Scitronics DSP1000OT900 Conveyor Belt Scale User Manual Instruction Manual
Scitronics Inc. Conveyor Belt Scale Instruction Manual
Contents
- 1. Instruction Manual
- 2. LINX HP Receiver Module Guide
Instruction Manual
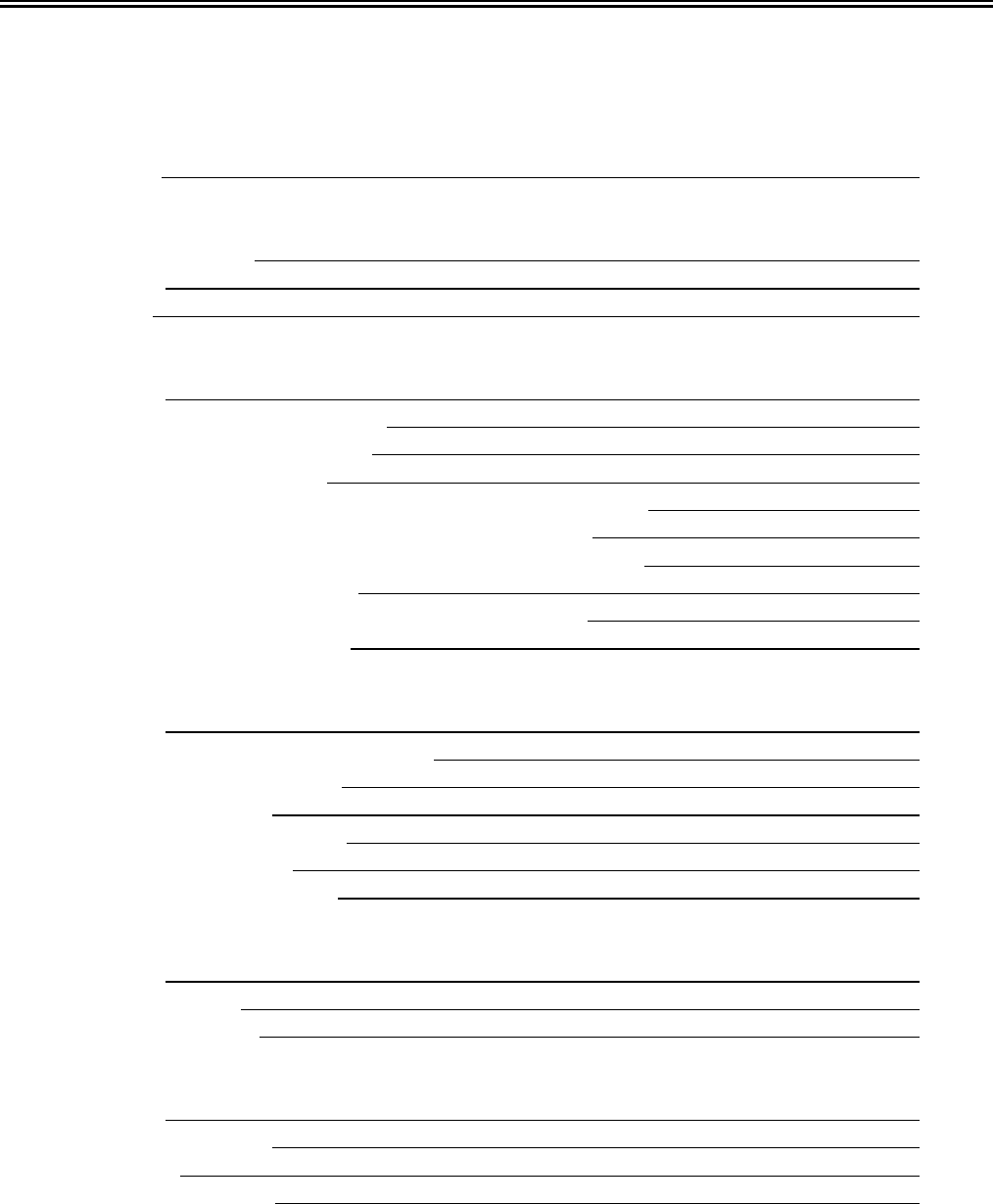
Table of Contents
Table of Contents
Warranty iv
Section 1 Introduction
Using This Manual 1-1
Overview 1-2
Features 1-3
Section 2 Installation
Overview 2-1
Unpacking the Belt Scale System 2-1
Installing the Belt Scale System 2-1
Mounting the Processor 2-2
Modifying the Mounting the Weigh Idler to the Belt Scale 2-3
Mounting the Belt Scale Assembly on the Conveyor 2-3
Mounting the Bridge Transducer Circuit Board Enclosure 2-5
Installing the Speed Sensor 2-5
Attaching the Load Cell to the Belt Scale Assembly 2-6
Wiring the Belt Scale System 2-6
Section 3 Programming the Processor
Overview 3-1
Becoming Familiar with the Processor 3-1
Processor Screen Display 3-2
Processor Keypad 3-2
Programming the Setup Data 3-3
Initial Programming 3-3
Changing the Setup Data 3-19
Section 4 Calibration
Overview 4-1
Initial Calibration 4-1
Routine Calibration 4-3
Section 5 Maintenance and Troubleshooting
Overview 5-1
Diagnostic Messages 5-1
Spare Parts 5-1
Routine Maintenance 5-1
i
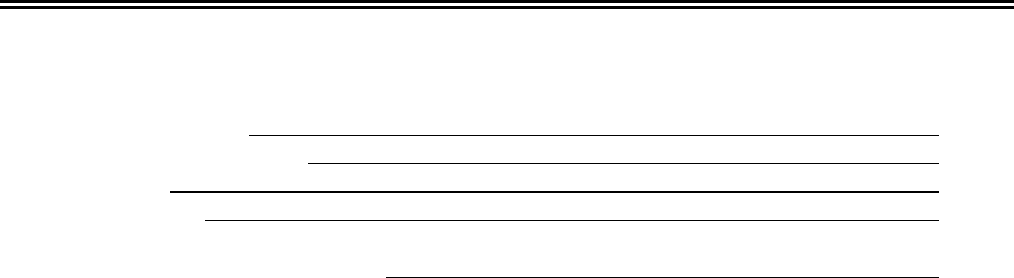
SciTronics Model CS 1000
Section 6 System Specifications
Belt Scale System 6-1
Digital Signal Processor 6-1
Load Cell 6-1
Speed Sensor 6-1
Section 7 Custom Applications 7-1
ii
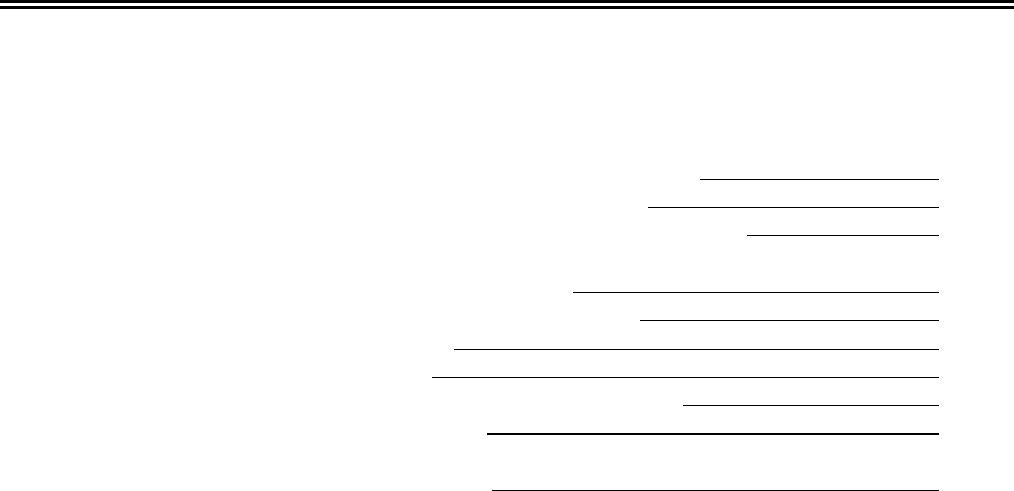
Table of Contents
List of Illustrations
Figure 2-1 Digital Signal Processor Dimensional Drawing 2-2
Figure 2-2 Mounting the Belt Scale on the Conveyor 2-4
Figure 2-3 Wiring Diagram for the Standard Belt Scale System 2-7
Figure 2-4 Wiring Diagram for the Belt Scale System with the
Optional DR4200 Chart Recorder 2-8
Figure 3-1 Model CS 1000 Digital Signal Processor 3-1
Figure 3-2 Processor Menu Tree 3-4
Figure 4-1 Calibration Record 4-4
Figure 7-1 Printer Cover on the Digital Signal Processor 7-3
Figure 7-2 Printer Ribbon Cartridge 7-3
Table 3-1 Programming Data Table 3-5
iii

SciTronics Model CS 1000
Warranty
SciTronics warrants all products of its manufacture to be free from defects in material and
workmanship. This warranty is effective for three years from the date of shipment to the
original Purchaser.
Upon notification by the Purchaser, SciTronics will correct any defects in equipment of its
manufacture either by repair in our plant or by supply of replacement parts to the Purchaser.
SciTronics must decide to its own satisfaction that the equipment is defective and has not
developed malfunctions as a result of misuse, modification, abnormal conditions of
operation, or attempted service not authorized by SciTronics.
SciTronics will not accept any product returned for refund or approve any backcharge for
labor, materials, or other costs incurred by the Purchaser or others in modification,
adjustment, service, or repair of SciTronics equipment unless such return or backcharge has
been authorized in writing to the Purchaser.
Any special test or requirement placed upon SciTronics products or products of other
manufacture used in SciTronics systems must be mutually agreed upon in writing by
SciTronics and the Purchaser prior to the date of shipment.
SciTronics reserves the right to make changes in design or construction of its products at any
time without incurring any obligation to make any changes whatsoever on units previously
purchased.
This warranty is expressly made by SciTronics and accepted by the Purchaser in lieu of all
other warranties, including warranties of merchantability and fitness for particular purpose,
whether written, oral, express, implied, or statutory. SciTronics shall not be liable for normal
wear and tear nor for any contingent, incidental, or consequential damage or expense due to
partial or complete inoperability of its products for any reason whatsoever. In no event shall
SciTronics’ liability exceed the original purchase price of the equipment.
Note : This equipment has been tested and found to comply with the limits for a Class A digital device,
pursuant to part 15 of the FCC Rules. These limits are designed to provide reasonable protection against
harmful interference when the equipment is operated in a commercial environment. This equipment
generates, uses, and can radiate radio frequency energy and, if not installed and used in accordance with
the instruction manual, may cause harmful interference to radio communications. Operation of this
equipment in a residential area is likely to cause harmful interference in which case the user will be
required to correct the interference at his own expense.
iv
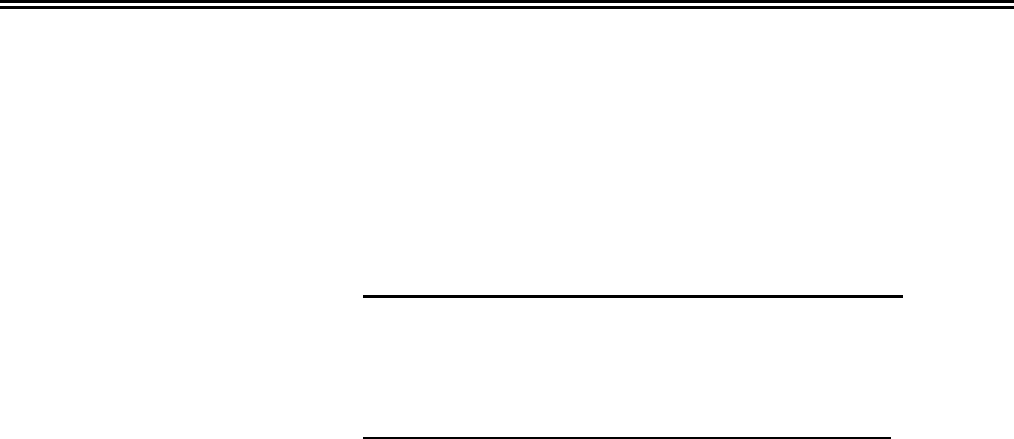
Section 1 Introduction
Section 1 Introduction
Using This Manual This manual contains the installation, operation, and maintenance
instructions for your SciTronics Model CS 1000 Belt Scale (belt
scale system).
_____________________________________________
NOTE
The warranty for your belt scale system is on page iv
in this manual. Be sure to read it so you are aware of its
provisions and exclusions.
____________________________________________
This manual is arranged in the following sections so that you can find
the information you need quickly and easily:
• Section 1 Introduction
describes the organization of this manual and provides a
general description of the belt scale system.
• Section 2 Installation
provides instructions for mechanical and electrical installation of
the belt scale system.
• Section 3 Programming the Processor
describes how to program the digital signal processor for initial
setup and any time data needs to be changed.
• Section 4 Calibration
explains how to perform electronic calibration of the belt
scale using the digital signal processor.
• Section 5 Maintenance and Troubleshooting
provides the necessary information for routinely maintaining
the belt scale system.
• Section 6 System Specifications
list the specification data for the belt scale system.
• Section 7 Custom Applications
explains the features unique to your specific belt scale system.
1-1

SciTronics Model CS 1000
Overview The SciTronics belt scale system is installed on a conveyor and
weighs material in transfer. It is designed for such applications as
rock crushing plants, asphalt and concrete products batch plants,
ore processing plants, coal preparation plants, recycling plants,
paper and wood processing plants, food processing plants, and
fertilizer plants.
The belt scale system consists of the following components:
• belt scale assembly with bridge transducer electronics
• speed sensor
• digital signal processor
The rigid steel construction of the belt scale assembly ensures
permanent alignment with the conveyor. The precision NTEP-
approved strain gauge load cell accurately weighs the material
being conveyed. The weight signal from the load cell is converted
to a digital computer signal in the bridge transducer signal
conditioner and transmitted to the digital signal processor.
The speed sensor outputs the speed signal that is proportional to
the velocity of the belt. The signal is converted to a digital
computer signal in the bridge transducer signal conditioner and
transmitted to the digital signal processor.
The digital signal processor receives the weight and speed signals,
performs calculations, and displays values for rate, total weight,
and belt speed in selectable standard engineering units (tons,
pounds, tonnes, or kilograms). The processor screen display is a
high-intensity, 4-line by 20-character alphanumeric display that is
adjustable to high, medium, or low intensity. The screen-saver
feature automatically turns the display off during inactive periods
to prevent damage to the screen. Using the screen menus and
processor keypad, the operator easily steps through programming
of the setup data.
The multiple scale interface network allows connection of up to
four scales to each digital signal processor.
1-2

Section 1 Introduction
Features The belt scale system has the following features:
• Accurate to ±0.5% (approved installations).
• Adjustable intensity, 4-line, 20-character vacuum fluorescent
display with screen saver.
• Easily programmable setup data.
• Full-time self-diagnostics.
• Real-time clock calendar.
• Multiple scale interface.
• Manufactured to CEMA standards.
• Optional printer or computer interface (plug-in PC board).
• Optional plug-in cards for relay outputs and 4-20 mA
outputs.
• Optional speed sensor selection for variable speed belt.
• Optional LCD Display Model DSP1000LCD
1-3

SciTronics Model CS 1000
1-4
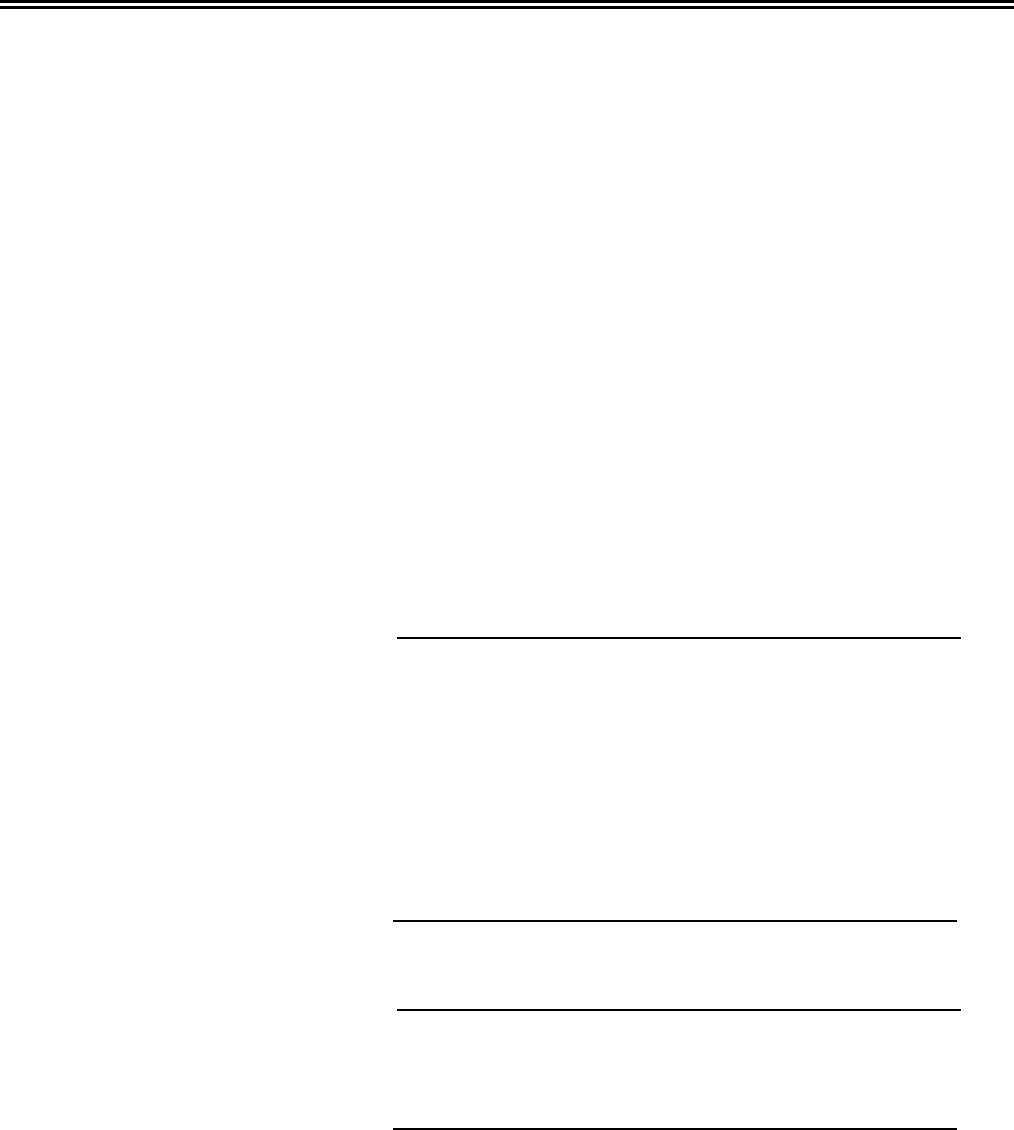
Section 2 Installation
Section 2 Installation
Overview This section provides instruction for mechanical and electrical
installation of the belt scale system.
Unpacking the Belt 1. Remove the belt scale assembly and speed sensor from the
Scale System pallet.
2. Place the shipping container containing the digital signal
processor on a stable surface and open it, taking care not to
damage the contents.
3. Inspect the contents and report any shipping damage or
missing parts to the carrier as soon as possible (most carriers
will not consider a claim unless notified within 15 days of
delivery).
__________________________________________
NOTE
The bill of lading for this shipment is an acknowledgment
by the carrier of the receipt of the equipment in good
condition. SciTronics is not responsible for any loss or
damage incurred during shipment. Note any damaged or
missing parts on the carrier’s delivery receipt. Sign the
notation and have the carrier’s driver also sign it. The
consignee is responsible for initiating claims against the
carrier.
__________________________________________
Installing the Belt __________________________________________
Scale System WARNING
To prevent bodily injury, be sure that the conveyor is
locked out before beginning installation.
__________________________________________
2-1
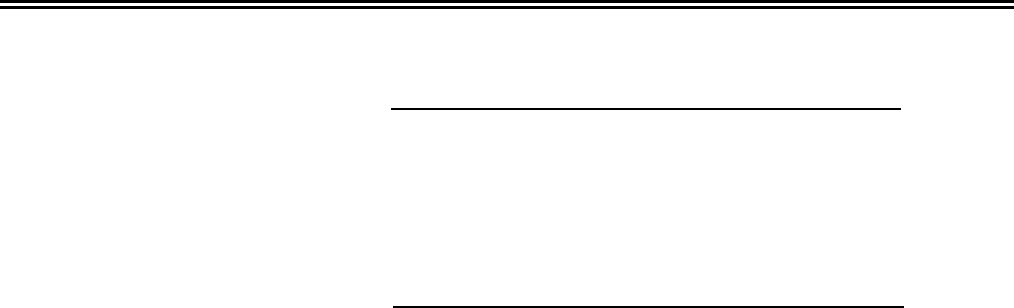
SciTronics Model CS 1000
______________________________________
CAUTION
1. Whenever possible, be sure to install the belt scale
on the conveyor in a location where it is protected
from the weather. Wind can cause weighing errors.
2. Curvature or upturn in the conveyor is serious.
Consult the factory before mounting the scale.
______________________________________
Mounting the Processor 1. Select a location close to a 115 V power source that is within
1,000 ft (304.8m) of the scale and where the processor will
not be exposed to excessive vibration, heat, and moisture. If
mounting the processor outside, be sure to place it in a
vandal-proof enclosure.
2. Secure the processor to a wall or support at a height where
the screen display can be easily seen and the keypad is
accessible. Be sure there is sufficient clearance to open the
enclosure. Refer to Figure 2-1 for dimensional specifications.
2-2
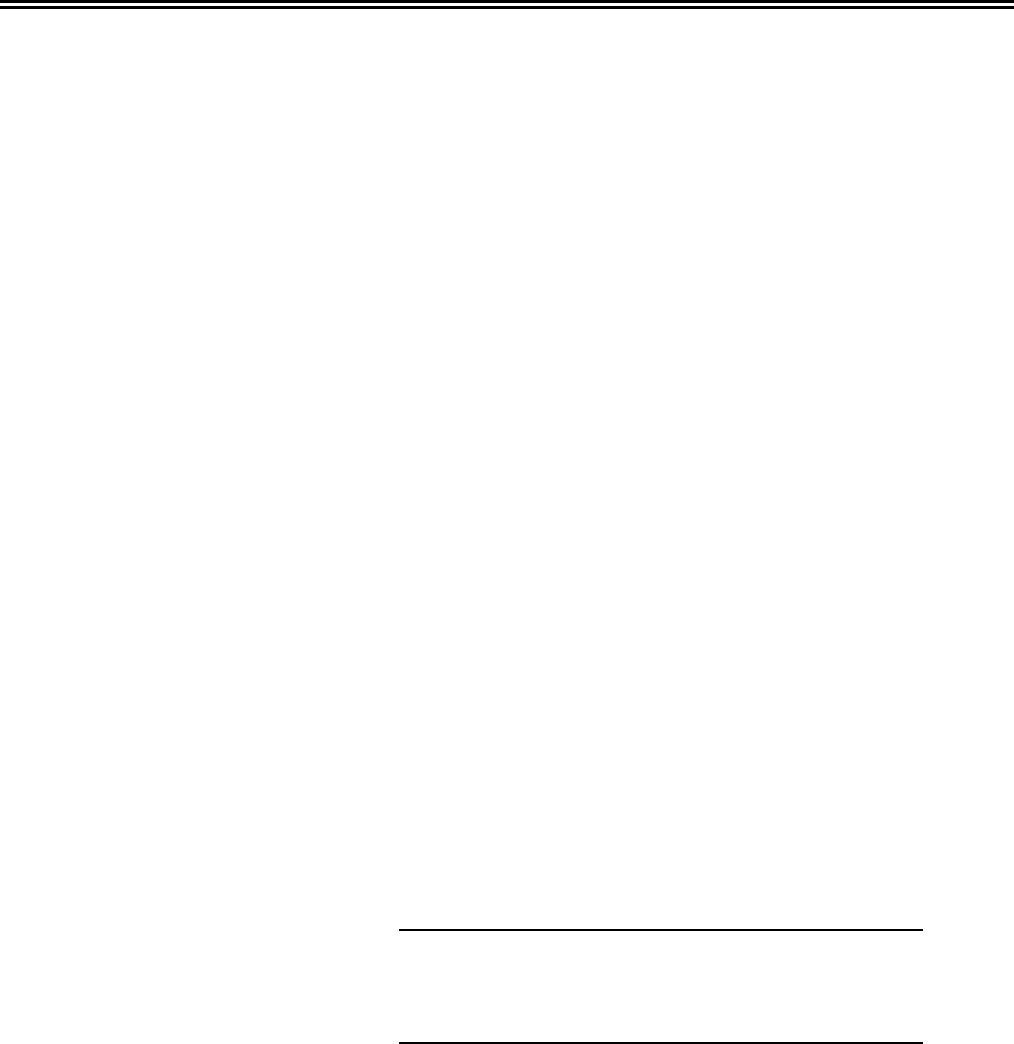
Section 2 Installation
Modifying & Mounting The weigh idler (the idler to be mounted to the scale) must be
the Weigh Idler to the modified to fit the scale mounting pads and then mounted to the
Belt Scale scale:
1. Select an idler identical to the idlers that will be in the
weighing section of the conveyor. The idler must be in good
condition - the rollers must turn freely and have good
concentricity.
2. Saw cut or torch cut the existing mounting feet to remove
them from the idler.
3. Sometimes it is necessary to remove material from the idler
that may weaken the roller support. If so, reinforce the end
brackets by welding a “gusset” between the vertical end
bracket and the horizontal piece.
4. Place the idler on the new mounting pads, which are bolted
the scale assembly. Center the idler from side to side on the
pads. Check for sufficient clearance - approximately ½ in.
(13 mm) - between the bottom of the idler and the scale frame.
5. Center the idlers exactly 18 in. (457 mm) from the rear pivot
support and the center of the end idler rollers, typically to the
grease fitting.
6. Clamp in place. Check for squareness from corner to corner
and check the dimensions.
_______________________________________
CAUTION
To prevent damage to the load cell, disconnect it and
remove it from the housing.
_______________________________________
7. Weld the idler to the new mounting pads.
Mounting the Belt Scale Place the belt scale assembly where a minimum of belt stress or
Assembly on the deformation can occur (that is, away from the loading area and the
Conveyor head pulley). Referring to Figure 2-2, install the belt scale assembly
by doing the following:
1. Raise the belt clear of the idlers in the weigh section.
2. Loosen three idlers on each side of the scale. If your conveyor
is very short, reduce the scale section to two idlers on each
side. Aligning longer sections can improve performance. 2-3
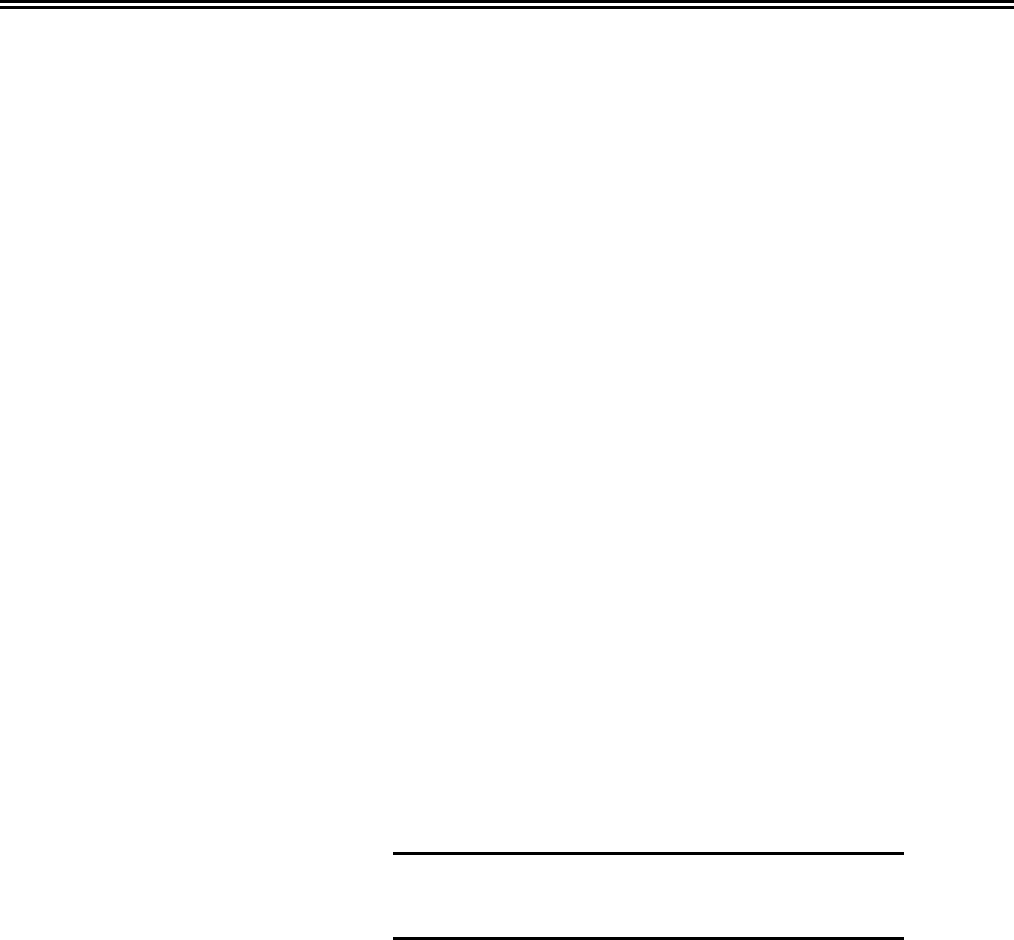
SciTronics Model CS 1000
3. Mark the center of each roller.
4. Place two 1/8 in. (3mm) shims (a total of ¼ in.) under the feet
of both the +3 and -3 idlers.
5. Stretch three string lines over the center marks on the +3/-3
idlers. Bolt the idlers down exactly six spaces or weigh spans
apart. For example, for a 36 in. (91cm) weigh span, attach
the +3/-3 idlers exactly 18 ft (5.49 m) center to center and
square with the conveyor.
6. Shim the belt scale assembly to obtain 1/32 in (.8mm)
clearance below the string line.
7. Shim the +1/-1 idlers to 1/32 in (.8mm) clearance.
______________________________________
CAUTION
Poor alignment will affect scale accuracy.
______________________________________
8. Shim the remaining idlers according to step 7, aligning all
center marks. Bolt the idlers down lightly. Check again after
tightening the bolts.
9. When the belt scale and the idlers are securely attached,
remove one of the 1/8 in (3mm) shims from the +3/-3
idlers and reattach the +3/-3 idlers into position. The entire
belt scale section is now flat between the +2/-2 idlers and 1/16
in (.8mm) higher than the +3/-3 idlers.
2-4
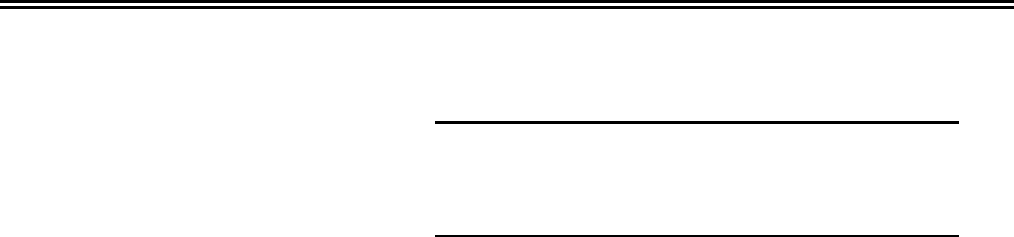
Section 2 Installation
_______________________________________
CAUTION
To prevent damage to the load cell, disconnect it and
remove it from the housing.
_______________________________________
10. Tack weld ¼ in (6mm) on each idler foot to prevent it from
moving out of position. For extra stability and to minimize
twisting on portable conveyors, tack weld all idlers.
11. Remove the string lines and lower the belt. Run the conveyor
and adjust the tension until the belt runs true in the center of
the idlers. Check that all the idlers in the scale area turn freely
from the pressure of the empty moving belt.
Mounting the Bridge Mount the bridge transducer circuit board enclosure between the
Transducer Circuit processor and the belt scale so that it is within 6 ft (1.8m) of the
Board Enclosure belt scale assembly.
Installing the Speed The “Belt Rider” speed sensor is shipped assembled and ready for
Sensor installation on the conveyor. For convenience, install the speed
sensor just behind the scale in the mounting holes provided. The
factory provides an adequate length of cable to allow placing the
speed sensor a sufficient distance in front or behind (but not over)
any return idlers. If necessary, the speed sensor can be installed in
front of the scale if the above guidelines are followed.
Install the speed sensor by doing the following:
1. Place the speed sensor on the conveyor stringers.
2. Center the speed sensor wheel on the belt.
3. Square the speed sensor mounting pipe to the conveyor.
4. Mark and drill the mounting holes in the stringers - drill a ¼ in
(6mm) clearance hole.
5. Using the ¼ in X 2 in (6mmX51mm) bolts provided, bolt
the speed sensor to the conveyor.
2-5
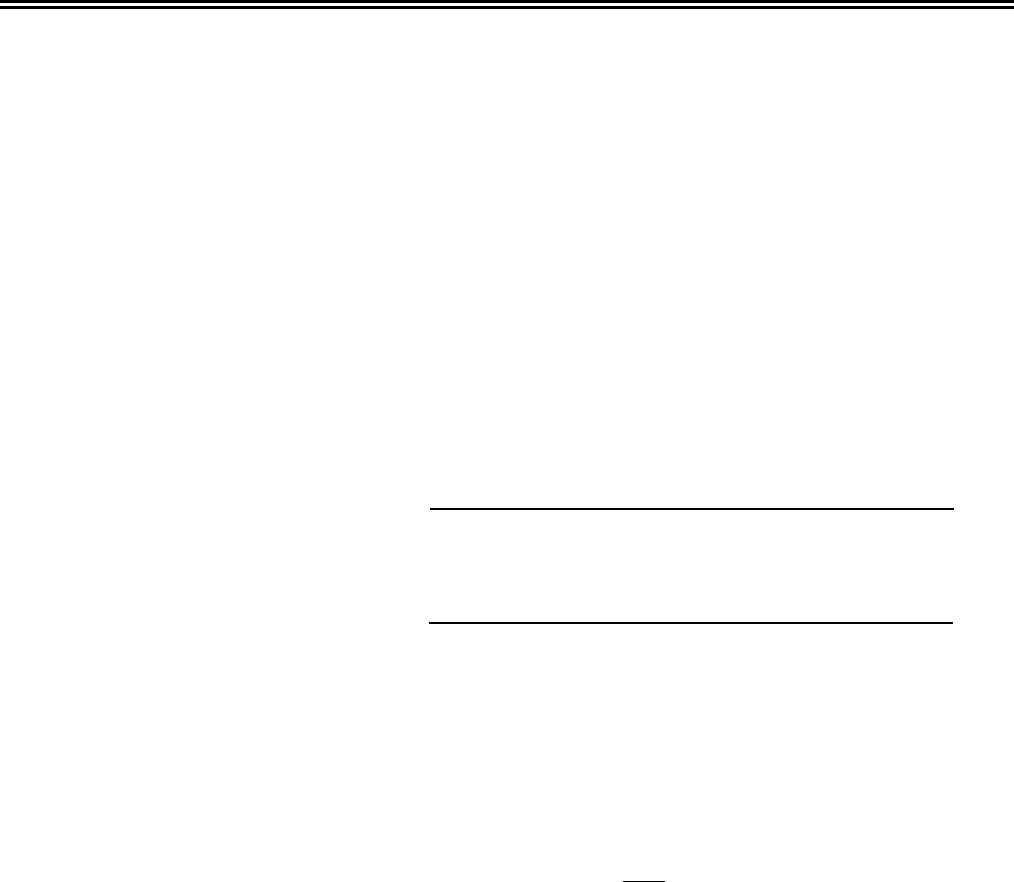
SciTronics Model CS 1000
Attaching the Load Cell The factory disconnects the load cell before shipping the belt scale
to the Belt Scale assembly. Attach the load cell to the belt scale assembly by doing
Assembly the following:
1. Remove the cover panel of the scale. Locate the T-handle
Allen wrench and the load cell and remove them.
2. Using the Allen wrench, remove the 3/8 in (10mm) bolt from
the belt scale assembly.
3. Insert the bolt into the load cell and attach the load cell to the
belt scale assembly using the wrench.
Wiring the Belt _______________________________________
WARNING
Be sure that the power is off before wiring the belt scale
system.
_______________________________________
Consider the following before making electrical connections:
• Do not shorten the load cell cable. The wire length
to load cell temperature compensation.
• Do not route the load cell or signal cables in the same
conduit as the power wires or any large source of electrical
noise.
• Connect the shields only where shown.
• Check that all wires are tight in their connectors - this is
especially important for load cell connections.
• Earth ground all enclosures and conduit.
Referring to the wiring diagram in Figure 2-3 on page 2-7, wire the
belt scale system:
1. Open the processor enclosure by releasing the two latches on
the right side of the enclosure (when facing the front of the
enclosure). Refer to Figure 2-1 on page 2-2. Supply 115 V
power to terminals H, N, and G on the processor circuit
board. Using the 25-ft wire (7.6-m) provided by the factory,
connect terminals 10, 12, and 19 on the processor circuit
board to terminals 10, 12, and 19 on the bridge transducer
circuit board and the shield to G. Close the processor
enclosure and latch the door.
2-6

Section 2 Installation
2. Using the 4-ft (1.2-m) flexible Sealtite conduit provided by
the factory, connect the load cell terminals to the bridge
transducer circuit board terminals: GRN to 25, RED to 22,
BLK to 20, WHT to 29, and the shield to G.
3. Using the 10-ft (3-m) cable provided by the factory, connect
the speed sensor terminals to the bridge transducer circuit
board terminals: BLK to 30 and WHT to 39.
4. Supply 115 V power to terminals H, N, and G on the bridge
transducer circuit board.
2-7

SciTronics Model CS 1000
2-8

Section 3 Programming the Processor
Section 3 Programming the Processor
Overview This section describes how to program the digital signal processor
for your specific application. Refer to the information in this
section on Initial Programming on page 3-3 for initial setup of the
processor and to Changing the Setup Data on page 3-19 any time
the data needs to be changed.
Becoming Familiar The processor (as shown in Figure 3-1) has a screen display that
with the Processor shows the Main Menu and each submenu as the operator steps
through the screens during programming. The operator can view
the changes made to each selection before saving the change.
Values are entered and selections are made using the pressure-
sensitive keypad. When the operator leaves a field after making a
change, this change is automatically saved. During normal oper-
ation of the belt scale, values for total weight, rate, and belt speed
are shown in the screen display.
3-1

SciTronics Model CS 1000
Processor Screen The screen display (as shown in Figure 3-1 on page 3-1) is a 4-line,
Display 20-character vacuum fluorescent display. The intensity of the
display can be set for high, medium, or low. The screen-saver
feature uses a sleep timer to turn off the display during inactive
periods so that an image does not become permanently burned into
the screen.
Processor Keypad The pressure-sensitive keypad (as shown in Figure 3-1 on page
3-1) consists of 11 dedicated function keys.
ZERO
Zeros out the tare weight during initial and routine calibration.
Refer to Section 4 - Calibration for more information on
calibration.
RESET TOTAL
Resets the totals being displayed.
DISPLAY
Allows the operator to select the screens in the DISPLAY mode.
TEST CAL
Used to check calibration of the belt scale. Refer to Section 4 -
Calibration for more information on calibration.
PRINT
Initiates printing of a report showing either hourly totals or grand
totals as preprogrammed at the factory.
PROG
Selects the PROGRAM function and allows the operator to scroll
through the submenus of the Main Menu and fields of the
submenus.
ENTER
Accesses a submenu in the PROGRAM function.
EXIT
Closes a submenu and returns the operator to the Main Menu in
the PROGRAM function. At the Main Menu, pressing this key
returns the operator to the DISPLAY function.
3-2
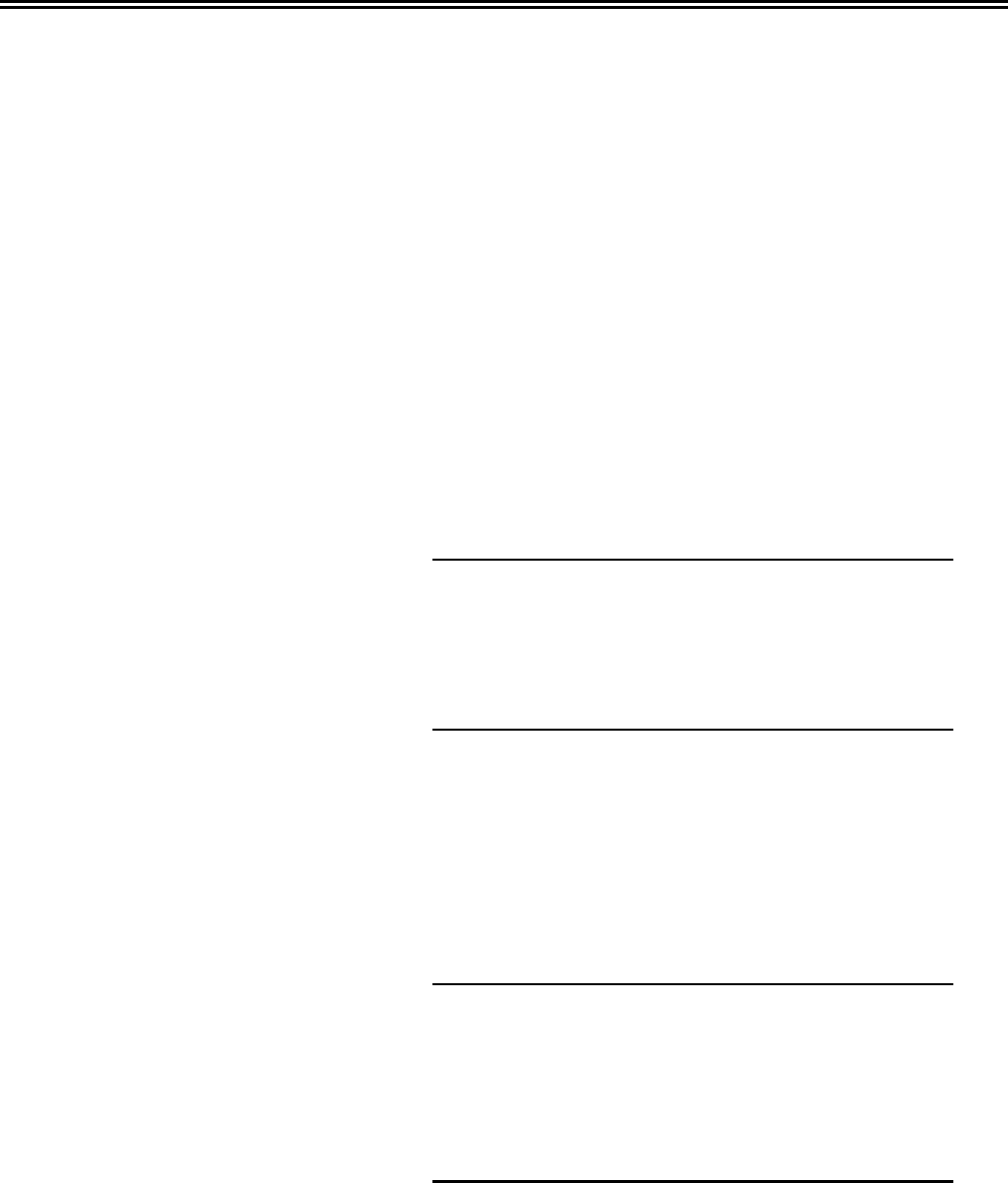
Section 3 Programming the Processor
SELECTION
Activates a selection or value in a field for making a change to it in
the PROGRAM function. When changing a numeric value, use
this key to move to each digit.
DECR/INCR
Used to change a numeric value in a field or to scroll through the
selections in a field in the PROGRAM function. Press the INCR
key to increase the value of a specific digit and the DECR key to
decrease the value of a specific digit.
Programming the
Setup Data
Initial Programming _______________________________________
NOTE
The processor screens shown are examples only. The
units of measure displayed will depend on the operator’s
selections in Mode 10: units of measurement in the
scale set up submenu.
_______________________________________
1. Apply power to the processor by plugging it into an outlet.
The first screen in the DISPLAY function appears in the
screen display.
2. Press the PROG key for approximately 3 seconds until the
Main Menu of the PROGRAM function appears on the
screen.
_______________________________________
NOTE
The flow chart in Figure 3-2 on page 3-4 shows the
submenus and fields within each submenu. Table 3-1
on pages 3-5to3-7 lists the fields in each submenu and
valid entries for each field in a submenu. Refer to these
as necessary during programming.
_______________________________________
3-3
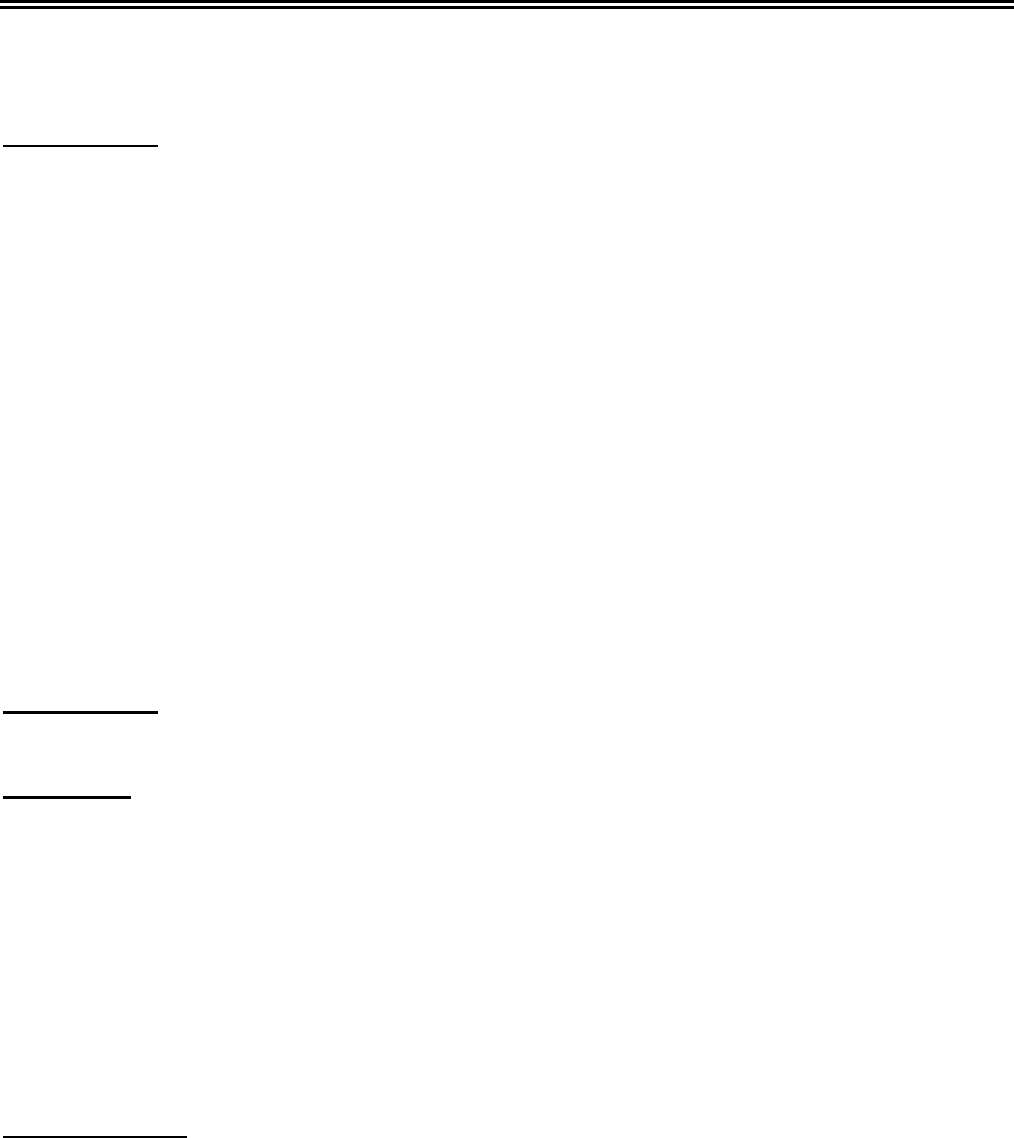
SciTronics Model CS 1000
Figure 3-2 Processor Menu Tree
Scale Set-Up:
Mode 1: Weigh Span
Mode 2: Belt Length
Mode 3: Load Span Adjustment
Mode 4: Calibration (0000.00 pounds)
Mode 5: Moisture Content (00.0 percent)
Mode 6: AZT
Mode 7: Tracking Time
Mode 8: Auto Zero Tracking
Mode 9: Test Cal Function (Calibrate / Test)
Mode 10: Test Cal Timing Source (Minutes / Belt Revolutions)
Mode 11: Test Cal Time Interval (Min or Rev. selection of Mode 10)
Mode 12: Belt Speed Span Adjustment
Mode 13: Units of Measurement
Mode 14: Damping
Mode 15: Total Decimal Point
Mode 16: Rate Decimal Point
Mode 17: Belt Speed Decimal Point
Mode 18: Terminal 9 Input Function
Material Test:
Scale 1: Test Total
Serial Port:
Mode 1: Baud Rate
Mode 2: Bits Per Character
Mode 3: Parity
Mode 4: Station I.D.
Mode 5: Time
Mode 6: Date
Mode 7: Clock Mode
Mode 8: Reset Total or Print Command
Mode 9: Print Net Total (Yes / No)
Mode 10: Print on the Hour (Yes / No)
Control Relay 1:
Mode 1: Function
Mode 2: Logic
Mode 3: Pulse Width
Mode 4: Pulse Scale
Mode 5: Alarm Delay
3-4
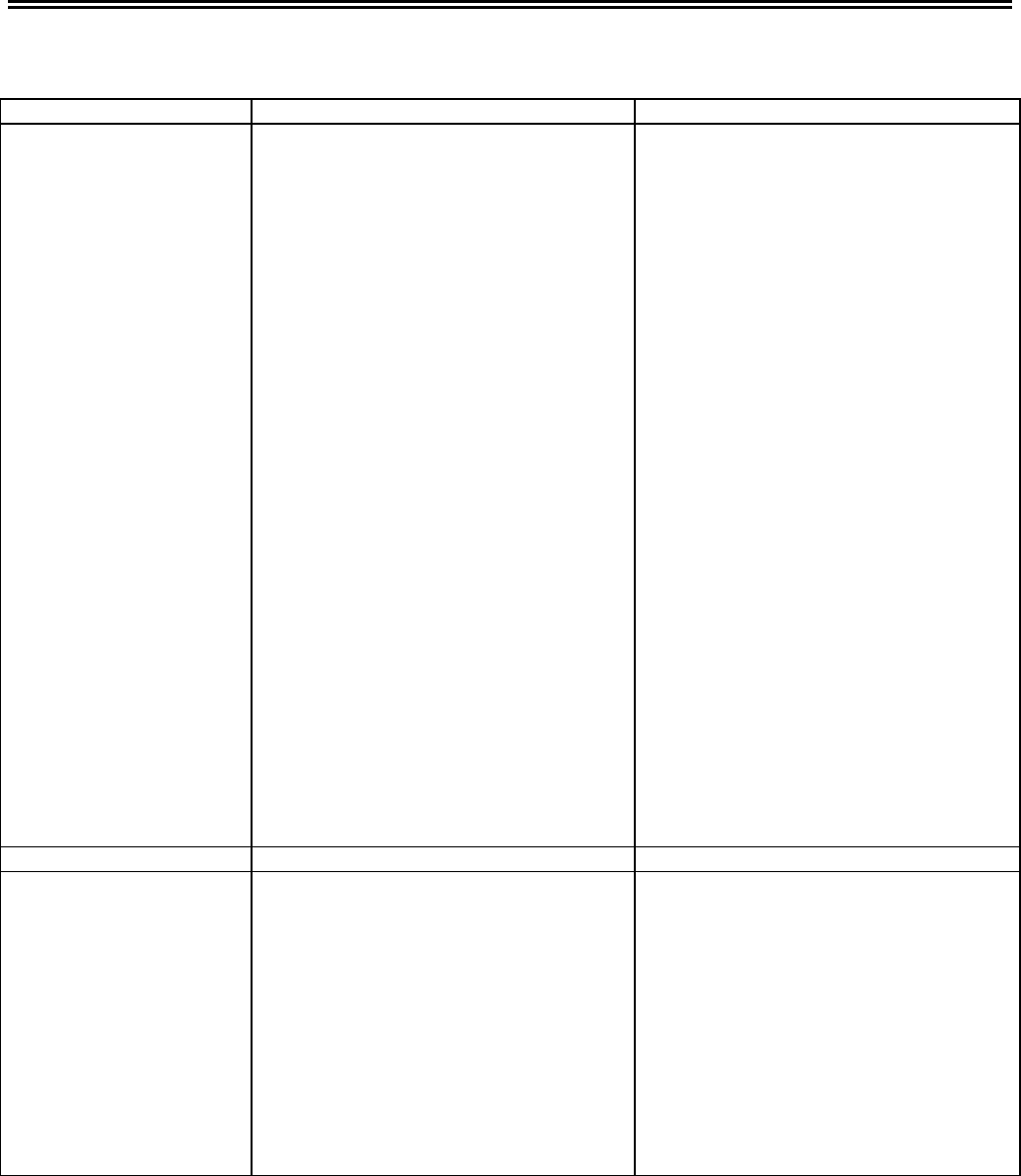
Section 3 Programming the Processor
Table 3-1 Programming Data Table
Submenu Item Valid Entries
Scale Set Up Mode 1: weigh span
Mode 2: belt length
Mode 3: rate span adjustment
Mode 4: azt (auto zero time) set point
Mode 5: tracking time interval
Mode 6: auto zero time interval
Mode 7: cal test timing source
Mode 8: cal test time interval
Mode 9: belt speed span adjustment
Mode 10 : units of Measurement
Mode 11: damping
Mode 12: total decimal point
Mode 13: rate decimal point
Mode 14: belt speed decimal point
Mode 15: terminal 9 input function
00.000 to 99.999*
0000.00 to 9999.99*
0000.00 to 9999.99 reference
00.00 to 99.99*
01 to 99 belt revs
01 to 99 belt revs
Minutes
Belt Revolutions
01 to 99 belt revs
0000.00 to 9999.99 reference
Tons Per Hour
Tons Per Minute
Pounds Per Hour
Pounds Per Minute
Tonnes Per Hour
Tonnes Per Minute
Kilograms Per Hour
Kilograms Per Minute
00.00 to 99.99 reference
Ones
Tenths
Hundredths
Ones
Tenths
Hundredths
Ones
Tenths
Hundredths
Interlock
Print Command
Reset Alarm
Material Test scale 1: test total 0000.00 to 9999.99*
Serial Port Mode 1: baud rate
Mode 2: bits per character
Mode 3: parity
Mode 4: station I.D.
Mode 5: time
1200
2400
4800
9600
19.2K
Seven
Eight
None
Odd
Even
A-P
Format - Hour:Min:Sec
Example: 11:52:09
* The units displayed depend on the operator’s selection in the Units of Measurement mode (Mode 10) of the Scale Set Up
submenu.
3-5
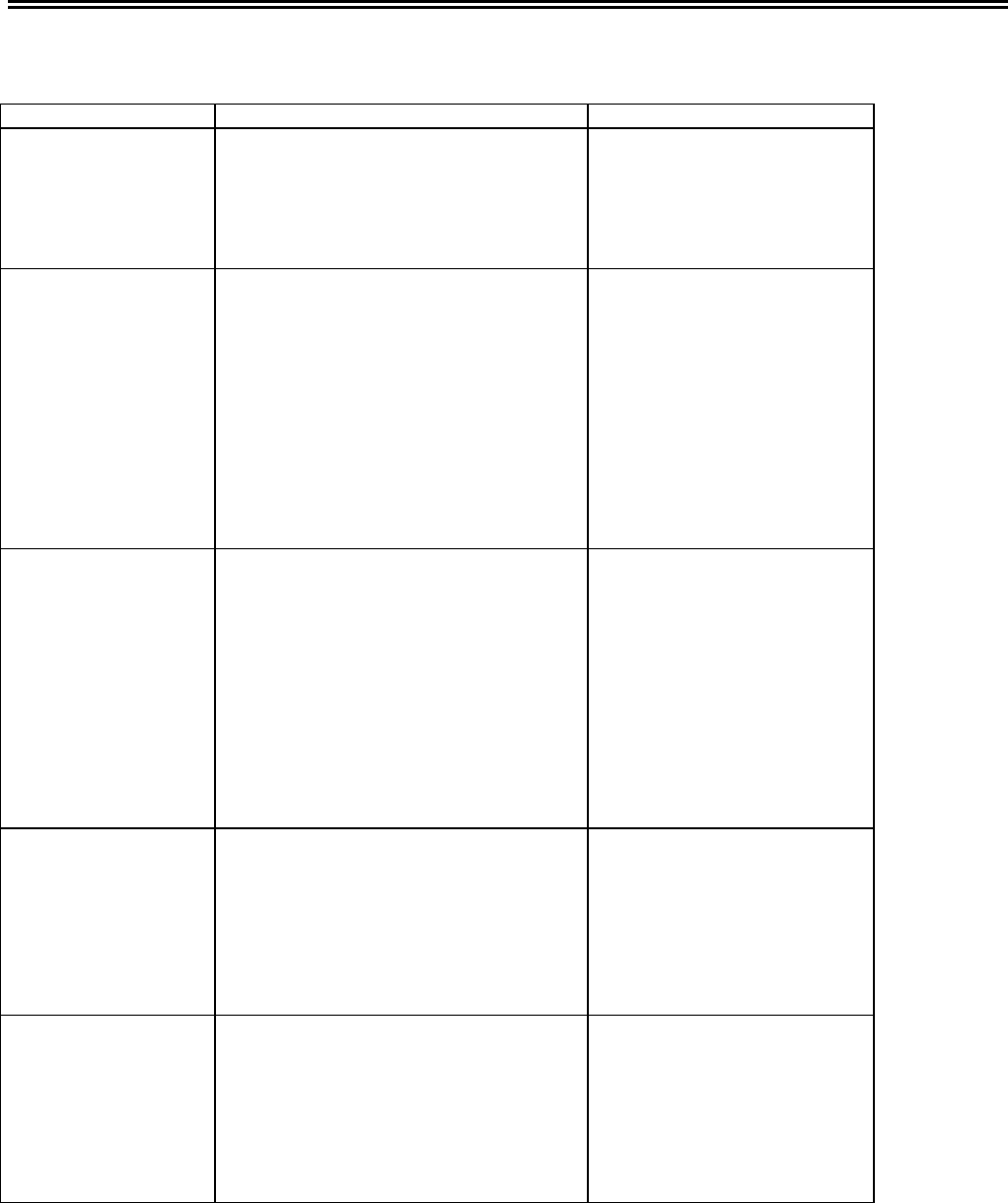
SciTronics Model CS 1000
Table 3-1 Programming Data Table (continued)
Submenu Item Valid Entries
Serial Port (continued) Mode 6: date
Mode 7: clock mode
Mode 8: reset total on print command
Mode 9: print on the hour
Format - month-day-year
Example: 04-11-95
AM
PM
Yes/No
Yes/No
Control Relay 1 Mode 1: function
Mode 2: logic
Mode 3: pulse width
Mode 4: pulse scale
Mode 5: alarm delay
Mode 6: low rate alarm setpoint
Mode 7: high rate alarm setpoint
Mode 8: low speed alarm setpoint
Mode 9: high speed alarm setpoint
pulse repeater
high/low alarm
diagnostic alarm
normally open
normally closed
.00 to .99 seconds
0000.0 to 9999.99*
.00 to .99 seconds
0000.00 to 9999.99*
0000.00 to 9999.99*
0000.00 to 9999.99*
0000.00 to 9999.99*
Control Relay 2 Mode 1: function
Mode 2: logic
Mode 3: pulse width
Mode 4: pulse scale
Mode 5: alarm delay
Mode 6: low rate alarm setpoint
Mode 7: high rate alarm setpoint
Mode 8: low speed alarm setpoint
Mode 9: high speed alarm setpoint
pulse repeater
high/low alarm
diagnostic alarm
normally open
normally closed
.00 to .99 seconds
0000.00 to 9999.99*
.00 to .99 seconds
0000.00 to 9999.99*
0000.00 to 9999.99*
0000.00 to 9999.99*
0000.00 to 9999.99*
Milliamp Output 1 Mode 1: function
Mode 2: offset
Mode 3: full scale
Mode 4: pulse width
Mode 5: pulse scale
rate output
belt speed output
lbs/foot output
pulse repeater
0.000 to 9.999 milliamps
Milliamp Output 2 Mode 1: function
Mode 2: offset
Mode 3: full scale
Mode 4: pulse width
Mode 5: pulse scale
rate output
belt speed output
lbs/foot output
pulse repeater
0.000 to 9.999 milliamps
0000.00 to 9999.99*
.00 to .99 seconds
0000.00 to 9999.99*
*The units displayed depend on the operator’s selection in Mode 10: units of measurement in the scale set up submenu.
3-6
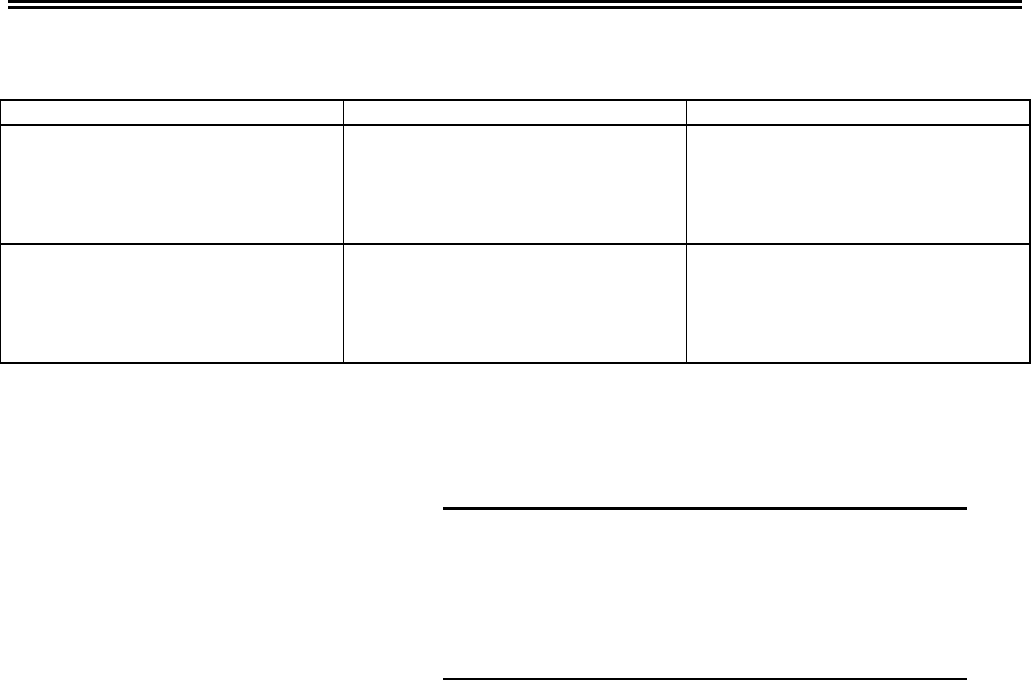
Section 3 Programming the Processor
Table 3-1 Programming Data Table (Continued)
Submenu Item Valid Entries
Mode 1: lock zero
Mode 2: lock reset
Mode 3: lock test cal
Mode 4: lock print
Mode 5: lock code
Yes / No
Yes / No
Yes / No
Yes / No
6 digits
Display Mode 1: display intensity
Mode 2: screen saver
Mode 3: demo mode
High
Medium
Low
00 to 99 minutes
On / Off
_______________________________________
NOTE
The procedure for Initial Programming is organized
so that the operator can access the first submenu in the
Main Menu and continue in order through each
submenu until all data has been programmed.
_______________________________________
Program each submenu as appropriate for your application:
SCALE SET UP SUBMENU
In the scale set up submenu, the operator enters belt scale system
parameters that will be used by the processor in its internal
calculations during calibration and normal operation.
To program the scale set up submenu:
1. At the Main Menu, press the ENTER key. The scale set up
submenu appears on the screen displaying Mode 1: weigh
span. The weigh span of the belt scale is the exact on-
center distance between the first advance and the first
retreat idler from the scale carriage, divided by two. Enter
this value (00.000 to 99.999) into the weigh span field
using the SELECT key to move to each digit and the
INCR and DECR keys to scroll through the numbers until
the appropriate value appears in the field. Press the PROG
key to move to Mode 2.
3-7

SciTronics Model CS 1000
2. Mode 2: belt length appears on the screen. Belt length is the
length of one complete revolution of the belt. Enter this value
(0000.00 to 9999.99) into the belt length field using the
SELECT key to move to each digit and the INCR and DECR
keys to scroll through the numbers until the appropriate value
appears in the field. Press the PROG key to move to Mode 3.
3. Mode 3: rate span adjustment appears on the screen. Rate
span adjustment is the value used by the processor during
calibration to manually adjust the scale system. This field has
been set by the factory but it can be changed as necessary. It
may be necessary to change this field during the calibration
process. Enter this value (0000.00 to 9999.99) into the rate
span adjustment field using the SELECT key to move to
each digit and the INCR and DECR keys to scroll through the
numbers until the appropriate value appears in the field. Press
the PROG key to move to Mode 4.
4. Mode 4: azt set point appears on the screen. When the rate
falls below the value set in this field, the processor starts to
track for the length of time indicated in the tracking and auto
zero time interval fields. Do not enter a value above the
lowest normal material flow rate. Setting this field at 00.00
disables auto zero tracking. Enter a value (00.00 to 99.99)
into the azt set point field using the SLELECT key to move to
each digit and the INCR and DECR keys to scroll through
the numbers until the appropriate value appears in the field.
Press the PROG key to move to Mode 5.
5. Mode 5: tracking time interval appears on the screen.
Tracking time interval is the number of belt revolutions to be
used by the processor during a zero tracking cycle. Enter a
value the allows for a 5 to 6 minute zero tracking cycle so
that the auto zero cycle does not start before the conveyor belt
has emptied. Enter a value (01 to 99 belt revolutions) into the
tracking time interval field using the SELECT key to move
to each digit and the INCR and DECR keys to scroll through
the numbers until the appropriate value appears in the field.
Press the PROG key to move to Mode 6.
3-8

Section 3 Programming the Processor
6. Mode 6: auto zero time interval appears on the screen. Auto
zero time interval is the number of belt revolutions during an
auto zero cycle. Although valid entries in this field range from
01 to 99 belt revolutions, typically, a value of 2 to 3 belt
revolutions is recommended. Enter a value into the auto zero
time interval field using the SELECT key to move to each
digit and the INCR and DECR keys to scroll through the
numbers until the appropriate value appears in the field. Press
the PROG key to move to Mode 7.
7. Mode 7: cal test timing source appears on the screen. Valid
selections in this field are minutes or belt revs. If the
operator selects belt revolutions, the processor uses belt
length and speed to determine the duration of the test cycle. If
the operator selects minutes, the actual number of minutes
entered determines the length of the cycle. Make your selection
using the SELECT key to activate the current selection (it will
blink) and the INCR and DECR keys to scroll through the
selections. When the desired selection appears on the screen,
press the SELECT key and the selection will stop blinking.
Press the PROG key to move to Mode 8.
8. Mode 8: cal test time interval appears on the screen.
Calibration test time interval is the number of belt revolutions
or minutes (depending on your selection in the cal test timing
source field) used by the processor during the calibration test.
Enter a value in the cal test time interval field (01 to 99 belt
revolutions) using the SELECT key to move to each digit and
the INCR and DECR keys to scroll through the numbers until
the appropriate value appears in the field. Press the PROG key
to move to Mode 9.
9. Mode 9: belt speed span adjustment appears on the screen.
Belt speed span adjustment is the value used by the processor to
calculate flow rate. This field is set by the factory but can be
manually changed when necessary to compensate for a
discrepancy between the actual weight in total tons and the
indicated weight in total tons. Enter the value (0000.00 to
9999.99) into the belt speed span adjustment field using the
SELECT key to move to each digit and the INCR and DECR
keys to scroll through the numbers until the appropriate value
appears in the field. Press the PROG key to move to Mode 10.
3-9

SciTronics Model CS 1000
10. Mode 10: units of measurement appears on the screen. This
field allows the operator to choose English or metric units of
measure (tons per hour, tons per minute, pounds per hour,
pounds per minute, tonnes per hour, tonnes per minute,
kilograms per hour, or kilograms per minute). The selection
in this field is used for the totals in the DISPLAY function
and for values as appropriate in the PROGRAM function.
Whenever this field is changed, the processor automatically
changes all applicable fields. Use the SELECT key to activate
the current selection (it will blink) and the INCR and DECR
keys to scroll through the selections. When the desired
selection appears on the screen, press the SELECT key and
the selection will stop blinking. Press the PROG key to move
to Mode 11.
11. Mode 11: damping appears on the screen. The value entered
in this field indicates the amount of weight change (typically in
pounds) to smooth the rate display when there are rapid input
variations. Enter the value (00.00 to 99.99) into the damping
field using the SELECT key to move to each digit and the
INCR and DECR keys to scroll through the numbers until the
appropriate value appears in the field. Press the PROG key to
move to Mode 12.
12. Mode 12: total decimal point appears on the screen. In this
field, the operator determines how many decimal places will
be used in the total displayed on the screen in the DISPLAY
function. Use the SELECT key to activate the current
selection (it will blink) and the INCR and DECR keys to
scroll through the selections (ones, tenths, and hundredths).
When the desired selection appears on the screen, press the
SELECT key and the selection will stop blinking. Press the
PROG key to move to Mode 13.
13. Mode 13: rate decimal point appears on the screen. In this
field, the operator determines how many decimal places will
be used in the rate displayed on the screen in the DISPLAY
function. Use the SELECT key to activate the current
selection (it will blink) and the INCR and DECR keys to
scroll through the selections (ones, tenths, and hundredths).
When the desired selection appears on the screen, press the
SELECT key and the selection will stop blinking. Press the
PROG key to move to Mode 14.
3-10

Section 3 Programming the Processor
14. Mode 14: belt speed decimal point appears on the screen.
This field allows the operator to determine how many decimal
places will be used in the belt speed displayed on the screen in
the DISPLAY function. Use the SELECT key to activate the
current selection (it will blink) and the INCR and DECR keys
to scroll through the selections (ones, tenths, and
hundredths). When the desired selection appears on the
screen, press the SELECT key and the selection will stop
blinking. Press the PROG key to move to Mode 15.
15. Mode 15: terminal 9 input function appears on the screen.
This field allows the operator to jumper terminal 9 to an
outside circuit. If this terminal is not needed, leave the default
setting (interlock). Use the SELECT key to activate the
current selection (it will blink) and the INCR and DECR keys
to scroll through the selections (interlock, remote reset, print
command, and reset alarm). When the desired selection
appears on the screen, press the SELECT key to leave this
submenu and return to the MAIN MENU.
MATERIAL TEST SUBMENU
The operator uses the material test submenu for calibrating the
belt scale. Refer to Section 4 - Calibration for more information
on this submenu.
SERIAL PORT SUBMENU
The serial port submenu is used to enter the settings required for
connection to a remote computer.
To program the serial port submenu:
1. Press the PROG key to move to the serial port submenu.
Press the ENTER key to display the first field in the
submenu.
3-11

SciTronics Model CS 1000
2. Mode 1: baud rate appears on the screen. The baud rate is
the speed in bits per second at which data is transmitted
between the processor and the remote computer. Use the
SELECT key to activate the current selection (it will blink) and
the INCR and DECR keys to scroll through the selections
(1200, 2400, 4800, 9600, and 19.2K). When the desired
selection appears on the screen, press the SELECT key and the
selection will stop blinking. Press the PROG key to move to
Mode 2.
3. Mode 2: bits per character appears on the screen. This field
determines the desired word length that will match the setting of
the remote device. It does not include stop, start, or parity bits.
Use the SELECT key to activate the current selection (it will
blink) and the INCR and DECR keys to scroll through the
selections (seven and eight). When the desired selection
appears on the screen, press the SELECT key and the selection
will stop blinking. Press the PROG key to move to Mode 3.
4. Mode 3: parity appears on the screen. Parity is the method use
to check errors in data transmission. Use the SELECT key to
activate the current selection (it will blink) and the INCR and
DECR keys to scroll through the selections (none, odd, and
even). When the desired selection appears on the screen, press
the SELECT key and the selection will stop blinking. Press the
PROG key to move to Mode 4.
5. Mode 4: station I.D. appears on the screen. Use the SELECT
key to activate the current selection (it will blink) and the INCR
and DECR keys to scroll through the selections (A-P). When
the desired selection appears on the screen, press the SELECT
key and the selection will stop blinking. B-P are used for
multiple hookups of processors. Press the PROG key to move
to Mode 5.
6. Mode 5: time appears on the screen. The operator enters the
current time in this field. When a report is printed, the time the
report was generated is printed on the report. Enter the current
time in hours, minutes, and seconds (for example: 11:52:09)
using the SELECT key to move to each digit and the INCR
and DECR keys to scroll through the numbers until the
complete time appears in the field. Press the PROG key to
move to Mode 6.
3-12

Section 3 Programming the Processor
7. Mode 6: date appears on the screen. The operator enters the
current date in this field. When a report is printed, the date the
report was generated is printed of the report. Enter the current
date in a month-day-year format (for example: 07-11-95) using
the SELECT key to move to each digit and the INCR and
DECR keys to scroll through the numbers until the complete
date appears in the field. Press the PROG key to move to Mode
7.
8. Mode 7: clock mode appears on the screen. The operator
selects a.m. if the current time is before noon or p.m. if the
current time is after noon using the SELECT key to activate the
current selection (it will blink) and the INCR and DECR keys
to scroll through the selections. When the desired selection
appears on the screen, press the SELECT key and the selection
will stop blinking. Press the PROG key to move to Mode 8.
9. Mode 8: reset total on print command appears on the screen
screen. The operator indicates in this field if the total should be
automatically reset after printing by using the SELECT key to
activate the current selection (it will blink) and the INCR and
DECR keys to scroll through the selections (yes and no). When
the desired selection appears on the screen, press the SELECT
key and the selection will stop blinking. Press the PROG key to
move to Mode 9.
10. Mode 9: print on the hour appears on the screen. The
operator indicates in this field if printing on the hour is desired
by using the SELECT key to activate the current selection (it
will blink) and the INCR and DECR keys to scroll through the
selections (yes and no). When the desired selection appears on
the screen, press the SELECT key and the selection will stop
blinking. Press the EXIT key to leave this submenu and return
to the Main Menu.
CONTROL RELAY 1 SUBMENU / CONTROL RELAY 2
SUBMENU
The control relays 1 and 2 allow the operator to program the
processor for more than one function. For example, the operator
may want each control relay programmed for a different alarm or
one control relay programmed for pulse repeater and one for an
alarm.
3-13

SciTronics Model CS 1000
To program the control relay 1 and 2 submenus:
1. Press the PROG key to move to the control relay 1
submenu. Press the ENTER key to display Mode 1.
2. Mode 1: function appears on the screen. Valid selections in
this field are pulse repeater, high/low alarm, and diagnostic
alarm. Make your selection using the SELECT key to activate
the current selection (it will blink) and the INCR and DECR
keys to scroll through the selections. When the desired selection
appears on the screen, press the SELECT key and the selection
will stop blinking. Press the PROG key to move to Mode 2.
3. Mode 2: logic appears on the screen. Valid selections in this
field are normally open or normally closed. Make your
selection using the SELECT key to activate the current
selection (it will blink) and the INCR and DECR keys to scroll
through the selections. When the desired selection appears on
the screen, press the SELECT key and the selection will stop
blinking. Press the PROG key to move to Mode 3.
4. Mode 3: pulse width appears on the screen. Enter the value
desired (.00 to .99 seconds) into the pulse width field using the
SELECT key to move to each digit and the INCR and DECR
keys to scroll through the numbers until the appropriate value
appears in the field. Press the PROG key to move to Mode 4.
5. Mode 4: pulse scale appears on the screen. The pulse output
is scaled at the value entered in this field. Enter the value
desired (0000.00 to 9999.99) into the pulse scale field using the
SELECT key to move to each digit and the INCR and DECR
keys to scroll through the numbers until the appropriate value
appears in the field. Press the PROG key to move to Mode 5.
6. Mode 5: alarm delay appears on the screen. Enter the value
desired (00 to 99 seconds) into the alarm delay field using the
SELECT key to move to each digit and the INCR and DECR
keys to scroll through the numbers until the appropriate value
appears in the field. The value entered in this field indicates the
length of time is seconds during an alarm condition before the
operator is alerted. Press the PROG key to move to Mode 6.
3-14

Section 3 Programming the Processor
7. Mode 6: low rate alarm set point appears on the screen.
When the rate falls below the value set in this field, the
processor alerts the operator to an alarm condition. Enter the
value desired (0000.00 to 9999.99) into the low rate alarm set
point field using the SELECT key to move to each digit and
the INCR and DECR keys to scroll through the numbers until
the appropriate value appears in the field. Press the PROG key
to move to Mode 7.
8. Mode 7: high rate alarm set point appears on the screen.
When the rate moves above the value set in this field, the
processor alerts the operator to an alarm condition. Enter the
value desired (0000.00 to 9999.99) into the high rate alarm set
point field using the SELECT key to move to each digit and
the INCR and DECR keys to scroll through the numbers until
the appropriate value appears in the field. Press the PROG key
to move to Mode 8.
9. Mode 8: low speed alarm set point appears on the screen.
When the speed moves below the value set in this field, the
processor alerts the operator to an alarm condition. Enter the
value desired (0000.00 to 9999.99) into the low speed alarm
set point field using the SELECT key to move to each digit
and the INCR and DECR keys to scroll through the numbers
until the appropriate value appears in the field. Press the PROG
key to move to Mode 9.
10. Mode 9: high speed alarm set point appears on the screen.
When the speed moves above the value set in this field, the
processor alerts the operator to an alarm condition. Enter the
value desired (0000.00 to 9999.99) into the high speed alarm
set point field using the SELECT key to move to each digit
and the INCR and DECR keys to scroll through the numbers
until the appropriate value appears in the field. Press the EXIT
key to leave this submenu and return to the Main Menu.
11. To program control relay 2, press the PROG key once to
move to the control relay 2 submenu. Follow steps 2-10 above
to complete the procedure for programming control relay 2.
3-15