Carrier Streamline Scroll 69Nt20 531 300 Users Manual
69NT20-531-300 to the manual 8fc7d515-9b87-4f39-8beb-1d381b46bd70
2015-01-24
: Carrier Carrier-Streamline-Scroll-69Nt20-531-300-Users-Manual-311021 carrier-streamline-scroll-69nt20-531-300-users-manual-311021 carrier pdf
Open the PDF directly: View PDF .
Page Count: 93
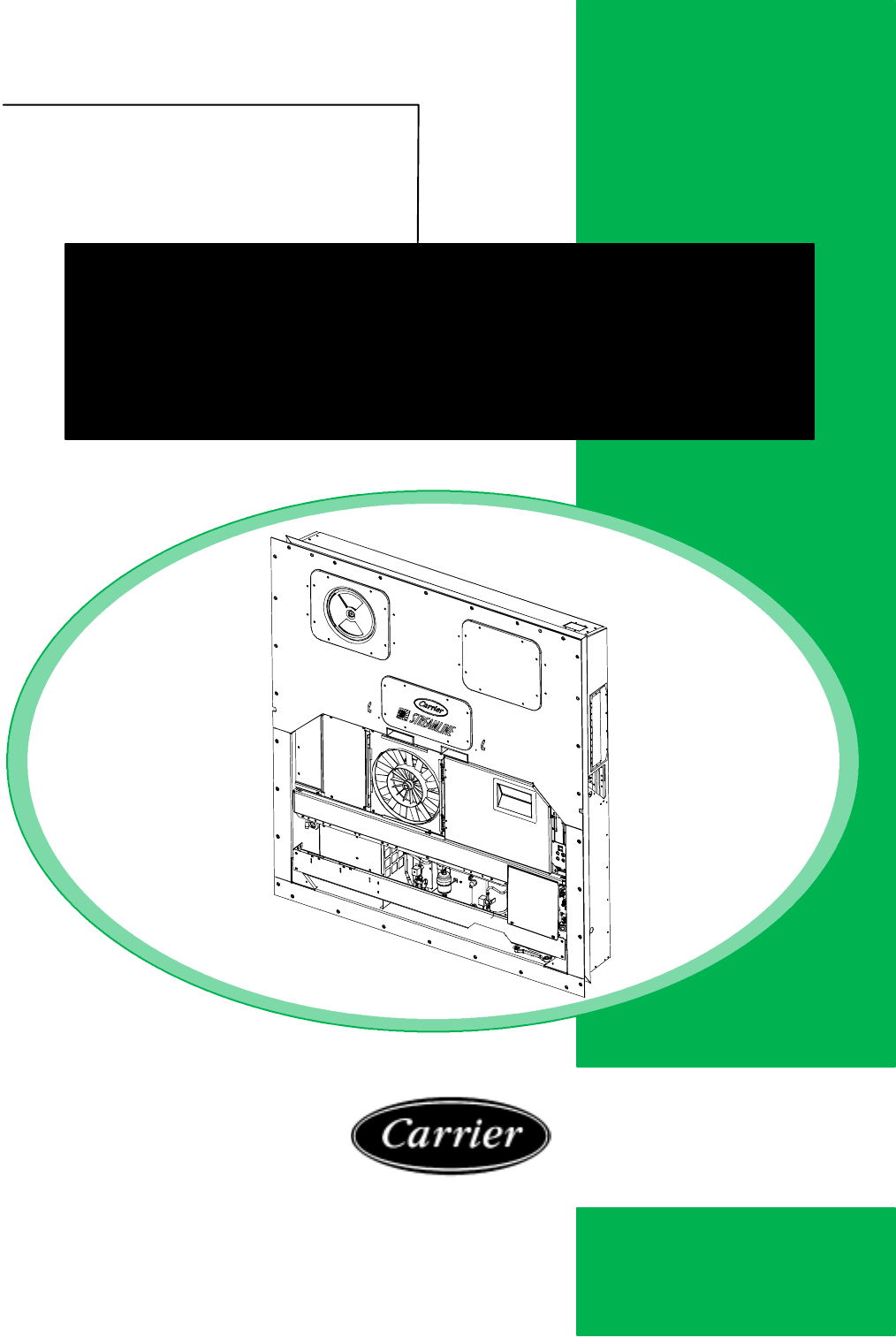
Model 69NT20-531-300
Streamline Scroll
T-309 Rev A
Carrier
Transicold
Container
Refrigeration
Operation
&Service

OPERATION AND SERVICE MANUAL
CONTAINER REFRIGERATION UNIT
MODEL
69NT20-531-300
Streamline Scroll
Carrier Transicold. A member of the United Technologies Corporation family. Stock symbol UTX.
Carrier Transicold Divsion, Carrier Corporation, P.O. Box 4805, Syracuse, N.Y. 13221 U. S. A.
ã2002 CarrierCorporation DPrinted in U. S. A. 07/02
T-309
Safety-1
SAFETY SUMMARY
GENERAL SAFETY NOTICES
The following general safety notices supplement the specific warnings and cautions appearing elsewhere in this
manual. They are recommended precautions that must be understood and applied during operation and maintenance
oftheequipmentcoveredherein.Thegeneralsafetynoticesarepresentedinthefollowingthreesectionslabeled:First
Aid, Operating Precautions and Maintenance Precautions. A listing of the specific warnings and cautions appearing
elsewhere in the manual follows the general safety notices.
FIRST AID
Aninjury,nomatterhowslight,shouldnevergounattended.Alwaysobtainfirstaidormedicalattentionimmediately.
OPERATING PRECAUTIONS
Always wear safety glasses.
Keep hands, clothing and tools clear of the evaporator and condenser fans.
Noworkshouldbeperformedontheunituntilallcircuitbreakers,start-stopswitchesareturnedoff,andpowersupply
is disconnected.
Always work in pairs. Never work on the equipment alone.
In case of severe vibration or unusual noise, stop the unit and investigate.
MAINTENANCE PRECAUTIONS
Beware of unannounced starting of the evaporator and condenser fans. Do not open the condenser fan grille or
evaporator access panels before turning power off, disconnecting and securing the power plug.
Besurepoweristurnedoffbeforeworkingonmotors,controllers,solenoidvalvesandelectricalcontrolswitches.Tag
circuit breaker and power supply to prevent accidental energizing of circuit.
Do not bypass any electrical safety devices, e.g. bridging an overload, or using any sort of jumper wires. Problems
with the system should be diagnosed, and any necessary repairs performed, by qualified service personnel.
Whenperforminganyarcweldingontheunitorcontainer,disconnectallwireharnessconnectorsfromthemodulesin
both control boxes. Do not remove wire harness from the modules unlessyou are grounded to the unit frame with a
static safe wrist strap.
In case of electrical fire, open circuit switch and extinguish with CO2(never use water).
UNIT LABEL IDENTIFICATION
To help identify the label hazards on the unit and explain the level of awareness each one carries, an explanation is
given with the appropriate consequences:
DANGER -- means an immediate hazard which WILL result in severe personal injury or death.
WARNING -- means to warn against hazards or unsafe conditions which COULD result in severe personal injury or
death.
CAUTION -- means to warn against potential hazard or unsafe practice which could result in minor personal injury,
product or property damage.
SPECIFIC WARNING AND CAUTION STATEMENTS
The statements listed below are applicable to the refrigeration unit and appear elsewhere in this manual. These
recommended precautions must be understood and applied during operation and maintenance of the equipment
covered herein. WARNING
Beware of unannounced starting of the evaporator and condenser fans. The unit may cycle the fans
and compressor unexpectedly as control requirements dictate.
WARNING
Do not attempt to removepower plug(s)beforeturning OFF start-stop switch (ST), unit circuitbreak-
er(s) and external power source.
WARNING
Make sure the power plugs are clean and dry before connecting to any power receptacle.
Safety-2
T-309
WARNING
Make sure thatthe unit circuit breaker(s) (CB-1 & CB-2) and the START-STOP switch (ST) are in the
“O” (OFF) position before connecting to any electrical power source.
WARNING
Never use air for leak testing. It has been determined that pressurized, mixtures of refrigerant and air
can undergo combustion when exposed to an ignition source.
WARNING
Make sure power to the unit is OFF and power plug disconnected before replacing the compressor.
WARNING
Before disassembly of the compressor make sure to relieve the internal pressure very carefully by
slightly loosening the couplings to break the seal.
WARNING
Oakite No. 32 is an acid. Be sure that the acid is slowly added to the water. DO NOT PUT WATER
INTO THE ACID -- this will cause spattering and excessive heat.
WARNING
Wear rubber gloves and wash the solution from the skin immediately if accidental contact occurs. Do
not allow the solution to splash onto concrete.
WARNING
Always turn OFFthe unitcircuit breakers (CB-1 & CB-2) and disconnect main power supplybefore
working on moving parts.
WARNING
Make sure power to the unit is OFF and power plug disconnected before removing capacitor(s).
WARNING
With power OFF discharge the capacitor before disconnecting the circuit wiring.
WARNING
Do not use a nitrogen cylinder without a pressure regulator. Do not use oxygen in or near a refrigera-
tion system as an explosion may occur.
WARNING
Do not open the condenser fan grille before turning power OFF and disconnecting power plug.
WARNING
The Unit Power Plug Must Be Disconnected To Remove Power From Circuit Breaker Cb1
CAUTION
Donotremovewireharnesses fromcontrollermodulesunlessyouaregroundedtotheunitframewith
a static safe wrist strap.
CAUTION
Unplugallcontrollermodulewireharnessconnectorsbeforeperformingarcweldingonanypartofthe
container.
CAUTION
When condenser water flow is below 11 lpm (3 gpm) or when water-cooled operation is not in use, the
CFS switch MUST be set to position ”1” or the unit will not operate properly.
CAUTION
Pre-trip inspection should not be performed with critical temperature cargoes in the container.
T-309
Safety-3
CAUTION
When Pre-Trip key is pressed, economy, dehumidification and bulb modewill bedeactivated. Atthe
completion of Pre-Trip activity, economy, dehumidification and bulb mode must be reactivated.
CAUTION
When a failure occurs during automatic testing the unit will suspend operationawaiting operatorin-
tervention.
CAUTION
When Pre--Trip test Auto 2 runs to completion without being interrupted, the unit will terminate pre-
trip and display“Auto2”“end.”Theunitwillsuspendoperationuntil theuserdepresses theENTER
key!
CAUTION
Toprevent trappingliquid refrigerant inthemanifold gaugesetbe suresetis broughtto suctionpres-
sure before disconnecting.
CAUTION
Thescroll compressorachieves lowsuction pressurevery quickly. Do not use the compressor toevacu-
ate the system below zero psig. Never operate the compressor with the suction or discharge service
valves closed (frontseated). Internaldamage willresult fromoperating thecompressor ina deep vacu-
um.
CAUTION
Use only Carrier Transicold approved Polyol Ester Oil (POE) -- Mobil ST32 compressor oil with
R-134a.Buyinquantitiesofonequartorsmaller.Whenusingthishygroscopicoil,immediatelyreseal.
Do not leave container of oil open or contamination will occur.
CAUTION
Takenecessarysteps(placeplywoodovercoiloruseslingonmotor)topreventmotorfrom fallinginto
condenser coil.
CAUTION
DONOTdisassemblepistonfromNEWsuctionmodulatingvalvepowerheadassembly.Doingsomay
result in damage to piston.
CAUTION
The unit must be OFF whenever a programming card is inserted or removed from the controller pro-
gramming port.
CAUTION
Do not allow moisture to enter wire splice area as this may affect the sensor resistance.

iT309
TABLE OF CONTENTS
PARAGRAPH NUMBER Page
GENERAL SAFETY NOTICES Safety-1.....................................................
FIRST AID Safety-1......................................................................
OPERATING PRECAUTIONS Safety-1......................................................
MAINTENANCE PRECAUTIONS Safety-1..................................................
UNIT LABEL IDENTIFICATION Safety-1...................................................
SPECIFIC WARNING AND CAUTION STATEMENTS Safety-1.................................
INTRODUCTION 1-1..............................................................................
1.1 INTRODUCTION 1-1..............................................................
1.2 CONFIGURATION IDENTIFICATION 1-1.............................................
1.3 OPTION DESCRIPTIONS 1-1.......................................................
1.3.1 Battery 1-1....................................................................
1.3.2 Dehumidification 1-1............................................................
1.3.3 Control Box 1-1................................................................
1.3.5 Pressure Readout 1-1............................................................
1.3.6 Interrogator 1-1................................................................
1.3.7 Remote Monitoring 1-1..........................................................
1.3.8 Communications 1-1............................................................
1.3.9 Compressor 1-1................................................................
1.3.10 Back Panels 1-1................................................................
1.3.11 460 Volt Cable 1-2.............................................................
1.3.12 Cable Restraint 1-2..............................................................
1.3.13 Upper Air (Fresh Air Make Up) 1-2................................................
1.3.14 Evaporator 1-2.................................................................
1.3.15 Evaporator Fan Operation 1-2.....................................................
1.3.16 Labels 1-2.....................................................................
1.3.17 Plate Set 1-2...................................................................
1.3.18 Controller 1-2..................................................................
1.3.19 Stepper Drive 1-2...............................................................
1.3.20 Condenser Grille 1-2............................................................
DESCRIPTION 2-1...............................................................................
2.1 GENERAL DESCRIPTION 2-1......................................................
2.1.1 Refrigeration Unit -- Front Section 2-1..............................................
2.1.2 Fresh Air Makeup Vent 2-1.......................................................
2.1.3 Evaporator Section 2-2...........................................................
2.1.4 Compressor Section 2-3..........................................................
2.1.5 Air Cooled Condenser Section 2-4.................................................
2.1.6 Control Box Section 2-5.........................................................
2.1.7 Communications Interface Module 2-5..............................................
2.2 REFRIGERATION SYSTEM DATA 2-6...............................................
2.3 ELECTRICAL DATA 2-7...........................................................
2.4 SAFETY AND PROTECTIVE DEVICES 2-8...........................................
2.5 REFRIGERATION CIRCUIT 2-9.....................................................
ii
T309
TABLE OF CONTENTS (cont)
2.5.1 Standard Operation 2-9..........................................................
2.5.2 Economized Operation 2-9.........................................................
2.5.3 Unloaded Operation 2-9...........................................................
MICROPROCESSOR 3-1..........................................................................
3.1 TEMPERATURE CONTROL MICROPROCESSOR SYSTEM 3-1..........................
3.1.1 Key Pad 3-2...................................................................
3.1.2 Display Module 3-2.............................................................
3.1.3 Controller 3-3..................................................................
3.2 CONTROLLER SOFTWARE 3-3.....................................................
3.2.1 Configuration Software (Configuration Variables) 3-3..................................
3.2.2 Operational Software (Function codes) 3-4...........................................
3.3 MODES OF OPERATION 3-4.......................................................
3.3.1 Temperature Control -- Perishable Mode 3-4..........................................
3.3.2 Defrost Interval 3-4.............................................................
3.3.3 Failure Action 3-4..............................................................
3.3.4 Generator Protection 3-4.........................................................
3.3.5 Compressor High Temperature, Low Pressure Protection. 3-4............................
3.3.6 Perishable Mode -- Conventional 3-4................................................
3.3.7 Perishable Mode -- Economy 3-5...................................................
3.3.8 Perishable Mode -- Dehumidification 3-5............................................
3.3.9 Perishable, Dehumidification -- Bulb Mode 3-5.......................................
3.3.10 Temperature Control -- Frozen Mode 3-6.............................................
3.3.11 Frozen Mode -- Conventional 3-6..................................................
3.4 CONTROLLER ALARMS 3-6.......................................................
3.5. UNIT PRE-TRIP DIAGNOSTICS 3-7.................................................
3.6 DataCORDER 3-7.................................................................
3.6.1 Description 3-7.................................................................
3.6.2 DataCORDER Software 3-7......................................................
3.6.3 Sensor Configuration (dCF02) 3-8.................................................
3.6.4 Logging Interval (dCF03) 3-10.....................................................
3.6.5 Thermistor Format (dCF04) 3-10...................................................
3.6.6 Sampling Type (dCF05 & dCF06) 3-10..............................................
3.6.7 Alarm Configuration (dCF07 -- dCF10) 3-10..........................................
3.6.8 DataCORDER Power-Up 3-10.....................................................
3.6.9 Pre-Trip Data Recording 3-10......................................................
3.6.10 DataCORDER Communications 3-10................................................
3.6.11 USDA Cold Treatment 3-11.......................................................
3.6.12 USDA Cold Treatment Procedure 3-11...............................................
3.6.13 DataCORDER Alarms 3-12........................................................
3.6.14 ISO Trip Header 3-12............................................................
iii T309
TABLE OF CONTENTS (cont)
OPERATION 4-1.................................................................................
4.1 INSPECTION (Before Starting) 4-1...................................................
4.2 CONNECT POWER 4-1............................................................
4.2.1 Connection To 380/460 vac Power 4-1..............................................
4.3 ADJUST FRESH AIR MAKEUP VENT 4-1............................................
4.3.1 Upper Fresh Air Makeup Vent 4-1..................................................
4.4 CONNECT REMOTE MONITORING
RECEPTACLE 4-2......................................................................
4.5 STARTING AND STOPPING INSTRUCTIONS 4-2......................................
4.5.1 Starting the Unit 4-2.............................................................
4.5.2 Stopping the Unit 4-2............................................................
4.6 START--UP INSPECTION 4-2.......................................................
4.6.1 Physical Inspection 4-2..........................................................
4.6.2 Check Controller Function Codes 4-2...............................................
4.6.3 Complete Inspection 4-2.........................................................
4.7 PRE-TRIP DIAGNOSIS 4-2.........................................................
4.8 OBSERVE UNIT OPERATION 4-3...................................................
4.8.1 Probe Check 4-3................................................................
4.9 SEQUENCE OF OPERATION 4-4......................................................
4.9.1 Sequence Of operation -- Compressor Phase Sequence 4-5................................
4.9.2 Sequence Of Operation -- Perishable Mode Cooling 4-5..................................
4.9.3 Sequence Of Operation --
Perishable Mode Heating 4-6...........................................................
4.9.4 Sequence Of operation -- Frozen Mode Cooling 4-6.....................................
4.9.5 Sequence Of Operation -- Defrost 4-6...............................................
TROUBLESHOOTING 5-1.........................................................................
5.1 UNIT WILL NOT START OR STARTS THEN STOPS 5-1................................
5.2 UNIT OPERATES LONG OR CONTINUOUSLY IN COOLING 5-1.........................
5.3 UNIT RUNS BUT HAS INSUFFICIENT COOLING 5-2..................................
5.4 UNIT WILL NOT HEAT OR HAS INSUFFICIENT HEATING 5-2..........................
5.5 UNIT WILL NOT TERMINATE HEATING 5-2.........................................
5.6 UNIT WILL NOT DEFROST PROPERLY 5-2..........................................
5.7 ABNORMAL PRESSURES (COOLING) 5-3...........................................
5.8 ABNORMAL NOISE OR VIBRATIONS 5-3............................................
5.9 CONTROLLER MALFUNCTION 5-4.................................................
5.10 NO EVAPORATOR AIR FLOW OR RESTRICTED AIR FLOW 5-4.........................
5.11 THERMOSTATIC EXPANSION VALVE MALFUNCTION 5-4.............................
5.12 AUTOTRANSFORMER MALFUNCTION 5-4..........................................
5.13 WATER-COOLED CONDENSER OR WATER PRESSURE SWITCH 5-4....................
5.14 COMPRESSOR OPERATING IN REVERSE 5-5........................................
5.15 ABNORMAL TEMPERATURES 5-5..................................................
5.16 ABNORMAL CURRENTS 5-5.......................................................
iv
T309
TABLE OF CONTENTS (cont)
SERVICE 6-1....................................................................................
6.1 SECTION LAYOUT 6-1............................................................
6.2 SERVICE VALVES 6-1.............................................................
6.3. MANIFOLD GAUGE SET 6-1.......................................................
6.4 PUMPING THE UNIT DOWN 6-2....................................................
6.5 REFRIGERANT LEAK CHECKING 6-3...............................................
6.6 EVACUATION AND DEHYDRATION 6-3.............................................
6.6.1 General 6-3....................................................................
6.6.2 Preparation 6-3.................................................................
6.6.3 Procedure - Complete system 6-3..................................................
6.6.4 Procedure - Partial System 6-4.....................................................
6.7 REFRIGERANT CHARGE 6-5.......................................................
6.7.1 Checking the Refrigerant Charge 6-5................................................
6.7.2 Adding Refrigerant to System (Full Charge) 6-5.......................................
6.7.3 Adding Refrigerant to System (Partial Charge) 6-5.....................................
6.8 COMPRESSOR -- Model RSH105 6-5.................................................
6.8.1 Removal and Replacement of Compressor 6-5........................................
6.9 COMPRESSOR OIL LEVEL 6-7.....................................................
6.10 HIGH PRESSURE SWITCH 6-7......................................................
6.10.1 Replacing High Pressure Switch 6-7................................................
6.10.2 Checking High Pressure Switch 6-8................................................
6.11 CONDENSER COIL 6-8............................................................
6.12 CONDENSER FAN AND MOTOR ASSEMBLY 6-8.....................................
6.13 FILTER-DRIER 6-8................................................................
6.14 EXPANSION VALVES 6-9..........................................................
6.14.1 Checking Superheat. 6-9.........................................................
6.14.2 Valve Replacement 6-9..........................................................
6.15 EVAPORATOR COIL AND HEATER
ASSEMBLY 6-10........................................................................
6.15.1 Evaporator Coil Replacement 6-10..................................................
6.15.2 Evaporator Heater Replacement 6-10................................................
6.16 ECONOMIZER, UNLOADER, LIQUID INJECTION AND OIL RETURN SOLENOID VALVE 6-11
6.17 EVAPORATOR FAN AND MOTOR ASSEMBLY 6-11....................................
6.17.1 Replacing The Evaporator Fan Assembly 6-12.........................................
6.18 EVAPORATOR FAN MOTOR CAPACITORS 6-12.......................................
6.18.1 When To Check For A Defective Capacitor 6-12.......................................
6.18.2 Removing The Capacitor 6-12......................................................
6.18.3 Checking The Capacitor 6-12......................................................
6.19 VALVE OVERRIDE CONTROLS 6-13.................................................
6.20 SUCTION MODULATION VALVE 6-13................................................
6.20.1 Precheck Procedure 6-14..........................................................
6.20.2 Checking The Stepper valve 6-14...................................................
6.21 CONTROLLER AND EXPANSION MODULE 6-14......................................
vT309
6.21.1 Handling Modules 6-14...........................................................
6.21.2 Controller Trouble-Shooting 6-15...................................................
6.21.3 Controller Programming Procedure 6-15..............................................
6.21.4 Removing and Installing a Module 6-16..............................................
6.22 TEMPERATURE SENSOR SERVICE 6-16..............................................
6.22.1 Sensor Checkout Procedure 6-16....................................................
6.22.2 Sensor Replacement 6-17..........................................................
6.22.3 Sensor Re--Installation 6-18........................................................
6.23 MAINTENANCE OF PAINTED SURFACES 6-18........................................
6.24 COMPOSITE CONTROL BOX REPAIRS 6-18...........................................
6.24.1 Introduction 6-18................................................................
6.24.2 Cracks 6-19....................................................................
6.24.3 Chips And Holes 6-19............................................................
6.24.4 Inserts 6-19.....................................................................
6.24.5 Door Hinge Inserts 6-19...........................................................
6.25 COMMUNICATIONS INTERFACE MODULE INSTALLATION 6-22........................
ELECTRICAL WIRING SCHEMATIC 7-1............................................................
7.1 INTRODUCTION 7-1..............................................................

vi
T309
LIST OF ILLUSTRATIONS
FIGURE NUMBER Page
Figure 2-1 Refrigeration Unit -- Front Section 2-1...............................................
Figure 2-2 Evaporator Section 2-2............................................................
Figure 2-3 Compressor Section 2-3...........................................................
Figure 2-4 Condenser Section 2-4............................................................
Figure 2-5 Control Box Section 2-5...........................................................
Figure 2-6 Refrigeration Circuit Schematic -- Standard Operation 2-10................................
Figure 2-7 Refrigeration Circuit Schematic -- Economized Operation 2-11.............................
Figure 2-8 Refrigeration Circuit Schematic -- Unloaded Operation 2-11...............................
Figure 3- 1 Temperature Control System 3-1...................................................
Figure 3- 2 Key Pad 3-2....................................................................
Figure 3- 3 Display Module 3-2..............................................................
Figure 3- 4 Control and Expansion Modules 3-3.................................................
Figure 3- 5 Standard Configuration Download Report 3-9.........................................
Figure 3- 6 Data Reader 3-11.................................................................
Figure 4-1 Make Up Air Flow Chart 4-1.......................................................
Figure 4-2 Controller Operation -- Perishable Mode 4-4...........................................
Figure 4-3 Controller Operation -- Frozen Mode 4-5..............................................
Figure 4-4 Perishable Mode 4-5..............................................................
Figure 4-5 Perishable Mode Heating 4-6.......................................................
Figure 4-6 Frozen Mode 4-6................................................................
Figure 4-7 Defrost 4-7.....................................................................
Figure 6-1 Service Valve 6-1................................................................
Figure 6-2 Suction Service Valve 6-1.........................................................
Figure 6-3 Manifold Gauge Set 6-1...........................................................
Figure 6-4 R-134a Manifold Gauge/Hose Set 6-2................................................
Figure 6-5. Refrigeration System Service Connections 6-3.........................................
Figure 6-6. Compressor Service Connections 6-4................................................
Figure 6-7 Compressor Upper Mounting 6-6....................................................
Figure 6-8 Compressor Lower Mounting 6-6...................................................
Figure 6-9 High Pressure Switch Testing 6-8...................................................
Figure 6-10 Thermostatic Expansion Valve Bulb 6-9.............................................
Figure 6-11 Evaporator Expansion Valve 6-9...................................................
Figure 6-12 Hermetic Thermostatic Expansion Valve Brazing Procedure 6-10..........................
Figure 6-13 Economizer Expansion Valve 6-10..................................................
Figure 6-14. Unloader Solenoid Valve 6-11.....................................................
Figure 6-15. Oil Return Solenoid Valve (ORV), Economizer Solenoid Valve (ESV),
Liquid Injection Solenoid Valve (LIV) 6-11...........................................
Figure 6-16. Evaporator Fan Assembly 6-12.....................................................
Figure 6-17 Suction Modulation Valve (SMV) 6-13...............................................
Figure 6-18 Controller Section of the Control Box 6-15............................................
Figure 6-19 Sensor Types 6-16...............................................................
Figure 6-20 Typical Sensor and Cable Splice 6-17................................................
Figure 6-21 Supply Sensor Positioning 6-18.....................................................

vii T309
LIST OF ILLUSTRATIONS
FIGURE NUMBER Page
Figure 6-22 Return Sensor Positioning 6-18.....................................................
Figure 6-23 Door Hinge Repair 6-19...........................................................
Figure 6-24. Insert Location 6-21.............................................................
Figure 6-25. Communications Interface Installation 6-22...........................................
Figure 7-1 LEGEND 7-1...................................................................
Figure 7-2 SCHEMATIC DIAGRAM 7-2......................................................
Figure 7-3 WIRING DIAGRAM 7-3.........................................................
LIST OF TABLES
TABLE NUMBER Page
Table 2-1 Safety and Protective Devices 2-8.....................................................
Table 3-1 Key Pad Function 3-2..............................................................
Table 3-2 DataCORDER Configuration Variables 3-8.............................................
Table 3-3 DataCORDER Standard Configurations 3-8.............................................
Table 3-4 Controller Configuration Variables 3-13.................................................
Table 3-5 Controller Function Codes 3-14.......................................................
Table 3-6 Controller Alarm Indications 3-17.....................................................
Table 3-7 Controller Pre-Trip Test Codes 3-21....................................................
Table 3-8 DataCORDER Function Code Assignments 3-25..........................................
Table 3-9 DataCORDER Pre-Trip Result Records 3-26.............................................
Table 3-10 DataCORDER Alarm Indications 3-27.................................................
Table 6-1 Compressor Kit 6-6................................................................
Table 6-2 Sensor Temperature/Resistance Chart (+/--.002%) 6-17.....................................
Table 6-3 Crack, Chip & Hole Repair Kit 6-20....................................................
Table 6-4 Insert Repair Kit 6-20...............................................................
Table 6-5 Drill Information 6-20...............................................................
Table 6-6 Recommended Bolt Torque Values 6-22.................................................
Table 6-7 R-134a Temperature - Pressure Chart 6-23...............................................
1-1 T-309
SECTION 1
INTRODUCTION
1.1 INTRODUCTION
The Carrier Transicold model 69NT20--531-300 units
are of lightweight aluminum frame construction,
designedtofitinthefrontofacontainerandserveasthe
container front wall.
They are one piece, self-contained, all electric units
which are fitted with cooling and heating systems to
provide precise temperature control.
The units are supplied with a complete charge of
refrigerant R-134a and compressor lubricating oil and
are ready for operation upon installation. Forklift
pockets are provided for unit installation and removal.
The base unit operates on nominal 380/460 volt, 3
phase, 50/60 hertz power. An optional autotransformer
maybefittedtoallowoperationonnominal190/230,3
phase, 50/60hertzpower. Power forthe control system
is provided by a transformer which steps the supply
power down to 18 and 24 volts, single phase.
The controller is a Carrier Transicold Micro-Link 2i
microprocessor. The controller will operate
automatically to select cooling, holding or heating as
required to maintain the desired set point temperature
within very close limits.
The controller is fitted with a keypad and display for
viewing orchanging operatingparameters. Thedisplay
isalsoequippedwithlightstoindicatevariousmodesof
operation.
1.2 CONFIGURATION IDENTIFICATION
Unit identification information is provided on a model
plate located to the left of the economizer. The plate
provides the unit model number and the unit parts
identification number (PID). The model number
identifies the overall unit configuration while the PID
provides information on specific optional equipment,
factory provision to allow for field installation of
optional equipment and differences in detailed parts.
Configuration identification for the models covered
herein areprovided in the Carrier Transicold Container
Unit Matrixmanual, publicationT--300. Printedcopies
of the T--300 may be obtained from Carrier Transicold.
Also,aweeklyupdatedcopymaybefoundattheCarrier
Web site, www.carrier.refrigeration.com.
1.3 OPTION DESCRIPTIONS
Variousoptionsmaybefactoryorfieldfittedto thebase
unit. Brief descriptions of the options are provided in
the following subparagraphs.
1.3.1 Battery
The controller may be fitted with standard replaceable
batteries or a rechargeable battery pack.
1.3.2 Dehumidification
The unit may be fitted with a humidity sensor. This
sensor allows setting of a humidity set point in the
controller. In the dehumidification mode the controller
willoperatetoreduceinternalcontainermoisturelevel.
1.3.3 Control Box
The control box is constructed of composite material
and may be fitted with a lockable door.
1.3.4 Temperature Readout
The unit may be fitted with suction and discharge
temperature sensors. The sensor readings may be
viewed on the controller display.
1.3.5 Pressure Readout
Theunitmaybefittedwithfactoryinstalledsuctionand
discharge pressure gauges. The unit is fitted with
suctionanddischargetransducers.Thereadingsmaybe
viewed on the controller display.
1.3.6 Interrogator
UnitsthatusetheDataCORDERfunctionarefittedwith
interrogator receptacles for connection of equipment to
download the recorded data. Two receptacles may be
fitted, one accessible from the front of the unit and the
other mounted inside the container (with the USDA
receptacles).
1.3.7 Remote Monitoring
The unit may be fitted with a remote monitoring
receptacle. This item allows connection of remote
indicators for COOL, DEFROST and IN RANGE.
1.3.8 Communications
Theunitmaybefittedwithacommunicationsinterface
module. The communications interface module is a
slave module which allows communication with a
master central monitoring station. The module will
respond to communication and return information over
the main power line. Refer to the ship master system
technical manual for further information.
1.3.9 Compressor
The unit is fitted with a scroll compressor.
1.3.10 Back Panels
Back panel designs that may be fitted include panels of
aluminumand stainlesssteel. Panels maybe fittedwith
access doors and/or hinge mounting.
1-2
T-309
1.3.11 460 Volt Cable
Various power cable and plug designs are available for
the main 460 volt supply. The plug options tailor the
cables to each customers requirements.
1.3.12 Cable Restraint
Various designs are available for storage of the power
cables. These options are variations of the compressor
section front cover.
1.3.13 Upper Air (Fresh Air Make Up)
The unit may be fitted with an upper fresh air makeup
assembly. These assemblies are supplied in two
designs, the standard design and themicro design. The
openings may also be fitted with screens.
1.3.14 Evaporator
Theunit is fitted with an evaporator coiland ahermetic
thermal expansion valve.
1.3.15 Evaporator Fan Operation
The units are fitted with Normal Evaporator Fan
Operation, opening of an evaporator fan internal
protector will shut down the unit.
1.3.16 Labels
Operating Instruction and Function Code listing labels
will differ depending on the options installed. For
example, additional operating instructions arerequired
to describe start--up of a unit equipped with an
autotransformer. Where the labels are available with
additional languages, they are listed in the parts list.
1.3.17 Plate Set
Each unit is equipped with a tethered set of wiring
schematic and wiring diagram plates.
The plate sets are ordered using a seven digit basepart
numberandatwodigitdashnumber. (See UnitMatrix
Manual, T-300)
1.3.18 Controller
Replacement controllers may be ordered as a universal
un--configured controller (without configuration
software) or configured.
1.3.19 Stepper Drive
All the units covered by this manual have suction
modulatingvalveswhichacttocontrolsystemcapacity.
Unitsindicatedasbeingfittedwith“stepperdrive”have
digital control motors fitted to the suction modulating
valve to open and close the valve in steps as required.
1.3.20 Condenser Grille
Two styles of condenser grilles are available, direct
bolted grilles and hinged grilles.

T-309
2-1
SECTION 2
DESCRIPTION
2.1 GENERAL DESCRIPTION
2.1.1 Refrigeration Unit -- Front Section
The unit is designed so that the majority of the
components are accessible from the front, see
Figure 2-1.Theupperaccesspanelsallowentryintothe
evaporator section, and the center access panel allows
access to the evaporator expansion valve, unloader
valve, suction modulation valve and evaporator coil
heaters.Theunitmodelnumber,serialnumberandparts
identificationnumbercanbefoundontheserialplateto
the left of the economizer.
2.1.2 Fresh Air Makeup Vent
Thefunctionoftheupperorlowermakeupairventisto
provide ventilation for commodities that require fresh
air circulation.
1
2
3
8
4
11
5
12
14
9
15
13
10
6
7
16
1. Access Panel (Evap. Fan #1)
2. Access Panel (Heaters, Suction Modulating
Valve, Unloader Valve & Evaporator
Expansion Valve)
3. Fork Lift Pockets
4. Control Box
5. Compressor
6. Receiver or Water Cooled Condenser
7. Economizer
8. Unit Serial Number, Model Number and
Parts Identification Number (PID) Plate
9. Power Cables and Plug
10. Condenser Fan
11. Interrogator Connector (Front left)
12. Blank Cover (Temperature Recorder Location)
13. Blank Cover (Lower Fresh Air Makeup Vent
Location)
14. Upper Fresh Air Makeup Vent
15. Access Panel (Evap. Fan #2)
16. Compressor Protection Panel (cutaway view)
Figure 2-1 Refrigeration Unit -- Front Section

2-2T-309
2.1.3 Evaporator Section
The evaporator section (Figure 2-2) contains the return
recorder sensor, return temperature sensor, evaporator
expansion valve, unloader valve, suction modulation
valve, dual-speed evaporator fans (EM1 and EM2),
evaporator coil and heater, defrost heaters, defrost
temperature sensor, heat termination thermostat and
suction temperature sensor.
The evaporator fans circulate air through the container
by pulling it in the top of the unit, directing it through
the evaporator coil, where it is heated or cooled, and
discharging it at the bottom.
Theevaporatorcomponentsareaccessiblebyremoving
the upper rear panel (as shown in the illustration) orby
removing the front access panels.
14
11 12
12
3
4
57
8
15
9
16
13
10 17 6
1. Evaporator Fan Motor #1
2. Return Recorder/Temperature Sensor
3. Humidity Sensor
4. Evaporator Fan Motor #2
5. Defrost Temperature Sensor
6. Heater Termination Thermostat
7. Evaporator Coil
8. Evaporator Coil Heaters
9. Evaporator Expansion Valve Bulb
10. Evaporator Expansion Valve
11. Low Side Access Valve
12. Suction Modulating Valve
13. Suction Temperature Sensor
14. To Compressor
15. From Coil
16. To Coil
17. Unloader Solenoid Valve
Figure 2-2 Evaporator Section

T-309
2-3
2.1.4 Compressor Section
The compressor section includes the compressor (with
high pressure switch) and the oil separator.
This section also contains the oil return solenoid,
compressor power plug, the discharge pressure
transducer, discharge temperature sensor and the
suction pressure transducers.
The supply temperature sensor, supply recorder sensor
and ambient sensor are located at the left side of the
compressor.
11
12
1
2
3
4
5
7
910
17 18 19
20
21
22
16
15
8
11
13
23
14
11
Discharge
Connection
(Hidden)
Economizer
Connection
Suction
Connection
Oil Return
Connection
6
1. Compressor Guard
2. Supply Temperature/Supply Recorder Sensor
Assembly
3. Ambient Sensor
4. Supply Air Thermometer Port (location)
5. Oil Drain
6. Compressor
7. Compressor Sight Glass
8 Compressor Power Plug
9. Discharge Service Valve
10. High Pressure Switch
11. Access Valve
12. Economizer Service Valve
13. Suction Service Valve
14. Discharge Temperature Sensor
15. Oil Return Service Valve
16. Discharge Pressure Transducer
17. Oil Return Solenoid Valve
18. Oil Separator
19. From Economizer
20. To Condenser
21. From Suction Modulating Valve
22. Suction Strainer
23. Suction Pressure Transducer
Figure 2-3 Compressor Section

2-4T-309
2.1.5 Air Cooled Condenser Section
The air cooled condenser section (Figure 2-4) consists
of the condenser fan, condenser coil, receiver, sight
glass/moisture indicator, liquid line service valve,
filter-drier and fusible plug.
Thecondenserfanpulls airinthebottom ofthecoiland
it is discharged horizontally out through the condenser
fan grille.
This section also contains the economizer, economizer
solenoid valve, economizer expansion valve and the
liquid injection solenoid valve.
567
17
1
24
3
811
9
12
15
14
16
27
18
19
20
21
22
23
24
25
26
10 13
1. Grille and Venturi Assembly
2. Condenser Fan
3. Key
4. Condenser Fan Motor
5. Condenser Coil
6. Condenser Motor Mounting Bracket
7. Condenser Coil Cover
8. Economizer
9. To Evaporator Expansion Valve
10. Liquid Injection Solenoid Valve
11. From Condenser
12. To Condenser
13. To Compressor Economizer Connection
14. To Unloader Solenoid Valve
15. From Compressor Discharge
16. Discharge Pressure Transducer
17. Oil Separator
18. To Oil Return Solenoid
19. Receiver
20. Sight Glass/Moisture Indicator
21. Sight Glass
22. Fusible Plug
23. Access Valve
24. Liquid Line Service Valve
25. Filter-Drier
26. Economizer Expansion Valve
27. Economizer Solenoid Valve
Figure 2-4 Condenser Section

T-309
2-5
2.1.6 Control Box Section
The control box (Figure 2-5) includes the manual
operationswitches;circuitbreaker(CB-1);compressor,
fan and heater contactors; control power transformer;
fuses; key pad;display module; current sensormodule;
controller module expansion module and the
communications interface module.
2.1.7 Communications Interface Module
The communications interface module is a slave
module which allow communication with a master
central monitoring station. The module will respondto
communication and return information over the main
powerline.Refertothemastersystemtechnicalmanual
for further information.
1920 151718
12 3 4 5 6 7
10 911
14
8
121316
1. Compressor Phase A Contactor
2. Compressor Phase B Contactor
3. Heater Contactor
4. Display Module
5. Communications Interface Module
6. Controller/DataCORDER Module (Controller)
7. Expansion Module
8. Key Pad
9. Start-Stop Switch
10. Remote Monitoring Receptacle
11. Manual Defrost Switch
12. Condenser Fan Switch
13. Controller Battery Pack
14. Interrogator Connector (Box Location)
15. Control Transformer
16. Evaporator Fan Contactor - High
17. Evaporator Fan Contactor - Low
18. Condenser Fan Contactor
19. Circuit Breaker -- 460V
20. Current Sensor Module
Figure 2-5 Control Box Section

2-6T-309
2.2 REFRIGERATION SYSTEM DATA
Model RSH105
Weight (Dry) 46.5 kg (103 lb)
a
C
o
m
p
r
e
s
s
o
r
/
M
o
t
o
r
Approved Oil Mobil ST32
a
.
C
o
m
p
r
e
s
s
o
r
/
M
o
t
o
r
Assembly Oil Charge 2957 ml (100 ounces)
y
Oil Sight Glass The oil level range, with the compressor off,
should be between the bottom and one-eighth
level of the sight glass.
b. Evaporator Expansion
Valve Superheat Verify at --18 _C
(0 _F) container box
temperature 4.4to6.7_C(8to12_F)
c. Economizer Expansion
Valve Superheat 4.4 to 11.1 _C(8to20_F)
d
H
e
a
t
e
r
T
e
r
m
i
n
a
t
i
o
n
T
h
e
r
m
o
s
t
a
t
Opens 54 (¦3) _C = 130 (¦5) _F
d
.
H
eater
T
erm
i
nat
i
on
T
h
ermostat Closes 38 (¦4) _C = 100 (¦7) _F
e
H
i
g
h
P
r
e
s
s
u
r
e
S
w
i
t
c
h
Cutout 25 (¦1.0) kg/cm@= 350 (¦10) psig
e.
H
i
g
h
P
ressure
S
w
i
tc
h
Cut-In 18 (¦0.7) kg/cm@= 250 (¦10) psig
Unit Configuration Charge Requirements -- R-134a
W
a
t
e
r
C
o
o
l
e
d
4--Row Coil
f. Refrigerant Charge Water-Cooled
Condenser 5.33 kg
(11.75 lbs)
Receiver 4.99kg
(11.0 lbs)
g
F
u
s
i
b
l
e
P
l
u
g
Melting point 99 _C = (210 _F)
g.
F
us
i
b
l
e
P
l
ug Torque 6.2 to 6.9 mkg (45 to 50 ft-lbs)
h. Sight Glass/Moisture Indicator Torque 8.9 to 9.7 mkg (65 to 70 ft-lbs)
i
R
u
p
t
u
r
e
D
i
s
c
Bursts at 35 ¦5% kg/cm@= (500 ¦5% psig)
i
.
R
upture
D
i
sc Torque 6.2 to 6.9 mkg (45 to 50 ft-lbs)
j. Unit Weight Refer to unit model number plate.
k
W
a
t
e
r
P
r
e
s
s
u
r
e
S
w
i
t
c
h
Cut-In 0.5 ¦0.2 kg/cm@(7 ¦3psig)
k
.
W
ater
P
ressure
S
w
i
tc
h
Cutout 1.6 ¦0.4 kg/cm@(22 ¦5psig)

T-309
2-7
2.3 ELECTRICAL DATA
CB-1 Trips at 29 amps
a. Circuit Breaker CB-2 (50 amp) Trips at 62.5 amps
a
.
C
i
r
c
u
i
t
B
r
e
a
k
e
r
CB-2 (70 amp) Trips at 87.5 amps
b. Compressor
Motor Full Load Amps (FLA) 13 amps @ 460 vac
380 vac, Single Phase,
50 hz 460 vac, Single Phase,
60 hz
c
.
C
o
n
d
e
n
s
e
r
F
a
n
Full Load Amps 1.3 amps 1.6 amps
c
.
C
o
n
d
e
n
s
e
r
F
a
n
Motor Horsepower 0.43 hp 0.75 hp
Rotations Per Minute 1425 rpm 1725 rpm
Voltage and Frequency 360 -- 460 vac ¦2.5 hz 400 -- 500 vac ¦2.5 hz
Bearing Lubrication Factory lubricated, additional grease not required.
Rotation Counter-clockwise when viewed from shaft end.
Number of Heaters 4
d. Eva
p
orator Coil Rating 750 watts +5/--10% each @ 230 vac
d
.
E
v
a
p
o
r
a
t
o
r
C
o
i
l
Heaters Resistance (cold) 66.8 to 77.2 ohms @ 20 _C(68_F)
Type Sheath
380 vac/50 hz 460 vac/60 hz
Full Load Amps
High Speed 1.6 2.0
Full Load Amps
Low Speed 0.8 1.0
Nominal Horsepower
High Speed 0.70 0.84
e
.
E
v
a
p
o
r
a
t
o
r
F
a
n
Nominal Horsepower
Low Speed 0.09 0.11
e
.
E
v
a
p
o
r
a
t
o
r
F
a
n
Motor(s) Rotations Per Minute
High Speed 2850 rpm 3450 rpm
Rotations Per Minute
Low Speed 1425 rpm 1750 rpm
Voltage and Frequency 360 -- 460 vac ±1.25 hz 400 -- 500 vac ±1.5 hz
Voltage & Frequency us-
ing power autotransformer 180 -- 230 vac ±1.25hz 200 -- 250 vac ±1.5 hz
Bearing Lubrication Factory lubricated, additional grease not required
Rotation CW when viewed from shaft end
Control Circuit 10 amps (F3)
f. Fuses Controller/DataCORDER 5amps(F1&F2)
f
.
F
u
s
e
s
Expansion Module 10 amps (F4)

2-8T-309
PARAGRAPH 2.3 -- Continued
Orange wire Power
Red wire Output
Brown wire Ground
Input voltage 5vdc
g
H
u
m
i
d
i
t
y
S
e
n
s
o
r
Output voltage 0to3.3vdc
g.
H
um
i
d
i
ty
S
ensor Output voltage readings verses relative humidity (RH) percentage:
30% 0.99 V
50% 1.65 V
70% 2.31 V
90% 2.97 V
2.4 SAFETY AND PROTECTIVE DEVICES
Unit components are protected from damage by safety
and protective devices listed in the following table.
Thesedevicesmonitortheunitoperatingconditionsand
open a set of electrical contacts when an unsafe
condition occurs.
Open safety switchcontacts oneitherorbothofdevices
IP-CP or HPS will shut down the compressor.
Open safety switch contacts on deviceIP-CM will shut
down the condenser fan motor.
Theentirerefrigerationunitwillshutdown ifoneofthe
following safety devices open: (a) Circuit Breaker(s);
(b)Fuse(F3/15A);or(c)EvaporatorFanMotorInternal
Protector(s) -- (IP-EM).
Table 2-1 Safety and Protective Devices
UNSAFE CONDITION DEVICE DEVICE SETTING
Circuit Breaker (CB-1) -- Manual Reset Trips at 29 amps (460 vac)
Excessive current draw Circuit Breaker (CB-2, 50 amp) --Manual Reset Trips at 62.5 amps (230 vac)
Circuit Breaker (CB-2, 70 amp) --Manual Reset Trips at 87.5 amps (230 vac)
Excessive current draw in the
control circuit Fuse (F3) 10 amp rating
Excessive current draw by the
controller Fuse (F1 & F2) 5 amp rating
Excessive current draw by the
expansion module Fuse (F4) 10 amp rating
Excessive condenser fan mo-
tor winding temperature Internal Protector (IP-CM) -- Automatic Reset N/A
Excessive compressor motor
winding temperature Internal Protector (IP-CP) -- Automatic Reset N/A
Excessive evaporator fan mo-
tor(s) winding temperature Internal Protector(s) (IP-EM) -- Automatic Reset N/A
Abnormal pressures/tempera-
tures in the high refrigerant
side
Fusible Plug -- Used on the Receiver
Rupture Disc -- Used on the Water-Cooled Con-
denser
93 _C = (200 _F)
35 kg/cm@= (500 psig)
Abnormally high discharge
pressure High Pressure Switch (HPS) Opens at 25 kg/cm@
(350 psig)
T-309
2-9
2.5 REFRIGERATION CIRCUIT
2.5.1 Standard Operation
Starting at the compressor, (see Figure 2-6, upper
schematic) the suction gas is compressed to a higher
pressure and temperature.
Inthestandardmode,boththeeconomizerandunloader
solenoid valves are closed. The gas flows through the
discharge service valve into the oil separator. In the
separator, oil is removedfrom therefrigerant and stored
forreturntothecompressorwhentheoilreturnsolenoid
valveisopenedbythecontroller.Theoilreturnsolenoid
valveisanormallyopenvalvewhichallowsreturnofoil
during the off cycle.
The refrigerant gas continues into the air-cooled
condenser. When operating with the air-cooled
condenser active, air flowing across the coil fins and
tubes cools the gas to saturation temperature. By
removing latent heat, the gas condenses to a high
pressure/high temperature liquid and flows to the
receiver which stores the additional charge necessary
for low temperature operation.
Whenoperatingwiththewatercooledcondenseractive
(see Figure 2-6, lower schematic), the refrigerant gas
passes through the air cooled condenser and enters the
watercooled condensershell. Thewater flowinginside
thetubing coolsthe gas to saturationtemperatureinthe
same manner as the air passing over the air cooled
condenser. The refrigerant condenses on the outside of
the tubes and exits as a high temperature liquid. The
water cooled condenser also acts as a receiver, storing
excess refrigerant.
The liquid refrigerant continues through the liquid line
service valve, the filter-drier (which keeps refrigerant
clean and dry) and the economizer (which is not active
during standard operation) tothe evaporator expansion
valve. As the liquid refrigerant passes through the
variable orifice of the expansion valve, some of it
vaporizes into a gas (flash gas). Heat is absorbed from
the return air by the balance of the liquid, causing it to
vaporize in the evaporator coil. The vapor then flows
through the suction modulation valve to the
compressor.
Theevaporatorexpansionvalveisactivatedbythebulb
strapped to the suction line near the evaporator outlet.
The valve maintains a constant superheat at the coil
outlet regardless of load conditions.
On systems fitted with a water pressure switch, the
condenser fan will be off when there is sufficient
pressure to open the switch. If water pressure drops
below the switch cut out setting, the condenser fan will
be automatically started. When operating a system
fitted with a condenser fan switch, the condenser fan
willbeoffwhentheswitchisplacedinthe“O”position.
The condenser fan will be on when the switch is placed
in the “I” position.
2.5.2 Economized Operation
Intheeconomizedmodethefrozenrangeandpulldown
capacityoftheunitisincreasedbysubcoolingtheliquid
refrigerant entering the evaporator expansion valve.
Overall efficiency is increased because the gas leaving
the economizer enters the compressor at a higher
pressure, therefore requiring less energy to compress it
to the required condensing conditions.
During economized operation, flow of refrigerant
through the main refrigerant system is identical to the
standard mode. (The unloader solenoid valve is
de--energized [closed] by the controller.)
Liquid refrigerant for use in the economizer circuit is
taken from the main liquid line as it leaves the
filter--drier(seeFigure 2-7).Theflowisactivatedwhen
the controller energizes the economizer solenoidvalve.
The liquid refrigerant flows through the economizer
expansion valve and the economizer internal passages
absorbingheatfromtheliquidrefrigerantflowingtothe
evaporator expansion valve. The resultant “medium”
temperature/pressure gas enters the compressor at the
economizer service valve.
2.5.3 Unloaded Operation
The system will operate in the unloaded mode during
periods of low load, during periods of required
discharge pressure or current limiting, and during
start--up.
During unloaded operation, flow of refrigerant through
the main refrigerant system is identical to the standard
mode. (The economizer solenoid valve is de--energized
[closed] by the controller.)
In the unloaded mode, a portion of the mid--stage
compressed gas is bypassed to decrease compressor
capacity. The flow is activated when the controller
opens the unloader solenoid valve (see Figure 2-7.
Opening of the valve creates a bypass from the
economizerservicevalvethroughtheunloadersolenoid
valve and into the suction line on the outlet side of the
suction pressure modulation valve.
Asloadonthesystemdecreases,thesuctionmodulating
valve decreases flow of refrigerant to the compressor.
This action balances the compressor capacity with the
loadandpreventsoperationwithlowcoiltemperatures.
In this mode of operation, the liquid injection solenoid
valve will open as required to provide sufficient liquid
refrigerant flow into the suction line for cooling of the
compressor motor.

2-10T-309
EVAPORATOR
CONDENSER
TXV
TXV BULB SMV
COMPRESSOR
COMPRESSOR
OIL SEPARATOR
ORV
FILTER
DRIER
RUPTURE DISC
WATER COOLED
CONDENSER
OIL RETURN
SERVICE VALVE
ORV
DPT
CPDS
DISCHARGE
SERVICE
CONNECTION
HPS
ECONOMIZER
SERVICE
CONNECTION
SPT
SUCTION SERVICE
CONNECTION
QUENCH
TXV
BULB
CPSS
STANDARD OPERATION WITH RECEIVER
STANDARD OPERATION WITH WATER COOLED CONDENSER
STS
DPT
CPDS
RECEIVER
FUSIBLE PLUG SIGHT GLASS
MOISTURE INDICATOR
LIQUID LINE
SERVICE
CONNECTION
FILTER
DRIER
ECONOMIZER
TXV
ESV
ECONOMIZER
ECONOMIZER TXV BULB
HPS
OIL RETURN
SERVICE VALVE
DISCHARGE
SERVICE
CONNECTION
SPT
SUCTION SERVICE
CONNECTION
USV
LOW SIDE ACCESS VALVE
DISCHARGE LIQUID SUCTION
ESV
ECONOMIZER
TXV
LIQUID LINE
SERVICE
CONNECTION
SIGHTGLASS/
MOISTURE INDICATOR
ECONOMIZER
SERVICE
CONNECTION
ECONOMIZER
LIV
EVAPORATOR
CONDENSER
TXV
TXV BULB SMV
ECONOMIZER TXV BULB
USV
LOW SIDE ACCESS VALVE
LIV
Figure 2-6 Refrigeration Circuit Schematic -- Standard Operation

T-309
2-11
LIQUID ECONOMIZER PRESSURE
ECONOMIZER
ECONOMIZER
SERVICE
CONNECTION
ESV
ECONOMIZER
TXV
LIQUID LINE
SERVICE CONNECTION
OIL SEPARATOR
RECEIVER
EVAPORATOR
CONDENSER
TXV
TXV BULB SMV
ECONOMIZER TXV BULB
LOW SIDE ACCESS VALVE
LIV
Figure 2-7 Refrigeration Circuit Schematic -- Economized Operation
LIQUID ECONOMIZER PRESSURE
TXV
TXV BULB SMV
SUCTION SERVICE
CONNECTION
USV
SUCTION
OIL SEPARATOR
RECEIVER
ECONOMIZER TXV BULB
LIV
Figure 2-8 Refrigeration Circuit Schematic -- Unloaded Operation

3-1 T-309
SECTION 3
MICROPROCESSOR
3.1 TEMPERATURE CONTROL MICROPRO-
CESSOR SYSTEM
The temperature control Micro-Link 2i microprocessor
system (see Figure 3- 1) consists of a key pad, display
module, the control module & expansion module set
(controller) and interconnecting wiring. The controller
houses the temperature control software and the
DataCORDER Software. The temperature control
software functions to operate the unit components as
required to provide the desired cargo temperature and
humidity. The DataCORDER software functions to
record unit operatingparameters and cargotemperature
parameters for future retrieval. Coverage of the
temperaturecontrolsoftwarebeginswithparagraph3.2.
Coverageof the DataCORDER software is provided in
paragraph 3.6.
The key pad and display module serve to provide user
accessandreadouts forbothofthe controllerfunctions,
temperature control and DataCORDER. The functions
are accessed by key pad selections and viewed on the
displaymodule.Thecomponentsaredesignedtopermit
ease of installation and removal.
TO
DISPLAY
CONTROL MODULE DISPLAY MODULE
KEY PAD
CONFIGURATION
SOFTWARE
CONFIGURATION
VARIABLE
(CnF##)
TEMPERATURE CONTROL SOFTWARE
ALARMS
(AL<70) PRE--TRIP INTERROGATION
CONNECTOR
DATAREADER
Computer Device
With DataLine
Software
DataCORDER SOFTWARE
OPERATIONAL
SOFTWARE
FUNCTION
CODE (Cd)
TO
DISPLAY
CONFIGURATION
SOFTWARE
CONFIGURATION
VARIABLE
(dCF## read only)
ALARMS
(AL>69) DATA
STORAGE
MEMORY
OPERATIONAL
SOFTWARE
FUNCTION
CODE (dC) TO
DISPLAY
(Scrollback)
EXPANSION MODULE
C
O
N
T
R
O
L
L
E
R
Figure 3- 1 Temperature Control System

3-2T-309
3.1.1 Key Pad
The key pad (Figure 3- 2) is mountedon the right-hand
side of the control box. The key pad consists of eleven
pushbuttonswitchesthatactastheuser’sinterfacewith
the controller. Descriptions of the switch functions are
provided in Table 3-1.
ENTER
BATTERY
POWER
DEFROST
INTERVAL
CODE
SELECT PRE
TRIP
ALARM
LIST
ALT.
MODE
RETURN
SUPPLY _C
_F
Figure 3- 2 Key Pad
COOL HEAT DEFROST IN RANGEALARM SUPPLY RETURN
SETPOINT/Code AIR TEMPERATURE/Data
Figure 3- 3 Display Module
3.1.2 Display Module
The display module (Figure 3- 3) consists of two
backlightedfivedigitLCDdisplaysandsevenindicator
lights. The indicator lights include:
1. Cool -- White LED: Energized when the refrigerant
compressor is energized.
2. Heat--OrangeLED:Energizedtoindicateheaterop-
eration in the heat or defrost mode.
3. Defrost--OrangeLED:Energizedwhentheunitisin
the defrost mode.
4. In-Range -- Green LED: Energized when the con-
trolled temperature probe is within specified toler-
ance of set point.
Table 3-1 Key Pad Function
KEY FUNCTION
Code Select Accesses function codes.
Pre-Trip Displays the pre-trip selection menu. Dis-
continues pre-trip in progress.
Alarm List Displays alarm list and clears the alarm
queue.
Defrost
Interval Displays selected defrost interval.
Enter Confirms a selection or saves a selection
to the controller.
Arrow Up Change or scroll a selection upward Pre-
trip advance or test interruption.
Arrow
Down Change or scroll a selection downward.
Pre-trip repeat backward.
Return/
Supply Displays non-controlling probe tempera-
ture (momentary display).
_C/_F
Displays alternate English/Metric scale
(momentary display). When set to _F,
pressure is displayed in psig and vacuum
in “/hg. “P” appears after the value to in-
dicate psig and “i” appears for inches of
mercury.
When set to _C. pressure readings are in
bars. “b” appears after the value to indi-
cate bars.
Battery
Power Initiate battery backup mode to allow set
point and function code selection if AC
power is not connected.
ALT Mode
This key is pressed to switch the functions
from the temperature software to the Da-
taCORDER Software. The remaining keys
function the same as described above ex-
cept the readings or changes are made to
the DataCORDER programming..
NOTE
The controlling probe in the perishable range
will be the SUPPLY air probe and the control-
ling probe in the frozen range will be the
RETURN air probe.
5. Supply--YellowLED:Energizedwhenthesupplyair
probe is used for control. When this LED is illumi-
nated, the temperature displayed inthe AIR TEMPER-
ATURE display is the reading at the supply air probe.
This LEDwill flash if dehumidification orhumidifi-
cation is enabled.
6. Return--YellowLED:Energizedwhenthereturnair
probe is used for control. When this LED is illumi-
nated, the temperature displayed in the AIR TEM-
PERATUREdisplayisthereadingatthereturnairpro-
be. This LED will flash if dehumidification or
humidification is enabled.
7. Alarm-- RedLED:Energizedwhenthereis anactive
or an inactive shutdown alarm in the alarm queue

3-3 T-309
8
12 33 3 3 345 67
1333 3 3
9
1. Mounting Screw
2. Micro-Link 2i Control/DataCORDER Module
3. Connectors
4. Test Points
5. Fuses
6. Control Circuit Power Connection
(Location: In back of controller)
7. Software Programming Port
8. Battery Pack
9. Expansion Module
Figure 3- 4 Control and Expansion Modules
3.1.3 Controller
CAUTION
Do not remove wire harnesses from control-
ler modules unless you are grounded to the
unit frame with a static safe wrist strap.
CAUTION
Unplug all controller module wire harness
connectors before performing arc welding
on any part of the container.
NOTE
Do not attempt to service the controller mod-
ules. Breaking the seal will void the warranty.
The Micro--Link 2i controller is a dual module
microprocessorasshowninFigure 3- 4.Itisfittedwith
test points, harness connectors and a software card
programming port.
3.2 CONTROLLER SOFTWARE
The controller software is a custom designed program
that is subdivided into the Configuration Software and
the Operational Software. The controller software
performs the following functions:
a. Control supply or return air temperature to required
limits, provide modulated refrigeration operation,
economized operation, unloaded operation, electric
heatcontrolanddefrost.Defrostisperformedtoclear
build up of frost and ice and ensure proper air flow
across the coil.
b. Providedefaultindependentreadoutsofsetpointand
supply or return air temperatures.
c. Provideability to read and (if applicable) modify the
Configuration Software Variables, Operating Soft-
ware Function Codes and Alarm Code Indications.
d. ProvideaPre-Tripstep-by-stepcheckoutofrefrigera-
tion unit performance including: proper component
operation, electronicand refrigeration control opera-
tion, heater operation, probe calibration, pressure
limiting and current limiting settings.
e. Provide battery powered ability to access or change
selected codes and set point without AC power con-
nected
f. Providetheabilitytoreprogramthesoftwarethrough
theuseofamemorycard.Thememorycardautomat-
icallydownloadsnewsoftwaretothecontrollerwhen
inserted.
3.2.1 Configuration Software (Configuration Vari-
ables)
The Configuration Software is a variable listing of the
components available for use by the Operational
Software. This software is factory installed in
accordancewiththeequipment fitted and options listed
on the original purchase order. Changes to the
Configuration Software are required only when a new
controller hase been installed or a physical change has
beenmadetotheunitsuchastheadditionorremovalof
an option. A Configuration Variable list is provided in
Table 3-4. Change to the factory installed
Configuration Software is achieved via a configuration
card or communications.
3-4T-309
3.2.2 Operational Software (Function codes)
The Operational Software is the actual operation
programming of the controller which activates or
deactivatescomponentsinaccordancewithcurrentunit
operating conditions and operator selected modes of
operation.
TheprogrammingisdividedintofunctionCodes.Some
of the codes are read only while the remaining codes
may be user configured. The value of the user
configurable codes can be assigned in accordance with
user desired mode of operation. A list of the function
codes is provided in Table 3-5.
To access the function codes, perform the following:
a. Press the CODE SELECT key, then press an arrow
key until the left window displays the desired code
number.
b. The right window will display the value of this item
for five seconds before returning to the normal dis-
play mode.
c. If a longer time is desired, press the ENTER key to
extend the time to 30 seconds.
3.3 MODES OF OPERATION
The Operational Software responds to various inputs.
These inputs come from the temperature and pressure
sensors,thetemperaturesetpoint,thesettingsofthethe
configuration variables and the function code
assignments. The action taken by the Operational
Software will change if any one of the inputs changes.
Overall interaction of the inputs is described as a
“mode” of operation. The modes of operation include,
perishable (chill) mode and frozen mode. Descriptions
of the controller interaction and modes ofoperation are
provided in the following sub paragraphs.
3.3.1 Temperature Control -- Perishable Mode
With configuration variable CnF26 (Heat Lockout
Temperature) set to --10_C the perishable mode of
operation is active with set points at or above --10_C
(+14_F). With the variable set to --5_C, the perishable
mode is active at or above --5_C(+23_F). Refer to
Table 3-4.
When in the perishable mode the controller maintains
the supply air temperature at set point, the SUPPLY
indicatorlightwillbeilluminatedonthedisplaymodule
and the default reading on the display window will be
the supply temperature sensor reading.
When the supply air temperature enters the in-range
temperature tolerance (as selected at function code
Cd30), the in-range light will energize.
3.3.2 Defrost Interval
Function code Cd27 may be operator set to initiate
defrostatintervalsof3,6,9, 12or24hours.Itmayalso
be set to OFF (no defrost). The factory default is 12
hours. (Refer to Table 3-5).
3.3.3 Failure Action
Function code Cd29 may be operator set to allow
continued operation in the event the control sensorsare
reading out of range. The factory default is full system
shutdown. (Refer to Table 3-5).
3.3.4 Generator Protection
Function codes Cd31(Stagger Start, Offset Time) and
Cd32 (Current Limit) may be operator set to control
startupsequenceofmultipleunitsandoperatingcurrent
draw.Thefactorydefaultallowsondemandstarting(no
delay) of units and normal current draw. Refer to
Table 3-5.
3.3.5 Compressor High Temperature, Low Pres-
sure Protection.
The controller monitors compressor suction and
discharge temperatures and pressures. If the discharge
temperature exceeds a certain limit, the liquidinjection
valve is opened to provide sufficient liquid refrigerant
flow into the economizer line to reduce the discharge
temperature. If the liquid injection is unable to reduce
the discharge temperature sufficiently and the
temperature exceeds the allowed limit, the compressor
will cycleoff ona 3 minute timer. The compressor will
alsocycleoffinasimilarmannerifthesuctionpressure
fallsbelowtheallowedlimit.Condenserandevaporator
fans continue to operate during the compressor off
cycle.
3.3.6 Perishable Mode -- Conventional
The unit is capable of maintaining supply air
temperatureto within ¦0.25_C(¦0.5_F) ofset point.
Supply air temperature is controlled by positioning of
the suction modulation valve (SMV), cycling of the
compressor and cycling of the heaters.
When cooling from a temperature that is more than
2.5_C (4.5_F)abovesetpoint,thesystemwillbe in the
perishable pull down mode. It will be in economized
operation with a target SMV position of 100% open.
However, pressure and current limit functions may
restrict the valve, if either exceeds the preset value.
Once set point is reached, the unit will transition to the
perishable steady state mode. This results in unloaded
operation with some restriction of the SMV. TheSMV
will continue to close and restrict refrigerant flow until
the capacity of the unit and the load are balanced.
If the SMV is at minimum modulation, the controller
has determined that cooling is not required, or the
controllerlogicdeterminessuctionpressureisatthelow
pressure limit, the unit will transition to the perishable
idle mode. The compressor is turned off and the
evaporator fans continue to run to circulate air
throughout the container. If temperature rises above set
point +0.2_C, the unit will transition back to the
perishable steady state mode
If the temperature drops to 0.5_C (0.9_F) below set
point, the unit will transition to the perishable heating
3-5 T-309
mode and the heaters will be energized . The unit will
transition back to the perishable idle mode when the
temperature rises to 0.2_C (0.4_F) below the set point
and the heaters will de-energize
3.3.7 Perishable Mode -- Economy
The economy mode is an extension oftheconventional
mode. The mode is activated when the setting of
function code Cd34 is “ON”. Economy mode is
provided for power saving purposes. Economy mode
could be utilized in the transportation of temperature
tolerant cargo or non-respiration items which do not
require high airflow for removing respiration heat.
Thereis noactivedisplayindicatorthat economymode
has been activated. To check for economy mode,
perform a manual display of code Cd34.
In order to achieve economy mode, a perishable set
point must be selected prior to activation. When
economy mode is active, the evaporator fans will be
controlled as follows:
At the start of each cooling or heating cycle, the
evaporator fans will be run in high speed for three
minutes. They will then be switched to low speed any
time the supply air temperature is within ¦0.25_C
(0.45_F)ofthesetpointandthereturnairtemperatureis
less than or equal to the supply air temperature + 3_C
(5.4_F). The fans will continue to run in low speed for
onehour.Attheendofthehour,theevaporatorfanswill
switchbacktohighspeedandthecyclewillberepeated.
If bulb modeis active, the economy fan activity will be
overwritten.
3.3.8 Perishable Mode -- Dehumidification
The dehumidification mode is provided to reduce the
humidity levels inside the container. The mode is
activated when a humidity value is set at at function
code Cd33.The displaymodule SUPPLYled willflash
ON and OFF every second to indicate that the
dehumidification mode is active. Once the Mode is
active and the following conditions are satisfied, the
controller will activate the heat relay to begin
dehumidification.
1. The humidity sensor reading is above the set point.
2. The unit is in the perishable steady state mode and
supply airtemperature isless than 0.25_C aboveset
point.
3. Theheaterdebouncetimer(threeminutes)hastimed
out.
4. Heater termination thermostat (HTT) is closed.
If theaboveconditions are truetheevaporator fans will
switch from high to low speed operation. The
evaporatorfanspeedwillswitcheveryhourthereafteras
long as all conditions are met (see Bulb Mode section
for different evaporator fan speed options). If any
condition except for item (1) becomes false OR if the
relative humidity sensed is 2% below the
dehumidification set point, the high speed evaporator
fans will be energized.
In the dehumidification mode power is applied to the
defrost and drain pan heaters. This added heat load
causes the controller to open the suction modulating
valve to match the increased heat load while still
holding the supply airtemperaturevery closeto the set
point.
Opening the modulating valvereduces the temperature
oftheevaporatorcoilsurface,whichincreasestherateat
which water is condensed from the passing air.
Removing water from the air reduces the relative
humidity. When the relative humidity sensed is 2%
belowthesetpoint, thecontrollerde-energizestheheat
relay. The controller will continue to cycle heating to
maintainrelativehumiditybelowtheselectedsetpoint.
If the mode is terminated by a condition other than the
humidity sensor, e.g., an out-of-range or compressor
shutdown condition, the heat relay is de-energized
immediately.
Two timers are activated in the dehumidificationmode
toprevent rapidcyclingandconsequent contactorwear.
They are:
1. Heater debounce timer (three minutes).
2. Out-of-range timer (five minutes).
The heater debounce timer is started whenever the
heater contactor status is changed. The heat contactor
remains energized (or de-energized) for at least three
minutes even if the set point criteria are satisfied.
The out-of-range timer is started to maintain heater
operationduring atemporaryout-of-rangecondition.If
the supply air temperature remains outside of the user
selectedin-rangesettingformorethanfiveminutes,the
heaters will be de-energized to allow the system to
recover. The out-of-range timer starts as soon as the
temperature exceeds thein-range tolerance value set by
function code Cd30.
3.3.9 Perishable, Dehumidification -- Bulb Mode
Bulb mode is an extension of the dehumidification
modewhichallowschangestotheevaporatorfanspeed
and/or defrost termination set points.
Bulb mode is active when configuration code Cd35 is
set to “Bulb”. Once the bulb mode is activated, the user
maythenchangethedehumidificationmodeevaporator
fan operation from the default (speed alternates from
low to high each hour) to constant low or constant high
speed. This is done by toggling function code Cd36
fromitsdefaultof“alt”to“Lo”or“Hi”asdesired.Iflow
speedevaporatorfanoperationisselected,thisgivesthe
user the additional capability of selecting
dehumidification set points from 60 to 95% (instead of
the normal 65 to 95%).
In addition, if bulb modeis active, function codeCd37
may be set to override theprevious defrosttermination
thermostat settings. (Refer to paragraph 4.9.5.) The
temperatureatwhichthedefrostterminationthermostat
will be considered “open” may be changed [in 0.1_C
(0.2_F) increments] to any value between 25.6_C
(78_F)and4_C(39.2_F).Thetemperatureatwhichthe
defrost termination thermostat is considered closed for
interval timer start or demand defrost is 10_Cfor
“open” values from 25.6_C(78_F) down to a 10_C
setting. For “open” values lower than 10_C, the
“closed” values will decrease to the same value as the
“open” setting. Bulb mode is terminated when:
3-6T-309
1. Bulb mode code Cd35 is set to “Nor.”
2. Dehumidification code Cd33 is set to “Off.”
3. The user changes the set point to one
that is in the frozen range.
When bulb mode is disabled by any of the above, the
evaporatorfanoperationfordehumidificationrevertsto
“alt”andtheDTSterminationsettingresetstothevalue
determinedbycontrollerconfigurationvariableCnF41.
3.3.10 Temperature Control -- Frozen Mode
With configuration variable CnF26 (Heat Lockout
Temperature)setto--10_Cthefrozenmodeofoperation
is active with set points at or below --10_C(+14_F).
Withthevariablesetto --5_C,the frozenmodeis active
at or below --5_C(+23_F).
When in the frozen mode the controller maintains the
return air temperature at set point, the RETURN
indicatorlightwillbeilluminatedonthedisplaymodule
and the default reading on the display window will be
the return air probe reading.
When the return air temperature enters the in-range
temperature tolerance as selected at function code
Cd30, the in-range light will energize.
3.3.11 Frozen Mode -- Conventional
Frozen range cargos are not sensitive to minor
temperature changes. The method of temperature
control employed in this range takes advantage of this
facttogreatlyimprovetheenergyefficiencyoftheunit.
Temperaturecontrolinthefrozenrangeisaccomplished
bycyclingthecompressoronandoffastheloaddemand
requires.
When cooling from a temperature that is more than
2.5_C (4.5_F)abovesetpoint,thesystemwillbe in the
frozenpulldownmode.Itwilltransitiontoeconomized
operation with a target SMV position of 100% open.
However, pressure and current limit functions may
restrict the valve, if either exceeds the preset value.
Once set point is reached, the unit will transition to the
frozen steady state mode. (Economized operation with
maximum allowed suction modulating valve opening.)
When temperature drops to set point minus 0.2_Cand
thecompressorhasrunforatleastfiveminutes,theunit
will transition to the frozen idle mode. The compressor
is turned off and the evaporator fans continue to run to
circulate air throughout the container. If temperature
rises above set point +0.2_C, the unit will transition
back to the frozen steady state mode.
If the temperaturedrops 10_C below set point, the unit
will transition to the frozen “heating” mode. In the
frozen heating mode the evaporator fansare broughtto
high speed. The unit will transition back to the frozen
steadystatemodewhenthetemperaturerisesbacktothe
transition point.
3.3.12 Frozen Mode -- Economy
In order to activate economy frozen mode operation, a
frozen set point temperature must be selected. The
economymodeisactivewhenfunctioncodeCd34isset
to “ON”. When economy mode frozen is active, the
system will perform normal frozen mode operations
except that the entire refrigeration system, excluding
the controller, will be turned off when the control
temperature is less than or equal to the set point -- 2_C.
After an off-cycle period of 60 minutes, the unit will
turn on high speed evaporator fans for three minutes,
and then check the control temperature. If the control
temperature is greater than or equal to the set point +
0.2_C.,theunitwillrestarttherefrigerationsystemand
continue to cool until the previously mentioned
off-cycle temperature criteria are met. If the control
temperature is less than the set point + 0.2_C, the unit
will turn off the evaporator fans and restart another 60
minute off-cycle.
3.4 CONTROLLER ALARMS
Alarm display is an independent controller software
function. If an operating parameter is outside of
expected range or a components does not return the
correct signals back to the controller an alarm is
generated. A listing of the alarms is provided in
Table 3-6.
The alarm philosophy balances the protection of the
refrigeration unit and that of therefrigerated cargo.The
action taken when anerror is detected always considers
thesurvivalofthecargo.Rechecksaremadetoconfirm
that an error actually exists.
Somealarmsrequiringcompressorshutdownhavetime
delays beforeand afterto try to keepthe compressoron
line. An example is alarm code “LO”, (low main
voltage), when a voltage drop of over 25% occurs, an
indication is given on the display, but the unit will
continue to run.
When an Alarm Occurs:
a. The red alarm light will illuminate for alarm code
numbers 13, 17, 20, 21, 22, 23, 24, 25, 26, and 27.
b. If a detectable problem is found to exist, its alarm
code will be alternately displayed with the set point
on the left display.
c. Theusershould scrollthroughthealarmlisttodeter-
minewhatalarms existor haveexisted. Alarmsmust
bediagnosedandcorrectedbeforetheAlarmListcan
be cleared.
To Display Alarm Codes :
a. While in the Default Display mode, press the
ALARMLISTkey.ThisaccessestheAlarmListDis-
playMode,whichdisplaysanyalarmsarchivedinthe
Alarm Queue.
b. The alarm queue stores up to 16 alarms in the se-
quence in which they occurred. The user may scroll
through the list by depressing an ARROW key.
c. The left display will show “AL##,” where ## is the
alarm number sequentially in the queue.
d. The right display will show the actual alarm code.
“AA##” will display for an active alarm, where“##”
isthealarmcode. Or“IA##”will displayfor an inac-
tive alarm. See Table 3-6.
3-7 T-309
e. “END” is displayed to indicate the end of the alarm
list if any alarms are active.
f. “CLEAr” is displayed if all alarms are inactive. The
alarmqueuemaythanbeclearedbypressingtheEN-
TER key. The alarm list will clear and “-- -- -- -- --”
will be displayed.
3.5. UNIT PRE-TRIP DIAGNOSTICS
Pre--Trip Diagnostics is an independent controller
function which will suspend normal refrigeration
controller activities and provide preprogrammed test
routines. The test routines include Auto Mode testing,
which automatically preforms a pre programmed
sequenced of tests, or Manual Mode testing, which
allows the operator to select and run any of the
individual tests. CAUTION
Pre-tripinspectionshouldnotbeperformed
with critical temperaturecargoes in thecon-
tainer. CAUTION
When Pre-Trip key is pressed, economy, de-
humidification and bulb mode will be deac-
tivated. AtthecompletionofPre-Tripactivi-
ty, economy, dehumidification and bulb
mode must be reactivated.
Testing may be initiated by use of the Key Pad or via
communication, but when initiated by communication
the controller will execute the entire battery of tests
(auto mode).
At the end of a pre-trip test, the message “P,” “rSLts”
(pretestresults)will be displayed. Pressing theENTER
keywillallowtheusertoseethe resultsforallsubtests.
The results will be displayed as “PASS” or “FAIL” for
all the tests run to completion.
Adetaileddescriptionofthepre-triptestsandtestcodes
isprovidedin Table 3-7.detailedoperatinginstructions
are provided in paragraph 4.7.
3.6 DataCORDER
3.6.1 Description
The Carrier Transicold “DataCORDER,” software is
integratedintothecontrollerandservesto eliminatethe
temperature recorder and paper chart. The
DataCORDER functions may be accessed by key pad
selectionsandviewedonthedisplaymodule.Theunitis
also fitted with interrogation connections (see
Figure 3- 1) which may be used with the Carrier
Transicold Data Reader to down load data. A personal
computer with Carrier Transicold Data View software
may also be used to download data and configure
settings. The DataCORDER consists of:
Configuration Software
Operational Software
Data Storage Memory
Real Time Clock (with internal battery backup)
Six thermistor inputs
Interrogation Connections
Power supply (battery pack).
The DataCORDER performs the following functions:
a. Logs data at 15, 30, 60 or 120 minute intervals and
storestwoyears’ofdata(basedononehourinterval).
b. Records and displays alarms on the display module.
c. Records results of pre--trip testing.
d. RecordsDataCORDERandtemperaturecontrolsoft-
ware generated data and events as follows:
Container ID Change
Software Upgrades
Alarm Activity
Battery Low (Battery Pack)
Data Retrieval
Defrost Start and End
Dehumidification Start and End
Power Loss (w/wo battery pack)
Power Up (w/wo battery pack)
Remote Probe Temperatures in the Container
(USDA Cold treatment and Cargo probe recording)
Return Air Temperature
Set Point Change
Supply Air Temperature
RealTimeClockBattery(InternalBattery)Replace-
ment
Real Time Clock Modification
Trip Start
ISO Trip Header (When entered via Interrogation
program)
Economy Mode Start and End
“Auto 2” Pre-Trip Start and End
Bulb Mode Start
Bulb Mode changes
Bulb Mode End
USDA Trip Comment
Humidification Start and End
USDA Probe Calibration
3.6.2 DataCORDER Software
The DataCORDER Software is subdivided into the
Configuration Software, Operational Software and the
Data Memory.
a. Operational Software
The Operational Software reads and interprets inputs
for use by the Configuration Software. The inputs are
labeled Function Codes. There are 35 functions (see
Table 3-8) which the operator may access to examine
the current input data or stored data. To access these
codes, do the following:
1 Press the ALT. MODE & CODE SELECT keys.
2 Press an arrowkey until theleftwindow displaysthe
desired code number. The right window will display
the value of this item for five seconds before return-
ing to the normal display mode.
3 If a longer time is desired, press the ENTER key to
extend the time to 30 seconds.

3-8T-309
Table 3-2 DataCORDER Configuration Variables
CONFIGURATION NO. TITLE DEFAULT OPTION
dCF01 (Future Use) -- -- -- --
dCF02 Sensor Configuration 2 2,5,6,9,54,64,94
dCF03 Logging Interval (Minutes) 60 15,30,60,120
dCF04 Thermistor Format Short Low, Normal
dCF05 Thermistor Sampling Type AA,b,C
dCF06 Controlled Atmosphere/Humidity Sampling Type AA,b
dCF07 Alarm Configuration USDA Sensor 1 AAuto, On, Off
dCF08 Alarm Configuration USDA Sensor 2 AAuto, On, Off
dCF09 Alarm Configuration USDA Sensor 3 AAuto, On, Off
dCF10 Alarm Configuration Cargo Sensor AAuto, On, Off
b. Configuration Software
The configuration software controls the recording and
alarmfunctionsoftheDataCORDER.Reprogramming
tothefactoryinstalledconfigurationisachievedviathe
same configuration card as the unit control module
software. Changes to the unit DataCORDER
configuration may be made made using the Data View
integration device. A listing of the configuration
variables is provided in Table 3-2. Descriptions of
DataCORDER operation for each variable setting are
provided in the following paragraphs.
3.6.3 Sensor Configuration (dCF02)
Two modes of operation may be configured, the
Standard Mode and the Generic Mode.
a. Standard Mode
In the standard mode, the user may configure the
DataCORDER to record data using one of seven
standard configurations. Standard configuration
variables, with descriptions, are listed in Table 3-3.
Thesixthermistorinputs(supply,return,USDA#1,#2,
#3 and cargo probe) and thehumidity sensor input will
be generated by the DataCORDER. An example of a
report using a standard configuration is shown in
Figure 3- 5.
NOTE
The DataCORDER software uses the supply
and return recorder sensors (SRS,RRS). The
temperature control software uses the supply
and return temperature sensors (STS,RTS) .
b. Generic Mode
Thegenericrecordingmodeallowsuserselection ofthe
network data points to be recorded. The user may select
up to a total of eight data points for recording. A listof
the data points available for recording follows.
Changing the configuration to generic and selecting
which data points to record may be done using the
Carrier Transicold Data Retrieval Program.
1. Control mode
2. Control temperature
3. Frequency
4. Humidity
5. Phase A current
6. Phase B current
7. Phase C current
8. Main voltage
9. Suction modulation valve percentage
10. Discrete outputs (Bit mapped -- require special
handling if used)
11. Discrete inputs (Bit mapped -- require special
handling if used)
12. Ambient sensor
13. Compressor suction sensor
14. Compressor discharge sensor
15. Return temperature sensor
16. Supply temperature sensor
17 Defrost temperature sensor
18. Discharge pressure transducer
19. Suction pressure transducer
20. Condenser pressure transducer
Table 3-3 DataCORDER Standard Configurations
Standard
Config. Description
2sensors
(dCF02=2) 2 thermistor inputs(supply & return)
5sensors
(dCF02=5) 2 thermistor inputs(supply & return)
3 USDA thermistor inputs
6sensors
(dCF02=6) 2 thermistor inputs(supply & return)
3 USDA thermistor inputs
1 humidity input
9sensors
(dCF02=9) Not Applicable
6sensors
(dCF02=54) 2 thermistor inputs(supply & return)
3 USDA thermistor inputs
1 cargo probe (thermistor input)
7sensors
(dCF02=64)
2 thermistor inputs(supply & return)
3 USDA thermistor inputs
1 humidity input
1 cargo probe (thermistor input)
10 sensors
(dCF02=94)
2 thermistor inputs(supply & return)
3 USDA thermistor inputs
1 humidity input
1 cargo probe (thermistor input)
3 C.A. inputs (NOT APPLICABLE)

3-9 T-309
Raw Data Report for ABC1234567
May 31, 2001 to Jun 04, 2001
System Configuration at the Time of Interrogation:
Interrogated On Sept05, 2001
Extracted by DataLine Rev 1.0.0
Controller Software: 5120
Controller Serial #: 04163552
Bill of Lading #: 1
Origin: Origin Date:
Destination: Discharge Date:
Comment: DataLine Tool
Probe Calibration Readings: USDA1: 0.0 USDA2: 0.0 USDA3: 0.0 Cargo: 0.0
Temperature Units: Centigrade
________________________________________________________________________________________
May 31, 2001
Setpoint: 1.66, Container : Serial : 04189552
9 Sensors Logged at 15 Minute Interval
Sensor Format Resolution
Figure 3- 5 Standard Configuration Download Report
3-10T-309
3.6.4 Logging Interval (dCF03)
The user may select four different time intervals
between data recordings. Data is logged at exact
intervals in accordance with the real time clock. The
clock is factory set at Greenwich Mean Time (GMT).
3.6.5 Thermistor Format (dCF04)
The user may configure the format in which the
thermistorreadingsarerecorded.Theshortresolutionis
a1byteformatandthelongresolutionisa2byteformat.
Theshortrequireslessmemoryandrecordstemperature
in0.25°C(0.45°F)stepswhenintheperishablemodeor
0.5°C (0.9°F) steps when in the frozen mode. The long
records temperature in 0.01°C (0.02°F) steps for the
entire range.
3.6.6 Sampling Type (dCF05 & dCF06)
Three types of data sampling are available, average,
snapshot and USDA. When configured to average, the
average of readings taken every minute over the
recording period is recorded. When configured to
snapshot, the sensor reading at the log intervale timeis
recorded. When USDA is configured the supply and
return temperature readings are averaged and the 3
USDA probe readings are snapshot.
3.6.7 Alarm Configuration (dCF07 -- dCF10)
The USDA and cargo probe alarms may be configured
to OFF, ON or AUTO.
IfaprobealarmisconfiguredtoOFF,thenthealarmfor
this probe is always disabled.
IfaprobealarmisconfiguredtoON,thentheassociated
alarm is always enabled.
If the probes are configured to AUTO, they act as a
group. This function is designed to assist users who
keep their DataCORDER configured for USDA
recording, but do not install the probes forevery trip.If
all the probes are disconnected, no alarms areactivated.
As soon asone of theprobes is installed, thenall ofthe
alarmsareenabledandtheremainingprobesthatarenot
installed will give active alarm indications.
The DataCORDER will record the initiation of a
pre-trip test (refer to paragraph 3.5) and the results of
each of the tests included in pre--trip. The data is
time-stamped and may be extracted via the Data
Retrieval program. Refer to Table 3-9 for a description
of the data stored in the DataCORDER for each
corresponding Pre-Trip test.
3.6.8 DataCORDER Power-Up
The DataCORDER may be powered up in any one of
four ways:
1. Normal AC power: The DataCORDER is powered
up when the unit is turned on via the stop-start switch.
2. ControllerDCbatterypackpower:Ifabatterypack
is installed, the DataCORDER will power up for
communication when an interrogation cable is plugged
into an interrogation receptacle.
3. External DC battery packpower: A 12 volt battery
pack may also be plugged into the back of the
interrogation cable, which is then plugged into an
interrogation port. No controller battery pack is
required with this method.
4. Real Time Clock demand: If the DataCORDER is
equipped with a charged battery pack and AC power is
not present, the DataCORDER will power up when the
real time clock indicates that a data recording should
take place. When the DataCORDER is finished
recording, it will power down.
During DataCORDER power-up, while using
battery-pack power, the controller will perform a
hardware voltage check on the battery. If the hardware
checkpasses,theController willenergizeandperforma
software battery voltage check before DataCORDER
logging. If either test fails, the real time clock battery
power-up will be disabled until the next AC power
cycle. Further DataCORDER temperature logging will
be prohibited until that time.
An alarm will be generated when the battery voltage
transitions from good to bad indicating that the battery
pack needs recharging. If the alarm condition persists
for more than 24 hours on continuous AC power, the
battery pack needs replacement.
3.6.9 Pre-Trip Data Recording
The DataCORDER will record the initiation of a
pre-trip test (refer to paragraph 3.5) and the results of
each of the tests included in pre--trip. The data is
time-stamped and may be extracted via the Data
Retrieval program. Refer to Table 3-9 for a description
of the data stored in the DataCORDER for each
corresponding Pre-Trip test.
3.6.10 DataCORDER Communications
Data retrieval from the DataCORDER can be
accomplished by using one of the following;
DataReader, DataLine/DataView or a communications
interface module.
a. DataReader
The Carrier Transicold Data Reader (see Figure 3- 6)is
asimpletooperatehandhelddevicedesignedtoextract
data from the DataCORDER and then upload it to a
personal computer. The Data Reader has the ability to
storemultipledatafiles.RefertoDataRetrievalmanual
62-02575 for a more detailed explanation of the
DataReader

3-11 T-309
DataReader
Figure 3- 6 Data Reader
b. DataView
The DataView software for a personal computer is
supplied on a floppy disk. This software allows
interrogation, configuration variable assignment,
screen view of the data, hard copy report generation,
cold treatment probe calibration, cold treatment
initialization and file management. Refer to Data
Retrieval manual 62-02575 for a more detailed
explanation of the DataView interrogation software.
c. Communications Interface Module
The communications interface module is a slave
module which allows communication with a master
central monitoring station. The module will respondto
communication and return information over the main
power line.
With a remote monitoring unit installed, all functions
andselectablefeaturesthatareaccessibleattheunitmay
be performed at the master station. Retrieval of all
DataCORDER reportsmay also beperformed. Referto
the master system technical manual for further
information.
d. DataLine
The DataLINE software for a personal computer is
supplied on both floppy disks and CD. This software
allows interrogation, configuration variable
assignment, screen view of the data, hard copy report
generation, cold treatment probe calibration and file
management.RefertoDataRetrievalmanual62-10629
for a more detailed explanation of the DataLINE
interrogation software. The DataLine manual may be
found on the net at www.contaner.carrier.com
3.6.11 USDA Cold Treatment
Sustained cold temperature has been employed as an
effective postharvest method for the control of
Mediterranean and certain other tropical fruit flies.
Exposing infested fruit to temperatures of 2.2 degrees
Celsius (36_F) or below for specific periods results in
the mortality of the various stages of this group of
insects.
In response to the demand to replace fumigation with
this environmentally sound process, Carrier has
integrated Cold Treatment capability into its
microprocessor system. These units have the ability to
maintain supply air temperature within one-quarter
degreeCelsiusofsetpointandrecordminutechangesin
product temperature within the DataCORDER
memory, thus meeting USDA criteria. Information on
USDA is provided in the following subparagraphs
a. USDA Recording
A special type of recording is used for USDA cold
treatment purposes. Cold treatment recording requires
threeremotetemperatureprobesbeplacedatprescribed
locations in the cargo. Provision is made to connect
these probes to the DataCORDER via receptacles
locatedat therearleft-handsideoftheunit.Fourorfive
receptacles are provided. The four three-pin receptacles
are for the probes. The five pin receptacle is the rear
connection for the Interrogator. The probe receptacles
are sized to accept plugs with tricam coupling locking
devices. A label on the back panel of the unit shows
which receptacle is used for each probe.
The standard DataCORDER report displays the supply
and return air temperatures. The cold treatment report
displaysUSDA#1, #2, #3 andthe supplyand returnair
temperatures. Cold treatment recording is backed upby
a battery so recording can continue if AC power is lost.
b. USDA/ Message Trip Comment
AspecialfeatureisincorporatedinDataLine/DataView
which allows the user to enter a USDA (or other)
message in the header of a data report. The maximum
messagelengthis 78 characters. Onlyonemessagewill
be recorded per day.
3.6.12 USDA Cold Treatment Procedure
The following is a summary of the steps required to
initiate a USDA Cold Treatment.
a. Calibrate the three USDA probes by ice bathing the
probes and performing the calibration function with
theDataReader, DataView orDataLine. This calibra-
tion procedure determines the probe offsets and
stores them in the controllerfor usein generatingthe
cold treatment report. Refer to the Data Retrieval
manual 62-02575 for more details.
b. Pre-coolthecontainertothetreatmenttemperatureor
below.
c..InstalltheDataCORDERmodulebatterypack(ifnot
already installed).
d. Place the three probes. The probes areplaced intothe
pulpoftheproduct(atthelocationsdefinedinthefol-
lowing table) as the product is loaded.

3-12T-309
Sensor 1 Place in pulp of the product located next
to the return air intake.
Sensor 2
Place in pulp of the product five feet
from the end of the load for 40 foot con-
tainers, or three feet from the end of the
load for 20 foot containers. This probe
should be placed in a center carton at
one-half the height of the load.
Sensor 3
Place in pulp of product five feet from
the end of the load for 40 foot containers
or three feet from the end of the load for
20 foot containers. This probe should be
placed in a carton at a side wall at one-
half the height of the load.
e. To initiate USDA Recording, connect the personal
computer and perform the configuration as follows,
using either the Data View or Data Line software:
1. Enter ISO header information
2. Enter a trip comment if desired
3. Configure the DataCORDER for five probes (s, r,
P1, P2, P3) (dcf02=5)
4. Configure the logging interval for one hour.
5. Set the sensor configuration to “USDA”.
6. Configure for two byte memory storage format
(dcf04=LONG).
7. Perform a “trip start”
3.6.13 DataCORDER Alarms
The alarm display is an independent DataCORDER
function. If an operating parameter is outside of the
expected range or a component does not return the
correct values back to the DataCORDER an alarm is
generated.TheDataCORDERcontainsabufferofupto
eight alarms. A listing of the DataCORDER alarms is
provided in Table 3-10, page 3-27. Refer to paragraph
3.6.7 for configuration information.
To display alarm codes:
a. While in the Default Display mode, press the ALT.
MODE&ALARMLISTkeys.Thisaccesses theDa-
taCORDER Alarm List Display Mode, which dis-
plays any alarms stored in the Alarm Queue.
b. ToscrolltotheendofthealarmlistpresstheUPAR-
ROW. Depressing the DOWN ARROW key will
scroll the list backward.
c. The left display will show “AL#” where # is the
alarms number in the queue. The right display will
show “AA##,” if the alarm is active, where ## is the
alarmnumber. “IA##,”willshowifthealarmisinac-
tive
d. “END” is displayed to indicate the end of the alarm
list if any alarms are active. “CLEAr” is displayed if
all the alarms in the list are inactive.
e. If no alarms are active, the Alarm Queue may be
cleared. The exception to this rule is the DataCORD-
ERAlarmQueueFullalarm(AL91),whichdoesnot
have to beinactive in order to clear the alarm list. To
Clear the Alarm List:
1. Press the ALT. MODE & ALARM LIST keys.
2. PresstheUP/DOWNARROWkeyuntil“CLEAr”is
displayed.
3. Press the ENTER key. The alarm list will clear and
“-- -- -- -- --” will be displayed.
4. Press the ALARM LIST key. “AL” will show on the
leftdisplayand“-- -- -- -- --”ontherightdisplaywhen
there are no alarms in the list.
5. Upon clearing of the Alarm Queue, the Alarm light
will be turned off.
3.6.14 ISO Trip Header
DataLine provides the user with an interface to
view/modify current settings of the ISO trip header
through the ISO Trip Header screen.
The ISO Trip Header screen is displayed when the user
clicks on the “ISO Trip Header” button in the “Trip
Functions” Group Box on the System Tools screen.
F9 function -- Provides the user with a shortcut for
manually triggering the refresh operation.Before
sending modified parameter values, the user must
ensure that a successful connection is established with
the Controller.
IftheconnectionisestablishedwiththeDataCorder,the
current contents of the ISO Trip Header from the
DataCorder will be displayed in each field. If the
connection is not established with the DataCorder, all
fields on the screen will bedisplayed as “X’s”.If at any
time during the display of the ISO Trip Header screen
the connection is not established or is lost, the user is
alerted to the status of the connection.
After modifying the values and ensuring a successful
connectionhasbeenmadewiththeDataCorder, clickon
the “Send” button to send the modified parameter
values.
ThemaximumallowedlengthoftheISOTripHeaderis
128 characters.If the user tries to refresh the screen or
close the utility without sending the changes made on
the screen to the DataCorder, the user is alerted with a
message.

3-13 T-309
Table 3-4 Controller Configuration Variables
NOTES
1. Configuration numbers not listed are not used in this application. Theseitems may appear when loading
configuration software to the controller but changes will not be recognized by the controller programming.
CONFIGURATION
NUMBER TITLE DEFAULT OPTION
CnF02 Evaporator Fan Speed dS (Dual) SS (Single)
CnF04 Dehumidification Mode On OFF
CnF11 Defrost “Off” Selection noOFF OFF
CnF16 DataCORDER Present On (Yes) OFF (No)
CnF22 Economy Mode Option OFF Std, Full
CnF23 Defrost Interval Timer Save Option noSAv SAv
CnF24 Long Pre Trip Test Sequence Enabled On Off
CnF25 Pre-Trip Test Points/Results Recording Option rSLtS dAtA
CnF26 Heat Lockout Change Option Set to --10_CSet to --5_C
CnF28 Bulb Mode Option NOr bULb
CnF31 Probe Check Option Std SPEC
CnF33 Snap Freeze Option OFF SnAP
CnF34 Degree Celsius Lockout Option bOth _F
CnF37 Electronic Temperature Recorder rEtUR (Return) suPPl, BOth

3-14T-309
Table 3-5 Controller Function Codes (Sheet 1 of 3)
Code
No. TITLE DESCRIPTION
Note: If the function is not applicable, the display will read “-- -- -- -- --”
Display Only Functions
Cd01 Suction Modulation
Valve Opening (%) Displays the SMV percent open. The right display reads 100% when the valve is
fully open. The valve will usually be at 10% on start up of the unit except in very
high ambient temperatures.
Cd02 Not Applicable Not used
Cd03 Compressor Motor
Current The current sensor measures current draw in lines L1 & L2 by all of the high
voltage components. It also measures current draw in compressor motor leg T3.
The compressor leg T3 current is displayed.
Cd04
Cd05
Cd06
Line Current,
Phase A
Line Current,
Phase B
Line Current,
Phase C
The current sensor measures current on two legs. The third unmeasured leg is cal-
culated based on a current algorithm. The current measured is used for control
and diagnostic purposes. For control processing, the highest of the Phase A and B
current values is used for current limiting purposes. For diagnostic processing,
the current draws are used to monitor component energization.. Whenever a heat-
er or a motor is turned ON or OFF, the current draw increase/reduction for that
activity is measured. The current draw is then tested to determine if it falls within
the expected range of values for the component. Failure of this test will result in a
pre-trip failure or a control alarm indication.
Cd07 Main Power Voltage The main supply voltage is displayed.
Cd08 Main Power Fre-
quency The value of the main power frequency is displayed in Hertz. The frequency dis-
played will be halved if either fuse F1 or F2 is bad (alarm code AL21).
Cd09 Ambient Tempera-
ture The ambient sensor reading is displayed.
Cd10 Compressor Suction
Temperature Compressor suction temperature sensor reading is displayed.
Cd11 Compressor Dis-
charge Temperature Compressor discharge temperature sensor reading is displayed.
Cd12 Compressor Suction
Pressure Compressor suction pressure transducer reading is displayed.
Cd13 Not Applicable Not used
Cd14 Compressor Dis-
charge Pressure Compressor discharge pressure transducer reading is displayed.
Cd15 Unloader Valve The status of the valve is displayed (Open - Closed).
Cd16 Compressor Motor
Hour Meter Records total hours of compressor run time. Total hours are recorded in incre-
ments of 10 hours (i.e., 3000 hours is displayed as 300).
Cd17 Relative Humidity
(%) Humidity sensor reading is displayed. This code displays the relative humidity, as
a percent value.
Cd18 Software Revision # The software revision number is displayed.
Cd19 Battery Check
This code checks the Controller/DataCORDER battery pack. While the test is
running, “btest” will flash on the right display, followed by the result. “PASS”
will be displayed for battery voltages greater than 7.0 volts. “FAIL” will be dis-
played for battery voltages between 4.5 and 7.0 volts, and “-- -- -- -- --” will be
displayed for battery voltages less than 4.5 volts. After the result is displayed for
four seconds, “btest” will again be displayed, and the user may continue to scroll
through the various codes.
Cd20 Config/Model # This code indicates the dash number of the model for which the Controller is con-
figured (i.e., if the unit is a 69NT40-531-100, the display will show “31100”).
Cd21 Economizer Valve The status of the valve is displayed (Open - Closed).

3-15 T-309
Table 3-5 Controller Function Codes (Sheet 2 of 3)ff
Cd22 Compressor State The status of the compressor is displayed (Off, On).
Cd23 Evaporator Fan Displays the current evaporator fan state (high, low or off).
Cd24 Controlled
Atmosphere State Not used in this application
Cd25 Compressor Run
Time Remaining
Until Defrost This code displays the time remaining until the unit goes into defrost (in tenths of
an hour). This value is based on the actual accumulated compressor running time.
Cd26 Defrost Temperature
Sensor Reading Defrost temperature sensor reading is displayed.
Configurable Functions
NOTE
Function codes Cd27 through Cd37 are user-selectable functions. The operator can change the value of
these functions to meet the operational needs of the container.
Cd27 Defrost Interval
(Hours)
The defrost interval is the time between defrost cycles. Five selectable values are
available: 3, 6, 9, 12 or 24 hours. The factory default value is 12 hours. Follow-
ing a start--up or after termination of a defrost, the time will not begin counting
down until the defrost temperature sensor (DTS) reading falls below set point. If
the reading of DTS rises above set point any time during the timer count down,
the interval is reset and the countdown begins over. If DTS fails, alarm code
AL60 is activated and control switches over to the the return temperature sensor.
The controller will act in the same manner as with the DTS except the return tem-
perature sensor reading will be used.
Defrost Interval Timer Value (Configuration variable CnF23): If the software is
configured to “SAv” (save) for this option, then the value of the defrost interval
timer will be saved at power down and restored at power up. This option prevents
short power interruptions from resetting an almost expired defrost interval, and
possibly delaying a needed defrost cycle.
NOTE
The defrost interval timer counts only during compressor run time.
Cd28 Temperature Units
(_Cor_F)
This code determines the temperature units (_Cor_F) which will be used for all
temperature displays. The user selects _Cor_F by selecting function code Cd28
and pushing the ENTER key. The factory default value is Celsius units.
NOTE
This function code will display “--- --- --- --- --- “ if Configuration Variable
CnF34 is set to _F.
Cd29 Failure Action
(Mode)
If all of the control sensors are out of range (alarm code AL26) or there is a probe
circuit calibration failure (alarm code AL27), the unit will enter the shutdown
state defined by this setting. The user selects one of four possible actions as fol-
lows:
A-- FullCooling(compressorison,economizedoperation.SMVsubjecttopressure
and current limit.)
B -- PartialCooling (Compressoris on, standardoperation.SMVsubjecttopressure
and current limit.)
C -- EvaporatorFan Only(Compressoris off, evaporatorfanson high speed, not ap-
plicable with frozen set points.
D -- Full System Shutdown -- Factory Default (shut down every component in the
unit)
Cd30 In-Range Tolerance
The in-range tolerance will determine the band of temperatures around the set
point which will be designated as in-range. If the control temperature is in-range,
the in-range light will be illuminated. There are four possible values:
1=¦0.5_C(¦0.9_F)
2=¦1.0_C(¦1.8_F)
3=¦1.5_C(¦2.7_F)
4=¦2.0_C(¦3.6_F) -- Factory Default

3-16T-309
Table 3-5 Controller Function Codes (Sheet 3 of 3)
Cd31 Stagger Start Offset
Time (Seconds)
The stagger start offset time is the amount of time that the unit will delay at start-
up, thus allowing multiple units to stagger their control initiation when all units
are powered up together. The eight possible offset values are:
0 (Factory Default), 3, 6, 9, 12, 15, 18 or 21 seconds
Cd32 Current Limit
(Amperes)
The current limit is the maximum current draw allowed on any phase at any time.
Limiting the unit’s current reduces the load on the main power supply. This is
accomplished by reducing the SMV position until current draw is reduced to the
set point. When desirable, the limit can be lowered. Note, however, that capacity
is also reduced. The five values for 460vac operation are: 15, 17, 19, 21 (Factory
Default), 23
Cd33 Perishable Mode
Dehumidification
Control (% RH)
Relative humidity set point is available only on units configured for dehumidifi-
cation. When the mode is activated, the control probe LED flashes on and off ev-
ery second to alert the user. If not configured, the mode is permanently deacti-
vated and “-- -- -- -- --”willdisplay.Thevaluecanbesetto“OFF.”“TEST,”ora
range of 65 to 95% relative humidity in increments of 1%. [If bulb mode is active
(code Cd35) and “Lo” speed evaporator motors are selected (code Cd36) then set
point ranges from 60 to 95%.] When “TEST” is selected or test set point is
entered, the heat LED should illuminate, indicating that dehumidification mode is
activated. After a period of five minutes in the “TEST” mode has elapsed, the
previously selected mode is reinstated.
Cd34 Economy Mode
(On--Off) Economy mode is a user selectable mode of operation provided for power saving
purposes.
Cd35 Bulb Mode
Bulb mode is a user selectable mode of operation that is an extension of dehu-
midification control (Cd33). If dehumidification is set to “Off,” code Cd35 will
display “Nor” and the user will be unable to change it. After a dehumidification
set point has been selected and entered for code Cd33, the user may then change
code Cd35 to “bulb.” After bulb has been selected and entered, the user may then
utilize function codes Cd36 and Cd37 to make the desired changes.
Cd36 Evaporator Speed
Select
This code is enabled only if in the dehumidification mode (code Cd33) and bulb
mode (Cd35) has been set to “bulb”. If these conditions are not met, “alt” will be
displayed (indicating that the evaporator fans will alternate their speed) and the
display cannot be changed. If a dehumidification set point has been selected along
with bulb mode then “alt” may be selected for alternating speed, “Lo” for low
speed evaporator fan only, or “Hi” for high speed evaporator fan only. If a setting
other than “alt” has been selected and bulb mode is deactivated in any manner,
then selection reverts back to “alt.”
Cd37 Defrost Termination
Temperature Setting
(Bulb Mode)
This code, as with function code Cd36, is used with bulb mode and dehumidifica-
tion. If bulb mode is active, this code allows the user to change the temperature
defrost will terminate. It allows the user to change the setting within a range of
4_C to 25.6_Cin0.1_C (0.2_F) increments. This value is changed using the UP/
DOWN ARROW keys, followed by the ENTER key when the desired value is
displayed. If bulb mode is deactivated, the DTS setting returns to the default.
Display Only Functions -- Continued
Cd38 Secondary Supply
Temperature Sensor
Code Cd38 will display the current secondary supply temperature sensor reading
for units configured for four probes. If the unit is configured with a DataCORD-
ER, Cd38 will display “-- -- -- -- --.” If the DataCORDER suffers a failure,
(AL55) Cd38 will display the supply recorder sensor reading.
Cd39 Secondary Return
Temperature Sensor
Code Cd39 will display the current secondary return temperature sensor reading
for units configured for four probes. If the unit is configured with a DataCORD-
ER, Cd39 will display “-- -- -- -- --.” If the DataCORDER suffers a failure,
(AL55) Cd39 will display the return recorder sensor reading.
Cd40 Container Identifica-
tion Number Code Cd40 is configured at commissioning to read a valid container identifica-
tion number. The reading will not display alpha characters, only the numeric por-
tion of the number will display.
Cd41 Valve Override SERVICE FUNCTION: This code is used for troubleshooting and allows manu-
al positioning of the economizer, unloader, suction modulation and oil return
valves. Refer to paragraph 6.19 for operating instructions.
Cd42 Oil Return Valve The status of the valve is displayed (Open - Closed).

3-17 T-309
Table 3-6 Controller Alarm Indications (Sheet 1 of 4)
Code
No. TITLE DESCRIPTION
AL13 Expansion Module
Alarm 13 is triggered if the control module has lost communication with the ex-
pansion module for more than five minutes or communication fails within the
first 15 seconds on power up. This alarm triggers failure action C (evaporator fan
only) or D (all machinery off) of Function Code Cd29 if the unit has a perishable
set point. Failure action D (all machinery off) is triggered if the unit has a frozen
set point
AL14 Phase Sequence
Failure -- Electronic
Alarm 14 is triggered if the electronic phase detection system is unable to deter-
mine the correct phase relationship. DIRCHECK will be displayed while the
relationship is determined. If the system is unable to determine the proper rela-
tionship alarm 14 will remain active. Additiotnal information on phase detection
may be displayed at Function Code Cd41. If the right most digit of Code Cd41 is
3 or 4, this indicates incorrect motor or sensor wiring. If the right most digit is 5,
this indicates a failed current sensor assembly.
AL15 Loss Cooling Future Expansion
AL16 Compressor Current
High Alarm 16 is triggered if compressor current draw is 15% over calculated maxi-
mum for 10 minutes out of the last hour. The alarm is display only and will trig-
ger off when the compressor operates for one hour without over current.
AL17 Phase Sequence
Failure -- Pressure
Alarm 17 is triggered if a compressor start in both directions fails to generate
sufficient pressure differential. The controller will attempt restart every twenty
minutes and deactivate the alarm if successful. This alarm triggers failure action
C (evaporator fan only) or D (all machinery off) of Function Code Cd29 if the
unit has a perishable set point. Failure action D (all machinery off) is triggered if
the unit has a frozen set point
AL18 Discharge Pressure
High Alarm 18 is triggered if discharge pressure is 10% over calculated maximum for
10 minutes within the last hour. The alarm is display only and will trigger off
when the compressor operates for one hour without overpressure.
AL19 Discharge Tempera-
ture High Alarm 19 is triggered if discharge temperature exceeds 135_C (275_F) for 10
minutes within the last hour. The alarm is display only and will trigger off when
the compressor operates for one hour without over temperature.
AL20 Control Circuit Fuse
Open (24 vac) Alarm 20 is triggered by control power fuse (F3) opening and will cause the soft-
ware shutdown of all control units. This alarm will remain active until the fuse is
replaced.
AL21 Micro Circuit Fuse
Open (18 vac)
Alarm 21 is triggered by one of the fuses (F1/F2) being opened on 18 volts AC
power supply to the Controller. The suction modulation valve (SMV) will be
opened and current limiting is halted. Temperature control will be maintained by
cycling the compressor.
AL22 Evaporator Fan Mo-
tor Safety Alarm 22 responds to the evaporator motor internal protectors. The alarm is trig-
gered by opening of either internal protector. It will disable all control units until
the motor protector resets and the unit is power cycled.
AL23 Loss of Phase B
Alarm 23 is triggered if low current draw is detected on phase B and IPCP, HPS
or IPEM is not tripped. If the compressor should be running, the controller will
initiate a start up every five minutes and trigger off if current reappears. If the
evaporator fan motors only should be running, the alarm will trigger off is cur-
rent reappears. This alarm triggers failure action C (evaporator fan only) or D
(all machinery off) of Function Code Cd29 if the unit has a perishable set point.
Failure action D (all machinery off) is triggered if the unit has a frozen set point
AL24 Compressor Motor
Safety
Alarm 24 is triggered when compressor is not drawing any current. It also trig-
gers failure action ”C” or ”D” set by function Code 29 for perishable setpoint, or
”D” for frozen setpoint. This alarm will remain active until compressor draws
current.

3-18T-309
Table 3-6 Controller Alarm Indications (Sheet 2 of 4)
AL25 Condenser Fan Mo-
tor Safety
Alarm 25 is triggered by the opening of the condenser motor internal protector
and will disable all control units except for the evaporator fans. This alarm will
remain active until the motor protector resets. This alarm triggers failure action
C (evaporator fan only) or D (all machinery off) of Function Code Cd29 if the
unit has a perishable set point. Failure action D (all machinery off) is triggered if
the unit has a frozen set point
AL26 All Supply and Re-
turn temperature
Control Sensors
Failure
Alarm 26 is triggered if the Controller determines that all of the control sensors
are out-of-range. This can occur for box temperatures outside the range of --50_C
to +70_C(--58_F to +158_F). This alarm triggers the failure action code set by
Function Code Cd29.
AL27 A/D Accuracy Fail-
ure
The Controller has a built-in Analog to Digital (A-D) converter, used to convert
analog readings (i.e. temperature sensors, current sensors, etc.) to digital read-
ings. The Controller continuously performs calibration tests on the A-D con-
verter. If the A-D converter fails to calibrate for 30 consecutive seconds, this
alarm is activated.This alarm will be inactivated as soon as the A-D converter
calibrates.
AL28 Low Suction Pres-
sure
Alarm 28 is triggered if suction pressure is below 2 psia and alarm 66 (Suction
Pressure Transducer Failure) is not active. This alarm will be inactivated when
suction pressure rises above 2 psia for three continuous minutes. This alarm trig-
gers failure action C (evaporator fan only) or D (all machinery off) as determined
by User Selectable Failure Response if the unit has a perishable set point; Failure
action D (all machinery off) if the unit has a frozen set point. Reset SMV.
AL51 Alarm List Failure
During start-up diagnostics, the EEPROM is examined to determine validity of
its contents. This is done by testing the set point and the alarm list. If the con-
tents are invalid, Alarm 51 is activated. During control processing, any operation
involving alarm list activity that results in an error will cause Alarm 51 to be ac-
tivated. Alarm 51 is a “display only” alarm and is not written into the alarm list.
Pressing the ENTER key when “CLEAr” is displayed will result in an attempt to
clear the alarm list. If that action is successful (all alarms are inactive), Alarm 51
will be reset.
AL52 AlarmListFull Alarm 52 is activated whenever the alarm list is determined to be full; at start-up
or after recording an alarm in the list. Alarm 52 is displayed, but is not recorded
in the alarm list. This alarm can be reset by clearing the alarm list. This can be
done only if all alarms written in the list are inactive.
AL53 Battery Pack Failure Alarm 53 is caused by the battery pack charge being too low to provide sufficient
power for battery-backed recording. Renew replaceable batteries. If this alarm
occurs on start up, allow a unit fitted with rechargeable batteries to operate for up
to 24 hours to charge rechargeable batteries sufficiently to deactivate the alarm
AL54 Primary Supply
Temperature Sensor
Failure (STS)
Alarm 54 is activated by an invalid primary supply temperature sensor reading
that is sensed outside the range of --50 to +70_C(--58_F to +158_F) or if the
probe check logic has determined there is a fault with this sensor. If Alarm 54 is
activated and the primary supply is the control sensor, the secondary supply sen-
sor will be used for control if the unit is so equipped. If the unit does not have a
secondary supply temperature sensor, and AL54 is activated, the primary return
sensor reading, minus 2_C will be used for control.
NOTE
The P5 Pre-Trip test must be run to inactivate the alarm
AL55 DataCORDER
Failure This alarm activates to indicate the DataCORDER has a software failure. To
clear this alarm, reconfigure the unit to the current model number. This failure
may be the result of a voltage dip in access of 25%.

3-19 T-309
Table 3-6 Controller Alarm Indications (Sheet 3 of 4)
AL56 Primary Return
Temperature Sensor
Failure (RTS)
Alarm 56 is activated by an invalid primary return temperature sensor reading
that is outside the range of --50 to +70_C(--58_F to +158_F). If Alarm 56 is acti-
vated and the primary return is the control sensor, the secondary return sensor
will be used for control if the unit is so equipped. If the unit is not equipped with
a secondary return temperature sensor or it fails, the primary supply sensor will
be used for control.
NOTE
The P5 Pre-Trip test must be run to inactivate the alarm.
AL57 Ambient Tempera-
ture Sensor Failure Alarm 57 is triggered by an ambient temperature reading outside the valid range
from --50_C(--58_F) to +70_C (+158_F).
AL58 Compressor High
Pressure Safety Alarm 58 is triggered when the compressor high discharge pressure safety switch
remains open for at least one minute. This alarm will remain active until the pres-
sure switch resets, at which time the compressor will restart.
AL59 Heat Termination
Thermostat Alarm 59 is triggered by the opening of the heat termination thermostat and will
result in the disabling of the heater. This alarm will remain active until the ther-
mostat resets.
AL60 Defrost Temperature
Sensor Failure
Alarm 60 is an indication of a probable failure of the defrost temperature sensor
(DTS). It is triggered by the opening of the heat termination thermostat (HTT) or
the failure of the DTS to go above set point within two hours of defrost initia-
tion. After one-half hour with a frozen range set point, or one-half hour of contin-
uous compressor run time, if the return air falls below 7_C(45_F), the Controller
checks to ensure the DTS reading has dropped to 10_C or below. If not, a DTS
failure alarm is given and the defrost mode is operated using the return tempera-
ture sensor. The defrost mode will be terminated after one hour by the Controller.
AL61 Heaters Failure Alarm 61 is triggered by detection of improper amperage resulting from heater
activation or deactivation. Each phase of the power source is checked for proper
amperage.This alarm is a display alarm with no resulting failure action, and will
be reset by a proper amp draw of the heater.
AL62 Compressor Circuit
Failure
Alarm 62 is triggered by improper current draw increase (or decrease) resulting
from compressor turn on (or off). The compressor is expected to draw a mini-
mum of 2 amps; failure to do so will activate the alarm. This is a display alarm
with no associated failure action and will be reset by a proper amp draw of the
compressor.
AL63 Current Over Limit
Alarm 63 is triggered by the current limiting system. If the compressor is ON
and current limiting procedures cannot maintain a current level below the user
selected limit, the current limit alarm is activated. This alarm is a display alarm
and is inactivated by power cycling the unit, changing the current limit via the
code select Cd32, or if the current decreases below the activation level.
AL64 Discharge Tempera-
ture Over Limit Alarm 64 is triggered if the discharge temperature sensed is outside the range of
-- 6 0 _C(--76_F) to 175_C (347_F), or if the sensor is out of range. This is a dis-
play alarm and has no associated failure action.
AL65 Discharge Pressure
Transducer Failure Alarm 65 is triggered if a compressor discharge transducer is out of range. This is
a display alarm and has no associated failure action.
AL66 Suction Pressure
Transducer Failure Alarm 66 is triggered if a suction pressure transducer is out of range. This is a
display alarm and has no associated failure action.
AL67 Humidity Sensor
Failure Alarm 67 is triggered by a humidity sensor reading outside the valid range of 0%
to 100% relative humidity. If alarm AL67 is triggered when the dehumidification
mode is activated, then the dehumidification mode will be deactivated.
AL69 Suction Temperature
Sensor Failure Alarm 69 is triggered by a suction temperature sensor reading outside the valid
range of --60_C(--76_F) to 150_C (302_F). This is a display alarm and has no
associated failure action.

3-20T-309
Table 3-6 Controller Alarm Indications (Sheet 4 of 4)
NOTE
If the Controller is configured for four probes without a DataCORDER, the DataCORDER alarms AL70
and AL71 will be processed as Controller alarms AL70 and AL71. Refer to Table 3-10.
The Controller performs self-check routines. if an internal failure occurs, an
“ERR” alarm will appear on the display. This is an indication the Controller
needs to be replaced.
ERROR DESCRIPTION
ERR 0 -- RAM failure Indicates that the Controller working memory has
failed.
ERR Internal
M
i
c
r
o
p
r
o
c
e
s
s
o
r
EER 1 -- Program
Memory failure Indicates a problem with the Controller program.
E
R
R
#
M
i
croprocessor
Failure EER 2 -- Watchdog
time--out The Controller program has entered a mode whereby
the Controller program has stopped executing.
EER 3 -- On board timer
failure The on board timers are no longer operational.
Timed items such as; defrost, etc. may not work.
EER 4 -- Internal counter
failure Internal multi-purpose counters have failed. These
counters are used for timers and other items.
EER 5 -- A-D failure The Controller’s Analog to Digital (A-D) converter
has failed.
Entr
StPt Enter Setpoint
(Press Arrow &
Enter) The Controller is prompting the operator to enter a set point.
LO
Low Main Voltage
(Function Codes
Cd27--38 disabled
and NO alarm
stored.)
This message will be alternately displayed with the set point whenever the sup-
ply voltage is less than 75% of its proper value.

3-21 T-309
Table 3-7 Controller Pre-Trip Test Codes (Sheet 1 of 4)
Code
No. TITLE DESCRIPTION
NOTE
“Auto” or “Auto1” menu includes the: P0, P1, P2, P3, P4, P5, P6 and rSLts. “Auto2” menu
includes P0, P1, P2, P3, P4, P5, P6, P7, P8, P9, P10 and rSLts.
P0--0 Pre-Trip Initiated All lights and display segments will be energized for five seconds at the start of
the pre-trip. Since the unit cannot recognize lights and display failures, there are
no test codes or results associated with this phase of pre-trip.
P1-0 Heaters Turned On Setup: Heater must start in the OFF condition, and then be turned on. A current
draw test is done after 15 seconds.
Pass/Fail Criteria: Passes if current draw change is within the range specified.
P1-1 Heaters Turned Off Setup: Heater must start in the ON condition, and then be turned off. A current
draw test is done after 10 seconds.
Pass/Fail Criteria: Passes if current draw change is within the range specified.
P2-0 Condenser Fan On Requirements: Water pressure switch or condenser fan switch input must be
closed.
Setup: Condenser fan is turned ON, a current draw test is done after 15 seconds.
Pass/Fail Criteria: Passes if current draw change is within the range specified.
P2-1 Condenser Fan Off Setup: Condenser fan is turned OFF, a current draw test is done after 10 sec-
onds.
Pass/Fail Criteria: Passes if current draw change is within the range specified.
P3 Low Speed Evapora-
tor Fans Requirements: The unit must be equipped with a low speed evaporator fan, as
determined by the Evaporator Fan speed select configuration variable.
P3-0 Low Speed Evapora-
tor Fan Motors On
Setup: The high speed evaporator fans will be turned on for 10 seconds, then off
for two seconds, then the low speed evaporator fans are turned on. A current
draw test is done after 60 seconds.
Pass/Fail Criteria: Passes if change in current draw is within the range speci-
fied. Fails if AL11 or AL12 activates during test.
P3-1 Low Speed Evapora-
tor Fan Motors Off
Setup: The low speed Evaporator Fan is turned off, a current draw test is done
after 10 seconds.
Pass/Fail Criteria: Passes if change in current draw is within the range speci-
fied. Fails if AL11 or AL12 activates during test.
P4-0 High Speed Evapo-
rator Fan Motors On
Setup: The high speed Evaporator Fan is turned on, a current draw test is done
after 60 seconds.
Pass/Fail Criteria: Passes if change in current draw is within the range speci-
fied. Fails if AL11 or AL12 activates during test.
P4-1 High Speed Evapo-
rator Fan Motors Off
Setup: The high speed Evaporator Fan is turned off, a current draw test is done
after 10 seconds.
Pass/Fail Criteria: Passes if change in current draw is within the range speci-
fied. Fails if AL11 or AL12 activates during test.
P5-0 Supply/Return Probe
Test
Setup: The High Speed Evaporator Fan is turned on and run for eight minutes,
with all other outputs de-energized.
Pass/Fail Criteria: A temperature comparison is made between the return and
supply probes.
NOTE
If this test fails, “P5-0” and “FAIL” will be displayed. If both Probe tests
(this test and the PRIMARY/ SECONDARY) pass, the display will read
“P5” “PASS.”

3-22T-309
Table 3-7 Controller Pre-Trip Test Codes (Sheet 2 of 4)
P5-1 Supply Probe Test
Requirements: For units equipped with secondary supply probe only.
Pass/Fail Criteria: The temperature difference between primary and secondary probe
(supply) is compared.
NOTE
Ifthistestfails,“P5-1”andFAILwillbedisplayed.IfbothProbetests(this
and the SUPPLY/ RETURN TEST)pass, because of the multiple tests,the
display will read ’P 5’ ’PASS’.
P5-2 Return Probe Test
Requirements: For units equipped with secondary return probe only.
Pass/Fail Criteria: The temperature difference between primary and secondary
probe (return) is compared.
NOTES
1. If this test fails, “P5-2” and“FAIL” will be displayed. Ifboth Probetests
(this test and the SUPPLY/ RETURN) pass, because of the multiple
tests, the display will read “P 5,” “PASS.”
2. The results of Pre-Trip tests 5-0, 5-1 and 5-2 will be used to activate or
clear control probe alarms.
P6 Refrigerant Probes,
Compressor
and
Refrigeration valves
Setup: The system is operated through a sequence of events to test the compo-
nents. The sequence is: Step 1, de--energize all outputs; Step 2, start unit with
unloader valve open. Open then close the suction modulation valve. Monitor
suction pressure; Step 3, open suction modulation valve to a known position;
Step 4, close suction modulation valve to a know position; Step 5, open econo-
mizer valve; Step 6, close unloader valve; Step 7, open unloader valve; Step 8,
close economizer valve; Step 9, de--energize all outputs.
P6-0 Discharge
Thermistor Test If alarm 64 is activated any time during the first 45 second period of Step 1, the
test fails.
P6-1 Suction
Thermistor Test If alarm 69 is activated any time during the first 45 second period of Step 1, the
test fails.
P6-2 Discharge Pressure
Sensor Test If alarm 65 is activated any time during the first 45 second period of Step 1, the
test fails.
P6-3 Suction Pressure
Sensor Test If alarm 66 is activated any time during the first 45 second period of Step 1, the
test fails.
P6-4 Compressor Current
Draw Test Compressor current is tested before and after start up. If current does not in-
crease, the test fails.
P6-5 Suction Modulation
Valve Test Suction pressure is measured before and after the valve opens. If suction pres-
sure does not increase, the test fails.
P6-6 Economizer
Valve Test Suction pressure is measured during Steps 4 and 5. If suction pressure does not
increase, the test fails.
P6-7 Unloader Valve Test Suction pressure is measured during Steps 6 and 7. If suction pressure does not
increase, the test fails.

3-23 T-309
Table 3-7 Temperature Controller Pre-Trip Test Codes (Sheet 3 of 4)
NOTE
P7-0 through P10 are included with the “Auto2” only.
P7-0 High Pressure
S
i
t
h
C
l
d
NOTE
This test is skipped if the sensed ambient temperature is less than 7_C
(45_F), the return air temperature is less than --17.8_C(0_F), the water
pressure switch is open or the condenser fan switch is open.
g
Switch Closed Setup: With the unit running, the condenser fan is de-energized, and a 15 minute
timer is started.
Pass/Fail Criteria: The test fails if high pressure switch fails to open in 15 min-
utes.
P7-1 High Pressure
Switch Open
Requirements: Test P7-0 must pass for this test to execute. Setup: The con-
denser fan is started and a 60 second timer is started.
Pass/Fail Criteria: Passes the test if the high pressure switch (HPS) closes
within the 60 second time limit, otherwise, it fails.
P8-0 Perishable Mode
Heat Test
Setup: If the container temperature is below 15.6°C(60_F), the set point is
changed to 15.6°C, and a 180 minute timer is started. The left display will read
“P8-0.” The control will then heat the container until 15.6°C is reached. If the
container temperature is above 15.6°C at the start of the test, then the test pro-
ceeds immediately to test P8-1 and the left display will change to “P8-1.”
Pass/Fail Criteria: The test fails if the 180 minute timer expires before the con-
trol temperature reaches set point. The display will read “P8-0,” “FAIL.”
P8-1 Perishable Mode
Pull Down Test
Requirements: Control temperature must be at least 15.6°C(60_F).
Setup: The set point is changed to 0°C(32_F), and a 180 minute timer is
started. The left display will read “P8-1,” the right display will show the supply
air temperature. The unit will then start to pull down the temperature to the 0°C
set point.
Pass/Fail Criteria: The test passes if the container temperature reaches set point
before the 180 minute timer expires.
P8-2 Perishable Mode
Maintain Tempera-
ture Test
Requirements: Test P8-1 must pass for this test to execute. This test is skipped
if the DATAcorder is not configured or available.
Setup: The left display will read “P8-2,” and the right display will show the sup-
ply air temperature. A two hour timer is started. The unit will be required to
maintain the temperature to within + or -- 0.5_C (0.9_F) of set point until a Da-
taCORDER recording is executed. The recorder supply probe temperature run-
ning total (and its associated readings counter) will be zeroed out for the remain-
der of the recording period at the start of this test, so that the actual value
recorded in the DataCORDER will be an average of only this test’s results. Once
a recording interval is complete, the average recorder supply temperature will be
recorded in the DataCORDER, as well as stored in memory for use in applying
the test pass/fail criteria.
Pass/Fail Criteria: If the recorded temperature is within +/-- 0.5_C. of set point
from test start to DataCORDER recording, the test passes. If the average temper-
ature is outside of the tolerance range at the recording, the test fails and will
auto--repeat by starting P8--0 over.
P9-0 Defrost Test
Setup: The defrost temperature sensor (DTS) reading will be displayed on the
left display. The right display will show the supply air temperature. The unit will
run FULL COOL for 30 minutes maximum until the DTT is considered closed.
Once the DTT is considered closed, the unit simulates defrost by running the
heaters for up to two hours, or until the DTT is considered open.
Pass/Fail Criteria: The test fails if: the DTT is not considered closed after the
30 minutes of full cooling, HTT opens when DTT is considered closed or if re-
turn air temperature rises above 49/50_C (120/122_F).

3-24T-309
Table 3-7 Controller Pre-Trip Test Codes (Sheet 4 of 4)
P10-0 Frozen Mode
Heat Test
Setup: If the container temperature is below 7.2_C(45_F), the set point is
changedto7.2_C and a 180 minute timer is started. The control will then be
placed in the equivalent of normal heating. If the container temperature is above
7.2_C at the start of the test, then the test proceeds immediately to test 10--1.
During this test, the control temperature will be shown in the right display.
Pass/Fail Criteria: The test fails if the 180 minute timer expires before the con-
trol temperate reaches set point --0.3_C (0.17_F). If the test fails it will not auto--
repeat. There is no pass display for this test, once the control temperature reaches
set point, the test proceeds to test 10--1
P10-1 Frozen Mode Pull
Down Test
Requirements: Control temperature must be at least 7.2_C(45_F)
Setup: The set point is changed to --17.8_C(0_F). The system will then attempt
to pull don the Control temperature to set point using normal frozen mode cool-
ing. During this test, the control temperate will be shown on the right display
Pass/Fail Criteria: If the control temperature does not reach set point --0.3_C
(0.17_F) before the 180 minute timer expires the test fails and will auto--repeat
by starting P10--0 over..
P10-2 Frozen Mode
Maintain
Temperature Test
Requirements: Test P10-1 must pass for this test to execute. This test is skipped
if the DATAcorder is not configured or available.
Setup: During this test, the left display will read “P10-2,” and the right display
will show the supply air temperature. A two hour timer is started. The unit will
be required to maintain the temperature to within + 0.5_C (0.9_F)/--1.3_C
(2.3_F) of set point until a DataCORDER recording is executed. The recorder
supply probe temperature running total (and its associated readings counter) will
be zeroed out for the remainder of the recording period at the start of this test, so
that the actual value recorded in the DataCORDER will be an average of only
this test’s results. Once a recording interval is complete, the average recorder
supply temperature will be recorded in the DataCORDER, as well as stored in
memory for use in applying the test pass/fail criteria.
Pass/Fail Criteria: If the recorded temperature is within +0.5_C (0.9_F)/--1.3_C
(2.3_F) of set point from test start to DataCORDER recording, the test passes. If
the average temperature is outside of the tolerance range at the recording, the test
fails and will auto--repeat by starting P10--0 over.

3-25 T-309
Table 3-8 DataCORDER Function Code Assignments
NOTE
Inapplicable Functions Display “-- -- -- -- --”
To Access: Press ALT. MODE key
Code
No. TITLE DESCRIPTION
dC1 Recorder Supply
Temperature Current reading of the supply recorder sensor.
dC2 Recorder Return
Temperature Current reading of the return recorder sensor.
dC3-5 USDA 1,2,3 Tem-
peratures Current readings of the three USDA probes.
dC6-13 Network Data
Points 1-8 Current values of the network data points (as configured). Data point 1 (Code
6) is generally the humidity sensor and its value is obtained from the Control-
ler once every minute.
dC14 CargoProbe4Tem-
perature Current reading of the cargo probe #4.
dC15-19 Future Expansion These codes are for future expansion, and are not in use at this time.
dC20-24 Temperature Sensors
1-5 Calibration Current calibration offset values for each of the five probes: supply, return,
USDA #1, #2, and #3. These values are entered via the interrogation pro-
gram.
dC25 Future Expansion This code is for future expansion, and is not in use at this time..
dC26,27 S/N, Left 4, Right 4 The DataCORDER serial number consists of eight characters. Function code
dC26 contains the first four characters. Function code dC27 contains the last
four characters. (This serial number is the same as the Controller serial num-
ber)
dC28 Minimum Days Left An approximation of the number of logging days remaining until the Data-
CORDER starts to overwrite the existing data.
dC29 Days Stored Number of days of data that are currently stored in the DataCORDER.
dC30 Date of last Trip
start The date when a Trip Start was initiated by the user. In addition, if the system
goes without power for seven continuous days or longer, a trip start will auto-
matically be generated on the next AC power up.
dC31 Battery Test Shows the current status of the optional battery pack.
PASS: Battery pack is fully charged.
FAIL: Battery pack voltage is low.
dC32 Time: Hour, Minute Current time on the real time clock (RTC) in the DataCORDER.
dC33 Date: Month, Day Current date (month and day) on the RTC in the DataCORDER.
dC34 Date: Year Current year on the RTC in the DataCORDER.
dC35 Cargo Probe 4
Calibration Current calibration value for the Cargo Probe. This value is an input via the
interrogation program.

3-26T-309
Table 3-9 DataCORDER Pre-Trip Result Records
Test
No. TITLE DATA
1-0 Heater On Pass/Fail/Skip Result, Change in current for Phase A, B and C
1-1 Heater Off Pass/Fail/Skip Result, Change in currents for Phase A, B and C
2-0 Condenser Fan On Pass/Fail/Skip Result, Water pressure switch (WPS) -- Open/Closed,
Change in currents for Phase A, B and C
2-1 Condenser Fan Off Pass/Fail/Skip Result, Change in currents for Phase A, B and C
3-0 Low Speed Evaporator Fan
On Pass/Fail/Skip Result, Change in currents for Phase A, B and C
3-1 Low Speed Evaporator Fan
On Pass/Fail/Skip Result, Change in currents for Phase A, B and C
4-0 High Speed Evaporator Fan
On Pass/Fail/Skip Result, Change in currents for Phase A, B and C
4-1 High Speed Evaporator Fan
On Pass/Fail/Skip Result, Change in currents for Phase A, B and C
5-0 Supply/Return Probe Test Pass/Fail/Skip Result, STS, RTS, SRS and RRS
5-1 Secondary Supply Probe Test Pass/Fail/Skip
5-2 Secondary Return Probe Test Pass/Fail/Skip
6-0 Discharge Thermistor Test Pass/Fail/Skip
6-1 Suction Thermistor Test Pass/Fail/Skip
6-2 Discharge Pressure Sensor
Test Pass/Fail/Skip
6-3 Suction Pressure Sensor Test Pass/Fail/Skip
6-4 Compressor Current Draw
Test Pass/Fail/Skip
6-5 Suction Modulation valve Test Pass/Fail/Skip
6-6 Economizer Valve Test Pass/Fail/Skip
6-7 Unloader Valve Test Pass/Fail/Skip
7-0 High Pressure Switch Closed Pass/Fail/Skip Result, AMBS, DPT or CPT (if equipped)
Input values that component opens
7-1 High Pressure Switch Open Pass/Fail/Skip Result, STS, DPT or CPT (if equipped)
Input values that component closes
8-0 Perishable Mode Heat Test Pass/Fail/Skip Result, STS, time it takes to heat to 16_C(60_F)
8-1 Perishable Mode Pull Down
Test Pass/Fail/Skip Result, STS, time it takes to pull down to 0_C(32_F)
8-2 Perishable Mode Maintain
Test Pass/Fail/Skip Result, Averaged DataCORDER supply temperature
(SRS) over last recording interval.
9-0 Defrost Test Pass/Fail/Skip Result, DTS reading at end of test, line voltage, line
frequency, time in defrost.
10-0 Frozen Mode Heat Test Pass/Fail/Skip Result, STS, time unit is in heat.
10-1 Frozen Mode Pull Down Test Pass/Fail/Skip Result, STS, time to pull down unit to --17.8_C(0_F).
10-2 Frozen Mode Maintain Test Pass/Fail/Skip Result, Averaged DataCORDER return temperature
(RRS) over last recording interval.

3-27 T-309
Table 3-10 DataCORDER Alarm Indications
To Access: Press ALT. MODE key
Code No. TITLE DESCRIPTION
dAL70 Recorder Supply
Temperature Out of
Range
The supply recorder sensor reading is outside of the range of --50_Cto
70_C(--58_F to +158_F) or, the probe check logic has determined there is
a fault with this sensor.
NOTE
The P5 Pre-Trip test must be run to inactivate the alarm.
dAL71 Recorder Return Tem-
perature Out of Range
The return recorder sensor reading is outside of the range of --50_Cto
70_C(--58_F to +158_F) or, the probe check logic has determined there is
a fault with this sensor.
NOTE
The P5 Pre-Trip test must be run to inactivate the alarm.
dAL72-74 USDA Temperatures
1, 2, 3 Out of Range The USDA probe temperature reading is sensed outside of --50 to 70°C
(--58to158°F) range.
dAL75 Cargo Probe 4 Out of
Range The cargo probe temperature reading is outside of --50 to 70°C(--58to
158°F) range.
dAL76, 77 Future Expansion These alarms are for future expansion, and are not in use at this time.
dAL78-85 Network Data Point
1 -- 8 Out of Range
The network data point is outside of its specified range. The DataCORD-
ER is configured by default to record the supply and return recorder sen-
sors. The DataCORDER may be configured to record up to 8 additional
network data points. An alarm number (AL78 to AL85) is assigned to
each configured point. When an alarm occurs, the DataCORDER must be
interrogated to identify the data point assigned. When a humidity sensor is
installed, it is usually assigned to AL78.
dAL86 RTC Battery Low The Real Time Clock (RTC) backup battery is too low to adequately
maintain the RTC reading.
dAL87 RTC Failure An invalid date or time has been detected. This situation may be corrected
by changing the Real Time Clock (RTC) to a valid value using the Data-
View.
dAL88 DataCORDER
EEPROM Failure A write of critical DataCORDER information to the EEPROM has failed.
dAL89 Flash Memory Error An error has been detected in the process of writing daily data to the non-
volatile FLASH memory.
dAL90 Future Expansion This alarm is for future expansion, and is not in use at this time.
dAL91 AlarmListFull The DataCORDER alarm queue is determined to be full (eight alarms).

T-309
4-1
SECTION 4
OPERATION
4.1 INSPECTION (Before Starting)
WARNING
Beware of unannounced starting of the
evaporator and condenser fans. The unit
may cycle the fans and compressor unex-
pectedly as control requirements dictate.
a. Ifcontainer is empty, check insidefor the following:
1. Check channels or “T” bar floor for cleanliness.
Channels must be free of debris for proper air cir-
culation.
2. Checkcontainerpanels,insulationanddoorsealsfor
damage. Effect permanent or temporary repairs.
3. Visuallycheckevaporatorfanmotormountingbolts
for proper securement (refer to paragraph 6.17).
4. Checkfordirtorgreaseonevaporatorfanorfandeck
and clean if necessary.
5. Check evaporator coil for cleanliness or obstruc-
tions. Wash with fresh water.
6. Checkdefrostdrainpansanddrainlinesforobstruc-
tions and clear if necessary. Wash with fresh water.
7. Checkpanelsonrefrigerationunitforlooseboltsand
condition of panels. Make sure T.I.R. devices arein
place on access panels.
b. Check condenser coil for cleanliness. Wash with
fresh water.
c. Open control box door. Check for loose electrical
connections or hardware.
d. Check color of moisture-liquid indicator.
e. Check oil level in compressor sight glass.
4.2 CONNECT POWER
WARNING
Do not attempt to remove power plug(s) be-
fore turning OFF start-stop switch (ST),
unit circuit breaker(s) and external power
source.
WARNING
Makesurethepowerplugsarecleananddry
before connecting to any power receptacle.
4.2.1 Connection To 380/460 vac Power
1. Make sure start-stop switch (ST, on control panel)
and circuit breaker (CB-1, in the control box) are in
position “0” (OFF).
2. Plug the 460 vac (yellow) cable into a de-energized
380/460 vac, 3-phase power source. Energize the
power source. Place circuit breaker (CB-1) in posi-
tion “I” (ON). Close and secure control box door.
4.3 ADJUST FRESH AIR MAKEUP VENT
The purpose of the fresh air makeup vent is to provide
ventilation for commodities that require fresh air
circulation. The vent must be closed when transporting
frozen foods.
Air exchange depends on static pressure differential,
whichwillvarydependingonthecontainerandhowthe
container is loaded.
4.3.1 Upper Fresh Air Makeup Vent
Two slots and a stop are designed into the disc for air
flowadjustments.Thefirstslotallowsfora0to30%air
flow, and the second slot allows for a 30 to 100% air
flow. To adjust the percentage of air flow, loosen the
wingnutandrotatethediscuntilthedesiredpercentage
of air flow matches with the arrow. Tighten the wing
nut. To clear the gap between the slots,loosen thewing
nut until the disc clears the stop. Figure 4-1 gives air
exchange values for an empty container. Higher values
can be expected for a fully loaded container.
0
30
60
90
120
150
180
210
240
0 102030405060708090100
AIR
FLOW
(CMH)
1-!/2”
PERCENT OPEN
69NT FRESH AIR MAKEUP
T-BAR
2-%/8”
3”
T-BAR
T-BAR
ZERO EXTERNAL STATIC 50HZ
For 60HZ operation multiply curves by 1.2
Figure 4-1 Make Up Air Flow Chart

T-309 4-2
4.4 CONNECT REMOTE MONITORING
RECEPTACLE
If remote monitoring is required, connect remote
monitorplugatunitreceptacle.(Seeitem9,Figure 2-5.)
When the remote monitor plug is connected to the
remote monitoring receptacle, the following remote
circuits are energized:
CIRCUIT FUNCTION
Sockets B to A Energizes remote cool light
Sockets C to A Energizes remote defrost light
Sockets D to A Energizes remote in-range light
4.5 STARTING AND STOPPING INSTRUCTIONS
WARNING
Make sure that the unit circuit breaker(s)
(CB-1 & CB-2) and the START-STOP
switch(ST)areinthe“O”(OFF)positionbe-
fore connecting to any electrical power
source.
4.5.1 Starting the Unit
1. Withpowerproperlyapplied,thefreshairdamperset
and (if required) the water cooled condenser con-
nected, (refer to paragraphs 4.2 & 4.3) place the
START-STOP switch to “I” (ON).
NOTE
Withinthefirst30secondstheelectronicphase
detection system will check for proper com-
pressor rotation. If rotation is not correct, the
compressorwill be stopped and restarted inthe
oppositedirection.Ifthecompressorisproduc-
ing unusually loud and continuous noise after
the first 30 seconds of operation, stop the unit
and investigate.
2. Continue with Start Up Inspection, paragraph 4.6.
4.5.2 Stopping the Unit
To stop the unit, place the START-STOP switch in
position “0” (OFF).
4.6 START--UP INSPECTION
4.6.1 Physical Inspection
a. Check rotation of condenser and evaporator fans.
b. Checkcompressor oillevel. (Refer to paragraph6.9.)
4.6.2 Check Controller Function Codes
Check and, if required, reset controller Function Codes
(Cd27 through Cd39) in accordance with desired
operating parameters. Refer to paragraph 3.2.2.
DataCORDER
a. Check and, if required, set the DataCORDER Con-
figuration in accordance with desired recording pa-
rameter. Refer to paragraph 3.6.3.
b. Enter a “Trip Start”. To enter a “trip Start”, do the
following:
1. Depress the ALT MODE key and scroll to Code
dC30.
2. Depress and hold the ENTER key for five seconds.
3. The “Trip Start” event will be entered in the Data-
CORDER.
4.6.3 Complete Inspection
Allow unit to run for 5 minutes to stabilize conditions
andperform apre--trip diagnosisinaccordancewiththe
following paragraph.
4.7 PRE-TRIP DIAGNOSIS
CAUTION
Pre-tripinspectionshouldnotbeperformed
with critical temperaturecargoes in thecon-
tainer.
CAUTION
When Pre-Trip key is pressed, economy, de-
humidification and bulb mode will be deac-
tivated. AtthecompletionofPre-Tripactivi-
ty, economy, dehumidification and bulb
mode must be reactivated.
Pre-Trip diagnosis provides automatic testing of the
unit components using internal measurements and
comparison logic. The program will provide a “PASS”
or “FAIL” display to indicate test results.
The testing begins with access to a pre-trip selection
menu. Theuser mayhavetheoption of selecting oneof
two automatic tests. These tests will automatically
perform a series of individual pre--trip tests. The user
may also scroll down to select any of the individual
tests.Whenonlytheshortsequenceisconfigureditwill
appear as “AUtO” in the display, otherwise “AUtO1”
will indicate the short sequence and “AUtO2” will
indicatethelongsequence.Thetestshortsequencewill
runtestsP0 throughP6. Thelongtestsequencewillrun
tests P0 through P10.
A detailed description ofthe pre-trip test codes is listed
in Table 3-7, page 3-21. If no selection is made, the
pre-trip menu selection process will terminate
automatically. However, dehumidification and bulb
mode must be reactivated manually if required.
Scrolling down to the “rSLts” code and pressing
ENTER will allow the userto scroll through theresults
ofthelastpre--triptestingrun.Ifnopre--testinghasbeen
run(oranindividualtesthasnotbeenrun)sincetheunit
was powered up “--------” will be displayed.
To start a pre--trip test, do the following:
NOTE
1. Priortostartingtests,verifythatunitvoltage
(Function Code Cd 07) is within tolerance
and unit amperage draw (Function Codes
Cd04, Cd05, Cd06) are within expected
limits. Otherwise, tests may fail incorrectly.
2. All alarms must be rectified and cleared
before starting tests.
T-309
4-3
3. Pre-trip may also be initiated via
communications. The operation is thesame
asforthekeypadinitiationdescribedbelow
except that should a test fail, the pre-trip
mode will automatically terminate. When
initiatedviacommunications,atestmaynot
be interrupted with an arrow key, but the
pre-trip mode can be terminated with the
PRE-TRIP key.
a. Press the PRE-TRIP key. This accesses a test selec-
tion menu.
b. TO RUN AN AUTOMATIC TEST: Scroll through
the selections by pressing the UP ARROW or
DOWNARROWkeystodisplayAUTO,AUTO1or
AUTO 2 as desired and then press the AUTO key.
1. The unit will execute the series of tests without any
need for direct user interface. These tests vary in
length, depending on the component under test.
2. Whiletestsarerunning,“P#-#”willappearontheleft
display, where the #’s indicate the test number and
sub-test. The right display will show a countdown
time in minutes and seconds, indicating how much
time there is left remaining in the test.
CAUTION
When a failure occurs during automatic
testing the unit will suspend operation
awaiting operator intervention.
Whenanautomatictestfails,itwillberepeatedonce.
Arepeatedtestfailurewillcause“FAIL”tobeshown
ontherightdisplay,withthecorrespondingtestnum-
ber to the left. The user may then press the DOWN
ARROWtorepeatthetest,theUPARROWtoskipto
the next test or the PRE--TRIP key to terminate test-
ing. The unit will wait indefinitely, until the user
manually enters a command.
CAUTION
When Pre--Trip test Auto 2 runs to comple-
tion without being interrupted, the unit will
terminate pre-trip and display “Auto 2”
“end.”Theunitwillsuspendoperationuntil
the user depresses the ENTER key!
WhenanAuto1runstocompletionwithoutafailure,
theunit will exit thepre-tripmode, andreturn tonor-
mal control operation. However, dehumidification
and bulb mode must be reactivated manually if re-
quired.
c. TO RUN AN INDIVIDUAL TEST: Scroll through
the selections by pressing the UP ARROW or
DOWN ARROW keys to display an individual test
code. Pressing ENTER when the desired test code is
displayed.
1. Individually selected tests, other than the LED/Dis-
play test, will perform the operations necessary to
verify the operation of the component. At the con-
clusion, PASS or FAILwill bedisplayed. Thismes-
sage will remain displayed for up to three minutes,
during which time a user may select another test. If
the three minute time period expires, the unit will
terminate pre-trip and return to control mode opera-
tion.
2. While the tests are being executed, the user may ter-
minatethepre-tripdiagnosticsbypressingandhold-
ing the PRE-TRIP key. The unit will then resume
normal operation. If the user decides to terminate a
test but remain at the test selection menu, the user
may press the UP ARROW key. When this is done
all test outputs will be de-energized and the test
selection menu will be displayed.
3. Throughout the duration of any pre-trip test except
the P-7 high pressure switch tests, the current and
pressure limiting processes are active .
d. Pre-Trip Test Results
At the end of the pre-trip test selection menu, the
message “P,” “rSLts” (pre--trip results) will be
displayed. Pressing theENTER key will allow the user
toseetheresultsforall subtests(i.e., 1-0, 1-1, etc).The
resultswillbedisplayedas“PASS”or“FAIL”forallthe
tests run to completion since power up. If a test has not
beenrunsincepowerup, “-- -- -- -- --”willbedisplayed.
Once all pre--test activity is completed,
dehumidification and bulb mode must be reactivated
manually if required.
4.8 OBSERVE UNIT OPERATION
4.8.1 Probe Check
IftheDataCORDERisofforinalarmthecontrollerwill
revert to a four probe configuration which includes the
DataCORDER supply and return air probes as the
secondary controller probes. The controller
continuously performs probe diagnosis testing which
compares the four probes. If the probe diagnosis result
indicates a probe problem exists, the controller will
perform a probe check to identify the probe(s) in error.
a. Probe Diagnostic Logic -- Standard
Iftheprobecheckoption(controllerconfigurationcode
CnF31) is configured for standard, the criteria used for
comparisonbetweentheprimaryandsecondarycontrol
probes is:
1_C(1.8_F)forperishablesetpointsor2_C(3.6_F)
for frozen set points.
If25ormoreof30readingstakenwithina30minute
periodareoutside ofthe limit, then adefrost is initi-
ated and a probe check is performed.
Inthis configuration, aprobecheckwill be run as apart
of every normal (time initiated) defrost.
b. Probe Diagnostic Logic -- Special
If the probe check option is configured for special the
abovecriteriaareapplicable.Adefrostwithprobecheck
will be initiated if 25 of 30 readings or 10 consecutive
readings are outside of the limits
In this configuration, a probe check will not be run as a
part of a normal defrost, but only as a part of a defrost
initiated due to a diagnostic reading outside of the
limits.
c.The30minutetimerwillberesetateachofthefollow-
ing conditions:

T-309 4-4
1. At every power up.
2. At the end of every defrost.
3. After every diagnostic check that does not fall out-
side of the limits as outlined above.
d. Probe Check
A defrost cycle probe check is accomplished by
energizing just the evaporatormotors for eight minutes
at the end of the normal defrost. At the endof the eight
minute period the probes will be compared to a set of
predetermined limits. The defrost indicator will remain
on throughout this period.
Any probe(s) determined to be outside the limits will
cause the appropriate alarm code(s) to be displayed to
identify which probe(s) needs to be replaced. The P5
Pre-Trip test must be run to inactivate alarms.
4.9 SEQUENCE OF OPERATION
General operation sequences for cooling, heating and
defrost are provided in the following subparagraphs.
Schematic representation of controller action are
provided in Figure 4-2 and Figure 4-3.Referto Section 3
for detailed descriptions of special events and timers
thatareincorporatedbythecontrollerinspecificmodes
of operation.
SET POINT
PULL DOWN RISING
TEMPERATURE
-- 0 . 5 _C
(0.9_F)
--0.20_C
+.20_C
HEATING
HEATING
AIR CIRCULATION
+2.5_C
(4.5_F)
UNLOADED OPERATION
MODULATED
COOLING
UNLOADED
AIR CIRCULATION
SET POINT
+.20_C
HEATING
+2.5_C
(4.5_F)
FALLING
TEMPERATURE
MODULATED
COOLING
UNLOADED
-- 0 . 5 _C
(0.9_F)
AIR CIRCULATION
NOTE: TEMPERATURES INDICATIONS ARE ABOVE OR BELOW SET POINT
START UNLOADED,
TRANSITION TO
ECONOMIZED
OPERATION
--0.20_C
Figure 4-2 Controller Operation -- Perishable Mode

T-309
4-5
SET POINT
FALLING
TEMPERATURE RISING
TEMPERATURE
--0.20_C
+.20_C
COOLING
ECONOMIZED
AIR CIRCULATION
START UNLOADED,
TRANSITION TO
ECONOMIZED
OPERATION
NOTE: TEMPERATURES INDICATIONS ARE ABOVE OR BELOW SET POINT
AIR CIRCULATION
Figure 4-3 Controller Operation -- Frozen Mode
CONTROL TRANSFORMER
POWER TO
CONTROLLER
SIGNAL TO
CONTROLLER
ENERGIZED
DE--ENERGIZED
FOR FULL DIAGRAM AND
LEGEND, SEE SECTION 7
NOTE: HIGH SPEED EVAPORATOR FAN SHOWN. FOR LOW SPEED
CONTACT TE IS DE--ENERGIZED AND CONTACT TV IS ENERGIZED
TD T6 PA PB
T6 PB PA
USV
ESV
TU
TS
Figure 4-4 Perishable Mode
4.9.1 Sequence Of operation -- Compressor Phase
Sequence
The controller logic will check for proper compressor
rotation. If the compressor is rotating in the wrong
direction, the controller will energize or de--energize
relay T6 as required (see Figure 4-4). Energizing relay
T6willswitchoperationfromcompressorcontactorPA
to compressor contactor PB. De--energizing relay T6
will switch operation from compressorcontactor PB to
compressorcontactorPA. Compressorcontactors PA is
wired to run the compressor on L1, L2, and L3.
Compressor contactor PB is wired to run the
compressor on L2, L1 and L3 thus providing reverse
rotation .
4.9.2 Sequence Of Operation -- Perishable Mode
Cooling
NOTE
Inthe Conventional PerishableMode ofopera-
tiontheevaporatormotorsruninhighspeed.In
the Economy Perishable Modethe fan speed is
varied.
a. With supply air temperature above set point and de-
creasing, the unit will be cooling with the condenser
fanmotor(CF), compressormotor (PAor PB),evap-
oratorfanmotors(EF)energizedandtheCOOLlight
illuminated. (See Figure 4-4.) Also, if current or
pressure limiting is not active, thecontroller will en-
ergize relay TS to open the economizer solenoid
valve (ESV) and placethe unit in economizedopera-
tion.
b. When the air temperature decreases to a predeter-
mined tolerance aboveset point, the in-range light is
illuminated.
c. As the air temperature continues to fall, modulating
cooling starts at approximately 2.5_C (4.5_F) above
set point. (See Figure 4-2.) At set point, relay TS is
de--energized to close the economizer solenoid valve
and relay TU is energized to open the unolader sole-

T-309 4-6
noid valve changing from economized operation to
unloaded operation. (As shown in Figure 4-5)
d. The controllermonitors thesupply air. Once thesup-
plyairfallsbelowsetpointthecontrollerperiodically
recordsthesupplyairtemperature,setpointandtime.
Acalculationisthenperformedto determinetemper-
ature drift from set point over time.
e. If thecalculation determinescooling is no longerre-
quired,contactsTDandTNareopenedtode-energize
compressormotorandcondenserfanmotor.Thecool
light is also de-energized.
f. Theevaporatorfanmotorscontinuetoruntocirculate
air throughout the container. The in-range light re-
mains illuminated as long as the supply air is within
tolerance of set point.
g. If the supply air temperature increases to 0.2_C
(0.4_F) aboveset point andthe threeminute off time
has elapsed, relays TD, TU and TN are energized to
restart the compressor and condenser fan motors in
unloaded operation. The cool light is also illumi-
nated.
CONTROL TRANSFORMER
POWER TO
CONTROLLER
SIGNAL TO
CONTROLLER
ENERGIZED
DE--ENERGIZED
FOR FULL DIAGRAM AND
LEGEND, SEE SECTION 7
NOTE: HIGH SPEED EVAPORATOR FAN SHOWN. FOR LOW SPEED
CONTACT TE IS DE--ENERGIZED AND CONTACT TV IS ENERGIZED
TD T6 PA PB
T6 PB PA
USV
ESV
TU
TS
Figure 4-5 Perishable Mode Heating
4.9.3 Sequence Of Operation --
Perishable Mode Heating
a. If the air temperature decreases 0.5_C (0.9_F)below
set point, the system enters the heating mode. (See
Figure 4-2). The controller closes contacts TH (see
Figure 4-5)to allowpowerflowthroughthe heatter-
mination thermostat (HTT) to energize the heaters
(HR).TheHEATlightisalsoilluminated.Theevapo-
rator fans continue to run to circulate air throughout
the container.
b. When the temperature rises to 0.2_C (0.4_F) above
set point, contact TH opens to de--energize theheat-
ers.TheHEATlightisalsode--energized.Theevapo-
rator fans continue to run to circulate air throughout
the container.
c. A safety heater termination thermostat (HTT), at-
tached to an evaporator coil support, will open the
heating circuit if overheating occurs.
4.9.4 Sequence Of operation -- Frozen Mode Cool-
ing
a. With supply air temperature above set point and de-
creasing, theunit will transition to economized cool-
ing with the condenser fan motor (CF), compressor
motor (CH), economizer solenoid valve (ESV), low
speed evaporator fan motors (ES) energized and the
COOL light illuminated. (See Figure 4-6.)
b.When the air temperature decreases to a predeter-
mined tolerance aboveset point, the in-range light is
illuminated.
CONTROL TRANSFORMER
POWER TO
CONTROLLER
SIGNAL TO
CONTROLLER
ENERGIZED
DE--ENERGIZED
FOR FULL DIAGRAM AND
LEGEND, SEE SECTION 7
TD T6 PA PB
T6 PB PA
USV
ESV
TU
TS
Figure 4-6 Frozen Mode
c. When the return air temperature decreases to 0.2_C
(0.4_F) belowset point, contacts TD, TSand TNare
opened to de-energize the compressor, economizer
solenoid valve and condenser fan motors. The cool
light is also de-energized.
d. The evaporator fan motors continue to run in low
speed to circulate air throughout the container. The
in-range light remains illuminated as long as the re-
turn air is within tolerance of set point.
e. When return air temperature is 10_C(18_F) ormore
below set point, the evaporator fans are brought to
high speed.
f. When the return air temperature increases to 0.2_C
(0.4_F) aboveset point andthe threeminute off time
has elapsed, relays TD, TS and TN are energizes to
restartthecompressorandcondenserfanmotors.The
cool light is illuminated.
4.9.5 Sequence Of Operation -- Defrost
The defrost cycle may consist of up to three distinct
operations.Thefirstisde-icingofthecoil,thesecondis
a probe check cycle and the third is snap freeze.

T-309
4-7
Defrost may be initiated by any one of the following
methods:
1. The manual defrost switch (MDS) is closed by the
user.
2. The user sends a defrost command by communica-
tions.
3. The defrost interval timer (controller function code
Cd27) reaches the defrost interval set by the user.
4. The controller probe diagnostic logic determines
thataprobecheckisnecessarybasedonthetempera-
ture values currently reported by the supply and re-
turn probes.
5. If the controller is programmed with the Demand
Defrost option (Future) and theoption is set to“IN”
the unit will enter defrost if it has been in operation
for over 2.5 hours without reaching set point.
CONTROL TRANSFORMER
POWER TO
CONTROLLER
SIGNAL TO
CONTROLLER
ENERGIZED
DE--ENERGIZED
FOR FULL DIAGRAM AND
LEGEND, SEE SECTION 7
TD T6 PA PB
T6 PB PA
USV
ESV
TU
TS
Figure 4-7 Defrost
Defrost may be initiated any time the defrost
temperature sensor reading falls below the controller
defrost termination thermostat set point. Defrost will
terminate when the defrost temperature sensor reading
risesabovethedefrostterminationthermostatsetpoint.
The defrost termination thermostat is not a physical
component. It is a controller setting that acts as a
thermostat, “closing” (allowing defrost) when the
defrosttemperaturesensorreadingisbelowthesetpoint
and“opening”(terminatingorpreventingdefrost)when
thesensortemperaturereadingisabovesetpoint.When
the unit is operating in bulb mode (refer to paragraph
3.3.9), special settings may be applicable.
If the controller is programmed with the Lower DTT
setting option the defrost termination thermostat set
pointmaybeconfiguredtothedefaultof25.6_C(78_F)
orloweredto18_C(64_F).Whenarequestfordefrostis
made by use of the manual defrost switch,
communications or probe check the unit will enter
defrost if the defrost temperature thermostat reading is
at or below the defrost termination thermostat setting.
Defrost will terminate with the defrost temperature
sensor reading rises above the defrost termination
thermostat setting. When a request for defrost is made
bythedefrostintermaletimerorbydemanddefrost,the
defrosttemperaturesettingsettingmust bebelow10_C
(50_F).
When the defrost mode is initiated the controller opens
contacts TD, TN and TE (or TV) to de-energize the
compressor, condenser fan and evaporator fans. The
COOL light is also de--energized.
The controller then closes TH to supply power to the
heaters. The defrost light is illuminated.
Whenthedefrosttemperaturesensorreadingrisestothe
defrost termination thermostat setting, the de--icing
operation is terminated.
If defrost does not terminate correctly and temperature
reaches the set point of the heat termination thermostat
(HTT) the thermostat will open to de--energize the
heaters. If termination does not occurwithin 2.0 hours,
the controller will terminate defrost. An alarm will be
given of a possible DTS failure.
If probe check (controller function code CnF31) is
configured to special, the unit will proceed to the next
operation (snap freeze or terminate defrost). If the code
is configured to standard, the unit will perform aprobe
check. The purpose of the probe check is to detect
malfunctions or drift in the sensed temperature that is
too small to be detected by the normal sensor out of
rangetests.Thesystemwillrunforeightminutesinthis
condition.Attheendoftheeightminutes,probealarms
will be set or cleared based on the conditions seen.
When the return air falls to 7_C(45_F), the controller
checks to ensure the defrost temperature sensor (DTS)
reading has dropped to 10_C or below. If it has not, a
DTS failure alarm is given and the defrost mode is
operated by the return temperature sensor (RTS).
If controller function codeCnF33 is configured tosnap
freeze, the controller will sequence to this operation.
The snap freeze consists of running the compressor
without the evaporator fans in operation for a period of
four minutes with the suction modulation valve fully
open. When the snap freeze is completed, defrost is
formally terminated.

5-1 T-309
SECTION 5
TROUBLESHOOTING
CONDITION POSSIBLE CAUSE REMEDY/
REFERENCE
SECTION
5.1 UNIT WILL NOT START OR STARTS THEN STOPS
External power source OFF Turn on
No power to unit Start-Stop switch OFF or defective Check
N
o
p
o
w
e
r
t
o
u
n
i
t
Circuit breaker tripped or OFF Check
Circuit breaker OFF or defective Check
L
o
s
s
o
f
c
o
n
t
r
o
l
p
o
w
e
r
Control transformer defective Replace
L
oss of control po
w
er Fuse (F3) blown Check
Start-Stop switch OFF or defective Check
Evaporator fan motor internal protector open 6.17
Condenser fan motor internal protector open 6.12
Compressor internal protector open 6.8
Component(s) Not Operating High pressure switch open 5.7
C
o
m
p
o
n
e
n
t
(
s
)
N
o
t
O
p
e
r
a
t
i
n
g
Heat termination thermostat open Replace
Loss of communication with expansion module Check Wiring
Malfunction of current sensor Replace
Low line voltage Check
Com
p
ressor hums
,
but does not Single phasing Check
C
o
m
p
r
e
s
s
o
r
h
u
m
s
,
b
u
t
d
o
e
s
n
o
t
start Shorted or grounded motor windings 6.8
Compressor seized 6.8
5.2 UNIT OPERATES LONG OR CONTINUOUSLY IN COOLING
C
o
n
t
a
i
n
e
r
Hot load Normal
Container Defective box insulation or air leak Repair
Shortage of refrigerant 6.7.1
Evaporator coil covered with ice 5.6
Evaporator coil plugged with debris 6.15
Evaporator fan(s) rotating backwards 6.15/6.17
Defective evaporator fan motor/capacitor 6.18
Air bypass around evaporator coil Check
Controller set too low Reset
Refrigeration System Compressor service valves or liquid line shutoff valve par-
tially closed Open valves
completely
Dirty condenser 6.11
Compressor worn 6.8
Current limit (function code Cd32) set to wrong value 3.5.5
Suction modulation valve lost track of step count Power cycle
Suction modulation valve malfunction 6.20
Economizer solenoid valve or TXV malfunction 6.14, 6.19
Unloader valve stuck open 6.19

5-2T-309
CONDITION POSSIBLE CAUSE REMEDY/
REFERENCE
SECTION
5.3 UNIT RUNS BUT HAS INSUFFICIENT COOLING
Abnormal pressures 5.7
Abnormal temperatures 5.15
Abnormal currents 5.16
Controller malfunction 5.9
Evaporator fan or motor defective 6.17
Shortage of refrigerant 6.7.1
Refrigeration System Suction modulation valve lost track of step count Power cycle
Suction modulation valve malfunction 6.20
Compressor service valves or liquid line shutoff valve par-
tially closed Open valves
completely
Economizer solenoid valve or TXV malfunction 6.14, 6.19
Unloader valve stuck open 6.19
Frost on coil 5.10
5.4 UNIT WILL NOT HEAT OR HAS INSUFFICIENT HEATING
Start-Stop switch OFF or defective Check
No operation of any kind Circuit breaker OFF or defective Check
N
o
o
p
e
r
a
t
i
o
n
o
f
a
n
y
k
i
n
d
External power source OFF Turn ON
Circuit breaker or fuse defective Replace
Control Transformer defective Replace
No control power Evaporator fan internal motor protector open 6.17
N
o
c
o
n
t
r
o
l
p
o
w
e
r
Heat relay defective Check
Heater termination thermostat open 6.15
Heater(s) defective 6.15
Heater contactor or coil defective Replace
Evaporator fan motor(s) defective or rotating backwards 6.15/6.17
Unit
w
ill not heat or has insuffi- Evaporator fan motor contactor defective Replace
U
n
i
t
w
i
l
l
n
o
t
h
e
a
t
o
r
h
a
s
i
n
s
u
f
f
i
-
cient heat Controller malfunction 5.9
Defective wiring Replace
Loose terminal connections Tighten
Low line voltage 2.3
5.5 UNIT WILL NOT TERMINATE HEATING
Controller improperly set Reset
U
n
i
t
f
a
i
l
s
t
o
s
t
o
p
h
e
a
t
i
n
g
Controller malfunction 5.9
U
n
i
t
f
a
i
l
s
t
o
s
t
o
p
h
e
a
t
i
n
g
Heater termination thermostat remains closed along with
the heat relay 6.15
5.6 UNIT WILL NOT DEFROST PROPERLY
Defrost timer malfunction (Cd27) Table 3-5
Loose terminal connections Tighten/
Will not initiate defrost Defective wiring Replace
W
i
l
l
n
o
t
i
n
i
t
i
a
t
e
d
e
f
r
o
s
t
automatically Defrost temperature sensor defective or heat termination
thermostat open Replace
Heater contactor or coil defective Replace
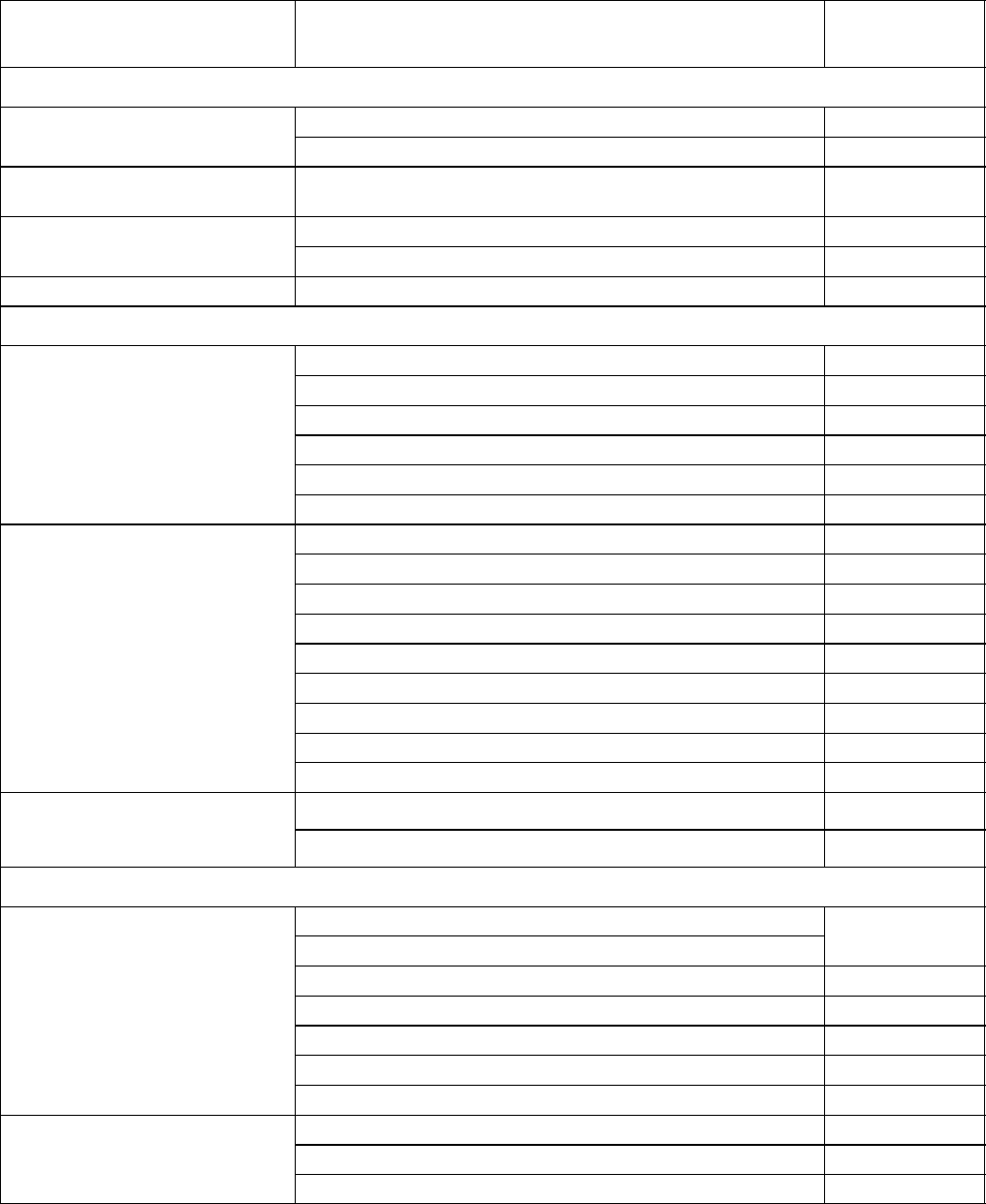
5-3 T-309
CONDITION POSSIBLE CAUSE REMEDY/
REFERENCE
SECTION
5.6 UNIT WILL NOT DEFROST PROPERLY -- Continued
Will not initiate defrost Manual defrost switch defective Replace
W
i
l
l
n
o
t
i
n
i
t
i
a
t
e
d
e
f
r
o
s
t
manually Defrost temperature sensor open 4.9.5
Initiates but relay (DR) drops
out Low line voltage 2.3
I
n
i
t
i
a
t
e
s
b
u
t
d
o
e
s
n
o
t
d
e
f
r
o
s
t
Heater contactor or coil defective Replace
Initiates but does not defrost Heater(s) burned out 6.15
Frequent defrost Wet load Normal
5.7 ABNORMAL PRESSURES (COOLING)
Condenser coil dirty 6.11
Condenser fan rotating backwards 6.12
H
i
g
h
d
i
s
c
h
a
r
g
e
p
r
e
s
s
u
r
e
Condenser fan inoperative 6.12
High discharge pressure Refrigerant overcharge or noncondensibles 6.7.1
Discharge service valve partially closed Open
Suction modulation valve malfunction 6.20
Faulty suction pressure transducer Replace
Suction service valve partially closed Open
Filter-drier partially plugged 6.13
Low refrigerant charge 6.7.1
Low suction pressure Expansion valve defective 6.14
L
o
w
s
u
c
t
i
o
n
p
r
e
s
s
u
r
e
No evaporator air flow or restricted air flow 6.15
Excessive frost on evaporator coil 5.6
Evaporator fan(s) rotating backwards 2.3
Suction modulation valve malfunction 6.20
Suction and discharge pressures
t
e
n
d
t
o
e
q
u
a
l
i
z
e
w
h
e
n
u
n
i
t
i
s
Compressor operating in reverse 5.14
ten
d
to equa
l
i
ze
w
h
en un
i
t
i
s
operating Compressor cycling/stopped Check
5.8 ABNORMAL NOISE OR VIBRATIONS
Compressor start up after an extended shutdown
N
o
r
m
a
l
Brief chattering when manually shut down Normal
Compressor operating in reverse 5.14
Compressor Loose mounting bolts or worn resilient mounts Tighten/Replace
C
o
m
p
r
e
s
s
o
r
Loose upper mounting 6.8.1 step r.
Liquid slugging 6.14
Insufficient oil 6.9
Bent, loose or striking venturi Check
Condenser or Evaporator Fan Worn motor bearings 6.12/6.17
C
o
n
d
e
n
s
e
r
o
r
E
v
a
p
o
r
a
t
o
r
F
a
n
Bent motor shaft 6.12/6.17

5-4T-309
CONDITION POSSIBLE CAUSE REMEDY/
REFERENCE
SECTION
5.9 CONTROLLER MALFUNCTION
Defective Sensor 6.22
Defective wiring Check
Will not control Fuse (F1, F2, F3) blown Replace
W
i
l
l
n
o
t
c
o
n
t
r
o
l
Stepper motor suction modulation valve circuit malfunction 6.20
Low refrigerant charge 6.7
5.10 NO EVAPORATOR AIR FLOW OR RESTRICTED AIR FLOW
E
v
a
p
o
r
a
t
o
r
c
o
i
l
b
l
o
c
k
e
d
Frost on coil 5.6
Evaporator coil blocked Dirty coil 6.15
Evaporator fan motor internal protector open 6.17
N
o
o
r
p
a
r
t
i
a
l
e
v
a
p
o
r
a
t
o
r
a
i
r
f
l
o
w
Evaporator fan motor(s) defective 6.17
No or partial evaporator air flo
w
Evaporator fan(s) loose or defective 6.17
Evaporator fan contactor defective Replace
5.11 THERMOSTATIC EXPANSION VALVE MALFUNCTION
Low refrigerant charge 6.7.1
External equalizer line plugged Open
Wax, oil or dirt plugging valve or orifice Ice formation at
valve seat 6.14
Low suction pressure with high
s
p
e
r
h
e
a
t
Superheat not correct 6.7.1
superheat Power assembly failure
Loss of element/bulb charge
6
1
4
Broken capillary 6.14
Foreign material in valve
H
i
h
i
i
h
l
Superheat setting too low 6.14
High suction pressure
w
ith lo
w
s
u
p
e
r
h
e
a
t
External equalizer line plugged Ice holding valve open Open
super
h
ea
t
Foreign material in valve 6.14
Liquid slugging in compressor Pin and seat of expansion valve eroded or held open by for-
eign material
6
1
4
F
l
u
c
t
u
a
t
i
n
g
s
u
c
t
i
o
n
p
r
e
s
s
u
r
e
Improper bulb location or installation 6.14
Fluctuating suction pressure Low superheat setting
5.12 AUTOTRANSFORMER MALFUNCTION
U
n
i
t
w
i
l
l
n
o
t
s
t
a
r
t
Circuit breaker (CB-1 or CB-2) tripped Check
Unit
w
ill not start Power source not turned ON Check
5.13 WATER-COOLED CONDENSER OR WATER PRESSURE SWITCH
C
o
n
d
e
n
s
e
r
f
a
n
s
t
a
r
t
s
a
n
d
s
t
o
p
s
Water pressure switch malfunction Check
Condenser fan starts and stops Water supply interruption Check

5-5 T-309
CONDITION POSSIBLE CAUSE REMEDY/
REFERENCE
SECTION
5.14 COMPRESSOR OPERATING IN REVERSE
CAUTION
Allowingthe scroll compressorto operate in reverse formore than two minuteswill result in internal
compressor damage. Turn the start--stop switch OFF immediately.
Incorrect wiring of compressor
Electrical Incorrect wiring of compressor contactor(s) Check
E
l
e
c
t
r
i
c
a
l
Incorrect wiring of current sensor
C
h
e
c
k
5.15 ABNORMAL TEMPERATURES
Discharge temperature sensor drifting high Replace
Failed economizer, TXV or solenoid valve Replace
High discharge temperature Plugged economizer, TXV or solenoid valve Replace
H
i
g
h
d
i
s
c
h
a
r
g
e
t
e
m
p
e
r
a
t
u
r
e
Loose or insufficiently clamped sensor Replace
Failed liquid injection solenoid valve Replace
L
o
w
s
u
c
t
i
o
n
t
e
m
p
e
r
a
t
u
r
e
Discharge temperature sensor drifting low Replace
L
o
w
suction temperature Loose or insufficiently clamped sensor Replace
5.16 ABNORMAL CURRENTS
Unit reads abnormal currents Current sensor wiring Check

6-1 T-309
SECTION 6
SERVICE
NOTE
Toavoiddamagetotheearth’sozonelayer,usearefrigerantrecoverysystemwheneverremovingrefrigerant.
When working with refrigerants you must comply with all local government environmental laws. In the
U.S.A., refer to EPA section 608.
WARNING
Neveruse airfor leak testing. Ithas beende-
termined that pressurized, mixtures of re-
frigerant and air can undergo combustion
when exposed to an ignition source.
6.1 SECTION LAYOUT
Service procedures are provided herein beginning with
refrigeration system service, then refrigeration system
component service, electrical system service,
temperature recorder service and general service. Refer
to the Table Of Contents to locate specific topics.
6.2 SERVICE VALVES
The compressor suction, compressor discharge,
compressor economizer, oil return and the liquid line
service valves (see Figure 6-1) are provided with a
double seat and an access valve which enable servicing
of the compressor and refrigerant lines. Turning the
valve stem clockwise (all the way forward) will
frontseat the valve to close off the line connection and
open a path to the access valve. Turning the stem
counterclockwise (all the way out) will backseat the
valve to open the line connection and close off the path
to the access valve.
With the valve stem midway between frontseat and
backseat,bothoftheservicevalveconnectionsareopen
to the access valve path.
For example, the valve stem is first fully backseated
whenconnectingamanifoldgaugetomeasurepressure.
Then, thevalveis opened1/4 to 1/2 turnto measure the
pressure.
VALVE
FRONTSEATED
(Clockwise)
VALVE
BACKSEATED
(Counterclockwise)
5
1
23
4
1. Line Connection
2. Access Valve
3. Stem Cap
4. Valve stem
5. Compressor Or Filter
Drier Inlet Connection
Figure 6-1 Service Valve
VALVE
FRONTSEATED
(Clockwise)
VALVE
BACKSEATED
(Counterclockwise)
5
1
23
4
1. Line Connection
2. Access Valve
3. Stem Cap
4. Valve stem
5. Compressor Inlet
Connection
Figure 6-2 Suction Service Valve
OPENED (Backseated )
HAND VALVE CLOSED (Frontseated)
HAND VALVE
SUCTION
PRESSURE
GAUGE
DISCHARGE
PRESSURE
GAUGE
ABC
A. CONNECTION TO LOW SIDE OF SYSTEM
B. CONNECTION TO EITHER:
REFRIGERANT CYLINDER OR
OIL CONTAINER
C. CONNECTION TO HIGH SIDE OF SYSTEM
Figure 6-3 Manifold Gauge Set
6.3. MANIFOLD GAUGE SET
The manifold gauge set (see Figure 6-3) is used to
determine system operating pressure, add refrigerant
charge, and to equalize or evacuate the system.
When the suction pressure hand valve is frontseated
(turnedallthewayin),thesuction(low)pressurecanbe
checked. When the discharge pressure hand valve is
frontseated, the discharge (high) pressure can be
checked. When both valves are open (turned
counter-clockwiseall thewayout), high pressurevapor
will flow into the low side. When the suction pressure
valve is open and the discharge pressure valveshut, the

6-2T-309
system can be charged. Oil can also be added to the
system.
A R-134a manifold gauge/hose set with self-sealing
hoses (see Figure 6-4) is required for service of the
models covered within this manual. The manifold
gauge/hose set is available from Carrier Transicold.
(Carrier Transicold P/N 07-00294-00, which includes
items1through6,Figure 6-4.)Toperformserviceusing
the manifold gage/hose set, do the following:
a. Preparing Manifold Gauge/Hose Set For Use
1. Ifthemanifoldgauge/hosesetisneworwasexposed
to the atmosphere it will need to be evacuated to
remove contaminants and air as follows:
2. Backseat (turn counterclockwise)both field service
couplings (see Figure 6-4) and midseat both hand
valves.
3. Connect the yellow hose to a vacuum pump and re-
frigerant 134a cylinder.
OPENED
(Backseated )
HAND VALVE
CLOSED
(Frontseated)
HAND VALVE
SUCTION
PRESSURE
GAUGE
DISCHARGE
PRESSURE
GAUGE
To Low Side
Access Valve To High Side
Access Valve
Red Knob
Blue Knob
1
43
YELLOW
2
45
6
3
RED
3
BLUE
2
1. Manifold Gauge Set
2. Hose Fitting (0.5-16 Acme)
3. Refrigeration and/or Evacuation Hose
. (SAE J2196/R-134a)
4. Hose Fitting w/O-ring (M14 x 1.5)
5. High Side Field Service Coupling
6. Low Side Field Service Coupling
Figure 6-4 R-134a Manifold Gauge/Hose Set
7. Evacuate to 10 inches of vacuum and then charge
withR-134atoaslightlypositivepressureof0.1kg/
cm@(1.0 psig).
8. Front seat both manifold gauge set valves and dis-
connect from cylinder. The gauge set is now ready
for use.
b. Connecting Manifold Gauge/Hose Set
To connect the manifold gauge/hose set for reading
pressures, do the following:
1. Remove service valve stem cap and check to make
sure it is backseated. Remove access valve cap. (See
Figure 6-1)
2. Connect the field service coupling (see Figure 6-4)
to the access valve.
3. Turn the field service coupling knob clockwise,
which will open the system to the gauge set.
4. To read system pressures: slightly midseat the ser-
vice valve.
5. Repeattheproceduretoconnecttheothersideofthe
gauge set.
CAUTION
Topreventtrappingliquid refrigerantin the
manifold gauge set be sure set is brought to
suction pressure before disconnecting.
c. Removing the Manifold Gauge Set
1. While the compressor is still ON, backseat the high
side service valve.
2. Midseat bothhand valveson the manifold gaugeset
and allow the pressure in the manifold gauge set to
bedrawndowntolowsidepressure.Thisreturnsany
liquidthatmaybeinthehighsidehosetothesystem.
3. Backseat the low side service valve. Backseat both
field service couplings and frontseat both manifold
set valves. Remove the couplings from the access
valves.
4. Install both service valve stem caps and serviceport
caps (finger-tight only).
6.4 PUMPING THE UNIT DOWN
To service the filter-drier, economizer, expansion
valves, moisture-liquid indicator, suction modulation
valve, economizer solenoid valve, unloader solenoid
valve or evaporator coil, pump the refrigerant into the
high side as follows:
CAUTION
The scroll compressor achieves low suction
pressure very quickly. Do not operate the
compressorinadeepvacuum, internaldam-
age will result.
a. Attach manifold gauge set to the compressorsuction
and discharge service valves. Refer to paragraph 6.3.
b. Start the unit and run in the frozen mode (controller
set below --10°C)for10to15minutes.
c. CheckfunctioncodeCd21(refertoparagraph3.2.2).
The economizer solenoid valve should be open. If
not, continue to run until the valve opens.
d. Frontseat the oil return service valve then, frontseat
theliquidlineservicevalve.Placestart-stopswitchin
theOFF position whenthe suctionreaches a positive
pressure of 0.1 kg/cm@(1.0 psig).
e. Frontseat the economizer service valve and then
frontseat the suction and discharge service valves.
Therefrigerantwillbetrappedbetweenthecompres-
sor suction service valve and the liquid line valve.
f. Before opening up any part of the system, a slight
positive pressure should beindicated on thepressure

6-3 T-309
gauge. If a vacuum is indicated, emit refrigerant by
crackingtheliquidlinevalvemomentarilytobuildup
a slight positive pressure.
g. Whenopeninguptherefrigerantsystem,certainparts
mayfrost.Allowtheparttowarmtoambienttemper-
ature before dismantling. This avoids internal con-
densation which puts moisture in the system.
h. After repairs have been made, be sure to perform a
refrigerant leak check (refer to paragraph 6.5), and
evacuate and dehydrate the low side (refer to para-
graph 6.6).
i. Check refrigerant charge (refer to paragraph 6.7).
6.5 REFRIGERANT LEAK CHECKING
WARNING
Never use air for leak testing. It has been
determined that pressurized, air-rich mix-
tures of refrigerants and air can undergo
combustion when exposed to an ignition
source.
a. The recommended procedure for finding leaks in a
systemiswithaR-134aelectronicleakdetector.Test-
ingjointswithsoapsudsissatisfactoryonlyforlocat-
ing large leaks.
b. Ifthesystemiswithoutrefrigerant,chargethesystem
with refrigerant 134a to build up pressure between
2.1to3.5kg/cm@(30to50psig).Toensurecomplete
pressurization of the system, refrigerant should be
charged at the compressor suction and economizer
servicevalvesandtheliquidlineservicevalve.Also,
the area between the suction modulating valve and
evaporatorexpansion valve maynot beopen tothese
charging points. Pressurebetween thesecomponents
maybechecked atthelowsideaccessvalve(item11,
Figure 2-2) or by checking that the suction modulat-
ing valve is more than 10% open at controller func-
tion code Cd01. The suction modulating valve may
beopenedbyuseofthecontrollerfunctioncodeCd41
valve override control (refer to paragraph 6.19). Re-
move refrigerant cylinderandleak-check allconnec-
tions.
NOTE
Only refrigerant 134a should be used to pres-
surize the system. Any other gas or vapor will
contaminate the system, which will require
additional purging and evacuation of the sys-
tem.
c. If required, remove refrigerant using a refrigerant
recovery system and repair any leaks.
d. Evacuateand dehydrate the unit.(Refer toparagraph
6.6.)
e. Charge unit per paragraph 6.7.
6.6 EVACUATION AND DEHYDRATION
6.6.1 General
Moisture is the deadly enemy of refrigeration systems.
The presence of moisture in a refrigeration system can
have many undesirable effects. The most common are
copper plating, acid sludge formation, “freezing-up”of
metering devices by freewater, and formation of acids,
resulting in metal corrosion.
6.6.2 Preparation
a. Evacuateand dehydrateonly after pressure leak test.
(Refer to paragraph 6.5.)
b. Essential tools to properly evacuate and dehydrate
any systeminclude avacuum pump (8 m3/hr= 5 cfm
volume displacement) and an electronic vacuum
gauge. (The pump is available from Carrier Trans-
icold, P/N 07-00176-11.)
c. If possible, keep the ambient temperature above
15.6_C(60_F) to speed evaporation of moisture. If
the ambient temperature is lower than 15.6_C
(60_F), ice might form before moisture removal is
complete.Heatlampsoralternatesourcesofheatmay
be used to raise the system temperature.
d. Additionaltimemaybesavedduringa completesys-
tem pump down by replaceing the filter-drier with a
section of coppertubing and the appropriatefittings.
Installation of a new drier may be performed during
the charging procedure.
6
4
5
D
S
23
11 9
10
1
7
8
1. Liquid Service Valve
2. Receiver or Water
Cooled Condenser
3. Compressor
4. Discharge Service
Valve
5. Economizer Service
Valve
6. Suction Service Valve
7. Vacuum Pump
8. Electronic Vacuum
Gauge
9. Manifold Gauge Set
10. Refrigerant Cylinder
11. Reclaimer
Figure 6-5. Refrigeration System Service
Connections
6.6.3 Procedure - Complete system

6-4T-309
a. Remove all refrigerant using a refrigerant recovery
system.
b. Therecommendedmethodtoevacuateanddehydrate
thesystem is to connect evacuation hosesatthecom-
pressor suction, compressor economizer and liquid
line service valve (see Figure 6-5). Be sure the ser-
vice hoses are suited for evacuation purposes.
c. The area between the suction modulating valve and
evaporator expansion valve may not be open to the
access valves. To ensure evacuation of this area,
check that the suction modulating valveis morethan
10% open at controller function code Cd01. If re-
quired, the suction modulating valvemay beopened
by use of the controller function code Cd41 valve
overridecontrol.Ifpoweris not availabletoopenthe
valve, the area may be evacuated by connecting an
additional hose at the low side access valve (item 11,
Figure 2-2).
d. Testtheevacuationsetupforleaksbybackseatingthe
unit service valves and drawing a deep vacuum with
thevacuumpumpandgaugevalvesopen.Shutoffthe
pump and check to see if the vacuum holds. Repair
leaks if necessary.
e. Midseat the refrigerant system service valves.
f. Openthevacuumpumpandelectronicvacuumgauge
valves,iftheyarenotalready open. Start thevacuum
pump. Evacuate unit until the electronic vacuum
gauge indicates 2000 microns. Close the electronic
vacuumgaugeandvacuumpumpvalves.Shutoffthe
vacuumpump.Waitafewminutestobesurethevac-
uum holds.
g. Break the vacuum with clean dry refrigerant 134a
gas. Raise system pressure to approximately 0.2 kg/
cm@(2 psig), monitoring it with the compound
gauge.
h. Remove refrigerant using a refrigerant recovery sys-
tem.
i. Repeat steps f.and g. one time.
j. Removethecoppertubingandchangethefilter-drier.
Evacuate unit to 500 microns. Close the electronic
vacuumgaugeandvacuumpumpvalves.Shutoffthe
vacuum pump. Wait five minutes to see if vacuum
holds. This procedure checks for residual moisture
and/or leaks.
k. With a vacuumstill in the unit,the refrigerantcharge
may bedrawninto the systemfromarefrigerant con-
tainer on weight scales. Continue to paragraph 6.7
6
4
5
7
DS
10
123
8
9
1. Receiver or Water
Cooled Condenser
2. Compressor
3. Discharge Service
Valve
4. Economizer Service
Valve
5. Suction Service Valve
6. Vacuum Pump
7. Electronic Vacuum
Gauge
8. Manifold Gauge Set
9. Refrigerant Cylinder
10. Reclaimer
Figure 6-6. Compressor Service Connections
6.6.4 Procedure - Partial System
a. If the refrigerant charge has been removed from the
compressorforservice,evacuateonlythecompressor
by connecting the evacuation set--up at the compres-
sor service valves. (See Figure 6-6.) Follow evacua-
tion procedures of the preceding paragraph except
leave compressor service valves frontseated until
evacuation is completed.
b. If refrigerant charge has been removed from the low
side only, evacuate the low side by connecting the
evacuation set--up at the compressor suction and
economizer service valves and the liquid service
valveexceptleavetheservicevalvesfrontseateduntil
evacuation is completed.
c. Once evacuation has been completed and the pump
has been isolated, fully backseat the service valvesto
isolate the service connections and then continue
with checking and, if required, adding refrigerant in
accordance with normal procedures
6-5 T-309
6.7 REFRIGERANT CHARGE
6.7.1 Checking the Refrigerant Charge
NOTE
To avoiddamagetothe earth’sozonelayer, use
arefrigerant recoverysystem wheneverremov-
ing refrigerant. When working with refriger-
ants you must comply with all local govern-
ment environmental laws. In the U.S.A., refer
to EPA section 608.
a. Connect the gauge manifold to the compressor dis-
chargeandsuctionservicevalves.Forunitsoperating
on a water cooled condenser, change over to air
cooled operation.
b. Bring the container temperature to approximately
1.7_C(35_F)or--17.8_C(0_F).Thensetthecontrol-
lerset point to --25_C(--13_F) to ensurethat thesuc-
tion modulation valve is fully open. (Position of the
suctionmodulating valve may be checked atcontrol-
ler function code Cd01.)
c. Partially block the condenser coil inlet air. Increase
theareablockeduntilthecompressordischargepres-
sureisraisedtoapproximately12kg/cm@(175psig).
d. Onunitsequippedwithareceiver,thelevelshouldbe
between the glasses. On units equipped with a water
cooled condenser, the level should be at the centerof
theglass.Iftherefrigerantlevelisnotcorrect,contin-
uewiththefollowingparagraphstoaddorremovere-
frigerant as required.
6.7.2 Adding Refrigerant to System (Full Charge)
a. Evacuate unit and leave in deep vacuum. (Refer to
paragraph 6.6.)
b. Place cylinderof R-134aon scaleand connectcharg-
ing line from cylinder to liquid line valve. Purge
charginglineatliquidlinevalveandthennoteweight
of cylinder and refrigerant.
c. Openliquidvalveoncylinder. Openliquidlinevalve
half-way and allow theliquid refrigerantto flow into
theunituntilthecorrectweightofrefrigerant(referto
paragraph2.2) has been added asindicated by scales.
NOTE
It may be necessary to finish charging unit
through suction service valve in gas form, due
to pressure rise in high side of the system.
(Refer to section paragraph 6.7.3)
d. Backseatmanualliquid linevalve(tocloseoffgauge
port). Close liquid valve on cylinder.
e. Start unit in cooling mode. Run approximately 10
minutes and check the refrigerant charge.
6.7.3 Adding Refrigerant to System (Partial
Charge)
a. Examine the unitrefrigerant system foranyevidence
of leaks. Repair as necessary. (Refer to paragraph
6.5.)
b. Maintain the conditions outlined in paragraph 6.7.1
c. Fully backseat the suction service valve and remove
the service port cap.
d. Connect charging line between suction service valve
port and cylinder of refrigerant R-134a. Open
VAPOR valve.
e. Partially frontseat (turn clockwise) the suction ser-
vicevalveandslowlyaddchargeuntiltherefrigerant
appearsattheproperlevel.Becarefulnottofrontseat
the suction valve fully, if the compressor is operated
in a vacuum internal damage may result.
6.8 COMPRESSOR -- Model RSH105
WARNING
Make sure power to the unit is OFF and
power plug disconnected before replacing
the compressor.
WARNING
Before disassembly of the compressor make
sure to relieve the internal pressure very
carefully by slightly loosening the couplings
to break the seal.
CAUTION
The scroll compressor achieves low suction
pressure very quickly. Do not use the com-
pressor to evacuate the system below zero
psig. Never operate the compressor with the
suction or discharge service valves closed
(frontseated). Internal damage will result
from operating the compressor in a deep
vacuum.
6.8.1 Removal and Replacement of Compressor
NOTE
Servicecompressorcontainsanitrogencharge.
Due to the hygroscopic nature of the oil, time
the compressor is left open to the atmosphere
should be minimized as much as possible.
a. Procure areplacement compressor kit. Alist ofitems
contained in the compressor kit is provided in
Table 6-1.
b. Ifthecompressorisoperational, pumpthe unitdown
(refer to paragraph 6.4).

6-6T-309
Table 6-1 Compressor Kit
Item Component Qty
1Compressor 1
2Service Valve Seal 3
3Mylar Washers 4
4Wire Tie 2
5Oil Sight Glass Plug 1
6Resilient Mount 4
7Upper Shock Mount Ring 1
8Upper Shock Mount Bushing 1
9Compressor Power Plug O--Ring 1
10 SST Washers 8
c. If the compressor is not operational, turn the unit
start--stop switch (ST) and unit circuit breaker
(CB--1)OFF.Disconnectpowertotheunitandfront--
seatthedischarge,suction,economizer,andoilreturn
service valves.
Remove all remaining refrigerant from the compres-
sor using a refrigerant recovery system. Connect
hoses to suction, economizer and discharge service
valves ports. Evacuate compressor to 500 microns
(75.9 cm Hg vacuum = 29.9 inches Hg vacuum).
d. Make sure power to the unit is OFF and unit power
plug disconnected. Disconnect the power plug from
the compressor.
e. Loosenandbreakthesealatfittingsfromthesuction,
discharge, economizer, and the oil return service
valves. Remove fittings and discard service valve
seals, retain oil return valve O--ring.
f. Remove the entire compressor upper mounting
bracket assembly,(see Figure 6-7) by removing the
fourcapscrewsattachingittotheunitandthe32--mm
bolt from the compressor mounting bracket.
Upper Shock Mount
Bushing(KitItem8) Upper Shock Mount
Ring (Kit Item 7)
Shoulder Bolt
32mm Bolt
Figure 6-7 Compressor Upper Mounting
Resilient Mount
(Kit Item 6)
Mylar Washer
(Kit Item 3)
Mylar Protector
(Retain)
Base Plate
(Retain)
Mylar Protector
(Retain)
SST Washer
(Kit Item 10)
SST Washer
(Kit Item 10)
Figure 6-8 Compressor Lower Mounting
g. Replace the upper mounting bracket shock mount
ring and bushing (kit items 7and 8). Reassemble the
bracketinthesamemannerastheoriginalandtorque
the shoulder bolt to 2.8 mkg (20 ft--lbs.).
h. Remove the male coupling from the top of the sight
glassontheoldcompressorandhandassembletothe
oil return valve coupling for safe keeping. Plug the
top of the replacement compressor sight glass with
the plug (kit item 5) to prevent spilling oil.
i. Remove the lowermounting bolts and hardware(see
Figure 6-8). Using plugs from replacementcompres-
sor,plugconnectionsonoldcompressor.Removethe
old compressor. Refer to paragraph 2.2for compres-
sor weight. Return plugs to replacement compressor.
j. The replacement compressor is shipped with an oil
charge of 591ml (20 ounces). Beforesliding the new
compressorintheunit,removetheoilsightglassplug
and (using a small funnel) charge the compressor
with an additional 1893ml (64 ounces) Castrol--Ice-
maticSW20(POEoil).Reassembletheoilsightglass
plugtoavoidspillingoilwhenslidingthecompressor
in the unit.
k. Securethebaseplateandmylarprotectorstothecom-
pressorwithwireties(kititem4), andplacethecom-
pressor in the unit.
l. Cut and remove the wire ties that were used to hold
the base plate and protectors to the compressor. Us-
ing new resilient mounts, SST washers and mylar
washers(kititems3,6&10).Installthefourmount-
ing screws loosely.
m.Installthemalecoupling(removedinsteph.)intothe
sight glass port.

6-7 T-309
n. Place the new service seals (kit item 2) at the com-
pressorservice ports, connect thefour servicevalves
loosely.
o. Torquethefourresilientmountscrewsto6.2mkg(45
ft--lbs).
p. Torque the four service valves to:
Service Valve Torque
Suction or Discharge 11 to 13.8 mkg
(80 to 100 ft--lbs.)
Economizer 6.9to8.3mkg
(50to60ft--lbs.)
Oil Return 1.4to1.66mkg
(10to12ft--lbs.)
q. Reassemble the top mounting bracket (see
Figure 6-7) by hand tightening the 32--mm (1¼
--inch)boltandtorquingthefourmountingscrewsto
0.9 mkg (6.5 ft--lbs). Align the mounting so that the
ringandbushingassemblyarefreewithnocompres-
sion.
r. Torque the32mm bolt to 1.5 mkg (11 ft--lbs.). While
maintaining the free movement of the shock mount,
torque the four mounting screws to 0.9 mkg (6.5 ft--
lbs.).
s. Replace the power plug O--Ring with new ring (kit
item9).Insertthepowerplugintothecompressorfit-
ting. Be sure plug is fully seated into the fitting and
then thread the coupling nut a minimum of 5 turns.
t. Leakcheckand evacuatethe compressorto 1000 mi-
crons. Refer to paragraphs 6.5 and 6.6
u. Run the unit for at least 15 minutes and check the oil
and refrigerant levels. Refer to paragraphs 6.7 and
6.9.
6.9 COMPRESSOR OIL LEVEL
CAUTION
Use only Carrier Transicold approved
Polyol Ester Oil (POE) -- Mobil ST32 com-
pressor oil with R-134a. Buy in quantities of
onequartorsmaller.Whenusingthishygro-
scopic oil, immediately reseal. Do not leave
container of oil open or contamination will
occur.
a. Checking the Oil Level in the Compressor
1 Ideally, ambient temperature should be between
40_F and 100_F.
2 Operatetheunitincoolingmodeforatleast20min-
utes.
3 Check the controller function code Cd1 for the suc-
tion modulation valve(SMV) position.It should be
at least 20% open.
4 Locatetheoilsightglassonthesideofthecompres-
sor (item 7, Figure 2-3).
5 TurnStart/Stopswitch offandallowoiltodraininto
compressor sump. Oil level must be visible in the
sightglass.Ifitisnotvisible,oilmustbeaddedtothe
compressor.
b. Adding Oil with Compressor in System
1. The recommended method is to add oil using an oil
pump at the oil return service valve (see item 15,
Figure 2-3)
2. Inan emergencywhere an oil pumpis not available,
oilmaybedrawnintothecompressorthroughtheoil
return service valve.
Connect the suction connection of the gauge man-
ifold to the compressor oil return valve port, and
immersethe common connection ofthe gaugeman-
ifold in an open container of refrigeration oil.
Extreme care must be taken to ensure the manifold
common connection remains immersed in oil at all
times.Otherwiseairandmoisturewillbedrawninto
the compressor. Crack the oil return service valve
andgaugevalvetoventasmallamountofrefrigerant
throughthecommonconnectionandtheoiltopurge
the lines of air. Close the gauge manifold valve.
With theunit running, turn thesuction servicevalve
toward frontseat and induce a vacuum in the com-
pressor crankcase. Do not allow the compressor to
pull below 127mm/hg (5 “/hg). SLOWLY crack the
suction gauge manifold valve and oil will flow
throughtheoilreturnservicevalveintothecompres-
sor. Add oil as necessary.
3 Run unit for 20 minutes in cooling mode. Check oil
level at the compressor sight glass.
c. Removing Oil from the Compressor:
1 If the oil level is above the sight glass, oil must be
removed from the compressor.
2 Perform a compressor pump down, refer to section
6.4.
3 Removetheoilplug,anddrainoiluntilalevelcanbe
seen in the sight glass.
4 Run unit for 20 minutes in cooling mode. Check oil
level at the compressor sight glass.
6.10 HIGH PRESSURE SWITCH
6.10.1 Replacing High Pressure Switch
a. Turn unit start-stop switch OFF. Frontseat the suc-
tion, discharge, economizer and oil return service
valves to isolate compressor. Remove the refrigerant
from the compressor.
b. Disconnect wiring from defective switch. The high
pressure switch is located on the discharge service
valve and is removed by turning counterclockwise.
(See Figure 2-3.)
c. Install a new high pressure switch after verifying
switch settings. (Refer to paragraph 6.10.2.)
d. Evacuate and dehydrate the compressor per para-
graph 6.6.

6-8T-309
6.10.2 Checking High Pressure Switch
WARNING
Do not use a nitrogen cylinder without a
pressure regulator. Do not use oxygen in or
near a refrigeration system as an explosion
may occur.
NOTE
The high pressure switch is non-adjustable.
a. Remove switch as outlined in paragraph 6.10.1
b. Connect ohmmeter or continuity light across switch
terminals. Ohm meter will indicate no resistance or
continuity light will be illuminated if the switch
closed after relieving compressor pressure.
c. Connect hose to a cylinder of dry nitrogen. (See
Figure 6-9.)
1. Cylinder Valve
and Gauge
2. Pressure Regulator
3. Nitrogen Cylinder
4. Pressure Gauge
(0 to 36 kg/cm@=
0 to 400 psig)
5. Bleed-Off Valve
6. 1/4 inch Connection
1
2
3
4
5
6
Figure 6-9 High Pressure Switch Testing
d. Set nitrogen pressure regulator at 26.4 kg/cm@(375
psig) with bleed-off valve closed.
e. Close valve on cylinder and open bleed-off valve.
f. Open cylinder valve. Slowly close bleed-off valveto
increase pressure on switch. The switch should open
at a static pressure up to 25 kg/cm@(350 psig). If a
lightisused,lightwillgoout.Ifanohmmeterisused,
the meter will indicate open circuit.
g. Slowlyopenbleed-offvalvetodecreasethepressure.
The switch should close at 18 kg/cm@(250 psig).
6.11 CONDENSER COIL
The condenser consists of a series of parallel copper
tubes expanded into copper fins. The condenser coil
mustbecleanedwithfreshwaterorsteamsotheairflow
is not restricted. To replace the coil, do the following:
WARNING
Do not open the condenser fan grille before
turning power OFF and disconnecting
power plug.
a. Using a refrigerant reclaim system, remove the
refrigerant charge.
b. Remove the condenser coil guard.
c. Unsolder discharge line and remove the line to the
receiver or water-cooled condenser.
d. Remove coil mounting hardware and remove the
coil.
e. Install replacement coil and solder connections.
f. Leak-check the coil connections per paragraph para-
graph 6.5. Evacuate the unit per paragraph 6.6 then
charge the unit with refrigerant per paragraph 6.7.
6.12 CONDENSER FAN AND MOTOR ASSEMBLY
WARNING
Do not open condenser fan grille before
turning power OFF and disconnecting
power plug.
The condenser fan rotates counter-clockwise (viewed
from front of unit), pulls air through the the condenser
coil,anddischargeshorizontallythroughthefrontofthe
unit. To replace motor assembly:
a. Open condenser fan screen guard.
b. Loosen two square head set screws on fan. (Thread
sealer has been applied to set screws at installation.)
Disconnect wiring from motor junction box.
CAUTION
Take necessary steps (place plywood over
coil or use sling on motor) to prevent motor
from falling into condenser coil.
c. Remove motor mounting hardware and replace the
motor. It is recommended that new locknuts be used
when replacing motor. Connect wiring per wiring
diagram.
d. Install fan loosely on motor shaft (hub side in). DO
NOTUSEFORCE.Ifnecessary,tapthehubonly,not
the hub nuts or bolts. Install venturi. Apply “Loctite
H”tofansetscrews.Adjustfanwithinventurisothat
the outer edge of the fan is within 2.0 ±.07 mm
(0.08”¦0.03”)from theoutside ofthe orificeopen-
ing. Spin fan by hand to check clearance.
e. Close and secure condenser fan screen guard.
f. Apply power to unit and check fan rotation. If fan
motor rotates backward, reverse wire numbers 5 and
8.
6.13 FILTER-DRIER
Onunitsequippedwithawater-cooledcondenser, ifthe
sight glass appears to be flashing or bubbles are
constantly moving through the sight glass when the
suction modulation valve is fully open, the unit may
havea lowrefrigerant chargeor thefilter-drier couldbe
partially plugged.
a. To Check Filter-Drier
1. Testforarestrictedorpluggedfilter-drierbyfeeling
the liquid line inlet and outlet connections of the
driercartridge.Iftheoutletsidefeelscoolerthanthe
inlet side, then the filter-drier should be changed.

6-9 T-309
2. Check the moisture-liquid indicator if the indicator
showsahighlevelofmoisture,thefilter-driershould
be replaced.
b. To Replace Filter-Drier
1. Pump down the unit (refer to paragraph 6.4 and
replace filter-drier.
2. Evacuate the low side in accordance with paragraph
6.6.
3. Afterunitisinoperation,inspectformoistureinsys-
tem and check charge.
6.14 EXPANSION VALVES
Two expansion valves are used, the evaporator
expansion valve (item 9, Figure 2-2), and the
economizer expansion valve (item 26, Figure 2-4) .The
expansionvalvesareautomaticdeviceswhichmaintain
constant superheat of the refrigerant gas leaving at the
pointofbulbattachmentregardlessof suctionpressure.
The valve functions are:
1. Automatic control of the refrigerant flow to match
the load.
2. Prevention of liquid refrigerant entering the com-
pressor.
Unless the valve is defective, it seldom requires
maintenance other than periodic inspection to ensure
thatthethermalbulbistightlysecuredtothesuctionline
and wrapped with insulating compound. (See
Figure 6-10.)
1
2
3
4
1. Suction Line
2. TXV Bulb Clamp 3. Nut and Bolt
4. TXV Bulb
Figure 6-10 Thermostatic Expansion Valve Bulb
6.14.1 Checking Superheat.
NOTE
Propersuperheatmeasurementfortheevapora-
tor expansion valve should be completed at
-- 1 8 _C(0_F) container box temperature where
possible. If the economizer valve is suspect, it
should be replaced.
a. Open the heater access panel (see Figure 2-1) to ex-
pose the evaporator expansion valve.
b. Attachatemperaturesensorneartheexpansionvalve
bulb and insulate. Make surethe suctionline is clean
and that firm contact is made with the sensor.
c. Connectanaccurategaugetotheserviceportdirectly
upstream of the suction modulating valve.
d. Setthetemperaturesetpointto --18_C(0_F),andrun
unit until conditions stabilize.
e. Thereadingsmaycyclefromahightoalowreading.
Take readings of temperature and pressure every
three to five minutes for a total of 5or 6 readings
f. From the temperature/pressure chart (Table 6-7), de-
termine the saturation temperature corresponding to
the evaporator outlet test pressures at the suction
modulation valve.
g. Subtract the saturation temperatures determined in
stepf.fromthetemperaturesmeasuredinstep e..The
difference is the superheat of the suction gas. Deter-
mine the average superheatIt shouldbe 4.5to 6.7 °C
(8 to 12 °F)
6.14.2 Valve Replacement
a. Removing the Expansion Valve
NOTES
1. TheTXV’sarehermeticvalvesanddonot
have adjustable superheat.
2. All connections on the evaporator TXV are
bi---metallic, copper on the inside and
stainless on the outside. When brazing,
bi---metallic connections heat up very
quickly.
1
6
5
43
2
1. Evaporator Expansion Valve
2. Non-adjustable Superheat Stem
3. Equalizer Connection
4. Inlet Connection
5. Outlet Connection
6. Expansion Valve Bulb
Figure 6-11 Evaporator Expansion Valve

6-10T-309
Copper Tube
(Apply heat for
10-15 seconds)
Bi-metallic Tube Connection
(Apply heat for 2-5 seconds) Use of a wet cloth is not neces-
sary due to rapid heat dissipation
of the bi--metallic connections
Braze Rod
(’Sil-Phos” = 5.5% Silver, 6% Phosphorus)
Figure 6-12 Hermetic Thermostatic Expansion Valve Brazing Procedure
INLET
OUTLET
Figure 6-13 Economizer Expansion Valve
1. Pump down the unit per paragraph 6.4.
2. Removecushionclampslocatedontheinletandout-
let lines.
3. Unbrazetheequalizerconnection(ifapplicable),the
outlet connection and then the inlet connection.
4. Removeinsulation(Presstite)fromexpansionvalve
bulb.
5. Unstrapthebulb,locatedbelowthecenterofthesuc-
tion line (4 o’clock position), and remove thevalve.
b. Installing the Expansion Valve
1. Clean the suction line with sandpaper before instal-
ling bulb to ensure proper heat transfer. Apply ther-
mal grease to the indentation in the suction line.
2. Strap the thermal bulb to the suction line, making
sure bulb is placed firmly into the suction line. See
Figure 6-10 for bulb placement.
3. Insulate the thermal bulb.
4. The economizer expansion valves should be
wrapped in a soaked cloth for brazing. See
Figure 6-12. Braze inlet connection to inlet line
5. Braze outlet connection to outlet line.
6. Reinstall the cushion clamps on inlet and outlet
lines.
7. If applicable, braze the equalizer connection to the
equalizer line.
8. Check superheat (refer to step 6.14.1).
6.15 EVAPORATOR COIL AND HEATER
ASSEMBLY
The evaporator section, including the coil, should be
cleaned regularly. The preferred cleaning fluid is fresh
waterorsteam.AnotherrecommendedcleanerisOakite
202 or similar, following manufacturer’s instructions.
The two drain pan hoses are routed behind the
condenser fan motor and compressor. The drain pan
line(s) must be open to ensure adequate drainage.
6.15.1 Evaporator Coil Replacement
a. Pump unit down. (Refer to paragraph 6.4.)
b. With power OFF and power plug removed, remove
thescrewssecuringthepanelcoveringtheevaporator
section (upper panel).
c. Disconnect the defrost heater wiring.
d. Disconnect the defrost temperature sensor (see Fig-
ure Figure 2-2 from the coil. .
e. Remove middle coil support.
f. Remove the mounting hardware from the coil.
g. Unsolderthetwocoil connections, oneat thedistrib-
utor and the other at the coil header.
h. After defective coil is removed from unit, remove
defrost heaters and install on replacement coil.
i. Install coil assembly by reversing above steps.
j. Leak check connections per paragraph 6.5. Evacuate
the unit per paragraph 6.6 and add refrigerant charge
per paragraph 6.7.
6.15.2 Evaporator Heater Replacement
a.Beforeservicingunit,makesuretheunitcircuitbreak-
ers (CB-1& CB-2) andthe start-stopswitch (ST) are
intheOFFposition,andthatthepowerplugandcable
are disconnected.
b. Remove the lower access panel (Figure 2-1) by
removing the T.I.R. locking device lockwire and
mounting screws.

6-11 T-309
c. Determine which heater(s) need replacing by check-
ing resistance on each heater. Refer to paragraph 2.3
for heater resistance values
d. Remove hold-down clamp securing heaters to coil.
e. Lift the bent end of the heater (with the opposite end
down and away from coil). Move heater to the side
enough to clear the heater end support and remove.
6.16 ECONOMIZER, UNLOADER, LIQUID INJEC-
TION AND OIL RETURN SOLENOID VALVE
a. Replacing the Coil
NOTE
Thecoilmay bereplacedwithoutremovingthe
refrigerant.
1 Be sure electrical power is removed from the unit.
Disconnect leads. Remove top screw and washer.
Lift off coil. (See Figure 6-14 or Figure 6-15)
2 Verify coil type, voltage and frequency of old and
newcoil.Thisinformationappearsonthecoilhous-
ing.
b. Replacing Valve Internal Parts (Unloader
Solenoid Only)
1 Pump down the unit. Refer to paragraph 6.4.
2 Be sure electrical power is removed from the unit.
Disconnect leads. Remove top screw and washer.
Lift off coil. (See Figure 6-14)
3 Remove the top screw (see Figure 6-14), washer ,
and coil assembly.
4 Loosen the enclosing tube locknut.
5 Remove enclosing tube and locknut assembly. The
gasket is inside the enclosing tube.
6 Remove seat disc from inside ofbody and checkfor
obstructions and foreign material.
7 Placetheseatdiscintothevalvebodywiththesmall-
er diameter end facing up.
8 Install stem and plunger.
9 Place the enclosing tube locknut over the enclosing
tube. Install spacer over enclosing tube making sure
it is seated properly in the enclosing tube locknut.
Tighten enclosing tube locknut to a torque value of
2.78 mkg (20 ft-lb). Do not overtighten.
10 Install coil assembly, washer and top screw.
11 Evacuateanddehydratethesystem.(Refertosection
6.6.) Charge unit with refrigerant per section 6.7.
12 Start unit and check operation.
c. Replacing Valve
1 To replace the unloader, liquid injection or econo-
mizervalve,pumpdowntheunit.Refertoparagraph
6.4. To replace the oil return valve, remove the re-
frigerant charge.
2 Be sure electrical power is removed from the unit.
Disconnect leads. Remove top screw and washer.
Lift off coil. (See Figure 6-14 or Figure 6-15)
3 Unbraze valve from unit and braze new valve in
place
4 Install coil. Evacuate low side and place unit back
in operation. Check charge.
1
9
8
7
6
5
4
3
2
1. Top Screw
2. Washer
3. Coil
4. Locknut
5. Enclosing Tube
6. Gasket
7. Stem and Plunger
8. Seat Disc
9. Body
Figure 6-14. Unloader Solenoid Valve
1
2
3
4
1. Slotted Screw
2. Washer
3. Coil
4. Enclosing Tube and
Body
Figure 6-15. Oil Return Solenoid Valve (ORV),
Economizer Solenoid Valve (ESV), Liquid
Injection Solenoid Valve (LIV)
6.17 EVAPORATOR FAN AND MOTOR ASSEMBLY
The evaporator fans circulate air throughout the
container bypulling airin the top ofthe unit. The airis
forced through the evaporator coil where it is either
heated or cooledand thendischarged out the bottom of

6-12T-309
the refrigeration unit into the container. The fan motor
bearings are factory lubricated and do not require
additional grease.
6.17.1 Replacing The Evaporator Fan Assembly
WARNING
Always turn OFF the unit circuit breakers
(CB-1 & CB-2) and disconnect main power
supply before working on moving parts.
a. Remove upper access panel (see Figure 2-2) by
removing mounting bolts and T.I.R. locking device.
Reach insideofunit and removetheTy-Rapsecuring
the wire harness loop. Then unplug the connector by
twisting to unlock and pulling to separate. NOTE: It
maybeeasiertounplugtheconnectorwiththemotor
assembly partially pulled out (after step b).
b. Remove the four mounting bolts that secure the mo-
tor--fan assembly to the unit.
c. Slide the fan assembly out from the unit and place it
on a sturdy work surface.
d. Remove the motor and fan from the assembly.
e. Replace the motor.
f. Lubricate the fan motor shaft with a graphite--oil
solution (Never--Seez) and apply thread sealer (Loc-
tite H, brown in color) to the two fan set screws.
Installfanonthemotorshaft,sothatthecouplingsur-
face will be even with the end of the motor shaft.
g. Install the fan assembly in reverse order of removal.
Apply power momentarily to check for proper fan
rotation(refertoparagraph2.3).Ifthefanspinsback-
wards, than motor wiring or motor is defective.
Replace access panel making sure that panel does not
leak. Lock--wire the T.I.R. locking device(s).
1
2
3
4
5
6
7
89
1. Bracket
2. Flat washer, 3/8
3. Bolt, 3/8-16 x 1.00
4. Locknut, 5/16-18
5. Flat washer, 5/16
6. Cap Screw, Hxhd
5/16-18 x 1.25
7. Fan
8. Shim
9. Evaporator Motor
Figure 6-16. Evaporator Fan Assembly
6.18 EVAPORATOR FAN MOTOR CAPACITORS
The evaporator fan motors are of the permanent-split
capacitor type. The motor is equipped with one
capacitor used in the high speed circuit and another
capacitor used for the low speed circuit.
6.18.1 When To Check For A Defective Capacitor
a. Fanmotorwillnotchangespeed.Forexample:inthe
conventionalperishablemode,themotorsshouldrun
in high speed. In the economy perishable mode they
shouldswitchspeedsandinthefrozenmode,themo-
tors should run in low speed.
NOTE
The evaporator fan motors will always start in
high speed.
b. Motor running in wrong direction (after checking
for correct wiring application).
c. Motor will not start, and IP-EM’s are not open.
6.18.2 Removing The Capacitor
WARNING
Make sure power to the unit is OFF and
power plug disconnected before removing
capacitor(s).
The capacitors are located on the motor and above the
evaporator fan deck they may be removed by two
methods:
1If container is empty, open upper rear panel of the
unit.Thecapacitormaybeservicedafterdisconnect-
ing power plug.
2If container is full,turn theunit power OFF anddis-
connect power plug. Remove the evaporator fan
motor access panel. (See see Figure 2-1). For
removal oftheevaporatorfan assembly,refertosec-
tion 6.17. WARNING
WithpowerOFFdischargethecapacitorbe-
fore disconnecting the circuit wiring.
6.18.3 Checking The Capacitor
If the capacitor is suspected of malfunction, you may
choosetosimplyreplaceit.Directreplacementrequires
a capacitor of the same value. Two methods for
checking capacitor function are:
1. Volt-ohmmeter set on RX 10,000 ohms.
Connect ohmmeter leads across the capacitorterminals
and observe the meter needle. If the capacitor is good,
the needle will make a rapid swing toward zero
resistance and then gradually swing back toward avery
high resistance reading.
If the capacitor has failed open, the ohmmeter needle
will not move when the meter probes touch the
terminals. If the capacitor is shorted, the needle will
swing to zero resistance position and stay there.
2. Capacitor analyzer:
The function of the analyzer is to read the microfarad
value ofa capacitor and to detect insulation breakdown

6-13 T-309
under load conditions. The important advantages of a
analyzer are its ability to locate capacitors that have
failed to hold their microfarad ratings, or those thatare
breaking down internally during operation. It is also
useful in identifying capacitors when their microfarad
rating marks have become unreadable.
6.19 VALVE OVERRIDE CONTROLS
CAUTION
DONOTdisassemblepistonfromNEWsuc-
tion modulating valve powerhead assembly.
Doing so may result in damage to piston.
Controller function code Cd41 is a configurable code
that allows timed operation of the automatic valves for
troubleshooting.Threetestsequencesareprovided.The
first, capacity mode (CAP), allows alignment of the
unloader and economizer solenoid valves in the
standard, unloaded and economized operating
configurations. The second, SMV % Setting (SM)
allows opening of the suction modulating valve to
various percentages and the third, Oil Valve Setting
(OIL)andLiquidValveSetting(LIV)allowsopeningor
closing of the oil return solenoid valve and the liquid
injection solenoid valve. A fourth selection is also
provided to enter a time period of up to three minutes,
during which the override(s) are active. If the timer is
active, valve override selections will take place
immediately. If thetimeris not active, changes will not
take place for a few seconds after the timer is started.
When the timer times out, override function is
automatically terminated and the valves return to
normal machinery control. To operate the override, do
the following:
a. PresstheCODESELECTkeythenpressanARROW
key until Cd41 is displayed in the left window. The
right window will display a controller communica-
tions code.
b. Press the ENTER key. The left display will show a
test name alternating with the test setting or time re-
maining.UseanARROWkeytoscrolltothedesired
test. Press theENTER key and SELCt will appear in
the left display.
c. Use an ARROW key to scroll to the desired setting,
and then press the ENTER key. Selections available
for each of the tests are provided in the following
table.
d. If the timer is not operating, follow the aboveproce-
dure to display the timer. Use an ARROW key to
scrolltothedesiredtimeintervalandpressENTERto
start the timer.
e. The above described sequence may be repeated dur-
ing the timer cycle to change to another override.
Right Display Available Selections
CAP
(Capacity Mode) AUtO
(Normal Control)
(
p
y
)
UnLd
(Unloader = Open
Economizer = Closed)
Std
(Unloader = closed
Economizer = closed)
ECOn
(Unloader = closed
Economizer = open)
SM
(SMV % Setting) AUtO
(Normal Control)
0
3
4
6
12
25
50
100
OIL
(Oil Valve Setting) AUto
(Normal Control)
(
g
)
CLOSE
OPEn
LIV
(Liquid Valve Setting, if
l
i
b
l
)
AUto
(Normal Control)
(
q
g
,
applicable) CLOSE
OPEn
tIM
(Timer) 000(0 minutes/0 Seconds)
In 30 second increments to
300(3 minutes/ 0 seconds)
6.20 SUCTION MODULATION VALVE
On start up of the unit, the valve will reset to a known
open position. This is accomplished by assuming the
valve was fully open, driving it fully closed, resetting
the percentage open to zero, then opening to a known
10% staging position.
2-1/8 inch Nut
FROM COIL
FROM UNLOADER TO COMPRESSOR
Figure 6-17 Suction Modulation Valve (SMV)
6-14T-309
6.20.1 Precheck Procedure
a. Check unit for abnormal operation.
b. Check charge. If refrigerant is low repair as required
and again check operation.
c. If sufficient capacity cannot be maintained or unit is
tripping excessively on high pressure switch (HPS)
in high ambients, check coils and clean if required.
d. If capacity or control cannot be maintained turn unit
OFF, then back ON. This will reset the valve in the
event the controller lost communication with the
valve, and may correct the problem.
NOTE
Carefully listen to the valve. During reset, the
valve will make a ratcheting noise that may be
heard or felt as it is attempting to close. If this
canbeheardorfelt,itindicatesthatthecontrol-
leranddrivemoduleareattemptingtoclosethe
valve, and may serveas a quick indicationthat
the drive is in working order.
e. Operationofthevalvemaybecheckedusingthecon-
troller valve override program, function code Cd41.
Refer to paragraph 6.19 for valve override test in-
structions.
6.20.2 Checking The Stepper valve
a. Checking with ohmmeter
Disconnect the four pin connector to the stepper SMV.
With a reliable digital ohmmeter, check the winding
resistance.Innormalambient,thevalveshould have72
to 84 ohms measured on the red/green (a-b terminals)
and on the white/black (c-d terminals) leads. If an
infinite or zero reading occurs, check connections and
replace the motor.
b. Checking with SMA-12 portable stepper drive tester
The SMA-12 portable stepper drive tester (Carrier
Transicold P/N 07-00375-00) is a battery operated
stepperdrivewhichwillopenandclosetheSMV,which
allows a more thorough check of the operating
mechanism.
To check operation:
1. Stoptheunit,disconnectthefourpinconnectorfrom
thesteppermoduletothevalve(seeFigure 6-17)and
attachtheSMA-12stepperdrivetotheconnectorgo-
ingtothevalve.
2. Set the SMA-12 pulse per second (PPS)to onePPS
and either open or close valve. Each LED should
lightsequentiallyuntilallfourarelit.AnyLEDfail-
ing to light indicatesan open on that leg which indi-
catesapoorconnectionoranopencoil.Repairorre-
place as required to achieve proper operation.
CAUTION
The scroll compressor achieves low suction
pressure very quickly. Do not operate the
compressorinadeepvacuum, internaldam-
age will result.
3. Restartunit, setthesteprateto200PPS onSMA-12
forthevalve,andclosesteppervalvewhilewatching
the suction gauge. Within one minute the suction
pressurewillgointoavacuum.Thisisanindication
that the valve is moving.
4. If no change in suction pressure is detected, check
for resistance (refer to step 6.20.2), and check con-
nectionsforpropercontinuityandretest.Ifthevalve
is functioning and all connections and motor resist-
ance are good, check the controller and expansion
module.
CAUTION
DONOTdisassemblepistonfromNEWsuc-
tion modulating valve powerhead assembly.
Doing so may result in damage to piston.
5. If thevalve is determined as faulty after completing
theabovesteps,performalowsidepumpdown.Re-
movevalvepowerheadassembly,andreplacewitha
NEWvalvepowerheadassembly,torquenutto35ft-
lb, evacuate low side, and open all service valves.
6.21 CONTROLLER AND EXPANSION MODULE
6.21.1 Handling Modules
CAUTION
Do not remove wire harnesses from module
unless you are grounded to the unit frame
with a static safe wrist strap.
CAUTION
Unplug all module connectors before per-
forming arc welding on any part of the con-
tainer.
The guidelines and cautions provided herein should be
followed when handling the modules. These
precautions and procedures should be implemented
when replacing a module, when doing any arc welding
on the unit, or when service to the refrigeration unit
requires handling and removal of a module.

6-15 T-309
12
3
4
5
2
1. Controller Software
Programming Port
2. Mounting Screw
3. Controller
4. Expansion Module
5. Test Points
Figure 6-18 Controller Section of the Control Box
a. Obtain a grounding wrist strap (Carrier Transicold
part number 07--00--304--00)and a static dissipation
mat (Carrier Transicold part number 07--00304--00.
The wrist strap, when properly grounded, will dissi-
pate any potential buildup on thebody. The dissipa-
tion mat will provide a static-free work surface on
which to place and/or service the modules.
b. Disconnect and secure power to the unit.
c. Placestrap on wrist and attach the ground end to any
exposed unpainted metal area on the refrigeration
unit frame (bolts, screws, etc.).
d. Carefullyremovethemodule.Donottouchanyofthe
electrical connections if possible. Place the module
on the static mat.
e. Thestrapshould bewornduringanyserviceworkon
a module, even when it is placed on the mat.
6.21.2 Controller Trouble-Shooting
Agroupoftestpoints(TP,seeFigure 6-18)areprovided
on the controller for trouble-shooting electrical circuits
(seeschematicdiagram, section7).Adescriptionofthe
test points follows:
NOTE
Use a digital voltmeter to measure ac voltage
between TP’s and ground (TP9), except for
TP8.
TP1
Thistestpointenablestheusertocheckifthecontroller
unloader solenoid valve relay (TU) is open or closed.
TP2
This test point enables the user to check if the high
pressure switch (HPS) is open or closed.
TP3
This test point enables the user to check if the water
pressure switch (WP) contact is open or closed.
TP 4
This test point enables the user to check if the internal
protectorforthecondenserfanmotor(IP-CM)isopenor
closed.
TP 5
This test point enables the user to check if the internal
protectors for the evaporator fan motors (IP-EM1 or
IP-EM2) are open or closed.
TP 6
This test point is not used in this application.
TP 7
Thistestpointenablestheusertocheckifthecontroller
economizer solenoid valve relay (TS) is open or closed
TP 8
This test point enables the user to check power to the
suction modulator valve.
TP 9
This test point is the chassis (unit frame) ground
connection.
TP 10
This test point enables the user to check if the heat
terminationthermostat(HTT)contactisopenorclosed.
6.21.3 Controller Programming Procedure
Toloadnewsoftwareintothemodule,theprogramming
card is inserted into the programming/software port.
CAUTION
The unitmustbeOFFwheneveraprogram-
ming card is inserted or removed from the
controller programming port.
NOTE
Themetal door on theprogramming card must
be facing to the left when inserting.
a. Procedure for loading Operational Software
1. Turn unit OFF, via start-stop switch (ST).
2. Insert the programming card for Operational Soft-
ware into the programming/software port. (See
Figure 6-18)
3. Turn unit ON, via start-stop switch (ST).
4. The Display module will alternate back and forth
between the messages “rEV XXXX” and “Press
EntR”. (If a defective card is being used theDisplay
will blink the message “bAd CArd”. Turn start-stop
switch OFF and remove the card.)

6-16T-309
5. Press the ENTER key on the keypad.
6. TheDisplaywillshowthemessage“ProSoFt.”This
message will last for up to one minute.
7. The Display modulewill read “Pro donE” when the
software loading has loaded. (If a problem occurs
while loading the software: the Display will blink
the message “Pro FAIL” or “bad 12V”. Turn start-
stop switch OFF and remove the card.)
8. Turn unit OFF, via start-stop switch (ST).
9. Remove the programming card from the program-
ming/softwareportandreturntheunitto normalop-
eration by placing the start-stop switch in the ON
position.
b. Procedure for loading Configuration Software
1. Turn unit OFF using start-stop switch (ST).
2. Insert the programming card, for Configuration
Software, into theprogramming/software port. (See
Figure 6-18.)
3. Turn unit ON using start-stop switch (ST).
4. The Display module will show “nt40” on the left
LCD display and “531###” on the right LCD dis-
play.“###”willindicatethedashnumberforagiven
unit modelnumber, usethe UP orDOWNARROW
key to scroll through the list to obtain the proper
model dash number. For example, to program a
model number 69NT40-531-05, press the UP or
DOWN ARROW key until the right display shows
“nt40” on the right display and “53105” on the left.
(If a defective card is being used, the Display will
blink the message “bAd CArd”. Turn start-stop
switch OFF and remove the card.)
5. Press the ENTER key on the keypad.
6. When the software loading has successfully com-
pleted, the Display will show the message “EEPrM
donE.” (If a problem occurs while loading the soft-
ware,theDisplaywillblinkthemessage“ProFAIL”
or “bad 12V.” Turn start-stop switch OFF and
remove the card.)
7. Turn unit OFF using start-stop switch (ST).
8. Remove the programming card from the program-
ming/softwareportandreturntheunitto normalop-
eration by placing the start-stop switch in the ON
position.
6.21.4 Removing and Installing a Module
a. Removal:
1. Disconnect all front wire harness connectors and
move wiring out of way.
2 The lower controller mounting isslotted, loosen the
topmountingscrew(seeFigure 6-18)andliftupand
out.
3 Disconnectthebackconnectorsandremovemodule.
4 When removing the replacement module from its
packaging,notehowitispackaged.Whenreturning
the old module for service, place it in the packaging
in thesamemanneras thereplacement. Thepackag-
ing has been designed to protect the module from
both physical and electrostatic discharge damage
during storage and transit.
b.Installation:
Install the module by reversing the removal steps.
Torque values for mounting screws (item 2, see
Figure 6-18) are 0.23 mkg (20 inch-pounds). Torque
value for the connectors is 0.12 mkg (10 inch-pounds).
6.22 TEMPERATURE SENSOR SERVICE
Procedures for service of the Return Recorder, Return
Temperature, Supply Recorder, Supply Temperature,
Ambient, Defrost Temperature, Compressor Discharge
and Compressor Suction temperature sensors are
provided in the following sub paragraphs.
6.22.1 Sensor Checkout Procedure
Sensor 40 mm (1 1/2 inch)
6.3 mm (1/4 inch)
Mounting Stud Type
Sensor 40 mm (1-1/2 inches)
6.3 mm (1/4 inch)
Bulb Type
Dual Sensor 40 mm (1-1/2 inches)
6.3 mm (1/4 inch)
Figure 6-19 Sensor Types
To check a sensor reading, do the following:
a. Removethesensorandplaceina0_C(32_F)ice-wa-
ter bath. The ice-water bath is prepared by filling an
insulated container (of sufficient size to completely
immersebulb)withicecubesorchippedice,thenfill-
ing voids between ice with water and agitating until
mixture reaches 0_C(32_F) measured on a labora-
tory thermometer.
b. Start unit and check sensor reading on the control
panel.Thereadingshouldbe0_C(32_F). If theread-
ing is correct, reinstall sensor; if it is not, continue
with the following.
c. Turn unit OFF and disconnect power supply.
d. Refertoparagraph6.21andremovecontrollertogain
access to the sensor plugs.

6-17 T-309
Table 6-2 Sensor Temperature/Resistance Chart
(+/--.002%)
Temperature Resistance
_
__
_C_
__
_F(Ohms)
C
F
AMBS,
CPSS,
DTS, RTS,
RRS, STS,
SRS
CPDS
-- 3 0 -- 2 2 177,000 1,770,000
-- 2 5 -- 1 3 130,400 1,340,000
-- 2 0 -- 4 97,070 970,700
-- 1 5 5 72,900 729,000
-- 1 0 14 55,330 553,000
-- 5 23 43,200 423,300
0 32 32,650 326,500
5 41 25,390 253,900
10 50 19,900 199,000
15 59 15,700 157,100
20 68 12,490 124,900
25 77 10,000 100,000
30 86 8,060 80,600
35 95 6,530 65,300
40 104 5,330 53,300
45 113 4,370 43,700
50 122 3,600 36,000
55 131 2,900 29,000
60 140 2,490 24,900
65 149 2,080 20,800
65 158 1,750 17,500
e. Using the plug connector marked “EC”, that is con-
nected to the back ofthe controller, locate thesensor
wires (RRS, RTS, SRS, STS, AMBS, DTS, CPDS
ORCPSSasrequired).Followthosewirestothecon-
nector and using the pins of the plug, measure the
resistance. Values are provided in Table 6-2.
Dueto thevariations andinaccuraciesinohmmeters,
thermometers or other test equipment, a reading
within 2% of the chart value would indicate a good
sensor. Ifa sensor is defective, the resistancereading
will usually be much higher or lower than the resis-
tance values given.
6.22.2 Sensor Replacement
a. Turn unit power OFF, disconnect power supply and
remove sensor assembly from unit.
b. Cut wire(s) 5 cm (2 inches) from shoulder of defec-
tive sensor and discard the defective probe only.
c. Cut one wire of existing cable 40 mm (1-1/2 inch)
shorter than the other wire.
d. Cut one replacement sensor wire (opposite color)
back 40 mm (1-1/2 inch). (See Figure 6-19.)
e. Stripbackinsulationonallwiring6.3mm(1/4inch).
f. Slide a large piece of heat shrink tubing over the
cable, and place the two small pieces of heat shrink
tubing, one over each wire, before adding crimp fit-
tings as shown in Figure 6-20.
Sensor (Typical)
Cable Heat Shrink
Tubing (3)
Large Heat Shrink
Tubing (1)
Figure 6-20 Typical Sensor and Cable Splice
g. Slip crimp fittings over dressed wires (keeping wire
colors together). Make sure wires are pushed into
crimpfittingsasfaraspossibleandcrimpwithcrimp-
ing tool.
h. Solder spliced wires with a 60% tin and 40% lead
Rosincore solder.
i. Slide heat shrink tubing over splice so that ends of
tubing cover both ends of crimp as shown in
Figure 6-20.
j. Heattubingtoshrinkoversplice.Makesureallseams
are sealed tightly against the wiring to prevent mois-
ture.
k. Slide large heat shrink tubing over both splices and
shrink.
CAUTION
Do not allow moisture to enter wire splice
area as this may affect the sensor resistance.
l. Position sensor in unit as shown in m.Figure 6-21
Slip crimp fittings over dressed wires (keeping wire
colors together). Make sure wires are pushed into
crimp fittings as far as possible and crimp with
crimping tool. and re--check sensor resistance.
n. Reinstall sensor, refer to paragraph 6.22.3.
NOTE
The P5 Pre-Trip test must be run to inactivate
probe alarms (refer to paragraph 4.7).

6-18T-309
SRS probe
STS probe
Supply
Air
Stream
Mounting
Clamp
Supply Sensor
Sensor
Wires
Back Panel
2.5” Drip Loop
T.I.R. Bolts
Gasketed
Support
Plate
Gasket
Mounting
Plate
Insulation
Gasketed
Cover
Figure 6-21 Supply Sensor Positioning
6.22.3 Sensor Re--Installation
a. Sensors STS and SRS
Toproperlypositionasupplysensor,thesensormustbe
fully inserted into the probe holder. Do not allow heat
shrink covering to contact the probeholder. For proper
placement ofthesensor, besure topositiontheenlarged
positioning section of the sensor against the the side of
the mounting clamp. This positioning will give the
sensor the optimum amount of exposure to the supply
air stream, and will allow the Controller to operate
correctly. See Figure 6-21.
b Sensors RRS and RTS
ReinstallthereturnsensorasshowninFigure 6-22.For
proper placement of the return sensor, be sure to
position the enlarged positioning section of the sensor
against the the side of the mounting clamp.
Return Sensor
Mounting
Clamp 1.50 in.
(38.1cm)
Figure 6-22 Return Sensor Positioning
c Sensor DTS
The DTS sensor must have insulating material placed
completely over the sensor to insure the coil metal
temperature is sensed.
6.23 MAINTENANCE OF PAINTED SURFACES
The refrigeration unit is protected by a special paint
system against the corrosive atmosphere in which it
normallyoperates.However,shouldthepaintsystembe
damaged,thebasemetalcancorrode.Inordertoprotect
the refrigeration unit from the highly corrosive sea
atmosphere, or if the protective paint system is
scratched or damaged, clean area to bare metal using a
wirebrush,emerypaperorequivalentcleaningmethod.
Immediately following cleaning, apply 2--part epoxy
paint to the area. and allow to dry. After the first coat
dries, apply a second coat.
6.24 COMPOSITE CONTROL BOX REPAIRS
6.24.1 Introduction
This procedure provides instructions for repair of the
Carrier Transicold composite control box. Damage to
the control box may be in the form of a chip or hole, a
crack, a damaged thread insert or damage to the door
hingeinserts.Generally,theobjectoftherepairmustbe
to ensuresufficient strength is restored to the damaged
area and the repair must keep the box water tight.
Informationonrepairkitsandrepairproceduresforeach
typeofdamageisprovidedinthefollowingparagraphs.
Ambient temperature must be above 7°C(45°F) for
proper curing of epoxy repairs.

6-19 T-309
6.24.2 Cracks
Cracksinthecontrol boxarerepairedusingafiberglass
patch over the damaged area. Materials required are
includedintheFiberglassPatchKitsuppliedwithCrack
Repair Kit, Carrier Transicold part number
76-00724-00SV (see Table 6-3).
a. The surface must be clean and dry. Roughen the sur-
face with sandpaper to ensure a good bond.
b. Cut the fiberglass cloth to allow a 25mm (1--inch)
overlap around the area to be repaired.
c. Stretch and position the cloth over the area to be re-
paired and secure it with masking tape.
d. Make up sufficient epoxy glue to cover the cloth by
mixingequalpartsofresinandhardener. Saturatethe
cloth with the epoxy glue, spreading evenly.
e. Remove the tape and overlap the edge of the cloth
approximately 6 to 12 mm (1/4” to 1/2”) with glue.
f. Epoxy will dry in 45--60 minutes. When completely
cured (12 hours), use sandpaper to smooth edges of
the patch.
6.24.3 Chips And Holes
Chips and holes in the control box are repaired using a
piece of aluminum or stainless steel to cover the
damagedarea.Thematerialcanbecuttosuitandriveted
in place. An adhesive sealant must be used to make the
repairwatertight.Theadhesivesealant(Sikaflex221)is
included in Crack Repair Kit Carrier Transicold part
number76-00724-00SV(seeTable 6-3).Donotusean
acetone based silicone sealant (Which can be
identified by a vinegar--like odor).
a. To make up the patch, cut a piece of aluminum or
stainlesssteelsothatitwill overlapthedamagedarea
by at least 40 mm (1 1/2”) on all sides.
b. Choose rivet locations and drill the rivet holes in the
correspondinglocationsonthecontrolboxandpatch
piece.
c. Apply the adhesive sealant around the damaged area
to form a seal between the control box and the patch
piece.
d. Rivet the patch piece in place.
e. File smooth any rough edges (including rivets) that
may come into contact with wires.
6.24.4 Inserts
The threaded brass inserts that are molded into the
control box will need to be replaced if the threads
become stripped, or if the insert becomes loose. The
inserts and epoxy are contained in repair kit, Carrier
Transicold part number 76-50084-00 (see Table 6-4).
There are 6 different inserts used in the control box.
Refer to Figure 6-24 for the locations of the various
inserts.
NOTE
Anepoxyapplicationgunisalsoneeded,Carri-
er Transicold part number 07 -- 00391 -- 00.
The damaged insert must be removed from the control
box. Table 6-5 identifies the drill size and drill depthto
beusedforeachinsert.Astopringshouldbeusedonthe
drill bit to limit the depth.
a. Center the drill bit on the insert and drill to the pre-
scribed depth.
b. Remove the chips from the drilled hole.
c. Mix the two component epoxy and fill the hole 1/2
way to the top with epoxy.
d. Press the insert in until it is flush with the surface.
e. Wipe away any excess epoxy. The part is ready for
service after the bond material has hardened and is
tack free (approximately 20 minutes)
6.24.5 Door Hinge Inserts
Ifthedoorhingeshavebeenpulledfromthecontrolbox
drillandreinstallthehingeasshowninFigure 6-23and
described in the following steps.
Figure 6-23 Door Hinge Repair
Materials needed:
1. Cut two square pieces of 3 mm thick (1/8 inch) alu-
minum or stainless steel approximately 40 mm (1
5/8”) square. These squares will serve as backing
plates.
2. Two nuts, bolts (10 -- 24 x 1”) and washers for each
insert that needs repair.
a. Drill a 1/4” hole in the center of each square backing
plate.
b. Pass the bolts through the bolts holes in the door
hinge, then through the control box at the location
where the hinge insert pulled out.
c. From inside the control box, slide the backingplates
over the bolts and secure in place with the washers
and nuts.

6-20T-309
Table 6-3 Crack, Chip & Hole Repair Kit
ITEM DESCRIPTION PART NUMBER Qty
1Crack Repair Kit -- Includes 76--00724--00SV 1
2Fiberglass Patch Kit (Loctite FK--98 or 80265)... 76--00724--00Z 10
3Sikaflex 221 Adhesive Sealant (Sikaflex 232--361)... 02--00067--02Z 10
4Instruction Sheet... 98--02339--00 10
Table 6-4 Insert Repair Kit
ITEM DESCRIPTION PART NUMBER Qty
1Insert Repair Kit -- Includes 76--50084--00 1
2Insert - 17.53 x 9.91 mm (..690 x .390 in) 1/4--20 Threads... 34--06231--01 10
3Insert - 15.88 x 6.35 mm (.625 x .250 in) 10-24 Threads... 34--06231--03 10
4Insert - 25.15 x 7.54 mm (.990 x .297 in) 10-24 Threads... 34--06231--04 10
5Insert - 10.16 x 9.53 mm (.400 x .375 in) 10-24 Threads... 34--06231--05 10
6Insert - 12.7 x 9.91 mm (.5 x .390 in) 1/4--20 Threads... 34--06231--06 10
7Insert - 9.53 x 6.76 mm (.375 x .266 in) 10-24 Threads... 34--06231--07 10
8Durabond Epoxy E20--HP (Loctite 29314)... 02--0082--00 1
9Static Mixing Tube (Loctite 983440)... 07--00390--00 1
10 Instruction Sheet... 98--02338--00 1
Note: Insert repair procedures require use of an Application Gun, Carrier part number 07--00391--00
Table 6-5 Drill Information
Item Insert part number Drill size and depth
1 34- 06231- 01 10.3 mm x 17.8 mm deep (.404 in. x .700 in. deep)
2 34- 06231- 03 6.8 mm x 16.3 mm deep (.266 in. x .640 in. deep)
3 34- 06231- 04 7.9 mm x 25.4 mm deep (.3125 in. x 1.0 in. deep)
4 34- 06231- 05 6.9 mm (.270 in.) Drill completely through.
5 34- 06231- 06 10.3 mm (.404 in.) Drill completely through.
6 34- 06231- 07 6.8 mm (.266 in.) Drill completely through.

6-21 T-309
03
03
03
03
04
04
03
01
07
07
05
05
06
INSERT PART NUMBERS 34--06231--## WHERE THE ## IS AS INDICATED
Figure 6-24. Insert Location

6-22T-309
6.25 COMMUNICATIONS INTERFACE MODULE
INSTALLATION
Communications
interface Module
CB1
Figure 6-25. Communications Interface
Installation
Units with communication interface module provision
havetherequiredwiringinstalled.Theprovisionwiring
kit (part number 76--00685--00), includes three
pre--addressed wires installed between the circuit
breakerandcommunicationinterfacemodulelocations.
These wires are to be connected to the module and
circuit breaker to allow the module to communicate
over the power system. To install the module, do the
following:
WARNING
The Unit Power Plug Must Be Disconnected
To Remove Power From Circuit Breaker
Cb1
a.. CB1 is connected to the power system, see wiring
schematic. Ensure that the unit power is off AND
that the unit power plug is disconnected.
b.. Open control box, see Figure 6-25 and removelow
voltage shield. Open high voltage shield.
c.. Remove the circuit breaker panel, with circuit
breaker, from the control box.
d.. Locate, wires CB21/CIA3, CB22/CIA5 and
CB23/CIA7 that have been tied back in the wire
harness.Removetheprotectiveheatshrinkfromthe
ends of the wires.
e.. Attach the three wires as addressed to the LOAD
side of the circuit breaker.
f.. Refit the circuit breaker panel.
g. Fit the new RMU into the unit.
h. Remove plugs CIA, CIB and CID from the wiring
harness and attach to the module.
.i. Replace the low voltage shield.
Table 6-6 Recommended Bolt Torque Values
BOLT DIA. THREADS TORQUE MKG
FREE SPINNING
#4
#6
#8
#10
1/4
5/16
3/8
7/16
1/2
9/16
5/8
3/4
40
32
32
24
20
18
16
14
13
12
11
10
5.2 in-lbs
9.6 in-lbs
20 in-lbs
23 in-lbs
75 in-lbs
11 ft-lbs
20 ft-lbs
31 ft-lbs
43 ft-lbs
57 ft-lbs
92 ft-lbs
124 ft-lbs
0.05
0.11
0.23
0.26
0.86
1.52
2.76
4.28
5.94
7.88
12.72
17.14
NONFREE SPINNING (LOCKNUTS ETC.)
1/4
5/16
3/8
7/16
1/2
9/16
5/8
3/4
20
18
16
14
13
12
11
10
82.5 in-lbs
145.2 in-lbs
22.0 ft-lbs
34.1 ft-lbs
47.3 ft-lbs
62.7 ft-lbs
101.2 ft-lbs
136.4 ft-lbs
0.95
1.67
3.04
4.71
6.54
8.67
13.99
18.86

6-23 T-309
Table 6-7 R-134a Temperature - Pressure Chart
Temperature Vacuum
_
__
_F_
__
_C “/hg cm/hg kg/cm@
@@
@bar
-- 4 0 -- 4 0 14.6 49.4 37.08 0.49
.35 .37 12.3 41.6 31.25 0.42
-- 3 0 -- 3 4 9.7 32.8 24.64 0.33
-- 2 5 -- 3 2 6.7 22.7 17.00 0.23
-- 2 0 -- 2 9 3.5 11.9 8.89 0.12
-- 1 8 -- 2 8 2.1 7.1 5.33 0.07
-- 1 6 -- 2 7 0.6 2.0 1.52 0.02
Temperature Pressure
_
__
_F_
__
_Cpsig kPa kg/cm@
@@
@bar
-- 1 4 -- 2 6 0.4 1.1 0.03 0.03
-- 1 2 -- 2 4 1.2 8.3 0.08 0.08
-- 1 0 -- 2 3 2.0 13.8 0.14 0.14
-- 8 -- 2 2 2.9 20.0 0.20 0.20
-- 6 -- 2 1 3.7 25.5 0.26 0.26
-- 4 -- 2 0 4.6 31.7 0.32 0.32
-- 2 -- 1 9 5.6 36.6 0.39 0.39
0-- 1 8 6.5 44.8 0.46 0.45
2-- 1 7 7.6 52.4 0.53 0.52
4-- 1 6 8.6 59.3 0.60 0.59
6-- 1 4 9.7 66.9 0.68 0.67
8-- 1 3 10.8 74.5 0.76 0.74
10 -- 1 2 12.0 82.7 0.84 0.83
12 -- 11 13.2 91.0 0.93 0.91
14 -- 1 0 14.5 100.0 1.02 1.00
16 -- 9 15.8 108.9 1.11 1.09
18 -- 8 17.1 117.9 1.20 1.18
20 -- 7 18.5 127.6 1.30 1.28
22 -- 6 19.9 137.2 1.40 1.37
24 -- 4 21.4 147.6 1.50 1.48
26 -- 3 22.9 157.9 1.61 1.58
Temperature Pressure
_
__
_F_
__
_Cpsig kPa kg/cm@
@@
@bar
28 -- 2 24.5 168.9 1.72 1.69
30 -- 1 26.1 180.0 1.84 1.80
32 0 27.8 191.7 1.95 1.92
34 1 29.6 204.1 2.08 2.04
36 2 31.3 215.8 2.20 2.16
38 3 33.2 228.9 2.33 2.29
40 4 35.1 242.0 2.47 2.42
45 7 40.1 276.5 2.82 2.76
50 10 45.5 313.7 3.20 3.14
55 13 51.2 353.0 3.60 3.53
60 16 57.4 395.8 4.04 3.96
65 18 64.1 441.0 4.51 4.42
70 21 71.1 490.2 5.00 4.90
75 24 78.7 542.6 5.53 5.43
80 27 86.7 597.8 6.10 5.98
85 29 95.3 657.1 6.70 6.57
90 32 104.3 719.1 7.33 7.19
95 35 114.0 786.0 8.01 7.86
100 38 124.2 856.4 8.73 8.56
105 41 135.0 930.8 9.49 9.31
110 43 146.4 1009 10.29 10.09
115 46 158.4 1092 11.14 10.92
120 49 171.2 1180 12.04 11.80
125 52 184.6 1273 12.98 12.73
130 54 198.7 1370 13.97 13.70
135 57 213.6 1473 15.02 14.73
140 60 229.2 1580 16.11 15.80
145 63 245.6 1693 17.27 16.93
150 66 262.9 1813 18.48 18.13
155 68 281.1 1938 19.76 19.37

7-1 T-309
SECTION 7
ELECTRICAL WIRING SCHEMATIC
7.1 INTRODUCTION
This section contains the Electrical Schematics and Wiring Diagrams. The diagrams are presented as follows:
Figure 7-1 Provides the legend for use with all figures.
Figure 7-2 Provides the basic schematic diagram.
Figure 7-3 Provides the basic wiring diagram.
Sequence of operation descriptions for the various modes of operation are provided in paragraph 4.9
SYMBOL DESCRIPTION (Schematic Location)
AMBS AMBIENT SENSOR (C--21)
C CONTROLLERS (H-21, H-23)
CB1 CIRCUIT BREAKER -- 460 VOLT (J--1)
CB2 CIRCUIT BREAKER -- AUTOTRANSFORMER (C--1)
CF CONDENSER FAN CONTACTOR (M--12, N--5)
CI COMMUNICATIONS INTERFACE MODULE (A--3)
CL COOL LIGHT (J--7)
CM CONDENSER FAN MOTOR (H--12, T-5)
CP COMPRESSOR MOTOR (T--1)
CPDS COMPRESSOR DISCHARGE SENSOR (A--22)
CPSS COMPRESSOR SUCTION SENSOR (D--21)
CR CHART RECORDER [TEMPERATURE RECORDER]
(K-16)
CS CURRENT SENSOR (M--1)
DHBL DEFROST HEATER -- BOTTOM LEFT (T--4)
DHBR DEFROST HEATER -- BOTTOM RIGHT (R--4)
DHTL DEFROST HEATER -- TOP LEFT (T--4)
DHTR DEFROST HEATER -- TOP RIGHT (R--4)
DL DEFROST LIGHT (J--6)
DPT DISCHARGE PRESSURE TRANSDUCER (J--22)
DTS DEFROST TEMPERATURE SENSOR (B--22)
DVM DUAL VOLTAGE MODULE (D--1)
DVR DUAL VOLTAGE RECEPTACLE (F--1)
E1 EVAPORATOR FAN CONTACTOR [HIGH]
(L--13,L--14,P--7,P--10)
EM EVAPORATOR FAN MOTOR (E--13,G--13,T--8,T--11)
ES EVAPORATOR FAN CONTACTOR [LOW]
( M -- 14 , P -- 7, P -- 11 )
ESV ECONOMIZER SOLENOID VALVE (K--17)
F FUSE (C--6,D--20,E--20,H--4)
FLA FULL LOAD AMPS
HPS HIGH PRESSURE SWITCH (G--11)
HR HEATER CONTACTOR (L--15, N--3)
HS HUMIDITY SENSOR (F--21)
HTT HEAT TERMINATION THERMOSTAT (G--15)
IC INTERROGATOR CONNECTOR [FRONT/REAR]
(P--22,P--21)
IP INTERNAL PROTECTOR (E--13,G--13,H--12)
IRL IN RANGE LIGHT (J8)
LIV LIQUID INJECTION SOLENOID VALVE (K-18)
MDS MANUAL DEFROST SWITCH (E--19)
LEGEND
SYMBOL DESCRIPTION (Schematic Location)
ORV OIL RETURN SOLENOID VALVE (N--24, H-9)
PA COMPRESSOR PHASE CONTACTOR (L--11,M--10,P1)
PB COMPRESSOR PHASE CONTACTOR (L--10,M--11,P2)
PR PROBE RECEPTACLE [USDA]
D--21,L--22,M--22)
RM REMOTE MONITORING RECEPTACLE
(J-6,J--7,K--6,K--7,K--8)
RRS RETURN RECORDER SENSOR (K--21)
RTS RETURN TEMPERATURE SENSOR (B--21)
SMV SUCTION MODULATING VALVE (K--24)
SPT SUCTION PRESSURE TRANSDUCER (H--21)
SRS SUPPLY RECORDER SENSOR (K--22)
ST START -- STOP SWITCH (K--4)
STS SUPPLY TEMPERATURE SENSOR (A--21)
TCC TransFRESH COMMUNICATIONS
CONNECTOR (D-4)
TD CONTROLLER RELAY -- COOLING (H11)
TE CONTROLLER RELAY -- HIGH
SPEED EVAPORATOR FANS
(K--13)
TFC TransFRESH CONTROLLER (G--5)
TH CONTROLLER RELAY -- HEATING (K--15)
TN CONTROLLER RELAY -- CONDENSER FAN (K--12)
TP TEST POINT (F--17,G--12,H--11,J--12,
J--13,J--15,M--19)
TR TRANSFORMER (M--3)
TRANS AUTO TRANSFORMER 230/460 (D--1)
TRC TransFRESH REAR CONNECTOR (E--5)
TS CONTROLLER RELAY -- ECONOMIZER SOLENOID
VALVE (E--17)
TT CONTROLLER RELAY -- COOLING (C--11)
TU CONTROLLER RELAY -- UNLOADER SOLENOID
VALVE (E--16)
TV CONTROLLER RELAY -- LOW SPEED EVAPORATOR
FANS (K--14)
T1 CONTROLLER RELAY -- RM COOL (G--7)
T2 CONTROLLER RELAY -- RM DEFROST (G--6)
T4 CONTROLLER RELAY -- RM INRANGE (G--8)
T6 CONTROLLER RELAY -- COMPRESSOR PHASE
SEQUENCING (K--10,K--11)
USV UNLOADER SOLENOID VALVE (K--16)
WP WATER PRESSURE SWITCH (E--12)
Figure 7-1 LEGEND

7-2T-309
Figure 7-2 SCHEMATIC DIAGRAM

7-3 T-309
Figure 7-3 WIRING DIAGRAM (Sheet 1 of 2)

7-4T-309
Figure 7-3 WIRING DIAGRAM (Sheet 2 of 2)
Index-1 T-309
INDEX
A
Air Cooled Condenser Section, 2-4
Alarm, 3-6, 3-10, 3-12, 3-17, 3-27
B
Battery, 1-1
C
Capacitors, 6-12
Checking Superheat, 6-9
Communications, 1-1
Communications Interface Module, 3-11, 6-21
Compressor, 1-1, 6-5
Compressor Phase Sequence, 4-5
Compressor Section, 2-3
Condenser Coil, 1-1, 6-8
Condenser Fan, 6-8
Configuration Identification, 1-1
Configuration Software, 3-3, 3-8
Configuration Variables, 3-13
Control Box, 1-1, 2-5, 6-18
Controller, 3-3, 6-14
Controller Software, 3-3
D
DataCORDER, 3-7, 3-10, 4-2
DataCORDER Software, 3-7
DataReader, 3-11
DataView, 3-11
Defrost Interval, 3-4
Defrost Mode, 4-7
Dehumidification, 1-1
Display Module, 3-2
E
Evacuation, 6-3
Evaporator, 6-10
Evaporator Fan, 6-12
Evaporator Section, 2-2
Expansion Module, 3-1, 6-14
Expansion Valves, 6-10
F
Failure Action, 3-4
Filter--Drier, 6-8
Fresh Air Makeup, 2-1, 4-1
Frozen Mode, 4-6
Frozen Mode -- Conventional, 3-6
Frozen Mode -- Economy, 3-6
Function Code, 3-14, 3-25
G
General Description, 2-1
Generator Protection, 3-4
H
Heat Lockout, 3-4, 3-6
Heater, 6-10
Heating Mode, 4-6
High Pressure Switch, 6-7
I
Inspection, 4-1, 4-2
Interrogator, 1-1
Introduction, 1-1
Index-2
T-309
INDEX
K
Key Pad, 3-2
L
Leak Checking, 6-3
Logging Interval, 3-10
M
Manifold Gauge Set, 6-1
Microporcessor System, 3-1
Modes Of Operation, 3-4
O
Oil, 6-7
Operational Software, 3-4, 3-7
Option Descriptions, 1-1
P
Painted Surfaces, 6-17
Perishable Mode -- Bulb, 3-5
Perishable Mode -- Conventional, 3-4
Perishable Mode -- Dehumidification, 3-5
Perishable Mode -- Economy, 3-5
Power, 4-1
Pre--Trip, 3-7, 3-10, 3-21, 3-26, 4-2
Pressure Readout, 1-1
Probe Check, 4-3
Pumping Down, 6-2
R
Refrigerant Charge, 6-4
Refrigeration Circuit, 2-10
Refrigeration System Data, 2-6
Refrigeration Unit -- Front Section, 2-1
Remote Monitoring, 1-1
S
Safety and Protective Devices, 2-8
Sampling Type, 3-10
Scroll Back , 3-10
Sensor Configuration, 3-8
Sequence Of Operation, 4-5
Service Valves, 6-1
Solenoid Valves, 6-10
Starting, 4-2
Stopping, 4-2
Suction Modulating Valve, 6-13
T
Temperature Control, 3-4, 3-6
Temperature Sensor, 6-17
Thermistor Format, 3-10
Torque Values, 6-21
U
Upper Air, 1-2
V
Valve Override Controls, 6-12
W
Wiring Schematic, 7-1