Craftsman 137216200 User Manual SCROLL SAW Manuals And Guides L0312350
CRAFTSMAN Saw Scroll Manual L0312350 CRAFTSMAN Saw Scroll Owner's Manual, CRAFTSMAN Saw Scroll installation guides
User Manual: Craftsman 137216200 137216200 CRAFTSMAN SCROLL SAW - Manuals and Guides View the owners manual for your CRAFTSMAN SCROLL SAW #137216200. Home:Tool Parts:Craftsman Parts:Craftsman SCROLL SAW Manual
Open the PDF directly: View PDF .
Page Count: 24
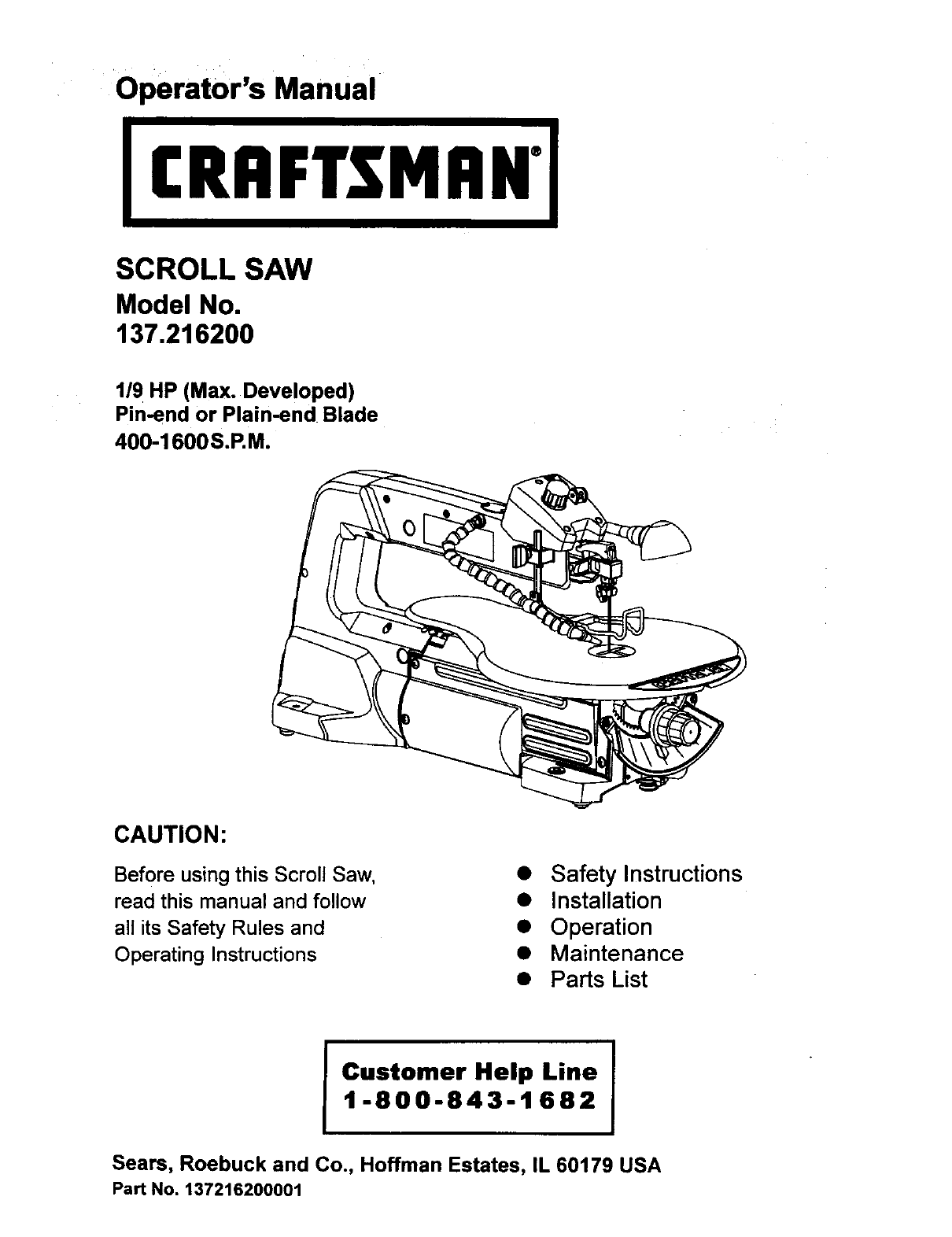
Operator's Manual
i CRRFTSMRN'J
SCROLL SAW
Model No.
137.216200
1/9 HP (Max. Developed)
Pin-end or Plain-end Blade
400-1600S.RM.
CAUTION:
Before using this Scroll Saw,
read this manual and follow
all its Safety Rules and
Operating Instructions
• Safety Instructions
• Installation
• Operation
• Maintenance
• Parts List
Customer Help Line
1-800-843-1682
Sears, Roebuck and Co., Hoffman Estates, IL 60179 USA
Part No, 137216200001

SECTION PAGE
Product Specifications ............................................................................................................... 2
Warning .................................................................................................................................... 2
Safety Instructions ..................................................................................................................... 3
Accessories and Attachments ...................................................................................................... 6
Carton Contents ......................................................................................................................... 6
Know Your Scroll Saw .................................................................................................................................. 8
Glossary of Terms ...................................................................................................................... 9
Assembly and Adjustments ......................................................................................................... t0
Bsalc saw Operation..................................................................................................................... 14
Maintenance .............................................................................................................................. 17
Troubleshooting Guide ............................................................................................................... 18
Parts ........................................................................................................................................ 20
FULL ONE YEAR WARRANTY
if this Scroll Saw fails due to a defect in material or workmanship within one year of date of purchase,
Sears will at its option repair or replace it free of charge.
Return this Scroll Saw to a Sears Service Center for repair, or to place of purchase for replacement.
This warranty gives you specific legal rights, and you may also have other rights which may vary from
state to state.
Sears, Roebuck and Co., Dept. 817 WA, Hoffman Estates, IL 60179
Some dustcreated by power sanding sawing,grinding,drillingand otherconstructionactivitiescontainschemicals
knownto the state of Californiato cause cancer, birthdefectsor other reproductve harm Some examplesof these
chemicalsare: •Lead from lead-basedpaints
• Crystalline silicafrom bricks, cement andother masonry products
• Arsenic and chromiumfrom chemicallytreatedlumber
Your riskfrom these exposuresvades, dependingon howoftenyoudothistype of work. To reduceyour exposureto
these chemicals,work in a well ventilatedarea andworkwith approvedsafetyequipmentsuch as dustmasksthat are
speciallydesigned to filter out microscopicparticles.
Motor
Power source ......... 120 V, 60 Hz, 1.4Amp., Ac
Speed ...................... 400 ~ 1600 spm
Speed control .......... Electronic
Blade
Type ..................... Pin-end or Plain-end
Depth of Throat ....... 20-114"
Blade Stroke .......... 3/4"
Depth of 45"Cut .... 1-1/8" Left; 3/4" Right
Depth of 90"Cut .... 2-1/4"
Table
Size ...................... 23-23/32" X15-11/16"
Tilt ........................ 45"Left; Right
SAWDUST BLOWER ...... Yes
To avoid electrical hazards, fire hazards, or damage to
the tool, use proper circuit protection. Use aseparate
electrical circuit for your tools.
Your scrollsaw is wired at the factory for 120V operation.
Connect to a 120V, 15 AMP branch circuit and use a 15
Amp time delay fuse or circuit breaker. To avoid shockor
fire, replace power cord immediately if it is worn, cut or
damaged in any way.

GENERAL SAFETY INSTRUCTIONS
BEFORE USING THE SCROLL SAW
Safety is a combinationof common sense, stayingalert
and knowinghowto use your scrollsaw.
_k_ll_ [_
Toavoid mistakesthat could cause seriousinjury,do not
plugthe ScrollSaw in untilyou have road and
understoodthe following.
1. READ and become familiar with the entire Operator's
Manual. LEARN the tool'sapplication,limitationsand
possiblehazards.
2. KEEP GUARDS IN PLACE and inworkingorder.
3. REMOVE ADJUSTING KEYS AND WRENCHES.
From the habitof checkingto see that keysand
adjustingwrenches are removed from the toolbefore
turningON.
4. KEEP WORK AREA CLEAN. Clutterodareas and
benchesinviteaccidents.
5. DON'T USE IN DANGEROUS ENVIRONMENT.
Don't use power toolsin damp and wet locations,or
exposethem to rain. Keepwork area well lighted.
6. KEEP CHILDREN AWAY.All visitorsshouldbe kepta
safe distancefromwork area.
7. MAKE WORKSHOP CHILD PROOF withpadlocks,
master switches,or by removingstarterkeys.
8. DON'T FORCE THE TOOL. It will do the job better
and safer at the rate for which itwas designed.
9. USE THE RIGHT TOOL. Do not force toolor
attachmentto do a job for which itwas notdesigned.
10.USE PROPER EXTENSION CORD. Make sureyour
extensioncord is in goodcondition.When usingan
extensioncord, be sure to use one heavy enoughto
carrythe currantyour productwill draw.An
undersizedcord willresult ina drop inline voltage
and in lossof powerwhichwillcause the toolto
overheat.The table on page 5showsthe correctsize
to use dependingon cord lengthand nameplate
ampere rating.If in doubt, use the next heavier gauge.
The smallerthe gauge number,the heavier the cord
11.WEAR PROPER APPAREL. Do not wear loose
clothing, gloves, neckties, rings, bracelets, or other
jewelry which may get caught in moving parts.
Non-slip footwear is recommended• Wear protective
hair covering to contain long hair.
12.ALWAYSWEAR EYE PROTECTION. Any scrollsaw
can throw foreignobjectsinto the eyes and could
cause permanenteye damage. ALWAYSwear Safety
Goggles(notglasses)that comply withANSI Safety
standardZ87.1. Everydayeyeglasseshave only
impact-rosistancelenses. They ARE NOT safety
glasses.Safety Gogglesare availableat Sears.
NOTE: Glasses or gogglesnotin compliance with
ANSI Z87.1 couldcause seriousinjurywhenthey
break.
13.WEAR A FACE MASK OR DUST MASK. Sawing
operationproducesdust.
14.SECURE WORK. Use clamps ora vise to holdwork
when practical.It's safer than usingyour hand andit
frees bothhandsto operatetool.
15.DISCONNECT TOOLS before servicing;when
changingaccessoriessuchas blades, bits,cutters,
and the like.
16.REDUCE THE RISK OF UNINTENTIONAL
STARTING. Make sureswitchis inOFF position
before pluggingin.
17.USE RECOMMENDED ACCESSORIES. Consultthe
Operator'sManualfor recommendedaccessories.
The use of improperaccessoriesmay cause riskof
injuryto persons.
18.NEVER STAND ON TOOL. Seriousinjurycould
occur if the tool is tippedor if the cuttingtoolis
unintentionallycontacted.
19.CHECK FOR DAMAGED PARTS. Before further use
of the too!,a guardor other partthat is damaged
shouldbe carefully checkedto determinethat it will
operate properlyand performits intendedfunction -
checkfor alignmentof movingparts,bindingof
movingparts, breakage of parts,mounting,and any
otherconditionsthat mayaffect itsoperation.A guard
orother partthat is damaged shouldbe properly
repairedor replaced.
20.NEVER LEAVE TOOL RUNNING UNATTENDED.
TURN POWER "OFF". Don't leave tooluntilit comes
to a completestop.
21.DON'T OVERREACH. Keep properfootingand
balance at all times•
22.MAINTAIN TOOLS WITH CARE. Keep tools sharp
andclean for best and safest performance.Follow
instructionsfor lubricatingand changingaccassodes.
23.DIRECTION OF FEED. Feed work into a blade or
cutter against the direction of rotation of the blade or
cutter only.
24.DO NOT operatethe tool if youare underthe
influence of any drugs,alcoholor medicationthat
couldaffectyour abilityto use the toolproberly.
3

25.DUST GENERATED from certain materialscan be
hazardousto your health.Always operate the saw in
well-ventilatedarea and providefor properdust
removal.Use dustcollectionsystemswhenever
possible.
SPECIFIC SAFETY INSTRUCTIONS FOR
SCROLL SAWS
1. READ AND UNDERSTAND all safetyinstructions
and operatingproceduresthroughoutthe manual.
2. DO NOT operate the scrollsaw untilit is completely
assembled and installedaccordingto the instructions.
3. SHOULD any part of scrollsaw be missing,damaged,
or fail in any way, or any electricalcomponent fail to
performproperly,shut offthe switchand removethe
plugfrom the powersupplyoutlet.Replace missing,
damaged, or failed parts before resumingoperation.
4. IF YOU ARE NOT thoroughlyfamiliar withthe
operationof the scrollsaw, obtainadvice from your
supervisor,instructor,or other qualifiedperson.
5. SERIOUS INJURY couldoccur if the tooltipsover or
you accidentallyhitthe cuttingtool.Do notstore
anythingabove or near the tool.
6. AVOID INJURY from unexpectedsaw movement.
Place the saw on a firm level surfacewhere the saw
doesnot rock, and boltor clamp the saw to its
support.
7. YOUR SCROLL SAW MUST BE SECURELY
FASTENED to a standor workbench.If there is any
tendencyfor the standor workbenchto move during
operation,the standor workbench MUST be fastened
to the floor.
8. THIS SCROLL SAW is intended for indooruse only.
9. TENSION BLADE PROPERLY before startingthe
saw. Recheck and adjusttension as needed.
10.BLADE TEETH MUST POINT downwardtowardthe
table.
I1.TABLE MUST BE CLEARED of all debris before
operating saw, Do not perform layout, set up or
assemble work on the table when the saw is in
operation.
12.TO PREVENT INJURIES, avoid awkwardhandor
fingerpositions,where a suddenslip couldcause a
handto move intothe blade whenoperatingthe saw.
13.HOLD WORKPIECE FIRMLY againstthe scrollsaw
table top.
14.NEVER CUT MATERIAL that is too smallto be held
safely.
15.DO NOT USE dullor bent blades.
16.TURN THE SAW OFF AND UNPLUG THE CORD if
the blade bindsin the saw kerf whilebeingbacked
out of the workpiece,usuallycaused by sawdust
cloggingthe kerf. If thishappens, turnoff the scroll
sawand unplugthe powercord. Wedge open the kerf
and backthe blade outof the workpieca.
17.DO NOT feed the materialtoo fast whilecutting.Only
feed the workpieceat the rate the saw willcut.
18.TURN THE POWER OFF, remove the switchkey and
make surethe scrollsaw comes to a completestop
beforeinstallingor removingan accessory,and
beforeleaving the workarea.
19.DO NOT START the saw with workpiecepressing
againstthe blade. Slowly feed the workpieceinto the
movingblade.
20.WHEN CUTTING a large workpiece.MAKE SURE
the materialis supportedat table height,
21.EXERCISE CAUTION when cuttingworkpiecesthat
are roundor irregularly shaped, workpiecescan pinch
the blade.
22.ALWAYS release blade tensionbefore looseningthe
blade holderscrew.
23.MAKE CERTAIN tabletiltinglock is tightenedbefore
startingthe machine.
24.NEVER REACH underthe scrollsawtable when
motoris running.
25.CHECK FOR DAMAGED PARTS beforeeach use.
Checkfor alignmentof movingparts, bindingof
movingparts, breakage of parts, mountingor any
otherconditionsthat may affectoperation.Parts that
are damaged shouldbe properly repairedor replaced
before usingthe tool.
26.THINK SAFETY.
4

ELECTRICAL REQUIREMENTS
GROUNDING INSTRUCTIONS
IN THE EVENT OF A MALFUNCTION OR
BREAKDOWN, groundingprovidesa pathof least
resistance for electriccurrentand reducesthe risk of
electricshock.This tool is equippedwith an electriccord
that has an equipmentgroundingconductorand a
groundingplug.The plugMUST be pluggedinto a
matching receptaclethat is propertyinstalledand
groundedin accordancewithALL localcodes and
ordinances.
DO NOT MODIFY THE PLUG PROVIDED. If it will notfit
the receptacle,have the properreceptacle installedby a
qualifiedelectrician.
IMPROPER CONNECTION of the equipmentgrounding
conductorcan result in riskof electric shock.The
conductorwith green insulation(withor withoutyellow
stripes)is the equipmentgroundingconductor.If repair
or replacement of the electriccord or plugis necessary,
DO NOT connectthe equipment groundingconductorto
alive terminal.
CHECK witha qualified electrician orservice person if
youdo notcompletelyunderstandthe grounding
instructions, or if you are not sure the tool is properly
grounded.
USE ONLY 3-WIRE EXTENSION CORDS THAT HAVE
3-PRONG GROUNDING PLUGS AND 3-POLE
RECEPTACLES THAT ACCEPT THE TOOL'S PLUG.
REPAIR OR REPLACE DAMAGED OR WORN CORD
IMMEDIATELY.
GUIDELINES FOR EXTENSION CORDS
USE PROPER EXTENSION CORD. Make sure your
extensioncord is ingood condition. When using an
extension cord, be sure to use one heavy enoughto
carrythe currentyour productwill draw. An undersized
cord will cause a drop in linevoltage, resulting inloss of
power and cause overheating.The table belowshows
the correctsize to use dependingon cordlengthand
nameplateampere rating.If in doubt,use the next
heaviergauge. The smallerthe gauge number,the
heavier the cord.
This tool is intendedfor use ona circuitthat has a
receptaclelikethe one illustratedin FIGURE A.
FIGURE A showsa 3-prong electricalplugand
receptaclethat has a groundingconductor.If a proper
groundedreceptacle is notavailable, an adapter
(FIGURE B) can be used to temporarilyconnectthisplug
to a 2-contactgroundedreceptacle.The temporary
adaptershouldbe used onlyuntila properlygrounded
receptacle can be installedby aqualified technician.The
adapter (FIGURE B) has a rigid lug extendingfrom it that
MUST be connected to a permanent earthground,such
as a properlygroundedreceptacle box.The Canadian
ElectricalCode prohibitsthe use of the adapters.
CAUTION: In all cases, make certain the receptacleis
properlygrounded.If youare not sure, have a qualified
electriciancheck the receptacle.
This toolis for indooruse only. Do not expose to rain or
use indamp locations.
Fig, A 3-Prong Plug
JZ
! I Grounding Prong
ProperlyGrounded
_ 3-Prong Receptacle
Fig. B
Grounding Lug
-- Make Sure This
is Connected to a
Known Ground
_- 2-Prong
Receptacle
Be sure your extension cord is properly wired and in
good condition. Always replace a damaged extension
cord or have it repaired by a qualified person before
using it. Protect your extension cords from sharp objects,
excessive heat and damp or wet areas
V_llll hVdIlLVi[l_;111[l1:11;[el :l =t:l 1:1_I_-I[l] _[_ll] _.|I1[€! F±VIVL_
Use a separate electrical circuit for your tools. This circuit
must not be less than # 12 wire and should be protected
with a 15 Amp time delay fuse. Before connecting the
motor to the power line, make sure the switch is in the
OFF position and the electric current is rated the same
as the current stamped on the motor nameplate, running
at a lower voltage will damage the motor.
This tool must be grounded while in use to protect the
operator from electrical shock.
(When using 120 volts only)
Ampere Rating Total length of cord in feet
More than not more than 25' 50' 100' 150'
0 6 18 16 16 14
6 10 18 16 14 12
10 12 16 16 14 12
12 16 14 12 notrecommended
5

AVAILABLE ACCESSORIES UNPACKING AND CHECKING CONTENTS
•Toavoid injury,do notattempt to modify thistoolor
any accessoriesnot recommended for use withthis
tool.Any suchalteration or modificationis misuse
and couldresult ina hazardousconditionleadingto
possibleseriousinjury.
•Use onlyaccessories availablefrom Sears for this
scrollsaw. Followinstructionsthat accompany
accessories.Use of improperaccessoriesmay
cause hazards.
V_sityourSears Hardware Departmentor see the Sears
Powerand Handtool catalog for the following
accessodes:
ITEM
Pin-endsaw blades
Plain-endsaw blades
Scrollsaw handbook
Scrollsaw pattern kit
Sears may offer other accessoriesnot listed in this
manual.
See your nearest Sears storeor Power and Hand Tool
Catalogfor other accessories.
Do not use any accessoryunless youhave completely
read the instructionsor Operator's Manual for that
accessory.
•To avoidinjury,if any part is missingor damaged, do
not plugthe scrollsaw in untilthe missingor damaged
part is replaced,and assemblyis complete.
•To avoidfire and toxicreaction,neveruse gasoline,
naphtha,acetone, lacquer,thinner,or similarhighly
volatilesolventsto clean the scrollsaw.
Carefullyunpackthe scrollsaw and all carton contents.
Compare them to the following list and illustrationsto
make surethat they are all there.
To remove the scrollsaw from the carton, liftthe saw by
the back of the upperframe.
ITEM DESCRIPTION QUANTITY
A. Scrollsaw 1
B. Blades (2 Pin-endand 2 Plain-end) 4
C. Hex wrench 1
D. Knob 1
STAND:
E. Leg withleg flange 1
F. Legs 3
G. Top bracket 2
H. Top bracket 2
I. Bottom bracket (short) 2
J. Bottom bracket (long) 2
K. Foot pads 3
L. Bolt 1
MNut 1
N. Mounting hex Bolt 4
O. Flatwashers 4
P. Screws 20
Q. Nuts 24
6

UNPACKINGYOURSCROLL SAW
la • i
,• • p
L
B
tI
E
K
i
J
I
J
I
\/
F
J
¢
o
I
Q
I
\/
L M
I
I
G
V_
N
/
o
_lJ o
i
I
/
o
/
®Q
Q_
0
D
Ar_
0
0
0
J
H
P
I J
Q
7

Bladeguardassembly Variablespeed
lockknob controlknob
tensionlever
-Bladelockknob
adeguard
foot
Mountinghole
UpperArm
Work light
Worktable
Bevel scale
Table lock knob
Sawdust collection Blade storage
8

SCROLL SAW TERMS
BEVEL SCALE- Represents the degree of table angle,from
0"to45", when the table is tiltedfor bevel cutting.
BLADE GUARD ASSEMBLY - Guards the blade arid keeps
your workpiece from rising. Helps protect fingers from blade
contact.
BLADE GUARD ASSEMBLY LOCK KNOB - Allowsyou to
raise or lowerthe foot, and lockit at the desiredheight.
BLADE HOLDERS - Retain and positionthe blades.
BLADE STORAGE - Providesconvenient easy access to
extrablades orwrenches.
QUICK RELEASE TENSION LEVER - Quicklyloosensand
retightensthe blade to its original tension. The tension Lever
quicklysets and resets the blade tension when performing
interiorcuttingoperationsor changing blades.
SAWDUST BLOWER - Keeps sawdustfrom coveringthe line
of sightfor more accurate cuts. The best results occur when
the blower tubeis directedtoward the blade and workpiece.
SAWDUST COLLECTION PORT - Allowsvacuum
attachmentsor hose to be used to remove the sawdustfrom
underthe table and base.
TABLE LOCK KNOB - Securelylocks the table at the angle
desired for bevel cutting.
VARIABLE SPEED ON/OFF CONTROL KNOB - Variable
switchdial allows greater versatilitywhen cuttinga varietyof
materials. Pull the controlknobOUT to turn the scrollsaw ON.
Adjustthe speed to the desired setting, between 400 to1600
strokesper minute (SPM), by turningthe controlknob
clockwise or counter clockwise. Push the controlknobIN to
turnthe scroll saw OFF.
WOODWORKING TERMS (FIG. A)
KERF - The slot cutby the blade.
LEADING EDGE - The front edge of the workpiecewhich is
pushed intothe blade.
SAW BLADE PATH- Area or line of sightof the workpiece
moving in linetowardthe saw blade edge.
BLADE TOOTH SET - The total blade cutwidth, basedon the
distancefrom the outsidepoint of one bent toothto the outside
pointof the next benttooth.
TRAILING EDGE - The edge of the workpiecethat the
sawblade willcutthroughlast.
SURFACE - Top of workpiecabeing cut.
WORKPIECE - Material on which the cuttingoperationis
being performed.
FEED - Rate of movingworkpieceintothe blade.
DEFLECTION - Slightmovement of blade inthe horizontal
directionwhile the blade is movinginlineduringcutting
operations.This may be caused bythe blade followingthe
grain or the pathof least resistance.
Leading Edge
Kerr
Sudace
Saw blade Path
Workpiece Trailing Edge
9
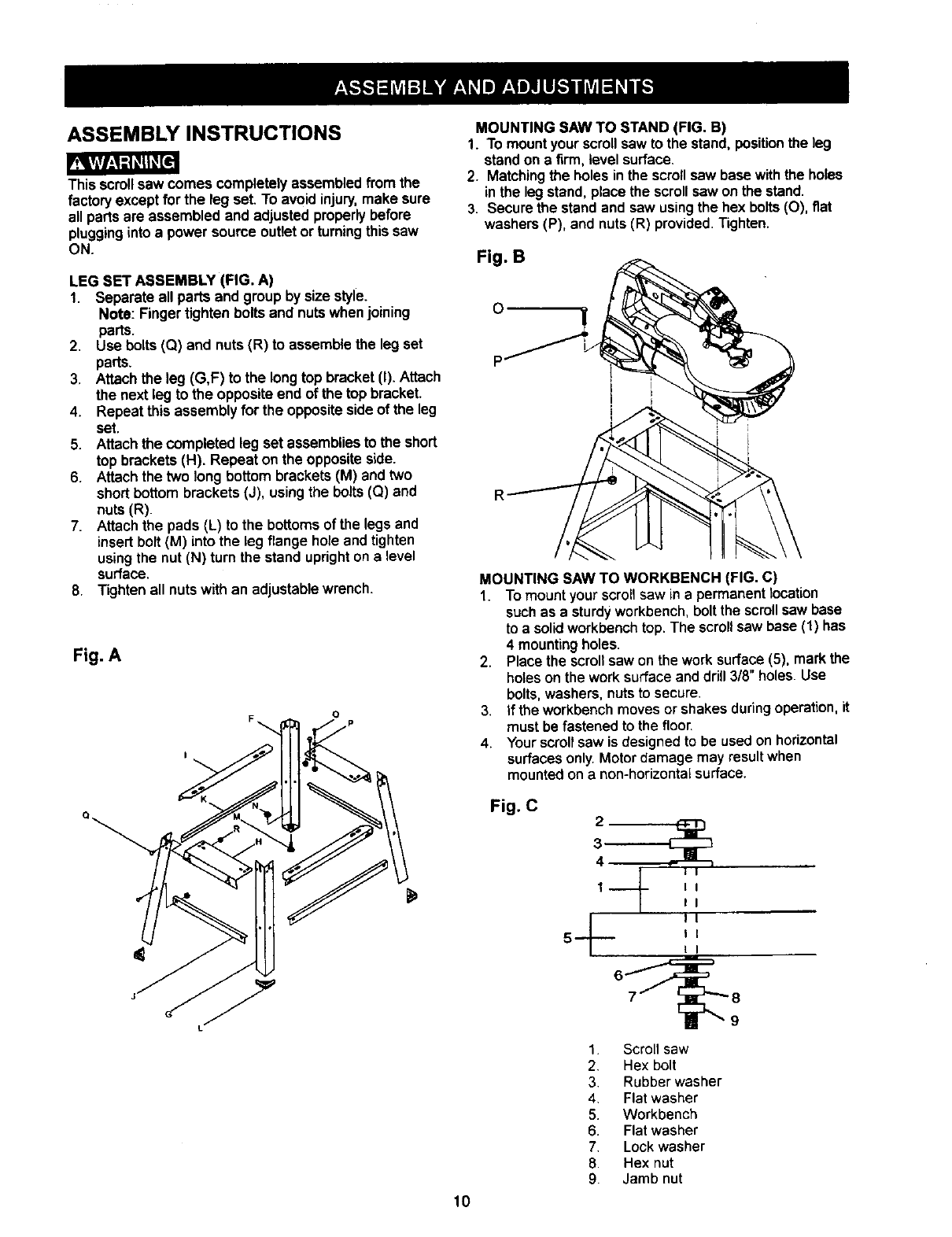
ASSEMBLY INSTRUCTIONS
This scrollsaw comes completelyassembledfrom the
factory except for the leg set. To avoid injury,make sure
all partsare assembled and adjusted properlybefore
pluggingintoa power source outletor turningthissaw
ON.
LEG SET ASSEMBLY (FIG. A)
1. Separate all parts and group by size style.
Note: Finger tightenbolts and nutswhenjoining
parts.
2. Use bolts (Q) and nuts(R) to assemblethe leg set
parts.
3. Attachthe leg (G,F) to the longtop bracket(I). Attach
the next leg to the opposite end of the top bracket.
4. Repeat thisassembly for the oppositeside ofthe leg
set.
5. Attach the completed leg set assembliesto the short
top brackets(H). Repeat on the oppositeside.
6. Attach the two longbottom brackets(M) and two
shortbottom brackets(J), usingthe bolts(Q) and
nuts (R).
7. Attachthe pads (L) to the bottomsof the legsand
insertbolt(M) into the legflange hole andtighten
usingthe nut (N) turn the stand uprighton a level
surface.
8. Tighten all nutswithan adjustablewrench.
Fig. A
F_ O
I
MOUNTING SAW TO STAND (FIG. B)
1. To mountyour scrollsaw to the stand,positionthe leg
standon a firm, levelsurface.
2. Matchingthe holes inthe scrollsaw base withthe holes
inthe legstand, placethe scrollsaw on the stand.
3. Securethe standand saw usingthe hex bolts(O), fiat
washers(P), and nuts(R) provided.Tighten.
Fig. B
O
P
MOUNTING SAW TO WORKBENCH (FIG. C)
1. Tomountyour scrollsaw in a permanentlocation
suchas a sturdyworkbench,boltthe scrollsaw base
to a solidworkbenchtop. The scrollsaw base (1) has
4mounting holes.
2. Placethe scrollsaw onthe worksurface(5), mark the
holeson the worksurfaceanddrill3/8" holes.Use
bolts,washers, nutsto secure.
3. If the workbenchmovesor shakes duringoperation,it
mustbe fastened to the floor.
4. Your scrollsaw isdesignedto be usedon horizontal
surfacesonly.Motordamage may resultwhen
mountedon a non-horizontalsurface.
lO
Fig. C
3
4
II I
II
@ "
5I K
I I
1. Scroll saw
2. Hex bolt
3. Rubber washer
4. Flat washer
5. Workbench
6. Flat washer
7. Lock washer
8. Hex nut
9. Jamb nut

BLADE STORAGE (FIG. D)
The bladestorage (1) is located underthe table. Pull out
the blade storage (1) to open. The blade storage
convenientlystoresyour hex wrenches, and bothPin and
Plainend blades.
Fig. D
SAWDUST COLLECTION PORT (FIG. E)
To keep your saw cutting efficiently,you mustkeep the
sawbase free of sawdustbuildup. For that purpose,this
saw has asawdustcollectionport (1) thatwill accepta
vacuumhose (notprovided).
If excessive sawdustbuildupdoes occurinsidethe saw
base, there is ametal plate (2) attachedby fourscrewsto
the left sideof the saw (as viewed from the front). Take
outthe screws and removethe metal plate. Clean outthe
sawdustmanuallyor witha wet]dryvacuum. Reattachthe
metal plate.
Fig. E
2
BLADE REMOVAL AND INSTALLATION
PLAIN-END BLADE REMOVAL AND INSTALLATION
This scroll saw accepts 5 inch plain-end or pin-end
blades to cut a wide variety of materials.
Plain-end type blades are recommended whenever fine,
accurate, and intricate work is being performed on 3/4" or
thinner material. It will take slightly longer to install and
tension the blade, but you will be able to use finer blades
for cutting a thinner kerf.
To avoid injury from accidental starting, always turn the
switch OFF and remove power cord plug from power
source before removing or replacing the blade.
PLAIN-END BLADE REMOVAL (FIG. F, G, H, I)
1.To removethe blade (1), first loosenthe bladetension
by liftingthe quick releasetensionlever(2) locatedon
the saw's bladearm (3). (Fig, F)
Fig. F
2. Loosen the upper blade holder (4) by turning the quick
release knob (5) counterclockwise(Fig. G).
Note: The hex set screw (6) onthe left sideis used
for fineadjustmentsand onlyneedsto be adjustedff
the blade is not perpendicular to the table.
Fig. G
6
3.Tilt the table to 0° and tightenthe bevel knob (7).
Loosen the lower blade holder screw (9) underthe
table on the left sideof the lower blade holder (8) by
turning counterclockwise. (Fig+H)
Fig. H
9
\,l
11

4.Removetheblade(1),from the upper (4) and lower
blade holders(8) by pullingforward and liftingthe blade
throughthe access hole (10) in the table (11). (Fig. I)
Fig. I 2
1
10
(3
PIN-END BLADE REMOVAL AND INSTALLATION
To preventpersonalinjury, always turnthe saw OFF and
disconnectthe plugfrom sourcebefore changingblades
or makingadjustments.
Pin-end type blades are thicker for stability and for faster
assembly. These blades are required for faster cutting of
material 3/4" thickness or greater. Also, use whenever
less precision or thicker kerf cutting is acceptable.
Note: When installingpin-end blades, the set screws
located on the upperand lower blade holdersshouldnot
be over or undertightened.The slotmustbe slightly
wider thanthe thicknessof the blade.After the blade is
installed,the blade tension mechanismwill keep the
pin-endin place.
PIN-END BLADE REMOVAL (FIG. J, K)
1. To remove the blade (1), loosen the tension by lifting
up the quick release tension lever (2) (Fig, J)
Fig. J
PLAIN-END BLADE INSTALLATION (FIG. F, G, H, I)
CAUTION: In order to avoid uncontrollable lifting of the
workpiece, the teeth of the blade should ALWAYS point
downward.
1. Install the blade (1) through the access hole (10) in
the table (11) with teeth pointing down.
2. Insert the new blade (1) into the lower blade holder
slot (13), then tighten the hex set screw (8). (Fig. I)
3. Tilt the table to the 0°bevel setting and lock the
bevel knob (7). (Fig. H)
4. Insert the other end of the blade into the upper blade
holder slot (12) and then tighten the quick release
knob (2) (Fig. G).
Note: Apply slight downward pressure against the
upper blade arm (7) when installing the blade into the
upper blade holder. (Fig. K)
5 Tighten the tension on the blade (1) by turning the
quick release lever (2) clockwise. Push the lock lever
downward. Check the tension on the blade. If too
loose, turn lever clockwise; do not make too tight or
blade will easily break in use. (Fig. F)
Note: The quick release lever handle must always be
clown to make the tension adjustments. Release the
quick release lever upward only during blade
changing operations If the blade is over-tightened,
the lever is difficult to lower
2,
3.
Remove the blade (1) from the upper (3) and lower (4)
blade holder by pulling it forward to release, then lift
the blade through the access hole (5). (Fig. K)
Fig. K
J j5
[_ 4
Tilt the table (6) to a 45 angle and lock the bevel
lock knob to view lower blade holder (4). (Fig. K)
Note: Appiy slight downward pressure on the upper
blade arm (7) of the saw when removing the blade
from the upper blade holder.
12

PIN-END BLADE INSTALLATION ( FIG. L,M )
CAUTION: In orderto avoid uncontrollableliftingof the
workpiece, the teeth of the blade shouldalwayspoint
downward.
1. Install the blade (1) by insertingone end of itthrough
the access hole (6) or throat plateinthe table. Hook
the lower blade pin inthe pinrecess in the lower
blade holder (5) and then the upperblade pin inthe
upperblade holder (4)(Fig. L).
Fig. L
16
7
BLADE GUARD ASSEMBLY ADJUSTMENT (FIG. N)
When cuttingat angles,the bladeguard assembly(1)
shouldbe adjustedso it is parallelto the table and rests
fiat abovethe workpiece.
1. Toadjust,loosenthe screw(2), tiltthe foot so it's
parallelto table and tightenthe screw.
2. Loosenthe knob(3) to raise or lowerthe foot untilit
just restson topof the workpiece.Tightenknob.
Fig. N
2
2. Check to see that the pins are properly located in the
upper (4) and the lower (5) blade holders and move
the table (7) to the 0° bevel position by unlocking
the bevel lock knob.
3. To tension the blade (1), lower the quick release
tension lever (2). Check the tension on the blade; if
tension is too tight, turn the levercounterclockwise. If
tension is too loose, turn the lever clockwise (Fig. M).
Note: If the blade is over tensioned, the lever will be
difficult to lower and could result in damage to the
blade holder or blade arm assembly.
Fig. M
SAWDUST BLOWER (FIG. O)
The sawdustblower(1) should be positioned to point at
the blade and workpiece to blow sawdust out of the
line-of-sight when cutting. It is not designed to blow all of
the sawdust off the table.
Fig. O
.3

BLADE SELECTION (FIG. P) VARIABLE SPEED CONTROL ONIOFF SWITCH
P_kVlVhl;]_qLr_q_
Toavoid injuryfrom accidentalstarting,alwaysturn the
switch"OFF" and unplugthe scrollsaw before moving,
replacingthe blade, or making adjustments.
This scrollsaw accepts 5" lengthbladeswith awide
varietyof blade thickness and widths. The type of
materialand intricaciesof cuttingoperations(size of
radiusor curve)will determine the numberof teeth per
inch.As a general rule,always select the narrowest
bladesfor intricatecurve cuttingand the widestbladesfor
straightand large curve cuttingoperations.
The following table representssuggestionsfor various
materials.When purchasingblades, referto the back of
the packagefor the best use of blades and speeds on
variousmaterials.Use thistable as a guide, but practice
andyour ownpersonal preference willbe the best
selectionmethod.
Fig. P
9.5 - 15 3O - 4815- 28
TEETH/
INCH
TPI*
9.5-15
15-28
3048
BLADE BLADE
WIDTH THICKNESS
INCH INCH
0.110 0.018
.055-.110 .010-.018
.024-.041 .012-.019
*TPI: Teeth per inch
** SPM: Strokes per minute
BLADE/
SPM** MATERIAL CUT
Medium turnson
400-1200 114"to 1-314"wood,
soft metal and
hardwoods
Small turnson 1/8"
800-1800 to 1-1/2" wood, soft
metal, hardwoods
Use very slow
Varies speeds on non-
ferrous metals and
hardwoods
Note: When using blades, sometimes speeds must
change to compensate for smaller curves, radii, or
smaller diameters. Thinner blades will have more
possibilities for blade deflection when cutting angles
which are not perpendicular to the table. Read BASIC
SCROLL SAW OPERATION for more suggestions.
Note: The blade must be installed with the teeth pointing
downward, as shown in FIG. P, to prevent the workpiece
from being pulled upward by the saw blade action.
For yourown safety,always push the controlknobOFF
whenthe scrollsaw is notin use.Also, inthe case of
powerfailure pushthe knob OFF. Removethe plugfrom
the power sourceoutletto avoidaccidentalstarting.
The variablespeed controlallowsgreater versatilityto cut
a varietyof materialssuchas wood,plastics,non-ferrous
metals, etc. Dependingon the hardness and thicknessof
material,the saw speed shouldbe reduced to allowthe
blade teeth to remove cut materialfrom the kerf.
REPLACING THE BULB
1. Use only a (10 watt maximum), candelabra base bulb.
Turnthe lightswitchOFF and unplugthe saw.
2. Removeold bulb. Replace new bulbintosocket.
VARIABLE SPEED SWITCH (FIG. Q)
Your saw is equipped with a variable speed dial (1).
Adjust the blade stroke rate by rotating the dial. To
increase speed, rotate dial clockwise.To reduce speed,
rotatedial counterclockwise.
ON/OFF SWITCH (FIG. Q)
To turn power ON or OFF push the power switch (2).
OVERLOAD BREAKER (FIG. Q, R)
When the motor becomes too hot during operation,the
overloadbreaker (3) will cause the motor to stop
automaticallyto preventdamage to the motor.Pushinon
the toggleswitch(2) to turn saw OFF and do notrestart
untilthe motorhas hadtime to coot.Push inon the
breaker switch(3) and switchthe toggleswitch(2) to ON
to startthe saw
Fig. Q 2
f
Fig. R
14

RECOMMENDATIONSFORCUTTING
1, When feeding the workpieceintothe blade do not
force the leadingedge of the workpieceintothe blade
becausethe blade will deflect, reducingthe accuracy
of cut and possiblybreakingthe blade.Allow the saw
to cut material by guidingthe workpieceintothe
blade as it cuts.
2. The blade teeth cut material ONLY on the down
stroke.
3. Youmust guide the wood intothe blade slowly
becausethe teeth of the bladeare very smalland
wood is removedonly on the down stroke.
4. There is a learningcurvefor each personwhowants
to use thissaw. Duringthat periodof time it is
expectedthat some bladeswill break untilyoulearn
howto use the saw and receivethe greatestbenefit
from the blades.
5. Best resultsare achieved when cuttingwoodless
thanone inchthick.
6. When cutting wood thicker than one inch the user
must guide the wood very, very slowlyinto the blade
and take extra care not to bend or twist the blade
while cutting in order to maximize blade life.
7. Teeth on scrollsaw blades wear outand must be
replacedfrequentlyfor best cuttingresults.Scro, saw
bladesgenerally stay sharp for 1/2 to 2 hoursof
cutting.
8. To get accurate cuts be prepared to compensate for
the blade's tendency to follow the wood grain as you
are cutting.
9, This scrollsaw is intended to cutwood or wood
products.Preciousand non-ferrousmaterials perform
well on scrollsaws that have very slowspeed
capability,and shouldbe lubricated with machine oil
orbeeswax.
10. When choosing a blade to use withyour scrollsaw,
use very fine, narrow blades to scrollcut thin wood of
1/4-inch or less thickness. Use wider blades for
thicker materials but wider blades will reduce the
ability to cut tight curves.
11. Blades wear faster when cutting abrasive materials
likeplywoodor particleboard. Angle cuttingin
hardwoodsreduces blade toothset faster due to
blade deflection.
FREEHAND CUTTING (FIG. S)
To avoidinjuryfrom an accidentalstart,make Surethe
switchis in the OFF position and the plugis not
connected to the powe( sourceouUet.
1. Lay outdesired design, or securedesign to the
workpiece(1).
2. Raise the blade guardassembly(2) by loosening the
heightadjustmentknob (3).
3.
4.
Positionthe workpieceagainst the blade (3) and
lowerthe blade guard assemblyagainstthe top
surfaceof the workpiece.
Secure the blade guard assembly(2) by tightening
the heightadjustmentknob (3).
5. Remove the workpiecefrom the bladeprior to tuming
the scroll saw ON. Pull the speed control knob (4) out
and setthe desired speed by turning the control knob
clockwise or counterclockwise.
CAUTION: In order to avoid uncontrollable lifting of
the workpieceand to reduce blade breakage,do not
pullthe controlknob ON while the workpieceis
againstthe blade..
6. Slowly feed the workpieceinto the blade, pressing
the workpiece down against the table while cutting.
CAUTION : Do notforce the leading edge of the
workpieceinto the blade. The blade will deflect,
reducingaccuracyof cut,and may break.
7. When the cut is complete, move the trailingedge of
the workpiece beyond the blade guard foot. Push the
controlknob in to turn the scroll saw OFE
Fig. S
15

ANGLEcu'n'ING(FIG.T) RIPORSTRAIGHTLINECUTTING(FIG.U)
Toavoidinjuryfrom an accidentalstarting,make surethe
switchis in the OFF positionand the plugis not
connectedto the power source outletbefore moving,
replacingthe blade or making adjustments.
1.Lay outor secure design to workpiece(1).
2. Move the blade guardassembly (2) to the highest
positionby looseningthe heightadjustmentknob (3)
and retighten.
3. Tiltthe table (4) to the desired angle by loosening the
bevel lock handle (5) and moving the table to the
proper angle, using the degree scale (6) and the
pointer (7).
4. Tighten the bevel lock knob (5).
5. Loosen the blade guard screw (8), and tiltthe blade
guardto the same angle as the table (4). Retightan the
blade guard screw.
6. Position the workpiece on the left and right side of the
blade (9). Lower the blade guard assembly against the
surface by loosening the height adjustment knob (3).
7. Follow items 4-8 under FREEHAND CUTTING
OPERATION.
Fig. T
'\ 1
4
Toavoid injuryfrom an accidentalstarting,make surethe
switchis inthe OFF positionand the plugis not
connectedto the powersource outletbefore moving,
replacingthe blade or making adjustments.
Tools Needed
QUANTITY
2
1
1
DESCRIPTION
Small C-clamps
Ruleror measuring tape
12" Straight scrap of wood
(Thickness to match workpiece)
1. Raise the blade guard assembly (1) by loosening the
height adjustment knob (2) on the right side of the
upper blade arm. Position the straight edge (4)
parallel to the blade at the desired ripping distance.
2. Clamp the straight edge (4) to the table (5).
3. Recheck your measurements, using the workpiece to
be cut, and make sure the scrap wood is secure.
4. Position the workpiece against the blade and place
the blade guard assembly (1) against the top surface
of the workpiece.
5. Secure the blade guard assembly in place by
tightening the height adjustment knob.
6. Remove the workpiece from the blade prior to turning
the scroll saw ON. Pull the speed knob control out
and set the desired speed by turning the control knob
clockwise or counterclockwise.
CAUTION: In order to avoid uncontrollable lifting
of the workpiece and reduce blade breakage, do not
pull the control knob ON while the workplace is
against the blade.
7. Position the workpiece against the straight edge (4)
prior to touching the leading edge of the workpiece
against the blade (3).
8. Slowly feed the workpiece into the blade, guiding the
workpiece against the straight edge and pressing the
workpiece down against the table while cutting.
CAUTION: Do not force the leading edge of the
workpiece into the blade. The blade will deflect,
reducing accuracy of cut, and may break.
9. When the cut is complete, move the trailing edge of
the workpiece beyond the blade guard assembly.
Push the controlknob in to turn the scroll saw OFE
NOTE: When cutting a narrow workpiece use push
sticks.
Fig. U
16

INTERIOR CUTTING (FIG. V) ....
1. Lay outthe designonthe workpiece(I). DrillaI/4"
hole inthe workpiece. P_Wkvlv/_,Wd _11_[_
2. Release the tensionknob (2), and removethe blade (3).
Refer to BLADE REMOVAL AND INSTALLATION.
3. Place the workpieceon the saw tablewiththe
workpiecehole over the access hole(4) in the table.
4. Installthe blade (3) throughthe hole inthe workpiece
and access hole (4) and lower the quickrelease
tensionlever(2).
5. Followthe process, items 3-g, under FREEHAND
CUTTING OPERATIONS.
6. When finished making the interiorscrollcuts turn the
scrollsaw OFF, remove the blade from the blade holder,
and remove the workpiecefrom the table.
Fig. V
For yourownsafety,turn the switchOFF and removethe
plug from the power source before maintainingor
lubricatingyour saw.
GENERAL
An occasionalcoat of paste wax onthe worktable will
allowthe wood beingcut to glidesmoothlyacrossthe
worksurface.
MOTOR
1. If the powercord isworn, cut, or damaged in anyway,
have it replacedimmediately.
2. Do not attemptto oil the motor bearings or servicethe
motor internal parts.
UPPER ARM BEARINGS (FIG. W)
Lubricate the upperarm bearings after every 50 hoursof
use.
1. Carefully lay the saw on its side.
2. Loosenthe bushing withan 8mm hex key.
3. Squirt agenerous amount of SAE 20 (lightweight)oil (11
around the shaft end and bearing (2).
4. Let the oil penetrate the bearing assembly overnight.
5. Replace and tighten. Turnthe scroll saw over and
repeat on the other side.
Fig. W
17

TROUBLESHOOTING GUIDE
To avoid injuryfrom accidentalstarting,alwaysturn switchOFF and unplugthe scrollsaw before moving,
replacingthe blade or making adjustments.
Contact your Sears ServiceCenter if for any reasonthe motorwillnotrun.
PROBLEM CAUSE REMEDY
Breakingblades 1. Wrong tension. 1.Adjustbladetension.
2. Overworkingblades. 2. Reducefeed rate.
3. Wrong blade application. 3. Use narrowblade.
4. Twistingblade inwood. 4. Avoidsidepressureon blade.
Motorwill not run. 1. Defectivecord or plug. 1. Replace defectivepartsbefore usingsaw again.
2. Defectivemotor. 2. Call Sears Service Center.Anyattempt to repair
3. Blownovedoadbreaker, thismotor may create a HAZARD unlessrepair
is done bya qualifiedtechnician.
3. Pushthe motorswitchto the OFF position.Let
the motorcoo!.
Excessive vibration.
NOTE: There will
always be some
vibrationpresentwhen
the saw is running
because of motor
operation.
1. Improper mountingof
saw.
2. Unsuitablemounting
surface.
3. Loosetable or table
resting against motor.
4. Loose motormounting.
1. See mounting instructionsin this manualfor
proper mounting technique.
2. The heavier yourworkbenchis the less
vibrationwilloccur.Aplywoodworkbenchwill
notbe as goodwork surfaceas the same size
solidlumber.Use common sense inchoosinga
mountingsurface.
3. Tightenthe table lockknob.
4. Tightenmotor mountingscrew.
Blade not inline with 1. Blade holders not 1. Loosen cap screws holding blade holder to
blade arm motion, aligned, blade arms. Adjust position of blade holders,
Retighten cap screw.
18

19

20" SCROLL SAW MODEL NO. 137.216200
When servicinguse only CRAFTSMAN replacementparts. Use of nay other parts may create a HAZARD orcause
productdamage.
Any attempt to repair or replace electricalpartson thisscrollsawmay create a HAZARD unlessrepairis done bya
qualifiedservicetechnician. Repair serviceis availableat yournearestSears ServiceCenter,
ORDER ONLY BY MODEL NUMBER AND PART NUMBER
Key Pad No. Der.cdptlon Size Q_y Key Pad No. Descdpflon Size
1 11A00101 PLUNGER HANDLE 81 16721602 BELLOWS
2 2501MBDN31 FLAT WASHER _0X18-1 5 62 11A12901 PLUG HOUSING
3 14403301 SPRING 83 2636BBDA07 CR RE COUNT HD SCREW M4XO.7-8
4 11A00401 TENSION HANDLE B4 2504MZC004 EXTERNAL TOOTH LOCK WASHER
5 11AB0601 TILTING SCALE 55 2653MZDE11 CR RE TRUSS HO TAPPING SCREW M4X16*12
6 1 tA00701 TRUNNION 8RACKET 56 18515401 RETAINING RING
7 2668BBDA08 CI_ RE. PAN HD. SCREW M4X0.7-10 67 2620BSDC05 CR,RE PAN HO SCREW SWASHER M6X1 025
8 26171BBLB19 HEX SOC. HD. CAP BOLT M6X1 0-12 68 19A10701 PLUNGER HOUSING
9 2637BBDA70 CR RE. TRUSS HD SCREW M6X1,0-23 59 2617BBLC20 HEX.SOCKET HDCAP SCREWS M6XI 0-25
10 11A01101 NEEDLE POINTER
Oty
_'o__.2_o_7_._ _0_L,. ,u:E?F.._.u_...............................................................................
11 11A01201 BRACKET TILT
12 2983AL5010 STEEL BALL
13 16203001 COMPRESSION SPRING
14 2668BBDA25 CR. RE. PAN HD SCREW M5X08 16
15 11A01601 DUST COLLECTOR JOINT
16 N/A
17 2603BBLA66 HEX SOC SET SCREW M10X1._12
18 2602BBLA58 HEX. SOC HD. CAP SOLT M8X1 25*35
19 N/A
Z1 11A13901 TRADE-MARK LABEL
Z2 16702001A2 BEARING SEAT ASS'Y
73 20105PBA05 SPHERICAL BEARING
74 11A15802 BUSH
?5 14701101 WASHER
?6 11A16002A1 ECCENTRIC ASS'Y
T/ 181O50O2 BLADE
?8 15802104 BLADE
?9 17104403A1 HOLDER BLADE ASS'Y
20 11A02201 BASE 1 _0 11A16801A1 BOTTOM ARM ROCKER ASS'Y
21 2705FBD108 NUT CHUCK MBX1 25 T=8
22 11A02401 TABLE
23 11A02501 INSERT
24 2668BBDA24 CR, RE, PAN HD SCREW MSX0 8-12
25 11A02701 RETAINING CLIP
26 11A02801 BLADE BOX I
27 2138MBL703 WRENCH HF_X, 3-57 1
25 2617BBLB58 HEX,SOCKET HD,CAP SCREWS M8X1 25-35 1
29 N/A
.:_,..,,.__0_'_C_pL.S_R.!_..W'_S,HE_...............................'_._.............................
31 11A03401 CAUTION LABEL
32 2501MWTN63 FLAT WASHER _p25 5X35-2 5
33 11A03601 TRADE=MARK LABEL
34 2637BBOA39 CR RE TRUSS HO, SCREW M6X1 O-12
35 11A10101 PLATE COVER
36 11A10201 LABEL
37 16730102A1 AIR DUCT ASS'Y
38 16730001 PVC HOSE
39 11A10501 CLAMP PLATE
:_L.?_.....,_.EX..S_L._ET..'%REW......................_6_.6 ..................
41 11A10701 PLUNGER HOUSING
42 11A10901 SUPPORT ROD
43 16700805 CLAMP HANDLE
44 11Al1101 CLAMPER
45 11Al1202 HOUSING
46 18402702 DUST SHIELD
47 2660PBCK40 CR RE PAN HD TAPPING SCREW M5X16-50
48 11Al1501 CONNECTOR BOX
49 11A11601A1 CONTROLLER ASS'Y
131 2501MBDN06 FLATWASHER _ 6X13-1
t32 2705FBD105 NUT CHUCK MSX08 T=5
1 33 15802301 BEARING SEAT
I_4 2602BBLA08 HEX SOC HD CAPBOLT M4X07-10
2 35 14706601 SET P{J_TE
36 2617BBLO13 HEX SOCKET HD CAP SCREWS M5X0.840
)7 11A17901A1 LINGAGE BAR ASS'Y
38 11A18001 EXTENSSION SPRING
)9 2677SBDAA3 CR.RE PAN HD ROUND NECK SCRE M4X0.7*7 5
)1 18105001 BLADE PLAIN 12.5
)2 17102701 BLADE PIN 10T
)3 15802103 BLADE PIN 18T
)4 8586128827 MOTOR
)5 2637BBDA39 CHORE TRUSS HO SCREW M6X1 0-12
)6 2617BBLC21 HEX SCCKET HD CAP SCREWS M6X1 0-16
)7 11A25401 SWITCH BOX
)5 2660MBCE14 CR.RE PAN HD TAPPING SCREW M4X16-16
)9 11A25601 SWITCH BOX COVER
IO0 ,_P BCK !5...... CR.RE...I_:_r_.1_[_.TAPP!NG.SCREW .....M4X18:20 ...............
101 2852U55722 ROCKER SWITCH
102 1IA25901 INDICATED BUTTON
103 2701FBO107 HEX. NUT MBX1 25 T=
104 2501NBDN59 FL_T WASHER 5/32X13/32=
105 2660MSCK16 CR.RE PAN HD TAPPING SCREW MSX08-10
,06 1IA26302 HOUSING RIGHT
'07 19A10101 CLAMP-CORD
08 11A26501A1 LAMP ASS'Y
09 11A27C01 STICKER
._L...2_PMBC_O_....._.R:RE:.£'_ff._O.:[ft_!'_P..S_E"Y.M.?_._...................._.L_9_p.!2%.........C_M£:_(__{_.............................................................................
51 11A11801 CONNECTOR BOX COVER 11 2660MBCB14 CRRE PANHO TAPPING SCREW
52 2660PBCK23 CR RE PAN HD TAPPING SCREW M4X18 25 12 1_A27301 WARNING LABEL
53 2553055714 CtRCU}T BREAKER SWITCH
2801UBHA07 STRAIN RELIEF
56 280655581 YLEAD W_RE ASS*y
56 2807BBQ8HB POWER CABLE
57 19A10901 SHAFT PIVOT
58 2501MBDN21 FLAT WASHER _pBX16-1 4
59 2506MBN606 WAVE WASHER
60 2705FBD106 NUT CHUCK
20

56
54
51
53
524
65
64 49
56
88 <
86
43
I
10 9
6
4• 0
m
r_
az "Z
o
".4
io
o)

ORDER ONLY BY MODEL NUMBER AND PART NUMBER
Key Part No. Descrlptiof
1 17010103 SPACER
2 17050111 SUPPORT BRACKET
3 17050511 BOTTOM SUPPORT BRACKET
4 2672BBDA54 CAP HD. SQ.NECK BOLT
5 17050313 UPPER SUPPORT BRACKET
S_e Q_/
3
L=7483 3
L=428 1
M8x1.25-16 20
L=243 2
6 2708FBD112 SERRATED TOOTHED HEXAGON FLANG NUT M8x1.25 T=7.5 24
7 17050412 BOTTOM SUPPORT BRACKET L=810 2
8 17050215 UPPER SUPPORT L=630 2
9 17050112 SUPPORT BRACKET L=748.3 1
10 2701QBD509 HEX. NUT 318"X16UNC T=8 1
11 1A213201 SPACER 1
12 2601BBDA66 HEX. HD. BOLT MSx1.25-70 4
13 2501MBDN21 FLATWASHER fp8x16-1.4 4
14 17050510 BOTTOM SUPPORT BRACKET L=428 1
22

20" SCROLL SAW MODEL NO. 137.216200
STAND
3
_3
23

For repair of major brand appliances in your own home...
no matter who made it, no matter who sold it7
1-800-4.-MY-HOM EsuAnytime,day or night
(1-800-469-4663)
www.sears.com
To bring in products such as vacuums, lawn equipment and electronics
for repair, cell for the location of your nearest Sears Parts & Repair Center.
1-800-488-1222 Anytime, day or night
www.sears.com
For the replacement parts, accessories and owner's manuals
that you need to do-it-yourself, call Sears PartsDirect s"!
1-800-366-PART sa.m.- 11 p.m. CST,
(1-800-366-7278) 7 days a week
www.sears.condpartsdirect
To purchase or inquire about a Sears Service Agreement:
1-800-827-6655
7 a.m. - 5 p.m. CST, Mon. - Sat.
Para pedir servicio de reparacibn a domicilio,
y para ordenar piezaS con entrega a domicilio:
1-886-SU-HOGAR s.
(1-888-784-6427)
IS ARS !
HorneCentral"
._4_
_:_
Au Canada pour service en fran_.ais: ! _!_
1.877.LE.FOYER s" _
(1 877 533-6937) ..........
....._:_iiiiiiiiiili:
OSears, Roebu d_ and Co.
®Regist_ed Trademark /i,* Trademark o( Seam, Roebuck and Co.
Mama Registrada /TM Marc_ de F;ibnca de Sears, Roebuck and Co.
2/2002