Alliance Laundry Systems Hf150 Users Manual
HF185 to the manual 3bd5ab53-3439-494f-b497-5b35799f29d7
2015-02-05
: Alliance-Laundry-Systems Alliance-Laundry-Systems-Hf150-Users-Manual-506599 alliance-laundry-systems-hf150-users-manual-506599 alliance-laundry-systems pdf
Open the PDF directly: View PDF .
Page Count: 46
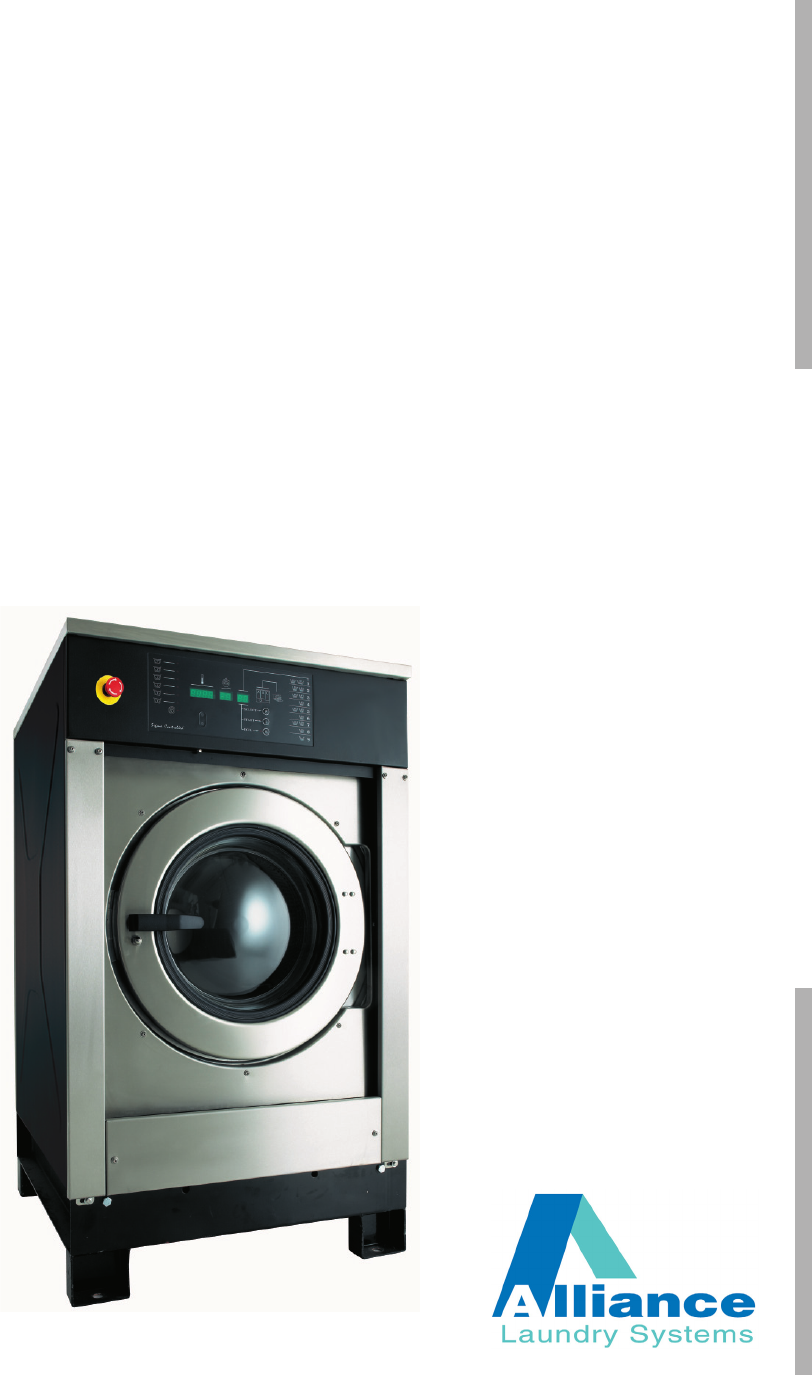
HF150, HF185, HF234, HF304
Instruction manual
Washer Extractors
Technical specications
Installation instructions
Maintenance
for corresponding “CHF” and “IHF” models,
see page 5 for complete model list
Part No. D0289R8
Code: 249/00390/10
May 2011

1
2
3
4
3
Contents
Contents
Model Numbers .............................................................................................. 5
Safety and Environmental Informations ...................................................... 6
Safety .......................................................................................................... 6
Environmental .............................................................................................. 7
Explanation of Safety Messages ................................................................. 8
Important Safety Instructions ....................................................................... 9
Operator Safety ......................................................................................... 11
Technical data and dimensions ................................................................. 12
Technical data HF150, IHF150, IHF033, CHF150, CHF033 ..................... 12
Dimensions HF150, IHF150, IHF033, CHF150, CHF033 .......................... 13
Technical data HF185, IHF185, IHF045, CHF185, CHF045 ..................... 14
Dimensions HF185, IHF185, IHF045, CHF185, CHF045 .......................... 15
Technical data HF234, IHF234, IHF055, CHF234, CHF055 ..................... 16
Dimensions HF234, IHF234, IHF055, CHF234, CHF055 .......................... 17
Technical data HF304, IHF304, IHF075, CHF304, CHF075 ..................... 18
Dimensions HF304, IHF304, IHF075, CHF304, CHF075 .......................... 19
Installation and Connection Instructions .................................................. 20
Surface ...................................................................................................... 20
Out of balance switch ................................................................................ 20
Removal of the transport safety ................................................................. 21
Mounting Bolt Hole Locations for machines, HF150, IHF150, IHF033,
CHF150, CHF033 ...................................................................................... 22
Mounting Bolt Hole Locations for machines, HF185, IHF185, IHF045,
CHF185, CHF045 ...................................................................................... 23
Mounting Bolt Hole Locations for machines, HF234, IHF234, IHF055,
CHF234, CHF055 ...................................................................................... 24
Mounting Bolt Hole Locations for machines, HF304, IHF304, IHF075,
CHF304, CHF075 ...................................................................................... 25
Water connection .......................................................................................26
Water drain ................................................................................................26
Electrical installation .................................................................................. 27
Main power connection .............................................................................. 29
Electrical Specifications HF150, IHF150, IHF033, CHF150, CHF033 ...... 31
Electrical Specifications HF185, IHF185, IHF045, CHF185, CHF045 ....... 32
Electrical Specifications HF234, IHF234, IHF055, CHF234, CHF055 ....... 33
Electrical Specifications HF304, IHF304, IHF075, CHF304, CHF075 ....... 34
Liquid soap connection (option) ................................................................. 35
Connection of a central operating panel for coin machines (option) ......... 37

5
6
7
8
9
4
Steam connection ........................................................................................ 38
Technical remarks ....................................................................................... 39
Internal connections of the electrical heating ............................................ 39
Maintenance instruction of the machine ................................................... 40
End of day .................................................................................................. 40
General maintenance ................................................................................ 40
Periodical maintenance ............................................................................. 40
Annual maintenance .................................................................................. 41
Contact Information ..................................................................................... 42
Nameplate ................................................................................................. 42
Repair and after-sales service .................................................................... 44

5
Model Numbers 1
HF150
HF185
HF234
HF304
HX55
HX75
xHF150yyHyyyyyy
xHF185yyHyyyyyy
xHF234yyHyyyyyy
xHF304yyHyyyyyy
xHF033yyHyyyyyy
xHF045yyHyyyyyy
xHF055yyHyyyyyy
xHF075yyHyyyyyy
Build-up
Model numbers CHF033
CHF045
CHF055
CHF055ANHX1
CHF055MNHX1
CHF075
CHF075ANHP1
CHF075ANHQ1
CHF150
CHF185
CHF234
CHF304
IHF033
IHF033ANHX1
IHF045
IHF045ANHX1
IHF055
IHF055ANHX1
IHF055ZNHX1
IHF075
IHF075ANHN1
IHF075ANHQ1
IHF150
IHF150MNHX1
IHF150ZNHP1
IHF185
IHF185ANHN1
IHF185ANHP1
IHF185ANHX1
IHF185YNHP1
IHF185ZNHP1
IHF185ZNHX1
IHF234
IHF234ANHN1
IHF234ANHP1
IHF234ANHQ1
IHF234MNHP1
IHF234MNHX1
IHF234ZNHP1
IHF234ZNHX1
IHF234ANHX1
IHF304
IHF304ANHP1
IHF304MNHP1
IHF304ZNHP1

6
2
Safety and Environmental Informations
Safety
CAUTION LABELS
Please familiarize yourself with the following standard warning symbols. They are
used throughout this manual and on the equipment to alert you to possible hazards.
Anyone operating or servicing this equipment must understand these symbols and
must follow all safety rules in this manual.
ELECTRICAL HAZARD
This symbol alerts you to the presence of a dangerous voltage, which could cause a
serious shock resulting in personal injury or death.
CONSULT MANUAL
This symbol warns you to consult the manual for important instructions concerning
the machine and possible hazards.
MOVING PARTS HAZARD
This symbol alerts you to the presence of possible dangerous moving parts within
the machine. Guards should always be in place when the machine is in operation. Be
very careful when servicing the drive system.
PINCHING HAZARD
This warning symbol indicates the presence of a pinch point on the machine. This is
a place where your hand might be pinched or crushed, resulting in a severe injury.
Make sure you understand these hazards and keep all body parts clear of them.
HOT SURFACE HAZARD
This symbol indicates the presence of a potentially hot surface. Some machine
surfaces and parts may become extremely hot during normal operation and should
not be touched.
ATTENTION
This symbol identies information about practices or circumstances that can lead to
personal injury or death, property damage, or economic loss.

7
2
Environmental
Disposal of Unit
This appliance is marked according to the European directive
2002/96/EC on Waste Electrical and Electronic Equipment (WEEE).
This symbol on the product or on its packaging indicates that this
product shall not be treated as household waste. Instead it shall be
handed over to the applicable collection point for the recycling of
electrical and electronic equipment. Ensuring this product is disposed
of correctly, you will help prevent potential negative consequences
for the environment and human health, which could otherwise be
caused by inappropriate waste handling of this product. The recycling
of materials will help to conserve natural resources. For more detailed
information about recycling of this product, please contact your local
distributor resources.

8
Explanation of Safety Messages
Throughout this manual and on machine decals, you will nd precautionary statements (“DANGER”,
“WARNING” and “CAUTION”) followed by specic instructions. These precautions are intended for the
personal safety of the operator, user, servicer, and those maintaining the machine.
DANGER
Indicates an imminently hazardous situation that, if not
avoided, will cause severe personal injury or death.
WARNING
Indicates a hazardous situation that, if not avoided, could
cause severe personal injury or death.
CAUTION
Indicates a hazardous situation that, if not avoided, may
cause minor or moderate personal injury or property
damage.
Safety Decals
Safety decals appear at crucial locations on the machine. Failure to maintain legible safety decals could
result in injury to the operator or service technician.
To provide personal safety and keep the machine in proper working order, follow all maintenance and
safety procedures presented in this manual. If questions regarding safety arise, contact the manufacturer
immediately.
Use manufacturer-authorized spare parts to avoid safety hazards.
Additional precautionary statements (“IMPORTANT” and “NOTE”) are followed by specic instructions.
IMPORTANT: The word “IMPORTANT” is used to inform the reader of specic procedures where
minor machine damage will occur if the procedure is not followed.
NOTE: The word “NOTE” is used to communicate installation, operation, maintenance or servicing
information that is important but not hazard related.
2

9
Important Safety Instructions
WARNING
To reduce the risk of re, electric shock, serious injury or
death to persons when using your washer, follow these
basic precautions:
1. Read all instructions before using the washer.
2. Refer to the GROUNDING INSTRUCTIONS in the installation Manual for the proper grounding of the
washer.
3. Do not wash textiles that have been previously cleaned, washed, soaked, or spotted with gasoline,
dry-cleaning solvents, or other ammable or explosive substances as they give off vapors that could
ignite or explode.
4. Do not add gasoline, dry-cleaning solvents, or other ammable or explosive substances to the wash
water. These substances give off vapors that could ignite or explode.
5. Under certain conditions, hydrogen gas may be produced in a hot water system that has not been
used for two weeks or more. HYDROGEN GAS IS EXPLOSIVE. If the hot water system has not been
used for such a period, before using a washing machine or combination washer-dryer, turn on all hot
water faucets and let the water ow from each for several minutes. This will release any accumulated
hydrogen gas. The gas is ammable, do not smoke or use an open ame during this time.
6. Do not allow children to play on or in the washer. This appliance is not intended for use by young
children or inrm persons without supervision. Young children should be supervised to ensure that
they do not play with the appliance.
7. Before the washer is removed from service or discarded, remove the door to the washing
compartment.
8. Do not reach into the washer if the wash drum is moving. This is an imminently hazardous situation
that, if not avoided, will cause severe personal injury or death.
9. Do not install or store the washer where it will be exposed to water and/or weather.
10. Do not tamper with the controls.
11. Do not repair or replace any part of the washer, or attempt any servicing unless specically
recommended in the user-maintenance instructions or in published user-repair instructions that the
user understands and has the skills to carry out.
12. To reduce the risk of an electric shock or re, DO NOT use an extension cord or an adapter to connect
the washer to an electrical power source.
13. Use a washer only for its intended purpose, washing textiles.
14. ALWAYS disconnect the washer from the electrical supply before attempting any service. Disconnect
the power cord by grasping the plug, not the cord.
15. Install the washer according to the INSTALLATION INSTRUCTIONS. All connections for water, drain,
electrical power and grounding must comply with local codes and be made by licensed personnel
when required.
16. To reduce the risk of re, textiles which have traces of any ammable substances such as vegetable
oil, cooking oil, machine oil, ammable chemicals, thinner, etc., or anything containing wax or
chemicals such as in mops and cleaning cloths, must not be put into the washer. These ammable
substances may cause the fabric to catch on re.
17. Do not use fabric softeners or products to eliminate static unless recommended by the manufacturer of
the fabric softener or product.
18. Keep washer in good condition. Bumping or dropping the washer can damage safety features. If this
occurs, have washer checked by a qualied service person.
19. Replace worn power cords and/or loose plugs.
20. Be sure water connections have a shut-off valve and that ll hose connections are tight. CLOSE the
shut-off valves at the end of each wash day.
2

10
22
21. Loading door MUST BE CLOSED any time the washer is to ll, tumble, or spin. DO NOT bypass the
loading door switch by permitting the washer to operate with the loading door open.
22. Always read and follow manufacturer’s instructions on packages of laundry and cleaning aids. Heed all
warnings or precautions. To reduce the risk of poisoning or chemical burns, keep them out of the reach
of children at all times (preferably in a locked cabinet).
23. Always follow the fabric care instructions supplied by the textile manufacturer.
24. Never operate the washer with any guards and/or panels removed.
25. DO NOT operate the washer with missing or broken parts.
26. DO NOT bypass any safety devices.
27. Failure to install, maintain, and/or operate this washer according to the manufacturer’s instructions
may result in conditions which can produce bodily injury and/or property damage.
28. It is recommended that the machine be installed by qualied technicians.
29. Before starting repairs or maintenance, shut off all power and water supplies.
30. To prevent re and explosion:
Keep the area around the machine free from inammable or combustible products.
NOTE: The WARNINGS and IMPORTANT SAFETY INSTRUCTIONS appearing in this manual are not
meant to cover all possible conditions and situations that may occur. Common sense, caution, and
care must be exercised when installing, maintaining, or operating the washer.
Any problems or conditions not understood should be reported to the dealer, distributor, service agent, or
the manufacturer.
SAVE THESE INSTRUCTIONS

11
Operator Safety
WARNING
NEVER insert hands or objects into basket until it has
completely stopped. Doing so could result in serious
injury.
To ensure the safety of machine operators, the following maintenance checks must be performed daily:
1. Prior to operating the machine, verify that all warning signs are present and legible. Missing or illegible
signs must be replaced immediately. Make certain that spares are available.
2. Check door interlock before starting operation of the machine:
a. Attempt to start the machine with the door open. The machine should not start with the door open.
b. Close the door without locking it and attempt to start the machine. The machine should not start with
the door unlocked.
c. Close and lock the door and start a cycle. Attempt to open the door while the cycle is in progress.
The door should not open.
If the door lock and interlock are not functioning properly, call a service technician.
3. Do not attempt to operate the machine if any of the following conditions are present:
a. The door does not remain securely locked during the entire cycle.
b. Excessively high water level is evident.
c. Machine is not connected to a properly grounded circuit.
Do not bypass any safety devices in the machine.
WARNING
Never operate the machine with a bypassed or
disconnected balance system. Operating the machine
with severe out-of-balance loads could result in personal
injury and serious equipment damage.
SAVE THESE INSTRUCTIONS
2

3
12
3
Technical data HF150, IHF150, IHF033, CHF150, CHF033
Technical data and dimensions
METRIC US
Capacity (dry weight) Ratio [kg/Lit]
1:11 13,2 kg 29.10 lb.
1:10 14,5 kg 31.97 lb.
1:9 16,1 kg 35.49 lb.
Cylinder
Diameter 680 mm 26.77 inch
Depth 400 mm 15.75 inch
Volume 145 Lit 5.12 ft³
Cabinet
Height 1376 mm 54.15 inch
Width 780 mm 30.71 inch
Depth 840 mm 33.07 inch
Front loading
Diameter door opening 400 mm 15.75 inch
Height under door 472 mm 18.58 inch
To center 745 mm 29.33 inch
Speed
Wash 10 - 50 tr/min - RPM
Distribution 85 tr/min - RPM
Spin 250 - 1000 tr/min - RPM
G-factor
High spin 380
Dynamic bottom load (N/Hz)
1010/16
Motor (3-phase)
4p. 1470 tr/min 2,2 kW / 2,95 HP
Drain valve
2"
Water supply
Hard, soft, warm water 3/4"
Steam connection
Steam connection 3/8"
Heating
Electrical 230/400 V 12 kW - 15 kW - 18 kW
Electrical 400V 21 kW - 24 kW
Steam 6 bar
Warm water (without additional heating) X
Warm water (with additional heating) X
Packing dimensions
(H x W x D) mm - inch 1500x850x950 mm - 59.06x33.46x37.40 inch
Weight
Net 368 kg 811.30 lb.
Gross 383 kg 844.37 Ib.

170 [6.69]
K
185 [7.29]
35 [1.38]
L
E
D
C
B
A
IG
F
109 [4.3]
1015 [39.96]
1066 [41.95]
1108 [43.6]
1141 [44.9]
105 [4.13]
704 [27.7]
332 [13.05]
267 [10.49]
202 [7.93]
1376 [54.15]
1348 [53.07]
780 [30.71]
680 [26.77]50 [1.97] 50 [1.97]
472 [18.58]
34 [1.34]
220 [8.66]
86.5 [3.41]
34 [1.34]
88 [3.47]
665 [26.18]
733 [28.86]
753 [29.65]
13
3
Dimensions HF150, IHF150, IHF033, CHF150, CHF033
A. Ventilation soap dispenser
B. Liquid soap connections
C. Hard water connections 3/4"
D. Warm water connections 3/4"
E. Soft water connections 3/4"
F. Connection clamps
G. Electrical connections
I. Ventilation tub
K. Drain valve
L. Steam connections
Legend: metric mm [inches]

14
3
METRIC US
Capacity (dry weight) Ratio [kg/Lit]
1:11 16,5 kg 36.38 lb.
1:10 18,1 kg 39.90 lb.
1:9 20,1 kg 44.31 lb.
Cylinder
Diameter 680 mm 26.77 inch
Depth 500 mm 19.69 inch
Volume 181 Lit 6.39 ft³
Cabinet
Height 1376 mm 54.15 inch
Width 780 mm 30.71 inch
Depth 940 mm 37.01 inch
Front loading
Diameter door opening 400 mm 15.75 inch
Height under door 472 mm 18.58 inch
To center 745 mm 29.33 inch
Speed
Wash 10 - 50 tr/min - RPM
Distribution 85 tr/min - RPM
Spin 250 - 1000 tr/min - RPM
G-factor
High spin 380
Dynamic bottom load (N/Hz)
1090/16
Motor (3-phase)
4p. 1470 tr/min 2,2 kW / 2,95 HP
Drain valve
2"
Water supply
Hard, soft, warm water 3/4"
Steam connection
Steam connection 3/8"
Heating
Electrical 230/400 V 12 kW - 15 kW - 18 kW
Electrical 400V 21 - 24 kW
Steam 6 bar
Warm water (without additional heating) X
Warm water (with additional heating) X
Packing dimensions
(H x W x D) mm - inch 1500x850x1020 mm - 59.06x33.46x40.16 inch
Weight
Net 391 kg 862.01 lb.
Gross 418 kg 921.53 Ib.
Technical data HF185, IHF185, IHF045, CHF185, CHF045

34 [1.34]
220 [8.66]
86.5 [3.41]
34 [1.34]
88 [3.47]
765 [30.12]
833 [32.8]
853 [33.58]
1376 [54.15]
1348 [53.07]
780 [30.71]
680 [26.77]50 [1.97] 50 [1.97]
472 [18.58]
170 [6.69]
K
185 [7.29]
35 [1.38]
L
E
D
C
B
A
IG
F
109 [4.3]
1015 [39.96]
1066 [41.95]
1108 [43.6]
1141 [44.9]
105 [4.13]
704 [27.7]
332 [13.05]
267 [10.49]
202 [7.93]
15
3
Dimensions HF185, IHF185, IHF045, CHF185, CHF045
Legend: metric mm [inches]
A. Ventilation soap dispenser
B. Liquid soap connections
C. Hard water connections 3/4"
D. Warm water connections 3/4"
E. Soft water connections 3/4"
F. Connection clamps
G. Electrical connections
I. Ventilation tub
K. Drain valve
L. Steam connections

16
3
METRIC US
Capacity (dry weight) Ratio [kg/Lit]
1:11 21,3 kg 46.96 lb.
1:10 23,4 kg 51.59 lb.
1:9 26 kg 57.32 lb.
Cylinder
Diameter 750 mm 29.53 inch
Depth 530 mm 20.87 inch
Volume 234 Lit 8.26 ft³
Cabinet
Height 1528 mm 60.14 inch
Width 900 mm 35.43 inch
Depth 996 mm 39.21 inch
Front loading
Diameter door opening 400 mm 15.75 inch
Height under door 533 mm 20.96 inch
To center 805 mm 31.69 inch
Speed
Wash 10 - 50 tr/min - RPM
Distribution 85 tr/min - RPM
Spin 250 - 1000 tr/min - RPM
G-factor
High spin 419
Dynamic bottom load (N/Hz)
2300/16
Motor (3-phase)
4p. 1470 tr/min 3 kW / 4,02 HP
Drain valve
3"
Water supply
Hard, soft, warm water 3/4"
Steam connection
Steam connection 1/2"
Heating
Electrical 230/400 V 12 kW - 15 kW - 18 kW
Electrical 400V 21 kW - 24 kW
Steam 6 bar
Warm water (without additional heating) X
Warm water (with additional heating) X
Packing dimensions
(H x W x D) mm - inch 1700x970x1100 mm - 66.93x38.19x43.31 inch
Weight
Net 534 kg 1177.27 lb.
Gross 584 kg 1287.50 lb.
Technical data HF234, IHF234, IHF055, CHF234, CHF055

720 [28.35]
1266 [49.82]
1386 [54.57]
156 [6.12]
251 [9.88]
346 [13.62]
CDE
35 [1.38]
L
B
A
1126.9 [44.36]
105 [4.13]
165 [6.5]
K
116 [4.57]
G
I
1500 [59.05]
738 [29.05]
900 [35.43]
81 [3.19] 81 [3.19]
1528 [60.14]
533 [20.96]
70 [2.76] 926 [36.46]
900 [35.43]
830 [32.68]35 [1.38] 35 [1.38]
65 [2.56]
H
240 [9.45]
3
F
H
17
Dimensions HF234, IHF234, IHF055, CHF234, CHF055
Legend: metric mm [inches]
A. Ventilation soap dispenser
B. Liquid soap connections
C. Hard water connections 3/4"
D. Warm water connections 3/4"
E. Soft water connections 3/4"
F. Connection clamps
G. Electrical connections
H. Emergency button
I. Ventilation tub
K. Drain valve
L. Steam connections

18
3
METRIC US
Capacity (dry weight) Ratio [kg/Lit]
1:11 27,6 kg 60.85 lb.
1:10 30,4 kg 67.02 lb.
1:9 33,7 kg 74.30 lb.
Cylinder
Diameter 850 mm 33.46 inch
Depth 537 mm 21.14 inch
Volume 304 Lit 10.74 ft³
Cabinet
Height 1558 mm 61.32 inch
Width 1060 mm 41.73 inch
Depth 1147 mm 45.16 inch
Front loading
Diameter door opening 400 mm 15.75 inch
Height under door 567 mm 22.32 inch
To center 845 mm 33.27 inch
Speed
Wash 10 - 50 tr/min - RPM
Distribution 85 tr/min - RPM
Spin 250 - 1000 tr/min - RPM
G-factor
High spin 475
Dynamic bottom load (N/Hz)
2340/16
Motor (3-phase)
4p. 1470 tr/min 4 kW / 5,36 HP
Drain valve
3"
Water supply
Hard, soft, warm water 3/4"
Steam connection
Steam connection 1/2"
Heating
Electrical 230/400 V 18 kW
Electrical 400V 21 kW - 24 kW
Steam 6 bar
Warm water (without additional heating) X
Warm water (with additional heating) X
Packing dimensions
(H x W x D) mm - inch 1740x1120x1260 mm - 68.50x44.09x49.61inch
Weight
Net 731 kg 1611.58 lb.
Gross 781 kg 1721.81 lb.
Technical data HF304, IHF304, IHF075, CHF304, CHF075

247 [9.72]
1403 [55.24]
105 [4.13]
170 [6.69]
35 [1.38]
580 [22.83]
1312 [51.65]
L
367.5 [14.47]
187 [7.36]
488 [19.21]
1167 [45.93]
IG
E
D
C
B
A
K
1530 [60.24]
97.5 [3.84] 865 [34.06] 97.5 [3.84]
1060 [41.73]
1558 [61.32]
567 [22.32]
40 [1.57] 960 [37.8] 40 [1.57]
1040 [40.94]
1065 [41.93]82 [3.23]
245 [9.65]
71.5 [2.81]
HH
F
19
3
Dimensions HF304, IHF304, IHF075, CHF304, CHF075
Legend: metric mm [inches]
A. Ventilation soap dispenser
B. Liquid soap connections
C. Hard water connections 3/4"
D. Warm water connections 3/4"
E. Soft water connections 3/4"
F. Connection clamps
G. Electrical connections
H. Emergency button
I. Ventilation tub
K. Drain valve
L. Steam connections

Label 1
1/2
1/2
1/3
Label 2
20
4
Installation and Connection Instructions
Surface
CAUTION
Ensure that the machine is installed on a level oor of
sufcient strength and that the recommended clearances
for inspection and maintenance are provided. Never allow
the inspection and maintenance space to be blocked.
The machine must be placed on a at, solid surface (metal base,
concrete or solid ground). When using a metal base or with machines with
steam heating, the machine must be anchored on the 4 provided
locations (A) (See Label 1) in the base. (See Mounting Bolt Hole
Locations). The height of the pad should not exceed 203 mm - 8 inch.
The machine must be placed entirely level. For easy maintenance it is
recommended to keep a minimal distance of 600 mm - 23.62 inch between
the wall and the back of the machine.
If several machines are placed next to each another, there should be a
minimal distance of 30 mm - 1.18 inch between each machine.
The out of balance switch is mounted on the solid part of the machine.
There is a window around the probe of the out of balance switch that is
mounted on the movable part of the machine.
When the machine goes out of balance by overloading or uneven
distribution of the linen, the out of balance switch will interrupt this action
to prevent damage to the machine.
Important
Out of balance switch
To guarantee good functioning, the probe should be centered
horizontally and vertically at 1/3 from the bottom of the out of
balance window (when machine drum is empty). (See Label 2)
Window
Probe

HF234-304
Label 3
Label 4
HF150-185
4
21
To prevent damage during transportation, the machine has been equipped
with four red transport brackets to eliminate every possible movement of
the tub.
After the machine has been placed level, take off the service panel and
back panel to remove these transport brackets. (See Labels 3 and 4)
Important
Removal of the transport safety
The machine must never be activated before removing
these transport brackets.

680 [26.77]
780 [30.71]
50 [1.97] 50 [1.97]
34 [1.34]34 [1.34]
Ø22 [Ø0.87]
665 [26.18]
733 [28.86]
22
4
Mounting Bolt Hole Locations for machines, HF150, IHF150, IHF033, CHF150, CHF033
Legend: metric mm [inches]

680 [26.77]
780 [30.71]
50 [1.97] 50 [1.97]
34 [1.34]34 [1.34]
Ø22 [Ø0.87]
765 [30.12]
833 [32.8]
23
4
Mounting Bolt Hole Locations for machines, HF185, IHF185, IHF045, CHF185, CHF045
Legend: metric mm [inches]

Ø22 [Ø0.87]
738 [29.05]
830 [32.68]
81 [3.19] 81 [3.19]
35 [1.38] 35 [1.38]
900 [35.43]
900 [35.43]
24
Mounting Bolt Hole Locations for machines, HF234, IHF234, IHF055, CHF234, CHF055
4
Legend: metric mm [inches]

4
1060 [41.73]
Ø22 [Ø0.87]
865 [34.06]97.5 [3.84] 97.5 [3.84]
960 [37.8]
1040 [40.94]
40 [1.57] 40 [1.57]
25
Mounting Bolt Hole Locations for machines, HF304, IHF304, IHF075, CHF304, CHF075
Legend: metric mm [inches]

26
4
The machine is delivered with hoses with 3/4" connections. These hoses t the water
inlet valves of the machine and the main water inlet taps. All the inlet valves have to be
connected. To ensure the optimal functioning of the water inlet valves, the water pressure
on the inlet should be between 3 and 5 bar (40 and 80 psi). If the pressure is too low, the
cycle time will increase considerably.
In case of boiler fed machines, a minimum of hot water of 90°C - 194°F should be
available per unit. (See Table 1)
MODEL Min Contents Boiler
METRIC US
For the HF150, IHF150, IHF033, CHF150, CHF033 110 l. 3.88 ft³
For the HF185, IHF185, IHF045, CHF185, CHF045 130 l. 4.59 ft³
For the HF234, IHF234, IHF055, CHF234, CHF055 150 l. 5.30 ft³
For the HF304, IHF304, IHF075, CHF304, CHF075 180 l. 6.36 ft³
MODEL Inlet ow capacity per minute (Gallons / Liters)
INTERNATIONAL US
For the HF150, 185 4.23 / 16 5.28 / 20
For the HF234, 304 7.93 + 13.2 / 30 + 50 7.93 + 13.2 / 30 + 50
Water connection
The diameter of the main drain should be adapted to the water ow and the number of
machines. It should be sufcient to handle at least 80 l/min - 21.13 gal./min (HF150-
185) and 160 l/min - 42.26 gal./min (HF234-304) per machine.
It is necessary to connect the main drain at least on one side to an open air-brake to
allow ventilation.
The machine is equipped with a drain valve with 2" outer diameter (50 mm) for HF150-
185 and with 3" outer diameter (80 mm) for HF234-304. This drain valve should be
connected to the drain by means of the drain elbow which is delivered with the machine.
Water drain
Table 1
Table 2
To comply with the WRAS water regulations: an 'approved' single check valve or
some other no less effective backow prevention device shall be tted at the point of
connection(s) between the supply and the tting (IRN R150).

4
27
Electrical installation
Important
Electrical ratings are subject to changes. Refer to serial plate decal for electrical ratings information
specic to your machine.
WARNING
Hazardous Voltage. Can cause shock, burn or cause
death. Allow machine power to remain off for two minutes
prior to working in and around AC inverter drive.
WARNING
Hazardous Voltage. Can cause shock, burn or death.
Verify that a ground wire from a proven earth ground is
connected to the lug near the input power block on this
machine.
The AC inverter drive requires a clean power supply free from voltage spikes and surges. A voltage
monitor should be used to check incoming power. The customer’s local power company may
provide such a monitor.
If input voltage measures above 240V for a 220V drive or above 480V for a 400V drive, ask the
power company to lower the voltage. As an alternative, a step-down transformer kit is available
from the distributor.
The AC drive provides overload protection for the drive motor. However, a separate single or
three-phase circuit breaker must be installed for complete electrical overload protection. This
prevents damage to the motor by disconnecting all legs if one should be lost accidentally. Check
the data plate on the back of the washer-extractor or consult Table 3 through 6 for circuit breaker
requirements.
IMPORTANT: Do NOT use fuses in place of a circuit breaker.
For installation in the United States or Canada, branch circuit protection must be provided
according to National and Local Codes. The branch circuit breaker must be of the inverse time or
instantaneous trip type at the values given in the technical specications for each machine.
Use a circuit breaker of the minimal type of 10kA interrupt current.
CAUTION
Do not use a voltage or phase converter on any variable speed machine.
The washer-extractor should be connected to an individual branch circuit not shared with lighting or
another electrical device.
The connection should be shielded in a liquid tight or approved exible conduit with proper
conductors of correct size installed in accordance with the National Electric Code or other
applicable codes. The connection must be made by a qualied electrician using the wiring diagram
provided with the washer-extractor, or according to accepted European standards for CE-approved
equipment.

4
28
Use wire sizes indicated in Table 3 through 6 for runs up to 50 feet.
Use next larger size for runs of 50 to 100 feet. Use two sizes larger for runs greater than 100 feet.
For personal safety and proper operation, the washer-extractor must be grounded in accordance
with state and local standards. If such standards are not available, grounding must conform to
the National Electric Code, article 250. The ground connection must be made to a proven earth
ground, not to a water pipe, gas pipe, or another metal pipe. Provide the necessary equipotential
connections according to the local electrical prescriptions.
GROUNDING INSTRUCTIONS
This appliance must be connected to a grounded metal, permanent wiring system; or an equipment-
grounding conductor must be run with the circuit conductors and connected to the equipment-
grounding terminal or lead on the appliance.
IMPORTANT: Alliance Laundry Systems Warranty does not cover components that fail as a
result of improper input voltage.

4
Label 5
29
Connection label:
Machine power connections are made at the back of the machine. Three or four conductor power cable
is the recommended method (See chapter electrical specs for minimum cable requirements, if local
electrical codes exceed these requirements, follow local codes). The number of conductors in this cable
and the proper connection points for the cable wires shall be determined by the machine and power
requirements. All machines must have a ground wire and be properly grounded. The ground wire must
be insulated with a green/yellow color. This wire is normally within the power cable but can also be a
separate wire run along side the power cable if properly sized.
Never run a machine that does not have a ground wire. This ground wire must be connected to
the machine grounding lug found near the main switch. This lug is identied with the international
“protective earth” symbol and the letters “PE”. Failure to connect this ground wire can lead to an unsafe
machine condition leading to machine damage and/or operator injury or death. This wire must be
connected to earth ground at far end.
Machine Power Cable Connections:
Remove main switch cover plate at back of machine (see chapter dimensions part (F)). Run power cable
through the cabinet knock-out located directly below the cover plate. Before installing, obtain and install
a cord-grip to hold the cable in place. Never rely upon the electrical connections to hold cable in place.
Allow some slack in this cable outside of the machine to form a drip-loop between the supply power circuit
breaker and the machine knock-out. Connect power cable wires as directed below. Always connect the
ground wire rst and remove last.
Wiring based on the supply power and machine design (voltage/frequency):
440-480 Volts, 3-Phase, 3-wire or 4-wire + PE, 50 or 60 Hertz Conguration (Named: N-Voltage):
With supply power of: 440-480 Volts, 3-phase, 3-wire, after connecting the green/yellow PE ground wire,
connect one wire to each of the bottom terminals of the power contactor switch marked: “L1,L2,L3”. When
this supply power has four wires, connect this 4th wire, identied as a neutral wire, to the bottom terminal
of the auxiliary contactor on the power contactor switch marked: “N”. Connect the remaining power wires
as rst noted.
380-415 Volts, 3-Phase, 4-wire + PE, 50 or 60 Hertz Conguration (Named: P-Voltage):
With supply power of: 380-415 Volts, 3-phase, 4-wire, after connecting the green/yellow PE ground wire,
follow the directions of the four wire system for 440-480 Volt conguration.
Main power connection

4
30
200-240 Volts, 3-Phase, 3-wire + PE, 50 or 60 Hertz Conguration (Named: Q-Voltage or 3-phase X-Voltage):
With supply power of: 200-240 Volts, 3-phase, 3-wire, after connecting the green/yellow PE ground wire, connect one power
wire to each of the terminals at the bottom of the power contactor switch marked: “L1,L2,L3”.
200-240 volts, 1-Phase, 2-wire + PE, 50 Hertz (called 1-phase, 50 Hz X-voltage):
With supply power of: 200-240 Volts, 1-phase, 2-wire, 50Hz, after connecting the green/yellow PE ground wire, connect
the power wire to the “L1” bottom terminal of the power contactor switch and the other wire, identied as the neutral wire,
to the bottom terminal of the auxiliary contactor on the power contactor switch marked: “N”.
200-240 volts, 1-Phase, 2-wire + PE, 60 Hertz (called 1-phase, 60 Hz X-voltage):
With supply power of: 200-240 Volts, 1-phase, 2-wire, 60Hz, after connecting the green/yellow PE ground wire, connect
one power wire to the “L1” and power wire to the “L2” of the bottom terminals of the power contactor switch.
After connection, check the spin direction. The cylinder must spin in the clockwise direction.
A wrong spin direction can damage the motor and can also cause water to spurt from the soap dispenser.
In case of wrong spin direction: switch the terminal clamps of the motor circuit “R” and “S” of the connecting cable or
change the connection at the terminal block switching the L1 and L2 wires.

4
31
WARNING
The washer-extractor should be connected to an individual branch
circuit not shared with lighting or other equipment.
Electrical Specications HF150, IHF150, IHF033, CHF150, CHF033
150 liters / 33 pounds
Boiler Fed/Steam Heat Electric Heat
Code
Voltage
Cycle
Phase
Wire
Full Load Amps
Recommended Circuit
Breaker (US-market)
AWG/mm2
kW Standard
Heating Elements
Full Load Amps
Recommended
Circuit Breaker (US-
market)
AWG/mm2
US NON-US US NON-US
N 440-480 50/60 3 3+PE 6 15 10 14/2.5
6x3 kW
32 40 40 8/10.0
P 380-415 50/60 3 3+N+PE 18 20 20 12/4.0 44 50 50 8/10.0
Q 200-240 50/60 3 3+PE 18 20 20 12/4.0 63 70 70 4/25.0
X 200-240 50/60 1/3 2/3+PE 18 20 20 12/4.0 N/A N/A N/A N/A
Alternative Electric Heat Options
N 440-480 50/60 3 3+PE
6x2 kW
23 30 32 10/6.0
P 380-415 50/60 3 3+N+PE 36 40 40 8/10.0
Q 200-240 50/60 3 3+PE 49 60 60 6/16.0
X 200-240 50/60 1/3 2/3+PE N/A N/A N/A N/A
N 440-480 50/60 3 3+PE
3x3 kW +
3x2 kW
28 40 40 8/10.0
P 380-415 50/60 3 3+N+PE 40 50 50 8/10.0
Q 200-240 50/60 3 3+PE 56 60 60 6/16.0
X 200-240 50/60 1/3 2/3+PE N/A N/A N/A N/A
N 440-480 50/60 3 3+PE
3x3 kW +
3x4 kW
36 40 40 8/10.0
P 380-415 50/60 3 3+N+PE 49 60 60 6/16.0
Q 200-240 50/60 3 3+PE N/A N/A N/A N/A
X 200-240 50/60 1/3 2/3+PE N/A N/A N/A N/A
N 440-480 50/60 3 3+PE
6x4 kW
41 50 50 8/10.0
P 380-415 50/60 3 3+N+PE 53 60 60 6/16.0
Q 200-240 50/60 3 3+PE N/A N/A N/A N/A
X 200-240 50/60 1/3 2/3+PE N/A N/A N/A N/A
Table 3

4
32
WARNING
The washer-extractor should be connected to an individual branch
circuit not shared with lighting or other equipment.
Electrical Specications HF185, IHF185, IHF045, CHF185, CHF045
185 liters / 45 pounds
Boiler Fed/Steam Heat Electric Heat
Code
Voltage
Cycle
Phase
Wire
Full Load Amps
Recommended Circuit
Breaker (US-market)
AWG/mm2
kW Standard
Heating Elements
Full Load Amps
Recommended
Circuit Breaker (US-
market)
AWG/mm2
US NON-US US NON-US
N 440-480 50/60 3 3+PE 6 15 10 14/2.5
6x3 kW
32 40 40 8/10.0
P 380-415 50/60 3 3+N+PE 18 20 20 12/4.0 44 50 50 8/10.0
Q 200-240 50/60 3 3+PE 18 20 20 12/4.0 63 70 70 4/25.0
X 200-240 50/60 1/3 2/3+PE 18 20 20 12/4.0 N/A N/A N/A N/A
Alternative Electric Heat Options
N 440-480 50/60 3 3+PE
6x2 kW
23 30 32 10/6.0
P 380-415 50/60 3 3+N+PE 36 40 40 8/10.0
Q 200-240 50/60 3 3+PE 49 60 60 6/16.0
X 200-240 50/60 1/3 2/3+PE N/A N/A N/A N/A
N 440-480 50/60 3 3+PE
3x3 kW +
3x2 kW
28 40 40 8/10.0
P 380-415 50/60 3 3+N+PE 40 50 50 8/10.0
Q 200-240 50/60 3 3+PE 56 60 60 6/16.0
X 200-240 50/60 1/3 2/3+PE N/A N/A N/A N/A
N 440-480 50/60 3 3+PE
3x3 kW +
3x4 kW
36 40 40 8/10.0
P 380-415 50/60 3 3+N+PE 49 60 60 6/16.0
Q 200-240 50/60 3 3+PE N/A N/A N/A N/A
X 200-240 50/60 1/3 2/3+PE N/A N/A N/A N/A
N 440-480 50/60 3 3+PE
6x4 kW
41 50 50 8/10.0
P 380-415 50/60 3 3+N+PE 53 60 60 6/16.0
Q 200-240 50/60 3 3+PE N/A N/A N/A N/A
X 200-240 50/60 1/3 2/3+PE N/A N/A N/A N/A
Table 4

4
33
WARNING
The washer-extractor should be connected to an individual branch
circuit not shared with lighting or other equipment.
Electrical Specications HF234, IHF234, IHF055, CHF234, CHF055
234 liters / 55 pounds
Boiler Fed/Steam Heat Electric Heat
Code
Voltage
Cycle
Phase
Wire
Full Load Amps
Recommended Circuit
Breaker (US-market)
AWG/mm2
kW Standard
Heating Elements
Full Load Amps
Recommended
Circuit Breaker (US-
market)
AWG/mm2
US NON-US US NON-US
N 440-480 50/60 3 3+PE 8 15 10 14/2.5
6x3 kW
34 40 40 8/10.0
P 380-415 50/60 3 3+N+PE 25 30 30 10/6.0 51 60 60 6/16.0
Q 200-240 50/60 3 3+PE 25 30 30 10/6.0 70 80 80 4/25.0
X 200-240 50/60 1/3 2/3+PE 25 30 30 10/6.0 N/A N/A N/A N/A
Alternative Electric Heat Options
N 440-480 50/60 3 3+PE
6x2 kW
25 30 32 10/6.0
P 380-415 50/60 3 3+N+PE 42 50 50 8/10.0
Q 200-240 50/60 3 3+PE 55 60 60 6/16.0
X 200-240 50/60 1/3 2/3+PE N/A N/A N/A N/A
N 440-480 50/60 3 3+PE
3x3 kW +
3x2 kW
29 40 40 8/10.0
P 380-415 50/60 3 3+N+PE 47 50 50 8/10.0
Q 200-240 50/60 3 3+PE 63 70 70 4/25.0
X 200-240 50/60 1/3 2/3+PE N/A N/A N/A N/A
N 440-480 50/60 3 3+PE
3x3 kW +
3x4 kW
38 50 50 8/10.0
P 380-415 50/60 3 3+N+PE 55 60 60 6/16.0
Q 200-240 50/60 3 3+PE N/A N/A N/A N/A
X 200-240 50/60 1/3 2/3+PE N/A N/A N/A N/A
N 440-480 50/60 3 3+PE
6x4 kW
42 50 50 8/10.0
P 380-415 50/60 3 3+N+PE 60 70 70 4/25.0
Q 200-240 50/60 3 3+PE N/A N/A N/A N/A
X 200-240 50/60 1/3 2/3+PE N/A N/A N/A N/A
Table 5

4
34
WARNING
The washer-extractor should be connected to an individual branch
circuit not shared with lighting or other equipment.
Electrical Specications HF304, IHF304, IHF075, CHF304, CHF075
304 liters / 75 pounds
Boiler Fed/Steam Heat Electric Heat
Code
Voltage
Cycle
Phase
Wire
Full Load Amps
Recommended Circuit
Breaker (US-market)
AWG/mm2
kW Standard
Heating Elements
Full Load Amps
Recommended
Circuit Breaker (US-
market)
AWG/mm2
US NON-US US NON-US
N 440-480 50/60 3 3+PE 16 20 20 12/4.0
6x3 kW
42 50 50 8/10.0
P 380-415 50/60 3 3+N+PE 25 30 32 10/6.0 51 60 60 6/16.0
Q 200-240 50/60 3 3+PE 25 30 32 10/6.0 71 80 80 4/25.0
X 200-240 50/60 1/3 2/3+PE N/A N/A N/A N/A N/A N/A N/A N/A
Alternative Electric Heat Options
N 440-480 50/60 3 3+PE
3x3 kW +
3x4 kW
46 50 50 8/10.0
P 380-415 50/60 3 3+N+PE 56 60 60 6/16.0
Q 200-240 50/60 3 3+PE N/A N/A N/A N/A
X 200-240 50/60 1/3 2/3+PE N/A N/A N/A N/A
N 440-480 50/60 3 3+PE
6x4 kW
51 60 60 6/16.0
P 380-415 50/60 3 3+N+PE 60 70 70 4/25.0
Q 200-240 50/60 3 3+PE N/A N/A N/A N/A
X 200-240 50/60 1/3 2/3+PE N/A N/A N/A N/A
N 440-480 50/60 3 3+PE
3x6 kW +
3x4 kW
59 70 70 4/25.0
P 380-415 50/60 3 3+N+PE 69 80 80 4/25.0
Q 200-240 50/60 3 3+PE N/A N/A N/A N/A
X 200-240 50/60 1/3 2/3+PE N/A N/A N/A N/A
Table 6

Label 6
Label 7
4
35
The liquid soap connection consists of 8 connections for liquid soap
(See Label 6).
The central opening is used for ventilation.
Liquid soap connection (option)
Connection of the liquid soap hoses
WARNING
Dangerous Chemicals. May damage eyes and skin. Wear eye and
hand protection when handling chemicals; always avoid direct
contact with raw chemicals. Read the manufacturer’s directions for
accidental contact before handling chemicals. Ensure an eye-rinse
facility and an emergency shower are within easy reach. Check at
regular intervals for chemical leaks.
CAUTION
Drill out plugs and nipples before making supply hose connection.
Failure to do so can cause buildup of pressure and risk a tubing
rupture.
Electrical connection of the liquid soap pumps
On machines equipped with a liquid soap connection, connect the wires directly on
the print board next to the ground wire connection (option). Connect as indicated on
the wiring diagram.
The two connectors on the right give a tension of 220V ~ (max. 4A) which can
be applied to drive 220V ~ soap pumps. If more than 4A is required, an external
tension will have to be used. 6 connections have been provided, of which one (S6)
can be used to drive a waterproong pump (e.g. for rain coats, etc.). (See Label 7)

Label 8
Label 9
Label 10
4
36
The 220V can be transformed to other values to drive other type soap pumps.
Example: pumps 24V ~. (See Label 8)
Also, pumps with different operating tension can be combined.
Example: 5 pumps 220V ~ and 1 pump 24V ~. (See Label 9)
With an external tension 24V DC (See Label 10)

Label 11 Label 12 Label 13
Label 14
4
A
37
Connection of a central operating
panel for coin machines (option)
WARNING
To reduce the risk of electric shock, disconnect this appliance from
the power supply before attempting any user maintenance. Turning
the controls to the OFF position does not disconnect this appliance
from the power supply.
At the backside above the main connectors, you nd a printboard, to which the
central operating panel for coin machines can be connected.
The right connectors form a potential free output contact as a result of which the
operating panel detects when the machine is activated or not.
The left connectors receive the signal, by means of which a machine is chosen
through the operating panel.
There are 3 different variations possible according to the output voltage of the
operating panel. (See Labels 11, 12 and 13)
IMPORTANT:
If a machine is equipped with this kind of printboard or if a printboard has been
built in, the resistance of the cycle contact (A) may no longer be present on
the main printboard. (See Label 14)
When this resistance is present, it has to be cut out of the main printboard.

5
2345 3 1
6
7
7
7
38
Steam connection
Machines with steam heating must have a steam valve between the steam
installation and the machine.
WARNING
Never touch internal or external steam pipes, connections,
or components. These surfaces can be extremely hot and
will cause severe burns. The steam must be turned off and
the pipe, connections, and components allowed to cool
before the pipe can be touched.
Steam Supply Information
MODEL
Steam inlet
connection, inch
Number of
steam inlets
Recommended
pressure, bar
Recommended
pressure, psi
Maximum
pressure, bar
Maximum
pressure, psi
For the HF150, IHF150, IHF033, CHF150, CHF033 3/8 1 2.0 - 5.5 30 - 80 5.5 80
For the HF185, IHF185, IHF045, CHF185, CHF045 3/8 1 2.0 - 5.5 30 - 80 5.5 80
For the HF234, IHF234, IHF055, CHF234, CHF055 1/2 1 2.0 - 5.5 30 - 80 5.5 80
For the HF304, IHF304, IHF075, CHF304, CHF075 1/2 1 2.0 - 5.5 30 - 80 5.5 80
With direct steam injection into the machine (See Table 7)
1. Steam pipe
2. Steam cut-off valve
3. Pipe coupling
4. Steam lter
5. Magnetic steam valve
6. Curve MF
7. Steam hose with appropriate pipe coupling
Table 7

6
Label 15 Label 16
39
Internal connections of the electrical heating
NOTE:
Other executions are available as options.
3 AC
1 AC
Technical remarks
Heating 3x230V R5 3x400V R5
4,2kw 3x1,4kw See Label 15 LC1D0901 See Label 16 LC1D0901
6kw 3x2kw See Label 15 LC1D0901 See Label 16 LC1D0901
9kw 3x3kw See Label 15 LC1D1810 See Label 16 LC1D0901
12kw 3x4kw -------- -------- See Label 15 LC1D0901
12kw 3x2kw
3x2kw
See Label 15
See Label 15
LC1D1810
LC1D1810
See Label 16 LC1D1810
15kw 3x2kw
3x3kw
See Label 15
See Label 15
LC1D1810
LC1D1810
See Label 16 LC1D1810
18kw 3x3kw
3x3kw
See Label 15
See Label 15
LC1D1810
LC1D1810
See Label 16 LC1D1810
21kw 3x3kw
3x4kw
-------- -------- See Label 16
See Label 15
LC1D1810
LC1D1810
24kw 3x4kw
3x4kw
-------- -------- See Label 15
See Label 15
LC1D1810
LC1D1810
Heating R5
3kw LC1D0901
B = Black Br = Brown
Gy = Grey Bu = Blue
R = Red W = White
Table 8
Table 9
"Delta" conguration "WYE" conguration

7
40
Maintenance instruction of the machine
Clean the entire cabinet of the machine regularly and remove all traces of soap,
etc....
Remove all detergent residue in the soap dispenser with hot water.
Clean the door gasket and remove all detergents and other products.
Shut off the main water, steam, and power connections at the end of each day.
Do not change the setting of the water inlet taps on boiler fed machines once
these have been installed.
It is recommended to leave the door and soap dispenser open after use, to
ventilate the machine.
Check for proper door lock operation on a daily basis.
General maintenance
The V-belts of the motors should be retightened after two to three months when
rst used. This is necessary because these belts are subject to a one-time
stretching when rst used. If this is not done, the belt starts to slip after a few
months and will break shortly afterwards.
Check the water inlet lters to make sure they are not blocked by calcication.
Check the drain valve for obstructions.
If a machine frequently skips the nal spin, check whether the probe of the out of
balance switch is still in the appropriate position, that is horizontally centered and
vertically 1/3 from the bottom inside the window. (When the drum is empty).
Lubricate the bearings after every 200 hours of operation or replace the automatic
lubricator annually.
Periodical maintenance
Clean AC drive lter:
a. Snap off external plastic cover which contains lter.
b. Remove foam lter from cover.
c. Wash lter with warm water and allow to air dry. Filter can be vacuumed clean.
End of day
WARNING
To reduce the risk of electric shock, disconnect this appliance
from the power supply before attempting any user maintenance.
Turning the controls to the OFF position does not disconnect this
appliance from the power supply.
Before starting wiring or inspection, power must be switched OFF,
check to make sure that the operation panel indicator is off.
Any person who is involved in wiring or inspection shall wait for
at least 10 minutes after the power supply has been switched OFF
and check that there is no residual voltage using a tester or the
like. The capacitor of the inverter or the EMC lter is charged with
a high voltage for some time after power OFF, and it is dangerous.

7
41
Verify that the belts are running in the middle of the basket pulley.
Verify the belt tension according to the table below. Belt tension measurements
should be taken as close as possible to the center of the belt span (see gure).
Annual maintenance
Belt tension:
Belt tension testing table
Model Belt Frequency (Hz) Tension force (N) Deection (mm) Deection force
MIN
MAX
MIN
MAX
at MIN
tension
at MAX
tension
MAX
HF150 10J 1549 91 111 708 1050 7,3 5,3 50
HF185 10J 1549 91 111 708 1050 7,3 5,3 50
HF234 10J 1663 87 92 821 1050 7,4 6,6 50
HF304 10PK 2120 62 67 1067 1182 10,6 5,6 75
1 Deection
2 Span length

8
Label 17
Label 18
42
Contact Information
Nameplate
Nameplate Location
The nameplate is located at the rear of the machine. Always provide the machine’s serial
number and model number when ordering parts or when seeking technical
assistance. See Labels 17 and 18.

8
43
Replacement Parts
If literature or replacement parts are required, contact the source from which the
machine was purchased or contact the phone numbers or websites shown on the
nameplate.
Position of the Serial plate

9
44
In case of important malfunctions and deciencies, which you cannot resolve
yourself, contact your distributor.
Repair and after-sales service
Machine : Type: ......................................................................................
Program: ................................................................................
Date of installation: ................................................................
Installed by: ...........................................................................
Serial number: .......................................................................
Operation voltage and frequency: .........................................
Distributor : Name: ....................................................................................
Address: ................................................................................
Tel.: ........................................................................................
Alliance Laundry Systems
Shephard Street, PO BOX 990
Ripon, WI 54971-0990
United States
Tel: 001 920 748 3121 - Fax: 001 920 748 1645
www.comlaundry.com
Alliance International bvba
Nieuwstraat 146 - B-8560 Wevelgem (Belgium)
Tel. +32 56 41 20 54 - Fax +32 56 41 86 74
info@alliancels.eu - www.alliancels.eu