Canon Lbp 3260 Users Manual Cover Face
canonlbp5055570 f5be1656-387f-4b5c-a196-d8c135cfeaaf Canon Printer 3260 User Guide |
2015-01-23
: Canon Canon-Lbp-3260-Users-Manual-242254 canon-lbp-3260-users-manual-242254 canon pdf
Open the PDF directly: View PDF .
Page Count: 234 [warning: Documents this large are best viewed by clicking the View PDF Link!]
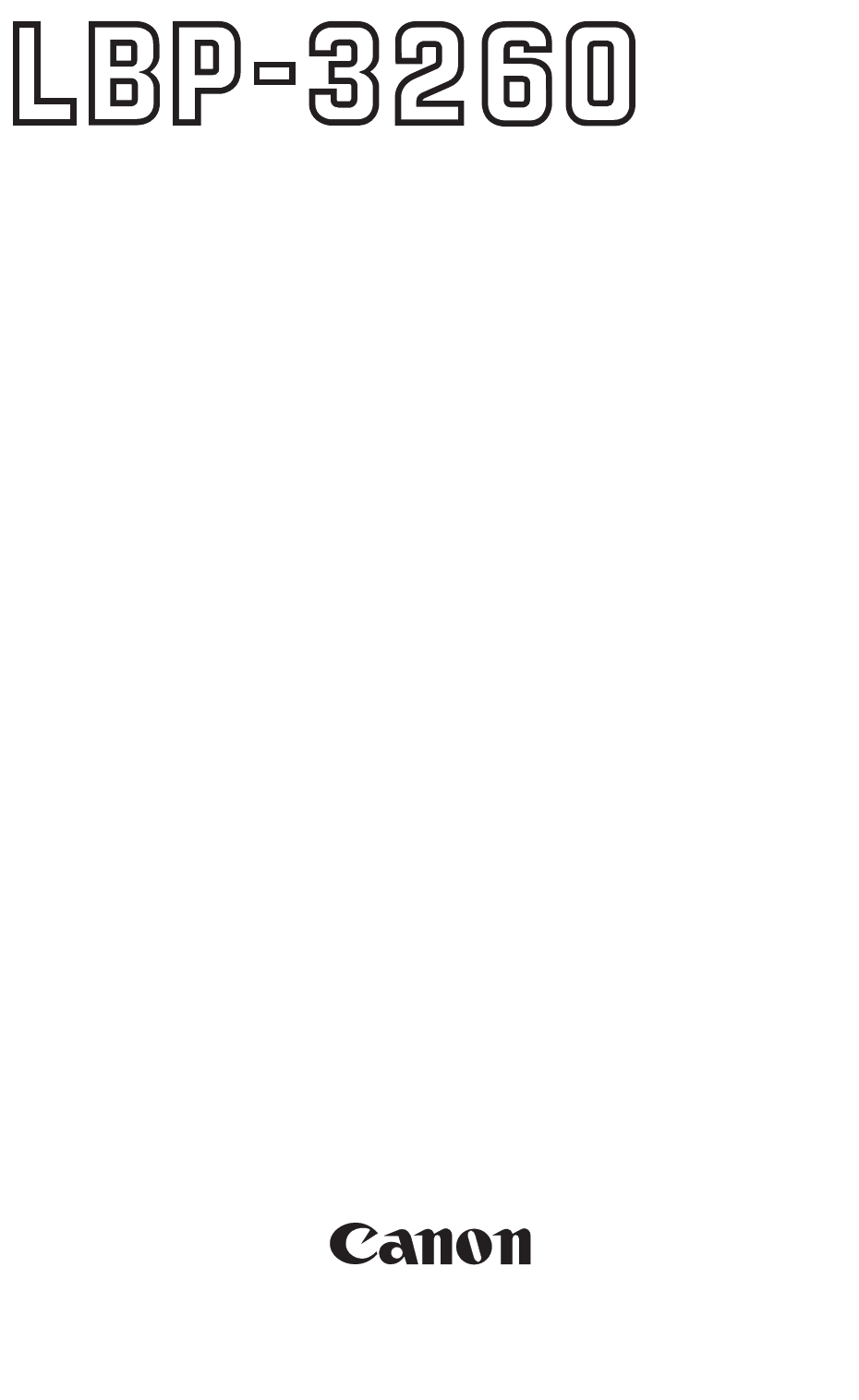
SERVICE
MANUAL
REVISION 0
COPYRIGHT 1999 CANON INC. CANON LBP-3260 REV.0 JAN. 1999 PRINTED IN JAPAN (IMPRIME AU JAPON)
RY8-1390-000
JAN. 1999
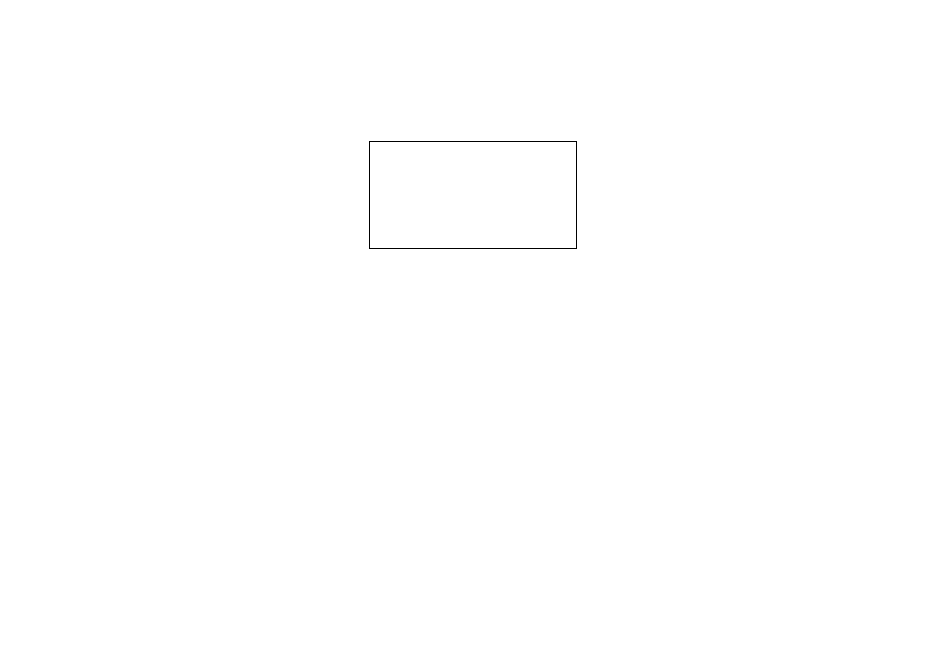
COPYRIGHT © 1999 CANON INC
Printed in Japan
Imprimé au Japon
Use of this manual should be
strictly supervised to avoid
disclosure of confidential
information.
Prepared by
PERIPHERAL PRODUCTS QUALITY ADVANCEMENT DIV.
PERIPHERAL PRODUCTS TECHNICAL DOCUMENTATION DEPT.
CANON INC.
5-1, Hakusan 7-chome, Toride-City, Ibaraki-Pref. 302-8501, Japan
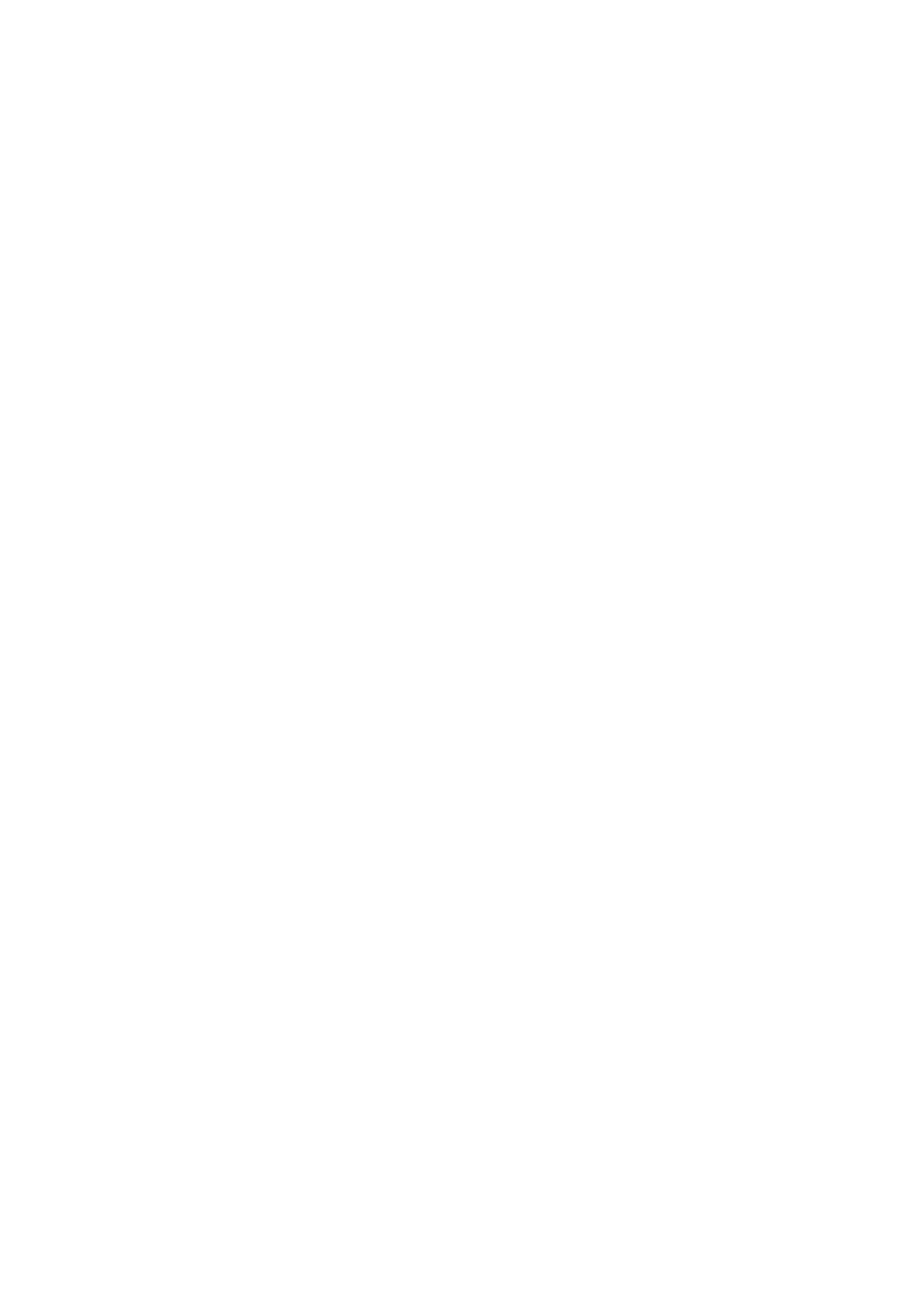
PREFACE
This Service Manual contains basic information required for after-sales service of the laser beam
printer LBP-3260 (hereinafter referred to as the "printer"). This information is vital to the ser-
vice technician in maintaining the high print quality and performance of the printer.
This manual consists of the following chapters:
Chapter 1: Product information
Features, specifications, operation, and installation
Chapter 2: Operation and Timing
A description of the operating principles and timing sequences of the electrical and
mechanical systems.
Chapter 3: The Mechanical System
Explanation of mechanical operation, disassembly, reassembly and adjustment pro-
cedures
Chapter 4: Troubleshooting
Troubleshooting procedures, reference values and adjustments, maintenance and
servicing, etc.
Appendix: General timing chart, general circuit diagram, etc.
Information in this manual is subject to change as the product is improved or redesigned. All
relevant information in such cases will be supplied in the Service Information Bulletins.
A thorough understanding of this printer, based on information in this Manual and Service
Information bulletins, is required for maintaining its performance and for locating and repairing
the causes of malfunctions.
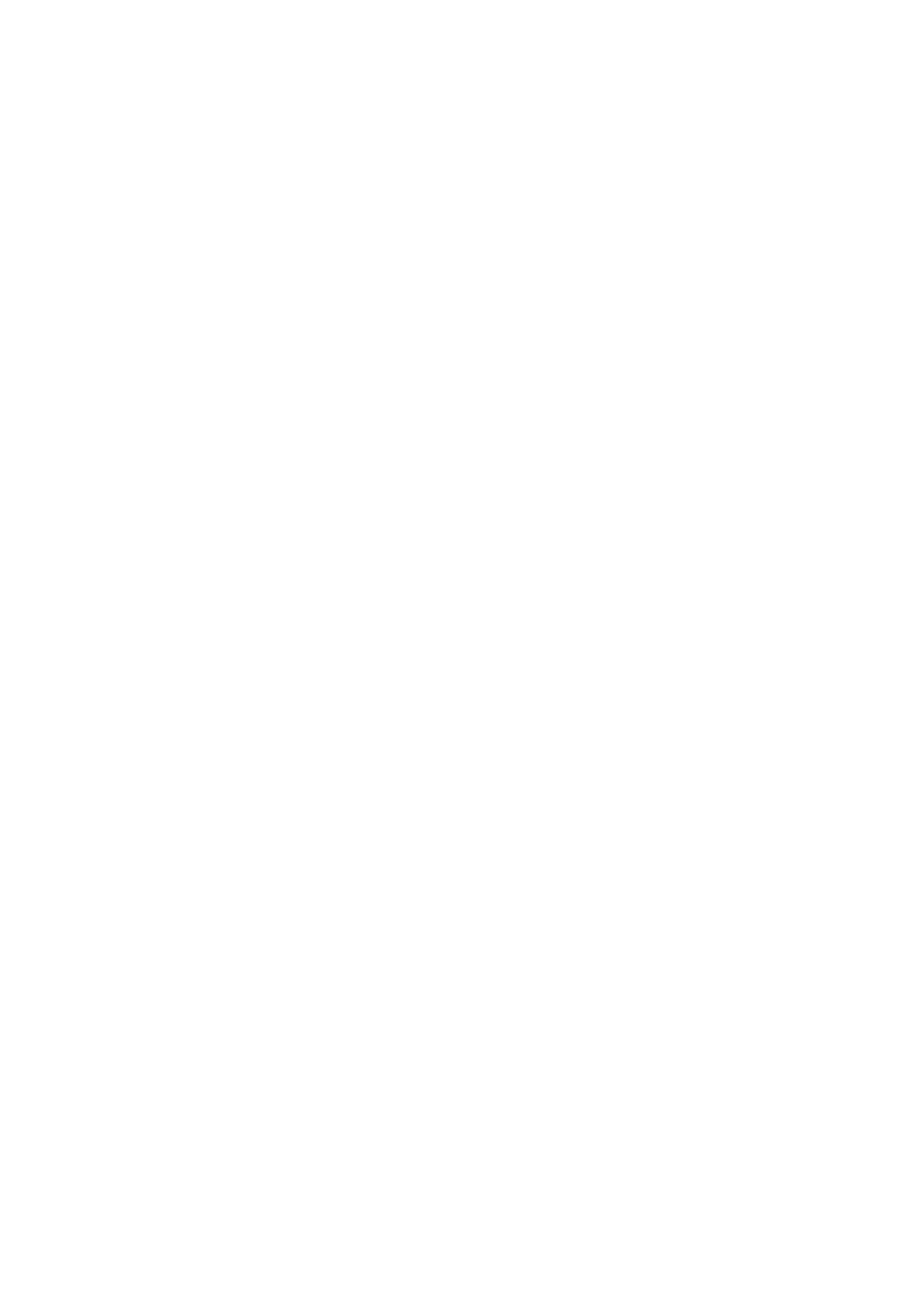
DTP system
This manual was produced on an Apple PowerMacintosh 9500/233 personal computer and output by an
Apple LaserWriter 16/600 PS laser beam printer; final pages were printed on DAINIPPON SCREEN MFG
CO. LTD DT-R3100.
All graphics were produced with Macromedia FreeHand (J), and all documents and page layouts were
created with QuarkXPress (E).
The video images were captured with SONY degital video camcorder and Radius PhotoDV capture board
system, and modified with Adobe Photoshop(J).
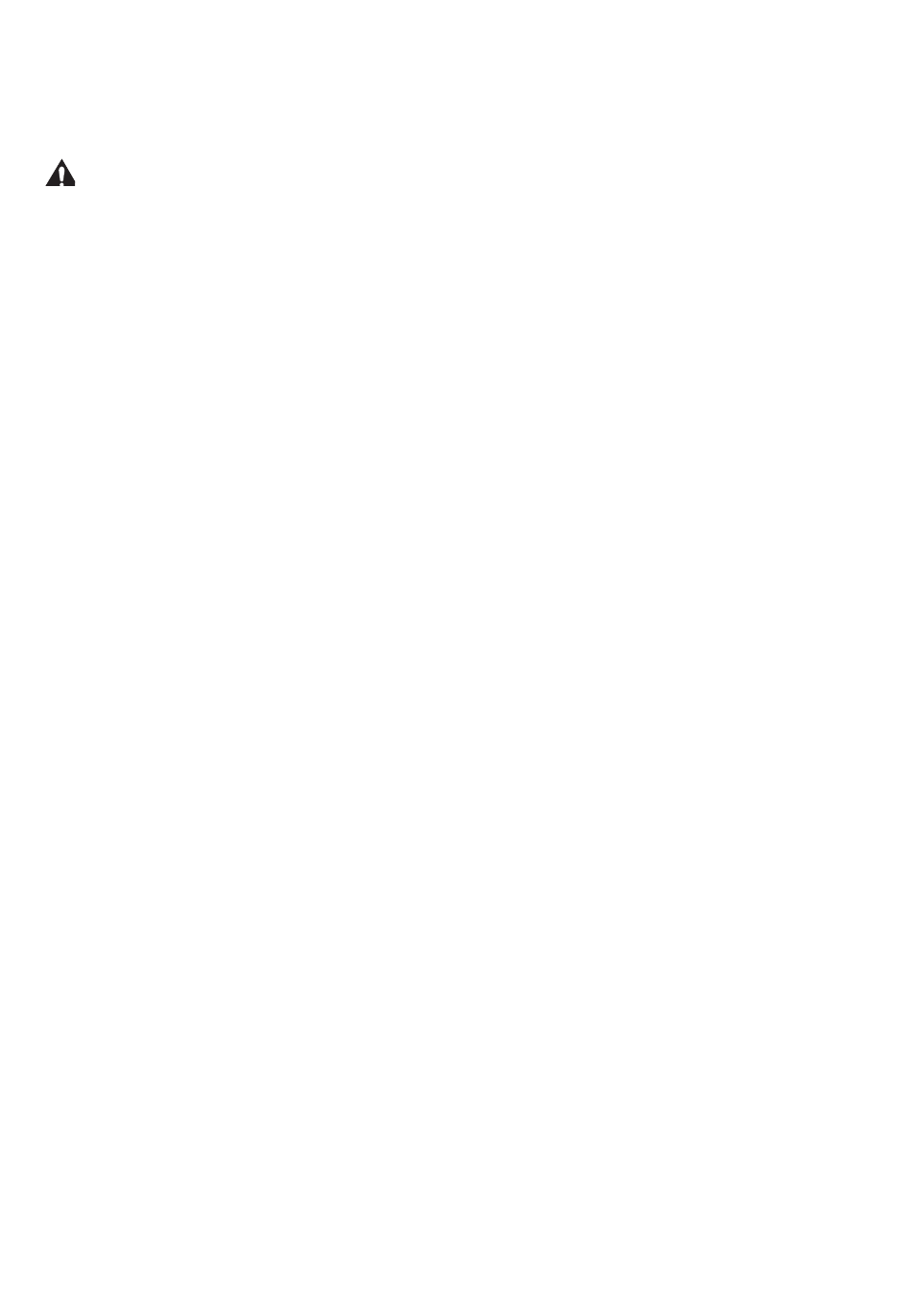
CONTENTS
CHAPTER 1 PRODUCT INFORMATION
I. FEATURES ............................ 1-1
II. SPECIFICATIONS .................. 1-3
III. SAFETY INFORMATION .... 1-6
IV. PARTS OF THE PRINTER ...... 1-7
V. INSTALLATION ...................... 1-9
VI. MAINTENANCE AND
SERVICING BY THE
CUSTOMER ........................... 1-18
VII. OPERATION .......................... 1-21
CHAPTER 2 OPERATION AND TIMING
CHAPTER 3 THE MECHANICAL SYSTEM
I. BASIC OPERATION ................. 2-1
A. Functions.......................... 2-1
B. Basic Operation Sequences 2-2
C. Power On Sequence ........... 2-3
II. ENGINE CONTROL SYSTEM.... 2-4
A. DC Controller Circuit ........ 2-4
B. Fixing Control ................... 2-10
C. High-Voltage Power
Supply............................... 2-16
D. Power Supply..................... 2-19
E. Video Interface Control ..... 2-21
F. Other Controls .................. 2-23
III. LASER/SCANNER SYSTEM..... 2-26
A. Outline.............................. 2-26
B. Laser Control Circuit......... 2-27
C. Scanning System............... 2-30
IV. IMAGE FORMATION SYSTEM . 2-32
A. Outline.............................. 2-32
B. Printing Process ................ 2-34
V. PICK-UP/FEED SYSTEM......... 2-42
A. Outline.............................. 2-42
B. Paper Pick-up .................... 2-45
C. Fixing and Delivery Unit.... 2-57
D. Paper Jam Detection ......... 2-59
VI. OVERALL CONTROL SYSTEM. 2-61
A. Video Controller PCB......... 2-61
B. Control Panel .................... 2-65
C. Self Test............................ 2-66
I. PREFACE ............................... 3-1
II. EXTERNALS ........................... 3-2
A. Locations .......................... 3-2
B. Control Panel Unit............. 3-7
III. MAIN UNITS ........................... 3-8
A. Laser/Scanner Unit ........... 3-8
B. Drive Unit ......................... 3-8
C. Pick-up Unit ...................... 3-9
D. Multi-purpose Tray Pick-up
Unit.................................. 3-12
E. Registration Roller Unit .... 3-12
F. Delivery Unit..................... 3-13
G. Fixing Unit ........................ 3-13
H. Feed Unit .......................... 3-14
IV. MAIN PARTS .......................... 3-15
A. Locations .......................... 3-15
B. Multi-purpose Tray Pick-up
Roller ............................... 3-16
C. Separation Pad .................. 3-16
D. Pick-up/Feed/Separation
Rollers ............................. 3-17
E. Registration Lower Roller.. 3-17
F. Transfer Charging Roller ... 3-18
G. Fixing Roller Heater .......... 3-18
H. Fixing Upper Roller ........... 3-19
I. Fixing Lower Roller ........... 3-22
J. Cleaning Roller.................. 3-23
V. SWITCHES/SENSORS............. 3-24
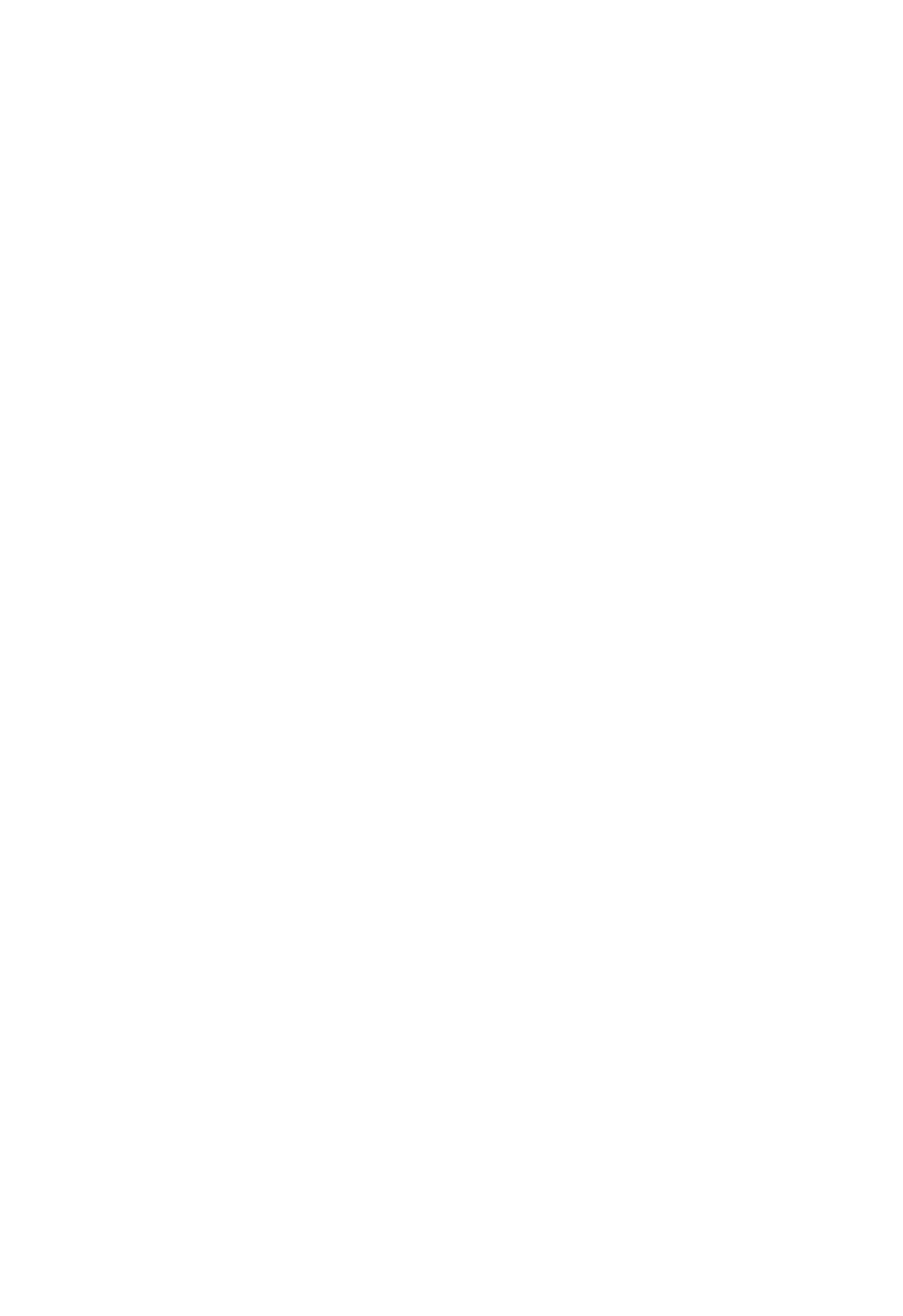
A. Locations .......................... 3-24
B. Thermoswitch ................... 3-25
C. Door Switch ...................... 3-25
D. Upper Cassette Paper-size
Sensing Switch/Lower Cassette
Paper-size Sensing Switch . 3-26
E. Thermistor ........................ 3-26
F. Registration Paper Sensor . 3-27
G. Pick-up Unit Paper Sensor. 3-28
H. Pick-up Unit Door Sensor .. 3-28
I. Lower Cassette Sensor/
Upper Cassette Sensor/
Lower Cassette Paper-level
Sensor 1/Lower Cassette
Paper-level Sensor 2/Upper
Cassette Paper-level Sensor 1/
Upper Cassette Paper-level
Sensor 2/Lower Cassette
Paper-out Sensor/Upper
Cassette Paper-out Sensor. 3-29
J. Multi-purpose Tray Paper
Sensor /Lifting Plate
Position Sensor ................. 3-29
K. Face-down Tray Paper Full
Sensor /Face-down Tray
Delivery Sensor /Fixing
Unit Delivery Sensor ......... 3-30
VI. CLUTCHS/SOLENOIDS ........... 3-31
A. Locations .......................... 3-31
B. Multi-purpose Tray Pick-up
Clutch ............................... 3-32
C. Feed Clutch....................... 3-32
D. Registration Clutch ........... 3-33
E. Lifting Plate Solenoid ........ 3-33
F. Cassette Pick-up Solenoid . 3-34
G. Face-up Solenoid Unit ....... 3-34
VII. MOTORS/FANS ...................... 3-35
A. Locations .......................... 3-35
B. Main Motor........................ 3-36
C. Pick-up Motor.................... 3-36
D. Fans ................................. 3-37
VIII.PCBS...................................... 3-41
A. Locations .......................... 3-41
B. Video Controller PCB Unit . 3-42
C. DC Controller PCB ............ 3-43
D. Pick-up PCB ..................... 3-44
E. Multi-purpose Tray PCB ... 3-44
F. Switch/Sensor PCB .......... 3-45
G. High-voltage Power Supply
Unit .................................. 3-47
H. Cassette Paper-size Sensing
PCB .................................. 3-47
I. Power Supply ................... 3-48
I. PREFACE ............................... 4-1
A. Malfunction Diagnosis
Flowchart ......................... 4-1
B. Initial Check ..................... 4-4
C. Test Print .......................... 4-5
II. IMAGE DEFECTS.................... 4-8
III. PAPER JAMS
TROUBLESHOOTING .............. 4-14
IV. PAPER TRANSPORT
TROUBLESHOOTING .............. 4-18
V. MALFUNCTION
TROUBLESHOOTING .............. 4-20
VI. MALFUNCTION STATUS
TROUBLESHOOTING .............. 4-21
VII. MEASUREMENT AND
ADJUSTMENT ........................ 4-28
A. Mechanical Adjustment ..... 4-28
B. Electrical Adjustment........ 4-29
C. Variable Resistors, LEDs,
Test Pins, Jumpers and
Switches on PCBs.............. 4-30
VIII.MAINTENANCE AND
CHAPTER 4 TROUBLESHOOTING
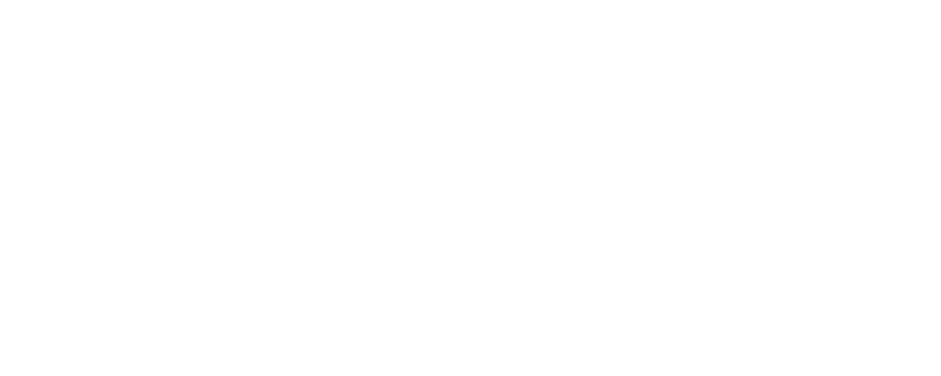
APPENDIX
I. GENERAL TIMING CHART ...... A-1
II. GENERAL CIRCUIT DIAGRAM A-3
III. LIST OF SIGNALS................... A-5
IV. MESSAGES TABLE ................. A-11
SERVICING............................. 4-35
A. Periodic Replacement
Parts ................................ 4-35
B. Expected Service Life of
Consumable Parts.............. 4-35
C. Periodic Service ................ 4-35
D. Cleaning during a Service
Visit .................................. 4-36
E. Standard Tools .................. 4-38
F. Special Tools ..................... 4-39
G. Special Tools (printer driver
tester) Explanation........... 4-40
H. Solvents and Oil List ......... 4-47
IX. LOCATION OF CONNECTORS . 4-48
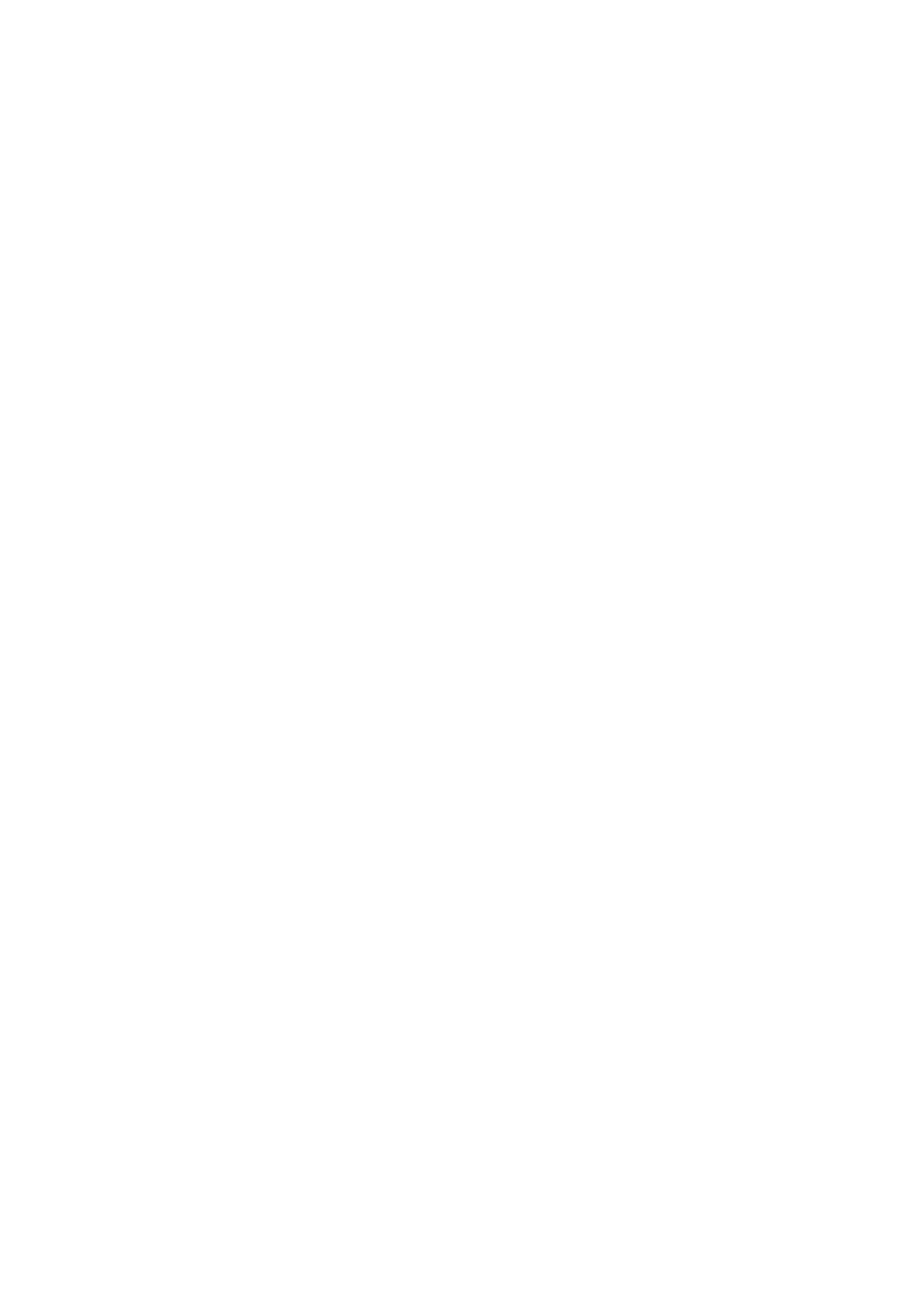
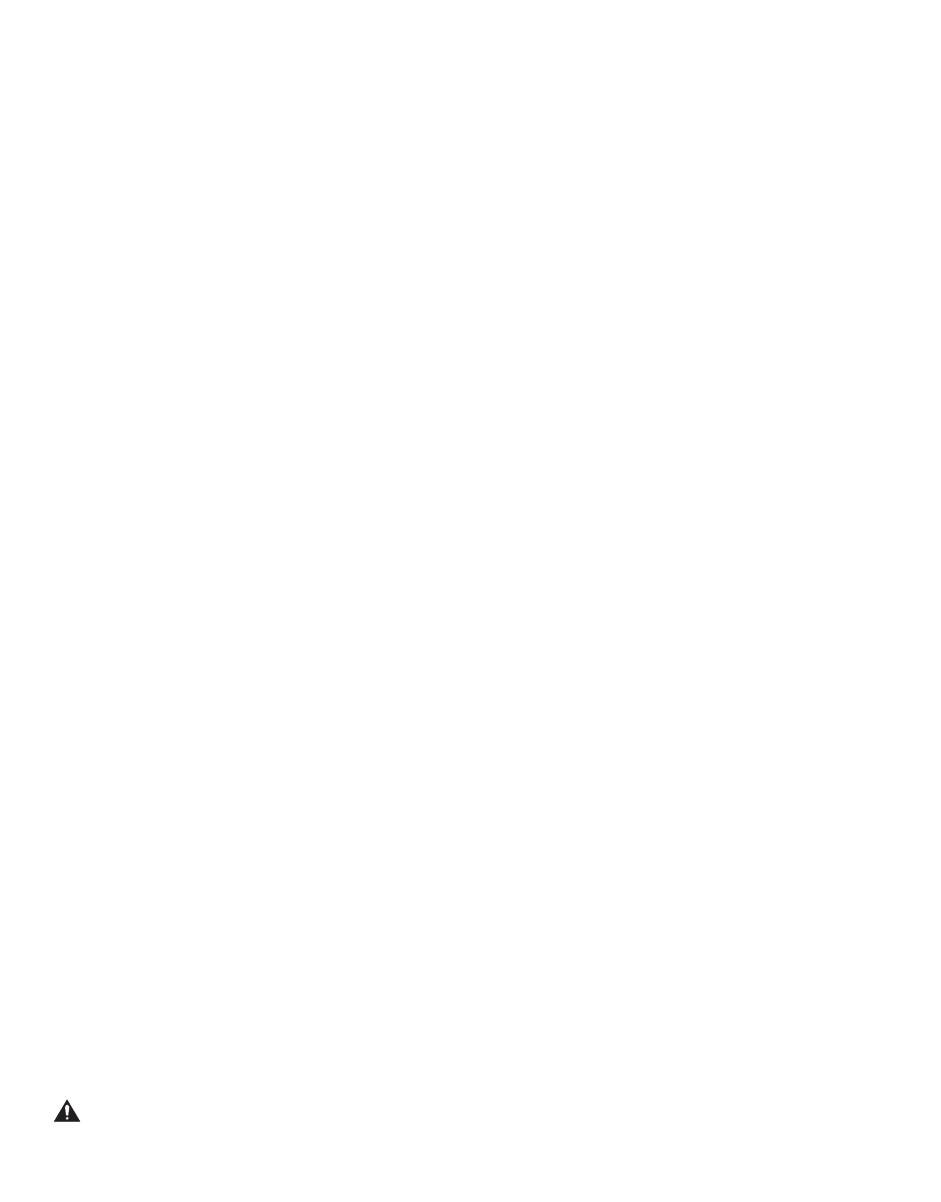
CHAPTER 1
PRODUCT INFORMATION
I. FEATURES ............................ 1-1
II. SPECIFICATIONS .................. 1-3
III. SAFETY INFORMATION .... 1-6
IV. PARTS OF THE PRINTER ...... 1-7
V. INSTALLATION ...................... 1-9
VI. MAINTENANCE AND
SERVICING BY THE
CUSTOMER ........................... 1-18
VII. OPERATION .......................... 1-21
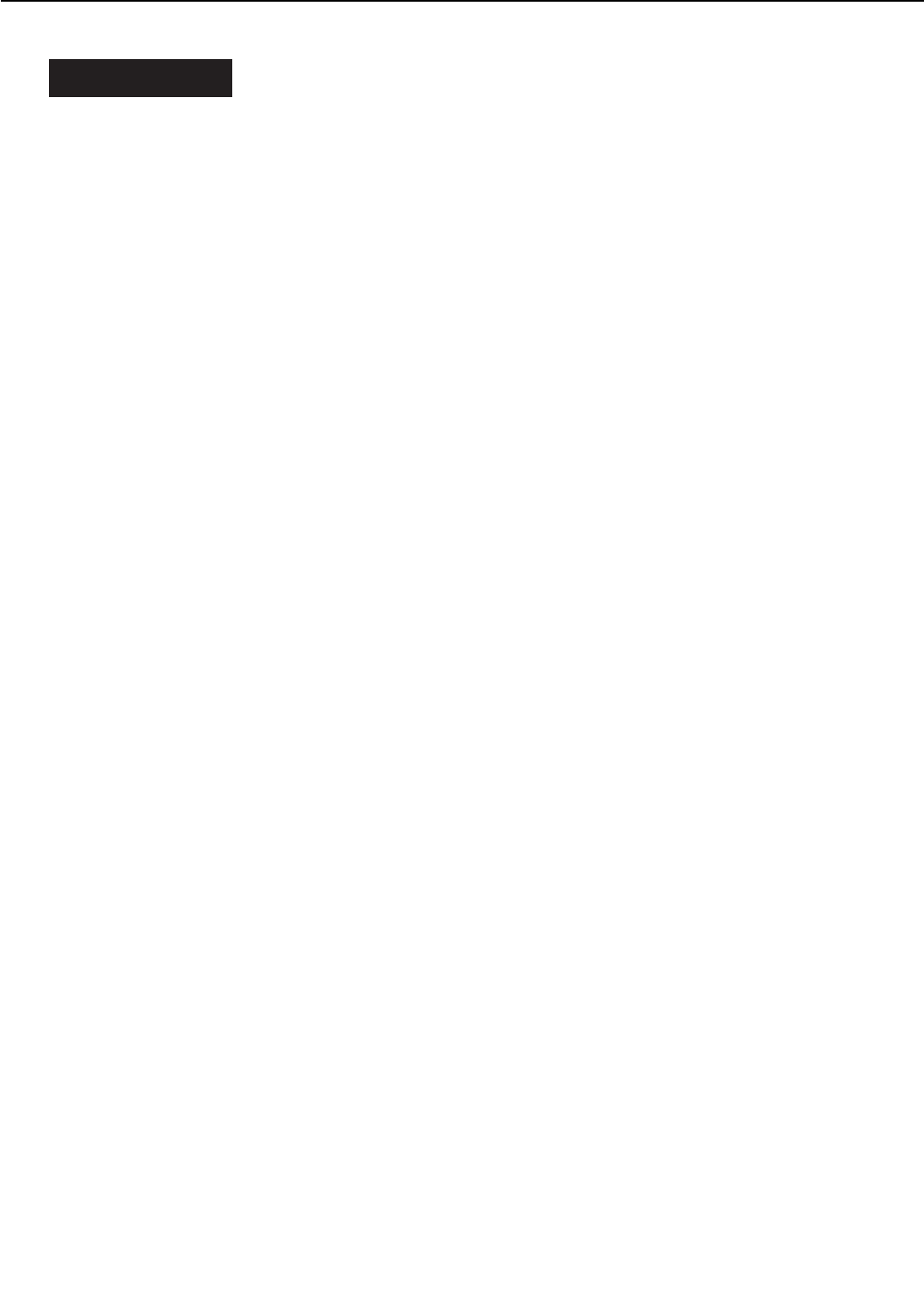
I. FEATURES
1. High speed printing
Equipped with Motorola's PowerPC 603e, the printer is capable of printing about 32 pages per
minute (A4/Letter).
2. Superior print quality
Combination of high resolution printing at 600 DPI and the use of super fine toner offers clear
print images.
3. Duplex printing
With the optional duplexing unit installed, the printer can print on both sides of paper.
4. Continuous printing
With the optional paper deck installed in the printer in addition to the standard equipped multi-
purpose tray and upper and lower cassettes, up to about 3,100 sheets of paper (75g/m2) can be
loaded, enabling continuous printing in large volume.
5. 6-way paper pick-up
Optional 2x500 sheet paper deck and envelope feeder in addition to the standard equipped
multi-purpose tray and upper and lower cassettes offer 6-way paper pick-up. The printer can
change the paper pick-up source automatically according to the paper type in addition to the
paper size.
6. Delivery
With the optional staple stacker installed in addition to the standard face-down tray, up to 2,300
sheets of A4 or Letter size paper (75g/m2) can be delivered (simple stacking).
7. Various delivery methods
With the optional sorter attached to the printer, paper can be delivered in 4 modes: mail box, job
separator, stacker and collator.
8. Memory saving technology
Memory Reduction Technology accomplishes printing at 600 DPI with standard equipped mem-
ory (8 MB). It also decreases errors, such as memory over flow, and provides stable printing.
9. Energy saving/Toner saving
The printer cuts off the power to the fixing heater when it remains idle for a specified length of
time. It can also reduce toner consumption by selecting the economy mode to print light images
with less toner.
10.Automatic emulation switching
The printer supports Hewlett-Packard's enhanced PCL6. With the optional PostScript ROM
DIMM (Canon Translator Module A-72) installed, the printer can automatically switch between
the standard PCL and Adobe®PostScript®3™.
11.Automatic interface switching
In addition to the standard built-in bicentronics parallel port, optional interfaces can be
installed in the printer. The printer can automatically switch between the parallel and expan-
sion interface according to which interface port the data sent from the host computer enters.
1 - 1
CHAPTER 1
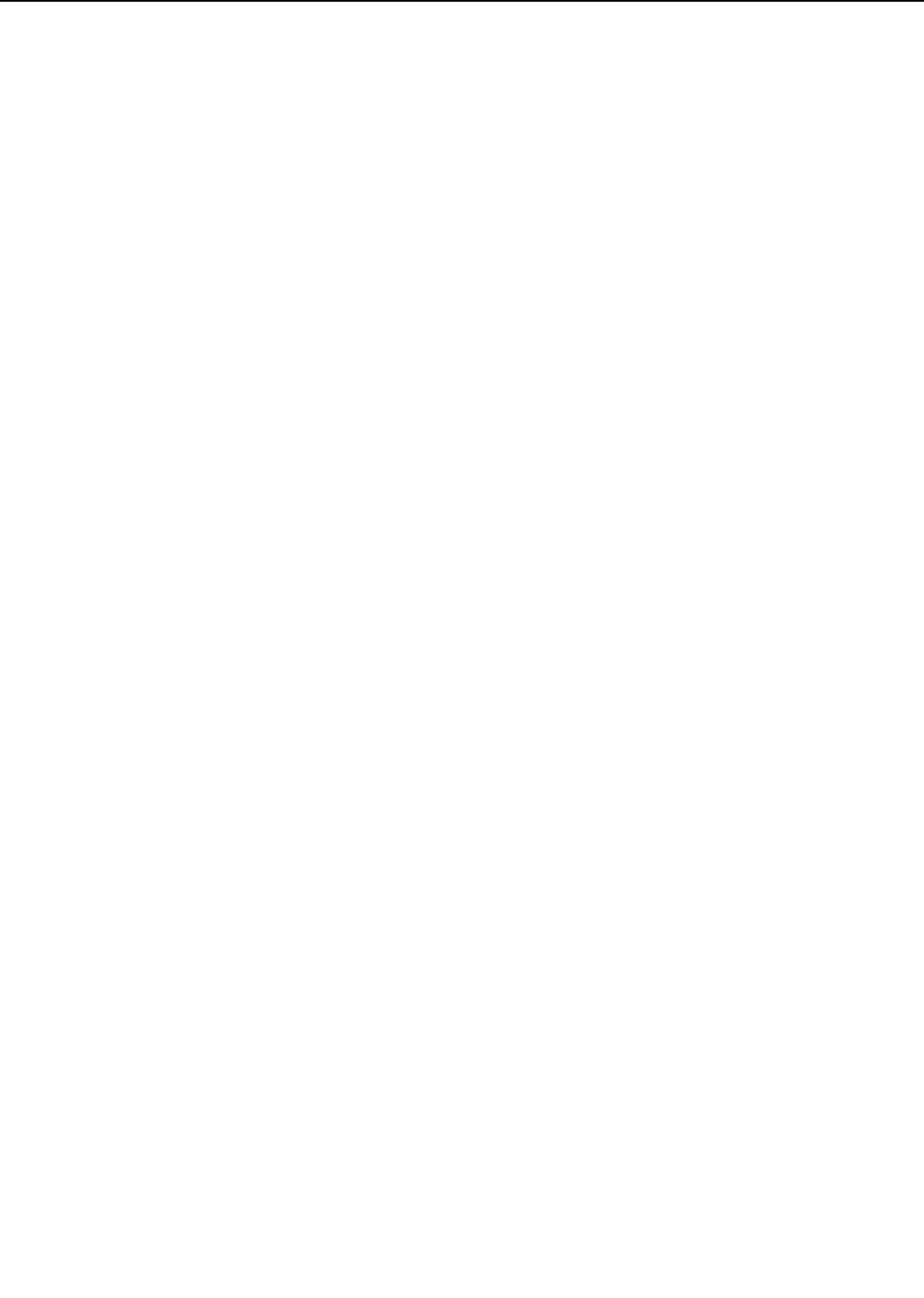
This page intentionally left blank
1 - 2
CHAPTER 1
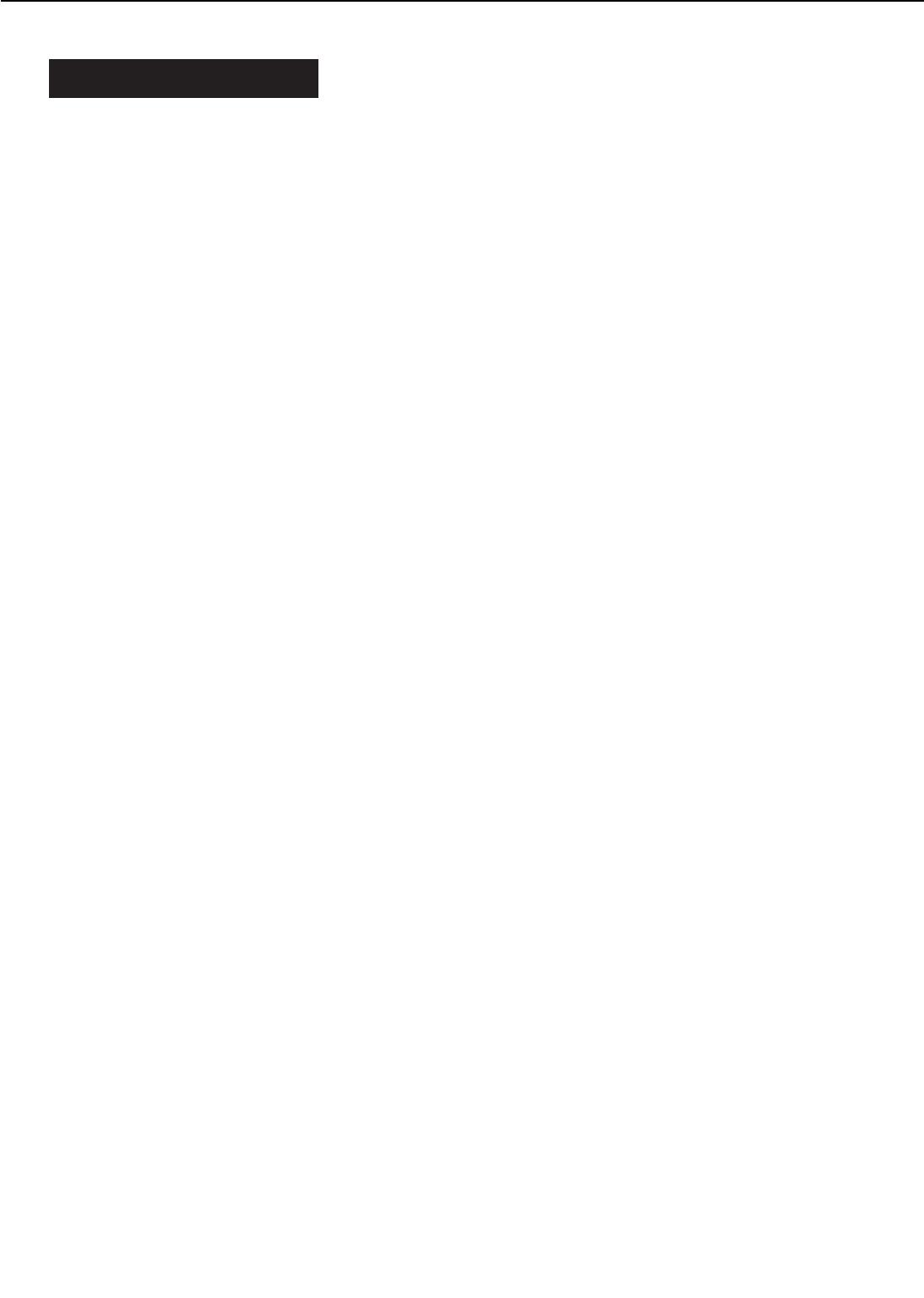
II. SPECIFICATIONS
A. Printer
1. Printer Engine
1) Type Desktop page printer (console type when paper deck is installed)
2) Printing method Electrophotography
3) Printing speed (Note 1) About 32 pages/min. (A4/Letter), about 18 pages/min. (A3)
4) First print time (Note 2) 12.9 sec. or less (A4), 14.3 sec. or less (A3)
5) Wait time (Note 3) 90 sec. or less
6) Resolution
Horizontal 600 DPI
Vertical 600 DPI
7) Image formation system
Laser Semiconductor laser
Scanning system Rotating six-faced prism mirror (Scanning mirror)
Photosensitive drum OPC
Charging Roller charging
Exposure Laser scanning
Toner Magnetic single-component dry toner
Development Toner projection development
Toner supply By EP-72 cartridge replacement (about 20,000 A4- or Letter-sized
prints; with "DENSITY" in "CONFIG MENU" set to "7" and 4% dot
density)
Transfer Roller transfer
Separation Curvature/discharge bias
Cleaning Blade
Fixing Heated rollers (600W, 450W)
8) Paper pick-up Multi-purpose tray
Cassette
Envelope feeder EF-9 (option)
2,000 Sheet paper deck PD-82 (option)
2x500 Sheet paper deck PD-82K (option)
Print paper Plain paper, colored paper, labels, OHT, envelopes, rough paper,
bond paper, tarnsparency paper, recycled paper, letterhead
Paper sizes
Multi-purpose tray Min. 98.4mm(W) ×190.5mm(L) to max. 297mm(W) ×432mm(L)
sized plain paper (64g/m2to 128g/m2recommended paper) and
paper mentioned above.
Upper cassette B4, A4, Legal, Letter-sized plain paper (64g/m2to 105g/m2rec-
ommended paper), and colored paper.
Lower cassette A3, B4, A4, Ledger, Legal, Letter-sized plain paper (64g/m2to
105g/m2recommended paper), and colored paper.
Multi-purpose tray
capacity 10mm stack (about 100 sheets of 75g/m2paper)
Cassette capacity 50mm stack (about 500 sheets of 75g/m2paper)
Cassette types
Upper cassette Universal (accommodates B4, A4, Legal, Letter sizes)
Lower cassette Universal (accommodates A3, B4, A4, Ledger, Legal, Letter sizes)
9) Print delivery Face-down/face-up
10) Print tray capacity
Face-down About 500 sheets (75g/m2paper)
Face-up About 100 sheets (75g/m2paper)
1 - 3
CHAPTER 1

11) Duplex print
Auto-duplexing When duplex unit (option) is installed, and plain paper (64g/m2to
105g/m2recommended paper) only.
Manual duplexing
(Note 4) Plain paper (64g/m2to 128g/m2recommended paper) on multi-
purpose tray only.
12) Environment
Temperature 10 to 32.5°C
Humidity 20 to 80%RH
Air pressure 760 to 1013hPa (560 ~ 760mmHg/equivalent to 0 ~ 2,600m above
the sea level)
13) Maximum power
consumption About 1,220W (20°C room temperature, rated voltage)
14) Noise level (Officially announced level based on ISO 9296)
Sound power level (1B=10dB) 6.9B or less (printing)
5.3B or less (standby)
Sound pressure level 54dB or less (printing)
(Bystander position) 38dB or less (standby)
15) Dimensions 566 (w) ×520 (D) ×540 (H) mm (excluding some projections)
16) Weight About 50kg (printer)
Aabout 3.4kg (cartridge)
17) Line voltage requirements
220 to 240V (-10%, +6%) 50/60Hz (±2Hz)
18) Options Duplex unit DU-82, envelope feeder EF-9, 2000 sheet paper deck
PD-82, 2x500 sheet paper deck PD-82K, sorter S-82, stapler
stacker SS-72
Notes: 1. A test print at room temperature of 20°C with rated voltage input.
2. When the printer is in READY state at a room temperature of 20°C, the time from
reception of the PRINT signal from the video controller until an A4 or A3-sized print
is delivered onto the face-down tray.
3. At a room temperature of 20°C with rated voltage input, the time from turning ON
the printer until the end of the WAIT period.
4. When manual duplexing, correct the curl of the print delivered in the face-down tray
before setting it in the multi-purpose tray.
2. Video Controller
1) CPU RISC processor: Motorola PowerPC 603e
2) RAM Standard: 8MB
Maximum: 40MB
3) ROM 4MB
4) ROM DIMM socket 2
5) RAM DIMM socket 3
6) Host interface Standard: IEEE 1284 compliant parallel
Option: expansion interface (Ethernet, Token Ring)
7) Language Standard: PCL 5e/PCL 6
Option: Adobe®PostScript®3™
8) Resident fonts 45 Scalable fonts (MicroType font), 8 Bitmap font
9) Optional fonts 136 fonts
10) Scaler UFST
1 - 4
CHAPTER 1
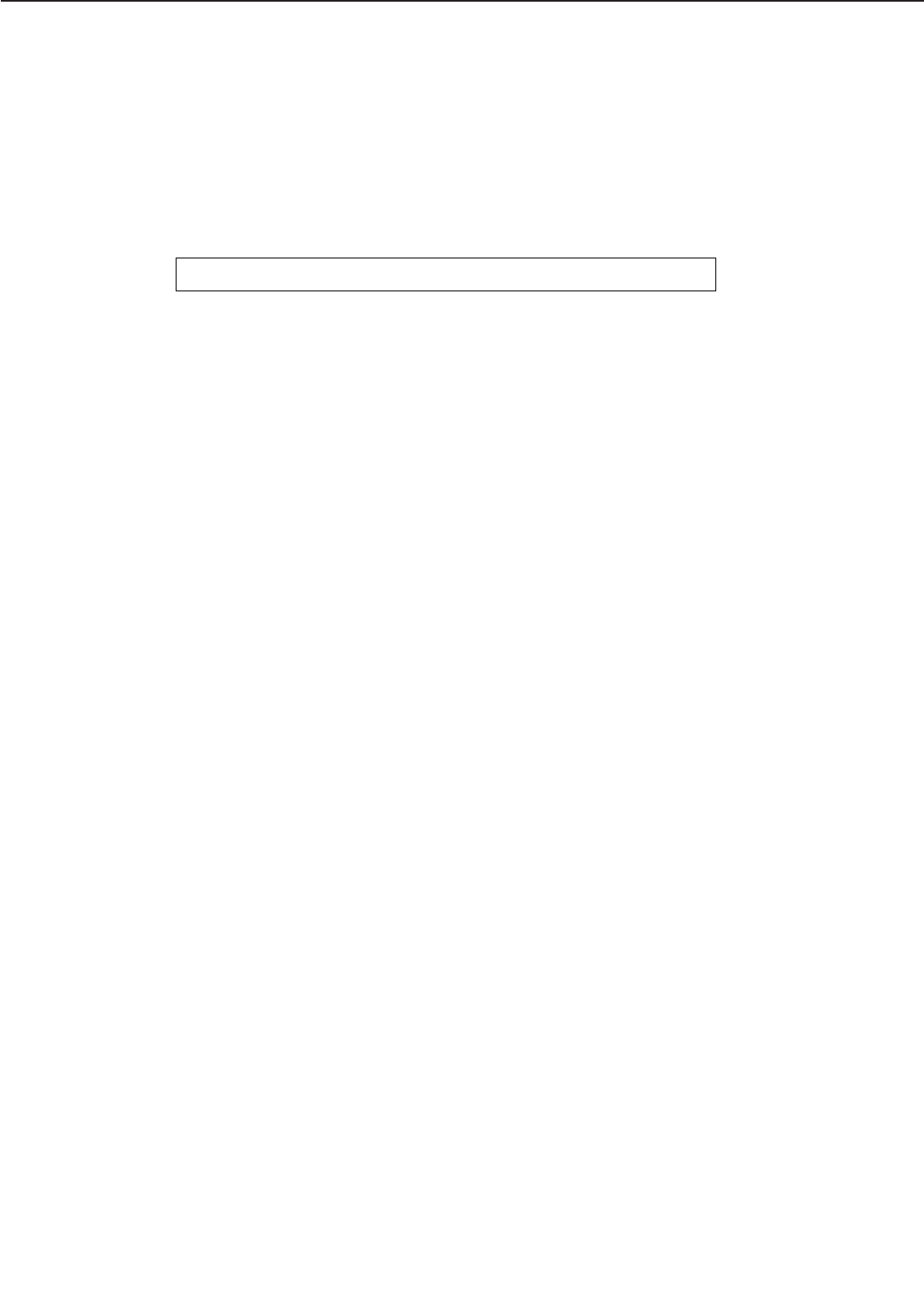
B. Option
1. Hard disk
1) Memory 2.16GB
2) Interface ATA-3 (IDE)
3) Dimensions 70 (w) ×12.7 (D) ×100 (H) mm (excluding mounting materials and
connector.)
4) Weight About 0.15kg
5) Power supply DC5V (supplied from the printer)
Specifications are subject to change with product modification.
1 - 5
CHAPTER 1
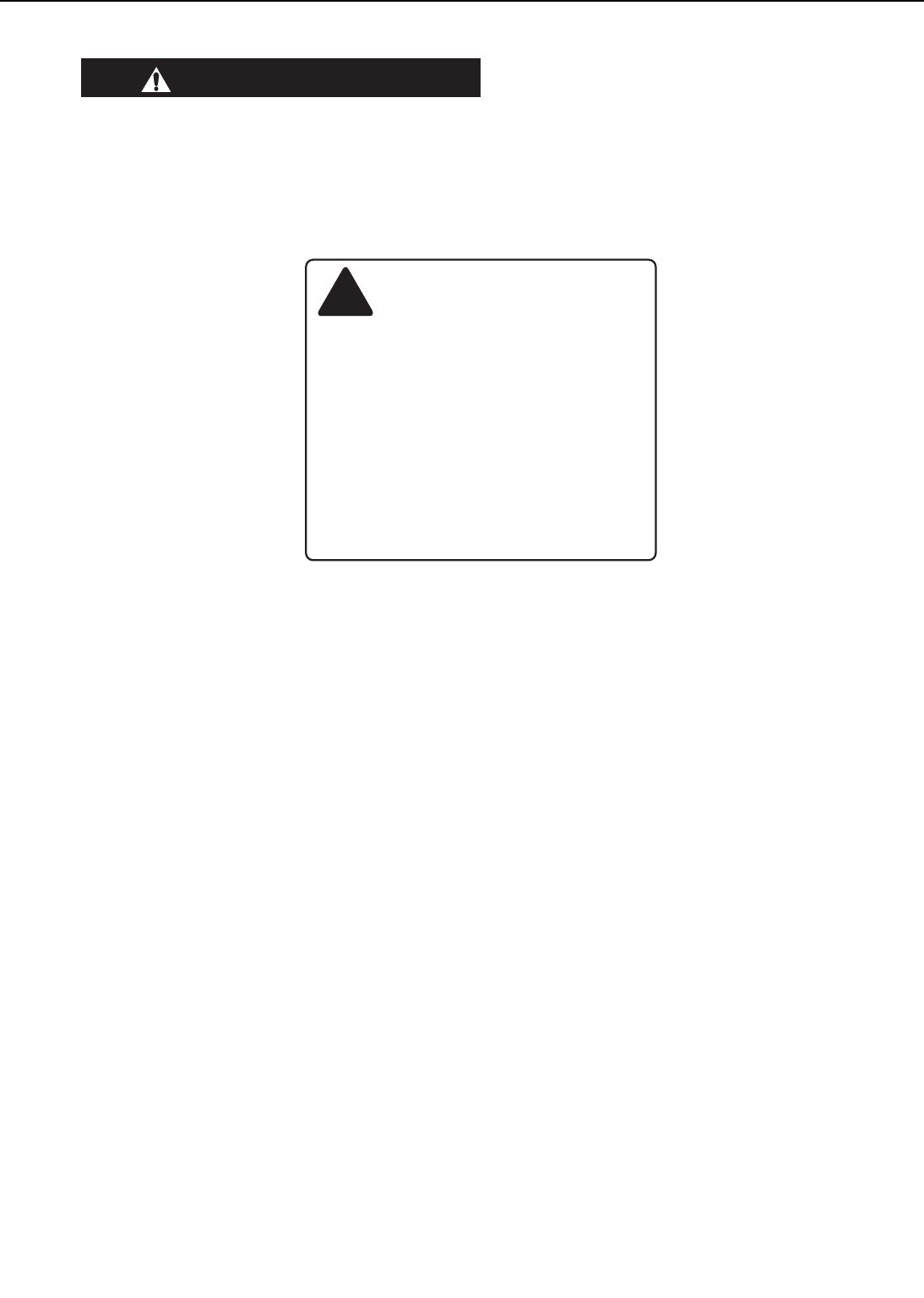
III. SAFETY INFORMATION
A. Laser Safety
An invisible laser beam is irradiated within the laser/scanner unit.
Since the laser beam can injure the eye if it strikes it, be sure not to disassemble the
laser/scanner unit. It cannot be adjusted in the field, anyway.
The label shown below is attached to the laser/scanner unit cover.
Figure 1-3-1
B. Toner Safety
Composed of plastic and minute colored components, toner is a non-poisonous substance.
If toner adheres to your skin or clothes, remove as much of it as possible with dry tissue
paper, then wash with cold water. If you use hot water, the toner will gel and become difficult
to remove.
As toner easily breaks down vinyl materials, avoid letting toner come into contact with vinyl.
C. Ozone Safety
An infinitesimal amount of ozone gas (O3) is generated during corona discharge from the charg-
ing roller used in this printer. The ozone gas is emitted only when the printer is operating.
This printer meets the ozone emission reference value set by Underwriters Laboratory (UL) at
the time it is shipped from the factory.
D. Power Supply Unit Safety
Care is needed as even though the printer switch may be OFF, there is a possibility that a cur-
rent may still flow on the primary side. Be sure to remove the power plug before disassembly
and assembly of this printer.
1 - 6
CHAPTER 1
!
Invisible laser radiation when open.
AVOID DIRECT EXPOSURE TO BEAM.
DANGER-
INVISIBLE LASER RADIATION WHEN OPEN.
AVOID EXPOSURE TO BEAM.
CAUTION
-
RAYONNEMENT LASER INVISIBLE EN CAS D'O UVERTURE.
EXPOSITION DANGEREUSE AU FAISCEAU.
ATTENTION
-
UNSICHTBARE LASERSTRAHLUNG.WENN ABDECKUNG GEÖFFNET.
NICHT DEM STRAHL AUSSETZEN.
VORSICHT
-
RADIAZIONE LASER INVISIBILE IN CASO DI APERTURA.
EVITARE L'ESPOSIZIONE AL FASCIO.
ATTENZIONE
-
RADIACION LASER INVISIBLE CUANDO SE ABRE.
EVITAR EXPONERSE AL RAYO.
PRECAUCION
-
AVATTAESSA OLET ALTTIINA NÄKYMÄTTÖMÄLLE
LASERSÄTEILYLLE. ÄLÄ KATSO SÄTEESEEN.
VARO!
-
OSYNLIG LASERSTRÅLNING NAR DENNA DEL ÄR ÖPPNAD.
BETRAKTA EJ STRÅLEN.
VARNING!
-
USYNLIG LASER STRÅLING,NÅR DENNE ER ÅBEN.
UNDGÅ BESTRÅLING.
ADVARSEL!
-
USYNLIG LASERSTRÅLING NÅR DEKSEL ÅPNES.
UNNGÅ EKSPONERING FOR STRÅLEN.
ADVARSEL
-
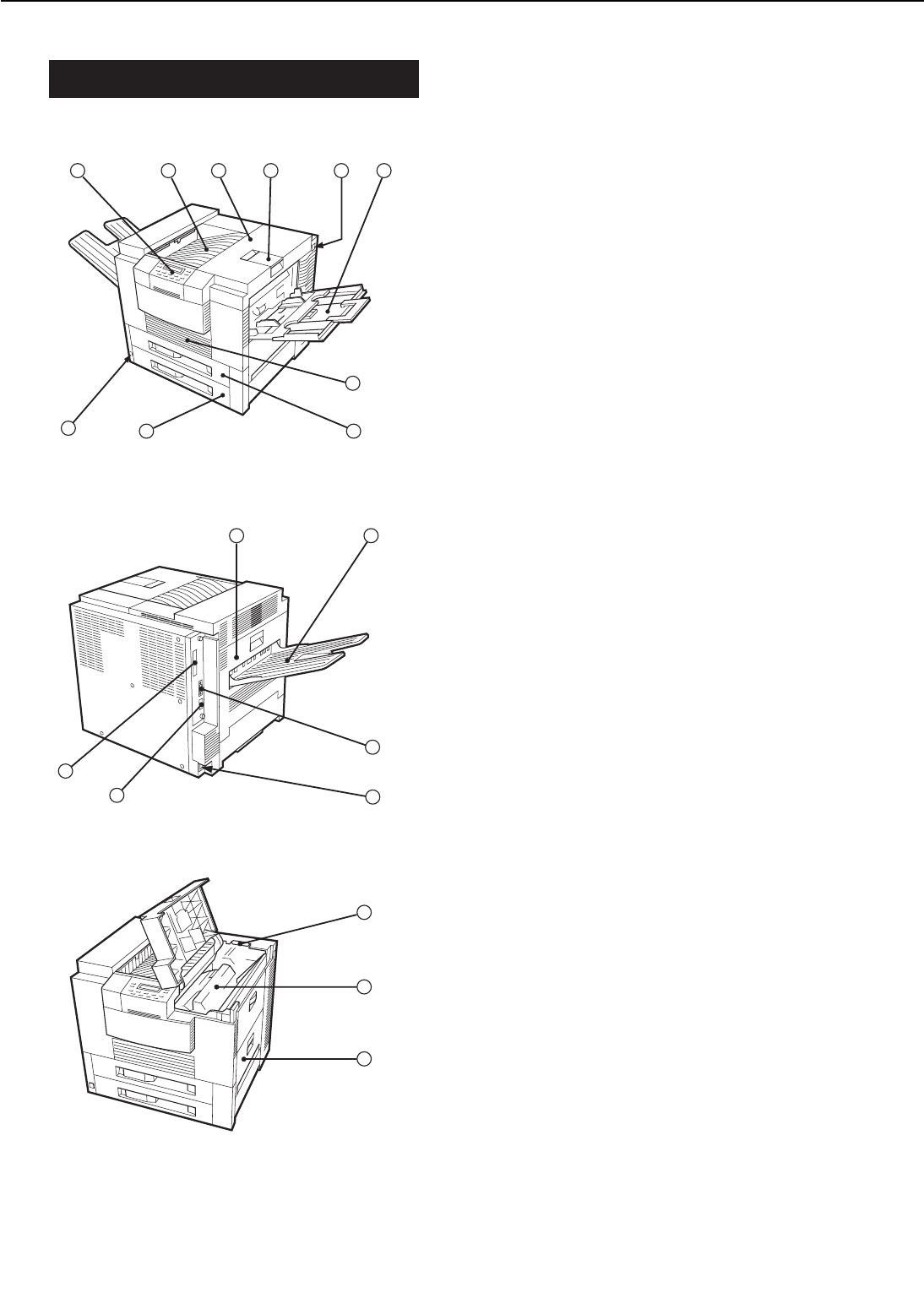
IV. PARTS OF THE PRINTER
A. External Views
Figure 1-4-1
Figure 1-4-2
Figure 1-4-3
1: Operation panel unit
2: Face-down tray
3: Upper cover
4: Delivery stopper
5: Test print switch
6: Multi-purpose tray
7: Duplex unit door
8: Upper cassette
9: Lower cassette
10: Power switch
11: Delivery cover
12: Face-up tray
13: Parallel interface connector
14: Power receptacle
15: Option interface connector (option)
16: Expansion board slot
17: Cleaning brush
18: EP-72 cartridge
19: Pick-up unit door
1 - 7
CHAPTER 1
123456
10 98
7
11 12
13
14
15
16
17
18
19

B. Cross-sectional Views
Figure 1-4-4
1: Face-up tray 13: Multi-purpose tray
2: Face-up delivery roller 14: Feed roller 1
3: Face-down delivery roller 15: Feed roller 2
4: Upper fixing roller 16: Separation roller
5: Laser/scanner unit 17: Pick-up roller
6: Primary charging roller 18: Transfer charging roller
7: Photosensitive drum 19: Upper cassette
8: Developing cylinder 20: Lower cassette
9: EP-72 cartridge 21: Lower fixing roller
10: Registration roller 22: Duplex deflector
11: Multi-purpose tray pick-up roller 23: Face-up deflector
12: Separation pad
1 - 8
CHAPTER 1
12 3 4 5 6 76 8 9
10 11 12 13
141516171821
22
23 19
20
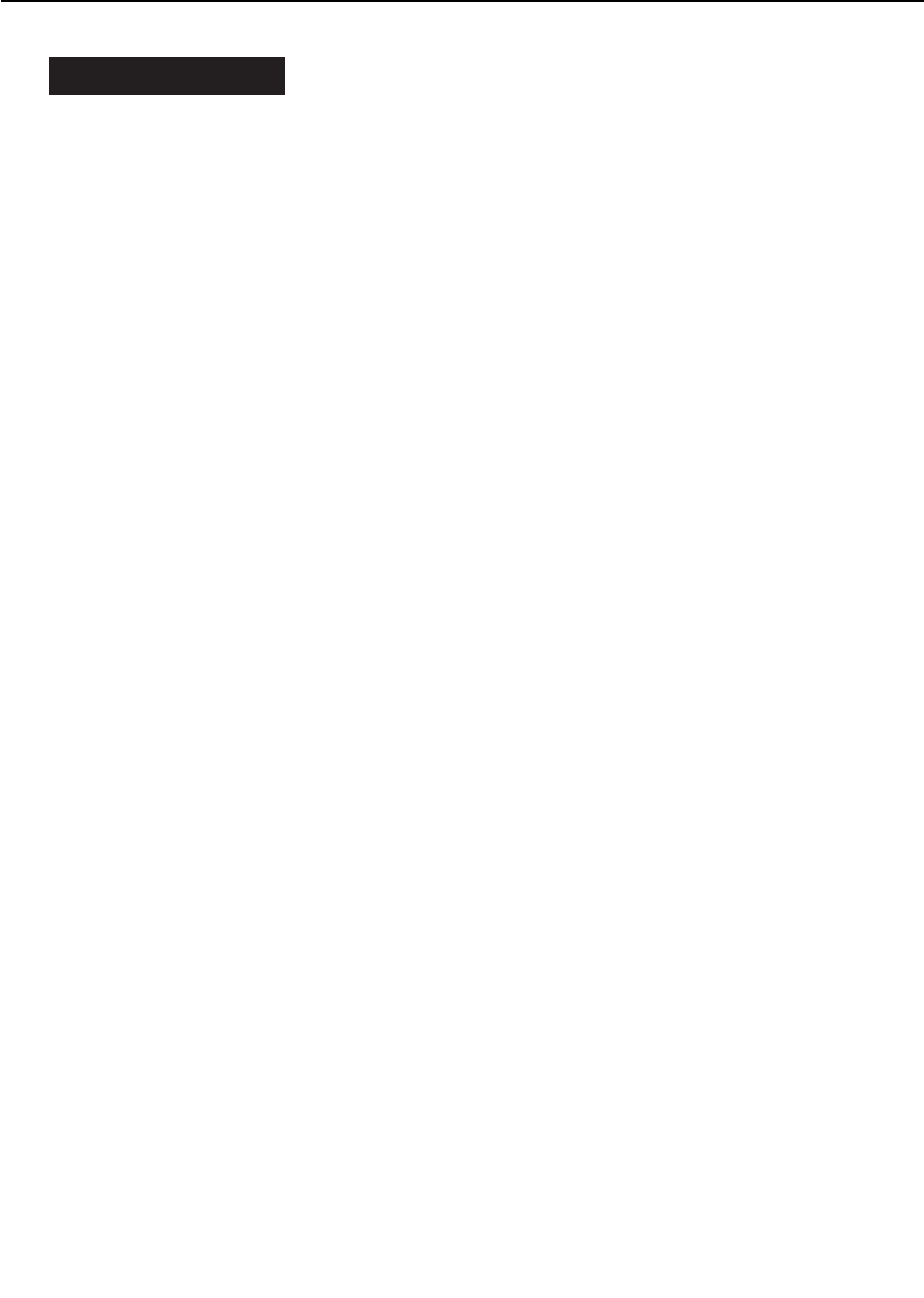
V. INSTALLATION
A. Notes
This printer is packaged and shipped from the factory after careful adjustments and rigorous
inspections.
When installing the printer, it is important to demonstrate its performance in the same way as
when it passes the factory inspection.
The service engineer must sufficiently understand the performance of the printer, install it
correctly in a location with an appropriate environment, and conduct sufficient checks of the
unit.
B. Location Selection
Before taking the printer to the customer's premises, you should confirm the following condi-
tions at the installation location.
1. Power supply
Use the following power supplies:
• Alternating current (AC): -10%, +6% of the rated voltage
• Power frequency: 50/60Hz±2Hz
2. Operating environment
Install in a location that meets the following conditions:
• Level, flat surface
• Temperature, humidity within the following ranges:
Surrounding temperature: 10to 32.5°C
Surrounding humidity: 20 to 80%RH (relative humidity), without condensation
• Cool, well-ventilated space
Do not install in the following locations:
• Exposed to direct sunlight
If you cannot avoid such a location, hang heavy curtains, etc. to shut out the direct sunlight.
• Near magnets and devices that emit a magnetic field.
• Areas with vibration
• Dusty places
• Near fire or water
3. Installation space
Install the printer a suitable distance from the wall, leaving enough room to operate it (see Figure
1-5-1).
When installing the printer on a desk, etc., be sure that it is large enough to accommodate
the printer's feet (rubber pads) and sturdy enough to hold its weight.
1 - 9
CHAPTER 1
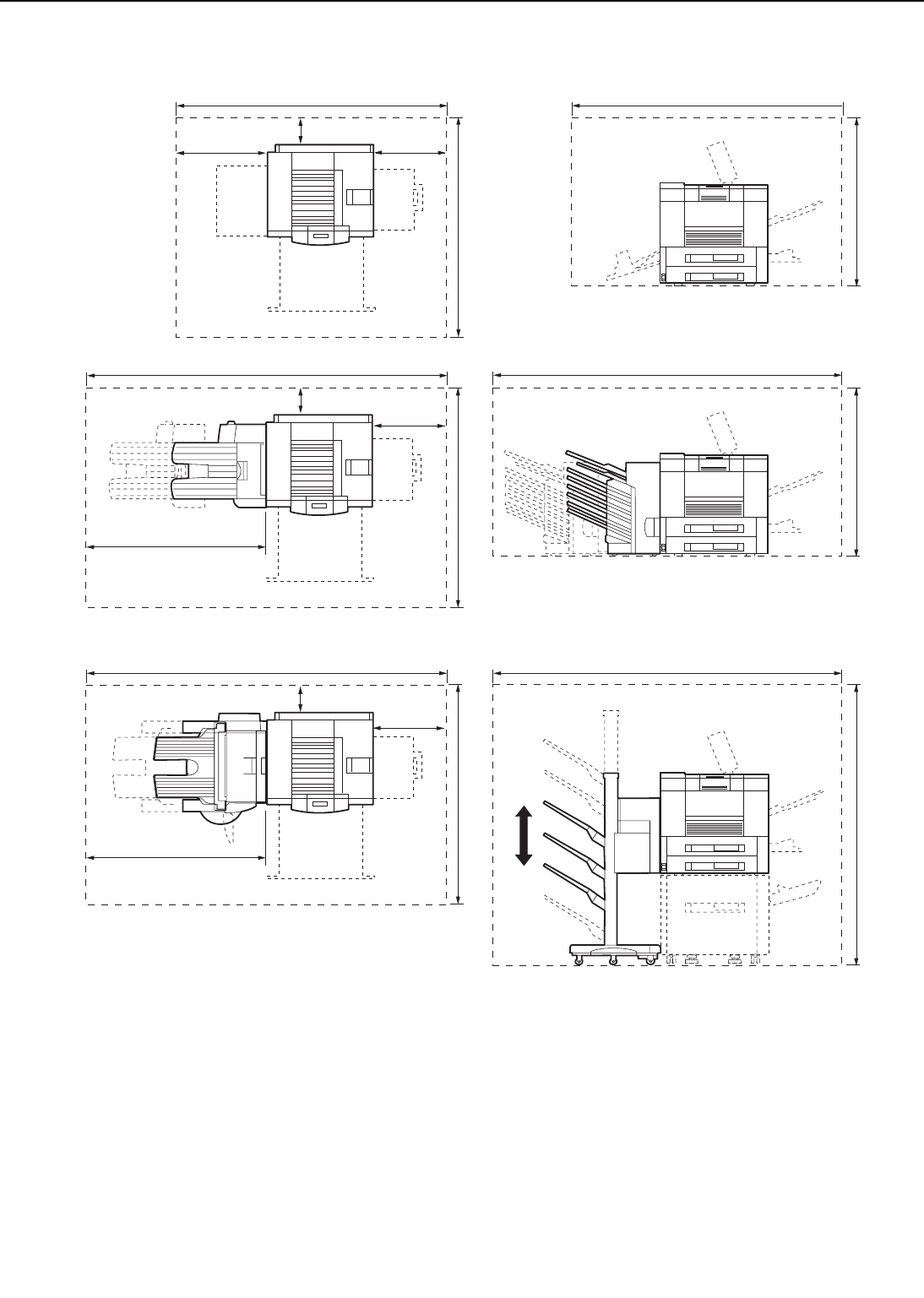
Figure 1-5-1
1 - 10
CHAPTER 1
900mm 100mm 834mm
2300mm
1500mm
2300mm
900mm
2600mm
2600mm
1200mm
900mm1380mm
2600mm
2600mm
834mm
100mm
100mm 834mm
1200mm
1500mm1500mm
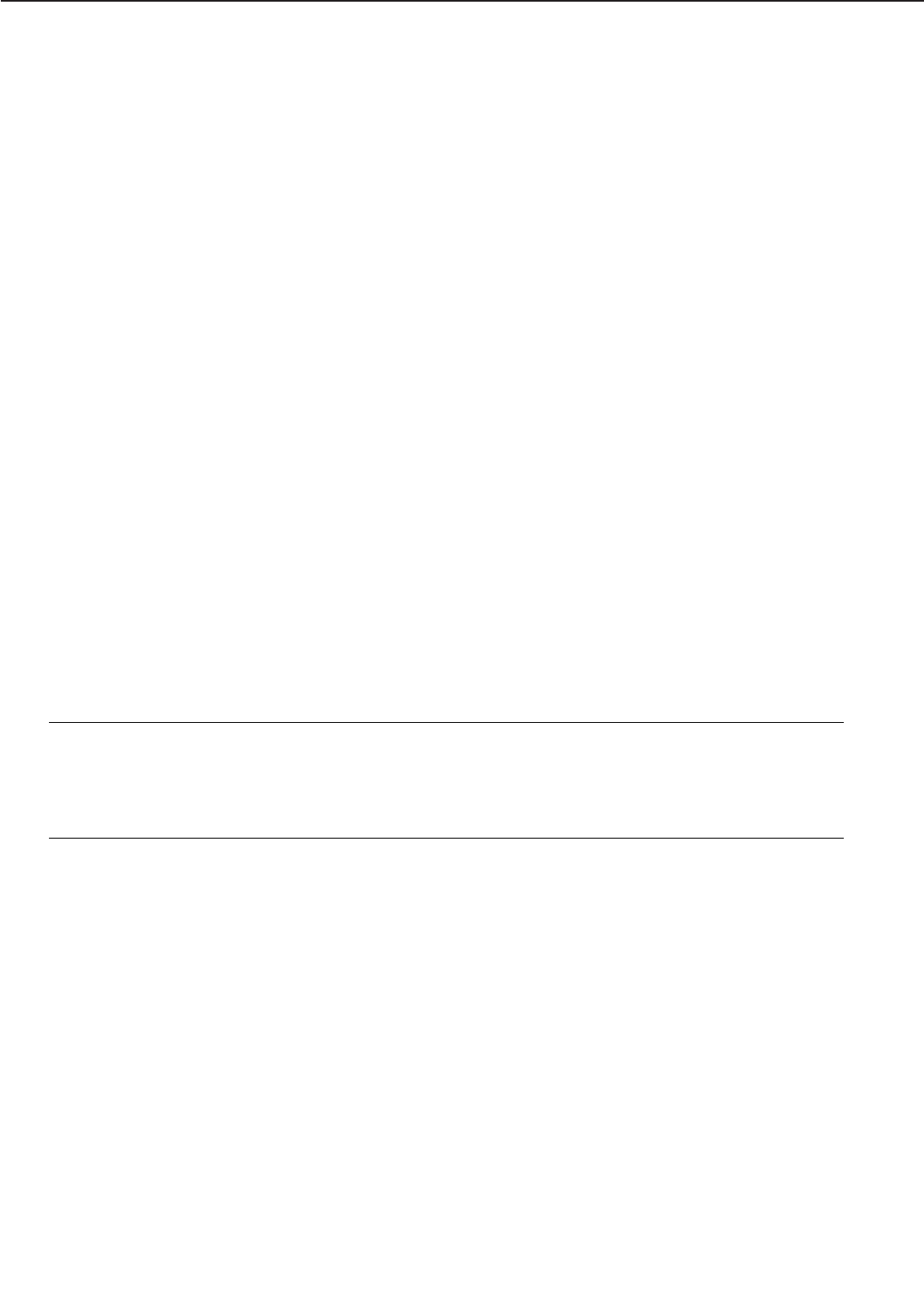
C. Unpacking and Installation
Condensation will form on metal surfaces when brought into a warm room from the cold.
Therefore, when moving the printer to a warm environment, leave it packed in its box for at least
an hour to acclimatize to room temperature.
1. Printer
1) Open the printer packaging.
2) Take out the accessories. Confirm that the power cord, cartridge, and face-up tray are
included.
3) The printer weighs approx. 50kg, therefore 4 people may be needed to lift the printer and to
move to the installation area.
4) Take the plastic bag off the printer and peel the tape off each part. Check that none of the
covers were scratched or deformed during shipment.
5) Open the delivery cover, and remove the pressure release spacer from the fixing unit.
6) Open the upper cover, and remove the tape and the packing materials from inside the print-
er.
7) Pull the two cassettes out of the printer and remove the packaging from the cassette.
2. Cartridge
1) Open the bag holding the cartridge and take out the cartridge.
2) Remove the tape and the black sheet from the cartridge.
3) Hold the cartridge on each side as shown in figure 1-5-2 and slowly rock it 5 to 6 times to
evenly distribute the toner.
4) Place the cartridge on a flat surface. While holding down on the top of the cartridge with one
hand, grasp the tab with the other and gently pull out the sealing tape.
5) Open the upper cover of the printer, and load the cartridge with both hands. Slowly insert it
until it firmly contacts with the back of the slot.
3. Unpacking and installing the hard disk
Note: 1. Before handling the hard disk, be sure to touch the metal part of the printer to dis-
charge electrical static from you body in order to avoid causing damage to the PCB
by the difference in static charge at that time.
2. When removing the PCB at the back of the printer, be sure not to touch the electrical
parts on the PCB. Make sure not to touch especially the electrical elements.
1) Open the hard disk packaging.
2) Remove the pad and then take out the hard disk from its box.
3) Remove the plastic bag holding the hard disk.
4) If the optional expansion board is installed in the printer, remove the board.
5) Loosen the 2 screws at the left back of the printer and pull out the PCB.
1 - 11
CHAPTER 1
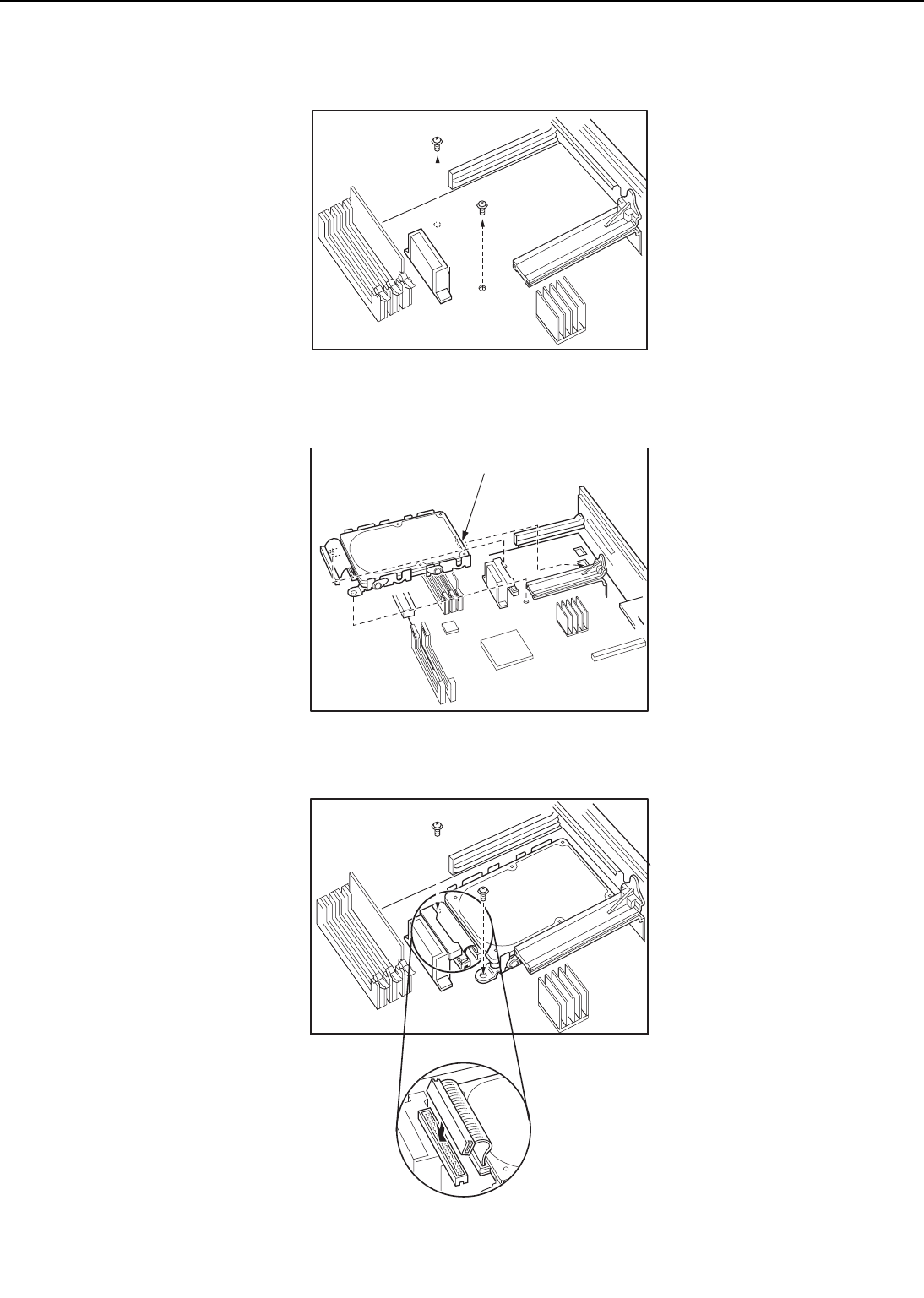
6) Remove the 2 screws on the PCB.
Figure 1-5-2
7) Insert the claw of the hard disk into the hole of the PCB.
Figure 1-5-3
8) Fix the hard disk with the enclosed 2 screws and then connect the connector.
Figure 1-5-4
1 - 12
CHAPTER 1
Hook
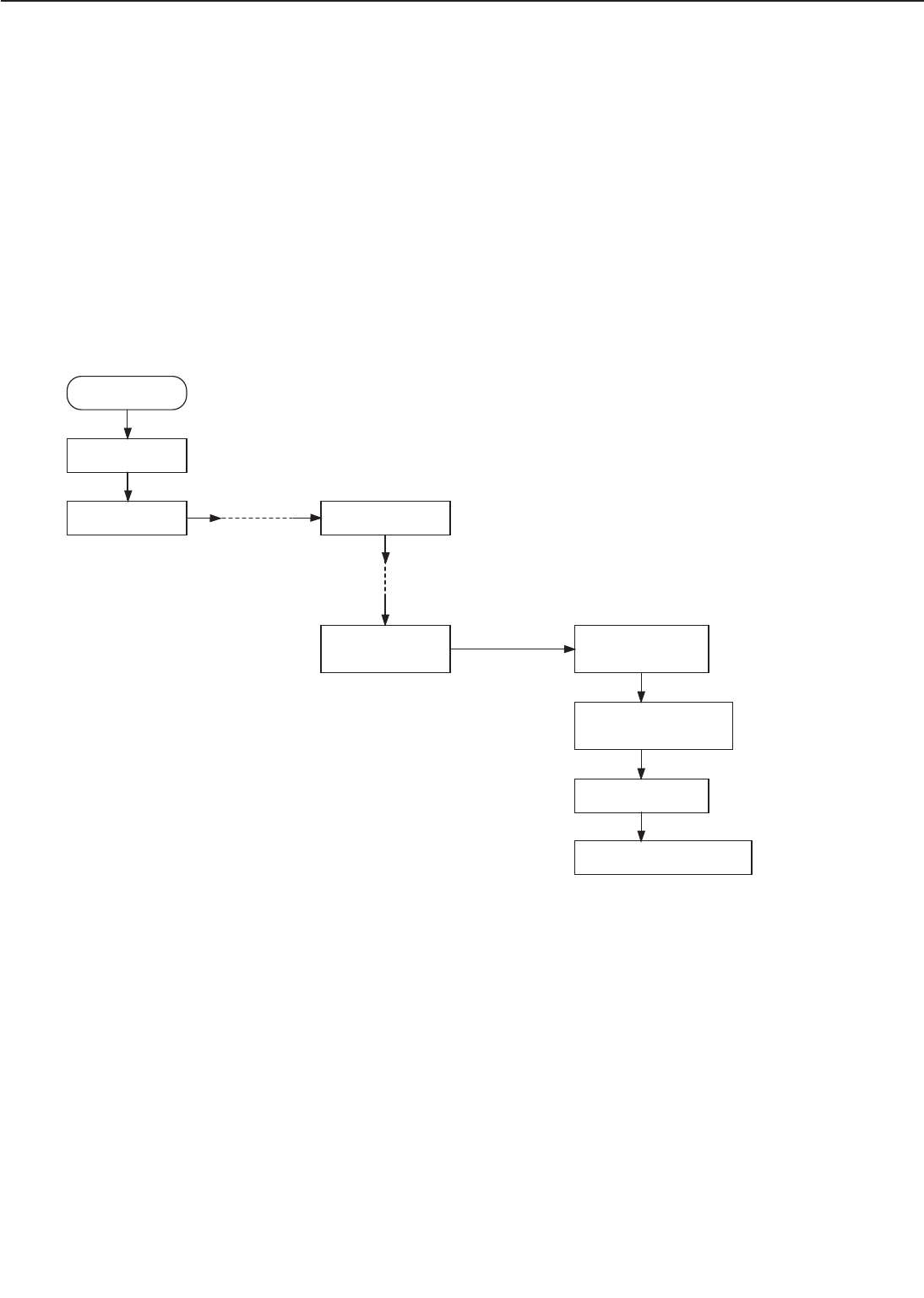
9) Install the PCB into the printer and fix it with 2 screws.
10) Turn ON the printer switch.
11) Press the On Line key when the printer becomes READY to take the printer off-line.
12) Press the Menu key to select "CONFIG MENU."
13) Press the Item key to select "FORMAT DISK."
14) Press the Enter key.
"+FORMAT DISK -IGNORE DISK" appears in the display.
15) Press the +Plus/-Minus key.
"+REALLY FORMAT -IGNORE DISK" appears in the display.
16) Press the +Plus/-Minus key.
"FORMATTING..." appears in the display, Disk LED lights up and formatting starts.
17) When the printer completes formatting the hard disk, "DISK FMT RESTART" appears in the
display, and the printer restarts automatically.
Figure 1-5-5
1 - 13
CHAPTER 1
Power On
READY
PAUSED
Press On Line key
Press Menu key CONFIG MENU
CONFIG MENU
FORMAT DISK
Press Item key
Press Enter key +FORMAT DISK
-IGNORE DISK
Press +Plus/-Minus key
+REALLY FORMAT
-IGNORE DISK
Press +Plus/-Minus key
FORMATTING...
DISK FMT RESTART
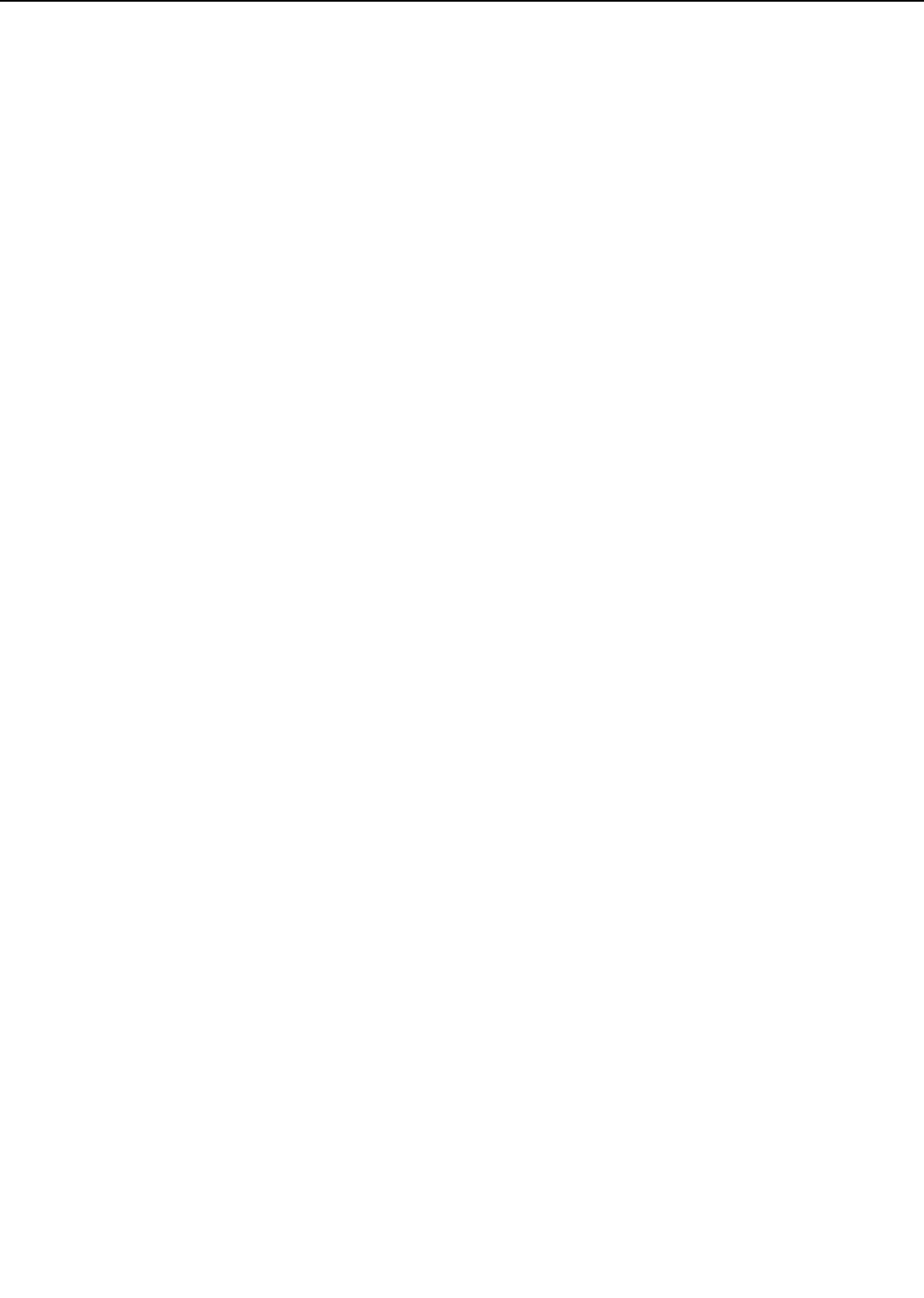
4. Operation confirmation
1) Load paper in the lower cassette.
2) Insert the power plug into the outlet and the printer, then turn the power switch ON.
After the printer enters STANDBY mode, press the test print switch to make a test print.
Check that the density of the output image is correct
3) Clean around the printer and ensure that it is ready for use at anytime.
5. Operation precautions
1) Turn ON the power of external equipment then the printer. Turn the power OFF in the
reverse sequence. If the power of external equipment is turned ON/OFF while the printer is
ON, noise may be transmitted through the connection cable between the external equipment
and the printer, and error may occur on the printer.
2) Turn off the power of both the printer and the external equipment before plugging/unplug-
ging the connector between the two. Doing so while the power is ON could cause malfunc-
tions.
1 - 14
CHAPTER 1
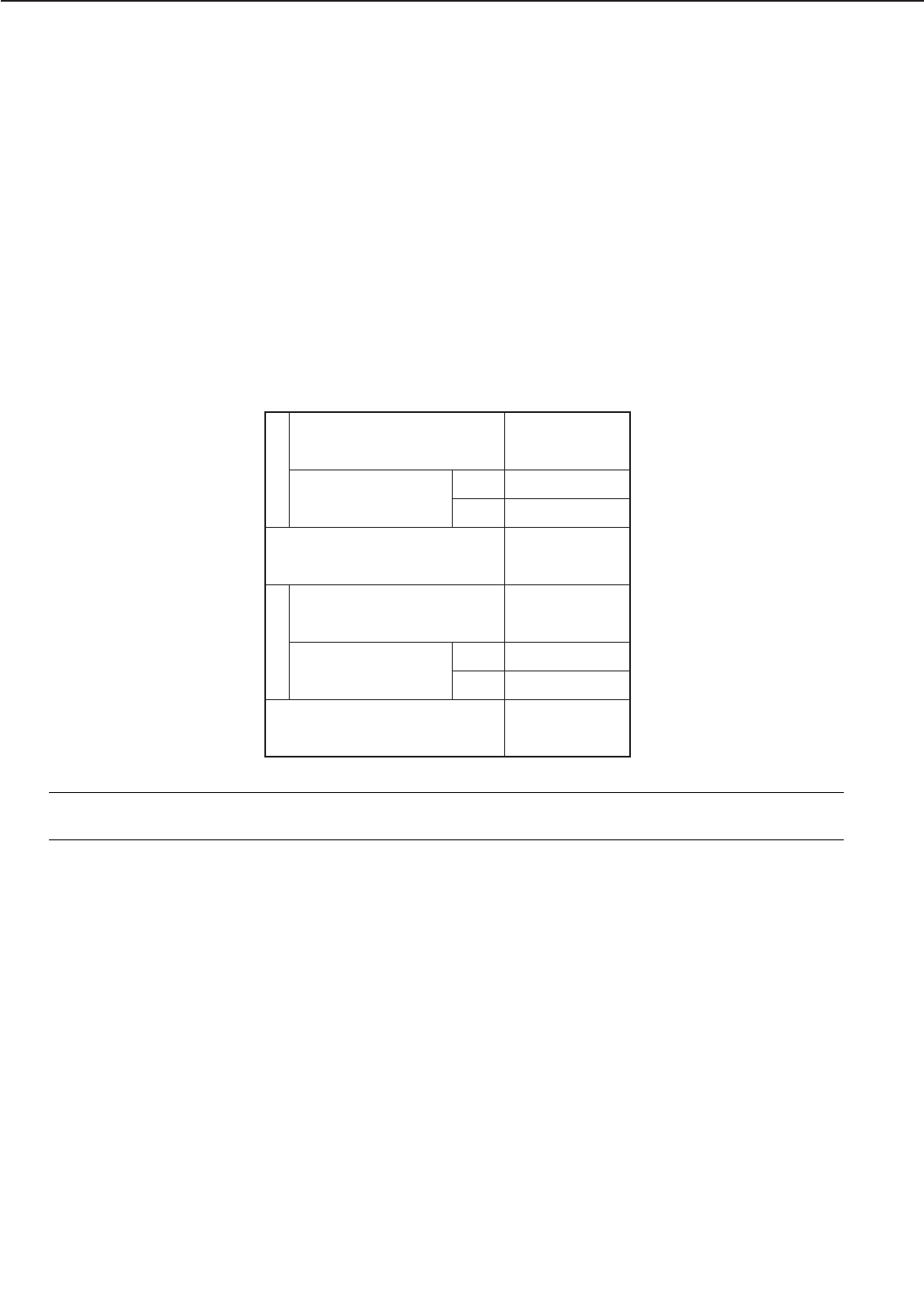
D. Storing, Handling the EP-72 Cartridge
Whether the cartridge is still sealed in its box or installed in the printer, the effect of the natur-
al environment will change it over time regardless of the number of prints. As the progression of
this natural change depends on the storage or installation environment, take sufficient care in
storing and handling the cartridges.
1. Before unsealing the box
When the cartridge is stored in a warehouse, workshop, etc., be sure to keep it within the ranges
shown in Table 1-5-1. Note the following points:
1) Avoid locations in direct sunlight.
2) Do not leave in areas exposed to strong vibration.
3) Do not bump or drop.
Table 1-5-1 Storage temperature and humidity conditions
Note: Total storage time is the valid time span following the manufacture date displayed on
the cartridge box.
2. After unsealing the box
As an organic photoconductor (OPC) is used in the photosensitive drum, it will deteriorate if
exposed to strong light. As there is toner in the cartridge, be sure to explain to the customer the
need to be careful in handling and storing unsealed cartridges.
a. Storage environment
1) Be sure to store in the aluminum bag.
2) Avoid locations exposed to direct sunlight, near windows, etc. Do not leave them in cars for
any extended period of time as heat can damage the cartridges.
3) Avoid high, low, and changeable temperature/humidity locations.
4) Avoid sites with corrosive gases (pesticides) or salt in the air.
5) Store the cartridge within a range of 0 to 35°C.
6) Do not leave cartridges near CRT displays, disk drives or floppy disks.
7) Store the cartridges out of reach of children.
1 - 15
CHAPTER 1
Normal (total storage time ×
9/10)
Temperature
Severe (total storage
time ×1/10)
Air pressure
Temperature change (within
3 minutes or so)
0to35°C
35 to 40°C
40°C→15°C
–20°C→25°C
35 to 85% RH
85 to 95% RH
10 to 35% RH
345 to 1013 hPa
(460 to 760 mmHg)
High
Low –20 to 0°C
Normal (total storage time ×
9/10)
Severe (total storage
time 1/10)
High
Low
Relative humidity
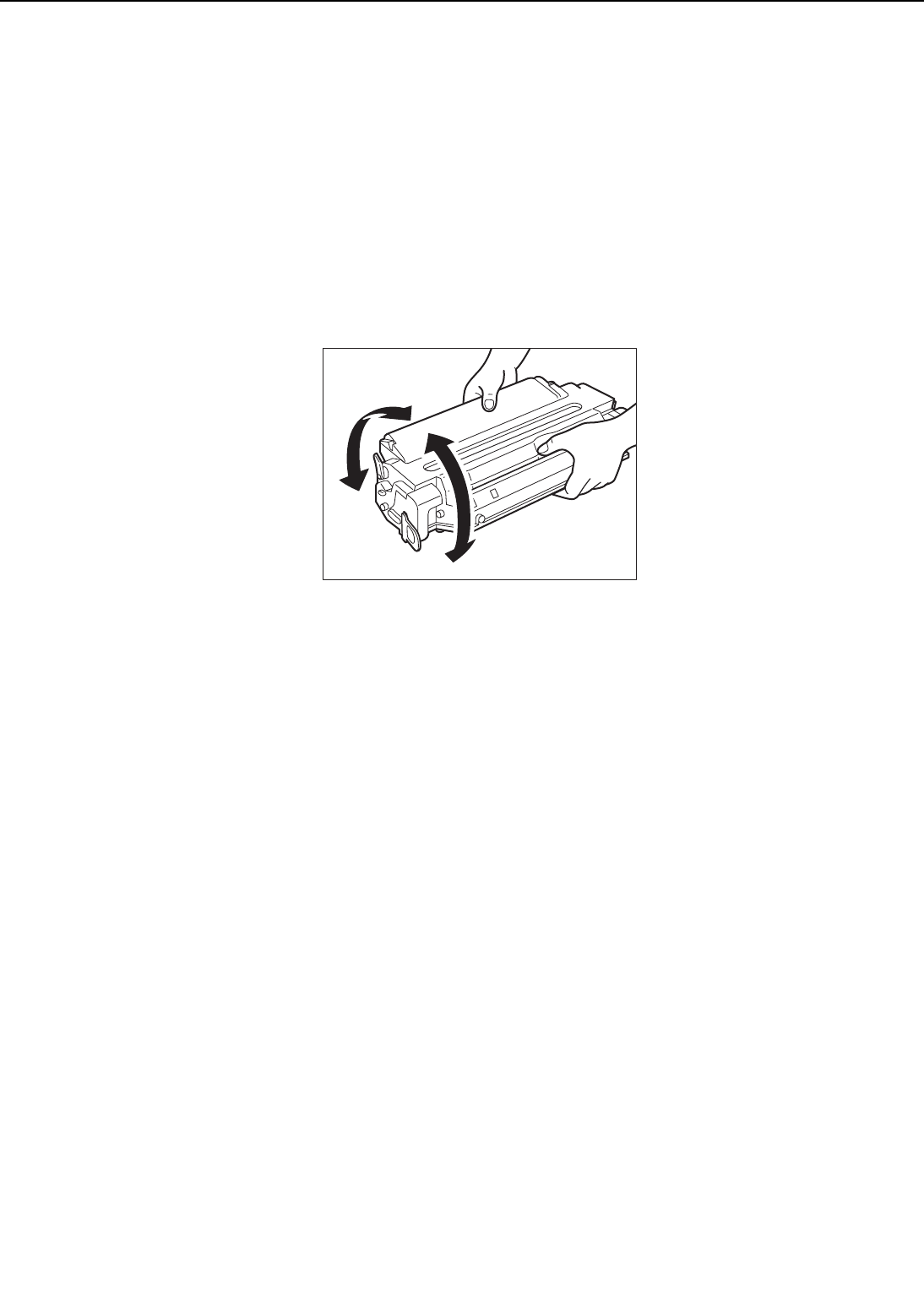
b. Effective life
Cartridges are effective for 2.5 years following the date of manufacture, which is displayed in an
abbreviated form on the cartridge. The cartridge life span is also displayed (month and year) on
the cartridge box as 2.5 years from the date of manufacture. Cartridges should be used within
their life spans, as image quality will deteriorate after the expiry date.
3. Handling
1) When loading a new cartridge into the printer, or when the toner in an already loaded car-
tridge hardens and blank spots appear on output images, hold the cartridge at each end as
shown in the below figure and slowly rock it about 45° in each direction 5 to 6 times. This
will evenly distribute the toner, and then reload it into the printer. Do not shake the cartridge
in any other way, as toner may leak from the developing cylinder or the cleaning unit.
Figure 1-5-6
To ensure that toner does not leak and dirty the images, be sure to print 3 to 5 pages of test
patterns after loading the cartridge in the printer.
2) When transporting the printer, remove the cartridges.
Either insert the cartridge in the aluminum bag or wrap it in a thick cloth to ensure light
does not penetrate it.
3) Do not leave the cartridge near CRT displays, disk drives, or floppy disks.
The magnetism generated by the cartridge may destroy their data.
4) As the photosensitive drum is sensitive to strong light, do not expose the cartridge to direct
sunlight or strong light (1500 lux or more). If it is exposed to strong light, blank spots or
black lines may appear on images.
Should this happen, temporarily turn OFF the printer. The distorted images such as blank
spots or black lines are likely to disappear. However, if the drum was exposed to strong light
for a long period of time, it is possible the black lines, etc., will remain.
5) Do not open the photosensitive drum protective shield by hand nor touch the drum surface.
Do not clean the drum.
6) Do not place the cartridge on its end or upside down. Always place it with the label side fac-
ing upward.
7) Do not disassemble the cartridge.
1 - 16
CHAPTER 1
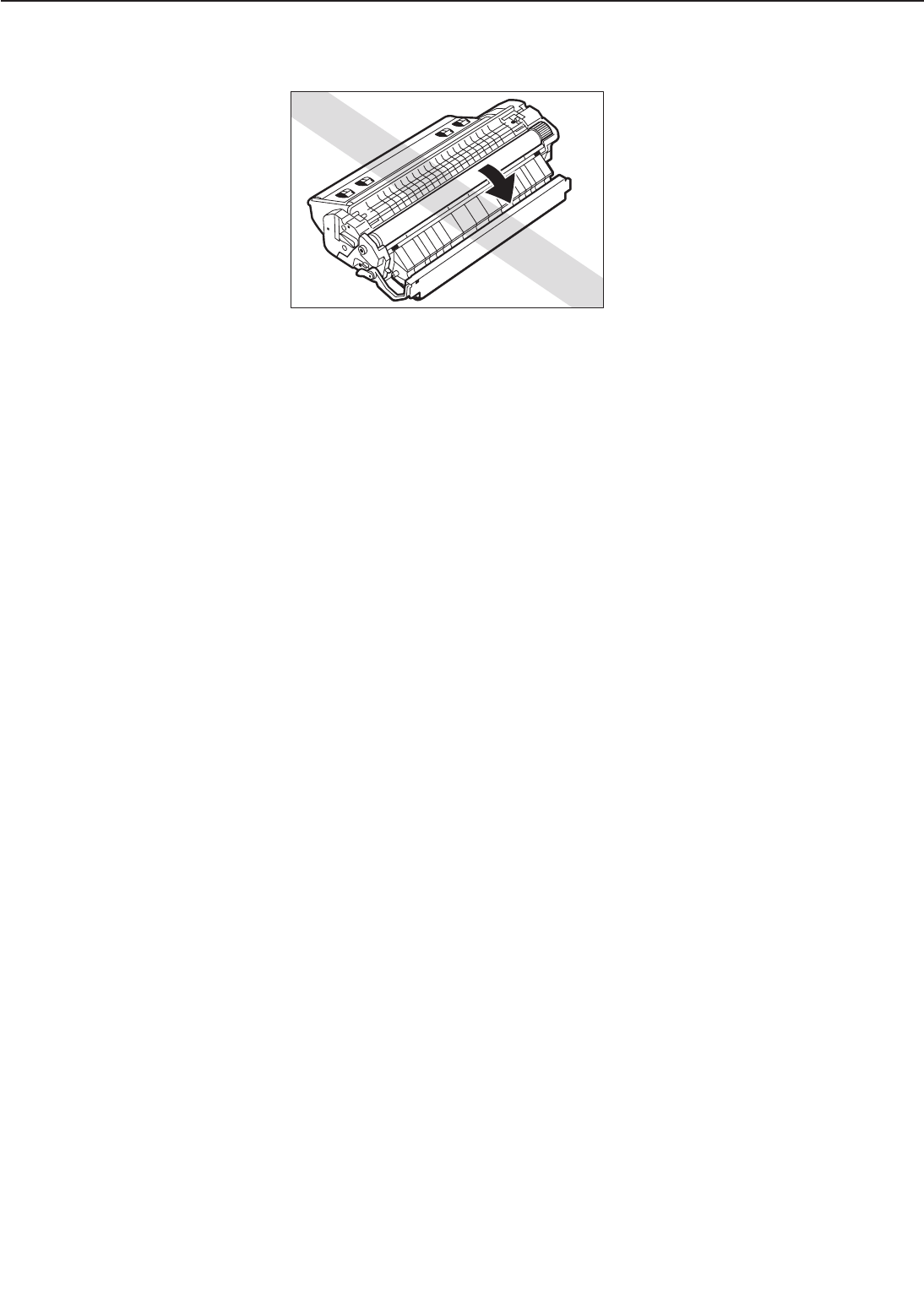
Figure 1-5-7
1 - 17
CHAPTER 1
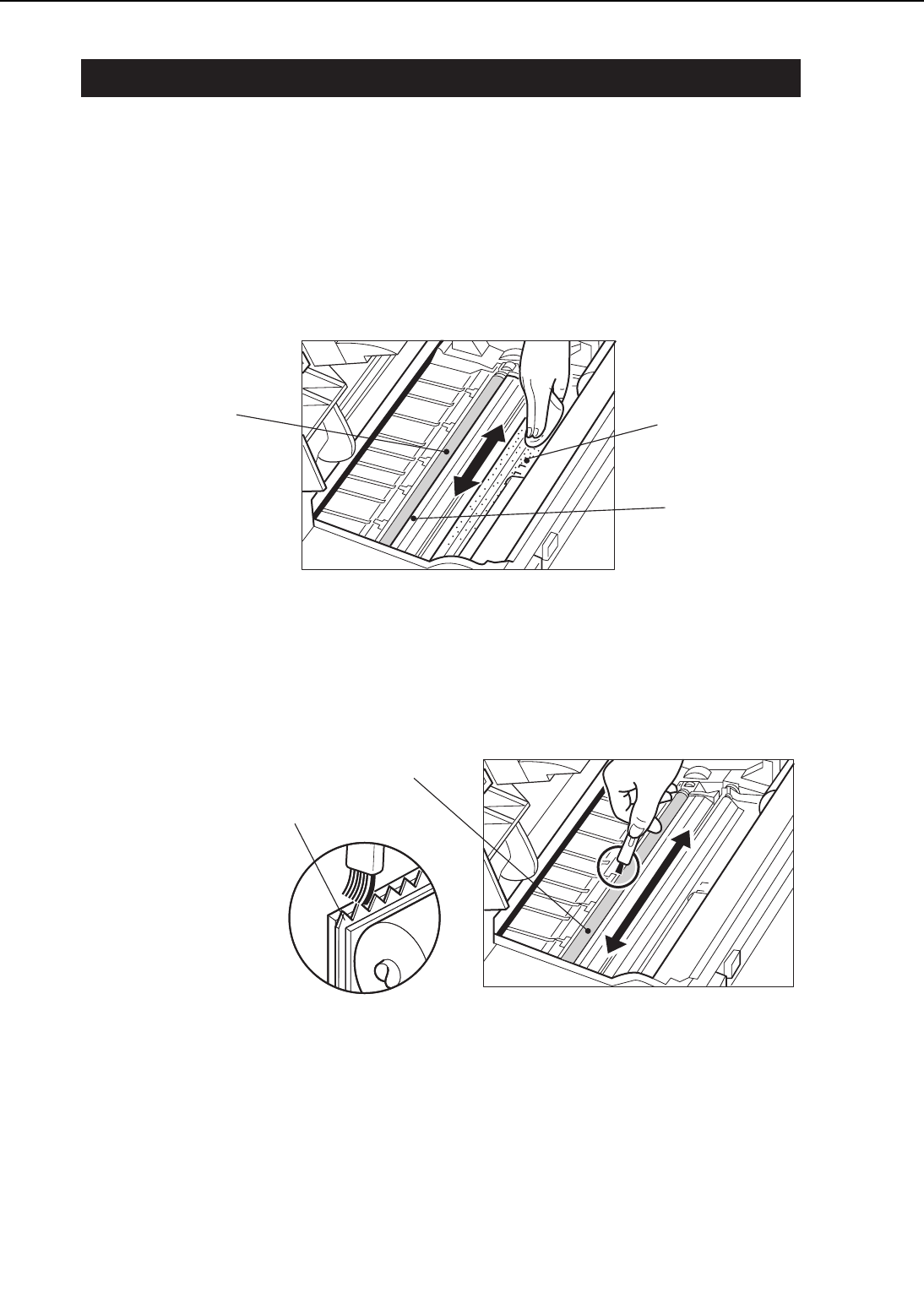
VI. MAINTENANCE AND SERVICING BY THE CUSTOMER
To maintain the optimum performance of the printer, the following maintenance should be per-
formed by the customer.
1. Cartridge
Shake or replace the cartridge as the occasion demands.
2. Transfer guide, registration guide
When replacing the cartridge, clean the transfer guide and registration guide with soft flannel
cloth.
Figure 1-6-1
3. Static charge eliminator
When replacing the cartridge, clean the static charge eliminator with the cleaning brush
attached inside the printer.
Figure 1-6-2
1 - 18
CHAPTER 1
Transfer chargin
g
roller
Transfer guide
(metal part)
Registration guide
(metal part)
Transfer charging roller
Static charge eliminator
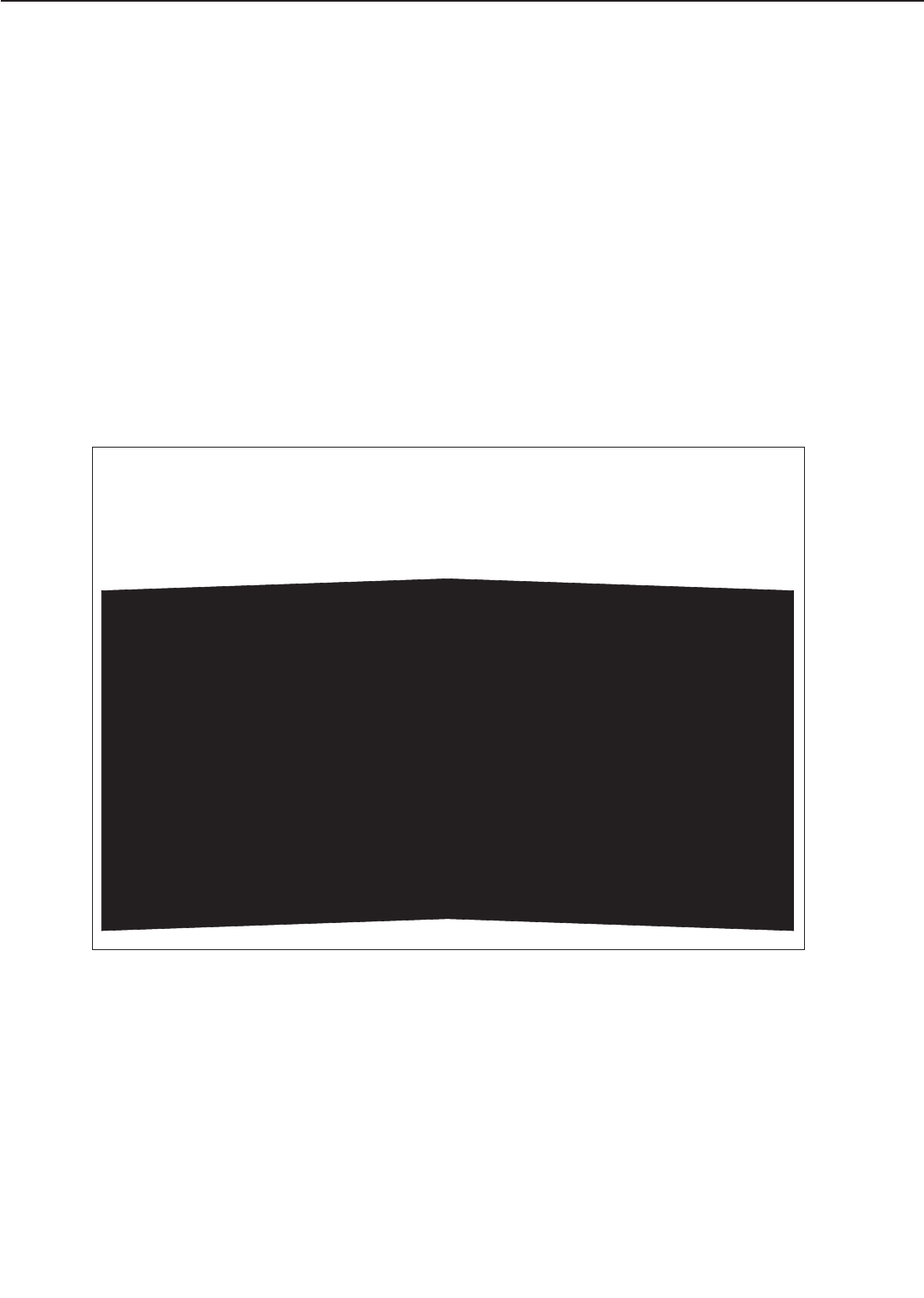
4. Fixing unit
When replacing the cartridge, clean the fixing unit following the procedure below.
1) Open the multi-purpose tray and load one sheet of A4 or Letter size paper into the tray.
2) Press the On Line key to take the printer off-line.
3) Press the Menu key to select "PCL MENU."
4) Press the Item key to select "PAGESIZE."
5) Press the +Plus/-Minus key to select either A4 or Letter, and then press the Enter key.
6) Press the Menu key to select "FEEDER MENU."
7) Press the Item key to select "MPTSIZE."
8) Press the +Plus/-Minus key to select either A4 or Letter, and then press the Enter key.
9) Press the Menu key to select "TEST MENU."
10) Press the Item key to select "CLEANING PAGE" , and then press the Enter key. "LOAD PLAIN
A4 (or LETTER) IN MANUAL" will appear in the display and the Continue LED and Form Feed
LED will light up.
11) Press the Continue key to print the Cleaning Page. "LOAD BLANK SIDE UP IN MANUAL" will
appear and the Continue LED will light up.
Figure 1-6-3
1 - 19
CHAPTER 1
Load this sheet, this side down, in MPT
Læg dette ark, med denne side nedad, i universalbakke
Laad dit vel met deze kant naar beneden in MPT
Lattaa tämä arkki, tämä puoli alaspäin, MPT:hen
Introduire cette page, ce côté vers le bas, dans le tiroir polyvalent
Legen Sie dieses Blatt mit dieser Seite nach unten in den MPT ein
Caricare questa pagina, con questa facciata verso il basso, nel MDT
Legg i arket med denne siden ned i den manuelle materen
Coloque esta página, com este lado para baixo, no MPT
Cargue esta hoja en MPT, con esta cara hacia abajo
Lägg detta ark med textsidan nedåt på din MPT
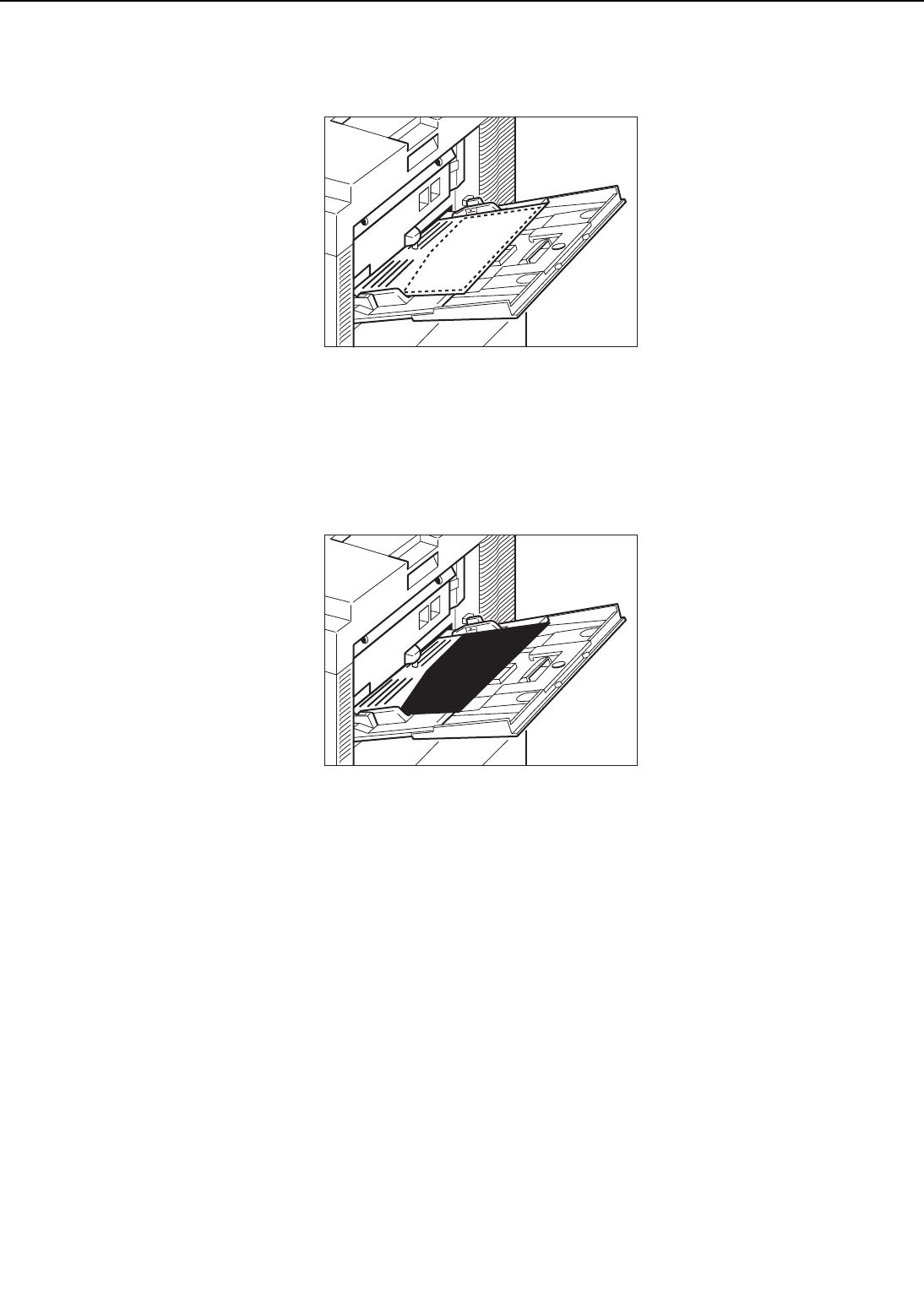
12) Place the printed Cleaning Page into the multi-purpose tray with the printed side face-down.
Figure 1-6-4
13) Press the Continue key to feed the Cleaning Page on the other side of the paper. "LOAD
CLEANING PAGE IN MANUAL" will appear and the Continue LED will light up.
14) Place the Cleaning Page into the multi-purpose tray.
Figure 1-6-5
15) Press the Continue key to feed the Cleaning Page through the printer to clean the fixing unit.
1 - 20
CHAPTER 1

VII. OPERATION
A. The Operation Panel
The operation panel is used to perform basic printer operations, make printer configuration
changes that software applications cannot control, identify available typefaces, and check the
status of the printer.
The operation panel consists of the status indication display, nine indicator lights, and seven
menu and operation keys.
Figure 1-7-1
· Error indicator: 1
On:
An error has occurred and printing has stopped. Check the display for a message describing the
problem.
Off:
Operation is normal and there is no error.
· Power indicator: 2
On:
The printer is ready to print.
Flashing:
The printer is warming up. Wait until the light stays on before you start printing operations.
Off:
1 - 21
CHAPTER 1
Power
Error
On Line Continue Form Feed
Menu Item +Plus/-Minus Shift
Reset Enter
Staple
Disk
1 2 345 6 7 8
9
10
1112
14 13
1617 15
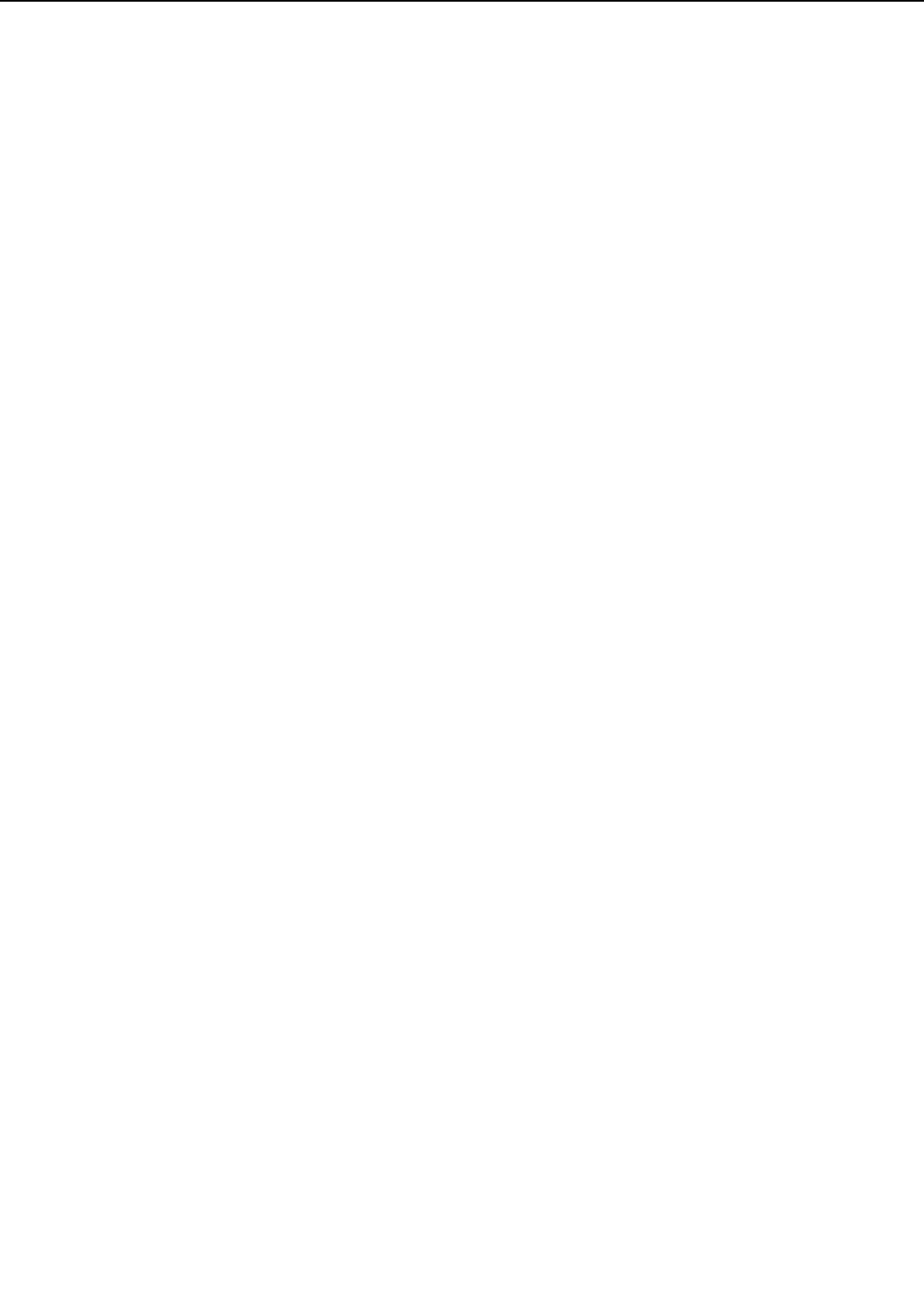
The printer cannot print.
· Continue indicator: 3
On:
Indicates the Continue button may be pressed to exit current condition. For instance, if the mes-
sage TONER LOW appears in the display panel, press Continue to continue printing but be sure
to change the toner as soon as possible.
Off:
Operation is normal.
· Status indication display: 4
The two-line, 20-digit display tells you what is happening inside the printer and shows you the
menus and settings which can be changed. The display keeps you informed about the printer's
operation status, lets you make menu selections, warns you about problems and identifies
errors.
· Form Feed key: 5
Performs a Form Feed and prints data remaining in the FORM printer. If the Form Feed indica-
tor is on, data remains in the printer (only with PCL). Press ON LINE to take the printer off-line.
Press Form Feed to print the remaining data.
· Reset key: 6
Accesses the RESET menu so you can select RESET PRINTER or RESET MENU. If you choose
RESET PRINTER all resources in the memory (soft fonts, macros, stored page data, and so on)
are erased, but the menu items selected are unaffected. If you choose RESET MENU the facto-
ry default values are restored for most menu items.
· Disk indicator: 7
On:
The disk is being accessed (for fonts, etc.).
Off:
The disk is not being accessed.
· Staple indicator: 8
On:
Stapling has been selected for the current print job.
Off:
Stapling has not been selected.
· Enter key: 9
Saves a value you selected for an item in the menu. An asterisk (*) marks the the current default
setting.
· Shift key: 10
Press Shift and another key to access the alternate function of dual-function keys. The two func-
tions on dual function keys are separated by a slash in the key name on the printer control
panel.
· +Plus/-Minus key: 11
With an item name displayed, press to +Plus/-Minus step through the item's values. Press and
hold down Shift then press +Plus/-Minus to step through the values in reverse order. Some item
have a large range of numbers from which to choose a value. For example, for COPIES you can
1 - 22
CHAPTER 1
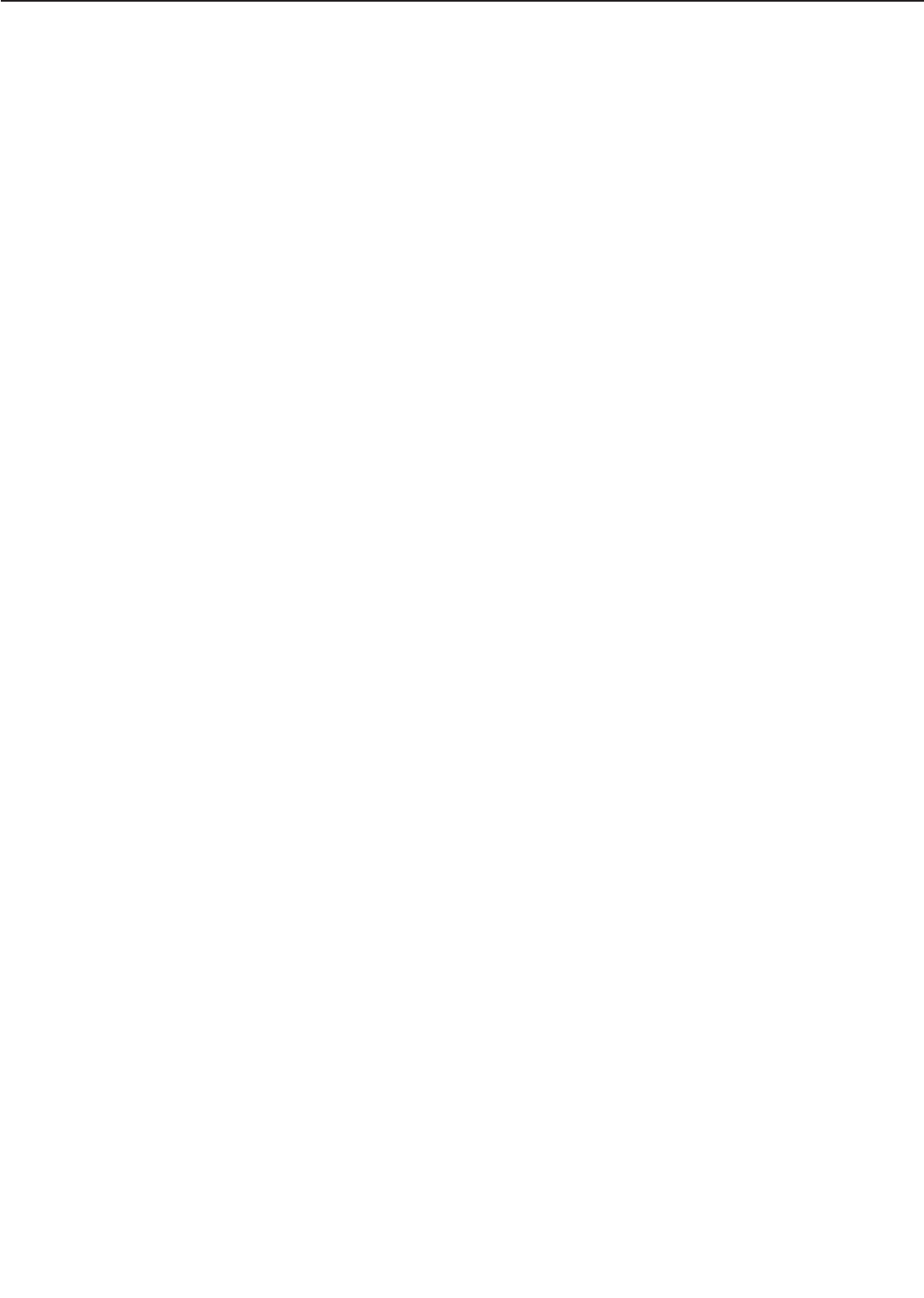
set a value from 1 to 999. In this case, to rapidly step through the values, press and hold down
+Plus/-Minus.
· Form Feed indicator: 12
On:
Indicates that a page is currently being composed in the printer's memory. To print the page
before it is completed, take the printer off-line and press the Form Feed key.
Off:
No print data is currently stored in the printer's memory.
· Item key: 13
With a menu name displayed, press the Item key to scroll through all the items on the menu
and return to the first item. To scroll back through the items in the opposite direction, press
the Shift and Item keys. Depending on what options you have installed, some items may not
appear.
· Continue key: 14
Restarts printing after the printer displays a message and halts printing. For most situations
after you press Continue, the message clears and printing resumes.
When the multi-purpose tray is used as a manual feed station (when MANUAL FEED=ON),
you have to press the Continue key every time you need to feed a single sheet of paper.
· Menu key: 15
With the printer off-line, press the Menu key to scroll through the menu names and return to
the first menu name. To scroll back through the menu names in the opposite direction, press
the SHIFT and MENU keys. Depending on what options have been installed, some menu names
may not appear.
· On Line key: 16
Takes the printer off-line and back on-line. When the On Line indicator is on, the printer is on-
line and ready to receive data and print. When the On Line indicator is off, the printer is off-
line and the other keys on the control panel can be used to view and change settings.
· On Line indicator: 17
On:
The printer is on-line (power on, warmed up, and ready to receive data from the host computer
for printing). Before you begin a print job, always check this indicator is on.
Flashing:
The printer is processig a print job. Do not turn the power off, otherwize you may lose print data.
Off:
The printer is off-line. You can now use the printer control panel keys to view and change set-
tings. When off-line, the printer cannot accept data for printing.
1 - 23
CHAPTER 1
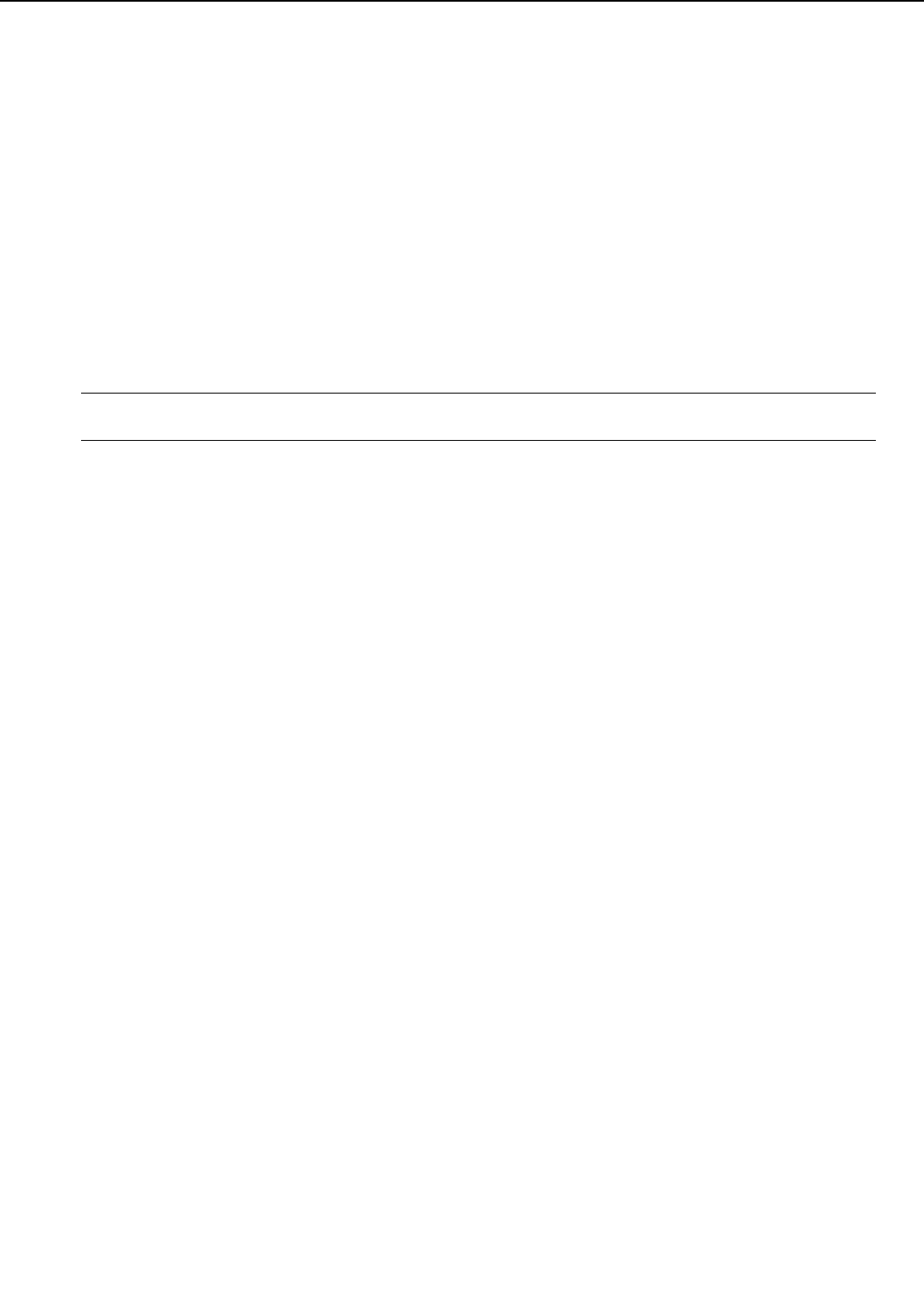
B. Operation Panel Menus
You can access the following menus though the operation panel:
· PCL MENU
· PS MENU (Note 1)
· FEEDER MENU
· CONFIG MENU
· MEMCONFIG MENU
· PARALLEL MENU
· LOCALTALK MENU (Note 2)
· ETHERNET MENU (Note 2)
· TOKEN RING MENU (Note 2)
· TEST MENU
· LANGUAGE MENU
Notes: 1. Menus that appear after the PostScript option has been installed.
2. Menus that appear after an option has been installed such as Network modules.
1. Accessing and selecting menu items
Follow these steps to access the menus and make selections:
1) Check the operation panel and be sure the JOB indicator is off.
2) Press the On Line key to set the printer off-line. The On Line indicator goes off.
3) Press the Menu key to display the name of the first menu. Press the Menu key until you see
the Menu.
4) Press the Item key to display the name of the first item on the menu. Press the Menu key
until you see the item.
5) Press the +Plus/-Minus key until you display the values you want to change.
6) If you want to change the setting, press the +Plus/-Minus key until the value you want is
displayed. Then press the Enter key.
7) Press the On Line key to set the printer on-line.
Figure 1-7-2 list the Menu Operation Flow.
2. Restoring the default settings
There are several types of default settings:
■Factory default settings are those set for each menu item at the factory. The printer uses
these settings changed.
■Temporary default settings are those set by the application software for the current print job.
■Permanent default settings are those set through the operation panel. These selections
remain in effect even when the printer is turned off, or send a different request through the
application.
3. Resetting the default values
The printer can be reset in three ways:
■The reset printer function clears the memory of all fonts, macros, and page information but
does not affect the menu settings.
1 - 24
CHAPTER 1
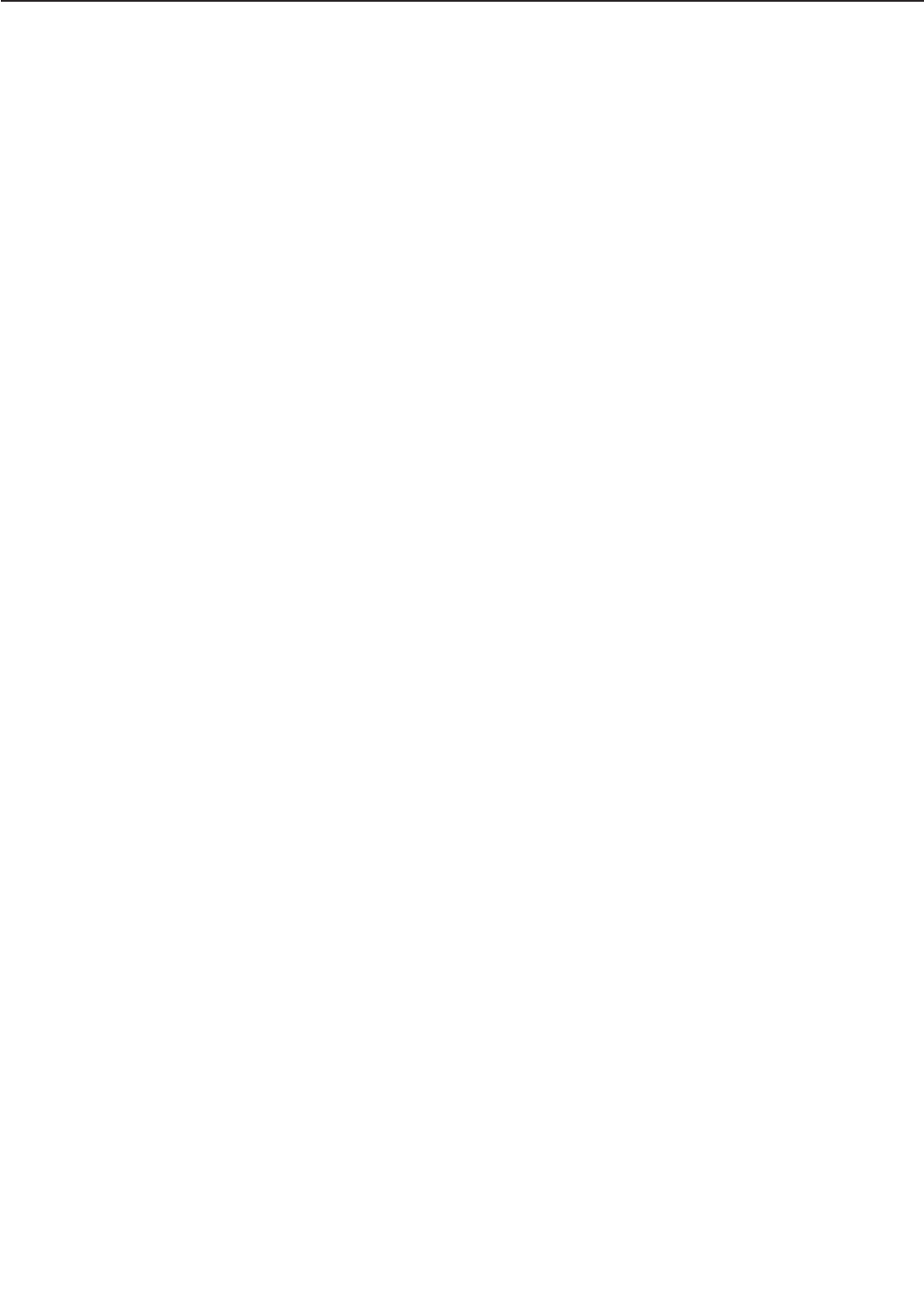
■The reset menu function performs a printer reset to clear all fonts, macros, and page infor-
mation but returns some of the menu settings to their original factory defaults.
■A cold reset clears the memory and restores all menu settings to their factory settings with
the exception of the page count value, multi-purpose tray page size, envelope feeder size, and
display language.
To perform a cold reset, press and hold down the On Line key while you turn on the print-
er. The printer displays the message COLD RESET followed by WARMING UP. When the
printer comes on-line, the factory default settings are restored.
1 - 25
CHAPTER 1
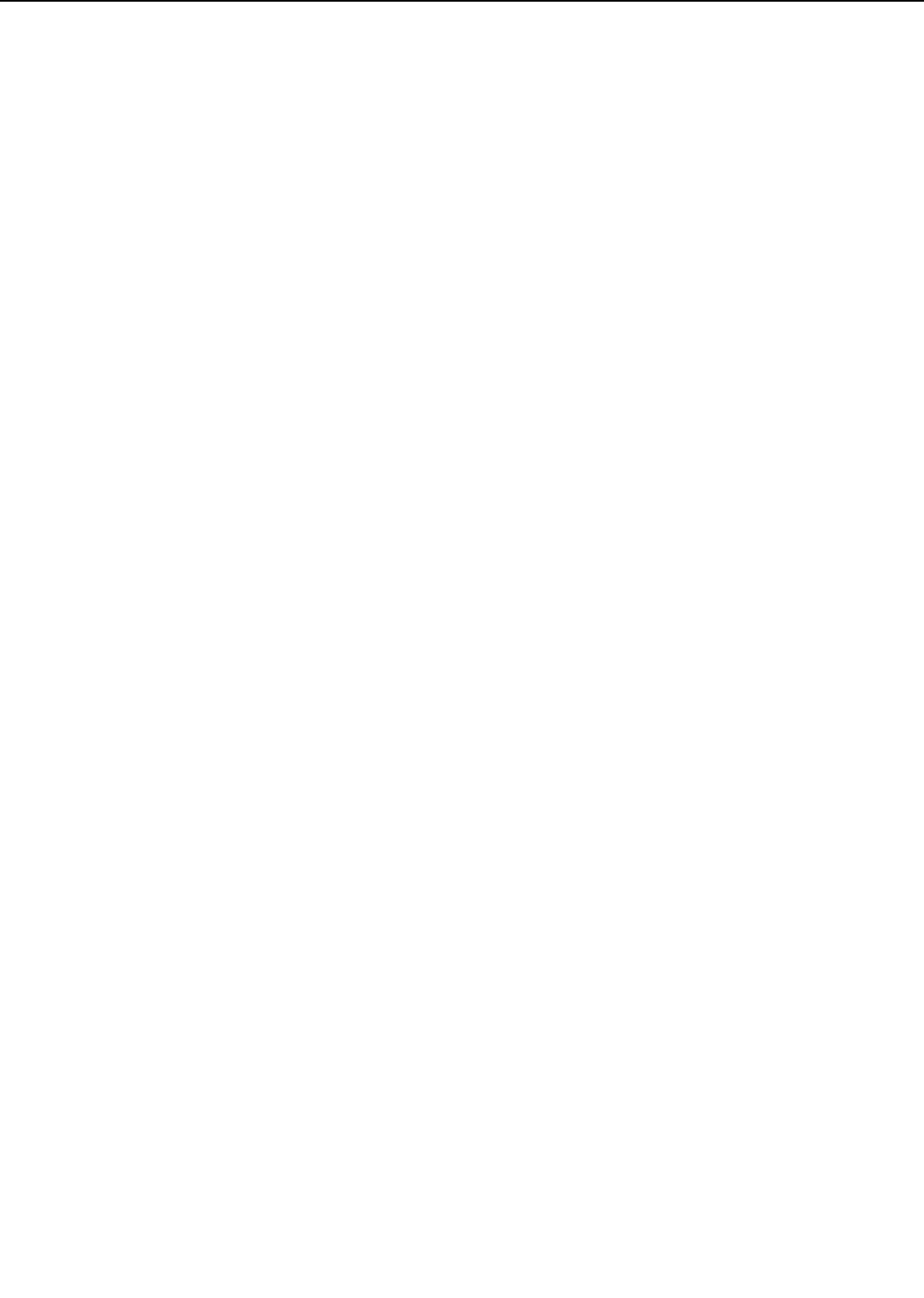
This page intentionally left blank
1 - 26
CHAPTER 1
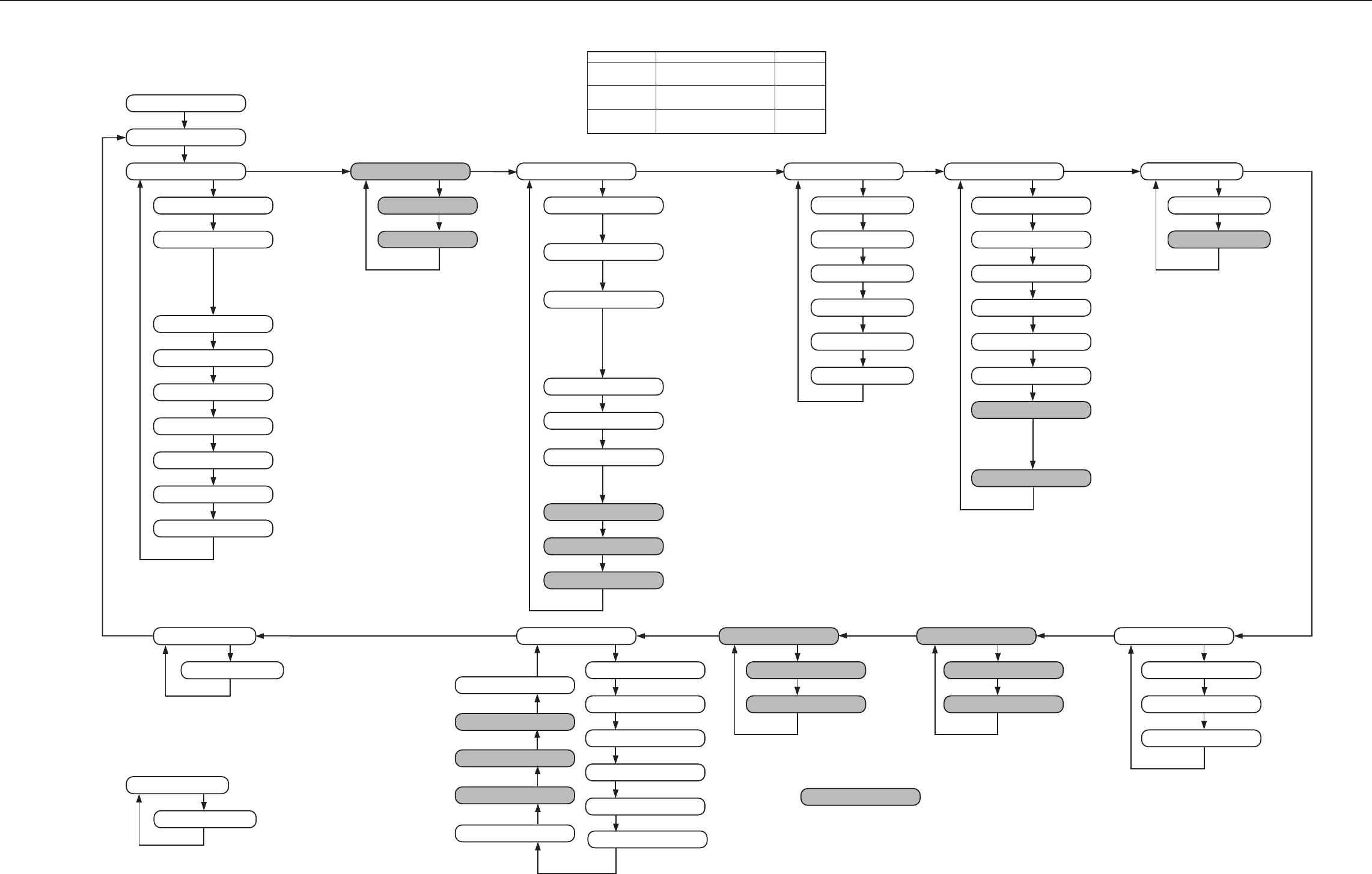
CHAPTER 1
1-27
Figure 1-7-2
READY
PAUSED
PCL MENU
COPIES=1
PAGESIZE=LETTER
FEEDER MENU
FEED=DECK
7 BIN SORTER MODE=MAILBOX
TRAY SWITCH=ON
OUTPUT=TOP OUTPUT BIN
MANUAL=OFF
MPTSIZE=LETTER
ENVSIZE=COM10
DUPLEX=OFF
BINDING=LONG
CONFIG MENU
JAMRECOVERY=OFF
AUTOCONT=ON
DENSITY=7
ECONOMY MODE=OFF
REFINE=ON
FORMAT DISK
FORMAT FLASH
PARALLEL MENU
PERSONALITY=AUTO
BIDIRECTION=ON
I/O TIMEOUT=15
ETHERNET MENU
PERSONALITY=AUTO
I/O TIMEOUT=15
TOKEN RING MENU
PERSONALITY=AUTO
I/O TIMEOUT=15
TEST MENU
SHOW PAGE COUNT
TEST PRINT
PRINT PS FONTS
PRINT PCL FONTS
PRINT PS DEMO
PRINT PCL DEMO
CONTINUOUS TEST
CLEANING PAGE
PRINT ETHER CONFIG
PRINT TOKEN CONFIG
PWRSAV=30MIN
LANGUAGE MENU
LANG=ENGLISH
RESET MENU
RESET=PRINTER
1to999
A3, A4, A5, B4,
11x17, EXEC,
COM10, DL,
MONARCH, C5,
B5-JIS, B5-ISO,
LEGAL
ORIENTATION=PORTRAIT
FORM=60 LINES
FNTSRC=INTERNAL
FONTNUM=0
PT.SIZE=12.00
PITCH=10.00
SYMSET=ROMAN-8
LANDSCAPE
5to128
SOFT
1to999
4.00 to 99.75
0.44 to 99.99
ISO L1, ISO L2, ISO L5, PC-8, PC-8 D/N, PC-850,
PC-852, PC-8TK, WIN L1, WIN L2, WIN L5,
DESKTOP, PS TEXT, VIN INTL, VN US, MS PUBL,
MATH-8, PS MATH, VN MATH, PI FONT, LEGAL,
ISO 4, ISO 6, ISO 11, ISO 15, ISO 17, ISO 21, ISO
60, ISO 69, WIN 3.0
PAPER TYPE MENU
UPPER=PLAIN
LOWER=PLAIN
DECK= PLAIN
DECK1=PLAIN
DECK2=PLAIN
MAT=PLAIN
PS MENU
COPIES=1
PRINT ERRS=OFF
1to999
ON
The following options
are available for all items:
PLAIN, LETTERHEAD, BOND,
RECYCLED, COLOR,
CARDSTOCK, LABELS,
TRANSPARENCY, ROUGH,
CUSTOM1, CUSTOM2,
CUSTOM3, CUSTOM4,
CUSTOM5, CUSTOM6
DECK1, DECK2(if installed),
LOWER, UPPER, MPT,
ENVELOPE(if installed)
JOB SEPARATION, STACKER,
SORTING,
+TO CONFIRM/-CANCEL
SIDE OUTPUT BIN, SORTER BIN-UP,
BIN1=MAILBOX1, BIN2=MAILBOX2,
BIN3=MAILBOX3, BIN4=MAILBOX4,
BIN5=MAILBOX5, BIN6=MAILBOX6,
BIN7=MAILBOX7,
SORTER BIN-UP, 7 BIN SORTER,
BIN7=MAILBOX7,
SORTER BIN-UP, 7 BIN SORTER
OFF
ON
LEAGAL, A3, A4, A5, 11x17,
EXEC, COM10, CUSTOM
MONARCH, C5, DL, B4, B5-JIS,
B5-ISO
C5, DL, B5-ISO,
MONARCH
ON
SHORT
OFF
ON
0to15
+FORMAT DISK
-IGNORE DISK
+REALLY FORMAT
-IGNORE DISK
OFF
+FORMAT FLASH
-IGNORE FLASH
+REALLY FORMAT
-IGNORE FLASH
ON
ON
ON
PS, PCL
OFF
5to300
PS, PCL
5to300
PS, PCL
5to300
DANISH, DUTCH, FINNISH,
FRENCH, GERMAN,
ITALIAN, NORWEGIAN,
SWEDISH PORTUGUESE,
SPANISH
MENU
1HR, 2HR, 3HR, 4HR,
OFF, 15MIN
MEMCONFIG MENU
PCL SAVE=OFF
PS3 SAVE=OFF
Press ON LINE to take the printer off-line.
Press MENU to display the name of the first menu.
Press +PLUS/-MINUS to select the item.
Press ENTER to select the value.
(if installed)
(if installed)
(if installed)
*
*
*
*
*
*
*
*
*
*
*
*
**
*
*
*
*
*
*
*
*
*
*
*
*
*
*
*
*
*
*
*
*
*
*
*
*
*
*
*
*
AT: Press: To move:
Menu level
Item level
Item level
MENU
SHIFT and MENU
ITEM
SHIFT and ITEM
+PLUS/-MINUS
SHIFT and +PLUS/-MINUS
Forward
Back
Forward
Back
Forward
Back
Shaded menus appear after an option has been installed. E.g. A-72 module with
the Adobe PostScript 3 software or Network cards.
If there is insufficient memory, MEMCONFIG may not appear in PostScript mode,
even after the A-72 module has been installed. MEMCONFIG usually appears in
PCL mode.
STAPLE TEST
To open the RESET menu, press RESET.
Press +Plus/-Minus to select PRINTER or MENU.
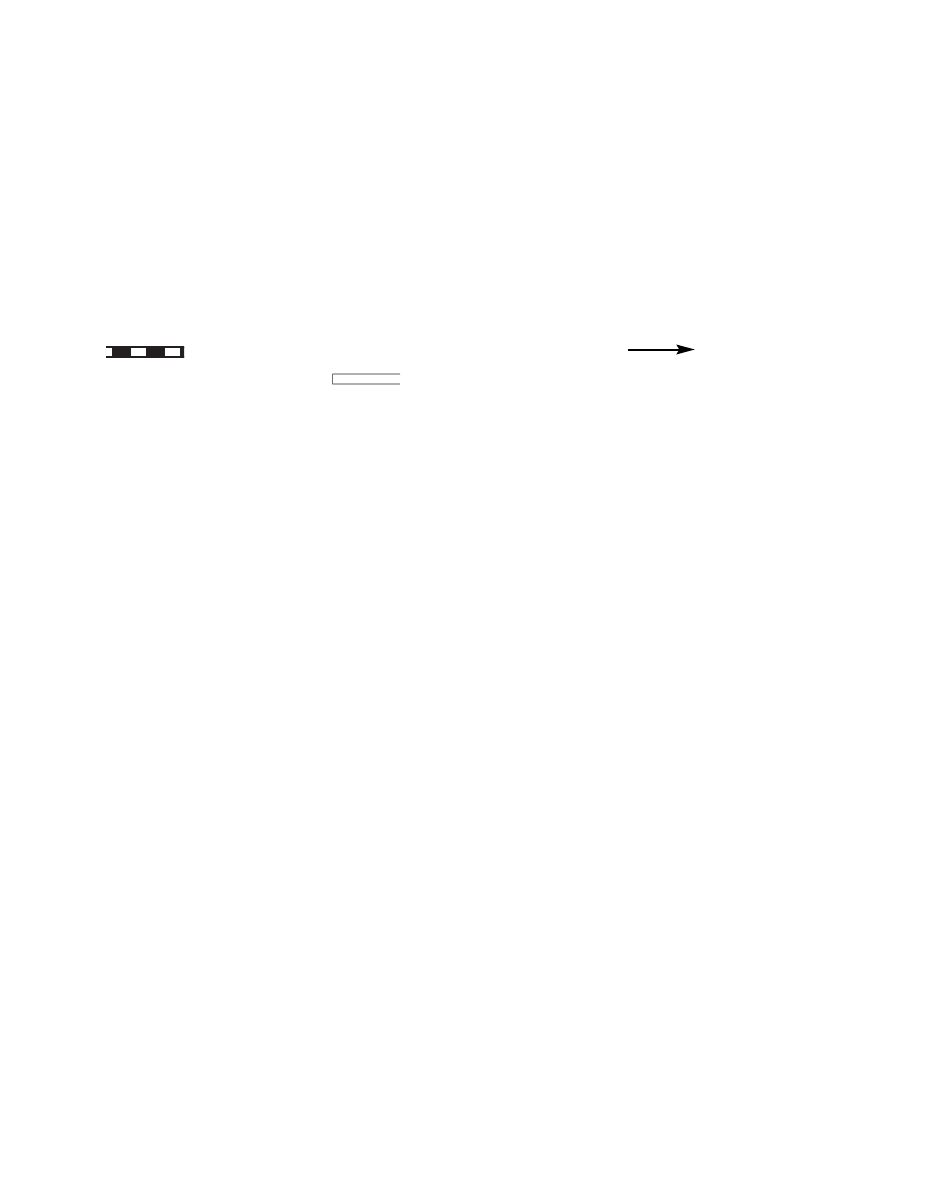
CHAPTER 2
OPERATION AND TIMING
1. This chapter describes the printer functions, the relationships between mechanisms and cir-
cuits, and the timing of operations. Mechanical linkages are indicated by black and white
lines ( ), the flow of control signals by solid arrows ( ), and the flow of groups
of signals by outline arrows ( ).
2. An active-high signal is indicated by "H" or by a signal name without a slash in front of it,
such as "PSNS." An active-low signal is indicated by "L" or by a signal name with a slash in
front of, such as "/SCNON."
A signal that is "H" or has a name without a slash is active at the supply voltage level
(indicating that the signal is being output), and inactive at ground level (indicating that the
signal is not being output).
A signal that is "L" or has a slash in front of its name is active at ground level, and inac-
tive at the supply voltage level.
There is a microcomputer in this printer. But as the internal operation of the microcom-
puter cannot be checked, an explanation of the operation of the microcomputer has been left
out.
As it is assumed that no repair will be made to customer circuit boards, the explanation
of board circuits is limited to an outline using block diagrams. So there are two types of cir-
cuit explanations; (1) everything from the sensor to the input sections of the major circuit
boards, (2) everything from the output sections of the major circuit boards to the loads.
These are explained with block diagrams according to the function.
I. BASIC OPERATION ................ 2-1
II. ENGINE CONTROL SYSTEM .. 2-4
III. LASER/SCANNER SYSTEM .... 2-26
IV. IMAGE FORMATION SYSTEM . 2-32
V. PICK-UP/FEED SYSTEM ........ 2-42
VI. OVERALL CONTROL SYSTEM. 2-61
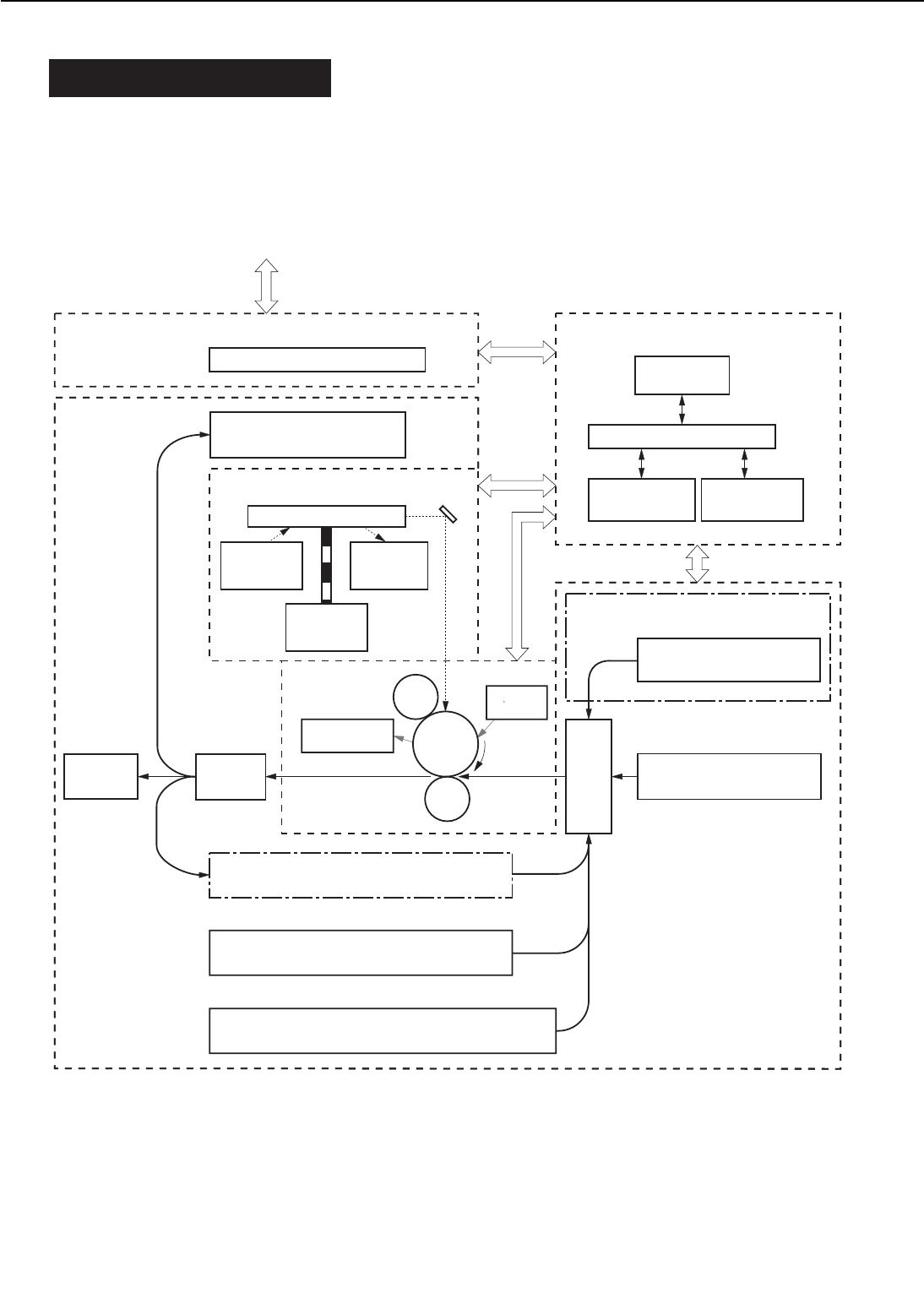
I. BASIC OPERATION
A. Functions
Printer functions can be divided into four groups: the engine control system, the laser/scanner
unit, the image formation system, the paper pick-up/feed system.
Figure 2-1-1
2 - 1
CHAPTER 2
Cleaning
unit
Fixing
unit
Develop-
ing unit
IMAGE
FORMATION
SYSTEM
Duplexing unit (option)
Transfer
charging
roller
Primary
charging
roller
Photos
ensitive
drum
Upper cassette
Lower cassette
Face-up
tray
Face-down tray
LASER/SCANNER UNIT
Scanning mirror
Scanner
motor
BD circuit
Pick-up
control unit
Multi-purpose tray
Envelope feeder (optional)
Envelope feeder
pick-up unit
PAPER PICK-UP/FEED
SYSTEM
ENGIN CONTROL SYSTEM
OVERALL CONTROL SYSTEM
Operation
panel
Low-voltage
power supply
High-voltage
power supply
To external device (host computer, etc.)
DC controller PCB
Video controller PCB
Laser diode
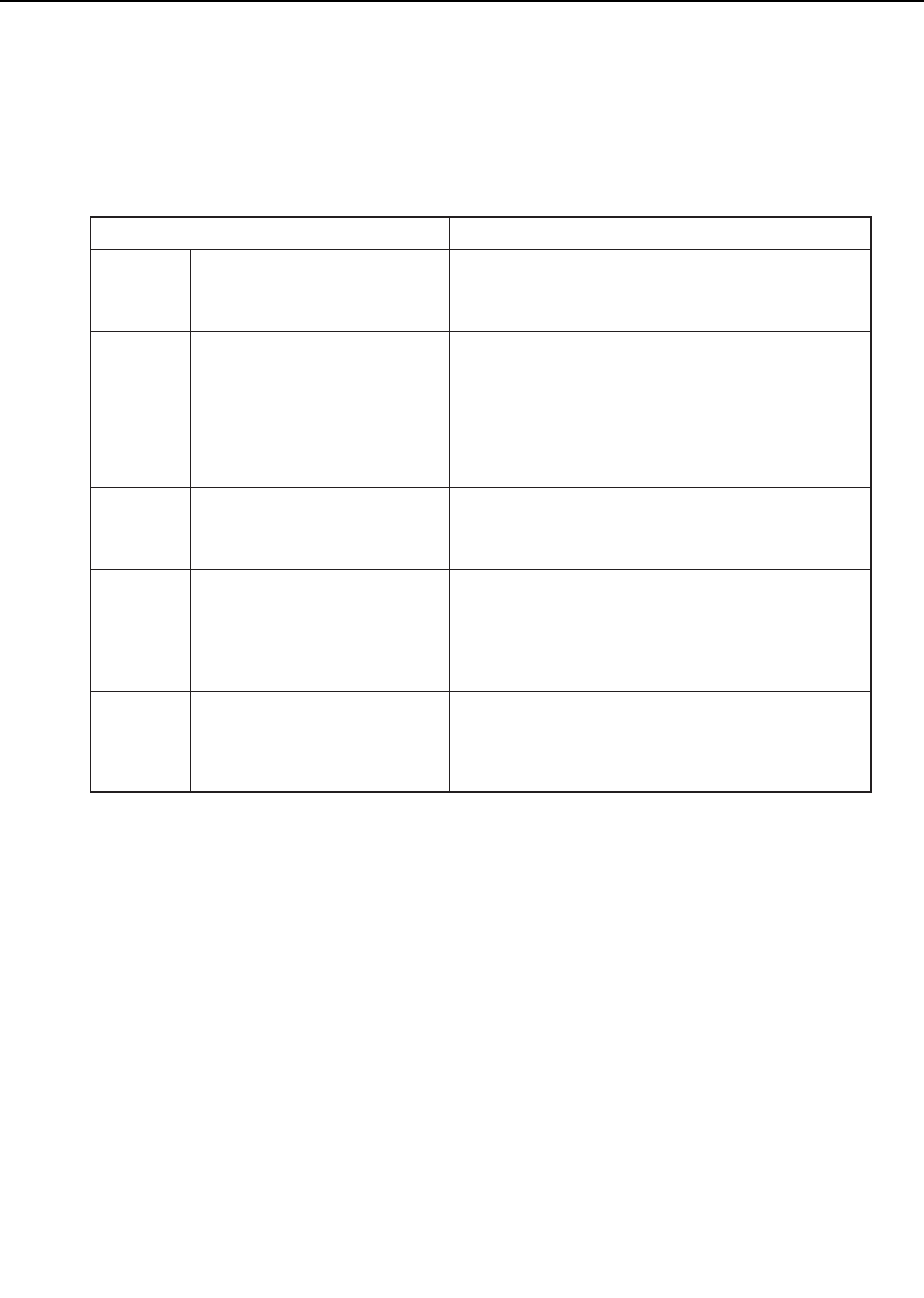
B. Basic Operation Sequences
Operation sequences of the printer are controlled by the microcomputer on the DC controller
PCB. Descriptions of each period from ON until the main motor stops are as shown below. See
the appendix for timing chart.
Table 2-1-1
2 - 2
CHAPTER 2
Purpose Remark
From power-ON until the fixing
roller temperature reaches 170°C.
(Less than 90 sec.)
Period
From the end of the WAIT period
until a /PRNT signal is input from
the video controller, or from the
end of the LSTR period until a
/PRNT signal is input from the
video controller or until the power
is switched OFF.
After the /PRNT signal has been
input from the video controller
until the scanner motor becomes
ready (about 7 seconds).
From the end of the INTR period
until the primary DC voltage
switches OFF.
After the primary DC voltage turns
OFF until the main motor stops.
Warms up the fixing rollers to
put the printer in the standby
mode. Cleans the transfer
charging roller.
Maintains the printing
temperature of the fixing roller
so that the printer is ready to
print.
To stabilize the sensitivity of
the drum in preparation for
printing and to clean the
transfer charging roller.
To form an image on the
photosensitive drum according
to the VDO and /VDO signals
input from the video controller
and to transfer the image to
paper.
To deliver the final page and
to clean the transfer charging
roller.
If a /PRNT signal is input
from the video controller,
the INITIAL ROTATIONS
period begins
immediately.
WAIT
(WAIT
period)
STBY
(STANDBY)
INTR
(INITIAL
ROTATIONS
period)
PRINT
(Print)
LSTR
(LAST
ROTATIONS
period)
During this period, the
printer checks if the car-
tridge is installed and if
there is toner in it.
If the printer stays in the
standby mode for longer
than five hours, it drives
the main motor for one
second to rotate the
fixing roller, to prevent it
from deforming.
During this period, the
printer maintains the
printing temperature of
the fixing rollers.
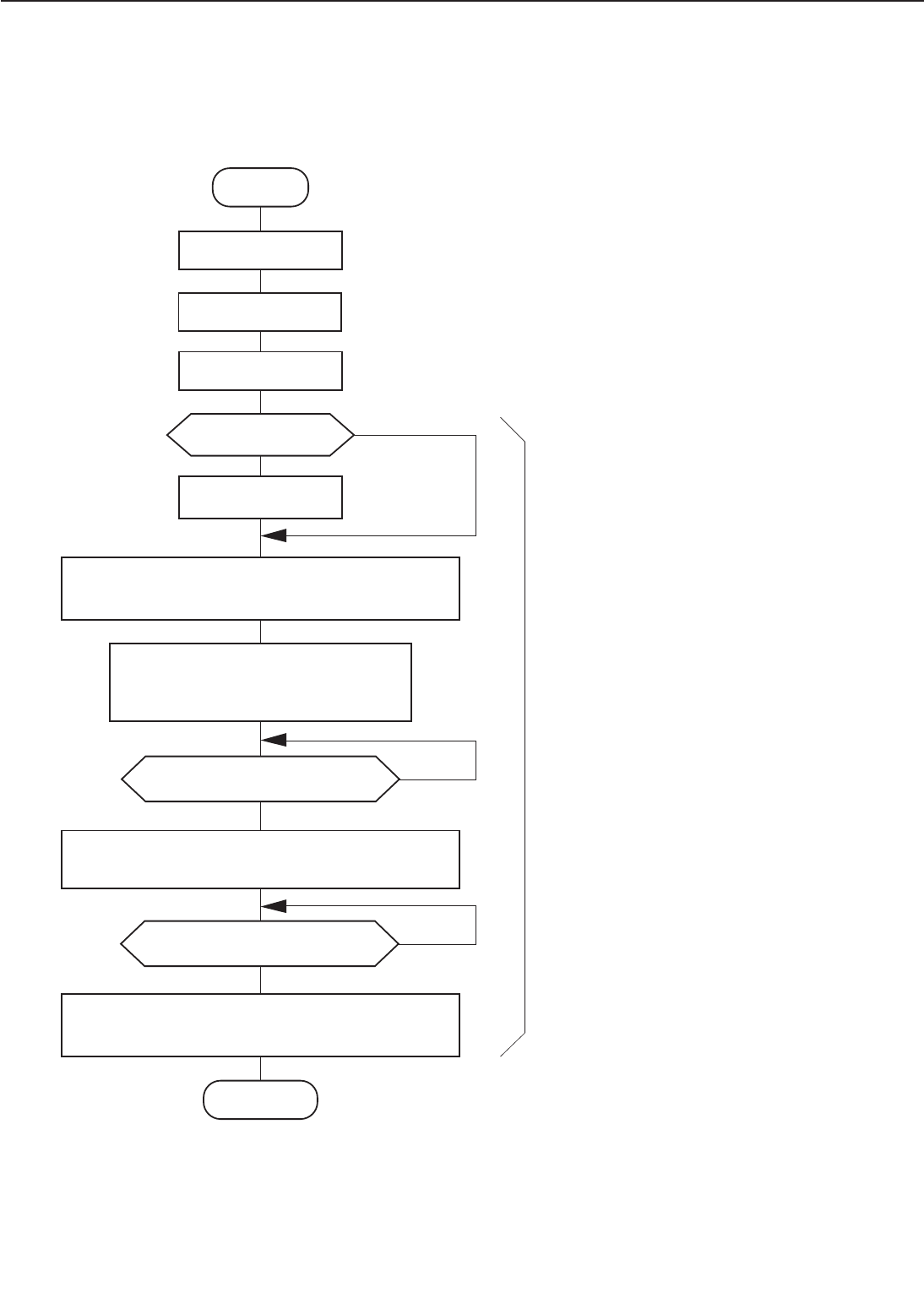
C. Power On Sequences
Sequences of the printer from power ON until it enters the standby mode are as shown below.
Figure 2-1-2
2 - 3
CHAPTER 2
NO
NO
During this period, checks if there is
residual paper in the printer. If automatic
paper delivery is required as a result of
the check, residual paper is delivered
automatically.
Power ON
CPU initialization
Duplexing unit
initialization
Duplexing unit
connection
Fixing heater ON
Main motor, scanner motor, pick-up roller, registration
roller, primary AC, transfer negative bias ON
Development AC bias ON (Checks if
the cartridge is installed and if there is
toner in it)
Main motor, scanner motor, pick-up roller, registration
roller, primary AC, transfer negative bias ON
Main motor, scanner motor, pick-up roller, registration
roller, primary AC, transfer negative bias ON
Standby
NO
/PPRDY signal output
Has fixing temperature
reached 170 C?
Has fixing temperature
reached 145˚ C?
˚
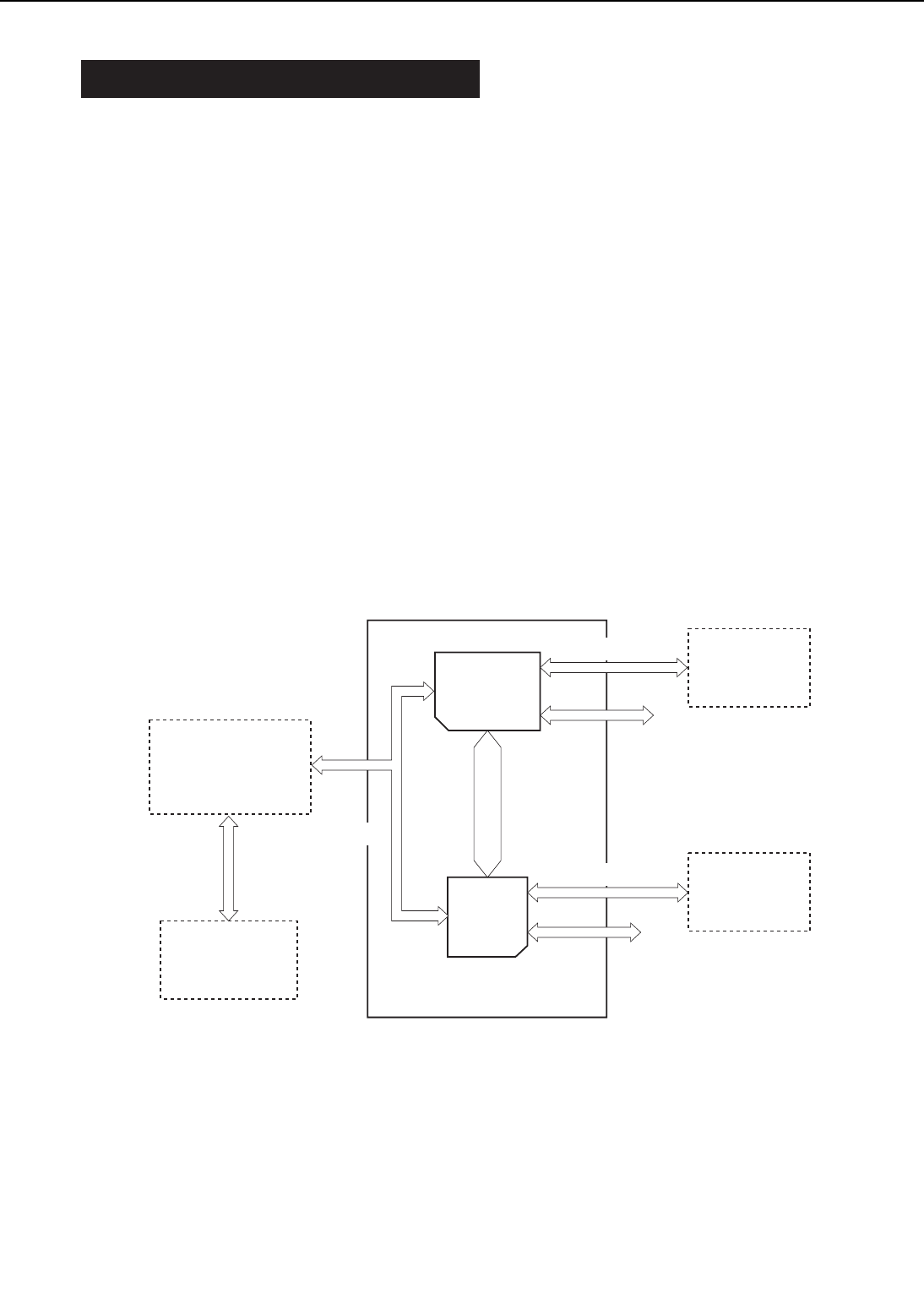
II. ENGINE CONTROL SYSTEM
A. DC Controller Circuit
1. Outline
Operation sequences of the printer are controlled by the CPU of this circuit. When DC power is
supplied from the power supply by turning ON the power switch of the printer and the printer
enters the standby mode, the CPU outputs the signals that drive the loads such as laser diode,
motors, and solenoids, based on the print start command and image data.
2. Explanation of operations of each block
a. CPU (IC201)
An 8-bit single chip microcomputer (UPD78056) by NEC is used.
The CPU is a one-chip type in which ROM and RAM are built in, and controls the operation of
the engine according to the control program stored in the ROM.
b. Gate array (IC202)
Its functions are to:
1) control the laser/scanner,
2) control the video interface,
3) communicate with the envelope feeder,
4) communicate with the printer driver tester, and
5) operate as the expansion I/O.
Figure 2-2-1
2 - 4
CHAPTER 2
Bus
Envelope feeder
Serial line
DC controller
Duplex unit
I/O
I/O
IC 201
CPU
IC 202
Gate array
Serial line
Serial line
Serial line
Video controller
Option controller
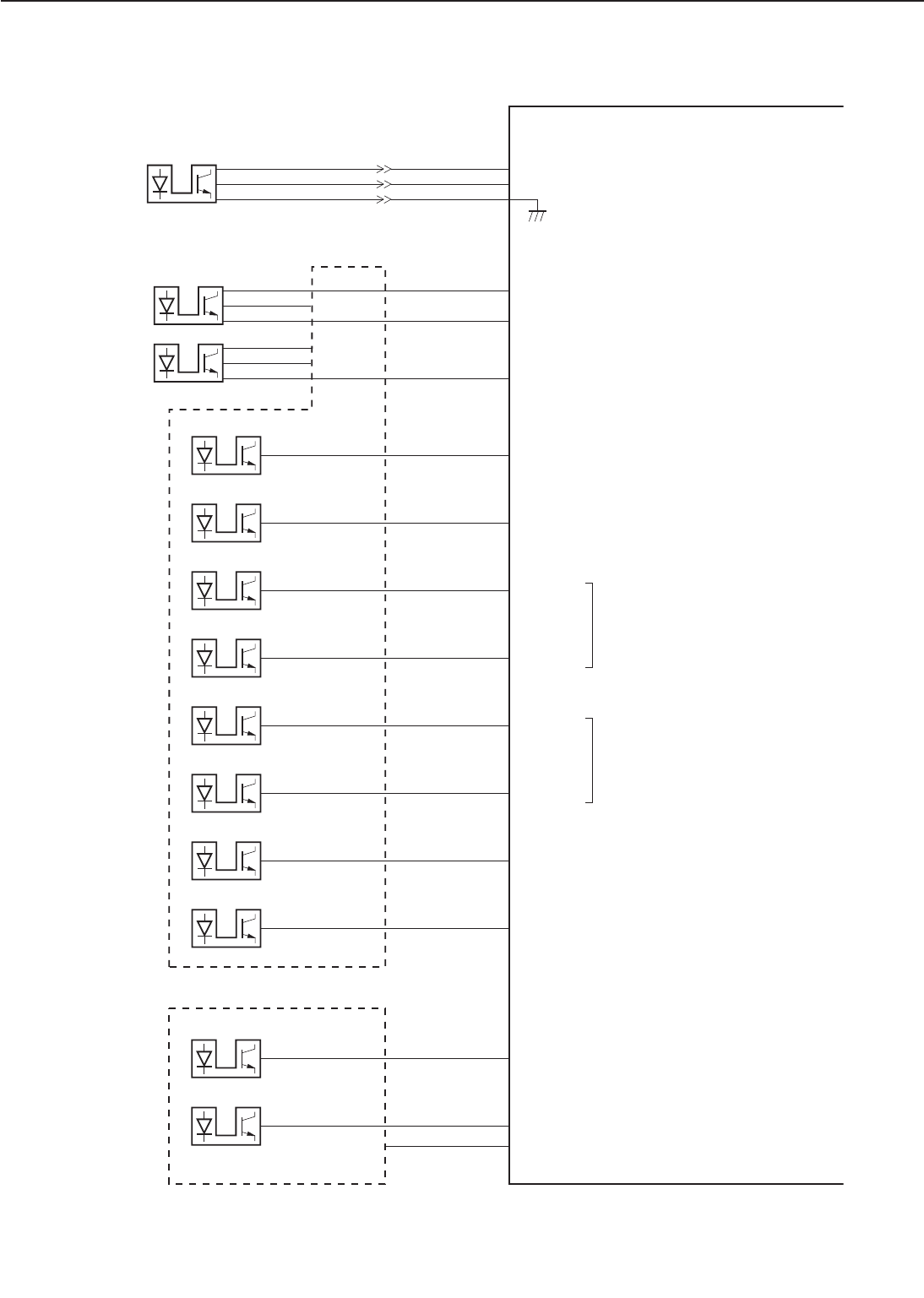
3. DC Controller Input/Output Signals
Figure 2-2-2
2 - 5
CHAPTER 2
PS1 J209-5
-3
-4 /REGS
J13-3
-2
-1
J1205-1
-2
-3
PS2
J14-3
-2
-1
J1206-1
-2
-3
PS3
P5VB1
GND
/FEEDS
P5VB1
GND
/RDOORS
J11-3
-1
-2
PS1201
PS1202
PS1203
PS1204
PS1205
PS1206
PS1207
PS1208
-8
-16
-10
-14
-6
-12
/FEEDS
/RDOORS
LDECKC
-6-16 UDECKC
-12-10 LPVS2
-13-7 LPVS1
-14-8 UPVS2
-15-5 UPVS1
-11-9 /LDECKS
-5-15 /UDECKS
P5VB1
P5VB1
PS1301
PS1302
J214-7J1301-7 /MPTPS
-6-6 MPTLS
-3-3 P5VB1
J219-18J1201-4
J15-3
-1
-2
J14-1
-3
-2
DC controller PCB
"L" when the sensor detects paper.
Registration
paper
sensor
Pick-up unit
paper sensor
Pick-up PCB
Paper pick-up
unit door
sensor
Lower cassette
sensor
Upper cassette
sensor
Lower cassette
paper-level
sensor 1
Lower cassette
paper-level
sensor 2
Upper cassette
paper-level
sensor 1
Upper cassette
paper-level
sensor 2
Lower cassette
paper-out
sensor
Upper cassette
paper-out
sensor
"H" when the pick-up unit door is
open.
"H" when the sensor detects the
lower cassette.
"H" when the sensor detects the
upper cassette.
These sensors detect the amount
of paper remaining in the lower
cassette.
"L" when there is paper in the
lower cassette.
These sensors detect the amount
of paper remaining in the upper
cassette.
"L" when there is paper in the
upper cassette.
Multi-purpose
tray paper
sensor
Lifting plate
position sensor
"L" when there is paper on the
multi-purpose tray.
"H" when the lifting plate has risen.
Multi-purpose tray PCB
"L" when the sensor detects paper
.
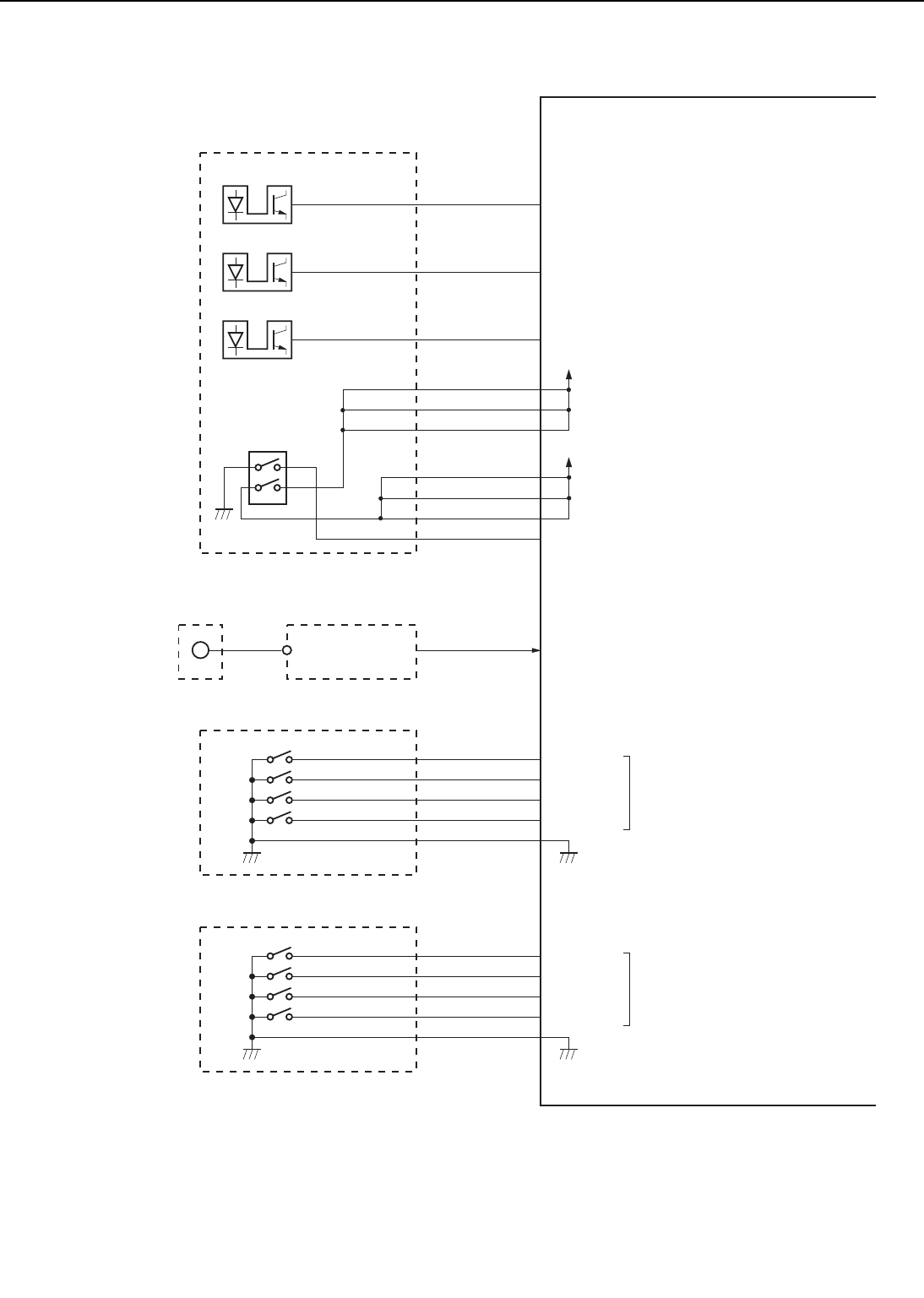
Figure 2-2-3
2 - 6
CHAPTER 2
PS1401
PS1402
PS1403
J205-7J1401-10 FDFULS
-9-12 FDOUTS
-8-11 FPOUTS
-6-9 UDOORS
SW1401
+24VB
+24VA
J221-1
-2
-3
-1
-2
-4
J205-3
-4
-5
-5
-7
-8
ANTIN J220-A10 TONSNS
J701-A10
TB705
J215-5
-4
-3
-2
-1
J1601A-1
-2
-3
-4
-5
SW1601
SW1602
SW1603
SW1604
LSIZE1
LSIZE2
LSIZE3
LSIZE4
J215-10
-9
-8
-7
-6
J1601B-1
-2
-3
-4
-5
SW1601
SW1602
SW1603
SW1604
USIZE1
USIZE2
USIZE3
USIZE4
DC controller PCB
Face-down
tray paper full
sensor
Face-down
tray delivery
sensor
Fixing unit
delivery sensor
"H" when the face-down tray is
fully loaded with paper.
"H" when the sensor detects paper.
"H" when either the upper or
delivery cover is open.
Switch/sensor PCB
Door switch
"H" when the sensor detects paper.
EP-72 cartridge
Toner
sensor Detects no cartridge installed and
toner out.
High-voltage power
supply PCB
Detects the lower cassette
paper-size.
Lower cassette
paper-size
sensing switch
Cassette paper-size sensing switch PCB
Detects the upper cassette
paper-size.
Upper cassette
paper-size
sensing switch
Cassette paper-size sensing switch
PCB
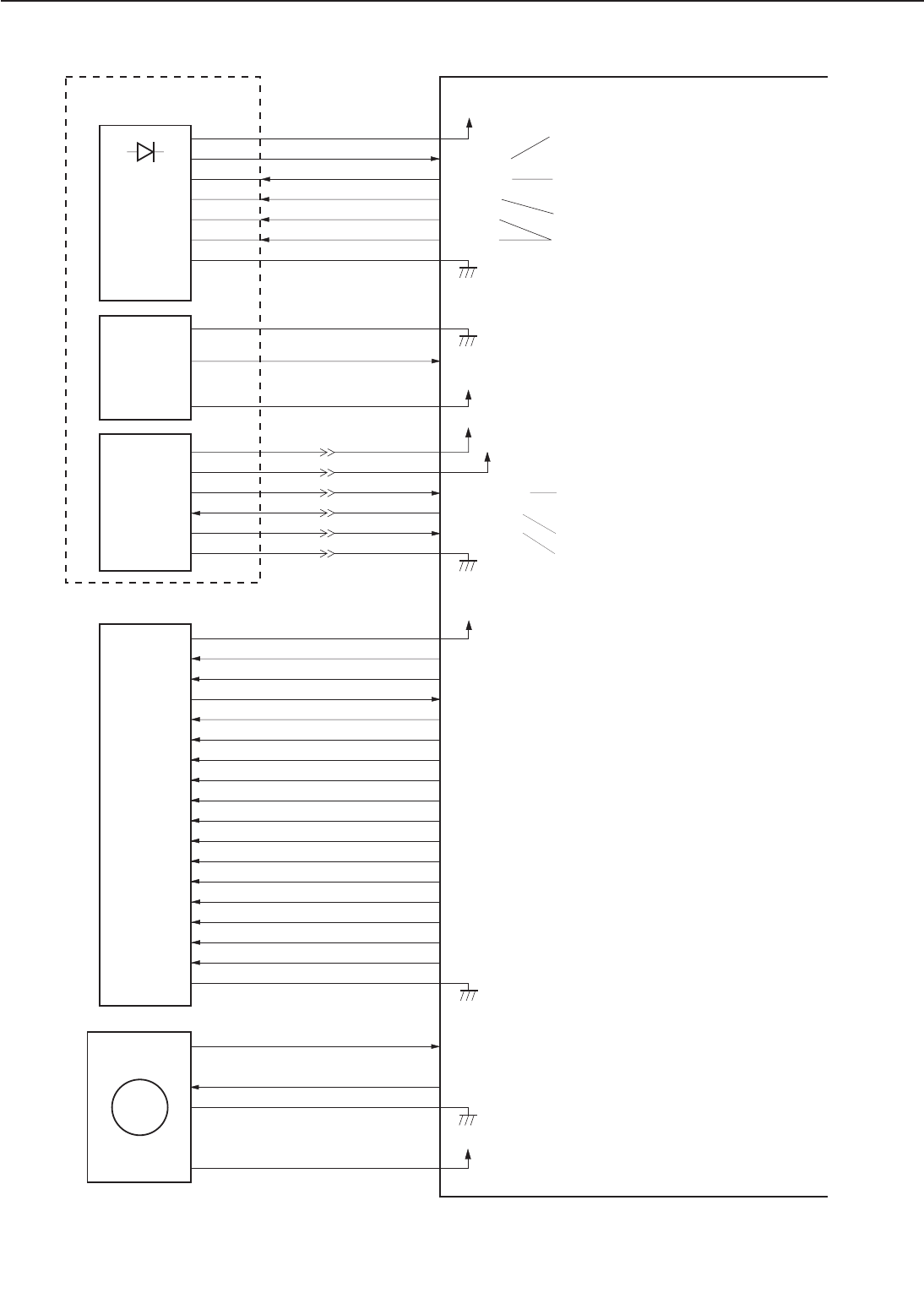
Figure 2-2-4
2 - 7
CHAPTER 2
TRFVCNT
/TRFNVD
TRFVSNS
/HRLBD
/TRFCCD
/DCHGBD
/TRFCLK
/DCHGUP
HVTCLK
/DEVACD
PRIACCLK
DEVACCLK
/PRIACD
/DEVDCD
/PRIDCD
DENADJ
Transfer bias drive signal
Transfer negative bias drive signal
Transfer bias monitor signal
Fixing roller bias drive signal
Transfer bias constant current drive signal
Discharge bias drive signal
Transfer bias frequency output signal
Discharge bias switch signal
High voltage bias frequency output signal
Developing AC bias drive signal
Primary AC bias frequency output signal
Developing AC bias frequency output signal
Primary AC bias drive signal
Developing DC bias drive signal
Primary DC bias drive signal
Image density adjustment signal
Analog signal in proportion to the laser
intensity is input.
J202-4
-2
-11
-10
-7
-9
-3/-5/-8
J1001-8
-10
-1
-2
-5
-3
-4/-7/-9
+5V
+24VB
DRVES
/LENBL
/LON
VDO
/VDO
J220
-A12/-B12
-A1
-B1
-A2
-B2
-A3
-B3
-A4
-B4
-A6
-A7
-B7
-A8
-B8
-A9
-B9
-B10
-A11/-B11
+5V
J206-1/-2J6-3/-4
/BDI
-4
-3
-1
-2
/SCNRDY
/SCND
SCNCLK
J207-7
-1
-2
-3
-5
-4/-6
J1-1
-7
-6
-5
-3
-2/-4
+24VA
-1
-7
-6
-5
-3
-2/-4
+5V
-1
-7
-6
-5
-3
-2/-4
J18
J701
-A12/-B12
-A1
-B1
-A2
-B2
-A3
-B3
-A4
-B4
-A6
-A7
-B7
-A8
-B8
-A9
-B9
-B10
-A11/-B11
J218-1
-2
-3/-4
-5/-6
/MMRDY
/MMOTD
J12-1
-2
-3/-4
-5/-6
+24VB
MT1
DC controller PCB
Laser diode
Laser driver
Laser/scanner unit
High-voltage
power
supply PCB
"L" when the scanner motor reaches the
prescribed speed.
"L" to drive the scanner motor.
Scanner motor reference clock signal.
Scanner
motor
BD PCB BD input signal (pulse)
"L" when the main motor runs normally.
"L" to run the main motor.
Main motor
"L" to switch the laser ON according to the VDO and
/VDO signals.
"L" to turn thelaser ONcompulsively.
The laser is turned ON only when the /LENBL, VDO,
and /VDO are "L", "H", and "L" respectively. (LOW-
VOLTAGE DIFFERENTIAL signal)
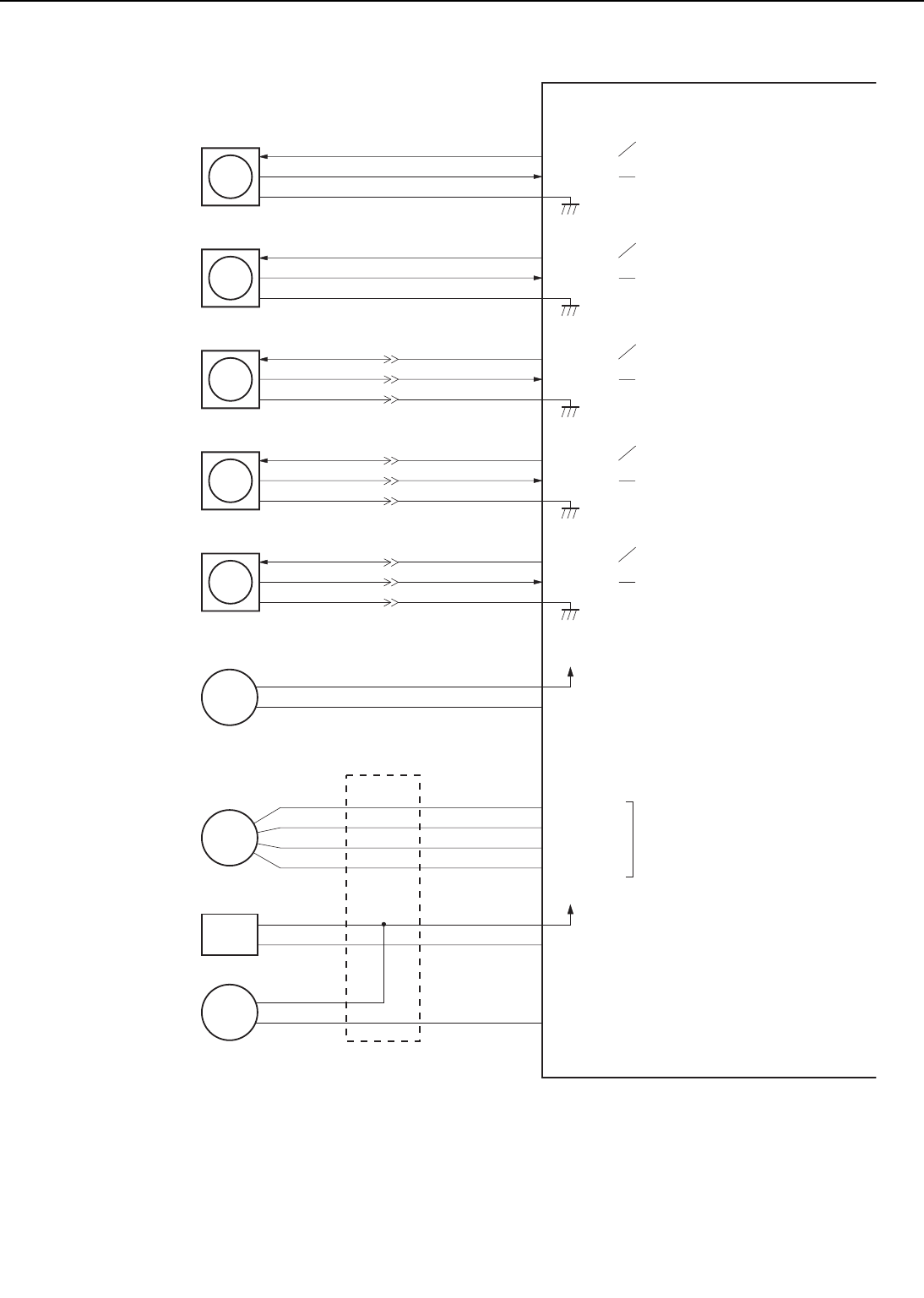
Figure 2-2-5
2 - 8
CHAPTER 2
+24VA
FAN1D
/FAN1S
J208-1
-2
-3
FAN1
FAN2D
/FAN2S
J216-1
-2
-3
FAN2
FAN3D
/FAN3S
J210-1
-2
-3
FAN3
FAN4D
/FAN4S
J225-1
-2
-3
FAN4
J26-1
-2
-3
J13-1
-2
-3
+24VA
J209-2
-1
J17-2
-1 /REGCLD
CL1 J16-1
-2
J1202-1
-2
-3
-4
SMT1
J1204-2
-1
CL2
J1203-2
-1
SL1
FEDAD
FEDAND
FEDBD
FEDBND
/PUPSLD
J219-2
-1
-4
-3
J1201-20
-19
-18
-17
-9-11
/FEEDCLD
-7-13
FAN5D
/FAN5S
J229-1
-2
-3
FAN5
J34-3
-2
-1
J35-1
-2
-3
J12-3
-2
-1
J25-3
-2
-1
DC controller PCB
"H" to rotate at high speed, "L" to
rotate at low speed.
"L" when the exhaust fan runs
normally.
Power supply
fan
"H" to rotate at high speed, "L" to
rotate at low speed.
"L" when the exhaust fan runs
normally.
Fixing unit/
Scanner unit
fan
"H" to rotate at high speed, "L" to
rotate at low speed.
"L" when the suction fan runs
normally.
Electrical unit
fan
"H" to rotate at high speed, "L" to
rotate at low speed.
"L" when the exhaust fan runs
normally.
Fixing unit fan
Registration
clutch "L" to run the registration roller.
Paper pick-up
motor
Feed clutch
Cassette feed
solenoid
Pick-up PCB
"L" to turn the feed roller.
"L" to lower the arm.
Pick-up motor rotation control
signal
"H" to rotate at high speed, "L" t
o
rotate at low speed.
"L" when the exhaust fan runs
normally.
Multi-purpose
tray fan
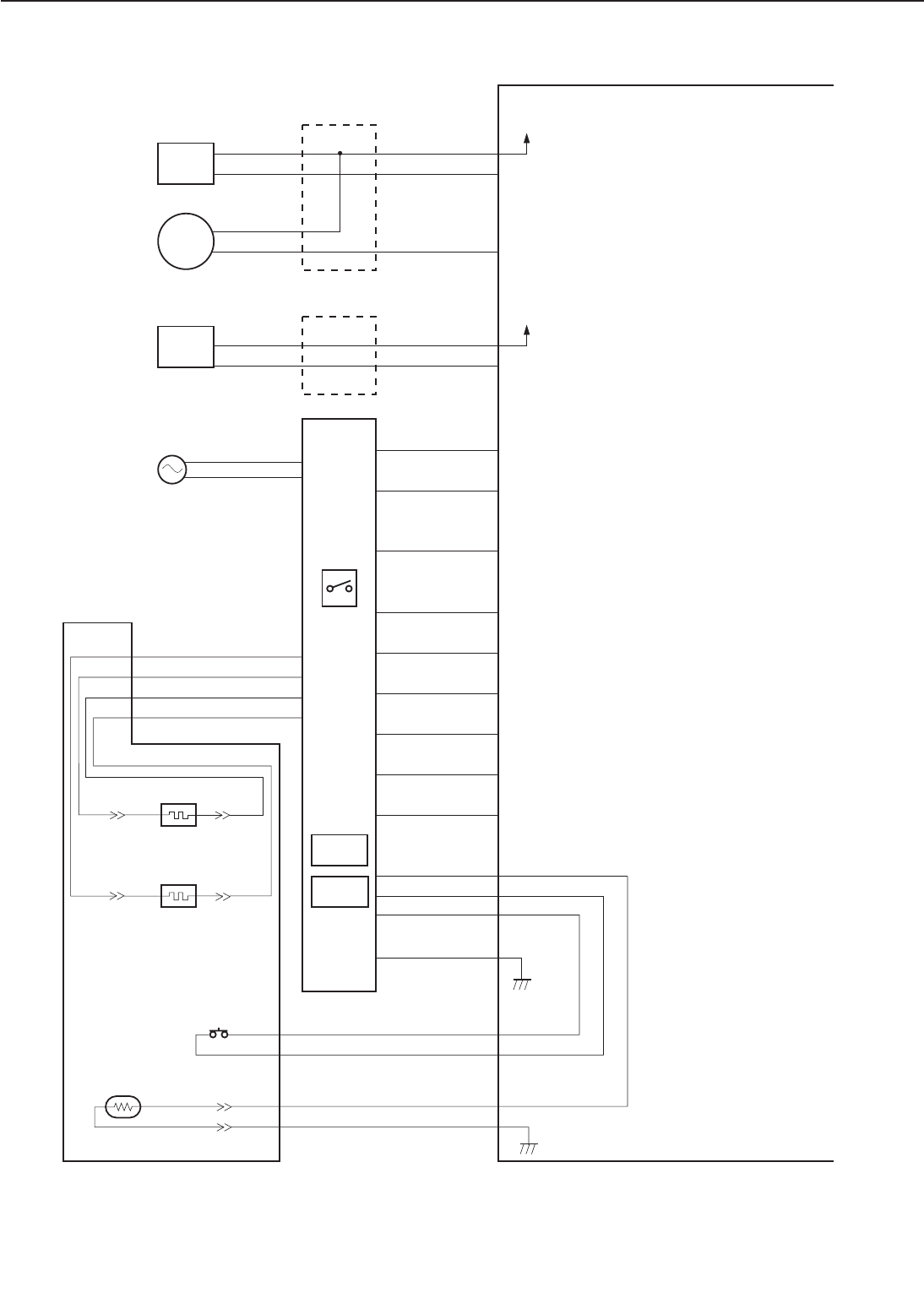
Figure 2-2-6
2 - 9
CHAPTER 2
+24VA
J1303-2
-1
CL3
J1302-2
-1
SL2 /MPTSLD
-5-5
/MTPCLD
-4-4
+24VA
J1402-2
-1
SL3 /FUSLD
J205-10J1401-13
H2
H1
S101
RLD
/FSRD1
/FSRD2
FSRDE
FSRCT
SUPSLT
/RLDSNS
PSTYP
/REMT24
J217-2
-6
-7
-8
-9
-10
-11
-12
-13
-1
-3
-5
-4
RY151
J54
J55
J10-1
-4
-3
-2
J50-6
J50-4
J50-3
J50-5 FSRN1
FSRL1
FSRL2
FSRN2
J214-2J1301-2
J222-2
-3
FSRTH
J50B-5
-4
TH J56-2
-1
J51-2
-1
J222-1
-4
TSWOUT
TSWIN
J50B-6
-3
TSW
J52
J53
J102-2
-6
-7
-8
-9
-10
-11
-12
-13
-1
-3
-5
-4
DC controller PCB
Manual feed
clutch
Lifting plate
solenoid
Multi-purpose tray PCB
"L" to rotate the manual feeding
pick-up roller.
"L" to drive the lifting plate. If the
plate is up it will drop, if down it will
rise.
Face-up
solenoid
Switch/sensor PCB
"L" to deliver printed paper face up.
Fixing main heater
Fixing sub heater
Thermo-switch
Fixing unit
Power
supply
Power
switch
Relay
AC power
The voltage drops as the
fixing roller temperature
rises.
Fixing roller
surface
temperature
sensor
RY152
"L" to turn OFF the relay and interrupt
the power to the fixing heater.
The main heater is turned ON when
the FSRDE signal is output and this
signal is "L."
The sub heater is turned ON when
the FSRDE signal is output and this
signal is "L."
Fixing heater drive enable signal
(pulse signal)
"L" when the current transformer
detects the power to the fixing heater.
Inverter circuit control signal.
"L" when the relay is turned ON.
"L" when the line voltage is 200V (for
200V model only)
When "L", the power supply uni
t
outputs 24V to the DC controller.
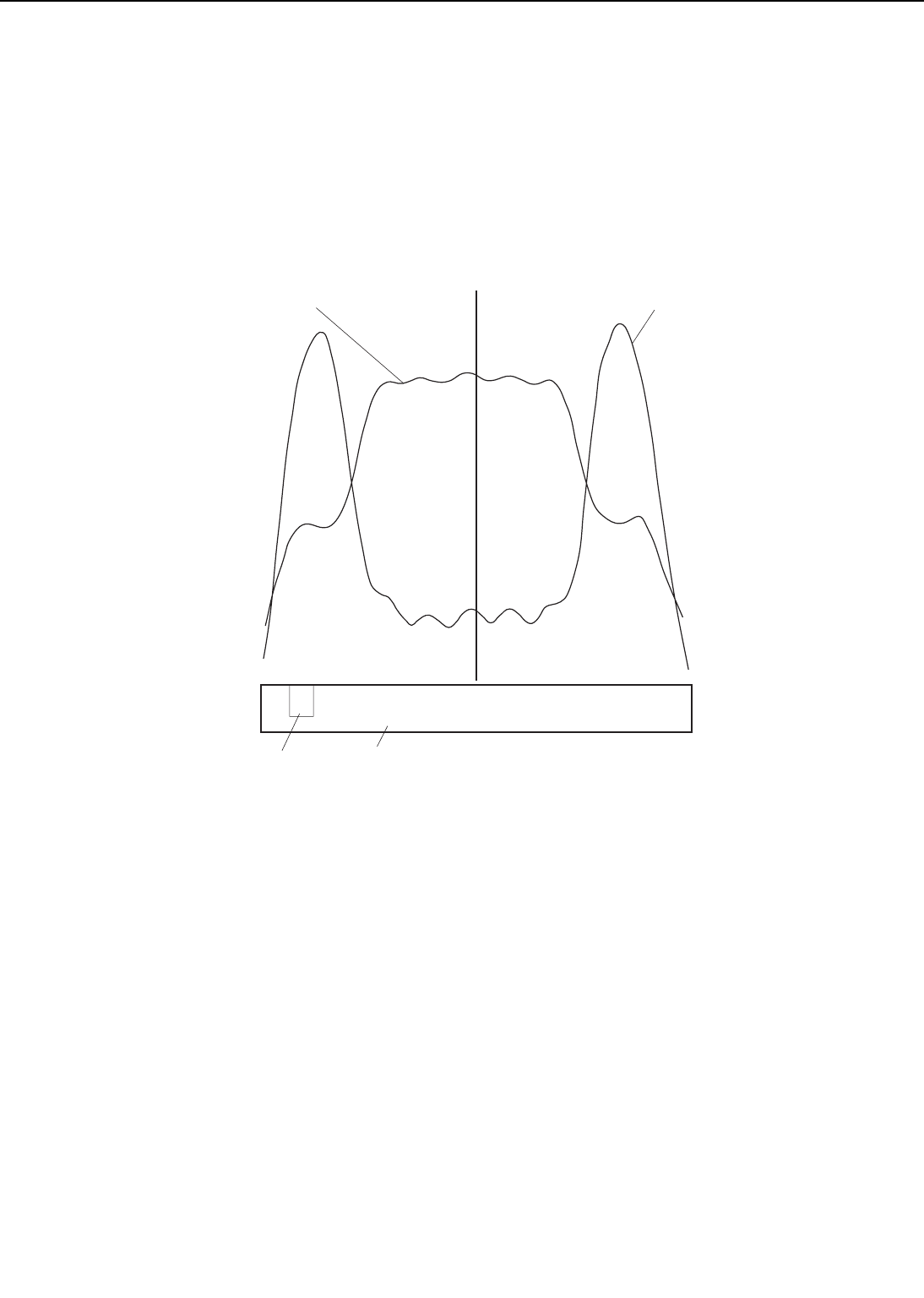
B. Fixing Control
1. Fixing temperature control
The upper fixing roller contains two heaters: fixing main heater (H1: 600W) and fixing sub heater
(H2: 450W). The fixing main heater heats the center of the upper roller, and the fixing sub heater
mainly heats both ends of the upper roller. The figure below shows the light distribution of the
heaters.
Figure 2-2-7
The surface temperature of the fixing roller is detected by the thermistor (TH1) on the fixing
roller. As the surface temperature rises, the resistance of TH1 decreases, and the voltage of the
FIXING ROLLER TEMPERATURE DETECTION signal (FSRTH) lowers.
The CPU (IC201) on the DC controller controls the FIXING MAIN HEATER DRIVE signal
(/FSRD1), FIXING SUB HEATER DRIVE signal (/FSRD2), FIXING HEATER DRIVE ENABLE sig-
nal (FSRDE), and INVERTER CIRCUIT DRIVE signal (SUPSLT) based on the voltage of the
FSRTH signal in order to bring the surface temperature of the fixing roller to the specified value.
This printer sets the TH-L/H signal to "H" when the fixing roller temperature is low (during
warm-up) and to "L" when the temperature is high (during normal temperature control) in order
to improve the accuracy of the FSRTH signal detection.
Table 2-2-1 shows the fixing roller target temperature during wait, standby, and print peri-
ods.
When it receives a /PRNT signal from the video controller, the CPU starts the fixing heater
print temperature control. The target fixing temperature and print speed at that point is shown
in Table 2-2-1. When you make duplex print or select "ROUGH" in "PAPER TYPE MENU" from
the control panel, the target fixing temperature and print speed are different from that of nor-
mal printing.
2 - 10
CHAPTER 2
Fixing main heater
Fixing upper roller
The center of the upper roller
Thermistor
Surface temperature of the
upper fixing roller
Drive
side
Fixing sub heater
°C
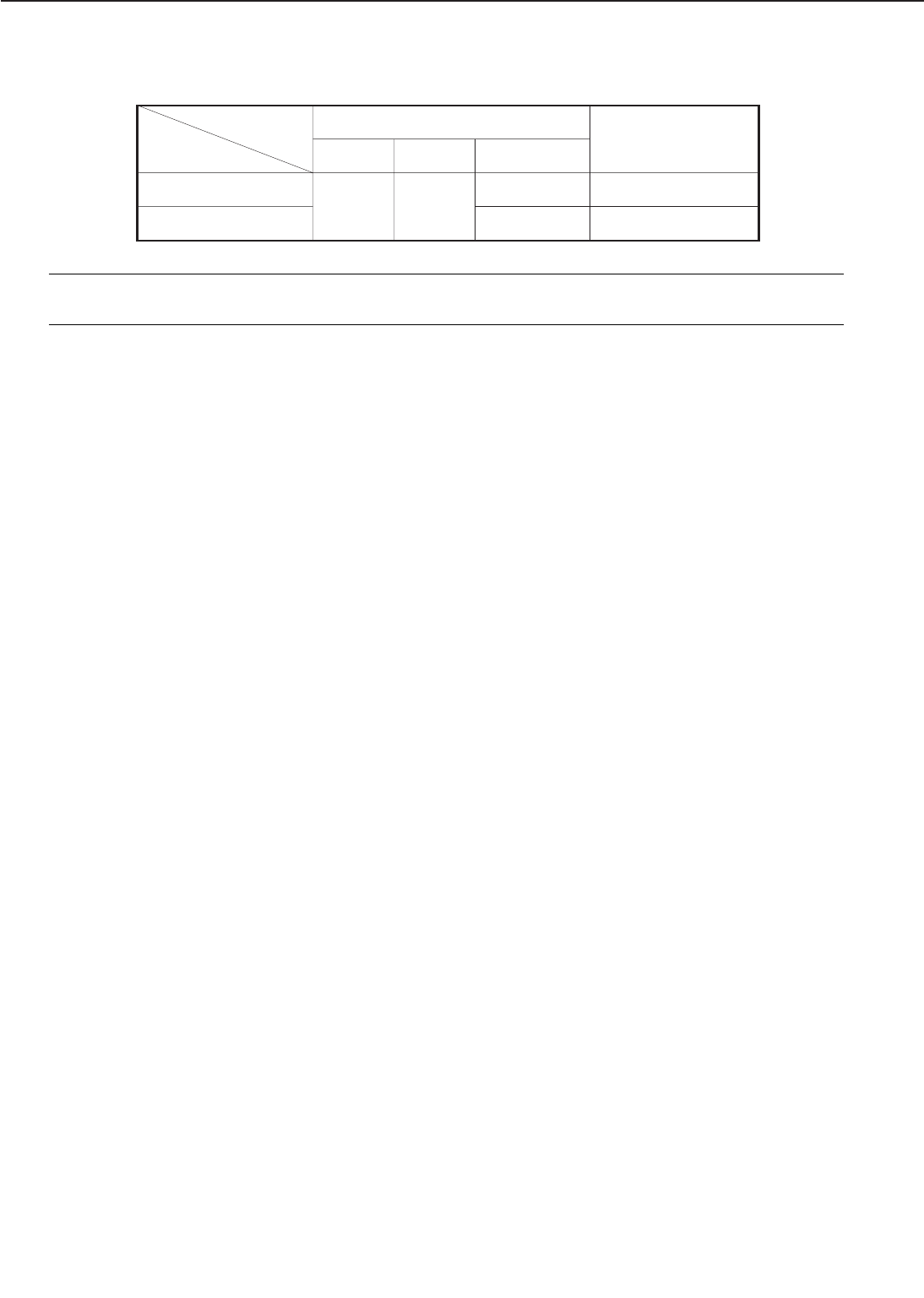
Table 2-2-1
Notes: 1. The target temperature for the first page in duplex print is 5°C lower.
2. The print speed in the above table is for A4 or Letter sized paper.
2 - 11
CHAPTER 2
190
195
Normal mode
Rough mode 169170 32
24
WAIT PRINT
Target temperature
STBY
PRINT SPEED
(ppm)
(˚C)
(note 1)
(note 2)
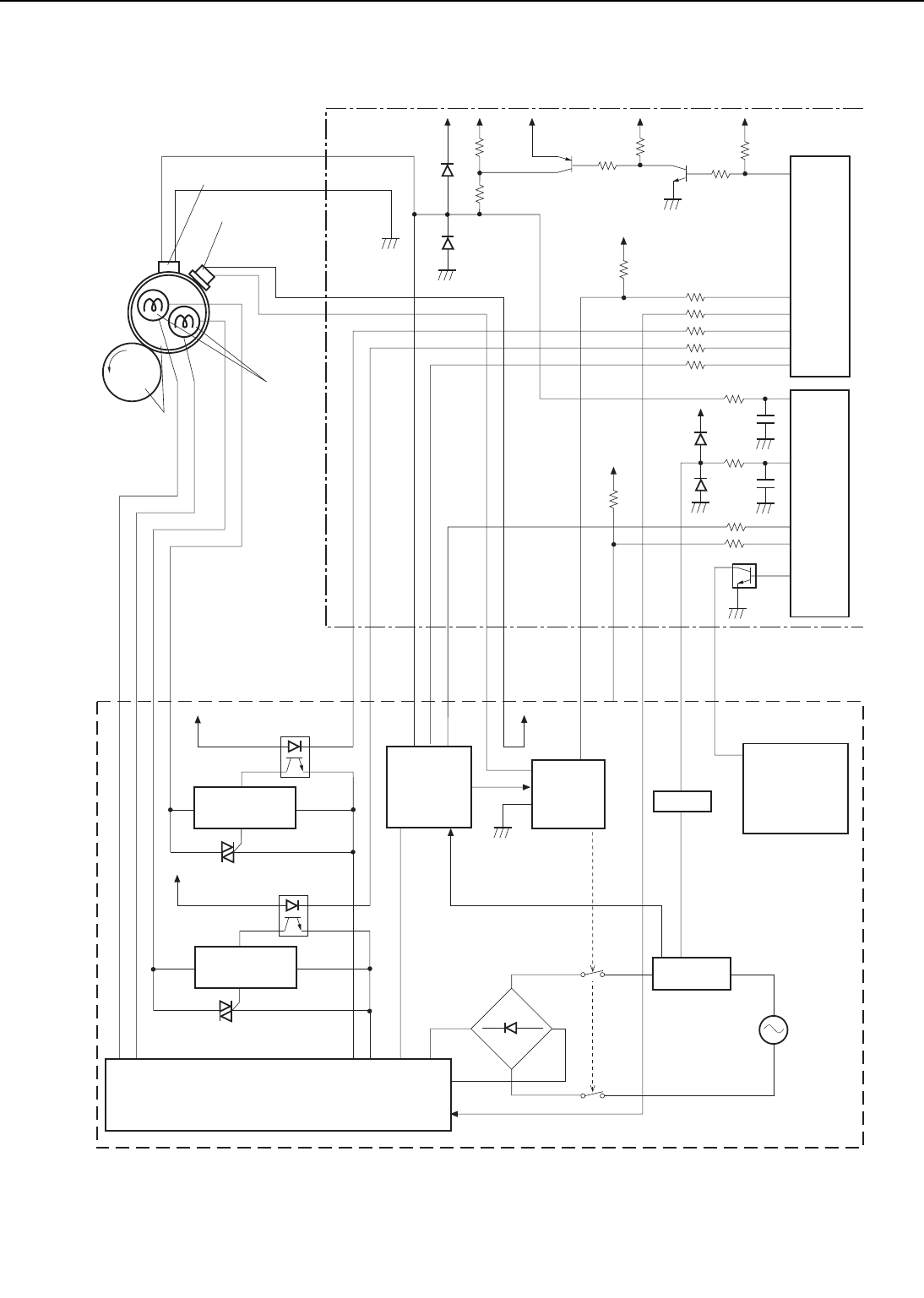
Figure 2-2-8
2 - 12
CHAPTER 2
51
129
128
125
126
122
FSRTH
GNDTH
DA21
DA20
DC15
DC16
DC12
P30/T00
P33/T11
DB21
P34/T12
CPU
IC201
44
47
+5V +5V +5V +5V +5V
Q206
48
C221
Q207
Q208
/FSRD1
/FSRD2
FSRTH
RLD
FSRDE
+24V
+5V
+5V
TSWIN
TSWOUT
/RLDSNS
SUPSLT
FSRCT
/REMT24
TSWOUT
TSWIN
J222-1
-4
J222-2
-3
P12/
AN12
78
C296
PSTYP
P15
1
J217-6
-7
J217-1
-2
-8
J217-3
-5
J217-11
J217-12
J217-10
J217-9
J217-13
FSRL1
FSRL2
FSRN2
FSRN1
J10-2
-3
-4
-1
+5V
+5V
AMP
+5V
GATE
ARRAY
IC202
Current
transformer
Low-voltage
power supply
circuit
Fixing
roller
Fixing
roller
heater
Thermistor
Thermoswitch
Safety
circuit
DC controller PCB
Power supply unit
Relay
drive
circuit
Triac drive
circuit
Triac drive
circuit
Inverter control circuit
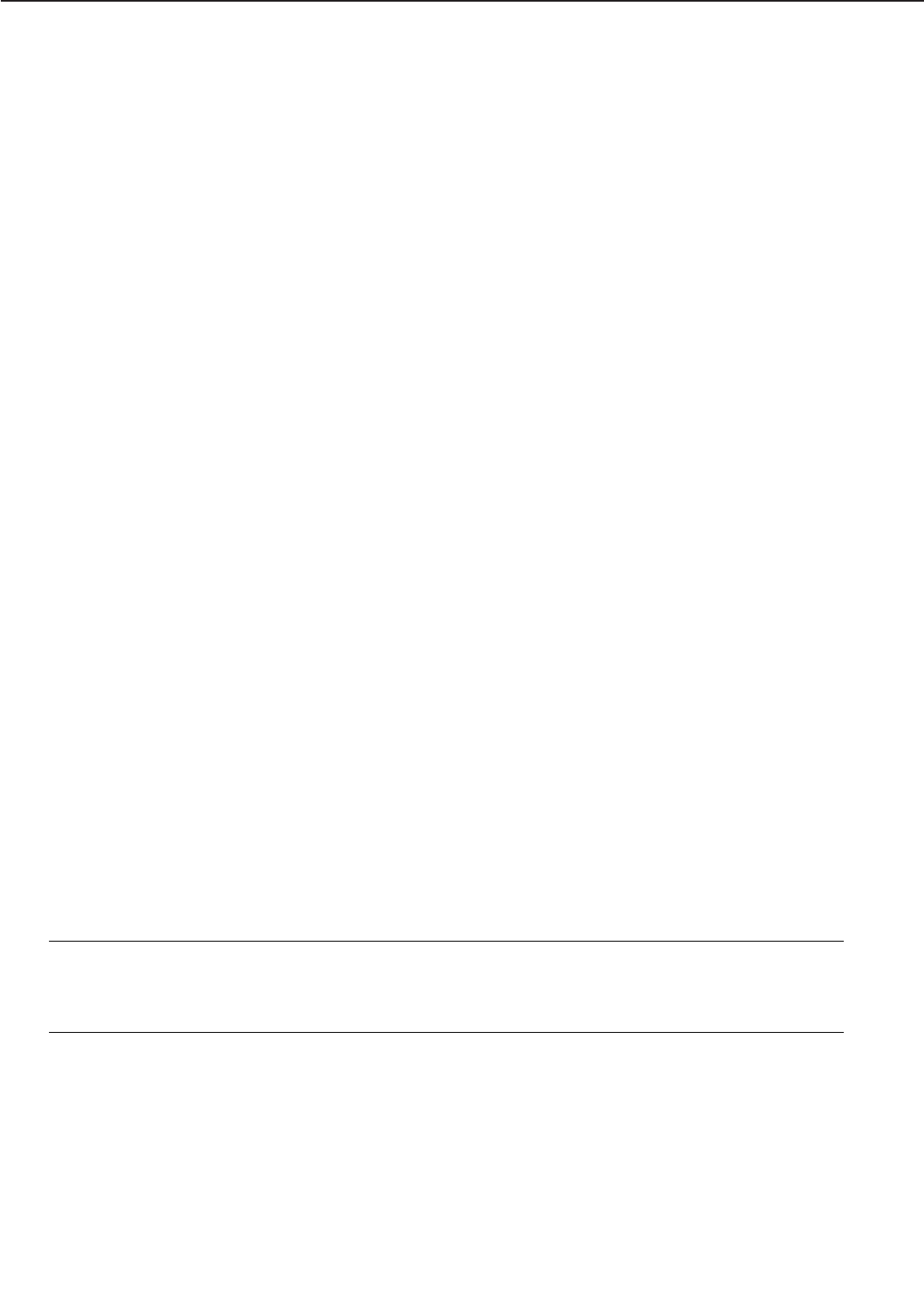
2. Protective function
The printer has three protection functions to prevent abnormal temperature rise of the fixing
roller.
• The CPU monitors the thermistor voltage. If the thermistor voltage becomes lower than
about 1.0V (230°C), the CPU identifies the fixing unit failure, and interrupts power to the
fixing unit and reports it to the video controller.
• If the surface temperature of the upper fixing roller rises abnormally and the thermistor volt-
age falls below about 0.8V (235°C), the safety circuit in the power supply interrupts power
to the fixing roller heater regardless of outputs from the CPU.
• If the surface temperature of the upper fixing roller rises abnormally and the thermoswitch
temperature exceeds 200°C, the thermoswitch turns off and cuts power to the fixing roller
heater.
3. Fixing unit failure detection
The CPU assesses a fixing unit failure in the following cases and reports it to the video controller.
a. Thermistor broken wire detection
The detected voltage of the thermistor is 4.6V or more when the thermistor voltage detection
mode (note) is in the error detection mode after the fixing heater is activated.
b. Maximum temperature detection
The fixing temperature rises abnormally and the temperature detected by the thermistor exceeds
about 230°C, during standby or printing.
c. Warmup error detection
The fixing unit does not reach the target temperature (see Table 2-2-1) within 180 seconds after
the start of warm-up.
d. Broken wire detection after the fixing unit is ready
The temperature detected by the thermistor is 150°C, or below during standby or printing.
e. Heater current detection
• The CPU detects a fixing heater broken wire if the FIXING HEATER CURRENT SENSE signal
(FSRCT) level is same as the all heaters OFF level when the fixing main heater or/and fixing
sub heater is/are driven.
• The CPU detects a fixing heater excursion if the FIXING HEATER CURRENT SENSE signal
(FSRCT) level is higher than the fixing main heater and fixing sub heater ON level when the
fixing main heater or/and fixing sub heater is/are OFF.
• The CPU detects a fixing heater excursion if the FIXING HEATER CURRENT SENSE signal
(FSRCT) level is higher than the specified value when both heaters are OFF.
Note: There are two thermistor voltage detection modes: error detection mode and normal
mode. In the error detection mode, sensitivity in the initial range (low temperature
range) is increased to improve detection accuracy. When the thermistor temperature
exceeds 60°C , it changes to the normal mode.
If the CPU detects a fixing unit failure, it does the following:
1) Stops the fixing roller heater.
2) Sets the RELAY DRIVE signal (RLD) to “L”, and turns the relay in the power supply OFF to
interrupt the power to the fixing roller heater.
3) Reports the fixing unit failure to the video controller.
2 - 13
CHAPTER 2
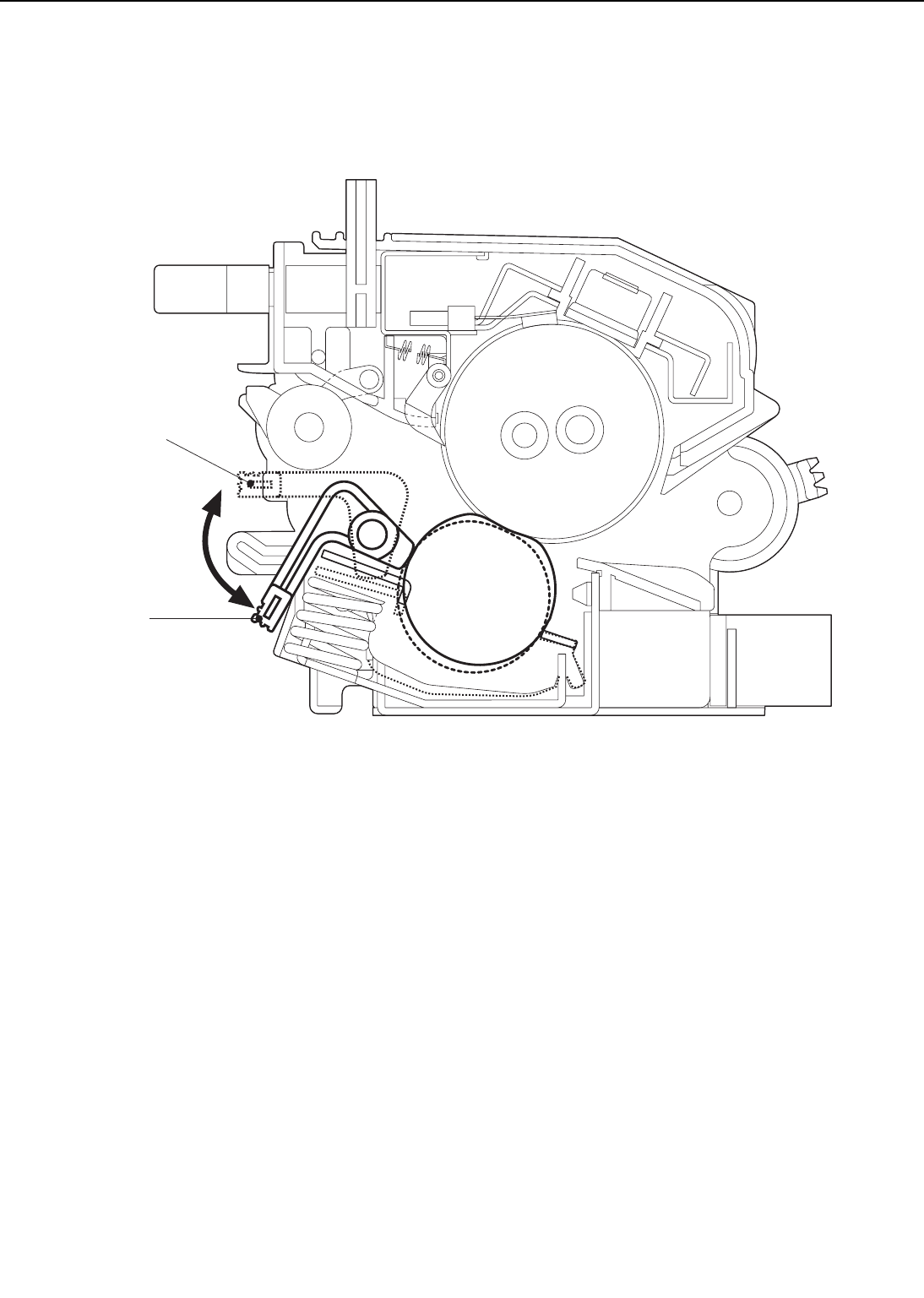
4. Envelope position lever function
This printer can adjust the nip width in two steps by changing the spring pressure of the lower
fixing roller. If an envelope wrinkles after it is printed, set the envelope position lever to the enve-
lope position.
➀ Normal mode
➁ Envelope mode
Figure 2-2-9
2 - 14
CHAPTER 2
➀
➁
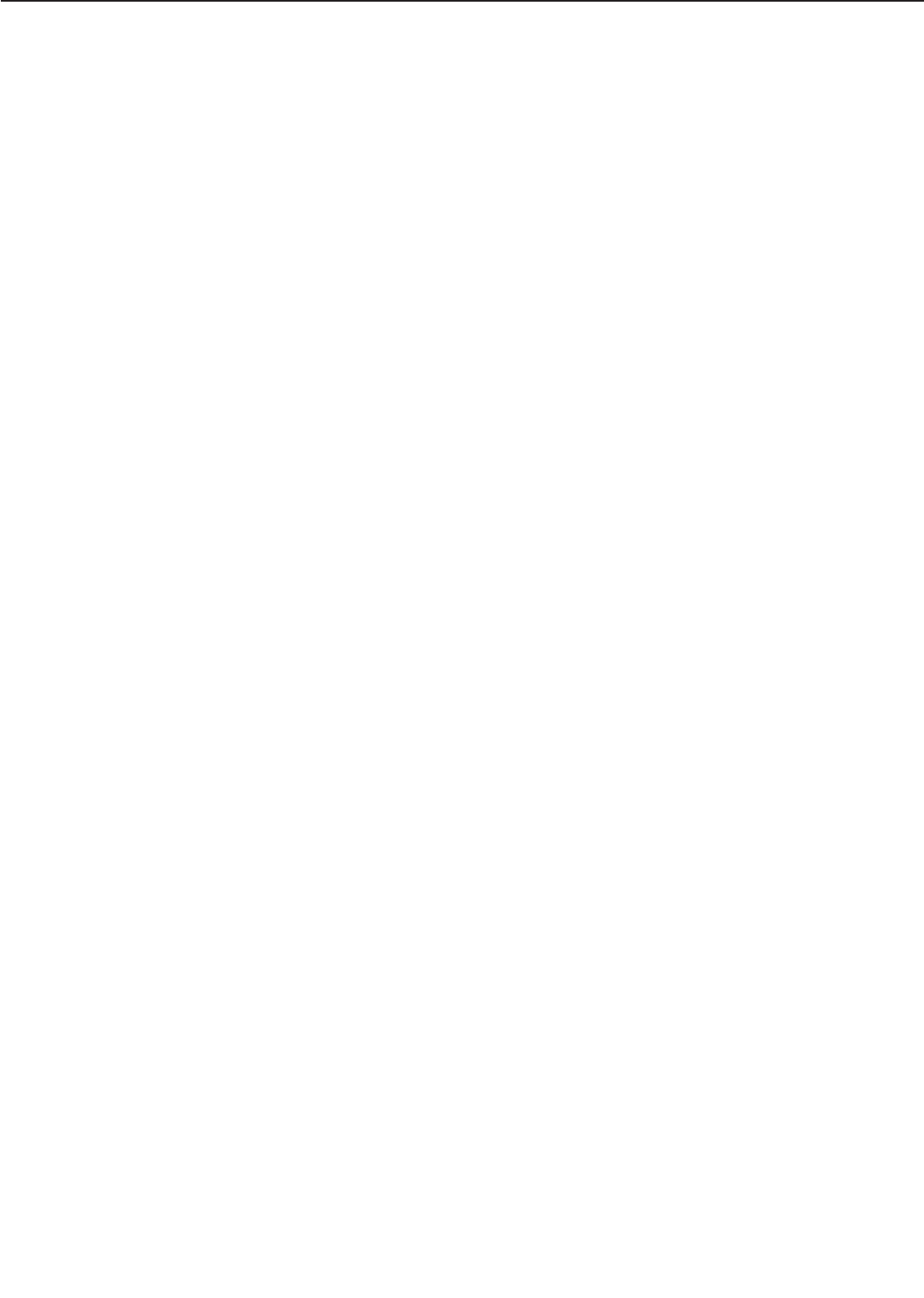
2 - 15
CHAPTER 2
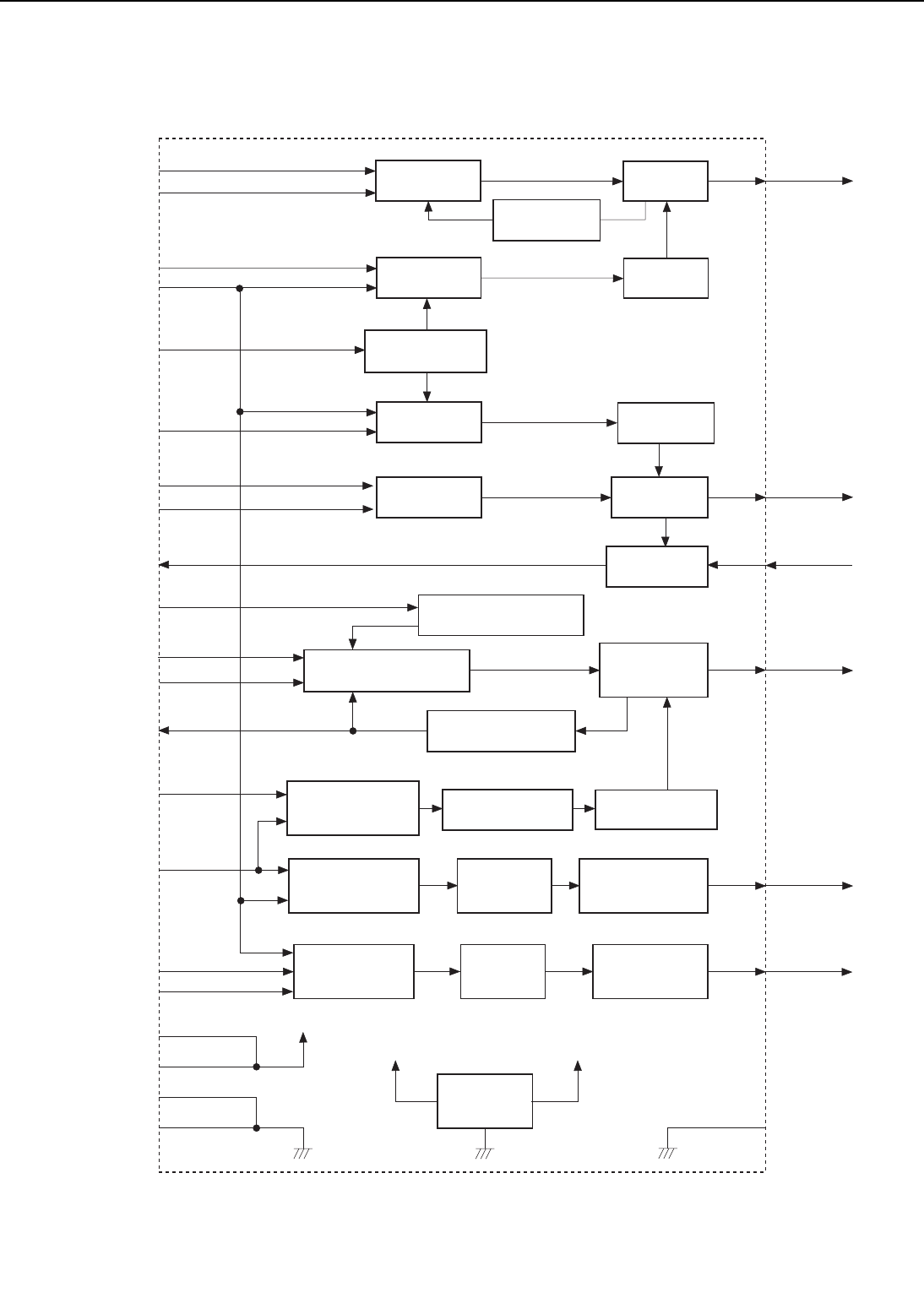
C. High-Voltage Power Supply
Figure 2-2-10
2 - 16
CHAPTER 2
J701-B2
J701-B4
J701-B3
/TRFCCD
J701-A10
/DEVACD
J701-A7
J701-B7 PR1
TB702
TB703
[T705]
TB706
TB705
[T701]
[T703]
[T706]
[T708]
[T707]
TB704
+24VB
+24VB
+24V
GND
GND
AC Transformer
Drive Circuit
Upper Fixing Roller
Voltage Transformer
Drive Circuit
Upper Fixing
Roller Voltage
Transformer
Discharge
Voltage
Generator Circuit
Discharge
Voltage
Transformer
Discharge Voltage
Transformer Drive
Circuit
Transfer Constant Current
Control Circuit
Transfer Negative
Voltage Transformer
Transfer Negative
Voltage Transformer
Drive Circuit
Transfer Positive Voltage
Transformer Drive Circuit
AC Transformer
Drive Circuit
Developing AC
Transformer
Transfer Positive
Voltage
Transformer
Primary AC
Transformer TB701
DEV
DCHGB
HRLB
/HRLBD
/DCHGUP
/DCHGBD
J701-A2
J701-A4
TONSNS
DEVACCLK
J701-A8
PR1ACCLK
J701-A12
J701-B12
J701-A11
J701-B11 GND
To primary
charging roller
To developing
cylinder
From toner
sensor
To transfer
charging roller
To static charge
eliminator
To upper fixing
roller
+24V +21.5V
Reference
Voltage
Power Supply
AC Current
detection Circuit
Toner detection
Circuit
Negative Voltage
Generation Circuit
Upper Fixing Roller
Voltage generation
Circuit
TRFCLK
TRFVSNS
TRFVCNT
/TRFNVD
[T702]
AC Transformer
Drive Circuit Primary DC
Transformer
/PR1DCD
[T704]
DC Transformer
Drive Circuit
/DEVDCD Developing DC
Transformer
TONANT
Transfer Positive
Voltage Sense Circuit
/PR1ACD
J701-B8
J701-B9
J701-A6 HVTCLK
DENADJ
J701-B10
J701-A9
J701-A3
J701-A1
J701-B1
Image Density
Adjustment Circuit
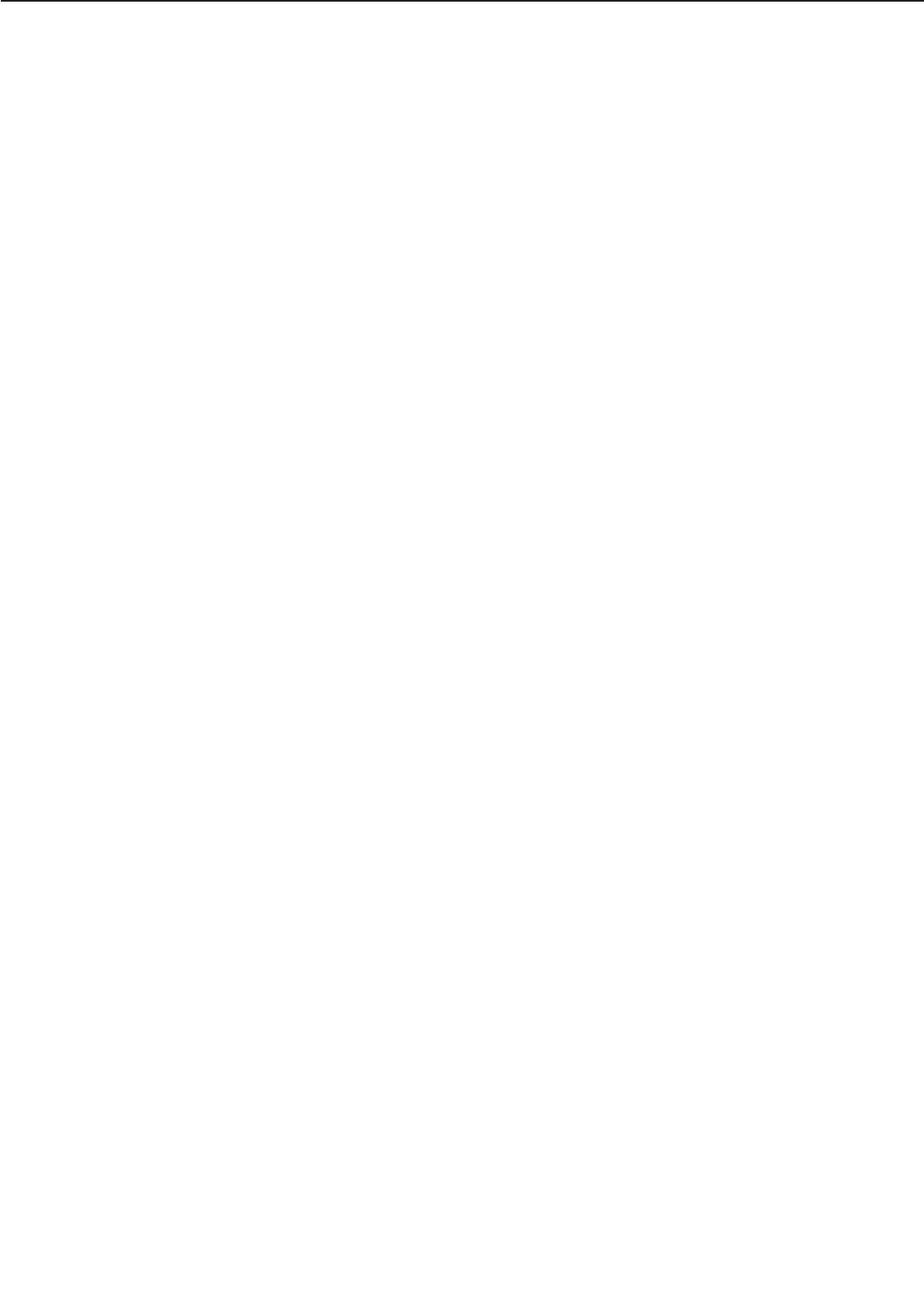
1. Outline
In response to the instruction from the microprocessor (CPU) on the DC controller PCB, the
high-voltage power supply applies a voltage to the primary charging roller, developing cylinder,
transfer charging roller, static charge eliminator, and upper fixing roller. It applies a voltage of
DC voltage and AC voltage to the primary charging roller and developing cylinder, applies a pos-
itive or negative DC voltage to the transfer charging roller, and a negative DC voltage to the sta-
tic charge eliminator and the upper fixing roller.
2. Principle of operation
a. Primary charging roller voltage generation
When the /PRNT signal sent from the video controller becomes “L”, initial rotation starts, and
the DC controller sets the PRIMARY AC BIAS DRIVE signal (/PRIACD) to "L." The circuit then
applies the primary AC bias to the primary charging roller. After the specified period of time has
elapsed the PRIMARY DC BIAS DRIVE signal (/PR1DCD) goes “L” and the voltage superimpos-
ing primary AC bias onto primary DC bias is applied to the primary charging roller.
The primary DC bias changes with the developing DC bias according to the IMAGE DENSITY
ADJUSTMENT signal (DENADJ) sent from the DC controller.
b. Developing bias generation
When the DEVELOPING DC BIAS DRIVE signal (/DEVDCD) from the DC controller becomes “L”,
a developing DC bias is applied to the developing cylinder.
When the VERTICAL SYNC signal (/VSYNC) is sent from the video controller, the DC con-
troller outputs the DEVELOPING AC BIAS DRIVE signal (/DEVACD) and DEVELOPING AC BIAS
FREQUENCY OUTPUT signal (/DEVACCLK). This circuit then applies the voltage superimpos-
ing developing DC bias and developing AC bias to the developing cylinder.
The developing DC bias changes according to the IMAGE DENSITY ADJUSTMENT signal
(DENADJ), making the image density adjustable.
c. Transfer charging roller voltage generation
The negative, between-page, and print bias are applied to the transfer charging roller according
to the print sequence.
The negative bias voltage is applied to the transfer charging roller at an appropriate timing to
move the toner attached to the transfer charging roller onto the photosensitive drum to clean the
roller.
For the between-page bias, a positive low voltage is applied to the transfer charging roller at
an appropriate timing so that the toner remaining on the photosensitive drum is not attracted
to the transfer charging roller.
For print bias, a positive voltage is applied to the transfer charging roller in order to transfer
the toner on the photosensitive drum surface to the paper.
When the /PRNT signal sent from the video controller becomes “L”, initial rotation starts and
a negative bias is applied to the roller for a certain time to clean the transfer charging roller.
Between-page bias is then applied, and a print bias is applied to the transfer charging roller after
the prescribed time has elapsed since the /VSYNC signal going “L”.
A print bias is applied during the print sequence to transfer the toner onto the paper. A
between-page bias is applied between pages.
After the completion of printing, a between-page bias and a negative bias are applied again to
clean the transfer charging roller.
d. Generation of print voltage to the discharger
2 voltage loads, high and low output bias are applied to the discharger according to the various
print sequences.
The discharger bias drive signal (/DCHGBD) output from the DC Controller is “L”, and when
2 - 17
CHAPTER 2
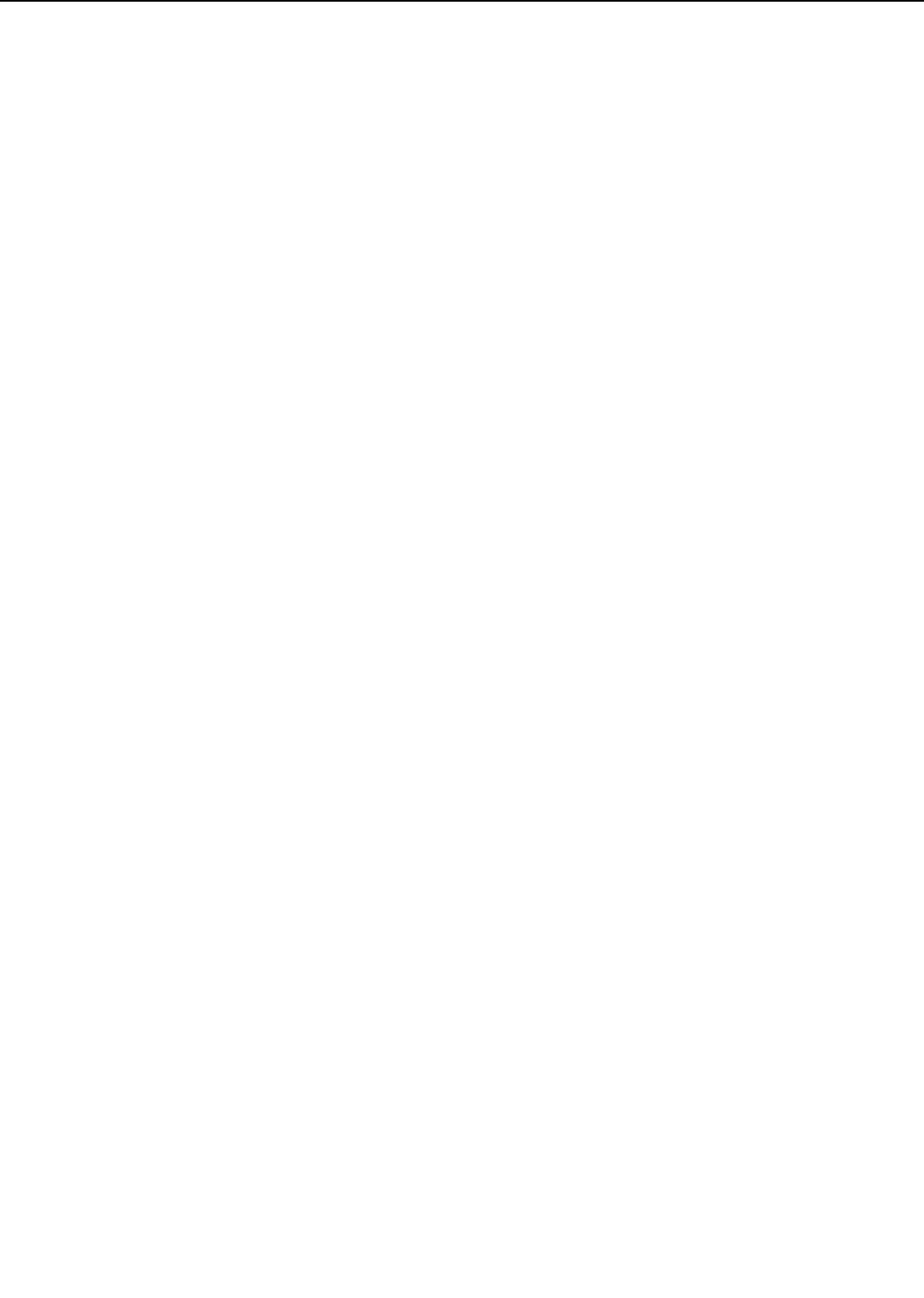
the discharger bias switch signal (/DCHGUP) turns “H” the low output bias changes to “L” and
the circuit applies a high voltage output bias. The high voltage output bias is applied only at
the trailing edge of a single side print and during the second side of a duplex print.
e. Toner sensing/cartridge sensing
The EP-72 cartridge has a toner sensor.
The DC controller detects the toner level and whether a cartridge is installed when the devel-
oping AC bias is applied to the developing cylinder by the DEVELOPING AC BIAS DRIVE signal
by checking the TONER LEVEL signal (TONSNS) voltage.
2 - 18
CHAPTER 2
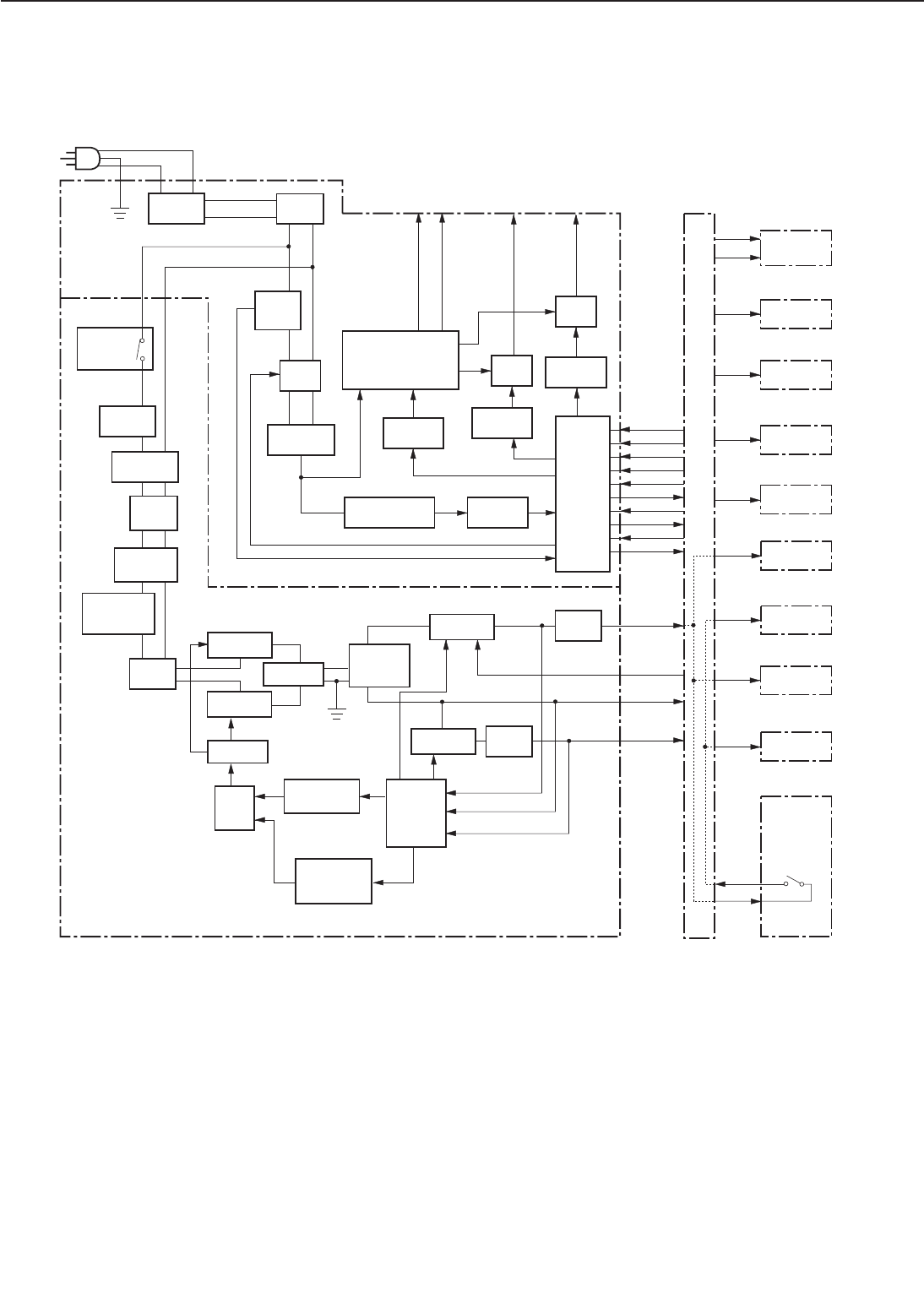
D. Power Supply
1. Outline
Figure 2-2-11
AC power is supplied to the low-voltage power supply when the main switch (S101) is turned
ON. The low-voltage power supply generates the required +24VDC, +5VDC and +3.3VDC for the
printer. +24VDC is supplied to the DC controller from the low-voltage power supply when the
DC controller sets the REMOTE 24V signal (/REMT24) to "L."
+24VDC is supplied to the high-voltage power supply PCB, +5VDC main motor, scanner motor,
and fans. +5VDC is used for sensors and ICs on the DC controller PCB.
+24VDC is divided into +24VA which is normally supplied from the power supply and +24VB
which is shut OFF when the door switch (SW1401) is turned OFF by opening the top cover or
2 - 19
CHAPTER 2
FSRTH
RLD
/FSRD1
/FSRD2
/FSRDE
/FSRCT
SUPSLT
/RLDSNS
TSWIN
TSWOUT
+5V
+24VA
+24VB
+5V
+24VA
+5V
+24VB
+24VA
+5V
+24VB
Over-current
detection circuit
Current
and
voltage
detection
circuit
+5V control
photocoupler
+3.3V
+5V
/REMT24
+24V
+3.3V
+5V
Converter
Current
transfor
-mer
Safety
circuit
Heater
drive
circuit
Triac
Current
fuse
Relay
Circuit
breaker Noise
filter
Transformer
Power
switch
(S101)
Power supply
Low-voltage power supply circuit
Video
controller PCB
Scanner
motor
Main motor
Sensors
Switch
/sensor
PCB
Door
switch
(SW1401)
Laser driver
Solenoids
Clutches
Operation
panel
High-voltage
power supply
To fixing roller heater DC controller
BD PCB
Triac
Phototriac
coupler
Phototriac
coupler
Phototriac
coupler
Control
IC
Switching
FET
Switching
FET
Switching
FET
Switching
FET
Transformer
Noise
filter
Phototriac
coupler
Rectificat
ion circuit
Rectificat
ion circuit
Filter
circuit
Filter
circuit
Filter
circuit
Rectificat
ion filter
circuit
Rush curren
t
prevention
circuit
Abnormal
voltage latch
photocoupler
Inverter control
circuit
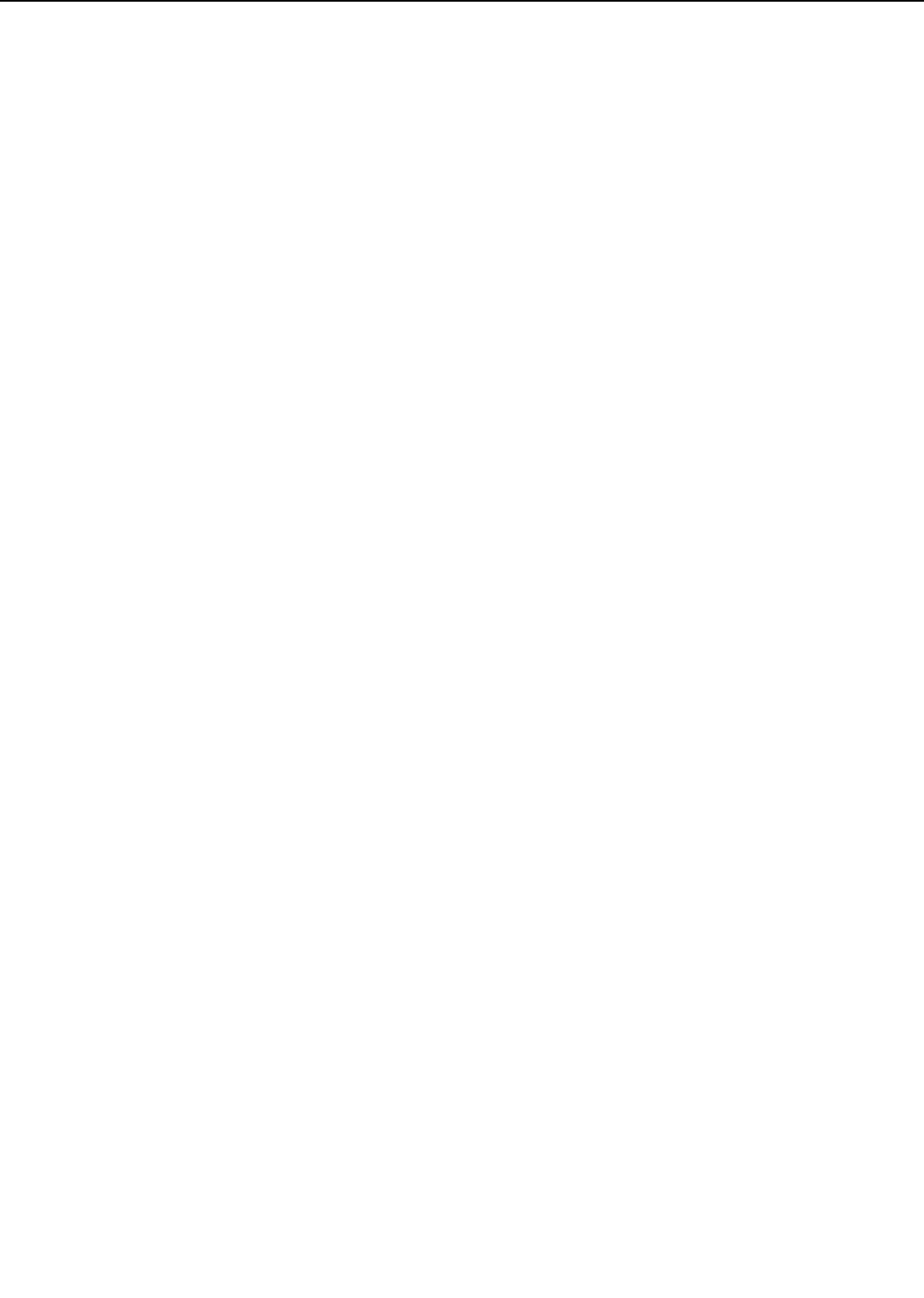
delivery cover.
+5VDC is divided into +5V which is normally supplied to the ICs on the DC controller PCB
from the power supply and +5V for power-saving mode (P5VB1). Supply of +5V for the power-
saving mode is stopped when the sleep command is received from the video controller. During
standby mode and periods when printing is not possible (when /RDY signal is “H”), the +5V is
supplied OFF and ON.
The DC controller PCB generates +5VC and supplies it to the laser driver.
This is shown in the block diagram below.
2. Protective Function
The +24VDC, +5VDC, and +3.3VDC power supply circuits have an over-current protective func-
tion and over-voltage protective function, which automatically interrupt output voltage to pro-
tect the circuits when a short circuit or other troubles on the load side result in over-current
flow or abnormal voltage.
If the over-current/over-voltage protective functions are activated, and no DC voltage is out-
put from the power supply circuits, turn OFF the power switch, rectify the trouble on the load,
and then turn ON the power switch again. Wait at least for 2 minutes before turning the power
switch ON again.
If over-current flows through the AC line, the circuit breaker in the power supply is turned
OFF to cut off the output voltage.
2 - 20
CHAPTER 2
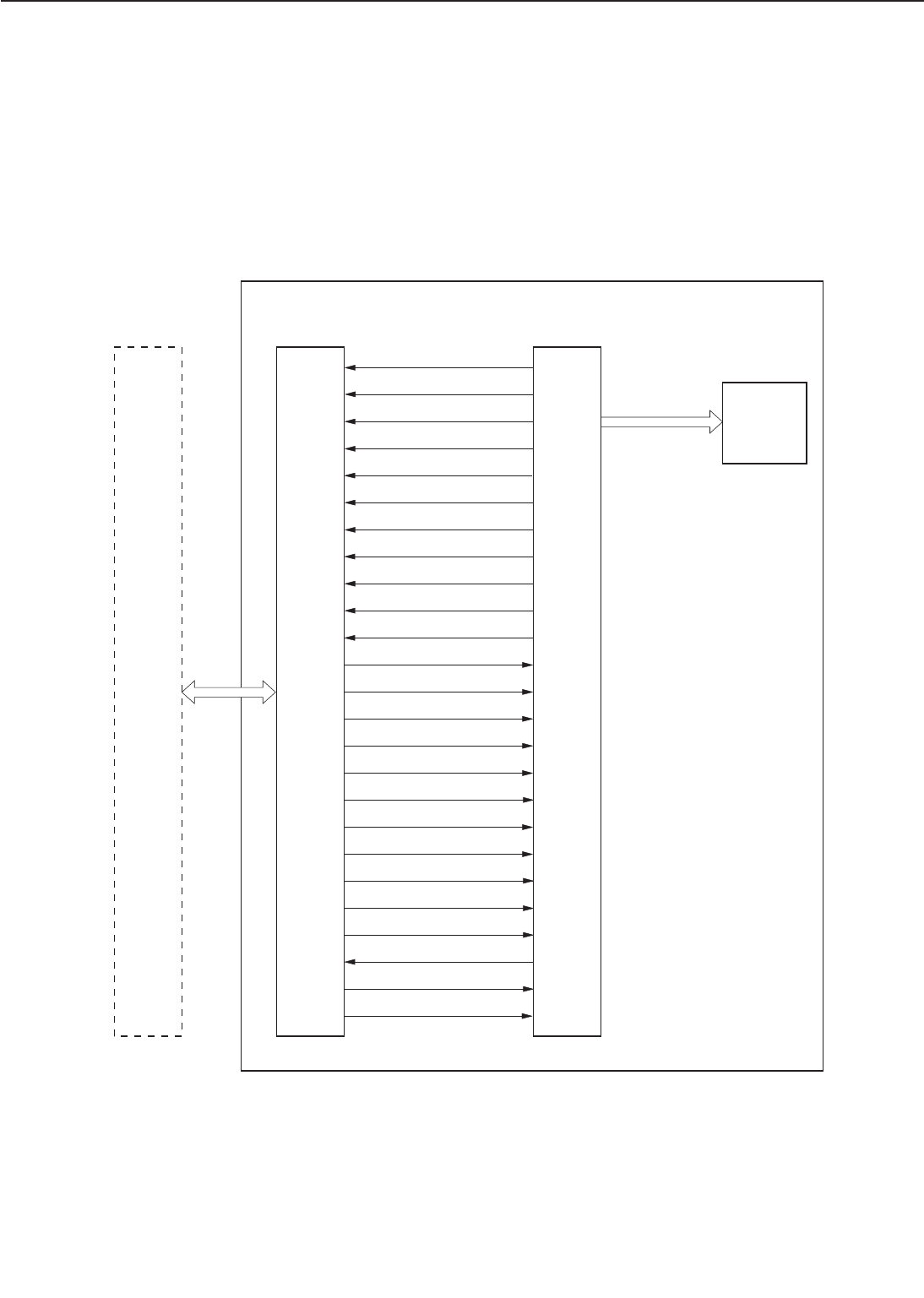
E. Video Interface Control
1. Outline
To connect the printer to an external device, such as a host computer, a video controller PCB
(interface PCB) is needed.
This section explains the kinds of interface signals exchanged between the printer and the
video controller PCB, and gives information concerning the sequence of printer operation mak-
ing use of interface signals.
a. Video interface signals
Figure 2-2-12
2 - 21
CHAPTER 2
/BD
/PPRDY
/RDY
/VSREQ
/SBSY
/STS
/CCRT
/PCLK
/PDLV
/PFED
/SPCHG
/CBSY
/PRNT
/VSYNC
/PRFD
/CPRDY
VDO
/VDO
/CMD
/CCLK
CPSEL
/FPCS
/FPO
/FPI
FPCK
Video controller
PCB
External device
(host computer, etc.)
Printer
DC controller
PCB
LASER DRIVE
signal
(VDO, /VDO)
Laser
driver
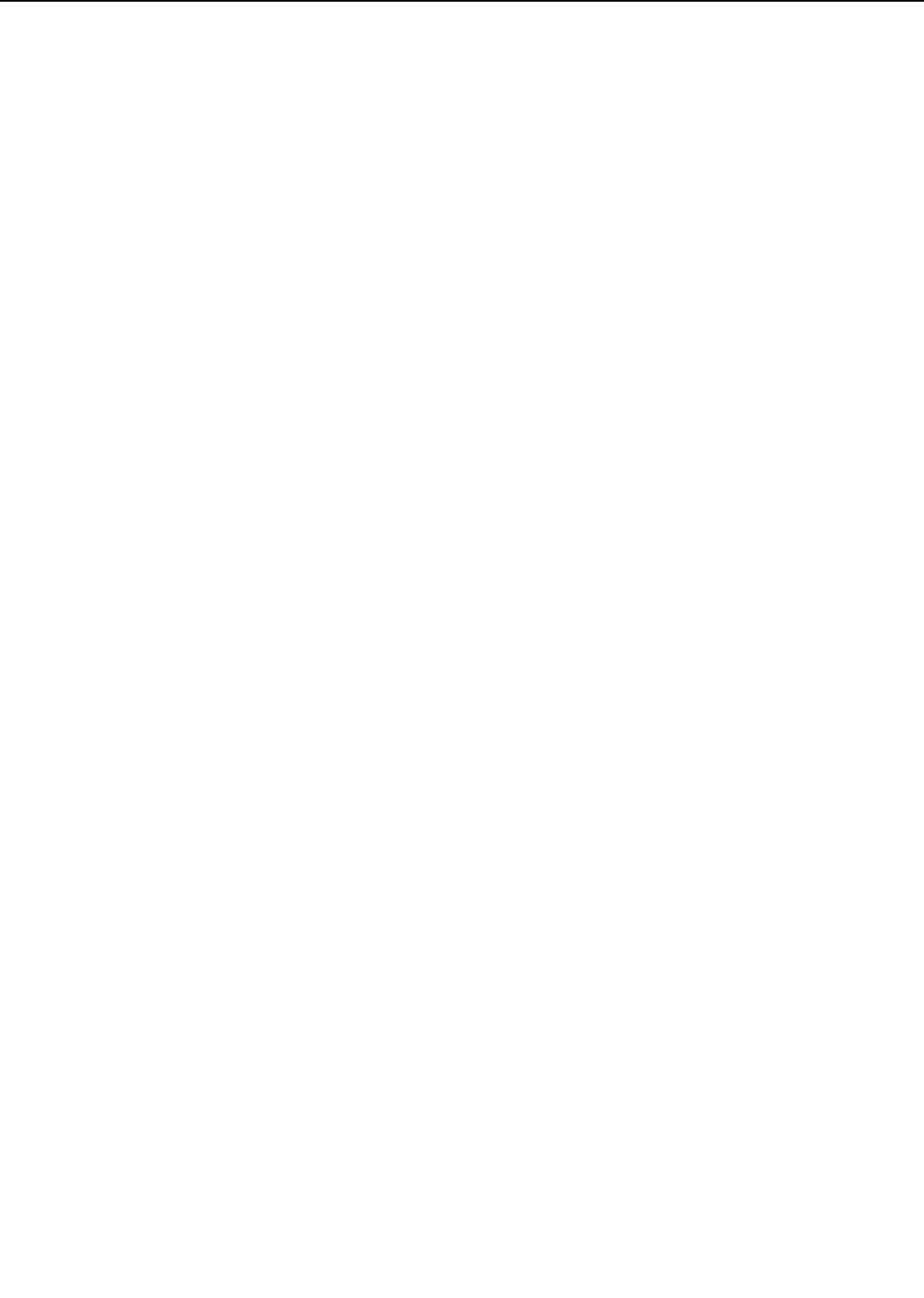
2. Operation
When the power is switched ON, the printer enters WAIT mode.
At the end of the WAIT mode, the DC controller sends the READY signal (/RDY) to the video
controller to inform it that printer is ready to print.
When the /RDY signal is “L” and data for a page is prepared, the video controller sends the
PRINT signal (/PRNT) to the DC controller.
When the DC controller receives the /PRNT signal, it starts the operation of the INITIAL
ROTATIONS (INTR) period.
At the end of the INTR period, the DC controller sends the VERTICAL SYNC REQUEST sig-
nal (/VSREQ) to the video controller.
The video controller receives the /VSREQ signal, and sends the VERTICAL SYNC signal
(/VSYNC) to the DC controller. When the /VSYNC signal is received, the print sequence is start-
ed.
The video controller sends the VIDEO signals (VDO, /VDO) synchronized with the HORI-
ZONTAL SYNC signal (/BD) and VERTICAL SYNC signal (/VSYNC) from the DC controller to the
laser driver through the DC controller.The VIDEO signals (VDO, /VDO) are sent to the laser dri-
ver as two low-voltage differential signals.
In response to the VIDEO signals (VDO, /VDO), the laser driver switches the laser diode ON
and OFF.
The laser beam is scanned repeatedly across the photosensitive drum with the scanning mir-
ror to form the latent electrostatic image of the original image.
The latent electrostatic image on the photosensitive drum is transferred onto the paper in the
electronic photographic process, and the paper is sent out through the face-down or face-up
trays.
When a page is being printed, the DC controller checks for other /PRNT or /VSYNC signals
from the video controller.
If none have arrived, the DC controller begins operation of the last rotations period (LSTR).
At the end of this period, the printer enters standby (STBY) mode.
If other /PRNT or /VSYNC signals arrive-during printing, the print sequence continues. The
last rotations operation is performed and the printer enters standby mode.
2 - 22
CHAPTER 2
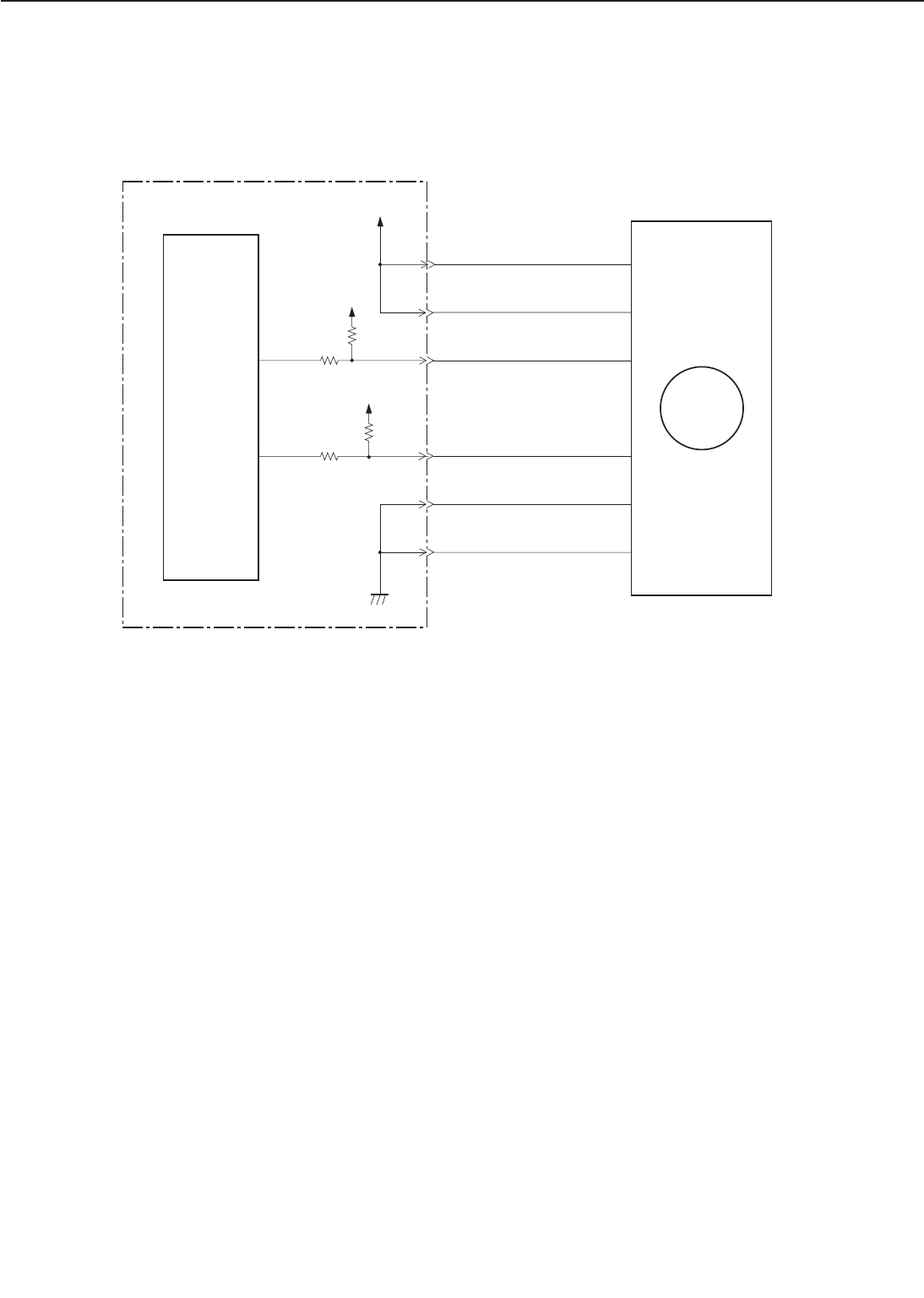
F. Other Controls
1. Main motor control
Figure below shows the main motor control circuit.
Figure 2-2-13
The main motor is a DC brushless motor with hall elements, and is unified with the motor drive
circuit.
The CPU (IC201) sets the MAIN MOTOR DRIVE signal (/MMOTD) to “L” and rotates the main
motor.
When the main motor rotates and reaches its specified speed, it sets the MAIN MOTOR
READY signal (/MMRDY) to “L.”
The CPU notifies the video controller PCB of a main motor failure in the following cases:
1) The /MMRDY signal does not become “L” withing 2.5 seconds after from the main motor
rotation starts.
2) The /MMRDY signal becomes “L” once, but becomes “H” for more than 0.1 seconds contin-
uously during the specified speed rotation.
2 - 23
CHAPTER 2
CPU
-2
39
-3
-4
M
-1
-6
J218-5
/MMOTD
MT1
/MMRDY
+5V
38
P62
+5V
IC201
-2
-3
-4
-1
-6
J36-5
P63
Main motor
DC controller PCB
+24VB
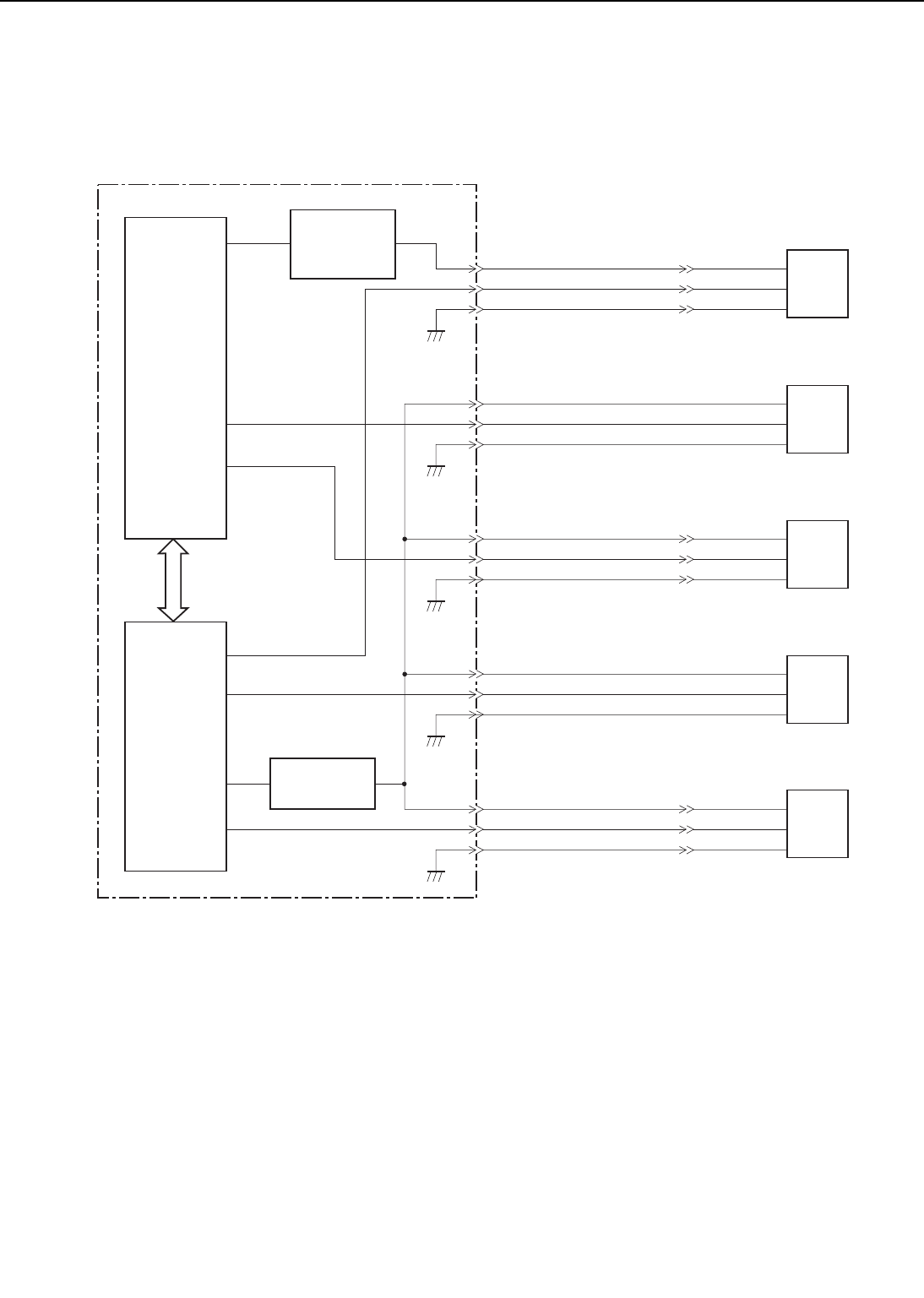
2. Fan motor control
This printer has 4 heat exhausting fans and an air intake fan. They are DC brushless motors.
The figure below shows the fan motor control circuit.
Figure 2-2-14
When the power switch of the printer is turned ON, the CPU (IC201) on the DC controller sets
the No.53 pin to "H" and rotates the multi-purpose tray fan (FM5) at half speed for about 15 sec-
onds. The CPU sets the No.65 pin to "H" via the gate array (IC202), and rotates the power sup-
ply fan (FM1), fixing unit/scanner fan (FM2), electrical unit fan (FM3), and fixing unit fan (FM4)
at half speed.
When it receives a /PRNT signal from the video controller, the CPU rotates FM1, FM2, FM3,
and FM4 at full speed and FM5 at half speed (full speed in case of duplex printing). When the
main motor drive stops after printing, the CPU rotates FM1, FM2, FM3, and FM4 at full speed
for about 30 seconds then at half speed. The CPU rotates FM5 at half speed for about 30 sec-
onds (full speed for about 30 seconds in case of duplex printing).
The drive voltages output from the fan motor drive circuit and multi-purpose tray fan motor
2 - 24
CHAPTER 2
FM5
J35-1
-2
-3
FAN5D
/FAN5S
GND
J34-3
-2
-1
J229-1
-2
-3
FM2
FAN2D
/FAN2S
GND
J216-1
-2
-3
FM3
J13-1
-2
-3
FAN3D
/FAN3S
GND
J12-3
-2
-1
J210-1
-2
-3
FM1
FAN1D
/FAN1S
GND
J208-1
-2
-3
FM4
J26-1
-2
-3
FAN4D
/FAN4S
GND
J25-3
-2
-1
J225-1
-2
-3
Multi-purpose
tray fan motor
drive circuit
Fan motor
drive circuit
65
DC14
IC202
(G.A.)
52
37
64
61
124
53
DA04
DA05
DA03
P121
P120
P61
IC201
(CUP)
DC controller PCB
Power supply
fan
Fixing unit/
Scanner unit
fan
Electrical unit
fan
Fixing unit fan
Multi-purpose
tray fan
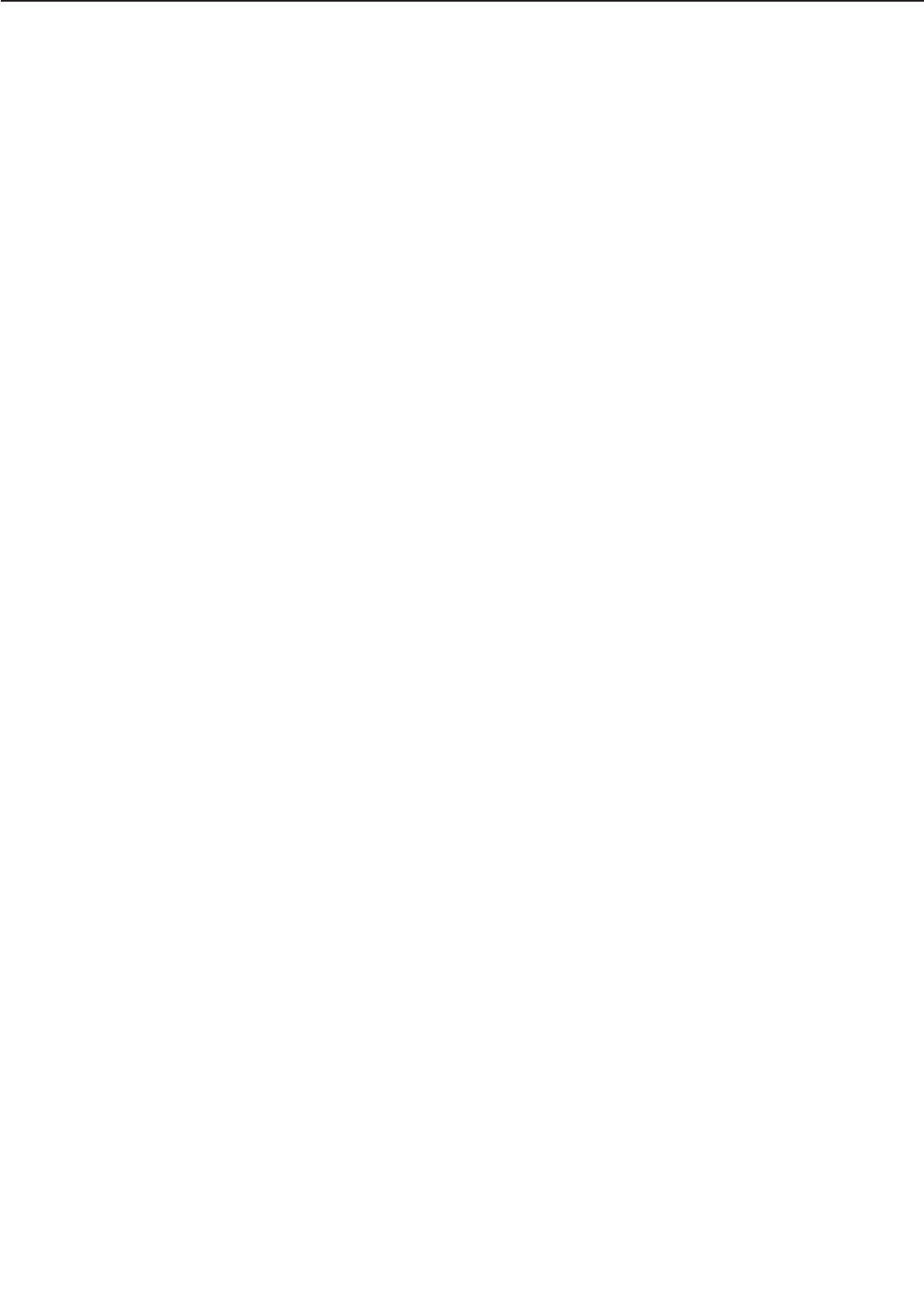
drive circuit switch the fun motor rotation speed between full and half speed.
The CPU assesses a fan motor failure and reports it to the video controller, if the FAN LOCK
DETECTION signals (/FAN1S, /FAN2S, /FAN3S, /FAN4S, /FAN5S) stay "L" for about 1.5 sec-
onds or more for 3 times at 5 seconds intervals while the fan motors are ON.
2 - 25
CHAPTER 2
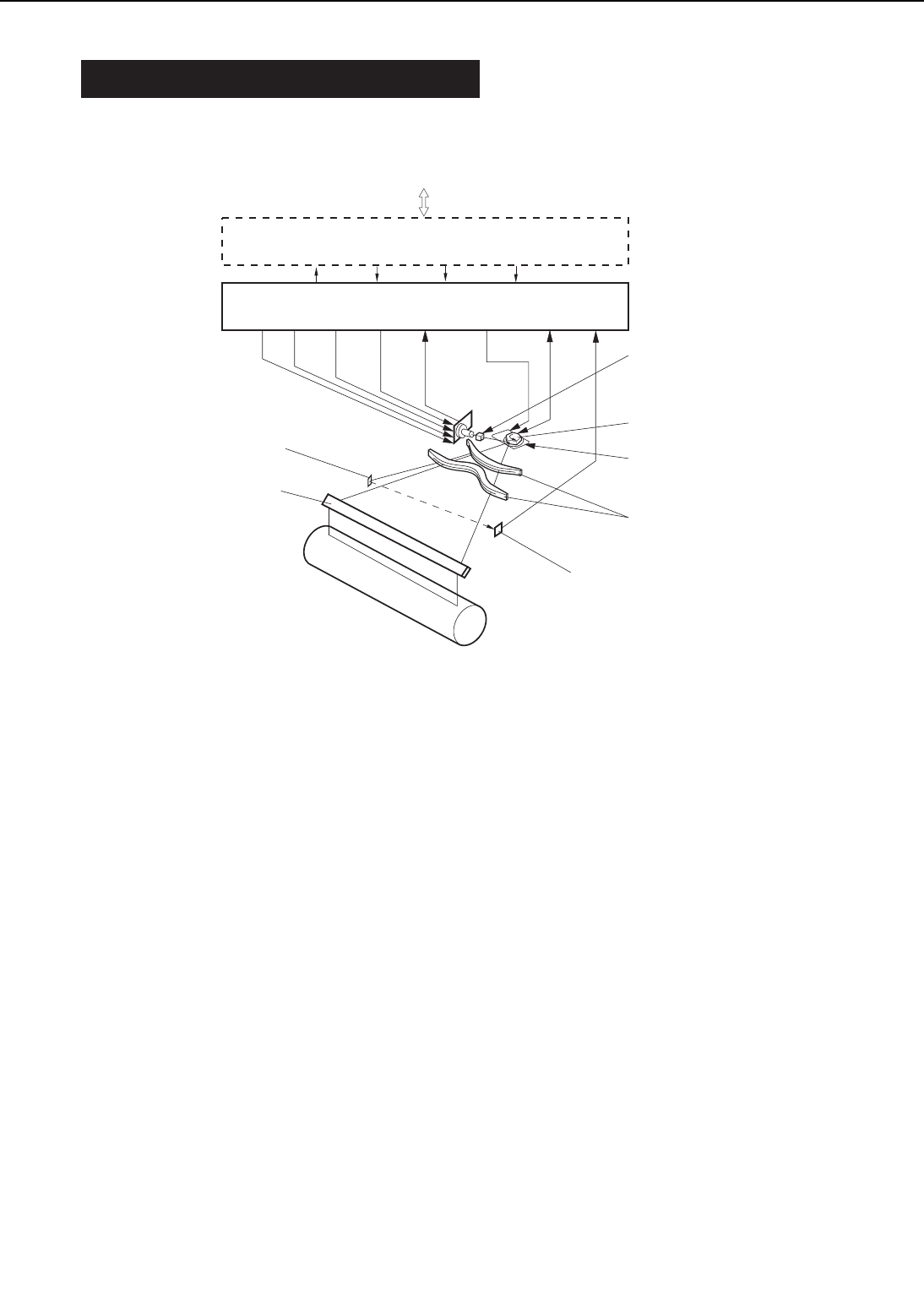
III. LASER/SCANNER SYSTEM
A. Outline
Figure 2-3-1
The DC controller PCB receives the VIDEO signals (/VDO, VDO) from the video controller PCB
and sends then to the laser driver in the laser/scanner unit.
The laser driver turns the laser diode ON and OFF according to the video signal (/VDO, VDO)
and generates the modulated laser beam only when the VIDEO ENABLE signal (/LENBL) from
the DC controller is “L.”
The modulated laser beam is aligned by a collimator lens and a cylindrical lens into a paral-
lel beam which strikes the scanning mirror that is rotating at a specified speed.
The beam reflected from the scanning mirror is brought to a point of focus on the photosen-
sitive drum with the focusing lens and the mirror located in front of the scanning mirror.
As the scanning mirror rotates at a specified speed, the beam is scanned across the drum at
a specified speed.
The drum also rotates at a specified speed and the laser beam successively scans across its
surface. Thus the laser beam builds up an image on the drum surface.
2 - 26
CHAPTER 2
/VSYNC /VDO VDO
/BDIVDO /SCNRDY/LENBL DRVES/LON/VDO
/BD
/SCND
External device
Video controller PCB
DC controller
Photosensitive drum
BD mirror
Cylindrical lens
Focusing lens
Scanning mirror
Scanner motor
Laser driver
Mirror
BD PCB
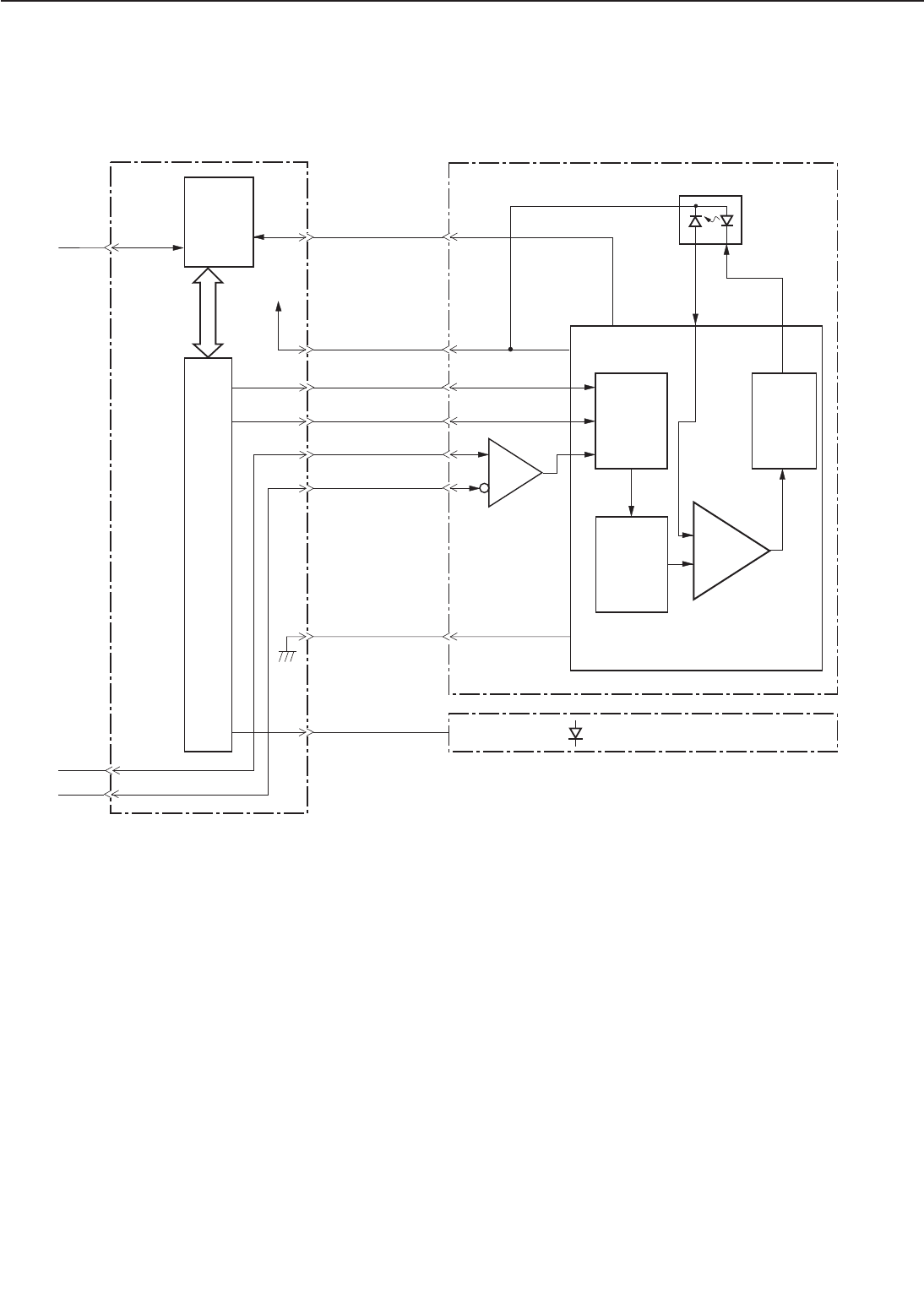
B. Laser Control Circuit
1. Outline
Figure 2-3-2
This circuit switches ON and OFF the laser diode (LD) with a constant intensity in response to
the video signals (/VDO, VDO) sent from the video controller PCB.
The /VDO and VDO signals are converted into the low voltage differential signals to suppress
radiation noise from the video controller PCB and sent to the DC controller PCB, and then sent
to the receiver in the laser driver circuit. The receiver demodulates the low voltage differential
signals and transmits it as a VIDEO OUT signal (/VDOUT) to the logic circuit in the laser driver
IC.
If the VIDEO ENABLE signal (/LENBL) from the microprocessor (CPU: IC201) is “L”, the laser
driver circuit turns the laser diode ON and OFF according to the /VDOUT signal.
The CPU monitors the LASER FAILURE DETECTION signal (DRVES) sent from the laser dri-
ver PCB to check whether the laser diode is generating laser normally or not.
The CPU emits laser forcibly when the /BDI signal is not input for 0.7 continuous seconds
from the BD PCB while the scanner motor runs at the specified speed, and notifies the video
controller of the BD failure when the DRVES signal is 3.805V or less and the laser failure when
2 - 27
CHAPTER 2
/VDO
J1001-8
-C2
/LENBL
48
NENBL
/LON -2
49
NLON
/VDO
DRVES
J202
-2
PD
LD
CPU
66
/PRNT
J201-C6 P05/
INTPS
GND
VCC
IC201
J202-4
-11
-10
-9
/BDI
J206
-3 J6-2
56
NBDI
-7
-5/-8
-1
-3
-5
-4/-7
VDO
/VDOUT
VDO
-C1
IC202
G.A.
80
P14/
AN14
J1001
-10
Logic IC
Drive IC
Analog
adder
circuit
DC controller PCB Laser driver PCB
Laser driver IC
(Photo diode)
(Laser diode)
BD PCB
Receiver
Power
adjustment
circuit
+5V
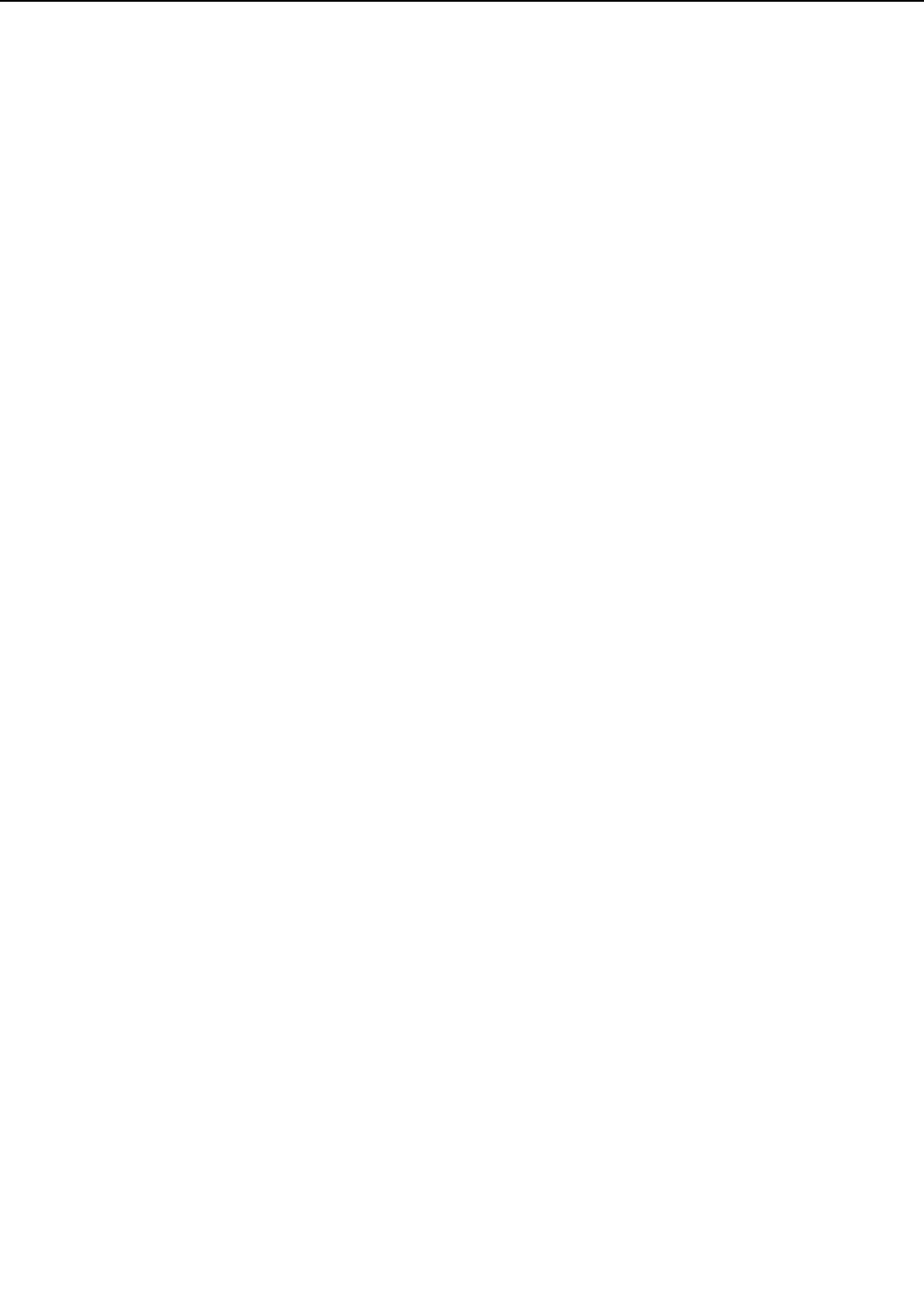
it exceeds 3.805V.
2. Automatic power control of laser diode
The laser driver IC controls the automatic power control (APC) of the laser diode so that the laser
diode emits a beam of constant intensity.
When the FORCED LASER ON signal (/LON) becomes “L,” or the VIDEO ENABLE signal
(/ENBL) and /VDOUT signal become “L,” the laser diode emits light according to the standard
voltage of the laser driver PCB. The photo diode in the laser diode detects the beam intensity
and feeds back the corresponding current value to the control amplification circuit. It is then
compared with the current value set in the power adjustment circuit, and the intensity of the
current to the laser diode is controlled.
The printer uses the APC method that conducts the beam intensity detection and control for
each dot while the laser driver is emitting laser. While in the conventional method, the beam
intensity was measured by emitting laser for a certain period of time between pages or during
unblinking, this method controls the laser output, detecting the intensity of the laser which is
actually forming an image. Therefore, the APC of this printer has higher reliability of control
over the conventional APC.
3. Horizontal synchronization control
The CPU generates an UNBLANKING signal inside the IC201 based on the BD input signal
(/BDI) sent from the BD PCB of the laser/scanner unit.
IC201 sets the FORCED LASER ON signal (/LON) to “L” during unblanking period. The laser
driver turns the laser diode ON when the /LON signal is “L.”
The laser beam turned ON by the /LON signal is reflected at the small fixed BD mirror locat-
ed in the light path where the laser beam scanning starts, and is input to the BD PCB in the
laser/scanner unit.
The BD PCB detects the laser beam, generates a BD INPUT signal (/BDI), and sends it to the
CPU. The CPU generates a BEAM DETECTION signal (/BD) according to the /BDI signal and
sends it to the video controller PCB.
4. Laser diode emission control
Based on the paper size data, the CPU generates a VIDEO ENABLE signal (/LENBL) and sends
it to the logic circuit of the laser driver IC. The /VDOUT signal is masked by the /LENBL sig-
nal in the logic circuit, which controls the emission period of the laser diode.
The paper size data is supplied to the CPU by the cassette paper size switches for cassette
pick-up and by the paper size specification command from the video controller PCB for multi-
purpose tray pick-up.
The CPU generates the IMAGE TOP ERASE AND BOTTOM ERASE signal (TOPE) and HORI-
ZONTAL IMAGE MASK signal (MSK) according to the paper size data. (TOPE and MSK are used
inside the CPU and are not output externally.)
To prevent the laser beam from writing on non-image area during the non-unblanking peri-
od, the CPU sets the VIDEO ENABLE signal (/LENBL) to “L” only when the TOPE and MSK sig-
nals are “L.” The laser driver turns the laser diode ON when the /LENBL signal and /VDOUT
signal are “L.”
2 - 28
CHAPTER 2
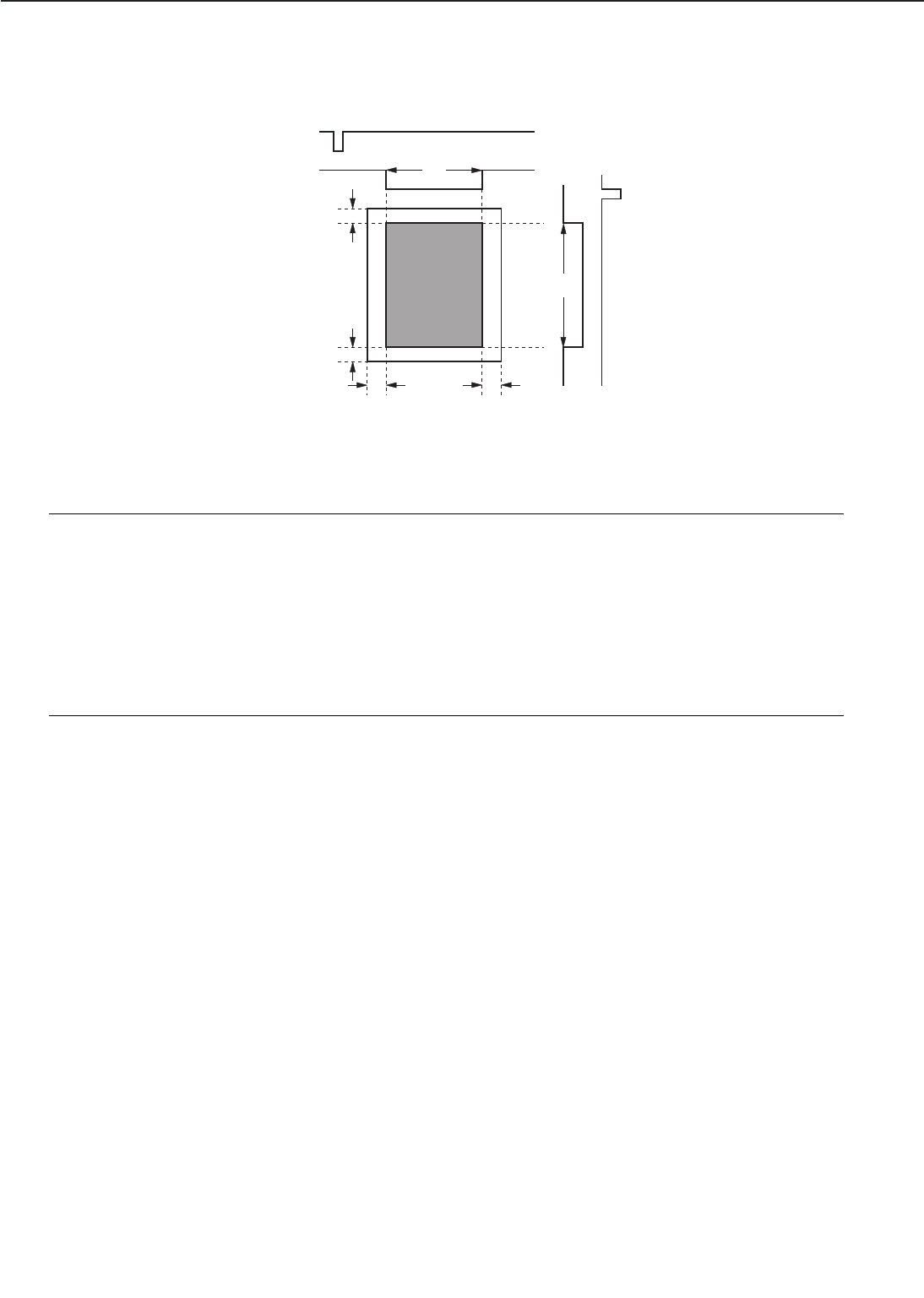
Figure 2-3-3
Notes: 1. The shaded area indicates the area where the laser beam writes on the drum.
2. T1 and T2 vary according to the paper size. If no paper size is specified by the paper
size specification command from the video controller during manual feed, the print-
er does not recognize the paper width. So the T1 and T2 values are assumed to be
UNIVERSAL size (297.0mm x 635.0mm), the maximum paper width for this printer.
3. The CPU determines the actual size of the paper being fed by detecting the time from
the leading edge of the paper passes through the registration paper sensor (PS1) until
its trailing edge clears the sensor. The image is then masked according to the detect-
ed paper size.
2 - 29
CHAPTER 2
/BD
MSK
TOPE
T2
T1
2mm2mm
3mm 3mm
/VSYNC
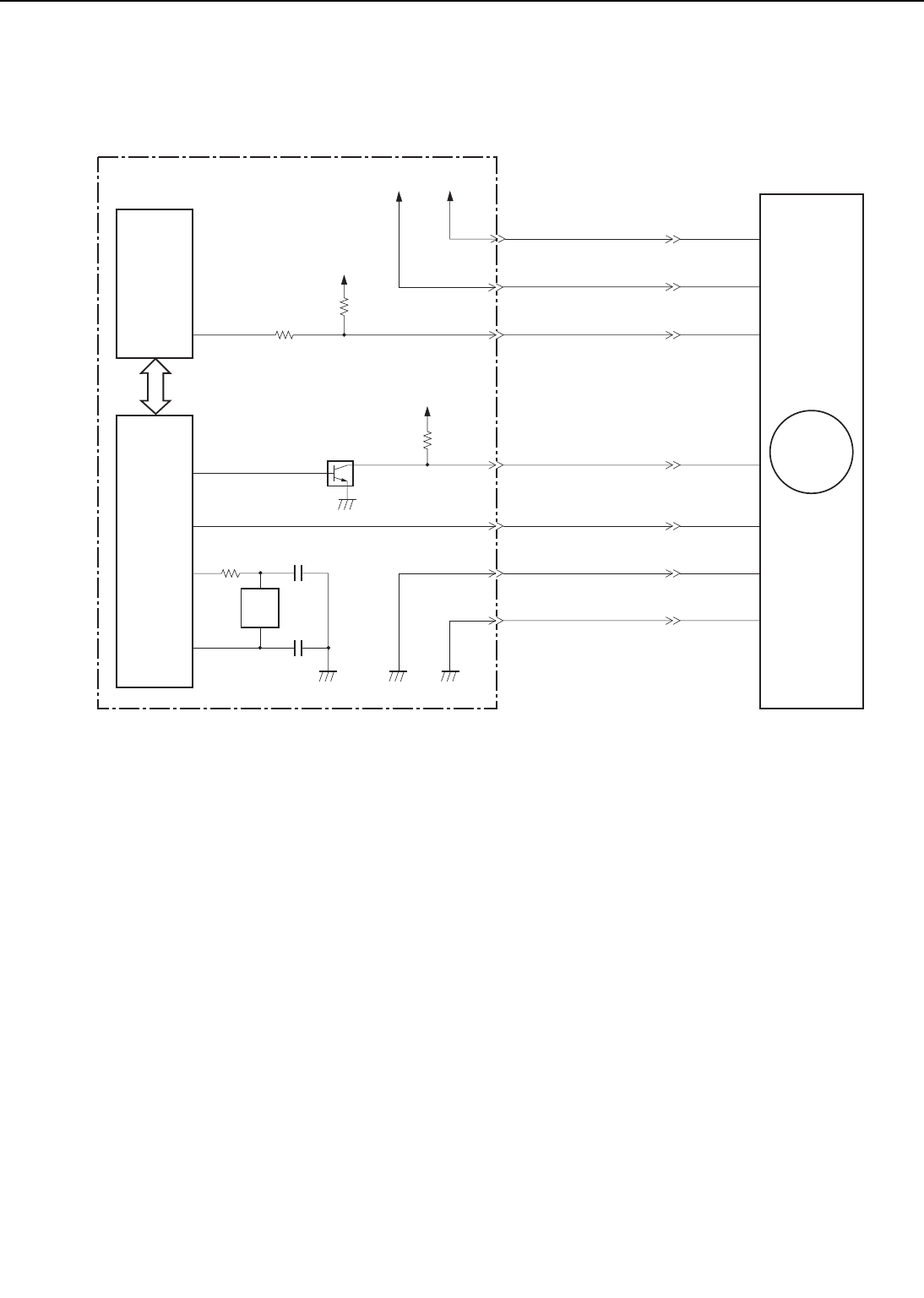
C. Scanning System
Figure below shows the scanner motor control circuit.
Figure 2-3-4
The scanner motor is a three-phase, eight-pole DC brushless motor with a HALL element. It
forms a unit with the scanner driver, which controls the scanner motor rotation at a constant
speed.
When the printer is turned ON, the oscillation frequency of the crystal oscillator (X202) is
divided by the gate array (IC202), and the /SCNCLK signal is sent to the scanner driver.
When the /PRNT signal sent to the CPU (IC201) on the DC controller becomes “L”, the CPU
sets the /SCND signal to “L” through the gate array. When it goes “L”, the scanner driver rotates
the scanner motor using the SCNCLK signal. When the scanner motor reaches its prescribed
speed, the scanner driver sets the SCANNER MOTOR READY signal (/SCNRDY) signal to “L”.
The CPU on the DC controller PCB monitors the /SCNRDY signal to make sure that the scan-
ner motor runs at the correct speed.
The CPU notifies the video controller of a scanner failure in the following cases:
a. When the /SCNRDY signal does not become “L” within 30 seconds after the scanner motor
starts rotation.
b. When the /SCNRDY signal goes “H” for 1.5 continuous seconds after going “L.”
2 - 30
CHAPTER 2
52
DB22 M
J207-7
-1
-2
-3
-5
-4
-6
M1
73
+5V
+5V
+5V
X202
54
70
71
SCNCLK
X1AO
X1AI
XT1/P07
IC202
(G.A.)
IC201
(CPU)
/SCNRDY
/SCND
/SCNCLK
GND
24VGND
J1-1
-7
-6
-5
-3
-4
-2
J18
-1
-7
-6
-5
-3
-4
-2
DC controller PCB
Scanner motor
+24VA
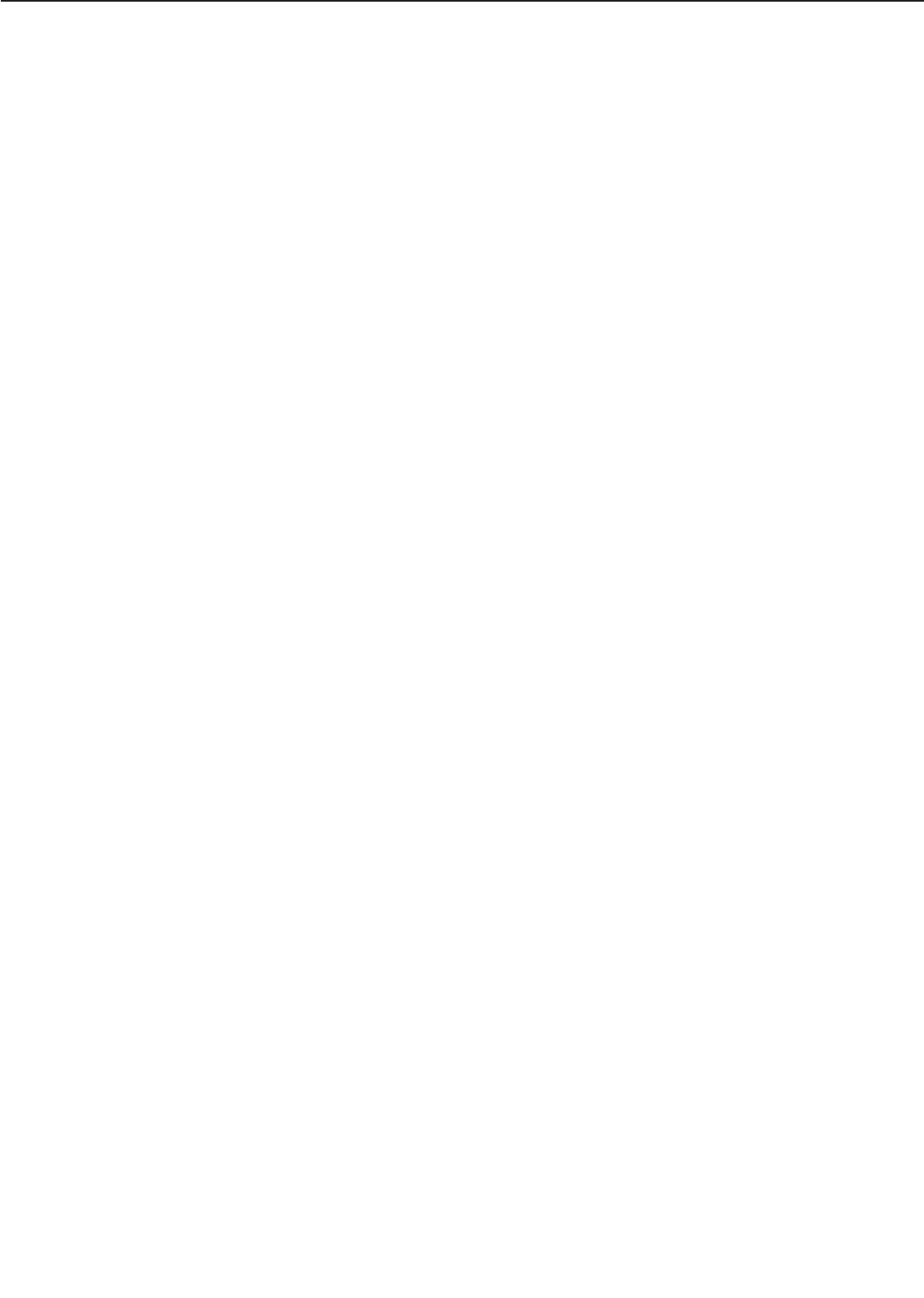
This page intentionally left blank
2 - 31
CHAPTER 2
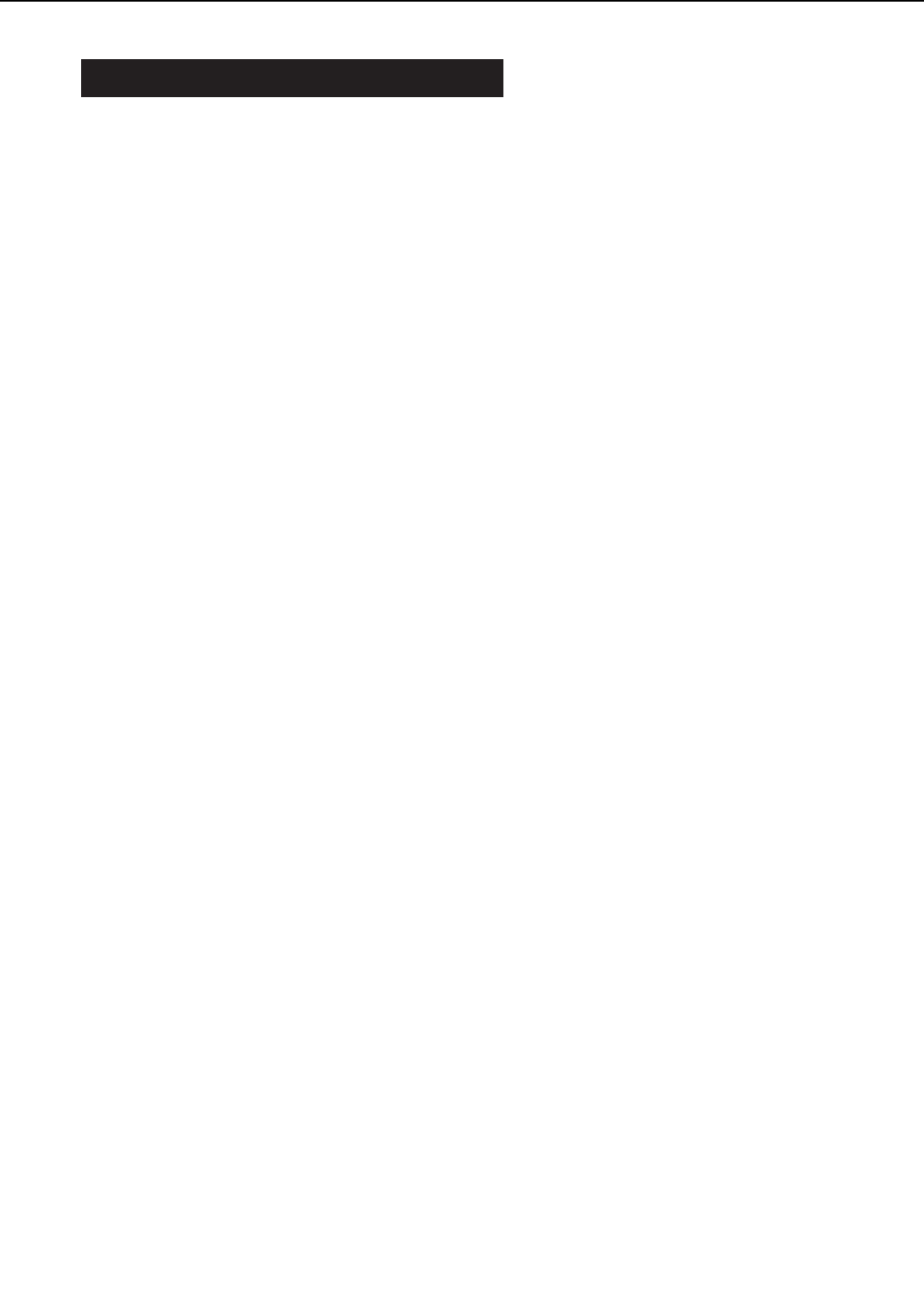
IV. IMAGE FORMATION SYSTEM
A. Outline
The image formation system is the central hub of the printer, and consists of the photosensitive
drum, developing unit and charging roller etc.
When the PRINT signal (/PRNT) is sent from the video controller to the DC controller, the DC
controller drives the main motor to rotate the photosensitive drum with the laser diode, devel-
oping cylinder, primary charging roller, and transfer charging roller.
The primary charging roller uniformly applies a negative charge on the surface of the photo-
sensitive drum. To form a latent image on the photosensitive drum, the laser beam modulated
by the VIDEO signals (VDO, /VDO) is exposed to the photosensitive drum surface.
The latent image formed on the photosensitive drum is changed to a visible image by the toner
on the developing cylinder then transferred onto paper by the transfer charging roller. Residual
toner on the photosensitive drum surface is scraped off by the cleaning blade. The potential on
the drum is made uniform by the primary charging roller in preparation for the next latent
image.
The cartridge has a toner sensor that detects whether there is enough toner remaining and
whether the cartridge is installed.
If the toner in the cartridge becomes lower than the prescribed level or there is no cartridge
installed in the printer, the high-voltage power supply notifies the DC controller through the
TONER LEVEL signal.
2 - 32
CHAPTER 2
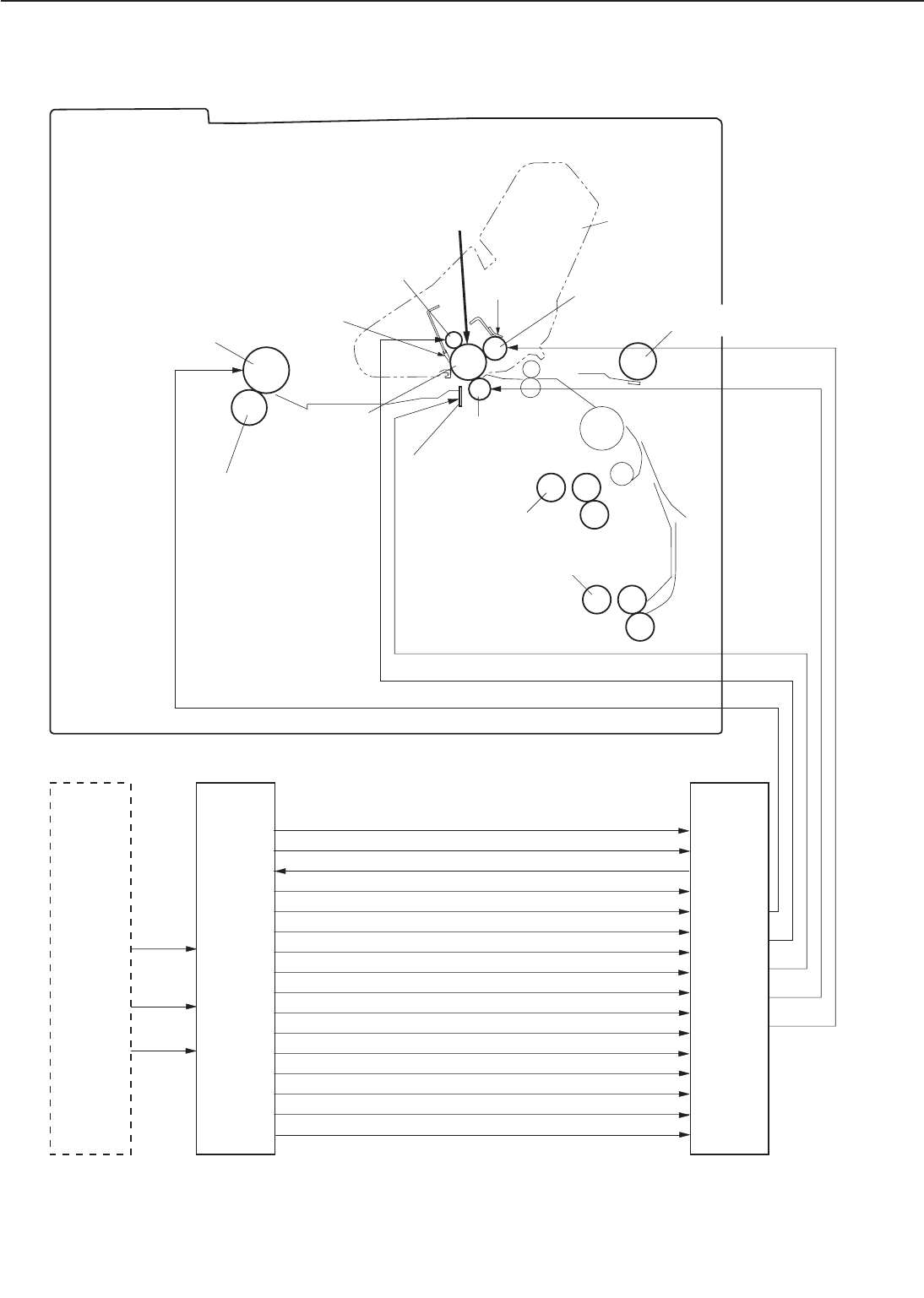
Figure 2-4-1
2 - 33
CHAPTER 2
/PRNT
VDO
/VDO
Cleaning blade
Cartridge
Static charge
eliminator
Transfer charging
roller
Lower fixing roller
Upper fixing roller
Photo-
sensitive
drum
Primary charging roller
Laser beam
Blade Developing cylinder
Manual feeding pick-up roller
Lower cassette
pick-up roller
Video
controller
PCB
DC
controller
PCB
High-
voltage
power
supply
Upper cassette
pick-up roller
Transfer bias drive signal (TRFVCNT)
Transfer negative bias drive signal (/TRFNVD)
Transfer bias monitor signal (TRFVSNS)
Fixing roller bias drive signal (/HRLBD)
Transfer bias constant current drive signal (/TRFCCD)
Discharge bias drive signal (/DCHGBD)
Transfer bias frequency output signal (/TRFCLK)
Discharge bias switch signal (/DCHGUP)
High voltage bias frequency output signal (HVTCLK)
Developing AC bias drive signal (/DEVACD)
Primary AC bias frequency output signal (PR1ACCLK)
Developing AC bias frequency output signal (DEVACCLK)
Primary AC bias drive signal (/PR1ACD)
Developing DC bias drive signal (/DEVDCD)
Primary DC bias drive signal (/PR1DCD)
Image density adjustment signal (DENADJ)
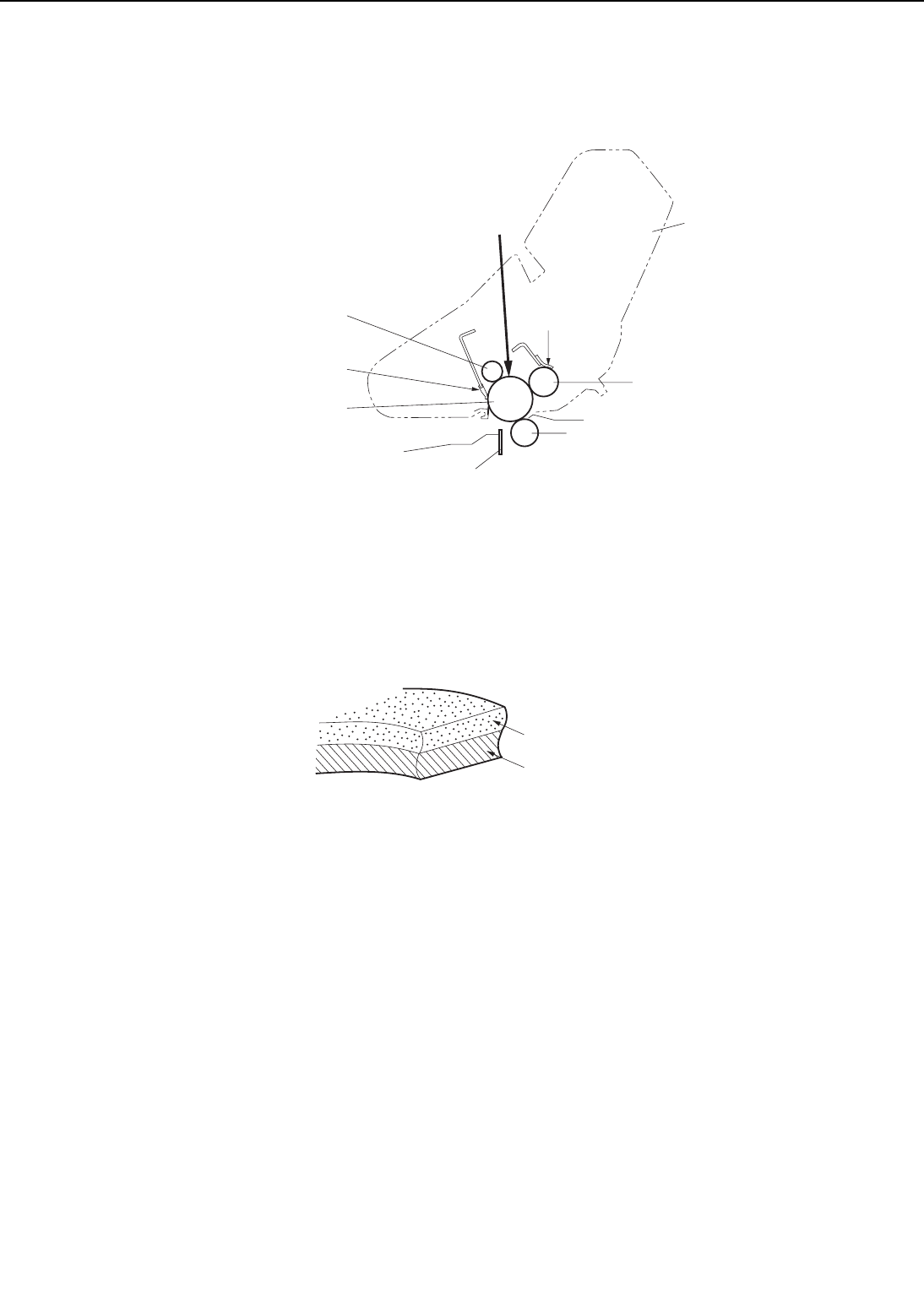
B. Printing Process
A major portion of the image formation system is contained with a cartridge as shown in Figure
2-4-2.
Figure 2-4-2
This printer’s cartridge has a seamless photosensitive drum with a two-layer surface shown
in Figure 2-4-3.
The outer layer of the drum consists of an organic photoconductor (OPC) and the base is alu-
minum.
Figure 2-4-3
The printing process can be divided into five major stages.
1. Electrostatic latent image formation stage
Step 1 Primary charge (-)
Step 2 Scanning exposure
2. Developing stage
Step 3 Development
3. Transfer stage
Step 4 Transfer (+)
Step 5 Separation
4. Fixing stage
Step 6 Fixing
Step 7 Fixing roller cleaning
2 - 34
CHAPTER 2
Cleaning blade
Photosensitive drum
Primary charging roller
Cartridge
Laser beam
Blade
Developing cylinder
Static charge eliminator
Transfer charging roller
Photoconductive
layer
Base
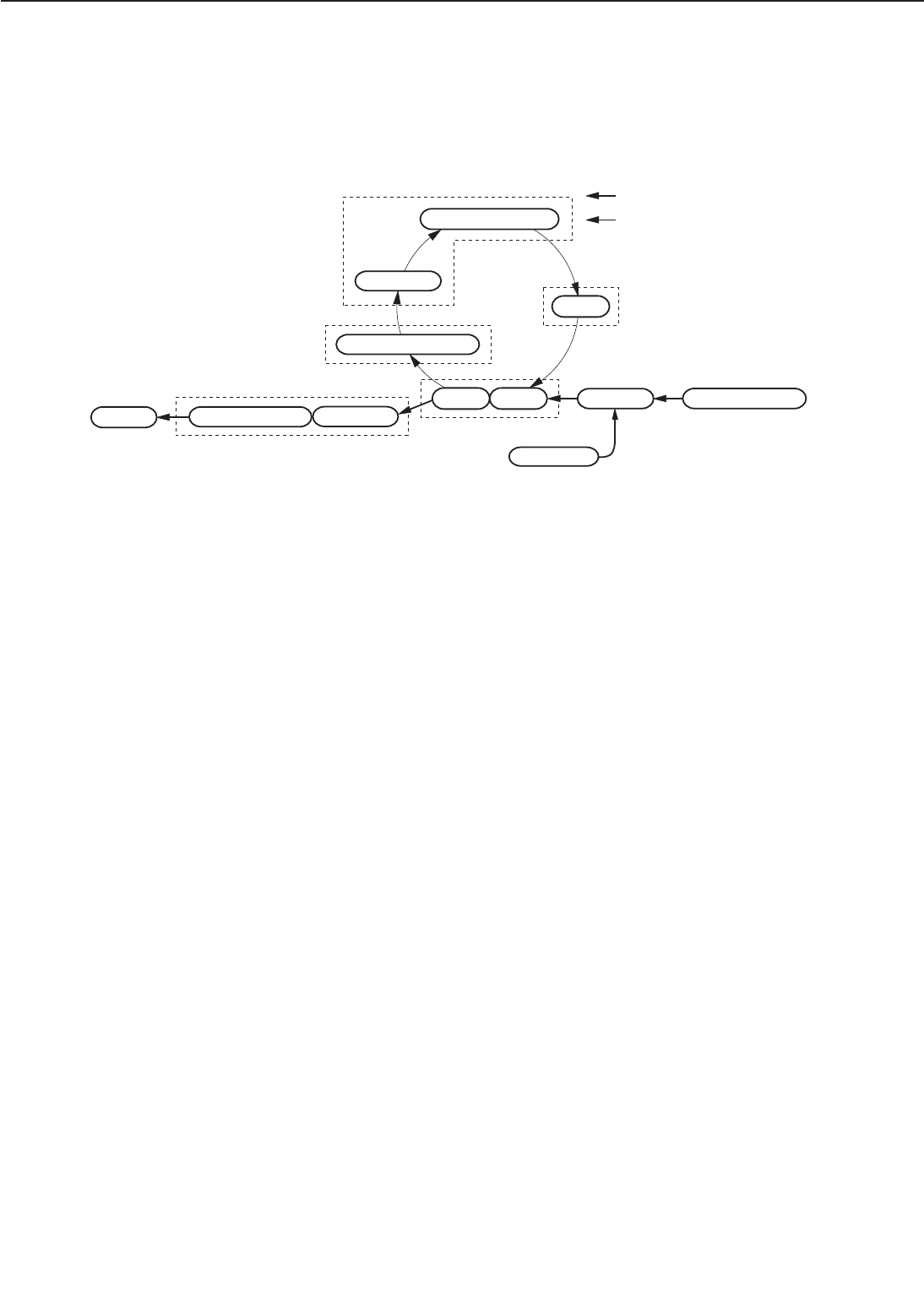
5. Drum cleaning stage
Step 8 Drum cleaning
Figure 2-4-4
2 - 35
CHAPTER 2
Drum cleaning stage
3. Develop-
ment
Fixing stage
Transfer stage
Electrostatic latent image
formation stage
Developing stage
Multi-purpose tray feed
Paper path
Direction of drum rotation
2. Scanning exposure
1. Primary charge
8. Drum cleaning
Print delivery 6. Fixing
5. Separa-
tion 4. Transfer Registration
Cassette feed
7. Fixing rollre cleaning
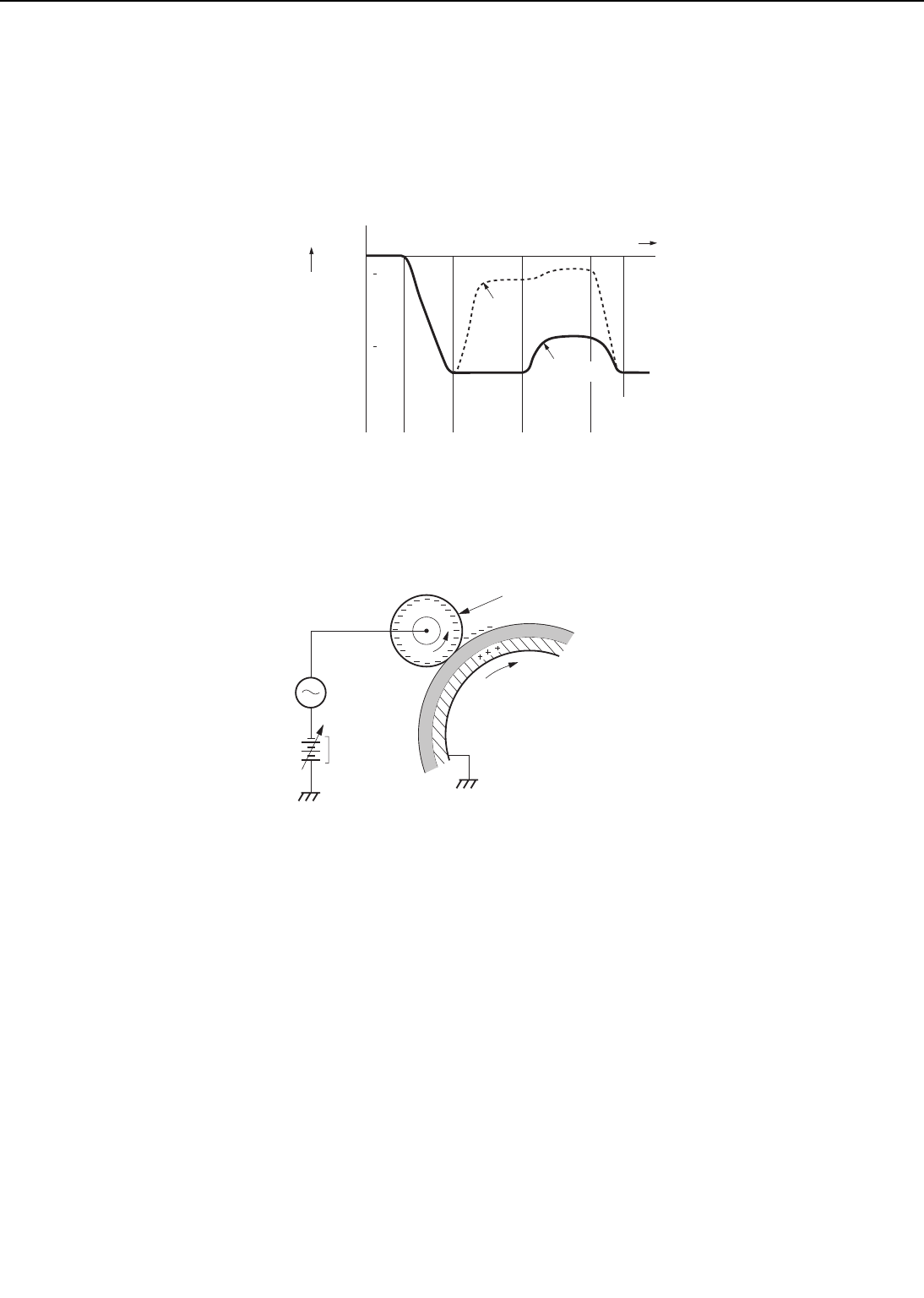
1. Electrostatic latent image formation stage
This stage follows two steps to produce an electrostatic latent image on the photosensitive drum.
At the end of the stage, negative charges remain on the unexposed “dark” areas, where the
laser beam struck (exposed) the drum surface.
This image of negative charges on the drum is invisible to the eye, so it is referred to as an
called an “electrostatic latent image.”
Figure 2-4-5
Step 1 Primary charge
Figure 2-4-6
For preparation of the latent image formation, a uniform negative potential is applied to the pho-
tosensitive drum surface. For primary charge, the printer uses the charging method, which
directly charges the drum.
The primary charging roller is made of conductive rubber. In addition to DC bias, AC bias
has been applied to the primary charging roller to keep the potential on the drum’s surface uni-
form. The DC bias is changed with the developing DC bias.
2 - 36
CHAPTER 2
0
-100
-500
Time (t)
Surface potential (V)
Exposed area
Scanning
exposure
(step 2)
Transfer
(step 4)
Primary
charge
(step 1)
Primary
charge
(step 1)
Unexposed
area
Photosensitive drum
Primary charging roller
AC bias
DC bias
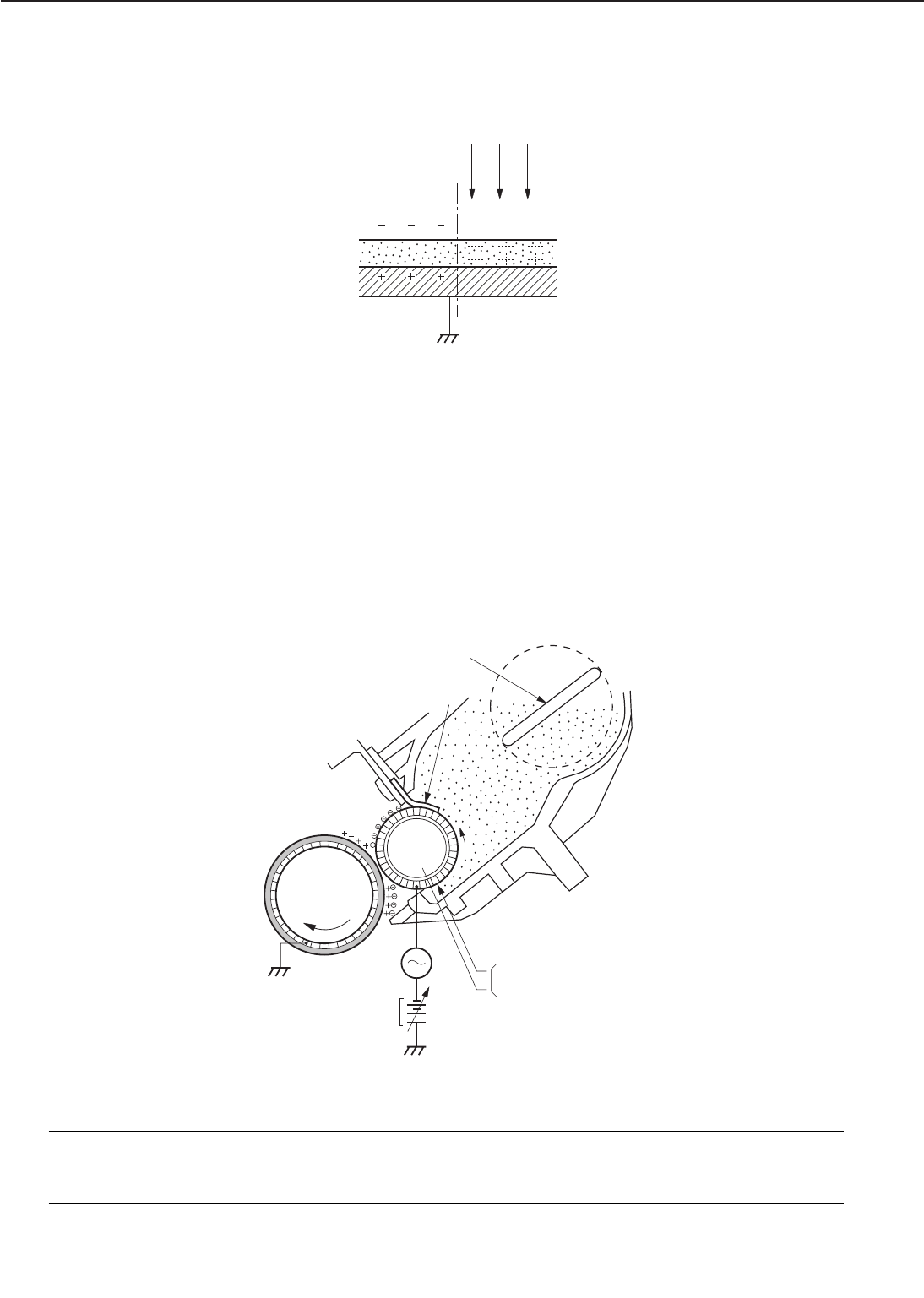
Step 2 Scanning exposure
Figure 2-4-7
When the laser beam scans the drum surface, it causes the charge to be neutralized in the areas
struck by the laser beam. These areas on the drum surface form the electrostatic latent image.
2. Development stage
Particles of toner are placed onto the electrostatic latent image on the surface of the drum to cre-
ate a visible image. This printer uses the toner projection development method with a single-
component toner.
Step 3 Development
Figure 2-4-8
Note: Charges on the exposed area of the photosensitive drum are shown as positive in this
figure. In actuality they are negative, but they are more positive than those on the devel-
oping cylinder.
2 - 37
CHAPTER 2
Laser beam
Unexposed area Exposed area
Blade
Stirring
Photo-
sensitive
drum
AC bias
DC bias
Developing cylinder
Cylinder
Magnet
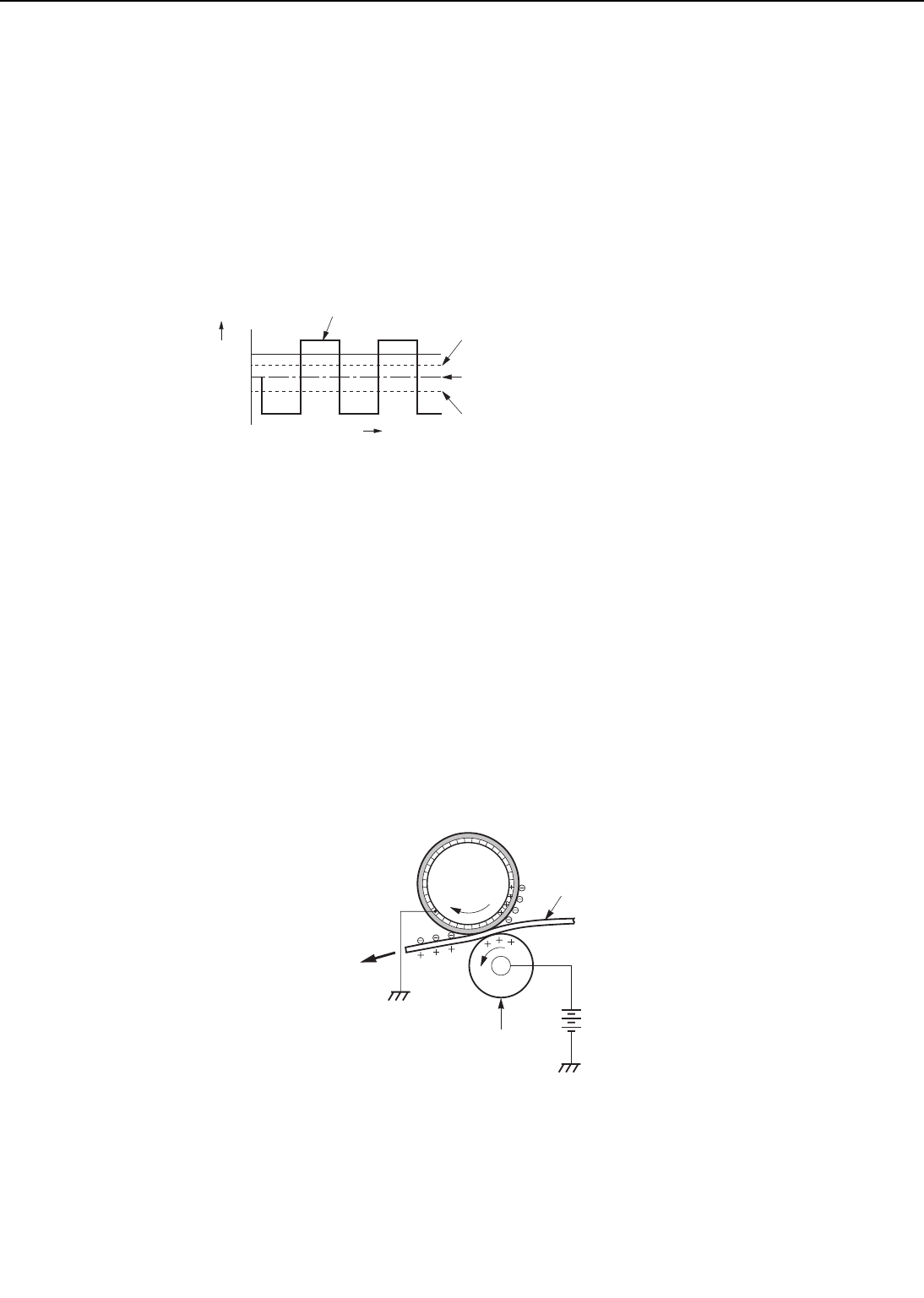
As shown in Figure 2-4-8, the developing unit consists of a developing cylinder and a rubber
blade. The developing cylinder rotates around a fixed internal magnet.
The single-component toner consists of magnetite and a resin binder, and is held to the cylin-
der by magnetic attraction. The toner is an insulator, and acquires a negative charge from fric-
tion of the rotating cylinder.
The areas on the drum that were exposed to the laser beam have a higher potential (are less
negative) than the negatively charged toner particles on the developing cylinder. When these
areas approach the cylinder, the potential difference projects the toner particles to them.
This is called toner projection, making the latent image on the drum visible.
Figure 2-4-9
An AC bias is applied to the developing cylinder to help project the toner particles to the drum
surface and improve the contrast of the printed image. The center voltage of the AC bias (1600
Vp-p) varies with the DC bias voltage. The change in the DC bias changes the potential differ-
ence between the cylinder and drum so the density of the print can be adjusted. It can be done
through a command from an external device.
This printer has a stirring mechanism in the cartridge to ensure that toner is applied smooth-
ly to the cylinder.
3. Transfer stage
In the transfer stage, the toner image is transferred from the drum surface to the paper.
Step 4 Transfer
Figure 2-4-10
A positive charge applied to the back of the paper attracts the negatively charged toner particles
to the paper.
2 - 38
CHAPTER 2
Voltage (V)
Developing cylinder surface potential
Drum surface potential (exposed area)
Drum surface potential (unexposed area)
+
V
-
V
0
Time t
DC bias
Paper
Transfer charging roller
Photo-
sensitive
drum
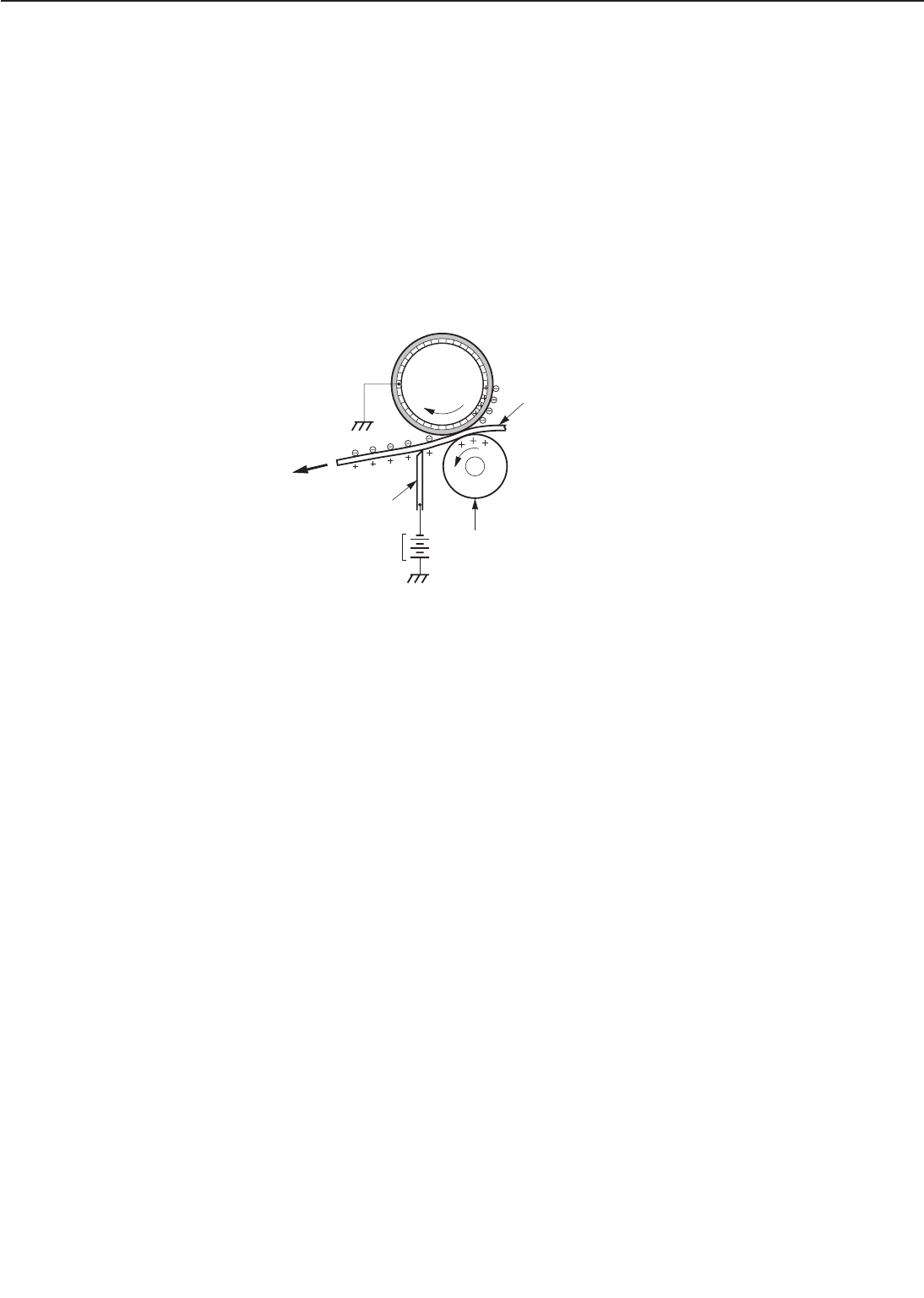
Reference:
If the image on the photosensitive drum is not completely transferred onto the paper due to jam-
ming, etc., the toner may adhere to the transfer charging roller. The printer removes the toner
from the transfer charging roller by switching the transfer voltage between positive and negative
in the specified sequence. During wait mode, initial rotation, and last rotation, the printer sets
the primary DC voltage to 0V to make the charge on the drum 0V. At the same time, the trans-
fer voltage is set to negative to remove the toner with a negative charge from the transfer charg-
ing roller to the drum. The transfer charging roller is cleaned by removing the toner on its sur-
face to the drum.
Step 5 Separation
Figure 2-4-11
The stiffness of the paper causes it to separate from the drum. Thin paper or curled sheets to
be duplex printed may not separate, but remain wrapped around the drum. To prevent this, a
negative bias is applied to the static charge eliminator to reduce electrostatic adhesion between
the drum and paper and facilitate separation.
To stabilize the paper feed system and prevent droplets on the printed image at low temper-
ature and humidity, the charge on the back of the paper is reduced by the static charge elimi-
nator after transfer.
2 - 39
CHAPTER 2
Paper
Transfer charging roller
Photo-
sensitive
drum
Static charge
eliminator
DC bias
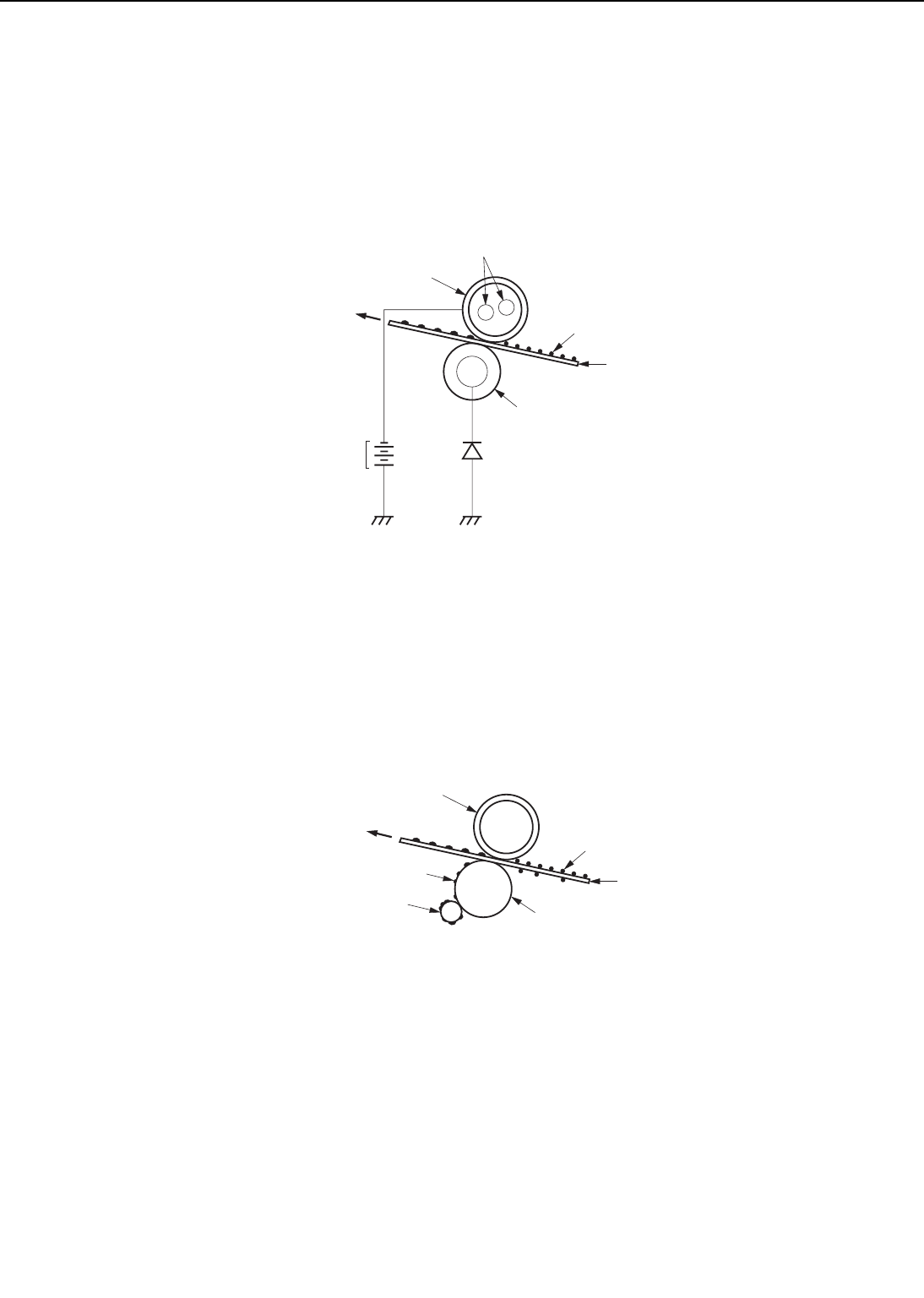
4. Fixing stage
The toner image transferred onto the paper in the transfer stage is held only by electrostatic
attraction and a slight physical adhesion, so even a light touch will smear the image.
In the fixing stage, the toner image is fixed by heating the paper and applying pressure. This
fuses the toner particles onto the paper to create a permanent image.
Step 6 Fixing
Figure 2-4-12
The upper and lower fixing roller surfaces are covered with teflon tubes with a very low adhesive
property.
The negative DC bias is applied to the upper fixing roller to prevent the toner from adhering
to the rollers.
Step 7 Fixing roller cleaning
Figure 2-4-13
In the fixing stage, not all the toner particles are fixed to the paper. In some cases, toner parti-
cles on the back of the paper are adhered to the lower roller.
The fixing cleaning roller cleans the lower fixing roller by attracting the residual toner on the
lower fixing roller.
2 - 40
CHAPTER 2
Lower fixing roller
Upper fixing roller
Halogen heater
Paper
Toner
DC bias
Lower roller
Upper roller
Paper
Toner
Residual toner
Fixing cleaning roller
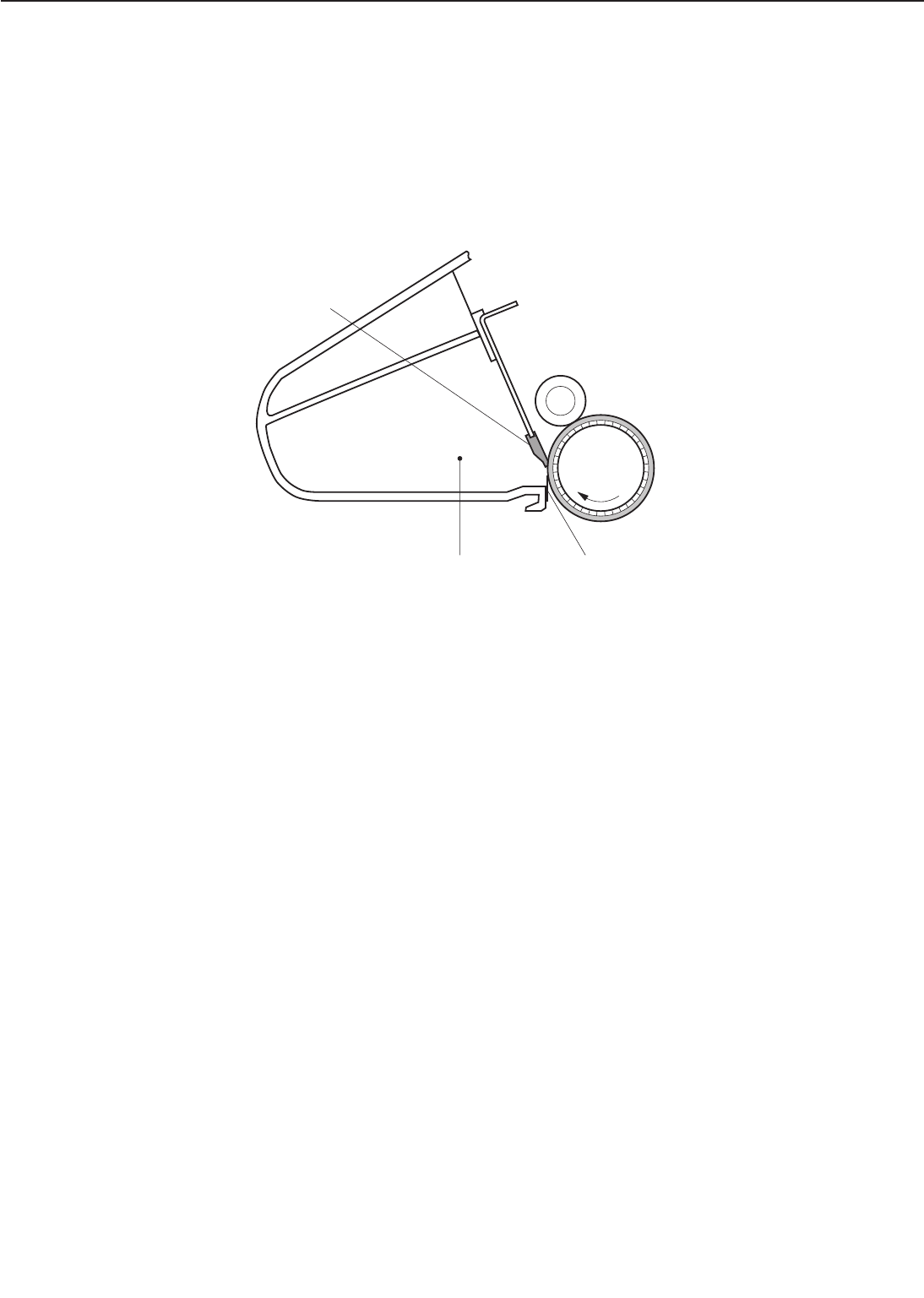
5. Drum cleaning stage
In the transfer stage, not all the toner is transferred to the paper. Some remains on the photo-
sensitive drum.
This residual toner is cleaned off in the drum cleaning stage so that the next print image will
be clear and distinct.
Step 8 Drum cleaning
Figure 2-4-14
The residual toner on the drum surface is scraped away with the cleaning blade to clean the
drum surface in preparation for the next print. The removed toner is collected in the cleaner
container.
2 - 41
CHAPTER 2
Cleaner container
Cleaning blade
Sweeper strip
Photo-
sensitive
drum
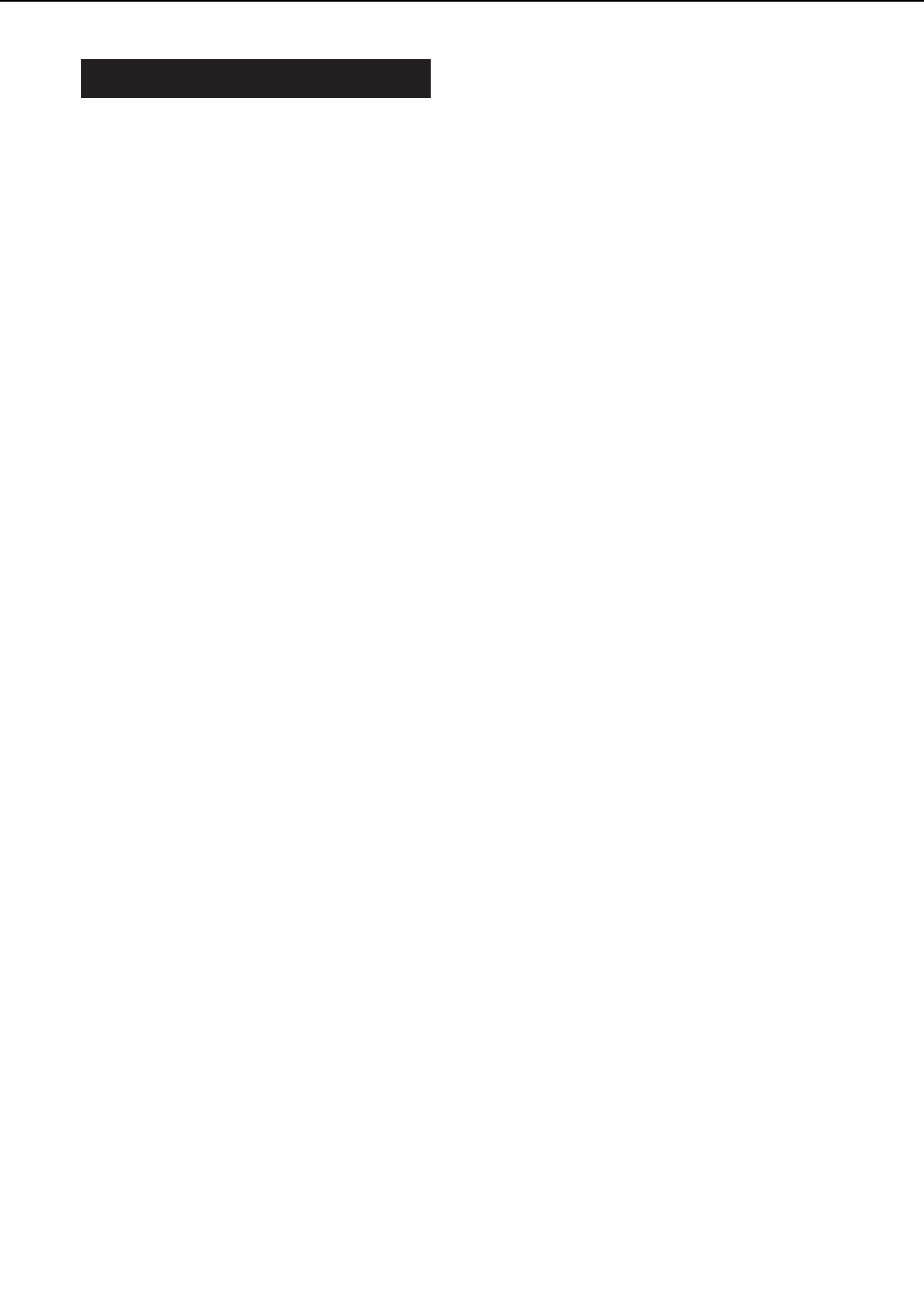
V. PICK-UP/FEED SYSTEM
A. Outline
Presence of paper on the multi-purpose tray is detected by the multi-purpose tray paper sensor
(PS1301), and presence of paper in the upper and lower cassettes is detected by the cassette
paper-out sensor (PS1207 or PS1208).
If the cassette pick-up motor (SMT1) in the paper pick-up unit rotates for cassette feeding,
pick-up roller, feed roller 1, and separation roller turn to feed a sheet of paper into the printer.
If the manual feed clutch (CL3) in the manual feed pick-up unit engages for manual feeding,
the manual feeding pick-up roller turns and feeds a sheet of paper from the multi-purpose tray
into the printer.
The paper is controlled by the registration roller so that the leading edge of the toner image
on the photosensitive drum matches the leading edge of the paper. The paper is fed, transferred,
then separated from the drum, fed to the fixing unit, and delivered onto the face-up or face-down
tray.
There are four photointerrupters (PS1, PS2, PS1402, and PS1403) on the paper path for sens-
ing paper reaching or passing through each area.
If the paper does not reach or clear each sensor within the pre-set time, the microprocessor
on the DC controller assumes a paper jam has occurred and notifies the video controller.
2 - 42
CHAPTER 2
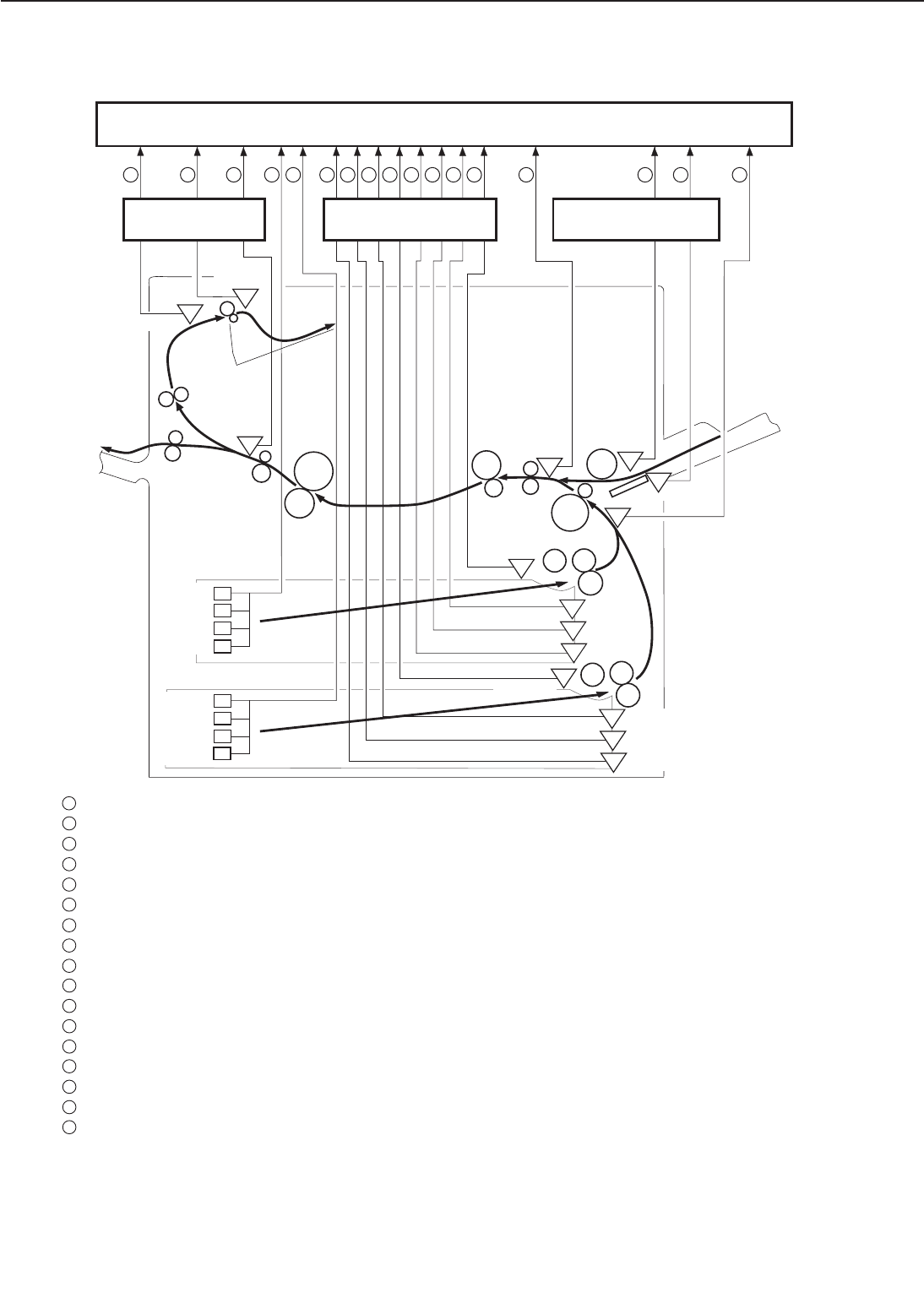
Figure 2-5-1
2 - 43
CHAPTER 2
PS1: Registration paper sensor
PS2: Pick-up unit paper sensor
PS1201: Lower cassette sensor
PS1202: Upper cassette sensor
PS1203: Lower cassette paper-level sensor 1
PS1204: Lower cassette paper-level sensor 2
PS1205: Upper cassette paper-level sensor 1
PS1206: Upper cassette paper-level sensor 2
PS1207: Lower cassette paper-out sensor
PS1208: Upper cassette paper-out sensor
PS1301: Multi-purpose tray paper sensor
PS1302: Lifting plate position sensor
PS1401: Face-down tray paper full sensor
PS1402: Face-down tray delivery sensor
PS1403: Fixing unit delivery sensor
SW1601: Cassette paper-size sensing switch
SW1602: Cassette paper-size sensing switch
SW1603: Cassette paper-size sensing switch
SW1604: Cassette paper-size sensing switch
DC controller PCB
PS1201
PS1207
PS1202
PS1208
PS2
PS1301
PS1
PS1403
PS1402
SW1601
SW1602
SW1603
SW1604
SW1601
SW1602
SW1603
SW1604
PS1401
PS1205
PS1206
PS1203
PS1204
321 4 5 6 7 8 910 11 12 13 14 15
PS1302
Multi-purpose tray PCB
16 17
Switch/sensor PCB
3
2
1
4
5
6
7
8
9
10
11
12
13
14
15
16
17
: FACE-DOWN TRAY DELIVERY SENSE signal (FDOUTS)
: FACE-DOWN TRAY PAPER FULL SENSE signal (FDFULS)
: FIXING UNIT DELIVERY SENSE signal (/FPOUTS)
: UPPER CASSETTE PAPER-SIZE SENSE signal
: LOWER CASSETTE PAPER-SIZE SENSE signal
: LOWER CASSETTE PAPER-LEVEL SENSE signal 1 (LPVS1)
: LOWER CASSETTE PAPER-LEVEL SENSE signal 2 (LPVS2)
: LOWER CASSETTE SENSE signal (/LDECKC)
: LOWER CASSETTE PAPER-OUT SENSE signal (/LDECKS)
: UPPER CASSETTE PAPER-LEVEL SENSE signal 1 (UPVS1)
: UPPER CASSETTE PAPER-LEVEL SENSE signal 2 (UPVS2)
: UPPER CASSETTE SENSE signal (/UDECKC)
: UPPER CASSETTE PAPER-OUT SENSE signal (/UDECKS)
: REGISTRATION PAPER SENSE signal (/REGS)
: MULTI-PURPOSE TRAY PAPER SENSE signal (/MPTPS)
: LIFTING PLATE SENSE signal (/MPTLS)
: PICK-UP UNIT PAPER SENSE signal (/FEEDS)
Pick-up PCB
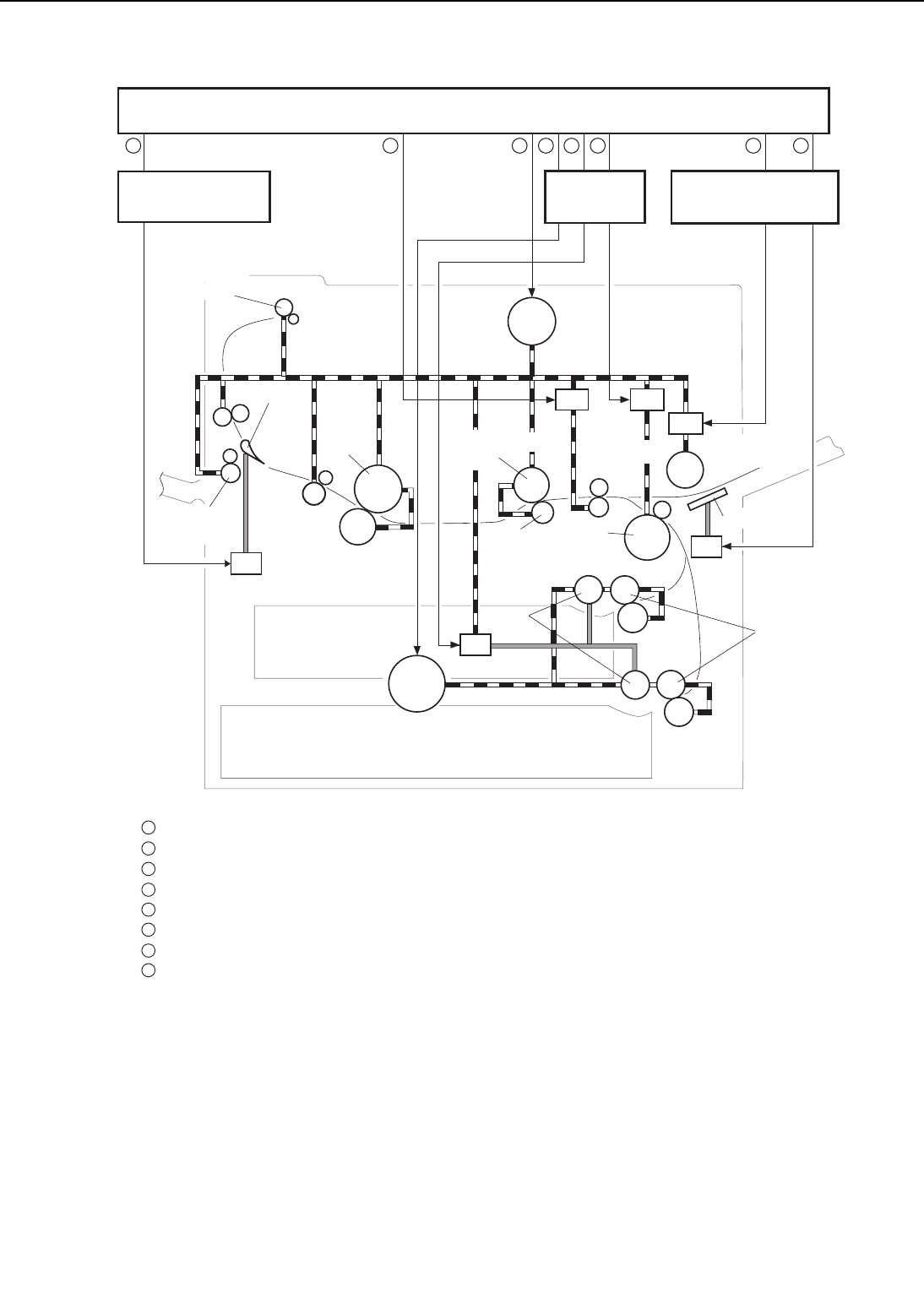
Figure 2-5-2
2 - 44
CHAPTER 2
SL2
SL3
CL2
CL3
CL1
SL1
321 4 5 6 7 8
Pick-up PCB Multi-purpose tray PCB
Switch/sensor PCB
Face-down
delivery roller
Flapper
Face-up
delivery roller
Fixing unit
delivery
roller
Upper
fixing
roller
Lower
fixing
roller
MT1: Main motor
SMT1: Cassette pick-up motor
SL1: Cassette pick-up solenoid
SL2: Lifting plate solenoid
SL3: Face-up solenoid
CL1: Registration clutch
CL2: Feed clutch
CL3: Manual feed clutch
Manual feeding
pick-up roller
Transfer
charging
roller
Feed
roller 2
Feed
roller 1
Lifting plate
Upper cassette
Lower cassette
Separation
roller
Separation
roller
Pick-up
roller
Registration
roller
Photosensitive
drum
3
2
1
4
5
6
7
8
: FACE-UP SOLENOID DRIVE signal (/FUSLD)
: REGISTRATION CLUTCH DRIVE signal (/REGCLD)
: MAIN MOTOR DRIVE signal (MMRDY)
: PICK-UP MOTOR DRIVE signal
: FEED CLUTCH DRIVE signal (/FEEDCLD)
: CASSETTE PICK-UP SOLENOID DRIVE signal (/PUPSLD)
: MANUAL FEED CLUTCH DRIVE signal (/MPTCLD)
: LIFTING PLATE SOLENOID DRIVE signal (/MPTSLD)
DC controllerPCB
MT1
SMT1
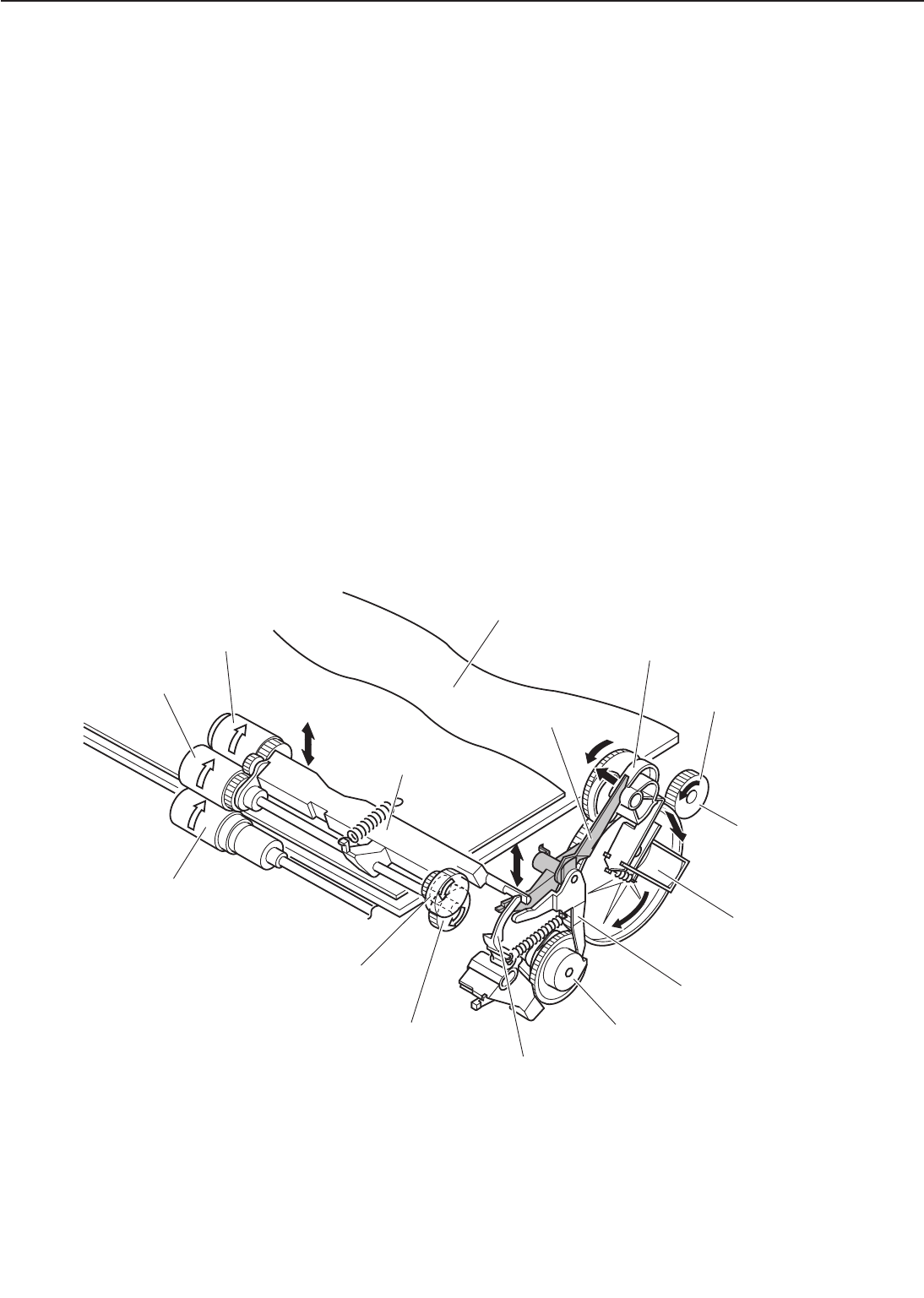
B. Paper Pick-up
1. Pick-up operation
This printer conducts paper pick-up operation by lifting the paper to the paper pick-up position
with the lifter and lowering the rotating cassette pick-up roller to the paper level.
Paper pick-up operation is conducted only when the multi-input tray driver receives the pick-
up command from the option controller. The pick-up roller is lowered to the paper level by the
rotational force of the main motor (MT1). At the same time, the pick-up roller is rotated by the
rotational force of the pick-up motor.
Paper pick-up operation is conducted as follows.
On receiving the /PRNT from the video controller PCB, the DC controller PCB runs the main
motor (MT1) and the pick-up motor (SMT1). When the cassette pick-up solenoid (SL1) is turned
ON, the main motor rotates the cassette pick-up cam via the gear to drive the shaft drive arm.
At the same time, the rotational force of the pick-up motor is transmitted to the cassette pick-
up roller via the feed roller gear. As a result, the rotating cassette pick-up roller goes down to
the paper level, picks up a sheet of paper, goes up to the paper pick-up standby position, and
stops rotation.
When the pick-up motor rotates clockwise, the paper is picked up from the upper cassette by
rotating the cassette pick-up roller, feed roller 1 and separation roller of the upper cassette.
When the pick-up motor rotates counterclockwise, the paper is picked up from the lower cas-
sette by driving the cassette pick-up roller, feed roller 1 and separation roller of the lower cas-
sette.
Figure 2-5-3
2 - 45
CHAPTER 2
Pick-up roller
Feed roller 1
Separation roller
Pick-up roller shaft
Cassette pick-up cam
Cassettte pick-up
solenoid
Lift-up cam
Print paper
Pick-up motor drive
Main motor drive
Gear
Lift-up release arm
Pick-up roller shaft fixing arm
Feed roller gear
Shaft drive arm
Paper lifting plate
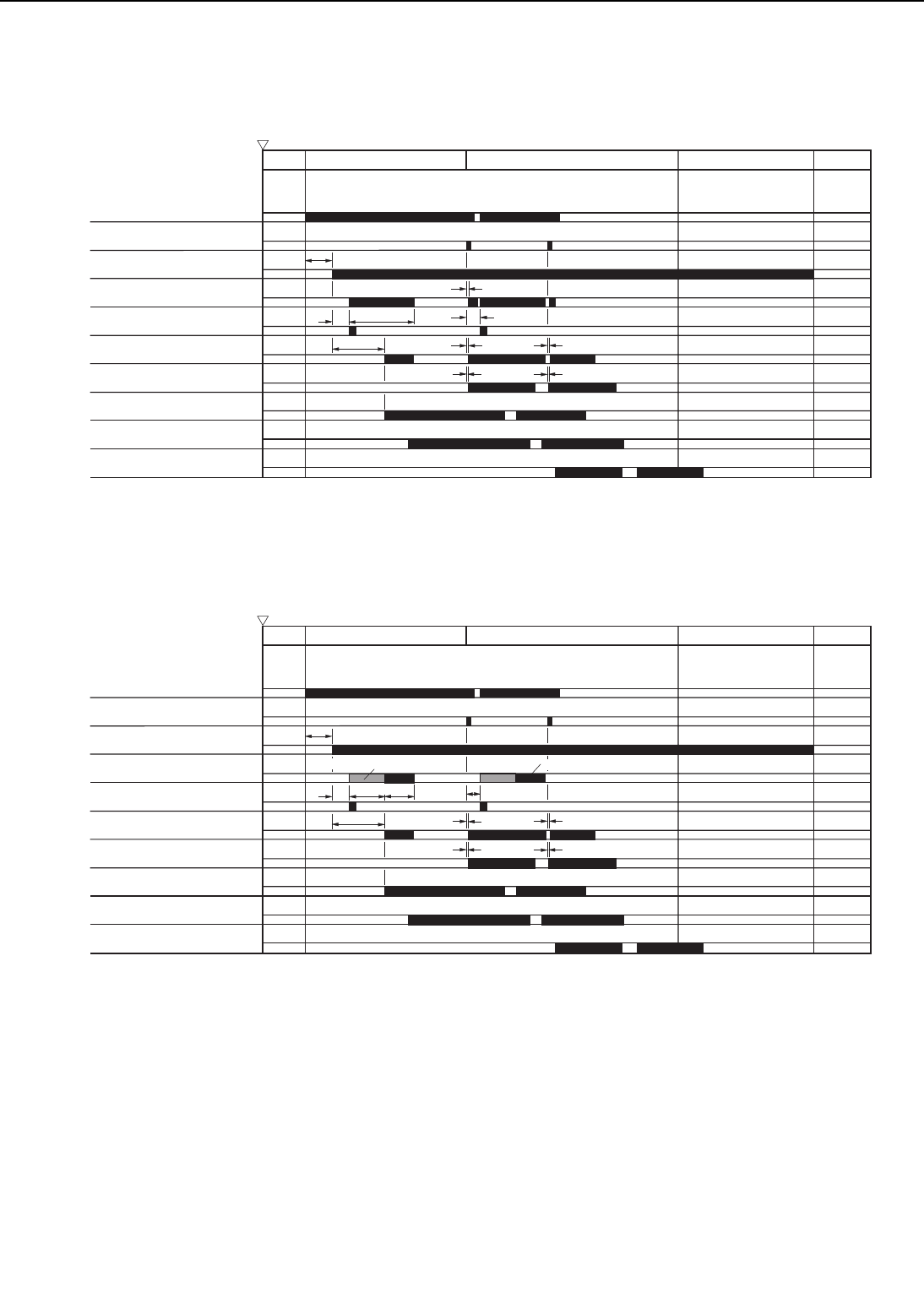
Figure 2-5-4
Figure 2-5-5
2 - 46
CHAPTER 2
STBY INTR PRINT STBY
LSTR
3.0
1.97
0.5
0.03
0.5
0.06
0.03
0.06
0.06
About 1.5
Power switch ON
PRINT signal (/PRNT)
VERTICAL SYNC signal (/VSYNC)
Main motor (MT1)
Pick-up motor (SMT1)
Cassette pick-up solenoid (SL1)
Feed clutch (CL2)
Registration clutch (CL1)
Pick-up unit paper sensor (PS2)
Registration paper sensor (PS1)
Fixing unit paper sensor (PS1403)
• Pick-up timing from the upper cassette (A4 : tow pages continuously print)
(Unit: Seconds)
STBY INTR PRINT STBY
LSTR
3.0
About 1.1
0.52
0.03
0.52
0.06 0.06
0.03
(Unit: Seconds)
Power switch ON
PRINT signal (/PRNT)
VERTICAL SYNC signal (/VSYNC)
Main motor (MT1)
Pick-up motor (SMT1)
Cassette pick-up solenoid (SL1)
Feed clutch (CL2)
Registration clutch (CL1)
Pick-up unit paper sensor (PS2)
Registration paper sensor (PS1)
Fixing unit paper sensor (PS1403)
• Pick-up timing from the lower cassette (A4 : tow pages continuously print)
Reverse high-speed rotation
About 0.9
About 1.5
Reverse rotation
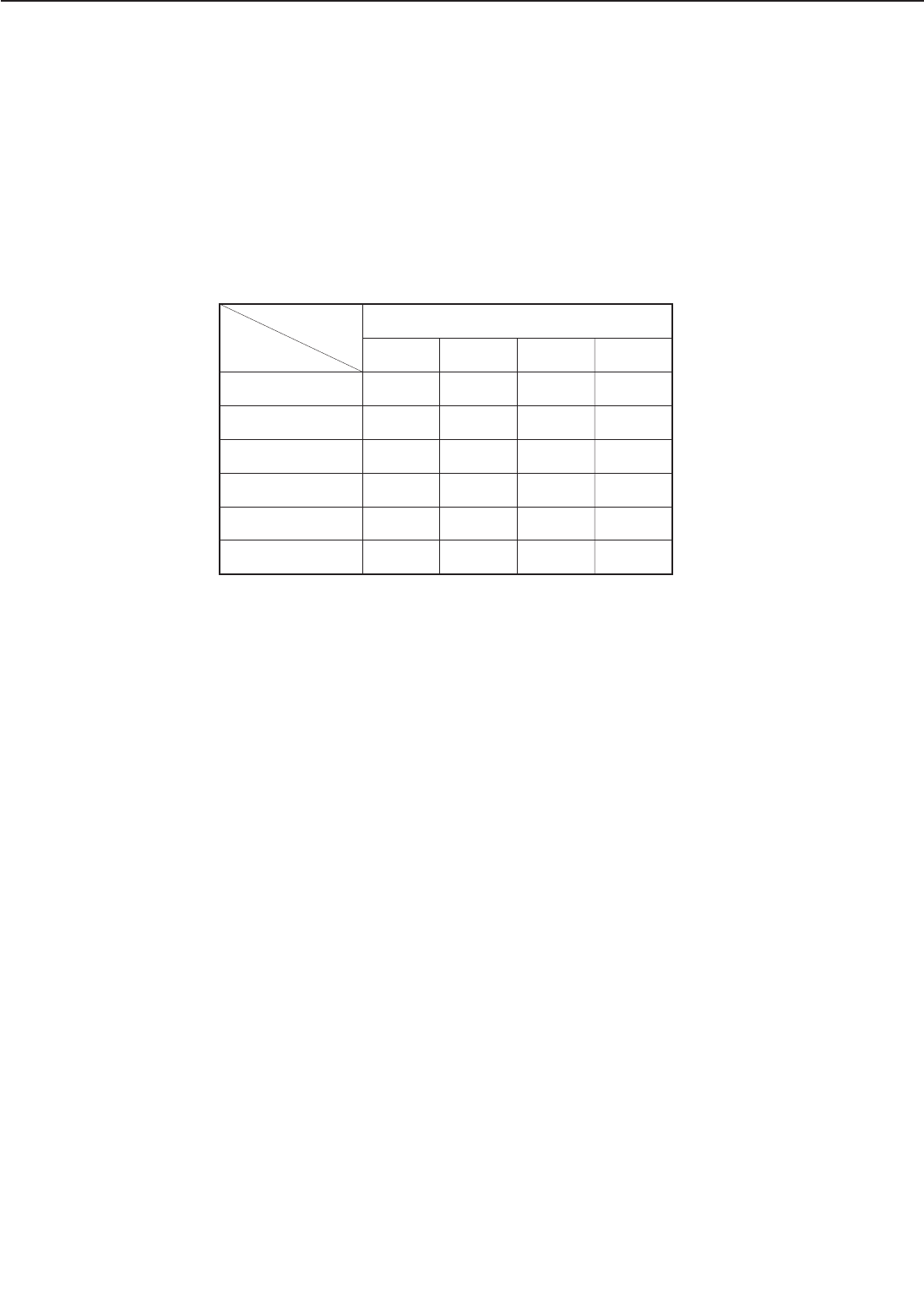
a. Cassette detection/cassette paper size detection/cassette paper level detection
The upper and lower cassettes detection is executed by the upper cassette sensor (PS1202) and
the lower cassette sensor (PS1201). The paper detection in the upper and lower cassettes is exe-
cuted by the upper cassette paper out sensor (PS1208) and the lower cassette paper out sensor
(PS1207). The paper size detection is executed by the upper and lower cassette paper size detec-
tion switches (SW1601 to SW1604) installed to each cassette. Each cassette has the four
switches. The combinations of the cassette paper size detection switches are shown in Table 2-
5-1.
Table 2-5-1
The remaining paper level in the cassette is detected according to the lifter position. The lifter
contains a light blocking plate which blocks two sensors on the pick-up PCB. The lifter position
is detected by these sensors. And, as a result, the remaining paper level in the cassette is detect-
ed.
The remaining paper level in the upper cassette is detected by the combination of outputs
from the upper cassette paper level sensor 1 (PS1205) and the upper cassette paper level sen-
sor 2 (PS1206). The paper level in the lower cassette is detected by the combination of outputs
from the lower cassette paper level sensor 1 (1203) and the lower cassette paper level sensor 2
(PS1204). Figure 2-5-6 shows the combinations of PS1205/PS1203 and PS1206/PS1204.
2 - 47
CHAPTER 2
SW1601
OFF
OFF
ON
ON
OFF
OFF
SW1602
OFF
ON
OFF
ON
OFF
OFF
SW1603
OFF
OFF
OFF
OFF
OFF
ON
SW1604
OFF
OFF
OFF
OFF
ON
OFF
Cassette paper-size sensing switch
Paper size
Ledger
A3
B4
Legal
Letter
A4
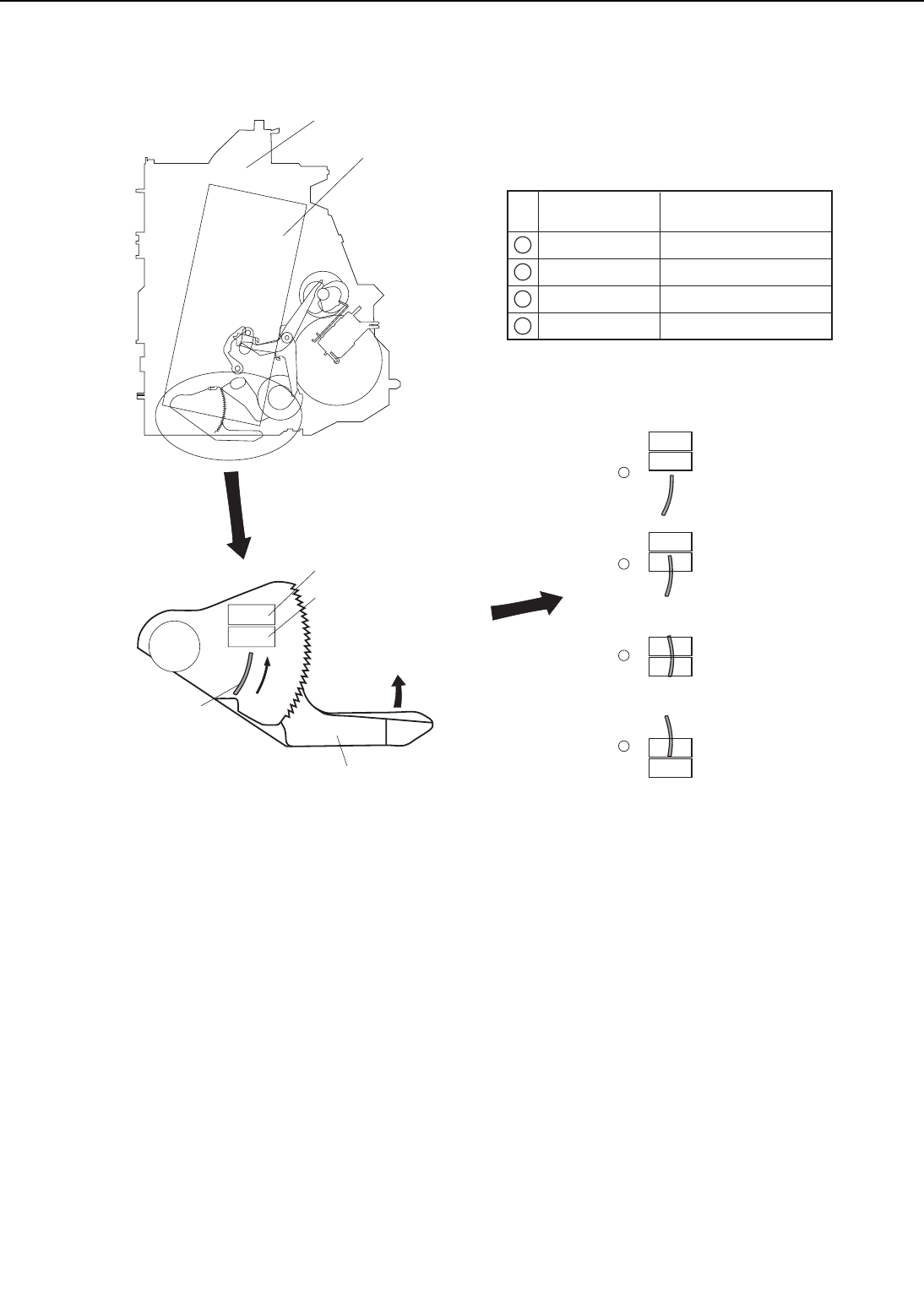
Figure 2-5-6
2 - 48
CHAPTER 2
PS1203 or PS1205
Lifter
PS1204 or PS1206
Pick-up unit
Pick-up PCB
Light blocking
plate
Remaining
paper level Remaining number
of sheets (note)
Almost full
High
Low
Almost empty
430 sheetes or more
200 - 490 sheetes
50 - 260 sheetes
110 sheetes or less
Note : Plain paper (75g/m2recommended paper)
4
3
2
1
1
2
3
4
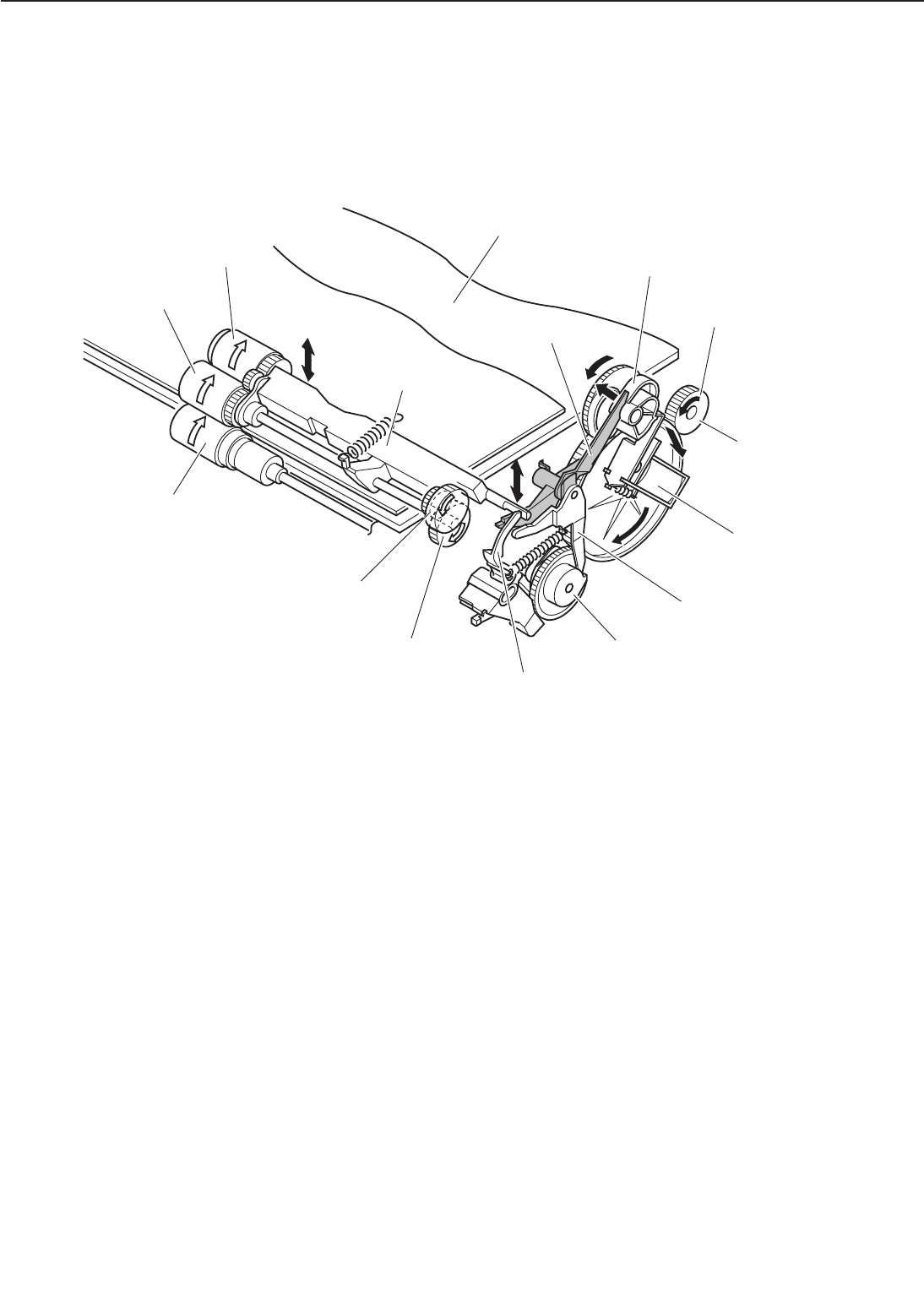
b. Lift-up operation
The lift-up operation is executed by the multi-input tray drive motor when a cassette is installed
or the pick-up roller shaft is set lower than certain level due to the paper reduce.
The two cases for the lift-up operation are as follows.
Figure 2-5-7
2 - 49
CHAPTER 2
Pick-up roller
Feed roller 1
Separation roller
Pick-up roller shaft
Cassette pick-up cam
Cassettte pick-up
solenoid
Lift-up cam
Print paper
Pick-up motor drive
Main motor drive
Gear
Lift-up release arm
Pick-up roller shaft fixing arm
Feed roller gear
Shaft drive arm
Paper lifting plate
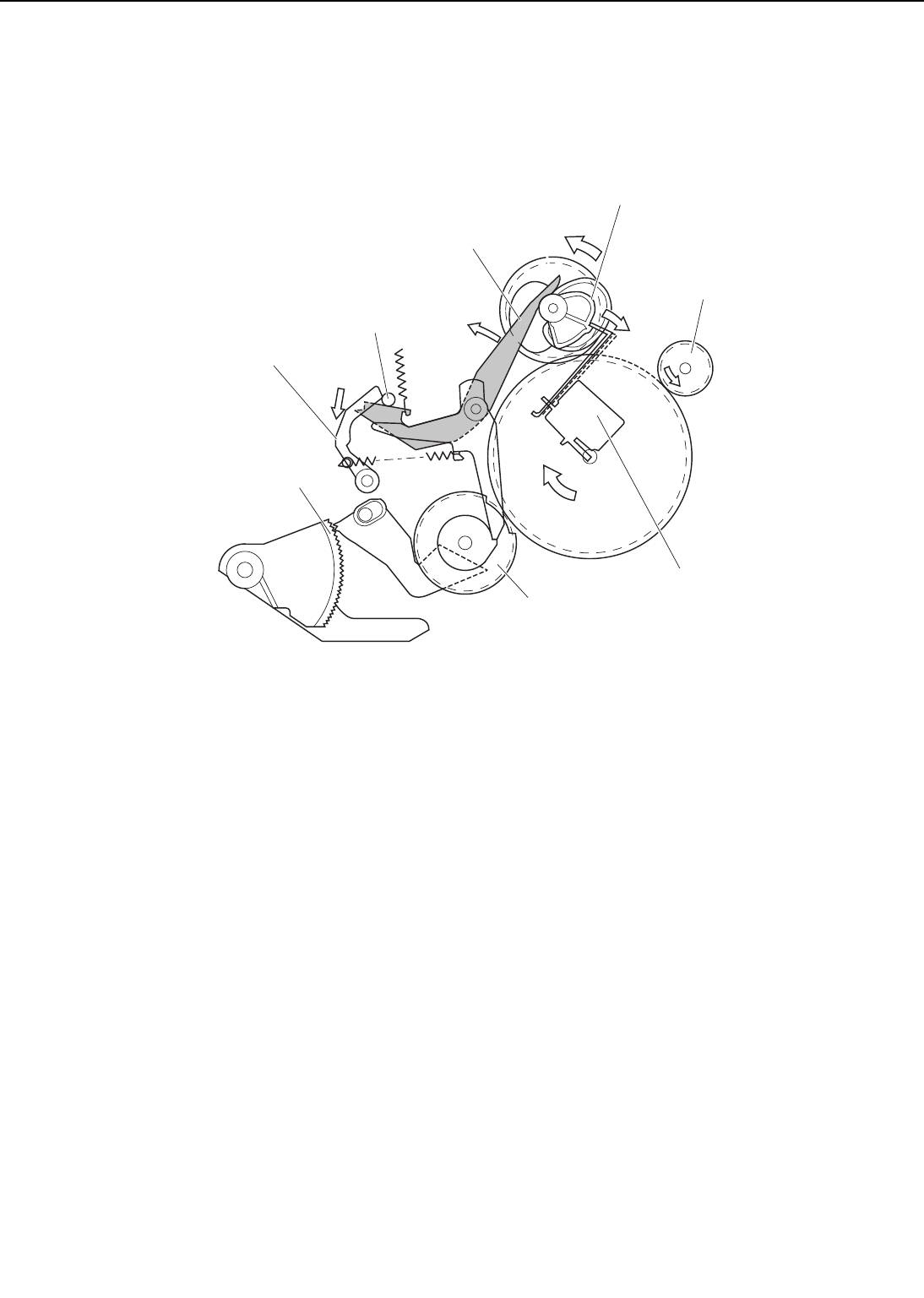
1) Cassette is installed
➀When a cassette is installed, the multi-input tray drive motor rotates, and the cassette paper
pick-up solenoid (SL3) is turned ON. Then, the shaft drive arm is driven by the cassette
paper pick-up cam rotation through the gear.
Figure 2-5-8
2 - 50
CHAPTER 2
Main motor drive
Lifter gear
Lift-up cam
Pick-up roller shfat fixing arm
Pick-up roller shaft
Cassette pick-up solenoid
Cassette pick-up cam
Shaft drive arm
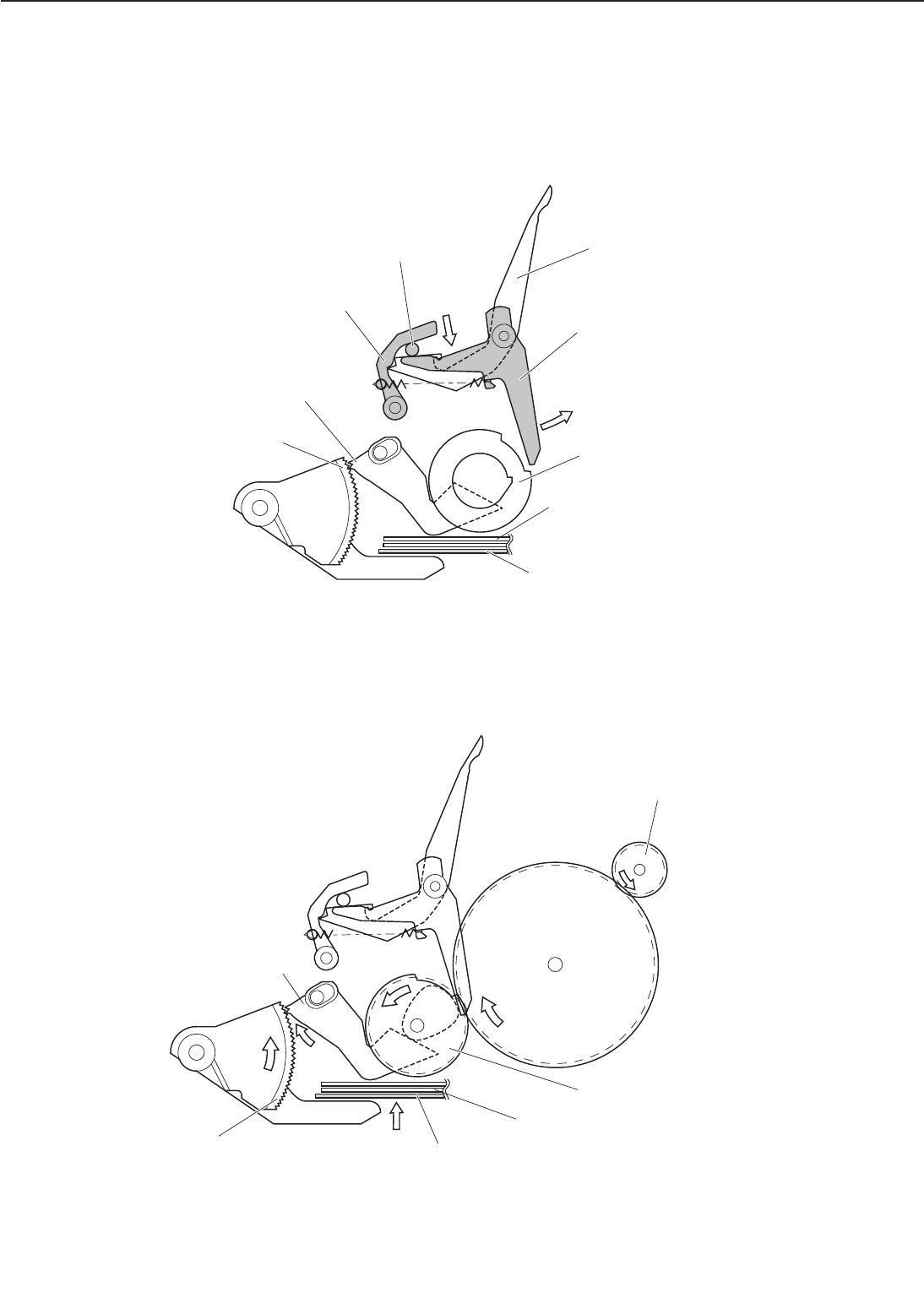
➁As the shaft drive arm goes down, the pick-up roller shaft goes down. Then, the lift-up
release arm is pushed, and the lift-up cam is unfixed. At the same time, the shaft drive arm
is fixed to the pick-up roller shaft fixing arm, and the pick-up roller shaft is stopped in the
designated position.
Figure 2-5-9
➂The lift up cam starts rotating when unfixed, and the lift up arm pushes up the lifter gear
by one tooth. The paper lifting plate is lifted by repeating this operation.
Figure 2-5-10
2 - 51
CHAPTER 2
Lifter gear Lift-up cam
Lift-up arm
Lift-up release arm
Pick-up roller shaft fixing arm
Pick-up roller shaft shaft drive arm
Paper lifting plate
Print paper
Lifter gear
Lift-up cam
Lift-up arm
Paper lifting plate
Print paper
Main motor drive
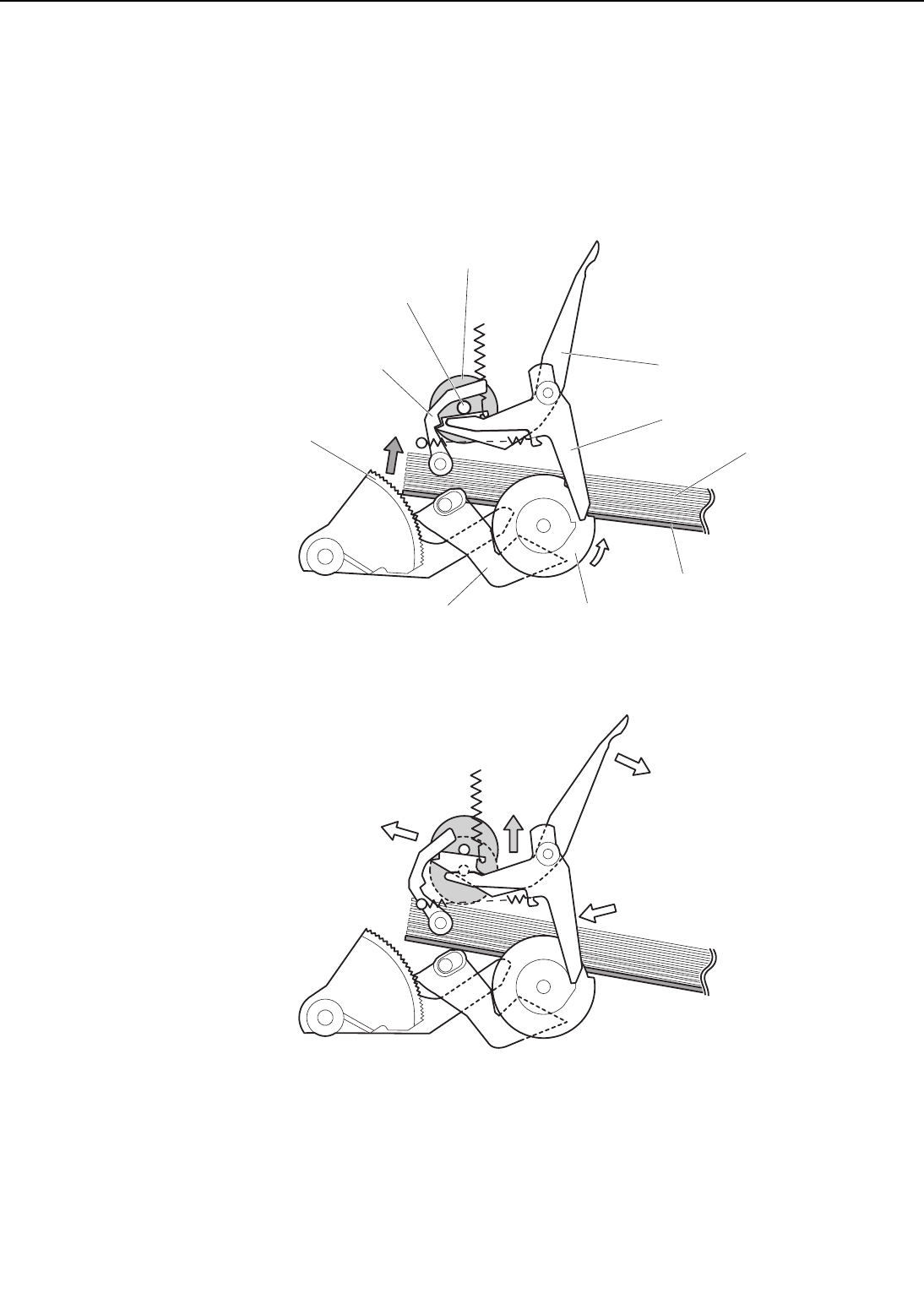
➃The pick-up roller shaft is lifted up when the paper on the paper lifting plate touches the
pick-up roller. Then, the fixing arm is released, and the lift-up release arm lifts up the pick-
up roller shaft to the waiting position by force of the spring. At the same time, the lift-up cam
is fixed by driving the pick-up roller shaft fixing arm and the lift-up release arm. Then, the
lift-up arm is stopped, and the lift-up operation is completed.
Figure 2-5-11
2 - 52
CHAPTER 2
Pick-up roller shaft fixing arm
Pick-up roller shaft
Shaft drive arm
Lifter gear
Lift-up cam
Paper lifting plate
Lift-up release arm
Cassette pick-up roller
Lift-up arm
Print paper
• Lift-up operation
• Completion of lift-up operation
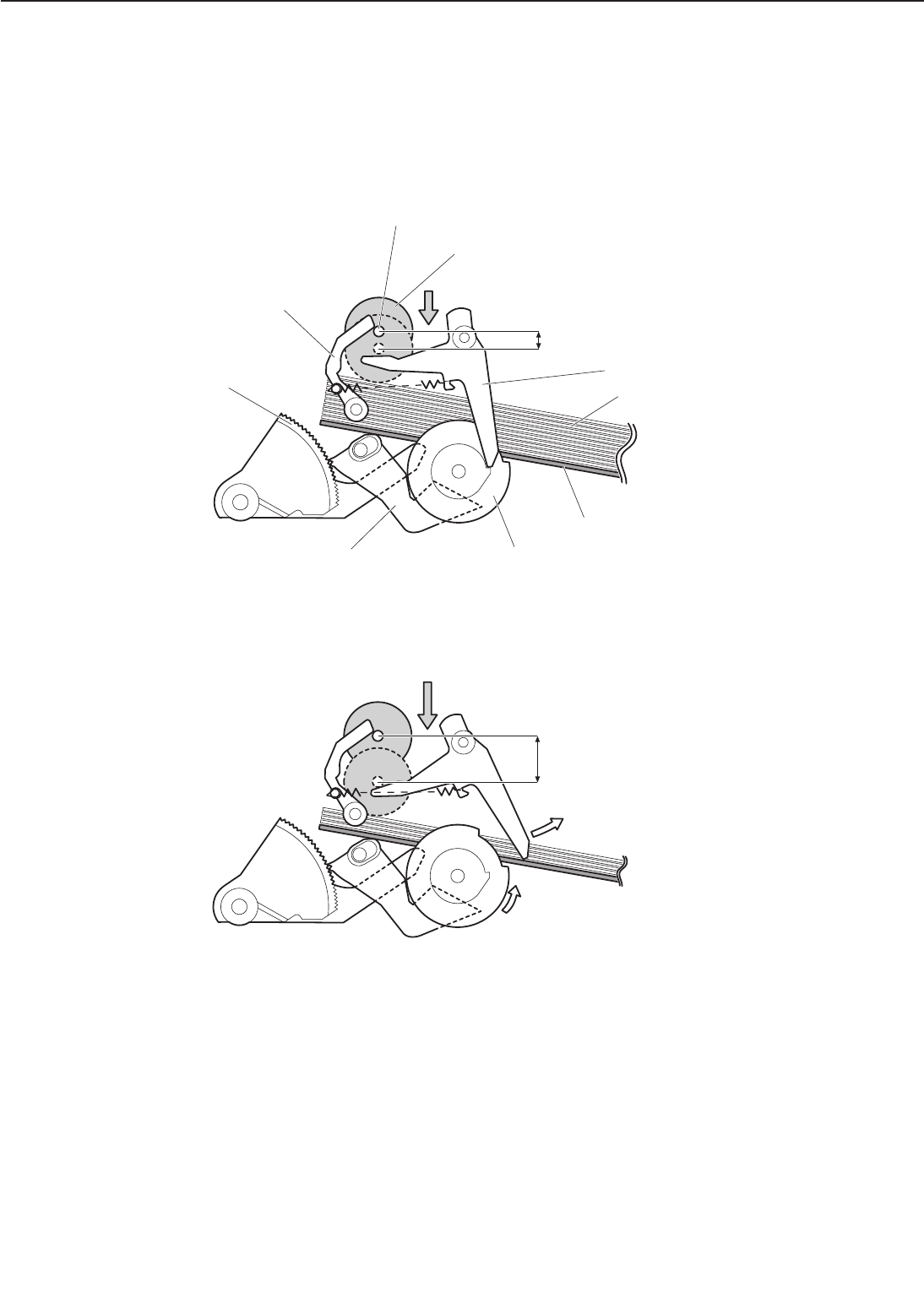
2) Paper level is lower than certain level
➀As the paper level lowers, the moving distance of the pick-up roller increases. When the
moving distance reaches the specified value, the pick-up roller shaft pushes the lift up
release arm, and the lift up cam is unfixed.
Figure 2-5-12
2 - 53
CHAPTER 2
Lift-up arm
Pick-up roller shaft fixing arm
Pick-up roller shaft
Lifter gear
Lift-up cam
Paper lifting plate
Lift-up release arm
Cassette pick-up roller shaft
Print paper
• Certain paper level
Moving distance of pick-up roller
Falling width of pick-up roller
• Less than certain paper level
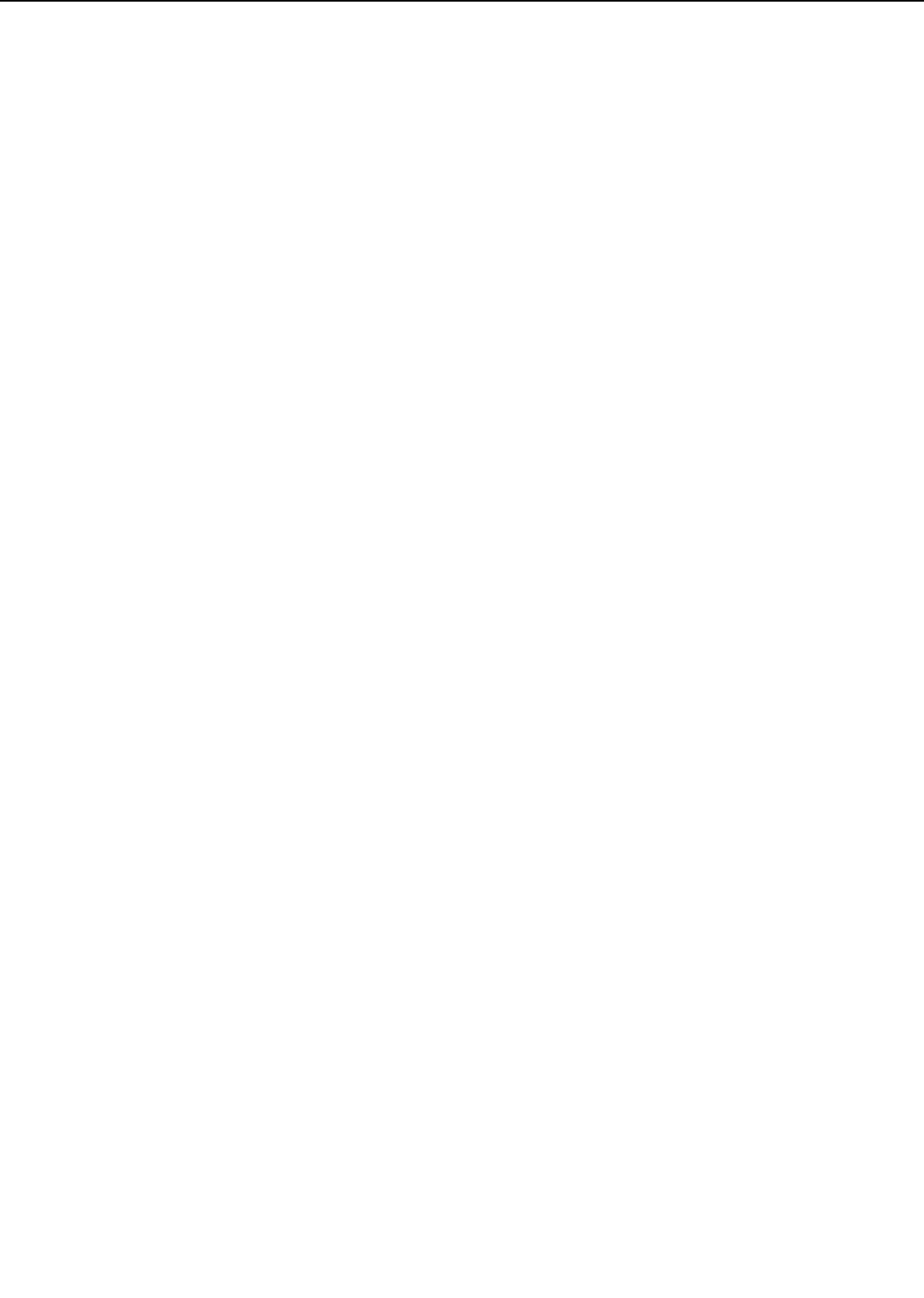
➁When the lift-up cam is unfixed, the lift-up arm lifts up the lifter gear one tooth by the rota-
tion of the lift-up cam. The paper lifting plate is lifted up by repeating the operation. (See
Figure 2-5-10)
➂When the paper on the paper lifting plate touches the pick-up roller, the pick-up roller shaft
is lifted up. Then, the fixing arm is released, and the lift-up release arm lifts up the pick-up
roller shaft to the waiting position by force of the spring. At the same time, the pick-up roller
shaft fixing arm and the lift up release arm are driven to fix the lift up cam. As a result, the
lift up arm is stopped and lift up operation is competed. (See Figure 2-5-11)
2 - 54
CHAPTER 2

c. Multi-feed prevention mechanism
When feeding from the cassette, the printer uses the separation roller to prevent multi-feeding.
Normally, the separation roller is imparted with a rotational force opposite to that of the feed
roller. However, since the separation roller is equipped with a torque limiter, it rotates with feed
roller 1 by transmission of its rotational force via the transported paper. On the other hand, if
multiple sheets of paper are picked up, the low friction force between the sheets of paper result
in a weak rotational force being transmitted to the separation roller from feed roller 1.
Consequently, the separation roller’s own rotational force separates the extra sheet.
Figure 2-5-13
2 - 55
CHAPTER 2
Pick-up roller Feed roller 1
Print paper
Driving force transmitted from the pick-up motor
through the torque limiter.
Separation roller
Driving force
transmitted from feed
roller 1
Normal
Muitifeed
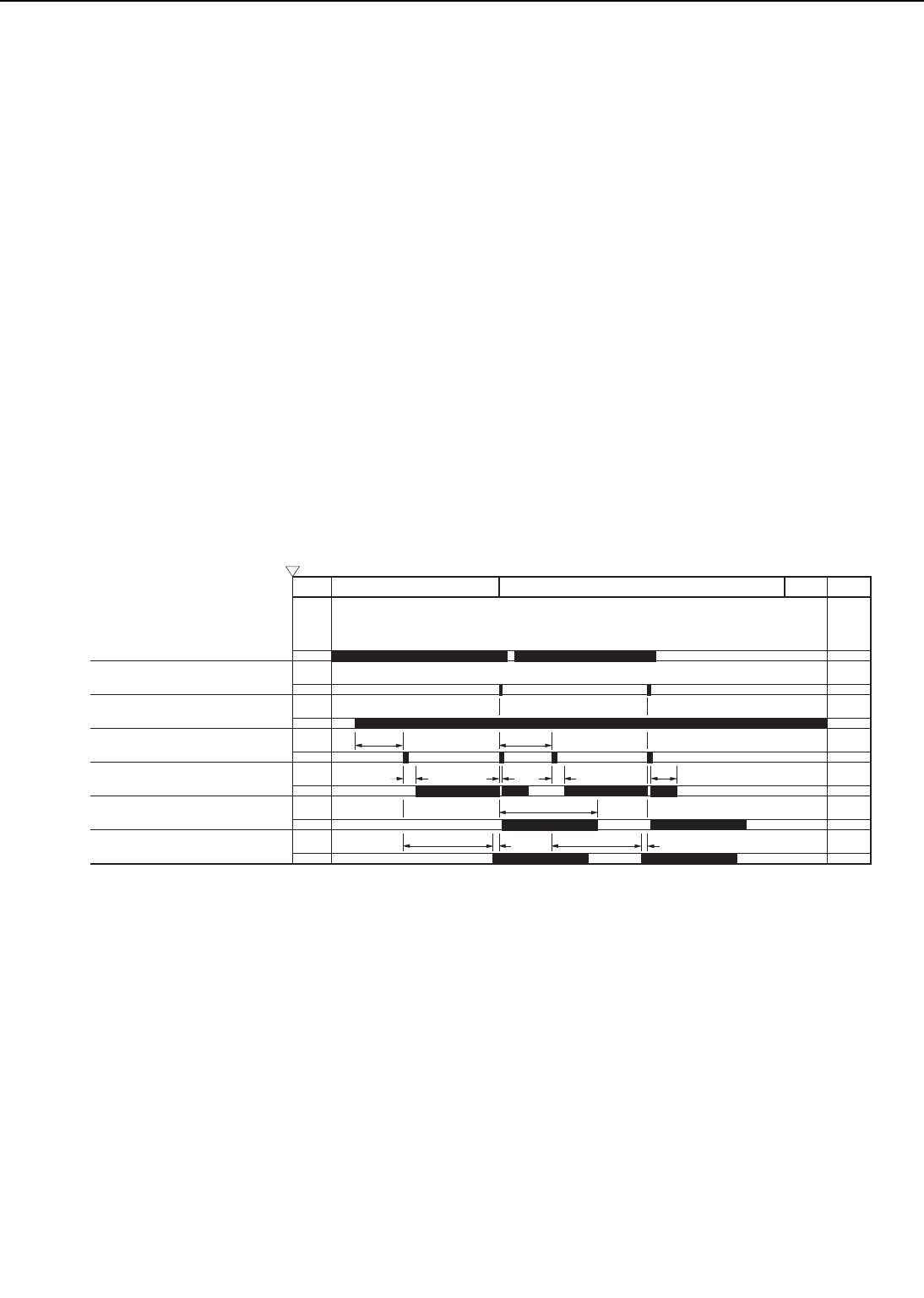
2. Manual feed (multi-purpose tray)
The presence of paper on the multi-purpose tray is detected by the multi-purpose tray paper
sensor (PS1301).
When the DC controller receives the /PRNT signal from the video controller, the lifting plate
solenoid (SL2) turns ON, the lifting plate is unlocked (the lifting plate rises), and the paper
touches the pick-up roller.
The lifting plate position is detected by the lifting plate position sensor (PS1302). If the sen-
sor detects that the lifting plate is up while waiting, SL2 is turned ON to lower the lifting plate.
The manual feed clutch (CL3) turns ON, and the main motor (MT1) power is transmitted to
the manual feeding pick-up roller.
Paper pressed against the manual feeding pick-up roller by the lifting plate is picked up by
the pick-up roller. Unnecessary sheets are removed by the separation pad, and one sheet is fed
into the printer by feed roller 2. The subsequent operations are almost the same as for those of
cassette feeding, except that SL2 is turned ON again right after the rotation of the registration
roller to lower the lifting plate.
The CPU turns ON SL2 to lower the lifting plate. If it is normal, the lifting plate position sen-
sor detects the lifting plate within about 0.5 seconds. The CPU notifies the video controller of a
lifting plate position failure if the lifting plate position sensor fails to detect the lifting plate 5
times in a row when the CPU repeats this operation 5 times.
Figure 2-5-14
2 - 56
CHAPTER 2
PRINT
STBY INTR LSTR STBY
3.0
0.27
0.14
1.87
0.03 0.27
2.03
0.14
1.87
0.55
About1.1
(Unit: Seconds)
Power switch ON
PRINT signal (/PRNT)
VERTICAL SYNC signal (/VSYNC)
Main motor (MT1)
Lifting plate solenoid (SL2)
Manual feed clutch (CL3)
Registration clutch (CL1)
Registration paper sensor (PS1)
• Pick-up timing from the manual feed (A4 : two pages continuously print)
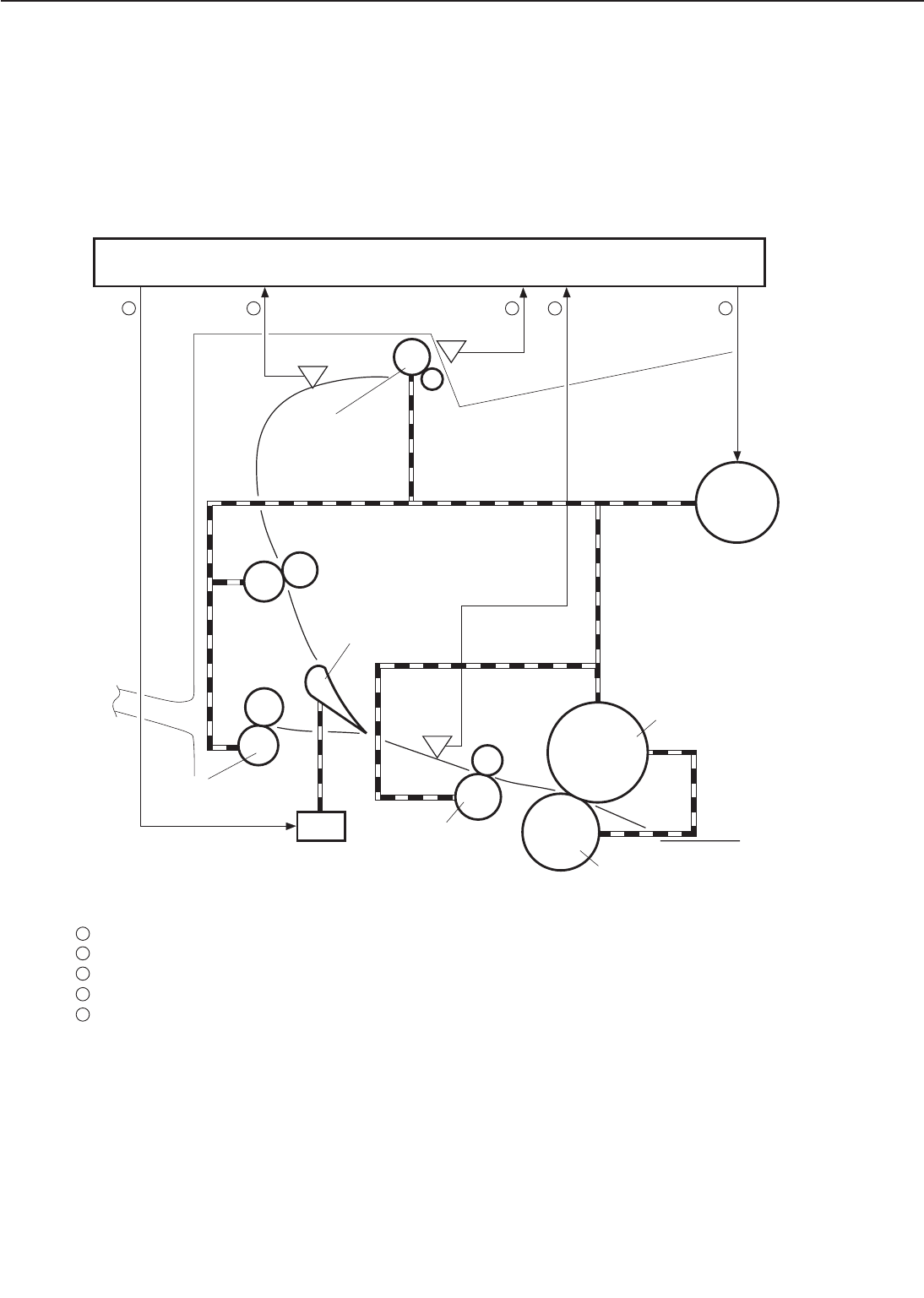
C. Fixing and Delivery Unit
The upper and lower rollers of the fixing unit, and the face-up and face-down delivery rollers are
driven by the main motor (MT1).
The paper separated from the photosensitive drum is fed into the fixing unit, and sent from
the fixing unit by the fixing roller and fixing unit delivery roller.
The paper sent from the fixing unit is detected by the fixing unit delivery sensor (PS1403).
Figure 2-5-15
2 - 57
CHAPTER 2
PS1401
PS1402
PS1403
MT1
SL3
Upper fixing roller
DC controller PCB
PS1401: Face-down tray paper full sensor
PS1402: Face-down tray delivery sensor
PS1403: Fixing unit delivery sensor
SL3: Face-up solenoid
MT1: Main motor
Face-up
delivery roller
Flapper
Fixing unit
delivery roller
Lower fixing roller
: FACE-UP SOLENOID DRIVE signal (/FUSLD)
: FACE-DOWN TRAY DELIVERY SENSE signal (FDOUTS)
: FACE-DOWN TRAY PAPER FULL SENSE signal (FDFULS)
: FIXING UNIT DELIVERY SENSE signal (/FPOUTS)
: MAIN MOTOR DRIVE signal (/MMOTD)
32
145
3
2
1
4
5
Face-down
delivery roller
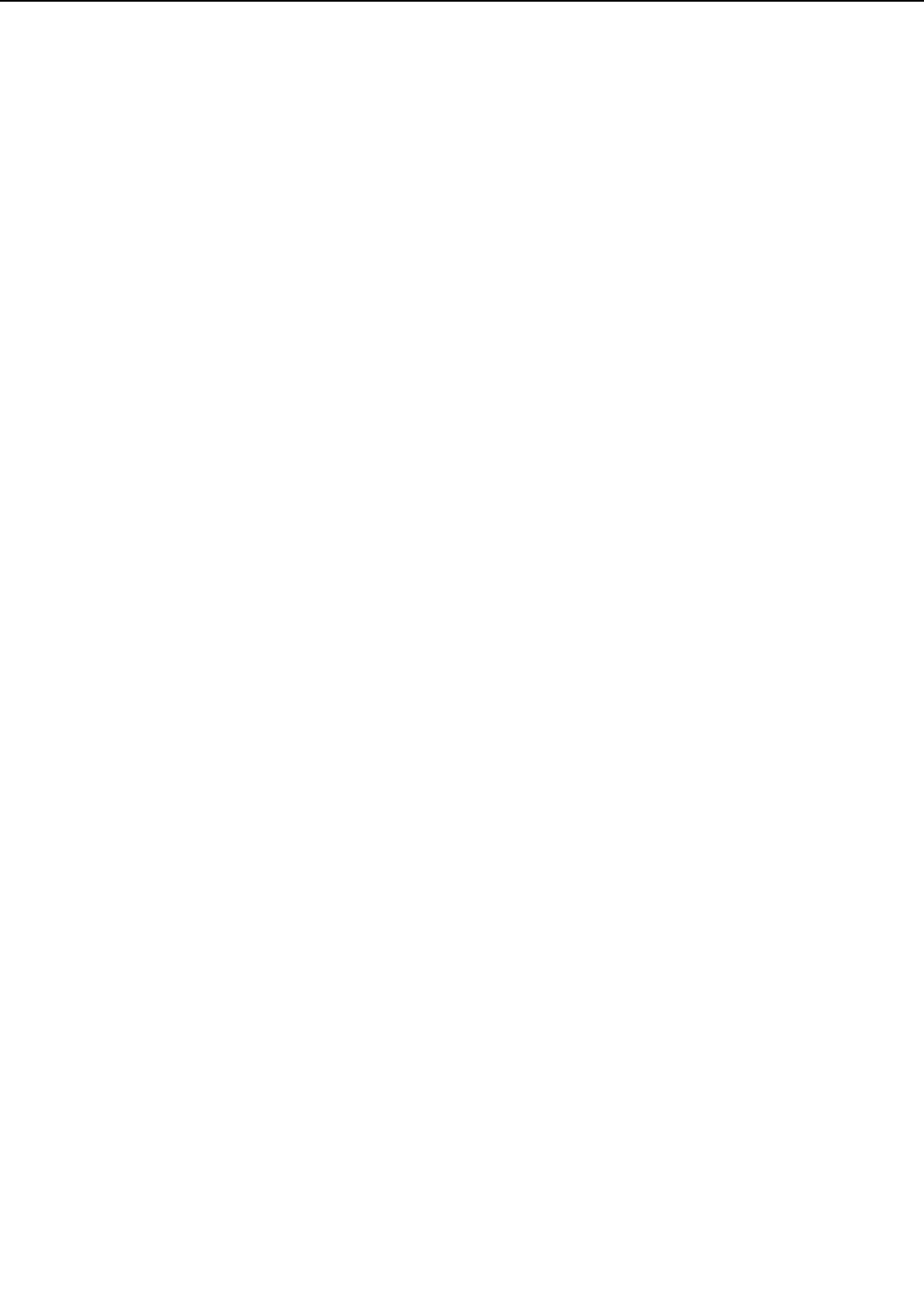
The printer switches between face-up and face-down tray delivery with the face-up deflector.
When the FACE-UP SOLENOID DRIVE signal (/FUSLD) becomes “L”, the face-up solenoid (SL3)
moves the face-up deflector to the face-up tray and the paper is delivered through the face-up
tray. If /FUSLD is “H”, the paper is delivered through the face-down tray on the top of the print-
er.
The paper delivered through the face-down tray is detected by the face-down tray delivery
sensor (PS1402). When the face-down tray becomes full, this is detected by the face-down tray
paper full sensor (PS1401).
2 - 58
CHAPTER 2
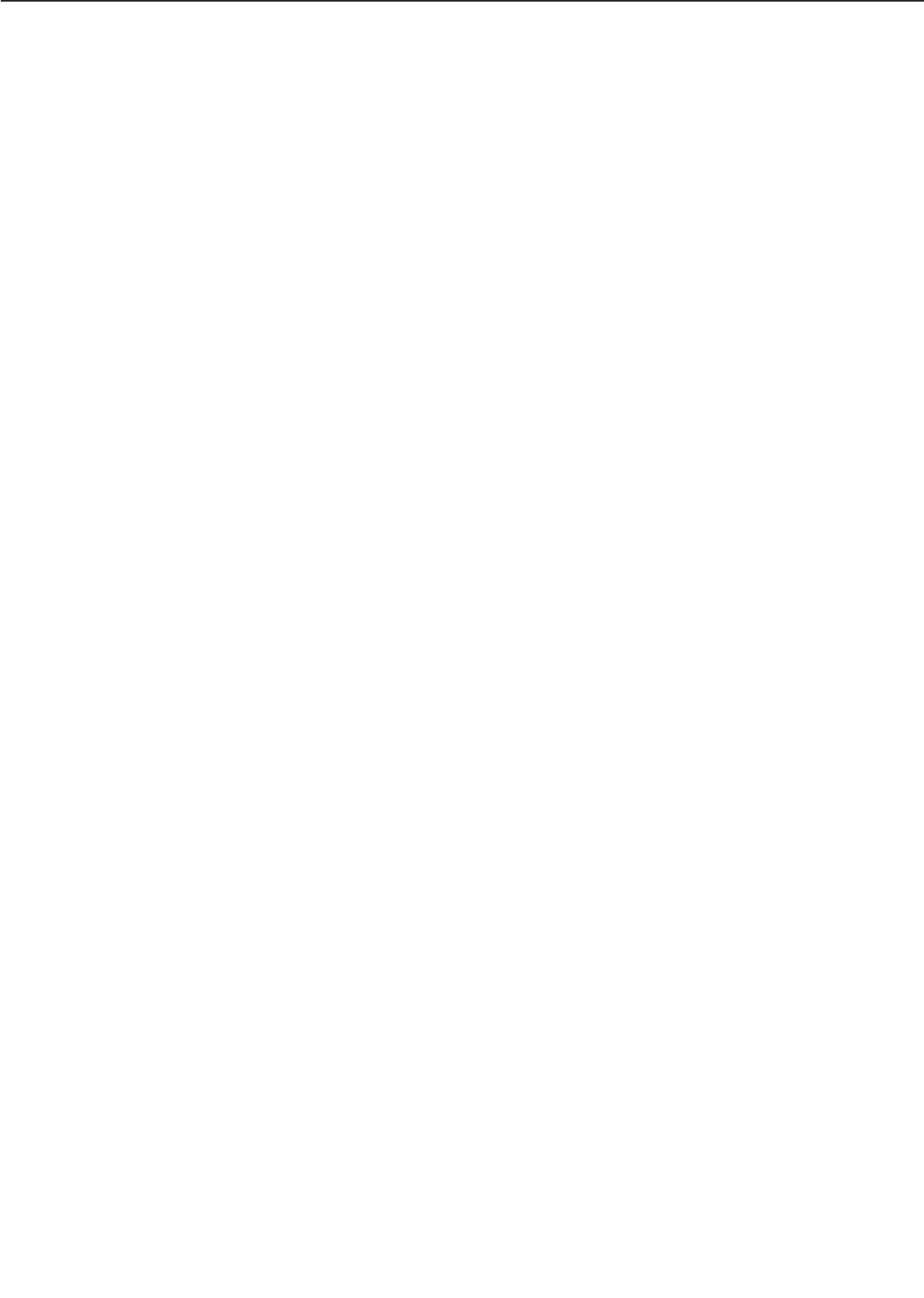
D. Paper Jam Detection
The following paper sensors are provided to detect whether paper is present and whether the
paper is fed normally.
• Registration paper sensor (PS1)
• Pick-up unit paper sensor (PS2)
• Fixing unit delivery sensor (PS1403)
• Face-down tray delivery sensor (PS1402)
The microprocessor (CPU) determines whether paper is jammed by checking whether paper
is present or absent at the sensors, at times stored in memory.
If the CPU determines that a jam has occurred, it stops print operation and notifies the jam
to the video controller.
1. Pick-up delay jam 1
The CPU assesses a pick-up delay jam 1 if the paper does not reach the pick-up unit paper sen-
sor (PS2) within the specified period of time after the pick-up operation.
Upper/lower cassettes: about 6.4 seconds
Duplexing unit (Option): about 2.4 seconds
Paper deck (Option): about 7.0 seconds
2. Pick-up delay jam 2
The CPU assesses a pick-up delay jam 2 if the registration paper sensor (PS1) cannot detect the
leading edge of the paper within about 0.7 seconds after the pick-up unit paper sensor (PS2)
detects the leading edge of the paper.
The CPU also assesses a pick-up delay jam 2 if the registration paper sensor (PS1) cannot
detect the leading edge of the paper within about 9.5 seconds after start of pick-up operation
from the multi-purpose tray or envelope feeder.
3. Fixing unit delivery delay jam
The CPU assesses a fixing unit delivery delay jam if the leading edge of the paper does not reach
the fixing unit deliver sensor (PS1403) within about 2.2 seconds after receiving the VERTICAL
SYNC signal (/VSYNC).
4. Fixing unit delivery stationary jam
The CPU assesses a fixing unit delivery stationary jam if the trailing edge of the paper does not
pass through the fixing unit delivery sensor (PS1403) within the specified period of time (T1)
after receiving the VERTICAL SYNC signal (/VSYNC).
Ledger=about 5.3 seconds, Legal=about 4.7 seconds, Letter=about 3.8 seconds,
A3=about 5.2 seconds, B4=about 4.8 seconds, A4=about 3.7 seconds
5. Face-down delivery delay jam
The CPU assesses a face-down delivery delay jam if the leading edge of the paper does not reach
the face-down tray delivery sensor (PS1402) within about 3.9 seconds after receiving the VER-
TICAL SYNC signal (/VSYNC).
6. Face-down delivery stationary jam
The CPU assesses a face-down delivery stationary jam if the trailing edge of the paper does not
pass through the face-down tray delivery sensor (PS1402) within the specified period of time (T2)
after receiving the VERTICAL SYNC signal (/VSYNC).
Ledger=about 7.0 seconds, Legal=about 6.4 seconds, Letter=about 5.5 seconds,
A3=about 6.9 seconds, B4=about 6.5 seconds, A4=about 5.4 seconds
2 - 59
CHAPTER 2
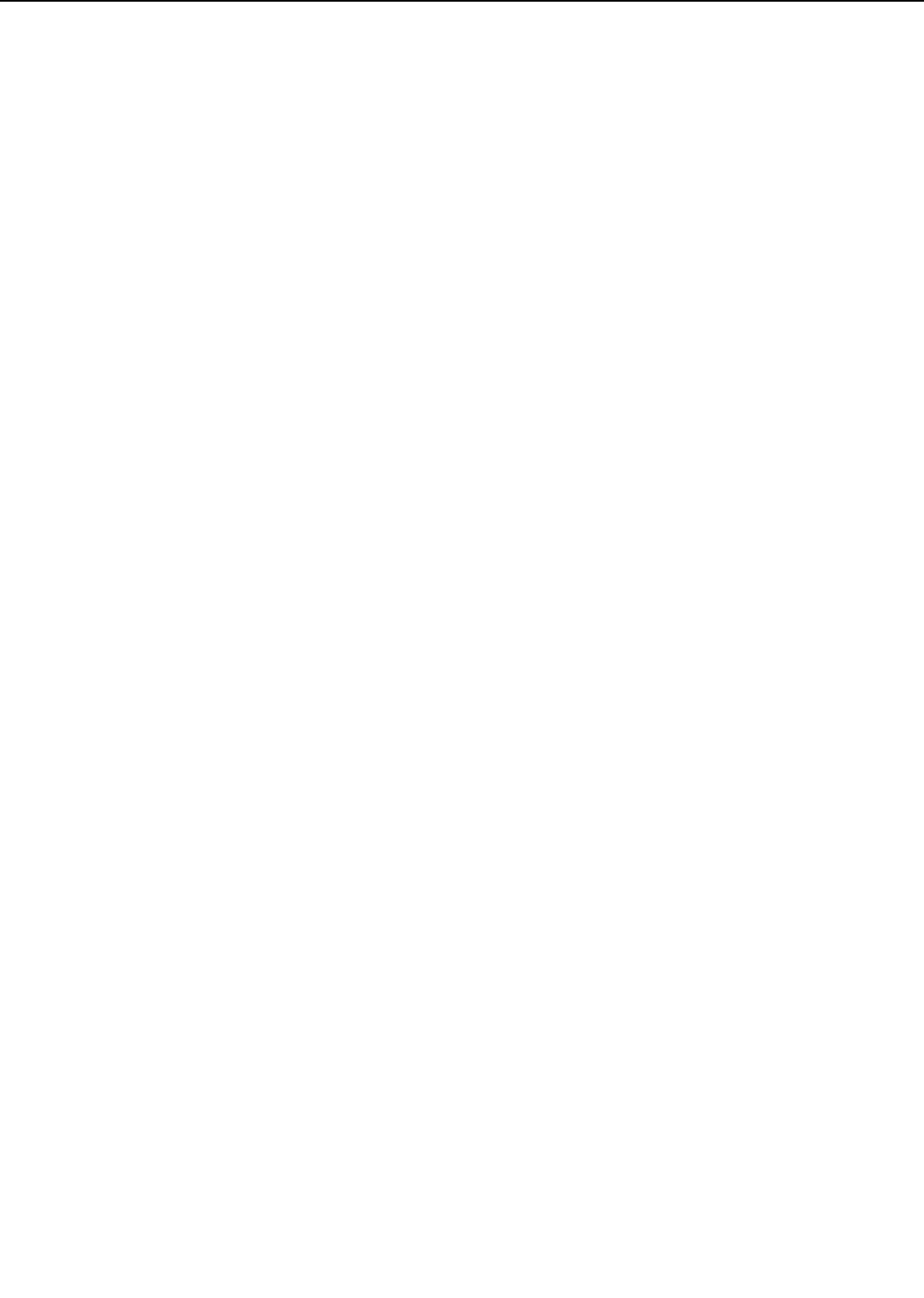
7. Residual paper jam
a. The CPU assesses a residual paper jam if the fixing unit delivery sensor (PS1403) detects the
paper after the power-ON.
b. The CPU assesses a residual paper jam if it does not receive an automatic delivery command
within 3 minutes after notifying the video controller of the presence of paper which can be
automatically delivered out of the printer.
c. The CPU assesses a residual paper jam if one of the following sensors detects the paper after
the printer has performed an automatic delivery of the relevant paper after the power switch
is turned ON and the fixing roller has reached the specified temperature (150°C).
• Registration paper sensor (PS1)
• Pick-up unit paper sensor (PS2)
• Fixing unit delivery sensor (PS1403)
• Face-down tray delivery sensor (PS1402)
2 - 60
CHAPTER 2
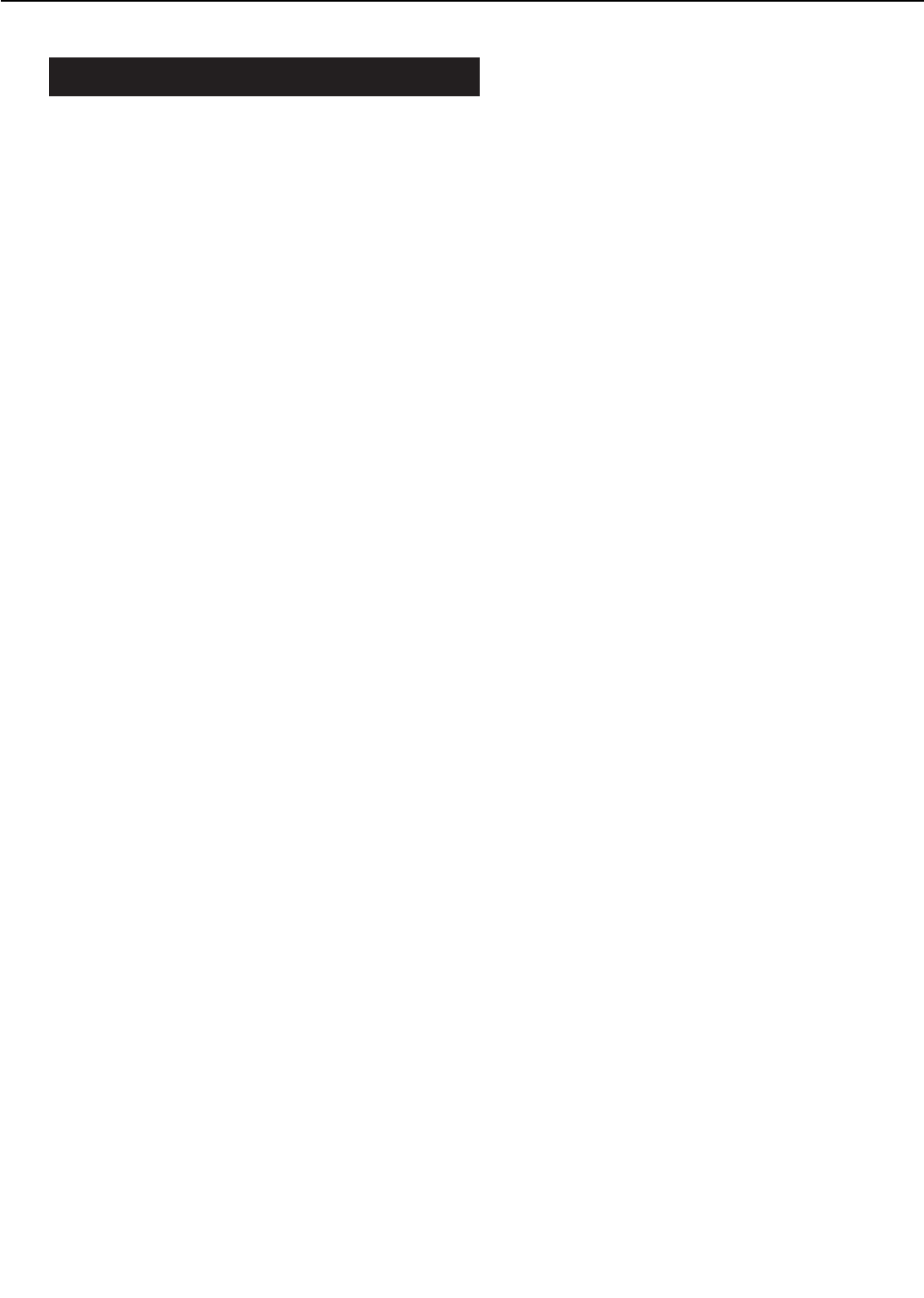
VI. OVERALL CONTROL SYSTEM
A. Video Controller PCB
1. Outline
The video controller PCB receives print data consisting of code or image data sent from the exter-
nal device (host computer, etc.) through the interface cable.
The print data including the contents specified by the control panel is analyzed, processed
and converted into the dot data within this PCB. The dot data is sent to the engine controller
PCB to turn ON/OFF the laser diode.
Figure 2-6-1 shows the location of the ICs on this PCB and Figure 2-6-2 shows the block dia-
gram.
2. Functions by block
a. CPU (IC15)
The CPU is Motorola made 32 bit RISC microprocessor (PPC603e) and its operation frequency is
100MHz. The CPU controls the operation of the video controller PCB according to the control
program stored in the ROM.
b. ASIC (IC21)
The ASIC is a graphic co-processor and has the following functions.
1) DRAM control
2) ROM control
3) Video interface control
4) IEEE 1284 parallel port interface control
5) I/O bus interface support
c. AIR (IC2)
The smoothing control circuit and SRAM are built in the AIR.
Its main functions are as follows.
1) Image smoothing control
2) EEPROM control
3) Control panel interface control
d. DRAM
8-MB DRAM is installed on the video controller PCB.
72 pin DIMM of 4-MB, 8-MB or 16-MB can be installed in the 2 slots on the PCB.
e. ROM DIMM
4-MB ROM is installed on the video controller PCB. In addition, a ROM is installed on the
firmware ROM DIMM. The ROM DIMM is installed in the connector J4 on the video controller
PCB.
The user can install 4-MB or 8-MB ROM DIMM in the left connector J2 and the middle con-
nector J3. The right connector J4 is exclusively for the firmware ROM DIMM.
f. EEPROM (IC11)
The EEPROM has a memory capacity of 4-KB and is used to store the factory default values and
values modified by the control panel.
2 - 61
CHAPTER 2
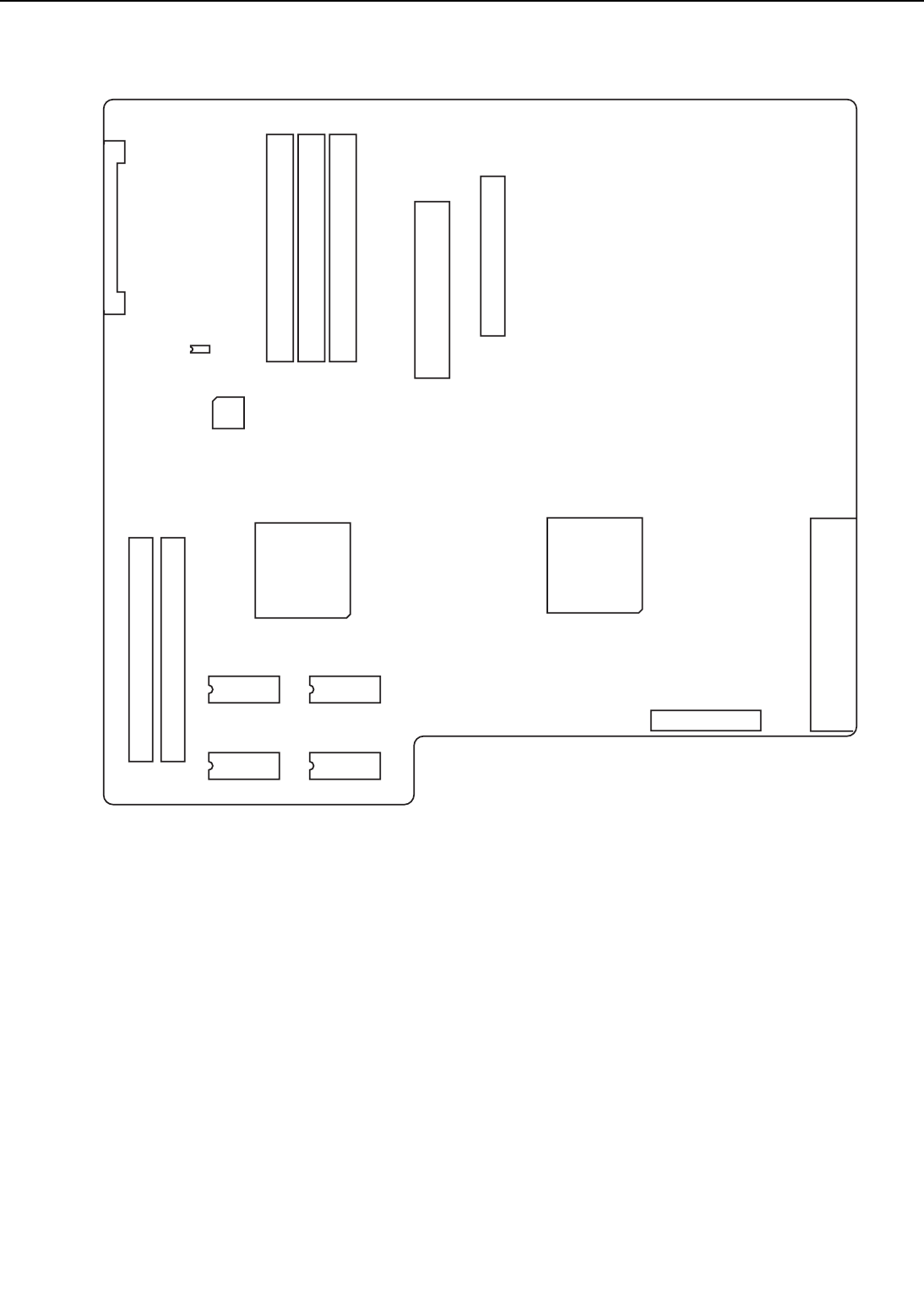
Figure 2-6-1
2 - 62
CHAPTER 2
J1 J4J3J2
ROM DIMM 0
ROM DIMM 1
ROM DIMM 2
J11
J10
IC27
EEPROM
AIR
IC2
J6 J7 IC10
DRAM
(16M) DRAM
(16M)
ASIC
IC15
CPU
J8
J9
RAM DIMM 0
RAM DIMM 1
DRAM
(16M) DRAM
(16M)
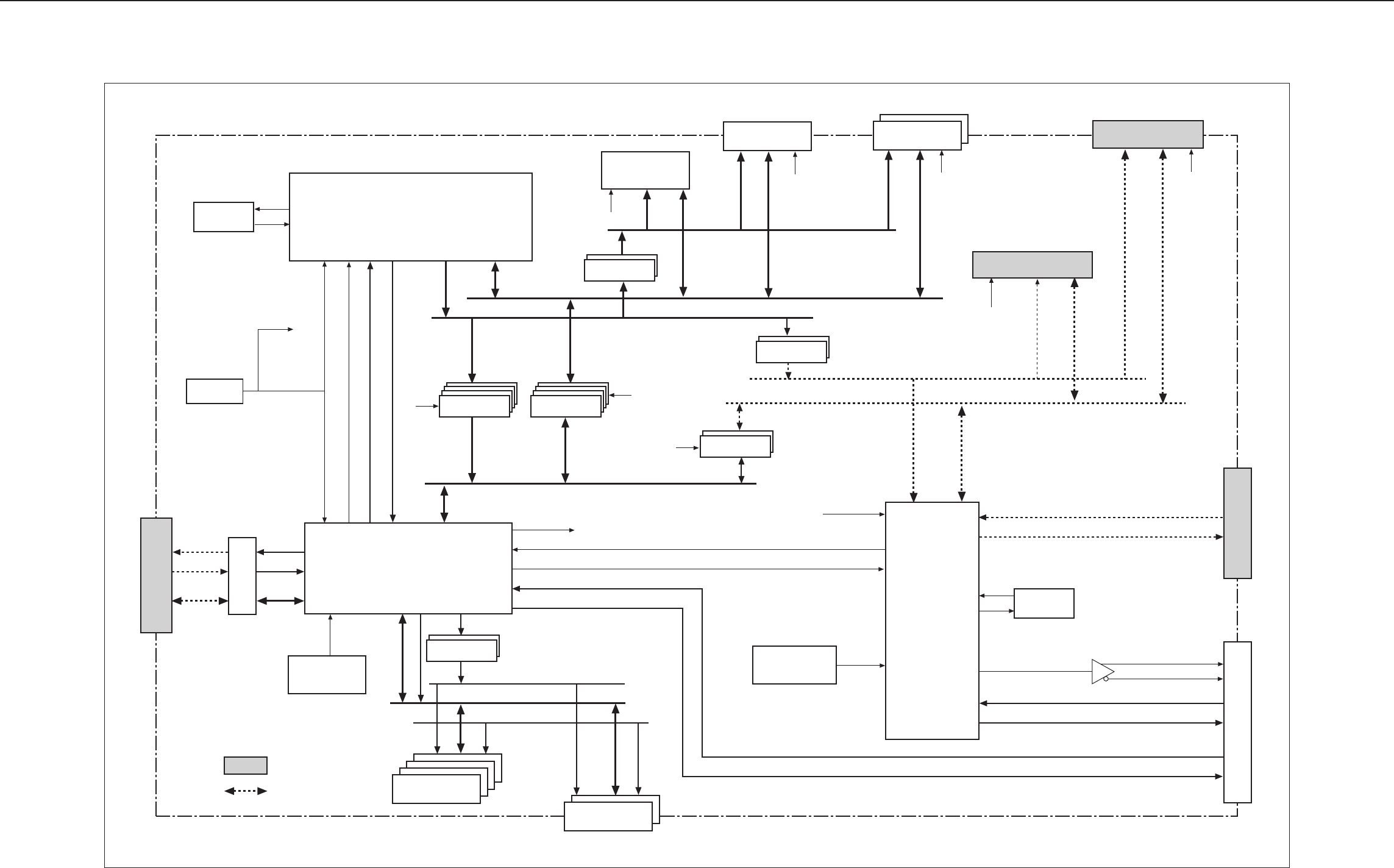
2-63
Video contoroller PCB Block Diagram
Figure 2-6-2
AIR
X´TAL
(14.37038MHz) nVDO
X´TAL
(66.6666MHz)
CPUCLK (33.3MHz)
<J4> <J2/3>
for option
(72pin, 2slot)
for hard disk
(44pin, 2.1GB)
IOA [6:2]
IOD [11:0]
IOA [4:2]
IOA [23, 17:2]
for network board
(50pin, PSIO)
<J11>
<J6/7>
for option
(72pin, 2slot)
<J9>
<J8>
<J1>
ASIC
CPU
PPC603e (100/33)
for option controller
(20pin)
to host computer
(36pin)
to DC controller
(48pin)
CHAPTER 2
EEPROM
Option controller I/FEngine
RAM (8MB)
RAM DIMM
LVCR2245 ✕2
MA [10:0], nCAS [3:0], nWE
MD [31:0]
nRAS [7:0]
nA8 VDO
nA8 LSYNC, VCLK
Buffer
IEEE1284
LVTH245 ✕4 LVTH245 ✕4
LVCR2245 ✕2
LVCR2245 ✕2
LVC827 ✕2
MASK ROM
(4MB)
Firm DIMM Extension I/O
Hard disk I/O
RESET
nRESET
nA0E
nGCS
nD0E
AD [31:0]
A [31:0]
D [31:0]
A [26:8]
ROM Cont.
ROM Cont.
ROM DIMM
ROM Cont.
I/O Cont.
IOA [23, 17:2]
IOD [15:0]
I/O Cont.
Cont.
I/O Cont.
: Operates at 5V
: 5V signals
Note
JTAG
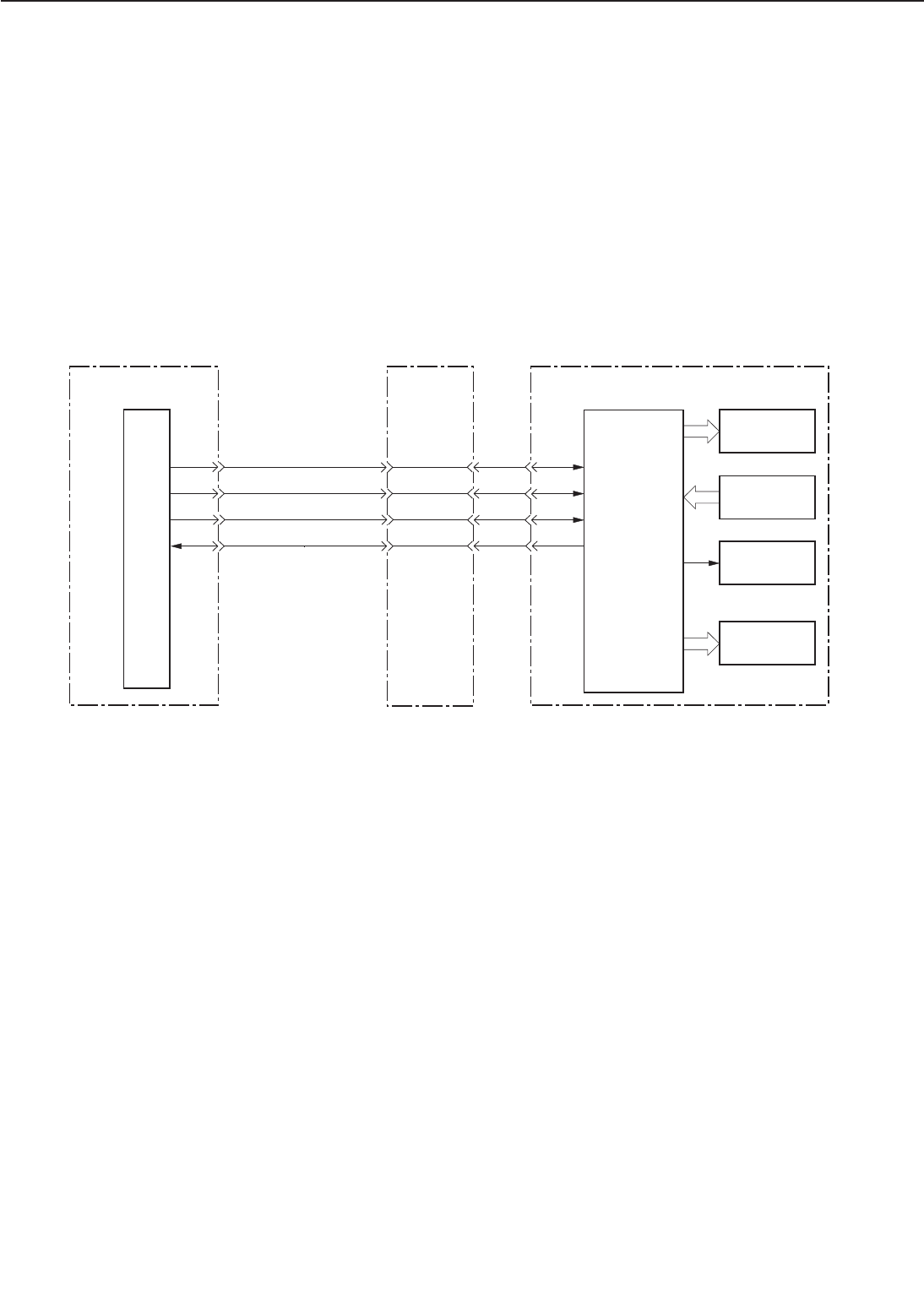
B. Control Panel
1. Outline
The control panel contains a LCD (20 characters x 2 lines), 9 switches, and 7 LEDs.
The control panel is connected to the video controller PCB and has the functions listed below.
a. Displays status and error messages in the LCD.
b. Displays operation condition with the LED.
c. Changes Menus and values with the switches.
2. Operation
The LCD and LEDs on the control panel are controlled by the signals output from the video con-
troller. The signals generated by the switches on the panel are input to the video controller.
Figure 2-6-3
2 - 65
CHAPTER 2
nFP CLK
J6-C13 J3-3
nFP CS J3-4
J3-5
J3-6
LEDs
LCD
CPU Switches
IC10
Video controller PCB
AIR nFP DI
nFP OD
J6-A14
J6-C14
J6-B14
DC controller PCB Control panel
Beeper
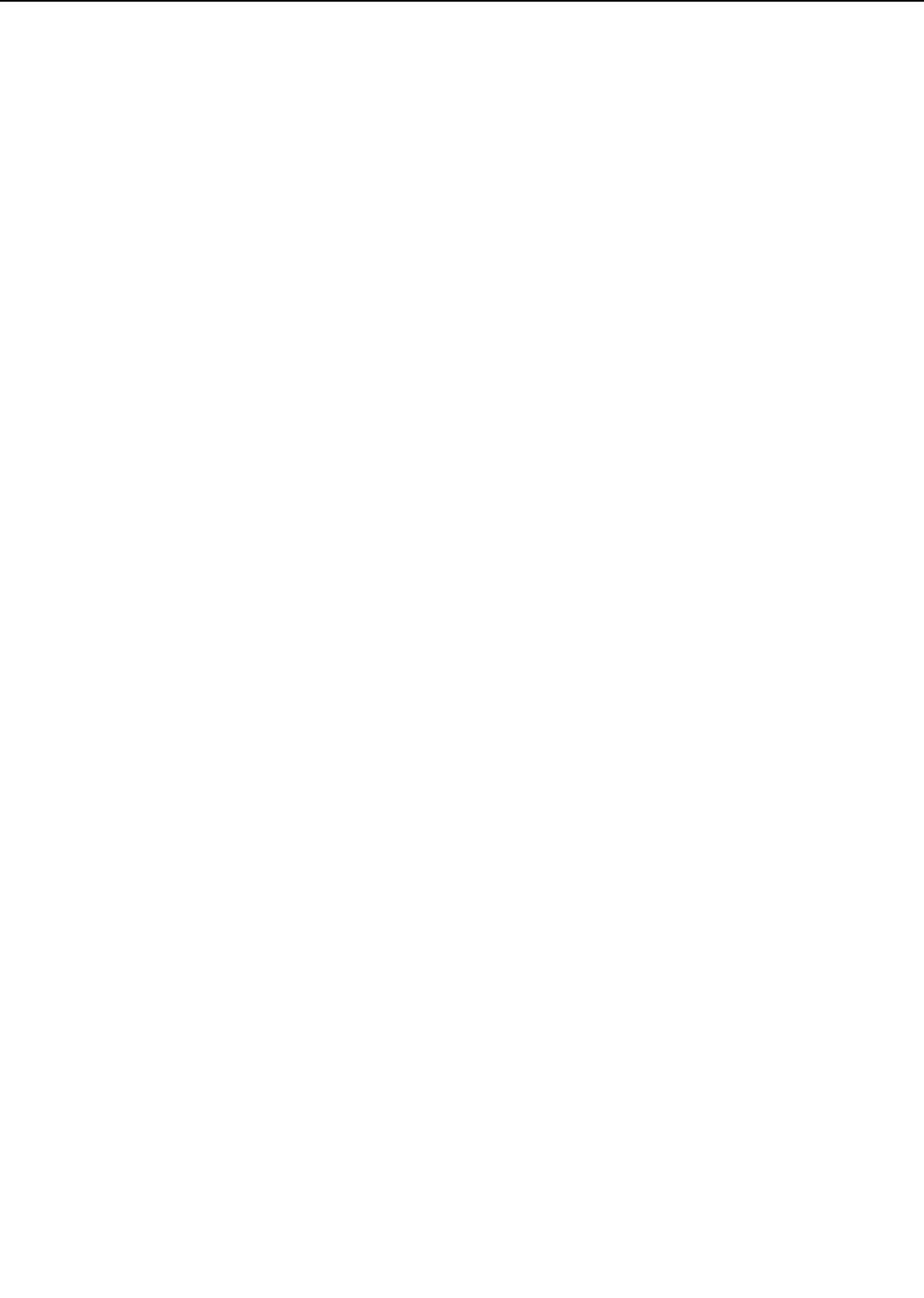
C. Self Test
The printer executes the self diagnostic program of the video controller to check the condition of
the video controller at the power-ON. This function is called self test.
There are two types of self tests: power-ON self test and power-ON key sequence.
1. Power-ON self test
Every time the printer is turned ON, the power-ON self test is conducted following the procedure
stated below.
1) Tests all the DRAMs on the video controller. Error found here will be displayed in the LCD
as a service call.
2) Tests the program ROM, font ROM and optional ROM. Error found here will be displayed in
the LCD as a service call.
3) Checks inside of the CPU. Error found here will be displayed in the LCD as a service call.
4) Completes the test. If an error is reported from the engine controller at this point, it will be
displayed in the LCD.
5) Displays "READY" in the LCD and prints the PCL demo-page automatically.
2. Power-ON key sequence
Pressing specified keys simultaneously at the power-ON executes the specific functions. Among
the following operations, only the Cold Reset sequence is for the user.
a. Cold Reset
Turn ON the printer with the On Line key pressed.
The Cold Reset resets all the printer settings to the factory default values.
b. Check Sum Functions
Turn ON the printer with the On Line and Enter keys pressed (PPG Check Sum). Or, turn ON
the printer with the On Lien and Reset keys pressed (PS Check Sum).
The printer performs the check sum on the requested ROM bank. The calculated check sum
will be displayed in the LCD.
c. Factory Reset Function (A4/LTR)
To reset the paper size default to A4, turn ON the printer with the Menu, Item and Shift keys
pressed.
To reset the paper size default to Letter, turn ON the printer with the Menu, Item, and
Plus/Minus keys pressed.
The printer uses the selected paper size (A4/Letter) as the default value, resets the page count
to "0", and executes the Cold Reset. The Cold Reset executed hereafter will maintain the paper
size selected here.
d. Panel Check Function
The Panel Check Function performs the control panel diagnosis and test sequence. The
sequences in the Panel Check Function are as follows.
1) Turn ON the printer with the On Line and Shift keys pressed. "PANEL CHECK" message will
appear in the LCD.
2) Step 3 to 11 can be executed as many times as you wish in any order.
3) Pressing the On Line key illuminates the top left half of the LCD (10 columns). Releasing the
key will clear the display.
4) Pressing the Continue key illuminates the top right half (10 columns) of the LCD. Releasing
the key will clear the display.
5) Pressing the Form Feed key illuminates the top line of the LCD (20 columns). Releasing the
key will clear the display.
2 - 66
CHAPTER 2
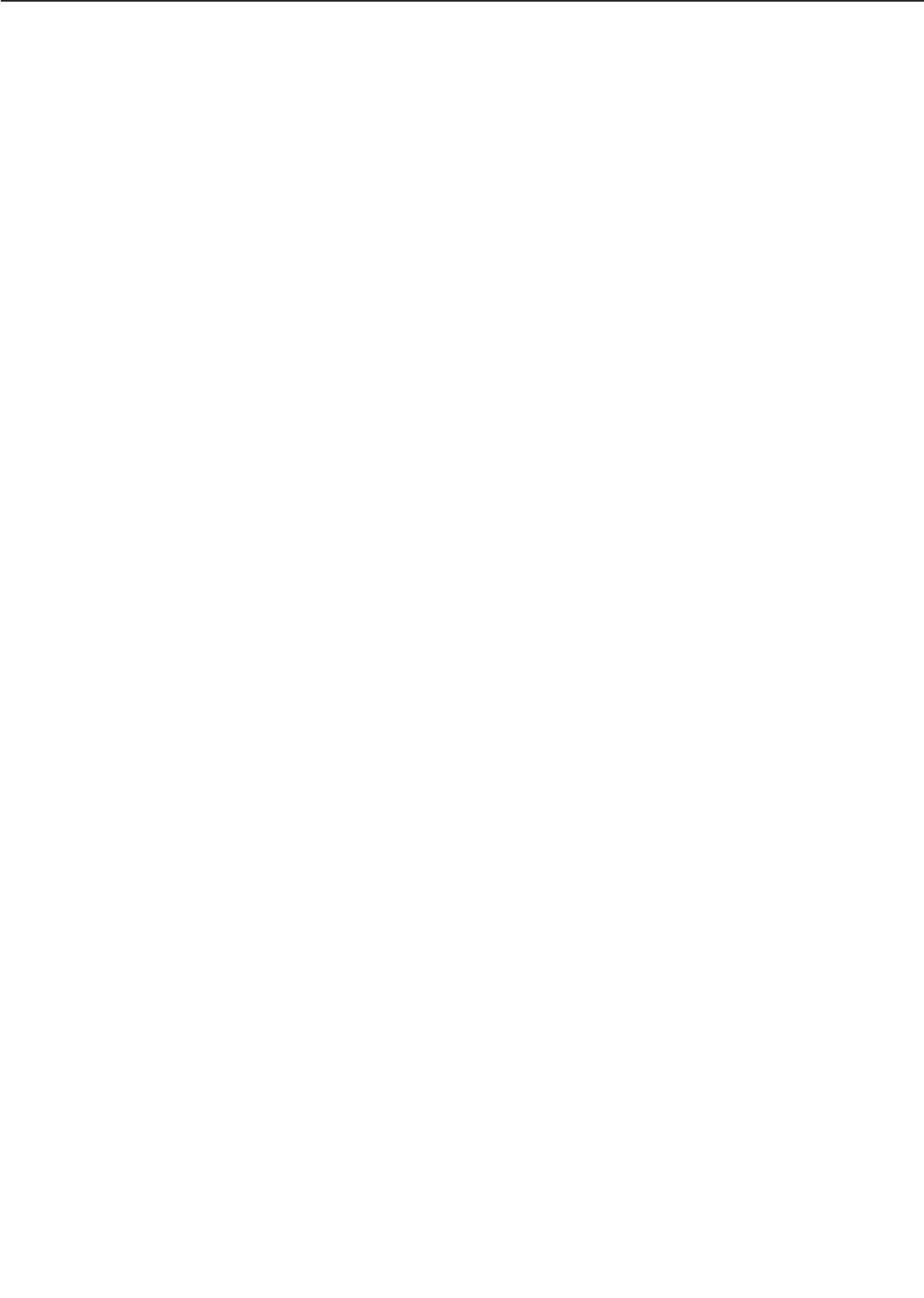
6) Pressing the Reset key illuminates the every other column of the top line of the LCD.
Releasing the key will clear the display.
7) Pressing the Enter key displays "OPERATION CHECK" message. Releasing the key will clear
the message.
8) Pressing the Menu key displays "OPERATION CHECK" message. Releasing the key will clear
the message.
9) Pressing the Item key displays "OPERATION CHECK" message. Releasing the key will clear
the message.
10) Pressing the Shift key illuminates the top line of the LCD (20 columns). Releasing the key
will clear the display.
11) Pressing the +Plus/-Minus key displays "OPERATION CHECK" message. Releasing the key
will clear the message.
12) When all the keys have been tested, "PANEL CHECK DONE" message appears and the DISK,
STAPLE and CONTINUE LEDs keep flashing. The message starts to move in circles in about
60 seconds. This conditions is kept until the printer is turned OFF.
e. Update flash
Turn ON the printer with the Enter and Shift keys pressed.
This function supplies the flash menu for managing/down loading the firmware.
2 - 67
CHAPTER 2
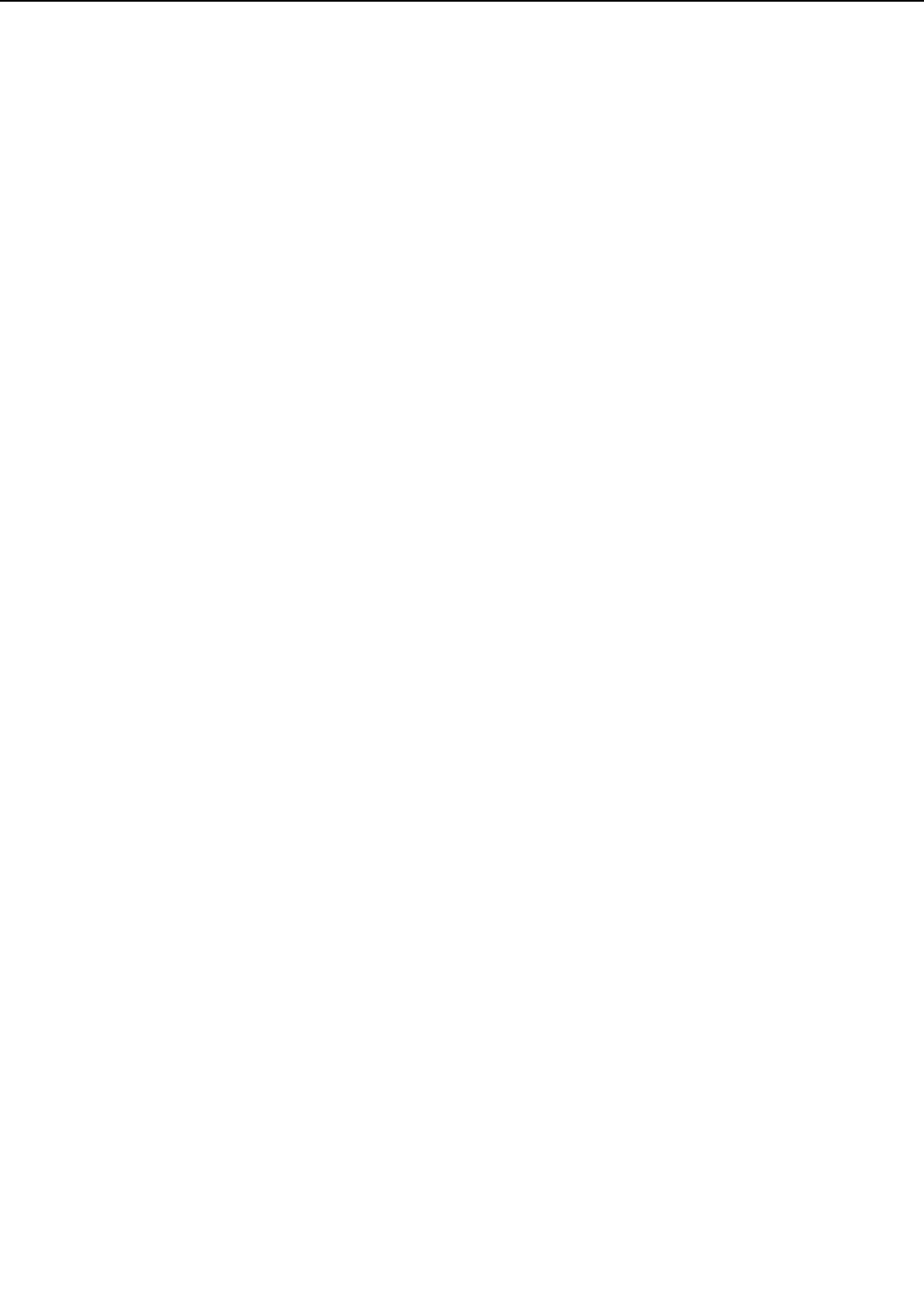
2 - 68
CHAPTER 2
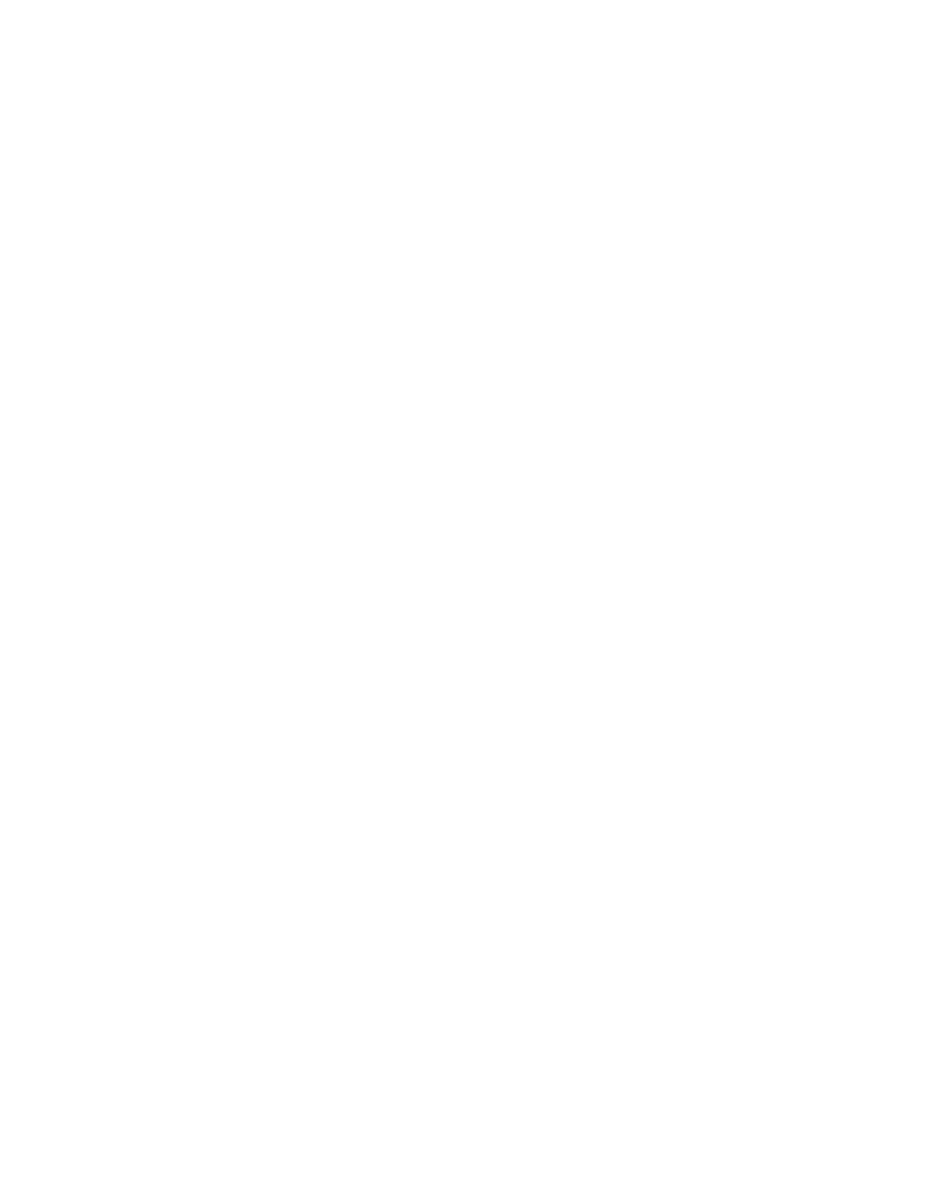
CHAPTER 3
THE MECHANICAL SYSTEM
I. PREFACE ............................... 3-1
II. EXTERNALS ........................... 3-2
III. MAIN UNITS ........................... 3-8
IV. MAIN PARTS .......................... 3-15
V. SWITCHES/SENSORS............. 3-24
VI. CLUTCHS/SOLENOIDS ........... 3-31
VII. MOTORS/FANS ...................... 3-35
VIII.PCBS...................................... 3-41
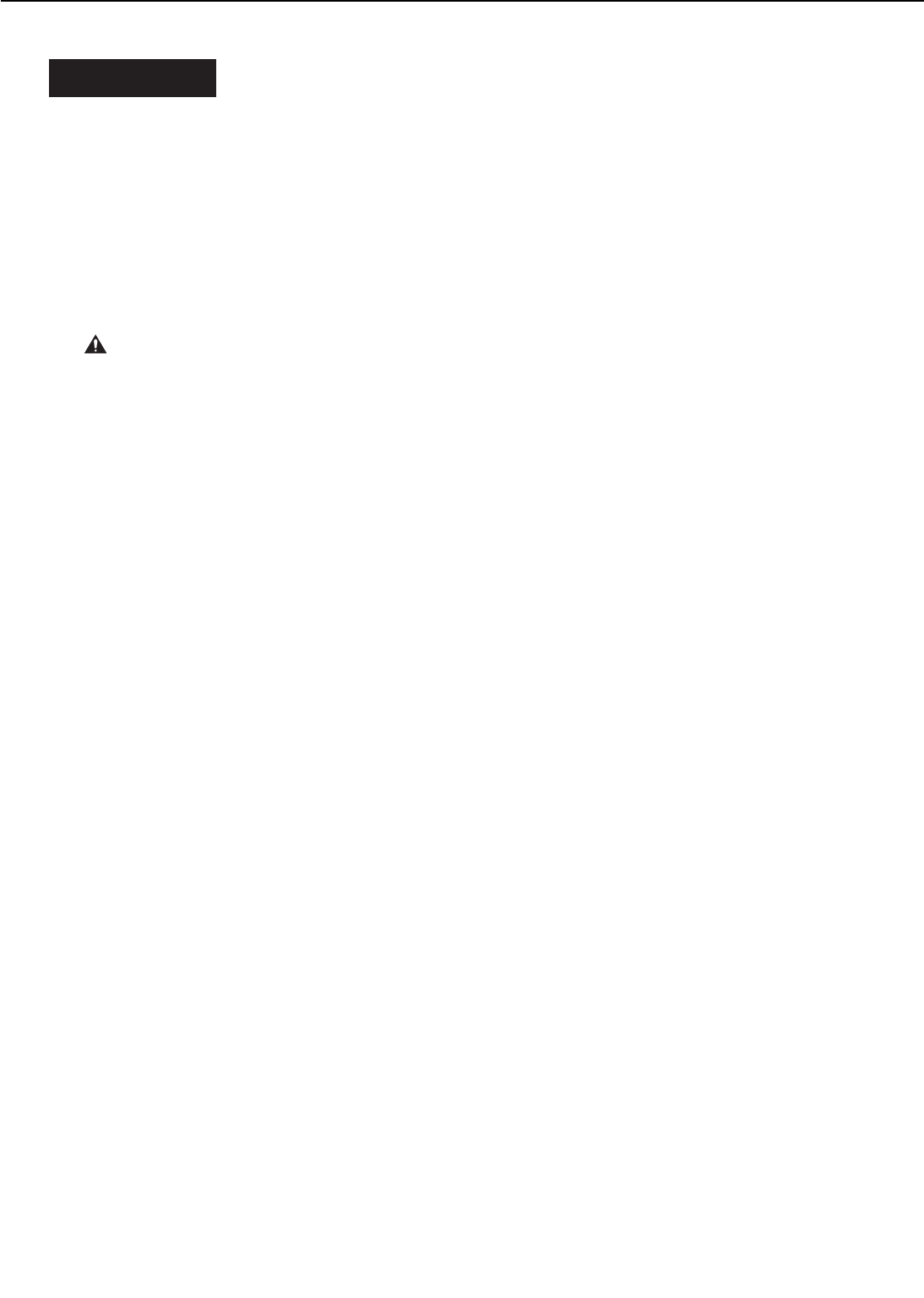
I. PREFACE
This chapter describes disassembly and reassembly procedures of the printer.
The service technician is to find the factor of the failure according to the "Chapter 4
Troubleshooting" and to follow the disassembly procedures in this chapter to replace the defec-
tive part(s). Replacement of consumable part(s) is also to be conducted according to the proce-
dures described in this chapter.
Note the following precautions during disassembly or reassembly.
1.At disassembly, reassembly, or transportation of the printer, remove the toner cartridge as
necessary. When the cartridge is out of the printer, put it in a protective bag to prevent light
from affecting it.
2. CAUTION: Before servicing the printer, disconnect its power cord from the electrical out-
let.
3.Assembly is the reverse of disassembly unless otherwise specified.
4. Note the lengths, diameters, and locations of screws as you remove them. When reassem-
bling the printer, be sure to use them in their original locations.
5.As a general rule, do not operate the printer with any parts removed.
6.Discharge electrical static from your body by touching the metal frame of the printer prior to
handling the PCBs in order to avoid causing damage by the difference in static charge at that
time.
3 - 1
CHAPTER 3
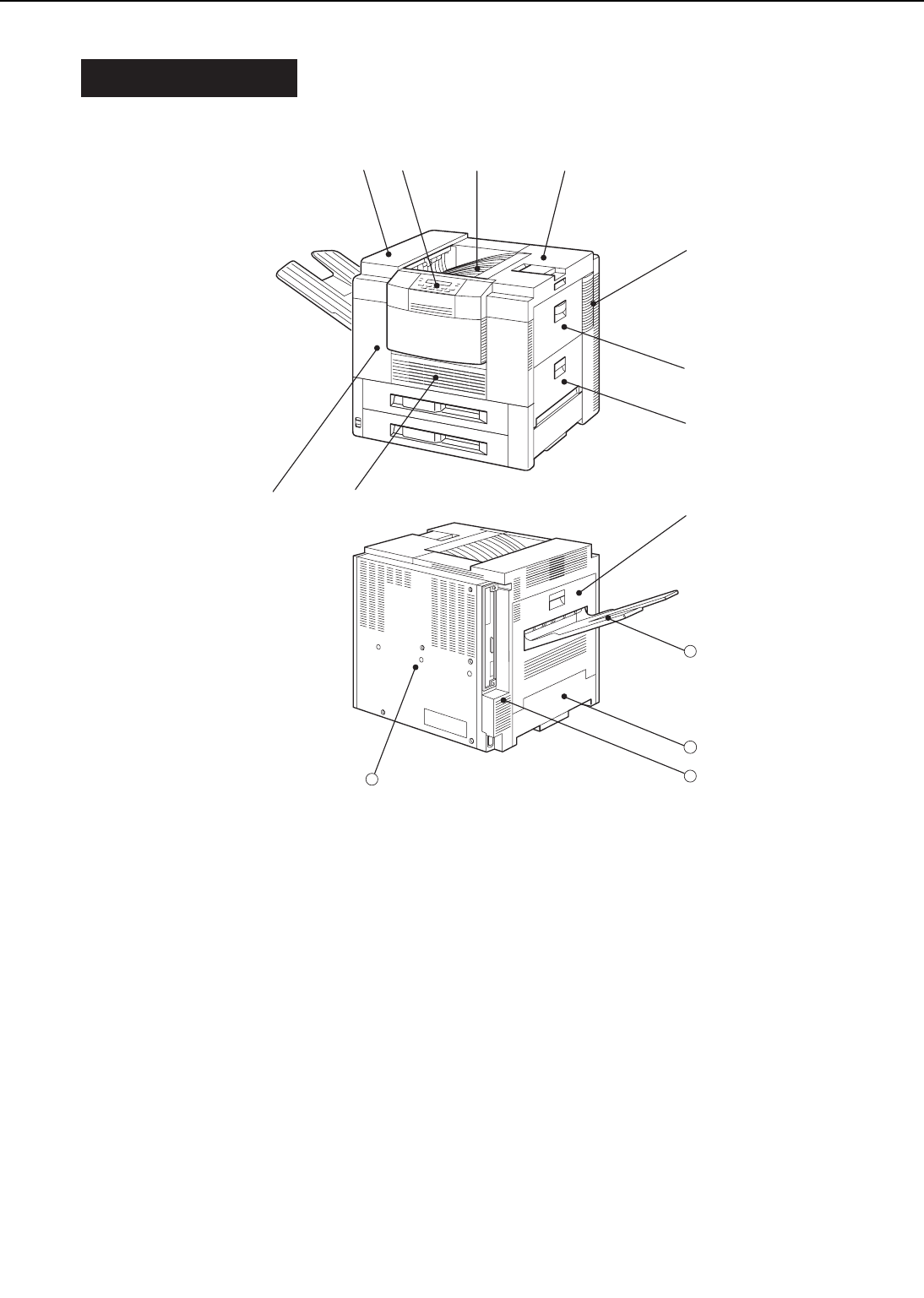
II. EXTERNALS
A. Locations
1: Upper cover unit 2: Operation panel unit
3: Face-down tray 4: Upper cover
5: Right rear cover 6: Multi-purpose tray
7: Pick-up unit door 8: Duplexing unit door
9: Front cover 10: Delivery cover unit
11: Face-up tray 12: Left lower cover
13: Left rear cover 14: Rear cover
Figure 3-2-1
Follow the procedures below to remove the cover(s) as required when cleaning, inspecting, or
repairing inside the printer.
The procedures for the covers, which can be removed simply by removing screws without
removing other parts, are omitted.
3 - 2
CHAPTER 3
11
13
14
➉
➀➁ ➂ ➃
➄
➅
➆
➇➈
12
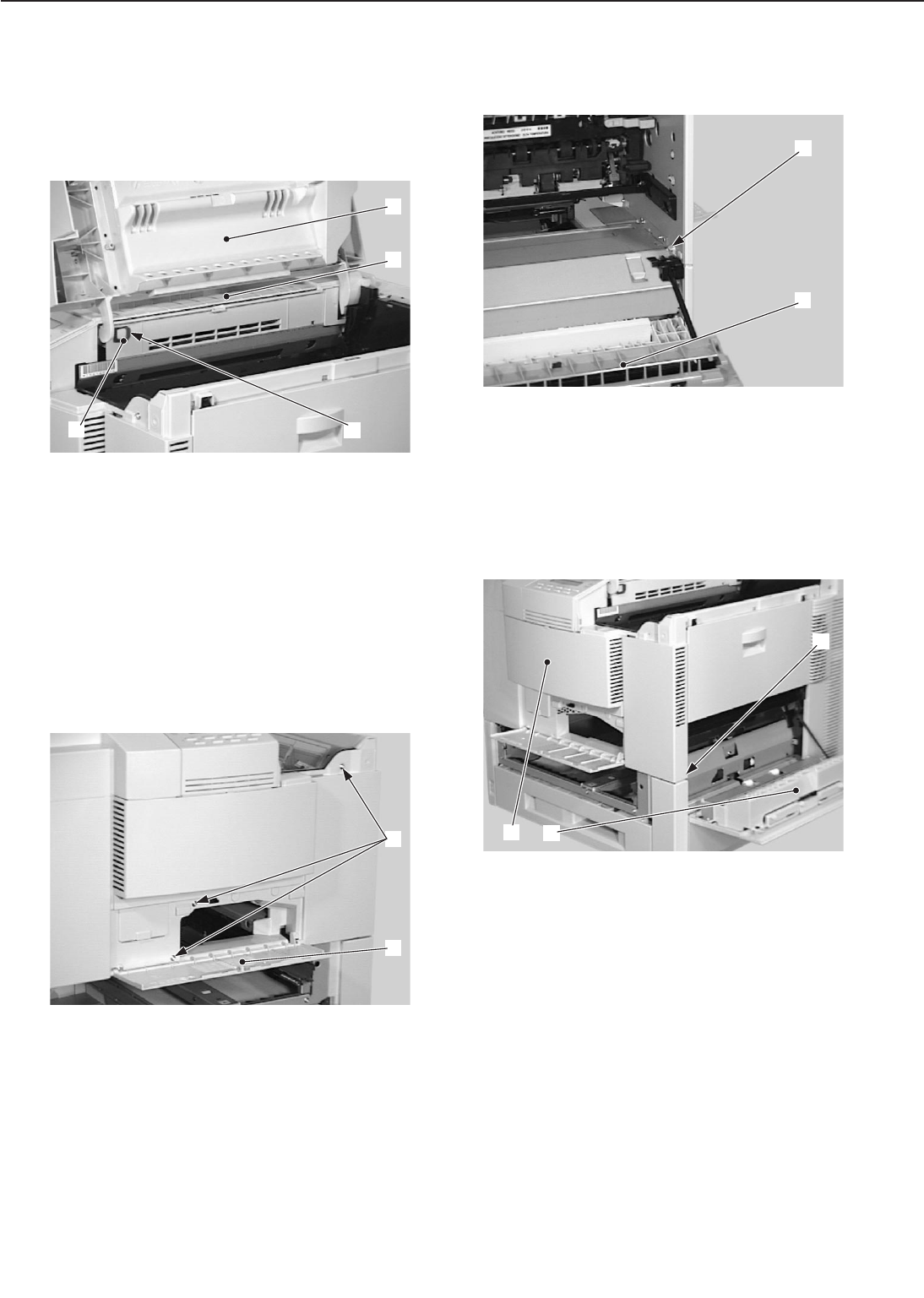
1. Face-down tray
1) Open the upper cover.
2) Holding the knob, remove the lock lever.
Close the upper cover and then take out
the face-down tray.
➀Upper cover ➁Knob
➂Lock lever ➃Face-down tray
Figure 3-2-2
2. Front cover
1) Remove the upper cassette.
2) Open the upper cover.
3) Open the duplexing unit door.
4) Remove the 3 screws.
➀Duplexing unit door
➁Screws
Figure 3-2-3
5) Open the delivery cover unit and
unhook the claw.
➀Delivery cover unit
➁Claw
Figure 3-2-4
6) Open the pick-up unit door, unhook the
claw, and then remove the front cover.
➀Pick-up unit door
➁Claw
➂Front cover
Figure 3-2-5
3 - 3
CHAPTER 3
➀
➃
➂➁
➀
➁
➀
➂
➁
➁
➀
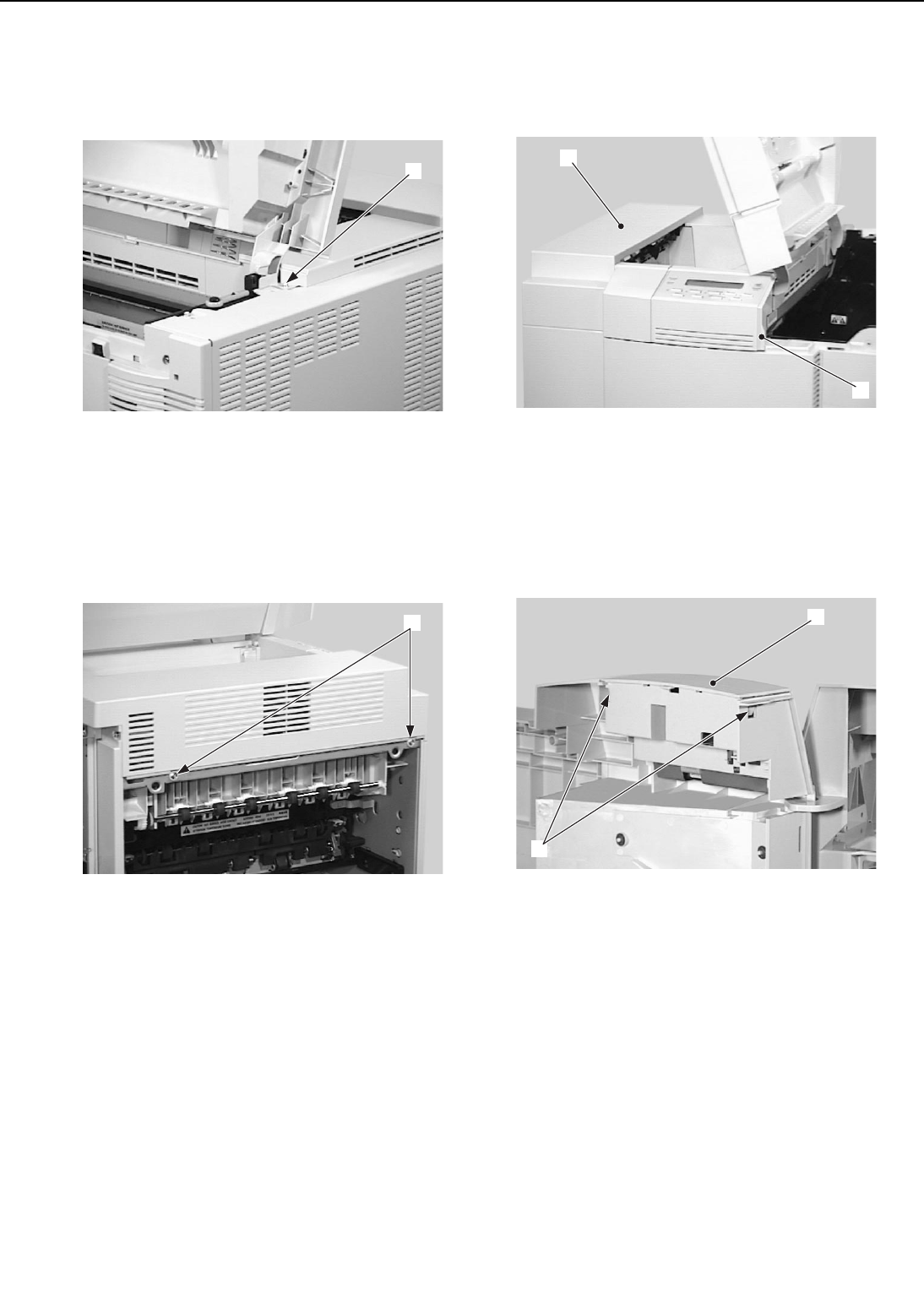
3. Upper cover unit
1) Remove the face-down tray.
2) Remove the 2 screws.
➀Screws
Figure 3-2-6
3) Open the delivery cover unit and then
remove the 2 screws.
➀Screws
Figure 3-2-7
4) Pulling the knob toward you, lift the
upper cover unit and disconnect the
connector from the inside.
➀Knob ➁Upper cover unit
Figure 3-2-8
5) Unhook the 2 claws and then remove
the control panel unit.
➀Claws ➁Control panel unit
Figure 3-2-9
3 - 4
CHAPTER 3
➁
➀
➀
➁
➀
➀
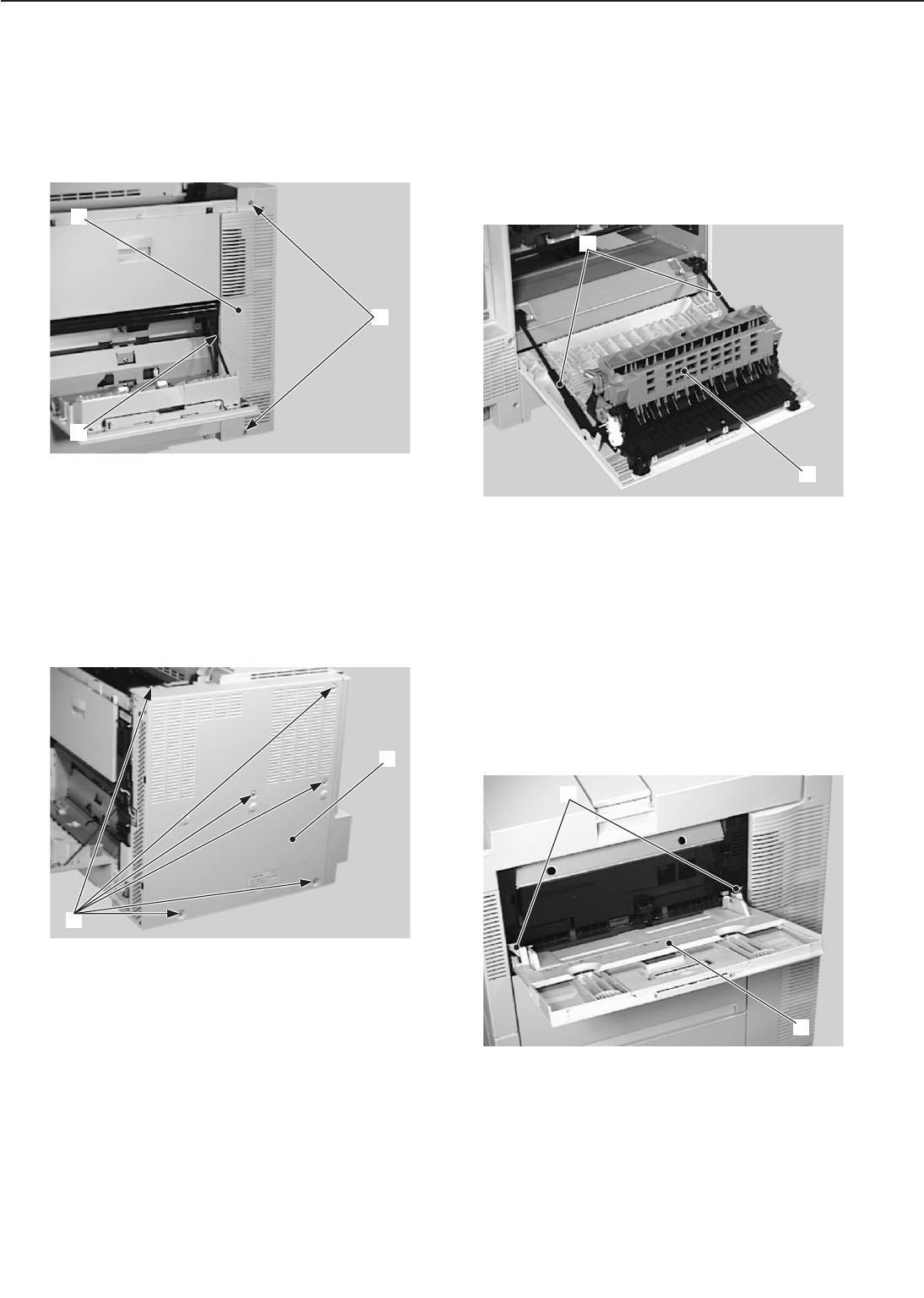
4. Rear cover
1) Open the upper cover.
2) Open the pick-up unit door.
3) Remove the 2 screws, unhook the claw,
and then remove the right rear cover.
➀Screws ➁Claw
➂Right rear cover
Figure 3-2-10
4) Remove the 6 screws and then the rear
cover.
➀Screws ➁Rear cover
Figure 3-2-11
5. Delivery cover unit
1) Open the delivery cover unit.
2) Remove the 2 rods that hold the delivery
cover unit to the printer.
3) Lifting up the delivery cover unit slight-
ly, remove the right and then the left
side of the unit.
➀Delivery cover unit
➁Rods
Figure 3-2-12
6. Multi-purpose tray
1) Open the multi-purpose tray.
2) Unhook the 2 claws that hold the multi-
purpose tray to the printer and pull out
the tray toward you.
➀Claws
➁Multi-purpose tray
Figure 3-2-13
3 - 5
CHAPTER 3
➀
➁
➂
➁
➀
➁
➀
➀
➁
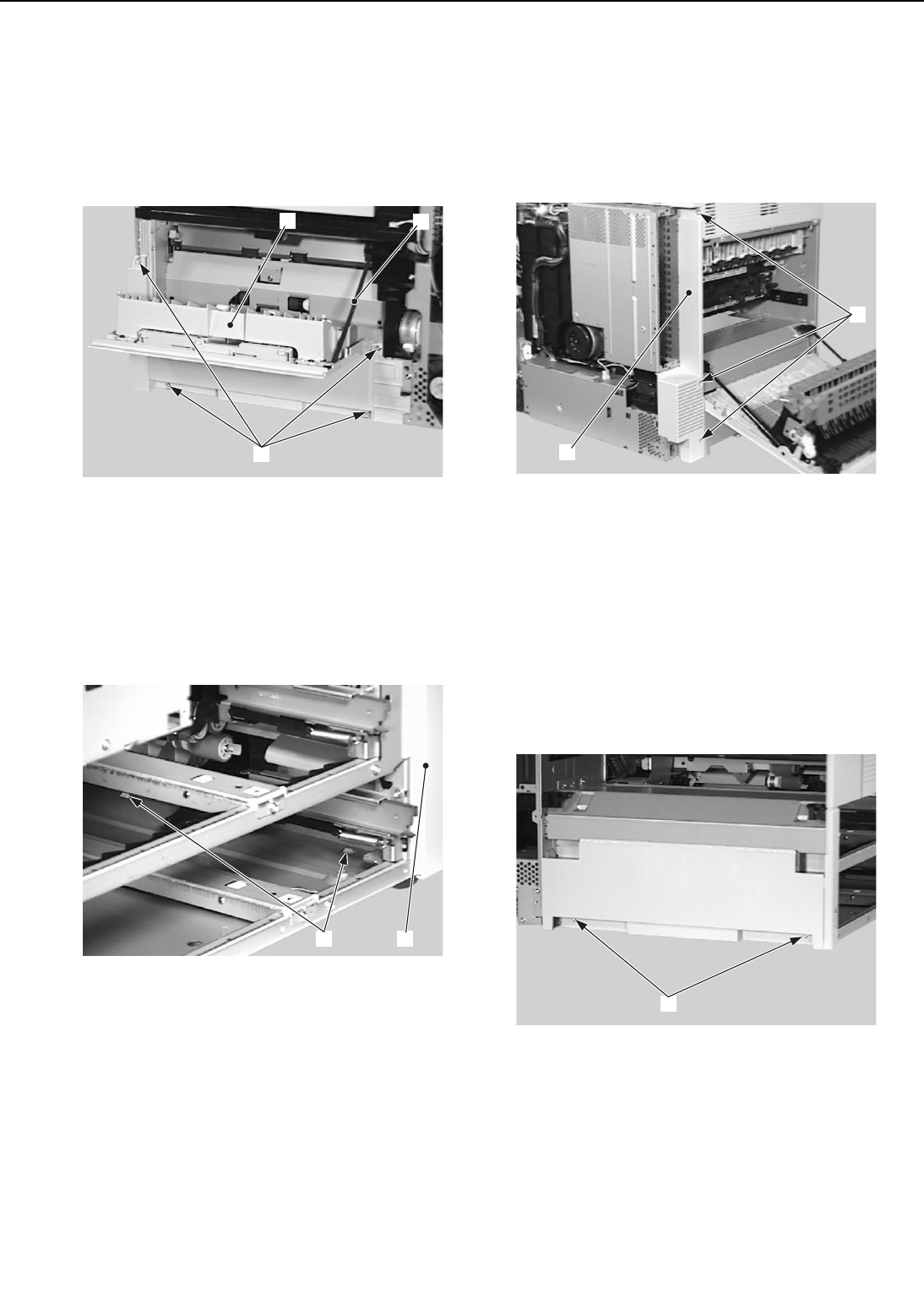
7. Right cover unit
1) Remove the upper and lower cassettes.
2) Remove the front cover.
3) Remove the right rear cover.
4) Remove the hinge and then the 4 screws
from the right cover unit.
➀Right cover unit ➁Hinge
➂Screws
Figure 3-2-14
5) Unhook the 2 claws from the inside and
then remove the right cover unit.
➀Claws ➁Right cover unit
Figure 3-2-15
8. Left rear cover
1) Remove the rear cover.
2) Open the delivery cover unit.
3) Remove the 3 screws and then the left
rear cover.
➀Screws ➁Left rear cover
Figure 3-2-16
9. Left lower cover
1) Remove the upper and lower cassettes.
2) Remove the rear cover.
3) Remove the left rear cover.
4) Remove the delivery cover unit.
5) Remove the 2 screws.
➀Screws
Figure 3-2-17
3 - 6
CHAPTER 3
➂
➀➁
➁
➀
➀
➁
➀
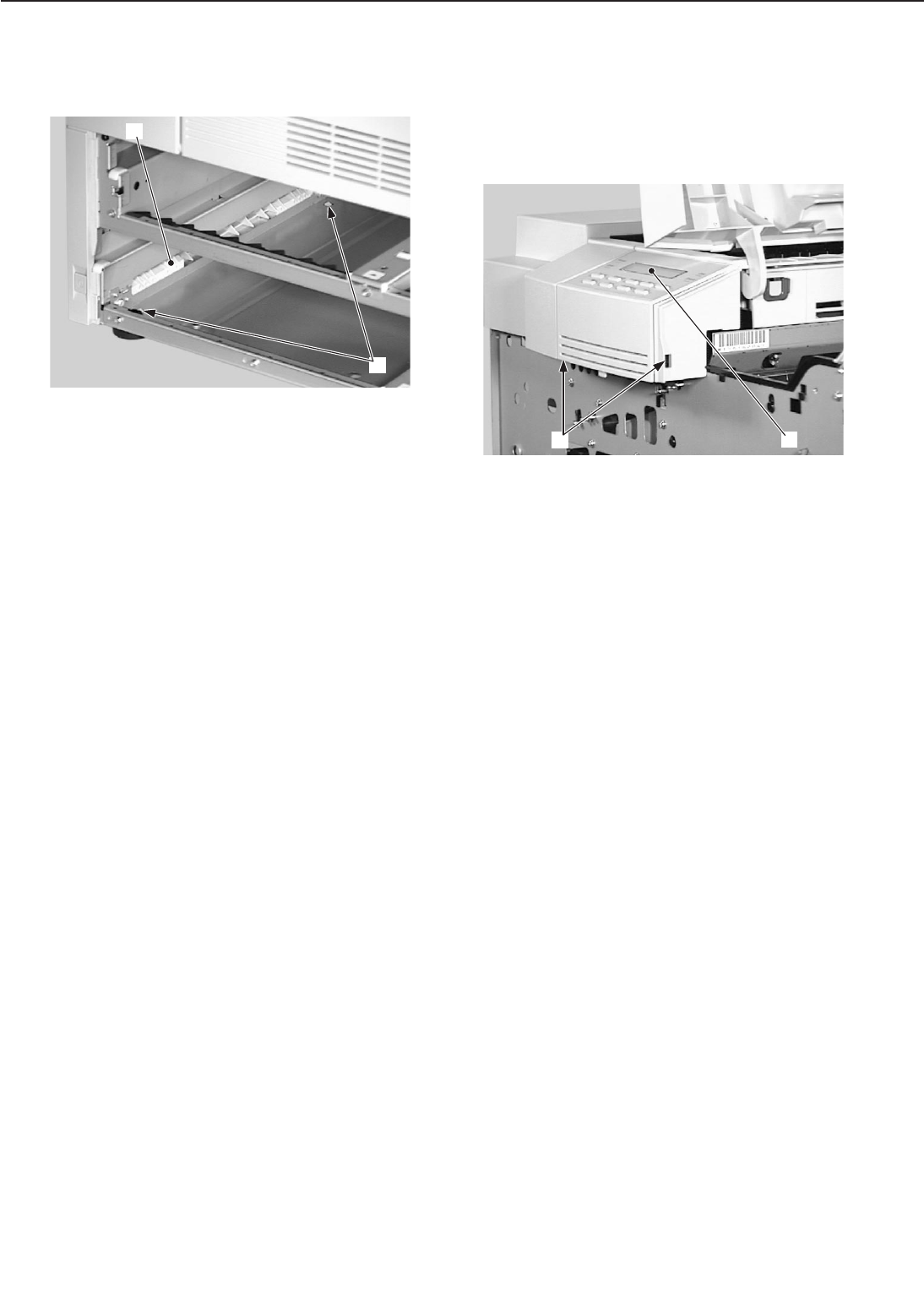
6) Unhook the 2 claws from the inside and
then remove the left lower cover.
➀Claws ➁Left lower cover
Figure 3-2-18
B. Control Panel Unit
1) Remove the front cover.
2) Unhook the 2 claws. Lifting the control
panel unit, disconnect the connector
from the inside.
➀Claws ➁Control panel unit
Figure 3-2-19
3 - 7
CHAPTER 3
➀
➁
➁
➀
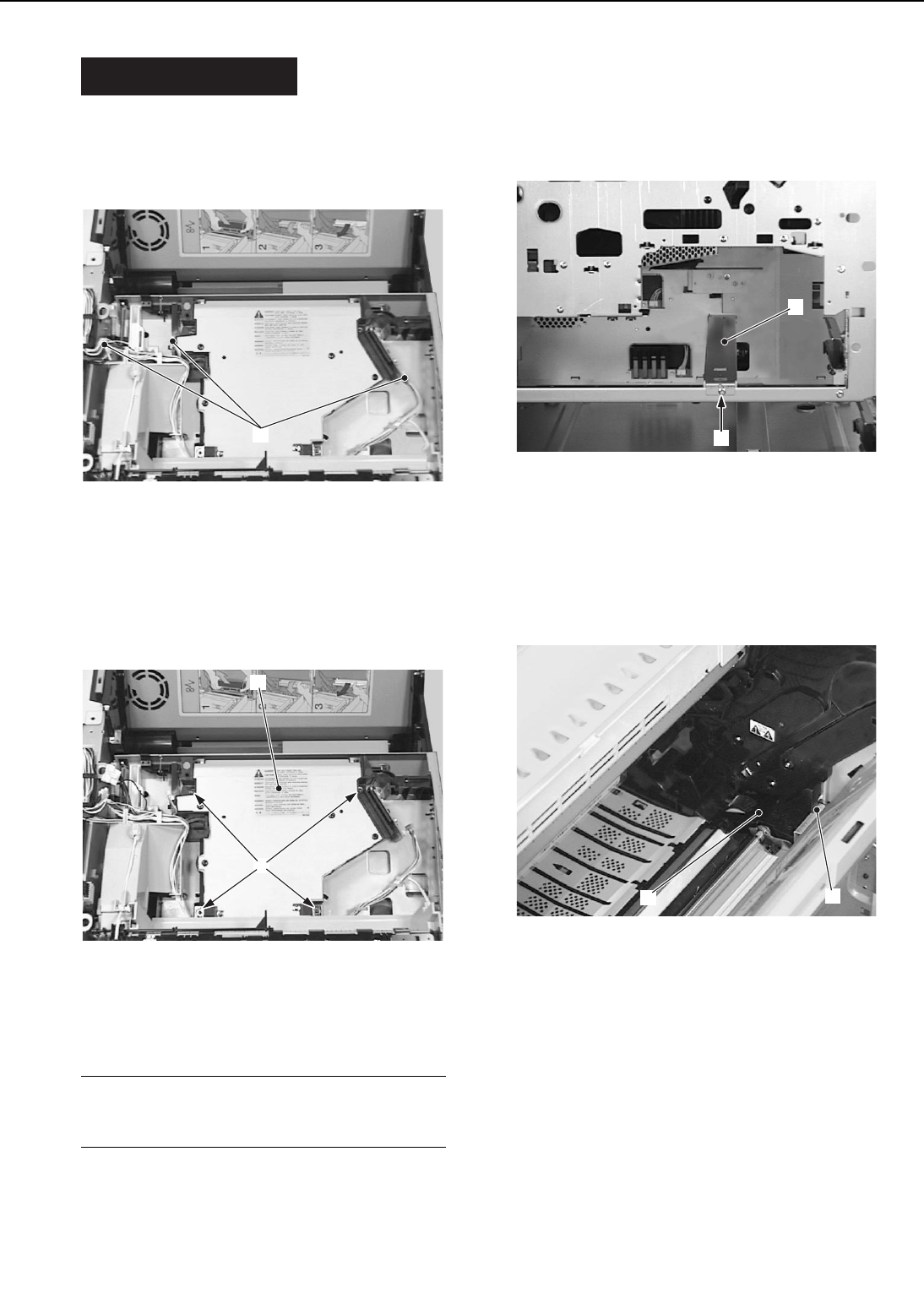
III. MAIN UNITS
A. Laser/Scanner Unit
1) Remove the upper cover unit.
2) Disconnect the 3 connectors from the
laser/scanner unit.
➀Connectors
Figure 3-3-1
3) Remove the 4 screws and the laser/
scanner unit.
➀Screws ➁Laser/scanner unit
Figure 3-3-2
Note: Do not disassemble the laser/scan-
ner unit as it cannot be adjusted in
the field
B. Drive Unit
1) Remove the pick-up unit following steps
1-7 on Page 3-9.
2) Remove the screw, and then the cas-
sette stay.
➀Screw ➁Cassette stay
Figure 3-3-3
3) Disconnect the claw, and then the
clutch cover.
➀Claw ➁Clutch cover
Figure 3-3-4
3 - 8
CHAPTER 3
➀
➁
➀
➀
➁
➀
➁
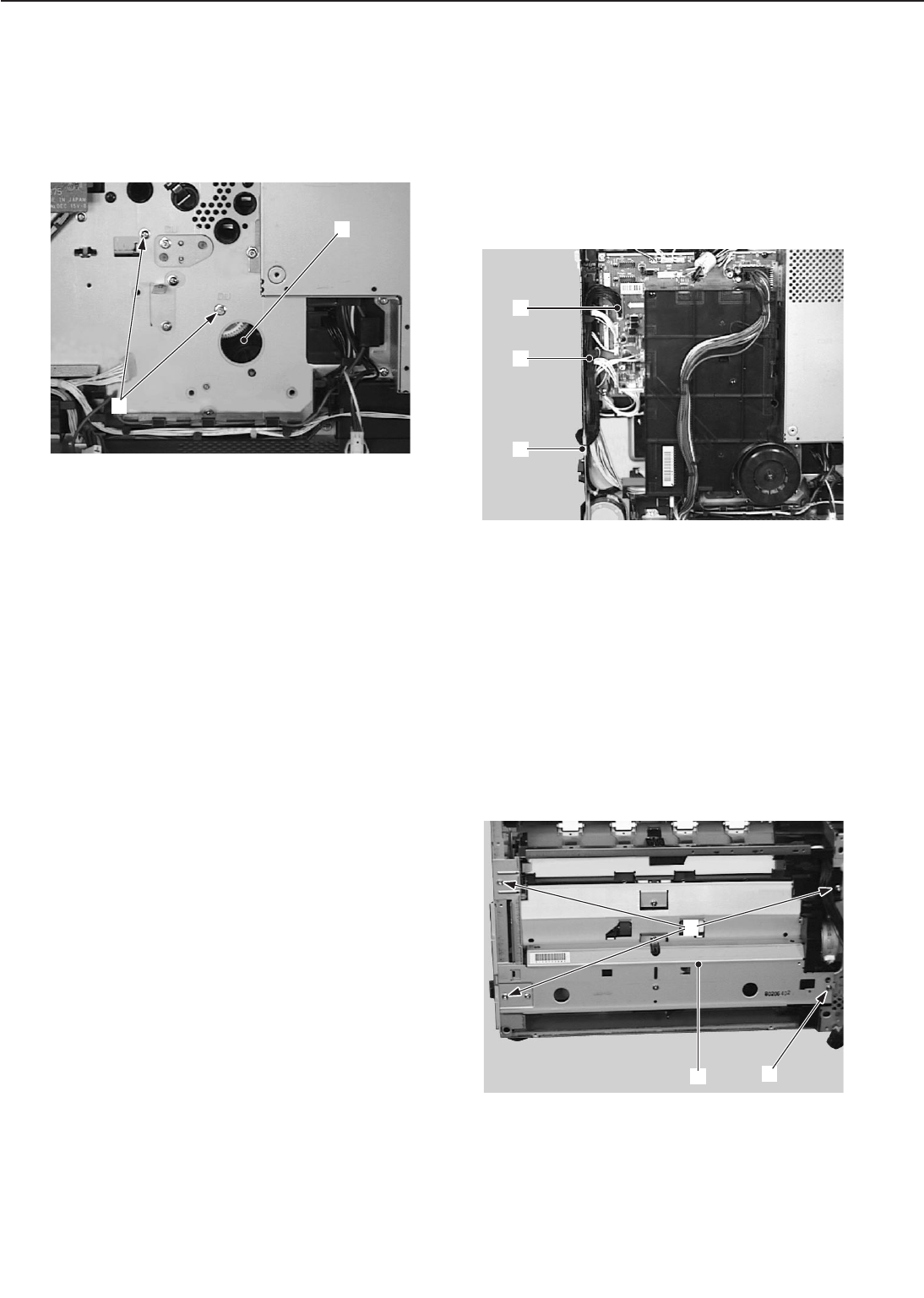
4) Remove the high-voltage power supply
unit following steps 1-3 on Page 3-47.
5) Undo the connector, remove the 4
screws and then the main motor.
6) Remove the 2 screws and the drive unit.
➀Screws ➁Drive unit
Figure 3-3-5
C. Pick-up Unit
1) Pull out the upper and lower cassettes.
2) Perform steps 1-6 on Page 3-12 to
remove the multi-purpose tray pick-up
unit.
3) Remove the right cover.
4) Undo the connector and remove the
cable from the cable guide.
➀Connector ➁Cable
➂Cable guide
Figure 3-3-6
5) Perform steps 1-2 on Page 3-17 to
remove the pick-up, feed and separation
rollers.
6) Remove the screw (M3x10).
7) Remove the 3 screws (M3x8), and take
out the pick-up unit.
➀Screw (M3×10) ➁Screw (M3×8)
➂Pick-up unit
Figure 3-3-7
3 - 9
CHAPTER 3
➀
➁
➂
➀
➁
➀
➁
➂
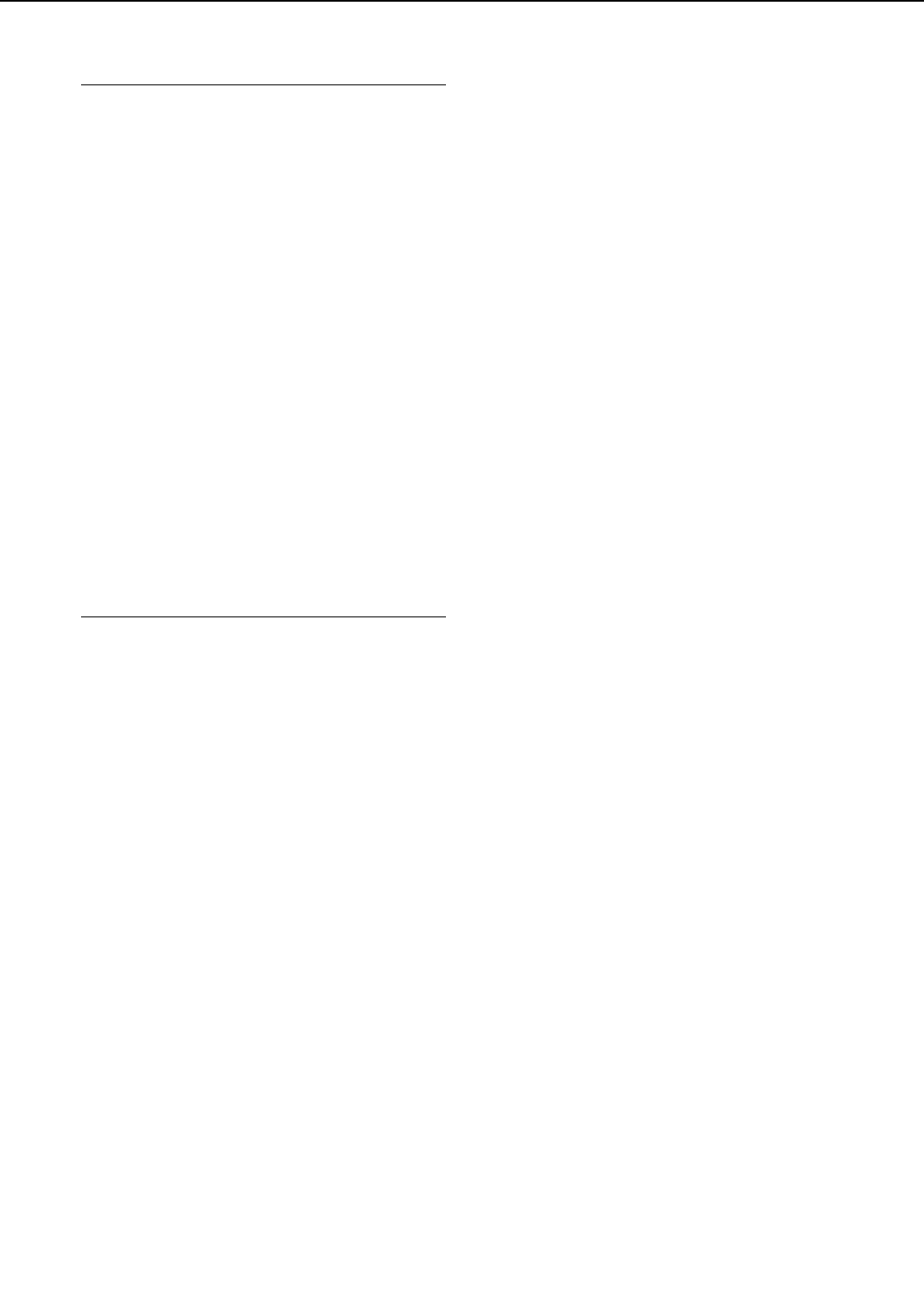
Notes: 1. While replacing parts in the
pick-up unit, to prevent grease
from getting on the pick-up, feed
and separation rollers, be sure
to remove them before working
on the unit. Take care not to get
grease on the paper feed guide.
2. Be sure to grease the parts
shown in figure 3-3-8 when
exchanging, to prevent noise.
The type of grease (do not use
grease other than the specified
type) and the method of applica-
tion is explained below:
Apply about one drop (1mm
diameter) of HY9-0007 to the
contact surface (a) of the roller
holder (1) and shaft (2).
Apply a few drops (total:5mm
diameter) of CK-8009 to 3 or
more continuous cogs of the
parts 3 to 9.
Apply CK-8009 to the whole cog
surface of the lifter (10) thinly.
3 - 10
CHAPTER 3
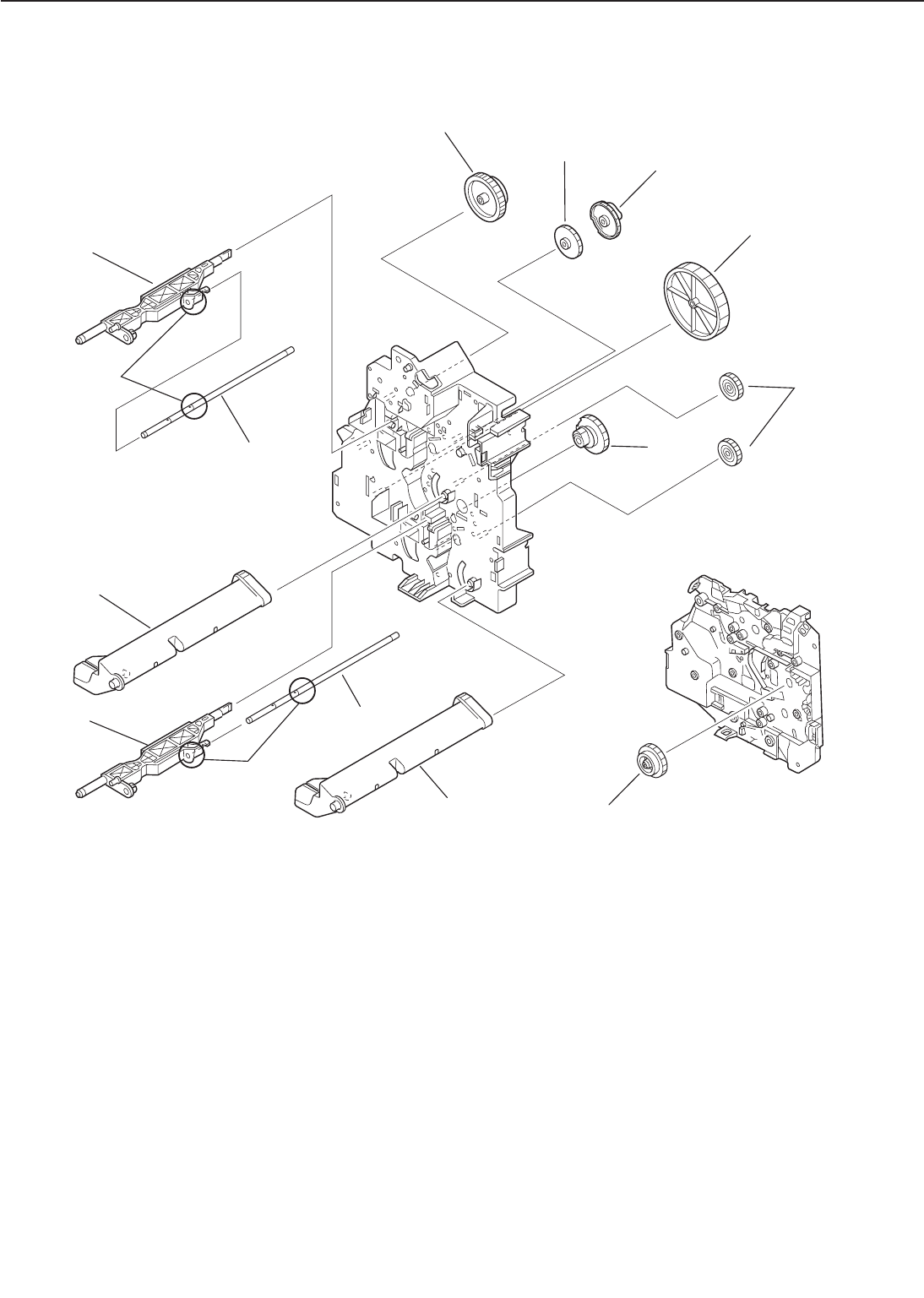
➀Roller holder ➁Shaft
➂57T gear ➃Upper lift-up cam
➄Pick-up cam ➅100T gear
➆20T/41T gear ➇Lower lift-up cam
➈31T/47T gear ➉Lifter
Figure 3-3-8
3 - 11
CHAPTER 3
➉
➀
➁
➂
➃➄
➅
➆
➇
➈
➀➁
➉
a
a
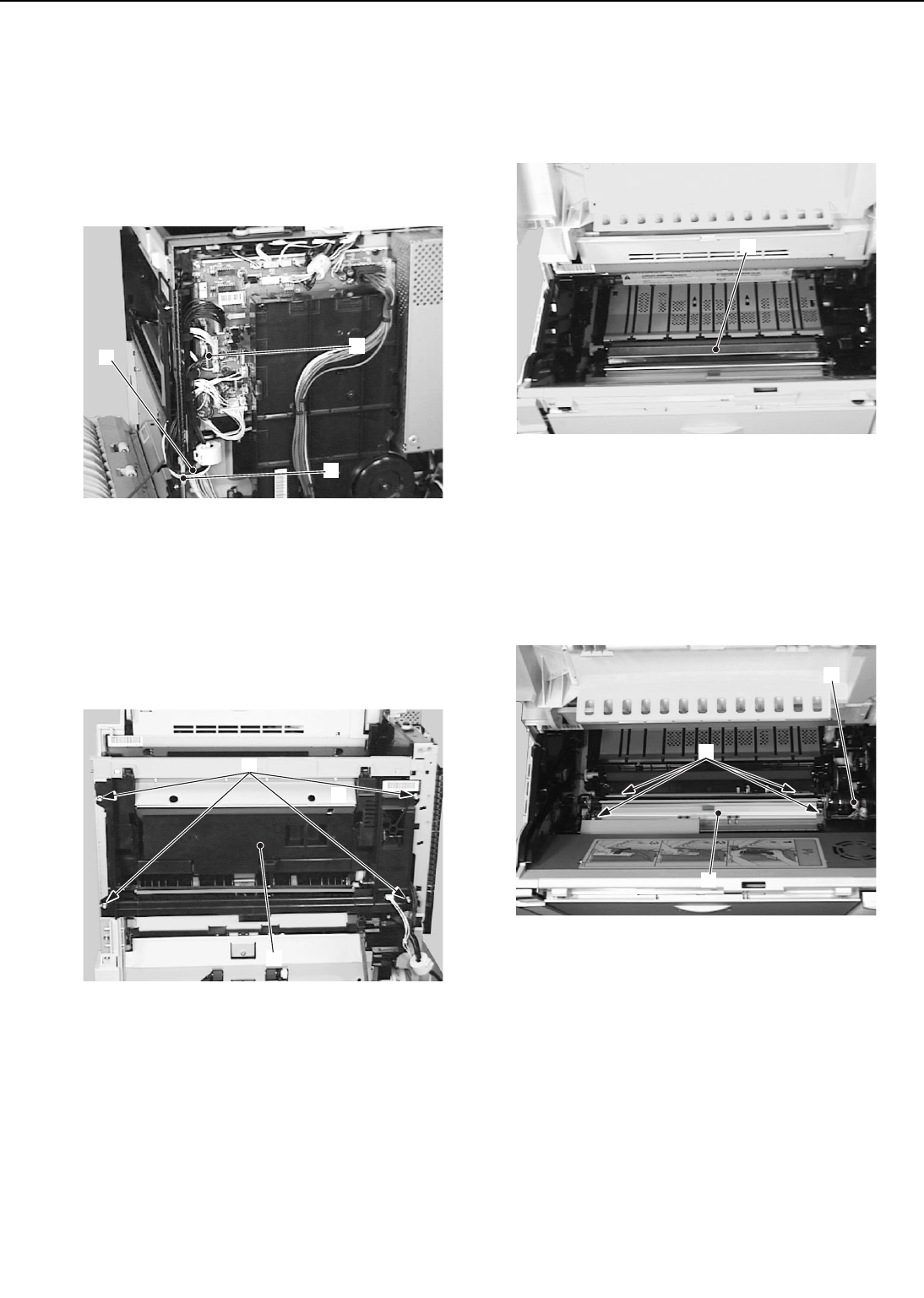
D. Multi-purpose Tray Pick-up Unit
1) Remove the front cover.
2) Remove the rear cover.
3) Remove the multi-purpose tray.
4) Open the pick-up unit door.
5) Disconnect the 2 connectors, and then
remove the cable from the cable guide.
➀Connectors ➁Cable guide
➂Cable
Figure 3-3-9
6) Remove the 4 screws, and then the
multi-purpose tray pick-up unit.
➀Screws
➁Multi-purpose tray pick-up unit
Figure 3-3-10
E. Registration Roller Unit
1) Open the upper cover.
2) Remove the clutch cover.
3) Open the transfer charging roller guide.
➀Transfer charging roller guide
Figure 3-3-11
4) Undo the connector.
5) Remove the 4 screws and take out the
registration roller unit.
➀Connector
➁Screws
➂Registration roller unit
Figure 3-3-12
3 - 12
CHAPTER 3
➁
➂➀
➀
➁
➀
➂
➀
➁
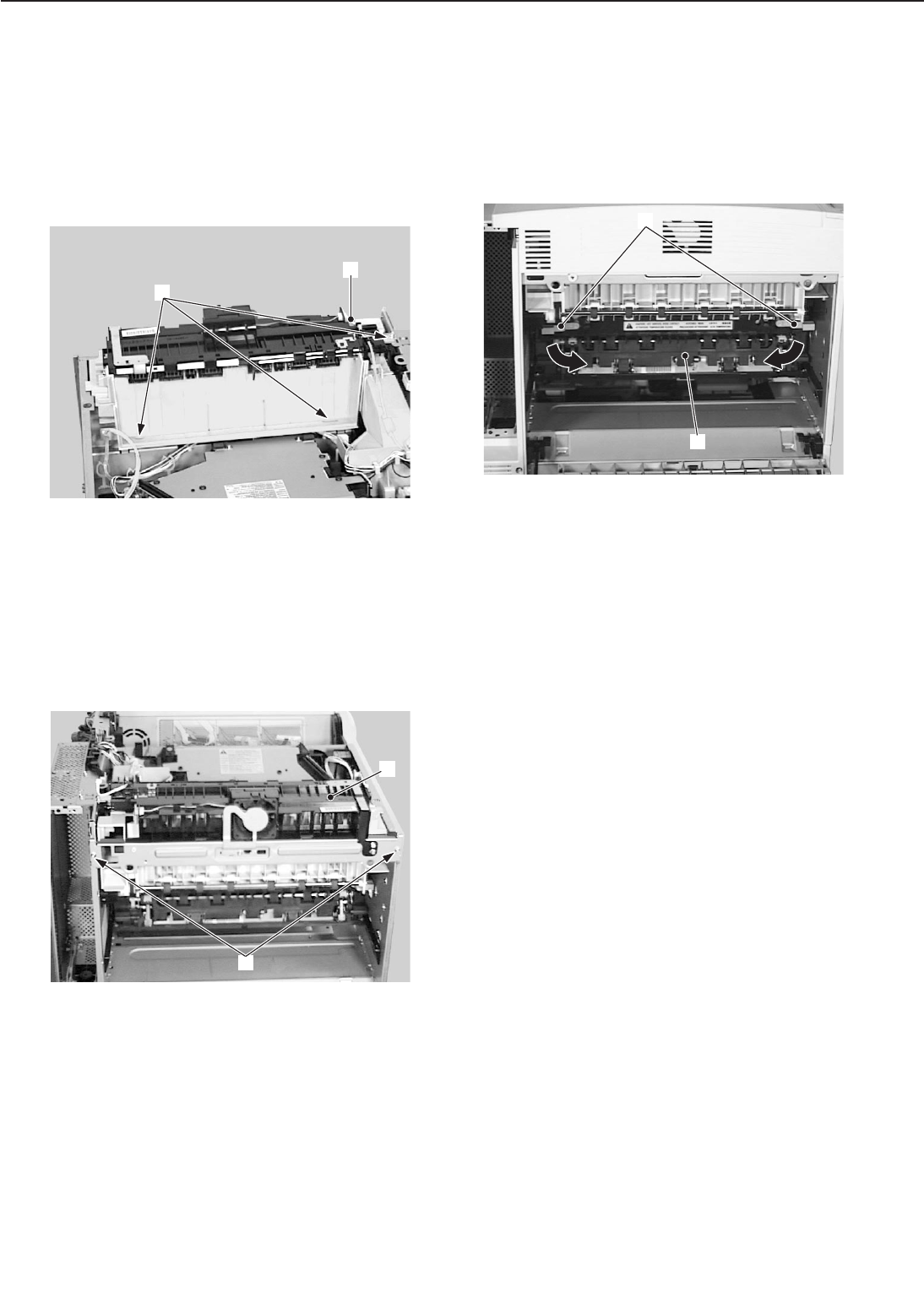
F. Delivery Unit
1) Remove the upper cover unit.
2) Remove the front cover.
3) Remove the right rear and rear covers.
4) Remove the left rear cover.
5) Disconnect the connector and remove
the 3 screws.
➀Connector ➁Screws
Figure 3-3-13
6) Remove the 2 screws.
7) Slightly lift the delivery unit up then
pull it out toward you.
➀Screws ➁Delivery unit
Figure 3-3-14
G. Fixing Unit
1) Open the delivery cover unit.
2) Move the 2 fastening levers of the fixing
unit in the direction of the arrow, slight-
ly lift the fixing unit, and pull it out
toward you.
➀Fixing unit fastening levers
➁Fixing unit
Figure 3-3-15
3 - 13
CHAPTER 3
➁
➀
➀
➁
➀
➁
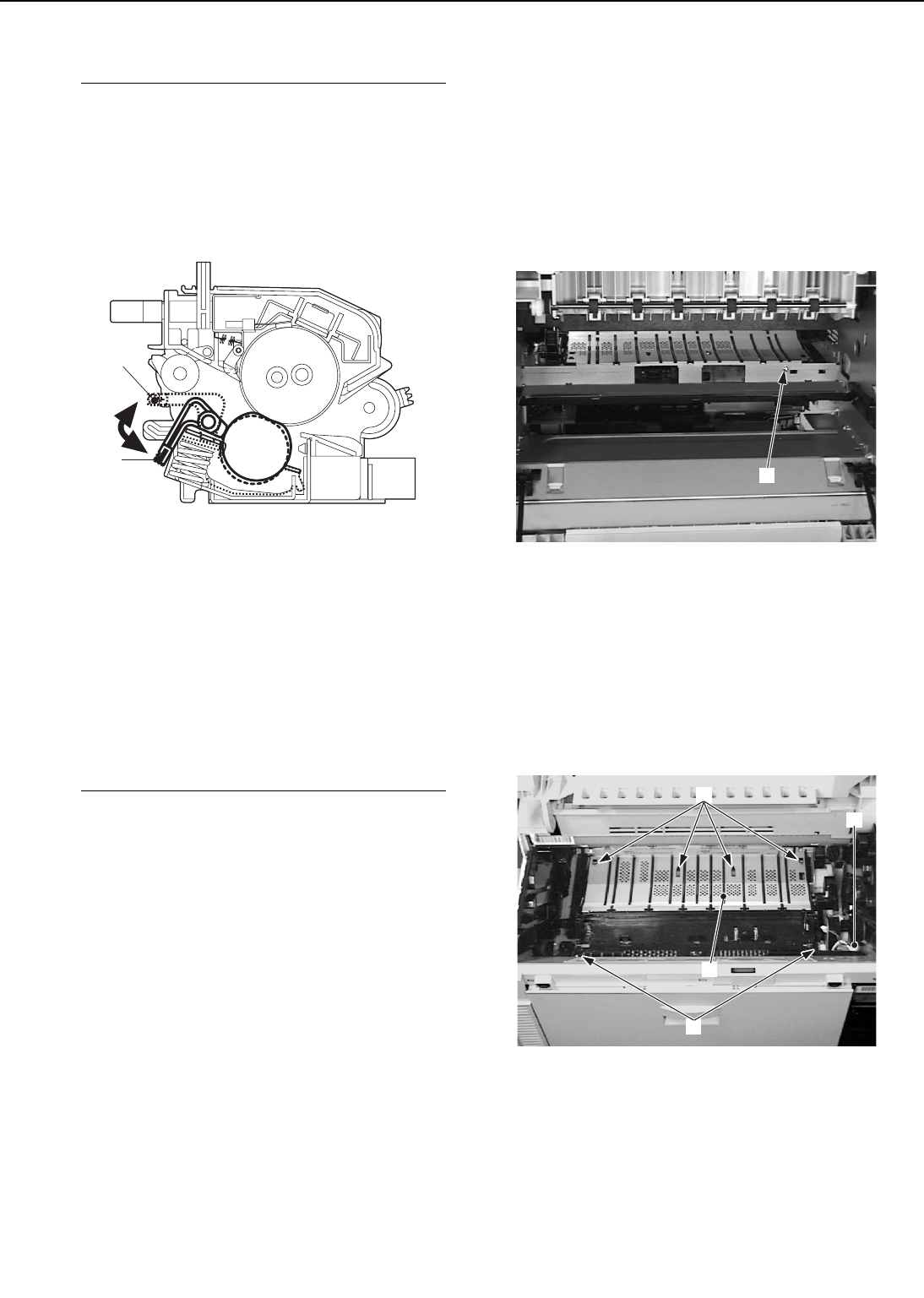
Notes: 1. When replacing the fixing unit,
be sure to confirm the location
of the fixing unit envelope lever
before replacement and then
position it the same way after
installing the new fixing unit.
➀Normal mode ➁Envelope mode
Figure 3-3-16
2. Make sure to turn the power
OFF and unplug the power cord
before replacing the fixing unit.
After power-OFF, wait for a
while to allow the fixing unit to
cool down.
H. Feed Unit
1) Remove the registration roller unit fol-
lowing steps 1-5 on Page 3-12.
2) Remove the transfer charging roller.
3) Remove the fixing unit following steps
1-2 on Page 3-13.
4) Remove the high-voltage power supply
unit following steps 1-2 on Page 3-47.
5) Remove the screw.
➀Screw
Figure 3-3-17
6) Disconnect the connector.
7) Remove the 2 screws.
8) Remove the 4 claws and then the feed
unit.
➀Connector ➁Screws
➂Claws ➃Feed unit
Figure 3-3-18
3 - 14
CHAPTER 3
➀
➁
➀
➁
➀
➃
➂
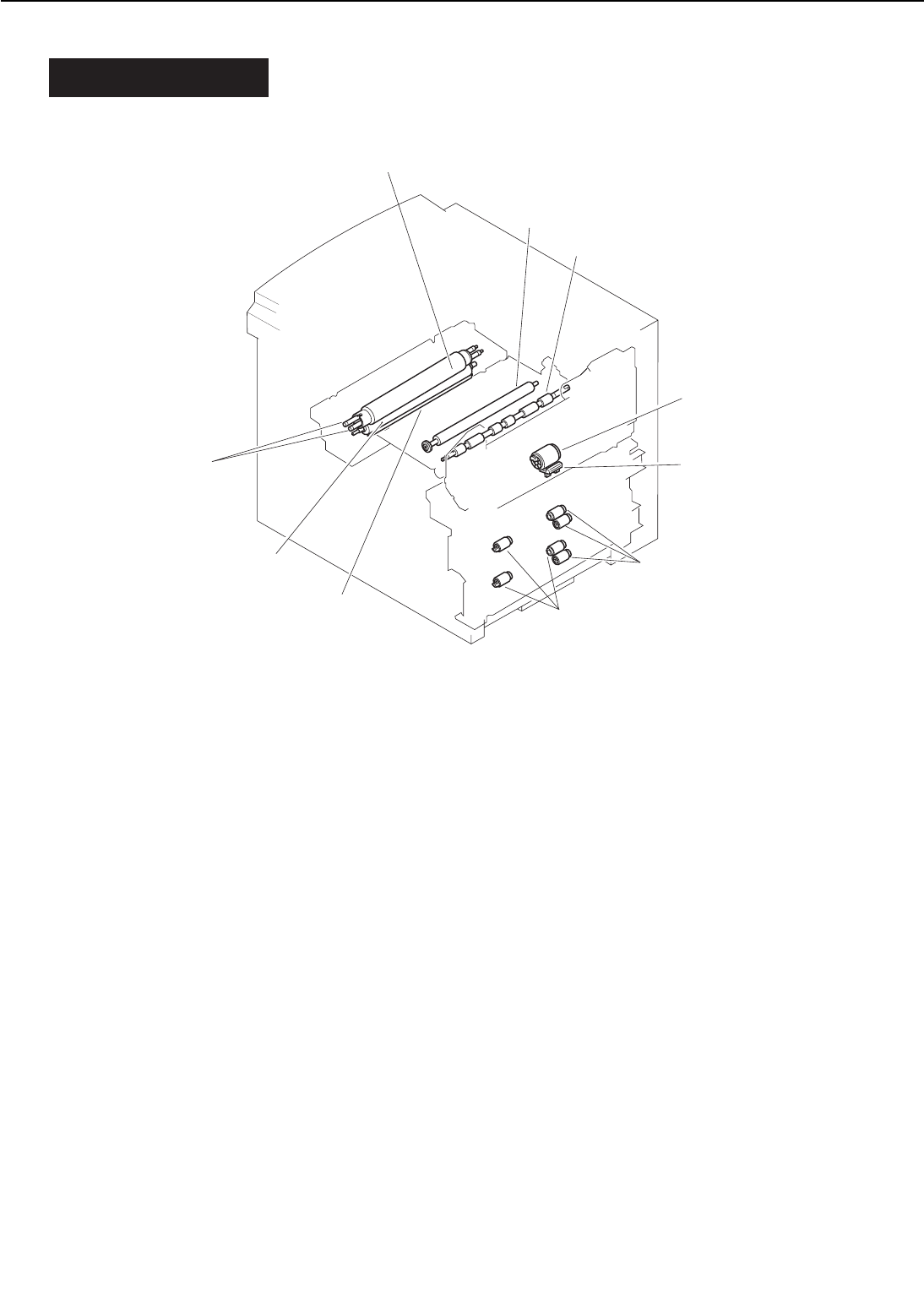
IV. MAIN PARTS
A. Locations
➀Multi-purpose tray pick-up roller ➁Separation pad
➂Pick-up/Feed/Separation rollers ➃Registration lower roller
➄Transfer charging roller ➅Fixing roller heater
➆Fixing upper roller ➇Fixing lower roller
➈Cleaning roller
Figure 3-4-1
3 - 15
CHAPTER 3
➀
➁
➂
➃
➄
➅
➆
➇
➈➂
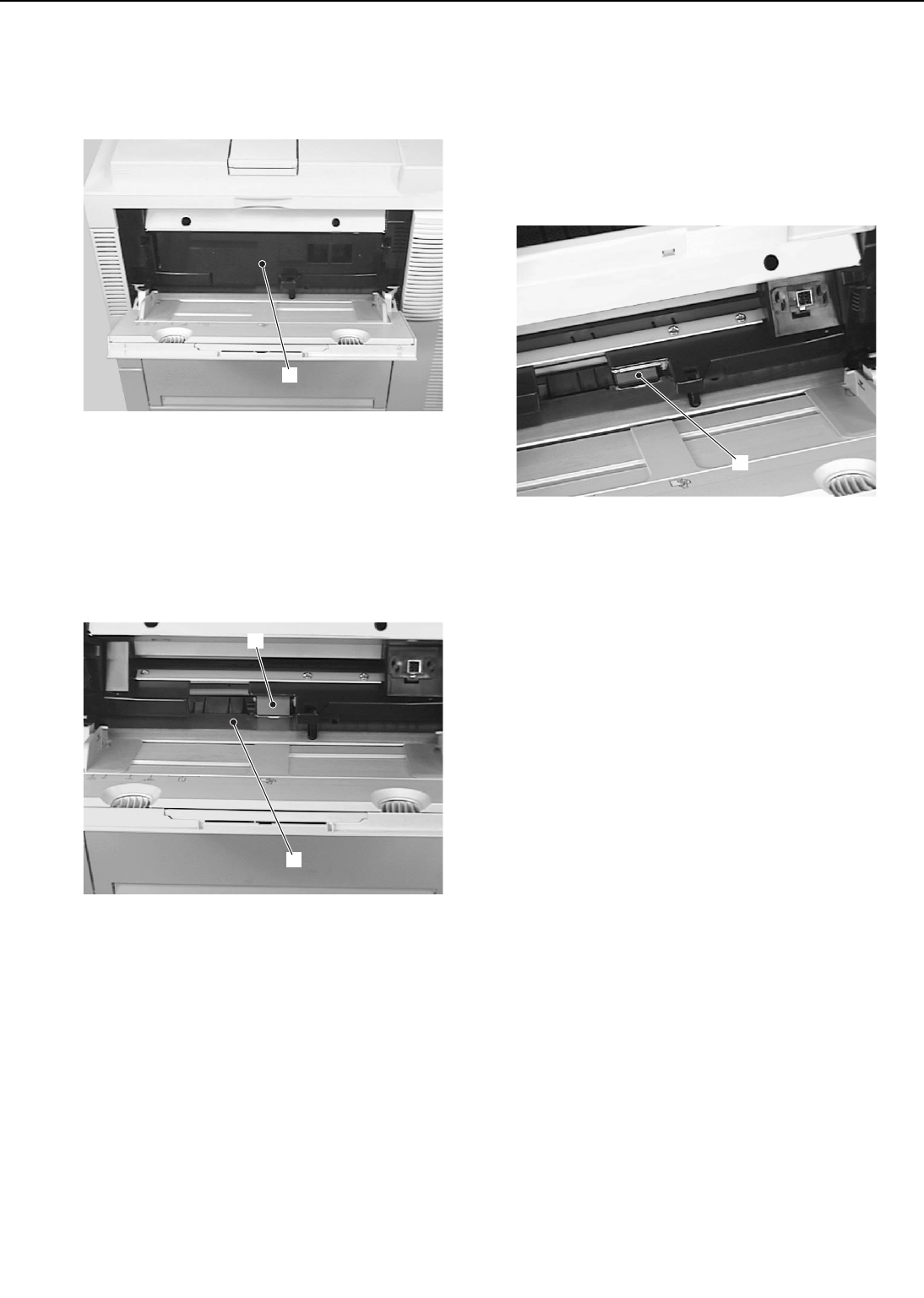
B. Multi-purpose Tray Pick-up Roller
1) Open the multi-purpose tray.
2) Remove the cover.
➀Cover
Figure 3-4-2
3) While pressing the lifting plate, grasp
the multi-purpose tray pick-up roller
knob, and pull out the roller.
➀Lifting plate
➁Multi-purpose tray pick-up roller
Figure 3-4-3
C. Separation Pad
1) Open the multi-purpose tray.
2) Remove the cover.
3) Remove the multi-purpose tray pick-up
roller.
4) Use a flat-bladed screwdriver to remove
the separation pad.
➀Separation pad
Figure 3-4-4
3 - 16
CHAPTER 3
➀
➀
➁
➀
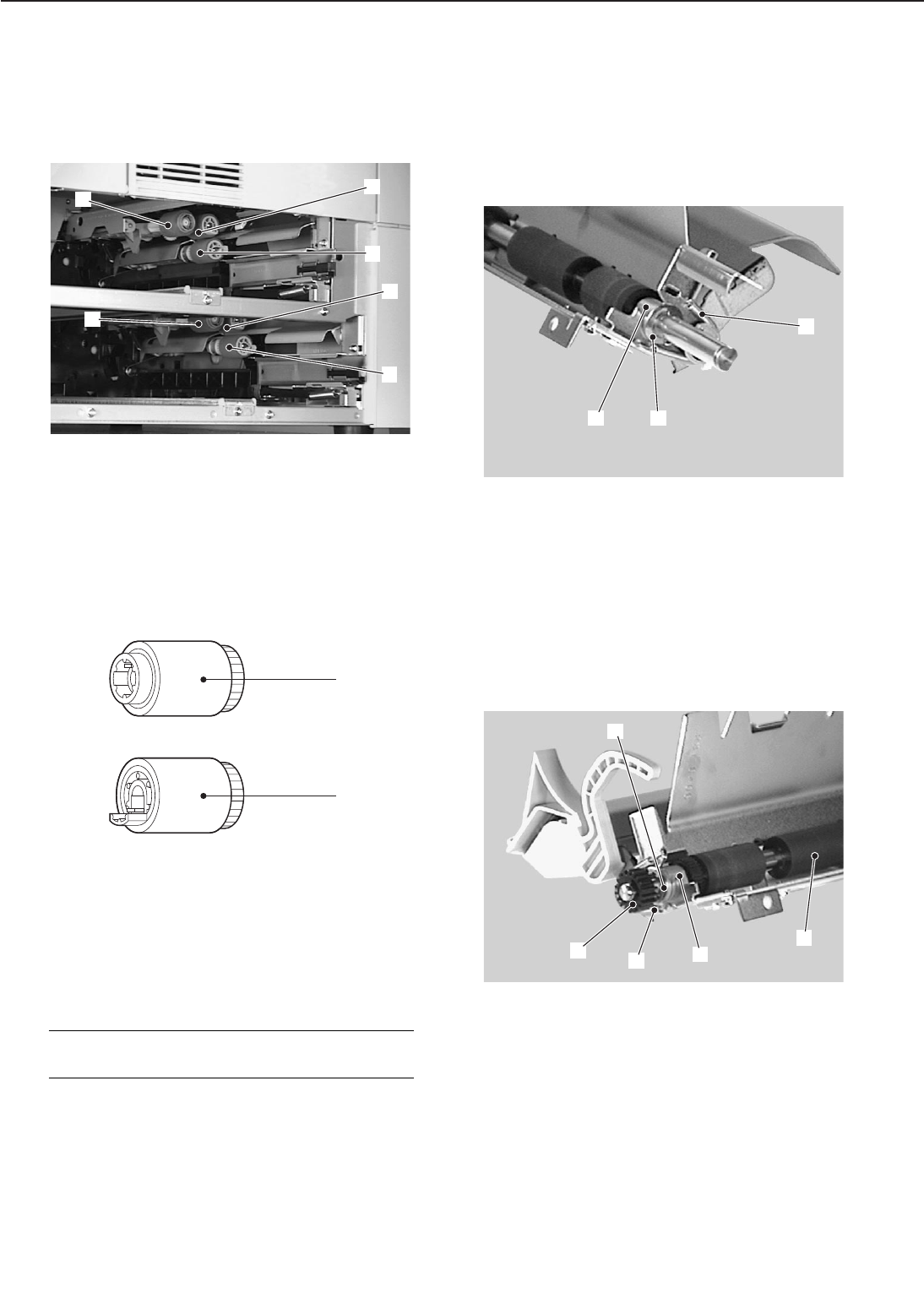
D. Pick-up/Feed/Separation Rollers
1) Pull out the upper and lower cassettes.
2) Grasp the knobs of each roller and pull
the rollers out of the printer.
➀Pick-up roller ➁Feed roller
➂Separation roller
Figure 3-4-5
➀Pick-up roller
➁Feed roller/Separation roller
Figure 3-4-6
Note: Be sure to replace the feed roller
and the separation roller together.
E. Registration Lower Roller
1) Remove the registration roller unit fol-
lowing steps 1-5 on Page 3-12.
2) Remove the registration clutch.
3) Remove the spring, the E-ring and the
bushing.
➀Spring ➁E-ring
➂Bushing
Figure 3-4-7
4) Remove the gear, the spring, the E-ring,
the bushing, and then the registration
lower roller.
➀Gear
➁Spring
➂E-ring
➃Bushing
➄Registration lower roller
Figure 3-4-8
3 - 17
CHAPTER 3
➀
➁
➂
➁
➂
➀
➀
➁
➀
➁➂
➀
➂
➄
➁➃
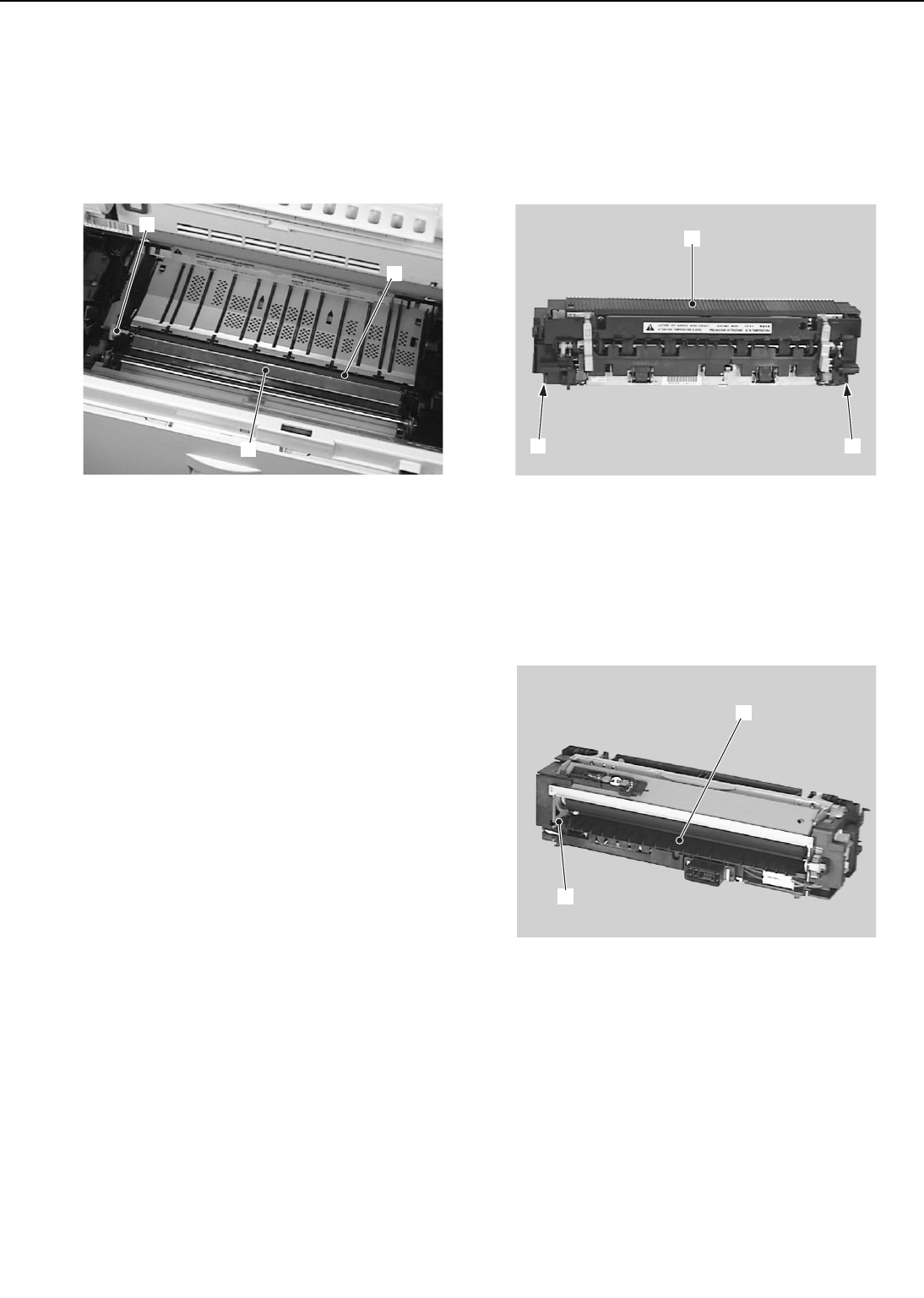
F. Transfer Charging Roller
1) Open the upper cover.
2) Open the transfer charging roller guide.
3) Pinch the gear, lift it slightly, and slide
it to the left. Remove the transfer
charging roller.
➀Transfer charging roller guide
➁Gear
➂Transfer charging roller
Figure 3-4-9
< Notes for reassembly >
Hold the shaft and bushing, not the sponge
area, of the transfer charging roller when
installing the roller.
G. Fixing Roller Heater
1) Remove the fixing unit following steps
1-2 on Page 3-13.
2) Disconnect the 2 claws that hold the
wire cover to the fixing unit, and then
remove the wire cover.
➀Claws ➁Wire cover
Figure 3-4-10
3) Unhook the claw, and then remove the
fixing entry guide.
➀Claw ➁Fixing entry guide
Figure 3-4-11
3 - 18
CHAPTER 3
➁
➀
➀
➁
➀
➁
➂
➀
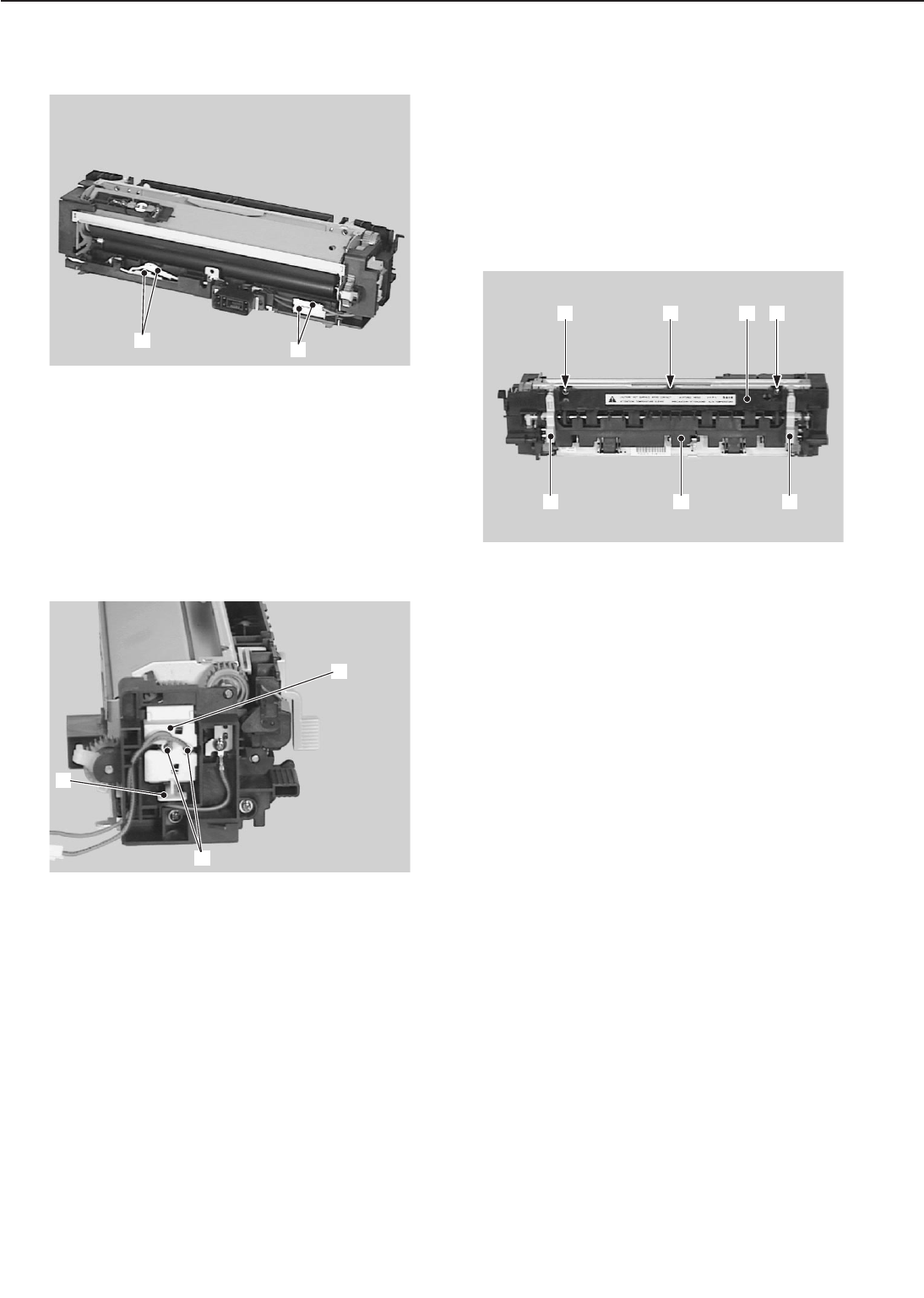
4) Take out the 4 connectors.
➀Connectors
Figure 3-4-12
5) Disconnect the heater claw of the hold-
er and remove the holder. Then, gently
pull out the fixing heater from the fixing
upper roller.
➀Claw
➁Heater holder
➂Fixing roller heater
Figure 3-4-13
H. Fixing Upper Roller
1) Remove the fixing unit following steps
1-2 on Page 3-13.
2) Hold up the left and right levers in the
direction of the arrow.
3) Remove the 2 screws.
4) Remove the claw then remove the sepa-
ration upper guide while pulling out the
separation lower guide.
➀Fixing unit fastening levers
➁Screws
➂Claw
➃Separation lower guide
➄Separation upper guide
Figure 3-4-14
3 - 19
CHAPTER 3
➃
➄➁➂
➀➀
➁
➀➀
➀
➁
➂
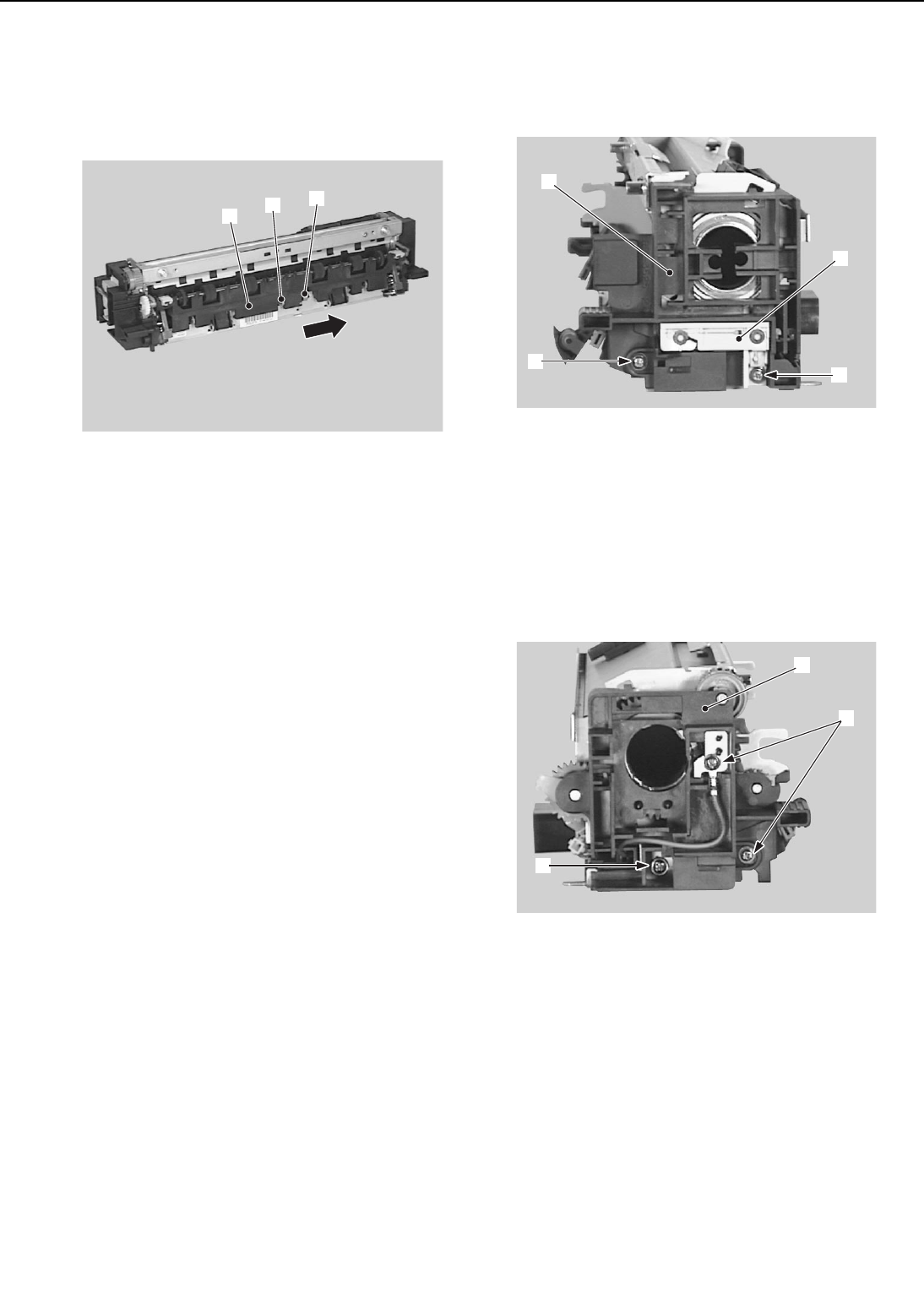
5) Remove the E-ring and the spring, then
pull out the separation lower guide
toward you and slide it off in the direc-
tion of the arrow.
➀E-ring
➁Spring
➂Separation lower guide
Figure 3-4-15
6) Remove the fixing roller heater following
steps 2-5 on Page 3-18.
7) Remove the thermoswitch following step
3 on Page 3-25.
8) Remove the thermistor following steps
3-4 on Page 3-26.
9) Remove the screw and diode holder.
10) Remove the screw and the right fixing
cover.
➀Screw ➁Diode holder
➂Screw ➃Right fixing rcover
Figure 3-4-16
11) Remove the 2 screws (M3), stepped
screw, and then the left fixing cover.
12) Remove the 4 gears.
➀Screws (M3) ➁Stepped screw
➂Left fixing cover
Figure 3-4-17
3 - 20
CHAPTER 3
➀➁
➂
➃
➂➀
➁
➁
➀
➂
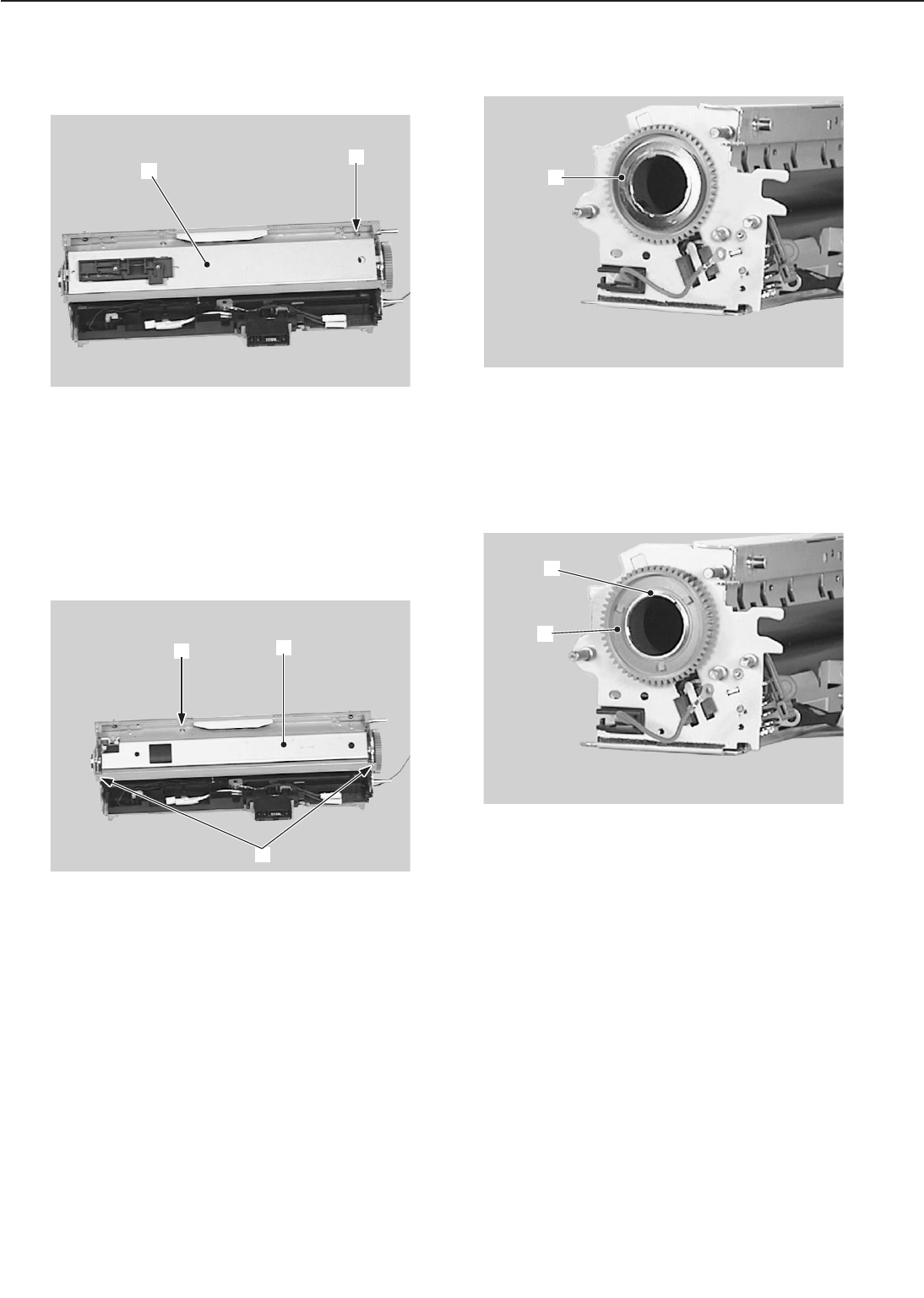
13) Remove the screw, and the ther-
moswitch stay.
➀Screw
➁Thermoswitch stay
Figure 3-4-18
14) Remove the screw, undo the 2 claws,
and take off the fixing roller cover.
➀Screw
➁Claw
➂Fixing roller cover
Figure 3-4-19
15) Remove the grounding ring.
➀Grounding ring
Figure 3-4-20
16) Remove the C-ring and the gear.
➀C-ring ➁Gear
Figure 3-4-21
3 - 21
CHAPTER 3
➀➂
➁
➀
➁
➀
➀
➁
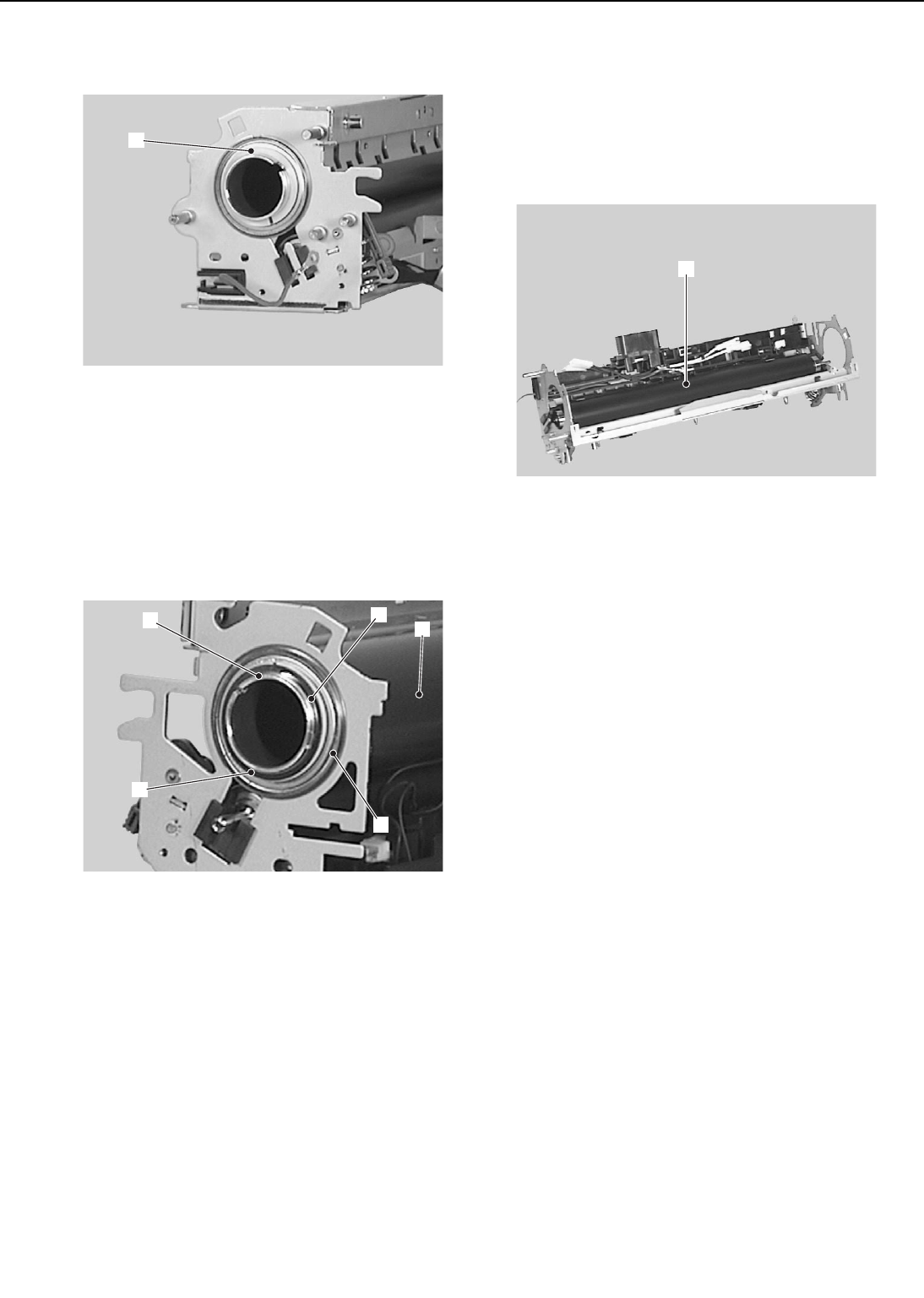
17) Removing the insulating bushing.
➀Insulating bushing
Figure 3-4-22
18) Remove the C-ring, O-ring and insulat-
ing bushing.
19) Remove the bearing and the fixing
upper roller.
➀C-ring
➁O-ring
➂Insulating bushing
➃Bearing
➄Fixing upper roller
Figure 3-4-23
I. Fixing Lower Roller
1) Remove the fixing unit following steps
1-2 on Page 3-13.
2) Remove the fixing upper roller following
steps 2-19 from Page 3-19.
3) Remove the fixing lower roller.
➀Fixing lower roller
Figure 3-4-24
3 - 22
CHAPTER 3
➀
➀
➃
➄
➀
➁
➂
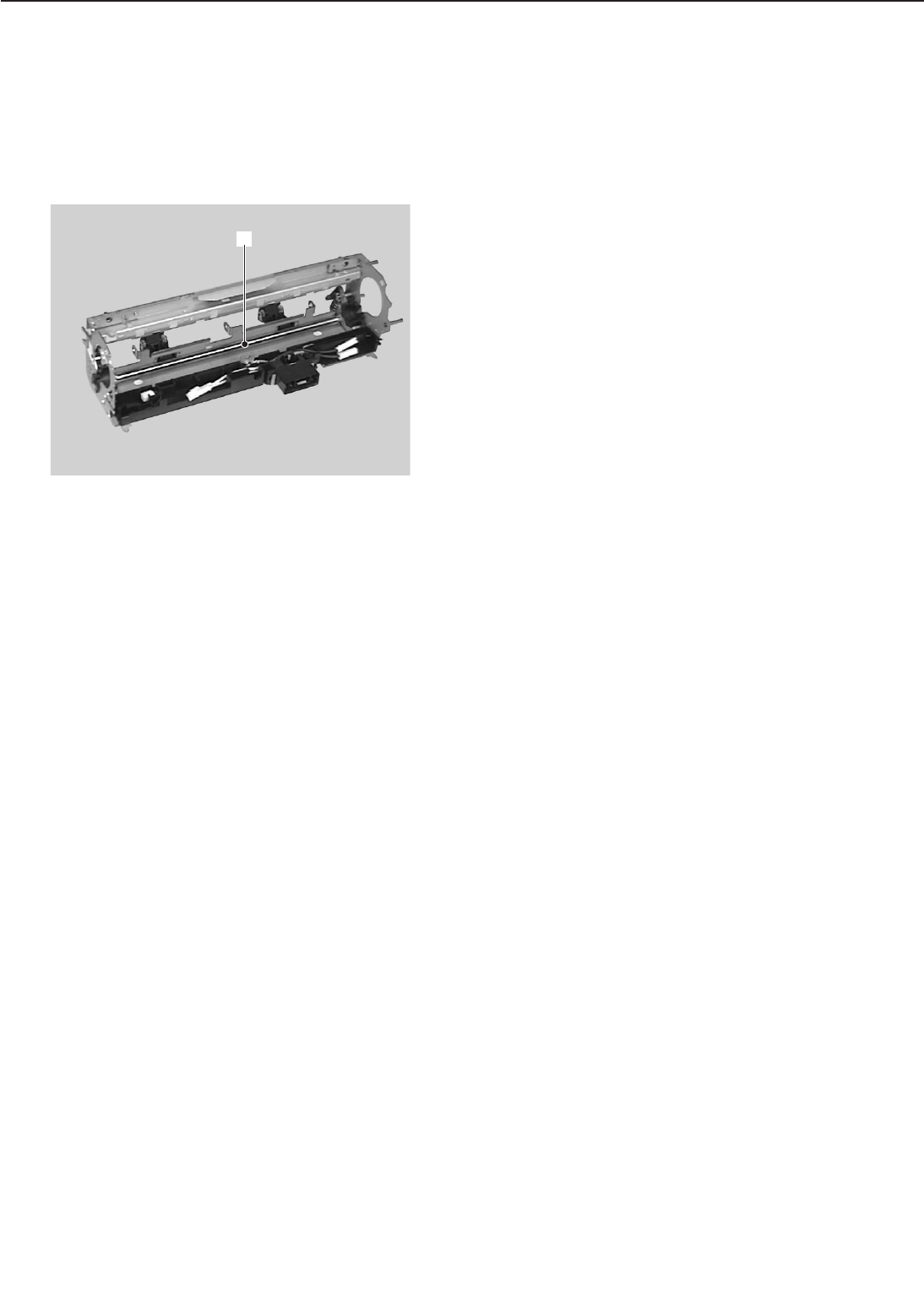
J. Cleaning Roller
1) Remove the fixing unit following steps
1-2 on Page 3-13.
2) Remove the fixing lower roller following
steps 2-3 on Page 3-22.
3) Remove the cleaning roller.
➀Cleaning roller
Figure 3-4-25
3 - 23
CHAPTER 3
➀
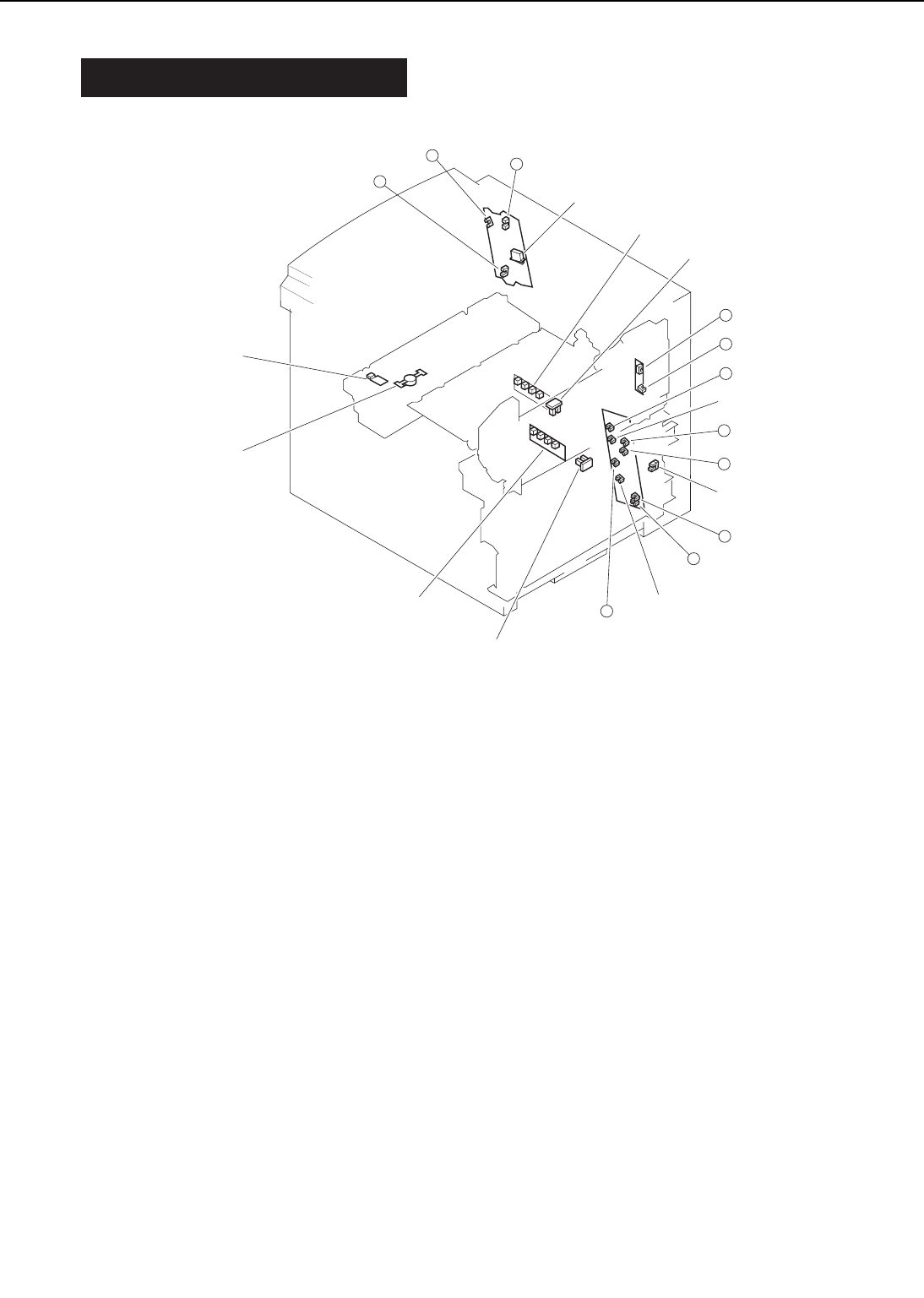
V. SWITCHES/SENSORS
A. Locations
1: Thermoswitch 2: Door switch
3: Upper cassette paper-size sensing switch 4: Lower cassette paper-size sensing switch
5: Thermistor 6: Registration paper sensor
7: Pick-up unit paper sensor 8: Pick-up unit door sensor
9: Lower cassette sensor 10: Upper cassette sensor
11: Lower cassette paper-level sensor 1 12: Lower cassette paper-level sensor 2
13: Upper cassette paper-level sensor 1 14: Upper cassette paper-level sensor 2
15: Lower cassette paper-out sensor 16: Upper cassette paper-out sensor
17: Multi-purpose tray paper sensor 18: Lifting plate position sensor
19: Face-down tray paper full sensor 20: Face-down tray delivery sensor
21: Fixing unit delivery sensor
Figure 3-5-1
3 - 24
CHAPTER 3
19
21
20
15
11
12
13
14
18
16
17
➉
➀
➁
➂
➃
➄
➅
➆
➇
➈
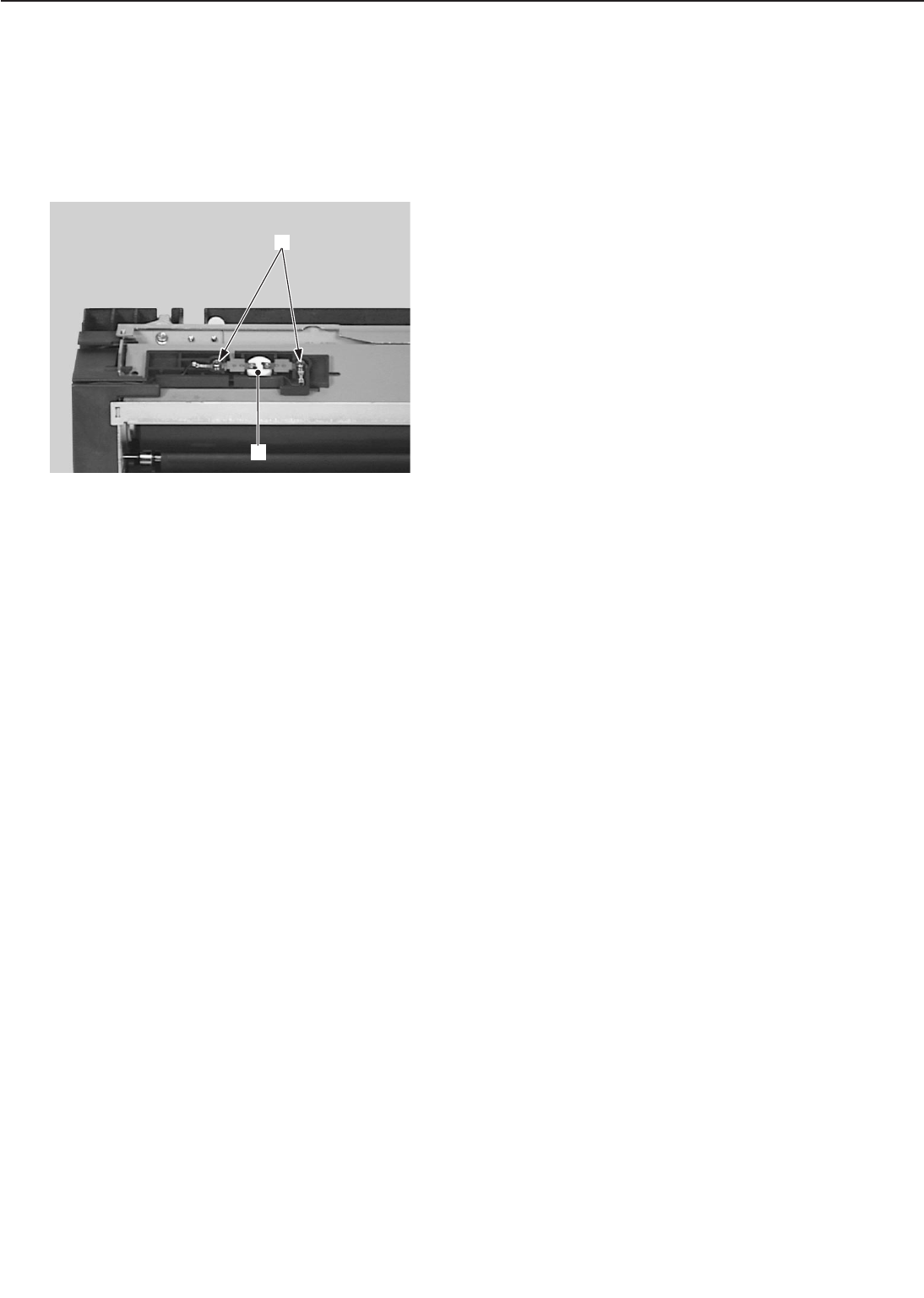
B. Thermoswitch
1) Remove the fixing unit following steps
1-2 on Page 3-13.
2) Remove the wire cover.
3) Remove the 2 screws and then the lead
wire and the thermoswitch.
➀Screws ➁Thermoswitch
Figure 3-5-2
C. Door Switch
1) Remove the switch/sensor PCB follow-
ing steps 1-10 on Page 3-45.
3 - 25
CHAPTER 3
➀
➁
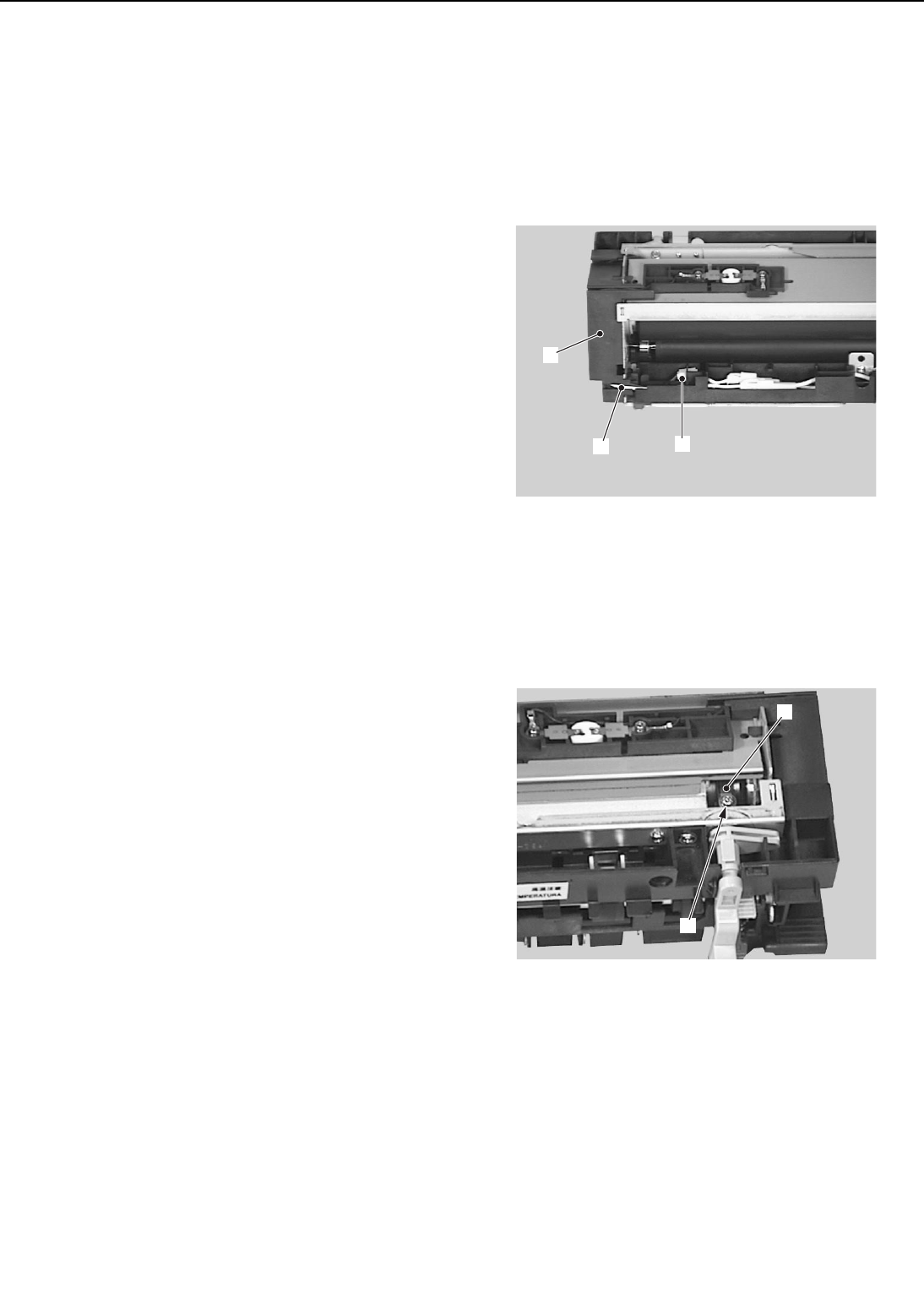
D. Upper Cassette Paper-size Sensing
Switch/Lower Cassette Paper-size
Sensing Switch
1) Remove the cassette paper-size sensing
PCB following steps 1-4 on Page 3-47.
E. Thermistor
1) Remove the fixing unit following steps
1-2 on Page 3-13.
2) Remove the wire cover.
3) Remove the fixing entry guide.
4) Disconnect the connector and remove
the cable from the fixing left cover.
➀Connector ➁Fixing left cover
➂Cable
Figure 3-5-3
5) Remove the screw and the thermistor.
➀Screw ➁Thermistor
Figure 3-5-4
<Note on reassembly>
When installing the thermistor, ensure that
its detection surface is uniformly contact-
ing the fixing upper roller surface.
If it is not making an uniform contact,
3 - 26
CHAPTER 3
➀
➂
➁
➀
➁
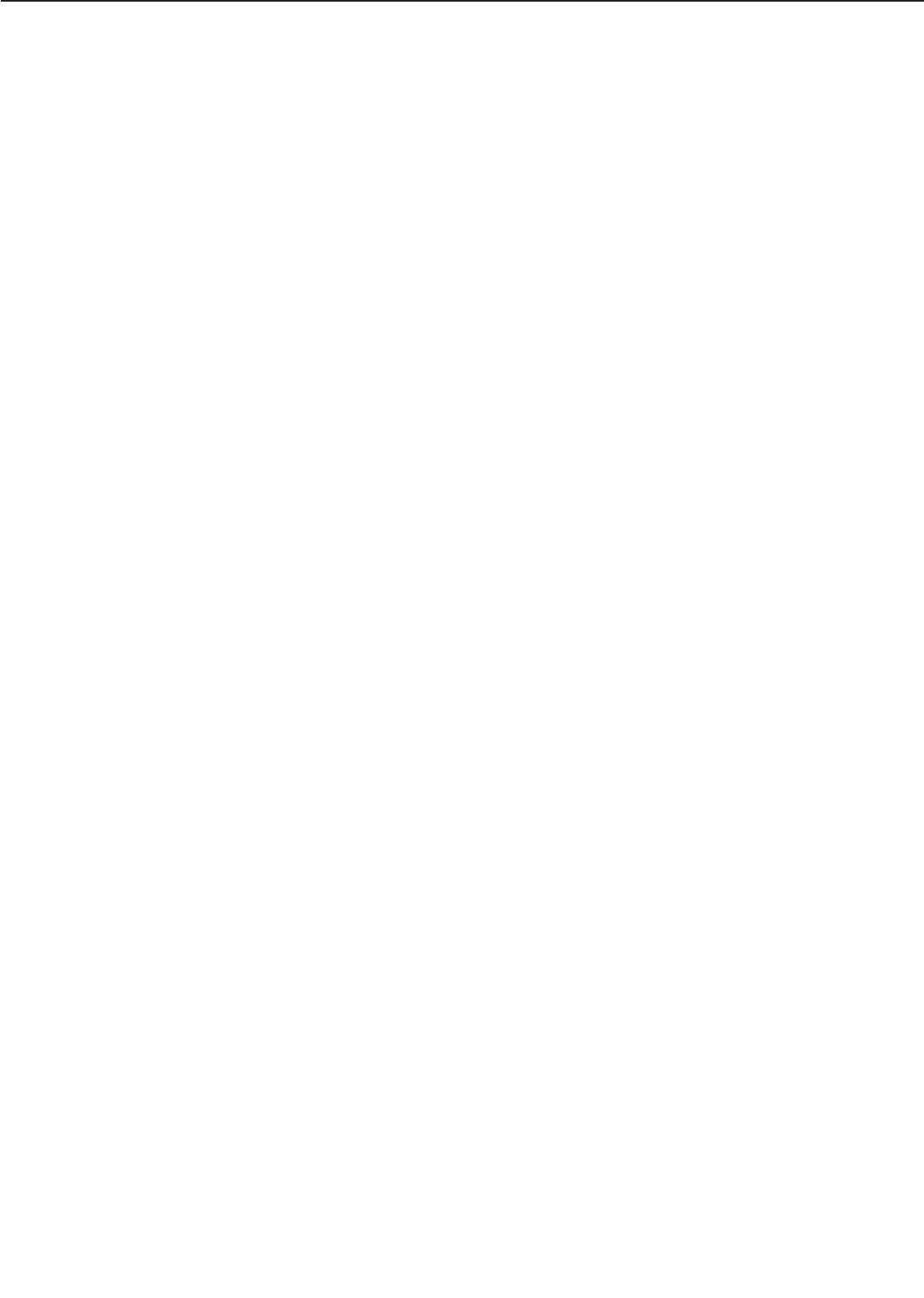
check that the plate spring has not
deformed.
F. Registration Paper Sensor
1) Remove the feed unit following steps 1-
7 on Page 3-14.
2) Disconnect the connector from the back
of the feed unit, and then remove the
registration paper sensor.
3 - 27
CHAPTER 3
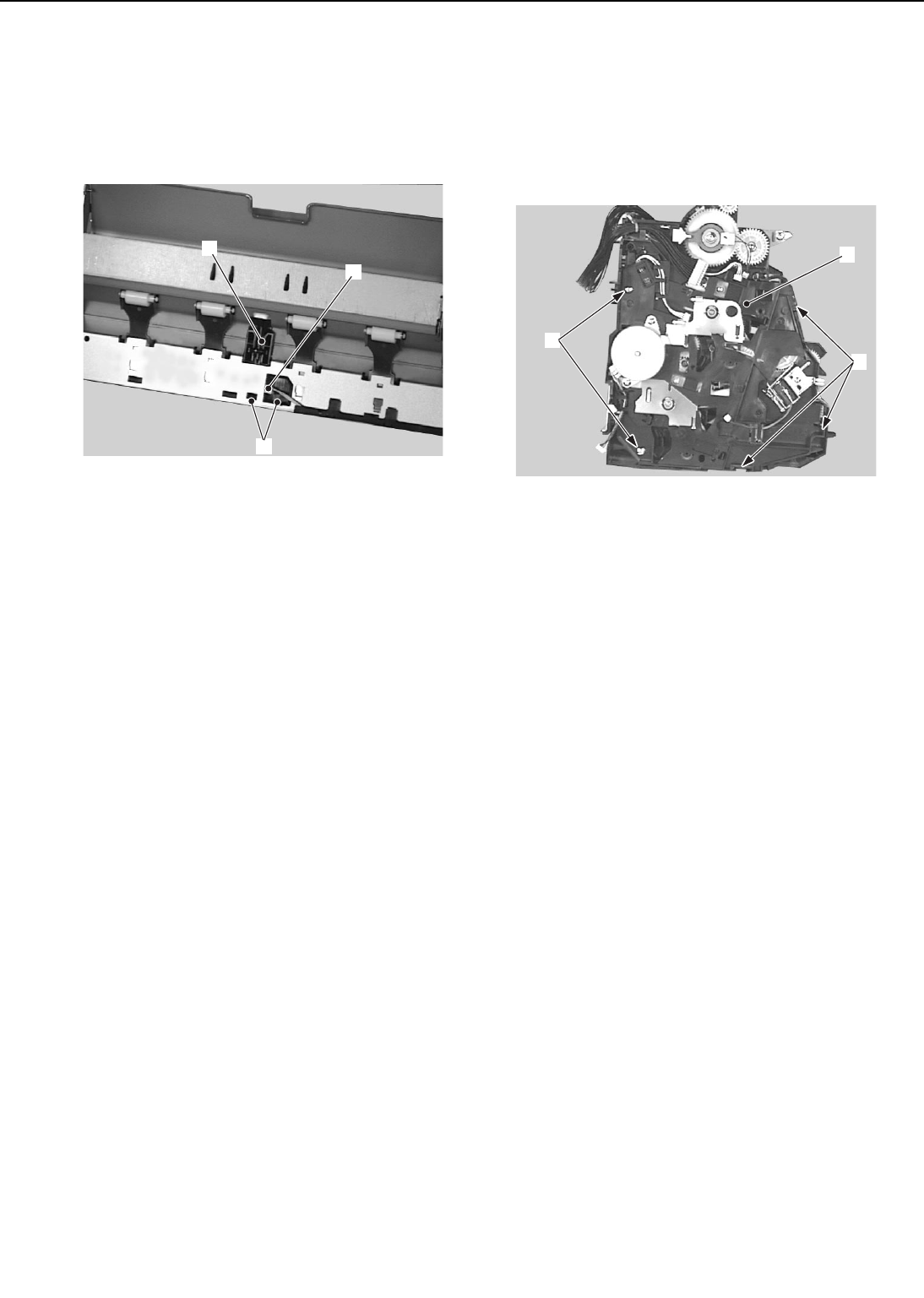
G. Pick-up Unit Paper Sensor
1) Remove the pick-up unit following steps
1-7 on Page 3-9.
2) Disconnect the connector, and then
remove the 2 claws and the sensor unit.
➀Connector ➁Claws
➂Sensor unit
Figure 3-5-5
3) Remove the pick-up unit paper sensor
from the sensor unit.
H. Pick-up Unit Door Sensor
1) Remove the pick-up PCB following steps
1-3 on Page 3-44.
2) Remove the 2 screws.
3) Unhook the 2 claws and remove the
gear cover.
➀Screws ➁Claws
➂Gear cover
Figure 3-5-6
4) Disconnect the connector from the gear
cover, and remove the pick-up unit door
sensor.
3 - 28
CHAPTER 3
➀
➁
➂
➀
➂
➁
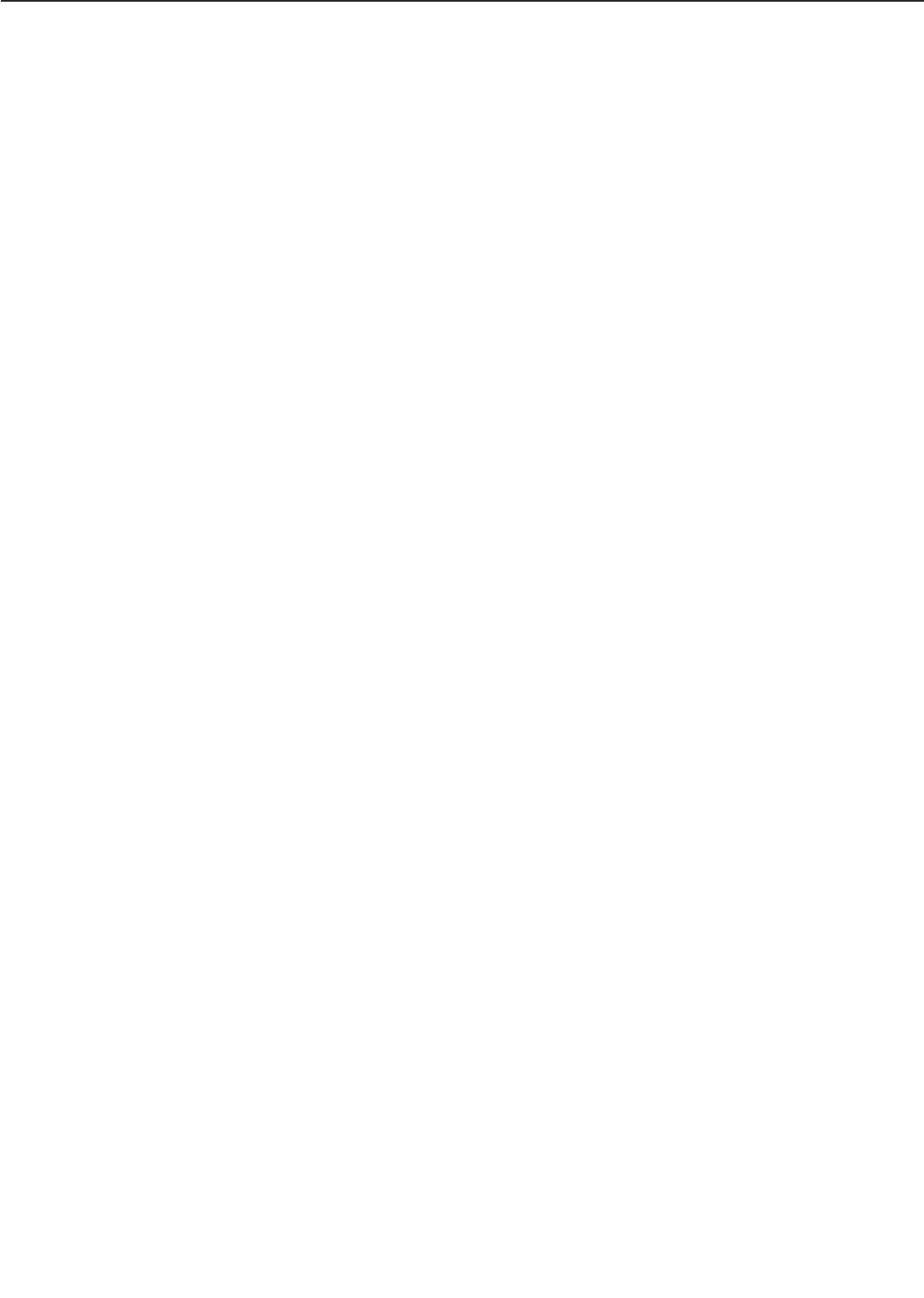
I. Lower Cassette Sensor/Upper
Cassette Sensor/Lower Cassette
Paper-level Sensor 1/Lower Cassette
Paper-level Sensor 2/Upper Cassette
Paper-level Sensor 1/Upper Cassette
Paper-level Sensor 2/Lower Cassette
Paper-out Sensor/Upper Cassette
Paper-out Sensor
1) Remove the pick-up PCB following steps
1-3 on Page 3-44.
J. Multi-purpose Tray Paper Sensor
/Lifting Plate Position Sensor
1) Remove the Multi-purpose tray PCB fol-
lowing steps 1-7 on Page 3-44.
3 - 29
CHAPTER 3
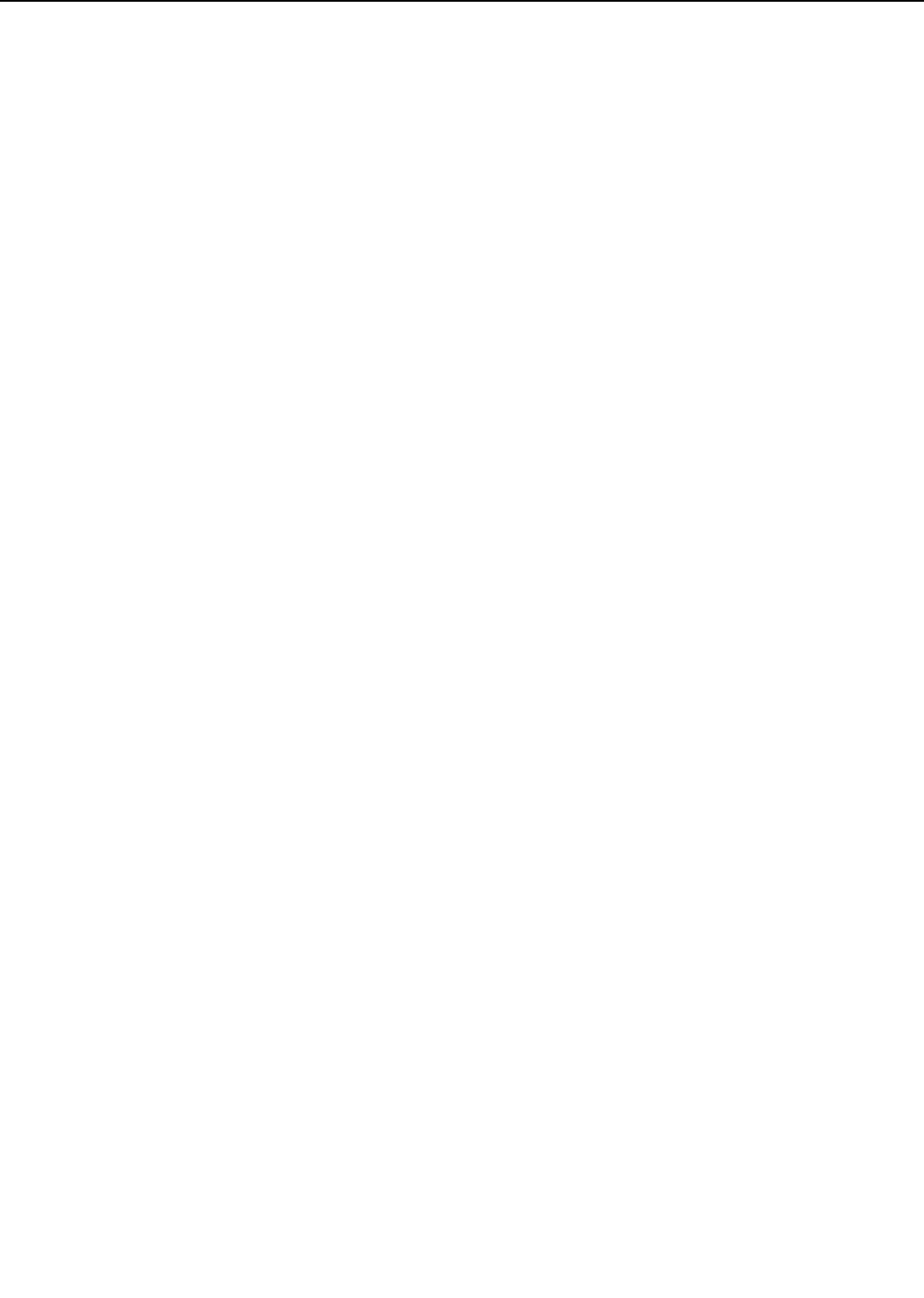
K. Face-down Tray Paper Full Sensor
/Face-down Tray Delivery Sensor
/Fixing Unit Delivery Sensor
1) Remove the switch/sensor PCB follow-
ing steps 1-11 on Page 3-45.
3 - 30
CHAPTER 3
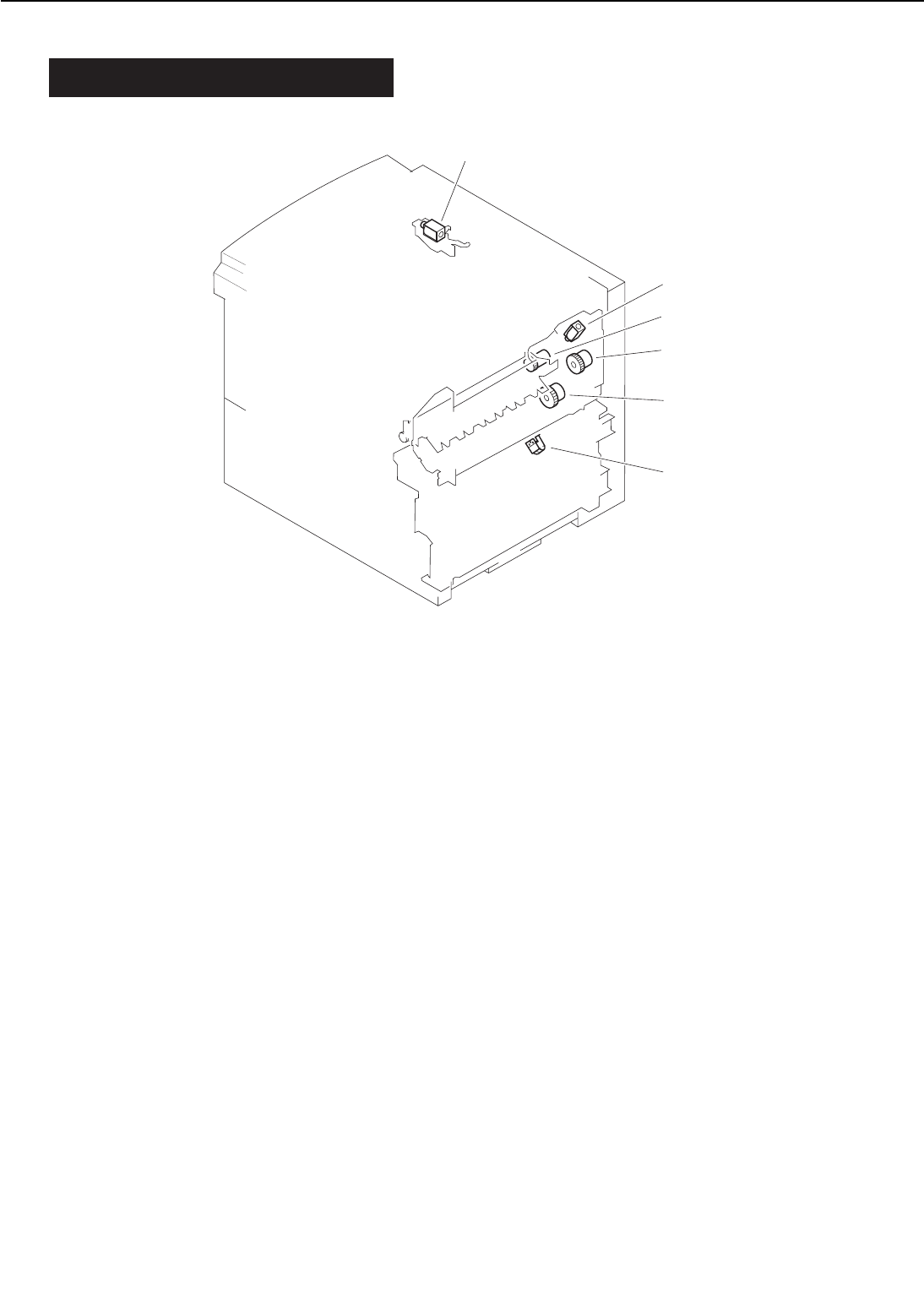
VI. CLUTCHS/SOLENOIDS
A. Locations
➀Multi-purpose tray pick-up clutch ➁Feed clutch
➂Registration clutch ➃Lifting plate solenoid
➄Cassette pick-up solenoid ➅Face-up solenoid
Figure 3-6-1
3 - 31
CHAPTER 3
➀
➁
➂
➃
➄
➅
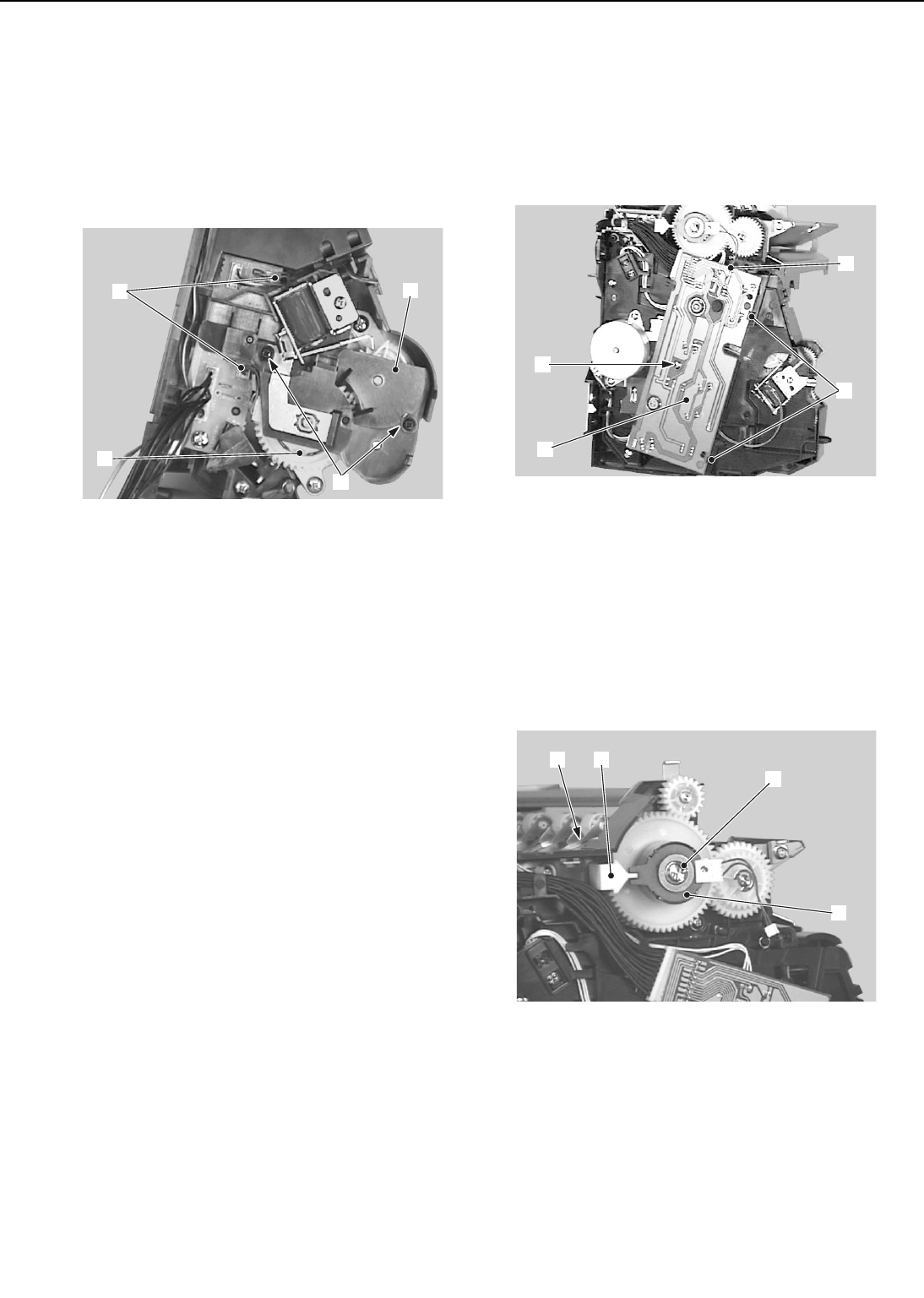
B. Multi-purpose Tray Pick-up Clutch
1) Remove the multi-purpose tray pick-up
unit following steps 1-6 on Page 3-12.
2) Disconnect the 2 connectors.
3) Remove the 2 screws, the clutch cover
unit, and then the multi-purpose tray
pick-up clutch.
➀Connector
➁Screws
➂Clucth cover unit
➃Multi-purpose tray pick-up clutch
Figure 3-6-2
C. Feed Clutch
1) Remove the pick-up unit following steps
1-7 on Page 3-9.
2) Disconnect the connector.
3) Remove the screw, and disconnect the 2
claws to remove the pick-up PCB.
➀Connector ➁Screw
➂Claws ➃Pick-up PCB
Figure 3-6-3
4) Undo the claw and remove the clutch
fixing plate.
5) Remove the E-ring, and then the feed
clutch.
➀Claw ➁Clutch fixing plate
➂E-ring ➃Feed clutch
Figure 3-6-4
3 - 32
CHAPTER 3
➁
➀➂
➃
➁
➀
➂
➃
➀➁
➃
➂
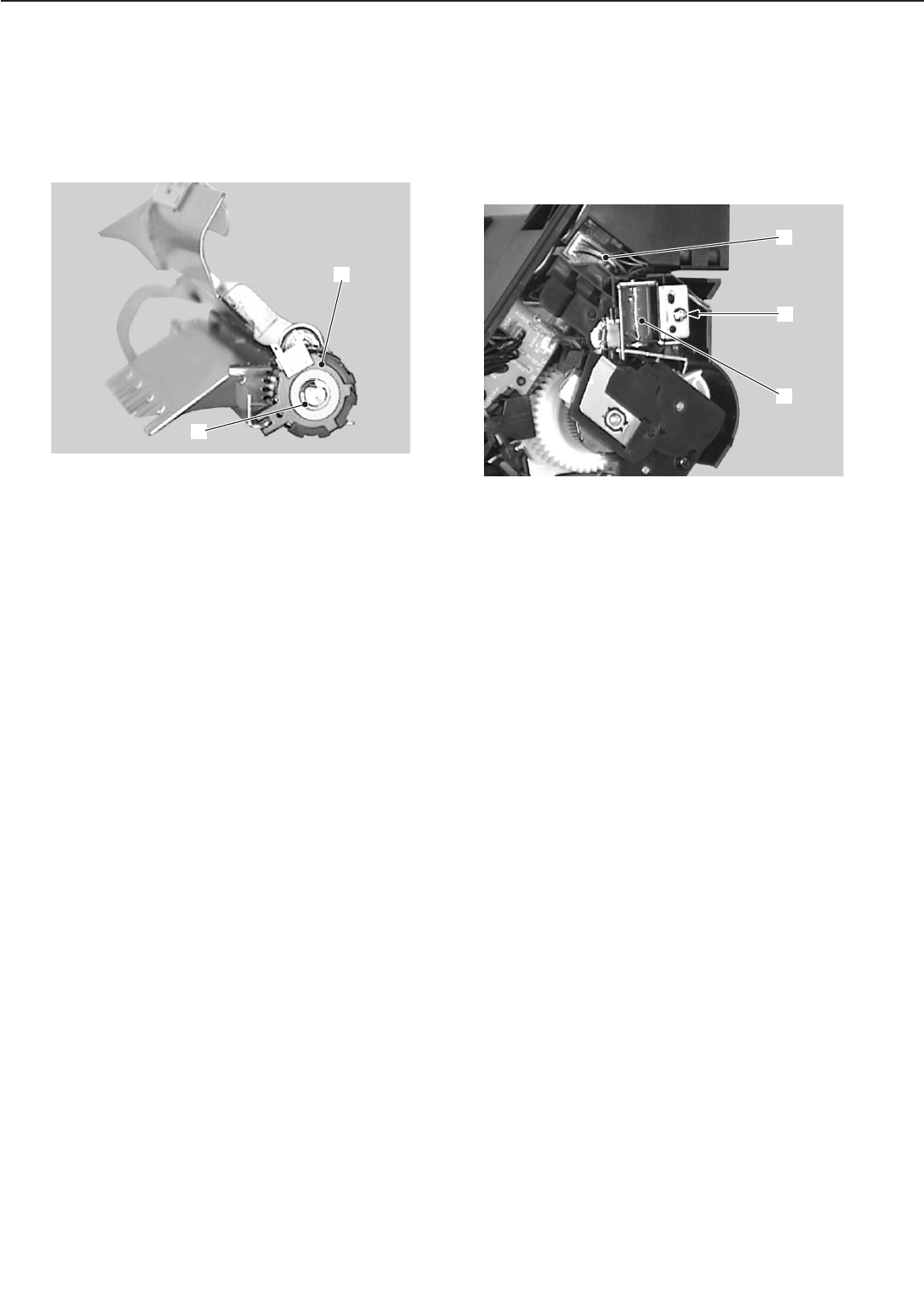
D. Registration Clutch
1) Remove the registration roller unit fol-
lowing steps 1-5 on Page 3-12.
2) Remove the E-ring and the registration
clutch.
➀E-ring ➁Registration clutch
Figure 3-6-5
E. Lifting Plate Solenoid
1) Remove the multi-purpose tray pick-up
unit following steps 1-6 on Page 3-12.
2) Disconnect the connector.
3) Remove the screw and then the lifting
plate solenoid.
➀Connector
➁Screw
➂Lifting plate solenoid
Figure 3-6-6
3 - 33
CHAPTER 3
➀
➁
➀
➁
➂
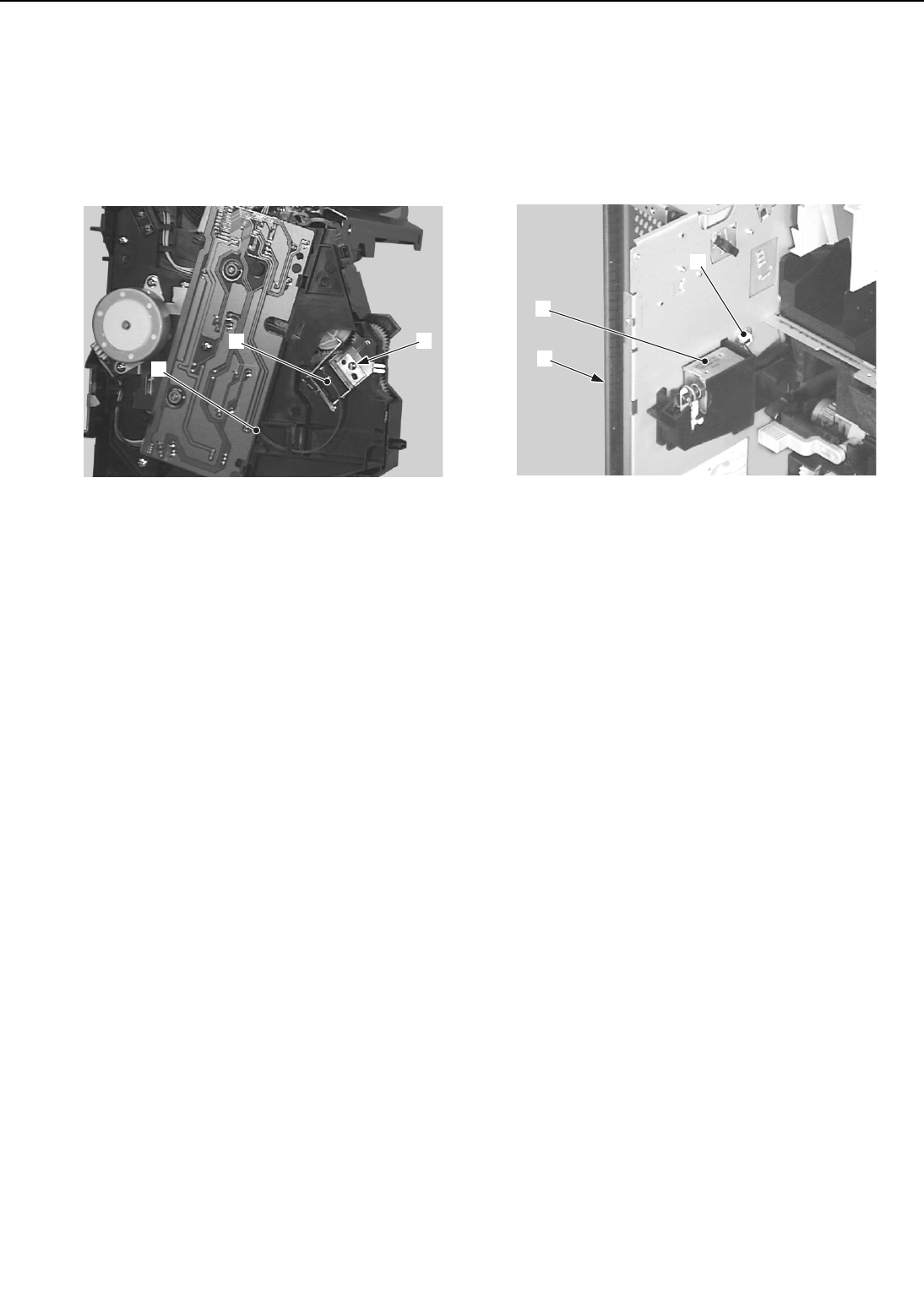
F. Cassette Pick-up Solenoid
1) Remove the pick-up unit following steps
1-7 on Page 3-9.
2) Disconnect the connector.
3) Remove the screw and take out the cas-
sette pick-up solenoid.
➀Connector
➁Screw
➂Cassette pick-up solenoid
Figure 3-6-7
G. Face-up Solenoid Unit
1) Remove the delivery unit following steps
1-7 on Page 3-13.
2) Disconnect the connector.
3) Remove the screw and then the face-up
solenoid unit
➀Connector
➁Screw
➂Face-up solenoid unit
Figure 3-6-8
3 - 34
CHAPTER 3
➁
➀
➂
➁
➀
➂
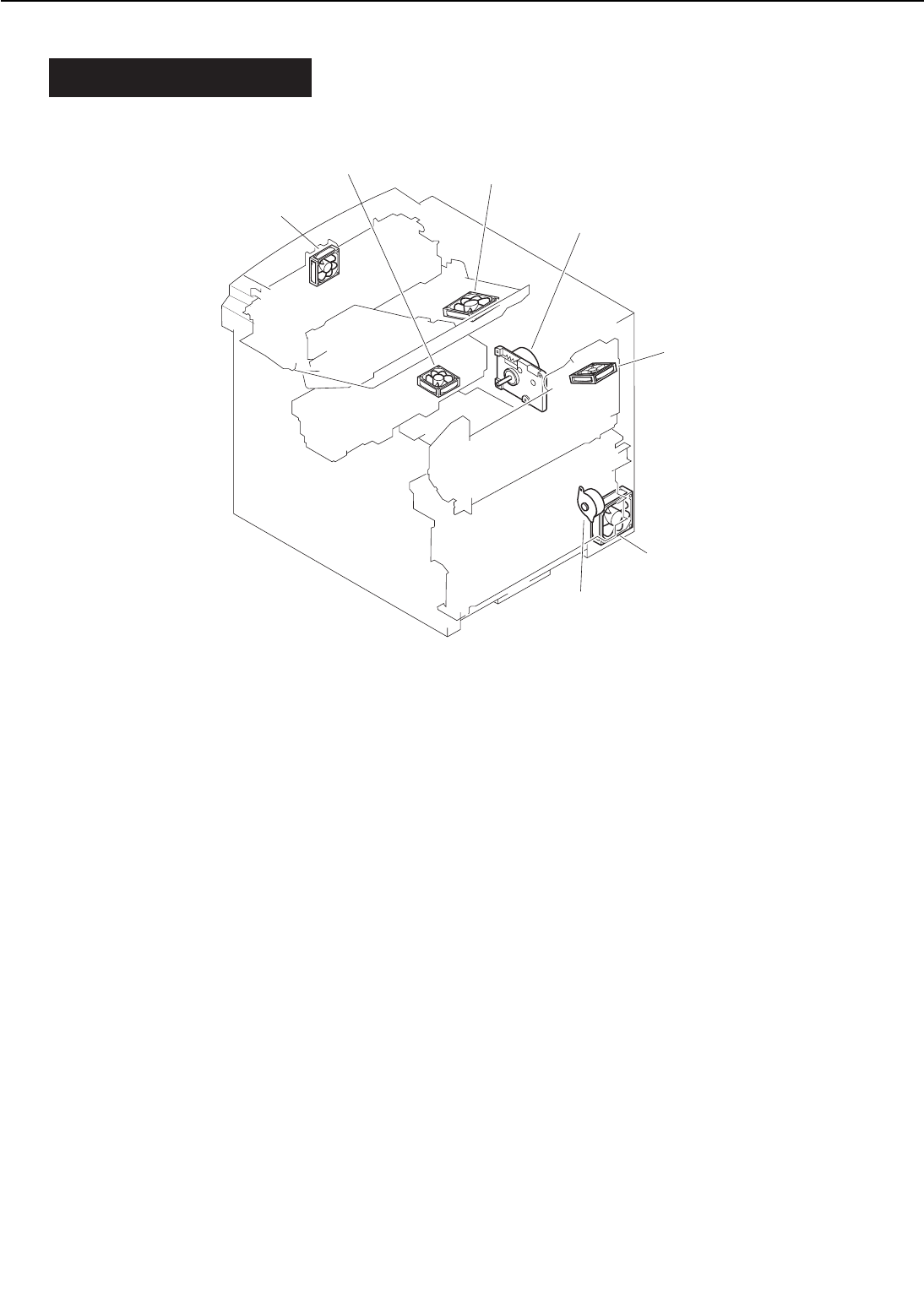
VII. MOTORS/FANS
A. Locations
➀Main motor ➁Pick-up motor
➂Fixing unit/scanner unit fan ➃Power supply fan
➄Electrical unit fan ➅Fixing unit fan
➆Multi-purpose tray pick-up unit fan
Figure 3-7-1
3 - 35
CHAPTER 3
➀
➁
➂
➃
➄
➅
➆
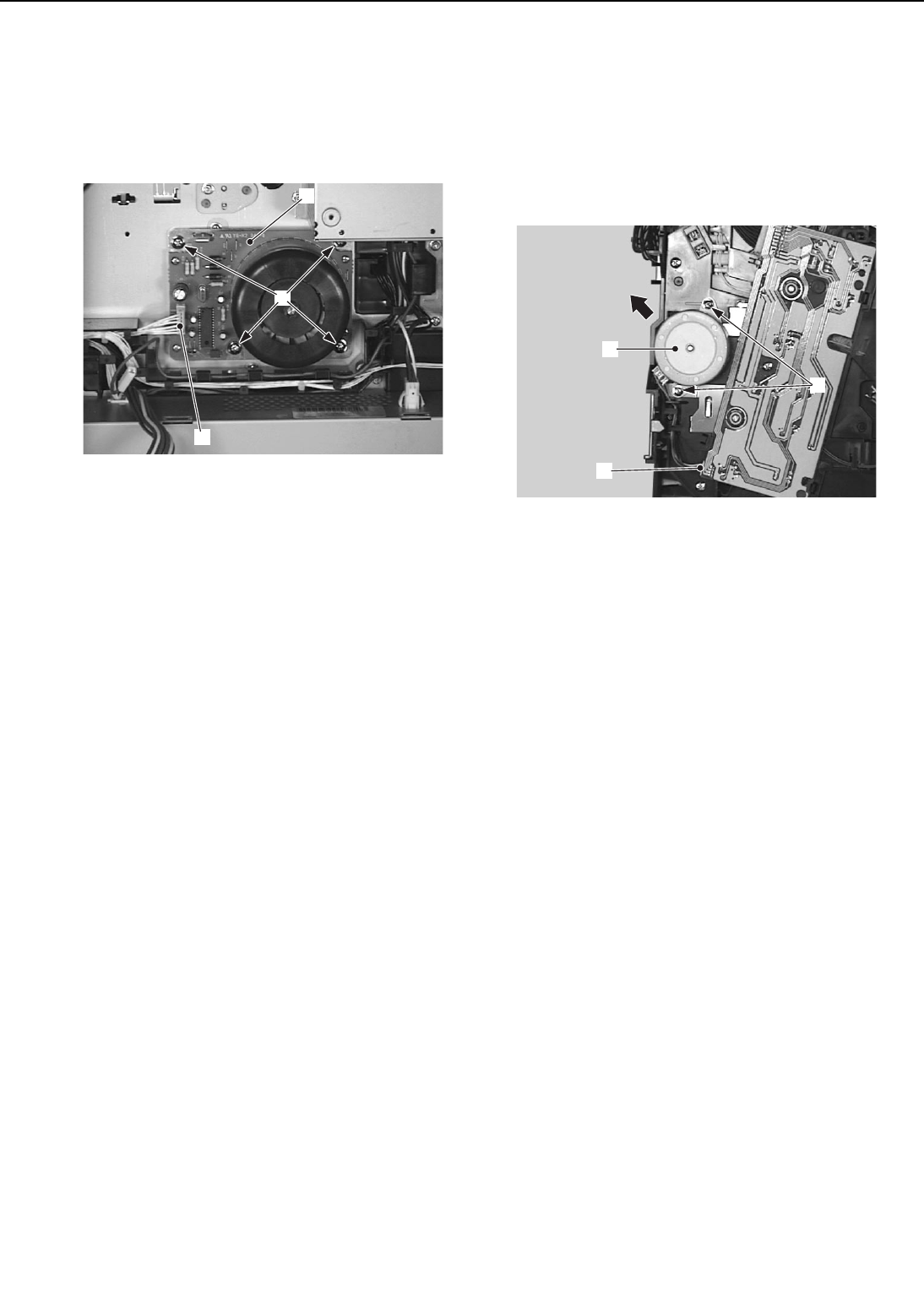
B. Main Motor
1) Remove the high-voltage power supply
unit following steps 1-3 on Page 3-47.
2) Undo the connector, remove the 4
screws and then the main motor.
➀Connector ➁Screws
➂Main motor
Figure 3-7-2
C. Pick-up Motor
1) Remove the pick-up unit following steps
1-7 on Page 3-9.
2) Undo the connector.
3) Remove the 2 screws, and slide the
pick-up motor out in the direction of the
arrow.
➀Connector ➁Screws
➂Pick-up motor
Figure 3-7-3
3 - 36
CHAPTER 3
➂
➀
➁
➁
➀
➂
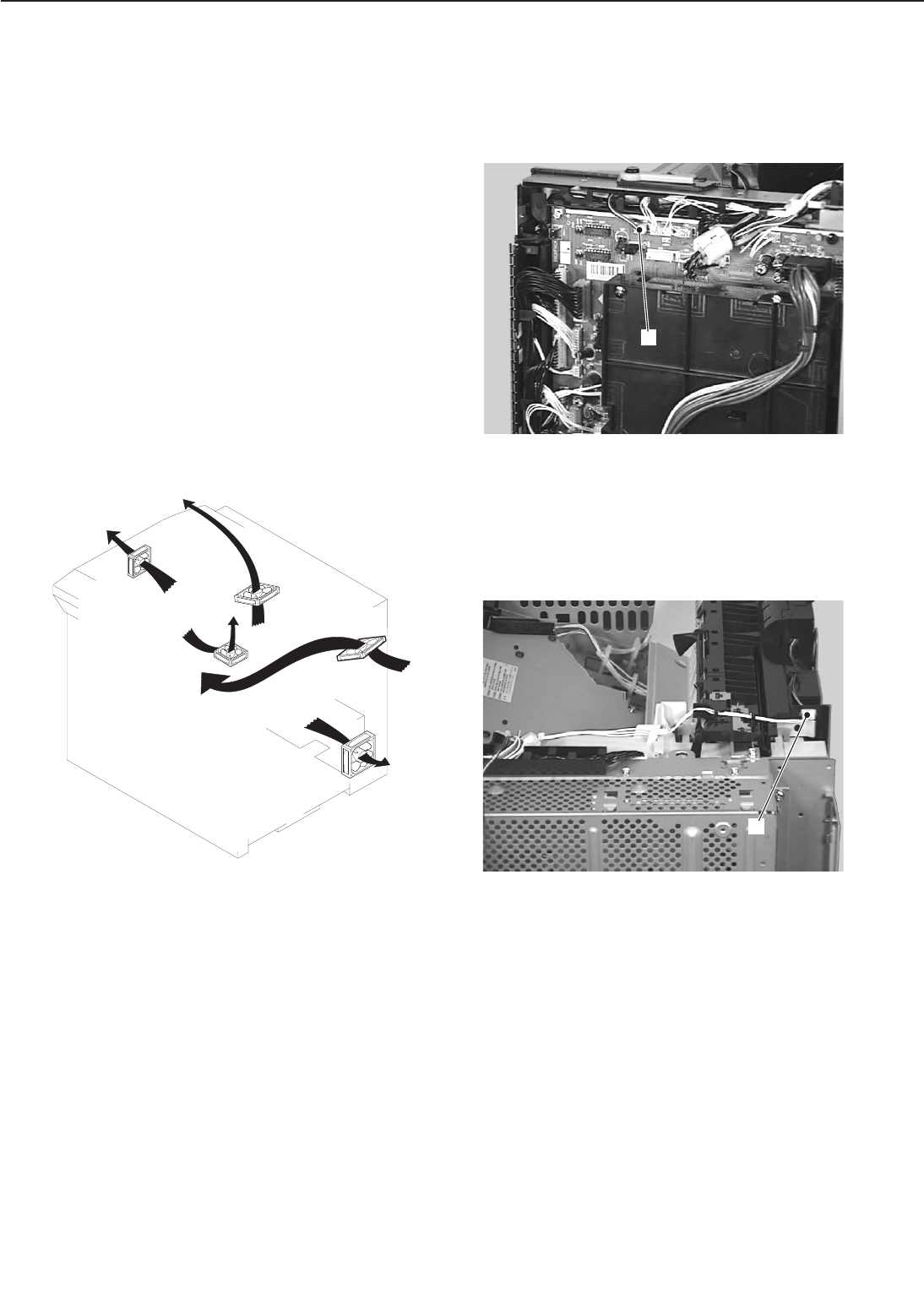
D. Fans
1. Summary
There are 4 fan motors installed to circu-
late air within the printer and prevent
the internal temperature from rising.
• Fixing unit/scanner unit fan (FM1):
Blows air from the fixing unit and the
scanner unit vicinity.
• Power supply fan (FM2):
Blows air from the power supply.
• Electrical unit fan (FM3):
Intake fan for the video controller unit.
• Fixing unit fan (FM4):
Blows air from the fixing unit vicinity.
• Multi-purpose tray pick-up unit fan
(FM5):
Blows air to the cartridge and
laser/scanner unit vicinity.
Figure 3-7-4
2. Fixing unit/scanner unit fan
1) Remove the right rear and rear covers.
2) Remove the upper cover unit.
3) Disconnect the connector.
➀Connector
Figure 3-7-5
4) Disconnect the connector.
➀Connector
Figure 3-7-6
3 - 37
CHAPTER 3
FAM 2
FAM 1
FAM 4
FAM 5
FAM 3
➀
➀
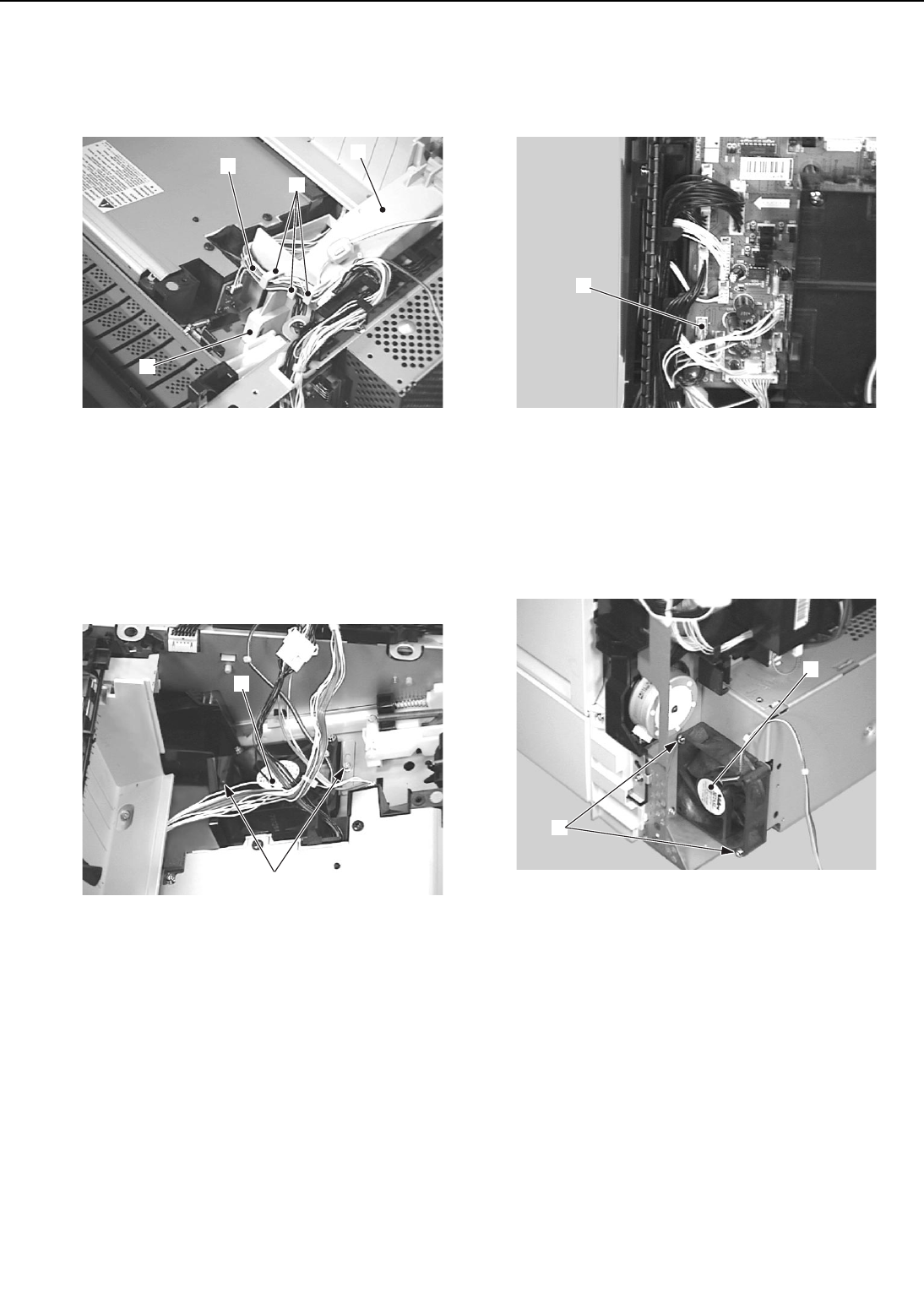
5) Remove the cable from the guide.
6) Unhook the claw, then remove the fan
duct.
➀Cable ➁Cable guide
➂Claw ➃Fan duct
Figure 3-7-7
7) Remove the 2 screws, and then the fix-
ing unit/scanner unit fan.
➀Screws
➁Fixing unit/scanner unit fan
Figure 3-7-8
3. Power supply fan
1) Remove the right rear and rear covers.
2) Disconnect the connector.
➀Connector
Figure 3-7-9
3) Remove the 2 screws, and then the
power supply fan.
➀Screws ➁Power supply fan
Figure 3-7-10
3 - 38
CHAPTER 3
➀
➀
➁
➂
➀➃
➁
➀
➁
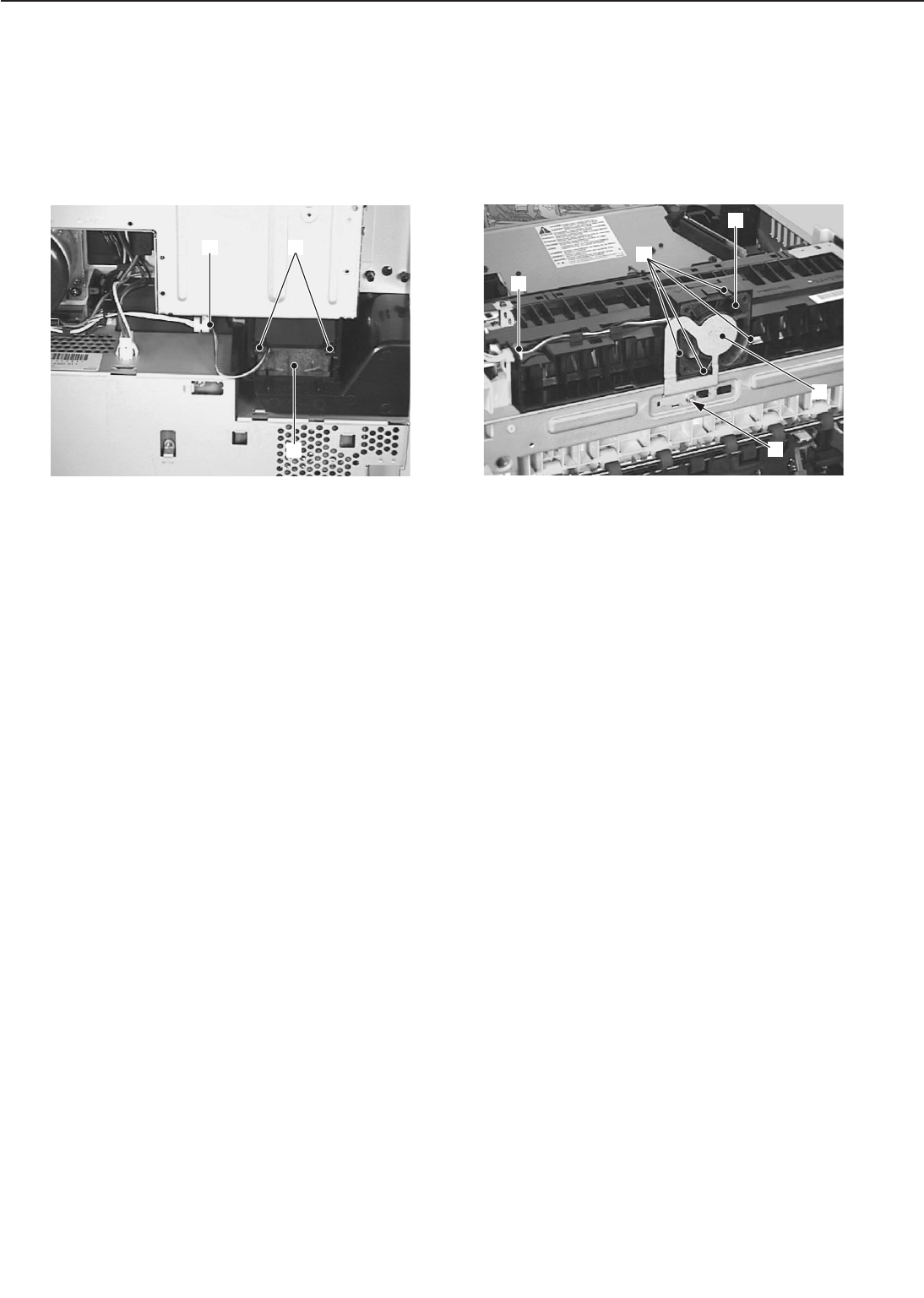
4. Electrical unit fan
1) Remove the right rear and rear covers.
2) Remove the left rear cover.
3) Undo the connector.
4) Pinch the 2 claws holding the electrical
unit fan and pull out the fan.
➀Connector
➁Claws
➂Electrical unit fan
Figure 3-7-11
5. Fixing unit fan
1) Remove the upper cover unit.
2) Undo the connector.
3) Remove the screw, and then the fan
grounding plate. Disconnect the 4
claws to remove the fixing unit fan.
➀Connector
➁Screw
➂Fan grounding plate
➃Claws
➄Fixing unit fan
Figure 3-7-12
3 - 39
CHAPTER 3
➀➁
➂
➁
➃
➂
➀
➄
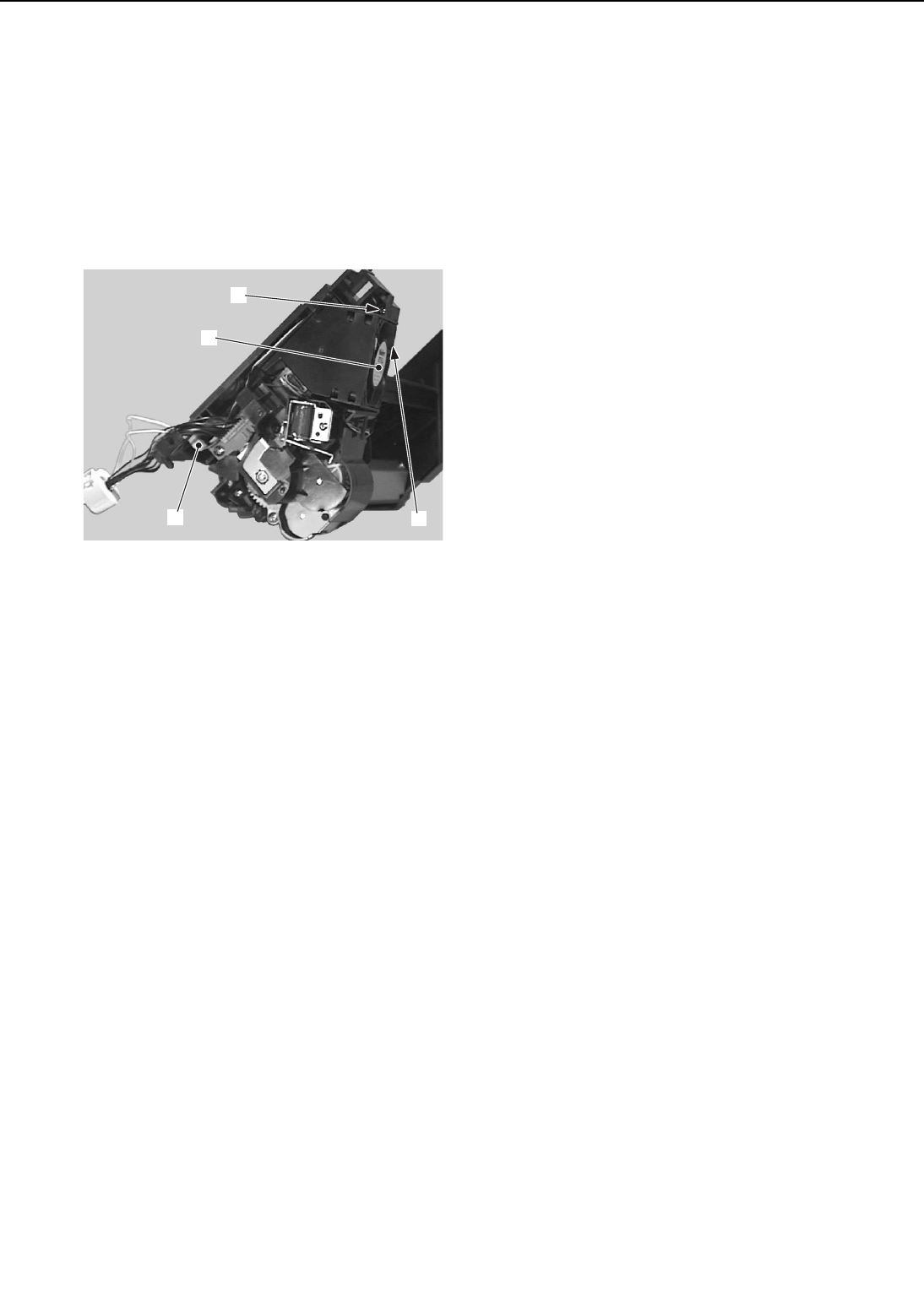
6. Multi-purpose tray pick-up unit fan
1) Remove the multi-purpose tray pick-up
unit following steps 1-6 on Page 3-12.
2) Disconnect the connector.
3) Remove the screw, claw, and then the
fan duct together the multi-purpose
tray pick-up unit fan.
4) Remove the multi-purpose tray pick-up
unit fan from the fan duct.
➀Connector
➁Screw
➂Claw
➃Multi-purpose tray pick-up unit fan
Figure 3-7-13
3 - 40
CHAPTER 3
➁
➂
➃
➀
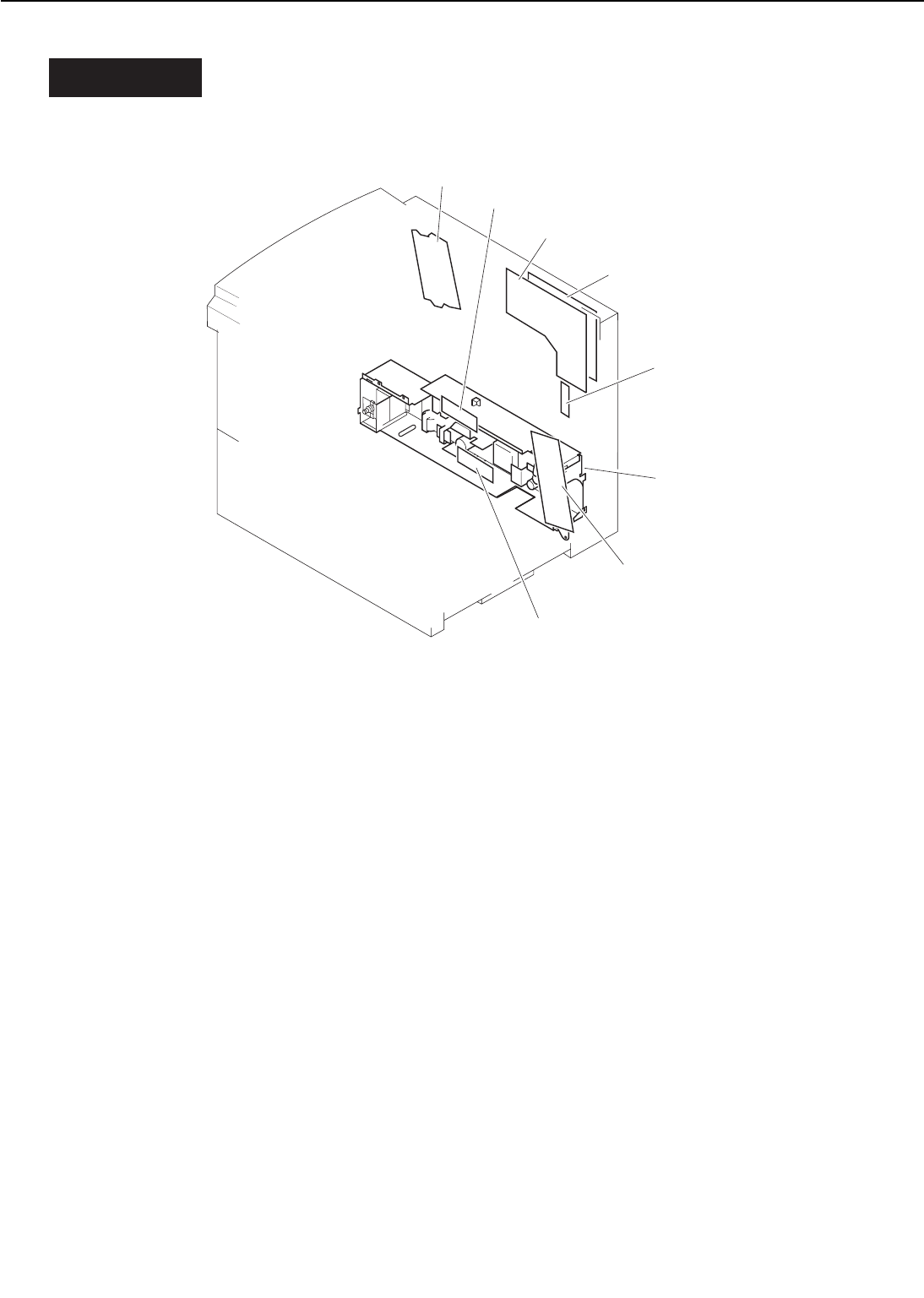
VIII. PCBS
A. Locations
➀DC controller PCB ➁Pick-up PCB
➂Multi-purpose tray PCB ➃Switch/sensor PCB
➄High-voltage power supply PCB ➅Upper cassette paper-size sensing PCB
➆Lower cassette paper-size sensing PCB ➇Power supply
Figure 3-8-1
3 - 41
CHAPTER 3
➀
➁
➂
➃
➄
➅
➆
➇
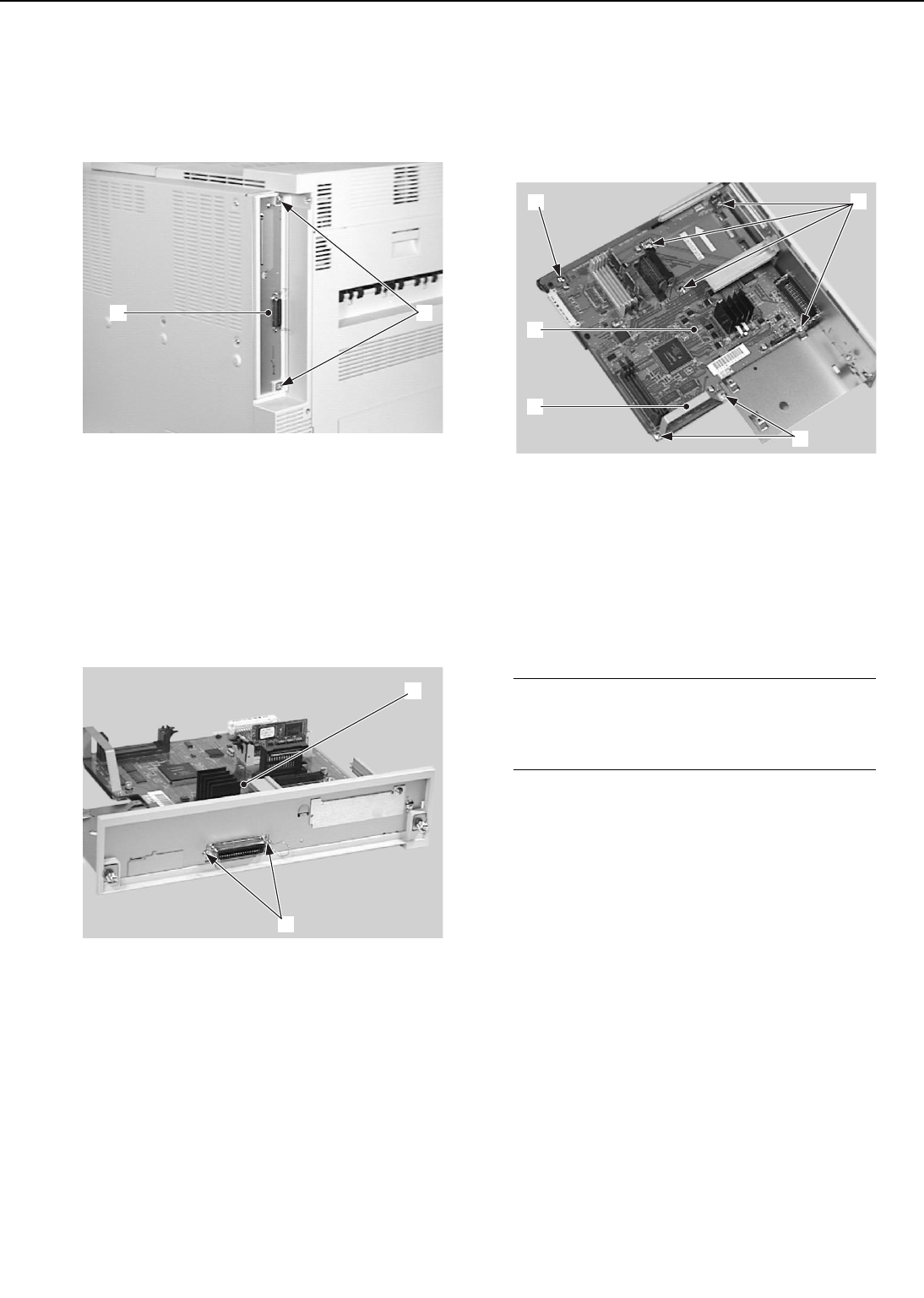
B. Video Controller PCB Unit
1. Removal from the printer
1) Loosen the 2 screws then pull out the
video controller PCB unit.
➀Screws
➁Video controller PCB unit
Figure 3-8-2
2. Disassembly/reassembly
a. Video Controller PCB
1) Remove the 2 screws.
➀Video controller PCB ➁Screws
Figure 3-8-3
2) Remove the 2 screws (M3) and the
guide.
3) Remove the 1 screw (M4) and the 4
screws (M3), then take out the video
controller PCB.
➀Screw (M3)
➁Guide
➂Screws (M4)
➃Screws (M3)
➄Video controller PCB
Figure 3-8-4
Note: If you removed ROM DIMM or RAM
DIMM when you repaced the video
controller PCB, reinstall it on the
new video controller PCB.
3 - 42
CHAPTER 3
➁➀
➀
➁
➁
➄
➂
➀
➃
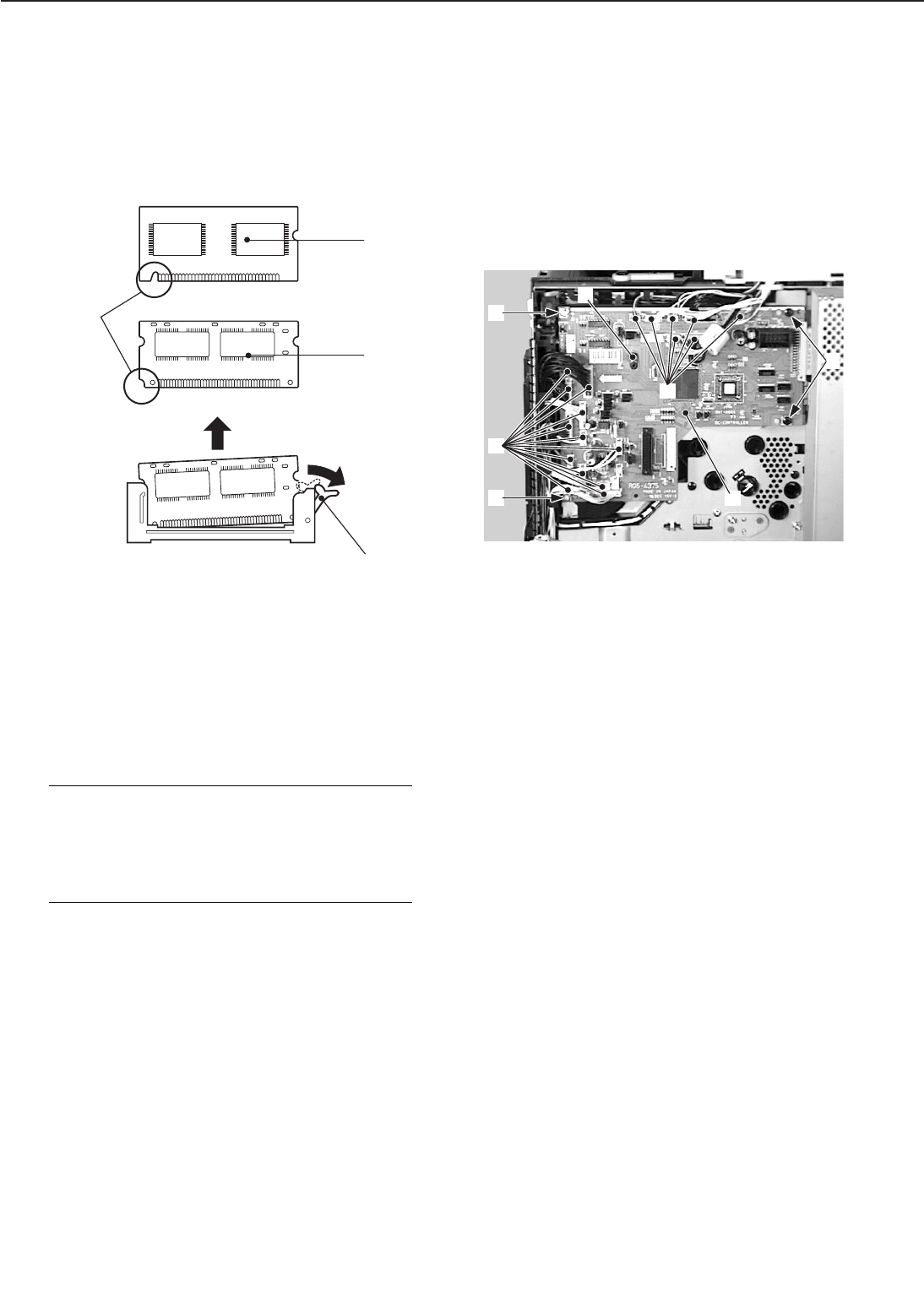
b. Removal of RAM DIMM/ROM DIMM
(option)
1) Push down the socket lever to remove
the RAM DIMM or ROM DIMM. Be sure
not to touch the elements.
➀Socket lever
➁RAM DIMM
➂ROM DIMM
➃Cutout
Figure 3-8-5
Note: When installing the RAM DIMM or
ROM DIMM onto the video con-
troller PCB, note that the shape of
the RAM DIMM cutout differs from
that of the ROM DIMM cutout.
C. DC Controller PCB
1) Remove the high-voltage power supply
unit following steps 1-3 on Page 3-47.
2) Disconnect the 19 connectors from the
DC controller PCB.
3) Remove the 2 screws (M3) and the 2
screws (M4).
4) Unhook the claw, and then remove the
DC controller PCB.
➀Connectors
➁Screws (M3)
➂Screws (M4)
➃Claw
➄DC controller PCB
Figure 3-8-6
3 - 43
CHAPTER 3
➁
➁
➂
➀
➃
➄
➀
➀
➁
➂
➃
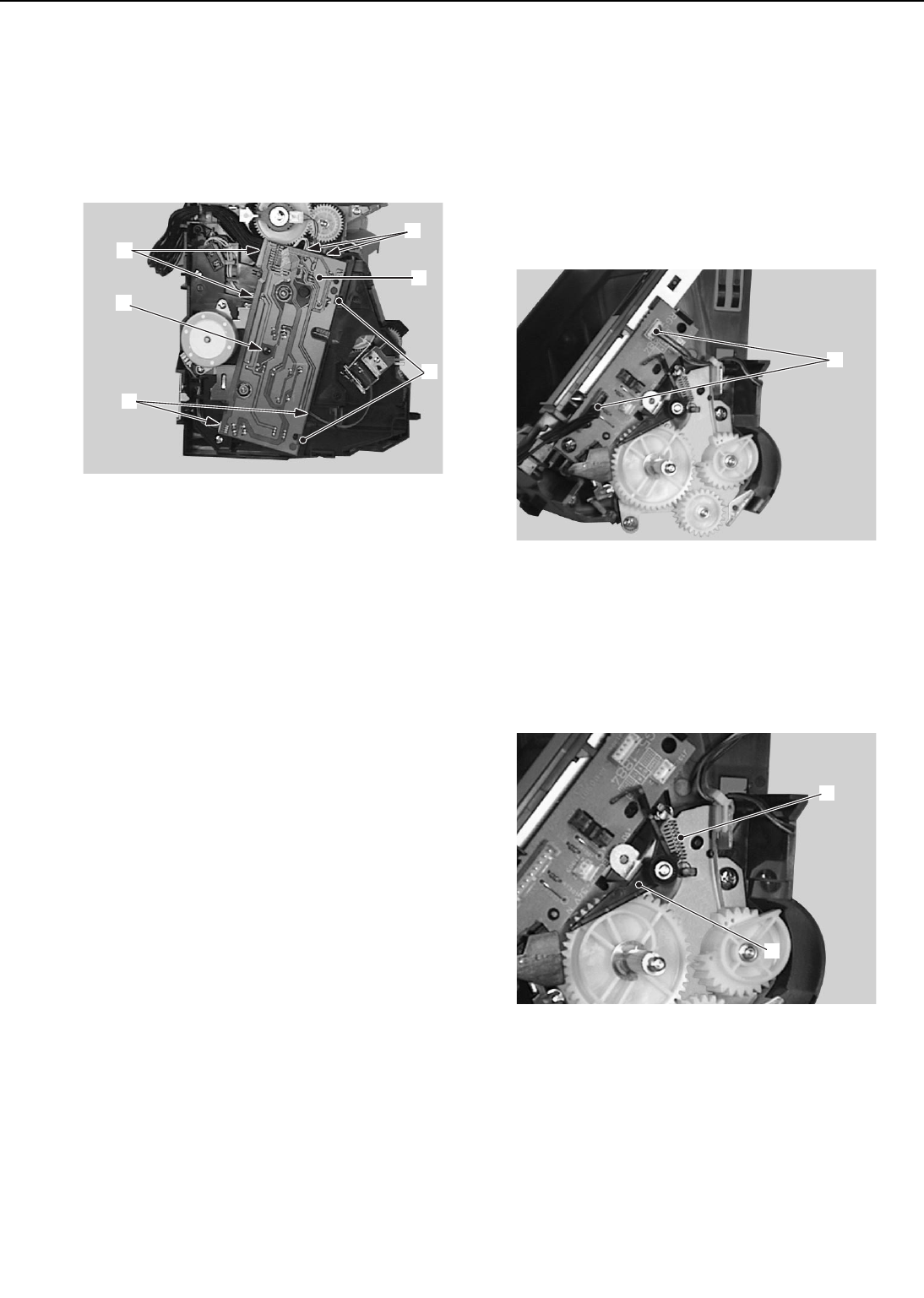
D. Pick-up PCB
1) Remove the pick-up unit following steps
1-7 on Page 3-9.
2) Disconnect the 6 connectors.
3) Remove the screw, disconnect the 2
claws, and take out the pick-up PCB.
➀Connectors ➁Screw
➂Claws ➃Pick-up PCB
Figure 3-8-7
E. Multi-purpose Tray PCB
1) Remove the multi-purpose tray pick-up
unit following steps 1-6 on Page 3-12.
2) Remove the multi-purpose tray pick-up
unit fan following steps 2-3 on Page 3-
40.
3) Remove the multi-purpose tray pick-up
clutch following steps 2-3 on Page 3-32.
4) Disconnect the 2 connectors
➀Connector
Figure 3-8-8
5) Remove the spring and then the lifting
plate position detection arm.
➀Spring
➁Lifting plate position detection arm
Figure 3-8-9
3 - 44
CHAPTER 3
➀
➀
➁
➃
➀
➂
➀
➁
➀
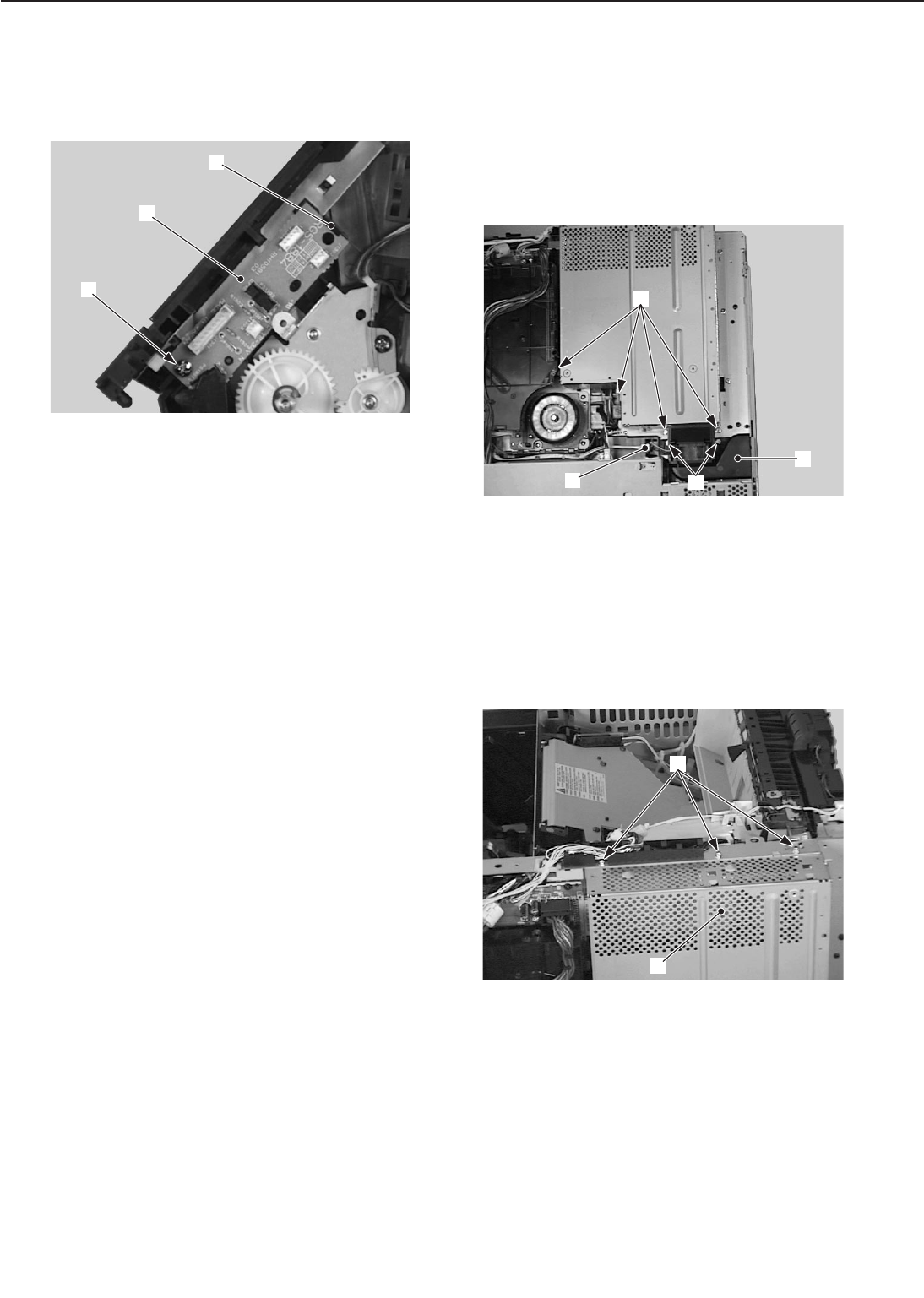
6) Remove the screw
7) Unhook the claw, and then remove the
multi-purpose tray PCB.
➀Screw
➁Claw
➂Multi-purpose tray PCB
Figure 3-8-10
F. Switch/Sensor PCB
1) Remove the upper cover unit.
2) Remove the right rear and rear covers.
3) Remove the left rear cover.
4) Remove the connector, the 2 screws,
and then the fan duct.
5) Remove the 4 screws.
➀Connector ➁Screws
➂Fan duct ➃Screws
Figure 3-8-11
6) Remove the 3 screws and the shield
cover.
➀Screws ➁Shield cover
Figure 3-8-12
3 - 45
CHAPTER 3
➂
➀
➁
➃
➁
➀
➂
➀
➁
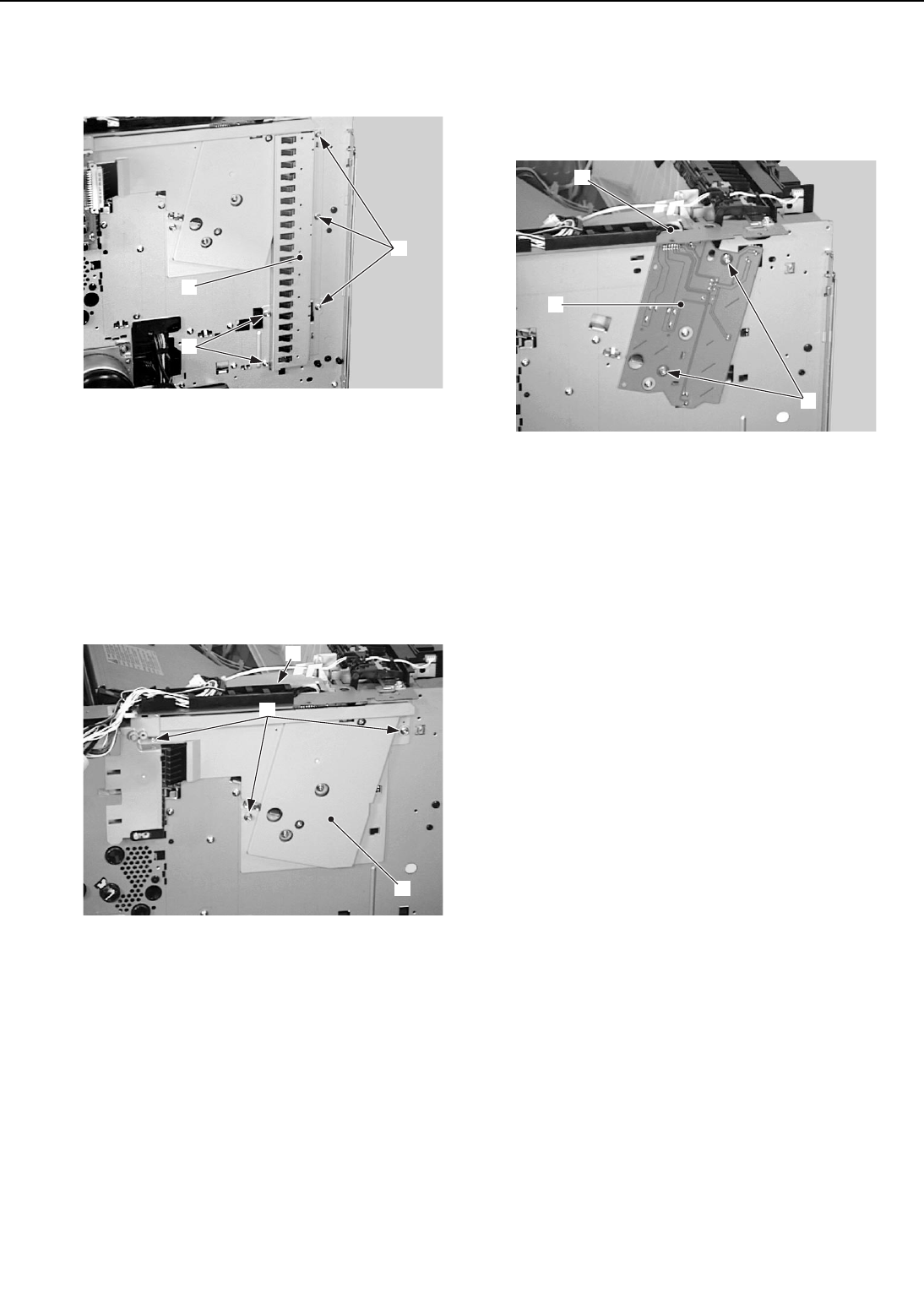
7) Remove the 5 screws and the shield
plate.
➀Screws ➁Shield plate
Figure 3-8-13
8) Remove the DC controller PCB following
steps 1-4 on Page 3-43.
9) Remove the 3 screws.
10) Remove the claw and take out the DC
controller mounting plate.
➀Screws
➁Claw
➂DC controller mounting plate
Figure 3-8-14
11) Disconnect the connector, remove the 2
screws, and pull out the board.
Disconnect the other connector and
remove the switch/sensor PCB.
➀Connectors
➁Screws
➂Switch/sensor PCB
Figure 3-8-15
3 - 46
CHAPTER 3
➀
➀
➁
➀
➁
➂
➂
➁
➀
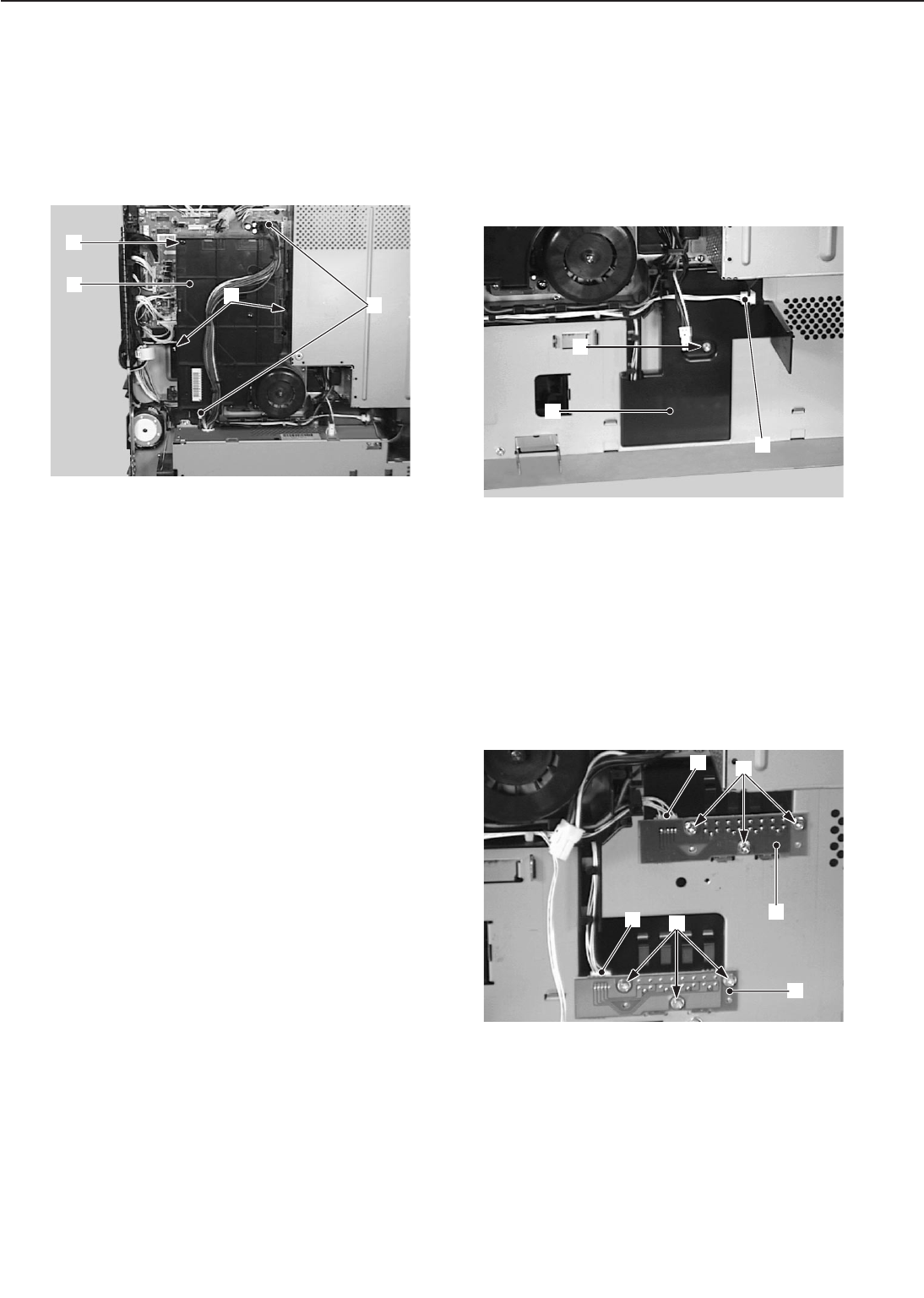
G. High-voltage Power Supply Unit
1) Remove the right rear and rear covers.
2) Disconnect the 2 connectors.
3) Remove the screw (M4), the 2 screws
(M3), and then the high-voltage power
supply unit.
➀Connectors
➁Screws (M4)
➂Screws (M3)
➃High-voltage power supply unit
Figure 3-8-16
H. Cassette Paper-size Sensing PCB
1) Remove the cassettes.
2) Remove the power supply following
steps 1-7 on Page 3-48.
3) Disconnect the connector, remove the
screw, then take out the cassette paper-
size sensing cover.
➀Connector
➁Screw
➂Cassette paper-size sensing cover
Figure 3-8-17
4) Disconnect the connector and remove
the 3 screws from each PCB, then take
out the cassette-size sensing PCBs.
➀Connectors
➁Screws
➂Upper-cassette paper-size sensing PCB
➃Lower-cassette paper-size sensing PCB
Figure 3-8-18
3 - 47
CHAPTER 3
➃
➁
➂➀
➁
➂
➀
➃
➀
➂
➁
➁
➀
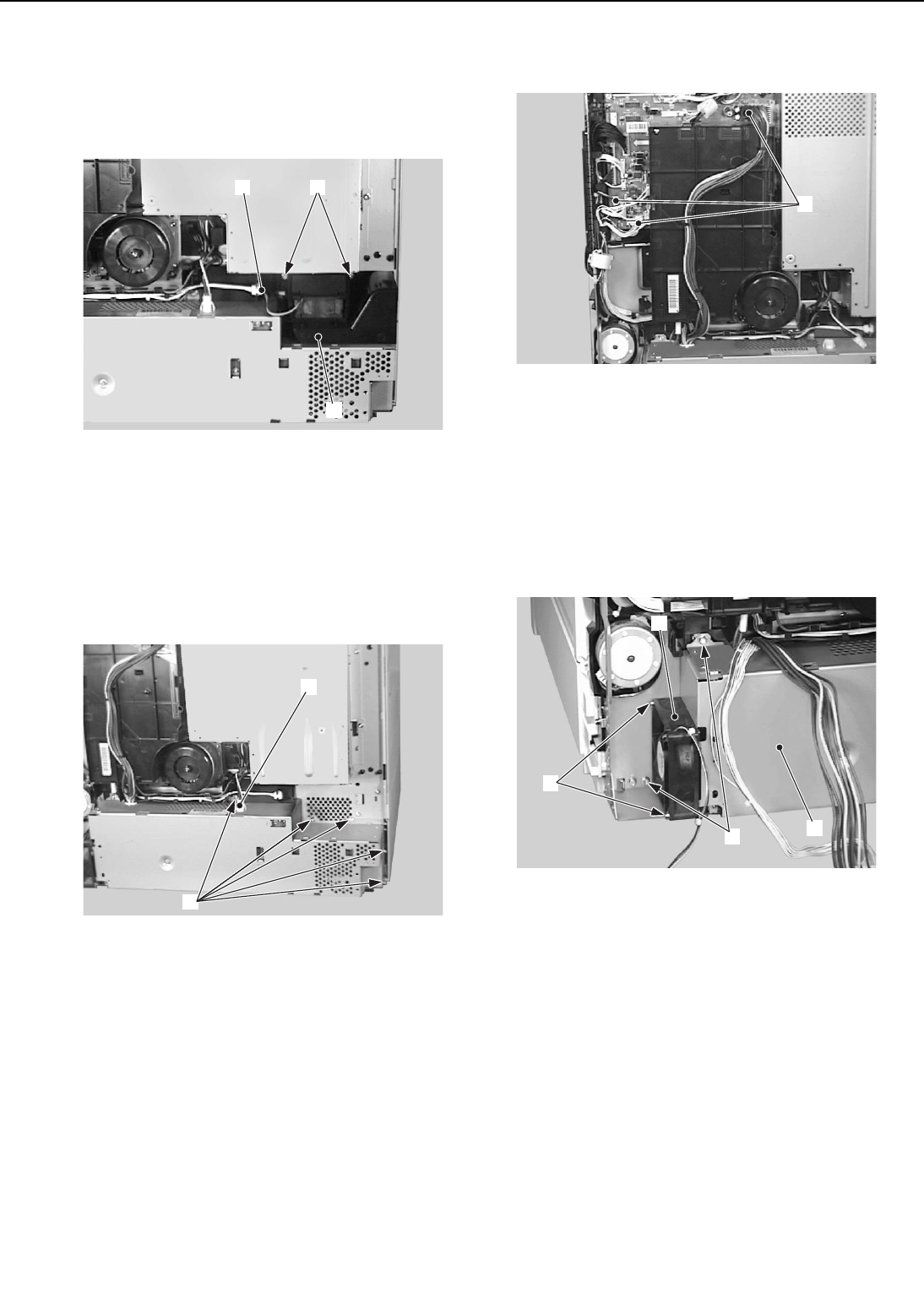
I. Power Supply
1) Remove the left rear and rear covers.
2) Disconnect the connector, remove the 2
screws, then take out the fan duct.
➀Connector ➁Screws
➂Fan duct
Figure 3-8-19
3) Remove the connector.
4) Take out the 5 screws.
➀Connector ➁Screws
Figure 3-8-20
5) Remove the 3 connectors.
➀Connectors
Figure 3-8-21
6) Remove the 2 screws and the power
supply unit fan.
7) Remove the 2 screws and take off the
power supply unit.
➀Screws ➁Power supply fan
➂Screws ➃Power supply
Figure 3-8-22
3 - 48
CHAPTER 3
➀
➀
➂
➁
➃
➁
➀
➂
➁
➀
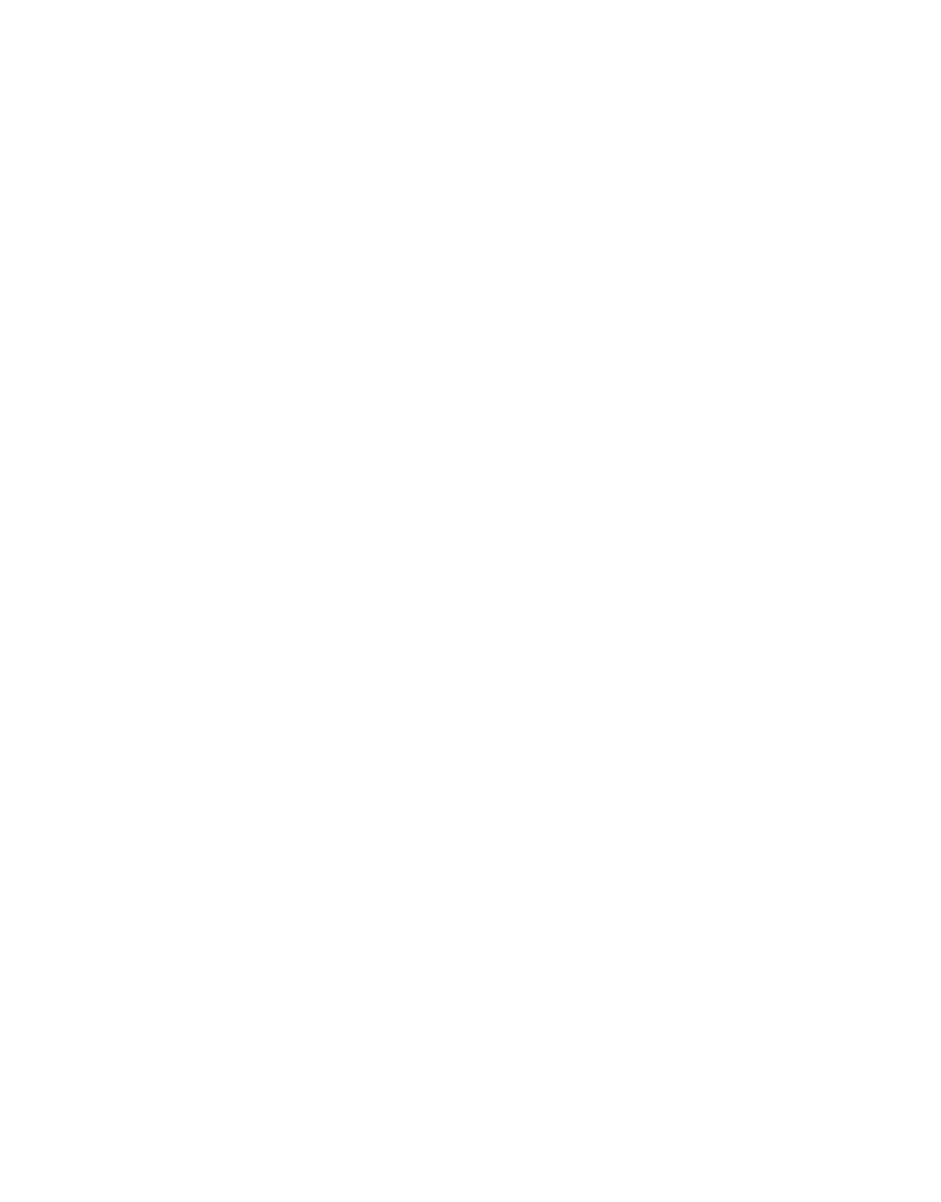
CHAPTER 4
TROUBLESHOOTING
I. PREFACE ............................... 4-1
II. IMAGE DEFECTS.................... 4-8
III. PAPER JAMS
TROUBLESHOOTING .............. 4-14
IV. PAPER TRANSPORT
TROUBLESHOOTING .............. 4-18
V. MALFUNCTION
TROUBLESHOOTING .............. 4-20
VI. MALFUNCTION STATUS
TROUBLESHOOTING .............. 4-21
VII. MEASUREMENT AND
ADJUSTMENT ........................ 4-28
VIII.MAINTENANCE AND
SERVICING............................. 4-35
IX. LOCATION OF CONNECTORS . 4-48
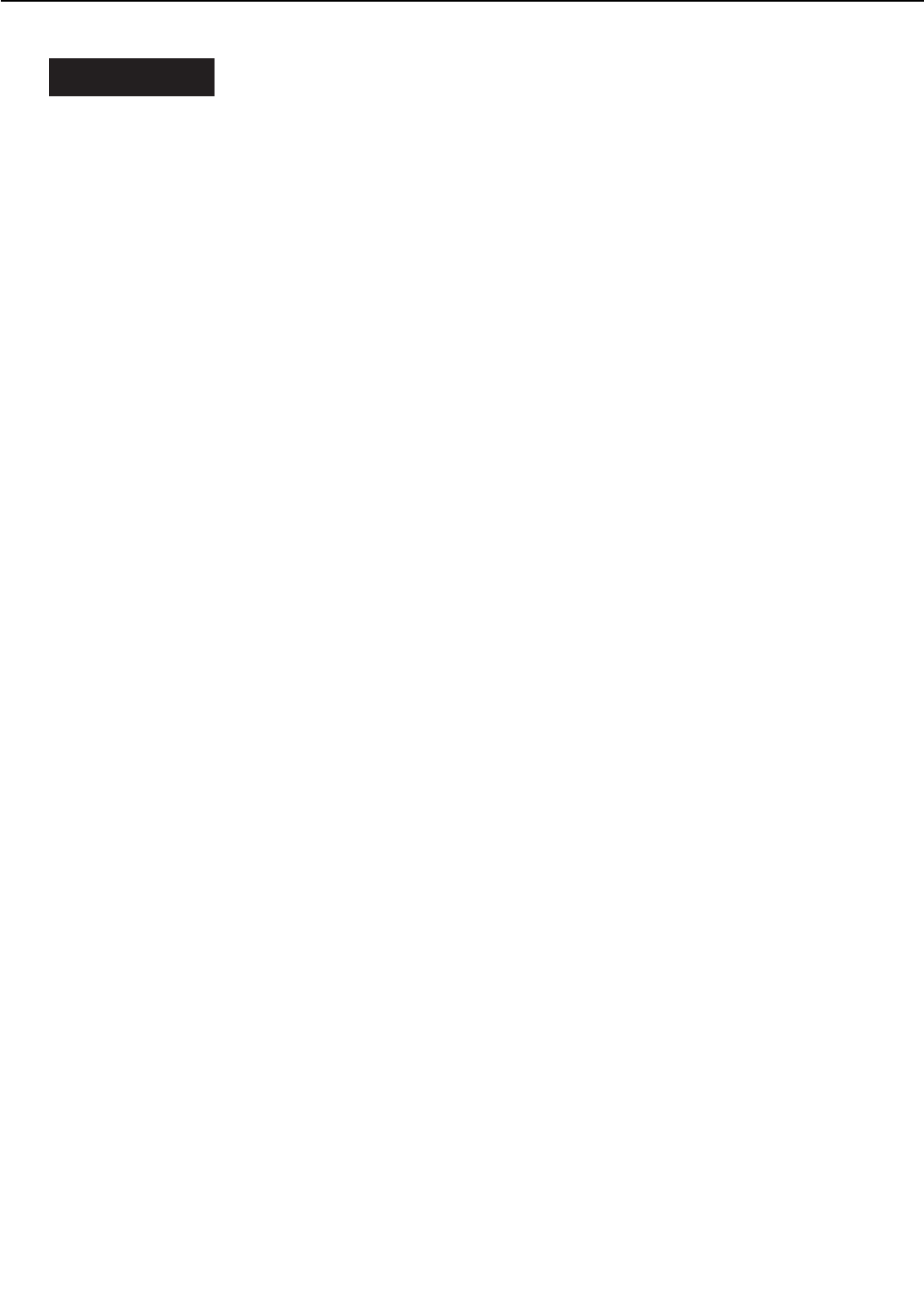
I. PREFACE
A. Malfunction Diagnosis Flowchart
The malfunctions that occur in the printer fall into five main factors; “image defects,” “paper
jams,” “paper transport troubleshooting,” “malfunction troubleshooting,” and “malfunction sta-
tus troubleshooting.”
If a malfunction occurred in the printer, the service technician is to find the factor according
to the malfunction diagnosis flowchart and to clear the problem following the action procedure
for each malfunction.
Make sure the following points at the execution of troubleshooting.
• Be sure that the connector has no poor contact when measuring the voltage at the specified
terminal of the connector.
• Before handling PCBs, be sure to touch a metal part of the printer to discharge static elec-
tricity, as it can cause damage to the PCBs.
• Do not attempt to disassemble the laser/scanner unit as it cannot be adjusted in the field.
4 - 1
CHAPTER 4
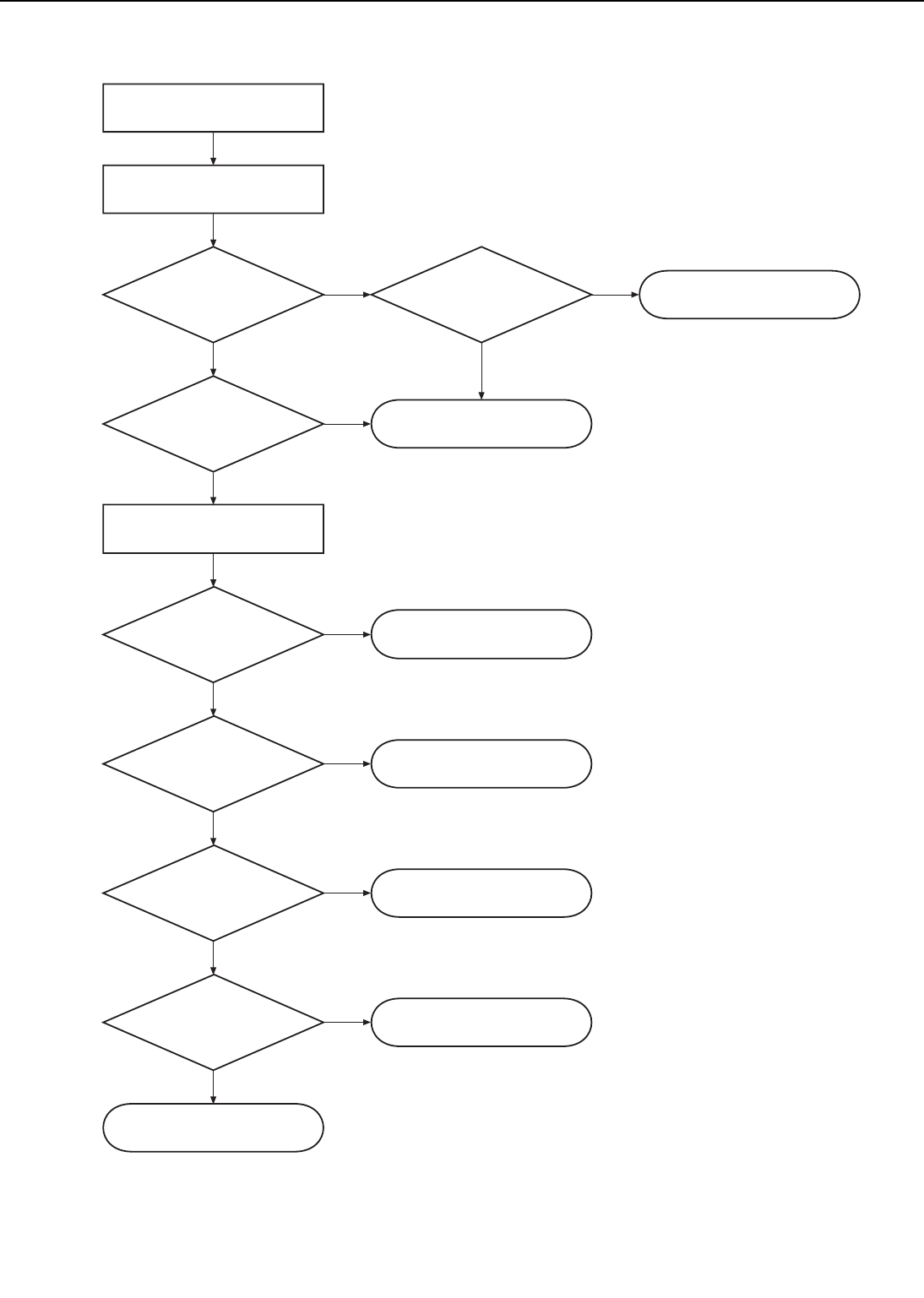
Figure 4-1-1
4 - 2
CHAPTER 4
Is test print executable?
(Note 1)
Refer to the item, "paper jams"
Power ON
Displays "READY"?
Make a test print
Occurs paper jam?
Initial check execution
Delivers paper
normally?
Occurs image
defect?
(Note 2)
Refer to the item, "image defects"
Refer to the item, "malfunction
status troubleshooting"
END
Displays "operator call"
or "service call"?
Refer to the item, "malfunction
status troubleshooting"
Refer to the item, "malfunction
troubleshooting"
Refer to the item, "paper
transport troubleshooting"
No
No
Yes
Yes
Yes
No
No
Yes
No
Yes
Yes
No
Displays "operator call"
or "service call"?
No
Yes
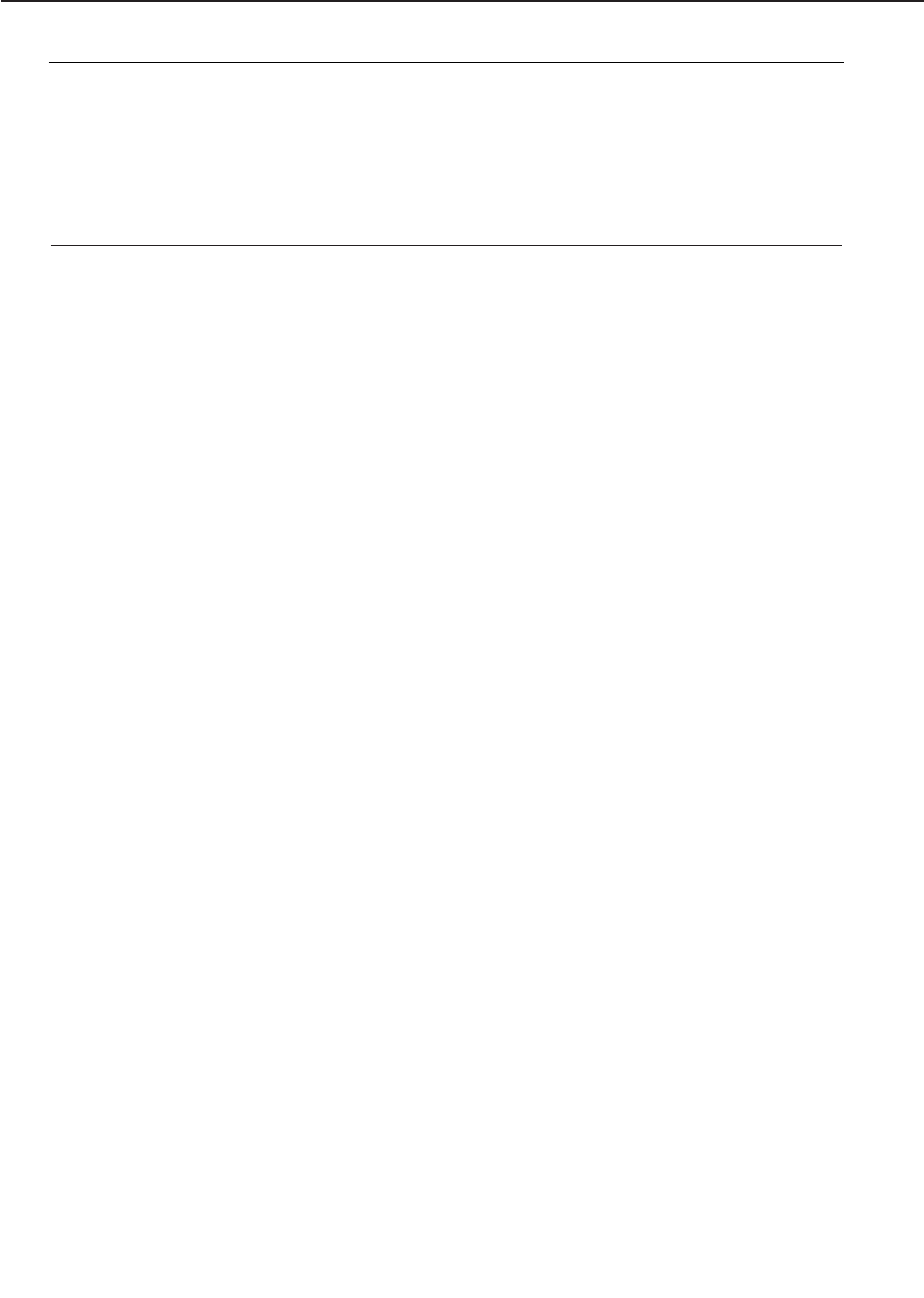
Notes : 1. Before executing a test print, make sure to select the same pick-up source and deliv-
ery source that were used when the malfunction occurred according to the informa-
tion given by the user.
If the information is not available, make test prints with all feasible combination of
paper source and delivery source in the printer, and find out the factor.
2. The image defect occurred at the user side might not re-occur on its test print.
In this case, make a print from external device and infer the factor by the output
image. Then, find the factor according to the item, "image defects."
4 - 3
CHAPTER 4
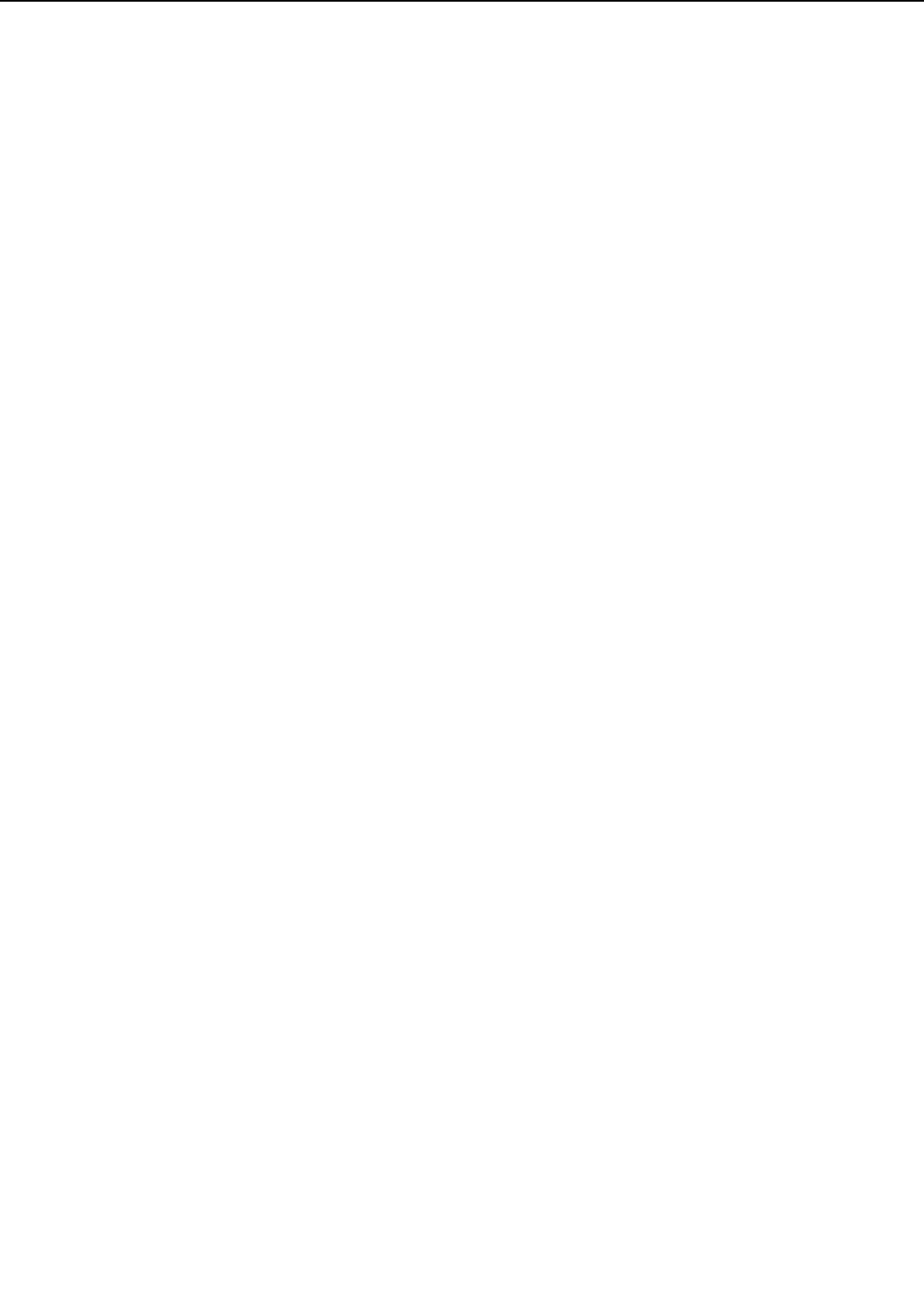
B. Initial Check
Check the following items before making a diagnosis of malfunction. If any failure is found, the
service technician is to clear the problem and to give the instruction to the user.
1. Installation environment
Make sure that the requirements stated below meet when installing printer:
a. The power supply voltage is from -10% to +6% of the rated voltage.
b. The printer is securely installed on a level surface.
c. The room temperature is kept between 10°C and 32.5°C, and the relative humidity, between
20% and 80%.
d. Avoid sites generating ammonia gas, high temperature or high humidity (near water faucet,
kettle, humidifier), cold places, open flames and dusty areas.
e. Avoid sites exposed to direct sunlight. If unavoidable, advise the customer to hang curtains.
f. A well-ventilated place.
g. Make sure that the power plug is inserted to the printer and the outlet securely.
2. Paper checks
a. The recommended paper for this printer is used.
b. The paper is not damp.
3. Paper sets
a. The paper is set to the pick-up source within the specified volume.
b. The paper is set to the selected pick-up source correctly.
c. The cassette is installed in the printer correctly.
4. EP-72 cartridge sets
The cartridge is installed in the printer correctly.
5. Condensation
During winter, particularly when moving the printer into a warm room from a cold location such
as a warehouse, various problems can occur due to condensation in the printer.
Example)
a. Condensation in the optical system (six-faced mirror, reflecting mirror, lens, etc.) will result
in light output images.
b. As the photosensitive drum is cold, the resistance of the photoconductive layer is high. This
will lead to incorrect contrast.
If condensation appears, leave the printer ON for 10 to 20 minutes.
If a cartridge is opened soon after being moved from a cold room to a warm room, condensa-
tion may appear inside the cartridge and may cause various image defects.
Be sure to instruct the customer that it is necessary to leave the cartridge sealed for one to
two hours at room temperature to allow it to acclimatize.
4 - 4
CHAPTER 4
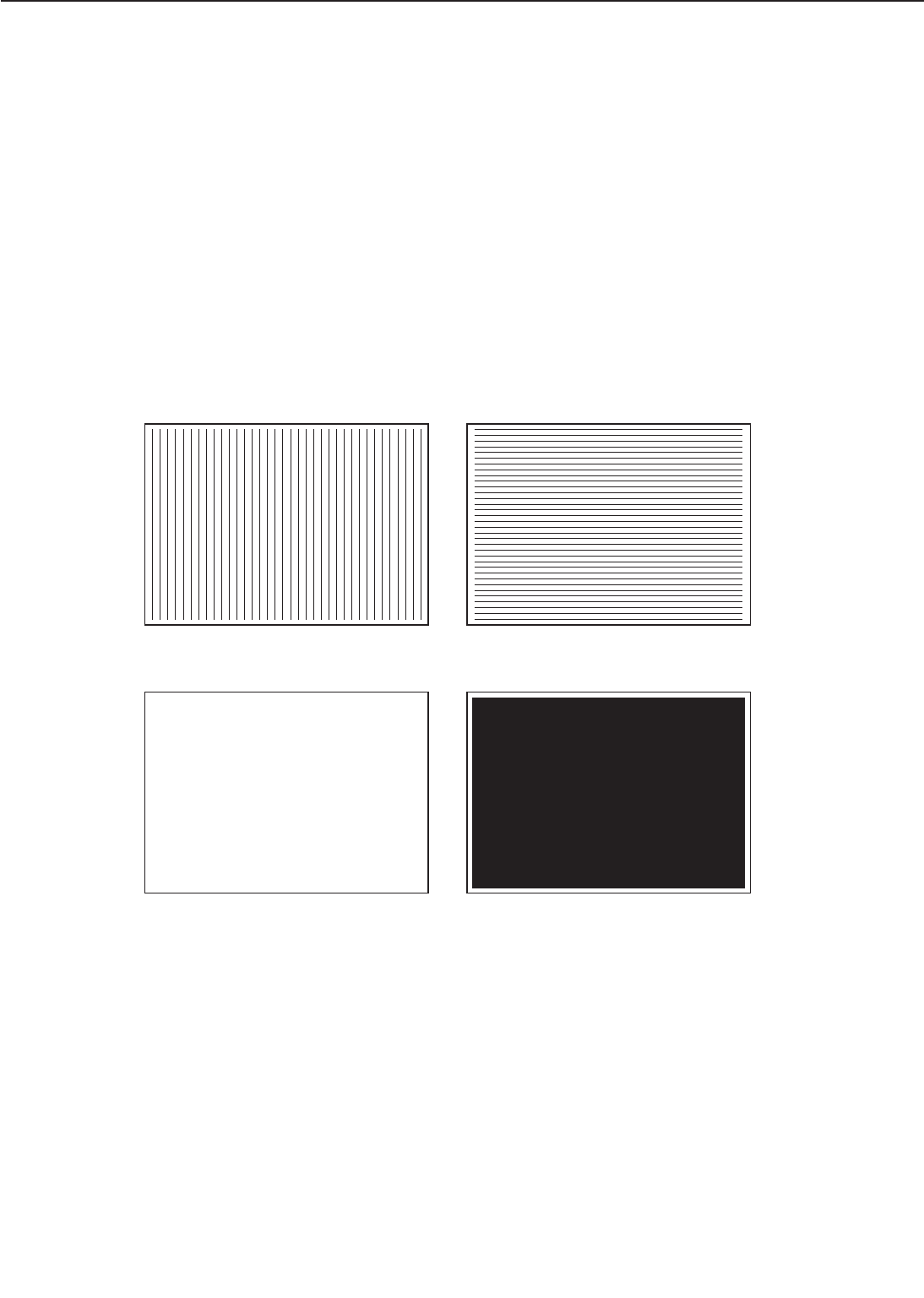
C. Test Print
The test print is divided into two types: engine test print and controller test print.
If a malfunction occurs in this printer, make a test print and assess the abnormality of the
printer.
1. Engine test print
Test print patterns of horizontal lines are printed in this test print. The test prints can be made
by using the printer driver tester which can make all four test patterns (vertical lines, horizon-
tal lines, solid black and solid white), or the test print switch located on the right side of the
printer (see Figure 1-4-1).
One print of test pattern can be made by pressing the switch once when the power is turned
ON and the "READY" appears on the display. If the switch is held down, test prints are made
continuously.
Make sure that paper is loaded into the lower cassette before pressing the switch as this is
where the paper is picked up from.
Figure 4-1-2
4 - 5
CHAPTER 4
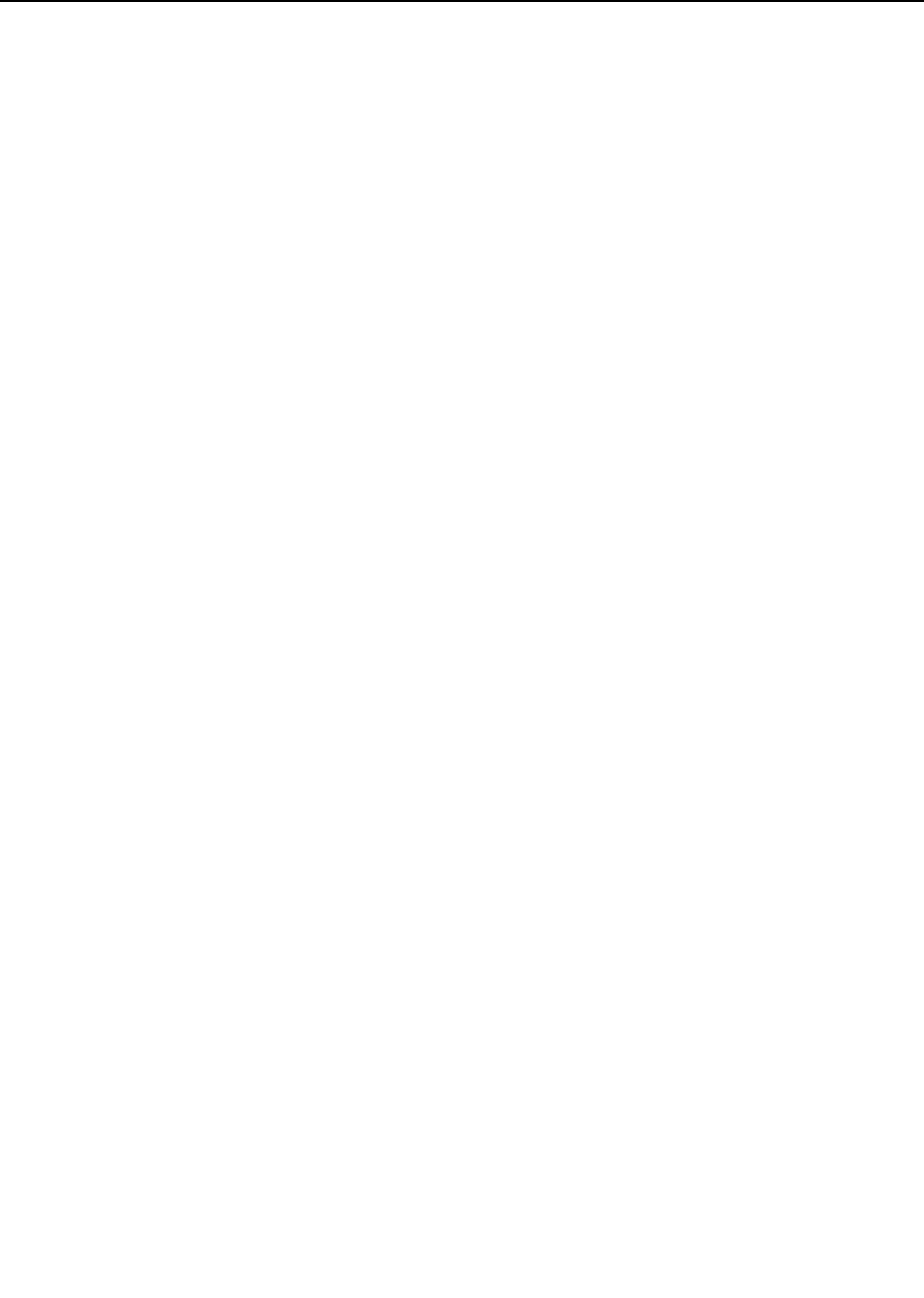
2. Controller test print
The following items can be printed by selecting and executing a TEST MENU:
•SHOW PAGE COUNT
Displays the total number of pages printed. The total page number is only shown briefly on
the display but does not print. The page count prints in the TEST PRINT.
•TEST PRINT
Make a Test Print. The Test Print lists the printing environment settings and also displays
the graphic and text printing capabilities.
•PRINT PS FONTS
Available only after the Translator Module A-72 for Adobe PostScript Level 3 module has been
installed. Prints the PS Font List.
•PRINT PCL FONTS
Prints the PCL Font List.
•PRINT PS DEMO
Available only after the Translator Module A-72 for Adobe PostScript Level 3 module has been
installed. Prints the PS demonstration page.
•PRINT PCL DEMO
Prints the PCL demonstration page.
•CONTINUOUS TEST
Make continuous Test Prints.
•STAPLE TEST
Available only when the staple stacker SS-72 is installed. Use "STAPLE TEST" when you
replaced the staple cartridge.
•CLEANING PAGE
Use "CLEANING PAGE" to print cleaning patterns to clean the fixing unit when an image
defect occurred and its cause is suspected to be the fixing unit. Refer to "Maintenance and ser-
vicing by the customer" in Chapter 1 for details.
Follow these steps to make a Test Print:
1) Press the On Line key to set the printer off-line. The On line indicator should be OFF and
"PAUSED" appears in display.
2) Press the Menu key until you see "TEST MENU" in the top line.
3) Press the Item key until you see "TEST PRINT" in the bottom line.
4) Press the Enter key to start printing a Test Print.
5) After the pages are printed, press the On Line key to put the printer on-line.
Use the Test Print to verify the operation panel selections, system configurations (memory and
options), and print quality.
4 - 6
CHAPTER 4
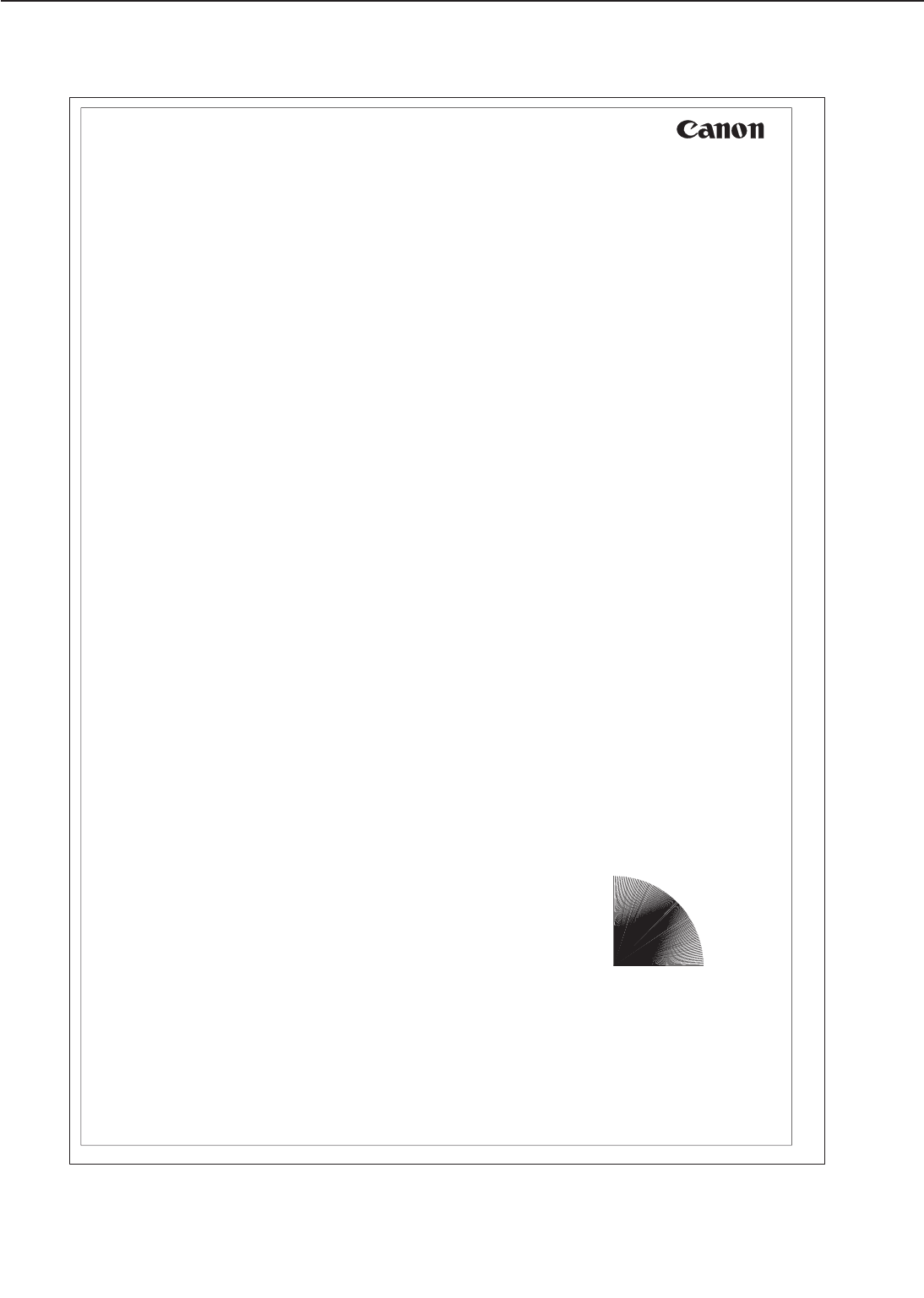
Figure 4-1-3
4 - 7
CHAPTER 4
Canon Inc., LBP-3260 Printer
Configuration Page
Canon, the Canon logo and LBP are trademarks of Canon Inc.
PCL and PCL5 are trademarks of Hewlett-Packard Company.
PCL MENU
COPIES = 1
PAGESIZE = A4
ORIENTATION = PORTRAIT
FORM = 64LINES
FNTSRC = INTERNAL
FONTNUM = 0
PT.SIZE = 12.00
PITCH = 10.00
SYMSET = ROMAN-8
FEEDER MENU
FEED = LOWER
7 BIN SORTER MODE = STACKING
OUTPUT = 7 BIN SORTER
FORM = 64LINES
TRAY SWITCH = ON
MANUAL = OFF
MPTSIZE = A4
CONFIG MENU
JAMRECOVERY = ON
AUTOCONT = OFF
DENSITY = 7
PWRSAV = 15 MIN
ECONOMY MODE = OFF
REFINE = ON
MEMCONFIG MENU
PCL SAVE = OFF
PARALLEL MENU
BIDIRECTION = ON
I/O TIMEOUT = 15
TEST MENU
SHOW PAGE COUNT
TEST PRINT
PRINT PCL FONTS
PRINT PCL DEMO
CONTINUOUS TEST
LANGUAGE MENU
LANG = ENGLISH
PAPER TYPE MENU
UPPER = PLAIN
LOWER = PLAIN
MPT = PLAIN
RESET MENU/PRINTER
RESET = PRINTER
RESET = MENU
INSTALLED OPTIONS
7 BIN SORTER
3-SPEED 7-BIN SORTER VER 5.7
TOTAL MEMORY = 8 MB
AUTOSENSED PAPER
UPPER = A4
LOWER = A4
PRINTER DETAILS
CODE LEVELS
CTL B1.0408/14/98
ENGINE OC
OPTC 05.10
PCL 1.4.10
PAGE COUNT = 1
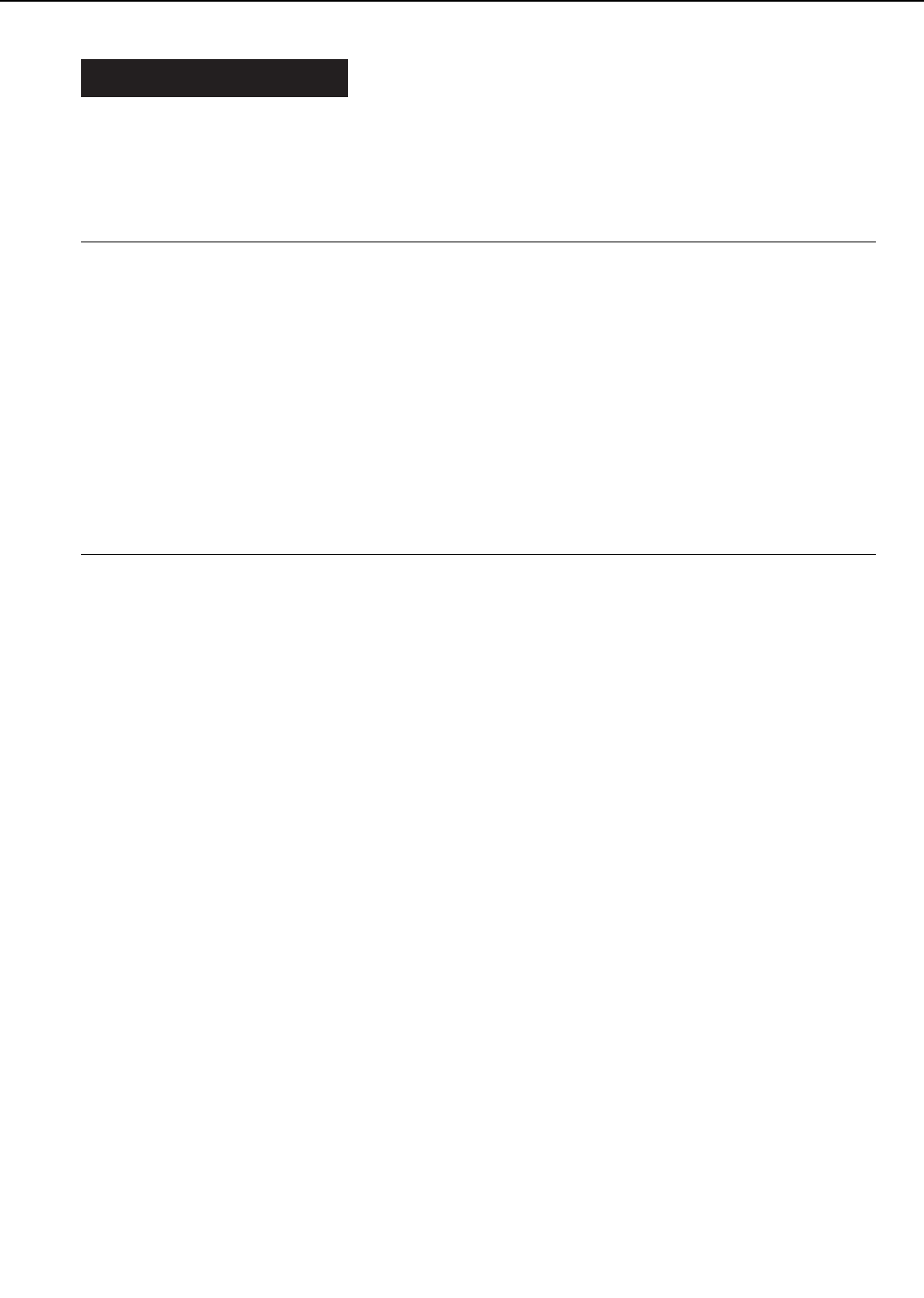
II. IMAGE DEFECTS
If the factor of the malfunction is identified as “image defects” by the malfunction diagnosis flow-
chart (Figure 4-1-1), find out the cause of the failure according to the table below and clear the
problem.
Table 4-2-1
• I-1 Light: Output very light image
• I-2 Dark: Output very dark image
• I-3 Completely Blank: Output no image
• I-4 All Black: Output all black paper
• I-5 Dots in Vertical Lines : Output white dots on the paper
• I-6 Dirt on Back of Paper: Output dirt on the back of the paper
• I-7 Vertical Lines: Output vertical lines on the paper
• I-8 Black Horizontal Lines: Output horizontal lines on the paper
• I-9 Dirt: Output dirt on surface of the paper
• I-10 Blank Spots: Output image with blank spots
• I-11 White Vertical Lines: Output white vertical lines on the paper
• I-12 White Horizontal Lines: Output white horizontal lines on the paper
• I-13 Poor Fixing: Output the image with poorly fixed toner
• I-14 Image Distortion: Output distorted image
II-1. Light
<Possible causes>
1. The image density is not adjusted correctly.
Action: Adjust the image density by operating the external device.
2. Open the upper cover and remove the EP-72 cartridge while a print is being made. Open the
drum protective shield of the EP-72 cartridge and check the toner image on the photosensi-
tive drum. If the toner image has not been transferred to the paper properly, go to step 3.
If the toner image on the drum is faint, go to step 6.
Do not open the drum protective shield for more than 10 seconds.
3. The transfer charging roller contact of the high-voltage power supply is not making a good
connection with the contact of the transfer charging roller shaft.
Action: If the contacts are dirty, clean them. If the problem continues after cleaning, or
parts are deformed or damaged, replace them.
4. The transfer charging roller is deformed or has deteriorated.
Action: Replace the roller.
5. The high-voltage power supply PCB is defective.
Action: Replace the high-voltage power supply PCB.
6. The DC controller PCB is defective.
Action: Replace the DC controller PCB.
4 - 8
CHAPTER 4
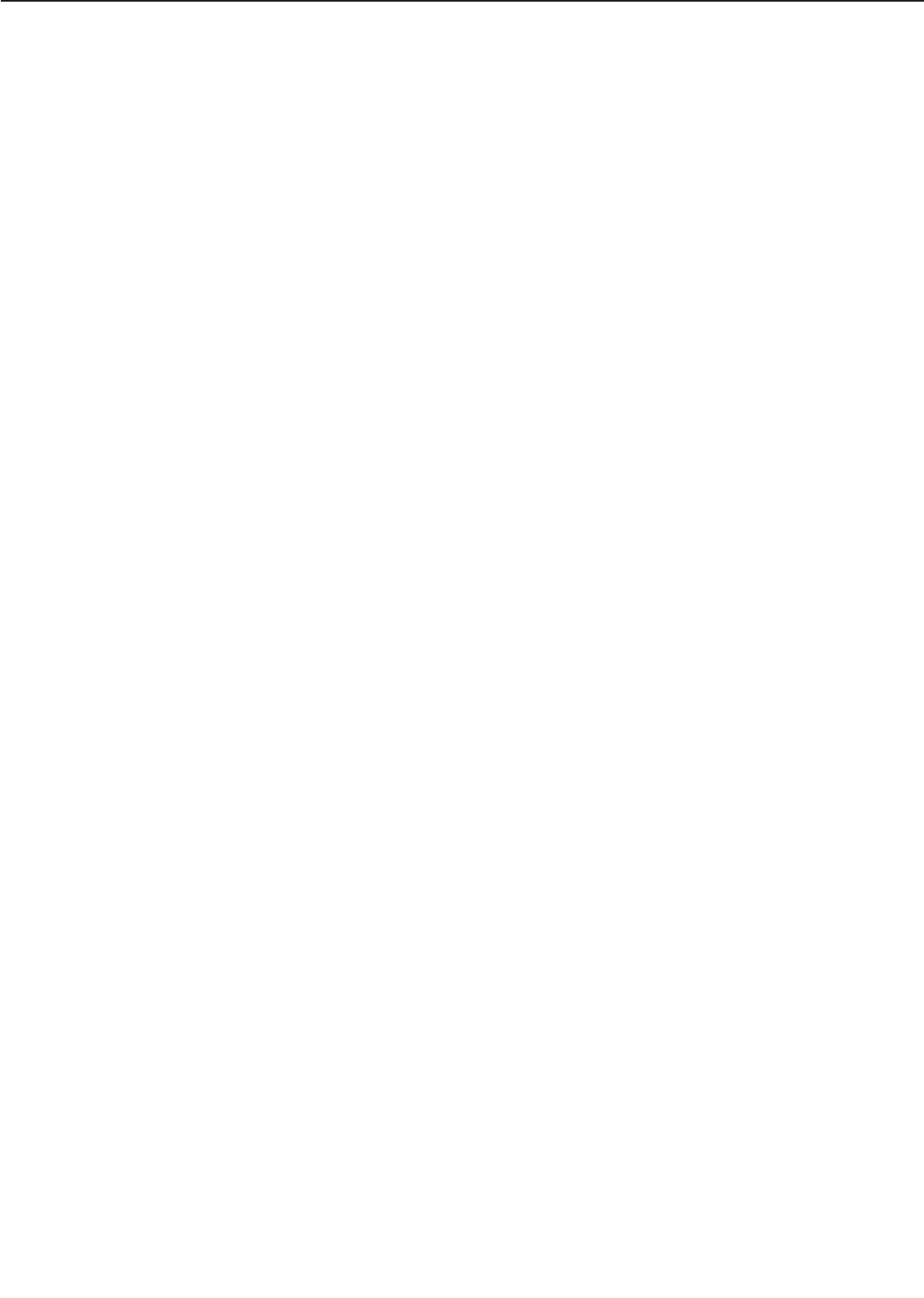
II-2. Dark
<Possible causes>
1. The image density is not adjusted correctly.
Action: Adjust the image density by operating the external device.
2. The drum grounding contact of the high-voltage power supply is not making a good connec-
tion with the cartridge contact.
Action: If the contacts are dirty, clean them. If the problem continues after cleaning, or
parts are deformed or damaged, replace them.
3. The primary bias contact of the high-voltage power supply is not making a good connection
with the cartridge contact.
Action: If the contacts are dirty, clean them. If the problem continues after cleaning, or
parts are deformed or damaged, replace them.
4. The high-voltage power supply PCB is defective.
Action: Replace the high-voltage power supply PCB.
5. The DC controller PCB is defective.
Action: Replace the DC controller PCB.
II-3. Completely blank
<Possible causes>
1. The projection for opening and closing the laser shutter of the EP-72 cartridge is damaged.
Action: Replace the cartridge.
2. The laser shutter arm or laser shutter is malfunctioning or damaged.
Action: If the laser shutter arm or laser shutter does not move smoothly, or parts are dam-
aged, replace them.
3. The developing bias contact of the high-voltage power supply is not making a good connec-
tion with the cartridge contact.
Action: If the contacts are dirty, clean them. If the problem continues after cleaning, or
parts are deformed or damaged, replace them.
4. The high-voltage power supply PCB is defective.
Action: Replace the high-voltage power supply PCB.
5. The DC controller PCB is defective.
Action: Replace the DC controller PCB.
II-4. All black
<Possible causes>
1. The primary bias contact of the high-voltage power supply is not making a good connection
with the cartridge contact.
Action: If the contacts are dirty, clean them. If the problem continues after cleaning, or
parts are deformed or damaged, replace them.
2. Defective primary charging roller
4 - 9
CHAPTER 4
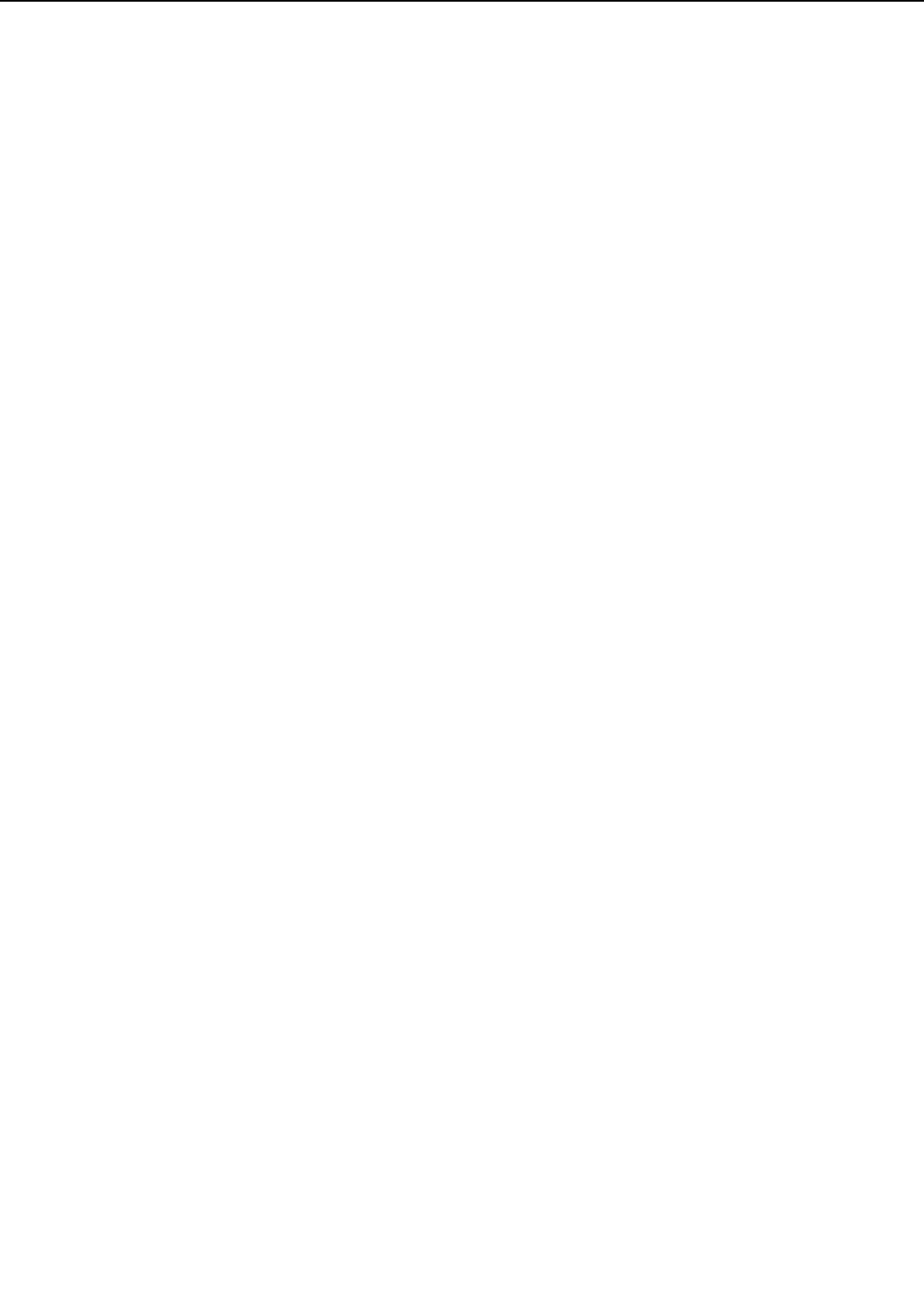
Action: Replace the cartridge.
3. The high-voltage power supply PCB is defective.
Action: Replace the high-voltage power supply PCB.
4. The DC controller PCB is defective.
Action: Replace the DC controller PCB.
II-5. Dots in vertical line
<Possible causes>
1. Static charge eliminator is dirty.
Action: Clean the eliminator with brush.
2. The static charge eliminator contact of the high-voltage power supply is not making a good
connection with the static charge eliminator contact.
Action: If the contacts are dirty, clean them. If the problem continues after cleaning, or
parts are deformed or damaged, replace them.
3. The transfer charging roller is deformed or has deteriorated.
Action: Replace the transfer charging roller.
4. The high-voltage power supply PCB is defective.
Action: Replace the high-voltage power supply PCB.
5. The DC controller PCB is defective.
Action: Replace the DC controller PCB.
II-6. Dirt on back of paper
<Possible causes>
1. Dirty paper
Action: Replace the paper with new one. Advise the customer on how to store paper.
2. Periodical stain (pick-up roller, transfer charging roller, lower fixing roller)
Action: Referring to Table 4-2-1 on page 4-11, identify the dirty roller(s) and clean the dirty
areas. If the dirt cannot be removed, replace the dirty roller(s).
3. The feed guide or fixing entry guide is dirty.
Action: Clean dirty parts.
II-7. Vertical lines
<Possible causes>
1. Circumferential scars on the photosensitive drum
Action: Replace the cartridge
2. The upper fixing roller is scratched.
Action: Remove the cause of the damage and replace the roller.
4 - 10
CHAPTER 4
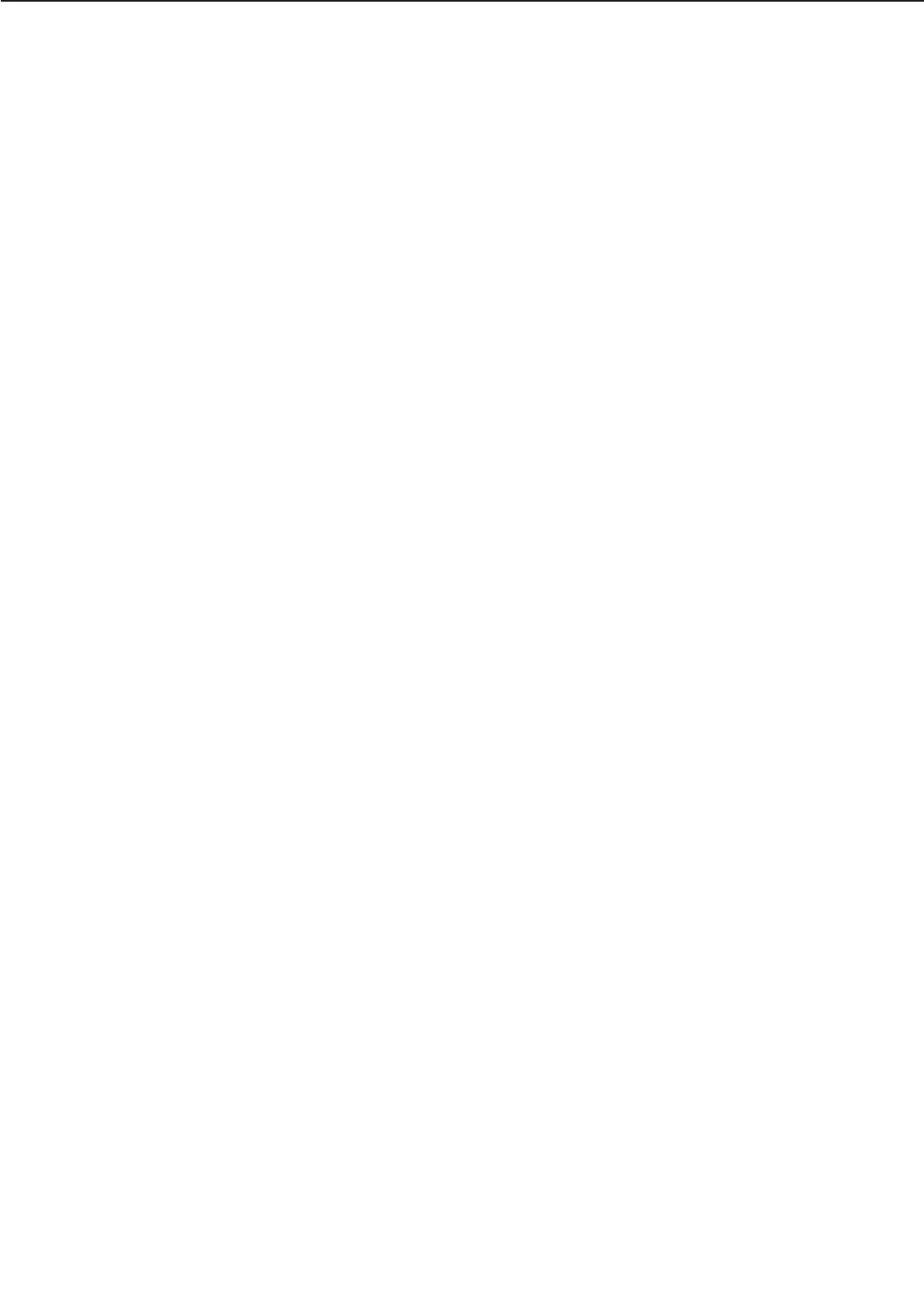
II-8. Black horizontal lines
<Possible causes>
1. Horizontal scar(s) on photosensitive drum
Action: Replace the cartridge.
2. The upper fixing roller is dirty, deformed, or worn.
Action: Replace the upper fixing roller.
II-9. Dirt
<Possible causes>
1. The print paper is dirty.
Action: Replace with new paper. Advise the customer how to store print paper.
2. Periodical stain (separation roller, transfer charging roller, upper fixing roller, EP-72 car-
tridge)
Action: Referring to Table 4-2-1 on page 4-11, identify the dirty roller(s) and clean the dirty
areas. If the dirt cannot be removed, replace the dirty roller(s).
3. Dirty delivery roller
Action: Clean the delivery roller.
II-10. Blank spots
<Possible causes>
1. Lack of toner
Action: Remove the cartridge from the printer. Rock the cartridge in the way described in
the chapter 1, and then install it back in the printer. If the problem persists, replace
the cartridge.
2. The transfer charging roller is dirty or deformed.
Action: Replace the transfer charging roller.
3. Defective photosensitive drum or developing cylinder
Action: Replace the cartridge.
II-11. White vertical lines
<Possible causes>
1. Lack of toner
Action: Remove the cartridge from the printer. Rock the cartridge in the way described in
the chapter 1, and then install it back in the printer. If the problem persists, replace
the cartridge.
2. Circumferential scars on the photosensitive drum
Action: Replace the cartridge.
3. Defective developing cylinder
Action: Replace the cartridge.
4. Foreign materials are on the laser outlet of the printer or the laser inlet of the cartridge.
4 - 11
CHAPTER 4
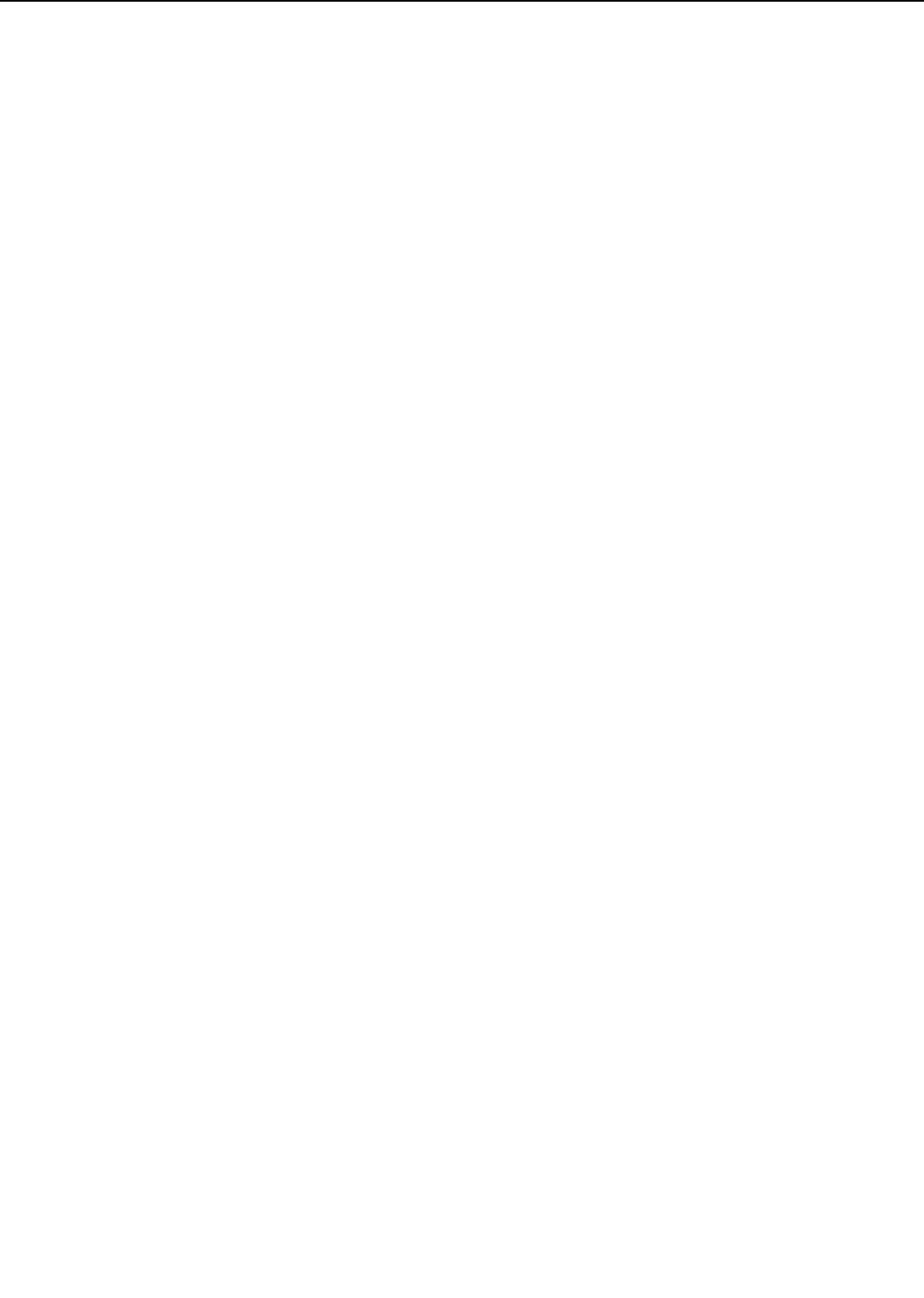
Action: Remove the foreign materials.
5. The upper fixing roller surface is damaged or dented.
Action: Replace the upper fixing roller.
6. The mirror in the laser/scanner unit is dirty.
Action: Replace the laser/scanner unit.
II-12. White horizontal lines
<Possible causes>
1. Horizontal scar(s) on the photosensitive drum
Action: Replace the cartridge.
2. Upper fixing roller is defective.
Action: Replace the upper fixing roller.
II-13. Poor fixing
<Possible causes>
1. The envelope position lever of the fixing unit is raised.
Action: Push down the lever.
2. The nip width of the fixing unit is not correct.
Action: Replace the fixing unit.
3. The fixing roller surface is damaged or dented.
Action: Replace the roller.
4. The lower fixing roller is dirty.
Action: Clean the roller. If it cannot be cleaned, replace the roller.
5. The thermistor has deteriorated.
Action: Replace the thermistor.
II-14. Image distortion
<Possible causes>
1. Connectors on the DC controller PCB are loose.
Action: Reconnect the J202, J206, and J207 connectors properly.
2. The laser/scanner unit connectors are loose.
Action: Reconnect J1001, J1 and J6.
3. The laser/scanner unit is faulty.
Action: Replace the laser/scanner unit.
4. The DC controller PCB is defective.
Action: Replace the DC controller PCB.
4 - 12
CHAPTER 4
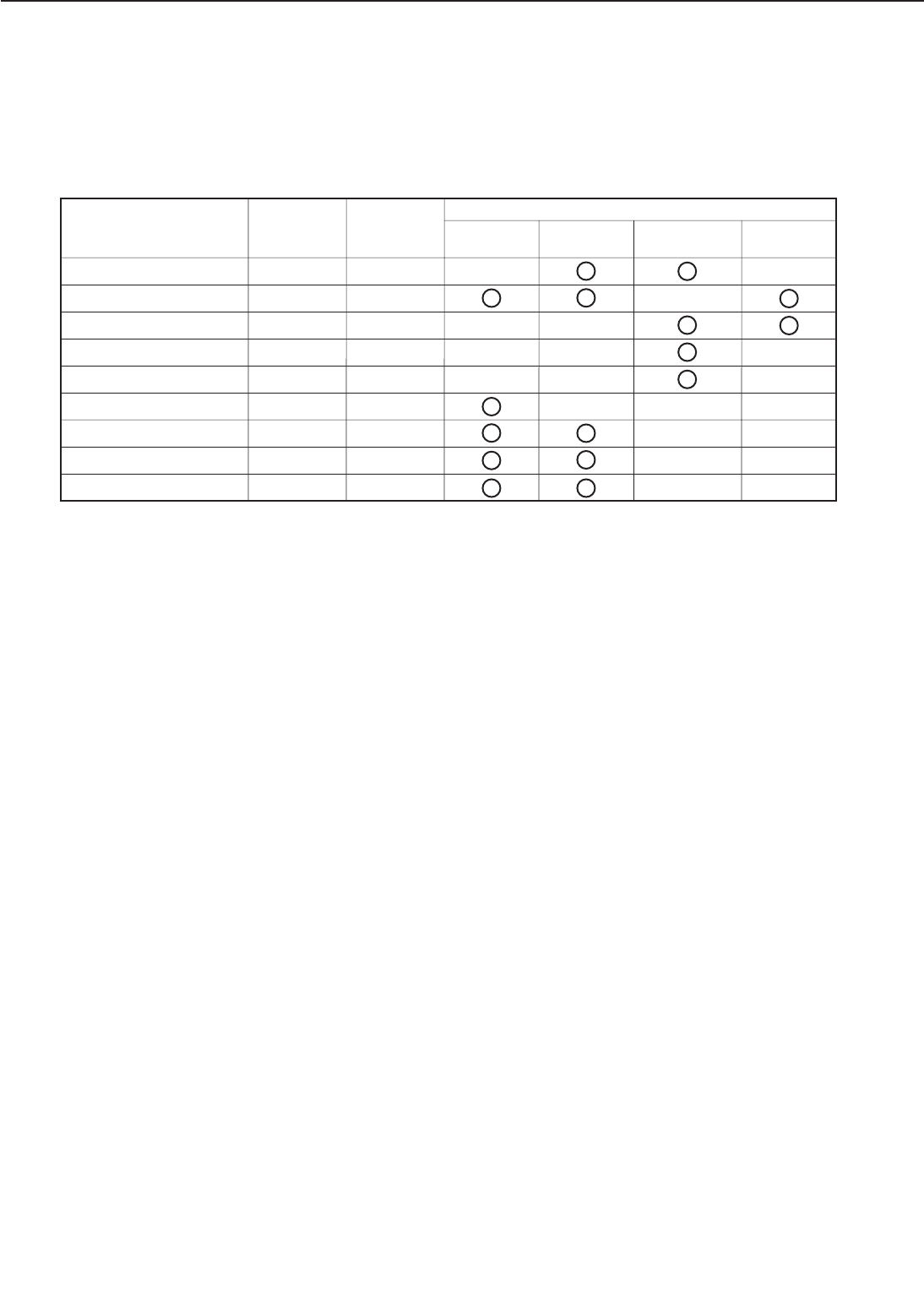
Table 4-2-2
4 - 13
CHAPTER 4
Dirt
Diameter
(mm)
Phenomenon
Transfer charging roller
Upper fixing roller
Lower fixing roller
Pick-up roller
Feed roller
Separation roller
Photosensitive drum
Developing cylinder
Primary charging roller
Period on
image (mm) Blank spot Dirt on back
of paper
17.15
45
32
24
24
24
30
20
14
Poor fixing
Problem location
About 54
About 141
About 100
About 75
About 75
About 75
About 94
About 52
About 44
Periods of appearance of dirt, blank spots on images
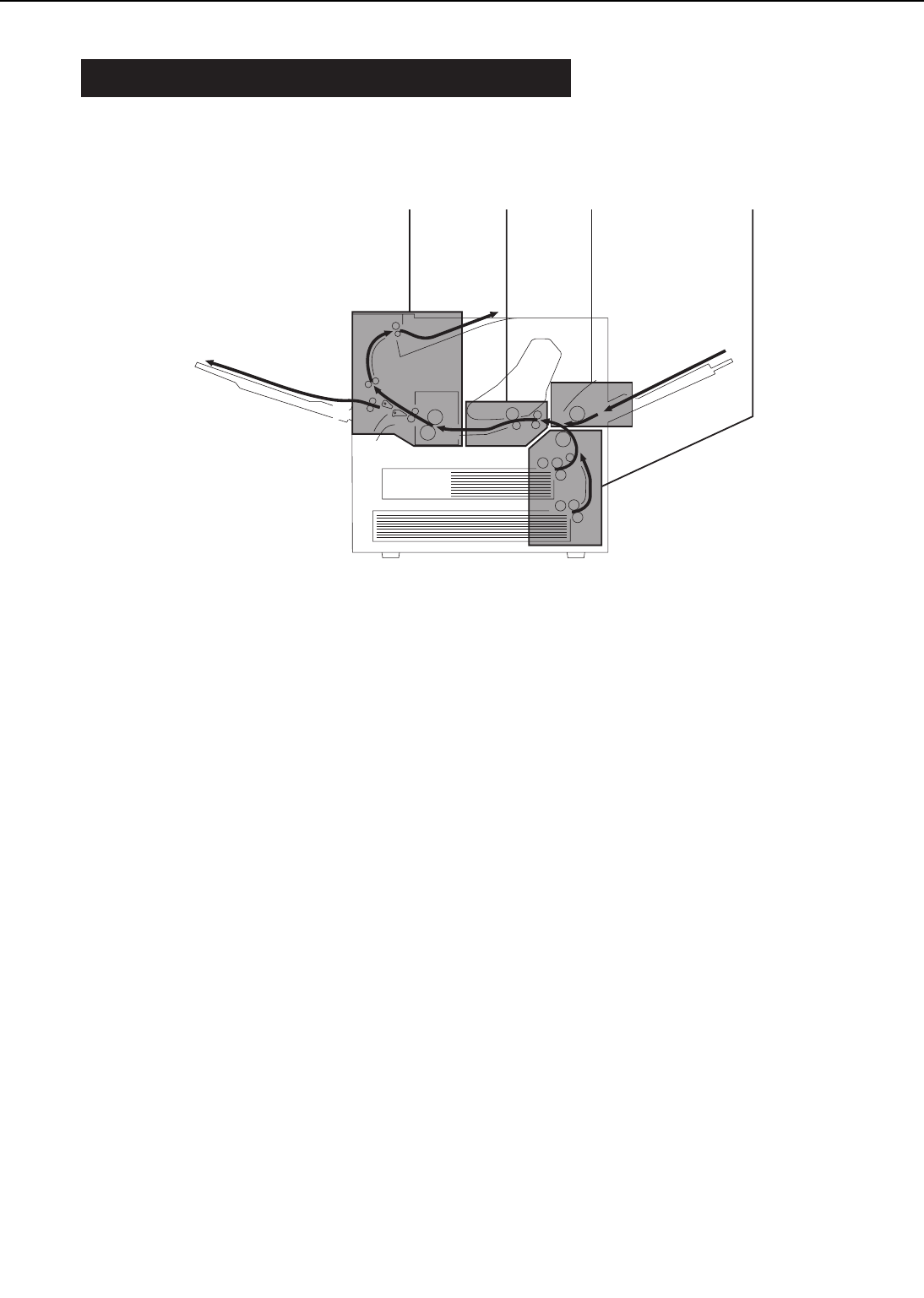
III. PAPER JAMS TROUBLESHOOTING
Paper passes through 4 major sections of the printer.
Figure 4-3-1
III-1: Multi-purpose tray pick-up block
III-2: Cassette pick-up block
III-3: Transfer and feed block
III-4: Fixing and delivery block
If the factor of the malfunction is identified as “paper jams” by the malfunction diagnosis flow-
chart (Figure 4-1-1), check the block in which the paper jam occurred, and find out the defec-
tive part.
4 - 14
CHAPTER 4
➀➁➂ ➃
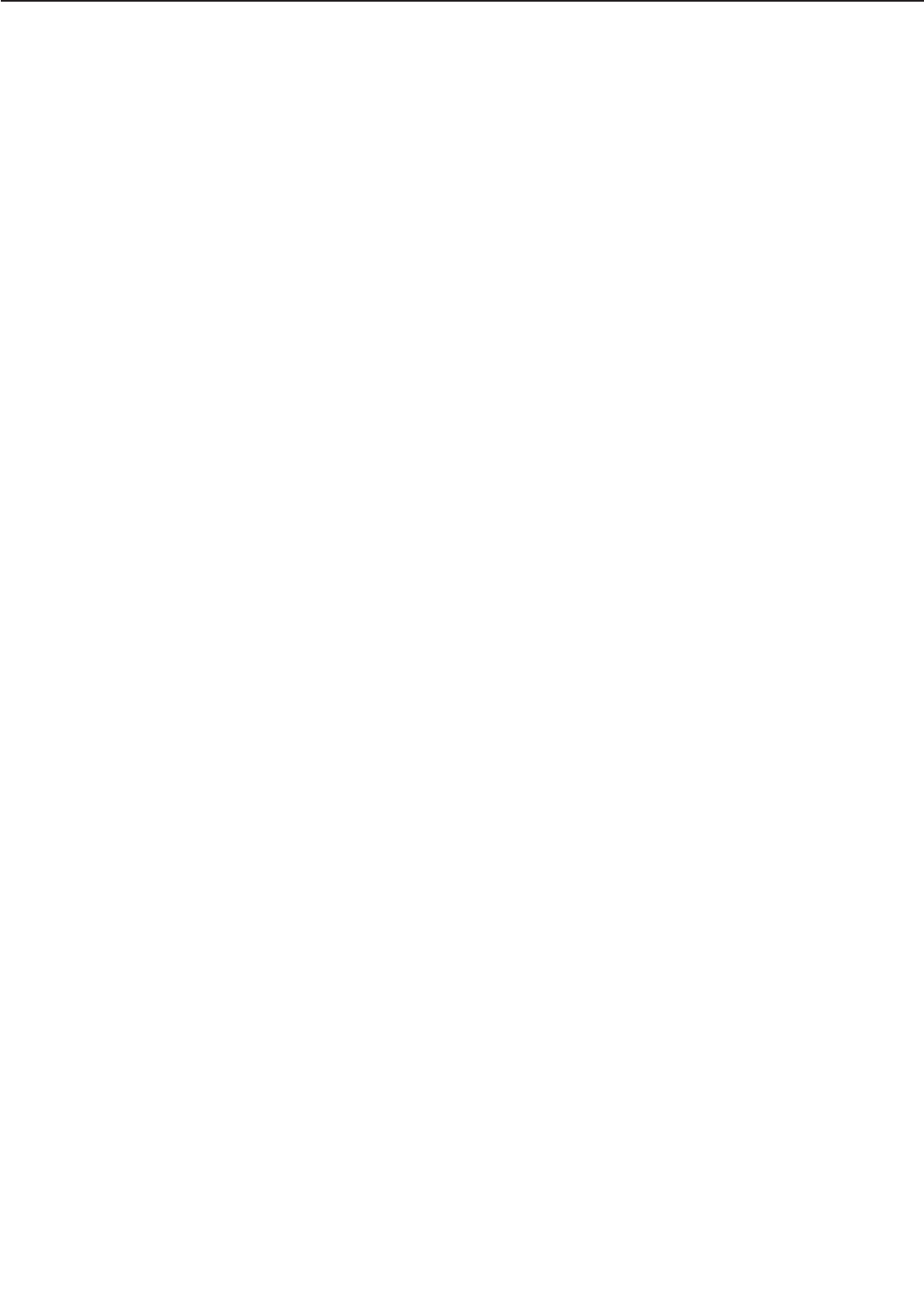
III-1. Multi-purpose tray pick-up block
<Possible causes>
1. Curled paper
Action: Straighten the paper, and then instruct the user.
2. The multi-purpose tray pick-up roller is worn, deformed, or dirty.
Action: Clean the tray pick-up roller if it is dirty. Replace if worn or deformed.
3. Spring of the sensor is out of place or defective
Action: Set the spring in the right position. Replace it if defective.
4. Gears are damaged.
Action: Remove the multi-purpose tray pick-up unit and check the gears. Replace any
damaged gears.
5. The multi-purpose tray pick-up clutch is defective.
Action: Remove the multi-purpose tray pick-up unit and disconnect multi-purpose tray
pick-up clutch connector J1303 from the multi-purpose tray PCB. Measure the
resistance between connector J1303-1 and J1303-2 on the cable side. If it is not
about 155Ω, replace the multi-purpose tray pick-up clutch.
6. The multi-purpose tray PCB is defective.
Action: Replace the multi-purpose tray PCB.
7. The DC controller PCB is defective.
Action: Replace the DC controller PCB.
III-2. Cassette pick-up block
<Possible causes>
1. The print paper is bent.
Action: Replace the paper.
2. The cassette pick-up roller, separation roller, or feed roller is worn or deformed.
Action: Replace if worn or deformed. Replace the separation roller and the feed roller
together.
3. Pick-up drive unit is damaged.
Action: Remove the pick-up unit and replace any damaged parts.
4. The pick-up motor is defective.
Action: Use the printer driver tester to rotate the paper pick-up motor. If it does not rotate,
replace it.
5. The cassette pick-up solenoid is defective.
Action: Remove the pick-up unit, and disconnect cassette pick-up solenoid connector
J1203 from the pick-up PCB. Measure the resistance between connector J1203-1
and J1203-2 on the cable side. If it is not about 190Ω, replace the cassette pick-
up solenoid.
6. The pick-up PCB is defective.
4 - 15
CHAPTER 4
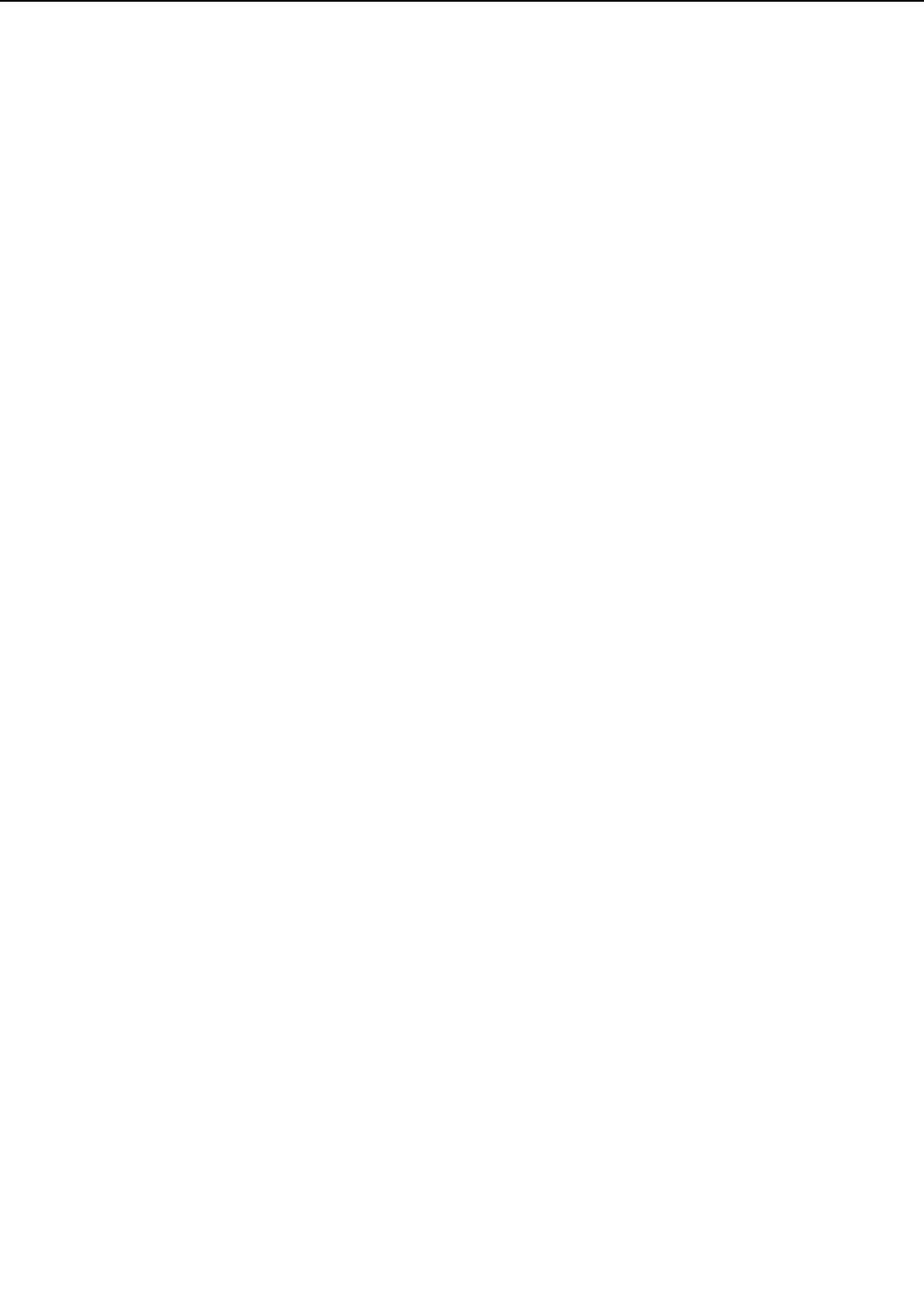
Action: Replace the pick-up PCB.
7. The DC controller PCB is defective.
Action: Replace the DC controller PCB.
III-3. Transfer and feed block
<Possible causes>
1. The registration roller is worn, deformed, or dirty.
Action: Clean the registration roller if it is dirty. Replace if worn or deformed.
2. Transfer charging roller does not rotate smoothly.
Action: Replace the transfer sub roller. Replace any worn gear(s).
3. Registration paper sensor lever does not move smoothly, or is damaged.
Action: Adjust the lever so that it moves smoothly. Replace it if damaged.
4. Registration roller drive gears are damaged.
Action: Replace any damaged gears.
5. The registration clutch is defective.
Action: Disconnect registration clutch connector J17. Measure the resistance between con-
nector J17-1 and J17-2 on the cable side. If it is not about 210Ω, replace the reg-
istration clutch.
6. The DC controller PCB is defective.
Action: Replace the DC controller PCB.
III-4. Fixing and delivery block
<Possible causes>
1. Paper longer than the paper length set by the user was loaded during manual feeding.
Action: Advise the user to replace it with the set paper size.
2. The fixing roller does not rotate smoothly.
Action: Check whether any gears are worn or fractured.
3. The fixing entry guide is dirty, damaged, or clogged with toner.
Action: Clean the guide.
4. The fixing separation guide is dirty, damaged, or clogged with toner.
Action: Clean the guide.
5. The fixing separation claw is worn or damaged.
Action: Replace the claw.
6. The upper or lower fixing roller is deformed or damaged.
Action: Replace deformed or damaged rollers.
7. The nip width of the lower fixing roller is not correct.
Action: Replace the fixing unit.
4 - 16
CHAPTER 4
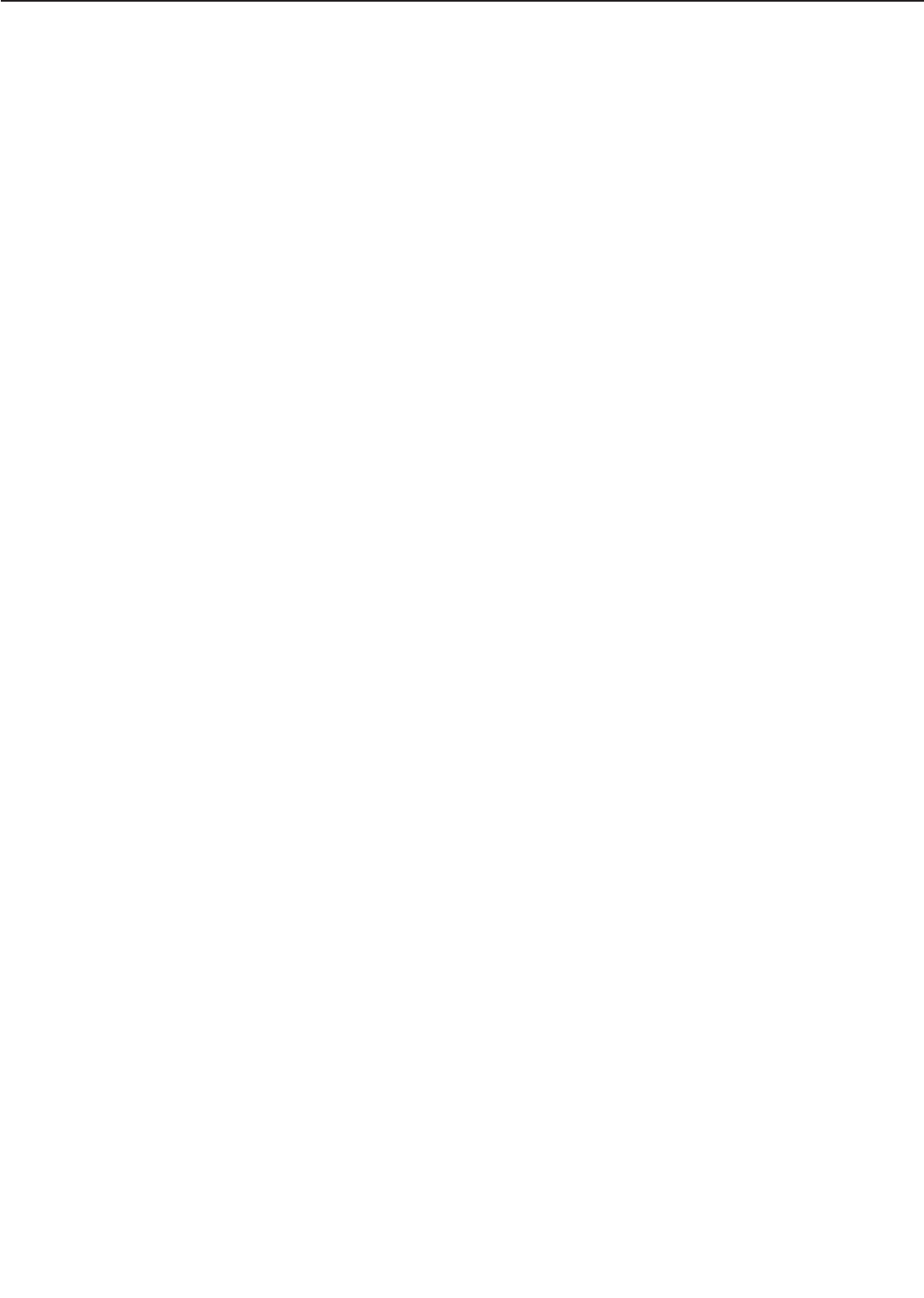
8. The fixing unit delivery sensor lever does not move smoothly or is damaged.
Action: Adjust the lever so that it moves smoothly. If it is damaged, replace it.
9. The fixing unit delivery roller is worn.
Action: Replace the fixing unit delivery roller.
10. The fixing unit delivery roller does not rotate smoothly.
Action: Check the gears, and replace any worn or fractured gear(s).
11. The face-down delivery roller does not rotate smoothly.
Action: Check the gears, and replace any worn or fractured gear(s).
12. Defective fixing unit delivery sensor.
Action: Replace the sensor.
4 - 17
CHAPTER 4
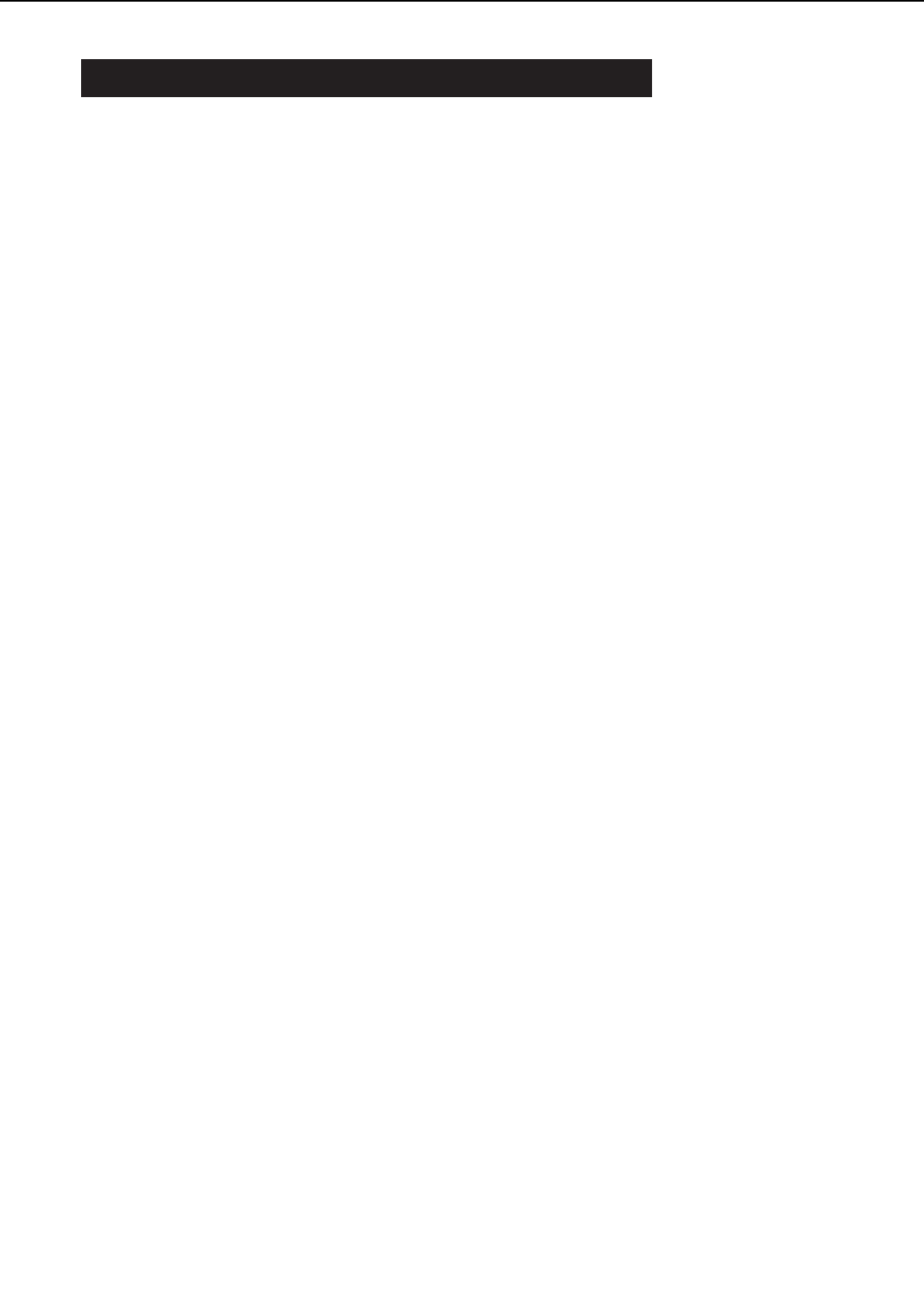
IV. PAPER TRANSPORT TROUBLESHOOTING
If the factor of the malfunction is identified as “paper transport troubleshooting” by the mal-
function diagnosis flowchart (Figure 4-1-1), execute the followings and mend the defect.
IV-1. Multiple Paper Feed
<Possible causes>
1. If this problem occurs with the multi-purpose tray, perform step 4 and subsequent steps.
2. The separation roller is worn or deformed.
Action: Replace the separation roller together with the feed roller.
3. The spring is defective.
Action: Replace the spring that pulls the separation roller.
4. The separation pad surface is worn.
Action: Replace the separation pad together with the multi-purpose tray pick-up roller.
5. The spring is defective.
Action: Replace the spring of the separation pad.
IV-2. Wrinkles/folded leading edge
<Possible causes>
1. Curled paper
Action: A devise the user to straighten the paper.
2. After executing a test print, open the top cover before the paper enters the fixing unit. If the
paper is wrinkled at this point, go to step 6).
3. The fixing entry guide is dirty.
Action: Clean the guide.
4. The lower fixing roller is dirty.
Action: Clean the lower fixing roller.
5. The fixing roller is deformed or worn.
Action: Replace the worn or deformed roller.
6. Paper dust or dirt is accumulated on the feed roller, registration roller, or feed guide.
Action: Clean the dirty areas.
7. Scarred or dirty feed guide
Action: Check the paper path. Replace any scarred or deformed guide(s).
IV-3. Skew
<Possible causes>
1. Paper dust or dirt is adhering to the registration rollers or the feed guide.
Action: Remove the paper dust or dirt.
4 - 18
CHAPTER 4
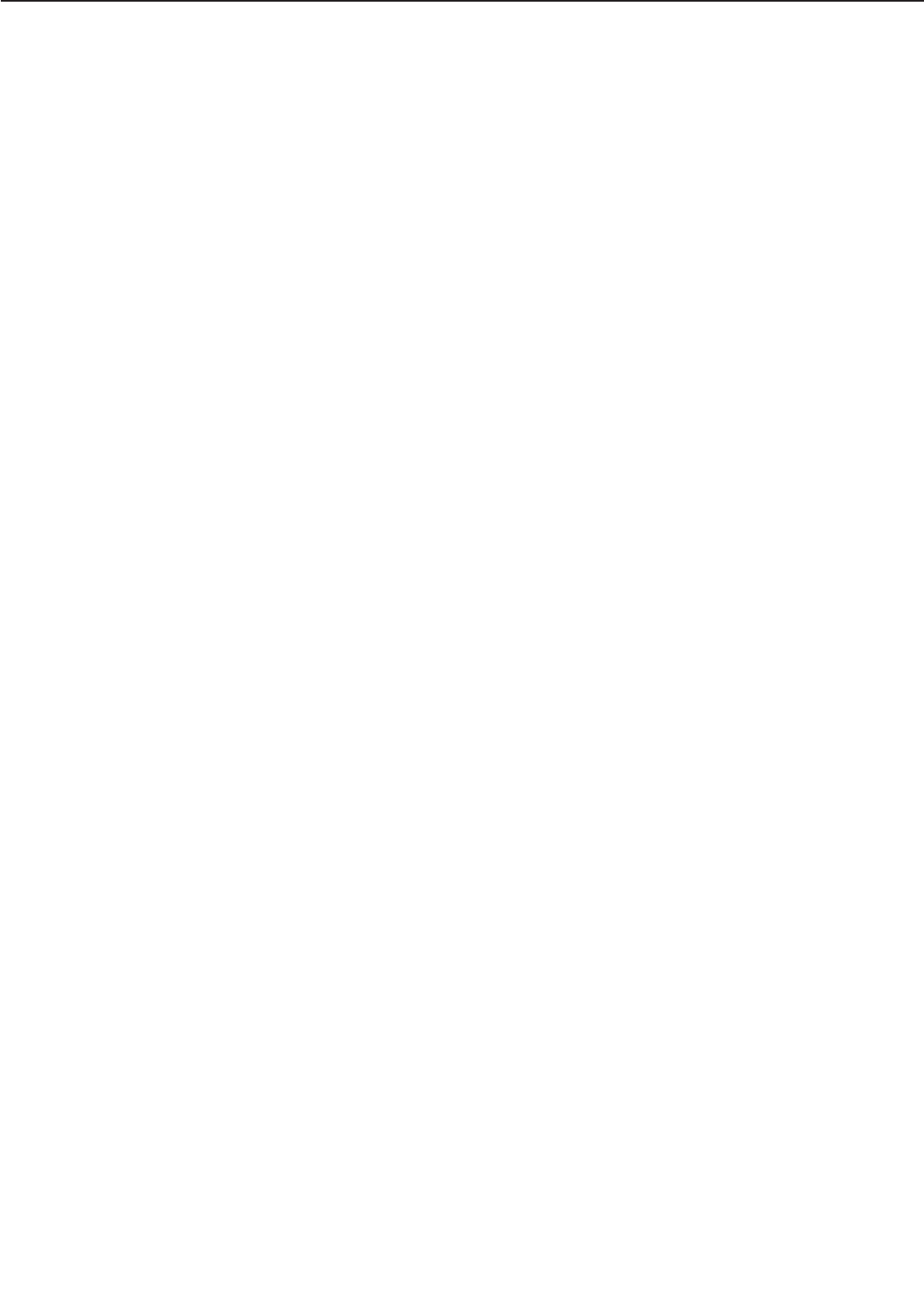
2. The spring of the registration roller unit is out of place.
Action: If the spring is out of place, set it in the right position or replace it with new one.
4 - 19
CHAPTER 4
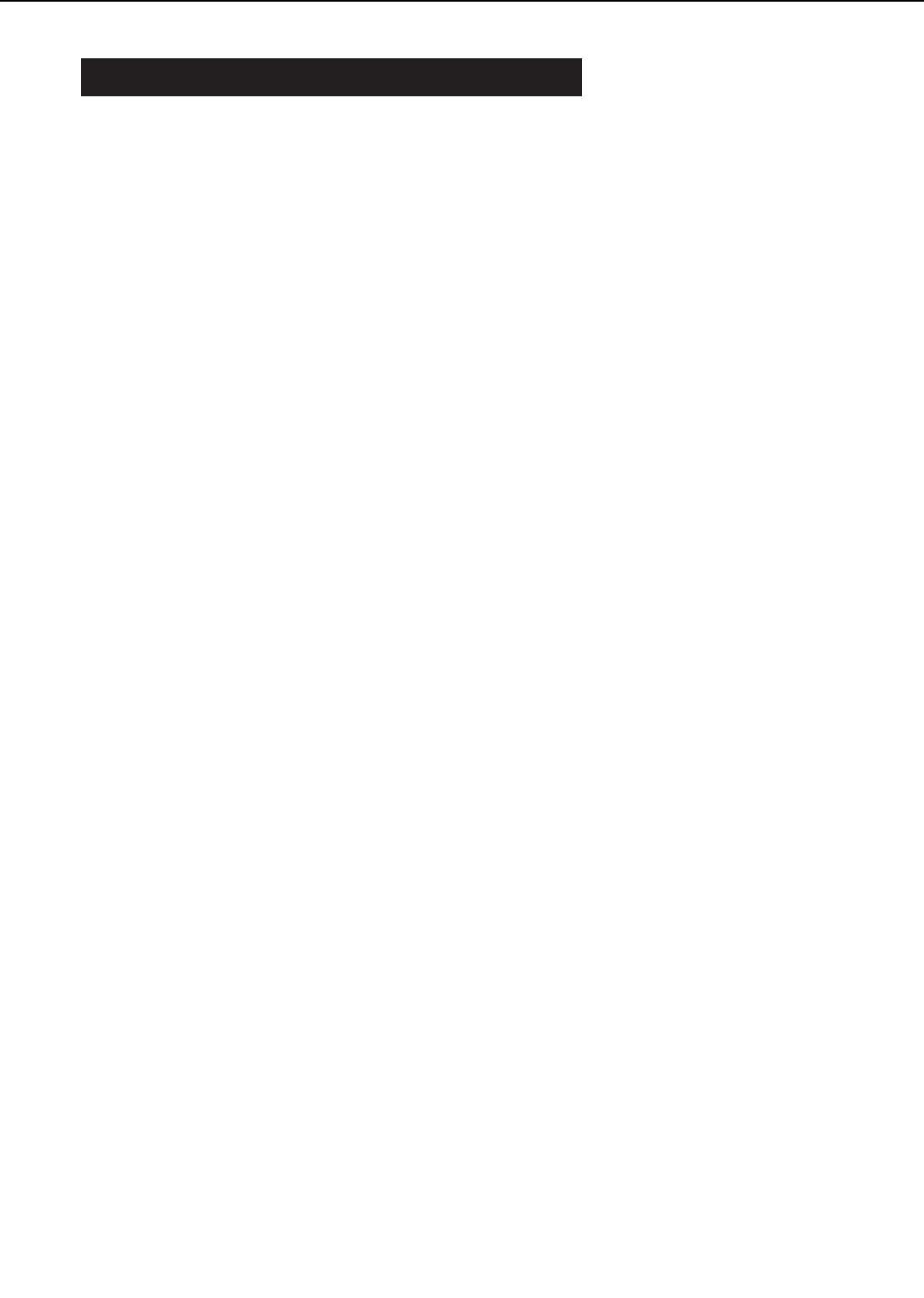
V. MALFUNCTION TROUBLESHOOTING
If the factor of the malfunction is identified as “malfunction troubleshooting” by the malfunction
diagnosis flowchart (Figure 4-1-1), execute the followings and mend the malfunction.
V-1. No AC Power Input
<Possible causes>
1. The correct voltage is not present at the outlet.
Action: Inform the customer that the correct line voltage is not available at the outlet.
2. The power cord is not firmly plugged into the printer, the option (with power receptacle), and
the outlet.
Action: Push the power plugs in firmly.
3. The circuit breaker is OFF.
Action: Remove the power supply. Press the circuit breaker button to set the circuit break-
er ON.
Turn the circuit breaker ON 30 seconds after it is activated (turned OFF).
Before plugging the power cord into the outlet, turn the power switch ON and
check the AC line circuit short and the circuit breaker states (continuity and
contact resistance) using a multimeter.
4. The power supply is defective.
Action: Replace the power supply.
V-2. No DC Power Input
<Possible causes>
1. The AC power is not present.
Action: Make a check using the steps of E-1 “No AC Power Input”.
2. The overcurrent/overvoltage detection circuit is active.
Action: If the problem is not rectified when the power switch is turned OFF and ON again,
find the cause of activation of the overcurrent/overvoltage detection circuit of the
power supply. Turn the power switch OFF for 2 minutes then turn it ON again.
3. The fuse has blown.
Action: Remove the power supply and replace the fuse.
4. The power supply is defective.
Action: Turn the power switch OFF and disconnect the connector J204 from the DC con-
troller PCB. Plug the power cable and turn the power switch ON. Measure the DC
power supply output of the connector J204. Do not short the connector. If the cor-
rect value is not output, replace the power supply.
5. Wiring, DC load, DC controller PCB
Action: Turn the power switch OFF. Check the wiring from the DC controller PCB and the
DC load. If they are normal, replace the DC controller PCB.
4 - 20
CHAPTER 4
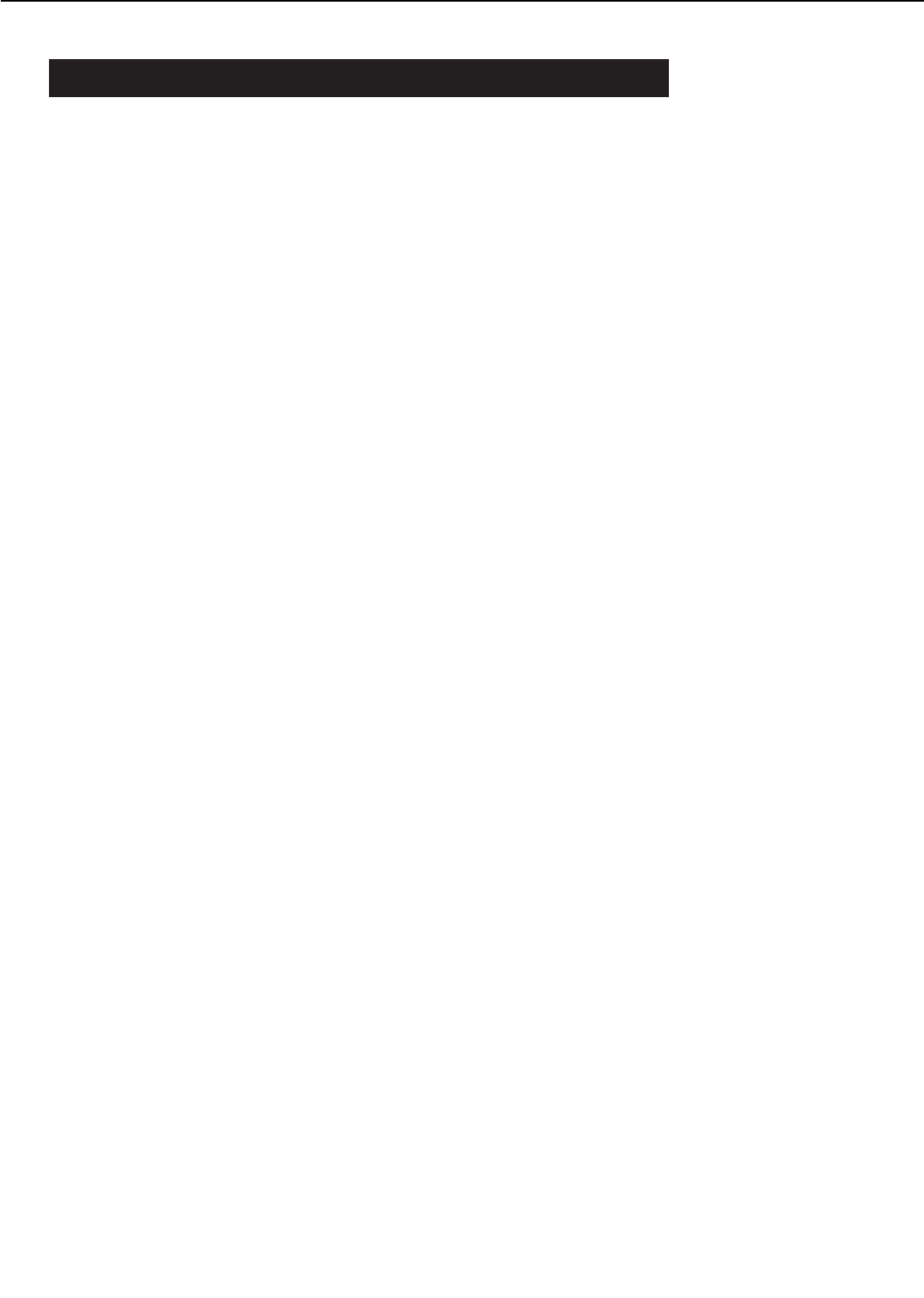
VI. MALFUNCTION STATUS TROUBLESHOOTING
If the factor of the malfunction is identified as “malfunction status troubleshooting” by the mal-
function diagnosis flowchart (Figure 4-1-1), execute the followings and mend the malfunction.
VI-1. "10.1 ERROR FUSER CALL FOR SERVICE"
Fixing unit failure (abnormal low temperature)
"10.2 ERROR FUSER CALL FOR SERVICE"
Fixing unit failure (abnormal Warm-up)
<Possible causes>
1. The rated voltage of the fixing unit installed in the printer differs from the line voltage.
Action: Replace the fixing unit.
2. The thermistor is dirty.
Action: If the thermistor contact area of the upper fixing roller is dirty, clean it.
3. The thermistor is not installed correctly.
Action: If the thermistor is not evenly contacting the upper fixing roller, re-install the ther-
mistor correctly.
4. The thermistor wire is broken.
Action: Turn the power OFF and remove the fixing unit. Measure the resistance between
the fixing unit connector J50B-5 (FSRTH) and J50B-4 (GNDTH). If the resistance
is not between about 190kΩand 290kΩ(room temperature of 25°C), check the
wiring from connector J222 on the DC controller PCB to the thermistor. If it is nor-
mal, replace the thermistor.
5. The main heater wire is broken.
Action: Remove the fixing unit. If there is no continuity between the fixing unit connector
J50-3 (FSRN1: the upper right terminal of the left connector) and J51-5 (FSRN2: the
upper right terminal of the right connector), replace the main heater.
6. The sub heater wire is broken.
Action: Remove the fixing unit. If there is no continuity between the fixing unit connector
J50-4 (FSRL1: the lower right terminal of the left connector) and J51-6 (FSRL2: the
lower right terminal of the right connector), replace the sub heater.
7. The thermoswitch is open.
Action: Remove the fixing unit and wiring cover. If there is no continuity between ther-
moswitch terminals, replace the thermoswitch.
8. The fixing unit drive circuit is defective.
Action: Replace the power supply unit.
9. The DC controller PCB is defective.
Action: Replace the DC controller PCB.
4 - 21
CHAPTER 4
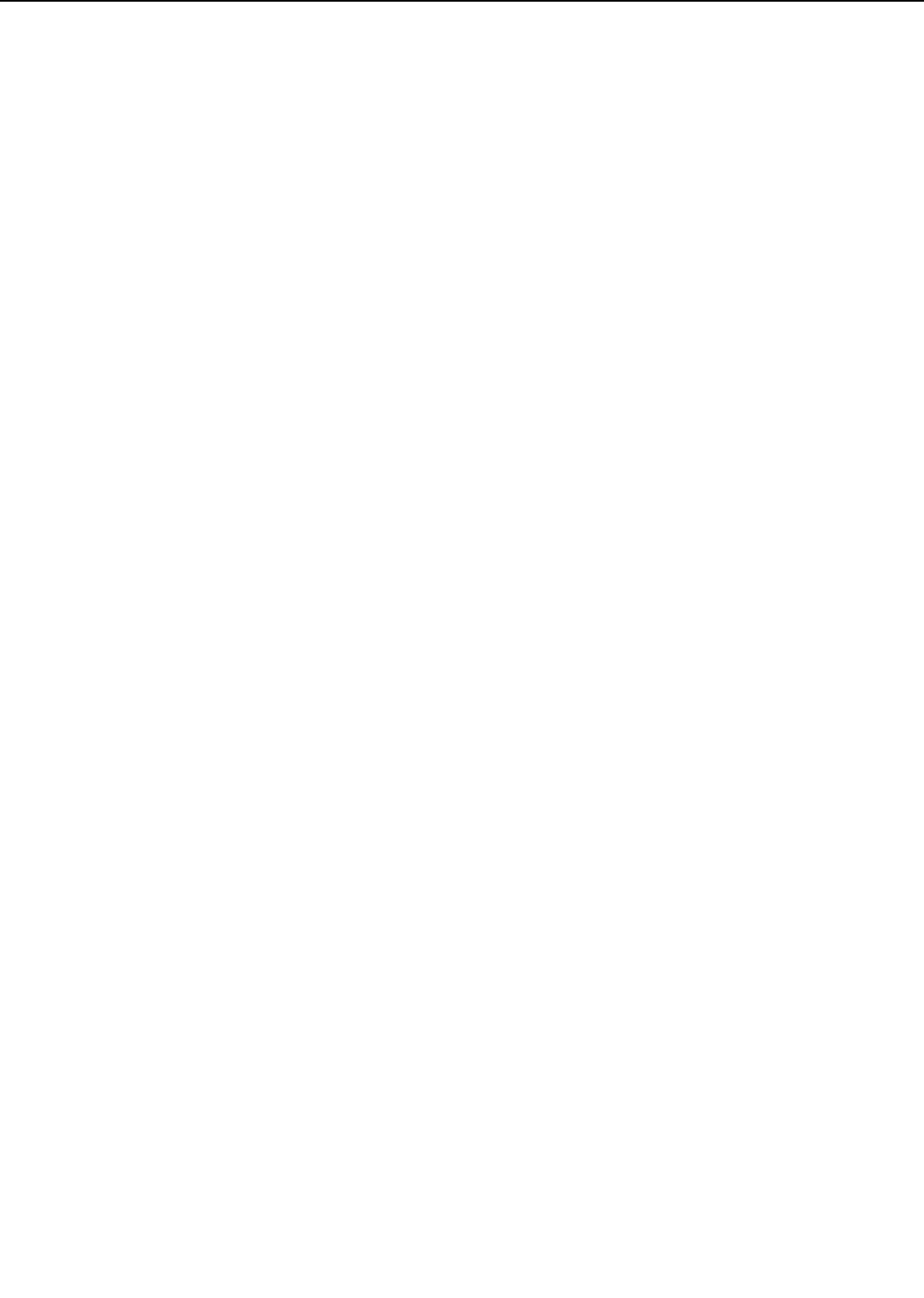
VI-2. "10.3 ERROR FUSER CALL FOR SERVICE"
Fixing unit failure (abnormal high temperature)
<Possible causes>
1. The thermistor has shorted.
Action: Turn the power OFF and remove the fixing unit. Measure the resistance between
the fixing unit connector J50B-5 (FSRTH) and J50B-4 (GNDTH). The connector
J50B is the upper terminal of the left connector. If the resistance is 1kΩor less,
check the wiring from connector J222 on the DC controller PCB to the thermistor.
If it is normal, replace the thermistor.
2. The fixing unit drive circuit in the power supply is defective.
Action: Replace the power supply.
3. The DC controller PCB is defective.
Action: Replace the DC controller PCB.
VI-3. "10.4 ERROR FUSER CALL FOR SERVICE"
Fixing unit failure (wrong type)
<Possible causes>
1. The rated voltage of the fixing unit does not match the line voltage.
Action: Replace the fixing unit.
2. The type detection circuit in the power supply is defective.
Action: Replace the power supply.
3. The DC controller PCB is defective.
Action: Replace the DC controller PCB.
VI-4. "11.1 ERROR SCANNER CALL FOR SERVICE" Scanner motor malfunction
"11.2 ERROR SCANNER CALL FOR SERVICE" Scanner motor malfunction
<Possible causes>
1. The scanner motor drive line connectors are loose.
Action: Reconnect connector J1 on the scanner driver PCB, intermediate connector J18,
and connector J207 on the DC controller PCB.
2. The scanner motor driver is defective.
Action: Use the printer driver tester to rotate the scanner motor. If it does not rotate,
replace the laser/scanner unit.
3. The DC controller PCB is defective.
Action: Replace the DC controller PCB.
VI-5. "11.3 ERROR SCANNER CALL FOR SERVICE" BD malfunction
"11.4 ERROR LASER CALL FOR SERVICE" Laser malfunction
<Possible causes>
1. The BD signal line connector is loose.
Action: Reconnect connector J6 on the BD PCB and J206 on the DC controller PCB.
4 - 22
CHAPTER 4
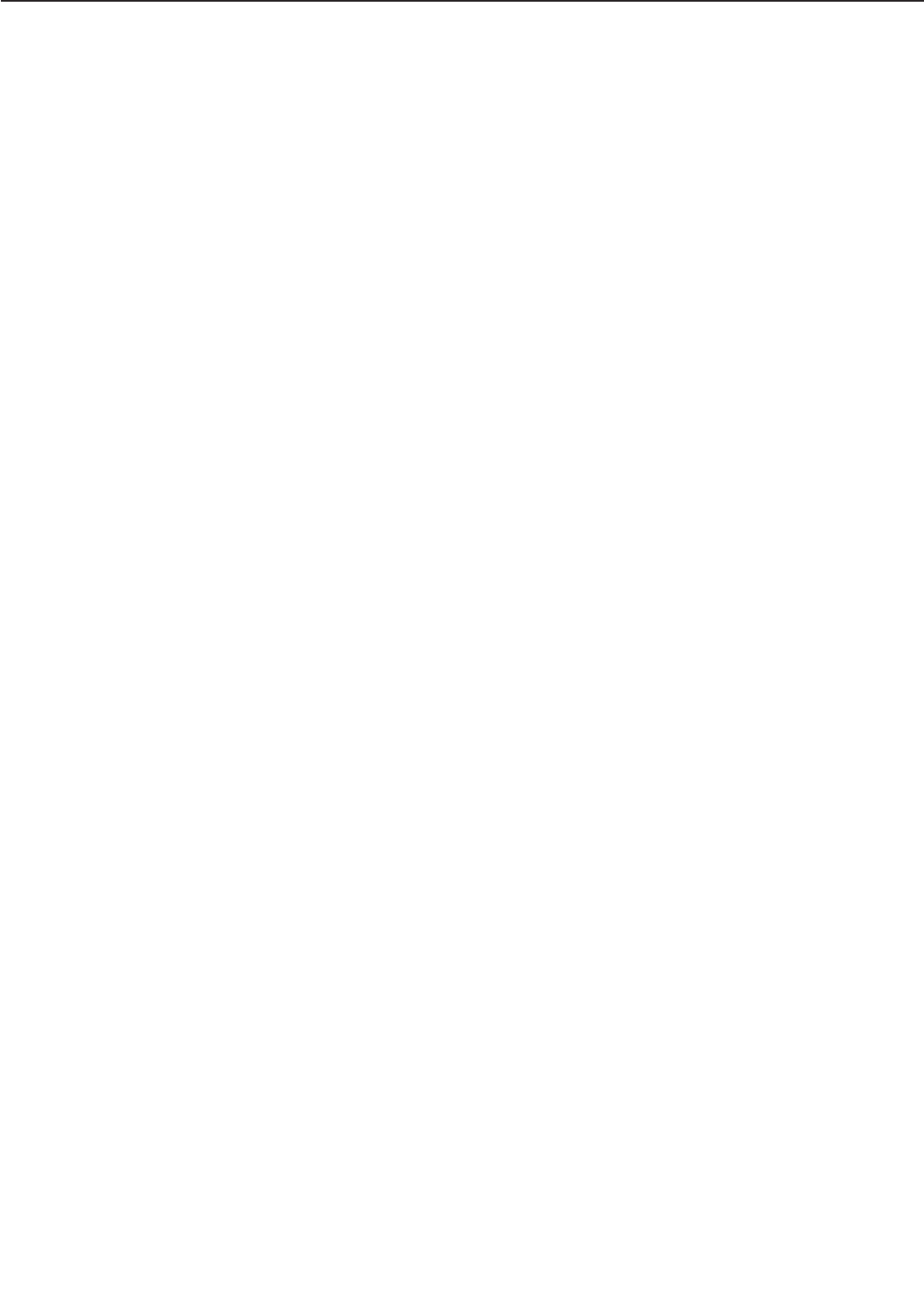
2. The laser drive signal line connectors are loose.
Action: Reconnect connector J1001 on the laser driver PCB, and connector J202 on the DC
controller PCB.
3. The laser/scanner unit is defective.
Action: Replace the laser/scanner unit.
4. The DC controller PCB is defective.
Action: Replace the DC controller PCB.
VI-6. "12.1 ERROR MOTOR CALL FOR SERVICE" Faulty main motor
"12.2 ERROR MOTOR CALL FOR SERVICE" Faulty main motor
<Possible causes>
1. The main motor drive signal line connectors are loose.
Action: Reconnect connector J12 of the main motor and connector J218 on the DC con-
troller PCB.
2. The door switch on the switch/sensor PCB is defective.
Action: Remove connectors J205 and J221 on the DC controller PCB. If J205-3 (+24V) and
J221-1 (+24VB) on the cable side do not conduct when the door switch (SW1401) is
ON, replace the switch/sensor PCB.
3. The main motor is defective.
Action: Use the printer driver tester to rotate the main motor. If it does not rotate, replace
it.
4. The DC controller PCB is defective.
Action: Replace the DC controller PCB.
VI-7. "13.1 ERROR FAM 1 CALL FOR SERVICE" Electrical unit fan (FM3) failure
<Possible causes>
1. The FM3 drive signal line connector is loose.
Action: Reconnect connector J210 on the DC controller PCB and connectors J12 and J13.
2. The electrical unit fan is defective.
Action: Disconnect connector J210 on the DC controller PCB. Turn the power switch ON
and measure the voltage between connector J210-1 (FAN3D) and J210-3 (GND) on
the DC controller PCB. If the voltage changes from 0 to more than 18V, replace the
electrical unit fan.
3. The DC controller PCB is defective.
Action: Replace the DC controller PCB.
VI-8. "13.2 ERROR FAM 2 CALL FOR SERVICE" Power supply fan (FM2) failure
<Possible causes>
1. The FM2 drive signal line connector is loose.
Action: Reconnect connector J216 on the DC controller PCB.
2. The power supply fan is defective.
4 - 23
CHAPTER 4
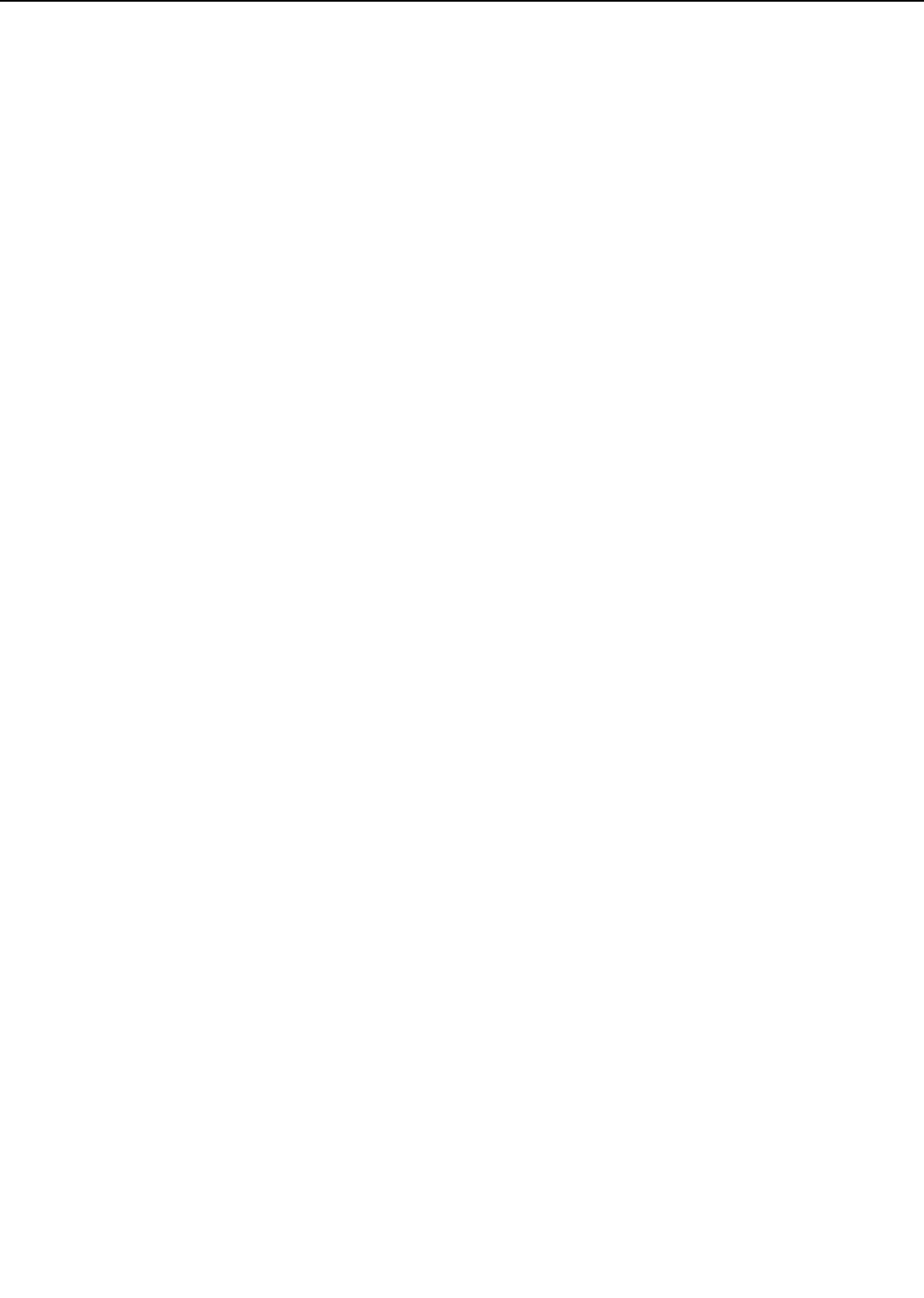
Action: Disconnect connector J216 on the DC controller PCB. Turn the power switch ON
and measure the voltage between connector J216-1 (FAN2D) and J216-3 (GND) on
the DC controller PCB. If the voltage changes from 0 to more than 18V, replace the
power supply fan.
3. The DC controller PCB is defective.
Action: Replace the DC controller PCB.
VI-9. "13.3 ERROR FAM 3 CALL FOR SERVICE" Fixing unit/scanner fan (FM1) failure
<Possible causes>
1. The FM1 drive signal line connector is loose.
Action: Reconnect connector J208 on the DC controller PCB.
2. The fixing unit/scanner fan is defective.
Action: Disconnect connector J208 on the DC controller PCB. Turn the power switch ON
and measure the voltage between connector J208-1 (FAN1D) and J208-3 (GND) on
the DC controller PCB. If the voltage changes from 0 to more than 18V, replace the
fixing unit/scanner fan.
3. The DC controller PCB is defective.
Action: Replace the DC controller PCB.
VI-10. "13.4 ERROR FAM 4 CALL FOR SERVICE" Fixing unit fan (FM4) failure
<Possible causes>
1. The FM4 drive signal line connector is loose.
Action: Reconnect connector J225 on the DC controller PCB and connectors J25 and J26.
2. The fixing unit fan is defective.
Action: Disconnect connector J225 on the DC controller PCB. Turn the power switch ON
and measure the voltage between connector J225-1 (FAN4D) and J225-3 (GND) on
the DC controller PCB. If the voltage changes from 0 to more than 18V, replace the
fixing unit fan.
3. The DC controller PCB is defective.
Action: Replace the DC controller PCB.
VI-11. "13.5 ERROR FAM 5 CALL FOR SERVICE"
Multi-purpose tray pick-up unit fan (FM5) failure
<Possible causes>
1. The FM5 drive signal line connector is loose.
Action: Reconnect connector J229 on the DC controller PCB and connectors J34 and J35.
2. The multi-purpose tray pick-up unit fan is defective.
Action: Disconnect connector J229 on the DC controller PCB. Turn the power switch ON
and measure the voltage between connector J229-1 (FAN5D) and J229-3 (GND) on
the DC controller PCB. If the voltage changes from 0 to more than 18V, replace the
multi-purpose tray pick-up unit fan.
3. The DC controller PCB is defective.
4 - 24
CHAPTER 4
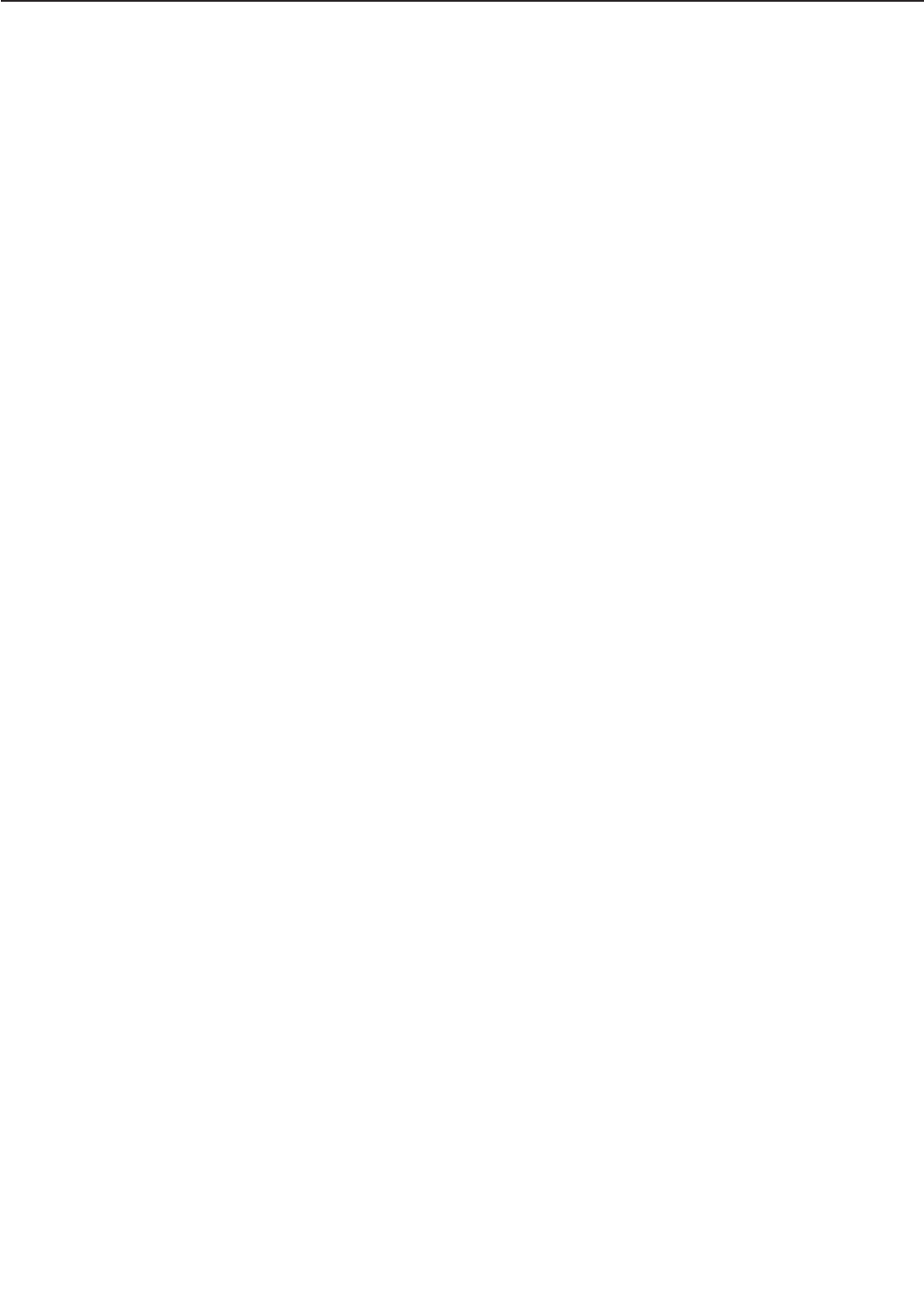
Action: Replace the DC controller PCB.
VI-12. "14.1 ERROR AUX TRAY CALL FOR SERVICE" Lifting plate failure
<Possible causes>
1. Lifting plate drive unit parts are damaged.
Action: Replace any damaged parts.
2. The lifting plate position sensor is defective.
Action: Check the sensor state using the printer driver tester. If it is defective, replace the
multi-purpose tray PCB.
3. The lifting plate solenoid is defective.
Action: Disconnect lifting plate solenoid connector J1302. Measure the resistance between
connector J1302-1 and J1302-2 on the cable side. If it is not about 160Ω, replace
the lifting plate solenoid.
4. The DC controller PCB is defective.
Action: Replace the DC controller PCB.
VI-13. "TONER CARTRIDGE MISSING" message appears when it is installed
<Possible causes>
1. The developing bias contact of the high-voltage power supply is not making a good connec-
tion with the cartridge contact.
Action: If the contacts are dirty, clean them. If the problem continues after cleaning, or
parts are deformed or damaged, replace them.
2. Defective cartridge
Action: Replace the cartridge.
3. The high-voltage power supply PCB is defective.
Action: Replace the high-voltage power supply PCB.
4. The DC controller PCB is defective.
Action: Replace the DC controller PCB.
VI-14. "LOAD <MEDIA> <SIZE> IN MPT" message appears when the specified sized paper
is in the multi-purpose tray
<Possible causes>
1. Damaged paper detection lever
Action: Replace the defective lever.
2. Defective multi-purpose tray paper sensor
Action: Replace the multi-purpose tray PCB.
3. The DC controller PCB is defective.
Action: Replace the DC controller PCB.
4 - 25
CHAPTER 4
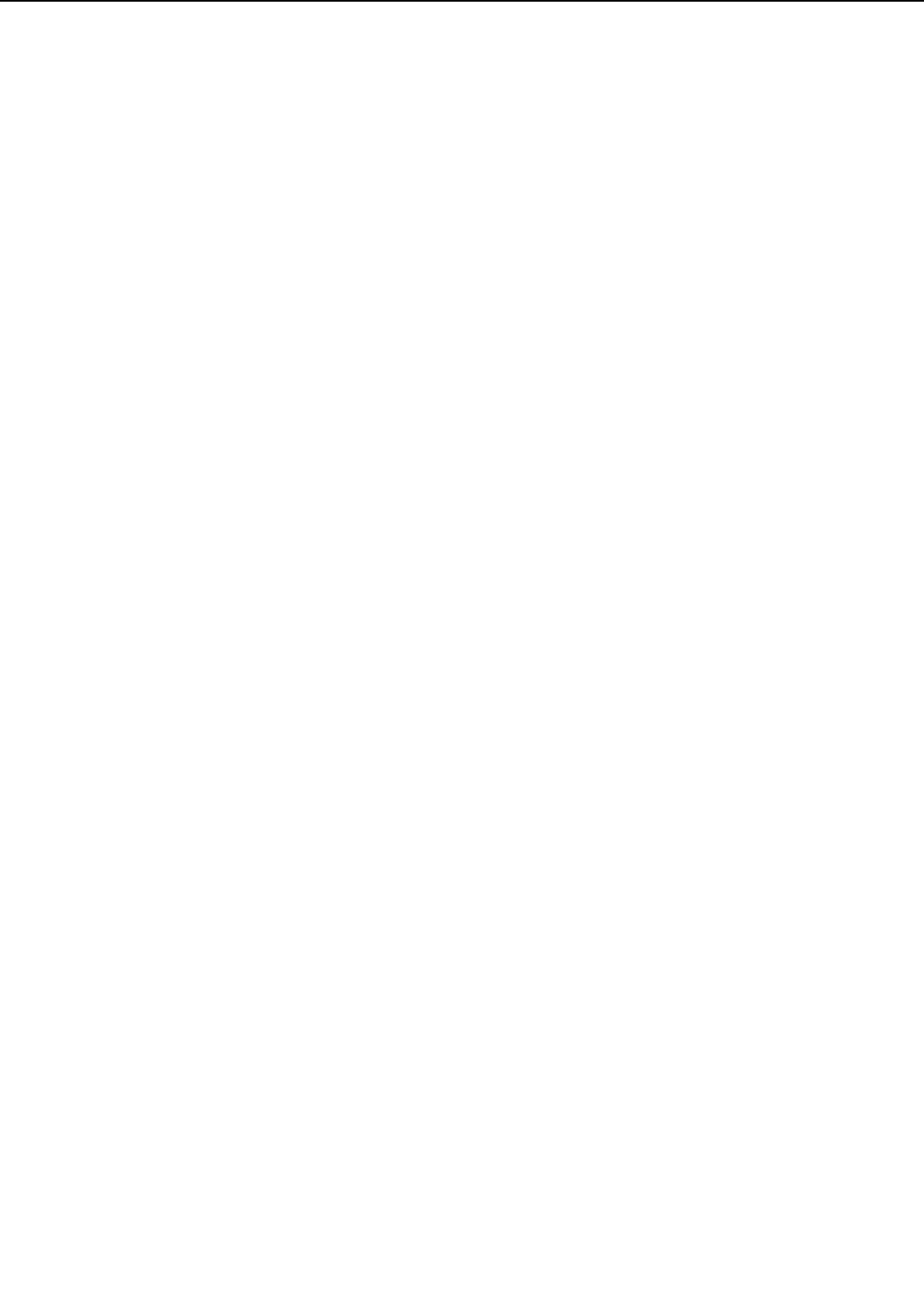
VI-15. Displays "LOAD<MEDIA><SIZE> IN UPPER" or "LOAD<MEDIA><SIZE>IN LOWER"
when the specified cassette is loaded with paper.
<Possible causes>
1. Pull out the upper and lower cassettes, and install the specified cassette in the printer. If
the lifter does not lift, perform step 5 and subsequent steps.
2. Damaged paper detection lever
Action: Replace the defective lever.
3. Defective upper cassette paper-out sensor/lower cassette paper-out sensor
Action: Replace the pick-up PCB.
4. The DC controller PCB is defective.
Action: Replace the DC controller PCB.
5. Pick-up drive unit is damaged.
Action: Remove the pick-up unit and replace any damaged parts.
6. The cassette pick-up solenoid is defective.
Action: Remove the pick-up unit, and disconnect cassette pick-up solenoid connector
J1203 from the pick-up PCB. Measure the resistance between connectors J1203-
1 and J1203-2 on the cable side. If it is not about 160Ω, replace the cassette pick-
up solenoid.
7. The pick-up PCB is defective.
Action: Replace the pick-up PCB.
8. The DC controller PCB is defective.
Action: Replace the DC controller PCB.
VI-16. "PAPER JAM" message appears when the paper jam has not occurred, and the
printer cannot be in READY mode.
<Possible causes>
1. Registration paper sensor lever does not move smoothly, or is damaged.
Action: Adjust the lever so that it moves smoothly. Replace it if damaged.
2. Pick-up unit sensor lever does not move smoothly, or is damaged.
Action: Adjust the lever so that it moves smoothly. Replace it if damaged.
3. Fixing unit delivery sensor lever does not move smoothly, or is damaged.
Action: Adjust the lever so that it moves smoothly. Replace it if damaged.
4. Face-down tray delivery sensor lever does not move smoothly, or is damaged.
Action: Adjust the lever so that it moves smoothly. Replace it if damaged.
5. Sensor failure
Action: Using the printer driver tester, check the condition of the sensors. If the LED of the
tester does not light up when the sensor lever is shifted, replace the sensor.
4 - 26
CHAPTER 4
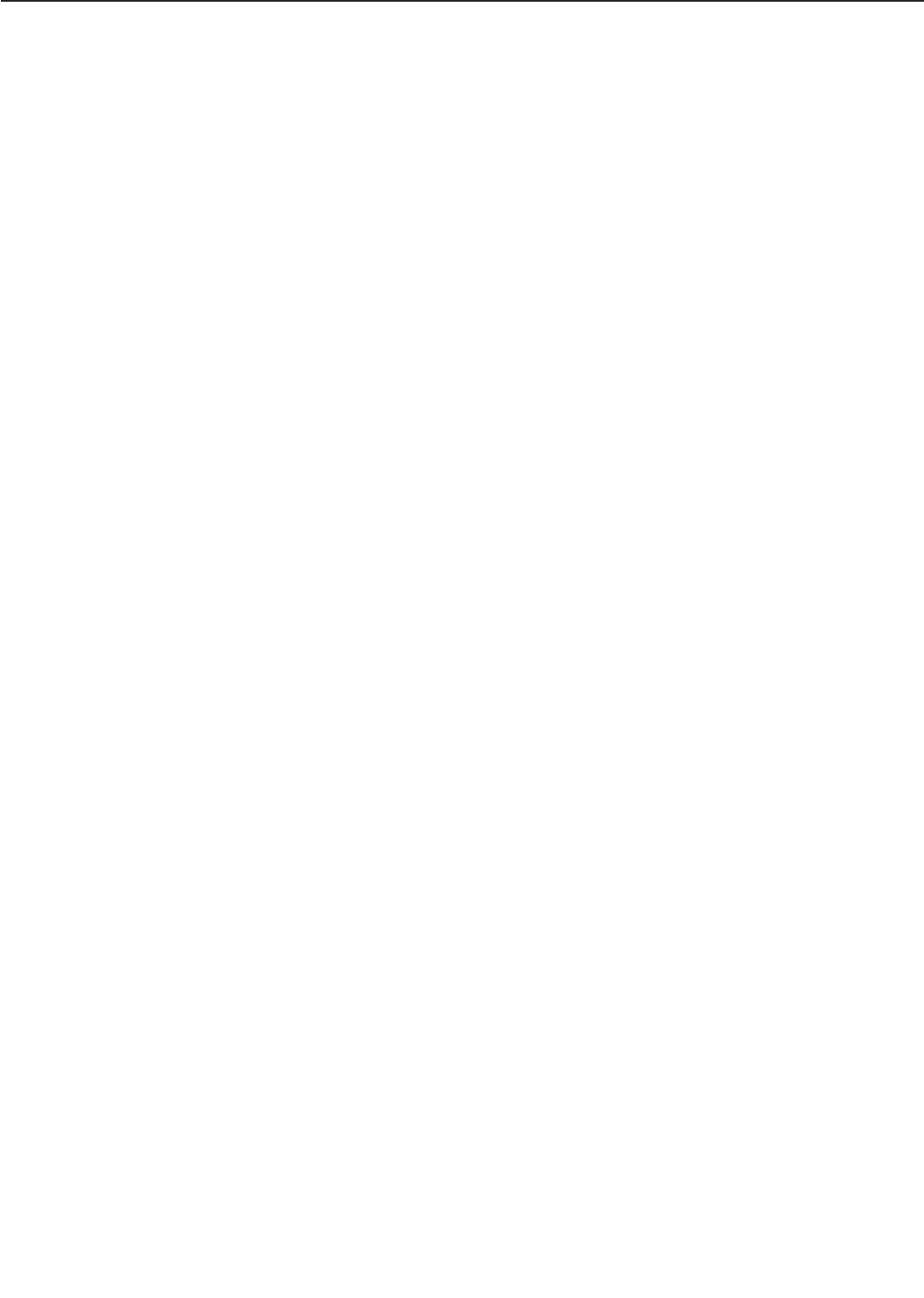
VI-17. "PRINTER OPEN" message appears when the cover is closed.
<Possible causes>
1. The projection for the delivery cover is damaged.
Action: Replace the delivery cover.
2. The projection for the upper cover is damaged.
Action: Replace the upper cover.
3. The projection for the pick-up unit door is damaged.
Action: Replace the pick-up unit door.
4. The pick-up unit door sensor is defective.
Action: Using the printer driver tester, check the condition of the sensor. If the LED of the
tester does not light up when the pick-up unit door is opened, replace the sensor.
5. Interlock arm does not move smoothly, or is damaged.
Action: Adjust the arm so that it moves smoothly. Replace it if damaged.
6. Connector is loose.
Action: Reconnect connector J1401 on the switch/sensor PCB and connectors J205 and
J221 on the DC controller PCB.
7. The door switch is defective.
Action: Replace the switch/sensor PCB.
8. The DC controller PCB is defective.
Action: Replace the DC controller PCB.
4 - 27
CHAPTER 4
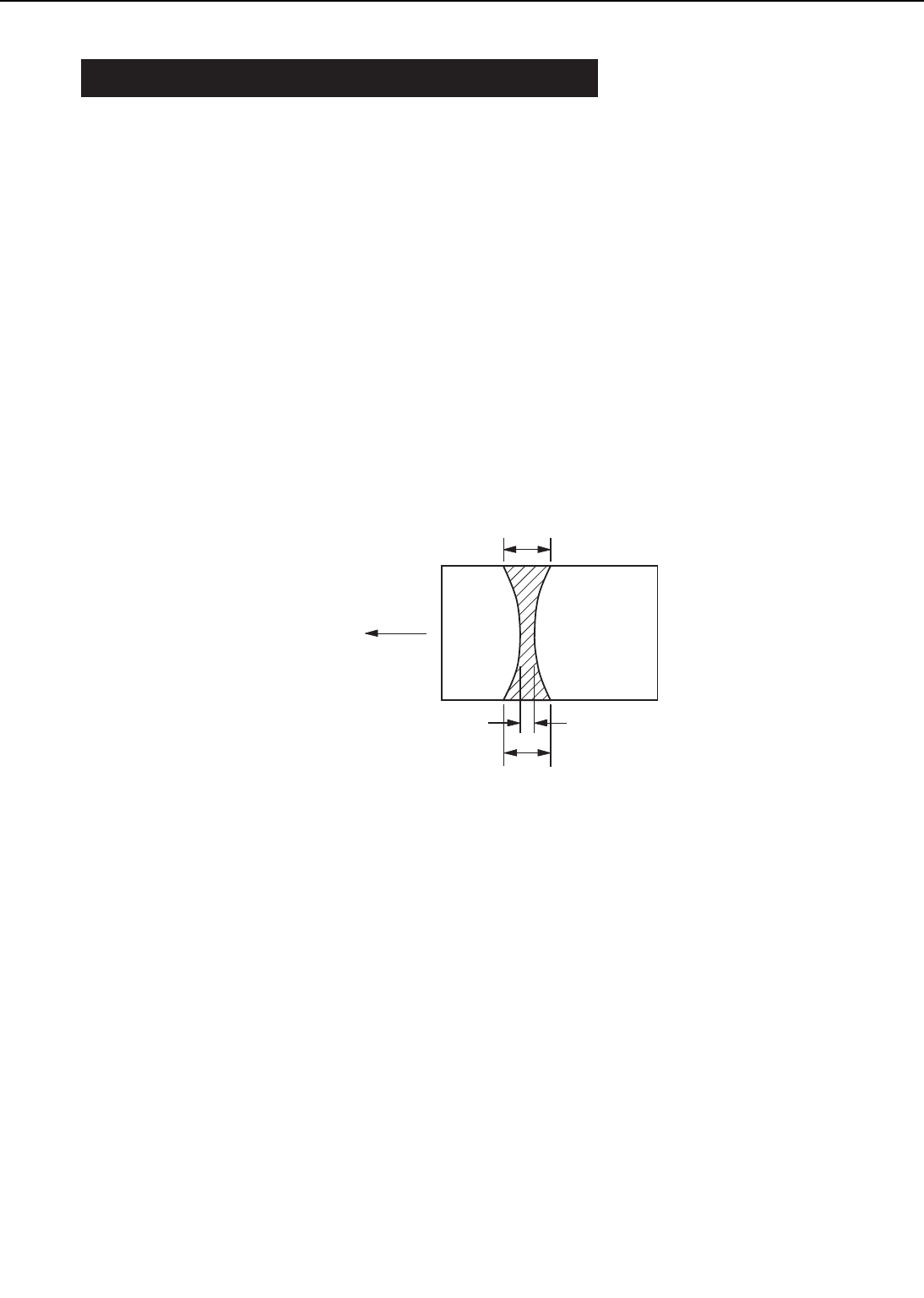
VII. MEASUREMENT AND ADJUSTMENT
A. Mechanical Adjustment
1. Checking the nip width of the lower fixing roller
The fixing unit is not designed to allow adjustment of the pressure (nip width); however, the
incorrect nip width can cause fixing problems.
Follow the procedures below to check the nip width:
1) Make an all-black print using an EP-72 cartridge, and take the print to the customer’s site.
(Use the printer driver tester to output an all-black print.)
2) Place the all-black print in the lower cassette of the printer, with the printed side facing
down.
3) Press the test print switch.
4) Turn OFF the printer when the leading edge of the print emerges at the face-down tray. Turn
ON the printer 10 seconds later, and operate the printer to deliver the print.
5) Measure the width of the glossy band across the paper and check that it meets the require-
ments as shown in Figure 4-7-1.
• Center (a) : 6.5 ± 1.0mm
• Left/right side (b) : 6.9 ± 1.0mm
• Difference between right side and left side (|b-c|) : 1.0mm or less
• Difference between right/left sides and center (b-a, c-a) : 1.5mm or less
Figure 4-7-1
2. Side registration adjustment of the cassette
When the side registration of the cassette is not aligned, this adjustment needs to be made.
The side registration adjustment levers (see Figure 4-7-2) in the upper and lower cassettes
are adjusted in the factory. Therefore, there is no need to make any adjustments when installing
the printer. However, when either upper or lower cassette is replaced in the field, re-adjustment
of the left margin is necessary. This procedure is outlined below.
1) Load 20 to 30 sheets of paper into the cassette. Then, using the printer driver tester, print
several pages of all-black or horizontal line test prints.
2) Measure the distance (a) between the left edge of the page to the edge of the printed pattern
(see Figure 4-7-2). Measure several test prints to find the average distance.
3) Move the side registration adjustment lever based on Figure 4-7-2 so that the distance mea-
sured in step 2) become 3.0mm. (one notch alters length (a) by 0.5mm.)
For example, if the average length of step 2) is 2.0mm, by moving the lever 2 steps clockwise
the necessary adjustment of 1.0mm can be made.
4) Make several more test prints. Make sure that the left margin is 3.0mm by repeating step
2) above.
If the margin needs further adjustment, repeat steps 1) to 3) again.
4 - 28
CHAPTER 4
Center of A3-
sized paper
Feed-out direction
b
b
a
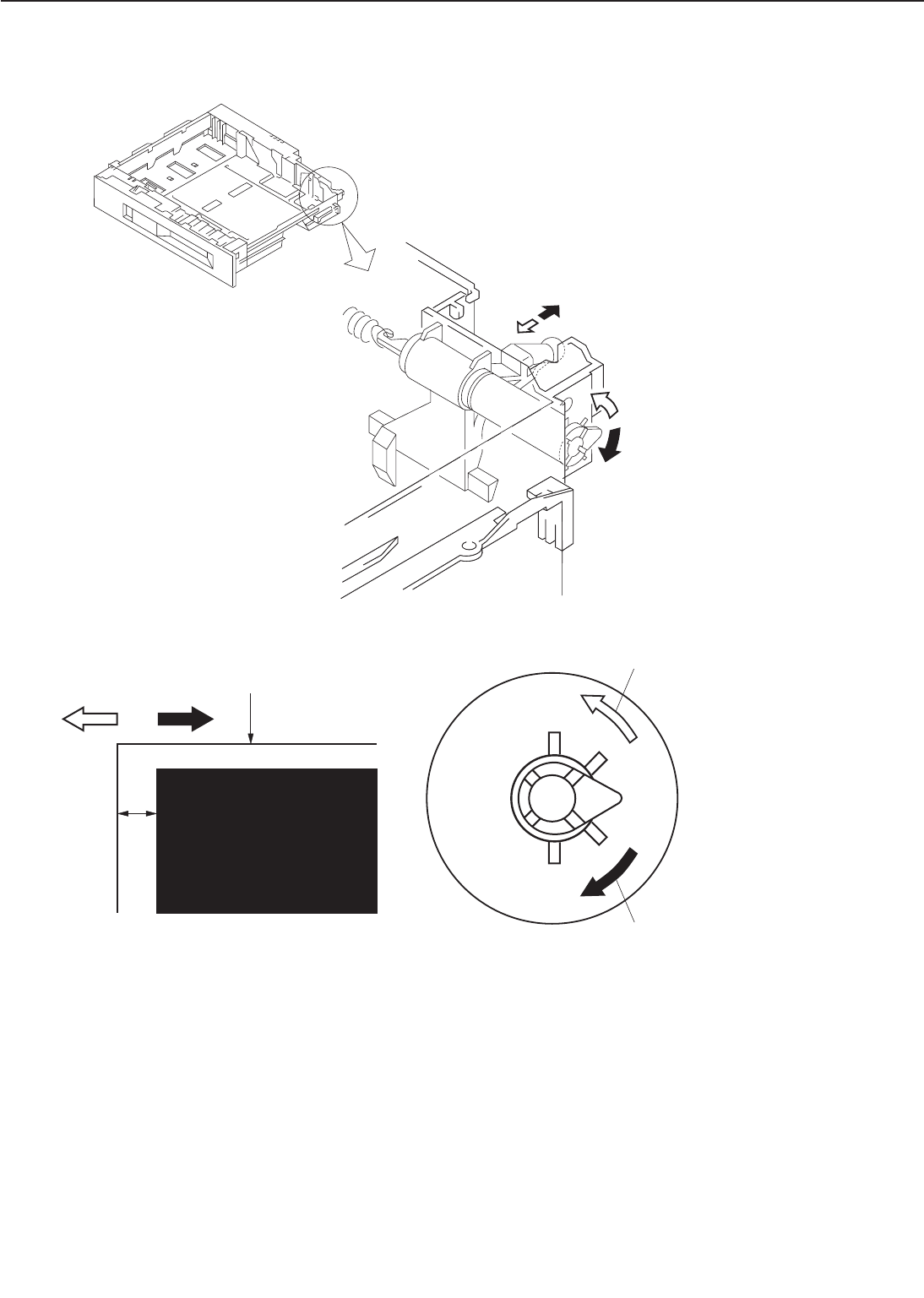
Figure 4-7-2
B. Electrical Adjustment
• No electrical adjustment for this printer.
4 - 29
CHAPTER 4
Leading edge of paper
a
The value of "a" drops by 0.5mm
for each notch moved.
The value of "a" rises by 0.5mm
for each notch moved.
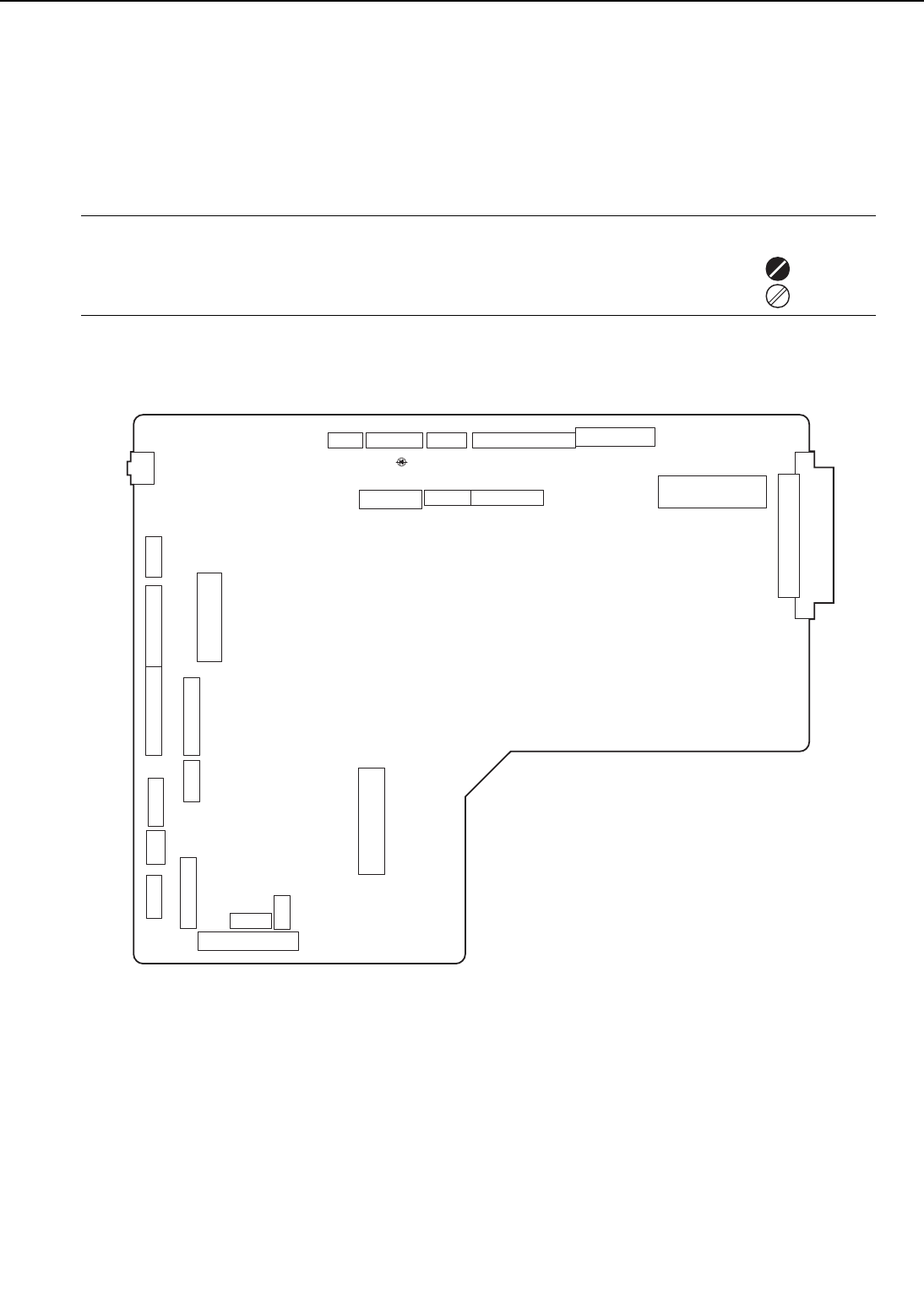
C. Variable Resistors, LEDs, Test Pins, Jumpers and Switches on PCBs
Only the variable resistors, LEDs, test pins, jumpers, and switches required for after-sales ser-
vice in the field are listed below.
All other variable resistors, test pins, etc. are for the factory use only. The adjustment and
check using these test pins, etc. require special tools, measuring instruments and high preci-
sion. Do not touch them in the field.
Notes: 1. Some LEDs receive leakage current during normal operation, thus glow dimly even
when they should be OFF.
2. Variable resistor which may be adjusted in the field are marked .........
Variable resistor which may not be adjusted in the field are marked ...
1. DC controller PCB
Figure 4-7-3
4 - 30
CHAPTER 4
J212
LED201
J206 J207
J208
J229
J217
J203
J225 J205 J202
J210
J220
J201
J223
J215
J218
J221 J216 J209 J214 J213 J222
J219
SW201
J204
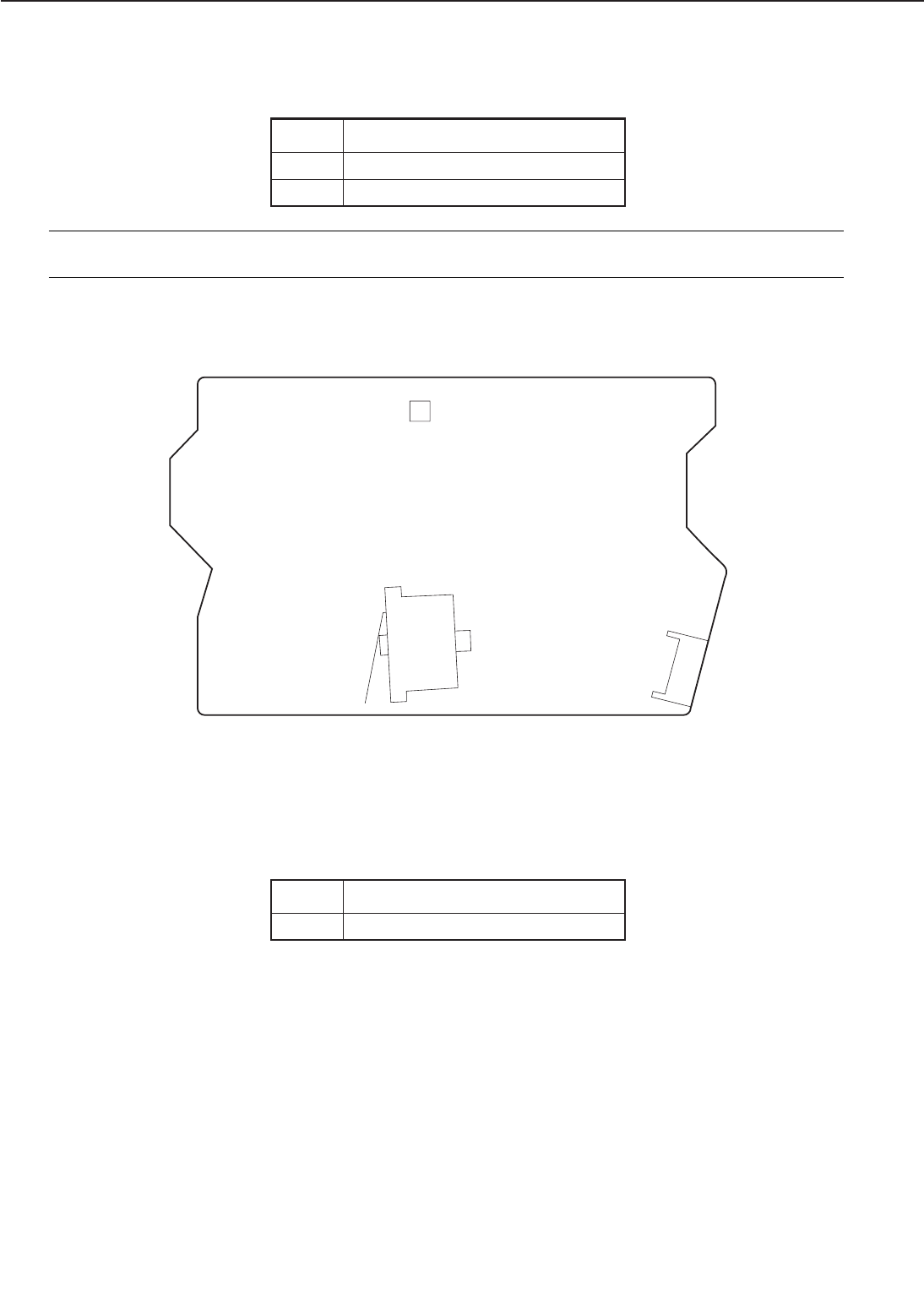
Table 4-7-1
Note: Sensor check is available only when the service mode is specified by the printer driver
tester. (Refer to the operating manual of the printer driver tester for details.)
2. Switch/sensor PCB
Figure 4-7-4
Table 4-7-2
4 - 31
CHAPTER 4
Test print switch
Sensor check (Note)
SW No.
SW201
LED201
Function
Door switch
SW No.
SW1401
Function
J1402
21
SW1401
3
1
2
4J1401
1
14
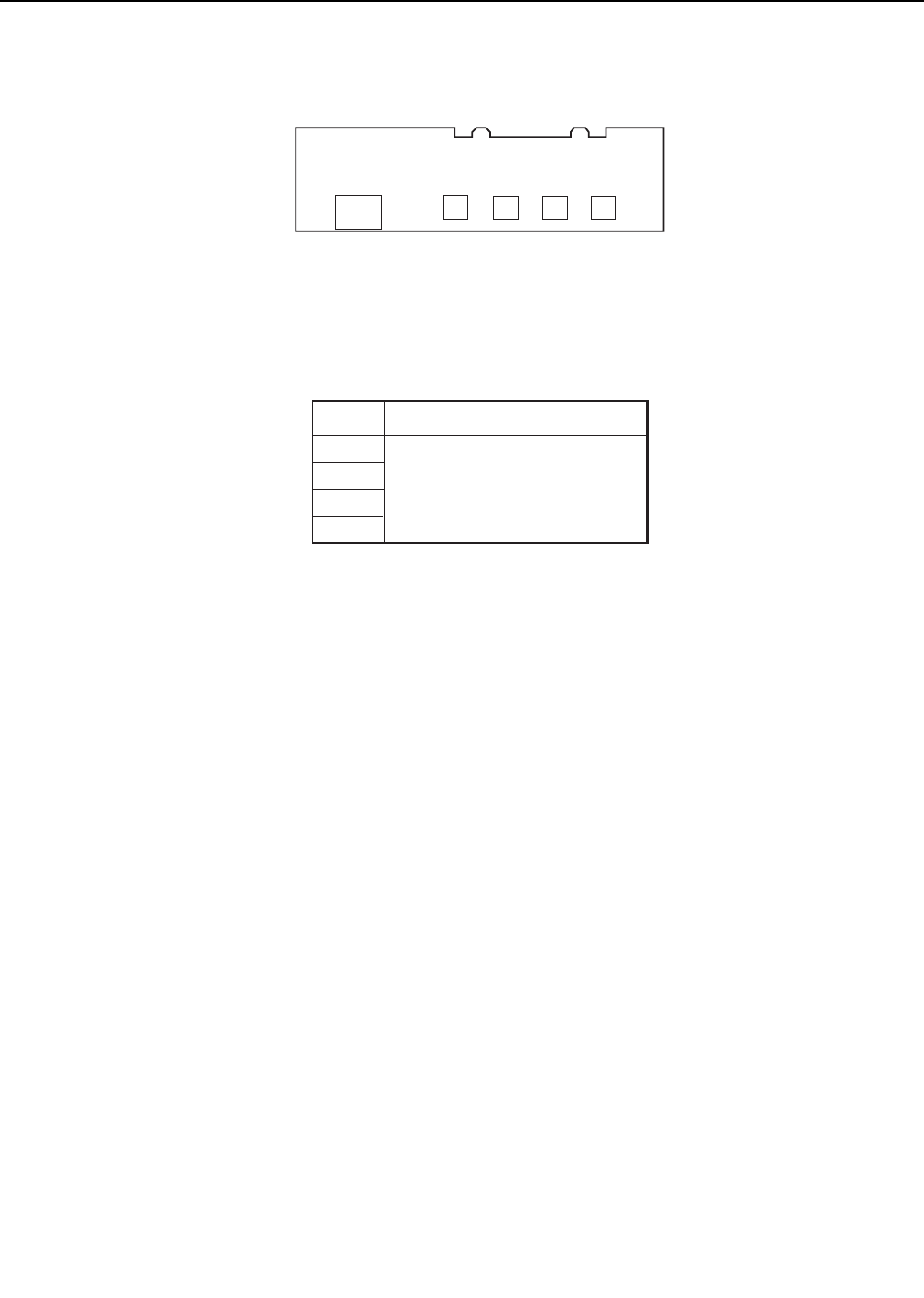
3. Cassette paper size detection PCB
Figure 4-7-5
Table 4-7-3
4 - 32
CHAPTER 4
J1601 51 SW1604 SW1603 SW1602 SW1601
Cassette paper-size sensing
switch
(See page 2-47.)
SW No.
SW1601
SW1602
SW1603
SW1604
Function
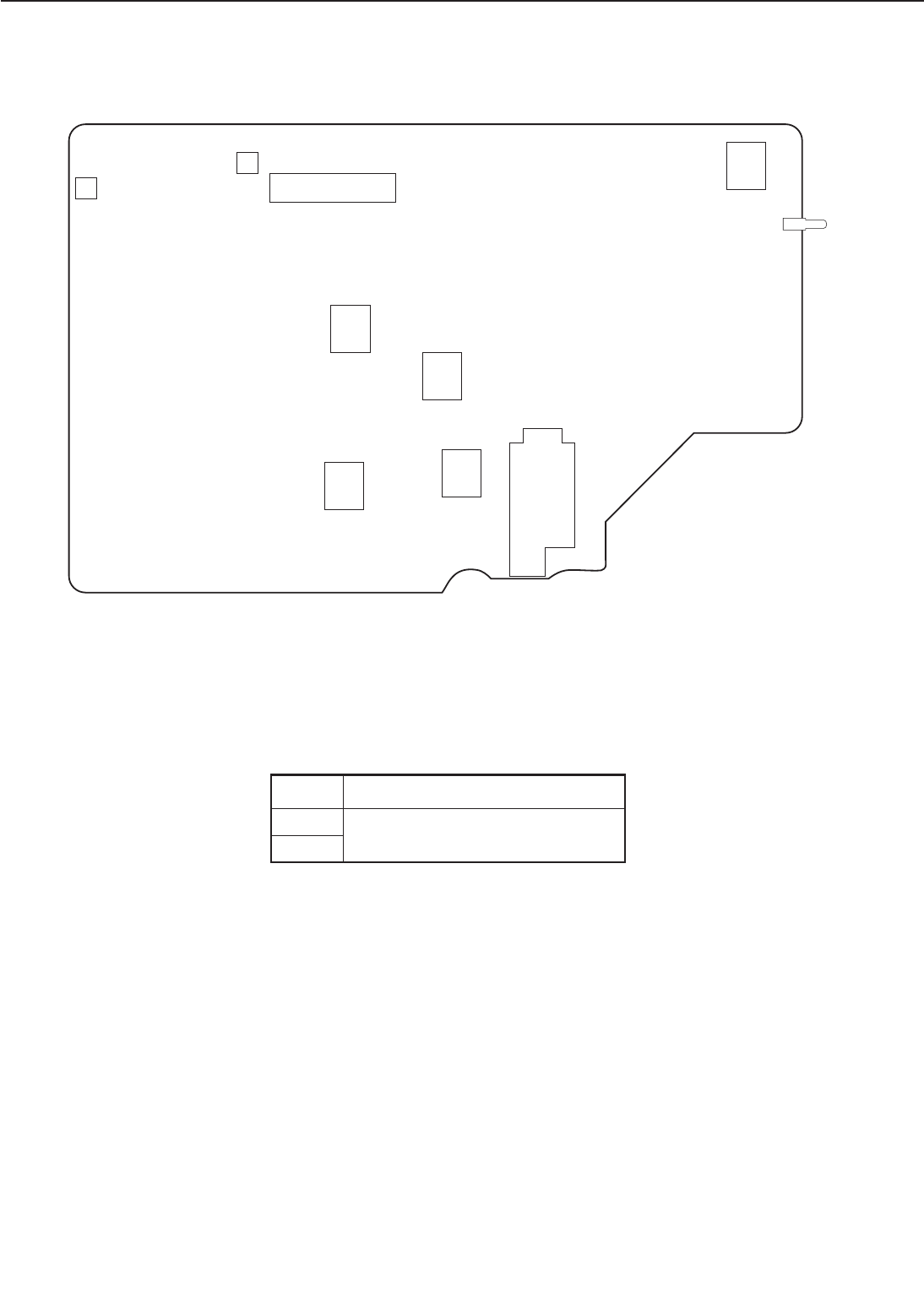
4. High-voltage power supply PCB
Figure 4-7-6
Table 4-7-4
4 - 33
CHAPTER 4
VR701
B12
A12
6
J701
VR702
A1
B1
TB703
TB702
TB701 TB704
T704
5
2
1
7
TB706
TB705
For factory use
VR No.
VR701
VR702
Function
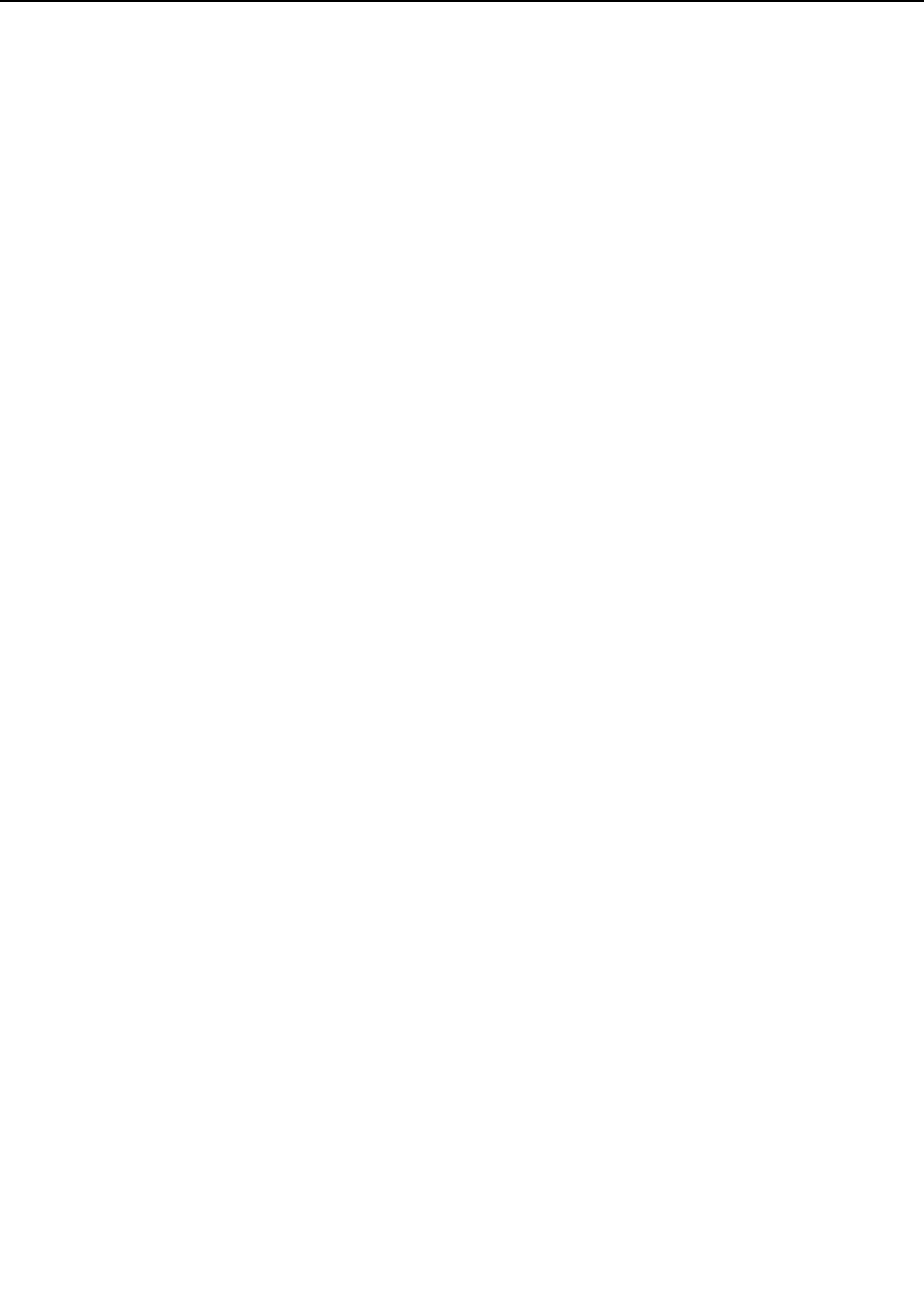
This page intentionally left blank
4 - 34
CHAPTER 4
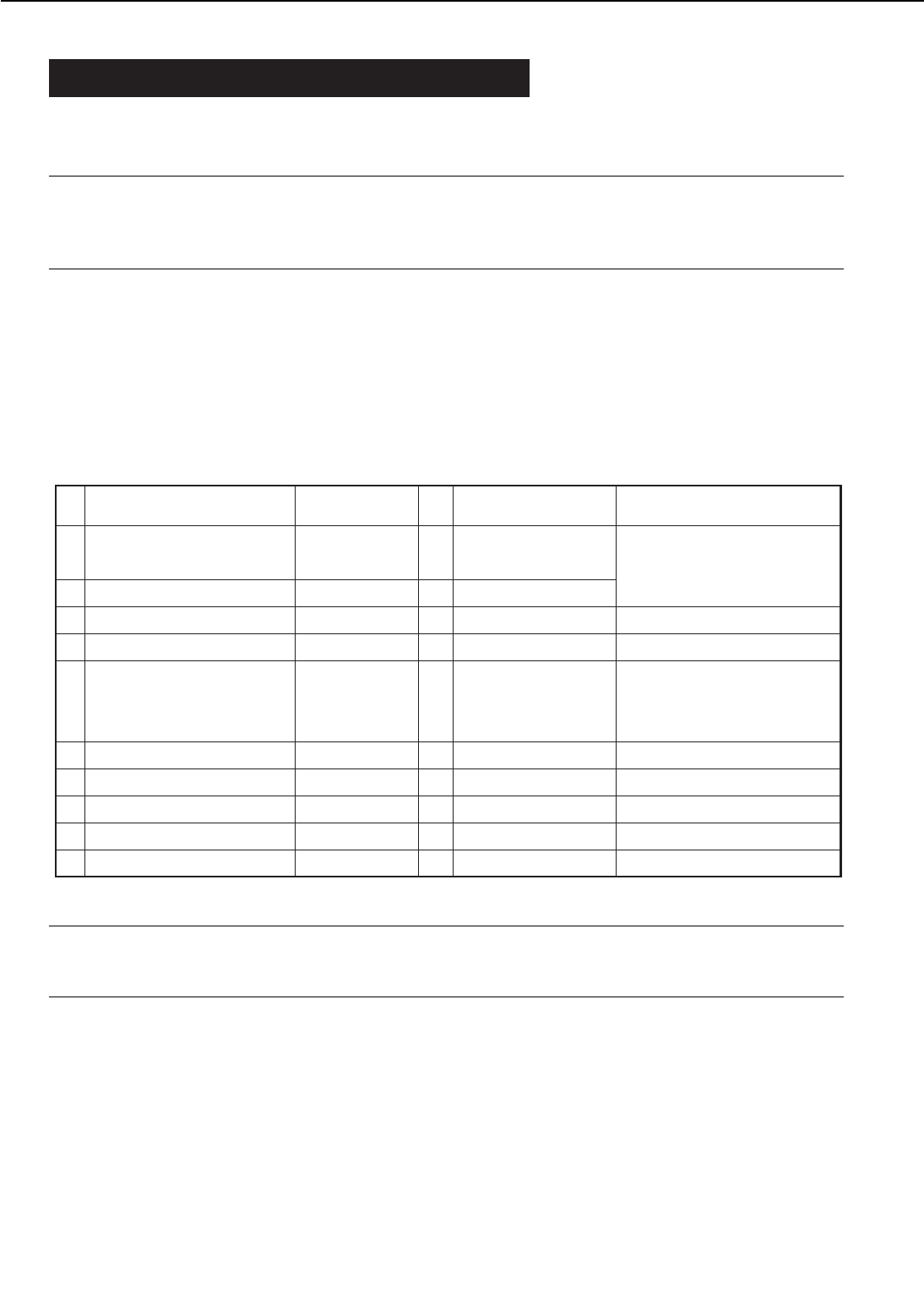
VIII. MAINTENANCE AND SERVICING
A.Periodic Replacement Parts
•No parts require periodic replacement in this printer.
Note: Periodic replacement parts are the parts that must be replaced at regular intervals, even
if they are functioning properly and show no signs of wear. (Failure of these parts can
seriously affect the performance.) These parts should be replaced during a regular
service visit closest to the end of the parts expected life.
B.Expected Service Life of Consumable Parts
Shown below are the average life expectancies (number of prints) of parts that may need to be
replace due to deterioration or damage at least once prior to the elapse of the warranty period
of the printer. These parts should be replace when faulty.
Table 4-8-1
Notes: 1.The values above are only estimates based on part data, and are subject to change.
2.2 pages are counted as 1 print in case of duplexing. Expected life of the fixing unit
is 350,000 pages when it is used only in the normal mode.
C.Periodic Service
•The printer has no parts that require periodic servicing.
4 - 35
CHAPTER 4
PartNo. Remarks
1
2
3
4
5
6
7
8
9
10
Multi-purposetraypick-
uproller
Separationpad
Fixingunit
Transferchargingroller
Feedrollerandseparation
roller
Powersupplyfan
Electricalunitfan
Fixingunitfan
Fixingunit/scannerfan
Multi-purposetrayfan
No. Partname
RB1-9526-000
RF5-2703-000
RG5-4319-000
RF9-1394-000
RF5-1834-000
RH7-1266-000
RH7-1271-000
RH7-1289-000
RH7-1396-000
RH7-1397-000
Replacethemulti-purpose
traypick-uprollerand
separationpadtogether.
220-240V
Forbothupperandlowerrollers.
Replacethefeedrollersand
separationrollerstogether.
Qt’y Expectedlife
1
1
1
1
4
1
1
1
1
1
200,000prints
200,000prints
350,000pages(Note2)
350,000pages(Note2)
350,000prints
25,000hours
25,000hours
25,000hours
25,000hours
25,000hours
AsofDecember,1998
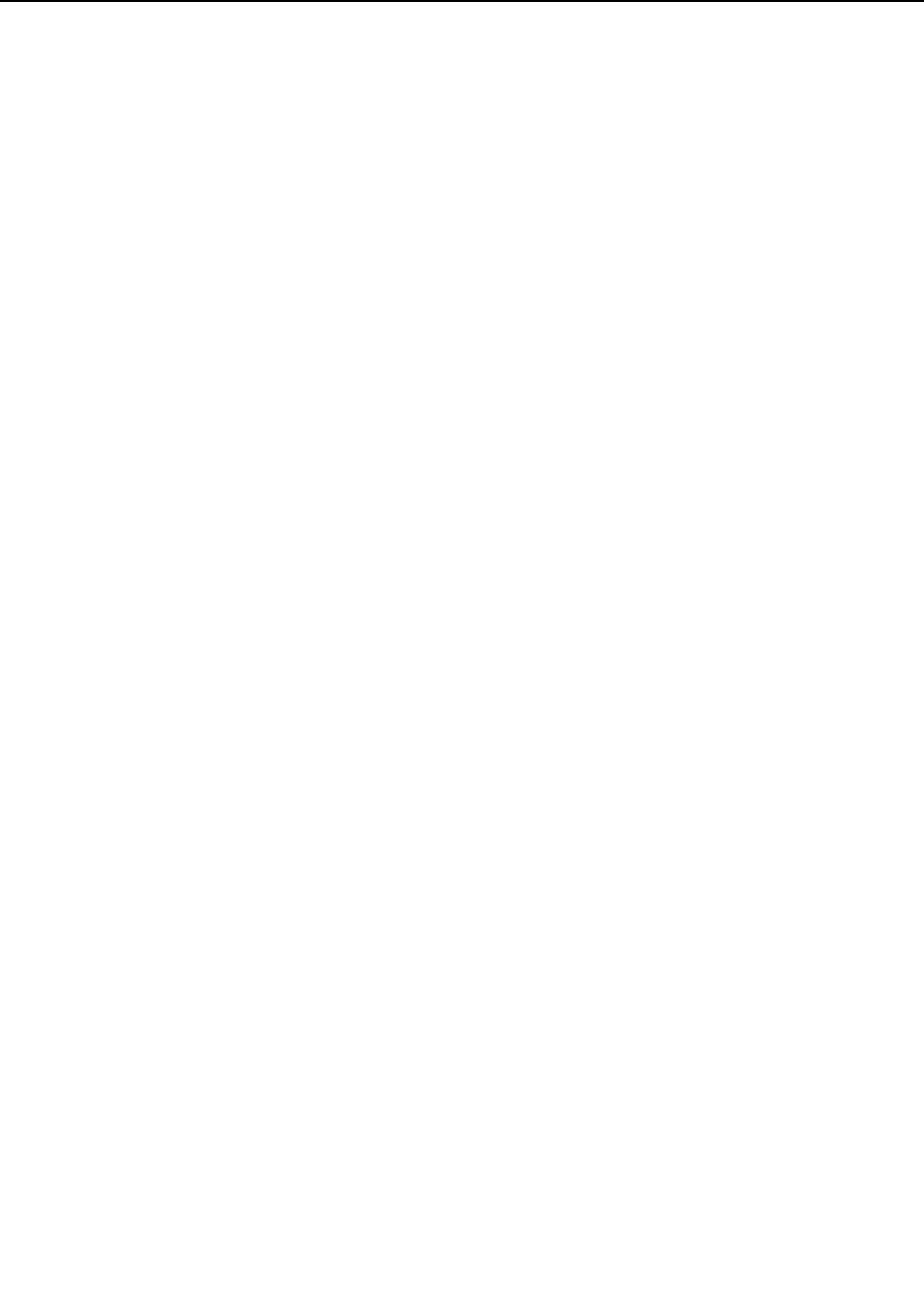
D. Cleaning during a Service Visit
Following the procedures below, clean the printer during service visit.
1. Transfer charging roller
As a general rule, the transfer charging roller is not to be touched or cleaned. If it is unavoid-
able, clean the roller with dry lint free paper (which produces little paper dust). Do not use water
or solvent. Make sure not to contaminate the roller with solvent or oil.
2. Multi-purpose tray pick-up roller, cassette pick-up roller, separation roller, and feed
roller
Clean with lint-free paper, either dry or moistened with ethyl/isopropyl alcohol.
3. Separation pad
Clean with lint-free paper.
4. Registration roller unit
Clean with lint-free paper. If badly contaminated, use it with ethyl/isopropyl alcohol for rubber
parts and MEK(methyl ethyl ketone) for other parts. Avoid skew or paper jams caused by
removal of the springs.
5. Transfer guide unit
Clean with soft, dry flannel cloth.
6. Static charge eliminator
Clean with brush.
7. Feed guide unit
Clean with lint-free paper.
8. Fixing unit
• Fixing entry guide
Clean with lint-free paper moistened with MEK.
• Fixing separation guide
Clean lightly with lint-free paper moistened with MEK, only to remove the toner deposit.
• Fixing separation claw
Clean lightly with lint-free paper moistened with MEK, only to remove the toner deposit. Replace
if badly worn.
4 - 36
CHAPTER 4
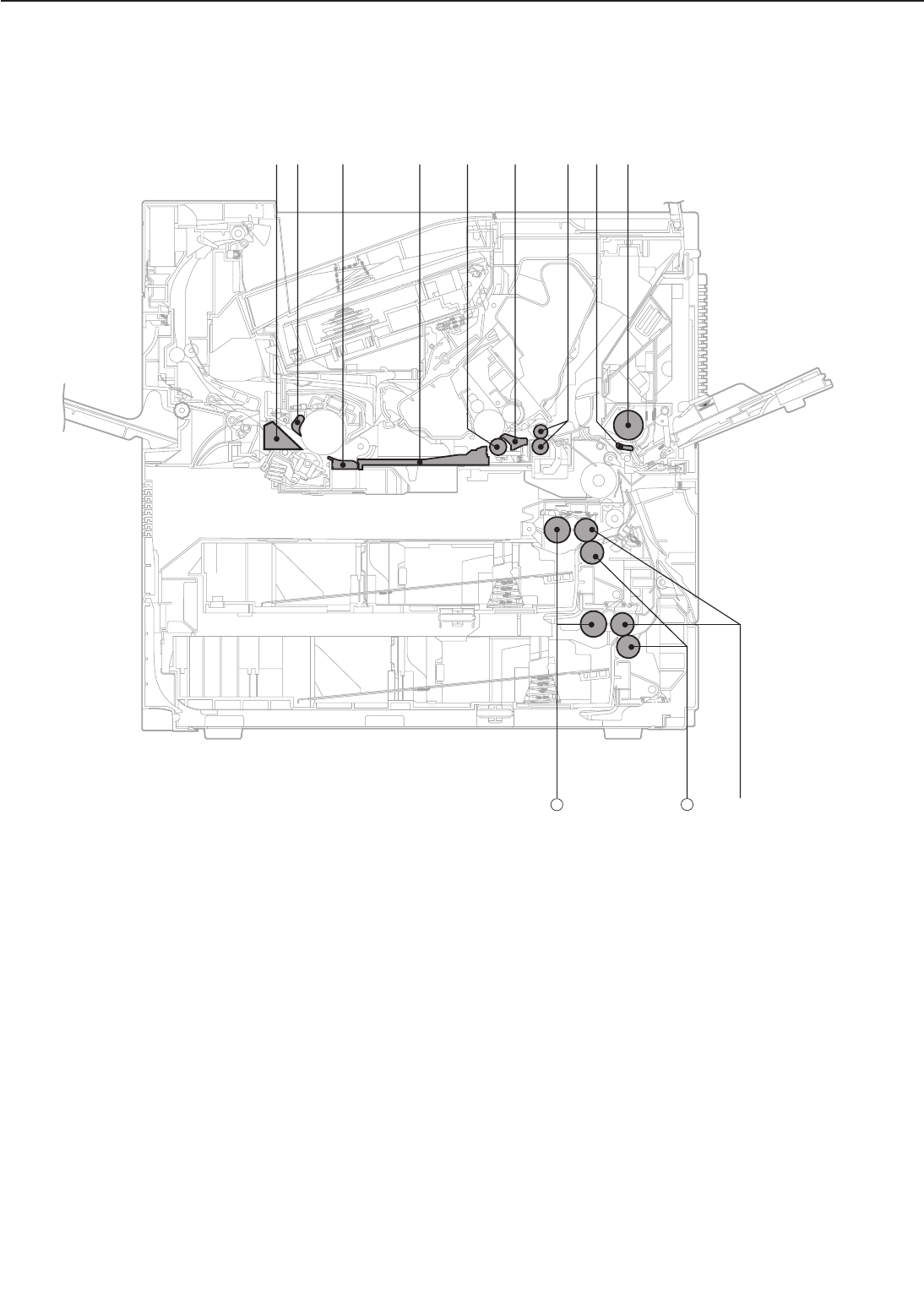
Figure 4-8-1
1: Fixing separation guide 7: Registration roller unit
2: Fixing separation claw 8: Separation pad
3: Fixing entry guide 9: Multi-purpose tray pick-up roller
4: Feed guide 10: Feed roller
5: Transfer charging roller 11: Separation roller
6: Transfer guide 12: Pick-up roller
4 - 37
CHAPTER 4
➉
➀➁➂➃➄
➅➆➇➈
12 11
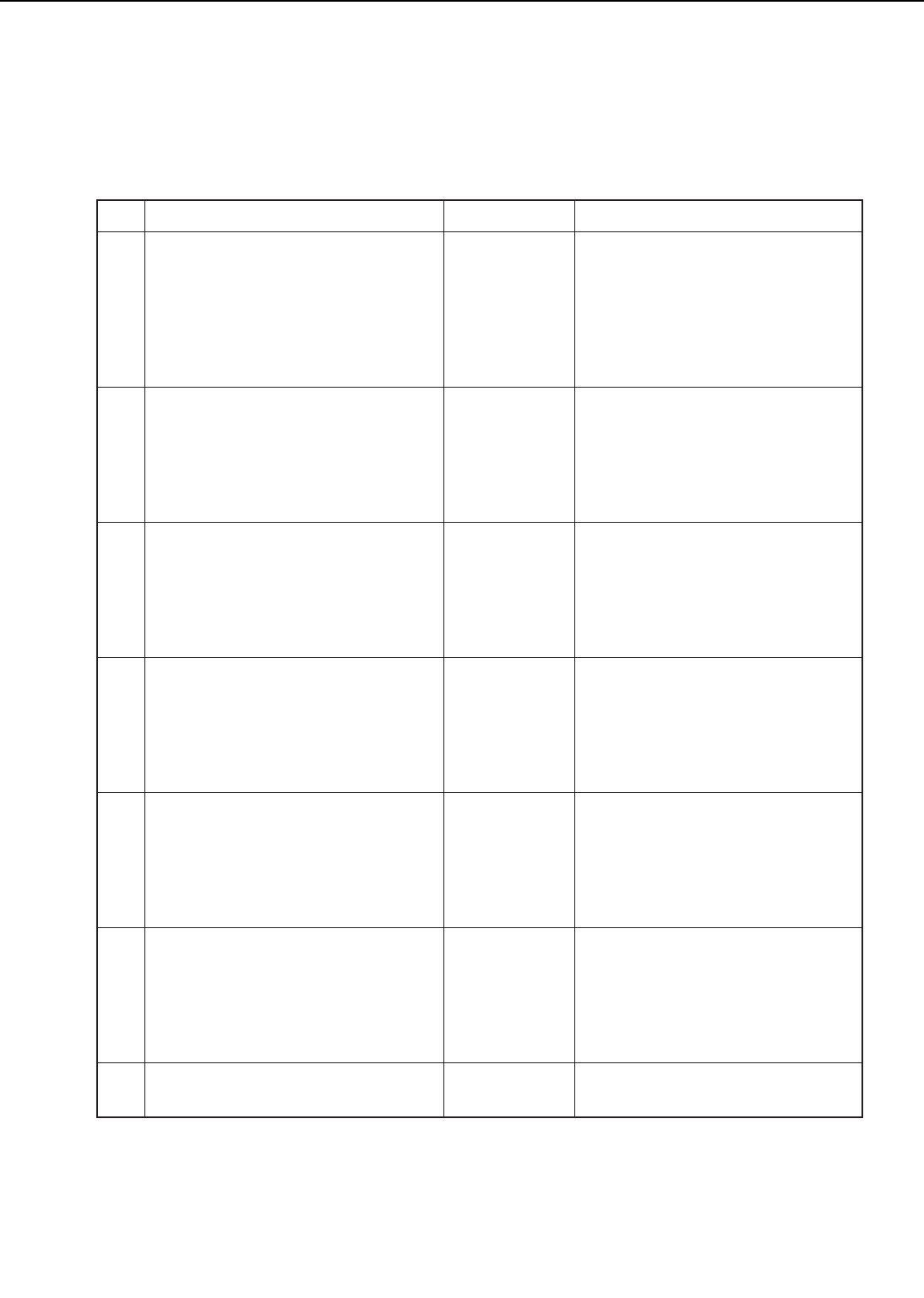
E. Standard Tools
The standard tools required for servicing the printer are listed below.
Table 4-8-2
4 - 38
CHAPTER 4
Tool No. Remarks
1
2
3
4
5
6
7
8
9
10
11
12
13
14
15
16
17
18
19
20
21
22
23
24
25
26
27
28
29
30
31
32
Tool case
Jumper wire
Thickness gauge
Compression spring scale
Phillips screwdriver
Phillips screwdriver
Phillips screwdriver
Phillips screwdriver
Flat-blade screwdriver
Precision flat-blade screwdriver set
Allen wrench set
File, fine
Allen (hex) screwdriver
Diagonal cutting pliers
Needle-nose pliers
Pliers
Retaining ring pliers
Crimper
Tweezers
Ruler
Soldering iron
Mallet, plastic head
Brush
Penlight
Plastic bottle
Solder
Desoldering wick
Lint-free paper
Soldering iron
Oiler
Plastic jar
Digital multimeter
No. Tool name
TKN-0001
TKN-0069
CK-0057
CK-0058
CK-0101
CK-0104
CK-0105
CK-0106
CK-0111
CK-0114
CK-0151
CK-0161
CK-0170
CK-0201
CK-0202
CK-0203
CK-0205
CK-0218
CK-0302
CK-0303
CK-0309
CK-0314
CK-0315
CK-0327
CK-0328
CK-0329
CK-0330
CK-0336
CK-0348
CK-0349
CK-0351
FY9-2032
With clips
0.02 mm to 0.3 mm
For checking cassette spring
strength (0–600 g)
M4, M5 length: 363mm
M3, M4 length: 155mm
M4, M5 length: 191mm
M4, M5 length: 85mm
Set of 6
Set of 5
M4 length: 107mm
For shaft rings
150 mm (for measuring)
100 V, 30 W
100cc
ø1.5 (mm) × 1(m)
1.5 mm
500 SH/PKG
240 V, 30 W
30cc
30cc
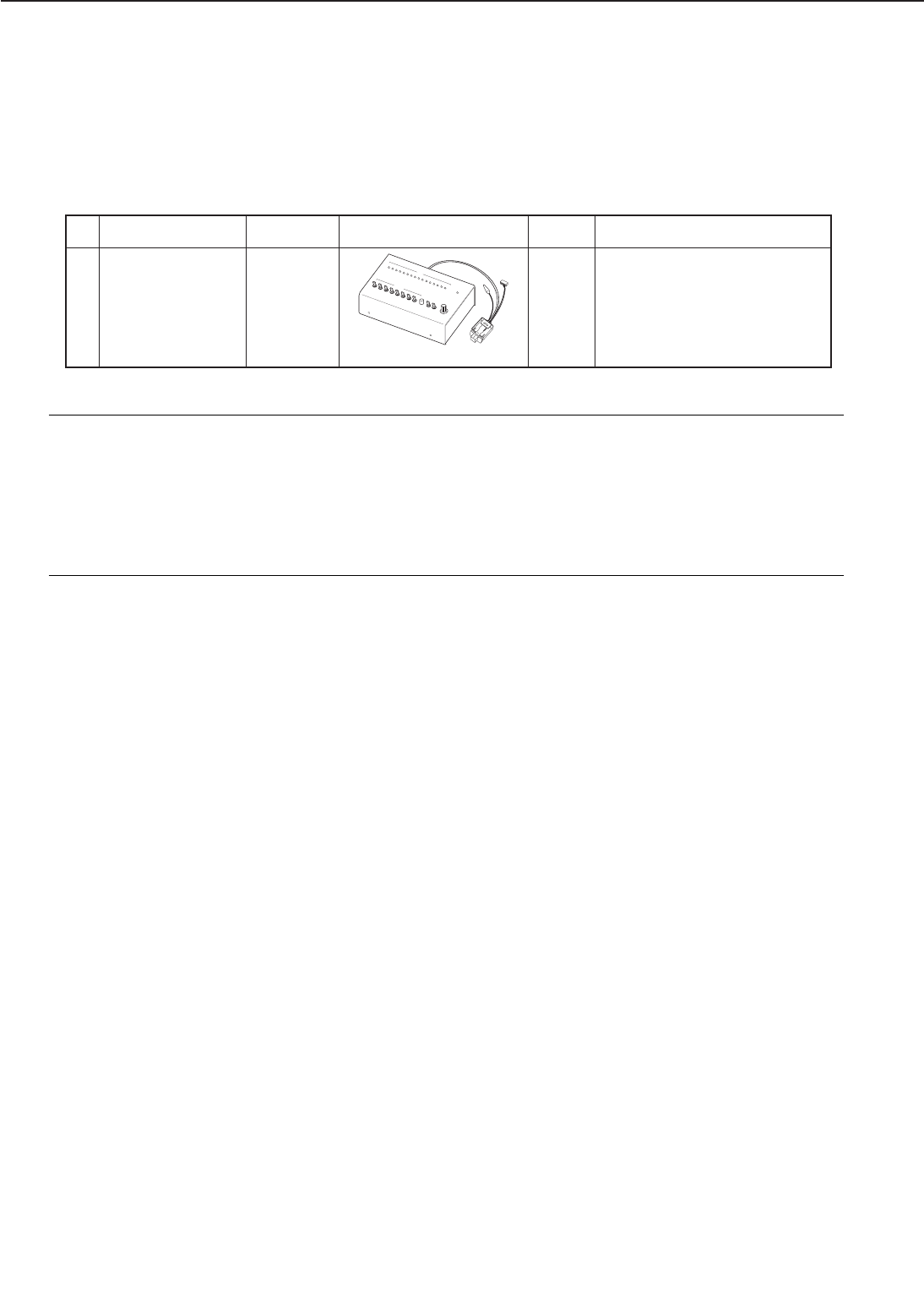
F. Special Tools
In addition to the standard tools, the following special tools are required for servicing the print-
er.
Table 4-8-3
Note: Ranks
A: Tools used for part replacement or adjustment on site.
B: Tools used on site or in regions.
These tools include tools used for failure analysis, and tools which are difficult to
carry around.
C: Tools used in the workshop.
These tools include the tools used for PCB and unit repairs.
4 - 39
CHAPTER 4
Tool No. Application/remarks
1 Printer driver
tester
No. Tool name
RY9-0104 Used for checking printer
operations.
Shape RANK
B
DATA
DATA SET
bit 16 bit 15 bit 14 bit 13 bit 12 b it 11 bit 10 bit9 bit 8 bit 7 b it 6 bit 5 bit 4 bit 3 b it 2 bit 1
DC24V
bit2
1
0
bit3
1
0
bit4
1
0
bit5
1
0
bit6
1
0
bit7
1
0
bit8
1
0
ENTER TEST
PRINT MODE SELECT
ON
OFF 1
DISPLAY
SET UP
2
3
567
8
9
10
11
CANON INC.
MADE IN JAPAN
RY9-0104
PRINTER DRIVER
bit1
1
0
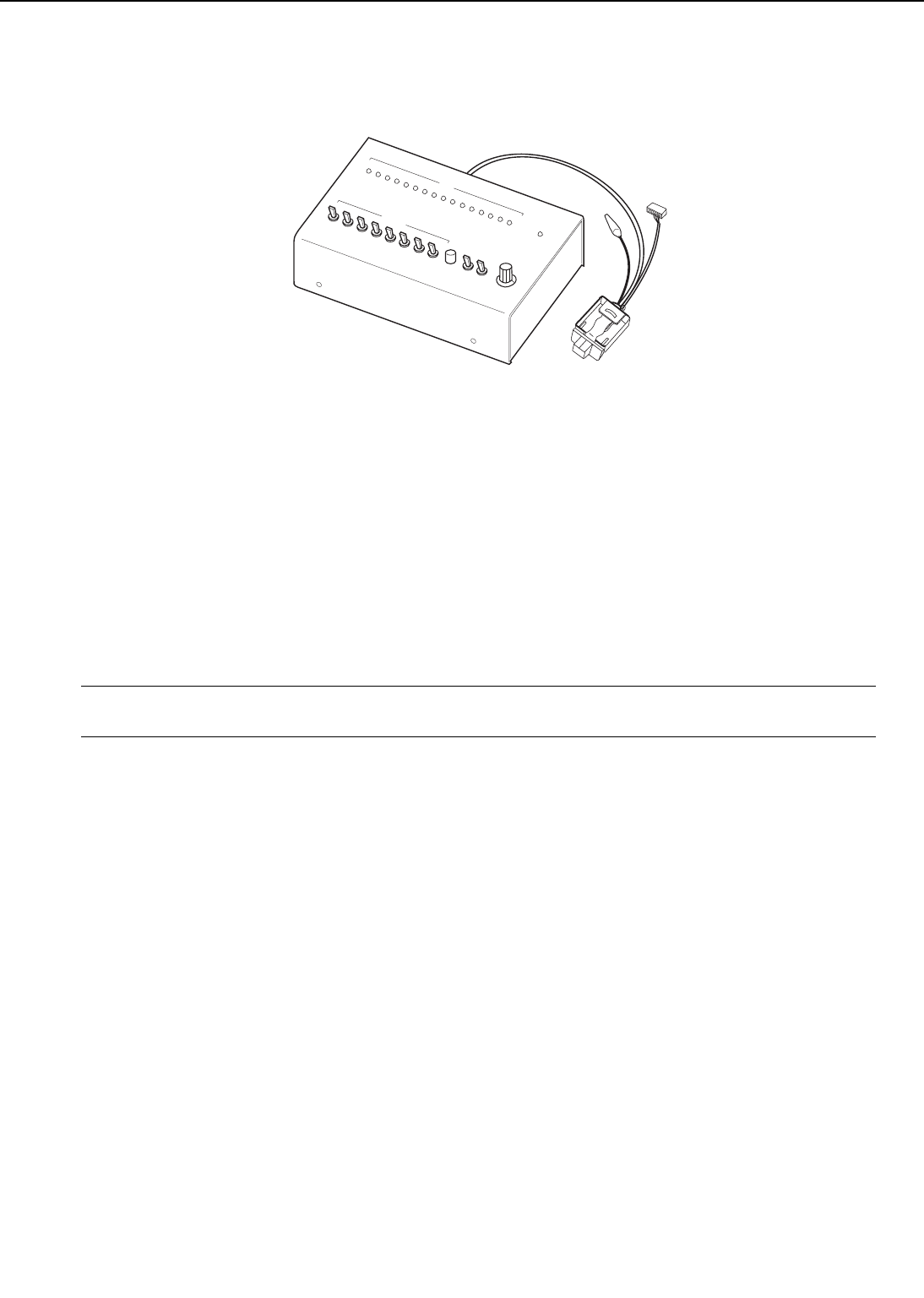
G. Special Tools (printer driver tester) Explanation
Figure 4-8-2
1. Outline
The tester runs the printer independently to test operation of printer and options (duplexing unit
and envelope feeder). It has three uses which are outlined below;
a. Commands the printer to print out solid black, horizontal lines, vertical lines and solid blank
images. It can also select the pick-up and delivery trays and simplex and duplex print.
b. Monitors the status of the sensors, and forcibly operates the various solenoids and motors.
c. In the event of a printer failure, the error information sent from the printer to the video con-
troller (external device) can be displayed on the tester LED.
Note: This manual covers the basic operation of the printer driver tester. For more defailed
explanation please refer to the operation manual attached to the tester.
4 - 40
CHAPTER 4
DATA
DATA SET
bit 16 bit 15 bit 14 bit 13 bit 12 bit 11 bit 10 bit 9 bit 8 bit 7 bit 6 bit 5 bit 4 bit 3 bit 2 bit 1
DC24V
bit 2
1
0
bit 3
1
0
bit 4
1
0
bit 5
1
0
bit 6
1
0
bit 7
1
0
bit 8
1
0
ENTER TEST
PRINT MODE SELECT
ON
OFF 1
DISPLAY
SET UP
2
3
567
8
9
10
11
CANON INC.
MADE IN JAPAN
RY9-0104
PRINTER DRIVER
bit 1
1
0
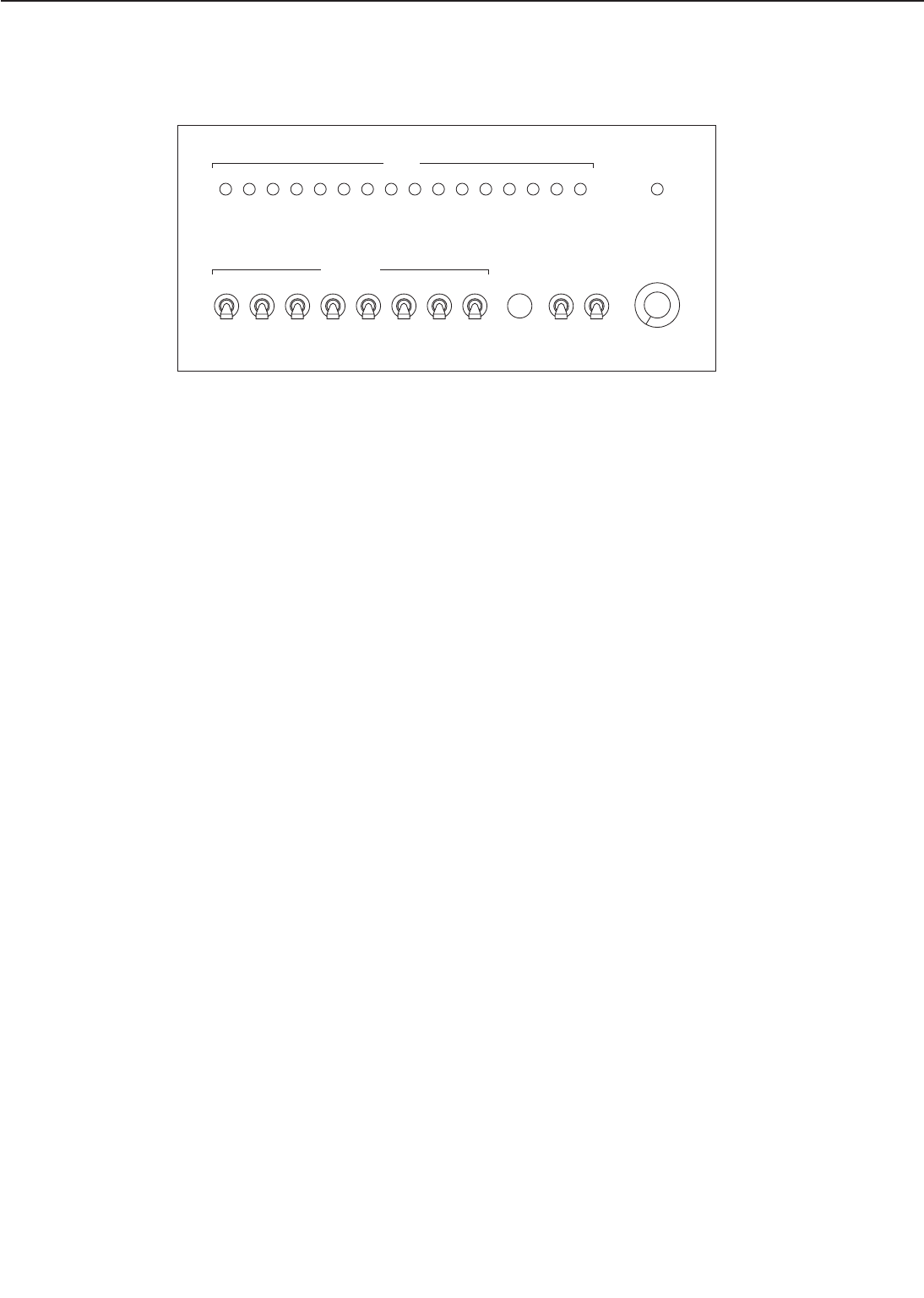
2. Operation Panel
Figure 4-8-3
DATA LED
Monitors the status of the various loads and sensors sent from the printer with the 16 LEDs.
+24VA LED
Lights up when +24VA is being supplied to the tester.
TEST PRINT switch
When set to "ON", test patterns set by the DATA SET switches are printed.
MODE SELECT switch
To select the various modes. See table 4-8-4.
DISPLAY/SET UP switch
Switches between DISPLAY and SET UP.
DISPLAY: Mode to display the status of the various sensors and loads sent from the printer with
the DATA LED.
SET UP: Mode to set data with the DATA SET switches.
DATA SET switch
Sets the various data sent to the printer. See in table 4-8-4.
ENTER switch
Inputs data set by the DATA SET switches.
4 - 41
CHAPTER 4
DATA
DATA SET
bit 16 bit 15 bit 14 bit 13 bit 12 bit 11 bit 10 bit 9 bit 8 bit 7 bit 6 bit 5 bit 4 bit 3 bit 2 bit 1
DC24V
bit 2
1
0
bit 3
1
0
bit 4
1
0
bit 5
1
0
bit 6
1
0
bit 7
1
0
bit 8
1
0
ENTER TEST
PRINT MODE SELECT
ON
OFF 1
DISPLAY
SET UP 2
3
4
567
8
9
10
11
CANON INC.
MADE IN JAPAN
RY9-0104
PRINTER DRIVER
bit 1
1
0
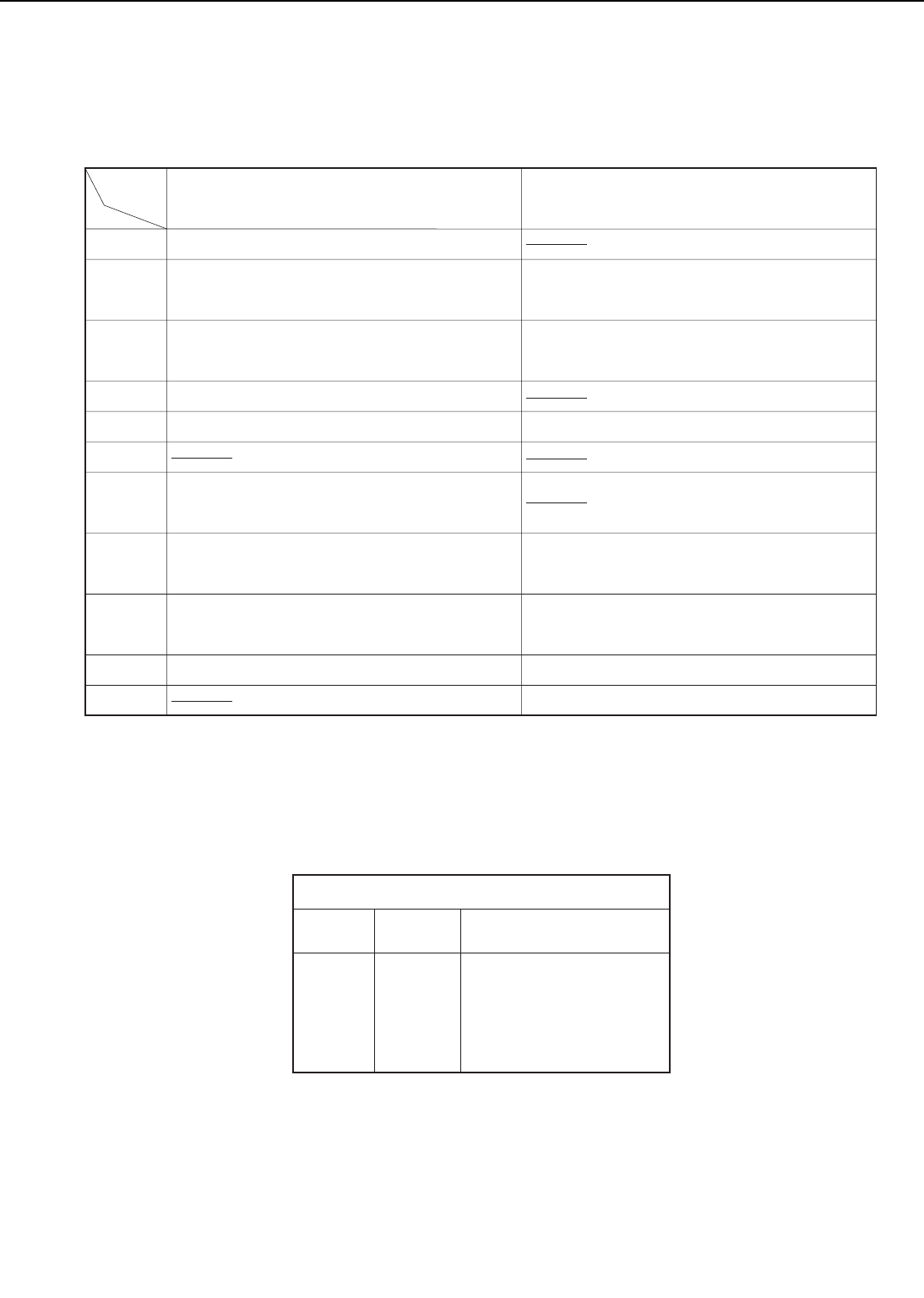
Table 4-8-4
3. Connector Signal Chart
Table 4-8-5
4 - 42
CHAPTER 4
Mode
Operator call/ service call
Service call/ misprint details/ warning/ fan
malfunction details 2 (72X)
Pick-up unit configuration/ select pick-up
unit/ pick-up unit paper-out
Sensor status (WX)/ Sensor status 1 (72X)
Select paper size/ select print density
Upper and lower cassette paper size detection
data/ Sensor status 2 (72X)
Cause of paper jam/ fan malfunction details
(WX)/ fan malfunction details 1 (72X)
Paper transport system electrical parts status/
Sensor status 3 (72X)
Motor status
Print density select
Ready inhibit/ forced laser emission (WX)/
sleep setting
Multi-purpose tray paper size select
Test print paper pick-up/ delivery slot
allocation/ pattern setting
Paper transport system electrical parts drive 1
Paper transport system electrical parts drive 2
Paper transport system electrical parts drive 3
DISPLAY SET UP
1
2
3
4
5
6
7
8
9
10
11
DISPLAY
/SET UP (displays the status of the sensors
and loads sent from the printer)
(sets up various data sent to the
printer)
J1-1
J1-2
J1-3
J1-4
Pin No. Signal
name Function
+24VA
IN
OUT
GND
+24VA
Serial line (input)
Serial line (output)
GND
Connector 1
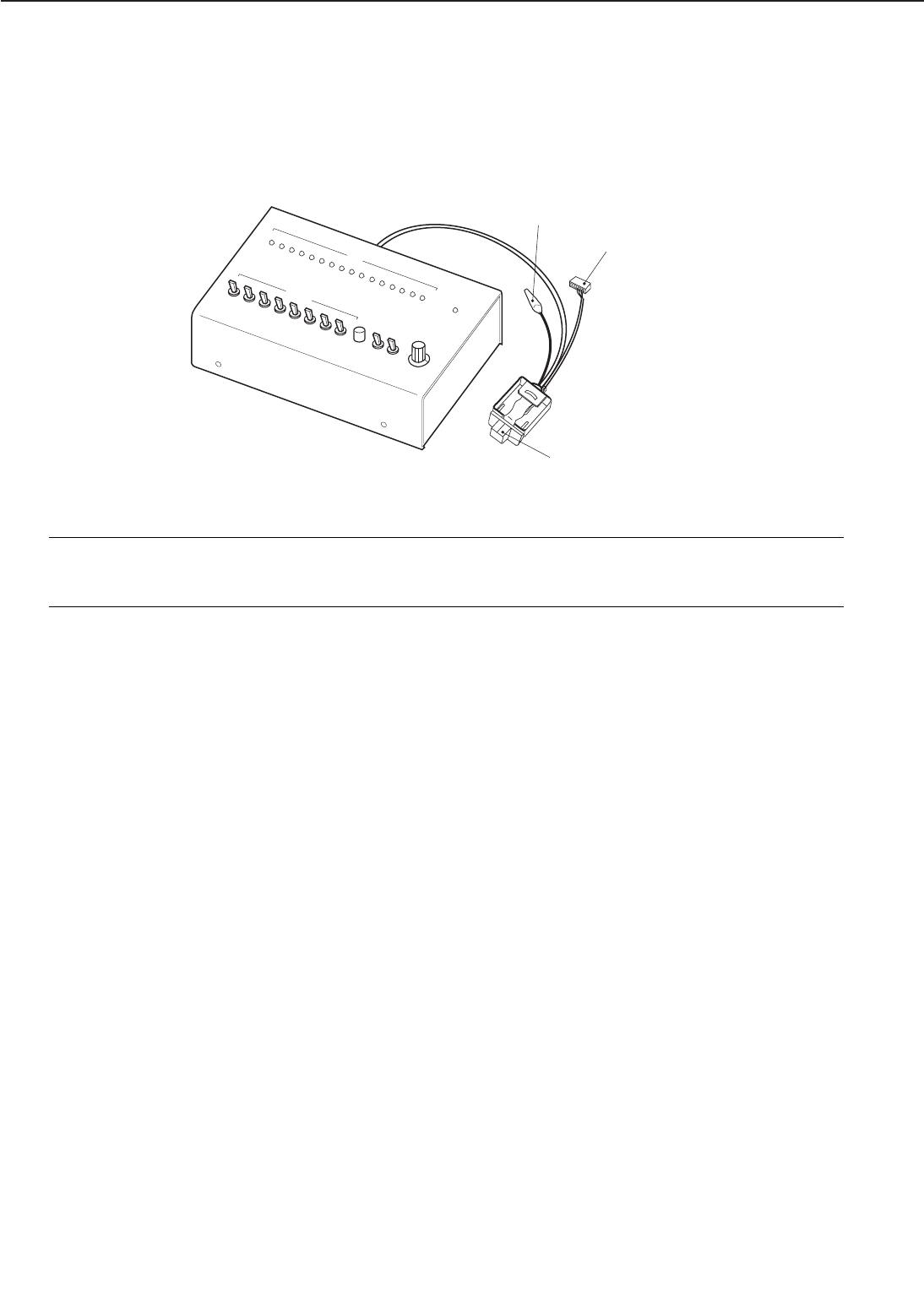
4. Operation Method
a. Preparation
1) Switch OFF the printer.
2) Connect the tester connector 1 to the envelope feeder connector (J24) in the printer.
3) Turn ON the printer.
4) When the printer is in standby mode, start performing checks with the tester.
Figure 4-8-4
Note: When operating the printer driver tester, electrostatic energy can cause operation fail-
ures. Therefore, when connecting the tester be sure to touch a metal part of the print-
er with your hand to discharge any electrostatic energy.
4 - 43
CHAPTER 4
DATA
DATA SET
bit 16 bit 15 bit 14 bit 13 bit 12 bit 11 bit 10 bit 9 bit 8 bit 7 bit 6 bit 5 bit 4 bit 3 bit 2 bit 1
DC24V
bit 2
1
0
bit 3
1
0
bit 4
1
0
bit 5
1
0
bit 6
1
0
bit 7
1
0
bit 8
1
0
ENTER TEST
PRINT MODE SELECT
ON
OFF 1
DISPLAY
SET UP
2
3
567
8
9
10
11
CANON INC.
MADE IN JAPAN
RY9-0104
PRINTER DRIVER
bit 1
1
0
Connector 2
Connector 1
Clip
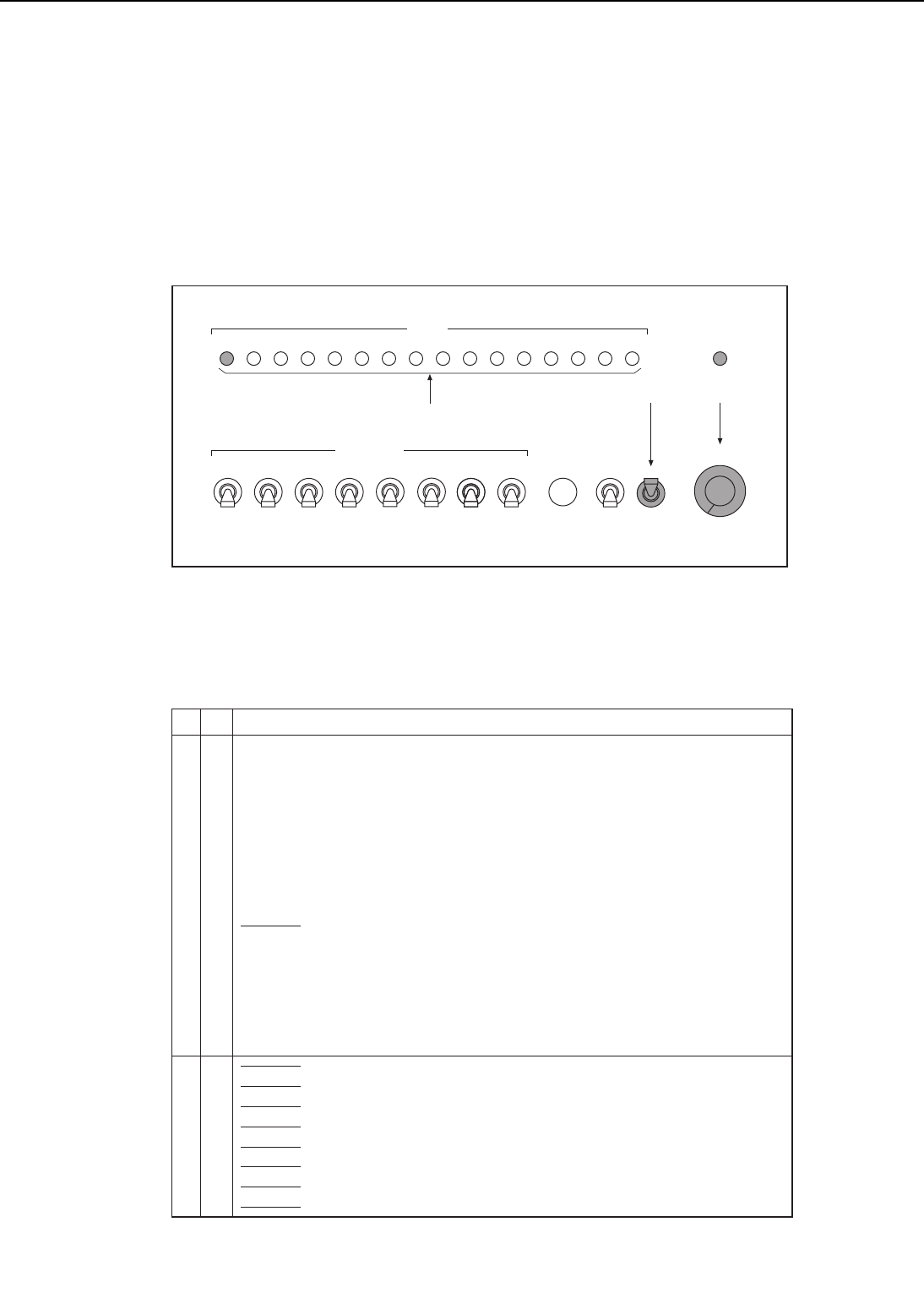
b. Confirming Printer Status
Select DISPLAY with the DISPLAY/SET UP switch. Check can be made with the LED display
(see table 4-8-7).
For example, when checking the contents of operator call/ service call, follow the directions
below.
1) After the printer has entered standby mode, set the DISPLAY/SET UP switch to "DISPLAY".
2) Set the MODE SELECT to "1".
3) Look up the corresponding chart for the bit that is lit up by a DATA LED.
For example, when a fixing unit failure occurs, the LED of bit 16 will light up.
Figure 4-8-5
Table 4-8-6
4 - 44
CHAPTER 4
DATA
DATA SET
bit 16 bit 15 bit 14 bit 13 bit 12 bit 11 bit 10 bit 9 bit 8 bit 7 bit 6 bit 5 bit 4 bit 3 bit 2 bit 1
DC24V
bit 2
1
0
bit 3
1
0
bit 4
1
0
bit 5
1
0
bit 6
1
0
bit 7
1
0
bit 8
1
0
ENTER TEST
PRINT MODE SELECT
ON
OFF 1
DISPLAY
SET UP 2
3
4
567
8
9
10
11
CANON INC.
MADE IN JAPAN
RY9-0104
PRINTER DRIVER
bit 1
1
0
➀➁
➂
16
15
14
13
12
11
10
9
8
7
6
5
4
3
2
1
8
7
6
5
4
3
2
1
Fixing unit malfunction
BD malfunction
Laser malfunction
Main motor malfunction
Scanner motor malfunction
Fan motor malfunction
Duplex pick-up roller malfunction (When duplexing unit is installed)
Lifting plate malfunction
Side registration guide malfunction (When duplexing unit is installed)
Misprint
Cartridge-out
Paper-out
Door open
Jam
Printer ready
Display Content Details/ Set Up Content Details
D
I
S
P
L
A
Y
S
E
T
U
P
bit
Mode select 1
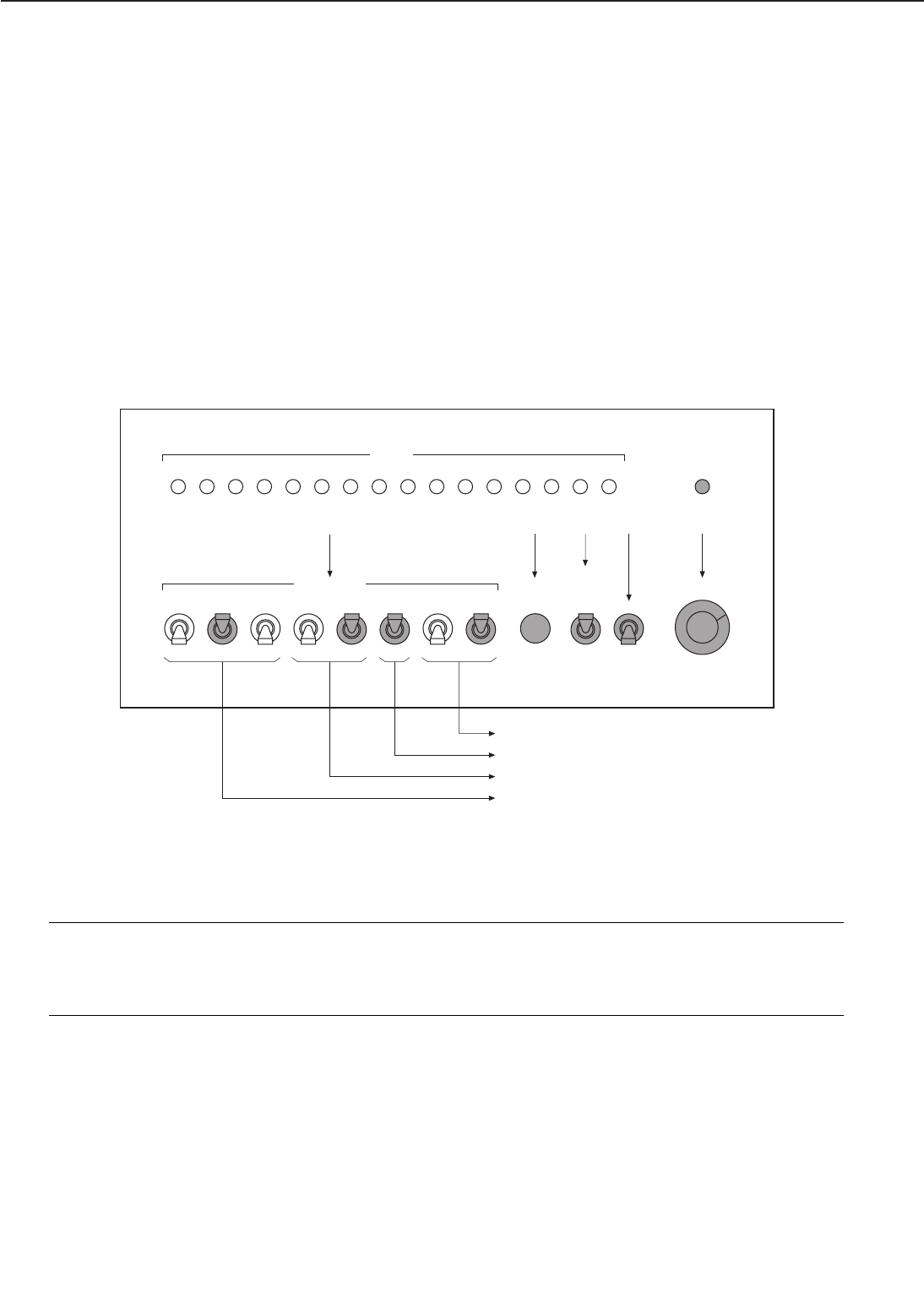
c. Itemize the Data Set
Select SET UP with the DISPLAY/SET UP switch. Various settings and commands can be made
according to the DATA SET (see table 4-8-4).
For example, when commanding a test print pick-up, delivery tray allocation or pattern set-
ting operation, follow the steps below by operating the the tester. (when you want to have paper
picked-up from the multi-purpose tray, duplex-print a horizontal line test print pattern and
deliver it through the face up tray.)
1) When the printer has entered standby mode, set the DISPLAY/SET UP switch on the tester
to "SET UP".
2) Set the MODE SELECT to "8".
3) Set DATA SET switch bit 8 to 0, bit 7 to 1, bit 6 to 0, bit 5 to 0, bit 4 to 1, bit 3 to 1, bit2 to
0 and bit 1 to 1 (see Table 4-8-7).
4) Press the ENTER switch.
5) By turning the TEST PRINT switch ON once, a test print can be made.
Figure 4-8-6
Notes: 1. After setting a test print in this mode, the data will remain the same even if the test
print is set in another mode.
2. By keeping the TEST PRINT switch "ON", continuous test prints will be made.
3. When setting the image pattern to "All black", do not make duplex prints.
4 - 45
CHAPTER 4
DATA
DATA SET
bit 16 bit 15 bit 14 bit 13 bit 12 bit 11 bit 10 bit 9 bit 8 bit 7 bit 6 bit 5 bit 4 bit 3 bit 2 bit 1
DC24V
bit 2
1
0
bit 3
1
0
bit 4
1
0
bit 5
1
0
bit 6
1
0
bit 7
1
0
bit 8
1
0
ENTER TEST
PRINT MODE SELECT
ON
OFF 1
DISPLAY
SET UP 2
3
4
567
8
9
10
11
CANON INC.
MADE IN JAPAN
RY9-0104
PRINTER DRIVER
bit 1
1
0
➀➁➂➃➄
Horizontal lines (image pattern) setting
Duplex print setting
Face-up tray delivery allocation
Multi-purpose tray pick-up allocation
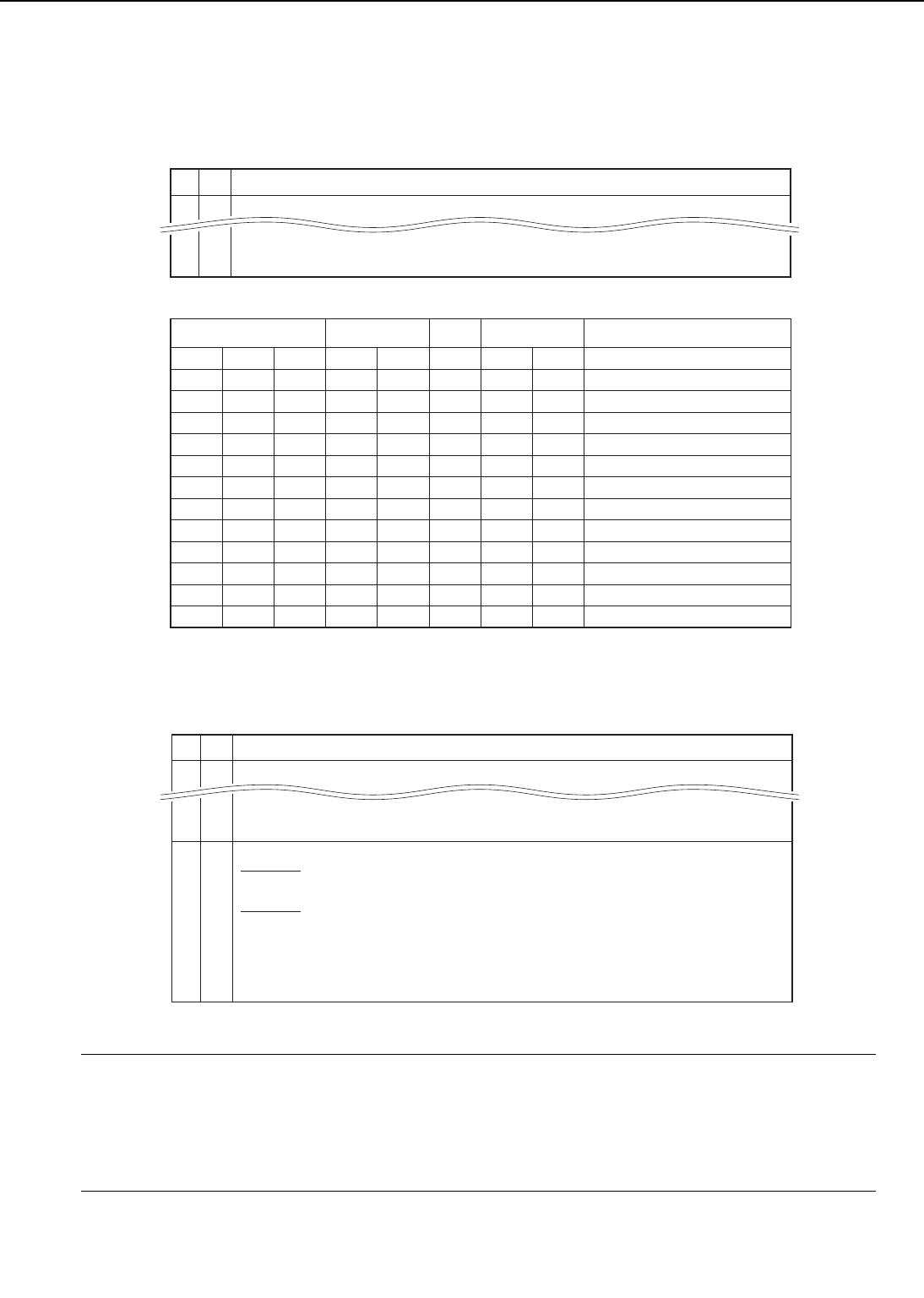
Table 4-8-7
Table 4-8-8
Notes: 1. When performing the ready inhibit setting, set MODE SELECT to "3" and turn ON the
printer while pressing the ENTER switch.
2. Deep mode halts all drives. (stop +24V supply)
Nap mode halts all drives except the fan motor.
3. The sleep mode setting can not be released. When releasing, turn the printer power
ON/OFF again.
4 - 46
CHAPTER 4
16
2
1
Initial residual jam
Electrical unit fan malfunction
Fixing unit fan malfunction
Display content details
SET UP
Lower cassette pick-up
Upper cassette pick-up
Multi-purpose tray pick-up
Envelope feeder pick-up
Face-down tray delivery
Face-up tray delivery
Single side print
Duplex print
Vertical lines
Horizontal lines
All-white
All-black
bit 8
0
0
0
0
bit 7
0
0
1
1
bit 6
0
1
0
1
bit 5
0
0
bit 4
0
1
bit 3
0
1
bit 2
0
0
1
1
bit 1
0
1
0
1
Print
mode
Pick-up slot Delivery slot Image pattern
bit
Mode select 8
16
2
1
8
7
6
5
4
3
2
1
Lights when the upper cassette pick-up function is ready in the printer
Lights when there are envelopes loaded in the envelope feeder.
Lights when paper is present at the re-feed position
RDYINH set (Note 1)
Forced laser emission (WX only)
Service mode (1: start, 0: stop) (72X only)
Display panel light up test (WX only)
Sleep mode (1: deep mode, 0: nap mode) (Note 2)
Sleep set (Note 3)
Display Content Details/ Set Up Content Details
S
E
T
U
P
bit
Mode select 3
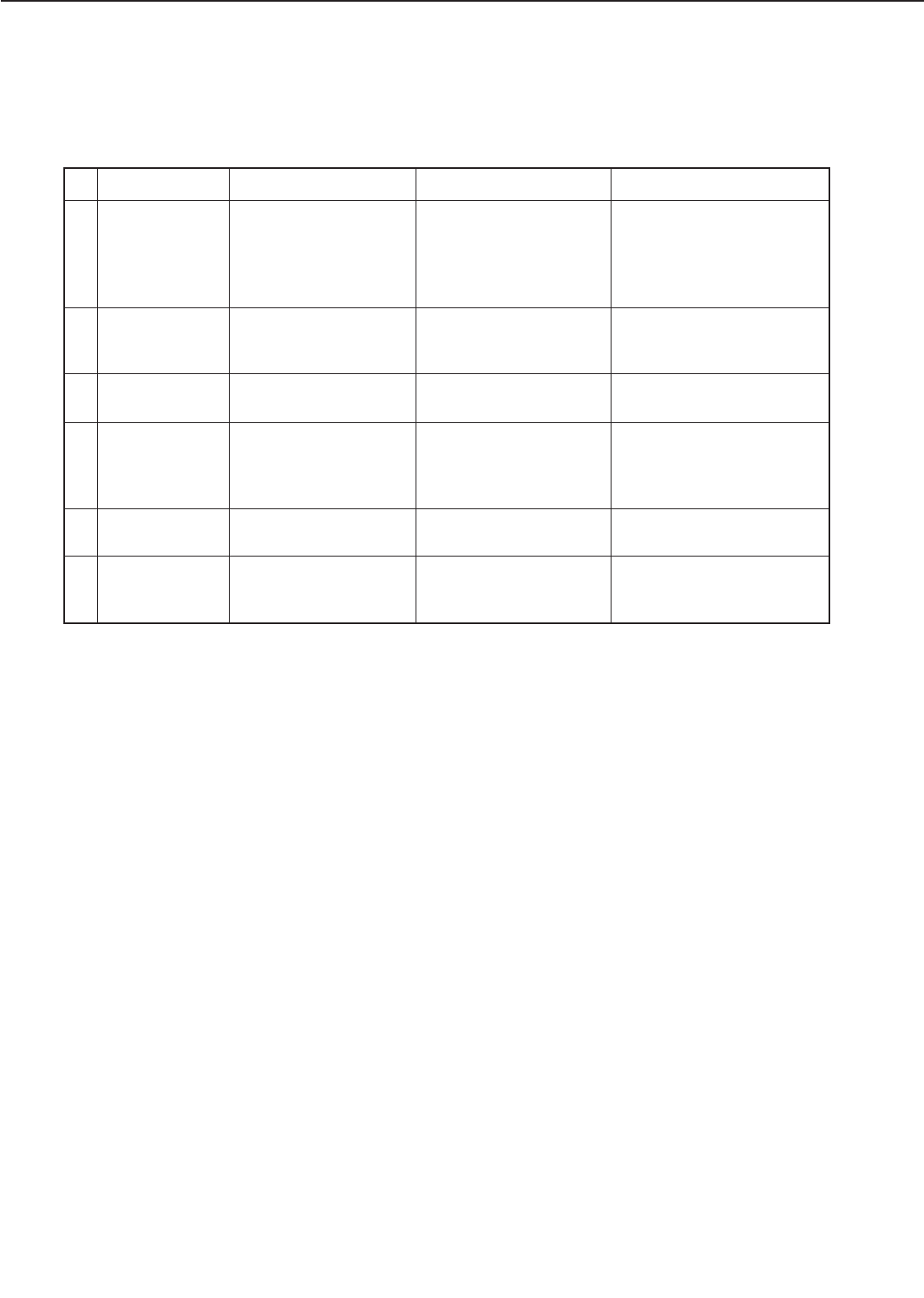
H. Solvents and Oil List
Table 4-8-9
4 - 47
CHAPTER 4
Components Remarks
1
2
Alcohol: ethyl
(pure or
denatured) or
isopropyl (pure
or denatured)
No. Material name
C2H5OH,
(CH3)2CHOH
•
•
Use
Cleaning: plastic,
rubber
CH3CO-C2H5
Purchase locally
Flammable: keep away
from flame
MEK (methyl
ethyl ketone)
Cleaning: oil and toner
stains
•
•
Purchase locally
Highly flammable: keep
away from flame
Lubricating oil Petroleum mineral oilApply between gear
and shaft
• Tool No. CK-8003
(100 ml bottle)
Lubricating
agent
Special oil
Special solid lubricating
material
Lithium soap
Apply to gears • Tool No. HY9-0007
(20 g tube)
3
4
Lubricating
agent
Lithium oilApply to gears of the
pick-up unit
•5
Lubricating
agent
Apply to gears of the
pick-up unit
(Refer to Chapter 3)
•6
Tool No. CK-8005
(40 g bottle)
Tool No. CK-8009
(20 g tube)
Poly αolefin oil
Lithium soap
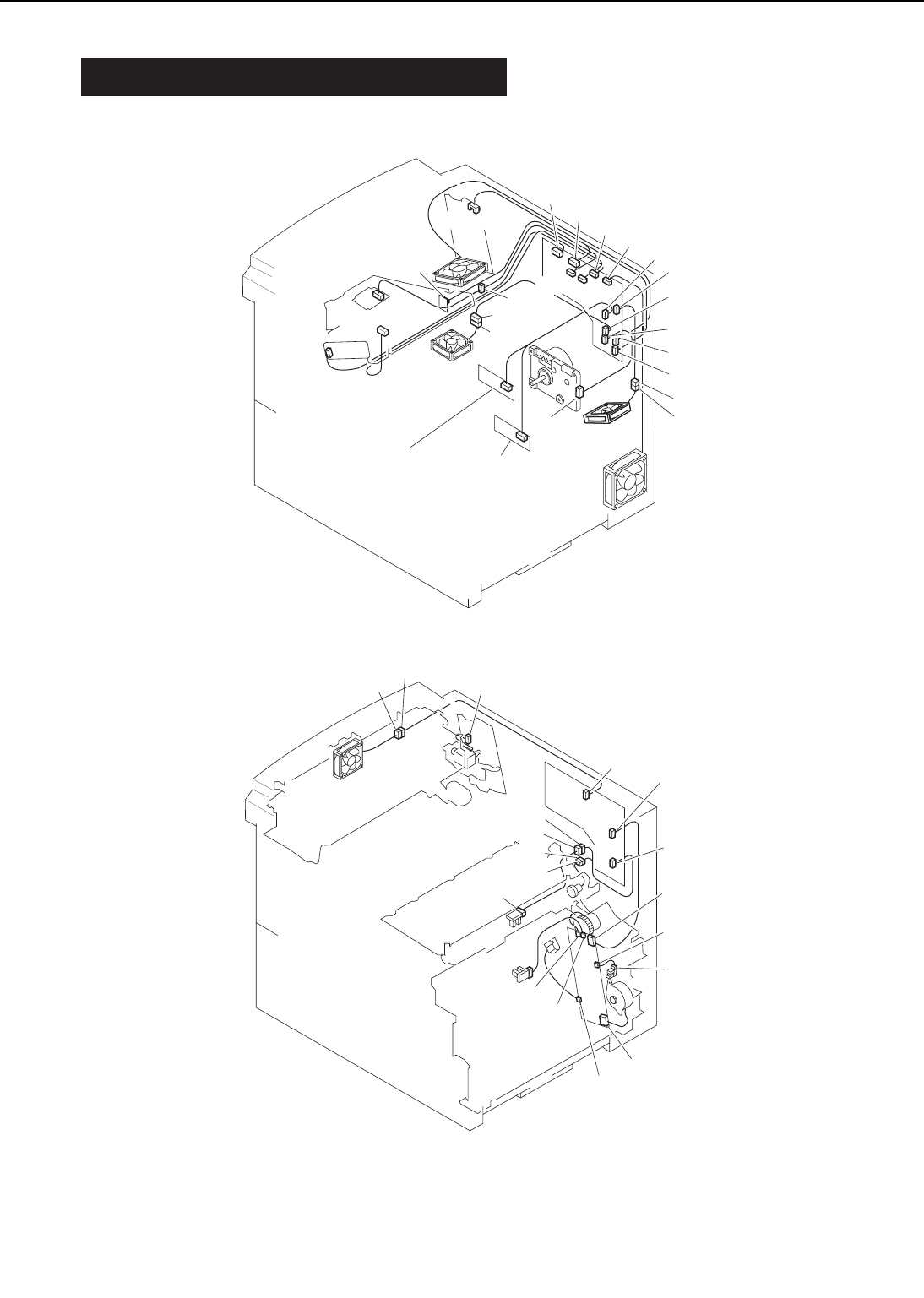
IX. LOCATION OF CONNECTORS
Figure 4-9-1
4 - 48
CHAPTER 4
J1001
J1 J18
J1601A J1601B
J12
J1401
J202
J206
J205
J203
J208
J215
J210
J218
J216
J221
J25
J225
J209
J219
J14
J15
J16
J17
J13
J1204
J1203
J1205
J1202
J1201
J1206
J14
J12
J13
J26 J1402
J207
J6
J11
J34
J35
J229
J3
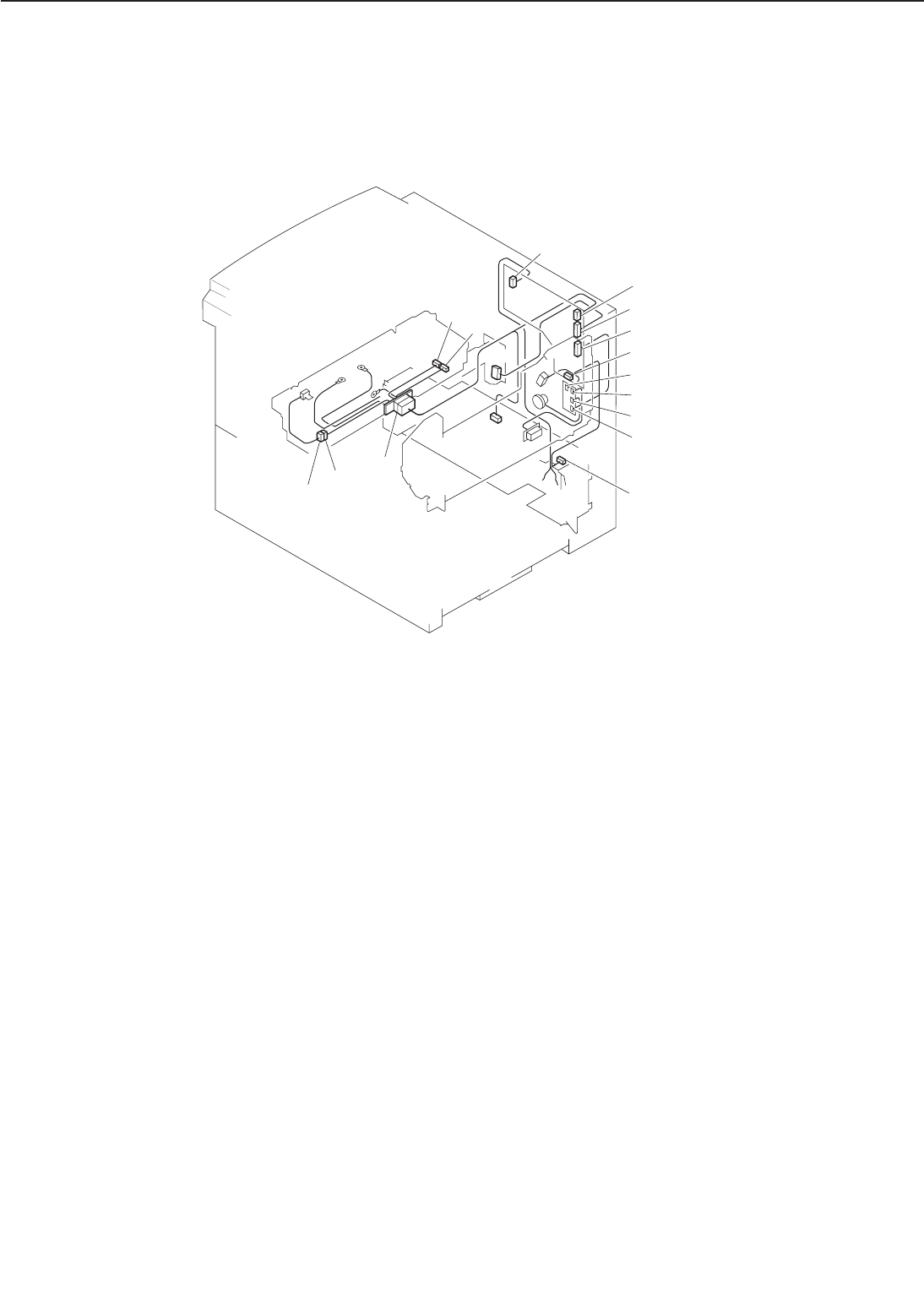
Figure 4-9-2
4 - 49
CHAPTER 4
J56 J51 J50
J54
J55
J19
J10
J24
J204
J213
J214
J222
J1302
J1304
J1303
J1301
J102
J217
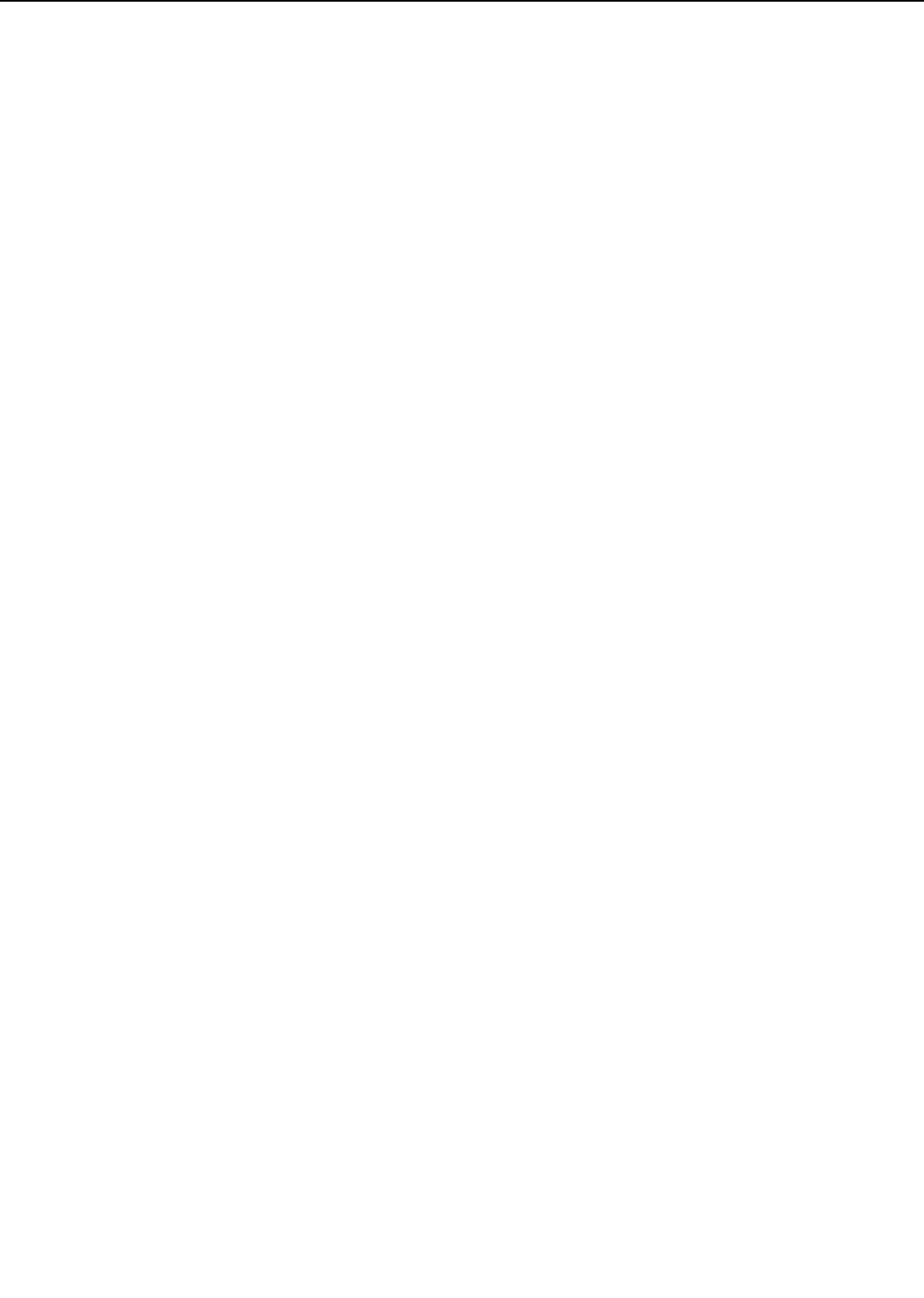
4 - 50
CHAPTER 4
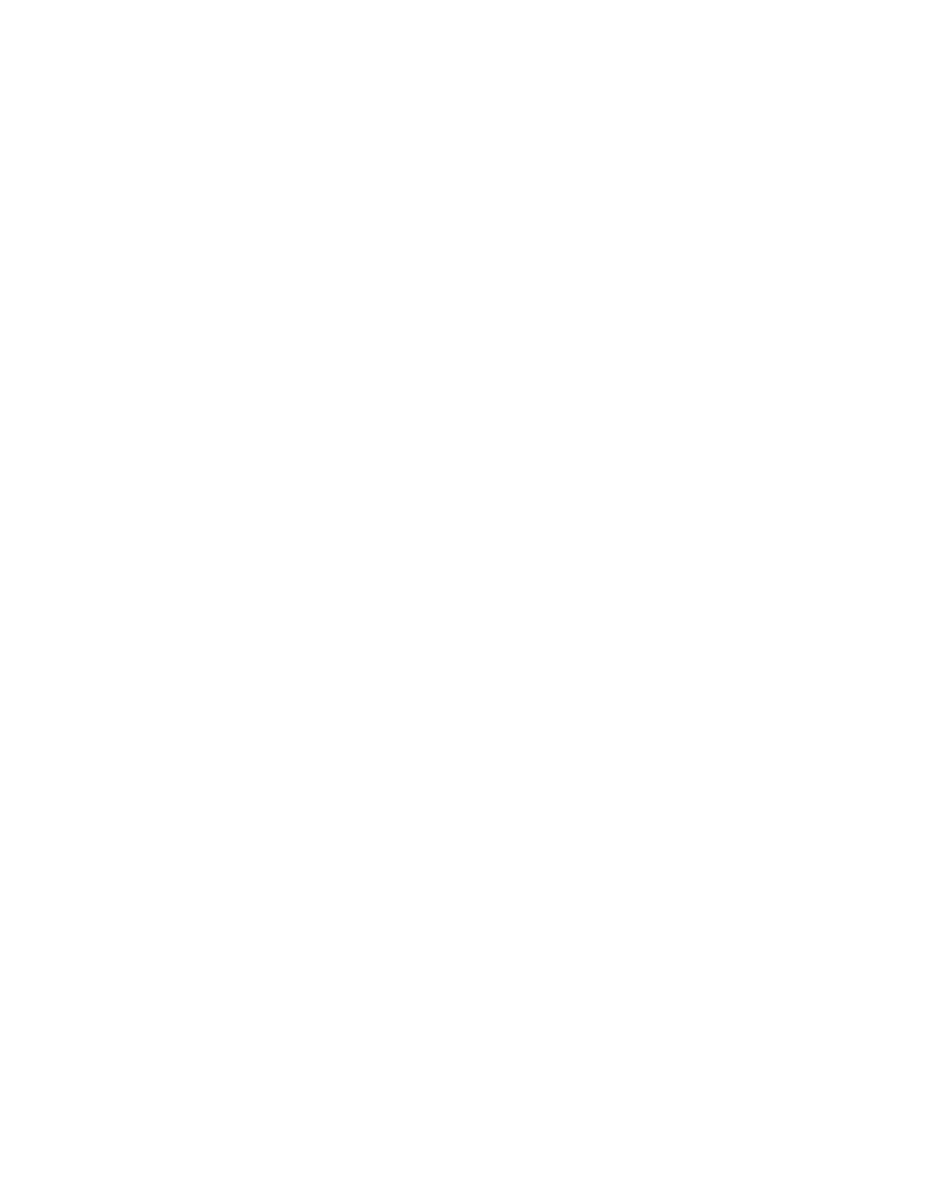
APPENDIX
I. GENERAL TIMING CHART ..... A-1
II. GENERAL CIRCUIT DIAGRAM A-3
III. LIST OF SIGNALS .................. A-5
IV. MESSAGES TABLE ................ A-11
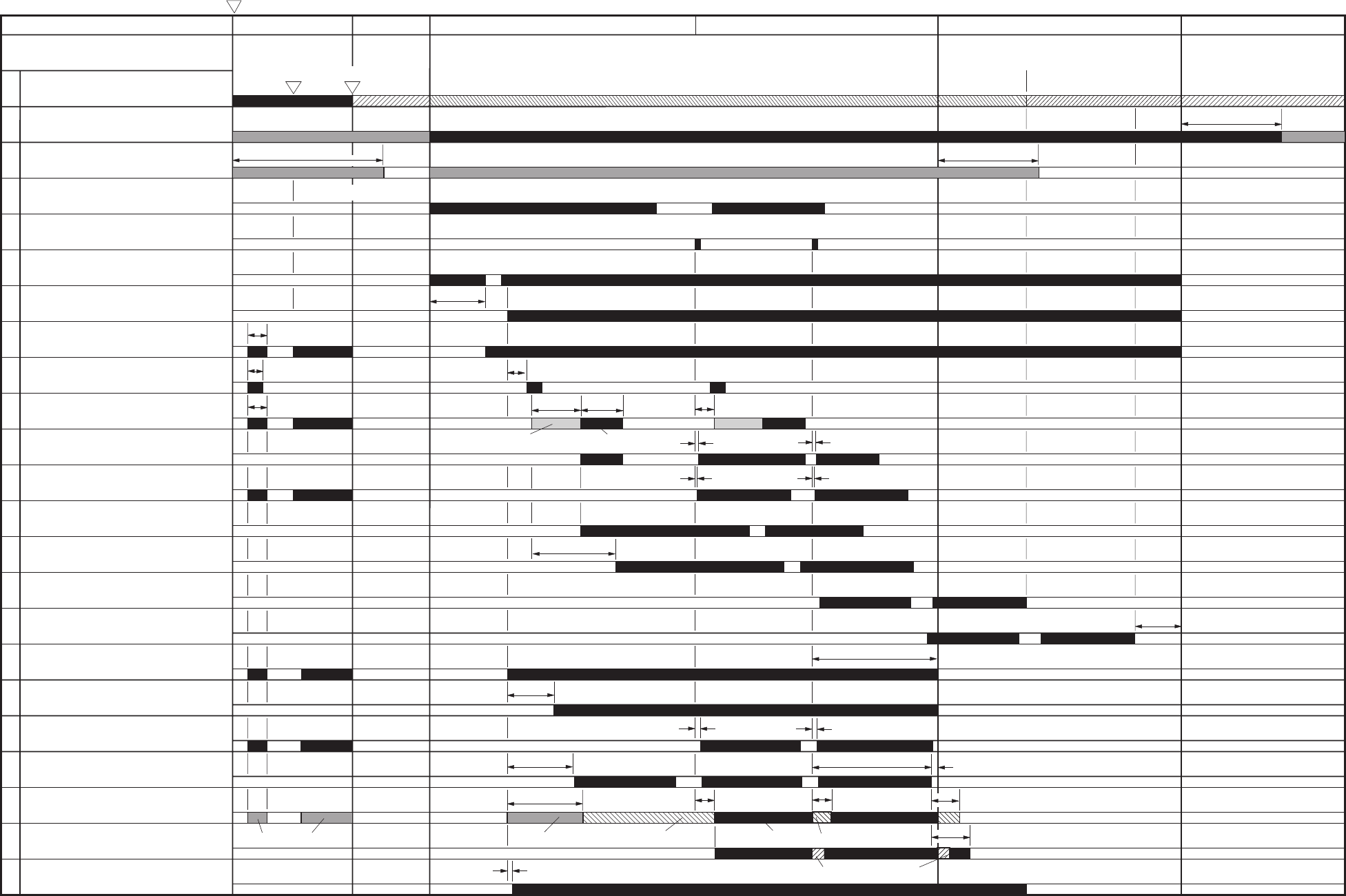
A-1
•Timing chart for two consecutive prints on A4 paper (Lower cassette feed - face-down tray delivery)
I. GENERAL TIMING CHART
1
2
3
4
5
6
7
8
9
10
11
12
13
14
15
16
17
18
19
20
21
22
23
STBYWAIT STBYINTR PRINT LSTR
3.25
0.52
0.82
0.31 0.37
0.52
0.77
0.05 0.05
0.31
0.2
0.04
0.01
0.04
0.01
0.1
1.74 0.05
0.47
1.79
About 15.0
(Unit: Seconds)
Fixing roller heater (H1, H2)
Fan (FM1, FM2, FM3, FM4)
Fan (FM5)
PRINT signal (/PRNT)
VERTICAL SYNC signal (/VSYNC)
Scanner motor (M1)
Scanner motor ready (/SCNRDY)
Main motor (MT1)
Cassette pick-up solenoid (SL1)
Pick-up motor (SMT1)
Feed clutch (CL2)
Registration clutch (CL1)
Pick-up unit paper sensor (PS2)
Registration paper sensor (PS1)
Fixing unit delivery sensor (PS1403)
Face-down tray delivery sensor (PS1402)
Primary voltage (AC)
Primary voltage (DC)
Developing bias (AC)
Developing bias (DC)
Transfer voltage
Static charge eliminator bias
Upper fixing roller bias
Operation
Power switch ON
High-speed rotationLow-speed rotation
169°C
control 190°C control
160°C170°C190°C
control
Rotation
About 1.5
High-speed rotation
Low-speed rotation
169°C control 169°C control
About 1.2
About 1.5 About 0.9
About 1.5
About 0.7
About
1.1
About 30.0
About 30.0
Between-page bias Print bias
Negative bias Negative bias
High-voltage bias
Between-page bias
Low-speed rotation
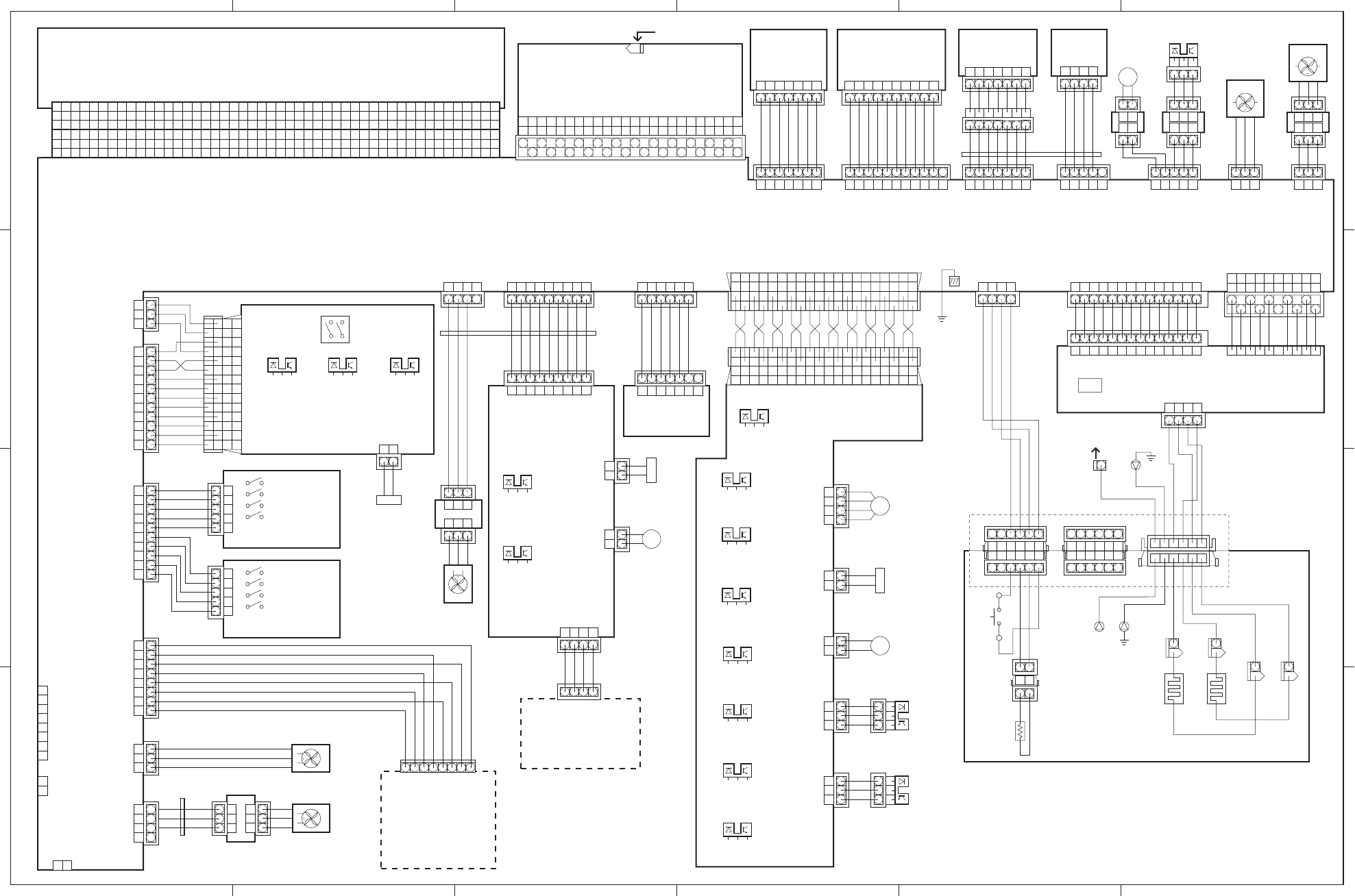
654321
D
C
B
A
A-3
II.@æH}
II. GENERAL CIRCUIT DIAGRAM-1/2
PS1302
PS1301
SL2
CL
CL3
SMT1
M
CL2
CL
SL1
PS2
1
2
3
3
2
1
1
2
3
PS3
1
2
3
3
2
1
1
2
3
PS1201
PS1202
PS1203
PS1204
PS1205
PS1206
PS1207
PS1208
PS1
CL
A1
B1
C1
A2
B2
C2
A3
B3
C3
A4
B4
C4
A5
B5
C5
A6
B6
C6
A7
B7
C7
A8
B8
C8
A9
B9
C9
A10
B10
C10
A11
B11
C11
A12
B12
C12
A13
B13
C13
A14
B14
C14
A15
B15
C15
A16
B16
C16
A16
B16
C16
A15
B15
C15
A14
B14
C14
A13
B13
C13
A12
B12
C12
A11
B11
C11
A10
B10
C10
A9
B9
C9
A8
B8
C8
A7
B7
C7
A6
B6
C6
A5
B5
C5
A4
B4
C4
A3
B3
C3
A2
B2
C2
A1
B1
C1
A1
B1
A2
B2
A3
B3
A4
B4
A5
B5
A6
B6
A7
B7
A8
B8
A9
B9
A10
B10
A11
B11
A12
B12
A1
B1
A2
B2
A3
B3
A4
B4
A5
B5
A6
B6
A7
B7
A8
B8
A9
B9
A10
B10
A11
B11
A12
B12
12 FAN1
CL1
J14 J15
J16 J17
J18
J1001
J3
J701
J201
GND
GND
VDO
GND
GND
/VDO
/FPCS
/FPO
/FPI
reserved
reserved
FPCK
/VSREQ
/RDY
/PPRDY
/VSYNC
/CPRDY
/PRNT
/STS
/SBSY
/PCLK
/CMD
/CBSY
/CCLK
CPSEL
/PRFD
/CCRT
/SPCHG
/PFED
/PDLV
3.3V
3.3V
3.3V
3.3V
3.3V
3.3V
+5V
+5V
+5V
+5V
+5V
+5V
GND
GND
GND
GND
GND
/BD
TRFVCNT
/
TRFNVD
TRFVSNS
/HRLBD
/
TRFCCD
/DCHGBD
TRFCLK
/DCHGUP
N.C.
N.C.
HVTCLK
N.C.
/DEVACD
PRJACCLK
DEVACCLK
/PRJACD
/DEVDCD
/PRJACD
TONSNS
DENADJ
24VGND
24VGND
+24VB
+24VB
J220
J203
J202
J207
J209
J208
/FPO
/FPI
/FPCS
FPCK
+5V
+5V
GND
/LENBL
/LON
/VDO
GND
VDO
N.C.
GND
+5V
GND
DRVES
GND
+5V
/SCNRDY
/SCND
GND
/SCNCLK
24VGND
+24VA
/REGCLD
+24VA
/REGS
GND
P5VB1
FAN1D
/FAN1S
24VGND
J204
J217
J222
J219
J218
J214
24VGND
+24VA
P5VB1
/MPTCLD
/MPTSLD
MPTLS
/MPTPS
ENVCMD
ENVSTS
FEDAND
FEDAD
FEDBND
FEDBD
/UDECKS
UDECKC
/FEEDCLD
/FEEDS
/PUPSLD
LDECKC
/LDECKS
LPVS2
LPVS1
UPVS2
UPVS1
/
RDOORS
+24VA
P5VB1
GND
GND
/MMRDY
/MMOTD
24VGND
24VGND
+24VB
+24VB
TSWOUT
FSRTH
GNDTH
TSWIN
FSRTH
RLD
TSWIN
GND
TSWOUT
/FSRD1
/FSRD2
FSRDE
FSRCT
SUPSLT
/RLDSNS
PSTYP
/REMT24
N.C.
+5V
3.3V
+5V
3.3V
GND
GND
GND
24VGND
+24V
24VGND
FSRN1
FSRL1
FSRL2
FSRN2
J102
J10
TB51
J1201
J12
MT1
J1301
1
2
J223
TONSNS
GND
2
1
2
1
2
1
2
1
J1302
J1303
+24VA
/MPTSLD
+24VA
/MPTCLD
J50
A
B
1
J54
J55
J52
TB53
TB50
1
2
3
4
1
2
3
4
2
1
2
1
2
1
2
1
3
2
1
3
2
1
J13
J14
FEDAD
FEDAND
FEDBD
FEDBND
+24VA
/PUPSLD
+24VA
/FEEDCLD
/FEEDS
GND
P5VB1
/RDOORS
GND
P5VB1
J1206
J1205
J1204
J1203
J1202
J11
SW101
J212
1
2
3
4
5
6
7
8
3.3V
+5V
GND
FSRTH
GND
SVIN
SVOUT
+24VA
/REGCLD
24VGND
1
2
1
2
3
4
5
6
7
8
9
10
1
2
3
4
5
6
7
8
9
10
J215
J213
GND
LSIZE4
LSIZE3
LSIZE2
LSIZE1
GND
USIZE4
USIZE3
USIZE2
USIZE1
5
4
3
2
1
5
4
3
2
1
5
4
3
2
1
5
4
3
2
1
J1601A
J1601B
SW1601
SW1602
SW1603
SW1604
SW1601
SW1602
SW1603
SW1604
1
2
3
1
2
3
4
5
6
7
8
9
10
11
1
2
3
4
5
6
7
8
9
10
11
12
13
14
1
2
3
4
5
6
7
8
9
10
11
12
13
14
1
2
3
1
2
3
4
5
6
7
8
9
10
11
J221
J205
+24VB
+24VB
+24VB
GND
GND
+24VA
+24VA
+24VA
UDOORS
FDFULS
/FPOUTS
FDOUTS
/FUSLD
P5VB1
J1401 SW1401
PS1403PS1402PS1401
J19
8
7
6
5
4
3
2
1
8
7
6
5
4
3
2
1
24VGND
24VGND
/DUPCLK
DUPCMD
/DUPSTS
/DUPIDS
+24VA
+24VA
J228
SL3
/FUSLD
+24VA
J1402
SL
123456789
123456789
123456789
123456789 123456
1234567
FAN5D
/FAN5S
24VGND
24VGND
FAN5
1234
123
321
321
123456
12345678910
1234
123456
123456
1234
TB52
J53
TB54
2
1
2
J56 J51
TB705
123456
12
12
1234567
7654321
1234
7654321 12
21
21
J12 J13
J210
FAN3D
/FAN3S
24VGND
123
123
123
123
321
321
123
123
123
123
123
321
321
12345
12345
123456789
10
123456789
10
987654321
1011
987654321
1011
J6
J1
7654321
7654321
7654321
7654321
1234567
1234567
4321
4321
12345
J206
GND
GND
/BDI
+5V
GND
12345
1234567891011121314
1234567891011121314151617181920
2019181716151413121110987654321
1234567891011121314151617181920
2019181716151413121110987654321
J204
1234567891011121314
1234567891011121314
1234567891011121314
123456
123456 123456
654321
654321
654321
654321
J229
1234567
1234
J34J35
A1B1A2B2A3B3A4B4A5B5
A1B1A2B2A3B3A4B4A5B5
FAN3
TB705
123
3
2
1
3
2
1
J216
GND
/FAN2S
FAN2D
FAN2
1
2
3
4
1
2
3
4
J225
FAN4D
/FAN4S
24VGND
GND
3
2
1
3
2
1
1
2
3
1
2
3
J25
FAN4
J26
1
2
3
4
1
2
3
4
1
2
3
4
+24VA
ENVCMD
ENVSTS
GND
J24 J1304
12345678
FGND
Video controller
Duplexing unit
(option)
Cassette-size
sensing switch PCB
DC controller PCB
Switch/sensor
PCB
Fixing unit fan
Face-down
tray paper full
sensor
Face-down
tray delivery
sensor
Fixing unit
delivery
sensor
Face-up
solenoid
Door switch
Power supply fan
Cassette-size
sensing switch PCB
Main motor
Multi-purpose
tray PCB
Multi-purpose
tray paper sensor
Lifting plate
position sensor
Lifting plate
solenoid
Manual feed
clutch
Pick-up PCB
Lower cassette
sensor
Upper cassette
sensor
Lower cassette
paper-level
sensor 1
Lower cassette
paper-level
sensor 2
Upper cassette
paper-level
sensor 1
Upper cassette
paper-level
sensor 2
Lower cassette
paper-out
sensor
Upper cassette
paper-out sensor
Pick-up motor
Cassette pick-up
solenoid
Feed clutch
Pick-up unit
paper sensor
Pick-up unit
door sensor
Power supply
Fixing unit
Envelope feeder
(option)
Power switch
HVT
Operation
panel Laser driver
PCB
Scanner
motor BD
PCB
Fixing unit/
Scanner unit
fan
Registration
clutch
Registration
paper sensor Electrical
unit fan
Thermistor
Thermoswitch
Fixing main heater
Fixing sub heater
To HVT
From fixing unit
Ferrite core
Ferrite
core
Ferrite
core
Multi-purpose
tray fan
TSW
TH
H1
H2
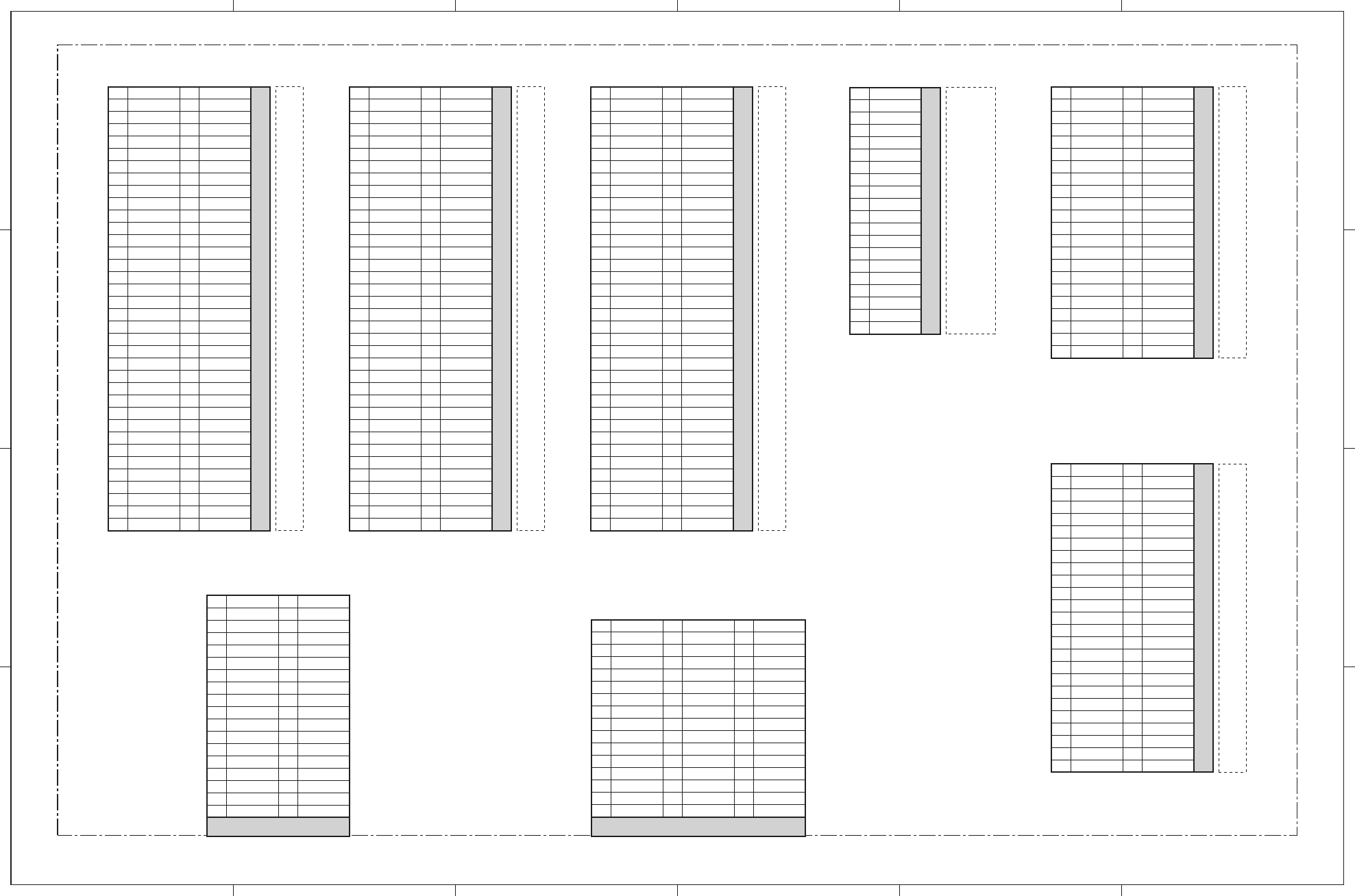
654321
D
C
B
A
A-4
II. GENERAL CIRCUIT DIAGRAM-2/2
Video controller PCB
Firmware ROM DIMM
J2
A1
A2
A3
A4
A5
A6
A7
A8
A9
A10
A11
A12
A13
A14
A15
A16
A17
A18
A19
A20
A21
A22
A23
A24
A25
A26
A27
A28
A29
A30
A31
A32
A33
A34
A35
A36
GND
D31
D29
D27
D25
D23
D21
D19
D17
GND
D15
D13
D11
D9
D7
D5
D3
D1
A2EV
VCC
A3EV
AA25
AA23
AA21
AA19
AA17
AA15
AA13
AA11
AA9
WnR
nRCS1
nRCS3
nRD0
nRD1
GND
VCC
D30
D28
D26
D24
D22
D20
D18
D16
GND
D14
D12
D10
D8
D6
D4
D2
D0
A2OD
GND
AA26
AA24
AA22
AA20
AA18
AA16
AA14
AA12
AA10
AA8
A3OD
nRCS0D
nRCS2
nWR0
nWR1
VCC
B1
B2
B3
B4
B5
B6
B7
B8
B9
B10
B11
B12
B13
B14
B15
B16
B17
B18
B19
B20
B21
B22
B23
B24
B25
B26
B27
B28
B29
B30
B31
B32
B33
B34
B35
B36
Optional ROM DIMM
J3/4
A1
A2
A3
A4
A5
A6
A7
A8
A9
A10
A11
A12
A13
A14
A15
A16
A17
A18
A19
A20
A21
A22
A23
A24
A25
A26
A27
A28
A29
A30
A31
A32
A33
A34
A35
A36
GND
D31
D29
D27
D25
D23
D21
D19
D17
GND
D15
D13
D11
D9
D7
D5
D3
D1
A2EV
VCC
A3EV
AA25
AA23
AA21
AA19
AA17
AA15
AA13
AA11
AA9
WnR
nRCS1
nRCS3
nRD0
nRD1
GND
VCC
D30
D28
D26
D24
D22
D20
D18
D16
GND
D14
D12
D10
D8
D6
D4
D2
D0
A2OD
GND
AA26
AA24
AA22
AA20
AA18
AA16
AA14
AA12
AA10
AA8
A3OD
nRCS0D
nRCS2
nWR0
nWR1
VCC
B1
B2
B3
B4
B5
B6
B7
B8
B9
B10
B11
B12
B13
B14
B15
B16
B17
B18
B19
B20
B21
B22
B23
B24
B25
B26
B27
B28
B29
B30
B31
B32
B33
B34
B35
B36
Optional RAM DIMM
J6/7
MD31
MD29
MD27
MD25
VCC
BMA0
BMA2
BMA4
BMA6
N.C.
MD22
MD20
MD18
BMA7
VCC
BMA9
nBAS2
N.C.
MD14
nBCAS3
nBCAS0
nBCAS2
N.C.
N.C.
MD12
MD10
MD8
MD7
MD5
MD4
MD2
MD0
N.C.
N.C.
N.C.
GND
GND
MD30
MD28
MD26
MD24
N.C.
BMA1
BMA3
BMA5
BMA10
MD23
MD21
MD19
MD17
N.C.
BMA8
nBAS3
MD16
MD15
GND
nBCAS1
nBCAS2
nBCAS3
WRITE*
MD13
MD11
MD9
N.C.
MD6
MD3
VCC
MD1
N.C.
N.C.
N.C.
N.C.
A1
A2
A3
A4
A5
A6
A7
A8
A9
A10
A11
A12
A13
A14
A15
A16
A17
A18
A19
A20
A21
A22
A23
A24
A25
A26
A27
A28
A29
A30
A31
A32
A33
A34
A35
A36
B1
B2
B3
B4
B5
B6
B7
B8
B9
B10
B11
B12
B13
B14
B15
B16
B17
B18
B19
B20
B21
B22
B23
B24
B25
B26
B27
B28
B29
B30
B31
B32
B33
B34
B35
B36
To host computer
J9
GND
GND
GND
GND
GND
GND
GND
GND
GND
GND
GND
GND
nINIT
nFAULT
N.C.
N.C.
N.C.
nSELIN
nSTROBE
D0
D1
D2
D3
D4
D5
D6
D7
nACK
BUSY
PERROR
SELECT
nAUTOFD
N.C.
GND
GND
PP 5V
1
2
3
4
5
6
7
8
9
10
11
12
13
14
15
16
17
18
19
20
21
22
23
24
25
26
27
28
29
30
31
32
33
34
35
36
To DC controller PCB
J1
GND
GND
VCC (5V)
VCC (5V)
VCC (3.3V)
VCC (3.3V)
nPFED
nPRFD
nCBSY
nSBSY
nCPRDY
nRDY
N.C.
nFP_OD
GND
GND
GND
GND
VCC (5V)
VCC (5V)
VCC (3.3V)
VCC (3.3V)
nSPCHG
CPSEL
nCMD
nSTS
nVSYNC
nVSREQ
N.C.
nFP_CS
GND
GND
A1
A2
A3
A4
A5
A6
A7
A8
A9
A10
A11
A12
A13
A14
A15
A16
nBD
GND
VCC (5V)
VCC (5V)
VCC (3.3V)
VCC (3.3V)
nPDLV
nCCRT
nCCLK
N.C.
nPRNT
nPPRDY
nFP_CK
nFP_ID
nVDO
VDO
B1
B2
B3
B4
B5
B6
B7
B8
B9
B10
B11
B12
B13
B14
B15
B16
C1
C2
C3
C4
C5
C6
C7
C8
C9
C10
C11
C12
C13
C14
C15
C16
Option controller interface board
(option)
J8
GND
GND
nTX
nCLK
nCLKEN
nRX
N.C.
nSTROBE
N.C.
N.C.
N.C.
nRETURN
nSPCHG
nPFED
nPRINT
nVSYNC
RESET
N.C.
VCC
VCC
1
2
3
4
5
6
7
8
9
10
11
12
13
14
15
16
17
18
19
20
Hard disk (option)
J10
nWR0
GND
nRD0
GND
N.C.
N.C.
N.C.
GND
nIDE INT
N.C.
IOA3
N.C.
IOA2
IOA4
nIDECS
IOA5
nIDE LED
GND
VCC
VCC
GND
N.C.
nHREST
GND
IOD7
IOD8
IOD6
IOD9
IOD5
IOD10
IOD4
IOD11
IOD3
IOD12
IOD2
IOD13
IOD1
IOD14
IOD0
IOD15
GND
N.C.
N.C.
GND
1
2
3
4
5
6
7
8
9
10
11
12
13
14
15
16
17
18
19
20
21
22
23
24
25
26
27
28
29
30
31
32
33
34
35
36
37
38
39
40
41
42
43
44
Expansion interface board
(option)
J11
GND
nWAIT
WnR
nRD0
IOA23
N.C.
GND
IOD1
IOD3
IOD5
IOD7
IOD9
IOD11
IOD13
IOD15
GND
IOA3
IOA5
IOA7
IOA9
IOA11
IOA13
IOA15
IOA17
GND
VCC
nPS INT
nHRESET
nWR0
nPSIOCS
N.C.
GND
IOD0
IOD2
IOD4
IOD6
IOD8
IOD10
IOD12
IOD14
GND
IOA2
IOA4
IOA6
IOA8
IOA10
IOA12
IOA14
IOD16
VCC
1
2
3
4
5
6
7
8
9
10
11
12
13
14
15
16
17
18
19
20
21
22
23
24
25
26
27
28
29
30
31
32
33
34
35
36
37
38
39
40
41
42
43
44
45
46
47
48
49
50
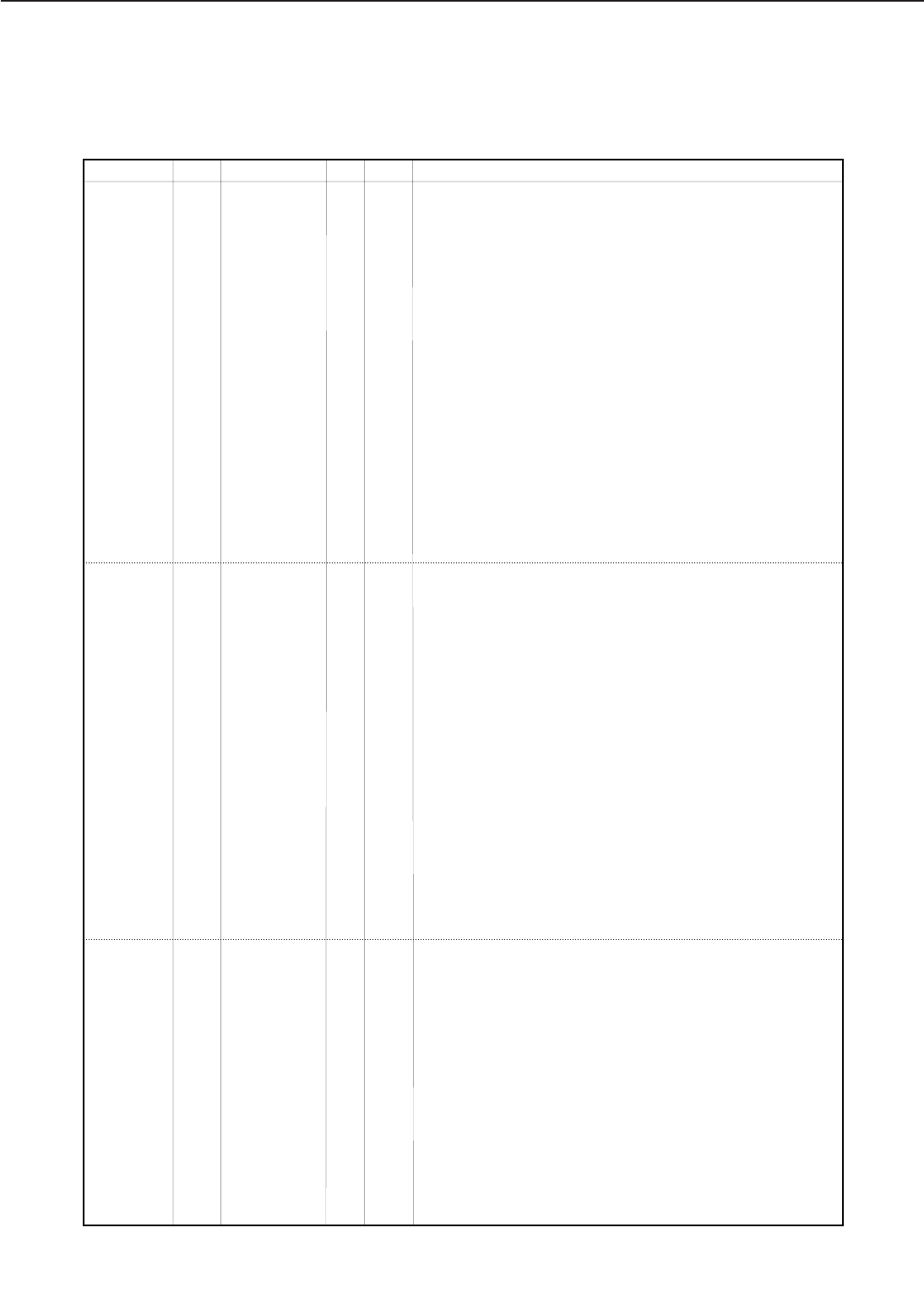
III. LIST OF SIGNALS
A. Input/output signals to/from DC controller PCB
A - 5
APPENDIX
J201 A1 GND
A2 GND
A3 /FPCS I L OPERATION PANEL CONTROLLER CHIP SELECT signal
A4 Reservrd
A5 /VSREQ O P VSYNC REQUEST signal
A6 /VSYNC I P VERTICAL SYNC signal
A7 /STS O L STATUS signal
A8 /CMD I L COMMAND signal
A9 /CPSEL I ANALOG COMTROLLER POWER SELCT signal
A10 /SPCHG O L SPEED CHANGE signal
A11 3.3V O
A12 3.3V O
A13 +5V O
A14 +5V O
A15 GND
A16 GND
B1 GND
B2 GND
B3 /FPO O L OPERATION PANEL SERIAL OUTPUT signal
B4 Reserved
B5 /RDY O L READY signal
B6 /CPRDY I L CONTROLLER POWER READY signal
B7 /SBSY O L STATUS BUSY signal
B8 /CBSY I L COMMAND BUSY signal
B9 /PRFD I L PRE-FEED signal
B10 /PFED O L PAPER FEED signal
B11 3.3V O
B12 3.3V O
B13 +5V O
B14 +5V O
B15 GND
B16 GND
C1 VDO I H VIDEO signal
C2 /VDO I L VIDEO signal
C3 /FPI I L OPERATION PANEL SERIAL INPUT signal
C4 FPCK I P OPERATION PANEL SERIAL CLOCK signal
C5 /PPRDY I L PRINTER POWER READY signal
C6 /PRNT I L PRINT signal
C7 /PCLK O P PRINTER CLOCK signal
C8 /CCLK I P CONTROLLER CLOCK signal
C9 /CCRT O L CONDITION CHANGE REPORT
C10 /PDLV O L PAPER DELIVERY signal
C11 3.3V O
C12 3.3V O
Connector Pin Abbreviation I/O Logic Signal name
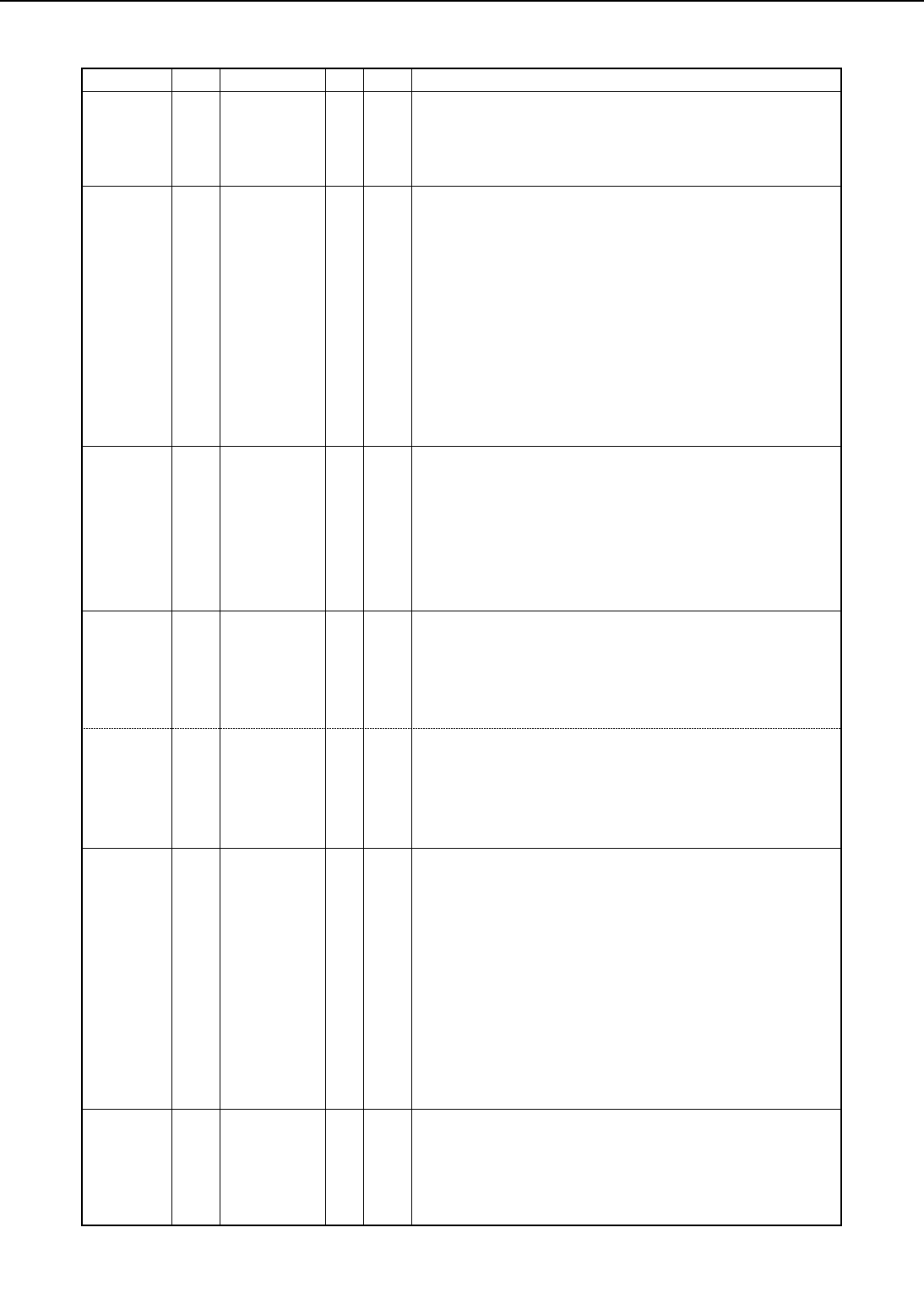
A - 6
APPENDIX
J201 C13 +5V O
C14 +5V O
C15 GND
C16 /BD O P BEAM DETECTION signal
J202 1 GND
2 DRVES I ANALOG LASER MALFUNCTION DETECTION signal
3 GNP
45VO
5 GND
6 N.C.
7 VDO O H VIDEO signal
8 GND
9 /VDO O L VIDEO signal
10 /LON O L LASER ON signal
11 /LENBL O L VIDEO ERABLE signal
J203 1 /FPO O L OPERATION PANEL SERIAL OUTPUT signal
2 /FPI I L OPERATION PANEL SERIAL INPUT signal
3 /FPCS O L OPERATION PANEL CONTROLLER CHIP SELECT signal
4 FPCK I P OPERATION PANEL SERIAL CLOCK signal
5 +5V O
6 +5V O
7 GND
J204 A1 +5V I
A2 +5V I
A3 GND
A4 GND
A5 24V I
B1 3.3V I
B2 3.3V I
B3 GND
B4 24VGND
B5 24VGND
J205 1 GND
2 GND
3 +24VA O
4 +24VA O
5 +24VA O
6 UDOORS I H UPPER DOOR OPEN SENSE signal
7 FDFULS I H FACE-DOWN TRAY PAPER FULL SENSE signal
8 /FPOUTS I H FIXING UNIT DELIVERY SENSE signal
9 FDOUTS I H FACE-DOWN TRAY DELIVERY SENSE signal
10 /FUSLD O L FACE-UP SOLENOID DRIVE signal
11 P5VB1 O
J206 1 GND
2 GND
3 /BDI I P BEAM DETECTION INPUT signal
4 +5V
5 GND
Connector Pin Abbreviation I/O Logic Signal name
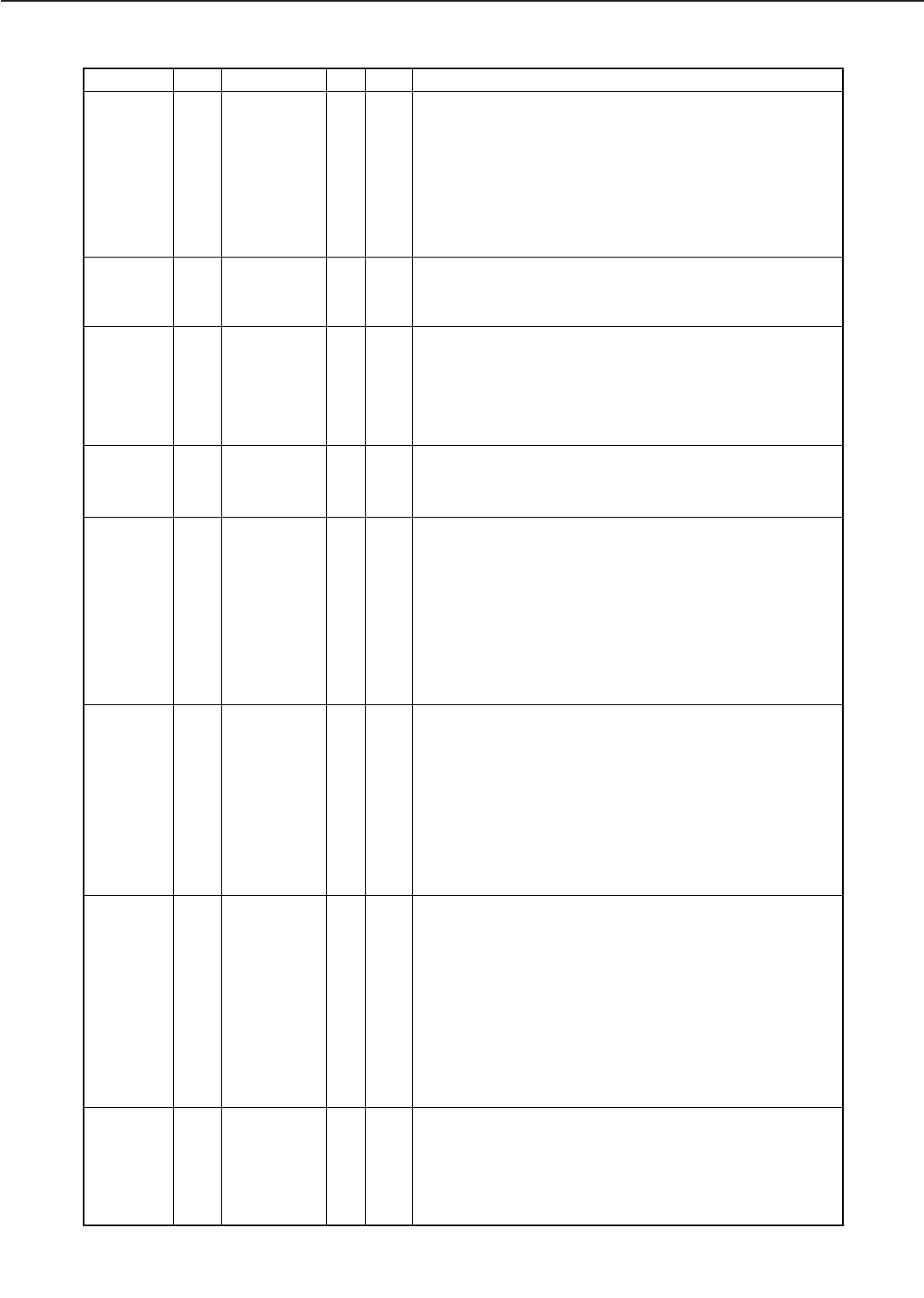
A - 7
APPENDIX
J207 1 +5V
2 /SCNRDY I L SCANNER MOTOR READY signal
3 /SCND O L SCANNER MOTOR DRIVE signal
4 GND
5 /SCNCLK O P SCANNER MOTOR CONTOL CLOCK signal
6 24VGND
7 +24VA O
J208 1 FAN1D O ANALOG FAN MOTOR 1 DRIVE signal
2 /FAN1S I L FAN MOTOR 1 ROTATING DETECTION signal
3 24VGND
J209 1 /REGCLD O L REGISTRATION CLUTCH DRIVE signal
2 +24VA O
3 /REGS I L REGISTRATION PAPER SENSE signal
4 GND
5 P5VB1 O
J210 1 FAN3D O ANALOG FAN MOTOR 3 DRIVE signal
2 /FAN3S I L FAN MOTOR 3 ROTATING DETECTION signal
3 24VGND
J212 1 3.3V O
2 +5V O
3 GND
4 FSRTH I ANALOG FIXING ROLLER TEMPERATURE SENSE signal
5 GND
6 SVIN I SERVICE STATUS signal
7 SVOUT O SERVICE COMMAND signal
8 +24VA O
J213 1 +24VA O
2 +24VA O
3 /DUPIDS I L DUPLEXING UNIT SENSE signal
4 /DUPSTS I L DUPLEXING UNIT STATUS signal
5 DUPCMD O H DUPLEXING UNIT COMMAND signal
6 /DUPCLK O P STATAS CLOCK signal
7 24VGND
8 24VGND
J214 1 24VGND
2 +24VA O
3 P5VB1 O
4 /MPTCLD O L MANUAL FEED CLUTCH DRIVE signal
5 /MPTSLD O L LIFTING PLATE SOLENOID DRIVE signal
6 MPTLS I H LIFTING PLATE SENSE signal
7 /MPTPS I L MULTI-PURPOSE TRAY PAPER SENSE signal
8 ENVCMD O ENVELOPE FEEDER COMMAND signal
9 ENVSTS I ENVELOPE FEEDER STATUS signal
J215 1 GND
2 LSIZE4 I L LOWER CASSETTE PAPER SIZE SENSE signal
3 LSIZE3 I L LOWER CASSETTE PAPER SIZE SENSE signal
4 LSIZE2 I L LOWER CASSETTE PAPER SIZE SENSE signal
5 LSIZE1 I L LOWER CASSETTE PAPER SIZE SENSE signal
Connector Pin Abbreviation I/O Logic Signal name
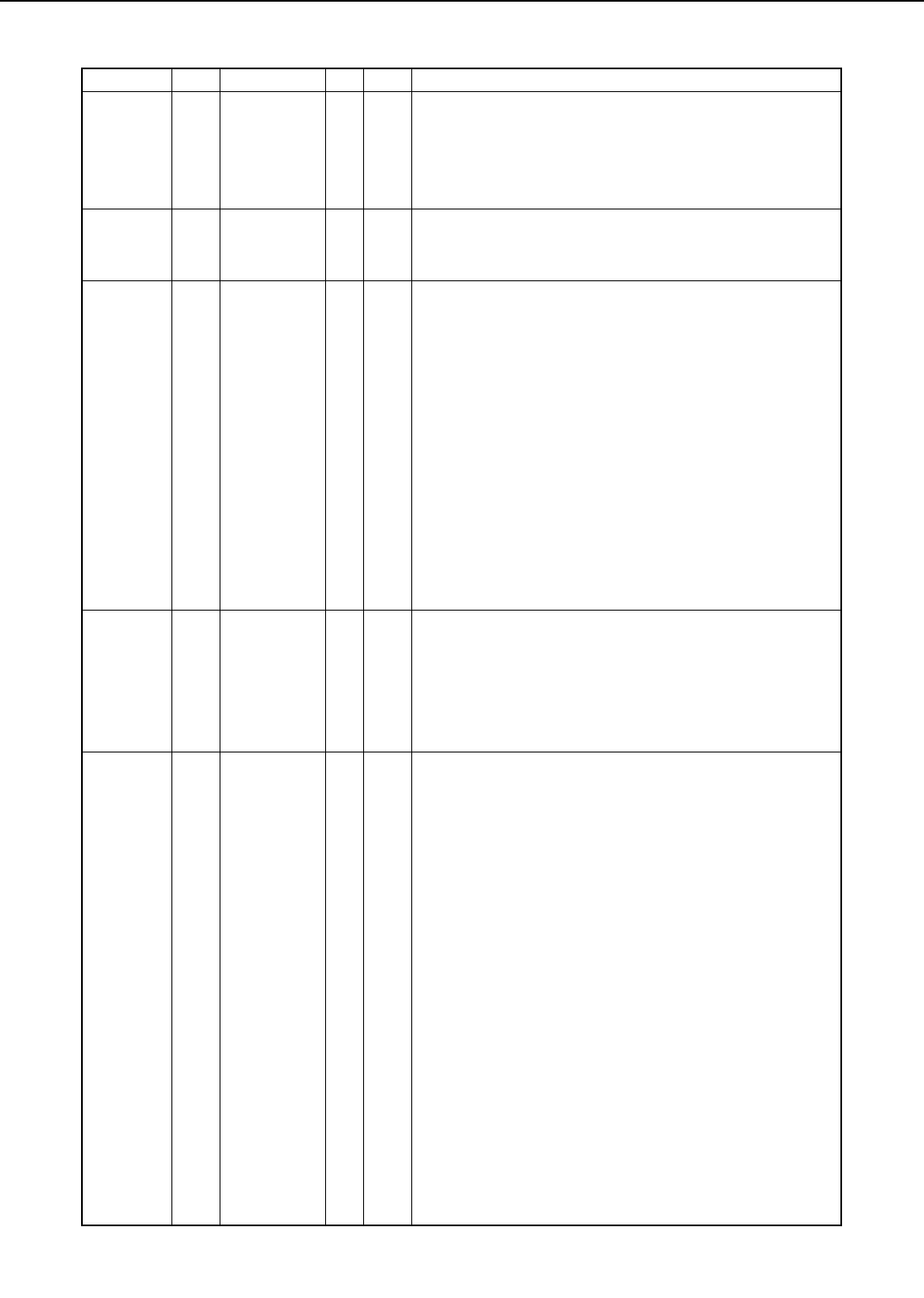
A - 8
APPENDIX
J215 6 GND
7 USIZE4 I L UPPER CASSETTE PAPER SIZE SENSE signal
8 USIZE3 I L UPPER CASSETTE PAPER SIZE SENSE signal
9 USIZE2 I L UPPER CASSETTE PAPER SIZE SENSE signal
10 USIZE1 I L UPPER CASSETTE PAPER SIZE SENSE signal
J216 1 FAN2D O ANALOG FAN MOTOR 2 DRIVE signal
2 /FAN2S I L FAN MOTOR 2 ROTATING DETECTION signal
3 24VGND
J217 1 FSRTH I ANALOG FIXING ROLLER TEMPERATURE SENSE signal
2 RLD O H RELAY DRIVE signal
3 TSWIN
4 GND
5 TSWOUT
6 /FSRD1 O L FIXING MAIN HEATER DRIVE signal
7 /FSRD2 O L FIXING SUB HEATER DRIVE signal
8 FSRDE O H FIXING HEATER DRIVE ENABLE signal
9 FSRCT I ANALOG FIXING HEATER CURRENT SENSE signal
10 SUPSLT O H INVERTER CIRCUIT CONTROL signal
11 /RLDSNS I L RELAY DETECTION SENSE signal
12 PSTYP I POWER SUPPLY TYPE SENSE signal
13 REMT24 O L 24V DRIVE signal
14 N.C.
J218 1 /MMRDY I L MAIN MOTOR READY signal
2 /MMOTD O L MAIN MOTOR DRIVE signal
3 24VGND
4 24VGND
5 +24VB O
6 +24VB O
J219 1 FEDAND O PICK-UP MOTOR CONTROL signal
2 FEDAD O PICK-UP MOTOR CONTROL signal
3 FEDBND O PICK-UP MOTOR CONTROL signal
4 FEDBD O PICK-UP MOTOR CONTROL signal
5 /UDECKS I L UPPER CASSETTE PAPER-OUT SENSE signal
6 UDECKC I H UPPER CASSETTE SENSE signal
7 /FEEDCLD O L FEED CLUTCH DRIVE signal
8 /FEEDS I L PICK-UP UNIT PAPER SENSE signal
9 /PUPSLD O L CASSETTE PICK-UP SOLENOID DRIVE signal
10 LDECKC I H LOWER CASSETTE PAPER-OUT SENSE signal
11 /LDECKS I L LOWER CASSETTE SENSE signal
12 LPVS2 I LOWER CASSETTE PAPER-LEVEL SENSE signal 2
13 LPVS1 I LOWER CASSETTE PAPER-LEVEL SENSE signal 1
14 UPVS2 I UPPER CASSETTE PAPER-LEVEL SENSE signal 2
15 UPVS1 I UPPER CASSETTE PAPER-LEVEL SENSE signal 1
16 /RDOORS I H PIK-UP UNIT DOOR OPEN SENSE signal
17 +24VA O
18 P5VB1 O
19 GND
20 GND
Connector Pin Abbreviation I/O Logic Signal name
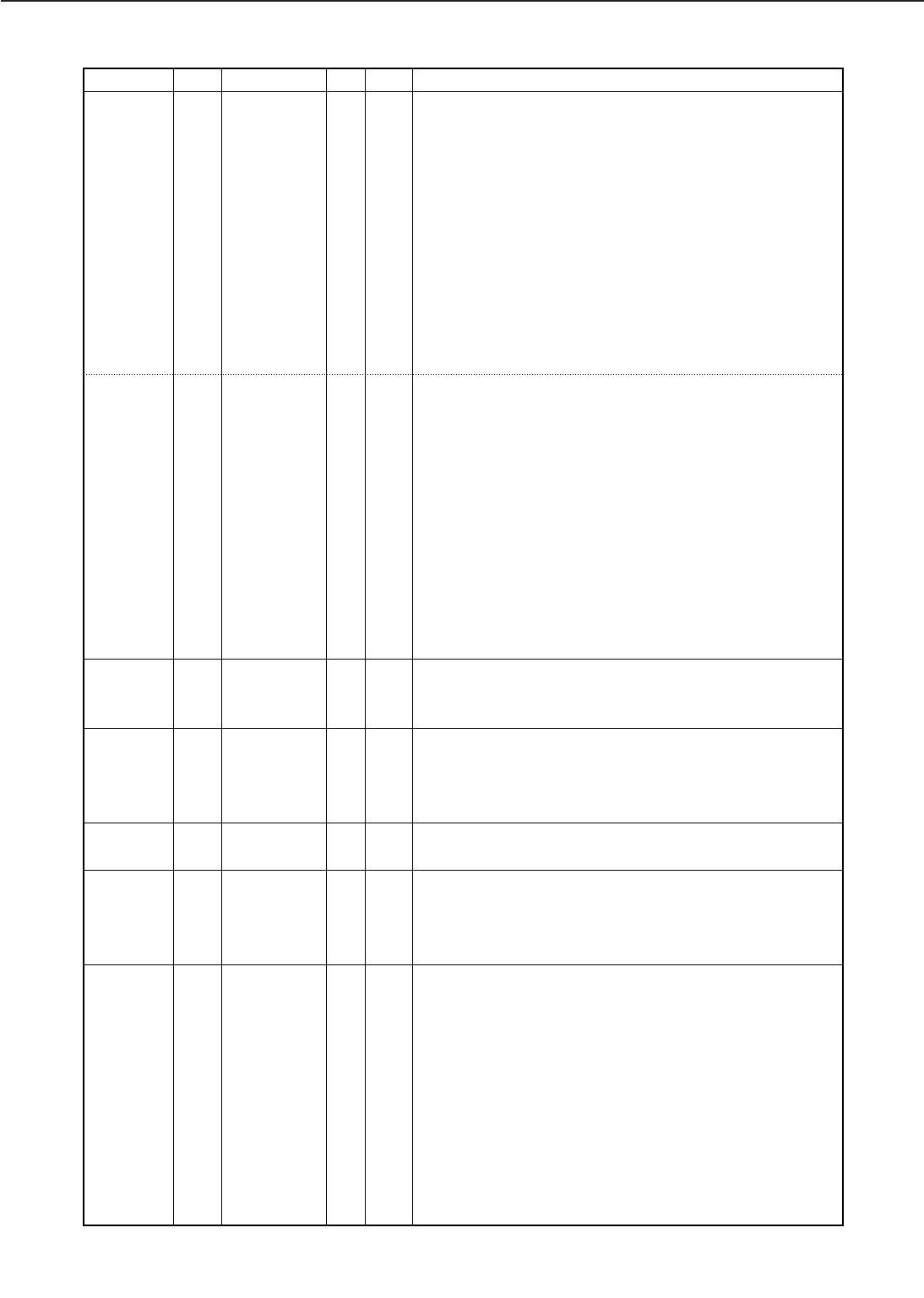
A - 9
APPENDIX
J220 A1 TRFVCNT O ANALOG TRANSFER BIAS CONTROLL signal
A2 TRFVSNS I ANALOG TRANSFER BIAS MONITOR signal
A3 /TRFCCD O L TRANSFER BIAS CONSTANT CURRENT DRIVE signal
A4 TRFCLK O P TRANSFER BIAS FREQUENCY OUTPUT signal
A5 N.C.
A6 HVTCLK O P HIGH-VOLTAGE BIAS FREQUENCY OUT PUT signal
A7 /DEVACD O L DEVELOPING AC BIAS DRIVE signal
A8 DEVACCLK O P DEVELOPING AC BIAS FREQUENCY OUT PUT signal
A9 /DEVDCD O L DEVELOPING DC BIAS DRIVE signal
A10 TONSNS I ANALOG TONER LEVEL signal
A11 24VGND
A12 24VB O
B1 /TRFNVD O L TRANSFER NEGATIVE BIAS DRIVE signal
B2 /HRLBD O L FIXING ROLLER BIAS DRIVE signal
B3 /DCHGBD O L DISCHARGE BIAS DRIVE signal
B4 /DCHGUP O L DISCHARGE BIAS SWITCH signal
B5 N.C.
B6 N.C.
B7 PRIACCLK O P PRIMARY AC BIAS FREQVENCY OUTPUT signal
B8 /PRIACD O L PRIMARY AC BIAS DRIVE signal
B9 /PRIDCD I L PRIMARY DC BIAS DRIVE signal
B10 DENADJ O ANALOG IMAGE DENSITY AD JUSTMENT signal
B11 24VGND
B12 24VB O
J221 1 +24VB I
2 +24VB I
3 +24VB I
J222 1 TSWOUT
2 FSRTH I ANALOG FIXING ROLLER TEMPERATURE SENSE signal
3 GNDTH
4 TSWIN
J223 1 TONSNS I ANALOG TONER LEVEL signal
2 GND
J225 1 FAN4D O H FAN MOTOR 4 DRIVE signal
2 /FAN4S I L FAN MOTOR 4 ROTATING DETECTION signal
3 24VGND
4 GND
J229 1 FAN5D O ANALOG FAN MOTOR 5 DRIVE signal
2 /FANS5 I L FAN MOTOR 5 ROTATING DETECTION signal
3 24VGND
4 24VGND
Connector Pin Abbreviation I/O Logic Signal name
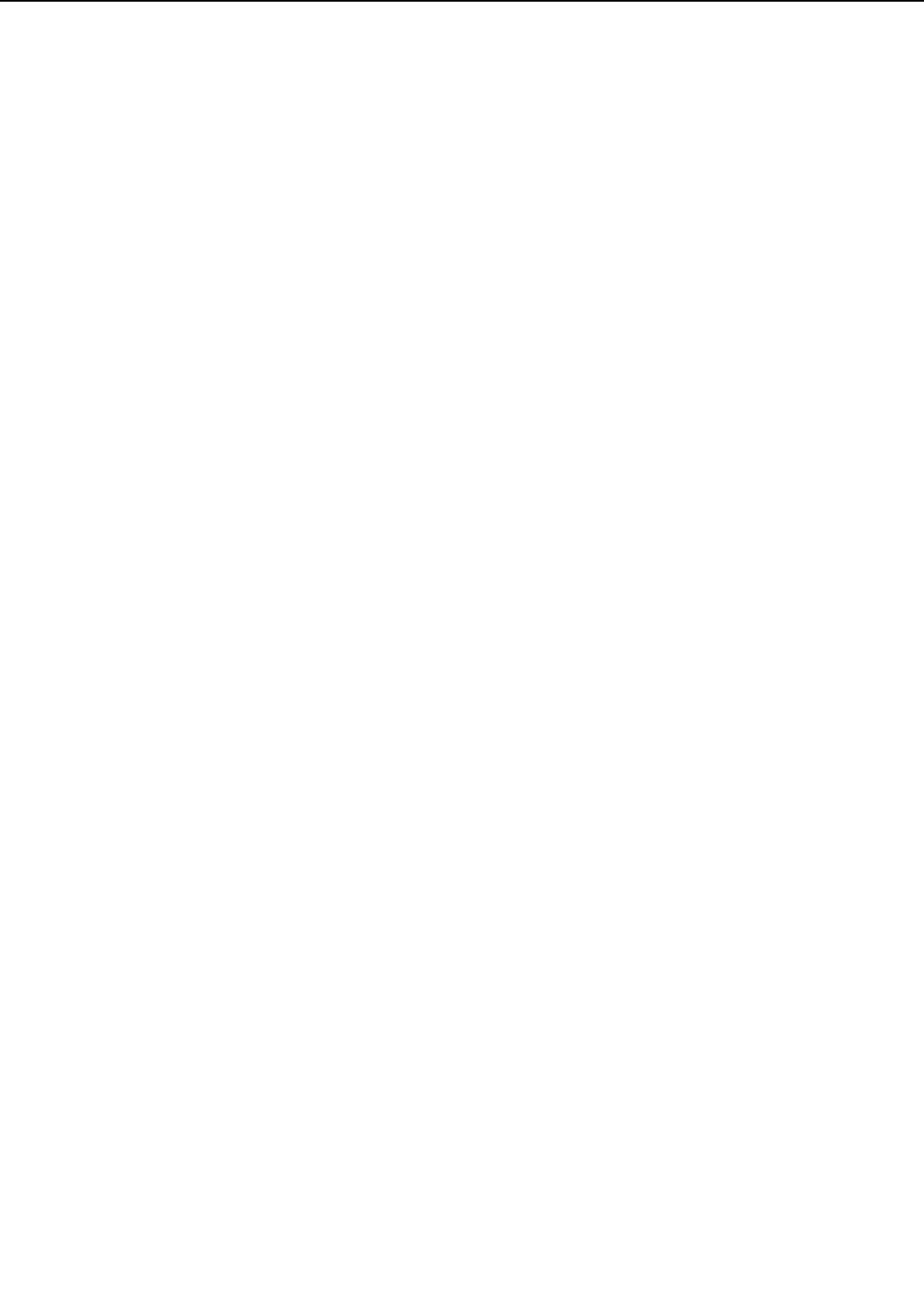
A - 10
APPENDIX
This page intentionally left blank
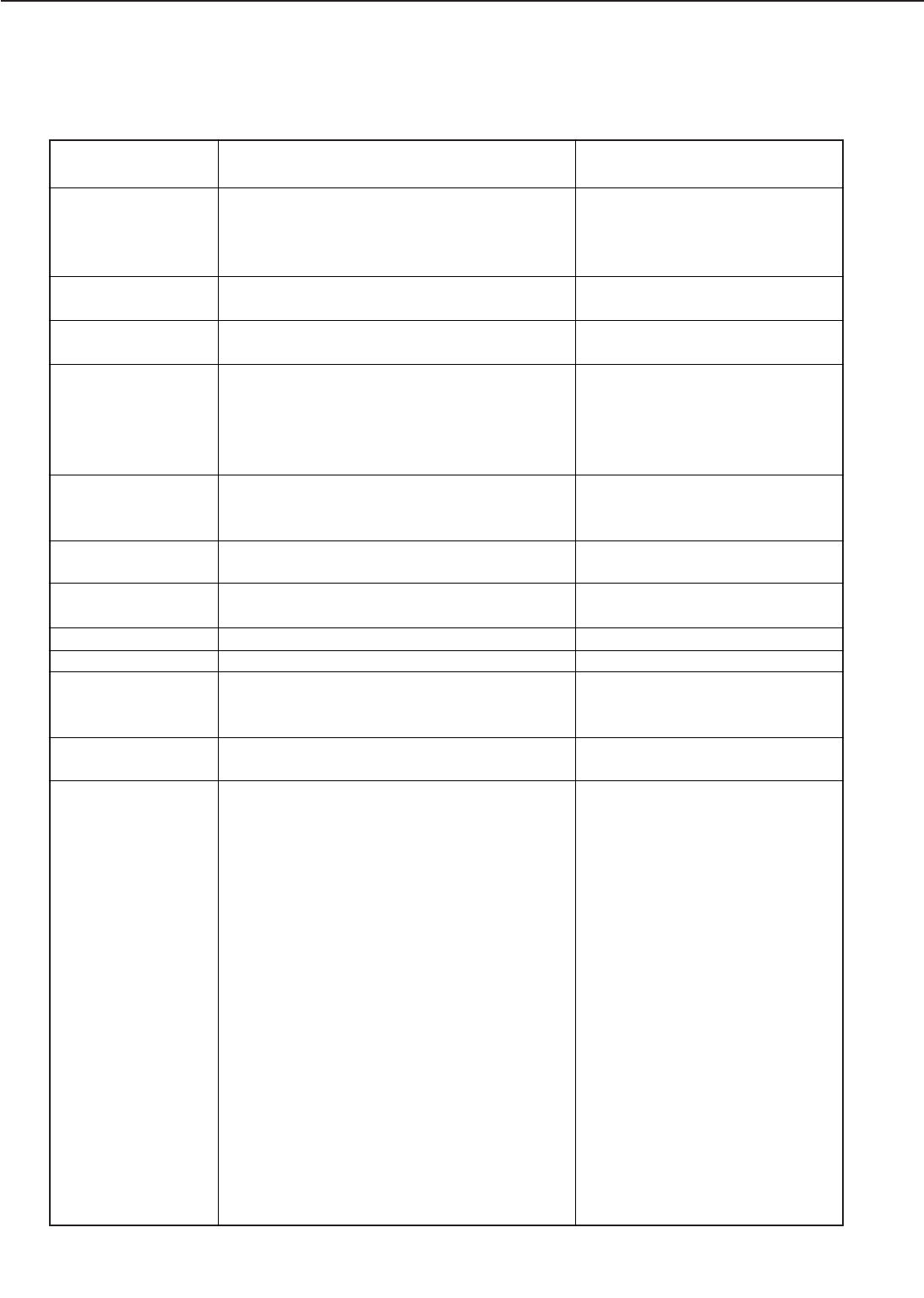
IV. MESSAGES TABLE
A - 11
APPENDIX
COLD RESET
COLD RESET A4
COLD RESET LTR
CONTEXT SAVE
ADJUSTED
CONTEXT SAVE
CHANGE
WARMING UP...
I/O INITIALIZING
READY
PAUSED
PRINTING...
KEY NOT VALID
RESET TO SAVE
Displays when the COLD RESET (Letter or A4)
Power-On sequence is selected.
Displays when Factory Reset - A4
Power-on sequence is selected.
Displays when Factory Reset - LTR
Power-on sequence is selected.
Context Saving mechanism modified by OS.
Displayed when printer powered on with con-
text saving enabled, but due to manual recon-
figuration, there is not enough memory to
support it.
Context saving mechanism modified by USER.
Displayed when going online after modifying
context saving.
Printer is warming up.
This message displays when one of the net-
work boads is being initialized.
Printer is ready to receive data and print.
Printer is OFFLINE.
Usually displayed when printing an item from
the TEST MENU, or when attempting to go
Offline while the printer is busy.
Displays when a key is pressed that is not
enabled at this time.
RESET verification prompt. This message will
appear momentarily and then PAUSED. When
a menu item was changed before the printer
releases the port on which the last job was
processed, such as in the middle of a job, or
before the port timed out.
RESET TO SAVE doesn't display or take
effect for the following menu items:
Parallel menu
-bidirectional=on/off
Config menu
-density
-pwrsav
paper type menu
-upper
-lower
-deck
-mpt
feeder menu
-mptsize
No action required although the
printer will be reset to its factory
defaults and any unique settings
will have to be reset.
No action required.
No action required.
Press Continue key to continue.
Press Continue and printer will
reboot to enable its new state.
Wait until the printer has warmed
up and displays "READY".
No action required.
No action required.
Press ONLINE.
No action required
Press the correct key to complete
the current function.
Two options are available:
1. Press the reset key to enter
the RESET menu and save
the information immediately.
This will terminate the cur-
rent job, deleting temporary
fonts, macros and buffered
data.
2. Press ONLINE and the cur-
rent job will resume where it
left off. The menu items
changed will not take effect
until the next end of job.
Message Meaning Action
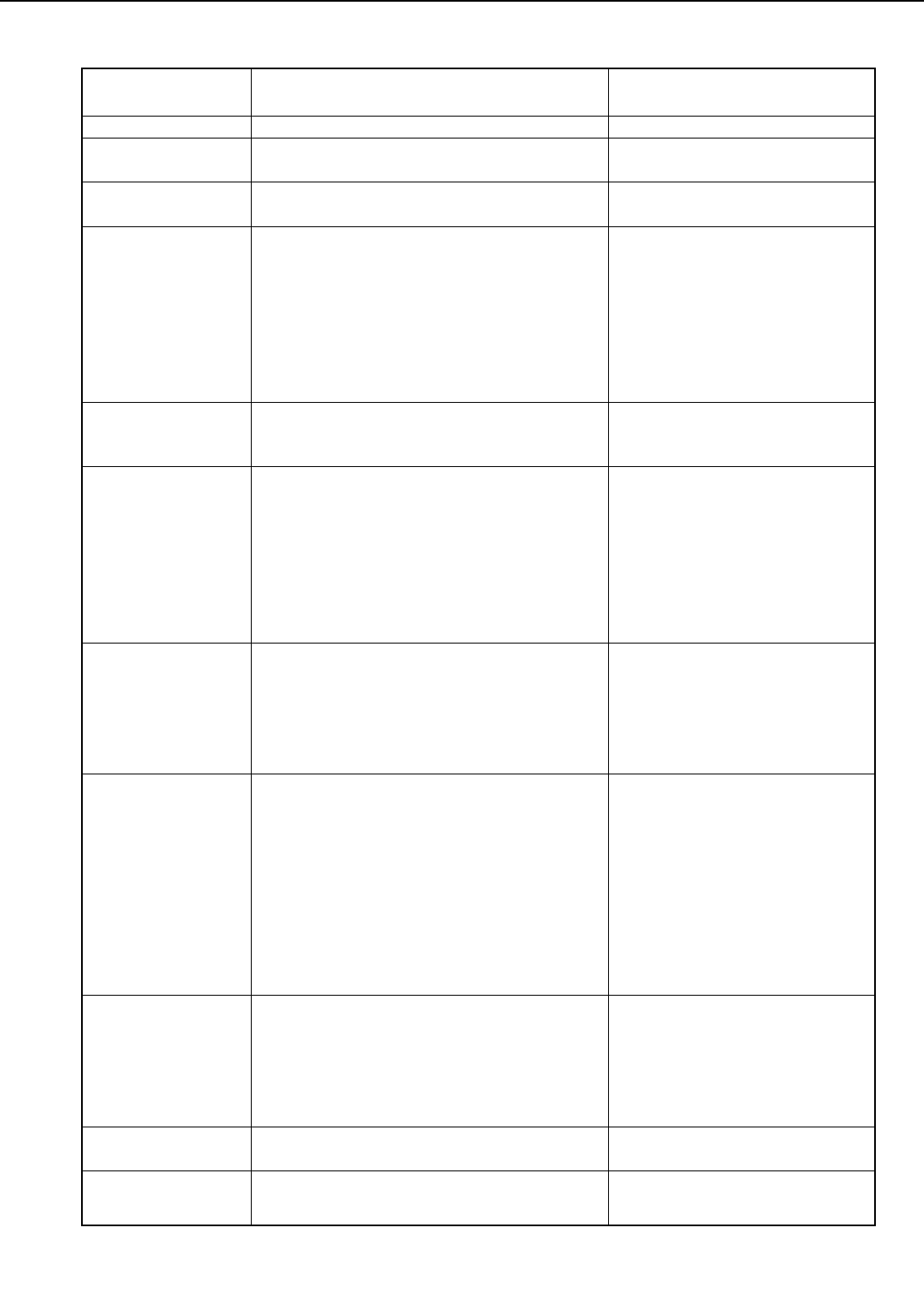
A - 12
APPENDIX
RESETTING PRINT-
ER
RESTORING
DEFAULTS
MEMORY OVER-
FLOW
READY
MRT COMPRES-
SION
+ FORMAT DISK\
- IGNORE DISK
+ REALLY FORMAT
- IGNORE DISK
START DISK TEST
ENTER ENDS TEST
FORMATTING...
DSK FMT RESTART
-envsize
Displays when TEST/RESET PRINTER item is
selected
Displays when TEST/FACTORY DEFAULTS
item is selected.
Memory overflow. The printer received more
data than it can fit into its available memory.
This can happen if too many soft fonts,
macros, or graphics which are too complex are
received.
Printer has invoked MRT Compression
because of lossy compression.
Either a request has been made to format the
disk or the printer has determined that the
disk needs formatting (engin a new unformat-
ted disk is installed when power up).
The operator is being asked to verify the disk
formatting is really wanted.
This is in response to the foregoing message.
Start testing the hard disk
Stop testing the hard disk
This message displays when the disk is being
formatted.
The operator has formatted the disk and the
operation has completed. The system will
No action required
No action required.
The job will resume after 10 sec-
onds if AUTOCONT is ON.
Otherwise press the Continue key
to resume printing. Check the
page that ejects since the page
could not be processed as
requested. Also simplify the job or
add additional memory.
No action required.
Press + to format the disk or press
- to ignore the disk.
For new/unformatted disk: If
press - to ignore disk, the printer
goes to "READY".
Any attempt to write to the
disk will be flushed since the disk
has not been formatted.
Press + to verify that the disk is to
be formatted or press - to skip
formatting the disk. This message
will not display for new/unfor-
matted disk (engin. The disk is to
be formatted for the 1st time)
Press Enter to start disk testing.
Note: This operation will cause
the disk to format when
press enter to end test. If
the printer is powered off
during the disk test, the
message + FORMAT
DISK \ - IGNORE DISK
will appear when the
printer is powered on.
Press Enter to end disk testing.
Note: The disk will be format-
ted and the printer will
reboot automatically
when press Enter to end
disk test.
No action required.
Press the Continue key for the
printer to reboot.
Message Meaning Action
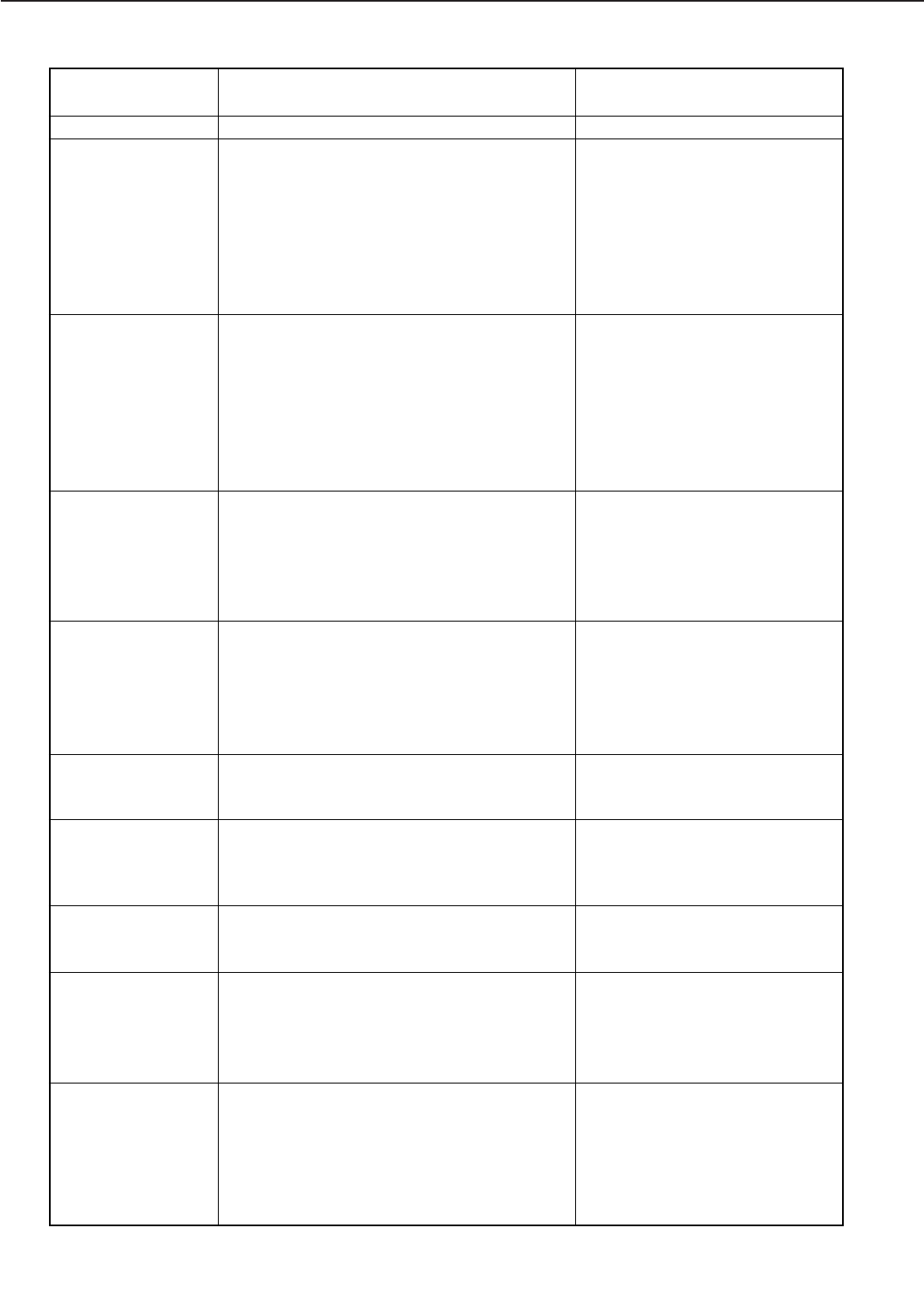
A - 13
APPENDIX
DISK ALMOST FULL
DISK FULL
READY
# OF ###
+ FORMAT FLASH
- IGNORE FLASH
+ REALLY FORMAT
- IGNORE FLASH
FLASH
FORMATTING...
FLASH FORMAT
RESTART
FLASH OVERFLOW
FLASH ERROR
restart after the continue key is pressed.
Warning message when the Disk is 70+% full.
Disk is 95% full. The printer goes offline (also
at power up with a "disk full" installed). If
AUTOCONT is ON, the printer will resume
back online after 10 seconds. If continue to
send files to the disk that larger than the 5%
left on the disk, the files will be flushed or
printed out as text.
Mopier is activated. ### is the total mopier
count. # is the increment count up to ###.
Mopier is only available when the hard disk is
installed.
A request has been made to format the flash
rom
The operator is being asked to verify the flash
rom formatting is really wanted. This is in
response to the foregoing message.
This message is displayed while the flash is
being formatted. This message also displays
when the printer is booting up with an unfor-
matted or bad flash.
The operator has formatted the flash and the
operation has completed. The system will
restart after the continue key is pressed.
The printer received more fonts/macros data
than it can fit into its FLASH ROM. The print-
er is "OFFLINE" when this message is dis-
played.
Error causes by flash format failure, read or
write failure.
Delete pcl/ps, fonts/macros/files
or format the disk to clear the
message. The message doesn't
clear with power cycle or COLD
RESET. This message has lower
priority than printer error mes-
sages such as "toner low" or
"memory overflow".
Delete pcl/ps, fonts/macros/files
or format the disk to clear the
message. The message doesn't
clear with power cycle or COLD
RESET. This message has lower
priority than printer error mes-
sages such as "toner low" or
"memory overflow".
No action required. This message
is temporarily displayed for the
duration of the printer's process-
ing time. @PJL RDYMSG DISPLAY
will have higher priority than "#
OF ###" message.
Press + to format the flash or
press - to ignore the flash. For
new/unformatted flash: the print-
er will automatically format the
flash without any message display
when the printer is booting up.
Press + to verify that the flash is to
be formatted or press - to skip for-
matting the flash.
No action required.
Press the Continue key for the
printer to reboot.
Press the Continue key for the
printer to go back to "READY".
Formatting or deleting
Fonts/macros should be per-
formed to regain more rom space.
Printer goes offline. Job will be
flushed in error occurs while
receiving data. Turn printer off
and on. The printer will attempt to
reformat the flash when it's boot-
ing up. If the attempt to reformat
Message Meaning Action
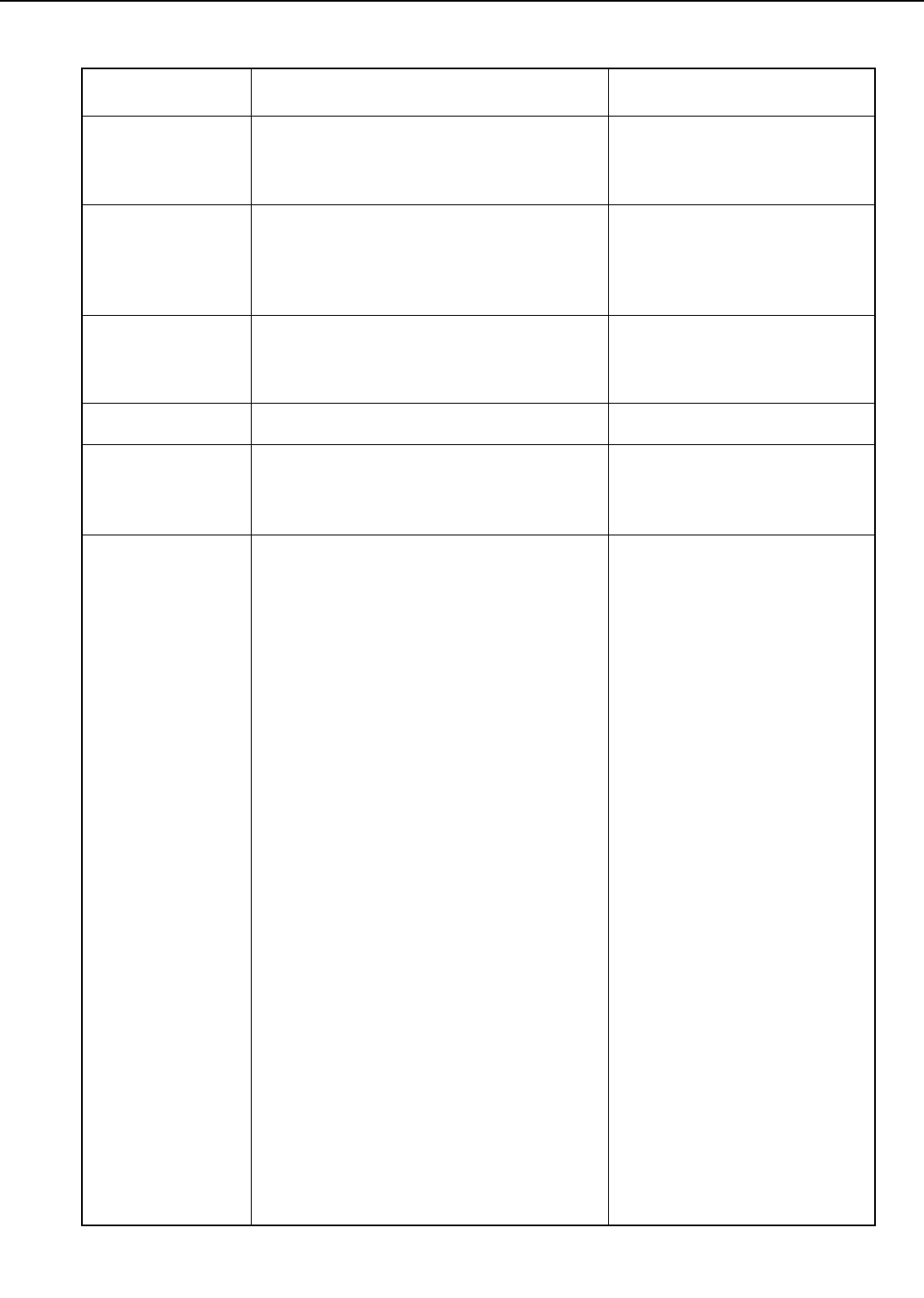
A - 14
APPENDIX
####
+TO CONFIRM/-
CANCEL
READY
TONER LOW
TONER CART
MISSING
PRINTING TO STD
TRAY
LOAD <MEDIA>
<SIZE> IN <TRAY>
Where #### = MAILBOX, JOB SEPARATION,
STACKER, or SORTING. The operator is being
asked to confirm the mode change in the
sorter is really wanted. This is in response to
the foregoing message.
Toner is low.
Toner cartridge is missing.
Display (for the duration that the printer takes
to process the job) when the bin(s) in the
sorter are full and the output is directed to the
standard tray.
Load the specified tray with paper size.
Size:
LETTER - Letter paper size.
LEGAL - Legal paper size.
11X17 - Ledger paper size.
A3 - A3 paper size.
A4 - A4 paper size.
A5 - A5 paper size.
11x17 paper size.
EXEC - Executive paper size.
COM10 - Commercial #10 envelope.
MONARCH - Monarch envelope.
DL - DL envelope.
C5 - C5 envelope.
B5JIS - B5 paper size.
B5ISO - B5 envelope.
B4 - B4 paper size.
CUSTOM - Custom paper size.
ANY - Unknown paper size.
Tray:
UPPER - Internal upper cassette.
LOWER - Internal lower cassette.
DECK - 2000 sheet Large Capacity tray.
DECK1 - Upper cassette of 2x500 deck.
DECK2 - Lower cassette of 2x500 deck.
MPT - Multi-purpose tray.
ENV. - Envelope feeder.
ANY TRAY - any paper tray that can support
Letter, Legal, B4 or A4
the flash fails, FLASH ERROR will
be displayed. Remove the faulty
flash rom and replace with new
flash.
Press + to accept (confirm) the
mode change in the sorter or
press - to cancel the mode
change.
Replace the toner cartridge as
soon as possible. The printer will
continue to operate, but the
images will degrade.
Add toner cartridge.
No action required.
The specified tray must be loaded
with the specified paper size and
media type.
Depending upon circumstances,
the Continue key may be required
to continue the job. If the printer
is printing and a tray runs out of
paper, for instance, simply load-
ing the tray and closing it will
cause the printer to continue nor-
mally. If, however, the printer
does not contain the required
paper size or media type, the user
must select/change the media
type from front panel. Open the
tray and load the appropriate
media type/paper size into the
specified tray. The printer will
resume printing after the tray is
reinstalled. In the case of manual
feed (discussed following), the
Continue key must always be
pressed.
Message Meaning Action
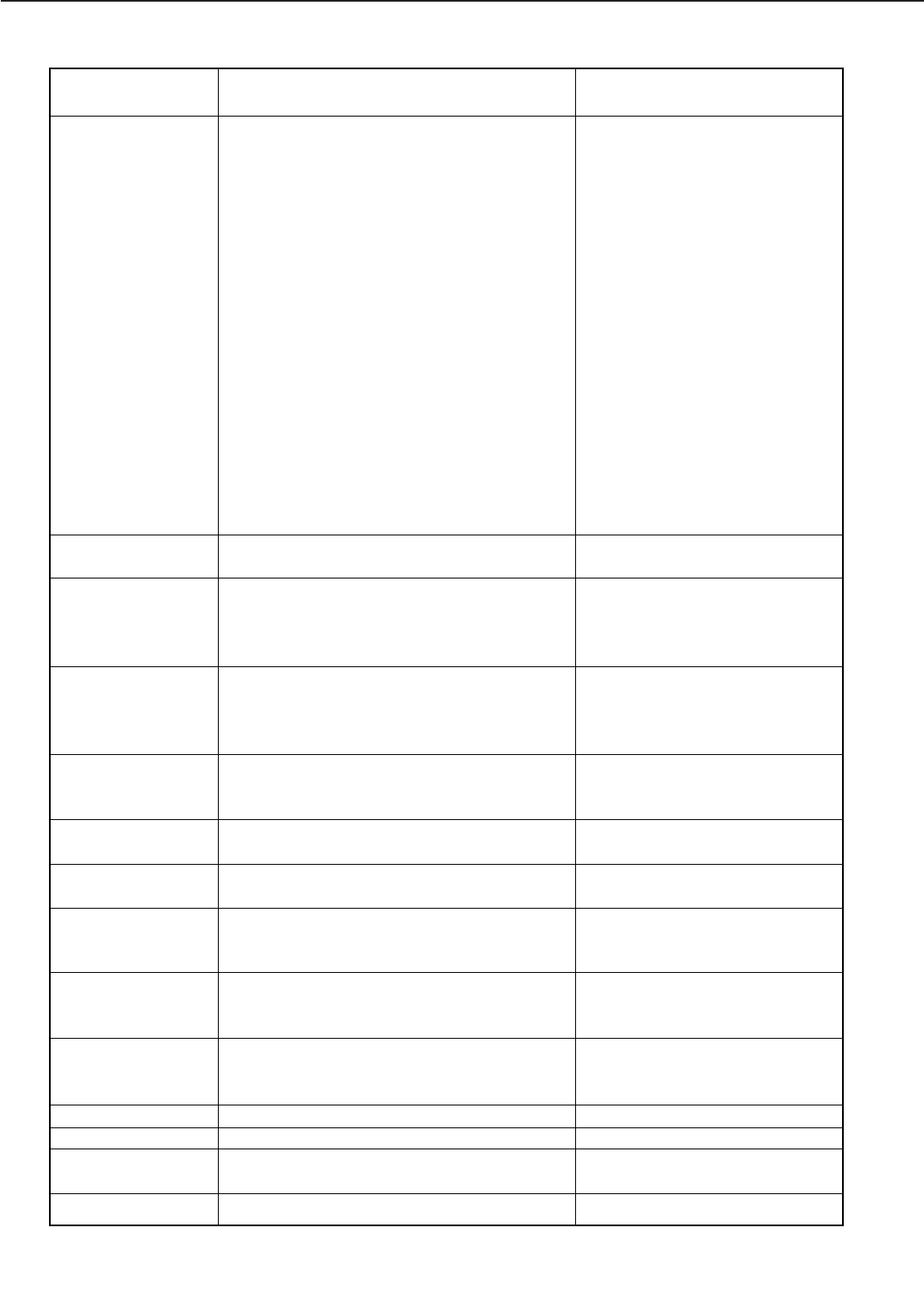
A - 15
APPENDIX
LOAD <MEDIA>
<SIZE> IN MANUAL
LOAD BLANK SIDE
UP IN MANUAL
LOAD CLEANING
PAGE IN MANUAL
LOAD STAPLES
UPPER TRAY
IN MOTION
LOWER TRAY
IN MOTION
DECK TRAY
IN MOTION
DECK1 TRAY
IN MOTION
DECK2 TRAY
IN MOTION
UPPER MISSING
LOWER MISSING
DECK MISSING
DECK1 MISSING
Media Type:
PLAIN - Plain
LETTERHEAD - Letterhead
TRANSPARENCY - Transparency
LABELS - Labels
BOND - Bond
RECYCLED - Recycled
COLOR - Color
CARDSTOCK - Cardstock
ROUGH - Rough paper
CUSTOM1 - or user defined media type
CUSTOM2 - or user defined media type
CUSTOM3 - or user defined media type
CUSTOM4 - or user defined media type
CUSTOM5 - or user defined media type
CUSTOM6 - or user defined media type
Note: User defined media type name can be
up to 15 maximum characters long.
Load multi-purpose tray with paper size. Like
"Load" but for manual feed only.
This message displays right after the front
side of the cleaning page has been created.
This message displays right after a cleaning
page has been created.
Staples low. Only the current job will be sta-
pled.
The upper cassette is repositioning the stack
after new paper was loaded.
The lower cassette is repositioning the stack
after new paper was loaded.
The paper tray in the 2,000 sheet deck is repo-
sitioning the stack after new paper was
loaded.
The upper cassette in the 2x500 sheet deck is
repositioning the stack after new paper was
loaded.
The lower cassette in the 2x500 sheet deck is
repositioning the stack after new paper was
loaded.
The specified upper cassette is missing.
The specified lower cassette is missing.
The specified deck (2,000 sheet deck) is miss-
ing.
The specified upper cassette (2x500 sheet
Press the Continue key to resume
printing.
Load the blank side face-up in the
multi-purpose tray. Press the
Continue key to create the other
side of the cleaning page.
Load the cleaning page face-down
in the multi-purpose tray. Press
the CONTINUE READY key to
start cleaning.
Load staples. The printer will
resume to READY. The printer is
now ready to staple.
No Action Required.
No Action Required.
No Action Required.
No Action Required.
No Action Required.
Reinsert the upper cassette.
Reinsert the lower cassette.
Reinsert the deck.
Reinsert the upper cassette.
Message Meaning Action

A - 16
APPENDIX
DECK2 MISSING
OUTPUT FULL
STD. TRAY
OUTPUT FULL
CHECK BIN 1
OUTPUT FULL
CHECK BIN 2
OUTPUT FULL
CHECK BIN 3
OUTPUT FULL
SORTER BIN UP
CHECK SORTER
BIN
REMOVE ALL
PAPER
PRINTER OPEN
COVER OPEN
STACKER
COVER OPEN
SORTER
COVER OPEN
PAPER JAM
WRONG PAPER
SIZE
CHECK INPUT TRAY
OPEN FRONT
COVER
OPEN LEFT COVER
OPEN RIGHT
COVER
OPEN TOP COVER
1 PAPER JAM
2 PAPER JAM
3 PAPER JAM
4 PAPER JAM
5 PAPER JAM
6 PAPER JAM
7 PAPER JAM
8 PAPER JAM
9 PAPER JAM
deck) is missing.
The specified lower cassette (2x500 sheet
deck) is missing.
The specified face-down tray is paper full.
The specified output tray of the stapler stack-
er is paper full.
The specified output tray of the stapler stack-
er is paper full.
The specified output tray of the stapler stack-
er is paper full.
The specified output bin (face-up bin of the
sorter) is paper full.
For use only when the sorting mode of the
sorter is selected. Any or all of the bins of the
sorter are paper full or not empty.
Top, right or left (side) cover is open.
2,000 sheet or 2x500 sheet deck right cover
(paper path) is open.
Stapler stacker top or front (stapler door)
cover is open.
Sorter top or front cover is open.
A paper size mismatch has occurred. More
than one paper size has been found in the
same tray.
A paper jam occurred near the input tray.
A paper jam occurred near the front cover.
A paper jam occurred near the left cover.
A paper jam occurred near the right cover.
A paper jam occurred near the top cover.
Paper jam has occurred somewhere in the
paper path.
Paper jam has occurred in the input paper
path.
Paper jam has occurred in the input paper
path.
Paper jam has occurred in the fixing unit area.
Paper jam has occurred in the fixing unit area.
Paper jam has occurred near the face-down
tray.
Paper jam has occurred near the face-down
tray.
Paper jam has occurred in the fixing unit area.
Paper jam has occurred near the duplexing
Reinsert the lower cassette.
Remove the paper from the face-
down tray.
Remove the paper from the tray
(Bin1 of the stapler stacker).
Remove the paper from the tray
(Bin2 of the stapler stacker.
Remove the paper from the tray
(Bin3 of the stapler stacker).
Remove the paper from the tray.
Remove the paper from all the
bins (bin# 1 to 7 of the sorter).
Close all cover doors.
Close the right cover door.
Close all cover doors.
Close all cover doors.
Inspect the trays for mismatched
paper and correct. Remove all
jammed paper and insert the cor-
rect paper size in the tray. Close
all covers to go back to READY.
Check the area specified.
Remove the jammed paper from
the paper path. The top cover
must be opened and closed to
resume printing.
Message Meaning Action
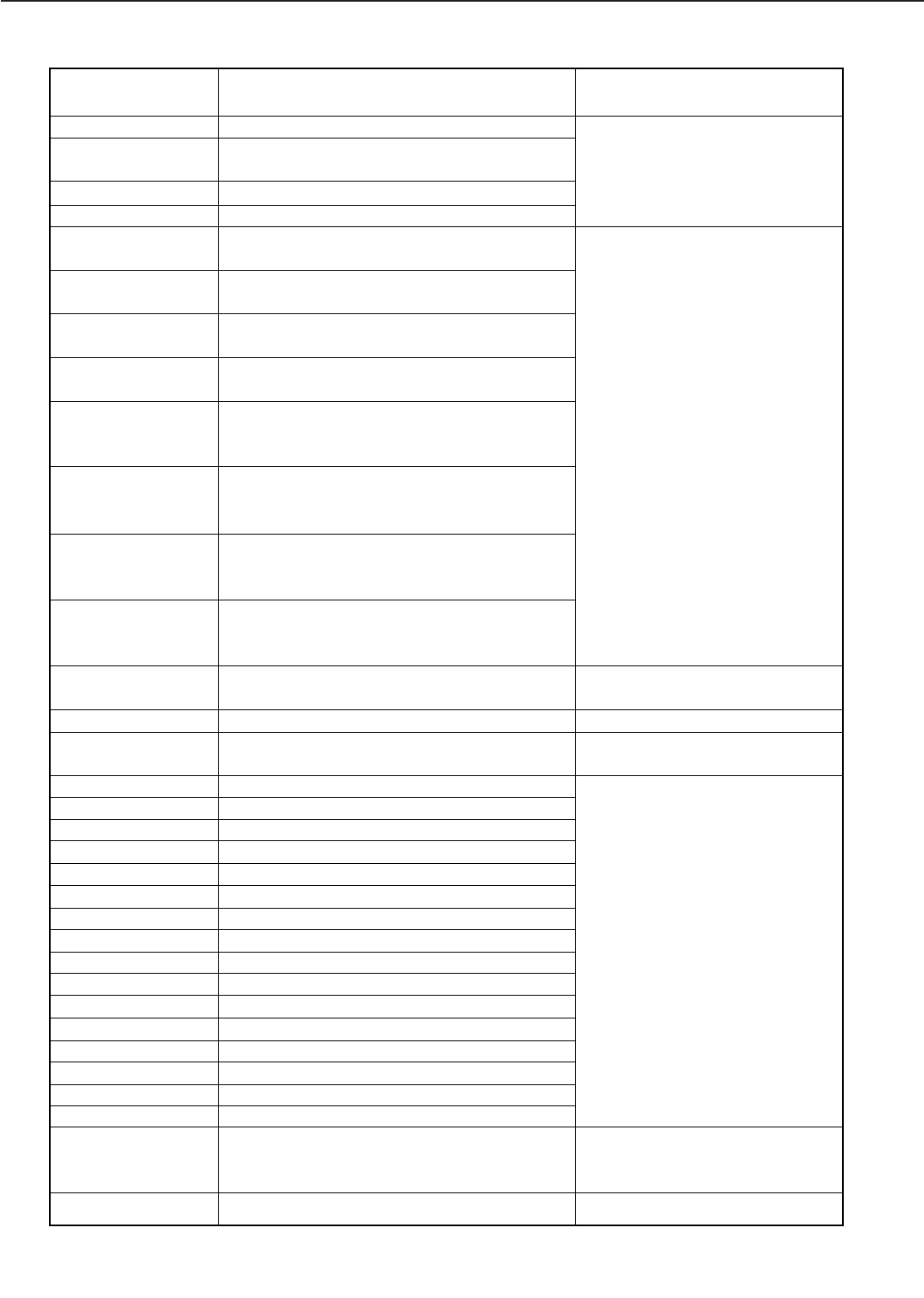
A - 17
APPENDIX
10 PAPER JAM
11 PAPER JAM
12 PAPER JAM
13.1 PAPER JAM
CHECK DECK
13.2 PAPER JAM
CHECK DECK
13.3 PAPER JAM
CHECK DECK
13.4 PAPER JAM
CHECK DECK
14.1 PAPER JAM
OPEN RIGHT
COVER
14.2 PAPER JAM
OPEN RIGHT
COVER
14.3 PAPER JAM
OPEN RIGHT
COVER
14.4 PAPER JAM
OPEN RIGHT
COVER
CHECK INPUT
AREA
OPEN TOP COVER
CHECK OUTPUT
BINS
15.1 STACKER JAM
15.2 STACKER JAM
15.3 STACKER JAM
15.4 STACKER JAM
16.1 STACKER JAM
16.2 STACKER JAM
16.3 STACKER JAM
16.4 STACKER JAM
17.1 STACKER JAM
17.2 STACKER JAM
17.3 STACKER JAM
17.4 STACKER JAM
18.1 STACKER JAM
18.2 STACKER JAM
18.3 STACKER JAM
18.4 STACKER JAM
STAPLE JAM
OPEN STAPLER
COVER
19.1 SORTER JAM
unit.
Paper jam has occurred near the duplexing
unit.
Paper jam has occurred in the duplexing unit.
Paper jam has occurred in the duplexing unit.
Paper jam has occurred in the 2,000 sheet
deck or 2x500 sheet deck.
Paper jam has occurred in the 2,000 sheet
deck or 2x500 sheet deck.
Paper jam has occurred in the 2,000 sheet
deck or 2x500 sheet deck.
Paper jam has occurred in the 2,000 sheet
deck or 2x500 sheet deck.
Paper jam has occurred in the right cover.
Paper jam has occurred in the right cover.
Paper jam has occurred in the right cover.
Paper jam has occurred in the right cover.
A paper jam occurred near the input tray.
A paper jam occurred near the top cover.
A paper jam occurred at the stapler stacker
output bins.
Jam at entrance sensor - Initial Jam
Jam at entrance sensor - Stay Jam
Jam at entrance sensor - Delay Jam
Jam at entrance sensor - Early Jam
Jam at reversing sensor - Initial Jam.
Jam at reversing sensor - Stay Jam.
Jam at reversing sensor - Delay Jam.
Jam at reversing sensor - Early Jam.
Jam at delivery paper sensor - Initial Jam
Jam at delivery paper sensor - Stay Jam
Jam at delivery paper sensor - Delay Jam
Jam at delivery paper sensor - Early Jam
Jam at staple tray paper sensor - Initial Jam
Jam at staple tray paper sensor - Stay Jam
Jam at staple tray paper sensor - Delay Jam
Jam at staple tray paper sensor
Jam near the stapler
Jam at entrance sensor - Initial Jam
Check the deck. Remove the
jammed paper from the paper
path. The top cover must be
opened and closed to resume
printing.
Check the area specified.
Check the area specified.
Check the area specified.
Check the stapler stacker.
Remove jammed paper and close
cover.
Clear jam
Check the soter. Remove jammed
Message Meaning Action
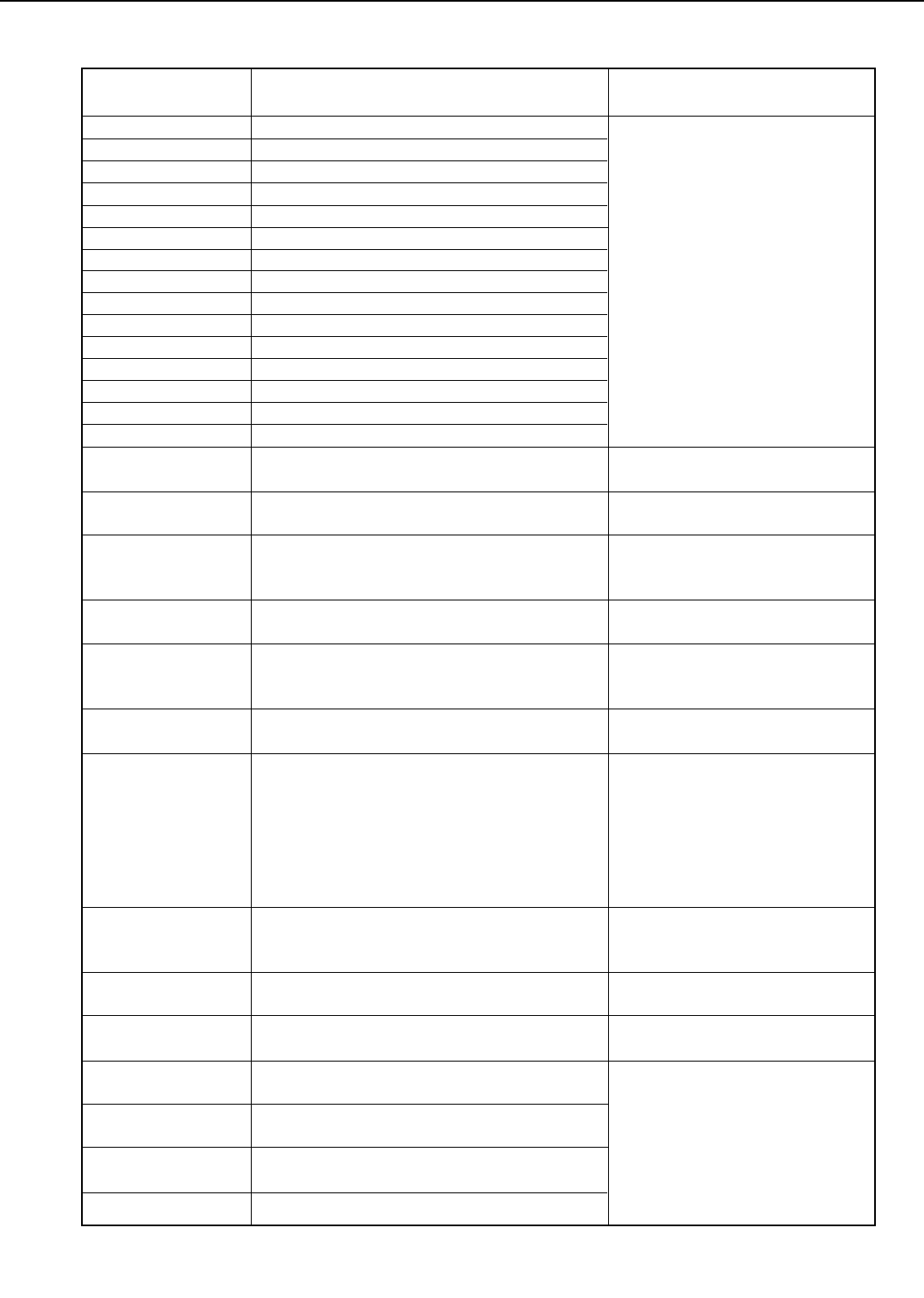
A - 18
APPENDIX
19.2 SORTER JAM
19.3 SORTER JAM
19.4 SORTER JAM
20.1 SORTER JAM
20.2 SORTER JAM
20.3 SORTER JAM
20.4 SORTER JAM
21.1 SORTER JAM
21.2 SORTER JAM
21.3 SORTER JAM
21.4 SORTER JAM
22.1 SORTER JAM
22.2 SORTER JAM
22.3 SORTER JAM
22.4 SORTER JAM
DUPLEX
OPTION ERROR
ENVELOPE
OPTION ERROR
OPTIONS
CONTROLLER
OPT CONTROLLER
ERROR
OPT CONTROLLER
COMMUNICATIONS
ERROR
ERROR DISK
CALL FOR SERVICE
MEMORY ALLOC
ERROR
PS OPTION
ERROR
ETHERNET
OPTION ERROR
TOKEN RING
OPTION ERROR
10.1 ERROR FUSER
CALL FOR SERVICE
10.2 ERROR FUSER
CALL FOR SERVICE
10.3 ERROR FUSER
CALL FOR SERVICE
10.4 ERROR FUSER
Jam at entrance sensor - Stay Jam
Jam at entrance sensor - Delay Jam
Jam at entrance sensor - Early Jam
Jam at reversing sensor - Initial Jam
Jam at reversing sensor - Stay Jam
Jam at reversing sensor - Delay Jam
Jam at reversing sensor - Early Jam
Jam at vertical path sensor - Initial Jam
Jam at vertical path sensor - Stay Jam
Jam at vertical path sensor - Delay Jam
Jam at vertical path sensor - Early Jam
Jam at face-up delivery sensor - Initial Jam
Jam at face-up delivery sensor - Stay Jam
Jam at face-up delivery sensor - Delay Jam
Jam at face-up delivery sensor - Early Jam
The duplexing unit has been removed or is no
longer properly seated.
The envelope feeder has been removed or is no
longer properly seated.
Option controller error with 2,000 sheet deck
or 2x500 sheet deck.
There is a problem with the Options Controller
Cable(s) are not connected in or there is a
problem with the Options Controller
Hard Drive Failure - Read Error -
GRS has been unable to allocate the memory
it needs.
Option PS ROM (DIMM) diagnostic error.
The Ethernet boad is not communicating with
the controller.
The Token Ring boad is not communicating
with the controller.
Fixing unit failure (Abnormally low tempera-
ture/warm up time out).
Fixing unit failure (Abnormally low tempera-
ture/warm up time out).
Fixing unit failure (Abnormally high tempera-
ture).
Fixing unit failure (wrong type).
paper and close cover.
Re-insert the duplexing unit into
the printer.
Re-insert the envelope feeder into
the printer.
Re-connect the 2,000 sheet deck
or 2x500 sheet deck to the print-
er.
Replace the option controller.
Reconnect cable(s) or replace the
option controller.
Replace the hard disk.
The job will resume after 10 sec-
onds if AUTOCONT is ON.
Otherwise press the CONTINUE
key to resume printing. Check the
page that ejects since the image
could not be processed as
requested.
An option ROM has failed its
startup checksum and needs to
be reprogrammed or replaced.
Replace the Ethernet boad
Replace the Token Ring boad
Perform the troubleshooting pro-
cedure described in section VI of
Chapter 4.
Note: If this error occurs,
switch off the printer for
15 minutes and then
switch the printer back
Message Meaning Action
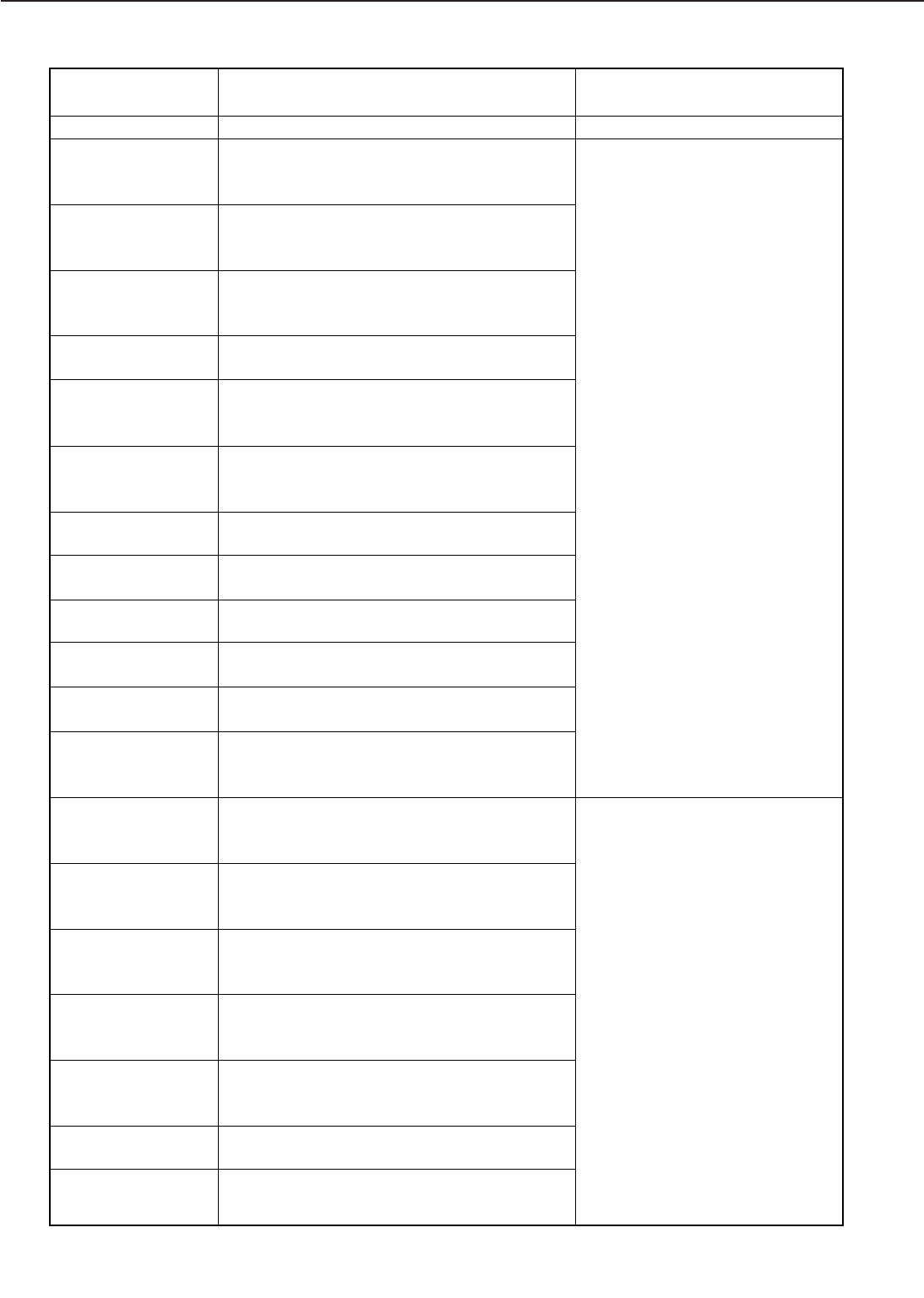
A - 19
APPENDIX
CALL FOR SERVICE
11.1 ERROR SCAN-
NER
CALL FOR SERVICE
11.2 ERROR SCAN-
NER
CALL FOR SERVICE
11.3 ERROR SCAN-
NER
CALL FOR SERVICE
11.4 ERROR LASER
CALL FOR SERVICE
12.1 ERROR
MOTOR
CALL FOR SERVICE
12.2 ERROR
MOTOR
CALL FOR SERVICE
13.1 ERROR FAN1
CALL FOR SERVICE
13.2 ERROR FAN2
CALL FOR SERVICE
13.3 ERROR FAN 3
CALL FOR SERVICE
13.4 ERROR FAN 4
CALL FOR SERVICE
13.5 ERROR FAN 5
CALL FOR SERVICE
14.1 ERROR AUX
TRAY
CALL FOR SERVICE
15.1 ERROR
STACKER
CALL FOR SERVICE
15.2 ERROR
STACKER
CALL FOR SERVICE
15.3 ERROR
STACKER
CALL FOR SERVICE
15.4 ERROR
STACKER
CALL FOR SERVICE
15.5 ERROR
STACKER
CALL FOR SERVICE
16 ERROR
CALL FOR SERVICE
16.1 ERROR
STACKER
Scanner motor malfunction (start up).
Scanner motor malfunction (rotation).
BD/Laser malfunction
BD/Laser malfunction
Main motor malfunction (start up)
Main motor malfunction (rotation)
Fan motor 1 failure - controller
Fan motor 2 failure - power supply
Fan motor 3 failure - exhaust1
Fan motor 4 failure - exhaust2
Fan motor 5 failure - multiple
Lifting plate failure
Malfunction of paper delivery motor
Malfunction of stapler shift motor
Malfunction of staple motor
Malfunction of lignment plate shift motor
Malfunction of tray unit elevation motor
Unknown Engine Error.
Malfunction of shutter
on.
Perform the troubleshooting pro-
cedure described in section VI of
Chapter 4.
Refer to Chapter 4 (troubleshoot-
ing) of the stapler stacker service
manual.
Message Meaning Action
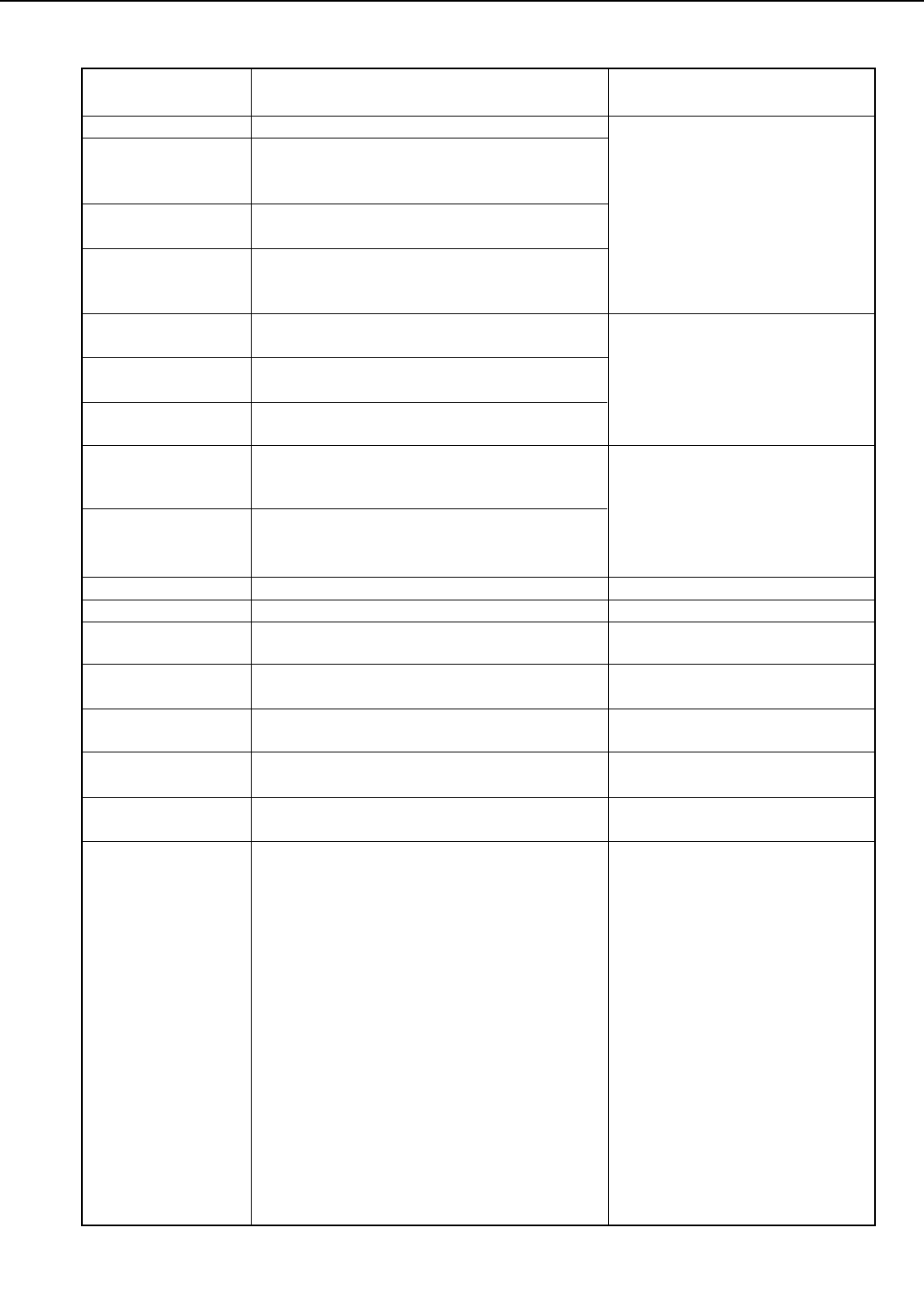
A - 20
APPENDIX
CALL FOR SERVICE
16.2 ERROR
STACKER
CALL FOR SERVICE
17 ERROR
CALL FOR SERVICE
17.1 ERROR
STACKER
CALL FOR SERVICE
18 UPPER ERROR
CALL FOR SERVICE
18.1 ERROR DECK
CALL FOR SERVICE
18.2 ERROR DECK
CALL FOR SERVICE
19.1 ERROR
SORTER
CALL FOR SERVICE
19.2 ERROR
SORTER
CALL FOR SERVICE
32 DISK ERROR
33 DISK ERROR
SRAM ERROR
CALL SERVICE
OPERATION CHECK
PAGES: ####
PANEL CHECK
PANEL CHECK
DONE
Malfunction of swing-guide
Unknown Stacker Error.
Malfunction of paper full sensor
Malfunction of UPPER tray
Malfunction of 2,000 sheet deck or 2x500
sheet deck delivery motor
Malfunction of 2,000 sheet deck or 2x500
sheet deck lifter
Malfunction of face-down deflector solenoid 1
Malfunction of face-down deflector solenoid 2
Hard drive failure - Write error -
Hard drive failure - Read failure -
The AIR Chip has failed.
This is the control panel diagnostic mode.
Displays under TEST when SHOW PAGE
COUNT is selected. #### is number of pages.
Displays during a panel check function
Displays when panel check function is com-
plete
Refer to Chapter 4 (troubleshoot-
ing) of the 2,000 sheet deck or
2x500 sheet deck service manual.
Refer to Chapter 4 (troubleshoot-
ing) of the soter service manual.
Replace the hard disk.
Replace the hard disk.
Replace the video controller PCB.
Factory Usage Only. See section
on diagnostics.
No action required.
Proceed with the panel check
function.
Power cycle printer
Message Meaning Action
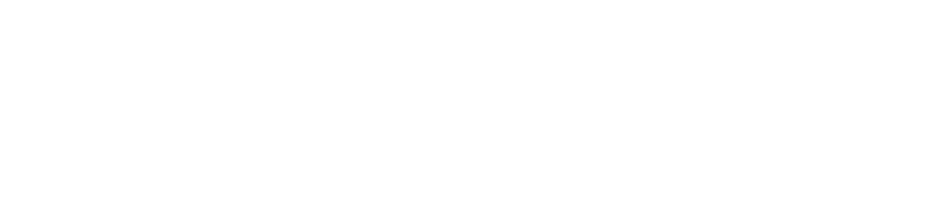
Prepared by
PERIPHERAL PRODUCTS QUALITY ADVANCEMENT DIV.
PERIPHERAL PRODUCTS TECHNICAL DOCUMENTATION DEPT.
CANON INC
Printed in Japan
REVISION 0 ( JAN. 1999 )
5-1, Hakusan 7–chome, Toride-City, Ibaraki-Pref. 302-8501, Japan
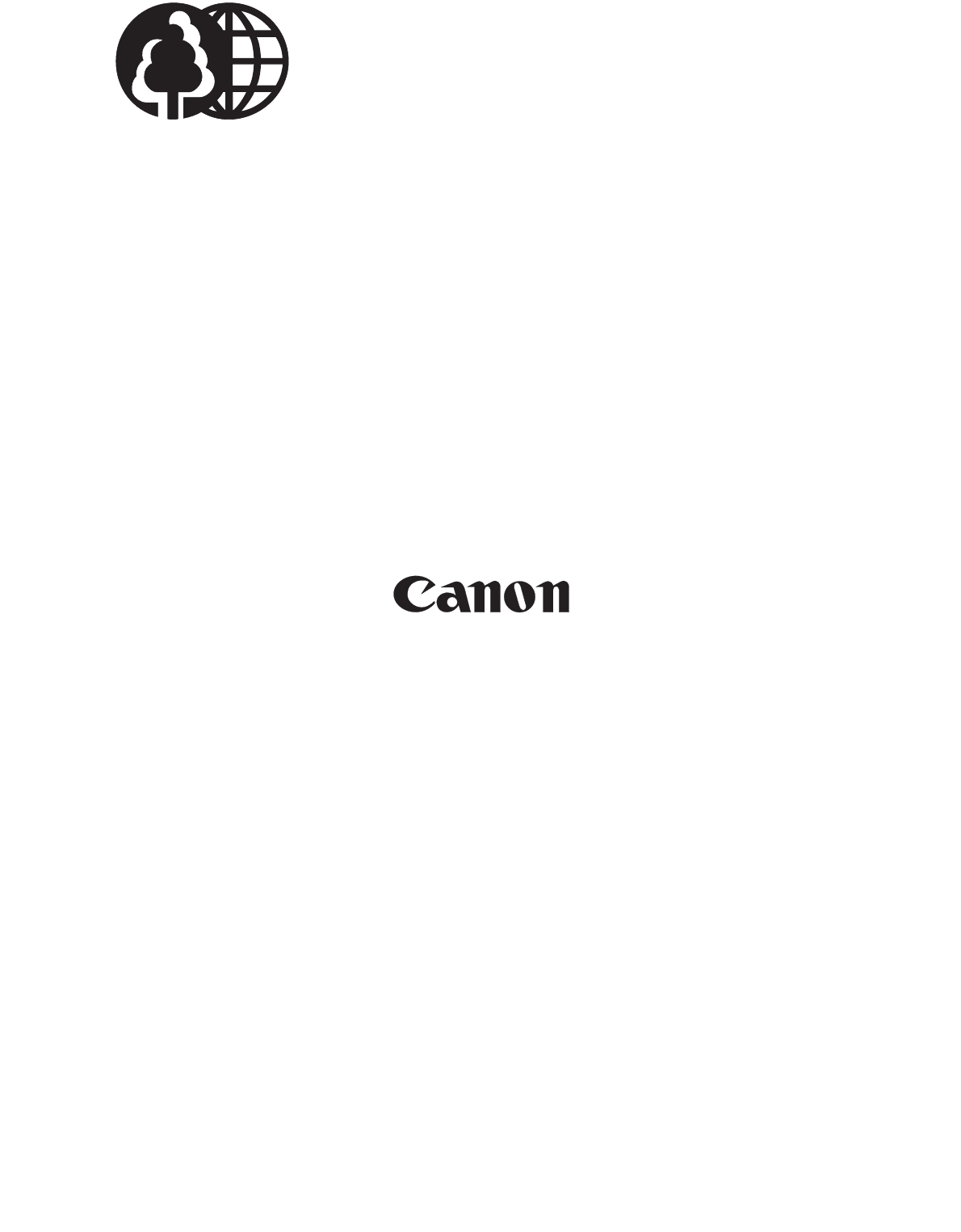
PRINTED IN JAPAN (IMPRIME AU JAPON) 0199AT0.70 CANON INC.
The printing paper contains
70% waste paper.