Accutech Security HWHY-660017 RFID Controller activates LF RFID Tags at Portals of egress and responds as per customer needs User Manual 1 UM25 outsidecover
Innovative Control Systems Inc RFID Controller activates LF RFID Tags at Portals of egress and responds as per customer needs 1 UM25 outsidecover
Exhibit D Users Manual per 2 1033 b3
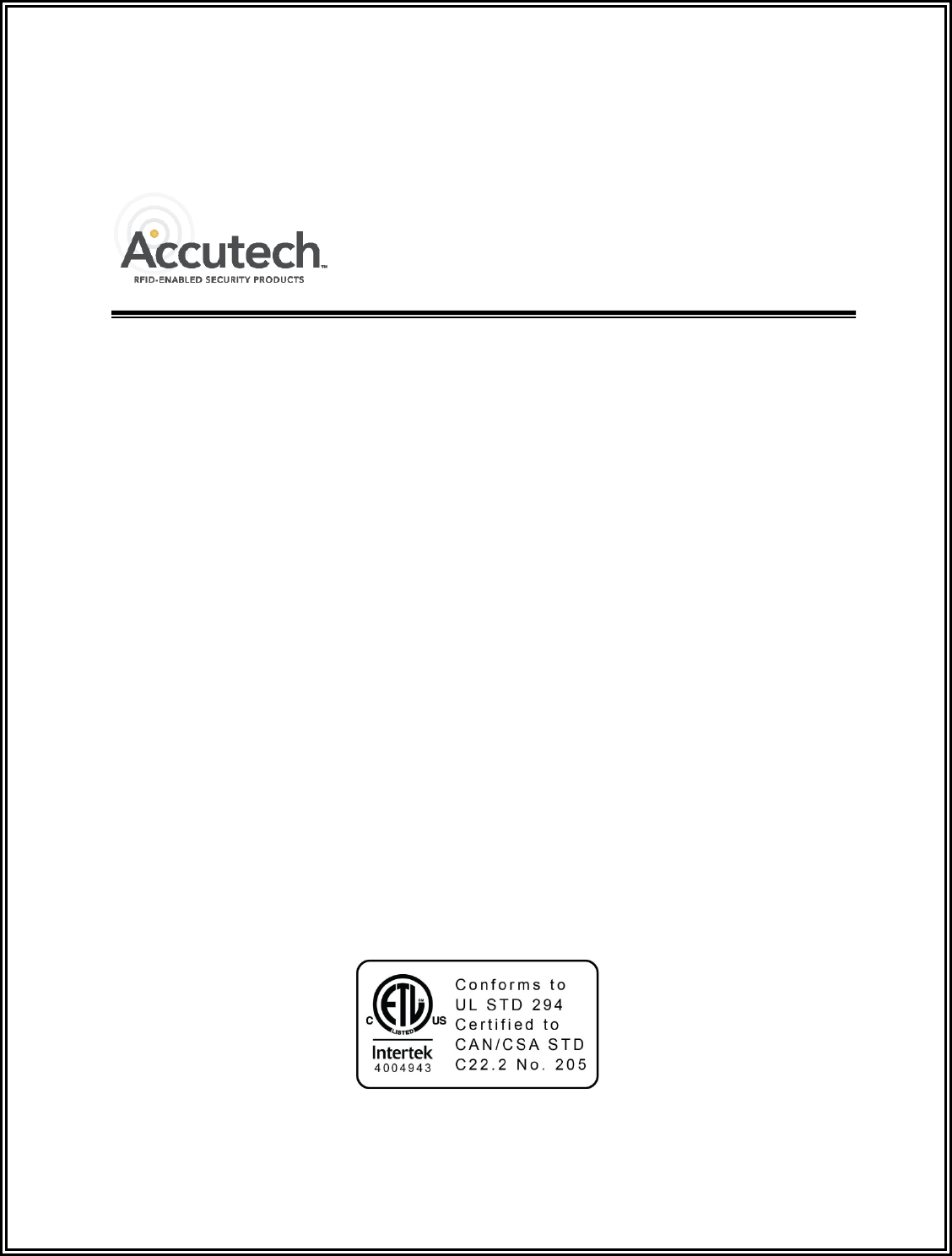
ES 2100 / ES 2200 / IS 3200 / BR 4200
User Manual
800-356-2671 | Accutech | www.AccutechSecurity.com

ES 2100 / ES 2200 / IS 3200 / BR 4200
User Manual
800-356-2671 | Accutech | www.AccutechSecurity.com
Version 2.5
DOC.970002
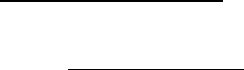
ICS/ACCUTECH LIMITED WARRANTY
Innovative Control Systems, Inc. (ICS) warrants its Accutech™ equipment (Product) against defect in
materials and workmanship under normal use for one (1) year from the date of product shipment.
Defective equipment will be either repaired or replaced at ICS’ discretion, free of charge to the Customer
during the warranty period. ICS will supply labor depending on contract to repair or replace defective
equipment, free of charge, during the warranty period only if ICS or an ICS-certified subcontractor hired by
ICS installed such equipment.
In addition, ICS warrants its Accutech™ LC 1200 / ES 2200 / IS 3200 / BR 4200 System Tags against
defects in materials and workmanship under normal use and service for a period of one (1) year from the
date of shipment.
If a Tag fails during the warranty period due to defects in material and workmanship, ICS will at its sole
discretion, repair or replace the Tag with like quality product free of charge, although overnight shipping
charges may apply. Broken BR Tag clasps or broken LT/SB/CB Tag strap slots are not covered by
warranty.
Returned merchandise will only be accepted within 30 days of shipping with a valid Return Merchandise
Authorization (RMA) number that is requested for full credit towards your account (less a 25% restocking
fee) if the product is returned unused, in its original packaging, and not damaged. No product will be
accepted for credit after 30 days from shipment date. All Tag sales are final.
Furthermore, the express limited warranty of ICS shall be the sole and exclusive warranty of ICS, and ICS
hereby disclaims all other warranties, express, implied or statutory, including but not limited, all other
implied warranties of merchantability or fitness for a particular purpose. In no way should ICS be liable for
special, incidental, or consequential damages. ICS reserves the right to change such limited warranty from
time to time upon thirty (30) days written notice.
Computers and monitors provided by ICS shall not be submitted for repair to ICS but instead shall be
submitted directly to their respective manufacturer and serviced under their inherent manufacturer warranty
policy present at the time of purchase. Customer shall be responsible for registering any and all warranty
requirements.
ICS assumes no responsibility if any Product shall fail to function during any warranty period by reason of
any one or more of the following causes:
Abuse or misuse of the Product or failure to operate the Product in accordance with operating instructions or
specifications.
Improper preventive maintenance of the Product.
Alteration or modification of the Product not specifically approved in writing by ICS.
Improper installation, repair, modification, or servicing the Product performed by any unauthorized service
personnel.
Equipment or cabling damaged by unauthorized personnel knowingly or unknowingly.
Use or operation of the Product in conjunction with any accessories or auxiliary equipment not specifically
approved in writing by ICS.
Acts of God, including, but not limited to, natural disaster, fire, explosions, flood, accidents and the like.
24-hour, 7-days-a-week, 365-days-a-year over the phone technical support at 1-800-356-2671
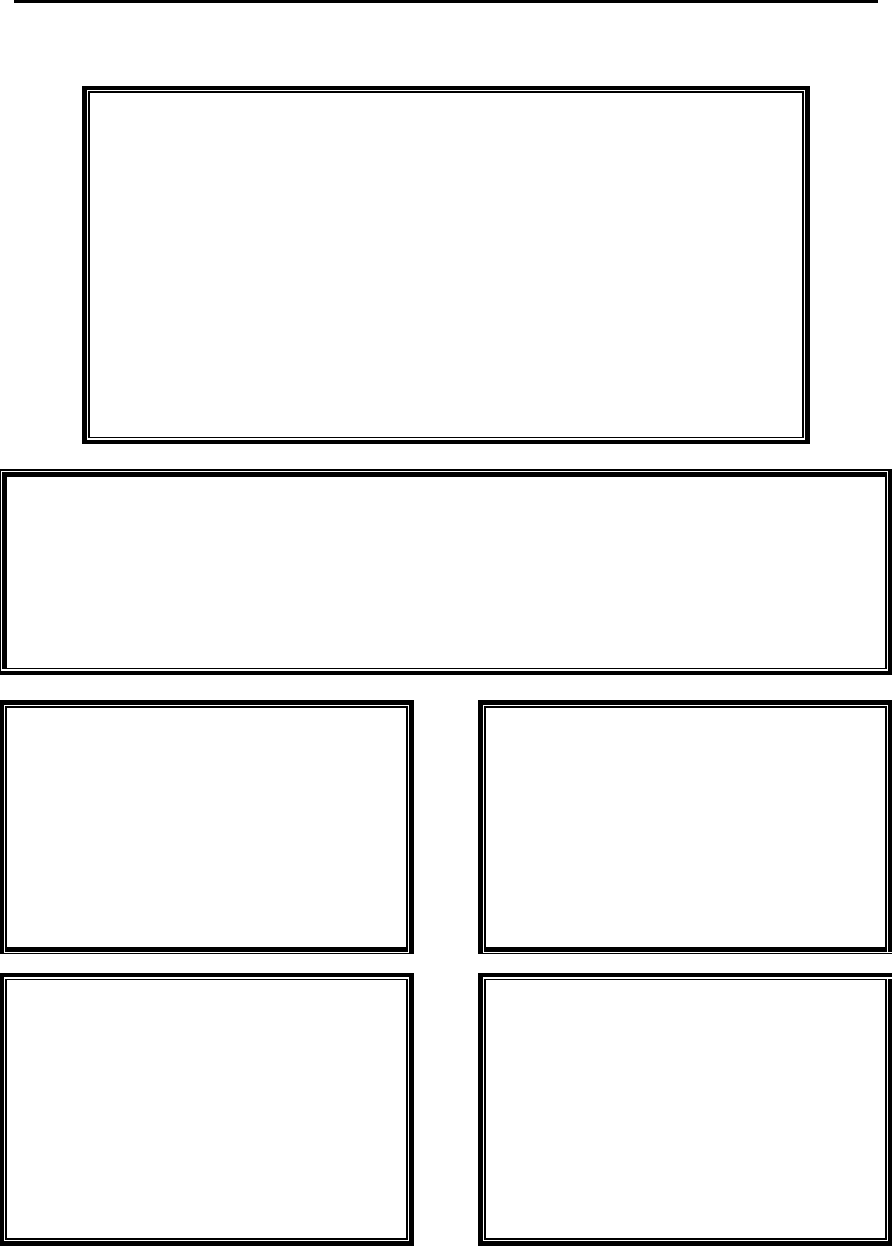
User Manual Preface
IMPORTANT FCC & DOC INFORMATION
Note: This equipment has been tested and found to comply with the limits for a Class B digital
device, pursuant to Part 15 of the FCC Rules. These limits are designed to provide reasonable
protection against harmful interference in a residential installation. This equipment generates, uses
and can radiate radio frequency energy and, if not installed and used in accordance with the
instructions, may cause harmful interference to radio communications. However, there is no
guarantee that interference will not occur in a particular installation. If this equipment does cause
harmful interference to radio or television reception, which can be determined by turning the
equipment off and on, the user is encouraged to try to correct the interference by one or more of
the following measures:
Reorient or relocate the receiving antenna.
Increase the separation between the equipment and receiver.
Connect the equipment into an output on a circuit different from that to which the receiver is
connected.
Consult the dealer or an experienced radio/TV technician for help.
Canadian D.O.C. Statement
This digital apparatus does not exceed the Class B limits for radio noise emissions from digital appartus as set out in the radio
interference regulations of the Canadian Department of Communications.
Le present appareil numerique n,emet pas de bruits radiolectriques depassant les limits appliques aux appereils numeriques de Class B
prescrites dans le rglement sur le brouillage radiolectrique dicte par le ministere des Communications du Canada.
FCC ID/DOC for the ES Sensor:
FCC ID: JM7-IGWT-662002
Canada IC: 2683A-662002
This device complies with Part 15 of the FCC rules.
Operation is subject to the following two conditions:
(1) This device may not cause harmful interference,
and (2) this device must accept any interference
received, including interference that may cause
undesired operation.
FCC ID/DOC for the ES Controller:
FCC ID: JM7-ITYS-700035
Canada 2683 102 312
This device complies with Part 15 of the FCC rules.
Operation is subject to the following two conditions:
(1) This device may not cause harmful interference,
and (2) this device must accept any interference
received, including interference that may cause
undesired operation.
FCC ID/DOC for the
Zone/Auxiliary Receiver:
FCC ID: JM7-IGWT-660076
Canada IC: 2683A-660076
This device complies with Part 15 of the FCC rules.
Operation is subject to the following two conditions:
(1) This device may not cause harmful interference,
and (2) this device must accept any interference
received, including interference that may cause
undesired operation.
FCC ID/DOC for the S-TAD:
FCC ID: JM7-IGWT-662008
Canada IC: 2683A-662008
This device complies with Part 15 of the FCC rules.
Operation is subject to the following two conditions:
(1) This device may not cause harmful interference,
and (2) this device must accept any interference
received, including interference that may cause
undesired operation.
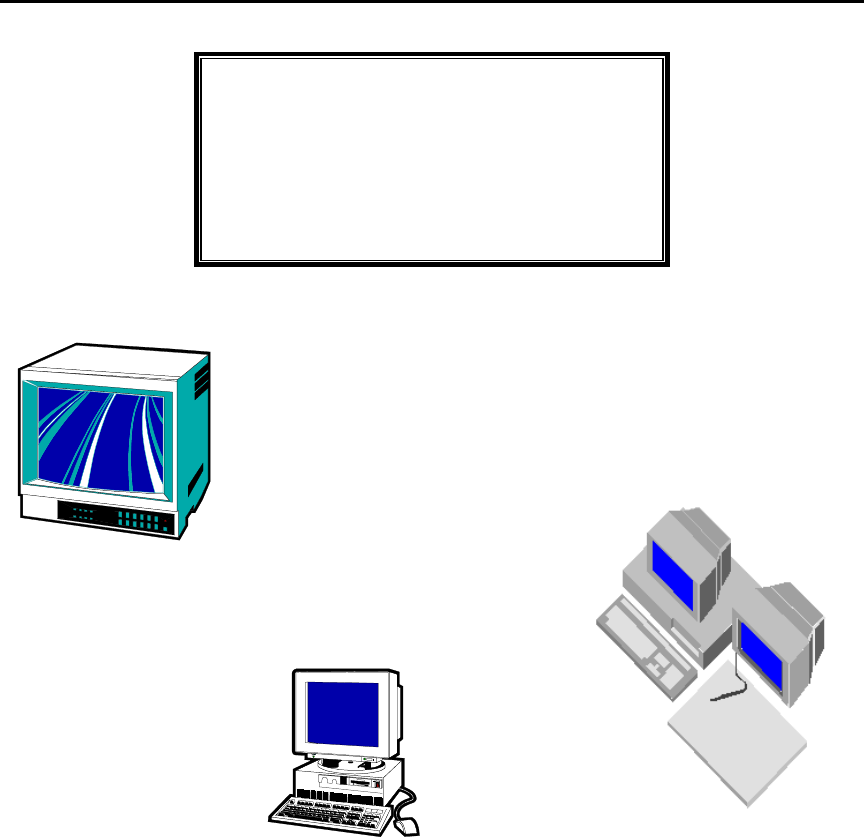
Preface User Manual
IMPORTANT:
Keep all Televisions, Computers, X-ray
equipment, etc. at least 10 feet away from the ES
Receiver. This includes equipment located on the
other side of walls and doors.
Picture the area around the monitored zone as
a big globe with the receive antenna as the
center. Keep all sources of interference outside
this globe.
IMPORTANT NOTICE
:
Do not store ES Sensor(s) within 3 feet of
ANY of the sources of electrical noise listed
on this page. These sources can reduce
sensor activation. This activation can lead
to possible undesirable responses from the
system.
Common Sources of Interference Include:
Television Sets
Computer Monitors
Medical Monitoring Equipment
Electric Motors
Electrical Distribution Panels and
Transformers
Fluorescent Lighting
Some Electronic Washers and Dryers
X-ray and other Imaging Equipment
Unshielded Computer Cables
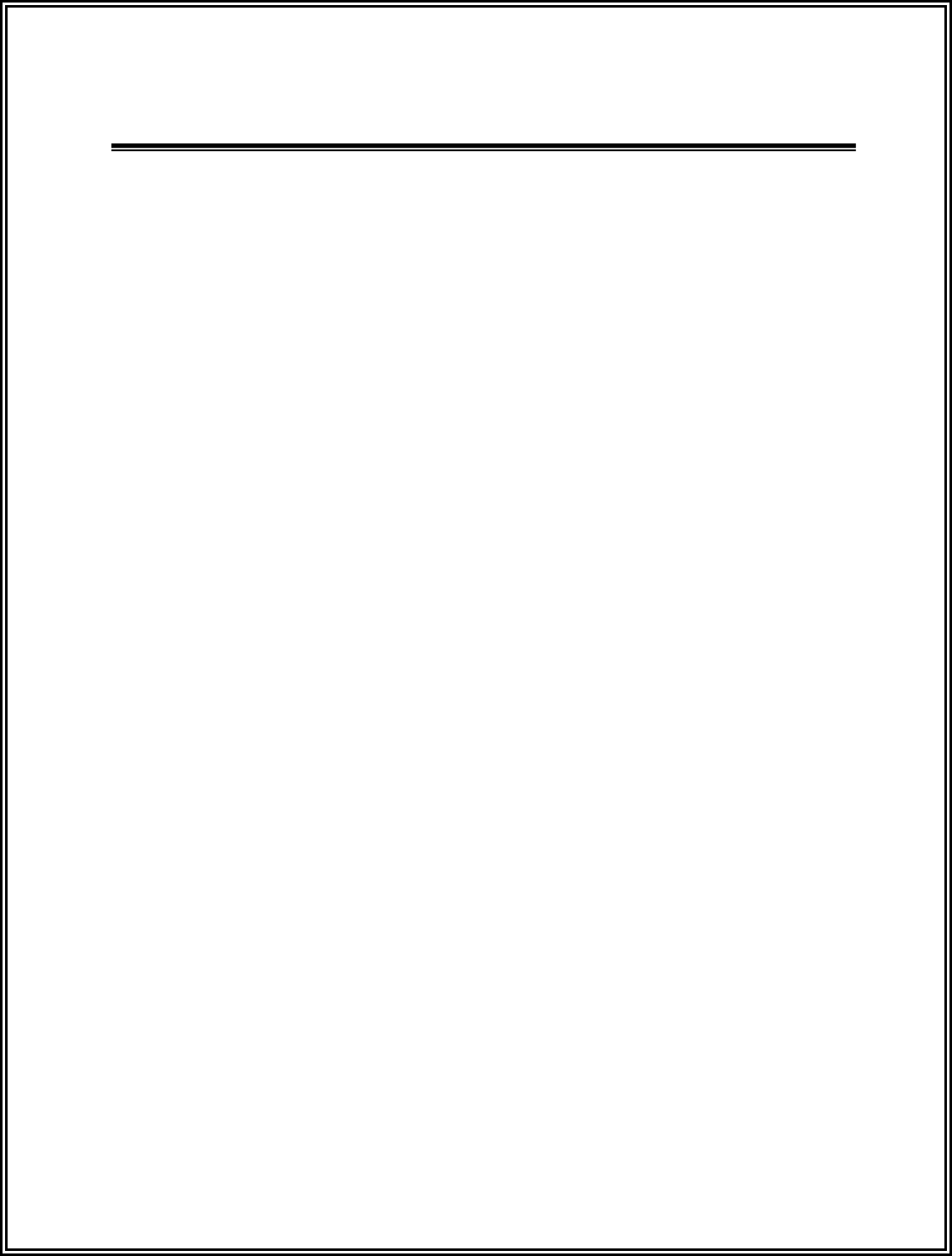
800-356-2671 | Accutech | www.AccutechSecurity.com
Contents
Chapter 1: The Accutech Systems
ES 2200 System
1
-
1
IS 3200 System
1
-
2
BR 4200 System
1
-
2
Cut Band System
1
-
2
Alarms
1
-
3
How Accutech Systems Work
1
-
3
Addressing Alarms
1
-
4
Escorting
1
-
6
Chapter 2: System Components
Controller
2
-
2
Receiver
2
-
2
Keypad
2
-
2
Magnetic Switch
2
-
2
Passive Infrared Reader (PIR)
2
-
3
Tx Wand Antenna
2
-
3
Tri
-
Axis Antenna
2
-
3
ES 2200 System Tags
2
-
4
IS 3200 System Tags
2
-
4
BR 4200 System Tags
2
-
5
Cut Band System Tags
2
-
5
Secure Tag Activator/Deactivator (S
-
TAD)
2
-
6
PC
2
-
6
Tag Test Station (TTS)
2
-
7
Accutech Software
2
-
7
Multiplexer
2
-
7
Power Supply
2
-
7
Auxiliary Receiver (BR 4200 only)
2
-
7
Graphic Display Panel (GDP)
2
-
8
Staff Alert Panel (SAP)
2
-
8
Magnetic Locks
2
-
8
Elevator Deactivation Circuitry
2
-
9
Automatic Door Deactivation
2
-
9
Band Alarm Lockdown
2
-
9
Fire Panel Interface (FPI)
2
-
9
Local Alarm
2
-
9
Multi
-
Tone Local Alarm (MTLA)
2
-
10
Central Alarm
2
-
10
Speakers
2
-
10
Voice Alarm
2
-
10
Strobe Light
2
-
10
Push Button Override (PBO)
2
-
11
Timer
2
-
11
Chapter 3: Tags
ES 2200 System Tags
3
-
1
IS 3200 System Tags
3
-
1
BR 4200 System Tags
3
-
2
Cut Band System Tags
3
-
2
Tag Barcodes
3
-
3
Visual Pulse LED
3
-
3
LED Tag
3
-
4
Attaching Tags
3
-
6
Tag and Band Maintenance
3
-
10
Chapter 4: The S-TAD
Powering the S
-
TAD On/Off
4
-
1
Unlocking the S
-
TAD
4
-
1
Activating/Deactivating Tags
4
-
2
Programming Mode
4
-
3
Enable/Disable Band Alarm Sounder
4
-
3
Set Unlock Timeout
4
-
3
Summary of LEDs
4
-
4
Chapter 5: The Keypad
Keypad Operation
5
-
1
Initiating
the First Relay (Reset/Escort)
5
-
1
Initiating the Second Relay (Anti
-
Tailgate)
5
-
1
How to enter user codes
5
-
2
How to set the relay time
5
-
3
DAP Instructions
5
-
6
Chapter 6: The Accutech Software
Chapter 7: Facility Performance Testing
Testing Tags
7
-
1
Zone Functions Tested
7
-
1
Test Equipment Required
7
-
1
Zone, Lock Test
7
-
2
Zone, Egress Test (3000 and 3101 Locks)
7
-
3
Zone, Delayed Egress Test (3101)
7
-
3
Zone, Hallway Test
7
-
4
Zone, Elevator Deactivation Test
7
-
5
Door Ajar Test
7
-
5
Loiter Test
7
-
6
System Supervisor Test (Tx)
7
-
7
System Supervisor Test (Rx)
7
-
7
Fire Panel Interface (FPI) Test
7
-
7
Band Alarm Test (BR 4200 Systems only)
7
-
8
FAQ
F
-
1
Glossary
G
-
1
Index
I
-
1
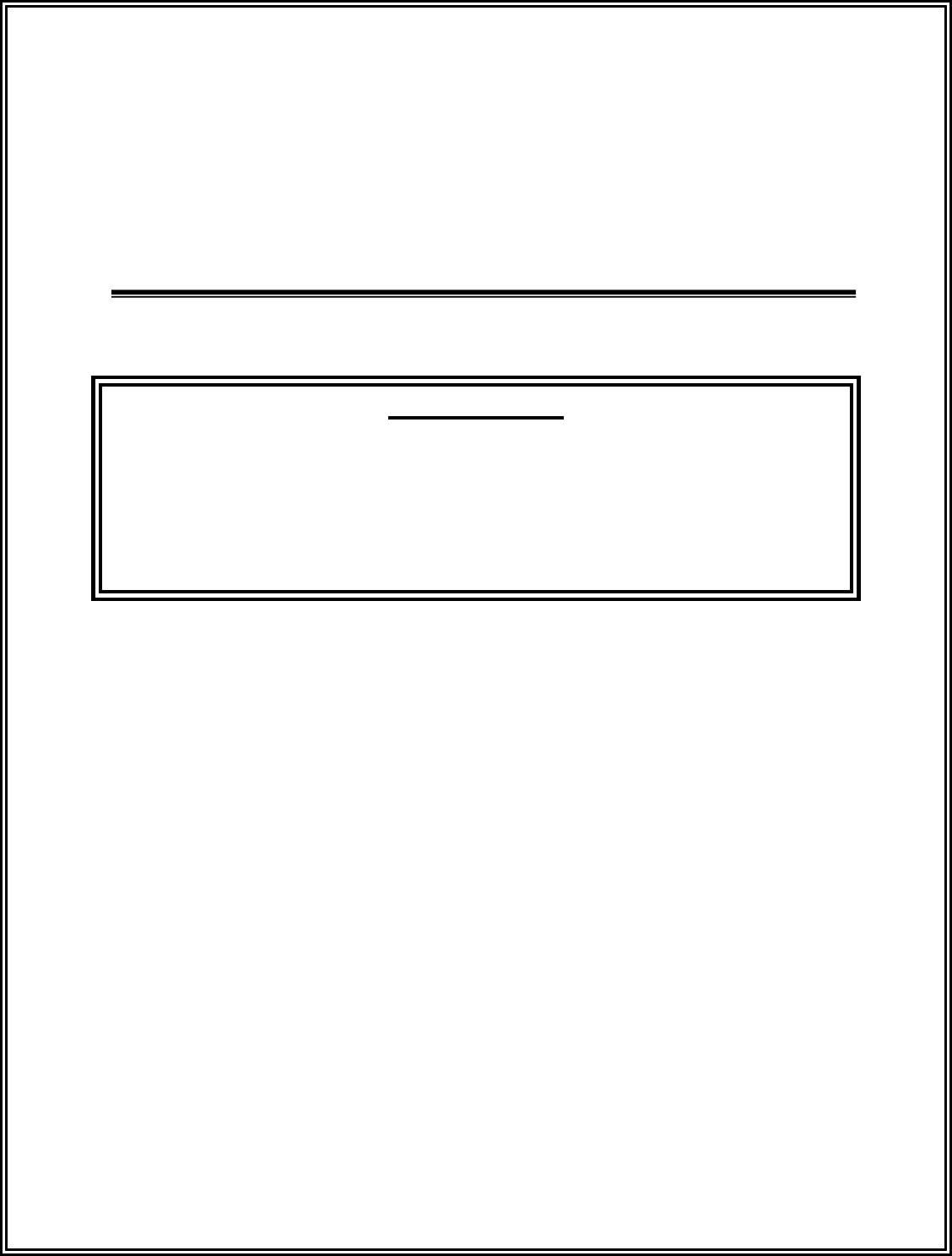
User Manual
Chapter 1:
The Accutech Systems
IMPORTANT:
No Security System can replace human vigilance. Creating a safe environment requires the
combined efforts of nursing, physicians, security, and patients. Global policies, procedures,
and processes on patient care should be discussed and disseminated. Education,
communication, and coordination are key. No level of security can replace an informed and
knowledgeable staff. Any electronic or physical security system should be considered as a
supplemental deterrent, but by no means an end-all.

User Manual The Accutech Systems 1-
1
The Accutech Systems
ES 2200 System
IS 3200 System
BR 4200 System
Cut Band System
Alarms
How Accutech Systems Work
Addressing Alarms
Escorting
Throughout this manual, when referring to the
various applications of the system, the term
“Tag” is used to represent all possible
applications of the system (i.e., a resident, a
patient, an infant, pediatrics, or an asset).
Furthermore, the terms “ingress” and “egress”
will be encountered. They are another way of
saying “coming and going” or “entering and
exiting” respectively.
The ES 2200 System is our platform system
from which all Accutech System’s are built.
Each subsequent system adds on to the system
before. Each system can be easily upgraded as
facility needs change and technology advances.
ES 2200 System
The function of the ES 2200 System is to alert
facility personnel of the possible egress of a
monitored resident.
The ES 2200 can be utilized for special care
residents suffering from wandering malady or
tendencies of straying into unauthorized areas or
leaving a facility, pediatric patients, asset
security, and/or infant security. The system is
designed so that each monitored zone is a stand-
alone system.
The ES 2200 System works with ES 2200
System Tags (LT/SB22) and consists of:
a Controller
a Transmit Antenna*
a Receiver
a Magnetic Switch (door zones) or
a Passive Infrared Reader (PIR)
(hallway and elevators zones)
a Keypad
a Local Alarm*
* Multiple options are available for these
components. In most cases a Tx Wand Antenna is
used for the Transmit Antenna, however, in special
circumstances a variation of the Tx Wand antenna
can be used. Furthermore, there are various options
available for a Local Alarm.
When a Tag enters a monitored zone, the system
can automatically:
lock doors
deactivate elevators
sound alarms
flash strobe lights
trigger visual displays
(e.g., SAPs, GDPs, as well as PCs in IS
3200 and BR 4200 Systems)
The Controller can be mounted on the wall near
the point of egress or can be mounted out of
sight in an utility or equipment closet.
A Tx Wand Antenna is mounted on the wall at
the point of egress.
The Receiver is mounted internally (inside the
Controller) when the Controller is located at the
zone or externally (near the monitored zone)
when the Controller is located remotely.

1-2 The Accutech Systems Us
er Manual
Virtually any hallway, doorway, stairwell, or
elevator can be made to sense a Tag and then
trigger audial and/or visual alarms to prompt a
staff response.
All cable used in Accutech Systems is plenum-
rated.
By adding options, most egress opportunities
can be eliminated without restricting staff,
visitors, and non-monitored residents movement.
Additional options that further enhance your
ability to prevent unescorted egress include:
Magnetic Lock(s)
Elevator Deactivation Unit(s)
Central Alarm
Door Ajar alarm
Loiter alarm
Staff Alert Panels (SAPs)
Graphic Displays Panels (GDPs)
Secure Tag Activator/Deactivator
(STAD)
STADs are capable of reading a Tag’s low
battery indicator and can assist in finding lost
Tags. However, ES 2200 Tags and/or VP
conversion Tags do not support the low battery
indicator.
IS 3200 System
The IS 3200 System is the ES 2200 System plus:
a computer(s)
the Accutech Software
a Tag Test Station
a Multiplexer(s)
a Power Supply(s)
The IS 3200 System uses IS 3200 System Tags
(LT/SB32) that are placed on the monitored
resident or asset. Once assigned, the computer
associates a name, room number, and any other
pertinent information about the resident/asset
with that Tag.
BR 4200 System
The BR 4200 System is intended for infant
security.
The function of the BR 4200 System is to alert
facility personnel of the possible abduction of an
infant.
The BR 4200 System is the IS 3200 System
plus:
BR 4200 Auxiliary Receivers
(as needed)
The BR 4200 System uses BR 4200 System
Tags (BR42) that are placed on infants. In
addition to the functionality of IS 3200 System
Tags, BR 4200 System Tags feature Intelli-Band
Technology, which will trigger alarms (audial
and/or visual) if the band is removed or
tampered with. Additional optional alarms (local
or central) can announce when a band alarm
incident has occurred.
Cut Band System
The function of the Cut Band System is to alert
facility personnel of the possible adduction of a
child. The Cut Band System is the BR 4200
System with Cut Band Tags, which will trigger
alarms (visual and/or audial) if the band is cut.

User Manual The Accutech Systems 1-3
Alarms
Egress
Door Ajar (Optional)
Loiter (Optional)
Supervisor
Band Alarm (BR 4200 systems only)
NOTE: In this manual, Egress alarms are
referred to as “Alarms.” Other alarm types are
referred to by name (i.e., Door Ajar, Loiter,
Supervisor, Band Alarm).
Egress
An alarm (i.e., an Egress alarm) occurs
whenever a Tag enters a monitored zone and the
door is opened or a PIR is tripped.
Door Ajar (Optional)
A Door Ajar alarm occurs when a door is open
for longer than the preset time (adjustable).
Loiter (Optional)
A Loiter alarm occurs when a Tag lingers in a
monitored zone for longer than the preset time
(adjustable).
Supervisor
A Supervisor alarm occurs when the TX or RX
performance of the system has been altered due
to tampering or inadvertent acts such as cut
wires, antenna damage.
Band Alarm (BR 4200 systems only)
A Band Alarm occurs when a BR42 Tag band is
loosened, cut, saturated, removed, or tampered
with.
How Accutech Systems Work
Double-conditioning
Door zones
Elevator zones
Hallway zones
This section explains how Accutech Systems
react to a Tag entering a monitored door,
elevator, or hallway as well as alarm definitions.
Double conditioning
At most zones, two conditions are required to
generate an alarm. For example, at a door zone,
a Tag must be detected in the zone and the door
opened or, in hallway zones, a Tag must be
detected in the zone and PIR detection to
generate an alarm. Double conditioning (set
during installation) helps prevent nuisance
alarms.
Door zones
When a Tag enters a monitored door zone, the
system will detect the Tag. At that moment
(provided the door is closed, has a Magnetic
Lock(s), and the Lock is unobstructed) the
Magnetic Lock will energize, locking the door.
The Lock will remain locked for as long as the
Tag is in the monitored zone. When the Tag
leaves the monitored zone, the door will unlock
after an adjustable period of time (unless it is set
to latch when an alarm occurs).
Egress
If a Tag enters a monitored door zone with or
without a Magnetic Lock(s) and the door is
already open (or is opened while the Tag is in
the zone), the Accutech System will go into
alarm.
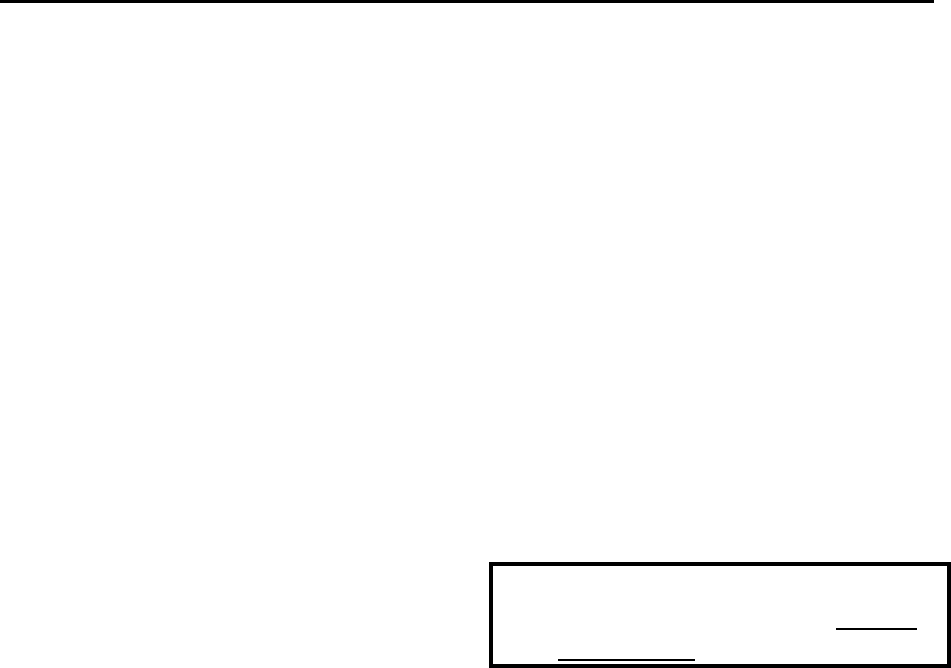
1-4 The Accutech Systems
User Manual
Loiter
An optional Loiter function is available to alert
staff personnel if a Tag is lingering in a
monitored zone. The time setting is adjustable
(10-110 seconds) and is factory set for
approximately 15 seconds.
Door Ajar
An optional Door Ajar function is also available
to alert staff personnel if the door in a monitored
zone has been held open for too long. The time
range can be set for immediate or from 10 to 110
seconds and is factory set for approximately 15
seconds.
Elevator zones
Elevator Deactivation Circuitry restricts the
wearer of a Tag from using an elevator.
Egress
If a Tag enters a monitored elevator zone, the
elevator’s call button on that floor will be
deactivated (Call buttons on other floors are
unaffected and no one is restricted from coming
to the floor).
When a Tag is in the zone and the elevator doors
are closed, the doors will remained closed.
When a Tag is in the zone (or approaches the
zone) and the elevator doors are open, the doors
will remain open and an alarm will sound.
If the elevator car is en route to the floor when a
Tag approaches the zone, the elevator will arrive
on the floor, the door(s) will open, and the
system will alarm.
Hallway zones
Egress
If a Tag enters a monitored hallway zone, the
system will detect the Tag and the PIR will
detect motion. The system can then sound
alarms, trigger visual displays and, in special
circumstances, lock nearby doors.
Addressing Alarms
Addressing Egress alarms
Addressing Door Ajar alarms
Addressing Loiter alarms
Addressing Supervisor alarms
Addressing Band Alarms
(BR 4200 systems only)
NOTE:
Whenever an alarm occurs, always go to the
alarm location to address the alarm.
Addressing Egress alarms
An Egress alarm occurs whenever a Tag enters a
monitored zone and the door is opened or a PIR
is tripped.
When an Egress alarm occurs:
1. Go to the alarm location and take
appropriate action.
2. After taking appropriate action, you may
clear the alarm by entering a valid code
into the zone Keypad and, if necessary,
clear the alarm on the PC.
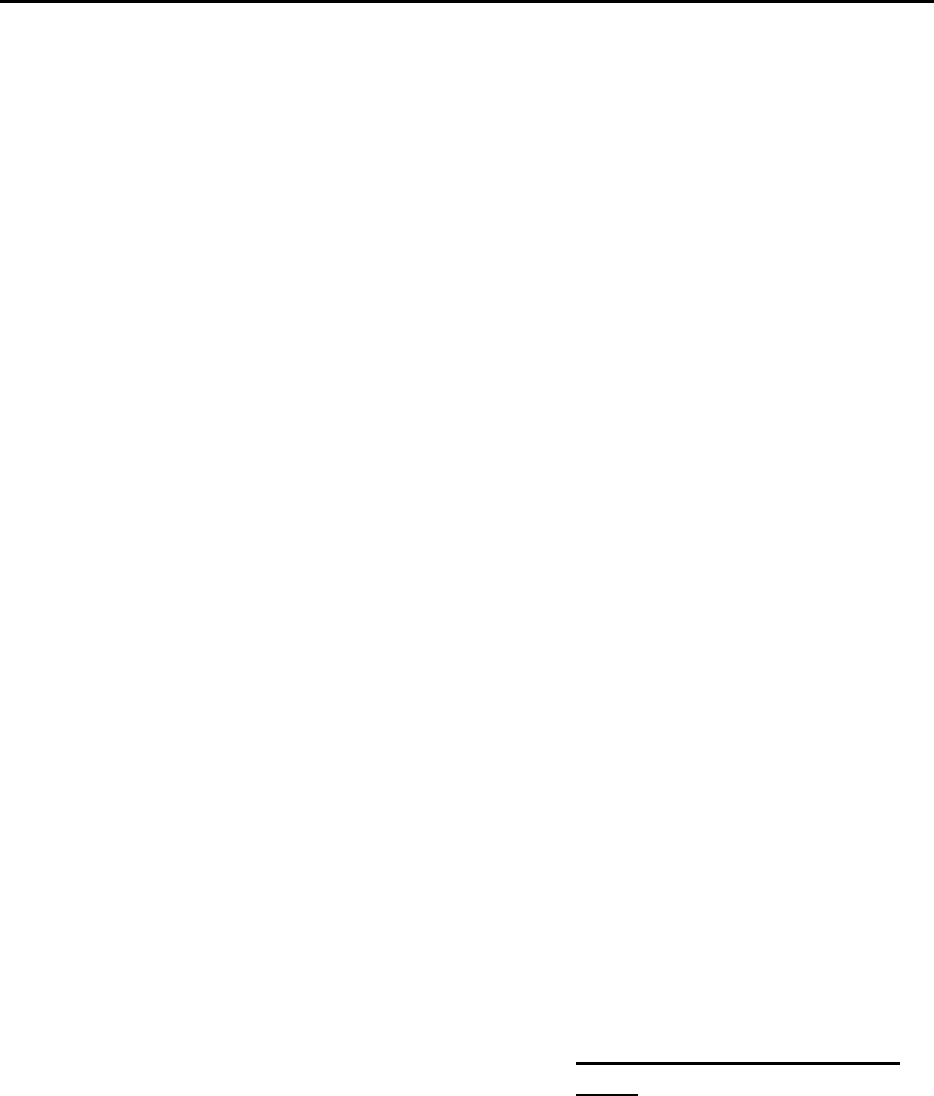
User Manual The Accutech Systems 1-
5
Addressing Door Ajar alarms
A Door Ajar alarm occurs when a door is open
for longer than the preset allotted time.
When a Door Ajar alarm occurs:
1. Go to the alarm location and check to
see if the door is propped open or not
completely closed.
2. Close the door completely.
3. The system may automatically reset or,
if necessary, enter a valid code into the
zone Keypad and/or clear the alarm on
the PC.
Addressing Loiter alarms
A Loiter alarm occurs when a Tag lingers in a
monitored zone for longer than the preset
allotted time.
When a Loiter alarm occurs:
1. Go to the alarm location and check the
following:
a. If a person is loitering in that
zone’s Tx Activation Field?
b. Is a Tag from an adjacent room
being activated by this zone? If
so, call your service technician
for help in addressing this issue.
c. Is there is a misplaced Tag in
the zone?
2. After removing the cause, the system
may automatically reset or, if necessary,
enter a valid code into the Keypad
and/or clear the alarm on the PC.
Addressing Supervisor alarms
A Supervisor alarm occurs when the
performance of the system has been altered due
to tampering or inadvertent acts such as cut
wires, antenna damage, or interference.
When a Supervisor alarm occurs:
1. Go to the alarm location and look for
visible damage to the Accutech
equipment.
2. Check for and remove any objects near
the zone equipment that may be causing
interference (metal carts, monitors or
other medical equipment as well as
personnel using wireless communication
devices).
3. If you locate and correct the cause, the
Supervisor alarm will cease. If
necessary, clear the alarm on the PC.
4. If not, call your service technician for
further assistance.
NOTE: Receiver-related supervise
events can be reset by the Keypad for
the duration of the supervise interval.
This will silence the alarm for up to 16
hours.
Addressing Band Alarms
(BR 4200 systems only)
A Band Alarm occurs when a BR42 Tag band is
loosened, cut, saturated, removed or tampered
with.
When a Band Alarm occurs:
1. Locate and assure the safety of the
infant.
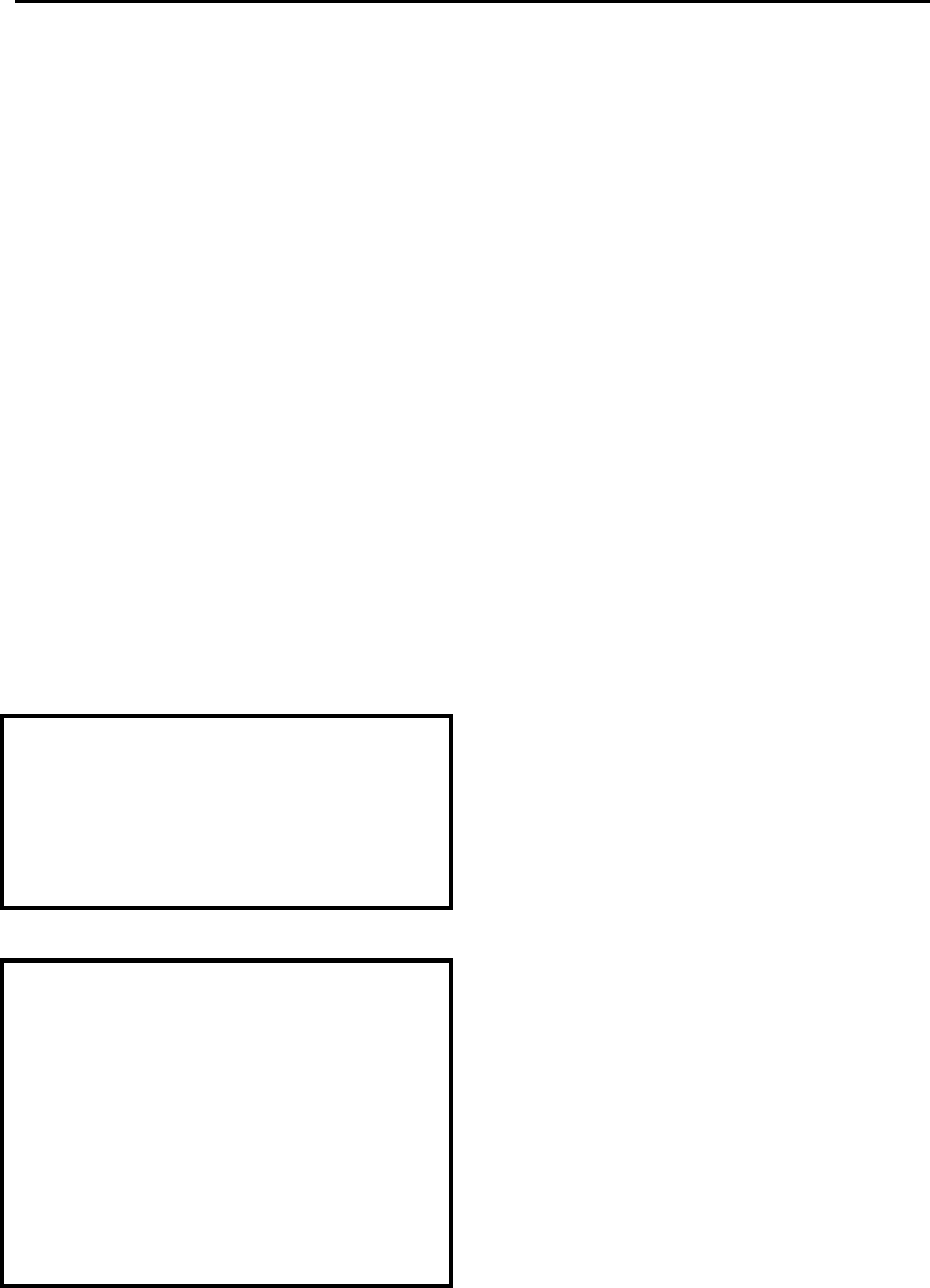
1-6 The Accutech Systems Us
er Manual
2. After locating the infant, if you can find
no obvious reason for the alarm, check
the following:
a. Is the band snug around the
infant’s extremity and the
conductive fiber stripes are in
good contact with the infant’s
skin? If not, snug up the band.
b. Is excess band material properly
trimmed? If not, trim
appropriately.
c. Is the band wet? If so, replace
the band.
d. Is the Cam Lock completely
closed? If not, snap it closed.
3. After verifying the above, enter a valid
code into any Keypad and, if necessary,
clear the alarm on the PC.
Escorting
DISCLAIMER:
The following instructions are intended as a
guidance document only. Each facility should
review these recommendations and modify as
necessary to meet their own unique security
requirements.
NOTICE:
While escorting Tags, be aware of “tailgating.”
Tailgating is the practice of Tags lingering near
a monitored zone (usually an exit point) until an
authorized escort passes through the zone then
immediately following behind through the zone.
To prevent tailgating, be aware of all traffic near
a monitored zone and once you are through the
monitored zone wait until the escort time has
timed-out before proceeding.
To escort Tags through a monitored zone, use
the following instructions:
1. Enter a valid code into the zone’s
Keypad. This will invoke the Keypad’s
Escort function. The Keypad’s Escort
function will allow the Tag to pass
through the monitored zone for the
designated Escort time. The duration of
the Escort function is adjustable from 0
to 98 seconds (factory set at 15 seconds).
2. Escort the Tag through the zone.
NOTE: For slower moving residents,
you may have to invoke the Escort
function again. However, if this is the
case, an alarm may sound. Therefore,
take into consideration the Escort time
duration at that zone. If the door handles
slow moving residents often, consider
extending the Escort time or using a
wheelchair to escort residents.
3. To prevent tailgating, once you are
through the zone wait until the escort
time has timed-out before proceeding
(the green LED will extinguish).
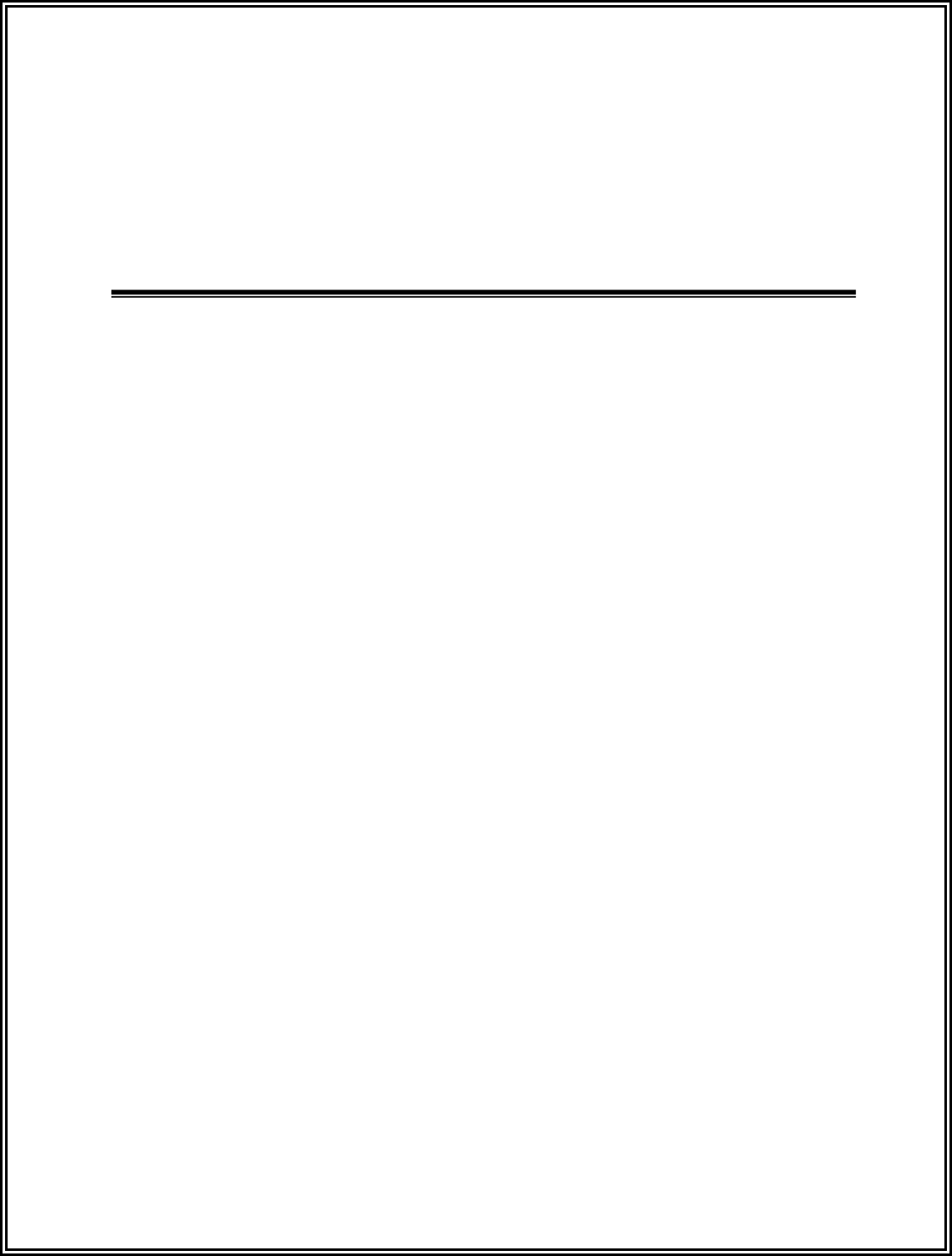
User Manual
Chapter 2:
System Components

User Manual System Components 2-
1
System Components
This section contains a brief description and a
simple graphic (not to scale) for each component
and its role in the Accutech System.
NOTE: Accutech reserves the right to substitute
comparable components.
Since each facility’s system is unique to its
particular needs, check off the components that
your system has.
ALL SYSTEMS COMPONENTS:
Controller
Receiver
Keypad
Magnetic Switch (with Door zones)
Passive Infrared Reader (PIR)
(with Elevator and Hallway zones)
TRANSMIT ANTENNA:
Tx Wand Antenna
Tri-Axis Antenna
TAGS:
ES 2200 System Tags (LT/SB22)
IS 3200 System Tags (LT/SB32)
BR 4200 System Tags (BR42)
Cut Band Tags
TESTERS:
Secure Tag Activator/Deactivator (S-TAD)
Tag Activator/Deactivator (TAD)
IS 3200 and BR 4200 COMPONENTS:
PC
Tag Test Station (TTS)
Accutech Software
Multiplexer
Power Supply
Auxiliary Receivers (BR 4200 only)
ALERT PANELS:
Graphic Display Panel (GDP)
Staff Alert Panel (SAP)
RESTRAINTS:
Magnetic Lock, 3000 Series
Magnetic Lock, 3101 Series
(Delayed Egress)
Elevator Deactivation
Automatic Door Deactivation
Band Alarm Lockdown
Fire Panel Interface (FPI)
(required for systems with Magnetic Locks
and/or Elevator Deactivation)
ALARMS:
Local Alarm
Multi-Tone Local Alarm
Central Alarm
Speakers
Voice Alarm
Strobe Light
ADDITIONAL OPTIONS:
Push Button Override (PBO)
Timer
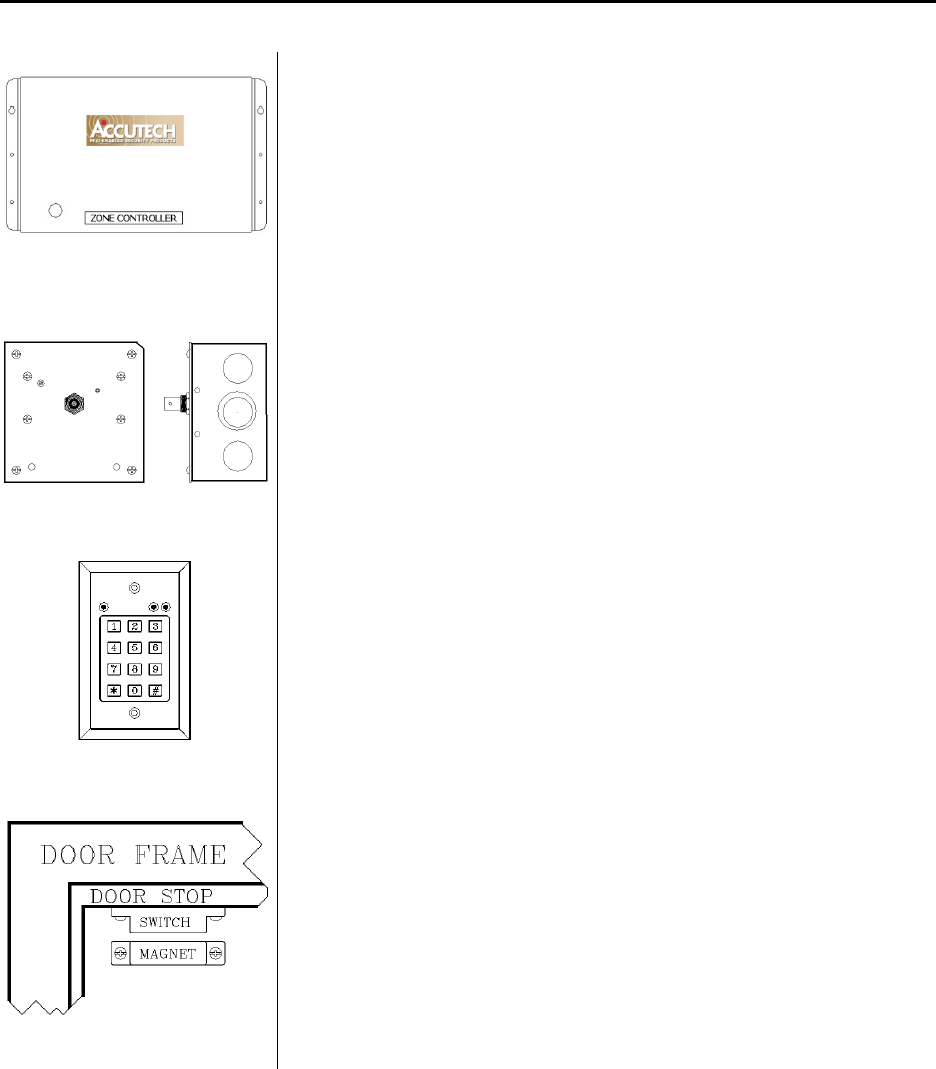
2-2 System Components User Manual
Figure 2.1 The Controller
Controller
The Controller (Figure 2.1) coordinates and controls all of the devices
and functions of the Accutech Security System.
Figure 2.2 Receiver
Receiver
The Receiver (Figure 2.2) picks up the signal from an activated Tag
and relays it to the Controller and the Multiplexer. Receivers can be
internally or remotely mounted near a monitored zone.
Figure 2.3 Keypad
Keypad
The Keypad (Figure 2.3) is used to escort residents or infants through a
monitored zone and to reset zone equipment once an alarm has
occurred.
Figure 2.4 Magnetic Switch
Magnetic Switch
The Magnetic Switch (Figure 2.4) is used on a door when alarm
activation is not desired unless the door is opened.
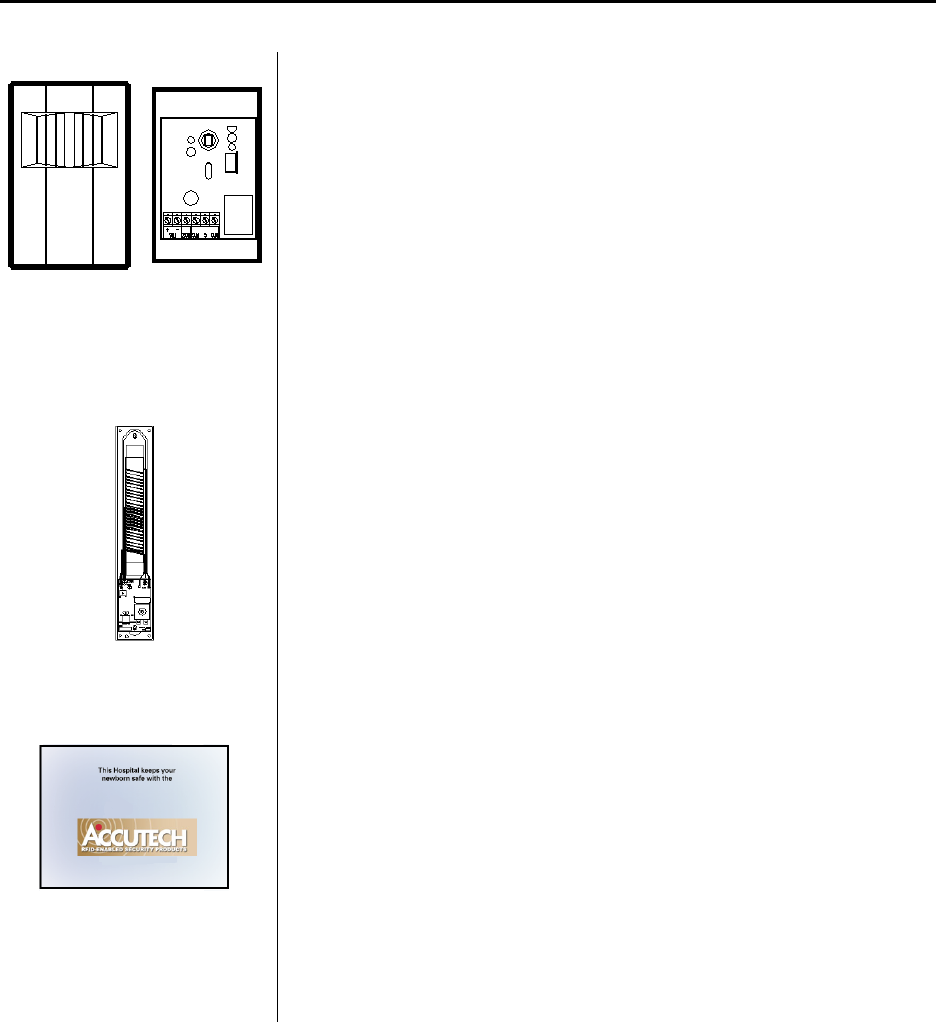
User Manual System Components 2-3
Figure 2.5
Passive Infrared Reader (PIR)
Passive Infrared Reader (PIR)
A Passive Infrared Reader (PIR) (Figure 2.5) is a device that uses a
infrared sensor to monitor doors, hallways, corridors, and
passageways.
Like the Magnetic Switch, the PIR is used in areas where alarm
activation is not desired immediately upon Tag detection. It can also
be used in hallways or other areas where a Magnetic Switch would not
be feasible.
Figure 2.6
Tx Wand Antenna
Tx Wand Antenna
The Tx Wand Antenna (Figure 2.6) generates a Tag-activating signal
near a monitored zone. This signal is referred to as the “Tx Activation
Field.”
Figure 2.7
Tri-Axis Antenna
Tri-Axis Antenna
The Tri-Axis Antenna (Figure 2.7) is a variation of the Tx Wand
antenna.
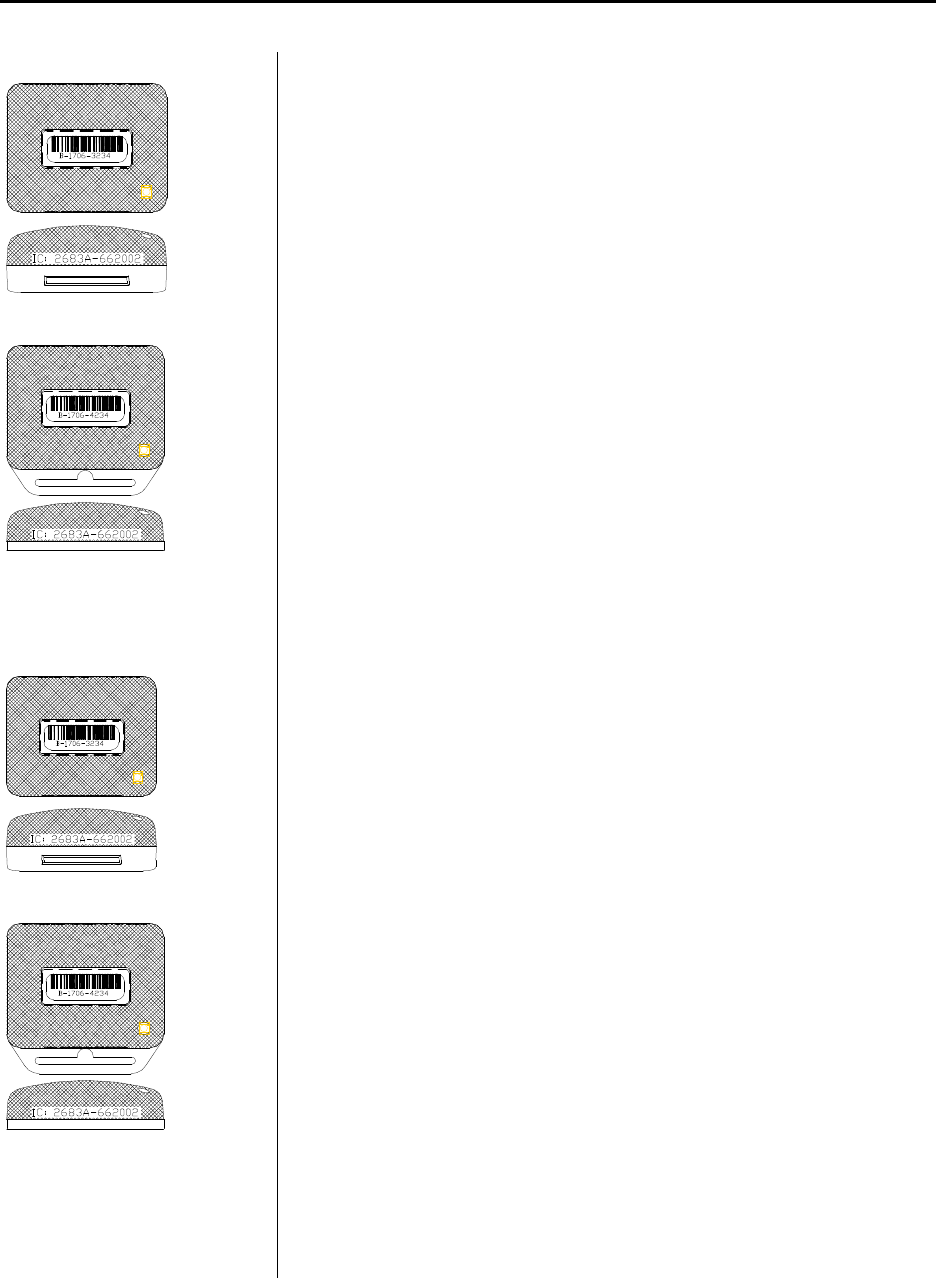
2-4 System Components User Manual
LT22
or
SB22
Figure 2.8
ES 2200 System Tag
(band not shown)
ES 2200 System Tags
The ES 2200 System Tag (Figure 2.8) is a small wristwatch-sized
device that is worn by a resident or attached to an asset.
Two models are available:
LT = Long Term resident care
SB = Slotted Back; to be used on infants and assets
When the Tag enters a monitored zone, the system detects the Tag and
responds by sending a signal via the Receiver to the Controller. This
information is processed by the Controller for appropriate control
action or response at the zone.
Tags are attached to residents/assets with a nylon-mesh-reinforced
vinyl band.
LT32
or
SB32
Figure 2.9
IS 3200 System Tag
(band not shown)
IS 3200 System Tags
In addition to the look and functionality of ES 2200 System Tags, IS
3200 System Tags (Figure 2.9) are assigned to a specific resident or
asset (via the Tag Test Station and a computer with the Accutech
Software). The computer then associates a name, room number, and
any other helpful comments about the resident or asset with that Tag.
When the Tag enters a monitored zone, the system detects the Tag and
responds by sending a signal via the Receiver to the Controller and the
Multiplexer. This information is processed by the Controller for
appropriate control action or response at the zone while the
Multiplexer sends the information to a computer with the Accutech
Software and/or to Graphic Display Panels (GDPs). This information
is processed by the Controller and the Multiplexer for appropriate
control action or response at the zone.
Tags are attached to residents/assets with a nylon-mesh-reinforced
vinyl band.
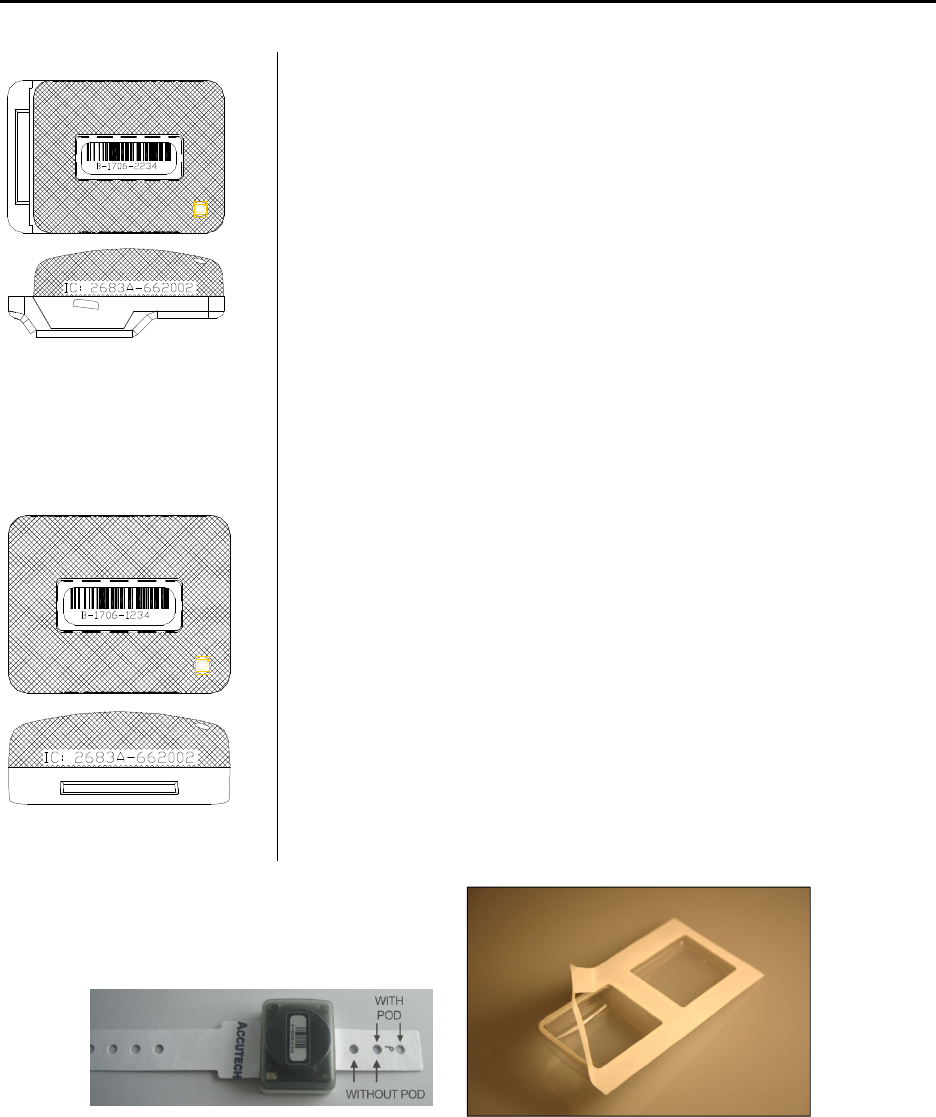
User Manual System Components 2-5
BR42
Figure 2.10
BR 4200 System Tag
(band not shown)
BR 4200 System Tags
In addition to the functionality of an IS 3200 System Tag, the BR 4200
System Tag (Figure 2.10) will alarm if the band is loosened, cut,
saturated, removed or tampered with.
BR 4200 System Tags are attached to infants with a conductive-fiber-
striped cloth band.
Figure 2.11
Cut Band Tag
Cut Band Tag
Similar to the functionality of a BR 4200 System Tag, Cut Band Tags
(Figure 2.11) will alarm if the band is cut and is designed for use in
pediatrics applications.
Cut Band Tags are attached to patients with a band (Figure 2.13) and
plastic covers (Figure 2.14), are activated/deactivated using an
S-TAD unit, and contain a visual pulse LED. Using plastic covers with
a Cut Band Tag will significantly reduce the need for sanitizing the
Tag between applications.
Figure 2.13 Cut Band band Figure 2.14 Plastic Covers
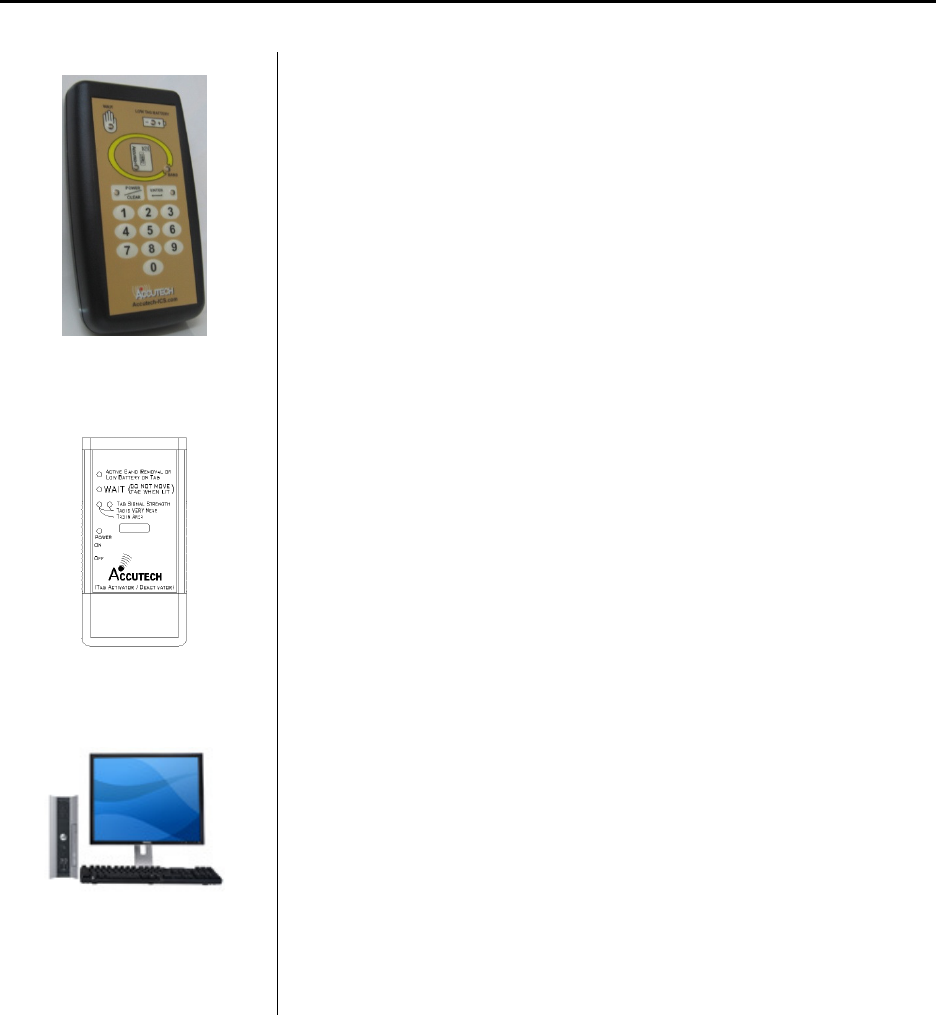
2-6 System Components User Manual
Figure 2.15
S-TAD
Secure Tag Activator/Deactivator (S-TAD)
The S-TAD (Secure Tag Activator/Deactivator) is used to check the
functionality of an Accutech Tag. Accutech Tags operate by internal
battery. Over the course of normal operation, Tags eventually lose
battery power and the Tags will need to be replaced. The S-TAD is
used to determine if a Tag has sufficient battery power to respond to
an activating signal.
Figure 2.16
The TAD
Tag Activator/Deactivator (TAD)
TAD (Tag Activator/Deactivator) is used to check the functionality of
an Accutech Tag. Accutech Tags operate by internal battery. Over the
course of normal operation, Tags eventually lose battery power and the
Tags will need to be replaced. The TAD is used to determine if a Tag
has sufficient battery power to respond to an activating signal. The
TAD was replaced by the S-TAD in late 2008.
Figure 2.17 PC
PC
A PC (Figure 2.17) is required for IS 3200 and BR 4200 Systems.
The Accutech Software is installed on each monitoring PC and is used
to display incoming event information. Using the facility’s floor plan
as the background, zone-specific icons (i.e., doors, elevators,
stairwells, hallways, and BR 4200 Auxiliary Receivers) are placed at
each monitored zone’s location and become animated when an alarm
occurs.
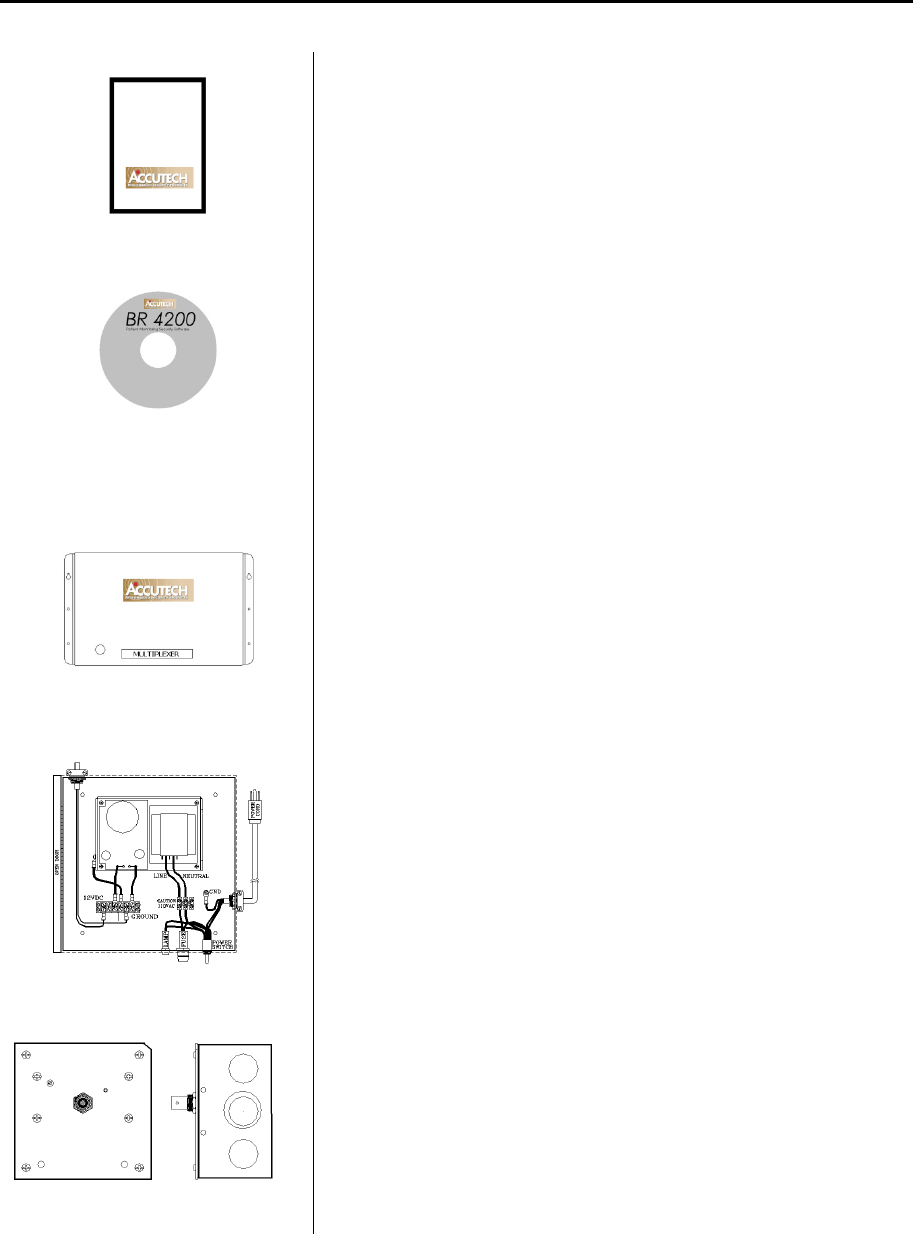
User Manual System Components 2-7
Figure 2.18 Tag Test Station
Tag Test Station (TTS)
The Tag Test Station (TTS) (Figure 2.18) is used for Tag
assignments, checking for low Tag battery, and verifying the Tag
number.
Figure 2.19
Accutech Software example
Accutech Software
The Accutech Software (Figure 2.19) is installed on each
monitoring PC and is used to display incoming event information.
Using the facility’s floor plan as the background, zone-specific
icons (i.e., doors, elevators, stairwells, hallways, and BR 4200
Auxiliary Receivers) are placed at each monitored zone’s location
and become animated when an alarm occurs.
Figure 2.20 Multiplexer
Multiplexer
The Multiplexer (Figure 2.20) relays event information sent from
the Controller and Receivers to Graphic Display Panels (GDPs)
and to PCs with the Accutech Software.
Figure 2.21 Power Supply
Power Supply
The inclusion of multiple peripherals into the Accutech System
may require more power than the Controller can provide. In these
cases, a Power Supply (Figure 2.21) is added to the system to meet
the additional power requirements.
Figure 2.22 Auxiliary Receiver
Auxiliary Receiver
The Auxiliary Receiver (Figure 2.22) picks up the signal from an
activated Tag and relays it to the Controller and the Multiplexer.
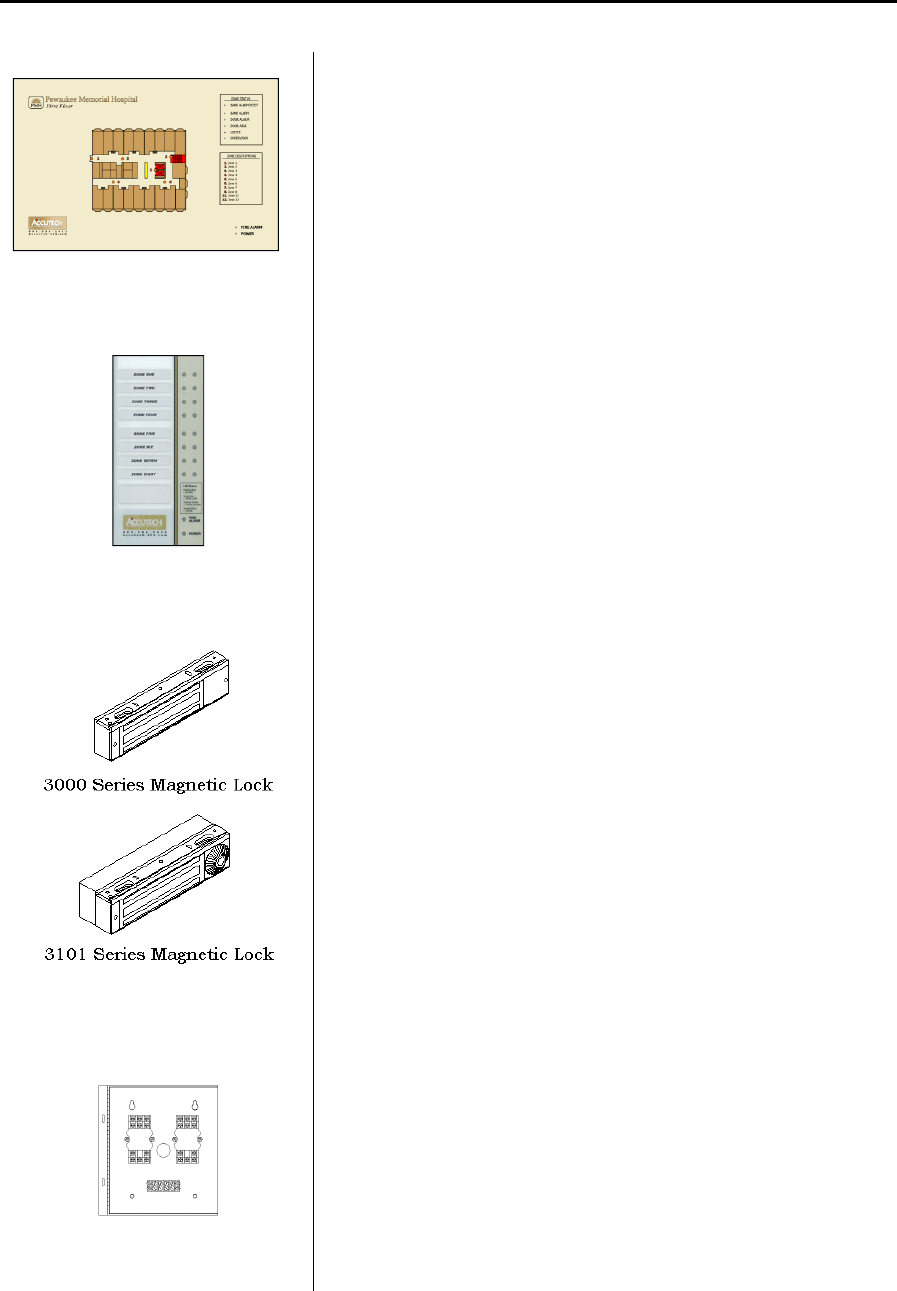
2-8 System Components User Manual
Figure 2.23
Graphic Display Panel (GDP)
Graphic Display Panel (GDP)
The Graphic Display Panel (GDP) (Figure 2.23) provides the staff
with a visual representation of the floor being monitored. GDPs
are custom-made to a facility’s floor plan and notify staff when
an alarm or event occurs in a monitored zone through a piezo
buzzer and alarm-specific LEDs.
Figure 2.24
Staff Alert Panel (SAP)
Staff Alert Panel (SAP)
The Staff Alert Panel (SAP) (Figure 2.24) notifies staff when an
alarm condition occurs in a monitored zone through a piezo
buzzer and alarm-specific LEDs.
Figure 2.25 Magnetic Locks
Magnetic Locks
Magnetic Locks (Figure 2.25) prevent unescorted egress.
The 3000 Series Magnetic Lock features:
1500-pound holding force
12V to 24V AC/DC
Unlocks instantly if the facility’s fire panel is activated
The 3101 Series Magnetic Lock features:
1200-pound holding force
12V AC/DC
Unlocks instantly if the facility’s fire panel is activated
NFPA101 Life Safety Code conformity (Delay Egress Circuitry)
a selectable nuisance delay
an Accutech-exclusive electromagnetic coil
an Accutech-exclusive firmware chip
Figure 2.26 Elevator Deactivation
Circuitry
Elevator Deactivation Circuitry
Elevator Deactivation Circuitry (Figure 2.26) is designed to
prevent someone (or an asset) wearing an Accutech tag from
using an elevator to leave a monitored floor. Using Relays
enclosed in the Elevator Deactivation Relay Cabinet, the Elevator
Company is able to interface with the Accutech System.
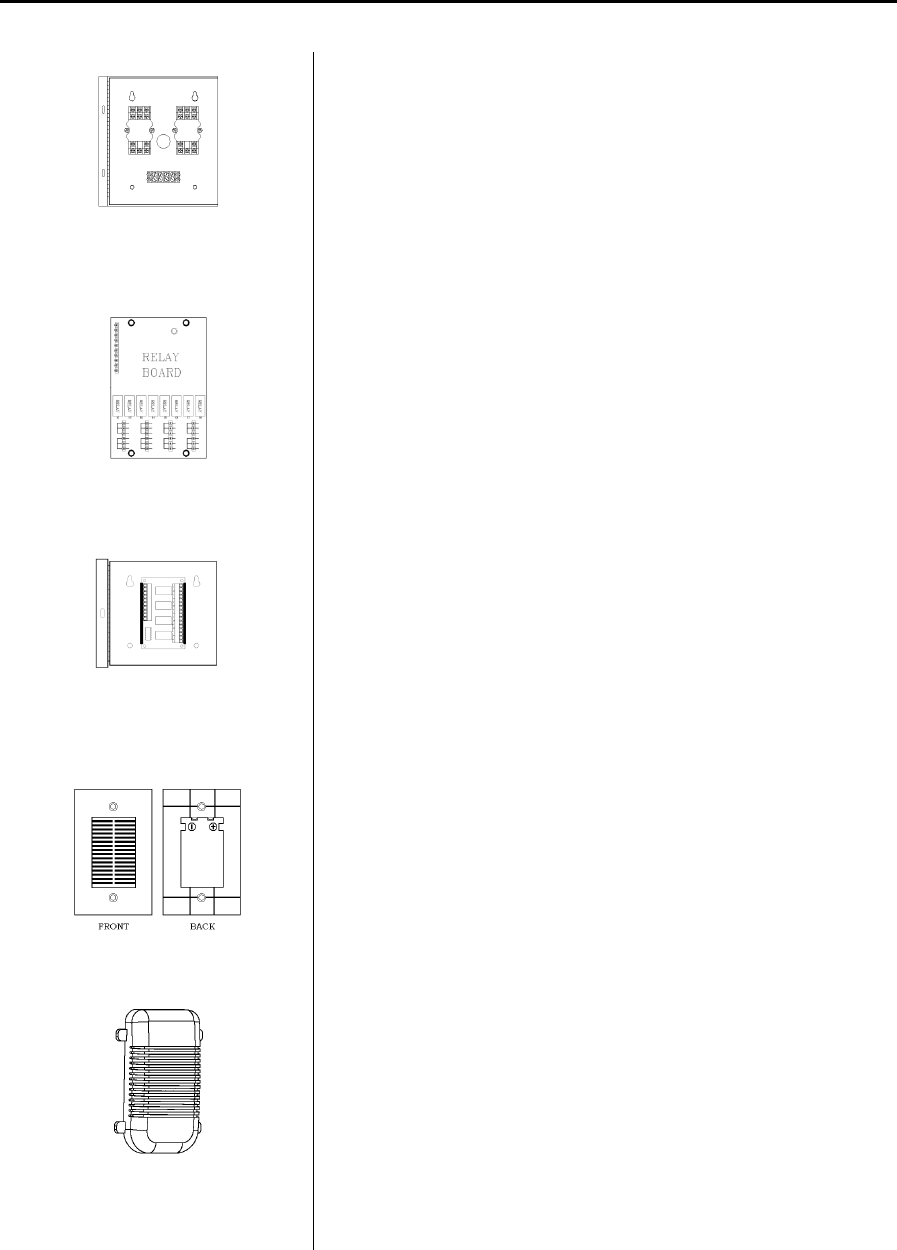
User Manual System Components 2-9
Figure 2.27
Automatic Door Deactivation
Automatic Door Deactivation
In automatic door applications (doors that open via a motion
sensor or push paddle) (Figure 2.27), the Accutech System can
deactivate this feature when a Tag enters a monitored zone’s Tx
Activation Field.
Figure 2.28
Band Alarm Lockdown
Band Alarm Lockdown
Band Alarm Lockdown (Figure 2.28) can engage specific facility
Magnetic Locks when a Band Alarm occurs.
Figure 2.29
Fire Panel Interface (FPI)
Fire Panel Interface (FPI)
The Fire Panel Interface (FPI) (Figure 2.29) ensures that in the
event of a fire alarm, the Magnetic Locks and Elevator
Deactivation Circuitry will disengage. Although the restraint
systems are disengaged, the system’s visual and audial alarms
will remain active.
Figure 2.30 Local Alarm
Local Alarm
The Local Alarm (Figure 2.30), a sounder, is intended to attract
attention near the monitored zone.
Figure 2.31
Multi-Tone Local Alarm
Multi-Tone Local Alarm (MTLA)
The Multi-Tone Local Alarm (MTLA) (Figure 2.31) can use 8
tone variations to attract attention near the monitored zone.
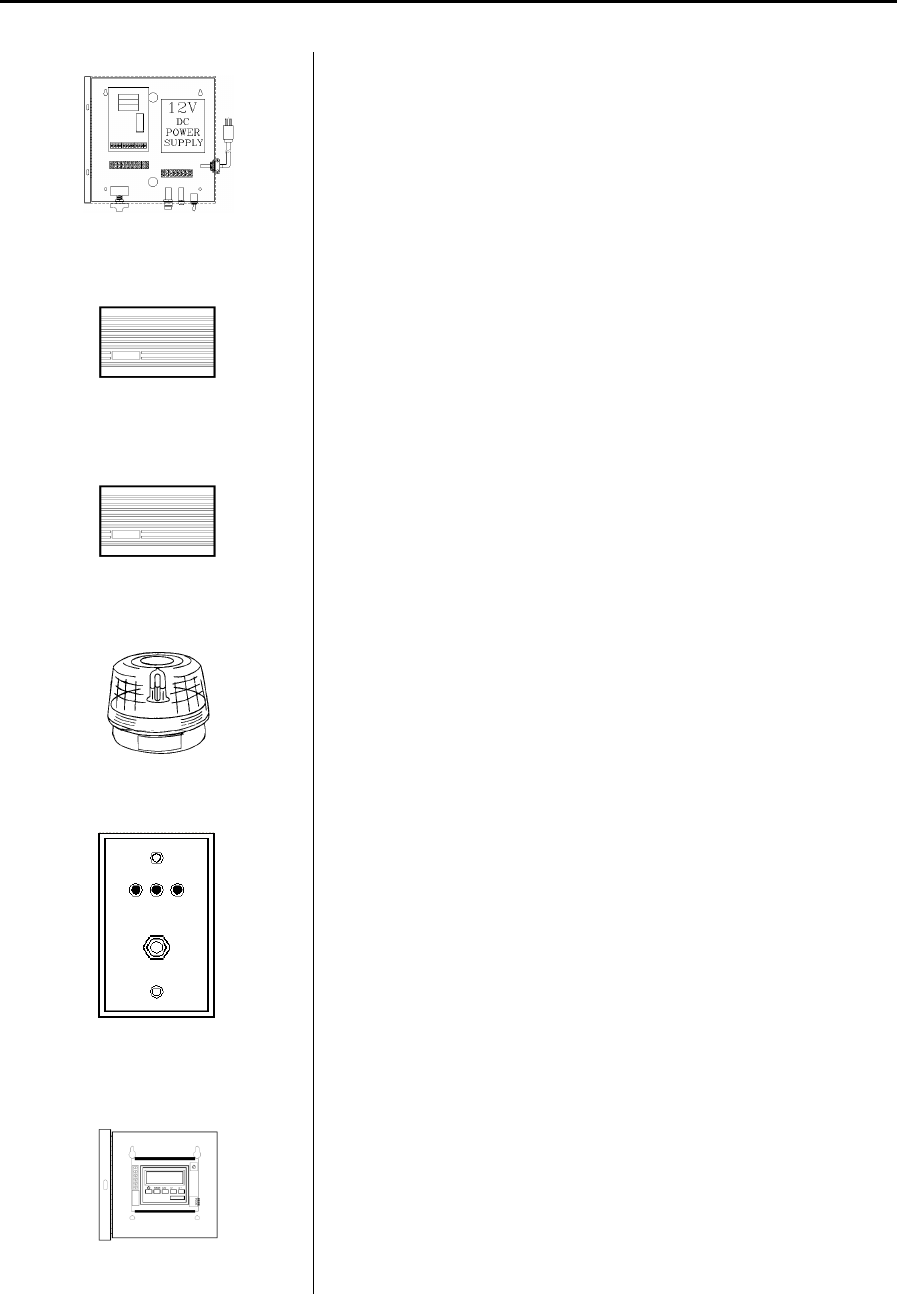
2-10 System Components User Manual
Figure 2.32 Central Alarm
Central Alarm
The Central Alarm (Figure 2.32) is a multi-tone alert. It consists of
a tone generator that drives Speakers (up to 5) located throughout
a facility. There are eight different tones available. You may
choose to assign a separate tone for each zone, share the same
tone for adjacent zones, or use one tone for all zones.
Figure 2.33 Speakers
Speakers
The 8-ohm Speakers (Figure 2.33) provided by Accutech are used
in conjunction with the Central Alarm.
Figure 2.34 Voice Alarm
Voice Alarm
The Voice Alarm (Figure 2.34), located at a monitored zone, will
repeat a recorded message (up to 20 seconds) continuously when
an alarm occurs.
Figure 2.35 Strobe Light
Strobe Light
A Strobe Light (Figure 2.35) can be used as another alarm
notification device.
Figure 2.36
Push Button Override (PBO)
Push Button Override (PBO)
The Push Button Override (PBO) (Figure 2.36) triggers the
Keypad’s Escort function; this option allows free access through
a monitored door from the non-Keypad side of the door.
Figure 2.37 Timer example
Timer
A Timer (Figure 2.37) allows the user to engage or disengage
certain system functions on a time schedule.
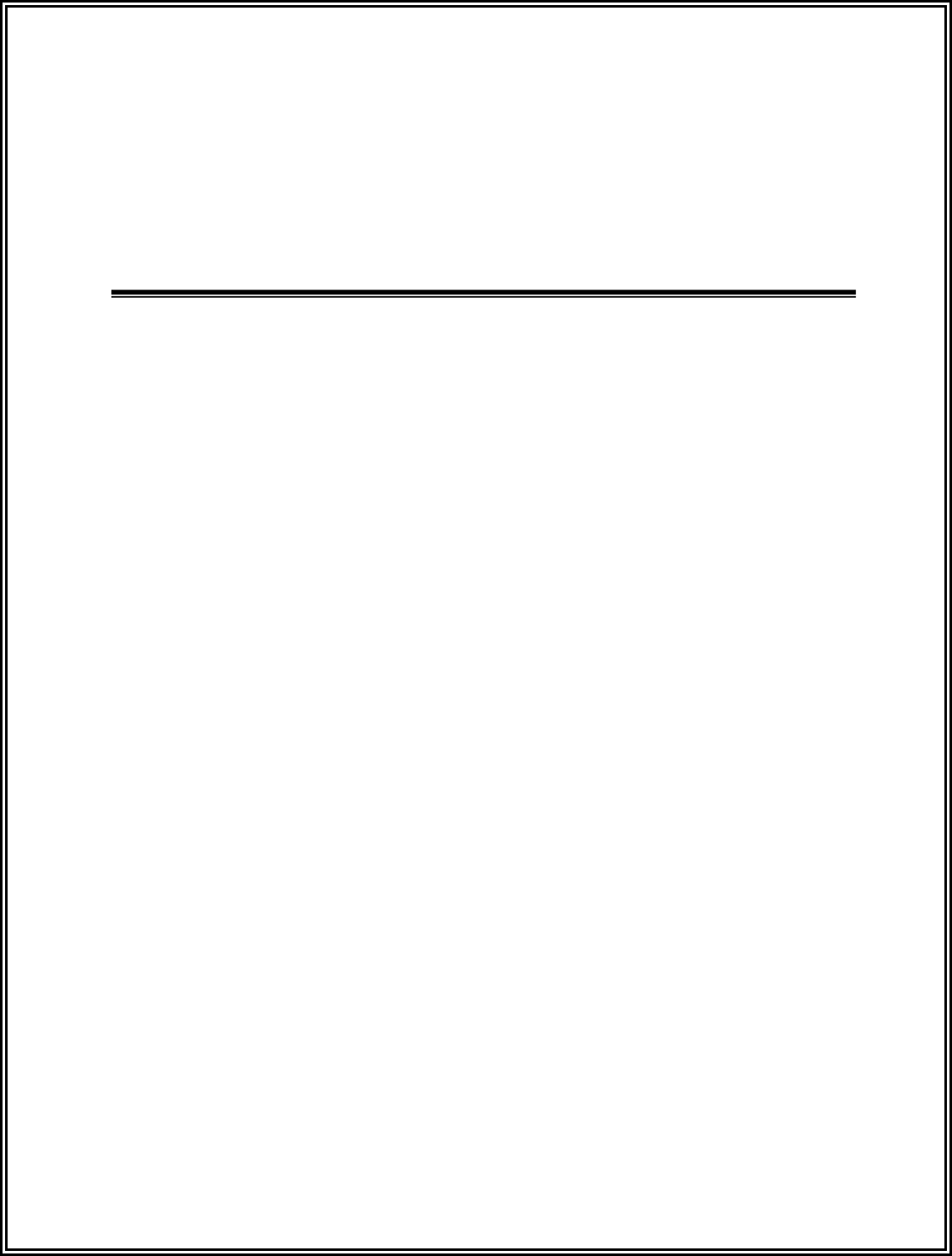
User Manual
Chapter 3:
Tags
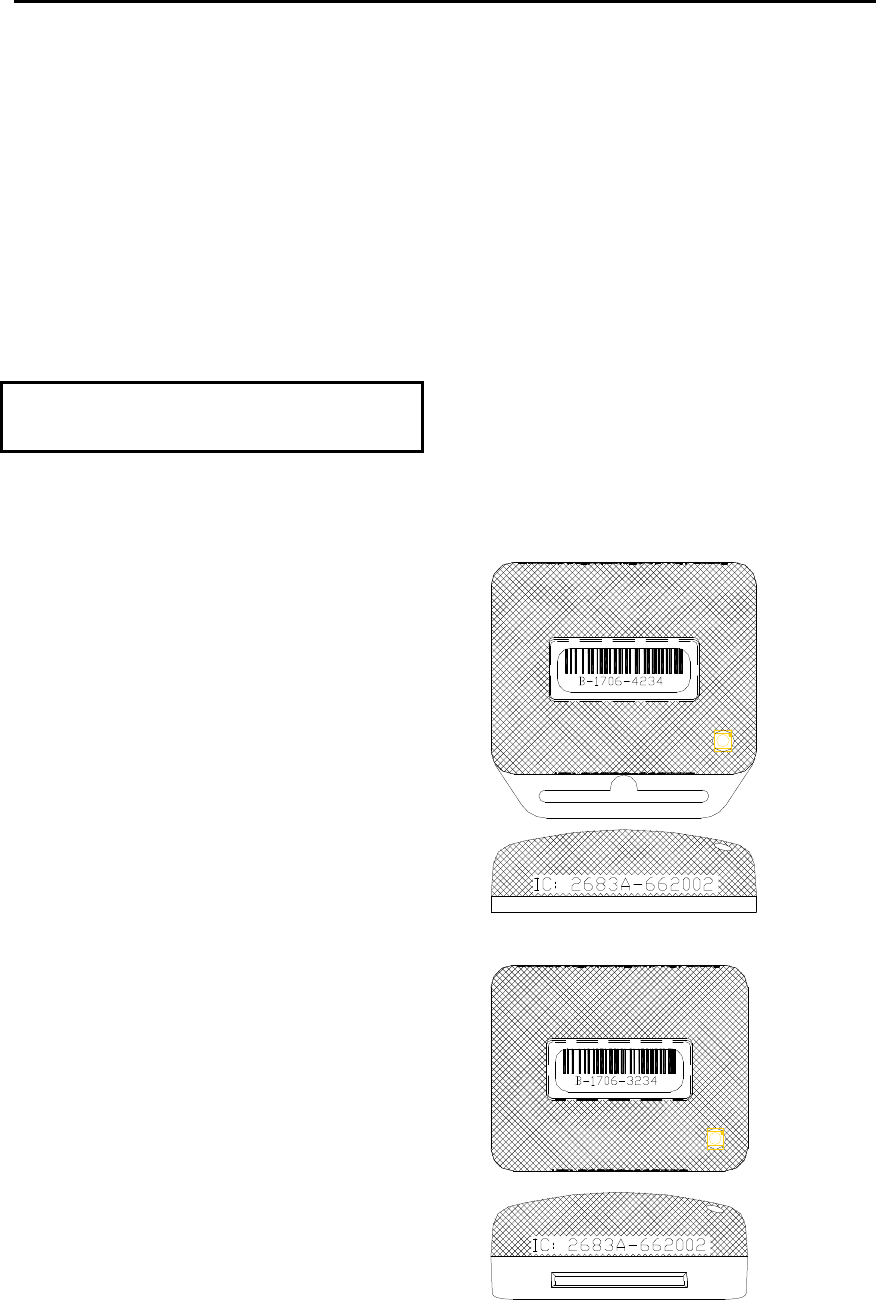
User Manual Tags 3-1
Tags
ES 2200 System Tags
IS 3200 System Tags
BR 4200 System Tags
Cut Band Tags
Tag barcodes
Visual Pulse LED
Tag base color chart
LED Tag
Attaching Tags
Tag and Band Maintenance
Note: The Tag Model CB’s Pod (plastic
covers) has not been evaluated by UL.
ES 2200 System Tags
ES 2200 System Tags (Figure 3.1 and 3.2) are
small wristwatch-sized devices worn by a
resident or attached to an asset. When a
resident or patient enters a Tx Activation
Field, the Tag sends a signal to the zone
Controller, via the Receiver. The zone
Controller processes this information for
appropriate control action or response (such
as sounding alarms, locking doors, and/or
deactivating elevators).
ES System 2200 Tags also contain a visual
pulse LED. Tags are activated/deactivated
with an S-TAD unit. Available in SB
(slotted back) or LT (long term) tag case
styles.
The ES 2200 System Tag band is made of
nylon-reinforced vinyl with nylon mesh. The
band is designed to resist tearing caused by
pulling or chewing on the band. However, if
the band becomes frayed or torn it will need
to be replaced. In long-term applications, the
band should be replaced periodically for
cleanliness.
IS 3200 System Tags
In addition to the functionality of an ES
2200 System Tag, IS 3200 System Tags
(Figure 3.1 and 3.2) are preprogrammed with
a number and assigned to a specific resident
or asset (via the Tag Test Station and
Accutech Software). Once assigned, the
computer associates a name, room number
and any other pertinent information about
the resident/asset with that Tag number.
IS 3200 System Tags also contain a visual
pulse LED. Tags are activated/deactivated
with an S-TAD unit. Available in SB
(slotted back) or LT (long term) tag case
styles.
Figure 3.1 SB Tag case style
Figure 3.2 LT Tag case style
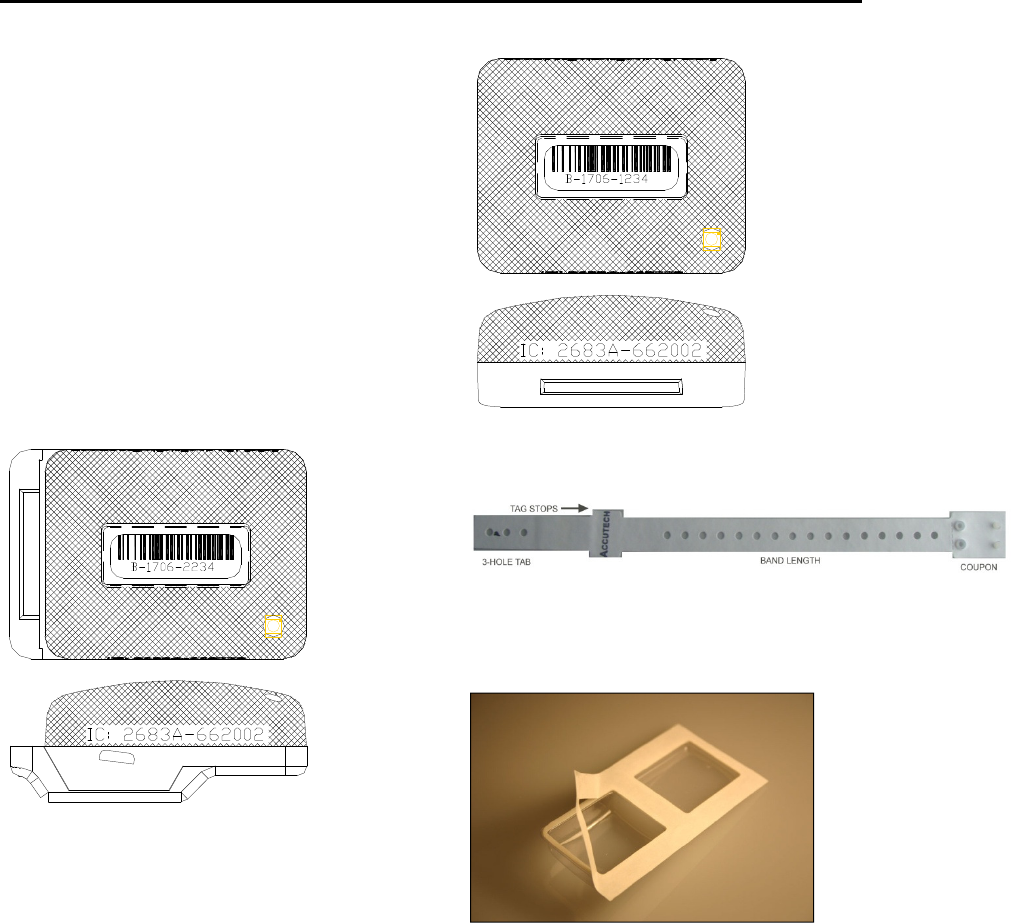
3-2 Tags User Manual
BR 4200 System Tags
In addition to the functionality of an IS 3200
System Tag, BR 4200 System Tags (Figure
3.3) will alarm if the band is removed or
tampered with in any way.
BR 4200 System Tags also contain a visual
pulse LED. Tags are activated/deactivated
with an S-TAD unit.
BR 4200 System Tags are attached to
infants with a conductive-fiber-striped cloth
band.
Figure 3.3 BR 4200 System Tag
Cut Band Tags
Similar to the functionality of a BR 4200
System Tag, Cut Band Tags (Figure 3.4) will
alarm if the band is cut, removed, or
tampered with in any way and is designed
for use in pediatric applications. Cut Band
Tags also contain a visual pulse LED.
The band (Figure 3.5) accommodates
various wrist/ankle lengths.
Using a pod (Figure 3.6) with a Cut Band
Tag will significantly reduce the need for
sanitizing the Tag between applications and
is water-resistant during use.
Figure 3.4 Cut Band Tag
Figure 3.5 Cut Band Band
Figure 3.6 Cut Band Pod

User Manual Tags 3-3
Tag barcodes
Tag barcodes (Figure 3.7) contain a Tag’s
manufacturing history.
Figure 3.7 Tag barcode example
The coding scheme is as follows:
M-WWYY-TSSS
”M” is the manufacturer designator.
”WWYY” is the date code.
(“1706” would mean the 17th week of 2006)
”T” is the tag type designator.
1 is for CB (Cut Band)
2 is for BR (Band Removal)
3 is for LT (Long Term)
4 is for SB (Slotted Back)
”SSS” is the serial number for that tag type
manufactured during that week.
Visual Pulse LED
The Visual Pulse LED indicates the Tag’s
current mode (see Table 3.1)
Table 3.1 Visual Pulse LED status
LED Light Pattern off on Tag LED Status
LT, SB Tags
None Tag is off.
Active, not in zone
Active, in zone
BR, CB Tags
None Tag is off.
Active, not in zone,
non-Band Alarm
Active, in zone
(may be in Band Alarm)
Active, not in zone
Band Alarm mode,
Tag base color chart
Tag tops are smoke-colored while the Tag
base color will vary based upon Tag type
(see Table 3.2).
Table 3.2 Tag base color chart
Tag Type Base Color
CB White
SB Gray
LT Gray
BR Yellow
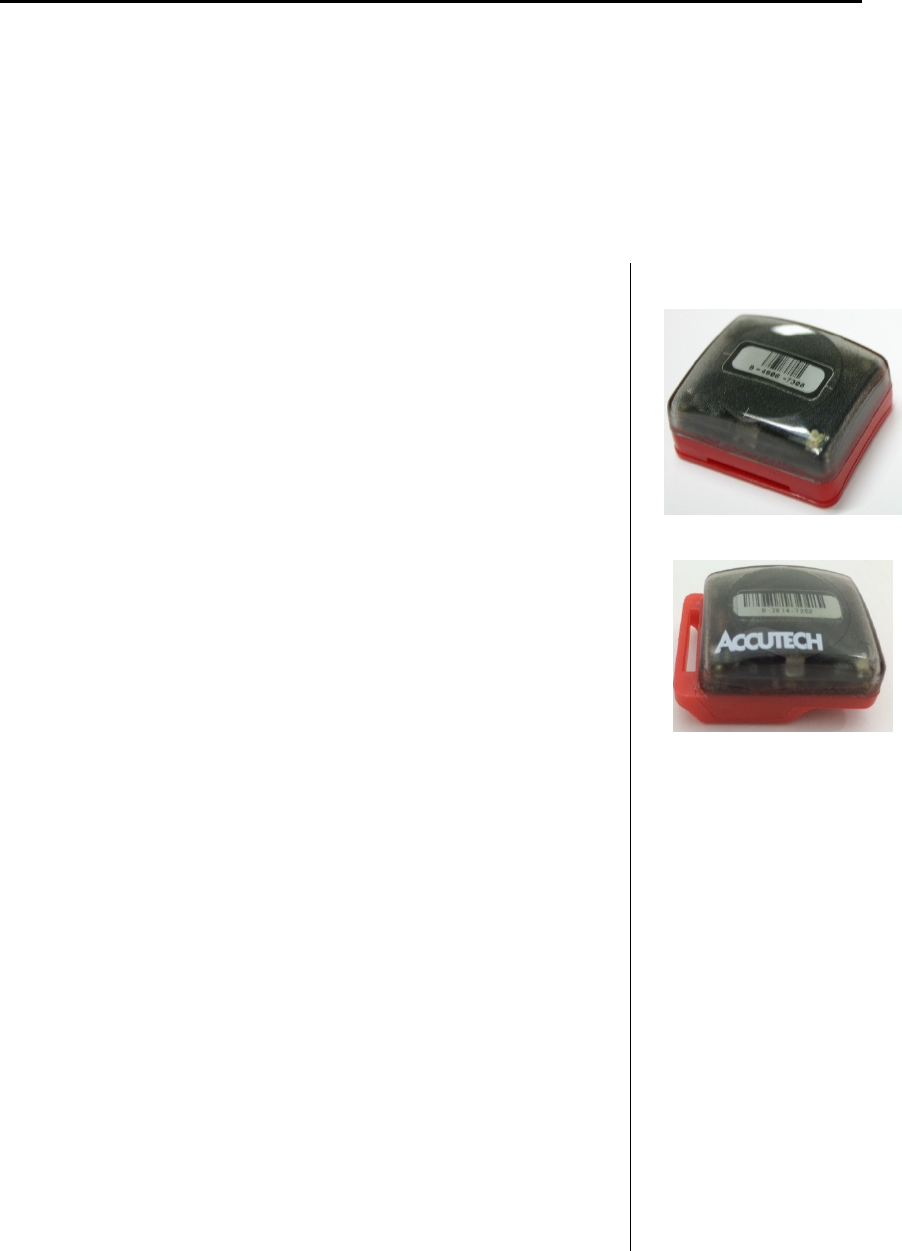
3-4 Tags User Manual
Test Tag
Verifying Proper Zone Coverage
Identifying Foreign Tag-Activating Sources
DISCLAIMER: Due to each facility’s unique environment, an LED Tag cannot give an exact measurement of zone
coverage; it can only give an estimation of zone coverage.
Verifying Proper Zone Coverage
An LED Tag (Figure 3.8) is used to verify proper zone coverage during
installation, adjustment, or testing of a monitored zone.
Proper zone coverage fully protects the intended area (door, elevator, hallway,
or any other passageway) without extending into other areas (in front, in back,
on sides, above, and beneath the intended area).
Monitored zones emit a Tag-activating signal called the Tx Activation Field.
When a Tag enters a zone’s TX Activation Field, the system will detect the
Tag and take appropriate action response.
A Test Tag can detect a zone’s TX Activation Field without causing alarms
making it a quick and easy way to verify proper zone coverage. This is not
only useful in ensuring complete zone coverage but also in locating areas
where a TX Activation Field may be extending into common areas and causing
nuisance alarms.
Figure 3.8 The ES/IS (top) and
BR Test Tag
To verify proper zone coverage with an Test Tag, use the following
instructions:
1. Using an S-TAD, activate the Test Tag.
NOTE: Once activated the Test Tag’s LED will change state when it is
in a Tx Activation Field. Therefore, to verify the Test Tag is active,
turn on the TAD and place the Test Tag near it. The Test Tag’s LED
will change state since an S-TAD has a small TX Activation Field
associated with it.
2. With the Test Tag in your hand, slowly approach each zone at various
angles and orientations. The Test Tag’s LED will change state when it
detects the zone’s TX Activation Field.
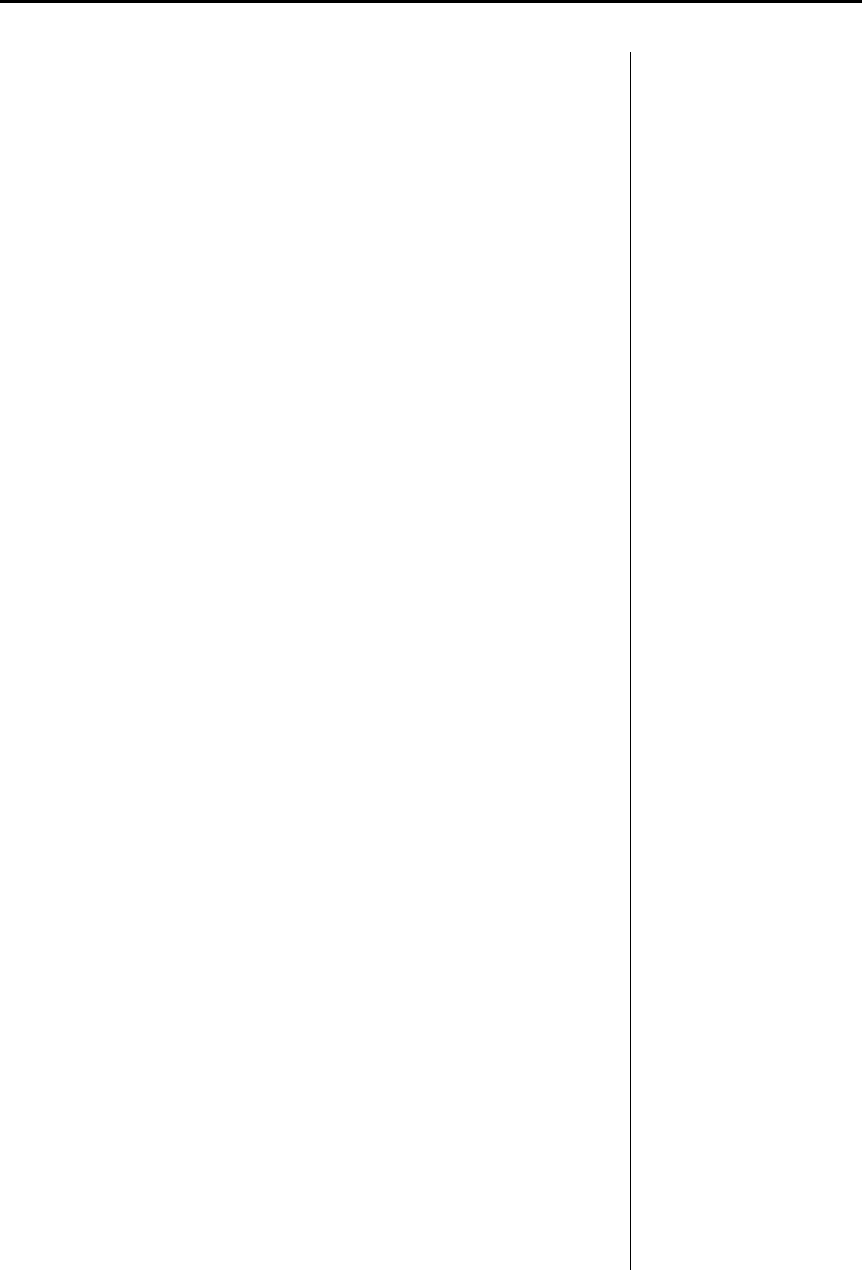
User Manual Tags 3-5
3. If you find that a zone’s coverage is at unacceptable levels (too small,
too big, extends too far in one direction), look for factors that may be
affecting the zone (food carts, medical equipment, and/or building
construction).
4. If you cannot locate any immediate causes, contact your system
maintenance technician for further assistance.
5.
When finished, deactivate the Test Tag using an S-TAD.
Identifying Foreign Tag-Activating Sources
In addition to verifying proper zone coverage, an LED Tag (Figure 3.3) can be
used to identify foreign Tag-activating sources to help preserve your Tags’
battery life and prevent nuisance alarms.
Monitored zones emit a Tag-activating signal called the TX Activation Field.
When a Tag enters a zone’s Tx Activation Field, it is activated. The system
detects the activated Tag and takes appropriate action response.
However, there are sources that can activate a Tag other than a TX Activation
Field. When Tags are activated by these “foreign” sources, battery life is
depleted and/or nuisance alarms can be caused. Therefore, identifying these
sources will prolong Tags battery life and prevent nuisance alarms.
To identify activating sources with a Test Tag, use the following instructions:
1. Using an S-TAD, activate the Test Tag.
NOTE: Once activated the Test Tag’s LED will change state when it is
in a TX Activation Field. Therefore, to verify the Test Tag is active,
turn on the TAD and place the Test Tag near it. The Test Tag’s LED
will change state since an S-TAD has a small TX Activation Field
associated with it.
2. With the Test Tag in your hand, slowly investigate each area for
possible activating sources*. The Test Tag’s LED will illuminate
when it detects an activating source. Note each activating source and
keep Tags away from those sources.
3. When finished, deactivate the Test Tag using an S-TAD.
*Some activating sources can be:
Computer Monitors
Unshielded computer cables
Television Sets
Medical Monitoring
equipment
X-ray and other imaging
equipment
Fluorescent Lighting
Wireless Communication
Devices
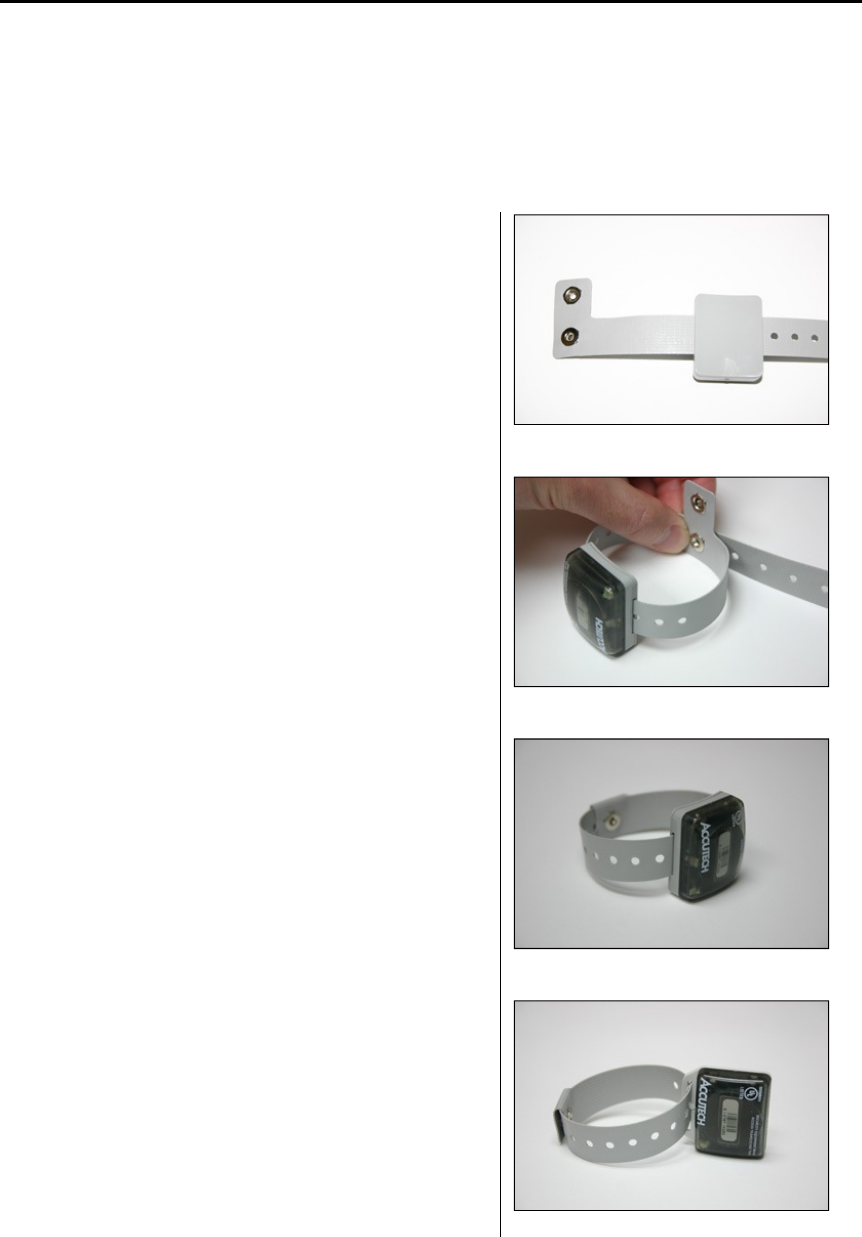
3-6 Tags User Manual
Attaching Tags
Attaching LT/SB Tags
Attaching BR42 Tags
Attaching Cut Band Tags with Pod
Removing a Cut Band Tag with Pod
Attaching LT/SB Tags
Note:
LT (Long Term) Tags are used for resident care.
SB (Slotted Back) Tags are used on small infants and assets.
All Tag bands are for one-time use only. For cleanliness and
sanitary reasons, Accutech recommends replacing applied
bands on a semi-monthly basis with a maximum of one
month between changes.
1. For LT Tags, with the snaps pointing in the
same direction as the Accutech logo, slide the
plastic band through the Slot.
(see Figure 3.9)
2. Adjust the band length to the nearest
accommodating hole for a comfortable fit
around the patient’s extremity.
Note: Once the band is secured it cannot be
adjusted.
3. Put the male part of the Snap through the
selected hole (see Figure 3.10).
4. Fold over the female part of the Snap and
secure to the male part by squeezing until they
snap together.
5. Using scissors, carefully trim any excess band
material (see Figure 3.11).
6. Using an S-TAD, activate the Tag.
7. Follow the same procedure for SB Tags.
(see Figure 3.12)
Figure 3.9: LT Tag with band
Figure 3.10: LT Tag with band
Figure 3.11: LT Tag with band secured
Figure 3.12. SB Tag with band secured

User Manual Tags 3-7
Attaching BR42 Tags
NOTE: The Soft Bracelet has conductive fiber stripes (Figure 3.13)
that must be in contact with both the infant’s skin and the gold
contacts on the Tag (Figure 3.14). The band must be routed
properly through the Tag case for the system to function properly.
Tags are typically attached to a wrist or ankle. For smaller infants,
placing the Tag around the thigh is also acceptable.
All Tag bands are for one-time use only. For cleanliness and
sanitary reasons, Accutech recommends replacing applied bands on
a semi-monthly basis with a maximum of one month between
changes.
1. Unsnap the Cam Lock (Figure 3.14).
2. Hold the Tag in your left hand with the Slot to
the right and the Cam facing up.
3. With the conductive fiber stripes facing the
Tag, slide the pointed end of the band up
through the Slot from underneath until the
folded end is snug next to the Slot (Figure
3.15).
4. Push the pointed end of the band (with the
conductive fiber stripes facing the gold
contacts on the Tag) through the Cam Lock
opening and form a 2-inch loop with the band
(Figure 3.16).
5. Slip the 2-inch loop over the infant’s extremity
and cinch the band until it is snug around the
infant’s extremity.
6. Make sure the conductive fiber stripes are in
good contact with the infant’s skin.
7. Snap the Cam Lock closed.
NOTE: Make sure the band is still snug
around the infant’s extremity. If necessary,
gently pull the band snug while the Cam Lock
is closed. Be careful not to overtighten; the
Cam Lock must be opened to loosen the band.
8. Using scissors, carefully trim any excess band
material so that the band does not protrude
beyond the end of the Tag case (Figure 3.17).
9. Using an S-TAD, activate the Tag.
Figure 3.13 The Soft Bracelet
Figure 3.14 Tag with Cam Lock open
Figure 3.15 BR42 Tag with band inserted
Figure 3.16 BR42 Tag with band in place
Figure 3.17 BR42 Tag with band in place
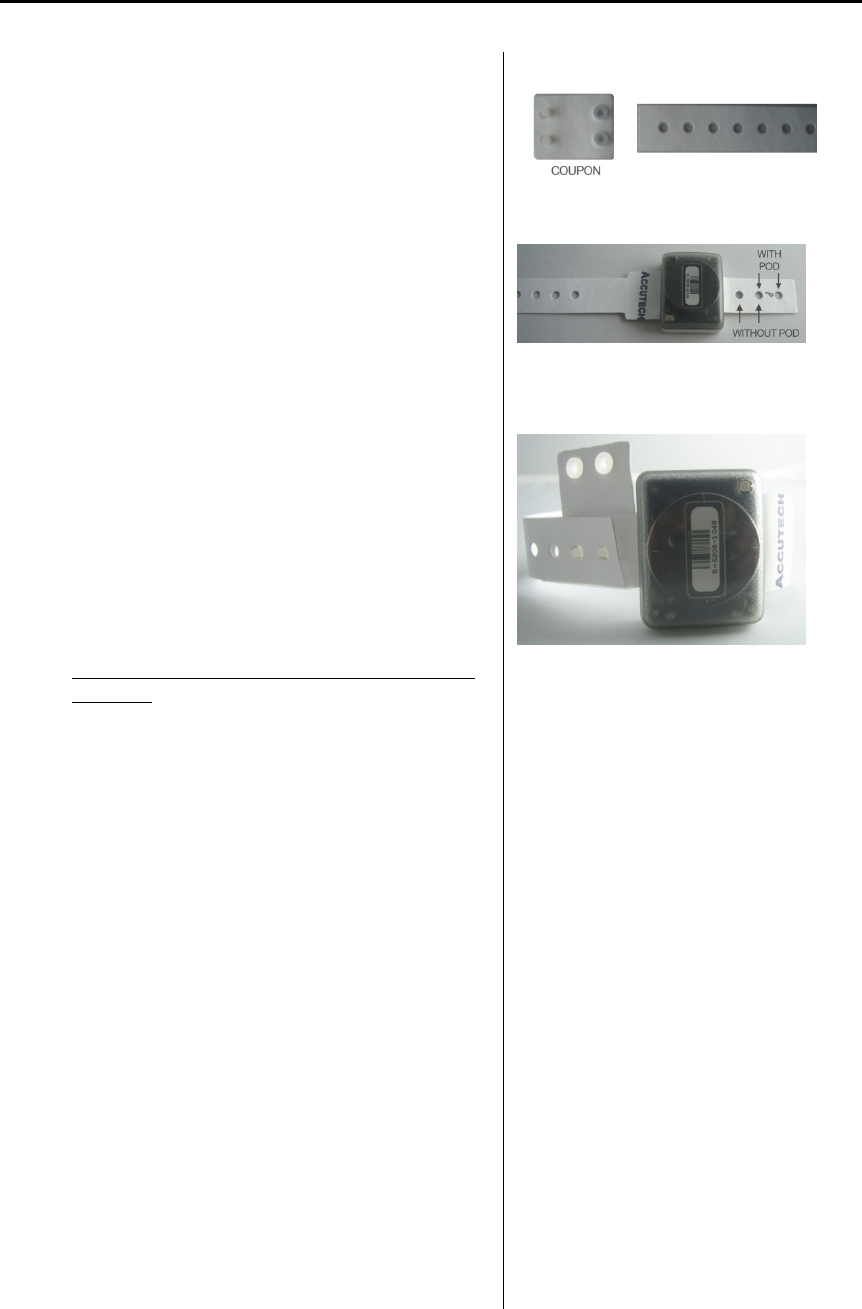
3-8 Tags User Manual
Attaching Cut Band Tags with Pod
Note: All Tag bands are for one-time use only. For
cleanliness and sanitary reasons, Accutech recommends
replacing applied bands on a semi-monthly basis with a
maximum of one month between changes.
1. OPTIONAL: Write the date when the band was
applied on the provided date lines __/__/__
located next to the Accutech logo on the Cut
Band. For cleanliness and sanitary reasons,
Accutech recommends replacing applied bands
on a semi-monthly basis with a maximum of one
month between changes. Writing the date will aid
in this schedule.
2. Using safety scissors, remove the coupon from
the snap band along the perforated line. Retain
the coupon (Figure 3.18).
3. With the Accutech name facing up, slide the 3-
hole tab section of the snap band through the Tag
slot until the Tag is against the Tag stops (Figure
3.19).
If not using a Pod, skip steps 3 & 4 and proceed
to Step 5.
4. OPTIONAL: Remove the top pod cover (the
large cover) from the cover strip and align it with
the top of the Tag (the side of the Tag that has the
Accutech logo) so that the two arrows on the top
pod cover point in the direction of the 3-hole tab
section. Being careful not to touch the adhesive
on the gasket, push the Tag into the cover until
the Tag is completely inside the cover and the
snap band is touching the adhesive gasket.
5. OPTIONAL: Remove the bottom pod cover (the
smaller cover) from the cover strip and place it
over the bottom side of the Tag so that the two
arrows on the bottom cover point in the direction
of the 3-hole tab section. Using your thumb and
forefinger, squeeze and run them along all fours
sides of the two pod pieces to ensure a tight
gasket seal.
6. Using the coupon, thread the male snaps through
the selected snap band holes (with pod or no pod)
of the 3-hole tab section from the bottom side up
(Figure 3.20).
Figure 3.18 Remove the coupon along the
perforated line and save for later use.
Figure 3.19 Slide the snap band through
the Tag slot. Determine which holes to use
(with or without pod)
Figure 3.20 Determine band length needed
and select holes. Position the coupon.
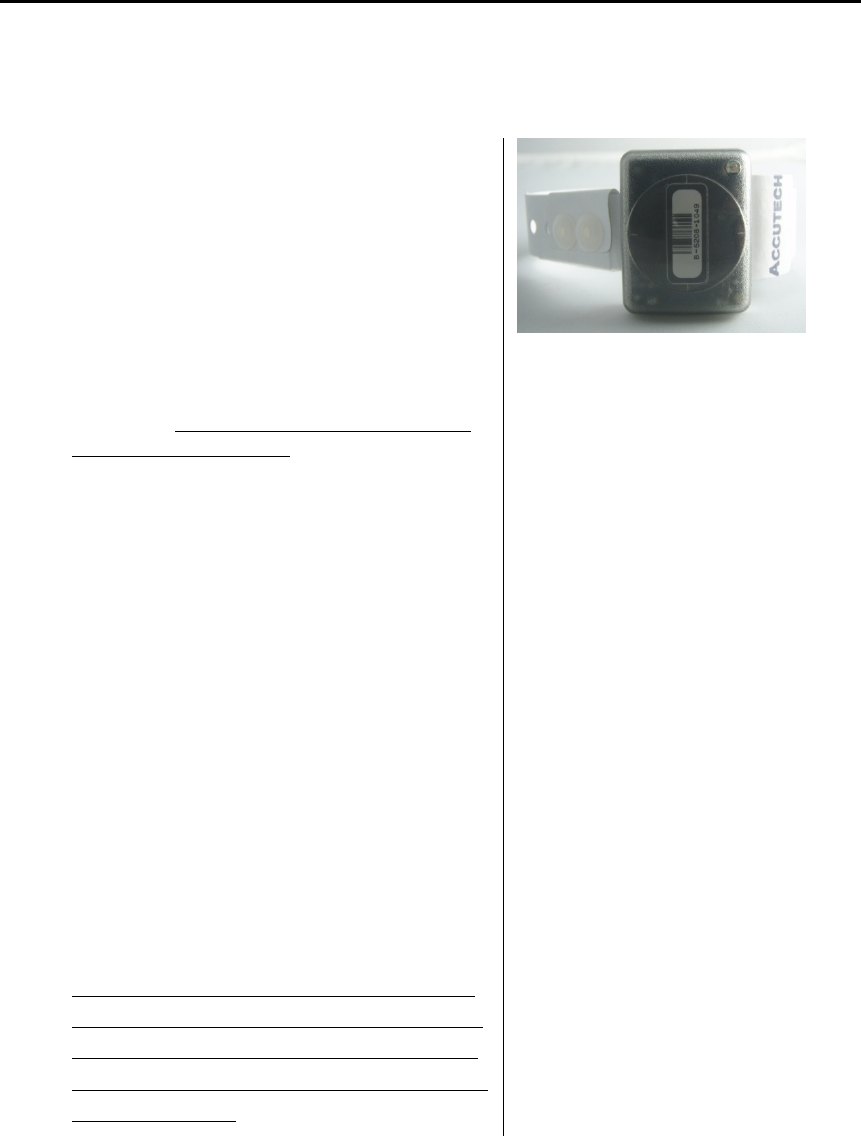
User Manual Tags 3-9
7. Wrap and overlap the band around the patient’s
wrist/ankle to determine the band length needed
and the holes to use by lining up the two male
snaps from the 3-hole tab section with two
overlapping holes from the band length section.
A properly fit snap band will not fall off the
patient nor will it restrict movement or blood
flow.
8. Fold over the coupon’s female snaps onto the
male snaps to secure the band. Press firmly on
each snap. Once locked together, the coupon
snaps cannot be adjusted. (Figure 3.21)
9. Carefully cut any excess band length material
and discard it.
10. Using an S-TAD (Secure Tag
Activator/Deactivator), activate the Tag.
The Tag’s red LED will blink rapidly to
indicate that the Tag is active.
Figure 3.21 Secure the snap band by
folding over the female snaps onto the
male snaps. Carefully cut any excess band
length material. Using an S-TAD activate
the Tag.
Removing a Cut Band Tag with Pod
1. Turn off the Tag with an S-TAD.
2. Carefully cut off the band from the patient’s
extremity.
3. If present, separate and remove the top and
bottom plastic covers from around the Tag.
4. Remove any residue left over from the plastic
cover gasket before pulling the band out of the
Tag slot. Failure to remove residue may result
in residue buildup inside the Tag slot rendering
the Tags unusable.
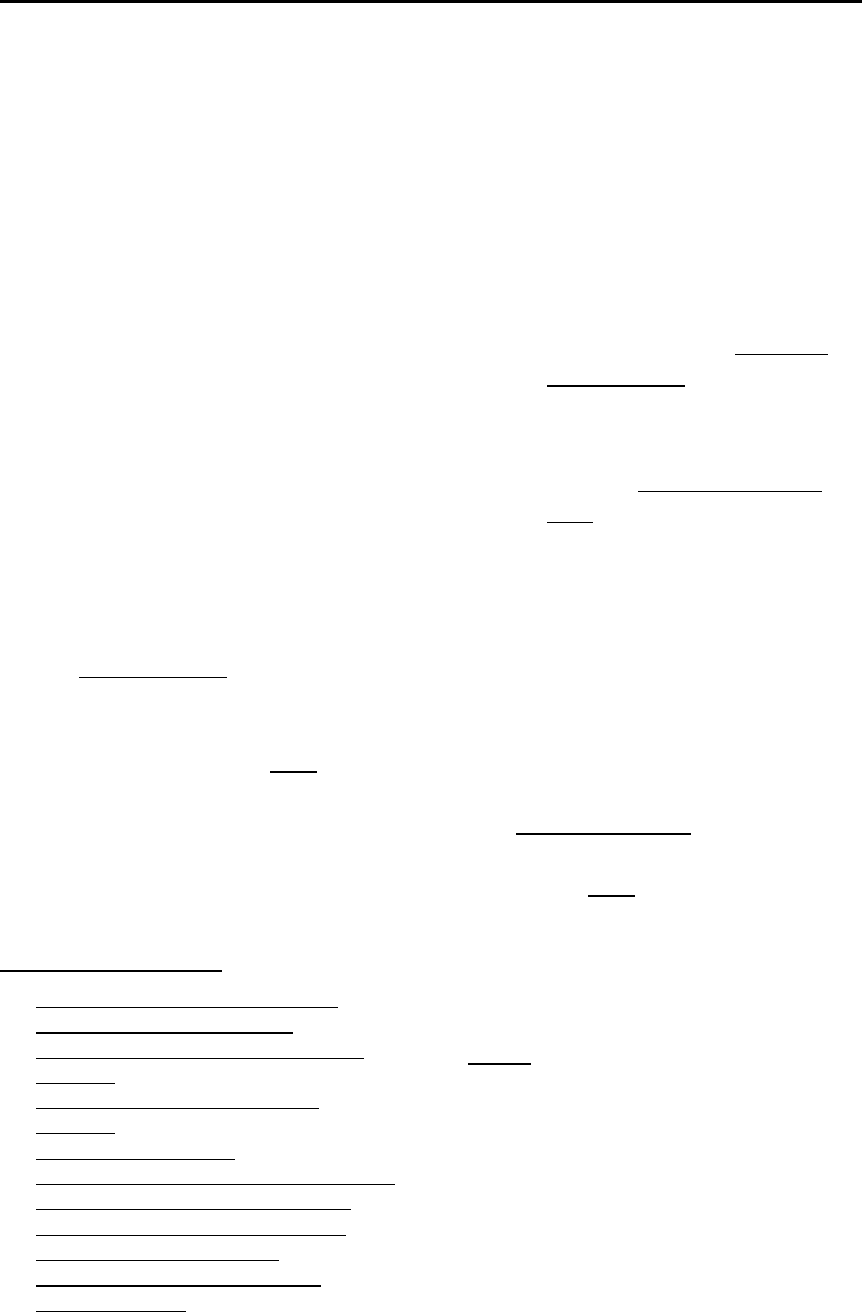
3-10 Tags User Manual
Tag and Band Maintenance
Testing Tags
Accutech Tags operate by internal battery.
Over the course of normal operation, Tags
eventually lose battery power and the Tags
will need to be replaced. The Tag battery is
not replaceable. For maximum protection of
residents or assets, Accutech recommends
that Tags be tested on a weekly basis. There
are many ways that you can test Tags:
Enter a monitored zone
(Software will report.)
With a S-TAD
The Keypad’s Auxiliary LED
(Yellow) will light when a Tag is
detected (Optional; additional wire
required).
Check Visual Pulse LED if present
BR and CB Tags only - Remove
Band Alarm band or Cut Band band
(alarm will sound).
Cleaning Tags
All Tags are reusable but they must be
cleaned and sanitized between applications.
In long-term applications, periodically
replace the bands and clean the Tags. There
are a few methods that can be used to clean
and sanitize Tags:
HOWEVER, DO NOT:
DO NOT submerge Tags in water
DO NOT soak Tags in water
DO NOT submerge Tags in cleaning
solutions
DO NOT soak Tags in cleaning
solutions
DO NOT use solvents
DO NOT use abrasive cleaners or cloths
DO NOT put Tags in an AutoClave
DO NOT put Tags in a dishwasher
DO NOT steam clean Tags
DO NOT put Tags in a washing
machine or dryer
Acceptable Tag Cleaning Methods:
Seek guidance with your Infection
Control representative for approved
cleaners that can be used on
plastics
Wipe down with 3% hydrogen
peroxide with water solution then
rinse with a water-dampened cloth
towel and wipe dry. (wipe only,
DO NOT soak.
Antibacterial wipes then rinse with
a water-dampened cloth towel and
wipe dry (wipe only, DO NOT
soak.
Cleaning Bands
All Tag bands are for one-time use only. For
cleanliness and sanitary reasons, Accutech
recommends replacing applied bands on a
semi-monthly basis with a maximum of one
month between changes.
Storing Tags: To preserve battery life,
Tags must be turned off with an S-TAD
during storage or periods of non-use. BR
and CB Tags must be deactivated to prevent
alarms when not use. In addition, Tags
should be stored away from sources of
electrical noise (see example list below) and
stored in a metal container with lid.
Do not store Tags within 3 feet of any of the
following sources of electrical noise:
Computer monitors
Unshielded computer cables
Television sets
Medical Monitoring Equipment
X-ray and other imaging equipment
Fluorescent Lighting
Storing Bands
Extra Tag bands should be stored in clean
and dry environment.
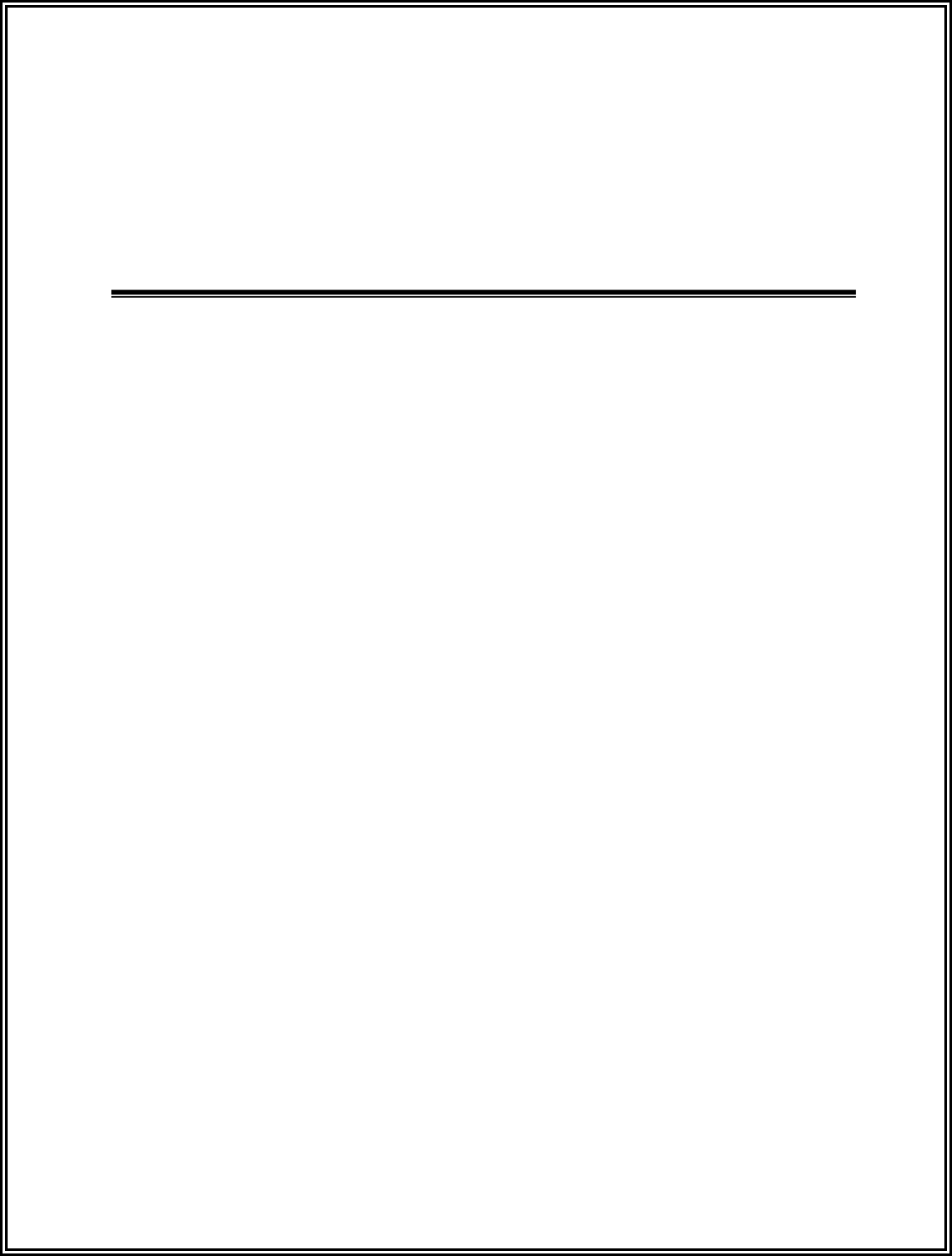
User Manual
Chapter 4:
The S-TAD
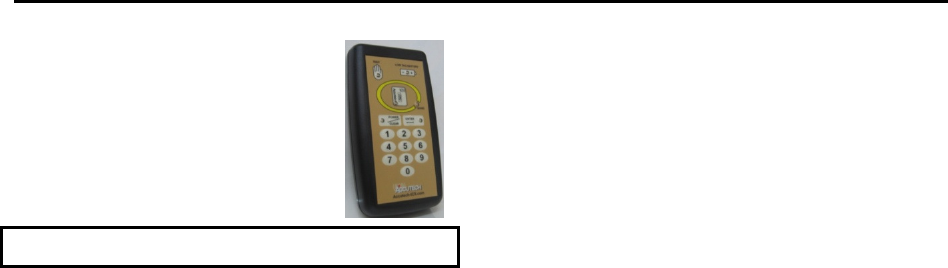
User Manual The S-TAD 4-1
The S-TAD
Powering the S-TAD On/Off
Unlocking the S-TAD
Activating/Deactivating Tags
Programming Mode
Note: The S-TAD has not been evaluated by UL.
The S-TAD (Secure Tag Activator/Deactivator)
is used to check the functionality of an Accutech
Tag. Accutech Tags operate by internal battery.
Over the course of normal operation, Tags
eventually lose battery power and the Tags will
need to be replaced. The Tag battery is not
replaceable. The S-TAD is used to determine if a
Tag has sufficient battery power to respond to an
activating signal. The S-TAD requires a 9-volt
lithium battery to operate.
Powering the S-TAD On/Off
The S-TAD includes a built-in power saving
feature that automatically turns off the S-TAD
after a period of inactivity.
1. Press the Power/Clear button
The Power/Clear LED illuminates (solid
green with wink).
The LED will remain lit for 1 minute.
While nearing the 1 minute mark, the
LED will begin to pulse until the LED
turns faster pulsing red and then
extinguishes while powering off the
S-TAD.
To extend the length of time, press the
Power/Clear button again anytime
before the LED turns off. Each press
will extend by 1 minute (up to 5 minutes
maximum).
2. Conversely you may manually power
off the S-TAD by pressing and holding
the Power/Clear button until the LED
turns solid red then let go and the Power
LED will extinguish.
Unlocking the S-TAD
For added security, access to
activating/deactivating Tags is locked via 4-digit
user codes. See Programming Mode for more
information about user codes.
1. Press the Power/Clear button.
The Power/Clear LED illuminates
(solid green with wink).
2. Using the number keypad, enter a valid
4-digit user code. Entering a valid code
will illuminate the Enter LED (solid
green) for about 5 seconds. Once the
Enter LED illuminates, press the Enter
button again. The WAIT LED will
illuminate (red) for 2 seconds to
confirm activation/deactivation action.
The Enter LED will then remain lit for 1
minute for the purpose of
activating/deactivating Tags.
Notes:
• The default user code is 7139.
See the Programming Mode section
to change the default user code.
• Entering an invalid code will
illuminate the Enter LED red.
Verify your user code is valid. Press
Power/Clear before reentering your
code to clear any inadvertent
previous entries.
• Once lit, each time you press the
Enter button will extend the Enter
LED life briefly (up to 1 minute by
default).
• Pressing the Power/Clear button will
clear out the user code. Otherwise,
after 1 minute of inactivity the Enter
LED will extinguish automatically.
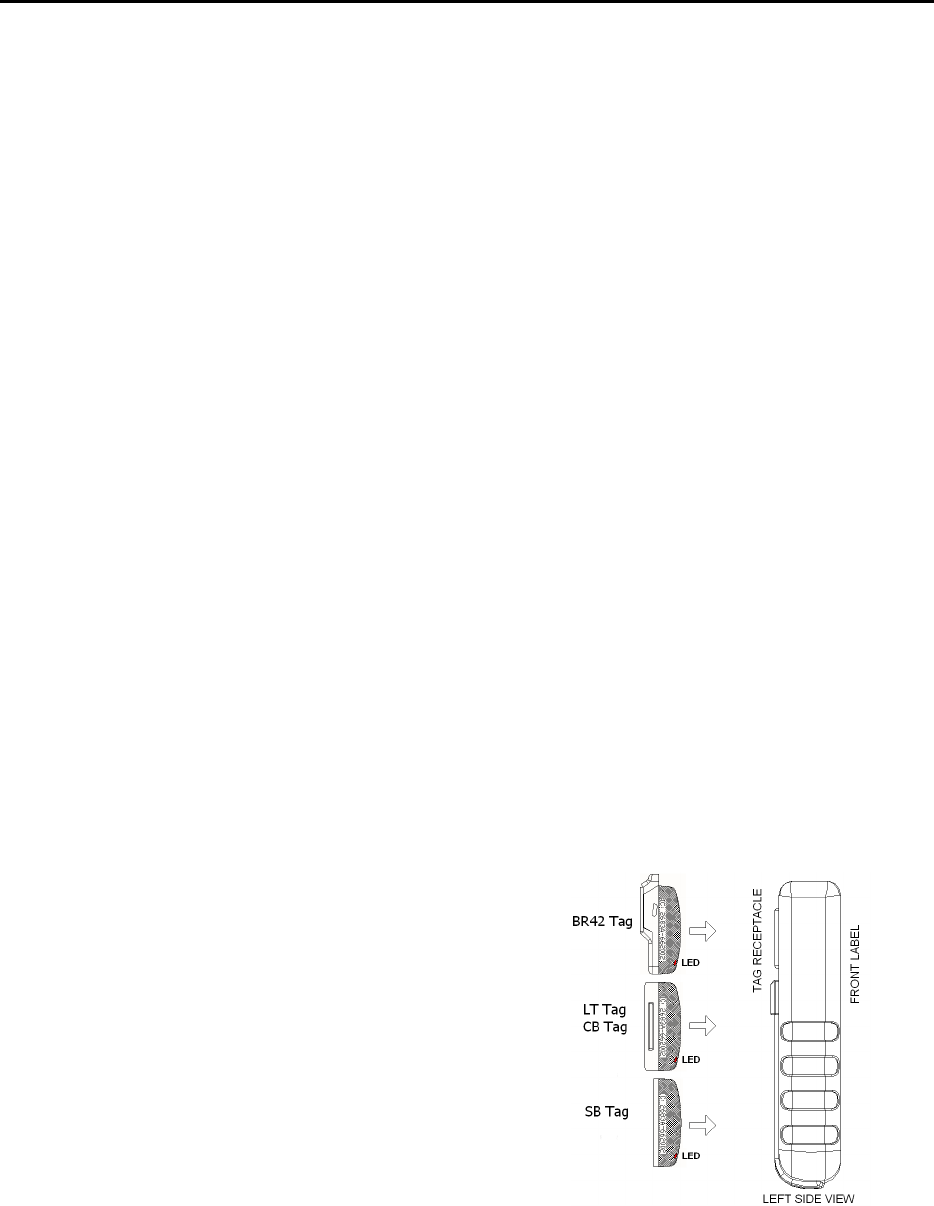
4-2 The S-TAD
User Manual
Activating/Deactivating Tags
The S-TAD can activate and deactivate Tags
preserving Tag battery life and preventing
nuisance alarms.
ACTIVATING
1. Unlock the S-TAD using your unique
4-digit user code.
2. On the back of the S-TAD, place the
inactive Tag in the correct orientation
within the Tag receptacle. On the front
of the S-TAD, the Tag graphic’s LED is
off (just like the physical Tag’s LED is
off).
3. Press the Enter button (green LED lit).
The Wait LED will illuminate (red) for
2 seconds. The Tag graphic’s LED on
the S-TAD will illuminate (pulsing
yellow) indicating the Tag is active (just
like the physical Tag’s LED will
illuminate).
4. If a Low Tag Battery condition is
detected, the Low Tag Battery LED will
illuminate red.
5. If a band alarm condition is detected, the
Band LED will illuminate red.
Likewise, if a band compromise
condition is detected, the Band LED will
illuminate half green and half red.
Note: Band alarm, band compromise,
and cut band conditions always take
precedence over a Low Tag Battery
condition, therefore, be sure to handle
the band-sensing Tag appropriately to
truly check for a Low Tag Battery
condition.
6. The S-TAD will still detect active Tags
and Low Battery conditions in the area
even after the Enter LED extinguishes.
However, you will have to unlock the S-
TAD again to be able to
activate/deactivate a Tag. Remember the
S-TAD will automatically lock after 1
minute of inactivity (by default).
DEACTIVATING
1. Unlock the S-TAD using your unique
4-digit user code.
2. On the back of the S-TAD, place the
active Tag in the correct orientation
within the Tag receptacle. On the front
of the S-TAD, the Tag graphic’s LED
will be pulsing yellow (just like the
physical Tag’s LED will be pulsing).
3. Press the Enter button (green LED lit).
The Wait LED will illuminate (red) for
2 seconds. The Tag graphic’s LED on
the S-TAD will extinguish indicating the
Tag is deactivated (just like the physical
Tag’s LED will extinguish).
Figure 6.9 S-TAD Tag Orientation

User Manual The S-TAD 4-3
Programming Mode
While in programming mode, the Enter button’s
LED winks quickly. In addition, the Enter button
LED will also indicate if a programming step
was completed successfully.
If the Enter button LED flashes green slowly the
operation completed correctly. 3 flashes on the
first entry, 5 flashes on the verify entry.
If the Enter button LED flashes red or yellow, an
entry error has occurred. If an entry error occurs,
press the Power/Clear button to cancel out and
start over.
To enter programming mode:
1. Press: Enter, Enter, Master Code, Enter,
Enter
Note: 198237645 is the default master
code.
2. While in programming mode, the Enter
button’s green LED winks quickly.
To exit programming mode:
1. Press: Power/Clear
2. Press: 0, Enter, 0, Enter
Programming mode exits and the Enter
button LED extinguishes.
Enable/Disable Sounders
(Band Alarm and/or Mother/Baby Match
sounder):
1. Enter Programming Mode
2. Press: 4, Enter, 4, Enter
(3 slow green flashes)
3. Press desired number (0 through 3) for
preferred S-TAD sounder option.
Press: 0 to disable both Band Alarm and
Mother/Baby Match sounder
Press: 1 to enable only Band Alarm
sounder,
Press: 2 to enable only Mother/Baby
Match sounder
Press: 3 to enable both Band Alarm and
Mother/Baby Match sounder
4. Then press Enter
(5 slow green flashes confirms)
5. Exit Programming Mode
Set Unlock Timeout:
1. Enter Programming Mode
2. Press: 5, Enter, 5, Enter
(3 slow green flashes)
3. Press: 1 through 5 for 1 to 5 minute
timeout
(5 slow green flashes confirms
4. Exit Programming Mode
To change the master code:
1. Enter Programming Mode
2. Press: 1, Enter, 1, Enter
(3 slow green flashes)
3. Press: The current 9-digit master code to
change, then Enter
(1 slow green flash if correct)
4. Press: New 9-digit master code, then
Enter
(1 slow green flash if correct)
5. Press: Same new 9-digit master code to
verify, then Enter
(5 slow green flashes confirms)
6. Exit Programming Mode
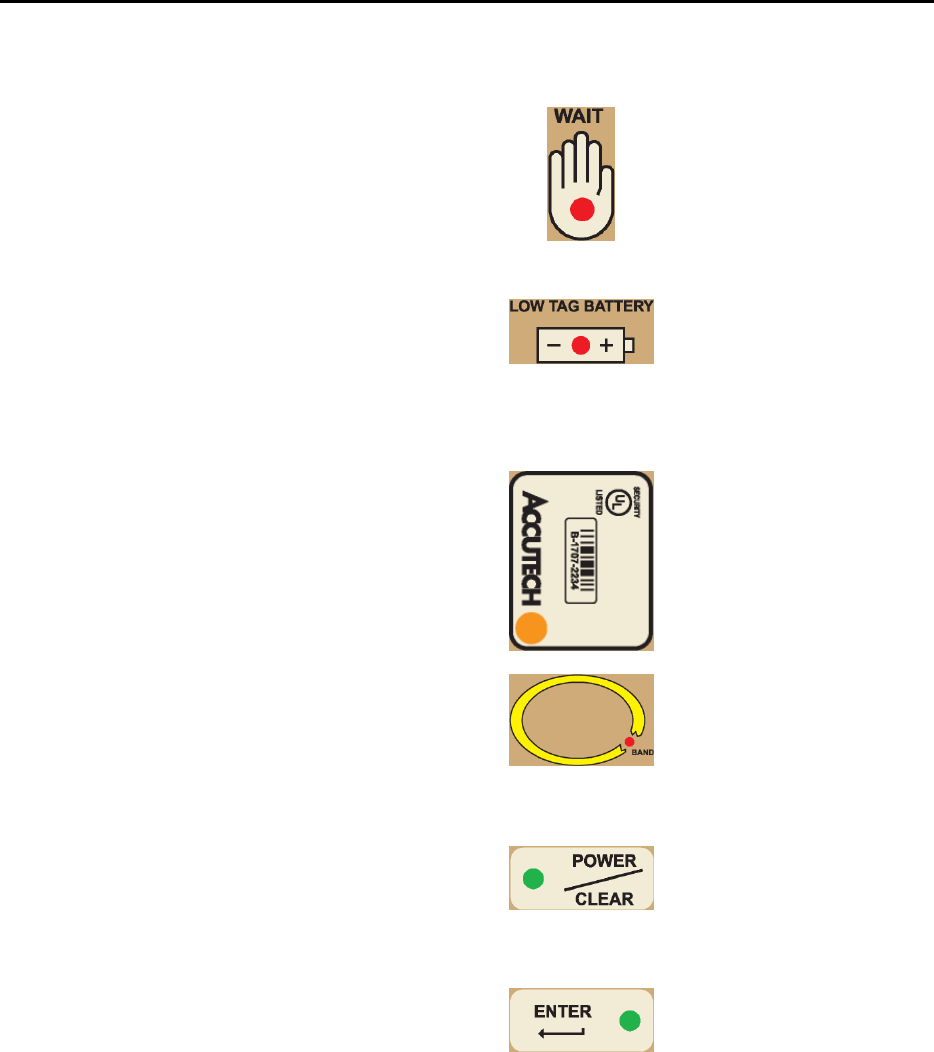
4-4 The S-TAD User
Manual
To add a user code:
1. Enter Programming Mode
2. Press: 2, Enter, 2, Enter
(3 slow green flashes)
3. Press: 4 digit user code to add, then
Enter
(1 slow green flash if correct)
Note: Maximum 121 codes.
4. Press: same 4-digit user code to verify,
then Enter
(5 slow green flashes confirms)
5. Repeat steps 3 & 4 to add another code.
When finished, exit Programming
Mode.
To delete a user code:
1. Enter Programming Mode
2. Press: 3, Enter, 3 Enter
(3 slow green flashes)
3. Press: 4 digit user code to delete, then
Enter
(1 slow green flash if correct)
4. Press: same 4-digit user code to verify,
then Enter
(5 slow green flashes confirms)
5. Repeat steps 3 & 4 to delete another
code. When finished, exit Programming
Mode
Summary of LEDs
WAIT LED
Tag is in the process of being
turned on or off or during
S-TAD unlocking.
LOW TAG BATTERY LED
A low tag battery is detected.
Replace Tag.
TAG LED
An active Tag is nearby.
BAND LED
A Band Alarm condition is
detected.
POWER/CLEAR LED
S-TAD is powered.
ENTER LED
S-TAD unlocked.

User Manual The S-TAD 4-5
Cleaning and Care
The S-TAD should be cleaned periodically using
antibacterial wipes (wipe, do not soak).
Do not use any abrasive cleaners or cloths.
When not in use the S-TAD should be stored in
a clean and dry environment.
The S-TAD requires a 9-volt lithium battery to
operate. Remove the protective boot to access
the battery compartment. Using the embossed
orientation guide, replace the 9-volt lithium
battery as needed.
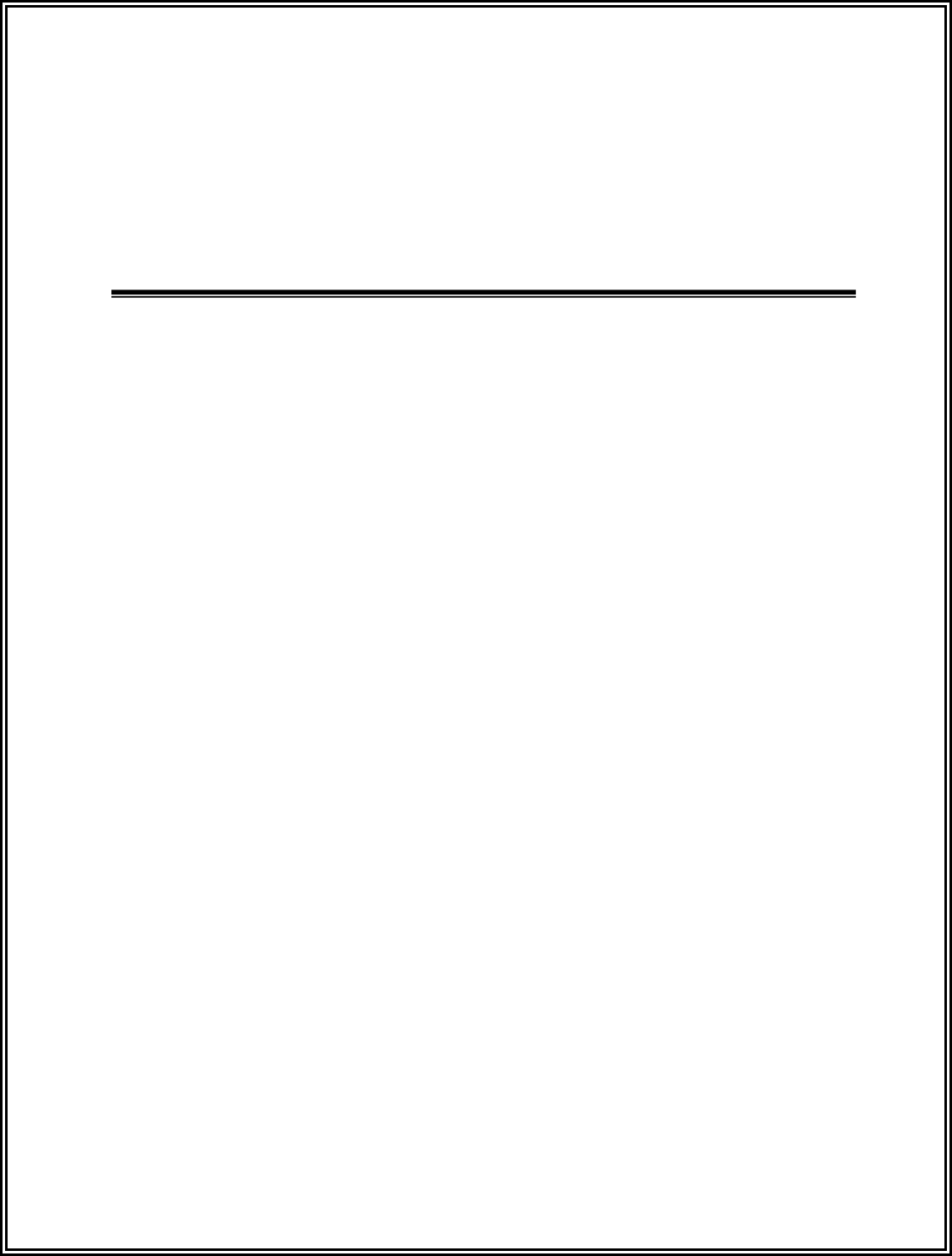
User Manual
Chapter 5:
The Keypad
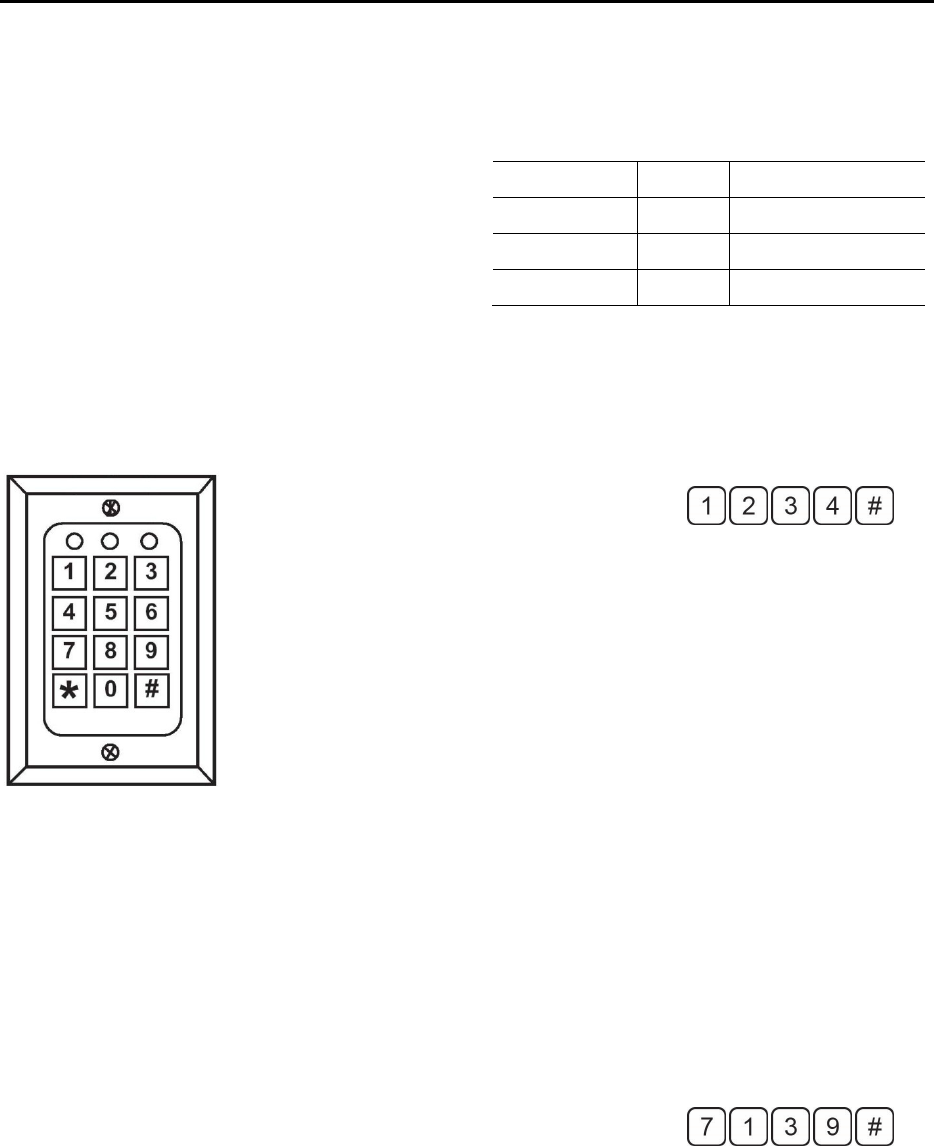
User Manual The Keypad 5-1
The Keypad (KP-103)
Programming
Programming
Initiating a Keypad Reset/Escort
Programming
How to enter user codes
How to delete user codes
How to set the relay time
How to set the installer code
The Keypad (Part # 650209) provided by
Accutech (the KP-103) is used to escort residents
through a monitored zone and to reset zone
equipment once an alarm has occurred.
The Keypad (KP-103)
Programming the Keypad is, in simple terms,
providing it with a set of instructions on how to
react in various contingencies. The Keypad must
be programmed as soon as all installation and
wiring have been completed. Later on, as
changes take place, partial or full
reprogramming may be carried out as many
times as necessary.
The Keypad has three LED indicators. See Table
5.1 for their functions during normal operation.
Table 5.1 Keypad LED Indicators
LED Status Function
Green On Output relay is active
Yellow On Monitors power input
Red On LC Unit is in alarm
* During programming, the green LED functions
differently.
Initiating the First Relay (Reset/Escort)
To initiate the first relay, enter a valid user code
and press the [#] key. The green LED will light.
Accutech Default is .
Keypad Resets are used to reset zone equipment
after an alarm has been addressed. When you
initiate a Keypad Reset, all zone equipment and
alarms will be reset. However, if the alarm
condition is not properly corrected, the alarm
will resume.
The Keypad’s Escort function is used to escort
Tags through a monitored zone without
triggering alarms. When you initiate the Escort
function, for the duration of the Escort time, you
will be able to escort the Tag through the door,
hallway, or use an elevator without triggering
alarms.
Initiating the Second Relay (Anti-Tailgate)
To initiate the second relay, enter a valid user
code and press the [#] key. The green LED will
light.
Accutech Default is .
The second relay is an anti-tailgate feature that
will allow unimpeded passage through the exit
point without triggering an alarm; however, any
banded tailgater attempting to subsequently
pass-through will trigger an alarm event.
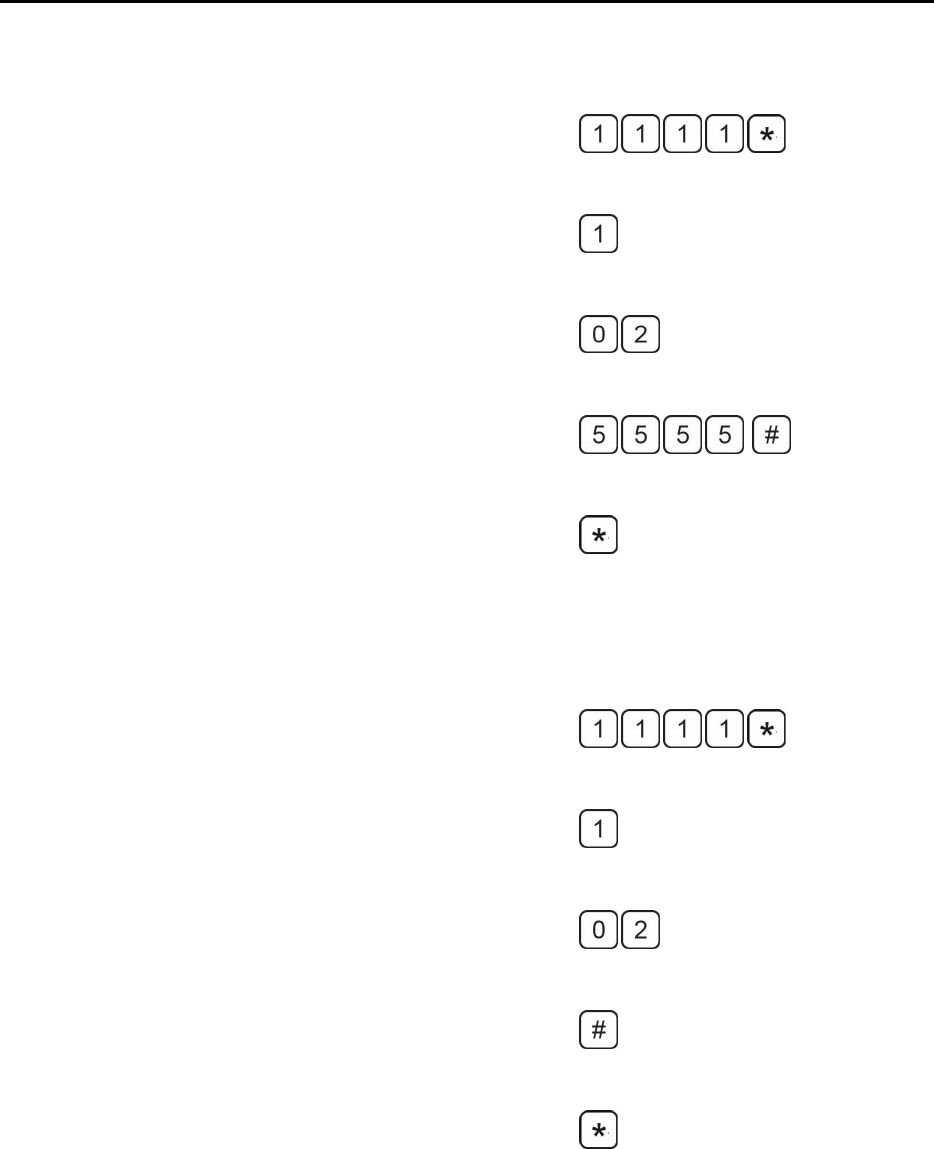
5-2 The Keypad
User Manual
How to enter user codes (First Relay)
Note: First Relay user numbers are two digits
and range from 01-99.
1. Enter the installer code [1][1][1][1][*] to
enter program mode. You will hear two
beeps.
2. Enter [1] to select relay 1
3. Then enter the desired user number
(for example 02) then enter the new user
code (for example 5555) followed by
the [#] key. You will hear two beeps.
4. Continue programming for additional
user codes as desired (for example 03,
9999, #).
5. When finished, enter [*] to exit program
mode and return the Keypad normal
operation mode.
How to delete user codes (First Relay)
1. Enter the installer code [1][1][1][1][*] to
enter program mode. You will hear two
beeps.
2. Enter [1] to select relay 1
3. Then enter the desired user number (for
example 02) then the [#] key.
You will hear two beeps.
4. Continue deleting additional user codes
as desired (for example 03, #).
5. When finished, enter [*] to exit program
mode and return the Keypad normal
operation mode.
(enter programming mode)
(selects relay 1)
(selects user code 02)
(selects 5555 as the code)
(exits programming mode)
(enter programming mode)
(selects relay 1)
(selects user code 02)
(deletes user code 02)
(exits programming mode)

User Manual The Keypad 5-3
How to set the relay time (First Relay)
Note: The relay time is factory set to 15 seconds
by Accutech.
To change the relay time:
1. Enter the installer code [1][1][1][1][*] to
enter program mode. You will hear two
beeps.
2. Enter [4][0] then the desired relay time
(1-999 seconds), then the [#] key.
You will hear two beeps.
3. Enter [*] to exit program mode and
return the Keypad normal operation
mode.
(enter programming mode)
(selects timer for relay 1)
(sets timer to 15 seconds)
(exits programming mode)
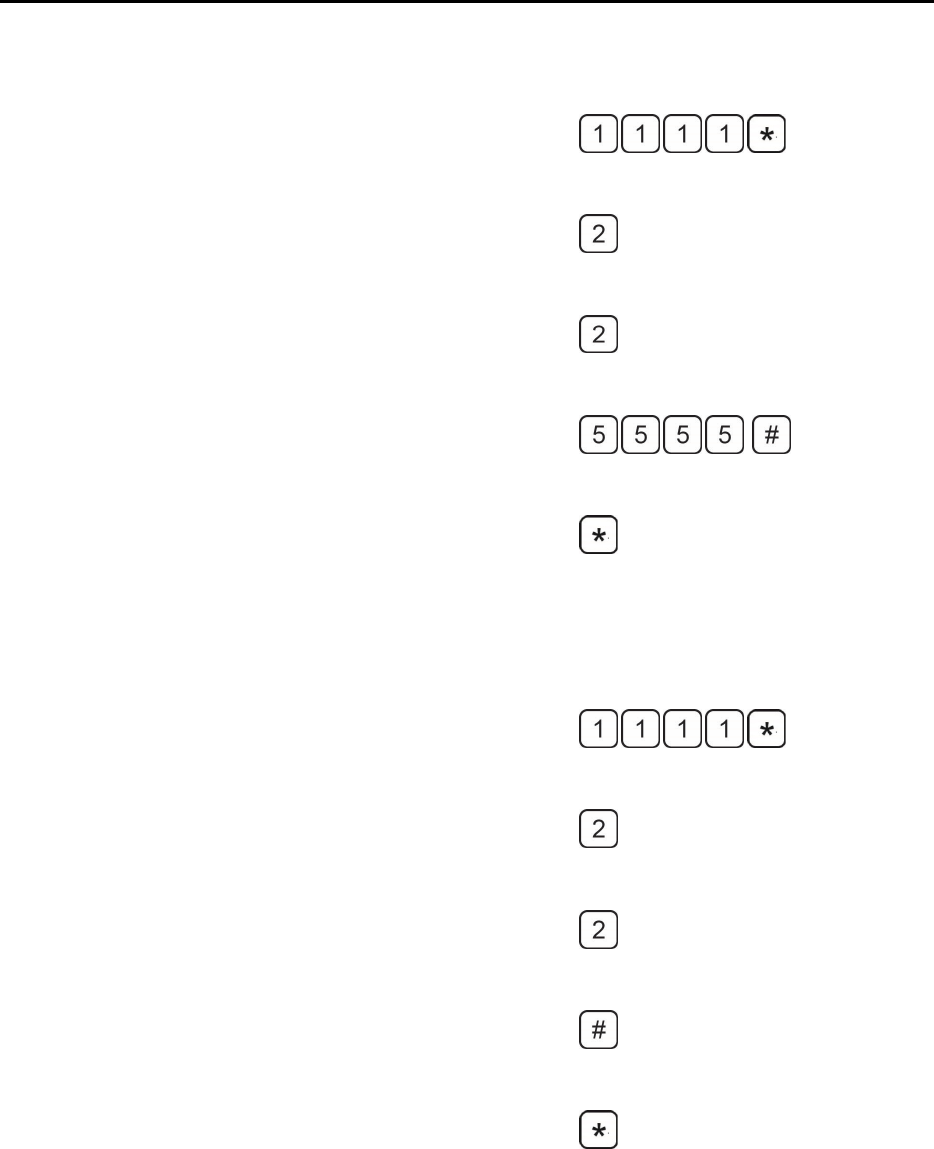
5-4 The Keypad
User Manual
How to enter user codes (Second Relay)
Note: Second Relay user numbers are one digit
and range from 1 to 9.
1. Enter the installer code [1][1][1][1][*] to
enter program mode. You will hear two
beeps.
2. Enter [2] to select relay 2
3. Then enter the desired user number (for
example 2) then enter the new user code
(for example 5555) followed by the [#]
key. You will hear two beeps.
4. Continue programming for additional
user codes as desired (for example 03,
9999, #).
5. When finished, enter [*] to exit program
mode and return the Keypad normal
operation mode.
How to delete user codes (Second Relay)
1. Enter the installer code [1][1][1][1][*] to
enter program mode. You will hear two
beeps.
2. Enter [2] to select relay 2
3. Then enter the desired user number (for
example 2) then the [#] key.
You will hear two beeps.
4. Continue deleting additional user codes
as desired (for example 03, #).
5. When finished, enter [*] to exit program
mode and return the Keypad normal
operation mode.
(enter programming mode)
(selects relay 2)
(selects user code 2)
(selects 5555 as the code)
(exits programming mode)
(enter programming mode)
(selects relay 2)
(selects user code02)
(deletes user code 2)
(exits programming mode)
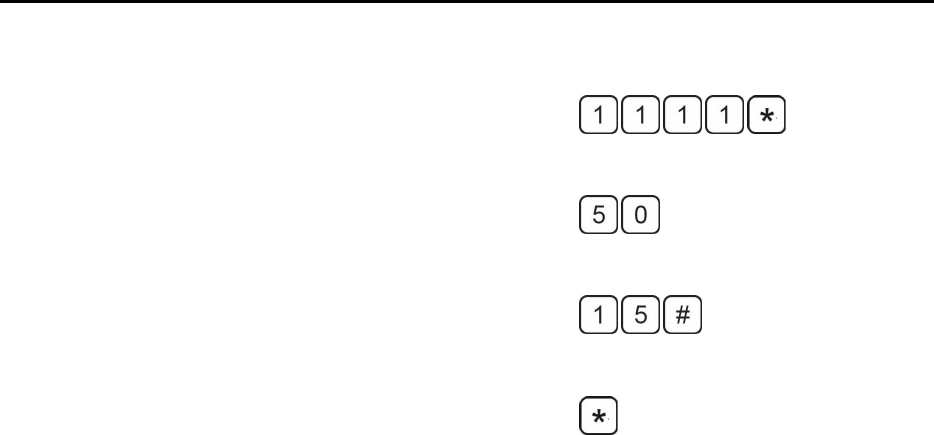
User Manual The Keypad 5-5
How to set the relay time (Second Relay)
Note: The relay time is factory set to 15 seconds
by Accutech.
To change the relay time:
1. Enter the installer code [1][1][1][1][*] to
enter program mode. You will hear two
beeps.
2. Enter [5][0] then the desired relay time
(1-999 seconds), then the [#] key.
You will hear two beeps.
3. Enter [*] to exit program mode and
return the Keypad normal operation
mode.
(enter programming mode)
(selects timer for relay 2)
(sets timer to 15 seconds)
(exits programming mode)
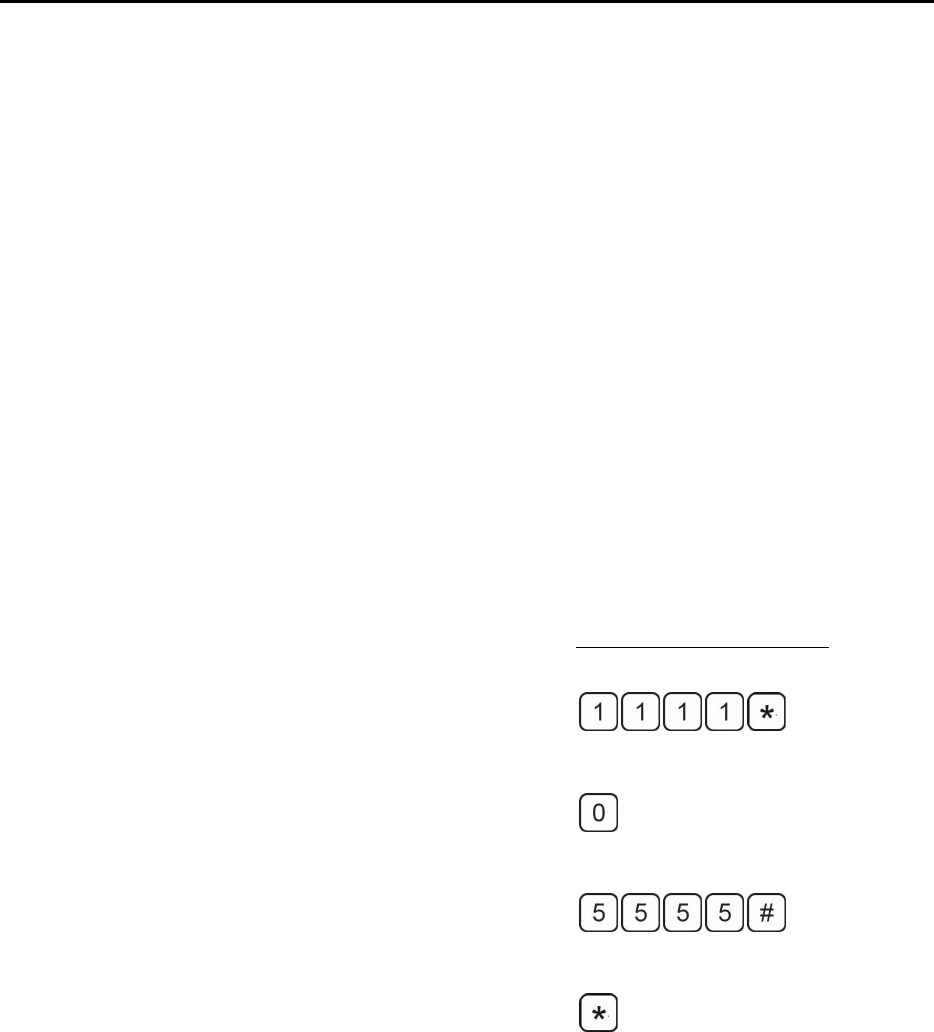
5-6 The Keypad User Manual
DAP Instructions
Note: DAP (Direct Access Programming) should
only be used if the Keypad programming has
become unstable (that is, if during programming
steps you continually receive 5 beeps between
steps). DAP programming will reset the KP-103
keypad to Accutech factory settings.
1. Remove power and keypad
faceplate from back box.
2. Move DAP jumper from OFF
position to ON position.
3. Apply power to keypad.
4. Move DAP jumper back to OFF
position.
5. Enter [8][9][0][1][#] to Initialize
(2 beeps)
6. Enter [0] (to select User Code 0)
7. Enter [1][1][1][1][#] to designate
the new Installer Code (2 beeps)
8. Enter [4][0] then [1][5] (to set to 15
seconds), then [#] (2 beeps)
9. Enter [5][0] then [1][5] (to set to 15
seconds), then [#] (2 beeps)
10. Enter [1], then [0][1] (to select User
Code 01), then [1][2][3][4][#]
(2 beeps)
11. Enter [2], then [1], then
[7][1][3][9][#] (2 beeps)
12. Enter [*] to exit (2 beeps)
How to change the installer code
Note: The original installer code is 0000. If the
installer code is unknown (or differs from the
Accutech preprogrammed 1111) and you need to
revert back to this code, go to the DAP
instructions section.
1. Enter the installer code [1][1][1][1][*] to
enter program mode. You will hear two
beeps.
2. Enter [0] then the new desired installer
code number (4-8 digits) then the [#]
key. You will hear two beeps.
3. When finished, enter [*] to exit program
mode and return the Keypad normal
operation mode.
Changing the Installer Code:
(enter programming mode)
(selects user code 0)
(sets 5555 to be the new code)
(exits programming mode)
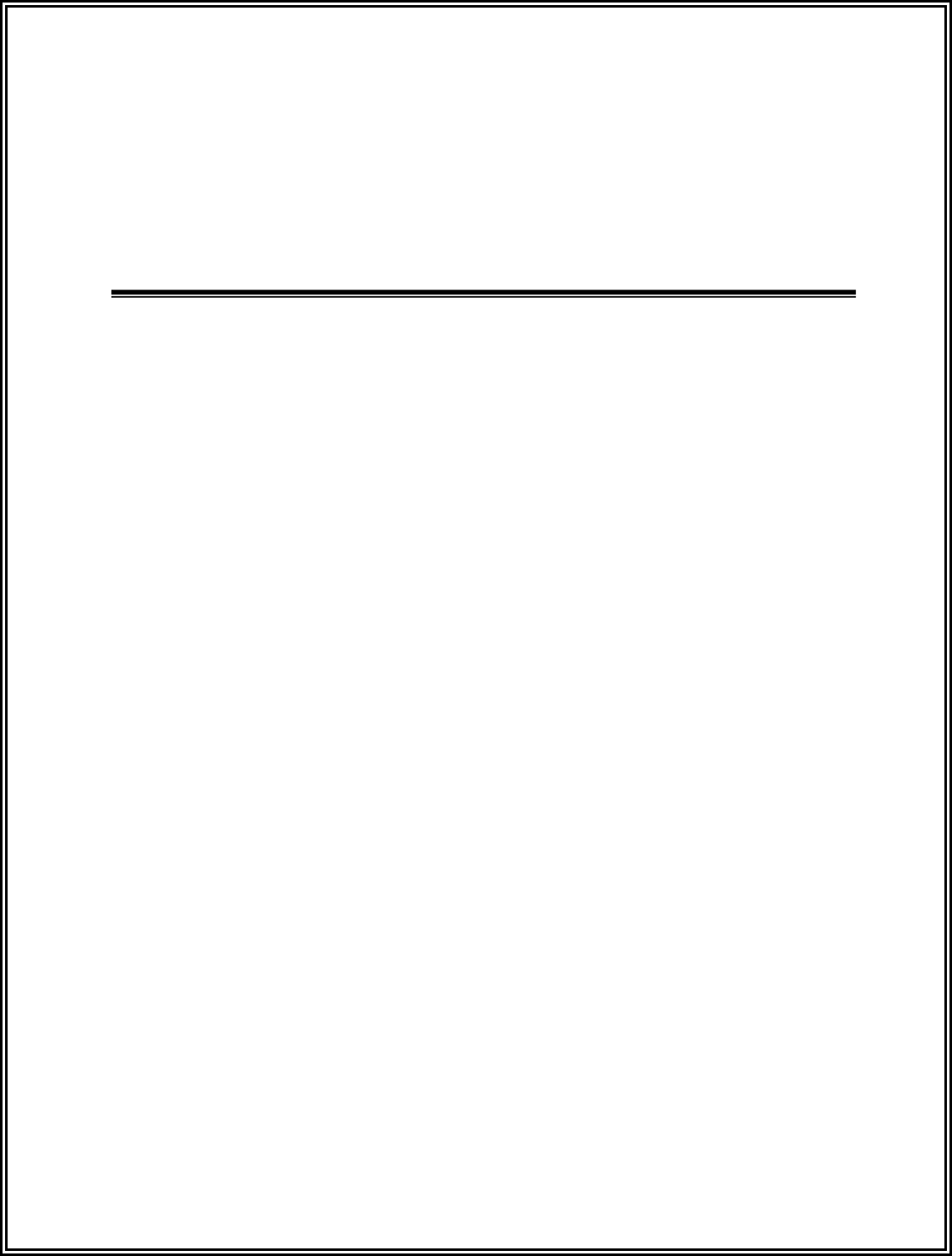
User Manual
Chapter 6:
The Accutech Software
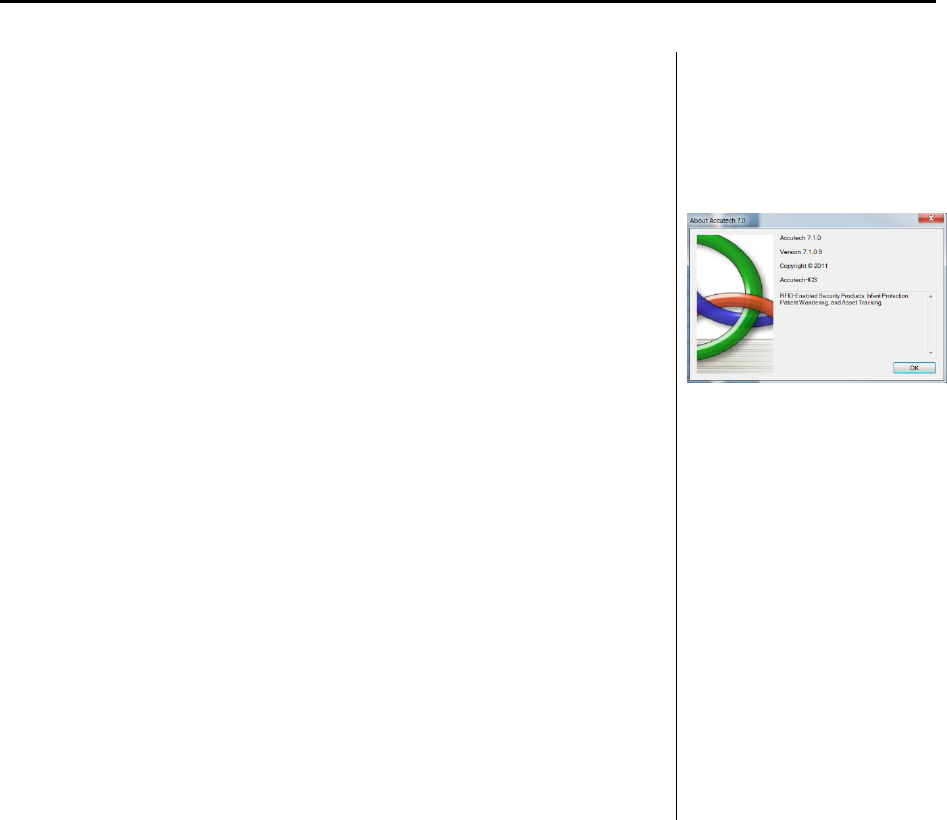
User Manual The Accutech Software 6-
1
The Accutech Software
Accutech Security Systems are NOT computer –dependent. The software
is for notification and reporting purposes only and does not affect nor
control the physical Accutech Security System components.
The following chapter details Accutech Software 7.0.
Software features will vary depending upon your version number, build,
and system settings.
The Accutech Software is installed on each monitoring computer and is
used to display incoming active event information.
Using the facility’s floor plan as the background, zone-specific icons
(i.e., doors, elevators, stairwells, hallway, and band removal receivers)
are placed at each monitored zone’s location and become animated when
an alarm event occurs.
Floor plans can be monitored locally or remotely.
Customizable event handing (displaying, logging, and clearing)
Tags are assigned to specific patients, residents, infants or assets.
Customizable savable/printable Reports
(sort by start date/end date, event type, zone location, and or Tag number)
Automatic daily database backup.

6-2 The Accutech Software U
ser Manual
Login
A valid login is required to open the Accutech 7.0 User Interface for a
specified server. Valid logins (User Name and Password combinations)
are created within Accutech 7.0 from the Operators menu. The options
available to each Operator within the Accutech 7.0 User Interface are
determined from the Operator Privileges menu.
These instructions assume the Database Server and Comm Server
Windows Services are installed and running.
To login the Accutech Software, use the following instructions:
1. Double-click the Accutech icon (1) on the Desktop.
The Login dialog appears.
2. Select the desired server from the Server pull-down list (2)
The Server is the name of the computer where the SQL database
resides.
3. Complete the User Name and Password text fields (2) then select
the Login button.
Default User Name is admin
Default Password is admin
4. Select the button.
The Accutech 7.0 user interface appears.
5. For view additional servers, from inside the Accutech software
user interface, select the button and repeat the process.
6. When viewing multiple areas, areas will be displayed in a tabbed
view.
Logout
For security reasons, it is strongly advised that the Accutech Software
never be closed (or minimized). Closing the Software in no way disables
the system or alarms. However, alarm events will not be logged when
the software is closed.
1
Accutech 7.0 icon
2
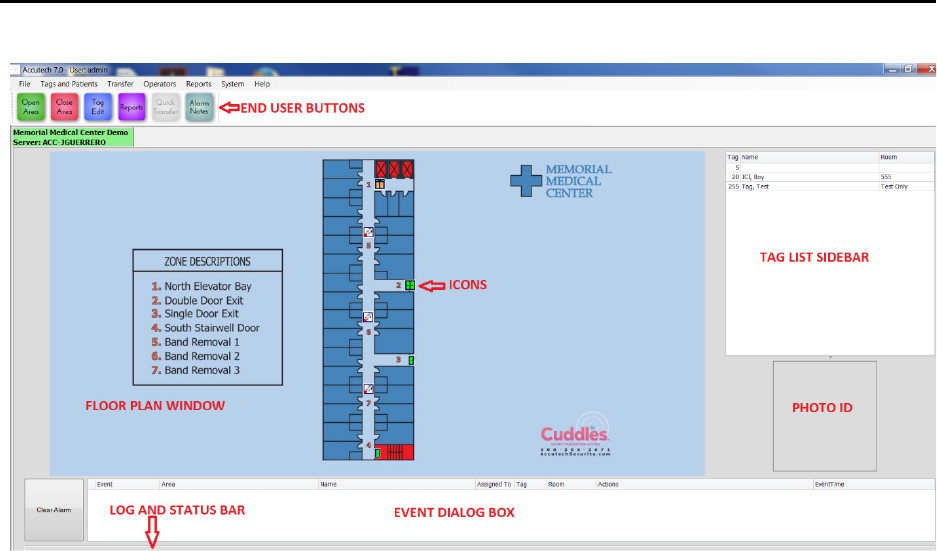
User Manual The Accutech Software 6-
3
7.0 User Interface
User Interface
1. End User buttons – quick access to the most commonly used software operations
2. Floor plan window – displays monitored exit points and Band Alarm Receiver locations
3. Tag List sidebar – displays the area’s currently assigned Tags (Tag number, name, and room)
4. Photo ID – displays Photo ID of the Tag assignment upon alarm event
5. Event Dialog box – displays incoming alarm event information (user action required to clear)
6. Log and Status bar – display incoming alarm event information in YELLOW (no user action
required)
Icons
The Accutech Software uses architectural-specific icons to represent monitored zones in the Floor plan
window. Icons are dormant until an event triggers them into active state. When alarming, icons cycle
between dormant, transitional, and active state. If a dormant icon is clicked on, the zone number and
name will appear in a dialog box; this is the ID state. If an active icon is clicked on, the Alarm
Information dialog box appears.
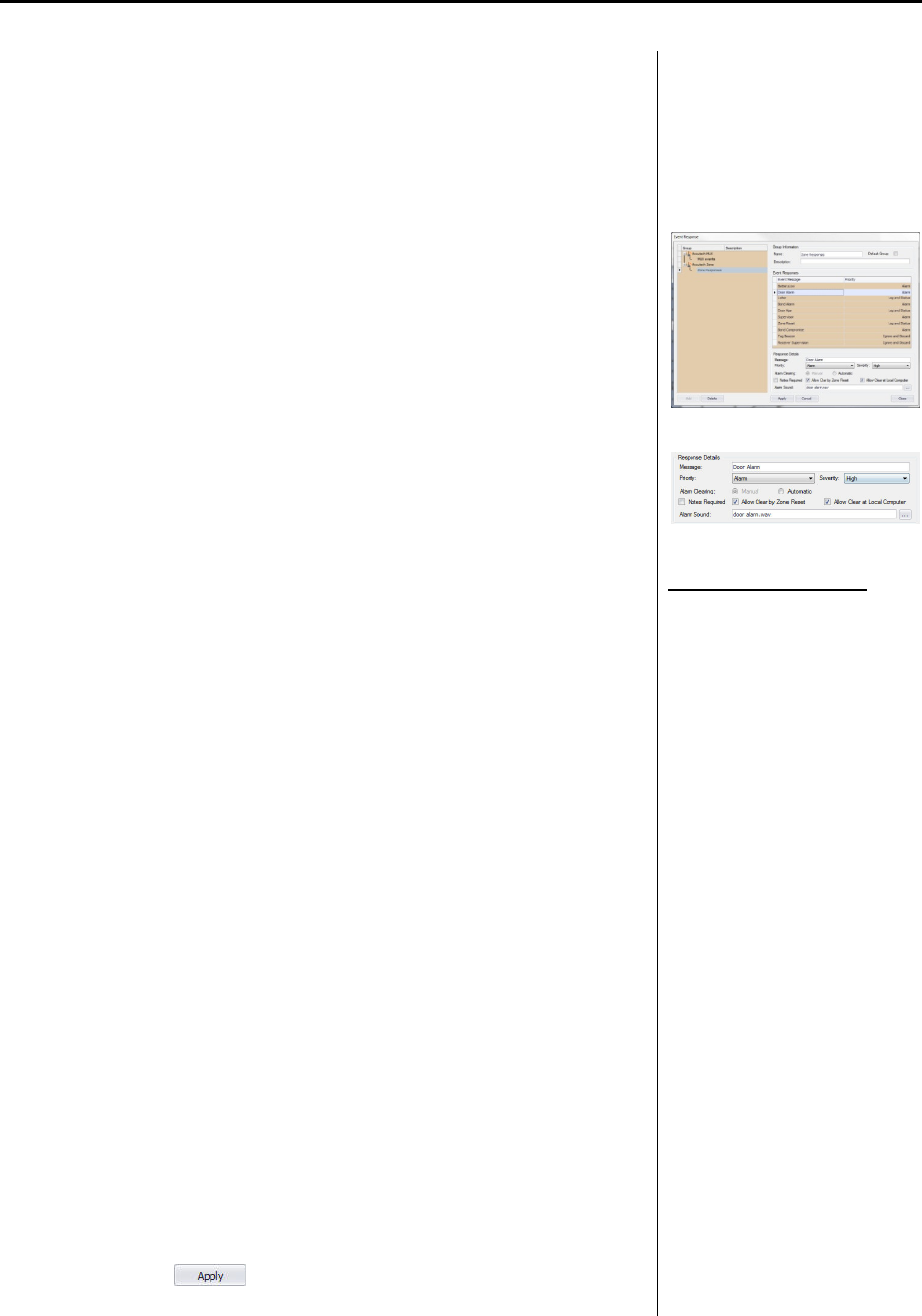
6-4 The Accutech Software User Manual
Event Groups
Event Groups define how alarm events are displayed, cleared, and
alerted (sound files) within the Accutech Software.
To set the Event Groups, use the following instructions:
1. From the System menu, select Event Groups.
The Event Response dialog appears.
2. Expand the Group tree to display Accutech Zone, then highlight
Zone Responses (the Event Reponses and Response Details
become accessible).
3. The Event Reponses section displays all alarm events and their
current priority setting.
4. To change a priority setting, from the Event Reponses section,
select the desired alarm event, then from the Response Details
section set the desired parameters.
5. The color an event appears in the Event Dialog box is
determined by the Severity pull-down list. High is red, Medium
is yellow, and Low is green.
6. The method an alarm can be cleared from the software is
determined by the Alarm Clearing radio buttons and checkboxes.
Remember the Accutech software does not control nor affect
the physical exit point equipment. Clearing an alarm from
the software does not clear or reset the exit point equipment.
Address the causing condition of the alarm event at the exit
point before clearing the alarm event from the software.
Manual – User action is required to clear the alarm from the software
(i.e., select the alarm event, then select the Clear button).
Automatic – The alarm is cleared from the software after a
user-defined duration of time.
Allow Clear by Zone Reset – A valid Keypad reset code entered at the exit
point Keypad will clear the alarm from the software.
Allow Clear at Local Computer – enables/disables the Clear button from the
software user interface.
7. The alarm event sound is determined by the Alarm Sound
setting. Use one of the Accutech provided alarm-specific .wav
files or another compatible sound file as desired. During
multiple alarm events, the alarm sounds will cycle.
8. Select the button to save all settings before exiting the
Response dialog box.
Priority Alarm Options
Ignore and Discard
The event does not appear.
The event is not logged.
Just Log the Event
The event does not appear.
The event is logged.
Log and Status
The event is displayed yellow in
the Status Bar for 20 seconds.
The event is logged.
Alarm
The event is displayed red in the
Event Dialog box.
The event is logged.
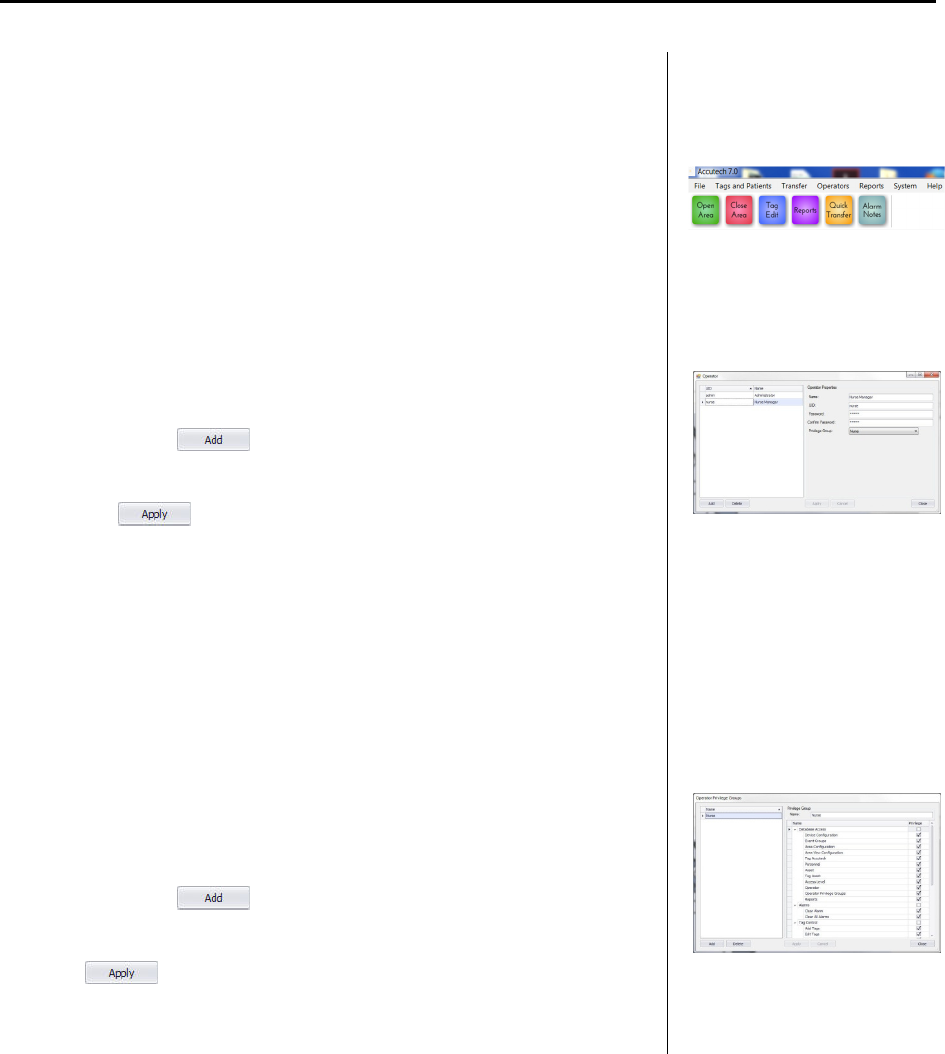
User Manual The Accutech Software 6-
5
Operators
A valid login is required to open the Accutech 7.0 User Interface for a
specified server. Valid logins (User Name and Password combinations)
are created within Accutech 7.0 from the Operators menu. The options
available to each Operator within the Accutech 7.0 User Interface are
determined from the Operator Privileges menu. The default User Name
is admin and the default Password is admin.
To create a new Operator, use the following instructions:
1. From the Operators (1) file menu, select Operator
The Operator dialog box (2) appears.
2. Select the button
3. Complete the Operator Properties section as desired then select
the button.
4. The Privilege Group is the rule set the Operator will follow.
Privilege Groups are set from the Operator Privileges
Operator Privilege Groups
A Privilege Group is the rule set the Operator will follow either allowing
access or denying access to specific software functions.
To create a new Privilege Group, use the following instructions:
1. From the Operators (1) file menu, select Operator Privileges
The Operator Privilege Groups dialog (3) box appears.
2. Select the button
3. Complete the Privilege Group section as desired then select the
button.
1
2
3

6-6 The Accutech Software U
ser Manual
Alarm Events
How an alarm event is displayed in the Accutech 7.0 software is
determined by the Event Response setting under Event Groups. The most
common Event Responses settings are Alarm and Log and Status.
If the alarm event is set to ALARM :
1. The zone icon location will flash
2. The event information will appear RED in the Event Dialog box
3. The event will be logged
4. An audible will sound (if enabled)
If the alarm event is set to LOG AND STATUS :
1. The event information will appear in the Log and Status bar
2. The event will be logged

User Manual The Accutech Software 6-
7
Clearing alarm events
How an alarm event is displayed in the Accutech 7.0 software is
determined by the Event Response setting for that alarm event type
under Event Groups.
The most common Event Response settings are Manual Clear, Allow
Clear by Zone Reset, and Automatically Clear.
Always go to the alarm location and take appropriate action to address
the causing condition. An alarm event will continue to display on the
software unless the causing condition is remedied.
If the alarm event is set to, Manual Clear, select the alarm event in the
Event Dialog box (3) and select Clear Alarm button (note: the alarm
event must be red/white). Alternatively, you may select the active
flashing icon location (4) (which will allow for notes (4) to be associated
with the alarm event in Reports) and then select the Clear Alarm button
(3). If the Alarm event is solid red (2), you cannot clear the alarm event
on the computer screen until the alarm is cleared at the exit point or the
band alarm is addressed.
If the alarm event is set to Allow Clear by Zone Reset, the alarm will
automatically clear when a valid Keypad reset code is entered into the
zone’s Keypad.
If the alarm event is set to Automatically Clear, the alarm will
automatically clear when the user-selected time duration expires.
1
2
3
4
5
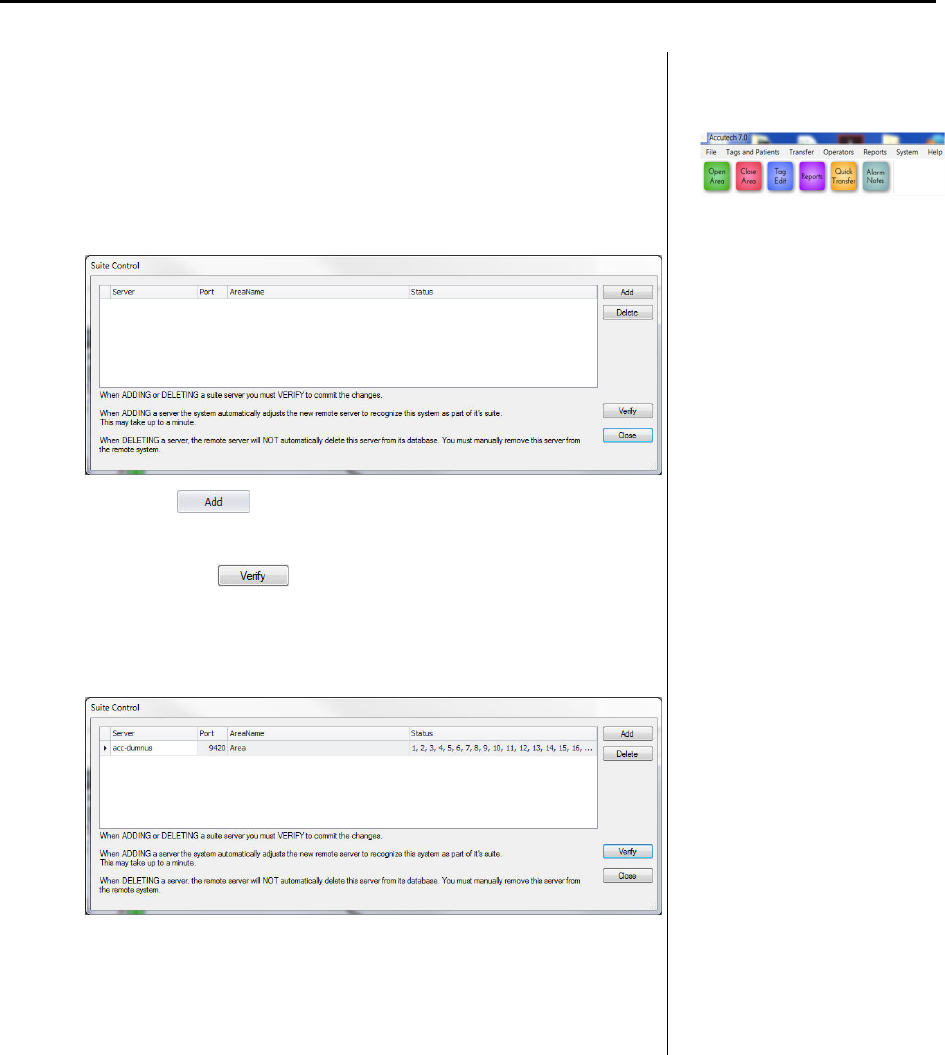
6-8 The Accutech Software U
ser Manual
Suite Control
Suite Control allows for Tag Transfer between two Server databases.
To add a Server to Suite Control, use the following instructions:
1. From the System file menu (1), select Suite Control
The Suite Control dialog appears.
2. Select the button
3. In the Server column, enter the computer name of a server and
then select the button
4. If successful, the Area Name column and Status columns will
populate. The Status column lists the current Tags in the server’s
database.
5. Add additional servers as desired.
1
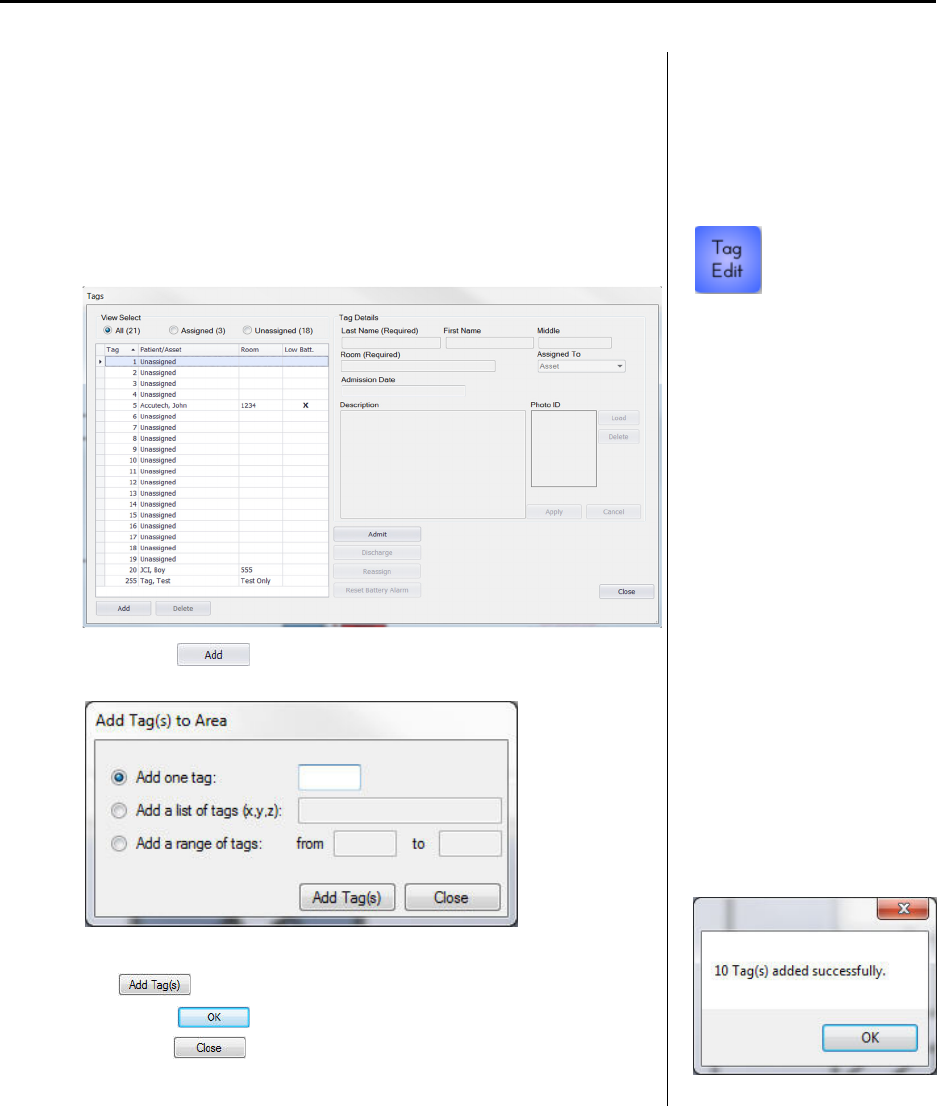
User Manual The Accutech Software 6-
9
Adding Tags
Upon initial installation, add all available Tags intended for use in the
monitored area into the server database.
To add a Tag to the server database, use the following instructions:
1. Select the Tags Edit (1) button
The Tags dialog appears.
2. Select the button
The Add Tag(s) to Area dialog box appears.
3. Enter an individual Tag, list of Tags, or range of Tags and select
the button. A confirmation window will appear (2).
Select the button of the confirmation window then
select the button of the Add Tag(s) to Area dialog box.
The Tags appear in the Tags list.
1
2
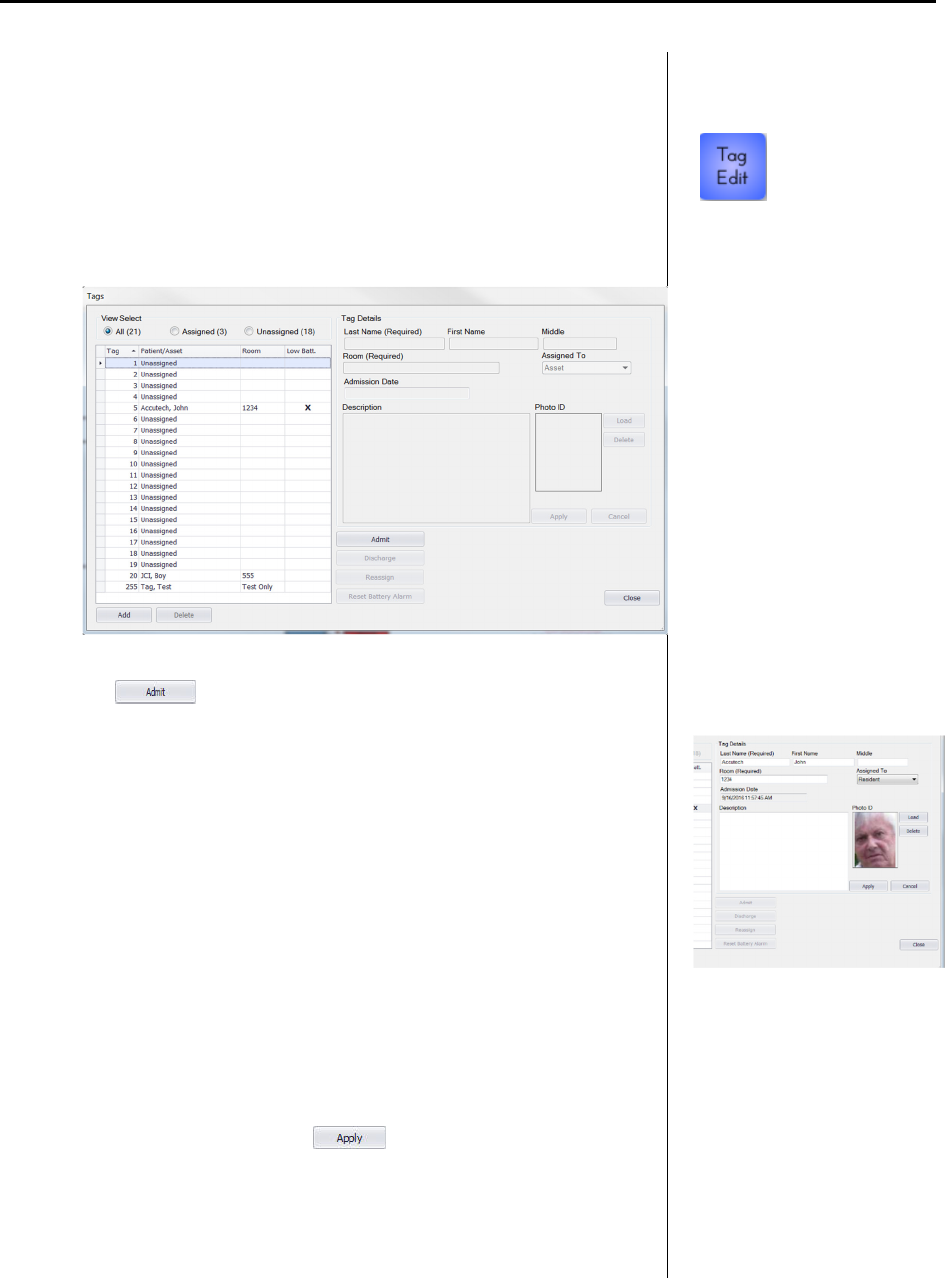
6-10 The Accutech Software Us
er Manual
Assigning a Tag
Tag assignment associated a name, room number, and photo ID for
display in the Accutech 7.0 software when an alarm event occurs.
To assign a Tag, use the following instructions:
1. Select the Tag Edit (1) button.
The Tags dialog appears.
2. Highlight the desired Tag number from the Tag list and select
the button. The Tags Details section becomes
accessible (2). Complete the Tag Details section:
a. The Last Name - required
b. First Name and or middle
c. Room – required
d. Assigned To – select from: Asset, Baby, Personnel, Patient,
Resident
e. Photo ID
3. The user can also associate a Photo ID (2) with the Tag
assignment by selecting the Load button, then the Load Image
button, browsing to the photo location, selecting the photo,
selecting the Open button, cropping the photo as desired, and
finally selecting the OK button.
4. When finished, select the button.
The Tag list updates with the entered information and the
assignment is listed in the Tag list sidebar of the user interface.
An admission date will automatically be associated with the tag
assignment.
1
2
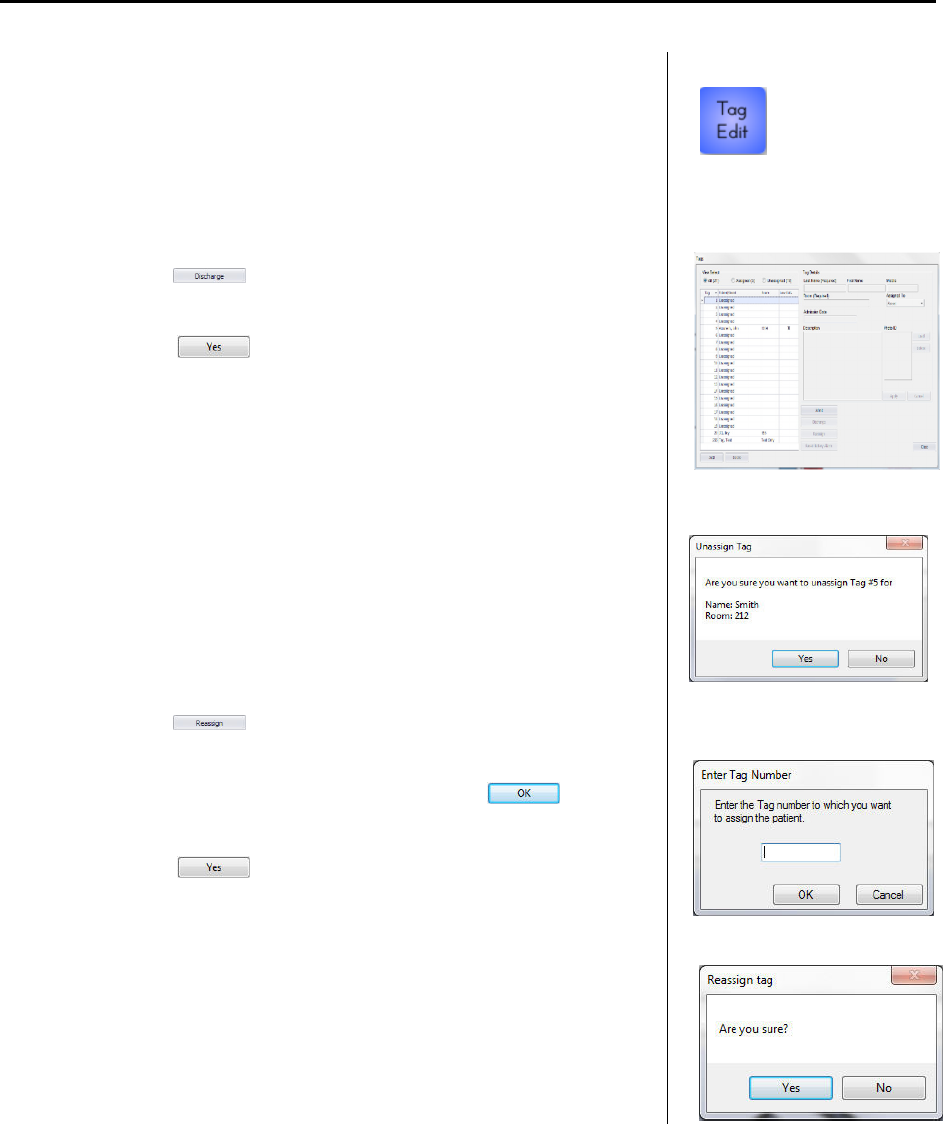
User Manual The Accutech Software 6-
11
Unassigning a Tag
To unassign a Tag, use the following instructions:
1. Select the Tag Edit (1) button.
The Tags dialog box (2) appears.
2. Highlight the desired assigned Tag number from the Tag list and
select the button. A confirmation window appears (3).
3. Select the button.
The Tag is unassigned. The Tag list and Tag list sidebar updates
accordingly.
Reassigning a Tag
To reassign a Tag (to another Tag number without having to re-enter Tag
Details information), use the following instructions:
1. Select the Tag Edit (1) button.
The Tags dialog box (2) appears.
2. Highlight the desired assigned Tag number from the Tag list and
select the button.
The Enter Tag Number dialog box appears (4).
3. Enter an available Tag number and select the button. A
confirmation window appears (5).
4. Select the
The Tag is reassigned. The Tag list and Tag list sidebar updates
accordingly.
1
2
3
4
5
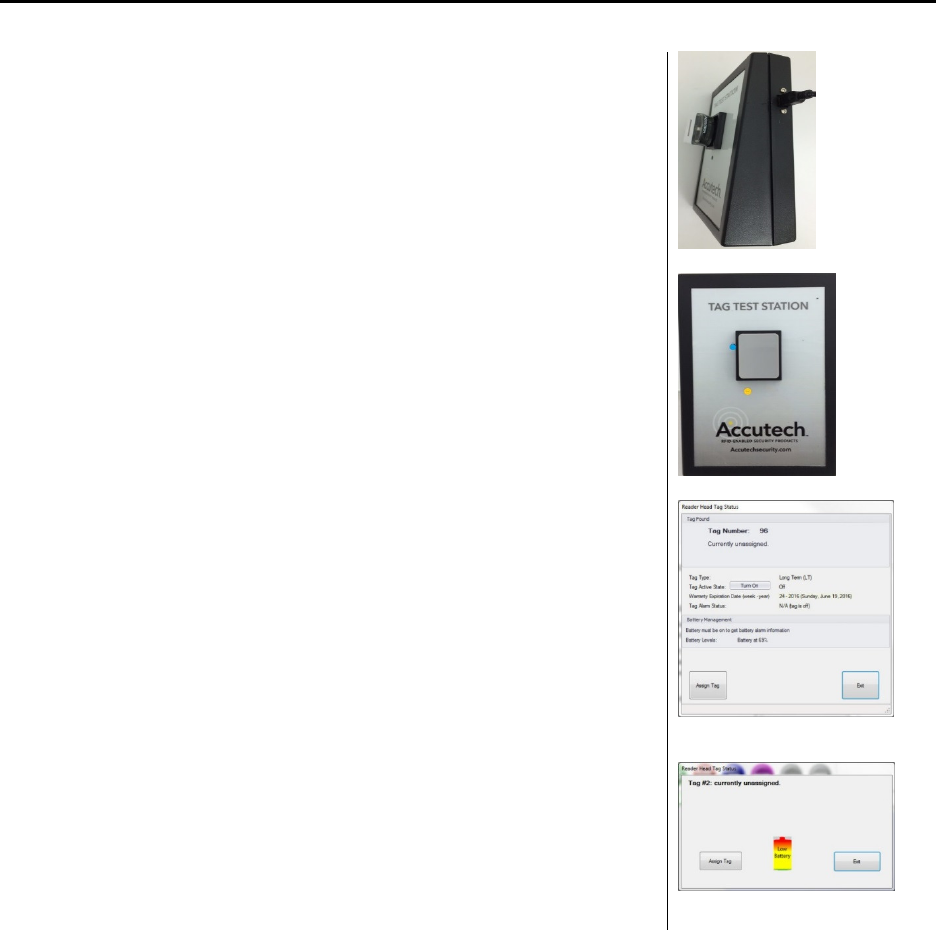
6-12 The Accutech Software Us
er Manual
USB Tag Test Station
The USB Tag Test Station verifies a Tags ID number, tag type, useful
battery level, warranty date and manufacture date without having to
activate the tag with an STAD. It will also allow you to generate a report
on tags that were tested. The USB TTS will only work with Accutech 7.0
Software.
Using the Tag Test Station
Once the TTS fully reads the data from the tag, the software will
provide:
1. The tag #
2. The bar code #, which indicates the manufacture date. eg.4209
indicates week and year
3. Tag State – whether the tag is in an OFF or ON state. You can then
turn the tag on for use at this time if it is an LT tag. Or if the tag is
already on, you can turn the tag off for storage purposes.
4. Tag Type – LT, SB, CB, BR
5. End of Warranty Date
6. Battery Level – 1-100% indicates USEFUL tag battery life and means
the tag is good. 0% indicates the tag needs to be replaced. Do not
continue to use a tag with 0% indicated.
Note: you cannot activate a BR tag with the TTS. However, you can
deactivate an active BR tag if placed on the TTS.
Generating a Report
Once the TTS fully reads the data from the tag, the software will
log the information a report can be created for future reference.
Tag Currently assigned
Tag Low Battery
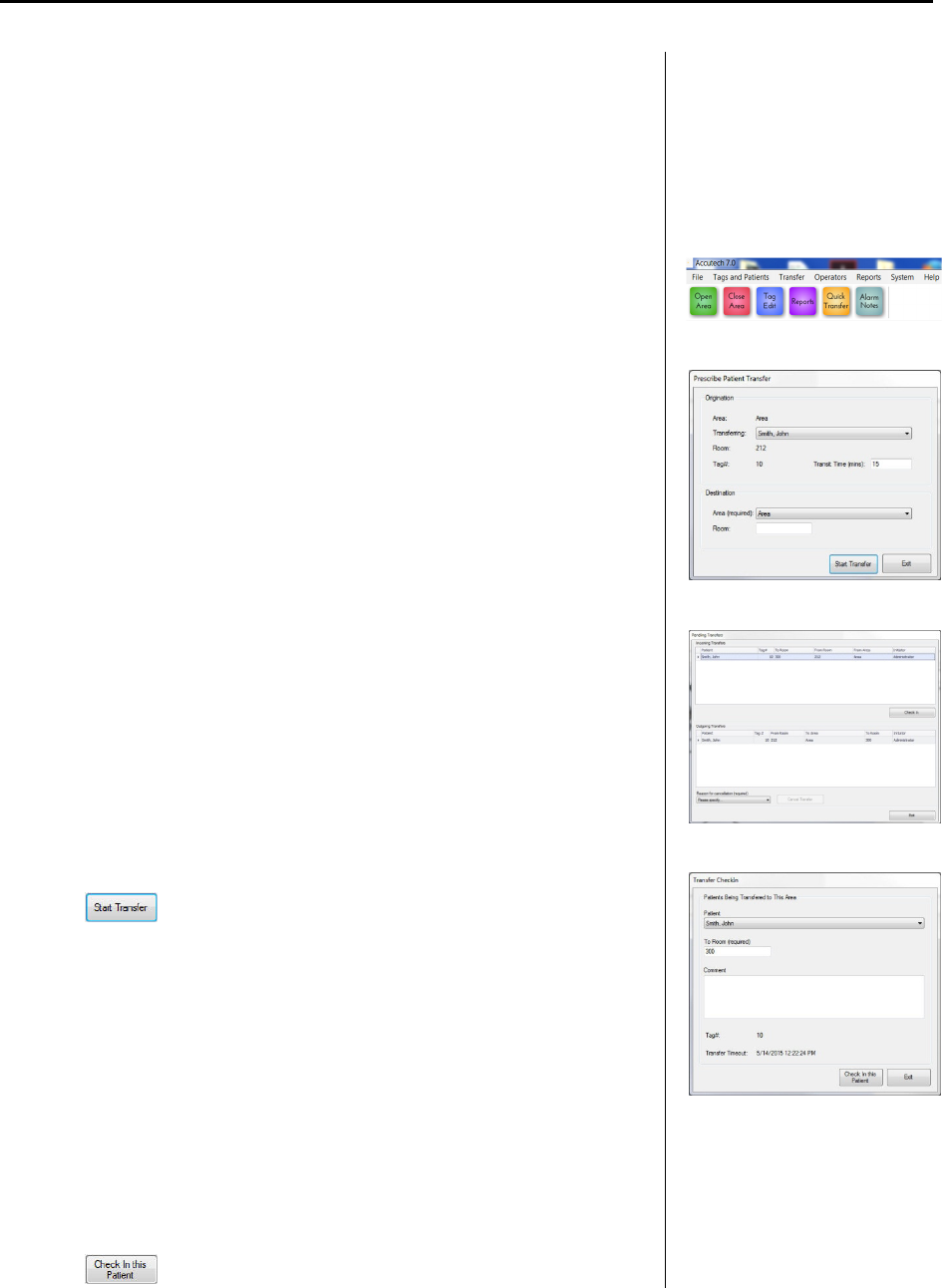
User Manual The Accutech Software 6-13
Tag Transfer
Tag Transfer is the process of transferring Tag Details between two
server databases. At no time is the protection of the system
compromised. Any alarm event will register and display before, during,
or after a Tag Transfer. In installations with multiple servers
(i.e., multiple protected areas or floors), due to floor-to-floor
discrimination and potential global band removal lockdown protocol,
the Accutech Software requires Tags to be designated in their respective
databases where they are in use and physically reside. Utilize Tag
Transfer for staff escorted transfer of currently assigned Tags. Use Quick
Transfer for transfer of unassigned Tag inventory.
These instructions assume Suite Control settings are already established.
To Transfer an assigned Tag, use the following instructions:
1. From the Transfer file menu (1), select CheckOut (2).
The Prescribe Patient Transfer dialog box appears.
2. From the Transferring pull-down list, select the desired assigned
Tag.
3. Adjust the Transfer Time (mins) text field as desired to allot
enough time to complete the transfer. If the Transfer time is
exceeded, a Transfer Timeout dialog box will appear. Once the
Transfer Timeout dialog box appears, the user will need to
cancel or extend the Transfer Time.
4. From the Destination Area pull-down list, select the desired area.
5. Once all Check Out parameters are set as desired, select the
button.
6. The transfer is started and moved to Pending Transfers
(Transfers file menu > Pending). The Pending Transfer dialog
box (3) displays all current Incoming and Outgoing Transfer in
progress, allows transfer cancellation, and allows transfer Check
In.
7. Once the staff escort arrives at the destination area, from the
Transfer file menu, select Check In. The Transfer CheckIn
dialog box (4) appears.
8. From the Patient pull-down list, select the desired Tag, edit the
Room and Comments text fields as desired, and select the
button to complete the transfer.
1
2
3
4
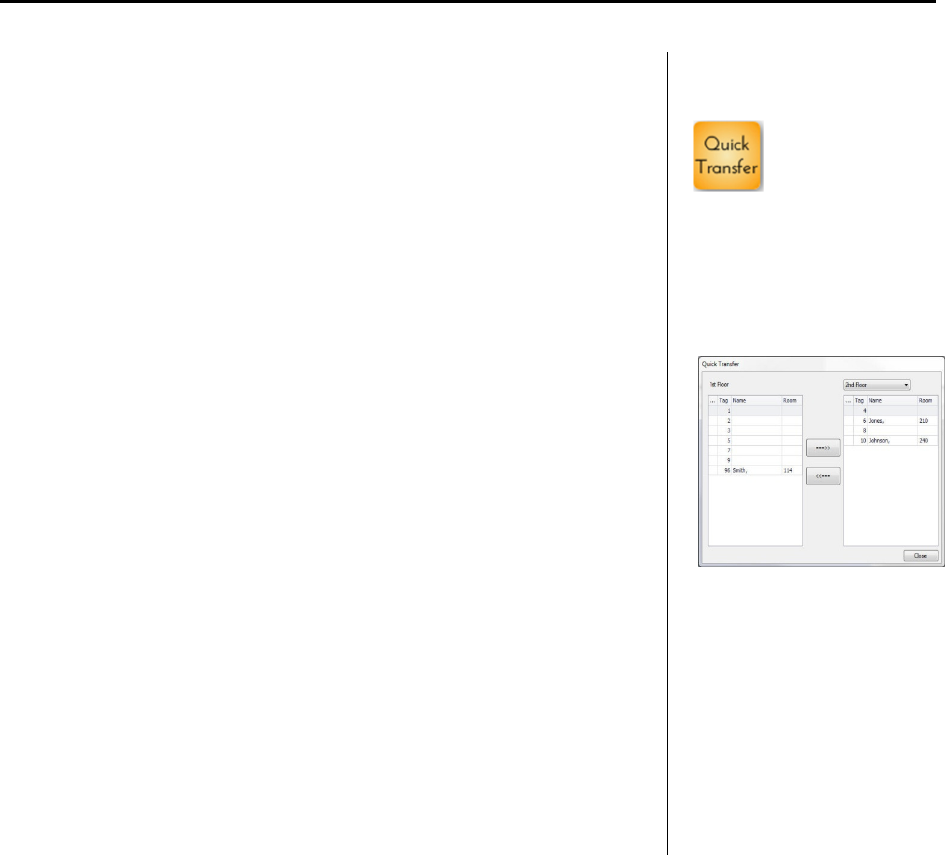
6-14 The Accutech Software Us
er Manual
Quick Transfer
Tag Transfer is the process of transferring Tag Details between two
server databases. At no time is the protection of the system
compromised. Any alarm event will register and display before, during,
or after a Tag Transfer. In installations with multiple servers
(i.e., multiple protected areas or floors), due to floor-to-floor
discrimination and potential global band removal lockdown protocol,
the Accutech Software requires Tags to be designated in their respective
databases where they are in use and physically reside. Utilize Tag
Transfer for staff escorted transfer of currently assigned Tags. Use Quick
Transfer for transfer of unassigned Tag inventory.
These instructions assume Suite Control settings are already established.
To Quick Transfer a Tag, use the following instructions:
1. Select the Quick Transfer button (1).
The Quick Transfer dialog box appears (2).
The current database is listed in the left column.
Available databases are listed in the right column.
2. From the Area Name pull-down list, select the desired database.
3. Select the desired Tag and use the right and left arrow buttons to
transfer accordingly.
4. When finished, select the close button to exit.
1
2
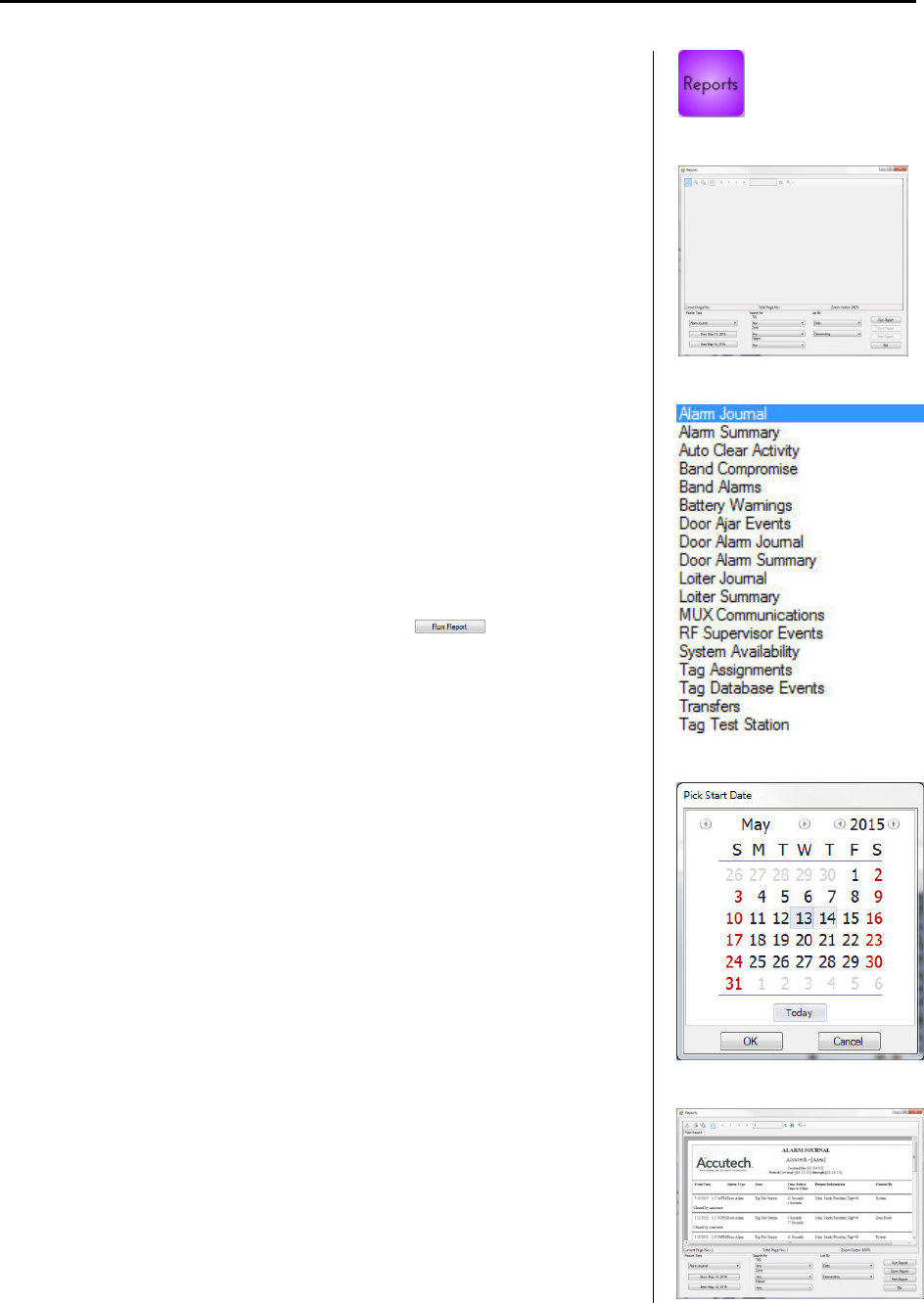
User Manual The Accutech Software 6-15
Reports
Alarm events set to log under Event Groups can be queried to examine
alarm frequency, duration, and patterns. Use this information to make
adjustments to zone equipment to alleviate staff alarm fatigue or during
system evaluations from internal or external parties. Reports may be
saved to various electronic file formats or sent to available printers.
To generate a Report, use the following instructions:
1. Select the Reports button.
The Reports dialog box (2) appears.
2. Select the desired report from Report Type pull-down list (3).
3. Select the desired Start and End Date parameters from their
respective buttons (4).
4. Select the parameters desired under the Search for and List By
section to further filter report results
5. Once all parameters are set, select the button.
The report is generated and displayed.
6. Save or Print the Report as desired.
1
2
3
4
5
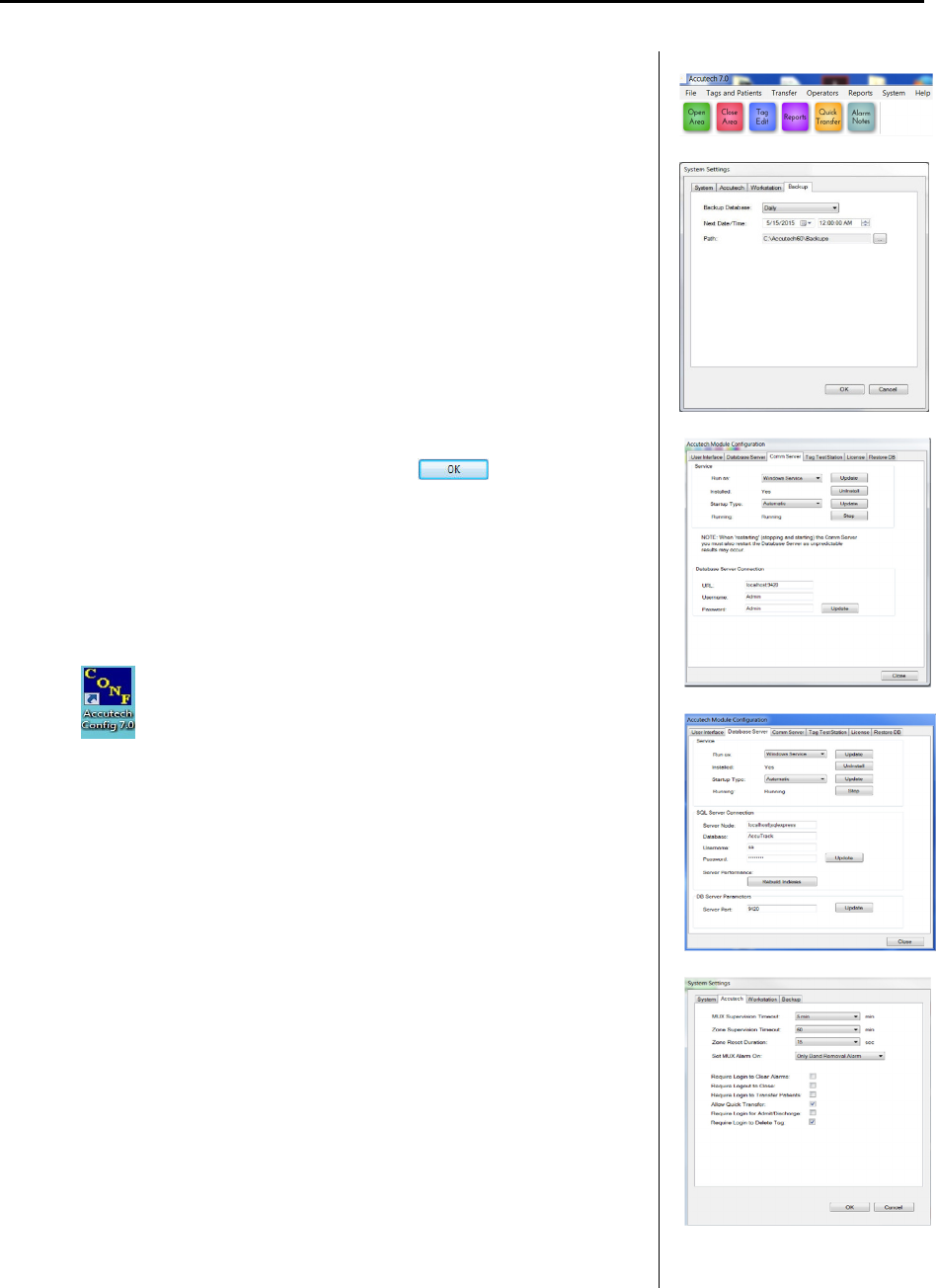
6-16 The Accutech Software Use
r Manual
Automatic Backups
Accutech Software 7.0 will automatically backup the server database
daily. To modify backup schedule and save location, use the following
instructions:
1. From the System menu (1), select Settings
The System Settings dialog box appears.
2. Select the Backup tab (2)
3. Adjust the Backup Database pull-down list (Daily or Weekly) as
desired
4. Adjust the Save Path location as desired
5. Once all parameters are set, select the button to exit
Trouble Shooting
In the event the software stops generating alarms,
1. Check the Database Server and or Comm server settings. Open
the Accutech Config 7.0 Icon from your desktop.
The Accutech Module Configuration dialog box appears. Check
both the Database Server tab (4) and the Comm Server tab (5).
The following settings should be selected in the service area:
Run As: Windows Service – (change and update if it isn’t)
Installed: Yes (install if it isn’t)
Startup Type: Automatic (change and update if it isn’t)
Running: Running (start if it is stopped)
2. Check “Only Band Removal Only Alarm”. From the System
menu (1), select Settings, The System Settings dialog box
appears. Select the WorkStation Tab (5). Next to Set MUX
Alarm On: “Only Band Removal Alarm” should be selected.
3. Restart computer. If the problem persists contact IT, your local
service provider or call 800-356-2671 for support.
1
2
3
4
5
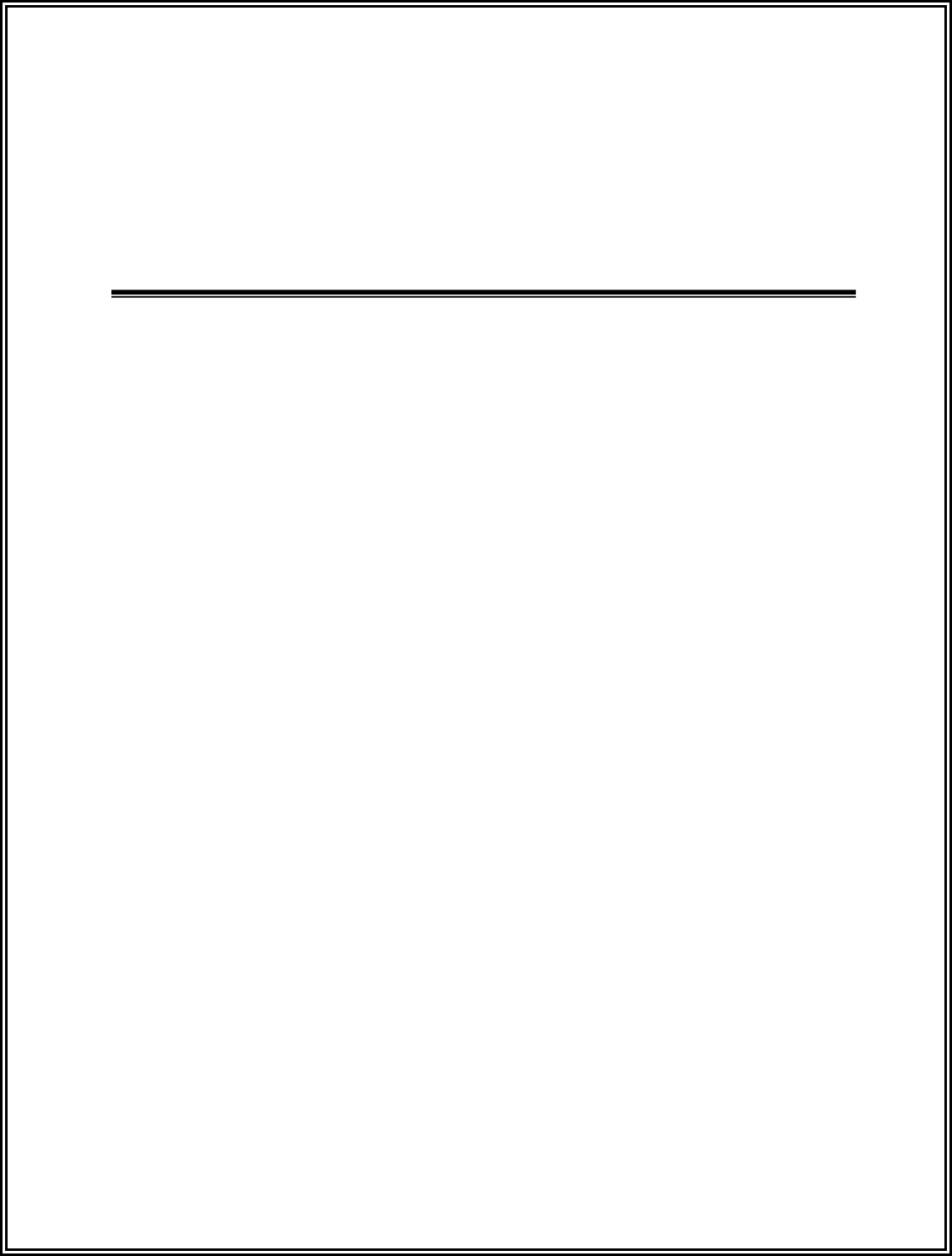
User Manual
Chapter 7:
Facility Performance Testing
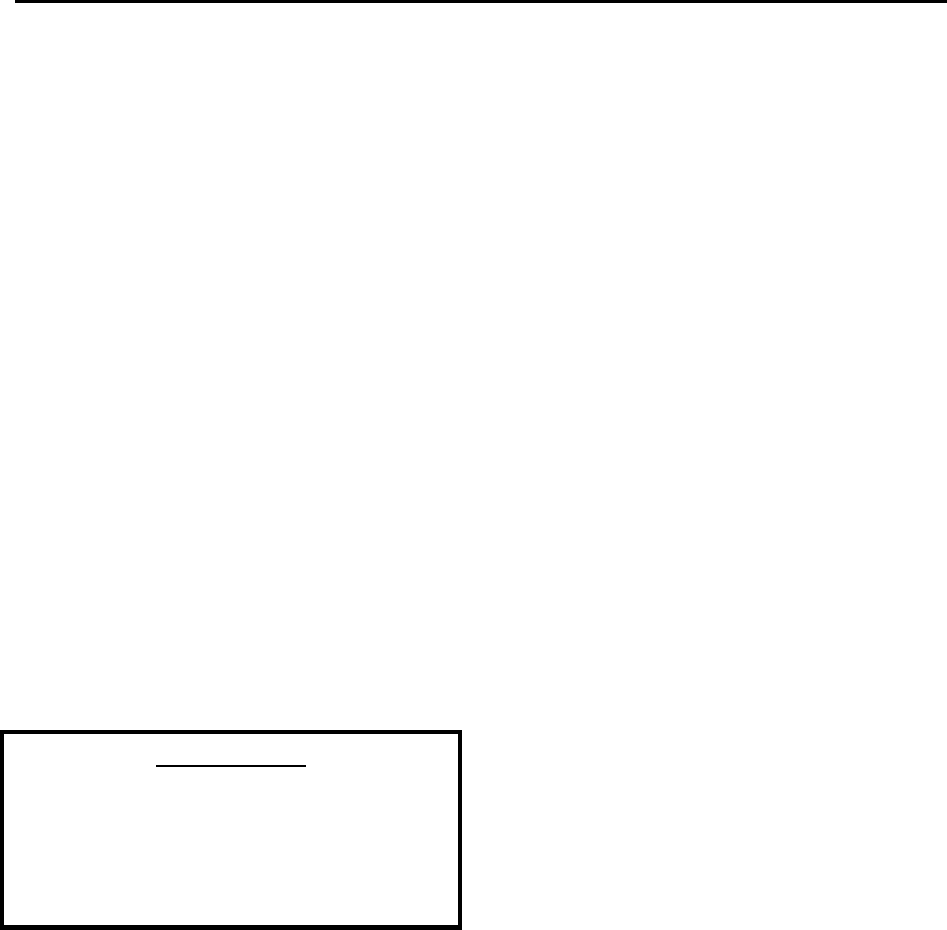
User Manual Facility Performance Testing 7-1
Facility Performance Testing
Zone Functions Tested
Test Equipment Required
Zone, Lock Test
Zone, Egress Test
(3000 and 3101 Magnetic Locks)
Zone, Delayed Egress Test
(3101 Magnetic Locks only)
Zone, Hallway Test
Zone, Elevator Deactivation Test
Door Ajar Test
Loiter Test
System Supervisor Test (Tx)
System Supervisor Test (Rx)
Fire Panel Interface (FPI) Test
Band Alarm Test (BR 4200 Systems only)
NOTE: These tests should only be performed by
trained personnel.
This document defines the recommended
periodic testing procedures for the Accutech
security systems. Accutech recommends that
these tests be performed (at the minimum) on a
monthly basis.
DISCLAIMER:
This chapter is intended as a guidance
document only. Each facility should review
these recommendations and modify as
necessary to meet their own unique security
requirements.
Periodic testing of these critical performance
functions can help prevent undetected security
system failures.
Zone Functions Tested
Accutech systems respond to RF signals
generated by the Tags. Most conditions occur at
a monitored zone, although, Band Alarms can
occur anywhere. In addition, the Accutech
System monitors non-Tag-related zone functions
such as Door Ajar and Supervisor. The RF
signals we will be concerned with during these
tests are:
Zone – triggered when a Tag
approaches or lingers at a doorway, an
elevator, or other monitored zone
Band Alarm (BR 4200 Systems only) –
triggered when a BR 42 Tag band is
loosened, cut, saturated, removed, or
tampered with.
Each exit point around the area of protection
should be evaluated to determine:
if doors lock and/or elevators disable when
a Tag approaches
if alarms are generated due to passage of a
Tag through an exit point
if Band Alarm functions are operating
correctly (BR 4200 Systems only)
if events are correctly logged in the system
computer(s) when chosen in the software
to do so
Test Equipment Required
You will need to designate Tags to be used
solely for testing purposes only.
For ES 2200 and IS 3200 Systems, designate
one Tag for testing zone alarms.
For BR 4200 Systems, you can designate one
Tag for testing zone alarms and Band Alarms or
designate one Tag for each alarm test.
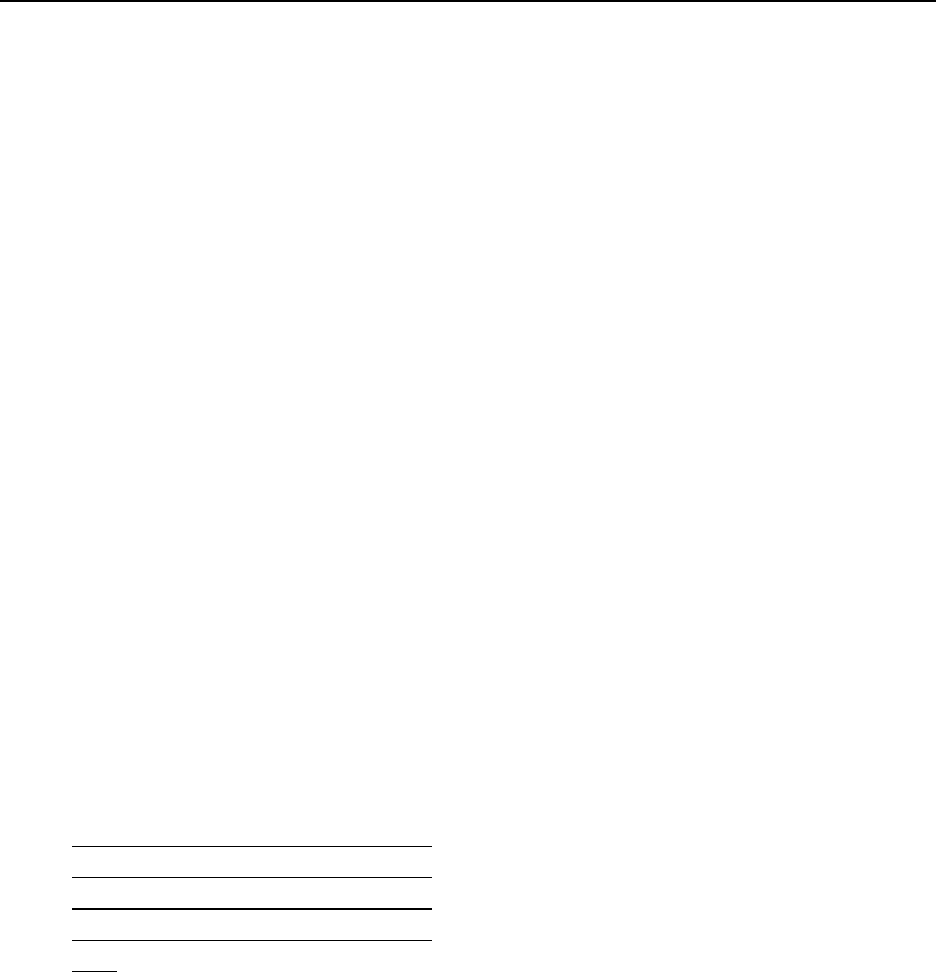
7-2 Facility Performance Testing User Manual
For IS 3200 and BR 4200 Systems, Tags
designated for testing purposes should be
assigned on the system under the patient names
“Test Tag – Zone” and “Test Tag – Band
Alarm” and the numbers 255 and 254
respectively, so that it will be clear to anyone
viewing the alarm pop-up messages or alarm
reports that these events were related to system
testing.
Zone, Lock Test
When a Tag approaches a monitored door zone
equipped with Locks, the Lock should engage.
When the Tag leaves the monitored zone, the
Lock should disengage. This test will evaluate
this operation.
NOTE: In the event of a fire, all Locks are
disabled and the door can be opened
immediately.
Test results should be written down and kept in a
test log. Make your own, or use the included, to
ensure that every monitored zone is tested.
These test reports should become part of your
permanent quality assurance records.
1. Notify staff and security that you will be
testing zone performance and alarms
may be generated. They should pay
special attention to traffic during this
time.
2. While not in a monitored zone, use an
S-TAD to activate the test Tag.
3. Hold the test Tag in your hand and
approach each monitored door zone.
4. Each door should lock as you approach.
NOTE: You may be able to hear the lock
“click” as it changes states. Otherwise,
For 3000 Series Magnetic Locks, you
can push on the door to verify the Lock
is engaged. For 3101 Series Magnetic
Locks, the LED will turn from green to
red when the Lock is engaged.
However, do not open the door; this test
is intended only for verifying that a door
locks when a Tag approaches. If you
wish to verify the operation of Delayed
Egress Circuitry for 3101 Locks, see
page 7-3.
5. As you approach each zone, try varying
your approach angle (i.e., straight on,
from the sides, down low, etc.). Make
sure there is adequate coverage from all
angles leading to the monitored zone.
6. Record the results (pass or fail).
7. If the test fails to lock the door:
a. Notify staff and security of the
vulnerable area.
b. Check for visible damage or
tampering to the zone equipment.
c. Have a maintenance technician
verify power to the zone equipment.
d. Have a maintenance technician
verify the FPI is set properly.
e. Call your Accutech Representative.
8. To reset the Lock, deactivate the test
Tag or leave the monitored zone.
Depending upon your settings, the Lock
may disengage itself automatically.
Otherwise enter a Keypad Reset code.
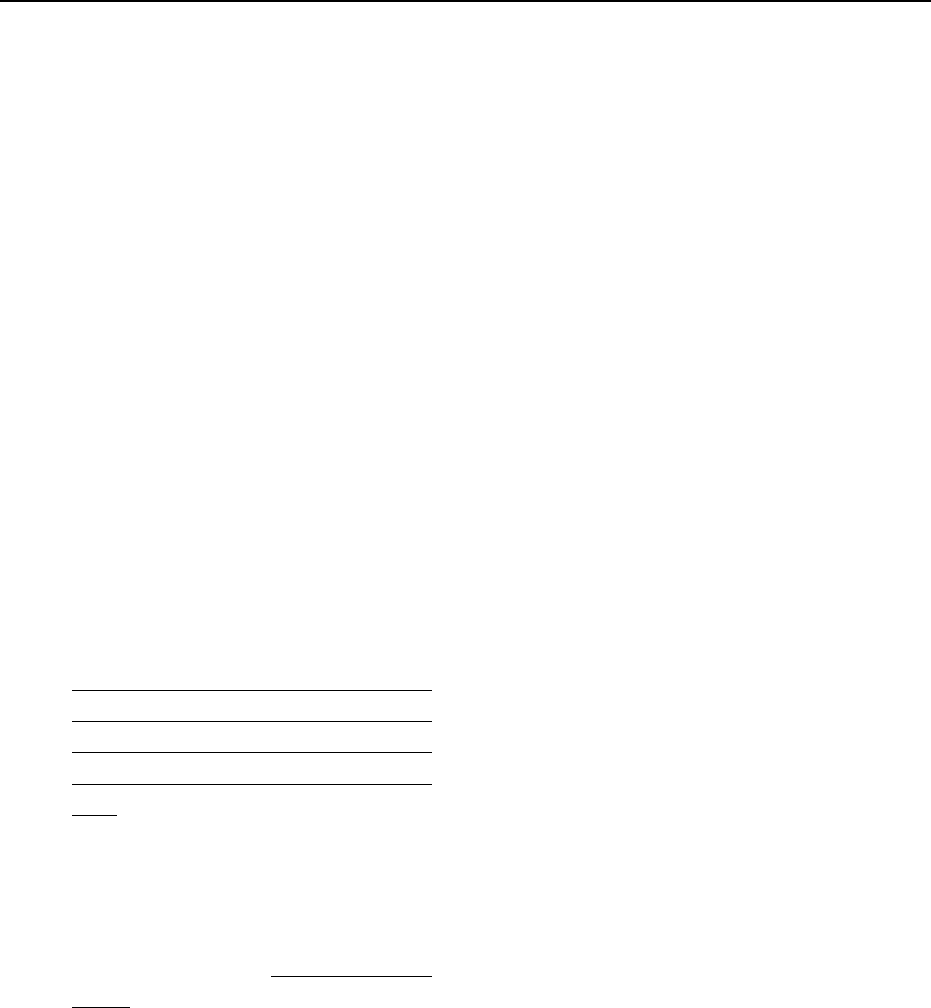
User Manual Facility Performance Testing 7-
3
Zone, Egress Test
(3000 and 3101 Magnetic Locks)
Most monitored door zones equipped with
Locks are configured to generate an alarm if a
Tag is detected in the zone and the door is open.
This test will evaluate this operation. For
hallways zones, see page 7-4.
NOTE: In the event of a fire, all Locks are
disabled and the door can be opened
immediately.
This test should be conducted selectively; create
a rotating schedule to test a different set of zones
each time that periodic testing is conducted.
Test results should be written down and kept in a
test log. Make your own, or use the included, to
ensure that every monitored zone is tested.
These test reports should become part of your
permanent quality assurance records.
1. Notify staff and security that you will be
testing zone performance and alarms
will be generated. They should pay
special attention to traffic during this
time.
2. Prop the door open.
3. While not in the zone, use an S-TAD to
activate the test Tag.
4. Approach the door. An alarm should
sound.
5. Verify that the central computer
correctly logged this alarm and that any
networked computer also sees the alarm.
6. Record the results (pass or fail).
7. If the test fails to cause an alarm:
a. Notify staff and security of the
vulnerable area.
b. Check for visible damage or
tampering to the zone equipment.
c. Have a maintenance technician
verify power to the zone equipment
d. Have a maintenance technician
verify the FPI is set properly
e. Call your Accutech Representative.
8. To reset the zone, enter a Keypad reset,
deactivate the test Tag, and close the
door completely, and if necessary, clear
the alarm on the PC.
Zone, Delayed Egress Test
(3101 Magnetic Locks only)
Delayed Egress Circuitry is a feature of the
Accutech 3101 Magnetic Lock that, due to fire
and life safety codes, allows free egress through
a door after 15 seconds (plus a 1 to 3 second
nuisance delay) of constant force is applied. This
test will evaluate this operation.
NOTE: In the event of a fire, Delayed Egress
Circuitry is disabled and the door can be opened
immediately.
This test should be conducted selectively; create
a rotating schedule to test a different set of zones
each time that periodic testing is conducted.
Test results should be written down and kept in a
test log. Make your own, or use the included, to
ensure that every monitored zone is tested.
These test reports should become part of your
permanent quality assurance records.
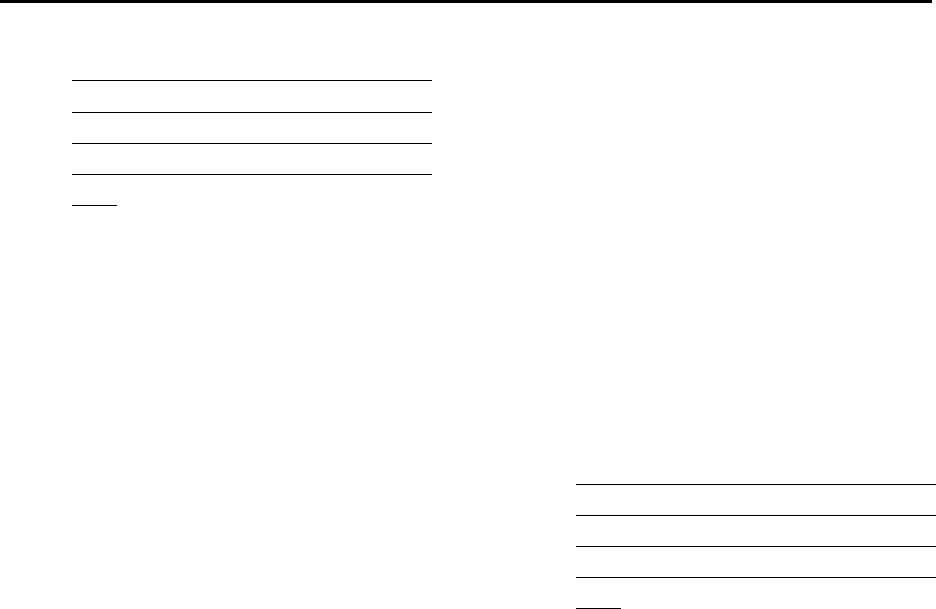
7-4 Facility Performance Testing User Manual
1. Notify staff and security that you will be
testing zone performance and alarms
will be generated. They should pay
special attention to traffic during this
time.
2. While not in the zone, use an S-TAD to
activate the test Tag.
3. Approach the door.
4. The Lock should engage.
NOTE: The LED on the Lock will turn
from green to red when the Lock is
engaged.
5. Remember once the Lock is engaged, in
order to open the door, you have invoke
the Delayed Egress Circuitry feature. To
do this, press on the door for the
duration of the nuisance delay (1 to 3
seconds) and the delayed egress
countdown (15 to 30 seconds) then the
Lock will disengage and you can open
the door.
NOTE: During the delayed egress
countdown the Lock’s piezo will beep.
After you open the door, the Lock’s
piezo will sound continuously.
6. Verify that the central computer
correctly logged this alarm and that any
networked computer also sees the alarm.
7. Record the results (pass or fail).
8. If the test fails to cause an alarm:
a. Notify staff and security of the
vulnerable area.
b. Check for visible damage or
tampering to the zone equipment.
c. Have a maintenance technician
verify power to the zone equipment.
d. Have a maintenance technician
verify the FPI is set properly.
e. Call your Accutech Representative.
9. To reset the zone, enter a Keypad reset,
deactivate the test Tag, close the door
completely, and, if necessary, clear the
alarm on the PC.
Zone, Hallway Test
Two conditions are required to generate an
alarm at a hallway zone: Tag detection and PIR
detection. This test will evaluate this operation.
1. Notify staff and security that you will be
testing zone performance and alarms
will be generated. They should pay
special attention to traffic during this
time.
2. Using an S-TAD, activate the test Tag.
3. Enter the monitored hallway zone and
move in the path of the PIR. An alarm
should be generated and an alarm may
sound.
4. Verify this alarm is logged on the
central computer and any other remote
computers networked to it.
5. Record the results (pass or fail).
6. If the test fails to cause an alarm:
a. Notify staff and security of the
vulnerable area.

User Manual Facility Performance Testing 7-
5
b. Check for visible damage or
tampering to the zone equipment.
c. Have a maintenance technician
verify power to the zone equipment
d. Call your Accutech Representative.
7. To reset the zone, enter a Keypad reset,
deactivate the test Tag, and, if
necessary, clear the alarm on the PC.
Zone, Elevator Deactivation Test
When a Tag approaches an elevator zone the
elevator call buttons will be disabled. This test
will evaluate this operation.
1. Notify staff and security that you will be
testing zone performance and alarms
will be generated. They should pay
special attention to traffic during this
time.
2. Using an S-TAD, activate the test Tag.
3. Enter the elevator zone. The zone’s
response will depend on the state of the
elevator door(s):
a. Elevators with door(s) open will
disable as you approach and an
alarm will sound. The car will not
be able to leave the floor.
b. Elevators with door(s) closed will
have their call button(s) disabled.
c. Elevators en route will arrive, open,
and then an alarm will sound. The
car will not be able to leave the
floor.
4. Verify this alarm is logged on the
central computer and any other remote
computers networked to it.
5. Record the results (pass or fail)
6. If the test fails to cause an alarm:
a. Notify staff and security of the
vulnerable area.
b. Check for visible damage or
tampering to the zone equipment.
c. Have a maintenance technician
verify power to the zone equipment
d. Have a maintenance technician
verify the FPI is set properly
e. Call your Accutech Representative.
7. To reset the zone, deactivate the test Tag
and, if necessary, enter a Keypad reset
and clear the alarm on the PC.
Door Ajar Test
This test will evaluate the Door Ajar feature.
1. Notify staff and security that you will be
testing zone performance and alarms
will be generated. They should pay
special attention to traffic during this
time.
2. Without a Tag in the zone, prop the door
open.
3. Depending upon the time delay setting,
the door should register a Door Ajar
alarm after the predetermined time.
4. Record and verify the time setting.
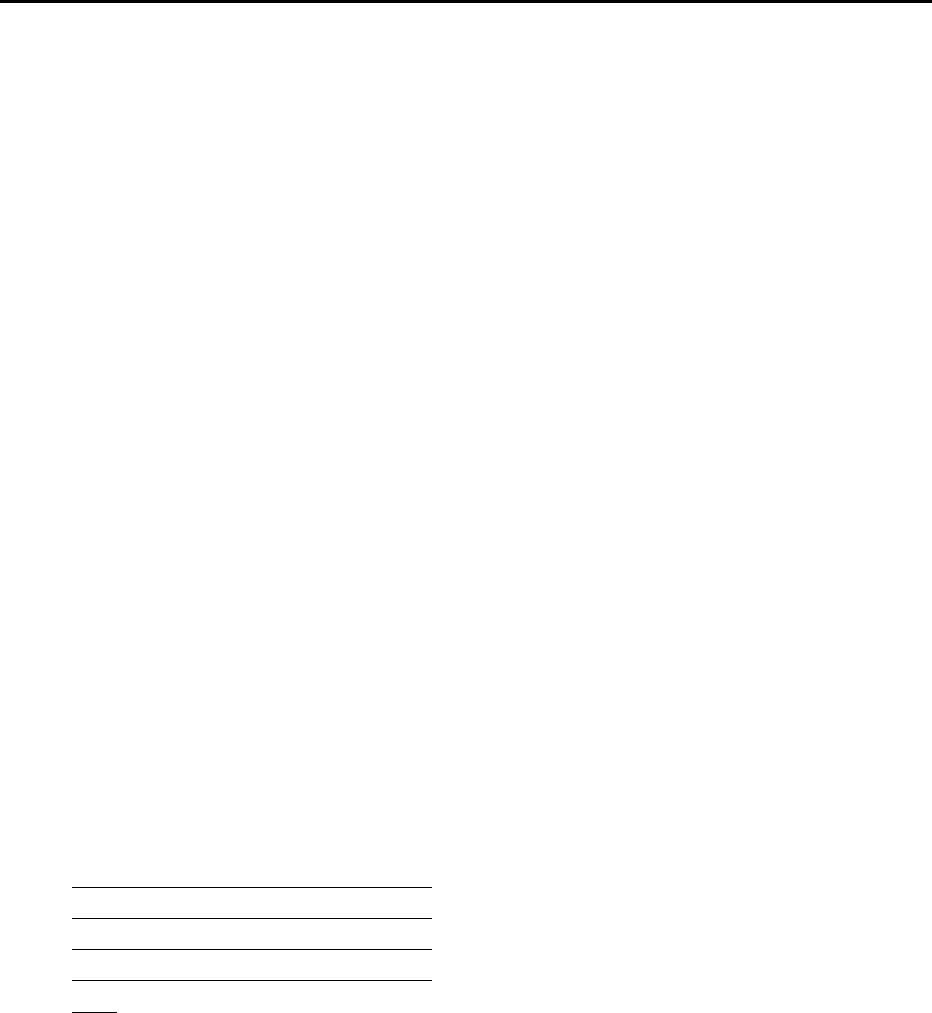
7-6 Facility Performance Testing User Manual
5. If Door Ajar is set in Event Preferences
to “Log and Status” or “Alarm”, verify
that the central computer correctly
logged this alarm and that any
networked computer also sees the alarm.
6. Record the results (pass or fail).
7. If the test fails to cause a Door Ajar
alarm:
a. Notify staff and security of the
vulnerable area.
b. Check for visible damage or
tampering to the zone equipment.
c. Have a maintenance technician
verify power to the zone equipment
d. Call your Accutech Representative.
8. To reset the zone, close the door
completely. Depending on settings, the
system may reset automatically or, if
necessary, enter a Keypad reset and
clear the alarm on the PC.
Loiter Test
This test will evaluate the Loiter feature
1. Notify staff and security that you will be
testing zone performance and alarms
will be generated. They should pay
special attention to traffic during this
time.
2. Using an S-TAD, activate the test Tag.
3. Enter a monitored zone and linger there.
NOTE: Be sure the door stays closed.
4. Depending upon the time delay settings,
the zone should register a Loiter alarm
after the predetermined time.
5. Verify and record the time setting.
6. If Loiter is set in Event Preferences to
“Log and Status” or “Alarm”, verify this
alarm is logged on the central computer
and any other remote computers
networked to it.
7. Record the results (pass or fail)
8. If the test fails to cause a Loiter alarm:
a. Notify staff and security of the
vulnerable area.
b. Check for visible damage or
tampering to the zone equipment.
c. Have a maintenance technician
verify power to the zone equipment
d. Call your Accutech Representative.
9. To reset the zone, deactivate the test Tag
and, if necessary, enter a Keypad reset
and clear the alarm on the PC.
10. Depending on settings, the system may
reset automatically or, if necessary,
enter a Keypad reset and clear the alarm
on the PC.
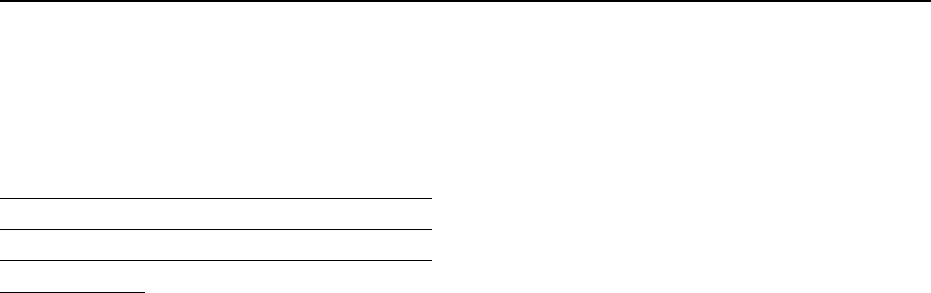
User Manual Facility Performance Testing 7-
7
System Supervisor Test (Tx)
This test will evaluate the System Supervisor
Test through a Tx wand antenna.
Notify staff and security that you will be testing
zone performance and alarms will be generated.
They should pay special attention to traffic
during this time.
1. Place a 4”x4”x2” electrical box (or an
equivalent piece of metal) next to the Tx
Wand Antenna. This will simulate a
damaged antenna.
2. A Supervisor alarm should register and
an alarm may sound.
3. Verify the alarm is logged on the central
computer and any other remote
computers networked to it.
4. Record the results (pass or fail).
5. If the test fails to cause a Supervisor
alarm:
a. Notify staff and security of the
vulnerable area.
b. Check for visible damage or
tampering to the zone equipment.
c. Have a maintenance technician
verify power to the zone equipment
d. Call your Accutech Representative.
6. Remove the electrical box away (or
equivalent) from the Tx Wand Antenna.
The Supervisor alarm will cease. If
necessary, clear the alarm on the PC.
System Supervisor Text (Rx)
Each time a Tag is detected in a zone (as has
been the case in each of the previous tests) the
Zone Receiver functionality is tested.
In addition, Receivers are self-tested on a
predetermined interval (set during installation).
Therefore, it is not necessary to perform a test
dedicated to testing the System Supervisor
through Zone Receivers. However, if you would
prefer to do so, consult your system maintenance
technician for assistance.
Fire Panel Interface (FPI) Test
State codes require that all Lock and Elevator
Deactivation Circuitry be wired into a facility’s
fire alarm system. In Accutech Systems this is
done via the Fire Panel Interface (FPI).
This is done so in the case of a fire, any Lock or
Elevator Deactivation unit disengages, allowing
free egress or ingress. For more information on
this policy, check your local codes.
This test should be performed concurrently with
your facility’s fire alarm test.
1. Using an S-TAD, activate a test Tag.
2. Activate your facility’s fire alarm.
NOTE: The LED on the FPI enclosure
will blink.
3. Proceed to each zone to be tested and
verify that doors are unlocked and
egress is possible. Elevators should be
inoperable due to the fire alarm.
4. Record the results (pass or fail).
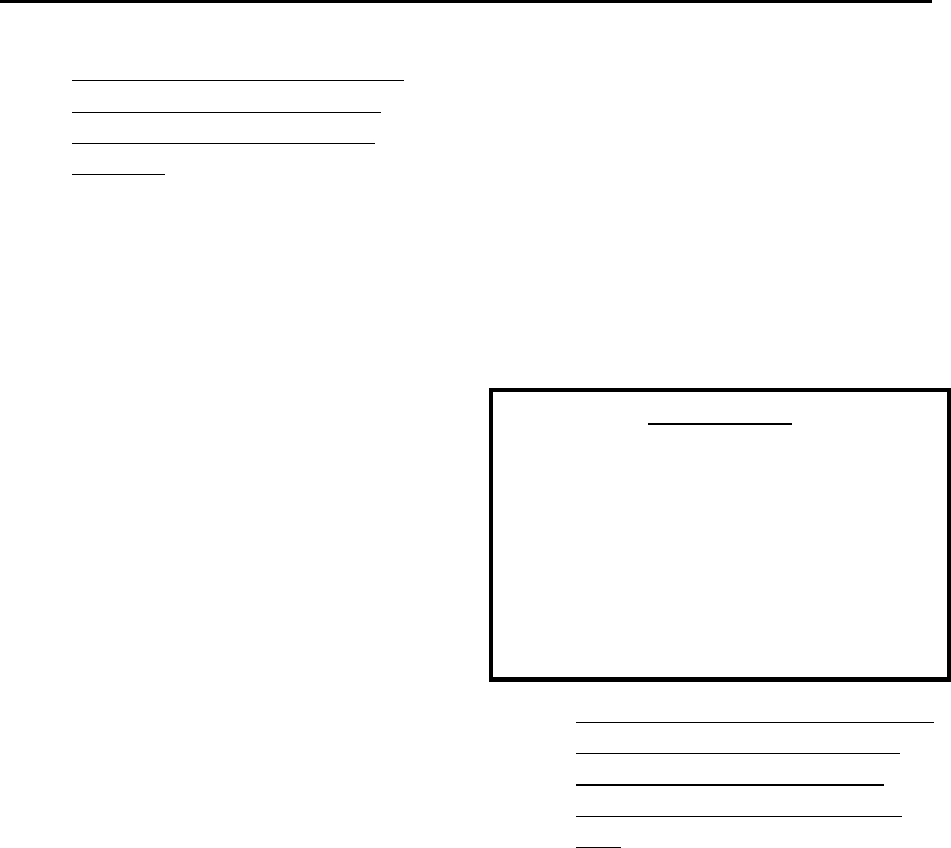
7-8 Facility Performance Testing User Manual
5. If a zone fails to disengage during the
fire alarm, call your system service
technician immediately for further
assistance.
6. After your facility’s fire alarm has been
reset the FPI may automatically reset or
press the Reset button on the outside of
the FPI enclosure to reset the FPI and
engage all restraints.
NOTE: The Reset button on the FPI
enclosure will not work during the fire
alarm. You must reset the fire alarm first
and then reset the FPI.
7. Return to each tested zone with the test
Tag and verify that doors now lock and
elevators disable as you approach.
8. Using an S-TAD, deactivate the test
Tag.
Band Alarm Test
(BR 4200 Systems only)
For this test you will need a BR42 Tag to
evaluate the Band Alarm function. Test results
should be written down and kept in a test log.
Select different locations within the protected
area(s) each time you conduct this test so that
you will evaluate all Receivers in the system on
a rotating basis. Remember to test both
Auxiliary and Zone Band Alarm Receivers.
IMPORTANT:
Band Alarms can be generated anywhere
within a facility, not just at exit points.
Repeat this test multiple times varying your
position each time within an area to assure
there is no place where a BR42 Tag can be
removed without being detected. This
includes bathrooms, visiting areas, storage
rooms, and laundry rooms.
1. Notify staff and security that you will be
testing zone performance and alarms
will be generated. They should pay
special attention to traffic during this
time.
2. With the cloth band, place the BR42 test
Tag snugly around your index finger.
3. Using an S-TAD, activate BR42 test
Tag.
Proceed to the area to be tested, remove
the Tag from your finger and place it
loosely in the palm of your hand. A
Band Alarm should be generated.
NOTE: If you are testing near a Zone
Receiver you may also generate Loiter
alarms during this test.

User Manual Facility Performance Testing 7-
9
4. Verify that the central computer
correctly logged this alarm and that any
networked computer also sees the alarm.
5. Record the results (pass or fail).
6. If the test fails to cause a Band Alarm:
a. Notify staff and security of the
vulnerable area.
b. Check for visible damage or
tampering to the zone equipment.
c. Have a maintenance technician
verify power to the zone equipment
d. Call your Accutech Representative.
7. To clear the alarm, deactivate the BR42
test Tag, enter a Keypad reset and, if
necessary, clear the alarm on the PC.
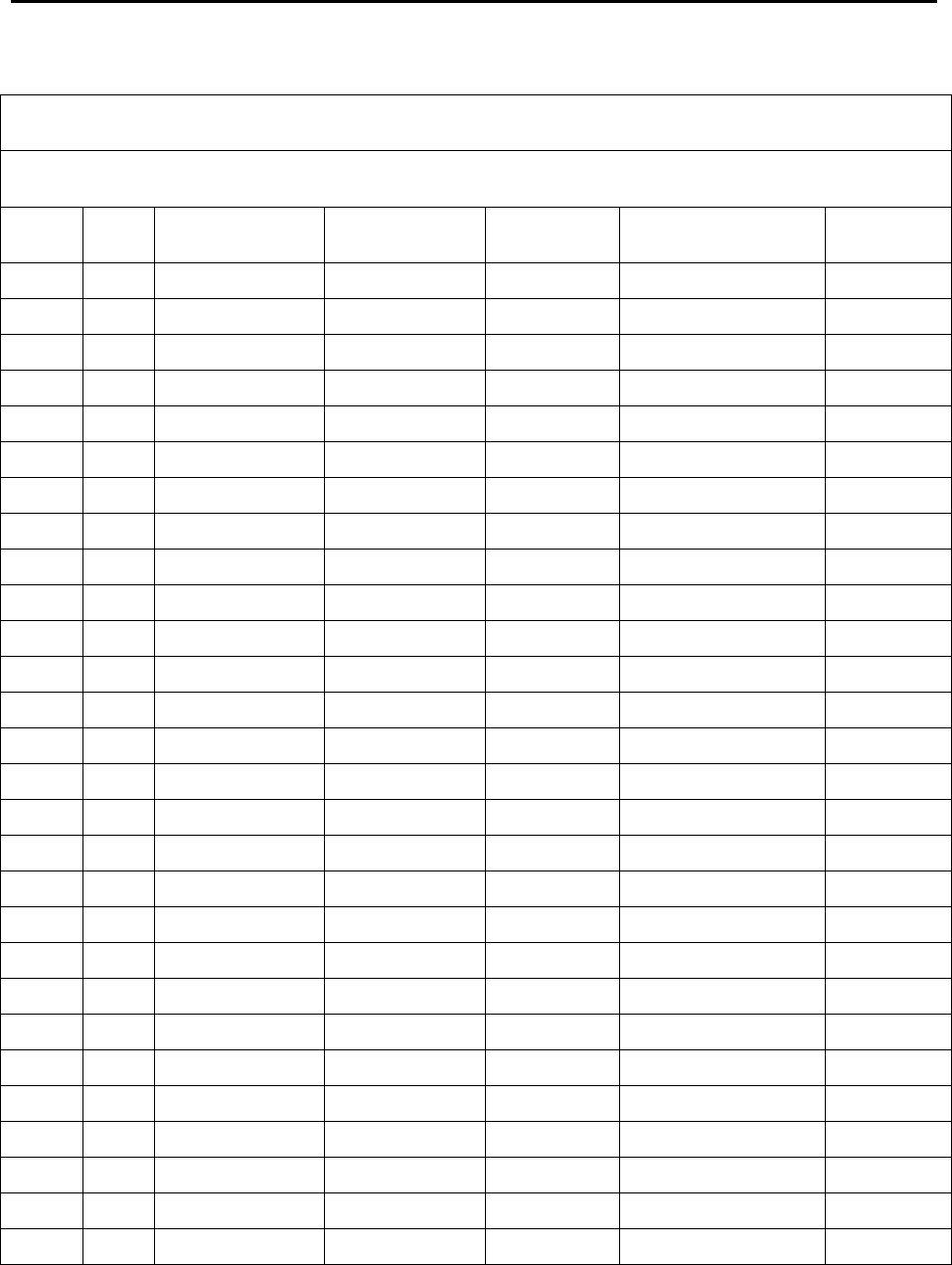
7-10 Facility Performance Testing User Manual
NOTE: Copy this form for future use.
FACILITY PERFORMANCE TEST LOG
Facility Name: Page __ of __
Date Floor Zone Name/Type Test Performed Results (P/F)
Comments Signature
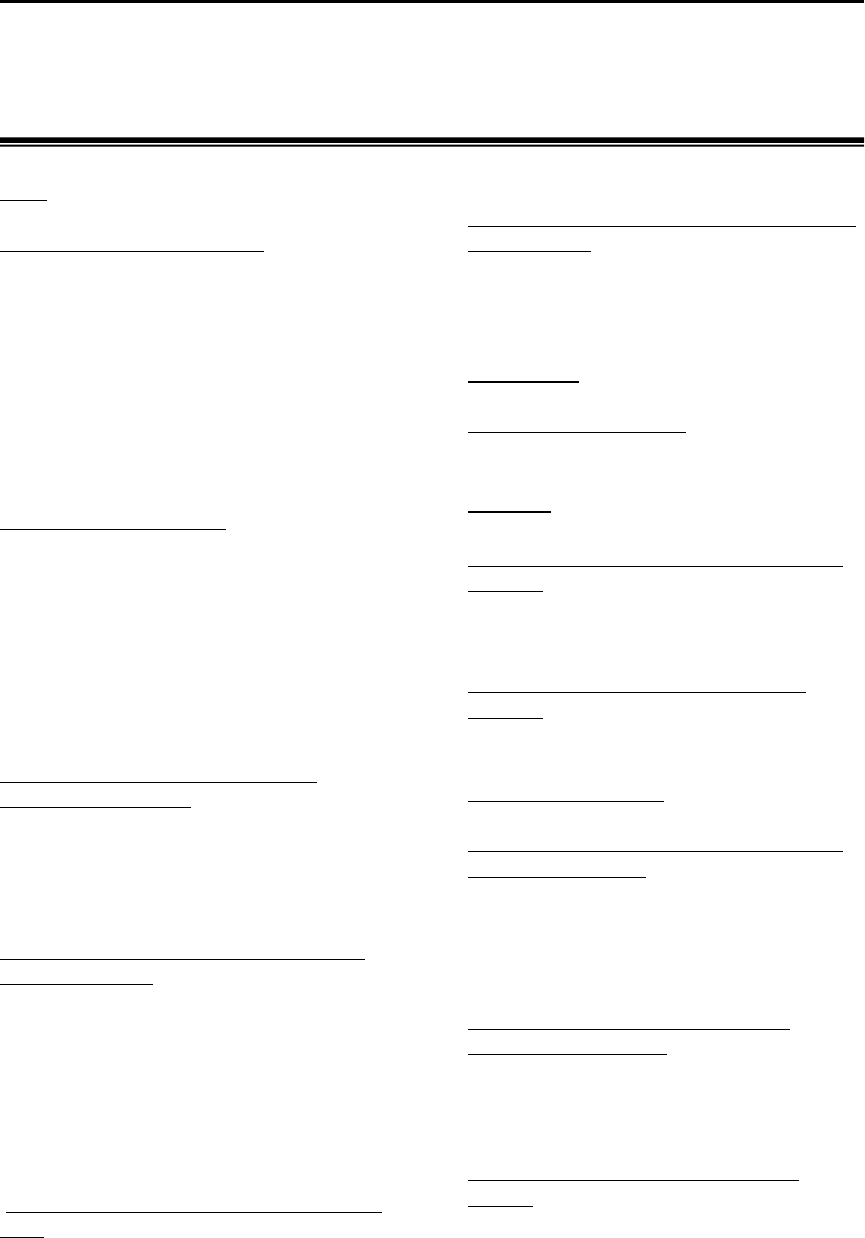
User Manual FAQ F-1
FAQ
Tag:
What can I use to clean Tags?
Use antibacterial wipes or a 3% hydrogen
peroxide solution (wipe, do not soak) to
clean Tags. ALWAYS RINSE WITH
WATER OR WIPE DOWN WITH A
DAMP CLOTH. THEN DRY TO
REMOVE ANY CHEMICAL RESIDUE.
UNAPPROVED CLEANERS CAN
AFFECT THE PLASTIC AND CAUSE IT
TO BREAK DOWN PREMATURELY.
How should I store Tags?
Ideally, to preserve battery life, Tags should
be turned off with an S-TAD. However, if
you do not have an S-TAD or your Tags are
always activated, Tags should be stored
away from
sources of electrical noise and stored in a
metal container with lid. BR42 Tags must be
turned off when not in use.
How can I be sure the Tag is on and
functioning properly?
You can test that a Tag is on and functioning
properly by the testing it with an S-TAD or
taking the Tag to a monitored zone (this may
cause alarms).
How often should I check a Tag’s battery
with my S-TAD?
Accutech recommends testing a Tag’s
battery during assignment of the
patient/infant then again during
unassignment prior to cleaning and
restocking of the Tag for new use. Periodic
weekly testing of Tags for long-term
patients is also recommended.
Can I replace or recharge the battery in the
Tag?
No. Once a Tag’s battery is drained, the Tag
will have to be replaced.
How long will the Tags last before I need to
replace them?
Accutech Tags operate by internal battery.
The Tags have been engineered for greater
than 1.5 years.
Tag Band:
Are Tag bands reusable?
No. Tag bands are for one-time use only.
S-TAD:
How long will the 9-volt battery last in the
S-TAD?
The life of the 9-volt battery in the S-TAD is
dependent upon usage.
Can I use a rechargeable battery in the
S-TAD?
Yes.
System (General):
If you are locking the doors, what happens
in the case of a fire?
Accutech follows NFPA codes and
regulations. Therefore, in the event of a fire,
all Accutech restraints will be disabled
(audial and visual alarms remain active).
If the PC shuts down, is the physical
security also disabled?
No. The Accutech Software is separate from
and does not affect nor control the physical
Accutech Security System components.
Can I adjust the Door Ajar and Loiter
Times?
Yes. Door Ajar and Loiter times are
adjustable. Contact your system
maintenance technician for further
assistance.
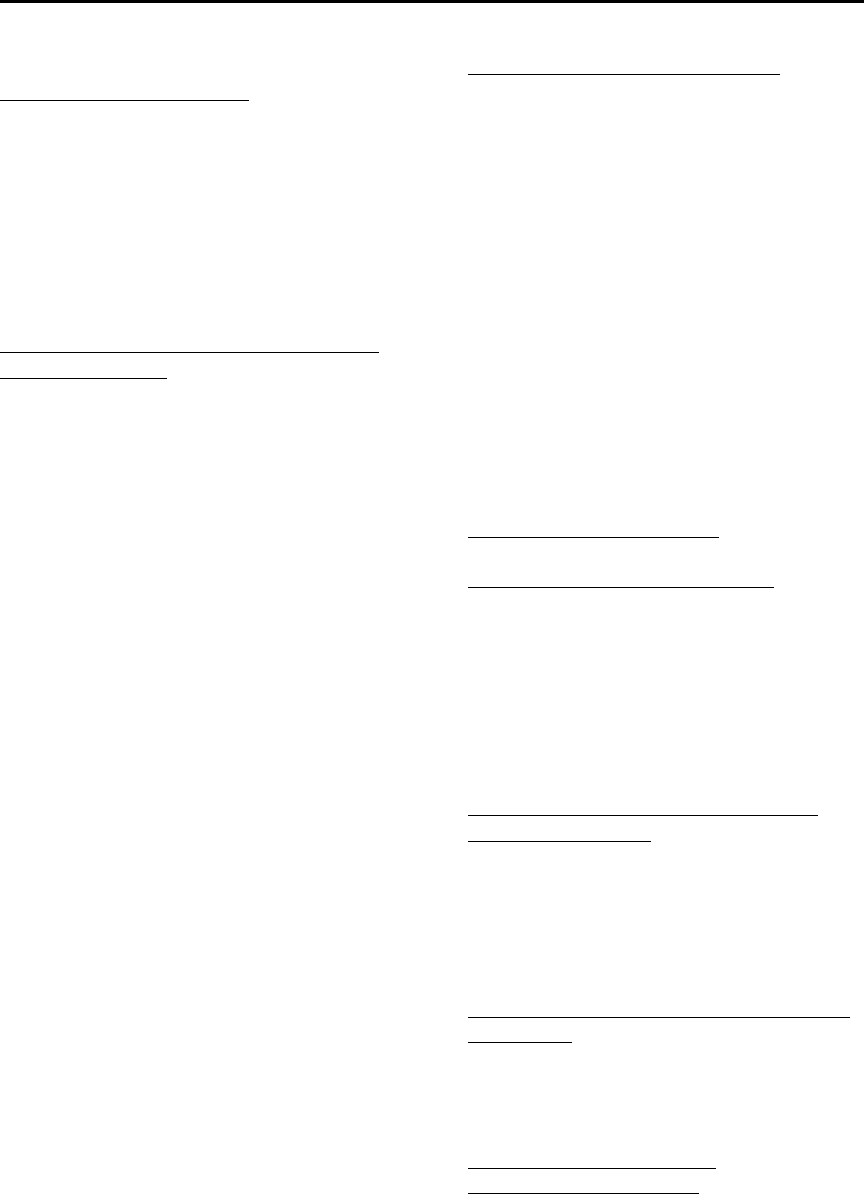
F-2 FAQ User Manual
Why do I get Loiter alarms?
Loiter alarms occur when a Tag lingers in a
monitored zone for longer than the preset
allotted time. If you experience an
abundance of Loiter alarms, consider that
your monitored zones may be extending into
common resident areas. Contact a
maintenance technician for further
assistance.
Why do I get a Band Alarm if the band has
not been removed?
Band Alarms occur when a BR42 Tag band
is loosened, cut, saturated, removed or
tampered with.
Is the band snug around the infant’s
extremity and the conductive fibers
are in good contact with the infant’s
skin? If not, snug up the band.
Is excess band material properly
trimmed? If not, trim appropriately.
Is the band wet? If so, replace the
band.
Is the Cam Lock completely closed?
If not, snap it closed.
Furthermore, due to the global response of
Band Alarms and possible overlapping of
zones to assure complete coverage, a single
Band Alarm event may register at multiple
zones.
As always, make sure your Tags are
handled, transported, and attached to infants
properly as well as turned off when not in
use.
How can I reduce nuisance alarms?
Nuisance alarms are typically caused by:
the mishandling of Tags
improper storage of Tags
Loiter alarm time being too brief
(passersby causing alarms or during
slow-moving patient transfers)
lost Tags
In addition, if you are experiencing an
abundance of nisance alarms, consider that
your monitored zones may be extending into
common resident areas and make sure your
Tags are handled, transported, and attached
properly as well as turned off when not in
use.
System (Maintenance):
How often should I test my zones?
Accutech recommends that Facility
Performance Testing (Chapter 7) be
performed (at the minimum) on a monthly
basis. However, each facility should review
and modify the testing procedures as
necessary to meet their own unique security
requirements.
Who do I contact if the system does not
seem to be working?
If you should need assistance with any part
of your Accutech Security System, contact
your system maintenance technician first,
then your local area Accutech
Representative.
Who do I call about upgrading or adding to
my system?
If you would like information about
upgrading or adding to your system, contact
your local area Accutech Representative.
How do I order replacement
Tags/Bands/Components?
If you would like to order replacement
Tags/Band/Components for your system,
contact your local area Accutech
Representative.
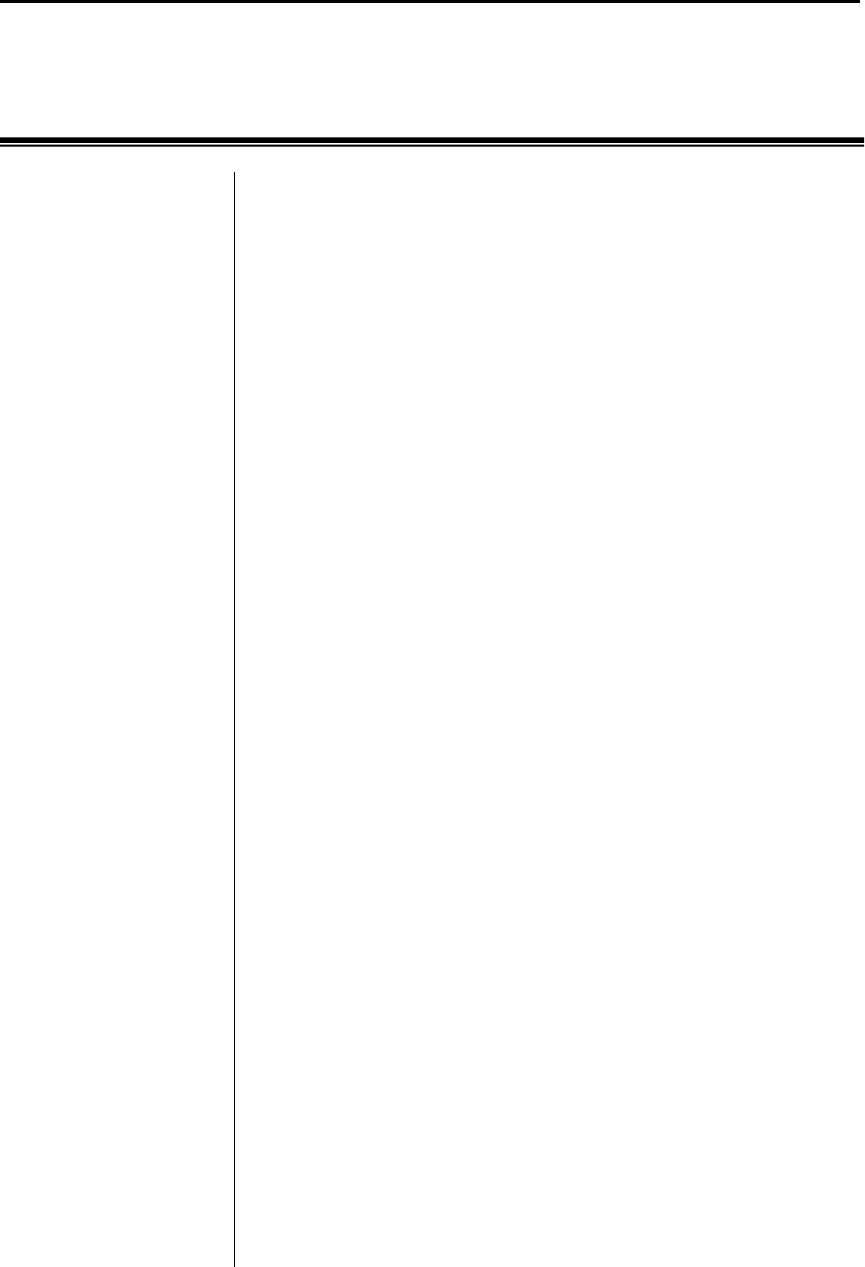
User Manual Glossary G-1
Glossary
Accutech Software The Accutech Software displays incoming event information from
monitored zones in real-time on a PC screen using the facility’s custom
floor plan as the background. Event information is stored in a database and
can be viewed as a printable Report. The Accutech Software is separate
from and does not affect nor control the physical Accutech Security System
or any of its components.
Auxiliary BR Receiver Used for complete facility-wide Band Alarm coverage, an external
Receiver that only detects Band Alarm events.
Band Alarm An alarm condition that occurs when an Accutech BR42 Tag is loosened,
cut, saturated, removed or tampered with.
BR 4200 System A complete infant security system featuring Intelli-Band Technology.
BR 4200 System Tag A small wristwatch-sized device that is worn by an infant. In addition to
the functionality of an IS 3200 System Tag, the BR 4200 System Tag
features Intelli-Band Technology, which will alarm if the band is removed
or tampered with.
Case sensitive A program’s ability to distinguish between uppercase (capital) and
lowercase (small) letters. Programs that distinguish between uppercase and
lowercase are said to be case sensitive.
Central Alarm A tone generator than can drive up to 5 speakers.
Controller The Controller coordinates and controls all of the devices and functions of
the Accutech Security Systems.
Delayed Egress Circuitry A feature of the Accutech 3101 Magnetic Lock that, due to fire and life
safety codes, allows free egress through a door after 15 seconds of constant
force. In the event of a fire alarm, the Delayed Egress Circuitry is disabled.
Door Ajar alarm An alarm condition that occurs when a door is open longer than the preset
time allowed.
Double conditioning A characteristic of a zone that requires two conditions to be met (such as
Tag detection and PIR detection) before an alarm is generated.

G-2 Glossary User Manual
Egress alarm An alarm condition that occurs when a Tag is in the Tx Activation Field
and a door is opened (or PIR detection).
Elevator
Deactivation Circuitry
Circuitry that deactivates an elevator’s call button(s) when a Tag is a
monitored elevator zone.
ES 2200 System A complete wanderer, asset, or infant security system.
ES 2200 System Tag A small wristwatch-sized device worn by a resident, infant, or attached to
an asset.
Escort Function A function of the Keypad used to escort Tags through a monitored zone
without triggering alarms.
Fire Panel Interface
(FPI)
A FPI ties Accutech Security System components into the facility’s fire
panel. Required if the system includes Magnetic Locks and/or Elevator
Deactivation Circuitry. In the event of a fire, Magnetic Locks and Elevator
Deactivation Circuitry are disabled. However, if there is still power to the
system, the alarms will still sound.
Floor-to-Floor Tag
discrimination
Set during installation, Floor-to-Floor Tag discrimination allows the
software to be configured so that predetermined ranges of Tags can be
designated to individual floors, thus when alarms occur they only appear on
PCs associated with that floor (This aids in reducing nuisance alarms from
bleed through especially in stacked zones). Regardless of what the PCs are
configured to see, zones will function as usual (i.e., locking doors and/or
sounding alarms if applicable).
Graphic Display Panel
(GDP)
A display panel, which provides staff with a representation of the floor
being monitored. GDPs are custom-made to a facility’s floor plan and
notify staff when an alarm condition occurs in a monitored zone through a
piezo buzzer and alarm-specific LEDs.
Intelli-Band Technology A feature of BR42 Tags, which will alarm if the band is loosened, cut,
saturated, removed, or tampered with.
IS 3200 System A complete wanderer, asset, or infant security system.
IS 3200 System Tag A small wristwatch-sized device that is worn by a resident, an infant, or
attached to an asset. They are assigned to a specific resident or asset (via
the Tag Test Station and Accutech Software). Once assigned, the computer
associates a name, room number, and any other pertinent information about
the resident/infant/asset with that Tag.
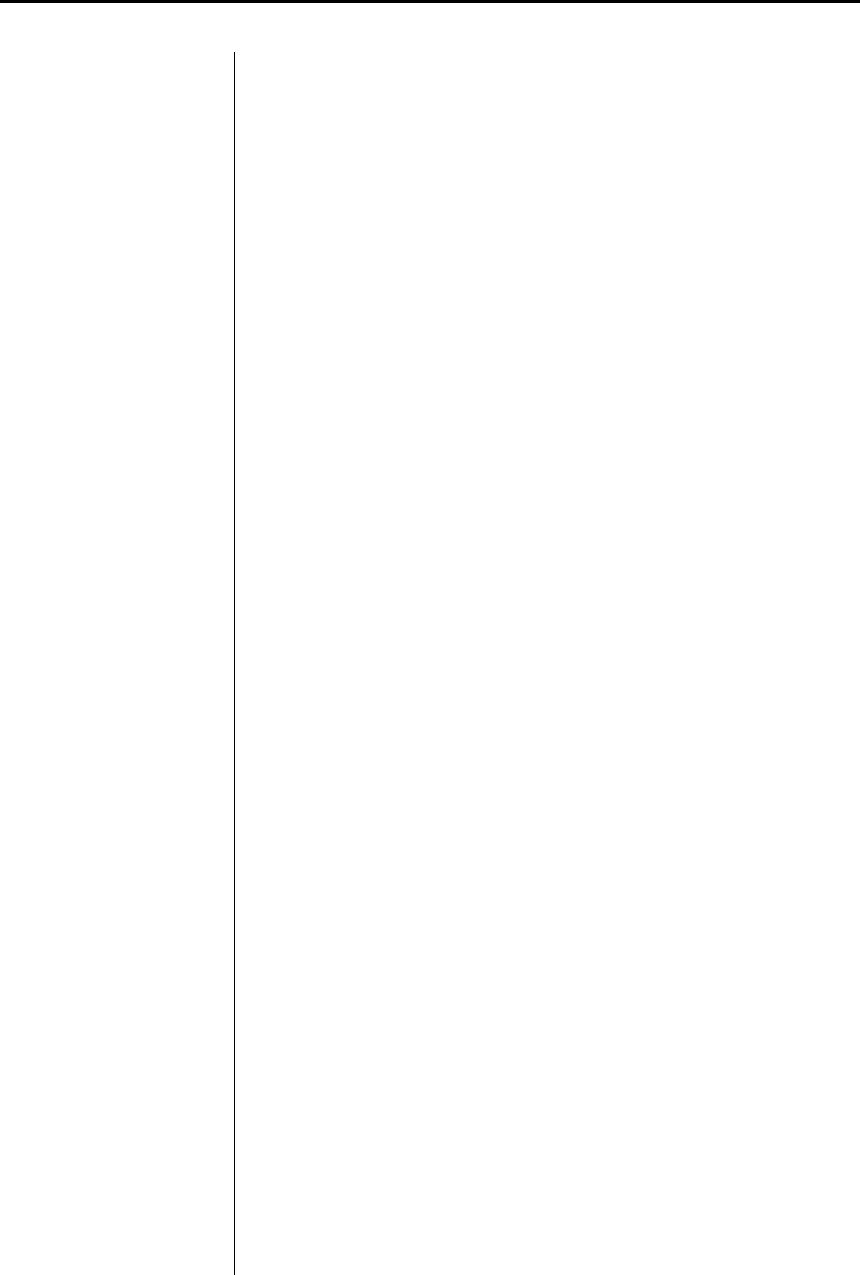
User Manual Glossary G-
3
Keypad A Keypad is used to reset zone equipment once an alarm has been
addressed (Keypad Reset) or to escort Tags through a monitored zone
without triggering alarms (Keypad Escort). The Keypad is also capable of
providing visual indicators for Tag detection, alarms, and escort time.
Keypad Reset A feature of the Keypad that is used to reset zone equipment after an alarm
has been addressed.
Test Tag A red Test Tag designed to verify proper zone coverage (without causing
alarms) during installation, adjustment, or testing of a monitored zone.
Local Alarm A single-tone sounder mounted at a monitored zone to attract attention
during alarms.
Loiter Alarm An alarm condition that occurs when a Tag lingers in the Tx Activation
Field for longer than the preset time.
LT “Long Term”, a Tag classification
Magnetic Lock A device using a magnetic coil and plate to lock a door when a Tag is
detected in the monitored door zone.
Magnetic Switch A device that monitors a door’s position (open or closed). A Magnetic
Switch is used on a door when alarm activation is not desired unless the
door is opened when a Tag in the monitored door zone.
Masking In PIR applications, limiting the infrared beam by placing stripes of tape
over the lens. In Software applications, during text insertion into a field,
characters are replaced with symbols (usually asterisks “*”) for privacy.
Master Code User Code Number 1 for the Keypad, used for Keypad programming
purposes only.
Monitored Zone Any door, hallway, stairwell, elevator, or other passageway that has a
Controller, Tx antenna, and Zone Receiver associated to it.
Multiplexer A device that relays event information from the Controller to SAPs, GDPs
and/or the Accutech Software.
Nuisance Alarms Undesired alarm activation stemming from such things as the mishandling
of Tags, improper storage of Tags, slow patient transferring, and/or Loiter
alarm time being too brief (passersby causing alarms).
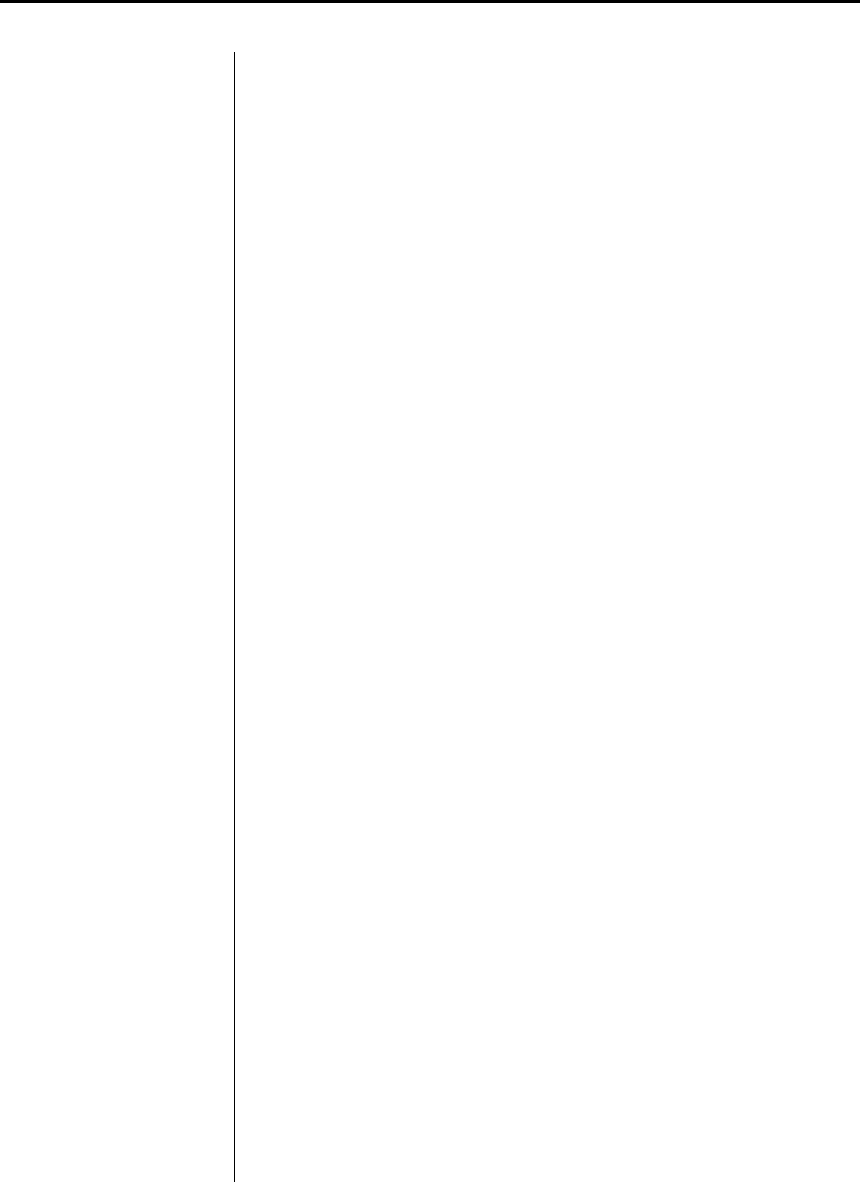
G-4 Glossary User Manual
Passive Infrared Reader
(PIR)
A device that uses an infrared light to detect motion.
Push Button Override
(PBO)
A switch (push button) that triggers the Keypad’s Escort function.
Program Shell An application of the Software that houses the displayed monitored area.
Receiver A device that detects the signal of an activated Tag, usually mounted in the
Controller above the drop ceiling or on the wall next to the door being
monitored. For centrally located systems, the Receiver is mounted
separately at the door. A short rubber duck antenna protrudes from the
cover.
SB “Slotted Back”, a Tag classification
S-TAD
Used to check the functionality of an Accutech Tag. Accutech Tags operate
by internal battery. Over the course of normal operation, Tags eventually
lose battery power and the Tags will need to be replaced. The S-TAD is
used to determine if a Tag has sufficient battery power to respond to an
activating signal. Secure Tag Activator/Deactivator.
Staff Alert Panel
(SAP)
A display panel used to indicate to staff where an Alarm, Door Ajar, Loiter,
or Supervise warning condition has occurred; it employs bi-color LEDs, a
Piezo Buzzer, and digital logic to control its outputs.
Supervisor A built-in self-diagnostic circuit of the Controller that continuously
monitors the Tx Activation Field and periodically simulates a Tag in the
zone.
Tag See ES 2200 System Tag, IS 3200 System Tag, or BR 4200 System Tag
Tag Test Station
(TTS)
A TTS is used in conjunction with the Accutech Software for Tag
assignments and to check the tags data information.
Tx Wand Antenna A device that generates a Tag-activating radio frequency signal. This signal
is referred to as a “Tx Activation Field.”
Tx Activation Field A radio frequency field created by a Tx antenna to detect Tags. Doors,
hallways, elevators, stairwells, and other passageways that have a Tx
Activation Field are commonly referred to as a “monitored zone.”

User Manual Index I-
1
Index
ALARMS
Band Alarm
1
-
3
Addressing
1
-
4
Door ajar alarm
1
-
3
Egress alarm
1
-
3
Loiter alarm
1
-
3
Supervisor alarm
1
-
3
Automatic Door Deactivation
2
-
9
Auxiliary Receiver
2
-
7
Band Alarm
1
-
3
Band Alarm Lockdown
2
-
9
BR 4200 System
1
-
2
BR 4200 System Tags
3
-
2
Central Alarm
2
-
10
Controller
2
-
2
Cut Band System
1
-
2
Cut Band System Tags
3
-
2
Door ajar alarm
1
-
3
Double Conditioning
1
-
3
Egress alarm
1
-
3
Elevator Deactivation
Circuitry
2
-
8
ES 2200 System
1
-
1
ES 2200 System Tags
3
-
1
Escorting
1
-
6
ESCORT FUNCTION
5
-
1
Facility Performance Testing
7
-
1
Band Alarm Test
7
-
8
Door Ajar Test
7
-
5
Fire Panel Interface (FPI) Test
7
-
7
Loiter Test
7
-
6
System Supervisor Test
7
-
7
Test Equipment Required
7
-
1
Zone, Egress Alarm Test
(3000 Series Magnetic Lock)
7-3
Zone, Egress Alarm Test
(3101 Series Magnetic Lock)
7-3
Zone, Elevator Deactivation Test
7
-
5
Zone, Hallway Test
7
-
4
Zone, Lock Test
7
-
2
Fire Panel Interface (FPI)
2
-
9
Graphic Display Panel (GDP)
2
-
8
HOW ACCUTECH SYSTEMS WORK
1
-
3
Door zones
1
-
3
Elevator zones
1
-
4
Hallway zones
1
-
4
IS 3200 System
1
-
2
IS 3200 System Tags
3
-
1
KEYPAD
Keypad Operation
5
-
1
Initiating the First Relay (Reset/Escort)
5
-
1
Initiating the Second Relay (Anti
-
Tailgate)
5
-
1
How to enter user codes
5
-
2
How to set the relay time
5
-
3
DAP Instructions
5
-
6
Test
Tag
3
-
4
Verifying Proper Zone Coverage
3
-
4
Identifying Tag
-
Activating Sources
3
-
5
Local Alarm
2
-
9
Loiter alarm
1
-
3
Lost Tags
4
-
2
Magnetic Locks
2
-
8
Magnetic Switch
2
-
2
MASTER CODE
5
-
2
Multiplexer
2
-
7
Multi
-
Tone Local Alarm
(MTLA)
2
-
9
Passive Infrared Reader (PIR)
2
-
3
Power Supply
2
-
7
Push Button Override
2
-
1
0
Receiver
2
-
2

Index I-2 User
Manual
SOFTWARE
Accutech Software
6
-
1
Speakers
2
-
10
Staff Alert Panel (SAP)
2
-
8
Strobe Light
2
-
10
Supervisor alarm
1
-
3
System Components
2
-
1
S-TAD
(Secure Tag Activator/Deactivator)
4
-
1
Activating/Deactivating Tags
4
-
2
Cleaning and Care
4
-
5
Enable/Disable Band Alarm Sounder
4
-
3
LEDS
4
-
4
Master Code
4
-
3
Powering the S
-
TAD On/Off
4
-
1
Programming Mode
4
-
3
Unlocking
4
-
1
Unlock Timeout
4
-
3
User Code
4
-
4
TAGS
Attaching
Cut Band Tags
3
-
8
BR42 Tags
3
-
7
LT/SB Tags
3
-
6
Cleaning
3
-
1
0
Removing Cut Band Tags
3
-
9
Storing
3
-
1
0
Testing
3
-
1
0
Tag Test Station (TTS)
2
-
7
Timer
2
-
10
Tri
-
Axis Antenna
2
-
3
Tx wand antenna
2
-
3
Voice Alarm
2
-
10