Cubic Defense Applications COM000-8 HF Transmitter User Manual Instruction and Maintenance Manual
Cubic Defense Applications HF Transmitter Instruction and Maintenance Manual
Contents
- 1. User Manual I
- 2. User Manual II
- 3. User Manual III
User Manual I
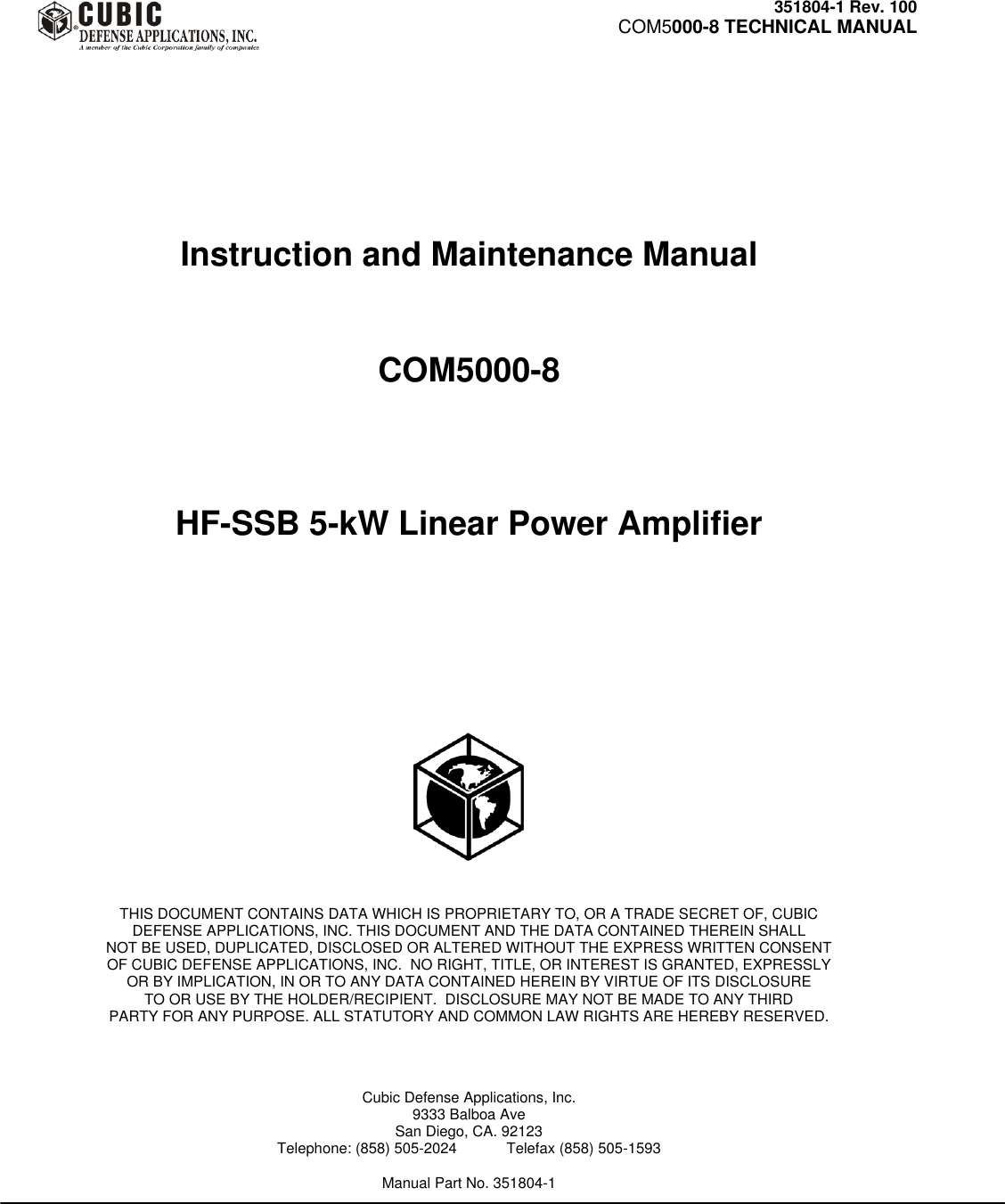
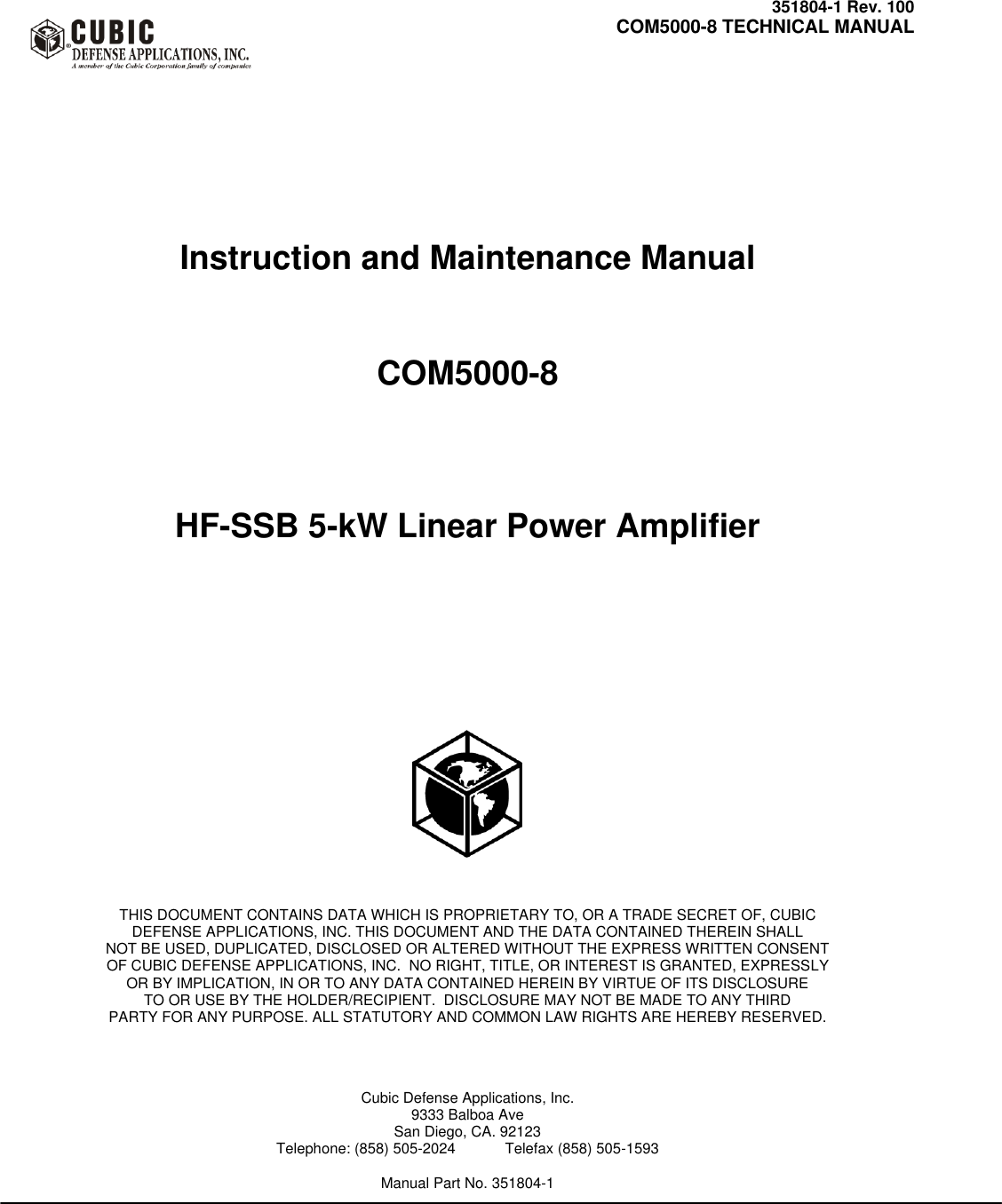
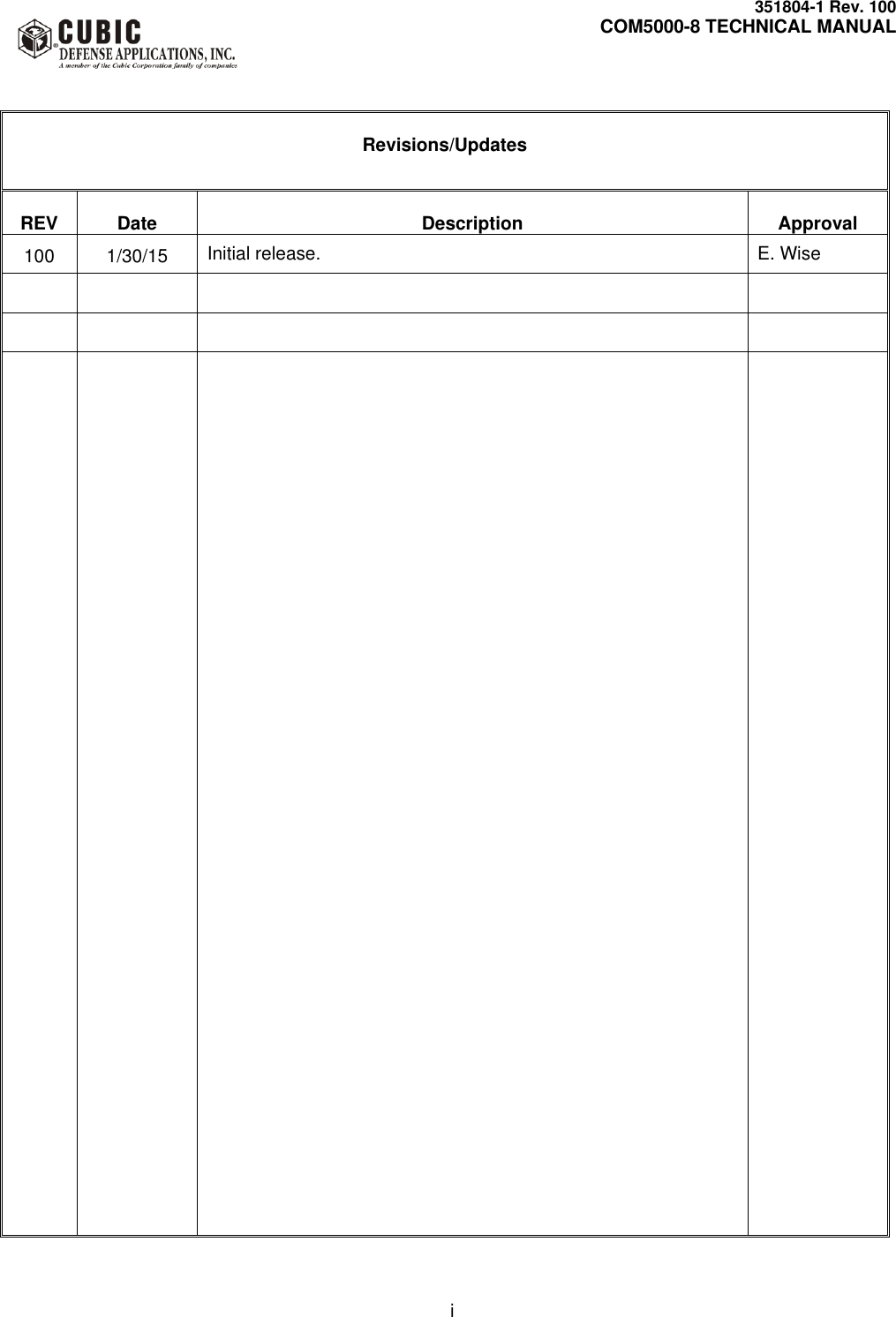
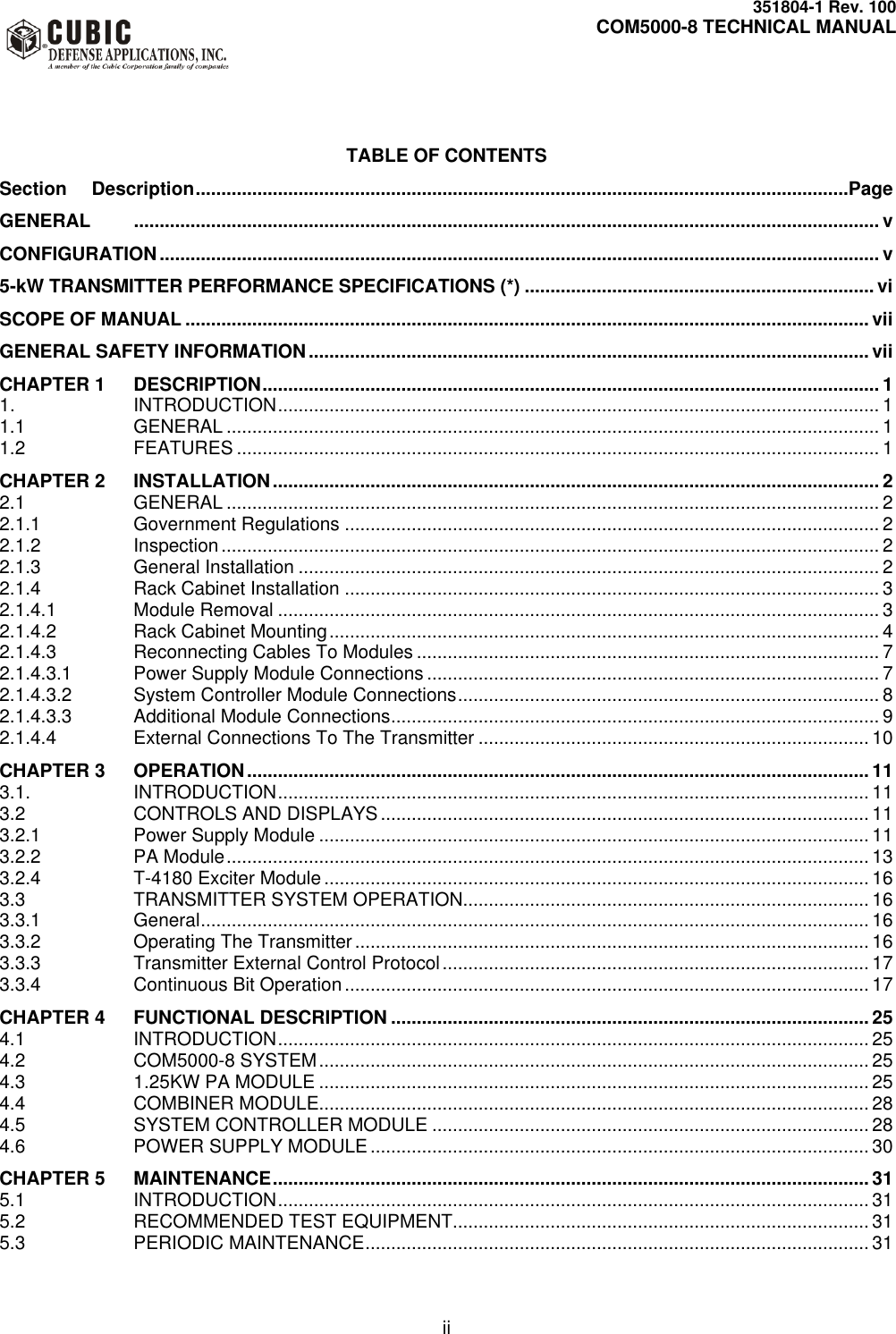
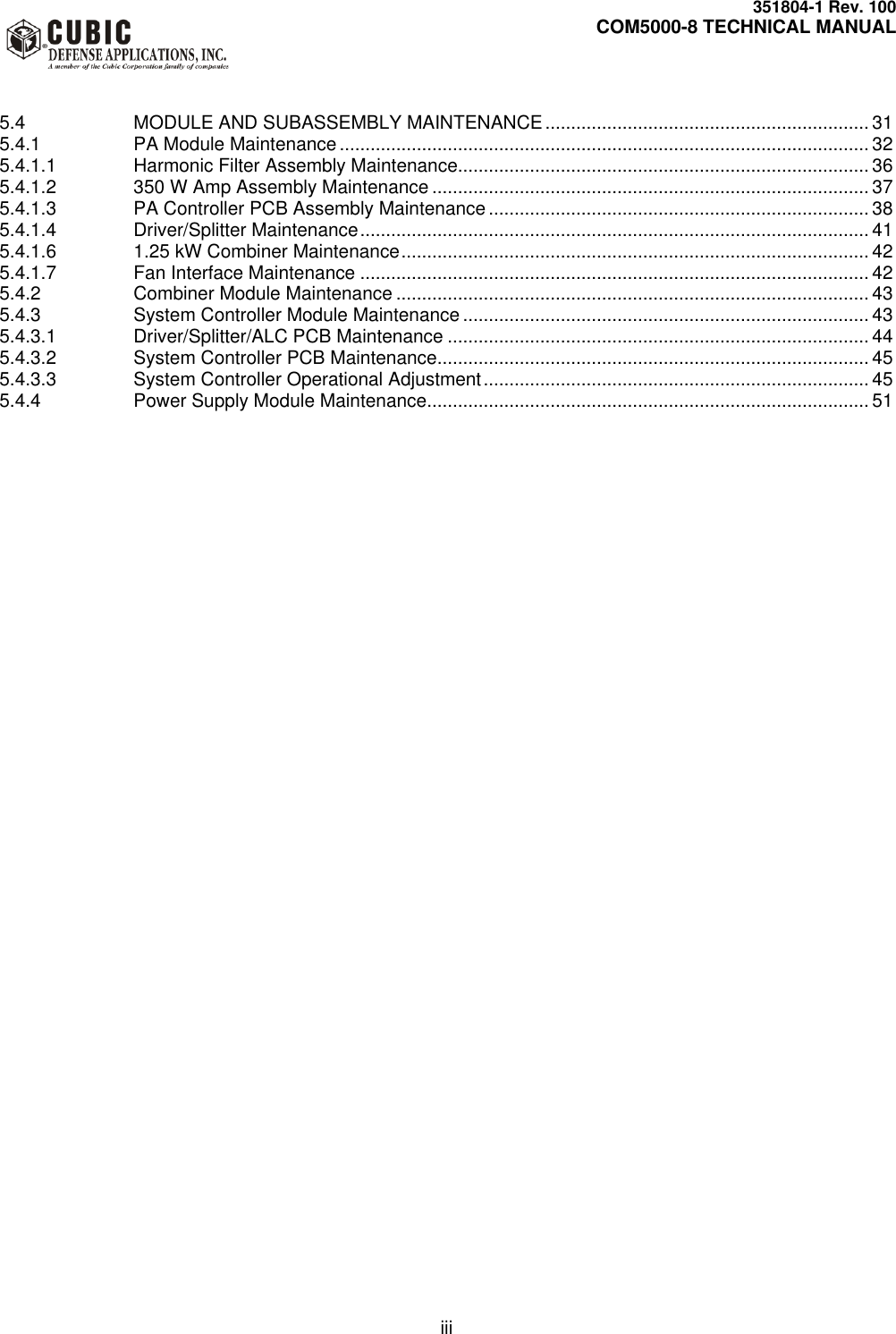
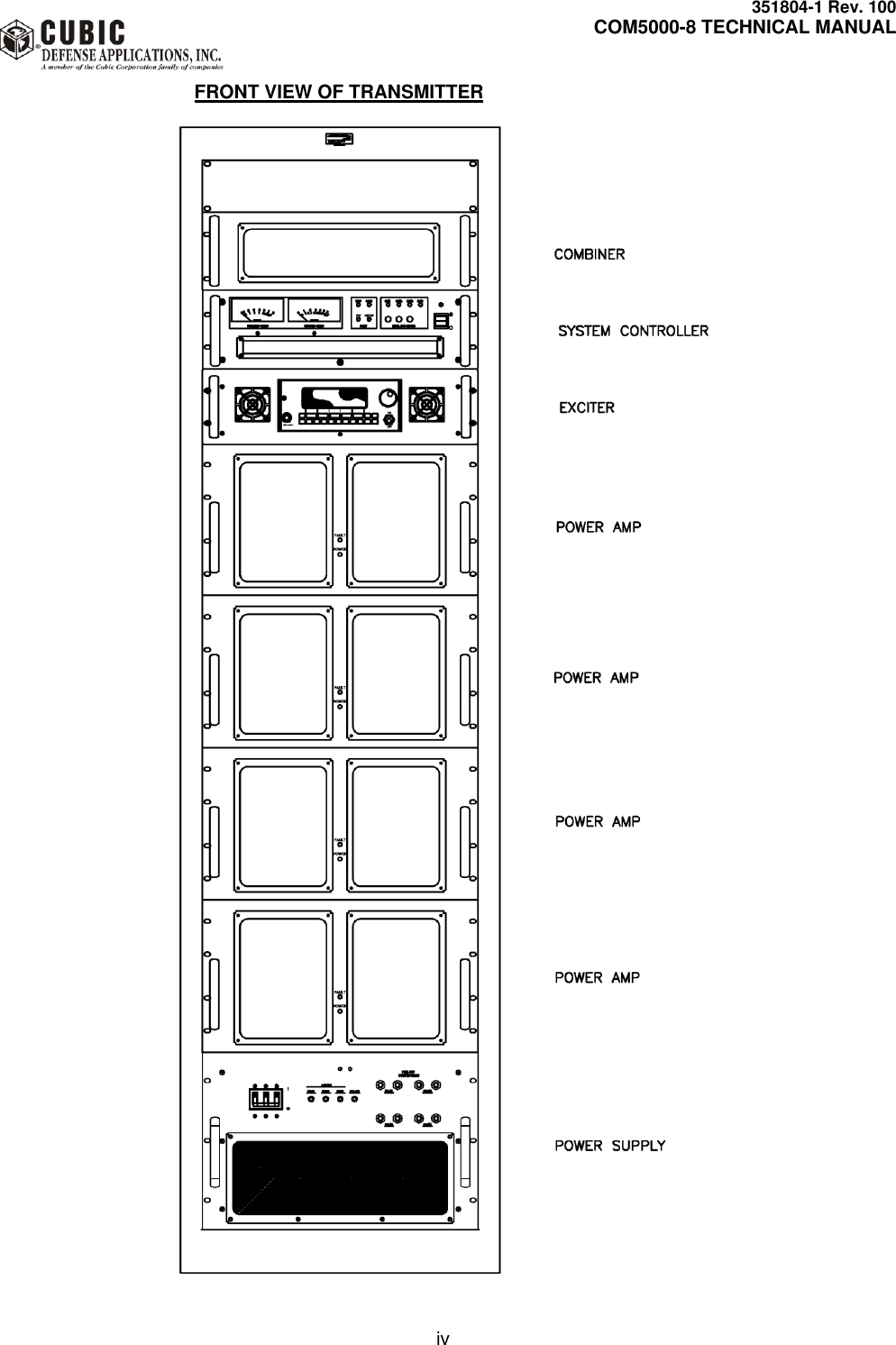
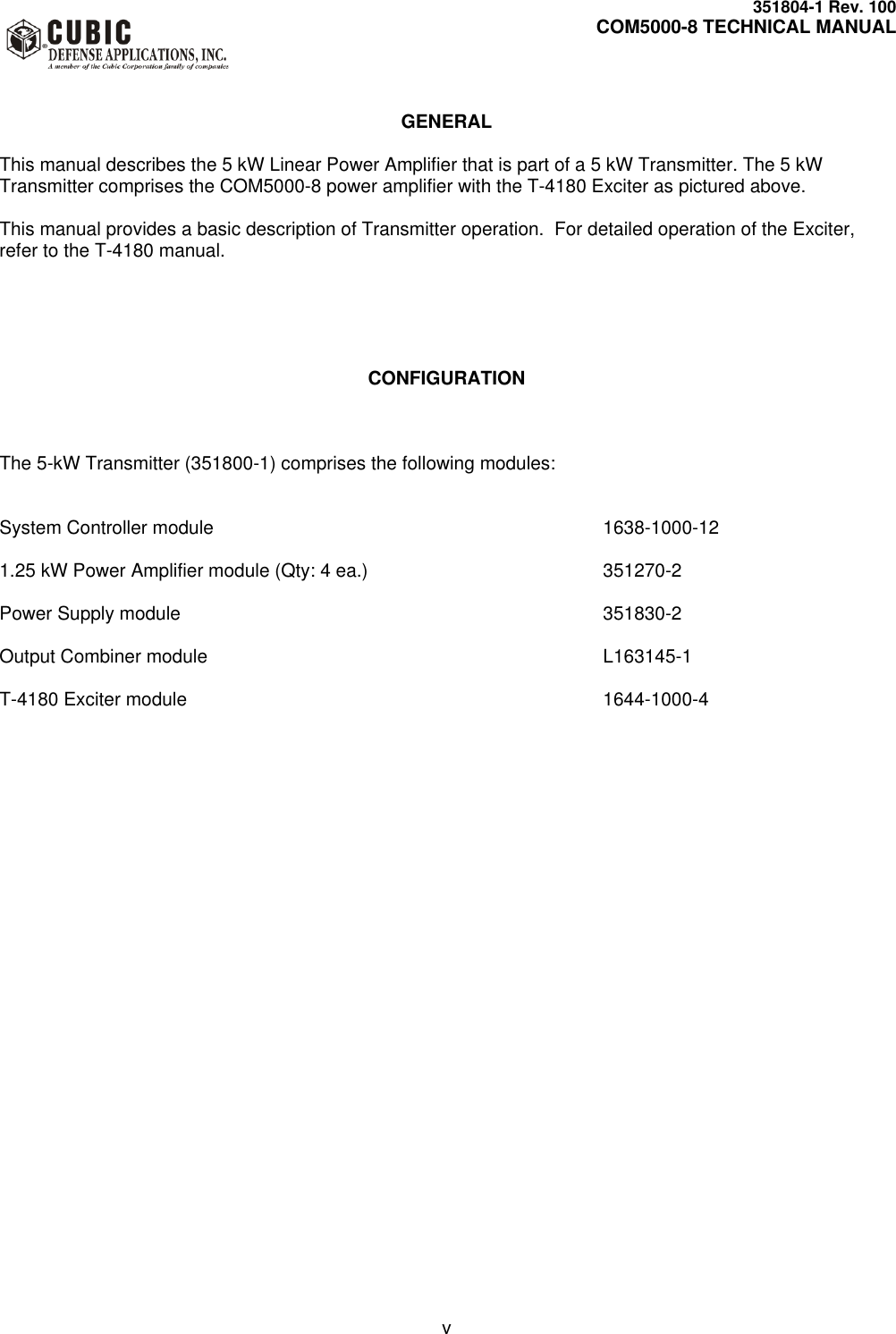

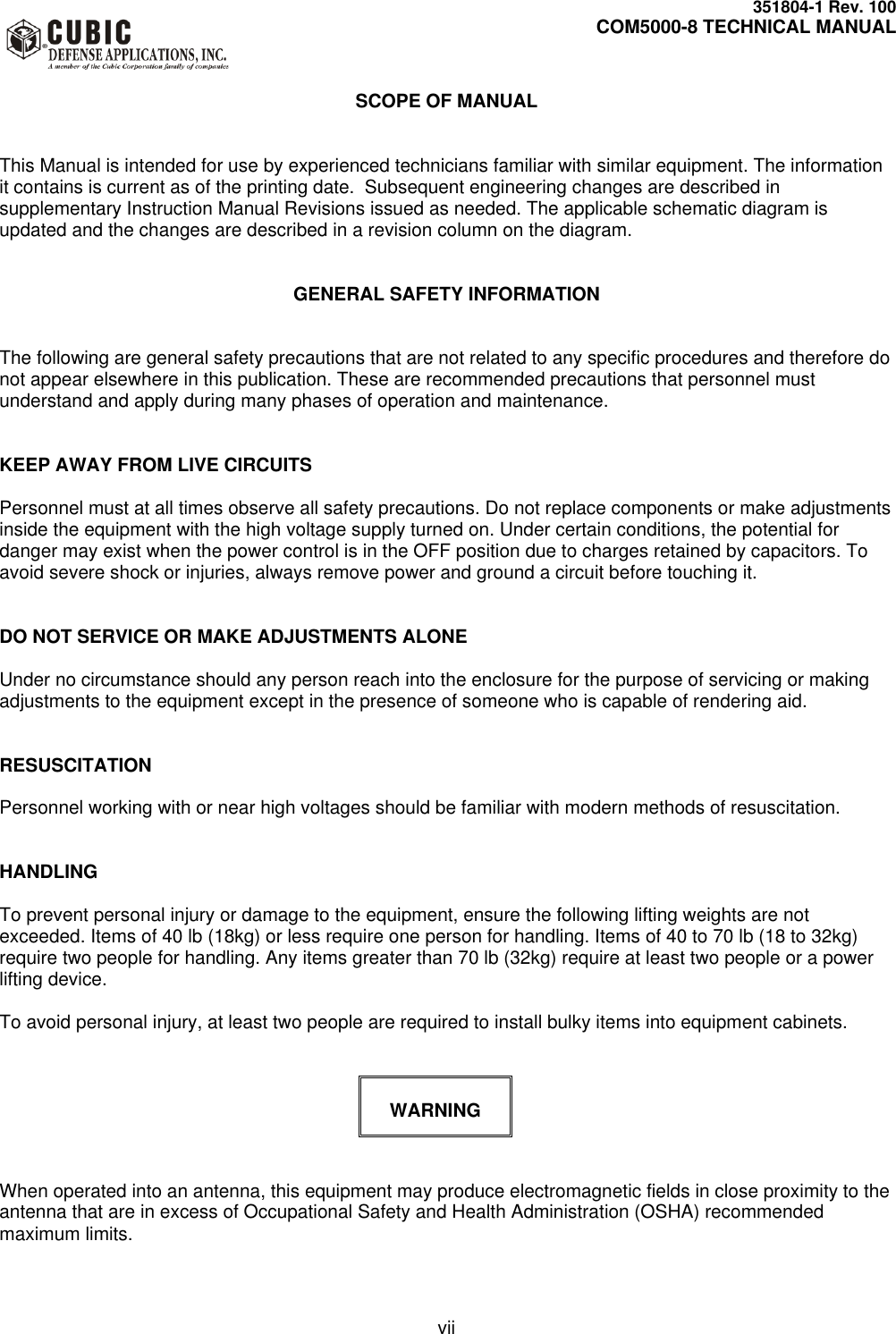
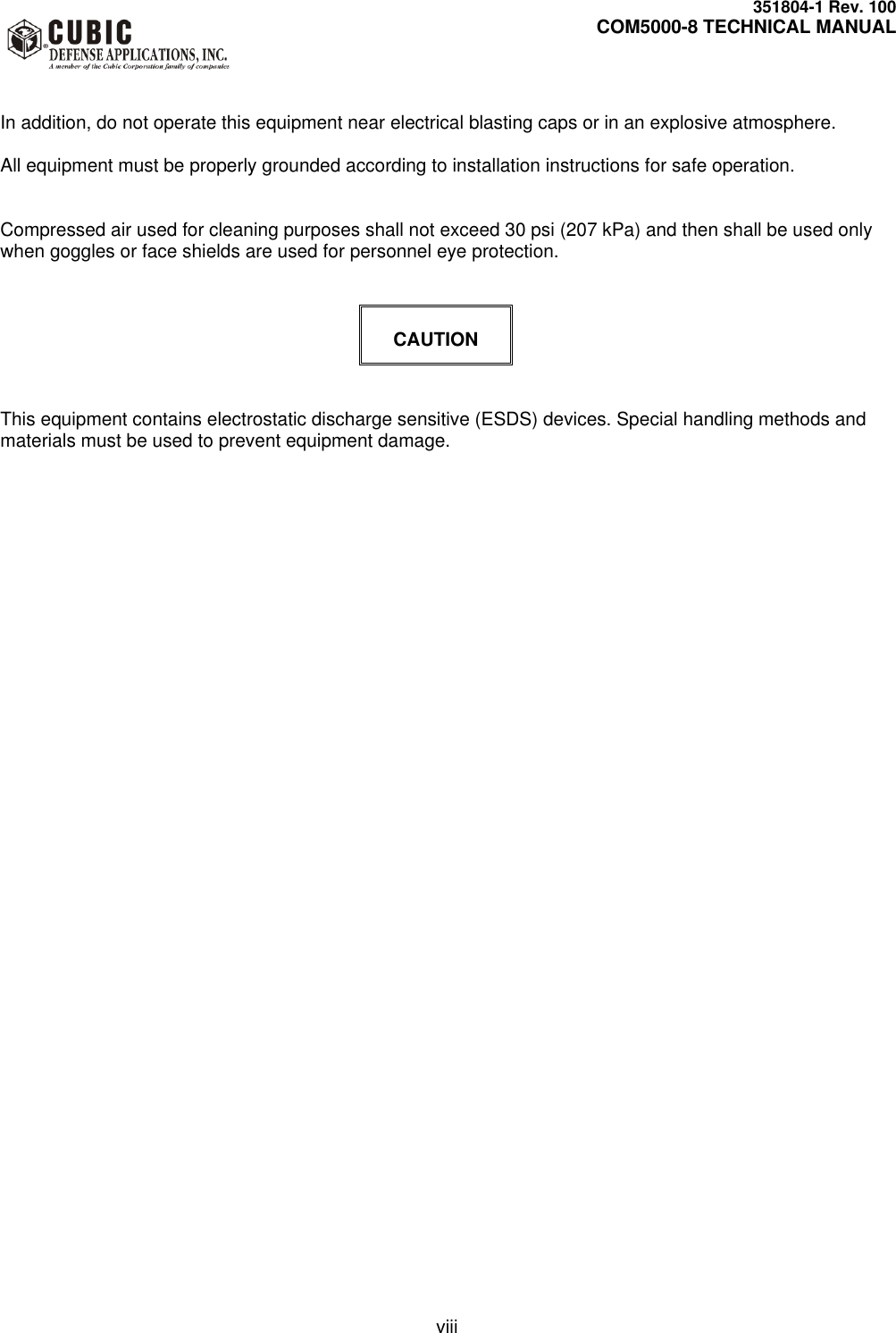

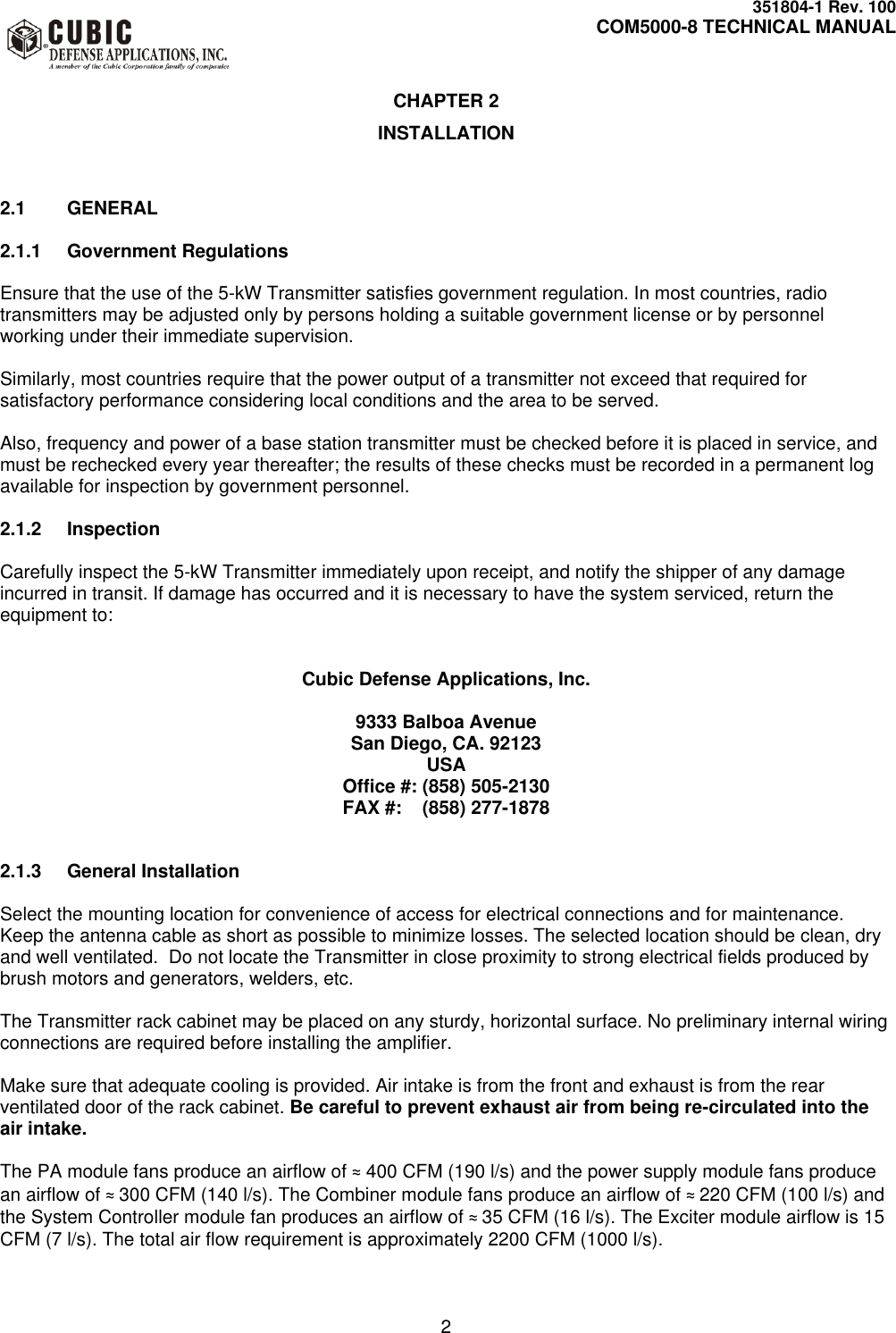
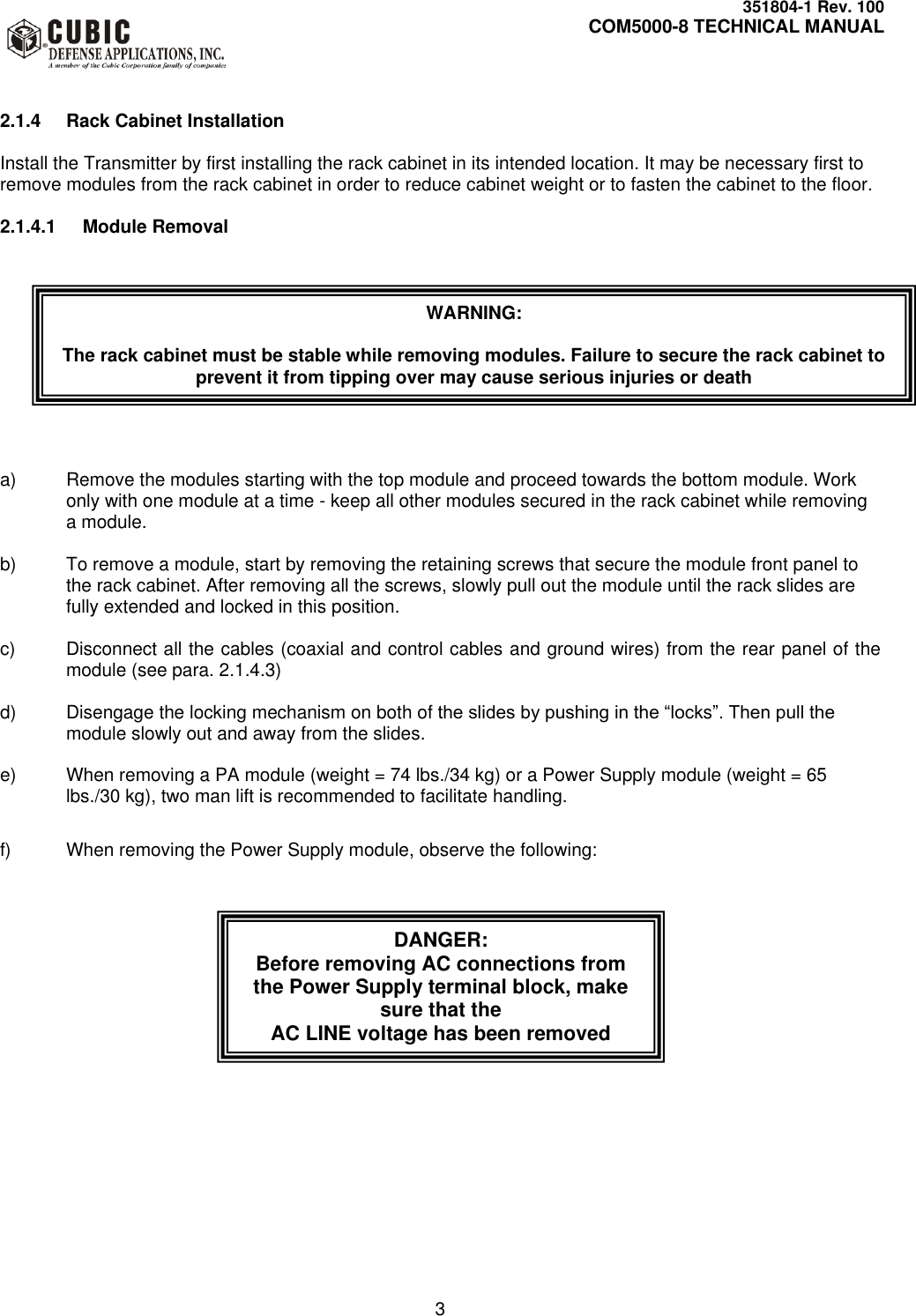
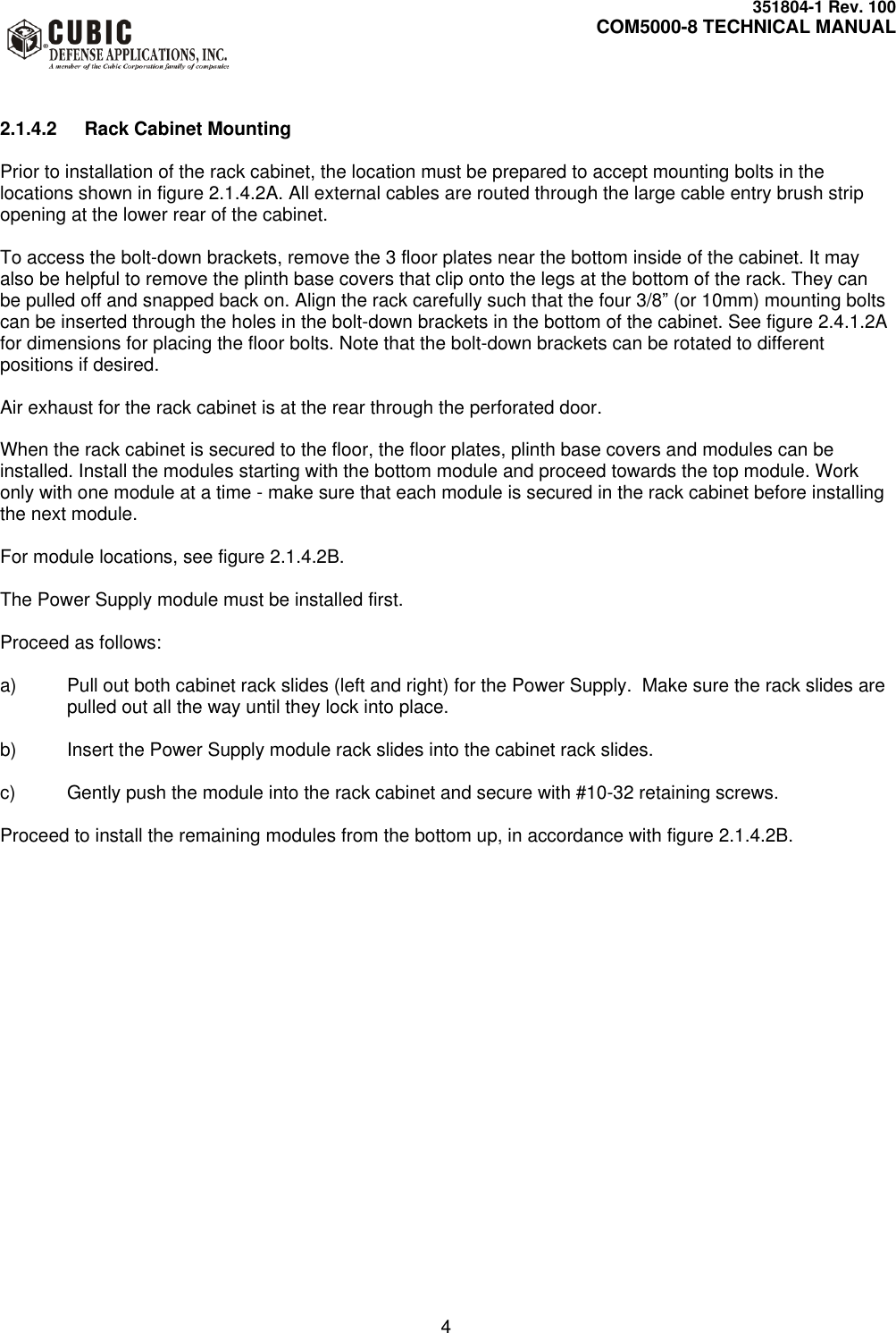
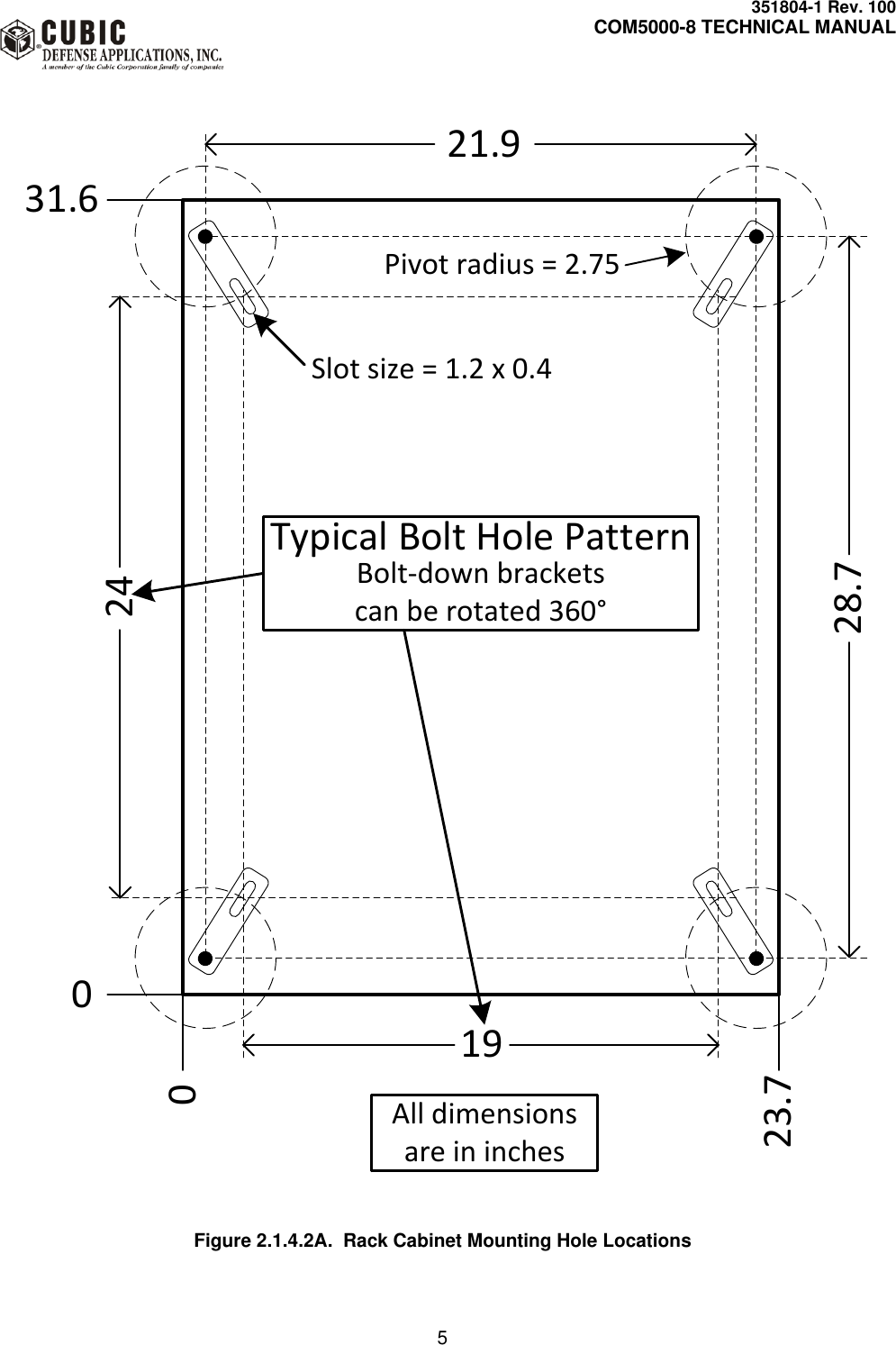
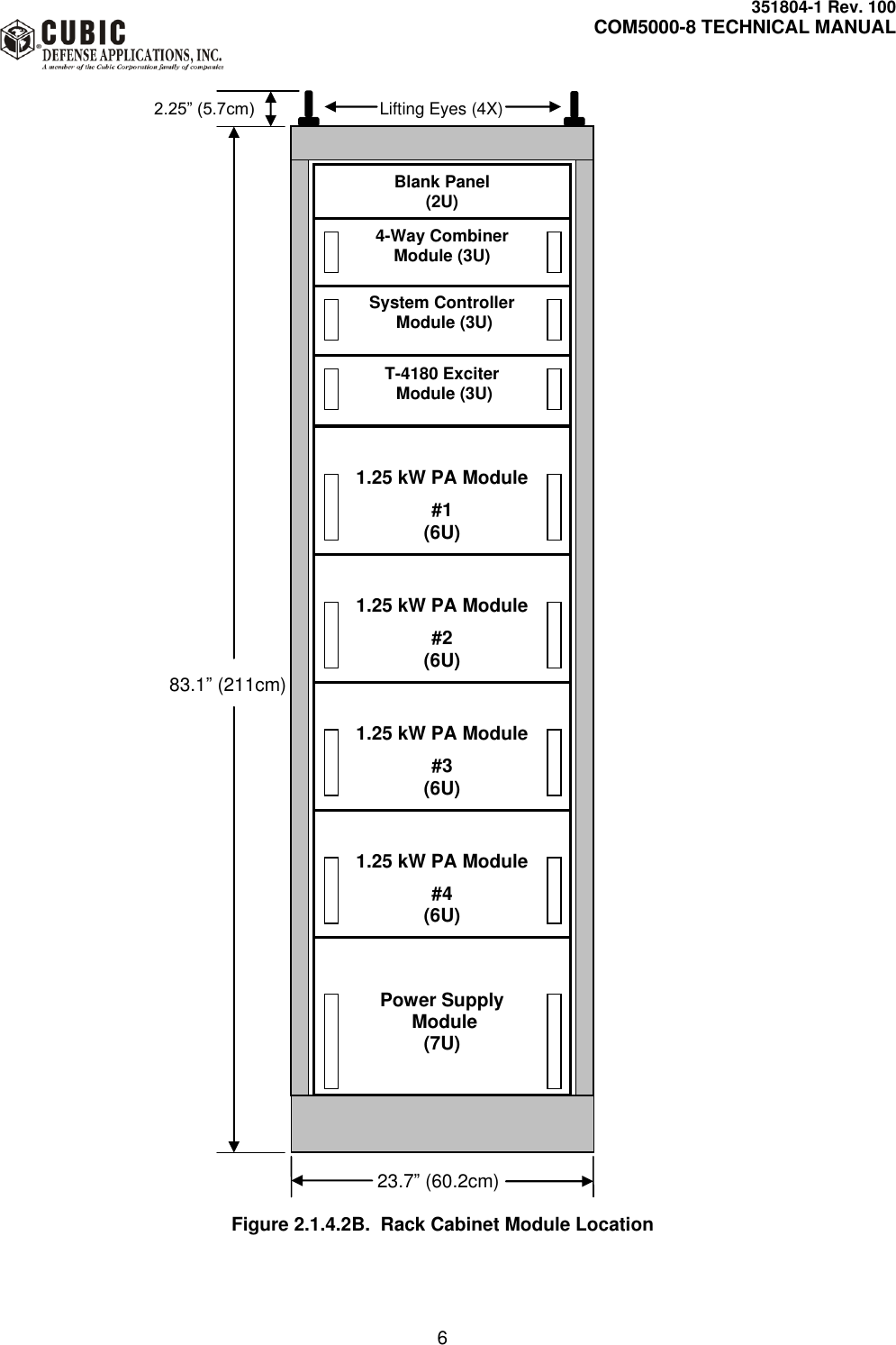
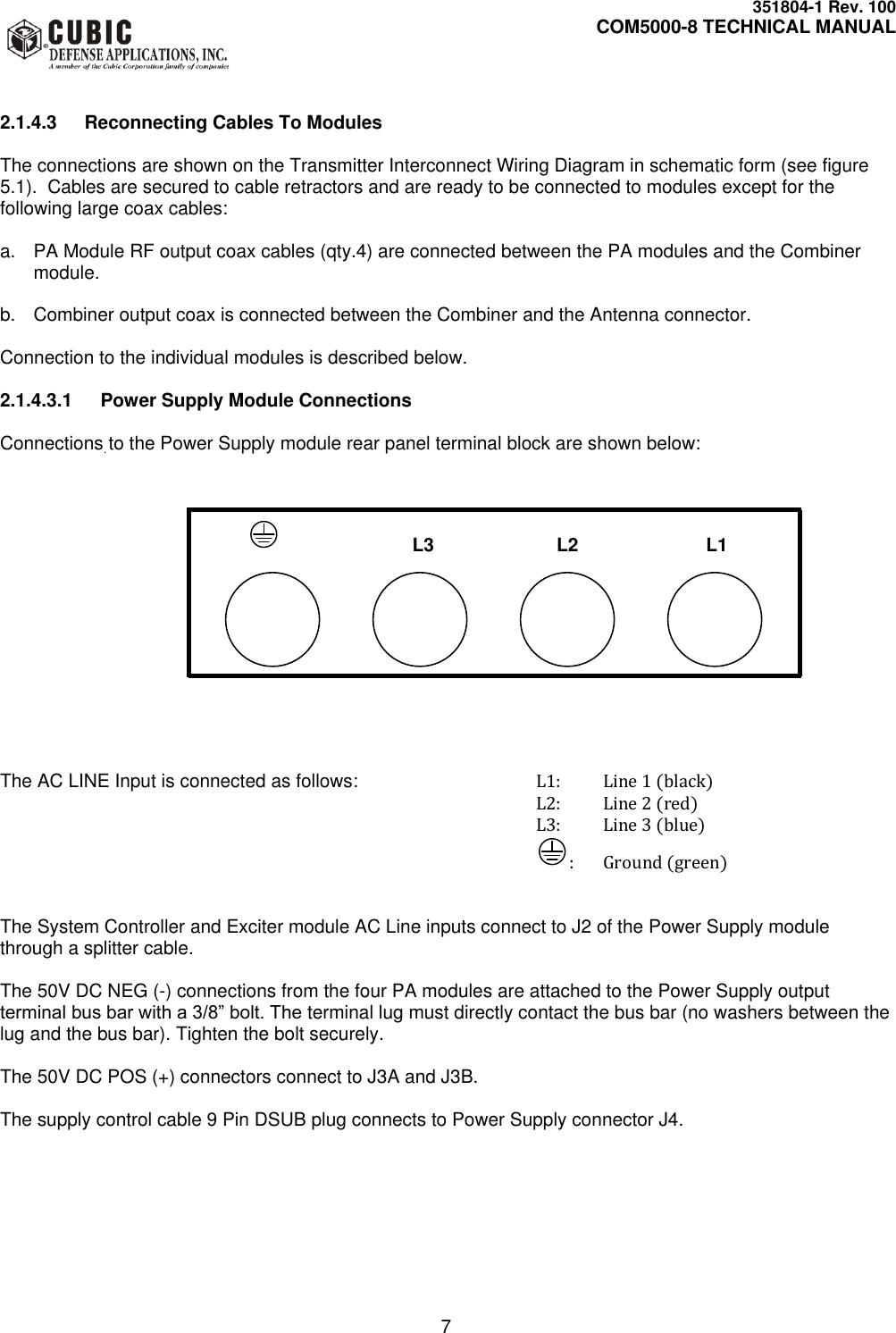
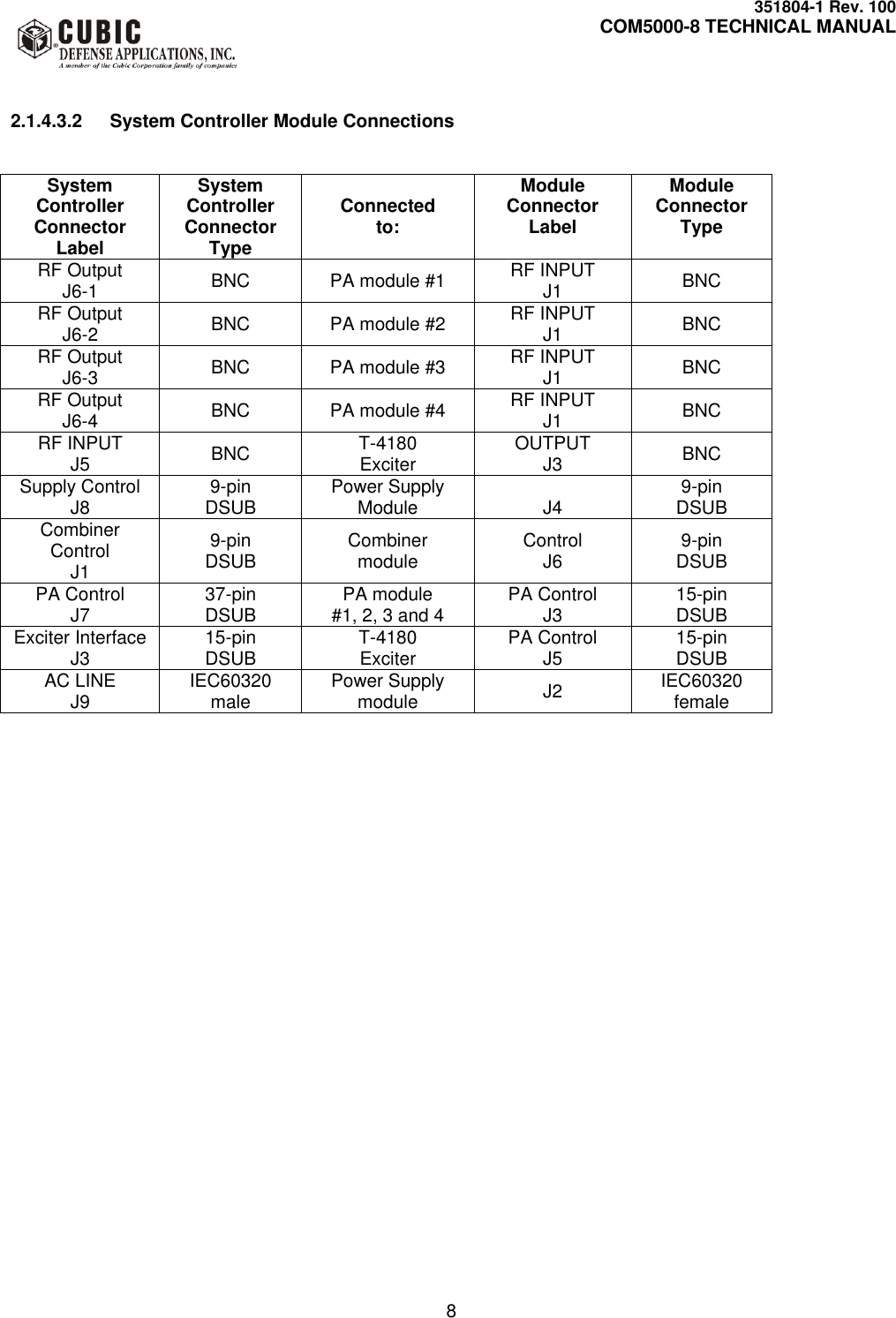
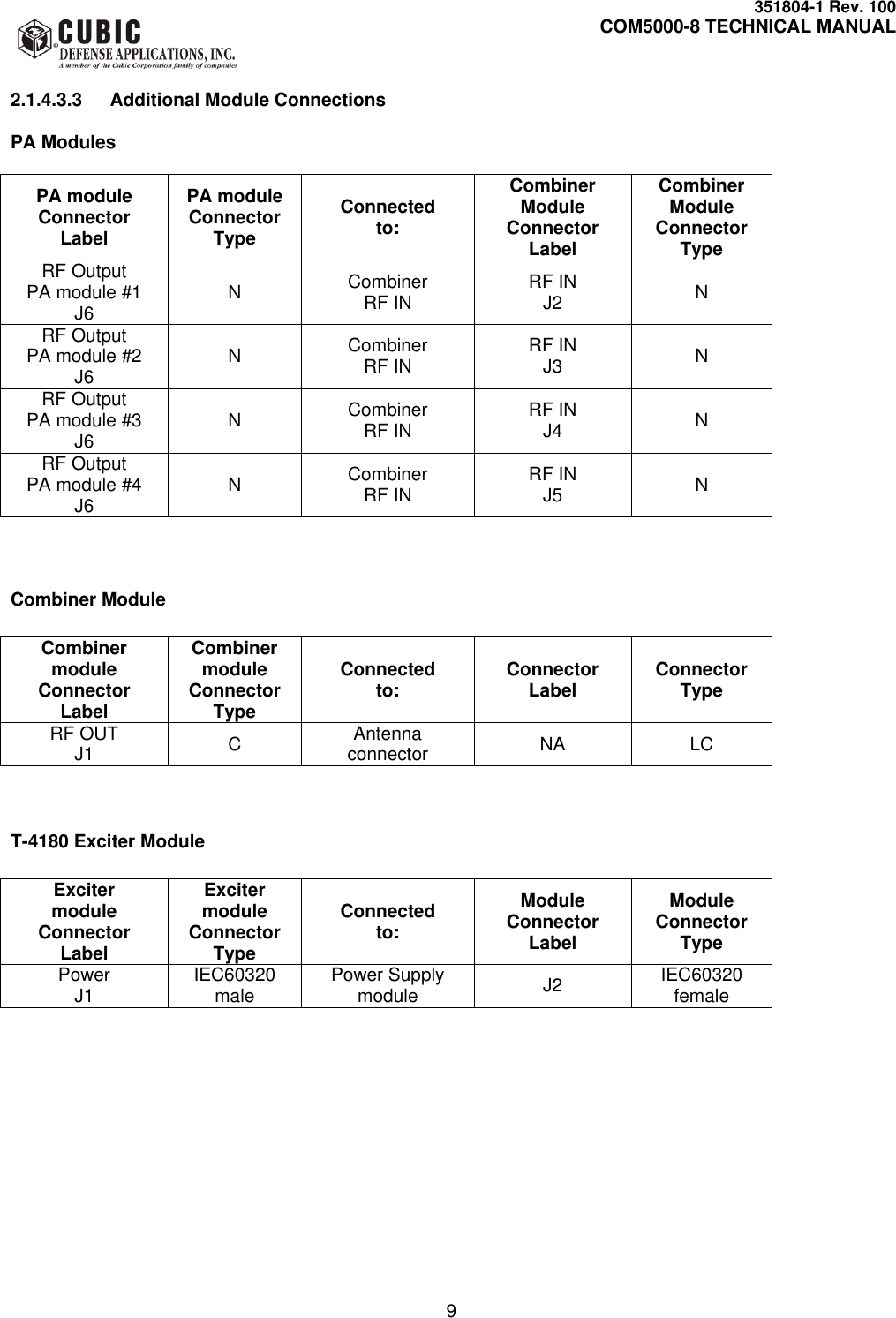
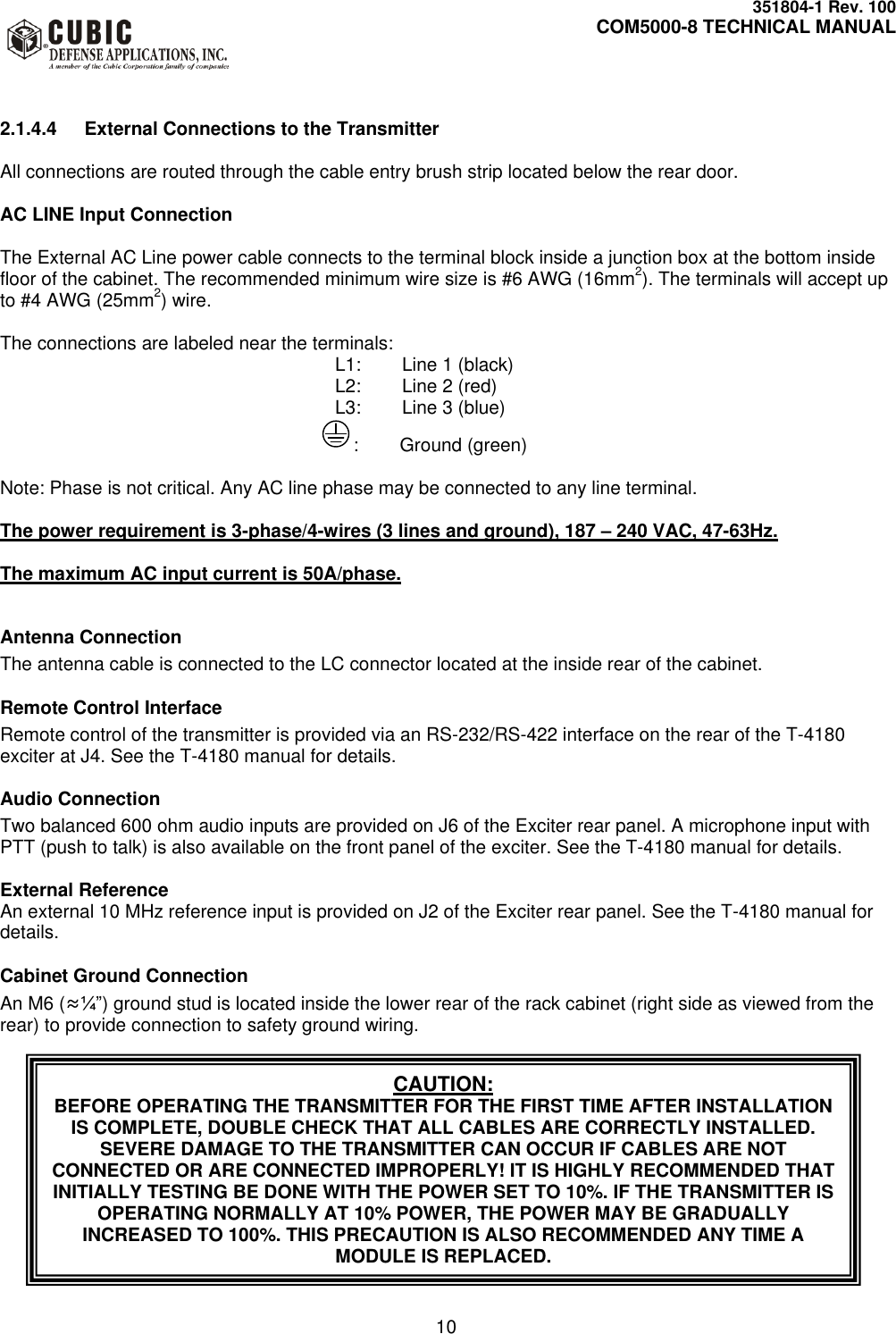
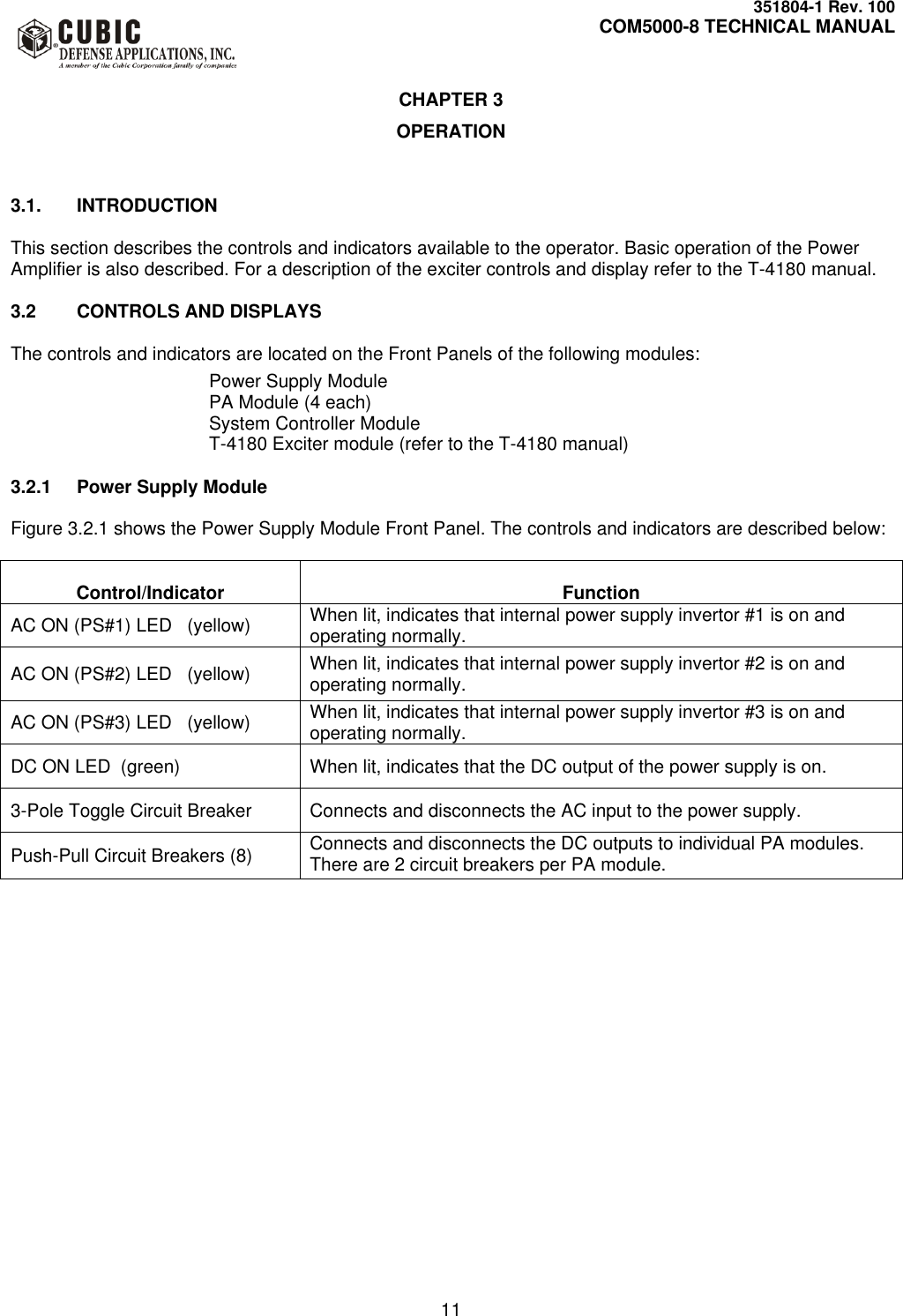
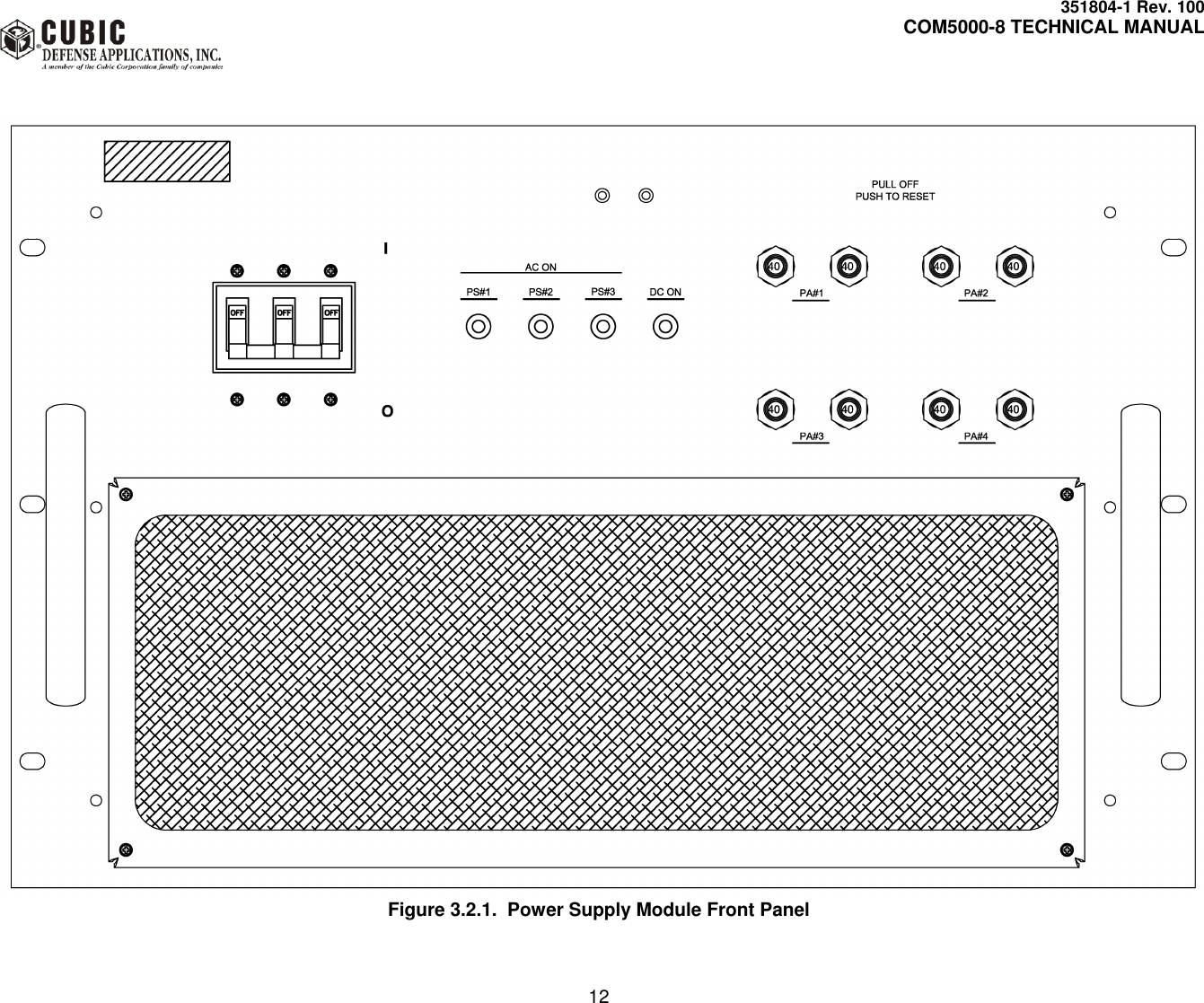
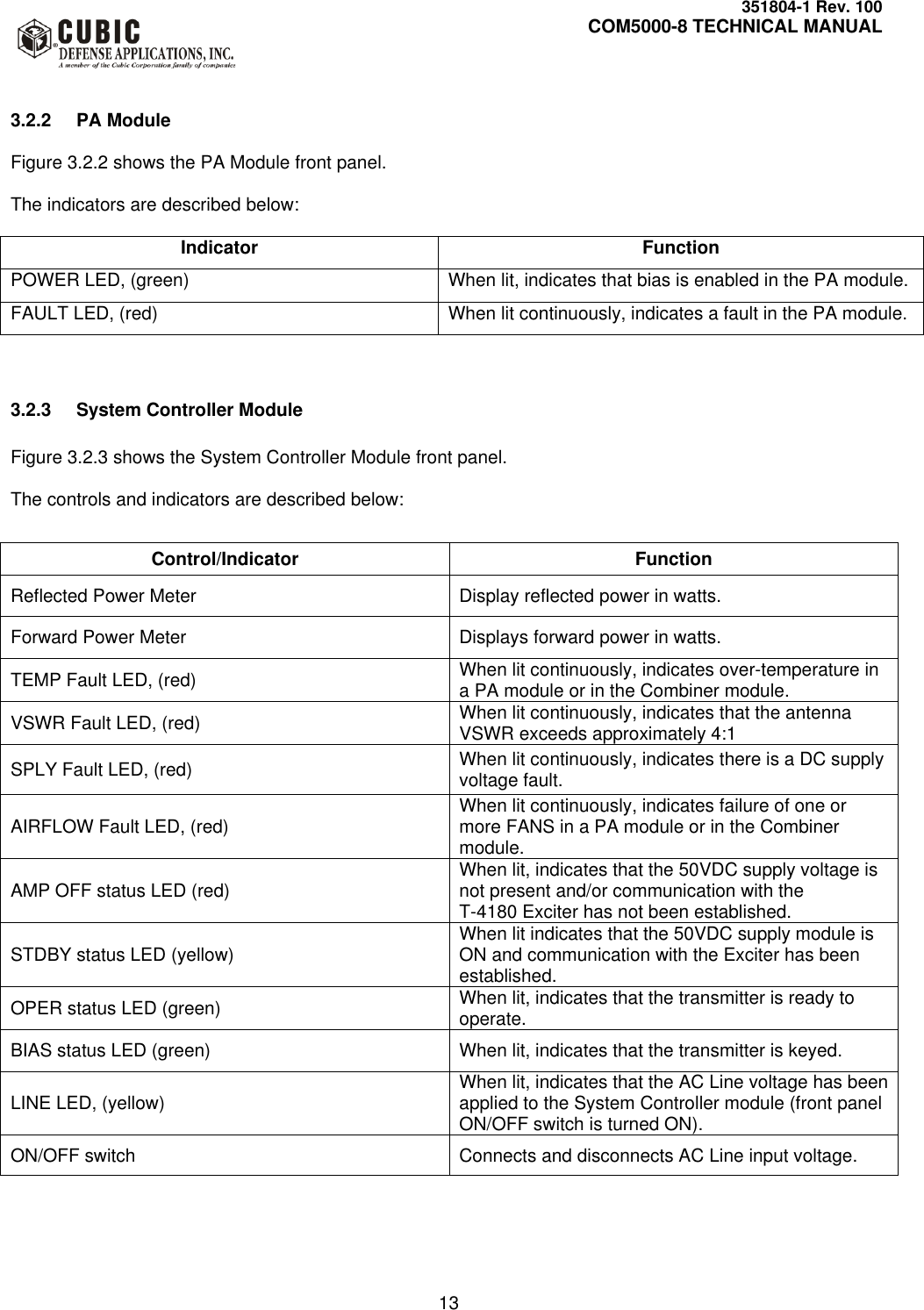
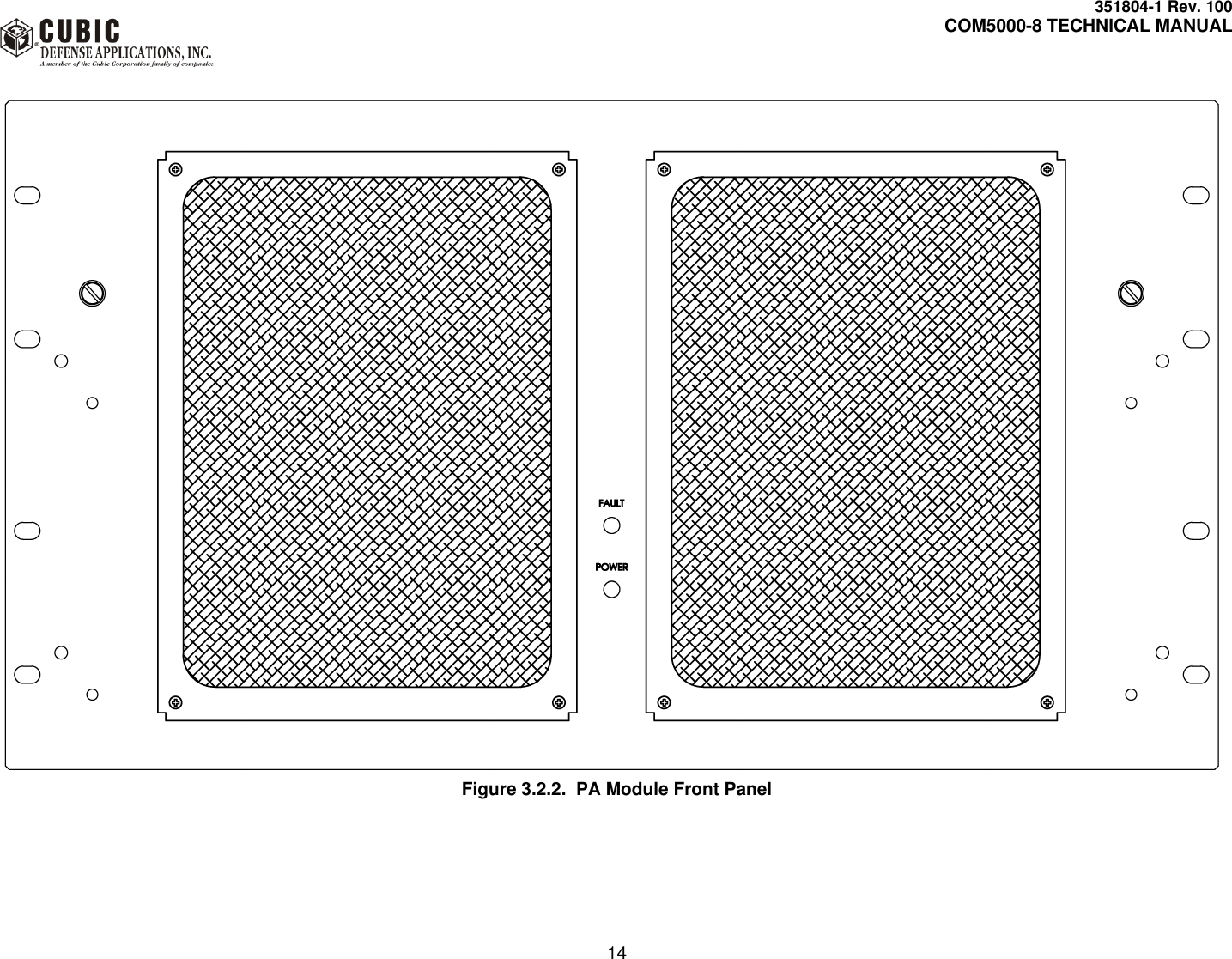
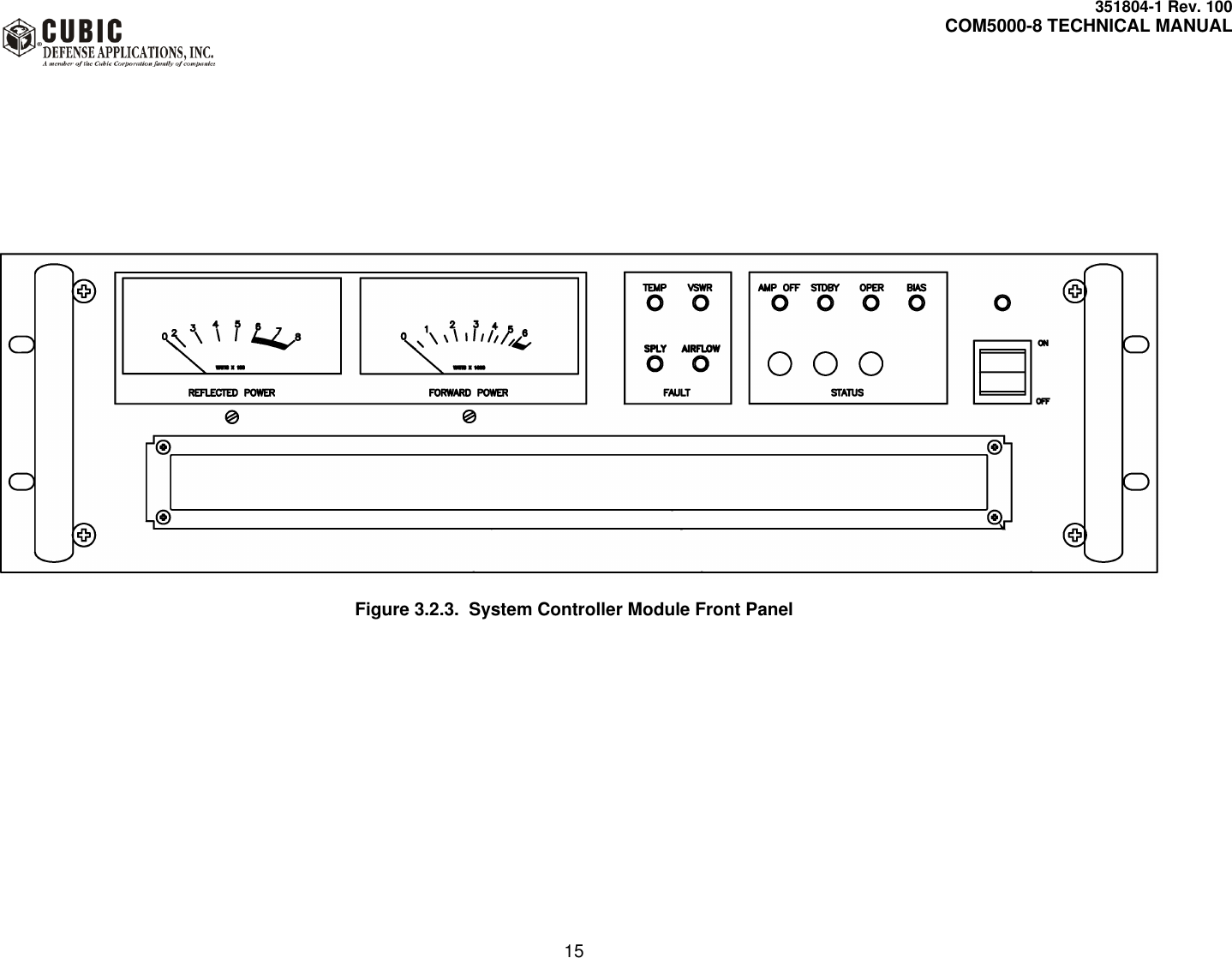
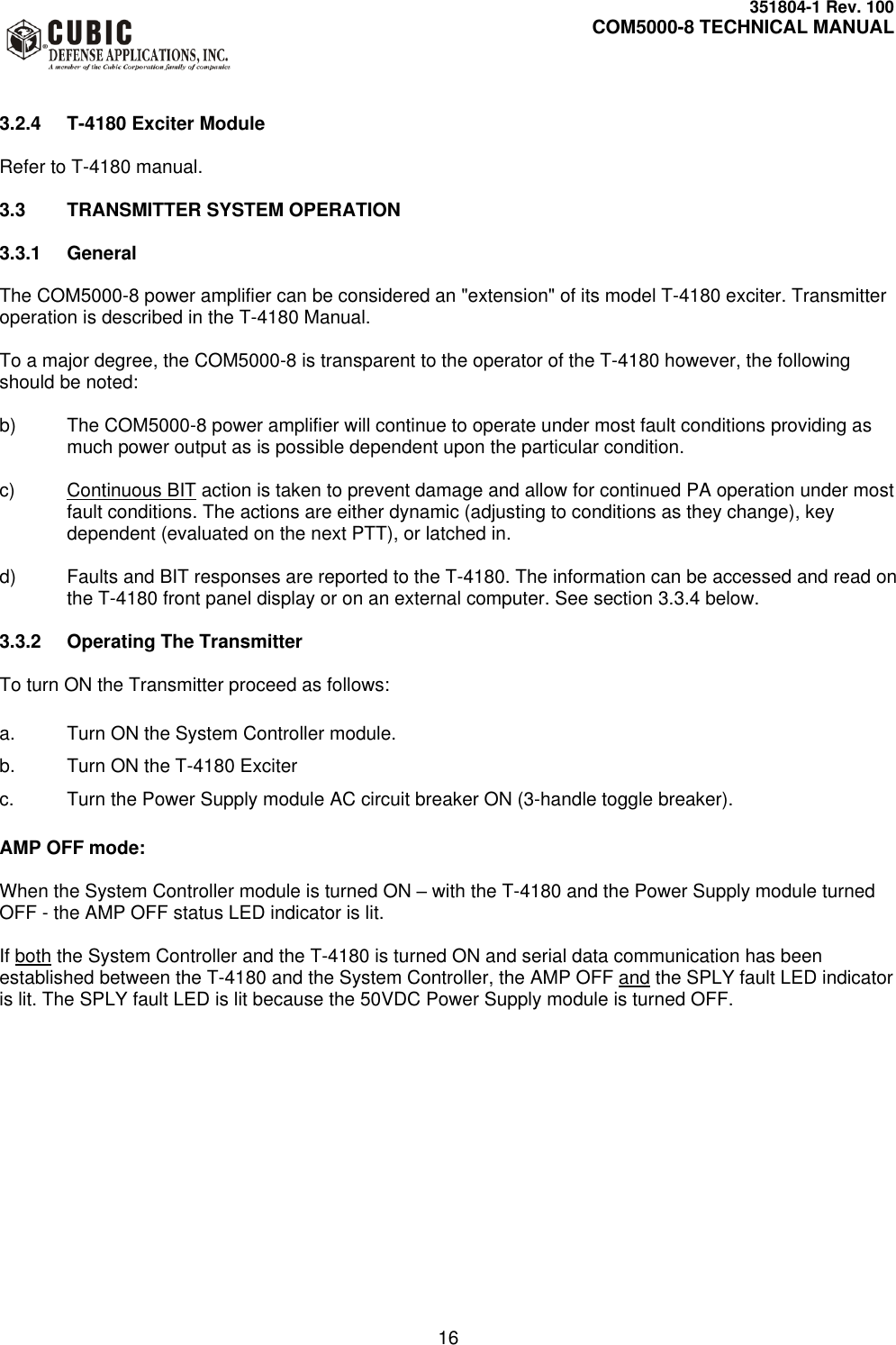
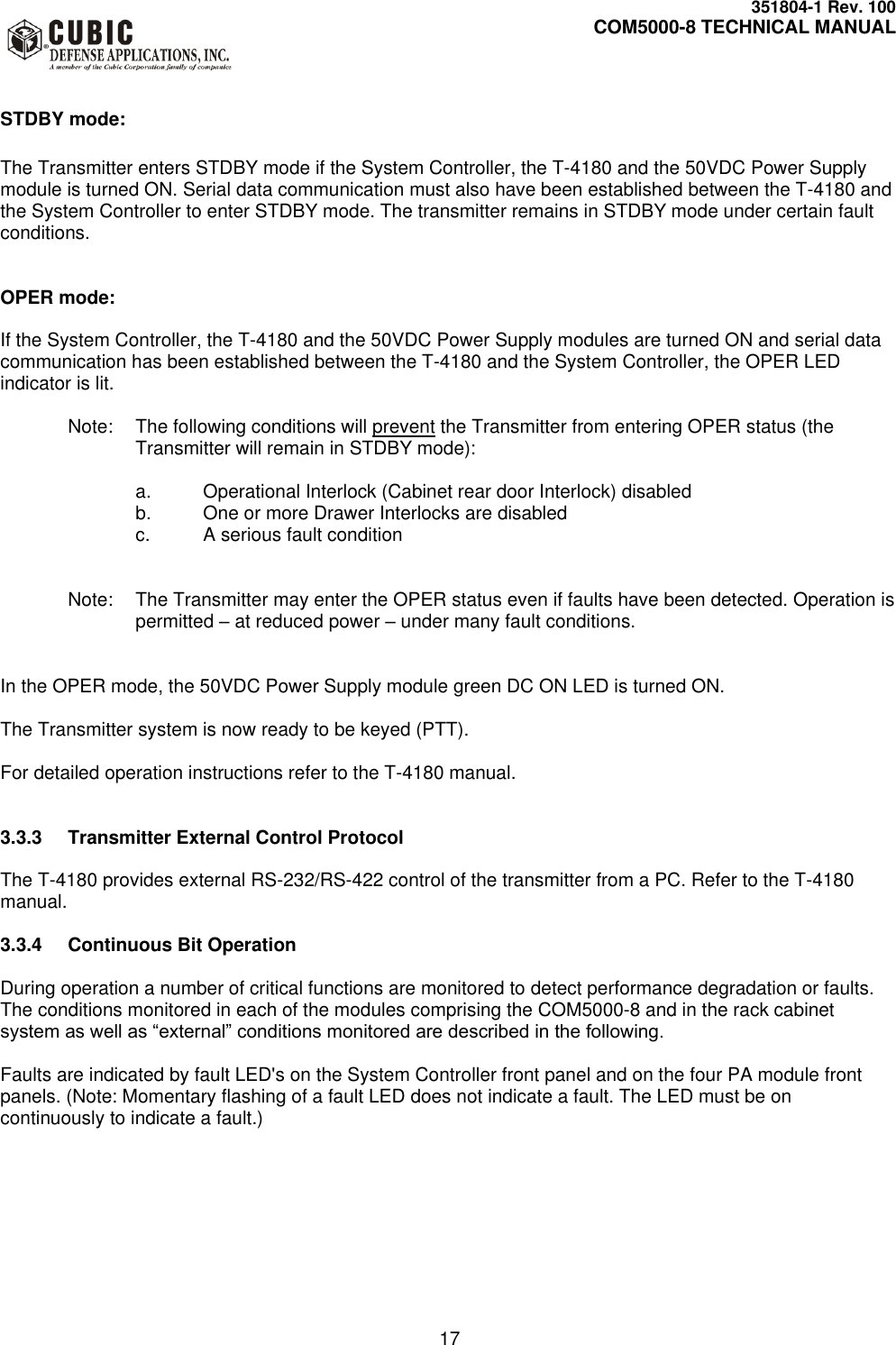
![351804-1 Rev. 100 COM5000-8 TECHNICAL MANUAL 18 In addition to the System Controller and PA module LED display, the T-4180 Status display will show operational parameters and specific fault conditions. The first of two T-4180 status screens is evoked as follows: From the T-4180 default screen press [NEXT] On the new screen press [PASTAT] The first of two status screen appears T-4180 Status screen #1: Press [MORE] to view the second status screen. T-4180 Status screen #2: The fault indications are as follows: a. On screen #1, if a fault is detected, "OK" will change to "FLT". b. "COMS" show status of serial communication with the PA module. If communication with a PA module is lost, “OK” will change to “FLT”. c. "FLTS" show PA module faults in HEX format. The definition is shown below. o A critical fault requires the 50V supply voltage to be turned OFF and then ON to reset the fault. o Most other faults are reset by un-keying and then re-keying the Transmitter. FREQ: 29.999 000 MHZ Antenna Intlock OK FWD POWER = 0000 WATTS Cabinet Intlock OK REV POWER = 000 WATTS Combiner Temp OK Combiner Fan OK SWR of 0.0:1 MORE RETURN FLTS P1 P2 P3 P4 000 000 000 000 COMS P1 P2 P3 P4 OK OK OK OK MORE RETURN](https://usermanual.wiki/Cubic-Defense-Applications/COM000-8.User-Manual-I/User-Guide-2770459-Page-28.png)
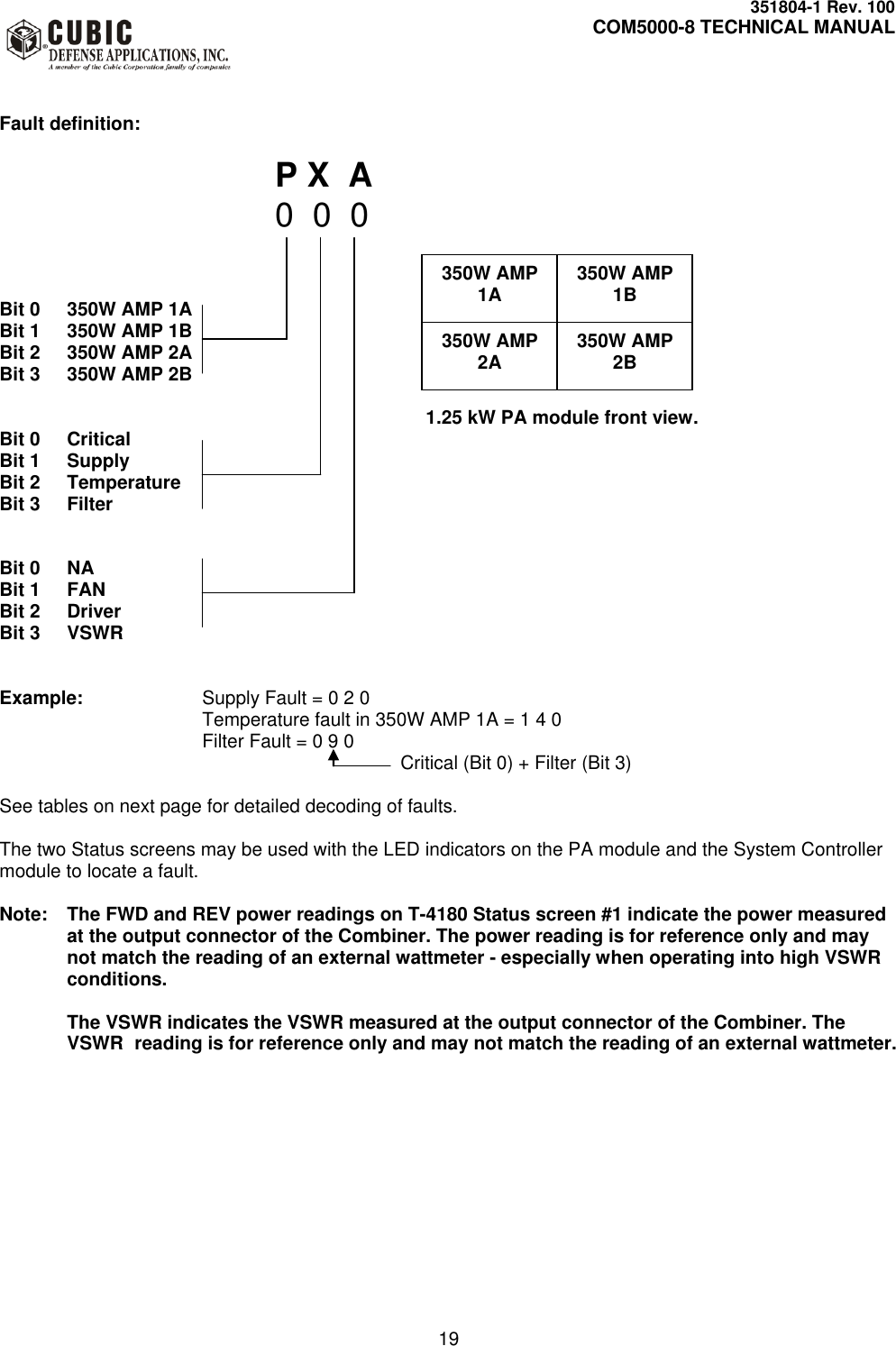

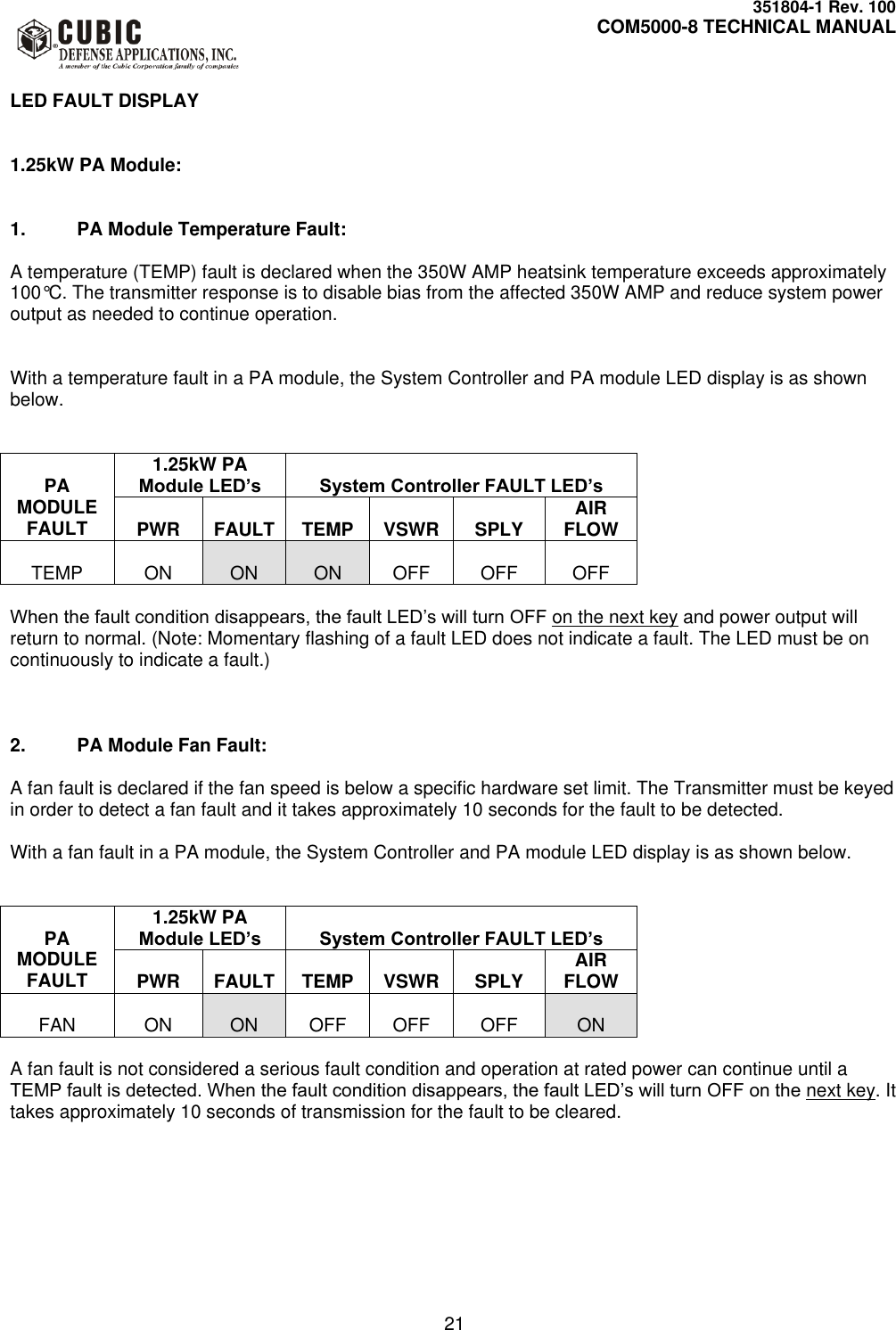
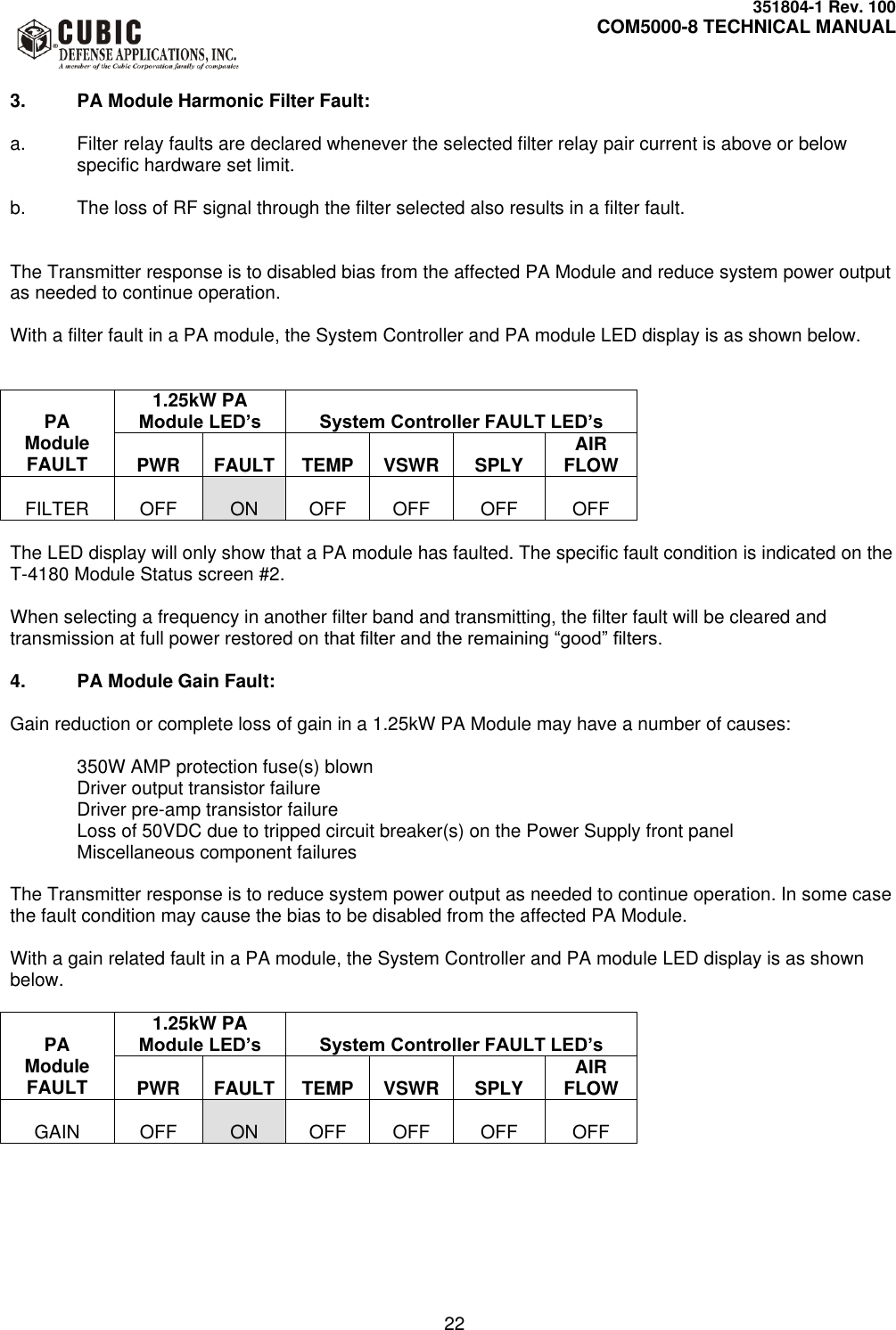
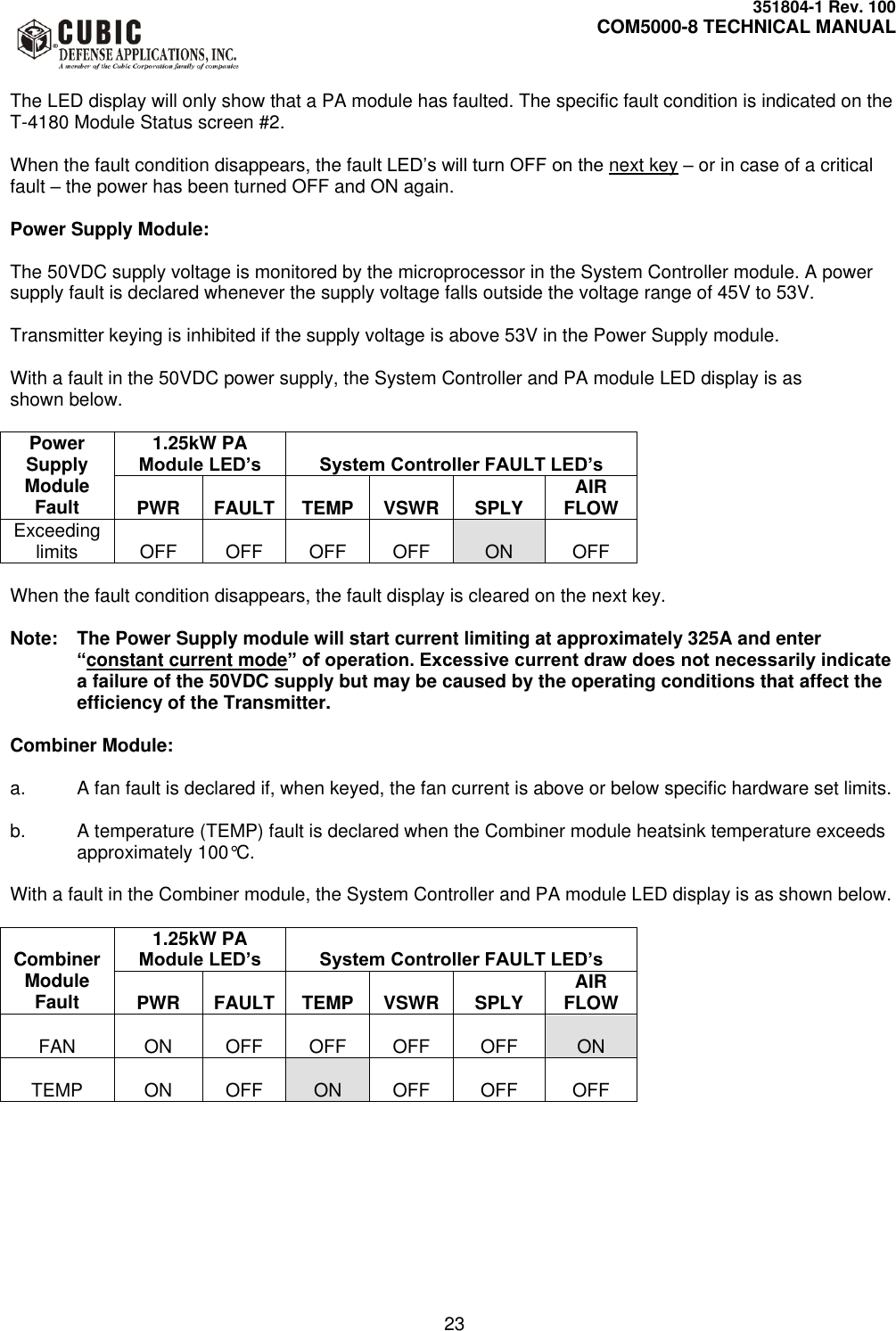
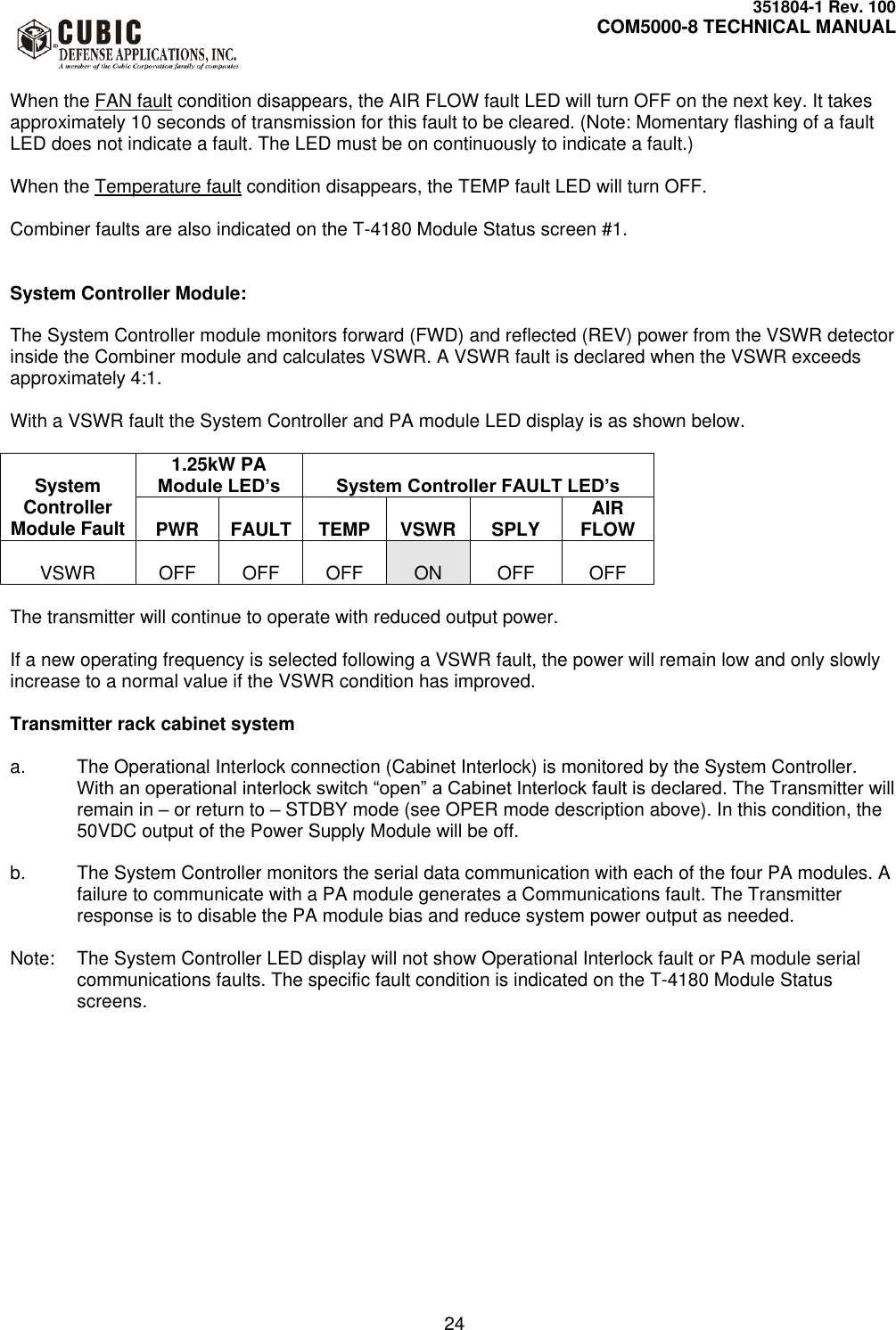
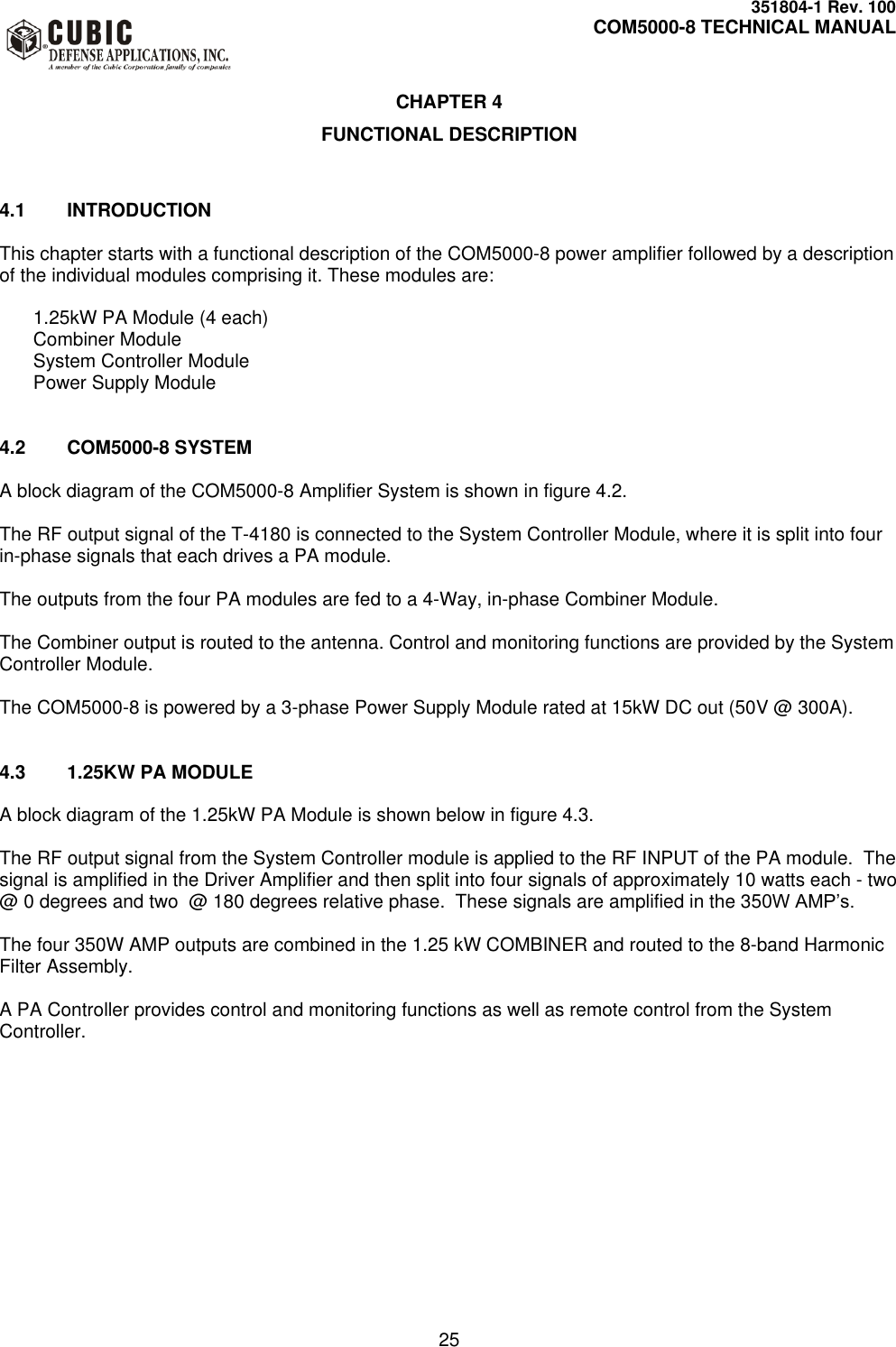
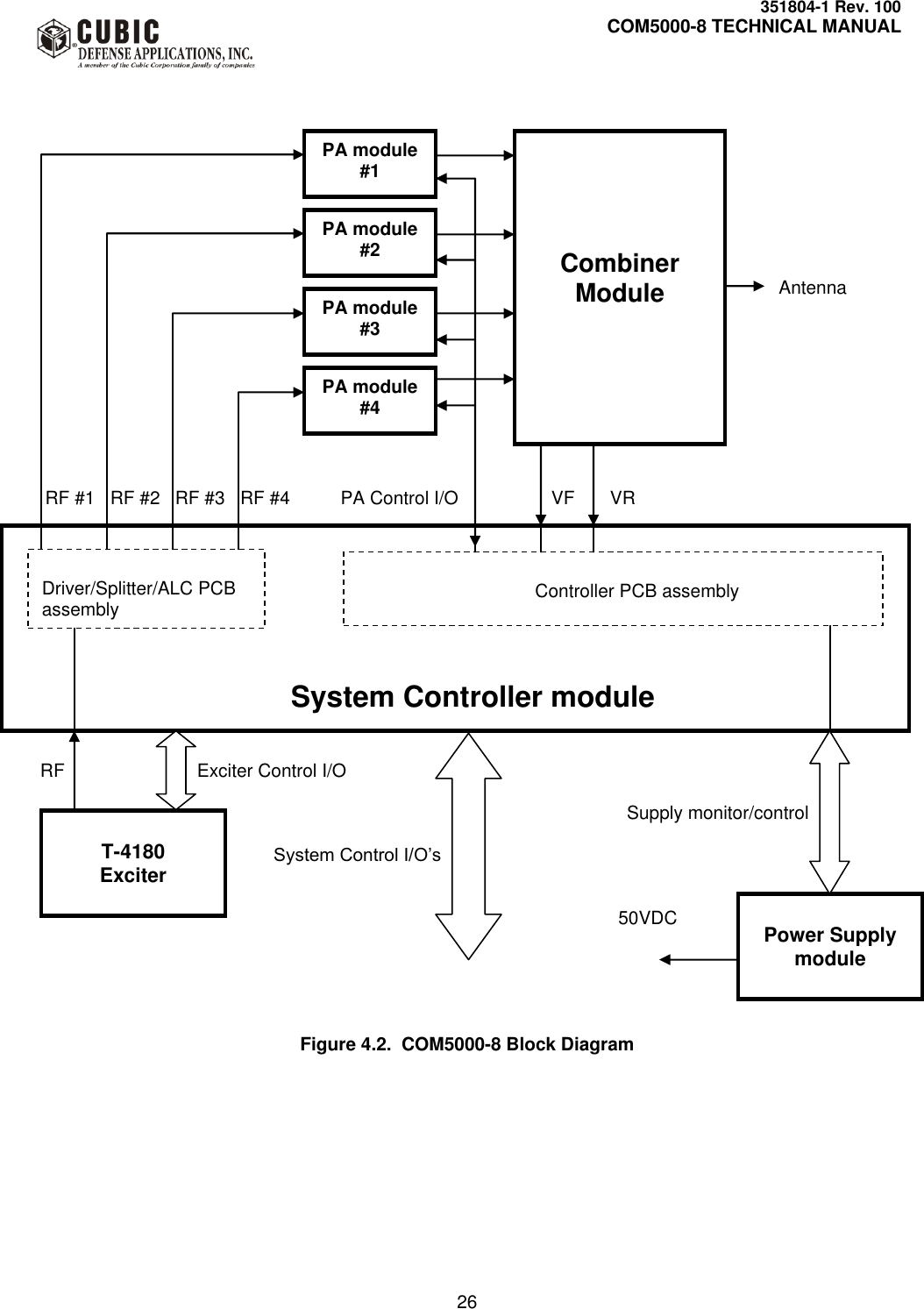
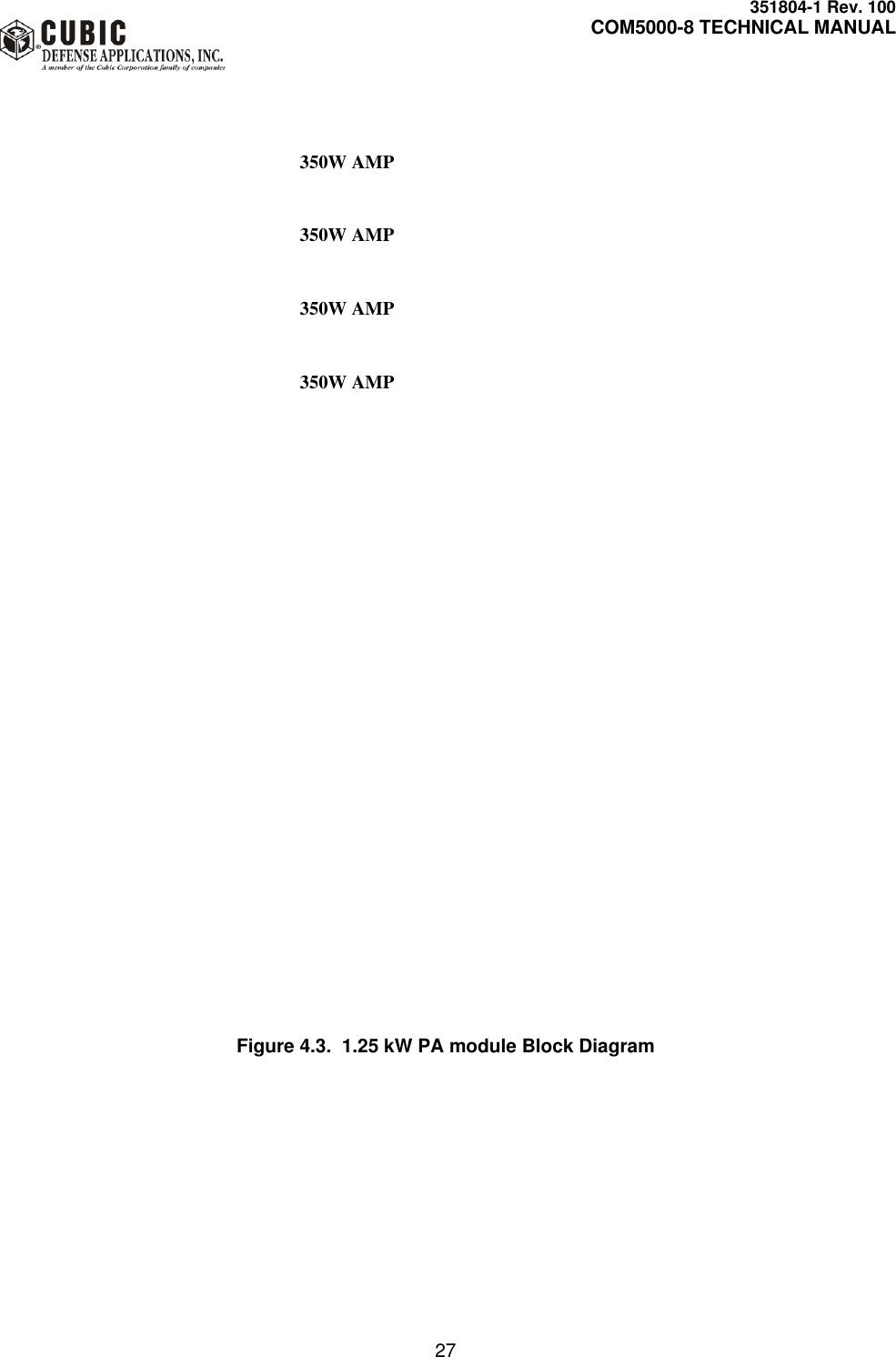
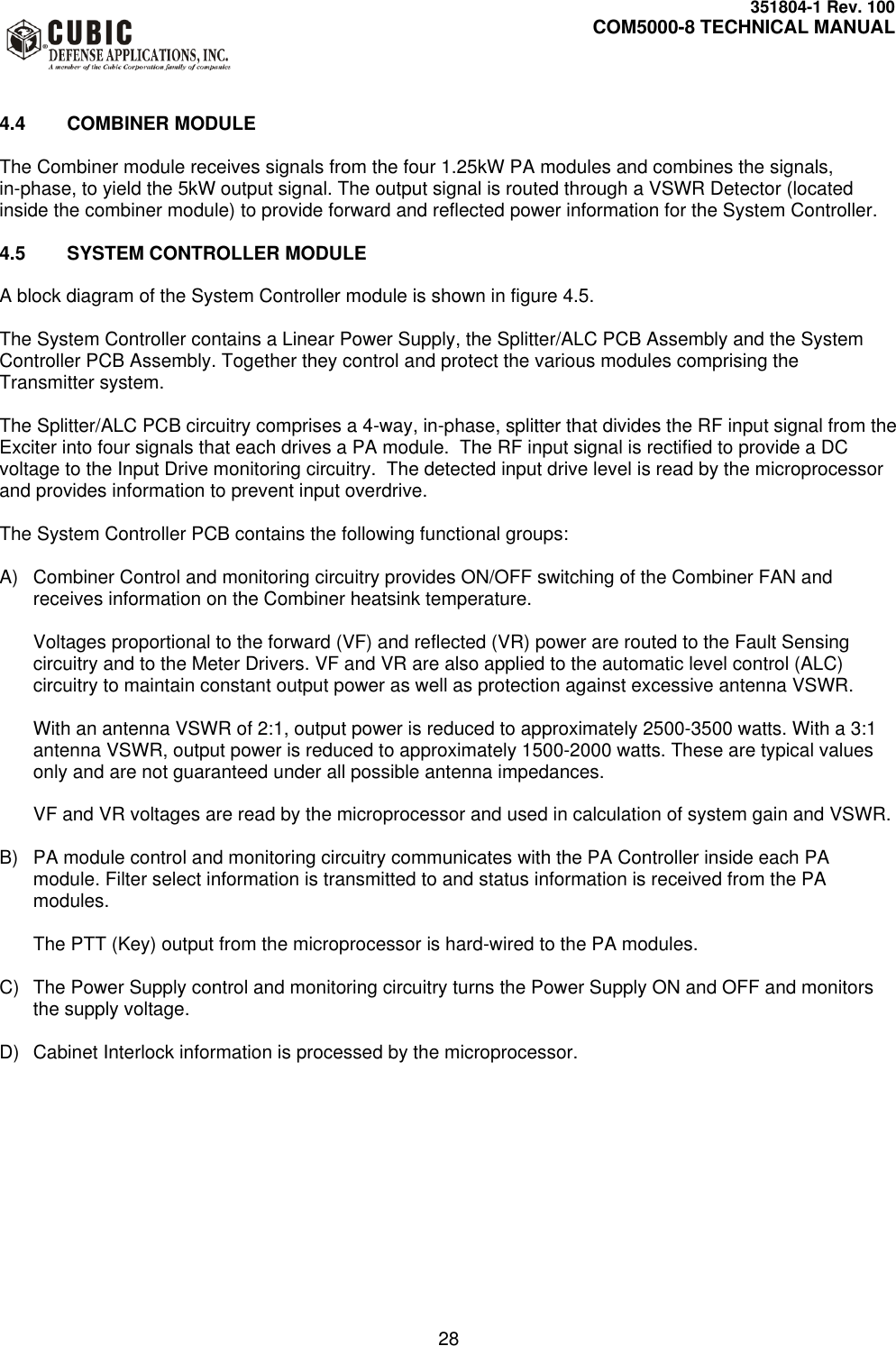
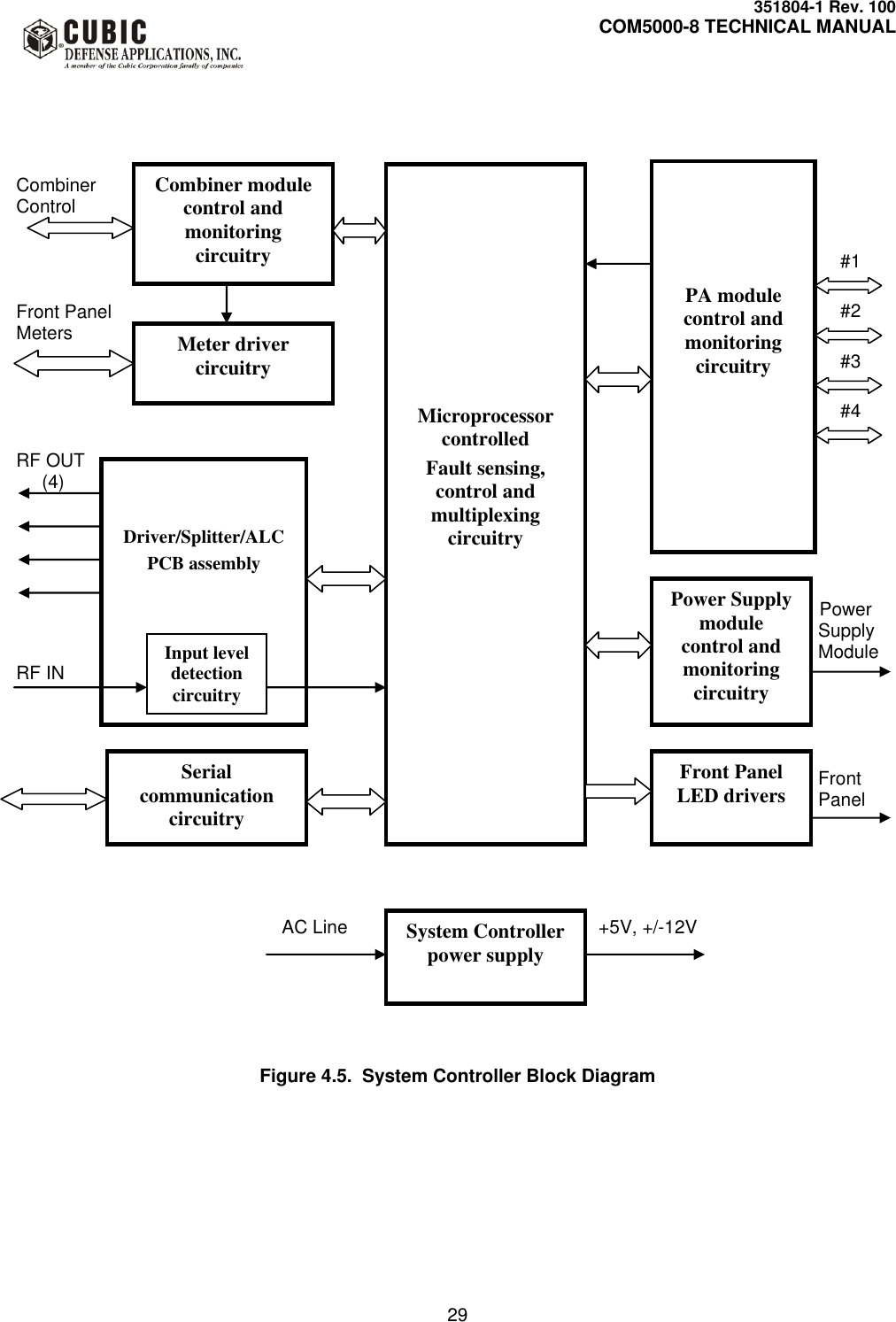
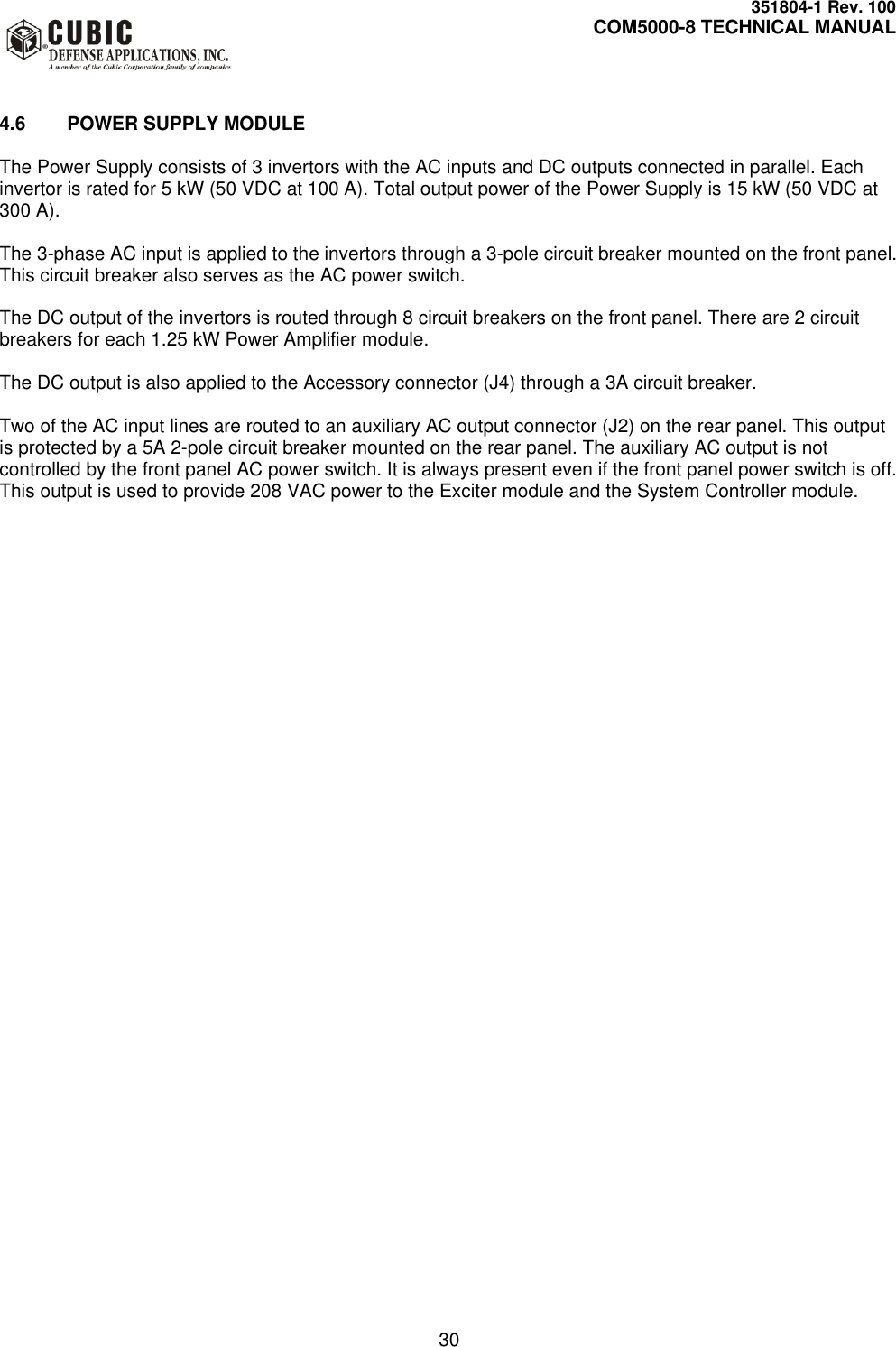
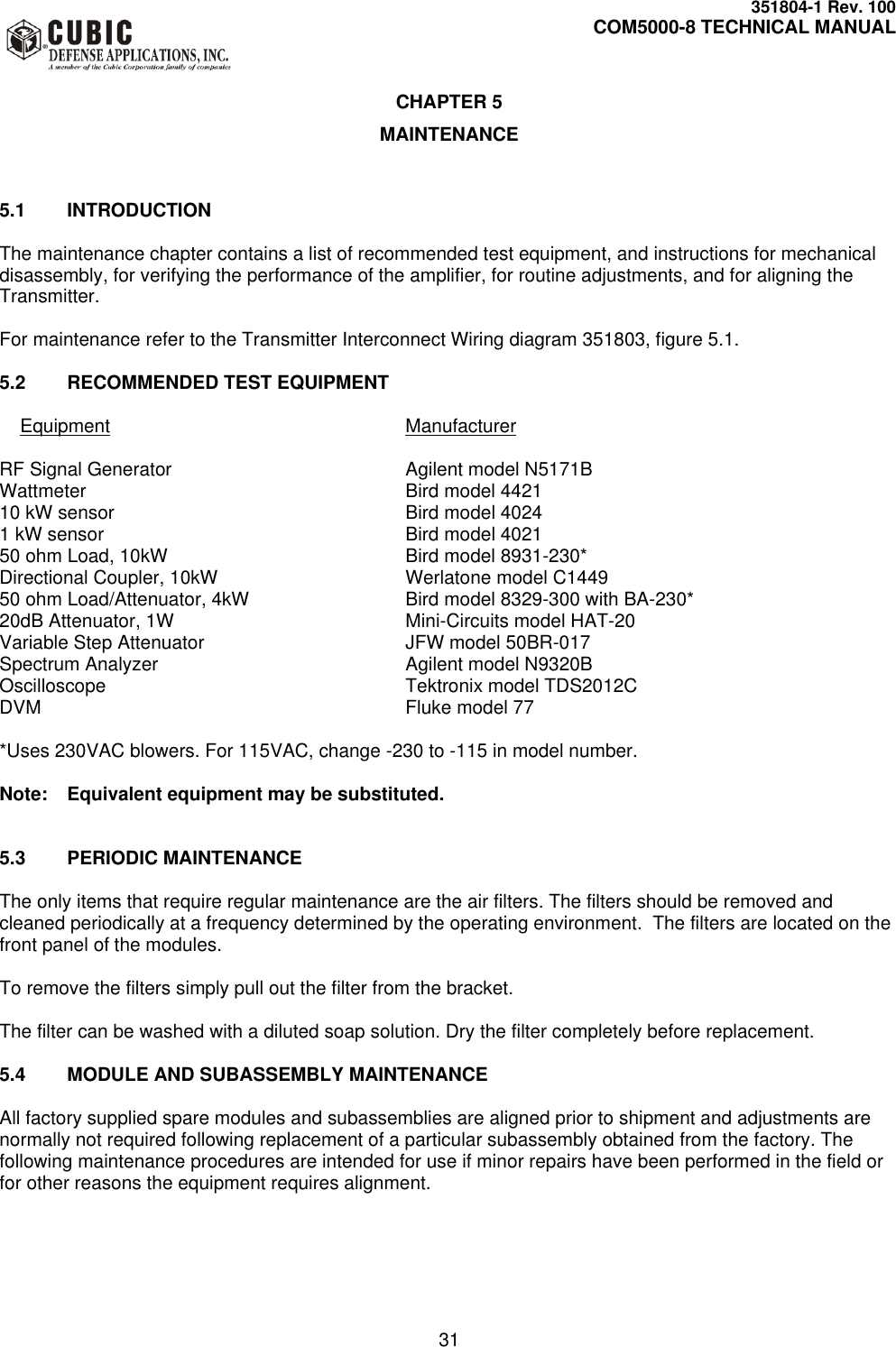
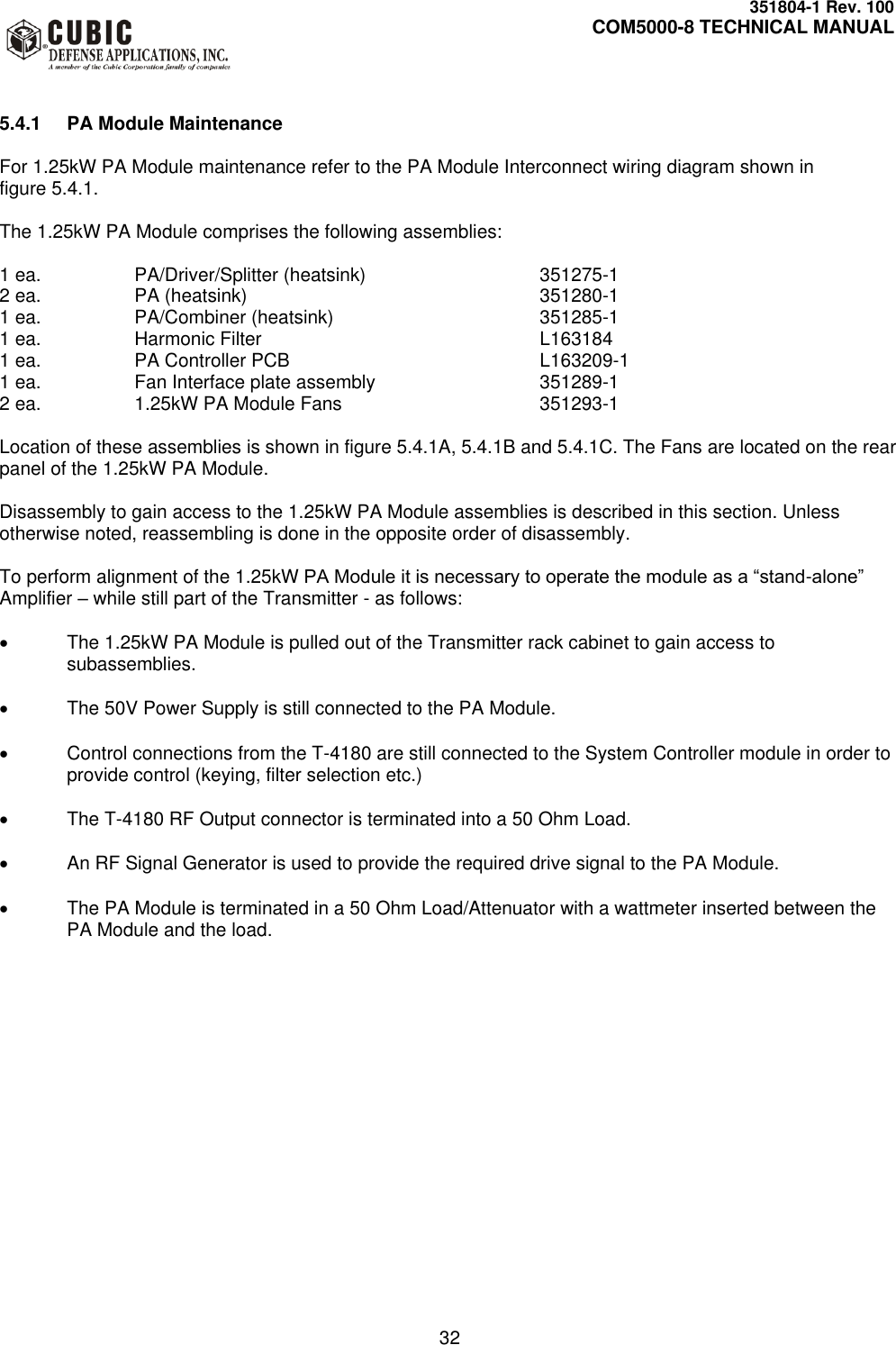
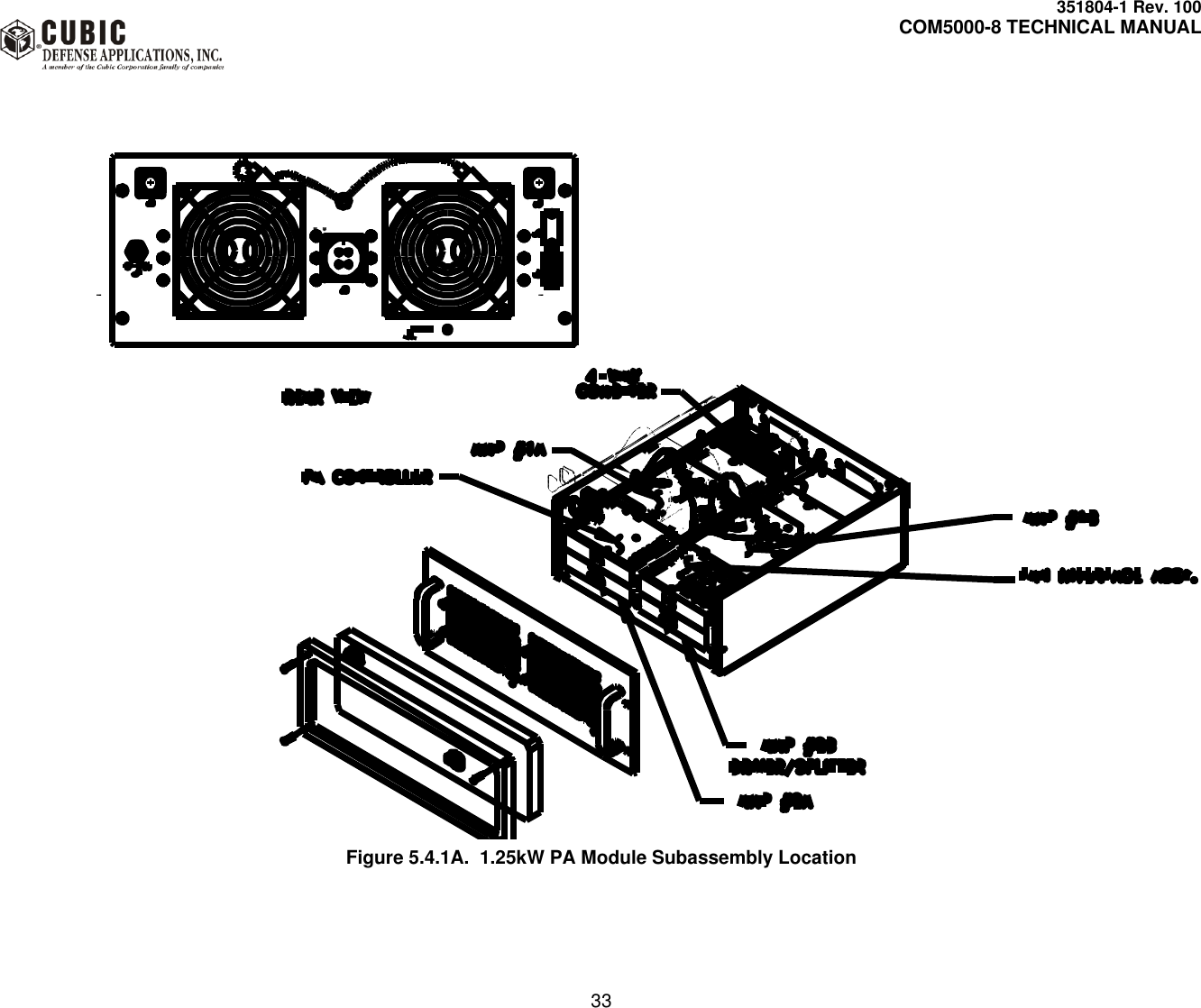
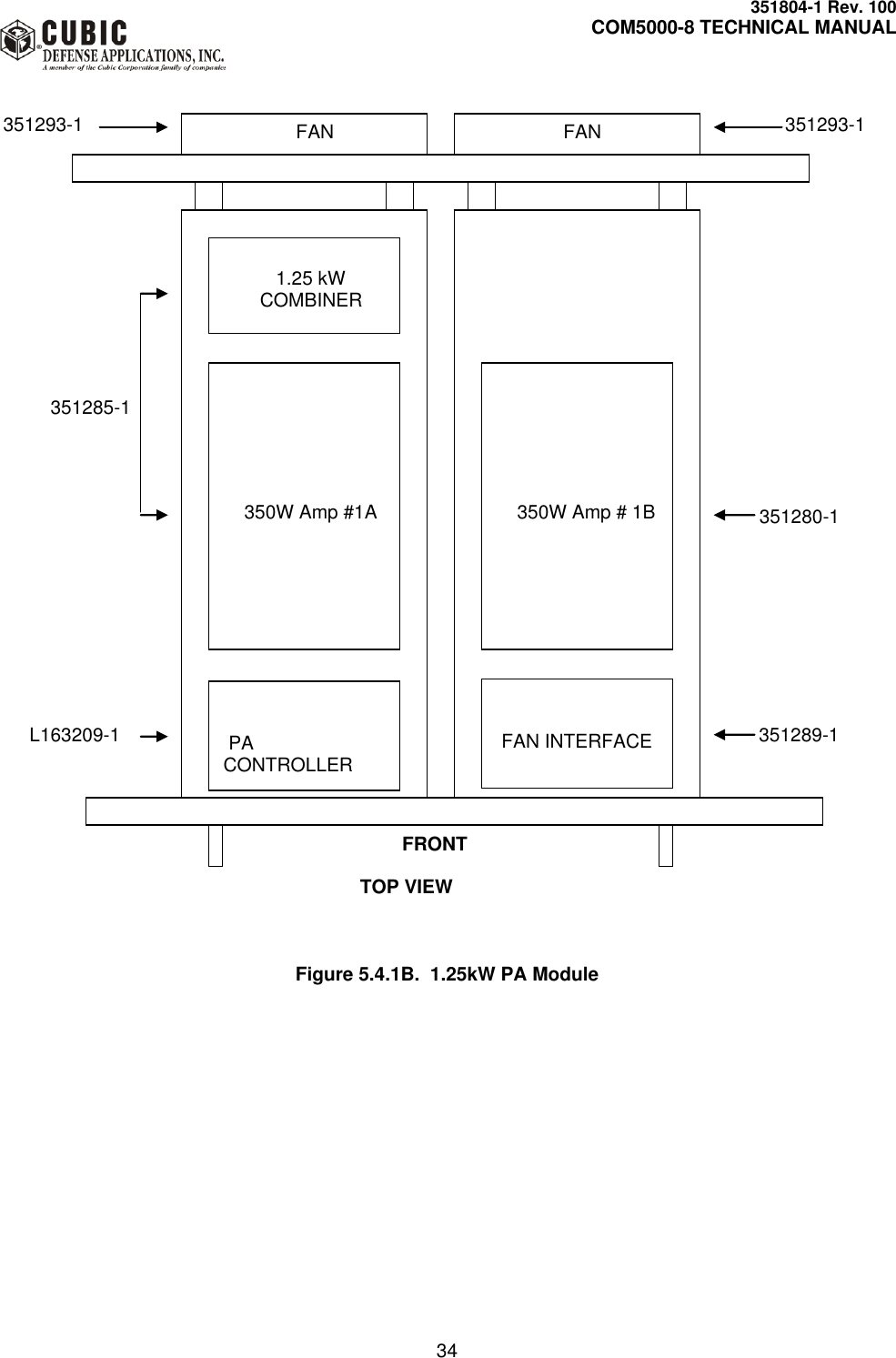
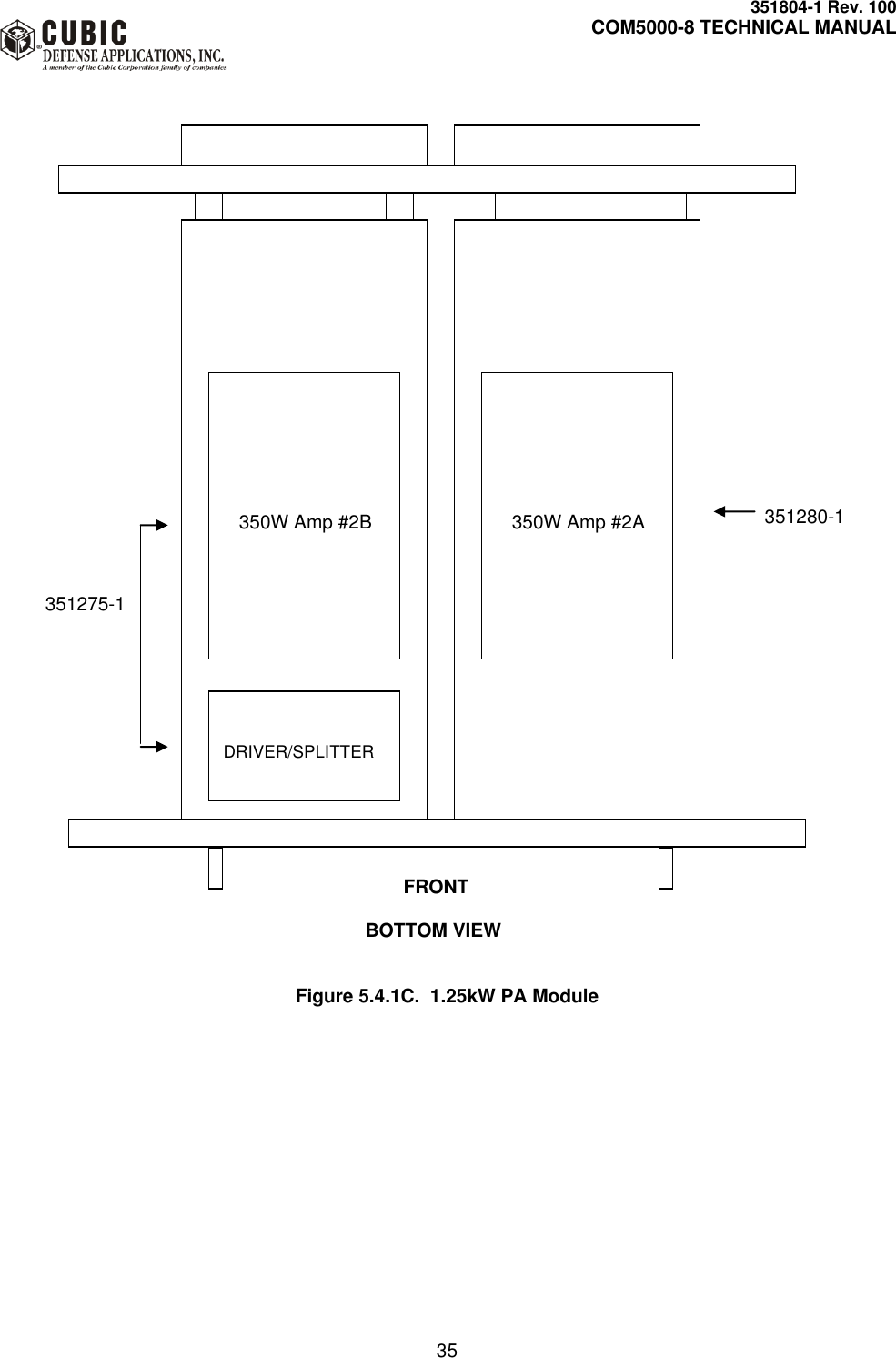
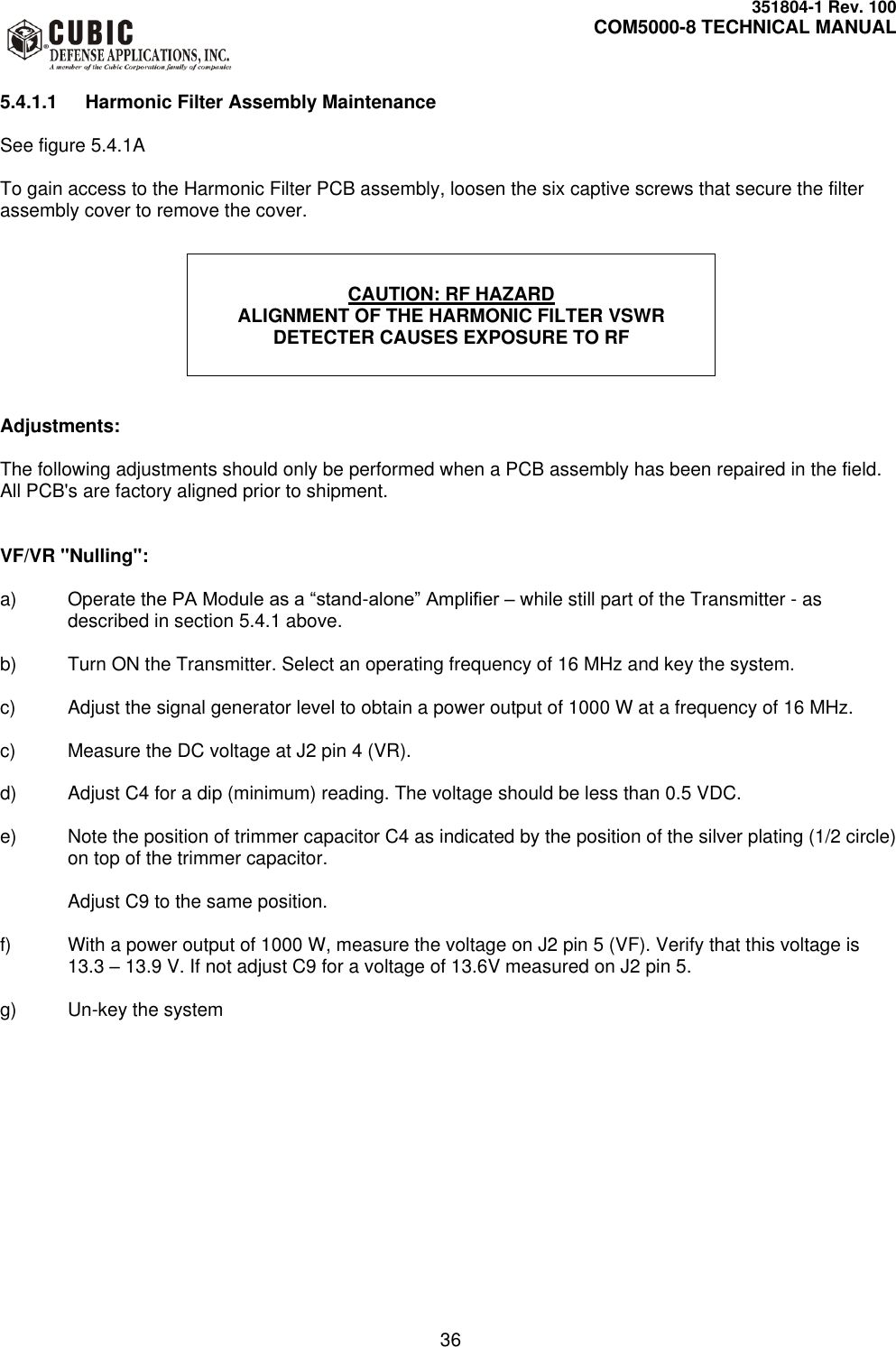
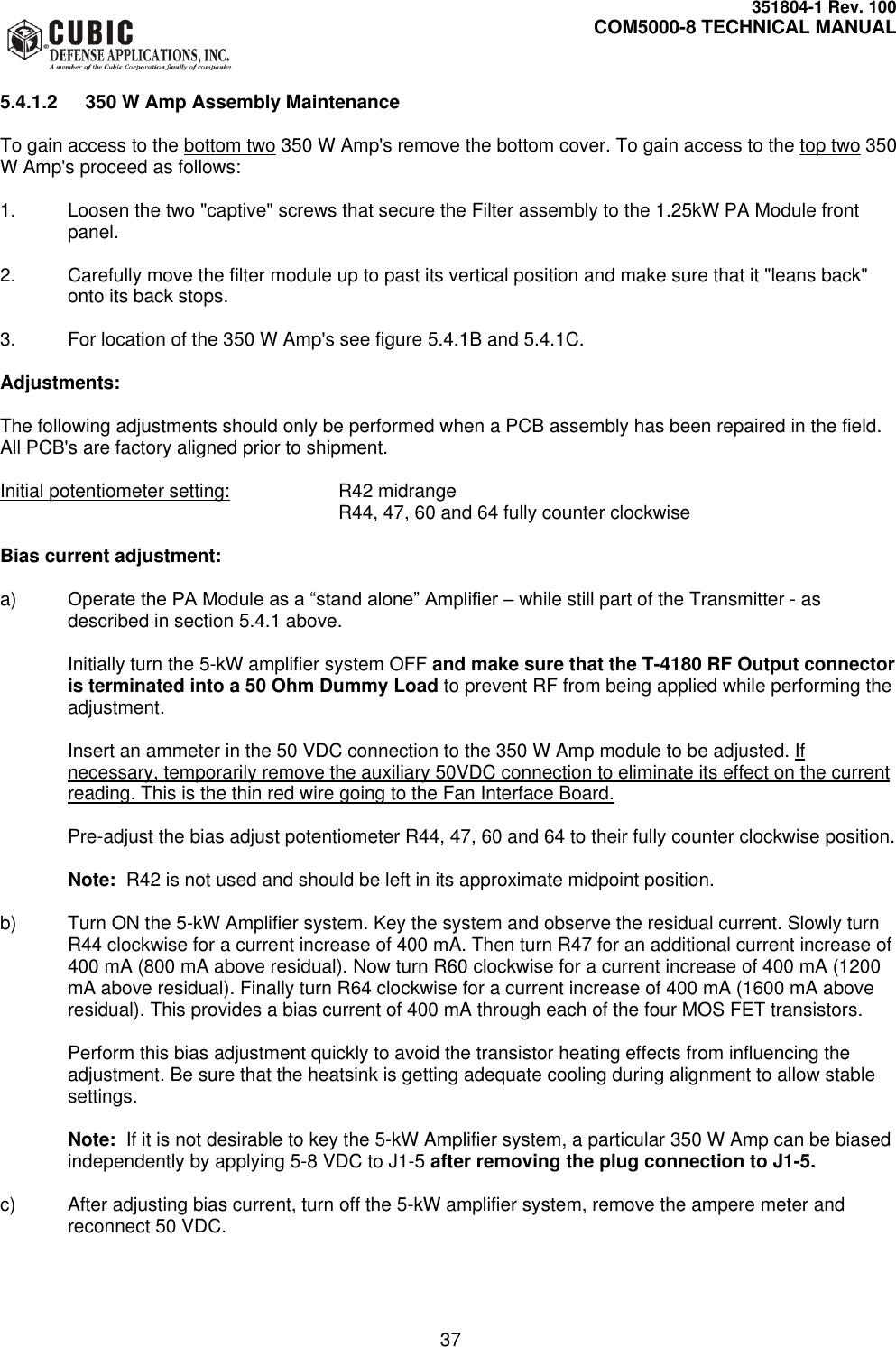
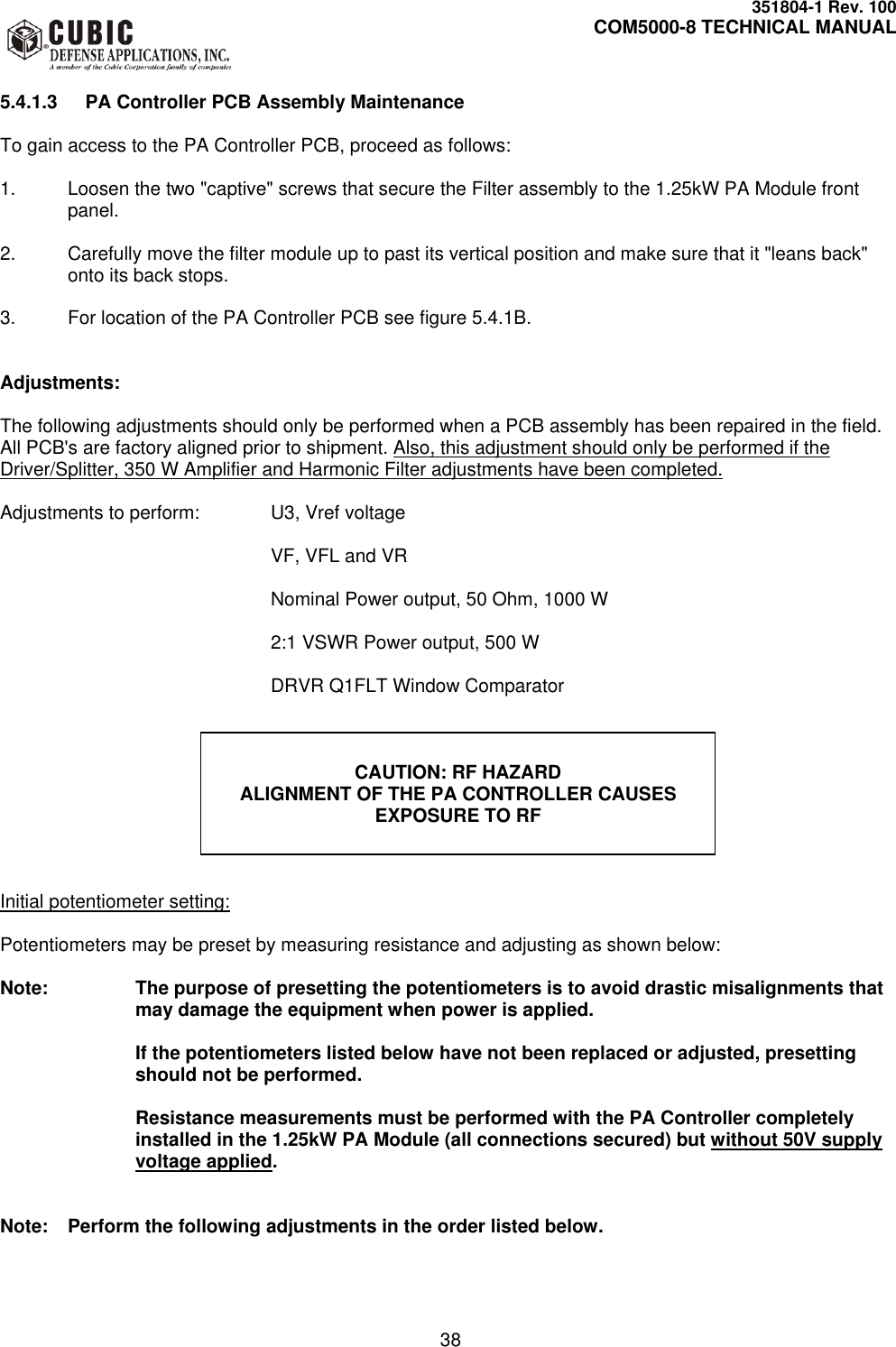
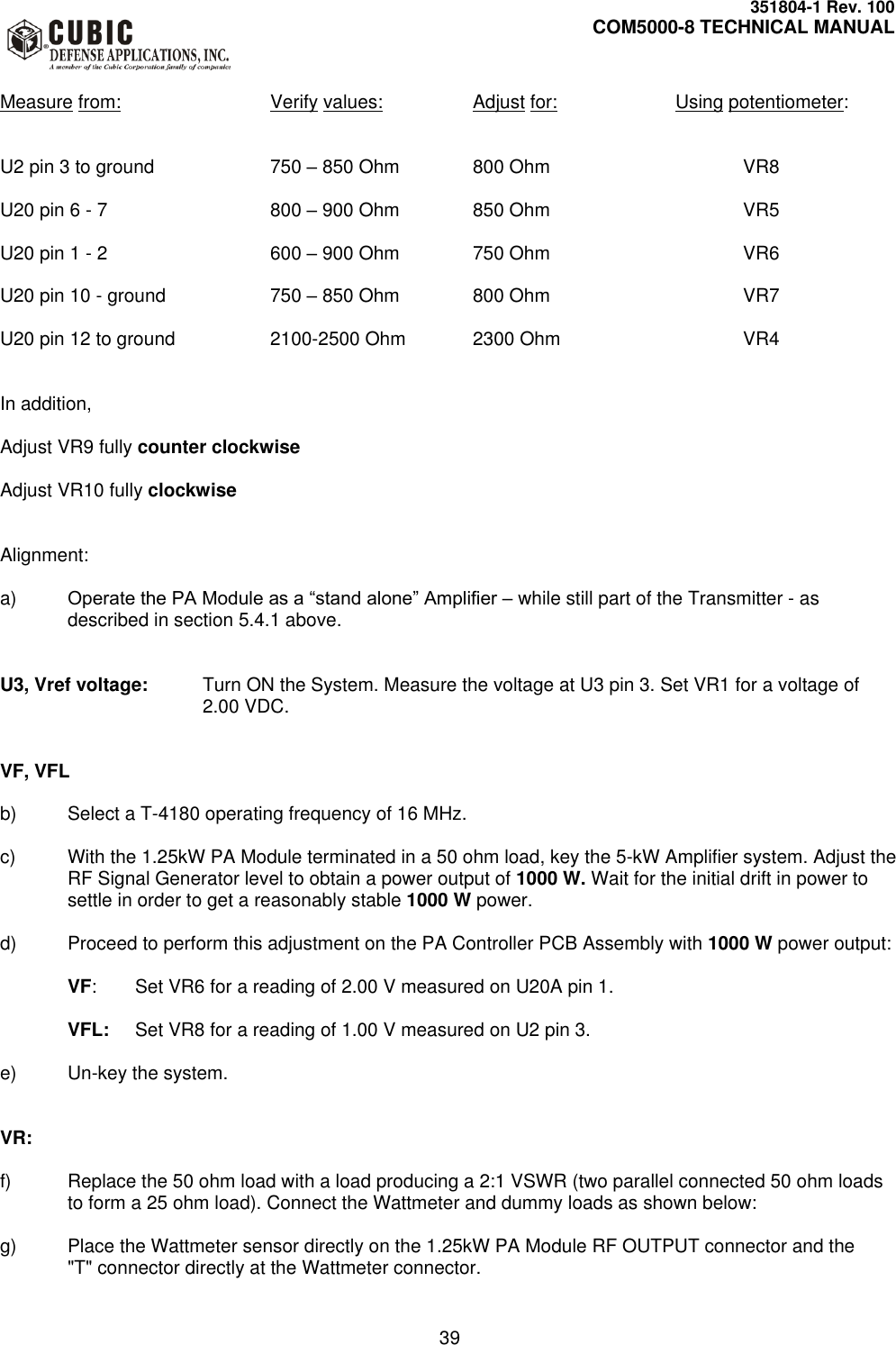
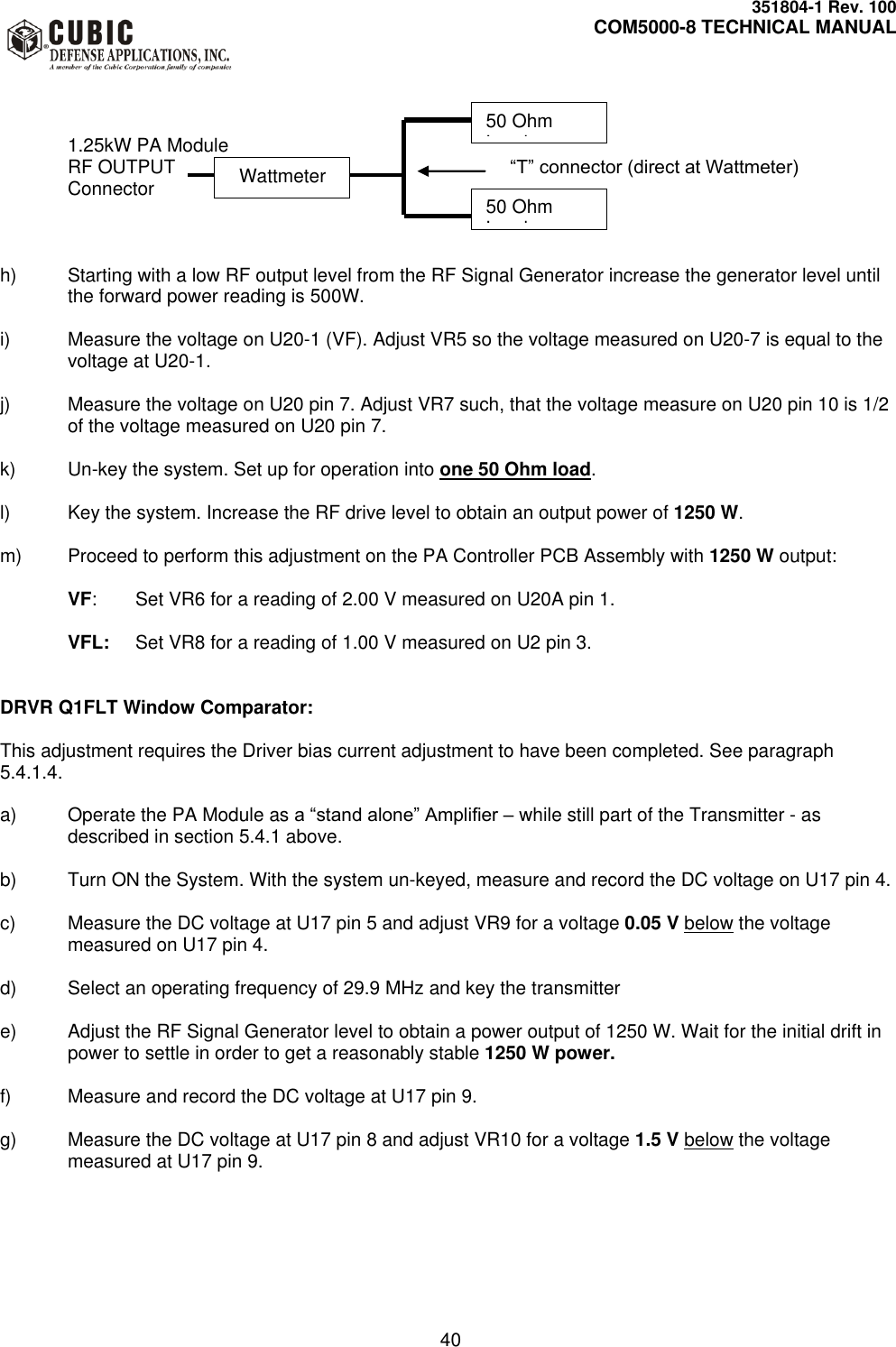
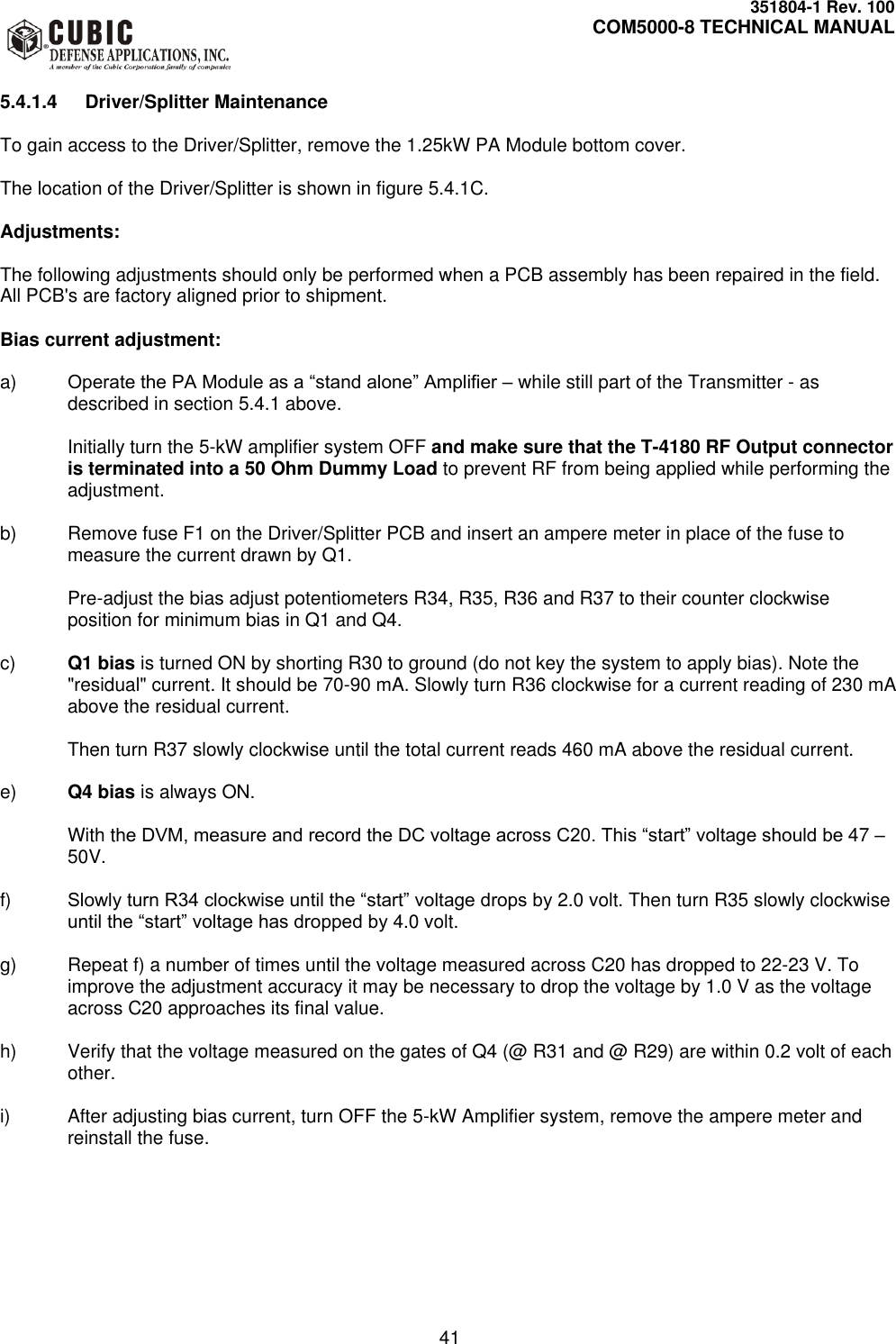
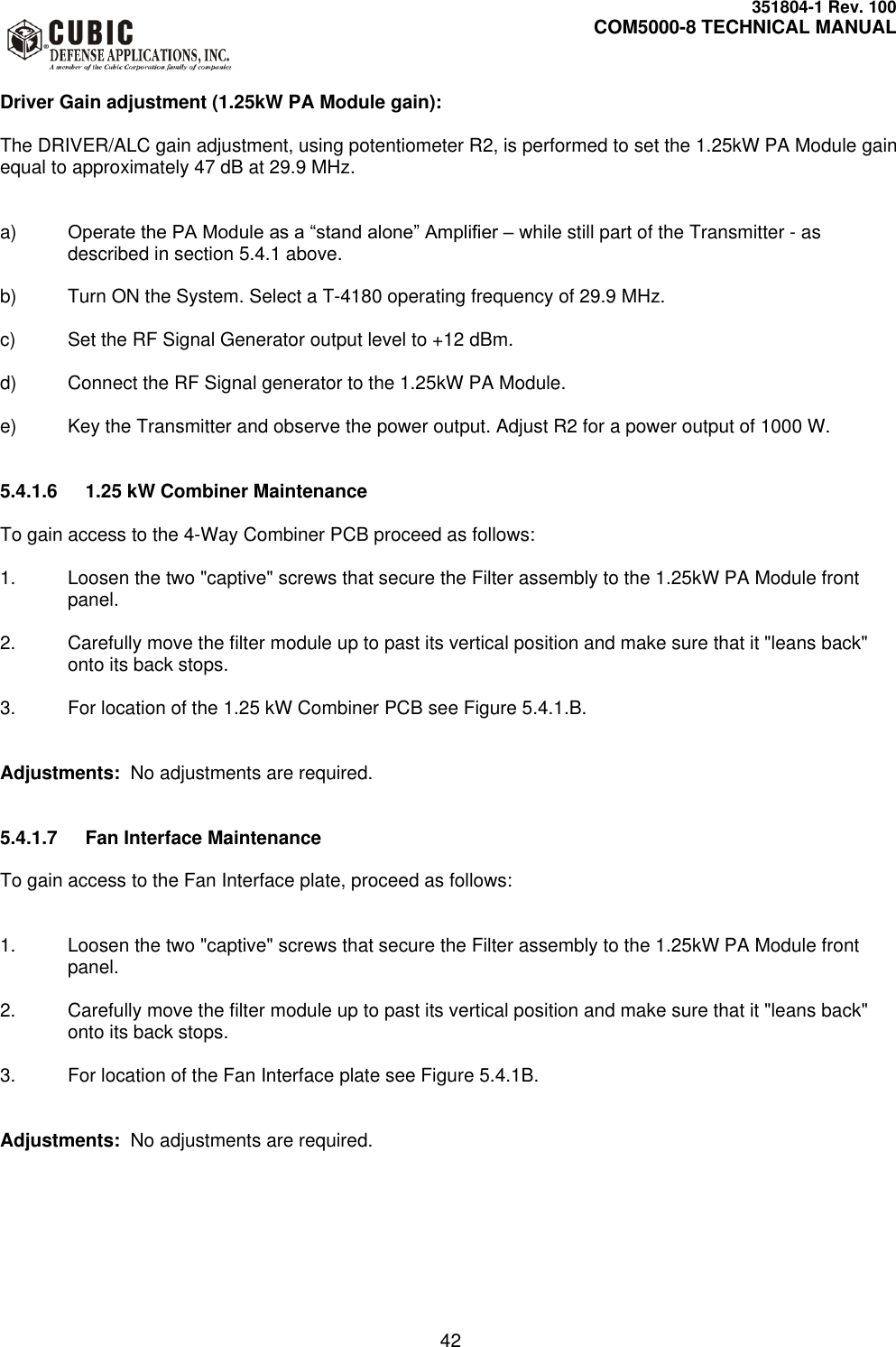
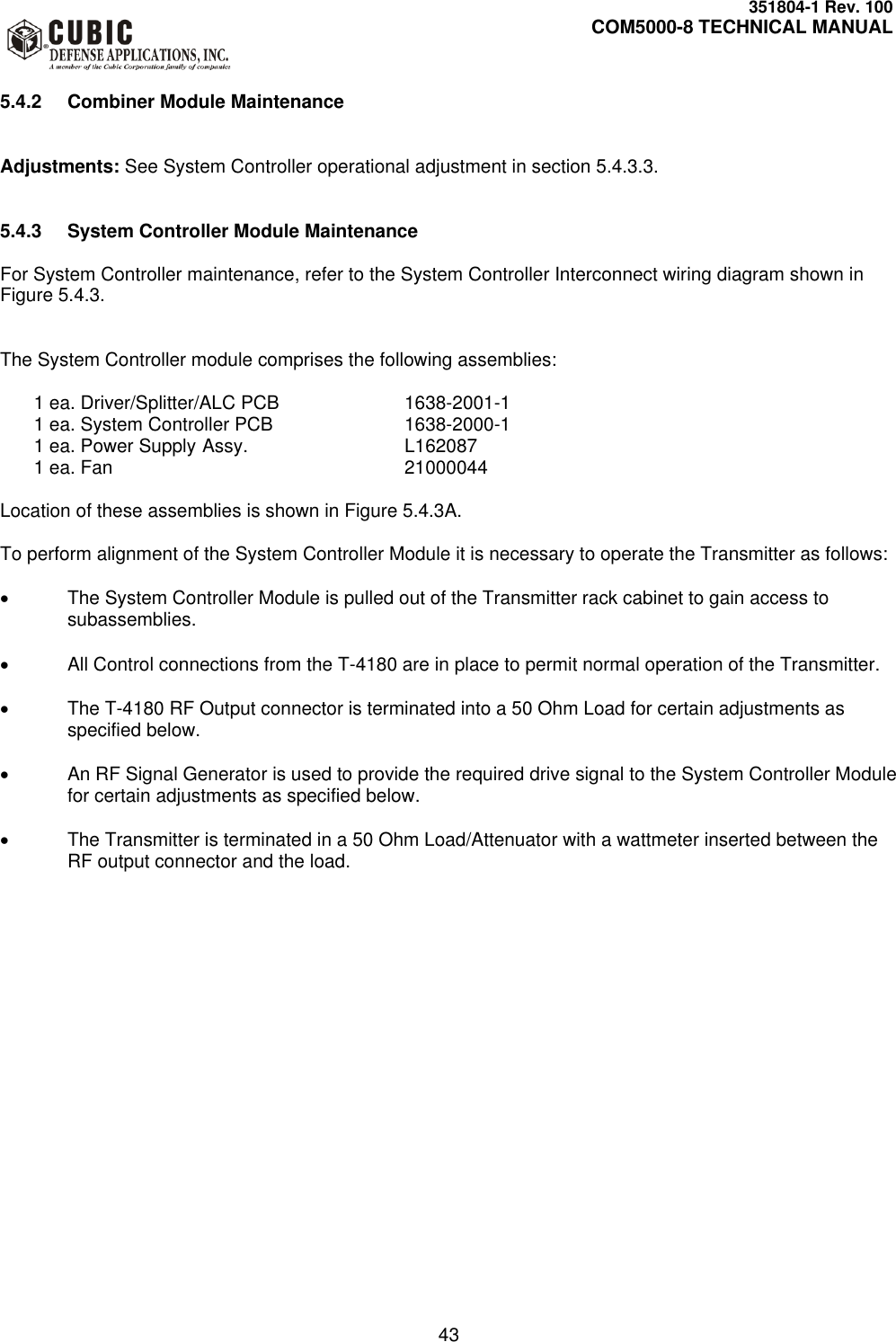
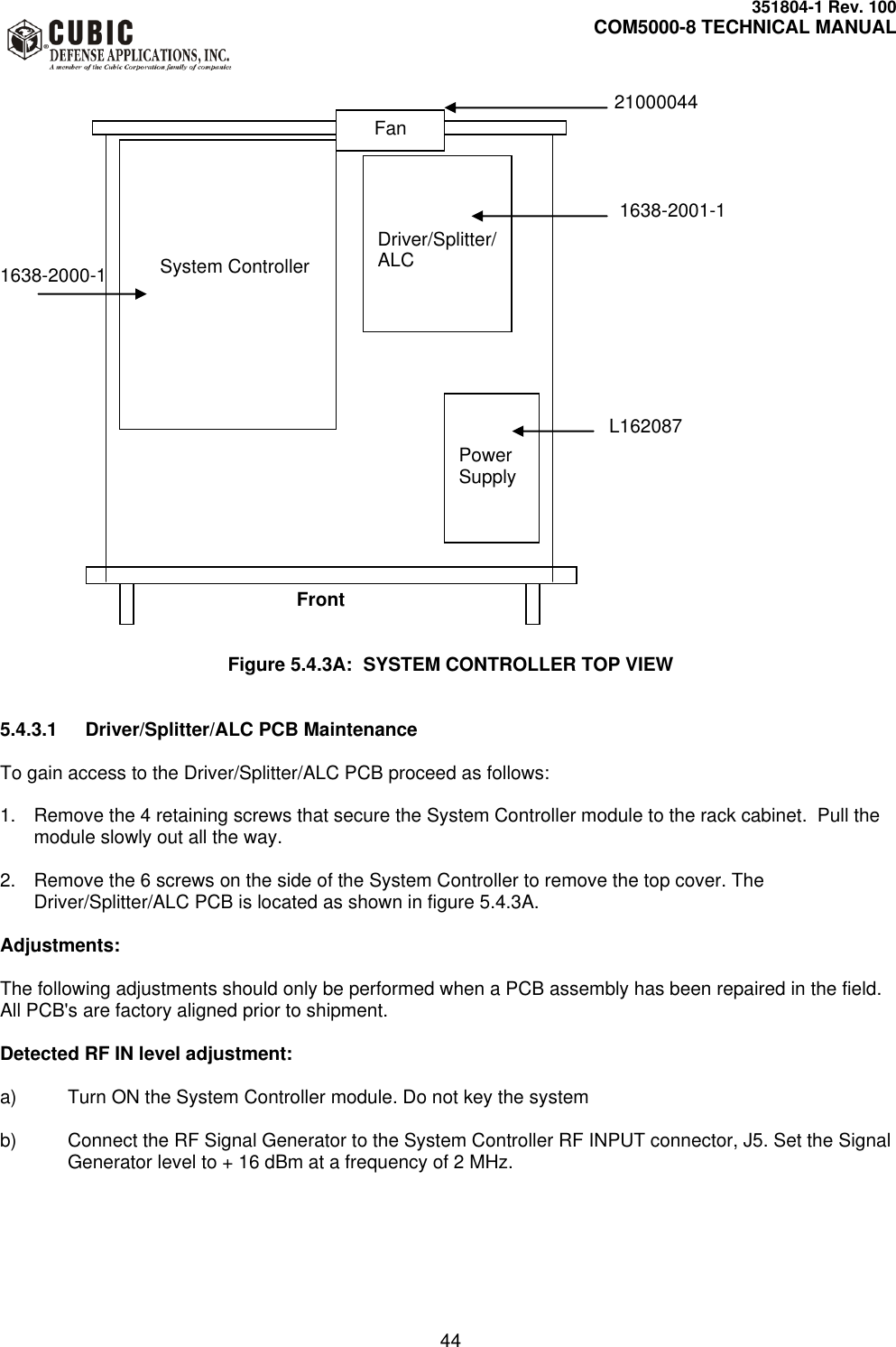
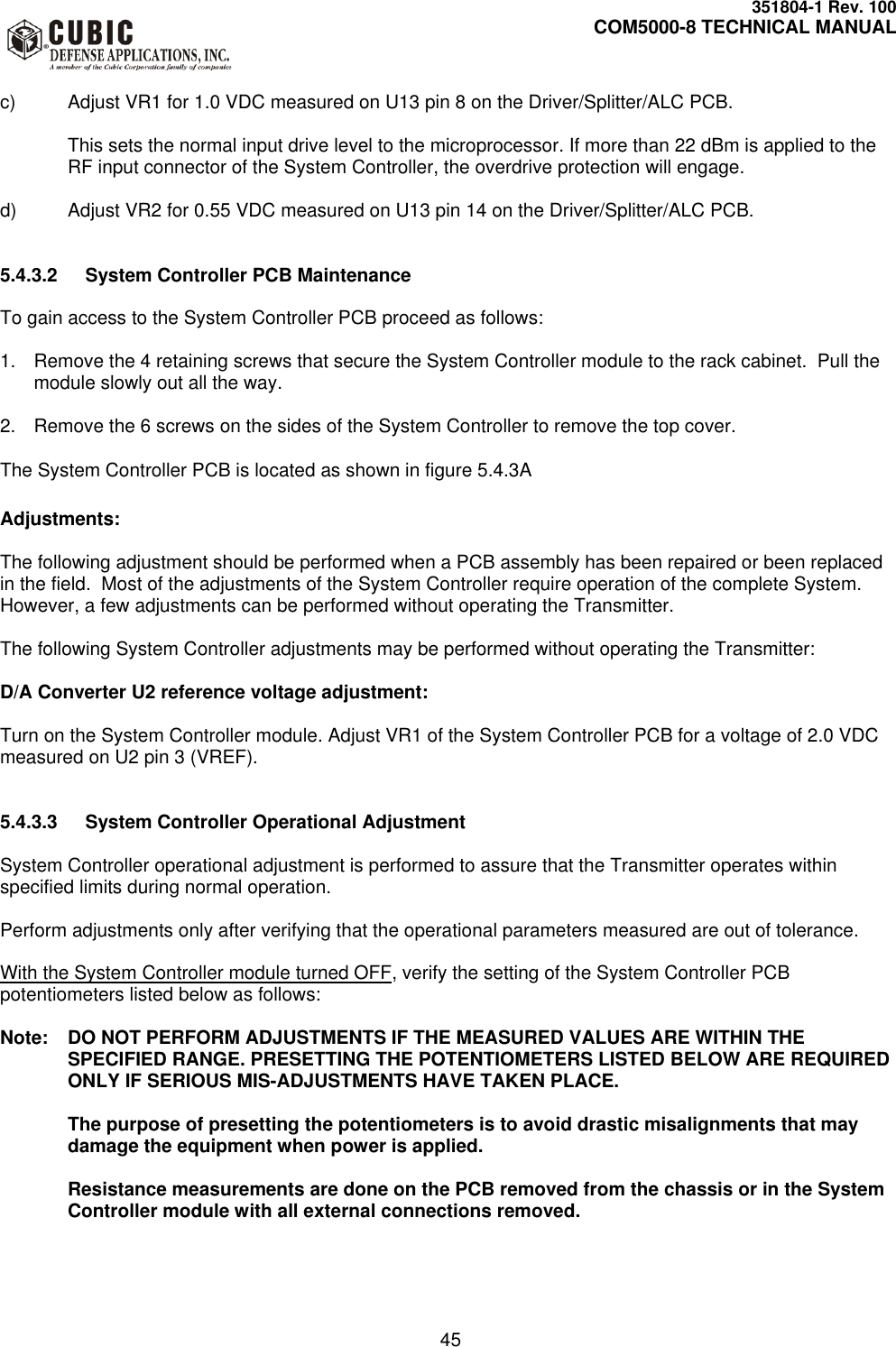
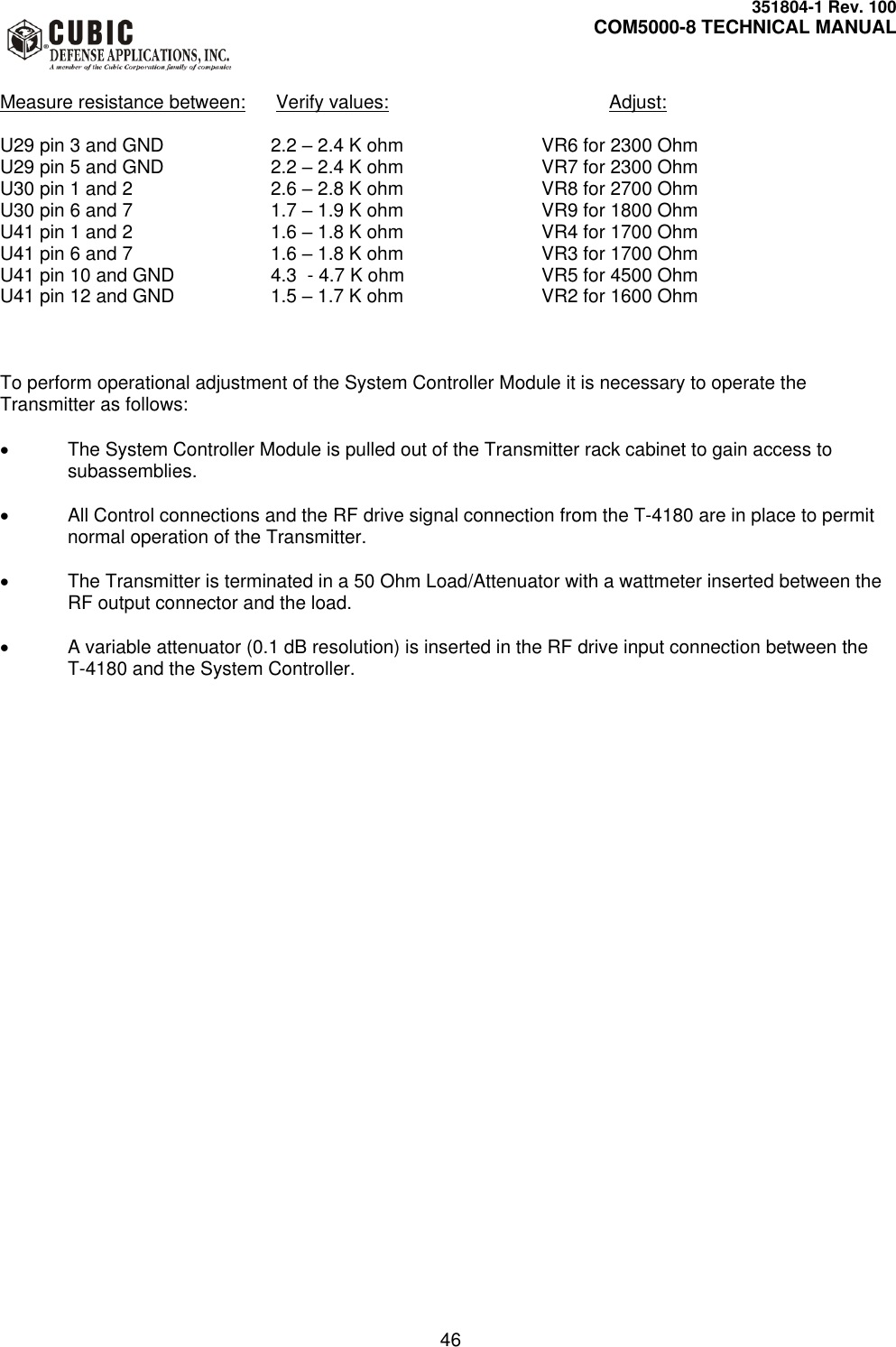
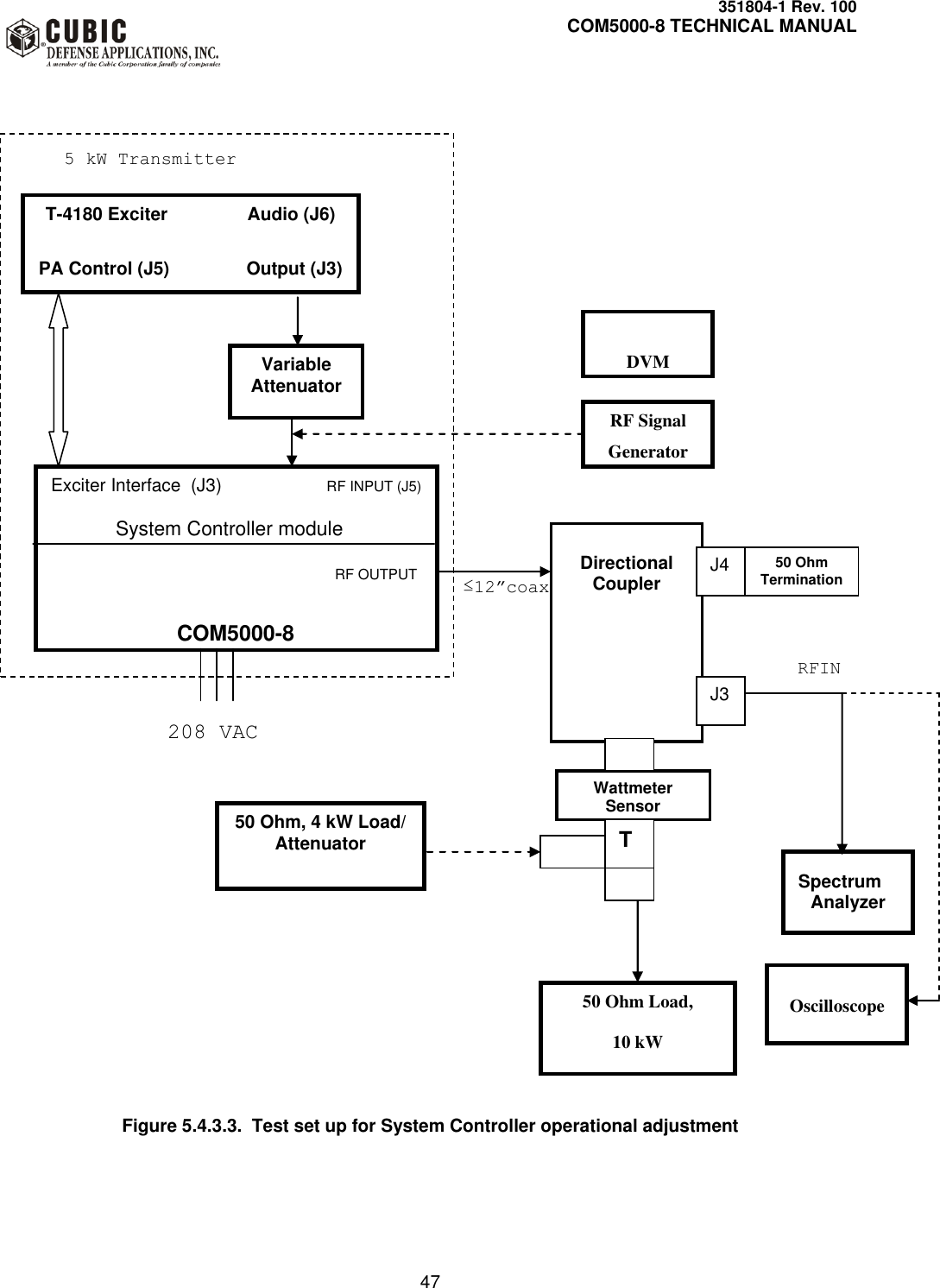
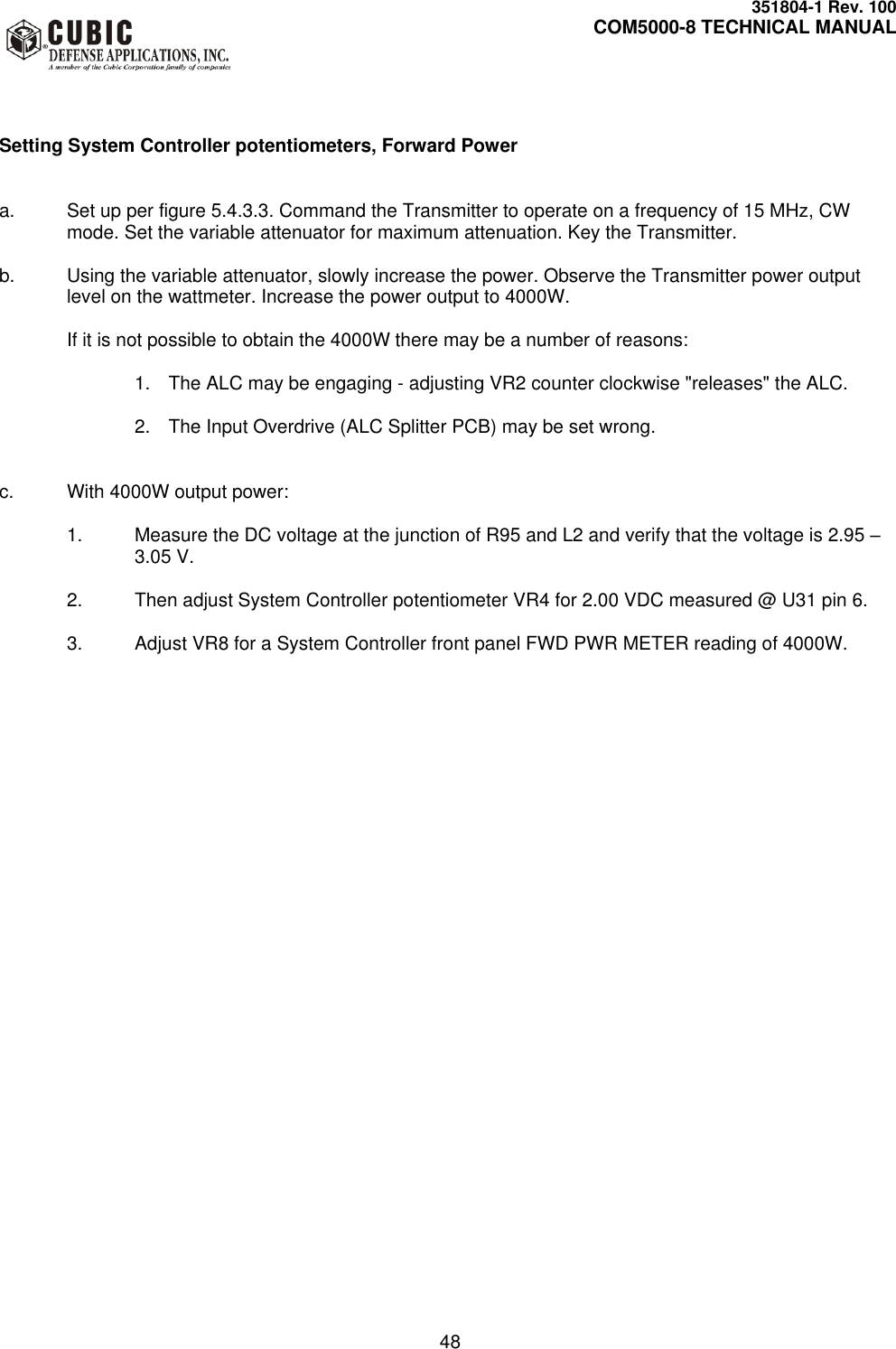
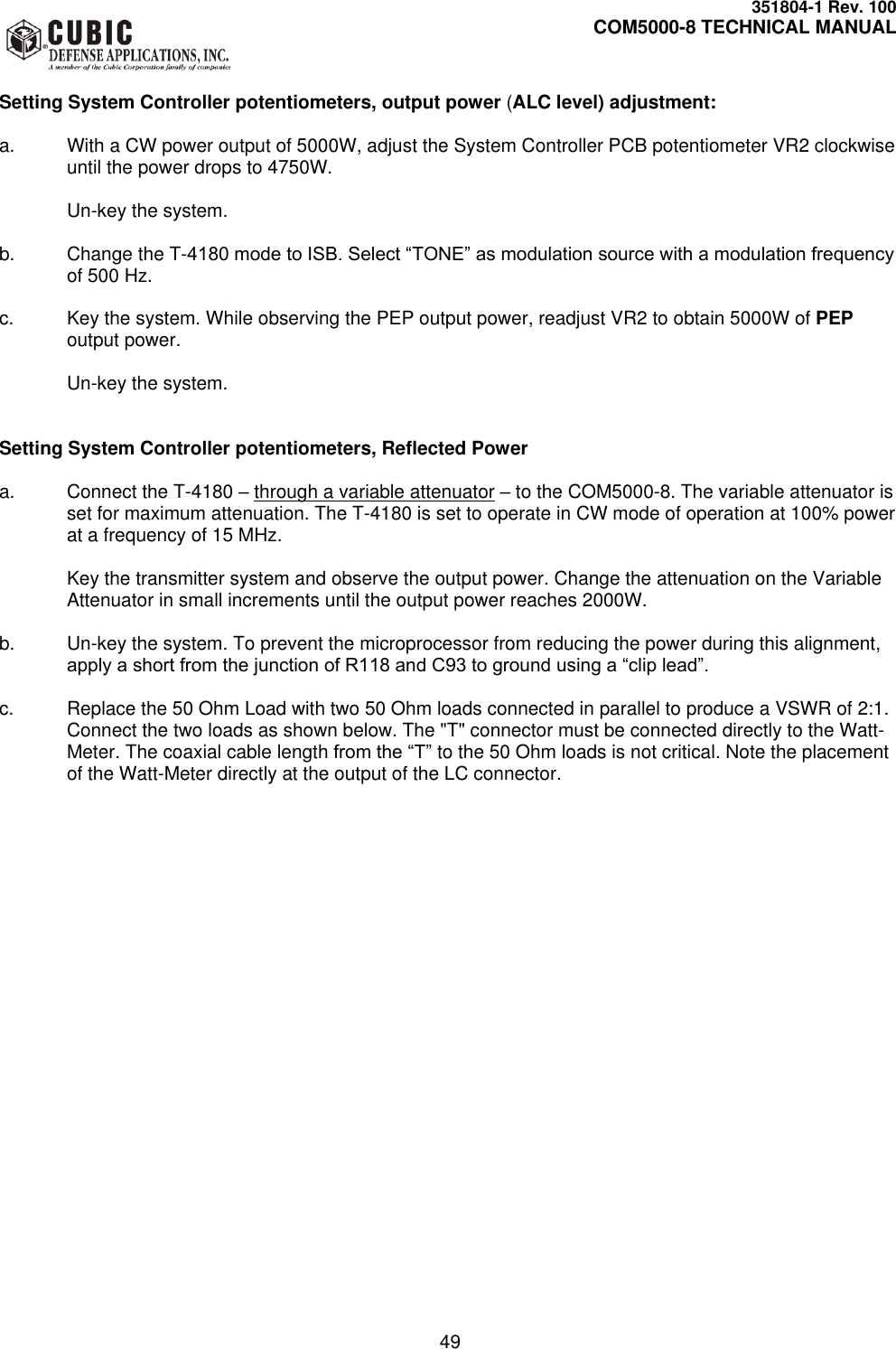
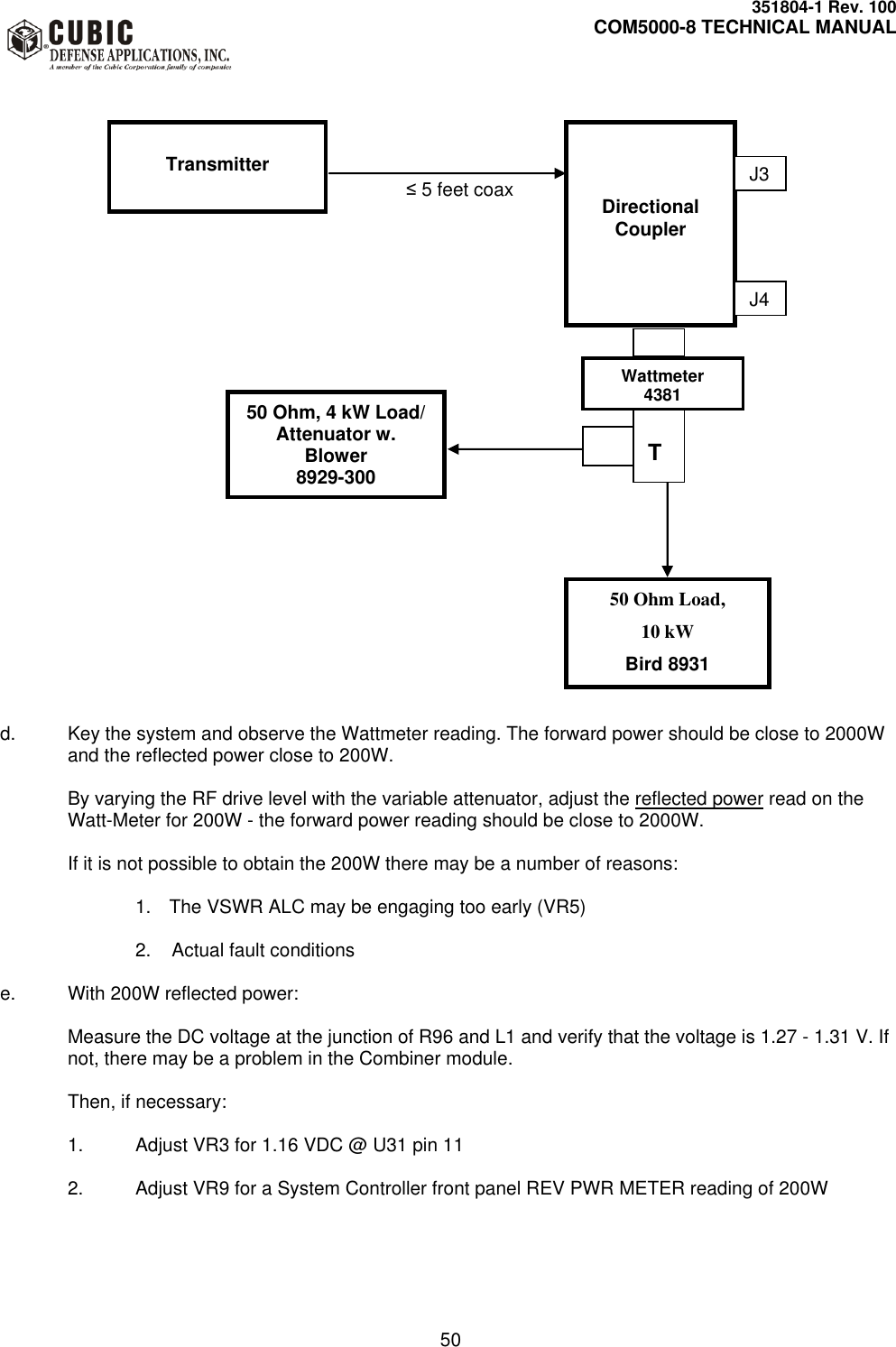
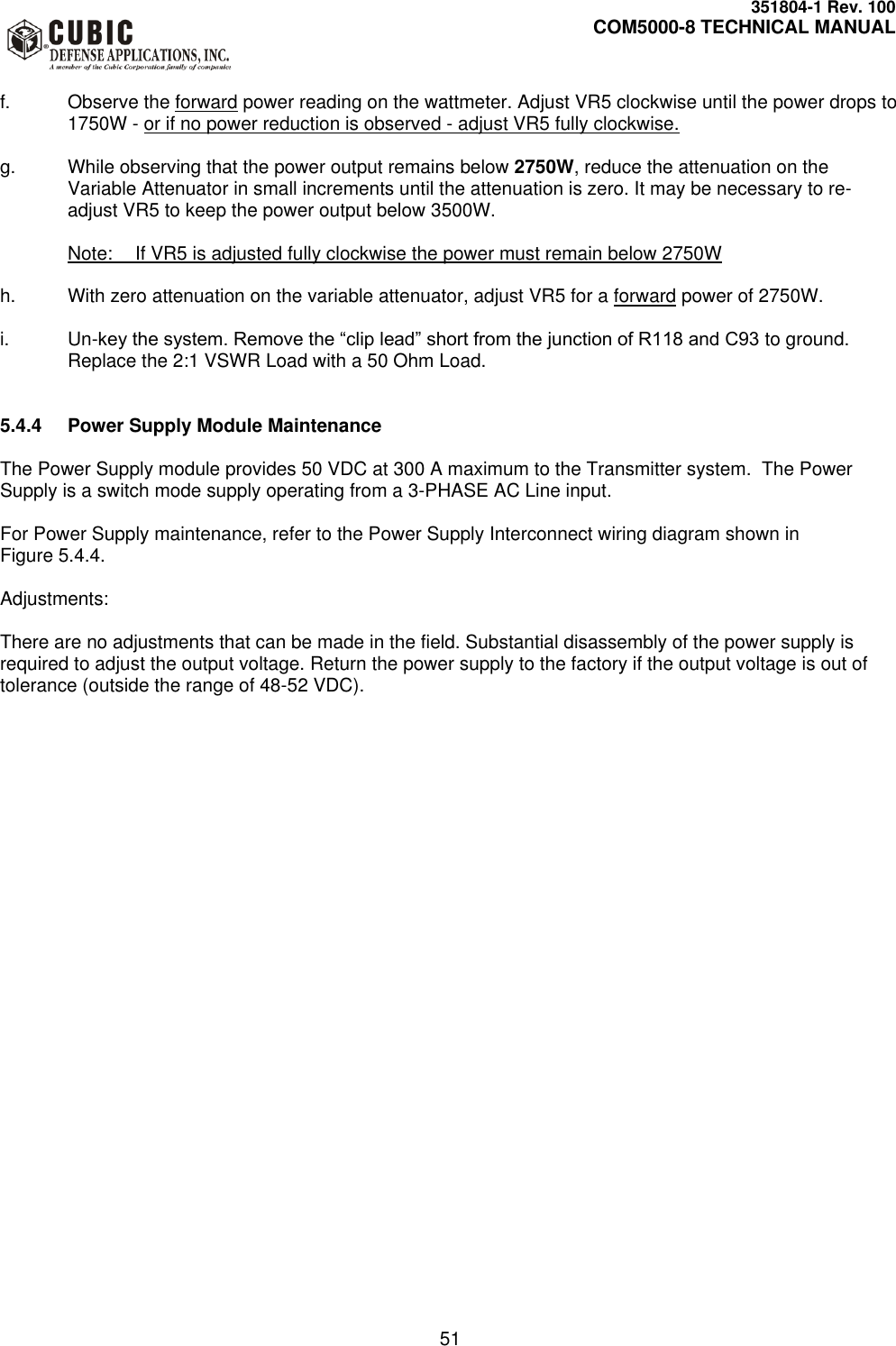
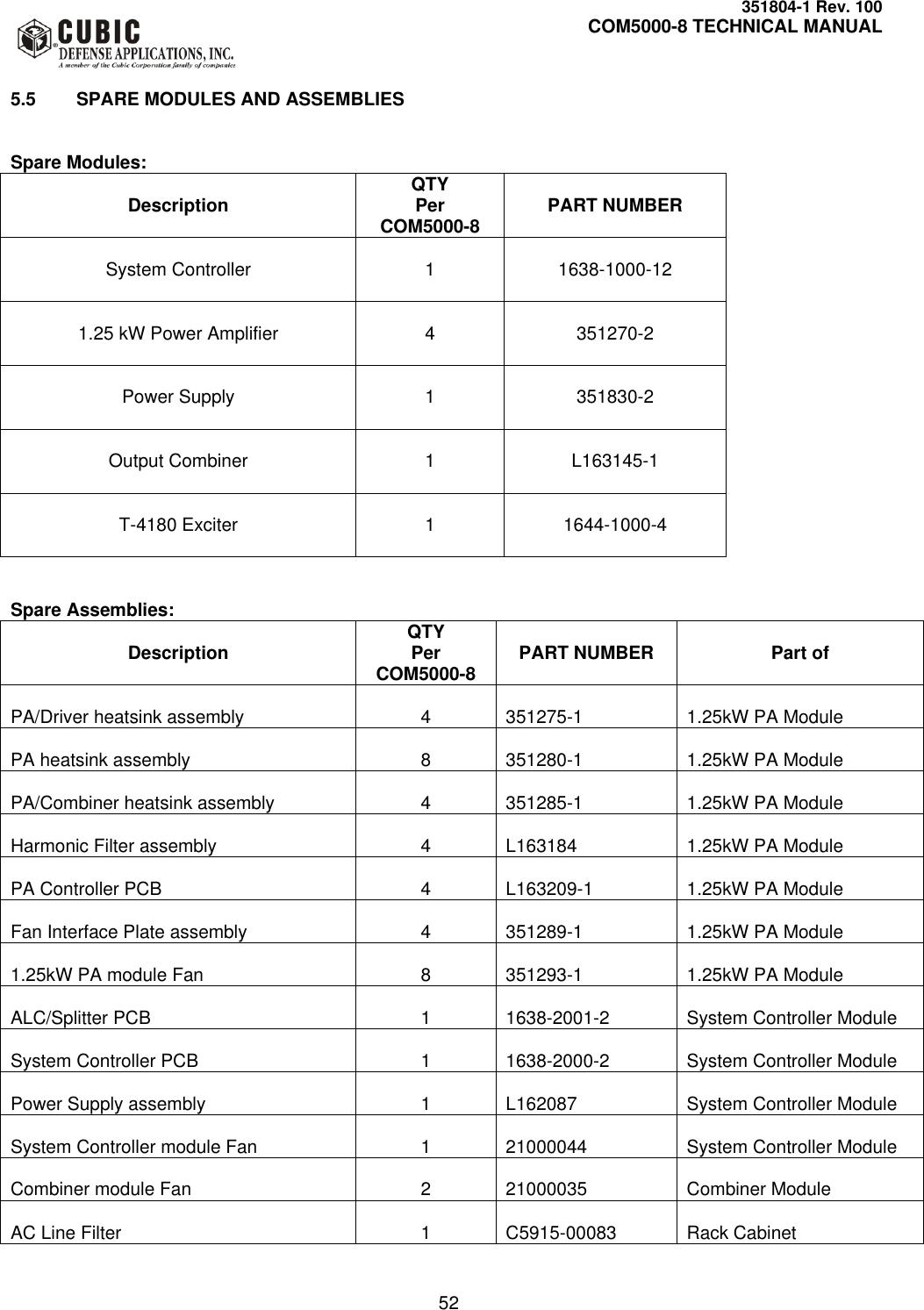
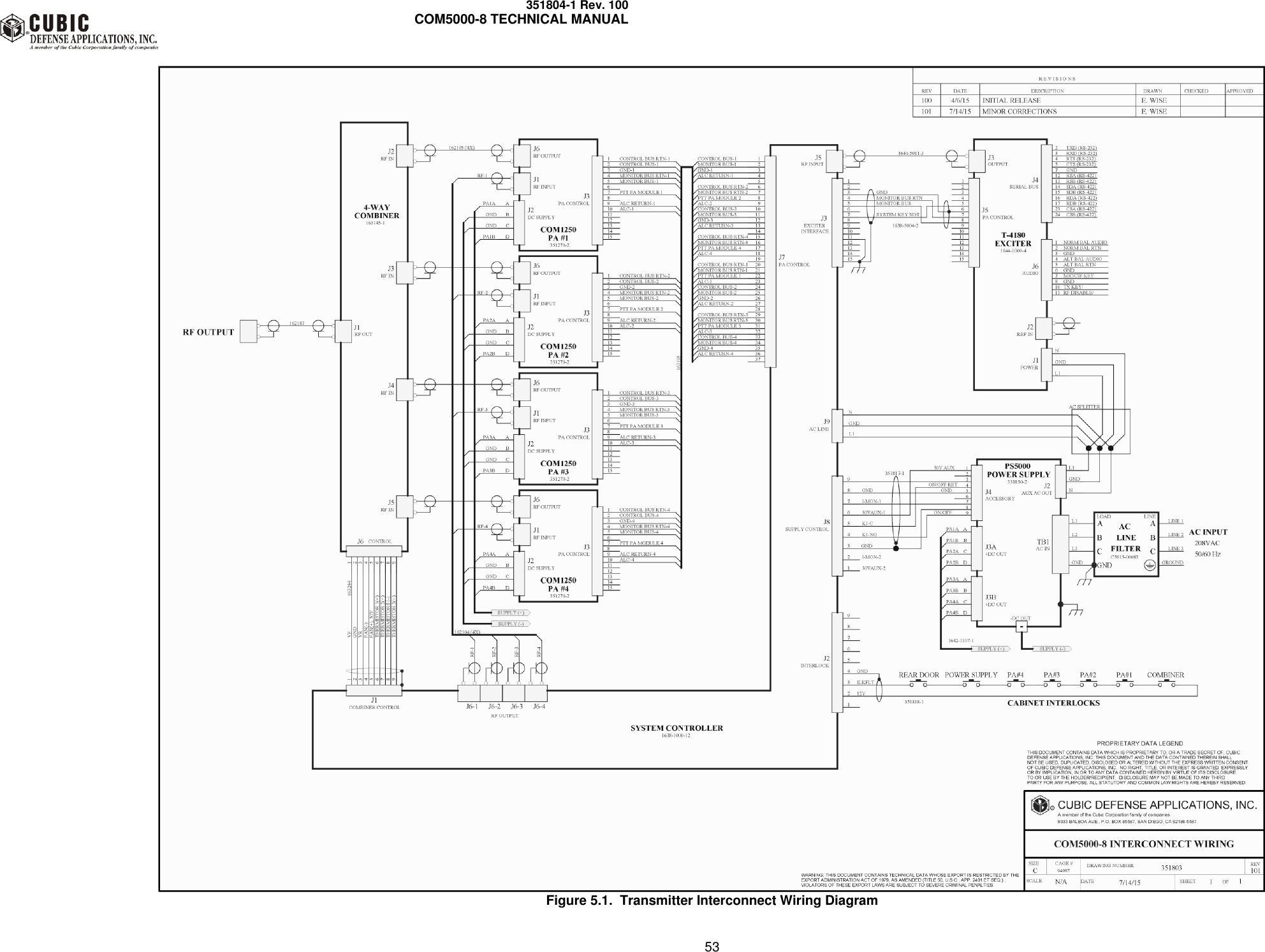
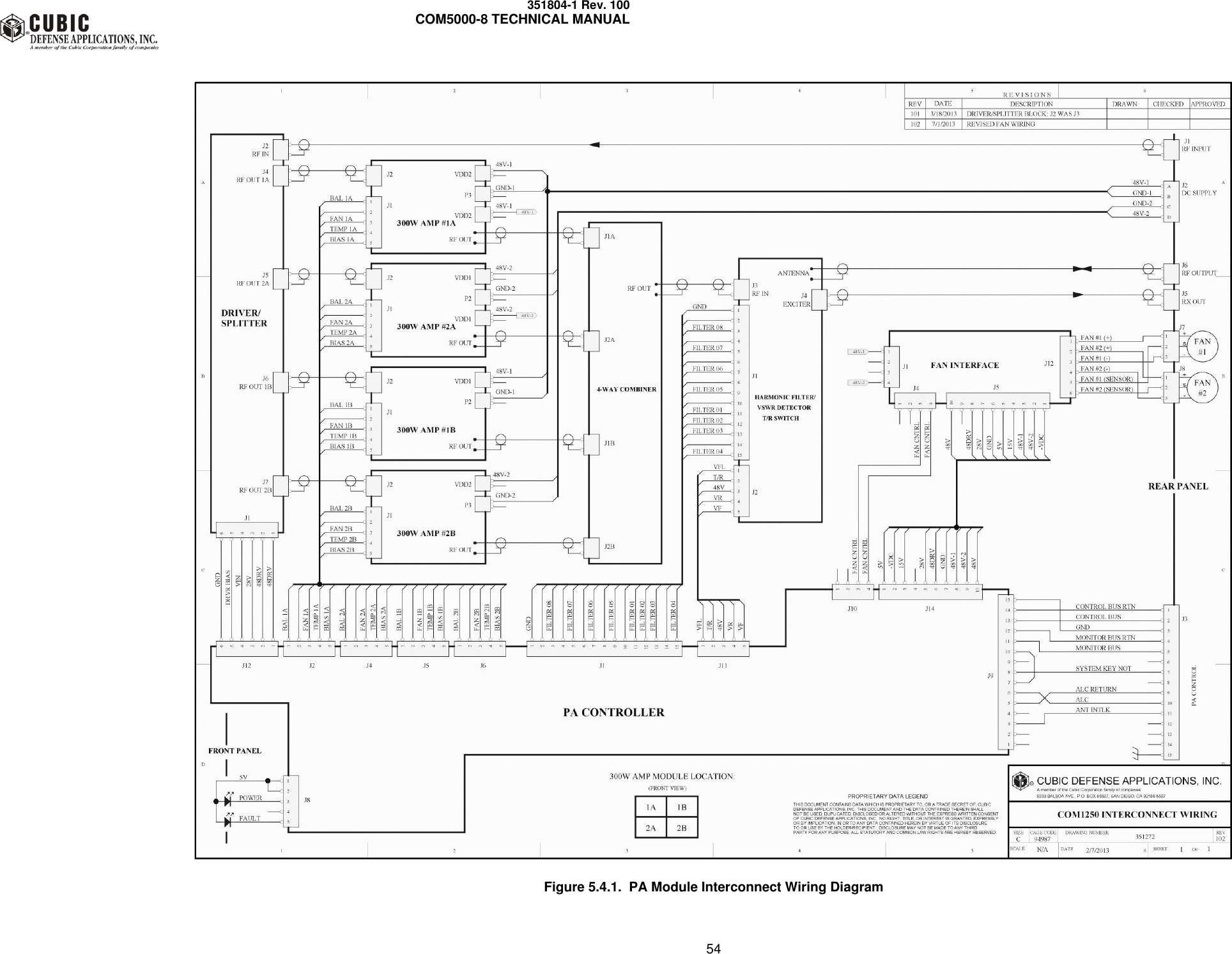
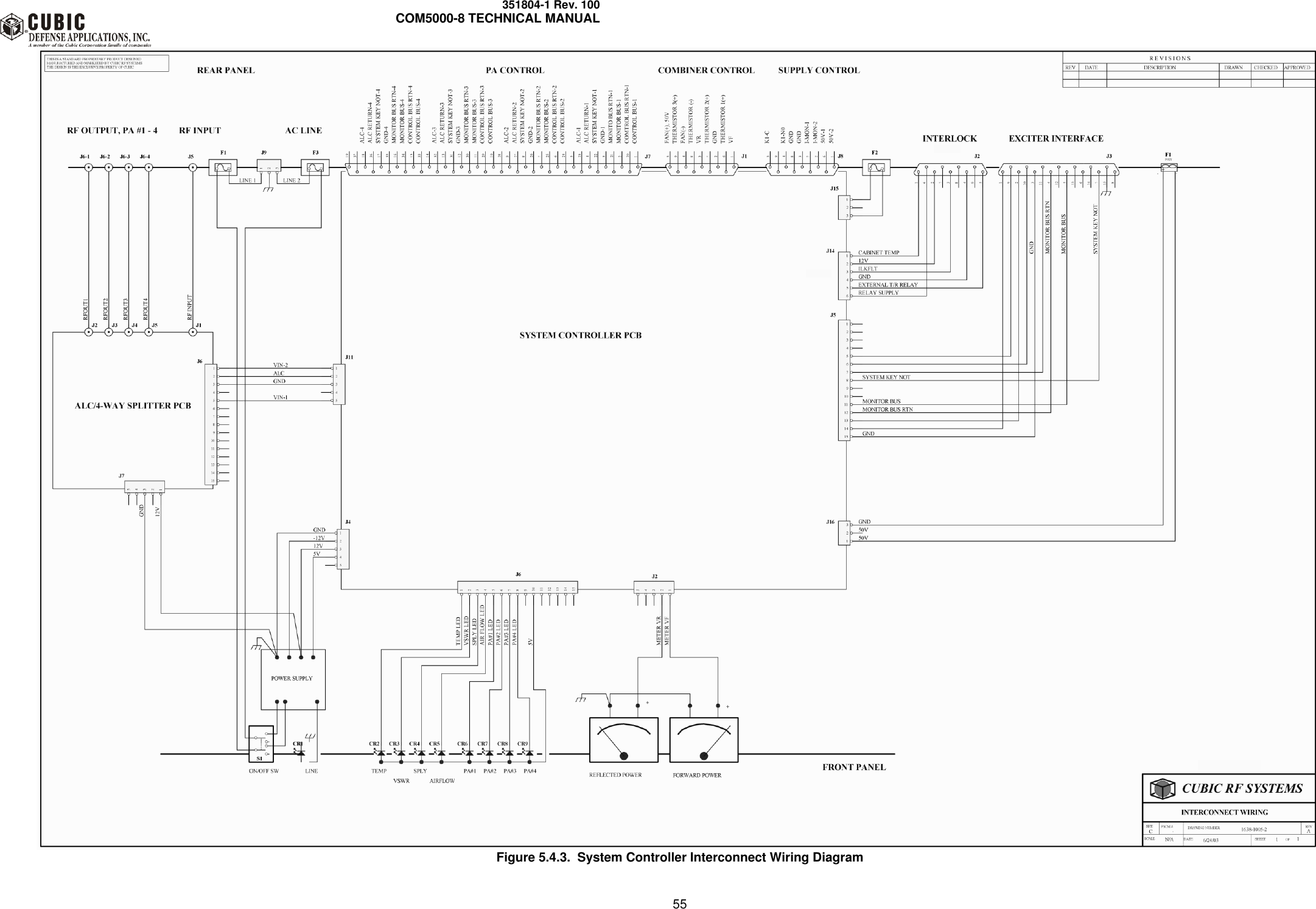
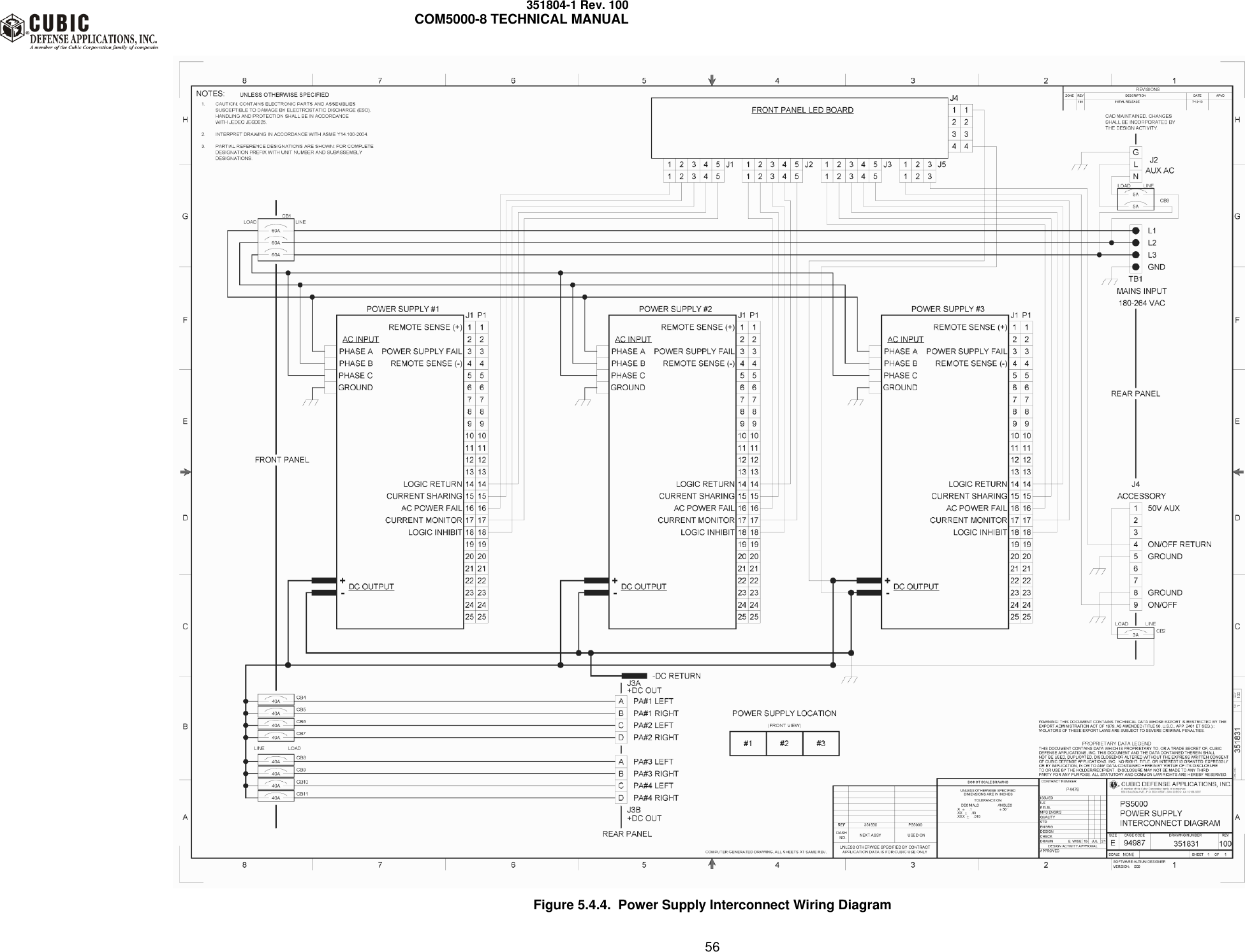