Craftsman 11329943 User Manual 10 INCH TILTING ARBOR BENCH SAW Manuals And Guides L0712532
CRAFTSMAN Saw Table Manual L0712532 CRAFTSMAN Saw Table Owner's Manual, CRAFTSMAN Saw Table installation guides
User Manual: Craftsman 11329943 11329943 CRAFTSMAN CRAFTSMAN 10-INCH TILTING ARBOR BENCH SAW - Manuals and Guides View the owners manual for your CRAFTSMAN CRAFTSMAN 10-INCH TILTING ARBOR BENCH SAW #11329943. Home:Tool Parts:Craftsman Parts:Craftsman CRAFTSMAN 10-INCH TILTING ARBOR BENCH SAW Manual
Open the PDF directly: View PDF .
Page Count: 32

CAUTION:
Read SAFETY
RULES and
INSTRUCTIONS
carefully
!
MODEL NO.
113.29943
IO-INCH TILTING
BENCH SA
assembly .operating ,, repair parts
Sears. Roebuck and Co., Chicago, IlL 60607 U,S.Ao
and Sirnpsons-Sears Lin_it_d. Toronto
Part No 62386

1. KNOW YOUR POWER TOO[
Read the owner's manual carefully. Learn its applica-
tion and limitations as well as the specific potential
hazards peculiar to this tool.
2. GROUND ALL TOOLS
third prong.
3. KEEP GUARDS IN PLACE
and in working order.
4. REMOVE ADJUSTING KEYS AND
WRENCHES
Form habit of checking to see that keys and adjusting
wrenches are removed from tool before turning on tool,
5. KEEP WORK AREA CLEAN
Cluttered areas and benches invite accidents.
6. AVOID DANGEROUS ENVIRONMENT
Don't use power tools in damp or wet locations. Keep
work area well illuminated.
7. KEEP CHILDREN AWAY
All visitors should be kept a safe distance from work
area.
8. MAKE WORKSHOP KID PROOF
--with padlocks, master switches, or by removing
starter keys.
9. DON'T FORCE TOOL
It will do the job better and be safer at the rate for
which it was designed.
10. USE RIGHT TOOL
Don't force tool or attachment to do a job it was not
designed for.
I 1. WEAR PROPER APPAREL
No loose clothing or jewelry to get caught in moving
parts.
12. USE SAFETY GLASSES
Also use face ordust mask if cutting operation is dusty.
13. SECURE WORK
Use clamps or a vise to hold work when practical. It's
safer than usingyour hand, frees both hands to oper-
ate tool.
14. DON'T OVERREACH
Keep your proper footing and balance at all times.
15. MAINTAIN TOOLS iN TOP
CONDITION
Keep tools sharp and clean for best and safest per-
formance. Follow instructions for lubricating and
changing accessories.
16. DgSCONNECT TOOLS
before servicing and when changing accessories such
Qs blades, bits, cutters.
17. AVOID ACCIDENTAL STARTING
Make sure switch is "OFF" before plugging in cord.
18. USE RECOMMENDED ACCESSORIES
Consult the owner's manual. Use of improper acces-
sories ma'/ be hazardous.
Copyright 1969 by Power Too] instifute, inc. AI| righ?s reserved.
The operation of any objects
being thrown into the eyes, which can result in severe eye
damage. Always wear safe_ glasses or eye shields before
commencing power tool operation. We recommend Wide
Vision Safety Mask for use over spectacles, or standard safety
glasses.., available at Sears retail or cata og stores
THIS SAFETY SEAL OF THE
POWER TOOL INSTITUTE ASSURES YOU...
I. That the manufacturer's power tools, including the particular tool
®associated w;_h the Seal, are produced in accordance with applicable
Standards For Safety of Underwriters' laboratories and American
National Standards (AI_SI).
2, That €omplloncu with applicable safety standards is assured by in-
dependent inspection and testing conducted by Underwriters" Labora-
tories (UL).
3, That every motorized t0o! is inspected under power.
4. That every tool has with it adequate instruct|ons and a llst of safety
rules for the protection of the user.
5. That the fool rnanufadurer is a member of the Power Tool Instffute and
is a sponsor of the Instltute's Consumer Safety Education Prog ram.

SASWTY INSTRUCT|ONS TO OP£RATOR
WARNING: Do not connect power cord
until _he following steps have been
satisfactorily completed:
a. READ CAREFULLY AND UNDERSTAND THE FOL-
LOWING INSTRUCTIONS and the "SAFETY RULES
FOR POWER TOOLS" ON PAGE 2.
b. Examination and operating familiarity with ON-OFF
switch, elevation control, bevel control, miter gauge,
and rip fence.
CAUTION: Always disconnect the power
cord when removing the table insert,
changing the cutting too{, or making
adjustments.
1. The saw should be baited down if there is any tendency
to tip over or move during normal operations. The
saw table should be approximately 36-inches above
the floor.
2. The saw work area should have adequate overhead,
non-glare light and adequate surrounding work space.
3. The saw should be positioned so neither the operator
nor o casual observer is forced to stand in llne with
the sow blade.
4. Kickbacks can cause serious injury. A"kickback" occurs
when a part of the workplace binds on the saw blade or
binds between the saw blade and the rip fence or other
fixed object, risesfrom the table, and is thrown toward
the operator. Kickbacks are usually caused by one or
more of the following conditions:
a. Failure to use a spreader when ripping, or failure to
maintain the spreader in alignment with the saw
blade.
b. Improperly conditioned (dull) saw that permits the
material to pinch on the out-feed edge of the saw
and rise from the table.
c. Failure to determine that the rip fence and the saw
blade are parallel to one another.
d. Ri0ping wood that has a twisted grain, does not
hove a straight edge to guide along the fence, or
wood that is twisted or not flat (which may rock on
the table and pinch the blade).
e. Confining the cut-off piece when ripping or cross-
cutting.
f. Ripping by applying the feed force to the section
of the workpiece that will become the cut-off (free)
piece (feed force when ripping should always be
applied between the saw blade and the fence -- use
push stick for narrow or short work).
g. Releasing workpiece before operation is complete;
not pushing the workplace all the way past the saw
blade.
5. Injury from kickbacks can be prevented or minimized
by:
a. Avoiding any of the causes noted above;
b. Making sure by trial before starting the cut that the
anti-kickback pawls will stop the kickback once it
has started (sharpen all points if they do not);
c. Keeping your face and body always out of line of
possible kickbacks, including turning the switch ON
and OFF.
d. Always wearing safety goggles.
e. Never use both the rip fence and miter gauge dur-
ing the same operation,
6. A large proportion of tilting arbor saw accidents is
caused by dull, badly set, improperly filed cutting tools,
by gum or resin adhering to cutting tools and by fence
misalignment (out of parallel). Such conditions cause
the materia{ to stick, jam, stall the saw, or kick-back at
the operator. Cracked saw blades should be discarded
immediately. Asaw blade can become cracked if it
wobbles or if it is not in balance. NEVER ATTEMPT TO
FREE A STALLED SAW BLADE WITHOUT TURNING
THE SAW OFF. Avoid potential injury by proper cutting
tool and machine maintenance.
7. Gloves should not be worn while operating the saw.
Loose flowing garments, jewelry (rings, wrist watches,
etc.), and neckties should never be worn. Long sleeves
should be roiled to above the elbows.
8. To protect your eyes, always wear safety goggles. In
addition, wear aface shield to protect against flying
particles. Ear protectors (ear plugs or muffs) should be
used during extended periods of operation.
9. Provide proper support for the workpiece, based on its
size and the type of operation to be performed; hold
the work firmly against the gauge or guide. Use a push
stick when ripping short work (under 6-inches fang), or
marrow work. Apush block or mi_r gauge hold-down
should be used when dadoing or molding.
10, Never use a length stop (such as the fence when cross-
cutting) on the free end or edge of the workplace. Never
hang onto or touch the free end of workplace, or a free
piece that is cut off, while power is "ON" and/or the
sawblade is rotating. In short, to guard against kick-
backs or other potential accidents, the cut-off piece in
any thru-sawing operation must never be confined it
must be allowed to move lalera!ly. Never use the rip
fence when cross-cutting, or the miter gauge when
ripping.
1 I. Cross-cutting operations are more conveniently worked
and with greater safety if an auxiliary wood facing is
attached to the miter gauge using the holes provided.
12. Do not leave a long board unsupported so the spring
of the board causes it to shift on the table. A support
should be used to catch the end of the board behind the
blade.
13. Never climb on or near the saw. Never leave the saw
with power on, or before the cutting tool has come to
a complete stop.
14. Avoid awkward operations and hand positions, where
asudden slip could cause a hand to move into a saw
blade or other cutting toot. Never reach in back of the
cutting tool with either hand to hold down the work-
piece.
(Continued an Next Page)
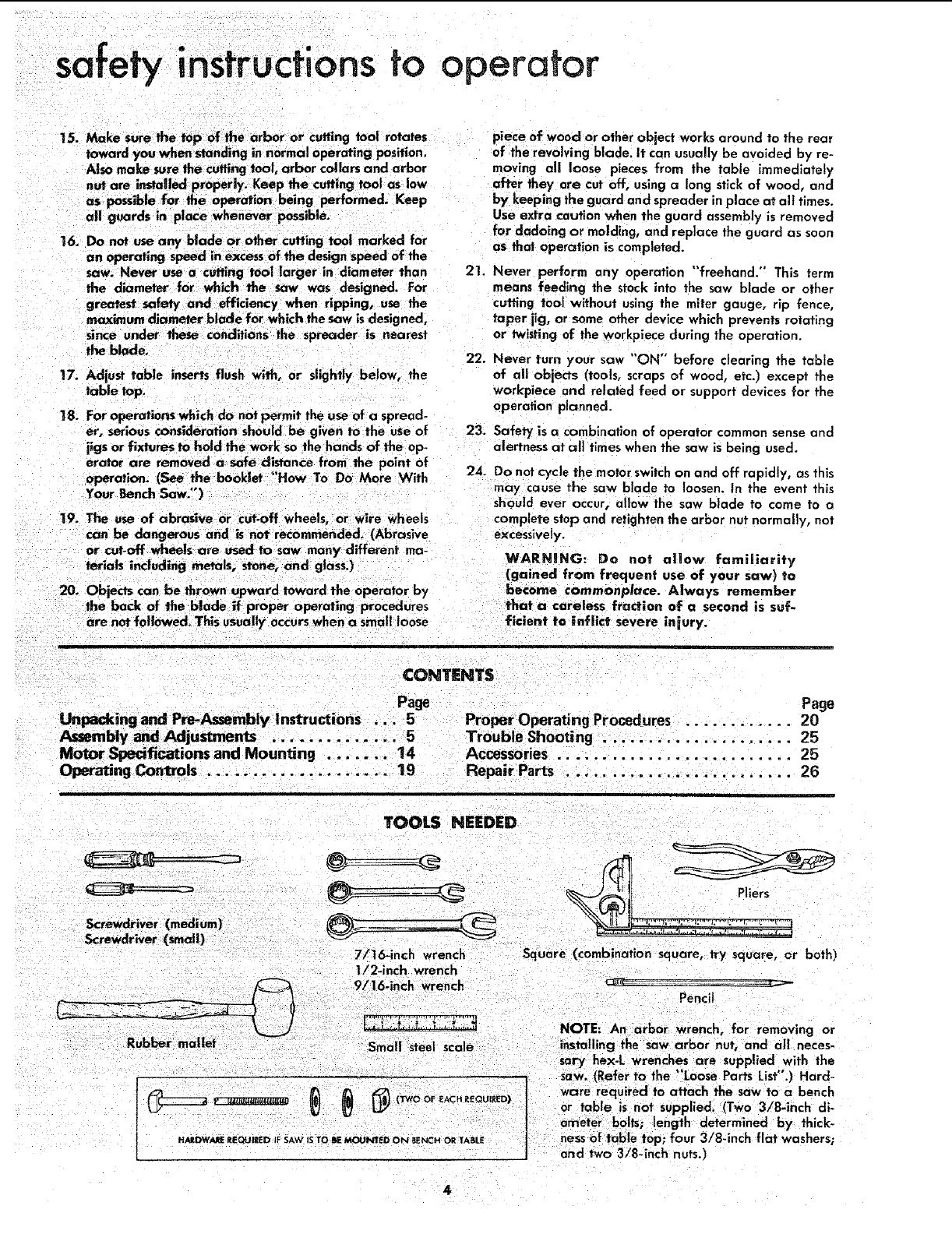
safety instructions to operator
15. Make sure the top of the arbor or cuffing tool rotates
toward you when standing in normal operating position.
Also make sure the cutting tool, arbor collars and arbor
nut are installed properly. Keep the cutting tool as law
as possible for the operation being performed, Keep
all guards in place whenever possible.
]6, Do not use any blade or other cuffing tool marked for
an operating speed in excessof the design speed of the
saw. Never use a cutting tool larger in diameter than
the diameter for which the saw was designed. For
greatest safety and efficiency when ripping, use the
maximum diameter blade for which the saw is designed,
since under these conditions the spreader is nearest
the blade,
]7. Adjust table inserts flush with, Or slightly below, the
table top.
18. For operations which do not permit the use of a spread-
er, serious consideration should be given to the use of
jigs or fixtures to hold the work so the hands of the op-
erator ore removed a safe distance from the point of
operation. (See the booklet "How To Do More _,Nith
Your Bench Saw.")
19. The use of abrasive or cut-off wheels, or wire wheels
can be dangerous and is not recommended. (Abrasive
or cut-off wheelsare used to saw many different ma-
terials including metals, stone, and glass.)
20. Objects can be thrown upward toward the operator by
the back of the blade if proper operating procedures
are not followed. This usually occurswhen a small loose
piece of wood or other object works around to the rear
of the revolving blade. It can usually be avoided by re-
moving all loose pieces from the table immediately
after they are cut off, using a long stick of wood, and
by keeping the guard and spreader in place at all times.
Use extra caution when the guard assembly is removed
for dadoing or molding, and replace the guard as soon
as that operation is completed.
21. Never perform any operation "freehand." This term
............ the stock into the saw blade or other
cutting tool without using the miter gauge, rip fence,
taper jig, or some other device which prevents rotating
or twisting of the workpiece during the operation.
22. Never turn your saw "ON" before clearing the table
of all objects (tools, scraps of wood, etc.) except the
workpiece and related feed or support devices for the
operation planned.
23. Safety is a combination of operator common sense and
alertness at all timeswhen the saw is being used.
24. Do not cycle the motor switchon and off rapidly, as this
may cause the saw blade to loosen. In the event this
should ever occur, allow the saw blade to come to a
complete step and retighten the arbar nut normally, not
excessively.
\!VARNENG: Do not allow familiarity
(gained from frequent use of your saw) to
became commonplace. Always remember
that a careless fraction of a second is suf-
ficient to inflict severe injury.
CONTENTS
Page Page
Unpacking and Pre-Assembly Instructions ... 5 Proper Operating Procedures .20
Motor Specifications and Mounting ....... 14 Accessories ............... 25
Operating Controls .................... 19 Repair Parts ......................... 26
TOOLS NEEDED
Screwdriver (medium)
Screwdriver (small)
Rubber mallet
7/16-inch wrench
1/2-inch wrench
9/16.inch wrench
-_,,._ 4, ,_.r,-1. j-. ,,,
Small steel scale
v_ls_utu_ _ (TWO OF EACH I_EQUIEED)
HARDWARE RIEQUIEEO IF SAW IS TO lie MOUNTED ON BENCH OR TASBE
Square (combination square, try square, or both)
Pencil
ware required to attach the saw to abench
or table is not supplied. (Two 3/8-inch di-
ameter bolls; length determined by thick-
nessof table top; four 3/8-inch flat washers;
arid two 3/8-inch nuts.l

unpacking and pre-assembJy
UNPACKINGAND PR[°A$SEMBLY
INSTRUCTIONS
UNPACKING AND CHECKING CONTENTS
This Craftsman Bench Saw is shipped complete in one carton
(without motor).
in order to prevent damage during shipment and facilitate
packaging, certain items have been removed at the factory
and must be assembled when received by the purchaser.
Remove all items from the package and identify them by
referring to figure 1. These "'loose" parts are listed below
and should be accounted for before discording any packing
material (See figure 1.)
LOOSE PARTS LIST
Key Ha.
(Fig. 1) Part Heine Qty
1Guard Assembly-Saw ......................... 1
ZFence Assembly-- Rip .......................... 1
3 Operating Instructions.......................... !
4 Handbook .................................... ]
5 Wrench, Arbor ................................ 1
6Gauge Assembly - Miter ........................ I
7 Rack- Table ................................. ]
8Bar Assembly -- Fence ........................ ]
9 Bag of Loose Parts ............................ ]
10 Hand-Wheel Assembly, Tilt 4-1/2 in.............. 1
11 V-BelL 1/2 x41 in.............................. ]
12 Pulley--V, Single Groove,2.1/2x5/8 in. Bore .... 1
13 Support Assembly - Motor ...................... !
14 Rod Assembly-Splitter ........................ 1
15 Support Assembly - Splitter ..................... 1
16 Guard, Belt ................................... ]
17 Clamp, Ring .................................. 1
Contentsof LooseParts Bale-- (KeyNo. 9, above)
Wrench, Hex-L,3/32 in.........................
Wrench.Hex-L 1/8 in......................... 1
Wrench,Hex-L, 5/32 in........................ 1
Wrench,flex-L, 1/16 in........................ 1
Bolt, Carriage, 5/16-t8 x 3/4 in................ 4
NuL Square, 5/16-18 ......................... 4
Washer, 11/32 x7/8 x 1/16 in................. 4
Loekwasher, 5/16 x .125 x .078 in. .............. 4
Screw,Mach., Rex Hd., 5/16.1S x5/8 in.......... 2
Spacer, FenceGuide Bar ...................... 3
Screw, Mach., Rd.-Rd.,Slotted, 1/4-20 x2in...... 3
Nut, Flex. t!4-20x7/16x3i]6 in.............. 3
Lockwasher,!/4x.109x.062 in............... 3
Screw, Mach., He×-ln-Hd. 5/16-18 x I in......... 2
Key (for Switch Lock) ......................... 2
Grommet ................................... ]
Clip, Cord .................................. 2
GENERJ_L INFOIIMATION
The instructions in this manual are presented in step-by-step
order and illustrated by numerous pictorial diagrams. Read
the instructions and observe the illustrations to insure a
correctly assembled and accurately adjusted saw.
Adjustments are carefully checked prior to packaging the
saw for shipment; however, rough handling in transit may
necessitate some readjustments. For this reason all adiust-
merits are presented in logical order.
Reference to the Repair Parts exp|oded drawings (and item
listings) may be helpful in acquiring a more thorough under-
standing of your Craftsman saw.
Assr BLY AND ADJUSTMENTS
1. Remove the rust-preventive coating from external
surfaces (saw table, etc.) with a cloth moistened with
kerosene.
:2. _nstail the tilt hand-wheel on tilt screw shaft and
secure it by tightening the set screw with a1/8-inch
hex-L wrench. (See figure 2.) Use pliers on the hex-L
wrench and tighten the set screw on the "flat" of tilt
screw. Exercise care against over-tlghtening to avoid
damaging the hand-wheel.
3. Rotate the tilt hand-whee| clockwise until it stops,
to set the saw blade in the vertical (90 °) position.
4. Remove the table insert, by inserting afinger into
the slot at one end of the insert and lifting it upward
and out. (See figure 3.)
T [LT HAND-WHEEL
\
HEX-L WRENCH
(I/8-1NCH)
Figure 2

adiustrnents
EL_VAT iON fl_D-WHE EL
F_u_ 4
ii
{NUT
5. Rotate the elevation hand-wheel clockwise until
it stops. This will position the saw blade at maximum
height (deepest cut) position. (See figure 4.)
6. Check tightness of saw arbor nut by wedging a
small block of wood between the saw blade and table
opening, as shown in figure 5, and, using the arbor
wrench supplied with the saw, tighten the nut. (The
nut rotates clockwise to tighten.)
7. Adjust Stop Collars as Follows:
a. Checking and Adjusting the O° Position....
(1) With the saw blade in deepest cut position,
check the tilt position of the saw b|ade by at-
tempting to rotate the tilt hand-wheel clockwise
until it will rotate no farther.
(2) Place asquare on the table top and against saw
blade. (See figure 6.) The blade should be at
exactly 90 degrees (perpendicular) to the table-
top surface. (Make sure the square is resting
against the flat surface of blade and is not
being held away by the "tooth-set" of the blade.)
(3) if the blade is not square with table top, rotate
the tilt hand-wheel counterclockwise until the
tilt mechanism movesa shortdistance away from
the stop collar on tilt screw. When the pointer
on tilt scale indicates approximately 10 degrees,
the stop collar can be reached. (See figures 7
and 9.)
(4) Loosen the two set screws in the stop collar,
located on the tilt screw nearest tilt hand-wheel,
with asmall screwdriver and rotate the stop
collar counterclockwise at least one turn. (See
Figure 6
_H /_ T,LT I
0_POSITION
Figure
/
.REAR OF SAW
SET
SCREW
_ T_LT
- SCREW
STOP " ____
COLLAR
SET
SCREW
Figure 8
(5)
(6)
Two slotted-head set screws (figure 8) are used
in each stop collar so that one of the screws
will always be accessible (with operator reach-
ing inside the saw base from the rear of saw,
figure 9)_ After adjusting the collar, it is only
necessary to tighten one of the set screws to
secure the Collar on the tilt screw.
Rotate the tilt hand-wheel clockwise until the
saw blade is perpendicular to the saw table--
Reach inside of saw base (figure 9) and rotate
the stop collar clockwise until it is in firm contact
with the saw cradle. Tighten one of the stop-
collar set screwsenough to keep the collar from
rotating on the tlit screw.
I

(7) Rotate the tilt hand-wheel counterclockwise ap-
proximately three turns, then rotate it clockwise
until it stops. Check the saw again with the
square as shown in figure 6. If the adjustment
is correct (blade square with table surface),
tighten the set screw in the stop collar securely.
NOTE: Several trial adjustments may be re-
quired in order to produce an accurate
adjustment of the stop collar. If the first trial
fails to produce an accurate setting, it is sug-
gested that the operator determine which
direction the stop collar needs to be rotated
for a correction and turn the collar in small
increments (checking each time) until the
adjustment is correct. Be sure to tighten one
of the collar set screws after each adjustment
to prevent the collar from slipping on the
tilt screw when it comes into contact with the
saw cradle.
(8) With the tilt hand-wheel rotated clockwise until
it stops (saw blade 90 ° with table surface),
check the tilt pointer on tilt gauge which should
be at exactly "0" (zero) degrees. (See figure 10.)
A close look will show a reflection of the pointer
tip on the mirror surface of the tilt scale on front
panel. In order to make surethat you are sighting
squarely with the scale, move your eye until the
tip of the pointer and its reflected image coincide.
(9) If the pointer is not aligned with the "0" mark,
bend the pointer carefully with pliers (figure
10) until it remains at "'0" when the pliers are
removed.
b. Checking and Adjusting the 45°Position.
fl )Rotate the tilt hand-wheel counterclockwise until
it will rotate no farther.
(2) Remove the scale from a combination square
and place the head of the square on table top
and against saw blade. (See figure 1I.) The saw
blade should be setting at exactly 45 degrees
with table top surface.
(3) Efthe acute angle between saw blade and table
top is not 45 degrees, rotate the tilt hand-wheel
clockwise until the tilt mechanism moves a short
distance away from the stop collar (located
farthest out toward the end of tilt screw, figure
12) so the collar can be reached for an adjust-
ment. When the tilt scale indicates approxi-
mately 35 degrees the collar will be accessible.
(4) Loosen the two set screws in the stop collar. (See
figures 8 and 12.) If, in preceding step (2), the
blade stopped with the acute angle greater than
45 degrees, rotate the stop collar counterclock-
wise (toward end of tilt screw). If the angle is
less than 45 degrees, rotate the collar clockwise
(away from end of tilt screw). For each trial
setting: move the stop collar a short distance
away from saw cradle (by rotating tilt hand-
wheel clockwise) loosen set screw, rotate the
stop collar a fraction of a turn in desired direc-
tion, tighten one of the set screws (figure 12)
and rotate the tilt hand-wheel counterclockwise
until it stops. Then measure the angle of saw
blade with table surface, as shown in figure 11.
\
I!_1 TILT
scREw
c. f
Figure 12
TABLE INSERT
Figure I3 _
Several trials will probc_bly be required to pro-
duce an accurate stop at the 45-degree position.
(5) Tighten one of the stop collar set screws securely
a{ter the adius_.ment has been completed.
NOTE: If the above adjustments have been
accurately performed, the saw will now have
a positive stop at "0" and "'45" degrees and
the pointer on tilt scale should stop at both
positions.
(6) Rotate the tilt hand-vcheel until it stops at the
"0'" position, as indicated by the pointer.
Adjust Table Insert as Follows:
a, Install the table inser,_ by" sliding it carefully into
position and pressing down firmly at both ends until
the spring clips on under'Side of insert "snap" into
position. (See figure 13.)

assembly and adiustments
c. Wffh the table insert in place, use a small scale or
straightedge to check near each of the four set screw
positions, in order to determine if the table ins_ert is
even with saw table surface at all four set screw
positions. (See figure 15.)
d. If an adjush_p_nt is _ry, rotate each of the
(See figure 15,) Make sure that ends of al! four set
screws are making conrad with table recess by
S_ING CLIP
,711
//'- Figu 14
9. Align Saw Blade With Table Grooves os F_|aws:
a. Checking for Correct Alignment.
(I) Check elevation and tlh hand-wheels to make
sure each is rotatad fully cleclcwisa -- to position
saw blade for deepest cut and sc!uare with
(2) Make n mark at _of one _tooth at rear
of b|ade just above table su_ce. (Se_ figure
16.) Select a tooth that is set toward the
right-hand side of saw.
b.
(4) Lay a pencil, or similar pointed tool, in the
depression lust ahead of miter gauge scale, with
pencil point toward Hie blade and hold pencil
in the depression with thumb of left hand as
shown. (See figure 163
15) Slide the miter gauge to a position which will
poi_t the pencil at the marked saw tooth. Hold
a small scale against the marked tooth and slide
the pencil toward the saw until the point rests
against the scale. With the left thumb, hold
the pencil securely in miter gauge head. it must
n(Mt mQ_.
(6) With the right hand, remove the scale and
rotate the saw blade until the marked tooth is
just above the saw table at the front, (See f_g-
ure 17.)
(7) Slide the miter gauge toward the front of saw
table untll the pencil is pointing 1owardl the
m_ed tooth. Insert the _le between Pencil
point and blade, as _hown in f',gure 17. If ti_
saw is parallel to table groove, the scale will
just slide into the gap _n the pencil point
and blade. If the sca|e will not enter, or is lOOSe
in the check Shownin figure 17, an adi ustment
of the table trunnions is required.
Adiusting Table Trunnions.
(l) Loca_ lbe three screwswhich secu_'eeach (front

(2)
permit each trunnion to "'stip ' when tapped with
a mallet or plastlc-tipped hammer. (If loosened
completely, it would be almost impossib_e to
achieve an accurate Qdiustment. )
Shift the two trunnions by topping them lightly
until the two measurements described in the pre-
ceding instructions are equal. Tighten the trun-
nion screws and recheck measurements to make
sure tightening screws did nat a_ter the setting.
Several trials may be required to produce an
accurate setting.
10. Ins_'ali the Table Rack,
a. Position the table rack against lower edge of fence
guide bar so that rack teeth are on upper edge of
rack and pointing outward. Align the three ho_es
in both parts. (See figures 19 and 20.)
b. Insert one of the three 1/4-20 x 2-inch screws
through holes at one end of rack and guide bar and
place a guide bar spacer on the end of the screw.
(See figure 19.) Insert the screw through the saw
table and install a 1!4-inch !ockwasher and 174-20
hex nut. Do not tighten the screw at this time.
c. Instalt the remaining two screws, spacers, Iockwash-
ers and nuts. Rotate these three screws into their nuts
until they are snug. Do not tighten them at this time,
11. Check and Adiust the Rip Fence as Follows:
Your Craftsman Rip Fence has been designed to pro-
vide accuracy, reliability and long llfe. In order for
your fence to work properly, it is imperative that it be
adjusted accurately. The fence is adjusted at the fac-
tory, but due to shipping hazards, and s_ight tolerance
buildup between individual saws, it is sometimes neces-
sary that your fence be adjusted to your particular saw.
Therefore, check your fence and adjust it (if necessary)
as outlined in the instructions that follow:
CAUTION: It is imperative that these instruc_
;'ions be followed precisely, as an incorrect
adiustment could damage the fence and the
fence guide bar attached to your saw.
a. Installation of Rip Fence.
(1) Raise the lock handle and position the rip fence
on the saw table, Do not latch the lock handle.
Lower the saw blade beneath the table surface
by rotating the elevation hand-wheel counter°
clockwise.
12) Slide the rip fence atong the guide bar while
watching the clearance between lower edge of
fence and table top. if any portion of the fence
(except sliding pad at rear) drags on the table
top, or if clearance between fence and table top
vades appreciably as the fence is moved, the
guide bar must be adius ted. This is accomplished
by tapping the guide bar slightly up or down
with a soft mallet until aconsistent clearance
exists over entire top surface of the table. The
screw holes in guide bar and table have suffici-
ent clearance around the attaching screws to
permit this adjustment-
(3) Tighten the 1/4-20 ×2qnch screws securely and
recheck to make sure tightening these screws did
not affect the guide bar setting.
FENCE
GUIDE BA!R
@ \
_ LC)CKWASHER
\ fl!4
NUT
(HEX., I/4-20)
RACK
SCREW
(I/4-20 × 2 _o.)
FENCE GUIDE
TEETH
TABLE RAC K
;REW
(1/4- 20 x 2 iN.)
Figure 20
i i
LOCKWASHER
( I/4 IN. _
b. Adjusting Pinion to Rack.
(1) Check for correct engagement (mesh) of teeth
on fence adjusting shaft pinion with the gear
teeth in lower edge of rack. (See figure 21.) The
pinion should be adiusted up or down so that

assembly and adjustments
Figure 22
Figure 23
gear teeth are in full contact lengthwise and
meshed as far as possible, just short of binding.
This adjustment is made as follows: Push the
fence adjusting knob all the way down, and
look underneath the rock to determine if the
pinion and rack teeth are aligned. (See figure
21.) If the pinion extends too far (or not far
enough) loosen the set screw (1, figure 221 with
a 5/32-1rich hex-L wrench and slide the knob
assembly on the pinion shaft (up or down) to
achieve proper alignment. Tighten the set screw
(1, figure 92).
(2) Adjust gear mesh (depth of tooth contact) by
loosening the set screw (3, figure 22) with a
5/32-inch hex-L wrench and rotate the eccen-
tric (4, figure 22) untll proper mesh is obtained.
Tighten the set screw after adjusting. Check for
proper operation at various points along the rack.
c. Checking for Parallelism of Rip Fence with
Table Groove.
(1) With the lock handle released {not latched), slide
the fence on the saw table so the front end of
the channel is flush with the side of one of the
two miter grooves. (See figure 23.) This can be
checked by using your fingers as shown to "'feel"
for correct alignment. Shift the rear of the fence
to the right or left slightly, causing fence not to
be square with the front edge of the table, nor
parallel to the miter groove.
(2) Push down on the lock handle carefully (do not
force) while watching the rear of the fence for
its correcting adion.
-, ,CAUTION: Do not force the lock handle.
If the handle does not lock down readily,
an adjustment is necessary -- and to force it
' ._ could cause damage to both the fence and
-! guide bar.
(3) The lock handle should lock in the clown position.
_'_ Do not force the handle, as it is not necessary
for the handle to be all the way down to lock
the fence. (See figure 24.) The rear of the fence
should move to correct itself, and do so parallel
I'flush) with the miter groove in saw table through-
Figure 24 out its full length. Alignment may be checked
with the forefingers to determine if the fence is
flush with the side of miter groove, as shown in
figures 23 and 24.
(4) tfthe lock handle responded as described above,
and the fence aligned itself with the table groove
at both enas, the fence is properly odiusted and
no further attention is necessary. If not, perform
the following adjustment routine.
d. Adjusting the Rip Fence Parallel to Table Groove.
(1) Remove the fence and turn it over. Then, with a
1/8-inch hex-L wrench, loosen the pawl set screw,
located just behind the fence pawl, approxi-
mately twotums. (See figure 25.)
(2) Using a 5/32-inch hex-L wrench, loosen the set
screw at the rear of the fence approximately
two turns. (See figure 26.) This screw is located
in thefence lock just inside the channel, as shown.
10

e.
(3) Place the fence back on saw table and notice
that the lock handle offers no resistance at any
position.
(4) Place the lock handle in "locked" position, and,
using a 1/8-inch hex-L wrench inserted into the
fence-pawl set screw from underneath the saw
table, tighten the set screw finger tight. (See
figure 27.) Do not use wrench or pliers- finger
tight only.
15) Raise the lock handle, push the fence to one side
(off square) at the rear. Then lock the fence with
the lock handle, while watching to make sure it
"corrects" itself. Repeat this operation two or
more times. The fence should "'correct" itself
each time it is locked.
(6) Raise the lock handle and align the fence with
the miter groove (at the front end of the groove)
as shown in figure 23. Push the lock handle dawn.
17) Check for correct alignment with saw table
groove for the full length of the fence. If it is
aligned at the front but out of alignment at the
rear, loosen the two hex-head screws on top of
the channel near the front (figure 28) just enough
to permit the channel to slip when tapped lightly
with the palm of one hand. Tap the channet at
the rear of the fence with one hand until it is
aligned with the table groove. Tighten the two
hex-head screws securely and recheck. More
than one triat may be required, as tightening
the screws may change the setting slightly.
(8) Check for "automatic correcting" by releasing
the lock lever, shifting the fence off square at
the rear, then locking it. The fence should square
itself automatically and be flush (parallel) with
the miter groove each time the handle is locked
down,
(9) Lock the fence with the lock handle, and, using
a5/32-inch hex-L wrench, tighten the fence lock
set screw at the rear, hand tight only. (See
figure 29.) Make sure the fence is "secure" to
the table at the rear.
NOTE: If the fence fails to square itself every-
time, check for any burr or foreign material
on the surface of the fence head where it
contacts the saw table. Also check for nicks
or burrs in edge of saw table_ Stone off any
irregularities on these surfaces.
Aligning Rip Fence Plastic indicators.
(1) If for any reason the tilt hand-wheel has been
rotated during preceding operations, rotate it
clockwise until it stops (tilt pointer at "O").
(2) Raise saw blade above the table surface by
rotating the elevation hand-wheel clockwise
(3) Position the rip fence on the right-hand side of
saw blade with the fence channel one inch from
the saw blade and lock the fence. Be sure to use
one of the teeth bent (set) to the right of blade
and measure from this tooth to the fence, since
this determines your width of cut. (See figure 30.)
This distance should be measured accurately
with a scale.
Figure 27
Figure 29
FENCE
l '
Figure 30
11

adiustments
(4) Set the right-hand indicator (a scribed line in
the plastic window) to "'1" inch on the guide-bur
scale, This is accomplished as follows:
(a) A close look will show a reflection of the
indicator line on the mirror surface of the
guide-bar scale. In order to make sure that
SCALE
(WITH MIRROR SURFACE)
WINDOW
REFLECTEDIMAGE
Figure 31
IND ICATOR LINE
IN PLASTIC WINDOw
!
$CREWS
Figure 32
LOCK HANDLE
ROD ASSEMBLY
STOP
PIN
SQUARE INDICATOR
BLOCK
Figure 33
yeu are sighting squarely above the scale,
move your eye until the indicator line and its
reflected image coincide. (See figure 31.1
(b) If an adiustrnent is required, loosen the two
screws cone at each end of the window] and
shift the plastic window untit the indicator
line is aligned with the "'!" inch line on the
scale, fSee figure 32.) Tighten the two screws
and recheck for accuracy. If the plastic win-
dow cannot be shifted far enough to provide
this alignment, loosen the screws that secure
the guide-bar scale to the gulde-bar at its
ends, shift the scale slightly and tighten the
screws. Then proceed to adjust the plastic
window as described above.
(c) When the fence is correctly adjusted and
moved to any position at the right of the saw
blade, the scale will indicate the width of
the desired cut. Make several trial settings
and check by measuring with a scale from
the fence to the blade.
NOTE: When properly adjusted, the indi-
cators may be used for most operations, thus
eliminating the need for actual measure-
ments, except for extreme requirements.
When sighting the indicator, always use the
system shown in figure 31 in order to make
sure the sight angle is correct.
(d) Move the fence to the left-hand side of saw
blade and adjust the left-hand indicator
(right-hand side of fence channel) in the
same manner as for the right-hand indicator.
NOTE: Remember, if the scale must be moved
when adjusting the left indicator, it will
change your settings on the right-hand indi-
cator which was previously set.
(5) Remove the rip fence from the saw to avoid
interference with subsequent adjustment routines.
12. Check and Adjust the Miter Gauge as Follows:
The miter gauge was set at the factory. During ship-
ment, however, rough handling might have disturbed
the setting, To assure maximum accuracy the "0" (zero)
degree stop should be checked and adjusted (if re-
quired) as follows:
a, Checking the Miter Gauge.
(1) Loosen the lock handle and push stop pin firmly
into the middle detent ("0"" position on the scale).
The stop pin will be seated more effectively if it
is rotated slightly as it is being "pushed" into
the detent. Tighten the lock handle firmly hand
tight, (See figure 33,)
(2) Using acombination square, check for an exact
90-degree angle between the miter gauge and
rod assembly. If this measurement is exactly 90
degrees, the adjustment has not been disturbed
and the gauge is-ready for use. If not accurate
at 90 degrees, adjust the gauge as follows:
12

b. Adiusting the Miter Gauge.
(1) Loosen the lock handle, disengage stop pin, hold
the square soLid{_ against the rod assembty a*._d
face and tighten lhe Jack handle firmly by hand
Always tighten the tack handle hand fight o_ly.
Do not use a wrench or pJiers_
(2) Recheck to make sure that tightening the iock
handle did not alter the setting. Remove the
square from the gauge.
(3) Loosen the two screws that attach the indicator
block to the rod assembly. Shift the indicator
block until the stop can be pushed solidly into
its detent. Hold the indicator btock aligned with
the rod assemb{_/and the stop pin seated firmly
in the detent and tighten the two screws.
(4) Loosen the lack handle and recheck for accuracy
with the combination square. (Make certain the
stop pin is fully seated.) Tighten the Jack handle
and readjust if necessary.
(5) After completing the above adiustment, _oasen
the pointer attaching screw, set pointer at "0"
(zero) and tighten the screw.
NOTE: Detents at the two 45-degree positions
are jig bored. When the gauge is adjusted
for 90-degree cut, the 45_degree positions
are col'root.
(6) Remove the miter gouge from saw tabJe until
remaining checks have been completed.
13. lnstaq! Saw Guard Assembly as Follows:
a. Installing Splitter BJede Bracket.
(1) Install the two 5/16-18xSi8-inch, hex-head
screws laosemy in holes at rear of saw cradle as
these screws cannot be installed after attaching
the splitter blade bracket_ (See figure 340 These
are the screws thai secure the motor support in
the cradle.
(2) tnstaH the splitter b;ade bracket with two 5/16-
18xl inch box-head screws. Tighten screws
finger tight at this time.
(3) Refer to figure 35 and hold the splitter rod to
the left of splitter support_ Rotate the splitterrod
so the "flat" on the rodis toward the operator.
Then slide the spJiffer rod into the spfitter sup-
port from the left until the pin (through the rod)
bottoms in the slots in splitter support. (See figure
35.) Tighten the thumb screw firmly against the
"'flat'" af splitter rod.
(4) Slide the splitter rod (attached to splitter sup-
port) into the sp{iii'er blade bracket until the
splitter blade is directly behind the saw blade.
(See figure 36.) Do not be concerned if the split-
ter bar does nat align with saw blade vertically
as this will be Corrected in the next step. "lFighten
the socket-head set screw in splitter blade bracket
with a 5/32-inch he×-L wrench.
C'EWHE* L t
5/,6 {1J
Figure 34 ""
PIN
\
TER SUPP©RI
\
13

ore i o
motor specihcat ons and mounhng
(5) With saw blade all the way up, MAKE SURE IT
IS 90 ° OR SQUARE WITH THE TABLE.Raise the
blade guard and by using a square, adjust the
spl_r vertically 90° (Square) to the table.
Tighten the two5/16-18 x 1-inch screwsto secure
thesplitter blade bracket to the cradle. Place a
large square or straight-edge alongside the
saw blade. If the splitter is not in line with the
saw blade, loosenthe sockethead set screw (See
figure 36) and move the splitterassembly to the
right or left so that it touches the square and is
in linewith the saw blade (See figure 37). Tighten
the set screw.
(6) Recheckto make sure the following screws are
tight:
The socket-head set screw Cfigure 36) that se-
cures the splitter rod, and the two hex-head
screws (figure 371 that attach the splitter blade
bracket to saw cradle. Sight along splitter bar
and saw blade again after tightening these
screwsto make surealignment was not disturbed.
NOTE: After the splitter blade is properly
aligned, always remove the guard by loosen-
ing the thumb screw _figure 35) and sliding
the assembly off the splitter rod. This will
avoid upsetting any of the alignment adjust-
ments, as the pin in the splitter rod will serve
asa "stop" when the guard is installed.
CAUTION: When cleaning the plastic guard
is necessary, wipe surfaces with a clean, dry
cloth. Do not use solvent of any kind.
MOTORSPECIFICATIONS& MOUNTING
1. This Craftsman Saw is designed for use with a 3450 rpm
motor. The saw arbor has a 2-1/2-1nch diameter pulley
_-_ attached and a 2-1/2-inch diameter motor pulley is sup-
plied for driving the saw at the proper speed of 3450 rpm
through a 1 to 1 motor to saw ratio.
CAUTION: Do not install a larger diameter
pullev on the motor as it would drive the saw
blade at speeds which would be dangerous.
_,ivl The following Craftsman motors are recom-
./"/ 0 ..
?_ mended, available at any Sears Retad Store
J or Catalog Order House:
_¥E Catalog No. RPM Horsepower Vo|ts
/- J_:_ _'_ _l
/99KT121 c 3450 10120
99KT1220C 3450 1 110-120 or 230
/t: _ fi_r wil°l!imt_fP_it aab_r_:t_ c_mmu::ddehdamn°_gteP"cl°t:s
/_'_ / _ figuration that will not permit installation of the belt
/_'_ i guard.
IFiaureg 37 __l_ 3. The Craftsman motors recommended in the preceding
table may be connected for either right- or left-hand
rotation. Make sure that wiring connections are made
so the motor shaft will rotate in a clockwise direction
BLADE
_7 (when facing the drive end). (See figure 38.)
BELT GUARD
use 5/B
END OF
\\
Figure 38
4. Attach the Motor to Motor Base as Follows:
a. Position the motor with the 5/8-inch diameter shaft
at the right with mounting base in a vertical position.
(See figure 39.)
b. Positionthe motor support assembly as it would be
oriented if mountedon the saw cradle, with the motor
base against the motor mounting base.
c. Insert four 5/16-18 x3/4-inch carriage bolts (from
loose parts package) through the motor base and
motor mounting base. (See figure 39.)
d. Instal! an 11/32-inch flat washer, 5/164nch lock-
14

washer and 5/16-18 square nut on each carriage bolt
finger tight. (All parts are in loose parts package.)
e. Shift the motor mounting base on motor base until
the top edges of each are even and carriage bolts are
approximately centered in the slotted holes of the
motor base.
f. Tighten the four square nuts securely.
g. install shaft guard on left-hand end (1!2-inch
diameter) motor shaft, if not already in place. This
guard is supplied with the motor.
5. Install Motor and Support Assembly.
a. Position the blade slightly below the deepest cut posi-
tion end tilt pointer at "'0",
b. Install the motor pulley on motor shaft with the set
screw boss toward the outside. (See figure 39.) Do not
tighten the set screw at this time.
c. Place the drive belt over the saw arbor pulley by
reaching inside saw base, allowing it to hang tem-
porarily on this pulley.
d. Slide the two pins on motor support assembly into
their holes in saw cradle far enough to enable the belt
to be placed in the groove of motor pulley. Raise blade
to deepest cut position.
e. Grasp the motor with both hands as shown in figure
40 and lift up until the pivot arm screw is at the rear
of the slot, as shown. While holding the motor in this
position pull it rearward (toward operator) until the
drive belt is "snug" and tighten the two motor mount
clamp screws securely. The pivot arm screw should
still be at the rear of limit of its slot.
f. Release the motor and note that it remains at essen-
tially the same position as it was held. The motor base
will probably rotate slightly rearward, thus leaving
the pivot arm screw slightly away from the end of
its slot.
g. If the belt is _ot aligned with the two pulleys, which
can be readily seen by sighting along edges of both
pulleys, slide the motor pulley in or out an the shaft
as required and, when correctly aligned, tighten
pulley set screw with a 5/32-inch hex-L wrench.
NOTE: If correct pulley alignment cannot be
obtained by the preceding method, loosen the
square nuts on motor base, shift the motor
in desired direction and tighten the nuts.
h. Loosen the motor base clamp screws (both ends) and
rotate the motor so that the ventilation holes in the
shell of the motor are facing down and the capacitor
cover is on top (See figure 41). This will help prevenl
sawdust from entering the motor.
i. Lower the blade enough to permit removal of drive
belt from the arbor pulley and remove the belt in
preparation for installing the belt guard.
6. Install Belt Guard.
a. Place the guard clamp ring around right-hand end
of motor, slide the free end into the screw-type
fastener. (See figure 42.) While holding the two ends
together, rotate the screw in fastener with a screw-
LOCKWASHER THESE TWO CARRIAGE BOLT
(5/16 iN) EDGESEVEN (5/16-I_3/4 iN.)
Figure 39
MOTOR &'OUNT
MO]OR PULLEY Figure 40
Figure 42
15

and rnounfin
BELT GUARD
CLAMP RING
MOTOR POWER CORD
S
h.
driver./Cake sure the screw engages the openings in
the ring and rotate the screw until the clamp ring
diameter just leaves enough clearance on motor
frame for the guard to be slipped easily under the
ring.
Hold the belt guard as shown in figure 43 and insert
the drive belt into the guard as shown. The lower end
of belt should contact the inner wall of the guard
so it will pass over the motor pulley when the guard
is slipped into place.
Slide the guard on end of motor, while holding it as
shown in figure 44, and slide the clamp ring over
the edge of guard leaving edge of ring approximately
1/2-inch from edge of guard. Do not tighten the
clamp ring at this time.
d. Grasp the belt between thumb and forefinger as
shown in figure 44 and, while looking down into the
guard "hook" the lower loop of belt onto the motor
pulley. Shift the guard on motor to center the belt
in the guard.
e. Continue to hold the belt on motor pulley, rotate the
guard downward and "'hook" upper end of belt onto
the saw pulley inside the base.
f. Rotate the elevation hand-wheel clockwise until it
stops, to place the saw blade in its highest position.
g. Positionthe belt guard so the belt clears the inside
of the guard at the upper position approximately
1/4-inch and the guard does not touch the under-
side of saw table. (See figure 45.) Correct positioning
of the belt guard is important. If the belt should be
permitted to rub against the guard it would soon
wear as|ot in the guard.
h. Tighten the clamp ring to hold the guard securely
on motor.
i. Rotate the elevation hand-wheel counterclockwise to
lower the saw blade tothe lowest position and check
positionof guard, The beh should stillclear the inside
of the guard.
7. Adjusting Pivot Arm Screw.
This adjustment (figure 46) is necessary to prevent motor
vibration (screw too loose) and to permit the motor mount
to maintain correct belt tension whenever the saw blade is
raised or lowered with the elevation hand-wheel (screw
too" fight if belt tension is not maintained). When either of
these conditions are evident, adjust the screw as follows:
CAUTION: Do not tighten the pivot arm
screw to a locked position, as it would be
sheared off when the saw blade is raised.
a. Tightening or loosening the pivot arm screw (figure
MdTOR
Figure 45
16

PIVOT-ARM
SCREW,
_iER
AND FLAT WASHER
Figure 46
-MOTOR BASE
BELT GUARD
Figure 47
b. Apply a few drops of oil (SAE 10 or 20] to the flat
washer and in slot in motor base, and adjust the screw
in small increments until the motor base slides readily
in or out in response to blade elevation movement
throughout the full range.
c. After obtaining normal movement of motor bose,
observe the saw in operation after starting it as de-
scribed in subsequent instruction. If the motor base
tends to vibrate, tighten the screw a little at a time
until vibration is minimized. After eliminating vibra-
tion recheck as in preceding step b, to make sure the
base will still slip in response to blade elevatian
movements.
8. Connect and Position Motor Power Cord.
a. Feed the motor power curd through the large hole in
saw base. (See figure 44.)
b. Grasp the connector on end of motor power cord
and, while looking into the base, insert the plug into
the receptacle at rear of switch box. (See figure 47.)
c. Position the power cord as shown in figure 47, and
install two cord retaining clips on edge of saw bose
flange to secure the cord. Locate clips at approxi-
mate positions shown. Allow approximately 12 inches
of cord between the motor and saw base,
d. Hold the power cord and slide the grommet (on cord)
upto the base and insert it into the hole in base panel.
(See figure 48.)
MOUNTmNG SAW ON BENCH
Some usersprefer to mount the saw solidly by bolting it to
a bench or table top. The following method for mounting
the sow is recommended.
CAUTION: Make sure the saw mounting sur-
face of bench or table is even and free of
"'twist" in order to prevent distortion of saw
table when mounting bolts are lightened.
1. Select asturdy table or bench and plan the saw location
for convenience and accessibility.
2. Measure and mark the two hole locations in bench (or
table), using the dimensions shown in figure 49. [Dimen-
sions are given from hole centers.)
23-1/2
GROMMET i
\\
Figure 48
REAR OF BASE
Figure 49
17

motor specifications and mounting
3, Drill two holesin table at marked locations. Holes in saw
base are 7/16-inch in diameter. It is recommended that
3/8-inch bolts be used for mounting.
4. Cut an opening inthe table top undersawbase, in order
to prevent accumulation of sawdust inside the base. The
opening should be at least 12-inches, The actual size
will depend upon the type of table or bench being used.
5. Mount the saw with proper length bolts.
PERIODIC MAINTENANCE OPERATIONS
This Craftsman saw is a fine machine and should be given
the best of care. If kept clean andproperly lubricated, it
will provide many years of trouble-free service. There are
no specific maintenance time tables. However, operations
listed and described in paragraphs immediately following
should be performed when conditions or symptomssuggest
need for attention.
1. Removing Saw Blade.
NOTE: The saw blade, regardless of type
being used, should be kept sharp at all times.
Accurate and effective work cannot be
achieved with a dull blade. The saw arbor
has right-hand threads which causes the
arbor nut to become tighter in response to
saw rotation.
a. Remove the table insert, as described under "'Assem-
bly and Adjustments".
b. Slide a wedge shaped block of wood under a saw
tooth to wedge the blade and prevent rotation. CSee
figure 50.)
c. Using the arbor wrench supplied with the saw, rotate
the arbor nut counterclockwise to loosen it Remove
the nut and loose collar with fingers.
d. Remove the wood block and slide saw blade off the
arbor shaft.
2. Installing Saw Blade.
CAUTmON: Under no circumstances should a
blade with adiameter greater than 10 inches
be used with this saw.
ARBO_ WRENCH
WOOD BLOCK
a. Slide the new blade on arbor shaft, making sure saw
teeth are "'pointing'* toward the front of saw table.
install the loose collar and arbor nut finger tight.
b. Insert the wedge shaped wood block into the table
opening at the rear of saw blade and tighten the
arbor nut with the arbor wrench supplied wlth the
saw. (See figure 51.1 Remove the wood block.
c. install the table insert as described under "Assembly
and Adjustments".
3. Lubricate Saw When Needed.
Lubricant should be applied to friction points when they
appear dry upon visual inspection,or when friction increases
on the various controls.
f '_ .
Re er to the Repair Parts" exploded views and "Parts
List" for correct item names.
Figure 50
a_ The tilt and lift screws are self-cleaning, which pre-
ventsclogging or gummingof the threads, as the sharp
threads w_pe and clean the gear teeth. Apply a few
drops of SAE 20 or 30 oil as needed to keep parts
rotating smoothly.
b. The saw arbor bearings have been packed at the
factory with proper lubricant and require no addi-
tional lubrication. Other parts requiring lubrication
should be oiled frequently with SAE No. 20 or 30 o I.
The following parts should be lubricated regularly:
(1) Table trunnions.
(2) Lift screw and gear rack of assembled arbor.
WOOD BLOCK (3) Tilt screw block, tilt screw threads and tilt nut.
(4) Pivot pin and saw arbor housing guide.
(5) Clamp screw.
c. All points where aslip fit is necessary for adjustment
purposes should be oiled occasionally. (Pivot arm
screw, for example, figure 46.)
d. Attention should be given to moving parts in the rip
fence and miter gauge for cleanliness and lubrication.
/
Figure 51
1B

operating controls
e. To prevent the saw table surface from rusting, it should
be kept covered with afilm of Sears "Stop Rust" when
not in use. It can be wiped off with a cloth before
using. Treat other unpleted and unpainted parts and
surfaces with "Stop Rust".
SAW MITER
GAUGE RIP-FENCE
LOCK HANDLE
OPERAT NGCONTROLS
Before operating the saw, the operator should examine all
controls until thoroughly familiar with their functions, as well
as making sure that mechanisms respond to operation of
controls. (See figure 52.)
1. Elevation Hand-Wheel- located on the front of the
saw to raise or lower the saw blade.
2. Tilt Hand-Wheel -- located on left-hand side of saw to
control the angle of tilt. The saw blade can be tilted from
0 to 45 degrees, as indicated on the Tilt Scale. If the
angle of cut (tilt) must be extremely accurate, the angle
of the saw blade should be checked with a protractor,
or with a board known to be cut at the exact angle
required.
3. Rip Fence-the fence is operated by pushing in the
Fence Knob so that it engages a pinion gear with the
teeth on the Rack. Turning the knob after pushing it in
will cause the rip fence to move across the table. When
the knob is released, it becomes disengaged from the
pinion gear and the rip fence can be moved across the
table by hand. Keep the saw table and rip fence clean,
as dirt may prevent the rip fence from assuming proper
alignment when tightened.
4. Lock Handle--this handle is used to clamp the rip
fence in place after it has been moved to the desired
position.
5. Miter Gauge this gauge is used in table grooves as
aguide far the work-piece. The angle of the gauge can
be adjusted by loosening the clamp handJe and position-
ing the gauge as indicated by the dial and pointer on
the gauge.
6. Key-located at lower right of saw base, alongside
the ON-OFF switch, to lock the switch and prevent un-
authorized persons turning on the saw. The key must
be in the lock before the ON-OFF switch can be turned
on. (See figure 53.)
7, ON-OFF Switch -- also at lower right of saw base. The
switch lever is of unique design for maximum safety
protection. It is turned "on" by inserting the forefinger
under end of lever and pulling it outward. [See
figure 54.)
The switch can be turned off by thumb pressure (figure
55) or by striking it with any part of the body.
NOTE: At this point, plug in the power cord,
insert the key and turn itto the unlocked posi-
tion and pull the ON-OFF switch lever outto
start the saw (figure 54.) Turn off the ON-
OFF switch by pressing the lever inward (fig-
ure 55) to stop the saw.
FENCE KNOB
RACK
HAND WHEEL # SWITCH
ELEVATION
HAND WHEEL Figure 52
Figure 53
Figure 54
SWITCH LEVER
Figure 55
19

proper operating procedures
ORANG[
PUR_£
RIP CUTS DEPTH OF CUT
LOCK UflLOCK
MITER CUTS
tIGHT BLUE v'ELLOW
Figure 56
Figure 57
i,
WIDTH OF CUT-_
SOC KET-HEAD
rSCREWS
CUT INDICATOR
CUT-INDICATOR SHOES
Figure 58
P OPEROPEEATJNGPROCEDURES
COLOR CODED CONTROLS
In order to simplify operation of this bench saw, basic set-up
and operating adjustments are keyed to the controls to be
used in performing the operation with color discs applied
directly to the item involved. These set-up adjustments and
color-codes are illustrated on the front (trim) panel of the
saw. The colors and operations to which they are keyed
are as follows: (See figure 56.)
1. ORANGE-- Rip Cuts. An orange disc is located in the
end of fence locating knob. This knob is used for posi-
tioning the fence (with lock handle released) for the
desired width of board when ripping.
2. PURPLE--Depth of Cut. Apurple disc is located in the
end of the handle attached to the elevation hand-wheel.
Rotation of the elevation hand-wheel raises or lowers the
saw blade to provide the desired depth of cut.
3. LIGHT BLUE--Bevel Cut. Alight blue disc is located
in the end of the handle attached to the tilt hand-wheel.
Rotation of the tilt hand-wheel positions the saw blade
at the desired angle with saw table for the bevel cut
required, The angle is indicated by the pointer on the
tilt scale (located on front panel).
4. YELLOW-Miter Cuts. The miter gauge indicator
(pointer) is colored yellow. The pointer and miter gauge
scale are used for setting the gauge to produce the de-
sired -niter cut angle.
NOTE: For additional descriptions of con-
trois involved in the use of the saw, refer to
the paragraph "OPERATING CONTROLS".
CHECK AND ADJUST THE
EXACT-I-CUT gNDICATOR:
NOTE: This adjustment is listed at this point
since it is necessary TO operate the saw in
order to make the test.
The cut indicator ("Exact-I-Cut') located afew inchesahead
of the saw blade (figure 57), enables the operator to deter-
mine preciselywhere the cut in a particular board will occur,
provided the cut indicator shoes have been correctly posi-
tioned, it should be checked and adjusted (if necessary)
as follows:
1. Inspect the cut indicator housing (figure 58) to make
sure it is even or just slightly below the level of table
top surface. If too high, locate the two cut indicator
housing attaching screwsunderneath the saw table and
fig hten them until the housing is flush (or slightly below)
the table top surface. If the cut indicator housing is
too 10w, loosen the attaching screws until it is correctly
positioned. (The cut indicator housing has a spring.type
washer under it which permits it to be raised, or lowered,
in response to ffghtening or loosening the attaching
screws.
2. Position the saw blade in the 90 ° position (0 ° on tilt
scale), by rotating the tilt crank counterclockwise until
it will rotate no farther.
2O

3.
4.
With the saw running, place a straight board (preferably
hardwood) against the miter gauge and hold it securely.
Make a smaff cut and pull the miter gauge back until
the cut is directly on the "Exact-l-Cut". (See figure 57.)
If both cut indicator shoes are aligned with the edges
of the cut, no adjustment is required. If not aligned,
loosen the two socket, flat-head screws with a 1/16-inch
hex-L wrench and slide the cut indicator shoes laterally
until the edge of each shoe is aligned with its respective
edge of the cut in the board. (See figure 58.) Tighten
both screws and recheck for accuracy of the adiustment.
RIPPING
The process of sawing wood with the grain is known as
"ripping". it is generally done with the aid of a rip
fence as a guide to positio_ and maintain the work at
correct width for the desired cut. (See figure 59.) Since
the work is pushed along the fence, it must have a rea-
sonably straight edge to make sliding contact with the
fence. Also. work must make solid contact with the table,
so that it will not wobble. Provide a straight edge, even
if this means temporarily nailing of an auxiliary straight
edge board to the work. If workpiece is warped, turn
the hollow side down.
2. The saw guard should be used during all ripping opera-
tions. The guard has a splitter which prevents the saw
kerr from closing and binding the blade.
3. Set the rip fence to desired width of cut, either by using
the scale on the fence guide bar, or measuring the dis-
tance between blade and fence. The fence _sgenerally
used on right-hand side of blade. Stand a little to the
right of center to avoid being sprayed with sawdust and
to be clear of work in case of a kickback.
4. Start the saw and advance the work, using the left hand
to hold work down and right hand to push it forward. As
:ut nears completion, move the left hand to a safe dis-
tance from saw blade, and push work through with right
hand a Eone.
CAUTION: Never reach in back of blade with
either hand to hold work down.
When the distance between the fence and saw blade is
less than the width of your palm, do not attempt to push
work through by hand. Use a push stick or pull work
through from behind saw. (See figure 60.)
Do not leave along board unsupported so that the
spring of the board causes Jt to shift on the table. Use a
support to catch end of board behind the blade. If board
is quite long, use another support in front of saw blade.
(Figure 61 showsone type of support that is adjustable
for height and easily constructed.)
RESAWING
1. The process of cuffing thick boards into thinner ones is
known as "resawing". It is a ripping operation. (See
figure 62.) Small boards (up to 3-3/B-inch maximum
width) can be resawed in one pass, but larger boards
(up to 6-1/4-inch maximum) require two passes, one
along each edge of the board.
2. When two cuts from opposite edges are required, these
GUARD
Figure 59 ./
:USH STICK
i-INCH SQUARES. /"
Figure 60 Figure 61
I
RIGHT WRO
Figure 62 I F'g
should be made to overlap 112-inch from the approxi-
mate center of the board.
3. If the first cut is too deep, the kerf will close and bind
the saw on the second cut, with danger of kickback. Also,
when the kerf closes, the two sidesof the cut are no !anger
parallel to the saw blade, and the saw wilt cut into them
to spoil their appearance. (See figure 62.)
_,. Keep same face of board against fence when making
both cuts.
CROSSCUTTING
1. Sawing wood across the grain is known as "'crosscuffing".
(See figure 63.) Boards are milled with the grain running
the length of the board.
21

proper operating procedures
Figure 64 Figure 65 Figure 66
2. In crosscutting the long edge of the work is placed across
the table top, therefore, the miter gauge is used as a
guide instead of the fence. Most operators prefer to
use the left-hand table groove. In this case, the left
hand is used to h_]d the work in contact with the gauge.
The right hand is placed on the handle and used to
advance the work. If right-hand groove 'is used, hand
positions are reversed.
3. Ordinarily, the gauge is placed in the table groove with
bar in front. When work is so wide that it completely
covers the table in front of blade, the gauge should
be reversed.
4. Square crosscutting is done with the miter gauge set at
"0" (at oright angle to the slide and groove). (See
figure 64.) The splitter need not be removed, but it is
not needed for this operation.
5, Start the cut slowly and hold work firmly to table to
prevent kickback or chatter. (Loosely held pieces will
sometimes vibrate against the table wher_ crosscutting,
which tends to bind the saw blade and dull the teeth.)
6. An auxiliary wOOd extension bolted to the miter gauge
greatly improves the gauge as a support. (See figure 65.)
Sandpaper glued to the extension will help prevent side
creep of thework.
7, If the work overhangs the saw table enough to sag al
each end, provide supportsthe same as in ripping opera-
tions. The stop rod on the miter gauge, or a stop block
BEVEL AND MITER CUTS
1. Bevels From 1 to 45 degrees are cut by tilting the saw
blade.
2. Operations are the same as for ripping or crosscutting,
but work should be extra well supported to prevent creep.
3. Miters are crosscutsat an angle to the edge of the work.
(See figure 67.) The miter gauge is set at the required
angle to make the cut. Here also, precautions must be
taken to prevent creep.
THE DADO HEAD
1. The dado saw or head is a special set of blades for
cutting grooves and dodoswith a bench saw. (See figures
68 and 69.) (Dado heads may be purchased at any
Sears Retail Store or Catalog Order House.) The head
consists of two solid, stiff outside blades, and a number
of inside chipper blades. The outside blades are 1/8-
inch thick; there is one 1/4-inch, two 1/8-inch, and one
1/16-inch chipper blades. With these blades, grooves
of I/g-inch, 1/4-inch can be cut and additional widths
increased in stepsof 1/6-inch up to a maximum of 13/16-
inch and amaximum depth of 1-3/8-inches.
NOTE: Outside bladescan be used alone, chip-
pers cannot.
2. When using a full set of dado blades, do not use the
fastened to the extension, is used to fix position of loose collar. The width of the dado can be reduced while
left-hand edge of Work for measuring length of piece using the loose collar and two or more passes can be
to be cut off. (See figure 66.) made with the work to obtain the desired width of cut.
Figure 67
I/E" OUTSIDE SAVV
/4"CHt PE -,
_ C H IPPERSARRANI _GED
_/,_TO FALL IN GULLETS'-z
_OF OUTSIDE SAWSII_
V/ Z_ co, ,
'_I r-_ TEETH
Figure 68 RAKERTOOTH Figure 69
22

3. A dado insert must be used to replace the standard table
insert. When using a full 13/16*inch dado set, the arbor
cannot be tilted to 45 degrees without touching the
insert. Do not attempt to operate in this position. Also
when the dado is set for the maximum depth of cut
(1-3/8-1nches), be sure to spinthe blade by hand before
turning on the motor to make sure the blade does not
strike the dado insert. Whenever two or more chippers
are used, stagger the swaged ends as evenly as possible
around the circumference. Fractional adjustments in
thickness of the head can be made by using paper
washers between the outside blades and chippers.
4. Dado head operations are much the same as those with
a standard blade. Since the dado head takes a larger
bite, the work should be held more firmly. It is agood
practice to use a hold-down jig like the one shown in
figure 70.
5. When a groove wider than the dado head is required,
make two or more passes, The best method is to use a
notched stop block to position each successive cut. (See
figure 71.) The block is fastened to edge of table where
it can be used to position work before starting the cut,
but in a position that will not permit contact with work
during the cutting operation. Space the cuts so they
overlap slightly.
6. When cutting a gain (a groove that is closed at one end)
use a stop block to fix the end of the cut. (See figure 70.1
To locate the stop, place the work alongside the dado
head in position in which it will be when cut is finished.
Then rig the stop at the end of the work. When cuffing
astopped groove (which is closed at both ends) also use
a starting block, as shown in figure 72. This is located
in same manner as the stop block,
SANDING
A sanding wheel can be mounted on the saw arbor and the
tilting arbor of the saw" provides ahigh degree of versatility
for fine sanding operation. (See figure 73.)
STABmL|ZmNG WASHERS
FOR THmN BLADES
Stabilizing washers should be used only with thin blades.
When using these washers, the maximum depth of cut cannot
be obtained and the washers must be kept below the bottom
surface of the table insert.
Figure 71
Figure 72
Figure 70
//
Figure 73
23

procedures
Figure 74
SAW BASE
NSIDE|
BEARING RETAINER
\\
Figure 75
RELOCAT|NG THE TnLT HAND-WHEEL--
FROM LEFT SIDE TO RIGHT SIDE OF SAW
The design of this saw permits relocation of the tilt hand-
wheel by moving it from the left-hand side to the right-hand
side of the saw. Should the operator prefer this hand-wheel
on the right, the change maybe made as follows:
NOTE: Figures 74 and 75 show only the saw
base. The table and cradle have been left
out for darity.
1. Removal of Partsfrom Left-Ha nd Side. (See figu re 740
a. Loosen the set screw intilt hand-wheel with a5/32-
inch hex-L wrench and remove the tilt hand-wheel
from end of tilt screw. (See figure 74.)
b. Reach inside saw base from the rear and loosen two
set screws in each stop collar just enough to permit
the stop collars 1o rotate easily on tilt screw
c. Remove the stop collar located near the end of tilt
shaft.
d. Remove two No. 10 x7/1 6-inch pan-head screwsthat
secure the bearing retainers to the saw base with a
screwdriver.
e. Grasp 1he saw cradle by reaching nsde the base
from the rear end flit" the cradle until the end of
tiff screw is withdrawn into the base. The tilt bearing f.
shims will fall out and should be retrieved as they
must be re-lnstalled on the opposite side.
f. Slide the outsidebearing retainer off end of tilt screw
and tilt the cradle by hand (while guiding the end of
tilt screw into the hole) until the outer end of tilt screw g"
passes through the holein the saw base.
g. Reach inside the base with one hand and hold the
stop collar and inside bearing retainer and rotate the
2. instai_ing Parts on Right-Hand Side. (See figure 75.)
a. Insert the inner end of tilt screw through the hole in
right-hand side of saw base (figure 75) then reach
inside of base and slide the inner bearing retainer
on the tilt screw, with flat face of retainer toward the
tilt screw bearing. Start the stop collar on the threads
and rotate it a few inches onto the tilt screw.
b. Start the end of tilt screw into threads in saw cradle.
c. Continue to rotate the tiff screw clockwise into saw
cradle, while at the same time rotating the stop collar
outward on tilt screw, until the outer end of flit screw
emerges from the hole inside saw base. it may be
necessary to grasp the saw cradle and tilt it by hand
enough to permit the outer end of tilt screw to pass
through the hole and emerge into the base.
d. Slide the outside bearing retainer onto the tilt screw
(oriented so it wilt fit the bearing contour) and rotate
the tilt screw counterc!ockwise until the end passes
through the hole in the base.
e. Work the outside bearing retainer into position on
the bearing and inside the base and siide the inside
bearing retainer over the stop cellar and into position
on the bearing.
Hold inside and outside hearing retainers in place
against the base and start two No. 10 x 7/16-1nch
pan-head screws into their threads in the inside bear-
mg retainer. Leave the screws loose at this time.
Slide the same number of tilt bearing shims between
the bearing retainers as were removed from the same
location and tighten the two No. 10 x7/16-inch pan-
head screws securely.
tilt screw counterclockw se unt I free of the threads in h. Install the t!!t, hand-wheel and tighten the set screw
agalnstthe riot on ena of tilt screw
saw cradle. White still holding the inside retainer and
stop collar, continue to rotate the tilt screw until the i. Refer to "'Adjust Step Collars," under "'Assembly and
stop collar is free of the threads. Withdraw the tiff Adjustments' and adjust the saw b ade to stop at
screw from the hole in the base. 0 and 45 poslhons as described.
24

bl h °
frou e s ootung-accessornes
TROUBLESffOOTJHGCHART
TROUBLE
Motor will not run
Excessive vibration
Cannot make square cut
when crosscuMing
Cut binds, burns or
sta||s motor when
rippQng
PROBABLE CAUSE
1. Defective On-Off switch
2. Defective switch cord
3. Defective switch box
receptacle
4. Motor protector open-
circuit, broken
5, Low voltage
6. Defective motor
I. Improper motor tension
2. Blade out of balance
REMEDY
1, Miter gauge not
adjusted properly
2. Blade not properly
aligned
1. Dull blade with
improper tooth set
2, Warped board
3. Blade not properly
aligned
4. Rip fence not
properly aligned
5. Guard splitter out of
alignment
1. Stop collars not
properly adjusted
I. Dirt and need of
lubrication
I. Replace switch,
2, Replace switch cord,
3. Replace switch box receptacle,
4,
5.
6.
1.
2.
1.
2.
1.
Reset protector by pushing on red button, located on side
of motor (indicated by audible click).
Check power line for proper voltage.
Repair or replace the motor,
See "'Adjusting Pivot Arm Screw" under "Periodic
Maintenance Operations".
Use a different blade.
See "Check and Adjust the Miter Gauge" under
"Assembly and Adjustments".
See "Align Saw Blade with Table Grooves" under
"'Assembly and Adjustments",
Check set and sharpness of blade.
2. True up material,
3, See "Align Saw Blade with Table Grooves" under
"Assembly and Adjustments",
4. See "Check and Adjust the Rip Fence" under "Assembly
and Adjustments".
5. Align splitter with saw blade.
Blade not true at O° 1. See "Adjust Stop Collars" under "'Assembly and
or 45 °Adjustments".
Tilt and elevating screw 1. See "Lubricate Saw" under "Periodic Maintenance
hand-wheels turn hard Operations".
RECOMMENDED ACCESSORIES
Item Cat No.
BENCHSAWKNOW-HOW
BOOKLET.............. 9-2929
FLOORBASE ........... 9-2227
FLOORBASE ............. 9-1071
RUBBERWHEELS............ 9-2244
TABLEEXTENSION........ 9.28925
STOPRODS................ 9-29924
HOLDDOWNCLAMP ....... 9-29928
Item Cat.No. Item Cat.No.
HOLDDOWNSET 9.3230 MOLDINGHEADONLY- 43/_" 9-3200
UNIVERSALJIG ............. 9-3231 MOLDINGHEAD--5s/s"9-3215
TAPERJIG .......... 9.3233 DADOHEAD- 7" ....... 9-3257
DADOiNSERT ........ 9-29958 DADOHEAD- S" 9-3249
MOLDINGINSERT ........ 9-29959 BLADESTABILIZERS 94952
MOLDINGHEADSET- 7" 9-3217 SANDINGWHEEL........ 9-22723
MOLDINGHEADSET- 4¾" 9-3221 SAWBLADES....... SEECATALOG
MOLDINGHEADONLY- 7" 9.3214
The above recommended accessories are current and were
available at the time this manual was printed.
25

repair parts
I2
:102
101
J
18 19
87 23
10-iNCH TULTING ARBOR BENCH SAW
MODEL No. 113.29943
22
15 14
23
109
65
63
Figure |
108
51
45 46
/
26 49
26

10-_NCH TILTING ARBOR BENCH SAW, MODEL No. 113.29943
WHEN ORDERING REPAIR
IN THiS LIST:
1. THE PART NUMBER
2. THE PART NAME
PARTS, ALWAYS GIVE THE FOLLOWING iNFORMATiON AS SHOWN
3. THE MODEL NUMBER -- 113.29943
4. THE NAME OF ITEM .....10dNCH BENCH SAW
Always order by Part Number .....nat by Key Number
N5l
4
5
6
7
8
9
t0
11
27
28
29
30
31
32
33
34
,, , ,,
Part !
No. ]Description
62387
62287
62074
144630
62288
140879
62289
62290
60049
62228
62209
62212
133063
62211
62011
114604
115120
120399
114605
118774
_26218
30426
30419
6532
106751
30442
30420
3509
37158
35O8
448611
30646
63017
6362
t
FIGURE | PARTS LIST
No. !Pad
,No.
35 160175
36 13540
37 423571
38 60062
39 60205
40 60206
l
41 J6301i
42 I 62295
43 137899
44 i 62296
45 30653
46 6017g
47 37838
48 62297
49 448633
50 62298
51 62299
52 62300
53 37861
54 448001
55 102570
56 62250
57 111688
58 62301
60 602O7
61 71046
62 62302
63 145189
64 j62303
65 t 62304
62305
66 J 454896
67 J 60045
tDescripHon
_;Blade, Ch;sei Too_h
Wrench, Arbor
*_._rew, Math. w/Ext. Tooth
LockwQsher, 3/8-16 × 1", Hex_ Hd.
_Washer, .380 x 3/4 ×3/32 '_, Stee!
Spring, Screw Ctamp
_Screw, Tapping, 1/4-20 × 1-1/2",
Hexo Washer Hd., SteeI
Washer, Screw CIamp
Spacer, Screw Clamp
Nut, Tilt
Screw, Lift
"'0" Ring
Washer, Lift Spring
*Washer, Plaln, .629 x 7/8 x 1/64 '_,
Steel
Pointer, Lift 1
_'Screw, Tapping, No_ 10-32 x 3/8 _,
Hex_ Hd.
Base
Switch
Panel Assembly, Trim
Key
'_Screw, Tapping, No. 6*32 x 1/4 _',
Pan Hd.
Screw, Set, t/4-20 x 7/]6 _,
Socket Hd., Cup Pt.
Crank Assembly
*Screw, Type B, No. 8 x 5/!6",
Pan Hd.
Card
Rellef,Cable Strain
Connector, W_re
Outlet
*Screw, Type B, No. 10 x 7/16",
Pan Hd.
Retainer, inside Bearing
Sh_m, (,005 Thick) _!
Shim, (.010 Thick)
Screw, Mech, Hex. Ind. Hd.o
3/8-16 x 1/2 |
J
Ring, Retaining
Guard Assembly, Saw (See F;g. 4)
8nsert Assembly, Table
Catch, Spring
*Screw, Mack, No. 4 x 5/16",
Flat Hd°, Steel
insert, Table
*Screw, Set_ No_ 10_32 x 3/16 °_,
Hex. Socket kid., C_p Pt.
Table
Fence AssembJy, Rip (See Fig_ 1)
_Screw, Self-Tapping,
No. 4-40x 3/16", Pan Hd.
Tape, Fence
Gauge AssembJy, Miter (See Fig. 3)
Rack, Table
*Screw, Mech., 1/4-20 x 2 rr,
Rd. Hd, SIott_d
Bar, Fence Guide
Spacer, Fence Guide Bar
Lockwasher, External 1/4"
*Nut, He×., 1/4-20 x7/16 x 3/t6 _,
Steel
*Nut, Square, 5/16 x9/16 x7/32 I'
Lockwasher, External 5/16"
*Washer, 11/32 x 7/8 x 1 /16 r_, Steel
*Baff_ Carriage, 5/16-18 x 3/4"
Trunnion, Table
Housing Assembly, Arbor:
Consisting of items 24, 25, 26, 27,
28, 29, 30, 31 and 32
Arbor Assembly
Key, Arbor
Ring, Retaining
Housing, Arbor
Bearing, Arbor
R_ng, Bearing Retainer
Retainer, Arbor Bearing
*Screw, Tapping, No. 8_32 x 3/8",
Hex. Ind. Hd., Steel
Pul|ey
Cotlar, Loose
Nut, Arbor
27

repair
10-INCH TILTING ARBOR BENCH SAW, MODEL No. 113.29943
FIGURE IPARTS LIST-- (Continued)
Key
No.
69
72
73
74
75
76
77
78
79
80
81
82
83
84
85
86
87
9O
62306 "Bearing
62307 Retainer, Outside Bearing
37900 !Collar, Stop
62308 Screw, Tilt
62204 I Clip, Cord
30767 Washer, End Play (.005 Thick)
1
62309 Cradle Assembly
62310 ' Cradle
6534 _Pin, Pivot
9415812 *Screw, Mach., 5/16-18x5/8",
'Hex. Ind. Hd.
62312 iLink
37945 tBelt, V-Type, 1/2 ×41"
60044 iRing, Retaining
62293 ' Guard, Belt
91 62294
92 62292
93 60025
94 62111
95 273336
96 102582
97 436693
98 38747
99 38746
100 62257
101 38845
102 60195
103 60194
104 37836
105 30505
106 37837
107 114606
108 63467
109 63054
110 "115545
_11 62378
112 62376
A 62386
Description
Clamp, Ring
Support Guard
*Screw, Mach., 5/16-18 x 1fr,
Hex. Ind. lid.
Rod, Splitter
Pin, Rail
Screw, Set, 5/16-18 x 1/2",
Socket Hd., Cup Pt.
*Screw, Mach., No. 8-32 x3/8",
Pan lid.
Plate, Cut Indicator
Washer, Spring
Housing, Cut Indicator
Shoe, Cut Indicator
*Screw, No. 4-40, Flat Hex. Socket
Rec. lid.
Wrench, Hex.-L (1/16 rt)
Wrench, Hex.-L (3/32 It)
Wrench, Hex.-L (1/8")
Wrench, Hex.-L (5/32")
Lackwasher, Ext. Tooth
Cap, Flag Terminal
Ring, Retaining
mLockwasher, No. 10
"Cord
mOutlet
rOwners"Manual (Not Illustrated)
*Standard Hardware item--May be Purchased Locally.
tStock Item -- may be secured through the Hardware Departments of most Sears or Simpsons-Sears Retail Stores or
Catalog Order Houses.
mUsed on Canadian Model only.
SEARS, ROEBUCK AND CO. oSIMPSONS-SEARS LIMITED
28

10-NHCH TILTING ARBOR BENCH SAW, MODEL No. 113.29943
RmP FENCE ASSEMBLY--62290
12
13
Figure 2
FIGURE 2 PARTS LIST
1
62290
423350
2 62126
360049
4 62052
562051
6 62046
7436732
8 62291
9 62127
10 62130
11 62131
Description
Fence Assembly, Rip
*Screw, Mach., w/Ext. Tooth
Lockwasher, 3/8-t 6 x 1/2 It,
Hex. Hd., Steel
Channel Assembly, Fence
*Screw, Tapping, No. 4-40 x 3/16",
Pan Hd. Slotted, Cad. PI, Steel
Retainer, Fence Index
Indicator, Fence
Shoe, Cam Face
*Screw, Mach., No. 10-24 x 1/2",
Pan Hd. Slotted, Cad. PI. Steel
Handle, Fence Lock
Head, Fence
Bushing, Fence Adjusting Shaft
Spring, Fence Adjusting Shaft
* Standard Hardware Item -- May be Purchased Locally.
Key Part
No. No. Description
12 60067
13 62132
14 62049
15 62048
16 60230
17 30505
18 62129
19 62050
20 62047
21 62128
22 62055
23 62073
24 37837
25 60229
26 62053
*Screw, Set, 1/4-20x 1/4"0 Hex.
Socket Hd., Cup Pt.
Knob, Fence Adjusting
Spring, Squaring Pawl
Pawl, Fence
*Screw, Set, Lock, 1/4-20 x 1"
*Wrench, Hex.-k (1/8 _)
Shaft Assy., Fence Adjusting
Pin
Pin
Rod, Lock
Spring, Fence Lock
Lock, Fence
*Wrench, Hex.-L (5/32 rr)
Screw, Set, Lock, 5/16-18 x 1/2"
Support, Fence Lock
29

10-INCH TILTING ARBOR BENCH SA_f, MODEL No. 1 13.29943
MITER GAUGE ASSEMBLY -- 62209
J
1
13 12 ./
Figure3 _8"_-.-_ 7
2
3
FIGURE 3 PARTS LIST
Key
3
Part
62209 _";'Gauge Assembly, Miter
7!
3 893 Gauge, Miter
37895 Block, Miter Gauge Indicator
Key
No. No. , Description
8 *Screw, Mach., w/Lockwasher,
No. 8-32 x 5/8", Pan Hd. Slotted,
Cad. PI. Steel
9 139325 *Screw, Set, 1/4-20 x3/8 rr,
Hex. Socket Hd., Cone. Pt.
t0 62230 " Rod Assembly, Miter Gauge:
, , Consisting of Items 12, 13, 14
11 *Wrench, Hex.-L (1/8")
12 124824 _ *Nut, He×--5/16-18xl/2x3/16"
13 62225 Stud, Clamp
14 Stud, Pivot
* Standard Hardware Item- May be Purchased Loccilly.
tStock Item -- May be secured through the hardware departments of most Sears or Sl_mpsons-SearsRetail Stores or
Catalog Order Houses.
3O

10-_NCH TmLT|NG ARBOR BENCH SAV¢, MODEL No. 113.29943
GUARD ASSEMBLY SAW 62387
1
/
/
/
/
/
45\1
1
6
7
8
Figure 4
FIGURE 4 PARTS LiST
Key Part
No. No. Description
62387
160297
262391
362395
4 62389
562390
6 9414920
762136
862396
9 115120
Guard Assembly, Saw
Nut, Push
Pin, 1/4× 1-1/2"
Support, Guard
Guard, Saw
Pin, 1/4x 1-3/4 pr
*Washer, 17/64 x 5/8 x 1/16 r_
Spacer, Pawl
Pawl
*Nut, Hex, I/4-20 x 7/16 x 3/16 r_
Key Part
No. No.
10 62210
11 60204
12 62393
13 60017
14 62392
15 455481
!6 60004
17 62134
Description
Support, Splitter
*Screw, Thumb
Blade Assembly, Spreader
*Screw, Hex Ind. Hd., 1/4-20 x 5/8 tr
Pin, 1/4x1"
*Pin, Roll, 3/16 x 15/16"
Ring, Retaining, 1/4"
Spring, Paw1
*Standard Hardware Item- May be Purchased Locally.
31

I Sears
owners
manual
Soaps
SER VICE
is at
YOUR
SERVICE
wherever YOU
live or move
in the U.S.A.
How to ORDER Repair Parts
The Model Number will be found on a plate attached to your
Saw at the rear of the base. Always mention the Model Number
when requesting service or repair parts for your 10 Inch Bench
Saw.
All parts listed herein mav be ordered through SEARS,
ROEBUCK AND CO. or SIMPSONS-SEARS LIMITED. When
ordering parts by mail, selling prices will be furnished on
request or parts will be shipped at prevailing prices and you will
be billed accordingly.
WHEN ORDERING REPAIR PARTS, ALWAYS GIVE THE
FOLLOWING INFORMATION AS SHOWN IN THIS LIST.
1. The PART NUMBER
2. The PART DESCRIPTION
3. The MODEL NUMBER 113.29943
4. The NAME OF ITEM - 10 INCH BENCH SAW
L
Your Sears merchandise takes on added value when you
discover that Sears has over 2,000 Service Units through out the
country. Each is staffed by Sears-trained, professional
technicians using Sears approved parts and methods.
Sears, Roebuck and Co., Chicago, Ill. 60607 U.S.A.
and Simpsons-Sears Limited, Toronto
Form No. SP3947-2 Printed in U.S.A. 8/73