Craftsman 247298770 User Manual 5 H.P. CHAIN DRIVE REAR TINE TILLER Manuals And Guides 1008323L
User Manual: Craftsman 247298770 247298770 CRAFTSMAN CRAFTSMAN 5 H.P. CHAIN DRIVE REAR TINE TILLER - Manuals and Guides View the owners manual for your CRAFTSMAN CRAFTSMAN 5 H.P. CHAIN DRIVE REAR TINE TILLER #247298770. Home:Lawn & Garden Parts:Craftsman Parts:Craftsman CRAFTSMAN 5 H.P. CHAIN DRIVE REAR TINE TILLER Manual
Open the PDF directly: View PDF .
Page Count: 32

Sears
maliiual
CAUT :
Read SAFETY
RULESand
iNSTRUCTIONS
carefully
f
_RRFTSN_N_
.CHAJ
Ti E IVE
TILLE
o Assembly
oOperating
®Maintenance
. Repair Parts
8F__._RS, P, DEBU6-_ AND 03., Cht_I1. 60684 U_.A.
and S_NS-SEARS LI_MYI2!D, Toronto, Canada
i m , i,,,i,ii ...................................... ,,,,.,,?,
PART NO, 770_7763
........ IIIl/l'
PRINTED IN U,S,A,,
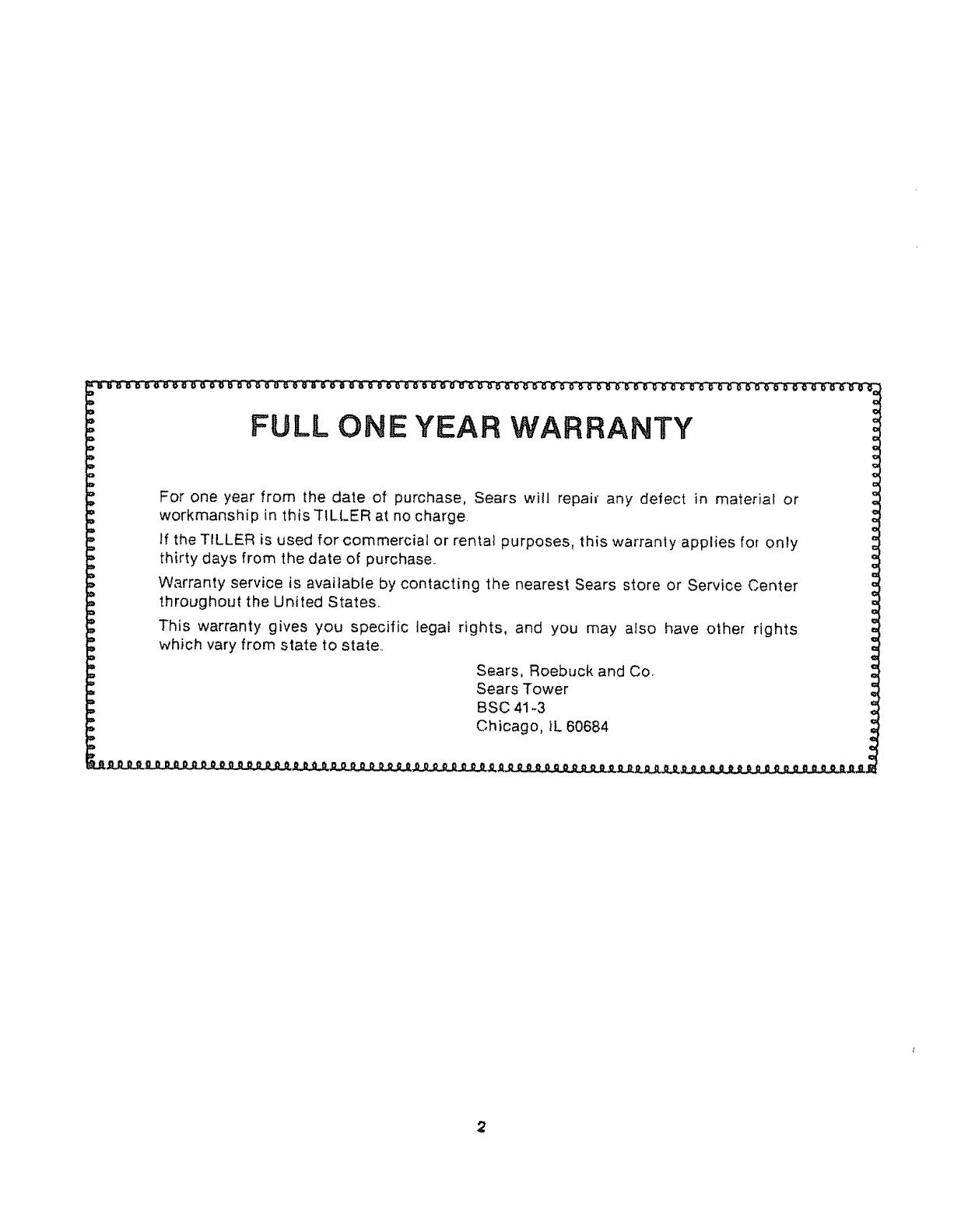
FULL ONE YEAR WARRANTY !
For one year from the date of purchase, Sears will repai_ any defect in material or
workmanship in this TILLER at no charge
If the TtLLER is used for commercial or rental purposes, this warranty applies for onry
thirty days from the date of purchase.
Warranty service is available by contacting the nearest Sears store or Service Center
throughout the United States..
This warranty gives you specific Jegai rights, and you may afso have other rights
which vary from state to state..
Sears, Roebuck and Coo
Sears Tower
BSC 41-3
Chicago, IL 60684
DODOg D Da 0 _J_ Q9_0_0 QD 0 D_ 000001_ D_ 000 QO 0000____90 na _oDa@ ooooooo D_ _
2

IMPORTANT
__is suggested that this manual be read in its entirety before attempting to assemble or operate Keep this
manual in a safe place for future reference and for ordering replacemen! parts
This unit is shipped WITHOUT GASOLINE orO1L After assembly, see operaiing section of this manual
for proper fuel and amount,.
Your tiller is a precision piece of power equipment, not a l::lay thing Therefore exercise extreme caution at
al! times
SAFE OPERATION PRACTICES FOR TILLERS
't. Read the Operating and Service Owner's
Manual carefully, Be thoroughly familiar with
the controls and the proper use of the equip-
ment..
2. Never allow children to operate a power tiller°
Only persons welt acquainted with these rules
of safe operation should be allowed to use
your tiller
11,
12.
1;3.
Do not fill gasoline tank while engine is
running. Spilling gasoline on hot engine may
cause a fire or explosion,
Do not run the engine while indoors, Exhaust
gases are deadly poisonous.
Be careful not to touch the muffler after the
engine has been running, it is hot.
3 Keep the area of operation clear of a]f
persons, particularly small children and pets.
4. Do not operate equipment when barefoot or
wearing open sandals Always wear substan-
tial footwear.
5. Do not wear loose fitting clothing that could
get caught on the tillen
6. Do not start the engine unless the shift tever
is in the neutral (N) position.
7. Do not stand in front of the tiller while
starting the engine.
8. Do not place feet and hands on or near the
tines when starting the engine or while the
engine is running.
9. Do not leave the tiller unattended with the
engine running,,
t0. Do not walk in front of the tiller while the
engine ts running.
14, Before any maintenance work is performed or
adjustments are made, remove the spark plug
wire and ground it on the engine block for
added safety.
15
l&
Use caution when tilling near buildings and
fences, rotating tines can cause damage or
injury.
Before attempting to remove rocks, bricks
and other objects from tines, stop the engine
and be sure the tines have stopped
completely. Disconnect t,he spark plug wire
and ground to prevent adctdental starting.
,
t8,
Check the tine and engine mounting bolts at
frequent intervals for proper tightness°
Keep all nuts, bolts and screws tight to be
sure the equipment is in safe working
condition
19. Never store the equipment with gasoline in
the tank inside of a building where fumes may
reach an open flame or spark, Allow the
engine to coot before storing In any
enclosure°

UNDEX
Warranty .................................... 2
Safe Operation Practices ..................... 3
Introduction ................................... 4
Contents in Hardware Pack ......................... 5
Tiller Identification ................................ 6
Assembly Instructions ......................... 7
Adjustments ..................................... 9
Con trots ....................................... t 0
Engine Preparation ............................... 13
Operation ........................................ 13
Tilling .......................................... 14
Tilling Hints ..................................... 15
Maintenance ................................. 15
Off-Season Storage ............................ ! 9
Transmission--Repair Parts .................. 20
Tiller-- Repair Parts ................................ 22
Parts Information ..................... Back Cover
INTRODUCTION
This Product has been designed, engineered and manufactured to give you the best possible dependability
and performance.
Should you experience any problem you cannot easily remedy, please contact your nearest Sears, or
Simpson-Sears Service Department. They have well qualified, competent trained technicians and the proper
tools to service or repair this unit.
PRE-ASSEMBLY
_NOTE
The right and teft side of your tiller
is determined from operator's posi-
tion.
Before any step is undertaken, the instructions for
that step should be read through.
3o Gas (regular)
4. Cleaning rag
PARTS IN CARTON
TOOLS REQUIRED:
1. (2) 7116" Socket, open or box wrench.
2. (1) 9t16" Socket, open or box wrench.
3, (1) V_" Flat Screwdriver.
4. (1) Adjustable Wrench.
MATERIALS REQUIRED:
1. Funnel (for gas and oil--NOTE: DO NOT MIX)
2. S.AoE.-30 O11--2¾ pints FIGURE 1.
4

C
E
GJG
FIGURE 2, (SHOWN IN FULL SCALE)
NOTE
THE LETTERS LISTED BELOW WILL BE
REFERRED TO THROUGHOUT THE FOLLOWING
TEXT FOR EASIER HARDWARE IDENTiFICA-
TION,
LIST OF CONTENTS IN HARDWARE PACK:
A (2) Shoulder Bolts
B (2) Flat Washers
C (2) BeltevitleWashe_s
D (2) Hex Nuts 318-18 Thread
E (t) Hex Screw 318-24 xi.,25" Long
F (t) Hex Screw !/4,20 x 1 ,,75" Long
G (3) Flat Washers 318"
H(2) Hex Locknuts 3/8-24 Thread
I(1) Gear Shift Knob
J (1) Compression Spring
K(2) Hair Pin Cotter
L (2) Serf Tapping Screws
M (1) Hex Nut _-.20Thread
N (1) Lever
O(1) Ferruie
P(1) Hex Jam Nut 3f8-24 Thread
F
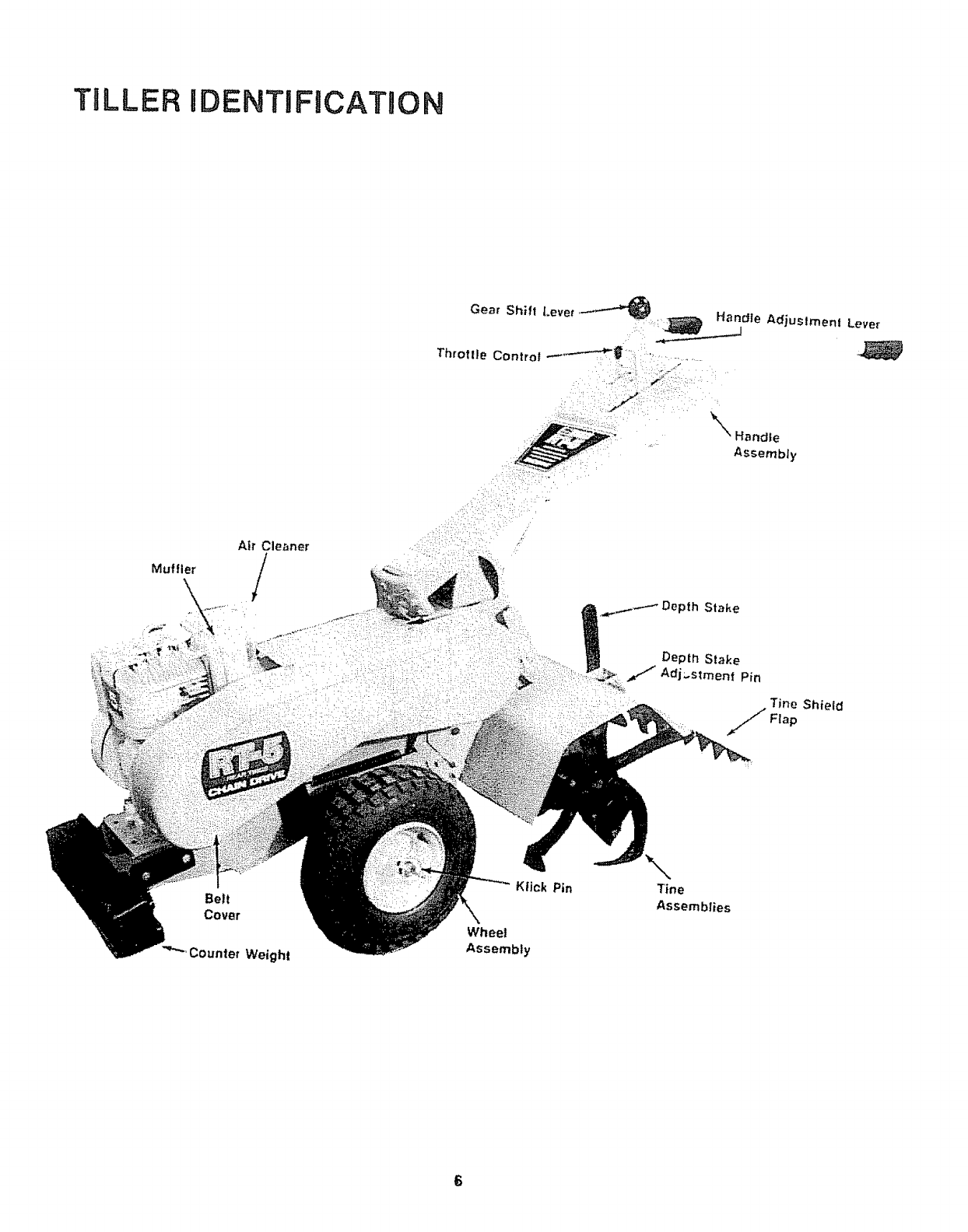
TILLER IDENTIFICATION
Depth Slake
Adj..stmen{ Pin
Shield
Belt
Cover
3ounter Weight
Klick Pin Tine
Assemblies
6

ASSEMBLY
INSTRUCTIONS
1 Handle Assembly
A Place the handle assembly in p,:;s,'",k)n Or:
the tiller so that the holes in handle Ime up
w_th holes in mountir, g bracket
g Place flat washer (B} and bellevi_le washer
(C) over shoulder on shoulder bolt (A)
Place shou}der bolt and two washers
through handle mounting holes and
secure with lie× nut (D) from the inside of
handle. See figure 4
DTip the tiller forward, so it rests on
counterweight Slide depth stake up
through titler as shown in figure 6, Pull
depth stake adjustment pin on tiller to
lock in place
FIGURE 6,
EAttach front end of depth bar assembly to
transmission housing Slip depth bar over
bolt and secure with hair pin cotter (K).
See figure 7
FIGURE 4.
C Remove depth stake from tiller and
preassemble depth stake to drag bar
assembly with hex screw (E), flat washer
(G) and hex Iocknut (H). See Figure 5
Tighten nut and bolt, but do not over
tightem Parts must pivot.
NOTE
Flat washer must go against slot on
drag bar assembly
FIGURE 5. 7
@
FIGURE 7
F_ Assemble notched edge of gear shift lever
so notch faces forward. Place gear shift
lever through slot in handle panel and
bottom hole over weld stud_ Secure with
flat washer (G), compression spring (J),
another flat washer (G) and hex locknut
(H)° See figure 8,
G. Tighten hex Iocknut until nut is flush with
stud. See figure 8

Thread ferrule [0) on other er_.d of gear
shift rod See figure 10
Secure ferrule in gear shift lever (as shown
in figure 11) with llair pin cotter (K),
FIGURE 8.
H. Thread hex jam nut (P) on one end of gear
shift rod, then thread gear shift rod into
ball joint on the top of pivot horn
assembly, 10 to 12 complete turns,
approximately 1,,t,inch. See figure 9,
FIGURE 9.
FIGURE 11.
K,,
L,,
To assemble the handle adjustment lever.
hook handle adjustment rod (already on
handle) into lever Hook to the outside
See figure 12
Place handle adjustment lever in place on
handle and secure with hex screw (F) and
tocknut (M) See figure 12 Do not over
tighten handle adjustment iever mt'sl
pivot freely.
FIGURE 10.
FIGURE 12.
M. Throttle Control Lever_
NOTE
The throttle control may have four
holes in the lever bracket, The holes
on the outside edge are to be used
for mounting on this unit° See figure
!3.
8

FIGURE 13.
2, Change oil after first 2 hours of operation and
every 25 hours thereafter_ Check oil every 8
operating hours.
Place throttle control lever up through the handle
panel and secure with two self tapping screws (L),
using a 1/4" fiat screwdriver.. See figure 14_
FIGURE 15.
3- Fill fuel tank with clean fresh regular grade of
gasoline. See figure 16..
FIGURE 14.
Engine is shipped without oil,
ENGINE
PREPARATION
1o Before starting, Fill crankcase with 2_A pints
of SAE 30 heavy duty detergent oil, Be sure
that engine is level, See figure 15,
FIGURE 16.
ADJUSTMENTS
After all assembly is completed, this
final adjustment must be made prior
to initial operation.
Gear Shift Rod Final Adjustment
1. Place ktick pins in freewheeling position. See
figure 17,

FIGURE 17.
2 Pull the depth bar adjustment pin and move
the depth stake all the way down. so the tines
DO NOT" touch the ground See figure 18
3 Block the front wheels as shown in figure 18
FIGURE 18.
4. Place the gear shift lever in Neutral (N)
position.
5, Place the throttle in the Start position
6. Pull choke lever out (if engine Is cold)
7. Start the engine_
8Engage the gear shift lever through the five
gears with the engine running and return to
Neutral (N)_
9. Stop the engine,
10o Remove the hair pin from ferrule and pull out
of gear shift lever,
11. Place gear shift lever in first gear (and pull
lever to rear of slot), Adjust the ferrule to fit
gear shift lever, and replace the hair pin,
10
Handle Adjustment Lever. (See figure t9 )
NOTE
Figure 19 is _,iewed from the bottom
of handle panel
A_ Use if not enough free play
B. Normal setting°
C, Use If pin wilt not withdraw completely from
bracket.
FIGURE 19.
To make the above adjustment loosen hex iocknut
and reposition the rod in Hole A, B or C.
Additional adjustment for the gear shift rod can be
made after lhe tiller has been in service for a
while
FIGURE 20.
When the belt has become worn and/or stretched
or the friction wheel has become worn, make the
following adjustment.
1. Move the control bracket to the bottom hole
on the pivot horn assembly and readjust the
gear shift rod, See figure 20_

CONTROLS
Location and Use°
t. Gear Shift Lever: The gear shift lever is
located in the center of handle Dane!.
A Forward (1 thru 5)--Move the lever to the
left and forward for each gear See figure
2rl
L_CAUTtON
DO not attempt to shift gears unless
engine is running°
E Neutral (N)--Move lever to center detent
See figure 22.
FIGURE 23.
.i:: :=
F. Reverse (R)--Pull the gear shift lever back
(upward) slowly to obtain reverse Always
use caution when using the reverse When
using reverse, if gear shift lever is
released it wtll snap back into neutral (N).
See figure 23.
FIGURE 21,
B o Use (1) first and (2) second gears when
breaking the sod for the first time
C. Use (3) third and (4) fourth gears when
tilling soil which has been tilled before,
D. Use(5) fifth gear for pulverizing soil.
2o Throttle Control: The throttEe control lever is
located on the right hand side of handle
panel and controls the engine speed.
FIGURE 22,
11
'2,,
FIGURE 24.
A. StopmPull lever back (upward) to stop the
engine. See figure 24.
B. Start--Push throttle control lever forward
(down) to start position. See figure 25.

4 HandleAdjustment: The handleacljus[men_
releaseis located on the right hand handle
bar_ See figure 27.
FIGURE 25,
3. Choke: The choke is located on the engine
just below the air cleaner, To choke the
engine pull the choke lever out., See figure 26.
FIGURE 28.
FIGURE 26.
RGURE 27.
FIGURE 29.
FIGURE 30.
12

S(;ue,:,_:'e up on hat]die adiustmen! iever
_:nd place ',he handle m one of n_ne Egt
;:,OSilionS See _Igures 2_ 29 30 a,"_::_ 2,1
NOTE
Figure 28 is viev,.ed frc_r'n !he fr(.,n_ c)f
filler for c;arily
FIGURE 31.
OPERATION
Your tiller has freewheeling and drive positions
A Freewheeling position is when the klick pin is
placed in the outer hole on wheel shaft, as
shown in 32.
Freewheeling is used for transporting the tiller to
and from the work area, with the engine off and
the gear shift lever in Neutral (N} position
:ii!:( :
FIGURE 32.
13
BDrive position is when the klick pin is
inserted into lhe _nside hole of ;,,,heel shall
(hole in wheelilub) as shown m figure 33
Drive position iS used for tilling
FIGURE 33.
TO START ENGINE:
_ CAUTION
BE SURE NO ONE IS STANDING IN
FRONT OF THE 'TILLER WI-'IILETHE
ENGINE lS RUNNING OR BEING
STARTED.
1 P}ace the gear shift lever in ne{_t_at (N)
position See figure 22
2, Place the throttle control lever in FAST
position See ligure 25
3 Choke engine Pull choke lever out, See figure
26. Once the engine starts, push the tever up
4, Stand at side of tiller, grasp lhe starter handle
and pull out rapidly, Return it slowly to the
engine, Repeat as necessary See figure 34,
FIGURE 3,4.

TILLING TILLING HINTS
FIGURE 35.
1. Adjust the depth stake by pulling the depth
stake adjustment pin. Release the depth
stake. See figure 35.
2. Lower the depth stake for shallow tilling and
raise the depth stake for deeper tilling.
3o Select gear on handle panel and tiller will
propel itself.
A. For tilling in sod, raise the depth stake so
the depth bar is one to two inches above
the tines.
This setting is used for breaking up the
sod and shallow cultivation. For further
depth ratse the depth stake and make one
or two more passes over the area.
B. For tilling loose and sandy soil, further
depth In tilling can be achieved by raising
the depth stake to its highest setting.
WARNiNG,e._,b.o4_..o _
When tilling, if a hard spot or rock is
encountered, the tines may rift the
back of the tiller out of the ground
and start to walk across the ground,
To correct this problem raise up on
the handles.
Soil conditions are important for proper tilling
The lines will not readily penetrate dry, hard soil
This may contribute to excessive bounce and
difficult handling of the tiller Hard soil should be
moistened prior to tilling,
Extremely wet soil will cause soil to bali up or
clump_
When tilling in the Fall, all vines and tong grass
should be removed. This will prevent vines trom
wrapping around the tine shaft which slows tilling
operation.
The best method will be determined by the soil
condition° In some soils, the desired depth is
obtained the first time over the garden. In other
soils, the desired depth is obtained by going over
the garden two or three times. In the latter case,
the depth stake should be raised before each
succeeding pass over the garden, and passes
should be made across the length and width of the
garden alternately. Rocks which are turned up
should be removed from the garden area°
Handle Pressure: Further control of tilling depth
and travel speed can be obtained by variation of
pressure on the handles.
When using the depth stake a downward pressure
on the handles will increase the working depth
and reduce the forward speed. An upward
pressure on the handles will reduce the working
depth and increase the forward speed. The type of
soil and working conditions will determine the
actual setting of the depth stake.
MAINTENANCE
BELT REPLACEMENT:
_CAUTION
Do not use an off-the-shelf belt,
If belt replacement is rc-quired, order belt or belts
by part number from your nearest Sears Service
Center.
Part No. 75443224 Part No. 75443221
518" x 26" Short Belt 5!8" x 52" Long Belt
Your tiller has been engineered with the above
belts and should not be replaced with an
off-the-shelf belt. The above belts are made of
special material (Kevtar Tensile) for longer life and
better Derformanceo
14

REMOVING AND REPLACING BELTS
1_ Remove bell cover remove three boils, two
nuts and !wo fiat washers. See figure 36.
_CAUTION
HOT muffter in the area of belt
cover Only remove the belt cover
when engine is cool
FIGURE 38,
4 Place the gear shift lever in one o! the forward
gears (as far forward as possible)
5 Pull the idler pulley down by hand and remove
the belt from idler pulley and transmission
pulley See figure 39
FIGURE 36.
2 To remove the front belt (short) pull gear shift
lever back to Reverse (R) position and hold,
With a 7t !6" wrench remove three screws and
Iockwashers holding the friction disc, See
figure 37°
FIGURE 39.
6. Remove the forward belt (short) from the
variable speed pulley and slip beit off the
engine pulley. See figure 40_
7. Remove rear belt (long) and replace with new
belts
FIGURE 37.
3. Hold the gear shift lever in Reverse (R)
position and slip the belt off engine pulley,
towards the engine as shown in figure 38
15
NOTE
Upon reassembly make sure the
short belt is inside the guide pins.
See figure 41_

FIGURE40,
FIGURE 41.
8o Reverse steps 1 through 7 for reassembfy.
NOTE
Upon reassembly of friction disc,
tighten three screws equally.
CARE AND MAINTENANCE:
Tran smission:
The transmission is pre-lubricated and sealed at
the factory. It requires no additional lubrication
unless the transmission is disassembled° To fill
with grease, lay the left half of the transmission
on its side, add 28 ounces of Plastilube #1 grease
and assemble the righ! half to it. This grease can
be purchased from your nearest authorized dealer.
(Order Part NOo737-0133.)
Engine:
1_ You MUST CHANGE THE OIL in the
crankcase after the first two hours of opera_
16
tion of your new engine and after each 25
hours of use thereafter to ensure proper lubri-
cation of internal parts for trouble free opera-
tion and to prevent costly repair due to
excessive wear. (Take care to remove dirt
around li!ler plug.) Be sure oil level is maim
tained full to point of overflowing Seefig{,re
42.
_. Oil Level
Oil Filler Plug
FIGURE 42_
TO change oil remove drain plug (figure 43) and tip
the tiller forward while engine is warm. Replace
drain plug. Remove oil fiiler cad and refill with
SAE 30 heavy duty detergent oil Replace filler
cap..
Oil Drain Plug
FIGURE 43,
2 Use only a good grade of fresh, clean, regular
gasoline Do not use gasoline that has been
sitting for a long period of time. Stale
gasoline may cause engine to run poorly or
not at all.
3_, Keep your engine CLEAN. Wipe off all spilled
fuel and oil Keep the engine clean of foreign
matter and be sure the cooling fins on the
cylinder are kept clean to permit proper air
circulation. You must REMEMBER that this is
an air cooled engine and free flow of air is
essential to proper engine performance and
life.
4_ Your must SERVICE YOUR AIR CLEANER,
The air cleaner prevents damaging dirt, dust,
etc.. from entering the carburetor and being
forced into the engine and is important to
engine life and performance.
To remove air cleaner: See figures 44 and 45.
A. Remove screw.
B.. Remove air cleaner carefully to prevent dirt
from entering carburetor.

C. Take air cleaner apart
D, Wash element in detergent and solution by
squeezing similar to a sponge
FIGURE 44.
E Wrap foam in cloth and squeeze dry.
F. Coat element with two tablespoons of engine
oil, squeeze to distribute and remove excess
oil. See figure 45.
G. Wipe air cleaner body with same solution to
remove excess oil.
H,, Reassemble (See figure 44,) by inserting
element into body and snapping cover into
place, fasten to carburetor with screw.
FIGURE 45.
NEVER RUN YOUR ENGINE WITHOUT
CLEANER COMPLETELY ASSEMBLED°
AIR
Carburetor Adjustment:
1. Never make unnecessary adjustments. The
factory settings are correct for most applica-
tions.
2. If adjustments are needed, proceed as
follows:
A.
B.,
Idle Adjusting
INITIAL ADJUSTMENT. See figure 46
Close needle valve (turn clockwise) then
open 1_,_ turns (lurn counterclockwise)
This initial adjustment will permit the
engine to be started and warmed up before
makine final adjustment
FINAL, ADJUSTMENT.. See _igure 46.. With
engine running at fast operating speed
(approximately 3,000 RPM without load)
close the needle valve (turn clockwise)
until engine starts to lose speed (lean
mixture), Then slowly open needle valve
(turn counterclockwise) pasl the point of
smoothest operation until engine just
begins to run unevenly This mixture
should be rich enough for best perform-
ance under load. Hold throttle in idling
position Turn idle speed adjusting screw
until fast idle is obtained (1.750 RPM),,
Test the engine and if it tends to stall or
die out, it usually indicates that the
mixture is slightly lean and it may be
necessary to open the needle valve slightly
to provide a richer mixture This richer
mixture may cause a slight unevenness in
idling
Screw ._. !._'P_--;_...._,
_"_-_ ":-2:'-,_ i;,..e
,_:.o,o::.::_:.,c':.' Needle Valve .:
FIGURE 46.
W NOTE
ALWAYS ALLOW SEVERAL SEC-
ONDS BETWEEN EACH ADJUST-
MENT FOR THE ENGINE CARBU-
RETOR TO REACT TO THE NEW
SETTING
3. Never attempt to change maximum engine
speed as THIS IS PRESET AT THE FACTORY.
Excessive speed, caused by by-passing the
governor, can cause extensive damage to your
engine.
SPARK PLUG:
1• Remove the spark plug each time you change
the oil and inspect it. See figure 47,
17

A. The electrodes should be kept clean and
free OF CARBON. The presence of carbon
or excess oil will greatly deter proper
engine performance.
FIGURE 47.
B. If possible, check the spark plug gap (area
between electrodes) using a wire feeler
gauge. This plug gap should be .030.
2. if you need a spark plug refer to the parts list
for the proper replacement spark plugo
ADJUSTMENT OF THROTTLE CONTROL CABLE
1, Place the throttle control lever in stop
position.
2. Loosen the casing clamp screw and move the
throttle control wire in as far as possible.
3. Tighten the casing clamp screw. See figure
48.
TIRE PRESSURE
Tires should be inflated from 8 to 15 p.sot.
1. Working outdoors, drain all fuel from the fuel
tank° Use a clean dry cloth to absorb the small
amount of fuel remaining in the tank, then run
the engine until all fuel in carburetor is
exhausted.
DO NOT DRAIN FUEL WHILE
SMOKING, OR IF NEAR AN OPEN
FIRE.
2. Drain all the oil from the crankcase (this
should be done after the engine has been
operated and is still warm) and refill the
crankcase with clean new oil. See figure 15.
3. Disconnect the spark plug wire and remove
the spark plug from the cylinder. Pour about
six drops of engine oil tnto the cylinder, and
then pull the recoil starter several times to
spread the oil on the cylinder wall. Replace
the spark plug, but DO NOT connect the wire.
4. Clean the engine and the entire tiller
thoroughly.
5. Wipe tines with oiled rag to prevent rust.
TILLER INSTRUCTIONS FOR WINTER
OPERATION (under 40 °F,)
Engine Lubrication. Drain the summer engine oil
while engine is warm_ Refill with new "winter
grade" oil. Run engine until warm to distribute the
new winter oil.
Use oil "for service" SC, SD, or SE. Use 5W-20 or
5W-30.tf not available, use !0W, or 10W-30.
FIGURE 48.
OFF-SEASON STORAGE
If the tiller is to be inoperative for aperiod longer
than 30 days, the following precautions are
recommended. Keep your tiller in a weatherproof
dry area. If stored for over 30 days the following
steps will protect the essential engine parts from
gum deposits, 18
Fuel, Replace any summer gasoline on hand or in
the fuel tank with fresh winter-grade gasoline. Use
lead-free or leaded "regular" grade automotive
gasoline. Winter fuels have additives for faster
starting. Keep fuel tank fuif.
_NOTE
Many automotive gasolines no long-
er contain "de-icer_" A can of gas-
line de-icer fluid added to your gaso-
line supply will help maintain the
engine's winter reliability.
Cold Starting Hints
1. Be sure to use proper winter-grade oi! and
gasoline,
2. Dectutch all possible external loads.
3, Set governor control at tow-speed position.
4. Turn carburetor needle valve approximately
!t8 turn counterclockwise. (Richer fuel
mixture) This will improve cold weather
starting and operation.

NOTES
19

Repair Parts 5 H.P. TilUer ModeB 247.298770
5t
29
_9
31 20
55
-. 52 53 54
12 ;3
.oT_iO.e_0o,,oceo°4
Plastilube #1 grease, Orderi
part no. 737-0133,, |
!
20

'T
REF., i PART
NO_ tNO
t i74t"0155
2 ! 04822
3 738-0379
4 7t4._0122
5 750..O379
6
7
8
9
10
1
15
18
19
20
21
22
23
i24
29
3O
Repair Parts Transmission 04878
................. "R I_-F'-]' PART i--
DESCRIPTION ND _ NO, 1 DESCRIPTION
Ball Bearing ' I 736-0329 iL-Wash '_ Scr "
Transmission Ass /--,-q _,. : :::' , :.0-03_8 H_.L Sleeve 3 c l D i"¸
7170210
750-.0378
04867
736-0259
1741-0t89
05034
_736-0329
!712-0138
1721-0102
736-02t9
736-0't69
7'12-0214
04872
736-0219
736-0169
7t0-041I
!7t0-060t
736-0242
72! -0162
721-0102
712-0138
Input Shaft 5,8- D_a
Sq Key3!16×3'1 ]., ":5 Lg
Spacer ,637 t D × }'_.1 0 D
x 85- Lc_. ,_
Sprocke 9- _. 50= Ph,'l_
Spacer 537 f -' 2. "_8! O D .5
x 1.44'" Lg "6
Tine _ha,t As:_ :. T
FI-Wasr ! O' I D x ! 62
OD .: 09 ' 8
Flange Bfg _; 00 D _.1 188 0
O.D ;,' t 12
Gasket_Housmg
Transmission Ass y._L t-_
Bearing Housing
L-Wash b_" Scr "
Hex Nut _4_-28Thd..*
Seal 1.0' I.D. xl 38" O E
Bell Wash 318'1 D.
L-Wash 318' Scr "
Hex Nu! 3/8-24 TI d "
Side Plate
Bell Wash 3!8 ;D
L-Wash 3f8' Scr "
Hex Scr 3f8-16 x 4..00" Lg*
Hex TaotiteSft6-'.8 x 75'
Lg
Bell Wash..345t D x 88
OD
Gasket_Side Ptale
Seal1,.0" t D xl.38' O D
Hex Nut 1/_-28 Thd.."
,_ ._-.8-0104
7_3-02 26
712-0375
7' 3-023 T
7_3-016-
7"_3-0154
750-031
i,,_ 7_,3-0222
f,I2 7,_8-018A
43 750-0374
_4 7,_1-0t89
I5 7,36-025£
;6 04873
_7 7! 3-022[
_8 750-03!4
_9 7! 0-0195
50 736-021 9
31 710-0629
52 736-01 59
53 736-0t19
54 710-0627
1
55_756-0297
D O x3..3SLg
Flange Brg :328 f D _ 713
3D ×,75
Cl_a_n #50--5 8 Pitch x 52
L nt,;s Eqciless
H.,', Cen: L-Nut 318-1(-; Thd
S[,, !":)c_et HUE, Ass y
#_20 Cha,.-_ _? Pitch × 57
-inks
M._sler Lii*,k '_2"P tch
S:,acer 1 fl"l D x 20 O D
x 68
Sprocket Ass y
F._nge Brg..6281 D _ 753
OD x75
Hub Sleeve 38 i D x 625
OD
Flange Brg. " 00 ! D x
1.I 88 O D
FI-Wash i 0 ; O x 1 (;2'
O_D
Axle Sheh A_s'y.
#_20 Chain _:," Pitch _ 42
Links Eqdtess
Spacerl.¢,' I D x20" O.D
Hex Sc',r '..,_-28x 62" Lg"
Betfevitle Wash
Hex Scr 318-24 x275' Lg.."
F,-Wash 5116' Scr"
L..Wash 5!11;" Scr"
Hex L-Scr 5'!6-24 x 75"
Lg*
Input Pu!_ey_Traqsmission
"Standard Hardware Items--May Be Purchased
Local ty.,
21

Repair Parts 5°HoPo TiB_erModel 247°298770
2
I
73 \,
4 5
4t
93 t3
37
22

Repair Parts
REF. PART
INo.I No. i
2 1746-0304 )
3 !747-0255
4 1710-0136
5:749-0268
6 1720-0180
7 _712-0107
8 04830
9 04831
10 749-0269
1! 720-0! 83
12 04892
13 714-0104
14 736-0101
'15 732-0!93
16 712-0214
17 04833
:t!8 710-0344
714-0115
20 732-0306
21 747-0256
22 747-0252
23 04804
24 710-0623 !
25 736-0169 1
26 710-0623
27 736-0169
26 736@101
29 712-0130
30 04879
3t 04909
32 04683
34 711-0599
35 742-0197
36 7I 0-0191
37 04857
38 736-0'I 69
39 712-0241
40 714-0145
4I 742-0! 98
42 i04855
46 736-0169
47 1712-0130
48 104878
49 1712-0267
5=H.P. Tiller ModeB 247.298770
DESCRIPTION REF
................. !NO
Hex Wash Hd Tan Scr #B -I-'_
x .50" Lg," 5_
52
53
54
,_5
56
57
58
9
(0
61
62
63
64
65
66
68
69
_t
72
Z3
15
76
77
78
79
80
84
85
8_
87
8_
89
9C
91
9_
9,.
9z
ThrottleControl A._sy
Comp
Handle Lock Rod
Hex Scr _,_-20 x 1 75 Lg °
Handle--R H
Gri p
, "I_
Hex Cen; L-N_4 : -J. Tt7:J
Clutch Grip
Handte Panel -'ss
Handle- LH
Ball }(nob ot8-_6 _hd
Clutcn Handle As."y,,
Hair Pin Cotter
Fl-Wash
Compression Spri:,g 88
QD _.8I Lg
Hex Nut 3!8-2,3 Thd"
Depth B:_r
HexScr 3!8-!6 x 1.50' Lj "
Cotte ,Pro _,8" D,_ x 1.00'
Lg"
Compression Spr,'_ 9
Depth Bar Adjustn;er! Pi.q
Hinge Rod
Tine Shield Hinge Flap
Ass'y.
Hez Wash., Hd. Self Tap Scr
3f8-1B x .75" Lc
L-Wash 3/8 ' Scr '
Hex Wash, Hd, Self Tap :;or
3t8-16 x .75" L9
L-Wash, 318" Scr "
Fi-Wash,
Hex Ins L-Nut 3/8-t6 T,_:t
Drag Bar Ass'y.
Inner Tine Adapte" Ass'y
Outer Tine Adapter Ass'y
Clevis Pin 318" Dia, x t 75'
Lg
Tine--L,.H
Hex Scr. 3f8-24 ), 1o25" Lg."
Outer Tine Ass'y, Comp -
L,H
L-Wash, 3t8" Sc[*
Hex Nut 318-24 Thd,*
Hair Pin Cotter
Tine--RH
Inner Tine Ass'y, 3omp -
L.Ho
L-Wash., 318" Scr *
Hex Ins. L-Nut 318-16 Thd.,
Transmission Ass'y, Cornp,
Hex Nut 5116-18 Thd.*
PART
NO.
736-01 t 9
04850
736-01 69
7t2-0116
714-0474
736,,0290
736,0119
738,0258
736.0105
710.0623
04841
7t 0 0601
7I 0-,0216
71401 t5
04796
7120130
73G0169
714-0474
04806
747-0278
723-0156
04812
712@221
711-0663
732-0"132
714-0474
736-0253
747-0254
726-011_
726-0108
7t2-0158
748-0516
04819
736-0289
738-0143
712-0267
T36-0119
71G0458
04792
746-0305
7I0-0152
712-0181
748-0!50
711-0198
712-0711
DESCRIPTION
L-Wash,. 5t16" Scr,*
Handle Post[loner Ass'y,
L-Wash., 3/8' Scr "
Hex Ins, L-Nut 3t8-24 Tha
Cotter Pm 1/8" Dia, x .75"
LG*
F!-V_ash 630 I D
x I.,0'" O D. x .,063
L-Wash, 5116 Scr.*
SMd, Scr 50 _ ,,25
Bellevtlle Wash
HexWash Hd Self Tap Scr
3'8-16 x 75" Lg,
.,,,)n rol Brk;
Hex Wash, Hd, Self Tap Scr
Hex Scr. 3/8-16x 75" Lg.*
CoRer Pin 1 i8" Dia x 100'"
Lgo*
Tree Sh,eld As,s'y
Hex Iqs L-Nut 3t8-_6 Thd,.
L-Wash 3 8"Scr"
Cotter Pin 1 I8" Dia, x ,,75-
Lg,*
Pivot Horn Assy.
Gea, Shift Rod
Rod End 31B-2,'- TnC
Pivot Brkt,, Ass y,,
Hex Ins L-Nut 5t8-I6 Thd,,
LocKing Pin
Compression Spring
CoHer Pin t/8' Di& x ..75"
Lg."
Bell, Wash 505 I.,D x 1,00"
O_D,,
Lower Handle Conbot Rod
Push Cap
Push Cap 3i8"' Rod
Hex Nut 5!16-'8 Thd*
Pivot Handle Brg
Pivot Handle Link
Bushing Wash
Shtd. Scr..500' Dia., x _,660
Hex Nut 5t16-!8 Thd,*
L-Wash 5t16" Scr.,"
Cam Bolt 5!16-1B x 1,75"
Lg,
Handle Mig. Brkt Ass'y_
Conduit and Wire
Hex Scr, 3!8-24 x 1 O0" lg,, °
Hex Top L-Nut 3!8q6 Thd
Sleeve Brg 50 I,D, x ,62
O_D,, x 1,12" Lg.
Ferrule
He, Jam Nut 3t8-24 Thd,
TINE CHART 4 '
Not Shown Inner Tine As'y. Comp,--R H 10 854 i
42 l Inner Tine Ass'y, Comp,_L. H,,t04855!
Not Shown IOuter Tine Ass'y. Comp.--R,, H ,,04856 I
37 !Outer TineASS'?,Comp,--L,H i 048___571
23

Repair Parts 5oH.P, TiBBerModel 247°298770
58 ..
54
I
t
,/
21
41
14
24

PART
NO.I NO.
1 752-0668
2 04869
3 736-01t-1
4 710-Dt2t
5 75a-3224
6 717-0343
7754-322"
8 750-338-
9756-92 c,'
10 736-01 59
11 736-01 _ :_
12 710-0627
t 3 7'12-0t 3'9
14 736-0169
15 756-0225
! 6 04836
17 736@329
18 7! 0-0230
i9 736-0133
20 7t0-0151
21 047q0
22 710-0599
33 05034
34 74'1-0155
37 714-0122
38 "138-0372
39 710-0502
40 736-01 69
4't 7t 0-0623
42 04878
43 712-01 38
44 741_0246
45 710-0347
46 716_0102
47 734-0832
73"_0833
7'34-0338
734,-O339
i 04874
I 04875
Parts 5=H.P. Tiller Mode 247,298770
i
i
i
DESCRIPTION ................... N{L. L__ NO ..... _ .......... DESCRIPTION
.b--_:,1! .....15 )I 7! 3-011BEngine B & S "' 30} '_ '-"" _ ''_ ,_ He< Sc" 5 !6-18 x -*-_Lg
Bell Cover SuF'por! Ass y
Internal L..-V',,as_ _ L,, r.
Hex Scr ' " :5
'V-Beh9 ,: ' _+
VariaLte Bp,,;e:: A:+
' -Beit 5 8 :2 L_+
Space: _37 t : .£,.., :
;4.t ;-
hq. ut :!. .,-:..... _ _ 1,_;_._.- e
Fi..W.3sr 5 16 3,':
L Wa:.q 5 6 S:;, "
He_×L "_ " :-'_15-2_ ;: 75 "
Hex :",s L44uI L_.6.._6 :'t::.
L-Wash 3/8" Sc,'.
Fi-ld,:_-.. ""_',_ D'_,._
FriclK)n 3;sC
L-Wa.sh.. :_ S,;r "
hex Scr _-'-28 _ _0 Lg
Fi-Wasb 375 i D x 1 _5
0 O :, ! 0
Hex "_ .....
,.,,o.-_- < .O0 Lq
Beit C,ov=_
Hex Wa._h Hd Se f "t'Bp Scr
Beanng .Housin£_
Bail Bea"ing
So, !.:,_y 3f16 x 7F. Ig
ShouJder Spacer
Hex Sell Tap Scr }t8-!6 <
1.25' Lg
L-Wash 3/8" Scr
Hex SF tap Scr 3B-16 >
75" Lg.
Transmission Ass_, C3m:)
Hex Nut !4-28 Thc..
Bearing 1.0"1 D x 1.12" Lg
Hex Scr 318-16 x I75' L
Snap Ring
Wheel Ass'y. Comp--R H
Wheel Ass'y. Comp._L.P'
(Not Shown1
Tire Only
Inner Tube Only
Wheel Hub Ass'y..-R H.
Wheel Hub Ass:y.-L.H,
(Not Shown:)
Hex Scr 318-24 x 1 00" Lzj "
5 ) i 04:360
,,m)-0t _0
{: ._ 71:'-0!L1
, --?,'0,:'_'C
_:_ 71 ]-02!g
5_
57
5_
5
6;
; 5t
i 63
_6_
i 7-i2-0;.)f7
; 735-01 ] 9
{,4B44
732-O! 53
34_64
712-0138
7t 2-0_ 30
04637
736-0256
[
!65 i 7" 1-04":.I
i 73s-03so
6,7 I 7t 0-0106
6_q . 7t 2,,0324
69 '04841
73 710-0623
71 .7'10-062t
72 , 736-01_ 9
74 _05080
,"_.= 756-0301
_6 710-0599
,77 04876
7B 736-0173
79 712-0117
7oo-0t , o
et 710-0195
j_2 710-0599
_[3 714-0105
_4 710-0380
_6 750-0382
_7 0_,863
r:8 751-o0233
9 750-0379
_770-7763
7j7-8517
Weigh! Mt.._ BrKt
Ft-.A'a_r, 5"_ I D x 7:3
') D. , 'h56
He,: Ser_. . !',ut 3 8-24
"f:d "
He:: Nu,!) i6 iST]d '
L-',.¢.aSP _'_t6 S:r "
;di Pi"Arm ,_ss /
-4-t,'_Cent L...Nu1 _ -28 Thd
-te_ ins _Nut 3/8-16-hd
/a iabie S_-_ee.lBrkt A.';s'y
:1 dash 625 I D x 1.25
O D
Coder Pir'l t_"' Dia x 75-
l_g"
Sh:_uloer Scr 5fl ._ 267
HexSr.:r "_20 xt 25"_g "
Hex Ins ,_hiLt _4-20 Tt}d
Con;ro_ Brkl
_e>: Wasr_ PId Se f Tap Scr
Hex Scr .=_6-18 x 50' Lg
L;Wash 5'16 Scr"
Friclion Wheel Ass'y.
Engine Pulley Ass'y 5_8 V
<75 tD
He.x Wash Hd Serf Taa Scr.
Belt Cove_ Ex:ensian Ass'y
Fl-Wast_ ";:" S:_ .
Hex Cenl L-Nut 1,_-28 Thc
Fl-Wash :.;_'" Sc_
Hex Scr. _4-2B x 62" Lg.."
Hex Wash Hal. Se;f Tap Ssr
Key 3/16).3!16 × 1 00" Lg
Hex Scr 5t16-t8 _ 175 Lg."
Spacer
Rear Bell -...,o,__rSuppo t
Brkt.
Muffler Deffe{:1or
Spacer.637 t D x .78t Q D
K.85:' Lg
Owner's Manual
Warranty Label
"Standard Hardware Items_May Be Purchased
Locally..
t-Not Illustrated
25

TILLERACCESSORIES
Hilling Plow (Must be used with "V" Bar Frame
Adapter)
Six Tang Cultivator (Recommended use of Depth
Gauge Wheels)
"V" Bar Frame Adapter (Recommended use of
Depth Gauge Wheels)
Four Shovel Cultivator(Must be used wilh "V" Bar
Frame Adapter)
Depth Gauge Wheels
Tine Cultivating Shields
Wheel Weights
Tire Chains (13" x 5")
32" Angle Dozer Blade
Front Hitch Mount (Required to mount 32" Angle
Dozer Blade)
26

Repair Parts
5-H.P. CHAIN DRIVE TILLER MODEL 247.298770
ENGINE MODEL, 130202 TYPE 08"15-03
5337
--20!
232
!72_6L3
,_....z";7 6i_)
5_
15
61_i,_z b2zil_
_,,5__F- _-_
31-35BGASKET SET]
REQUIRES SPECIAL TOOLS TO INS'FALL
SEE REPAIR INSTRUCTIONNtC_NUAL
27

Repair Parts
5-H.Po CHAIN DRIVE TILLER MODEL 247,298770
ENGINE MODEL 130202 TYPE 0815-03
\
373 _ 65,..._;
3O4 24
76 71 70 67
Z
305
REQUIRE8 SPECIAL
TOOLS TO INSTALL
SEE REPAIR INSTRUCTIONMANUAL
23
75
\
28

Repair Parts
5_H.P** CHAIN DRIVE TILLER MODEL 247.298770
ENGfNE MODEL 130202 TYPE 0815-03
62_
_ 124
,19j
534
Z67 f526
265
t63
29

Aepair Parts
5-H,P. CHAIN DRIVE TILLER MODEL 247.298770
ENGINE MODEL 130202 TYPE 0815-03
PARTS LIST FOR ENGINE MODEL NO. 130202_0815-03
REF, PART PART
NO. NO, DESCRIPTION NO,,
391977
297565
_ 89660
211542
7 *270383
8 294178
9 *27549
!0 93394
!1 66578
t2 *270080
*270125
*270126
13 93368
14 93369
15 91249
16 261148
18 297602
19 297603
20 294606
21 66768
22 93032
23 297229
24 61760
PISTON RING
298904
298305
298906
298907
298982
298983
298984
298985
26026
298909
298908
299430
221890
221876
92296
Cylinder Ass'y.
Bushing--Cylinder
NOTE: Requires special tools
for installation.
Seal--Oil
Head--Cylinder
Gasket--Cylinder Head
Breat her--Valve Chamber
Gasket--Valve Cover
REF,
NO,,
33 211119
34 261044
35 260552
36 26478
37 222443
40 93312
45 260642
46 211117
52 *27355
DESCRIPTION
Valve-- Exhau st
Valve-- Intake
Spring--Intake Valve
Spring--Exhaust Valve
Guard--Flywheel
Retainer--Valve Spring
Tappet --Valve
Gear--Cam
Gasket--Carburetor Mtg_ (2)
Screw--Breather Mtg. Sere
Grommet_Breather Tube
Gasket_Crankcase _ .015"
thick (Standard)
Gasket--Crankcase_.005"
thick
Gasket_Crankcase=.,009"
thick
Screw_Cylinder Head
(2-3132" lgo)
Screw_Cylinder Head
(2-I 5132" Ig.,)
Ptug_Pipe, _A" Std,, Square
Head
Crankshaft
Cover Ass'y_ _Crankcase
Bushing_Crankcase Cover
NOTE: Requires special toots
for installation,,
Seat_Oil
Plug--Oil Filler
Screw_Crankcase Cover
Mtgo Sere
Flywheel_Magneto
Key_Ftywheel
SETS:
NOTE: For Chrome Piston
Ring Set,_Stdo _ze--order
Part No. 299742.
Piston Ass'y_--Std.
Piston Ass'y._.,010" O,,S
Piston Ass'y.--O20" O.So
Piston Ass'y.--.030" OoS.
Ring Set--Std. Piston
Ring Set_.010" COS,, Piston
Ring Set--c020" O.S,, Piston
Ring Set--.030" O.S. Piston
Lock--Piston Pin
Pin Ass'y._Ptston--Std.
Pin Ass'yo-- Piston-- °005"
CoS.
Rod Ass'y.--Connecting
NOTE: For Connecting Rod
with .020" undersize Crankpin
Bore--order Noo 390459.
Dipper--Connecting Rod
Lock_Conno Rod Screw
Screw--Connecting Rod
55
56
57
58
59
6O
65
66
67
68
70
71
73
74
75
76
81
90
95
96
97
114
116
117
!18
124
147
148
149
152
154
! 63
180
181
190
191
1299431
295871
294303
66884
230228
66728
93067
298310
21"1383
63770
298436
22'1653
221923
93490
220865
68238
222263
299437
93499
211203
2992'12
66594
'65978
230590
i23433
193357
1230591
i22235
26336
260575
92634
27660
297600
392304
93341
"27911
Housing_ Rewind Starter
Puttey_ Rewind Starter
(includes 63" long rope)
If longer rope is required,
order rope no. 66894 and cut
to length.
Spring--Rewind Starter
Rope_Rewind Starter_
63" long
(For use with Plastic Pulley)
If longer rope is required,
order rope No. 66894 and cut
to length°
Pin--Starter Grip
Grip_Starter Rope
Screw_Stamped Steel Hsg..
Mtgo Sere
Clutch Ass'y,_Rewind Starter
Housing_Starter Clutch
Ball--Clutch
Ratchet_Rewind Starter
Washer_Ciutch Retainer
Screen_Starter Pul Iey
Screw_Sem
Washer_Spring
Washer_ Ratchet Sealing
Lock--Screw
Carburetor Ass'y.
Screw--Throttle Valve to
Shaft Sere
Throttle_Carburetor
Shaft and Lever,---Throttle
Gasket_Needle Valve Nut
Packing--Needle Valve
Nut--Needle Valve
Vatve_Needle
Screw_Hex Head
Seat_ Needle Valve
Washer--Needle Valve (2)
Spring--Needle Valve
Spring--Throttle Adjustment
Screw_Machine, Rd. Hd._
5-40 x 5 /8"
Gasket_Air Cleaner Mtg.
Tank Ass'y,--Fuel
Cap--Fuel Tank
Screw--Fuel Tank Mtg. Sem
Gasket--Fuel Tank Mtg. (2)
*Included in Gasket Set--Part No, 297615° 30

Repair Parts
5-H.Po CHAIN DRIVE TILLER MODEL 247.298770
ENGINE MODEL 130202 TYPE 0815.o3
"EF.j
200
201
202
203
204
308
333
335
337
340
341
PART
NO.
221480
260661
260678
297718
230844
93838
260695
391737
22155!
221517
93491
391966
220680
222450
260478
221535
93496
391313
299410
93158
221511
93042
221512
298316
934'14
2988O9
26018
93381
PARTS LIST FOR ENGINE MODEL NO. 130202-0815-03
Guide--Air
Link--Governor
Link--Throttle
Crank-- Bell
Bushi ngmGovernor Lever
(Flat)
NOTE: 230943 Bushing--
Governor Lever (with 1/2" dia..
Flange) or:
23688 Bushing--Governor
Lever (with 318" dia. Flange)
Used on type Nos. 0130, 0148,
0't74, 0181, 0184. 0185, 0194,
0196, 022!, 0230, 0233, 0237,
0239, 0247, 0255, 03'16, 0352,
0353, 0359, 0364, 0406, 0414,
0416, 0418,04t9, 0422, 0425,
0431, 0435, 0438, 0439, 0451,
0458, 0471, 0480, 048t, 0485,
0514, 0520, 0540, 0568, 0573,
0607, 0608, 0620, 0635, 0636.
Screw--Shoulder
65704
93042
345
346 93705
356
357
358
372
373
375
392
Spring--Governo _
Gear--Governor
Washer--Thrust
Lever--Governor Control
Rivet--Governor Control
Lever Mtg.
Lever Ass'y.--Governor_
For V4" Dia. Crank
Washer_Governor Lever
Washer_Governor Lever
(_A" loD,.)
Spring--Governor Link
Clamp_Oasing
Screw--Sere
Muffler_Exhaust
Housing_BIower
Screw_Blower Hsg, Mtg.
Shield_Cylinder
Screw_Cylinder Shield Mtg.
Sern
Cover_Cylinder Head
Armature--Magneto
Screw_Armature Mtg. Sere
Plug_Spark (with Gasket)
1_/2" High--37-42 M. Mo
Spring_-Breaker Arm
Sorew_Breaker Arm Mtg
Sere
59z
6O8
609
61z
6I3
614
615
616
621
626
634
643
676
684
725
851
220366
295413
91539
297615
220477
92987
294628
260455
270026
221377
93265
210959
93141
260374
93343
221514
230722
67838
93322
27987
297036
231079
92613
231082
390463
260694
391813
296811
93704
93306
93307
231077
297472
230749
270167
221321
222261
299060
221885
221798
DESCRIPTION
Plunger_ Breaker Point
Screw--Condenser Clamp
Mlg, Sem
Cover--Breaker Point and
Condenser
Screw--Dust Cover and
Flywheel Guard M_g
Wire--Ground
Key
Gasket Set
Clamp_Condenser
Nut_Hex
Breaker Points and Condenser
Set
Spring--Fuel Pump
Diaphragm
Diaphragm
Cap--Spring
Pin--Diaphragm Cover
Cover--Diaphragm
Screw_Diaphragm Cover
Spring--Connector
Screw--Tank Brkt, Mtg.. Sere
Clamp--Breather Tube
Tube_ Breather
Grommet-- Breather Tube
Screw_Air Cleaner
Element_Air Cleaner
Cleaner Ass'y _Air
Bushing_Governor Crank
I.D,)
Bolt_Governor Lever
Nut_Hex_10-24
Starter Ass'y, _Rewi nd
Spring--Throttle Link
Fuel Pipe and Clip Ass'y
Pipe_Fuet
Screw--Muffler Mtg.
Cotter--Hair Pin
Retainer_E-Ring
Crank--Governor (_,_" Dia. )
Switch--Stop
Spacer--Governor Crank
Washer, Throttle Shaft (Felt)
Cup--Air Cleaner
Deflector_ Exhaust
Needle Valve K,t
Shield_Heat
Cable Terminal,--lgnition
*included in Gasket Set--Part No.. 29761&

Sears
..... i i/ H i,, i
manual
EL O.
247=298=(70
HOW TO ORDER
REPAUR PARTS
The Model Number wil! be found slamped on a plate attached to the
chassis. Always mention the Model Number when requesting service or
repair parts for your fiUer.
All parts listed herein may be ordered through SEARS ROEBUCK AND CO
or SIMPSON SEARS LIMITED RETAIL or CATALOG STORE,
WHEN ORDERING REPAIR PARTS, ALWAYS GIVE THE FOLLOWING
INFORMATION AS SHOWN lN THIS LIST.
1 The PART NUMBER
2_ The MODEL NUMBER 247.298770
3. The PART DESCRIPTION
4 The NAME OF MERCHANDISE-- Tiller
if the parts you need are not stocked locally, your order will be
electronically transmitted to a Sears Repair Parts Distribution Center for
expedited handling,
Your Sears merchandise takes on added value when you discover that Sears
has over 2,000 Service Units throughout the country, Each is staffed by
Sears-trained, professional technicians,
ROEBUCK AND CO., Chill. 60684 U_A.
and __NS._--'HIAIqS L1lV_'r_, Toronto, Ca_da
PART NO. 770-,7763 PRINTED IN U.S.A,