Ziehl Abegg SE AMMODBUSW RF Module AM-MODBUS(-W) User Manual
Ziehl-Abegg AG RF Module AM-MODBUS(-W) Users Manual
Contents
- 1. installation instruction
- 2. operating instruction
installation instruction
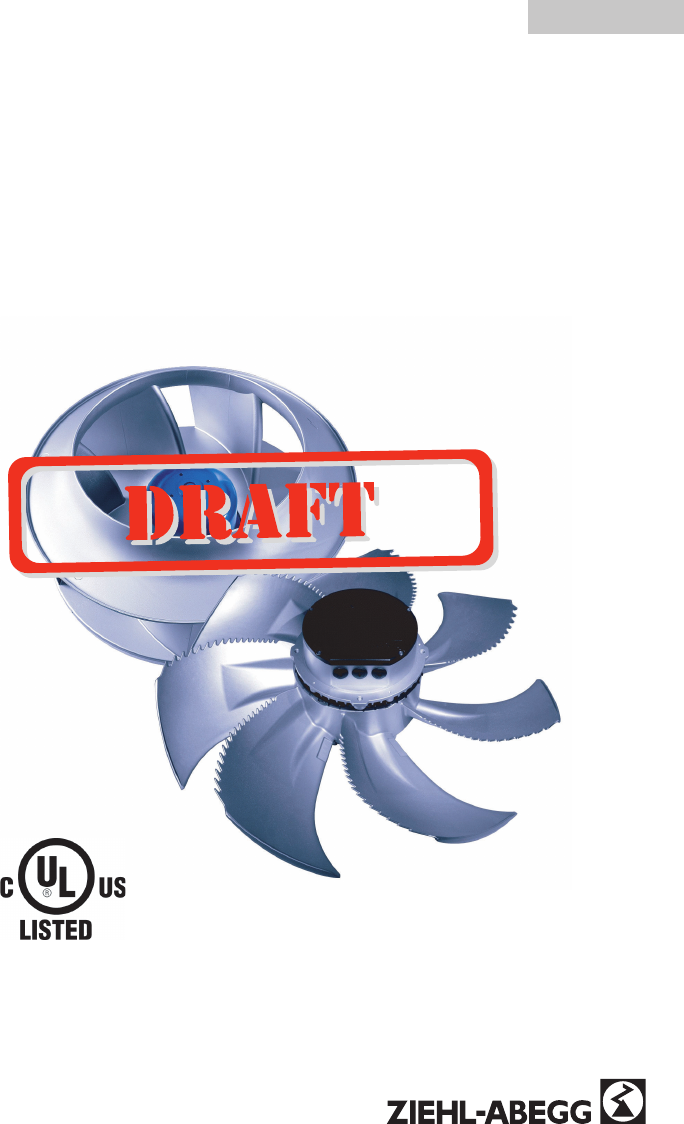
ECblue
Basic Version
EC-fans and motors with highest efciency
Assembly instructions
Software version: D1583...87A from Version 1.00
L-BAL-F046-GB 1203 Index 003 Part.-No. 00297758-GB
english
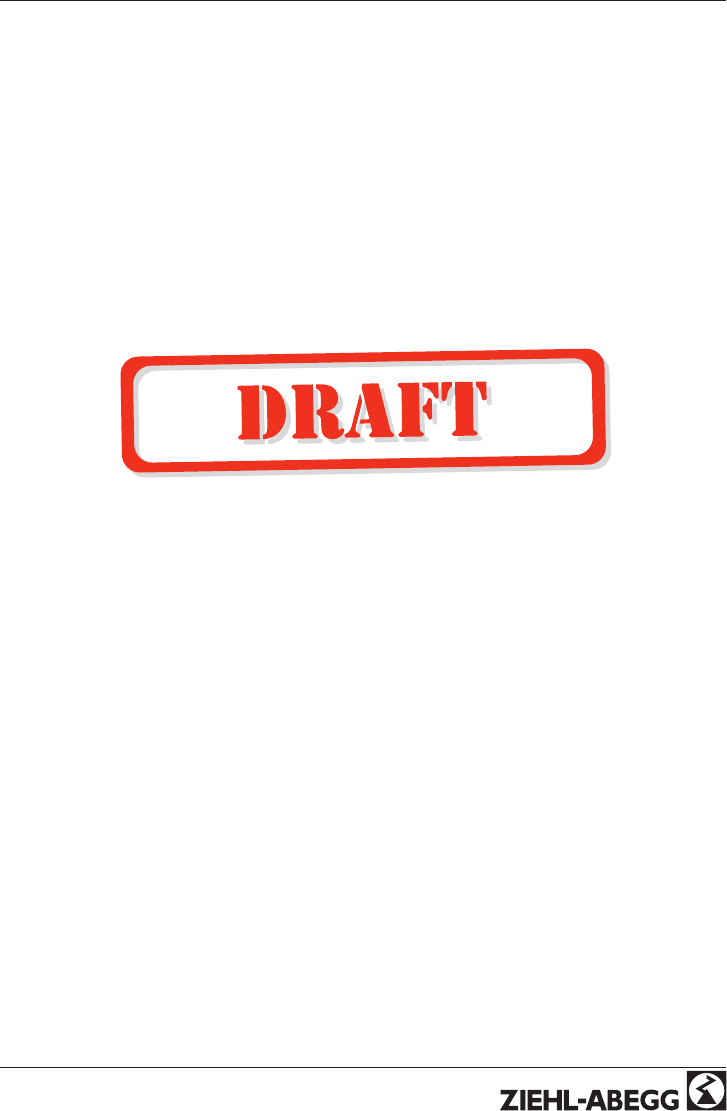
Content
1 General notes . . . . . . . . . . . . . . . . . . . . . . . . . . . . . . . . . . . . . . . . . . . . 5
1.1 Structure of the assembly instructions . . . . . . . . . . . . . . . . . . . . 5
1.2 Target group . . . . . . . . . . . . . . . . . . . . . . . . . . . . . . . . . . . . . . . . 5
1.3 Exclusion of liability . . . . . . . . . . . . . . . . . . . . . . . . . . . . . . . . . . 5
1.4 Copyright . . . . . . . . . . . . . . . . . . . . . . . . . . . . . . . . . . . . . . . . . . 5
2 Safety instructions . . . . . . . . . . . . . . . . . . . . . . . . . . . . . . . . . . . . . . . . 5
2.1 Intended use . . . . . . . . . . . . . . . . . . . . . . . . . . . . . . . . . . . . . . . 6
2.2 Improper use . . . . . . . . . . . . . . . . . . . . . . . . . . . . . . . . . . . . . . . 6
2.3 Explanations of symbols . . . . . . . . . . . . . . . . . . . . . . . . . . . . . . . 6
2.4 Product safety . . . . . . . . . . . . . . . . . . . . . . . . . . . . . . . . . . . . . . 7
2.5 Requirements placed on the personnel / due diligence . . . . . . . 7
2.6 In the Operation . . . . . . . . . . . . . . . . . . . . . . . . . . . . . . . . . . . . . 7
2.7 Working on device / Hazards through “residual voltage” . . . . . . 8
2.8 Modifications / interventions in the device . . . . . . . . . . . . . . . . . 9
2.9 Operator’s obligation of diligence . . . . . . . . . . . . . . . . . . . . . . . . 9
2.10 Employment of external personnel . . . . . . . . . . . . . . . . . . . . . . . 9
3 Product overview . . . . . . . . . . . . . . . . . . . . . . . . . . . . . . . . . . . . . . . . . 10
3.1 Application operational area . . . . . . . . . . . . . . . . . . . . . . . . . . . . 10
3.2 Functional description . . . . . . . . . . . . . . . . . . . . . . . . . . . . . . . . . 10
3.3 Ziehl-Abegg design criteria for long service life . . . . . . . . . . . . . 10
3.4 Transport . . . . . . . . . . . . . . . . . . . . . . . . . . . . . . . . . . . . . . . . . . 11
3.5 Storage . . . . . . . . . . . . . . . . . . . . . . . . . . . . . . . . . . . . . . . . . . . . 11
3.6 Disposal / recycling . . . . . . . . . . . . . . . . . . . . . . . . . . . . . . . . . . 11
4 Mounting . . . . . . . . . . . . . . . . . . . . . . . . . . . . . . . . . . . . . . . . . . . . . . . . 12
4.1 General notes . . . . . . . . . . . . . . . . . . . . . . . . . . . . . . . . . . . . . . . 12
4.2 Connection lead & terminal box . . . . . . . . . . . . . . . . . . . . . . . . . 12
4.3 Connection according UL and CSA in different applications . . . . 13
4.3.1 Connecting the conduit for NEC and CEC approval . . . . . . 13
4.3.2 Connection in NFPA 79 Applications . . . . . . . . . . . . . . . . . 14
4.4 Installation of axial fans . . . . . . . . . . . . . . . . . . . . . . . . . . . . . . . 15
4.4.1 Fan designs A, D, K, S and W (without nozzles) . . . . . . . . 15
4.4.2 Installation in an exhaust air stack, design T . . . . . . . . . . . 16
4.5 Mounting of centrifugal fans . . . . . . . . . . . . . . . . . . . . . . . . . . . . 18
4.5.1 Mounting of centrifugal fans, RH design . . . . . . . . . . . . . . 18
Assembly instructions ECblue
L-BAL-F046-GB 1203 Index 003 Part.-No. 00297758-GB
2/45

4.5.2 Erecting the equipment: Design ER...-..N... / ER...-..K... / GR...
19
4.5.3 Optimal installation distances according to for RH../ ER../ GR..
fans . . . . . . . . . . . . . . . . . . . . . . . . . . . . . . . . . . . . . . . 19
4.6 Mounting of motors . . . . . . . . . . . . . . . . . . . . . . . . . . . . . . . . . . . 20
4.7 Outdoor fans in a humid atmosphere . . . . . . . . . . . . . . . . . . . . . 20
4.8 Motorheating . . . . . . . . . . . . . . . . . . . . . . . . . . . . . . . . . . . . . . . 21
5 Electrical installation . . . . . . . . . . . . . . . . . . . . . . . . . . . . . . . . . . . . . . 21
5.1 Safety precautions . . . . . . . . . . . . . . . . . . . . . . . . . . . . . . . . . . . 21
5.2 Connection . . . . . . . . . . . . . . . . . . . . . . . . . . . . . . . . . . . . . . . . . 21
5.2.1 Motor size “D” and “G” .......................... 22
5.2.2 UL: note for cable entrances . . . . . . . . . . . . . . . . . . . . . . 23
5.3 EMC-compatible installation of control lines . . . . . . . . . . . . . . . . 23
5.4 Mains connection . . . . . . . . . . . . . . . . . . . . . . . . . . . . . . . . . . . . 23
5.4.1 Line voltage for 1~ types . . . . . . . . . . . . . . . . . . . . . . . . . 23
5.4.2 Line voltage for 3~ types . . . . . . . . . . . . . . . . . . . . . . . . . 24
5.4.3 Required quality attributes for the mains voltage . . . . . . . . . 24
5.4.4 Operating in IT-System . . . . . . . . . . . . . . . . . . . . . . . . . . 24
5.4.5 UL: Short-circuit protection for branch circuits (UL508C) . . . 25
5.5 Residual-current-operated protective device . . . . . . . . . . . . . . . . 25
5.6 Motor protection . . . . . . . . . . . . . . . . . . . . . . . . . . . . . . . . . . . . . 25
5.7 Analog input (0...10 V) for setting fan speed . . . . . . . . . . . . . . . 25
5.8 Output voltage +10 V . . . . . . . . . . . . . . . . . . . . . . . . . . . . . . . . . 27
5.9 Voltage supply for external devices, only motor sizes “D”, “G”
(+24 V, GND) . . . . . . . . . . . . . . . . . . . . . . . . . . . . . . . . . . . . . . 27
5.10 Enable, device ON / OFF (Digital In 1 = D1) . . . . . . . . . . . . . . . 28
5.11 Relay output (K1) . . . . . . . . . . . . . . . . . . . . . . . . . . . . . . . . . . . . 28
5.12 Potential at control voltage connections . . . . . . . . . . . . . . . . . . . 28
5.13 Add-on modules . . . . . . . . . . . . . . . . . . . . . . . . . . . . . . . . . . . . . 28
6 Start-up . . . . . . . . . . . . . . . . . . . . . . . . . . . . . . . . . . . . . . . . . . . . . . . . 30
6.1 Prerequisites for commissioning . . . . . . . . . . . . . . . . . . . . . . . . . 30
7 Diagnostics / Faults . . . . . . . . . . . . . . . . . . . . . . . . . . . . . . . . . . . . . . . 31
7.1 Trouble shooting . . . . . . . . . . . . . . . . . . . . . . . . . . . . . . . . . . . . . 31
7.2 Status Out with flash code . . . . . . . . . . . . . . . . . . . . . . . . . . . . 32
7.3 Behaviour in rotation by air current in reverse direction . . . . . . . 34
8 Service work . . . . . . . . . . . . . . . . . . . . . . . . . . . . . . . . . . . . . . . . . . . . . 35
8.1 Repairs / maintenance . . . . . . . . . . . . . . . . . . . . . . . . . . . . . . . . 35
Assembly instructions ECblue
L-BAL-F046-GB 1203 Index 003 Part.-No. 00297758-GB
3/45
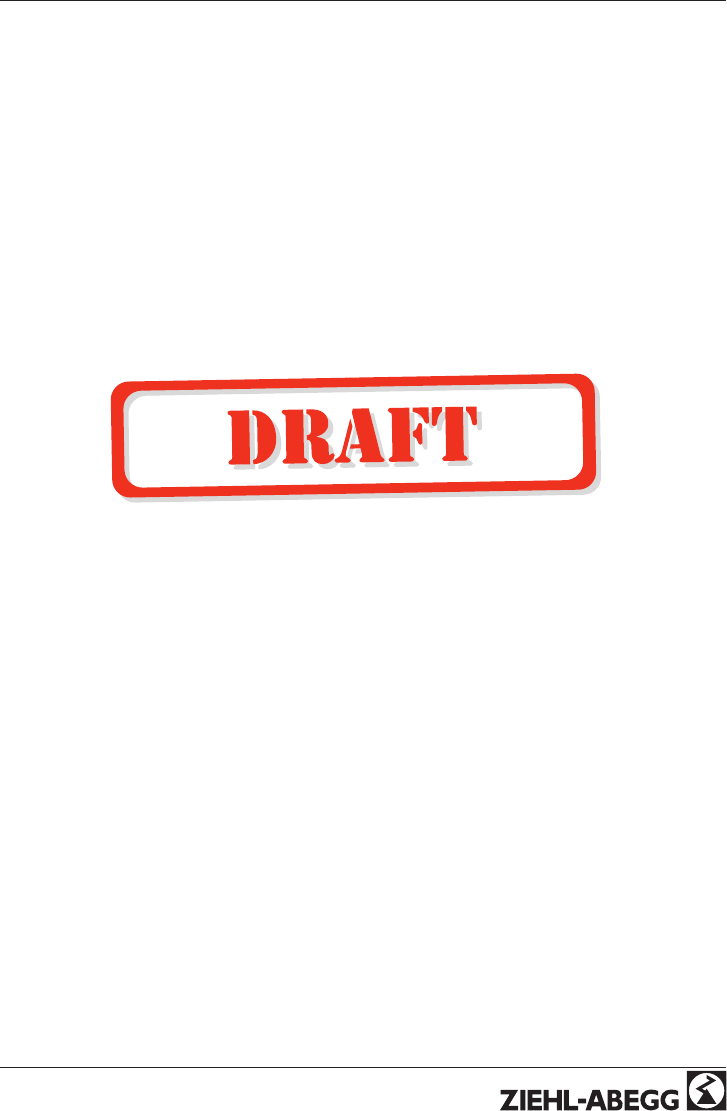
8.2 Cleaning . . . . . . . . . . . . . . . . . . . . . . . . . . . . . . . . . . . . . . . . . . . 35
9 Enclosure . . . . . . . . . . . . . . . . . . . . . . . . . . . . . . . . . . . . . . . . . . . . . . . 36
9.1 Technical data . . . . . . . . . . . . . . . . . . . . . . . . . . . . . . . . . . . . . . 36
9.1.1 UL: Ratings and dimensions: . . . . . . . . . . . . . . . . . . . . . . 38
9.1.2 UL: Overload protection . . . . . . . . . . . . . . . . . . . . . . . . . . 39
9.1.3 UL: Short Circuit Current Rating . . . . . . . . . . . . . . . . . . . . 40
9.2 Connection diagram . . . . . . . . . . . . . . . . . . . . . . . . . . . . . . . . . . 41
9.3 EC Declaration of Incorporation . . . . . . . . . . . . . . . . . . . . . . . . . 42
9.4 Index . . . . . . . . . . . . . . . . . . . . . . . . . . . . . . . . . . . . . . . . . . . . . 44
9.5 Manufacturer reference . . . . . . . . . . . . . . . . . . . . . . . . . . . . . . . 45
9.6 Service information . . . . . . . . . . . . . . . . . . . . . . . . . . . . . . . . . . . 45
Assembly instructions ECblue
L-BAL-F046-GB 1203 Index 003 Part.-No. 00297758-GB
4/45
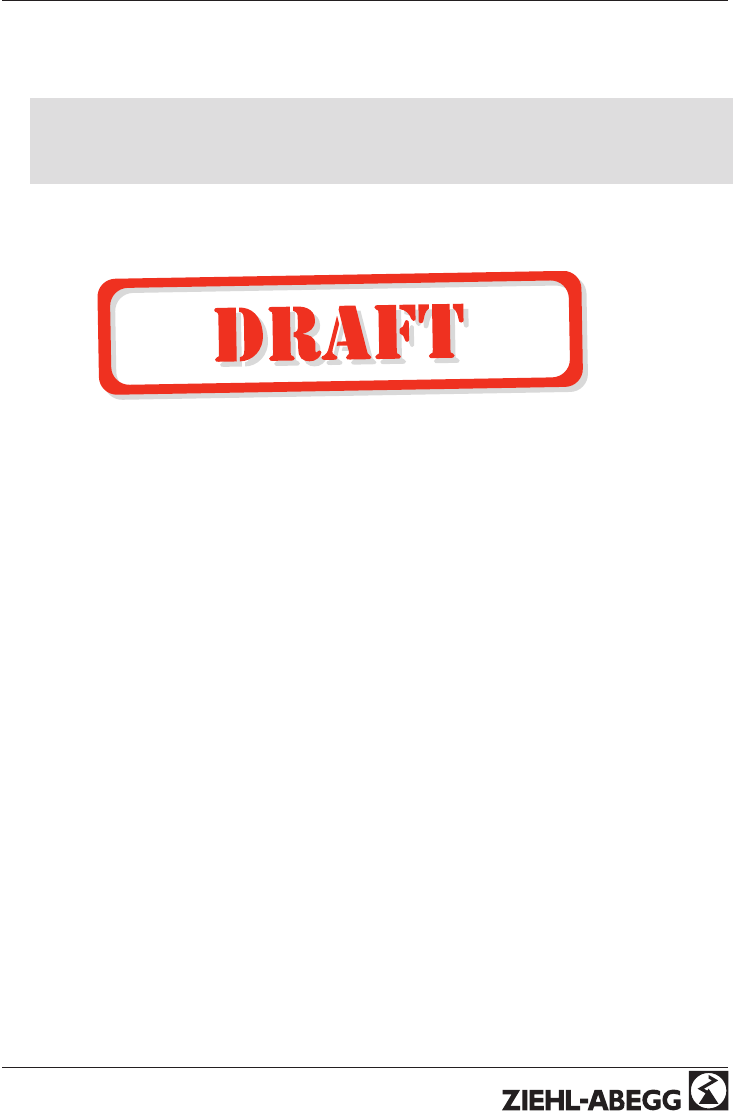
1 General notes
1.1 Structure of the assembly instructions
Before installation and start-up, read this assembly instructions carefully to en-
sure correct use!
We emphasize that these assembly instructions apply to specific units only, and
are in no way valid for the complete system!
Use these assembly instructions to work safely with and on the device. They contain
safety instructions that must be complied with as well as information that is required for
failure-free operation of the device.
Keep these assembly instructions together with the device. It must be ensured that all
persons that are to work on the device can refer to the assembly instructions at any time.
Keep the assembly instructions for continued use. They must be passed-on to all
successive owners, users and final customers.
1.2 Target group
The assembly instructions address persons entrusted with planning, installation, com-
missioning and maintenance and servicing and who have the corresponding qualifica-
tions and skills for their job.
1.3 Exclusion of liability
Concurrence between the contents of these assembly instructions and the described
hardware and software in the device has been examined. It is still possible that non-
compliances exist; no guarantee is assumed for complete conformity. To allow for future
developments, construction methods and technical data given are subject to alteration.
We do not accept any liability for possible errors or omissions in the information con-
tained in data, illustrations or drawings provided.
Ziehl-Abegg AG is not liable for damage due to misuse, incorrect use, improper use or
as a consequence of unauthorized repairs or modifications.
1.4 Copyright
These assembly instructions contain copyright protected information. The assembly
instructions may be neither completely nor partially photocopied, reproduced, translated
or put on data medium without previous explicit consent from Ziehl-Abegg AG. Infringe-
ments are liable for damages. All rights reserved, including those that arise through
patent issue or registration on a utility model.
2 Safety instructions
This chapter contains instructions to prevent personal injury and property damage.
These instructions do not lay claim to completeness. In case of questions and problems,
please consult our company technicians.
Assembly instructions ECblue General notes
L-BAL-F046-GB 1203 Index 003 Part.-No. 00297758-GB
5/45
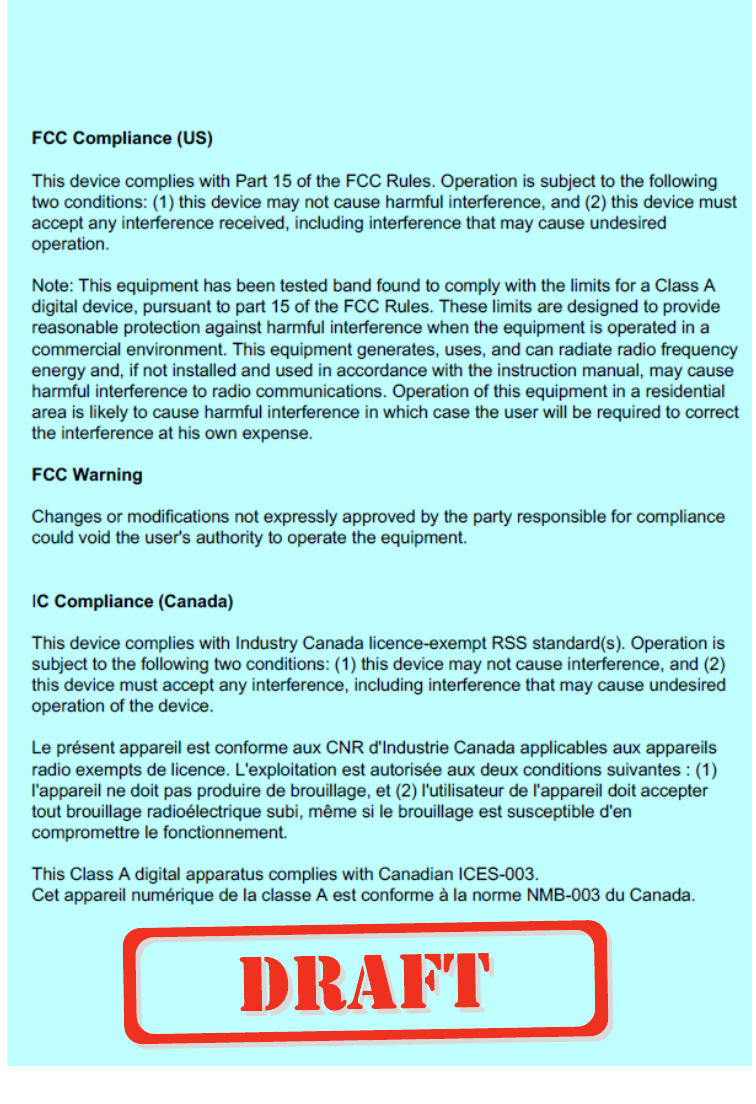
1.5 FCC/IC Statements
In case that the AM-MODBUS-W module or the AM-PREMIUM-W
module is installed in the ECblue, the following applies:
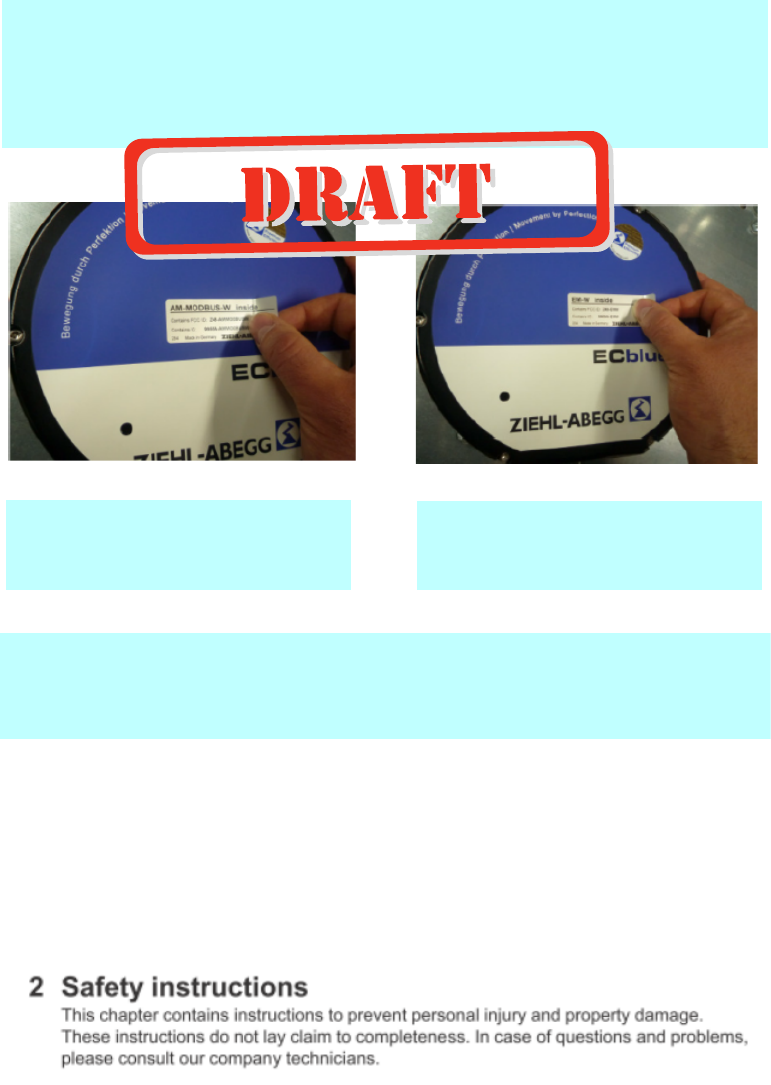
Note: If AM-MODBUS-W module or AM PREMIUM-W module is used
and installed by the user, the FCC/IC label (AM-MODBUS-W inside
label for AM-MODBUS-W module, EM-W inside label for AM-
PREMIUM-W module) have to stick on the housing of the ECblue.
Sticking the AM-MODBUS-W
inside label on the ECBlue
housing.
Sticking the EM-W inside label
on the ECBlue housing.
Note: The modules (AM-MODBUS-W and AM-PREMIUM-W) are stricly
limited for the integration and usage with host devices manufactured by
Ziehl-Abegg AG.
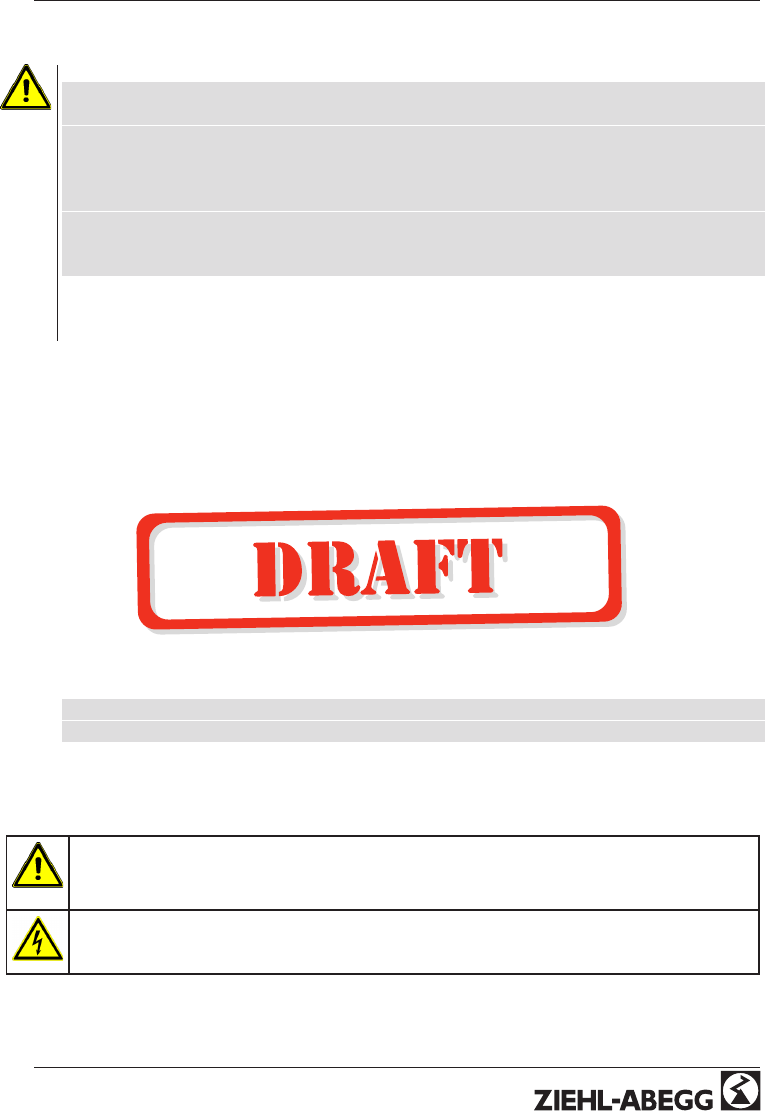
2.1 Intended use
Attention!
•The fans are only intended for the conveyance of air or mixtures similar to
air.
•Other uses which do not coincide with, or which exceed those specified will
be deemed unauthorised unless contractually agreed. Damages resulting
from such unauthorised uses will not be the liability of the manufacturer.
The user will assume sole liability.
•They must not be used in hazardous areas for the transfer of gas, mist
vapours or mixtures. Nor must they be used for the transfer of solid compo-
nents in the transfer medium.
•Reading these document and complying with all contained instructions -especially
the safety notifications contained therein -are considered part of intended use.
•To consider is also the documentation of attached components.
2.2 Improper use
Improper use / reasonably foreseeable misuse
•Conveyance of aggressive and explosive gaseous media.
•Use in an explosive atmosphere.
•Operation with iced up fan impeller.
•Conveyance of abrasive or adhesive media.
•Conveyance of liquid media.
•Use of the fan and add-on parts (e.g. safety grille) as a resting surface or climbing
aid.
•Unauthorised constructional modifications to the fan.
•Operation of the fan as a safety component or for the performance of safety-
relevant functions in the sense of EN ISO 13849-1.
•Blocking or braking of the fan by inserting objects.
•Loosening of the impeller from the motor.
•All applications not listed in the intended use.
Not the manufacturer, rather the operator of the frequency inverter is liable for any
personal harm or material damage arising from non-intended use.
2.3 Explanations of symbols
Safety instructions are highlighted with warning triangles and are depicted according to
the degree of hazard as follows.
Attention!
General hazardous area. Death or severe injury or significant property damage can
occur if the corresponding precautions are not taken!
Danger due to electric current
Warning of dangerous voltage or dangerous current.
Assembly instructions ECblue Safety instructions
L-BAL-F046-GB 1203 Index 003 Part.-No. 00297758-GB
6/45
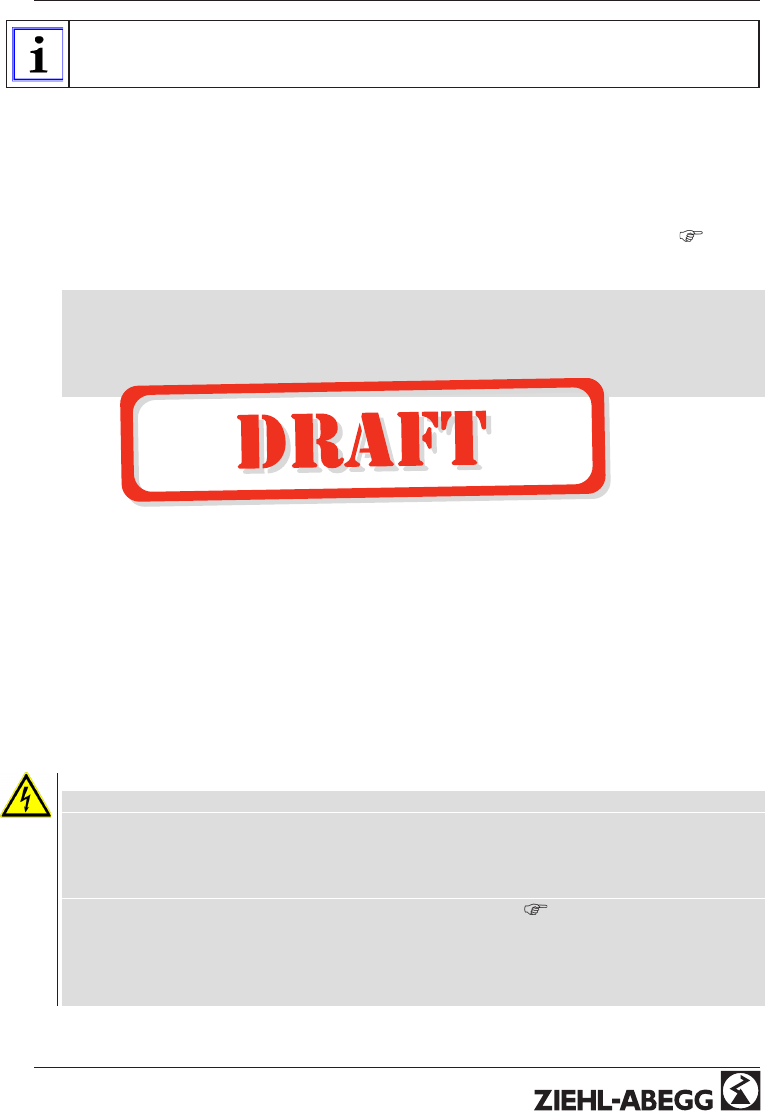
Information
Important additional information and advice for user.
2.4 Product safety
The device conforms to the state of the art at the time of delivery and is fundamentally
considered to be reliable. The device and its accessories must only be used in a flawless
condition and installed and operated in compliance with the assembly instructions and/or
operating instructions. Operating outside the device's technical specifications (
rating
plate and attachment / technical data) can lead to a defect in the device and additional
damage!
A separate fault and performance monitoring-system with an alarm signal function
is necessary in order to prevent personal injuries and material damages during
malfunctions and in case the device fails. Substitute operation must be taken into
consideration! The design and installation of the system must comply with local
regulations and directives.
2.5 Requirements placed on the personnel / due diligence
Persons entrusted with the planning, installation, commissioning and maintenance and
servicing in connection with the frequency inverter must have the corresponding qual-
ifications and skills for these jobs.
In addition, they must be knowledgeable about the safety regulations, EU directives,
rules for the prevention of accidents and the corresponding national as well as regional
and in-house regulations. Personnel to be trained or instructed and apprentices are only
permitted to work on the device under the supervision of an experienced person. This
also applies to personnel undergoing general training. Comply with the legal minimum
age.
This device is not intended to be used by people (including children) who have restricted
mental, sensory or intellectual abilities or who have a lack of experience and/or knowl-
edge.
2.6 In the Operation
Danger due to electric current
•Any faults detected in the electric system/modules/operating equipment must be
corrected immediately. If these faults are not corrected, the device/system is
potentially very dangerous. The device/system must therefore not be operated
when it is faulty.
•Fuses must always be replaced only, never repaired or bridged. The specifications
for maximum prefusing must always be adhered to (
Technical data). Only
fuses cited in the electrical circuit diagram may be used.
•When opening cable glands on the fan / motor, check the condition of the threaded
connections and seals. Always replace defective or brittle threaded connections
and seals.
Assembly instructions ECblue Safety instructions
L-BAL-F046-GB 1203 Index 003 Part.-No. 00297758-GB
7/45
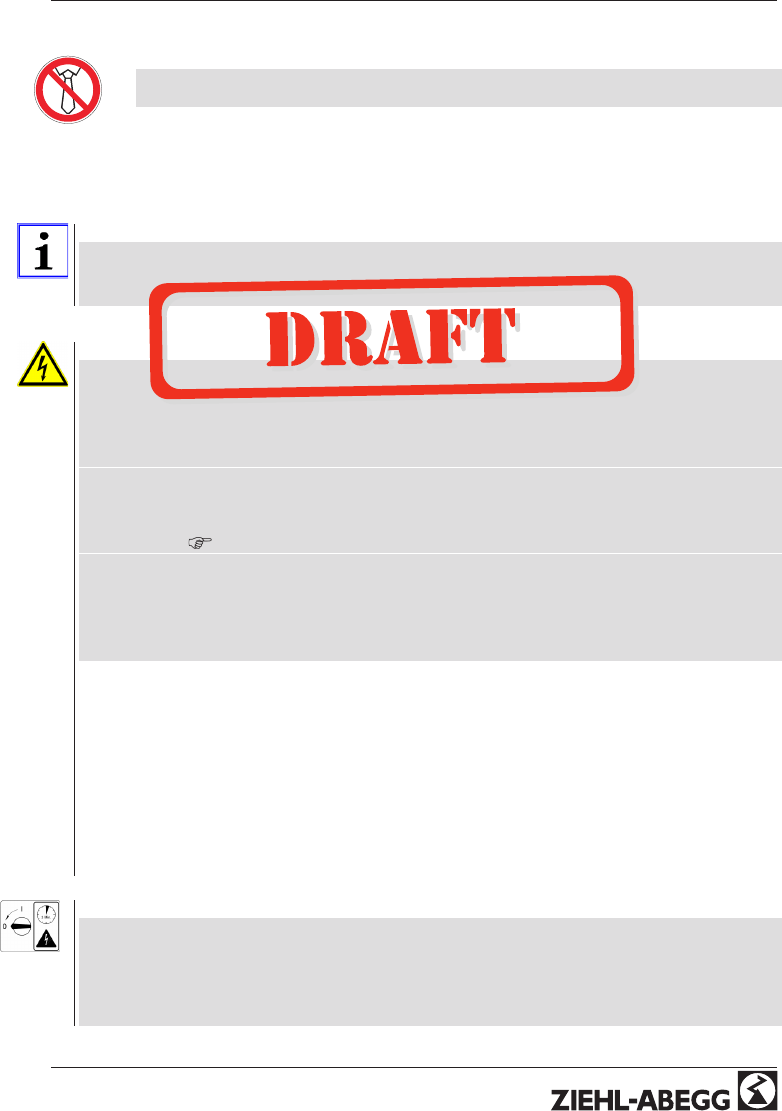
Attention, danger of being sucked in!
•Danger of being sucked in: Do not wear loose or hanging clothing, jewellery, etc.,
tie together long hair and cover it.
2.7 Working on device / Hazards through “residual voltage”
Information
Mounting, electrical connection, and start-up operation may only be carried out by
an electrical specialist in accordance with electrotechnical regulations (e.g. EN
50110 or EN 60204)!
Danger due to electric current
•It is generally forbidden to carry out work on electrical live parts. Protection
class of the device when open is IP 00! It is possible to touch hazardous
voltages directly!
•The rotor is not protected against indirect contact neither by supplementary
or reinforced insulation nor by connection to safety-earth in accordance
with EN 60204-1, therefore the system constructor must provide protection
by enclosure in accordance with EN 61140 before the motor is connected to
a power source. This protection can be achieved for example by a guard
grille (
Product overview: Application operational area and Installation:
General).
•When the motor runs independently due to air flowing through or if it
continues to run down after being turned off, dangerous voltages of over
50 V can arise on the motor internal connections through operation of the
generator.
•The safe isolation from the supply must be checked using a two-pole voltage
detector.
•Even after disconnecting the mains voltage, life-threatening charges can appear
between the protective earth “PE” and the mains connection.
•The protective earth is conducting high discharge currents (dependent on the
switching frequency, current-source voltage and motor capacity). Earthing in
compliance with EN specifications shall therefore be observed even for testing
and trial conditions (EN 50 178, Art. 5.2.11). Without earthing, dangerous voltages
can be present on the motor housing.
•Maintenance work may only be carried out by suitably qualified personnel.
Waiting period at least 3 minutes!
Through use of capacitors, danger of death exists even after switching off the
device through directly touching the energized parts or due to parts that have
become energized due to faults.
The controller housing may only be removed or opened when the power line has
been switched off and a period of three minutes has elapsed since switching it off.
Assembly instructions ECblue Safety instructions
L-BAL-F046-GB 1203 Index 003 Part.-No. 00297758-GB
8/45
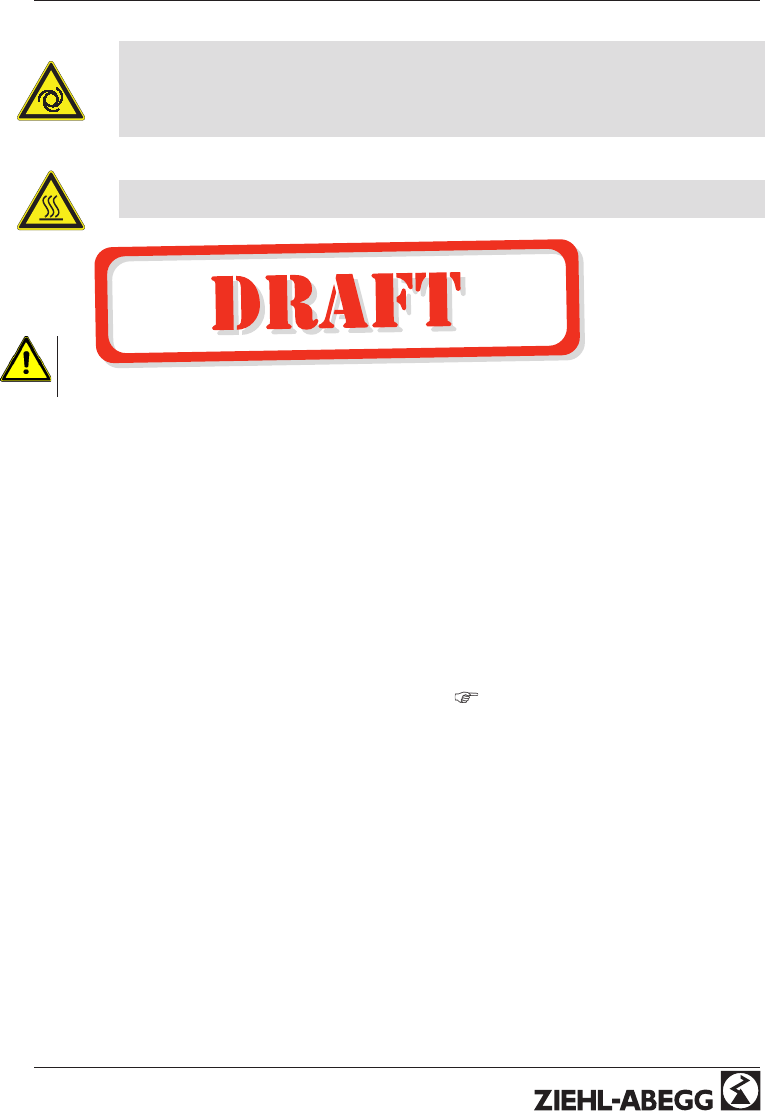
Attention, automatic restart!
•The fan / motor may switch on and off automatically for functional reasons.
•After power failure or mains disconnection an automatic restart of the fan takes
place after voltage return!
•Wait for the fan to come to a complete standstill before approaching it!
•In the AC external rotor motor the external rotor turns during operation!
Attention, hot surface!
•Temperatures of above 85 °C can occur on the motor surfaces, especially on the
controller housing!
2.8 Modifications / interventions in the device
Attention!
For reasons of safety, no unauthorized interventions or modifications may be made on
the device. All planned modifications must be authorized by the manufacturer in writing.
Use only genuine spare parts / genuine wearing parts / genuine accessories from Ziehl-
Abegg.These parts were specifically designed for the device. There is no guarantee that
parts from non-original sources are designed and manufactured in correspondence with
load and safety requirements.
Parts and optional equipment not supplied by Ziehl-Abegg are not approved by Ziehl-
Abegg for use.
2.9 Operator’s obligation of diligence
•The contractor or owner must also ensure that the electric systems and equipment
are operated and maintained in accordance with electro-technical regulations.
•The owner is obliged to ensure that the device are operated in perfect working
order only.
•The device may only be used as intended (
“Application”).
•You must periodically examine the safety equipment for their properly functioning
condition.
•The assembly instructions and/or operating instructions are always readily avail-
able at the location where the device is being used, are complete and are in
legible condition.
•These persons are regularly instructed in all applicable questions regarding occu-
pational safety and environmental protection and are knowledgeable regarding
the assembly instructions and/or operating instructions and, especially, are famil-
iar with the safety instructions contained therein.
•All safety and warning notices attached to the device are never removed and
remain legible.
2.10 Employment of external personnel
Maintenance and service work are frequently carried out by external employees who
often do not recognize the specific situations and the thus resulting dangers.These
persons must be comprehensively informed about the hazards in their area of activity.
Assembly instructions ECblue Safety instructions
L-BAL-F046-GB 1203 Index 003 Part.-No. 00297758-GB
9/45
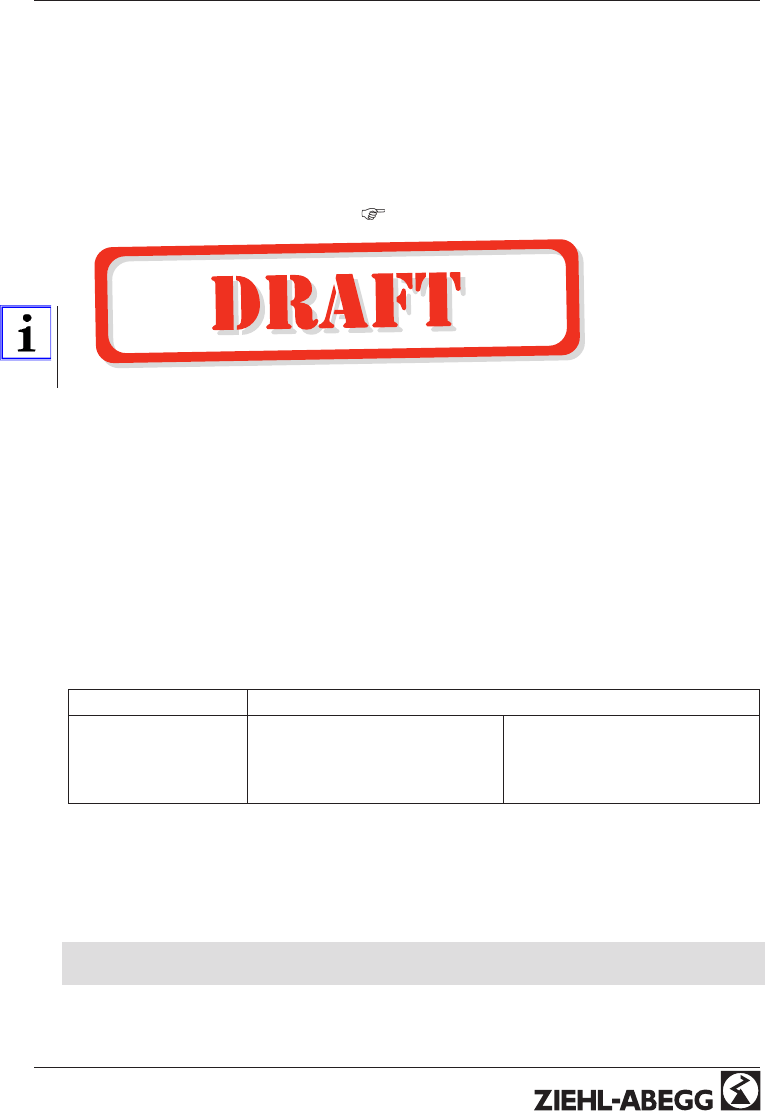
You must monitor their working methods in order to intervene in good time if necessary.
3 Product overview
3.1 Application operational area
The fans / motors are not ready-for-use products, but conceived as components for
ventilation systems (type designation
type label). The fans may only then be operated
when they are installed in accordance with their intended use, and safety has been
secured through protective devices in accordance with DIN EN ISO 13857 (DIN EN ISO
12100) or other structural protective measures.
Information
This assembly instructions describes the combination of motor and controller. Dependent
on application and version of the fan absolutely the resuming specifications are to be
considered!
3.2 Functional description
ECblue stands for EC fans and motors with maximum efficiency. Highly efficient, elec-
tronically switched external rotor motors with permanent magnets are used the speed of
which is controlled by the integrated controller.
The devices are constructed in accordance with the general requirement in DIN EN
61800-2 for adjustable speed electrical power systems and is intended for one-quadrant
drives.
ECblue fans and motors in different models and sizes are described in this assembly
manual. Connection, structure and technical details depend partly on the motor size.
The used motor sizes (D = 116, G = 152) are recognisable from the type designation.
Motors Type Example for fans with motor size “D”
MK116 -_ I _ . _ _ . _ _
MK152 -_ I _ . _ _ . _ _
Axial fans type:
•F _ _ _ _-_ I _. D _._ _ _ _
Centrifugal fans type:
•RH _ _ _-_ I _. D _._ _
•GR _ _ _-_ I _. D _._ _
•ER _ _ _-_ I _. D _._ _
3.3 Ziehl-Abegg design criteria for long service life
The service life of devices with power electronics is decisively dependent on the ambient
temperatures. The longer electronic components are exposed to high ambient temper-
atures, the faster the deterioration and the more probable the failures.
The device is designed with a service life of at least 40,000 h when S1 operated at
full power in the maximum permissible ambient-temperature environment.
In order to achieve this, the device protects itself by active temperature management.
Assembly instructions ECblue Product overview
L-BAL-F046-GB 1203 Index 003 Part.-No. 00297758-GB
10/45
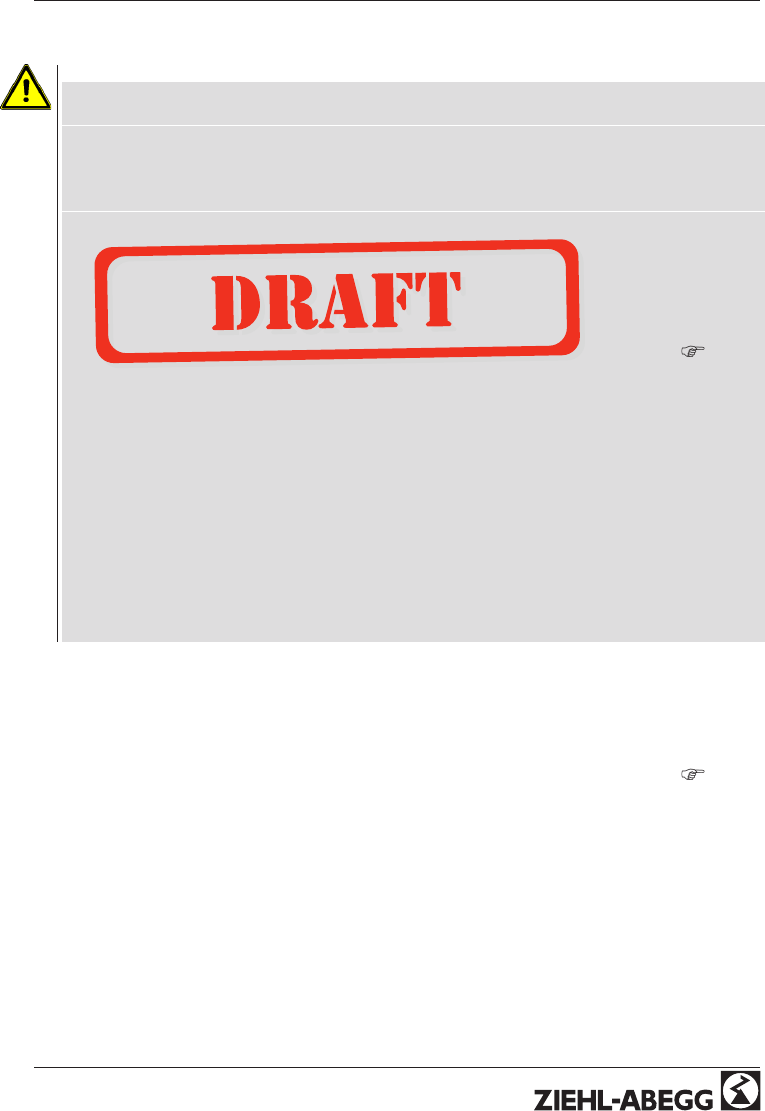
3.4 Transport
Attention!
•Ziehl-Abegg fans and motors are packed in the factory in accordance with the
respective, agreed, form of transportation.
•Always observe the weight specifications and the permissible carrying loads of
the means of transport.
•Transport the fan(s) either in their original packing or larger fans on the transport
devices provided (axial fans: holes drilled in support arms, wall ring plates and
motor block ; radial fans: holes drilled in the motor block, fastening brackets and
support plates) with suitable means of transport. Observe the weight specifica-
tions on the rating plate.
•Wear safety shoes and gloves for handling!
•Do not transport the fan by the connecting cable!
•Avoid shocks and impacts to the device during the transport.
•Avoid extreme heat or cold (temperature range for storage and transport
Technical data).
•Be on the alert for any damage to the packaging or the fan.
•Radial impellers or built-in fans type ER../GR.. are generally delivered on euro-
pallets, and can be transported using lift trucks.
•Fix pallets during transport.
•Do not stack pallets.
•Only handle with suitable hoisting gear.
•Construction ER../ GR..: Fan unit may only be lifted and transported when using
a suitable hoisting device (load spreader). Ensure sufficient cable or chain length.
•Position the lifting beam transversely to the motor axis. Pay attention to adequate
width of the lifting beam.
•Never stand underneath the suspended fan because defective transport
equipment could cause death.
3.5 Storage
•Store the fan / motor in the original packaging in a dry area protected from the
weather and protect it from dirt and weather until final installation.
•Do not stack pallets!
•Avoid extreme heat or cold (temperature range for storage and transport
Technical data).
•Inspect the motor bearings for proper operation prior to installation.
•Avoid prolonged storage; we recommend a maximum of one year (consult the
manufacturer before starting if stored for longer).
3.6 Disposal / recycling
Disposal must be carried out professionally and environmentally friendly in accordance
with the legal stipulations.
Assembly instructions ECblue Product overview
L-BAL-F046-GB 1203 Index 003 Part.-No. 00297758-GB
11/45
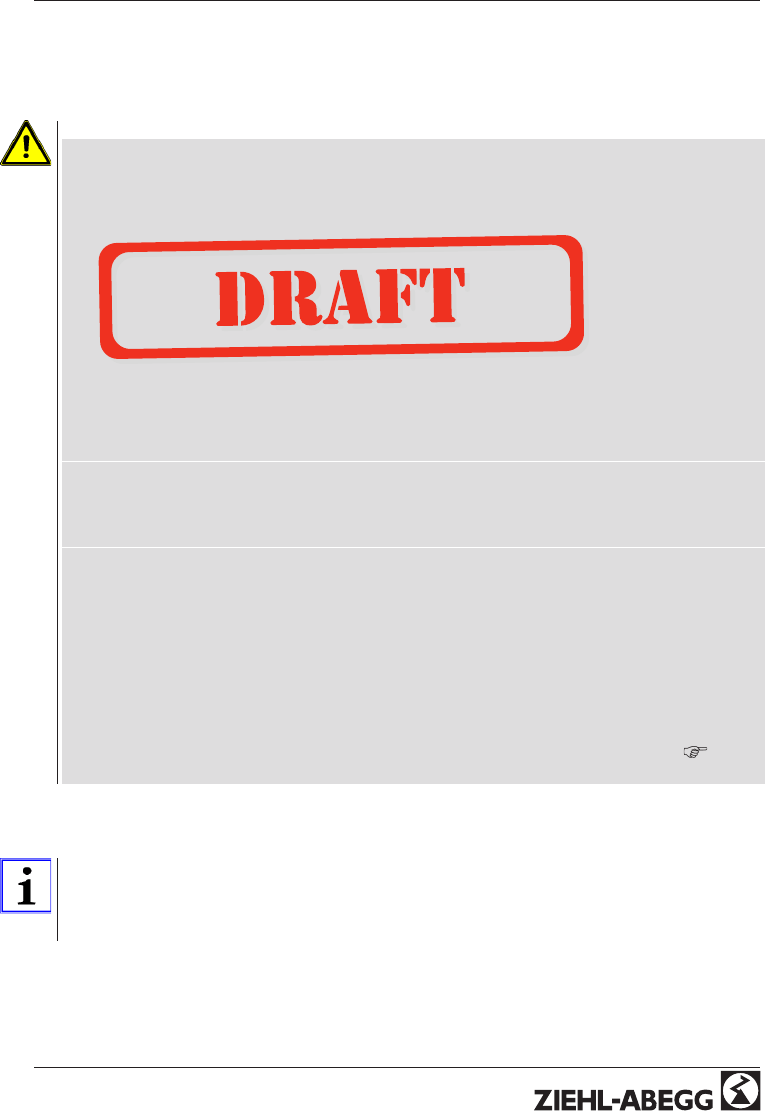
4 Mounting
4.1 General notes
Attention!
•Installation are only to be performed by trained service personnel. The system
manufacturer or the machine builder and/or the user is responsible that the
inherent installation and security information are harmonized with the valid stand-
ard and guidelines (DIN EN ISO 12100 / 13857).
•Lift the fan out of the packing with a hoisting unit (lifting beam). Only use the holes
in the motor block and the fastening brackets of the fan and the hook or fastening
bracket (depending on the design of the fan) as attachment points.
•The chain/rope may not touch the fan wheel when lifting with the lifting beam.
Other damage is possible.
•Check the fan for damage, e.g. transport damage, cracks or dents or damage to
the electric cables, before assembly.
•At a weight greater than 25 kg for men / 10 kg for women, the fan should be lifted
out by two persons (according to REFA). The values may differ from country to
country.
•Do not allow drilling chips, screws and other foreign bodies to reach the device
interior!
•Prior to installing the fan, it is to be checked whether the safety zone as per DIN
EN ISO 13857 and in household appliances as per DIN EN 60335 are met. If the
installation height (danger zone) above the reference level is greater than or equal
to 2700 mm and is not reduced by auxiliary means such as chairs, ladders, work
platforms or bases on vehicles, a guard grille against accidental contact is not
necessary at the fan.
•If the fan is located in danger zone, then the manufacturer or operator shall ensure
that hazards shall be prevented by appropriare protective constuctions which
meet the requirements to DIN EN ISO 13857.
•Custom designs must suit the prevailing conditions.
•Tighten the fastenings with the specified torques.
•Any use below -10 °C is dependent on not being subjected to unusual, sudden or
mechanical loads or stresses on the material (min. ambient temperature
Technical data).
4.2 Connection lead & terminal box
Information
In demanding environments (wet areas, open air installation) all connections must
incorporate water drainage curves. To ensure that water cannot penetrate through to the
controller housing from the connections install a terminal box lower than the fan.
Assembly instructions ECblue Mounting
L-BAL-F046-GB 1203 Index 003 Part.-No. 00297758-GB
12/45
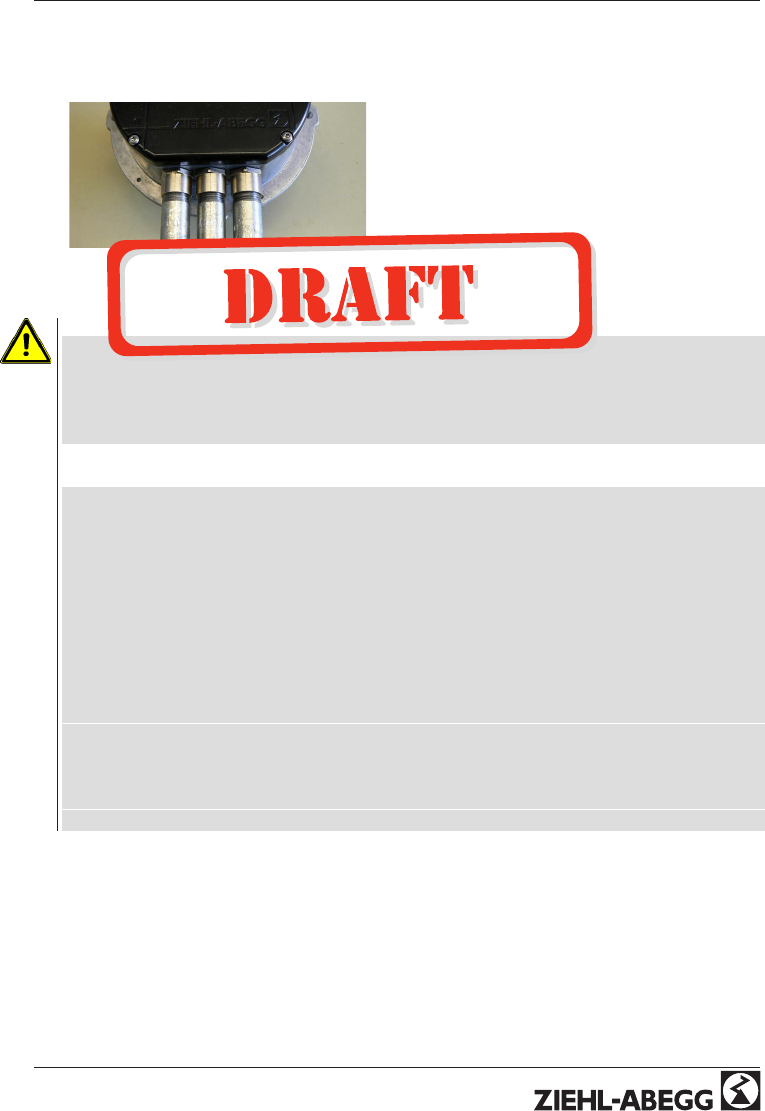
4.3 Connection according UL and CSA in different applications
4.3.1 Connecting the conduit for NEC and CEC approval
Conduits
Attention!
The fan type ECblue, series MK116 and MK152 with integrated variable speed drives,
for the North American economic region (noticeable on the rating plate) are approved as
power conversion equipment according to UL508C.
Furthermore, the motors have environmental type rating class 3 according UL50(E) for
outdoor use.
Compliance with the following specifications is mandatory for this:
•Metric to inches threaded adapters, used to connect the conduits, can be ordered
from Ziehl-Abegg AG in a package of 3:
–for MK116: part number 00297623
–for MK152: part number 00297624
•These are to be used to connect the motor in accordance with the specifications
of the NEC
®
(National Electrical Code, ANSI/NFPA 70) and UL508 corresponding
to the circumstances onsite.
•The electrician / plant contractor is responsible for correct connection of the
adapter and the conduits so that no damage can occur due to infiltrating moisture
or water. When sealing the conduit connections make sure the supplied O-rings
are used. When screwing the conduits into the thread adapters, use UL approved
sealing tape (e.g., Teflon tape).
•The locking screws used within the MK116 and MK152 series are only for ship-
ment. For installation the locking screws must be removed.
•It must be used a connection technology suitable for the environmental type rating
of the drive!
Assembly instructions ECblue Mounting
L-BAL-F046-GB 1203 Index 003 Part.-No. 00297758-GB
13/45
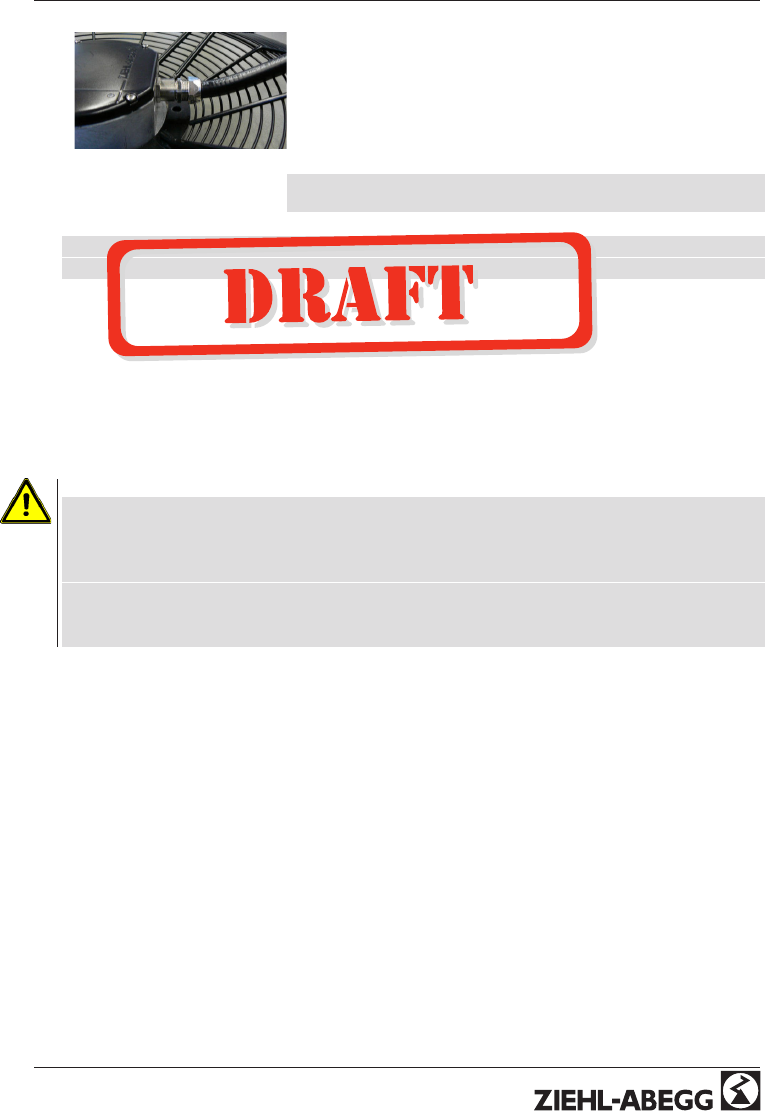
Alternative: flexible connection
If the connection of the conduits is not possible with the thread
adapter due to a lack of installation space, Ziehl-Abegg recom-
mends its customers use an UL514B approved flexible connection
hose system.
As an example it can also be used on equipment and machines.
However, applicable here is that the equipment / machine must be
configured / approved in accordance with UL508.
Possible suppliers: - Anamet, - Flexa GmbH, - Thomas & Betts
Attention! Ziehl-Abegg cannot provide any warranty on the envi-
ronmental type rating, class 3 for this.
Independent of the type and manner of the conduit / tube connection, correct connection
of the supply line(s), the safety of people and objects must be provided at all times.
4.3.2 Connection in NFPA 79 Applications
In applications where the NFPA 79 (Electrical Standard for industrial machinery) applies
the enclosed cable glands can be used.
The cable glands can be ordered additionally in packages of 3 from Ziehl-Abegg:
•for MK116: part number 00295308
•for MK152: part number 00296715
Attention!
•Independent of the type and manner of the conduit / tube connection, correct
connection of the supply line(s), the safety of people and objects must be provided
at all times.
•The locking screws used within the MK116 and MK152 series are only for ship-
ment. For installation the locking screws must be removed.
•It must be used a connection technology suitable for the environmental type rating
of the drive!
Assembly instructions ECblue Mounting
L-BAL-F046-GB 1203 Index 003 Part.-No. 00297758-GB
14/45
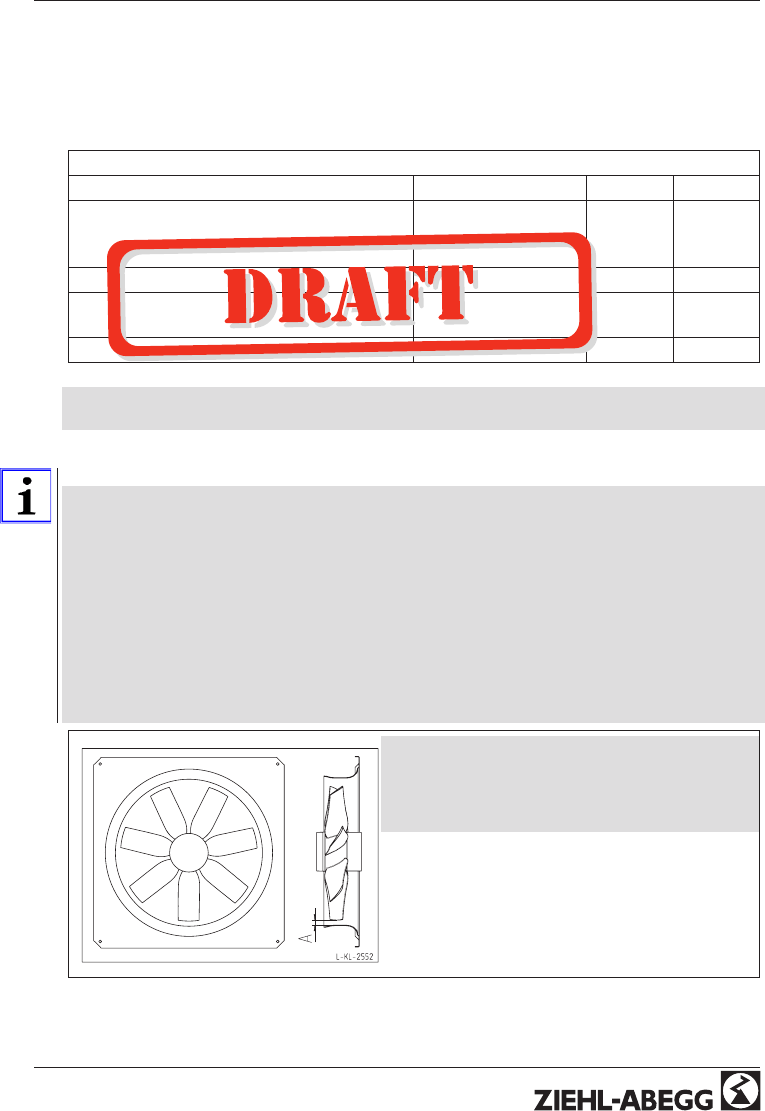
4.4 Installation of axial fans
4.4.1 Fan designs A, D, K, S and W (without nozzles)
For attachment to fixed motor flange use screws with property class 8.8 or A2-70
(stainless steel) to DIN EN ISO 4014 and provide with suitable screw locking.
Permissible tightening torques M
A
Motor size D D G
Thread size
M6
(Special application
with 5-pitch)
M8 M10
Property class 8.8, friction coefcient µges = 0.12 9.5 Nm 23 Nm 40 Nm
Stainless steel A2-70, friction coefcient µges =
0.12 7 Nm 17 Nm 33 Nm
Screw penetration ≥ 1.5 x d ≥ 1.5 x d ≥ 1.5 x d
When using screws with different friction values or strength classes, different tightening
torques may be necessary.
Information
•Pay attention to a sufficient screw-in length in the motor flange.
•Excess screw length not permissible and it may result in the rotor being brushed
against or blocked.
•Every screwing case is different. The tightening torque adapted to it must be
determined by the appropriate screw tests.
•Avoid structural damage or stress with installation. Make sure the surface is flat
and even.
•In the case of a vertical motor axis, the respective lower condensation drain hole
must be open.
•Fasten the fan connecting cable using cable ties to the guard grille or motor
braces.
A minimum head gap “A” of 2.5 mm in all installation
positions but especially in installation position H (hor-
izontal motor shaft) is necessary. Distortion due to
uneven surface may lead to fan failure due to brush-
ing against the fan wheel.
Assembly instructions ECblue Mounting
L-BAL-F046-GB 1203 Index 003 Part.-No. 00297758-GB
15/45

4.4.2 Installation in an exhaust air stack, design T
figure 1
Mark the mounting bracket (4) in accordance with fig. 1
in the chimney (3) using a 4x90° template, drill hole
center distance “a” in accordance with the mounting
bracket (4).
Fan size Adjustable diameter area
min. max.
F_063 640 660
F_071 725 745
F_080 815 835
F_091 915 935
Tighten the mounting bracket (4) and the support bracket (5) fig. 2 with screws (6) only
so far that the mounting bracket and support bracket do not dig into the chimney wall (3).
Self-locking nuts (7) are used for securing the screws. The enclosed protective caps (8)
are to be pushed onto the ends of the fan supports (1), fig. 2.
1
8
1
9/10
4
5
7
6
3
ai_kl_1905_1
figure 2
figure 3
Feed the fan (1) into the chimney in accordance with fig. 3, and center it in the mounting
bracket (4). In addition, the support is to be secured in accordance with fig. 2 by using
bolts (9/10).
Assembly instructions ECblue Mounting
L-BAL-F046-GB 1203 Index 003 Part.-No. 00297758-GB
16/45

The four support clamps (5) are used as support eyelets for additional fixings (e.g. by
standing ropes) in order to relieve the chimney of the weight of greater fans.
Installation set (Part.-No. 00291545)
Pos. Naming Each
1 Axial fan -
3 Chimney -
4 Mounting bracket 4
5 Support bracket 4
6 M8x70 screws DIN EN ISO 4014 8
7 M8 nuts DIN EN ISO 10511 self-locking 8
7a 8.4 washer DIN EN ISO 7089 8
8 Protective cap 4
9 M8x30 screws DIN EN ISO 4017 4
10 M8 nuts DIN EN ISO 10 511 self-locking 4
10a 8.4 washer DIN EN ISO 7089 4
All fastening elements made of stainless steel
Assembly instructions ECblue Mounting
L-BAL-F046-GB 1203 Index 003 Part.-No. 00297758-GB
17/45
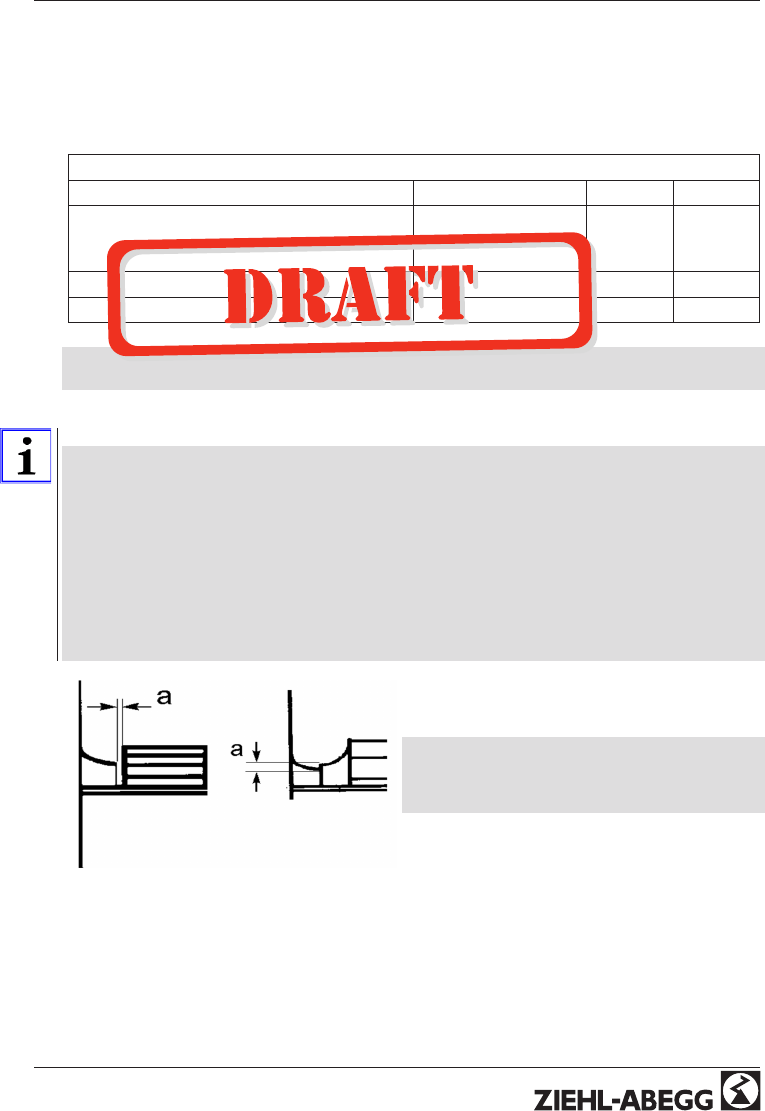
4.5 Mounting of centrifugal fans
4.5.1 Mounting of centrifugal fans, RH design
For attachment to fixed motor flange use screws with property class 8.8 to DIN EN ISO
4014 and provide with suitable screw locking.
Permissible tightening torques M
A
Motor size D D G
Thread size
M6
(Special application
with 5-pitch)
M8 M10
Property class 8.8, friction coefcient µges = 0.12 9.5 Nm 23 Nm 40 Nm
Screw penetration ≥ 1.5 x d ≥ 1.5 x d ≥ 1.5 x d
When using screws with different friction values or strength classes, different tightening
torques may be necessary.
Information
•Pay attention to a sufficient screw-in length in the motor flange.
•Excess screw length not permissible and it may result in the rotor being brushed
against or blocked.
•Every screwing case is different. The tightening torque adapted to it must be
determined by the appropriate screw tests.
•Avoid structural damage or stress with installation. Flange and mounting bracket
must be fixed flat on a level surface.
•In the case of a vertical motor axis, the respective lower condensation drain hole
must be open.
•The fan must be securely mounted, with vibration dampers if necessary.
Ensure that the clearance (gap) “a” see fig. be-
tween the fan impeller and the stationary housing
section is constant. Distortion due to uneven sur-
face may lead to fan failure.
Assembly instructions ECblue Mounting
L-BAL-F046-GB 1203 Index 003 Part.-No. 00297758-GB
18/45
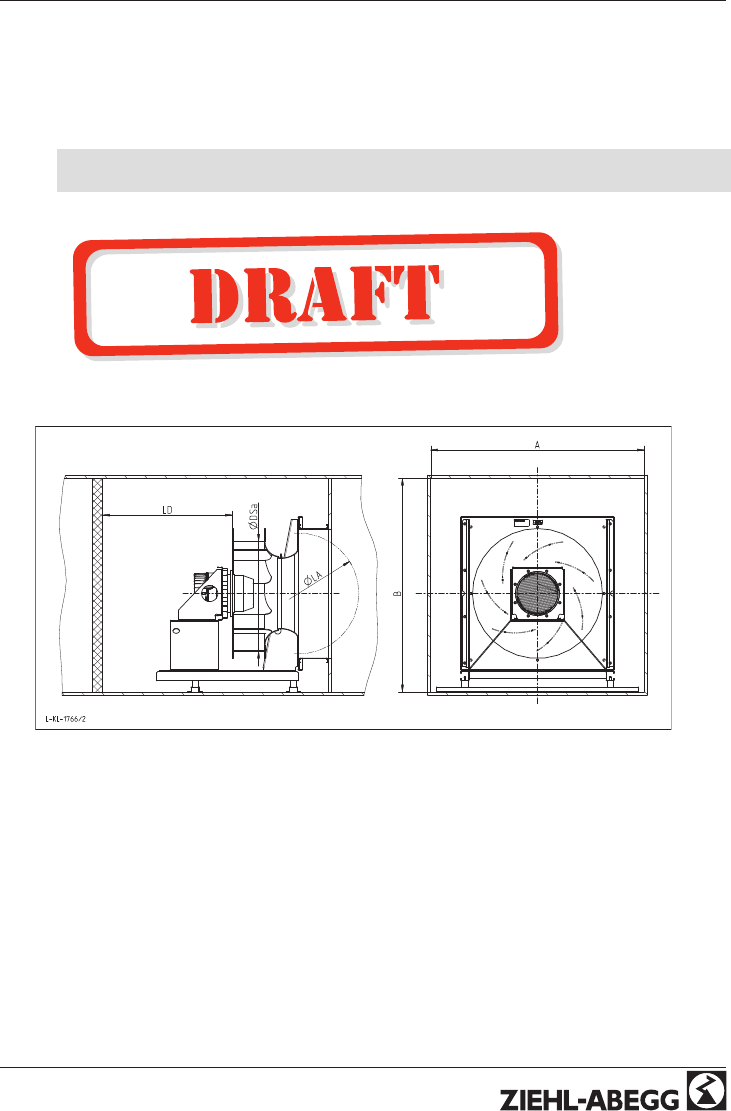
4.5.2 Erecting the equipment: Design ER...-..N... / ER...-..K... / GR...
•To avoid the transference of disruptive vibrations, we recommend de-coupling the
entire plug fan to avoid sounds transmitted through solids. (Spring and/or attenu-
ation units are not a constituent part of the standard scope of delivery). Look at
our catalogue for positioning the decoupling elements or request a dimensions
sheet stating the type designation and Part.-No.
•Attention: All contact points must be fixed securely. If the fixing is inad-
equate there is a risk of the fan overturning.
•Erect in the open air only if this is expressly mentioned and confirmed in the
ordering information. There is a risk of damage to the bearings if the fan remains
stopped in a moist environment. Avoid corrosion by suitable protective measures.
Roofing is required.
•Making your own alterations/conversions on the fan module is unacceptable -
safety risk.
•In the case of a vertical motor axis, the respective lower condensation drain hole
(if available) must be open.
4.5.3 Optimal installation distances according to for RH../ ER../ GR.. fans
•Distance on suction side: LA ≥ 0.5 x DSa*
•Distance on the pressure side: LD ≥ 1 x DSa
•Impeller blade external-diameter : Ø DSa
•Housing wall distances: A = 1.8 x DSa (A = B)
* In the case of disturbance flow (per example curved pipe at the suction side, flaps etc.)
LA ≥ 1 x DSa
Assembly instructions ECblue Mounting
L-BAL-F046-GB 1203 Index 003 Part.-No. 00297758-GB
19/45
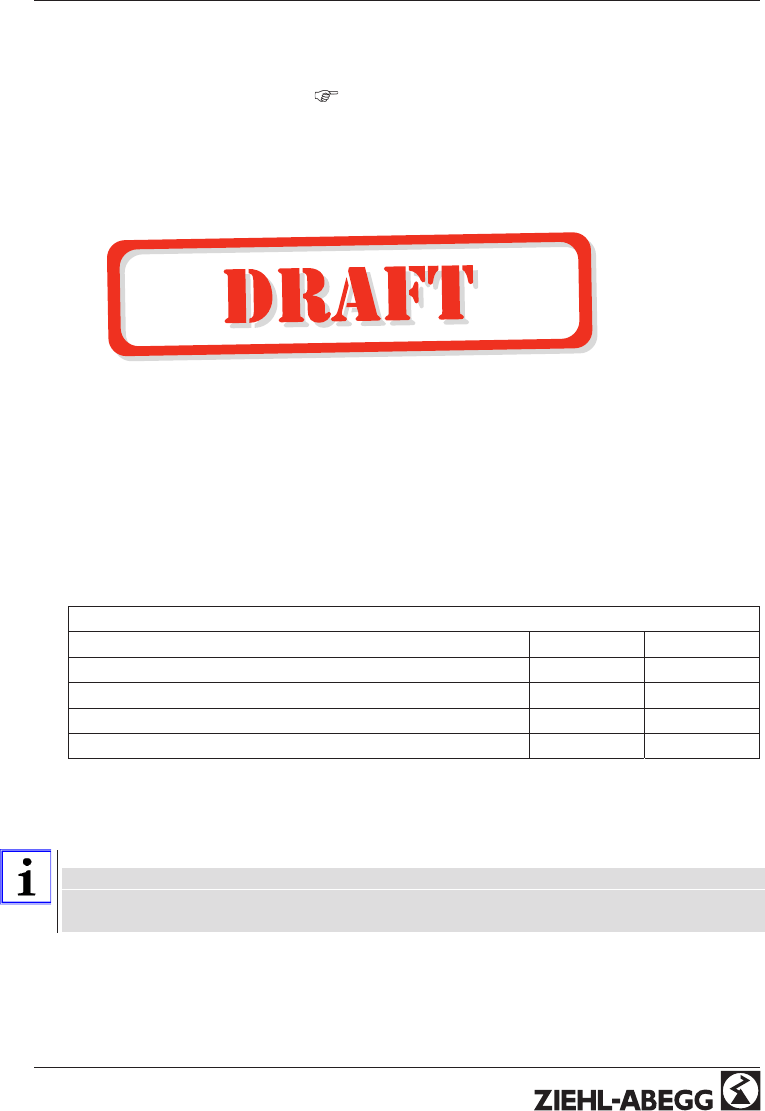
4.6 Mounting of motors
EC-motors design MK
Fastening to fixed motor flange
assembly of axial fans / fans of design A, D .. and
assembly of radial fans of design RH
•If the motor is used to drive fan impellers or other components, please note the
maximum permissible speeds of the impeller or the component to be driven.
•The max. permissible mass of the impeller ort he component to be driven must be
inquired from and confirmed in writing by Ziehl-Abegg.
Design K (with rotor flange) or D (with offset rotor flange) as a drive for fans:
•During assembly of the fan impellers or other components, no inadmissible force
may be applied to the motor bearing.
•Centre the fan impeller accurately and mount without tension on the rotor flange,
the fan wheel must lie flat.
•Use suitable screws for fastening the fan impeller on the rotor flange and fit as
suitable screw lock.
•Every screwing case must be tested for suitability.
•The permissible area pressing of the steel flange may never be exceeded
(depending on the contact surface).
•Too great a screw overhang is not permitted and can lead to scraping or blocking
of the rotor on the fixed motor flange.
•Motors are not balanced as standard, a complete balancing with mounted fan
impeller is necessary. The balancing must be done on the fan impeller. The
pertinent regulations must be observed.
Permissible tightening torques M
A
Motor size D G
Thread size M6 M8
Property class 8.8, friction coefcient µges = 0.12 9.5 Nm 23 Nm
Screw penetration ≥ 0.83 x d ≥ 0.83 x d
Max. permissible screw overhang 1.0 mm 1.5 mm
4.7 Outdoor fans in a humid atmosphere
Information
If a fan is stationary for long periods in a humid atmosphere, it should be switched
ON for minimum of two hours every month to remove any moisture that may have
condensed within the motor.
Assembly instructions ECblue Mounting
L-BAL-F046-GB 1203 Index 003 Part.-No. 00297758-GB
20/45
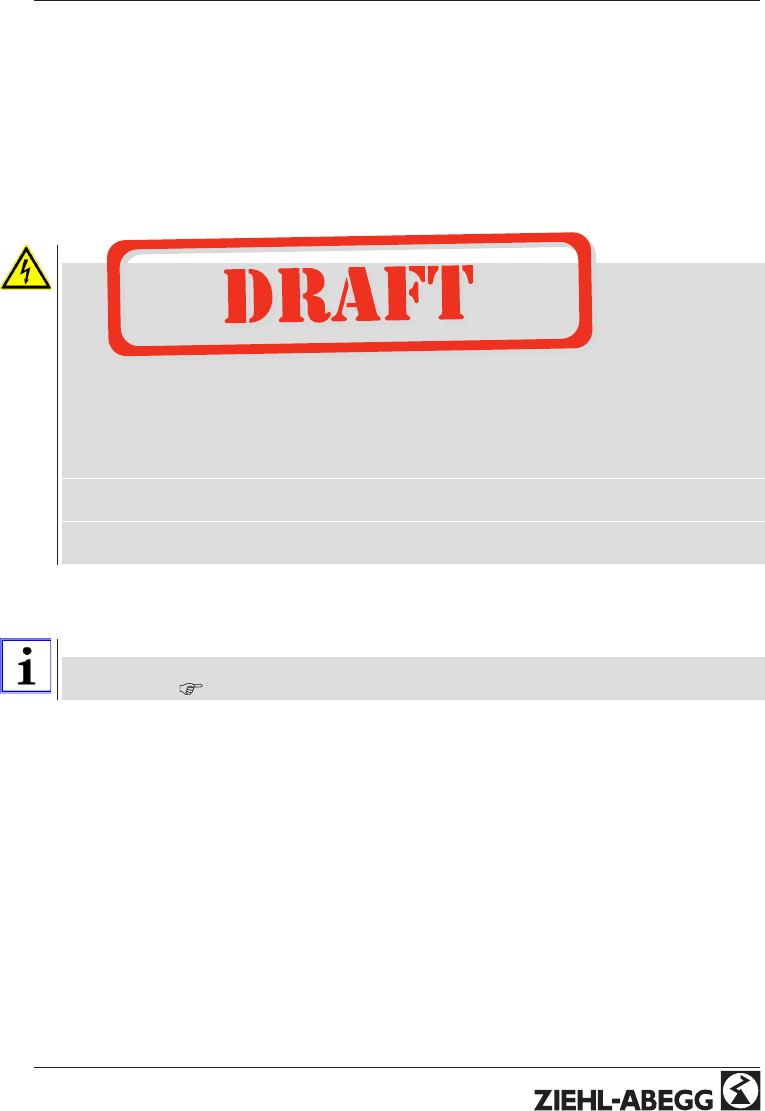
4.8 Motorheating
To prevent a stationary ventilator in a cold environment from jamming or freezing, the
Motorheating becomes automatically active at a controller interior temperature of -19 °C.
5 Electrical installation
5.1 Safety precautions
Danger due to electric current
•Work on electric components may only be carried out by trained electricians
or by persons instructed in electricity under the supervision of an electrician
in accordance with electrical engineering regulations.
•The 5 electrical safety rules must be observed!
•It is forbidden to carry out work on electrically live parts. Even after discon-
nection, the dc-link is still live. Always wait at least 3 minutes.
•A second person must always be present when working on energized parts
or lines who disconnects in case of emergency.
•Connect fan only to electrical circuits that can be disconnected with an all-
pole isolating switch.
•The device owner is responsible for the EMC of the entire plant according to
the locally applicable standards.
•Inspect electrical equipment periodically: retighten loose connections –
immediately replace damaged lines and cables.
5.2 Connection
Information
The respective connections are represented in the enclosure of this assembly
instructions (
Connection diagram)!
Assembly instructions ECblue Electrical installation
L-BAL-F046-GB 1203 Index 003 Part.-No. 00297758-GB
21/45
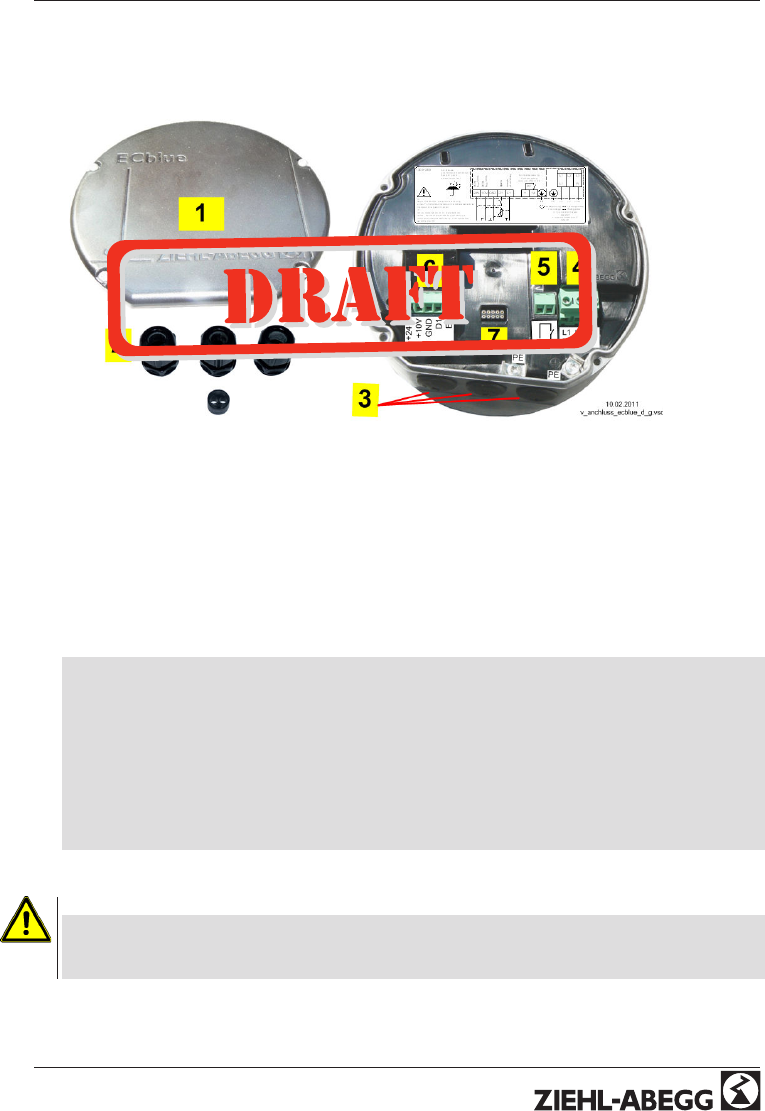
5.2.1 Motor size “D” and “G”
Fans with connection box (type: _ _ _ _ _-_ I _. D _._ _ _ _), (type: F _ _ _ _-_ I _. G _._
_ _ _)
1 Cover of controller housing
2 Cable glands + seal insert for two cables (applicable only if necessary)
- motor size “D”: 3 x M16 + 1 x seal insert with two holes 5 mm
- motor size “G”: 3 x M20 + 1 x seal insert with two holes 6 mm
3 Cable entry points with plastic fastener
4 Mains connection
5 Connection alarm relay
6 Connection contols
7 Slot for add-on module
Procedure:
1. Remove the cover from the controller housing for the connection.
2. All 3 cable entry points are in a sealed condition at delivery. Remove plastic
fastener if necessary, and insert enclosed cable glands, entry points that are not
used must remain sealed!
3. When using the seal insert for two cables it is not permissible to use the corre-
sponding cable gland with only one cable.
4. Insert and connect lines correctly.
5. Attach cover of controller housing again carefully in correct position before start-
up.
Attention!
•Temperatures up to 80 °C can be present on the controller housing.
•To connect, always use heat resistant wires or, as an alternative, silicon tubes.
•Remants from installation and foreign object may not remain on the inside!
Assembly instructions ECblue Electrical installation
L-BAL-F046-GB 1203 Index 003 Part.-No. 00297758-GB
22/45
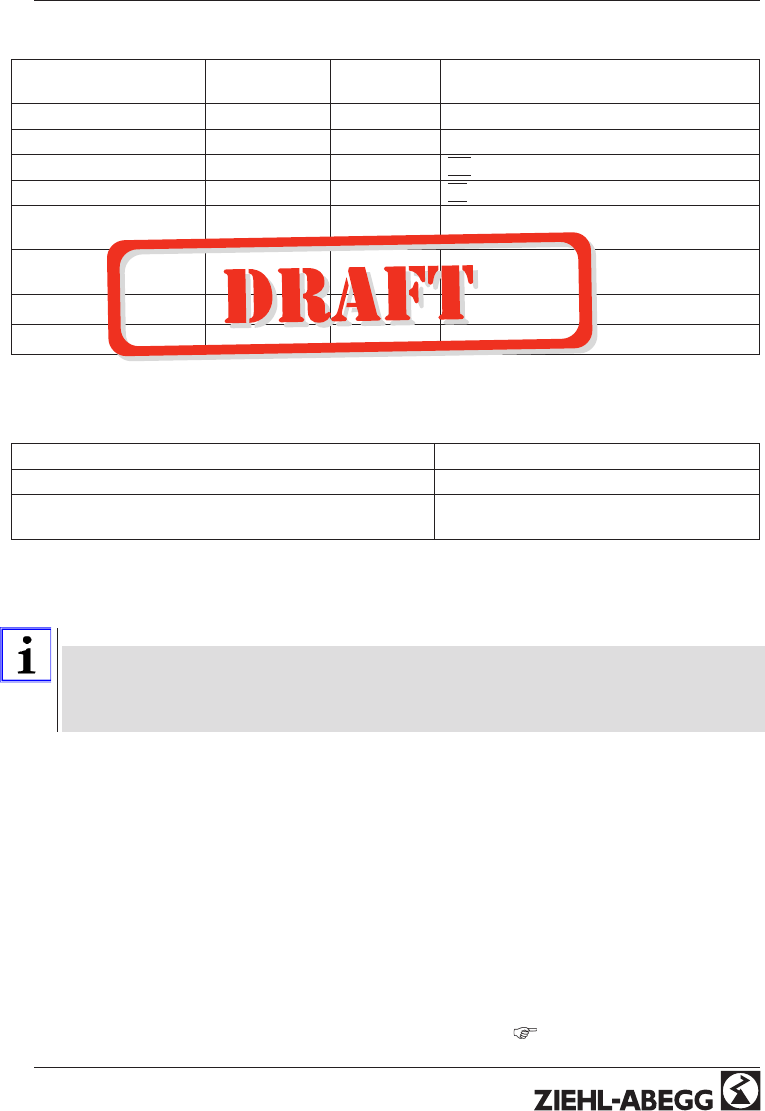
Permissible tightening torques M
A
Thread size Tightening
torque M
A
Remark
Cable gland M16 2.5 Nm Sealing area for cable diameter 4…10 mm
Cable gland M20 4 Nm Sealing area for cable diameter 6…12 mm
Locking screw M16 + M20 1.25 Nm
|
+
|
screwdriver
Locking screw M16 + M20 2.5 Nm
|
-
|
screwdriver
Cover of controller hous-
ing M4 2.3 Nm
Protective earth connec-
tion M4 2.5 Nm
Mains supply terminals M3 0.6 Nm
Fastening add-on module M4 1.3 Nm
Max. cross section of terminals
Mains connection: L1, N and/ or L1, L2, L3 max. 2.5 mm
2
and/or AWG12
Connection control: +24 V, +10 V, GND, D1, E1, K1 max. 1.5 mm
2
and/or AWG16
Add-on modules: 1.5 mm
2
(0.75 mm
2
with wire end sleeve)
and/or AWG16
5.2.2 UL: note for cable entrances
Information
According to UL the attached locking screws (made of plastic) are acceptable for trans-
port.
According to UL the supplied cable glands can be used without conduit when they are
being used in an installation according to NFPA79.
5.3 EMC-compatible installation of control lines
Pay attention to sufficient distance from powerlines and motor wires to prevent interfer-
ences. The control cable may not be longer than 30 m. Screened control cables must be
used when the cable length is longer than 20 m. When using a shielded cable connect
the shielding to one side only, i.e. only to the device with the protective earth (keep cable
short and with as little inductance as possible!).
5.4 Mains connection
5.4.1 Line voltage for 1~ types
Mains connection: PE, L1, and N. Here, it must be strictly observed that the mains
voltage lies within the allowable tolerance specifications (
technical data).
Assembly instructions ECblue Electrical installation
L-BAL-F046-GB 1203 Index 003 Part.-No. 00297758-GB
23/45
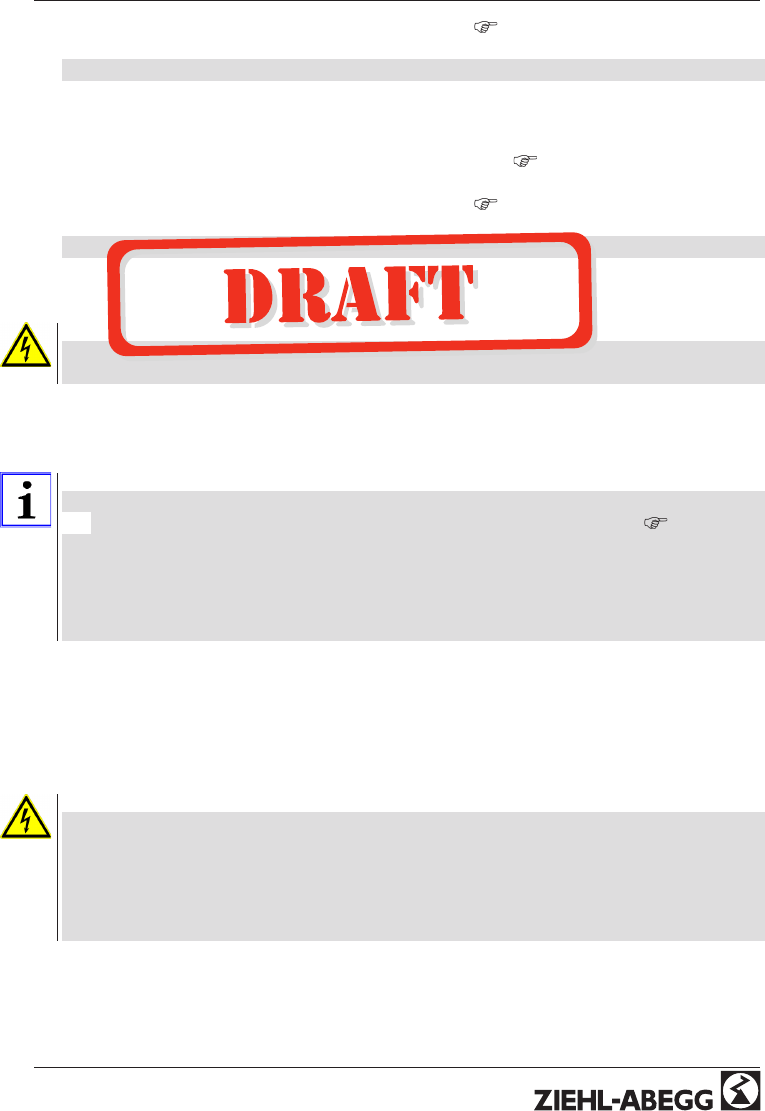
Alternatively a supply of DC voltage is possible (
Technical data).
The polarities on “L1” and “N” are irrelevant.
DC supply not UL approved!
5.4.2 Line voltage for 3~ types
Mains connection: PE, L1, L2 and L3. Here, it must be strictly observed that the mains
voltage lies within the allowable tolerance specifications (
technical data).
Alternatively a supply of DC voltage is possible (
Technical data).
Connect to any two terminal clips for “L1”, “L2” and “L3”, the polarity is irrelevant.
DC supply not UL approved!
5.4.3 Required quality attributes for the mains voltage
Danger due to electric current
The mains voltage must comply with the EN 50160 quality characteristics and the
defined standard voltages in IEC 60038!
5.4.4 Operating in IT-System
Information
• 3 ~ ECblue types are only in special version “IT” for the employment in IT-
System suitable! Special version “IT” not UL approved, line voltage
Technical
data.
• 1 ~ ECblue types can be used in IT-System in standard version. These may only
be used in 3 ~ IT-Systems if no higher voltage to the “PE” can occur than the
specified mains voltage of the device even in case of a fault to earth of a mains
phase which is not used by the device (of none of the two power supplies).
In order to ensure a trouble free operation in IT-System the “GND” potential of the
control ports have to be connected with the protective earth potential.
As a consequence of these connection must be considered for the control ports (excep-
tion floating relay contacts):
1. Connection only with wires, suitable for mains voltage and surrounding area.
2. Connection with suitable isolated amplifiers only.
Danger due to electric current
•In the IT-System the neutral point of voltage supply is not grounded; in the case of
a short-circuit between a phase (e.g. “L1”) and protective earth “PE” becomes the
protective earth potential = L1.
•Between the mains connection of the device and the protective earth “PE” is
in no case a higher voltage permissible than the indicated line voltage of
the device!
Assembly instructions ECblue Electrical installation
L-BAL-F046-GB 1203 Index 003 Part.-No. 00297758-GB
24/45
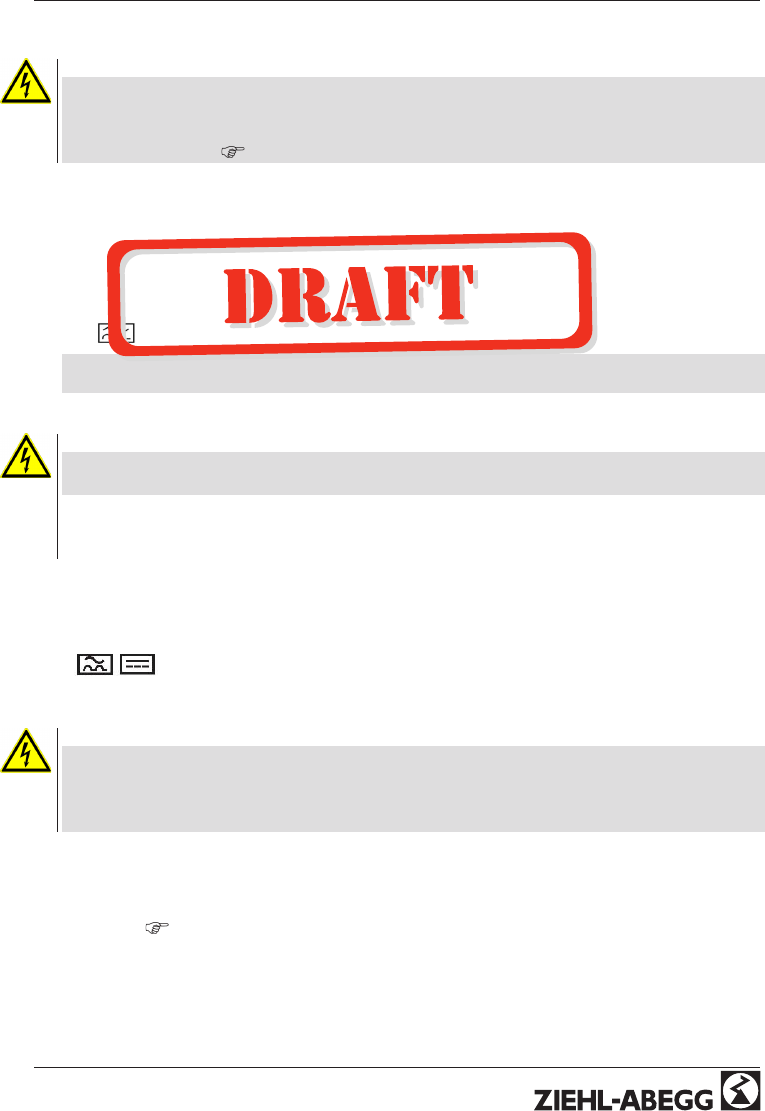
5.4.5 UL: Short-circuit protection for branch circuits (UL508C)
Danger due to electric current
This power conversion equipment is suitable for connection to electric circuits that
cannot supply more than 100 kA symmetrical current effective.
The fusing for the short-circuit protection must comply with the requirements in UL248
(further information
Assembly instructions / Technical data).
5.5 Residual-current-operated protective device
For 1 ~ fan types
Residual current circuit breaker (type A)
To ensure as high a degree of reliability as possible we recommend a release current of 300
mA, where a residual current circuit breaker (type A) is used.
Danger due to electric current
Exception: Mains connection between two phase conductors for supply networks 3 ~
230 V
For an installation of r.c.d. protection, it shall be observed that this must be of “universal-
current sensitivity”. In accordance with EN 50 178, Section. 5.2. other types of current-
operated protective devices may not be used.
For 3 ~ fan types
Residual current circuit breaker (type B)
Danger due to electric current
For an installation of r.c.d. protection, it shall be observed that this must be of
“universal-current sensitivity”. In accordance with EN 50 178, Section. 5.2. other
types of current-operated protective devices may not be used. To ensure as high a
degree of reliability as possible , we recommend a tripping current of 300 mA.
5.6 Motor protection
Integrated overload protection, preceding motor protection device unnecessary (max.
prefusing
Technical details).
5.7 Analog input (0...10 V) for setting fan speed
The unit has an analog input 0...10 V for setting fan speed.
Connection “GW E1 Viive” / “GND” (Analog In 1).
Alternatively speed setting with a PWM-signal is possible.
Assembly instructions ECblue Electrical installation
L-BAL-F046-GB 1203 Index 003 Part.-No. 00297758-GB
25/45
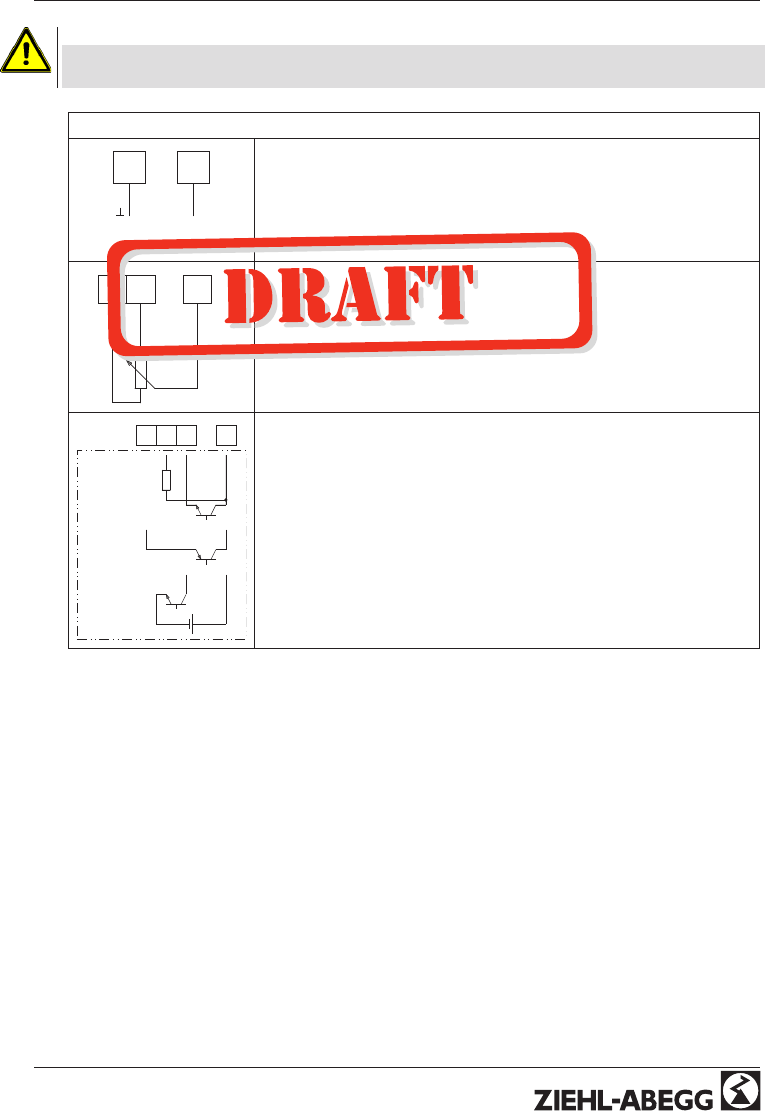
Attention!
Ensure correct polarity!
Never apply line voltage to analog inputs!
Possibilities for speed setting
0...10 V
+
GND E1
•Control via external setting signal 0...10 V
•By external wiring with a resistor (499 Ω / 0,25 W) between the
terminals “E1” and “GND” parallel to the input signal, activation
with a 0...20 mA signal is possible.
•The “AM-MODBUS” communication module enables a
inverted set-point signals to be programmed (10...0 V).
10V GND E1
10 kΩ
•Speed setting by 10 kΩ potentiometer at terminals “+10 V” and
“GND” pick-off at terminals “E1”.
10V GND E124V
PWM
f = 1...10 kHz
10 kΩ
10 V
GND
E1
24 V
E1
E1
GND
15...28 V
+
-
•Control by external setting signal PWM (connection “24 V” only
for motor sizes “D” and “G” available).
Assembly instructions ECblue Electrical installation
L-BAL-F046-GB 1203 Index 003 Part.-No. 00297758-GB
26/45
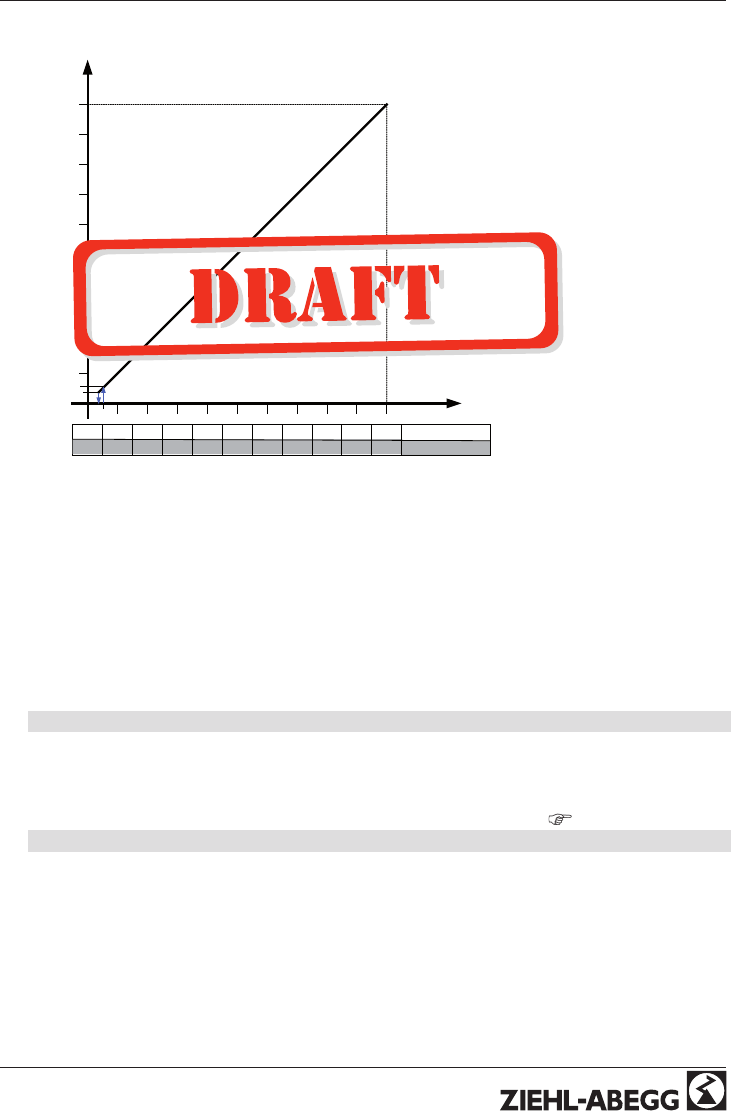
Diagram Setting signal and fan speed (Idealized principle diagram)
nM
100 %
0 1 2 3 4 5 6 7 8 9 10
0 10 20 30 40 50 60 70 80 90 100
0 – 10 V
0 – 100 % PWM
14.09.2011
v_nmotor@0_10v_pwm.vsd
Si
6 %
4.5 %
0.5 V
5 % PWM
50 %
nM Fan speed
100 % Rated Speed
6 % height of start speed
4.5 % height of stop speed
0.5 V / 5 % PWM value start analog input
Si Speed setting signal 0...10 V / 0...100 % PWM
5.8 Output voltage +10 V
Voltage supply e.g. for speed setting by external potentiometer.
Connection: “DC Out” - “GND” (I
max
10 mA).
It is not permissible to connect outputs of several devices to each other!
5.9 Voltage supply for external devices, only motor sizes “D”, “G”
(+24 V, GND)
Integrated voltage supply for external devices. Terminals “+ 24 V”(
Technical data).
It is not permissible to connect outputs of several devices to each other!
During an overload or short-circuit (24 V - GND), the control voltage (and thus the device)
is disconnected . Automatic start after elimination of the cause of error.
Assembly instructions ECblue Electrical installation
L-BAL-F046-GB 1203 Index 003 Part.-No. 00297758-GB
27/45
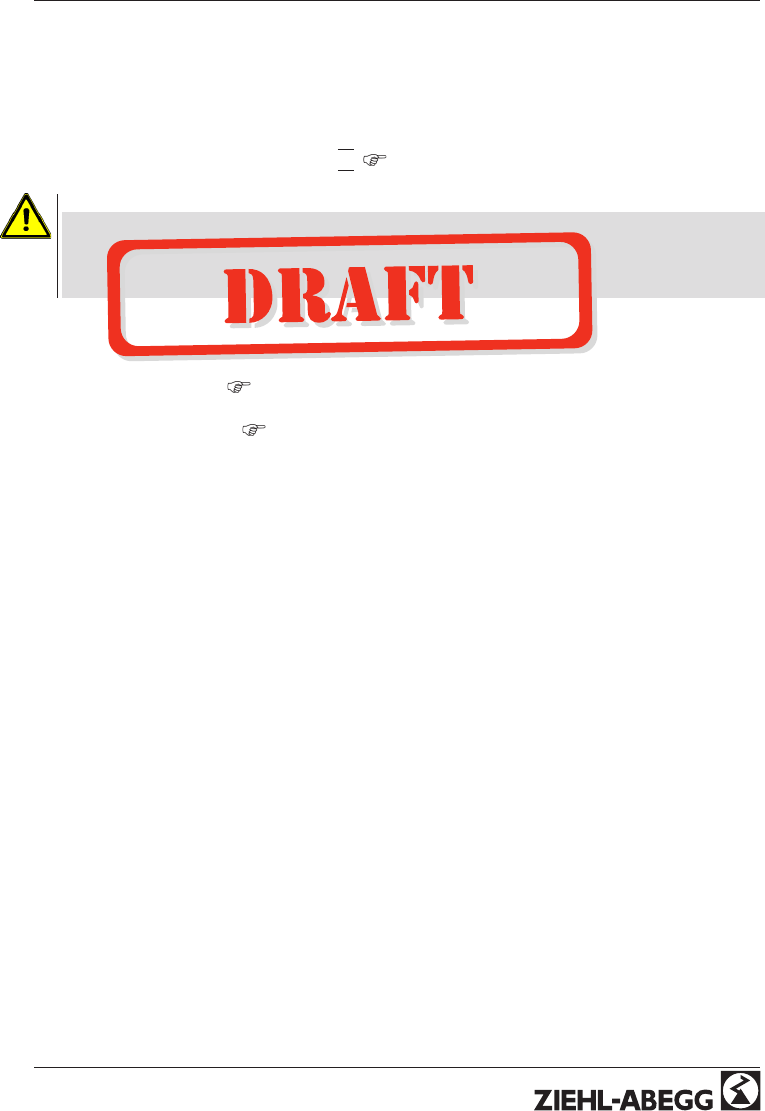
5.10 Enable, device ON / OFF (Digital In 1 = D1)
Electronic ON / OFF control via floating contact at terminals “D1” - “+24V” /
“+10V”
•Device “ON” for closed contact.
•Device “OFF” with opened contact.
Relay “K1” remains energized, connections 11 - 14 bridged.
Status Out with flash code:
|
1
|
(
Diagnostics / Faults).
Attention!
•No disconnection (isolation) when turned off by remote, in accordance with
VBG4 §6)!
•Never apply line voltage to the digital input!
•It is not permissible to connect inputs of several devices to each other!
5.11 Relay output (K1)
An external fault indicator is available over the potential-free contact of the built-in relay
(max. contact rating
Technical data and connection diagram).
For operation the relay is energized, connections “11” and “14” are bridged. For fault the
relay is de-energized (
Diagnostics / faults).
When switching off via enable (D1 = Digital In 1), the relay remains energized.
5.12 Potential at control voltage connections
The control voltage connections (< 50 V) relate to the joint GND potential (Exception:
Relay contacts are potential free). There is a potential separation between the control
voltage connections and the protective earth. It must be ensured that the maximum
external voltage at the control voltage connections cannot exceed 50V (between “GND”
terminals and “PE” protective earth). If necessary, a connection to the protective earth
potential can be established, install bridge between “GND” terminal and the “PE”
connection (terminal for screening).
5.13 Add-on modules
The assembly instructions and/or operating instructions available here describe the
“Basic Version”.
If required, an auxiliary module can be retrofitted to the designated slot for motor size
“D”, “G”. The auxiliary module is installed automatically. Manual installation or parameter-
isation is not required!
The extended scope of function is specified in the documentation for the auxiliary
module.
The range of additional modules is constantly being extended and adapted to market
requirements. The currently available additional modules can be requested from Ziehl-
Abegg.
Assembly instructions ECblue Electrical installation
L-BAL-F046-GB 1203 Index 003 Part.-No. 00297758-GB
28/45
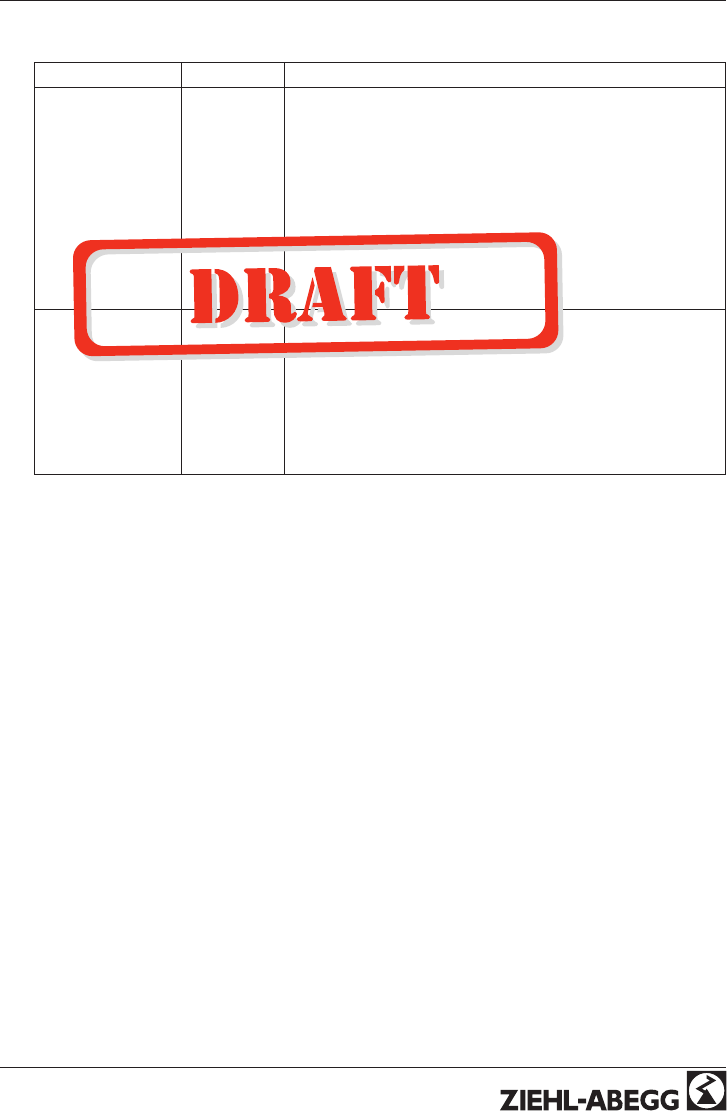
Examples for currently available additional modules
Type Part.-No. Function
AM-MODBUS
(for motor size “D”
and “G”)
349045 Communication module
Over the “AM-MODBUS” module can be communicated with
the controller of the fan. The module can be put in temporarily
for programming of desired functions during start-up or for
diagnostics. The connection to the control terminal is made by
a connecting cable or wirelessly by means of radio.
The module is left in the slot if it is to be integrated into a
module bus system or networked to several devices. The
addressing of ECblue fans takes place automatically, i.e. it is
not necessary to manually enter individual network addresses
for each fan.
AM-PREMIUM
(for motor size “D”
and “G”)
349046 Premium Module
When the “AM-PREMIUM” is plugged in the controller in the
fan is extended to become a full-grade multipurpose controller.
The “Premium module” provides not only an integrated
MODBUS interface, it also enables sensors to be connected
straight to the fan.
The module also comes with two analogue inputs and one
analogue output.
Assembly instructions ECblue Electrical installation
L-BAL-F046-GB 1203 Index 003 Part.-No. 00297758-GB
29/45
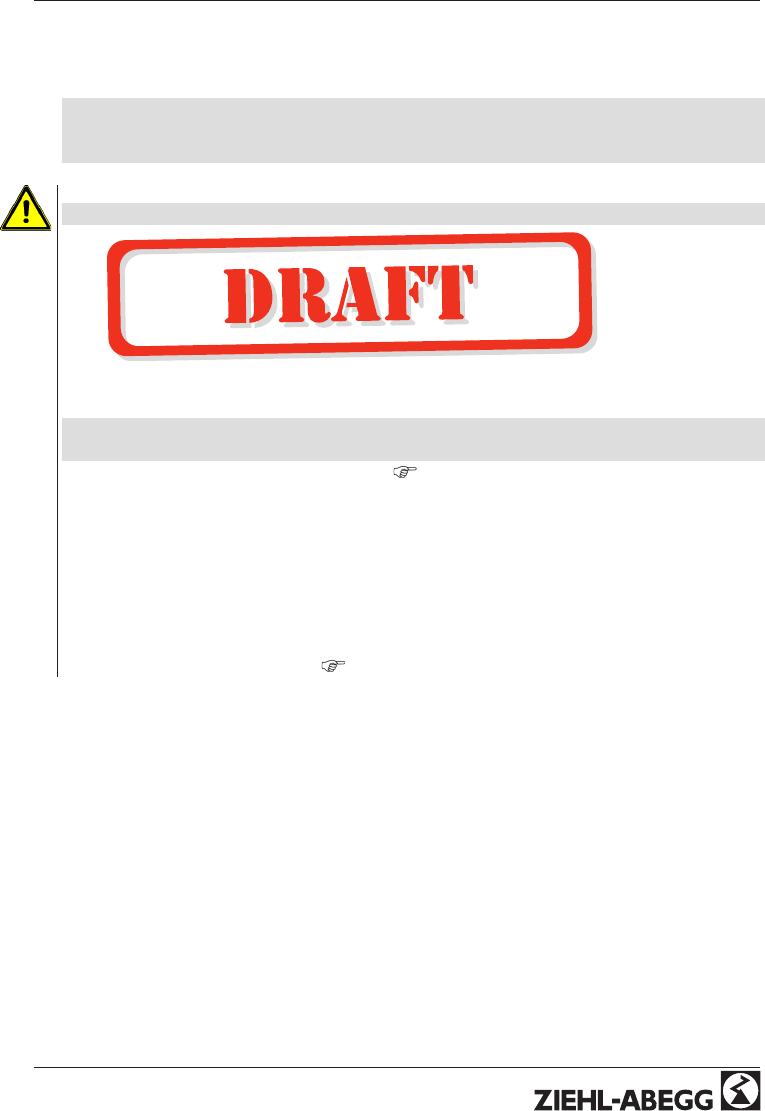
6 Start-up
6.1 Prerequisites for commissioning
During commissioning, unexpected and hazardous conditions can arise in the entire
installation due to defective adjustments, defective components or incorrect electrical
connections. Remove all persons and objects from the hazardous area.
Attention!
•Check before first-time start-up:
1. Installation and electrical connection have been properly completed?
2. Has any leftover installation material and other foreign material been removed
from the fan area?
3. That safety devices -if necessary- are mounted (EN ISO 13857)?
4. The impeller is out of reach?
5. Are the condensation water drains holes open or respectively closed according
to the suitable installation position?
6. Connection data complies with the specifications on the type plate?
•Commissioning may only take place if all safety instructions have been
checked and danger can be excluded.
–Check the direction of rotation (
rotation direction arrow on the fan blade,
impeller base plate or on the fan housing).
–Check for quiet, low vibration operation. Strong vibrations due to erratic
operation (unbalanced), e.g. caused by transportation damage or improper use,
can lead to failure.
–A-rated sound power levels of over 80 dB(A) are possible, see product
catalogue.
–Check for mechanical vibrations after installation into the system. If the
tolerances according to ISO 10816-1 are exceeded, it is possible to exclude
certain speed ranges (
Motor Setup or add-on module).
Assembly instructions ECblue Start-up
L-BAL-F046-GB 1203 Index 003 Part.-No. 00297758-GB
30/45
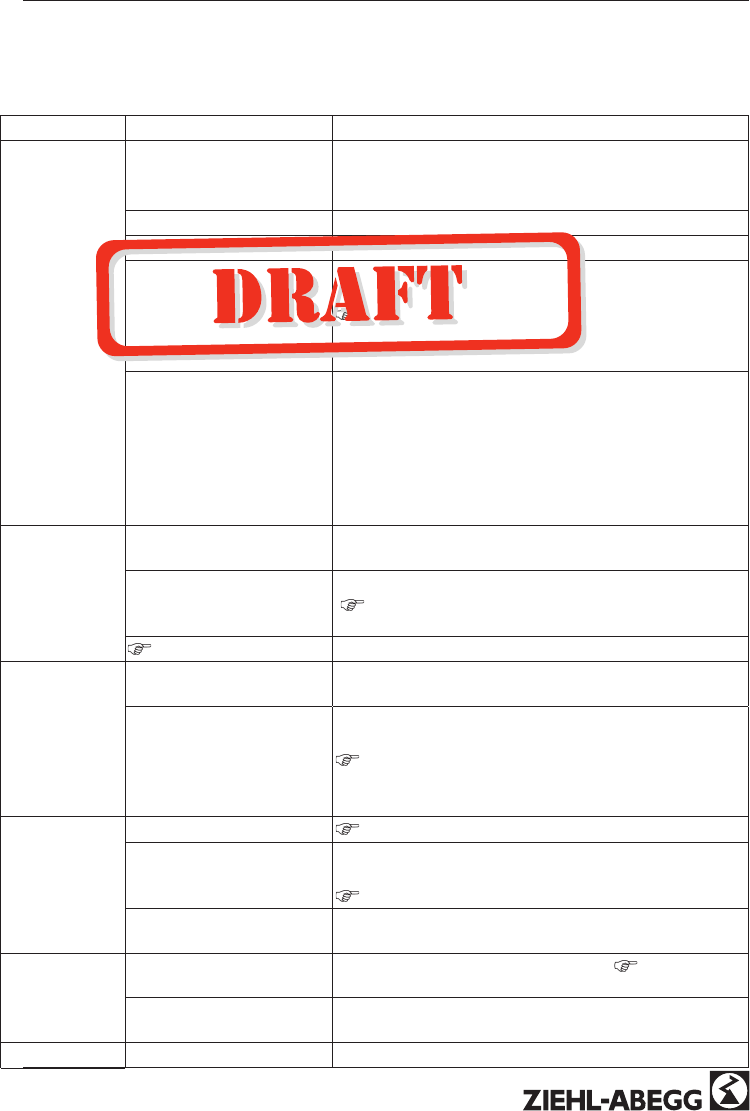
7 Diagnostics / Faults
7.1 Trouble shooting
Type of error Possible cause Remedial measures
Fan does not
run (anymore)
Failure line voltage
Failure of one phase
Under - or overvoltage
Check line voltage
Earth fault Check motor connection and line voltage
Short circuit winding Replace fan
Thermal motor protection
has triggered (motor is over-
heated)
Check for free air passages; remove foreign bodies if nec-
essary
"Impeller blocked or dirty"
Check temperature of supply air
Check voltage
Impeller blocked or dirty - Switch off power to the motor and secure against switch-
ing back on
- Check safe isolation from supply
- Remove safety grille
- Remove foreign bodies or soiling
- Remount the safety grille
- Further procedure as in the chapter “Start-up”
fan will not start Temperature too low for
bearing grease
Insert bearing with cold greasing
Air stream wrong direction
(Motor turns in wrong direc-
tion at high speed)
Check air stream
(
Behaviour in rotation by air current in reverse direction)
"Fan does not run"
Fan turns too
slowly
Impeller / blade scrapes /
brushes
When indicated clear foreign bodies / dirt from the fan
Active temperature manage-
ment effective
(Motor or electronics over-
heated)
Check for free air passages; remove foreign bodies if nec-
essary
"Impeller blocked or dirty"
Check temperature of supply air
Check installation space (air speed over heat sink)
Air flow to low Fan turns too slowly
"Fan turns too slowly"
Airways blocked Check for free air passages (supply/exhaust air vents,
filters)
"Impeller blocked or dirty"
Pressure loss different to
planned
Check fan selection
Vibrations Imbalance Check blades for damage, soiling or ice
"Impeller
blocked or dirty"
No or wrong vibration damp-
ers (only in radial)
Install correct vibration dampers
Unusual noises Bearing damaged / worn Change bearings
Assembly instructions ECblue Diagnostics / Faults
L-BAL-F046-GB 1203 Index 003 Part.-No. 00297758-GB
31/45
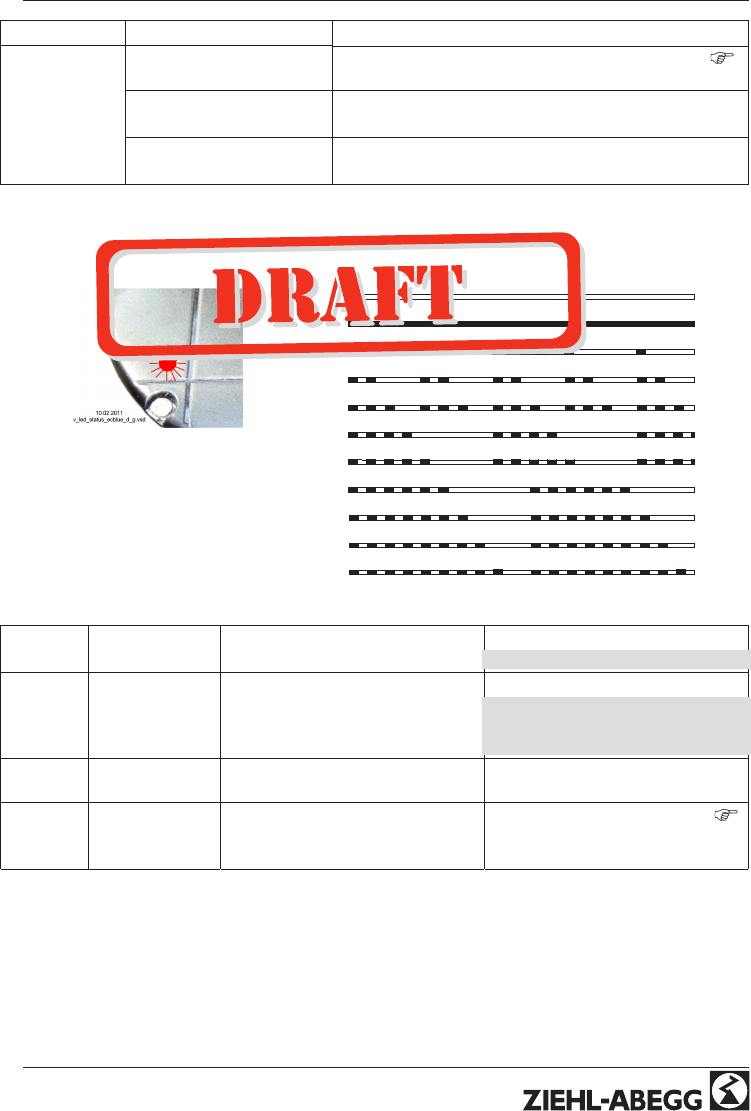
Type of error Possible cause Remedial measures
Impeller / blade scrapes /
brushes
When indicated clear foreign bodies / dirt from the fan
"Impeller blocked or dirty"
Operation beyond stall point
(for axial fans)
Check for free air passages (supply/exhaust air vents,
filters)
Wrong overlap on nozzle
(for centrifugal fans)
Observe the installation instructions
7.2 Status Out with flash code
For motor size “D” and “G” Status LED
integrated in cover.
11.02.2009
v_flash_explain.VSD
3 x
2 x
ON
OFF
4 x
5 x
6 x
1 x
7 x
8 x
9 x
LED Code Relays K1* Cause
Explanation
Reaction of Controller
Adjustment
OFF de-energized, 11
- 14 interrupted no line voltage
Line voltage available?
Unit switch OFF and automatically
ON when the voltage has been re-
stored
ON energized, 11 - 14
bridged Normal operation without fault
1 x energized, 11 - 14
bridged
no enable = OFF
Terminals “D1” - “24 V / 10 V” (Digital
In 1) not bridged.
Switch OFF by external contact (
digital input).
Assembly instructions ECblue Diagnostics / Faults
L-BAL-F046-GB 1203 Index 003 Part.-No. 00297758-GB
32/45
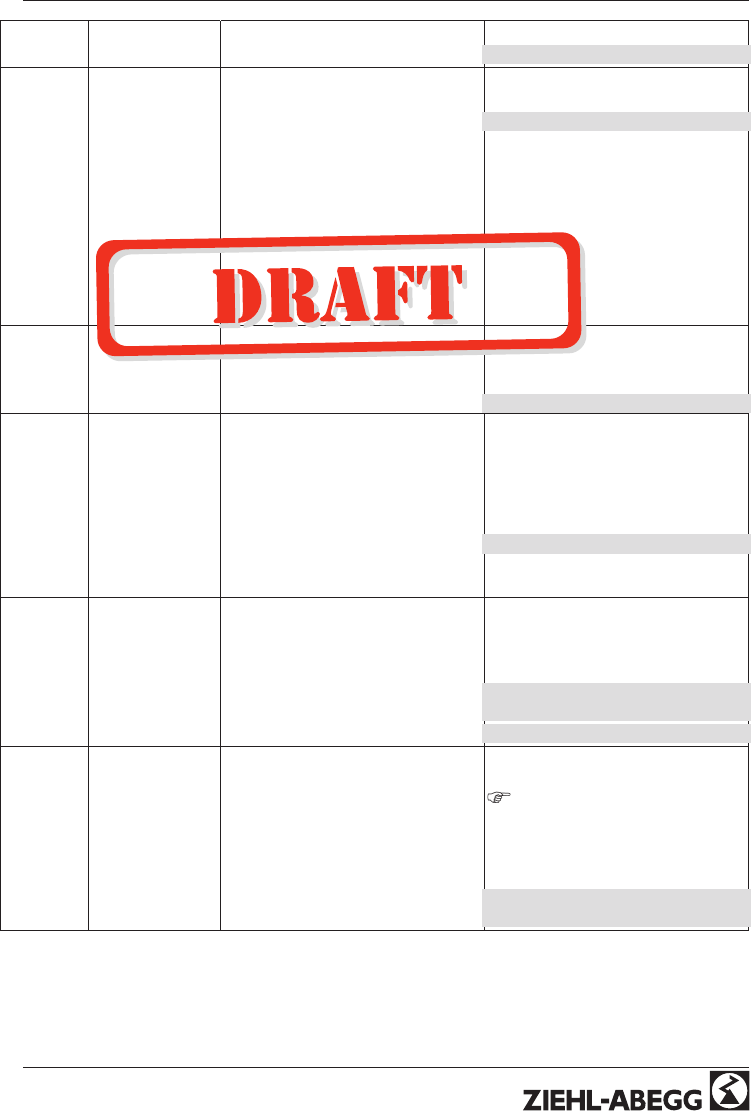
LED Code Relays K1* Cause
Explanation
Reaction of Controller
Adjustment
2 x energized, 11 - 14
bridged
Active temperature management
The device has an active tempera-
ture management to protect it from
damage due to too high inside tem-
peratures. In case of a temperature
rise above the fixed limits, the modu-
lation is reduced linearly. To prevent
the complete system being switched
off externally (in this operation per-
missible for the controller) in case of
reduced operation due to too high an
internal temperature, no fault mes-
sage is sent via the relay.
With a drop in temperature the mod-
ulation rises again llinear.
Check cooling of the controller
3 x de-energized, 11
- 14 interrupted
HALL-IC
Incorrect signal from the Hall-ICs,
error in the commutation.
Internal plug connection faulty.
The controller switches the motor off.
Automatic restart if no faults are rec-
ognised.
Replace fan / motor
4 x de-energized, 11
- 14 interrupted
Line failure (only for 3 ~ types)
The device is provided with a built-in
phase-monitoring function for the
mains supply. In the event of a mains
interruption (failure of a fuse or
mains phase) the unit switches off
after a delay (approx. 200 ms).
Only functioning with an adequate
load for the controller.
Following a shutoff, a startup attempt
is made after approximately 15 sec-
onds, if the voltage supply is high
enough. This keeps occurring until
all 3 supply phases are available
again.
Check power supply
5 x de-energized, 11
- 14 interrupted
Motor blocked
If after 8 seconds of commutation no
speed is measured > 0, the fault
“Motor blocked” is released.
EC-Controller switches off, renewed
attempt to start after about 2.5 sec.
Final shutoff, when fourth starting
test fails.
It is then necessary to have a reset
by disconnecting the line voltage.
Check if motor is freely rotatable.
6 x de-energized, 11
- 14 interrupted
IGBT Fault
Short circuit to earth or short circuit
of the motor winding.
EC-Controller switches off, renewed
attempt to start after about 60 sec.
Code 9.
Final shutoff, if - following a second
starting test – a second fault detec-
tion is detected within a period of 60
seconds.
It is then necessary to have a reset
by disconnecting the line voltage.
Assembly instructions ECblue Diagnostics / Faults
L-BAL-F046-GB 1203 Index 003 Part.-No. 00297758-GB
33/45
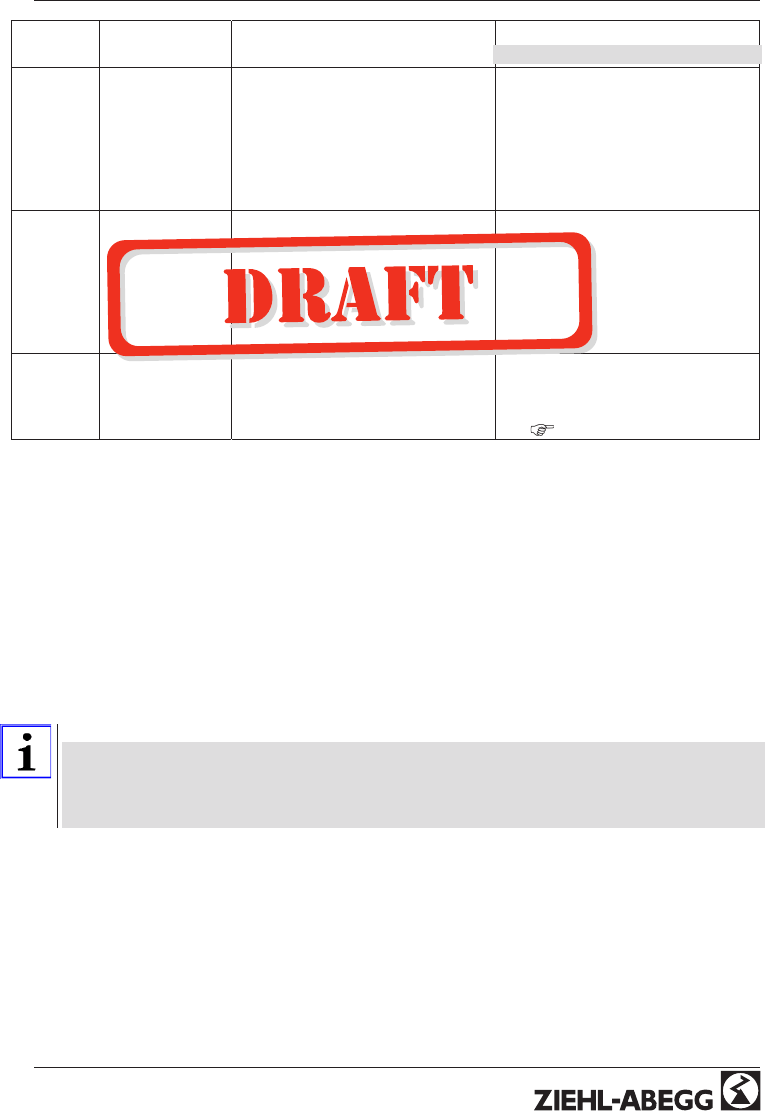
LED Code Relays K1* Cause
Explanation
Reaction of Controller
Adjustment
7 x de-energized, 11
- 14 interrupted
DC undervoltage
If the DC-link voltage drops below a
specified limit the device will switch
off.
If the DC-link voltage rises above the
limit within 75 seconds, then the
cotroller will attempt to start.
Should the DC-link voltage stay for
more than 75 seconds below the
limit, the device will switch off with a
fault message.
8 x de-energized, 11
- 14 interrupted
DC overvoltage
If the DC-link voltage increases
above a specified limit, the motor will
switch off.
Reason for excessively high input
voltage or alternator motor operation.
If the DC-link voltage drops below
the limit within 75 seconds, then the
cotroller will attempt to start.
Should the DC-link voltage stay
above the limit for more than 75 sec-
onds, the device will switch off with a
fault message.
9 x energized, 11 - 14
bridged
IGBT cooling down period IGBT cooling down period for approx.
60 sec.
Final shutoff after 2 cooling-off inter-
vals
Code 6.
* K1: programmed function at factory: Fault indication not inverted
7.3 Behaviour in rotation by air current in reverse direction
In the STOP state (no release, no preset signal, no voltage supply) the motor controller
does not intervene when the fan turns in the wrong direction (e.g. due to a draught).
If the fan is started while being driven in the opposite direction to that set, the speed is
reduced controlled to “0” and restarted in the set direction of rotation.
The higher the speed to be reduced, the longer this process lasts.
In cases in which the fan is driven very powerfully in the wrong direction, it may not be
possible to start the fan with the set direction of rotation.
Information
•Do not switch off line voltage that the fan can start again!
•Safe starting of fans is not guaranteed if it is started in reverse. If the application
demands safe starting, the machine manufacturer or owner must prevent reverse
driving rotation by suitable measures.
Assembly instructions ECblue Diagnostics / Faults
L-BAL-F046-GB 1203 Index 003 Part.-No. 00297758-GB
34/45
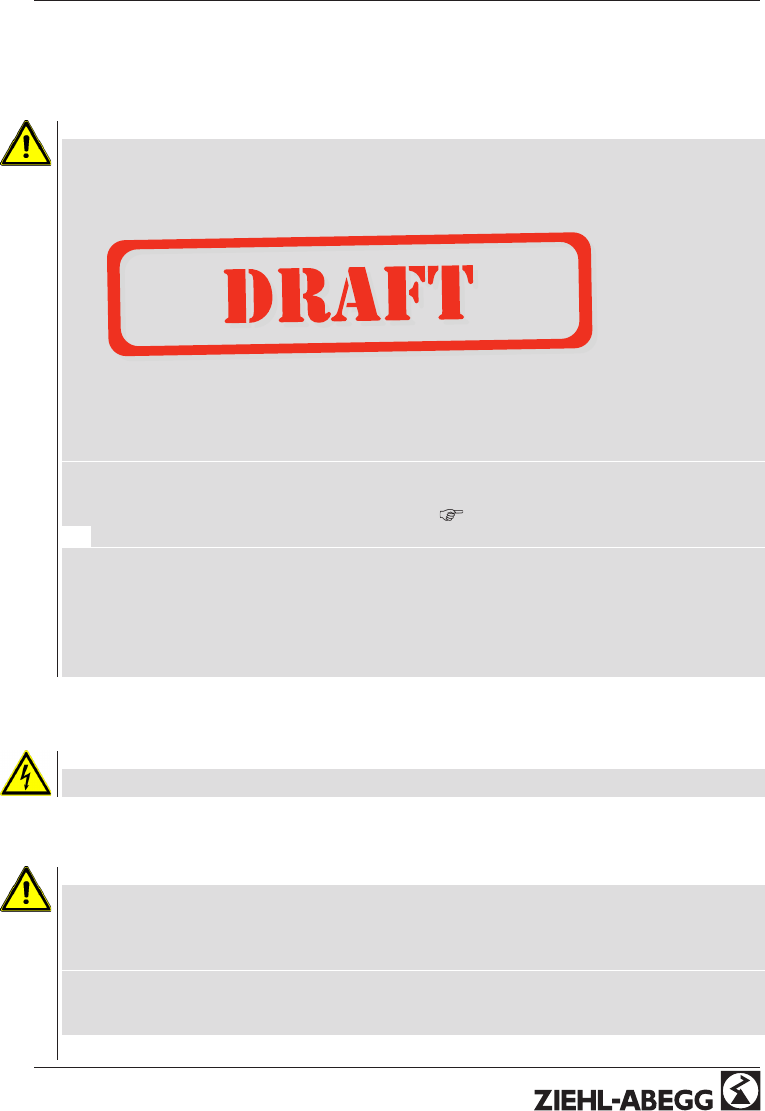
8 Service work
8.1 Repairs / maintenance
Attention!
•Allow maintenance work to be carried out by trained specialists only.
•Please observe the safety regulations and the worker´s protection rules by all
maintenance and service work (DIN EN 50 110, IEC 364).
•Before working on the fan, this must be disconnected from the power supply and
secured against switching back on!
•Keep the airways of the fan free - danger because of objects dropping out!
•No maintenance work at running fan!
•Watch out for vibration free motion!
•Depending on the application and the transfer medium the impeller has a natural
wear. Deposits on the impeller can lead to imbalance and thus to damages
(danger of endurance fracture). The impeller can disintegrate!
•Maintenance interval in accordance with the degree of contamination of the
impeller!
•In case of imbalance: Rebalance the impeller.
•Check the impeller, in particular the weld-seams, for possible cracks.
•Repair, e.g. by welding is prohibited!
•The fan or motor is maintenance-free due to the use of ball bearings with “life-long
lubrication”. At the end of the grease life (
Technical Data) it is necessary to
change the bearing. Please consult our Service Department in this case as for all
other damage (e.g. to the coil or electronics).
•Bolted-on wheels and/or wings may only be replaced by authorised Ziehl-Abegg
AG staff. The manufacturer shall not be liable for damage caused through improp-
er repair work.
•Regular inspection, and cleaning is necessary to prevent imbalance due to in-
gress of dirt.
8.2 Cleaning
Danger due to electric current
Voltage supply for motor must be interrupted and secured against restoration!
Attention!
•Do not use any aggressive, paint solvent cleaning agents when cleaning.
•Cleaning with a water jet:
–Make sure that no water gets into the inside of the motor and electronics, note
protection class (IP).
–Do not hold the jet spray directly on the motor openings and seals.
–During cleaning work using a jet spray, no guarantee is assumed regarding
corrosion formation / paint adhesion for unpainted / painted fans.
Assembly instructions ECblue Service work
L-BAL-F046-GB 1203 Index 003 Part.-No. 00297758-GB
35/45
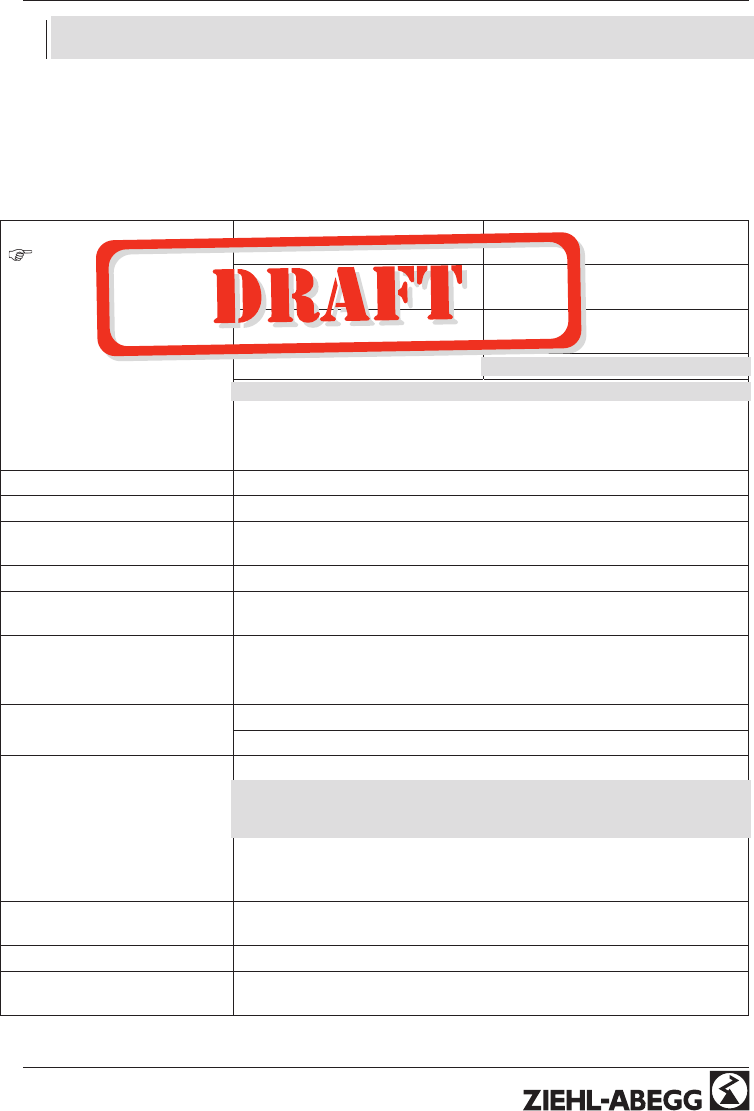
–After the cleaning process, the fan must be operated for 30 minutes at 80 to
100 % of maximum speed for drying purposes!
9 Enclosure
9.1 Technical data
Line voltage*
(
Rating-plate)
AC: 1 ~ 200...277 V (+/- 10 %),
50/60 Hz
DC: 280...400 V (+/- 10 %)
AC: 3 ~ 200...240 V (+/- 10 %),
50/60 Hz
DC: 280...340 V (+/- 10 %)
AC: 3 ~ 380...480 V (+/- 10 %),
50/60 Hz
DC: 500...680 V (+/- 10 %)
DC supply not UL approved!
Special version for IT-System (not UL approved!)
AC: 3 ~ 400 V (-15 up to +10 % ), 50/60 Hz
in TN-System or TT-System for this version
AC: 3 ~ 380...480 V (+/- 10 % ), 50/60 Hz
Maximal line fuse 16 A for all types 1 ~ and 3 ~
Max. cut-in current 126 A
Max. load limit integral of cut-in
current
1.22 A
2
s
Switching Freq. 16 kHz
Input resistance for signal set for
the rotational speed
R
i
> 100 kΩ
Specification speed setting sig-
nal PWM
Voltage: 15...28 VDC
Switching Frequency: 1...10 kHz
On-off ratio: 0...100 %
Voltage supply for external devi-
ces
+ 10 V, I
max
10 mA (short-circuit-proof)
+24 V ±20 %, I
max
70 mA (only for motor size “D”, “G”)
Permissible minimal and maxi-
mal ambient temperature for op-
eration
-25 °C...60 °C (up to 70 °C **)
Please see the technical documentation of the product for the minimum
and maximum ambient temperature valid for the respective fan; These
may deviate from the specified permissible ambient temperatures.
To avoid condensation the drive must be continuously energized due to
the application of heat, with interruptions such that cooling to the point of
condensation does not occur.
Max. permissible installation
height
height 1000 m amsl without derating
Permissible rel. humidity 85 % no condensation
Permissible temperature range
for storage and transport
Motor size “D” and “G”: -40...+80 °C
Assembly instructions ECblue Enclosure
L-BAL-F046-GB 1203 Index 003 Part.-No. 00297758-GB
36/45
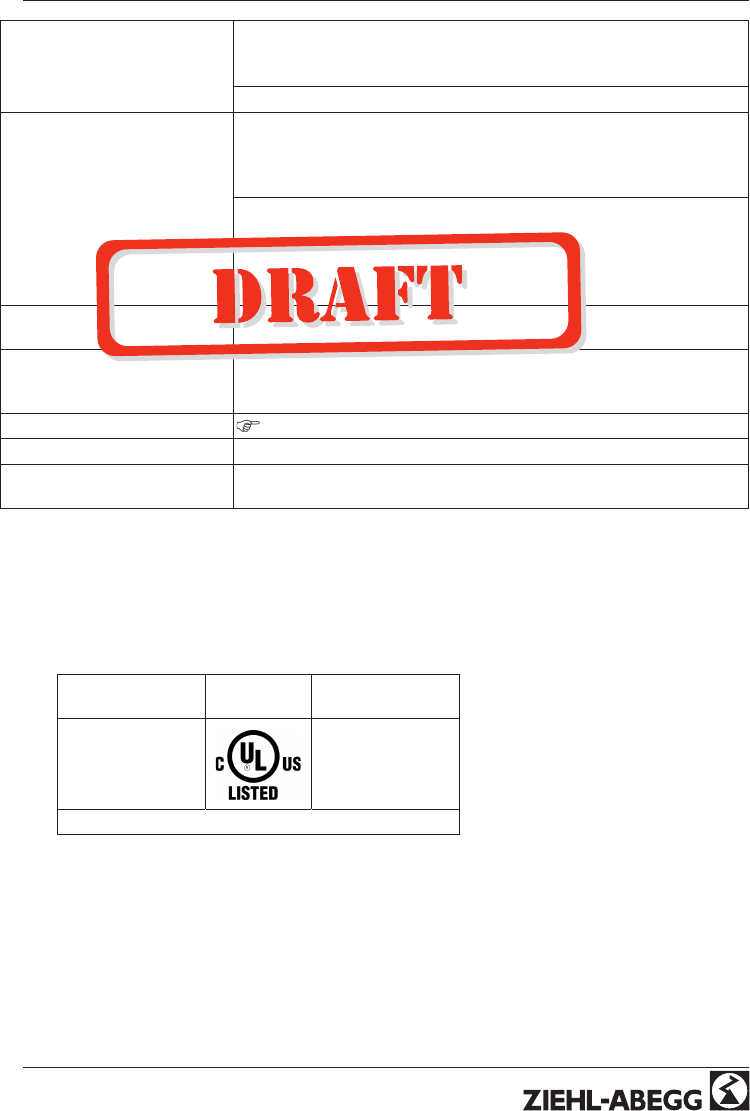
Electromagnetic compatibility for
the standard voltage 230 / 400
V according to IEC 60038
Interference emission EN 61000-6-3 (domestic household applications)
By special version for IT-System according to EN 61000-6-4 (industrial
applications)
Interference immunity EN 61000-6-2 (industrial applications)
Harmonics current according For 1 ~ types
Active power factor adjustment for sinusoidal input current (PFC = Power
- Factor - controller), harmonic current in accordance with EN 61000-3-2
are guaranteed.
For 3 ~ types
EN 61000-3-2 for a “professional unit”.
Please ask Ziehl-Abegg for the individual harmonic oscillation levels of
the current as a percentage of the fundamental oscillation of the rated
current.
Contact rating of the internal
relay
AC 250 V 2 A
Max. leakage current according
to the defined networks of EN
60990
< 3.5 mA
dB(A) values
product catalog
Ball bearings grease service-life during standard usage ca. 30 - 40,000 h
Protection class of motor ac-
cording to EN 60529
IP54
* Regarding the mains connection, the devices are to be classified as category “C2” devices
according to the relevant DIN EN 61800-2 The increased requirements placed on electrical
interference for category “C1” devices are complied with in addition.
** In case of a temperature increase above the predetermined threshold values modulation is
linearly reduced by active temperature management.
Authorization: FILE No.
E213826
UL 508c
Power Conversion
Equipment
62BN
Environment type rating: 3
Assembly instructions ECblue Enclosure
L-BAL-F046-GB 1203 Index 003 Part.-No. 00297758-GB
37/45
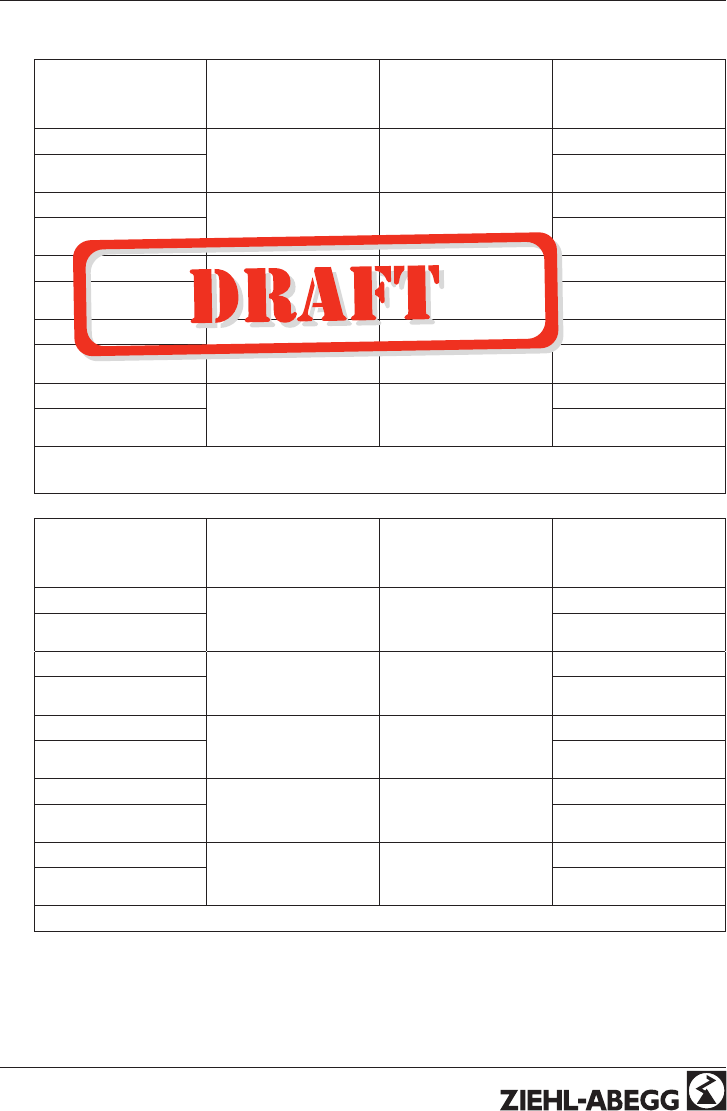
9.1.1 UL: Ratings and dimensions:
Model input: output:
Dimensions
(Ø x length)
[mm]
MK16-#I#.07.#A 3 x 380 - 480 Vac
2500 W, 4.0 - 3.2 A
50/60 Hz
2400 W / 16 kHz
4.7 A
460 Vac (rms)
200 x 167.7
MK116-#I#.11.#A 200 x 185.7
MK116-#I#.07.#B 3 x 200 - 240 Vac
2400 W, 6.0 A
50/60 Hz
2250 W / 16 kHz
7.7 A
230 Vac (rms)
200 x 167.7
MK116-#I#.11.#B 200 x 185.7
MK116-#I#.07.#C 1 x 200 - 277 Vac
1440 W, 5.2 A
50/60 Hz
1320 W / 16 kHz
3.3 A
340 Vac (rms)
200 x 167.7
MK116-#I#.11.#C 200 x 185.7
MK152-#I#.11.#A 3 x 380 - 480 Vac
4100 W, 6.6 - 5.2 A
50/60 Hz
3950 W / 16 kHz
7.2 A
460 Vac (rms)
275 x 220.8
MK152-#I#.17.#A 275 x 249.8
MK152-#I#.11.#B 3 x 200 - 240 Vac
3800 W, 9.7 A
50/60 Hz
3600 W / 16 kHz
11.6 A
230 Vac (rms)
275 x 220.8
MK152-#I#.17.#B 275 x 249.8
MK116 ambient temperature: 40 °C
MK152 ambient temperature: 50 °C
Model input: output:
Dimensions
(Ø x length)
[mm]
MK116-#I#.07.#A 3 x 380 - 480 Vac
2500 W, 3.2 - 3.6A
50/60 Hz
2350 W / 16 kHz
4.4 A
460 Vac (rms)
200 x 167.7
MK116-#I#.11.#A 200 x 185.7
MK116-#I#.07.#B 3 x 200 - 240 Vac
1420 W, 3.6 A
50/60 Hz
1360 W / 16 kHz
4.4 A
230 Vac (rms)
200 x 167.7
MK116-#I#.11.#B 200 x 185.7
MK116-#I#.07.#C 1 x 200 - 277 Vac
1000 W, 3.7 A
50/60 Hz
920 W / 16 kHz
2.3 A
340 Vac (rms)
200 x 167.7
MK116-#I#.11.#C 200 x 185.7
MK152-#I#.11.#A 3 x 380 - 480 Vac
4100 W, 6.6 - 5.2A
50/60 Hz
3950 W / 16 kHz
7.2 A
460 Vac (rms)
275 x 220.8
MK152-#I#.17.#A 275 x 249.8
MK152-#I#.11.#B 3 x 200 - 240 Vac
2900 W, 7.4 A
50/60 Hz
2750 W / 16 kHz
8.9 A
230 Vac (rms)
275 x 220.8
MK152-#I#.17.#B 275 x 249.8
Ambient temperature: 60 °C
Assembly instructions ECblue Enclosure
L-BAL-F046-GB 1203 Index 003 Part.-No. 00297758-GB
38/45
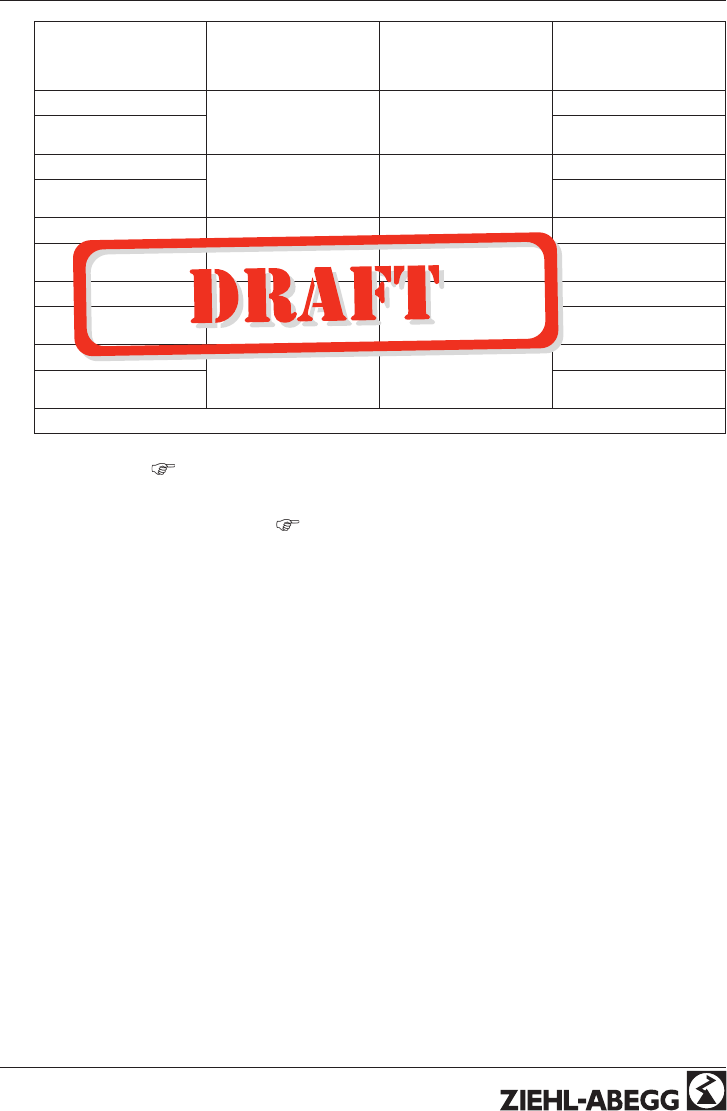
Model input: output:
Dimensions
(Ø x length)
[mm]
MK116-#I#.07.#A 3 x 380 - 480 Vac
190 W, 0.24 A
50/60 Hz
180 W / 16 kHz
0.3 A
460 Vac (rms)
200 x 167.7
MK116-#I#.11.#A 200 x 185.7
MK116-#I#.07.#B 3 x 380 - 240 Vac
95 W, 0.24A
50/60 Hz
90 W / 16 kHz
0.3 A
230 Vac (rms)
200 x 167.7
MK116-#I#.11.#B 200 x 185.7
MK116-#I#.07.#C 1 x 200 - 277 Vac
135 W, 0.49 A
50/60 Hz
124 W / 16 kHz
0.31 A
340 Vac (rms)
200 x 167.7
MK116-#I#.11.#C 200 x 185.7
MK152-#I#.11.#A 3 x 380 - 480 Vac
1820 W, 2.3 A
50/60 Hz
1740 W / 16 kHz
2.8 A
460 Vac (rms)
275 x 220.8
MK152-#I#.17.#A 275 x 249.8
MK152-#I#.11.#B 3 x 200 - 240 Vac
910 W, 2.3 A
50/60 Hz
870 W / 16 kHz
2.8 A
230 Vac (rms)
275 x 220.8
MK152-#I#.17.#B 275 x 249.8
Ambient temperature: 70 °C
#: Placeholder
Ziehl-Abegg Nomenclature
Power data of the motor in the fan standing nearby the above data on the rating-plate.
For further information to UL types
connection diagram.
9.1.2 UL: Overload protection
The integrated variable speed drives are equipped with a solid state motor overload
protection and a solid state short circuit protection.
The solid state motor overload protection protects the motor under overload conditions
by reducing current flow to the internal motor output terminals. This protection is
achieved through algorithms based on I
2
t of the current of the motor.
The overload protection circuitry is optimally configured to the specific motor and the
specific final application of the integrated variable speed drive.
This is typically 100 % of the full-load current of the motor. Changing the settings of the
solid state motor overload protection needs further discussion with Ziehl-Abegg AG.
Changing the settings without written permission of Ziehl-Abegg AG is not allowed.
The solid state short circuit protection acts to suspend current flow to the internal motor
output terminals upon sensing output current to the motor and bus voltage. The protec-
tion of the motor is comprised of hardware and firmware.
Assembly instructions ECblue Enclosure
L-BAL-F046-GB 1203 Index 003 Part.-No. 00297758-GB
39/45
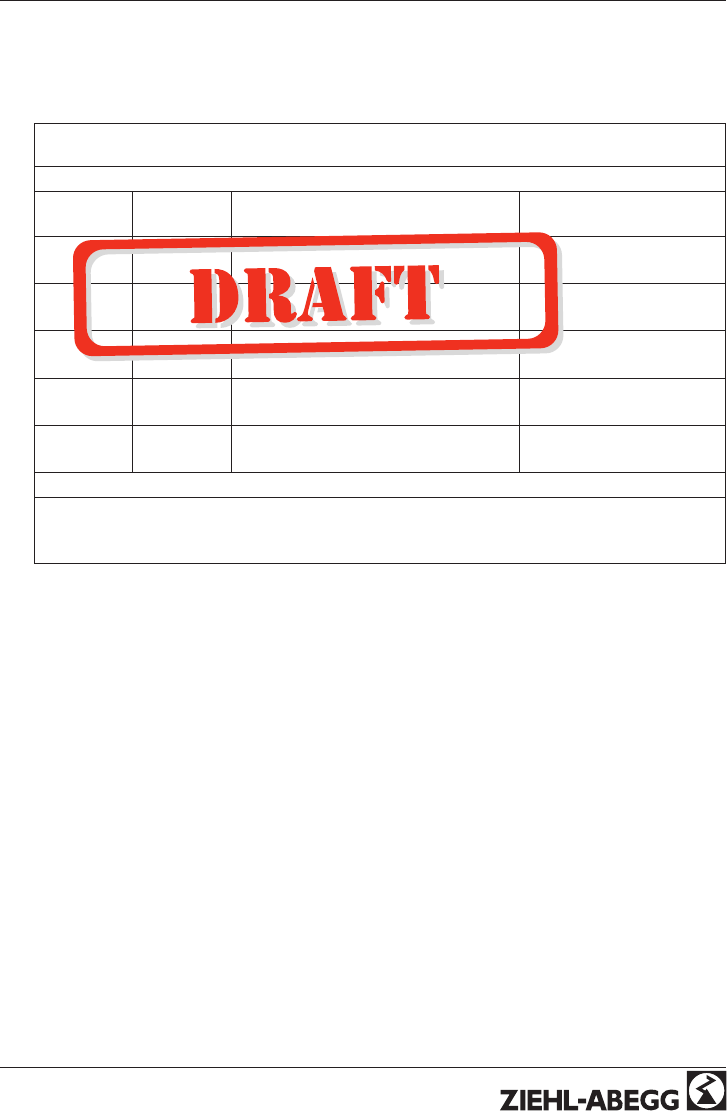
9.1.3 UL: Short Circuit Current Rating
The integrated variable speed drives are suitable to be used on a circuit capable of
delivering no more than 100 kA RMS symmetrical. Details can be found in the following
table.
The fusing for the short-circuit protection must comply with the requirements in UL248.
Tests were made with RK fuses without semiconductor protection:
Class fuses Maximum
AC Voltage
Rating of Fuse used motor type
RK1 277 V 20 A / 600 V
(e.g Ferraz Shawmut / TRS20R)
MK116- #I#.##.#C
RK5 240 V 25 A / 250 V
(e.g. Ferraz Shawmut / TR25R)
MK116- #I#.##.#B
RK5 240 V 50 A / 250 V
(e.g. Ferraz Shawmut / TR50R)
MK152- #I#.##.#B
RK5 480 V 15 A / 600 V
(e.g. Ferraz Shawmut / TR15R)
MK116- #I#.##.#A
RK5 480 V 30 A / 600 V
(e.g. Ferraz Shawmut / TR30R)
MK152- #I#.##.#A
Integrated solid state short circuit protection does not provide branch circuit protection.
Branch circuit protection must be provided in accordance with the National Electrical Code and any
additional local codes, or the equivalent.
Assembly instructions ECblue Enclosure
L-BAL-F046-GB 1203 Index 003 Part.-No. 00297758-GB
40/45
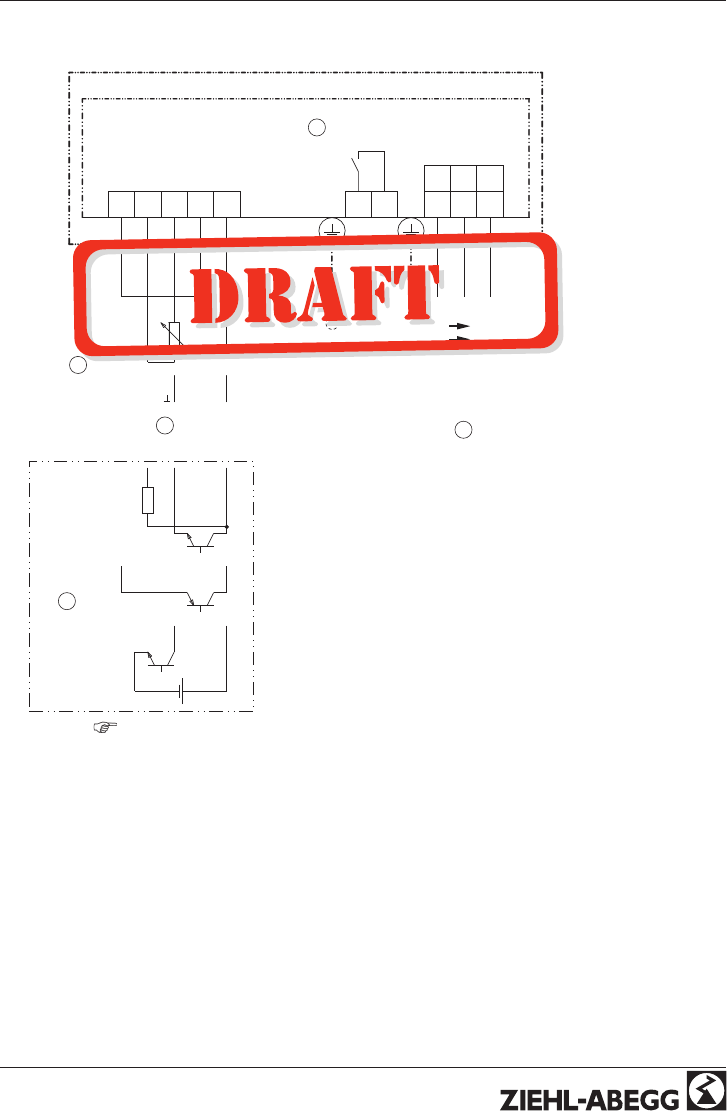
9.2 Connection diagram
24V 10V GND D1 E1 11 14
DC Out
(Imax = 70 mA)
DC Out
(Imax = 10 mA)
Digital In 1
Analog In 1
L3/NL2L1PE
L1
L2 L3
PE
L1
N
ECblue Basic (_ _ _ _ _-_I_.D_._ _ _ _), (_ _ _ _ _-_I_.G_._ _ _ _)
MOEA03K0
08.03.2011
K1
Kontaktbelastung
Contact rating
max. AC 250 V 2 A
Netzspannung Leistungsschild
Line voltage Rating-plate
Eingang
Input
0...10 V
+
PWM
f = 1...10 kHz
Externe Drehzahlvorgabe
External speed setting
5
3
4
2
10 kΩ
10 kΩ
10 V
GND
E1
24 V
E1
E1
GND
15...28 V
+
-
3 ~ Typ nur in Sonderausführung
für IT-System geeignet
3 ~ type only in special version
suitable for IT-System
1
1 Line voltage
rating plate (3 ~ type only in special version suitable for IT-System)
2 Contact rating max. AC 250 V 2 A
3 External speed setting
4 Input 0...10 V
5 PWM input, f = 1...10 kHz
UL: Input (Line)
•Cu connection leads with the following specifications must be employed:
–Minimum insulation temperature of 80 °C
–Terminal tightening torque for field block (L1, N, and/or L1, L2, L3) of 5 - 7 Lb In.
(Exception: spring-cage terminal for motor size "G" @ line voltage 3 ~ 200...240 V)
–Terminal tightening torque of 4.5 Lb In. for field block (K1)
–terminal tightening torque of 4.5 Lb In. for all other field blocks
–terminal tightening torque of 2.2 Lb In. for add-on modules
Assembly instructions ECblue Enclosure
L-BAL-F046-GB 1203 Index 003 Part.-No. 00297758-GB
41/45
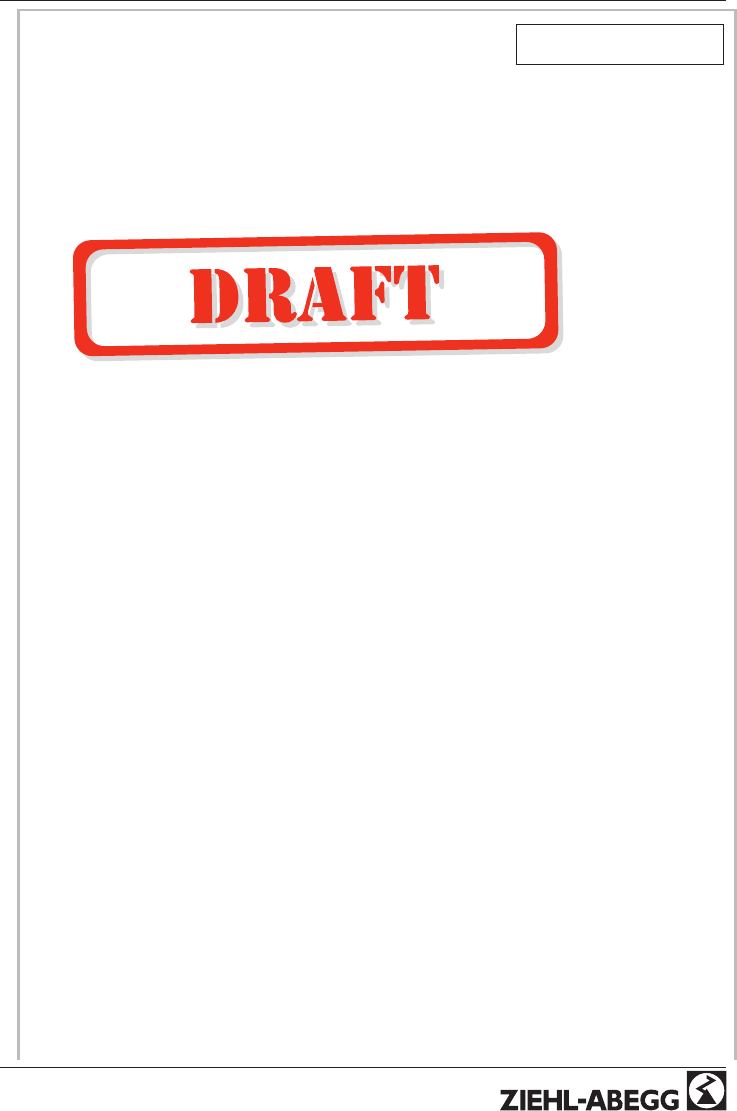
9.3 EC Declaration of Incorporation ZA87-GB-12/09 Index 000
00296702-GB
as defined by the EC Machinery Directive 2006/42/EC,
Annex II B
The design of the incomplete machine:
•Axial fan FA.., FB.., FC.., FE.., FS.., FT.., FH.., FL.., FN.., VR.., VN..
•Centrifugal fan RA.., RD.., RE.., RF.., RG.., RH.., RK.., RM.., RR.., RZ.., GR..,
ER..
•Cross-flow fan QK.., QR.., QT.., QD.., QG..
Motor type:
•Induction internal or external rotor motor (also with integrated frequency inverter)
•Electronically commutated internal or external rotor motor (also with integrated EC
controller)
complies with the requirements in Appendix I, Articles 1.1.2, 1.1.5, 1.4.1, 1.5.1 in
EC Machinery Directive 2006/42/EC.
The manufacturer is the Ziehl-Abegg AG
Heinz-Ziehl-Strasse
D-74653 Kuenzelsau
The following standards are applied:
EN 60204-1:2006 Safety of machinery; electrical equipment of machines; Part 1: Gen-
eral requirements
EN ISO
12100:2003
Safety of machinery; basic concepts, general principles for design
EN ISO
13857:2008
Safety of machinery; safety distances to prevent danger zones being
reached by the upper limbs
Note: The maintenance of the EN ISO 13857:2008 relates only to the
installed accidental contact protection, provided that it is part of the
scope of delivery.
The specific technical documentation in accordance with Appendix VII B has been
written and is available in its entirety.
The person authorised for compiling the specific technical documentation is: Dr. O. Sadi,
address see above.
The specific documentation will be transmitted to the official authorities on justified
request. The transmission can be electronic, on data carriers or on paper. All industrial
property rights remain with the above-mentioned manufacturer.
Assembly instructions ECblue EC Declaration of Incorporation
L-BAL-F046-GB 1203 Index 003 Part.-No. 00297758-GB
42/45
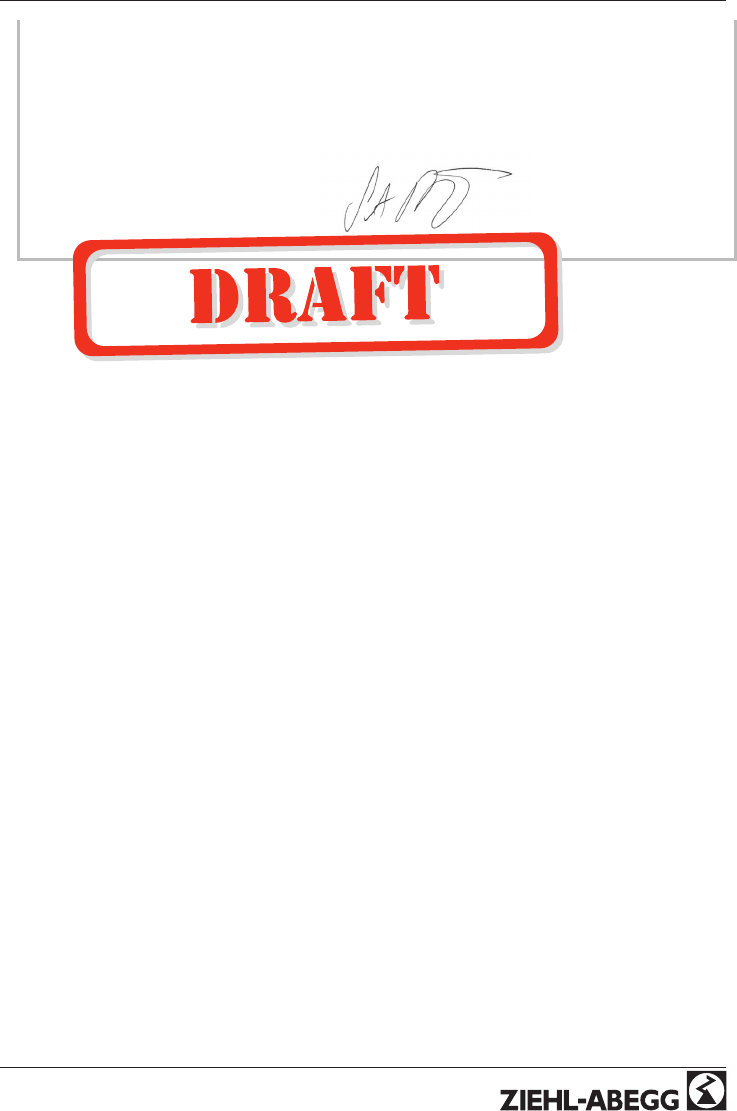
It is prohibited to commission this incomplete machine until it has been secured
that the machine into which it was incorporated complies with the stipulations of
the EC Machinery Directive.
Künzelsau, 29-Dec-2009 Dr. O. Sadi - Technical Manager Ventilation Technology
i.V.
Assembly instructions ECblue EC Declaration of Incorporation
L-BAL-F046-GB 1203 Index 003 Part.-No. 00297758-GB
43/45
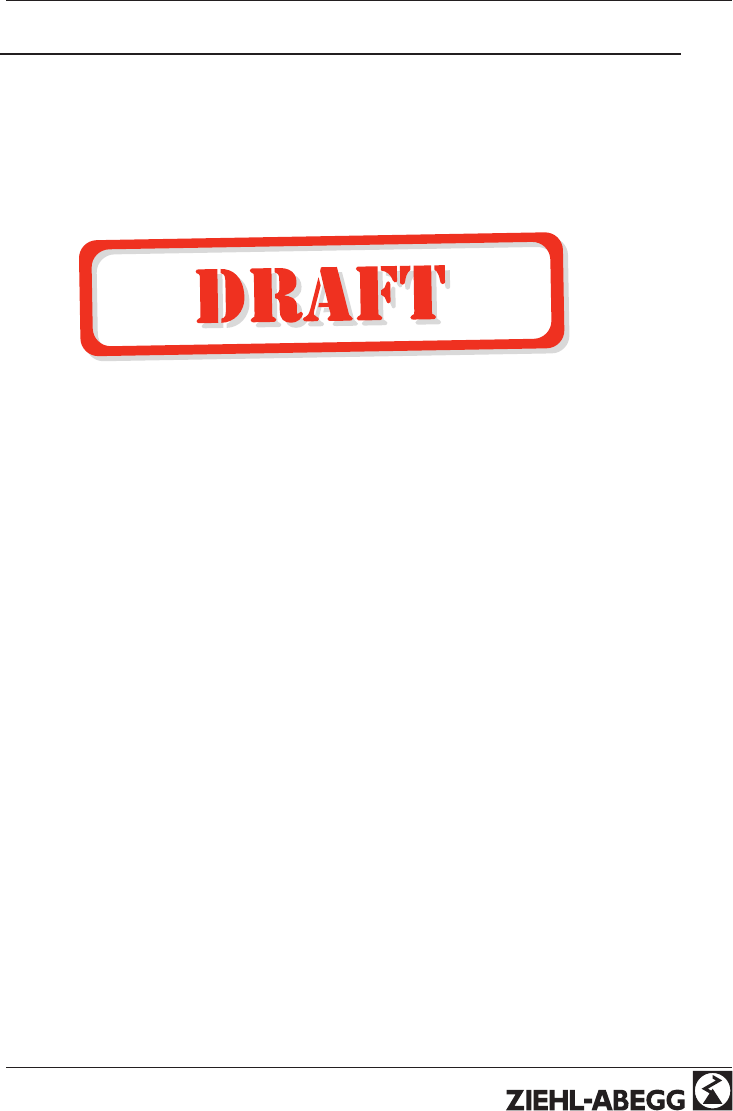
Assembly instructions ECblue EC Declaration of Incorporation
L-BAL-F046-GB 1203 Index 003 Part.-No. 00297758-GB
44/45
9.4 Index
A
air current 34
B
Bearing 31
C
change the bearing 35
Chimney 17
cleaning 35
condensation drain hole 15, 18
control cable 23
current-operated protective
devices 25
D
DC voltage 24
E
Enable 28
G
grease life 35
I
Imbalance 31
Input resistance 36
IT-System 24
L
leakage current 37
M
motor size 10
Motorheating 21
N
NFPA79 23
O
one-quadrant 10
Outdoor fans 20
P
PWM-signal 25
R
relay 28
Relay output 28
Residual current circuit
breaker 25
S
S1 operated 10
service life 10
Setting signal 27
sound power levels 30
Switching Freq. 36
T
Technical data 4, 36
temperature management 33
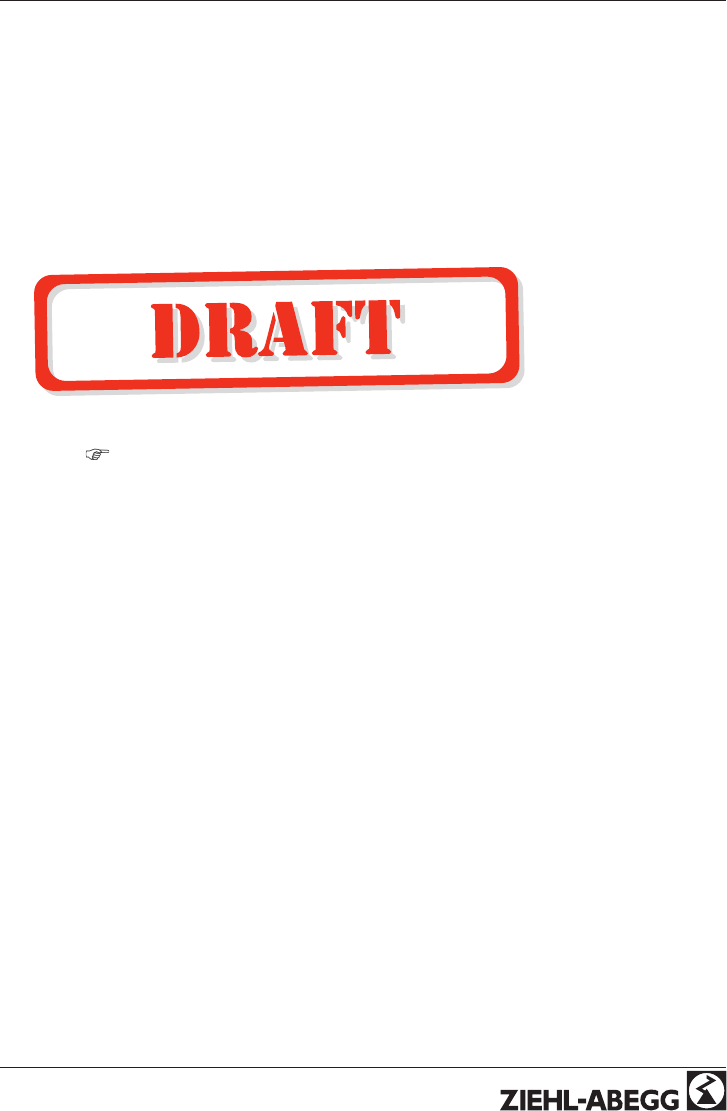
9.5 Manufacturer reference
Our products are manufactured in accordance with the relevant international regulations.
If you have any questions concerning the use of our products or plan special uses,
please contact:
Ziehl-Abegg AG
Heinz-Ziehl-Straße
74653 Künzelsau
Telephone: +49 (0) 7940 16-0
Telefax: +49 (0) 7940 16-504
info@ziehl-abegg.de
http://www.ziehl-abegg.de
9.6 Service information
If you have any technical questions while commissioning or regarding malfunctions,
please contact our V-STE support department for control systems - ventilation technol-
ogy.
Our worldwide contacts are available in our subsidiaries for deliveries outside of Ger-
many.
www.ziehl-abegg.com.
If you make returns for inspections or repairs we need certain information in order to
facilitate focused trouble shooting and fast repair. Please use our repair tickets for this. It
is provided to you after you have consulted our support department.
In addition, you can download it from our homepage. Download - Ventilation Technology
- Topic: Control Engineering - Document type: General documents.
Assembly instructions ECblue Index
L-BAL-F046-GB 1203 Index 003 Part.-No. 00297758-GB
45/45