Craftsman 11329461 User Manual 10 INCH ACCRA ARM RADIAL SAW Manuals And Guides L0712531
CRAFTSMAN Saw Radial Manual L0712531 CRAFTSMAN Saw Radial Owner's Manual, CRAFTSMAN Saw Radial installation guides
User Manual: Craftsman 11329461 11329461 CRAFTSMAN CRAFTSMAN 10 INCH ACCRA-ARM RADIAL SAW - Manuals and Guides View the owners manual for your CRAFTSMAN CRAFTSMAN 10 INCH ACCRA-ARM RADIAL SAW #11329461. Home:Tool Parts:Craftsman Parts:Craftsman CRAFTSMAN 10 INCH ACCRA-ARM RADIAL SAW Manual
Open the PDF directly: View PDF .
Page Count: 36
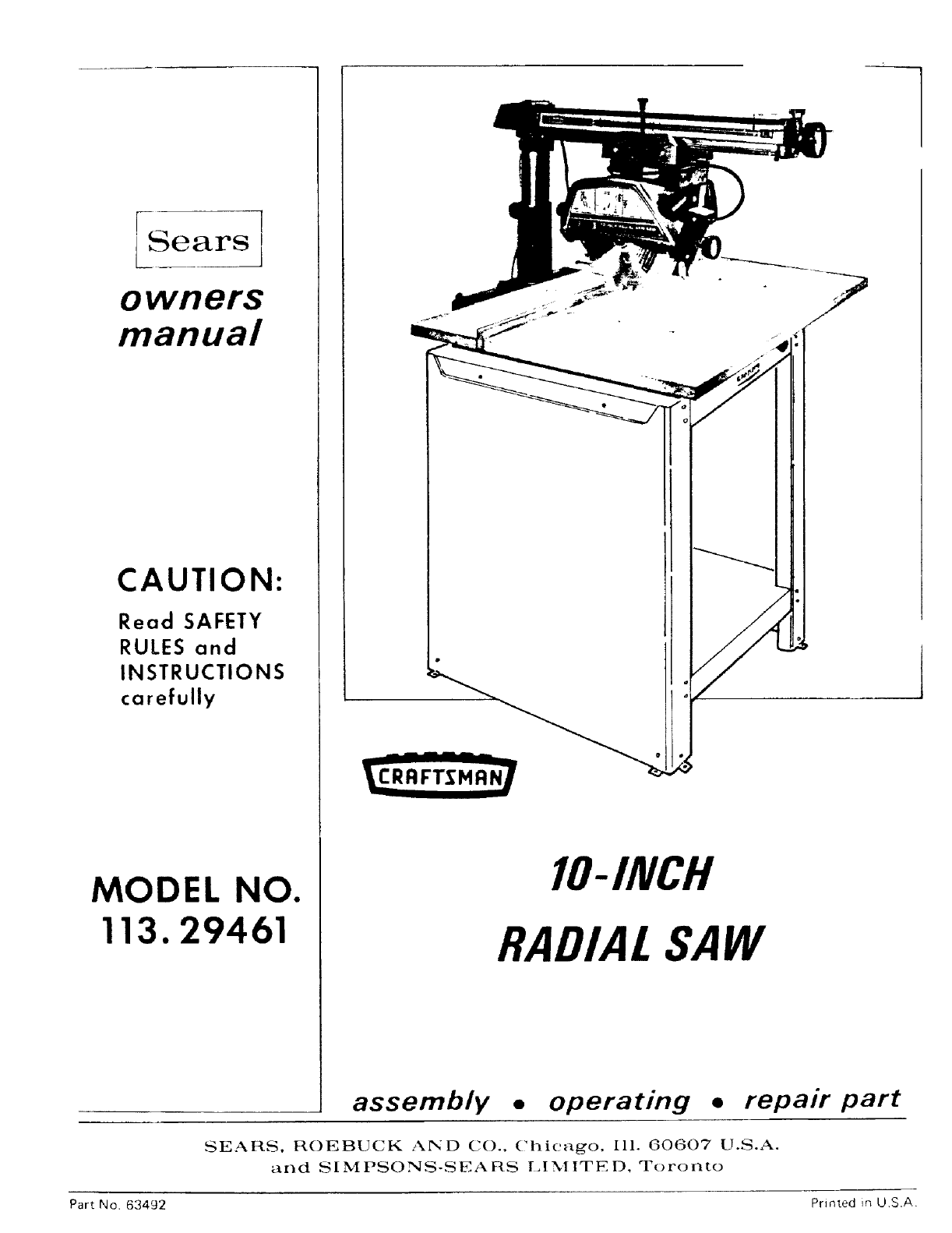
[Sears ]
owners
manual
CAUTION:
Read SAFETY
RULES and
INSTRUCTIONS
carefully
MODEL NO.
113.29461
IO-INCH
RADIAL SAW
assembly •operating •repair part
SEARS, ROEBUCK AP,,D CO.. (_hicago, Ill. 60607 U.S.A.
arid SIN_IPSONS-SEARS LINIITED, Toronto
Part No. 63492 Printed in U.S.A.

general safety rules for power tools
1. KNOW YOUR POWER TOOL
Read the owner's manual carefully. Learn its appli-
cation and limitations as well as the specific potential
hazards peculiar to this tool.
2. GROUND ALL TOOLS
If tool is equipped with three-prong plug, it should be
plugged into a three-hole grounded receptacle. If
adapter is used to accommodate two-prong receptacle,
the adapter wire must be attached to a known ground.
Never remove third prong.
3. KEEP GUARDS IN PLACE
and in working order.
4. REMOVE ADJUSTING KEYS
AND WRENCHES
Form habit of checking to see that keys and adjusting
wrenches are removed from tool before turning it on.
5. KEEP WORK AREA CLEAN
Cluttered areas and benche.s invite accidents.
6. AVOID DANGEROUS ENVIRONMENT
Don't use power tools in damp or wet locations. Keep
work area well lit.
7. KEEP CHILDREN AWAY
All visitors should be kept a safe distance from work
area.
8. MAKE WORKSHOP KID-PROOF
-- with padlocks, master switches, or by removing
starter keys.
9. DON'T FORCE TOOL
It will do the job better and safer at the rate for which
it was designed.
USE RIGHT TOOL
Don't force tool or attachment to do ajob it was not
designed for.
10.
11. WEAR PROPER APPAREL
No loose clothing or jewelry to get caught in moving
parts. Rubber-soled footwear is recommended for best
footing.
12. USE SAFETY GLASSES
Also use face or dust mask if cutting operation is dusty.
13. SECURE WORK
Use clamps or a vise to hold work when practical. It's
safer than using your hand, frees both hands to operate
tool.
14. DON'T OVERREACH
Keep proper footing and balance at all times.
15. MAINTAIN TOOLS WITH CARE
Keep tools sharp and clean for best and safest
performance. Follow instructions for lubricating and
changing accessories.
16. DISCONNECT TOOLS
before servicing; when changing accessories such as
blades, bits, cutters, etc.
17. AVOID ACCIDENTAL STARTING
Make sure switch is in "OFF" position before plugging
in.
18. USE RECOMMENDED ACCESSORIES
Consult the owner's manual for recommended acces-
sories. The use of improper accessories may cause
hazards.
19. NEVER STANDON TOOL
Serious injury could occur if the tool is tipped or if the
cutting tool is accidentally contacted.
20. CHECK DAMAGED PARTS
Before further use of the tool, a guard or other part
that is damaged should be carefully checked to assure
that it will operate properly and perform its intended
function -- check for alignment of moving parts,
binding of moving parts, breakage of parts, mounting
and any other conditions that may affect its operation.
A guard or other part that is damaged should be
properly repaired or replaced.
WEAR YOUR
Copyright 1969 I_y Power Tool Institute, in(:, All lightz reserved.
The operation of any power tool can result in foreign objects
being thrown into the eyes, which can result in severe eye
damage. Always wear safety glasses or eye shields before
commencing power tool operation. We recommend Wide
Vision Safety Mask for use over spectacles, or standard safety
glasses.., available at Sears retail or catalog stores.
THIS SAFETY SEAL OF THE
POWER TOOL INSTITUTE ASSURES YOU...
1, That the manufacturer's power tools, including the particular tool
associated with the Seal, are produced in accordance with applicable
Standards For Safety of Underwriters' Laboratories and American
Notional Standards (ANSI).
2. That compliance with applicable safety standard| is assured by in-
dependent inspection and testing conducted by Underwriters' Labora-
tories (UL),
3 That every motorized tool is inspected under power.
4. That every tool has with it adequate instructions and a llst of safety
rules for the protection of the uter.
5. That the tool manufacturer is a member of the Power Tool Institute and
_s a sponsor of the Instltute's Consumer Safety Education Program.

unpacking and preassembly
CONTENTS
Page
Unpacking and Preassembly Instructions ....... 3
Alignment Instructions ................ 5
Electrical Connections ................. 11
Operating Controls .................. 13
Basic Saw Operations ................. 15
Page
Trouble Shooting ................... 20
Motor Trouble Shooting Chart ............ 25
Guarantee ....................... 27
Repair Parts ...................... 28
C_
SCREWDRIVER (MEDIUM)
SCREWDRIVER (SMALL)
PLIERS
PENCIL
TOOLS NEEDED
7116-1NCH WRENCH
1/2-INCH WRENCH
9/16-INCH WRENCH
RUBBER MALLET
UNPACKING AND PREASSEMBLY INSTRUCTIONS
1. Unpacking and Checking Contents
Separate all "loose" parts from packaging materials and
check each item with figure t and "Table of Loose
Parts" to make sure all items are accounted for, before
discarding any packing material.
45
NUT
&
i 44 USED-- DISCARD)
I
KeyNo.
(Fi9. 1)
1
2
3
4
5
6
7
TABLE OF LOOSE PARTS QW.
Basic Saw assembly ...................
Rear table .......................
Table spacer ......................
Rip fence ........................
Front table .......................
"Owner's Manual" . ..................
Loose Parts Carton (containing the following items):
Hex-'L" Wrench, 1/8" ................ 1
Hex-'L"wrench, 3/16" ............... 1
Hex-"L"wrench, 1/4" . ............... 1
Elevation crank assembly ............... 1
Knob assembly, pull ................. 1
Switch key ...................... 2
Arbor wrench ..................... 1
Table clamp ..................... 2
Rip.scale indicator .................. 2
Twin nut (for attaching rip-scale indicator} .2
Machine screw, pan-halo,1/4-20x1"' .......... G
Washer, steel (flat), t7/64x518xl!32" ........ 7
Lockwasher, medium, 114" . ............. fi
Nut, hex., 1/4-20x7/t6x3/16" ............ 6
Machine screw, pan-hd., 6-32x7/16"' ........ 4
Nut-"T" . .....................
Setscrew, eup-pt....................
Machine screw, pan-hal., 114-20x1-1/4" . ......
Shaft wrench .....................
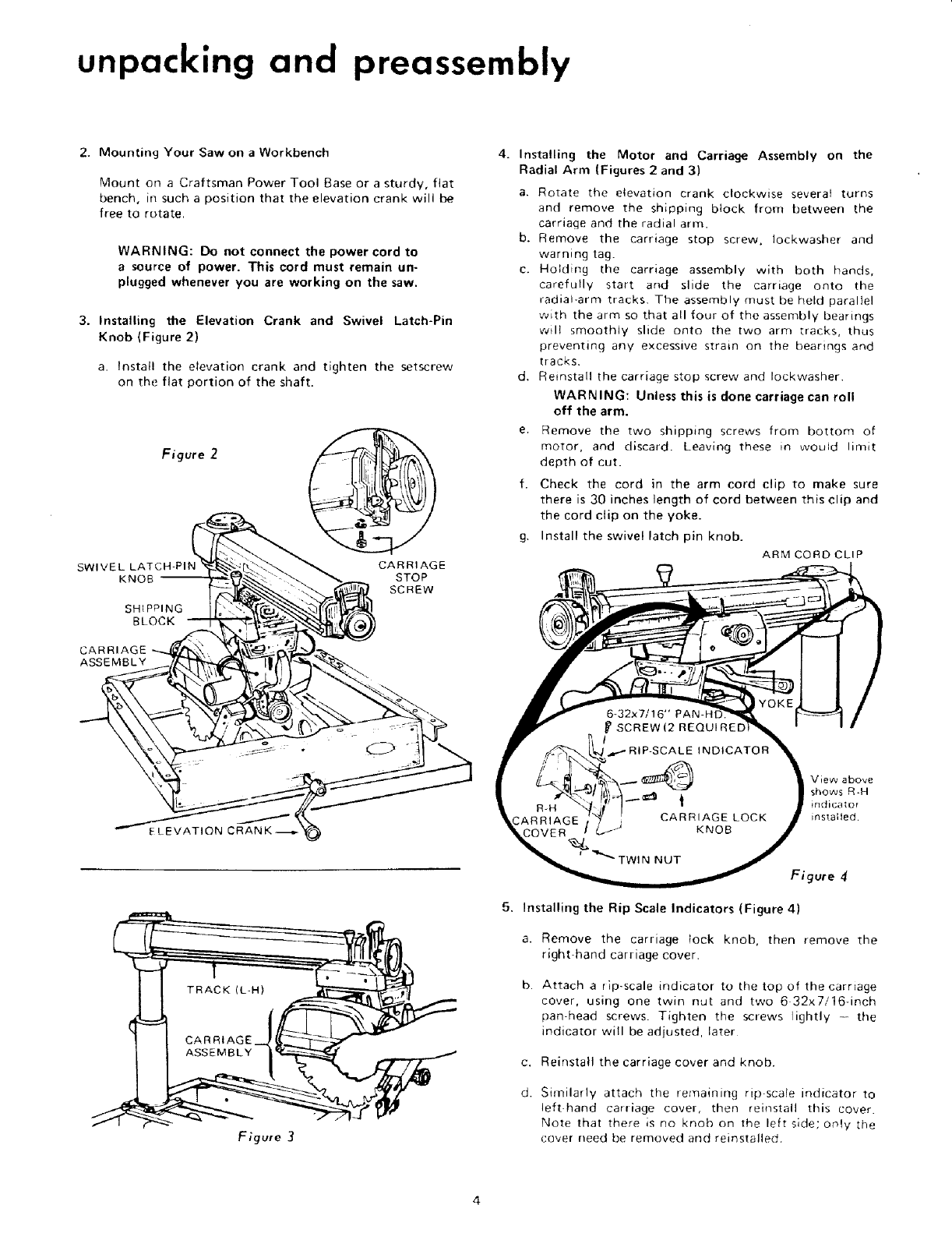
unpacking and preassembly
2. Mounting Your Saw on a Workbench
Mount on a Craftsman Power Tool Base or a sturdy, flat
bench, in such a position that the elevation crank will be
free to rotate,
WARNING: Do not connect the power cord to
asource of power. This cord must remain un-
plugged whenever you are working on the saw.
3. Installing the Elevation Crank and Swivel Latch-Pin
Knob (Figure 2)
a. Install the elevation crank and tighten the setscrew
on the flat portion of the shaft.
Figure 2 ,_
SWIVEL LATCH-PIf CARRIAGE
KNOB -- STOP
SCREW
SHIPPING
BLOCK
CARRIAGE
ASSEMBLY
ELEVATION C
Figure 3
4. Installing the Motor and Carriage Assembly on the
Radial Arm (Figures 2 and 3)
a. Rotate tbe elevation crank clockwise several turns
and remove the shipping block from between the
carriage and the radial arrn.
b. Remove the carriage stop screw. Iockwasher and
warning tag.
c. Holding the carriage assembly with both hands,
carefully start and slide the carriage onto the
radial-arm tracks. The assembly must be held parallel
with the arm so that all four of the assembly bearings
will smoothly slide onto the two arm tracks, thus
preventing any excessive strain on the bearings and
tracks.
d. Reinstall the carriage stop screw and Iockwasher.
WARNING: Unless this is done carriage can rol!
off the arm.
e. Remove the two shipping screws from bottom of
motor, and discard. Leaving these in would limit
depth of cut.
f. Check the cord in the arm cord clip to make sure
there is 30 inches length of cord between this clip and
the cord clip on the yoke.
g. Install the swivel latch pin knob.
ARM CORE) CLIP
View above
shows R-H
indicator
installed.
Figure 4
5. Installing the Rip Scale Indicators (Figure 4)
a. Remove the carriage lock knob, then remove the
right-hand carriage cover.
b. Attach a rip-scale indicator to the top of the carriage
cover, using one twin nut and two 6 32x7/16-inch
pan-head screws. Tighten the screws lightly -- the
indicator will be adjusted, later
c, Reinstall the carriage cover and knob.
Similarly attach the remaining rip-scale indicator to
left-hand carriage cover, then reinstall this cover
Note that there is no knob on the left side; only [he
cever need be removed and reinstalled.

assembly and adjustments
ALIGNMENT INSTRUCTIONS
GUARD ASSEMBLY LOCK KNOB
GUABDCLAM_
SCREW ;HT RECEPTACLE
LATCH-PIN HANDLE
BEVEL LOCK KNOB
Figure 5
NOTE: The following instructions are pre
sented in the most logical sequence in which
they can be done to ensure accurate perform
ance of your saw.
C.
d.
Loosen the guard-clamp screw and remove the guard
assembly.
Place the arbor wrench on the shaft nut and the shaft
wrench on the hex portion of motor shaft just inside
the saw blade.
Hold the shaft wrench and rotate the arbor wrench
downward to loosen the shaft nut. The motor shaft
has left-hand threads.
e. Remove shaft nut, outer collar, saw blade, and inner
collar.
f. Place the saw blade, nut, collars, and guard assembty
where they will be out of your way during the
following adjustment steps.
Figure 6
1. Removing the Guard and Saw Blade (Figures 4, 5 and 6)
a, Tight_:n the carriage lock knob.
b, Disconnect the too!-tight cord.
2. Adjusting the Table Supports Parallel to the Radial Arm
(Figures 7 through 10)
IMPORTANT: Precise adjustment of the table
supports is necessary to assure consistently
true sawing operations. If the table supports-
and the table - are not precisely squared with
the saw-blade travel in all operating positions,
the blade may not produce clean, uniform
cuts.
a.
b.
Loosen the bevel lock knob and hold the latch-pin
handle up
Swivel the motor counterclockwise until the saw end
of the shaft is pointing straight down Tighten the
lock knob.
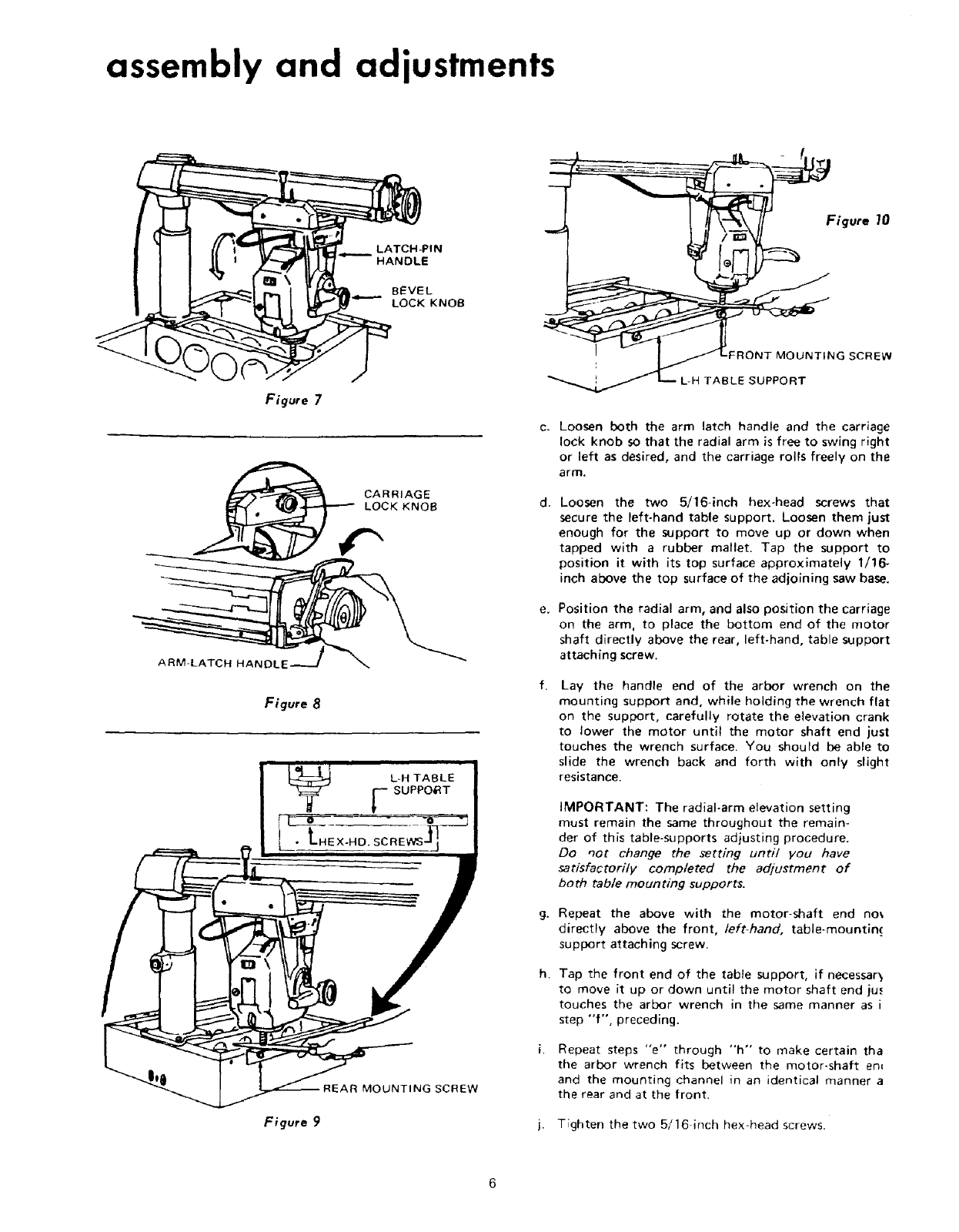
assembly and adjustments
LATCH-PIN
HANDLE
Figure 10
Figure 7
ARM-LATCH HANDLE
Figure 8
Figure 9
MOUNTING SCREW
-FRONT MOUNTING SCREW
L-H TABLE SUPPORT
d.
Loosen both the arm latch handle and the carriage
lock knob so that the radial arm is free to swing right
or left as desired, and the carriage rolls freely on the
arm.
Loosen the two 5/16-inch hex-head screws that
secure the left-hand table support. Loosen them just
enough for the support to move up or down when
tapped with a rubber mallet. Tap the support to
position it with its top surface approximately 1/16-
inch above the top surface of the adjoining saw base.
Position the radial arm, and also position the carriage
on the arm, to place the bottom end of the motor
shaft directly above the rear, left-hand, table support
attaching screw.
Lay the handle end of the arbor wrench on the
mounting support and, while holding the wrench flat
on the support, carefully rotate the elevation crank
to lower the motor until the motor shaft end just
touches the wrench surface. You should be able to
slide the wrench back and forth with only slight
resistance.
IMPORTANT: The radial-arm elevation setting
must remain the same throughout the remain-
der of this table-supports adjusting procedure.
Do qot change the setting until you have
satisfactorily completed the adjustment of
both table mounting supports.
Repeat the above with the motor-shaft end no_
directly above the front, left-hand, table-mountim
support attaching screw.
Tap the front end of the table support, if necessar3
to move it up or down until the motor shaft end ju,,
touches the arbor wrench in the same manner as i
step "f", preceding.
Repeat steps "e" through "h" to make certain tha
the arbor wrench fits between the motor-shaft en(
and the mounting channel in an identical manner a
the rear and at the front.
j. Tighten the two 5/16 inch hex-head screws.

U-CLIP
BASECROSS-MEMBER Figure 1/
k. Adjust the right-hand table support in exactly the
same manner, without altering the radial-arm eleva-
tion setting.
Loosen the bevel lock knob and, while holding the
bevel latch-pin handle up, rotate the motor to a
horizontal position - then release the latch-pin
handle so that the pin bottoms in its detent, and
tighten the lock knob.
m. Move the radial arm to 0 ° (center) position and lock
it by tightening the arm-latch handle.
3. Installing the Front Table (Figures 11 through 15)
P_ace the front table (largest) board upside down on
a workbench or the floor. It is upside down when the
face in which the screw holes are counterbored is at
bottom. Note that there are two holes near the
center of the board, one smaller in diameter than the
other. Drive the T-nut (furnished with loose parts)
into the smaller of these two center holes.
Turn the front table top side up and place it on the
table supports, locating it so that the six screw holes
near the board sides are aligned with their corre-
sponding holes in the two supports.
C. In each of the six boles located above the table
supports, place one 17/64-inch flat washer and one
1i4-20xl-inch pan-head machine screw. In the larger
of the two center holes place one 17!64-inch flat
washer and one 1/4-20xl 1!4-inch pan-head machine
screw - and start the screw into the U-nut on the
front of the saw base (but do not tighten it). In the
smaller center hole {with the T-nut underneath),
barely start the cup-point set-screw.
Install one 1!4-inch Iockwasher and one 1/4 20 hex
nut on each of the six screws in the table supports,
and tighten slightly. The board should be snug
against the supports, but not held too tightly to be
moved by tapping it firmly with a rubber mallet.
Figure 12
A CROSS_SECTIONA L
VIEW THROUGH
CENTER OF T-NUT
1t4 20x 1" PAN-HD. SCREW
FF17/64" FLAT WASHER
FRONT _ _, [----;/4t_i2Cx ,1 1/4"' PAN lid
TABLE [/ "_i v, , I
1/4-LOCK °
1/4-20 I ,__
HEX NUT _ _" Figure 73
NOTE: Setscrew is shown as it will
be when tightened. For step 3c it
must not touch the saw base.
CUP-POI NT SETSCREW_
Figure 14 FRONTTABLE_______
E
REAR TABLE BOAR Figure 15
1
FRONT TABLE
e. Move the carriage to its extreme rear position, and
tighten the carriage lock knob.
f. Lay the rear table board on edge across the front
table to serve as a straightedge. Sight under this
straightedge to determine whether the front table
board is high or low at its center.
g. If the front table is high at center, first tighten the
center (1/4-20x1-1/4-inch) hold-down screw until the
table is level - then tighten the leveling screw until
this screw is snug If table is low at center, hrst
tighten the leveling screw until the table is level -
then tighten the hold down screw.

assembly and adjustments
4. Squaring the Crosscut Travel (Figures 16 through 23)
a. Loosen the carriage lock knob, move the carriage to
the approximate center of the radial arm, then
retighten the lock knob.
b. Install the saw blade, as follows:
(1) Place on the motor shaft, in this order: 1) One of
the two blade collars, flat face out; 2) The blade,
with the teeth pointing in a clockwise direction
when you are facing saw-blade end of motor; 3)
The remaining blade collar, flat face against
blade; and 4) The shaft nut.
(2) Tighten the shaft nut as shown in Figure 17.
c. Loosen the arm-latch handle 1/4 turn (counterclock-
wisel, and make sure the yoke clamp handle and the
bevel lock knob are tight.
SAW BLADE_,_,_,_,_,_ Figure 16
OUTER __
COLLAB/_ MOTOR
SHAFT L.
NUT _ INNERCOLLAR
•-1
Figure 17
ARM LATCH LEVER
t
ARM LATCH
HANDLE
YOKE
HANDLE
o
BEVEL LOCK
KNOB
Figure 18
Figure 19
d,
Figure 20
CAUTION: WHENEVER YOU MOVE THE RADIAL
ARM BEYOND 45°LEFT OR RIGHT ALWAYS
EITHER PULL THE ARM-LATCH LEVER OUT, OR
COMPLETELY LOOSEN THE ARM-LATCH
HANDLE BY ROTATING IT COUNTERCLOCK-
WISE AS FAR AS POSSIBLE. THE ARM LOCK PIN
MUST BE RETRACTED WHENEVER THE ARM IS
ROTATED PAST 45 °LEFT OR RIGHT, OR THE
PIN WILL BE DAMAGED, REFER TO "PRECISION
INDEXING" IN THE "OPERATING CONTROLS"
SECTION FOR THE CORRECT PROCEDURE TO
FOLLOW WHEN ROTATING AND INDEXING THE
RADIAL ARM.
Hold the arm-latch lever out and move the radial arm
approximately 10 ° to the right. Release the arm-
latch lever and move the arm slowly to the left until
it indexes at the 0 ° position. Do not bump or iar
the arm. Tap the arm latch solidly with the palm of
your hand to seat the arm lock pin firmly.
Retighten the armdatch handle, !oosen the carriage
lock knob, and position the carriage to the rear of
the front table. By turning the elevation crank
counterclockwise, lower the blade until it just clears
the front table.
Place a framing square on the front table with its
short leg against the rear edge of the table and the
long leg lust contacting a tooth of the blade. Mark
this tooth ("A'" in the illustration) with a pencil,

MITER
SCALE
ATTACHING
SCREWS 0o
MARK
Figure 21 Figure 22
MITER
SCALE it'q[
MITER SCALE
INDICATOR
Figure 23
g. Now slowly move the carriage outward along the
radial arm. The tooth you have marked should just
touch the long leg of the square at all points. If it
does not, make the following adjustments:
(1) If your marked tooth moves into the square as
the carriage is moved outward, tap the left-front
edge of the table with a rubber mallet until you
can perform step "g" correctly.
(2) If the tooth movesawav from the square, tap the
right-front table edge to make the correction
(3) Recheck until you can perform step "'g" correct-
ly, then securely tighten all six of the front table
hold-down screws. Also refer to page 20, steps
'q" and "j" of Trouble Shooting Section.
h. Loosen the two miter-scale attaching screws and
rotate the scale to align its 0 ° mark with the
miter-scale indicator. Tighten the screws.
NOTE: This squaring of the crosscut travel will
simultaneously set both of the 45 ° index
positions of the radial arm.
5. Installing the Remaining Table Boards (Figure 24)
a. Position the rip fence, spacer board and rear table
board behind the front table board, as shown.
b. Install the two table clamps in the slots provided for
them at the rear of the saw base, and tighten them
securely.
NOTE: The life of your saw table will be
lengthened considerably if you will cover the
front table with a fitted piece of 1/4-inch
plywood. This should be tacked in place for
easy replacement. Use of such a cover will
allow, you to do all cutting into the cover,
rathe_ than your table top.
6. Setting the Bevel-Index Indicator (Figure 25)
a The bevel index indicator should read 0 ° on the
TABLE CLAMP
l
I
FRONTTABLE
REAR TABLE
SPACER
RIP FENCE Figure 24
__ Figure 25
_'_ k _ BEVEL INDEX
[ 0 OS,T,ON
\ tL )))Y7"----BEVEL'N°'cAT°R
BEVEL LOCK KNOB
bevel-index scale when the motor is locked (bevel
lock knob tightened) into position with the saw
blade vertical.
b. If necessary, loosen the indicator attaching screw,
adjust the indicator to theO °reading,then retighten
the attaching screw.

assembly and adjustments
7. Adjusting the Rip-Scale Indicators (Figures 26 --29)
NOTE: The two rip scales and indicators are
intended only for use in making quick settings.
For maximum accuracy of setting, make direct
measurements between the blade and the rip
fence.
a, Loosen the yoke clamp handle, hold the swivel
latch pin knob up, swivel the yoke until releasing the
swivel latch-pin knob will allow the yoke to index at
its 90 ° position, then retighten the yoke clamp
handle.
b. Loosen the carriage lock knob and move the carriage
until the saw blade just touches the rip fence. The
blade should be free to rotate while just scraping the
fence. Tighten the carriage lock knob.
c. Set the right-hand indicator at "0".
NOTE: With the rip fence positioned at
normal, as in figure 27, the bottom right-side
scale is used to read the saw-blade in-rip
setting. If the rip fence is moved to the
extreme rear position, the top scale is used.
YOKE
CLAMP
HANDLE
;WIVEL LATCH-PIN KNOB
CARRIAGE
LOCK KNOB
Figure 26
YOKE
RIP
FENCE
Figure 27 _ _-_
REAR TABLE BOARD- I _"
_NT TABLE
L,
FENCE
Figure 28
INDICATOR
IN-RIP
SCALE
CARRIAGE LOCK KNOB
_ _1 _
RIP FENCE J
Measure from the fence
to the nearest blade
tooth.
F--'FRONT TABLE
l _-_ SPACER BOARD
REAR TABLE BOARD Figure 29
d. Loosen carriage lock knob, position rip fence and
blade as shown in figure 29, tighten carriage lock
knob, and set left-hand indicator at "'12"'.
NOTE: The top left-side scale is used to read
the saw-blade out-rip setting whenever the rip
fence is at the extreme rear position. If fence
is at the normal position, the lower left-side
scale is used.
e. After completing the indicator adjustments, swivel
the yoke back to the 90 ° position.
8. Reinstalling the Guard and Adjusting the Anti-Kickback
and Spreader Assembly (Figure 30)
a. Carefully fit the guard assembly into position over
the saw blade, seating the inner guard flange in the
groove on the end of the motor.
b. Tighten the guard clamp screw.
c. Feed the tool-light cord end between the yoke and
the motor, and insert the plug into the receptacle on
top of the motor.
d=
e.
Loosen the wing nut, lower the anti-kickback assem-
bly to lowest position, then retighten the wing nut.
Sight (visually) to check for proper alignment of the
anti-kickback spreader with the saw blade. If the
spreader is misaligned, adjust it as follows: Loosen
the two hex-head screws th3t hold the anti-kickback
I0

electrical connections
mounting bracket, shift the spreader into alignment
with the saw blade, then retighten the two screws to
hold the bracket securely. Check to make sure the
spreader is aligned throughout its travel.
NOTE: Periodically check, and maintain sharp
tips on the anti-kickback pawls.
IMPORTANT: If you experience any diffi-
culty in obtaining trouble-free sawing opera-
tions, refer to the trouble-shooting section in
this manual.
9. Preparing Rear Table for Shaping (Figure 30)
For us_ of a Molding Head Cutter (page 17) the rear
table ruquires an opening for clearance of the motor
end Ct]t this opening as shown in figure 30 inset.
POWER SUPPLY AND
MOTOR CONNECTIONS
1. Motor Specifications
The A-C motor used in this saw is a capacitor-start,
non-reversible type having the following specifications:
Horsepower .............. 2.50 (developed) @120V.
2.50 (developed) @ 240V.
Voltage ........................ 120/240
Amperes ......................... 11/5.5
Hertz (_ycies) ........................ 60
Phase .......................... Single
RPM ............................ 3450
Rotation as viewed
from saw-blade end ................ Clockwise
CAUTION: YOUR SAW IS WIRED FOR 120V
OPERATION. CONNECT TO A 120V, 15-AMP.
BRANCH CIRCUIT AND USE A 15-AMP., TIME-
DELAY FUSE OR CIRCUIT BREAKER. IF THE
MOTOR IS RECOMMENDED FOR 240V OPERA-
TION, CONNECT TO A 15-AMP, BRANCH CIRCUIT
AND USE A 1B-AMP. TIME-DELAY FUSE OR CIR
CUlT BREAKER.
ELECTRICAL CONN ECTIONS
WARNING: CHANGES IN ELECTRICAL
CONNECTIONS SHOULD BE MADE BY A
QUALIFIED ELECTRICIAN.
1, Changing Motor Connections
a. Unde_ normal home workshop usage, and if proper
(full voltage is supplied to the motor, your saw will
operate efficiently on 120V, as connected at the
factory. However, if any of the following conditions
exists, it wi!l be advisable for you to reconnect the
motor for 24OV operation - to obtain the efficiency
and I)erformance for which your saw is designed:
(1) Continuous heavy-duty operations.
GUARD CLAMP
SCREW
TOOL-LIGHT- Figure 30
CORD RECEPTACLE
EYE
ANTI-KICKBACK
MOUNTING
BRACKET
ANTI-KI CKBACK
ASSEMBLY
WING NUT
FOR
SHAPING
3"---d, I
b.
(2) Either an undersized or an overloaded branch
circuit serving the saw motor.
(3) Low voltage supplied by the power source,
which the power company cannot correct.
Motor wiring connections for 120V (as made at the
factory) are described below. Necessary reconnec-
tions for 240V operation are also described follow-
ing. Whenever changing connections from 120V to
240V or vice-versa, make certain that a!l necessary
steps (including proper fusing of the branch circuit)
are completed.
2. Connections for 120V A.C. (Figure 31)
a. Remove nameplate cover from motor to expose
terminal board.
b. The wires inside of the motor must be connected as
follows:
(1) The orange-colored wire on number 6 terminal.
(2) The brown-colored wire on number 5 terminal.
c. Use the 120V power-cord plug furnished with your
saw.
FOR USE ON I?_OV!24-OV Figure31
_ROWN LEAD ON 5 7
BROW ORANGE
11

electrical connections
3. Connections for 240V A.C. (Figure 32)
a. The wires inside the motor terminal box must be
connected as fo!lows:
(1) The orange-colored wire on number 8terminal.
(21 The brown-colored wire on number 7 terminal.
b. Replace the 120V power-cord plug with a(3-blade)
240V plug, connecting the power-cord white and
black leads, respectively, to the two "hot" plug
blades - and connecting the power-cord grounding
wire to the third (neutral) plug blade.
c. Plug your saw into a 240V, 3-blade receptacle.
d. Make certain the receptacle is connected to a 240V
A-C power supply through a 240V branch circuit
having at least a 15-amp. capacity, and protected by
a 15 amp. time-delay fuse or circuit breaker.
Figure 32
As soon as the red button will snap into running
position, the saw may be started and operated normally,
by pulling out the saw switch to the "'ON" position.
Frequent opening of fuses or circuit breakers may result
if motor is overloaded, or if the motor circuit is fused
different!y from recommended. Overloading can occur if
you feed too rapidly or if your saw is misaligned so that
the blade heels. Do not use afuse of greater capacity
without consulting the power company.
Although the motor is designed for operation on the
voltage and frequency specified on motor nameplate,
normal loads will be handled safely on voltages not more
than 10% above or below the nameplate voltage. Heavy
loads, however, require that voltage at motor terminals
equals the voltage specified on nameplate.
Most motor troubles may be traced to loose or incorrect
connections, overloading, reduced input voltage Isuch as
small size wires in the supply circuit) or to an
overlylong supply circuit. Always check the connec-
tions, the load and the supply circuit, whenever the
motor fails to perform satisfactorily. Check wire sizes
and lengths with the table following.
FOR U3E ON I?-0V 240V
ORANGE LEAD ON 6 _t_
I_ROWN LEAD ON ,5 7
12345
BROW ORANGE
MOTOR SAFETY PROTECTION
NOTE: This motor should be blown out, or
"vacuumed", frequently to prevent sawdust
interference with normal motor ventilation.
Your saw motor is equipped with a manual-reset, thermal-
overload protector designed to open the power-line circuit
when the motor temperature exceeds a safe value (figure
33).
1. If the protector opens the line and stops the saw motor,
immediately press the saw switch to the "OFF" posi-
tion, and allow the motor to cool.
2. After cooling to a safe operating temperature, the
overload protector can be closed manually by pushing in
the red button on the top of the motor. If the red
button will not snap into place immediately, the motor
is still too hot and must be allowed to cool for a while
longer. (An audible click will indicate protector is
closed.)
U
_ ---4" \-_
,. I I_.j-T---
.L...._r
OVERLOAD PROT_ MOTOR
NAMEPLATE
Figure 33
WIRE SIZES
Length of the
Conductor
50 feet or less
100 feet or less
100 feet to 150 feet
150 feet to 200 feet
200 feet to 400 feet
The following table lists recommended wire sizes for
connecting the motor to the power source. These sizes
should be maintained for trouble-free operation of the saw.
If an extension cord is used, it should be a 120V or 240V,
3-wire type designed for ]rounding the tool.
Wire Size Required
(American Wire Gauge Number)
240 Volt Lines 120 Volt Lines
_114 NO. 12-
No. 12 No. 10
No. 10 No. 8
No. 8, No 6
No. 6 i No. 4
I
NOTE: For circuits of greater length, the wire
size must be increased proportionately in order
to deliver ample voltage to the saw motor.
12

U_,_t;_l Lt i ili_ LUlilIUI_
LOCATIONS AND FUNCTIONS OF CONTROLS
7
8
1. Arm-Latch Lever
2, Swivel Latch-Pin Knob
3. Rip Scale and Indicator
4. Miter Scale and Indicator
5. Carriage Lock Knob
6. Yoke Clamp Handle
7. Key
8. Latch-Pin Handle
9, Bevel-lnde× Scale
and Indicator
Figure 34
10. Elevation Crank
11, Bevel Lock Knob
12. Anti-Kickback and
Spreader Assembly
13. Guard Clamp Screw
14. Bevel Index Handle
15. On-Off Switch
16. Sawdust Chute
1"7. Sawdust-Chute Lock Knob
18. Arm-Latch Handle (Knob)
yo_J! _T
€
A series of six diagrams is located on the top surface of the
radial arm. These designate the controls that must be used
in basic set-ups and operating procedures. You should
become familiar with these diagrams and the operating
instructions that follow, before operating your saw.
1. Depth of Cut
a. The diagram shows the elevation crank (10, figure
34), which is used to raise and lower the saw blade.
b. Clockwise rotation raises the blade.., counter-
clockwise rotation lowers it. One complete turn of
the handle will raise or lower the saw blade 1/8-inch.
2. Angle of Cut
CAUTION: WHEN MOVING THE RADIAL ARM IN
ANY DIRECTION BEYOND 45 ° (LEFT OR RIGHT_,
ALWAYS PULL OUT THE ARM-LATCH LEVER (1,
FIGURE 34). OR LOOSEN THE LEVER BY RO-
TATING THE ARM-LATCH HANDLE (18}
COUNTERCLOCKWISE UNTIL IT STOPS, TO PRE-
VENT DAMAGING THE ARM-LOCK PIN, DAMAGE
OF THIS NATURE WOULD PREVENT PROPER IN-
DEXING OF THE RADIAL ARM AT THE 0 ° AND
45 ° POSITIONS (LEFT OR RIGHT}.
a. Two controls are involved in releasing, securing and
indexing the angle of the radial arm. These are: the
arm-latch handle (18, figure 34), and the arm-latch
lever (1).
WARNING: THE SAW SHOULD NEVER BE
OPERATED WITH THE SAW BLADE OUT-
SIDE OF THE TABLE AREA, EVEN
THOUGH THE RADIAL ARM CAN BE RO-
TATED A FULL 360 ° AND LOCKED IN ANY
POSITION.
b. The arm is unlocked from any position by a slight
counterclockwise rotation of the armlatch handle
and is locked in any desired miter position by
rotating the arm-latch handle clockwise until tight.
O O
The radial arm has positive stops at 0 and 45 left
and right, and is released from these index positions
by unlocking the arm-latch handle 1/4 turn, and
pulling out the arm-latch lever.
For the most positive and accurate settings at the
index positions, the following is recommended:
13

operating controls
(1) If the radial arm is already indexed, rotate the
arm-latch handle ( 18, figure 34) 1!4turn counter-
clockwise from the locked position, pull out the
arm-latch lever, and move the radial arm off the
index position_ Release the arm-latch lever.
(2) Move the radial arm into the desired index
position (do not bump or jar it) and push on the
arm-latch lever solidly with the palm of your
hand (figure 34 inset). This is very important as
it ensures proper seating of the arm lock pin in
the arm latch, thus always setting the arm at the
correct position.
(3) Lock the radial arm by rotating the arm-latch
handle clockwise until tight.
3. Yoke Pivot
a. Two controls are used in this operation. They ate:
the swivel latch-pin knob (2, figure 34) and the yoke
clamp handle (6, figure 34).
b. A swivel latch pin automatically indexes the yoke at
each 90 ° position. Lift the spring-loaded swivel
latch-pin knob to release this pin.
e. The yoke clamp handle locks the yoke to the carriage
in any position. Pull the handle forward to release
the yoke; push the handle rearward to secure the
yoke.
4. Carriage Lock
a. The carriage lock knob (5, figure 34) is rotated
clockwise to secure the carriage on the radial arm,
and counterclockwise to release it.
b. When performing a square or miter-angle crosscut,
the carriage lock knob must be rotated counterclock-
wise until the carriage is free to travel along the arm.
This knob should be tightened except when the
operator is ready to grasp the bevel index handle (14,
figure 34) and rnake a cut.
5. Blade Angle
a. The two controls used in angular positioning and
indexing of the motor, to provide the desired
saw blade (bevel) angle, are: the bevel lock knob (t 1,
figL_re 34) and the latch pin handle (8, figure 34).
b. The bevel-index scale (9, figure 34) indicates the
angular position of the motor with respect to
horizontal, from 0 ° to 90 ° in either vertical position.
c. The bevel latch pin automatically indexes the motor
at 0°, 45 ° and 90 ° up and down. Lift the spring
loaded latch-pin handle to release this pin. At any
other position, the latch pin does not engage.
d. The bevel lock knob locks the motor to the yoke
when the motor is in any position. Rotate the knob
cloekwise to lock, counterclockwise to unlock.
6. Power Switch and Key
a. This saw cannot be operated without the key, and
the key cannot be removed from the lock while the
saw motor is running.
b, To release the switch lever (15, figure 34) insert the
key (7, figure 34) in the slot and turn it counter-
clockwise until it stops. Rotate the key clockwise
to lock the switch.
c. To start the saw, engage your forefinger under the
left side of the switch lever and pull the lever
outward.
d lo stop the saw, simply push the switch lever with
finger or thumb.
WARNING: When leaving the saw unattended,
lock the ON-OFF switch and remove the key.
POSITIONING SAWDUST CHUTE, AND
ANTI-KICKBACK AND SPREADER
ASSEMBLY, FOR RIPPING
WARNING: NEVER POSITION THE GUARD
CHUTE OR ANTI-KICKBACK ASSEMBLY
WITH THE POWER ON. NEVER POSITION
THE ANTI-KICKBACK PAWLS BY GRASP-
ING THE PAWLS OR SPREADER.
For all crosscutting operations (those operations in which
the carriage is traveled along the radial arm to feed the saw
blade into the workpiece) both the sawdust chute (16,
figure 34) and the anti-kickback and spreader assembly (12,
figure 34) must be elevated to clear theworkpiece or the
fence, whichever is higher.
1. The Anti-Kickback and Spreader Assembly
b.
The anti-kickback and spreader assembly (12, figure
34) is used during ripping operations and is adjust-
able to accommodate the thickness of the board
being ripped. A wing nut in the guard secures the
assembly.
The anti-kickback and spreader assembly is posi-
tioned by grasping the top of the light housing
assembly (23, figure 3 on p. 30), I9osening the wing
nut, and raising or lowering the assembly until the
anti-kickback pawl point nearest the saw blade rests
on the top surface of the workpiece, with the bottom
edge of the pawls angled slightly downhill to the top
surface of the workpiece. (See figure 35.) Before
making the cut, check the effectiveness of the
anti-kickback pawls by placing the workpiece under
Figure 35
WORK
_I KICKBACK
14

basic saw operations
the pawls and attempting to slide it in the direction
of kickback. If the pawls do not catch, further
adjustment is necessary.
e
d.
e.
When positioning the anti-kickback and spreader
assembly for bevel ripping, lower the assembly until
the Iocknut just clears the workpiece. If the pawls do
not catch, further adjustment is necessary.
Before repositioning the yoke to the crosscut posi-
tion, false the anti-kickback assembly to the upper
limit and secure.
The tips of the anti-kickback pawls should be
checked occasionally and kept sharp.
2. The Sawdust Chute
a. The sawdust chute (16, figure 34) is used to help
prope! sawdust from the cut and provide a hold-
down for boards during ripping.
b The sawdust chute is positioned by grasping the
upper tab et lower end of chute, loosening the knob
(17, figure 34) and raising or lowering it to just clear
the top surface of the board being ripl_ed_'T-_ght_'_n_
the knob secures the chute.
c. Before repositionlng the yoke to the crosscut posi-
tion, raise the chute to the upper limit and secure.
IMPORTANT: In ripping operations the work-
piece is always fed from the sawdust chute side,
never from the anti-kickback side of the guard.
(See figures 41 and 42.)
PRECISION INDEXING
Experienced operators of precision equipment, such as your
Craftsman Radial-Arm Saw, normally acquire the habit of
indexing the machine in one direction only, whenever a
new setting is made in preparation for a different operation.
For example: when moving the radial arm to a new
position, it is advisable to move it slightly past the desired
index position, then return it slowly and carefully to latch
and lock it. Figure 34 inset shows the radial arm being se-
curely indexed by "tapping" the arm latch lever with the
palm of the hand. Swivel indexing and bevel indexing can
be accomplished in a similar manner This indexing tech-
nique tends to neutralize any stresses imposed upon the saw
components, and contributes to the high degree of accuracy
the saw is capable of producing when operated expertly.
BASIC SAW OPERATIONS
REQUIREMENTS FOR CROSSCUT
(OPERATIONS 1THROUGH 4)
1. Be sure you return the carriage to the full rearward posi-
tion at the conclusion of each cut. Never remove your
hand from the bevel index handle unless the carriage is
in this position. Allow the saw blade to come to a com-
plete stop before removing the workpiece from the saw
table.
2. Arbor nut must be tight and saw blade guard installed in
a horizontal position with anti-kickback device in full up
position.
3. Arm latch handle (knob) must be tight.
4. Work must be held firmly against table and fence. For
workpieces thicker than the fence is high, it is recom-
mended that a higher fence be cut (at least workpiece
thickness) and inserted for that operation being per-
formed. Always place the fence in the most forward
position (farthest from the column support) compatible
with the workpiece being processed and the operation
being performed. With the carriage fully retracted, the
blade should not contact the workpiece when placed
against the fence, within the stated capacities of your
saw.
5. Blade should be sharp and correctly set.
6. Hands must be kept well away from saw blade.
7. Yoke clamp handle must be in locked position.
8. Bevel index knob must be tight.
9. For operations No. 3 and No. 4, observe additional in
struetions under paragraph, "Operating Controls",
"Blade A_gle".
BEVEL
LOCK KNOB
CARRIAGE LOCK KNOB
YOKE CLAMP
HANDLE
Figure 36
OPERATION NO. 1 -- CROSSCUT
Crosscutting is the process of sawing the workpiece by pull-
ing the saw blade through it and using the fence as a sup-
port for the edge of the workpiece. Never crosscut free-
hand.
WARNING: BEFORE CROSSCUTTING, MAKE
SURE THE ARM LATCH, BEVEL LOCK AND
YOKE CLAMP ARE ALL SECURED, NEVER USE
ALENGTH STOP OR A FIXED GUIDE ON THE
FREE END OR EDGE OF AWORKPIECE. (SEE
INSTRUCTION 15 UNDER "'SAFETY INBTRUC-
TIONS TO OPERATOR".) DO NOT CROSSCUT
WORKPIECES THAT PLACE YOUR HANDS
CLOSE TO THE PATH OF THE SAW BLADE.
WHEN MORE EXPERIENCE IS GAINED BY
USING THE SAW, IT WILL BE NOTICED, THAT
WHEN PULLING THE SAW TOWARD YOU DUR-
ING CROSSCUTTING, THE BLADE TENDS TO
FEED ITSELF THROUGH THE WORK DUE TO
THE ROTATION OF THE BLADE AND THE
DIRECTION OF THE FEED. THEREFORE, THE
OPERATOR SHOULD DEVELOP THE HABIT OF
HOLDING HIS RIGHT ARM STRAIGHT FROM
THE SHOULDER TO THE WRIST.
15

basic saw operations
RADIAL ARM
RADIAL
ARM
CARRIAGE
Figure 37
ARM
Figure 38
OPERATION NO. 2 -- MITER CROSSCUT
Miter crosscutting is the process of sawing a board at any
angle other than a 90 ° (square) cut. (See figure 37.) The
45" miter angle is a popular one, since two boards cut at
45 ° can be assembled to form a 90 ° corner for producing a
square or rectangular frame. The radial arm is set to the
desired angle of cut, and the yoke and bevel settings are
o
indexed at 0 (and locked), as in square crosscutting. The
board being cut is held firmly against the fence, and the
carriage is pulled forward along the radial arrn to perform
the desired cut. As in "Operation No. 1", the carriage
should be returned to full rear position, and the saw blade
allowed to come to a complete stop, before removing the
workpiece from the saw table,
OPERATION NO. 3 -- BEVEL CROSSCUT
Bevel crosscutting is the process of sawing at 90 ° (square)
across the board with the saw blade set at an angle other
than 90 ° 1o the saw table (Bee figure 38.) The radial arm
and yoke are indexed at 0 ° and locked, but the bevel _sset
'co the de<,ired angle of cut. The board is held firmly against
the fence, and the carriage is pulled forward along the radial
arm to p_oduce the cut. The carriage should be _eturned to
RADIAL ARM
CARRIAGE
YOKE
Figure 40
full rearward position, and the saw blade allowed to come
to a complete stop, before removing the workpiece from
the saw table.
OPERATION NO. 4 -- COMPOUND
CROSSCUT
Compound crosscutting is a combination of miter and bevel
crosscutting. (See figure 39) The radial arm and bevel are
set to produce the desired cut; the yoke is indexed at 0 °
and locked. The board is held firmly against the fence, and
the carriage is pulled forward along the radial arm to
produce the cut. Again, the carriage should be returned to
full rearward position, and the saw blade allowed to come
to a complete stop, before removing the workpiece from
the saw table.
REQUIREMENTS FOR RIPPING
OPERATIONS 5 AND 6
1. Carriage lock knob must be tight.
2. Radial arm must'be locked in 0 ° position.
3. Saw blade must be parallel to fence, to minimize
possibility of kickbacks.
4. Work must be held firmly against table and fence while
feeding through.
5. Guard chute and anti-kickback pawls must be properly
set. Observe instructions under "ADJUSTING GUARD
CHUTE AND ANti-KICKBACK AND SPREADER
ASSEMBLY FOR RIPPING OPERATIONS", preceding.
16

YOKE
Figure 42
6. Blade should be sharp and correctly set.
7. Hands must be kept wellaway from saw blade.
8. When ripping narrow or short stock, always use a push
board.
OPERATION NO. 5 -- OUT-RIPPING
AND IN-RIPPING
1. Ripping is the process of sawing the workpiece by feed
ing it into the saw blade when using the fence as a guide
and as a positioning device to obtain the desired width
of cut.
WARNING: NEVER RIP FREE-HAND. BEFORE
RIPPING, MAKE SURE THE GUARD, SPREADER
AND ANTI-KICKBACK PAWLS ARE SET UP
PROPE R LY. ALSO, MAKE SURE THE SAW
BLADE IS PARALLEl WITH THE FENCE. NEVER
RIP WORKPIECES SHORTER THAN THE SAW
BLADE DIAMETER.
2. Since the work is pushed along the fence, it must have a
reasonably straight edge in order to make sliding contact
with the fence. Also, the work must make solid contact
with the table, so that it will not wobble. Provide a
straight edge, even if this means temporary nailing of an
auxiliary straight-edged board to the work. If the work-
piece is warped, turn the hollow side down,
3. Always use the saw guard and make sure the spreader is
correctly aligned with the saw kerr. Wood cut with the
grain tends to spring the kerr closed and bind the blade
and a kickback could occur.
4. Stand a little to one side of center to avoid being
sprayed with sawdust and to be clear of work in case of
kickback.
5. When ripping short or narrow work, always use a push
stick applied to the section of the workpiece between
the blade and fence . .. push the work past the blade so
it is clear of the blade. This procedure will minimize the
possibility of kickbacks.
Out-Ripping (See figure 41.1 The bevel is indexed and
locked at 0 °. The yoke is turned 90-degrees in a counter-
clockwise direction (viewed from above), from the crosscut
position. When you are standing in front of the saw, the
blade will rotate clockwise. Before positioning the guard
chute and anti kickback pawls, lower the blade to just cut
into the table. After positioning the guard chute and
anti-kickback pawls, the workpiece is fed from the chute
(left-hand) side of the guard, as shown. The "Out Rip"
scale is on the left-hand side of the radial arm,
OPERATION NO. 6 -- BEVEL RIPPING
Bevel ripping is either in-ripping or out-ripping as de_ribed
preceding, except the saw blade is tilted out of perpendicu-
lar to the saw table surface. Figure 42 shows a typical bevel
out-ripping operation. The bevel is set to the desired bevel
angle, and the yoke is positioned for in-ripping or out
ripping, as required. All requirements and observations
applicable to normal ripping operations also apply to bevel
ripping.
RECOMMENDED ACCESSORIES
ITEM CAT. NO. ITEM CAT. NO.
Cabinet ......................... 9 10315
Stand ........................... 9 1038
Bench .......................... 9-1071
Shaper Fence ..................... 9 2954
Hold-Down Attachment ............ 9 3230
Key Chuck ...................... 9 2980
Miter Vise ....................... 9 3279
Molding Head Guard - 7-Inch ...... 9-29524
Molding Head Guard - 8-Inch ........ 9-29523
Rotary Surface Planer - Carbide lip . 9 29513
Sanding Plate - 10-Inch ............ 9 22724
The above recommended accessories are
Sanding Wheel - 8Inch ............. 9 2274
Sanding Wheel - 10-Inch ........... 9 22723
Dust Collector .................... 9 16996
Taper Jig ....................... 9 3233
Satin Cut Dado - 7-Inch ............ 9-3257
Satin Cut Dado- 8-Inch ........... 9-3253
Heavy Duty Dado- 8Inch .......... 932473
Molding Head Single Cutter. ......... 9 3215
Molding Head Three Cutter .......... 9 3221
Sanding Drum -3-Inch ........... 9 25246
Lower Ring Guard ................. 9 29008
current and were available at the time this manual was printed
17

safety instructions to operator
1. Be sure to read the following instructions carefully
before operating the saw.
WARNING: DO NOT CONNECT POWER
CORD UNTIL THE FOLLOWING STEPS
HAVE BEEN SATISFACTORILY COM-
PLETED.
a. Assembly and installation.
b. Examination and operating familiarity with ON-
OFF switch, elevation control, bevel control, rip
control, and miter control.
c. Review and understanding of the operating proce-
dures which follow.
CAUTION: Always disconnect the power when
changing the sat-up, or making adjustments.
Shut off motor before performing layout work
on the saw table. ALWAYS return the carriage
to the full rear position after each crosscut Wpe
operation.
2. The saw should be bolted down.
3. Set carriage lock before moving machine.
4. Position your entire saw (or saw and bench) to slope
slightly rearward, so the carriage will not roll forward
due to gravity.
5. Kickbacks can cause serious injury. A kickback occurs
when a part of the workpiece binds on the saw blade
and the rip fence or other fixed object, rises from the
table, and is thrown toward the operator. Kickbacks
are usually caused by one or more of the following
conditions:
a. Failure to use a spreader when ripping, or failure to
maintain the spreader in alignment with the saw
blade.
b. Improperly conditioned (dull) saw that permits the
material to pinch on the out-feed edge of the saw
and rise from the table.
c, Failure to determine that the rip fence and the saw
blade are parallel to each other.
d. Ripping wood that has a twisted grain, does not
have a straight edge to guide along the fence, or
wood that is twisted or not fiat (which may rock on
the table and pinch the blade).
e. Confining the cut-off piece when ripping.
6.
B,
9,
10.
11.
Ripping by applying the feed force to the section of
the workpiece that will become the cut-off (free)
piece (feed force when ripping should always be
applied between the saw blade and the fence.., use
apush stick for narrow or short work),
g. Releasing workpiece before operation is complete...
not pushing the workpiece all the way past the saw
blade.
NOTE: Injury from kickbacks may be pre-
vented or minimized by:
Avoiding any of the causes noted above...
Making sure (by trial) before starting the cut
that the anti-kickback pawls will stop the kick-
back once it has started...
Keeping your face and body always out of line
of possible kickbacks, including turning the
switch ON and OFF ...
Always wearing safety goggles...
Whenever possible, perform rip, bevel rip, and plough
cuts with the saw in the out-rip position. This provides
the most stable setup (carriage bearings nearest the
column) and the greatest visibility of the sawblade.
The saw should be positioned when ripping so neither
the operator nor a casual observer is forced to stand in
line with the saw blade.
Before starting work, verify that no play exists in the
carriage and that arm, yoke, and bevel locks/clamps are
tight.
Use only accessories that are designed for this machine.
The saw work area should have adequate overhead,
non-glare light and adequate surrounding work space.
A large proportion of saw accidents is caused by dull,
badly set, improperly filed cutting tools, by gum or
resin adhering to cutting tools, and by fence misalign-
ment (out-of-parallel) with the sawblade. Such condi-
tions cause the material to stick, jam, stall the saw, or
kick-back at the operator. Cracked saw blades should
be discarded immediately. A sawblade can become
cracked if it wobbles or if it is not in balance. Never
attempt to free a statled saw blade without turning the
saw "OFF". Avoid potential injury by proper cutting
tool and machine maintenance."
CAUTION: DO NOT cycle the motor switch
ON and OFF rapidly, as this might cause the
saw blade to loosen. In the event this should
ever occur, allow the saw blade to come to a
complete stop and re-tighten the arbor nut nor-
mally, not excessively.
18

12. Gloves should not be worn while operating the saw.
Loose flowing garments, jewelry (rings, wrist watches,
etc.} and neckties should never be worn. Long sleeves
should be rolled to above the elbows.
13. Always wear safety goggles to protect the eyes. In addi-
tion. wear a face shield if the operation is dusty, and
ear protectors (plugs or muffs) during extended periods
of operation.
14. Provide proper support for the workpiece, based on its
size and the type of operation to be performed. Hold
the work firmly against the fence. When ripping short
workpieces (under 12-inches long) or narrow pieces
(under 6-inches wide), use a push stick applied to the
section of the workpiece between the blade and the
fence.
15. Never use a length stop on the free end or edge of the
workpiece. Never hang onto or touch the free end of
workp*ece, or a free piece that is cut off, while power
is "ON" and!or the saw blade is rotating. In short, to
guard against kickbacks or other potential accidents,
the cut-off piece in any thro-sawing operation must
never be confined -- it must be allowed to move laterally.
16. Do not leave a long board unsupported so the spring of
the board causes it to shift on the table. A support
should be used to catch the end of the board you are
supporting.
17. Make sure your fingers do not contact the terminals of
power or motor plugs when installing or removing the
plug to or from a live power source.
18. Never climb on or near the saw when power is on.
Never leave the saw with power on, or before the cut-
ting tool has come to a complete stop. Lock the motor
switch and put away the key when leaving the saw.
19. Avoid awkward hand positions, where a sudden slip
could cause a hand to move into a saw blade or other
cutting tool. Never reach in back of or around the
cutting toot with either hand to hold down the work-
piece.
CAUTION: Never reposition the GUARD
CHUTE or anti-kickback/spreader with power
ON.
20. Always position the GUARD CHUTE and the anti-
kickback and spreader assembly for rip type opera-
tions. Also make sure the cutting tool, arbor collars
and arbor nuts are installed properly. Keep guards in
place; use the proper guard.
21.
22.
Do not use any blade or other cutting tool marked for
an operating speed in excess of the design speed of the
saw. Never use a cutting tool larger in diameter than
the diameter for which the saw was designed. For
greatest safety and efficiency when ripping, use the
maximum diameter blade for which the saw is de-
signed, since under these conditions the spreader is
nearest the blade.
The use of abrasive or cut-off wheels, or wire wheels
can be dangerous and is not recommended. (Abrasive
or cut-off wheels are used to saw many different ma-
terials including metals, stone, and glass.)
23, Do not position the arm so the operation you are per-
forming permits the cutting tool to extend beyond the
edges of th_e table.
24. Never turn your radial arm saw "ON" before clearing
the table or work surface of all objects (tools, scraps of
wood, etc.) except the workpiece and related feed or
support devices for the operation planned_
25.
26.
27.
Objects can be thrown upward toward the operator by
the back of the blade if proper operating procedures
are not followed. This usually occurs when a small,
loose piece of wood or other object contacts the rear
of the revolving blade. It can be avoided by removing
all loose pieces from the table immediately after they
are made, using a long stick, and keeping the guard in
place at all times. Use extra caution when the guard
assembly is removed for molding, and replace the guard
as soon as that operation has been completed.
Never perform any operation "free hand". This term
means feeding the carriage into the workpiece or feed-
ing the workpiece into the saw blade or other cutting
tool without using the fence or some other device
which prevents rotation or twisting of the workpiece
during the operation. Never "rip" (cut with the grain)
narrow or long workpieces in the crosscut position...
feeding saw blade into the stationary workpiece. Never
make a miter cut with the arm in the 90 ° crosscut
position.
Safety is a combination of operator common sense and
alertness at all times when the saw is being used.
WARNING: DO NOT ALLOW FAMILIARITY
(GAINED FROM FREQUENT USE OF YOUR
SAW} TO BECOME COMMONPLACE" AU
WAYS REMEMBER THAT A CARELESS
FRACTION OF ASECOND IS SUFFICIENT
TO INFLICT SEVERE INJURY.
19

trouble shooting
TROUBLE SHOOTING
Even though the finest materials and precision workman-
ship have been incorporated into your Craftsman saw, it is
reasonable to expect some wear after long periods Gf use.
Adjustment facilities have been built into the saw to
compensate for this wear. Looseness due to wear, rough
handling, or improper adjustments will usually be indicated
by reduced accuracy or the inability of the saw to perform
as intended. The usual operating troubles are listed in the
following paragraphs, with the necessary corrections
described and illustrated.
1. LOOSENESS OF COLUMN TUBE IN COLUMN SUP-
PORT -ELEVATION CRANK OPERATES ROUGH-
LY, OR CHATTERS WHEN ROTATED
When this condition exists, square crosscuts are likely to
be difficult to make, and repeated cuts inaccurate.
Adjust the column tube key as follows:
a. Checking for Looseness of Column Tube in Column
Support (Figure 43).
ARM
Figure 43
(1) Tighten the arm-latch handle
(2) Grasp the arm-latch handle with one hand and
hold a finger of the other hand at the parting line
between the column tube and column support.
(3) Apply gentle side force to the radial art]] in
opposing directions. Any !ooseness bet_Jeen
column and column support (indicated by arrow
in figure 43) can be felt with finger.
(4) If looseness can be felt, perform the following
Jperations:
NOTE: Before attempting to adjust the
column tube key, the function of this adjust-
ment should be understood. Figure 44 shows a
sectional view through the column tube sup-
port (looking downward} at the column tube
key location By loosening the left-hand set-
screw and tightening the right-hand setscrew
the column tube key will be forced tighter into
the column tube keyway. Conversely, loosen-
ing the right-hand setscrew and tightening the
left-hand setscrew wilt retract the column key
out of the column tube keyway. The setscrew
in the outer end of the column tube key must
be loosened while adjustment is being made,
and tightened with medium firmness after the
adjustment has been completed. This screw
applies pressure on the nylon friction plug, and
provides smoother elevation movement of the
column tube ... and should be tightened to
provide maximum smoothness of operation.
References to right- and left-hand positions are
as indicated in the illustration.
b. Adjusting Column Tube Key (Figure 44)
COLUMN
SUPPORT
COLUMN TUBE
FRICTION
PLUG
INylon)
RACK-UP
(Righ t-Hd.} PLUG (Steel)
CREW
(Left-Hd.)
Figure 44
(1) Loosen the setscrew located in the center of the
column tube key (figure 44).
(2) Loosen the left-hand setscrew 1/4 turn.
(3) Tighten the right-hand setscrew.
(4) Tighten the left-hand setscrew.
(5) Rotate the elevation crank to raise and lower the
radial arm. If too tight, loosen the right-hand
setscrew slightly, and check again for smooth
operation. When correct, tighten the left-hand
setscrew.
(6) Tighten the setscrew located in the center of the
column tube key until smoothest operation is
obtained.
2. BLADE DOES NOT MAKE SQUARE CUTS, AND
ACCURATE REPEAT CUTS CANNOT BE MADE
If this condition exists the trouble might be due to any
one, or a combination of, the following conditions:
a. Looseness Between Column Tube and Column Sup-
port.
Adjust as described in preceding paragraph "1", a
and b.
b. Crosscut Travel Not Properly Adjusted.
Refer to "ALIGNMENT INSTRUCTIONS", step "4.
Squaring the Crosscut Travel", preceding. If crosscut
travel cannot be adjusted as described, refer to
paragraph "i", following.
c. Table Supports Not Properly Adjusted.
Correct adjustment of table supports can be checked
with satisfactory accuracy, without removing the
table boards, by checking at the various positions on
20
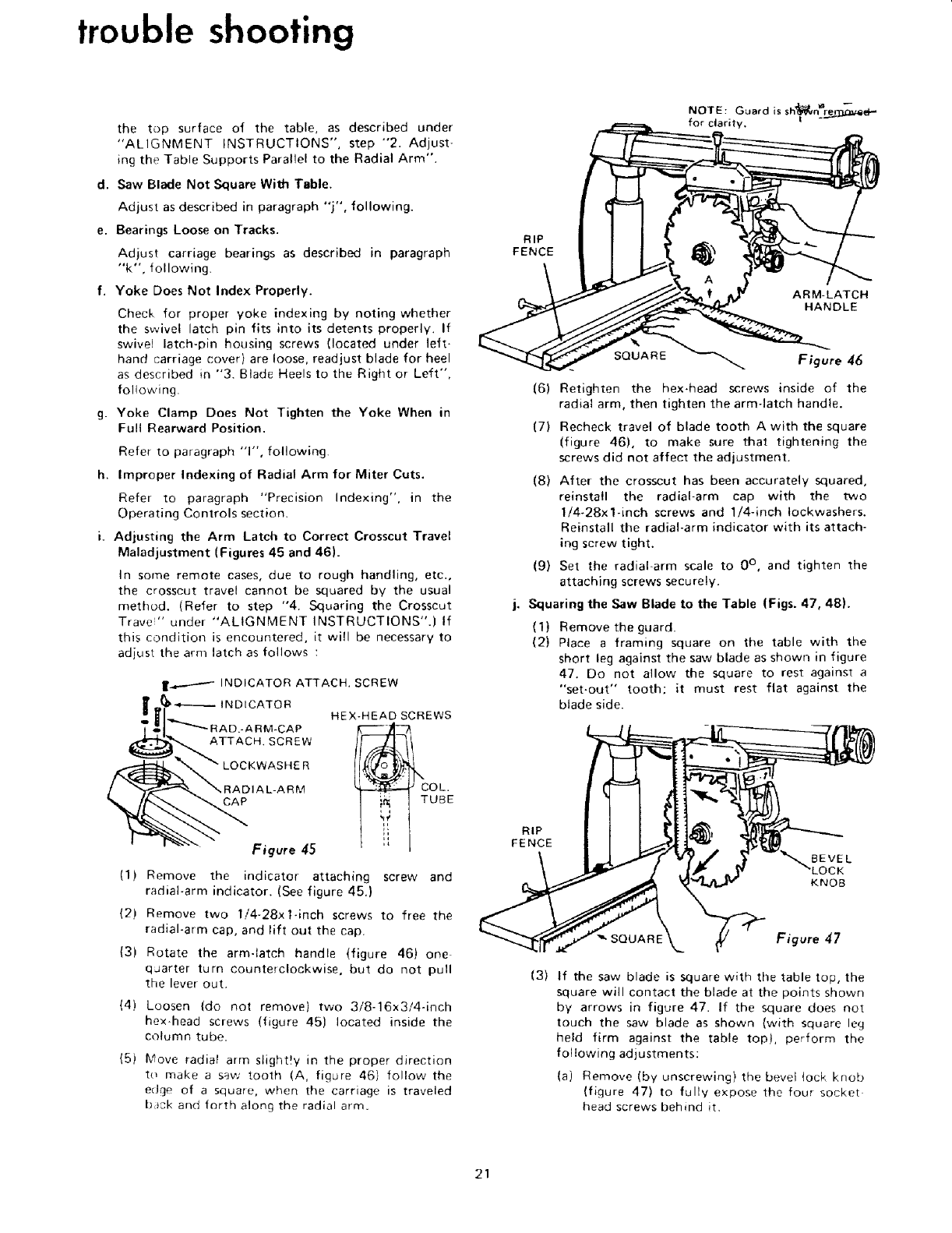
trouble shooting
the top surface of the table, as described under
"ALIGNMENT INSTRUCTIONS", step "2. Adjust-
ing the Table Supports Parallel to the Radial Arm".
d. Saw Blade Not Square With Table.
Adjust as described in paragraph "j", following.
e. Bearings Loose on Tracks.
Adjust carriage bearings as described in paragraph
"k", following.
f. Yoke Does Not Index Properly.
Check for proper yoke indexing by noting whether
the swivel latch pin fits into its detents properly. If
swivei latch-pin housing screws (located under left-
hand carriage cover) are loose, readjust blade for heel
as described in "3. Blade Heels to the Right or Left",
following.
g. Yoke Clamp Does Not Tighten the Yoke When in
Full Rearward Position.
Refe( to paragraph "1", following.
h. Improper Indexing of Radial Arm for Miter Cuts.
Refer to paragraph "Precision Indexing", in the
Operating Controls section.
i. Adjusting the Arm Latch to Correct Crosscut Travel
Maladjustment (Figures 45 and 46).
In some remote cases, due to rough handling, etc.,
the crosscut travel cannot be squared by the usual
method. (Refer to step "4. Squaring the Crosscut
Trave " under "ALIGNMENT INSTRUCTIONS".) If
this condition is encountered, it will be necessary to
adjust the arm latch as follows :
_/ INDICATOR ATTACH. SCREW
I t_ -,m------- INDICATOR HEX-HEAD SCREWS
_RAD.-ARM-CAP -- !
ATTACH. SCREW
LOCKWASHER _ }NCOL.
CAP TUBE
Figure 45
(1) Remove the indicator attaching screw and
radial-arm indicator. (See figure 45.)
(2) Remove two 1!4-28xl-inch screws to free the
radial-arm cap, and lift out the cap.
(3) Rotate the arm-latch handle (figure 46)one
quarter turn counterclockwise, but do not pull
the lever out.
(4)
(5}
Loosen (do not remove} two 3/8-16x3/4-inch
hex-head screws (figure 45) located inside the
column tube.
Move radial arm stight!y in the proper direction
t(_ make a saw tooth (A, figure 46) follow the
edge of a square, when the carriage is traveled
b_ck and forth along the radial arm.
RIP
FENCE
ARM-LATCH
HANDLE
SQUARE Figure 46
(6) Retighten the hex.head screws inside of the
radial arm, then tighten the arm-latch handle.
(7) Recheck travel of blade tooth A with the square
(figure 46), to make sure that tightening the
screws did not affect the adjustment.
(8) After the crosscut has been accurately squared,
reinstall the radial-arm cap with the two
1/4-28xl-inch screws and 1/4-inch Iockwashers.
Reinstall the radial-arm indicator with its attach-
ing screw tight.
(9) Set the radial-arm scale to 0 °, and tighten the
attaching screws securely.
j. Squaring the Saw Blade to the Table (Figs. 47, 48).
(1) Remove the guard.
(2) Place a framing square on the table with the
short leg against the saw blade as shown in figure
47. Do not allow the square to rest against a
"set-out" tooth; it must rest flat against the
blade side.
RIP
FENCE
BEVEL
"LOCK
KNOB
SQUAR Figure 47
(3) If the saw blade is square with tile table top, the
square will contact the blade at the points shown
by arrows in figure 47. If the square does not
touch the saw blade as shown (with square leg
held firm against the table top), perform the
following adjustments:
(a) Remove (by unscrewing) the bevel lock knob
(figure 47) to fully expose the four socket
head screws behind it.
21

F,gu,o,8!
SOCKET HD
SCREW
(4 Tolal)
_ BEVEL
INDEX
SCALE
)) BEVEL
INDICATOR
I
LOCK KNOB
(b) Using a 1/4-inch hex-L wrench, slightly
loosen the four socket-head screws (figure
48L
(c) Tilt the motor until the saw blade is square
with the table top as shown in figure 47.
Then, while holding the square firmly
against the saw blade and table top, apply
moderate force against the lower part of the
saw blade with your thumb, until approxi-
mately 1/32 inch clearance exists between
the square and the lower edge of the blade.
This is to compensate for the possible slight
shifting of the motor while the socket-head
screws are being tightened.
(d) Tighten the four socket-head screws and
replace the bevel lock knob (figure 48). It
may be necessary to perform several trial
operations before the saw blade remains
perfectly square with the table, after tighten
ing the four screws.
(4) After completing this adjustment, set the bevel
indicator to zero.
k, Adjusting Carriage Bearings (Figs. 49 through 52).
To test for looseness between the carriage bearings
and the tracks on the radial arm, lock the yoke-clamp
handle (figure 49), grasp the motor and carriage
assembly firmly with both hands, and apply a firm
rocking motion. If looseness exists, perform the
following steps :
NOTE: Adjustment is made on lefr-hand side, onlyo
(1) Remove left-hand carriage cover (figure 50).
(2) Loosen the two nuts (figure 51) just enough to
permit the two eccentric screws to turn. (See
figure 52.)
(3) Rotate one of the eccentric screws a partial turn
(left or right) as required to take up looseness,
Hold the head of the eccentric screw (figure 51)
m the position established by this method and
t_ghten the nut. Repeat this procedure for the
other eccentric screw. Correct adjustment exists
.vhen there is no play between the carriage and
the radial arm tracks, but the carriage moves
',0ack and forth freely.
(4) Reinstall the left-hand carriage cover (figure 50).
YOKE CLAMP
HANDLE
MOTOR AND CARRIAGE
ASSEMBLY
Fiqure 49
LEET_HD,
CARRIAGE
COVER
ATTACHING
SCREW
(2 Total)
Figure 50
._r_ .,_,.._ E c CENT R I C SCREW
k II II d_'_-,_--_CAR RIAGE
BEARING
PLAIN WASHER"_k--_I IIk\\"l_'_"{'_:'k-_ R'AOE
LOCKWASH E Rt"t_w__ NUT
Figure 52
22

trouble shooting
YOKE CLAMP LOCKING POSITION
ASSEMBLY -, DUE TO WEAR
""__ ._ _p....NO R MA L LOCKING
POSITION
_------_'_ LOOSENED
POSITION
_.._ _. YOKE CLAMP HANDLE
Figure 53
LOCKWASHER
Figure 54
CARRIAGE STOP
SCREW
HEX WRENCH
YOKE-CLAMP
ASSEMBLY
Figure 55
\\?
YOKE-CLAMP-HANDLE
YOKECLAMPASSEMBLY
YOKE CLAMP
HANDLE
Figure 56
I. Yoke Clamp Handle Adjustment (Figures 53 -56).
The normal locking position of the yoke-clamp
handle (figure 53) is approximately midway between
the two sides of the yoke. When sufficient wear has
occurred to permit the handle to move considerably
to the rear, or to strike the yoke before locking, the
handle may be adjusted as follows:
(1) Loosen the yoke-clamp handle.
(2) Remove the carriage stop screw and Iockwasher
(figure 54} with the 1/4 inch hex-L wrench.
(3}
(4)
(5)
Grasp the motor and carriage assembly and,
holding it parallel to the radial arm until all
bearing rollers are free of their tracks, move it
carefully off the end of the arm.
Rest the motor and carriage assembly on the saw
table and remove the lock screw (figure 55).
Using a screwdriver, rotate the yoke clamp
assembly (figure 56} clockwise until the next
hole will line up with the lock screw. (See figure
55.) Usually, rotating the yoke clamp assembly
one hole will correct this adjustment. However,
in some extreme cases it may be necessary to
rotate it two holes or more.
(6)
(7)
Align, install and tighten the lock screw. (See
figure 55.)
Hold the motor and carriage assembly parallel to
the radial arm and start the rear bearings onto the
tracks. Continue to hold the assembly parallel to
the tracks until the forward bearings are on the
tracks.
18) Slide the carriage rearward on the radial arm and
reinstall the carriage stop screw and Iockwasher
(figure 54).
3. BLADE HEELS TO THE RIGHT OR LEFT
A blade is said to "'heel"whenit is out of alignment with
the direction in which it is forced to travel. Figure 57
shows a saw blade heeling to the right. The result of
even a minor degree of heeling can be detected by the
tooth marks left on the side of the saw kerf (cut edge)
of the board. When using a taper ground blade, even a
small degree of heeling will cause the wood to smoke
because of the frictional heat produced. When ripping,
heeling can cause kickbacks.
--_ - "_-_ _,, BLADE H-EELING TO RIGHT
/DIRECTION OF BLADE TRAVEL
WIDENED
KERF '--- ,- DIRECTION OF ATTEMPTED
BLADE TRAVEL
Figure 57
23

LEFT-HD,
COVER
RIP
FENCE
a. Evidence of Blade Heel
(1) Crosscutting
Figure 58
(a) Heeling to the right will tend to slide the
workpiece toward the right along the rip
fence, as the cut is being made, and will
make square cutting almost impossible.
(b) Heeling to the left will tend to slide the
board to the left along the fence.
(2) Miter Cutting - Same as for crosscutting, except
to a lesser or greater degree, depending upon the
angle°
(3) In-Ripping
(a) Heeling to the right will force the workpiece
against the rip fence.
(b) Heeling to the teft will force the workpiece
away from the fence.
(4} Out-Ripping - The exact reverse of in-ripping
b. Checking for Blade Heel.
(1) Loosen the guard clamp screw and remove the
g_:ard,
(2) Place asquare against the rip fence and the saw
blade, as shown in figure 58. The long leg of the
square must be held firmly against both the rip
fence and the table top, and the short leg must
not touch any of the teeth on the saw blade.
(3) If the square does not touch the blade at both of
the two points shown in figure 5B, a heel
condition exists (either to the left or right).
e. Adjusting to Eliminate Blade Heel.
(1) Remove the left-hand carriage cover (figure 58).
(2) Loosen the yoke-clamp handle (figure 56).
(3) Loosen (slightly) two hex-head screws (figure
59).
(4) R,_tate the yoke until the gap between the saw
blade and the square is eliminated.
(5) Iock the yoke with the yoke clamp handle, and
[iqhten the two he×-head screws (figure 59).
SCREWS LEFT-
HANO
SIDE
Figure 59
(6) Recheck for heel to make sure that tightening
the screws did not affect the setting,
(7) Reinstall the left-hand carriage cover.
4. WOOD SMOKES AND MOTOR SLOWS DOWN OR
STOPS, WHEN RIPPING
This can be caused by the following conditions :
a. A Dull Blade or a Warped Board.
Sharpen or replace the saw blade. Avoid the
attempted use of severely warped material.
b. Crosscut Not Properly Squared.
Adjust as described under "ALIGNMENT INSTRUC-
TIONS", step "4. Squaring the Crosscut Travel".
c. Radial Arm Not Securely Locked in 0 ° Position.
Refer to"PRECISION INDEXING" in the Operating
Controls section.
d. Blade Heels to the Right or Left.
Refer to paragraph "3. Blade Heels to the Right or
Left", preceding.
5. BOARD BINDS, OR PULLS AWAY FROM THE
FENCE, WHEN RIPPING
Refer to "Adjusting Guard Chute and Anti-Kickback
and Spreader Assembly for Ripping Operations" in the
Operating Controls section.
LUBRICATION
Your saw is precision built and should be kept clean and
properly lubricated. Before describing the various points
which may periodically require lubrication, IT IS MORE
IMPORTANT TO FIRST MENTION THE VARIOUS
POINTS WHICH SHOULD NOT BE LUBRICATED,
NO LUBRICATION REQUIRED
Do not lubricate the carriage ball bearings or the motor
bearings. These are sealed ball bearings and require no
added lubrication.
Do not lubricate between the radial arm cap and the radial
arm.
24

trouble shooting - motor
PERIODICALLY LUBRICATE THESE POINTS
Use SAE No. 10W-30 automotive engine oil. Refer to the
Parts Lists for locations, and lightly lubricate the following
points:
1. The rea_ bearing surface of the elevation crank shaft
assembly - and also the two meshed gears through
which this shaft drives the elevation shaft assembly.
There is an oil hole in the bracket at the rear end of the
etevatior, crank shaft, through which the rear bearing
surface can be oiled.
2. The threads of the elevation shaft assembly -- and also
the bottom bearing surface of this shaft where it is held
by the retaining plate. Use the oil hole at the center of
the radial-arm cap.
3. The bevel-latch pin.
4. The bearing surface of the swivel-latch pin in the
latch-pin housing.
5. The face of the column tube and keyway (by wiping
with alightly oiled cloth) to lubricate the surfaces that
bear against the key and the column support assembly,
ICAUTION: Excessive oil at any location will I
!
attract airborne dust particles and sawdust. I
TROUBLE SHOOTING CHART--MOTOR
NOTE: Motors used on wood-working tools are particularly and *-hould be blown out or "vacuumed" frequently to
susceptible _o the accumulation of sawdust and wood chips prevent interference with normal motor ventilation.
TROUBLE
Motor will not run.
Motor will not run and
fuses "BLOW".
Motor fails to develop
full power. (Power output
of motor decreases rapidly
with decrease in voltage at
motor terminals. For
example: a reduction of
10% in voltage causes a
reductior_ of 19% in
maximum power output
of which the motor is
capable, while a reduction
of 20% in voltage causes
reduction of 36% in
maximum power output.)
PROBABLE CAUSE
1. Protector open; circuit
broken.
2. Low voltage.
1. Short circuit in line, cord
or plug.
2. Short circuit in motor or
loose connections.
1. Power line overloaded with
lights, appliances and other
motors.
2. Undersize wires or circuit
too long.
3. General overloading of
power company's facitities.
(In many sections of the
country, demand for
electrical power exceeds
the capacity of existing gen-
erating and distribution
systems.)
4. h_correct fuses in power line.
REMEDY
1. Reset protector by pushing on red button, located
on top of motor (indicated by audible click).
2. Check power line for proper voltage.
1. Inspect line, cord and plug for damaged insulation
and shorted wires.
2. Inspect all terminals in motor for loose or shorted
terminals or worn insulation on wires.
1. Reduce the line load.
2. Increase wire sizes, or reduce length of wiring
3. Request a voltage check from the power company.
4. Install correct fuses.
25

TROUBLE SHOOTING CHART--MOTOR (Con't.
I
TROUBLE PROBABLE CAUSE I
q
Motor overheats. 1. Motor overloaded.
2. Improper cooling. (Air cir-
culation restricted through
...... motor due to sawdust, etc:)
Motor starts slowly or 1. Low Voltage - will not trip
fails to come up to full starting switch.
speed. 2. Starting switch not operat-
ing.
Starting switch in 1. Burned switch contacts
motor will not operate. (due to extended hold-in
2.
3.
Motor stalls (resulting in
blown fuses or tripped
circu it breakers).
1.
2.
3.
Frequent opening of 1.
fusesor circuit breakers. 2.
Brake fails to work.
!3.
periods caused by low
line voltage, etc.)
Loose or broken connec-
tions in motor.
Shorted capacitor.
Starting switch not operat-
ing.
Voltage too low to permit
motor to reach operating
speed.
Fuses or circuit breakers
do not have sufficient
capacity.
Motor overloaded.
Fuses or circuit breakers
do not have sufficient
capacity.
Starting switch no_ operat-
ing (motor does not reach
normal speed.)
Worn brake lining.
REMEDY
1. Correct overload condition.
2. Clean out sawdust to provide normal air
circulation through motor.
1. Correct low voltage condition.
2. Replace the starting switch.
1. Replace switch and check line voltage.
2. Check and repair wiring.
3. Test capacitor and replace if defective.
1. Replace switch.
2. Correct the low line voltage condition.
3. Replace fuses or circuit breakers with
proper capacity units,
1. Reduce motor load.
2. Replace fuses or circuit breakers.
3. Replace switch,
Replace brake lining.
26

POWER TOOL GUARANTEE
Craftsman power tools (or welders) are unconditionally
guaranteed for one year to give complete satisfaction or the
tool will be repaired free of charge.
This guarantee service is available through any of our Sears
stores or service centers throughout the United States or
Canada,
SEARS ROEBUCK AND CO. •SIMPSONS-SEARS LIMITED
27

repair parts
CRAFTSMAN IO-INCH RADIAL SAW, MODEL NO. 113.29461
33
SEE FIGURE 2
FOR EXPLODED
SEE FIGURE 5 ._
FOR EXPLODED VIEW 25
26
FIGURE I
28

PARTS LIST
CRAFTSMAN IO-INCH RADIAL SAW, MODEL NO. !13.29461
All parts illustrated in Figures 1through 5 and listed under part numbers may be ordered through any Sears Retail Store or
Catalog Order House. Order parts by mail from the Catalog Order House that serves the territory in which you live. In several
instances, part numbers are listed for COMPLETE ASSEMBLIES. All parts are shipped prepaid within the limits of the
Continental United States.
WNEN ORDERING REPAIR PARTS, ALWAYS GIVE THE FOLLOWING INFORMATION AS SHOWN ON THIS LIST:
1. THE PART NUMBER 3. THE MODEL NUMBER 113.29461
2. THE PART NAME 4. The NAME OF ITEM-- 10JNCH RADIAL SAW
Always order by Part Number - not by Key Number
Key Part
No. No. Description
1
2
3
4
5
6
7
8
9
10
11
12
13
14
15
16
17
18
19
20
21
22
FIGURE
63409
37863
63127
448337
131201
9421620
37435
30662
30482
37370
30489
30490
60044
443151
63O96
448039
6OO76
37372
37373
60030
63410
455872
Trim, Radial Arm
Arm, Radial
Track
*Screw, Type 23, 10-32 x 5/8,
Rd. Hd.
Lockwasher, 5/16 x .125 x .078
*Screw, Cap, 5/16 18 x I/2, Soc. Hd.
tWrench, Hex. "L", 1/4
Screw, Arm Lock
Pin Assembly, Arm Lock
Shaft Assembly, Arm Latch
Washer, Spring Support
Spring, Arm Latch
Ring, Retaining
Pin, Groove
Cap, Trim
*Screw, Type 23, 10-32 x 3/4,
Pan Hd.
Washer, .505 x 1-1/8 x 1/16
Lever, Arm Latch
Washer, Spring
Washer, .505 x 1 x 1/32
Knob Assembly, 3-1/4
*Screw, Mach. 1/4-20 x 1-1/4
Sems. Truss Hd.
PARTS LIST
Key Part
No. No. Description
23 30494
24 60175
25 30495
26 3540
27 63062
28 63146
29 30661
30 30479
31 131202
32 9415837
33 63098
34 448033
35 115109
36 191230
37 448001
38 37935
39 30559
4O 37418
41 30613
42 448011
63492
Collar
[tBlade, Saw, 10"
Nut, Shaft
Wrench, Arbor
Wrench, Shaft
Tube Assembly, Column
Shoe, Brake
Latch, Arm
*Lockwasher, 3/8 x .136 x.070
*Screw, Mach. 3/8 16 x 3/4 Hex.
Hd.
Plate, Cover
*Screw, Type 23, 10-32 x 3/8,
Pan Hd.
*Lockwasher, 1/4 x .109 x .062
*Screw, Mach., 1/4-28 x 1, Fil. Hd.
*Screw, Type 23, 6-32 x 1/4,
Pan Hd.
Washer, Fibre, .140 x ,250 x 1/32
Indicator
Cap, Radial Arm
Clamp, Cord
*Screw, Type 23, 8-32 x 3/8,
Pan Hd.
Owner's Manual (Not Illus.)
*Standard Hardware Item - May Be Purchased Locally.
tStock Item - May be secured through the Hardware Department of most Sears or Simpsons-Sears Retail Stores or
Catalog Order Houses.
NOTE: Shipping and handling charges for standard hardware items (identified by *) such as nuts, screws, washers, etc.,
make buying these items by mail uneconomical. To avoid shipping and handling charges, you may obtain most
of these locally.
29

repair parts
CRAFTSMAN IO-INCH RADIAL SAW, MODEL NO. 113.29461.1-4
v/,._
31
SEE FIGURE 446/"
FOil EXPLODED
v,EW 6,3 45 I
1
I
32
35
FIGURE 2
3O

CRAFTSMAN IO-INCH RADIAL SAW, MODEL NO. 113.29461
FIGURE 2 PARTS LIST
Key Pa_
No. No.
130566
2 63120
3 3O567
4 436664
5 63215
6 63415
7 63416
8 3O530
9 9415819
I0 60040
11 37388
12 63117
13 63148
14 131201
15 124824
16 30547
17 30548
19 30689
20 115999
21 63418
22 63467
23 37568
24 63419
25 441377
26 115543
27 448001
28 453676
29 30693
30 62299
31 63304
32 37861
33 63423
L
Description
Yoke, Clamp Assembly
Shoe, Carriage Lock
Bumper, No. 2
*Screw, Mach., 6-32 x 7/16, Pan
Hd.
Indicator, Rip Scale
Knob, Carriage Lock, 1-1/2
Cover, R. H., Carriage
Nut, Twin
"Screw, Mach., 5/16-18 x 1-1/2,
Hex Hd.
*Washer, .328 x 3/4 x 1/16
Sleeve, Bearing
Bearing, Carriage
Carriage Assembly
*Lockwasher, 5/16 x .125 x .078
*Nut, Hex., 5/16-18 x 1/2 x 3/16
Disk
Spring, Latch Pin
Pin, Bevel Latch
*Nut, Hex., 10-32 x 3/8 x 1/8
Clamp, Cord
Cap, Insulator
etAdaptor, Plug
Cord, with Plug
*Screw, Mach., 10-32 x 3/4 Pan Hd.
Washer, Lock
*Screw, Type 23, 6-32 x 1/4, Pan Hd.
Pin, Roll 1/8x 1
Handle, Latch Pin
Switch (Off-On)
Lock Assembly, Switch
Key, Safety Lock
Indicator, Bevel
Key Part Description
No. No.
34
35
36
37
38
39
40
41
42
43
44
45
46
47
48
49
5O
51
52
53
54
55
56
57
58
59
60
61
62
63
37935
6342O
9421626
63424
37403
37816
30664
3O665
30663
30558
60055
37859
63468
115109
6O021
63421
30613
448011
63118
436751
63417
30565
37387
63119
63422
30521
37494
60259
138540
Washer, Fibre, .140 x.250 x 1132
Knob, 2-1/4, Bevel Index
*Screw, Cap 5/16-18 x 1-1/2,
Socket Hd.
Handle, Bevel Index
Handle, Yoke
Washer, .630 x 1-1/8 x .093
Pad, Pressure
Shoe, Index Handle Brake
Expander
Motor (See Fig, 5)
Screw, Lock
Washer, Fibre, ,380 x 3/4 x 1/16
Ring, Hog
Support Assembly, Motor
*Lockwasher, 1/4 x .109 x .062
*Screw, Mach., 1/4-20 x 7/16,
Hex. Hd.
Yoke Assembly
Clamp, Cord
*Screw, Type 23, 8-32 x 3/8,
Pan Hd.
Housing, Latch Pin
*Screw, Type 23, 10-32 x 5/8,
Pan Hd.
Cover, LH., Carriage
Bumper, Carriage
Screw, Eccentric
Retainer, Spring
Knob Assembly
Spring, Swivel Latch
Pin, Swivel Latch
Screw, Mach. 5/16-18 x 1-1/2 Hex.
Wash. Hd.
Lockwasher, Ext. Tooth, 5/16 x 19/32
x 1/32
*Standard Hardware Item - May Be Purchased Locally.
tStock (tern - May be secured through the Hardware Department of most Sears or Simpsons-Sears Retail Stores or
Catalog Order Houses.
mNot Supplied in Canada.
31

Q
repatr parts
CRAFTSMAN IO-INCH RADIAL SAW, MODEL NO. 113.29461
30
1
29
2O 15
24
23
22 I11
I
16 15 FIGURE3
18
FIGURE 3 PARTS LIST
Key Part
No. No. Description
163411 Guard Assembly
2 63258 Elbow, Discharge
3 63337 Shoe, Guard
4 455488 Pin, Roll, 1/4 x 5/8
563039 Screw, Guard Clamp
6 63338 Bracket, Housing
7 9414920 *Washer, 17/64xSi8x 1/16
8 63339 Nut, Wing
9 131201 * Lockwasher, 5/16x .125 x .078
10 60078 *Screw, Mach., 5/16-18 x1/2, Hex. Hd.
11 63425 Cord with Plug
12 37875 Relief, Strain
13 60243 *Screw, Mach., 10-32 x 1-1/8, Pan Hd.
14 63341 Bushing, Kickback Pawl
15 63271 Pawl, Anti-Kickback
16 60041 *Washer, .198 x 9/16 x 1/32
• Standard Hardware Item - May Be Purchased Locally.
r
Key!
18
19
20
21
22
23
24
25
26
27
28
29
3O
tStock Item - May be secured through the Hardware Department of
Catalog Order Houses.
Part
No.
71046
163426
69013
I
i
i60012
111137
:60062
!63427
194O4365
94O4351
i60029
63428
i109091
!63345
!63344
Description
*Connector, Wire
Socket, Light
Bulb, Light, 115/125V, 25 Watt, Double
Contact, Bayonet Base, Appliance
Nut, Lock, 10-32
*Bolt, Carriage, 1/4-20 x 1/2 Rd. Hd.
*Washer, Plain .380 x 3/4 x 3/32
Housing, Light
*Screw, Mach., 8-32 x 5/16, Pan Hd.
*Screw, Type 23, 6-32 x 1/4, Pan Hd.
Nut, Lock, 8-32
Cap, Light Housing
*Bolt, Carriage, 1/4-20 x 1-1/4, Rd. Hd.
Chute, Guard
Knob Assembly, 1-1/2
most Sears or Simpsons-Sears Retail Stores or
32

repa,r parts
CRAFTSMAN IO-INCH RADIAL SAW, MODEL NO. 113.29461
15
16
FIGURE 4 PARTS LIST
Key Part
No. No.
-63490
-63491
1 448003
263437
2 63489
3 63438
4 448011
5 30613
6 63439
6 63487
7 63440
8 63441
9 63443
10 63442
11 63444
12 63445
13 63446
14 63447
15 30582
16 63448
*Standard Har
Description
Motor (Complete) (Domestic)
mMotor (Complete) (Canada)
*Screw, Type 23, 6 32 x 3/8 Pan Hd.
Nameplate W/Insulation (Domestic)
INameplate W/Insulation (Canada)
Receptacle
*Screw, Type 23, 8-32 x 3/8 Pan Hd.
Clamp Cord
Housing, Top (Domestic)
"Housing, Top (Canada)
Lead Assy., Brown
Lead Assy., Black
Lead Assy., Red
Lead, Btue
Cord Assembly
Insulation, Switch
Switch Assy., Starting (Including
Key No. 14)
Lead Assy., Red
Cap, Shaft
Plate, Instructions
ware Item -May Be Purchased Locally.
Key Part
No. No.
17 63449
18 140879
19 63450
20 63451
21 63452
22 115999
23 63453
23 63488
24 448O07
25 60248
26 63469
27 63454
28 37859
29 30573
30 448019
31 63455
32 37408
33 63456
34 133477
- 63486
tStock Item - May be secured through the Hardware Department of
Catalog Order Houses.
/_Supplied Detached Canada Only.
=Carlada Only.
Description
Fan Assembly (Includes Key Nos.
18 and 19)
Set Screw
Lining, Brake
Plate, Brake
Spring, Brake
*Nut, Hex., 10-32 x 1/8
Housing, Bottom (Domestic)
=Housing, Bottom (Canada)
*Screw, Type 23, 6-32 x 5/8 Pan Hd.
Screw, Stator
Bushing, Rubber
Panel Assembly
Ring-Hog
*Nut, Wire
*Screw, Type 23, 8-32 x 7/8 Pan Hd.
Capacitor
Protector, Manual Thermal
Washer, Dust
Screw, Mach., 8-32 x 1/4 Flat Hd.
APlug 240V (Not shown)
most Sears or Simpsons-Sears Retail Stores or
33

repair parts
CRAFTSMAN 10-INCH RADIAL SAW, MODEL NO. 113.29461
5 6
I
31
32
10
12 13
/14
21
FIGURE 5
34

CRAFTSMAN 10-INCH RADIAL SAW, MODEL NO. 113.29461
FIGURE 5 PARTS LIST
Key Part
No. No. Description
2
3
4
5
6
8
9
10
11
12
13
14
15
16
17
18
19
2O
21
22
23
24
25
102718
63078
63077
63079
63431
139416
9415839
63429
60128
60057
102707
63430
63432
63433
37384
60056
37880
37879
115109
115120
60013
131201
60078
30505
102570
Screw, Set, 5/16-18 x 1/2, Slotted,
Cup Pt.
Plug, Back-Up (Steel)
Plug, Friction (Nylon)
Key, Column Tube
Support, Column
Screw, Set, 3/8-16 x 5/8, Socket
Hd., Cone Pt.
*Screw, Mach., 3/8-16 x 1-1/8,
Hex. Hd.
Spacer Board, Table
*Washer, 17/64 x 5/8 x 1/32
*Screw, Mach., 1/4-20 x 1-1/4,
Pan Hd.
Screw, Set, 1/4-20 x 1/2, Slotted,
Cup Pt.
Table, Rear
Fence, Rip
Table, Front
T-Nut
*Screw, Mach., 1/4-20 x 1, Pan Hd.
Channel, Table Mtg., Right-Hand
Channel, Table Mtg., Left-Hand
*Lockwasher, 1/4 x .109 x .062
*Nut, Hex., 1/4-20 x 7/16 x 3/16
*Washer, 11/32 x 7/8 x 1/16
* Lockwasher, 5/16 x . 125 x .078
*Screw, Mach., 5/16-18 x 1/2,
Flex. Hd.
tWrench, Hex. "L", 1/8
Screw, Set, 1/4-20 x 3/8, Socket
Hd., Cup Pt.
Key Part Description
No. No.
26 63434
28 37862
29 443507
30 60143
31 60080
32 306O4
34 63404
35 634O5
36 60201
37 423561
38
39
40
41
42
43
44
45
46
47
48
49
50
51
30509
37428
37530
37383
118615
131202
9415836
63435
63436
60246
448649
30510
30508
37911
Crank Assembly (Includes Key
No. 25)
Clamp, Table
*Screw, Mach., 1/4-20 x 1/2,
Pan Hd.
*Washer, .266 x .562 x 3/64
Washer, .515 x 7/8 x 1/32
Washer, Oil Sling
Shaft Assembly, Elevation (Includes
Key No's. 35 & 36)
Washer, Keyed
Ring, Retaining
*Screw, Mach., 5/16-18 x 7/8
Seres,, Hex. Hd.
Washer, End Play (as required)
Plate, Retaining
Nut, "U" Clip, 1/4-20
Base Assembly
*Nut, Hex., 3/8-16 x 9/16 x 21/64
*Lockwasher, 3/8 x .141 x.094
*Screw, Mach., 3/8-16 x 5/8,
Hex. Hd.
Bushing
Bracket, Bearing
Nut, Lock
*Screw, Type 23, 1/4-20 x 3/4,
Hex. Hd.
Bracket, Elevation Shaft Bearing
Shaft Assembly, Elevation Crank
tWrench, Hex. "L", 3/16
*Standard Hardware Item - May Be Purchased Locally.
tStock Item - May be secured through the Hardware Department of most Sears or Simpsons-Sears Retail Stores or
Catalog Order Houses.
35

Sears
o wners
manual
MODEL NO.
113.29461
Sears
SERVICE
is at
YOUR
SERVICE
wherever YOU
live or move
in the U.S.A.
How to ORDER Repair,
The Model Number will be found on a plate attached to your
saw, at the left-hand side of the base. Always mention the
Model Number when requesting service or repair parts for your
10-INCH RADIAL SAW.
All parts listed herein may be ordered through SEARS,
ROEBUCK AND CO. or SIMPSONS-SEARS LIMITED. When
ordering parts by mail, selling prices will be furnished on re-
quest or parts will be shipped at prevailing prices and you will
be billed accordingly.
WHEN ORDERING REPAIR PARTS, ALWAYS GIVE THE
FOLLOWING INFORMATION AS SHOWN IN THIS LIST.
1. The PART NUMBER
3. The MODEL NUMBER
113.29461
2. The PART DESCRIPTION
4. The NAME OF ITEM -
10-INCH RADIAL SAW
Your Sears merchandise takes on added value when you dis-
cover that Sears has over 2,000 Service Units through out the
country. Each is staffed by Sears-trained, professional tech-
nicians using Sears approved parts and methods.
SEARS, ROEBUCK AND CO., Chicago, Ill. 60607 U.S.A.
and SIMPSONS-SEARS LII_4ITED, Toronto
Form No. SP3855-2 Printed in U,S.A. 1-73