Avitec FD-3100A Distributed Antenna System User Manual FiberDAS Manual
Avitec, AB Distributed Antenna System FiberDAS Manual
Avitec >
users manual
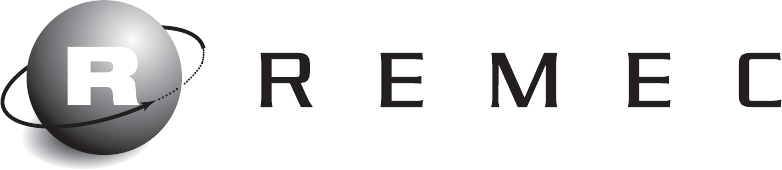
Operating Manual
FiberDAS Distributed Antenna System
FiberDAS Manual, Rev. E14
ii
Table of Contents
1 LINK DESCRIPTION .................................................................................................................................. 1-1
1.1 CAUTIONS AND WARNINGS ...................................................................................................................... 1-1
1.2 GENERAL DESCRIPTION............................................................................................................................ 1-2
1.2.1 Basic Principles ............................................................................................................................... 1-2
1.2.2 Functional Description.................................................................................................................... 1-3
1.3 SPECIFICATIONS ....................................................................................................................................... 1-7
2 INSTALLATION........................................................................................................................................... 2-1
2.1 GENERAL PROCEDURE.............................................................................................................................. 2-1
2.2 INSTALL FIBEROPTIC CABLES................................................................................................................... 2-5
2.2.1 Minimizing Optical Reflections ....................................................................................................... 2-5
2.2.2 Cleaning Optical Connectors .......................................................................................................... 2-6
2.3 SYSTEM ALARMS...................................................................................................................................... 2-7
2.4 HUB SHELF AND REMOTE POWER SUPPLY BATTERY CHARGE MONITORING AND REPLACEMENT ........... 2-7
2.4.1 Replacing the Hub Shelf Battery...................................................................................................... 2-8
2.4.2 Replacing the Remote Power Supply Battery .................................................................................. 2-8
2.5 INSTALLATION CHECKLIST ....................................................................................................................... 2-9
2.5.1 Inspect Received Items..................................................................................................................... 2-9
2.5.2 Recommended Tools ........................................................................................................................ 2-9
2.6 INSTALLING THE HUB SHELF .................................................................................................................... 2-9
2.6.1 Rack Installation.............................................................................................................................. 2-9
2.6.2 Connect Fiberoptic Cables ............................................................................................................ 2-10
2.6.3 Indentifying Remote Locations ...................................................................................................... 2-10
2.6.4 Serial Bus, Telephone and Local Alarm Connections ................................................................... 2-10
2.6.5 Mains Power and Fuses................................................................................................................. 2-10
2.6.6 RF Connections ............................................................................................................................. 2-11
2.7 INSTALLING THE REMOTE TRANSCEIVERS.............................................................................................. 2-11
3 MONITORING AND TROUBLESHOOTING.......................................................................................... 3-1
3.1 FIELD SUPPORT NUMBERS........................................................................................................................ 3-1
3.2 TROUBLESHOOTING TIPS .......................................................................................................................... 3-2
3.3 REGULATORY ........................................................................................................................................... 3-4
iii
iv

1 Link Description
1.1 Cautions and Warnings
Throughout this manual, these terms appear which highlight the care that should be exercised to ensure
personal safety and proper operation of the equipment.
WARNING: Warning statements identify conditions or practices that could result in injury
or loss of life.
CAUTION: Caution statements identify conditions or practices that could
result in damage to this product or other property.
CAUTION: any modifications to this device not expressly authorized by
Remec, Inc. could void the user’s authority to operate this device.
CLASS 1 LASER PRODUCT
FDA/CDRH Class 1 laser product. All versions of the FiberDAS are Class 1 lasers products per
CDRH, 21 CFR 1040 Laser Safety requirements. All versions are Class 1 laser products per EN
60825-1:1994.
NOTICE
UNTERMINATED OPTICAL RECEPTACLES MAY EMIT LASER RADIATION. DO NOT
VIEW WITH OPTICAL INSTRUMENTS.
1-1
1.2 General Description
The FiberDAS Fiberoptic Distributed Antenna System provides extended coverage of wireless networks
throughout buildings and campus environments. The Hub Shelf is a 3U (5.25 inch) high, 19-inch wide
rack-mounted chassis. The Hub Shelf holds up to 8 Hub Transceiver Plug-Ins. The Hub Shelf is located in
a communications equipment room in the building and is connected to the wireless base station or repeater
via hardline connection. The Hub Shelf may also be connected to the radios of a wireless PBX. Each Hub
Shelf is configured with up to eight Hub Transceiver plug-in cards. Each card is connected to up to two
Remote Transceivers via two pairs of singlemode fiberoptic lines. The Remote Transceiver Units are
distributed throughout the building as necessary to provide coverage. The Remote Transceivers are
mounted, generally, above the suspended ceiling but may be mounted near the ceiling inside the room if
need be. The aesthetic and low-profile design of the Remote Transceiver makes it relatively unobtrusive.
The plastic cover may even be removed and/or painted to match the décor. Each Remote Transceiver is
connected to Hub Shelf via two singlemode optical fibers. Each Remote Transceiver has one RF port
which is connected to a user-supplied indoor coverage antenna. This port may also be routed through an N-
way RF splitter to provide coverage from a number N antennas for the one Remote Transceiver. The
choice depends on the results of the engineering design for that particular structure as to the most cost-
effective way to provide uniform coverage. The Remote Transceiver is DC-powered, usually by the Remec
Central DC Power Supply. This is distributed from the power supply at the Hub location using the
conductor pairs in a composite fiber/conductor cable or by a separate two-wire cable pulled along with the
fiberoptic cable. The DC connector utilized at the Remote Transceiver can accommodate up to 14 AWG
wire.
The FiberDAS design is very versatile but certain options are available that target specific signal types and
applications. In addition to the single band versions from iDEN through UMTS, there are dual band
versions such as 800 MHz/1900 MHz and GSM900/GSM1800.
FiberDAS installation and setup is very simple. First, standard telcom grade singlemode fiberoptic cable
that is most suitable for the site is installed. The cable installer can terminate the cable on site easily with
the SC/UPC optical connectors. The Plug-Ins and Remote Transceivers of a given type are completely
interchangeable. The SC/UPC plugs directly into the Remote Transceiver at one end. The other end plugs
into an optical patch panel or directly into the Hub Shelf via an SC/UPC-to-SC/UPC adapter. If the patch
panel is used, SC/UPC-to-SC/UPC jumpers must be used to connect the Hub Shelf to the patch panel.
Built-in optical loss compensation automatically equalizes the gain in both the transmit and receive paths
so the transmit RF power is known for a given input RF power and the receive path sensitivity is
optimized. The only adjustment available is a manual setting for the static transmit power at the Remote
Transceiver which may be used to optimize coverage, if necessary. This is a one time adjustment during set
up.
1.2.1 Basic Principles
The FiberDAS operation is based on an analog RF fiberoptic link. The principles are illustrated in Figure 1.
Input RF signals are converted to light by direct intensity modulation of a semiconductor laser. This
modulated light is transmitted over optical fiber and detected by a semiconductor PIN photodiode. The
photodiode converts optical power to electrical current. This current is AC coupled and passed through a
load to recover the RF signal.
The basic RF loss in this link is determined by the inefficiencies of the conversions of RF to optical and
back. The fiber also contributes an RF loss equal to twice the optical loss. This is because the photodiode
converts optical power to electrical current and RF power is proportional to the square of the current. So,
for 1 km of fiber with a loss of 0.4 dB/km (this is typical at 1310 nm wavelength) the optical loss is 0.4 dB
1-2
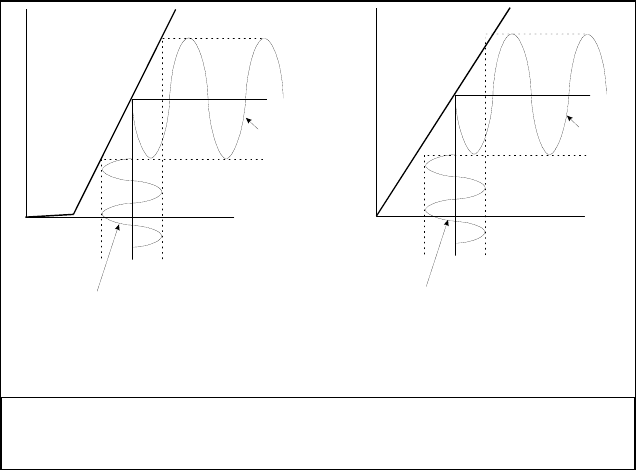
and the contribution to the
RF loss is 0.8 dB. In a real
installation, two optical
connectors will add
approximately 0.5 dB of
optical loss.
The laser and, to a much
lesser degree, the
photodiode, add noise and
distortion to the RF signal.
This RF performance is
characterized just as any
RF link in terms of dB loss,
noise figure, third order
intercept, etc.
The fiber path itself can
contribute noise and
distortion. In the
FiberDAS, the laser used is
a Fabry-Perot (FP) laser
instead of a Distributed Feedback (DFB). The DFB has a single spectral component. The FP laser has
multiple spectral components which can contribute noise and distortion for longer fiber runs. For the
distances used in the FiberDAS, this effect is not significant. Also, optical backscattering back into the
laser from less than perfect connections can cause additional noise and distortion. The FP lasers used in the
FiberDAS are much less sensitive to this than are DFB lasers. DFB lasers are also considerably more
expensive. However, if optical reflections are severe enough from a bad connection, the resulting optical
reflection may cause performance degradation even with FP lasers. To minimize this, SC/UPC optical
connectors with a return loss > 50 dB are used. Following standard practices in cleaning of the removable
optical connectors (see procedure outlined below) will keep the connections in spec and will avoid the
problems of performance degradation.
I
bias
I (mA) I (mA)
P (mW)
out
I
th
RF
Input
RF
Output (ac coupled
to remove dc component)
Optical
Output
Opti ca
l
Input
P (mW)
in
LASER DIODE
CHARACTERISTIC
PHOTODIODE
CHARACTERISTIC
Figure 1-1. Laser and photodiode characteristics.
1.2.2 Functional Description
The FiberDAS Fiberoptic Antenna System connects to the mobile coverage RF ports of a repeater or base
station as an extended coverage antenna. The Hub Shelf mounts in a standard 19 inch rack close to the
repeater or base station transmit and receive RF ports. Generally, the appropriate configuration of the Entry
Shelf is used for convenience in combining multiple BTS channels, duplexing the signals to separate
Transmit and Receive, combining, setting the proper RF levels and routing the combined Tx and Rx
signals to and from one or more Hub Shelves, as necessary. The Hub Shelf RF connections are made via
the RF connectors on the rear panel. Inside the chassis, the transmit signal is split and routed to the Hub
Transceiver Plug-Ins. Each plug-in is a dual fiberoptic transceiver. The Hub Shelf holds up to eight plug-
ins. Each plug-in interfaces with up to two Remote Transceivers by way of fiberoptic connections on the
Hub Shelf rear panel.
Transceiver optical output is the green connector. The Remote Transceiver units are generally mounted
above the false ceiling on a bulkhead or post. Each Remote Transceiver is connected to an indoor coverage
antenna by way of a customer-supplied flexible RF cable. Some indoor antennas are available with flexible
RF cable pigtails and an SMA connector termination. These units are distributed throughout the building or
campus as necessary to get full coverage. After installation, the transmit power from each Antenna Unit
may be adjusted manually by way of a rotary dip switch on the unit. This switch is indented in 2 dB steps.
This is a one time adjustment. For dual band units, there is a separate adjustment for each band.
1-3
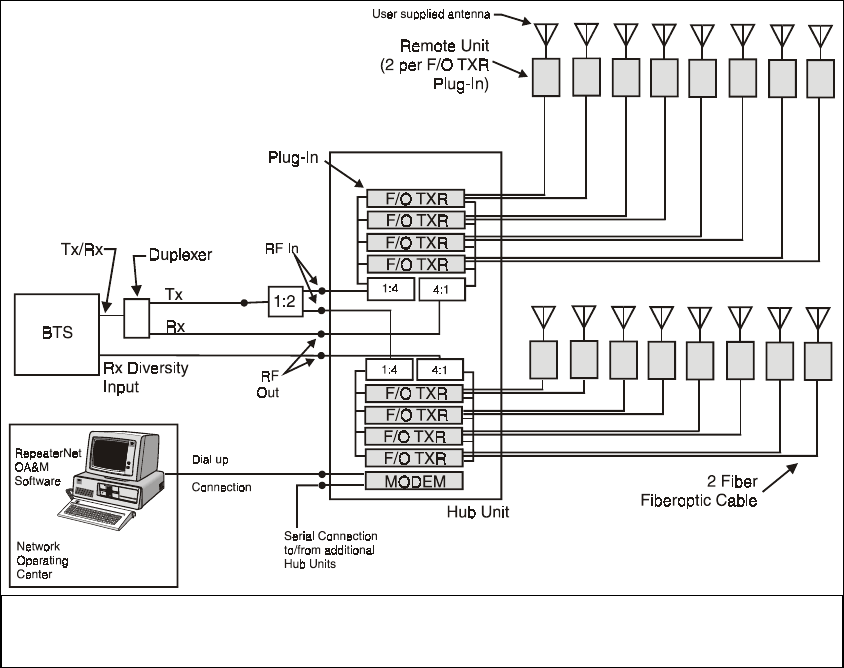
Figure 1-2. System Block Diagram.
The block diagram of the FiberDAS Fiberoptic Antenna System is shown in Figures 1-2 and 1-3. The input
transmit RF signal is split eight ways in the Hub Shelf. Each of these signals is routed to a Hub Transceiver
Plug-In where it is split in two and each path modulates the optical output of a solid state laser diode. This
optical output is routed through a singlemode optical fiber to one Remote Transceiver. The photodiode in
the Remote Transceiver detects this optical signal and outputs a proportional electrical current. This current
is ac coupled and passed through a load to recover the RF signal. The RF signal is amplified, filtered and
output to the antenna.
Depending on design requirements, a 1:2 or 1:4 may be used at the antenna port to route the signal to 1, 2
or 4 in-building coverage antennas. Several versions of the Remote Transceiver are available that are
optimized for specific formats such as AMPS, GSM900, GSM1800, etc. Dual band versions are available;
one providing simultaneous coverage for GSM900 and GSM1800 and one for PCS1900 and 800 MHz. In
these versions, a single RF port feeds a dual band antenna.
The output RF signal path includes a variable attenuator that permits the user to adjust the output level in 2
dB steps for optimum coverage. The RF subcarrier from the plug-in is detected at the photodiode output.
This level is used by the transmit AGC to set the downlink gain. The subcarrier is also amplified and
inserted into the uplink path. This signal is detected at the Hub Shelf Plug-In for the uplink AGC and Node
Function Alarm which acts the primary critical failure alarm. A loss of RF signal due to plug-in or Remote
Unit laser failure, photodiode failure or a break in the fiber path will trigger this alarm. Also, a failure of
any amplifier in the downlink path in the Remote Transceiver, shuts off the subcarrier in the return path
which, in turn, triggers the Node Function Alarm at the Hub.
The receive or uplink RF signal from the antenna is filtered and amplified then routed to the Remote
Transceiver laser. A fast ALC is included in this path which prevents RF overdrive damage to the laser
while recovering fast enough to minimize blocking for TDMA and GSM signals. The laser output in the
Remote Transceiver is then modulated by the receive RF signal and is transmitted through another
1-4
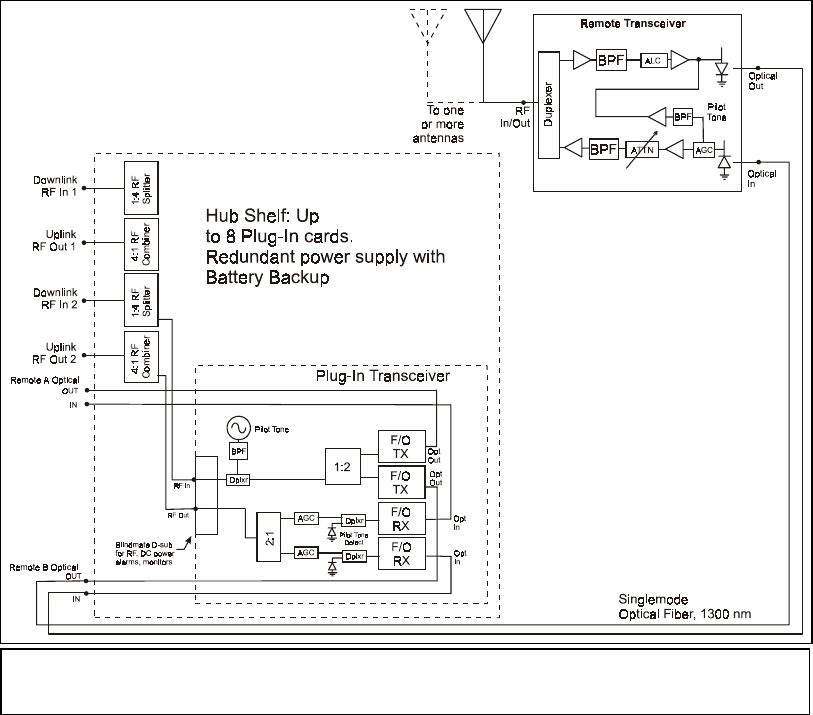
singlemode optical fiber back to the Hub Shelf Plug-In. Each of the two photodiodes in the Hub
Transceiver Plug-In recovers the RF signals from each of two Remote Transceivers. The pilot tone on each
signal is split off and detected. This is used for the Node Function alarm. This LED is normally green and
turns red if the pilot tone is not detected. This alarm also appears at the Hub Shelf rear panel DB37
connector as a TTL level critical alarm. It would also be reported to the NOC or service technician by the
modem card depending on how the user configured the system alarms.
The receive RF signal from each photodiode is combined in the Hub Transceiver Plug-In. These combined
outputs are combined again in the and output to the rear panel RF uplink connectors. The Hub Shelf is
divided into two halves. The RF signals from each half are combined and routed to separate rear panel N
connectors. The combined uplink signals from one half can be routed to the BTS main receive port while
the other RF output is routed to the BTS receive diversity port. This method provides an overall 3 dB
system sensitivity improvement compared to routing all of the uplink signals into one receive port (see
Figure 1-2). Alternatively, both outputs may be combined and routed to a single BTS receive port.
Figure 1-3. FiberDAS RF path block diagram.
1-5
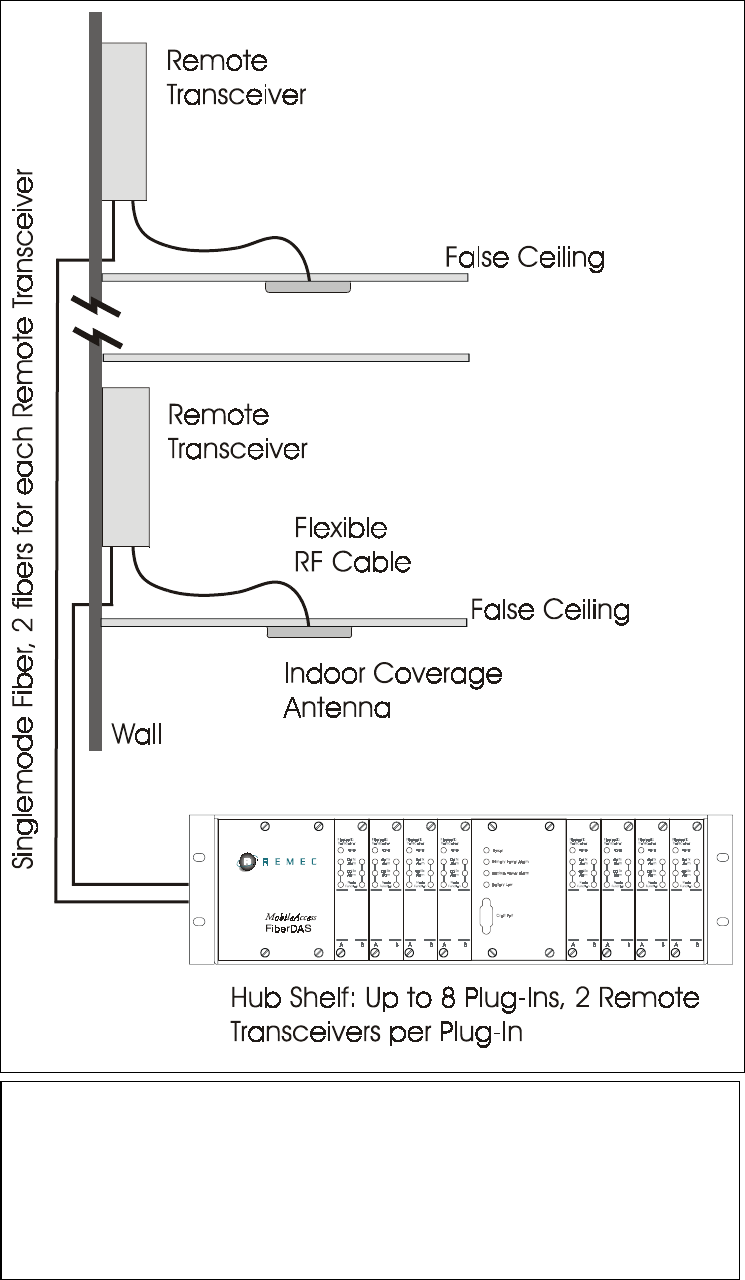
Figure 1-4. The Remote Transceivers are normally mounted above the false ceiling
but may be mounted in the room. Each Remote Transceiver is connected to the
Hub Shelf via 2 singlemode fibers. The Remote Transceiver is connected to a user-
supplied antenna via flexible RF cable. The Remote Transceivers may be powered
using the optional universal Remote Power Supply with battery backup, or using a
central power supply that distributes DC power along with the fiber over a
composite fiber/conductor cable.
1-6
1.3 Specifications
Description
This specification defines the uplink and downlink performance of the FiberDAS Fiberoptic Antenna
System. The terminal equipment consists of the Remote Transceiver and the Hub Transceiver Plug-In. The
latter is installed in the Hub Shelf. This system meets the requirements for GSM900, DCS1800 and
GSM1900 Class M3 micro-BTS as well as IS-136 TDMA, IS-95 CDMA, CDMA2000 and UMTS for
wireless PBX, in-building and campus coverage applications.
There are five frequency options for the FiberDAS: 850 MHz (AMPS), GSM900, DCS1800, PCS1900 and
UMTS. There are two downlink output power options: the P1 power option meets GSM 900 micro-BTS
M3 requirements and is available for the 850MHz and 900MHz versions only when they are part of a dual
band system. The P2 power option meets micro-BTS M3 requirements for 1800MHz and 1900MHz. For
850MHz and 900MHz, the High Power meets GSM micro-BTS power class M1 requirements and IS-136
in-building requirements for +20 dBm composite power. All of these system standards specifications are
met for optical loss of up to 4 dB.
RF Parameters (up to 4 dB optical loss)
Uplink
Frequency Range 850 MHz 824 - 849 MHz
GSM900 890 - 915 MHz
DCS1800 1710 - 1785 MHz
PCS1900 1850 - 1910 MHz
UMTS 1920 – 1980 MHz
Amplitude Flatness
824 – 849, 890 - 915 MHz; (Any 15 MHz band) ± 1.0 dB
DCS, PCS, UMTS (Any 15 MHz band) ± 1.5 dB
Noise Figure ≤ 13 dB
Low Noise Option (DCS, PCS and UMTS only) ≤ 7 dB
Input Third Order Intercept (IIP3), 2 carriers, -43 dBm/carrier ≥ -15 dBm
Low Noise Option (GSM1800/PCS1900) ≥ -25 dBm
High Dynamic Range Option ≥ 0 dBm
High Dynamic Range Option w/Low Noise ≥ -10 dBm
Link Gain (with external 20 dB attenuator; 30 dB attenuator with Low Noise Option, over full
band and 4 dB optical loss range)
850 MHz, GSM900 4 ± 2.0 dB
DCS, PCS, UMTS 4 ± 2.5 dB
Uplink Input ALC
Input RF Threshold - 25 dBm
Low Noise Option -35 dBm
High Dynamic Range Option -10 dBm
High Dynamic Range Option w/Low Noise -20 dBm
Range 30 dB
Response Time < 5 µsec
Gain Stability ± 1 dB
Input/Output Impedance 50 Ω
Input/Output VSWR ≤ 2 : 1
Downlink
Frequency Range 850 MHz 869 - 894 MHz
GSM900 935 - 960 MHz
GSM1800 1805 - 1880 MHz
1-7
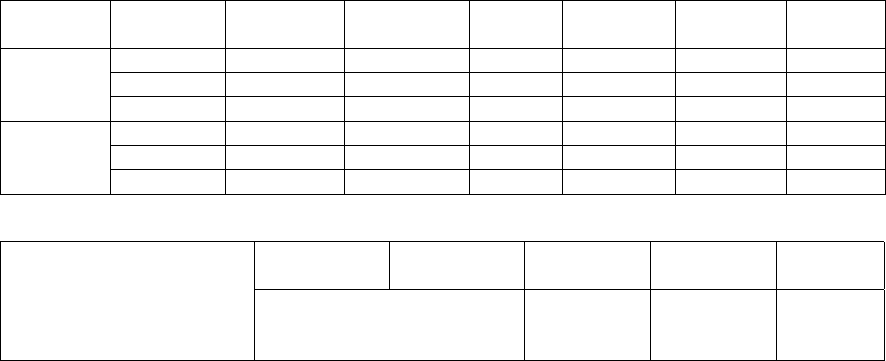
PCS1900 1930 - 1990 MHz
UMTS 2110 – 2170 MHz
Amplitude Flatness
850MHz, GSM900; (any 15 MHz band) ± 1.5 dB
850MHz, DCS, UMTS; (any 15 MHz band) ± 1.5 dB
Output Noise ≤ -95 dBm/Hz
Output Third Order Intercept
Option P1 +30 dBm
Option P2 +40 dBm
Output 1dB Compression (typical)
Option P1 +17 dBm
Option P2 +25 dBm
(Note: all single band systems are Power Option P2. Power Option P1 is only for the low band
in dual band systems. For example, the GSM900/DCS1800 dual band has Power Option P1 for
GSM900 and Power Option P2 for DCS1800. The same applies for the dual band 800MHz/PCS1900.)
Output Power/Carrier (dBm)
Power
Option
Number of
Carriers
GSM800 &
GSM900
DCS1800 &
GSM1900
EDGE CDMA TDMA UMTS
1 17.0 - - 11.0 17.0 -
2 8.0 - - 8.0 8.0 -
P1
4 5.0 - - 5.0 5.0 -
1 25.0 25.0 25.0 20.0 25.0 20.0
2 14.0 17.0 14.0 16.5 17.0 16.5
P2*
4 11.0 14.0 11.0 13.5 14.0 13.5
* For Dual Band Systems, the output power shown for Option P2 is reduced by 1 dB.
GSM800 &
GSM900
DCS1800 &
GSM1900
CDMA TDMA UMTS
Intermodulation &
Spurious Meets GSM 05.05 and 11.26 Meets IS-
95/97 and J-
STD-005
< -45 dBc
IMs for 2
Carriers
Meets
3GPP
TS25.104
Output Power Range ≥ 12 dB user adjustable (in 2 dB
increments at Remote Transceiver)
Input Power Threshold for Input Power Protect 11.5 to 15.5 dBm
Attenuation Step for Input Power Protect 10 dB
Gain at Maximum Output Power (output attenuator set at min, over full band and optical loss
range)
Output Power Option P1 4 ± 2.5 dB
Output Power Option P2 14 ± 2.5 dB
Gain Stability ± 1 dB
Input/Output Impedance 50 Ω
Input/Output VSWR ≤ 2 : 1
General
Loop back Carrier Frequency 100 MHz ± 10%
Optical Parameters
1-8
Wavelength 1310 ± 20 nm
Output Power
Remote Transceiver 1.2 mW
Hub Transceiver Plug-In 1.2 mW
Optical Connector
Hub Shelf SC/UPC, > 50 dB return loss
Remote Transceiver SC/UPC, > 50 dB return loss
Fiber Singlemode
Absolute Maximum Ratings
RF Input Power
Uplink +5 dBm
Low Noise Option -5 dBm
Downlink +26 dBm total
Photodiode Input Optical Power +2.3 mW
Electrical
Remote Transceiver +12 V to +28 V, 12 W (single
band), 20 W (dual band)
Remote Power Supply 100 to 240 VAC, 50/60 Hz
Hub Transceiver Plug-In 6 W, 0.5 A max
Hub Shelf 100 - 240 VAC, 50/60 Hz, 1.0 A
max
1-9
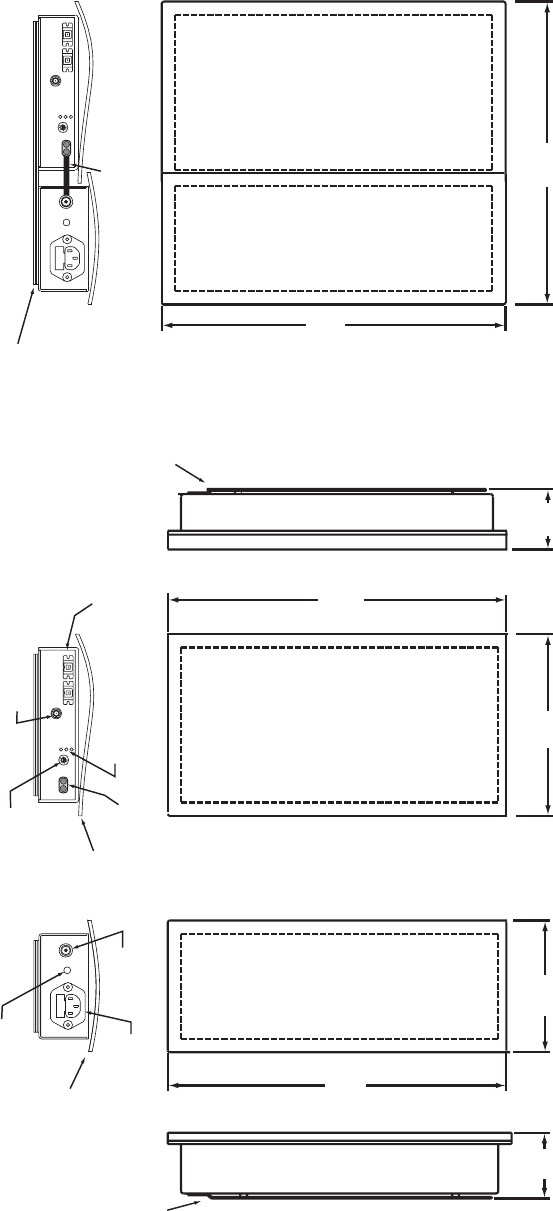
Mechanical
Remote Transceiver
Remote Transceiver
Weight 4.5 lbs. (2.04 kg) Net
Dimensions See outline drawing below
Remote AC Power Supply
Weight 4.8 lbs. (2.18 kg) Net
Dimensions See outline drawing below
DC Connector
Static RF Output
Power Adjust
(2 dB Steps)
Status LEDs
SMA RF Connector
to Antenna
Fiberoptic Connectors
(SC/APC)
Universal AC
Mains Power
Input
Battery Backup
Indicator/Shutoff
DC Power
Cable
2.46" 4.93" 6.80" 2.26" 11.33"
12.93"
12.93"
12.93"
Front Cover
Front Cover Shielded DC power cable
(6.25cm) (12.5cm)
(32.8cm)
(32.8cm)
(32.8cm)
(17.3cm) (5.7cm) (28.8cm)
Mounting brackets for each unit
snap together using connecting
bracket
Mounting
Bracket Mounting
Bracket
1-10
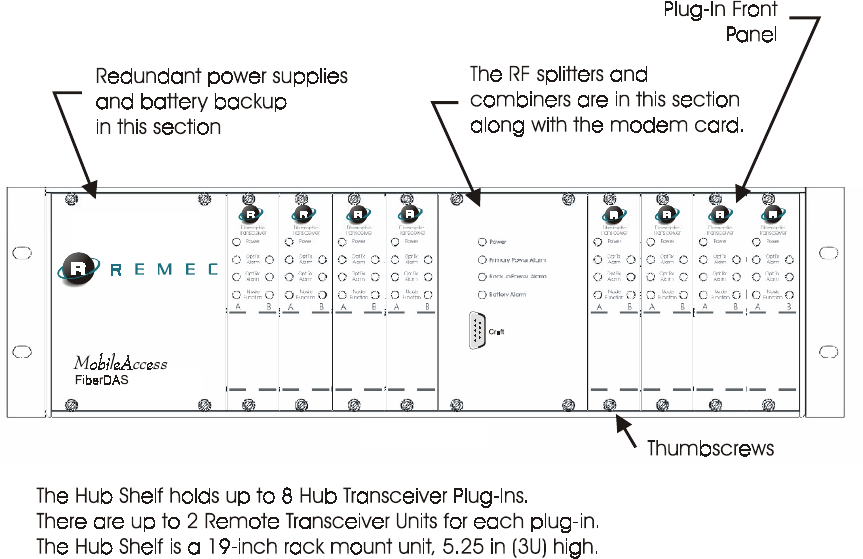
Hub Transceiver
Dimensions Plug-in card with 5.06” (12.85 mm)H x 1.2”
(3.05 cm) W front panel for Hub Shelf
Weight 0.9 lbs. (0.41 kg) Net
Hub Shelf
Dimensions 19”(48.26 cm), 3U (5.25”, 13.34 cm) H,
15.75” (40.01 cm)D rack mount
Weight 20 lbs. (9.1 kg) Net
1-11
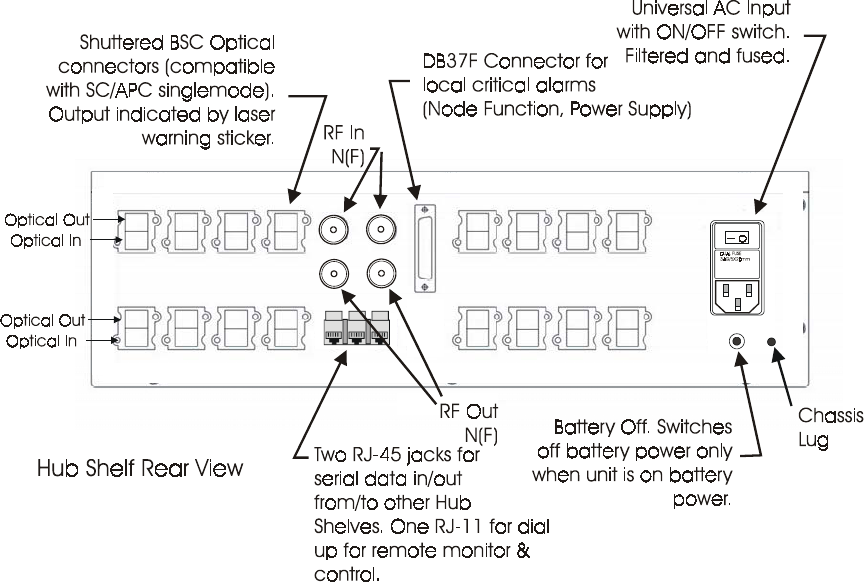
1-12

Alarms and Monitors
Remote Transceiver
Description
Power On (Green LED)
Laser Optical Power Low Alarm (active if laser output < 90% of factory set point:
Red Front panel LED)
Received Optical Power Low Warning (active if optical loss > 4.2 dB: Yellow
front panel LED)
Transmit Amplifier Failure Alarm (active if any amplifier in transmit path fails as
detected by bias current: Red LED. Also causes shutoff of subcarrier in uplink
path which triggers Node Function Alarm at plug-in.)
Hub Transceiver Plug-In Node Function (loopback carrier detect:
Front panel LED; normally Green, Red if
RF subcarrier level drops more than 10 dB)
Received Optical Power Low Warning
(active if optical loss > 4.2 dB: Yellow front
panel LED, normally OFF)
Laser Optical Power Low Alarm (active if
laser optical output power drops 10%): Red
Front panel LED, normally OFF)
Hub Shelf
LEDs Power On (Green, Normally ON)
Main Power Alarm (Red Front panel LED;
normally OFF)
Backup Power Alarm (Red Front panel
LED; normally OFF)
Battery Alarm (Yellow front panel LED,
active if battery backup charge is low;
normally OFF)
Alarms, Rear Panel DB-37 (See Table) Critical Alarms: these include all Node
Function Alarms and the Main and Backup
Power Supply Alarms.
Summary Contact Closure Alarm: active if
any alarm is active in chassis or plug-ins.
Dial-up Any critical alarm prompts the system to dial up
Remote Power Supply NOC. This is configured at
installation with a laptop computer via the front panel
Craft interface. Dial up connection is made with RJ-
11 interface on rear panel. The system may also be
polled through dial-up connection to get status of all
alarms and warnings.
Craft Interface (Front Panel) Used to configure system including naming
system and Remote Transceiver locations, set up
critical and minor alarms, and setting telephone
numbers of system, NOC and/or service pager. Also
1-13
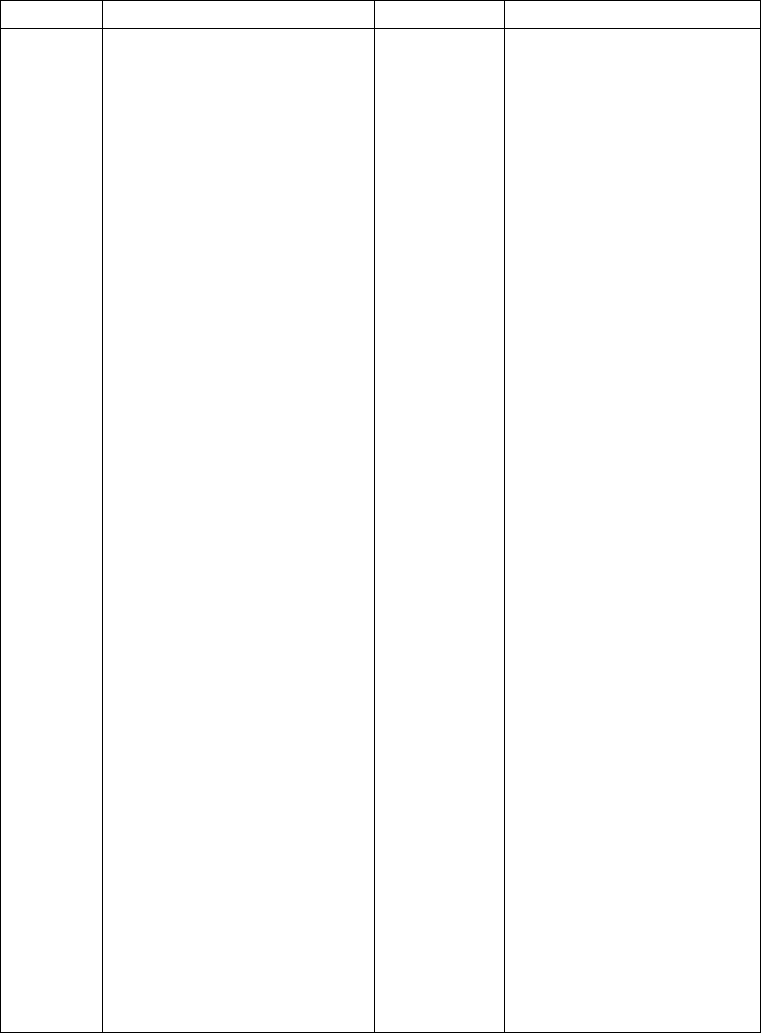
configures Hub Shelf as master or slave. Master
provides dial up connection for itself and daisy-
chained slave units. Connection to slave units via RJ-
45 jacks on rear.
DB-37 Pin Signal name Type Sense
1 1-A Node Function Alarm TTL Active Low
2 2-A Node Function Alarm TTL Active Low
3 3-A Node Function Alarm TTL Active Low
4 4-A Node Function Alarm TTL Active Low
5 5-A Node Function Alarm TTL Active Low
6 6-A Node Function Alarm TTL Active Low
7 7-A Node Function Alarm TTL Active Low
8 8-A Node Function Alarm TTL Active Low
9 Master P.S. Alarm TTL Active Low
10 Battery Alarm TTL Active Low
11 n.c.
12 n.c.
13 n.c.
14 n.c.
15 RTN
16 RTN
17 RTN
18 n.c.
19 n.c.
20 1-B Node Function Alarm TTL Active Low
21 2-B Node Function Alarm TTL Active Low
22 3-B Node Function Alarm TTL Active Low
23 4-B Node Function Alarm TTL Active Low
24 5-B Node Function Alarm TTL Active Low
25 6-B Node Function Alarm TTL Active Low
26 7-B Node Function Alarm TTL Active Low
27 8-B Node Function Alarm TTL Active Low
28 Back-up Power Supply Alarm TTL Active Low
29 n.c.
30 n.c.
31 n.c.
32 n.c.
33 n.c.
34 Summary Alarm N.C. Relay contact Connect to Common if O.K.
35 Summary Alarm Common Relay contact
36 Summary Alarm N.O. Relay contact Open if O.K.
37 n.c.
1-14
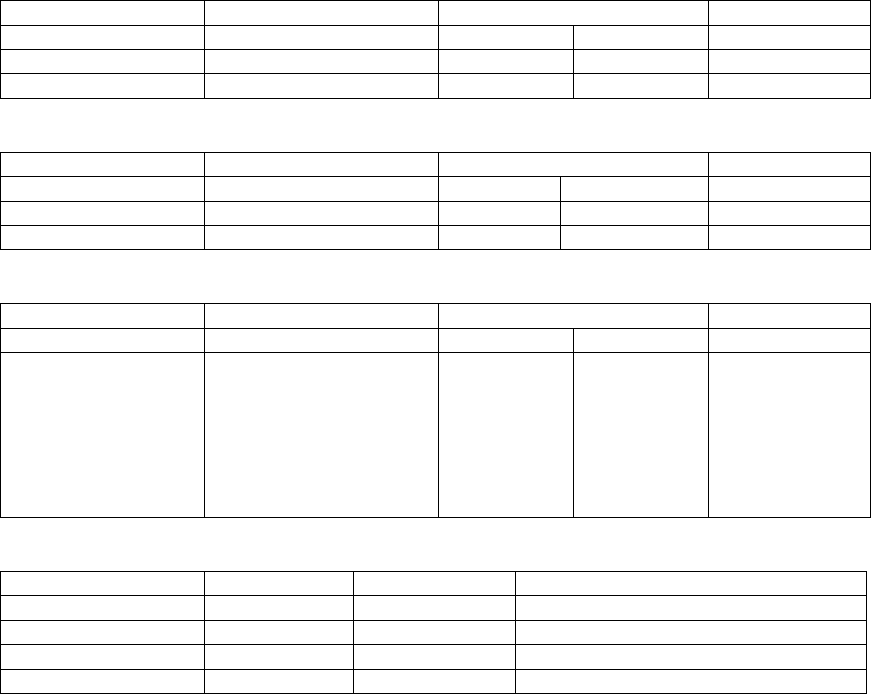
Environmental
Operating (ETSI EN 300 019-1-3)
Temperature Range +5 to +45°C
Rate of Temperature Change 0.5 °C/minute
Relative Humidity 5 to 85% RH, non-
condensing
Storage and Transportation
(ETSI 300 019-1-1 STORAGE, class 1.2)
(ETSI 300 019-1-2 TRANSPORTATION, class 2.3)
Temperature Range -40 to +70°C
Rate of Temperature Change 0.5°C/minute
Relative Humidity 10 to 100%
Vibration (Storage)
PARAMETER FREQUENCY RANGE SEVERITY DURATION
(Hz) Vel; mm/s Accel; m/s2
Sinusoidal 5 – 62 5.0 3x5 sweep cycles
Sinusoidal 62 - 200 2 3x5 sweep cycles
Vibration Test (Transportation)
PARAMETER FREQUENCY RANGE SEVERITY DURATION
(Hz) ASD: m2/s3 Rolloff: dB/oct
Random 5 – 20 0.96 3 x 10 mins
Random 20 - 500 -3 3 x 10 mins
Shock Test (Transportation)
PARAMETER SHOCK SPECTRUM SEVERITY DURATION
(Hz) Accel: m/s2 Number ms
Shock (m≤100kg) Half Sine 400 500 in each
of 6
directions
or
1000 in
normal
attitude
6
Drop Test (Transportation)
Regulatory UL, CSA, FCC Type
Acceptance for 800 MHz
and PCS versions.
PARAMETER MASS DROP HEIGHT NUMBER OF DROPS
(kg) (m)
Free Fall < 30 0.5 1 on each face or 2 in normal attitude
Free Fall 30 - 40 0.4 1 on each face or 2 in normal attitude
Free fall 40 - 50 0.3 1 on each face or 2 in normal attitude
CE Marking for GSM900
and GSM1800 versions
1-15
2 Installation
2.1 General Procedure
Generally, the fiberoptic and DC power cable, the antennas with flexible coaxial cable connections and the
Remote Transceiver mounting plates can be installed first. Then, the FiberDAS components, Hub Shelf,
Remote Transceiver Units and Remote Power Supplies (if any), can be added easily and the system
powered on.
Before installing and, in fact, before even receiving the FiberDAS units, one can have the fiberoptic cables
installed and tested. The network planning has been completed which has determined the type, number and
location of Remote Transceivers needed for optimum coverage and capacity.
Install and check the fiberoptic cables first. Use any high quality, telcom grade singlemode fiberoptic
cable. If the central DC Power Supply is used, either use a composite cable with a singlemode fiber pair
and a pair of wires built into the same cable, or pull a separate two-fiber fiberoptic cable and a two wire
DC connection together. The gauge or size of the wire to be used depends on the distance to the Remote
Unit. The SC/UPC optical connectors can be installed on site using the Seicor Unicam connector system.
One can learn how to install the Unicam SC/UPC connectors easily. However, the terminations must be
done carefully and well to ensure proper performance. Poor optical connections are by far the most
common cause for system performance degradation.
! Make sure to specify SC/UPC, not SC/PC. The standard SC/PC has an optical return loss < 27 dB
which can cause degradation of the system noise performance. SC/UPC specifies an “ultra” polish for
a return loss > 50 dB.
General practice is to terminate the fiberoptic cables at a patch panel near the Hub Shelf. In this case,
optical jumper cables will be needed to make the connection between the patch panel and the Hub Shelf.
During this process, label each cable at each end to indicate whether it is transmit or receive and which
Remote Transceiver it is associated with. As part of the planning, decide whether it would be good to pull
one or two additional fiber pairs to each Remote Transceiver to allow for future expansion. Also, leave a
service loop near the Remote Transceiver location in case the unit needs to be moved. Next, mount the Hub
Shelf in the rack and connect the fiberoptic cables. Do not connect the RF cables yet.
Mount the Remote Transceivers. Install the wall mounting brackets first. For mounting above a false
ceiling, the preferred method is to orient the bracket so that the end of the Remote Transceiver with the
connectors is pointing downwards. The unit could also be mounted horizontally with the connectors to one
side. When mounting inside the room, the preferred method is to place the Remote Transceiver near the
ceiling with the connectors pointing upwards. This permits the most aesthetic routing of the cables. The
plastic cover on the Remote Transceiver may be removed by loosening the six screws on the back of the
Unit. This permits the user to paint the cover to match the room décor. If the Remote Transceiver is to be
installed with the Remote Power Supply, install the two mounting brackets next to each other linking them
with the connector piece supplied with the power supply mounting bracket. This will give the most
aesthetic mounting with the proper spacing for an easy DC power connection. ( Note: the Remote AC
Power Supplies are not to be installed above a false ceiling.) Orient the bracket so that the threaded tab
will be at the same end as the connectors on the Remote Transceiver.
Before mounting the Remote to the bracket, attach the Optical RF and DC cables to the Remote. If the
plastic cover is not to be used, you may remove it by removing the four screws that hold it on. This will
make it easier to attach the cables.
2-1
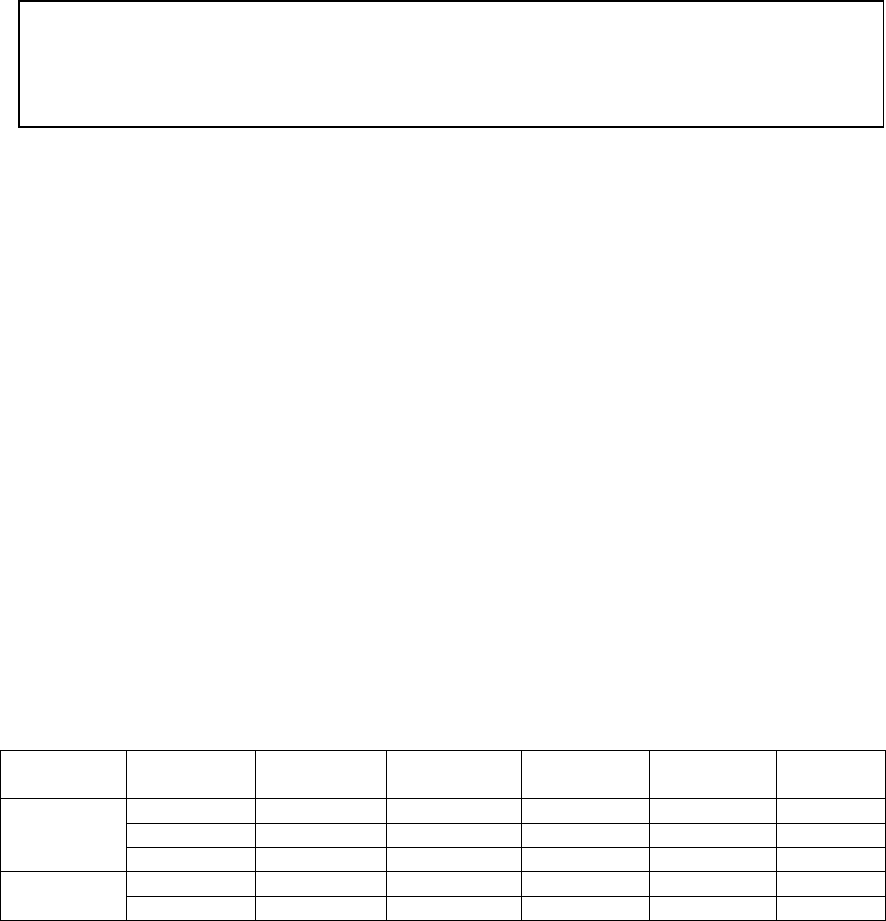
Place the Remote Transceiver so that the rear panel studs slide into the keyhole slots on the mounting
bracket. Secure the unit by tightening the captive thumbscrew on the Remote Transceiver to the threaded
hole in the mounting bracket. The Remote Power Supply installs in the same way. For the Remote Power
Supply, if the red NO AC LED is on, press the reset switch located next to the AC power connector which
turns off the battery backup (when the mains is not connected). For AC powered units, connect the AC
power cords to the building mains according to local building electrical codes. Connect DC power to the
Remote Transceiver by connecting the DC cable to the DC input connector on the Remote Transceiver.
Mount the indoor coverage antenna to the ceiling or wall as needed and connect it to the Remote
Transceiver with a flexible RF cable rated to cover the highest frequency in use.
The RF cable must have an SMA male connector for the connection to the Remote Transceiver. If the
antenna has a different RF connector, say, N or TNC, an RF adapter must be used. If more than one
antenna is to be connected to the Antenna port of the Remote Transceiver, connect the Antenna port to the
appropriate RF splitter with a short flexible coaxial RF coaxial cable rated to at least 2.5 GHz. Then
connect the antennas to each of the RF splitter ports with another length of RF coaxial cable rated to at
least 2.5 GHz. Plug in the transmit (downlink) fiberoptic cable connector into the OPTICAL IN on the
Remote Transceiver and the receive (uplink) fiberoptic cable connector into the OPTICAL OUT (Green)
on the Remote Transceiver.
From the initial network design, the output power required from each Remote Transceiver should be
known. This can be preset before power is turned on by turning the Output Power adjustments on each
Remote Transceiver. From the maximum output power rating for each Remote Transceiver, the power can
be reduced in 2 dB by turning the indented rotary DIP switch on the Remote Transceiver..
Turn the power on to the Remote Transceivers and on the Hub Shelf. Proper operation of the optical
system is indicated by a green Node Function LED on each of the Hub Transceiver Plug-Ins that is
connected to an active Remote Transceiver. All other alarm indicators should be OFF. A yellow LED at the
plug-in or at the Remote Transceiver indicates that the optical loss in that path is > 4 dB and is, therefore,
out of the range of the guaranteed specification.
Before connecting the Hub Shelf to the BTS or Repeater, check that the RF transmit power from the
source (BTS or repeater) is within the safe operating range of the FiberDAS and that it is at the level
required for proper noise and distortion performance according to the network design (see Table 1).
Table 1. Transmit (Downlink) Input RF Levels/carrier
Power
Option
Number of
Carriers
GSM800 &
GSM900
DCS1800 &
GSM1900
CDMA TDMA UMTS
1 13.0 - 8.0 13.0 -
2 4.0 - 4.0 4.0 -
P1
4 1.0 - 1.0 1.0 -
1 11.0 11.0 6.0 11.0 6.0
P2* 2 0.0 3.0 2.5 3.0 2.5
IMPORTANT NOTE! to comply with FCC RF Exposure compliance requirements, the following
antenna installation and device operating configurations must be satisfied:
Any antenna connected to this device must result in an ERP < 1.5W(800 and 900MHz) or < 3.0W
(1800MHz and 1900MHz)! and must be mounted such that there is at least 20 centimeter spacing
from the antenna structure and a human body.
2-2

4 -3.0 0.0 -0.5 0.0 -0.5
Connect the RF cables between the BTS or repeater and the Hub Shelf. The Remote Transceivers and the
plug-ins have been calibrated at the factory and the optical loss compensation in each Remote Power
Supply and plug-in automatically equalizes the gain in each link so that the specified link gain is always
met. The system is now operational and no further adjustment is necessary.
2-3
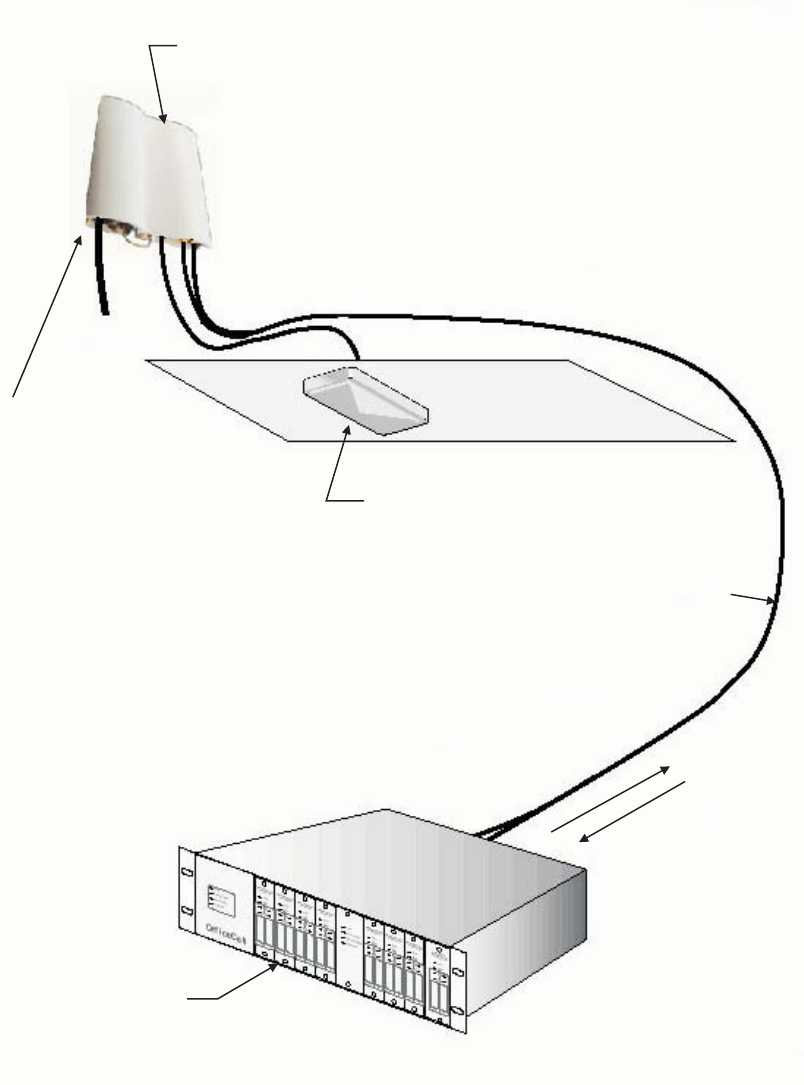
Remote Transceiver mounts
above false ceiling. Aesthetic
design permits mounting in room,
if necessary.
All optical and RF connectors along
with RF output adjust and LEDS at
same end for easy installation and servicing.
If Remote AC Power
Supply is used, it is attached
to common mounting plate
with the Remote Transceiver
Remote Transceiver connects
to any standard indoor coverage
antenna
Singlemode fiber pair up to 4 dB
optical loss to each Remote Transceiver,
1300 nm wavelength. Composite
cable may be used to distribute
DC power as well
RF Connects to BTS
or BDAs through the
passive Entry Shelf.
Alarms reported through modem to NOC
or pager via POTS connection. Also, to local
TTL, Summary and LED.
Hub Shelf
Hub Transceiver
Plug-Ins
FiberDAS
Installation
Figure 2-1. FiberDAS Installation
2-4
2.2 Install Fiberoptic Cables
Once the location for each of the Remote Transceivers has been determined, the fiberoptic cable can be
installed between the Hub Shelf and these locations. The cable length can be up to 5 km.
You need to know the following:
Optical Fiber Singlemode, 1310nm wavelength
Optical Loss Good quality fiber should have an optical loss of
< 0.4 dB/km at 1310nm. There will be additional
optical loss due to connectors and splices but there
should be no more than about 0.5 dB loss through a
connector mating (optical connections are sexless)
and less through a splice.
Optical Connectors SC/UPC connectors. The “U” refers to “Ultra Polish”
which gives an optical return loss > 50 dB. One can
procure cable assemblies that are pre-terminated,
however the SC/UPC can be installed in the field
using the Seicor Unicam connector. The Hub Shelf
also uses SC/UPC connectors. IMPORTANT
NOTE: MAKE SURE TO USE AN SC/UPC
TERMINATION: THIS CONNECTOR IS AN
“ULTRA POLISHED” CONNECTOR WITH AN
OPTICAL RETURN LOSS > 50 dB. A
STANDARD SC/PC TERMINATION HAS A
HIGH RETURN LOSS AND WILL DEGRADE
LINK NOISE AND LINEARITY PERFORMANCE.
Once the cable has been installed, the installer should check the quality of the optical path using an Optical
Time Domain Reflectometer (OTDR). This will check the optical path loss and the magnitude and location
of any reflections. The total return loss should be > 45 dB.
While checking the cables in this way, it is useful to label each cable near the connector as to which
Remote Transceiver it is for and whether it is for the transmit or receive path. Labelling the cable in this
way permits complete interconnection during installation with the system powered off. Otherwise, the
Remote Transceivers will have to be installed with the Hub Shelf power on with all fiberoptic cables
connected to it. This allows the installer to check which fiber is transmit by using an IR sensitive card (see
Recommended Tools).
2.2.1 Minimizing Optical Reflections
As discussed in the Functional Description, optical reflections can degrade the noise and linearity of a
fiberoptic link. In particular, reflections that reach the laser can be a problem. Keep all discrete reflections
to > 50 dB. The SC/UPC connectors are polished to a return loss >50 dB.
2-5
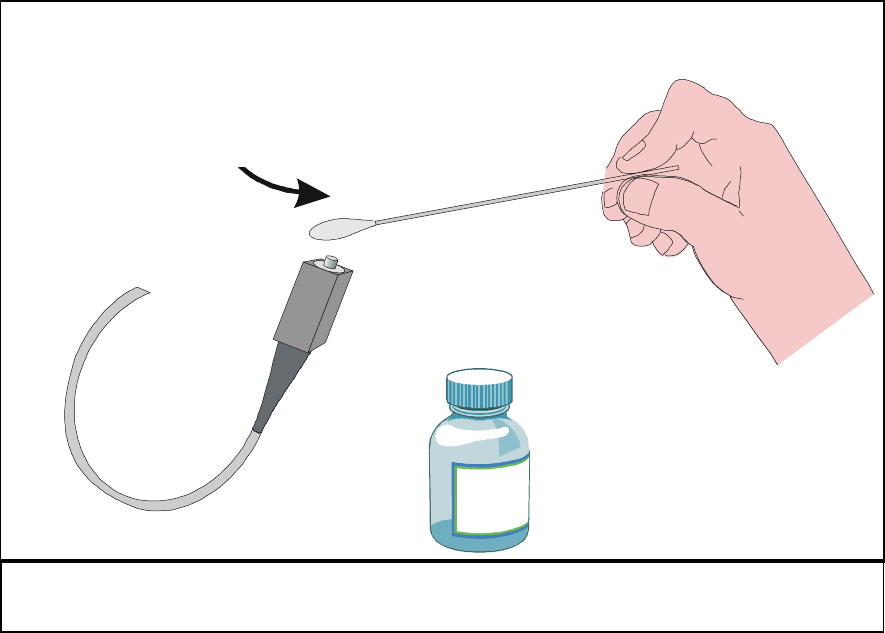
2.2.2 Cleaning Optical Connectors
Optical reflections from a discontinuity such as a poor connector interface appear on an RF spectrum
analyzer trace as stable variations in the noise floor amplitude that are periodic with RF frequency. If the
reflection is bad enough, it could impact the system performance. By far, the most common cause for a
large discrete reflection is a dirty optical connector. Remember that the optical aperture at the tip of the
fiberoptic connector is only 9 :m in diameter. A bit of dust or oil from a finger can easily interfere with or
block this light. Fortunately, it very easy to clean the connector. The procedures are indicated in the Figure.
Be sure to use the correct procedure for the given connector. When disconnected, cap the SC/UPC
connector to keep it clean and prevent scratching the tip of the ferrule.
Cleaning the SC/UPC optical connectors.
Swipe the tip of the ferrule 2 – 3 times with
a cotton swab soaked in alcohol. Let it air
dry. Do not use canned air to dry as this
may leave a residue.
Figure 2-2. Cleaning the optical connectors.
2-6
2.3 System Alarms
The FiberDAS has four ways of indicating alarms.
1. LEDs: the Hub Shelf and the Remote Transceiver have status indicators for power on and
alarm conditions.
2. Hub Shelf Rear Panel DB37 Connector: The “critical” alarms are available here as TTL
levels. In addition, three pins provide a contact closure summary alarm (see Alarms in the
specifications).
3. Craft serial port: The system status may be monitored locally with a computer through the
front panel Craft serial port. The main purpose of this port is initial system setup. This
includes specifying which alarms are critical, setting the local system telephone number and
specifying the action to be taken when there is a critical alarm (dial up the NOC or a service
technician’s pager). If more than one Hub Shelf is being used at the same location, one of the
hubs may be configured as the Master, reporting alarms for all connected Hubs. One can also
give the system an easily recognizable name as well as naming the Remote Transceiver
locations so that the system and the fault location may be easily identified at the Network
Operating Center (NOC) using the NMS.
4. Dial-Up: the system may be connected to a standard RJ-11 telephone jack through which it
communicates with the NOC or a service technician’s pager. Using network management
software at the NOC, the network administrator can poll and monitor thousands of remote
FiberDAS systems. The system and alarms can be configured by way of the front panel serial
port using the Remec MobileCraft software (see separate MobileCraft manual).
Using the alarms provided, the cause of a critical failure can be determined with high confidence. For
instance, if the Node Function alarm is associated with a Plug-In laser alarm, the Plug-In has failed and
must be replaced. If the Node Function alarm is associated with a Received Optical Power Low at the Plug-
In, either the Remote Transceiver laser has failed or the fiberoptic cable has been broken or damaged. The
service technician would come with a replacement Remote Transceiver. If, upon inspecting the Remote
Power Supply in question, the LEDs indicate no failure, the fiber path would have to be inspected. This
should be relatively easy to track down since damage would have to be associated with some other work
going on at the site or someone had deliberately disconnected the optical cable from the unit. Finally, a
Node Function alarm not associated with any other alarm at the Hub Shelf would indicate a failure of the
Remote Transceiver downlink amplifier chain. This would be confirmed by inspection of the Remote
Power Supply in question for that particular LED. The complete troubleshooting matrix is given at the end
of this manual and is included in the separate MobileCraft manual. Or, it can be used to program another
NMS to recommend the proper action to be taken.
2.4 Hub Shelf and Remote Power Supply Battery Charge Monitoring and
Replacement
Both the Hub Shelf and the Remote Power Supply have a battery backup. While connected to mains
power, the battery is kept charged by a charging circuit. Once AC mains power is first connected, the
charging circuit waits 48 hours before starting the battery test circuit. This circuit checks to open circuit
battery voltage every ten seconds. Once the circuit detects the battery voltage drops below approximately
12 Volts, the BATT LOW alarm is activated. At the beginning of life, the battery provides approximately
15 to 20 minutes of system backup. At end of life, the backup time is about 8 to 10 minutes. It is expected
that the batteries should be replaced every 1.5 to 2 years.
2-7

2.4.1 Replacing the Hub Shelf Battery
The battery must be replaced with the AC mains power off.
CAUTION: DOUBLE POLE/NEUTRAL FUSING
1. Turn off the AC mains power (rear panel switch)
2. Disconnect AC mains power cable
3. Press the BATT OFF switch on the rear panel to switch off the battery power to the Hub
Shelf
4. Pull the Hub Shelf out of the rack from the front on the chassis rack mount slides. Be careful
not to pull on rear panel cable assemblies, especially the fiberoptic cables.
5. Remove the Hub Shelf top cover.
6. Locate the battery on the left behind the power supplies.
7. Remove the battery bracket by loosening the screws. Lift off the bracket.
8. Disconnect the battery terminal wires by pulling them off.
9. Lift the battery out.
10. Install the replacement battery by reversing the process.
Spent batteries must be treated as hazardous waste and disposed of or recycled according to
local, state and federal guidelines
2.4.2 Replacing the Remote Power Supply Battery
The battery must be replaced with the AC mains power off.
1. Disconnect the AC mains power cable.
2. Press the BATT OFF switch on the power supply to switch off the battery power.
3. Disconnect the DC power connector from the Remote Transceiver.
4. Loosen the thumbscrew that secures the power supply to the mounting bracket.
5. Slide the power supply housing so as to release from the mounting bracket keyhole slots.
6. Remove the smaller cover on the back of the housing (the far end from the connectors).
7. Lift out the battery and pull off the terminal wires.
8. Install the replacement battery by reversing the process.
Spent batteries must be treated as hazardous waste and disposed of or recycled according to
local, state and federal guidelines.
2-8
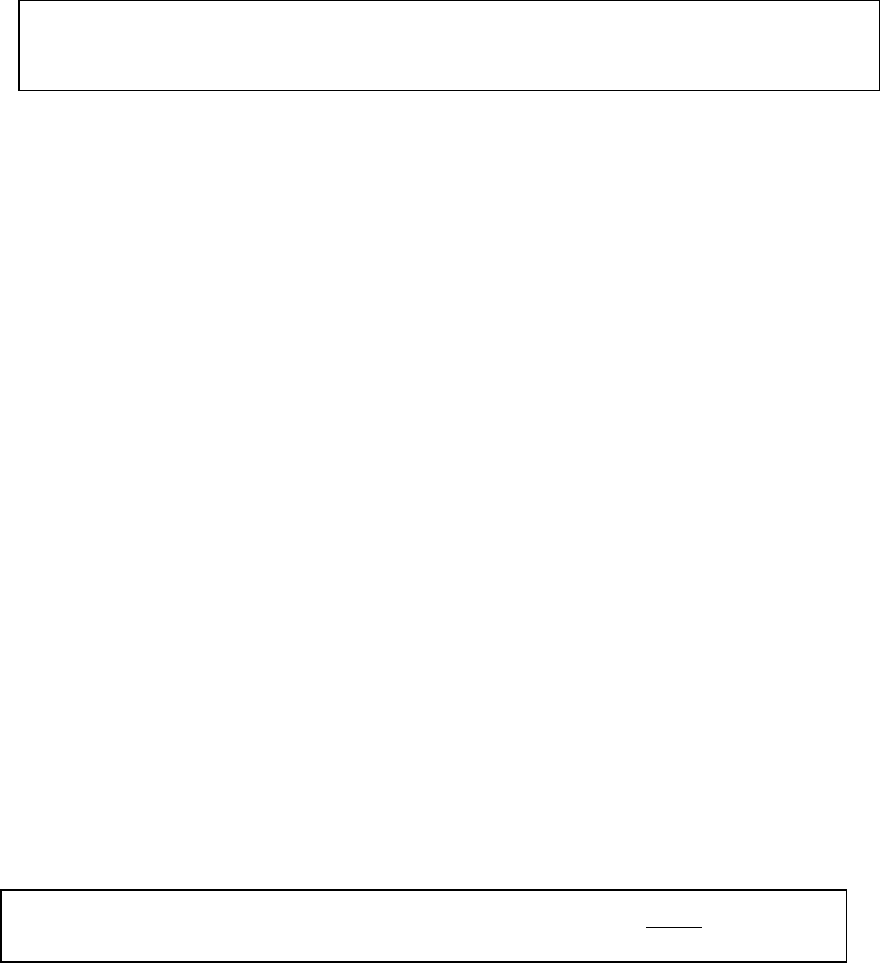
2.5 Installation Checklist
Once the fiberoptic cable has been installed properly, the FiberDAS installation and set up is simple.
2.5.1 Inspect Received Items
I
nspect all received items thoroughly. If any item has been damaged during shipping, report it to the
shipping company and to Remec in the U. S. at 408-747-1946. Also, contact the factory immediately
if any item is missing.
Packing List Checklist (as applicable)
Hub Shelf w/mounting hardware and AC power cord
Hub Transceiver Plug-In (s); these are installed in the chassis unless they are spares
Plug-In Termination Cards: these are plug-ins behind blank front panels installed on unused slots.
They provide 50Ω RF terminations to the internal RF splitters and combiners ensuring a balanced
load.
Two 1:2 RF splitter/combiners (supplied with the Hub Shelf)
Remote Transceiver (s): These will be in a separate box.
Remote Power Supplies (not included if user is supplying DC power to Remote Transceiver).
Mounting Brackets for Remote Transceiver and Remote Power Supply. Included with Remote
Transceiver and Remote Power Supply.
1 Operating Manual
2.5.2 Recommended Tools
Fiberoptic Connector Cleaning Kit: For the SC/UPC: cotton swabs, alcohol
IR sensitive card: used to detect active laser port and active fiber. (eg. Quantex Model Q-42-R)
Small screwdriver or Adjustment Tool for transmit output power rotary DIP switch
Screwdriver for mounting chassis in rack and Remote Transceivers on the wall
4 #6 panhead or M3.5 mounting screws for each Remote Transceiver.
Appropriate screws, washers and mounting hardware for rack mounting the Hub Shelf.
2.6 Installing the Hub Shelf
2.6.1 Rack Installation
The Hub Shelf mounts in a standard 19 inch rack close to the RF source (BTS or repeater). The chassis
should be supported at the sides as well as from the front flanges. The Hub Shelf 3U high chassis is also
available with rails as an option.
! Make sure that Hub Shelf is supported at both front and back in the rack. Do not mount with
front mounting ears only.
2-9

2.6.2 Connect Fiberoptic Cables
Before turning on the AC (or DC) power to the chassis, connect the fiberoptic cables at the rear panel.
During installation of the fiberoptic cables, each fiber should have been labelled as to which Remote
Transceiver it is to be connected to and whether it is for transmit or receive. The transmit or downlink
fibers are connected to the optical outputs on the rear panel. These are the red connectors with the laser
light warning labels. Make sure that the connectors used are associated with an active plug-in installed in
the chassis.
First, clean the tip of the connector on the cable according to the procedures in 2.2.2 above. Lift the spring
loaded cover on the Hub Shelf rear panel connector and, after orienting the connector so that the “key” on
the connector aligns with the slot in the mating adapter on the Hub rear panel, push in the SC/UPC cable
connector until firmly seated (the connector may or may not “click” into place; do not push too hard!!).
NOTICE
UNTERMINATED OPTICAL RECEPTACLES MAY EMIT LASER RADIATION. DO
NOT VIEW WITH OPTICAL INSTRUMENTS.
2.6.3 Indentifying Remote Locations
The front panel of each Plug-In has two 1.75” x 0.5” (4.4 cm x 1.3 cm) outlines labelled A and B which
can be used to affix standard “address” size labels (Avery 5167) to designate which Remote Transceiver is
connected to that path. These labels should correspond to the electronic names assigned to each path
through the front panel Craft serial port.
2.6.4 Serial Bus, Telephone and Local Alarm Connections
If more than one Hub Shelf is being used, connect the SERIAL DATA ports together using CAT-5
jumpers with RJ-45 connectors. The two SERIAL DATA ports on the rear panel are connected together;
two are provided to permit the use of simple jumpers when daisy-chaining several units.
Connect the LINE port to a POTS telephone jack for the dial-up modem connection.
If it is being used, connect the chassis to the local OA&M interface by way of the 37 pin D-Sub connector
on the rear panel of the Hub Shelf (see section 2.3: System Alarms).
2.6.5 Mains Power and Fuses
Turn on the chassis power. The AC powered version of the Hub Shelf operates on 100 to 240VAC. The
rear panel IEC receptacle is dual fused. The fuses used are FUSE, TIME LAG, 2 AMP, SLO-BLO
CAUTION: DOUBLE POLE/NEUTRAL FUSING
Certified power cords and ac plugs, appropriate for the country where equipment is installed,
shall be used for continued safety compliance.
Powering up the chassis will “light up” the fiber allowing those installing the Remote
Transceivers to identify the transmit and receive cables using an IR sensitive card (see Recommended
Tools) to see which fiber is emitting light. The fiber emitting light at the Remote Transceiver end is the
transmit path and is connected to the OPTICAL IN connector on the Remote Transceiver (after proper
cleaning; see section 2.2.2).
2-10
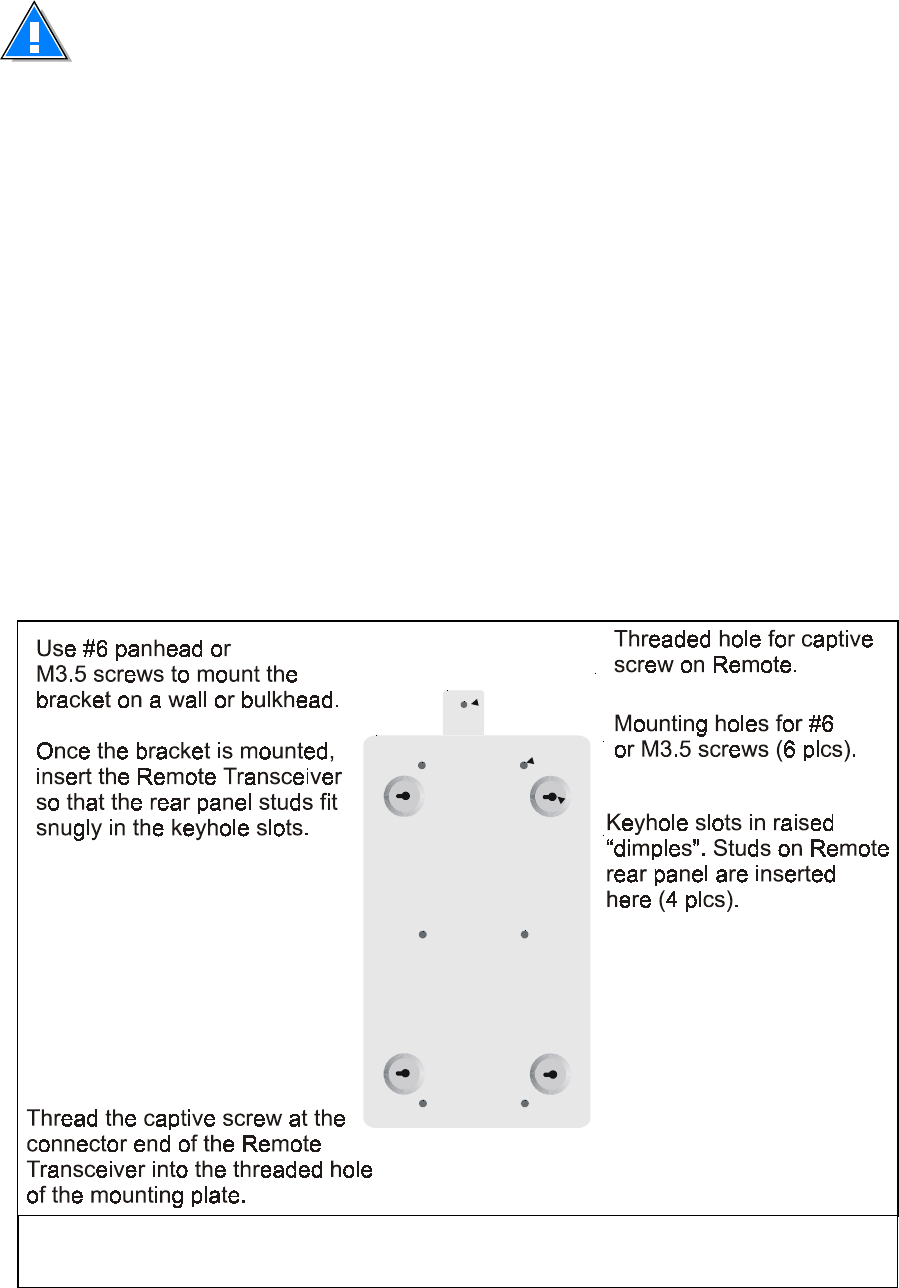
NOTICE: UNTERMINATED OPTICAL RECEPTACLES MAY EMIT LASER
RADIATION. DO NOT VIEW WITH OPTICAL INSTRUMENTS.
2.6.6 RF Connections
If the transmit RF signal from the BTS or repeater is to be routed to all the plug-ins in both sides of the
Hub Shelf, connect the external 1:2 RF splitter supplied with the Hub Shelf to both RF IN ports on the rear
panel. If the receive RF signals from all of the plug-ins in both halves of the Hub Shelf are to be routed to a
single receive port on the BTS or repeater, connect the other 2:1 RF combiner to both of the RF OUT ports
on the rear panel. If one of the RF OUT ports is to be connected to the BTS or repeater receive diversity
port, do not connect the RF combiner to the RF OUT port.
Connect the RF OUT to the BTS or repeater receive port(s).
Before connecting the RF transmit cables from the BTS or repeater to the RF IN of the Hub Shelf, verify
that the BTS or repeater RF output power levels are consistent with the desired output power at the Remote
Power Supply and will not overdrive or damage the FiberDAS Plug-Ins. Connect the BTS or repeater RF
transmit cables to the Hub Shelf.
2.7 Installing the Remote Transceivers
Each Remote Transceiver is usually mounted above the false ceiling against the wall with the connectors
pointing down for easy access. The Remote may also be mounted horizontally. In an area with no false
Figure 2-3. Remote Transceiver Mounting Plate. The Remote Power Supply uses a similar plate
and the two can be sna
pp
ed to
g
ether with the matin
g
bracket su
pp
lied.
2-11
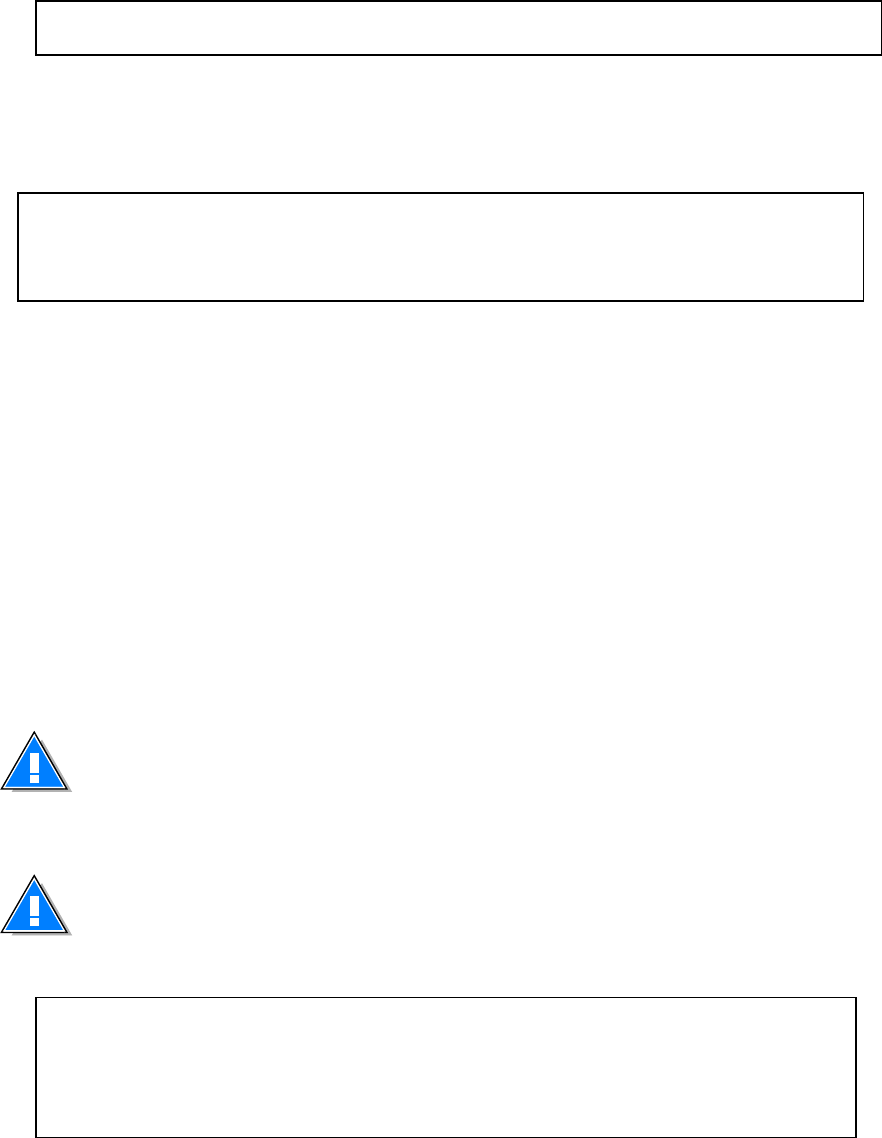
ceiling, it can be mounted in the room near the ceiling with the connectors pointing up. This permits a more
aesthetic routing of the cables in the wall-ceiling corner. The Remote Transceiver is connected to the Hub
Shelf with a singlemode fiberoptic cable with a maximum optical loss of 4 dB, including connectors and
patch panels.
! The minimum bend radius of the fiber is 2 inches (5 cm). Be careful not to kink the fiber.
To mount the Remote Transceiver, first install the mounting bracket. If the Remote Power Supply is being
used, snap the mounting brackets for the Remote and and the Remote Power Supply together using the
connector bracket that comes with the Remote Power Supply.
! The Remote Power Supply is not to be installed above a false ceiling. In these cases, always use
the Central DC Power Supply and pull the DC supply wires along with the fiber duringcable
installation.
The bracket is attached to a wall or bulkhead using #6 pahhead or M3.5 screws. The Remote Transceiver
(and Power Supply, if applicable) are mounted on the bracket by inserting the rear panel studs into the
keyhole slots in the bracket. Each Unit is secured to the bracket by threading the captive thumscrew
(located at the connector end of the unit) into the threaded hole in the tab on the bracket. See the figures
below for more detail.
It is easier to make all of the optical, RF and DC connections to the Remote Transceiver before mounting
the unit on the plate. If the plastic cover is not needed, it may be removed by removing the four screws that
hold it on. This will also make access to the connectors easier. However, even if the plastic cover is not
needed for aesthetic reasons, it may be desirable to install it to provide some protection from dust buildup.
The Remote Transceiver takes +12 to +28 VDC power through a field-installable Molex connector. If the
Remote Power Supply is being used, the DC connection is provided by simply plugging in the DC cable
from the Remote Power Supply to the Remote Transceiver. The Remote Power Supply should be powered
through a sheilded AC power cable installed according to local building codes. The Remote Power Supply
takes 100 to 240VAC. It is dual fused using a TIME LAG, 1 A, (SLO-BLO) fuse.
CAUTION: DOUBLE POLE/NEUTRAL FUSING
For DC versions , the terminals can take wires 18 AWG to 14 AWG. The choice will depend on the
voltage used and the distance from the power supply (see Specification, Electrical).
Certified power cords and ac plugs, appropriate for the country where equipment is installed,
shall be used for continued safety compliance.
Next, install the indoor coverage antenna according to the manufacturer’s instructions. Connect the antenna
IMPORTANT NOTE! to comply with FCC RF Exposure compliance requirements, the
following antenna installation and device operating configurations must be satisfied:
Any antenna connected to this device must result in an ERP < 1.5W(800 and 900MHz) or <
3.0W (1800MHz and 1900MHz)! and must be mounted such that there is at least 20centimeter
spacing from the antenna structure and a human body.
2-12
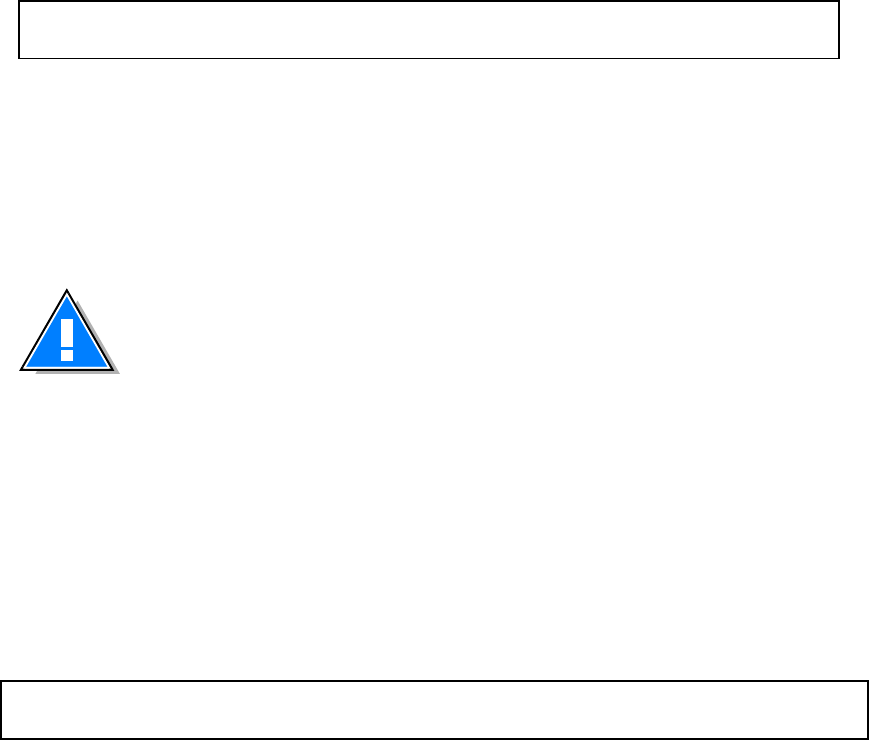
to the Remote Transceiver RF SMA connector using a flexible RF cable with VSWR < 1.5 : 1 at the
frequencies in use.
! RF SMA connectors should be tightened with a torque wrench set to 8 in-lbs. Do not
overtighten!
Connect the optical cable. The fiber for the transmit (downlink) path connects to the OPTICAL IN
connector. The fiber for the receive (uplink) path connects to the OPTICAL OUT connector (Green with
laser DANGER label). The fibers should be labelled accordingly during installation of the fiberoptic
cables. If not, they can be identified by turning the Hub Shelf power on with the plug-ins and fiberoptic
cables installed. Then, use an IR sensitive card (see Recommended Tools) to detect the light emitted from
the transmit fiber. Point the optical connector on each fiber at the card to see which fiber is emitting light
(you see a glowing spot on the card). This is the fiber for the transmit path. The other is for the receive
path.
NOTICE
UNTERMINATED OPTICAL RECEPTACLES MAY EMIT LASER RADIATION. DO
NOT VIEW WITH OPTICAL INSTRUMENTS.
Knowing the desired output power level from each Remote Transceiver as determined by the network
design, the Output RF Power can be preset before the system is powered up. Given the rated maximum
power from the Remote Transceiver, the antenna gain an the loss in the RF cable, the output RF power is
maximum when the Output Power adjustment is set at 0. The static output power can be reduced by turning
the adjustment. The adjustment is indented and each indent changes the output power by 2 dB.
Once all connections have been made, turn on the AC power (or DC power, depending on the option used)
to Hub Shelf and Remote Transceivers. Before connecting the transmit RF input from the source, check
that the level is that needed for optimum signal to noise and distortion as determined in the network design
(see Table 1 above). Connect the RF cables to the Hub Shelf.
! To prevent damage to the Hub Shelf plug-ins, do not exceed the maximum ratings for RF input to
the Hub Shelf !
2-13
3 Monitoring and Troubleshooting
3.1 Field Support Numbers
The tips given below should help pinpoint most link problems. Often, problems are a result of a poor
optical interface which is easily fixed by properly seating a connector or cleaning the connector. There are
no user serviceable parts in the FiberDAS. Faulty units must be returned to Remec Inc. for repair or
replacement. For technical support call:
USA 714-765-5823
United Kingdom +44 (0)1296 319319
Malaysia +603 7785 1270
3-1
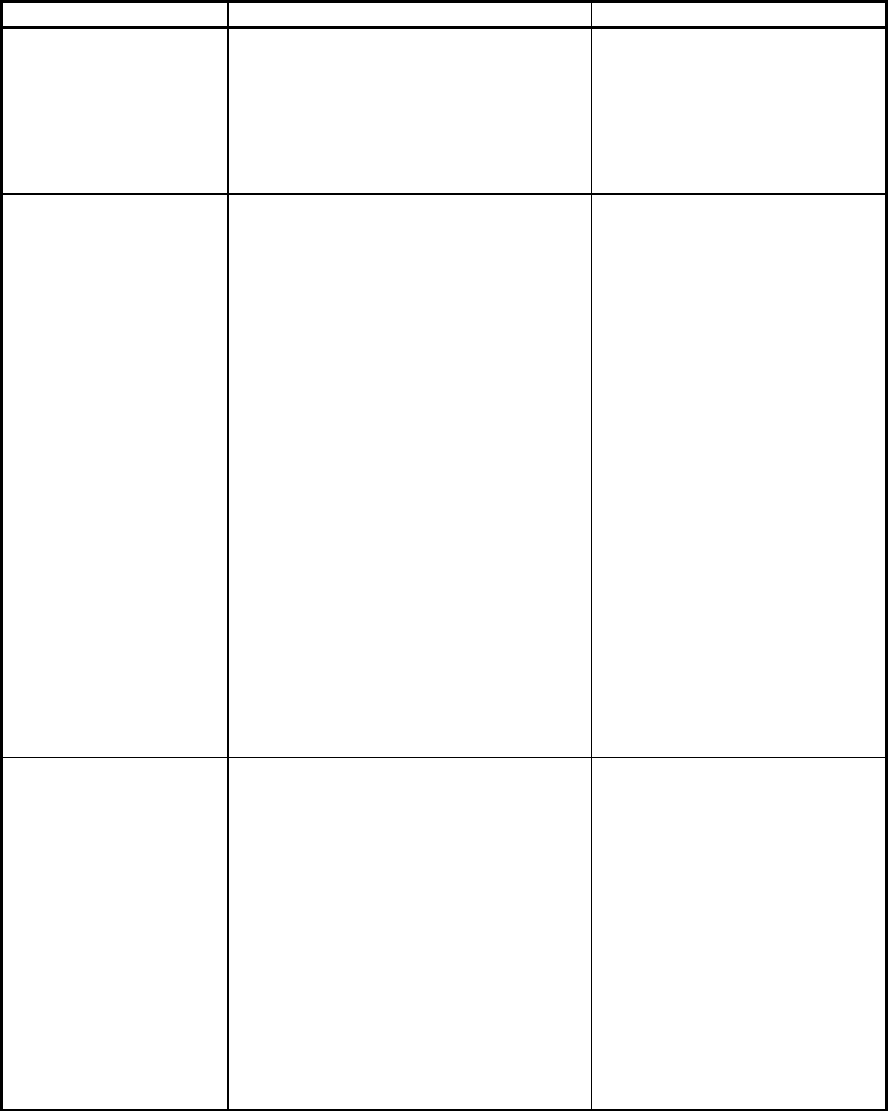
3.2 Troubleshooting Tips
Alarms Probable Cause Action*
Node Function 1. Remote Transceiver Downlink Tx
amplifier chain failure
2. Pilot tone oscillator malfunction
3. Pilot tone detector malfunction
1. If Remote Transceiver Rcvd
Opt Pwr LED is OFF, this
indicates downlink amplifier
chain failure: replace Remote
Transceiver.
2. Repair/replace failed Plug-In
3. Repair/replace failed Plug-In
1. Node Function
2. Received Opt Pwr
Low (Remote
Transceiver)
1. Problem in downlink fiber path:
optical loss too high: fiber run is
too long, connector not seated
properly, damaged or in need of
cleaning, damaged splice
2. Remote Transceiver photodiode
failure
1. Check Rcvd Optical
Power LED at Remote
Transceiver. If active
(Yellow), disconnect
downlink fiber and
check optical output
with light sensitive card.
If no light detected,
inspect fiber path, esp.
any connector recently
disconnected. Inspect for
proper seating. Clean
connectors. If necessary,
disconnect fiber from
FiberDASand check
fiber path with OTDR to
locate problem.
2. If fiber is OK, indicates
Remote Transceiver
photodiode failure:
replace Remote
Transceiver.
1. Node Function
2. Received Opt Pwr
Low (Plug-In)
1. Remote Transceiver laser failure
2. Problem in uplink fiber path:
optical loss too high: fiber run is
too long, connector not seated
properly, damaged or in need of
cleaning, damaged splice
3. Plug-In photodiode failure
1. Check Laser Alarm in
Remote Transceiver. If
active (Red), replace
Remote Power Supply.
2. If not, inspect fiber path,
esp. any connector
recently disconnected.
Inspect for proper
seating. Clean
connectors. If necessary,
disconnect fiber from
FiberDASand check
fiber path with OTDR to
locate problem.
3. Replace Plug-In
3-2
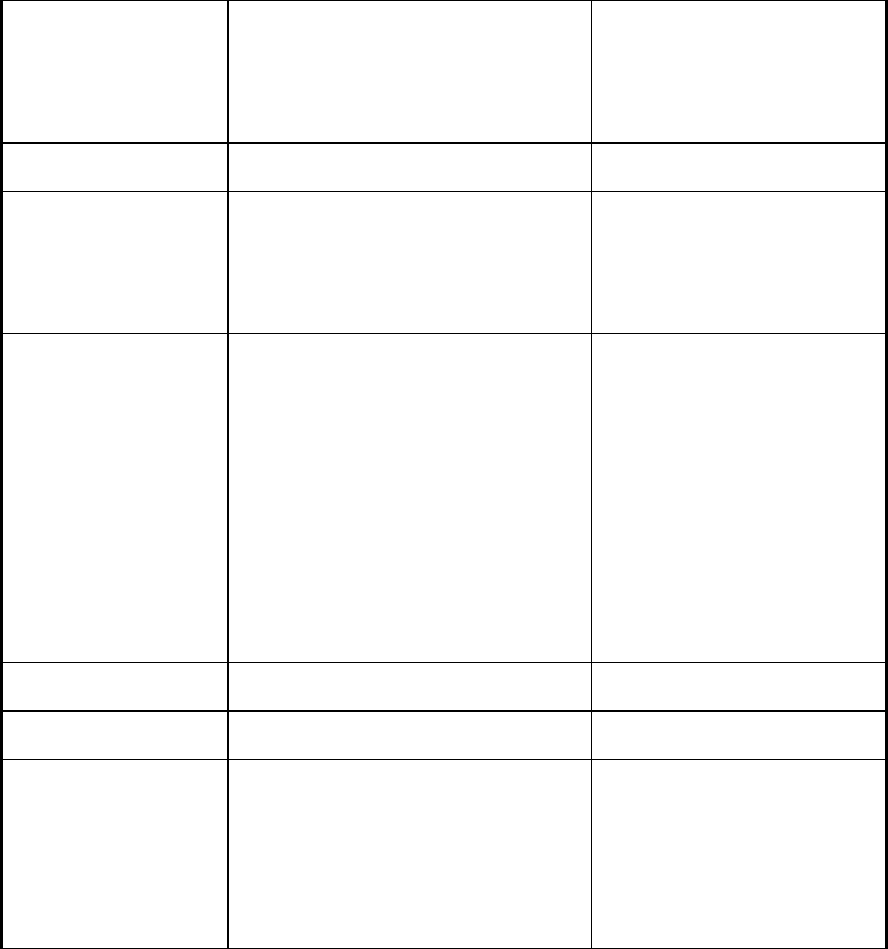
1. Node Function
2. Received Opt Pwr
Low
3. Laser Pwr Low (both
Hub Shelf Plug-In and
Remote Transceiver)
Failing or failed Plug-In laser Replace Plug-In
Laser Pwr Low (Hub
Shelf Plug-In)
Failing laser Replace unit Hub Shelf Plug-In
1. Laser Pwr Low
(either in Hub Shelf
Plug-In or Remote
Transceiver)
2. Received Opt Pwr
Low (opposite end)
Failing laser Repair/replace unit (Hub Shelf
Plug-In or Remote Transceiver)
Received Opt Pwr Low
(Hub Shelf Plug-In)
1. Failed/failing laser in Remote
Transceiver
2. Optical loss too high, link may
not be operating within
specifications. Fiber path may be
too long. Problem in fiber path:
connector not seated properly,
damaged or in need of cleaning,
damaged splice
1. Inspect Remote
Transceiver for Laser
Alarm LED on (Red). If
so, replace Remote
Transceiver
2. Inspect fiber path, esp.
any connector recently
disconnected. Inspect for
proper seating. Clean
connectors. If necessary,
disconnect fiber from
system and check fiber
path with OTDR to
locate problem.
Hub Shelf: Main Power
Alarm
Main Power Supply Failure (voltage
dropped more than 1 V from +15V)
Replace Main Power Supply
Hub Shelf: Backup
Power Supply Alarm
Backup Power Supply Failure (voltage
dropped more than 1 V from +15V)
Replace Backup Power Supply
Battery Alarm 1. During battery only operation this
would be normal after unit has been
on for 10 to 20 minutes. Should go
off after main power is restored and
battery charges up.
2. If main and/or backup power supplies
are OK, this indicates battery or
recharging circuit failure
1. No Problem
2. Replace Chassis
* All repairs of FiberDAS components must be performed by the factory
3-3
3.3 Regulatory
FCC Part 22, Part 24 and Part 68 Regulation
Versions of this equipment designated to operate in the PCS1900 frequency bands have been
certified as compliant with FCC Part 22. Versions designated to operate in the AMPS frequency
bands have been certified as compliant with FCC Part 24. Versions of the Hub Unit that include
the dial-up modem have been certified as compliant with FCC Part 68. Testing and certification
was executed by MET Laboratories, Baltimore, MD, USA.
FCC Part 15 Regulation
NOTE: this equipment has been tested and found to comply with the limits for a Class B digital
device, pursuant to Part 15 of the FCC rules. These limits are designed to provide reasonable
protection against harmful interference in a residential installation. This equipment generates, uses
and can radiate radio frequency energy and if not installed and used in accordance with the
instructions, may cause harmful interference to radio communications. However, there is no
guarantee that interference will not occur in a particular installation. If this equipment does cause
harmful interference to radio or television reception, which can be determined by turning the
equipment off and on, the user is encouraged to try to correct the interference by one or more of
the following measures:
• Reorient or relocate the receiving antenna
• Increase the separation between the equipment and receiver
• Connect the equipment into an outlet on a circuit different from that to which the receiver
is connected
• Consult the dealer or an experienced radio/TV technician for help.
Industry Canada
Versions of the Hub Unit that include the dial-up modem have been certified as compliant with
Industry Canada CS-03 Telecom regulations.
This Class B digital apparatus meets all requirements of the Canadian Interference-Causing
Equipment Regulations.
Cet appareil numérique de la classe B respecte toutes les exigencies du Regiement Canadien sur le
materiel brouilleur.
Testing and certification for Industry Canada compliance was carried out by MET Laboratories,
Baltimore, MD, USA.
UL
UL and CUL Safety certification testing and certification was provided by Underwriters
Laboratories, Inc., San Diego, CA, USA.
CE Mark
Versions of this equipment that are designated for operation in the GSM900, DCS1800 or UMTS
frequency bands each have a Technical Construction File certified as compliant with the Council
Directive 1999/5/EC, Articles 3.1 (a), 3.1 (b) and 3.2. Safety testing and certification was
executed by TÜV Product Service, San Diego, CA, USA. RF testing and compliance and
complete TCF certification was provided by BABT, Walton on Thames, Surrey, UK.
3-4