Arcade Virtua Cop 3 Ur Manual VC3 UPRIGHT MANUAL_Iss 0 User
2013-11-28
User Manual: Arcade Virtua Cop 3 Ur Manual
Open the PDF directly: View PDF .
Page Count: 116 [warning: Documents this large are best viewed by clicking the View PDF Link!]

420-6759-02UK REV 0
SERVICE MANUAL
UPRIGHT TYPE
Before using this product, read this SERVICE MANUAL carefully to understand the contents stated herein.
After reading this manual, be sure to keep it available nearby the product or somewhere convenient in order to
be able to refer to it whenever necessary.
Manufactured in the UK by
i
CONTENTS
1. BEFORE USING THIS PRODUCT........................................................................................................1
1.1. INSPECTIONS IMMEDIATELY AFTER TRANSPORTING THE PRODUCT TO THE LOCATION..2
2. INTRODUCTION TO THIS SERVICE MANUAL ...................................................................................4
3. INSTALLATION AND MAINTENANCE INSTRUCTIONS .....................................................................5
3.1. HANDLING AND INSTALLATION PRECAUTIONS ..........................................................................5
3.2. COIN HANDLING...............................................................................................................................5
3.3. NAME OF PARTS..............................................................................................................................6
3.4. ACCESSORIES .................................................................................................................................7
3.5. SHIPPING THE GAME BOARD.........................................................................................................8
3.6. SHIPPING THE MEDIA BOARD......................................................................................................10
3.7. SHIPPING THE GD-ROM DRIVE....................................................................................................11
3.8. ASSEMBLY INSTRUCTIONS..........................................................................................................12
3.8.1. INSTALLING THE DISPLAY CARD..........................................................................................13
3.8.2. INSTALLING THE FLOOR .......................................................................................................14
3.8.3. SECURING IN PLACE (LEG ADJUSTER ADJUSTMENT)......................................................18
3.8.4. INSTALLING THE FOOT PEDAL.............................................................................................19
3.8.5. COIN HANDLING INSTALLATION...........................................................................................24
3.8.5.1. WIRING CONNECTIONS..................................................................................................25
3.8.6. CONNECTION TO THE POWER SUPPLY..............................................................................26
3.8.7. ADJACENT CONTROL INTERFERENCE PREVENTION.......................................................27
3.9. ASSEMBLY CHECK.........................................................................................................................28
3.9.1. MEMORY TEST........................................................................................................................28
3.9.2. C.R.T. TEST .............................................................................................................................29
3.9.3. INPUT TEST .............................................................................................................................30
3.9.4. OUTPUT TEST .........................................................................................................................30
3.9.5. GUN ADJUSTMENT.................................................................................................................31
3.10. MOVING THE MACHINE .............................................................................................................32
3.11. CONTROLLER .............................................................................................................................34
3.11.1.1. REPLACING THE MICROSWITCH..................................................................................34
3.11.1.2. REPLACING THE SENSOR UNIT....................................................................................38
3.12. REPLACEMENT OF LED BOARD...............................................................................................39
3.13. REPLACEMENT OF FLUORESCENT LAMP AND START LAMPS ...........................................40
3.13.1. FLUORESCENT....................................................................................................................40
3.13.2. START LAMP REPLACEMENT............................................................................................41
3.14. GAME BOARD .............................................................................................................................42
3.14.1. REMOVING THE BOARD.....................................................................................................42
3.14.2. REMOVING THE GD-ROM DRIVE.......................................................................................44
3.15. COMPOSITION OF THE GAME BOARD ....................................................................................45
3.16. TROUBLESHOOTING .................................................................................................................46
3.17. FUSES..........................................................................................................................................47
4. PERIODIC CHECK AND INSPECTION ..............................................................................................48
4.1. CLEANING THE CABINET SURFACES..........................................................................................48
5. HOW TO PLAY....................................................................................................................................49
5.1. GAME CONTENTS..........................................................................................................................50
5.1.1. The Main Characters ................................................................................................................51
5.1.1.1. 1P Character: RAGE .........................................................................................................51
5.1.1.2. 2P Character: SMARTY.....................................................................................................51
5.1.2. Playing Virtua Cop 3..................................................................................................................51
5.1.2.1. Start a New Game .............................................................................................................51
5.1.2.2. Calibrating at the Start of the Game ..................................................................................51
5.1.2.3. Mission Select....................................................................................................................51
5.1.2.4. Game Screen.....................................................................................................................52
5.1.2.5. ES Gauge ..........................................................................................................................53
5.1.3. Game Over ...............................................................................................................................54
5.1.4. Continue....................................................................................................................................54
6. MAINTENANCE INSTRUCTIONS.......................................................................................................55
6.1. EXPLANATION OF TEST DATA AND DISPLAY ............................................................................55
6.2. INTERNAL SWITCHES AND COIN METERS.................................................................................56
6.3. SYSTEM TEST MODE.....................................................................................................................57
6.3.1. EXPLANATION OF TEST AND DATA DISPLAY .....................................................................57
6.3.2. SYSTEM TEST MENU MODE..................................................................................................58
ii
6.3.3. MEDIA BOARD TEST...............................................................................................................59
6.3.4. SYSTEM INFORMATION .........................................................................................................60
6.3.5. JVS TEST .................................................................................................................................61
6.3.6. INPUT TEST Screen.................................................................................................................62
6.3.7. SOUND TEST...........................................................................................................................63
6.3.8. C.R.T. TEST .............................................................................................................................64
6.3.9. COIN ASSIGNMENTS..............................................................................................................65
6.3.10. CLOCK SETTING .................................................................................................................67
6.3.11. NETWORK SETTING (CORE) .............................................................................................68
6.3.12. NETWORK SETTING (MEDIA) ............................................................................................69
6.4. GAME TEST MODE.........................................................................................................................70
6.4.1. INPUT TEST .............................................................................................................................71
6.4.2. OUTPUT TEST.........................................................................................................................72
6.4.3. GAME ASSIGNMENTS ............................................................................................................73
6.4.4. GUN ADJUSTMENT.................................................................................................................74
6.4.5. BOOKKEEPING........................................................................................................................75
6.4.6. BACKUP DATA CLEAR............................................................................................................77
7. COIN MECH INSTALLATION AND CREDIT BOARD SET UP...........................................................78
7.1. INTRODUCTION..............................................................................................................................78
7.1.1. PRICE OF PLAY SETTINGS UK .............................................................................................80
7.1.2. PRICE OF PLAY SETTINGS EURO ........................................................................................81
7.1.3. PRICE OF PLAY SETTINGS Austria-Czech-Denmark-Norway-Israel-France2 ......................82
8. DESIGN RELATED PARTS.................................................................................................................83
9. PARTS LIST ........................................................................................................................................84
9.1. VCT-10002UK ASSY CABINET VCT U/R .......................................................................................84
9.2. VCT-11002UK ASSY FRAMEWORK VCT U/R ...............................................................................87
9.3. NOA-1200UK ASSY CRT COVER UK.............................................................................................89
9.4. VCT-1200UK ASSY FOOT PEDAL DX............................................................................................90
9.5. VCT-1300 ASSY BILLBOARD .........................................................................................................91
9.6. VCT-1400UK ASSY CONTROL BOX VCT U/R...............................................................................92
9.7. VCT-1500UK ASSY FRONT PANEL VCT U/R FST........................................................................94
9.8. NOB-1710UK ASSY AC UNIT ........................................................................................................95
9.9. NOA-1750UK ASSY SERVICE DOOR ...........................................................................................95
9.10. VCT-2100-01 CONTROL UNIT EXP............................................................................................96
9.11. JPT-2030 SENSOR UNIT ............................................................................................................97
9.12. HDT-4100UK ASSY XMFR ..........................................................................................................98
9.13. CHT-4000UK ASSY ELEC ..........................................................................................................99
9.14. VCT-4800UK ASSY MAIN BD VCT U/R ...................................................................................100
9.15. VCT-5000UK ASSY FLOOR VCT U/R......................................................................................101
9.16. VCT-5100UK ASSY CCT VCT U/R...........................................................................................102
9.17. VCT-5150UK ASSY FENCE L U/R ............................................................................................104
9.18. VCT-5170UK ASSY FENCE R U/R............................................................................................105
9.19. VCT-5200UK ASSY FOOT BASE FRAME L..............................................................................106
9.20. VCT-5300UK ASSY FOOT BASE FRAME R.............................................................................107
9.21. HDT-6001UK ASSY WIRE L HDT U/R ......................................................................................108
9.22. HDT-INST-U ASSY INST KIT U/R .............................................................................................109
9.23. VCT-INST-SUB1-U ASSY SUB1 INST ......................................................................................109
9.24. VCT-INST-SUB2-U ASSY SUB2 INST ......................................................................................109
10. APPENDIX A - ELECTRICAL SCHEMATIC......................................................................................110
10.1. WIRE COLOURS .......................................................................................................................110
10.2. ELECTRICAL SCHEMATIC .......................................................................................................110

1
1. BEFORE USING THIS PRODUCT
To ensure safe usage be sure to read the following before using the product. The following instructions are intended
for the use of QUALIFIED SERVICE PERSONNEL ONLY.
If any activity is carried out on the product, this should be done only after carefully reading and sufficiently
understanding the instructions.
Only qualified service personnel should carry out maintenance on the product.
Depending on the potential risk, terms such as” WARNING!” “CAUTION” and “IMPORTANT!” are used where an
explanation is given that requires special attention. SEGA is not responsible for injury or damage caused by use in a
manner contrary to the instructions given in this document.
In order to prevent accidents warning stickers and printed instructions are applied in the places where a potentially
hazardous situation relating to the product could arise. Be sure to comply with these warnings.
Indicates that mishandling the product by disregarding this warning will cause a potentially
hazardous situation that can result in death or serious injury.
Indicates that mishandling the product by disregarding this caution will cause a potentially
hazardous situation that can result in personal injury and or material damage.
This is cautionary information that should be complied with when handling the product. Indicates
that mishandling the product by disregarding this will cause a potentially hazardous situation
that may not result in personal injury but could damage the product.
Be sure to turn off the power and disconnect from the mains supply before working on the machine.
Ensure that the correct fuses are fitted to the machine. Details of these are enclosed in the Service Manual.
Ensure that only qualified Service Engineers perform any maintenance work on the machine.
Specification changes, removal of equipment, conversion and/or additions not designated by SEGA are not permitted
and will invalidate this product’s CE conformity.
Warning labels or safety covers for personal protection etc, are component parts of the product. A potential hazard will
be created if the machine is operated while any parts have been removed. Do not operate the product if any doors, lids
or protective covers become damaged or lost. SEGA is not liable in any whatsoever for any injury and/or damage
caused by specification changes not designated by SEGA.
Before installing the product, check for the Electrical Specification Sticker, SEGA products have a sticker on which the
electrical specifications are detailed. Ensure that the product is compatible with the power supply voltage and
frequency requirements of the location in which the machine is to be installed.
Install and operate the machine only in places where appropriate lighting is available, allowing warning stickers to be
clearly read.
To ensure maximum safety for customers and operators, stickers and printed instructions describing potentially
hazardous situations are applied to potentially hazardous locations. Ensure that the product’s operating location has
sufficient lighting to allow any warnings to be read. If any sticker or printed warning is removed or defaced, do not
operate the machine until an identical item has replaced it.
Exercise great care when handling the monitor (applies only to product with monitor). Some of the monitor (TV) parts
are subject to high-tension voltage. Even after turning the power off some components are liable to high-tension
voltage. Only qualified service engineers should perform monitor repair and replacement.
In cases where commercially available monitors and printers are used, only the items relating to this product are
contained in this manual. Some commercially available equipment will have functions and reactions not referred to in
this manual. This manual should be read in conjunction with the specific manufacturer’s manual for such equipment.
Descriptions contained herein may be subject to change without prior notification.
The contents described herein are fully prepared with due care. However, should any question arise or errors be found
please contact SEGA AMUSEMENTS EUROPE LTD.

2
1.1. INSPECTIONS IMMEDIATELY AFTER TRANSPORTING THE PRODUCT
TO THE LOCATION
· Only QUALIFIED SERVICE PERSONNEL should carry out inspection.
Normally, at the time of shipment, SEGA products are in a state to allowing usage immediately after
transporting to the location. Nevertheless, an irregular situation may arise during transportation preventing
this. Before turning on the power, check the following points to ensure that the product has been transported
safely.
· Are then any dented parts or defects (cuts, etc.) on the external surfaces of the product.?
· Are castors and leg adjusters present and undamaged?
· Do the power supply voltage and frequency requirements meet with the local supply?
· Are all wiring connectors correctly and securely connected? Unless connected in the correct direction,
connector connections cannot be made successfully. Do not insert connectors forcibly.
· Are all IC’s of each IC BD firmly inserted?
· Does the power cord have any cuts or dents?
· Do fuses meet the specified rating?
· Are such units such as monitors, control equipment, IC BD, etc. firmly secured?
· Are all earth wires connected?
· Are all accessories available?
Can all doors and lids be opened with the accessory keys and/or tools?

3
CONCERNING THE STICKER DISPLAY CONCERNING WARNING STICKERS
SEGA product has stickers describing the product
manufacture number (Serial Number) and
electrical specification. If you require service
assistance you will require the Serial Number.
Identical machines may have different parts fitted
internally. Only by quoting the Serial Number will
the correct parts be identified.
SEGA product has warning displays on
stickers, labels or printed instructions
adhered/attached to or incorporated in the
places where hazardous situations can arise.
The warning displays are intended for the
accident prevention of customers and service
personnel.
(Actual machines may differ slightly from the illustration)
SPECIFICATIONS
Installation Space (cm): 76 (W) x 98 (L) Including Floor and Coin Tower
Height (cm): 210
Weight (kg): Approx. 152
Rated Voltage (VAC): 230
Rated Current (A): 2
Operating Temperature Range 5 - 40°C
Note: Descriptions in this manual are subject to change without prior notice.
4
2. INTRODUCTION TO THIS SERVICE MANUAL
SEGA ENTERPRISES LTD., supported by its experience in electronic high technology of VLSI’s,
microprocessors etc. and with a wealth of experience, have for more than 30 years been supplying various
innovative and popular games to the world market. This Service Manual is intended to provide detailed
descriptions together with all the necessary information covering the general operation of electronic
assemblies, electro-mechanicals, servicing controls, spare parts, etc. as regards this new SEGA product.
This manual is intended for those who have knowledge of electricity and technical expertise especially in
IC’s, CRT’s, microprocessors etc. Carefully read this manual to acquire sufficient knowledge before
working on the machine. Should there be any malfunction, non-technical personnel should under no
circumstances touch the internal systems. Should such a situation arise contact the nearest branch listed
below, or our head office.
SEGA AMUSEMENTS EUROPE LTD./ SEGA SERVICE CENTRE
Suite 3a
Oaks House
12 - 22 West Street
Epsom
Surrey
United Kingdom
KT18 7RG
Telephone: +44 (0) 1372 731820
Fax: +44 (0) 1372 731849

5
3. INSTALLATION AND MAINTENANCE INSTRUCTIONS
· Only QUALIFIED SERVICE PERSONNEL should carry out installation and
maintenance.
3.1. HANDLING AND INSTALLATION PRECAUTIONS
When installing or inspecting the machine, be very careful of the following points and pay attention to ensure
that the player can enjoy the game safely.
The game must NOT be installed under the following conditions:
· Outside, the game is designed for indoor use only.
· In areas directly exposed to sunlight, high humidity, dust, excessive heat or extreme cold.
· In locations that would present an obstacle in the case of an emergency i.e. near fire equipment or
emergency exits.
· On unstable surfaces or surfaces subject to vibration.
· Where liquids, other than routine cleaning, may come into contact with the game.
Important:
· Only Qualified Service Personnel should install this machine.
· Be sure to switch the supply power OFF and remove the mains supply plug from the machine before any
work is carried out on the machine.
· Do not attempt to repair the PCB’s (Printed Circuit Boards) yourself. This will void the warranty. The
PCB’s contain static sensitive devices that could be damaged.
· Always return a faulty part to your distributor with adequate packaging and protection.
· When removing the plug from the mains always grasp the plug not the cable.
· Do not use a fuse that does not meet the specified rating.
· Make sure all connections are secure before applying power.
· Ensure that the mains lead is not damaged. If the mains lead is damaged in any
way there could be a danger of electric shock or a fire hazard.
· Ensure that the power supply is fitted with circuit protection. Using the power
supply without circuit protection is a fire hazard.
3.2. COIN HANDLING
Standard Sega machines are fitted with a SR3 coin mechanism, however, as a service to our customers
Sega machines can be supplied with no coin mechanism or door allowing the customer to fit a coin handling
option from the approved list. Fit only the coin handling arrangements detailed below and follow the
instructions provided in section 4. Failure to fit the coin handling options detailed or failure to follow the
installation instructions will render the machine, under the CE marking directive, void.
Approved coin handling options:
· Coin controls SR3
· Generic mechanical
· Mars (MS111B1 and ME115)
· SECI RM4-G20

6
3.3. NAME OF PARTS
Width (cm) Length (cm) Height (cm)
CABINET 76 98 177
FLOOR 63 90 15
WHEN ASSEMBLED 93.5 184 210

7
3.4. ACCESSORIES
HDT-INST-U ASSY INST KIT U/R
Item Component Part Qty. Description Component Reference
1 VCT-5000UK 1 ASSY FLOOR VCT U/R
2 VCT-INST-SUB1-U 1 ASSY SUB1 INST
3 VCT-INST-SUB2-U 1 ASSY SUB2 INST
16 PK0323 1 INST KIT PACKING WEDGE
VCT-INST-SUB1-U ASSY SUB1 INST
ITEM PART NO. QTY DESCRIPTION COMPONENT REF.
2 VCT-5100UK 1 ASSY CCT VCT U/R
3 VCT-5150UK 1 ASSY FENCE L U/R
4 VCT-5170UK 1 ASSY FENCE R U/R
6 PK0337 1 INST KIT BOX VCT U/R
VCT-INST-SUB2-U ASSY SUB2 INST
ITEM PART NO. QTY DESCRIPTION COMPONENT REF.
1 VCT-1200UK 2 ASSEMBLY FOOT PEDAL DX
2 VCT-5200UK 1 ASSEMBLY FOOT BASE FRAME L
3 VCT-5300UK 1 ASSEMBLY FOOT BASE FRAME R
5 SAECE-114 1 DECLARATION OF CONFORMITY VCTU
7 CTA-0001 1 JOINT BRKT L
8 CTA-0002 1 JOINT BRKT R
9 VCT-3013UK 1 STICKER CONTROL PANEL CCT Multilingual
15 PK0336 1 BOX PEDAL VCT UPRIGHT
101 540-0006-01 1 WRENCH M4 TMP PRF
102 540-0015-01 1 WRENCH M6 TMP PRF
103 514-5078-5000 1 FUSE 5X20 CERAMIC SB 5000mA
104 OS1019 2 SELF SEAL BAG 9X12.3/4
105 440-CS0186UK 1 STICKER C EPILEPSY MULTI
201 030-000820-SB 2 M8X20 BLT W/S BLK (7)-1,(8)-1
202 068-852216-0B 2 M8 WSHR 22OD FLT BLK (7)-1,(8)-1
203 008-T00412-0B 2 M4X12 TMP PRF TH BLK (BILLBOARD)-2
204 SDW-0001UK 4 BLIND CAP UK (2)-2, (3)-2
301 600-7141-250 1 CABLE JVS TYPE A-B 250CM
402 420-6759-02UK 1 SERVICE MANUAL VCT U/R
403 420-5827 1 SERVICE MANUAL SANWA 31K
404 420-6620UK 1 SERVICE MANUAL GD ROM SYS
405 509-5080 2 SW MICRO TYPE (SS-5GL2)

8
3.5. SHIPPING THE GAME BOARD
Replacement or repair of the Game Board (Chihiro) for this product should be undertaken at
the appropriate repair centre. Be sure to follow the specifications below when requesting
repairs/sending the board to the repair centre. Not following the specifications may result in
the board not being accepted or in extra charges being made.
· Put the game board in the carton box as is. Do not carry out any disassembly or part
removal other than that specified.
· Follow the procedure and instructions regarding direction below when placing the Game
Board in the carton box.
· When packing the game board with the Media Board attached, do not remove the Key
Chip.
· When packing the game board with the Media Board detached, be sure to include the
AVIP Cable.
· When packing, attach the accessory stickers in the specified places on the Game Board
and carton box.
INSTRUCTIONS
1. Wrap the Chihiro Board in a plastic bag.
2. Place it on top of the bottom surface cushioning material. Turn the Filter Board to face the side with
the three honeycomb buffers. Packing it in the opposite direction may cause damage to the Filter
Board.
3. Insert corrugated cardboard into the space between the lateral honeycomb buffers of the bottom
surface cushioning material and stow the AVIP cable inside.
4. Place the Chihiro Board wrapped in the bottom surface cushioning material into the carton box. Use
the handles on the bottom surface cushioning material.
5. Place the upper surface cushioning material on top of the Chihiro Board. Be sure to align it in the
right direction, as it will not fit otherwise.
6. Close the top of the carton box and seal it tightly with adhesive tape.

9

10
3.6. SHIPPING THE MEDIA BOARD
When sending the Media Board for repairs, follow the specifications below and
request repairs or send the Board to your retailer/the repair centre.
Not following the specifications may result in the board not being accepted or in extra
charges being made. Also, mistaken handling can damage or result in loss of parts.
· Be sure to use the special purpose carton box included with this product.
· Do not remove the Key Chip. Send the board with the Key Chip attached.
· Undo the 10 screws holding the Media Board to the Main Board and pack the
Media Board. Do not carry out any disassembly or part removal other than that
specified in this manual.
· Pack the Media Board in the special purpose carton box as shown in the
explanatory diagram.
· The packing material in the carton box has a shock absorbing function. Be sure
to use it when packing. Do not bend or fold the material in a direction other than
that shown on the diagram.
· Do not pack any wires, cables, or screws together with the Board.
· Be sure to attach the special purpose carton box accessory sticker
"843-ããããB."

11
3.7. SHIPPING THE GD-ROM DRIVE
· When returning the GD-ROM DRIVE for repair or replacement, be sure to
package it in the original card transit box - THERE ARE NO USER-
SERVICEABLE PARTS INSIDE.
· Ensure the GD-ROM Disk is removed and the GD-ROM Drive Lid is replaced on
the unit, with fixing screw, before packaging. Also, remove the GD-ROM Drive
Bracket and store with the four screws for reuse.
· Failure to return the GD-ROM DRIVE in this manner may invalidate the warranty.

12
3.8. ASSEMBLY INSTRUCTIONS
· Perform the assembly by following the procedure herein stated. Failure to comply
with the instructions, for example, inserting the plug into an outlet at a stage not
mentioned in this manual can cause an electric shock
· Assembling should be performed as per this manual. Since this is a complex
machine, erroneous assembling can cause damage to the machine, or
malfunction to occur.
· Do not attempt to complete this work alone, a minimum of 2 people are required.
· Only QUALIFIED SERVICE PERSONNEL should carry out assembly.
When carrying out the assembly work, follow the procedure in the following sequence:
STEP 1 INSTALLING THE DISPLAY CARD
STEP 2 INSTALLING THE FLOOR
STEP 3 SECURING IN PLACE (LEG ADJUSTMENT)
STEP 4 INSTALLING THE FOOT PEDAL
STEP 5 COIN HANDLING INSTALLATION
STEP 6 CONNECTION TO THE POWER SUPPLY
STEP 7 ASSEMBLY CHECK
Note that the parts contained within the installation kit are required for the assembly work.
The following tools will be required when installing this machine, in addition to the tools provided with the
Installation Kit:

13
3.8.1. INSTALLING THE DISPLAY CARD
· Only QUALIFIED SERVICE PERSONNEL should carry out this operation.
1. Insert ASSY BILLBOARD to the top part of the cabinet
2. Secure with the two Tamperproof screws.

14
3.8.2. INSTALLING THE FLOOR
· Ensure all connections are secure - poor connections can cause electric shock or
short circuit.
· Take care not to damage wiring during installation, as this can cause electric
shock or short circuit.
· Please read these instructions carefully and follow them in step by step.
· IMPORTANT: We recommend that two (2) people carry out this operation,
as there are heavy components involved.
Tools Required: No1 Pozidriver, M8 Wrench or Socket.
1. Open the Installation box and remove its entire contents. Once the box is completely empty fold the four
open leaves back into the box (this will help to create a sturdier box as we intend to use it as a makeshift
table).
2. Turn the box upside down. Place the Floor Assembly and the Coin Tower onto the box as shown in figure 1.
Note:
The coin tower shown is for illustration only and will
differ slightly from the actual one used
3. Remove the Cashbox Base Plate by unscrewing the 2 x M4 Pozi Pan screws, located directly inside the
Cashbox Door.
4. Remove the Elbow Joint, which is attached to the free end of the Flexipipe.
5. Insert the Flexipipe into the hole located at the front end of the Floor. (Fig 2)
Note:
The coin tower shown is for illustration only and will
differ slightly from the actual one used
6. Offer the Coin Tower up onto the Floor (Fig 3) ensuring that the Flexipipe continues through the access
hole (Fig 4).

15
7. Secure the Coin Tower to the Floor using the 6x M8 Hex head bolts and M8 washers (provided) at location
shown in fig 5.
8. Move the Coin Tower and Floor Assembly onto its side (Fig 6) and thread the Flexihose through the ribs on
the underside of the Floor. (Fig 7)

16
9. Refit the Elbow joint onto the open end of the Flexipipe.
10. Fit the Joint Bracket onto the machine end of the Floor (Fig 8)
11. Offer the Floor to the machine and fit the Flexipipe Elbow Joint into the recess as shown in Fig 9.

17
12. Push the Floor uptight to the machine and secure it using the 2 x M8 Chrome Shoulder Bolts provided
(Fig 10 & 11).
13. Finally, secure Joint Brkt L and Joint Brkt R to the Floor and Adjustable feet using 2 x M8 Hex HD Bolts
Blk and 2 x M8 Washers Blk (Fig 12).

18
3.8.3. SECURING IN PLACE (LEG ADJUSTER ADJUSTMENT)
· Make sure all of the leg adjusters are in contact with the floor. If not the machine
may move and cause injury. This operation requires 2 people.
· Only QUALIFIED SERVICE PERSONNEL should carry out this operation.
This machine has four castors and two leg adjusters. When the installation position is decided, unscrew the
leg adjusters so that they raise both front castors 7mm from the floor. Make sure the machine is level.
1. Move the product into the installed position.
2. Slightly lower the 2 Adjusters on the cabinet
and install Joint Bracket L & R by inserting from
the rear, and secure to the floor using M8 hex
head bolts as shown. Now tighten the two M8
shoulder bolts.
3. After lowering the Adjusters fully downward,
tighten both Adjusters’ lock nuts fully upward.
4. The service door can now be refitted.
5. Unscrew the adjusters until they are in contact
the floor, and use a wrench to turn them further
until the front castors are raised approximately
7mm above the floor.
6. Tighten the locknut on the leg adjusters
upwards to lock the legs in position.

19
3.8.4. INSTALLING THE FOOT PEDAL
1. Attach the pedal and fence to the left and right of the controller cabinet. The foot base and fence have
right and left versions; make sure they are aligned correctly before attaching.

20
Instructions for attaching the L (left) side are included in this manual. The procedure for attaching the R
(right) side is the same.
2. Attach the foot base to the U-shaped
bracket sticking out from the side of the
controller cabinet by inserting it from the
side.
3. Secure the foot base with the following:
BOLTS (2) M8 x 20, w/spring washer, flat
washer used).
NUTS (2) M8 Flange Nut
4. Set foot base adjuster.

21
5. Attach the pedal to the foot base using 4 hexagonal bolts. Be sure not to tighten the hexagonal bolts
completely.
6. Pull wire from the pedal to the foot base and connect the connector on the end of the wire to the
connector on the U-shaped bracket. Use the cord clamp in the foot base to secure the wire.
7. Remove the 2 screws and remove the plate sash from the pedal.

22
8. Insert the fence into the pedal and attach with 4
hexagonal bolts. Use the large flat washers with the
hexagonal bolts used on the cabinet.
(M8 x 20, W/SPRING WASHER, FLAT WASHER).
9. Reattach the plate sash as it was before.
10. Securely tighten the 4 hexagonal bolts on the pedal.
11. Attach the base hole lid to the foot base and
attach 6 screws.

23
Ensure adequate ventilation is maintained as detailed below:
(Actual machines may differ slightly from the illustration)

24
3.8.5. COIN HANDLING INSTALLATION
· Only QUALIFIED SERVICE PERSONNEL should carry out this operation.
When fitting the coin mechanism to the door please refer to the specific manufacturers installation
instructions for that coin mechanism. To fit the door to the machine, follow the procedure below.
· Loosen all of the bolts on the frame which secure the clips.
· Turn all clips in towards the door.
· Position the door into the aperture in the machine.
· Turn the clips around so that they will hold the door in the
machine.
· Tighten all of the bolts.

25
3.8.5.1. WIRING CONNECTIONS.
COIN MECH LOOM INSTALLATION
C220B LM1006IDC
LM1006LAMP-0.1
· Attach the lamp holder to the bracket on the coin return
button.
· Attach one 15-way connector to the C220 coin mech.
· Attach the other 15-way connector to Validator A on the
credit board.
· Attach the 2-way connector to ‘LAMP’ on the VTS board.
GENERIC
MECHANICALS
LM1008
LM1008-LAMP
· Fit the two lamp holders behind the coin return buttons.
· Attach the blue cable and orange cable to one mech’s
microswitch switch.
· Attach the blue/green cable and orange/green cable to the
other mech’s microswitch.
· Attach the 2-way mate and lok plug to the 2-way mate and
lok cap provided.
· Attach one 15-way connector to Validator A and the other
to Validator B on the credit board
MARS MS111B1
MARS ME115
LM1007
LM1008-LAMP
· Fit the lamp holder to the bracket behind the coin return
button.
· Fit one of the 13-way connectors to the coin mech.
· Fit the other 13-way connector to Validator A on the credit
board. Note the 13-way connector is keyed and this key
must coincide with the key on the credit board.
SECI, C120, SR3 OWN LOOM AND
LM1006LAMP-0.1
· Attach the lamp holder to the bracket on the coin return
button.
· Attach the 2- connector to ‘LAMP’ on the VTS board.
· Attach the validator’s own loom to position A on the credit
board
VTS credit board assembly

26
3.8.6. CONNECTION TO THE POWER SUPPLY
· Be sure that the machine is not connected to the mains supply before attempting
this operation
· Only QUALIFIED SERVICE PERSONNEL should carry out this operation.
1. The AC Unit is located on the right hand side of the base unit, when viewing the screen. It houses the
IEC inlet, mains switch and fuse.
2. Ensure that all of the machine’s wires have been connected in accordance with the preceding sections
and that the mains switch is OFF.
3. Check that the operating voltage of the mains supply matches the machine (section 1.1).
4. Insert the IEC lead into the IEC inlet and the mains plug into a wall socket. If applicable, switch the wall
socket ON.
5. Stand clear of the machine and switch the mains switch ON.

27
3.8.7. ADJACENT CONTROL INTERFERENCE PREVENTION
· Be sure that the machine is not connected to the mains supply before
attempting this operation.
· Be careful not to damage wiring.
· The Game Board area should be accessed only if necessary.
· Only QUALIFIED SERVICE PERSONNEL should carry out this operation
When games with the same or similar infrared sensing system are installed side by side, interference may
occur causing malfunction or inaccuracy of the sensing system in adjacent games.
A removable wire harness controls the operating frequency of the gun sense system. Removal of this
harness switches from the default frequency to an alternate one.
Where game machines of the same or similar type are installed side by side, remove the jumper harness
(SPY-60010UK) from every other machine in the line.
1. Turn off the power.
2. Open the Control Panel Cover as detailed in section 3.12 of the Service Manual.
3. Locate the Sensor Board and remove SPY-60010UK WIRE HARNESS HIGH FREQUENCY
JUMPER as required.

28
3.9. ASSEMBLY CHECK
· Only QUALIFIED SERVICE PERSONNEL should carry out this operation.
In the TEST MODE, ensure that the assembly has been made correctly and IC Board is satisfactory (refer
to Section ).
In the test mode, perform the following test:
3.9.1. MEMORY TEST
When "MEDIA BOARD TEST" is selected from the System Test Mode Menu Screen the Game Board
memory is automatically tested. If the display beside each memory reads "GOOD", the Game Board is
functioning correctly.
Also, when "SYSTEM INFORMATION" is selected, Main Board and Media Board data for the Game Board
are displayed. If data is displayed correctly, the Game Board is functioning correctly.
MEDIA BOARD TEST screen
SYSTEM INFORMATION screen

29
3.9.2. C.R.T. TEST
In the TEST mode menu, selecting
C.R.T. TEST allows the screen (on
which the moniter is tested) to be
displayed. Although the moniter
adjustments have been made at the
time of shipment from the factory,
make judgment as to whether an
adjustment is needed by watching
the test mode screen. If it is
necessary, adjust the moniter by
referring to Monitor manual.

30
3.9.3. INPUT TEST
Selecting the INPUT TEST on the
game test mode menu screen
causes the screen (on which each
switch is tested) to be displayed.
Press each switch. If the display
beside each switch indicates "ON,"
the switch and wiring connections
are satisfactory.
3.9.4. OUTPUT TEST
Select OUTPUT TEST from the menu in the test mode to cause the screen (on which each lamp
and wiring connections are tested) to appear. Ensure that lamp light up satisfactorily.

31
3.9.5. GUN ADJUSTMENT
Before starting the operation, play the game by yourself and make sure that the gun readjustment is
not needed and that you can play the game without a problem. Although completed at the factory,
the gun adjustment may be necessary because after the adjustment the product has been
disassembled for packing and shipping.
Perform the above inspections also at the time of monthly inspection.
As for the gun adjustment described in above, confirm weekly that the gun is properly adjusted.

32
3.10. MOVING THE MACHINE
· When moving the machine, be sure to remove the plug from the power supply.
Moving the machine with the plug inserted can cause the power cord to be
damaged, resulting in a fire or electric shock.
· Separate the floor assembly from the cabinet before moving. Refer to section
3.8.2 for details.
· Retract the leg adjusters fully and ensure the casters make contact with the floor.
During movement pay careful attention so that the casters or leg adjusters do not
damage any other cabling laid on the floor. Such damage could result in a fire or
electric shock.
· Do not push the upper part of the cabinet. Failure to observe this can cause the
cabinet to fall forwards and result in accidents.
· When transporting the machine, be sure to hold the catch portion on the rear of
the cabinet with the castors making contact with the surface as shown below.
Inclining the machine by holding portions other than the catch or moving the
cabinet without retracting the adjusters can damage the cabinet and/or the floor
surface.
· Do not push the Billboard. Failure to observe this may damage the installation
portions and may cause unexpected accidents.
· Only QUALIFIED SERVICE PERSONNEL should carry out this operation.

33
(Actual machine may differ slightly from illustration)

34
3.11. CONTROLLER
· Follow these directions carefully to avoid damaging or losing small parts.
In the cases where the gun's operation is not satisfactory or the gun sight deviates from the direction in
which the control unit is pointed, the gun's interior parts may have been damaged. Replace the parts by
disassembling the gun using the following procedure.
Note: be sure to perform sighting check in the test mode when the gun parts are replaced.
3.11.1.1. REPLACING THE MICROSWITCH
To replace the Gun Controller's internal components, first separate the left shell (Cover L) and right shell
(Cover R). The controller's internal components are mounted on the right shell, so work with the gun lying on
its right side. To replace the Weapon Change Button microswitch, first remove the Weapon Change Button
from the right shell.
1. Turn power off.
2. Remove the 10 screws to separate the two shells.
3. With the right shell lying flat, carefully lift the
left shell from the right shell.
SCREW (10), black / M3 x 10, W/small flat &
spring washers

35
4. Remove the trigger microswitch from the right
shell.
MICROSWITCH / 509-5080
5. Remove the soldering and detach the
microswitch.
6. Remove the Change Button from the right
shell.
7. Remove the spring from the right shell.

36
8. Remove 1 screw and detach the microswitch
(with SW bracket attached) from the right
shell.
SCREW (1) / M3 x 8, W/flat & spring washers
9. Disconnect the microswitch wire connector.
10. Remove the 2 screws and remove the SW bracket from the microswitch.
SCREW (2) / M2 x 10, W/flat & spring washers

37
11. Remove the soldering and extract the microswitch.
12. Solder in the new microswitch and reassemble the Gun Controller. Be careful not to tighten the
screws too tightly.
13. Test the trigger (or Weapon Change Button) to make sure that the new microswitch functions
properly.

38
3.11.1.2. REPLACING THE SENSOR UNIT
1. Follow instructions (1) – (3) of “Replacing the Microswitch” to remove the left shell.
2. Detach the connector and pull out the sensor unit.
SENSOR UNIT / JPT-2030

39
3.12. REPLACEMENT OF LED BOARD
· Only QUALIFIED SERVICE PERSONNEL should carry out these procedures.
The operation of the ten LED boards located around the CRT can easily be checked by viewing from the
front with the power switched on. Two red points of light from the LEDs should be visible through each of
the ten black lenses: if any of the LEDs are not lit, the corresponding LED board(s) should be replaced as
follows.
1. Turn the power OFF.
2. Remove the Front Panel as described in section 3.13.1,
taking care to disconnect the LED board loom before fully
removing the Front Panel (see right).
3. To access the mounting screws for the malfunctioning LED
board(s), prise open the screw caps with a small flat head
screwdriver as shown.
4. Lay the Front Panel face down on a
soft surface (e.g. a blanket) to
prevent marking. Disconnect the
individual LED board(s) from the
loom and remove the two M3 nuts to
release the LED board.
5. Fit the replacement LED board and
reassemble in reverse order.
6. Adjust the gun calibration in the test
mode when the machine has been
reassembled (Section Error!
Reference source not found.)

40
3.13. REPLACEMENT OF FLUORESCENT LAMP AND START LAMPS
· Never touch places other than those specified. Touching places other than those
specified can cause electric shock and short circuit. Disconnect the machine from
the supply before attempting the replacement of any lamp.
· When performing work, be sure to turn power off. Working with power on can
cause an electric shock or short circuit.
· Hot fluorescent lamps can cause burns. Be very careful when replacing them.
· Use a secure step to improve access to the upper parts of the cabinet.
· Only QUALIFIED SERVICE PERSONNEL should replace lamps.
3.13.1. FLUORESCENT
1. Power OFF the machine and
remove the IEC lead from the
wall outlet.
2. Unlock the lock on the underside
of the Control Panel Base, and
open the Panel.
3. By using a flat bladed
screwdriver, carefully remove the
four screw caps from the front
panel.
4. Take out the four tamperproof
screws and the two lower
screws, and carefully take off the
Front Panel far enough to
disconnect the LED board loom
(refer to section 3.12). Once this
loom has been disconnected, the
Front Panel can be fully
removed.
5. Remove the four screws and the
Earth Link to allow the Billboard
Holder to be removed.
6. Disconnect the two end caps and
withdraw the Lamp upwards
through the two mounting clips to
remove the Fluorescent lamp.
7. After replacing the lamp,
reassemble in reverse order,
being sure to replace the Earth
Link between the Billboard
Holder and frame, and the LED
board loom.

41
3.13.2. START LAMP REPLACEMENT
1. Remove the control panel cover as shown by
removing the 5 screws holding it in position.
2. Carefully lift the control panel cover up until it is
possible to disconnect the wire harness plugs
attaching the start switches to the cabinet.
3. Turn the control panel cover over and remove the
micro switch from the start switch as shown
below.
4. Remove and replace the wedge lamp.
5. Reassemble the control panel cover to the gun
cabinet.
Note:
The coin tower shown is for illustration only and will
differ slightly from the actual one used

42
3.14. GAME BOARD
· Turn off the mains power and remove the power cord before opening the
machine.
· To prevent risk of shock or fire, be careful not to damage any wiring.
· The GAME BOARD should not require any work to be carried out upon it. All
settings and tests can be achieved without access to the GAME BOARD.
· Take anti-static precautions to avoid damaging the electronic parts.
· All work to be carried out by QUALIFIED SERVICE PERSONNEL
The GD-ROM Service Manual supplied with this product instructs you to remove the Key Chip when
shipping the Game Board. However, this product employs a dedicated Game Board, therefore do not
disassemble the Game Board, or remove the Key Chip.
3.14.1. REMOVING THE BOARD
1. Turn off the power.
2. Unlock and remove the Service Door.
3. Disconnect all harnesses linking the
Game Board assembly to the cabinet.
4. Remove the two M4 wing bolts and
carefully withdraw the assembly upwards
and out through the service opening
(see following page).

43
5. Remove all connectors from the filter board of the Game Board. Also remove the GD cable connector
from the DIMM Board.
6. Remove four screws securing the Game Board to the base.
7. Reassemble in reverse order.

44
3.14.2. REMOVING THE GD-ROM DRIVE
Take out the ASSY MAIN BD from the cabinet and remove the GD-ROM Drive from the ASSY MAIN BD as
follows:
1. Following the above procedure (steps 1 to 5), take out the ASSY MAIN BD.
2. Remove the GD cable connector and the power cord
connector from the GD-ROM Drive.
2. To remove the GD-ROM Drive, undo the 3 screws
shown.
3. Reassemble in reverse order.

45
3.15. COMPOSITION OF THE GAME BOARD

46
3.16. TROUBLESHOOTING
· Only QUALIFIED SERVICE PERSONNEL should carry out these procedures.
If a problem occurs, first check the wiring connections.
PROBLEMS CAUSE COUNTERMEASURES
When the main switch
is turned ON, the
machine is not
activated
The power is not ON. Firmly insert the plug into the outlet.
Incorrect power source/voltage. Make sure that the power supply/voltage
are correct.
AC Unit CIRCUIT PROTECTION
DEVICE (i.e. fuse) was activated due to
an instantaneous overcurrent.
First, remove the cause of overcurrent and
reinstate the circuit protection device to its
original status.
Then identify the cause of the fault on the
item which caused the overcurrent & fix.
The colour image on
the screen is incorrect
Incorrect monitor adjustment. Make appropriate adjustments.
SEE SECTION 6.3.8.
The on-screen image
of the monitor sways
and/or shrinks
The power source and voltage are not
correct.
Make sure that the power supply and
voltage are correct.
Sound is not emitted Sound volume adjustment is not correct. Adjust the volume setting on the VTS
bracket. SEE SECTION 6.2
Malfunctioning BD and Amp.
Perform Sound Test to check it. SEE
SECTION 6.3.7
Connector connection is incorrect Check connector connection from Base to
Speaker
Controller operation is
not satisfactory
Sighting is inaccurate due to
environmental conditions, etc.
Adjust the gun sighting alignment. SEE
SECTION Error! Reference source not
found.
Micro-switch malfunctioning Replace the micro-switch. SEE SECTION
3.11
Sensor BD is malfunctioning Replace the Sensor BD. SEE SECTION
3.11
The fluorescent lamp
does not light up
Fluorescent lamp needs replacement Replace the fluorescent lamp. SEE
SECTION 3.13.1
The connector is disconnected
Check connector connections in the
billboard case.

47
3.17. FUSES
· Never touch places other than those specified. Touching places other than those
specified can cause electric shock and short circuit. Disconnect the machine from
the supply before attempting the replacement of any fuse.
· Only QUALIFIED SERVICE PERSONNEL should replace FUSES.
· Only replace fuses with ones of the same value and type.
There are a number of fuses used on this machine to protect the user and the machine from damage. Only
replace the fuse once you have removed the cause of its failure. Detailed below is a list of the fuses used,
their location and if relevant PCB reference:
PART NUMBER LOCATION TYPE & DETAILS QTY
514-5078-3150 STEREO AMP REF. F1, F2 5x20mm CERAMIC SB 3.15A 2
514-5078-5000 IEC INLET REF. F1 5x20mm CERAMIC SB 5A 1
838-11856CE-02 CONN. BD. REF. F1 5x20mm CERAMIC SB 6.3A 1
There are also fuses located on the Monitor PCB. Refer to the relevant Monitor manual supplied to
reference these fuses.

48
4. PERIODIC CHECK AND INSPECTION
The items listed below require periodic check and maintenance to retain the performance of the machine
and ensure safe operation:
· Be sure to check annually to see if the power cords are damaged, the plug is
securely inserted and that there is no dust in the interior of the machine or
between the socket and the power cord. Using the product in an unclean
condition may cause a fire or electric shock.
DESCRIPTION WHAT TO CHECK INTERVAL
CABINET Check Adjusters’ contact with surface Daily
MONITOR Clean CRT face - (Do Not use water jet)
Check settings
Weekly
Monthly
GAME BD Setting check Monthly
CONTROL PANEL Input test Monthly
Speaker, sound Sound test, check volume adjustment Monthly
COIN SELECTOR Coin insertion test
Cleaning
Monthly
Tri-Monthly
POWER SUPPLY CORD Check condition Annually
INTERIOR Clean (Do Not use water jet) Annually
CABINET SURFACE Clean (Do Not use water jet) As required
4.1. CLEANING THE CABINET SURFACES
When the cabinet surfaces are badly soiled, remove stains with a soft cloth dipped in water or chemical
detergent (diluted with water) and squeezed dry - DO NOT USE A WATER JET. To avoid damaging
surface finish, do not use such solvents as thinner, benzene, etc. (other than ethyl alcohol), abrasives or
bleaching agents.

49
5. HOW TO PLAY
Use this section to confirm the machine is operating correctly; if the machine doesn’t operate as described
there may be a fault.
While power is connected, the billboard is continuously lit and demonstration footage and ranking data are
displayed on the screen. This ‘advertise’ mode will be accompanied by sound from both speakers unless
set otherwise in the TEST mode.
The 1P and 2P start buttons have integral lights that flash when a credit is inserted.
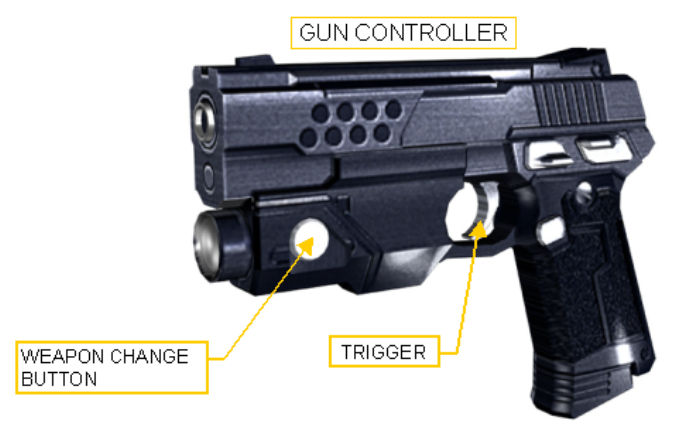
50
5.1. GAME CONTENTS
Press the appropriate START button to begin play as 1P or 2P. If enough credits for a game are remaining,
the other player’s START button will flash. Press the flashing START button to join a game.

51
5.1.1. The Main Characters
Virtua Cop 3 has two main characters, RAGE (1P) and SMARTY (2P). JANET appears as an allied
character during the game but cannot be controlled.
5.1.1.1. 1P Character: RAGE
Strong as an ox and just as uncontrollable, this
hothead tends to act before he thinks. That’s made
him something of a headache for the department.
5.1.1.2. 2P Character: SMARTY
Rage’s complete opposite, Smarty is a cautious,
brainy type who never loses his cool. He’s also the
best marksman in the precinct.
5.1.2. Playing Virtua Cop 3
5.1.2.1. Start a New Game
Press the START button to begin a new game. Mission Select follows.
5.1.2.2. Calibrating at the Start of the Game
The availability of calibration at the start of each game may be set in Test Mode. The following applies when
calibration on demand is enabled.
To enter the calibration screen, hold down the foot pedal, aim the gun controller at the screen, and press the
START button when starting the game. Aim the gun at the centre target and pull the trigger. When
calibration is complete, press the START button to exit to Mission Select.
5.1.2.3. Mission Select
Displays the three mission panels, Simple, Normal and Hard. Shoot the desired mission panel to start.
Players are free to start any mission they like.
When a mission has been completed, the game returns to Mission Select. The mission panel for the
completed mission reads “Complete” and cannot be selected. Select a different mission.

52
5.1.2.4. Game Screen
1. Points/Point Multiplier Meter
Total points earned are indicated by the eight digit number. After 3-point shots, Justice shots, and
other special attacks the name of the attack and points earned are shown beneath the score display.
The more enemies you shoot, the more the gauge above the score display lengthens. When the
gauge is completely filled, your level increases. The current level is shown inside the circle. A higher
level means more points for killing enemies, but you’ll lose a level if you take damage or shoot a
civilian!
2. Lock-On Sight
The Lock-On Sight automatically detects armed enemies and tells you when you’re being attacked.
The Lock-On Sight can lock on multiple enemies simultaneously. When the sight appears, enemies
are attacking. If you don’t fight back, you’re sure to take damage.
3. Bullets Left/Reload
Shows bullets remaining in current gun.
Shoot the gun away from the screen to reload your weapon.
4. Weapon Palette, Weapon Change
The player starts out with a Guardian II (10-round magazine, infinite reloads). Defeat special enemies
and destroy background objects to get special weapons. Acquiring a special weapon will add a
second weapon to the Weapon Palette. Use the Weapon Change button to switch between the
special weapon and the Guardian II. The weapon currently in use is shown on top, above the weapon
in stock. Special weapons can only be reloaded a limited number of times and cannot be reloaded
once ammunition runs out. Get Ammo items to increase the number of times the weapon may be
reloaded.
Special Weapons can be lost in three ways:
l When the reload count hits zero and all ammunition is used up
l When shot and hurt by an enemy
l By shooting a civilian
Knowing when to use which weapon is key.
5. Life
Shows life remaining. Getting shot by an enemy costs one life. Shooting a civilian also costs one life.
When all lives have been used up, the game is over.

53
5.1.2.5. ES Gauge
This shows the remaining energy in ES Mode. The ES Gauge falls during ES Mode and recovers when you
defeat enemies.
5.1.2.5.1. ES Mode (Exceeding Sense Mode)
Hold down the foot pedal to activate ES Mode.
ES Mode enhances your character’s senses, making time
appear to move slower. In ES Mode you can even see your
enemies’ bullets and shoot them down before they reach
you. Red bullets are especially damaging, so try to get
them before they get you!
ES Mode consumes the ES Gauge. When the ES Gauge
runs out of energy, you will be unable to use ES Mode.
Kill enemies to recover energy for the ES Gauge.

54
5.1.2.5.2. ES Attack (Exceeding Sense Attack)
ES Attack begins automatically in certain scenes.
ES Attack displays special targeting sights that show points
of particular vulnerability for a limited time. Speed and
accuracy are essential.
Hit all the targeted areas within the time given to clear the
ES Attack. The outcome of an ES Attack affects the rest of
the game’s story.
When targets are shown with energy gauges, shoot until
the energy gauge hits zero to clear the ES Attack.
5.1.3. Game Over
The game ends in one of three ways:
l When all lives have been lost
l When all three missions have been completed
l When the special “Extra Mission”* has been completed
[*]: When both the Simple and Normal missions have been completed successfully (in either order) and the
player defeats the boss of the Hard mission, a special scene is shown and the Extra Mission is unlocked.
5.1.4. Continue
When you run out of lives, “Continue” appears on the screen and a countdown begins. To continue, insert
sufficient coins and press the START button. If enough credits remain to continue, press the flashing
START button.

55
6. MAINTENANCE INSTRUCTIONS
6.1. EXPLANATION OF TEST DATA AND DISPLAY
Use the switches inside the Control Panel to enter the TEST MODE. This will allow you to carry out post
installation and periodic checks and adjustments. The following section details the function of each of the
tests:
Refer to the service manual supplied with the Monitor for detailed instructions.
ITEM DESCRIPTION INTERVAL
INSTALLATION OF
THE MACHINE
When the machine is installed perform the following checks:
· Check to see that each setting is as per the standard settings
input at the time of shipment.
· In the INPUT TEST mode, check each switch and V.R.
· In the OUTPUT TEST mode, check each of the lamps.
· In the MEMORY TEST mode check all of the IC’s on the IC BD.
Monthly
MEMORY · On the TEST MENU screen choosing the MEMORY TEST
allows self-test to be performed. In this test RAM & ROM are
tested.
Monthly
PERIODIC CHECKS Periodically perform the following
· MEMORY TEST.
· Ascertain each setting.
· In the INPUT TEST mode, test the control devices.
· In the OUTPUT TEST mode, check each of the lamps.
Monthly
CONTROL SYSTEM · In the INPUT TEST mode, check each switch and V.R.
· Adjust or replace each switch and V.R.
Monthly
MONITOR · In the CRT TEST mode, check to ensure the monitor is adjusted
correctly
· Clean screen (switch off machine and remove the plug)
Monthly
Weekly
IC BOARD MEMORY TEST
· In the SOUND TEST mode, check the sound related ROM’s
Monthly
DATA CHECK · Check such data as held in the bookkeeping screens, relating to
number and length of plays
Monthly
EXTERIOR
MAINTENANCE
· Clean surfaces
Monthly
COIN MECHANISM · Check switch operation (if fitted) Monthly

56
6.2. INTERNAL SWITCHES AND COIN METERS
· Never touch places other than those specified. Touching places not specified can
cause electric shock and short circuits
· Be careful not to damage wiring. Damaged wiring can cause electric shock and
short circuits.
· Adjust to the optimum sound volume considering the environmental requirements
of the installation location.
· If the COIN METER and the game board are electrically disconnected, game play
is not possible.
Open the Coin Chute door to access the VTS PCB. The function of each switch is as follows.
TEST BUTTON
(TEST SW)
Used to enter TEST mode. Also has function during TEST mode. Refer to the
later section detailing TEST mode.
SERVICE BUTTON
(SERVICE SW)
Gives credits without registering on the coin counter. Also used during TEST
mode.
DEMAG Eliminates colour unevenness from the monitor screen.
VOLUME CONTROL Adjusts the volume of the speakers.

57
6.3. SYSTEM TEST MODE
6.3.1. EXPLANATION OF TEST AND DATA DISPLAY
Perform the tests and data check periodically when installing the machine initially or collecting cash, or when
the machine does not function correctly. Perform checks in accordance with the explanations given in this
section.
The following shows tests and modes that should be utilized as applicable.
This product's basic system consists of the Chihiro game board and the GD-ROM drive. The system
enables you to play several games one after the other just by changing a GD-ROM disc that is to be set on
the GD-ROM drive.
Therefore the product supports, the following 2 test modes:
(1) System test mode for an automatic self-diagnostic test (generally used by every product that contains
the basic system) and a coin assignment (specifically used by this product)
and
(2) Game test mode for testing the input/output control devices and setting the difficulty level (specifically
used by this product).
· Any settings that are changed by users during TEST MODE are saved upon
exiting TEST MODE with the EXIT command in the SYSTEM MENU. If the
unit is powered off prior to exiting, changes to settings will not take effect.
· You may not enter GAME TEST MODE while the unit is reading from or
checking the GD-ROM. If error messages are displayed when exiting TEST
MODE, you should power the unit off and on again.
· In the manual for this product, "Media Board" and "DIMM" are one and the
same.
· Use with the specified settings. If settings other than those specified are
used, inappropriate operations or malfunction may occur.

58
6.3.2. SYSTEM TEST MENU MODE
System Test Mode can be used to check that the main circuit operations are correct, adjust Monitor colour,
and perform coin/credit settings.
However, this product can only be used with the settings shown below.
SOUND TEST - OUTPUT TYPE: STEREO
COIN ASSIGNMENTS - COIN CHUTE TYPE: COMMON
- SERVICE TYPE: COMMON
NETWORK SETTING (MEDIA) - NETWORK TYPE: NONE
1. Press the TEST Button after powering on the unit to display the following SYSTEM MENU.
2. Press the SERVICE Button to move the cursor to the desired test item.
3. Move the cursor to the desired item and press the TEST Button to display each test
screen.
4. Move the cursor to ENTER GAME TEST and press the TEST Button to enter the
individual test menus for each game. Refer to "9-3 GAME TEST MODE".
5. When testing is complete, move the cursor to EXIT and press the TEST Button. The
game advertisement screen should be displayed.

59
6.3.3. MEDIA BOARD TEST
Powering off the system during the MEDIA BOARD TEST with a DIMM BOARD
will erase the game programme data. It may be necessary to reload the data.
Always wait for the test to complete before attempting to exit.
MEDIA BOARD TEST is used to check the memory and IC on the MEDIA BOARD connected to the Chihiro.
Test screens and test times may differ depending on the type of MEDIA BOARD connected to the unit.
The following is the MEDIA BOARD TEST screen for a unit with a DIMM BOARD.
1. MEDIA BOARD TEST begins immediately upon entering this test mode.
2. If "GOOD" is displayed to the right of each item, the MEDIA BOARD components are
functioning properly.
3. After the test is complete, move the cursor to EXIT and press the TEST Button to return to the
SYSTEM MENU screen.

60
6.3.4. SYSTEM INFORMATION
Use SYSTEM INFORMATION to check version and other information for system programmes.
Screens may differ depending on the type of MEDIA BOARD connected to the unit.
The following is the SYSTEM INFORMATION screen for a unit with a DIMM BOARD.
Press the TEST Button to return to the SYSTEM MENU screen.
(A) REGION
The COUNTRY CODE of the MAIN BOARD.
(B) BOOT VERSION, QC FIRM VERSION, SC FIRM VERSION
Version information for the MAIN BOARD system programmes.
(C) SERIAL NO.
Serial number of the MAIN BOARD.
(D) DIMM BOARD + GDROM
Type of MEDIA BOARD. This example shows a DIMM BOARD with a GD-ROM DRIVE
connected.
(E) MEMORY SIZE
Capacity of DIMM memory installed on the DIMM BOARD.
(F) FIRM VERSION
Version information for the DIMM BOARD system programme.
(G) SERIAL NO.
Serial number of the DIMM BOARD.

61
6.3.5. JVS TEST
JVS TEST is used to verify the specs of the I/O BOARD connected to the Chihiro and to run input tests.
I/O BOARD specs are displayed initially.
Screens may differ depending on the type of I/O BOARD connected to the unit.
(1) Use the SERVICE Button to move the cursor to the desired test item.
(2) Move the cursor to INPUT TEST and press the TEST Button to enter the INPUT TEST
screen for the I/O BOARD currently displayed.
(3) When 2 or more I/O BOARDS are connected, move the cursor to NEXT NODE and
press the TEST Button to enter the test screen for the next I/O BOARD. The lower the
NODE number, the further away the node is from the Chihiro.
(4) Move the cursor to EXIT and press the TEST Button to return to the SYSTEM MENU
screen.

62
6.3.6. INPUT TEST Screen
(5) On-screen values change according to the input from switches and the volume.
(A) SYSTEM, PLAYER
Values change with input from control panel/other switches.
(B) COIN
Increases with input from the COIN SWITCH. The count is cleared when exiting
TEST MODE.
(C) ANALOG
Displays analog values from "0000" to "FFFF".
(6) Press the SERVICE and TEST Buttons simultaneously to return to the JVS TEST main
screen.

63
6.3.7. SOUND TEST
Use SOUND TEST to test sound output and to select the stereo/mono/surround setting.
(1) Use the SERVICE Button to move the cursor to the desired test item.
(2) Press the TEST Button to enter the selected item.
(A) OUTPUT TYPE (STEREO, MONO, SURROUND)
Select the sound output from the I/O PANEL audio output interface setting among
STEREO, MONO and SURROUND.
(B) RIGHT/LEFT SPEAKER (ON, OFF)
When set to "ON", the test sends a beep to each audio output interface. Only the
word "SPEAKER" is displayed when the OUTPUT TYPE is set to "MONO", and
when set to "ON", the test sends the same beep to both the left/right audio output
interfaces.
To test surround output, it is necessary to use a separate Audio Amp, and receive
signal from a terminal not in use at the time of shipping.
Note: Not available with this product.
(3) Move the cursor to EXIT and press the TEST Button to return to the SYSTEM MENU
screen.

64
6.3.8. C.R.T. TEST
Use the C.R.T. TEST to adjust monitor colours and verify screen size.
COLOUR CHECK Screen
(1) Monitor COLOUR CHECK screen is displayed initially.
Each of the colours (red, green and blue) is darkest at the far left and gets progressively
lighter (32 steps) towards the right.
Monitor brightness is set correctly if the white colour bar is black at the left edge and
white at the right edge.
(2) Press the TEST Button to proceed to the next page
SIZE CHECK Screen
(3) Adjust the CHECK GRID so that the entire GRID is displayed on the screen.
(4) Press the TEST Button to return to the SYSTEM MENU screen.

65
6.3.9. COIN ASSIGNMENTS
Use COIN ASSIGNMENTS to set the credit rate for each coin inserted.
(1) Use the SERVICE Button to move the cursor to the desired test item.
(2) Press the TEST Button to change the setting or to open the detailed settings.
(3) Move the cursor to EXIT and press the TEST Button to return to the SYSTEM MENU
screen.
(A) COIN CHUTE TYPE (COMMON, INDIVIDUAL)
Adjust settings according to the specs of the cabinet COIN CHUTE.
COMMON
This is for cabinets where a single COIN CHUTE is used by multiple players.
Coins inserted by each player are treated as common credits.
Up to 2 COIN CHUTES (#1 and #2) may be used. The (C) COIN TO CREDIT RATE
setting for COIN CHUTE #1 and #2 may be set differently.
INDIVIDUAL
This is for cabinets with individual COIN CHUTES for each player.
Coins inserted by each player are treated as individual player credits.
The (C) COIN TO CREDIT RATE setting is used by all COIN CHUTES.
(B) SERVICE TYPE (COMMON, INDIVIDUAL)
Use this to set the function of each SERVICE Button when there is more than one
SERVICE Button.
COMMON
Pressing any SERVICE Button enters service credits for all players.
INDIVIDUAL
Pressing the SERVICE Button enters service credits only for the corresponding player.

66
(C) COIN TO CREDIT RATE
Set the CREDIT RATE for each coin inserted.
The "r COIN(S) COUNT AS £ CREDIT(S)" setting indicates that "Inserting r coins
equals £ credits".
Set this to "FREE PLAY" to allow game play without credits.
When (A) COIN CHUTE TYPE is set to "COMMON", COIN CHUTE #2 settings are
restricted to some extent by the settings for COIN CHUTE #1.
(D) DETAIL SETTING
This mode allows for more detailed credit rate settings than the (C) COIN TO CREDIT
RATE setting.
Changes made in DETAIL SETTING override any (C) COIN TO CREDIT RATE settings.
DETAIL SETTING Screen
(E) COIN CHUTE MULTIPLIER
Use this to set how many coins will be counted for each coin inserted.
The "1 COIN COUNT AS r COIN(S)" setting indicates that "Each coin will be counted as
r coins".
When the (A) COIN CHUTE TYPE is set to "COMMON", the setting may be set
individually for COIN CHUTE #1 and #2.
(F) BONUS ADDER
Use this to set the number of coins calculated with the (E) COIN CHUTE MULTIPLIER
setting that need to be inserted to get 1 bonus coin. When the (A) COIN CHUTE TYPE is
set to "COMMON", the sum of the coins for COIN CHUTE #1 and #2 is used for the
calculation.
The "r COINS GIVE 1 EXTRA COIN" setting indicates that "For every r coins, 1 bonus
coin is given".
Set this to "NO BONUS ADDER" to disable bonus coins entirely.
(G) COIN TO CREDIT
Use this to set how many coins calculated with the (F) BONUS ADDER setting count as 1
credit.
The "r COIN(S) 1 CREDIT" setting indicates that "Every r coins equals 1 credit."

67
(H) GAME COST SETTING
Use this mode to set the number of credits required to start a game.
Screens may differ depending on the game.
(I) Set the number of credits required to start a game.
(J) Set the number of credits required to continue a game.
6.3.10. CLOCK SETTING
Use the SERVICE Button to move the cursor to the item to be set.
(1) Move the cursor to the desired item and press the TEST Button to increase values.
(2) The max value for YEAR is "2099"; further increases return the value to "2000".
(3) Move the cursor to EXIT and press the TEST Button to return to the SYSTEM MENU
screen.

68
6.3.11. NETWORK SETTING (CORE)
Use the LAN PORT attached to the Main Board, and carry out the settings necessary for network
communication.
*This game does not support network communication connections. *
THIS OPTION IS FOR POSSIBLE FUTURE GAMES ONLY.
SELECT EXIT AND GO DIRECTLY TO THE NEXT TEST MODE.
(1) Use the SERVICE Button to move the cursor to the desired test item.
(When setting IP ADDRESS, SUBNET MASK, GAME WAY or PRIMARY DNS, use the underline as a
guide.)
(2) Press the TEST Button to change the setting.
(3) Move the cursor to EXIT and press the TEST Button to return to the SYSTEM MENU screen.
(A) REMOTE (C)
This sets up whether a communication setting is automatic or manual.
ENABLE: Sets the communication setting automatically.
DISABLE: Sets the communication setting manually.
(B) IP ADDRESS (C)
This is one of the settings required for communication network. After setting the number, press TEST
Button on SET position to memorize the setting. If you set the REMOTE setting to ENABLE, you
cannot select this.
(C) SUBNET MASK (C)
This is one of the settings required for communication network. After setting the number, press TEST
Button on SET position to memorize the setting. If you set the REMOTE setting to ENABLE, you
cannot select this.
(D) GATE WAY (C)
This is one of the settings required for communication network. After setting the number, press TEST
Button on SET position to memorize the setting. If you set the REMOTE setting to ENABLE, you
cannot select this.
(E) PRIMARY DNS (C)
This is one of the settings required for communication network. After setting the number, press TEST
Button on SET position to memorize the setting. If you set the REMOTE setting to ENABLE, you
cannot select this.

69
(F) CURRENT
This displays the present setting value during a set-up of each item [(B), (C), (D), (E)]. Pressing TEST
Button on SET position, the settings are memorized and the screen is changed.
6.3.12. NETWORK SETTING (MEDIA)
*This game does not support network communication connections. *
THIS OPTION IS FOR POSSIBLE FUTURE GAMES ONLY.
SELECT EXIT AND GO DIRECTLY TO THE NEXT TEST MODE.
THIS GAME DOES NOT SUPPORT NETWORK COMMUNICATION CONNECTIONS.
Use NETWORK SETTING to establish and test network connections.
This is only displayed when a network enabled MEDIA BOARD is connected to the Chihiro.
In this game only the following error message will be displayed.

70
6.4. GAME TEST MODE
· When changing the game configuration, changes will not take effect until
the Game Test Mode has been completed. Be sure to exit the Game Test
Mode properly after configuration changes.
· Do not configure the game in ways not described in this text. It is possible
that the game will not function properly.
Select ENTER GAME TEST from the System Menu screen to display the Game Test Menu screen as
follows.
Use the SERVICE Button to move the cursor to the desired test item.
Press the TEST Button to enter the selected item’s test.
Performs tests, adjustments and settings for each of the Game Test Menu screen items below.
INPUT TEST: Tests each input device used in the game.
OUTPUT TEST: Tests each output device used in the game.
GAME ASSIGNMENTS: Adjusts game settings.
GUN SETTING: Performs sight settings for the game's Control Unit (Gun).
BOOKKEEPING: View all recorded game data.
BACKUP DATA CLEAR: Erase all game records.
After selecting an item, read the explanations below regarding operation.
After performing tests and adjustments, return to the Game Test Menu screen, select EXIT and press the
TEST Button.
You will return to the System Menu screen. Move the cursor to EXIT on the System Menu screen and press
the TEST Button to return to the Game Play screen.

71
6.4.1. INPUT TEST
Select INPUT TEST to display the following screen and check the status of input devices.
This test should be used periodically to check that each input device is functioning correctly.
The items refer to the following input devices.
● TRIGGER: The gun triggers.
● CHANGE: The controller’s weapon change button.
● PEDAL: The foot pedal.
● GUN-X: Ranges between 00 and FF when controller is pointed at screen.
● GUN-Y: Ranges between 00 and FF when controller is pointed at screen.
● SCREEN: Point controller at screen to change from OUT to IN.
● START: The player Start Buttons.
● SERVICE: The SERVICE Button.
● TEST: The TEST Button.
Input is normal if the display to the right of each item changes from OFF to ON when each input device is
operated.
Input is normal if the display to the right of SCREEN changes from OUT to IN and GUN-X and GUN-Y show
values between 00 and FF when the controller is pointed at the screen.
Press the SERVICE and TEST Buttons simultaneously to return to the Game Test Menu screen.

72
6.4.2. OUTPUT TEST
Select OUTPUT TEST to display the following screen and check the status of each lamp.
This test should be used periodically to check that the lamps are functioning correctly.
Press the SERVICE Button to move the cursor and the TEST Button to select. Displays ON when selected.
Actual screen may differ for depending on cabinet type.
The following is for the STANDARD (Upright) type screen.
Perform the tests as follows.
● PLAYER 1 START LAMP: Lights up the 1P START button.
● PLAYER 2 START LAMP: Lights up the 2P START button.
Move the cursor to EXIT and press the TEST Button to return to the Game Test Menu screen.

73
6.4.3. GAME ASSIGNMENTS
Select GAME ASSIGNMENTS to display the current game settings and make changes.
Perform the following settings for each item.
● DIFFICULTY: Set the game’s difficulty level. Five settings are available, from VERY EASY
to VERY HARD.
● LIFE: Set the number of lives each player starts the game with. Nine levels are
available.
● COLLISION: Set the size of targets. Five levels, from 1 to 5, are available. The higher the
level, the easier it is to hit targets.
● GUN LOOSENESS: Set gun looseness. Ten levels, from 0 to 9, are available. The higher the
level, the easier it is to hit targets.
● CALIBRATION: Toggle the availability of user calibration at the start of the game. Three
options are available.
1) OFF: Disable calibration.
2) ON (TYPE1): Always calibrate.
3) ON (TYPE2): Allow calibration if command is entered (start game with
controller aimed at screen and pedal held down).
● ADVERTISE SOUND: Turn advertising sound output ON/OFF.
● CABINET TYPE: Set cabinet type.
Set to either DELUXE or STANDARD. Be sure to set according to actual
cabinet type.
Changes to settings are not enabled until Test Mode is exited. After changing settings, be sure to exit Test
Mode.
After changing the settings, select EXIT and press the TEST Button to return to the Game Test Menu
screen.

74
6.4.4. GUN ADJUSTMENT
Select GUN ADJUSTMENT to display the following screen.
This screen allows you to adjust the gun using the five calibration targets (TOP, LEFT, CENTRE, RIGHT,
BOTTOM). Use each target to calibrate as follows.
Use the standard gun controller, carefully aim at the correct target and pull the trigger to calibrate the value.
Select between the calibration targets with the 1P and 2P START buttons or SERVICE button.
Details for each item are as follows.
● TOP x y: Set the TOP value.
The number on the left (x) is the horizontal component, and the number on the right
(y) is the vertical component. Aim the controller at the TOP target (white circle) and
pull the trigger to set the value. This will not affect horizontal calibration.
● LEFT x y: Set the LEFT value.
The number on the left (x) is the horizontal component, and the number on the right
(y) is the vertical component. Aim the controller at the LEFT target (white circles)
and pull the trigger to set the value. This will not affect vertical calibration.
● CENTRE x y: Set the CENTRE value.
The number on the left (x) is the horizontal component, and the number on the right
(y) is the vertical component. Aim the controller at the CENTRE target and pull the
trigger to set the CENTRE value.
● RIGHT x y: Set the RIGHT value.
The number on the left (x) is the horizontal component, and the number on the right
(y) is the vertical component. Aim the controller at the RIGHT circle and pull the
trigger to set the RIGHT value. This will not affect vertical calibration.
● BOTTOM x y: Set the BOTTOM value.
The number on the left (x) is the horizontal component, and the number on the right
(y) is the vertical component. Aim the controller at the BOTTOM circle and pull the
trigger to set the value. This will not affect horizontal calibration.
● DEFAULT: Restore calibration values to original settings.
● CANCEL: Restore calibration values to previous settings.

75
● CURSOR:
Select CURSOR and aim the controller at the screen to display a round cursor
(blue for 1P, red for 2P) where the controller hits the screen. Use this cursor to
check calibration.
● OUT OF SCREEN: Displays “OUT OF SCREEN” when the controller is pointed outside the screen.
Values cannot be set when the controller is out of screen.
Changes to settings are not enabled until the Test Mode is exited. After changing settings, be sure to exit
Test Mode.
After changing the settings, select EXIT and press the TEST Button to return to the Game Test Menu
screen.
6.4.5. BOOKKEEPING
Select BOOKKEEPING on the Game Test Menu screen to display the three screens of operating status
data.
Press the TEST Button on the BOOKKEEPING 1/3 and BOOKKEEPING 2/3 screens to move to the second
and third (BOOKKEEPING 3/3) screens. Press the TEST Button in the third screen to return to the Game
Test Menu screen.
The display items for the screen (Page 1 of 3) are as follows.
● COIN CHUTE #1: The number of coins inserted into Coin Slot 1.
● COIN CHUTE #2: The number of coins inserted into Coin Slot 2.
● TOTAL COINS: The total number of coins inserted into the coin slots.
● COIN CREDITS: The number of credits for the coins inserted.
● SERVICE CREDITS: The number of credits input by the SERVICE Button.
● TOTAL CREDITS: Total credits from coins and the SERVICE Button
Press the TEST Button to display the next screen.

76
The display items for the screen (Page 2 of 3) are as follows.
● NUMBER OF GAMES: The total number of games played by 1P and 2P.
● NUMBER OF GAME STARTS: Number of games started.
● NUMBER OF CONTINUES: Number of times game has been continued.
● NUMBER OF JOIN GAMES: Number of two-player games.
● TOTAL TIME The amount of time the unit has been in operation.
● PLAY TIME: The sum of 1P’s time played and 2P’s time played.
● LONGEST PLAY TIME The longest play time for one game.
● SHORTEST PLAY TIME The shortest play time for one game.
● AVERAGE PLAY TIME: The sum of all play times divided by the total number of games.
Press the TEST Button to display the next screen (Page 3 of 3).
PLAY TIME HISTOGRAM shows the number of plays and the respective play times. This histogram should
be referred to when setting the Game Difficulty.
This displays play times on a scale from 0M00S to 9M59S with 30-second intervals.
All play times over ten minutes are included in the item OVER 10M00S.
Press the TEST Button after viewing. You will return to the Game Test Menu screen.

77
6.4.6. BACKUP DATA CLEAR
Select BACKUP DETA CLEAR to clear the contents of BOOKKEEPING, ranking data and coin/credit data.
To clear data, use the SERVICE Button to move the cursor to YES (CLEAR) and then press the TEST
Button. When the data has been cleared, the message “COMPLETED” will be displayed.
Press the TEST Button again to return to the Game Test Menu screen.
Move the cursor to NO (CANCEL) and press the TEST Button to return to the Game Test Menu screen
without clearing the data.
Note that this operation does not affect GAME ASSIGNMENTS or GUN ADJUSTMENT settings.

78
7. COIN MECH INSTALLATION AND CREDIT BOARD SET UP
7.1. INTRODUCTION
Game credits between the Coin Mechanism and the game board for this machine are controlled by a VTS
board. This electronic circuit allows the price of play to be set for a range of different countries. These
functions are set on Dual In Line (DIL) PCB mounted switches.
SW1 is used to set the currency (or coin ratio) and SW3 the price of play. Refer to the Tables on the
following pages for the correct settings for your environment.
The VTS board pictured below is mounted in the Coin Chute Tower.
The VTS board is connected to the coin validator and lamps via a dedicated wiring harness depending upon
the coin validator used:
Wiring Harness Validator
LM1006 Coin Controls (15 way connector)
LM1007 Mars (13 way connector)
LM1008 Mechanical See note 2
N/A NRI See note 1
Notes
1. If NRI mechanisms are to be used, these should be ordered with the highest denomination coin on coin
path #1 and the lowest denomination on coin path #4. The VTS board should be then be set up for either
the UK or Switzerland settings. A minimum connecting lead length of 600mm is required.
2. Mechanical coin mechanisms may be connected in parallel allowing two identical mechanisms to be
fitted.
The VTS Board

Rev 1Updated:- 23/11/01 79
Credit Board Mode Settings Switch 3
Country Setting Switch 3 Setting Coin Validator Programming C120/SR3 Only
SW1 SW2 SW3 SW4 SW5 SW6 COIN1 COIN2 COIN3 COIN4 COIN5 COIN6 COIN7 COIN8 COIN9 COIN10 COIN11 COIN12
UK Coin Controls
C220 Parallel
OFF OFF OFF OFF £1 50p new 20p 10p - 50p old - -
UK Coin Controls
C220 Binary
ON OFF OFF OFF £1 50p new 20p 10p - 50p old - £2
UK Coin Controls
C220 Binary
OFF ON OFF OFF £1 50p new 20p 10p - £2 - 50p
old
UK Coin Controls
SR3 Parallel
ON ON OFF OFF £1 50p new 20p 10p - £2 - 50p
old
- - - -
UK
Euro
Coin Controls
SR3 Parallel
OFF OFF ON OFF £2
€2
£1
€1
50p new
50¢
20p
20¢
10p
10¢
- - - 50p old - - -
UK Mars ME/MS
111 Parallel
ON OFF ON OFF £1 £2 20p 10p 50p new 50p old
UK NRI Parallel OFF ON ON OFF 10p 20p 50p £1 £2 -
Belgium Parallel ON ON ON OFF - 50BFr 20BFr 5BFr
Holland Parallel OFF OFF OFF ON - 5NLG 2.5NLG 1NLG
Austria SR3 Parallel ON OFF OFF ON 20Sch 10Sch 5Sch 1Sch
Spain Coin Controls
C220 Binary
OFF ON OFF ON 500Pta 200Pta 100Pta 50Pta 25Pta 200Pt
old
50Pta
old
25Pta
old
Spain SR3/NRI
Parallel
ON ON OFF ON 500Pta 200Pta 100Pta 50Pta 25Pta - - 200Pta - 50Pta
old
25Pta
old
-
Spain Coin Controls
C220 Parallel
OFF OFF ON ON 100Pta 50Pta
new
- 25Pta
new
- 50Pta
old
- 25Pta
old
Portugal
Euro
Parallel ON OFF ON ON 200Es
€1
100Es
50¢
50Es - - - - -
TBA OFF TBA Please Note
The credit board automatically sets the validator for parallel and binary
operation through an output on pin 8 of the 17 way pinstrip. For the feature
to work it is necessary for the validator interconnecting cable to include at
wire at this position
ON TBA
Channels OFF Direct Mode
ON 2 channel Mode
Note: These switch settings are under constant review and may change due to world currency updates.
· Set SW 1 according to the option settings found in the relevant Price of Play Settings Table on the following pages.
· For Germany (DM), France (Fr) & Switzerland (SFr), use the appropriate existing setting shown above (from another country) that matches the coin ratios programmed into your coin mech.
· Set SW 3 on the VTS /Excel board as shown in the table above corresponding to the country required.

Rev 1Updated:- 23/11/01 80
7.1.1. PRICE OF PLAY SETTINGS UK
Price Bonus DIL Switch 1
Switch 1 Switch 2 Switch 3 Switch 4 Switch 5
1 10p No Bonus OFF OFF OFF OFF OFF
2 10p 6 = 50p ON OFF OFF OFF OFF
3 20p No Bonus OFF ON OFF OFF OFF
4 20p 3 = 50p 6 = £1 12 =£2 ON ON
OFF OFF OFF
5 30p No Bonus OFF OFF ON OFF OFF
6 30p 1.66 = 50p 4 = £1 8 = £2 ON OFF ON OFF OFF
7 30p 2 = 50p 4 = £1 OFF ON ON OFF OFF
8 30p AMLD * 3 = £1 6 = £2 ON ON ON
OFF OFF
9 40p No Bonus OFF OFF OFF ON OFF
10 40p 1.25 = 50p 3 = £1 6 = £2 ON OFF OFF ON OFF
11 50p No Bonus OFF ON OFF ON OFF
12 50p 3 = £1 6 = £2 ON ON
OFF ON OFF
13 50p 2 = £1 5 = £2 OFF OFF ON ON OFF
14 60p No Bonus ON OFF ON ON OFF
15 60p 2 = £1 4 = £2 OFF ON ON ON OFF
16 80p No Bonus ON ON ON ON OFF
17 80p 1.25 = £1 2 = £1.50 2.5 = £2 OFF OFF OFF OFF ON
18 £1 No Bonus ON OFF OFF OFF ON
19 £1 3 = £2 OFF ON OFF OFF ON
20 £1 2 = £2 5 = £4 ON ON
OFF OFF ON
21 £1.50 No Bonus OFF OFF ON OFF ON
22 £1.50 2 = £2 ON OFF ON OFF ON
23 £2 No Bonus OFF ON ON OFF ON
24 £2 3 = £5
ON ON ON
OFF ON
25 £3 No Bonus OFF OFF OFF ON ON
26 £3 2 = £5
ON OFF OFF ON ON
27 £5 No Bonus OFF ON OFF ON ON
28 £5 3 = £10
ON ON
OFF ON ON
29 £7.50 No Bonus OFF OFF ON ON ON
30 £7.50 2 = £10 ON OFF ON ON ON
31 £10 No Bonus OFF ON ON ON ON
32 Free Play ON ON ON ON ON

81
7.1.2. PRICE OF PLAY SETTINGS EURO
Price Bonus DIL Switch 1
Switch 1 Switch 2 Switch 3 Switch 4 Switch 5
1 10¢ No Bonus OFF OFF OFF OFF OFF
2 10¢ 6 = 50¢ ON OFF OFF OFF OFF
3 20¢ No Bonus OFF ON OFF OFF OFF
4 20¢ 3 = 50¢ 6 = €1 12 =€2 ON ON
OFF OFF OFF
5 30¢ No Bonus OFF OFF ON OFF OFF
6 30¢ 1.66 = 50¢ 4 = €1 8 = €2 ON OFF ON OFF OFF
7 30¢ 2 = 50¢ 4 = €1 OFF ON ON OFF OFF
8 30¢ AMLD * 3 = €1 6 = €2 ON ON ON
OFF OFF
9 40¢ No Bonus OFF OFF OFF ON OFF
10 40¢ 1.25 = 50¢ 3 = €1 6 = €2 ON OFF OFF ON OFF
11 50¢ No Bonus OFF ON OFF ON OFF
12 50¢ 3 = €1 6 = €2 ON ON
OFF ON OFF
13 50¢ 2 = €1 5 = €2 OFF OFF ON ON OFF
14 60¢ No Bonus ON OFF ON ON OFF
15 60¢ 2 = €1 4 = €2 OFF ON ON ON OFF
16 80¢ No Bonus ON ON ON ON OFF
17 80¢ 1.25 = £1 2 = €1.50 2.5 = €2 OFF OFF OFF OFF ON
18 €1 No Bonus ON OFF OFF OFF ON
19 €1 3 = €2 OFF ON OFF OFF ON
20 €1 2 = €2 5 = €4 ON ON
OFF OFF ON
21 €1.50 No Bonus OFF OFF ON OFF ON
22 €1.50 2 = €2 ON OFF ON OFF ON
23 €2 No Bonus OFF ON ON OFF ON
24 €2 3 = €5
ON ON ON
OFF ON
25 €3 No Bonus OFF OFF OFF ON ON
26 €3 2 = €5
ON OFF OFF ON ON
27 €5 No Bonus OFF ON OFF ON ON
28 €5 3 = €10 ON ON
OFF ON ON
29 €7.50 No Bonus OFF OFF ON ON ON
30 €7.50 2 = €10 ON OFF ON ON ON
31 €10 No Bonus OFF ON ON ON ON
32 Free Play ON ON ON ON ON

82
7.1.3. PRICE OF PLAY SETTINGS Austria-Czech-Denmark-Norway-Israel-
France2
Price Bonus Switch 1
Switch 1 Switch 2 Switch 3 Switch 4 Switch 5
1 1 No Bonus OFF OFF OFF OFF OFF
2 1 11 = 10
ON OFF OFF OFF OFF
3 1 6 = 5 OFF
ON OFF OFF OFF
4 2 No Bonus ON ON OFF OFF OFF
5 2 6 = 10 OFF OFF
ON OFF OFF
6 2 3 = 5 ON OFF ON OFF OFF
7 3 No Bonus OFF
ON ON OFF OFF
8 3 4 = 10
ON ON ON OFF OFF
9 3 2 = 5 OFF OFF OFF ON OFF
10 4 No Bonus ON OFF OFF ON OFF
11 4 3 = 10 OFF ON OFF ON OFF
12 5 No Bonus ON ON OFF ON OFF
13 5 3 = 10 OFF OFF ON ON
OFF
14 6 No Bonus ON OFF ON ON
OFF
15 6 4 = 20 OFF ON ON ON
OFF
16 8 No Bonus ON ON ON ON OFF
17 10 No Bonus OFF OFF OFF OFF ON
18 10 3 = 20 ON OFF OFF OFF ON
19 20 No Bonus OFF ON OFF OFF ON
20 20 3 = 50 ON ON OFF OFF ON
21 30 No Bonus OFF OFF ON OFF ON
22 30 2 = 50 ON OFF ON OFF ON
23 50 No Bonus OFF ON ON OFF ON
24 50 3 = 100
ON ON ON OFF ON
32 Free Play ON ON ON ON ON

83
8. DESIGN RELATED PARTS
For the Warning stickers refer to Section 1.
No. PART No. DESCRIPTION
1 VCT-5151-AUK STICKER FENCE FRAME L
2 VCT-5171-AUK STICKER FENCE FRAME R
3 VCT-3001UK BILLBOARD PLATE U/R
4 VCT-3002UK STICKER SIDE COVER L
5 VCT-3003UK STICKER SIDE COVER R
6 VCT-3005UK STICKER CONTROL PANEL NOB
7 VCT-3011UK STICKER SERVICE DOOR
8 VCT-3013UK STICKER CONTROL PANEL CCT
9 VCT-3018UK STICKER CASH DOOR
10 VCT-5002UK FLOOR PLATE ARTWORK

84
9. PARTS LIST
9.1. VCT-10002UK ASSY CABINET VCT U/R

85
ITEM PART NO. QTY DESCRIPTION COMPONENT REF.
1 VCT-11002UK 1 ASSY FRAMEWORK VCT U/R
2 NOA-1200UK 1 ASSY CRT COVER UK
3 VCT-1300 1 ASSY BILLBOARD
4 VCT-1400UK 1 ASSY CONTROL BOX HDT U/R COLOUR CHANGE
5 VCT-1500UK 1 ASSY FRONT PANEL HDT U/R FST COLOUR CHANGE
6 CHT-4000UK 1 ASSY ELEC
7 NOA-1750UK 1 ASSY SERVICE DOOR WHITE
8 NOA-1801UK 1 REAR HATCH FIX DOWN AT TOP ASSY (WHITE)
9 NOB-1001UK 1 FRAME COVER UR R
10 NOB-1002UK 1 FRAME COVER UR L
11 NOA-1003 1 ENDCAP R
12 NOA-1004 1 ENDCAP L
13 PTR-1005UK 1 REAR COVER UPPER BLACK
15 280-6617 4 BUSH FOR TV LONG
16 280-5113 4 COLLAR FOR NANAO MONITOR (101)-4
18 VCT-1006UK 4 SCR CAP COLOUR CHANGE
20 NOB-1710UK 1 ASSY AC UNIT WHITE
23 NOA-1009 2 WSHR PLATE (4)-2
24 RTS-1010UK 1 BILLBD HOLDER
25 NOA-1011 1 FL BRKT
27 HDT-4100UK 1 ASSY XFMR
29 NOB-1117UK 1 WATER GUARD CE
37 421-7020UK 2 STICKER CAUTION FORK AT BACK OF BASE BOX
41 LB1102 5 STICKER DANGEROUS VOLTAGE LID,LEFT OF DOOR,CRT,FL,CP
42 LB1104 1 STICKER CAUTION, HOT SURFACE FL COVER
44 VCT-3002UK 1 STICKER SIDE COVER L
45 VCT-3003UK 1 STICKER SIDE COVER R
51 VCT-3011UK 1 STICKER SERVICE DOOR
52 VCT-3018UK 1 STICKER CASH DOOR
101 200-5949 1 ASSY CLR DSPL 29 TYPE 31K UK
102 390-5695-40-CUK 1 FL TRAY 110V 40W (T12)
114 390-5695-40-DUK 1 FL TUBE 40W 600L 1.5"DIA
116 280-A02048-PM 5 ROUTER TWIST D20 SO4.8 PAN LG
117 280-A02000-A 4 ROUTER TWIST D20 ADH
118 280-A01248-PM 12 ROUTER TWIST D12 SO4.8 PAN MED
119 280-A01200-A 3 ROUTER TWIST D12 ADH
120 280-A00900-A 2 ROUTER TWIST D9 ADH
121 OS1230 1.18 FOAM STRIP 2mm X 10mm 2X0.59M TO 8
122 601-0460 10 CABLE TIE 100mm (29)-10
201 008-T00625-0C 14 M6X25 TMP PRF TH CRM (2)-6,(5)-4,(13)-4
202 030-000620-S 4 M6X20 BLT W/S PAS (4)-4
203 000-P00408 2 M4X8 MSCR PAN PAS FL TUBE CLIPS - 2
204 008-T00412-0C 6 M4X12 TMP PRF TH CRM (9,10)-2,(11,12)-1
205 008-T00412-0B 10 M4X12 TMP PRF TH BLK (20)-6,(24)-4
206 050-F00600 4 M6 NUT FLG SER PAS (101)-4
208 008-T00430-0B 2 M4X30 TMP PRF TH BLK TNG STOPPER CP & REAR LID
CONTINUED ON NEXT PAGE

86
CONTINUED FROM PREVIOUS PAGE
ITEM PART No. QTY DESCRIPTION COMPONENT REF.
209 030-000630-S 4 M6X30 BLT W/S PAS (27)-4
210 068-651616 4 M6 WSHR 16OD FLT PAS (27)-4
211 000-P00408-W 6 M4X8 MSCR PAN W/FS PAS (25)-2,EARTHS-4
214 000-P00416-W 4 M4X16 MSCR PAN W/FS PAS (5)-2,(11)-1,(12)-1
215 068-652516 4 M6 WSHR 25OD FLT PAS (101)-4
216 050-F00400 4 M4 NUT FLG SER PAS (102)-2,EARTHS-2
217 050-F00500 3 M5 NUT FLG SER PAS FRAME EARTHS - 3
218 010-P00408 4 M4X8 S-TITE PAN PAS (6)-4
219 060-F00400 4 M4 WSHR FORM A FLT PAS (6)-4
301 HDT-6001UK 1 ASSY WIRE L HDT U/R
302 NOB-60041UK 1 WIRE HARN AC EXT UK
303 NOA-60025 1 WIRE HARN SPEAKER R
311 600-7159-070 1 WIRE HARN JVS PWR 070CM
319 600-9010-44K 1 WIRE HARN EARTH 100mm M4/M4 BBOARD HOLDER TO FL BASE
320 NOB-60201UK 1 WIRE HARN FL NOB
321 600-9070-45K 1 WIRE HARN EARTH 700mm M4/M5 K BASE LID TO BASE
322 600-9080-45K 1 WIRE HARN EARTH 800mm M4/M5 K BASE TO RH FRAME (BOTTOM)
323 600-9025-56U 1 WIRE HARN EARTH 250mm M5/M6 MON CHASSIS TO RH FRAME TEMP
324 600-9055-45K 1 WIRE HARN EARTH 550mm M4/M5 K BASE TO LH FRAME BOTTOM

87
9.2. VCT-11002UK ASSY FRAMEWORK VCT U/R

88
ITEM PART NO. QTY DESCRIPTION COMPONENT REF.
1 VCT-1601UK 1 BASE BOX
2 NOB-1101UK 1 MAIN FRAME UR R
3 NOB-1102UK 1 MAIN FRAME UR L
4 NOA-1111X 1 LOWER BEAM
5 NOA-1112X 1 UPPER BEAM
6 NOA-1113 1 HOOF R
7 NOA-1114 1 HOOF L
11 NOA-1115UK 1 TNG REAR HATCH
102 601-5699X 2 LEG ADJUSTER BOLT M16x75 SEGA
103 601-10461UK 2 CASTOR 50 SWIVEL FRONT
104 601-10462UK 2 CASTOR 50 FIXED REAR
105 220-5575UK 1 LOCK
201 050-F00600 4 M6 NUT FLG SER PAS (2)-2,(3)-2
202 030-000620-S 14 M6X20 BLT W/S PAS (2,3)-3,(4,5)-4
203 068-652016 6 M6 WSHR 20OD FLT PAS (2)-3,(3)-3
204 050-F00500 2 M5 NUT FLG SER PAS (6)-1,(7)-1
205 000-P00408-W 2 M4X8 MSCR PAN W/FS PAS (6)-1,(7)-1
207 050-H01600 2 M16 NUT PAS (102)-2
208 FAS-200004 16 M6X14 SKT CAP BLK (103,4)-8EA
209 060-S00600-0B 16 M6 WSHR SPR BLK (103,4)-8EA

89
9.3. NOA-1200UK ASSY CRT COVER UK
No. PART NUMBER QTY DESCRIPTION COMPONENT REFERENCE
1 NOA-1201UK 1 CRT COVER
2 NOA-1202 1 SPEAKER BOX
3 RND-0037 0.38 TAPE SPEAKER BOX 2 SIDED (2)-0.19
101 130-5205 2 SPEAKER 40HM 10W 100 W/S
102 000-P00410-W 8 M4X10 MSCR POSI PAN W/FS (101)-8
103 340042 6 RIVET BULBEX 3/16 BF01-0630 (2)-6
301 NOA-60031 1 WIRE HARN SPEAKER L [NOT SHOWN]
302 NOA-60032 1 WIRE HARN SPEAKER R [NOT SHOWN]

90
9.4. VCT-1200UK ASSY FOOT PEDAL DX
ITEM PART NUMBER QTY DESCRIPTION COMPONENT REF.
1 VCT-1201UK 1 PEDAL BASE DX
2 VCT-1202UK 1 PEDAL
3 VCT-1203UK 1 FOOT PLATE (ARTWORK)
4 VCT-1204 1 COM SPRING
5 VCT-1205UK 1 SPRING COVER
6 VCT-1206UK 1 SHADE PLATE
7 VCT-1207UK 1 SENSOR BRKT
8 VCT-1208UK 1 WIRE COVER
9 VCT-1209 2 STOPPER RUBBER
10 VCT-1210 2 RUBBER CUSHION
11 VCT-1211UK 2 RUBBER CASE
12 VCT-1212UK 2 CUSHION
13 VCT-1213UK 1 PLATE SASH
101 370-5226 1 PHOTO SENSOR OMT-01DAMP NEW
103 280-6622-30030 4 SPACER TUBE
201 FAS-000102 3 M5X6 MSCR TH BLK (2)-3
202 FAS-290034 4 M5X15 LH CAP SCR STN (3)-4
203 000-F00512 2 M5X12 MSCR FH (5)-2
204 000-P00310 10 M3X10 MSCR PAN W/FS (11)-4,(7)-4,(12)-4
205 050-F00400 10 M4 FLG NUT (6)-2,(7)-2,(14)-2,(8)-4
206 000-T00408-0B 2 M4X8 MSCR TH BLK (13)-2
207 000-P00320-W 3 M3X20 MSCR PR W/FS (14)-2
208 050-H00400 1 M4 NUT HEX (1)-1
209 060-F00400 1 M4 FLT WSHR (1)-1
210 060-S00400 1 M4 SPR WSHR (1)-1
211 030-000620 1 M6X20 BLT W/S BLK (1)-4
301 VCT-64002 1 WH FOOT PEDALS

91
9.5. VCT-1300 ASSY BILLBOARD
No. PART NUMBER QTY DESCRIPTION COMPONENT REFERENCE
1 NOA-1301X 1 BILLBOARD PLATE
2 NOA-1302UK 1 BILLBOARD SHEET
3 VCT-3001UK 1 BILLBOARD PLATE U/R NOT SHOWN
201 008-T00408-OC 3 M4X8 MSCR TMP PRF TH CRM (2)-3

92
9.6. VCT-1400UK ASSY CONTROL BOX VCT U/R
ITEM PART NUMBER QTY DESCRIPTION COMPONENT REF.
1 SPY-1404UK 1 ADJUST PANEL BRKT
3 NOA-1401 1 CONTROL BOX LOWER
4 VCT-1402UK 1 CONTROL BOX UPPER COLOUR CHANGE
5 CQN-1055X 1 HINGE
6 NOA-1403 1 SHAFT
7 HOT-1520 2 LATCH N
8 HOT-1504 2 LATCH HOLDER
9 NOA-1404 1 TOR SPRING
10 HOT-1505UK 1 LKG TNG (101)-1
12 SPY-1406UK 1 REJECT COVER
14 VCT-3004UK 1 PANEL INSTRUCTION SPACE 5MM FOAMEX (ARTWORK)
15 NOA-1419 2 BRKT INST COVER (14)-2
16 NOA-1420 4 L WASHER (15)-4
17 SPX-1407UK 1 COIN ENTRY COVER
21 NOA-1415 2 LOCK BRKT
22 NOA-1418 2 DUMMY BTN
23 SPX-1403UK 1 CNTRL PANEL PLATE BLANK
24 SPY-1408UK 1 COIN EXIT COVER
25 VCT-3005UK 1 STICKER CONTROL PANEL NOB (23)-1
CONTINUED NEXT PAGE

93
CONTINUED FROM PREVIOUS PAGE
ITEM PART NUMBER QTY DESCRIPTION COMPONENT REF.
101 220-5575UK 1 LOCK
102 280-A00900-A 3 ROUTER TWIST D9 ADH
201 000-P00410-W 27 M4X10 MSCR PAN W/FS PAS (1,12,22)-2,(8,16,21)-4,(5)-9
202 050-H00600 2 M6 NUT PAS (7)-2
203 060-S00600 2 M6 WSHR SPR PAS (7)-2
204 050-F00300 2 M3 NUT FLG SER PAS (17)-2
205 031-000416-0B 6 M4X16 CRG BLT BLK (23)-6
206 050-F00400 6 M4 NUT FLG SER PAS (23)-6
207 068-441616 2 M4 WSHR 16OD FLT PAS (22)-2
209 065-E00600 2 DIA6 E RING (6)-2
210 000-P00412-W 1 M4X12 MSCR PAN W/FS PAS (24)-1
211 008-T00412-0C 1 M4X12 TMP PRF TH CRM (24)-1

94
9.7. VCT-1500UK ASSY FRONT PANEL VCT U/R FST
ITEM PART NO. QTY DESCRIPTION COMPONENT REF.
1 VCT-1501UK 1 FRONT PANEL VCT COLOUR CHANGE
2 SPY-1502-02UK 1 MASK NF SPY U/R
3 NOA-1503 1 LIGHT COVER
4 NOA-1504UK 1 PRISM PLATE
5 VCT-1505UK 1 LID GC COLOUR CHANGE
6 VCT-1506UK 2 LID VMS COLOUR CHANGE
7 NOA-1507 1 EMBLEM NAOMI
101 838-13145-02 10 LED BD GUN SENSE HOD
102 JPT-1082 10 IR COVER
103 SPY-1507-AUK 20 HEAD COVER M3 GREY (101)-20
104 SPY-1507-BUK 20 HEAD COVER BASE M3 (101)-20
105 280-A00900-A 2 ROUTER TWIST D9 ADH 2-(2)
201 050-U00300 20 M3 NUT NYLOK PAS (101)-20
202 000-P00410-W 13 M4X10 MSCR PAN W/FS PAS (2)-8,(5)-5
203 012-P03516 4 N6X5/8" S/TAP PAN PAS (4)-4
204 000-P00325 20 M3X25 MSCR PAN PAS (101)-20
205 068-330808-PN 20 M3 WSHR 8OD FLT NYLON (101)-20
301 SPY-61040UK 7 WIRE HARN MASK SHORT
302 SPY-61042UK 2 WIRE HARN MASK LONG
303 SPY-61041UK 1 WIRE HARN IC BD

95
9.8. NOB-1710UK ASSY AC UNIT
ITEM PART NO. QTY DESCRIPTION COMPONENT REF.
1 NOB-1711UK 1 AC BRKT NEW WHITE
3 LB1096 1 STICKER PROTECTIVE EARTH NEXT TO EARTH STUD ON INSIDE
4 421-6595-5000-T 1 STICKER FUSE 5000mA TYPE T NEXT TO IEC INLET ON OUTSIDE
101 EP1381 1 FILTER IEC & SW 6A ROXBURGH
111 514-5078-5000 1 FUSE 5X20 CERAMIC SB 5000mA
202 050-F00400 2 M4 NUT FLG SER PAS EARTH - 2
204 000-F00316 2 M3X16 MSCR CSK PAS (101)-2
301 NOB-60004UK 1 WIRE HARN AC OUT
303 600-9030-45K 1 WIRE HARN EARTH 300mm M4/M5 K AC BRKT TO XFMR
305 600-9025-44K 1 WIRE HARN EARTH 250mm M4/M4 AC BRKT TO BASE
306 600-9015-4FK 1 WIRE HARN EARTH 150MM
9.9. NOA-1750UK ASSY SERVICE DOOR
ITEM PART NO. QTY DESCRIPTION COMPONENT REF.
1 NOA-1751UK 1 SERVICE DOOR WHITE
2 DP-1167UK 1 TNG LKG UK
101 220-5575UK 1 LOCK
201 008-T00430-0C 1 M4X30 TMP PRF TH CRM DO UP 1/2 WAY SO TNG OPENS

96
9.10. VCT-2100-01 CONTROL UNIT EXP
Item Component Part Qty Description Component Reference
1 VCT-2101-01 1 COVER L EXP
2 VCT-2102-01 1 COVER R EXP
3 VCT-2103-01 1 HAMMER EXP
4 VCT-2104 1 TRIGGER
5 VCT-2105 1 CHANGE BUTTON
6 VCT-2106 1 SW BRKT
7 VCT-2107 1 COM SPRING
8 JPT-2030 1 SENSOR UNIT
9 125-5124 1 TORSION SPRING
101 280-5124-04 1 NYLON CLAMP NK04
102 310-5029-D20 1 SUMITUBE F D 20MM
103 509-5080 1 SW MICRO TYPE (SS-5GL2)
104 601-0460 1 PLASTIC TIE BELT 100 MM
201 000-P00308-W 2 M SCR PH W/FS M3 x 8 (6)-1, (101)-1
202 FAS-000099 10 M SCR PH W/SMALL FS BLK M3 x10 (1)-10
204 FAS-000101 2 M SCR PH W/FS M2.3 x 10 (103)-2
301 VCT-60011 1 WH CONTROL UNIT
302 VCT-60012 1 WH CHANGE SW

97
9.11. JPT-2030 SENSOR UNIT
ITEM NO. PART NO. DESCRIPTION NOTE
1 JPT-2031 SENSOR HOLDER
101 838-13144 SENSOR BD GUN SENSE
201 012-P00306 TAP SCR #2 PH 3X6

98
9.12. HDT-4100UK ASSY XMFR
No. PART NUMBER QTY DESCRIPTION COMPONENT REFERENCE
1 HDT-4101UK 1 XFMR BASE
3 838-11856CE-02 1 CONN BD W/FUSE 6.3A CE
101 560-5422UK 1 XFMR NOB
201 000-P00416-W 4 M4X16 MSCR POSI PAN W/FS (101)-4
202 068-441616 4 M4 WSHR 16OD FLT PAS (101)-4
203 012-P00325 2 N4X1" S/TAP POSI PAN PAS (3)-2 (102)-2

99
9.13. CHT-4000UK ASSY ELEC
ITEM PART NO. QTY DESCRIPTION COMPONENT REF
1 CTH-4001 1 ELEC BASE
2 NOM-4002 1 BRKT FOR PWR PROTECT UNIT
101 400-5443 1 SW REGU FOR CHIHIRO
103 838-13616 1 AUDIO POWER AMP 2CH
107 280-A02048-PM 4 ROUTER TWIST D20 SO4.8 PAN LG
108 601-6231-B095 9,5 EDGE TRIM NEW TYPE 0.91t (1) BACK EDGE IN MIDDLE
109 EP1317 1 FERRITE CORE ROUND CABLE CLAMP SW REGU OUTLET WIRES
110 280-A01248-PM 2 ROUTER TWIST D12 SO4.8 PAN MED
111 280-A02000-A 1 ROUTER TWIST D20 ADH
112 EP1364 1 FERRITE CORE ROUND CABLE CLAMP SW REGU INLET WIRES
113 610-0674 1 PWR PROTECT UNIT FOR CHIHIRO
201 010-P00408 4 M4X8 S-TITE PAN PAS (101)-4
202 010-P00308 4 M3X8 S-TITE PAN PAS (103)-4
303 HDT-60013UK 1 WIRE HARN SW REGU + CONDENSER
304 NOA-60014 1 WIRE HARN I/O BD PWR
305 NOB-60202UK 1 WIRE HARN AUDIO POWER-IN
306 600-7159-039 1 WIRE HARN JVS PWR 039CM

100
9.14. VCT-4800UK ASSY MAIN BD VCT U/R
ITEM PART NO. QTY DESCRIPTION COMPONENT REF.
1 SPY-4801UK 1 WOODEN BASE MAIN
2 843-0001D-12 1 ASSY CASE BOX COM NAO DIMM EXP
3 610-0617 1 GD-ROM DRIVE UNIT NAOMI SHIP BOX WITH MACHINE
4 105-5435 1 GD DRIVE BRKT STD
5 610-0652-0003 1 GD SOFT VCT
6 253-5508-0354 1 KEY CHIP
7 HDT-60100UK 1 WH POWER GD ROM
101 LB1101 1 STICKER WARNING BATTERY (2)-1
102 280-A01264-WX 5 ROUTER TWIST D12 SO6.4 WOOD X
103 LB1111 1 STICKER PLEASE RECYCLE (2)-1
201 000-P00416-W 7 M4X16 MSCR PAN W/FS PAS (2)-4,(4)-3
202 012-P00410-F 4 N8X3/8" S/TAP FLG PAS (3)-4
301 600-7249UK 1 WIRE HARN NAOMI GD DRIVER DC
307 600-7247-500 1 CABLE SCSI ST-L TYPE2 500MM

101
9.15. VCT-5000UK ASSY FLOOR VCT U/R
No. PART NUMBER QTY DESCRIPTION COMPONENT REFERENCE
1 VCT-5001UK 1 FLOOR BASE
2 VCT-5002UK 1 FLOOR PLATE ARTWORK SELF ADHESIVE ON REVERSE

102
9.16. VCT-5100UK ASSY CCT VCT U/R
ITEM PART NO. QTY DESCRIPTION COMPONENT REF.
1 VCT-5101UK 1 COINCHUTE TOWER
2 VCT-2100-01 2 CONTROL UNIT EXP NOT SHOWN
3 VCT-5102UK 1 CCT COVER
5 VCT-2199UK 2 GUN TETHER DX NOT SHOWN
7 VCT-5103UK 4 GUN HOLDER PLATE
8 SPY-5104UK 2 GUN CUSHION A
9 SPY-5105UK 2 GUN CUSHION B
10 SPY-5110UK 4 CUSHION BAR
12 VTS-STW-U 1 VTS BOARD UPRIGHT TYPE
13 DYN-0010UK 1 DENOMI PLATE
14 NCR-1103UK 1 CCT FLOOR
15 DUT-0302UK 1 COIN PATH PLATE
16 PP1087 1 BOX CASH FOR MINI DOOR
17 105-5216 2 CHAIN BRKT (2)-2
101 509-SPYU-YE 2 SW PB W/LAMP 6V YELLOW OVAL
102 838-13143-09 1 IC BD GUN SENSE SPY U/R
103 837-13551-92 1 I/O CONTROL BD FOR JVS
105 310-5287-29 2 CONN L29 32mm X PG29
106 310-5285-290100 1 FLEX TUBE 29 100CM
107 280-L00709-OS 4 STANDOFF 7OD 4ID 9L (102)-4
CONTINUED ON NEXT PAGE

103
CONTINUED FROM PREVIOUS PAGE
ITEM PART NO. QTY DESCRIPTION COMPONENT REF.
108 280-A02048-PM 3 ROUTER TWIST D20 SO4.8 PAN LG
109 280-L00805-0M 2 STANDOFF 8OD 5ID 4.8L (10)-2
110 310-5287-PG29 2 NUT LOCK PG29 BLACK (105)-1
201 000-T00412-0C 8 M4X12 MSCR TH CRM (7)-4,(8)-4
202 008-T00412-0B 17 M4X12 TMP PRF TH BLK (2)-8,(3)-5,(13)-4
203 000-P00416-W 18 M4X16 MSCR PAN W/FS PAS (9)-12,(12)-4,(14)-2
204 029-B00812-0B 4 M8X12 BLT BH BLK (4)-2,(5)-2
205 060-S00800-0B 4 M8 WSHR SPR BLK (4)-2,(5)-2
207 050-F00300 8 M3 NUT FLG SER PAS (102)-4,(103)-4
208 008-T00408-0C 4 M4X8 MSCR TH CRM (17)-4
210 000-P00408-W 5 M4X8 MSCR PAN W/FS PAS (15)-5
211 030-000820-SB 6 M8X20 BLT W/S BLK (2)-6
212 068-852216-0B 6 M8 WSHR 22OD FLT BLK (2)-6
213 060-F00300 4 M3 WSHR FORM A FLT PAS (18)-4
214 050-U00300 4 M3 NUT NYLOK PAS (18)-4
215 029-B00870-0B 4 M8X70 BLT BH BLK
216 060-S00800-0B 4 M8 WSHR SPR BLK
301 SPY-61052UK 1 WIRE HARN TUBE V0L CTRL
302 SPY-61053UK 1 WIRE HARN VTS SPY (NAO)
303 VCT-64001UK 1 WH I/O CONTROL
304 SPY-61044UK 1 WIRE HARN TUBE IC BD & DEMAG
306 600-6457-10UK 1 WIRE HARN START UK
307 600-6457-36UK 1 WIRE HARN START EX UK
308 SPY-60010UK 1 WIRE HARN HIGH FRQNCY JUMPER
309 600-7141-250 1 CABLE JVS TYPE A-B 250CM
310 RND-600002 2 WH GUN ADAPTOR
311 VCT-64003 1 WH EARTH FOOT PEDALS

104
9.17. VCT-5150UK ASSY FENCE L U/R
ITEM PART NO. QTY DESCRIPTION COMPONENT REF.
1 VCT-5151UK 1 DESIGN PLATE LHS
2 VCT-5151-AUK 1 STICKER DESIGN PLATE LHS
3 VCT-5152UK 1 FENCE FRAME L
201 008-T00416-0B 6 M4X8 TMP PRF TH BLK (1)-6
202 030-000820-SB 4 M8X20 BLT W/S BLK (2)-4
203 068-852216-0B 4 M8 WSHR 22OD FLT BLK (2)-4

105
9.18. VCT-5170UK ASSY FENCE R U/R
ITEM PART NO. QTY DESCRIPTION COMPONENT REF.
1 VCT-5171UK 1 DESIGN PLATE RHS
2 VCT-5171-AUK 1 STICKER DESIGN PLATE RHS
3 VCT-5172UK 1 FENCE FRAME R
201 008-T00416-0B 6 M4X8 TMP PRF TH BLK (1)-6
202 030-000820-SB 4 M8X20 BLT W/S BLK (2)-4
203 068-852216-0B 4 M8 WSHR 22OD FLT BLK (2)-4

106
9.19. VCT-5200UK ASSY FOOT BASE FRAME L
ITEM PART NO. QTY DESCRIPTION COMPONENT REF.
1 VCT-5201UK 1 FOOT BASE FRAME L
2 VCT-0003UK 1 BASE HOLE LID NOT SHOWN
101 601-5699X 1 LEG ADJUSTER BOLT M16 X 75 (1)-1
201 050-H01600-0B 1 M16 HEX NUT BLK (1)-1
202 068-651616-0B 4 M6 WSHR 16OD FLT BLK (1)-4
203 030-000616-SB 4 M6X16 BLT W/S BLK (1)-4
204 008-T00416-0B 6 M4X8 TMP PRF TH BLK (2)-6
205 030-000820-SB 2 M8X20 BLT W/S BLK (1)-2
206 050-F00800 2 M8 NUT FLG SER PAS (1)-2
207 068-852216-0B 4 M8 WSHR 22OD FLT BLK (1)-4

107
9.20. VCT-5300UK ASSY FOOT BASE FRAME R
ITEM PART NO. QTY DESCRIPTION COMPONENT REF
1 VCT-5311UK 1 FOOT BASE FRAME R
2 VCT-0003UK 1 BASE HOLE LID
101 601-5699X 1 LEG ADJUSTER BOLT M16 X 75 (1)-1
201 050-H01600-0B 1 M16 HEX NUT BLK (1)-1
202 068-651616-0B 4 M6 WSHR 16OD FLT BLK (1)-4
203 030-000616-SB 4 M6X16 BLT W/S BLK (1)-4
204 008-T00416-0B 6 M4X8 TMP PRF TH BLK (2)-6
205 030-000820-SB 2 M8X20 BLT W/S BLK (1)-2
206 050-F00800 2 M8 NUT FLG SER PAS (1)-2
207 068-852216-0B 4 M8 WSHR 22OD FLT BLK (1)-4

108
9.21. HDT-6001UK ASSY WIRE L HDT U/R
Item Component Part Qty Description Component Reference
101 601-0460 12 CABLE TIE 100mm
102 280-N01610-0B 0.40 SLIT HARN WRAP 16mm DIA 1M BLK
301 600-7009-2500 1 ASSY RGB CA D-SUB 15P 2500MM
302 NOB-60045 1 WIRE HARN SPEAKER L
303 NOB-60046 1 WIRE HARN SPEAKER R
304 SPY-61043UK 1 WIRE HARN IC BD & DEMAG EXT
305 600-7158-0100 1 CA AUDIO RCA TO RCA 2CH 100CM
306 HDT-61051UK 1 WIRE HARN DC SPLY & VOL CNTRL

109
9.22. HDT-INST-U ASSY INST KIT U/R
Item Component Part Qty. Description Component Reference
1 VCT-5000UK 1 ASSY FLOOR VCT U/R
2 VCT-INST-SUB1-U 1 ASSY SUB1 INST
3 VCT-INST-SUB2-U 1 ASSY SUB2 INST
16 PK0323 1 INST KIT PACKING WEDGE
9.23. VCT-INST-SUB1-U ASSY SUB1 INST
ITEM PART NO. QTY DESCRIPTION COMPONENT REF.
2 VCT-5100UK 1 ASSY CCT VCT U/R
3 VCT-5150UK 1 ASSY FENCE L U/R
4 VCT-5170UK 1 ASSY FENCE R U/R
6 PK0337 1 INST KIT BOX VCT U/R
9.24. VCT-INST-SUB2-U ASSY SUB2 INST
ITEM PART NO. QTY DESCRIPTION COMPONENT REF.
1 VCT-1200UK 2 ASSEMBLY FOOT PEDAL DX
2 VCT-5200UK 1 ASSEMBLY FOOT BASE FRAME L
3 VCT-5300UK 1 ASSEMBLY FOOT BASE FRAME R
5 SAECE-114 1 DECLARATION OF CONFORMITY VCTU
7 CTA-0001 1 JOINT BRKT L
8 CTA-0002 1 JOINT BRKT R
9 VCT-3013UK 1 STICKER CONTROL PANEL CCT Multilingual
15 PK0336 1 BOX PEDAL VCT UPRIGHT
101 540-0006-01 1 WRENCH M4 TMP PRF
102 540-0015-01 1 WRENCH M6 TMP PRF
103 514-5078-5000 1 FUSE 5X20 CERAMIC SB 5000mA
104 OS1019 2 SELF SEAL BAG 9X12.3/4
105 440-CS0186UK 1 STICKER C EPILEPSY MULTI
201 030-000820-SB 2 M8X20 BLT W/S BLK (7)-1,(8)-1
202 068-852216-0B 2 M8 WSHR 22OD FLT BLK (7)-1,(8)-1
203 008-T00412-0B 2 M4X12 TMP PRF TH BLK (BILLBOARD)-2
204 SDW-0001UK 4 BLIND CAP UK (2)-2, (3)-2
301 600-7141-250 1 CABLE JVS TYPE A-B 250CM
402 420-6759-02UK 1 SERVICE MANUAL VCT U/R
403 420-5827 1 SERVICE MANUAL SANWA 31K
404 420-6620UK 1 SERVICE MANUAL GD ROM SYS
405 509-5080 2 SW MICRO TYPE (SS-5GL2)

110
10. APPENDIX A - ELECTRICAL SCHEMATIC
10.1. WIRE COLOURS
THE WIRE COLOUR CODE IS AS FOLLOWS:
A PINK
B SKY BLUE
C BROWN
D PURPLE
E LIGHT GREEN
Wires other than those of any of the colours listed above will be displayed by 2 alphanumeric characters:
1 RED
2 BLUE
3 YELLOW
4 GREEN
5 WHITE
7 ORANGE
8 BLACK
9 GREY
If the right hand side numeral of the code is 0, then the wire will be of a single colour shown by the left hand
side numeral (see the list above).
Note 1: If the right hand side alphanumeric is not 0, that particular wire has a spiral colour code. The left
hand side character shows the base colour and the right hand side one, the spiral colour.
[Example] 51------------- WHITE/RED = WHITE wire with RED stripes
Note 2: The character following the wire colour code indicates the size of the wire.
K: AWG18, UL1015
L: AWG20, UL1007
None AWG22, UL1007
10.2. ELECTRICAL SCHEMATIC
The following pages contain the electrical schematic for this machine.

LOCATE A3 SCHEMATIC DRAWING 1 HERE

LOCATE A3 SCHEMATIC DRAWING 2 HERE

SEGA AMUSEMENTS EUROPE LTD./ SEGA SERVICE CENTRE
Suite 3a
Oaks House
12 - 22 West Street
Epsom
Surrey
United Kingdom
KT18 7RG
Telephone: +44 (0) 1372 731820
Fax: +44 (0) 1372 731849
ã SEGA 2002