Craftsman 315174710 User Manual ROUTER Manuals And Guides L0709179
CRAFTSMAN Router Manual L0709179 CRAFTSMAN Router Owner's Manual, CRAFTSMAN Router installation guides
User Manual: Craftsman 315174710 315174710 CRAFTSMAN ROUTER - Manuals and Guides View the owners manual for your CRAFTSMAN ROUTER #315174710. Home:Tool Parts:Craftsman Parts:Craftsman ROUTER Manual
Open the PDF directly: View PDF .
Page Count: 16

OWNER'S
MANUAL
MODEL NO.
315.174710
CAUTION:
Read Rules for
Safe Operation
and All Instruc-
tions Carefully
II III "111IIIIII
in,,i ...............
®
Router
Double Insulated
IlllIllllll I Illllllll I lll II'lllllI
Thank You for Buying
Craftsman Tools
_l in ,i.
Warranty
Introduction
Operation
Maintenance
,, Repair Parts
Designed exclusively for and sold only by
SEARS, ROEBUCK AND CO, Sears Tower, Chicago, IL 60684
612547-8! 5
4-92
®
PR}NTED IN U S A

, , iU,,ll ii i]
.................. HH
FULLONE YEARWARRANTYON CRAFTSMANROUTER
IfthisCraftsmanRoutertailsto givecompletesatisfactionwithinoneyearfromthedate of purchaseRETURNrr TO
THENEARESTSEARSSERVICECENTER/DEPARTMENTTHROUGHOUTTHEUNITEDSTATESandSearewilt
repairit,free of charge.
Ifthlsrouterisusedfor commercialor rentalpurposesthiswarrantyappliesforonly90daysfromthedateofpumhass,,
Thiswarrantygivesyou specific legalrights,andyoumay alsohaveotherrightswhichvary fromstate tostate.
SEARS,ROEBUCKAND CO,
DEPT.73tCR-W
SEARSTOWER
CHICAGO, IL 60684
,,,uu, ,ll, llllll ,, ,,,,i i i , ,HH I
INTRODUCTION
DOUBLE INSULATION Is a concept in safety, in electric
power tools, which eliminates the need for the usual three
wire grounded power cord and grounded supply system,
Wherever there is electric current in the tool there are two
complete sets of insulationto protectthe user, All exposed
metal parts are isolated from internal metal motor compo-
nents with protecting insulation.
READ ALL INSTRUCTIONS
IMPORTANT - Servicing of a tool with doubts Insulation
requires extreme care and knowledge of the system and
should be performed only by a qualified service technician.
For service we suggest you return the toot to your nearest
Sears Store for repatr_Always use originalfactory replace-
ment parts when servicing.
RULES FOR SAFE OPERATION
1, KNOW YOUR POWER TOOL - Read owner's manual carefully. Learn its applications and
limitations as welt as the specific potential hazards related to this tool,
2o GUARD AGAINST ELECTRICAL SHOCK BY PREVENTING BODY CONTACT WITH
GROUNDED SURFACES. For example: Pipes, radiators, ranges, refrigerator enclosures.
3. KEEP GUARDS IN PLACE and in working order.
4, KEEP WORK AREA CLEAN. Cluttered areas and benches invite accidents_
5. AVOID DANGEROUS ENVIRONMENT, Don:t use power tool in damp or wet locations or expose
to rain_ Keep work area well lit.
6. KEEP CHILDREN AND VISITORS AWAY. All visitors should wear safety glasses and be kept a
safe distance from work area. Do not let visitors contact tool or extension cord.
7. STORE IDLE TOOLS. When not in use tools should be stored in a dry, high or locked-up place -
out of the reach of children.
8. DON'T FORCE TOOL. It will do the job better and safer at the rate for which it was designed.
9. USE RIGHT TOOL. Don't force small tool or attachment to do the job of a heavy duty to.oL Don't
use tool for purpose not intended -for example - Don't use a circular saw for cutting tree limbs or
logs_
10. WEAR PROPER APPAREL. No loose clothing or jewelry to get caught in moving parts. Rubber
gloves and non-skid footwear are recommended when working outdoors. Also, wear protective
hair covering to contain tong hair and keep it from being drawn into air vents.
11. ALWAYS WEAR SAFETY GLASSES, Everyday eyeglasses have only impact_resistant lenses;
they are NOT safety glasses.
Page 2
2 Hll Ir"ll'l ,,,,_L- ....... ,i Ii ,=L' '1, _ " ,,r=_r= ..... _ .................... - _ .............

RULES FOR SAFE OPERATION (Continued)
12. PROTECT YOUR LUNGS, Wear a face or dust mask if operation Is dusty.
13, PROTECT YOUR HEARING, Wear hearing protection during extended periods of operation.
1_4o DON'T ABUSE CORD, Never carry tool by cord or yank it to disconnect from receptacle. Keep
cord from heat, oil and sharp edge&
15. SECURE WORK. Use clamps or a vise to hold work. Both hands are needed to operate the tool.
16. DON'T OVERREACH. Keep proper footing and balance at all times° Do not use on a ladder or
unstable support.
17. MAINTAIN TOOLS WITH CARE. Keep tools sharp at all times, and clean for best and safest
performance. Follow instructions for lubricating and changing accessories.
18, DISCONNECT TOOLS. When not in use, before servicing, or when changing attachments,
blades, bits, cutters, etc,, all tools should be disconnected from power supply.
19. REMOVE ADJUSTING KEYS AND WRENCHES. Form habit of checking to see that keys and
adjusting wrenches are removed from tool before turning it ono
20. AVOID ACCIDENTAL STARTING. Don't carry plugged-in tools with finger on switch. Be sure
switch is off when plugging in,
21, OUTDOOR USE EXTENSION CORDS. When tool is used outdoors, use only extension cords
suitable for use outdoor& Outdoor approved cords are mar_ed with the suffix W-A, for example -
SJTW-A or SJOW-A.
22. KEEP CUTTERS CLEAN AND SHARP. Sharp cutters minimize stalling and kickback,
23, KEEP HANDS AWAY FROM CUTTING AREA. Keep hands away from cutters. Do not reach
underneath work while cutter is rotating, Do not attempt to remove material while cutter is rotating.
24. NEVER USE IN AN EXPLOSIVE ATMOSPHERE. Normal sparking of the motor could ignite
fumes.
25. INSPECT TOOL CORDS PERIODICALLY and if damaged, have repaired at your nearest Sears
Repair Center. Stay constantly aware of cord location.
2& INSPECT EXTENSION CORDS PERIODICALLY and replace if damage&
27. KEEP HANDLES DRY, CLEAN, AND FREE FROM OIL AND GREASE. Always use a clean
cloth when cleaning. Never use brake fluids, gasoline, petroleum-based products or any strong
solvents to clean your tool,
28. STAY ALERT. Watch what you are doing and use common sense° Do not operate tool when you
are tired, Do not rush.
29. CHECK DAMAGED PARTS. Before flJrther use of the tool, a guard or other part that is damaged
should be carefulty checked to determine that it will operate properly and perform its intended
function° Check for alignment of moving parts, binding of moving parts, breakage of parts,
mounting, and any other conditions that may affect its operation, A guard or other part that is
damaged should be properly repaired or replaced by an authorized service center unless indi-
cated elsewhere in this instruction manual
30. DO NOT USE TOOL IF SWITCH DOES NOT TURN IT ON AND OFF° Have defective switches
replaced by an authorized service center.
31. Inspect for and remove aft nails from lumber before routing.
32° DRUGS, ALCOHOL, MEDICATION. Do not operate tool while under the influence of drugs,
alcohol, or any medication.
3& When servicing use only Identical Craftsman replacement parts.
34. SAVE THESE INSTRUCTIONS. Review them frequently and use them to instruct others who may
use this toot. If you loan someone this tool, loan them these instructions also.
Page 3

OPERATION
Your router is a versatile woodworking toot which will give you years of trouble-free performance It is engineered with the
professional in mind, but its ease of operation allows the amateur to produce work which ts beauttft,,_land precise.
KNOW YOUR ROUTER
Before attempting to use your router, familiarize yourself with all operating features and safety requirements, See Figure 1,
WRENCH
WRENCH
"LOCK.ON"
BUTTON
SPINDLE
CLAMPING
HANDLE
DEPTH
STOPRINGS
HANDLE
CHIP SHIELD SUBBASE Fig, 1
CHIP SHIELD
A clear plastic chip shieid is installed on the front of your router for protection against ftytng dust and chips. The shtetd is
designed to fit the front opening of the router base. See Figure 1. If necessary to remove chlp shield, squeeze the tabs on
each end and puil outward, To replace, squeeze the tabs at each end, fit into the opening, then ralease_ FOR YOUR
PROTECTION DO NOT USE ROUTER WITHOUT CHIP SHIELD PROPERLY IN PLACE.
"LOCK-ON" BUTTON
The switch of your router is equipped witha "lock-on" feature which is convenient when operating for extended periods of
time. To lock on, depress the trigger, push in the lock button located on the side of the handle, then while holding the lock
button pushed in, retease the trigger To release the lock, depress the trigger and release it See Figure 1.
WRENCH STORAGE AREA
Your router has a wrench storage area located on the top end cap portionof the motor houstng, When installingor removing
cutters remove the wrench from its storage area Proper storage of wrench when not in use w{II help reduce the possibttiity of
tosingwrench. S_a Figure 1,
The operation of any router can reautt In foreign objects being thrown Into your eyes, wht.ch
can result In severe eye damage, Before commencing power tool operation, always wear
safety goggles or safety grasses wtth side shietds and afurl face shield when needed. We
recommend Wide Vision Safety Mask for use over eyeglasses or standard safety glasses wlth
side shields, available at Sears Catalog Order or Retail Stores.
........................ ,,,,,i,H, H,i
Page 4

OPERATION
INSTALL1NG/REMOVING CUTTERS
See Figure2,
t+ UNPLUGYOUR ROUTER+
2. A Spindle lock is located on the front of the motor
housing See Figure 1, To activate lock, push spindle
lock tn and slide into lock position,
3. Place your muter upside down on tab{e, then turn collet
nut with wrench until lock mechanism interlocks See
Figure 2. NOTE: Spindle lock is spring loaded and will
snap into position when lock mechanism interlocks,
4.
6_
Remove cutters by turning coliet nut counterclockwise
enough to allow cutter to slip easily from colleL See
Figure2, The cotlet is machined to precision tolerances
to fit cutters with I/4" diameter shank size+
With your router sti+l upside down on table, insert shank
of cutter into collet L The shank of your cutter shoMd be
close to but not touching bottom of cotter+
Tighten the coltet nut securely by turning clockwise with
the wrench provided+ See Figure 2 Put spindle lock
back in unlock positlon+ Otherwise, the interlocking
mechanism of the spindle lock will not let you turn your
router oR.
DEPTHOF CUT ADJUSTMENTS
See Figures 3 and 4
We recommend thai cuts be made at a depth not exceeding
1/8" and that several passes be made to reach depths of cut
greater than 1/8"
TURN TO ACTIVATE
SPINDLE LOCK
CUTTER
TO LOCK
Fig. 2
TO UNLOCK
CLAMPING
LEVER
ELECTRICAL CONNECTION
Your router has a precision built electric motor+ ft should be
connected to a power supply that is 120 volts, 60 Hz, AC
only (normal household current). Do not operate this tool
on direct current (DC) A voltage drop of more than 10
percent will cause a loss of power and overheating If your
tool does not operate when plugged into an oulIet, double-
check the power supply rating
Page 5

OPERATION
DEPTH OF CUT ADJUSTMENTS (Continued)
1, UNPLUG YOUR ROUTER.
2Place your muter on a flat surface, unlock clamping
tever, and adjust until cutter is inside subbaso. See
Figure 3
3 Turn the depth adjusting ring until tip of cutter touches
flat surface, See Figure 4,
4 Position your router so that the cutter can extend below
the subbase for desired depth setting,
5 Turn the depth adjusting ring to obtain the desired depth
ot cuL The distance the cutter moves Can be read on
the depth adjusting ring. Use reference point on motor
housing to measure depth of cut° Each mark on the
depth adjusting ring indicates 1/64 inchchange in depth
setting.
6. Lock clamping lover, securing depth adjusting ring to
motor housing end base,
DEPTH STOP RINGS
See Figures 5 and 6
Your router is equipped with depth stop rings that will allow
you to set positive stops for operating your router at two
desired depths of cut
1 Release depth stop rings. To release: grasp depth stop
ring tabs with your thumb and index finger, then twisl
them apart as shown by the arrows in figure 5.
2. Using depth adiusling ring, sot cutter at lowest desired
depth of cut, Lock clamping lever. Position bottom depth
stop ring against depth adjusting ring. Hold depth stop
ring against depth adjusting ring and lock. See Figure 6.
Note: Depth stop ring ends snap together to lock
3 Unlock clamping lever and move depth adjusting ring to
set culler at second desired depth of cut Lock damping
fever Posilion top depth slop ring against depth adjusting
ring Hold deplh slop ring against depth adjusling ring
end lock See Figure 6 Note: Oeplh slop ring ends snap
together Io lock
Depth stop rings witl now provide a positive stop allowing you
to operate your rouler at two cutter depths
BASE cu'n'ER
Page 6
-_:_ ............ _T''"'"I"' . ' '11111I'll II' /'., '1'11'........ L'""' Z_I"L_ ..__ .........

OPERATION
RqUTING
_or case of operation and maintaining proper control, your
touter has two handles, one on each side ofthe router baser
When using your router hold it firmly with both hands as
shown infigumm7. Turn routeron and letmotor buildtoits full
speed, then gradually feed cutter into workplece. Remain
alertand watch what you are doing. DO NOT operate muter
Whenfatigued,
PROPER FEEDING
The rightfeed is neither too fast nor too slow. It ts the rate at
which the bit is being advanced firmly and surely to produce
a continuousspiral of uniform chipsmwithout hogging into
thewoodto make large individualchipsor,on theotherhand,
to create only sawdusL If you are making a smail diameter,
shallow groove in soft, dry wood, the proper feed may be
about as fast as you can travel your routeralong your guide
line. On the otherhand, ifthe bit is alargeone, thecutts deep
or thewood ishard to cut,the proper feed may be a very slow
oneoThen, again, a cross-graincutmay require a slowerpace
than an identicalwith grain cut inthe same workpisCeo
There Is no fixed rule. You will team by experience°., by
listening to the router motor and by feeling the progress of
cach cut. If at all possible, always test aouton a scrap piece
of the workpiece wood, beforehand.
RATE OF FEED
IMPORTANT:The whole "secret"of professionalroutingand
edge shaping lies inmaking a careful set-upfor the cutto be
made and In sclcctlng the proper rate of feed.
FORCE FEEDING
Clean, smooth routingand edge shaping can be done only
when the bit is revolving at a relatively high speed end is
takingvery small bites to producetiny,cleanlysevered chips.
If your muter is forced to move forward too fast, the RPM of
the bitbecomes slower than normal in relationto itsforward
movement.. As a result, the bit must take bigger bites as it
revoiveso "Bigger bites" mean bigger chips, and a roughcr
finish. Biggcr chips also require more powcr, which could
result in the router motor becoming overloaded.
Under extreme force-feeding conditions the relative RPM of
the bit can become so slow-._nd the bites it has to take so
large--that chips will bepadiatly knocked off (ratherthan fully
cutoff), with resultin_ splintering and gouging of theworkplace.
Sea Figure 8.
Your Craftsman Router is an extremely high-speed tool
(25,000 RPM no-load speed), and willmake clean, smooth
cuts if allowed to run freely Without the ovedoad of e forced
(too fast) feed. Three things that cause =forcefeeding" are blt
size, depth-of-cut, and workpiece characteristics° The larger
thebit orthe deeperthe cut, themore slowly thereutershould
be moved forward. If the wood is very hard, knotty, gummy or
damp, the operation must be slowed stilI more.
You can always detect "force feeding" by the sound of the
motor. Its high-pitched whine will sound Iowerand strongeras
it loses speed. Also, the strain of holding the tool will be
noticeably increased Page 7
=[jii
,i,,i................... Fig. 7
J
TOO SLOW Fig,8
TOO SLOW FEEDING
it is also possibleto spoil acutby movingthe router forward
too slowly° When it is advanced into the work too slowly, a
revolving bit does not dig into new wood fast enough to take
a bite; instead, itsimplyscrapesaway sawdust-_ikepadicles.
Scraping produces heel which can glaze, bum, or mar the
cut-- in extreme cases, can even overheat the bit so as to
destroyits hardness.
in addition, itis more difficult to control arouter when the bit
is scraping instead of cutting With practically no load on the
motor the bit will be revolving at close to top RPM, and wilt
have amuch greater than normal tendency to bounce offthe
sides of the cut (especially, if the wood has a pronounced
grain with hard and soft areas) As a result, the cut produced
may have rippled, insteadof straight sides See Figure 8
........................................ • .' I[I [i'

OPERATION
TOO SLOW FEEDING (Continued)
"Too.stow feeding" can also cause your routerto take off ina
wrong direction from the intended line of cut, Always grasp
and hold your router firmly with both hands when rout e
Ing.
You can detect "too-slow feeding" by the runawaytoo-highly
pitched sound of the motor; or by feeling the "wiggle" of the bit
inthe cut
DEPTH OF CUT
As previously mentioned, the depth of cut is important be-
cause it affects the rate of feed which, in turn, affects the
quality of a cut (and, atso, the possibility of damage to your
router motor and bit) A deep cut requires a slower feed than
a shallow one, and a too deep cut will cause you to slow the
feed so much thai the bit is no longer cutting, it is scraping,
instead.
Making a deep cut is never advisable. The smaller bits--
especia}[y those only !/16 inch in diameter --are easily
broken off when subjected to too much side thrust A large
enough bit may not be broken off, but if the cut is too deep a
rough cut will result-- and it may be very difficult to guide and
control the bit as desired For these reasons, we recommend
that you do not exceed 1/8 inch depth of cut in a single pass,
regardless of the bif size or the softness or condition of the
workptece_ See Figure 9
To make deeper cuts it is therefore necessary to make as
many successive passes as required, lowering the bit 1/8
inch for each new pass In order to save time, do all the cutting
necessary at one depth setting, before lowering the bit forthe
next pass This wtllatso assure a uniform depth when the final
pass _scompleted. See Figure 10.
DIRECTION OF FEED AND THRUST
The routermotor and bffrevolve inaclockwisedirection. This
gives the tool a slfght tendency to twist (tn your hands) in a
counterclockwise direction, especially when the motor revs
up (as at starting).
Because of the extremely high speed of bit rotation during a
"proper feeding" operation, there is very little kickback to
contend with under normal conditions. However, should the
bit strike a knot, hard grain, foreign object, etc. that would
affect the normal progress of thecuttingaction, there will be
a slight kickback---sufficient to spoil the trueness of your cut
if you are not prepared. Such a kickback is always in the
direction opposite to the direction of bit rotation.
TO guard against such a kickback, plan your set-up and
direction of feed so that youwill always be thrusting thetool--
tohold it against whatever you are using to guide the cut--in
the same direction that the teadingedge of the bit is moving
In shod, the thrust should be in a direction that keeps the
sharp edges of the bit continuously biting straight into new
(uncut) wood.
DEPTH
OF_UT
,, ,,,
14--- WIDTH OF CUT
_" FfO,9
i,H i ,,, i,
2ND. PASS
I,.1_1 1ST. PASS
--_""---""-_'_'_ Fig. 10
1ST, PASS
,,,H, GU,DEOUTS,DE
R_OTATIO._N ('_,_
GUIDE"
j ......
ROTATION
THRUST FEED
GUIDE INSIDE Fig, 11
, ,, i i i
ROUTING
Whenever you are routing a groove, your travelshould be In
a direction that places whatever guide you are using at the
right-hand side. In short, when the guide is positioned as
shown in the first partof Figure 11, tool travel should be _eft
to right and counterclockwise around curves. When the guide
is positionedas shown in the second part of Figure 11 tool
travel should be right to left and clockwise around curves. If
there is a choice, the first set-up is generally the easiest to
use In eithercase, the sideways thrust you useis against the
guide.
Page 8
H'IIH_ _L_ -.---.1 .................... __ =_._.__H'u .-- lUll'fill I ::_:: ........................: m: =. HI

OPERATION
STARTING AND ENDING A CUT
INTERNAL ROUTING
Tilt router and place on workpiece, letting edge of subbase
contact workpiece first Be careful not to let router bit contact
workpieceo Turn router on and let motor buffd to its full speed.
Gradually feed cutter into workpiece until subbase is level
with workpiece.
Upon completion of cut, tum motor off and let itcome to a
complete stop before removing router from work suflace_
EDGING WITH PILOT BITS
The arbor-type bits with pilotsare excellent for quick, easy,
edge shE/pingOfany workpiece edge that is either straight or
curved at a curvature as great orgreater thanthe radiusof the
bit to be used. The pilot prevents the bit from making too deep
a cut; and holding the pilot firmly incontact with theworkpiece
edge throughout prevents the cut from becoming too shallow.
Whenever the workpiece thickness together with the desired
depthof cut(as adjusted by router depth setting) are such that
onTythe top pad of the edge is to be shaped (reaving at least
a 1t16 Inothick uncut podion at bottom), the pilot can ride
against the uncut portion, which will serve to guide IL See
Figure t2 However, if the workpiece is too thin or the bit set
too low so that there will be no uncut edge to ride the pilot
against, an extraboa rd toact as agutde must be placed under
the workpieeeA This "guide" board must have exactiy the
same contour-- stra}ght or curved---as the workpiece edge.
If it is positioned so that its edge is flush wffh the workpieee
edge, the bit will make a funcut (in as faras the bit radius)_On
the other hand, ifthe guide is positioned as shown in F{gure
12 (out from the workpiece edge), the bit wit! make less than
a full cut -- which wiil after the shape of the finished edge.
NOTE: Any of the piloted bits can be used withoutapilot for
edge shaping withguides, as preceding The size (diameter)
of the pilotthat is used determines the maximum cut width
that can be made with the pilotagainst the workptece edge
(the small pilot exposes all of the b{t; the large one reduces
this amount by 1/16 inch)_
ROUTING WITH GUIDE BUSHINGS
__PILOT
TOP EDGE SHAPING
..,11 i .i ,,.,, .H , i ..... . _
WHOLE EDGE SHAPING Fig, 12
EDGEROUTING
Place router on workptece, making sure the router bit does
not contact workptece Turn router on and let motor build to
its full speed. Begin your cut, graduaBy feeding cutter into
workpteca_
Upon completion of cut, turn motor off and let it come to a
complete stop before removingrouter from work surface.
When using the Template Guide Bushings Cat. No_9-25082 withyour router, you must visuallycenterthe bit withthe bushing
before beginning your cut. Your router subbase may be adjusted by loosening the screws holding the subbase to your router
Be sure clamping lever is locked before centering bit in bushing, After centeringbit with bushing tighten screws firmly°
Page 9
J
I i,i] ..... .

SWITCH REPLACEMENT
See Figures 13 & 14
1, UNPLUG YOUR ROUTER.
MAINTENANCE
2, Remove screws (A) and handle cover (B). See Figure
13.
3, NOTE THE LOCATION OF THE MOLDED BEND RE-
LIEF (C) ON THE POWER HANDLE CORD, ALSO
NOTE ALL WIRING INTHE HANDLE AND HOW EACH
LEAD IS CONNECTED TO THE SWITCH° Connec*
lions and wiring position must be identical when instafl_
trig new switch, See Figure 13
4Remove leads from switch (D) by inserting a 1/32"
diameter nail or pin into switch teed receptacle and
putting on lead as shown in figure _4 Remove nail or
pin with a twisting, pulling motion
5o Make lead connectionsto new switch. Push each lead
as far as possible into proper switch receptacle. Pull on
leads to check lead connections withlead receptacles.
6. Locate switch in handle and place leads so they won',t
be pinched or contact screws when handle cover i_;
replaced
7Make sure molded bend relief (C) is correctly positioned
in switch handle, then replace handle cover and screws
8, Tighten all screws securely,
DEPTH ADJUSTING RING
ADJUSTMENTS OR REPLACEMENT
Tension on the depth adjusting ring has been factory set for
properly tightening depth of cut settings, However, extended
use may require that adjustments or replacement be made
to depth adjusting ring See Figures 15-1Z
1o UNPLUG YOUR ROUTER,
To make adjustments to depth adjusting ring=
2 _ghten or loosen lop screw in depth adjusting ring,
See Figure 15. Make adjustments with top screw onfy,
DEPTH
ADJUSTING I
BASE _
Page 10
C
D
Fig. 13
,, 11
LEAD
MOTOR
,HOUSING
DEPRESS LIP
Fig, 15

MAINTENANCE
DEPTH ADJUSTING RING
ADJUSTMENTS OR REPLACEMENT (Continued)
To replace depth adjusting ring;
3 Remove depth stop rings, To remove: Depress lip on
depth stop ring and sfide end of depth stop ring over Itp_
See Figure 15.
4, Remove screw from rear of depth adjusting ring. See
Figure 16_
5. Remove two screws on front of depth adjusting ring,
Also remove slide nut from pocket inside clamping le-
ver. NOTE = Depth adjusting ring replacement ls the
only time bottom screw should be removed.
6. Remove depth adjusting ring
7. Position new depth adjusting ring in place and secure
with the same screws and slide nut used to secure old
depth adjusting r_ng.
8. Make all adjustments with top screw (#10-32 x 15/16=
FiL Hd,) as mentioned previously. Bottom screw (#6-
19 x 1/2" Pan Hd,) should have up to amaximum 'U4"
(.250) clearance, allowing flexibility for top screw ad-
justments See Figure 17.
=ill
REAR OF DEPTH ADJUSTING RING
_EW
Fig. 16
FRONT OF DEPTH ADJUSTING RING
1/4" {.250) MAXIMUM CLEARANCE
Fig. 17
Page 11

MAINTENANCE
GENERAL
Only the parts shown on parts list, page 15, are intended to
be repaired or replaced by the customer All other parts
represent an important part of the double insulation system
and should be serviced only by a qualified Sears service
technician.
Avoid using solvents when eteaning plastic parts. Most
plastics are suscept+ble to various types of commercial
solvents and may be damaged by their use Use clean
cloths to remove dirt, carbon dust, etc
When electric tools are used on fiberglass boats, sports
cars, wallboard, spackling compounds, or plaster, it has
been found that they are subject to accelerated wear and
possible premature failure, as the fiberglass chips and
grindings are highly abrasive to bearings, brushes,
commulator, etc Consequently, it [s not recommended that
this tool be used for extended work on any fiberglass material,
wa!iboard; ° spack+ing compounds, or ptaster. During any
use on fiberglass it is extremely important that the tool is
cleaned frequently by blowing with an air jet
PROPER CARE OF CUTTERS
Get faster more accurate culting results by keeping cutters
clean and sharp. Remove atl accumulated pitch and gum from
cutters after each use
A cutter sharpening kit (Cat No 9-66501) is available from
Sears Catalog Order or Retail Stores
When sharpening cutters, sharpen only the inside of the
ct._tting edge Never grind the outside diameter Be sure when
sharpening the end of a cutter to grind the c+earance angle the
same as originally ground
EXTENSION CORDS
The use o{ any extens+on cord wit{ cause some _oss of power,
To keep the _oss to a minimum and to prevent toot overheat+
ing, follow the recommended cord sizes on the chart at the
right When toot is used outdoors, use only extension cords
suitable tor outdoor use and so marked Extension cords are
available at Sears Catatog Order or Retail Stores
PROPER CAREOFCOLLET
From time to time, it atso becomes necessary to clean your
coflet and coder nut To do so, simply remove col+e! nut from
coltet and clean the dust and chips that have collected Then
return collar nut to its original position
LUBRICATION
All of the bearings in this toot are _ubr[cated with a sufficient
amount of high grade lubricant for the life of the unit under
normal operating conditions. Therefore, no further lubrica-
tion is required
Extension Cord Length Wire Size A.W,.G.
0-25 Feet 18
25-50 Feet 16
50-100 Feet 14
y +
Page 12

ACCESSORIES
----- THE FOLLOWING RECOMMENDED ACCESSORIES ARE CURRENT AND WERE
AVAILABLE AT THE TIME THIS MANUAL WAS PRINTED.
Dovetail Template
Box Joint Temptate
MiU Works Molding Maker
BIs-Kit Plate Jointer Kit
Multi,Purpose Router Guide
(9-2579) Template Guide Bushings (9°25082)
(9-2580) Rout-A-Form Pantograph (9-25183)
(9-25254) Template Set (9-2573)
(9-25423) Sharpening Kit (9-66501)
(9-25179) Full View Router Base (9-25086)
NATIONl
PANEL I
tin'rim I
,, ,,,
VEINING
BffS
26330-1/_"
26329-3J16"
26_28-7/32"
26327-I14 =
DOUBLE EHD
45 ° 60•
V-GBQOV_
26333
CORE BOX
BIT
O
2632_"1/4"
;t6326-,1,_"
V-GROOVE
CHAMFER
O
;_6322_ft2"
"25S78-f/2"
STRAIGHT i
FACE
BITS
LI
25315-1t_"
26314_ _
25313-1/2"
26312-314"
_25524-114"
_25525-5/16"
"25827-1t2"
_2_506-314"
OMBI.,
NATION
STRAIGHT,
BEVEL
CUTTER
@
FO_
"2541
VEN_ER
cUTTER
STRAIGHT
"25413
BEVEL
HINGE
MORTISING
BIT
26336
CUTTER
BFI_
26,319,11_"
26318,I12 _
iRABBETi
BIT
E3]
i
1/4", 5/16_
26310
_25_82
OGEE j
i3/16_
2_305
i
ROMAN Of=
"25504,t14" I
F 7_,,_,o,T,,,,o.,,_' L_J
COVE I
iBIT I
I
i263ol.518" ]
i '25576-3/8" I
"2_575-.It_" I
&R _ 1
CHAMFER I
BIT I
26303 I
BEAD
QUARTER,
ROUND
BITS
25309_114"
2_308-3_B"
2_307.1_"
"25,_03,114"
"25586,,3/_"
"255_5,1Z2"
ARBOR
25_
WITH 2
SALL
BEARING,_
|112 &5ll_'
*2Sag5
The use of attachments or accessories not listed above might be hazardous.
HELPFUL HINTS
,/ Always clamp workplace securely before routing,
,/ A safe operator is one who thinks ahead,
,/ Always wear eye protectfon when routing.
,/ Make set-up adjustments carefully, Then double check. Measure twice and cutonce.
,/ Keep cutters ciean and properlysharpened.
,/' Don't let familiarity make you caretesso
,it Study all safety rules and do the Job safely.
,/ NEVER place your hands inJeopardy,
v" Make certain clamps can't loosen while In usa.
,/ Test difficult set-ups on scrap--Don't waste lumber.
,/ Pian each operation before you begin.
,/
v'
Clean your router frequently..This willprovide smoother operation of depth adjusting ring and clamping lever areas.
Shake router or blow with an air Iet to remove sawdust build-up
THINK SAFETY BY THINKING AHEAD.
Page 13
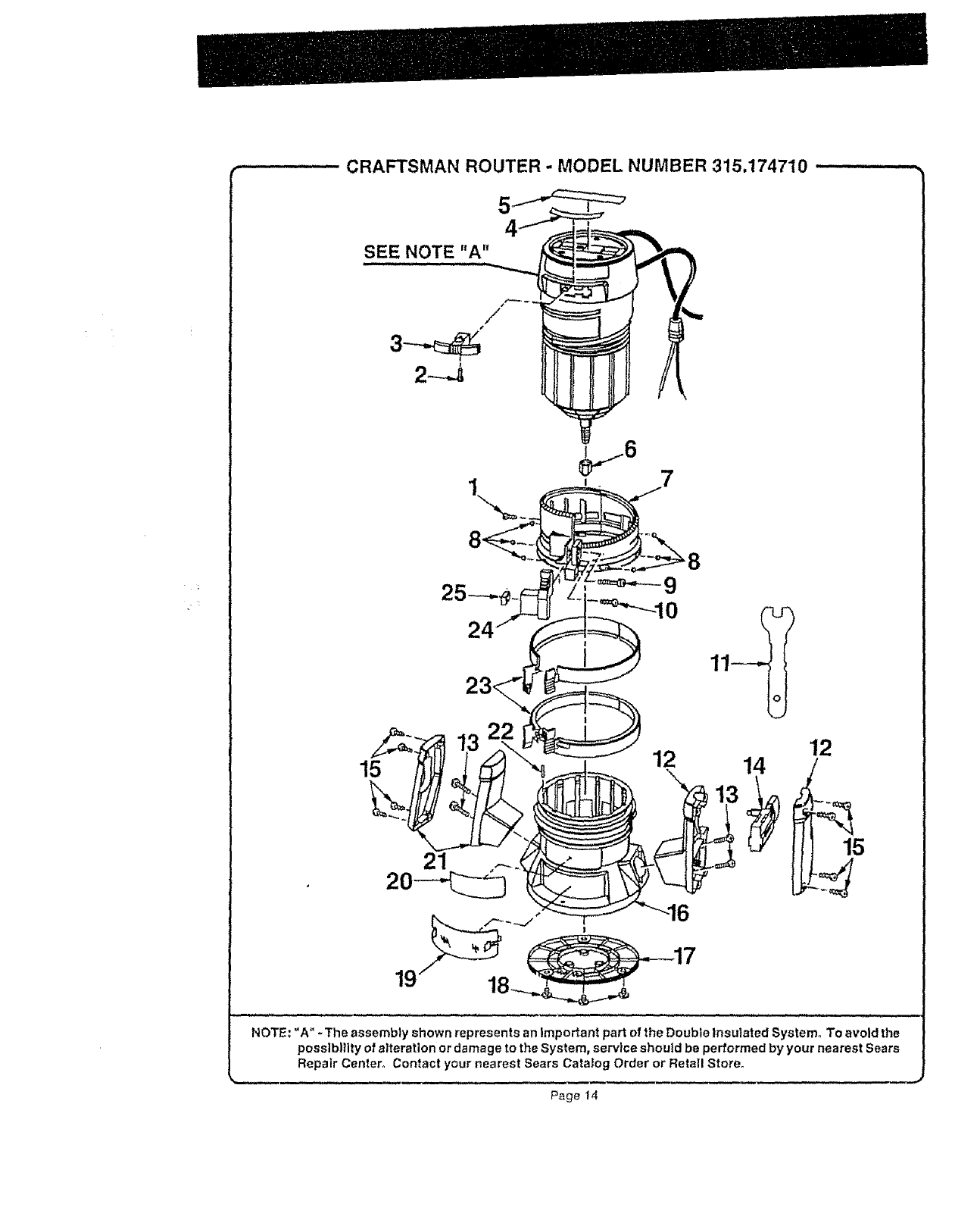
CRAFTSMAN ROUTER - MODEL NUMBER 315,174710 ..... ._
SEE NOTE "A"
9
15
21 12 1_ 12 5
NOTE: _A" - The assembly shown represents an important part of the Double Insulated System. To avoid the
possibility of alteration or damage to the System, service should be performed by your nearest Sears
Repair Center° Contact your nearest Sears Catalog Order or Retail Store.
Page !4
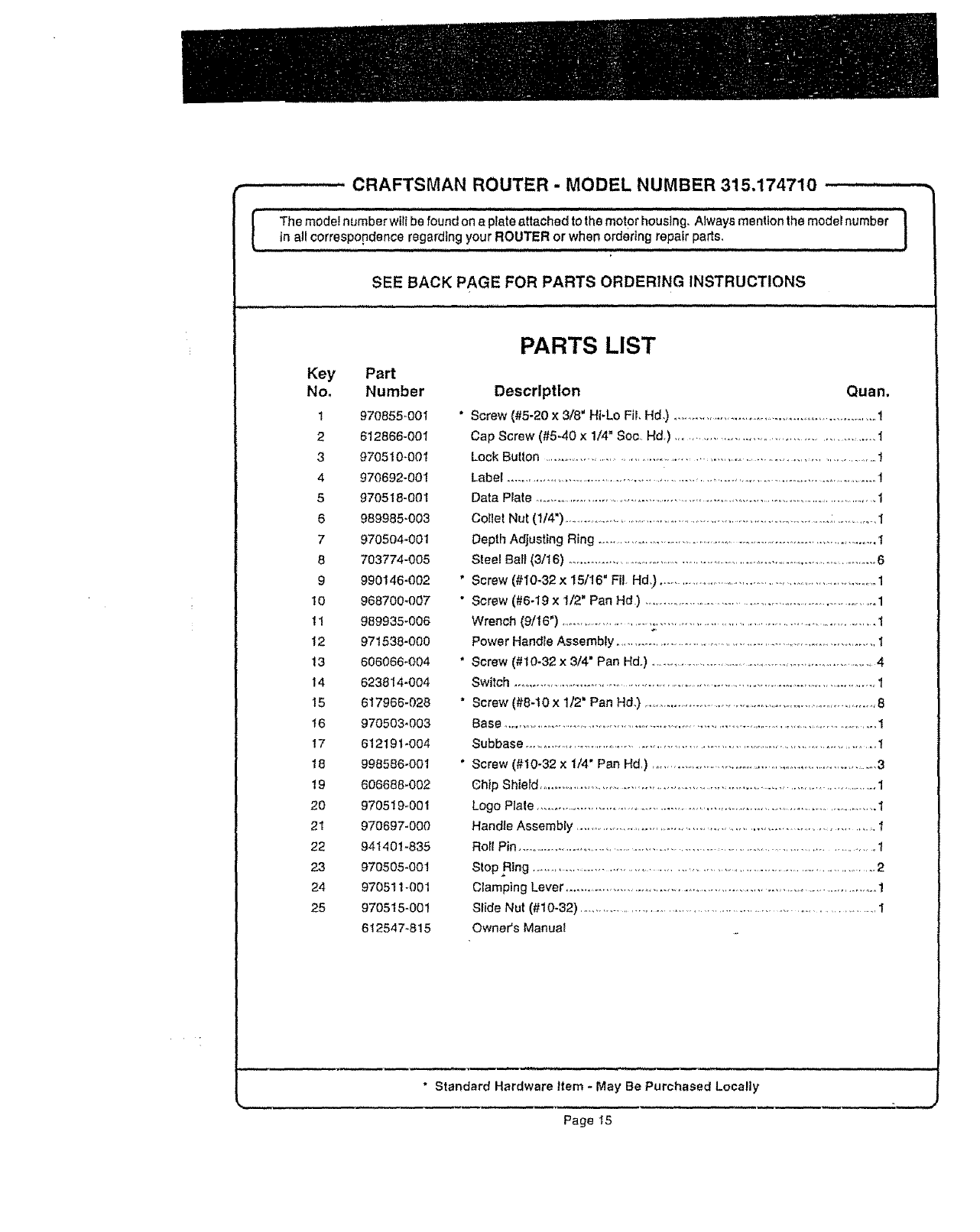
[
' " CRAFTSMAN ROUTER - MODEL NUMBER 315,174710 .......
, ,,, ,, ,, , , ,,i, ,,,,, , ,,,, ,,, ,,,,,,,,,t i,,,i,,,,,,, i , u
The model number will be found on a plateattached to themotor houslng. Always mention themodel number
in all correspondence regarding your ROUTER or when ordering repair parts, !
SEE BACK PAGE FOR PARTS ORDERING INSTRUCTIONS
Key Part
No. Number
1 970855-001
2 612866-001
3970510-001
4 970692-001
5 970518-001
6 989985-003
7 970504-001
8 703774-005
9 990146-002
t0 968700-007
11 989935-006
12 971538-000
13 606066-004
14 623814-004
15 617966-028
t6 970503_003
17 612191-004
18 998586-001
19 606688-002
20 9705t9-091
21 970697-000
22 94t401-835
23 970505-001
24 970511_001
25 9705t5-001
612547-815
PARTS LIST
Description Quan,
" Screw (#5-20 x 3/8" Hi-Lo FiL Hd.) ..............................................................!
Cap Screw (#5-40 x 1/4= Soc Hd,) ..................................................... 1
Lock Button ...................................................................................... t
Label ............................................. _.......................................................... 1
Data Plate ......................................................................................................1
Collet Nut (1/4")................................................................................:............ 1
Depth Adjusting Ring ................................................................................ t
Steel Baft (3/t6) .............................................................................................6
" Screw (#10-32 x 15/16" Fil, Hd,) .................................................................1
"Screw (#6-19 x 1/2" Pan Hal) ................................................................... 1
Wrench (9/t6") ......................... ,.:,.......................................................... 1
Power Handle Assembly ............................................................................... 1
" Screw (#10-32 x 3/4" Pan Hdo) ............................................................... 4
Switch ......................................................................................................... 1
" Screw (#8-10 x 1/2" Pan Hal,) ........................................................................8
Base ...................................................................................................................I
Subbase .................................................................................................. t
* Screw (#t0-32 x 1/4" Pan Hd,) ..................................................................3
Ghtp Shield .............................................................................................. 1
Logo Plate .................................................................................................. 1
Handle Assembly ..................................................................................... t
Roll Pin................................................................................................... 1
Stop Ring ........................................................................................... 2
Clamping Lever ........................................................................................ 1
Slide Nut (#t0-32) .......................................................................... 1
Owner's Manual
* Standard Hardware Item -May Be Purchased Locally
Page 15

OWNER'S
MANUAL
SERVICE
MODEL NO.
315.174710
HOW TO ORDER
REPAIR PARTS
CRRFTgMRN °
Router
Double Insulated
Now that you have purchased your Router, should a
need ever exist for repair parts or service, simply contact
any Sears Service Center and most Sears, Roebuck and
Co, stores. Be sure to provide all pertinent facts when
you call or visit°
The model number of your Router will be found on a plate
attached to the motor housing.
WHEN ORDERING REPAIR PARTS, ALWAYS GIVE
THE FOLLOWING INFORMATION:
,PART NUMBER • PART DESCRIPTION
.MODEL NUMBER • NAME OF ITEM
315.!74710 Router
All parts listed may be ordered from any Sears Service
Center and most Sears stores.
If the parts you need are not stocked locally, your order
will be electronically transmitted to a Sears Repair Parts
Distribution Center for handling,
SEARS, ROEBUCK AND CO, Sears Tower, Chicago, IL 60684