Craftsman 921153101 User Manual AIR COMPRESSOR Manuals And Guides L0512094
CRAFTSMAN Air compressor Manual L0512094 CRAFTSMAN Air compressor Owner's Manual, CRAFTSMAN Air compressor installation guides
921.153101 L0512094
User Manual: Craftsman 921153101 921153101 CRAFTSMAN AIR COMPRESSOR - Manuals and Guides View the owners manual for your CRAFTSMAN AIR COMPRESSOR #921153101. Home:Tool Parts:Craftsman Parts:Craftsman AIR COMPRESSOR Manual
Open the PDF directly: View PDF .
Page Count: 11
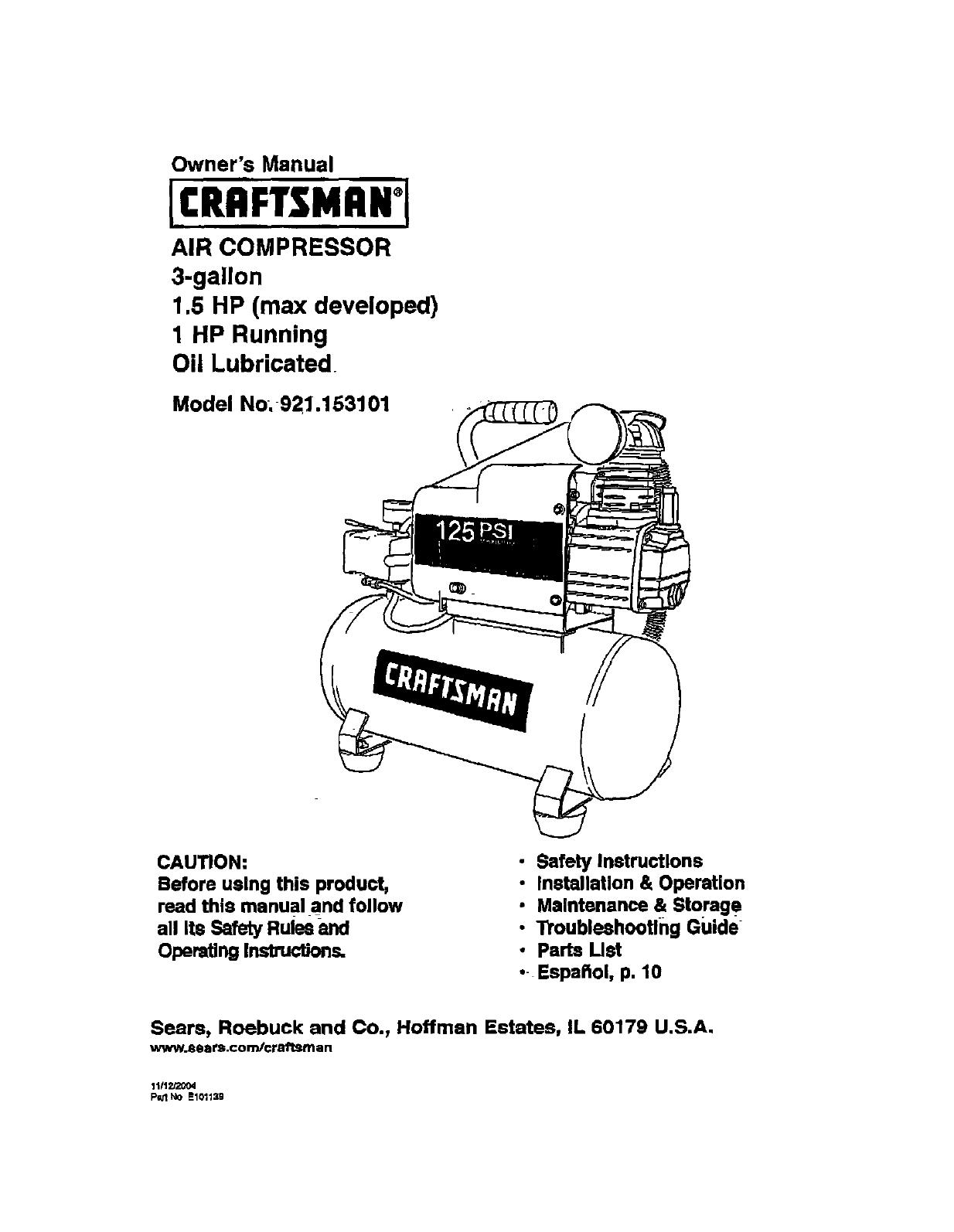
Owner's Manual
AIR COMPRESSOR
3-gallon
1.5 HP (max developed)
1 HP Running
Oil Lubricated
Model No_ 921.153101
CAUTION:
Before using this product,
read this manual and follow
all Its Safety Rules and
Opera'dngInsUuc'dons.
•Safety Instructions
• Installation & Operation
• Maintenance & Storag e
•"rroubleshootlng Guide
. Parts List
• Espaflol, p. 10
Sears, Roebuck and Co., Hoffman Estates, IL 60179 U.S.A.
www.sears.com/¢raftsman
11112Q004
P¢;1NO E10113G
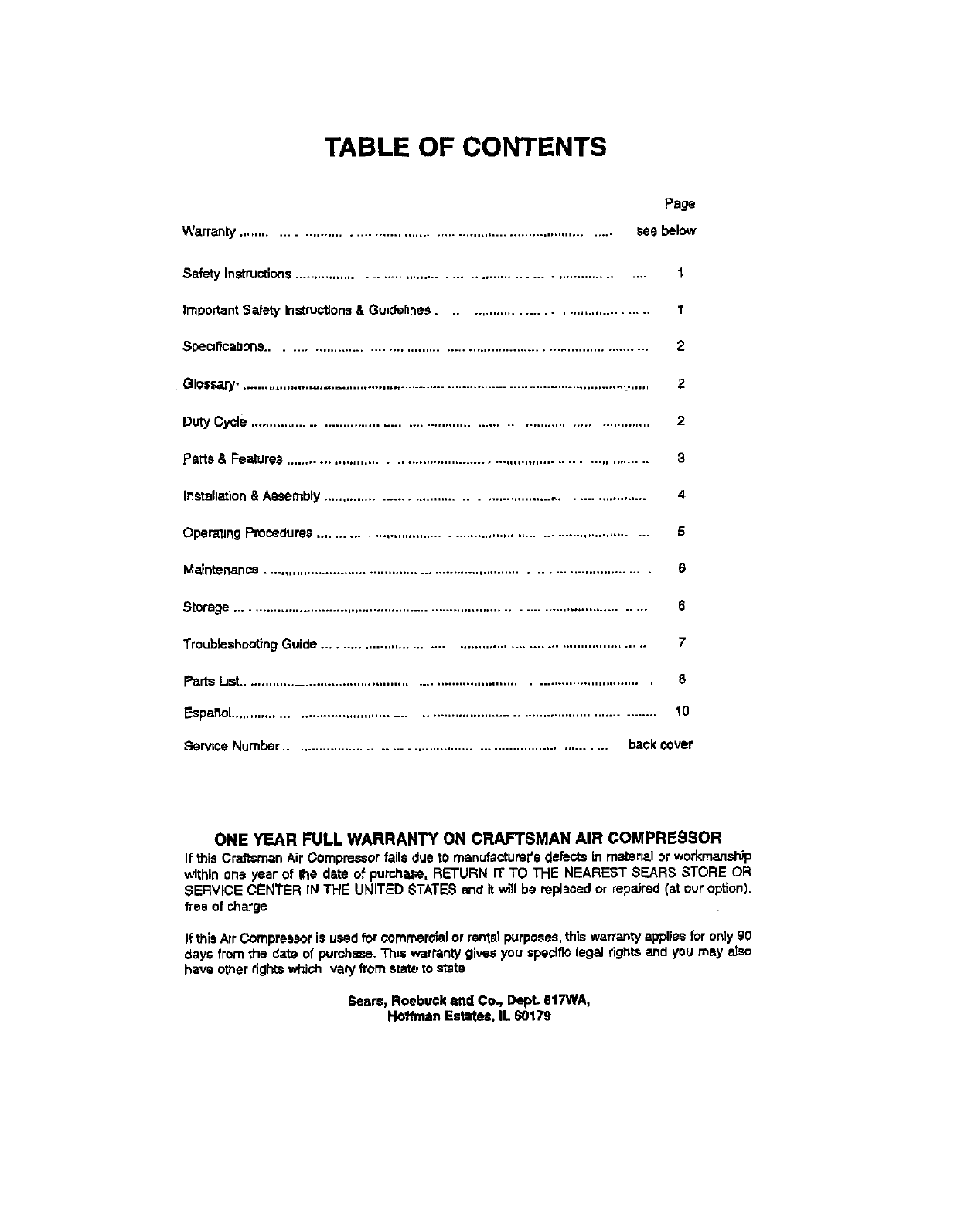
TABLE OF CONTENTS
Page
Warranty .................................................................................... see below
Safety Instructions........................................................................ 1
ImportantSafety Instructions& Guldef=ne_......................................... 1
Spec_ffcabol18....................................................................................... 2
(31os._'y-. ....................................................................................... _...... 2
Duty Cycle .......................................................................................... 2
PaRs & Features ................................................................................... 3
Installarion & Assembly ........................................................................ 4
Opera, rig Procedures .............................................................................. 5
Maintenance ............................................................................................ 6
Storage ...................................................................................................... 6
TroubleehDoOngGuide ......................................................................... 7
Parts IJet.................................................................................................... 8
Espahol ..................................................................................................... 10
Serwce Number ......................................................................... back sever
ONE YEAR FULL WARRANTY ON CRAFTSMAN AIR COMPRESSOR
If this Craftsman Air Compressor fails due to manufacturer's defects in matertal or workmanship
within one >,ear of Ihe date of purchase, RETURN IT TO THE NEAREST SEARS STORE OR
SERVICE CENTER IN THE UNITED STATES and it _,1"11be replaced or repaired (at our option),
free of charge
Ifthis Air Compressor is used for commarolalor ramal purposes,this warrat_y applies for only 90
days from the data of purchase. This warranty gives you specific legal rights and you may 8]se
have other rightswhich vary from state to stata
Sears, Roebuck and Co., DepL B17WA,
Hoffl_an Estates. IL 60178
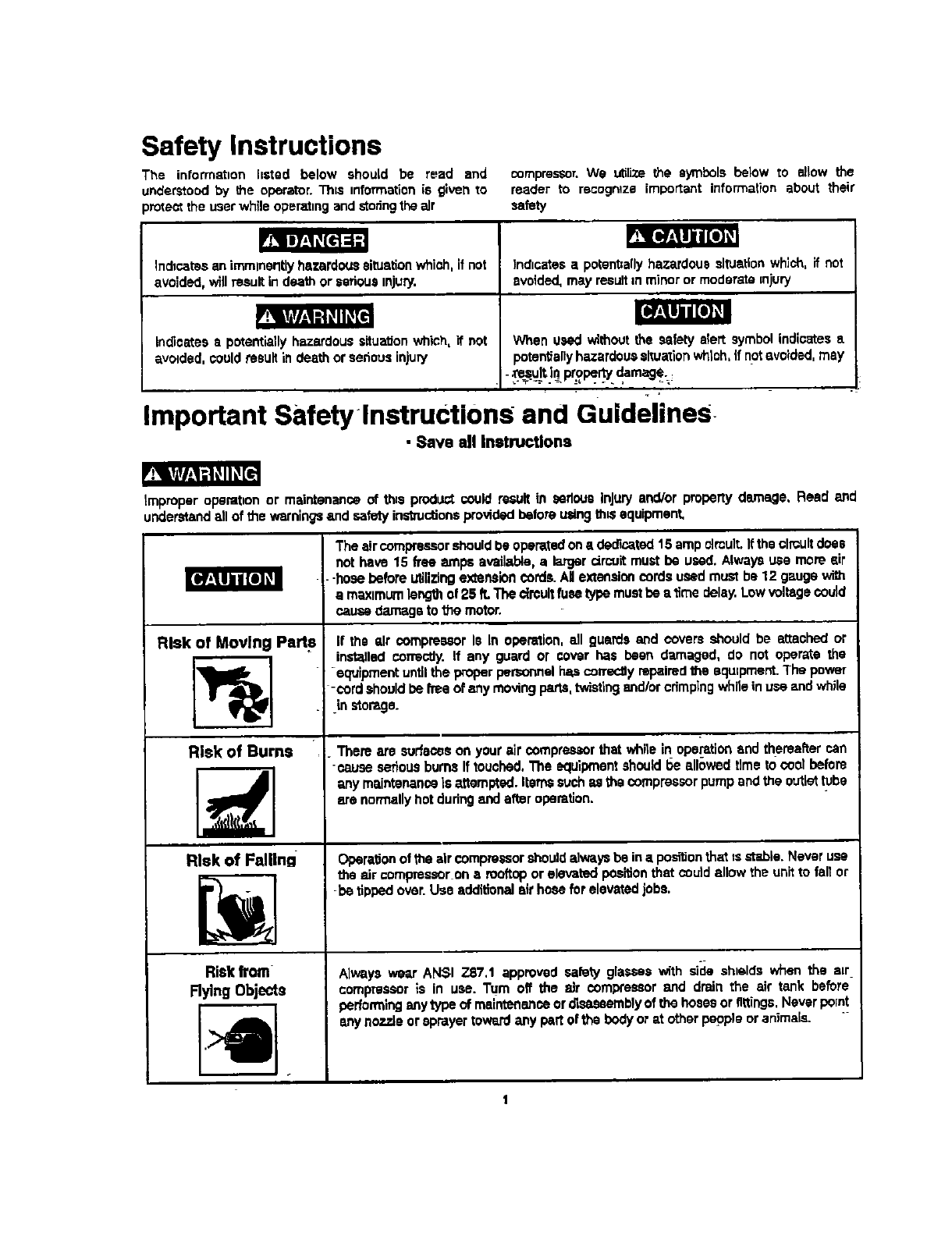
Safety Instructions
The informatton hated below should be read and
understood by the operator. Th=smformation is given to
_rote= the user while operating and stodngthe air
n.J[_:lll IIlia,
Indicatesan immlnerltlyhazardoussituationwhip,h, if not
avoided,willresultindeathor serioustnjury.
ind|cstea • potentiallyhazardoussitua'donwhich,if not
e,volded,couldresultindeath orserousinjury
_ompmsSor. We utilize the symbols below to allow the
reader to recogntza important information about their
safety
]ndtcates a potent=allyhazardous situation which, if not
avoided, may result=nminoror moderate injury
When used without the ssfaty start symbol indicates a
potentiallyhazardous situation which,if not=,voided, may
dam %
=•
Important Safety lnstructions and Guidelines
• Save all Instructions
V:__l_/-l=l_ll_[ll
tmpmperoperat=onor maintenanceof the=produd_couldresultin seriousInjuryend/orpropertydamage.Read end
understandell of the warningsand safetyinstructionsprovidedbeforeusingth_ equipment,
Risk of Moving Part s
Risk of Burns
Risk of Falling
Risk from
Rylng Objects
The air compressorshould be operatedon • dedicated 15 amp €lmult.Ifthe circuitdoes
not have 15 flee _nps available, a larger circuit must be used. Always use more sir
-hose before utilizingextension cords.AMexte_'_lencords used must be 12 gauge wi_
emaxtmum lengthof 25 P..The circuitfusetype mustbe e time delay. Low voltage could
cause damage to the motor.
If the sit €ompressor Is In operation, ell guards and covers should be attached or
installed correctly, If any guard or cover has been damaged, do not operate the
-equipment until the proper personnel has correctlyrepaired the aqulpmenL The power
-cord should be flee of any moving ptrts, twistingandlor crimpingwhilein use and while
in ston_ge.
There are surfaceson your air compressor that white in operation end thereafter can
-cause serious burns If touched, The equipment should t_e allowed time to cool before
any maintenanceis attempted. Iterr_ such _ the compressor pump andthe outlet tube
are normallyhot duringand after operttJon.
Operationof the air compressor should always be ina positionthat tsat'J_la. Never use
the air compressor on a rooftop or elevated positionthat could allow the unit to fell or
-be tipped over. Use additional sit hose for elevated jobs.
Alwayswear ANSI Z87,1 approvedsafetyglasseswith side shieldswhen the air
compressoris in use. Turn off the air compressor and drainthe air tank before
perfownlnganytypeof maintenanceordisassemblyof thehosesorfittings,Neverpoint
any nozzleorsprayertowardany pe_lofthe bodyor at otherpop_pieoranimals.
r
t
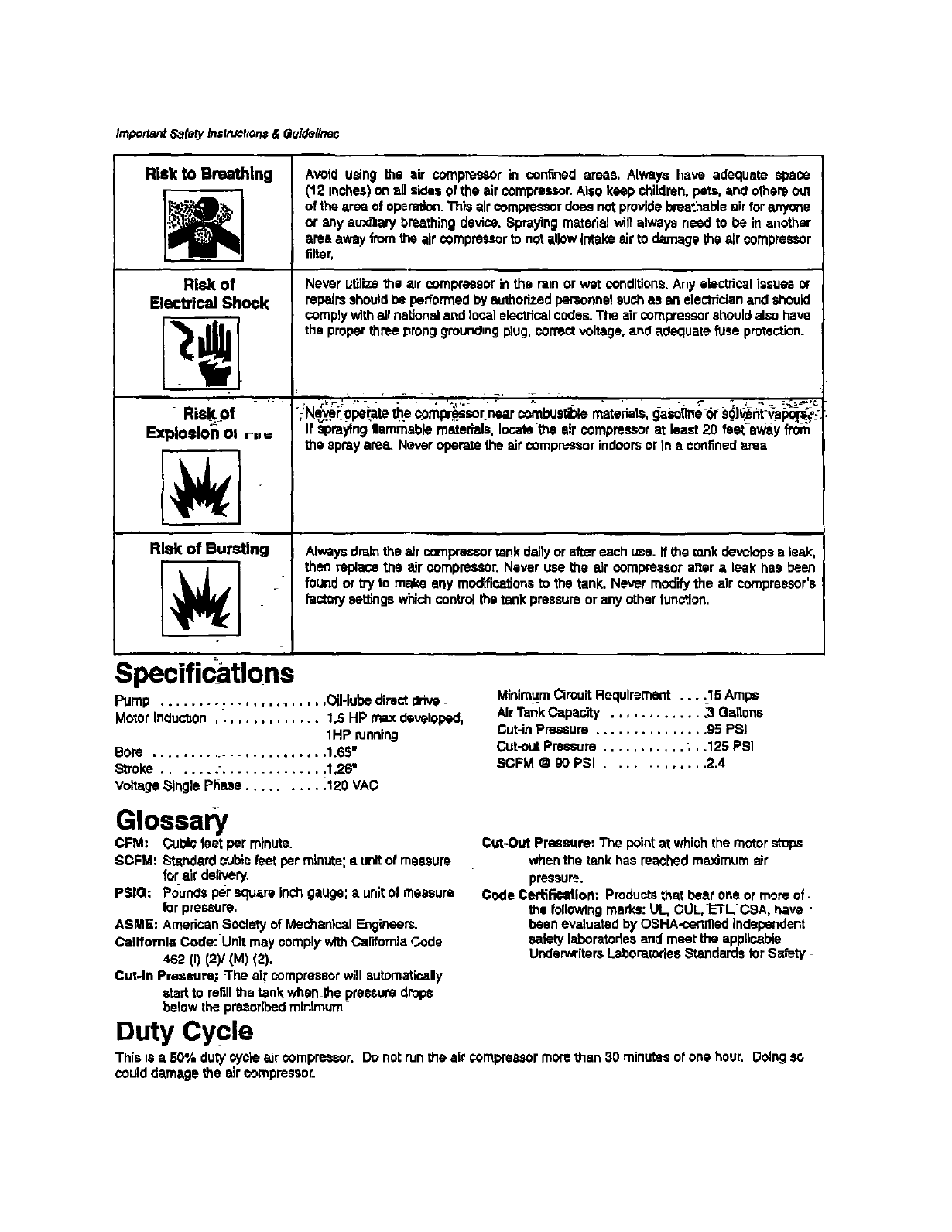
Important Safely Inslruel_On#& Guldellne_
Risk to Breathing
Risk of
Electrical Shock
Risk of
Exploslo_- oI r,,=
Risk of Bursting
Specdzcations
Avoidusingthe air compresSOr in conked areas, Always have adequate space
(12 Inshee) on aBsides of the air compressor.Also keep children, pats, and othersout
of the area of operation. This air ¢ompmesor does not provide breathable air for anyone
or any auxikary breathing device, _praying material will always need to be in another
areaaway from the air compressorto not allow Intake air to damage the air compressor
filter,
Never utilize the a_r ooml_'eeasrin the tam or wet conditions.Any e|ectdcal issues or
repairs should be performed by authorizedpemonnel such as on aiectT_cianand should
oomp]ywithall national and localelectrical codes. The air compressorshould also have
the proper three prong groundingplug, correctvoltage, and adequate _se protection.
;Ne._ operate the.compr_isor.neat oombusfible marshals,geeoUr_e01'e_oJ_nt-vapoFr_;
If spraying flammable materials, locatethe sir compressor at least 20 teat-sway fro_
the spray areal Never operate the air compressor indoorsor tn • confined area
Alway=draintheair cempres=ortankdailyorafter eachuse.If the tankdevelopsa task,
then replacethe air oompreasor.Neveruse the air compre_or afteraleek has been
foundorW to makeanymodificationsto thetank,Nevermodify the air compreesor's
faotofysettingswhichcontrolthe tankpressureoranyother function,
Pump ...................... Oil-lubedirect ddve-
Motor Indu_on .............. 1.5 HP max developed,
1HP funning
Bore ........................ 1.65w
_roke ....... ".............. 1,26"
Voltage Single Plisse ......... _120VAC
Minimum Circuit Requirement ...._15 Ampe
Air Tank Capac'W ............ .3 Ga,one
Cut-in Pressure ............... 95 PSI
Cut-out Pressure ........... ., .125 PSI
SCFM @ 90 PSI ............ 2.4
Glossary
CFM: Cubic feet per minute.
SCFM: _'_dard cub_r' feat per minute; aunitof measure
for air delivetT.
PSIG: Pounds per square Inch gauge: a unltof measure
for pressure.
ASME: American Soolety of Mechanical Engineer=.
Catlfomla Code:Unlt may oomplywith CaliforniaCode
462 (f) (2)/(M) (2).
CuHn Pressure; -The air compressorwill automatically
start to refillthe tank when the pressure drops
below the pre._oribedminimum
Duty Cycle
Cut-Out Pressure: The pointat which the motor steps
when the tank has reaohed maximum air
pressure,
Code Certification: Productsthat bear one or more of-
the followingmarks: UL, CUL,ETLCSA, have -
been evaluated by O_HA-certl_]edindependent
safety laboratoriesand meet the applicable
UnderwritersLabor_tariee Standards for Safety
This Is a50% dutycy_'ieair compressor.Donotruntheair €ompressormorethan 30 minutesof onehour. Doing
coulddamagethe =lr compressor.
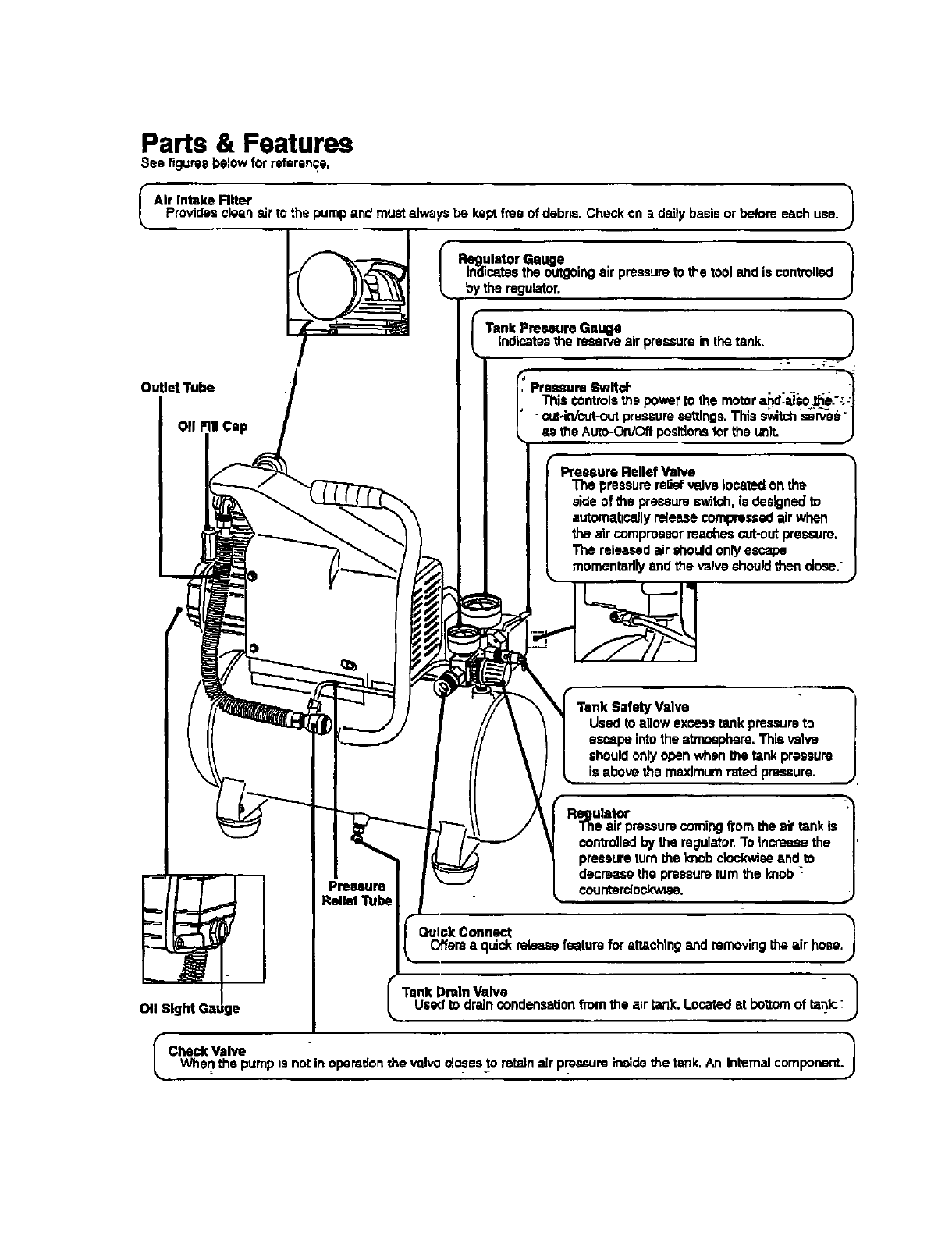
Parts & Features
See figures below for reference,
IAW Intake Rlter 1
Providesclean elf to the pump and must always be kept free of debris. Check on adaily basis or before each use.
OutletTube
on FillCap
Regulator Gauge 1
Indicates the outgoingair pressure to the tool and is controlled
by the regulator.
Tank Preemui'eGauge |
indicatesthe reserve air pressure in thetank.
-_ 7- .
Pressure 8wlt_ . . _
This controlsthe power to the motor aJ_d.al_e.--'.:_
cut4n/cut-out pressure settings.This switch .served"1
the AkRo-OniOffpositionsfor the unit, J
=Valve
The pressure relief valve located on the
side of the pressure switch, is designedto
automa,bcally release compressedair when
the air compressorreaches cut-outpressure,
The released air shouJdonly escape
momentarily and the valve shouldthen dose.
tValve
Used to allow excess tank pressure to
e_pe into the atmosphere, This valve
should only open when the tank preastJre
is above the maximum rated pressure.
Regutatcr '_
The air pressure coming from the air tank is |
con_olled by the regulator,To increasu the |
pressure turn the le_ob clePJxwieeand to |
decrease the pressureturn the knob _|
Pressure counterdockw;su. J
Relief Tube
Quick Connect 1Offers •quickrelease feature for sttashtngand removingthe air hose,
lTank DraIn Valve 1
011Sight Gatiga Used to drsJnoundensation from the a=rtank, Located st bottom of tank.:
ICheck valv_ 1
When the pump is not in operation the valve €losests retzdn=drpressure in,;de the tank, An internal component.
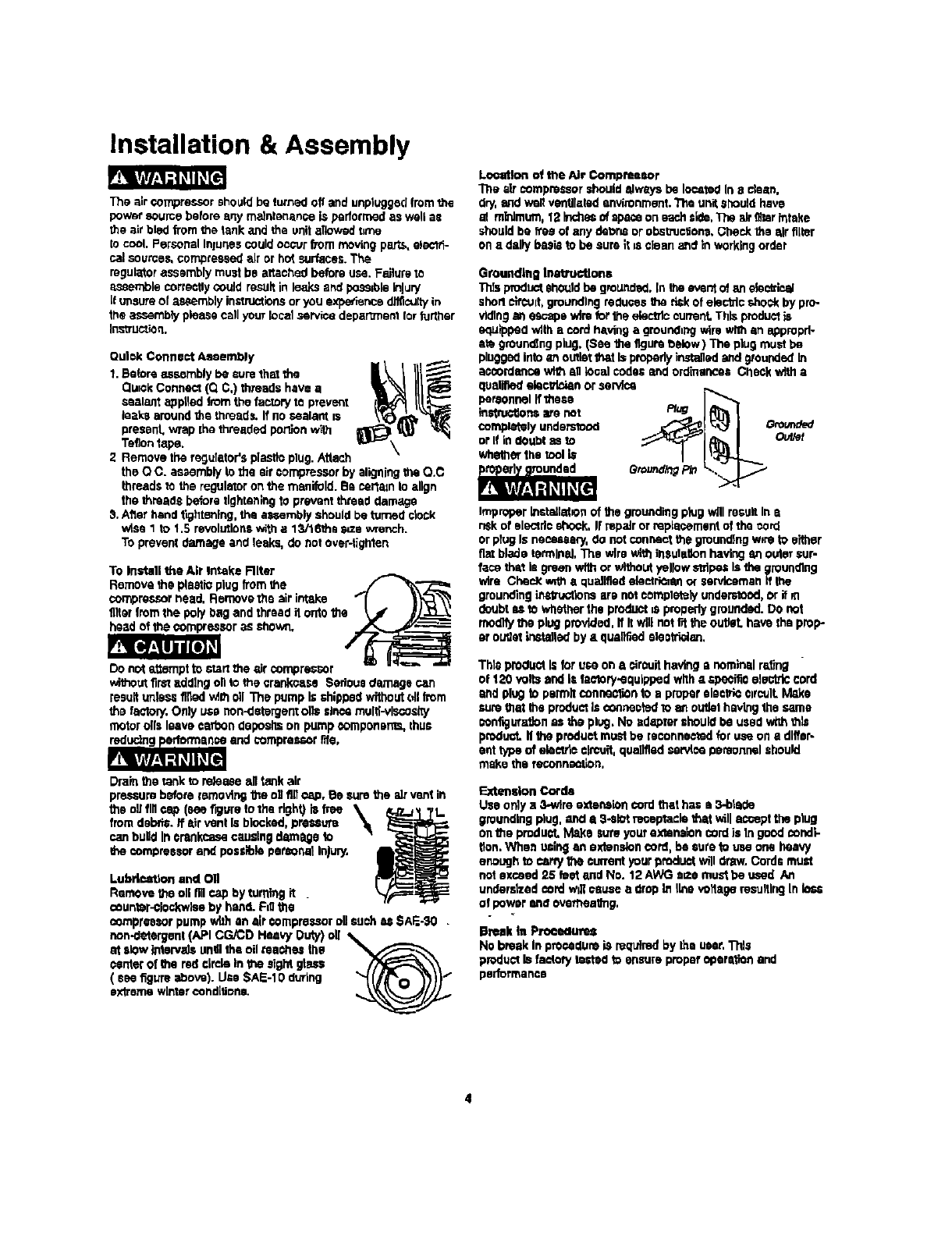
Installation & Assembly
The air compressor should be turned off and unptuggod Imm the
power coume betore any rnainrananoe is performed as well a=
the air bled from the tank and the unit allowed t_rne
to cool. Personal Inlunes could oOcvrfrom moving paris, elecld-
col sources, compressed elf or hot surfaces. The
mgulutor assembly must be a_eched before use, Failure to
assemble correctly could resultin lo_s end poss=bleinjury
It unsure of assembly instructionsor you expe(_encediffisul_ in
the assmmb;y please call your local .servicedeparlmem Iorforthsr
Instruction,
Qufok Connect Assembly
'L Before assembly be sure that the
Quick Connect (Q C,) threads have a
sealant applied from the factory m proven!
Iaa_ around the threads. If no sealant is
present, wrap [ha threaded portionW_l
Teflon tope.
2 Remove the regulator's plasito plug, Attach
the O C. assembly to the air compressor by aligning the Q,C
threads to the regulator on the manifold. Be certam ld align
the threads before tlghtenleg to prevent thread damage
3, After hand t_htening, the a_embly should be turned clock
wise 1 to 1,5 revolmlona with • 13ki6ths _ze wrench.
To prevent damage and leaks, do not over-tighten
To ths'taU the Air Intake Rlter
Remove the pleatlo plug from the _,/_ _"-'_
compressor head. Remove the air into,he "_( _'_
t]ifer from the poly bag and thread it onto the t_' j_
asr as shown.
Do not otternptto start the =drcomprasecr
withoutffrst adding oil to the crankcase Serious damage can
resuit unl_ fifled _th oil The pump Is shipped without ell from
the fectury.Only use non.detergent clio since multl-vlecos W
motor oils leave carbon itapos_ on pump ¢omp0nsms, thus
and compressor rife,
Drain the tank to I_leece all tank air
pressure betom removthg the oll _P._p, Be sure the air vent in
the 09 fill cap (see figure to the right) ;8 free _L_.,7_I ?L
from debris. If ntr vent Is blocked, pressure
can build In orankcase causing dam Nto
lee compressor and possPblo pereonat in_Jry.
Lubdeatton and Oil
Remove the oll tiffcap by turning it
counter-clockwise by hand. Fd] the
compressor pump v/_h an sir €ompressor ell such as SAF.-_0
non.detergent (API CG/CD Heevy Duty) oll
at slow thterv_ unlll the oil tee0hea the
eentor of the red oirelo In the sight itiass
(see figure above). Use SAE-10 during
extreme winter ¢onditfono.
Lo_-'Mlon of the Air Compmuor
The air compressor should oiwe.ys be Io_ted In n clean,
dry. and welt verdllated environment. The unit should have
ai mNmum, 12 Inchecof space on each side, The air m_arintake
shouldbe _ee of any debris or obstmc_ono, Check the air fi_tor
on a dally bogle to be sure _tis clean and in working order
Grounding Inatru_lone
TI_ productshould be greund_. In the eventof an decuir.al
sherl oh'cult, grounding reduses I_ risk of electric r.hock by pro-
vlrflngan escape wire for the eleclnfocurrant,This productis
equipped with • cord having o grounding wire with an agproprf-
ato gmun_ng plug. (See the figure below) The plug must be
plugged into an outlet that is properlyinstalled and grounded In
acmrdanco wi_ ag lOcal codas and ordinances Check with a
quaiiflod olec_ln_n or sense
personnel ff these
ins'b'ucfions arenot P/ug
complet$1y understood Omunde_
or If in doubt as to guilt
whether the tool is
Ground/noP/n
Improper install_on of the grounding p_ugwill result In It
risk of slocMe shock. IFrepair or replecomerd of the cord
or p_ugIs nuseseery, do not conne_ the grounding w_rsto either
fiat blade fermlnaL The wire wi_ insula_on having an outer sur-
face tha_ Is green with or without yellow stripe= Is _grounding
wire CheeX _a quaiffledethetri=an or serviceman If the
grounding ii%=d_.,ctin_are not completely understood, or if m
doubt as to _i_uther the product mpropedy grounded. DO not
modify the plug provided, If Itwill not th the oubeL havE)the prop
er ou'Jetinstalled by &qualified aiesfi'idan.
This pmduut Is for use on ,=cimuit having a nominal rot_ng
of 120 wits and is lectory-equltwed with e spa€tits aie_dc cord
und plug to pem_]t conno_lOn to a proper electric clrcolLMake
sure that the productIs connected to as outbt hav_g the same
sunfigur_gon as the plug, No adapter should be used withthis
product, H theproduct mutd be reconnected for use on adiffer-
ent type of eb¢_e circuit,quailfled servlse personnel should
mske ths reconn_fion,
ExtensionCords
Useonlya3-wireextensioncord met has e3..blade
groundingplug.andaS-slotnmsptanlothat willacceptthe plug
onl_e predu_ Ma_e sumyoursxtanaloncordis Ingoodcondi-
Ifon,Whenusingan extanaioncord,be sureto uaeone heavy
onDughto P.art_the currentyourproduutwill draw. Cordsmust
not escoed25 feetandNo. 12AWGsee must be ungd An
undersizedcord willceu.'u=adrop in linevoltage resultingInloss
el power and overileetthg,
BrenkIn Prooedure_
NobreakIn pro_dom is requiredby the usur,Trde
productIs factorylect_ to ensureproperoperationand
performanse
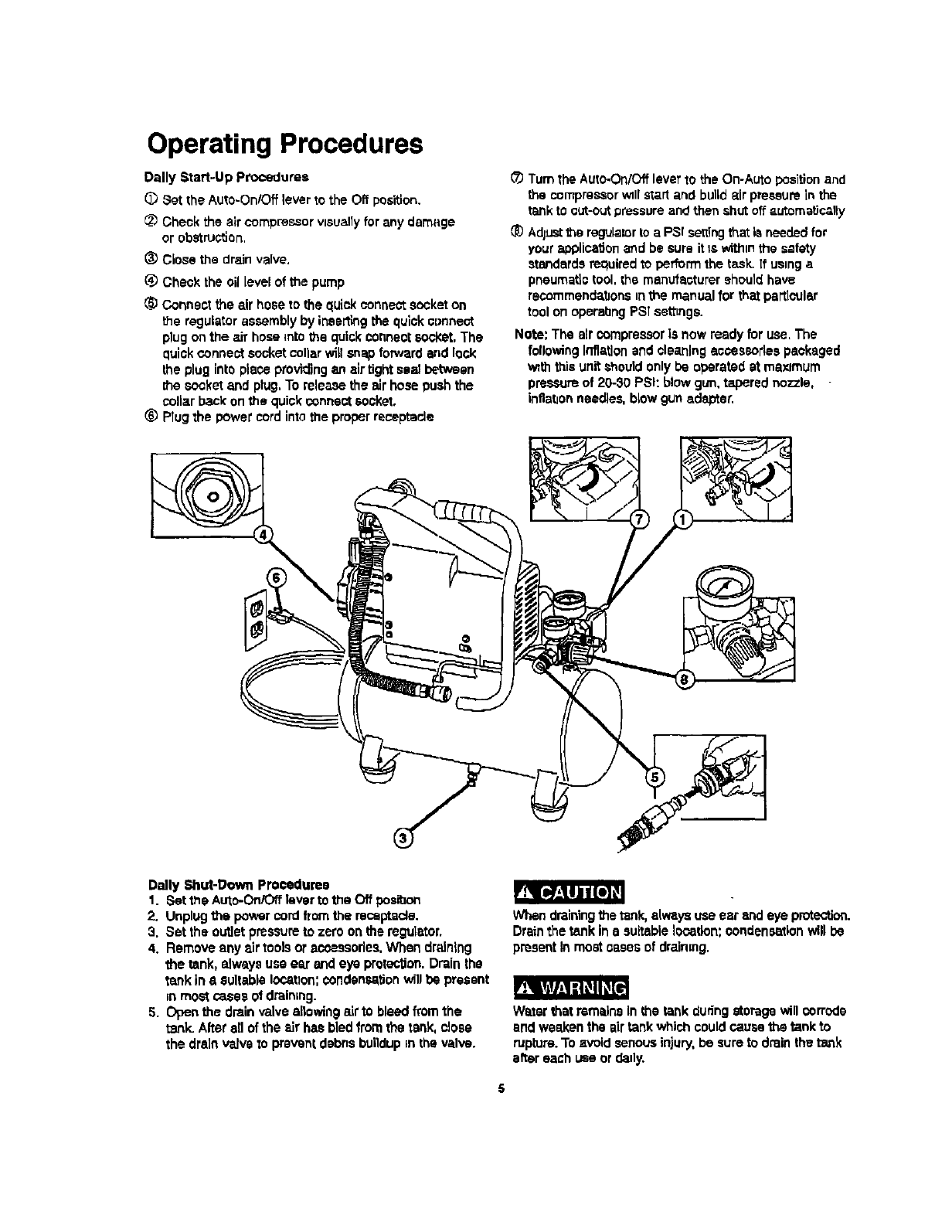
Operating Procedures
Daily Start-Up Procedures
O Set the Auto-On/Off lever to the Off position.
__ Check the air compressor visuallyfor any damage
or obstru_on,
_) Close the drain valve.
Check the oil level of the pump
Connect the air hose to the quick connectsocket on
the regulator assembly by ineerling the quickconnect
plugon the air hose rote the quick connect soci<at,The
quick connect socket collar will snap forward and lock
the plug into piece providingan airtight ssai between
=hesocket and plug,To relez_e the air hose pushthe
collar back onthe quickconnect socket.
_) Plug the power cord into the proper receptacle
_/_Turn the Auto-On/off lever to the On-Auto positionand
=he compressor v_llstart and build air pressure in the
tank to out-outpressureand then shut offautomatically
Ad}ustthe regula_r to a PSI se_lngthat Is needed for
your applica_onand be sure itts withmthe safety
standards requiredto performthe task. ff using a
pneumatictool, the manufacturershould have
recommendatJons=nthe manual for that particular
tool on eperabng PSI se_ngs.
Note: The aircompressor is now ready for use. The
following Inflationand cleaning aosessorlea packaged
v_ththis unit should only be operated at maximum
pres_Jre of 20-30 PSI: blow gun, tapered nozzle,
infla_on needles, blew gun adapter.
Dally Shut-Down Prooeduma
1. Set the Auto-On/Off laver to the Off posihan
2. Unplug the power cord from the receptacle.
3. Set the outletpressureto zero onthe regulator,
4. Remove any airtools or accessories,When draining
the tank, always use e_r and eye profectten.Drain the
tank in a suitable location;condensationwillbe present
=nmost cassa of draimng.
5. Open the drain valve allowingairto bleed fl'omthe
tank. After 811of the air has bled from the tank, close
the drain valve to preventdebns buildup=nthe valve.
P"REo,_r,,_llJ]l[o_
When drainingthe tank, always use ear and eye protection.
Drain the tank in asuitable location; condensation will be
present In most cases of dreinmg,
Water that remains in the tank dudng storage will corrode
and weaken the air tank which couldcause the tank to
rupture.To Avoid serious injury,be sure to drain the tank
after each usa or dady.
S
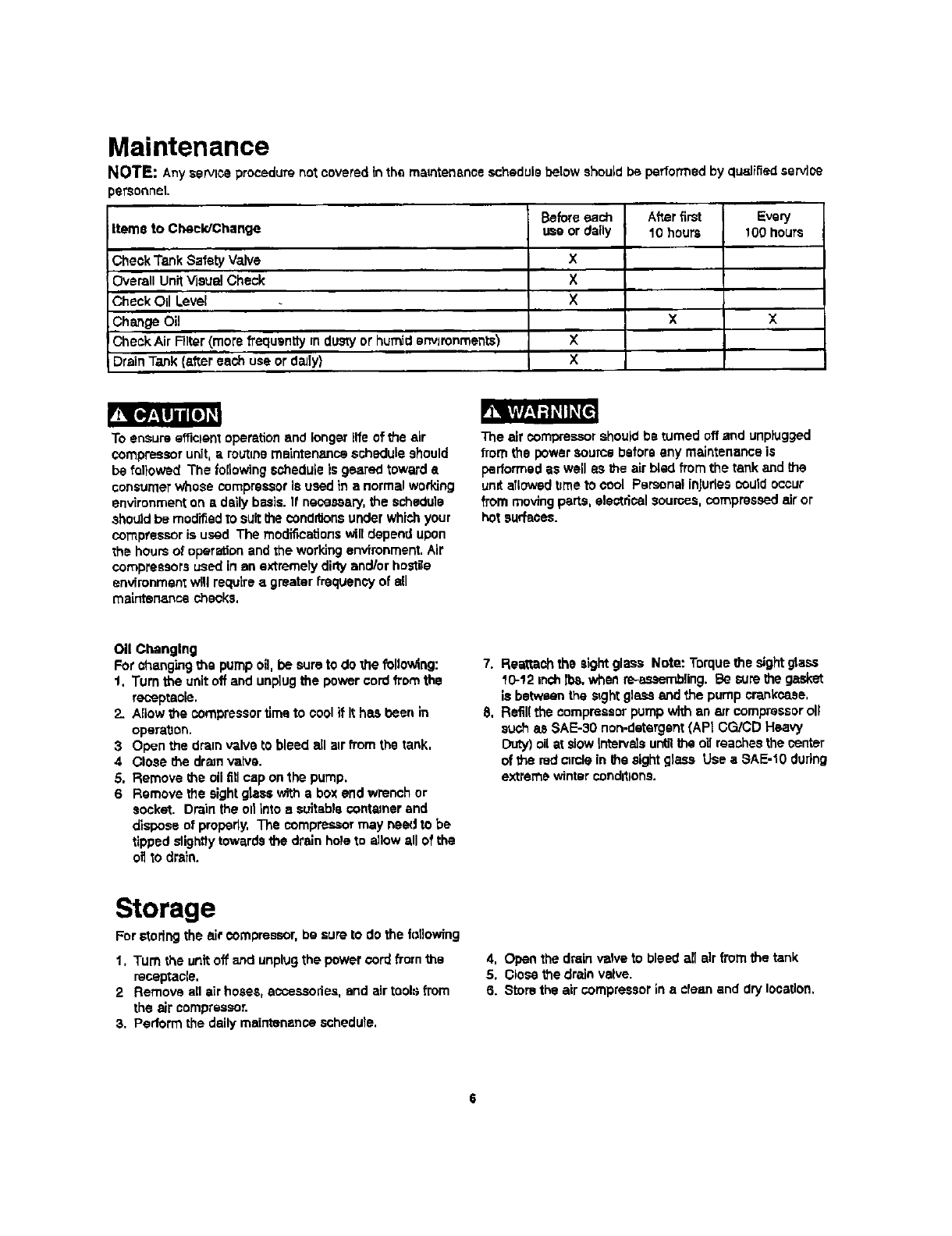
Maintenance
NOTE: Any service procedure not covered in the maintenance schedule below should be performed by qualified service
_ereoenet.
Items to Check/Change
Check Tank Safety Valve
Overall Unit Visual Check
Check Oil Level
Change Oil
Check Air RIter (more frequently =ndusty or humid environments)
Drain Tank (after each use or daily)
Before each
use or daily
X
X
X
X
X
Afterfirst
lO hours
X
Every
100 hours
z Irc tlji R
To ensure efficient operation and longer life of the air
compressor unit, a routine maintenance schedule should
be followed The following schedule is geared toward •
consumer whose compressorIs used in a normal working
environmenton a daily basis. If necessary,the schedule
should be modified TOsuit the condrl_ansunder which your
compressor is used The modifications wiltdepend upon
the hours of operation and the working environment. Air
compressors used in an extremely difo/end/or hostile
environmentwill require a greater frequency of ell
maintenance checks,
The air compressor should be turned off and unplugged
fromthe power source before any maintenance is
performed as well as the alr bled from the tank and the
unit aTIowedt=meto cool Psrscna! injuries could occur
from moving parts, electrical scum.s, compressed air or
hot surfa_J.
Oil Changing
For changing _e pump oil. be sureto do thefollowing:
t, Turn the unit off and unplug the power cord from the
receptacle.
2. Allow the compressor tLmato cool if It has bean in
opera'0on.
3 Open the dra=nvalve to bleed all air from the tank.
4Close the dram valve.
5. Remove the oil I_11cap on the pump.
6 Remove the sightglass with e box end wrench or
socket. Drain the oil Into a suitable sentaJner and
dispose of properly. The compressor may need to be
tipped slightlytowards the drain hole to allow all of the
oll to drain.
7. Reattaoh the sight glass Note: Torque the sightglass
10-12 inchll_, when re-assembling. Be surethe gasket
is betwsen the s_ghtglass and the pump crankcase,
8, Refill the compressor pump with an _ur compressor all
such as SAE-30 non-detergent (APt CG/CD Heavy
Duty) oil a_slow _ntervaisur_l the o'dreaches the center
of the red orcle in the sight glass Use a SAE-t0 during
extreme winter conditions,
Storage
For stodng the air compressor,be sure to do the fotlowing
1, Turn the unit off and unplug the power cord from the
receptacle.
2 Remove all air hoses, accessories, and air tools from
the air compressor.
3. Perform the daily maintenance schedule,
4. Open the drain valve to bleed all air from the tank
5. Close the drain valve.
6. Store the air compressor in a clean and dry location.
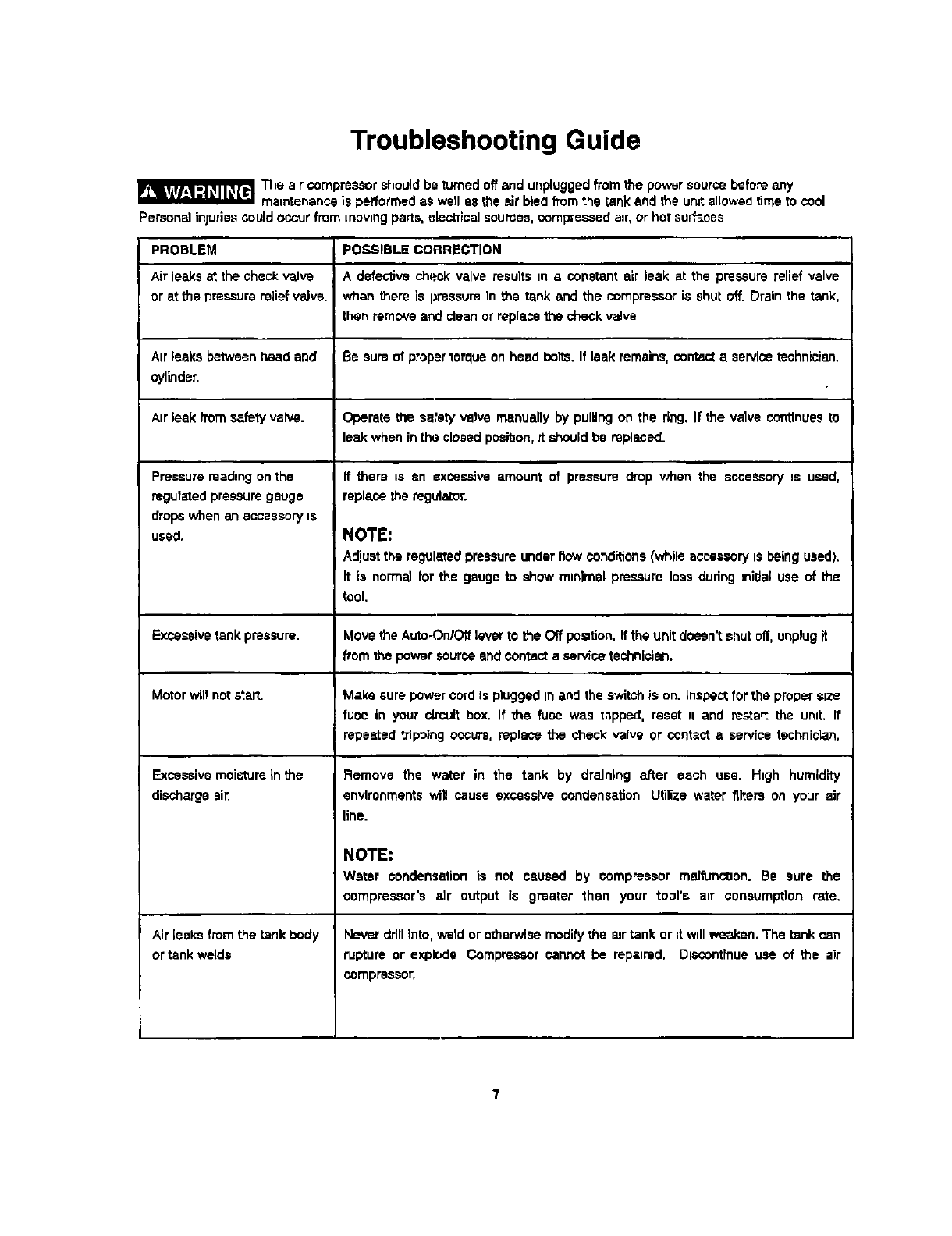
Troubleshooting Guide
_The air compressor shouldbe turned off and unpluggedfromthe power source before any
mamtenanse is performed as well as the _Jrbted from the tank and the unutallowed time to cool
Persona] inluries could occur from moving pans, _[ectrica] sources,compressed anr,or hot surfaces
PROBLEM POSglBLE CORRECTION
Air leaks at the check valve A defective chsok valve results in sconstant air leak at the pressure relief valve
or st the pressure reliefvalve, when there is pressure in the tank and the compressor is shut off. Drain the tank,
then remove and clean or replace the check valve
Air leaks between head and Be sum of proper torqueon head bolts. If leak rem,_ins,contactaservicetsohnician.
cylinder.
Anrleek fromsafety valve. Operate the safety valve manually by pulling on the dng, If the valve continues to
leak when in the closed posibon, tt should be replaced.
Pressure msding on the
regulated pressuregauge
drepswhenanecoeseory_e
used.
Excessive tank pressure.
Motor willnot e_aR,
Excessive moisture _rtthe
discharge sir.
Air leaks from the tank body
ortank welds
If there us an excessive amount of pressure drop when the accessory ns used,
replase the regulator.
NOTE:
Adjustthe regulated pressureunder flow conditions(while accessory is being used).
It is normal for the gauge to show minimal pressure loss dudng _niUaluse of the
tool,
Move the Auto-On/Off lever to the Off position. If the unit doesn't shut off, unplug it
from the power source end contact a service technician,
Make sure power cord isplugged In and the switchis on. inspectfor the proper size
rues in your circuit box. If the fuse was tnpped, reset Pl and restart the unnt. If
repeated tripping occurs, replace the check valve or contact a service technician,
Remove the water in the tank by draining after each usa. High humidity
environments will cause excessive condensation Utilize water/llter_ on your air
line.
NOTE:
Water condensationis not caused by compressorma]functnon.Be sure the
compreseor'sslr output is greater then your tool's anr coneumptfonrate.
Never drill into, weld or otherwise modify the air tank or it wnllweaken, The tank can
rupture or explode Compressor cannot be re_nred, DIscontfnue use of the air
compressor,
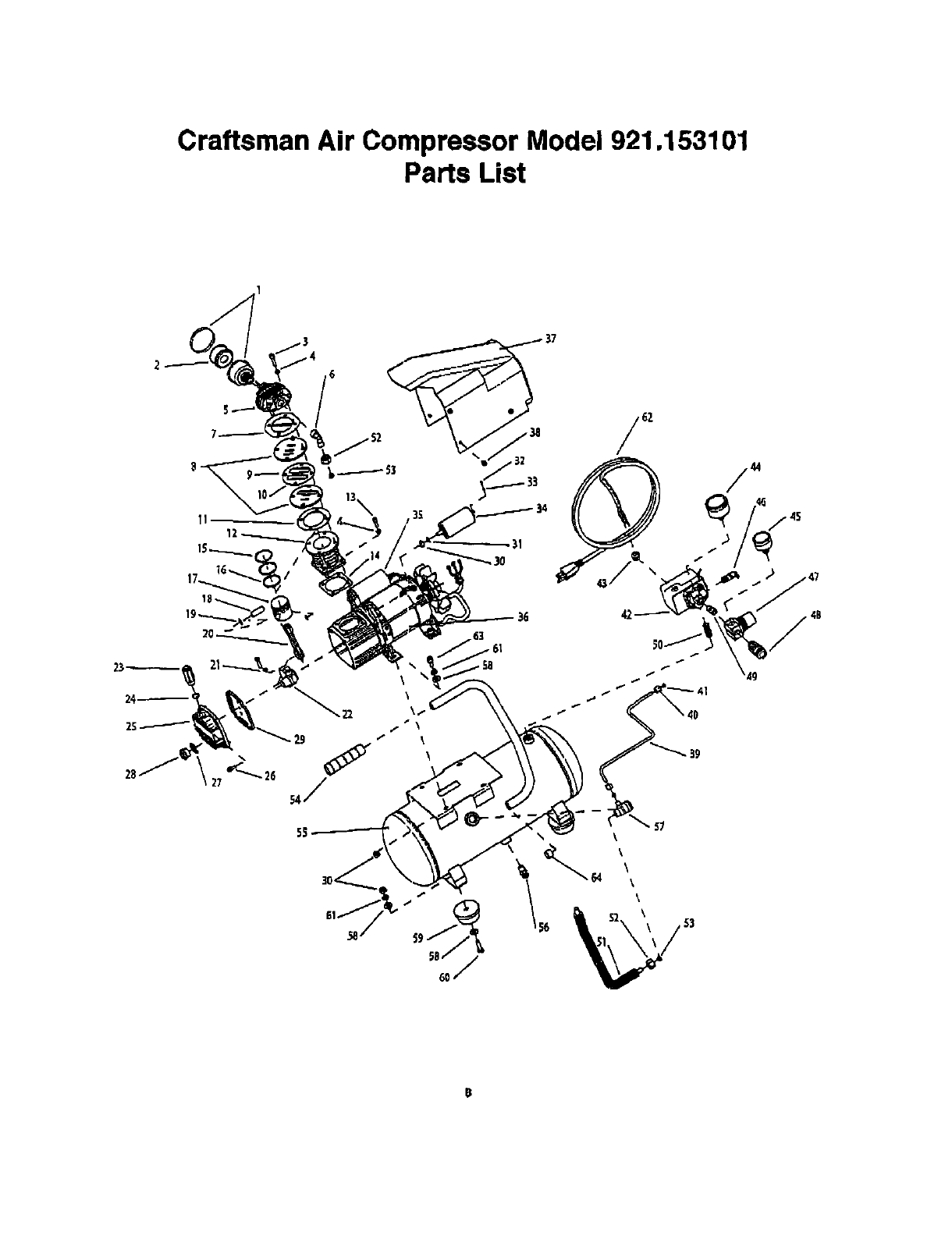
Craftsman Air Compressor Model 921.153101
Parts List
25i I
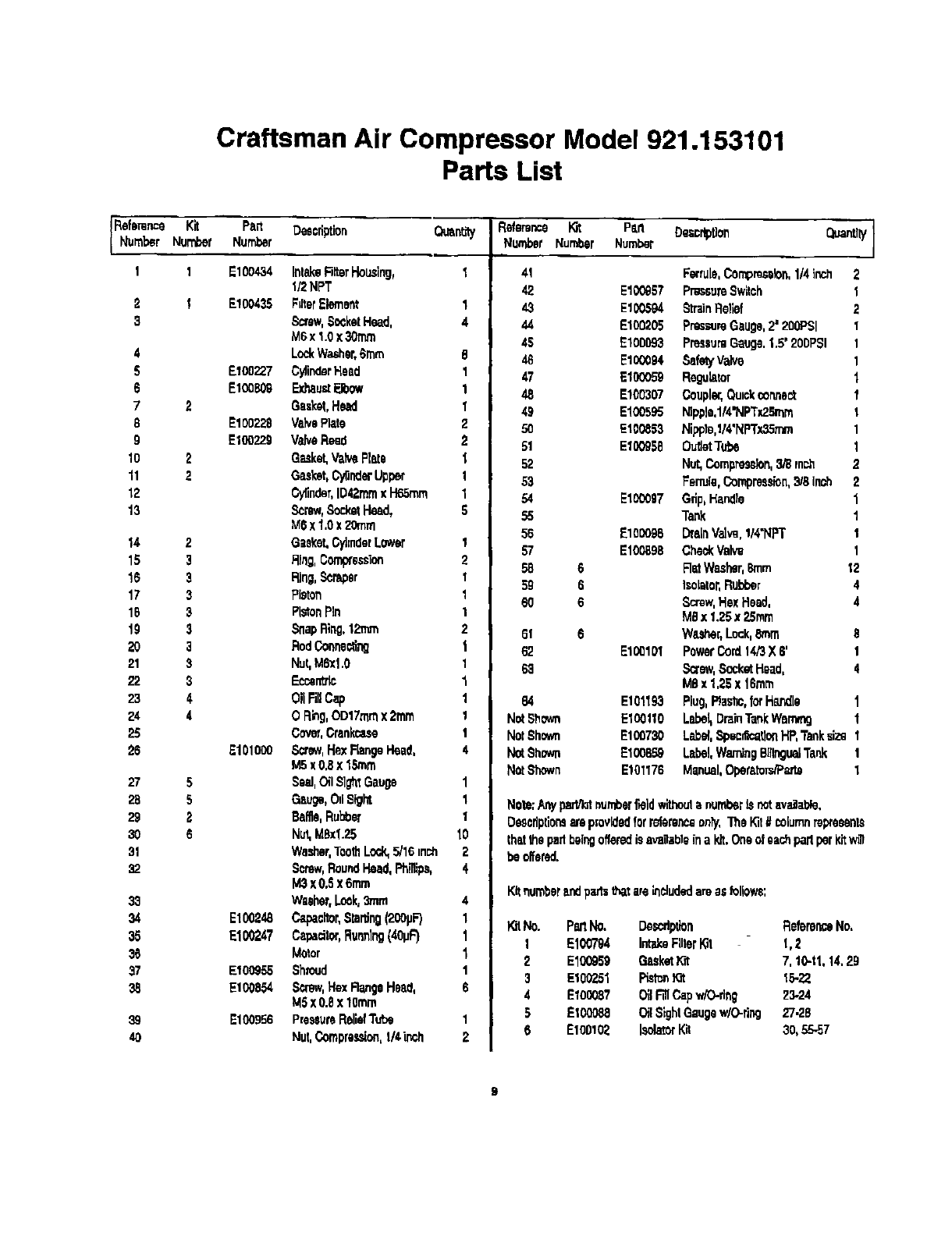
Craftsman Air Compressor Model 921.153101
Parts List
Reference Kk Pan Desedptioc QuanttLy
Number Number Number
1
2
3
4
5
6
7
8
9
10
11
12
13
14
15
16
17
lg
19
21
22
23
24
25
26
27
2g
29
3O
31
32
33
34
35
36
37
38
39
40
1 E100434 IntakeRhr Housing, 1
1/2NPT
!EI00435 FilterElement 1
9c_ew,SocketHead, 4
M6x t.0 x 30n'_ql
LockWasher,6ram B
EI00227 CylinderHeed 1
EIOOB09 ExhaustE_ow 1
2Gasket,Head I
E100228 Vo)vePlata 2
Et0022g ValveRead 2
2GMket,vaivePlate 1
2 G_lmt,cygnderUpper 1
Oyflndm,ID42mmx H65mm 1
Screw,SockatHead, g
M6x i.Ox 20ram
2 Gasket.GylmdorLower 1
3 Ring,Compress'_n 2
3 Ring,Scraper I
3 Pbt_ 1
3 PIslonPin 1
3 SnapRing,1gram 2
@RodConsec_ng 1
3 Nut,MBXl.0 1
$ Ecceatrlc I
4OilFinCap 1
4 O Ring,OD17mmx2ram 1
Cove,Crankcase I
E101000 Sorow,HexRangeHead, 4
M5x 0.8x 15mm
5Seal,OilSigh!Gauge 1
5Gauge,OilSight 1
2 Baffle,Rubber 1
6 Nut,Mgxl.25 10
Washer,Tea_ Lock_16 Inch 2
Screw,RoundHead,Phi_ps, 4
Mgx0.Sx6mm
wseher,Lock,3ram 4
E100248 Capadtot,Sta_ng(200pF) 1
E100247 Gabedlor,Rur_lng(40pF) 1
Motor I
EI00955 Shroud 1
E100854 SCrew,HexRangeHead, 6
MSx 0.8x 10mm
E100956 PressureRelidTz.Coe 1
Nut,Compression,I/4 inch 2
Reference _ Pro1 Description Quantity]
Number Number Number I
41 Ferrule,Corapreealon,1/4inch 2
42 E1008S7 PressureSwitch 1
43 E100594 StrainRailer 2
44 E100205 PressureGauge,2' 200PSI 1
4S E100093 PrsecuraGauge,1,5'200P$1 1
46 E1000N SafetyVefve 1
47 E100ogg Regulator 1
48 E100307 Coupler,Qu=ckconnent 1
49 E13O595 Mpp]e.l/4'NPTx2_mm I
50 S100853 Nipple,t/4'NPTx35mm 1
51 E10095B OutletTube 1
52 Nut,Compresek,n, 3/8inch 2
53 Ferrule,Compression,3/8Inch 2
54 E103Og7 Grip,Handle I
55 Tank 1
56 E100098 OialnValve,I/4"NFT 1
57 E13O898 Ch_ Valve 1
58 6 Rat Washer,Bmm 12
5g 6 Isolator,Rubber 4
60 6Screw,HaxHead, 4
MBx 125 x 25ram
BI 6 W_r, Lock,8ram 8
62 E100101 PowerCord14/3X g' t
63 Screw,SocketHead, 4
M@x 1._ x16ram
B4 EI01193 Plug,Plsehc,forHsr_[s 1
NotSho'_m El00110 Lebe_DrainTankWarning 1
NotShov,'n E100730 Label,Spec,fieatlonHP,Tanksize I
NotShown E100859 label, WarningB[llnguefTartk 1
NotShown E101176 Manual,Operato_JPm',a 1
Note:Anyp_ numberfmldwithoulenumberLgnotawaal_'e,
Oesedptlor_amprovidedforreferenceonty,The_t #colurnnrepresents
that1hepadbeingoffered_ ava_bleinakit.Oneofeachpartperkitw,1
beoffered.
Kitnumberandpzrts1hatareincludedareas follows:
No. Pro1No. Dezcdpdon Referent,No.
I E100794 Ir_ FilterK11 I, 2
2 E100959 GasketKzt 7. 10-tl, 14.29
3 E100251 Pla_ IQt 1522
4E100087 O_1FillGapw/O-rlng 23-24
5 Et00088 OilSightGaugew/O-ring 27.28
6 E10DI_ [€obtorKit 30,55-57