Bird Technologies Group 6138 Channelized Signal Booster User Manual Users manual
Bird Technologies Group Channelized Signal Booster Users manual
Users manual
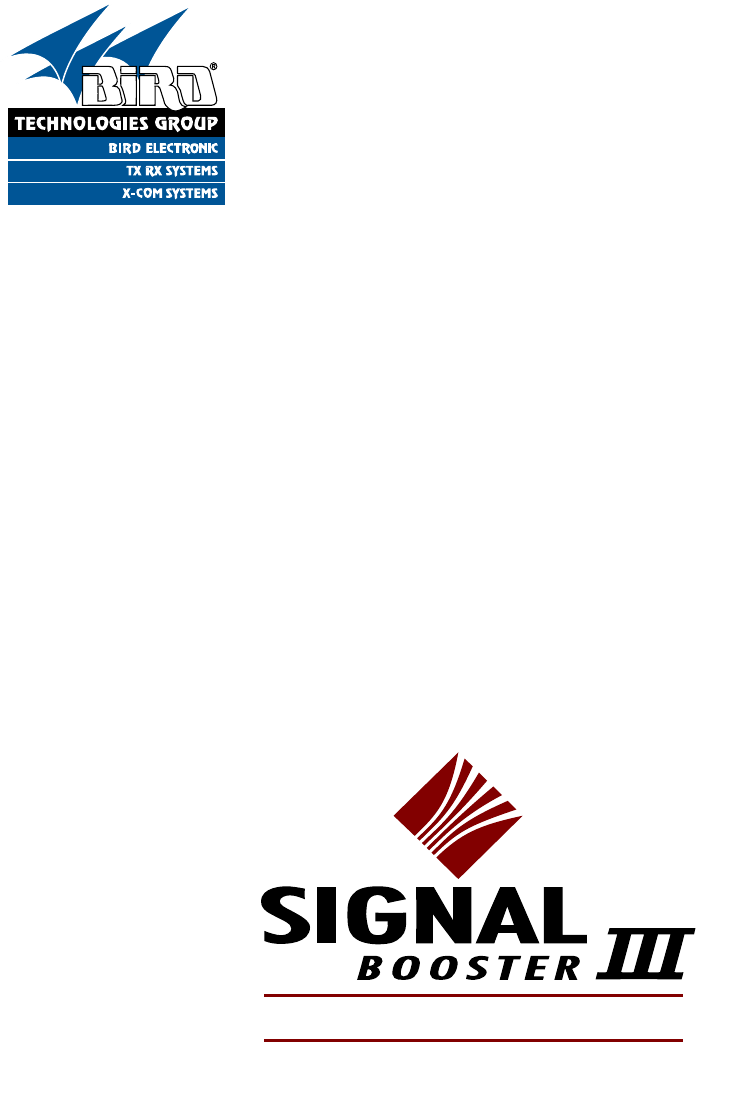
YOU'RE HEARD, LOUD AND CLEAR.
8625 Industrial Parkway, Angola, NY 14006 Tel: 716-549-4700 Fax: 716-549-4772 sales@birdrf.com www.bird-technologies.com
Installation and Operation Manual for
the SBIII Digital Signal Booster
Model 613-8
Manual Part Number
7-9485
DIGITAL TECHNOLOGY
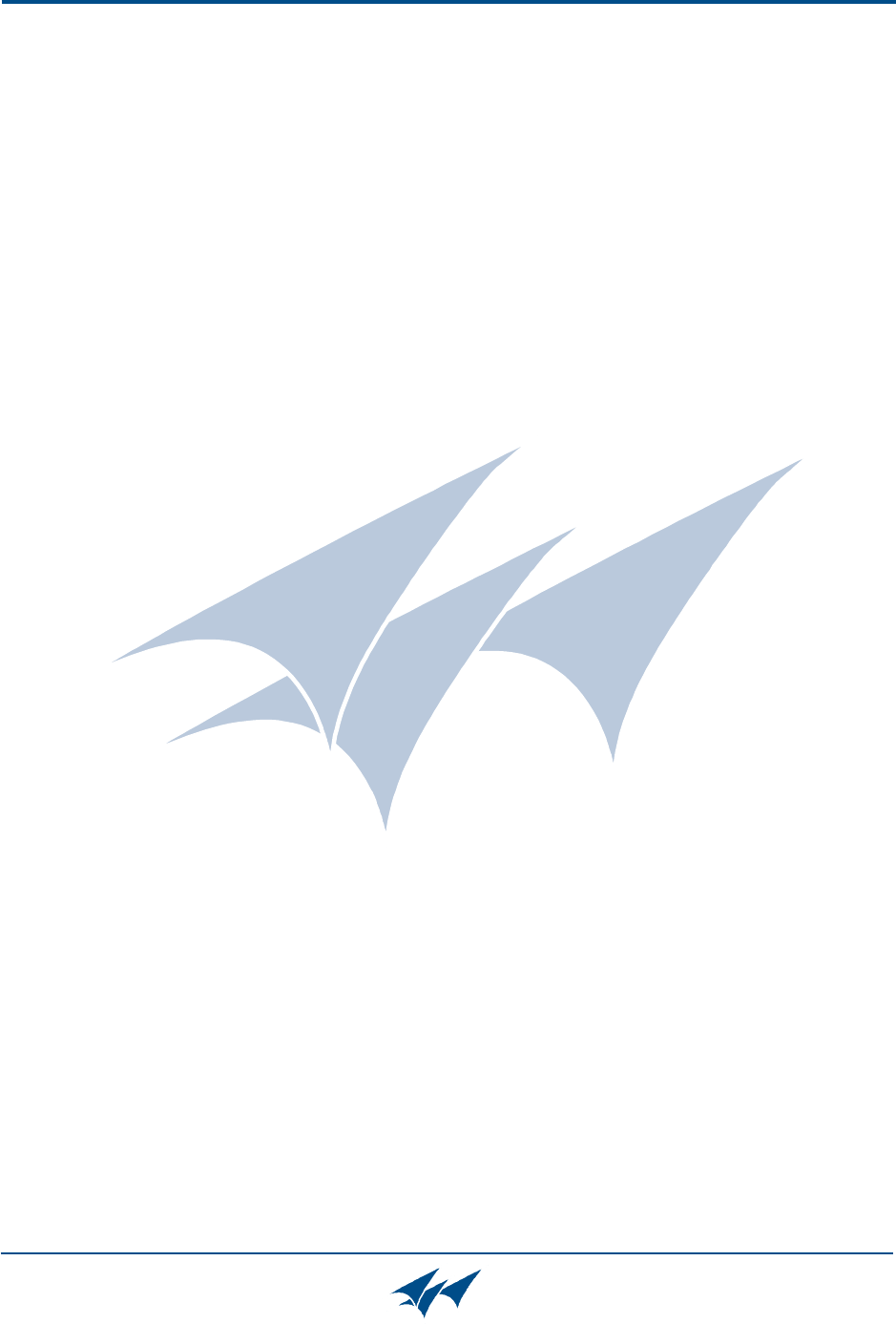
Warranty
This warranty applies for one year from shipping date.
TX RX Systems Inc. warrants its products to be free from defect in material and workmanship at the time of shipment.
Our obligation under warranty is limited to replacement or repair, at our option, of any such products that shall have
been defective at the time of manufacture. TX RX Systems Inc. reserves the right to replace with merchandise of
equal performance although not identical in every way to that originally sold. TX RX Systems Inc. is not liable for dam-
age caused by lightning or other natural disasters. No product will be accepted for repair or replacement without our
prior written approval. The purchaser must prepay all shipping charges on returned products. TX RX Systems Inc.
shall in no event be liable for consequential damages, installation costs or expense of any nature resulting from the
purchase or use of products, whether or not they are used in accordance with instructions. This warranty is in lieu of all
other warranties, either expressed or implied, including any implied warranty or merchantability of fitness. No repre-
sentative is authorized to assume for TX RX Systems Inc. any other liability or warranty than set forth above in con-
nection with our products or services.
TERMS AND CONDITIONS OF SALE
PRICES AND TERMS:
Prices are FOB seller’s plant in Angola, NY domestic packaging only, and are subject to change without notice. Fed-
eral, State and local sales or excise taxes are not included in prices. When Net 30 terms are applicable, payment is
due within 30 days of invoice date. All orders are subject to a $100.00 net minimum.
QUOTATIONS:
Only written quotations are valid.
ACCEPTANCE OF ORDERS:
Acceptance of orders is valid only when so acknowledged in writing by the seller.
SHIPPING:
Unless otherwise agreed at the time the order is placed, seller reserves the right to make partial shipments for which
payment shall be made in accordance with seller’s stated terms. Shipments are made with transportation charges col-
lect unless otherwise specified by the buyer. Seller’s best judgement will be used in routing, except that buyer’s routing
is used where practicable. The seller is not responsible for selection of most economical or timeliest routing.
CLAIMS:
All claims for damage or loss in transit must be made promptly by the buyer against the carrier. All claims for shortages
must be made within 30 days after date of shipment of material from the seller’s plant.
SPECIFICATION CHANGES OR MODIFICATIONS:
All designs and specifications of seller’s products are subject to change without notice provided the changes or modifi-
cations do not affect performance.
RETURN MATERIAL:
Product or material may be returned for credit only after written authorization from the seller, as to which seller shall
have sole discretion. In the event of such authorization, credit given shall not exceed 80 percent of the original pur-
chase. In no case will Seller authorize return of material more than 90 days after shipment from Seller’s plant. Credit
for returned material is issued by the Seller only to the original purchaser.
ORDER CANCELLATION OR ALTERATION:
Cancellation or alteration of acknowledged orders by the buyer will be accepted only on terms that protect the seller
against loss.
NON WARRANTY REPAIRS AND RETURN WORK:
Consult seller’s plant for pricing. Buyer must prepay all transportation charges to seller’s plant. Standard shipping pol-
icy set forth above shall apply with respect to return shipment from TX RX Systems Inc. to buyer.
DISCLAIMER
Product part numbering in photographs and drawings is accurate at time of printing. Part number labels on TX RX
products supersede part numbers given within this manual. Information is subject to change without notice.
Bird Technologies Group TX RX Systems Inc.
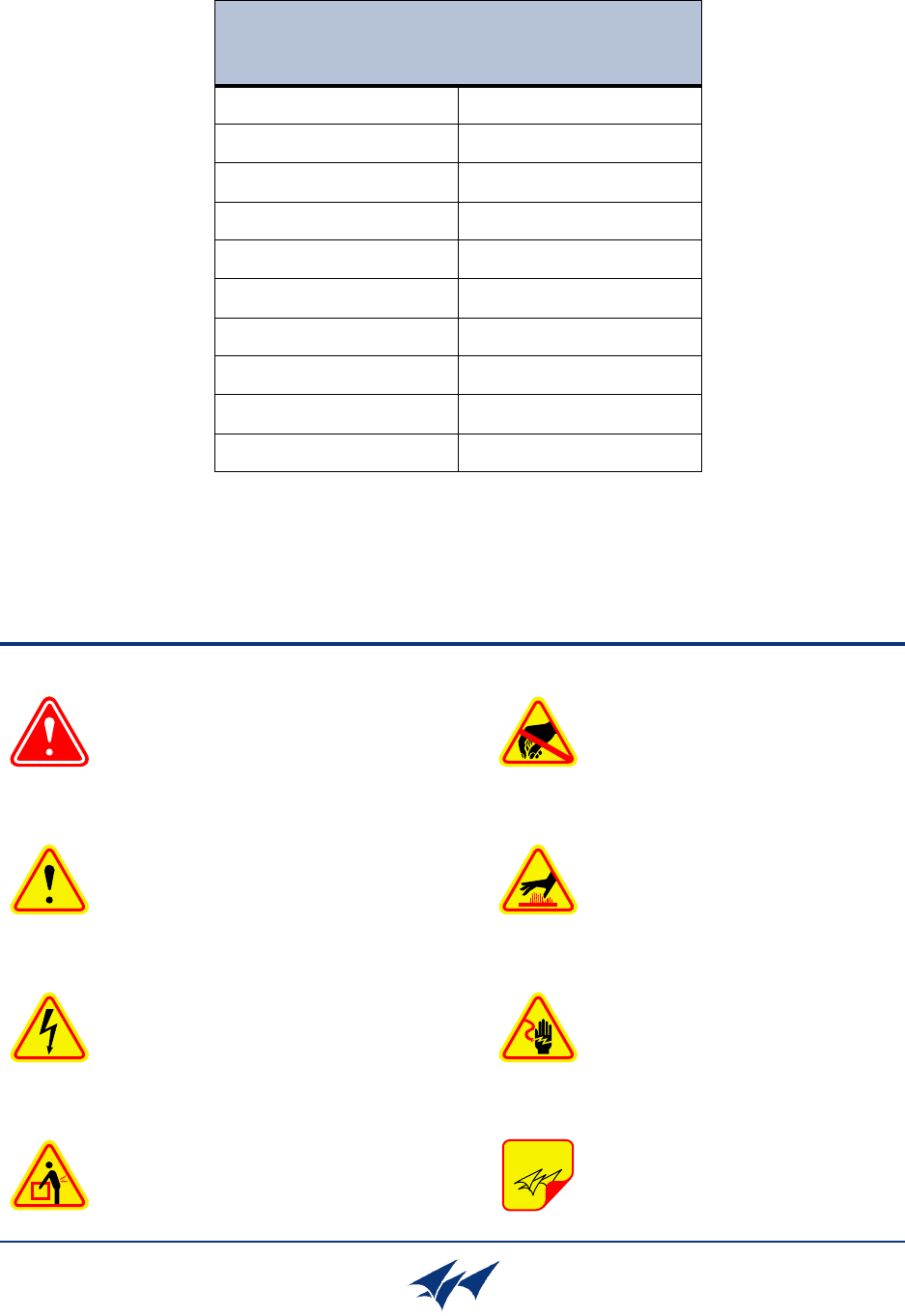
Symbols Commonly Used
WARNING
ESD Electrostatic Discharge
Hot Surface
Electrical Shock Hazard
Important Information
CAUTION or ATTENTION
High Voltage
Heavy Lifting
Bird Technologies Group TX RX Systems Inc.
NOTE
Manual Part Number 7-9485
Copyright © 2011 TX RX Systems, Inc.
First Printing: May 2011
Version Number Version Date
1 05/16/11
1.4 07/25/11
1.6 09/02/11
1.7 09/12/11
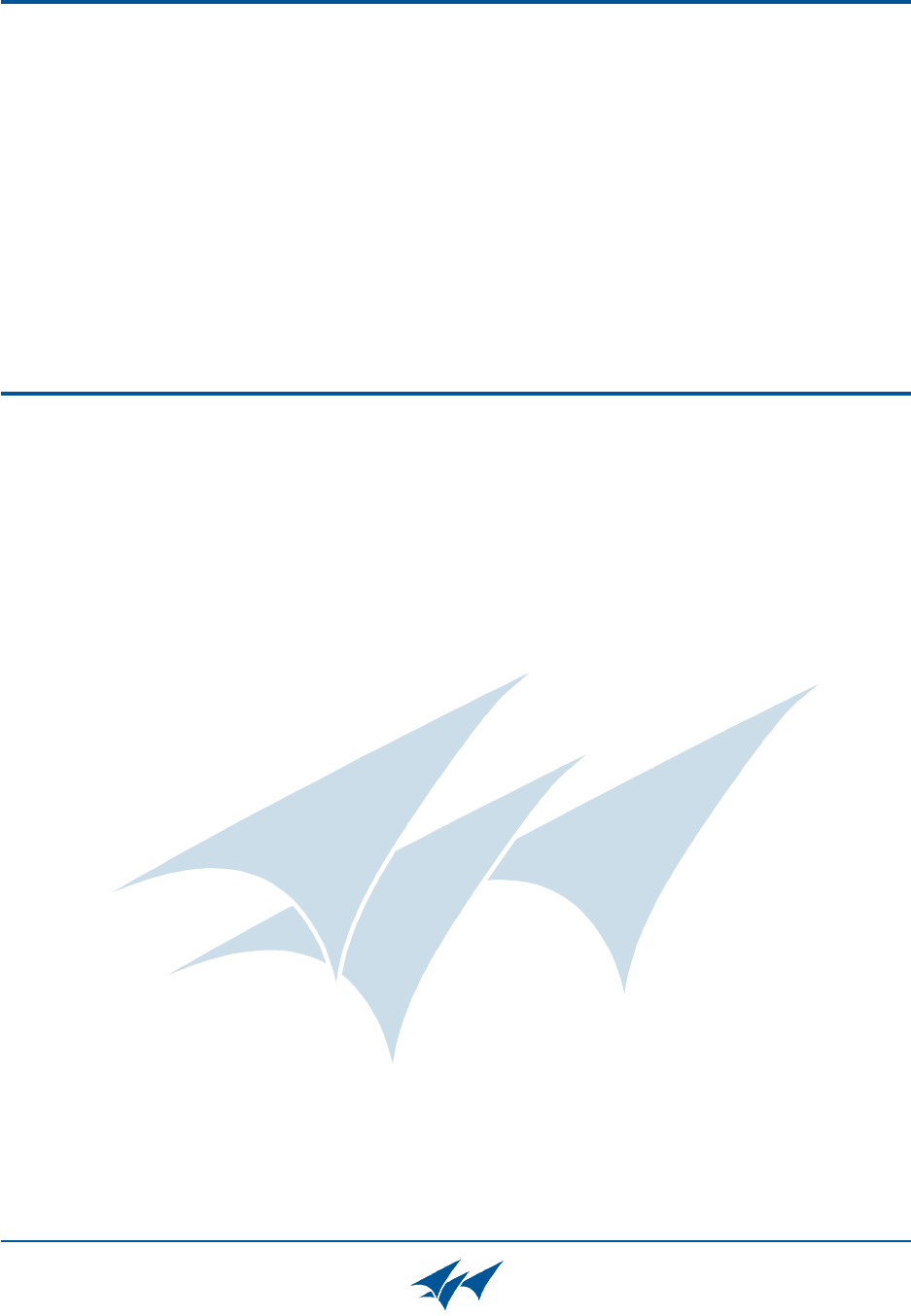
Contact Information
Changes to this Manual
Bird Technologies Group TX RX Systems Inc.
Sales Support at 716-217-3113
Customer Service at 716-217-3144
Technical Publications at 716-549-4700 extension 5019
We have made every effort to ensure this manual is accurate. If you discover any
errors, or if you have suggestions for improving this manual, please send your
comments to our Angola, New York facility to the attention of the Technical Publications
Department. This manual may be periodically updated. When inquiring about updates to
this manual refer to the manual part number and revision number on the revision page
following the front cover.
Table of Contents Manual 7-9485-1.7 09/12/11
Table of Contents
Overview............................................................................................................... 1
Down / Up Conversion......................................................................................... 2
Unpacking ............................................................................................................ 3
Installation............................................................................................................ 3
Location ............................................................................................................. 3
Mounting............................................................................................................. 3
Connections........................................................................................................ 3
Antenna Isolation ............................................................................................... 4
Required Equipment ......................................................................................... 5
Measurement Procedure .................................................................................. 5
RF Exposure (Exposition RF) ............................................................................ 6
Signal Flow Block Diagram ............................................................................... 6
Uplink and Downlink Input Signals ...................................................................... 6
Channel Module .................................................................................................. 8
Uplink and Downlink Output Signals ................................................................... 9
Operation.............................................................................................................. 9
Subassembly LED’s ........................................................................................... 9
Configuring the Channel Module ........................................................................ 9
Filters Tab ......................................................................................................... 11
Command Buttons .......................................................................................... 11
Filter Area ....................................................................................................... 12
Status Area ..................................................................................................... 12
Link Tab ............................................................................................................ 12
Command Buttons .......................................................................................... 12
Link and Settings Area.................................................................................... 13
Status Area ..................................................................................................... 13
Admin Tab......................................................................................................... 13
System Tab ....................................................................................................... 13
Figures and Tables
Figure 1: The Down / Up Converter Process ....................................................... 3
Figure 2: Cabinet Mounting ................................................................................. 4
Figure 3: Measuring Antenna Isolation................................................................. 5
Figure 4: Signal Flow Block Diagram ................................................................... 6
Figure 5: Booster Cabinet Front View .................................................................. 7
Figure 6: Enet Connector ..................................................................................... 9
Figure 7: Enter Your Password ............................................................................ 9
Figure 8: Web-Page Interface Filters Tab ........................................................... 10
Figure 9: Design Filter Interactive Display .......................................................... 10
Figure 10: Web-Page Interface Link Tab ............................................................ 11
Figure 11: Web-Page Interface Admin Tab......................................................... 12
Figure 12: Web-Page Interface System Tab ....................................................... 13
Table 1: Model number nomenclature................................................................... 1
Table 2: Specifications .......................................................................................... 2
Table 3: Subassembly LED Descriptions .............................................................. 8
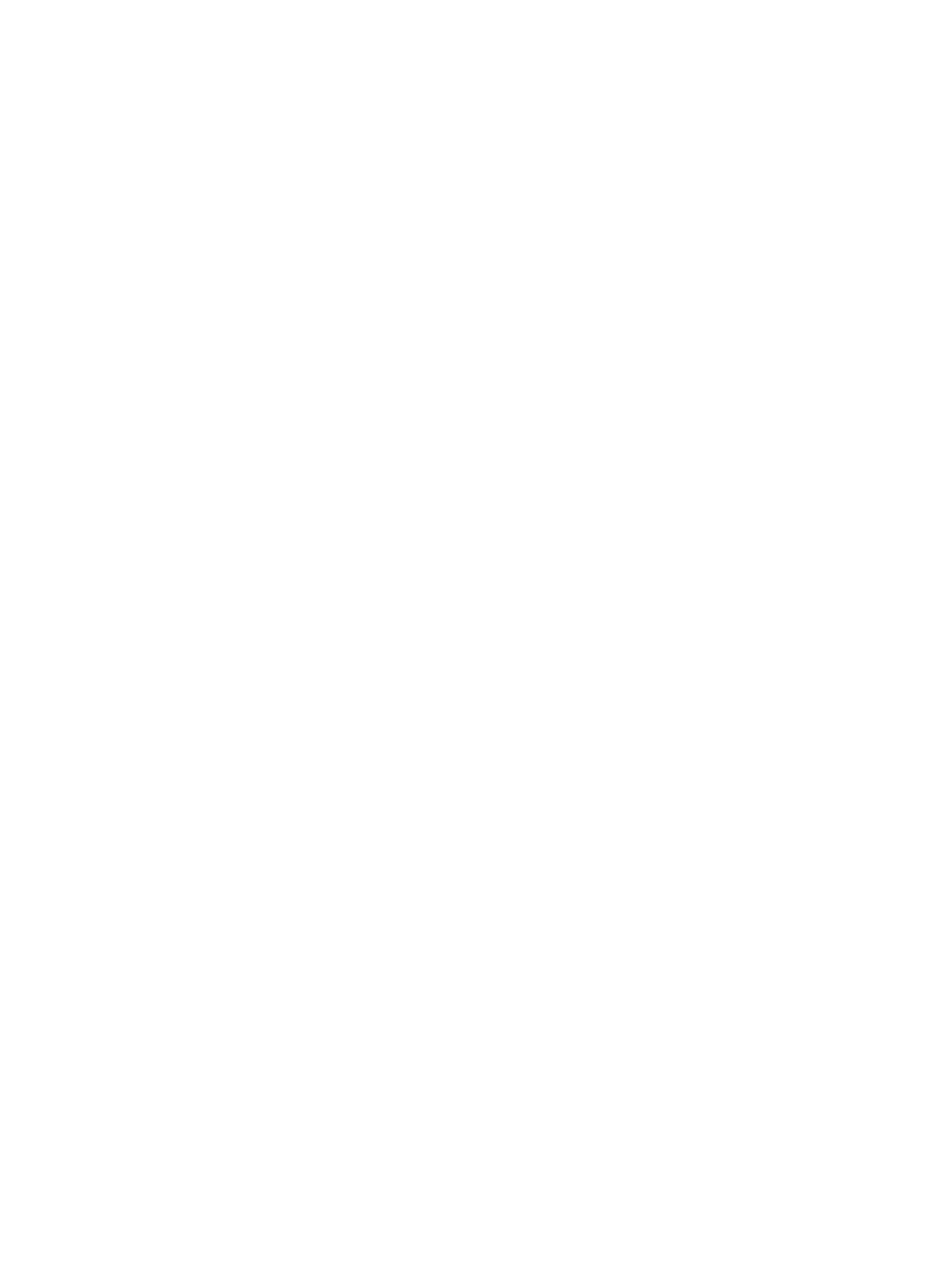
Table of Contents Manual 7-9485-1.7 09/12/11
Appendixes
Appendix A: Front Panel Ethernet Connectivity .................................................14
Ethernet Connectivity ..........................................................................................14
Direct Connection ..............................................................................................14
Required Equipment ........................................................................................14
Procedure ........................................................................................................14
Networked Connection ......................................................................................15
Required Equipment ........................................................................................15
Procedure ........................................................................................................17
Appendix B: Changing Your Service Computers IP Address.............................18
For Class A Unintentional Radiators
This equipment has been tested and found to comply with the limits for a Class A digital device, pursuant to Part
15 of the FCC rules. These limits are designed to provide resonable protection against harmful interference when
the equipment is operated in a commercial environment. This equipment generates, uses, and can radiate radio
frequency energy and, if not installed and used in accordance with the instruction manual, may cause harmful
interference to radio communications. Operation of this equipment in a residential area is likely to cause harmful
interference in which the user will be required to correct the interference at his own expense.
Pour Classe-A Radiateurs Involontaires
Cet équipement a été testé et jugé conforme avec les limites de la Classe-A des appareils numériques, suivants
à la Partie 15 des règlements de la FCC. Ces limites sont conçues pour fournir une protection raisonnable contre
les interférences dangereuses lorsque l'équipement est utilisé dans un environnement commercial. Cet équipe-
ment génère, utilise et peut émettre des fréquences radio et, s'il n'est pas installé et utilisé conformément aux
instructions du manuel, ceci peut causer des interférences dangereuses aux communications radio. Le fonction-
nement de cet équipement dans une zone résidentielle est susceptible de causer des interférences mauvaises
dans lequel l'utilisateur sera tenu pour responsable de corriger l'interférence à sa propre discrétion.
WARNING:
Changes or modifications which are not expressly approved by TXRX Systems
Inc. could void the user’s authority to operate the equipment.
AVERTISSEMENT:
Les changements ou modifications qui ne sont pas approuvés par
TXRX Systems Inc. pourrait annuler l'autorité de l'utilisateur de faire fonctionner l'équipement.
ATTENTION: This device complies with Part 15 of the FCC rules. Operation is subject to the following
two conditions: (1) this device may not cause harmful interference and (2) this device must accept any
interference received, including interference that may cause undesired operation.
ATTENTION : Cet appareil est conforme à la Partie 15 des règlements de la FCC. L'opération doit se
conformer aux deux conditions suivantes: (1) cet appareil ne peut causer d'interférences nuisibles et
(2) cet appareil doit accepter toute interférence reçue, y compris les interférences qui peuvent provo-
quer un fonctionnement indésirable.
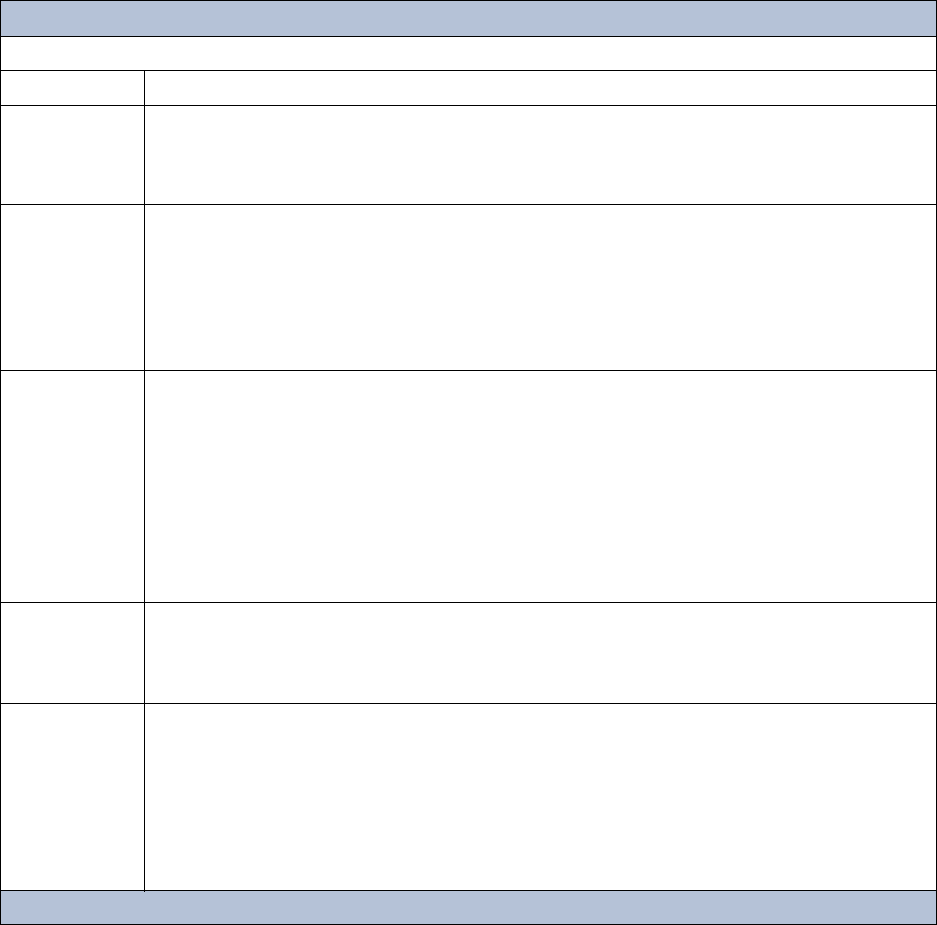
TX RX Systems Inc. Manual 7-9485-1.7 09/12/11 Page 1
OVERVIEW
Signal boosters extend radio coverage into areas
where abrupt propagation losses prevent reliable
communication. The system receives an RF signal,
raises its power level, and couples it to an antenna
so that it can be re-radiated. The TXRX model 613-
8 family of channelized signal boosters is designed
to operate in either the 700 or 800 MHz range.
Dual band models are available that include both
700 and 800 MHz systems in the same enclosure
box. The system is based on a module design with
each module capable of handling 14 or 30 carriers
in the uplink and downlink direction. The signal
booster is available in a variety of configurations as
shown in Table 1. The product model number is
used to describe each configuration available.
Model number nomenclature is described in table
1.
The size of the system can be tailored to the cus-
tomers needs by increasing or decreasing the
number of carriers used. Each module is bi-direc-
tional with one downlink and one uplink signal
branch. Each of the two branches in a module are
independently tunable to their required pass fre-
quencies via software interface. System specifica-
613-8XX-YYUD-Z-Options
(nomenclature breakdown)
613-8 Designates product as 700 - 800 MHz channelized signal booster
XX
Designates operating frequency band
9A = 806 - 869 MHz
3B = 763 - 805 MHz
3G = 763 - 869 MHz
YY
Designates how many modules used and number of filters available
A = 1 module with 14 filters
B = 1 module with 30 filters
AA = 2 modules with 14 filters each
BB = 2 modules with 30 filters each
AB = 1 module (700 MHz) with 14 filters and 1 module (800 MHz) with 30 filters
BA = 1 module (700 MHz) with 30 filters and 1 module (800 MHz) with 14 filters
UD
Designates the type of output for the uplink and downlink
HH = high power uplink and downlink
HL = high power uplink and low power downlink
LH = low power uplink and high power downlink
LL = low power for both uplink and downlink
FH = fiber output uplink and high power downlink
FL = fiber output uplink and low power downlink
HF = high power uplink and fiber output downlink
LF = low power uplink and fiber output downlink
FF = fiber uplink and fiber downlink
Z
Designates mounting style
RM = 19” rack mount
G1 = Painted enclosure
G2 = Stainless steel enclosure
Options
Designates the options that have been added
Blank = no options added
N = NFPA compliant (National Fire Protection Association)
P = 10 MHz high precision reference
D = -48 VDC
Q = Fiber input downlink only
R = Fiber input uplink only
S = Fiber input downlink and uplink
Table 1: Model number nomenclature.
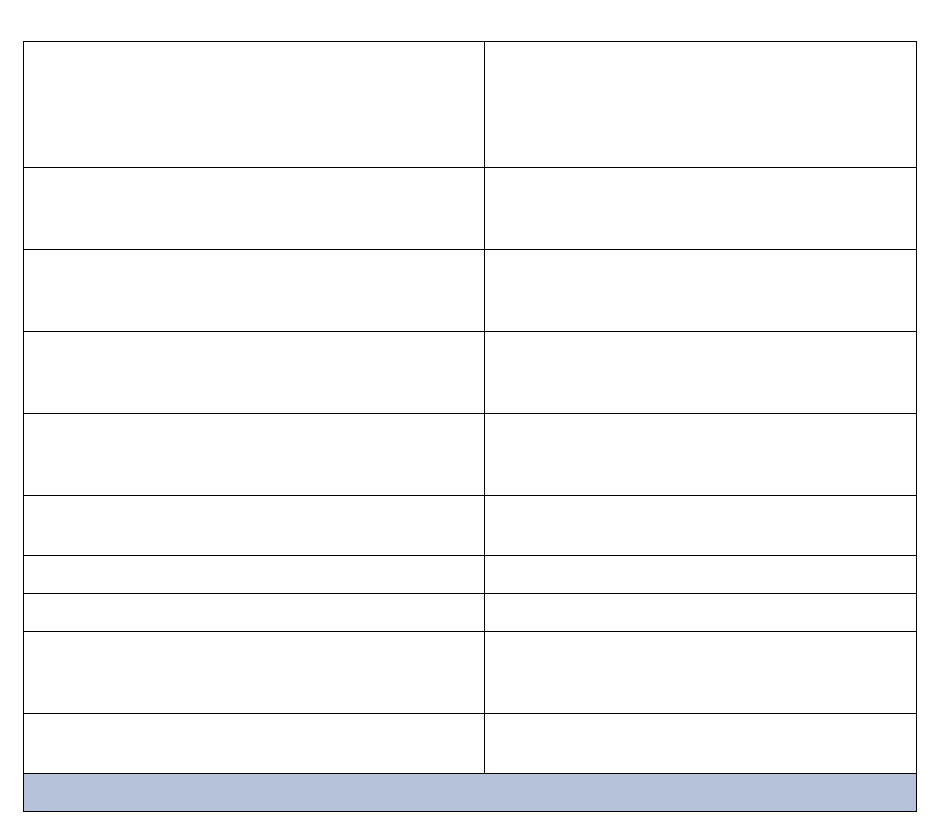
TX RX Systems Inc. Manual 7-9485-1.7 09/12/11 Page 2
tions for the 613-8 family of channelized signal
boosters are listed in Table 2.
Down / Up Conversion
A channelized signal booster has much in common
with a superheterodyne (superhet) receiver. The
incoming signal is converted to a lower frequency
so that single channel selectivity can be obtained.
It is then filtered. Unlike the superhet receiver how-
ever, the signal is not demodulated. Instead, it is
up-converted back to its original frequency where it
is further amplified to reach a useful power level.
Figure 1 shows a simplified block diagram that
illustrates the down/up conversion principle. An
incoming signal at (Freq IN) is amplified and
applied to the first mixer along with a signal from a
local oscillator (Freq LO). A third signal at an inter-
mediate frequency (Freq IF) is produced as a result
of the mixing. The intermediate frequency is given
by the following relationship:
(1) Freq IF = Freq IN - Freq LO
The IF signal from the mixer then passes through
digital filtering with single channel bandwidth
before being amplified and passed on to the sec-
ond mixer. The second mixer also receives the
same local oscillator signal (Freq LO). The result is
a mixing product frequency at the output of mixer
2. The output frequency (Freq OUT) is given by the
following relationship:
(2) Freq OUT = Freq IF + Freq LO
Substituting equation (1) for the “Freq IF” term in
equation (2) allows the “Freq LO” terms to be can-
celed yielding:
(3) Freq Out = Freq IN
Frequency Range (MHz)
763 - 775 and 793 - 805 (units sold in USA)
806 - 824 and 851 - 869 (units sold in USA)
764 - 776 and 794 - 806 (units sold in Canada)
806 - 824 and 851 - 869 (units sold in Canada)
Number of Carriers per Module
Low Density Model
High Density Model
14 uplink and downlink
30 uplink and downlink
Gain
Low Power Version
High Power Version
80 dB (min)
95 dB (min)
Maximum RF Bandwidth
700 MHz module
800 MHz module
12 MHz
15 MHz
Output Level
Low Power
High Power
-30 to 10 dBm composite
-15 to 25 dBm composite
Maximum Continuous Input Level Operational: -20 dBm
Static w/o damage: -10dBm
RF In/Out Impedance 50 Ohms
Alarms Form-C Contacts
Power
90 - 250 VAC, 50/60 Hz
or
- 48 VDC
Operating Temperature Range -30°C to +60°C
95% RH (non-condensing)
Table 2: Specifications.
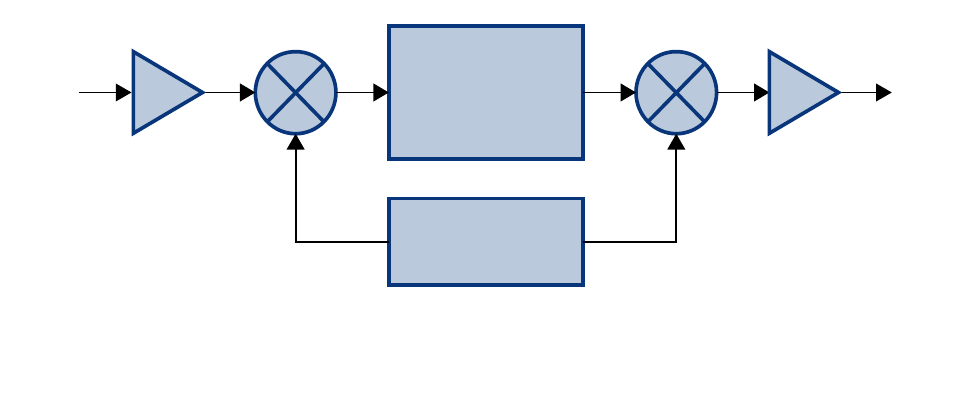
TX RX Systems Inc. Manual 7-9485-1.7 09/12/11 Page 3
The implication of equation (3) is that the frequency
stability of the signal that is processed by this type
of signal booster is not affected by the frequency
stability of the signal booster itself. Frequency sta-
bility depends only on the stability of the signal
source producing the signal to be boosted. A shift
in the LO frequency will cause the center of the fil-
ter bandwidth to move with respect to the signal.
For very narrow filter widths, the channel modules
LO may be locked to a high stability 10 MHz refer-
ence.
UNPACKING
It is important to report any visible damage to the
shipping company immediately. It is the customers
responsibility to file damage claims with the ship-
ping company within a short period of time (1 to 5
days). Care should be taken when removing the
unit from the packing box to avoid damage to the
unit.
INSTALLATION
The following sub-sections of the manual discuss
general considerations for installing the booster. All
work should be performed by qualified personnel
and in accordance with local codes.
Location
The layout of the signal distribution system will be
the prime factor in determining the mounting loca-
tion of this unit. However, safety and serviceability
are also key considerations. The unit should be
located where it can not be tampered with by the
general public, yet is easily accessible to service
personnel. Also, consider the weight of the unit and
the possibility for injur y if it sh ould become
detached from its mounting for any reason.
The booster needs to be installed such that there
can be unobstructed air flow around the equip-
ment. Insure that the heat sink fins are unob-
structed. The various subassemblies within the
equipment cabinet will stay warm during normal
operation so in the interest of equipment longevity,
avoid installation locations that carry hot exhaust
air or are continually hot.
Mounting
Figure 2 shows the mounting hole dimensions and
layout for the cabinet. Mount the cabinet using 3/8”
(10 MM) diameter steel bolts (not supplied). We
recommend flat washers on both ends and a lock
washer under the nut. Nut and bolt mounting is
preferred to the use of lag bolts. Use backer blocks
where necessary to spread the force over a larger
area. In areas of known seismic activity, additional
devices such as tether lines may be necessary.
Because Bird Technologies cannot anticipate all of
the possible mounting locations and the structure
types where these devices will be located, we rec-
ommend consulting local building inspectors, engi-
neering consultants or architects for advice on how
to properly mount objects of this type, size and
weight in your particular situation. It is the custom-
ers responsibility to make sure that these devices
are mounted safely and in compliance with building
codes.
Connections
All RF cabling connections to the booster should
be made and checked for correctness prior to pow-
ering up the system. N(f) bulkhead connectors are
available at the top of the booster enclosure box for
connection to the system antennas. Make sure the
Intermediate
Frequency
Signal
Processing
1st Mixer 2nd Mixer
RF OutRF In
Local
Oscillator
Figure 1: The down converter / up converter process.
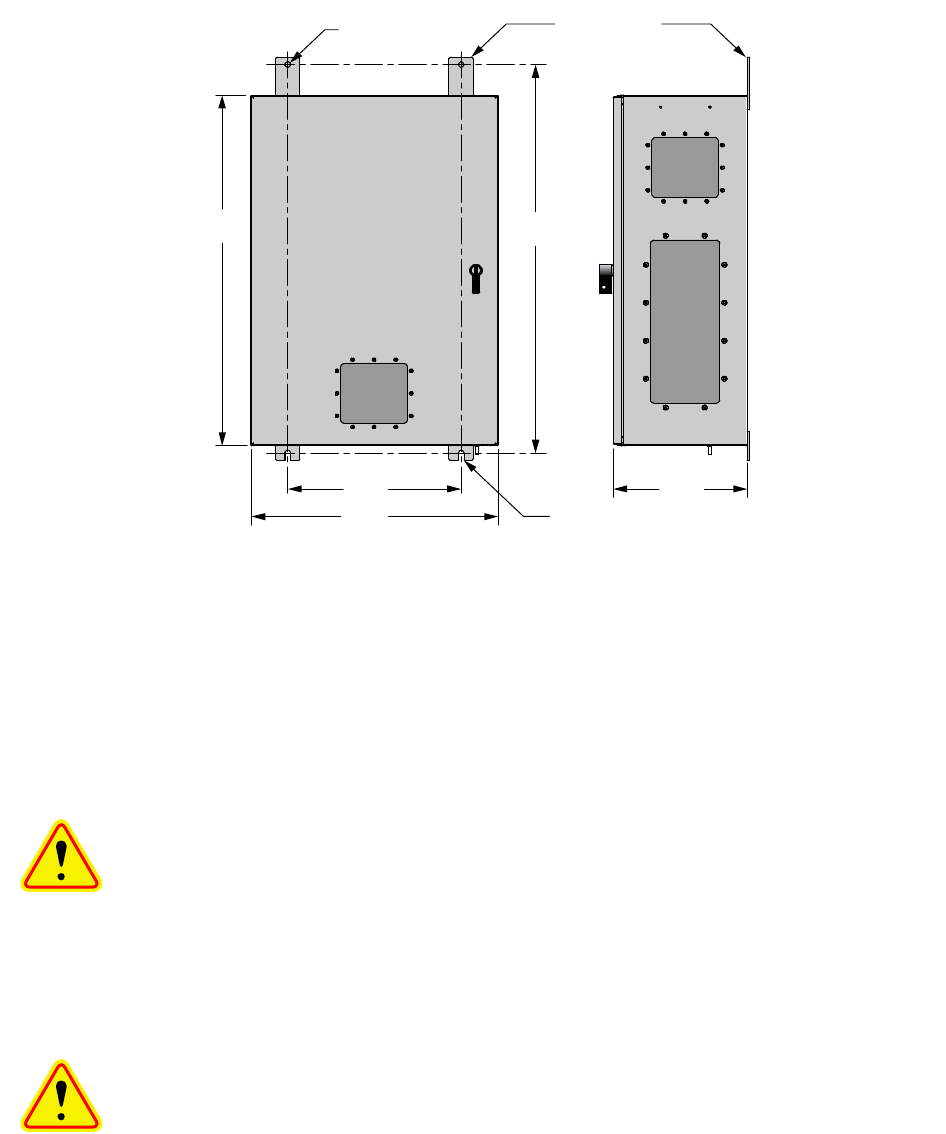
TX RX Systems Inc. Manual 7-9485-1.7 09/12/11 Page 4
correct branch of the antenna system is connected
to its corresponding uplink/downlink connector or
the system will not work properly. Using high qual-
ity connectors with gold center pins is advised.
Flexible jumper cables made of high quality coax
are also acceptable for connecting to rigid cable
sections.
Caution: The ERP (effective radi-
ated power) from the booster sys-
tem must not exceed +37 dBm (5
Watts) in order to remain compliant
with FCC regulations. The maxi-
mum power output from the booster is approxi-
mately +40 dBm. Depending on cable loss and
antenna gain, the output power of the booster may
need to be reduced accordingly.
Caution: The maximum continu-
o u s i n p u t p ow e r le ve l fo r t h is
booster is -20 dBm. Stronger input
signals will cause the unit to exceed
it’s IM specifications. Static input
signals greater than -10 dBm may
damage the unit.
Models of the booster are available for either AC or
DC operation. Based on the model number (see
table 1) the booster is designed to be plugged into
either a single phase AC line (110 VAC at 50/60
Hz) or a - 48 Volt DC source. A connector is avail-
able at the top of the equipment box for connecting
the AC or DC source voltage.
Antenna Isolation
Antenna isolation between uplink and downlink
should be measured before connecting the signal
booster to the antenna system. This step is neces-
sary to insure that no conditions exist that could
possibly damage the signal booster and should not
be skipped for even the most thoroughly designed
system.
Just like the feedback squeal that can occur when
the microphone and speaker get too close together
in a public address system, a signal booster can
start to self oscillate. This can occur when the iso-
lation between the Uplink and Downlink antennas
does not exceed the signal boosters gain by at
least 15 dB. Oscillation will reduce the effective-
ness of the system and may possibly damage
amplifier stages. Isolation values are relatively
easy to measure with a spectrum analyzer and sig-
nal generator.
0.44 Dia
(2 places)
0.44 wide slot (2 places)
33.2430.00
14.00 10.8
20.00
Mounting Tabs
(4 Places)
Figure 2: Cabinet mounting hole layout.
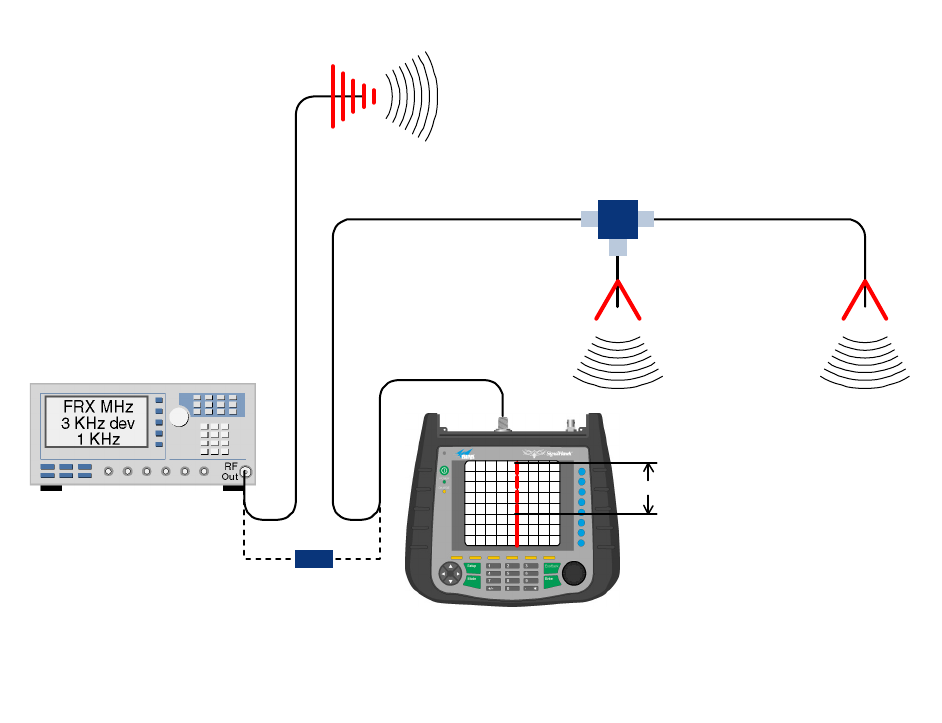
TX RX Systems Inc. Manual 7-9485-1.7 09/12/11 Page 5
REQUIRED EQUIPMENT
The following equipment is required in order to per-
form the antenna isolation measurements.
1) Signal generator for the frequencies of interest
capable of a 0 dBm output level. Modulation is
not necessary.
2) Bird Technologies “Signal Hawk” spectrum ana-
lyzer which will cover the frequencies of interest
and is capable of observing signal levels down
to -100 dBm or better.
3) Double shielded coaxial test cables made from
RG142, RG55 or RG223 coaxial cable.
MEASUREMENT PROCEDURE
To measure the antenna isolation perform the fol-
lowing in a step-by-step fashion.
1) Set the signal generator for a 0 dBm output level
at the center frequency of the boosters pass-
band.
2) Set the spectrum analyzer for the same center
frequency and a sweep width equal to or just
slightly greater than the passband chosen ear-
lier in step 1.
3) Temporarily connect the test leads of the signal
generator and spectrum analyzer together
using a female barrel connector, see Figure 3.
Observe the signal on the analyzer and adjust
the input attenuator of the spectrum analyzer
for a signal level that just reaches the 0 dBm
level at the top of the graticule.
4) Referring to figure 3, connect the generator test
lead to one side of the antenna system and the
spectrum analyzer to the other then observe the
signal level. The difference between the
observed level and 0 dBm is the isolation
between the sections. If the signal is too weak
to observe, the spectrum analyzer’s bandwidth
may have to be narrowed and it’s input attenua-
tion reduced. The isolation value measured
Signal Generator
External
Antenna
(YAGI)
Spectrum Analyzer
Isolation (dB)
Zero Loss
Reference
Internal
Signal Distribution
System
(Omni-directional
Antennas)
Figure 3: Typical test equipment interconnection for measuring antenna isolation.
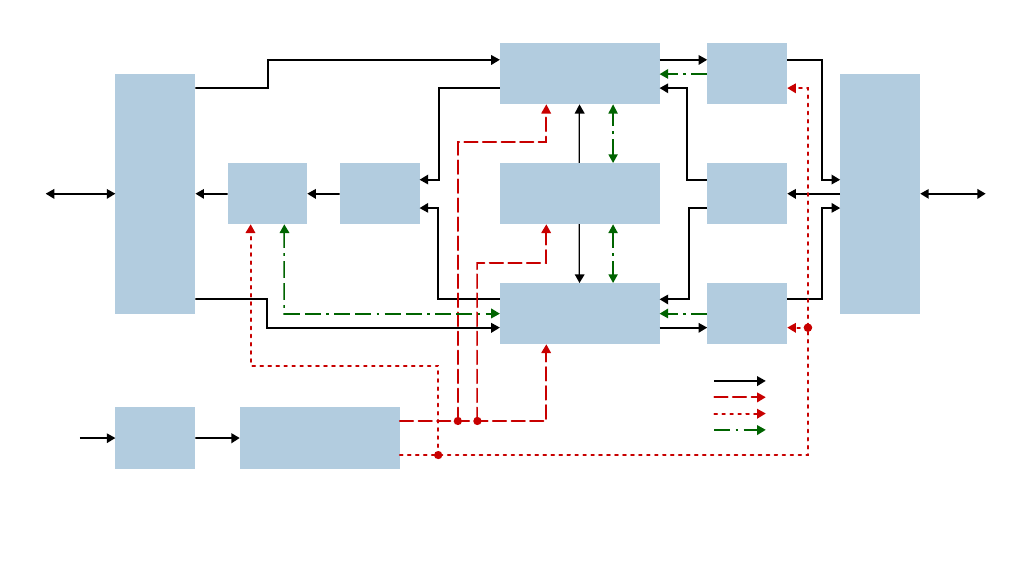
TX RX Systems Inc. Manual 7-9485-1.7 09/12/11 Page 6
should exceed the signal booster’s gain figure
by at least 15 dB.
5) Repeat step 4 again with the signal generator
set at the passband edges in order to see if the
isolation is remaining relatively constant over
the complete width of the passband.
6) Repeat the isolation measurements if neces-
sary at other system passbands to determine
the overall minimum isolation value for the sys-
tem. Physical modification of the antenna sys-
tem maybe required in order to reach an
acceptable minimum value.
RF EXPOSURE
To comply with FCC RF exposure compliance
requirements, a separation distance of at least 100
cm must be maintained between the antennas of
this device and all persons. This device must not
be co-located or operating in conjunction with any
other antenna or transmitter.
EXPOSITION RF
Pour conformer aux exigences d'exposition de
FCC RF, une distance de séparation d'au moins
100 cm doit être maintenue entre les antennes de
cet appareil et toutes les personnes. Cet appareil
ne doit pas être co-localisé ou exploités en con-
jonction avec toute autre antenne ou transmetteur.
SIGNAL FLOW BLOCK DIAGRAM
Figure 4 is the signal flow block diagram of the
standard channelized signal booster model 613-8.
Figure 5 shows the front view of the booster cabi-
net. The channel modules are bi-directional with
each module containing one downlink branch and
one uplink branch. The branches are functionally
identical because the same circuit board designs
are used in each branch. The uplink and downlink
branches may be programmed to any frequency in
the appropriate band.
Uplink and Downlink Input Signals
Uplink input signals (794 - 806 and 806 - 824) are
picked up by the DAS antenna and applied to the
triplexer. The uplink input signals pass through the
triplexer and are fed into a directional coupler
where they are distributed to the uplink input port of
both the 700 and 800 MHz channel modules.
Downlink input signals (764 - 776 and 851 - 869)
are picked up by the Donor antenna and applied to
the triplexer. The downlink input signals pass
through the triplexer and exit at either the 700 or
800 MHz output port. The 700 and 800 MHz down-
link inputs signals are then applied to the downlink
inputs of the respective 700 and 800 MHz channel
modules.
Channel Module
3-23350-1
Channel Module
3-23368-1
Control Module
3-23360-1
Hybrid
Coupler
3-5688
Hybrid
Coupler
3-5688
Power
Amp
3-23665
Power
Amp
3-23665
Power
Amp
3-23665
Line
Filter
8-23887
Triplexer
8-23088
Triplexer
8-23088
Donor
Antenna
AC
In
DAS
Antenna
Power Supply Module
+28VDC & +6VDC Output
3-23912
RF Connections
+6V Power
+28V Power
Communications
Figure 4: Signal flow block diagram of the channelized signal booster.
Dual band high power model shown as an example.
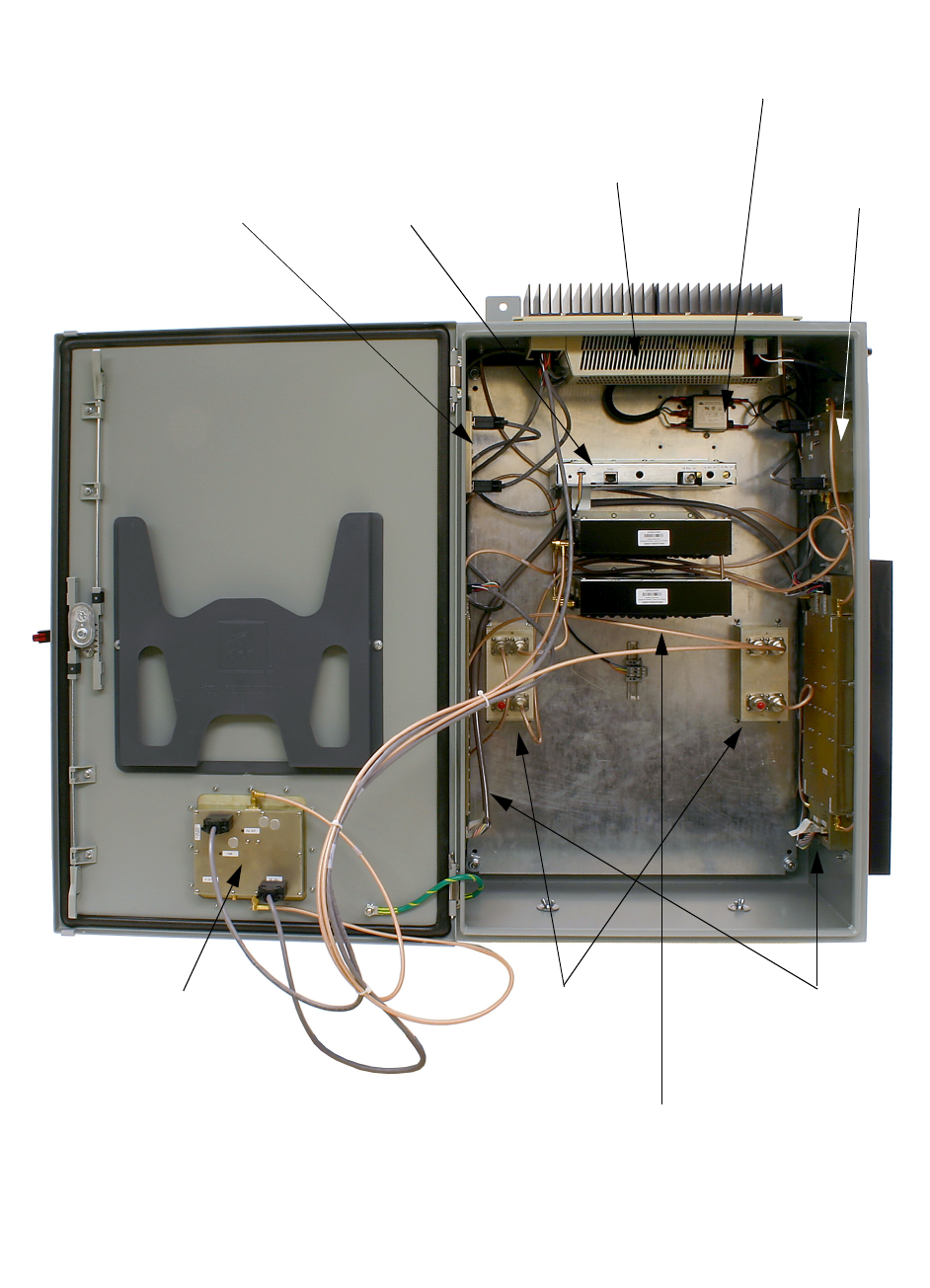
TX RX Systems Inc. Manual 7-9485-1.7 09/12/11 Page 7
Figure 5: Front view of the booster.
Power
Amplifier
Channel
Module
Triplexers
Power
Amplifier
Power
Amplifier
Control
Board
Line
Filter
Power
Supply
Directional
Coupler
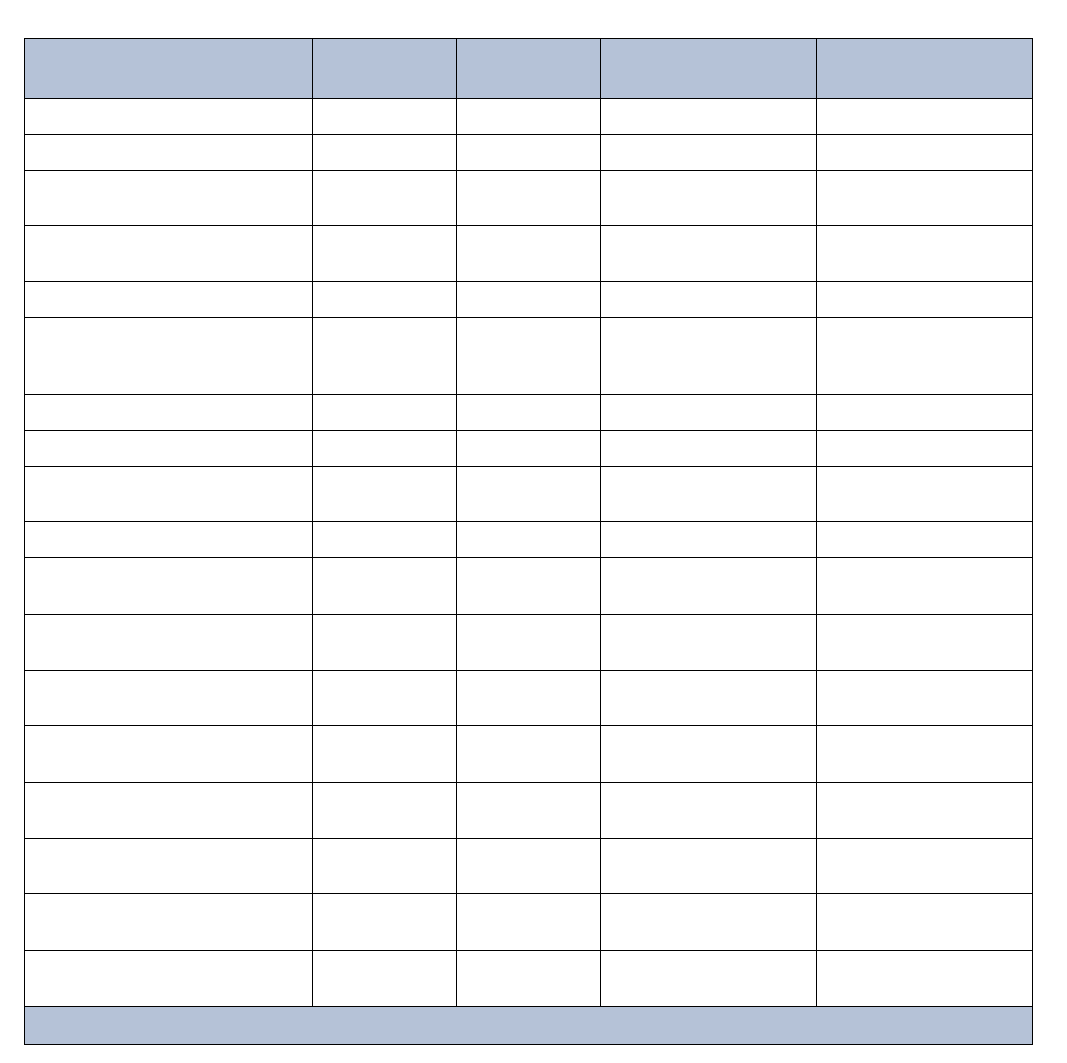
TX RX Systems Inc. Manual 7-9485-1.7 09/12/11 Page 8
Channel Module
The uplink input signals and the downlink input sig-
nals are applied to a down-converter board when
they enter the channel module. Within the channel
module input signals are down converted, digitized,
and DSP filtering is performed. There are two
styles of Channel modules available, a 14 channel
version and a 30 channel version. After DSP filter-
ing the analog signal is recreated and up converted
with an up-conver ter board to the original fre-
quency before being output from the channel mod-
ule at the downlink and uplink output ports.
Up converter boards are available in two different
styles including low level and high level. If the sig-
nal booster is a high-power model then a low level
up converter board is used in the channel module.
If the booster is a low power model then high level
Location Label Possible
States Causes Action
to take
Bottom of channel module DL/UL PWR Green solid FPGA successfully loaded None
Bottom of channel module DL/UL PWR Off Issue with board Return to factory
Bottom of channel module DL/UL COM Red flashes Exchanging data with con-
trol board None
Bottom of channel module DL/UL COM Red solid Exchanging data with con-
trol board None
Bottom of channel module DL/UL COM Off No data exchanging None
Bottom of channel module DL/UL COM
Always Off and it
is expected to
flash
No data exchanging Check cabling; return con-
trol board to factory
Bottom of channel module DL/UL DAC Red solid DAC overflow Lower output power setting
Bottom of channel module DL/UL DAC Off DAC normal operation None
Bottom of channel module DL/UL ADC Red solid ADC overflow Increase down converter
attenuation
Bottom of channel module DL/UL ADC Off ADC normal operation None
Control board Ctrl LED Off no power, no bootloader,
no program Return to factory
Control board Ctrl LED Orange bootloader installed, no
program
return to factory or per-
form field update
Control board Ctrl LED Red Control board detected a
fault
Address fault condition.
Contact factory
Control board Ctrl LED Green solid Control board normal oper-
ation None
Power Amplifier PWR Green solid 6 VDC supply to Amplifier
is OK None
Power Amplifier PWR Off No supply voltage check power supply and
cabling
Power Amplifier PA OFF Off Power Amp normal opera-
tion None
Power Amplifier PA OFF Red solid Over current, over temp Amp shut down, contact
factory
Table 3: Subassembly LED descriptions.
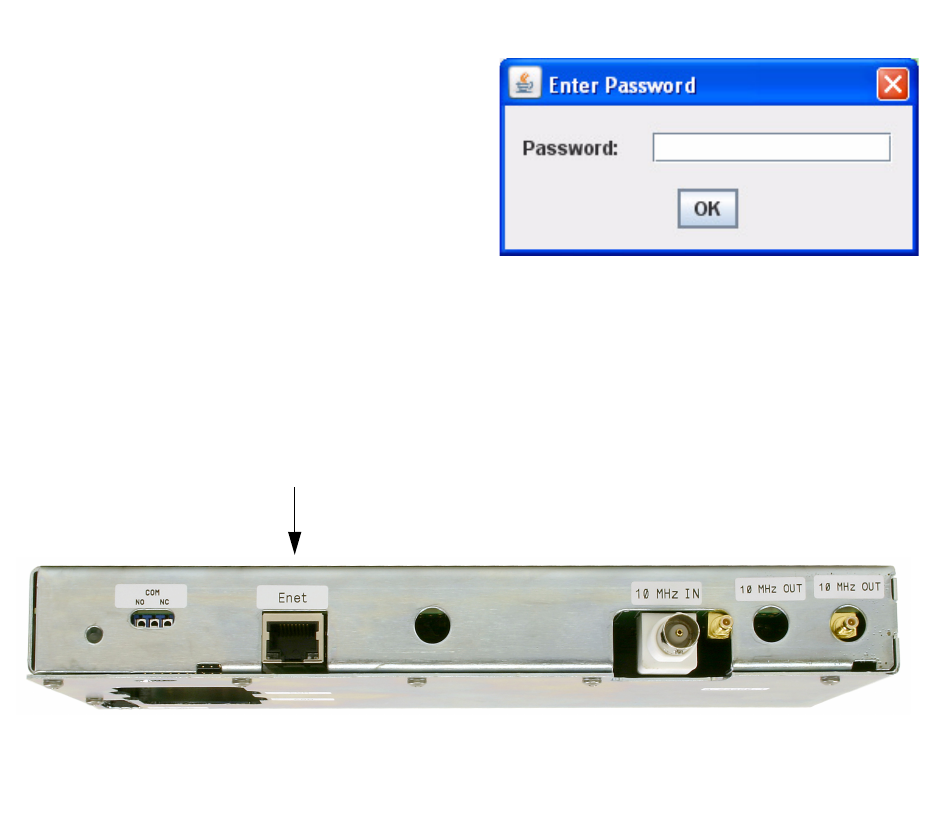
TX RX Systems Inc. Manual 7-9485-1.7 09/12/11 Page 9
up converter boards are used. Signal booster mod-
els that have the fiber-optic option installed in them
have enhanced down-converter boards that are
capable of dealing with the low level signals from
the optical conversion.
Uplink and Downlink Output Signals
Uplink and Downlink output signals leave the chan-
nel module at the UL OUT and DL OUT connectors
respectively. The 700 and 800 MHz uplink output
signals are combined with a directional coupler
then passed on to a power amplifier stage. The
output of the power amplifier is passed through a
triplexer then radiated from the donor antenna.
Downlink output signals leave the channel module
and are applied to a power amplifier stage. The
output of the power amplifier is passed through a
triplexer then radiated from the service antenna.
OPERATION
Power is applied to the channelized booster by
plugging in the AC or DC power cord (depending
on how th e system was configu red for input
power).
Subassembly LED’s
LED’s are located on several of the subassemblies
within the Booster cabinet. The function of each of
these indicator LED’s are listed in Table 3.
Configuring the Channel Module
The digital signal booster provides Ethernet con-
nectivity that allows access to a web-based inter-
face for programming the individual channels.
Programming will require connecting your laptop
computer to the Enet connector on the control
board. Figure 6 shows the connector. A standard
Ethernet crossover cable is used to make the con-
nection between your laptop and the booster cabi-
net. Refer to Appendix A at the back of this
manual for detailed instructions on how to properly
connect your computer to the Enet port of the
booster.
Once your laptop is properly connected to the sig-
nal booster, if password protection is enabled, the
password request box will appear in your web
browser as shown in Figure 7. Type in your pass-
word and press the OK button. The password box
will disappear and the web-based interface screen,
at the filters tab, will appear as shown in Figure 8.
The web based interface is divided into four pages
including FILTERS, LINK, ADMIN, and SYSTEM.
Each page contains a group of related functions.
Figure 7: Enter your password.
Figure 6: Enet connector on the control board.
Enet
Connector
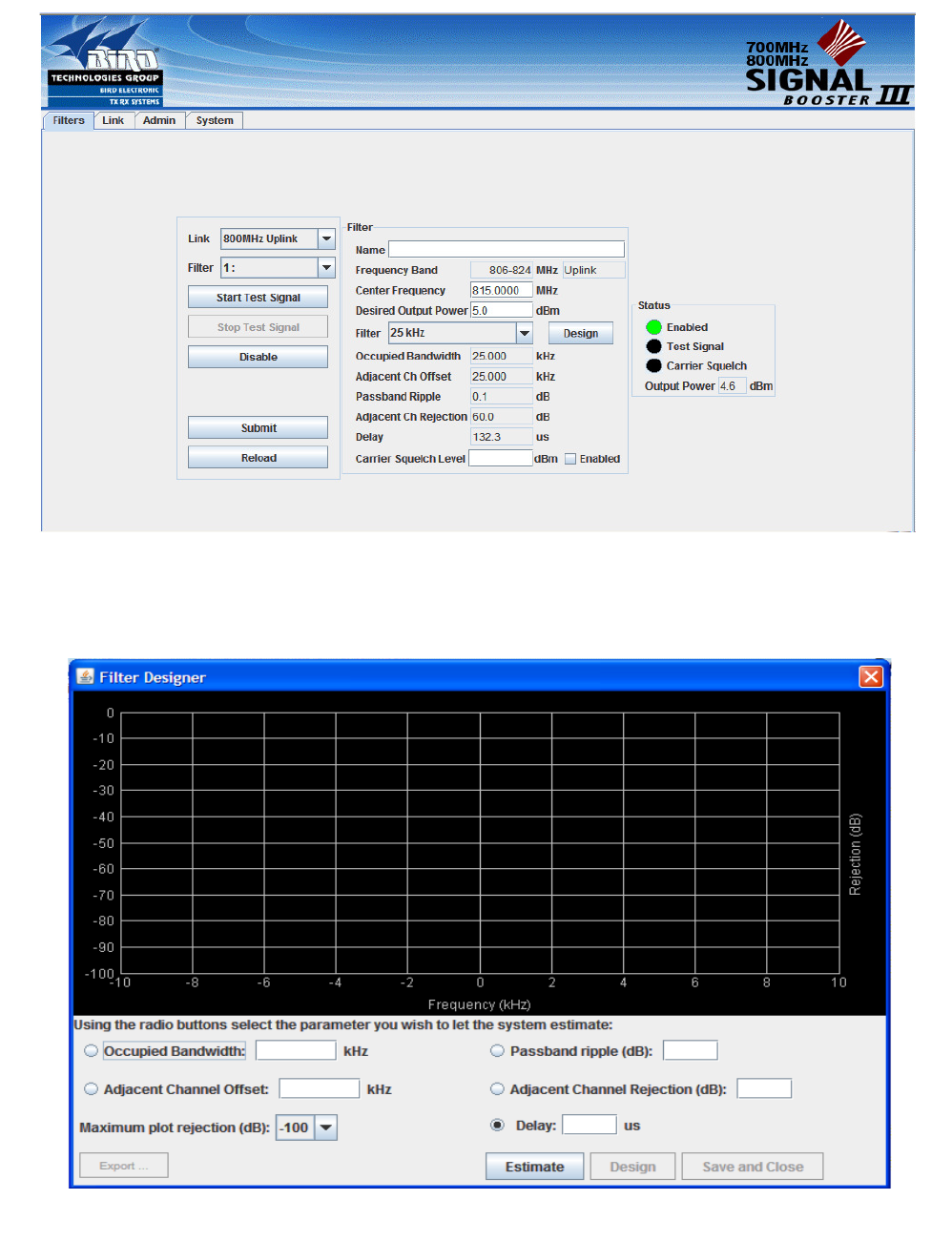
TX RX Systems Inc. Manual 7-9485-1.7 09/12/11 Page 10
Figure 8: The Web-Page Interface screen, filters tab.
Figure 9: The design filter interactive display screen.
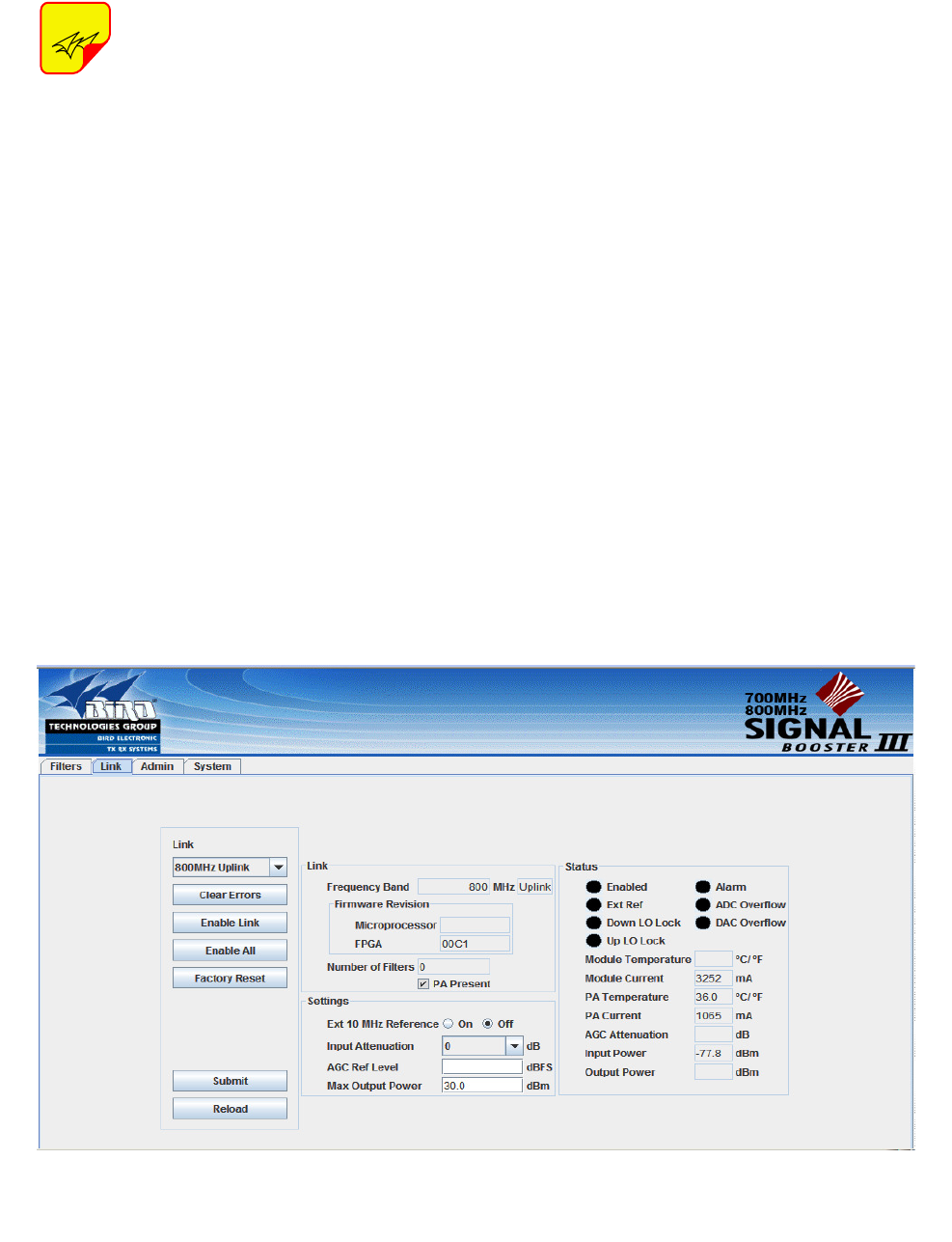
TX RX Systems Inc. Manual 7-9485-1.7 09/12/11 Page 11
O n c e yo u r p a ssw o r d h a s b e e n
entered and validated a 15 minute
inactivity timer is started. If the user
does not make any changes to the
web page interface the system will re-
arm security once the inactivity timer
expires. The user will then need to re-
enter the password.
Password protection is disabled by default when
your system leaves the factory. To enable pass-
word protection for your system perform the follow-
ing steps;
1) Launch the web page interface in your web
browser.
2) Click the “Admin” tab at the top of the interface
screen.
3) Click on the “Enable Password protection” box.
4) Enter your password. Write your password
down somewhere for safe keeping in case you
forget it. If you do forget your password you will
need to contact Bird Technologies Group to
obtain a default password.
5) Click the submit button to apply the changes.
Filters Tab
The filters tab is divided into three functional areas
which include a row of command buttons running
down the left side of the screen, a filter area in the
middle of the screen, and a status area on the right
side of the screen as shown in Figure 8. The filter
tab is designed to interact with one channel at a
time. The channel that is selected for interaction is
determined by the LINK and FILTER boxes on the
upper left of the screen. To change the filter chan-
nel that you are going to interact with click on the
arrow to display the full drop down box. Scroll
down the list until the desired channel is high-
lighted and click on it. The data displayed in the fil-
ter area of the display screen will now be for the
selected channel.
COMMAND BUTTONS
Clicking on a command button (located on the
extreme left hand side of the filters tab) performs
the associated task immediately. The submit and
reload buttons in the bottom left corner allow any
changes you make to the display/interface boxes
to be downloaded to the booster. The submit and
reload buttons act like a trigger sending any
changes you made in the interface boxes to the
NOTE
Figure 10: The Web-Page interface screen, link tab.
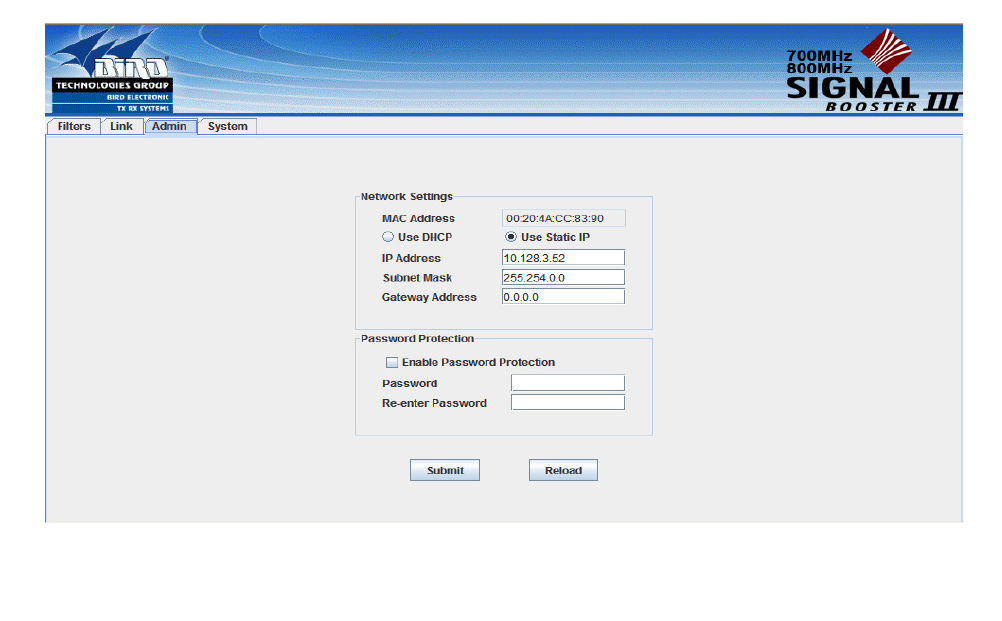
TX RX Systems Inc. Manual 7-9485-1.7 09/12/11 Page 12
channel module as well as updating any displayed
data from the module, but only after the button is
pressed.
FILTER AREA
This is a user interactive area where the field engi-
neer can program the operating characteristics of
the selected channel filter. Each parameter in the
settings area can be changed by clicking in the box
and typing in the new values or by pointing at an
arrow to display a drop down box. Most of the
adjustable parameters have adjustment limitations
as applicable. The parameters are self-explana-
tory. The changes you make are only applicable to
the selected channel filter. After you have made
changes to the various parameters press the “sub-
mit” command interface button (lower left corner of
the screen) in order to copy the changes into the
module itself.
When the “Design Filter” button is pressed a cus-
tom design template will be displayed as shown in
Figure 9. Remember the changes you make are
only applicable to the selected channel filter. After
you have made changes to the various parameters
press the “submit” command interface button
(lower left corner of the screen) in order to copy the
changes into the module itself.
STATUS AREA
The status area of the filters tab lets the user know
whether the channel is enabled, if the test signal is
on, if the carrier squelch is on, and what the output
power level is for that channel. A green bubble indi-
cates the parameter is on and a black bubble indi-
cates the parameter is off.
Link Tab
The link tab is divided into four functional areas
which include a row of command buttons running
down the left side of the screen, a link and settings
area in the middle of the screen, and a status area
on the right side of the screen as shown in Figure
10. The link tab is designed to interact with one
branch of a module at a time. The branch that is
selected for interaction is determined by the LINK
box on the upper left of the screen. To change the
branch that you are going to interact with click on
the arrow to display the full drop down box. Scroll
down the list until the desired branch is highlighted
and click on it. The data displayed in the link area
of the display screen will now be for the selected
branch.
COMMAND BUTTONS
Clicking on a command button (located on the
extreme left hand side of the filters tab) performs
Figure 11: The Web-Page Interface screen, admin tab.
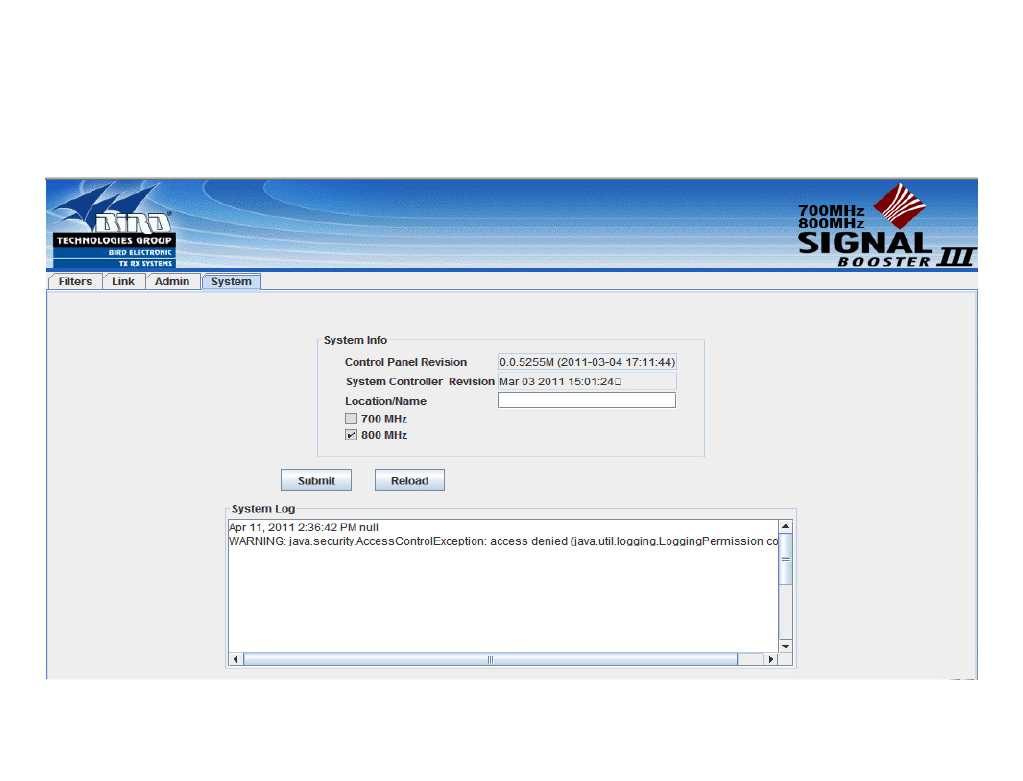
TX RX Systems Inc. Manual 7-9485-1.7 09/12/11 Page 13
the associated task immediately. The submit and
reload buttons in the bottom left corner allow any
changes you make to the display/interface boxes
to be downloaded to the booster. The submit and
reload buttons act like a trigger sending any
changes you made in the interface boxes to the
channel module as well as updating any displayed
data from the module, but only after the button is
pressed.
LINK AND SETTINGS AREA
This is a user interactive area where the field engi-
neer can program the operating characteristics of
the selected branch as shown in the settings area.
Each pa rameter in the settings a rea can be
changed by clicking in the box and typing in the
new values or by pointing at an arrow to display a
drop down box. Most of the adjustable parameters
have adjustment limitations as applicable. The
parameters are self-explanatory. The changes you
make are only applicable to the selected channel
filter. After you have made changes to the various
parameters press the “submit” command interface
button (lower left corner of the screen) in order to
copy the changes into the module itself. The link
portion of the area displays status information for
the branch.
STATUS AREA
The status area of the link tab lets the user know
the status of the module and power amplifier if
applicable. Parameters that can be turned on or off
have a bubble next to the parameter name. A
green bubble indicates the parameter is on and a
black bubble indicates the parameter is off.
Admin Tab
The admin tab allows the user to change the boost-
ers network settings and enable password protec-
tion for the web-based interface program. The
boxes on this page are interactive. To ma ke
changes click inside the box and a cursor will
appear. Refer to Figure 11.
System Tab
The system tab lists the control board software ver-
sions. A customer designated location name can
be recorded. There is also a system logbook avail-
able on this page. Refer to Figure 12.
Figure 12: The Web-Page Interface screen, system tab.
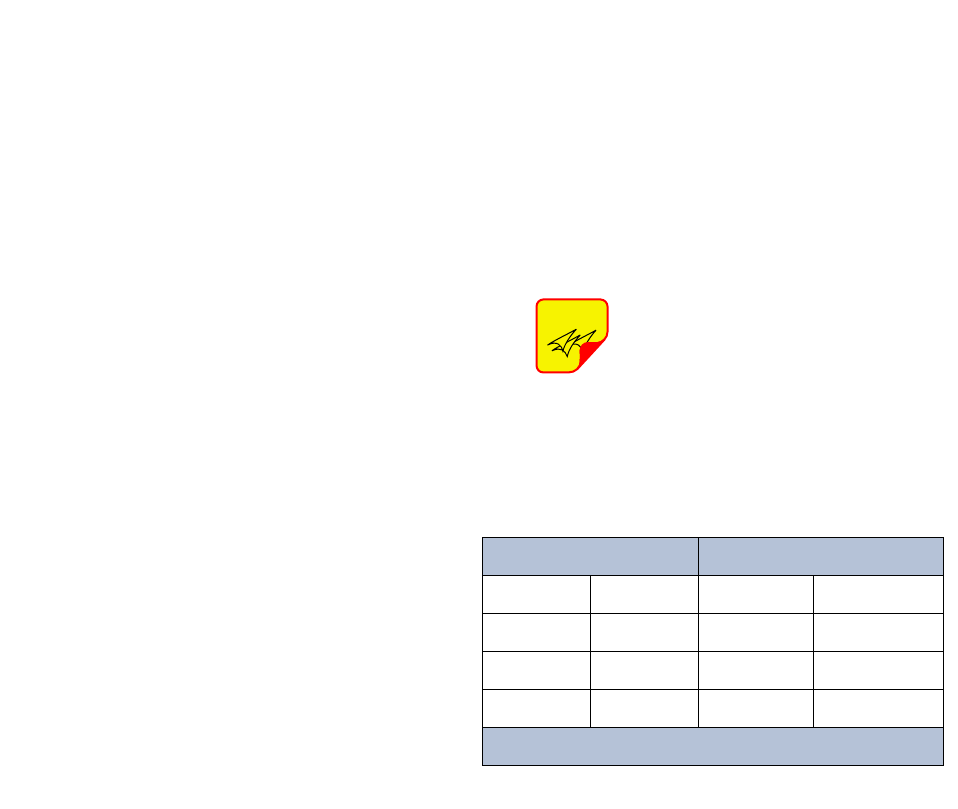
TX RX Systems Inc. Manual 7-9485-1.7 09/12/11 Page 14
ETHERNET CONNECTIVITY
The front panel User Interface connector on the
booster provides for 10/100 BASE-T Ethernet con-
nection using the TCP-IP protocol. This product
feature allows access to a web-based interface for
programming the individual modules within the
booster. The web based interface requires a JAVA
runtime environment (version 1.6.0 or later) to be
installed on your laptop. The JAVA software can be
downloaded free of charge from the Sun Microsys-
tems website found at “http://java.com/en/down-
load/index.jsp”. The channe lized booster is
shipped from the factory with a default IP address
of “192.168.1.1”.
Two connection schemes are discussed including
a direct connection from your laptop computer to
the booster front panel as well as connecting the
booster to a networked environment. A direct con-
nection (at the installation site) should be estab-
lished the first time you interface to the booster
using the fixed IP mentioned above. Once the ini-
tial communications are established the IP address
in the booster can be changed to permit a net-
worked connection (from a remote site such as
your office).
Direct Connection
Your initial connection to the booster system
should be a direct connection to the front panel
using an Ethernet crossover cable. Figure A1
shows the proper way to interconnect the equip-
ment as well as the pinout for a CAT-5 crossover
cable.
REQUIRED EQUIPMENT
Cat-5 Crossover Cable
Laptop Computer with a network interface card
installed. In addition, the JAVA run-time environ-
ment version 1.6.0 or later, and a web browser
such as Internet Explorer must also be installed on
the laptop.
PROCEDURE
To connect your laptop computer to the front panel
LAN port and access the web page interface, per-
form the following steps;
1) Insure the JAVA runtime environment software
is installed on your laptop.
2) Connect your laptop network port to the LAN
connector on the booster front panel using a
standard CAT-5 Crossover cable.
The front panel LAN connector
has two built-in bi-color status
LED’s which will aid you in estab-
lishing communications. The
meaning of each LED is shown in
Table A1.
3) The left-most (LINK) status LED built-in to the
LAN port connector should illuminate amber or
green indicating that a good physical connec-
tion is established between your computer and
the booster.
4) Insure that your laptop’s IP address is compati-
ble with the default address of the signal
booster system. This may require changes be
made to the Ethernet adaptor address on your
laptop (refer to Appendix B). Your laptop’s IP
address will need to be set to “192.168.1.2”
along with a subnet mask of “255.255.255.0”.
The right-most (ACTIVITY) status LED built-in
to the LAN port connector will turn amber or
green indicating good TCP-IP communications
are established between the laptop and the
booster.
NOTE
APPENDIX A
Front Panel Ethernet Connectivity
LINK LED
(left side)
ACTIVITY LED
(right side)
Color Meaning Color Meaning
Off No Link Off No Activity
Amber 10 Mbps Amber Half-Duplex
Green 100 Mbps Green Full-Duplex
Table A1: LAN port status LED’s
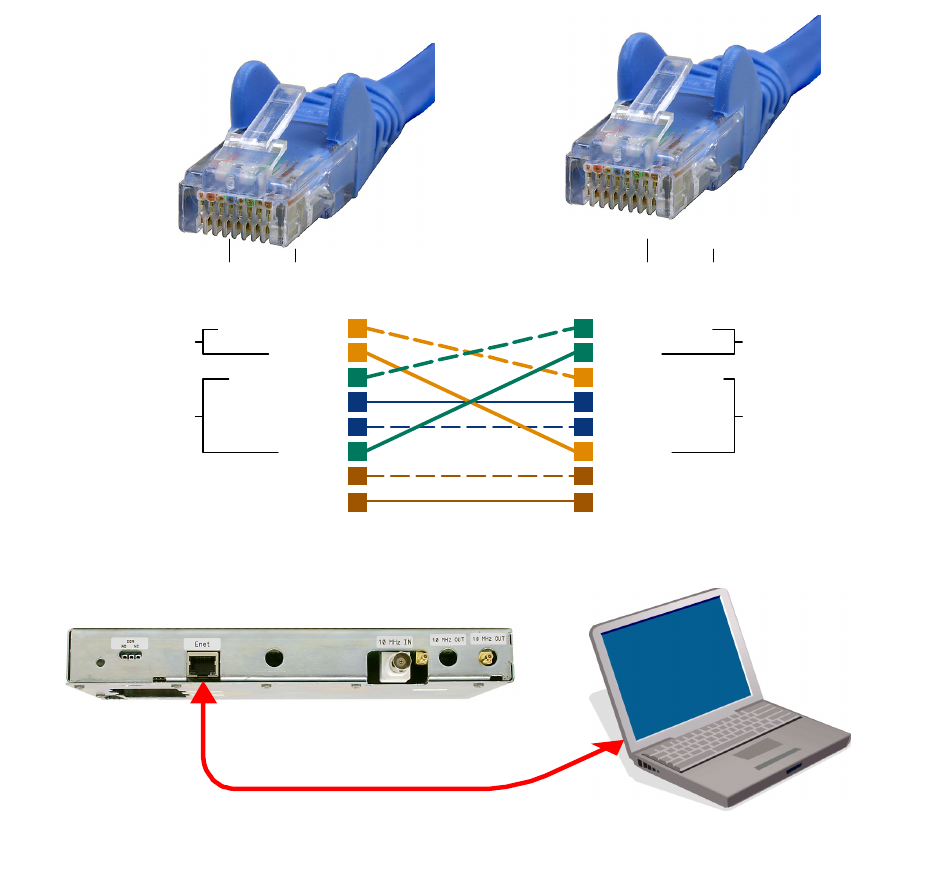
TX RX Systems Inc. Manual 7-9485-1.7 09/12/11 Page 15
5) Launch your web browser software on the lap-
top.
6) In your web browsers address box type-in the
address of the booster “http://192.168.1.1” and
press the ENTER key. The web page interface
to the booster should appear in your laptop’s
browser window. When you launch the web
page you may notice that the JAVA applet will
load first.
Networked Connection
Before attempting a networked connection to the
signal booster system consult with your IT support
personnel for information concerning the correct IP
address to use and any additional connectivity
issues such as firewalls. Once you have the correct
IP address you will need to direct connect to the
booster system as discussed in the earlier section
of this appendix and reconfigure the booster LAN
port with this new address. You can then connect
the signal booster system using a straight-through
CAT-5 cable to the networked environment and
interface to it from a remote computer. Figure A2
shows the proper way to interconnect the equip-
ment for a networked connection as well as the
pinout for a straight-thru CAT-5 cable.
REQUIRED EQUIPMENT
Cat-5 Straight-thru Cable
Laptop Computer with a network interface card
installed. In addition, the JAVA run-time environ-
1
4
7
6
3
5
8
2
1
4
7
6
3
5
8
2
Orange/White
Orange
Green/White
Blue
Blue/White
Green
Brown/White
Brown
Green/White
Green
Orange/White
Blue
Blue/White
Orange
Brown/White
Brown
Transmit (1 & 2)
Receive (3 & 6) Transmit (3 & 6)
Receive (1& 2)
Pins 4, 5, 7 and 8 are not used
Pin Pin
CAT-5 Cross-Over Cable
1 8 1 8
Figure A1: Direct connection to the booster using crossover cable.
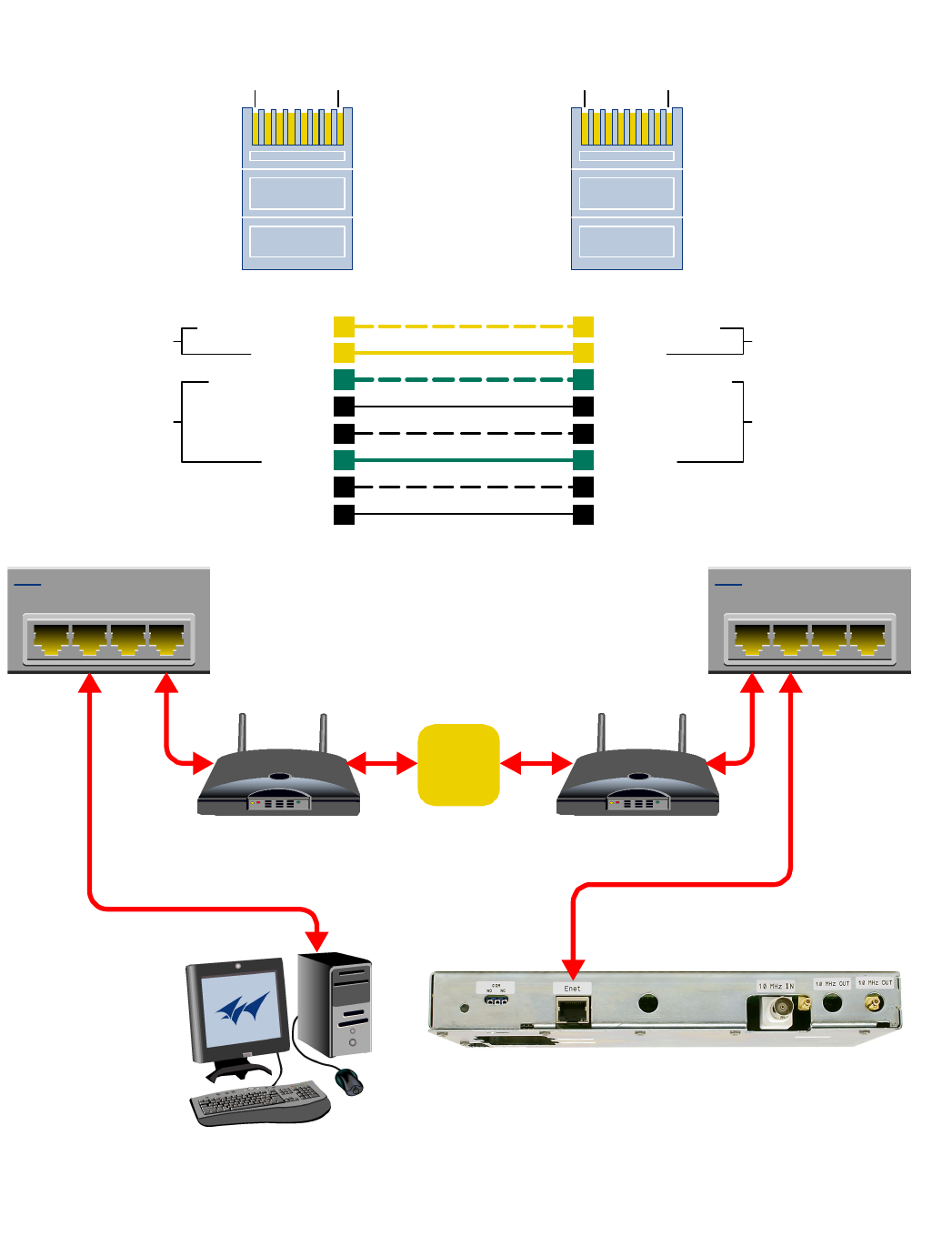
TX RX Systems Inc. Manual 7-9485-1.7 09/12/11 Page 16
1
4
7
6
3
5
8
2
1
4
7
6
3
5
8
2
Orange/White
Orange
Green/White
Blue
Blue/White
Green
Brown/White
Brown
Orange/White
Orange
Green/White
Blue
Blue/White
Green
Brown/White
Brown
Transmit (1 & 2)
Receive (3 & 6) Transmit (3 & 6)
Receive (1& 2)
Pins 4, 5, 7 and 8 are not used
Pin Pin
1234
4 Port Ethernet Hub
1 2 3 4
4 Port Ethernet Hub
CAT-5
Straight-Through
Cable
Modem/Router Modem/Router
Remote PC System
Internet
1 8 1 8
Figure A2: WAN connection to the booster using straight-through cable.
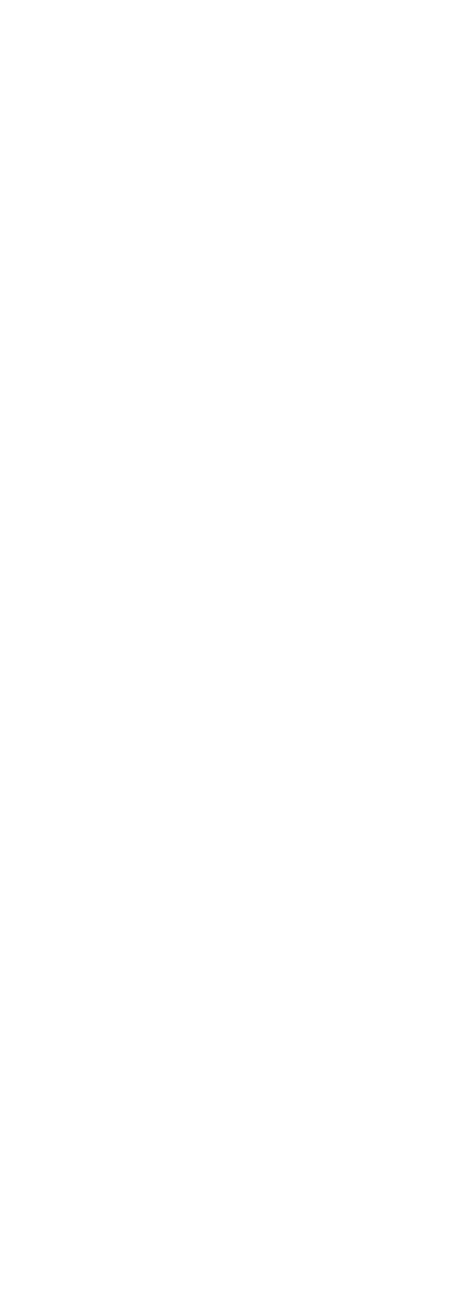
TX RX Systems Inc. Manual 7-9485-1.7 09/12/11 Page 17
ment version 1.6.0 or later, and a web browser
such as Internet Explorer must also be installed on
the laptop.
PROCEDURE
Before a networked connection can be established,
the booster LAN Port must be changed to an IP
address that’s compatible with your network. If you
are unsure how to determine this address check
with your IT support personnel. To connect the
booster LAN port to a networked environment and
access the web page interface, perform the follow-
ing steps;
1) Change the boosters LAN port IP address. To
do this, direct connect your laptop to the
booster as discussed in the earlier section of
this appendix titled “Direct Connection” and fol-
low steps 1 through 4.
2) Launch the configuration Applet in your web
browser.
3) Click the “Admin” tab at the top of the interface
display screen.
4) To be safe, take note of the settings currently
displayed.
5) Select the “User Static IP” radio button.
6) Enter the following settings provided by your
network administrator;
A) IP Address
B) Subnet Mask
C) Gateway Address
7) Click the “Submit” button to apply the changes.
8) Once the changes have been successfully
applied close your web browser.
9) Launch the configuration Applet in your web
browser using the newly entered IP address.
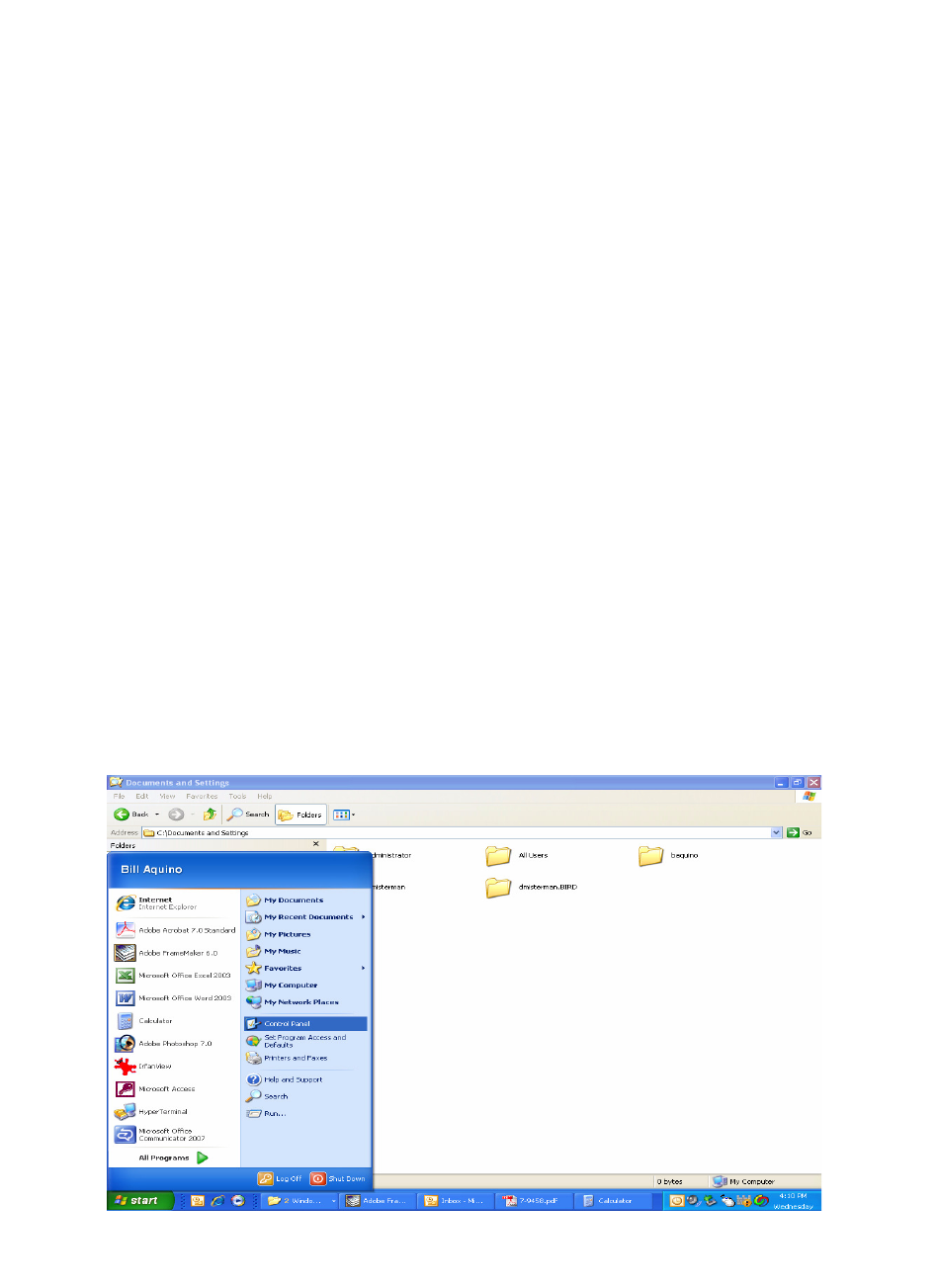
TX RX Systems Inc. Manual 7-9485-1.7 09/12/11 Page 18
When you initially direct connect your laptop ser-
vice computer to the booster it will be necessary to
change the computers IP address. The procedure
for doing this varies depending upon your operat-
ing system. As an example, this appendix illus-
trates how to make the change using the Microsoft
XP operating system. The procedure for other
operating systems will vary slightly from this exam-
ple. Consult with your IT support personnel if
needed. To change the IP address (assuming the
Microsoft XP operating system is being used) per-
form the following in a step-by-step fashion;
1) Select “Start” from the status menu.
2) Single click the “Control Panel” choice from the
“Start” pop-up menu as shown in Figure B1.
3) From the “Control Panel” icon selections double
click on the “Network Connections” icon. Refer
to Figure B2.
4) When the “Network Connections” folder opens
double click on the “Local Area Connection”
icon. See Figure B3.
5) The “Local Area Connection Status” box will
open. Single click the “Properties” tab as shown
in Figure B4. Note: If you do not have the cable
connected between the service computer and
the booster front panel the “Local Area Connec-
tion Status” box will not open. Instead proceed
to step 6.
6) The “Local Area Connection Properties” box will
open. Use the arrow buttons to scroll down the
list until the “Internet Protocol (TCP/IP)” choice
is highlighted as shown in Figure B5. Click the
“Properties” tab at the right-center of the box.
7) Select the “Use the following IP address” bub-
ble. Make sure the circle is filled-in. Refer to
Figure B6.
8) Enter the new IP address and subnet mask val-
ues as shown in Figure B7. To interface your
computer to the signal booster use an IP
address of “192.168.1.2” and a subnet mask of
“ 255.255.255.0”.
9) Click on the “OK” tab to initiate the changes.
This completes the procedure. Close any open
boxes.
APPENDIX B
Changing Your Service Computers IP Address
Figure B1: Choose the “Control panel” icon.
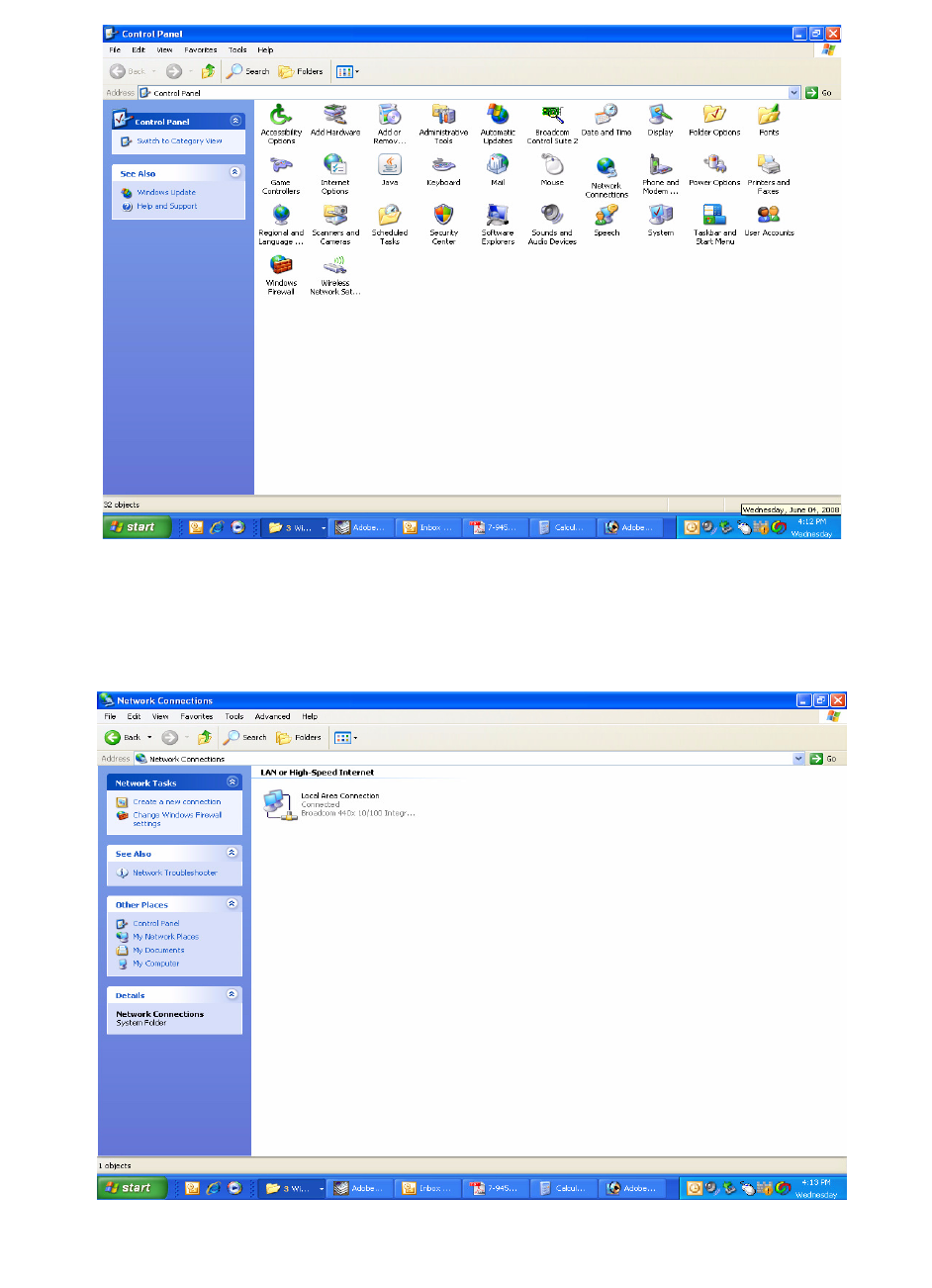
TX RX Systems Inc. Manual 7-9485-1.7 09/12/11 Page 19
Figure B2: Select the “Network Connections” icon.
Figure B3: Select the “Local Area Connection” icon.
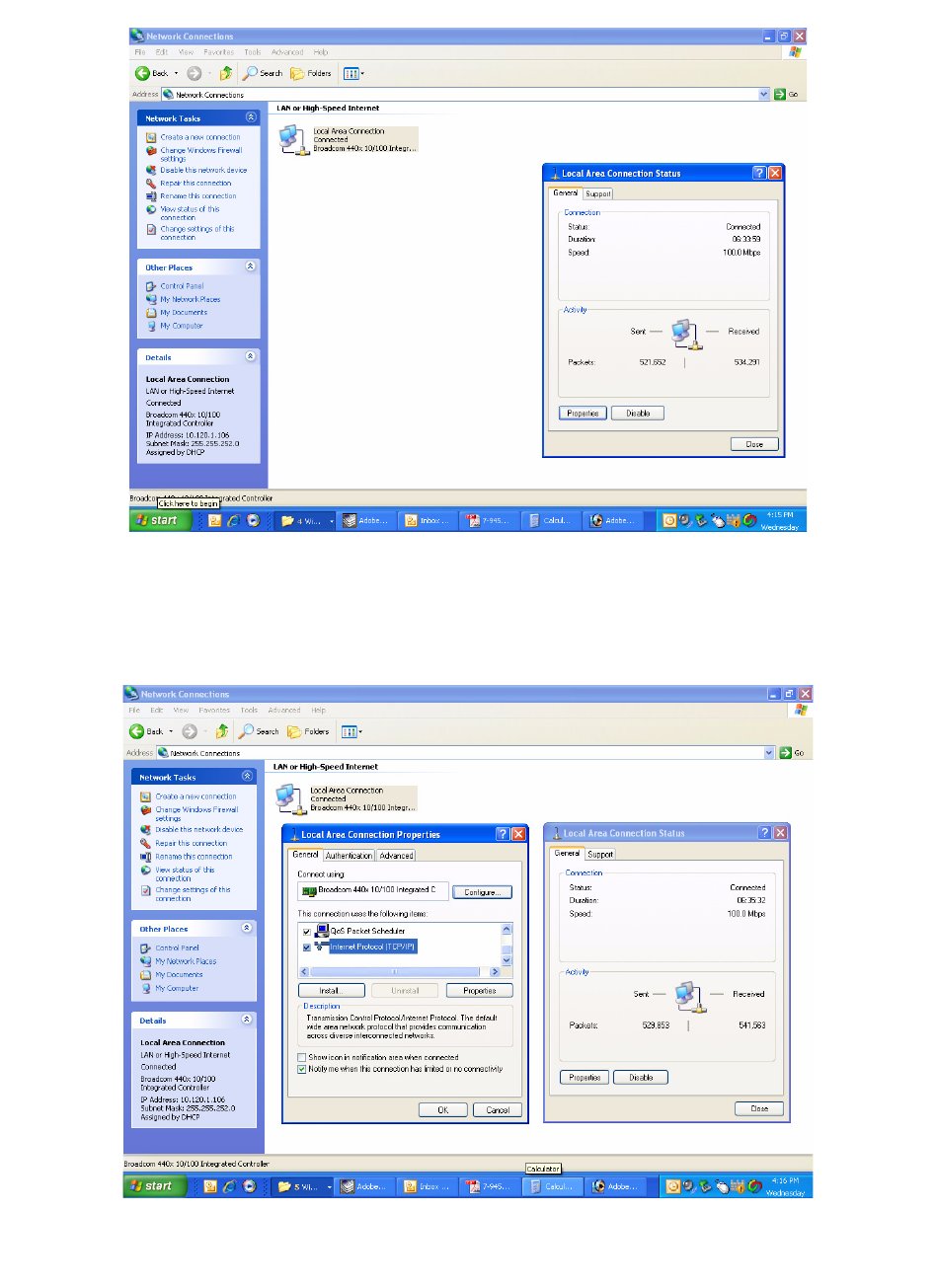
TX RX Systems Inc. Manual 7-9485-1.7 09/12/11 Page 20
Figure B4: Select the “Properties” tab.
Figure B5: Make sure the “Internet Protocol (TCP/IP)” choice is highlighted. Then select “OK”.
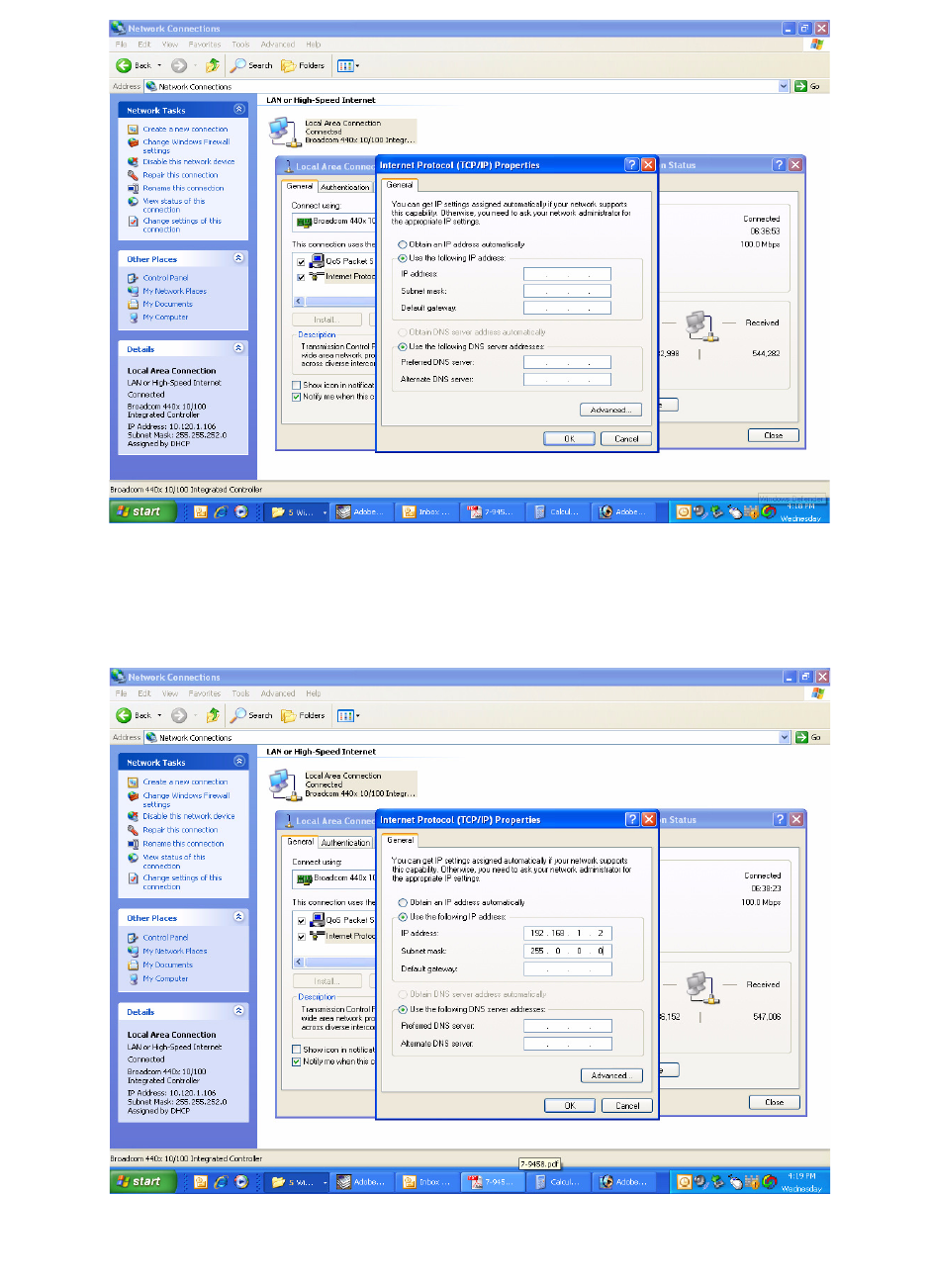
TX RX Systems Inc. Manual 7-9485-1.7 09/12/11 Page 21
Figure B6: Select “Use the Following IP Address”.
Figure B7: Enter the new IP Address and Subnet mask Values.
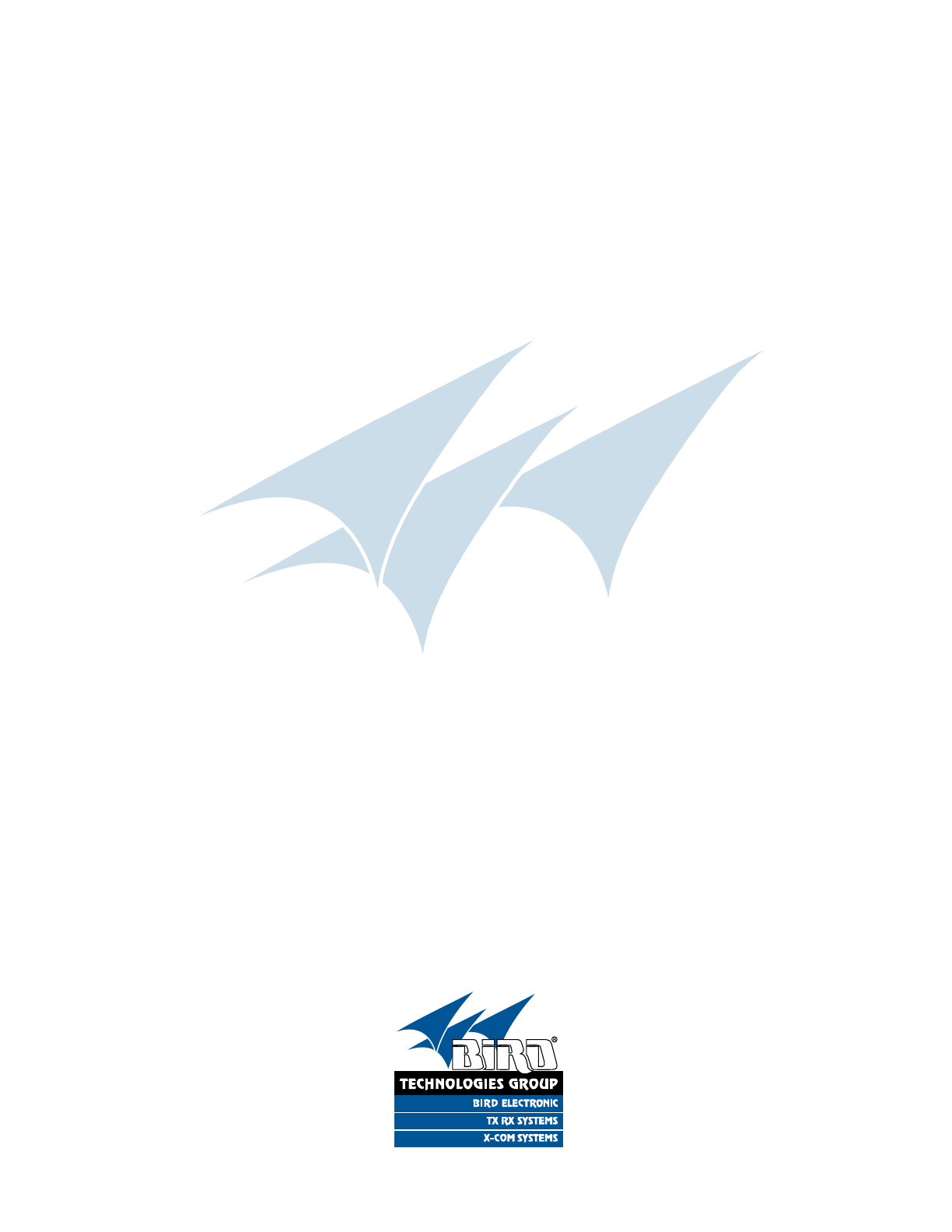
TX RX Systems Inc. Manual 7-9485-1.7 09/12/11 Page 22
8625 Industrial Parkway, Angola, NY 14006 Tel: 716-549-4700 Fax: 716-549-4772 sales@birdrf.com www.bird-technologies.com