CalAmp Wireless Networks BDD4T881 Paragon PD User Manual Annex A technical manual preliminary
CALAMP WIRELESS NETWORKS INC. Paragon PD Annex A technical manual preliminary
Contents
- 1. Annex A technical manual preliminary
- 2. Appendix A Preliminary version 2 00 April HC
Annex A technical manual preliminary

ParagonPD
Data Base Station
Technical Manual
Version 2.00
Preliminary, internal use
The entire contents of this manual and the Radio Installation Software
described in this manual are copyright 2000 by DATARADIO Inc.
Copyright DATARADIO Inc.
November 2000
Part no.: 120 20170-200
120 20170-200 ii ParagonPD Technical Manual
Table of Contents
1. PRODUCT OVERVIEW.....................................................................................................................................1
1.1 INTENDED AUDIENCE..........................................................................................................................................1
1.2 GENERAL DESCRIPTION ......................................................................................................................................1
1.2.1 Features: ..................................................................................................................................................1
1.3 FACTORY TECHNICAL SUPPORT..........................................................................................................................2
1.4 PRODUCT WARRANTY.........................................................................................................................................2
1.5 REPLACEMENT PARTS .........................................................................................................................................2
1.5.1 Factory Repair .........................................................................................................................................2
1.5.2 Model Designation...................................................................................................................................3
1.6 RADIO SERIES I OR II...........................................................................................................................................4
1.7 PACKAGING........................................................................................................................................................4
2. INSTALLATION..................................................................................................................................................4
2.1 OVERVIEW ..........................................................................................................................................................4
2.2 LOCATION ..........................................................................................................................................................4
2.3 ELECTRICAL........................................................................................................................................................4
2.3.1 Radio Assembly Power .............................................................................................................................7
2.3.2 BDLCPD assembly Power..........................................................................................................................8
2.4 ANTENNA ...........................................................................................................................................................8
2.4.1 Overview...................................................................................................................................................8
2.4.2 Cabling and Connection...........................................................................................................................8
2.5 COMPLETING THE PHYSICAL INSTALLATION. .......................................................................................................8
2.6 CHECKING OUT NORMAL OPERATION .................................................................................................................9
3. OPERATING DESCRIPTION............................................................................................................................9
3.1 RADIO ASSEMBLY...............................................................................................................................................9
3.1.1 Front panels .............................................................................................................................................9
3.1.1.1 Receiver module ................................................................................................................................. 9
3.1.1.2 Exciter module.................................................................................................................................. 10
3.1.1.3 Power Amp module .......................................................................................................................... 10
3.1.1.4 Speaker panel................................................................................................................................... 10
3.1.1.5 Dual Power Supply module................................................................................................................ 11
3.1.1.5.1 Rear Connections ......................................................................................................................... 11
3.1.2 Radio Assembly, rear panel....................................................................................................................11
3.1.2.1 Backplane PCB ................................................................................................................................ 11
3.2 BDLCPD............................................................................................................................................................12
3.2.1 BDLCPD Front panel...............................................................................................................................12
3.2.1.1 Front Switches.................................................................................................................................. 12
3.2.1.1.1 Reset........................................................................................................................................... 12
3.2.1.1.2 PF 1............................................................................................................................................ 12
LEDs and Indications.......................................................................................................................................... 14
3.2.1.2.1 Radio Network Indicators.............................................................................................................. 14
3.2.1.2.2 RS-232 Port Indicators.................................................................................................................. 14
3.2.1.2.3 Check and Power ......................................................................................................................... 15
3.2.1.2.4 Alarm Indicators........................................................................................................................... 15
3.2.2 BDLCPD Rear panel................................................................................................................................16
3.2.2.1 Signal Levels .................................................................................................................................... 16
3.2.2.2 Pin Functions.................................................................................................................................... 16
4. RIS PROGRAM.................................................................................................................................................17
4.1 OPERATION.......................................................................................................................................................18
4.2 TO CONNECT AND START RIS ...........................................................................................................................18
4.3 SCREEN.............................................................................................................................................................19
4.4 FUNCTIONS.......................................................................................................................................................19
120 20170-200 iii ParagonPD Technical Manual
4.4.1 Configuration to a file............................................................................................................................19
4.4.1.1 Connect Button................................................................................................................................. 20
4.4.1.2 “Get” button..................................................................................................................................... 20
4.4.1.3 “Get As” button................................................................................................................................ 20
4.4.2 Configuration from a File......................................................................................................................21
4.4.2.1 “Put From” button............................................................................................................................ 21
4.4.2.2 “Station Reset” button....................................................................................................................... 21
4.4.3 Special Functions...................................................................................................................................21
4.4.3.1 Banner Field and “i” button................................................................................................................ 21
4.4.3.2 Comments........................................................................................................................................ 21
4.4.3.3 Password ......................................................................................................................................... 22
4.4.4 Test Functions........................................................................................................................................22
4.4.4.1 Channel Selection.............................................................................................................................. 22
4.4.4.2 TXON Tests .................................................................................................................................... 22
4.4.4.2.1 Unmodulated Carrier..................................................................................................................... 22
4.4.4.2.2 Modulated Carrier......................................................................................................................... 22
4.4.4.3 Ping Button...................................................................................................................................... 23
4.4.4.4 Ping addresses.................................................................................................................................. 23
4.4.4.5 Flatness test button............................................................................................................................ 23
4.4.4.6 Random data test .............................................................................................................................. 23
5. TESTING AND TROUBLE-SHOOTING .......................................................................................................24
5.1 EQUIPMENT REQUIRED......................................................................................................................................24
5.2 RECOMMENDED CHECKS ..................................................................................................................................24
6. RADIO PROGRAMMING AND ADJUSTMENTS ........................................................................................28
6.1 SERIES I 800MHZ RADIO PROGRAMMING .........................................................................................................28
6.1.1 Recommended Items ...............................................................................................................................28
6.1.2 Introduction............................................................................................................................................28
6.1.3 File Creation..........................................................................................................................................29
6.1.4 Programming the EPROM .....................................................................................................................30
6.1.5 EPROM Installation...............................................................................................................................31
6.1.6 Channel Selection via DIP Switches......................................................................................................31
6.2 SERIES I 800MHZ RADIO TUNING.....................................................................................................................32
6.2.1 Test Equipment.......................................................................................................................................32
6.2.2 Receiver Module (T885).........................................................................................................................33
6.2.2.1 Initial Setup...................................................................................................................................... 33
6.2.2.2 Synthesizer Alignment ....................................................................................................................... 33
6.2.2.3 Front-End Alignment ......................................................................................................................... 33
6.2.2.4 SINAD and Linearity Check .............................................................................................................. 34
6.2.2.5 RSSI Adjustment.............................................................................................................................. 34
6.2.3 Exciter Module (T881)...........................................................................................................................35
6.2.3.1 Initial Setup...................................................................................................................................... 35
6.2.3.2 Synthesizer Alignment ....................................................................................................................... 35
6.2.3.3 TX Frequency Error Adjustment........................................................................................................ 35
6.2.3.4 Low Frequency Balance Adjustment................................................................................................... 36
6.2.3.5 Exciter Power Output........................................................................................................................ 36
6.2.4 Power Amplifier Module (T889) ............................................................................................................37
6.2.4.1 Power Amplifier Power Out............................................................................................................... 37
6.2.4.2 Forward Power Alarm Level.............................................................................................................. 37
6.2.4.3 Reverse Power Alarm Level (Optional)............................................................................................... 37
6.3 SERIES II RADIO PROGRAMMING.......................................................................................................................40
6.3.1 Recommended Items ...............................................................................................................................40
6.3.2 Module Programming ............................................................................................................................41
6.3.3 Channel Selection via DIP Switches......................................................................................................44
6.4 SERIES II RADIO TUNING ..................................................................................................................................45
6.4.1 Test Equipment.......................................................................................................................................45
6.4.2 Receiver module (T855 & T835) ............................................................................................................45
120 20170-200 iv ParagonPD Technical Manual
6.4.2.1 Initial Setup...................................................................................................................................... 45
6.4.2.2 Synthesizer Alignment ....................................................................................................................... 46
6.4.2.3 Front-End Alignment ......................................................................................................................... 46
6.4.2.4 SINAD and Linearity Check .............................................................................................................. 46
6.4.2.5 RSSI Adjustment (UHF: T855).......................................................................................................... 47
6.4.2.6 RSSI Adjustment (VHF: T835) .......................................................................................................... 48
6.4.3 Exciter Module (T857 or T837) .............................................................................................................49
6.4.3.1 Initial Setup...................................................................................................................................... 49
6.4.3.2 Synthesizer Alignment ....................................................................................................................... 49
6.4.3.3 TX Frequency Error Adjustment........................................................................................................ 49
6.4.3.4 Low-Frequency Balance Adjustment .................................................................................................. 50
6.4.3.5 Exciter Power Output........................................................................................................................ 51
6.4.4 Power Amplifier Module (T859 or T839)...............................................................................................51
6.4.4.1 Power Amplifier Power Output.......................................................................................................... 51
6.4.4.2 Forward Power Alarm Level.............................................................................................................. 51
6.4.4.3 Reverse Power Alarm Level (Optional)............................................................................................... 51
6.4.4.4 Tait T859 (UHF) Standard Tuning Procedure ..................................................................................... 52
6.4.4.5 Tait T859 Tuning for Best Efficiency ................................................................................................. 52
7. SPECIFICATIONS.............................................................................................................................................58
APPENDIX 1 - PARAGONPD DEVIATION ADJUST ...........................................................................................................57
FIGURE 1 – TYPICAL RADIO AND POWER SUPPLY ASSEMBLIES, FRONT VIEW .....................................................................5
FIGURE 2 - BDLCPD, FRONT VIEW ...................................................................................................................................5
FIGURE 3 – TYPICAL RADIO AND POWER SUPPLIES ASSEMBLY, REAR VIEW........................................................................6
FIGURE 4 - BDLCPD, REAR VIEW......................................................................................................................................6
FIGURE 5 - BDLCPD’S REAR CONNECTION, SWITCH AND FUSE.........................................................................................8
FIGURE 6 - RECEIVER MODULE FRONT PANEL ...................................................................................................................9
FIGURE 7 - EXCITER MODULE, FRONT PANEL..................................................................................................................10
FIGURE 8 - POWER AMP MODULE, FRONT PANEL............................................................................................................10
FIGURE 9 - SPEAKER PANEL............................................................................................................................................11
FIGURE 10 - DUAL POWER SUPPLY REAR CONNECTIONS................................................................................................11
FIGURE 11 - BDLCPD MEMBRANE SWITCHES..................................................................................................................12
FIGURE 12 - RF INDICATORS..........................................................................................................................................14
FIGURE 13 - RS-232 PORT LED INDICATORS.................................................................................................................14
FIGURE 14 - ALARMS LED INDICATORS ......................................................................................................................15
FIGURE 15 - BDLCPD Y CABLE AND PINOUT..................................................................................................................17
FIGURE 16 - RIS MAIN SCREEN ......................................................................................................................................19
FIGURE 17 - “CONNECT USING” DIALOG WINDOW .........................................................................................................20
FIGURE 18 - SERIES I RECEIVER SYSTEM INFORMATION.................................................................................................29
FIGURE 19 - SERIES I CHANNEL INFORMATION ..............................................................................................................30
FIGURE 20 - CHANNEL SELECTION VIA DIP SWITCHES ...................................................................................................32
FIGURE 21 - T885 RECEIVER TUNING CONTROL LOCATION ............................................................................................38
FIGURE 22 - T881 EXCITER TUNING CONTROLS LOCATION ............................................................................................39
FIGURE 23 - RECEIVER SYSTEM INFORMATION...............................................................................................................42
FIGURE 24 - RECEIVER CHANNEL INFORMATION SCREEN...............................................................................................42
FIGURE 25 - EXCITER SYSTEM INFORMATION SCREEN....................................................................................................43
FIGURE 26 - EXCITER CHANNEL INFORMATION SCREEN.................................................................................................43
FIGURE 27 - BACKPLANE DIP SWITCHES EXAMPLE - CHANNEL 5 SELECTED...................................................................44
FIGURE 28 - T855 AND T885, RSSI CURVE: VOLT TO DBM...........................................................................................47
FIGURE 29 - T835, RSSI CURVE: VOLT TO DBM............................................................................................................48
FIGURE 30 – T800-50-0001 BACKPLANE AND TEST PINS LOCATION ..............................................................................48
FIGURE 31 - T859 TUNING SETTINGS.............................................................................................................................52
FIGURE 32 - T855 RECEIVER TUNING CONTROLS LOCATION.........................................................................................53
FIGURE 33 - T857 EXCITER TUNING CONTROLS LOCATIONS .........................................................................................54
120 20170-200 vParagonPD Technical Manual
FIGURE 34 - T835 RECEIVER TUNING CONTROLS LOCATION.........................................................................................55
FIGURE 35 - T837 EXCITER TUNING CONTROLS LOCATION...........................................................................................56
TABLE 1 - POWER SUPPLY LEDS INDICATIONS ................................................................................................................7
TABLE 2- TX MODE SELECTION LEDS INDICATIONS ......................................................................................................13
TABLE 3 - TEST TRANSMISSIONS ...................................................................................................................................13
TABLE 4 - RS-232 LED FUNCTION SELECTION SEQUENCE............................................................................................14
TABLE 5 - RS-232 SIGNAL LEVELS.................................................................................................................................16
TABLE 6 - DTE PORT 9-PIN FUNTIONS...........................................................................................................................16
TABLE 7 - DTE PORT 25-PIN FUNCTIONS.......................................................................................................................16
TABLE 8 - TYPICAL CARRIER MODULATION ...................................................................................................................23
TABLE 9 - CHECKLIST A (AFTER INSTALLATION)............................................................................................................25
TABLE 10 - CHECKLIST B (GENERAL) ............................................................................................................................26

120 20170-200 vi ParagonPD Technical Manual
WHAT'S NEW IN VERSION 2.0
History
Preliminary – Version 2.0: November 2000
• Section 6 “Specifications”, Channel spacing limited to 25kHz only
Preliminary – Version 2.0: October 2000
• Further revision changes made to:
- Table 8 “Carrier Modulation”
- Section 6 “Specifications”.
Preliminary - Version 2.0: September 2000
• Further revision changes made to:
- Table 8 “Carrier Modulation”
- Table 10 “Checklist B, (General)”
- Section 6 “Specifications”.
Preliminary - Version 2.0: August 2000
• First release of SRRC4FSK modulated model, with speeds of up to 25.6
Kbps. Relevant changes made to:
- Section 1.2.1 “Features”
- Section 1.5.2 “Model Designation”
- Table 3 “Test transmissions”
Version 1.0: May 2000
• First released version, DGFSK modulated model, and speeds up to 19200
b/s.
120 20170-200 vii ParagonPD Technical Manual
Definitions
The following terms are used throughout this document.
Asynchronous Information that can be sent at random times, and not synchronized to a clock.
Transmission characters begin with a “start” bit and end with a “stop” bit.
AVL Automatic Vehicle Location. Optional feature that involves using GPS (Global
Positioning System) signals from the mobile unit by the Host PC.
BDLCPD Base Station Data Link Controller (PD = Parallel decode). An async radiomodem
designed to control the base station in mobile systems. A component of Para-
gonPD.
DBA Dataradio’s Dynamic Bandwidth Allocation protocol designed for short-
inquiry/long response applications such as dispatch systems. Latest enhancements
include support for occasional long messages inbound, and for Out-of-Band data
for AVL reports with no extra overhead.
DCE Data Communications Equipment. This designation defines the direction (input or
output) of the various RS-232 interface signals. Modems are always wired as
DCE.
DTE Data Terminal Equipment. This designation defines the direction (input or output)
of the various RS-232 interface signals. Most user equipment, as well as PCs, are
wired as DTE.
GeminiPD High specs mobile radiomodem. (PD = Parallel Decode)
Network Speed This is the bit rate on the RF link between units. Could be different from COM
port baud rate.
ParagonPD Factory-integrated industrial-grade data base station using Parallel Decode tech-
nology. Used in VIS mobile networks.
Parallel Decode Technology featuring dual receivers for added data decode sensitivity in multi-
path and fading environments (Patent Pending).
Refarming FCC’s strategy for using the radio spectrum more efficiently to meet future com-
munications requirements.
Radio Assembly Radio modules used in ParagonPD and available in two distinct series depending
on radio’s frequency band.
RIS Radio Installation Software. This software allows basic tests and unit configura-
tion.
RS-232 Industry–standard interface for serial data transfer.
VIS Vehicular Information Solutions. Dataradio’s name for a series of products spe-
cially designed for mobile data.
120 20170-200 ParagonPD Technical Manual1
1. PRODUCT OVERVIEW
This document provides the information required for the setting up, operation, testing and trouble-shooting
of the DATARADIO ParagonPD radio-modem base station.
1.1 Intended Audience
This document is intended for engineering, in-
stallation, and maintenance personnel.
1.2 General Description
ParagonPD product is a factory-integrated
industrial-grade data base station used in mobile
networks and is designed specifically to fit the
needs of vehicular applications.
It features dual receivers for added data decode
sensitivity in multi-path and fading environments.
When used with Dataradio’s state-of-the-art
GeminiPD mobile data solution, the system
delivers unequaled high-speed data performance
and unmatched effective throughput.
All ParagonPD models are supplied in a rack-
mount configuration that includes:
• A ParagonPD Radio assembly
• A contemporary, high-speed Dataradio
“Base Station Data Link Controller”
(BDLCPD).
ParagonPD units do not include the optional wire
line modem(s). Duplexer and backup power
units are custom furnished items. The laptop PC
and its application software are user-supplied
items.
1.2.1 Features:
• Dual receivers Parallel Decode technology
(Patent Pending)
• SRRC4FSK modulation capable of 25600
and 19200 b/s in 25 kHz channel spacing
• Sophisticated DSP-based modem design
provides added system performance and
fewer retries
• Available in VHF, UHF (Series II) and 800
MHz (Series I) radio bands
• Power output of 20W to 70W for
ParagonPD’s 800 MHz and of 20W to 100W
for VHF and UHF
• Supports high-efficiency Dataradio DBA
over-the-air protocol
• Over-the-air compatible with SRRC4FSK
modulated GeminiPD mobile products*
• Modular design in a rugged die-cast alumi-
num chassis
• Full-duplex operation
• ParagonPD units are factory-configured based
on each customer’s network system require-
ments
* Networks must use common bit and baud rates
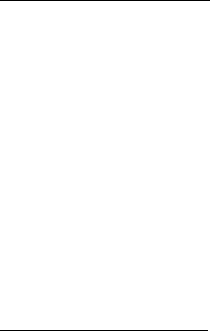
120 20170-200 ParagonPD Technical Manual2
1.3 Factory Technical Support
The Technical Support departments of
DATARADIO provide customer assistance on
technical problems and serve as an interface with
factory repair facilities. They can be reached in
the following ways:
DATARADIO Inc.
5500 Royalmount Ave, suite 200
Town of Mount Royal
Quebec, Canada H4P 1H7
Technical support hours: Monday to Friday 9:00
AM to 5:00 PM, Eastern Time
phone: +1 514 737-0020
fax: +1 514 737-7883
Email address: support@dataradio.com
or
DATARADIO Corp.
6160 Peachtree Dunwoody RD., suite C-200
Atlanta, Georgia 30328
Technical support hours: Monday to Friday 8:30
AM to 5:30 PM, Eastern Time
phone: 1 770 392-0002
fax: 1 770 392-9199
Email address: drctech@dataradio.com
1.4 Product Warranty
Warranty information may be obtained by con-
tacting your sales representative.
1.5 Replacement Parts
This product is usually not field-serviceable,
except by the replacement of individual radio
modules. Specialized equipment and training is
required to repair logic, modem boards and radio
modules.
Contact Technical Support for service informa-
tion before returning equipment. A Technical
Support representative may suggest a solution
eliminating the need to return equipment.
1.5.1 Factory Repair
When returning equipment for repair, you must
request an RMA (Returned Material Authoriza-
tion) number. The Tech Support representative
will ask you several questions to clearly identify
the problem. Please give the representative the
name of a contact person, who is familiar with
the problem, should a question arise during
servicing of the unit.
Customers are responsible for shipping charges
for returned units. Units in warranty will be re-
paired free of charge unless there is evidence of
abuse or damage beyond the terms of the war-
ranty. Units out of warranty will be subject to
service charges. Information about these charges
is available from Technical Support.
120 20170-200 ParagonPD Technical Manual3
1.5.2 Model Designation
To correctly identify your ParagonPD unit, check its catalog number label located on the rear of the
BDLCPD adjacent to the power connector.
The first four digits designate the model:
- BDDD = ParagonPD (DGFSK)
- BDD4 = ParagonPD (SRRC4FSK)
The next three digits designate the Band used:
- 83X = VHF, 100W
- 85X = UHF, 100W
- 88X = 800 MHz, 70W
The next digit designates the RF band of opera-
tion:
For the 83X band:
- 1 = 136 – 156 MHz
- 2 = 148 – 174 MHz
For the 85X band:
- 1 = 400 – 440 MHz
- 2 = 440 – 480 MHz
- 3 = 480 – 520 MHz
For the 88X band:
- 1 = 800 – 880 MHz (RX
850 – 870 MHz (TX)
- 2 = 870 – 960 MHz (RX)
(TX, 5W only)
The next digit designates the RF Bandwidth
used:
For the 83X band:
- 0 = 25 kHz full channel, 2.5 ppm*
- 5 = 12.5 kHz half channel, 2.5 ppm*
- 6 = 12.5 kHz half channel, 2.0 ppm* (U.S.
model only)
For the 85X band:
- 0 = 25 kHz full channel, 1 ppm*
- 5 = 12.5 kHz half channel, 1 ppm*
For the 88X band:
- 0 = 25 kHz full channel, 1.5 ppm*
- 5 = 12.5 kHz half channel, 1.5 ppm*
* denotes Frequency Stability
The next digit designates the transmitter power:
- 005 = 5 watt transmitter
- 070 = 70 watt transmitter (850-870 MHz
only)
- 100 = 100 watt transmitter
The next and last digit designates the Power
Source:
- 0 = Power supply deleted on order
- 2 = heavy-duty 120 VAC dual supplies
120 20170-200 ParagonPD Technical Manual4
1.6 Radio Series I or II
System-engineered installations use one of two
complements of ParagonPD radio modules. They
are assembled on a common chassis:
Series I models:
- 800 MHz frequency range radios
- Frequency programming is done via
EPROM. (This model does not use the pro-
gramming port of Series II models).
Series II models:
- VHF and UHF frequency range radios (800
MHz models will be available as Series II at
a later date)
- Frequency programming is done using soft-
ware via a programming port located on the
speaker front panel.
1.7 Packaging
Each ParagonPD product normally leaves the
factory packaged as follows:
• A Series I or II Dataradio base station “Ra-
dio assembly”
• A dual power supply assembly
• A Dataradio BDLCPD model
• A Radio Interface Cable to link the Radio
assembly to the BDLCPD:
18-inch long “Y” cable; DB-25 female to
dual DB-25 female (p/n 730 03374-102)
for connection between backplane PCBs
and BDLCPD.
• One standard seven-foot 120VAC power
cord
• Two DC power cables to connect the radio
assembly to the dual power supply assem-
bly.
• Courtesy small parts kit
Frequently, ParagonPD product components are
field-assembled prior to customer delivery.
The cabinetry may then be supplied in one of
several custom rack-mount configurations that
may also include fan, backhaul modems,
duplexer/filters/combiners, and ancillary
equipment.
If damage has occurred to the equipment during
shipment, file a claim with the carrier immedi-
ately.
2. Installation
2.1 Overview
The cabinet and rack-mount housing the Para-
gonPD’s Radio assembly and the BDLCPD is gen-
erally installed in a sheltered facility. Occasion-
ally located adjacent to the nerve center of the
user’s network, it is often located near tower
sites or at remote locations where it operates
unattended.
Furnishings needed include power, cabling and
installation of antenna, landline or microwave
modem and host PC or portable computer. De-
tails of these are outside the scope of this man-
ual. This manual covers the radio assembly and
the BDLCPD that includes the modem.
2.2 Location
Be sure to place the ParagonPD in such a way
that:
• The LEDs can be seen (as an aid in trouble-
shooting)
• Access to the antenna connector and to the
back connectors is possible without remov-
ing the unit
• Sufficient air may flow around the unit to
provide adequate cooling.
2.3 Electrical
Standard 120 VAC electrical power is required.
It should be capable of providing at least 10A.
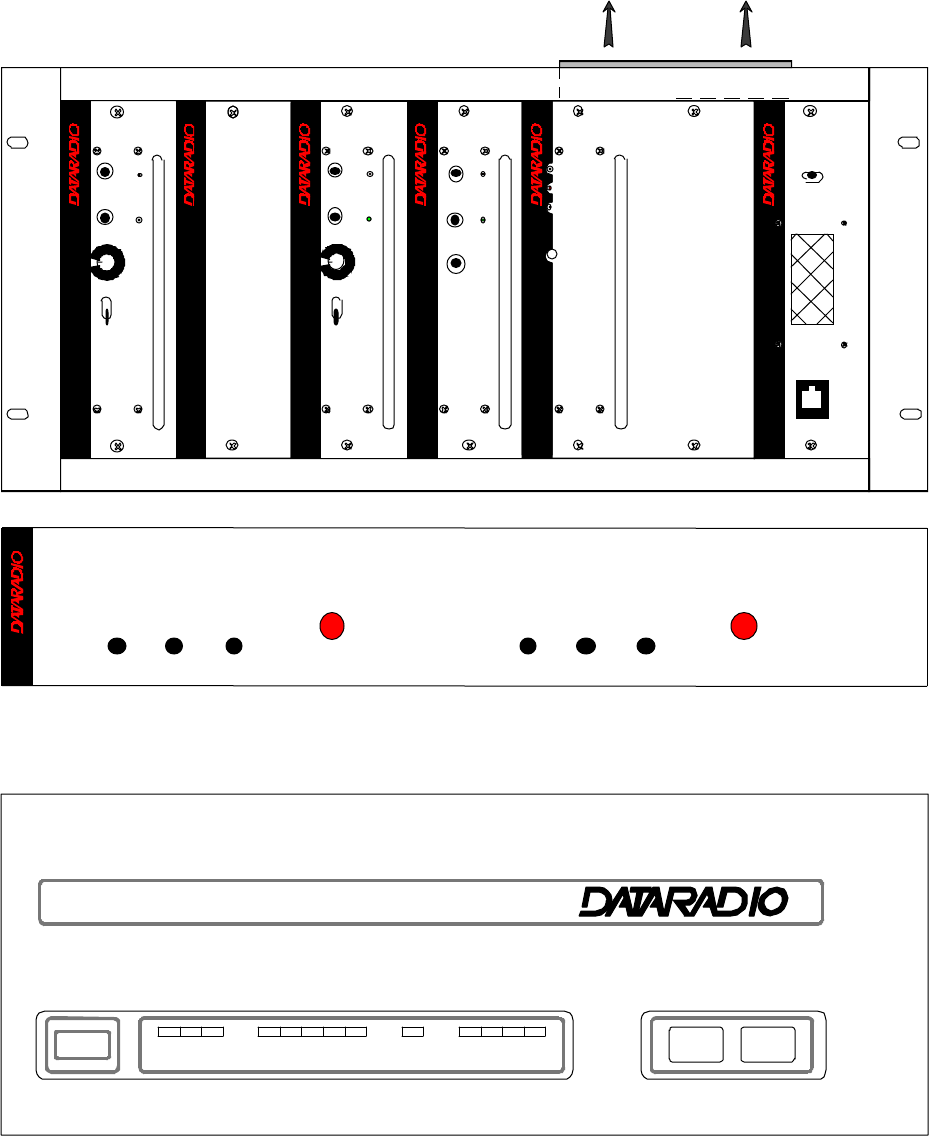
120 20170-200 ParagonPD Technical Manual5
Figure 1 – Typical radio and power supply assemblies, front view
Figure 2 - BDLCPD, front view
RESET
UFLFRMLMCK
ALARMSRF
TXRXCS
S-3 RS-232
CM FR FT RD TD
123 PF1
®
Re c e i v e r
®
Gating Gate
Line
Le vel Supply
®
Exciter
Ca r r i e r On
Line
Sensitivi ty
Supply
Microphon e
®
Pow er Am p li fi er
Low Forward Power
Supply
Hi gh Re ver se Po wer
Pow er
Sensitivi ty
Monitor
Volum e
Off
On
Monitor
Mute
Re c e i v e r
Gating Gate
Line
Le vel Supply
Sensitivi ty
Monitor
Volum e
Off
On
Monitor
Mute
Excellence in Radio
Communic at ion s
®
®
S peaker Panel
programming
port
RX2RX1
OFF
SP EAK ER
SELECT SWI TCH
Air Flow
OL Stby On Power
OL Stby On Power
T800 II
Slimline
®
Dual Power Supply Module
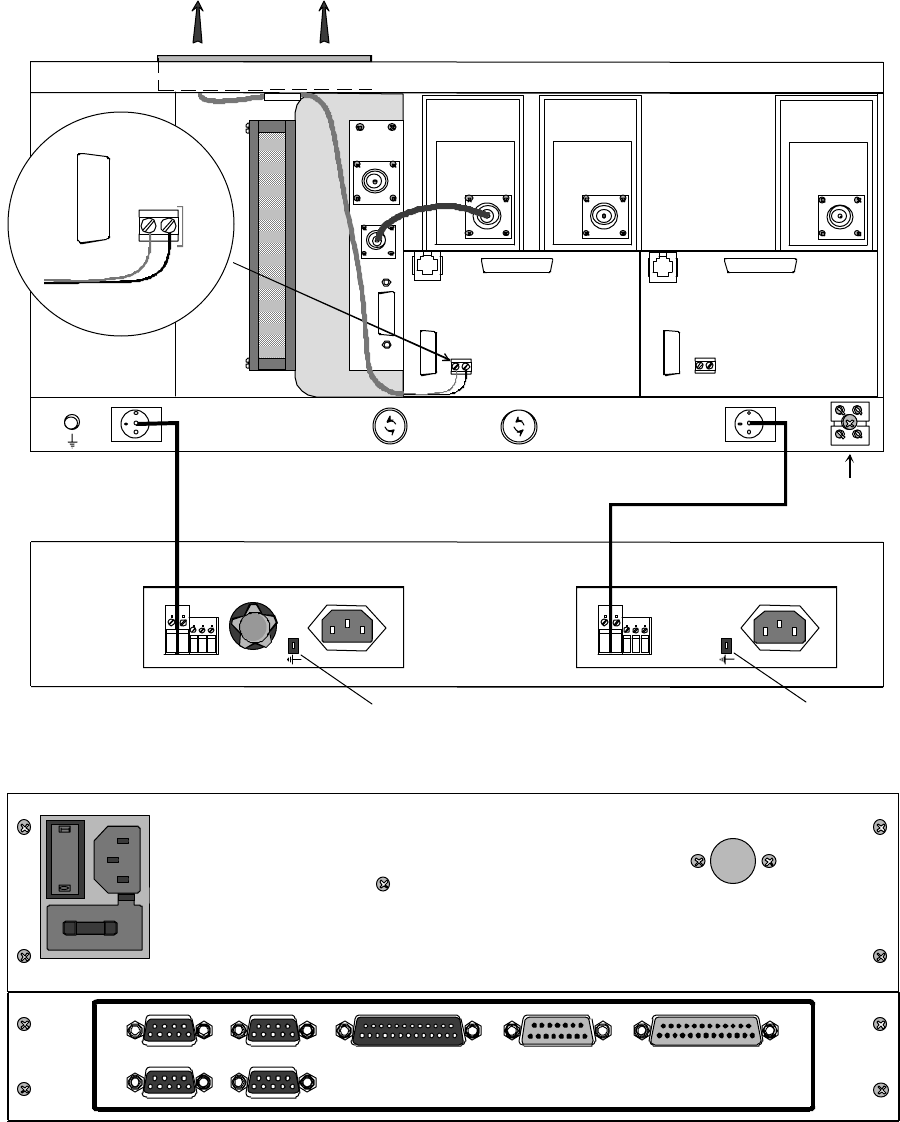
120 20170-200 ParagonPD Technical Manual6
Figure 3 – Typical radio and power supplies assembly, rear view
Figure 4 - BDLCPD, rear view
Emp loy er u n iqu em en t av ec
un fu sible de 25 0 V
Use on l y with a 250 V fu se
DEV. 3 RS-232
DEV. 5 R S-232
DEV. 2 RS-232
DEV. 4 R S-232
DEV. 1 RS-232 DEV. 6 DIG. I/O EXT. RADIO/TE ST
T808-10-00CA T807-10-00CA
REAR VIEW
Air Flow
GND
DC
INPUT 1
FUSE 1FUSE 2DC
INPUT 2 13.8 VDC
2 AM PS MAX.
F
U
S
E
F
U
S
E
F
U
S
E
F
U
S
E
F
U
S
E
F
U
S
E
+
-
+
-
+
-
+
-
GND
GND
T800-50-0001
No 1
PL1
SK5
T800-50-0001
No 2
PL1
SK5
_+_+
SK5
_+
FAN
CN2
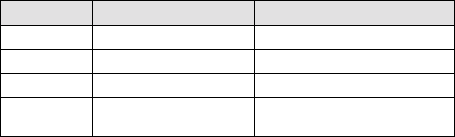
120 20170-200 ParagonPD Technical Manual7
2.3.1 Radio Assembly Power
Referring to Figure 3, the Radio assembly unit
receives two separate 13.8 VDC power inputs
from a “T800 Slimline” dual power supply typi-
cally rack-mounted right below the main assem-
bly radio chassis.
The T800 is made up of two separate power
supply units joined in a single chassis:
• A T807 using convection cooling is rated up
to 15A. It supplies all the radio modules
other than the Power Amplifier.
• A T808 using convection and fan cooling is
rated up to 25A. It supplies only the Power
Amplifier module.
Normally used at room ambient temperatures,
they can operate within specifications over a
range of –10 to +60 °C.
Note: Internal over-temperature protection
shuts down the main transformer above
105 degrees Celsius.
Both power supply modules are internally con-
nected to ground via their individual, rear-
connected, seven-foot standard 120 VAC power
cords. Nevertheless, each requires a separate
secure electrical ground connection. Individual
grounding tabs are provided next to the power
connectors.
Similarly, the Radio Assembly chassis requires a
secure ground connection. A threaded grounding
binding post fitted with a knurled binding-nut is
provided on the chassis next to DC input 2.
Separate grounding leads with appropriate con-
nectors are supplied (either in the courtesy
small-parts kit or with one end fastened to the
equipment.
A- For each of the power supply modules:
1. Fit one end of the grounding lead’s
push-on connector onto the ground-
ing tab.
B- For the Radio Assembly chassis:
1. Install the grounding lead’s lug over
the binding post and firmly hand-
tighten the binding-nut.
For both A and B
2. Fit the slotted connector (on the other
end of each of the grounding connector)
under a conveniently located screw on
the rack frame or other support surface.
Scrape away paint if needed to ensure
clean contact.
3. Apply anti-corrosion compound where
paint scraping was done.
4. Ensure by testing continuity that a se-
cure electrical and mechanical connec-
tion is achieved.
If a –DC rail (0V) is installed as part of the sys-
tem, the grounding leads may alternatively be
fitted to the rail terminal.
Caution:
Improper grounding between power
supply case and rack frame may result
in harmful voltage potentials and/or
miscellaneous power supply switching
noise problems in both receivers and
transmitter.
Press both red power buttons located on the front
of the module to have complete power distribu-
tion to the Radio assembly.
The power supply front panel LEDs indications
are:
Table 1 - Power Supply LEDs Indications
LED Color Indication
On Green Power enabled *
Stby Red Power disabled *
OL Steady Red Current Overload
On & OL Flashing green and
red respectively Over voltage
* To remove voltage from the power supply PCB, disconnect
the main power cords.
For LEDs descriptions, see section 3.2.1.2
The Radio assembly is fused at the rear of the
chassis:
• Fuse 1 is a 32-volt MDL (slow-blow) 10A
• Fuse 2 is a 32-volt MDL (slow-blow) 30A
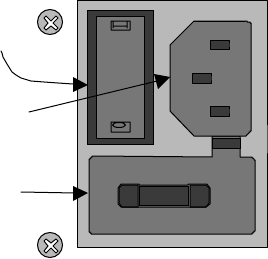
120 20170-200 ParagonPD Technical Manual8
2.3.2 BDLCPD assembly Power
The BDLCPD assembly uses a standard 120
VAC power cord. Plug this cord to the rear
power outlet shown in Figure 6.
To check or install a fuse:
1. Open the slide-out fuse drawer located be-
low the power connector.
2. Use a fine bladed screwdriver or a knife
blade and gently pry open.
3. Hold the fuse support in one hand and with
the other, lift the center plastic retainer until
it releases the fuse sliding base.
4. Replace or install a 250V, 2A fuse.
5. To complete the procedure, push the sliding
fuse base until it snaps under the retainer.
6. Re-insert the fuse drawer in its housing and
push until it is fully seated and closed.
When ready to apply power, use the ON-OFF
toggle power switch adjacent to the power con-
nector.
Figure 5 - BDLCPD’s rear connection, switch and fuse
2.4 Antenna
2.4.1 Overview
ParagonPD commonly uses three antennas (one
transmit and two receive) unless a duplexer is
used with one of the receive antennas; then only
two antennas would be needed. They should be
mounted according to any guidelines supplied
with the antennas. For antennas placement and
spacing, consult System Engineering.
2.4.2 Cabling and Connection
1- Route good quality 50-ohm double-shielded
coaxial cable(s) (e.g. RG-214 or Heliax)
from the selected antenna position(s) to the
ParagonPD Radio assembly.
2- Terminate the RX-1 and RX-2 cable ends at
the Receiver modules rear position with an
N-type connector.
3- Similarly, terminate the TX cable end at the
Power Amp’s module rear position with an
N-type connector.
Caution:
When terminating RF cables
use brand-name crimping tools
(such as AMP, Jensen, Crimp-
Master, etc…) of the correct
size for the cable and type of
connector used.
Common pliers are NOT ac-
ceptable.
2.5 Completing the physical
Installation.
ParagonPD products are factory-configured to
user’s requirements and are shipped ready to
run.
After new installations:
• Re-check that all connections are secure on
radio and BDLCPD assemblies (antennas,
PC, power cords etc.)
• Check that fuses are inserted.
• Turn both BDLCPD and radio power ON.
You are now ready to check for normal opera-
tion and to run the Radio Installation Software
(RIS) program for testing or trouble-shooting.
Any change(s) to the settings must be done via
files saved on diskette and loaded into the unit
using the RIS program.
Employer uniquement avec
un fu sible de 25 0 V
Use on l y with a 250 V fu s e
ON-OFF
Switch
120VAC
Connector
Fuse
Slide-out
Drawer
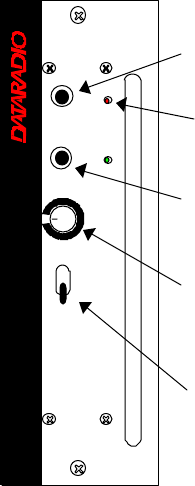
120 20170-200 ParagonPD Technical Manual9
2.6 Checking out Normal
Operation
1- Check that power is applied.
2- Check Radio assembly lights for proper op-
eration as per section 3.1.1
3- Check for proper operation of the BDLCPD’s
LEDs as per section 3.2.1.2.
4- Using the RIS program (described in section
4), and an in-line wattmeter, check forward
& reflected power to confirm antenna in-
stallations.
5- Using the RIS, check the RF link with a mo-
bile station that can be heard, by using the
RIS “Ping” feature. See section 4.4.4.3
If user application and a mobile station are
available, test the installation by going through a
normal sequence of transmitting and receiving
messages.
3. Operating Description
3.1 Radio Assembly
The Radio assembly component of each Paragon
product is made up of high performance synthe-
sized radio base station designed for single op-
eration. Referring to Figure 1 on page 5, the Ra-
dio Assembly’s modules are commonly installed
in a standard, 19-inch wide rack frame.
3.1.1 Front panels
The complement of modules is identical for:
Series I, (800 MHz model) and
Series II, (VHF and UHF models)*
* 800 MHz models will be available as Series II at a fu-
ture date)
• 2 Receivers
• Exciter
• Power Amplifier
• Speaker panel
• Dual Power Supply
3.1.1.1 Receiver module
The RX1 and RX2 receivers’ use identical front
panel controls and indicators. These are:
Figure 6 - Receiver module front panel
• Gating Sensitivity - sets the RF signal level
required to open the mute gate and allow
audio to pass to the speaker.
• Gate LED - indicates the status of the mute
circuit. It is lit when a signal above the mute
threshold is received.
Note:
“Gating Sensitivity” and “Gate LED” are
not functionally used except to allow lis-
tening to incoming receptions as a trouble-
shooting aid.
• Supply LED - is lit when DC power is ap-
plied. Fast Flashes when linked with
PGM800Win. Slow Flashes indicates VCO
(synthesizer) out of lock. Unequal Flashes
indicates internal communication error.
• Line Level - Not used
• Monitor Volume - The audio output delivers
up to one watt to the speaker. Always set
volume knob to minimum when not in use to
reduce current consumption.
Gating
Sensitivity
Gate
LED
Line
Level
Monitor
Volume
Monitor
Mute
On - Off
Receiver
®
Gating Gate
Line
Level Supply
Sensitivity
Monitor
Volume
Off
On
Monitor
Mute
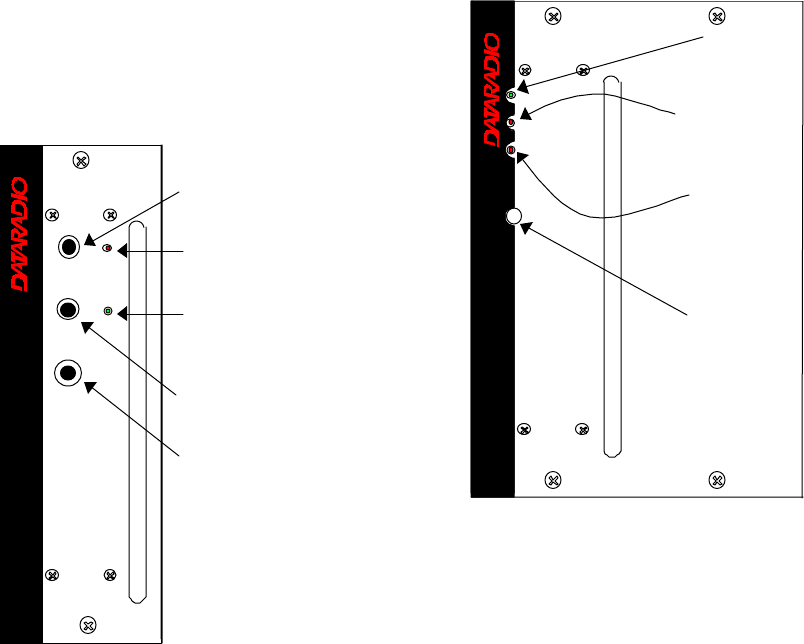
120 20170-200 ParagonPD Technical Manual10
• Monitor Mute switch - opens the mute, al-
lowing continuous monitoring of the audio
signal.
On = audio muted
3.1.1.2 Exciter module
The Exciter’s front panel controls and indicators
are:
Figure 7 - Exciter module, front panel
• Carrier Switch - momentarily keys the
transmitter ON while pressed (used for test
purposes only).
• On LED - is lit when transmitting
• Line Sensitivity – not used.
• Supply LED - is lit when DC power is ap-
plied. Fast Flashes when linked with
PGM800Win. Slow Flashes indicates VCO
(synthesizer) out of lock. Unequal Flashes
indicates internal communication error.
• Microphone Socket – not used.
3.1.1.3 Power Amp module
The Power Amp front panel and indicators are:
Figure 8 - Power Amp module, front panel
• Supply LED - is lit when DC power is ap-
plied.
• Low Forward Power LED - is lit when for-
ward power is below the level set, normally
80% of nominal forward power.
• High Reverse Power LED - is lit when high
reverse power is detected (e.g. VSWR= 3:1).
• Power - sets the PA output power:
- VHF & UHF: 20 – 100 Watts
- 800: 20-70 Watts
3.1.1.4 Speaker panel
Referring to Figure 9, the speaker panel is fitted
with a 4Ω speaker.
Both series of radio assemblies share the same
front panel fitted with an RJ11 connector. This
connector is used to allow programming the ra-
dio from the front of the unit via a programming
lead. This feature is exclusive to the Series II
modules.
Carrier
Switch
On
LED
Supply
LED
Line
Sensitivity
Microphone
Socket
®
Exciter
Carrier On
Line
Sensitivity
Supply
Microphone
®
Power Amplifier
Low Forward Power
Supply
High Rev erse Power
Pow er
Supply
LED
Low Forward
Power LED
High Reverse
Power LED
Power
Adjustment
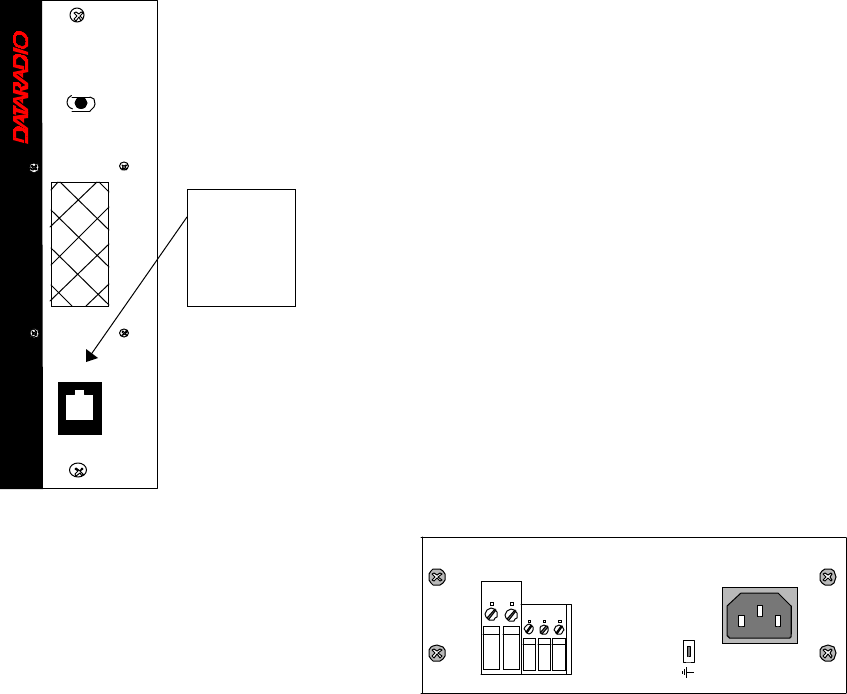
120 20170-200 ParagonPD Technical Manual11
If the speaker panel needs to be removed, a mir-
ror programming port connector is provided on
both backplanes.
Programming for Series I 800 MHz units is done
via EPROM and is detailed in section 6.1. The
RJ11 front port is covered (not used).
Figure 9 - Speaker panel
3.1.1.5 Dual Power Supply module
The Dual Power Supply module is made up of
two separate power supply units coupled in a
single chassis.
Refer to Table 1 on page 7 for tabular listing of
power supply LEDs indicators.
Refer to Figure 1 for the front panel LED layout.
This module has:
• Two “Power” red-colored pushbutton
switches - Push in for ON and release out
for OFF. Control complete power distribu-
tion to the Radio assembly
• Two “ON” LEDs - light green when push
button is ON; DC power is distributed to ra-
dio modules. Flash green in conjunction with
the “OL” LED when an over voltage condi-
tion is present.
• Two “Stby”- Standby voltage LED, lights
red when push button is off; AC power is
applied but DC is not distributed to radio
modules. To remove presence of voltage,
disconnect both power cords.
• Two “OL” LEDs - Monitor current overload,
light red when supply exceeds current limit
set; nominally 25Amps (T808 model).
Flashes red in conjunction with the ON LED
when an over current condition is present.
3.1.1.5.1 Rear Connections
Referring to Figure 10, (convection-cooled
model shown; fan-cooled model not illustrated),
the rear connections for each of the power sup-
ply are:
Fail Alarm –
Off: Power supply OK; approx. +Vout
(via 1k resistor - typ. 13.8V).
ON: Power supply failure; approx. -Vout
(via 11k resistors - typ. 0V)
+ Remote – Not used for Paragon
- Sense – Not used for Paragon
-VE – main ground (0V)
+13.8V – Mains DC output supply
Figure 10 - Dual Power Supply rear connections
Note: more power supply installation details
are covered in section 2.3.1
3.1.2 Radio Assembly, rear panel
3.1.2.1 Backplane PCB
Referring to Figure 3, two main backplanes are
used. Their main components are:
• RJ11 connector – Mirrors the one on the
front of the Speaker panel (series connected
to both backplanes). Used for programming
the Radio Assembly whenever the speaker
panel has been removed.
15A +
-
Ouput
Sense +
-
Re mote
Fail Alarm
13.6V
Max.
®
Speaker Panel
progra mm ing
port
RX2RX1
OFF
SP EAK ER
SELE CT SWI TCH
Not
Used with
800 MHz
Series I
model
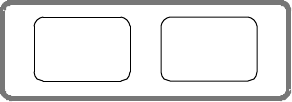
120 20170-200 ParagonPD Technical Manual12
This feature is exclusive to the Series II
model. Series I model’s programming is
done externally via EPROMs.
• DB-25M plug at PL1 (one side of the “Y”
cable on each PCB) – used to supply the re-
ceive signal to the BDLCPD’s single
“EXT.RADIO/TEST” DB-25F plug.
• Two channel-select DIP switches (SW1 and
SW2)
This feature is exclusive to the Series II
model.
• Cooling fan driver – CN2 located on back-
plane connects to the horizontally-mounted
fan on top of the Radio assembly and acti-
vated by BDLC’s PTT signal.
• Coaxial relay driver – not used.
3.2 BDLCPD
The rack-mounted BDLCPD is housed in a steel
case. It has no user serviceable parts. Unit’s con-
figuration is stored in flash memory (EEPROM).
3.2.1 BDLCPD Front panel
Referring to Figure 2, the front panel of the
BDLCPD has two cutouts across its length.
A- The left cutout groups the unit’s type label
and ten LED indicators:
• The S3 label designates the BDLCPD as a
“three Serial-port” model
(Ports 4 and 5 are reserved for future use)
• The RF group of 3 LEDs
• The RS-232 group of 5 LEDs
• A single CK LED
• The ALARMS group of 4 LEDs
B- The right cutout groups two tactile (mem-
brane) switches (PF1 and RESET).
3.2.1.1 Front Switches
Referring to Figure 11, the BDLCPD uses two
membrane-type switches labeled:
• RESET
• PF 1
These switches indicate contact by emitting a
short BEEP tone when pressed.
Figure 11 - BDLCPD membrane switches
3.2.1.1.1 Reset
Pressing Reset produces the same result as pow-
ering OFF and ON again. It restarts the micro-
processor, the peripherals and invokes the on-
board diagnostics. BDLCPD’s radio modules’
internal flash-memories are read and their values
are loaded in system SRAM CPU flash-memory.
Normally, pressing Reset results in one short
BEEP tone followed by all LEDs coming ON for
about four seconds. Then, the LEDs flash in a
“ripple” pattern for close to two seconds indi-
cating diagnostics are in progress. At the end of
this period, all LEDs should be OFF except CK
that should flash about six to eight times per
second.
Expect an additional two seconds delay for CK
to start flashing and the UF indicator to come
ON if the radio assembly is not connected or not
powered (see section 3.2.1.2.4 for Alarm de-
tails).
3.2.1.1.2 PF 1
PF 1 is a multi-function switch:
• It clears LED error indications
• It initiates test transmissions
• It sets the function of the RS-232 LEDs
PF1 RESET
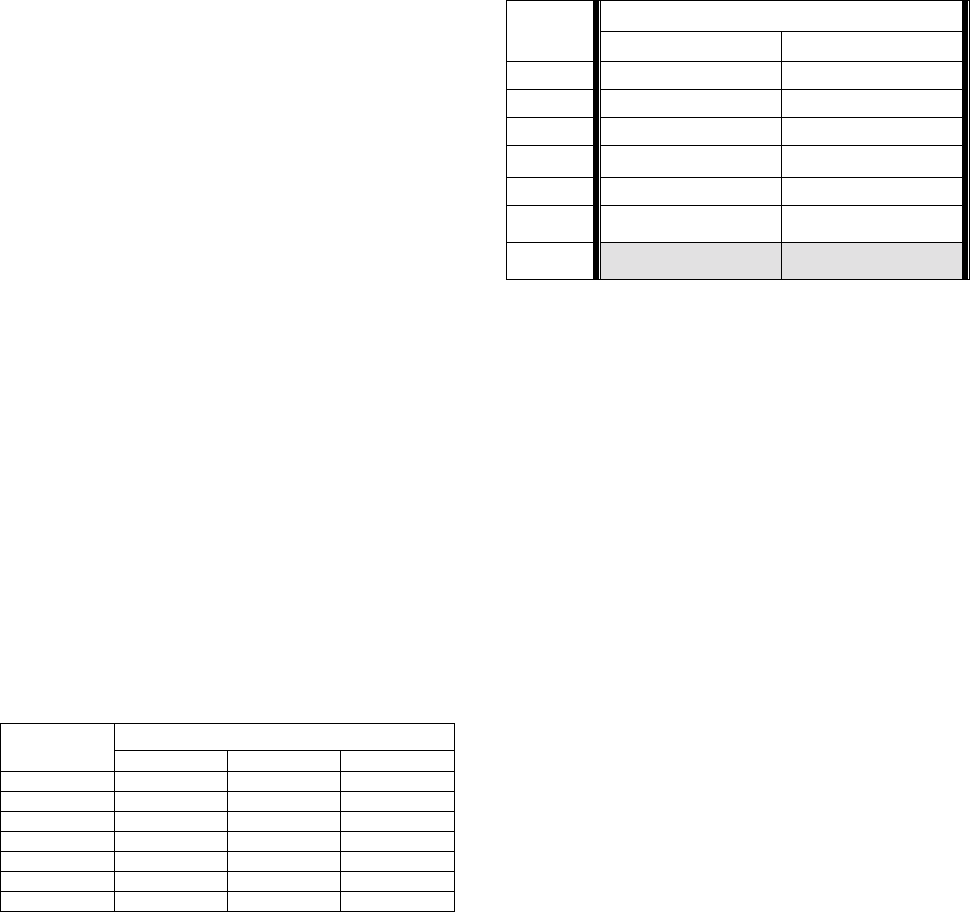
120 20170-200 ParagonPD Technical Manual13
3.2.1.1.2.1 Clearing Errors
Major and minor error LED indications remain lit
on the front panel until:
• The unit is RESET
• The unit is powered OFF and ON again
• PF 1 is pressed
The PF 1 switch can be pressed at any time to
clear an error display without affecting normal
operations.
3.2.1.1.2.2 Test Transmissions
To select a pattern and begin transmission, start
by pressing and holding PF1. It beeps once, all
five RS232 LEDs light; listen for a second beep
followed by a third beep. After two seconds, the
unit beeps and goes in “TX Select” mode with
only the three rightmost RS-232 LEDs now used
as selection indicators. Only release PF1 after
the third beep.
Following release:
• Start of selection must be made within two
seconds. If not, the unit will default to pat-
tern one and start test transmitting.
• PF1 may be pressed more than once. The
number of times it is pressed determines the
type of pattern that will be transmitted ac-
cording to Table 3
• Each pressing of PF1 extends the two-second
timer.
• The three rightmost RS-232 LEDs display
are used to indicate TX mode selection as
shown in Table 2.
Table 2- TX mode selection LEDs indications
Binary TX mode LED indicationsTX pattern
selected FT LED RD LED TD LED
1 Off Off On
2 Off On Off
3 Off On On
4 On Off Off
5 On Off On
6 On On Off
7OnOnOn
Once the type of transmission is selected, stop
pressing PF1, allow the two-seconds timer to run
down. Automatically, the BDLCPD turns its
transmitter ON, sends the selected “test pattern”
for 55 seconds and turns its transmitter OFF.
The TX LED in the RF group of indicators lights
in red while test transmitting. Pressing PF1 while
the 55 seconds test is in progress stops the test.
At the end of test transmission, BDLCPD opera-
tion returns to normal and the RX LED lights in
green (monitoring normal transmitter activity).
Table 3 - Test Transmissions
ParagonPD
# times
PF1 is
pressed 16000 b/s 25600 b/s
1 2400 Hz Dotting* 3200 Hz Dotting*
2 Do not use Do not use
3 100 Hz Square wave 100 Hz Square wave
4 Random data Random data
5 Unmod Unmod
61000 Hz sine
beacon mode 1000 Hz sine
beacon mode
71000 Hz sine wave
Adjustment tone 1000 Hz sine wave
Adjustment tone
* Dotting with reduced amplitude
Notes:
- A dotting pattern consists of alternating sequence of
1’s and 0’s
- The square wave is used for balancing transmitter
low frequency response
- The 1000 Hz sine can be used for transmitter distor-
tion measurements.
- Pattern 6 produces a transmission of 55 seconds
followed by 55 seconds of silence. Initial transmis-
sion in a sequence may be shorter than 55 seconds.
TX LED stays steadily red for duration of the test.
Press PF1 to terminate beacon mode.
3.2.1.1.2.3 RS-232 LED Function
Selection
The PF 1 button is used to select the RS-232
display mode as follows:
• If pressed ONCE (do not hold pressed):
- Clears Alarm indications
- CK LED stops flashing for 2 seconds
- During this time, one or all of the
RS-232 numbered LEDs (see Figure 13)
will light. If one LED lights, it denotes
the port to which the subsequent display
applies. If all numbered LEDs light, it
denotes that the normal 3-port display
mode is active.
The selected display remains active until

120 20170-200 ParagonPD Technical Manual14
manually changed or until RESET is
pressed or until power up.
Table 4 - RS-232 LED Function Selection Sequence
RS-232 LED Function Selection Sequence
ALL
1
2
3
4 (reserved)
5 (reserved)
TX LED in RF group lights with any and
all transmission
ALL
1
2
3
4 (reserved)
5 (reserved)
TX LED in RF group only lights with
an ACK or DATA transmission
• If, during the 2 seconds period that CK is not
flashing, PF 1 is pressed a second time, the
LED functions will advance one step from
top to bottom through the available options
in the order shown in Table 4.
• PF 1 may be pressed repeatedly during the 2
second period (extended with each press) to
advance to the desired numbered LED func-
tion option.
Once the desired RS-232 LED function is se-
lected, stop pressing PF1, allow the two-seconds
timer to run down. The BDLCPD returns to nor-
mal operation using the newly selected display.
3.2.1.2 LEDs and Indications
LEDs are used to indicate the operation status of
the BDLCPD. Although capable of displaying
three colors, only the green and red colors are
used for the BDLCPD. They are grouped by their
function:
• RF Group, displays radio channel status in
green
• RS-232 Group, displays serial port status in
green except the TX LED that also uses red
• ALARM Group, displays fault status in red
3.2.1.2.1 Radio Network Indicators
The Radio Network LEDs are useful when trou-
bleshooting as an indication of network activity.
It can help isolate transmission problems.
Figure 12 - RF indicators
CS Carrier Sense - Steady light indicates
that an incoming radio data signal is be-
ing detected by the DSP modem. CS
signal is not user-adjustable.
RX Receive Data – Flashing light indicates
unit is internally receiving data from the
radio network.
TX Transmitter ON – blinks green indicates
(depending on display mode selected):
• That a data packet or ACK (packet
acknowledgment) is being
transmitted.
• That an idle packet, data packet or
ACK is being sent. Test transmis-
sion display is done in red.
3.2.1.2.2 RS-232 Port Indicators
The RS-232 LEDs normally indicate port activ-
ity on the port selected. See section 3.2.1.1.2.3
above for instructions for selecting display
mode.
Figure 13 - RS-232 Port LED indicators
CM Command Mode - LED lights and re-
mains lit while the selected port is ac-
cessing the Command Processor. It lights
ON and OFF while being configured.
321 RS-232
CM FR FT RD TD
CS RX TX
RF
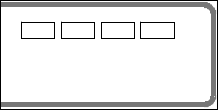
120 20170-200 ParagonPD Technical Manual15
FR Flow Control on Receive - the BDLCPD
has received a flow control signal from
the device connected to it. When it
lights, BDLCPD has stopped sending data
to the DTE. When LED goes out, the
port terminal is again ready to receive
data.
FT Flow Control on Transmit - the BDLCPD
has sent a flow control signal to the DTE
asking it to stop sending data. The LED
remains lit as long as the terminal is be-
ing held off.
RD Receive Data - when lit, it shows that the
Receive Data pin 3 on the RS-232 inter-
face connector is active. Since all
BDLCPD are configured as DCE, it
means that the DTE is receiving data
from the BDLCPD.
TD Transmit Data - shows the status of
Transmit Data pin 2 of the RS-232 inter-
face. When lit, the DTE is sending data
to the BDLCPD.
3.2.1.2.3 Check and Power
CK Check:
Normally flashing rapidly (about 6 cps),
indicates microprocessors are working
correctly and power is applied.
Not flashing indicates unit is not func-
tioning.
Blinking slowly (1 cps), indicates the
parameters contents of the flash memory
have been corrupted. The unit automati-
cally loads its set of factory default pa-
rameters and starts beeping at 20 sec-
onds intervals.
May also indicate DSP-modem re-
initialization has occurred
3.2.1.2.4 Alarm Indicators
All alarm conditions will cause the BDLCPD to
light one or more of the LED indicators. LEDs
remain ON when lit until cleared by either
pressing PF 1 (without affecting operation of the
unit) or RESET (cycling unit OFF and ON).
Figure 14 - ALARMS LED indicators
LM Local Minor Alarm - when lit, indicates
the presence of any of the following mi-
nor faults:
- Parity, framing or overrun error at any
RS-232 port.
- Out of buffers. No memory available
to accept data from a local terminal de-
vice. Usually denotes a flow control
problem.
- Flash memory error. At power-up or
reset, the unit detected a change in non-
volatile memory.
RM Remote Minor Alarm - when lit, indi-
cates any of the Local Minor Alarm
listed above have taken place at the re-
mote end of the link (i.e. the mobile the
local base station is currently communi-
cating with). It will also light when a
protocol error has been detected on the
network.
In a network using the “Host Link Ac-
tive” (MSC) feature, the RM LED,
flashing in-sync with the CK LED, indi-
cates that the link is down.
ALARMS
LM RM LF UF
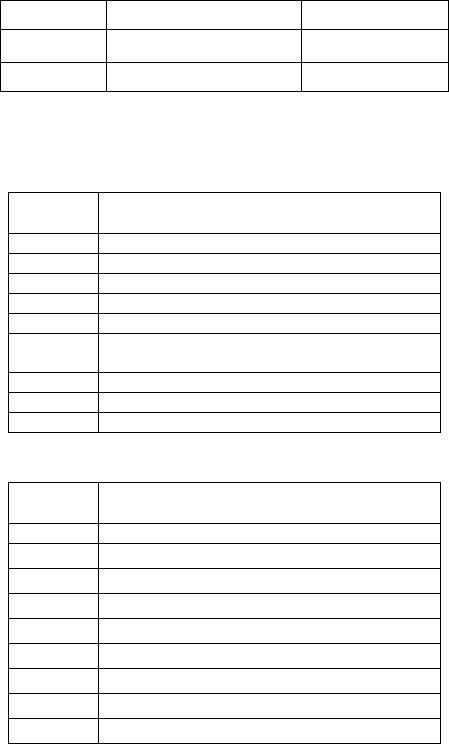
120 20170-200 ParagonPD Technical Manual16
LF Link Failure - when lit, indicates that the
base station fails to receive an ACK for
a packet sent and for all subsequent re-
tries. Some data has possibly been lost.
LF is not functional if all active ports are
set to NAR mode.
Link fails are inevitable during normal
operation (mobiles temporarily out of
range, in a tunnel, parked in a dead spot,
etc.). A lit LF LED is not normally
cause for concern.
UF Unit Failure - when lit, the unit requires
attention:
- the BDLCPD is not operable;
It may indicate detection of a system
software error trap.
- the BDLCPD is operable;
Indicates that on power-up, invalid data
was detected in the serial EEPROM chip
(located in the radio modules). It may
also indicate that connection to the radio
modules is incorrect or that radio power
is not applied.
The LM, RM and UF alarms also sound a beep
when a fault occurs. The LF alarm is silent.
3.2.2 BDLCPD Rear panel
Referring to Figure 4, the rear panel of the
BDLCPD has the following set of chassis con-
nectors:
• Four DE-9F connectors:
– DEV2 - usually connected to Datara-
dio’s RIS program (DMP/Setup 19200).
Can also be used with special user’s ap-
plication such as telephone modem
Note: connection to a telephone re-
quires the use of a DCE Crossover ca-
ble.
– DEV3 - Dedicated (9600)
– DEV4 and DEV5 - not used
• One DB-25F connector
- DEV1 - Connects to user’s application.
a) DMP 19200 for single-site installa-
tions
b) MSCP 19200 for multi-site installa-
tions
• One DA-15M connector:
- DEV6 Digital I/O - not used
• One DB-25M connector:
- EXT RADIO/TEST - connects to the
Radio assembly (see Figure 15)
3.2.2.1 Signal Levels
In the description of data signals in Table 7, the
following conventions are used:
Table 5 - RS-232 Signal levels
Term Alternates Signal level
ON Asserted, spacing +3 to +15 V
OFF Dropped, marking -3 to -15 V
3.2.2.2 Pin Functions
Table 6 - DTE Port 9-pin funtions
DE-9 F
pin # Function (RS-232 signal levels)
1 DCD – from ParagonPD, normally asserted
2 RXD – data from ParagonPD
3 TXD – data to ParagonPD
4 DTR – to ParagonPD, handshaking
5 Ground
6 DSR – from ParagonPD, tied to VCC through
current limiting resistor
7 RTS - to ParagonPD, handshaking
8 CTS – from ParagonPD, handshaking
9 Reserved
Table 7 - DTE Port 25-pin functions
DB-25F
pin # Function (RS-232 signal levels)
1 and 7 Ground
2TXD – data to BDLCPD
3RXD – data from BDLCPD
4RTS – to BDLCPD, must be asserted
5CTS – from BDLCPD, handshaking
6DSR – from BDLCPD, always +8V
8DCD – from BDLCPD, always asserted
9RI - from BDLCPD, always –8V
20 DTR – to BDLCPD, handshaking
We recommend the use of shielded 9-wire or 25-
wire cables with all pins connected.
Dataradio recommends the use of secure (i.e.
password protected and/or dial-back) modems in
any installation where dialup access is provided.
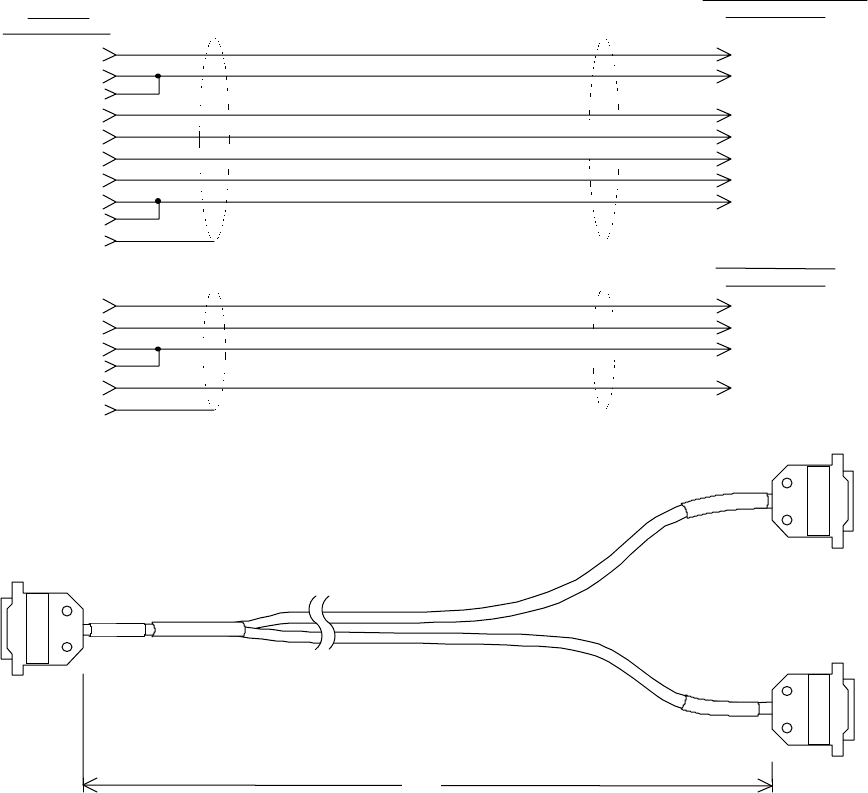
120 20170-200 ParagonPD Technical Manual17
Figure 15 - BDLCPD Y cable and pinout
4. RIS program
The Radio Installation Software (RIS) program is
used to:
• Check and troubleshoot ParagonPD.
• Save an existing configuration.
• Upload files for field configuring of units
(Requires intervention with technical sup-
port).
Important note:
The aggregate total baud rate for all active
ports on a BDLCPD must not exceed 30,000
for ParagonPD. Sustained simultaneous op-
eration on devices 1 and 3, using the fac-
tory settings for these ports, may result in
lost characters.
Using the factory settings, device 3 is in-
tended only for use during configuration and
should not be used simultaneously with data
traffic on device 1. For special user applica-
tion done while the BDLCPD is active, use
either device 2, or set device 3 to 2400
bauds.
DB-25 FEMALE (PL1)
BACKPLANE 1 / RX 1 & EXCITER
BDLC D212
18TXA TXA (fr om SK3 pin 8)11
1RX1 EEPROM (from SK1 pin
1
EXTIO_OUT1
3RXA ( 1) RX AUDIO 1 (from SK1 pin 6)24
9 RX RSSI (from SK1 pin 5)
RSSI (1) 16
6
PTT 15
SH I ELD
YELLOW
GRAY
GREEN
BLUE
ORANGE
17SH I ELD
RXA ( 2) RX AUDIO 1 (from SK1 pin 6)
24
9 RX RSSI (from SK1 pin 5)RSSI (2)
2GROUND (2) 13
SH I ELD
BROWN
VIOLET
RED
15SH I ELD
DB-25 FEMALE (P8)
EXTIO_IN1
10
22
GROUND (1) 4BLACK
EXTIO_OUT3 7 WHITE
EXTIO_IN3 24
TX KEY (f rom SK3 pi n 1 3)
13 GROUND
TX EEPROM (from SK3 pin 1)5
1
14
9EXTIO_OUT2
EXTIO_IN2 23
1 RX 2 EEPROM (from SK1 pin
GROUND
DB-25 FEMALE (PL1)
BACKPLANE 2 / RX 2
BLACK
18.00"
730-03374-102
L
E
F
T
(
R
X
1
-
E
x
)
R
I
G
H
T
(
R
X
2
)
TO BDLC
1)
1)
)
120 20170-200 ParagonPD Technical Manual18
To run the program, you will need:
- A PC or portable computer with a 486 class
CPU or better.
- 2 free megabytes of RAM.
- A hard disk.
- An available COM port.
- A serial mouse, with its own driver installed
is strongly recommend however most actions
can also be done using keyboard commands.
ParagonPD and Paragon products share the RIS
program with the MobilPac family of products. It
is available on diskette, Dataradio p/n 085
03355-00n. Please refer to the readme.txt file
included on the diskette for installation
instructions.
4.1 Operation
This support program is DOS-based and can be
run in MS-Windows © MS-DOS mode.
DO NOT have more than one copy of this pro-
gram loaded at any given time in separate win-
dows. Doing so creates COM port sharing con-
flicts and program failure.
It has the general look and feel of an MS-
Windows program. Mouse operation is the con-
ventional click, double-click plus click and drag
method. Only left mouse button operation is
supported.
Any command or selection shown in gray is ei-
ther unavailable or is awaiting another action
before activating.
Help in the program is available at all points by
pressing the F1 key. If a subject is highlighted,
the help displayed will be context sensitive. Oth-
erwise, the Index List is displayed.
4.2 To connect and start RIS
1- Connect a suitable 9-pin straight PC cable,
between the BDLCPD rear-mounted DEV2
port (see Figure 4), defined as DMP/setup
port (19200 bauds) at the time of manufac-
ture, and the port of the PC (or portable
computer) that will be running the RIS pro-
gram. If needed, a 9/25 pin-adapter and a 25-
pin PC cable may be used.
2- Check that ParagonPD is ON.
3- To run the Radio Service Software (RIS):
Note: Refer to the RIS Readme.txt file for
more details on how to set the Win-
dows environment, connect, install
and run this program.
• In DOS, change to the directory where
the program is installed and type
mpac_ris.exe and press ENTER.
• In WIN 3.x, click on File, then on Run,
type the path or browse to select, click
on OK to run mpac_ris.exe.
• In WIN 9x, click on Start, then on Run,
type the path or browse to select, click
on OK to run mpac_ris.exe.
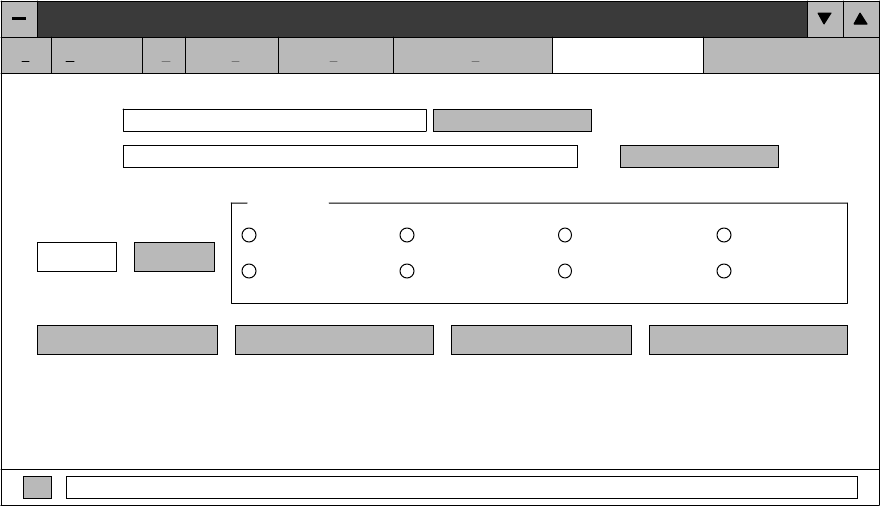
120 20170-200 ParagonPD Technical Manual19
Figure 16 - RIS main screen
4.3 Screen
The Radio Installation Software program uses
one main display screen. Referring to Figure 16,
starting from top and moving down to the bottom,
it has:
• A Button bar, containing the program’s six
main commands: Exit, Connect, Get, Get As,
Put From and Station Reset plus a Product
type field.
• A Data section, containing the Banner plus
the Comments and Password fields and their
related Put buttons.
• A Channel(s) section, grayed out in Para-
gonPD and Paragon family products.
• A Test section, containing the TXON, Flat-
ness and the Random data test buttons plus
the Ping button and its address field.
• An “i” square button, which opens up the
“About” window.
• A Status bar, for displaying standard user-
messages. Other messages appear in dialog
window boxes or in warning windows.
4.4 Functions
The RIS program is used to:
• Save an existing configuration from a unit to
a file.
• Take a configuration from a file and upload
it to a unit
• Check ParagonPD’s transmit functions
• Test and/or trouble-shoot installations
4.4.1 Configuration to a file
Saving the unit’s configuration to a file allows
the user to:
• Subsequently restore the configuration.
• Safeguard a copy as documentation of the
configuration.
Note: The configuration and status files are
ASCII files and may be e-mailed or faxed to
technical support when requested to do so.
Warning: Do NOT make any change to these
files unless called for in the trouble-shooting
section of this manual or by Dataradio’s System
Engineering or Technical Support departments.
Changing unknown parameters may render unit
inoperative.
Dataradio Radio Installation Program
Exit Get Get As Put From Station Reset VIS Products
Banner:
Comments:
Password:
Put Comments
Put Password
Channels
CHANNEL 1
CHANNEL 5
CHANNEL 2
CHANNEL 6
CHANNEL 3
CHANNEL 7
CHANNEL 4
CHANNEL 8
TXON (Modulated) TXON (Unmodulated)
Ping Address:
APing
i
Connect
Flatness test Random data test
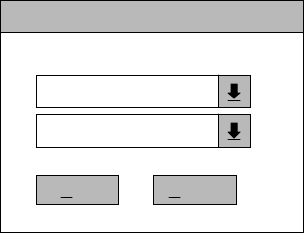
120 20170-200 ParagonPD Technical Manual20
Figure 17 - “Connect using” dialog window
4.4.1.1 Connect Button
The Connect button is used to establish the re-
quired communication link with the connected
ParagonPD unit.
1. Press the Connect button to open the “Con-
nect using ” dialog window (see above).
2. Select the appropriate COM port where the
ParagonPD’s RS-232 cable is connected on
your PC or portable computer and the port
speed (usually 19200) for the COM port
selected. This speed is independent of the
network bit rate. Bit rates from 2400 to
19200 are supported.
3. Click OK. This validates the options entered
and starts the connection sequence.
The program briefly displays pop-up window
messages as it establishes a communications link
with the equipment. Their content is not normally
user-sensitive and only denotes proper operation.
If an Error window opens, check the connections
and that the right options were selected in the
“Connect using” dialog window.
Selecting an incorrect port speed in the “Connect
using” window will result in the status bar re-
porting Connection failed!
When communication linking is complete:
• The Status bar reports Connection estab-
lished.
• All of the buttons grayed-out at startup be-
come available.
• The “Comment” and “Password” fields and
their respective Put buttons are activated.
• The product field indicates the product
model connected to.
• The Banner information is displayed.
4.4.1.2 “Get” button
After communication is established using the
Connect button, press the Get button to down-
load and automatically save the connected
BDLCPD configuration setting to a file named
with the unit's on-air address (as set at the time
of manufacture). The RIS status bar will then
report “All parameters are successfully re-
trieved and saved in file [unit's on-air ad-
dress].bp2. Any previous configuration in the
program is overwritten.
If you do not wish to overwrite an existing con-
figuration or prefer to name the file yourself, use
the Get As button.
Example: In a network using multiple BDLCPD
having a common address, using the “Get As”
button allows to uniquely name the files.
4.4.1.3 “Get As” button
After communication is established using the
Connect button, press the Get As button to:
• Open the “File, Save As” window with the
ASCII file *.bp2 (already selected).
• Save the connected BDLCPD’s operating
characteristics (configuration setting) to a
file, directory or drive of your choice.
The program will ask before overwriting an
existing file.
• Status bar reports “All parameters are suc-
cessfully retrieved and saved in [filename].
Connect using
COM1
9600
OK Cancel
120 20170-200 ParagonPD Technical Manual21
4.4.2 Configuration from a File
Loading a configuration from a file to a BDLCPD
is useful to:
• Restore the operating characteristics of a
unit (Requires intervention with technical
support.)
• Carry out field updates using Dataradio
system engineering supplied diskette(s).
Warning: Do NOT make any change to these
files unless called for in the trouble-shooting
section of this manual or by Dataradio’s System
Engineering or Technical Support departments.
Changing unknown parameters may render unit
inoperative.
4.4.2.1 “Put From” button
After communication linking is established using
the Connect button:
1- Press the Put From button on the button bar.
The program selects the bt2 filter file.
2- In the opened “File, Put From” window, lo-
cate the drive, directory and file name of the
relevant file.
• This may be a configuration saved ear-
lier from a unit.
• It can also be from a Dataradio (factory
or system engineering) diskette.
4- Select the appropriate file
5- Press the “OK” button. The status bar re-
ports: “[filename] is downloading into unit”
and up to 30 seconds later displays: “All pa-
rameters are saved. Apply Station Reset to
take effect!”.
6- Press the “Station Reset” button (unit will
beep). See the next paragraph for details.
4.4.2.2 “Station Reset” button
Press the Station Reset button as a last step after
doing a “Put From”. This action has the same
effect as when pressing the membrane switch
“Reset“ (see section 3.2.1.1.1 on page 12 for
details). Causes downloaded parameters from a
file or diskette to take effect in the connected
unit.
Pressing Station Reset is not required after doing
any Comments or Password configuration change
as these have their own Put Comments and Put
Password buttons.
Station Reset does not break the connection.
4.4.3 Special Functions
The following RIS fields and buttons are used to
gather specific information concerning the con-
nected BDLCPD:
• Banner field
• “i” button
• Comments field and Put Comments button
• Password and Put Password button
4.4.3.1 Banner Field and “i” button
This field displays a string made up of the serial
number of the connected unit followed by the
firmware(s) used and their version number.
Format For ParagonPD model is:
[on-air address]:firmware 1 name, its version #,
firmware 2 name, its version # (where name 1 is
for DSP and name 2 is for the main cpu).
ParagonPD's firmware(s) resides in flash
EPROM and are designed to allow field up-
grades.
When contacting your supplier, give the full ban-
ner string and the version of the RIS used. You
will find the version number in the “About” win-
dow. To open it, click the lower left square but-
ton (with a lowercase letter “i” in it).
The Banner field is blank prior to establishing a
link with the equipment using the Connect button.
4.4.3.2 Comments
1- Type comments directly in the “Comments”
field. These can be text up to 24 characters.
120 20170-200 ParagonPD Technical Manual22
Use this field to enter user-convenient de-
scription(s) (customer name, location,
etc…).
2- Press the button “Put Comments” to make
the entry permanent. This field may be left
blank.
On subsequent Connect, this field displays en-
tered comments. If no comment was entered, the
field will remain blank.
4.4.3.3 Password
The password feature is useful where two (or
more) fleets share the same radio channel. Mo-
biles without the proper password would still
receive the message but the contents would not
be intelligible.
1- Type your password directly in the “Pass-
word” field. It is a string of 32 hexadecimal
characters (exactly).
2- Press the button “Put Password” to make the
entry permanent. This field may be left
blank.
On subsequent Connect, this field will require
that the correct password be entered. If none was
entered, the field will remain blank.
Password information is NOT retrieved and
saved to a file, along with the configuration.
Clearing a Password is done by entering 32 zeros.
The Dataradio supplied password algorithm is
designed to thwart the casual observer only. It
provides a limited form of data privacy. There-
fore, if your security requirements are high, Da-
taradio urges you to use external encryption
technology such as Data Encryption Standard
(DES) in the Host and Mobiles computers.
4.4.4 Test Functions
The following RIS functions and buttons are
used to carry out testing or trouble-shooting on a
connected unit:
• TXON (Modulated) button
• TXON (Unmodulated) button
• Flatness test button
• Random data test button
• Ping Address and Ping button
Note:
While a button is in-use for test trans-
missions, all others are inoperative.
4.4.4.1 Channel Selection
ParagonPD uses its default radio channel. No
channel selection being available, all channels
are grayed-out.
4.4.4.2 TXON Tests
4.4.4.2.1 Unmodulated Carrier
Unmodulated carrier gives a clear carrier and is
frequently used for checking:
• Frequency error
• Forward and reflected power
Press the TXON (Unmodulated) button to trans-
mit an unmodulated test signal for 30 seconds on
its default channel or until pressed again.
The time remaining to test transmit is displayed
on the status bar.
4.4.4.2.2 Modulated Carrier
Test transmission generates a carrier modulated
with a test tone at a speed and a deviation level
that depends on network speed as detailed in
Table 8 below.
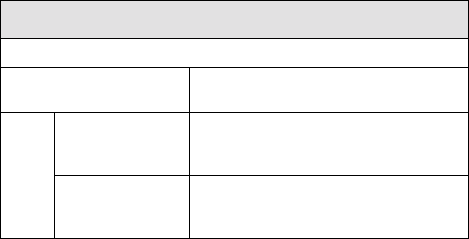
120 20170-200 ParagonPD Technical Manual23
Table 8 - Typical Carrier Modulation
Carrier Modulation
Full Channel
Network Speed
(b/s) Typical deviation in kHz
TX test tone in ( )
25600 ± 4.0
(1000 Hz)
SRRC4FSK
19200 ± 4.7
(1000 Hz)
This function is frequently used for checking
frequency deviation.
Press the TXON (Modulated) button to be-
gin transmitting a modulated test signal for
30 seconds or until pressed again.
The time remaining to test transmit is dis-
played on the status bar.
4.4.4.3 Ping Button
The Ping function checks connectivity by testing
the ability of ParagonPD to communicate with a
mobile unit by sending a short transmission
query and receiving a confirming response.
1- Specify the ping address (section 4.4.4.4)
2- Press the Ping button to start ping testing.
The time remaining to test transmit is dis-
played on the status bar.
3- The program sends a test query and contin-
ues transmitting pings at brief intervals.
As soon as a Ping test signal is returned from the
address selected, the status bar displays:
• “Ping Successful” and pinging stops.
• If no ping signal is received after 60 sec-
onds, ping testing stops and the status bar
displays “Ping Failed”.
4.4.4.4 Ping addresses
Addresses may be entered by typing directly in
the “Ping Address” field as an “Alpha-Mapped-
Nibble” (AMN) address for mobiles, consisting
of upper case letters in the range A-P. The valid
address range is A to GN (8 characters max.).
The program may display one of the following
messages on the status bar:
“Ping address is not in AMN or number format”
or
“Ping address is not in the range A – GN”
In either case, check that the address entered is
within the acceptable range, is of a valid format
and correctly typed.
4.4.4.5 Flatness test button
This complimentary feature has been added to
support the ParagonPD radio’s low-frequency
balance adjustment.
Tests generate a square wave at a frequency of
100 Hz.
Press the Flatness test button to transmit a
square wave test signal for 30 seconds or until
pressed again.
The time remaining to test transmit is displayed
on the status bar.
4.4.4.6 Random data test
Random data test transmissions are used for
checking low-frequency balance.
Refer to Table 10, at the “Low Frequency
Balance” (step 7).
Random data test requires the use of an IFR
COM-120B service monitor with option 03:
30KHz IF filter and its DC coupled demodulator
output selected.
Press the Random data test button to generate a
test signal on the channel selected for 30 seconds
or until pressed again.
The time remaining to test transmit is displayed
on the status bar.
120 20170-200 ParagonPD Technical Manual24
5. Testing and Trouble-
Shooting
The checks described below should be done at
time of installation, annual intervals or whenever
deterioration in performance is noted.
5.1 Equipment Required
• In-line watt meter (150W & 10 W ranges)
• Radio service monitor (IFR-120B with op-
tion 03: 30KHz IF filter or equivalent).
• RG-214 or RG-223 cable with N-Type male
connector to connect ParagonPD to the serv-
ice monitor.
Important note: Before proceeding make sure
that the service monitor has been calibrated
recently and has warmed up for at least the
time specified by its manufacturer.
Some reported frequency and deviation problems
have actually been erroneous indications from
service monitors that have not adequately
warmed up. This is particularly likely when field
service is done during winter months.
5.2 Recommended Checks
A) After an installation
1. LED Indications
2. Save “unit config” to a file
3. Transmitter Output Power
4. Transmitter Reflected Power
5. RF Link test between ParagonPD and mobile
unit(s)
B) For annual maintenance & trouble-shooting
Same checks as A) plus:
6. Carrier Frequency Error
7. TX Deviation
8. Low Frequency Balance
9. 12 dB SINAD
10. Receiver distortion
11. RSSI check

120 20170-200 ParagonPD Technical Manual25
Table 9 - Checklist A (after installation)
CHECKLIST A
(ParagonPD)
Recommended Check out after Installation
Step ACTION EXPECTED RESULTS at
25°
°°
°CMEASURE WITH IF NOT?
1Normal Power-up
Sequence
BDLCPD beeps once, all LEDs come ON for about four seconds, the green LEDs
then flash in a “ripple” pattern for close to two seconds. All LEDs go OFF except the
CK that should flash 6 to 8 times per second. For functions, see section 3.2.1.2
2Connect and save
unit config
Press RIS Get but-
ton
as per section 4.4.1
3Transmitter Output
Power
Press TX (Unmod)
VHF/UHF: 100 watts
800: 70 watts
+10%, -10%
Factory-settable down to
10 watts as per customer
request.
Service monitor set to
read power
or
150W in-line watt-
meter installed as
close as possible to
the unit antenna con-
nector.
1Refer to Checklist B
4Transmitter
Reflected Power
Press TXON (Un-
mod)
<5% of forward power or as
specified by Syst. Eng. 10W in-line wattmeter Check for bad connections,
damaged coax cable, etc.
5RF Link test
"Ping" a mobile “Ping Successful” as per sections
4.4.4.3
- Mobile is out of range
- Refer to factory technical
support.
1 (unless unit has been set a lower value). Note that readings less than 100 watts for VHF/UHF or 70 watts for 800 MHz models,
may be due to losses in cables used for testing. Check also your wattmeter frequency calibration curve. Do not be too ready to
condemn the transmitter or the RF feedline & antenna installation.
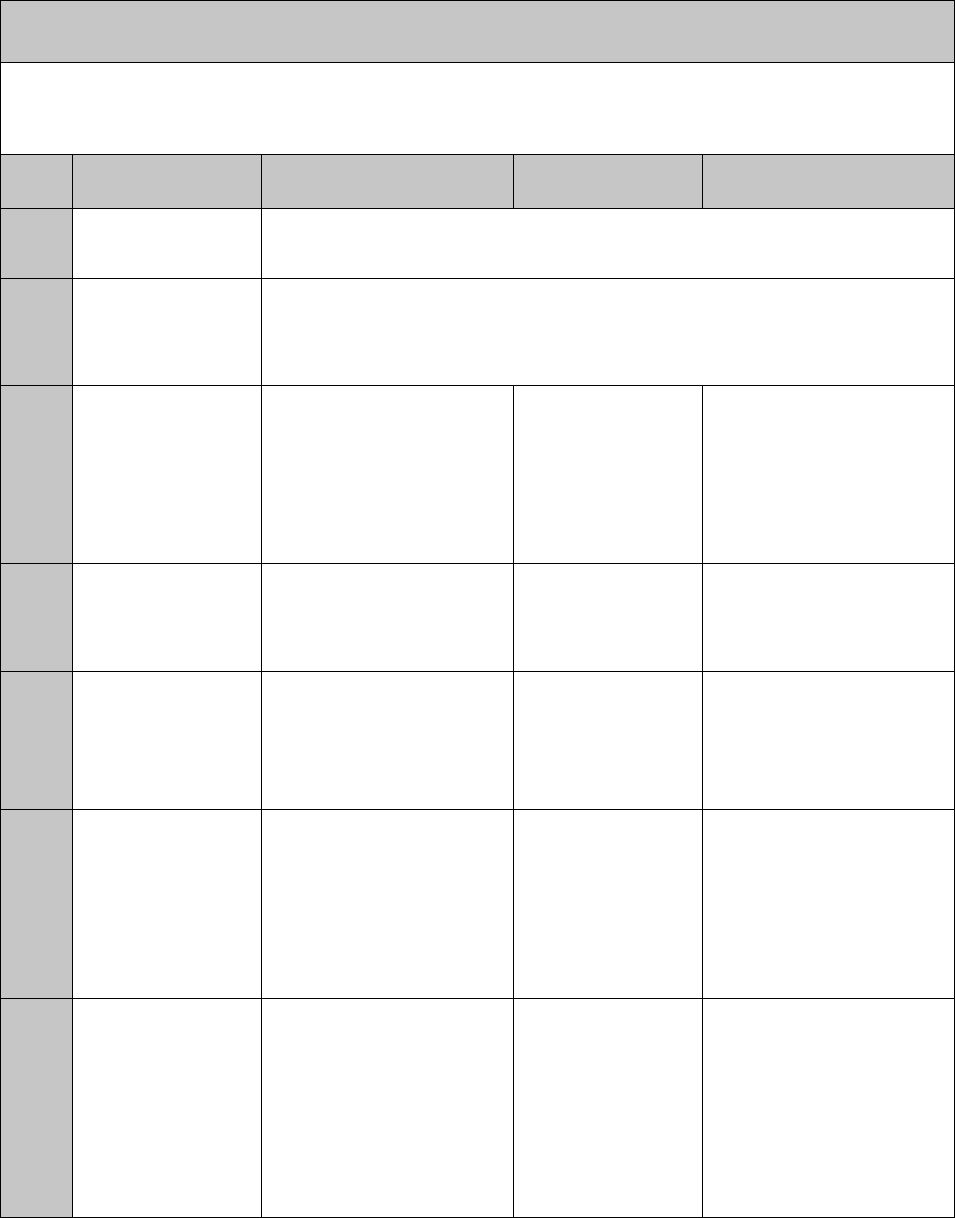
120 20170-200 ParagonPD Technical Manual26
Table 10 - Checklist B (General)
CHECKLIST B (ParagonPD)
General Check out (part1 of 2)
ParagonPD units are set and characterized at the factory to optimize performances.
It is not recommended to try readjusting units unless it is really required.
Misadjusting a unit may result in significant performance losses.
Step ACTION EXPECTED RESULTS at
25°
°°
°CMEASURE WITH IF NOT?
1Normal Power-up
Sequence
BDLCPD beeps once, all LEDs come ON for about four seconds, the green LEDs
then flash in a “ripple” pattern for close to two seconds. All LEDs go OFF except the
CK that should flash 6 to 8 times per second. For functions, see section 3.2.1.2
2Connect and save
unit config
Press RIS Get but-
ton
as per section 4.4.1
3
Transmitter Output
Power
Press TX ON (Un-
modulated)
VHF/UHF: 100 watts
800: 70 watts
+10%, -10%
Factory-settable down to 10
watts as per customer re-
quest.
Service monitor set
to read power
or
150W in-line watt-
meter installed as
close as possible to
the unit antenna
connector.
Adjust “Power” on the front
panel of the “Power Amp”
( see Figure 8)
4Transmitter
Reflected Power
Press TXON (Un-
modulated)
<5% of forward power or as
specified by Syst. Eng. 10 W in-line watt-
meter Check for bad connections,
damaged coax cable, etc.
5Carrier Frequency
Error
Press TX (Unmade) < ±300 Hz
Service monitor set
to read frequency
error
Adjust TCXO
(see inside Exciter module)
Figure 22 &
Figure 35
6TX Deviation
Press
TXON (Modulated)
Carrier will be
modulated with a 1
kHz tone.
SRRC4FSK, Full ch. unit:
25.6 kb/s: ±4.0 kHz
19.2 kb/s: ±4.7 kHz
Service monitor set
to read deviation
(IF filter set to Mid
or 30 kHz position)
Adjust according to Appendix
1 - ParagonPD Deviation
adjust on page 57
7Low Frequency
Balance
Press
TX Random data
test
a) Record deviation level
read from step 7
b) Record deviation read
from TX Random test
c) Difference between a)
and b) must be:
< 500 Hz
Service monitor set
to read deviation
(IF filter set to Mid
or 30 kHz position,
all audio filtering
disabled )
Refer to
Section 6.2.3.4 for Series I
and section 6.4.3.4 for Se-
ries II
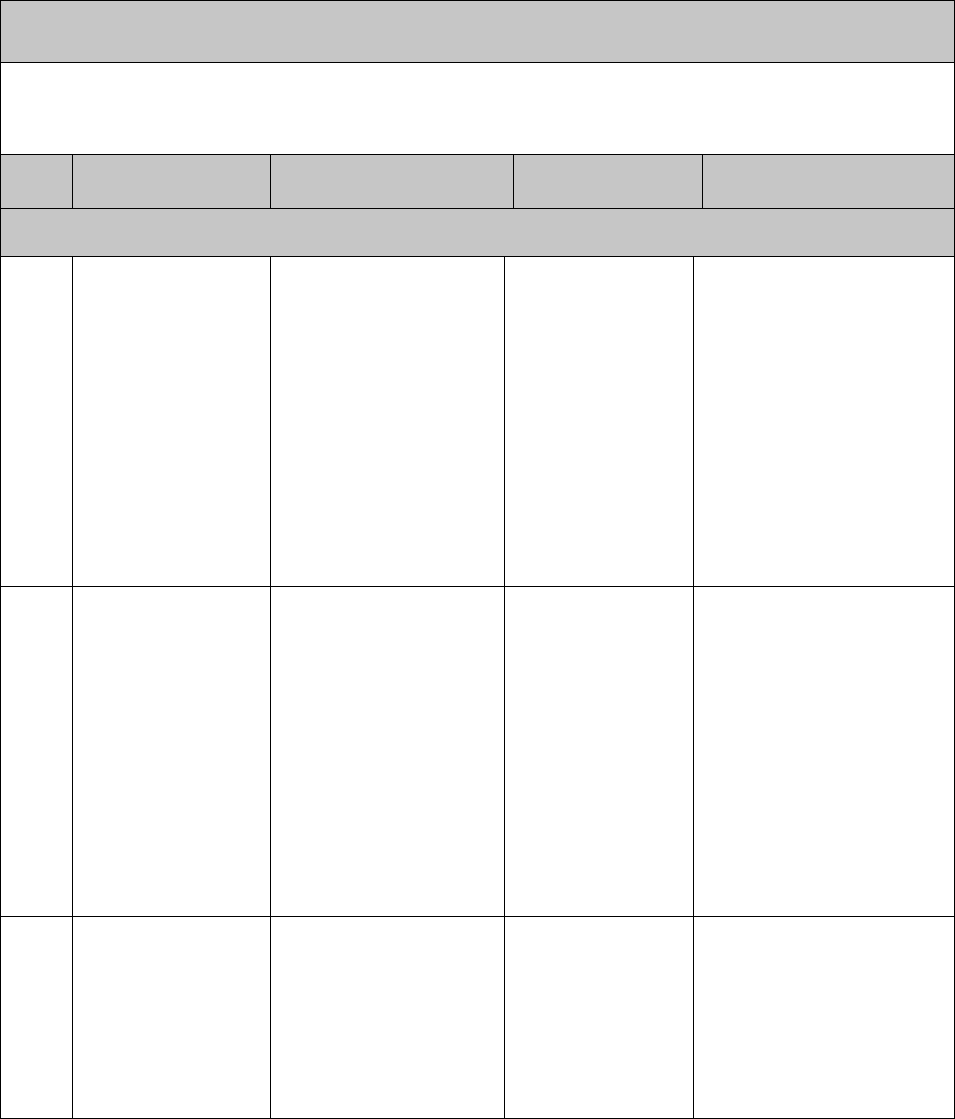
120 20170-200 ParagonPD Technical Manual27
CHECKLIST B (ParagonPD)
General Check out (part2 of 2)
ParagonPD units are set and characterized at the factory to optimize performances.
It is not recommended to try readjusting units unless it is really required.
Misadjusting unit may result in significant performance losses.
Step ACTION EXPECTED RESULTS at
25°
°°
°CMEASURE WITH IF NOT?
Set the service monitor to generate on the selected receive frequency. Verify alternately for both receivers.
The carrier should be modulated with a 1.0 kHz tone at deviation level specified below:
8
12 dB SINAD
(Dataradio wide band
measurement
method: no audio
filtering)
- For Full channel
unit, set deviation
to ±3 kHz.
- For Half channel
unit, set deviation
to ±1.5 kHz
Better than -110 dBm
(including cable loss)
- Backplane cor-
responding to
the receiver
being verified:
SK1, Pin 6 (see
Figure 30)
- Service monitor
(IFR) set to
SINAD
- IFR IF filter set
to MID position
or 30 kHz wide
filter.
Refer to section 6.2 for Series
I and to section 6.4 for Series
II
9Receiver distortion
(Dataradio wide band
measurement
method: no audio
filtering)
- Set service
monitor RF Gen
output to –70
dBm
- Deviation level
as per SINAD
above.
≤ 5.5 %
- Backplane cor-
responding to
the receiver
being verified:
SK1, Pin 6 (see
Figure 30)
- Service monitor
(IFR) set to
SINAD
- IFR IF filter set
to MID position
or 30 kHz wide
filter.
Refer to section 6.2 for Series
I and to section 6.4 for Series
II
10 RSSI
- Vary the RF level
output from –120
to –80 dBm
- Measure voltage
at each RSSI re-
ceiver ouputs
- 2VDC @ -110dBm
- 10dB/V ±0.2V
- Backplane cor-
responding to
the receiver
being verified:
SK1, Pin 5 (see
Figure 30)
- DC Voltmeter
measurement
Refer to section 6.2.2.5 for
Series I and to sections
6.4.2.5 or 6.4.2.6 for Series II
120 20170-200 ParagonPD Technical Manual28
6. Radio Programming and Adjustments
All receiver procedures detailed in this section should be done twice: once for the main receiver module
and a second time for the second receiver module. Connect to the relevant module and its corresponding
backplane PCB as required.
Both Series of ParagonPD radio module assemblies share the same backplane PCBs. Refer to section
3.1.2.1 for details. Programming for Series I is done via EPROMs while Series II uses of the RJ11 con-
nector present on the front of the Speaker panel and mirrored on both backplane boards (see section 6.3
below).
6.1 Series I 800MHz Radio Programming
This procedure describes the steps needed to program the ParagonPD’s Tait T800 Series I radio (half &
full channel) used in all ParagonPD 800 MHz versions. This procedure is a supplement to the Tait pro-
gramming procedure.
6.1.1 Recommended Items
T800win programming kit for Series I:
- PGM800Win programming software user's manual
- PGM800Win Windows based programming software
- EPROM Programmer BP MicroSystems’s model CP-1128 (suggested model)
- EPROM Programmer software BP MicroSystems’s (Version 3.08 or later)
- 27C64 EPROM (150 nanoseconds or faster)
- 486 PC or better, Ms-Windows 3.1 © or later
- Standard 25-pin parallel cable (terminated Male/Female)
6.1.2 Introduction
Before starting programming, have a PC running MS-Windows and the Tait PGM800Win software for Se-
ries I Base station. It will be needed to generate a binary file required in programming the EPROM.
This program supports the use of a mouse but may be used without one if required. Keyboard access fol-
lows the conventional MS-Windows © method as briefly described below:
- Press and hold the “Alt” key while pressing the relevant hotkey (indicated by an underlined letter on
the menu command).
- On a drop-down menu, press only the hotkey letter without pressing the “Alt” key.
- Use the “Tab” key to cycle available fields and the “Enter” key to validate entries. E.g. Pressing
“Alt”+F opens the File drop-down menu and pressing “A” opens the Save As directory service box.
For full description of the programming procedure, refer to the T800 Programming Software User’s Man-
ual.
• Receiver VCO and front-end alignment will be required when new receiver frequency is programmed
outside the radio tuning range: ± 3 MHz from previous center frequency.
• Exciter alignment will be required when new transmitter frequency is programmed outside the radio
tuning range: ± 4 MHz from previous center frequency.
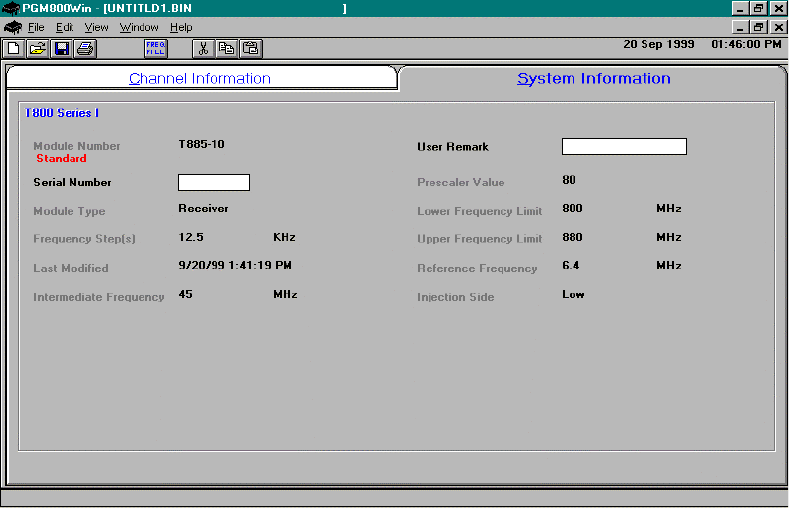
120 20170-200 ParagonPD Technical Manual29
6.1.3 File Creation
1. In WIN 3.x: Start by clicking on File, then on Run, type the path or browse to select the Tait pro-
gram, click OK to run PGM800Win executable program.
In WIN 9x: click on Start, then on Run, type the path or browse to select, click OK to run
PGM800Win.
2. In the Tait program’s Menu bar, click on “View”. On the drop-down menu, make sure that a check
mark is present in front of the “T800 EPROM” option. If not, click this option to activate it and
click on “View” again to verify that a check mark is now present.
3. Select File, New and choose the relevant unit model to program. Click on OK. The program dis-
plays a dual-tabbed virtual file folder.
4. Click the System Information tab; enter the unit’s serial number in the relevant field.
In the User Remarks field, you may enter user comments as required (up to 16 characters). Use as
a notepad (customer name, location, technical info etc...). Refer to Figure 18.
Click the Channel Information tab; click the relevant frequency field to make it active and type in
the required channel number in the frequency field. Refer to Figure 19
Figure 18 - Series I Receiver System Information
Warning:
DO NOT enter anything in the CTCSS fields. If there is already something in any of
those fields, erase their content(s). The indication should be 00.0
5. Select File, Save As. Enter an appropriate name in the “Filename” field. Always use the suffix
.bin for these binary files. Choose the relevant drive and directory to save under and click on OK.
6. Repeat file creation procedure for the Exciter, the main receiver and for the diversity receiver
modules as required.
7. Select File, Exit to leave the program.
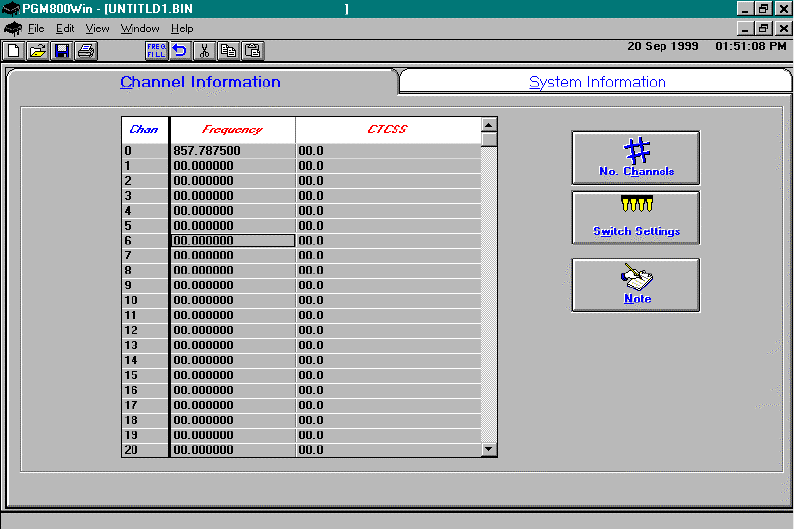
120 20170-200 ParagonPD Technical Manual30
Figure 19 - Series I Channel Information
6.1.4 Programming the EPROM
Connect a straight 25-pin ribbon parallel cable between the PC’s LPT1 port and the EPROM programmer.
Apply power to it.
At the DOS prompt, type bp.exe to open the EPROM program software.
ParagonPD uses three 27C64 EPROMs (150 nanoseconds or faster) in the Exciter and Receivers modules.
Repeat the following procedure for each EPROM as needed.
Carefully grasp between thumb and index the 27C64 EPROM chip to be tested and gently insert it with a
rocking motion in the EPROM Programmer socket until well seated.
Navigate the programmer’s screen using the keyboard directional arrows. The left and right keys move
through the available options and the up and down arrows select the function.
1. Move to and select “Buffer”
2. In the sub-menu, move to and select “Load”
3. Press ENTER
4. In the opened box, type in the directory path where the file created in paragraph 6.1.3 above is lo-
cated. In the list of filenames, move to the appropriate file and press ENTER once to complete the
selection and press ENTER a second time to load the file. This closes the directory service box.
The message “Load successful” displays until directional arrows are pressed again.
5. Move to and choose “Select”
6. Press ENTER
7. A selection box opens, in the “Device Selector:” field, type M27C64A. Move to and choose the
brand of EPROM. Press ENTER to close the selection box. The program is now ready to config-
ure the EPROM and the name of the device is displayed at the bottom of the screen.
8. Move to and select “Device”
120 20170-200 ParagonPD Technical Manual31
9. In the now opened sub-menu, move to and select “Program”.
10. Press ENTER. The program loads the binary file into the EPROM (approximately fifteen sec-
onds). The message “Function complete” displays until directional arrows are pressed again. *
11. Move to and select “Buffer”
12. In the now opened sub-menu, move to and select “Clear”
13. Press ENTER. The program displays at the bottom of the screen: “All buffers cleared”
14. Press ENTER
15. Move to and select “Quit”
16. Press ENTER
17. Remove configured EPROM from the EPROM Programmer
* If an “Error” message (and warning beep) appears during the procedure, it normally
indicates improper erasure of the EPROM. Replace it with a fresh one and start from
the beginning. The removed EPROM will need to be cycled through an EPROM
eraser.
6.1.5 EPROM Installation
Warning
Always use a grounding strap and wear an anti-static bracelet when working with sensitive cir-
cuitry or components susceptible to static discharge or transients damage.
1. Remove power to the radio
2. Unscrew #1 Pozidriv screw on the front panel to slide out the module.
3. Unscrew the fourteen #2 Pozidriv screws on the handle side and remove cover.
4. Using a small flat-bladed screwdriver, carefully slide the blade between the EPROM socket and
the chip (IC1) itself. Gently pry the chip away from its base and remove. The removed EPROM
will need to be cycled through an EPROM eraser. Refer to Figure 21 on page 38.
5. Install the appropriate EPROM by carefully grasping the chip between thumb and index and gently
inserting it with a rocking motion in its socket until well seated.
6. Select the channel configured in the EPROM as detailed in the next section.
6.1.6 Channel Selection via DIP Switches
Channel selection is done via DIP switches inside each module.
Example: To select channel 5, the DIP switch settings are as shown in Figure 20 below.
Notes:
- For channel 1 (one), switch #1 must be OFF and switches #2 through #7 must be ON.
- Always have switch #8 set to OFF.
- The EPROM and DIP switches locations are identical in both receiver and exciter modules (refer to
Figure 21 and to Figure 22.
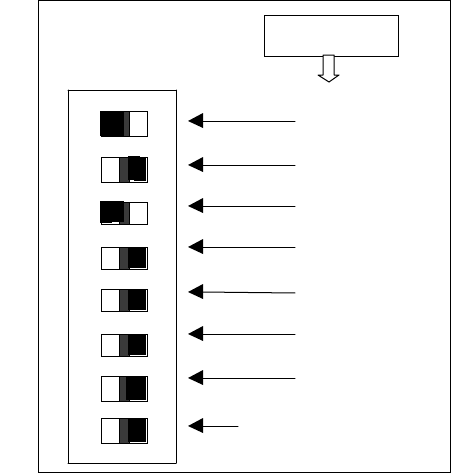
120 20170-200 ParagonPD Technical Manual32
Figure 20 - Channel Selection via DIP switches
6.2 Series I 800MHz Radio Tuning
This section covers some basic tuning and verification for the 800 MHz Series I base station modules.
6.2.1 Test Equipment
You will need the following test equipment:
- Digital multimeter and probes (e.g. Fluke 77)
- Digital or analog calibrated Oscilloscope (X1, X2 selectable)
- Calibrated COM-120B (with .001ppm TCXO and 30kHz IF options)
- 3 feet long double shielded N-M to BNC-M cable (RG-214 or RG-223)
- 2x 'BNC' to 'N' type adapters (e.g. Amphenol, Greenpar).
- Bird RF power meter with 150W / 50 ohm dummy load (optional)
- 1x Torx screwdriver #10
- Pozidriv screwdriver #1 & #2
- 1x six-inch adjustable wrench
- RF tuning/trimming tools.
- Extender Rail Kit for Series II chassis (T800-13-0000)
- 1x 6" coax cable N-M to BNC-M (provided with the ParagonPD to connect the exciter to the PA)
1
2
3
4
5
6
7
8
O
F
F
S
W
Binary Value
1
2
4
8
16
32
64
Always ON except when
default channel is required
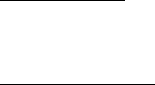
120 20170-200 ParagonPD Technical Manual33
6.2.2 Receiver Module (T885)
Note 1: Refer to Figure 21, page 38 for locating tuning controls
Note 2: When the synthesizer is unlocked, the front panel green LED called "Supply" will be flashing
showing that it needs to be re-tuned.
6.2.2.1 Initial Setup
This initial setup will be used during each receiver alignment procedures that follow:
1. Remove the receiver (T885) module from the ParagonPD rack frame
2. Remove the receiver top cover (nearest the handle).
3. Connect the ParagonPD extender Rail kit between the RX module and the empty chassis re-
ceiver slot.
4. Set the multimeter to read DC Volts.
5. Apply power to the ParagonPD.
6.2.2.2 Synthesizer Alignment
Single channel: Connect the multimeter to the long lead of L1 in the VCO (this measures the syn-
thesizer loop voltage). Tune VCO trimmer C6 for a synthesizer loop voltage of 7V
(working range is between 3V to 10V).
Multiple channels: Select the middle channel via the EPROM PCB DIP switch.
Adjust the VCO loop to 7V.
All channels should lie within the upper and lower limits of 10V and 3V respectively.
6.2.2.3 Front-End Alignment
1) IFR COM120B settings:
a) Connect a 3 feet long double shielded cable (N-M to BNC-M) between the IFR T/R output
and the receiver antenna connector.
b) Select the generator mode (GEN button) and set to the main receiver channel frequency
c) Select and turnon GEN2
d) Set the FM Deviation to ±3kHz (full channel) or ±1.5kHz (half channel) using 1 kHz sine
e) Select SINAD meter
2) Monitor the SINAD by connecting an X1 scope probe to the Demod O/P test point (close to
PL103 in the first section from the module front panel) or on the relevant backplane board at SK1
pin 6 (see Figure 30 for test point location).
3) Adjust the helical resonators #H1 to #H3 for best SINAD.
4) Continually decrease the RF level to reach 12dB SINAD, then re-do steps 3) and 4) again. (mini-
mum requirement to reach is 12 dB SINAD for –110 dBm)
5) Perform the SINAD linearity tests described in the next paragraphs below. If it fails to pass the
requirement, contact your Dataradio technical support.

120 20170-200 ParagonPD Technical Manual34
WARNING: Do not attempt to re-tune the IF stages (i.e. L312 to L318).
These adjustments do not need to be re-adjusted after frequency re-programming.
Touching these coils will have a direct impact on the DSP modem coefficient settings
and may significantly reduce the radio performances over data.
6.2.2.4 SINAD and Linearity Check
1. Apply the following settings to the IFR:
- Generator mode, Output T/R
- IFR TX frequency to match the main radio RX frequency
- Filter set to wide band (no audio filter)
- Select Gen2 (Modulating tone fixed to 1KHz). All other Gen must be off, except for “wide-
band”.
- Set deviation to ±3.0KHz for full channel or ±1.5KHz for half channel radios.
2. Lower the RF level to get a 12dB SINAD reading. Level must be better than -110dBm (including
cable loss).
3. Offset the IFR TX frequency 2KHz (full channel) or 1kHz (half channel) above the main radio RX
frequency, record the SINAD reading. It should remain within 1.5dB from the on frequency
SINAD reading.
4. Offset the IFR TX frequency 2KHz (full channel) or 1kHz (half channel) below the main radio RX
frequency, record the SINAD reading. It should remain within 1.5dB from the on-frequency
SINAD reading.
Note:
If one of the above requirements is not met, try to re-tune the front-end. If it is still “failed”,
contact your Dataradio technical support.
6.2.2.5 RSSI Adjustment
Note: This check is only recommended for ParagonPD model running DBA protocol 3.06.009 series or
later.
1. Apply an on-channel signal from the RF generator at a level of -110dBm with deviation of ±3kHz
(full channel) or ±1.5kHz (half channel) at 1kHz tone.
2. Adjust RV301 (RSSI level) to give 2.0V RSSI output when measured with a multimeter at SK301
pin 2 or on the relevant backplane board at SK1 pin 5 (see Figure 30 for test point location).
3. Vary the RF level in 10dB steps and check that the RSSI output voltage changes at a rate of a
10dB/V (±0.20VDC) over the range of –120dBm to –80dBm. If the requirement cannot be
reached, contact your Dataradio technical support.
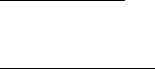
120 20170-200 ParagonPD Technical Manual35
6.2.3 Exciter Module (T881)
Note 1: Refer to Figure 22 on page 39 for locating tuning controls.
Note 2: When the synthesizer is unlocked, the front panel green LED called "Supply" will be flashing
showing that it needs to be re-tuned.
6.2.3.1 Initial Setup
1. Shut down power to the base station
2. Prepare the multimeter to read DC Volts.
3. Remove the exciter (T881) module from the base station rack frame
4. Remove the exciter top cover (nearest the handle).
5. Connect the ParagonPD Extender Rail kit between the exciter module and the empty chassis exciter
slot.
6. Connect a 3 feet long double shielded cable (N-M to BNC-M) between the IFR T/R output and
the exciter antenna connector.
7. Apply power to the base station
6.2.3.2 Synthesizer Alignment
Single channel: Connect the multimeter to the long lead of L1 in the VCO (this measures the syn-
thesizer loop voltage). Tune VCO trimmer C6 for a synthesizer loop voltage of 7VDC.
Multiple channels: Adjust the VCO loop to 7V using the middle frequency channel.
All channels should lie within the upper and lower limits of 10V and 3V respectively.
Note: Normally, the fast TX key option is installed and the synthesizer is always energized.
Where that option was not fitted, key the transmitter by pressing the front panel Carrier
button to make the above adjustment possible.
6.2.3.3 TX Frequency Error Adjustment
1. Apply the following settings to the IFR:
- Receiver mode
- IFR RX frequency to match the main radio TX frequency
- IF Filter (BW) set to 30KHz
- Zoom the RF Error window: select 10Khz range
2. Key the transmitter by pressing the front panel TX-key button and measure the carrier output fre-
quency. It should be within ±300 Hz. If it is not, adjust the TCXO to trim to meet the requirement,
preferably within 100Hz.
120 20170-200 ParagonPD Technical Manual36
6.2.3.4 Low Frequency Balance Adjustment
1. Apply the following settings to the IFR:
– Receiver mode and Oscilloscope display (Source: Demod Out Connector).
– IFR RX frequency to match the radio transmit frequency
– IF Filter set to 30KHz
– Zoom the Deviation window: select 10kHz Range and DC coupling.
2. Select the active or, the lowest (in the case of multi-channel base) frequency channel (via dip
switch)
3. Transmit a square wave by pressing the BDLCPD’s PF1 button and following the procedure out-
lined in section 3.2.1.1.2.2 or run on another computer the RIS program and press the Flatness test
button. Adjust RV-105 (REF MOD) close to the microphone connector, for best wave shape; no
damping, no overshoot. Record the deviation read.
4. If transmission has not ended by itself, press PF1 or RIS’ Flatness test button again to stop it. For
single-channel unit, proceed to step 7.
5. For multi-channel unit, select the highest frequency channel. Transmit a square wave by pressing
the BDLCPD’s PF1 button and following the procedure outlined in section 3.2.1.1.2.2 or run on
another computer the RIS program and press the Flatness test button. Record deviation again.
6. The difference in deviation between the two channels should be less than ±300 Hz. If not, re-
adjust RV105 to "average" the square wave shape on both channels until the spec is met.
7. To confirm the adjustment, select the active, or the lowest frequency channel. Compare the devia-
tion produced between:
- TX ON (Modulated) and
- Random data tests,
The difference should be lower than 300 Hz. For multi-channel unit, repeat this step on the highest
frequency channel.
8. Select the active channel. Transmit a TX ON (Modulated) adjustment tone by pressing the
BDLCPD’s PF1 button and following the procedure outlined in section 3.2.1.1.2.2 or run on an-
other computer the RIS program and press the TX ON (Modulated) button. Make sure that devia-
tion level read on the IFR correspond to model and bit rate in use (see Table 8 - Typical Carrier
Modulation). Re-adjust deviation as necessary referring to Checklist B - page 26.
6.2.3.5 Exciter Power Output
1. Apply the following settings to the IFR:
- Receiver mode, Output T/R
- IFR RX frequency to match the main radio TX frequency
- IF Filter set to 30KHz
- Select auto range in the Power reading window
- Connect the coaxial cable from the IFR T/R to the Exciter output connector
2. Key the Exciter by pressing the module PTT button. The output power must be:
- 800 MHz (T881) = 5W ±300mW.
3. If 5Watts is not reached, adjust helical #L300 for maximum power output (which should be at
least 7W); adjust RV356 down to 5W.
120 20170-200 ParagonPD Technical Manual37
6.2.4 Power Amplifier Module (T889)
1. Re-install the exciter module into the Paragon rack frame
2. Connect the Exciter module to the Power Amplifier
3. Connect the Power Amplifier output to the IFR T/R connector or to a stand-alone BIRD style power
meter, terminated with a 150W dummy load.
6.2.4.1 Power Amplifier Power Out
1. Set RV63 (Power adjustment, access on the front panel) fully clockwise.
2. Key the transmitter from the exciter Carrier button. The power output should exceed 90W.
3. Adjust RV69 (Driver power, access from the left end side) until the output power drops to 90W.
4. Adjust RV63 (Power) to reduce power output to its nominal value (70W) or lower as required.
5. Cable loss should be included in the reading.
6.2.4.2 Forward Power Alarm Level
1. Power up the T889 and adjust RV63 (Power) so that the output power is at the alarm level re-
quired, usually 20% lower than nominal value (e.g. 40W if the PA normally operates at 50W).
2. Adjust RV48 (Forward power Alarm set) so that the forward power alarm LED lights.
3. Adjust RV63 (Power) for the normal operating power level.
6.2.4.3 Reverse Power Alarm Level (Optional)
1. Power up the T889 and adjust RV63 (Power) for the normal operating power level.
2. Place a known mismatch of the required value (e.g. 3:1 VSWR) and adjust RV52 (reverse power
alarm set) so that the reverse power alarm LED lights.
Example: A VSWR of 3:1 can be simulated by connecting an undetermined 3 dB pad to the PA output.
This will result in a loss of 6 dB.
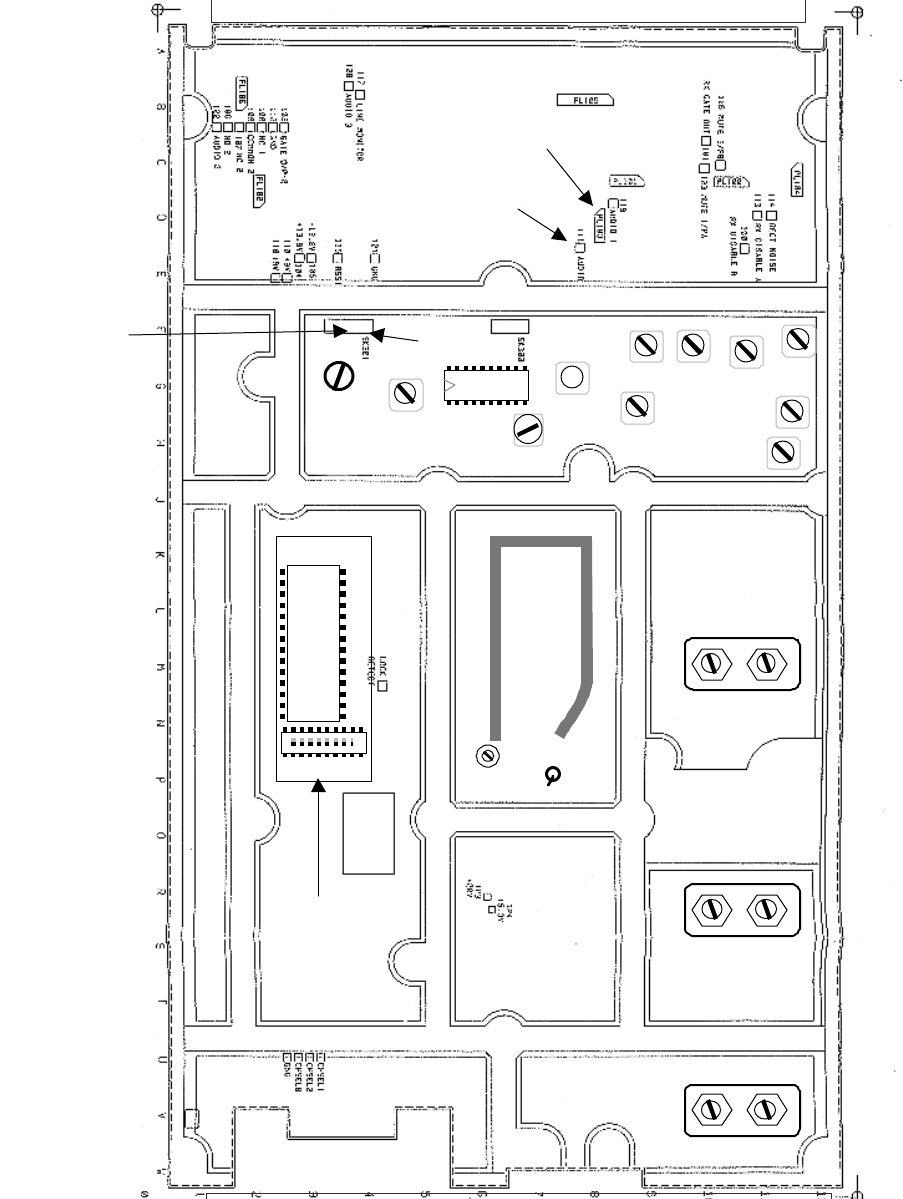
120 20170-200 ParagonPD Technical Manual38
Figure 21 - T885 Receiver tuning control location
RSSI Test point:
SK301 pin 2
Demod
output
PL103
CHANNEL
SELECTION
L312
L313
L314
L315
L316
L318
L319
L317
L321
L320
H1
H2
H3
C6
L1
IC1
12345678
FRONT
RSSI
SET
RV301
IC301
SK301
Pin 1
TCXO
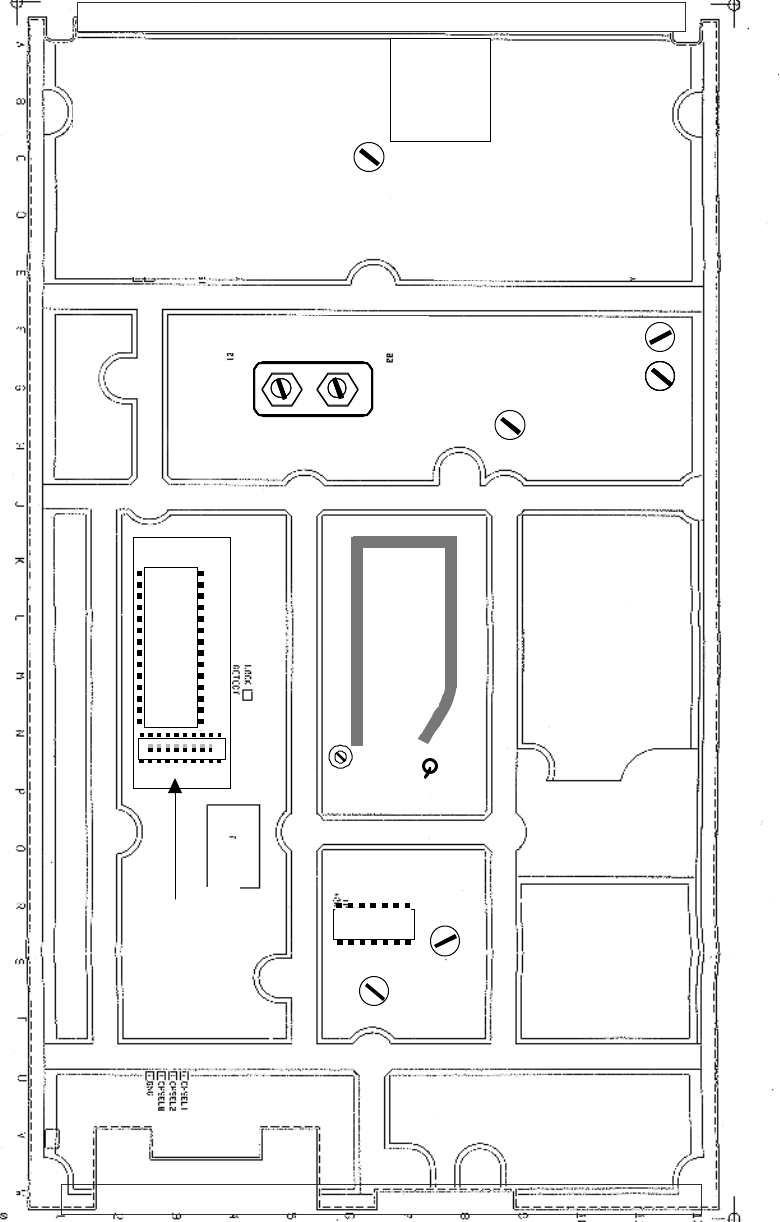
120 20170-200 ParagonPD Technical Manual39
Figure 22 - T881 Exciter tuning controls location
#L300
C6
L1
IC1
12345678
BACK
FRONT
TCXO
IC202
#L300
Temp
control
Hi-Temp
adjust
Power
Adjust
RV356
Tail
Timer
Tx Timer
Micro-phone
connector
Ref
Mod
RV105
CHANNEL
SELECTION
120 20170-200 ParagonPD Technical Manual40
6.3 Series II Radio Programming
This procedure describes the steps needed to program the UHF & VHF model that uses the ParagonPD
base station radios (half & full channels).
6.3.1 Recommended Items
- 486 PC or better, MS-Windows 3.1 © or later
- T800win programming kit for Series II:
- PGM800Win programming software user's manual
- PGM800Win Windows based programming software
- T800-01-0002 programming cable (DB-25 to RJ-45 cable)
- Standard 25-pin parallel cable (terminated Male/Female)
120 20170-200 ParagonPD Technical Manual41
6.3.2 Module Programming
Before starting programming, have a PC running MS-Windows © and the Tait PGM800Win soft-
ware for Series II Base station.
This program supports the use of a mouse but may be used without one if required. Keyboard
access follows the conventional MS-Windows © method as briefly described below:
- Press and hold the “Alt” key while pressing at the same time the relevant hotkey as indicated
by an underlined letter on the menu command.
- On a drop-down menu, press only the hotkey without pressing the “Alt” key.
- Use the “Tab” key to cycle available fields and the “Enter” key to validate entries. E.g.
Pressing “Alt”+F opens the File drop-down menu and pressing “A” opens the Save As di-
rectory service box.
Receiver VCO and front-end alignment will be required when new receiver frequency is pro-
grammed outside the radio tuning range:
UHF = ± 2.5 MHz from previous center frequency.
VHF = ± 1.5 MHz from previous center frequency.
Exciter and PA alignment will be required when new transmitter frequency is programmed outside
the radio tuning range:
VHF & UHF= ± 4 MHz from previous center frequency.
1. Connect the PC, via the supplied programming lead, to the speaker panel’s front-mounted
RJ11 connector.
2. Run Tait PGM800Win program and follow instructions found in the T800 Programming Soft-
ware User’s Manual to select the proper module to be programmed.
3. Program required channel's frequencies.
– Do not program any CTCSS tones on channels.
– Do not change any other parameters.
– Refer to Figure 23, Figure 24, Figure 25 and Figure 26 for screen program examples.
4. Save the base station programming info to a file for further reference.
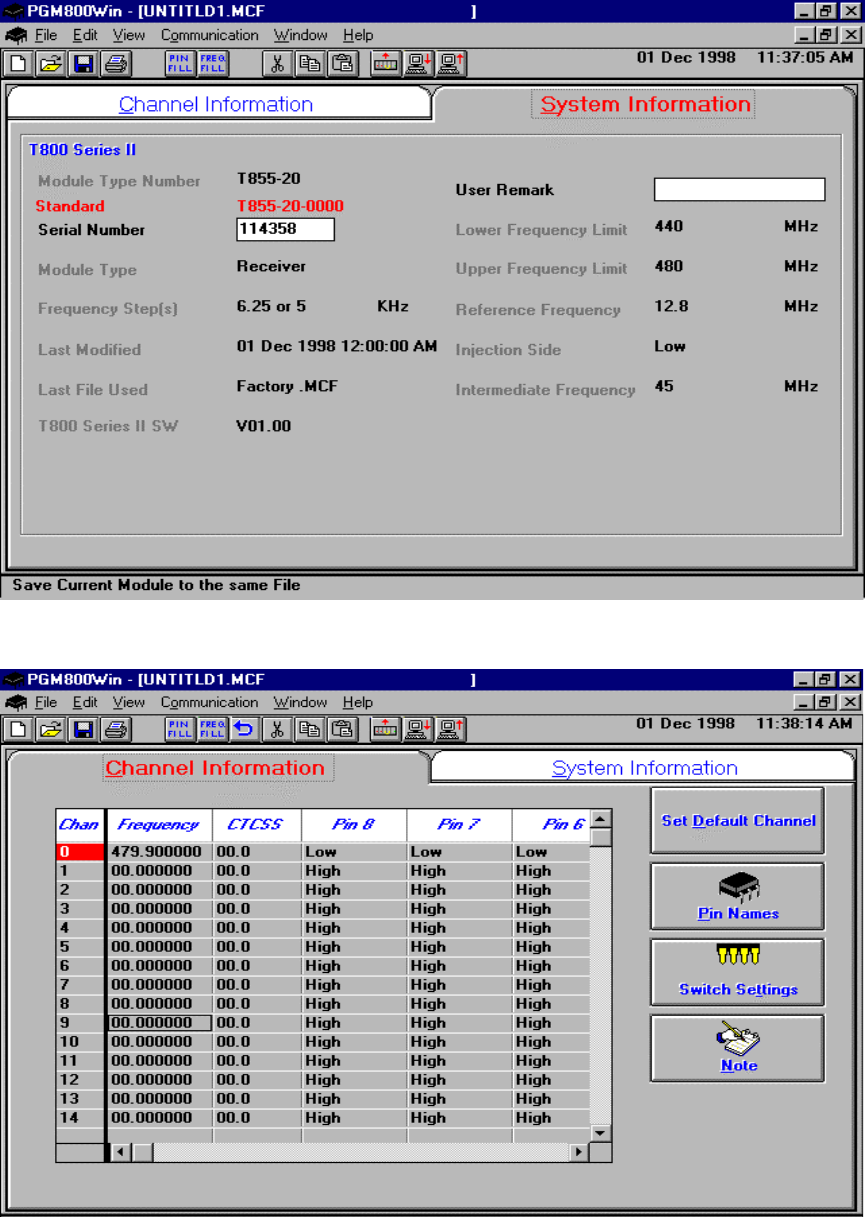
120 20170-200 ParagonPD Technical Manual42
Figure 23 - Receiver System Information
Figure 24 - Receiver Channel Information screen
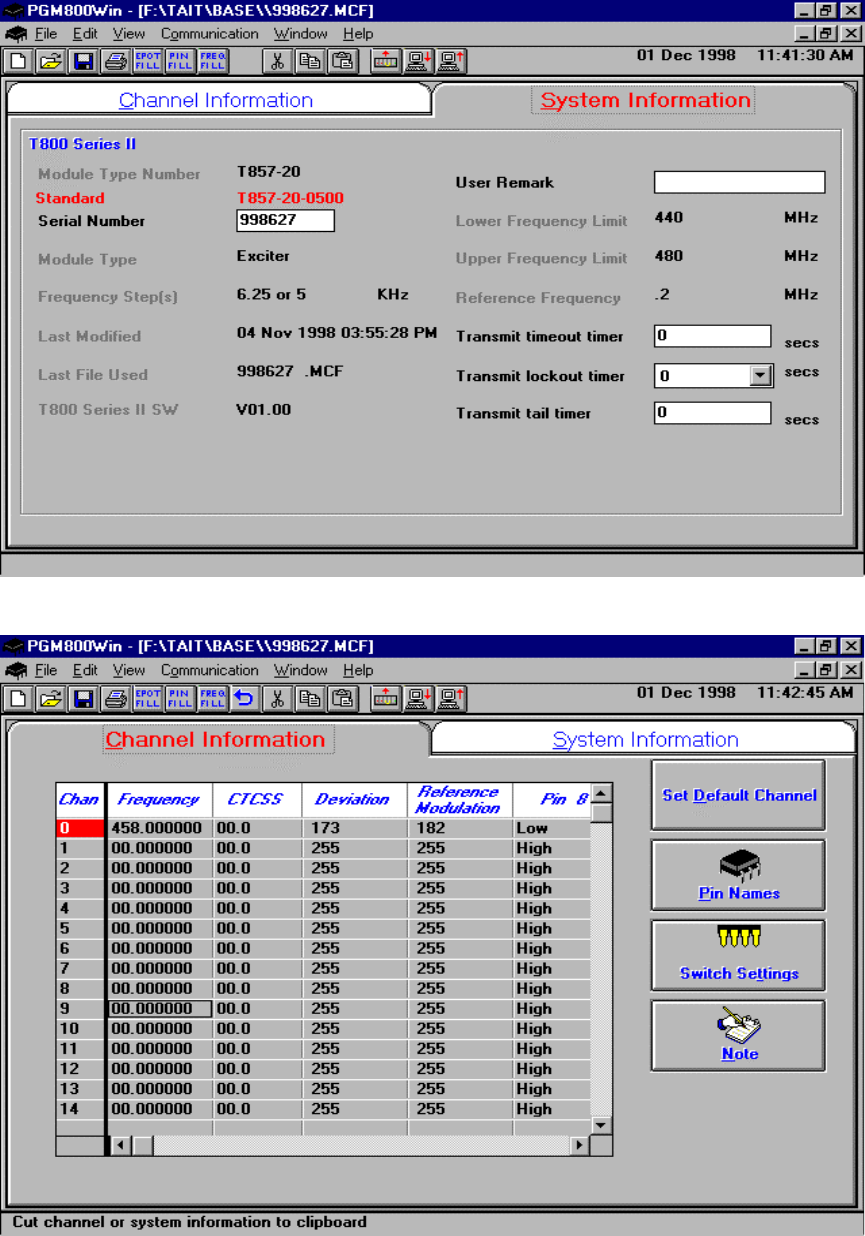
120 20170-200 ParagonPD Technical Manual43
Figure 25 - Exciter System Information screen
Figure 26 - Exciter Channel Information screen
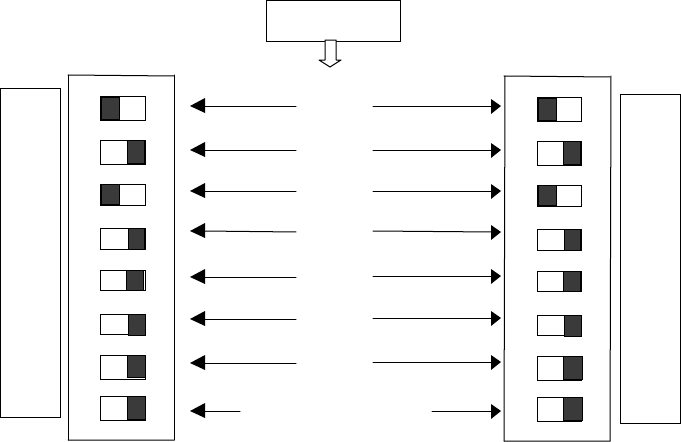
120 20170-200 ParagonPD Technical Manual44
6.3.3 Channel Selection via DIP Switches
The backplane-mounted DIP switch settings override the default channel programmed by
PGM800Win.
To set a default channel via the software, all DIP switches must be set to “OFF” (i.e. 00000000).
When a switch is “Off”, its binary count is active; when a switch is “ON” its binary count is inac-
tive.
The various DIP switch combinations of ON or OFF make up a binary total, which identifies the
channel number. To select a channel, set the appropriate DIP switch or switches to “OFF” to make
the binary count total the channel number you want. Set all other switches to “ON”.
It is recommended to set both SW1 (RX) and SW2 (TX) to the same settings.
Example: To select channel 5, set the DIP switches as shown in below:
Figure 27 - Backplane DIP switches example - Channel 5 selected
Binary Value
1
2
4
8
16
32
64
Always ON except when
default channel is required
CHANNEL SWITCH TX
CHANNEL SWITCH RX
1
2
3
4
5
6
7
8
O
F
F
1
2
3
4
5
6
7
8
O
F
F
120 20170-200 ParagonPD Technical Manual45
6.4 Series II Radio Tuning
This section covers some basic radio tuning and verification for VHF (T83x-xx) and UHF (T85x-
xx) Series II base station modules.
6.4.1 Test Equipment
- Digital multimeter & probes (e.g. Fluke 77)
- 1 HP 34330A Shunt 30A (UHF only, used for transmitter current measurement)
- Digital or analog calibrated Oscilloscope & scope probes (X1, X2 selectable)
- Calibrated COM-120B (.001ppm TCXO and 30kHz IF options)
- 3 feet long double shielded N-M to BNC-M cable (RG-214 or RG-223)
- 2x 'BNC' to 'N' type adapters (e.g. Amphenol, Greenpar).
- Bird RF power meter with 150W / 50 ohm dummy load (optional)
- 1x Torx screwdriver #10
- Pozidriv screwdriver #1 & #2
- 1x Six inch adjustable wrench
- RF tuning/trimming tools.
- Extender Rail Kit for Series II chassis (T800-13-0000)
- 1x 6" coax cable N-M to BNC-M (comes with the radio to connect the exciter to the PA)
6.4.2 Receiver module (T855 & T835)
Note 1: Refer to Figure 32 (T855) and to Figure 34 (T835) for locating tuning controls.
Note 2: When the synthesizer is unlocked, the front panel green LED called "Supply" will flash
indicating that it needs re-tuning.
Warning,
The LED will also flash when the unit is in setup mode while connected to the
PGM800win program.
6.4.2.1 Initial Setup
This initial setup will be used during all receiver alignment procedures described below:
1. Remove the receiver (T855 or T835) module from the ParagonPD rack frame
2. Remove the receiver top cover (nearest the handle).
3. Connect the ParagonPD Extender Rail Kit for Series II to the empty chassis receiver slot.
4. Prepare the multimeter to DC Volts.
5. Apply power to the ParagonPD.
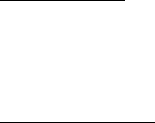
120 20170-200 ParagonPD Technical Manual46
6.4.2.2 Synthesizer Alignment
Single channel: Connect the multimeter to the long lead of L1 in the VCO (this measures the syn-
thesizer loop voltage).
1. T855 (UHF) Tune VCO trimmer C6 for a synthesizer loop voltage of 10V DC.
2. T835 (VHF). Tune VCO trimmer CV1 for a synthesizer loop voltage of 9VDC.
Multiple channels:
1. T855 (UHF) Adjust the VCO loop to 10V using the middle channel.
2. T835 (VHF) Adjust the VCO loop to 9V using the middle frequency channel.
3. All channels should lie within the upper and lower limits of respectively
All channels should lie within the upper and lower limits of 16V and 3V respectively for the T855
and within 13V and 5V for the T835.
6.4.2.3 Front-End Alignment
1. IFR COM120B settings:
a) Connect a 3 feet long double shielded cable (N-M to BNC-M) between the IFR T/R out-
put and the receiver antenna connector.
b) Select the generator mode (GEN button) and set to the main receiver channel frequency
c) Select and turnon GEN2
d) Set the FM Deviation to ±3kHz (full channel) or ±1.5kHz (half channel) using 1KHz sine
e) Select SINAD meter
f) Use a X1 scope probe connected to SINAD input and monitor the Discriminator O/P on
the backplane at SK1 pin 6 (RX-audio1). Alternately, it is also possible to monitor at the
receiver TP314 (T855) or at the receiver IC350 pin 7 (T835).
2. Adjust the helical resonators for best SINAD: #FL410 and #FL420 (T855) or L410, L420,
L460 and L470 (T835).
3. Continually decrease the RF level to reach 12dB SINAD, then re-do step 2) & 3) again.
(minimum requirement to reach is 12dB SINAD for -110dBm)
4. Perform the SINAD linearity tests described in paragraph 6.4.2.4. If it fails to pass the re-
quirement, contact your Dataradio technical support.
WARNING: Do NOT attempt to re-tune the IF stages
(i.e. L310 to L390 for T855, CV318 or L330 to L360 for T835).
These adjustments do not need to be re-adjusted after frequency re-
programming. Touching these coils will have a direct impact on the modem
DSP coefficient settings and may reduce significantly the radio performances
over data.
6.4.2.4 SINAD and Linearity Check
1. Apply the following settings to the IFR:
a) Generator mode, Output T/R
b) IFR TX frequency to match the main radio RX frequency
c) Filter set to wide band (no audio filter)
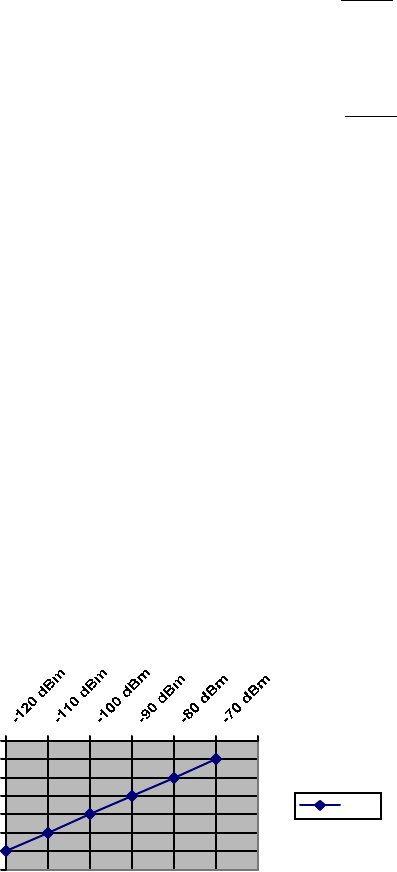
120 20170-200 ParagonPD Technical Manual47
d) Select Gen2 (Modulating tone fixed to 1KHz). All other Gen must be off.
e) Set deviation to ±3.0KHz for full channel or ±1.5KHz for half channel radios.
f) Use a X1 scope probe connected to IFR SINAD input and monitor the Discriminator O/P
on the backplane at SK1 pin 6 (RX-audio1). Alternately, it is also possible to monitor at
the receiver TP314 (T855) or at the receiver IC350 pin 7 (T835)
2. Lower the RF level to get a 12dB SINAD reading. Level must be better than -110dBm (in-
cluding cable loss).
3. Offset the IFR TX frequency 2kHz (full channel) or 1kHz (half channel) above the main radio
RX frequency, record the SINAD reading. It should remain within 1dB from the on frequency
SINAD reading. For T855, use above values, for T835 use 1.5kHz (full channel) or 0.8kHz
(half channel).
4. Offset the IFR TX frequency 2KHz (full channel) or 1kHz (half channel) below the main radio
RX frequency, record the SINAD reading. It should remain within 1dB from the on-frequency
SINAD reading. For T855, use above values, for T835 use 1.5kHz (full channel) or 0.8kHz
(half channel).
Note: If one of the above requirements is not met, try to re-tune the front-end. It
still failed, contact your Dataradio technical support.
6.4.2.5 RSSI Adjustment (UHF: T855)
Note: This check is only recommended for Paragon/R model running DBA protocol 3.06.009
series or later.
- Apply an on-channel signal from the RF generator at a level of -110dBm with deviation of
±3kHz (full channel) or ±1.5kHz (half channel) at 1kHz tone.
- Adjust RV320 (RSSI level) to give 2.0V RSSI output at SK330 pin 2 or on backplane SK1 pin
5 when measured with a voltmeter (See Figure 30).
- Vary the RF level in 10dB steps and check that the RSSI output voltage (SK1 pin5) changes at
a rate of a 10dB/V (±0.20VDC) over the range of –120 dBm to -80dBm (see Figure 28). If the
requirement cannot be reached, contact your Dataradio technical support.
Figure 28 - T855 and T885, RSSI Curve: volt to dBm
0
1
2
3
4
5
6
7
Volt
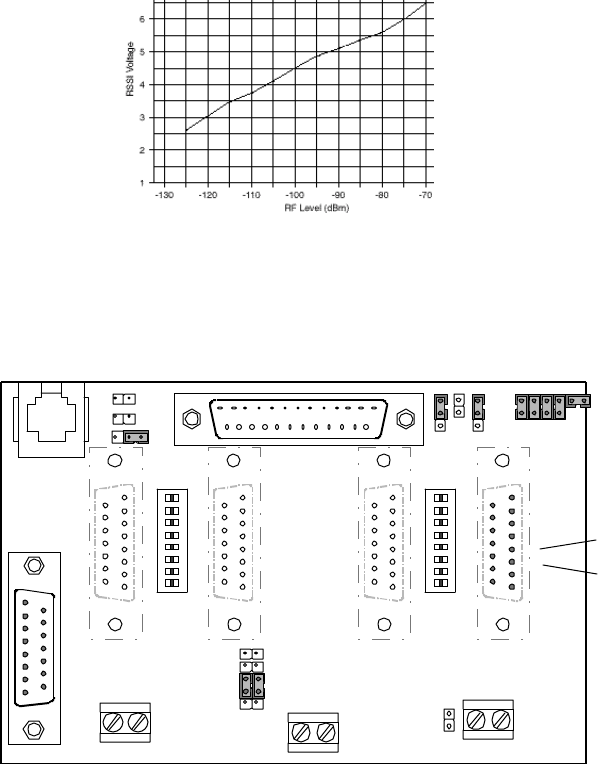
120 20170-200 ParagonPD Technical Manual48
6.4.2.6 RSSI Adjustment (VHF: T835)
Note: This check is only recommended for Paragon/R model running DBA protocol 3.06.009
series or later.
- Apply an on-channel signal from the RF generator at a level of -100dBm with deviation of
±3kHz (full channel) or ±1.5kHz (half channel) at 1kHz tone.
- Adjust RV320 (RSSI level) to give 4.5V RSSI output at RSSI test point (near of quad. Coil
L360) or on backplane SK1 pin 5 when measured with a voltmeter
- Vary the RF level in 15dB steps and check that the RSSI output voltage (SK1 pin5) changes at
a rate of a 15dB/V (+/- 0.30VDC) over the range of -120 dBm to -80dBm (see Figure 29). If
the requirement cannot be reached, contact your Dataradio technical support.
Figure 29 - T835, RSSI Curve: Volt to dBm
Figure 30 – T800-50-0001 Backplane and test pins location
1
2
3
4
5
6
7
8
O
F
F
1
2
3
4
5
6
7
8
O
F
F
SW2SW1
RX C HAN EL SWITC H
TX CHANEL SWITCH
OFF
ON
OFF
ON
PL1
SK1
1
5
6
RSSI ouput SK1 pin 5
RX-Audio1 SK1 pin 6
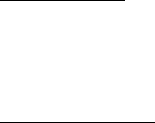
120 20170-200 ParagonPD Technical Manual49
6.4.3 Exciter Module (T857 or T837)
Note 1: Refer to Figure 33 (T857) and to Figure 35 (T837) for locating tuning controls and com-
ponents.
Note 2: When the synthesizer is unlocked, the front panel green LED called "Supply" will flash
indicating that it needs re-tuning.
Warning: The LED will also flash when the unit is in setup mode while connected to the
PGM800win program.
6.4.3.1 Initial Setup
1. Shut down power to the base station
2. Prepare the multimeter to DC Volts.
3. Remove the exciter (T857 or T837) module from the base station rack frame
4. Remove the exciter top cover (nearest the handle).
5. Connect a 3 feet long double shielded cable (N-M to BNC-M) between the IFR T/R out-
put and the exciter antenna connector.
6. Connect the ParagonPD Extender Rail Kit to the empty chassis exciter slot.
7. Apply power to the base station
6.4.3.2 Synthesizer Alignment
Single channel: Connect the multimeter to the long lead of L1 in the VCO (this measures the syn-
thesizer loop voltage).
1. T857 (UHF) Tune VCO trimmer C6 for a synthesizer loop voltage of 10V DC.
2. T837 (VHF). Tune VCO trimmer CV1 for a synthesizer loop voltage of 9VDC.
Multiple channels:
1. T857 (UHF) Adjust the VCO loop to 10V using the middle channel.
2. T837 (VHF) Adjust the VCO loop to 9V using the middle frequency channel.
All channels should lie within the upper and lower limits of 16V and 3V respectively for
the T857 and within 13V and 5V for the T837.
Note:
Normally, the fast TX key option is installed and the synthesizer is always ener-
gized. In the case where that option was not fitted, we must key the transmitter by
pressing the front panel Carrier button to make the above adjustment possible.
6.4.3.3 TX Frequency Error Adjustment
1. Apply the following settings to the IFR:
- Receiver mode
- IFR RX frequency to match the main radio TX frequency
- IF Filter set to 30KHz
- Zoom the RF Error window: select 10Khz range
120 20170-200 ParagonPD Technical Manual50
2. Key the transmitter by pressing the front panel TX-Key button and measure the carrier
output frequency. It should be within ±300 Hz. If it is not, adjust the TCXO to trim to
meet the requirement, preferably within 100Hz.
6.4.3.4 Low-Frequency Balance Adjustment
PGM800Win controls this adjustment. Electronic potentiometer (256 step) is used to allow chan-
nel adjustment of two-point modulation (Low freq. balance).
1. Apply the following settings to the IFR:
– Receiver mode and Oscilloscope display (Source Demod out connector, DC cou-
pled).
– IFR RX frequency to match the radio transmit frequency
– IF Filter set to 30KHz
– Zoom the Deviation window: select 10kHz Range and DC coupling.
2. Select the active or, the lowest (in the case of multi-channel base) frequency channel (via
dip switch)
3. Transmit a square wave by pressing the BDLCPD’s PF1 button and following the proce-
dure outlined in section 3.2.1.1.2.2 or run on another computer the RIS program and press
the Flatness test button. You can also run both programs on the same computer if two se-
rial COM ports are available.
4. Adjust IC220 via PGM800Win “reference modulation” to obtain the best square wave, no
damping, no overshoot. (You can use either the mouse or up and down arrow keys). Rec-
ord the deviation read.
5. If transmission has not ended by itself, press BDLCPD PF1 or press RIS’ Flatness test
button to stop it. For single-channel unit, proceed to step 7.
6. For multi-channel unit, select the highest frequency channel. Transmit a square wave by
pressing the BDLCPD’s PF1 button and following the procedure outlined in section
3.2.1.1.2.2 or run on another computer the RIS program and press the Flatness test button.
Record deviation again.
7. The difference in deviation between the two channels should be less than ±300Hz. If not,
re-adjust IC220 to "average" the square wave shape on both channels until the spec is
met.
8. To confirm the adjustment, select the active, or the lowest frequency channel. Compare
the deviation produced between:
- TX ON (Modulated) and
- Random data tests,
The difference should be lower than 300 Hz. For multi-channel unit, repeat this step on
the highest frequency channel.
8. Select the active channel. Transmit a TX ON (Modulated) adjustment tone by pressing
the BDLCPD’s PF1 button and following the procedure outlined in section 3.2.1.1.2.2 or
run on another computer the RIS program and press the TX ON (Modulated) button.
Make sure that deviation level read on the IFR correspond to model and bit rate in use
(see Table 8 - Typical Carrier Modulation). Re-adjust deviation as necessary referring to
the related Checklist (B for ParagonPD - page 26
120 20170-200 ParagonPD Technical Manual51
6.4.3.5 Exciter Power Output
1. Apply the following settings to the IFR:
- Receiver mode, Output T/R
- IFR RX frequency to match the main radio TX frequency
- IF Filter set to 30KHz
- Select auto range in the Power reading window
- Connect the coaxial cable from the IFR T/R to the Exciter output connector
2. Key the Exciter by pressing the module PTT button. The output power must be:
- VHF (T837) = 800 mW ±200mW
- UHF (T857) = 1W ±300mW
6.4.4 Power Amplifier Module (T859 or T839)
- Re-install the exciter module into the ParagonPD rack frame
- Connect the Exciter module to the Power Amplifier.
- Connect the Power Amplifier output to the IFR T/R connector or to a stand-alone BIRD
style power meter, terminated with a 150W dummy load.
- Forward and reverse power alarm set (control) are identified on the PA cover.
6.4.4.1 Power Amplifier Power Output
- Key the transmitter on the exciter and adjust the PA output for 100W using front panel
power control. If power cannot be reached, refer to section 6.4.4.4 for T859 UHF model
or to Tait T839 service manual for T839 model. Cable loss should be included in the
reading.
6.4.4.2 Forward Power Alarm Level
1. Power up the PA and adjust front panel power control so that the output power is at the
alarm level required, usually 20% lower than nominal value (e.g. 40W if the PA normally
operates at 50W).
2. Adjust the forward power alarm set (T859: RV48 or T839: RV101) so that the forward
power alarm LED lights.
3. Adjust front panel power control (T859: RV63 or T839: RV109) for the normal operating
power level
6.4.4.3 Reverse Power Alarm Level (Optional)
1. Power up the PA and adjust the front panel power control for the normal operating power
level.
2. Place a known mismatch of the required value (e.g. 3:1 VSWR) and adjust the reverse
power alarm set (T859: RV52 or T839: RV105) so that the reverse power alarm LED
lights.
Example:
A VSWR of 3:1 can be simulated by connecting an unterminated 3dB pad to the
PA output. This will result in a return loss of 6dB.
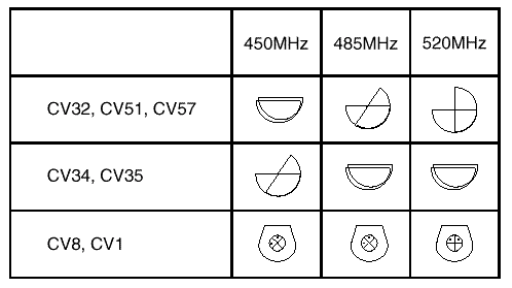
120 20170-200 ParagonPD Technical Manual52
6.4.4.4 Tait T859 (UHF) Standard Tuning Procedure
1. For sets with serial numbers following 217262, set RV69 (driver power level) fully
clockwise.
2. For all units, preset the tuning controls as shown in Figure 31
Figure 31 - T859 Tuning Settings
3. Set RV63 (front panel power control) fully clockwise.
4. Key on the exciter (press PTT button).
5. Adjust CV1 for maximum output.
6. Adjust CV8 for maximum output.
7. Adjust CV32 for maximum output.
8. Adjust CV51 and CV57 for maximum output.
9. Adjust CV34 and CV35 for maximum output.
10. Recheck all settings. The power output should exceed 110W.
11. For sets with serial numbers following 217262, adjust RV69 (driver power level)
until the output power drops to 110W.
12. For all units, adjust RV63 to reduce the power output to the required level (normally
100W).
6.4.4.5 Tait T859 Tuning for Best Efficiency
1. Insert a Shunt current device (HP 34330A Shunt 30A ) between the power supply red
wire and its 13.8Vdc output, then connect the shunt to the multimeter (VDC scale)
2. While transmitting, monitor the current. It should remain under 22A.
3. Retune CV32, CV51 and CV57 towards maximum capacitance to obtain minimum supply
current, but do not exceed a maximum drop of 0.5A per control.
4. Check that the supply current is <22A for 100W output power.
Note:
These control settings are normally very close to minimum supply current. If the cur-
rent is reduced too far, maximum power output will drop and 2f rejection may degrade.
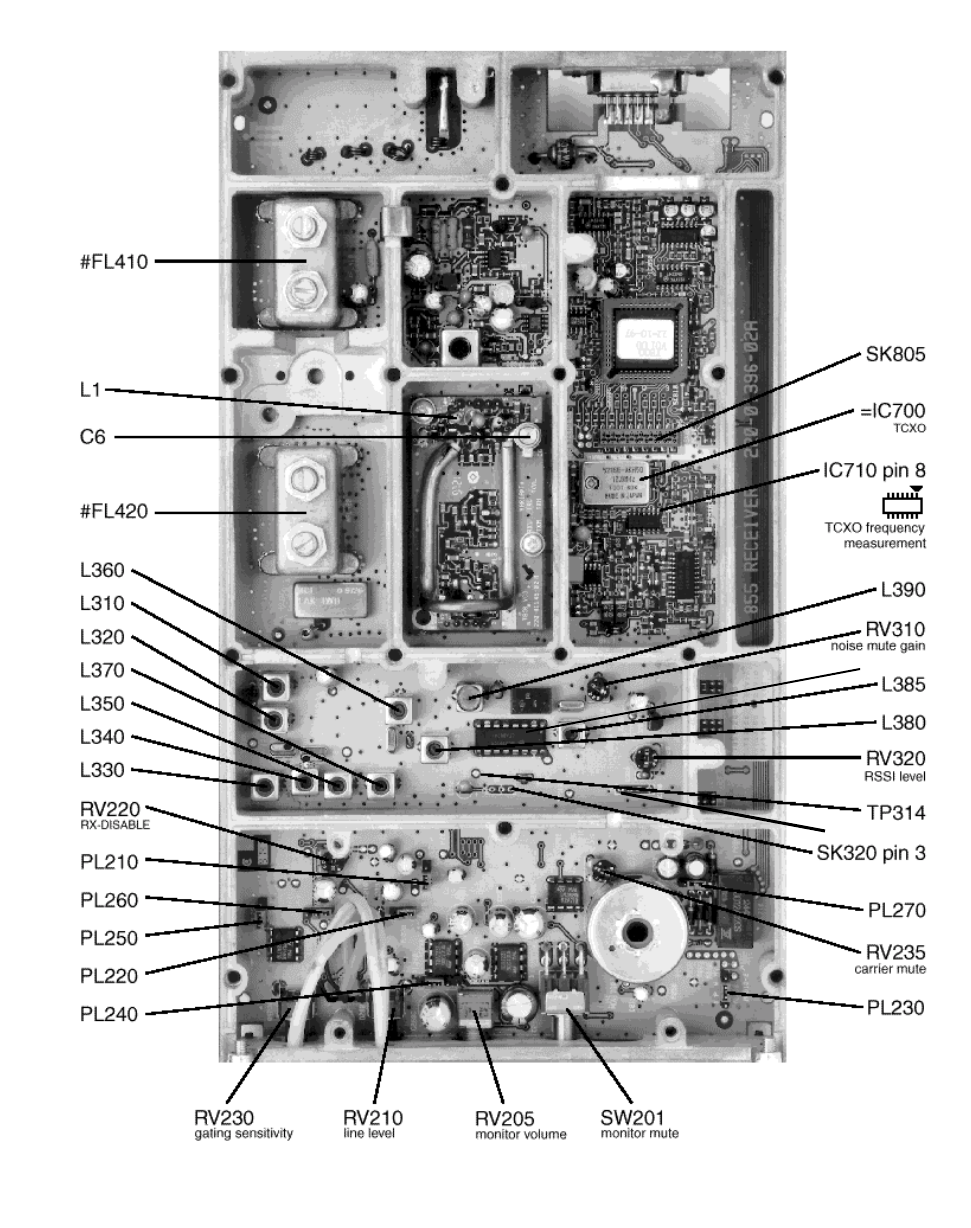
120 20170-200 ParagonPD Technical Manual53
Figure 32 - T855 Receiver Tuning Controls Location
IC 310
SK330 pin 2
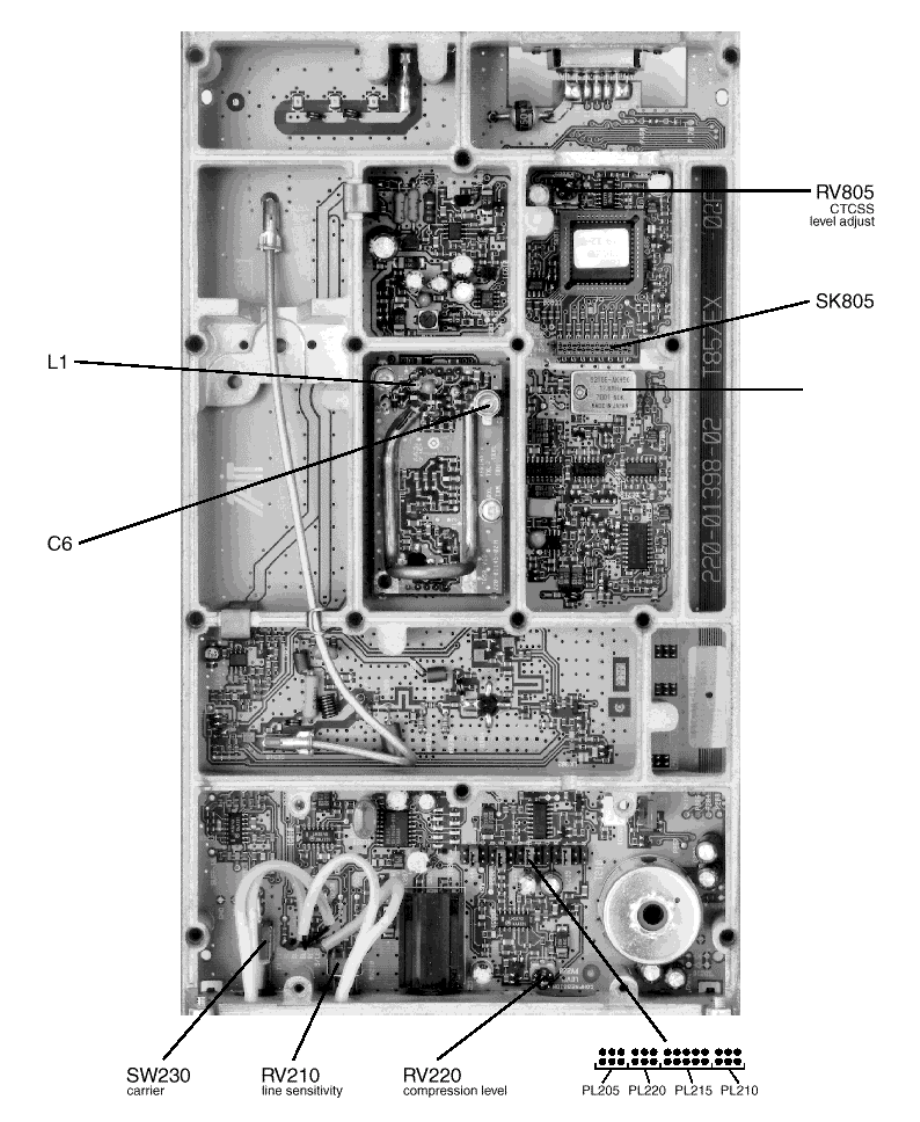
120 20170-200 ParagonPD Technical Manual54
Figure 33 - T857 Exciter Tuning Controls Locations
TCXO
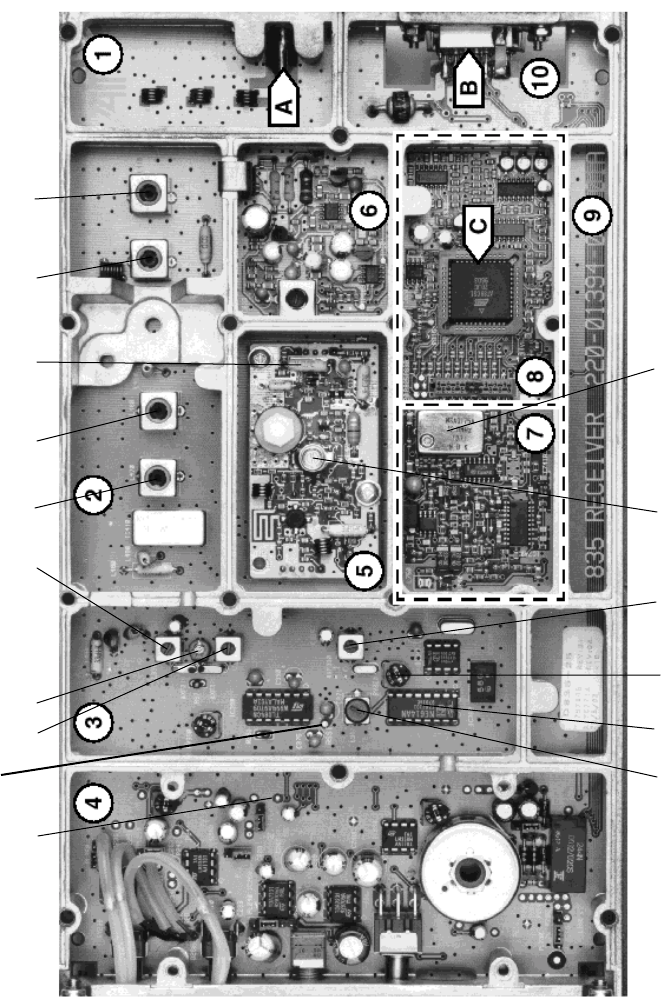
120 20170-200 ParagonPD Technical Manual55
Figure 34 - T835 Receiver Tuning Controls Location
L410
L420
L1
L460
L47
CV318
L340
RSSI
Test Point
P207
IC 700
CV1
L350
IC 350
L360
L330
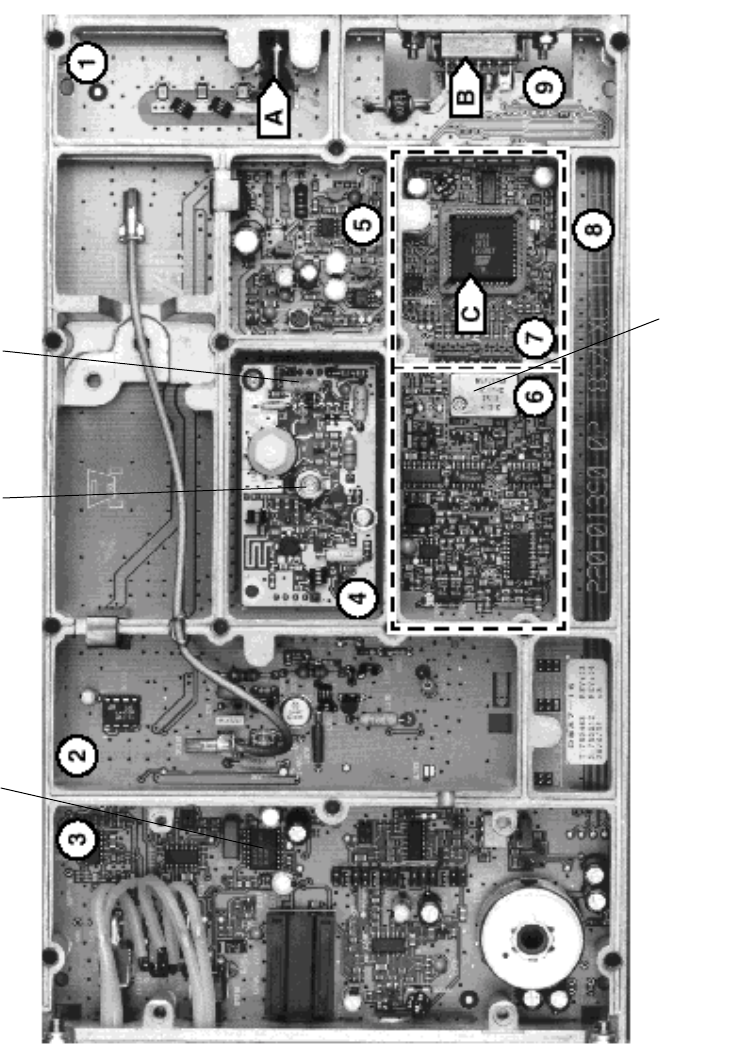
120 20170-200 ParagonPD Technical Manual56
Figure 35 - T837 Exciter Tuning Controls Location
L1
CV1
IC220
IC700
TCXO
120 20170-200 ParagonPD Technical Manual57
Appendix 1 - ParagonPD Deviation adjust
1. Using the RIS, press TX ON (Modulated) and record deviation level as read on the IFR.
2. Using Windows Notepad, Edit the .bp2 file named with the corresponding BDLCPD serial
number (e.g. abcd.bp1). “Save as” to another file name and keep it in case something goes
wrong while changing a parameter.
3. Locate the line labeled “Dev0 Par85=” and record the value beside the “=” sign. This is the
corresponding parameter value to the deviation read in step 1.
4. Apply the following formula to determine the new parameter value to be set:
(New Par85 value) = [(initial Par85 value) X (target deviation) / (deviation read)] + 2
5. Change the value in the file, “Save as” using the BDLCPD serial number file name.
6. Run the RIS again and do a “Put From”. From the opened window, select the file that you just
made the change to and then press “OK”
7. Again, check deviation level while pressing TX ON (Modulated). If fine-tuning of Par90 value
is still required, Edit the file again and re-do step 5 by changing directly the Par85 value by 1
or 2 up or down.
8. Re-check deviation level. If the level is now correct, press Stationreset to make the change
permanent.
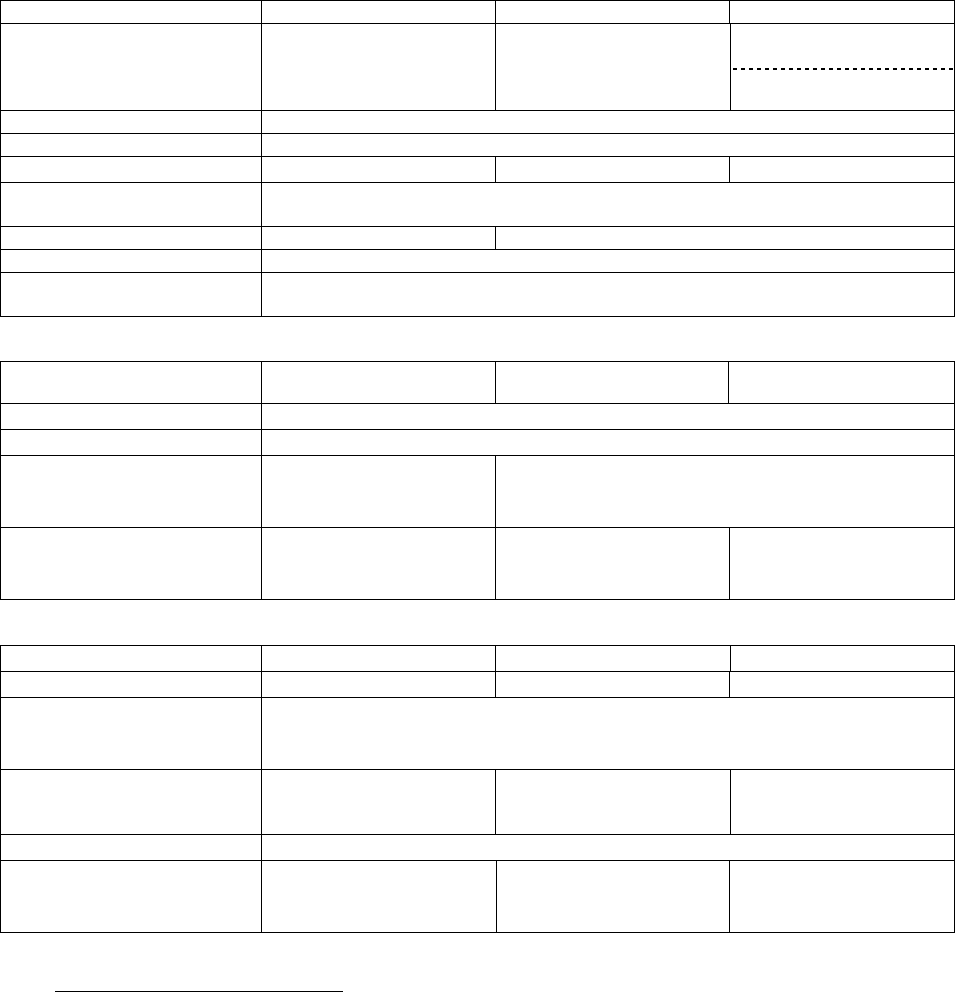
120 20170-200 ParagonPD Technical Manual58
7. Specifications
GENERAL
VHF UHF 800 MHz
Rx 800 - 880 MHz
Tx 850 - 870 MHz
Frequency 136 -156 MHz
148 -174 MHz
400 - 440 MHz1
440 - 480 MHz
480 - 520 MHz Rx 870 – 960 MHz
Tx 870 – 960 MHz 5W only
Cabinet Size 22.06” W x 75.82” H (without leveling feet) x 27.06: D
RF/Modem Assembly Size 19.0” W x 17.5.0” H x 12.5” D + 2.0” connector allowance
Frequency Stability 2.5 ppm 1.0 ppm 1.5 ppm
Rx Operating Voltage/
Current Consumption 120 VAC, 60 Hz, 13.8 VDC/ 6A max.
Tx Current Consumption 21A DC max. 24A DC max.
Channel spacing 25 kHz
Operating Temperature Range -30°C to +60°C (deleted power supply, catalog number ending with a 0)
-10°C to +60°C (with standard Dual Power Supply assembly, catalog number ending with a 2)
RECEIVER
Selectivity @ 25 kHz
@ 12.5 kHz
95 dB
89 dB
90 dB
85 dB
85 dB
80 dB
Sensitivity @ 12 dB SINAD -117 dBm
Spurious Response 100 dB
Intermodulation
- EIA 25 kHz
- EIA 300-096 12.5 kHz 85 dB
80 dB
85 dB
85 dB
Hum and Noise
- EIA
- ETS 300-096 N/A 55 dB
50 dB
50 dB
45 dB
TRANSMITTER
Rated Continuous RF Power 100W 100W 70W
Range of Adjustment 20 – 100 W 20 – 100 W 20 – 70 W
Spurious Emissions
- transmit
- standby
-36 dBm to 1 GHz/-30 dBm to 4 GHz
-57 dBm to 1 GHz/-47 dBm to 4 GHz
Hum and Noise
- narrow
- Wide
-50 dB
-55 dB
-50 dB
-55 dB
-45 dB
-50 dB
VSWR Stability 5:1 mismatch
Transmitter Sideband Noise
@ +/-25 kHz
@ +/- 1 MHz
-95 dBc
-105 dBc
-95 dBc
-105 dBc
-88 dBc
-100 dBc
1 WARNING: The frequency band 406 to 406.1 MHz is reserved for use by distress beacons and should not be programmed into the
unit.
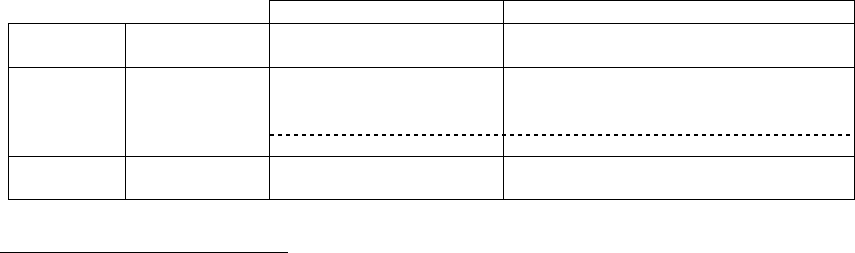
120 20170-200 ParagonPD Technical Manual59
FCC / IC CERTIFICATIONS *
FCC IC (DOC)
VHF 136 - 156 MHz
148 - 174 MHz
CASTEL0007
CASTEL0002
737195375A
737195376A
400 - 440 MHz 1CASTEL0021
UHF 440 - 480 MHz CASTEL0023 3993195401A
480 - 520 MHz CASTEL0025 N/A
800 MHz 800 - 870 MHz CAS8IPT889BW (100 Watts)
CAS8IPT881 (5Watts)
737194358
* Pending for Class II permissive change approvals or approval of request for FCC ID change
1 WARNING: The frequency band 406 to 406.1 MHz is reserved for use by distress beacons and should not be programmed into the
unit.