BTI Wireless MBSC700FRUM mBSC-CM RUM User Manual mBSC NMS
BTI Wireless mBSC-CM RUM mBSC NMS
Users Manual
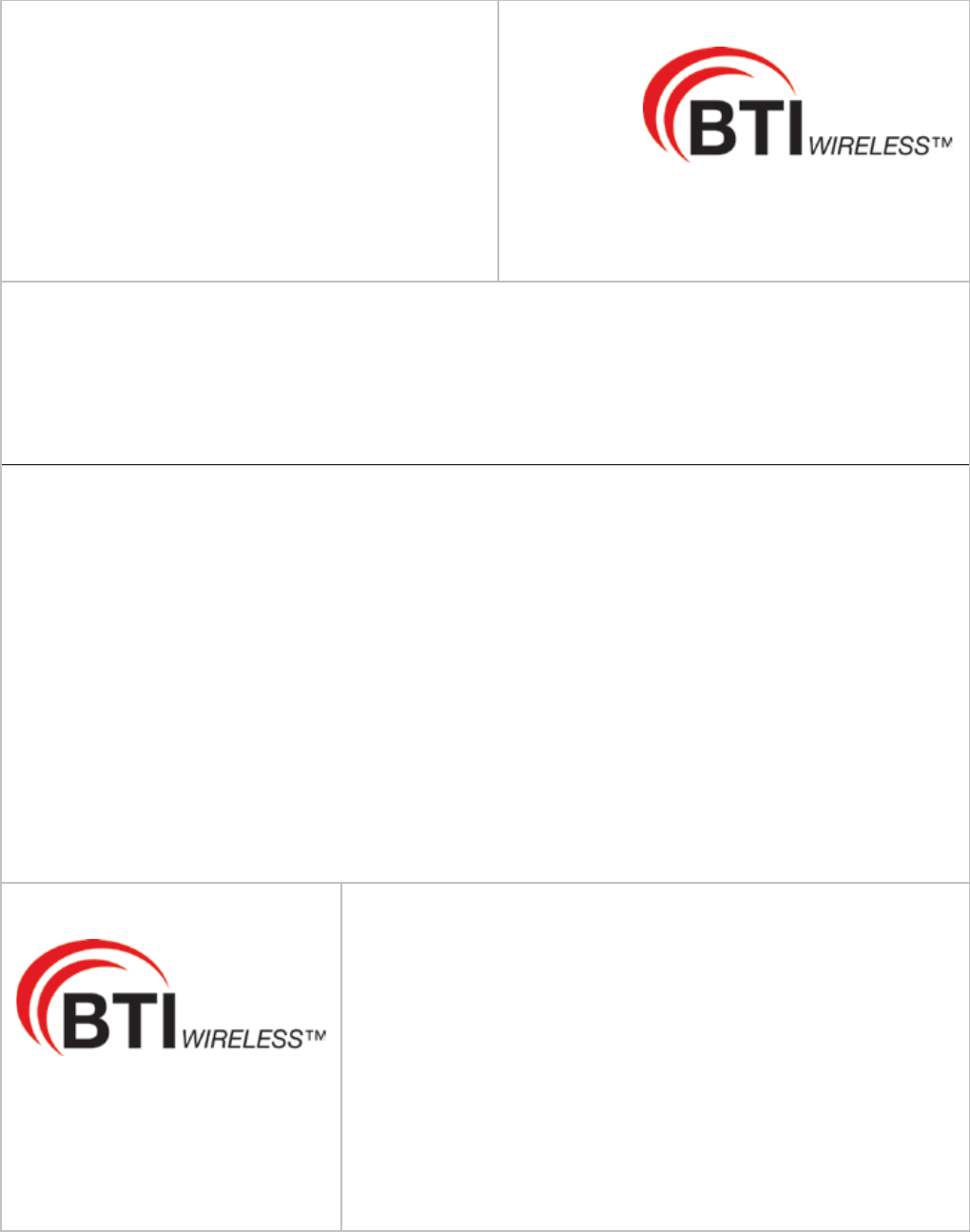
Document Name:
mBSC0700-005-RUXX
mBSC0700-002-RUXX
Revision:
001.02A
Effective Date:
12/15/2015
USER MANUAL
mBSC0700-005-RUXX
mBSC0700-002-RUXX
Medium-Power
Coverage Solution
6185 Phyllis Drive
Cypress, CA 90630
USA
PH: 714.230.8333
Visit our Website at www.BTIwireless.com
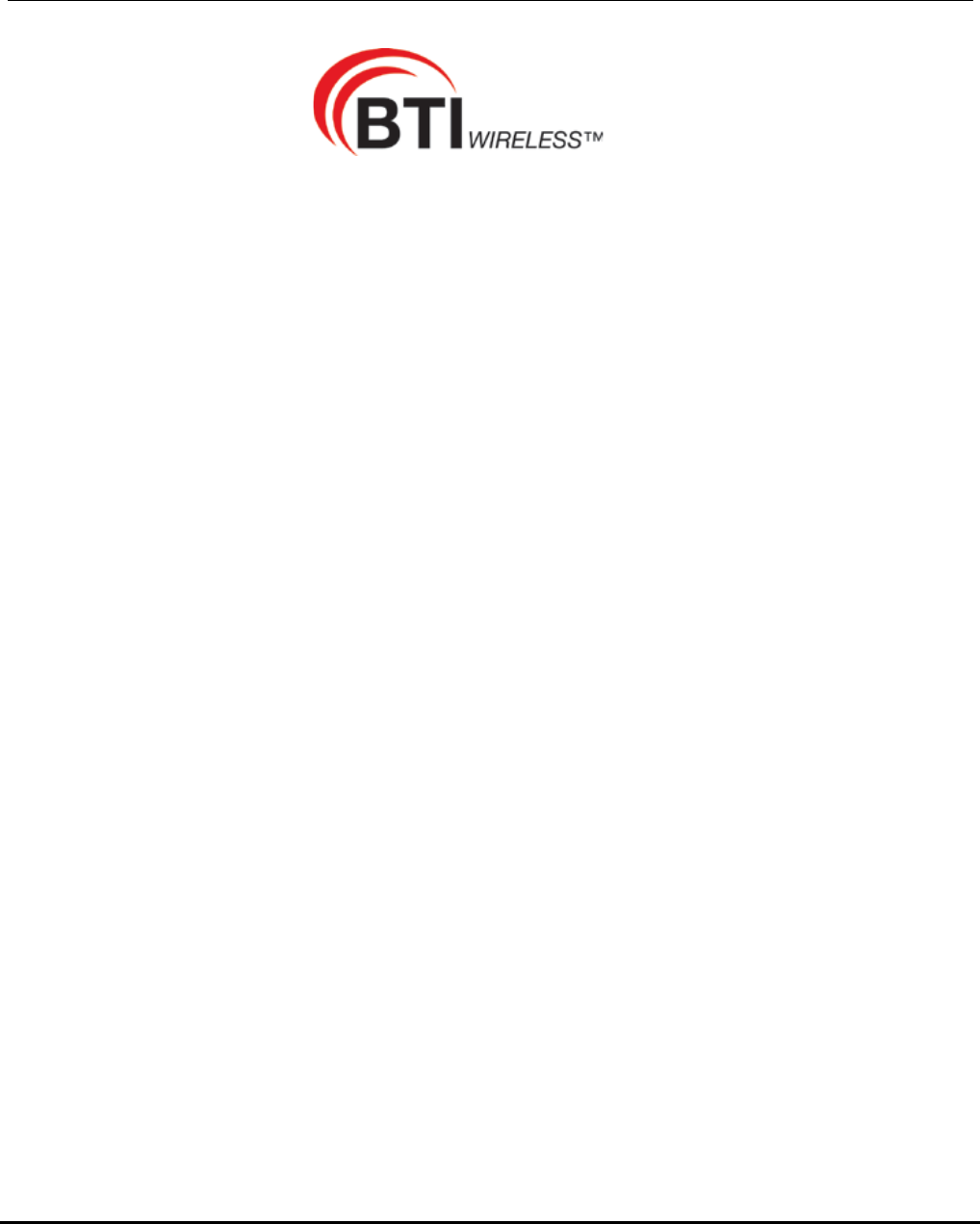
mBSC-CM RUM
BTI Wireless
6185 Phyllis Drive Unit D, Cypress, CA 90630
Phone: 1-714-230-8333
Website: www.btiwireless.com
mBSC-CM
Copyright © 2016 BTI Wireless All rights reserved.
No part of this publication may be reproduced, transmitted, transcribed, stored in a retrieval system, or translated into
any language, in any form or by any means, electronic, mechanical, photocopying, recording, or otherwise, without
prior written permission from BTI Wireless.
All copyright, confidential information, patents, design rights and all other intellectual property rights of whatsoever
nature contained herein are and shall remain the sole and exclusive property of BTI Wireless. The information
furnished herein is believed to be accurate and reliable.
However, no responsibility is assumed by BTI Wireless for its use, or for any infringements of patents or other rights of
third parties resulting from its use.
The BTI Wireless name and BTI Wireless logo are trademarks or registered trademarks of BTI Wireless
All other trademarks are the property of their respective owners
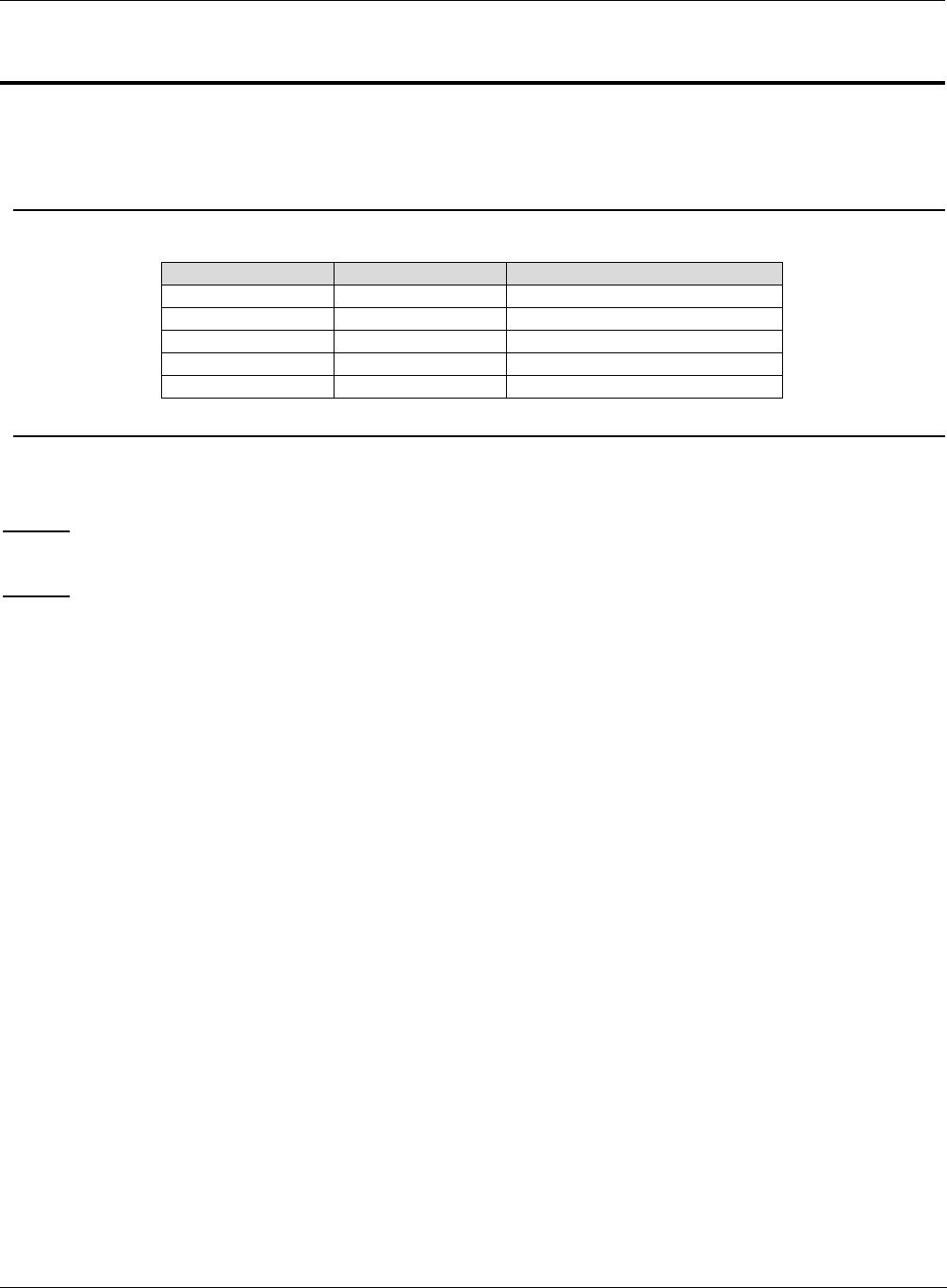
mBSC-CM RUM
©2015-2016 BTI Wireless Inc.
Document History
Paper copies are valid only on the day they are printed. Contact the author if you are in any doubt about the
accuracy of this document.
Revision History
Revision Number
Revision Date
Summary of Changes
001.00A
5/28/2013
Initial Release for NA
001.01A
4/15/2013
Updated for new EMS
001.02A
12/15/2015
Added new modules
GENERAL SAFETY PRECAUTIONS
Warning: Wet conditions increase the potential for receiving an electrical shock when installing or using electrically-powered
equipment. To prevent electrical shock, never install or use electrical equipment in a wet location or during a lighting storm.
Warning: This is NOT a CONSUMER device. It is designed for installation by FCC LICENSEES and QUALIFIED
INSTALLERS. You MUST have an FCC LICENSE or express consent of an FCC License to operate this device. Unauthorized
use may result in significant forfeiture penalties, including penalties in excess of $100,000 for each continuing violation.
Improper installation and operation of this equipment outside of the recommended installation procedures, and operation
beyond the designed operating specifications, and/or not in compliance with regulatory requirements, will revoke any warranty
and may:
Prevent the equipment from performing properly
Violate regulatory RF emissions requirements
Require removal of the equipment from service.
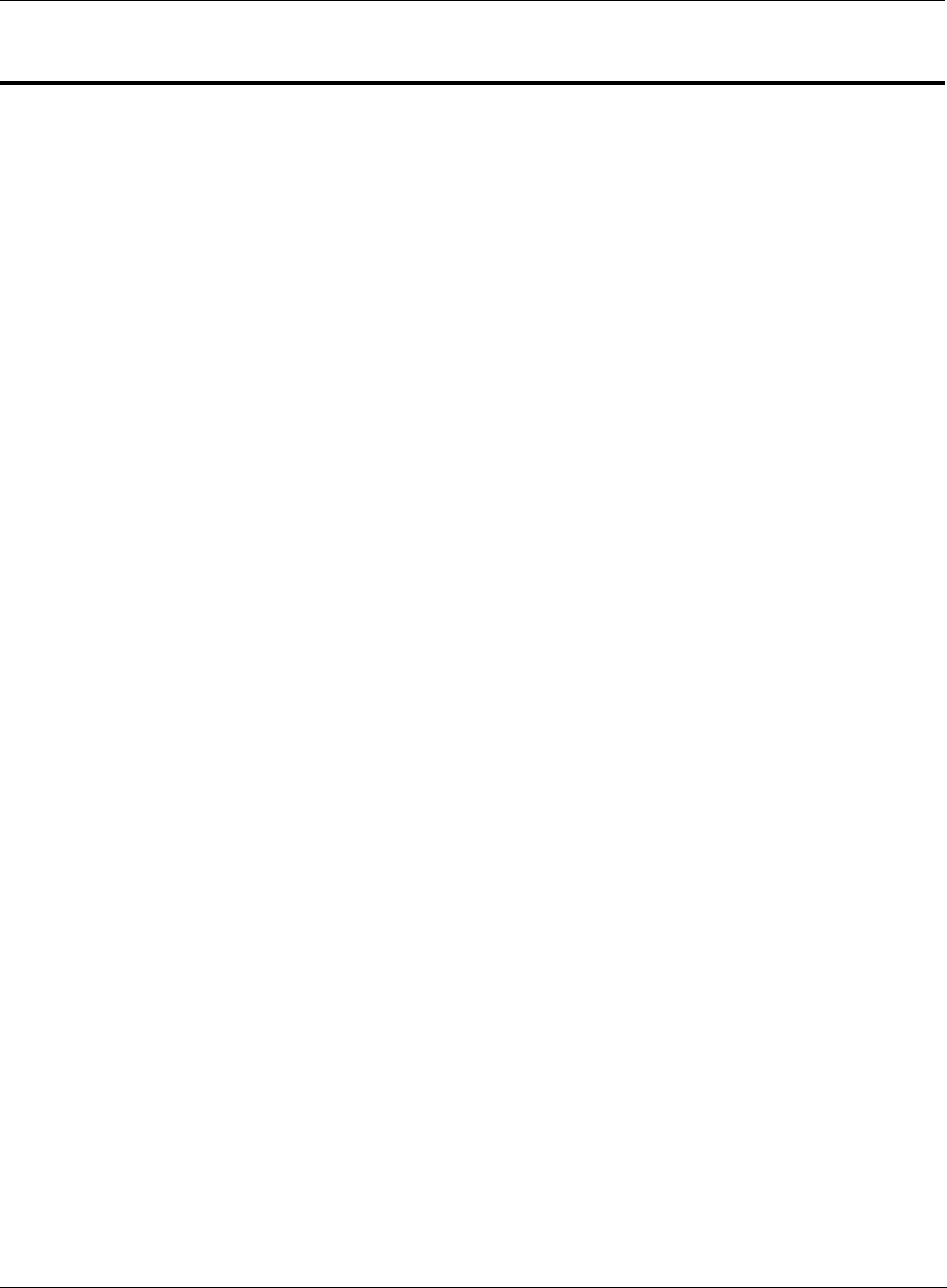
mBSC-CM RUM
©2015-2016 BTI Wireless Inc.
TABLE OF CONTENTS
1 INTRODUCTION 1
1.1 SYSTEM SOLUTION BLOCK DIAGRAM 1
1.1.1 Host Unit 1
1.1.2 Remote Node 2
2 SAFETY 3
3 SYSTEM OVERVIEW AND UNIT DESCRIPTION 4
3.1 SYSTEM OVERVIEW 4
3.1.1 Interface with BTS 5
3.1.2 Interface with Cellular Phones 5
3.1.3 Fiber Optic Transport 5
3.1.4 Powering 5
3.1.5 Cooling 5
3.1.6 Fault Detection and Alarm Reporting 5
3.2 HOST UNIT DESCRIPTION 6
3.2.1 Host Unit Components 6
3.2.2 Mounting 9
3.2.3 Fault Detection and Alarm Reporting 9
3.2.4 RF Signal Connections 9
3.2.5 Optical Connections 9
3.2.6 Powering 10
3.2.7 Host Unit Interface 10
3.3 REMOTE NODE DESCRIPTION 12
3.3.1 BCM Enclosure 12
3.3.2 Single-band RUM Enclosure 14
3.3.3 RTM 18
3.3.4 RPM 21
4 SYSTEM INSTALLATION 24
4.1 UNPACKING AND INSPECTION 24
4.2 INSTALLATION PREPARATION 24
4.2.1 Required Tools 24
4.2.2 Installation Location 24
4.2.3 Anti-corrosion and Shock-protection 25
4.2.4 Lighting, Ventilation and Fire Protection 25
4.2.5 Power Requirements 25
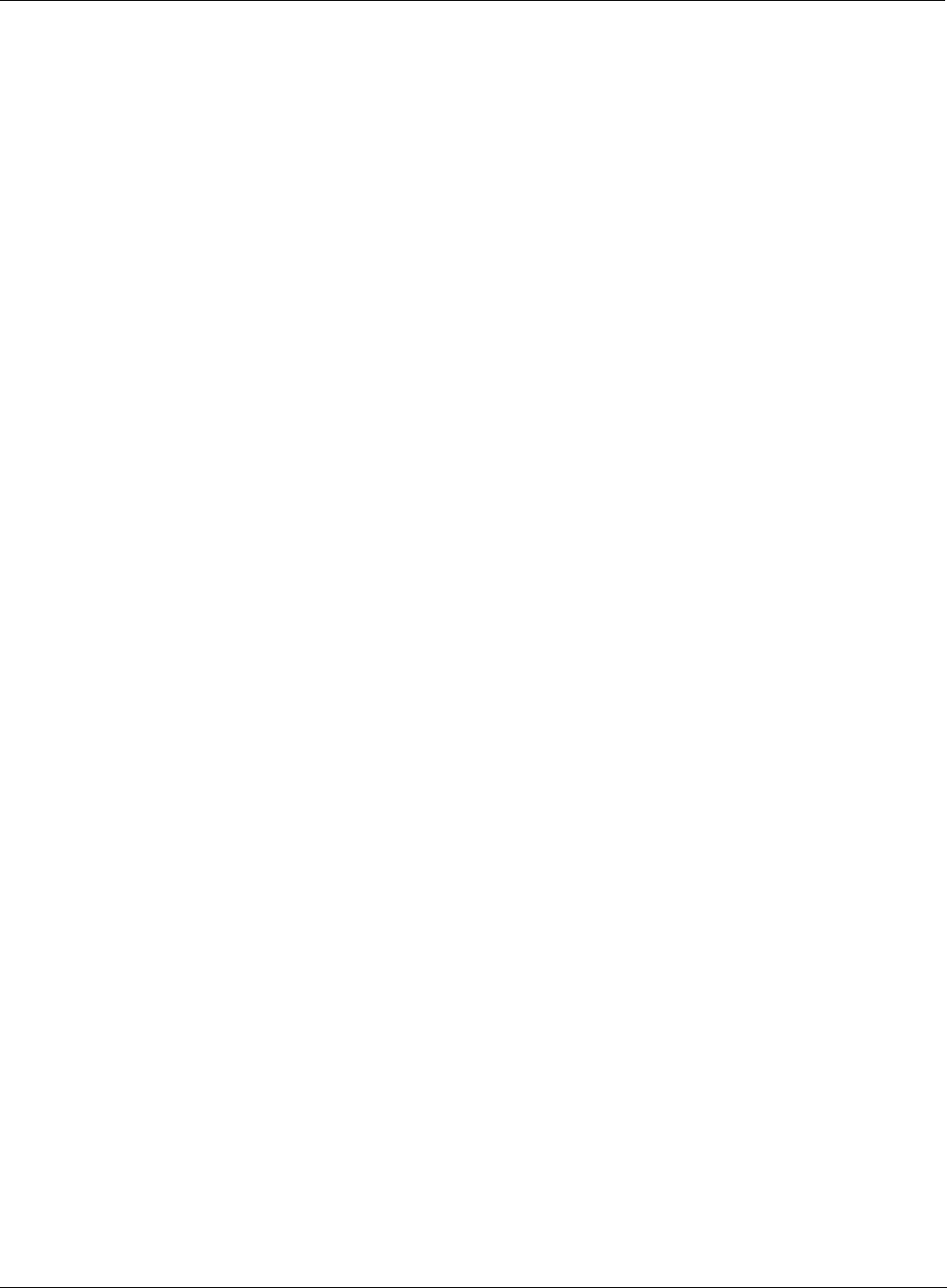
mBSC-CM RUM
©2015-2016 BTI Wireless Inc.
4.2.6 Lightning Protecting and Grounding 25
4.3 HOST UNIT INSTALLATION 25
4.3.1 Rack Mounting 25
4.3.2 Cable Connections 27
4.4 REMOTE NODE INSTALLATION 31
4.4.1 Cable Connections 32
4.5 INSTALLATION FINAL INSPECTION 36
4.5.1 Host Unit Connection Overview 37
4.5.2 Remote Node Connection Overview 38
4.5.3 mBSC-C Inspection Checklist 39
4.5.4 Cabling Inspection 39
4.6 SYSTEM TEST 39
5 SYSTEM MONITORING &CONFIGURATION 41
5.1 ACCESSING EMS LOCAL GUI 41
5.1.1 Using Ethernet Port 41
5.1.2 Using USB Port 42
5.1.3 Login to EMS Local GUI 43
5.2 NAVIGATING THE EMS LOCAL GUI 44
5.2.1 Topology Tool Bar 45
5.2.2 Upgrade/Password Functions 46
5.3 INSTALLATION & CONFIGURATION 46
5.3.1 Network & Communications 46
5.3.2 System Installation 48
5.3.3 Alarms 53
5.4 SYSTEM TUNING 55
5.4.1 BTS Signal Conditioning 55
5.4.2 Set Downlink Gain 55
5.4.3 Set Uplink Gain 58
5.4.4 Link Verification 60
5.5 MONITORING AND ALARMS 62
5.5.1 Operational Status 62
5.5.2 System Alarms 64
5.6 SYSTEM UPGRADE 65
5.6.1 Verify Software Versions 65
5.6.2 Upgrade component software 65
6 MAINTENANCE 66

mBSC-CM RUM
©2015-2016 BTI Wireless Inc.
6.1 ELECTROSTATIC DISCHARGE PRECAUTIONS 66
6.2 PREVENTATIVE MAINTENANCE 66
6.3 FAULT DETECTION AND ALARM REPORTING 66
6.4 TROUBLESHOOTING QUICK GUIDE 67
6.4.1 Host Unit Trouble Shooting 68
6.4.2 Remote Unit Trouble Shooting 69
7 TERMS, ACRONYMS & ABBREVIATIONS 70
8 PACKING LIST 71

mBSC-CM RUM
©2015-2016 BTI Wireless Inc.
LIST OF FIGURES
FIGURE 1BLOCK DIAGRAM OF HOST UNIT ................................................................................................................................. 1
FIGURE 2 BLOCK DIAGRAM OF REMOTE NODE .......................................................................................................................... 2
FIGURE 3MBSC SYSTEM FUNCTIONAL OVERVIEW ..................................................................................................................... 4
FIGURE 4 HOST UNIT .................................................................................................................................................................. 6
FIGURE 5BIU ............................................................................................................................................................................. 7
FIGURE 6FIU .............................................................................................................................................................................. 7
FIGURE 7 PSU ............................................................................................................................................................................ 8
FIGURE 8RCU ............................................................................................................................................................................ 9
FIGURE 9 HOST UNIT USER INTERFACE .................................................................................................................................... 11
FIGURE 10FIBER BCM ENCLOSURE OUTLINE .......................................................................................................................... 13
FIGURE 11FIBER BCM INTERIOR LAYOUT ............................................................................................................................... 13
FIGURE 12BCM ENCLOSURE USER INTERFACE ........................................................................................................................ 14
FIGURE 13SINGLE-BAND RU ENCLOSURE ................................................................................................................................ 15
FIGURE 14 SINGLE-BAND RU ENCLOSURE USER INTERFACE ................................................................................................... 17
FIGURE 15 RTM ENCLOSURE .................................................................................................................................................... 18
FIGURE 16 RTM INTERIOR LAYOUT ......................................................................................................................................... 19
FIGURE 17 RTM INTERFACE ..................................................................................................................................................... 21
FIGURE 18 RPM OUTLINE ........................................................................................................................................................ 22
FIGURE 19 RPM INTERIOR LAYOUT .......................................................................................................................................... 23
FIGURE 20 MOUNTING BRACKETS FOR 19” RACK INSTALLATION ............................................................................................ 26
FIGURE 21HOST UNIT-19” RACK MOUNTING VIEW ................................................................................................................. 26
FIGURE 22HOST UNIT GROUNDING STUD ................................................................................................................................ 27
FIGURE 23 GROUNDED HOST UNIT ........................................................................................................................................... 28
FIGURE 24 BTS QMA COAXIAL CABLE CONNECTION ............................................................................................................. 29
FIGURE 25SINGLE MODE PATCH CORD(E2000/APC) ............................................................................................................... 29
FIGURE 26E2000 FIBER OPTIC PORT ON HOST UNIT FIU ......................................................................................................... 29
FIGURE 27 48VDC HOST POWER CONNECTION ....................................................................................................................... 30
FIGURE 28IP CONNECTION FOR LOCAL GUI CONTROL ............................................................................................................. 31
FIGURE 29MODEM PORT ON RCU (DB9 MALE) ....................................................................................................................... 31
FIGURE 35 RF INTER-CONNECT BETWEEN BCM AND SINGLE-BAND RU ................................................................................. 33
FIGURE 36 RF INTER-CONNECT BETWEEN RTM AND SINGLE-BAND RU .................................................................................. 34
FIGURE 37 FIBER OPTIC CABLE CONNECTION TO RTM ENCLOSURE ........................................................................................ 35
FIGURE 38 RPM ....................................................................................................................................................................... 36
FIGURE 40HOST UNIT CONNECTION OVERVIEW ....................................................................................................................... 37
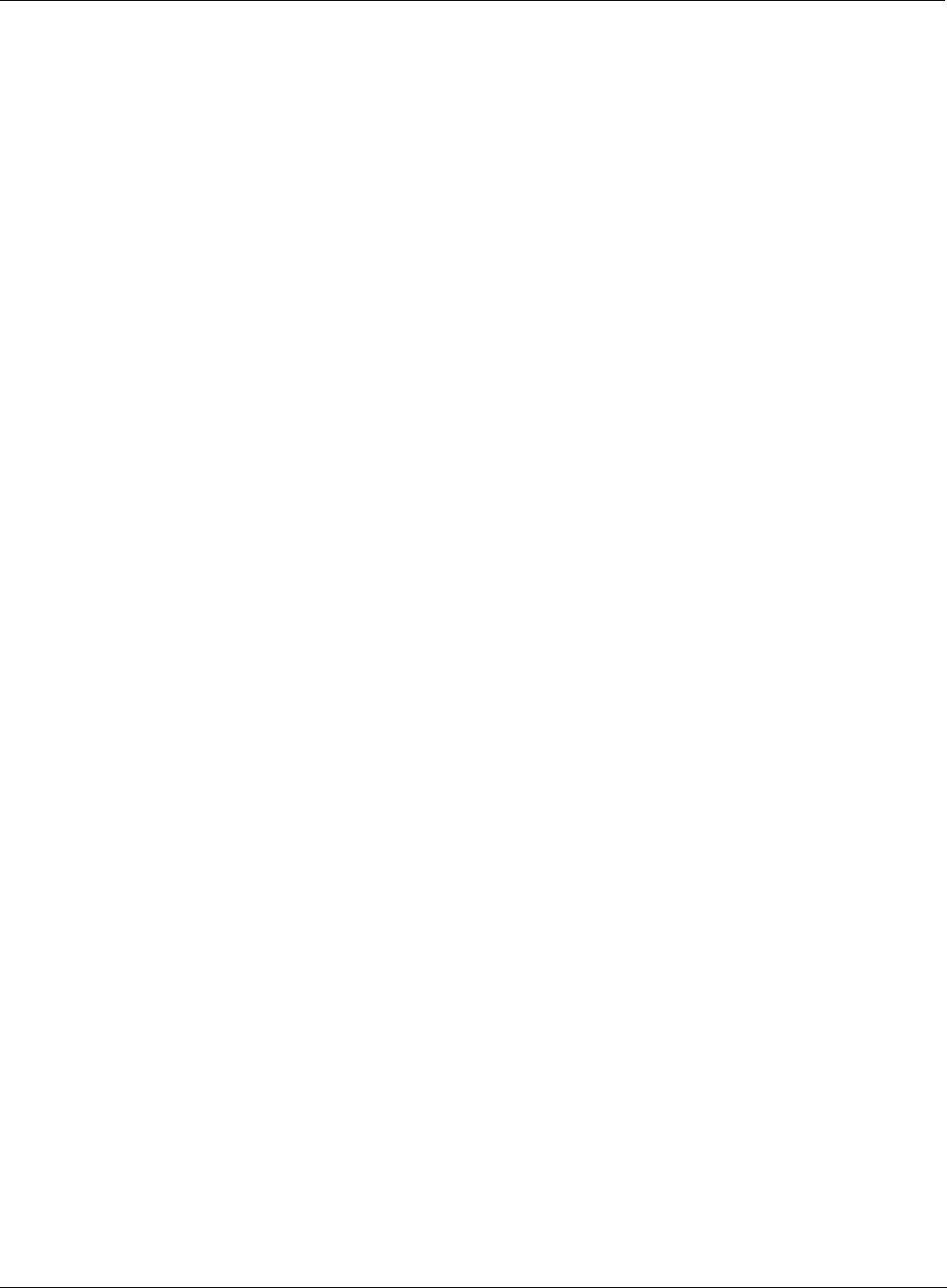
mBSC-CM RUM
©2015-2016 BTI Wireless Inc.
FIGURE 41 REMOTE NODE INTER-CONNECTION DIAGRAM ...................................................................................................... 38
FIGURE 42 FLOW CHART OF SYSTEM DEBUGGING ................................................................................................................... 40
FIGURE 43– EMS LOCAL GUI LOGIN ....................................................................................................................................... 43
FIGURE 44- MAIN PAGE EXPANDED TOPOLOGY ....................................................................................................................... 44
FIGURE 45- MAIN PAGE SUMMARY VIEW ................................................................................................................................. 45
FIGURE 46- RCU COMPONENT VIEW ....................................................................................................................................... 47
FIGURE 47- MAIN PAGE EQUIPMENT STATUS ............................................................................................................................ 49
FIGURE 48- FIU OPTICAL POWER LEVELS ................................................................................................................................ 50
FIGURE 49- RTM OPTICAL POWER LEVELS .............................................................................................................................. 51
FIGURE 50 - EMS LOCAL GUI SOFTWARE VERSION ................................................................................................................. 52
FIGURE 51 - COMPONENT SOFTWARE VERSIONS ...................................................................................................................... 52
FIGURE 52 – OPTICAL LINK ALARMS ........................................................................................................................................ 54
FIGURE 53 - BIU ATTENUATOR ................................................................................................................................................. 56
FIGURE 54 - RU ATTENUATOR .................................................................................................................................................. 58
FIGURE 55 – UP/DOWN LINK VERIFICATION ............................................................................................................................ 61
FIGURE 56 - HOST UNIT ALARM STATUS .................................................................................................................................. 62
FIGURE 57 - REMOTE NODE ALARM STATUS ............................................................................................................................ 63
FIGURE 58 - COMPONENT UPGRADE ......................................................................................................................................... 65
FIGURE 59HOST UNIT TROUBLE SHOOTING ............................................................................................................................. 68
FIGURE 60REMOTE UNIT TROUBLE SHOOTING ........................................................................................................................ 69

mBSC-CM RUM
©2015-2016 BTI Wireless Inc.
LIST OF TABLES
TABLE 1 HOST UNIT USER INTERFACE...................................................................................................................................... 10
TABLE 2HOST UNIT INDICATOR DESCRIPTION .......................................................................................................................... 12
TABLE 6BCM ENCLOSURE USER INTERFACE ........................................................................................................................... 14
TABLE 7 SINGLE-BAND RUM ENCLOSURE USER INTERFACE ................................................................................................... 17
TABLE 8 INDICATOR DESCRIPTION ............................................................................................................................................ 18
TABLE 3 RF-OPTIC TRANSCEIVER INTERFACE .......................................................................................................................... 19
TABLE 4 DB9 PINOUTS .......................................................................................................................................................... 19
TABLE 5 RF-OPTIC TRANSCEIVER INDICATORS ........................................................................................................................ 20
TABLE 6FIBER RTM ENCLOSURE USER INTERFACE ................................................................................................................. 21
TABLE 8 INDICATOR DESCRIPTION ............................................................................................................................................ 21
TABLE 10MBSC UNIT INSPECTION ........................................................................................................................................... 39
TABLE 11 CABLE INSPECTION ................................................................................................................................................... 39
TABLE 12LOCAL GUI DEFAULT USER ACCOUNTS .................................................................................................................... 43
TABLE 13 TOOL BAR FUNCTIONS ............................................................................................................................................. 45
TABLE 14 GENERAL GUI TOOLS .............................................................................................................................................. 46
TABLE 15SYSTEM ALARMS ...................................................................................................................................................... 64
TABLE 16 TROUBLESHOOTING QUICK GUIDE ........................................................................................................................... 67
TABLE 17 TERMS, ACRONYMS AND ABBREVIATIONS ................................................................................................................ 70
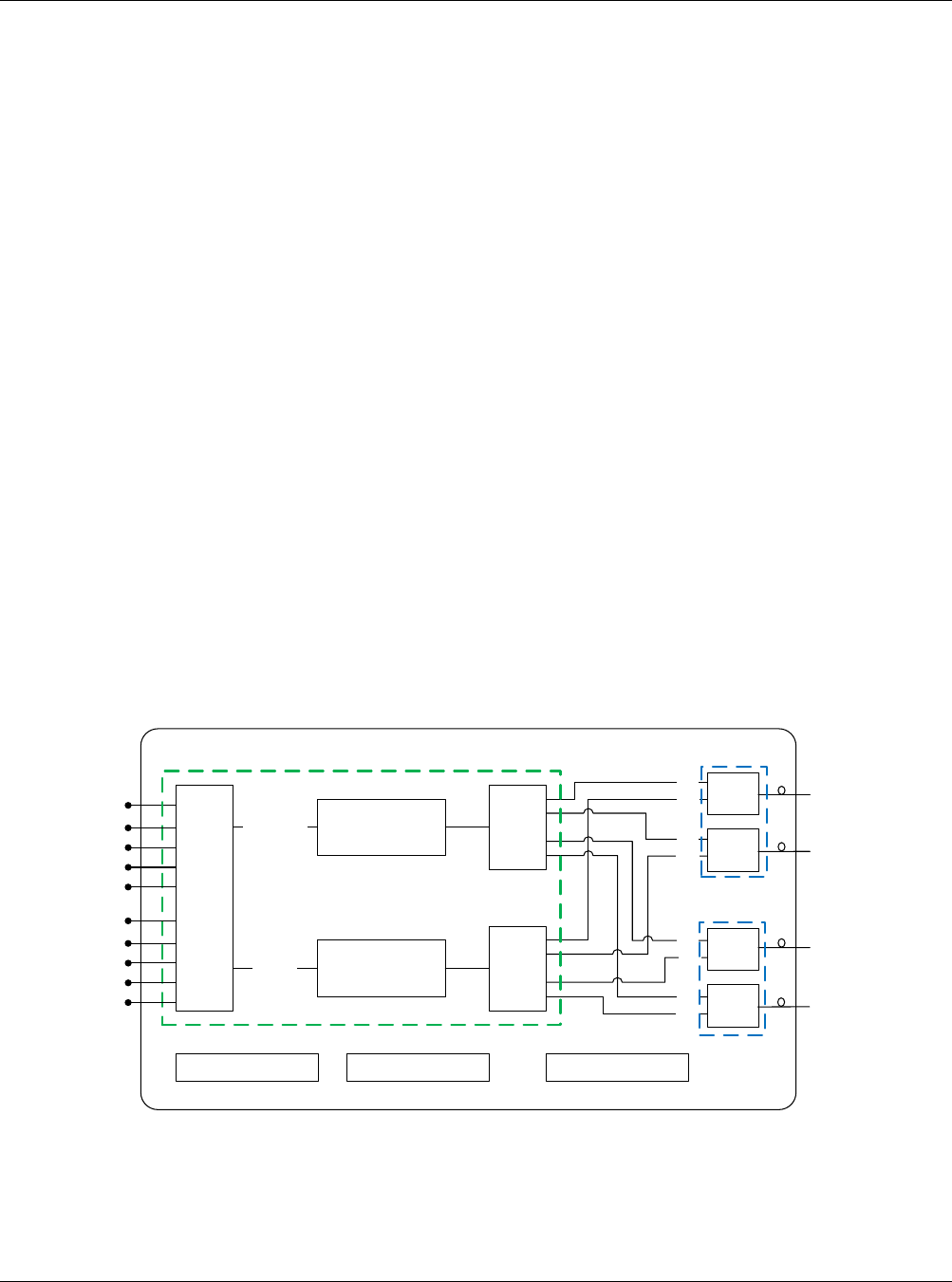
mBSC-CM RUM
mBSC-CM December 15, 2015
Page 1
1 Introduction
The MBSC-C Fiber Optic Coverage System is used to extend wireless coverage to specific areas in
building(s), or throughout a complex zone. The mBSC product family offers a flexible, scalable, modular
platform to improve signal quality and enhance the services to meet the increasing demands.
The MBSC-C system components include a Host Unit (HU) and a Remote Node. Each Host Unit can feed
up to eight multi-band Remote Nodes, each utilizing a single fiber. A Remote Node can accommodate
between one and five single-band bi-directional amplifiers (Remote Units) – install only the bands required
at the time of deployment. As requirements change, additional single-band units can be easily installed in
the field. This modular architecture provides optimum implementation flexibility, reduces initial cost, and
defers further investment until required.
1.1 System Solution Block Diagram
The MBSC-C platform allows flexible system deployment to support mixed mode 700~2700MHz services in
SISO configurations.
1.1.1 Host Unit
B
a
n
d
R
F
S
ig
n
a
l
P
r
o
c
e
s
s
in
g
F
ilt
e
r
in
g
E/O
Tx Gain &
Gain Ajustment
T
x
S
ig
n
a
l
S
p
lit
t
in
g
700
Rx Gain &
Gain Ajustment
R
x
S
ig
n
a
l
C
o
m
b
in
e
r
E/O
E/O
Tx1
Downlink
Uplink
E/O
Tx2
Tx3
Tx4
Rx1
Rx2
Rx3
Rx4
BIU-I FIU-I
PSU-I PSU-II RCU
0.7~2.6G
0.7~2.6G
FIU-II
HOST UNIT (4:1 Simulcast)
850
1900
2100
2600
700
850
1900
2100
2600
0.7~2.6G
0.7~2.6G
Figure 1Block Diagram of Host Unit
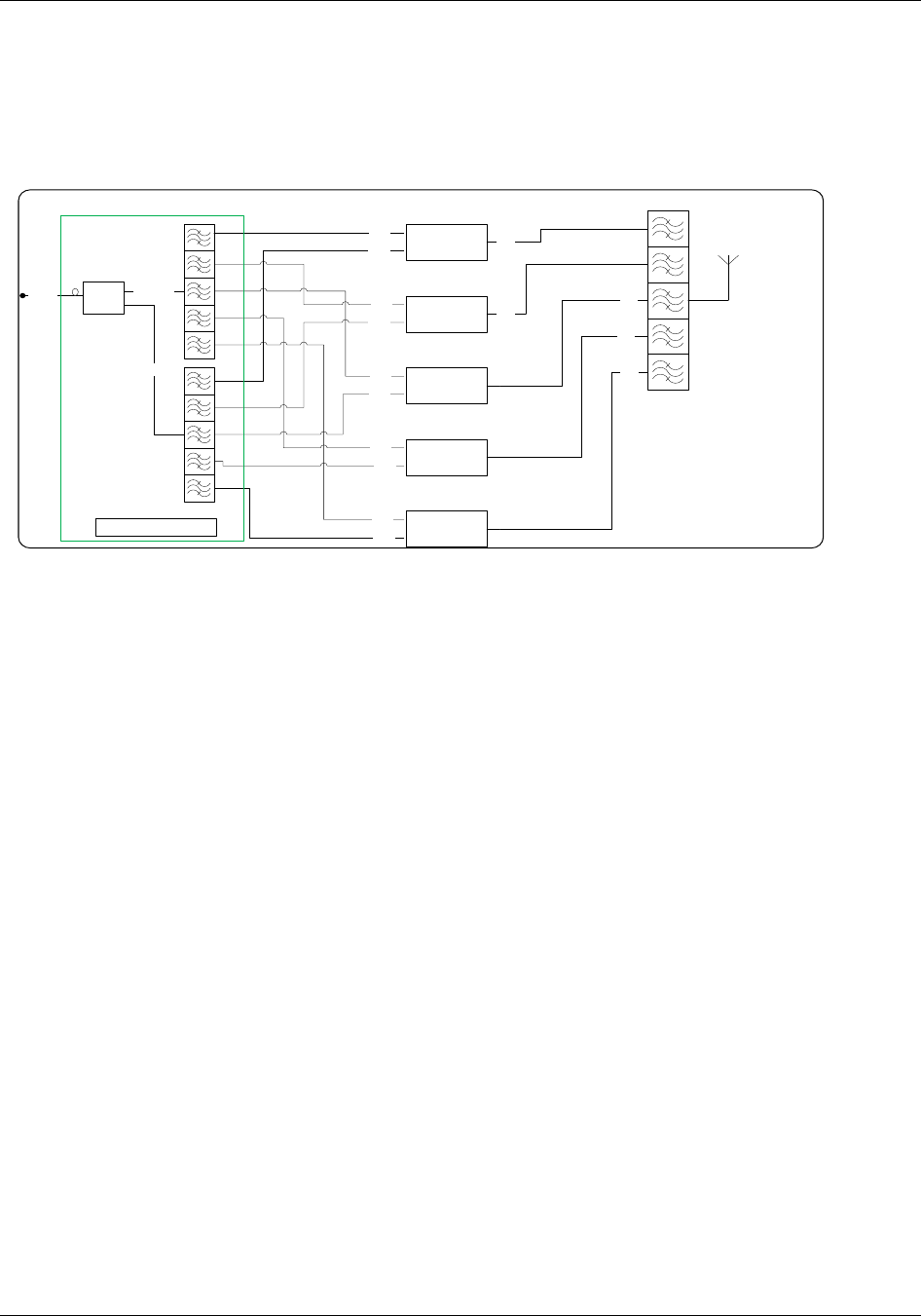
mBSC-CM RUM
mBSC-CM December 15, 2015
Page 2
1.1.2 Remote Node
Tx_0.7~2.6G
Tx_0.8
Rx_0.8
Tx_1.9
Tx_2.1
Rx_0.7
Rx_1.9
Rx_2.1
Rx_0.7~2.6G
O/E
0.7~2.6G
Tx_0.7
Tx_2.6
Rx_2.6
Control Unit #1
RTM
700MHz
UNIT
850MHz
UNIT
1900MHz
UNIT
2100MHz
UNIT
2600MHz
UNIT
Tx/Rx
Tx/Rx
Tx/Rx
Tx/Rx
BCM
Tx/Rx
RUM
RUM
RUM
RUM
RUM
Tx/Rx
Figure 2 Block Diagram of Remote Node
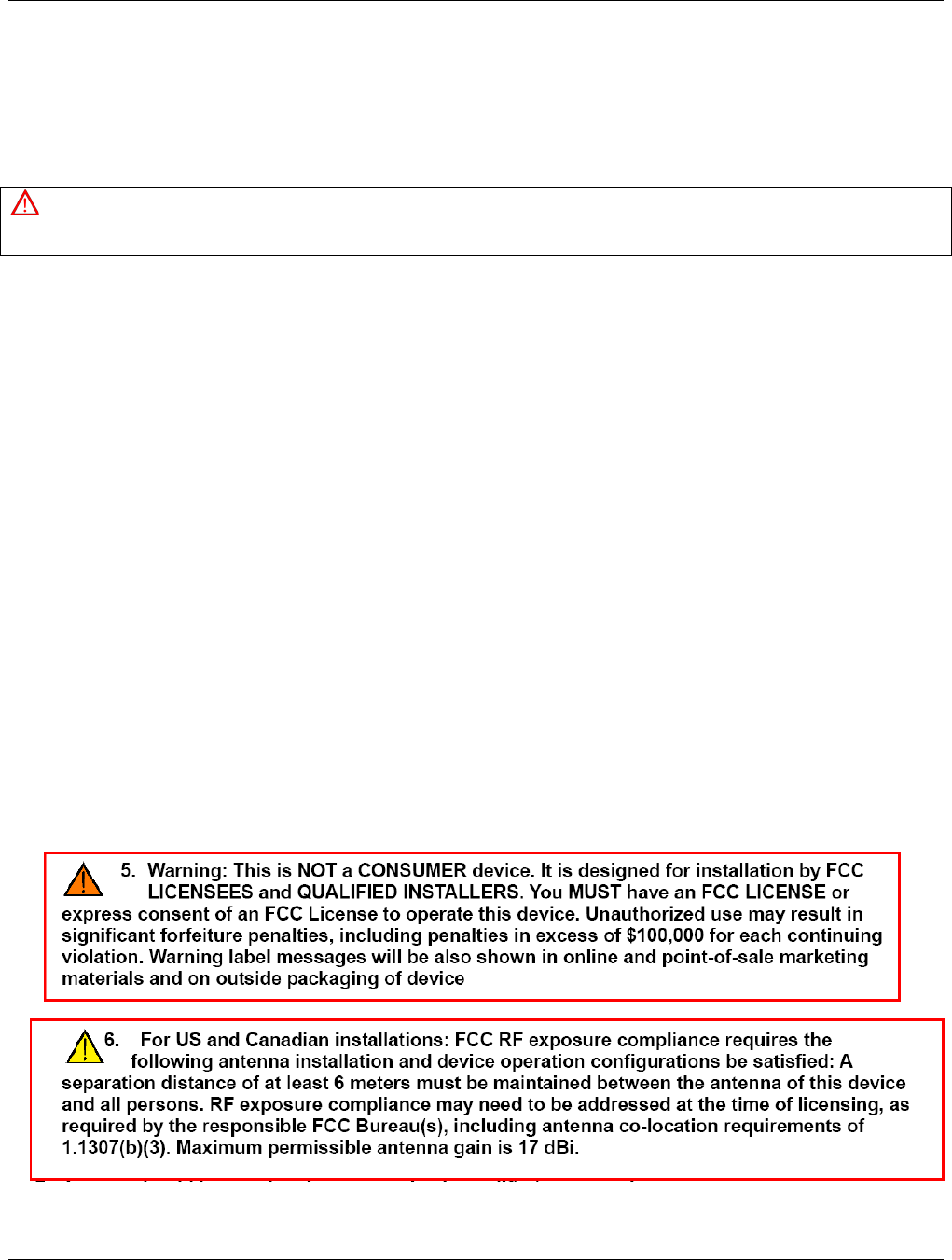
mBSC-CM RUM
mBSC-CM December 15, 2015
Page 3
2 Safety
Caution
All the following “Safety Precautions” must be observed during the entire installation and operation of the mBSC system.
1. The mBSC system is designed for maximum safety and reliability when installed, used, and maintained
by trained and qualified technicians in accordance with the procedures and instructions contained in
this manual. To assure the safe operation of your system, always follow the safety and operational
recommendations in this manual.
2. Read and understand all instructions and warnings before handing the mBSC system.
3. Warning: Do not install or operate mBSC system in the presence of flammable gases or fumes.
4. Warning: mBSC system produces high level of RF radiation.
5. Do not operate exposed circuitry or radiating elements with personnel in close proximity to radiating
source.
6. Persons with cardiac pacemakers should avoid exposure to RF radiating elements.
7. Exposing the human eye to high levels of radio-frequency radiation may result in the formation of
cataracts.
8. Warning: We do not provide the antenna; the antenna and other cable set provide by customs. Please
don’t use unauthorized antennas, cables, and/or coupling devices.
9. Warning: To avoid injuries or damage, use care and obtain assistance before lifting the mBSC unit.
10. Warning: mBSC system should be installed only in restricted access areas (dedicated equipment room,
equipment closet, or similarity designated areas) where access is controlled or where access can only
be gained by service personnel with a key or tool. Access to this equipment is restricted to qualified
service personnel only.
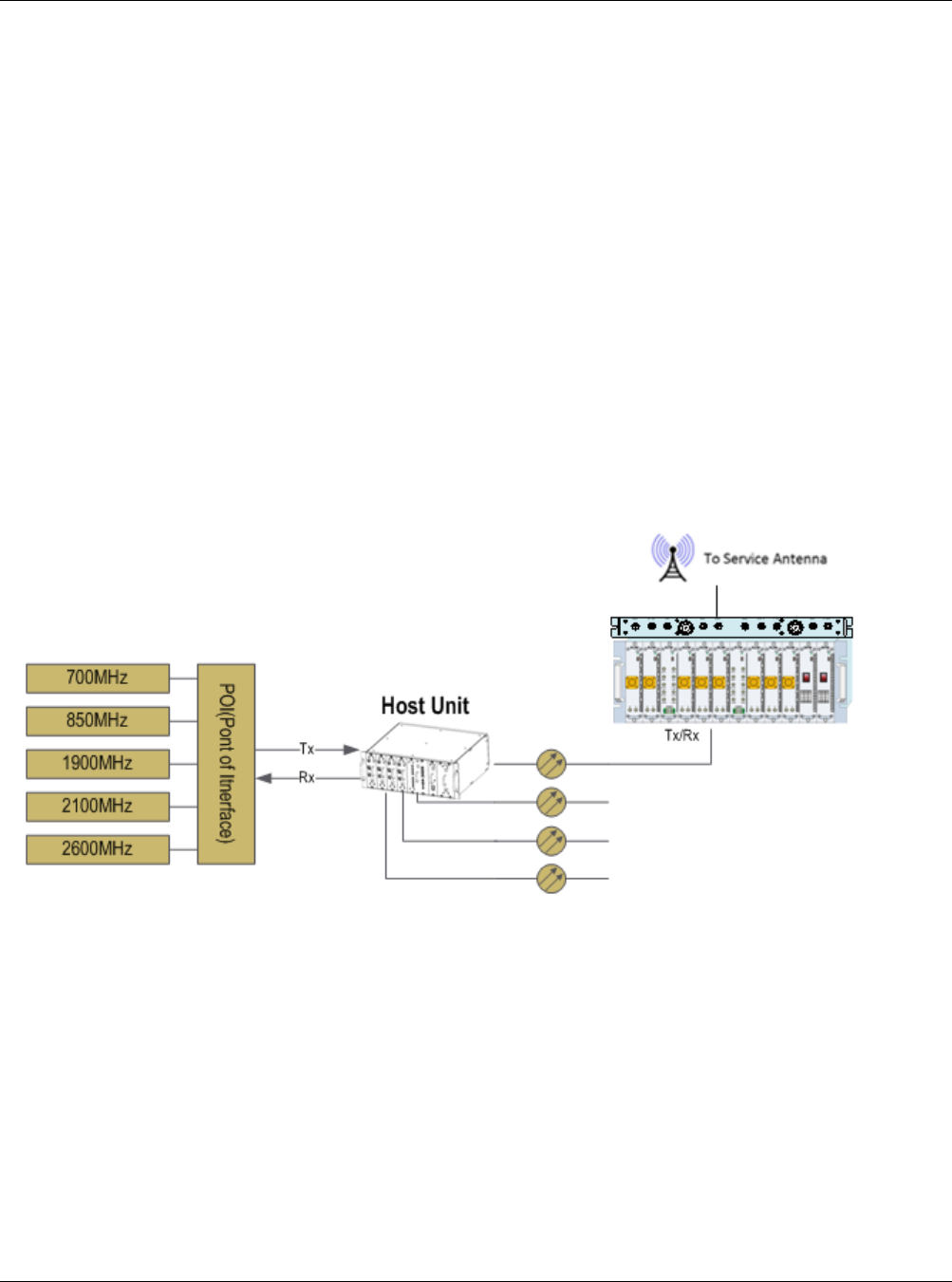
mBSC-CM RUM
mBSC-CM December 15, 2015
Page 4
3 System Overview and Unit Description
3.1 System Overview
The MBSC-C system is a multi-operator, multi-band and multi-technology coverage system that provides
in-building / venue coverage for up to five operating bands. Large buildings typically interfere with the
transmission or reception of cellular phone system signals by imposing high attenuation losses on the RF
signal. The mBSC system is designed to overcome these losses which otherwise make cellular
communications within buildings or structures difficult or impossible. With the mBSC system, cellular phone
RF signals can be distributed to the interior areas of any building or structure to eliminate dead spots and
improve reception.
The MBSC-C coverage solution interconnects to, and extends, the wireless service provider base station
equipment (BTS) and service antennas. A functional overview is illustrated below.
Figure 3mBSC System Functional Overview
The mBSC system provides downlink signal amplification and uplink sensitivity improvement for multi-band
RF signals, which may be comprised of multiple carriers and multiple standards.
The Host Unit provides the input interface for RF signals from a base transceiver station (BTS). The Host
Unit converts the RF signals into a digital format and distributes the digitized signal over fiber to multiple
output ports. An optional Multi-operator Point-of-Interface (POI) combines multiband BTS inputs from
several operators into a single TXin / RXout interface to the Host Unit. Refer to “SP-MBSC-C-POI” for
additional details.
The Remote Node receives the optical signals from the Host Unit, converts the signals back into RF and
interfaces with the service antennas to amplify the RF signals throughout the building. The Remote Node is
typically wall-mounted within an equipment room.

mBSC-CM RUM
mBSC-CM December 15, 2015
Page 5
3.1.1 Interface with BTS
The Host Unit is typically installed close to the wireless service provider BTS equipment. In the downlink
path the Host Unit combines RF signals from up to 5bands and feeds the combined signal to a fiber-optic
transceiver for transmission to the interconnected Remote Node(s).In the uplink path the Host Unit converts
a composite multi-band optical signal into independent RF signals for interconnection with the BTS receive
elements.
3.1.2 Interface with Cellular Phones
The mBSC Remote Node interfaces with the cellular phones through the service antennas. In the reverse
path, the Remote Node receives RF signals from cellular phones. In the forward path, the Remote Unit
transmits the RF signals to the cellular phones. A bi-directional antenna is connected to the mBSC Remote
Node to transmit and receive RF signals from the cellular phones.
3.1.3 Fiber Optic Transport
The Host Unit is connected to each Remote Node over a single optical fiber. The optical fibers must be
terminated withE2000/APC connectors for connection with the Host Unit and the Remote Node. For fiber
transmission, and remote node equipment is required, along with an additional optical fiber.
3.1.4 Powering
The Host Unit is powered by -48V DC which is supplied by either the equipment room power distribution
cabinet or an AC/DC converter. The Remote Node is powered by 110/220VAC, 50/60Hz power which is
supplied through a power supply distribution junction box.
3.1.5 Cooling
The Host Unit is cooled through cross-convection without fans.
The Remote Node contains multiple single-band Remote Units, which are cooled through continuous air
flow fans mounted on the top of each singe-band unit. A minimum of 200mm (7.87 inches) of clearance
space must be provided on both the top and the bottom sides of the Remote Node for air flow.
An alarm is provided that indicates if a high temperature condition occurs.
3.1.6 Fault Detection and Alarm Reporting
LED indicators are provided on the front panel of the Host Unit to indicate if the mBSC system is operating
as expected (normal) or if a fault is detected. In addition, normally open and closed alarm contacts (for both
major and minor alarms) are provided at the Host Unit for connection to a customer provided external alarm
system.
The mBSC system also includes a standalone (optional) Element Management System server, which
interconnects with each Host Unit in a multi-system deployment, and is used for system configuration, status
monitoring, and SNMP alarm reporting / management.

mBSC-CM RUM
mBSC-CM December 15, 2015
Page 6
3.2 Host Unit Description
As shown in Figure 4, the Host Unit is a standard 19”4U rack-mounted shelf, which serves as the BTS
servicing unit for the mBSC system. The Host Unit provides the following basic functions:
RF interface with BTS (Simplex TXin, RXout)
Optical interface to Remote Nodes
Conversion of the forward path(downlink) RF signals into up to four simulcast optical signals
Conversion of up to four reserve(uplink) optical signals to RF signals
Manages and monitors the system alarms and configurations
Provides alarm information to a local alarm or remote system
PSU
1
0
PSU
1
0
177(6.97")
482.6(19")
405.95
(15.98")
FIU
Opreate
FIBER2
TX2
RX2
FIBER1
TX1
RX1
FIU
Opreate
FIBER2
TX2
RX2
FIBER1
TX1
RX1
BIU
Opreate
Tx700
Rx4
IN
Rx3
IN
Rx2
IN
Rx1
IN
Tx4
OUT
Tx3
OUT
Tx2
OUT
Tx1
OUT
Tx850
Tx1900
Tx2100
Tx2600
Rx700
Rx850
Rx1900
Rx2100
Rx2600
RCU
Opreate
RJ45
RS232
Modem
USB
Figure 4 Host Unit
3.2.1 Host Unit Components
The Host Unit is a multi-slot chassis, consisting of 9 slots numbered from left to right: 1 through 9. Slots 7
through 9 are dedicated and specifically keyed for the Remote Control Unit (RCU) and two redundant Power
Supply Units (PSUs). The Host Unit also houses the Base Station Interface Units (BIU) and Fiber Interface
Units (FIU). The Host Unit allows any combination of BIU and FIU modules, up to six in total.
3.2.1.1 BIU (BTS Interface Unit)
The BIU is a frequency agnostic RF interface card that provides simplex TX input and RX output
connections to the BTS equipment. The BIU combines up to 5 bands of RF downlink signal into a composite
signal, which is then split across four TX out connectors for interconnection to up to four fiber modules
(simulcast). In the uplink path the BIU combines up to four separate multi-band uplink signals for distribution
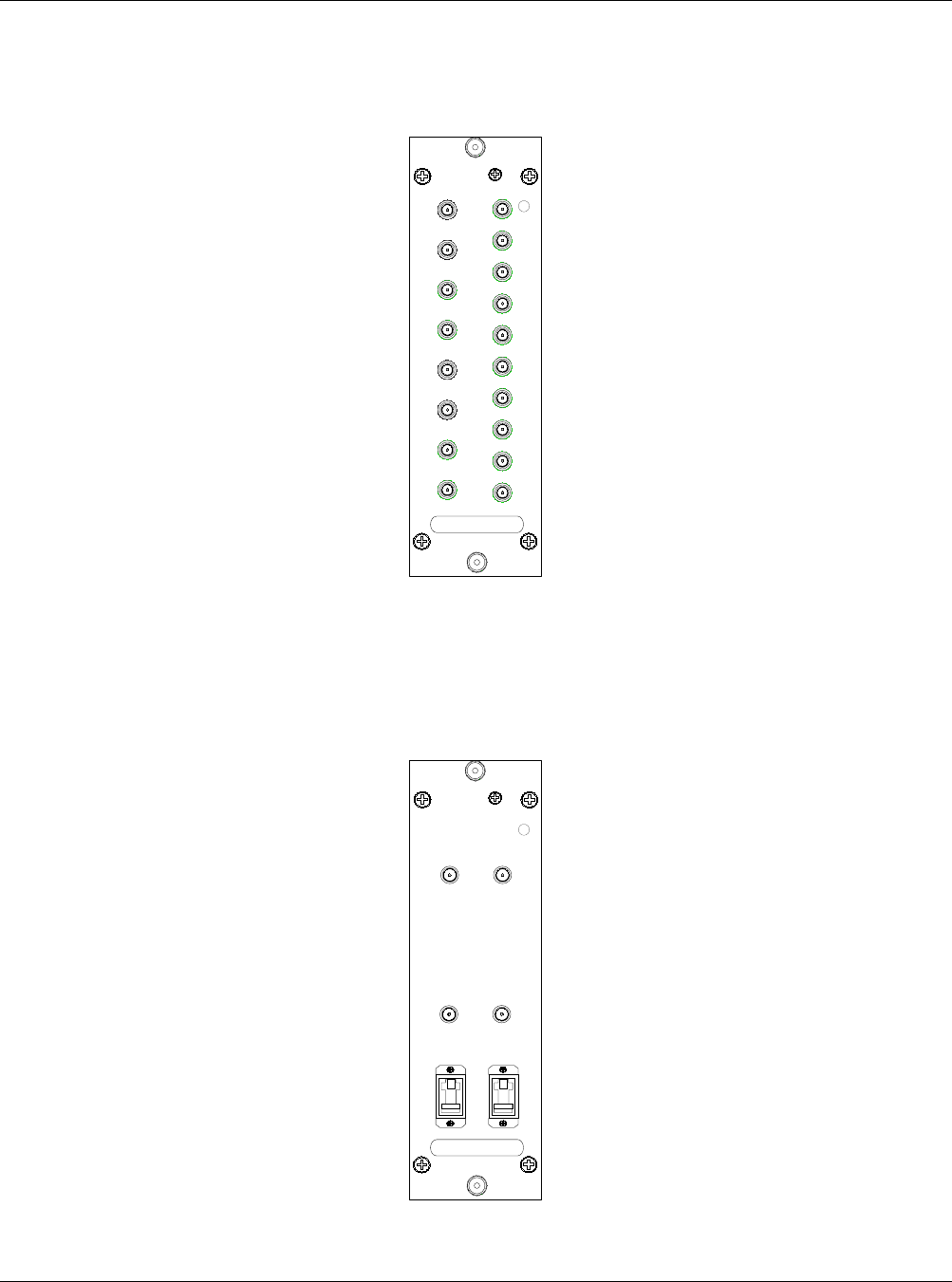
mBSC-CM RUM
mBSC-CM December 15, 2015
Page 7
to the BTS receivers. Internal splitters, combiners, and software controlled attenuators enable customized
designs to support various RF inputs scenarios.
BIU
Opreate
Tx700
Rx4
IN
Rx3
IN
Rx2
IN
Rx1
IN
Tx4
OUT
Tx3
OUT
Tx2
OUT
Tx1
OUT
Tx850
Tx1900
Tx2100
Tx2600
Rx700
Rx850
Rx1900
Rx2100
Rx2600
Figure 5BIU
3.2.1.2 FIU (Fiber Interface Unit)
The FIU provides the interface between the combined RF signals (BIU) and the optical fiber connections.
Each FIU is equipped for 2 independent bi-directional fiber connections.
FIU
Opreate
FIBER2
TX2
RX2
FIBER1
TX1
RX1
Figure 6FIU

mBSC-CM RUM
mBSC-CM December 15, 2015
Page 8
3.2.1.3 PSU (Power Supply Unit)
The Host Unit is powered by -48V DC. The PSU takes the -48 VDC input source power and provides voltage
conversion and distribution for the line cards installed within the host unit shelf. The host unit is equipped
with 2 independent PSU’s in parallel redundancy. Each PSU is hot swappable (one unit at a time only).
PSU
1
0
Figure 7 PSU
3.2.1.4 RCU (Remote Control Unit)
The RCU provides the control and interface for a local Operations and Maintenance Console (OMC) GUI,
and a remote Element Management System (EMS) server through Ethernet or modem connection
(optional).
The RCU is a hot swappable card and will not affect operation of the RF path if removed.
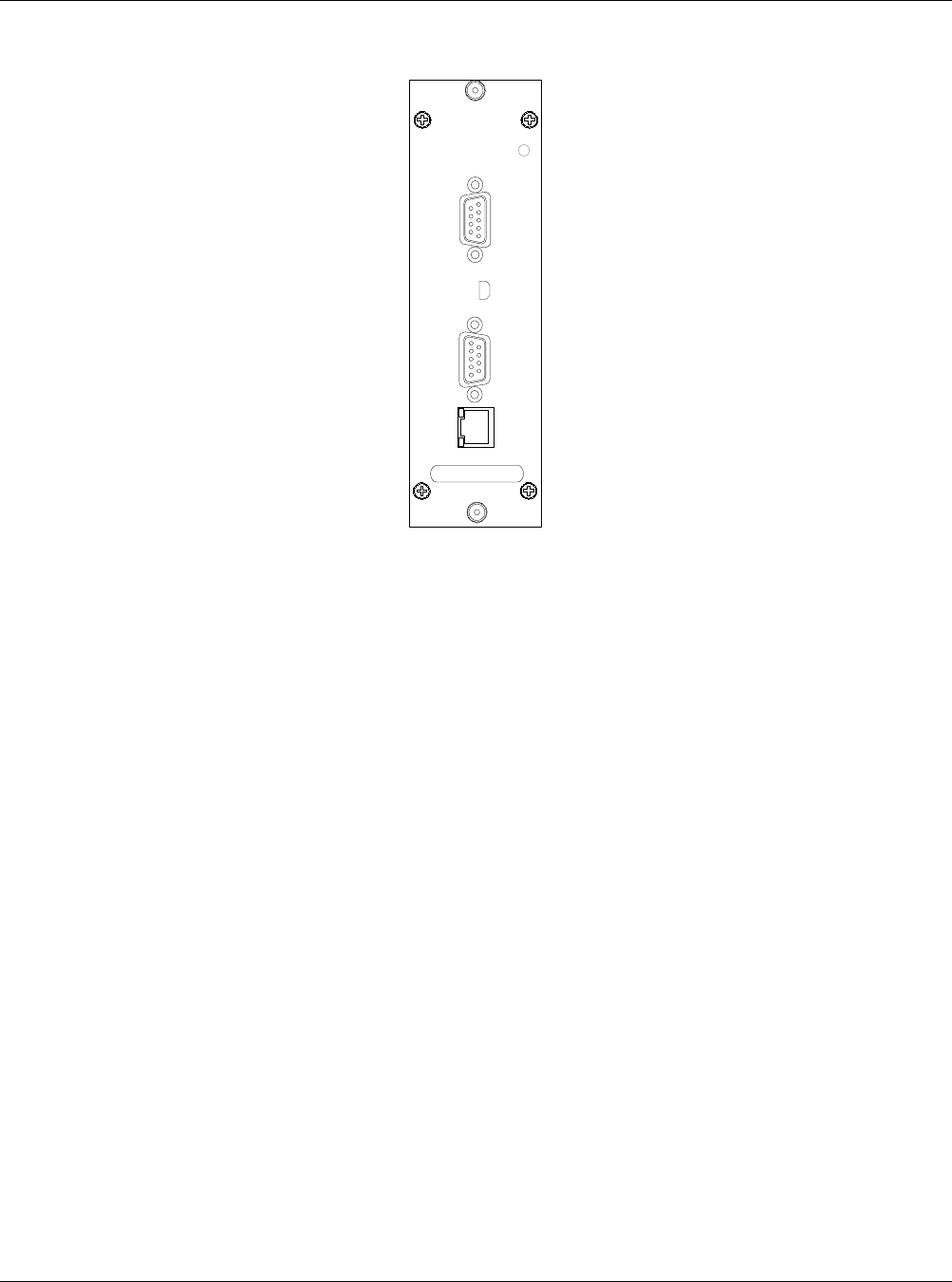
mBSC-CM RUM
mBSC-CM December 15, 2015
Page 9
RCU
Opreate
RJ45
RS232
Modem
USB
Figure 8RCU
3.2.2 Mounting
The Host Unit is intended for use in indoor, rack-mounted applications. For rack mounting, a pair of
mounting brackets is provided that allows the Host Unit to be mounted in a 19” equipment rack. When
rack-mounted, the front panel of the Host Unit is flush with the front of the rack.
3.2.3 Fault Detection and Alarm Reporting
The Host Unit detects internal circuitry faults and optical port faults. Various front panel LED indicators turn
from green to red if a fault is detected or an optical input is lost. A set of dry-contact alarm points(normally
open and normally closed) are also provided for interfacing with an external alarm system.
3.2.4 RF Signal Connections
RF signal connections with the BTS are supported through two QMA female connectors per RF Band (5
bands supported). One QMA connector per band is used for coaxial cable connection of the combined
downlink path (TXin) RF signal. The other QMA connector is used for coaxial cable connection of the
combined uplink path (RXout) RF signal.
Notes: The input RF signal level range to Host Unit is -10dBm - +10dBm, normally it is between -5~0dBm.
3.2.5 Optical Connections
The Host Unit optical connections to the Remote Unit are supported on the Fiber Interface Unit (FIU). Each
FIU supports two independent optical paths, each consisting of a status LED, two QMA RF connectors, and
anE2000/APC optical transceiver using single-mode fiber. Up to five bands of non-overlapping RF signal
can be transported across a single fiber.

mBSC-CM RUM
mBSC-CM December 15, 2015
Page 10
3.2.6 Powering
The Host Unit is powered by -48V DC through a DC power terminal block on the rear. An ON/OFF switch is
provided at the PSU front panel. The switch applies power to the Host Unit internal power supply, which
distributes the operating voltages to lines cards installed in the Host Unit shelf.
3.2.7 Host Unit Interface
The Host Unit interface consists of the various connectors, switches, terminals and LED indicators that are
provided on the front and rear panel. The Host Unit user interfaces are described in Table 1and indicated in
Figure 9.
Table 1 Host Unit User Interface
#
User Interface
Designation
Device Functional Description
PSU
1 ON/OFF Power switch Enable/disable Host Unit internal power supply
2 Power LED(Green/Off) Indicates if the PSU is powered on or off.
Note: The power input port is provided according to the power in type.
RCU
1 Modem (optional) DB9(male) Used for external wired modem connection
2 RS232 (optional) DB9(female) Local connection from PC/Laptop through serial cable
3 RJ45 RJ45 jack (female) Ethernet connection interface for NMS
4 USB Mini USB (female) Used for USB connection for local GUI
5 Operate LED(Green/Red) Indicates if the RCU is normal or faulty
BIU
1 Tx (700~2600) QMA female connector
Band-specific Downlink input from BTS
(one QMA per band, up to 5 bands)
2 Rx (700~2600) QMA female connector
Band-specific Uplink output to BTS
(one QMA per band, up to 5 bands)
3 Tx1~Tx4 QMA female connector
Combined multi-band Downlink signal output to up to four
independent fiber paths (on FIUs)
4 Rx1~Rx4 QMA female connector
Combines multi-band Uplink signal inputs from up to four
independent fiber paths (on FIUs)
5 Operate LED(Green/Red) Indicates if the BIU is normal or faulty
FIU
1 Tx (1~2) QMA female connector Composite Downlink RF input from BIU
2 Rx (1~2) QMA female connector Composite Uplink RF output to BIU
3 Fiber (1~2) E2000/APC WDM optical
transceiver Fiber connection to Remote Node (2 per FIU)
4 Operate LED(Green/Red) Indicates if the FIU is normal or faulty
Enclosure Rear Panel
1 Alarm In Screw-type terminal block Alarm contacts - inputs from an external alarm system
2 Alarm Out Screw-type terminal block Alarm contacts – outputs to an external alarm system
3 DEBUG DB19 male connector Local serial connection for debug by BTI staff only

mBSC-CM RUM
mBSC-CM December 15, 2015
Page 11
#
User Interface
Designation
Device Functional Description
4 Power Input Screw-type terminal block -48VDC power input
5 POI FAN (optional) Screw type terminal +12VDC for external power connection
6 NETWORK RJ45 jack (female) Optional Ethernet connection
PSU
1
0
PSU
1
0
FIU
Opreate
FIBER2
TX2
RX2
FIBER1
TX1
RX1
FIU
Opreate
FIBER2
TX2
RX2
FIBER1
TX1
RX1
BIU
Opreate
Tx700
Rx4
IN
Rx3
IN
Rx2
IN
Rx1
IN
Tx4
OUT
Tx3
OUT
Tx2
OUT
Tx1
OUT
Tx850
Tx1900
Tx2100
Tx2600
Rx700
Rx850
Rx1900
Rx2100
Rx2600
RCU
Opreate
RJ45
RS232
Modem
USB
Composite RF
Tx Connector
(1~2)
Composite RF
Rx Connector
(1~2)
Optical
Transceiver Port
(1~2)
LED
Indicator
Power ON/OFF
Switch
Ethernet
Connector
5-band RF Tx
Connector
(1~4)
RF Rx
Connector
(700~2600MHz)
RF Tx
Connector
(700~2600MHz)
5-band RF Rx
Connector
(1~4)
Serial Port
External Wired
Modem Connector
Front Panel
-48 VDC
redundant
connections
POI Fan Power
interface and monitor
Dry Contact (Form C) alarm output
Input Alarms
Rear Panel
Figure 9 Host Unit User Interface
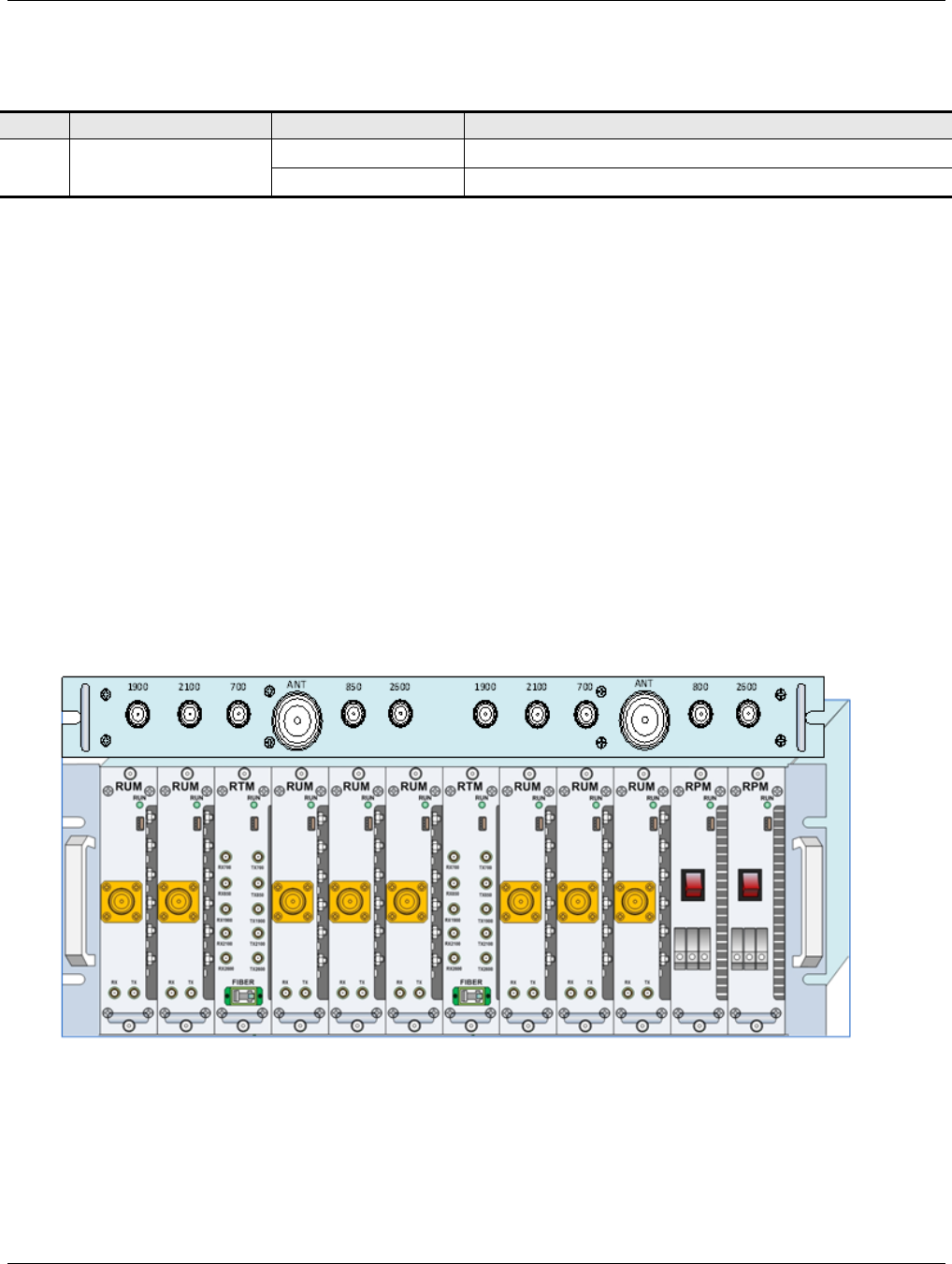
mBSC-CM RUM
mBSC-CM December 15, 2015
Page 12
Table 2Host Unit Indicator Description
#
Indicator
Status
Description
1 RUN Green(Flashing) Normal system operation
Red(Flashing) System fault detected
3.3 Remote Node Description
The Remote Node serves as the remote interface unit for the fiber optic mBSC system. It is a multi-slot
chassis and consisting of 12 slots numbered from left to right, enclosure for up to five RUMs (Remote Unite
Module), RTM (Remote Transmission Unit), RPM (Remote Power Module), BCM (Band Combiner Unit)
and Fan. The Remote Node provides the following basic functions:
RF interface to the mobile end-systems via an external service antenna
Optical interface to the Host Unit FIU
Conversion of the forward path(downlink) optical signal to original RF signal
Conversion of the reverse path(uplink) RF signal to an optical signal
Transports alarm status over the optical fiber
Supplies in-band messaging between the Host Unit and the Remote Node for Remote Node
alarms and configuration
3.3.1 BCM Enclosure
The BCM module provides function:
Combines the RF signals from each single-band RU Enclosure for duplex interconnection with the
service antenna
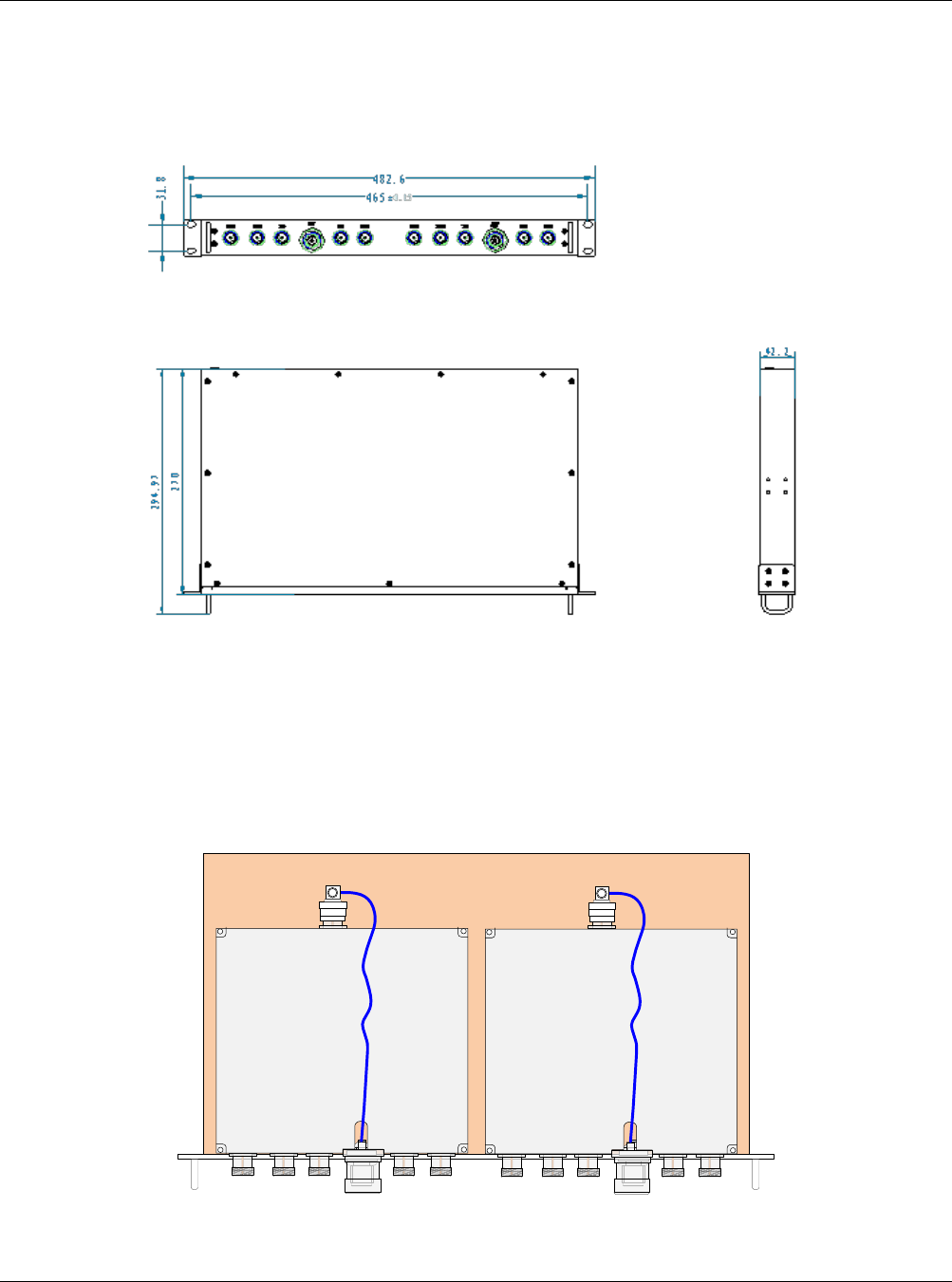
mBSC-CM RUM
mBSC-CM December 15, 2015
Page 13
Figure 10Fiber BCM Enclosure Outline
3.3.1.1 Primary Components
The fiber BCM enclosure interior layout, shown in Figure 11, is equipped to interface up to five bands
(700MHz, 850MHz, 1900MHz, 2100MHz and 2600MHz).
430MM
PCS1900 AWS2100 LTE700 CDMA800 2600
COM
PCS1900 AWS2100 LTE700 CDMA800 2600
COM
Figure 11Fiber BCM Interior Layout
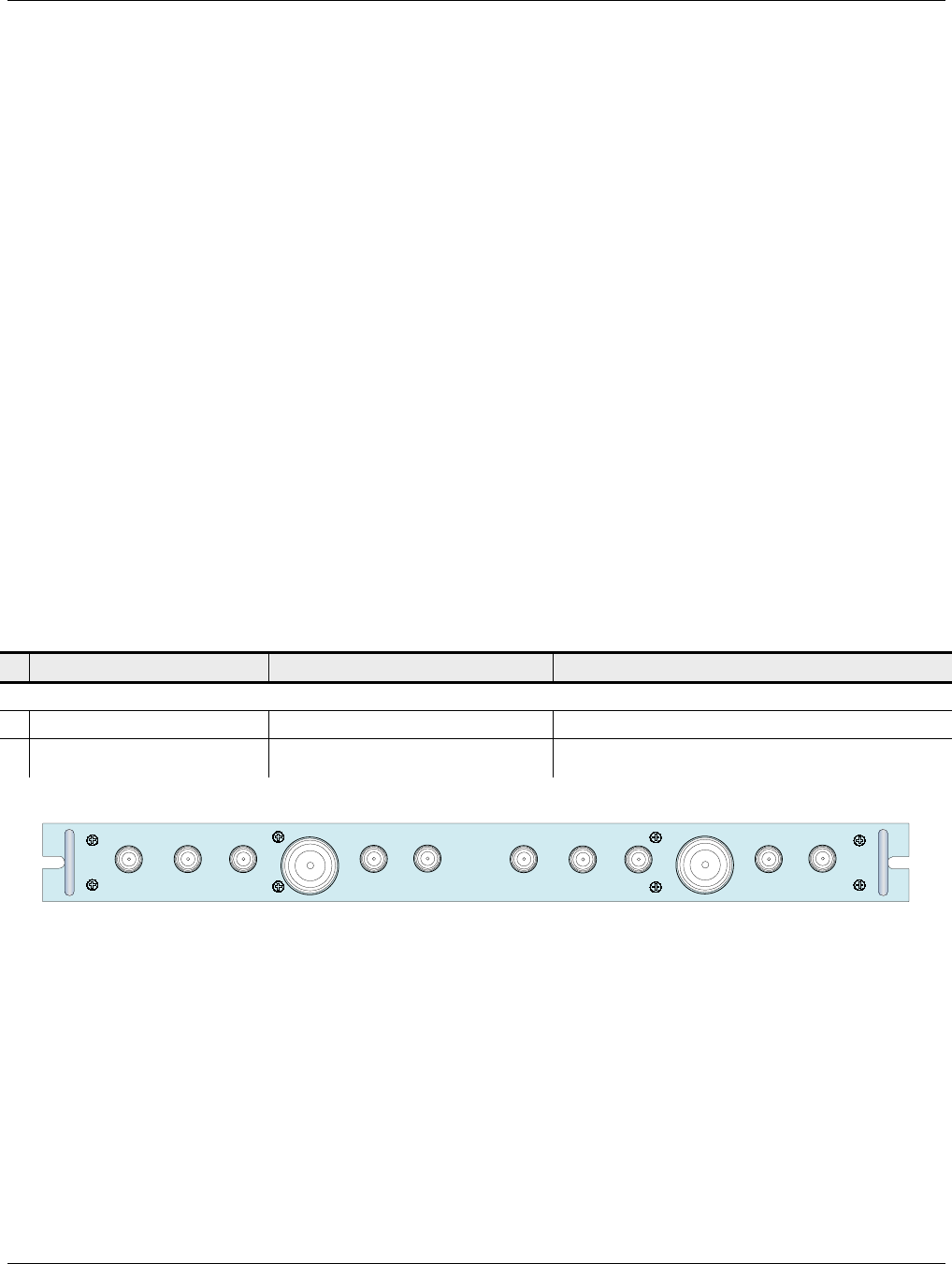
mBSC-CM RUM
mBSC-CM December 15, 2015
Page 14
3.3.1.2 Multiplexer
The multiplexer separates the various band frequencies respectively. The duplexer is used to make the
bi-directional signals into simplex signals and provides sufficient isolation.
3.3.1.3 Mounting
The BCM enclosure is installing on the 19’’ rack.
3.3.1.4 RF Connection
The RF signal connections with the antenna combiner are supported through 10 N-type female connectors.
These ten N-type connectors are used for coaxial cable connection to the Antenna ports of the single-band
RUM enclosures. Two 7/16 DIN connector is used to interface the combined multi-band RF signal to the
service antenna.
3.3.1.5 User Interface
The BCM enclosure interface consists of the two kinds of connectors that are provided on the front panel.
The BCM enclosure user interface is described in Table 6 and indicated in Figure 12.
Table 3BCM Enclosure User Interface
#
User Interface Designation
Device
Functional Description
Model BCM
5 ANT DIN female RF coaxial connector RF duplex Tx/Rx connection to antenna
6 700~2600 TxRx N female RF coaxial connector
RF duplex Tx/Rx inter-connection from ANT of
single-band RU
1900 2100 700 ANT ANT
7002100
1900
850 800
2600 2600
Combiner Model BCM
Figure 12BCM Enclosure User Interface
3.3.2 Single-band RUM Enclosure
The Single-band Remote Unit (RU) enclosure provides forward and reverse amplification of the RF signals
within the specified band. Its enclosure accommodates the remote single-band modules and protects them
from the environment. The enclosure consists of the housing, mounting brackets, and enclosed MCPA
(Multi-Carrier Power Amplifier), controller unit, duplexer modules. Figure 13 shows the single-band
enclosure dimensions.

mBSC-CM RUM
mBSC-CM December 15, 2015
Page 15
Figure 13Single-band RU Enclosure
3.3.2.1 Primary Components
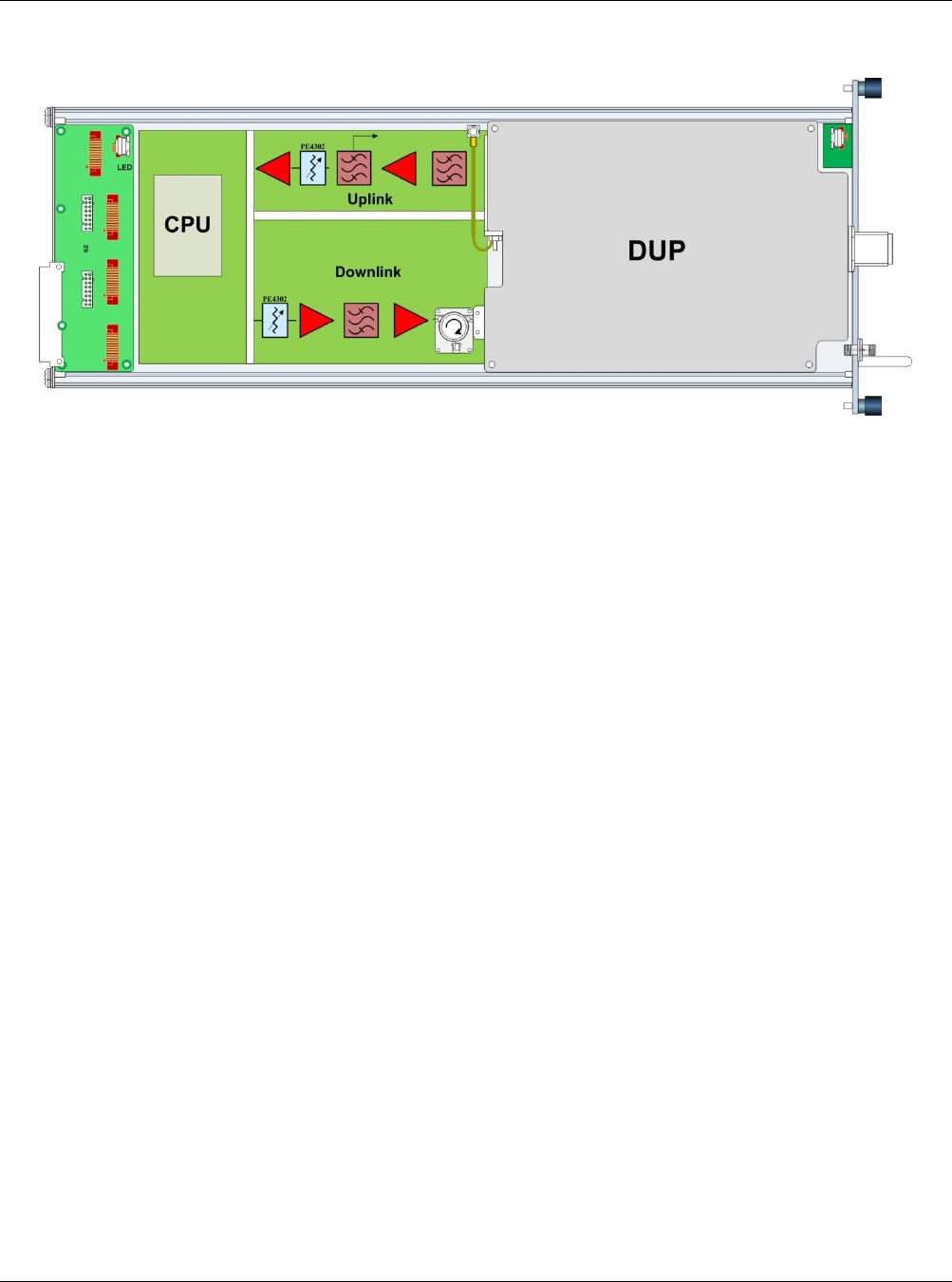
mBSC-CM RUM
mBSC-CM December 15, 2015
Page 16
3.3.2.1.1 Multi-Carrier Power Amplifier (MCPA) Modules
The MCPA Module is the heart of the mBSC RUM Enclosure. The MCPA Module boosts the BTS forward
link transmission signal. Operating on28VDC input, the MCPA Module produces 5W composite RF power
for each band (measured at output of the antenna combiner).
The mBSC system provides linear amplification of multi-carrier, mixed-mode signals in the 700MHz,
850MHz, 1900MHz, 2100MHz and 2600MHz frequency bands with the respective RU’s.
3.3.2.1.2 Duplexer
The duplexer is used to make the bi-directional signals into simplex signals and provides sufficient isolation
3.3.2.1.3 CPU(Central Processing Unite)
The CPU provides communications and monitors with power amplifier module or other functional module.
3.3.2.2 Mounting
The single-band RUM enclosure is plug in REMOTE NODE multi-slot chassis.
3.3.2.3 RF Connection
The RF signal connections with the single-band enclosure are supported through two QMA female coaxial
connectors and one N female connector. The two QMA female connectors are used for coaxial cable
connection (RF jumper) of the Tx and Rx RF signals between the RTM enclosure and the single-band RUM
enclosure. The N female connector is used for coaxial cable connection of the amplified duplex Tx/Rx RF
signal to the BCM enclosure.
3.3.2.4 Cooling
The single-band RUM enclosure is cooled by cooling fans in the bottom of the casing. A minimum of 200mm
(7.87 inches) of clearance space must be provided on both the top and the bottom sides of the Remote
Node for air convection.
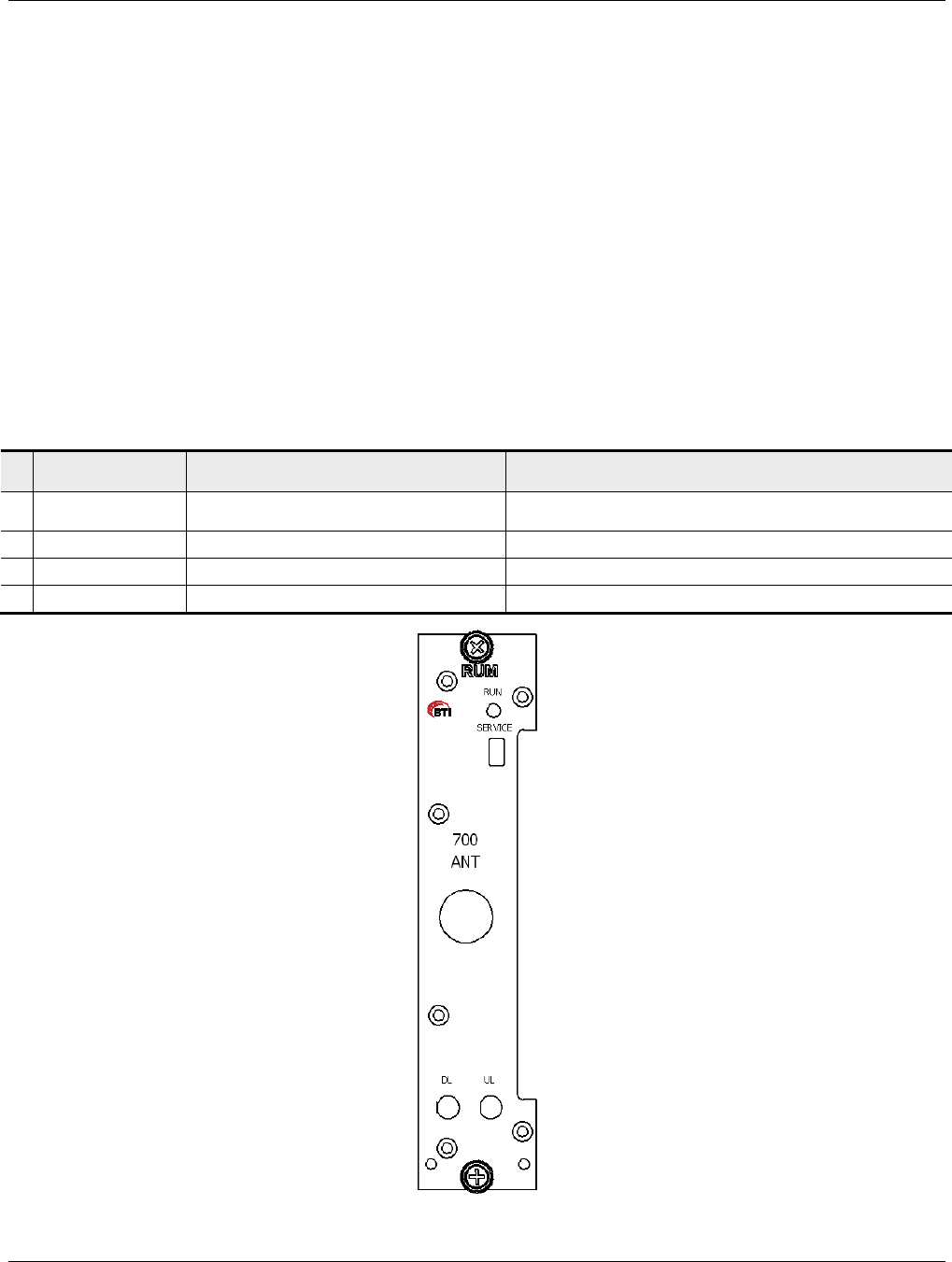
mBSC-CM RUM
mBSC-CM December 15, 2015
Page 17
An alarm is provided that indicates if a high temperature condition occurs.
3.3.2.5 Powering
The single-band RUM enclosure is equipped with connector board in the bottom of chassis that provides a
connection point for the DC power cable from RPM. The single-band RUM enclosure is powered by 28V
DC.
3.3.2.6 User Interface
The single-band RUM enclosure user interface includes the various connectors that are provided on the
exterior enclosure. The user interface is described in Table 7, and indicated in Figure 14.
Table 4 Single-band RUM Enclosure User Interface
#
User Interface
Designation
Device Functional Description
1 ANT
MINI-DIN or N type female RF coaxial
connector
RF (Tx/Rx) inter-connection to BCM enclosure
2 DL/UL QMA female coaxial connector RF inter-connection to RTM
3 Debug Mini USB connector Support local debugging
4 RUN LED (Green/Red/Off) Indicates if unit operation is normal or faulty.
Figure 14 Single-band RU Enclosure User Interface
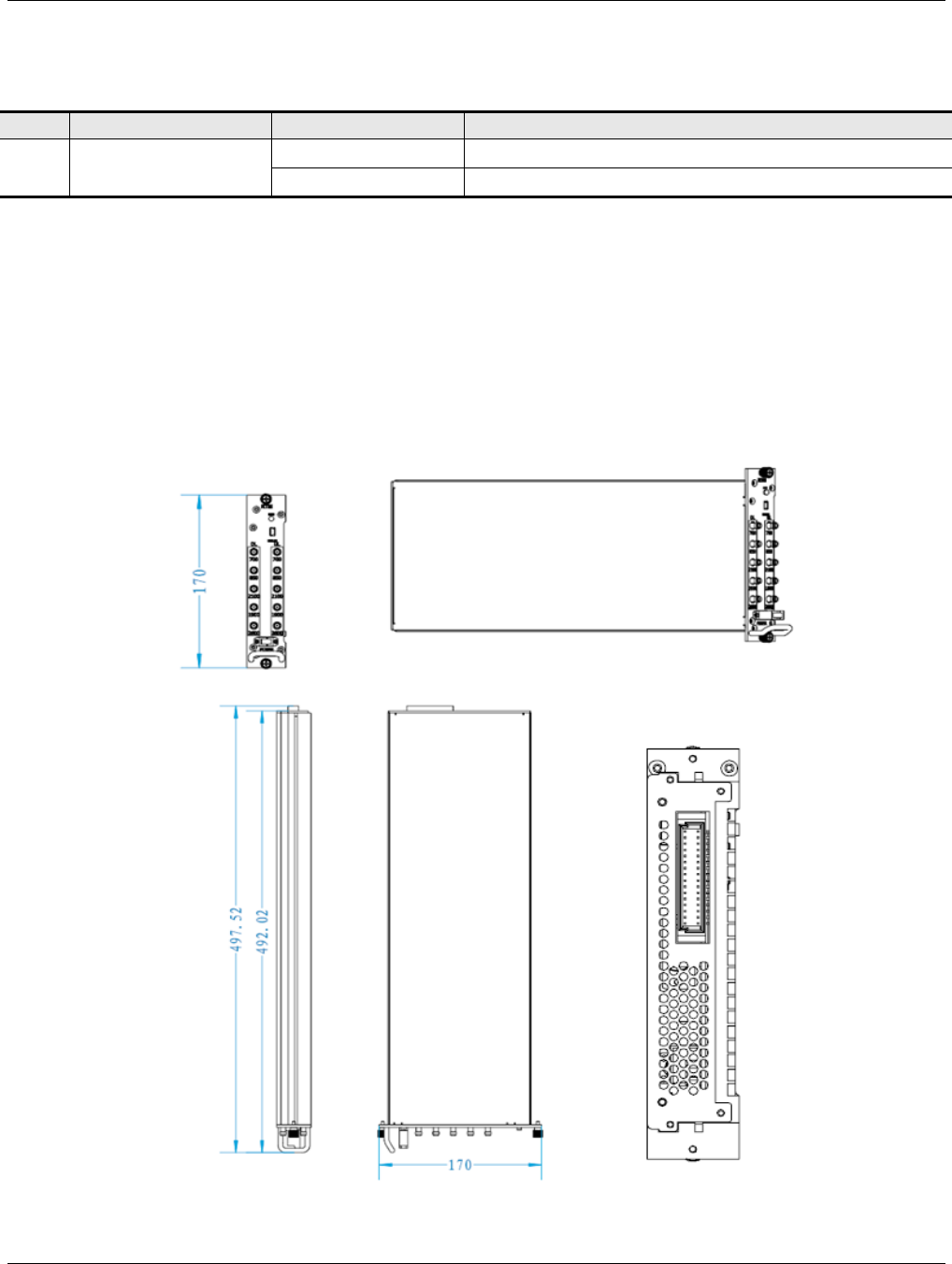
mBSC-CM RUM
mBSC-CM December 15, 2015
Page 18
Table 5 Indicator Description
#
Indicator
Status
Description
1 RUN Green(Flashing) System operating normally
Red(Flashing) System alarm
3.3.3 RTM
The RTM module provides two key functions:
1. Electrical-optical/optical-electrical signal conversion and separates the combined multi-band RF
signals into simplex connections for delivery to the respective single-band RU Enclosures
2. Combines the RF signals from each single-band RU Enclosure for duplex interconnection with the
service antenna
Figure 15 RTM enclosure

mBSC-CM RUM
mBSC-CM December 15, 2015
Page 19
3.3.3.1 Primary Components
3.3.3.1.1 Optical Modules
The RTM enclosure interior layout, shown in Figure 11, is equipped to interface up to five bands (700MHz,
850MHz, 1900MHz, 2100MHz and 2600MHz). The enclosure includes weatherproof housing, plug in plug in
CM multi-slot chassis and internal multiplexer, RF-optic transceiver, and control unit elements.
Figure 16 RTM Interior Layout
3.3.3.1.2 Multiplexer & Duplexer
The multiplexer separates the various band frequencies respectively. The duplexer is used to make the
bi-directional signals into simplex signals and provides sufficient isolation.
3.3.3.1.3 RF-Optic Transceiver
The RF-Optic Transceiver is an optical module providing conversion between RF signals and optical signals
over a single fiber. The optical module converts the downlink optical signal from the FIU module in the host
unit, and it also converts the uplink RF signal to an optical signal and simultaneously sends it back to FIU
module in the host unit for distribution to the BIU modules. A laser and received optical power monitor and
alarm are provided.
Table 6 RF-Optic Transceiver Interface
# Port Device Description
1 RF OUT QMA\SMA female coaxial connector RF output
2 RF IN QMA\SMA female coaxial connector RF input
3 OPTIC IN/OUT E2000/APC Fiber interface (HU & RN)
4 --- Ethernet Debug & monitoring
Table 7 DB9 PINOUTS
# PIN Definition Description
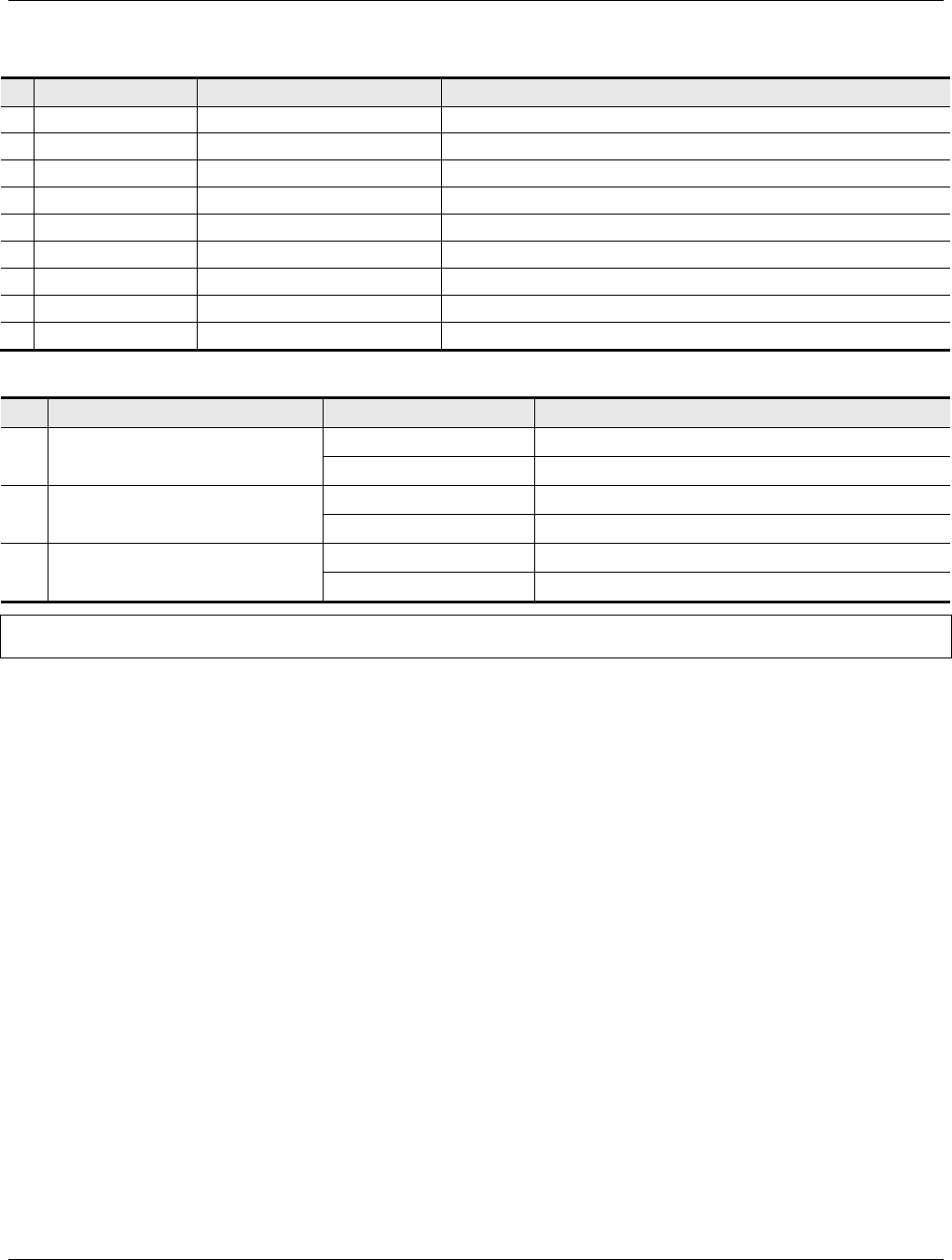
mBSC-CM RUM
mBSC-CM December 15, 2015
Page 20
#
PIN
Definition
Description
1 PIN1 NC
2 PIN2 GND
3 PIN3 VCC +12V DC
4 PIN4 TXD1/B1 Channel1: RS485-B1
5
PIN5
RXD1/A1
Channel1: RS485-A1
6 PIN6 RXD0/A0 Channel0: RS485-A0
7 PIN7 LD ALM Laser Device error
8 PIN8 TXD0/B0 Channel0: RS485-B0
9 PIN9 PD ALM Photo-detector error
Table 8 RF-Optic Transceiver Indicators
# Indicator Status Description
1 POWER Green Normal
Off No power supply
2 PD ALARM Off Photo-detector works
Red Photo-detector error
3 LD ALARM Off Laser Device works
Red Laser Device error
Notes: If the fiber is not connected properly, both of the HU and RN’s PD ALARM indicator will alarm (red LED). Otherwise the
indicator is off.
3.3.3.2 RF Connection
Optical Module: The RF signal connections with the optical fiber module are supported through 5 groups of
QMA female connectors. These five connector groups are used for coaxial cable inter-connection of the
simplex Tx and Rx RF signals to the single-band RUM enclosures.
3.3.3.3 Optical Port
The RTM enclosure uses anE2000/APC type optical transceiver for inter-connecting the optical fiber. The
transceiver supports single-mode (yellow) fiber.
3.3.3.4 Powering
The RTM enclosure is equipped with connector board in the bottom of chassis that provides a connection
point for the DC power cable from RPM.
3.3.3.5 User Interface
The RTM enclosure interface consists of the various connectors, terminals and LED indicators that are
provided on the front panel. The RTM enclosure user interface is described in Table 6and indicated in Figure
12.
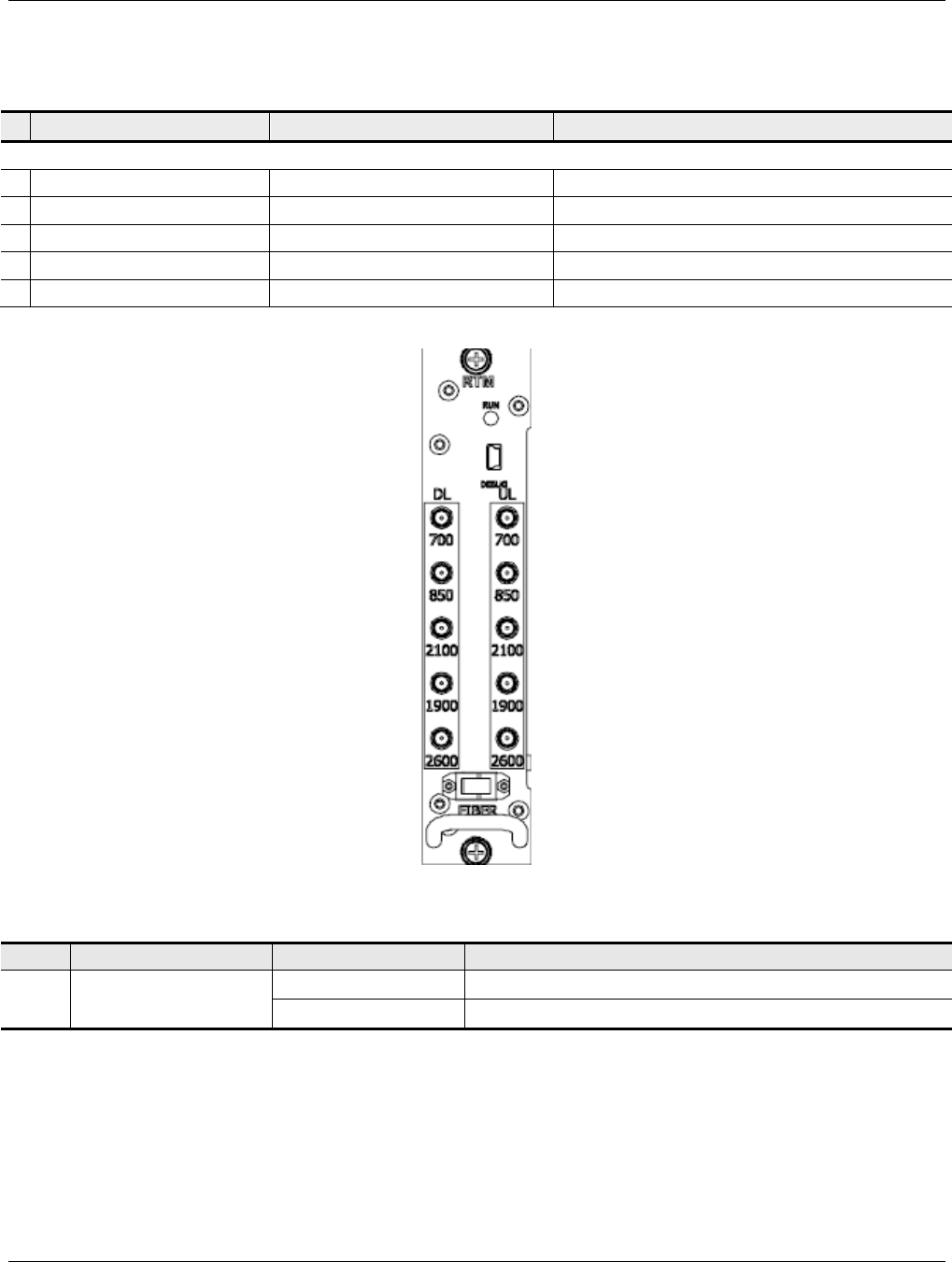
mBSC-CM RUM
mBSC-CM December 15, 2015
Page 21
Table 9Fiber RTM Enclosure User Interface
#
User Interface Designation
Device
Functional Description
Model RTM
1 Fiber E2000/APC optical connector Used for fiber connecting to host unit
2 RUN LED (Green/Red/Off) Indicates if Fiber/RF link is normal or faulty.
3 UL(700~2600) QMA female RF coaxial connector RF inter-connection to UL of RUM
4 DL(700~2600) QMA female RF coaxial connector RF inter-connection to DL of RUM
7 DEBUG Ethernet Support Local debugging
Figure 17 RTM interface
Table 10 Indicator Description
# Indicator Status Description
1 RUN Green(Flashing) System operating normally
Red(Flashing) System alarm
3.3.4 RPM
The RPM provides 28V DC power connection and distribution to each enclosure.
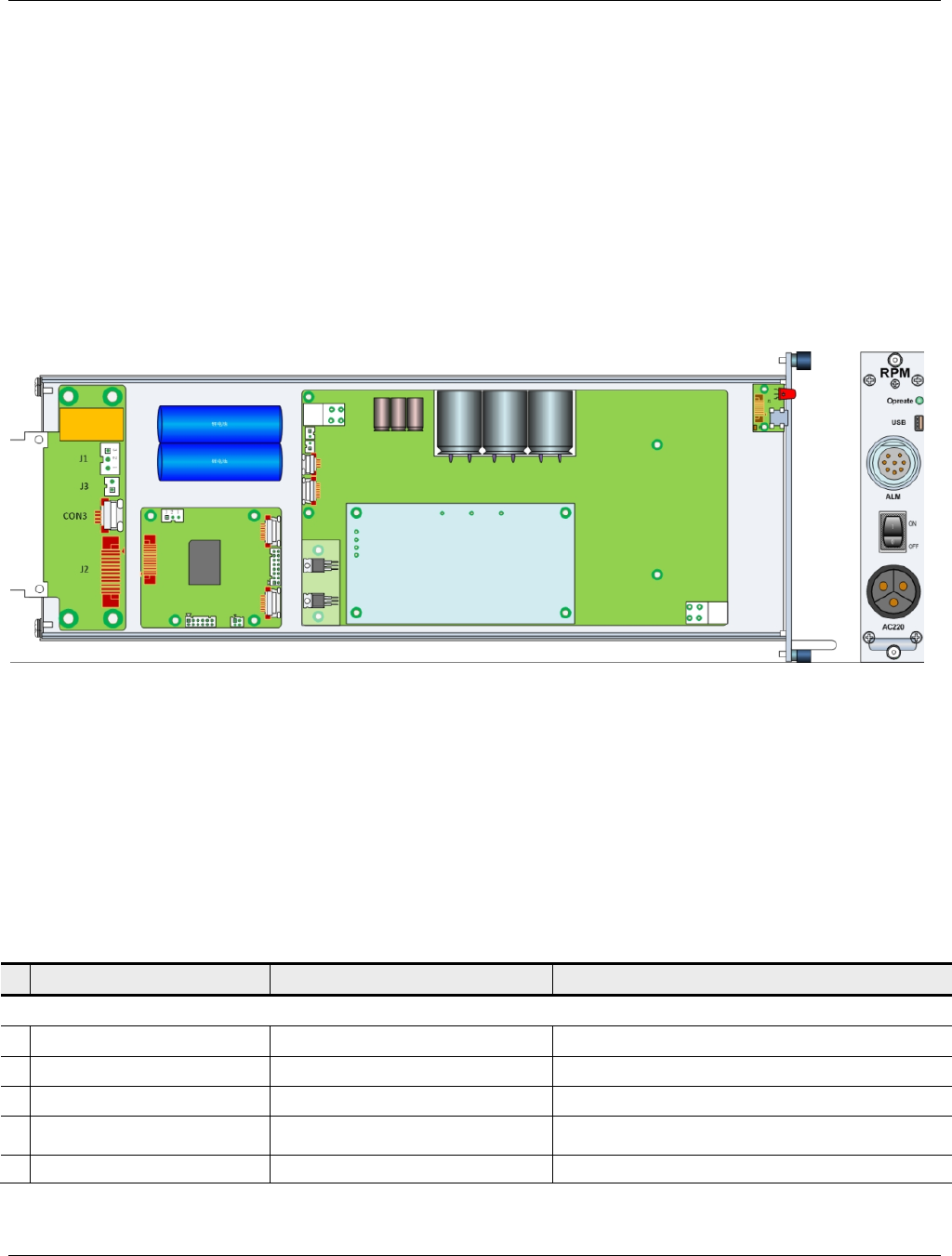
mBSC-CM RUM
mBSC-CM December 15, 2015
Page 23
chassis.
3.3.4.1.1 Power supply board
The RPM enclosure is equipped with a 3-wire AC power connector that provides a connection point for the
AC power cable. AC power input via power supply board convert to 28V DC distributed to RUMs and RTMs
by connector board on the bottom of RPM enclosure.
Power supply board provides 28V DC to battery board and control board.
Figure 19 RPM interior layout
3.3.4.1.2 Control board
Control board manages power supply alarm and report to NMS.
3.3.4.1.3 Battery board
When power supply board stops working, then battery board will provides control board work.
3.3.4.1.4 Interface
# User Interface Designation Device Functional Description
Model RPM
1 Switch Power Switch Used for turn on/off power
2 RUN LED (Green/Red/Off) Indicates if Fiber/RF link is normal or faulty.
3 Alarm 8-PIN circular plug Used for external alarm
4 AC 220V
3-wire\4wire circular push-plug
power connector
Used for connecting AC 110/220V power input.
7 DEBUG Mini USB connector Support Local debugging

mBSC-CM RUM
mBSC-CM December 15, 2015
Page 24
4 System Installation
4.1 Unpacking and Inspection
Every mBSC-C component has been tested and calibrated at the factory. Unpack the mBSC-C components
carefully after they arrive at the installation site. Open the wooden container and remove the foam padding.
If the equipment is damaged:
Immediately contact the transportation and notify them of the damage.
A claim should be filed with the carrier once the extent of any damage is assessed.
If possible, always inspect the equipment in the presence of the delivery person.
If the equipment is damaged and must be returned to BTI’s nearest RMA facility:
Log on the BTI website, or call 714-230-8333for a return authorization.
BTI will not accept returns without a RMA number.
Claims for loss or damage may not be withheld from BTI, nor may any payment due be with held pending
the outcome thereof.
BTI CANNOT be held responsible for the freight carrier’s performance.
4.2 Installation Preparation
4.2.1 Required Tools
The following equipment and tools may be required for a successful installation:
Multi-meter
Phillips screwdrivers
Flat blade screwdrivers
Wrenches
Drill
VSWR testing device
N adapters
RF testing cables
RF Power meter (part of hand-held tester)
4.2.2 Installation Location
The mBSC Host unit is typically installed within a 19” rack:

mBSC-CM RUM
mBSC-CM December 15, 2015
Page 25
The rack should be selected with adequate shelf space to accommodate the Host Unit equipment
with adequate space for ventilation around each component
The rack must be able to support the weight of the equipment to be installed
The mBSC Remote unit is typically installed on the wall:
The wall should be water-resistant, dry, non-caustic and without high-voltage power leaking.
The wall’s bearing capacity is more than 136kg.
Concrete wall sand brick walls are recommended, because those walls can accept expansion
screws. Masonry walls or sandy-dust walls are not suitable.
4.2.3 Anti-corrosion and Shock-protection
To safeguard products and operators, the installation location must be kept away from caustic or poisonous
pollutants. If the site can’t meet seismic standards, it must be properly reinforced.
4.2.4 Lighting, Ventilation and Fire Protection
The installation site should have enough illumination for installation and maintenance needs. Flammable
and explosive material should not be near the site.
4.2.5 Power Requirements
Nominal voltage:
Remote Unit: 110/220VAC +/- 20%, 50/60 Hz +/-5%.
Host Unit: -48VDC. Variable range: -36 ~ -72 V DC.
The power consumption of the mBSC Remote Node is approximately 220W per band. Make sure to select a
fuse or breaker with the proper capacity. A 10A breaker is recommended @ 220VAC.
4.2.6 Lightning Protecting and Grounding
The cross section of grounding cable should be no smaller than 25mm2. The grounding cable should be
connected to earth ground directly without any splices. Keep the grounding cable as short as possible.
MBSC0800S-005-RUCM11 system design complies with the criteria of IEC61000-4-5 and ETS 300
342-2/3.
4.3 Host Unit Installation
4.3.1 Rack Mounting
The Host Unit is a 19” 4U equipment shelf. When loading the Host Unit in a rack, make sure the mechanical

mBSC-CM RUM
mBSC-CM December 15, 2015
Page 26
loading of the rack is even to avoid a hazardous condition. The rack should safely support the combined
weight of all the equipment and be securely anchored. Installing the Host Unit in a room with sufficient air
circulation is recommended as the maximum ambient temperature for Host Unit is 60°C.
Use the following steps to install the Host Unit in the equipment rack:
1. The Host Unit is built with mounting bracket installed for 19” rack installation.
Figure 20 Mounting Brackets for 19” Rack Installation
2. Position the host unit in the designated mounting space in the rack as shown below.
3. Secure the mounting bracket to the rack using the four mounting screws provided.
Figure 21Host Unit-19” Rack Mounting View
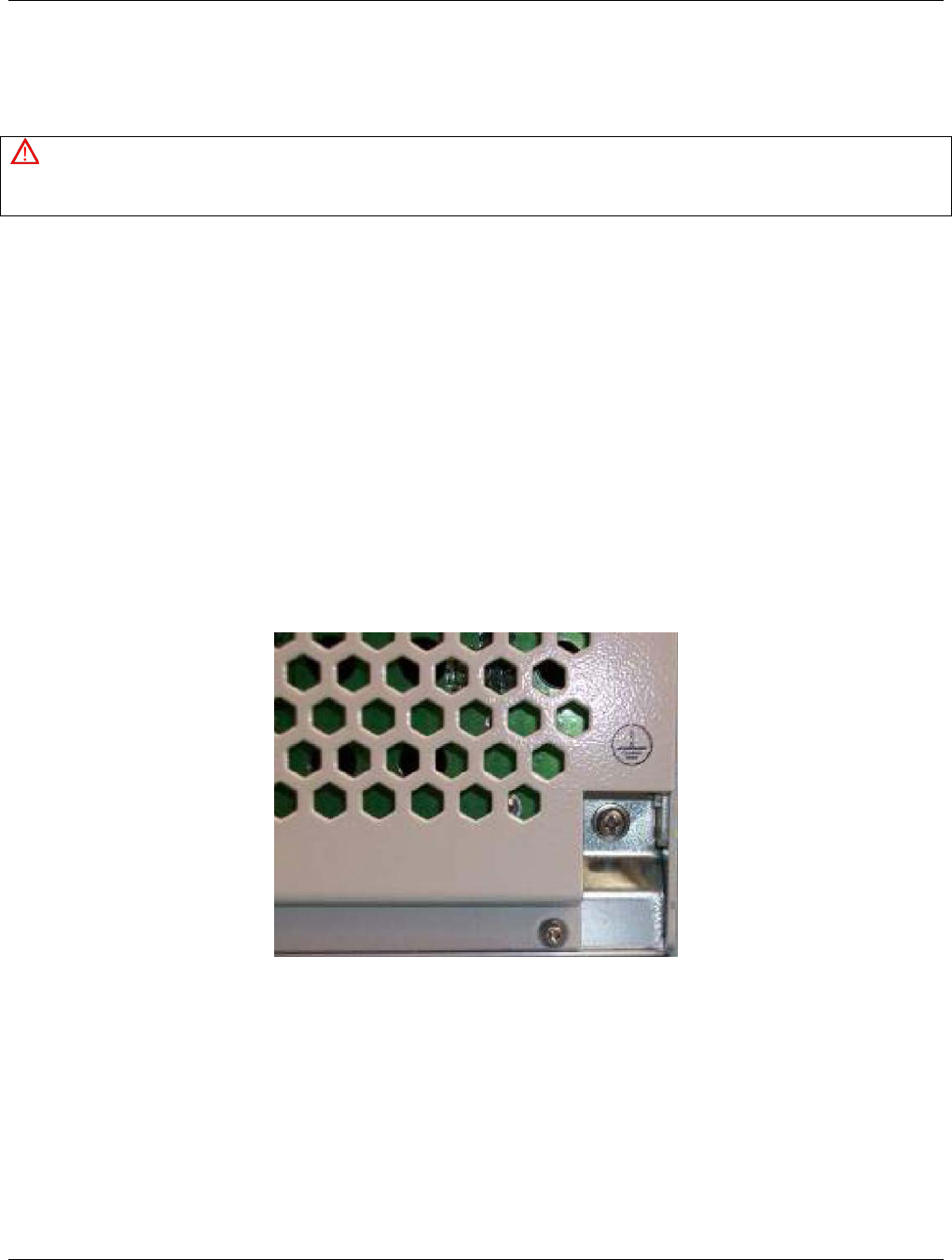
mBSC-CM RUM
mBSC-CM December 15, 2015
Page 27
4.3.2 Cable Connections
Note
The NEC(National Electrical Code) does not allow signal wires to share the same conduit with power wires unless the signal
cable’s voltage range is equal to the power wire’s voltage range.
Avoid bundling signal cable and grounding cable/power cable, keep them separate.
The power cable and RF inter-connection cables are supplied.
Check open and short circuits before installing the power cable.
4.3.2.1 Grounding
The host unit must be grounded. Do not connect external devices to the grounding connection.
Verify the host unit is securely grounded. If it is not securely grounded, use the following procedure to
ground the host unit:
1. Find the screw at the bottom right corner of the Host Unit as shown in Figure 19.
2. Loosen the screw located on the grounding connection.
3. Connect the cabinet mounted earth-bonding cable between the two lock and flat washers as shown
in Figure 20. Ensure the grounding surface is clean and free of paint, insulating material or
contaminants.
Figure 22Host Unit Grounding Stud
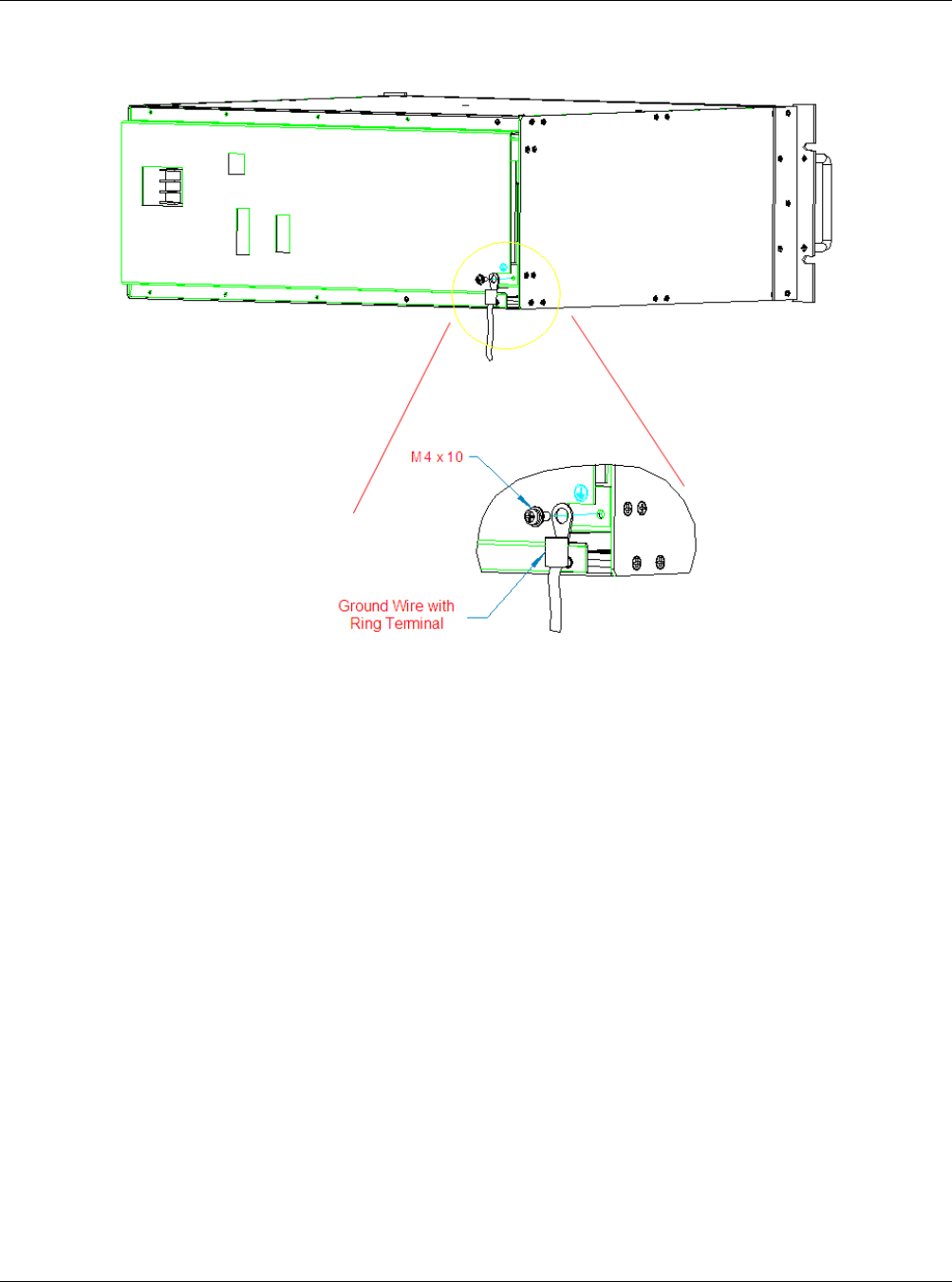
mBSC-CM RUM
mBSC-CM December 15, 2015
Page 28
Figure 23 Grounded Host Unit
4. Tighten the screw, making sure the cable is securely connected before moving to the next phase of
the installation.
4.3.2.2 Coaxial Cable Connections
The RF interface between the Host Unit and the BTS (or POI) is supported through Tx/Rx QMA female
connectors mounted on the Host Unit front panel.
The Host Unit should be mounted as close as possible to the BTS to minimize RF cable losses. Use the
following steps to route and connect the simplex path coaxial cables to the Host Unit:
1. Obtain the required lengths of high performance, flexible, low loss 50Ω coaxial communication
cable for all coaxial connections.
2. Route the RF Tx and Rx path coaxial cables between the Host Unit and BTS interface and cut to
the required length.
3. Terminate the cable with a QMA male connector.
4. Connect the Tx and Rx cables from the BTS to the Tx and Rx connectors on the BIU front panel
corresponding to the frequency band (e.g. Tx 700, Tx 850, Tx1900, Tx 2100 or Tx2600).
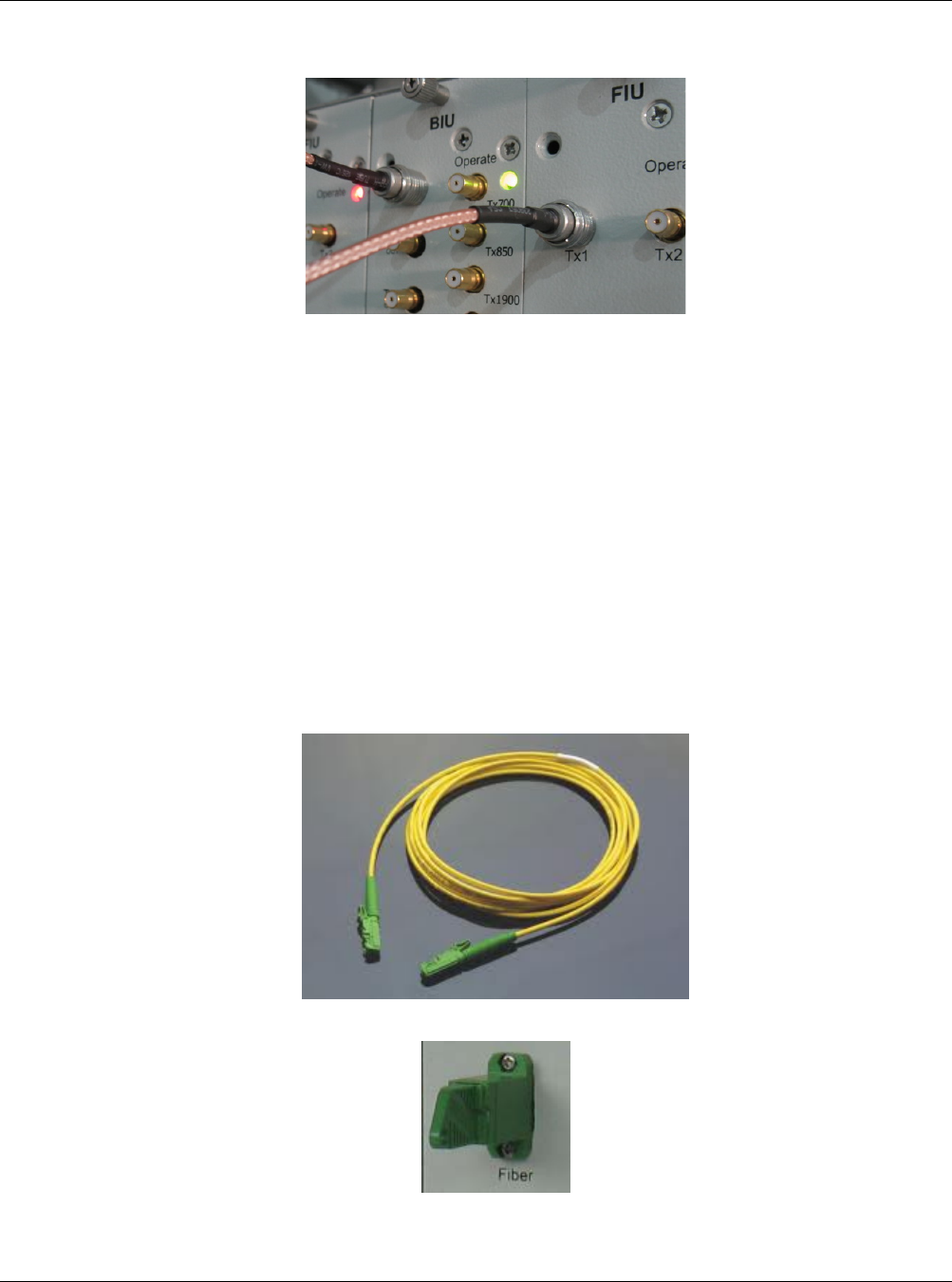
mBSC-CM RUM
mBSC-CM December 15, 2015
Page 29
Figure 24 BTS QMA Coaxial Cable Connection
5. Dress and secure cable at the Host Unit.
6. The RF inter-connection between the BIU and the FIU uses QMA to QMA jumper cables supplied
with the mBSC-C equipment.
4.3.2.3 Optical Connections
The optical interface between the Host Unit and the Remote Node is supported by an E2000/APC optical
adapter which is mounted on the FIU front panel. A single mode, E2000/APC patch cord may be used to
connect the Host Unit with Remote Node.
Use the following steps to connect the optical fibers:
1. Obtain one patch cord which is sufficient length to reach from Host Unit to the Remote Node.
2. Clean each patch cord connector following the patch cord supplier’s recommendation.
3. Push and secure the patch cord connector into the desired optical port on the Host Unit FIU
Figure 25Single Mode Patch Cord(E2000/APC)
Figure 26E2000 Fiber Optic Port on Host Unit FIU
4. Route the patch cords from the Host Unit to the Remote Node.
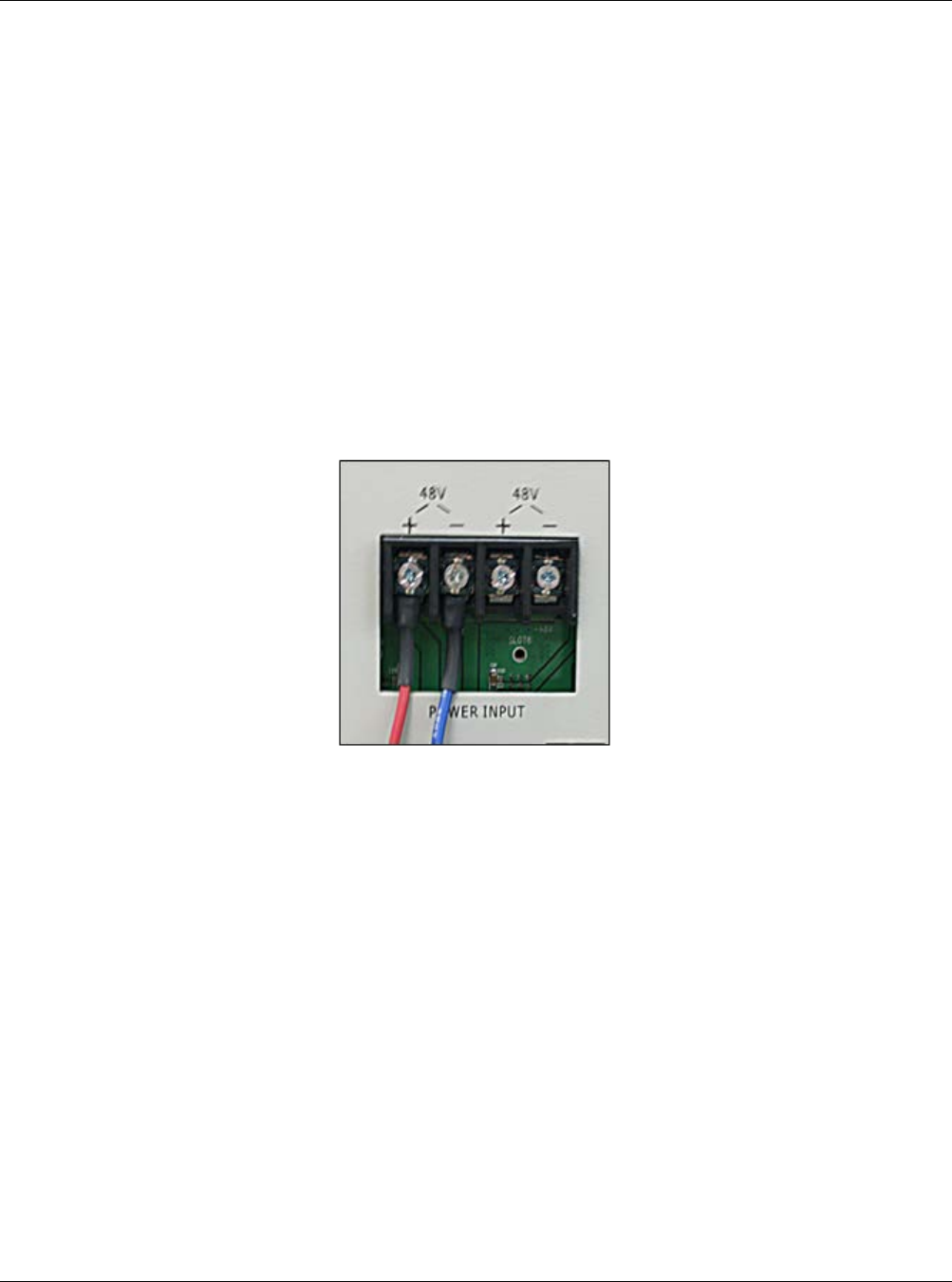
mBSC-CM RUM
mBSC-CM December 15, 2015
Page 30
5. Connect optical fiber to the Remote Node RTM fiber port.
4.3.2.4 DC Power Connection
The DC power interface of the Host Unit is provided by a 2-wire termination located on the HU rear panel. The DC
termination provides a connection point for the power cord which is provided separately with the HU. Use the
following procedure to install the DC power:
1. Locate the 48 VDC power cord which is provided separately with the HU.
2. Place both HU PS module power ON/OFF switches in the OFF position.
3. Connect one end of the power cord to the DC termination on the HU.
4. Connect the other end of the power cord to the 48VDC source.
5. Dress and secure cable per standard industry practice.
Figure 27 48VDC Host Power Connection
4.3.2.5 Local OMC Computer Connection
The primary communication interface between the mBSC system OMC and a local computer is provided by
a single RJ45 jack on the front panel of Host Unit (note: the USB port of the RCU card can also be used to
access the local OMC port). All the connected Remote Nodes can be monitored at the Host Unit side
through the fiber connection. The communication connector supports an IP interface. A CAT5 cable is used
for connecting the local computer to the mBSC Host Unit OMC interface.
To connect the OMC computer with the Host Unit:
1. Obtain the required length of CAT5 twisted pair cable with RJ45 connectors.
2. Route the cable between the OMC computer (or local switch/router) and Host Unit.
3. Connect the cable to the RJ45jack on the front panel of Host Unit RCU.
4. Connect the other end of the cable to the RJ45 jack on the OMC computer or local switch/router.
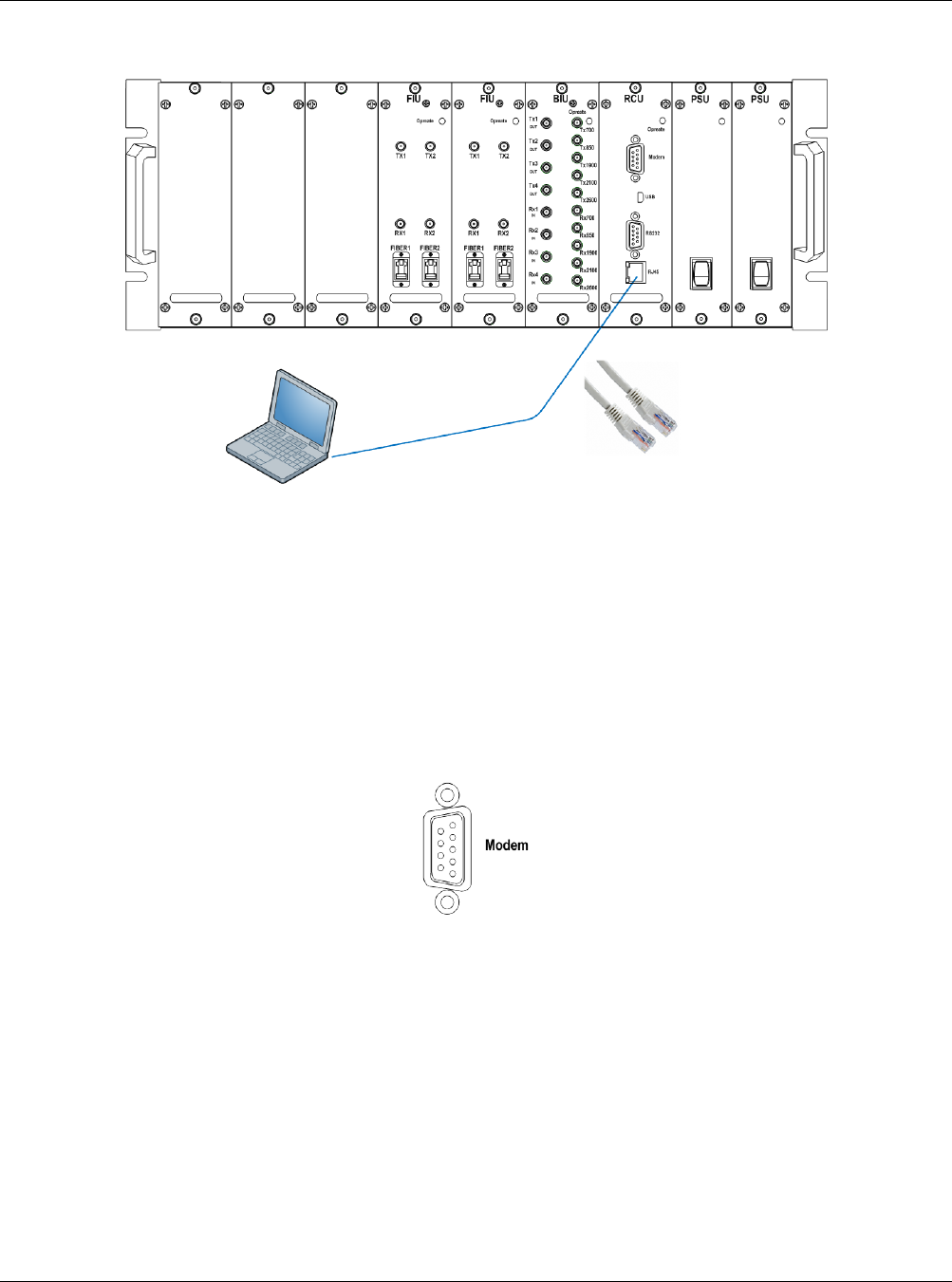
mBSC-CM RUM
mBSC-CM December 15, 2015
Page 31
Figure 28IP Connection for local GUI Control
4.3.2.6 Modem Connection (optional)
For remote operation, the mBSC-C system provides a serial modem connecter for external modem
connection.
To connect a modem with the host unit:
1. Route the modem cable between the modem and host unit.
2. Connect the modem cable with a DB9 female plug to the modem socket on the host unit’s RCU
front panel.
Figure 29Modem Port on RCU (DB9 male)
3. Connect the modem cable with DB9 male plug to the modem serial port.
4.4 Remote Node Installation
The remote unit is a 19” 4U equipment shelf. When loading the remote unit in a rack, make sure the
mechanical loading of the rack is even to avoid a hazardous condition. The rack should safely support the
combined weight of all the equipment and be securely anchored. Installing the remote unit in a room with
sufficient air circulation is recommended as the maximum ambient temperature for remote unit is 60°C.
remote unit install as same as HU device. Please refer to chapter 4.3.1.
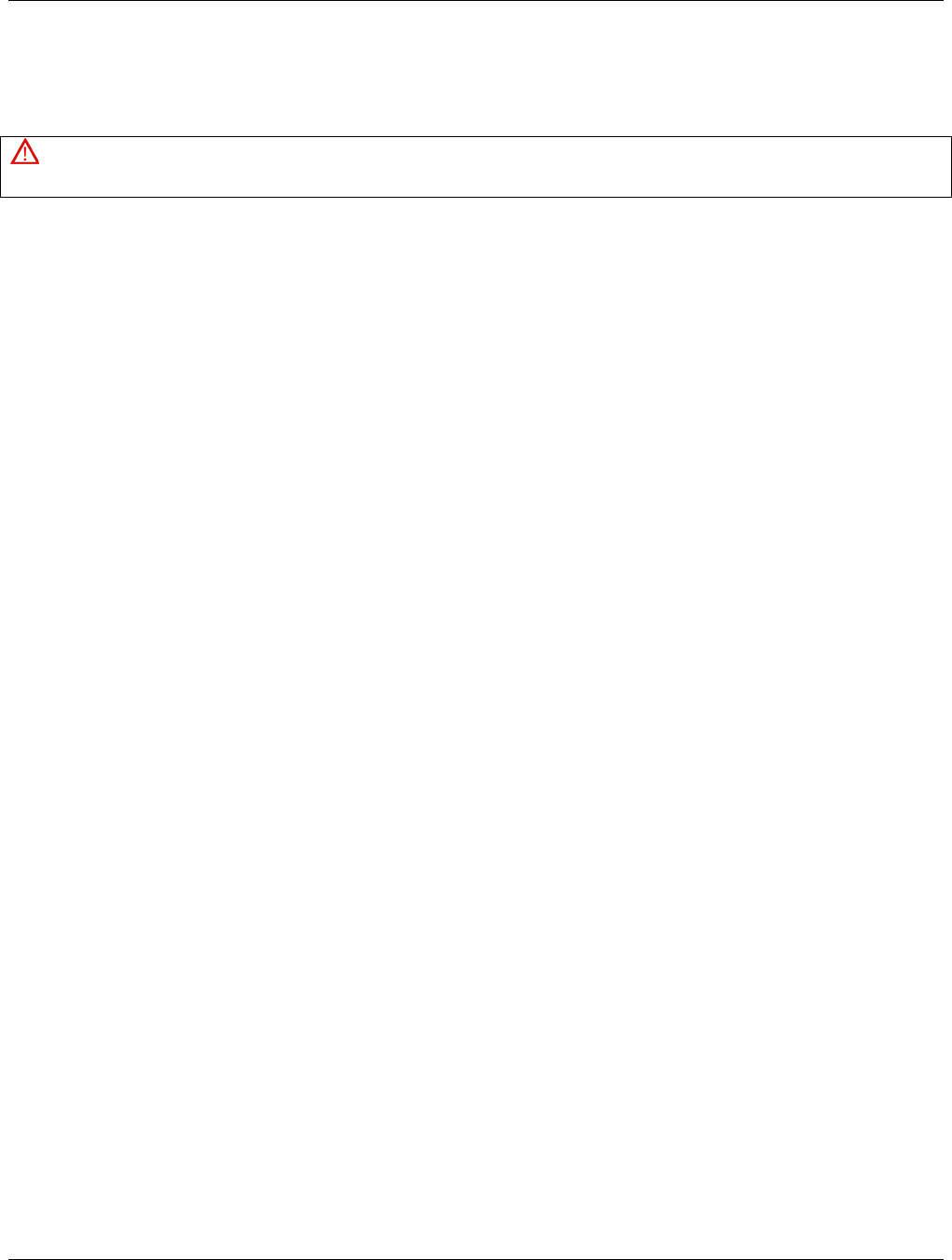
mBSC-CM RUM
mBSC-CM December 15, 2015
Page 32
4.4.1 Cable Connections
Attention
All the power switches must be switched off before cable installation.
Avoid bundling signal cable and grounding cable/power cable, keep them separate.
The power cable and RF inter-connection cables are supplied.
Check open and short circuits before installing the power cable.
4.4.1.1 Coaxial Cable Connections
The simplex low-power RF interface between the RTM enclosure and the single-band RUM enclosures is
supported through RF QMA female connectors mounted on the enclosure panel. The duplex high-power RF
interface between the single-band RU enclosures and the BCM enclosure, and to the service antennas, is
supported through Nfemale connectors mounted on the enclosure panel.
4.4.1.1.1 BCM to Single-band RU
To connect the coaxial cable between BCM enclosure and single-band RU enclosure:
1. Obtain the required lengths of high performance, flexible, low loss 50Ω coaxial communication
cable for all coaxial connections.
2. Route the RU ANT and BCM N connector coaxial cable between the BCM enclosure and
single-band enclosure interface and cut to the required length.
3. Dress and secure cable.

mBSC-CM RUM
mBSC-CM December 15, 2015
Page 33
Figure 30 RF Inter-Connect between BCM and Single-band RU
4.4.1.1.2 Single-band RUM to RTM
To connect the coaxial cable between RTM enclosure and single-band RUM enclosure:
1. Obtain the required lengths of high performance, flexible, low loss 50Ω coaxial communication
cable for all coaxial connections.
2. Route the RF UL/DL path coaxial cable between the RTM enclosure and single-band RUM
enclosure interface and cut to the required length.
3. Connect the UL/DL cable to the designated UL/DL connector on the panel of RTM enclosure and
the panel of the single-band RUM enclosure.
4. Dress and secure cable.
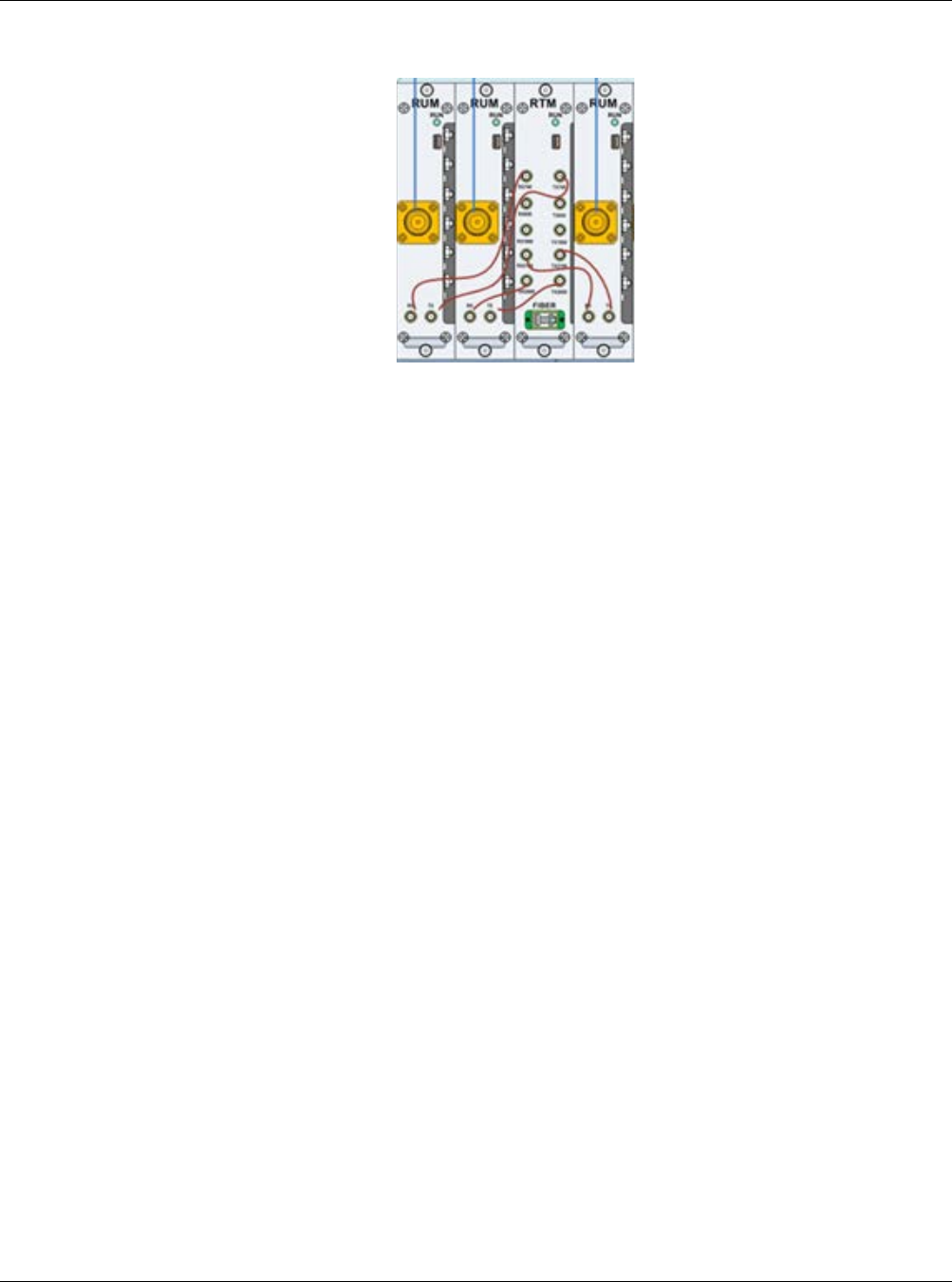
mBSC-CM RUM
mBSC-CM December 15, 2015
Page 34
Figure 31 RF Inter-Connect between RTM and Single-band RU
4.4.1.2 Antenna Cable Connection
Route a coaxial antenna cable from the antenna to the equipment enclosure. The cable must be terminated
with the proper connector for connecting to the antenna port on the panel of BCM enclosure.
Below is the procedure to install the antenna cable:
1. Remove the dust cap from the DIN type female connector located on the panel of the BCM
enclosure.
2. Route the coaxial antenna cable to the panel of the BCM enclosure panel.
3. Cut the antenna cable to the required length and terminate with the proper connector.
4. Connect the antenna cable to the BCM port.
4.4.1.3 Optical Connections
The optical interface between the RTM enclosure and the Host Unit is supported by duplex Tx/Rx optical
port(s). Each optical port consists of aE2000/APC optical adapter which is mounted on the RTM enclosure
panel. A single mode, E2000/APC patch cord may be used.
Use the following steps to connect the optical fibers:
1. Obtain one patch cord which is sufficient length to reach from fiber optic distribution box to RTM
panel.
2. Remove the dust caps the optical ports and from the patch cord connectors that will be connected.
3. Clean each patch cord connector following the patch cord supplier’s recommendation.
4. Screw-thread secures the patch cord connector into the optical port on the fiber optic distribution
box.
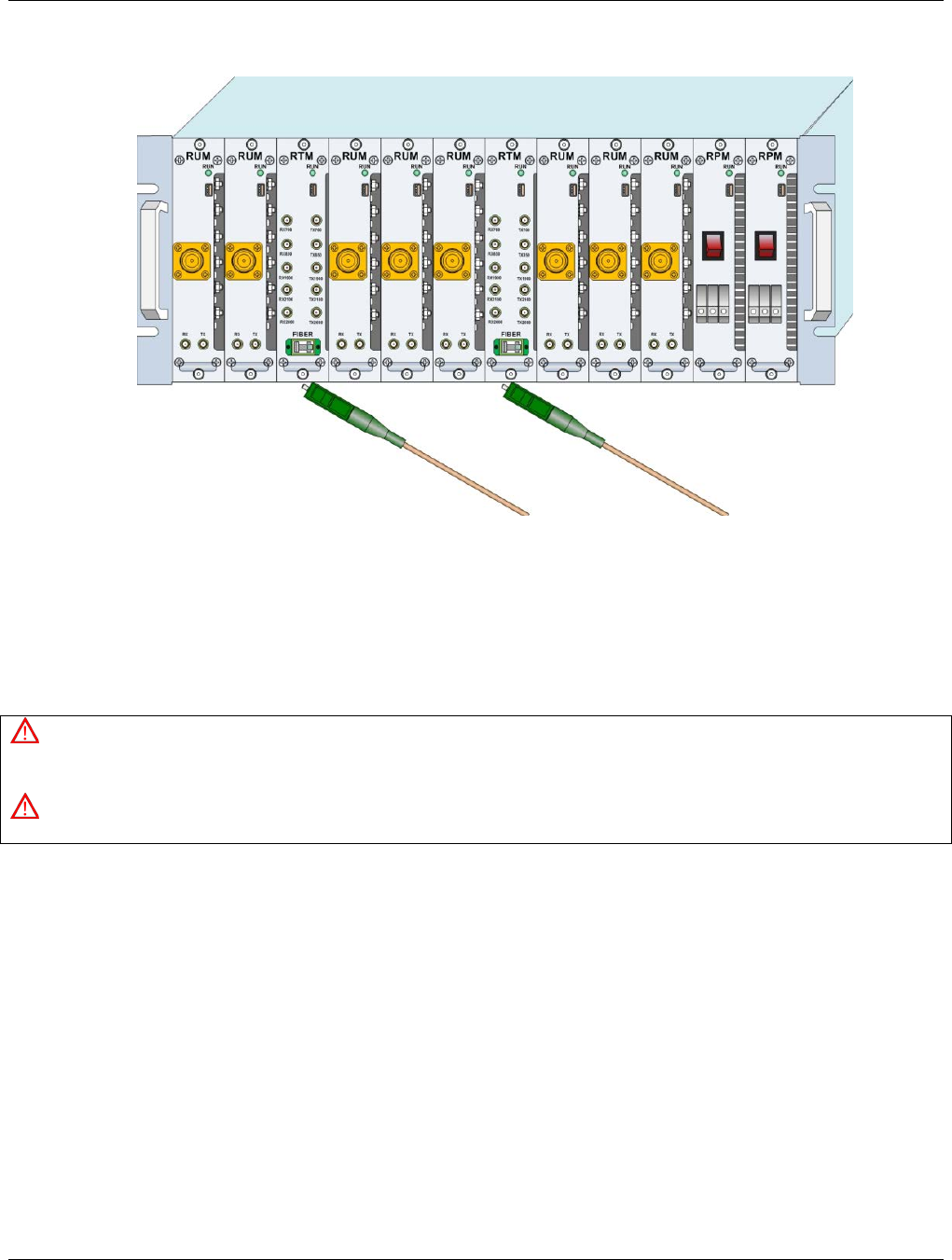
mBSC-CM RUM
mBSC-CM December 15, 2015
Page 35
Figure 32 Fiber Optic Cable Connection to RTM Enclosure
5. Route the patch cords from the fiber optic distribution box to the designated optical port on the
panel of the RTM enclosure.
6. Identify each optical fiber.
4.4.1.4 AC Power Connection
Danger
Use extreme caution when working with high voltage AC power. Ensure all power is disconnected before working on power
circuit.
Warning
Verify that the unit has been ground with an earth-bonding cable to the grounding connector.
A connectorized 3-wire power cable is provided with the RPM enclosures for the AC power connection, as
shown in Figure 36. The connectorized end of the power cable connects to the AC power port located on the
panel of the enclosure.
The AC power source must supply 110/220V AC(+/20% @50/60Hz) through a 15 Amp circuit breaker. The
AC power cable provides the wire leads for line, neutral and ground connections. The power cable must be
routed from the cabinet to an electrical junction box for connection to the AC power source. The power cable
is rated for indoor or outdoor use. Refer to the following procedure to install the AC power wiring:
1. Locate the RPM which is located at the multi-slot chassis of the Remote Node unite as shown in
Figure 35.

mBSC-CM RUM
mBSC-CM December 15, 2015
Page 36
Figure 33 RPM
2. Terminate the AC power supply wires that are required between the RPM and the local source of
AC power.
3. Tighten the coupling nut.
4.5 Installation Final Inspection
The following section provides a set of review procedures once the physical installation and connections are
complete. Leave the source AC power at the Host Unit and Remote Node in the OFF position (breaker open)
to prevent accidental power-up.

mBSC-CM RUM
mBSC-CM December 15, 2015
Page 37
4.5.1 Host Unit Connection Overview
RCU
Opreate
RJ45
RS232
Modem
USB
BIU
Opreate
Tx700
Rx4
IN
Rx3
IN
Rx2
IN
Rx1
IN
Tx4
OUT
Tx3
OUT
Tx2
OUT
Tx1
OUT
Tx850
Tx1900
Tx2100
Tx2600
Rx700
Rx850
Rx1900
Rx2100
Rx2600
PSU
1
0
PSU
1
0
FIU
Opreate
FIBER2
TX2
RX2
FIBER1
TX1
RX1
FIU
Opreate
FIBER2
TX2
RX2
FIBER1
TX1
RX1
Combined RF
Rx Signals
from BTS/POI
Combined RF
Tx Signals
from BTS/POI
T
o
r
e
m
o
t
e
u
n
i
t
#
1
T
o
r
e
m
o
t
e
u
n
i
t
#
2
T
o
r
e
m
o
t
e
u
n
i
t
#
3
T
o
r
e
m
o
t
e
u
n
i
t
#
4
E
t
h
e
r
n
e
t
P
o
r
t
Figure 34Host Unit Connection Overview
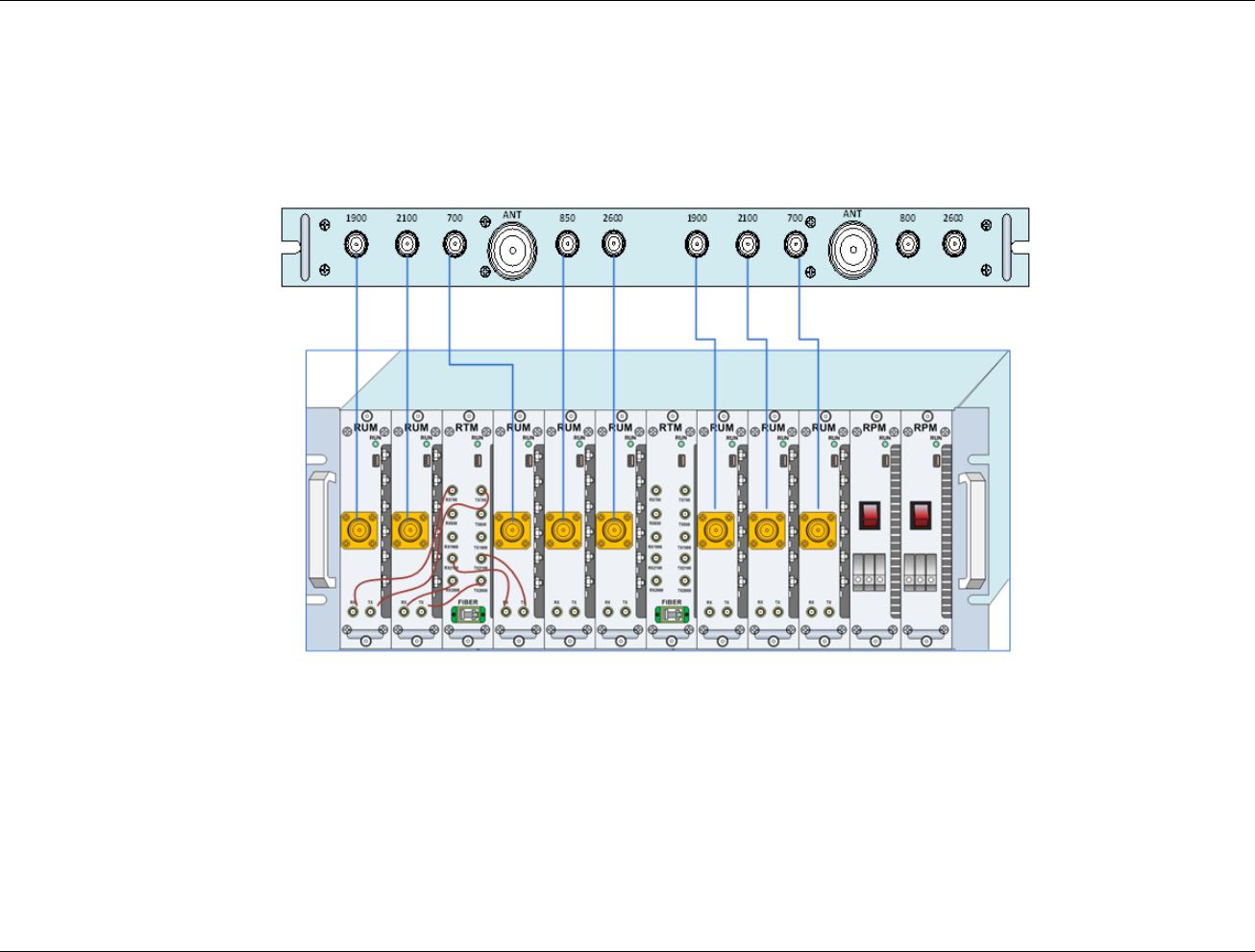
mBSC-CM RUM
mBSC-CM December 15, 2015
Page 38
4.5.2 Remote Node Connection Overview
Interconnection with Combiner Model BCM
Figure 35 Remote Node Inter-Connection Diagram
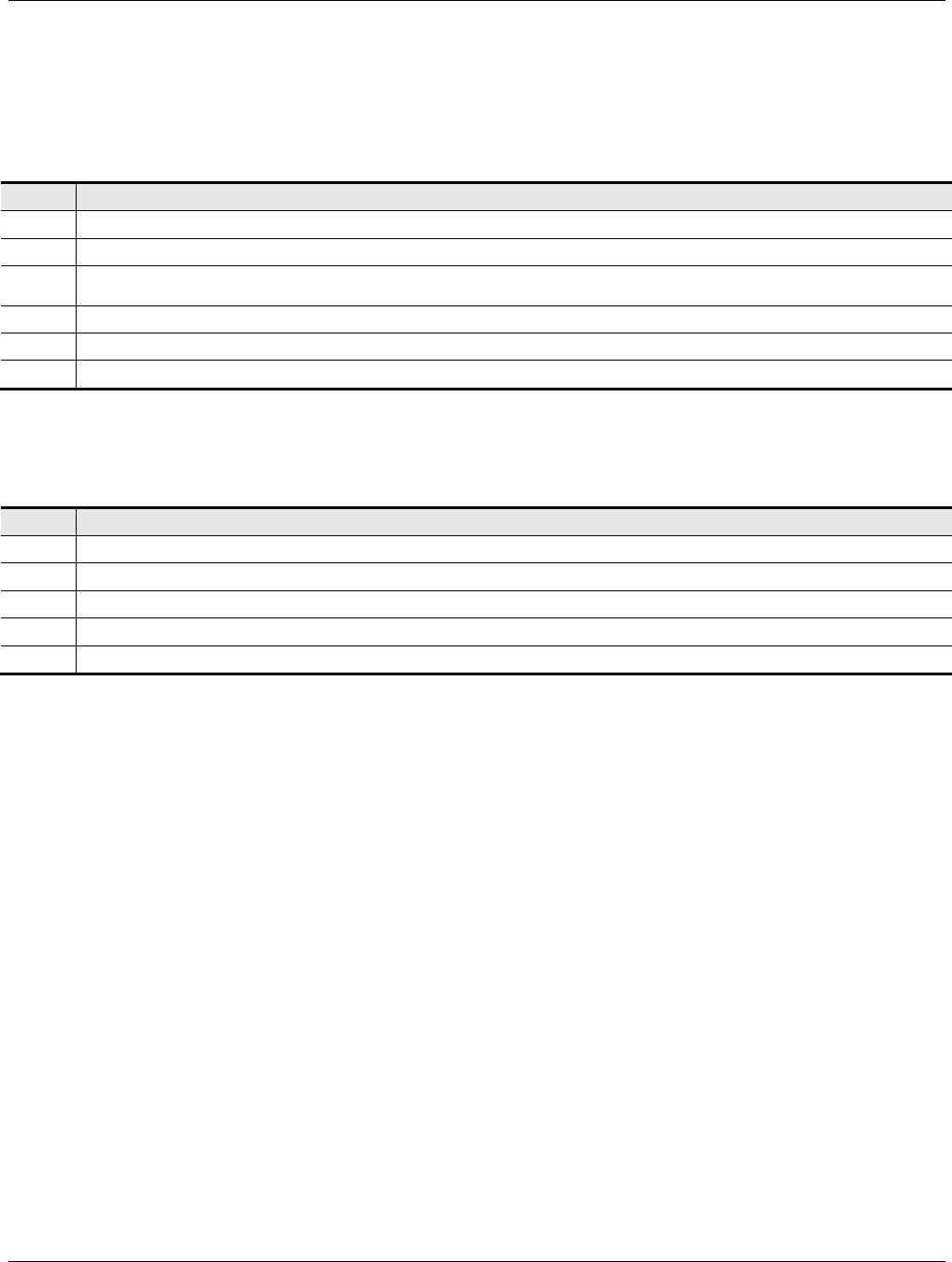
mBSC-CM RUM
mBSC-CM December 15, 2015
Page 39
4.5.3 mBSC-C Inspection Checklist
Table 11mBSC Unit Inspection
Item
Description
1 Stable and normal.
2 Properly fastened
3
Screws and nuts screwed tightly, without missing flat washers and spring washers. Spring washers must be on the
top of flat washers.
4 No cable damage.
5 Clean, no smudges or dust.
6 Connections between metallic parts must be reliable, to assure reliable electric connectivity.
4.5.4 Cabling Inspection
Table 12 Cable Inspection
Item Description
1 The connection of the cable is tight, not loose or damaged.
2 The cable shell not damaged.
3 Grounding cable is connected properly.
4 Cables are dressed neatly, power kept separate from signal.
5 The minimum bending radius of the cable is proper. (Shouldn’t be less than twenty times of the cable’s diameter.)
4.6 System Test
It is recommended to perform a system test after the physical installation and cabling has been inspected
and verified.
Use the following procedure to perform the system test:
Configure the attenuation both of the forward path and reverse path
Configure the parameters of Host Unit
VSWR testing: sweep test of cables and antenna
Configure the parameters of Remote Unit
Signal testing: indoor signal level testing
Effect testing: CQT/DT testing
Coverage Optimize: based on the signal & effect testing result, adjust the mBSC parameters to
optimize the coverage
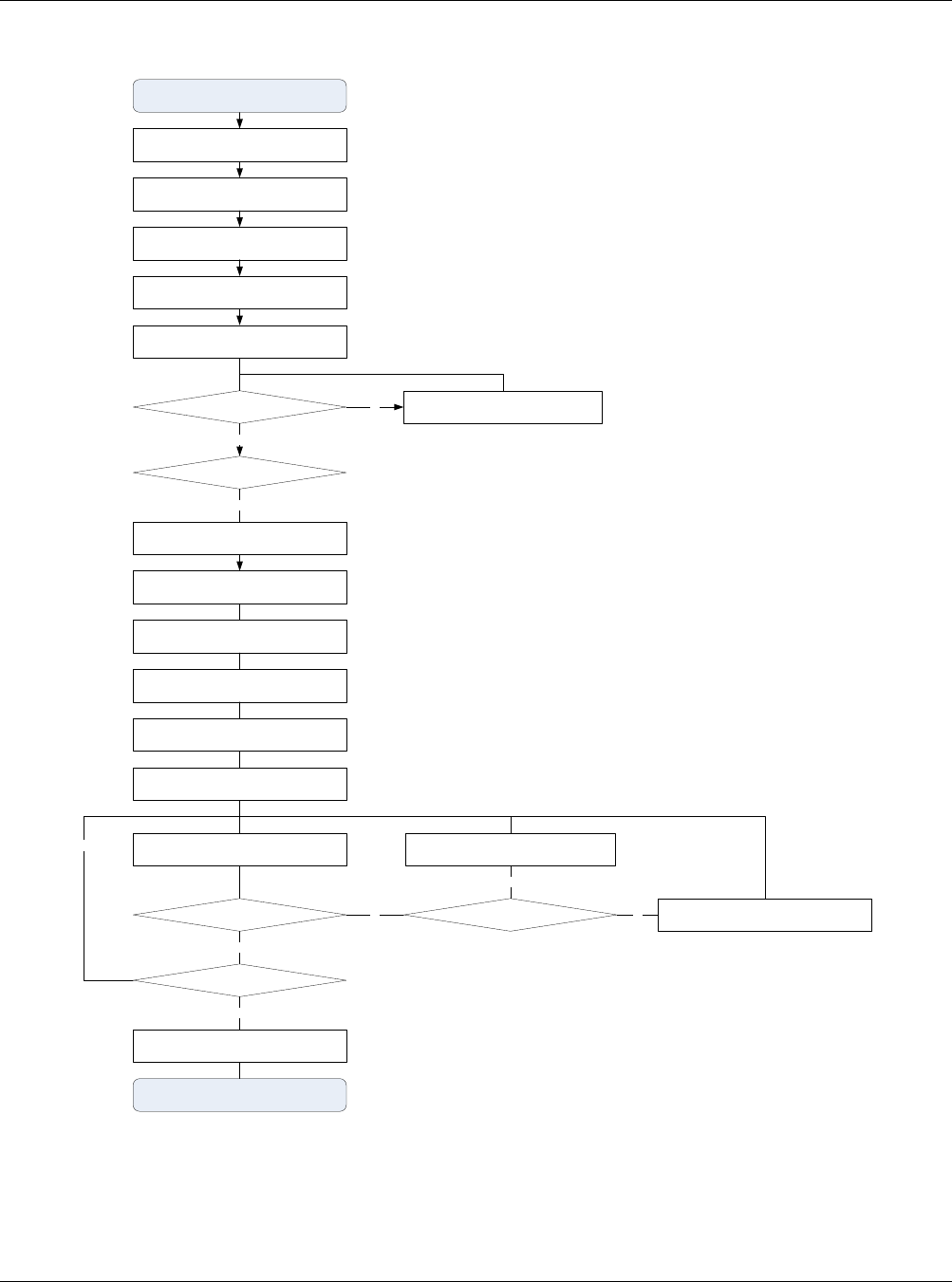
mBSC-CM RUM
mBSC-CM December 15, 2015
Page 40
HU installation & configuration
Reserve path signal level evaluation
RU VSWR is normal?
HU optical power level test
RU power on
Check connection of cable & antenna
Yes
No
Test Start
Test & Debug complete
HU RF signal input/output level adjustment
RU installation, cable & antenna connection
RU optical power lever is normal?
Yes
Reserve path pre-attenuation
RU forward path adjustment
RU reverse path adjustment
Forward path and reserve path balance
adjustment
RU parameter configuration
RU signal effect test
Coverage is normal?
Monitor & adjustment remotely
Yes
Adjust related parameters
mBSC Unit problem?
No
Yes
Adjust cable & antenna
No
HU noise figure is normal?
Yes
No
Figure 36 Flow Chart of System Debugging

mBSC-CM RUM
mBSC-CM December 15, 2015
Page 41
5 System Monitoring &Configuration
5.1 Accessing EMS Local GUI
The mBSC0800S-005-RUCM11 system supports local configuration through a web-based Element
Management System (EMS) graphical user interface (GUI) accessed through the RJ-45 and USB ports of
the Host Unit RCU card. The EMS local GUI is a web-based application supported by standard
web-browsers. Microsoft Internet Explorer® is recommended.
System configuration and monitoring can also be performed from a remote EMS Server. The EMS Server is
a multi-user platform that includes enhanced management capabilities for configuration, monitoring and
alarming. The EMS Server is required to generate SNMP alarms.
Note:It may take up to 3 minutes for the mBSC system to initialize, therefore it is recommended to only attempt to login to the
GUI after the mBSC system has completely started, otherwise the GUI may incorrectly display a message indicating that the
username and/or password are wrong (when in fact they may be correct).
5.1.1 Using Ethernet Port
Access to the EMS Local GUI through an RJ-45 Ethernet connection is provided on the RCU card in the
Host Unit shelf. The Ethernet port is the primary point of connection for the remote EMS Server. The EMS
Local GUI accessed through the Ethernet port is assigned the IP address 172.18.60.60 at the factory.
However, this IP address can be modified to suit the networking requirements of the installation (e.g. to allow
access across a Local Area Network).
Steps:
1. Obtain a CAT5 cable and connect it to the RJ45 port on the host unit RCU card, and connect the
other end into the RJ45 port on the laptop/computer. Depending on the model year of your computer,
a crossover cable may be required.
2. Start an Internet Explorer browser session on the laptop/computer, and enter the following URL to
connect to the Local GUI–“http://172.18.60.60”.
Note: The mBSC system does not provide DHCP service. To access the GUI you will need to configure the local computer
with a static IP address the same subnet as the local GUI.
Note: The EMS Local GUI is a single-user interface, and supports only a single user at a time. If the Ethernet interface is
connected to a Local Area Network, and more than one user is accessing the EMS Local GUI at the same time, inconsistent
operation may occur. Please use the EMS Server for multi-user applications.
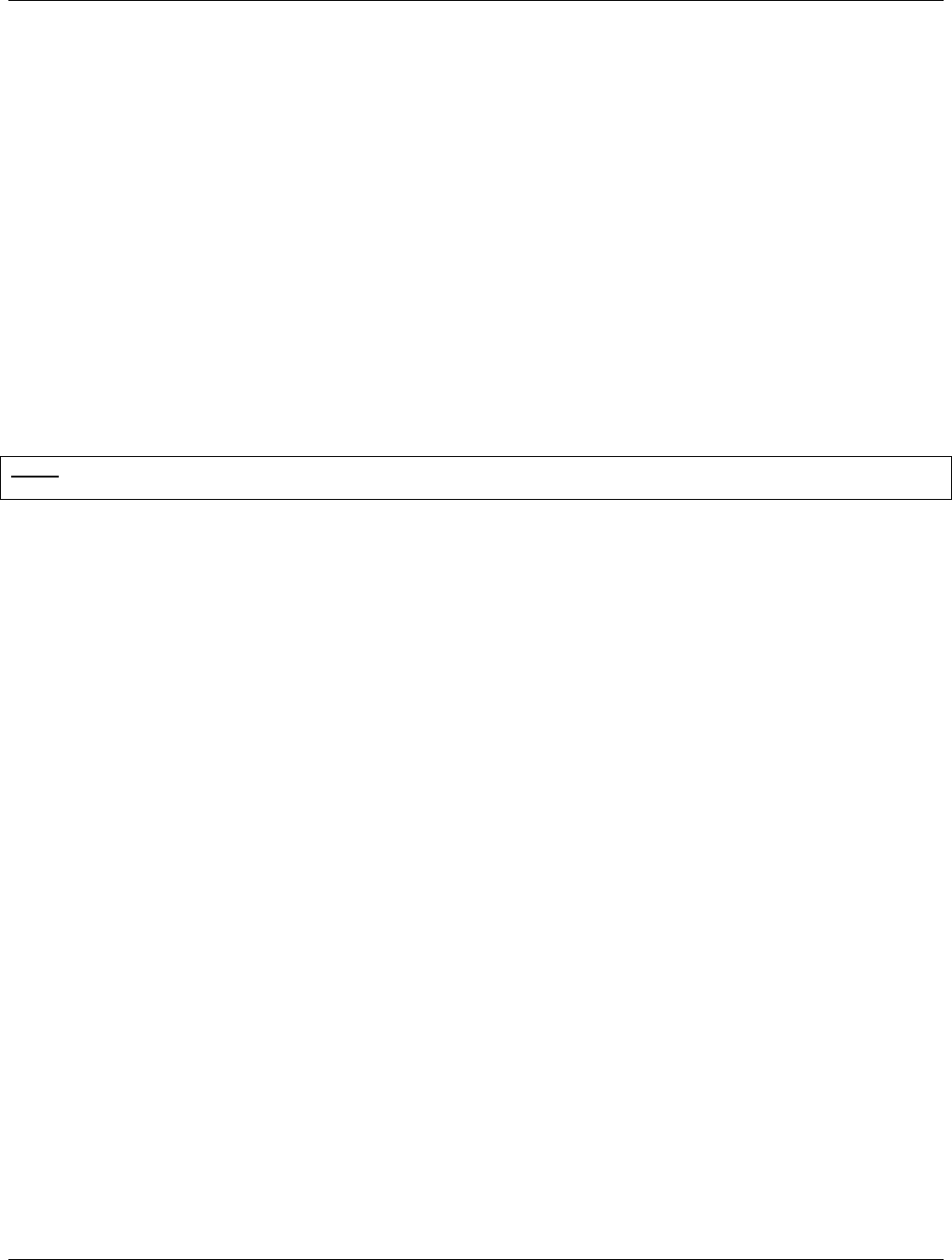
mBSC-CM RUM
mBSC-CM December 15, 2015
Page 42
5.1.2 Using USB Port
Access to the EMS Local GUI through a standard USB connection is also available at both the Host Unit
RCU card, and the RTM enclosure of the Remote Node. The EMS Local GUI has a fixed IP address
assignment when accessed through the USB port – it is set at the factory and cannot be changed.
Steps:
1. Install the USB-Ethernet driver on the laptop/computer. The laptop/computer must be connected
to the internet in order for the drivers to be automatically installed.
2. Obtain a USB cable and connect it to the USB port on the host unit and the laptop/computer.
3. Start an Internet Explorer browser session on the laptop/computer, and enter the following
URL–“http://192.168.5.220”.
Note: The mBSC system does not provide DHCP service. To access the GUI you may need to configure the local computer
with a static IP address the same subnet as the local GUI.
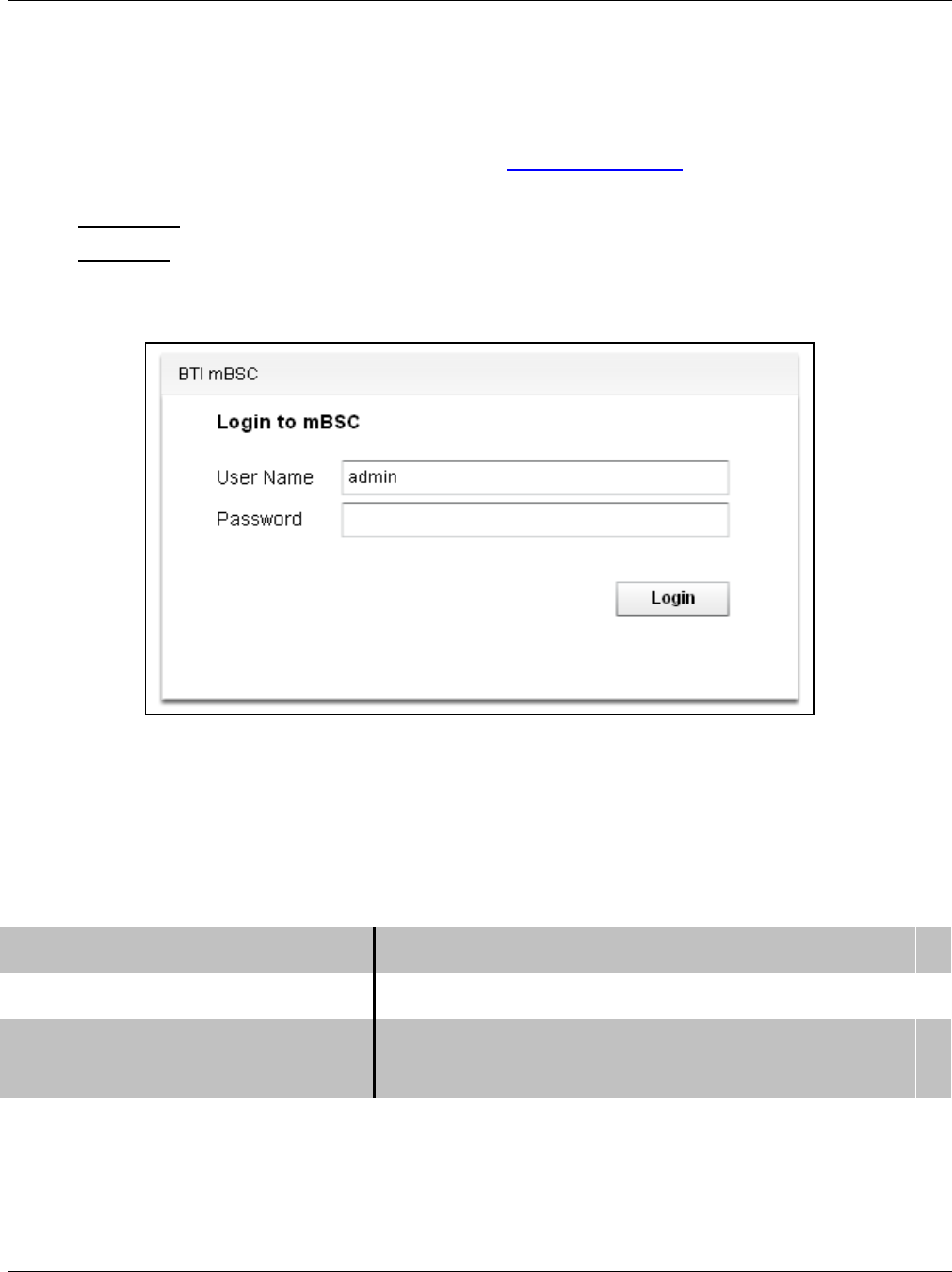
mBSC-CM RUM
mBSC-CM December 15, 2015
Page 43
Login to EMS Local GUI
Access the EMS Local GUI as follows:
1. Type the appropriate URL into the browser (e.g. http://192.168.5.220 for USB port). The dialog box
shown in Figure 40– EMS Local GUI Login will appear.
2. User name: Type in the user name provided for you to access the system (default = “admin”)
3. Password: Type in the password provided for you to access the system (default = “”)
4. Click Login
Figure 37– EMS Local GUI Login
The default user account for the EMS Local GUI is set at the factory as follows:
Table 13Local GUI Default User Accounts
Username Admin
Password (null)
Access Control Level Equipment properties view
Gain setting
The mBSC system administrator may have created different usernames and passwords for you to use.
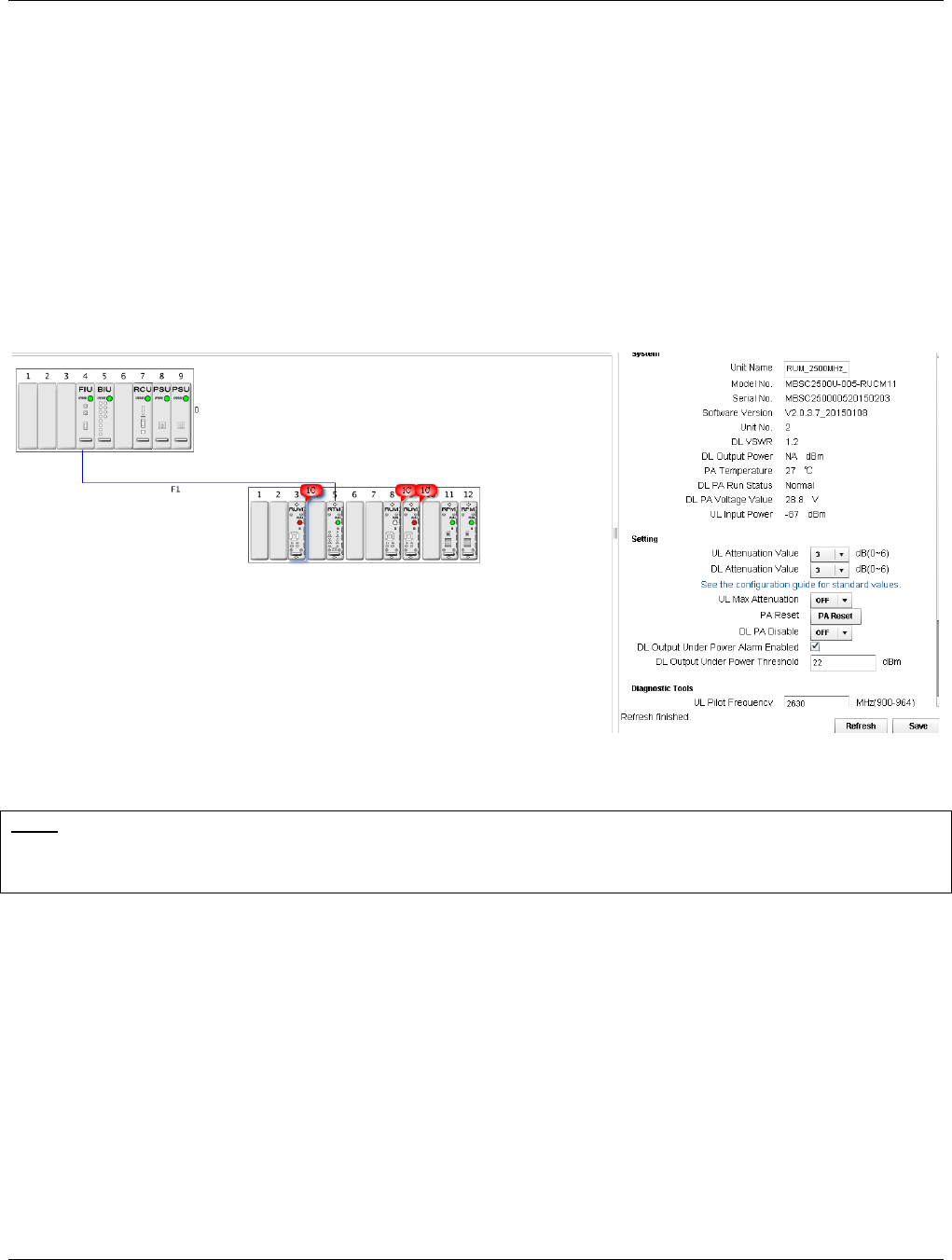
mBSC-CM RUM
mBSC-CM December 15, 2015
Page 44
5.2 Navigating the EMS Local GUI
When logged in to the EMS Local GUI, it displays the main page as shown in Figure 41. On the left side of
the main page the topology of the mBSC-C system you are connected to is automatically displayed. This
includes the Host Unit and the fiber attached Remote Nodes. On the right side is a floating window for
displaying system component properties.
Figure 38- Main Page Expanded Topology
Note: The EMS Local GUI will only display the nodes that are connected to the specific Host Unit shelf that you are connected
to. If the site has multiple Host Unit shelves (to support many Remote Nodes) then you will need to separately connect to each
shelf to perform configuration. The EMS Server, if provided, will enable connections to multiple connected Host Unit Shelves
and multiple installation sites.
In the topology window the system can be placed into a summary view by double-clicking on the Host Unit
shelf, or the Remote Node components.
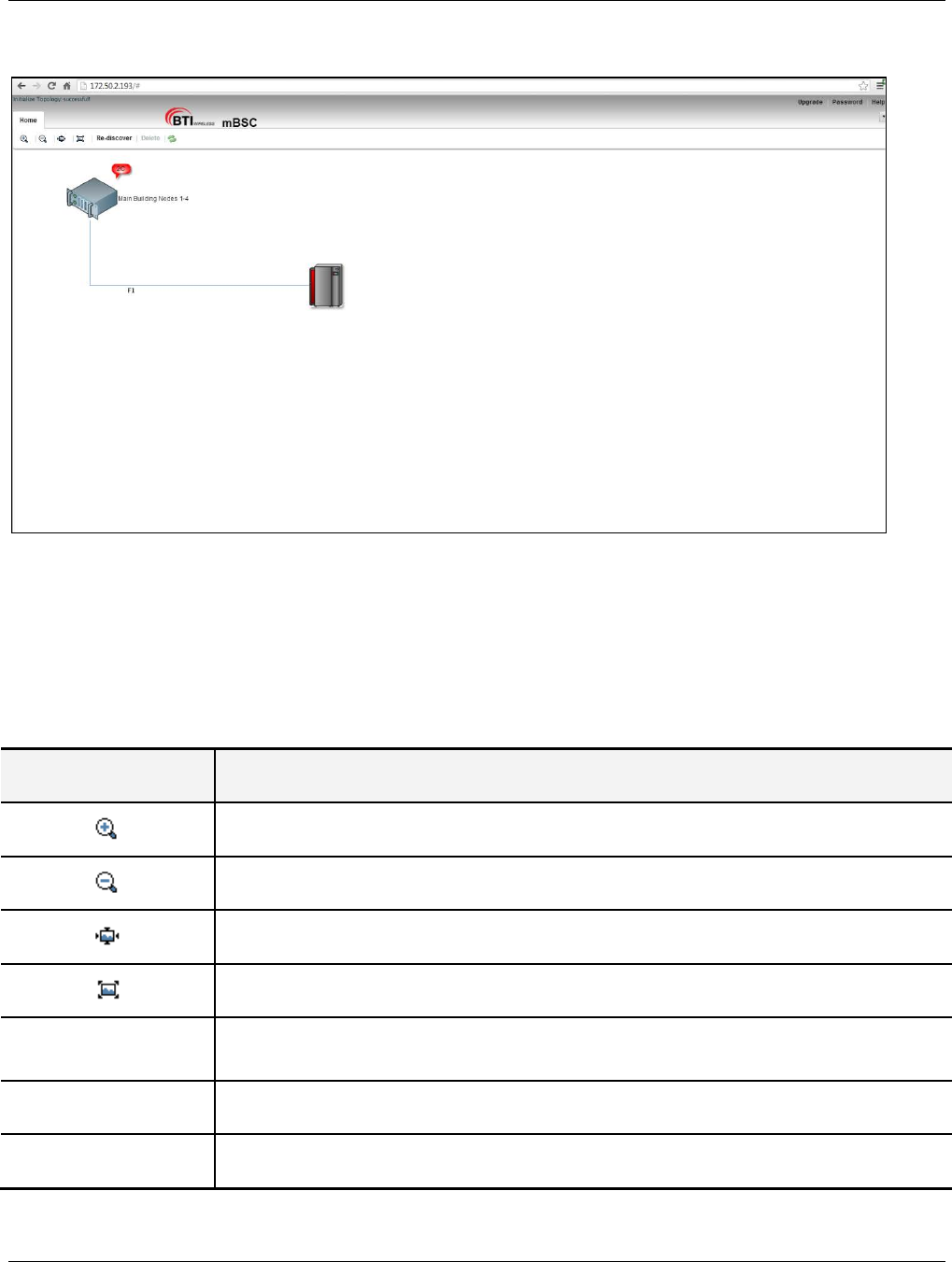
mBSC-CM RUM
mBSC-CM December 15, 2015
Page 45
Figure 39- Main Page Summary View
5.2.1 Topology Tool Bar
Various functions can be performed by clicking on the following icons.
Table 14 Tool Bar Functions
Tool Function
Zoom in – Zooms in the topology diagram
Zoom out – Zooms out the topology diagram
Reset – Resets the topology view to default
Overview – Resizes topology diagram to full screen
Re-discover Re-Discovery – Constructs the topology upon initial local GUI login or changes in system
configuration. This function is crucial to make sure topology structure is correct.
Delete Delete – Deletes a component from the Topology view
Refresh Refresh – Refreshes “real time” system topology

mBSC-CM RUM
mBSC-CM December 15, 2015
Page 46
5.2.2 Upgrade/Password Functions
The links in the upper right corner contain the Upgrade, Password, and Help functions.
Table 15 General GUI Tools
Function Description
Upgrade Perform a component software upgrade
Password Change the login password for current User
Help System information and Help
5.3 Installation & Configuration
5.3.1 Network & Communications
5.3.1.1 Change IP Address of RCU Ethernet port
In order to connect the RCU to a Local Area Network (for example, to allow remote access to the mBSC
from outside the Site) the user will need to change the IP address to the address required in their existing
network.
To change the IP address of the RCU Ethernet Port:
1. Click on the RCU in the topology diagram and the component window will pop up on the right as
shown in Figure 43- RCU Component View.
2. Locate the required fields and set the appropriate values.
a. Mode of Communication: must be set to Ethernet
b. Equipment IP Address: enter the value assigned to this HU shelf
c. Equipment Subnet Mask: enter appropriate subnet mask
d. Equipment Default gateway: enter assigned gateway
3. Click Save

mBSC-CM RUM
mBSC-CM December 15, 2015
Page 47
Figure 40- RCU Component View
5.3.1.2 Assign IP Address for Remote EMS Server
The mBSC-C system can also be managed from a remote EMS Server. To communicate with the remote
server the IP address must be reachable form the local network, and must be configured within the RCU.
To assign the IP address of the remote EMS Server:
1. Click on the RCU in the topology diagram and the component window will pop up on the right as
shown in Figure 43- RCU Component View.
2. Locate the required fields and set the appropriate values.

mBSC-CM RUM
mBSC-CM December 15, 2015
Page 48
a. NMS IP Address(IP4): enter the value assigned to the remote EMS Server
b. NMS IP Port: enter port (default value is 8008)
c. Equipment Default gateway: enter assigned gateway
3. Click Save
5.3.1.3 Assign HU Site Name/Number
Users can create a name or a site number for the Host Unit. This information is displayed in the Summary
View (Figure 42- Main Page Summary View), or is used in the EMS Server to distinguish between multiple
Host Shelves and/or multiple mBSC systems.
To assign the HU Site name/Number:
1. Click on the RCU in the topology diagram and the component window will pop up on the right as
shown in Figure 43- RCU Component View.
2. Locate the required fields and set the appropriate values:
a. Site Name/Number Info: enter the desired identifier
3. Click Save
5.3.2 System Installation
5.3.2.1 Verify Component Status
Once the system has been properly installed, check the status of each component in the Home tab, as
shown in Figure 44- Main Page Equipment Status.
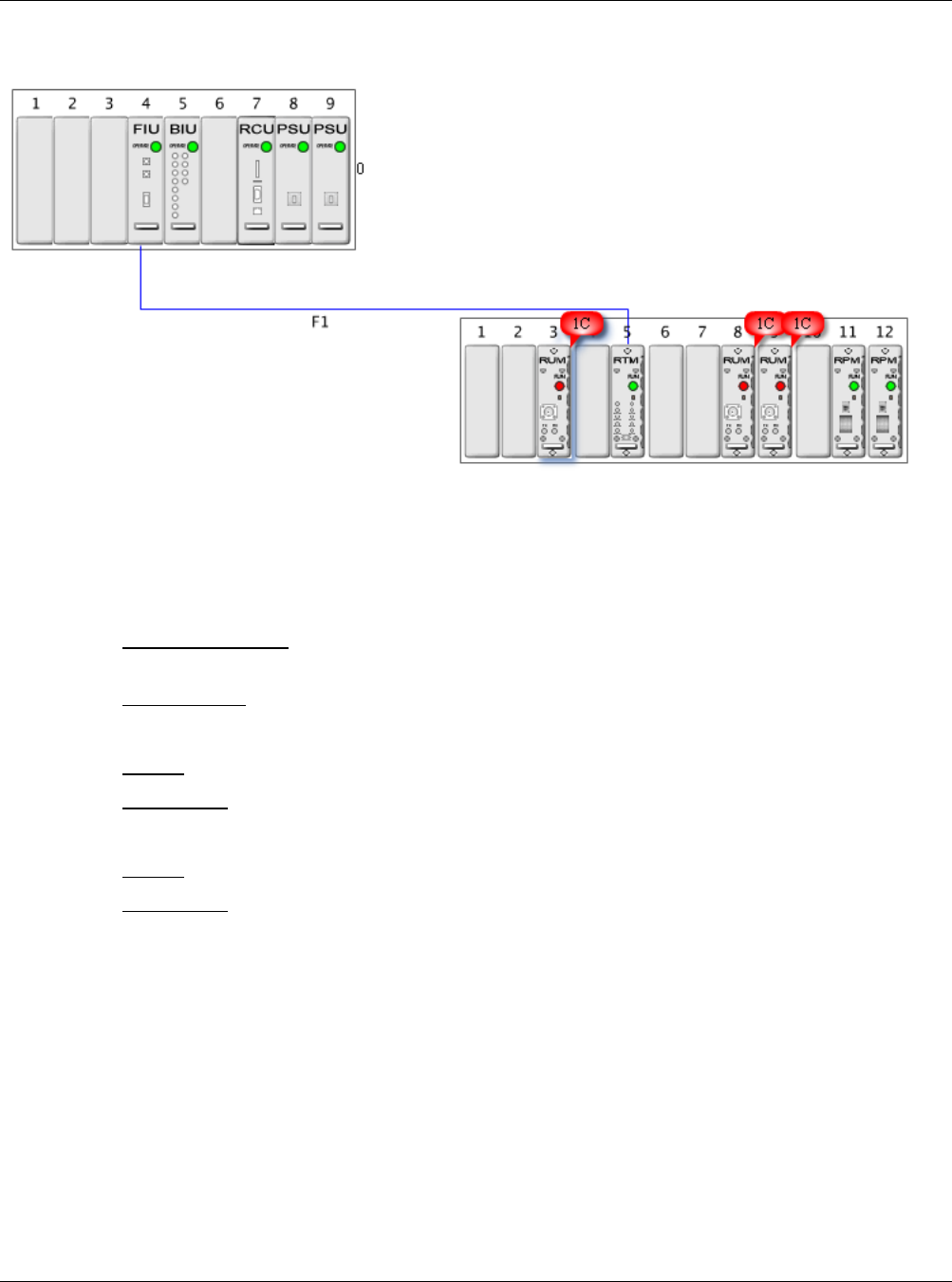
mBSC-CM RUM
mBSC-CM December 15, 2015
Page 49
Figure 41- Main Page Equipment Status
Check the current status of each component as follows:
1. Update Topology view:
a. Click Re-Discover: If new equipment (eg. Remote Node) has been added but does not yet
show up in the topology view
b. Click Refresh: If all components appear and to ensure current status is reflected
2. Review HU status indicators:
a. All OK: Component LEDs in the HU shelf indicate green state
b. Error/alarm: Component LEDs are flashing red, and a red “balloon” is present
3. Review Remote Node status indicators:
a. All OK: Component LEDs in the Remote Node indicate green state
b. Error/alarm: Component LEDs are flashing red, and a red “balloon” is present
If components appear with error conditions please see sections 5.3.3.1Optical Link Alarms and 5.5
Monitoring for details on error conditions.
5.3.2.2 Verify Optical Power Levels
The optical power levels at both ends of the fiber link (at the FIU of the Host Unit, and the CM of the Remote
Node) can be observed and verified through the EMS Local GUI.
Check optical power levels at the Host Unit as follows:
1. Click on the FIU in the topology diagram and the component window will pop up on the right as
shown in Figure 45- FIU Optical Power Levels.

mBSC-CM RUM
mBSC-CM December 15, 2015
Page 50
2. Optical Transceiver 1 Tx Power: the output power of the FIU 1 to the fiber.
a. Nominal value is: +4.0 dBm +/-1.5 dB (impacted by temperature)
3. Optical Transceiver 1 Rx Power: the input power of the FIU 1 from the fiber.
a. Acceptable range is:-15 dBm ~ +6dBm (impacted by fiber loss)
4. Optical Transceiver 2Tx Power: the output power of the FIU 2 to the fiber.
a. Nominal value is: +4.0 dBm +/-1.5 dB (impacted by temperature)
5. Optical Transceiver 2 Rx Power: the input power of the FIU 2 from the fiber.
a. Acceptable range is: -15 dBm ~ +6dBm (impacted by fiber loss)
Figure 42- FIU Optical Power Levels
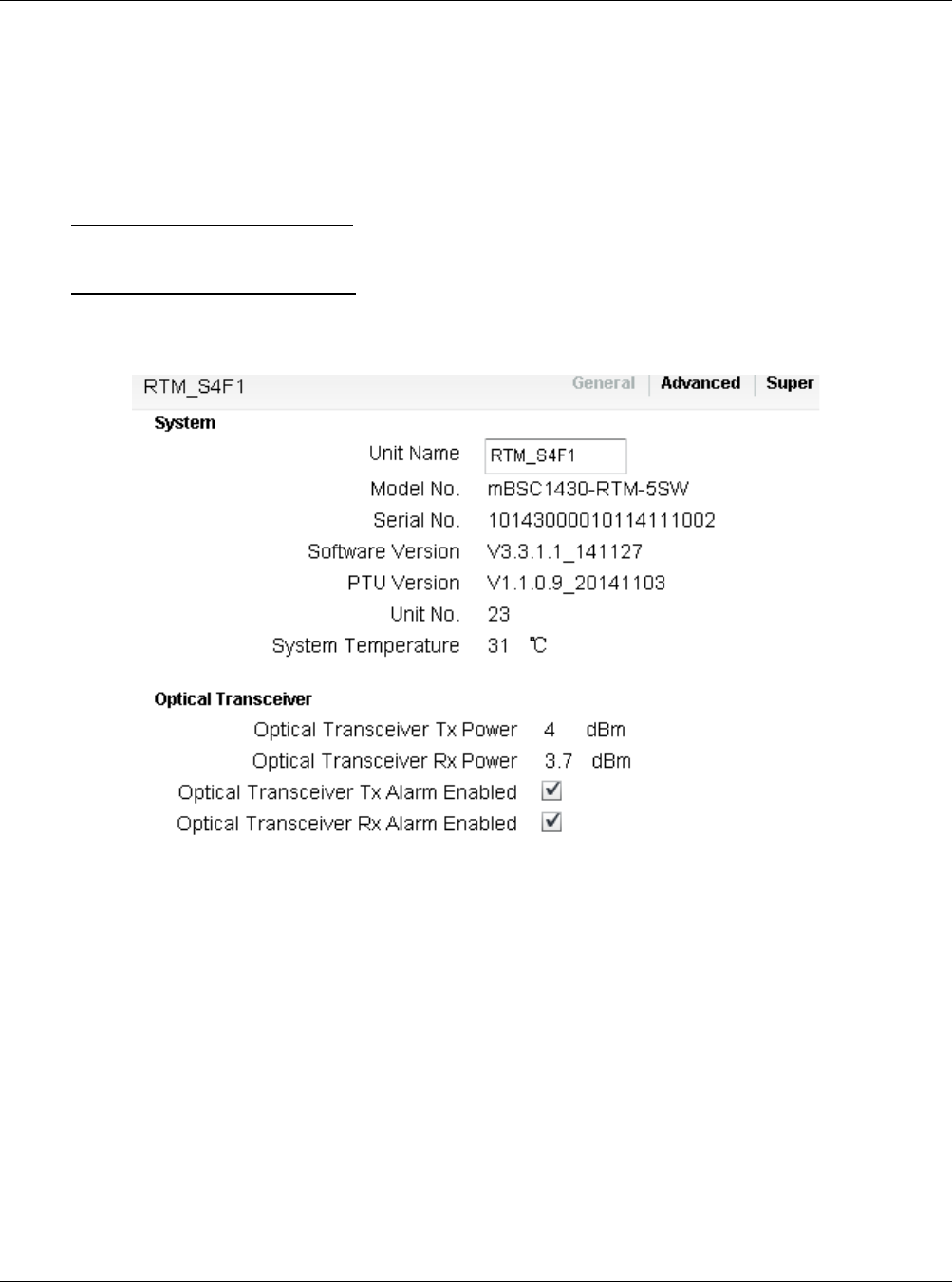
mBSC-CM RUM
mBSC-CM December 15, 2015
Page 51
Check optical power levels at the Remote Node as follows:
1. Click on the RTM in the topology diagram and the component window will pop up on the right as
shown in Figure 46- CM Optical Power Levels.
2. Optical Transceiver 1 Tx Power: the output power of the RTM 1 to the fiber.
a. Nominal value is: +4.0 dBm +/-1.5 dB (impacted by temperature)
3. Optical Transceiver 1 Rx Power: the input power of the RTM from the fiber.
a. Acceptable range is: -15 dBm ~ +6dBm (impacted by fiber loss)
Figure 43- RTM Optical Power Levels
5.3.2.3 Verify Software Versions
Click on Help in the upper right corner to verify the software version of the EMS Local GUI.
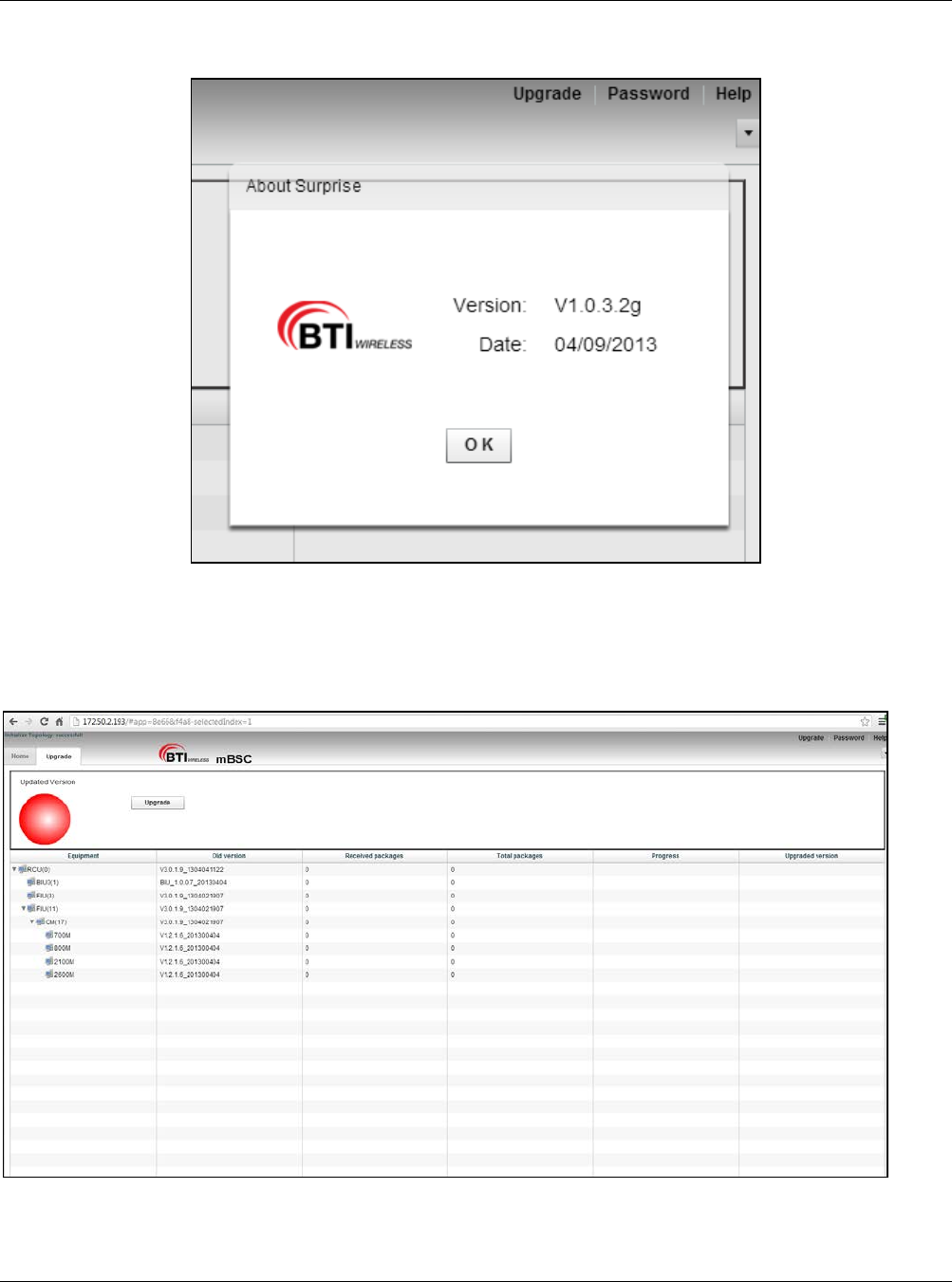
mBSC-CM RUM
mBSC-CM December 15, 2015
Page 52
Figure 44 - EMS Local GUI Software Version
To verify the software version installed on each component click on the Upgrade button in the top right:
Figure 45 - Component Software Versions
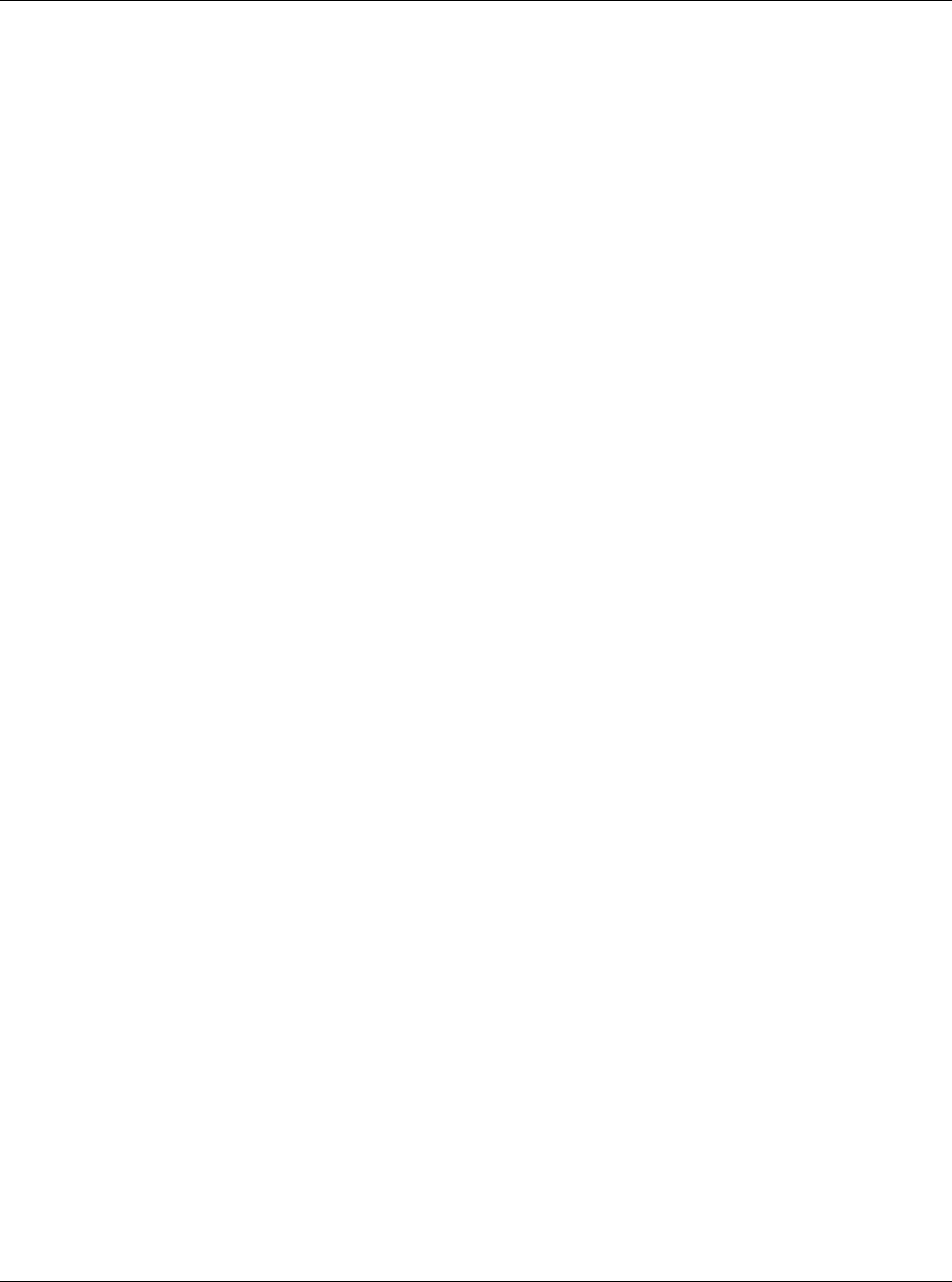
mBSC-CM RUM
mBSC-CM December 15, 2015
Page 53
5.3.3 Alarms
5.3.3.1 Optical Link Alarms
Optical Link alarms at the FIU will occur for various reasons:
1. Remote Node not in service: The Remote Node connected to the specific FIU link is not yet powered
up
2. Remote Node malfunctioning: connected to the specific FIU link is in an error state
3. Fiber issue: The fiber link between the specific FIU and the Remote Node has excessive loss
(possibly due to breakage or to dirty optical connectors)
4. No Remote Node: there is no plan to connect a Remote Node to the FIU (an FIU card supports two
links and one link is not used in this system).
In Figure 41- Main Page Expanded Topology the FIU in slot 3 is indicating an alarm state. Note the following
in Figure 49 – Optical Link Alarms:
1. The LED indicator for the FIU in slot 3 is not solid Green
a. A flashing red state indicates an alarm
2. There is a red “balloon” extending from the FIU in slot 3
a. The FIU supports two fiber connections: 1C indicates 1 alarm condition exists, 2C indicates 2
alarm conditions exist
3. There are no remote Nodes connected to the FIU in slot 3, and no fiber are extending from the FIU
a. In this case the HU recognizes there are no Remote Nodes connected
4. The FIU in Slot 6 is showing green operational status
a. No alarms are being reported, yet there is only one fiber extending from the FIU in connection
F1
b. Normally this FIU would report an alarm state for F2 (“1C” showing in the red alarm balloon)
c. No alarm state is shown because the user disabled Optical Transceiver 2 Alarms
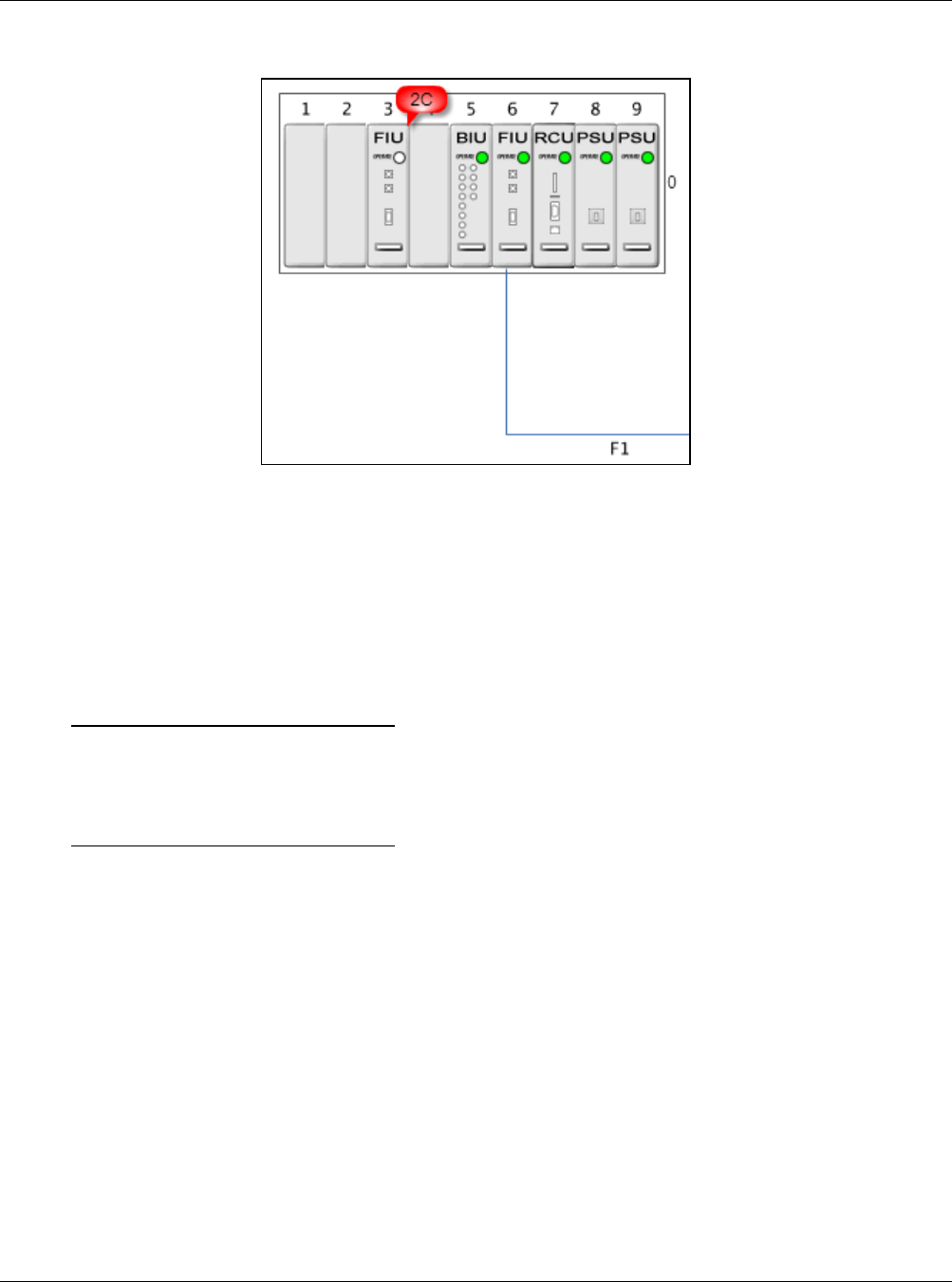
mBSC-CM RUM
mBSC-CM December 15, 2015
Page 54
Figure 46 – Optical Link Alarms
To disable optical transceiver alarms:
1. Click on the desired FIU in the topology window. The FIU component dialog box will appear as in
Figure 45- FIU Optical Power Levels
2. Optical transceiver 1 Alarm Enabled:
a. To enable alarms place a “check” in the box
b. To disable alarms clear the box
3. Optical transceiver 2 Alarm Enabled:
a. To enable alarms place a “check” in the box
b. To disable alarms clear the box
4. Click Save
5.3.3.2 Enable SNMP alarms
Support for SNMP in the mBSC-C system is provided through the remote EMS Server. For more information
about support for SNMP please refer to UM-MBSC-C-EMS.

mBSC-CM RUM
mBSC-CM December 15, 2015
Page 55
5.4 System Tuning
5.4.1 BTS Signal Conditioning
The interface from the operator BTS equipment to the MBSC0800S-005-RUCM11 is via simplex RF
connections to the BIU. The nominal downlink input to the BIU (TXin) is 0 dBm±1dB (range: -10dBm to
+10dBm). If the BTS signal downlink exceeds +10 dBm, or the signal is a composite duplex RF signal, then
RF signal conditioning will be required.
BTI provides a high-power Point of Interface to perform RF signal conditioning (mBSC-C-POI) The use and
operation of this component is outside the scope of this document.
5.4.2 Set Downlink Gain
It may be necessary to adjust the Downlink gain of the mBSC-C system in order to achieve a balanced
forward and reverse link, or to adjust for other conditions (input levels from the BTS, propagation
characteristics at different bands, specific RF design). The mBSC0800S-005-RUCM11 provides two points
of adjustment for downlink gain:
1. Software controlled attenuator for each band in the BIU
2. Software controlled attenuator in each band-specific Remote Unit
The determination of appropriate values for these parameters is outside the scope of this document.
5.4.2.1 Adjust BIU Downlink Attenuator
Adjust the BIU downlink value for each frequency band as follows:
1. Click on the BIU in the topology diagram and the component window will pops up on the right as
shown in Figure 50 - BIU Attenuator.
2. Downlink Attenuation Value (XXX MHz): Input the appropriate value for each frequency band (0dB –
25dB range)
3. Click Save
Note that the system will report an error message if the input value is out of range.
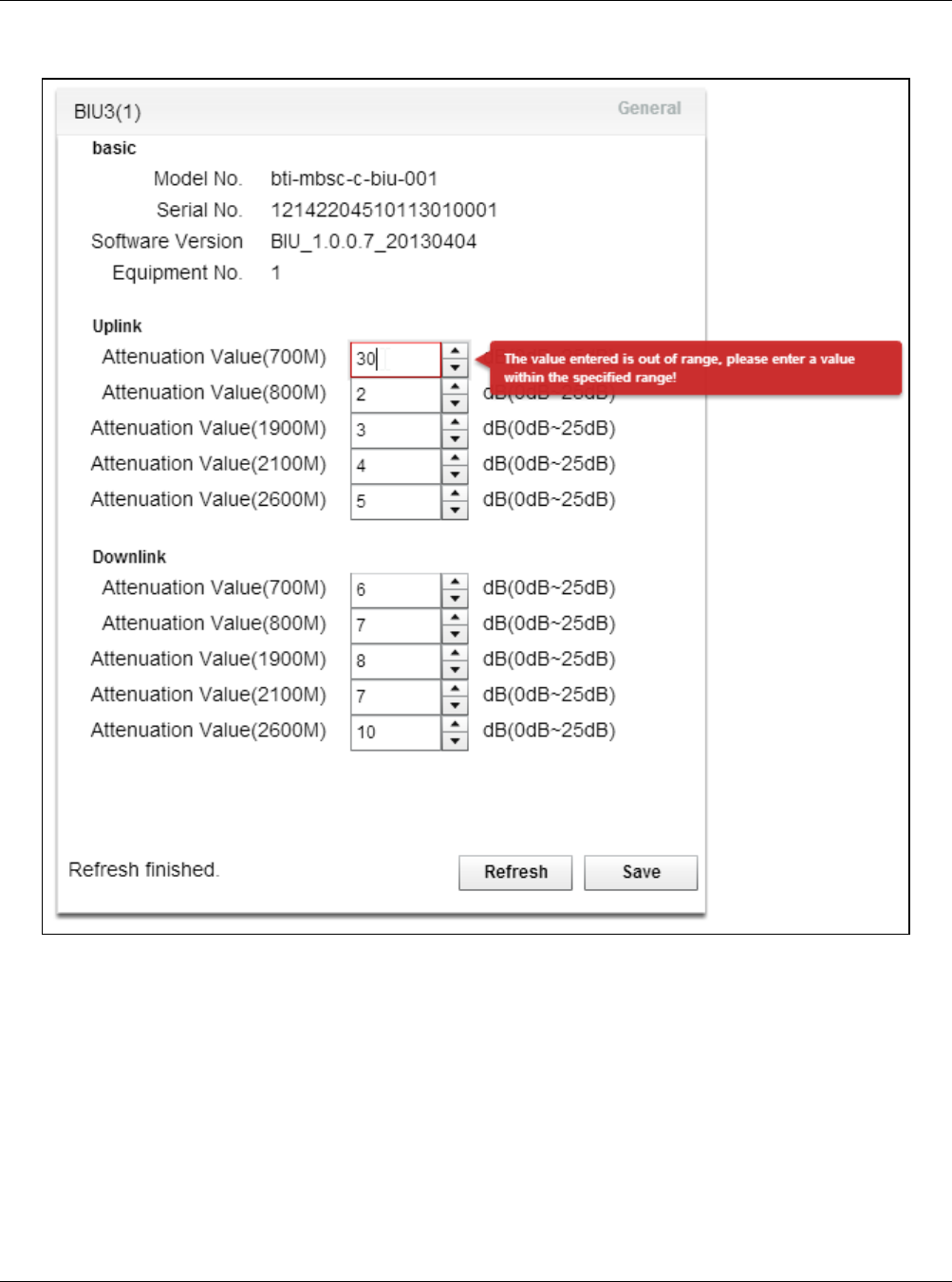
mBSC-CM RUM
mBSC-CM December 15, 2015
Page 56
Figure 47 - BIU Attenuator
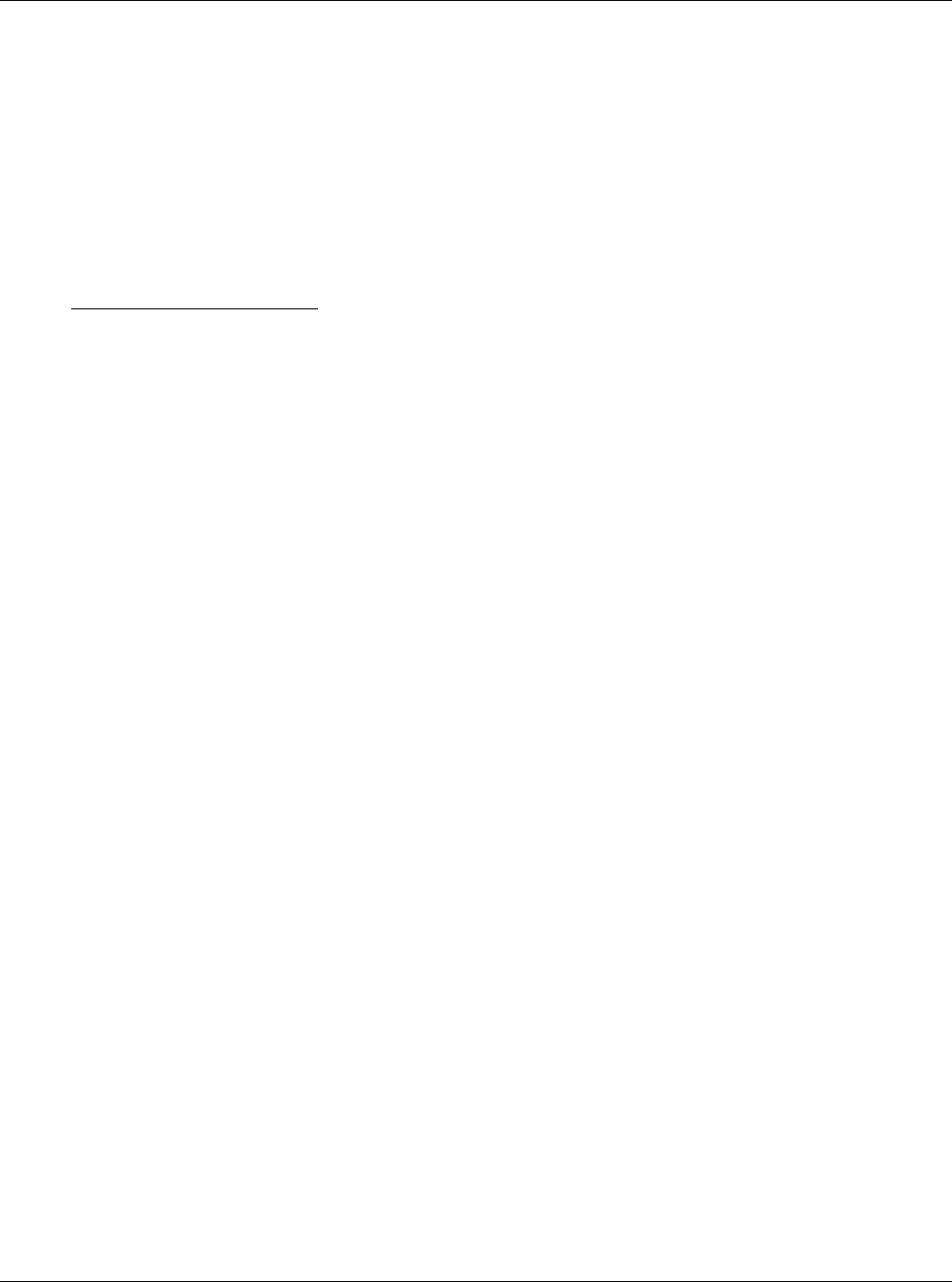
mBSC-CM RUM
mBSC-CM December 15, 2015
Page 57
5.4.2.2 Adjust RU Downlink Attenuator
Adjust the RU downlink value for the specific RU / frequency band as follows:
1. Click on the RU in the topology diagram and the component window will pops up on the right as
shown in Figure 51 - RU Attenuator.
2. Downlink Attenuation Value: Input the appropriate values (0dB – 6dB range)
3. Click Save
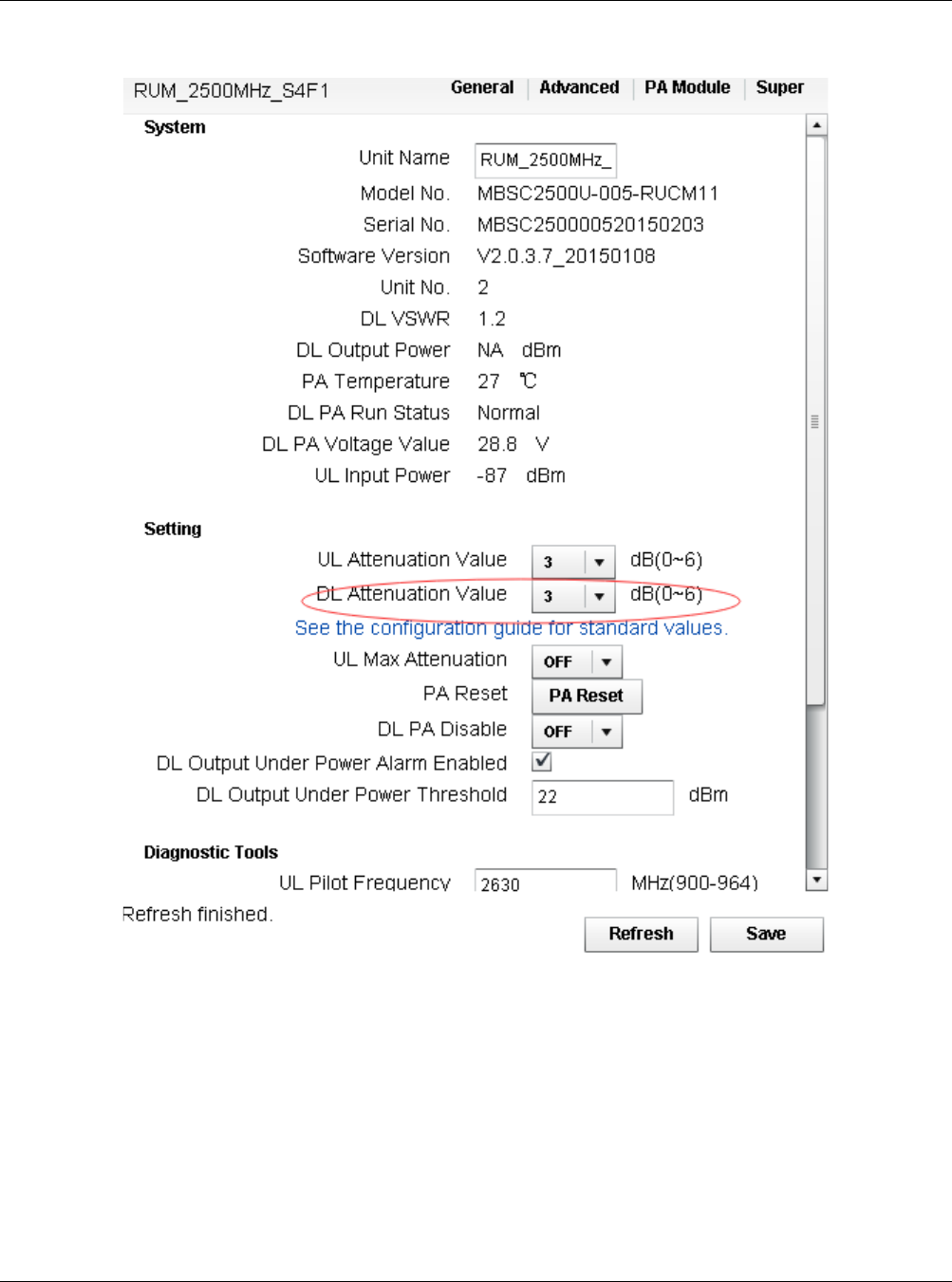
mBSC-CM RUM
mBSC-CM December 15, 2015
Page 58
Figure 48 - RU Attenuator
5.4.3 Set Uplink Gain
It may be necessary to adjust the Uplink gain of the mBSC-C system in order to achieve a balanced forward
and reverse link, or to adjust for other conditions (antenna placement, dynamic range requirements,
propagation characteristics at different bands, specific RF design). The mBSC0800S-005-RUCM11
provides two points of adjustment for uplink gain:
1. Software controlled attenuator for each band in the BIU
2. Software controlled attenuator in each band-specific Remote Unit
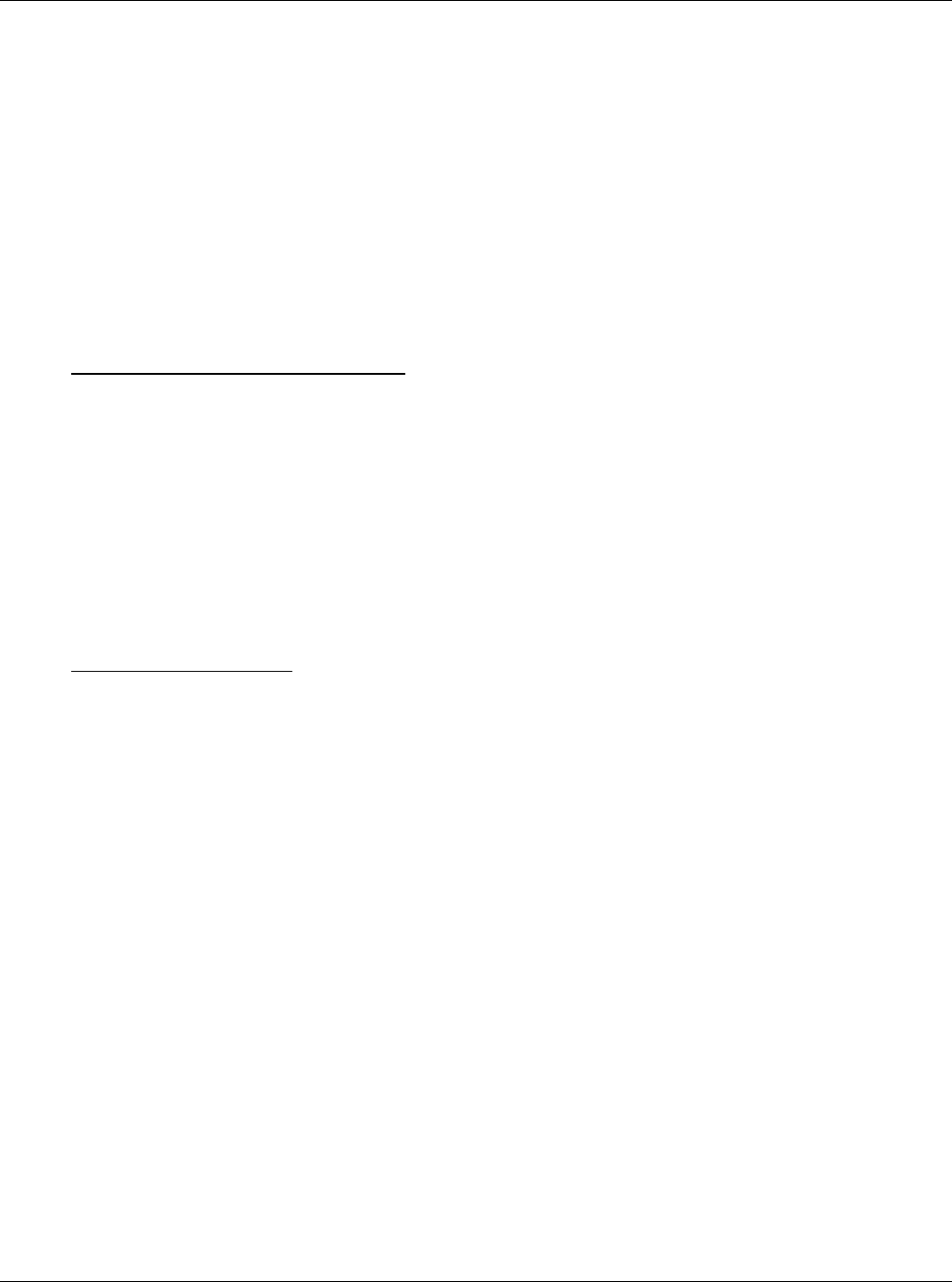
mBSC-CM RUM
mBSC-CM December 15, 2015
Page 59
The determination of appropriate values for these parameters is outside the scope of this document.
5.4.3.1 Adjust BIU Uplink Attenuator
Adjust the BIU uplink attenuation value for each frequency band as follows:
1. Click on the BIU in the topology diagram and the component window will pops up on the right as
shown in Figure 50 - BIU Attenuator.
2. Uplink Attenuation Value (XXX MHz): Input the appropriate value for each frequency band (0dB –
25dB range)
3. Click Save
5.4.3.2 Adjust RU Uplink Attenuator
Adjust the RU uplink attenuation value for the specific RU / frequency band as follows:
1. Click on the RU in the topology diagram and the component window will pops up on the right as
shown in Figure 51 - RU Attenuator.
2. Uplink Attenuation Value: Input the appropriate values (0dB – 6dB range)
3. Click Save

mBSC-CM RUM
mBSC-CM December 15, 2015
Page 60
5.4.4 Link Verification
The mBSC0800S-005-RUCM11 system is equipped with features that enable the downlink and uplink link to
be fine-tuned from the head-end location using common test equipment (RF signal generator and RF power
detector).
5.4.4.1 Verify End-to-End Downlink Gain
Each RU in the remote node is equipped with a calibrated Downlink Power Detector which will display the
average power at the output of the RU. By injecting an RF CW signal at each TXin port of the BIU the
end-to-end downlink system gain can be verified without additional test equipment required at the Remote
Node.
Verify the end-to-end Downlink Gain for each frequency band as follows:
1. Using an RF Signal generator inject a CW RF signal to the TXin port of the BIU
a. Set the frequency to the center of the spectrum to be used in the system (if the operator
licensed bands are not known set the frequency to center of the band – e.g. 2550 MHz for
TDD-LTE band)
b. Set the input RF power level to be 3 – 5 dB below the expected RF level to product maximum
output power at the RU to avoid accidental overdrive (e.g. if the gain is set so that 0dBm
input will produce +37 dBm at the output then start with -5dBm)
2. The resultant Downlink output power of the RU can be observed in two ways:
a. In the topology window the Downlink Output power is displayed next to the specific RU (e.g.
30.7 dBm indicated in the topology diagram by the 800MHz RU in Figure 52 – Up/Down Link
Verification)
b. Downlink Output Power: In the component window
3. Variations in filtering, amplifiers, and optical loss may cause the actual system gain to vary +/- 6 dB.
All paths can be normalized by adjusting downlink attenuation settings in the BIU.
4. This procedure should be repeated for each frequency band in the system
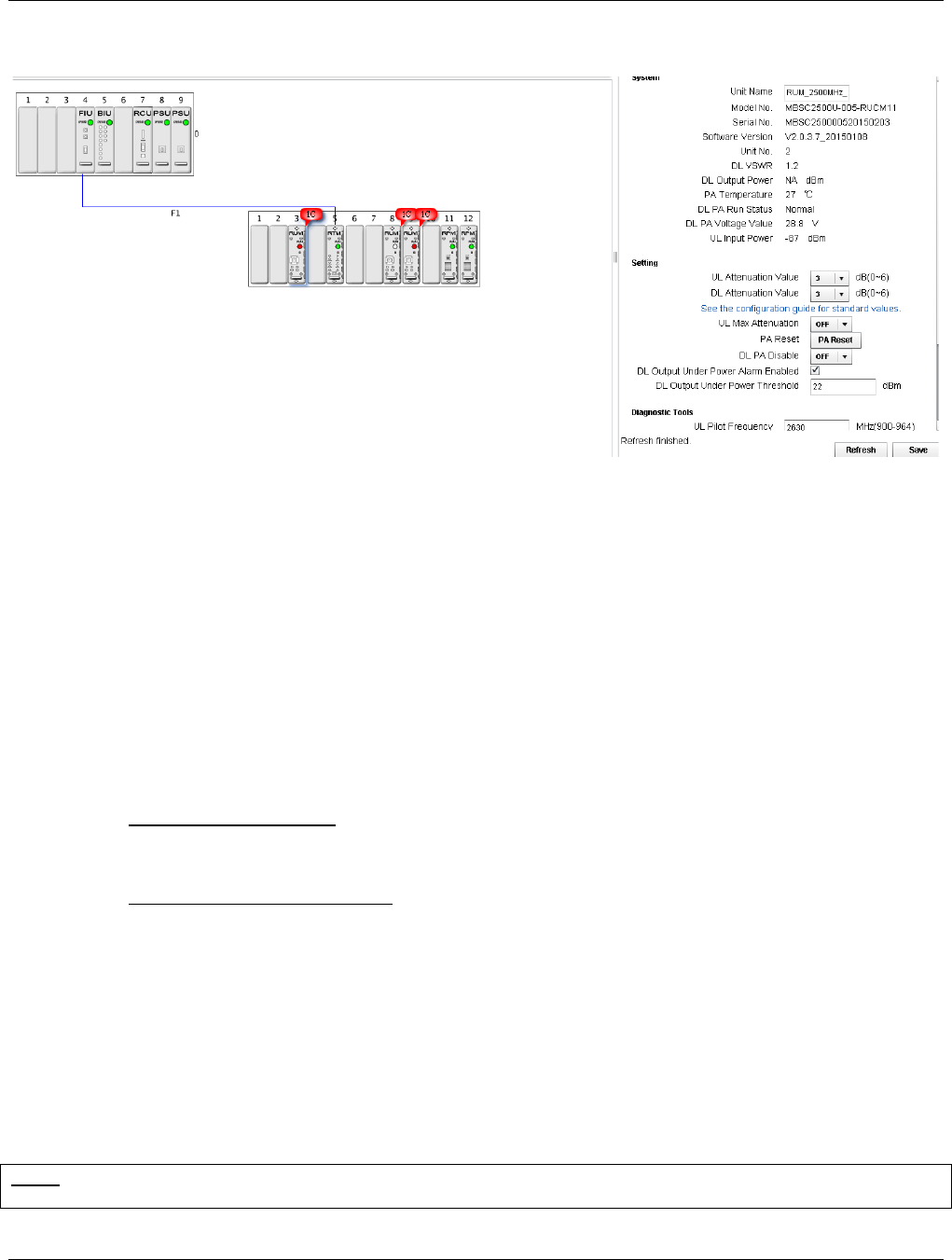
mBSC-CM RUM
mBSC-CM December 15, 2015
Page 61
Figure 49 – Up/Down Link Verification
5.4.4.2 Using Uplink Pilot Tone Generator
Each RU in the remote node is equipped with an Uplink Pilot Tone Generator which will generate a CW RF
tone out of the RU back towards the FIU and BIU.. By measuring the RF power at the RXout port of the BIU
the end-to-end uplink system gain can be verified, and band-to-band / node-to-node, variations calibrated
without additional test equipment required at the Remote Node.
Verify the end-to-end Uplink Gain for each frequency band as follows:
1. Click on the RU for the desired frequency band. The component window ;will pop up as shown in
Figure 52 – Up/Down Link Verification
a. Uplink Pilot Frequency: Set the frequency to the center of the spectrum to be used in the
system (if the operator licensed bands are not known set the frequency to center of the
band)
b. Uplink Pilot Frequency Switch: select ON from the drop-down box
c. Click Save to turn the Uplink Pilot generator ON
2. Connect an RF power meter to the corresponding RXout port of the BIU
a. A -6 dBm value in the Uplink Pilot Frequency Output Power field of the RU corresponds to an
equivalent signal of -60 dBm at the input to the RU
b. Variations in filtering, amplifiers, and optical loss may cause the actual system gain to vary +/-
6 dB. All paths can be normalized by adjusting uplink attenuation settings in the BIU.
3. This procedure should be repeated for each frequency band in the system
Note: Uplink Pilot Frequency Switch should be off during normal operations. This function is intended for testing, verifying,
and adjusting uplink performance and will interfere with normal operation of the system.

mBSC-CM RUM
mBSC-CM December 15, 2015
Page 62
5.5 Monitoring and Alarms
5.5.1 Operational Status
5.5.1.1 Host Unit
The EMS Local GUI graphical interface will notify users of an error or malfunction in the Host Unit with a red
popup “alarm indicator”. The alarms will also be displayed in the lower section of the component window.
Figure 50 - Host Unit Alarm Status
5.5.1.2 Remote Node
In the case of a Remote Node malfunction, the affected unit will also be marked with a red popup “alarm
indicator”. Figure 54 - Remote Node Alarm Status illustrates a condition where both fans of an RU are not
working (power cable disconnected):
1. The alarm indicator beside the affected RU in the topology view displays “2C”
2. Additional alarm status is shown in the lower right section of the RU component window.

mBSC-CM RUM
mBSC-CM December 15, 2015
Page 63
Figure 51 - Remote Node Alarm Status

mBSC-CM RUM
mBSC-CM December 15, 2015
Page 64
5.5.2 System Alarms
The mBSC0800S-005-RUCM11 provides alarm indications for equipment malfunctions or for conditions that
place the out of standard operating range (such as over-power). A complete list of alarm events, and the
originating product module, is provided in Table 15System Alarms.
These events are enabled by default factory settings, but can be disabled if desired.
These alarm events can be observed in multiples ways:
- In the EMS Local GUI in the network topology view and corresponding component parameter
windows
- In the Monitor window of the remote EMS Server
- As SNMP traps issued by the remote EMS Server (if enabled)
Table 16System Alarms
Item Equipment
Module
Alarm
ID
Alarm Name Description
1
Host Unit RCU
401500 Host/Remote Link
Optical RX signal is detected by the FIU
but no logical connection exists to the
Remote Node (CM)
2 423000 System Temperature
A system over-temperature alarm has
been reported
3
Host Unit FIU
401500 Host/Remote Link
Optical RX signal is detected by the FIU
but no logical connection exists to the
Remote Node (CM)
4 422000 Optical Transceiver 1
Low/No optical signal is detected on Link
1
5 422100 Optical Transceiver 2
Low/No optical signal is detected on Link
2
6
Remote
Node RTM
401500 Host/Remote Link
Optical RX signal is detected by the CM
but no logical connection exists to the
Host Unit (FIU)
7 423000 System Temperature
A system over-temperature alarm has
been reported
408301 Fan 1 Alarm Fan 1 is non-functioning (low current)
408302 Fan 2 Alarm Fan 2 is non-functioning (low current)
8 400100 Power Down
Power has been lost at the Remote Node
(internal battery backup enables alarm
delivery)
9
401920 PA Over VSWR High VSWR detected at output of PA
10 427000 PA Over Output Power PA output power exceed threshold
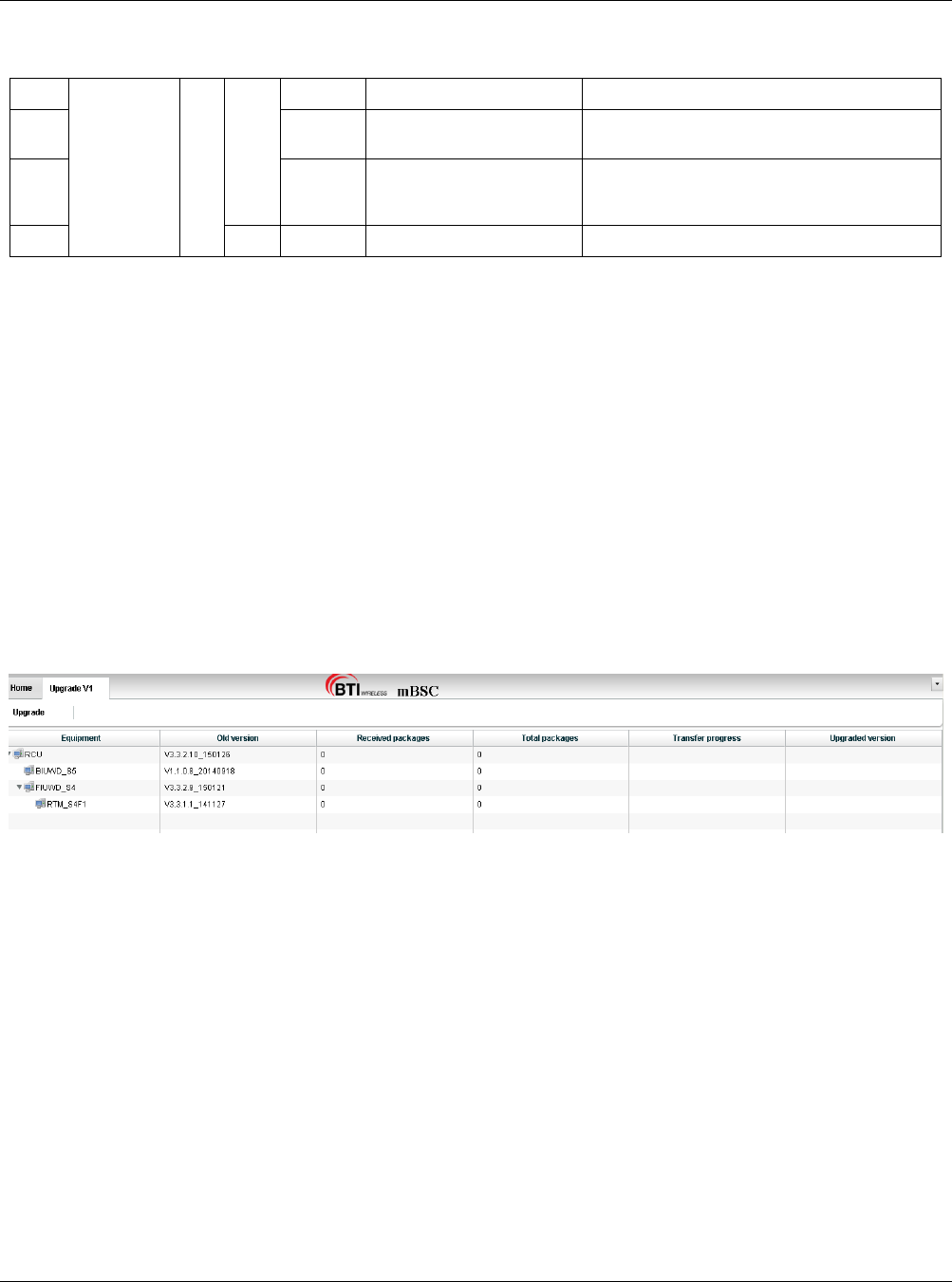
mBSC-CM RUM
mBSC-CM December 15, 2015
Page 65
11
Remote
Node
RU
PA
401620 PA Fault Alarm PA overdrive condition exists
12 400600
PA Over Temperature
Alarm
High temperature condition in final PA
stage
13 427100 PA Lower Gain Alarm Low gain condition (< 10dB) detected
14 SSM 401000 Uplink LNA Fault Alarm Internal LNA fault detected
5.6 System Upgrade
To conduct a system upgrade, navigate to the upper right section and click on “Upgrade”.
5.6.1 Verify Software Versions
Verify component versions in the second column of the Upgrade tab.
5.6.2 Upgrade component software
Click on the “Upgrade” button and locate the firmware file to start the component upgrade. Note: Each
component upgrade time differs from one another ranging from 5 minutes to 120 minutes.
Figure 52 - Component Upgrade

mBSC-CM RUM
mBSC-CM December 15, 2015
Page 66
6 Maintenance
Note: Check your sales order and equipment warranty before attempting to service or repair the mBSC-C system. Breaking
the seals on equipment under warranty will void the warranty. Do not return equipment for warranty or repair until proper
shipping instructions are received from the factory.
6.1 Electrostatic Discharge Precautions
The mBSC-C system modules contain assemblies and components which are sensitive to electrostatic
discharge (ESD). Carefully observe the precautions and recommended procedures to verify that system
reliability is not compromised due to component damage from static electricity.
The following precautions will significantly reduce the risk of system failure or malfunction due to ESD:
1. Always wear a grounded wrist strap while working around the system
2. Consider all assemblies, components and connections to be ESD sensitive
3. When unpacking circuit boards, interfaces and modules that are packaged separately from the
system, keep them in their conductive wrapping until they are ready to be installed.
4. Before removing or replacing any components, select a work area where potential static sources
are minimized
5. Handle circuit packs and boards by the grounded housings, avoiding contact with the connectors
6.2 Preventative Maintenance
The mBSC-C system requires minimal regular maintenance to ensure continuous and satisfactory operation.
Maintenance includes diagnosing and correcting the service problems as they occur. When an alarm is
reported, it is necessary to follow a troubleshooting procedure to identify the source of the problem.
The following are recommended routine maintenance procedures:
Check the indicator status LEDs (normal or alarm).
Prevent dust or grime from accumulating on the surface of heat sinks.
Check power output.
6.3 Fault Detection and Alarm Reporting
The mBSC-C on-board embedded firmware detects unit and system faults and reports them as system
alarms. The following methods may be used to report alarms:
Dry-contact alarm points
Status LEDs on system components
NMS (Local GUI, remote NMS, and SNMP Alarms)

mBSC-CM RUM
mBSC-CM December 15, 2015
Page 67
The mBSC-C Host Unit components are equipped with multiple LED indicators that show status and alarms
by displaying Green, Red or Off. Detailed descriptions of the LED indicators are provided respectively in
section 3.2.7Host Unit Interface.
The NMS software provides detailed alarm information which includes module level faults, circuit faults and
measured value faults such as door, RF power and temperature.
6.4 Troubleshooting Quick Guide
Use this section to quickly troubleshoot alarms and faults.
Table 17 Troubleshooting Quick Guide
Problem Quick Troubleshooting Steps / Possible Cause
No RF output
1) Optical path is faulty;
2) Downlink path BTS input signal is low/not present
3) Remote Node RU is faulty.
RF output power level is low
Measure the downlink output power at the output of the RU, and at the input to he antenna
1)Passive components between the RU and the antenna port are faulty;
2) Host Unit RF input connections are faulty;
3) Optical path is faulty;
4) RU is faulty.
Loss of phone service, but the
RF signal level is normal
1) Test calling in the coverage area of original BTS. It may be the BTS problem if the
situation is the same;
2) Measure the gain both of the forward path and reserve path to see whether they are
close;
3) RU LNA module is faulty.
Power supply is out of service
1) Measure the DC power input source. If the voltage is out of 48VDC +/- 20%, add a
regulated power supply between the power in connector and the power source.
2) The interior power unit is faulty.
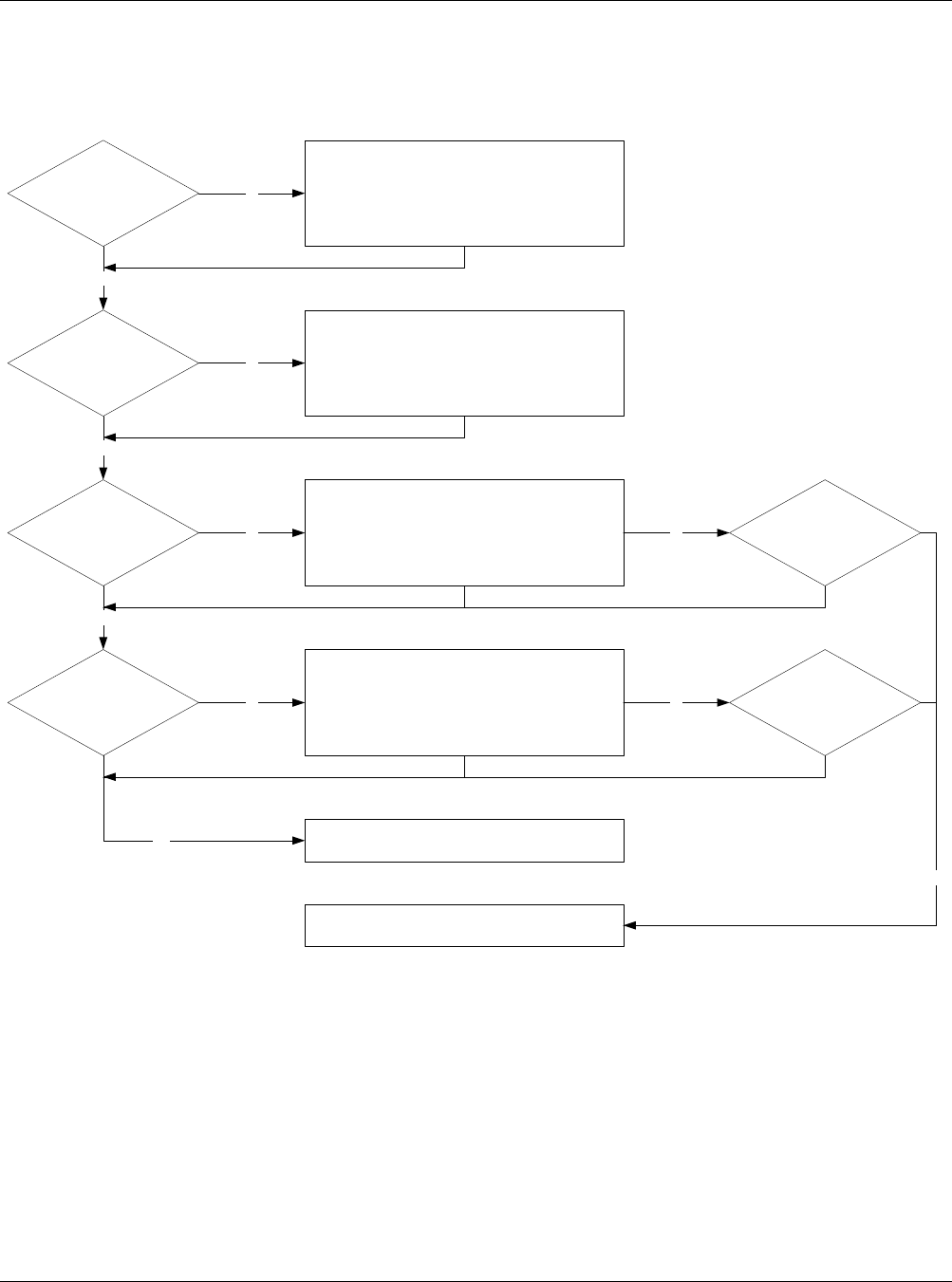
mBSC-CM RUM
mBSC-CM December 15, 2015
Page 68
6.4.1 Host Unit Trouble Shooting
Is the HU shelf
grounded?
Is the PSU LED
Green?
Check the grounding connection and connect
the ground cable to the HU
No
Yes
Check the power cable connection.
Check the power supply connection.
Check the PSU switch.
No
Is the BIU LED
Green?
Yes
Check for pin connector damage on the BIU. If
undamaged, reseat the board. Uninstall the BIU
and re-insert the BIU into the HU slot.
No No Spare BIU available?
Is the FIU LED
Green?
Yes
Check for pin connector damage on the FIU. If
undamaged, reseat the board. Uninstall the FIU
and re-insert the FIU into the HU slot.
LED in Red: both fiber connections are open
LED in Yellow: one fiber connection is open
No No Spare FIU available?
Installation complete and continue to NMS
installation
Yes
Contact local BTI customer service
No
Figure 53Host Unit Trouble Shooting
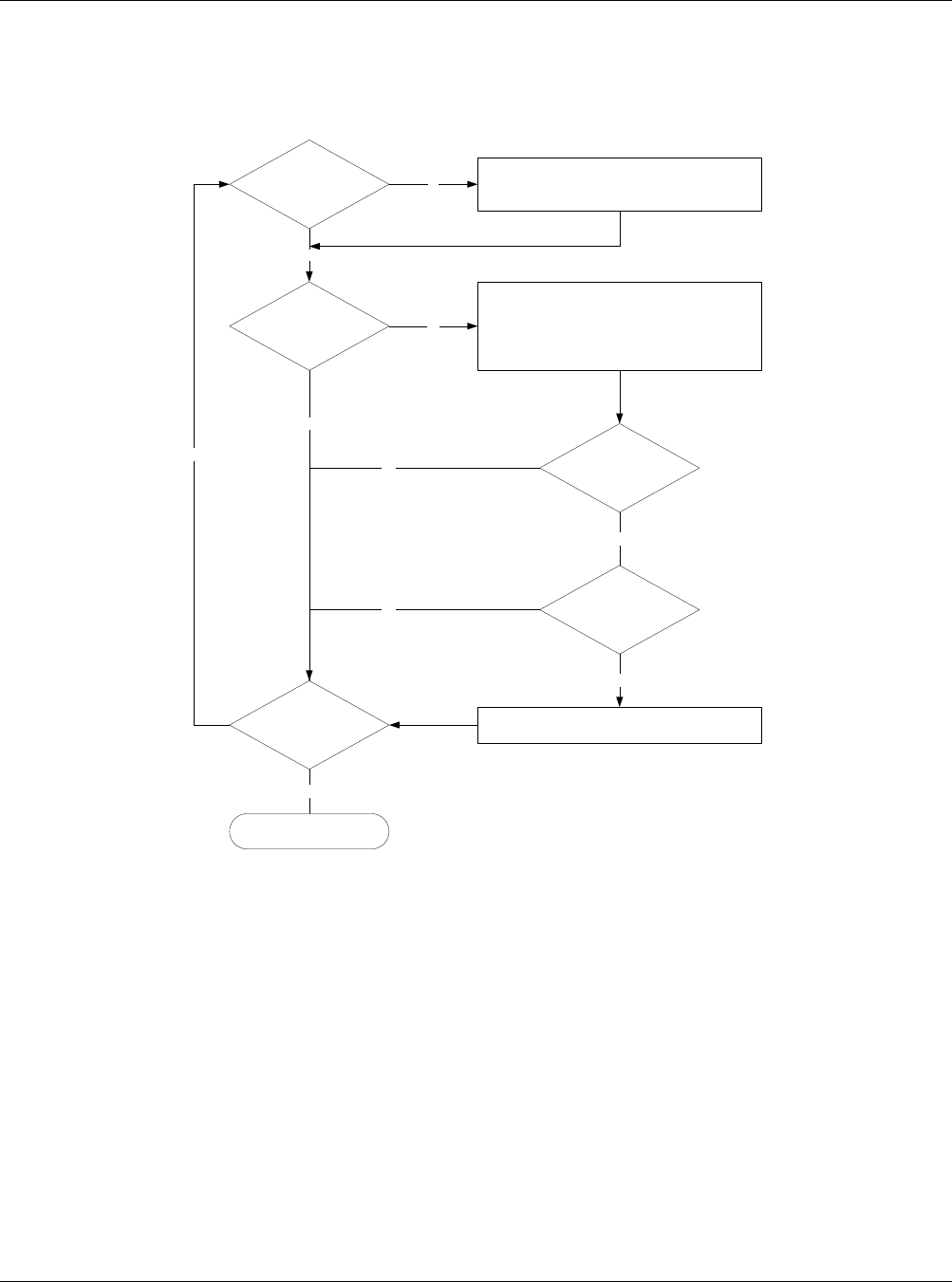
mBSC-CM RUM
mBSC-CM December 15, 2015
Page 69
6.4.2 Remote Unit Trouble Shooting
LED on?
LED status
• Check power switch
• Check mains cabling
• Check mains power
No
Yes
• Check the fiber cable connection on the fiber
CM-BTS enclosure
• Check that the HU is installed and power is on.
• Check the fiber cable connection on the HU.
red
Are all RU units
installed?
LED status green?
Spare FIU available?
Contact local BTI customer servcie
No
No
Installation status:
Complete or terminated
Yes
Yes
green
Yes
No
Figure 54Remote Unit Trouble Shooting
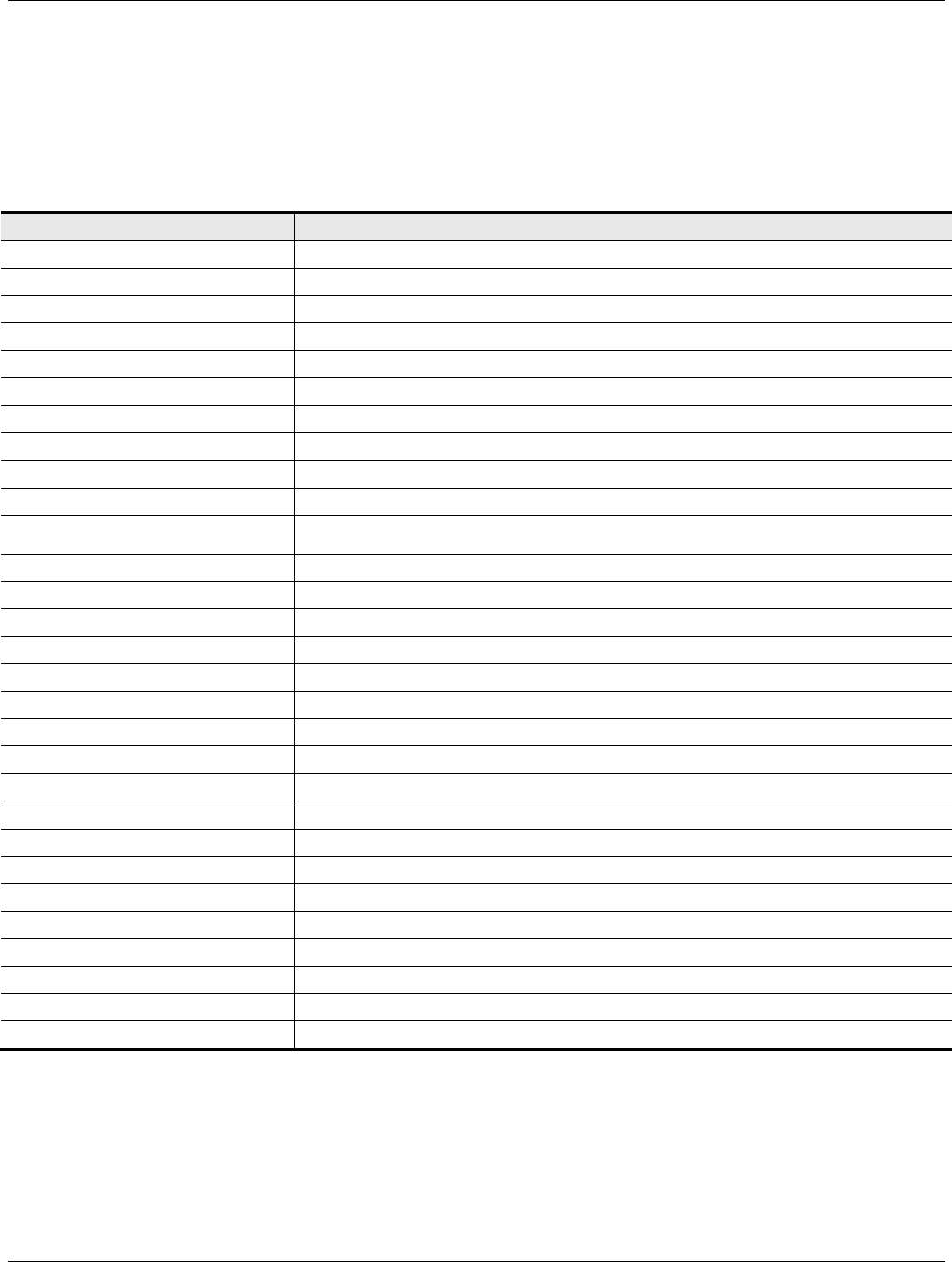
mBSC-CM RUM
mBSC-CM December 15, 2015
Page 70
7 Terms, Acronyms & Abbreviations
Table 18 Terms, Acronyms and Abbreviations
Terms/Acronyms/Abbreviation
Definition
ANT Antenna
AWG American Wire Gauge
BTS Base Transceiver Station or Base Transceiver System
C° Degree Celsius
COM Serial Communication Port
CQT Call Quality Test
dB Decibels
dBm Power measurement referenced to the specific power level of one milli watt
DCS Digital Cellular System
DIN Deutsches Insitut für Normung eV (German standardsinstitution)
7-16 DIN
German standards RF connector:
7mm OD of inner contact, 16mm ID of outer contact.
DL Downlink
DT Driver Test
EMC Electromagnetic Compatibility
GSM Global System for Mobile Communications
LED Light Emitting Diode
LNA Low Noise Amplifier
NMS Network & Monitoring System
MCPA Multi-carrier Power Amplifier
MHz Megahertz
MTBF Mean Time Between Failures
OMC Operation Monitor Center
PA Power Amplifier
RF Radio Frequency
RX Receive or Receiver
SMA Subminiature Type A coaxial connector
TX Transmit, Transmitter
UMTS Universal Mobile Telecommunications System
VSWR Voltage Standing Wave Ratio
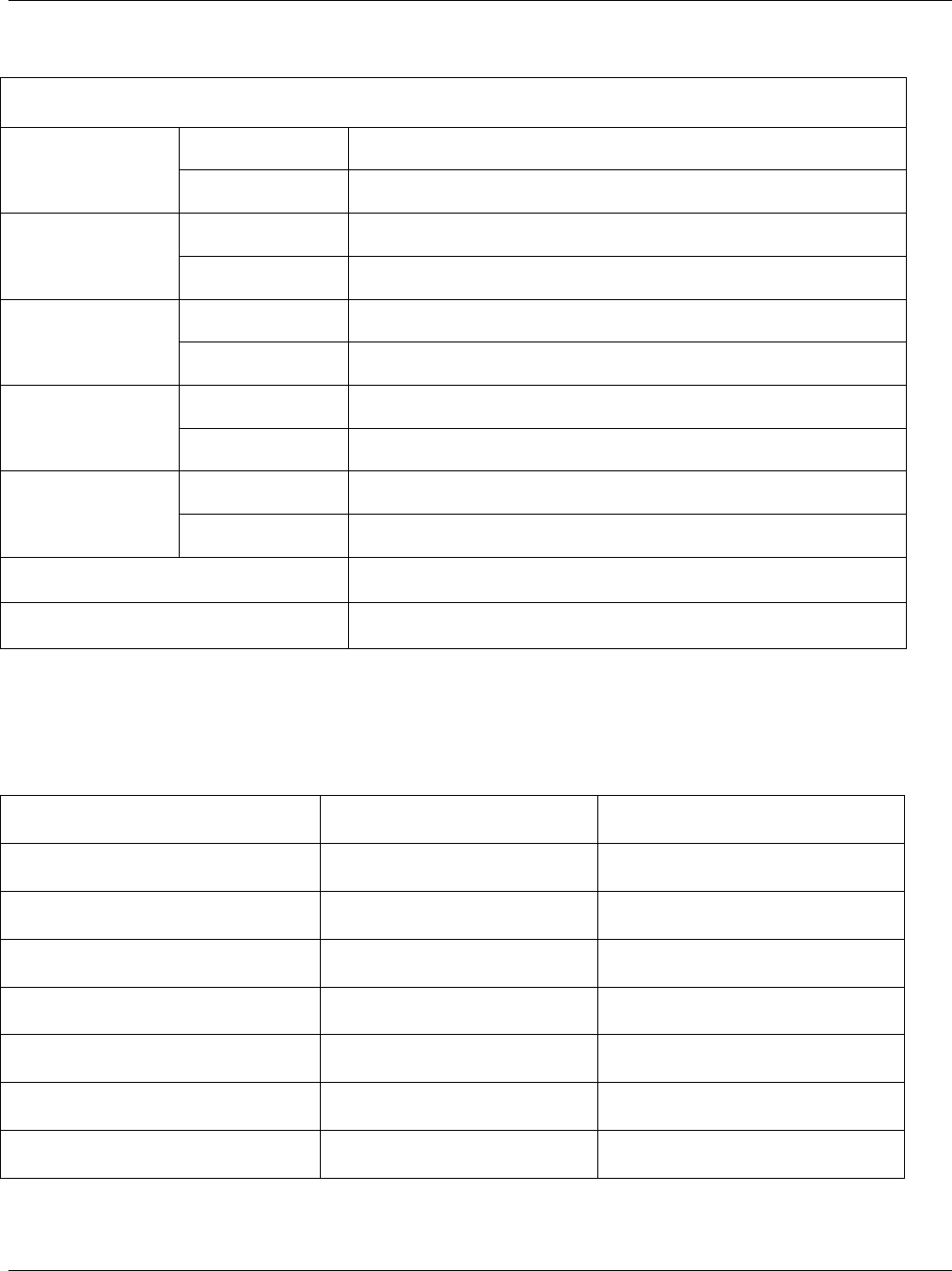
mBSC-CM RUM
mBSC-CM December 15, 2015
Page 71
Technical Parameter:
900MHz
Downlink 728MHz~746MHz/746MHz~757MHz
Uplink 698MHz~716MHz/776MHz~787MHz
Maximum Output
Power
Downlink 37.38dBm
Uplink 5.39dBm
Max Gain
Downlink 54.37dB
Uplink 62.42dB
Antenna Type
Downlink External antenna (N female)
Uplink External antenna (N female)
Antenna Gain
Downlink Maximum permissible antenna gain is 17dBi
Uplink Maximum permissible antenna gain is 17dBi
Type of modulation and Designator LTE(W7D)
Remark The EUT does not transmit over the air in the uplink direction.
8 Packing List
List brand quantity
mBSC0900S-005-RUCS12 BTI Wireless 1
mBSC1430-RTM-5SW BTI Wireless 1
mBSC1426-RPM-AC BTI Wireless 2
Fiber-cable(E2000-E2000) / 1
RF-Cable(QMA-QMA) / 2
Power cable / 1
mBSC1426-RACK-10S BTI Wireless 1
To submit your comments by mail, use the response card behind the front cover of your document, or

mBSC-CM RUM
mBSC-CM December 15, 2015
Page 72
write to the following address:
Attn: Publications Manager
BTI Wireless
6185 Phyllis Drive
Cypress, CA 90630
We appreciate your comments.
For US and Canadian installations: FCC RF exposure compliance requires the following antenna installation
and device operation configurations be satisfied:
A separation distance of at least 6 meters must be maintained between the antenna of this device and all
persons. RF exposure compliance may need to be addressed at the time of licensing, as required by the
responsible FCC Bureau(s), including antenna co-location requirements of 1.1307(b)(3). §2.1091
Maximum permissible antenna gain is 17dBi.
IC STATEMENT Operation is subject to the following two conditions:
(1) This device may not cause interference, and
(2) This device must accept any interference, including interference that may cause undesired operation of
the device.
Le présent appareil est conforme aux CNR d'Industrie Canada applicables aux appareils radio exempts de
licence.
L'exploitation est autorisée aux deux conditions suivantes :
(1) l'appareil ne doit pas produire de brouillage, et
(2) l'utilisateur de l'appareil doit accepter tout brouillage radioélectrique subi, même si le brouillage est
susceptible d'en compromettre le fonctionnement.
IC Radiation Exposure Statement
This equipment complies with IC radiation exposure limits set forth for an uncontrolled environment. This
equipment should be installed and operated with minimum distances 6 m between the radiator include
antenna & your body.
IC Déclaration sur la radio exposition
Cet équipement est conforme avec l'exposition aux radiations IC définies pour un environnement non contrôlé .
Cet équipement doit être installé et utilisé avec une distance minimale de 6 m de entre le radiateur inclure
l'antenne et votre corps.