CalAmp Wireless Networks MCUB5R User Manual preliminary version
CALAMP WIRELESS NETWORKS INC. preliminary version
preliminary version

Integra-TR
Technical Manual
Version 0.02
PRELIMINARY
The entire contents of this manual and the Software described
in this manual are copyright 1999 by Dataradio Inc.
Copyright DATARADIO Inc.
February 1999
Part no.: 120 4010x-002
i
Table of Contents
1. PRODUCT OVERVIEW................................................................................................................................... 1
1.1 INTENDED AUDIENCE ....................................................................................................................................... 1
1.2 GENERAL DESCRIPTION .................................................................................................................................... 1
1.2.1 Characteristics ........................................................................................................................................ 1
1.2.2 Accessories and options.......................................................................................................................... 1
1.3 CONFIGURATION ............................................................................................................................................... 1
1.4 FACTORY TECHNICAL SUPPORT........................................................................................................................ 2
1.5 PRODUCT WARRANTY ...................................................................................................................................... 2
1.6 REPLACEMENT PARTS....................................................................................................................................... 2
1.6.1 Factory Repair........................................................................................................................................ 2
1.7 PHYSICAL DESCRIPTION.................................................................................................................................... 2
1.8 DIAGNOSTICS.................................................................................................................................................... 2
1.8.1 Remote Commands.................................................................................................................................. 3
1.9 FIRMWARE UPGRADES...................................................................................................................................... 3
1.10 NETWORK APPLICATION............................................................................................................................... 3
1.10.1 RF Path and Communications Range................................................................................................. 3
1.10.2 Basic Connections .............................................................................................................................. 3
1.10.3 Common Characteristics ................................................................................................................... 3
1.10.4 Point to Point System.......................................................................................................................... 3
1.10.5 Point–Multipoint System..................................................................................................................... 4
1.10.6 Extending a Landline (Tail Circuit).................................................................................................... 4
2. FEATURES AND OPERATION...................................................................................................................... 5
2.1 OVERVIEW........................................................................................................................................................ 5
2.2 INTENDED AUDIENCE ....................................................................................................................................... 5
2.3 FRONT PANEL ................................................................................................................................................... 5
2.3.1 Antenna Connector ................................................................................................................................. 5
2.3.2 LED Indicators........................................................................................................................................ 5
2.3.3 Connection to DTE.................................................................................................................................. 5
2.3.4 Com Port................................................................................................................................................. 6
2.3.5 Setup Port................................................................................................................................................ 6
2.4 REAR PANEL..................................................................................................................................................... 7
2.4.1 Heat Sink................................................................................................................................................. 7
2.4.2 Power / Analog connector....................................................................................................................... 7
2.5 OPERATION....................................................................................................................................................... 7
2.5.1 Operating Modes..................................................................................................................................... 8
2.5.2 Data Forwarding Timer.......................................................................................................................... 8
2.5.3 Sending Break Signals ............................................................................................................................ 8
2.5.4 COM Port Baud Rates ............................................................................................................................ 8
2.5.5 Diagnostics.............................................................................................................................................. 8
2.5.6 Addressing............................................................................................................................................... 9
2.5.7 Station Type............................................................................................................................................. 9
2.6 ONLINE DIAGNOSTICS....................................................................................................................................... 9
2.6.1 Using an External Program for Online Diagnostics............................................................................... 9
2.6.2 Interpreting Diagnostic Results ............................................................................................................ 10
2.7 OFFLINE DIAGNOSTICS.................................................................................................................................... 12
2.8 LOW POWER OPERATION ................................................................................................................................13
2.8.1 Reduced Transmit Power...................................................................................................................... 13
2.8.2 Suspend Mode ....................................................................................................................................... 13
ii
2.8.3 Sleep Mode............................................................................................................................................ 13
2.8.4 Remote Unit Wake-up by DTE .............................................................................................................. 13
2.9 TRANSMITTER TIMEOUT ................................................................................................................................. 13
2.10 OPTIMIZING YOUR SYSTEM ........................................................................................................................ 14
3. MAINTENANCE ADJUSTMENTS............................................................................................................... 15
3.1 OVERVIEW AND MAINTENANCE INTERVALS ................................................................................................... 15
3.2 INTENDED AUDIENCE ..................................................................................................................................... 15
3.3 EQUIPMENT REQUIRED ................................................................................................................................... 15
3.4 TEST POINT..................................................................................................................................................... 15
3.5 BASIC ADJUSTMENTS...................................................................................................................................... 15
3.5.1 Preliminary Steps.................................................................................................................................. 15
3.5.2 After Adjustments are Done .................................................................................................................. 15
4. CIRCUIT DESCRIPTION.............................................................................................................................. 17
4.1 OVERVIEW...................................................................................................................................................... 17
4.2 INTENDED AUDIENCE ..................................................................................................................................... 17
4.3 CIRCUIT DESCRIPTION .................................................................................................................................... 17
4.3.1 Microprocessor Circuit......................................................................................................................... 17
4.3.2 RS232.................................................................................................................................................... 17
4.3.3 MODEM................................................................................................................................................ 17
4.3.4 TRANSMIT & RECEIVE DATA ............................................................................................................ 17
4.3.5 Integra-R A/D and DIGIPOT................................................................................................................ 18
4.3.6 Wake-Up Circuit ................................................................................................................................... 18
4.3.7 Power Supply ........................................................................................................................................ 18
TABLE 1 INTEGRA-T ACCESSORIES AND OPTIONS.......................................................................................................... 1
TABLE 2: COM PORT SIGNALS....................................................................................................................................... 6
TABLE 3: SETUP PORT SIGNALS ..................................................................................................................................... 6
TABLE 4: SWR / REV PWR .......................................................................................................................................... 12
TABLE 5: TESTS AND ADJUSTMENTS HALF AND FULL CHANNEL UNITS ............................................................................. 16
FIGURE 1 - BASIC CONNECTIONS REQUIRED................................................................................................................... 3
FIGURE 2 - POINT TO POINT SYSTEM.............................................................................................................................. 4
FIGURE 3 - POINT–MULTIPOINT SYSTEM ....................................................................................................................... 4
FIGURE 4 - TAIL CIRCUIT ............................................................................................................................................... 4
FIGURE 5 - DCE CROSSOVER CABLE FOR RTS-CTS MODE........................................................................................... 4
FIGURE 6 – INTEGRA-T FRONT PANEL............................................................................................................................ 5
FIGURE 7 – COM AND SETUP PORT CONNECTORS PIN LOCATIONS ................................................................................ 6
FIGURE 8 – 3-WIRE INTERFACE ...................................................................................................................................... 6
FIGURE 9 – INTEGRA-T REAR PANEL.............................................................................................................................. 7
FIGURE 10 - POWER / ANALOG CONNECTOR.................................................................................................................. 7
FIGURE 11- POWER / ANALOG CABLE ............................................................................................................................ 7
FIGURE 12 - LOGIC BOARD BLOCK DIAGRAM.............................................................................................................. 19
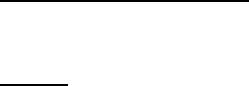
iii
What's New in this Version
Document various corrections
History
0.01: This version 0.01 of the first preliminary version of the Integra-TR technical manual will be re-
placing the Integra-T manual versions. The Integra-TR is compliant to the FCC refarming (19.2Kb/s in
25KHz channels and 9.6KHz in 12.5KHz channels).
iv
Definitions
The following terms are used throughout this document.
Bit dribble Extraneous bits delivered at the end of a data transmission. Equivalent to a
“squelch tail” in voice systems. Integra-T does not have bit dribble.
COM Port The Communications Port of Integra-T. This port is configured as DCE and is
designed to connect directly to DTE.
CTS Clear to Send. An RS-232 output signal from Integra-T indicating that it is ready
to accept data.
DCE Data Communications Equipment. This designation is applied to equipment such
as modems. DCE is designed to connect to DTE.
DOX Data Operated Transmit. A mode of operation in which Integra-T begins a
transmission as soon as data is presented to the RS-232 port.
DTE Data Terminal Equipment. This designation is applied to equipment such as ter-
minals, PCs, RTUs, PLCs, etc. DTE is designed to connect to DCE.
Network speed This is the bit rate on the RF link between units. Could be different from COM
port baud rate.
PLC Programmable Logic Controller. An intelligent device that can make decisions,
gather and report information, and control other devices.
RDS Radio Diagnostic Software. This software allows local and remote diagnostics of
Integra-T.
RRSS Remote Radio Setup Software. (Future expansion software package)
RSS Radio Service Software. This software allows configuration and testing of Inte-
gra-T.
RTS Request to Send. RS-232 input signal to Integra-T indicating that the DTE has
data to send. RTS may optionally be used as a transmit switch for Integra-T.
RTS mode A mode of operation in which Integra-T begins a transmission when RTS is
raised, and continues transmitting until RTS is dropped.
RTU Remote Terminal Unit. A SCADA device used to gather information or control
other devices.
SCADA Supervisory Control And Data Acquisition. A general term referring to systems
that gather data and/or perform control operations.
SETUP Port The configuration / diagnostic port of Integra-T. This port is designed to be con-
nected to a PC running the Integra RSS program.
Transparent A transparent unit transmits all data without regard to special characters, etc.
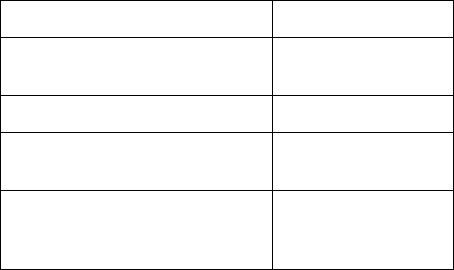
120 4010x-002 1Integra TR Technical Manual
1. PRODUCT OVERVIEW
This document provides the information re-
quired for the installation, operation and main-
tenance of the Dataradio Integra-TR radio-
modem.
1.1 Intended Audience
This manual is intended for use by system de-
signers, installers and maintenance technicians
1.2 General Description
Integra-TR is a high-speed transparent radio-
modem, FCC refarmed compliant, designed
specifically to fit the needs of SCADA,
telemetry and control applications. Integra-TR
provides the communication links among data
equipment for installations where wired com-
munication is impractical.
Integra-TR will work with most makes and
models of RTU, PLC and with their protocols
(usually polling). Configuration settings allow
tailoring for a variety of applications.
Integra-T supports:
1. Point to point Master–Slave or Peer to Peer
configurations in simplex or half-duplex
modes.
2. Point to multipoint Master–Slave configur-
ation in simplex or half-duplex modes.
Settings and connections for these configura-
tions are given later in this manual.
1.2.1 Characteristics
Integra-TR has the following characteristics:
• Selectable network speeds of 4800, 9600 for
half channel units and 4800, 9600 and
19.200 b/s for full channel units.
• Backward compatible with the Integra-T for
bit rate of 4800 and 9600 b/s (full channel
units only)
• One COM port for connection to DTE.
Speeds 300 - 19200 bauds.
• One Setup port, for configuration and
diagnostics.
• Built-in 5-watt transceiver, operating in the
VHF, UHF or 900 MHz communications
bands. Half-duplex or simplex operation.
• Fully transparent operation with error-free
data delivery.
• Allows transmission of “break” characters.
• DOX (Data Operated Transmit) or RTS
mode.
• Stations may be set as “master” or “remote”
to prevent remote stations from hearing each
other.
• Full local and remote diagnostics
• Two 8-bit analog inputs (0 - 10V).
• Low power consumption modes: “sleep”
and “suspend” modes (nominal 7mA).
• “12 VDC, negative ground”, device.
1.2.2 Accessories and options
Table 1 Integra-T Accessories and options
Accessory DR Part #
Local RSS & RDS software kit
(diskette and setup/data cable) 085 03281-0xx
Technical manual 120 40101-xxx
SMA Male – BNC Female
adapter 685 00832 –000
Cooling fan – factory option
(for high duty-cycle transmit
applications)
Catalog number /F
suffix.
For continuous-transmit applications, the “TX
Timeout” timer must be turned off (set to “dis-
able”) via the Radio Service Software (RSS).
1.3 Configuration
Operating characteristics of Integra-TR are con-
figured by means of Integra-TR’s Radio Service
Software (RSS) available from your sales repre-
sentative. Also available is Integra-T’s Radio
Diagnostic Software (RDS) which permits both
local and remote diagnostics. Remote Radio
Service Software (RRSS) to allow remote pro-
gramming is a future expansion. The RSS, RDS
and RRSS (future option) programs are MSDOS
based and will run on any 486 or higher PC (2
Megabytes memory required).
Integra-TR requires the use of the RSS for
both configuration and adjustment.
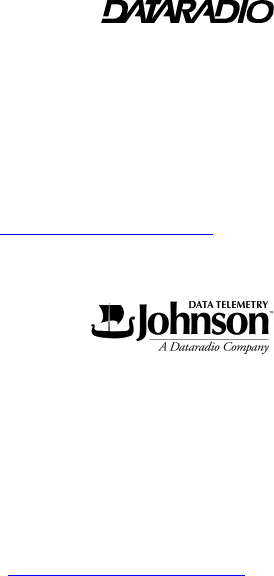
120 4010x-002 2Integra TR Technical Manual
1.4 Factory Technical Support
The Technical Support departments of Datara-
dio and Johnson Data Telemetry (JDT) provide
customer assistance on technical problems and
serve as an interface with factory repair facili-
ties. Technical support hours are respectively:
for Dataradio, 9:00 AM to 5:00 PM, Eastern
Time, Monday to Friday and for JDT, 7:30 AM
to 4:30PM, Central Time, Monday to Friday.
Technical support can be reached in the fol-
lowing ways:
For equipment purchased from Dataradio:
Dataradio Inc.
5500 Royalmount Ave, suite 200
Town of Mount Royal
Quebec, Canada H4P 1H7
phone: +1 514 737-0020
fax: +1 514 737-7883
Email address: support@dataradio.com
For equipment purchased from JDT:
Johnson Data Telemetry Corp.
Customer Service Department
299 Johnson Avenue, P.O. Box 1733
Waseca, MN 56093-0833
phone:1-800-992-7774 and
+1-507 835-6408
fax: +1-507-835-6648
Email address: support@johnsondata.com
1.5 Product Warranty
Warranty information may be obtained by con-
tacting your sales representative.
1.6 Replacement Parts
This product is normally not field-serviceable,
except by the replacement of complete units.
Specialized equipment and training is required
to repair logic boards and radio modules.
Contact Technical Support for service informa-
tion before returning equipment. A Technical
Support representative may suggest a solution
eliminating the need to return equipment.
1.6.1 Factory Repair
When returning equipment for repair, you must
request an RMA (returned merchandise authori-
zation) number. The Tech Support representa-
tive will ask you several questions to clearly
identify the problem. Please give the represen-
tative the name of a contact person, who is fa-
miliar with the problem, in case questions arise
during servicing of the unit.
Customers are responsible for shipping charges
for returned units. Units in warranty will be re-
paired free of charge unless there is evidence of
abuse or damage beyond the terms of the war-
ranty. Units out of warranty will be subject to
service charges. Information about these charges
is available from Technical Support.
1.7 Physical Description
Integra-TR consists of a logic PCB (which in-
cludes the modem circuitry) and a separate radio
module. The two boards plug directly together
and slide into the rails of an extruded aluminum
case. DTE connection is made via a front panel
connector. Power is applied through a connec-
tor, which also includes analog inputs, on the
rear panel. The unit is not hermetically sealed
and should be mounted in a suitable enclosure
where dust and/or a corrosive atmosphere are
anticipated. There are no external switches or
adjustments; operating parameters are set using
the RSS.
1.8 Diagnostics
Integra-TR has sophisticated built-in diagnostics
that may be transmitted automatically without
interfering with normal network operation. In
addition, commands to generate test transmis-
sions, etc., may be issued either locally or re-
motely.
Diagnostic information takes one of two forms:
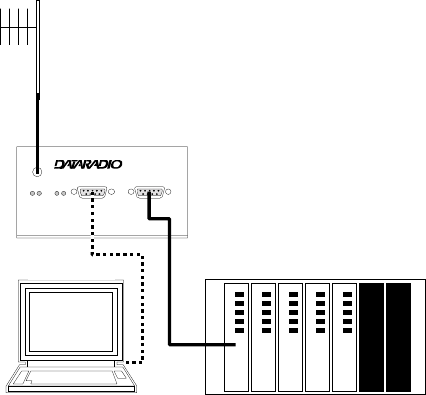
120 4010x-002 3Integra TR Technical Manual
Online diagnostics. Information is auto-
matically sent by each unit at the beginning
of every data transmission.
Offline diagnostics. Information is sent by a
specific unit in response to an inquiry made
locally or from another station.
Diagnostics are processed using the Integra-TR’
RDS.
1.8.1 Remote Commands
The upcoming Integra RRSS will allow config-
uring most functions and adjustments remotely
via the radio network.
Sending remote commands and receiving re-
sponses is done with the host application off-
line.
1.9 Firmware Upgrades
Integra-TR’s firmware resides in flash EPROM
and is designed to allow field upgrades.
Upgrades are done using a PC connected to In-
tegra-TR and do not require that the unit be
opened.
1.10 Network Application
Integra-TR is suited to a variety of network ap-
plications. Its primary design goal was to satisfy
the needs of SCADA systems using RTUs or
PLCs in either point to point or point–multipoint
service.
This section gives an overview of some common
configurations. Selection of “master” or “re-
mote” as well as data delivery conditions is
done using the Integra RSS.
1.10.1 RF Path and Communications
Range
Integra-TR is designed for use over distances up
to 30 miles (50 km) depending on terrain and
antenna system. To assure reliable commun-
ications, the RF (radio frequency) path between
stations should be studied by a competent pro-
fessional, who will then determine what anten-
nas are required, and whether or not a repeater is
needed.
1.10.2 Basic Connections
The connections required (except power) are
shown below in Figure 1.
While an RTU or PLC is shown in the diagram,
master stations often use a PC running an appli-
cation designed to communicate with remote
RTUs or PLCs.
The Setup PC is used for both configuration and
local and remote diagnostics. It may be left con-
nected at all times if desired, but is not required
for normal operation once the unit has been con-
figured.
Integra
®
Antenna
Integra
Setup PC
RTU or PLC
Figure 1 - Basic connections required
1.10.3 Common Characteristics
The networks described below share a number
of common characteristics.
1. The network speed (4800 or 9600 b/s) must
be the same for all stations in a network.
2. Unless otherwise noted, the default setting
of station type is “master” and data delivery
is “all”.
3. Transmission of online diagnostics may be
enabled or disabled at any station or stations
without affecting their ability to commun-
icate with other stations.
1.10.4 Point to Point System
A simple point to point connection is shown
below:
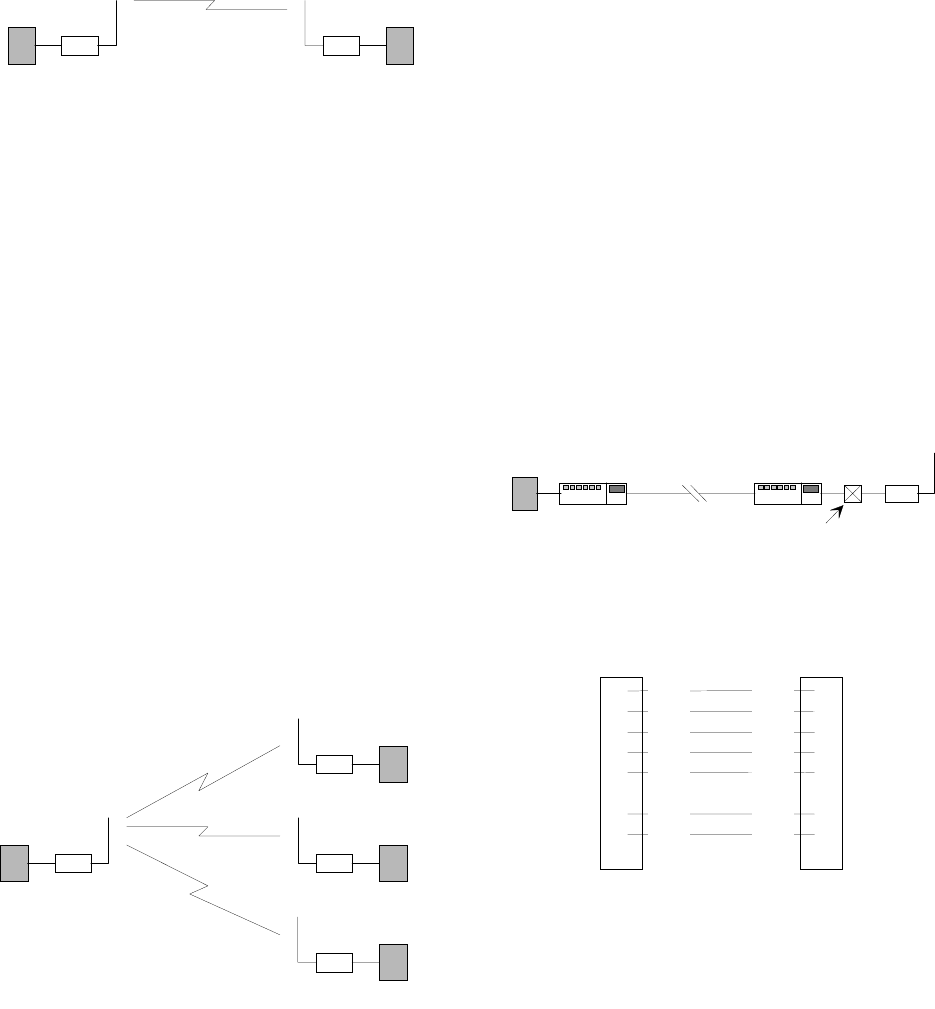
120 4010x-002 4Integra TR Technical Manual
DTE Integra DTE
Integra
Figure 2 - Point to Point System
In such a system, the user’s equipment (DTE)
may be set up in either a peer-to-peer or a mas-
ter slave configuration. The Integra-T’s may be
left in their default configuration, which is:
1. Both units set as “master”.
2. Both units set to deliver “all” data transmis-
sions.
Two other configurations that would work
equally well are:
1. One unit set to “master”, the other to “re-
mote”, delivery set to either “all” or “selec-
tive” data transmissions.
2. Both units set to “remote”, data delivery set
to “all”.
1.10.5 Point–Multipoint System
A basic point–multipoint system is shown
below:
remote
remote
remote
master
Figure 3 - Point–Multipoint System
If a half-duplex radio network is used (i.e. two
frequencies with the master station transmitting
and receiving on the reverse pair from the re-
motes) the Integra-TR’s may be left in their de-
fault configuration (station type “master” and
data delivery “all”). The master station can be
either full duplex or half-duplex.
If a simplex radio network is used (i.e. a single
frequency for all stations) we recommend that
the master Integra-TR be set to “master”, the
remotes to “remote” and all units to “selective”
data delivery. This will prevent remote stations
from hearing each other’s responses. Use this
setting also if a full duplex repeater is used.
1.10.6 Extending a Landline (Tail
Circuit)
Integra-TR may be used to extend a landline
circuit (giving access to difficult locations, etc.).
This type of connection is called a “tail circuit”
and is shown in Figure 4 below. The tail circuit
assembly may be used in any of the network
types described in the preceding sections.
line
modem line
modem
dedicated
line Integra T
DTE
DCE crossover
cable
Figure 4 - Tail Circuit
Note: The line modems should be full duplex
units.
1
2
3
4
5
6
7
8
9
DE-9M
7
3
2
8
5
1
4
DE-9M
DCD
RXD
TXD
DTR
GND
RTS
CTS
RTS
TXD
RXD
CTS
GND
DCD
DTR
Figure 5 - DCE Crossover Cable for RTS-CTS mode
However, some point-to-point FDX landline
modems or line drivers may require the use of
DOX mode and an alternate pinout for two of
the above lines.
All other lines remain as shown in Figure 5
above.
8
CTS
RTS
7
1
DCD
DTR
4
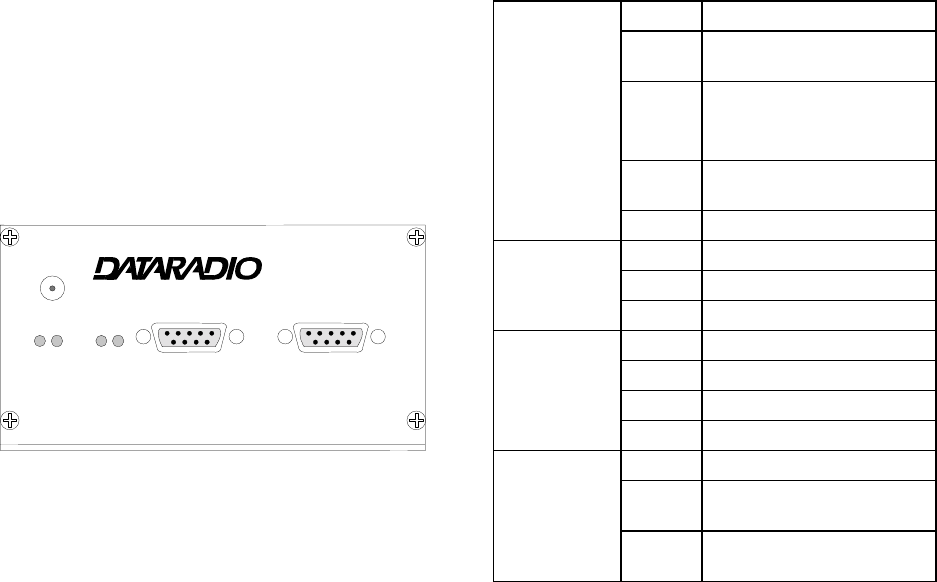
120 4010x-002 5Integra TR Technical Manual
2. Features and Operation
2.1 Overview
This chapter describes the connections,
indicators and operating characteristics of
Integra-TR.
2.2 Intended Audience
This chapter is intended for system design and
installation personnel.
2.3 Front Panel
Integra
®
ANT
SETUP COM
RUN CS RX RD
PWR SYN TX TD
Figure 6 – Integra-T front panel
The various front panel elements are described
in the following sections.
2.3.1 Antenna Connector
Antenna connector is a type SMA-female, 50
ohms.
Testing must be done with a 50-ohm dummy
load. Units operated with a “rubber duck” an-
tenna connected directly to the antenna con-
nector may exhibit unusual operating character-
istics and high levels of reverse power.
2.3.2 LED Indicators
Integra-TR has four two-color LED indicators.
Functions are shown in the following table:
RUN/PWR green normal operation
flash
green sleep mode (flashes dur-
ing wakeup)
flash
red &
green
setup mode, or loading
new application or new
bootloader
flash
red firmware error *
red CPU or PROM failure *
CS/SYN off no RF carrier
green Receive carrier present
red (reserved)
RX/TX off Idle
green receiving network data
yellow synthesizer unlocked
red transmitter is on
RD/TD off Idle
green RX data outgoing from
RS-232 port
red TX data incoming at RS-
232 port
* Contact technical support.
2.3.3 Connection to DTE
Integra-TR is configured as DCE. Most DTE
should be connected using a 9–conductor pin to
pin “straight” cable.
Some RTUs or PLCs may require a special ca-
ble to route the signals correctly. See the docu-
mentation for your data equipment for further
information.
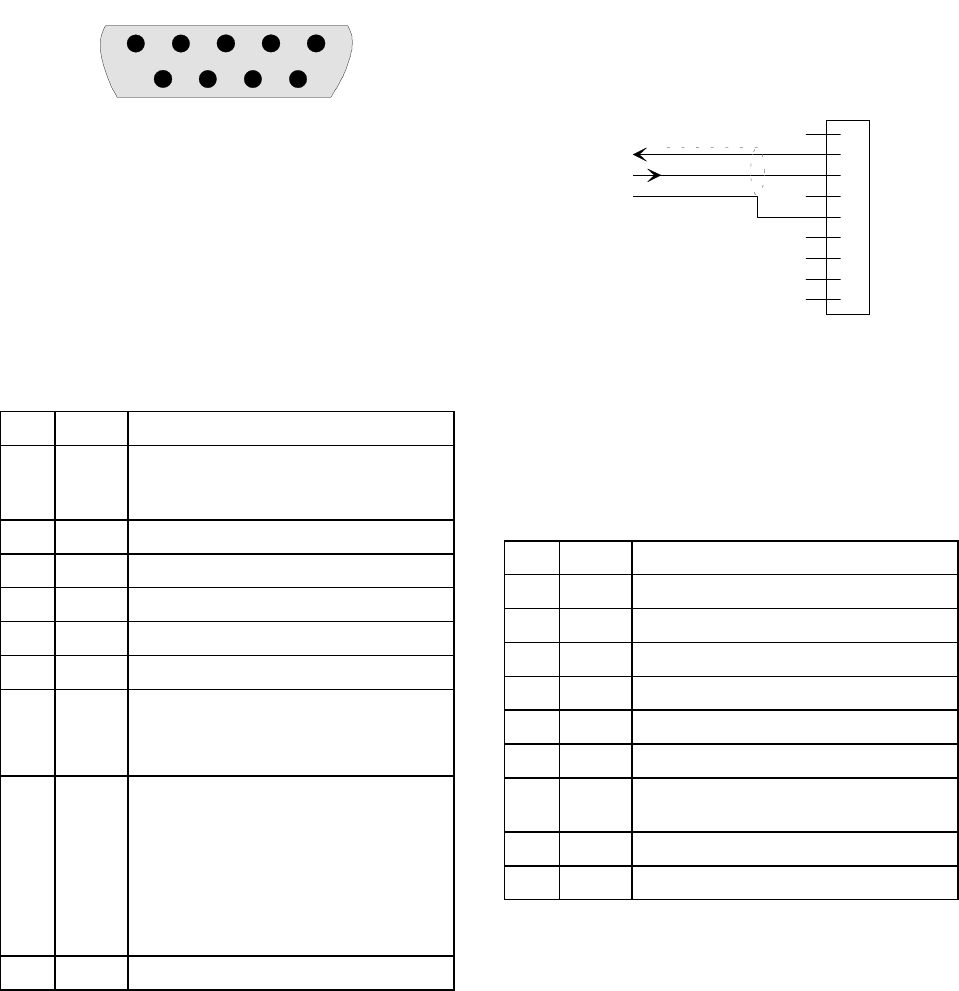
120 4010x-002 6Integra TR Technical Manual
2.3.3.1 Connector Pinout
For reference, the DE-9 F pinout is shown be-
low:
12345
6789
Figure 7 – COM and Setup Port connectors pin locations
2.3.4 Com Port
Baud rates from 300 – 9600 are supported. Un-
less required by your operating protocol, we
advise restricting port speed to be equal to or
less than the RF network speed.
Table 2: COM port signals
Pin Name Function
1 DCD Output: Always asserted or asserted
when RX data available (selectable
via RSS)
2 RXD Output: Data from Integra-T to DTE
3 TXD Input: Data from DTE to Integra-TR
4 DTR Input: Ignored
5 GND Signal and chassis ground
6 DSR Output: always positive (asserted)
7 RTS Input: Used as a “begin transmission”
signal in RTS mode.
Will “wake up” a unit in sleep mode.
8 CTS Output: Used for handshaking in RTS
mode and used for flow control in
DOX mode.
RTS mode: RTS/CTS delay is 4ms.
DOX mode: CTS always asserted,
except when data overflow is de-
tected.
9 RI Not internally connected, reserved
2.3.4.1 3-Wire Connection (DOX)
For DTE that lack RTS control, Integra-TR can
operate in DOX mode (Data Operated Transmit)
with only Transmit Data, Receive Data and
Ground (“3-wire interface”). Integra-T also sup-
ports CTS flow control for cases where the ter-
minal rate exceeds the network rate.
1
2
3
4
5
6
7
8
9
RXD
TXD
GND
DE-9M
Figure 8 – 3-wire interface
2.3.5 Setup Port
The Setup port uses a DE-9 female connector
configured as DCE. Signals are described in the
following table.
Table 3: Setup Port signals
Pin
Name
Function
1
DCD
Tied directly to DTR.
2
RXD
Data from Integra-T to setup PC
3
TXD
Data from setup PC to Integra-TR
4
DTR
Tied directly to DCD.
5
GND
Signal and chassis ground
6
DSR
Output; always positive (asserted)
7
RTS
Tied to CTS. Also monitored to “wake
up” unit from sleep mode.
8
CTS
Tied to RTS.
9
RI
not internally connected, reserved
The Setup port uses a proprietary commun-
ications protocol designed to work with the In-
tegra RSS, the upcoming RRSS and the RDS
programs. It is also designed to provide numeric
diagnostics information when connected to a PC
terminal emulator. For the format, see section
2.6.1.2.
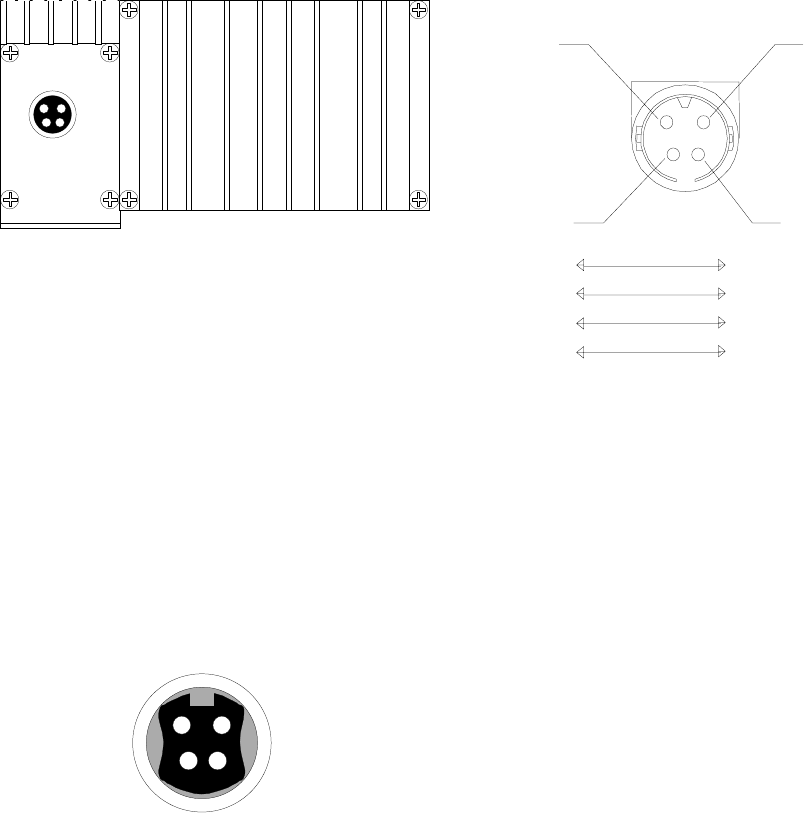
120 4010x-002 7Integra TR Technical Manual
2.4 Rear Panel
Figure 9 – Integra-T rear panel
The various elements are described in the fol-
lowing sections.
2.4.1 Heat Sink
The rear panel heat sink is essential for proper
operation of the Integra-TR transmitter. The unit
must be mounted in a location that permits free
air circulation past the heat sink. Cooling will be
best if the fins are vertical.
2.4.2 Power / Analog connector
The 4 pin power / analog connector pinout is
shown below:
+13.3 VDC (1) (2) GND
Analog in 1 (3) (4) Analog in 2 /
RX-TP
(red) (black)
(white)
(green)
Figure 10 - Power / Analog Connector
2.4.2.1 Power
Integra-TR’s power requires a filtered power
source of 13.3 VDC nominal (10 – 16 VDC
max.), negative ground with a 3.0 A rating.
An internal 3A fuse (surface-mount and not
field-replaceable) and a crowbar diode protect
the main RF power components from reverse
polarity. Application of more than 16 VDC will
damage the unit and is not covered by the war-
ranty.
WARNING: Do not exceed 16Vdc.
Power / Analog cable
PIN 4 PIN 3
PIN 2 PIN 1
SIGNAL2
SIGNAL1
GROUND
POWER
WHITE
GREEN
BLACK
RED
PIN 2
PIN 1
PIN 3
PIN 4
Figure 11- Power / Analog cable
2.4.2.2 Analog inputs
Two analog inputs are provided. Inputs are
scaled to 0–10 V and have a resolution of 8 bits
(1 part in 256). Inputs are referenced to chassis
ground.
The absolute maximum input voltage should be
no greater than 20 Vdc. These inputs are re-
verse-voltage protected.
Integra-TR allows the analog values to be read,
either locally or remotely, using the Offline Di-
agnostics function of the Integra RDS.
Analog in 2 (pin 4) can be switched (using the
Integra RSS) to perform as the demodulated sig-
nal level test point (RX-TP) which is half of the
voltage read at the RSSI bar graph.
If the analog inputs are not used, the green and
white wires should be cut back and/or taped to
prevent contact.
2.5 Operation
Integra-TR is designed for fully transparent op-
eration. This means that all binary values are
transmitted as data, with minimum time delays,
and without regard to their binary value.
“Break” signals can also be transmitted.
120 4010x-002 8Integra TR Technical Manual
Unlike most transparent radiomodems, Inte-
gra-TR eliminates “bit dribble” and allows DOX
operation. A CRC-16 error check is used so that
faulty data will not be delivered.
2.5.1 Operating Modes
Integra-TR has two operating modes, for its
COM port: (selectable via the RSS program)
DOX mode: The RS-232 port is monitored for
incoming data. Upon receipt of the first data
byte, the transmitter is turned on. The RTS
signal is ignored (note: RTS may still be
used as a wakeup signal for a unit that is
asleep).
RTS mode: The RTS signal is monitored for a
low–to–high transition. This transition
causes Integra-T to turn on its transmitter.
CTS is raised 4 ms later to accommodate
DTE that requires a CTS transition before it
can send data. The transmission will con-
tinue until RTS is dropped, or until the Tx
Timeout (see section 2.9) expires.
CTS is used as a handshaking/flow control sig-
nal in both modes. If Integra-T’s buffers fill,
CTS will be dropped as a signal to the DTE to
stop sending data. This condition is most likely
when the Data port speed exceeds the radio
network speed. In such cases, reduce the DTE
baud rate so that Integra-T buffers will not fill.
2.5.2 Data Forwarding Timer
The data forwarding timer can modify the tim-
ing between data blocks in a transmission to
accommodate some RTU’s special timing re-
quirements. Set to “normal” (15 ms) unless ad-
vised otherwise by technical support. Do not use
“fast” (5 ms) timer below 2400 b/s.
2.5.3 Sending Break Signals
Integra-TR may be configured to send “break”
signals, as required by some SCADA user pro-
tocols. A break signal is generated by holding
TXD in the zero state for longer than one char-
acter time. Indication of a break signal is carried
in a special data transmission to the remote sta-
tion, which in turn generates its own output
break signal.
At a port speed of 9600 b/s, the output break
signal has a duration of 10 to 20 ms, regardless
of the duration of the input break signal. These
times are scaled proportionally for other baud
rates. Integra-TR may also be set to ignore
“break” signals in order to prevent spurious
transmissions when terminal equipment is pow-
ered on and off.
2.5.4 COM Port Baud Rates
The COM port operates at standard baud rates
from 300 – 19200 b/s. Baud rate is set using the
Integra RSS and is independent of the network
speed setting.
We recommend that the COM port baud rate
be set to a speed not greater than the network
speed. Setting a COM port baud rate higher than
the network rate may result in data buffers fill-
ing, which in turn may cause Integra-TR to drop
CTS. This could have detrimental effects on
some protocols, particularly those that ignore
CTS.
The COM port will support 7 or 8 data bits, one
or two stop bits, and even, odd or no parity. Se-
lection is made via Integra RSS. These parame-
ters may be set differently on various Integra-T
units without affecting their ability to communi-
cate with each other.
2.5.5 Diagnostics
Online diagnostics may be included as part of an
extended header at the beginning of each trans-
mission. It may be enabled or disabled on a per-
unit basis without affecting inter–commun-
ication. Reception of online diagnostics is al-
ways enabled.
Enabling this option adds about 5 ms delay at
9600 b/s (10 ms at 4800 b/s) to each trans-
mission, but has no other effect on network op-
eration.
Online diagnostics for all audible stations is de-
livered out at the Setup Port. An ASCII diag-
nostic output is also available. Diagnostic in-
formation is normally collected at the master
station.
120 4010x-002 9Integra TR Technical Manual
Offline diagnostics are sent upon receipt of a
command from the Integra RDS, normally when
the host application is stopped or taken offline.
Since diagnostics transmissions are not under
the control of the SCADA user protocol, tempo-
rary network disruption will occur if both are
attempted simultaneously.
2.5.6 Addressing
Each Integra-TR is associated with three identi-
fication numbers (addresses):
ESN: The Electronic Serial Number is uniquely
assigned to each Integra-TR at time of manu-
facture and cannot be changed. It is identical
to the serial number printed on the label of the
unit. Integra-T uses this number for ident-
ification only; it does not form part of the on–
air protocol. The ESN of a remote unit may be
viewed with the RDS by doing a Remote GET.
Short ID: The short ID (maximum value of 254)
is used to identify Integra-TR for purposes of
diagnostics (both online and offline), remote
configuration and commands. The default
value of the short ID (set at factory) is calcu-
lated from the ESN. This value may be
changed via the Integra RSS. It is important
that all stations within a communicating group
have unique short IDs.
Station Type: This is a 1-bit value used to iden-
tify the station as a master or remote. See
2.5.7 below.
2.5.7 Station Type
On a simplex Integra-TR network, all remote
stations can hear the master, and many remote
stations can hear each other. Certain SCADA
user protocols are designed with the assumption
that remote stations can not hear the responses
to polls made by other remote stations.
To allow operation with such protocols in sim-
plex networks, Integra-TR has a simple ad-
dressing scheme. Stations may be designated as
master or remote. This sets a flag in the header
identifying the type of the originating station.
On the receive side, Integra-TR stations can be
set to accept all data, or accept data only if it
originates from a station of the opposite type
(selective). This choice is made by setting Data
Delivery to selective or all using the RSS.
2.6 Online Diagnostics
Online diagnostics, if enabled, are included with
every data transmission. Online diagnostics do
not interfere with normal network operation.
The following information is gathered and de-
livered via the Setup port:
• Unit’s “short ID”
• Inside case temperature: degrees C
• Supply voltage (B+): tenths of a volt
• Local received signal strength: dBm
• Remote received signal strength: dBm
• Forward power: tenths of a watt
• Reverse power: good / poor
• Receive quality: based on last 15 data
blocks received.
2.6.1 Using an External Program
for Online Diagnostics
The Setup port communicates with the RDS
using a proprietary protocol that is not docu-
mented in this manual. However, if a terminal,
or a PC running terminal software, is connected
to the Setup port, online diagnostic information
will be delivered in plain ASCII form.
For the purposes of the following discussion we
will refer to the proprietary data format as
RSS/RDS mode.
2.6.1.1 Initialization
When Integra-TR is powered on, it will attempt
to establish a link with the RSS/RDS and select
its output mode as follows:
1. If RTS is not exerted on the setup port, Inte-
gra-T will immediately switch to ASCII
mode.
2. If RTS is exerted on the setup port, Integra-
T will send an initialization message in
RSS/RDS mode and wait for the proper re-
sponse form the RSS or RDS.
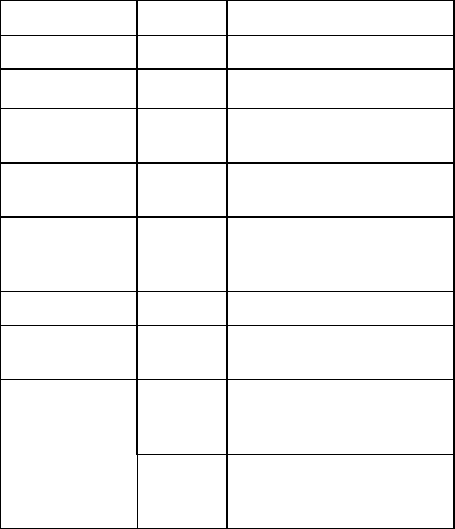
120 4010x-002 10 Integra TR Technical Manual
3. If there is no response, Integra-T will switch
to ASCII mode.
The cleanest interface for a user program exists
if the program initializes the PC serial port with
RTS false. This will disable the RSS/RDS mode
and only ASCII data will be output from the
port.
2.6.1.2 Online Diagnostic String
Format
In ASCII output mode, the setup port will output
a one line diagnostic string each time the unit
receives a transmission from another unit. No
other data will be output. The string consists of
a number of comma-delimited fields terminated
by a carriage return. Each field is a constant
length (with leading zeros if required), regard-
less of the value contained in the field, but the
fields are not all the same length.
The field definitions are shown in the table be-
low.
Name Length Description
Short ID 4 1 – 254
Temperature 3 Signed value in °C
B+ 4 Tenths of a volt from 6.0
to 18.8V
Remote RSSI 4 Signal strength received
by remote station
Local RSSI 4 Signal strength for this
remote as received by
local station
FWD power 4 Tenths of a watt.
Rev power 1 0 = good
1 = poor
RX quality 3 Number of good data
blocks received in the
last 15.
3 Number of total data
blocks detected, maxi-
mum 15.
Note: A data block is about 26 bytes long.
A typical diagnostic string, with its interpreta-
tion, is shown below:
0003,+28,13.1,-093,-088,4.7,1,015,015
Remote station # 3 reports that:
• its internal case temperature is +28°C,
• supply voltage is 13.1 VDC,
• it is receiving a signal of -93 dBm from the
master,
• the master is receiving a signal of -88 dBm
from station 003,
• the forward power is 4.7 watts,
• the reflected power is OK,
• 15 of the last 15 data blocks were received
correctly.
2.6.2 Interpreting Diagnostic
Results
Interpretation of the diagnostic results is similar
for both online and offline diagnostics. Where
differences exist, they will be noted in the text.
For simplicity, we continue to assume that diag-
nostics are being collected at the master station.
2.6.2.1 Short ID
Online diagnostic data is identified by the Short
ID of the unit. Users should make sure that all
units in a communicating group have unique
Short IDs.
2.6.2.2 Temperature
Internal case temperature of sending unit. This
is a 3-digit signed value in degrees C. This value
should remain within the limits of -30ºC to
+60ºC.
2.6.2.3 B+ Voltage
Current value of supply voltage. This is a 4 digit
signed value in volts, e.g. a value of 13.3 indi-
cates 13.3 VDC. This value should remain
within the limits of 10-16 VDC.
2.6.2.4 Remote RSSI
Displays the strength of the last valid data signal
received by a reporting remote unit.
In a polling type network, the last signal usually
originates from the polling master unit.
For the master itself, the last signal received is
that of the remote that answered the previous
poll.
120 4010x-002 11 Integra TR Technical Manual
This is a 4-digit value, including the leading mi-
nus sign, expressed in dBm with a typical accu-
racy of +/- 2dB. For example, a value of -090
indicates a signal strength of -90 dBm.
2.6.2.5 Local RSSI
Displays the strength of the last valid data signal
received by the connected Integra-TR unit. The
format described in the Remote RSSI section
above applies.
2.6.2.6 Interpreting RSSI Readings
Typical values of RSSI will be in the range of
-110 dBm to -60 dBm, with higher values (i.e.
less negative values) indicating a stronger sig-
nal.
Reliability of data reception depends largely on
signal strength. Good design practice calls for a
minimum 30 dB “fade margin”, based on a
threshold reception level of -107 dBm (1 uV) at
speed of 9600 b/s. Experience indicates that this
will give about 99.5% reliability.
Some representative performance values for
9600 b/s operation are given below. These val-
ues assume that the units are correctly aligned
and installed in a quiet location. Environments
with high electrical or RF noise levels will re-
quire an increase in the numbers shown to
achieve a given level of reliability.
-100 dBm. Approximately 50% reliability.
Fading may cause frequent data loss.
-90 dBm. Approximately 90% reliability. Fad-
ing will cause occasional data loss.
-80 dBm. Approximately 99% reliability. Rea-
sonable tolerance to most fading.
-70 dBm. Approximately 99.9% reliability with
high tolerance to fading.
If RSSI values drops seasonally, the most likely
cause is tree foliage, which can interfere with
radio transmissions during the spring and sum-
mer.
2.6.2.7 Forward Power
Approximate measure of transmit power. This is
a 4 digit value in watts rounded to the nearest
tenth. Note that this is an approximate value
that should be used for trend monitoring
only. It does not compare in accuracy with val-
ues obtained by a standard wattmeter.
2.6.2.8 Interpreting Power Readings
The values returned are approximate and should
not be regarded as an absolute indicator of per-
formance. For example, a unit that shows a for-
ward power of 4.5 watts may actually measure
at 5.0 watts on a lab quality wattmeter. For this
reason, these values should not be used to indi-
cate that a unit is out of spec or to compare one
unit to another.
However, the values returned are consistent
over time for any given unit. If statistics are kept
on a unit per unit basis, changes in forward or
reflected power are significant.
Therefore, the following conditions are worthy
of investigation.
1. Forward power output drops or rises by
more than 10% from its established value.
Reflected power remains low.
2. This indicates that the transmitter may need
alignment or that a component may be in
need of replacement.
3. Forward power output drops by more than
10% from its established value. Reflected
power shows an increase.
This indicates a possible antenna or feedline
problem that affects SWR (Standing Wave
Ratio).
2.6.2.9 Reverse Power
Approximate measure of reverse (reflected)
power. The value is returned differently for on-
line and offline diagnostics:
Online: The value returned is 0 if reverse power
is within acceptable limits, 1 if reverse power is
too high. The threshold is set to approximately
1/4 of the forward power value.
Offline: Value is in watts to the nearest tenth.
This value is intended as an indication of an-
tenna problems and will normally be used for
trend monitoring. Ideally it should close to be
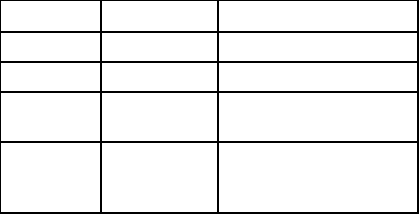
120 4010x-002 12 Integra TR Technical Manual
zero, but values up to about 15% of Forward
Power may be encountered in properly operating
systems.
2.6.2.10 Reverse Power and SWR
A reverse power reading above zero is an indi-
cation that the antenna, feedline or connectors
are damaged, corroded or improperly tuned.
This creates standing waves that are reported as
a Standing Wave Ratio (SWR).
The table below, based on a forward power of 5
watts (it may be scaled for lower power settings)
gives guidelines to interpreting these figures:
Table 4: SWR / Rev Pwr
SWR Rev Pwr Significance
1:1 0 ideal situation
1.5:1 0.2 normal operation
2:1 0.6 should be investi-
gated
3:1 or
greater 1.25 or
greater defective antenna,
feedline or connec-
tors.
In the case that the values returned by the built-
in diagnostics seem to indicate a problem, we
recommend verification by means of proper ra-
dio shop equipment.
2.6.2.11 RX Quality Indicator
This is the number of good received data trans-
missions out of the last 15.
The receive quality indicator value returned by
any remote unit to the master station is an indi-
cation of the reception quality on the outbound
path.
If the master station is monitored, either from a
remote station or by using a local GET STATS,
users should note that the receive quality indi-
cator thus returned is a composite value which
represents the average reception from the last 15
remotes. Any significant drop in the receive
quality indicator returned by the master station
is therefore likely to indicate a problem with the
master station receiver itself, rather than any one
remote station.
2.7 Offline Diagnostics
Offline diagnostics are returned in response to a
specific request to a particular station. Requests
are issued using the Integra RDS, either locally
or remotely from another station. This may
cause slight temporary network disruption.
The diagnostic information available is similar
to that available from online diagnostics with
the following additions:
Demodulated signal voltage: peak-to-peak
Analog 1 input voltage: 0 – 10 V in tenths
Analog 2 input voltage: 0 – 10 V in tenths
Reverse power: tenths of a watt rather than a
good / poor flag.
Note: Analog 1 and 2 have 8 bits of resolution.
120 4010x-002 13 Integra TR Technical Manual
2.8 Low Power Operation
To accommodate users, who operate sites with
limited available power, Integra-TR offers the
following power saving features:
1. Reduced transmit power
2. Suspend mode
3. Sleep mode
2.8.1 Reduced Transmit Power
Integra-TR’s transmitter is type-approved for
power levels less than 5 watts. Simply select the
desired power setting using the Integra RSS.
Reducing transmitter output power from 5 watts
to 1 watt will reduce maximum current con-
sumption by approximately 0.5A to 1.0 A de-
pending on radio model.
2.8.2 Suspend Mode
Note: as long as the RTS is asserted (on any
port), the unit will be kept awake.
In Suspend mode, remote stations remain in
“low power consumption mode” (nominal 7
mA), waking up periodically for about 100 ms
to check the presence of a carrier.
If a carrier is present, the unit will remain awake
for a period of time set by the Activity timeout.
At the end of that time, if a carrier is present or
if data has been decoded, the Activity timeout is
restarted.
If there is no carrier or no data was decoded, the
unit goes into “low power consumption mode”
for the duration of the Suspend period.
The Suspend period can be set via the RSS to
any value between 50 to 12000 ms in 50 ms
steps. Setting a value of 0 disables the Suspend
mode.
The Activity timeout can be set via the RSS to
any value between 1 and 255 seconds.
The same Activity timeout and Suspend period
values must be set for both master and re-
mote stations.
Master stations always remain awake. To make
sure those suspended remotes have time to wake
up for outbound master data transmission, the
master unit will automatically extend its start-
of-transmission synchronization time to slightly
exceed that of the remote stations’ Suspend pe-
riod. This is done only for the first transmission.
If the subsequent master transmissions begin
within the Activity timeout setting, it will then
begin with a normal start-of-transmission syn-
chronization time.
If the delay between master transmissions is
more than the Activity timeout, the next trans-
mission will be extended.
2.8.3 Sleep Mode
In this mode, the unit is always in low power
consumption (nominal 7 mA). Only asserting
RTS on the COM or the SETUP ports can wake-
up the unit. When the unit is sleeping, it cannot
detect the presence of a carrier. This mode can
be selected from the RSS.
The unit will be ready to receive a carrier and
decode data within 45 to 65 ms (depending on
radio model and temperature) after wake-up.
2.8.4 Remote Unit Wake-up by DTE
A Remote Terminal Unit (RTU) connected at an
Integra-TR (configured as remote) can be awak-
ened by raising either RTS inputs.
DOX mode: either COM or SETUP ports RTS
can be used for wake-up. Data from DTE cannot
wake-up the unit.
RTS mode: the SETUP port RTS can be used
for wake-up without causing transmission.
2.9 Transmitter Timeout
Integra-TR is equipped with a 30-second trans-
mitter timeout (Tx Timeout) designed to protect
both Integra-TR itself and the network in case a
transmitter becomes “stuck” on the air.
Should this happen with a remote station, the
master would be unable to hear some or all of
the other remote stations (depending on relative
120 4010x-002 14 Integra TR Technical Manual
signal strength), seriously disrupting network
operation.
The Tx Timeout is fixed at 30 seconds, and may
be enabled or disabled using the Integra RSS.
When active, the Tx Timeout disables the
transmitter. The timer can be reset by cycling
RTS off and back on again. In DOX mode the
timer will reset at the next break in the data
stream that exceeds the value set for the Data
Forwarding Timer. In either case, a new trans-
mission may begin immediately.
If your application software may occasionally
output data for longer than 30 seconds, the TX
TIMEOUT timer may be disabled. Warning:
Transmissions longer than 30 seconds may
exceed the duty cycle rating of the transmit-
ter and lead to shortened life or transmitter
failure.
However, for high-duty-cycle transmit applica-
tions, a fan is available as an option (contact
your sales representative). For continuous-
transmit application, the TX Timeout timer must
be turned off (set to “disable”).
2.10 Optimizing Your System
Detailed system engineering is beyond the scope
of this manual. However, there are some simple
tips that can be used to optimize performance of
a radio based SCADA or telemetry system.
Choose the best protocol. Some SCADA de-
vices allow a choice of more than one operating
protocol. In some cases, performance can be
improved by selecting a different protocol. Your
sales representative can advise you for many
common types of equipment, or a simple trial
and error process can be used to select the one
that performs best.
Check timer settings. Polling protocols issue a
poll, then wait a certain time for a response. In-
tegra-T adds a short amount of delay to each
poll and response (typically in the order of 60 to
70 ms). Timer settings that are too short may
cause erroneous indication of missed polls, in
which case the application may retry or continue
to cycle, ignoring the missed station. In this
case, the response may collide with the next
poll, further increasing errors. Setting an ade-
quate timer margin will avoid problems and
maximize performance.
Avoid flow control. Set the Com port baud rate
to a value less than or equal to the radio network
speed (4800, 9600 or 19200 b/s). In a polling
system, this will prevent buffer overflow with
possible missed transmissions. If the port baud
rate must be set higher than the radio network
speed, you may have to limit message length to
prevent possible buffer overflow. Integra-T will
always exert a flow control signal (CTS
dropped) if buffers are almost full, but not all
DTE honor such signals.
Use the highest suitable port baud rate, without
exceeding the radio network speed. Operating
an RTU at 1200 b/s on a 9600 b/s network will
increase data transmission delays and reduce
system performance.
Evaluate the need for online diagnostics. Ena-
bling online diagnostics increases delays by 5 to
10 ms (depending on speed). In critical appli-
cations, this extra delay can be eliminated by
disabling online diagnostics. Offline diagnostics
(diagnostics on request) remain available.
120 4010x-002 15 Integra TR Technical Manual
3. Maintenance adjustments
3.1 Overview and Mainte-
nance intervals
This chapter outlines the basic adjustment pro-
cedures required upon initial installation and
thereafter at annual maintenance intervals or
whenever deterioration in performance indicates
that adjustment may be required. Units are de-
livered from the factory properly aligned and
tested on the frequencies specified at time of
order. Adjustment beyond that described in this
chapter is not required unless radio modules
have been tampered with or repaired. In such
cases, we recommend complete factory re-
alignment, as special test jigs are required.
3.2 Intended Audience
This chapter is intended for use by installation
and maintenance personnel.
3.3 Equipment Required
The adjustments described below require the
following equipment:
1. 13.3 VDC / 5A regulated power supply.
2. Radio service monitor (IFR or equivalent).
3. Cable with SMA connector to connect Inte-
gra-T to the service monitor.
4. Integra Radio Service Software (RSS) kit.
5. A PC 486 or better to run the RSS.
6. Normal radio shop tools including align-
ment tools.
3.4 Test Point
For trouble shooting aid, there is one test point
available at pin 4 of the power/analog connector
(white wire). This demodulated signal meas-
urement is half the voltage read at the RSSI bar
graph.
Note: the RX-TP mode must be selected using
the Integra RSS.
3.5 Basic Adjustments
Basic adjustments to be performed are:
1. Transmitter power output
2. Transmitter frequency
3. Transmitter deviation
4. Demodulated signal level
5. Carrier Sense
3.5.1 Preliminary Steps
Important Note: Before proceeding make
sure that the service monitor has been cali-
brated recently and has warmed up for at
least the time specified by its manufacturer.
Some reported frequency and deviation prob-
lems have actually been erroneous indications
from service monitors that have not adequately
warmed up. This is particularly likely when
field service is done during winter months.
1. Connect the Integra-TR’s antenna connector
to the input of the service monitor using a
suitable length of 50-ohm cable. That input
should be able to support at least 5 watts.
2. Connect Integra-TR to a suitable power
supply and adjust the supply voltage to 13.3
volts (16 VDC maximum).
3. Using a suitable 9-conductor straight RS-
232 cable, connect the unit’s Setup port to
the RS-232 port of a PC and run the Integra
RSS program (INTRSS.exe) on the PC.
4. Press GET to get the configuration from the
unit.
5. From the Radio Settings window, accessed
by double-clicking the Radio Settings icon,
set the frequency to be used for testing.
Leave this window open and on top.
6. Follow the steps in the Table 4.
3.5.2 After Adjustments are Done
Adjustments made using the RSS are temporary
and must be made permanent as follows:
1. After all adjustments are completed satis-
factorily, press “PUT” to save the changes
permanently to the unit.
2. Press Station Reset to activate all configu-
ration changes.
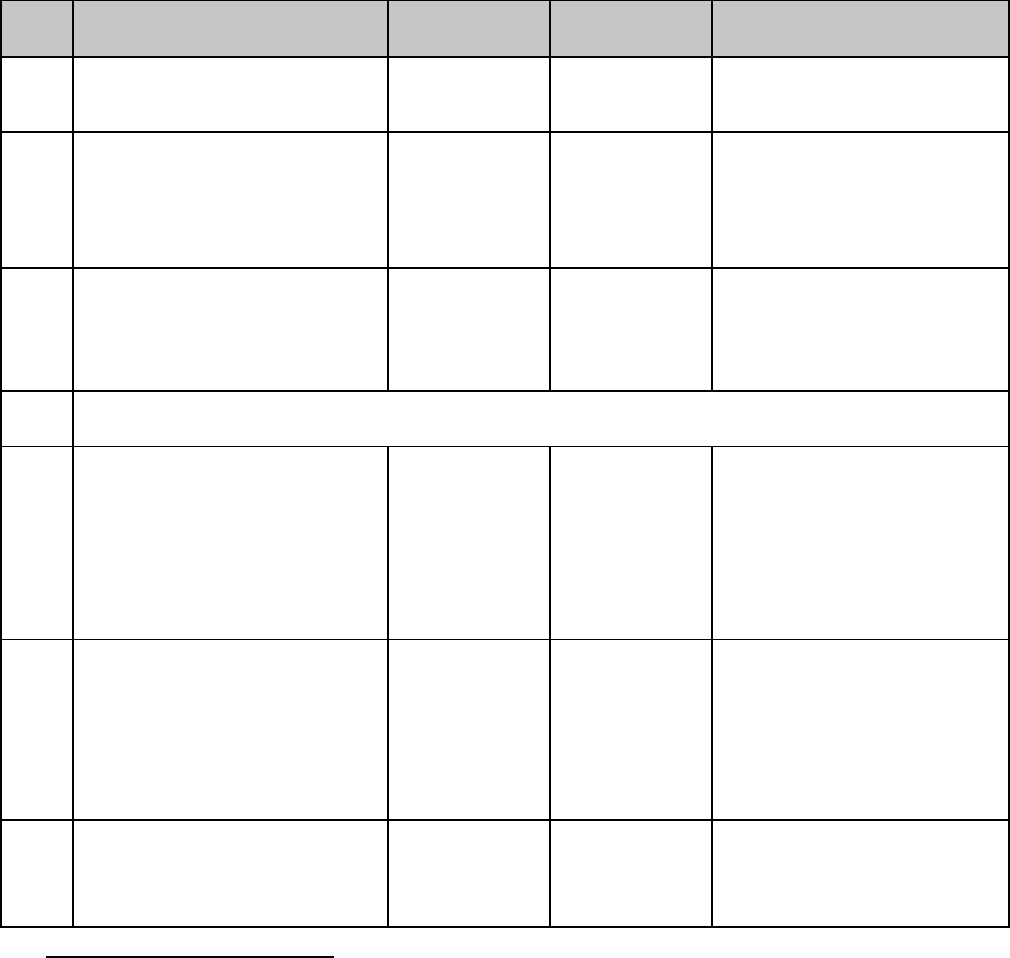
120 4010x-002 16 Integra TR Technical Manual
Table 5: Tests and adjustments half and full channel units
STEP ACTION EXPECTED
RESULTS MEASURE
WITH IF NOT?
1Output Power
Press TX Unmod
5 W1 +10%,
-20%
Service monitor
set to read power Adjust using the RSS Power Out
setting (255 is the maximum) or,
Refer to factory tech support.
2Frequency Error
Press TX Unmod
Within ± 300 Hz Service monitor
set to read fre-
quency
Adjust using the RSS Freq Warp
setting.
(Typical adjustment range is
1.5KHz) If found outside limits,
user is to call factory technical
support.
3Deviation
Press TX tone
For any bit rate speeds selected
Tol. +5%, -10%
For Full channel:
±4.0 kHz
For Half channel:
±2.5 kHz
Service monitor
set to read de-
viation with mid
(15-30 kHz) IF
filter.
Adjust using the RSS Deviation
setting if required.
4 Set the service monitor to generate a -80 dBm signal on the selected receive frequency. The signal should be
modulated with a 1.0 kHz tone at ± 3 kHz deviation. Set service monitor IF filter to mid (15-30 kHz), no audio filter.
5Demodulated Audio
Press CHK
For any bit rate speeds selected:
• For Full channel unit, set gen-
erator deviation to ±4.0 kHz
• For Half channel unit, set gen-
erator deviation to ±2.5 kHz.
2.0 Vpp ± 0.2 Bar graph in Ra-
dio Settings win-
dow.
Adjust using RXA adjust setting if
required.
612 dB SINAD
Set service monitor IF filter to mid
(15-30 kHz).
• For Full channel unit, set de-
viation to ±3 kHz.
• For Half channel unit, set de-
viation to ±1.5 KHz
≤ 0.5µV2Service monitor
set for SINAD. Refer to factory tech support
Note: Connect to the test audio
pin 4 of the power/analog con-
nector (white lead)3
7Distortion
Set service monitor IF filter to mid
(15-30 kHz).
< 3% Service monitor
set for
DISTORTION.
Refer to factory tech support.
Note: Connect to the test audio
pin 4 of the power/analog con-
nector (white lead)3
1 (unless you have set a lower value). Note that readings less than 5 watts may be due to losses in the cables used for testing. Check
also your wattmeter frequency calibration curve. Do not be too ready to condemn the transmitter.
2 if a psophometrically weighted filter is available on the service monitor, use 0.35 µV.
3 in the RSS’ Analog connector window, Check the RX-TP box. (Accessed by double-clicking the Analog Connector icon).
120 4010x-002 17 Integra TR Technical Manual
4. Circuit Description
4.1 Overview
This chapter describes the circuit operation of
the logic board.
4.2 Intended Audience
This chapter is intended for use by engineering
and service personnel.
4.3 Circuit Description
Refer to Figure 12 when reading the following
sections.
4.3.1 Microprocessor Circuit
For the microprocessor section, two Z84015
CMOS low power Intelligent Peripheral Con-
trollers are used. Each IPC is an 8-bit micro-
processor integrated with CTC, SIO, PIO Clock
Generator Controller and Watch Dog Timer.
One of the Z84015s (U17) is used in the normal
mode. The other Z84015 (U21) is used in the
evaluation mode and as such only the CTC, SIO
and PIO section are used. The CPU section is
disabled.
The first Z84015 Clock Generator uses a
19.6608 MHz crystal which provides a CPU
clock rate of 9.8304 MHz for both Z84015s. The
9.8304 MHz clock is further divided by 2 to
feed all 8 CTC (4 in each Z84015).
The 64K memory space of the Z84015 is di-
vided into two blocks of 32k each. The lower
32K is used for the firmware program and the
upper 32K by the CMOS RAM (U18). ). The
memory IC used for the program is a CMOS
FLASH (U22) with 1024 sectors of 128 bytes
each.
The dual Z84015 circuit provides up to 8 CTC,
4 SIO (Serial I/O) and 32 PIO (Parallel In-
put/Output) lines.
The CPU also provides the clock for the CPLD
modem.
4.3.2 RS232
The RS232 IC (U15) is used to interface the
application DE-9 connector to the SIO_B sec-
tion of U17, and the set-up DE-9 connector to
the SIO_A section of U21. When in sleep mode,
two receivers remain enabled, this is needed for
fast wakeup.
4.3.3 MODEM
The modem section is used to interface the se-
rial digital data to the transceiver.
The CPLD modem IC (U16) with a program-
mable Raise–Cosine filter (U10), operates in
DRCMSK mode at 4800, 9600 and 19200
bits/sec. It incorporates a 7-bit hardware scram-
bler and uses Differential (NRZI) encoding in
DRCMSK mode to minimize data pattern-
sensitivity. Electronic potentiometer U5B (E-
Pot), controlled by CPU U17, is used to set the
transmitter deviation by amplitude adjustment of
the baseband signal. Electronic potentiometer
U5C is also provided to adjust the frequency of
the RF carrier.
4.3.4 TRANSMIT & RECEIVE DATA
Transmit Data from the RS-232 port is level-
shifted to TTL by U15, then passed through the
CPU for further processing and convertion from
asynchronous to synchronous format. The
CPLD modem, U16 takes the digital data
stream from SIO-A of the CPU and synthesizes
to the constant-amplitude analog baseband sig-
nal, which is filtered by U10, buffered by U9B
then applied to radio module TXA at P1-6.
Received signals are applied to the RXA pin on
P1-13 amplified by U3A, whose gain is set by
the electronic potentiometer U5D, and then fil-
tered by U10. The same filter circuit is used for
transmission and reception: two analog multi-
plexer/demultiplexer gates (U8A and B) con-
trolled by TX_EN line are used for sharing. The
filter U10 cut-off frequency is programmable by
the CPLD, based on the data rate. The analog
signal is then buffered by U1D and fed to Peak
Detectors U3C, U3D and U3B, and to the slicer
circuit U1C via U1B. The raw data is then
passed to the CPLD modem U16 for descram-
bling and receive clock recovery. The resulting
120 4010x-002 18 Integra TR Technical Manual
synchronous bit stream is then fed to CPU, SIO-
A for further processing and convertion to
asynchronous format before delivery to the RS-
232 driver and to the user port.
4.3.5 Integra-R A/D and DIGIPOT
An 8 channel, 8-bit successive approximation
A/D converter, type ADC0838 (U4), is inter-
faced to CPU (U17) and Peripheral (U21).
CH0 and CH1 are connected to the positive and
negative peak detector of the modem section.
The software can thus read the positive or nega-
tive value of an RX signal, or using the differ-
ential mode, the actual peak-to-peak RX signal
value.
CH3 is used to measure the radio RSSI signal
which was amplified by U7A.
CH4 is connected to the radio diagnostic signal
(P3-14). This pin is used to output an analog
signal corresponding to the power output and
the reflected signal.
CH5 is connected to U6 (LM50), a temperature
sensor with a -40 to +125°C range.
CH6 is used to read the SWB+ voltage after
proper scaling into the 0-5 V range.
CH7 and CH8 are connected to EXT SIGNAL 1
and 2. A 2:1 divider and protection circuit is
inserted between both external signals and the
A/D.
The EXTERNAL SIGNAL 1 and 2 pins are also
connected to U21 at PB6 and PB7 through tran-
sistors Q3 and Q4, and thus can be used for
ANALOG INPUT or DIGITAL OUTPUT
(available on some Integra versions).
EXT_SIGNAL2 is also connected to the rx test
point RX-TP through U8A (74HC4066). Under
software control the RX-TP (scaled down by 2)
is thus available on the power connector for
trouble-shooting purposes.
A 4 channel digital potentiometer type (U5) is
used to adjust the RX SIGNAL, TX
MODULATION, CARRIER FREQUENCY and
CARRIER DETECT THRESHOLD.
An 8 channel, 8-bit successive approximation
A/D converter, type AD0838 (U9), is interfaced
to CPU (U18) and Peripheral (U20).
U19 generates a power-on reset for the CPU and
U6 is a temperature sensor used by the firmware
to compensate for variations in RSSI.
The RSSI signal from the transceiver is ampli-
fied and filtered by U7A, it is then compared to
a threshold value set by a digital potentiometer
(U5A). The output of the comparator (U7B) is
used to change the hold time of both peak de-
tectors at the beginning of the receive packet.
4.3.6 Wake-Up Circuit
The wake-up circuit for Integra-R consists of a
50 ms monostable circuit that is triggered by the
rising edge of a SLEEP signal from the CPU
(U17). The falling edge of this 50 ms pulse (end
of pulse) is connected to the \NMI of the CPU
and thus will wake up the CPU from SLEEP
mode after 50 ms.
When exiting SLEEP mode on a \NMI, the CPU
firmware will increment a counter, then return
to SLEEP until it reaches a limit set by a soft-
ware parameter. When the programmed count is
reached the CPU will wake up the radio and the
RS232 driver, program the synthesizer, and
watch for channel activity.
While in sleep mode (during the 50 ms pulse) an
active RTS from either communication port will
reset (terminate) the 50 ms pulse so that its fal-
ling edge will restart the CPU immediately.
The CPU will check to see if either RTS signal
is valid each time it is restarted by the \NMI.
The firmware will only start the sleep timer after
checking that all "wakeup" inputs are inactive.
4.3.7 Power Supply
The 13.3 volt DC power input is protected by a
3 amp fuse and reverse protected by a diode.
A 5 volt, low voltage regulator (U12) is used to
power all digital functions and another 5 volt,
low voltage regulator is used to control the
analog +5V_SW voltage in the sleep mode.
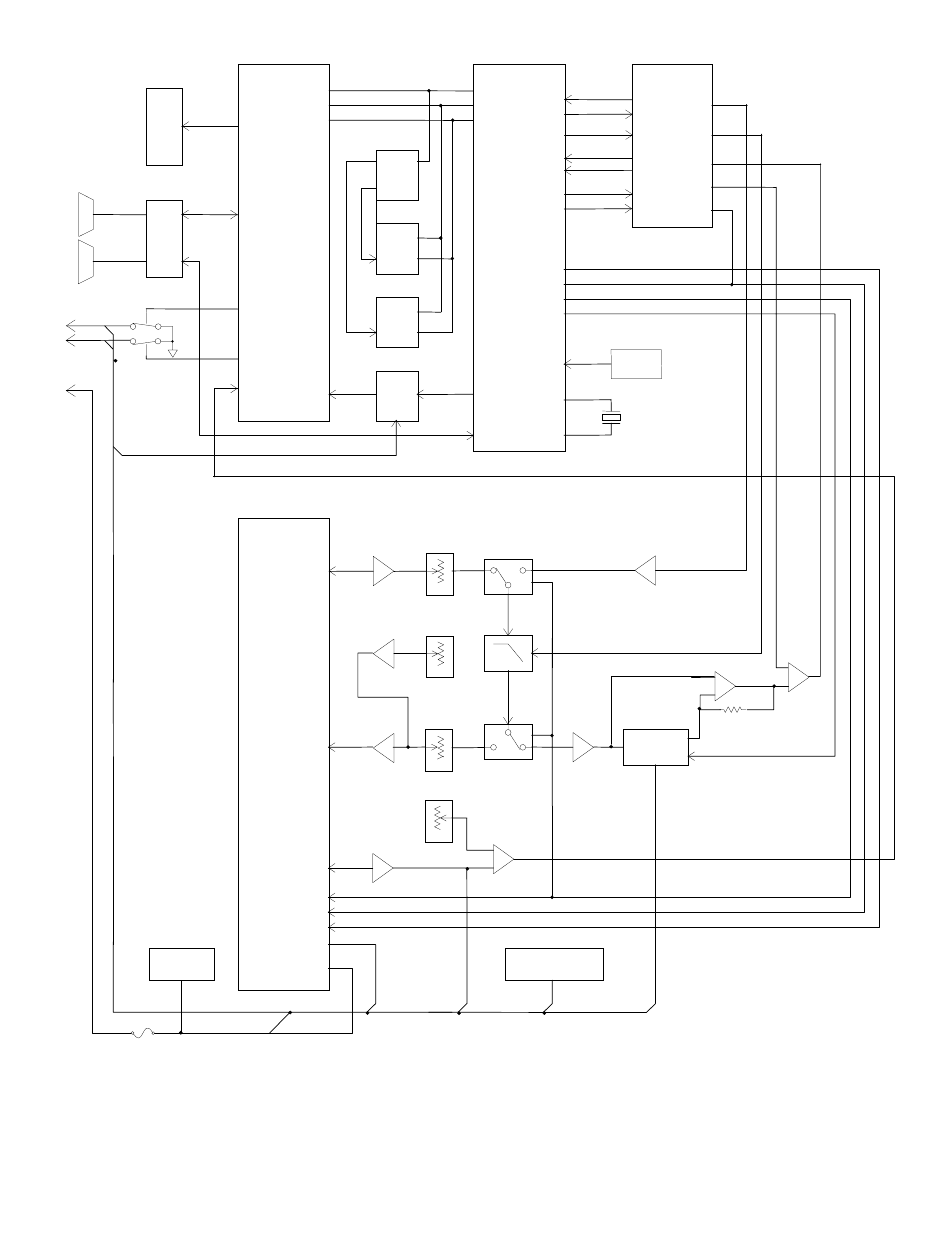
120 4010x-002 19 Integra TR Technical Manual
BI-
CO
LO
R
LE
D
RS
-
23
2
DR
IV
ER
DE9
DE9
SETUP
PORT
USER
PORT
U15
U21
PERIPHERAL
PA0-PA7
SIO-A
Q3
Q4
OUT
OUT-2
U17
CPU
MEM.
DECODE
U20A,B
ROM
U22
RAM
U18
A/D
U4
CONTROL BUS
DATA BUS
A
DDRESS BUS
CLK,DATA
SELECT
SIO-B
U16
TXC
TXD
CLOCK
RXC
CPLD
MODEM
RXD
MODE
SPEED
RADIO
MODULE
TXA
FILTER
CLOCK
RXS
SLICER
LEVEL
RX-EN
U1B
U5D
E-POT
U3A
RX GAIN
RXA
U5C
E-POT
U9D
WARP
U5B
E-POT
U9B
DEV
U5A
E-POT U7B
TXA
U8A
U10
U8B
RSSI
U1A
U1D PEAK
DETECT
U3C,D,B
U1C
FAST PEAK DETECT
TX-EN
TX ENABLE
RX-EN
RX ENABLE
SYNTH
SYNTHESIZER ENABLE-CLOCK-DATA
RESET
U19
X1
19.6MHz
CD
CARRIER DETECT
EXT 1
EXT 2
DIAG
U7A
TEMPERATURE
U6
SENSOR
5 VOLTS
U11,U12
REGULATOR SWB+
13.6 V OUT
F1
REV DESCRIPTION DATE
DATARADIO INC.
Check
Draft
Design P/N
SIZE BSHEET
Check
DOC/N
DATE
LEVEL
INTEGRA-R
LOGIC BLOCK DIAGRAM
210-03315-000 1 / 1
990302
990302
DUNG NGUYEN
EMISSION
0
Figure 12 - Logic Board Block Diagram
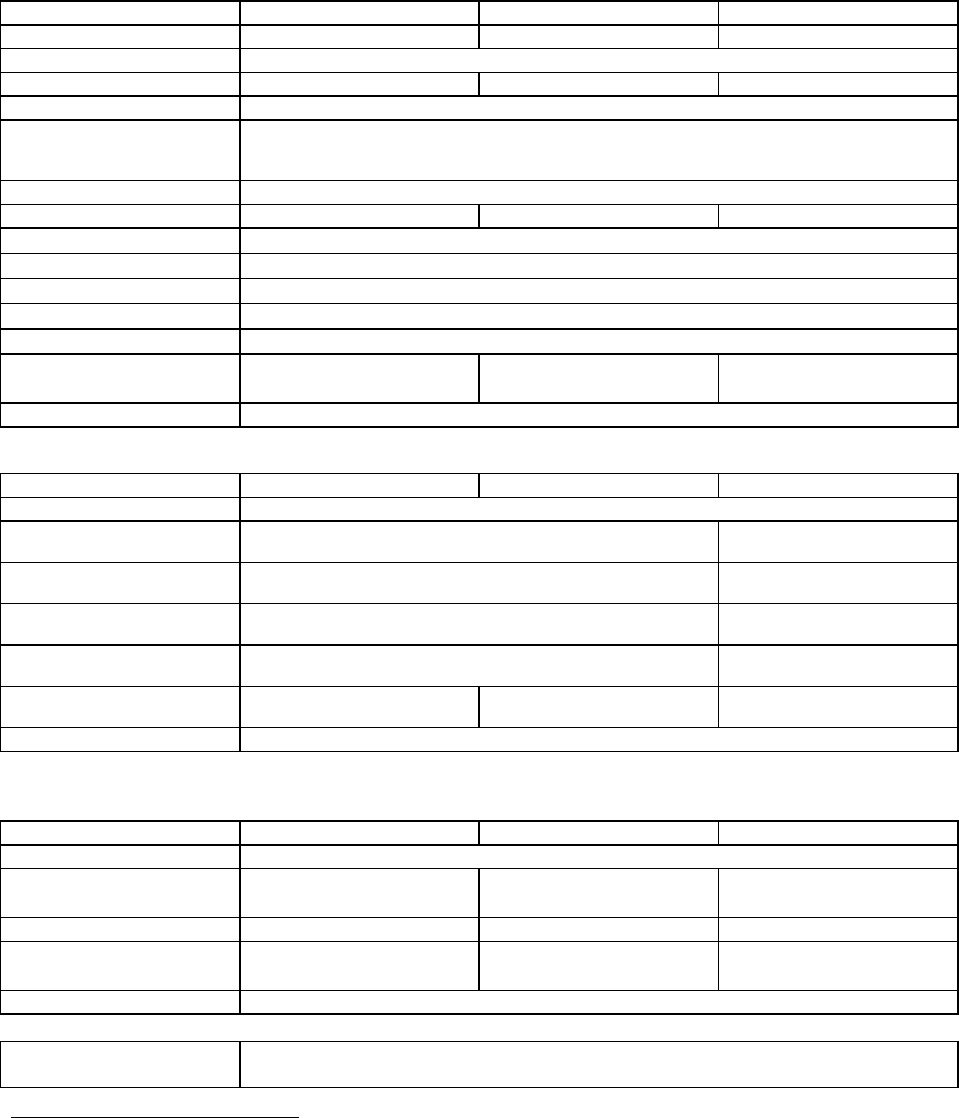
120 4010x-002 20 Integra TR Technical Manual
Specifications
GENERAL
VHF UHF 900 MHz
Frequency 132 - 174 MHz 403 - 512 MHz 928 - 960 MHz
Channels One channel. Frequency may be set locally or remotely.
Channel spacing 30 kHz 25 kHz 25 kHz
Operating temperature -30°C to +60°C
Supply voltage 10 - 16 VDC maximum (nominal 13.3 VDC)
Fuse protected input (internal surface mount 3A fuse: not field replaceable),
Input is also protected against reverse voltage.
RX Current drain at 13.3 VDC < 170 mA (with a terminal connected to Integra-T COM port)
TX Current drain at 13.3 VDC <1.8 A < 2.0 A < 2.5 A
Low power mode current drain 7 mA (nominal)
Cold start14 sec (typical)
Warm start RX245 to 60 msec (depending on radio model and temperature)
Warm start TX355 to 70 msec (depending on radio model and temperature)
TX turnon time415 ms typical
RX/TX bandwidth,
without tuning
18 MHz (132 - 150)
24 MHz (150 - 174)
16 MHz except
20 MHz (450 - 470)
32 MHz
Nominal Dimensions 4.5” W x 2.2” H x 4.75” D (11.4 x 5.6 x 12.1 cm)
RECEIVER
VHF UHF 900 MHz
Sensitivity 0.35 µV for 12 dB SINAD *
Selectivity (25 or 30 kHz) 75 dB typical
70 dB minimum
72 dB typical
65 dB minimum
Selectivity (12.5 or 15 kHz) 65 dB typical
60 dB minimum
63 dB typical
60 dB minimum
Intermodulation 75 dB typical
70 dB minimum
72 dB typical
70 dB minimum
Spurious rejection 75 dB typical
70 dB minimum
75 dB typical
70 dB minimum
FM hum & noise -48 dB typical
-45 dB max (30 kHz)
-48 dB typical
-45 dB max (25 kHz)
-43 dB typical
-40 dB max (25 kHz)
Conducted spurious < -57 dBm
* psophometrically weighted
TRANSMITTER
VHF UHF 900 MHz
RF power output 1 to 5 watts, software adjustable
Spurious and harmonics -63 dBc (-26 dBm) typ
-57 dBc (-20 dBm) max
-75 dBc (--38 dBm) typ
-63 dBc (-26 dBm) max
-75 dBc (-38 dBm) typ
-57 dBc (-20 dBm) max
Frequency stability 2.5 PPM 1.5 PPM 1.5 PPM
FM hum and noise -50 dB typical (30 kHz)
-45 dB max (30 kHz)
-50 dB typical (25 kHz)
-45 dB max (25 kHz)
-50 dB typical (25 kHz)
-40 dB (max (25 kHz)
Attack time < 7 ms
TX Duty cycle 50%, max TX time 30 seconds
100%, unlimited TX time with the cooling fan option
1 Cold start: This is the time from when DC power is applied, until the unit is fully ready to receive or transmit data.
2 Warm start RX: In low power modes (sleep or suspend), this is the Integra-T wake-up time for full receiver recovery.
3 Warm start TX: In low power modes (sleep or suspend), this is the Integra-T wake-up time for full transceiver operation.
4 TX turnon time: This is the typical RX to TX switching time for stable transmission.
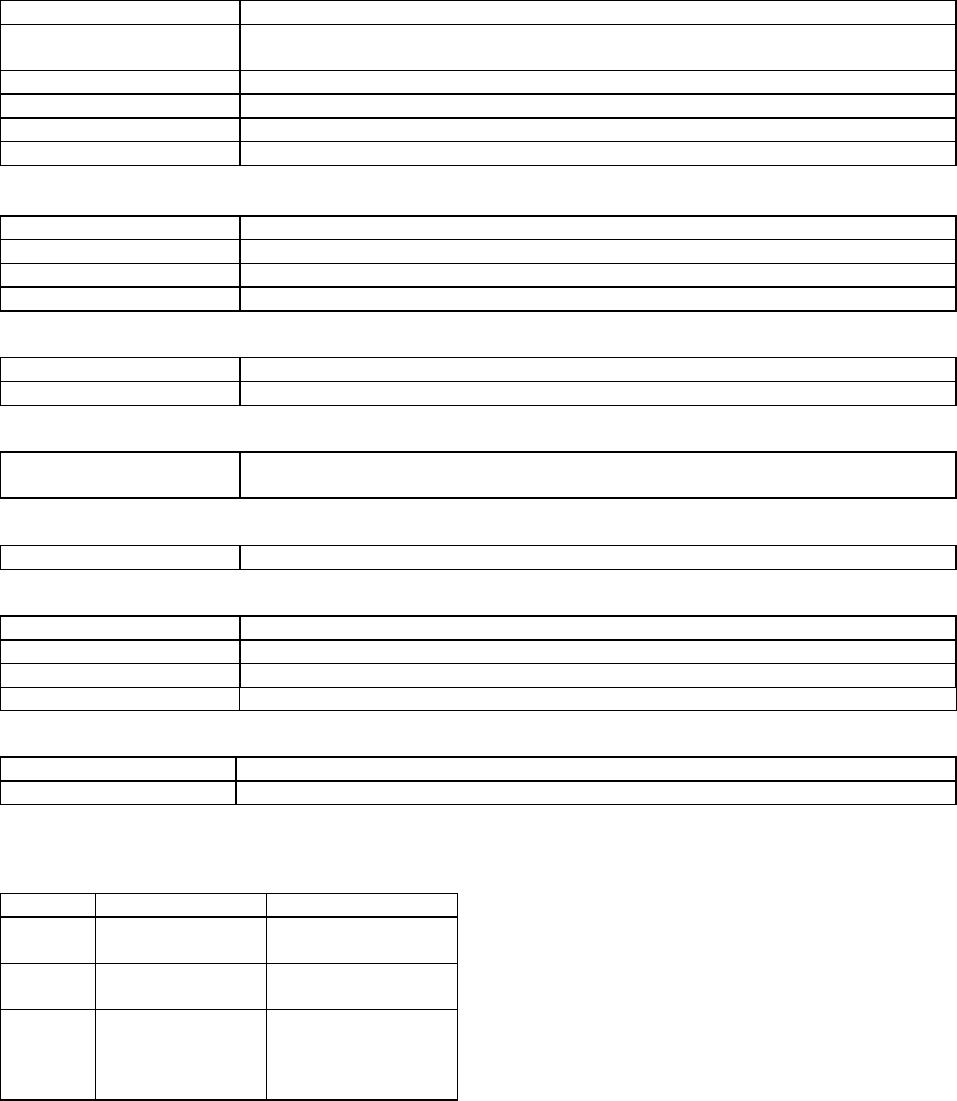
120 4010x-002 21 Integra TR Technical Manual
MODEM / LOGIC
Operation Simplex/half duplex
Data bit rates Full Channel: 4800 b/s, 9600 b/s and 19200 b/s
Half Channel: 4800 b/s, 9600 b/s
Modulation type DRCMSK (Differential Raise-Cosine Minimum Shift Keying)
RTS/CTS delay (RTS mode) 4 ms
Addressing 8 bit station address, 1 bit station type (master, remote)
Bit error rate (BER) better than 1 x 10 -6 at 1.0 µV (based on “block error rate”) @ 9600 b/s (Full Ch.)
COM PORT
Interface EIA RS-232C
Data rate 300 - 19200 b/s
Protocol Transparent, 7 or 8 data bits, 1 or 2 stop bits, even, odd or no parity
Transmit control RTS or DOX (data operated transmit)
SETUP/DIAG PORT
Data format Proprietary binary for setup, ASCII for diags
Data rate 9600 b/s
ANALOG INPUTS
Interface Two inputs, 0 - 10 VDC, 8 bits. May be read only via Offline diagnostics.
Absolute maximum input voltage < 20 Vdc. Inputs are reverse-voltage protected.
DISPLAY
4 two color status LEDs RUN/PWR, CS/SYN, RX/TX, RD/TD
CONNECTORS
RF SMA female
COM DE-9F
SETUP/DIAG DE-9F
Power / Analog Snap & lock 4-pin DC power jack
DIAGNOSTICS
Online Short ID, temperature, B+ voltage, local RSSI, remote RSSI, fwd and rev power, RX quality
Offline As for Online plus: demodulated signal voltage, analog input levels
FCC / IC CERTIFICATIONS
FCC (Pending) IC (DOC)
VHF EOTMCUA5R Pending
(19K4F1D) (16K0F1D)
UHF EOTMCUB5R Pending
(19K4F1D) (16K0F1D)
900 MHz EOTMCUC5R Pending
(16K6F1D) (16K6F1D)
(9K80F1D) (16K0F1D
(9K80F1D)
.
120 4010x-002 22 Integra TR Technical Manual
INDEX
A
addressing ................................................................. 9
adjustments
equipment required ............................................. 15
analog inputs ............................................................. 7
B
break signals.............................................................. 8
C
characteristics............................................................ 1
circuit description.................................................... 17
COM port
baud rates.............................................................. 8
commands, remote .................................................... 3
configuration............................................................. 1
connections ............................................................... 3
D
diagnostics............................................................. 3, 8
interpretation....................................................... 10
offline ................................................................. 12
online.................................................................... 9
online string format............................................. 10
using an external program..................................... 9
DOX mode................................................................ 8
DTE connections....................................................... 5
E
ESN........................................................................... 9
F
firmware upgrades..................................................... 3
L
LEDs......................................................................... 5
M
master........................................................................ 9
O
optimizing performance .......................................... 14
P
point to point............................................................. 4
point–multipoint........................................................ 4
power connector........................................................ 7
power saving ........................................................... 13
R
range (distance)......................................................... 3
remote ....................................................................... 9
RS-232 port............................................................... 6
RTS mode ................................................................. 8
S
setup port................................................................... 6
short address.............................................................. 9
signal quality........................................................... 12
sleep mode .............................................................. 13
station type................................................................ 9
T
tail circuit .................................................................. 4