Craftsman 875199590 User Manual AIR GREASE GUN Manuals And Guides L0705091
CRAFTSMAN Greasing equipment Manual L0705091 CRAFTSMAN Greasing equipment Owner's Manual, CRAFTSMAN Greasing equipment installation guides
User Manual: Craftsman 875199590 875199590 CRAFTSMAN AIR GREASE GUN - Manuals and Guides View the owners manual for your CRAFTSMAN AIR GREASE GUN #875199590. Home:Automotive Parts:Craftsman Parts:Craftsman AIR GREASE GUN Manual
Open the PDF directly: View PDF .
Page Count: 5
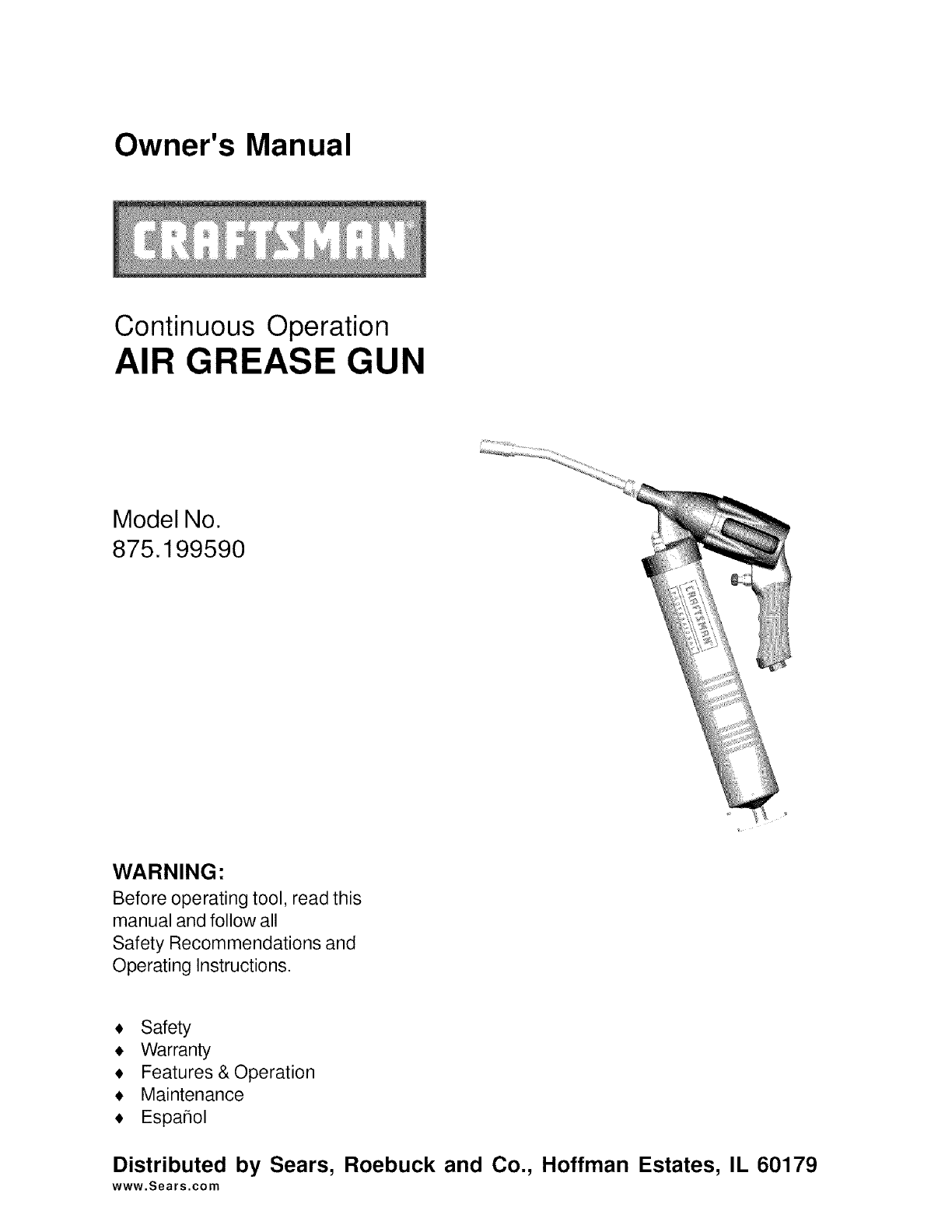
Owner's Manual
Continuous Operation
AIR GREASE GUN
Model No.
875.199590
WARNING:
Before operating tool, read this
manual and follow all
Safety Recommendations and
Operating Instructions.
Safety
, Warranty
Features & Operation
Maintenance
Espahol
Distributed by Sears, Roebuck and Co., Hoffman Estates, IL 60179
www.Sears.com
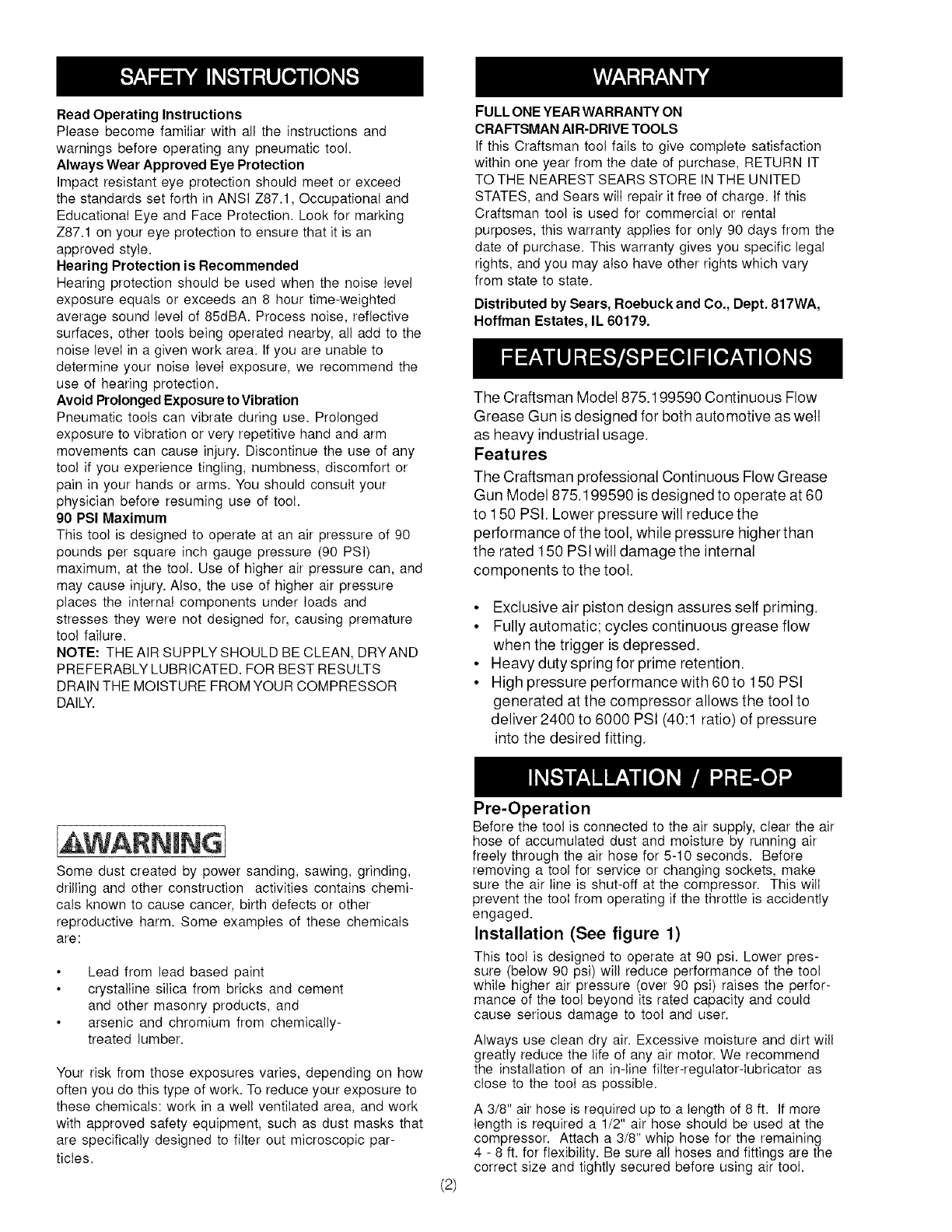
ReadOperatingInstructions
Please become familiar with all the instructions and
warnings before operating any pneumatic tool.
Always Wear Approved Eye Protection
impact resistant eye protection should meet or exceed
the standards set forth in ANSI Z87.1, Occupational and
Educational Eye and Face Protection. Look for marking
Z87.1 on your eye protection to ensure that it is an
approved style.
Hearing Protection is Recommended
Hearing protection should be used when the noise Ievel
exposure equals or exceeds an 8 hour time-weighted
average sound level of 85dBA. Process noise, reflective
surfaces, other tools being operated nearby, all add to the
noise level in a given work area. If you are unable to
determine your noise level exposure, we recommend the
use of hearing protection.
Avoid Prolonged Exposure to Vibration
Pneumatic tooIs can vibrate during use. Prolonged
exposure to vibration or very repetitive hand and arm
movements can cause injury. Discontinue the use of any
tool if you experience tingling, numbness, discomfort or
pain in your hands or arms. You should consult your
physician before resuming use of tool.
90 PSI Maximum
This tool is designed to operate at an air pressure of 90
pounds per square inch gauge pressure (90 PSi)
maximum, at the tool. Use of higher air pressure can, and
may cause injury. Also, the use of higher air pressure
places the internal components under loads and
stresses they were not designed for, causing premature
tool failure.
NOTE: THE AIR SUPPLY SHOULD BE CLEAN, DRYAND
PREFERABLY LUBRICATED. FOR BEST RESULTS
DRAIN THE MOISTURE FROM YOUR COMPRESSOR
DALLY.
FULL ONE YEAR WARRANTY ON
CRAFTSMAN AIR-DRIVE TOOLS
if this Craftsman tool fails to give complete satisfaction
within one year from the date of purchase, RETURN iT
TOTHE NEAREST SEARS STORE IN THE UNITED
STATES, and Sears will repair it free of charge, if this
Craftsman tool is used for commercial or rental
purposes, this warranty applies for only 90 days from the
date of purchase. This warranty gives you specific legal
rights, and you may also have other rights which vary
from state to state.
Distributed by Sears, Roebuck and Co., Dept. 817WA,
Hoffman Estates, IL 60179.
The Craftsman Model 875.199590 Continuous Flow
Grease Gun is designed for both automotive as well
as heavy industrial usage.
Features
The Craftsman professional Continuous Flow Grease
Gun Model 875.199590 is designed to operate at 60
to 150 PSI. Lower pressure will reduce the
performance of the tool, while pressure higher than
the rated 150 PSl will damage the internal
components to the tool.
• Exclusive air piston design assures self priming.
• Fully automatic; cycles continuous grease flow
when the trigger is depressed.
• Heavy duty spring for prime retention.
• High pressure performance with 60 to 150 PSI
generated at the compressor allows the tool to
deliver 2400 to 6000 PSI (40:1 ratio) of pressure
into the desired fitting.
Some dust created by power sanding, sawing, grinding,
drilling and other construction activities contains chemi-
cals known to cause cancer, birth defects or other
reproductive harm. Some examples of these chemicals
are:
Lead from lead based paint
crystalline silica from bricks and cement
and other masonry products, and
arsenic and chromium from chemically-
treated lumber.
Your risk from those exposures varies, depending on how
often you do this type of work. To reduce your exposure to
these chemicals: work in a well ventilated area, and work
with approved safety equipment, such as dust masks that
are specifically designed to filter out microscopic par-
ticles.
(2)
Pre-Operation
Before the tool is connected to the air supply, clear the air
hose of accumulated dust and moisture by running air
freely through the air hose for 5-10 seconds. Before
removing a tool for service or changing sockets, make
sure the air Iine is shut-off at the compressor. This wilI
prevent the tool from operating if the throttle is accidently
engaged.
Installation (See figure 1)
This tool is designed to operate at 90 psi. Lower pres-
sure (below 90 psi) will reduce performance of the tool
while higher air pressure (over 90 psi) raises the perfor-
mance of the tool beyond its rated capacity and could
cause serious damage to tool and user.
Always use clean dry air. Excessive moisture and dirt will
greatly reduce the life of any air motor. We recommend
the installation of an in-line filter-regulator-lubricator as
close to the tool as possible.
A 3/8" air hose is required up to a length of 8 ft. If more
length is required a 1/2" air hose should be used at the
compressor. Attach a 3/8" whip hose for the remaining
4 - 8 ft. for flexibility. Be sure all hoses and fittings are the
correct size and tightly secured before using air tool.
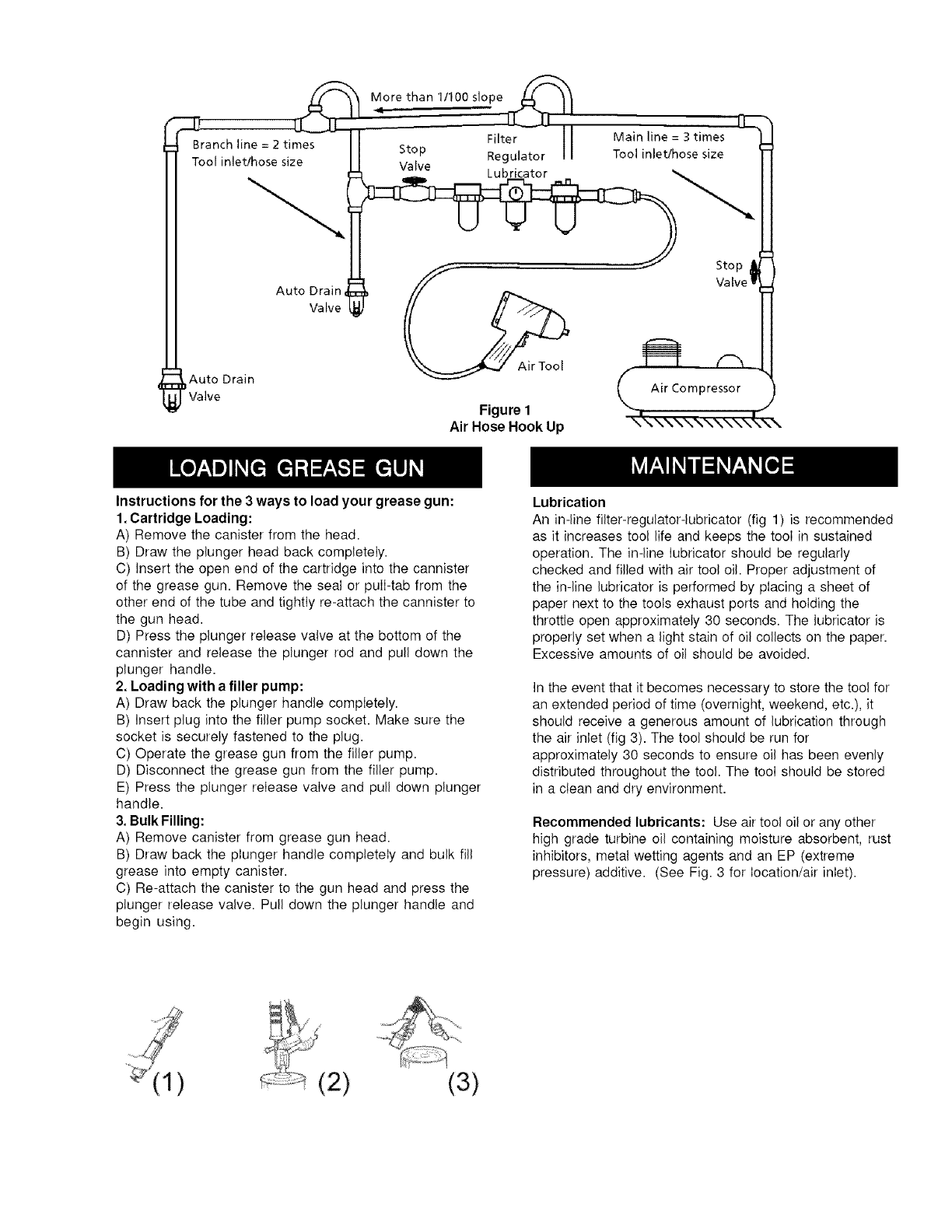
._ Morsethan 1/100slo.pe
ranch ne = 2 t Sto_ Filter Main line = 3 times
"r"f ........ I I _" Reaulator Tool inlet/hose size
I I iooi mien/nose size II Valve
I I Auto Drain _ AirTool I I
_'A:lve _Air Compressor
Figure I _l' •"
Air Hose Hook Up \\\\\\\\\\\\_x\\
Instructions for the 3 ways to load your grease gun:
1. Cartridge Loading:
A) Remove the canister from the head.
B) Draw the plunger head back completely.
C) Insert the open end of the cartridge into the cannister
of the grease gun. Remove the seal or pull-tab from the
other end of the tube and tightly re-attach the cannister to
the gun head.
D) Press the plunger release valve at the bottom of the
cannister and release the plunger rod and pull down the
plunger handle.
2. Loading with a filler pump:
A) Draw back the plunger handle completely.
B) Insert plug into the filler pump socket. Make sure the
socket is securely fastened to the plug.
C) Operate the grease gun from the filler pump.
D) Disconnect the grease gun from the filler pump.
E) Press the plunger release valve and pull down plunger
handle.
3. Bulk Filling:
A) Remove canister from grease gun head.
B) Draw back the plunger handle completely and bulk fill
grease into empty canister.
C) Re-attach the canister to the gun head and press the
plunger release valve. Pull down the plunger handle and
begin using.
Lubrication
An in-line filter-regulator-lubricator (fig 1) is recommended
as it increases tool life and keeps the tool in sustained
operation. The in-line lubricator should be regularly
checked and filled with air tool oil. Proper adjustment of
the in-line lubricator is performed by placing a sheet of
paper next to the tools exhaust ports and holding the
throttle open approximately 30 seconds. The lubricator is
properly set when a light stain of oil collects on the paper.
Excessive amounts of oil should be avoided.
In the event that it becomes necessary to store the tool for
an extended period of time (overnight, weekend, etc.), it
should receive a generous amount of lubrication through
the air inlet (fig 3). The tool should be run for
approximately 30 seconds to ensure oil has been evenly
distributed throughout the tool. The tool should be stored
in a clean and dry environment.
Recommended lubricants: Use air tool oil or any other
high grade turbine oil containing moisture absorbent, rust
inhibitors, metal wetting agents and an EP (extreme
pressure) additive. (See Fig. 3 for location/air inlet).
(3)
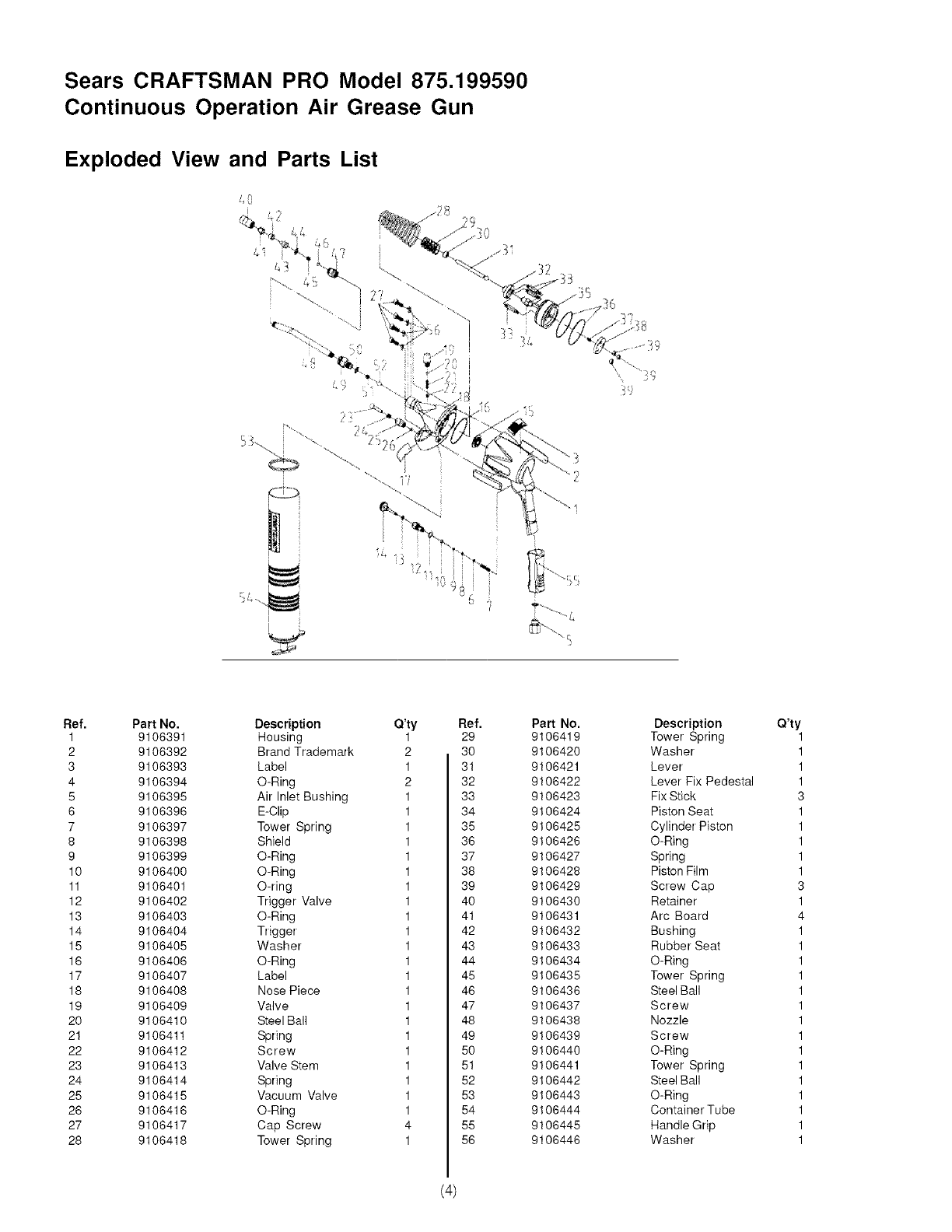
Sears CRAFTSMAN PRO Model 875.199590
Continuous Operation Air Grease Gun
Exploded View and Parts List
z+"
}2
I
Ref. Part No. Description Q'ty
1 9106391 Housing 1
2 9106392 Brand Trademark 2
3 9106393 Label 1
4 9106394 O-Ring 2
5 9106395 Air Inlet Bushing 1
6 9106398 E-Clip 1
7 9106397 Tower Spring 1
8 9106398 Shield 1
9 9106399 O-Ring 1
10 9106400 O-Ring 1
11 9106401 O-ring 1
12 9106402 Trigger Valve 1
13 9106403 O-Ring 1
14 9106404 Trigger 1
15 9106405 Washer 1
16 9106406 O-Ring 1
17 9106407 Label 1
18 9106408 Nose Piece 1
19 9106409 Valve 1
20 9106410 Steel Bali 1
21 9106411 Spring 1
22 9106412 Screw 1
23 9106413 Valve Stem 1
24 9106414 Spring 1
25 9106415 Vacuum Valve 1
26 9106416 O-Ring 1
27 9106417 Cap Screw 4
28 9106418 Tower Spring 1
Ref. Part No. Description Q'ty
29 9106419 Tower Spring 1
30 9106420 Washer 1
31 9106421 Lever 1
32 9106422 Lever Fix Pedestal 1
33 9106423 Fix Stick 3
34 9106424 Piston Seat 1
35 9106425 Cylinder Piston 1
36 9106426 O-Ring 1
37 9106427 Spring 1
38 9106428 Piston Film 1
39 9106429 Screw Cap 3
40 9106430 Retainer 1
41 9106431 Arc Board 4
42 9106432 Bushing 1
43 9106433 Rubber Seat 1
44 9106434 ©-Ring 1
45 9106435 Tower Spring 1
46 9106436 Steel Ball 1
47 9106437 Screw 1
48 9106438 Nozzle 1
49 9106439 Screw 1
50 9106440 O-Ring 1
51 9106441 Tower Spring 1
52 9106442 Steel Ball 1
53 9106443 O-Ring 1
54 9106444 Container Tube 1
55 9106445 Handle Grip 1
56 9106446 Washer 1
(4)
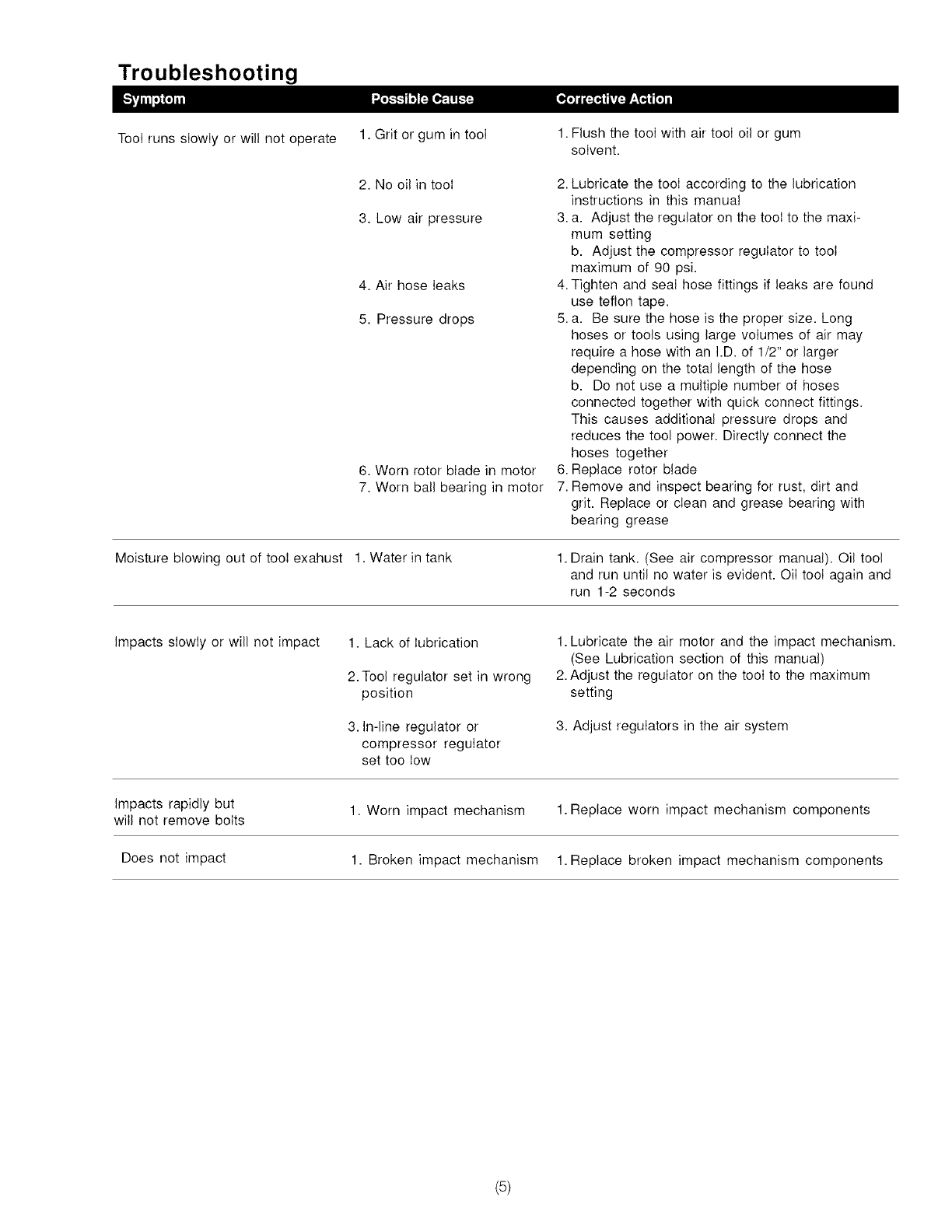
Troubleshooting
Tool runs slowly or will not operate 1. Grit or gum in tool 1. Flush the tool with air tool oil or gum
solvent.
2. No oil in tooI
3. Low air pressure
4. Air hose leaks
5. Pressure drops
6. Worn rotor blade in motor
7. Worn ball bearing in motor
2. Lubricate the tool according to the lubrication
instructions in this manuai
3. a. Adjust the regulator on the tool to the maxi-
mum setting
b. Adjust the compressor regulator to tool
maximum of 90 psi.
4. Tighten and seal hose fittings if leaks are found
use teflon tape.
5. a. Be sure the hose is the proper size. Long
hoses or tools using large volumes of air may
require a hose with an I.D. of 1/2" or larger
depending on the total length of the hose
b. Do not use a multiple number of hoses
connected together with quick connect fittings.
This causes additional pressure drops and
reduces the tool power. Directly connect the
hoses together
6. Replace rotor blade
7. Remove and inspect bearing for rust, dirt and
grit. Replace or clean and grease bearing with
bearing grease
Moisture blowing out of tool exahust 1. Water in tank 1. Drain tank. (See air compressor manual). Oil tool
and run until no water is evident. Oil tool again and
run 1-2 seconds
Impacts slowly or will not impact 1. Lack of lubrication 1. Lubricate the air motor and the impact mechanism.
(See Lubrication section of this manual)
2. Adjust the regulator on the tool to the maximum
setting
2. Tool regulator set in wrong
position
3. In-line regulator or
compressor regulator
set too low
3. Adjust regulators in the air system
Impacts rapidly but 1. Worn impact mechanism 1. Replace worn impact mechanism components
will not remove bolts
Does not impact 1. Broken impact mechanism 1. Replace broken impact mechanism components
(5)