Crown Equipment Rc 5500 Series Users Manual Product Specifications
RC 5500 Series to the manual 72db22d1-932a-4a6f-b5e7-c3e818aa64f5
2015-02-05
: Crown-Equipment Crown-Equipment-Rc-5500-Series-Users-Manual-535408 crown-equipment-rc-5500-series-users-manual-535408 crown-equipment pdf
Open the PDF directly: View PDF .
Page Count: 6
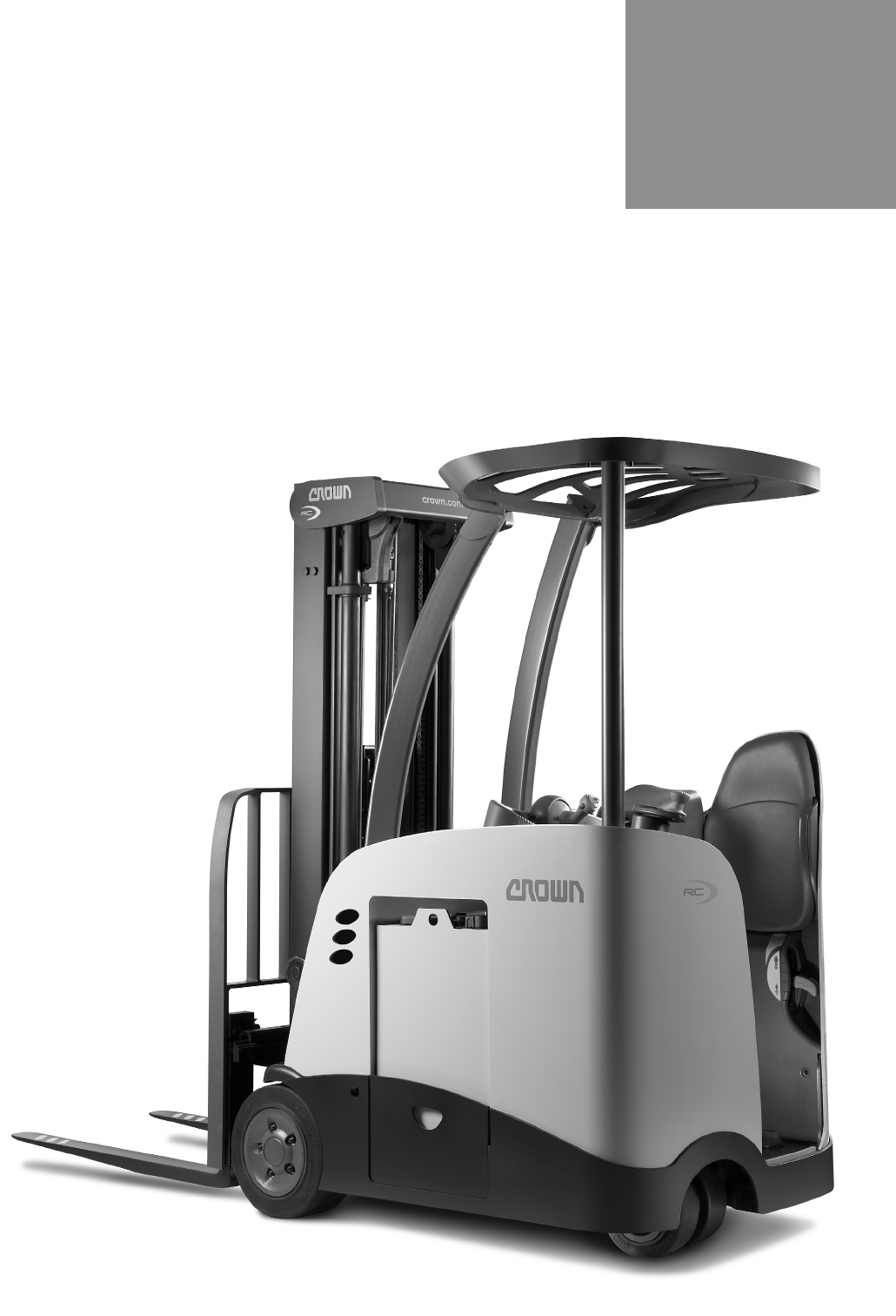
CSpecifications
RC 5500 Series
Stand-up Rider
Lift Truck
RC 5500
Series
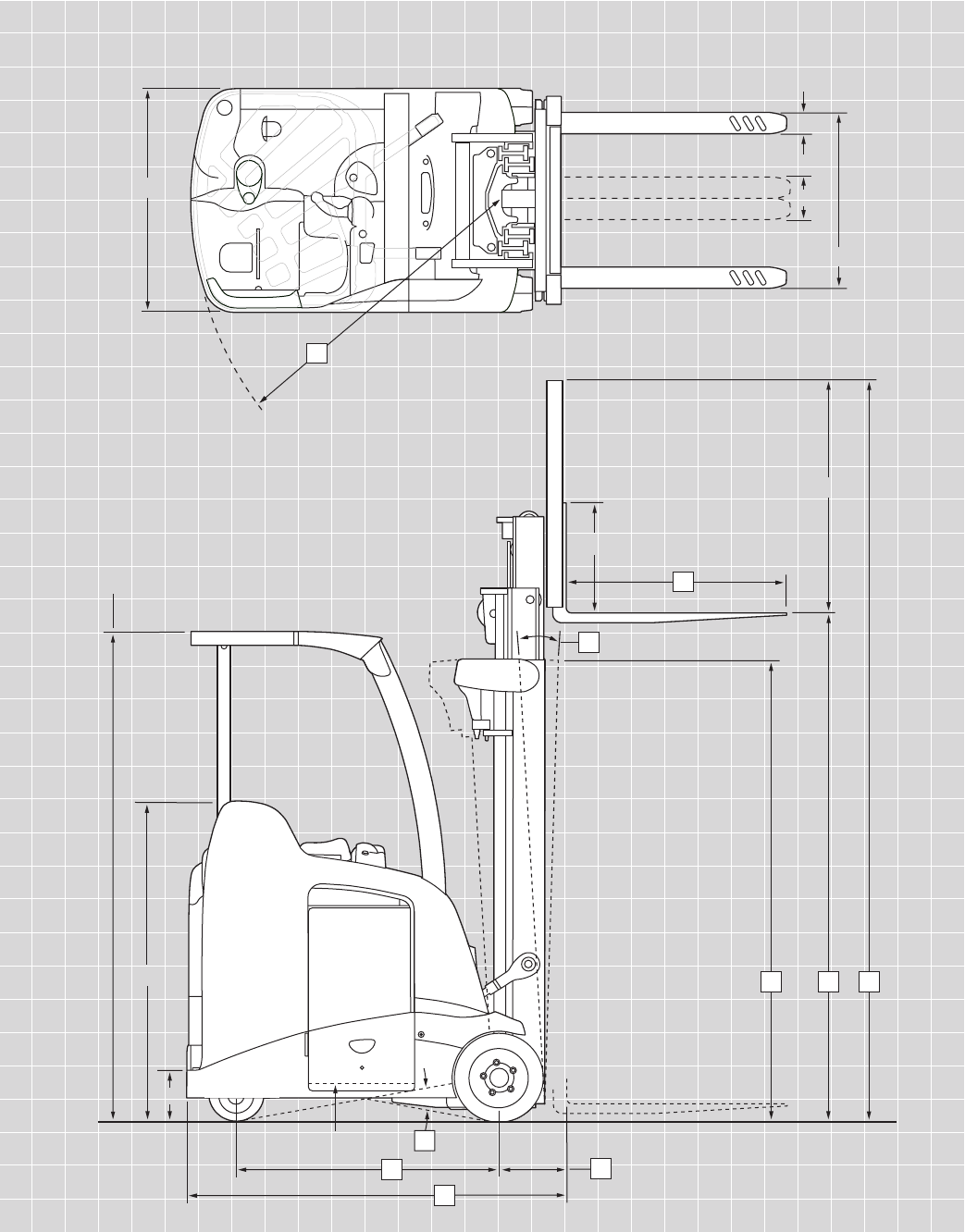
8"
33"
57.5"
9.5"
48"
19.8"
42"
4"
Height to top of
rollers 6.8"
88" Standard - 79.4" Head Clearance
84.5" Optional - 75.9" Head Clearance
21
17 9 18
22
15
38
42
14
13
CRC 5500 Series Stand-up Rider
Lift Truck

RC 5500 Series Specifications
1Manufacturer Crown Equipment Corporation
2Model RC 5510/15-30 5520/25-30 5530/35-30 5530/35-35 5540/45-40
3Load Capacity* Rated to 154 in lb 3000 3000 3000 3500 4000
4Load Center Fork Face to Load CG in 24
5Power Electric 36 Volts
6Operator Type Stand-up Rider Counterbalanced
7Tire Type Press-on Solid Cushion
8Wheels (x = driven) Number Front/Rear 2x / 2
9Mast Lifting Height in See Mast Chart
11 Free Lift Height† in See Mast Chart
12 Fork Carriage ITA Class II
13 Forks Standard L x W x T in
36 x 4 x 1.5 36 x 4 x 1.5 36 x 4 x 1.5 36 x 4 x 1.75 36 x 4 x 1.75
Optional Lengths in 30, 39, 42, 45, 48, 54, 60
14 Tilt B°/F° degree See Mast Chart
15 Headlength** in 62.9 65.2 67.5 67.7 70.1
16 Width Overall in 42
17 Height Mast Collapsed in See Mast Chart
18 Mast Extended† in See Mast Chart
21 Turning Radius in 51.7 54 56.2 56.2 58.6
22 Load Distance** Center of Wheel to Fork Face in 11.3 11.5
23 Aisle Width Right Angle Stack in Turn Radius + Load Distance + Load Length + Clearance
24 Speed Travel Empty/Loaded 36V mph 7.2/7.2
24A w/Productivity Package Empty/Loaded 36V mph 7.8/7.2
25 Speed Lift DC Empty/Loaded fpm 90/60 90/60 90/60 90/57 90/50
AC Empty/Loaded fpm 110/65 110/65 110/65 110/60 110/55
26 Speed Lower Empty/Loaded fpm 90/90
32 Weight, Less Battery lb 6350 6390 5929 6429 6457
33 Axle Load with Max Battery Unloaded Front lb 3992 4167 4522 4557 4850
34 Unloaded Rear lb 4337 4489 4057 4521 4678
35 Tires Number Front/Rear 2 / 2
36 Size Front in 16 x 7 x 10.5
37 Size Rear in 10 x 5 x 6.5
38 Wheelbase in 42.7 45 47.2 47.2 49.6
39 Tread Width Front - Drive in 35
Rear - Steer in 6.7
40 Ground Clearance, Loaded Lowest Point in 3.0
41 Center of Wheelbase in 4.2
42 Grade Clearance, Loaded %41 39 37 37 35
43 Brakes Service Foot - Motor
44 Parking Auto - Electric
45 Battery Type Lead Acid
Compartment B C D D E
46 Capacity AH 775 930 1085 1085 1240
KWH 27.2 32.6 38.1 38.1 43.6
47 Weight - Min lb 1710 1990 2280 2280 2600
Weight - Max lb 1980 2270 2650 2650 3070
Comp’t. Size - Max Length 13.6 15.9 18.2 18.2 20.5
Width 38.56
Height 31
48 Battery Floor Height
With Rollers
in 6.8
49 Motors Traction Motor, dia in 7.5
50 Lift Motor, dia DC/AC in 6.7/7.5
51 Operating Pressure For Attachments psi Up to 2500 psi
General Information
Dimensions
Speeds
ChassisBattery
* Optional masts, attachments, longer load dimensions and higher lifting heights may result in derating of the capacity. Contact your local dealer.
** Add 4.25 inches for quad masts; add 2 inches for sideshift option.
† Includes load backrest.
Performance specifications are based on a truck equipped with a 190" triple telescopic mast.
Weights
Motors
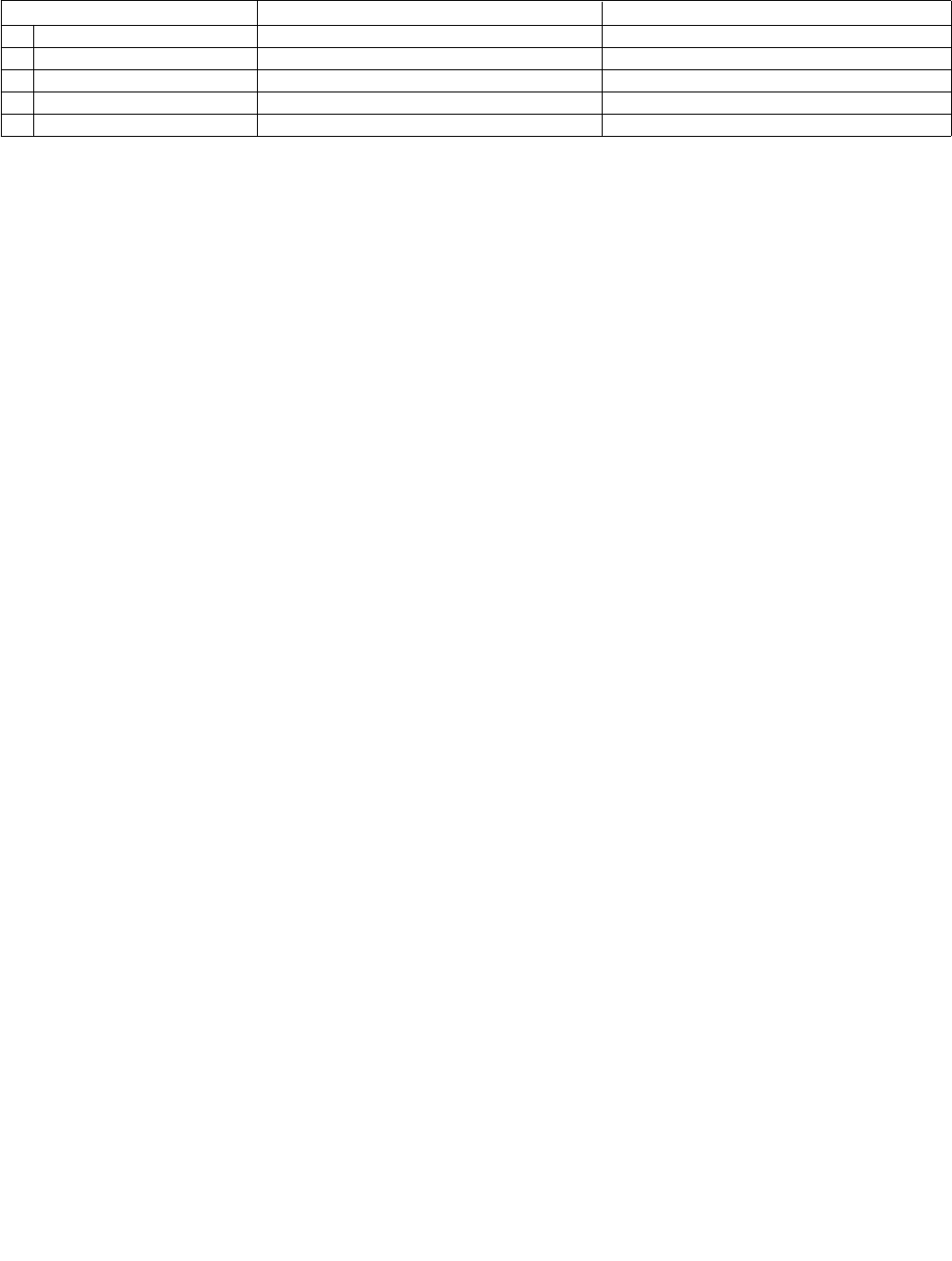
RC 5500 Series Specifications
RC 5500 Series Technical Information
Standard Equipment
1. Crown’s Access 1 2 3®
Comprehensive
System Control
2. e-GEN™ Braking System
with automatic parking brake
3. Intrinsic Stability System™
• Travel speed reduction and
appropriate brake control
when forks are above
free lift
• Forward tilt interlock
above staging
• Controlled tilt speeds
• Counterweight exceeds
required standards
• Cornering speed control
• Ramp hold
• Ramp speed control
4. FlexRide™ Suspension
5. Operator compartment
• Crown flexible side stance
• Padded back support with
integral side restraint
• Premium rubber floor mat
•
Padded arm rest
• Operator console with
desk top work surface
and storage
•
Entry bar
• Posture relief step
6. Multi-task control handle
7. Tilt position assist
8. Crown display
• Battery discharge indicator
with lift interrupt and
re-key feature
• Hour meters / travel
distance / stop watch
• Pin code access capable
• Event code display with five
(5) key navigation
• Access 1 2 3 diagnostics
• P1, P2, P3 Performance
tuning
9. AC traction system
10. 36-volt system
11. 350 amp battery connector
22. Audible travel alarms
23. Suspended floorboard
24. Positive/Negative
accessory cable
25. Work Assist™ Accessories
• Clip pad and hook
• Clamp
• Clamp and
mounting plate
• Operator fan
• Fire extinguisher
• Dome light
• Storage Pocket
Operator Compartment
Soft, rounded surfaces make
the compartment interior more
comfortable. Streamlined
exterior smooths entry/exit
for the operator.
A low floor height, (9.5") first
greets the operator. A patented
FlexRide suspended floor
provides a comfortable ride
for a wide range of operators.
A footrest provides postural
relief during stationary tasks,
complementing the largest
floorboard in its class.
Crown’s flexible side stance
allows the operator to change
positions to increase comfort
and productivity.
An entry bar with sensors auto-
matically slows travel and sounds
an audible alarm when activated,
encouraging safe foot positioning
inside the truck.
The Multi-Task Control Handle
naturally bridges Crown’s
current and past designs.
Intuitive operation is increased,
reducing the learning curve.
Blending of hydraulic control
functions and traction can
improve productivity. Control
handle activation forces are
reduced. Soft grip steer tiller
with hydrostatic steering reduces
operator fatigue.
12. InfoPoint®System with
Quick Reference Guide
13. Color-coded wiring
14. Battery rollers
15. Dual 10" cushion steer tires
16. Large 16" cushion drive tires
17. Crown-manufactured drive
and lift motors
18. High visibility power unit
19. Radial design overhead guard
with third post
20. High visibility mast with
in-line hose routing
21. Hydrostatic power steering
22. 5° forward tilt
23. 48" high load backrest
24. Reverse steering
Optional Equipment
1.
AC Hydraulics
2.
Productivity package
3. Operator compartment
wall padding
4. Adjustable armrest
5. Freezer and corrosion
conditioning
6. Sideshifter
7. Hydraulic valves for
attachments
8. Quick disconnect
hydraulic connectors
9. Forward steering
10. EE rating
11. InfoLink™ Ready System
12. Keyless on/off switch
13. Fork lengths
14. Polished and tapered forks
15. Load backrest heights
16. Non-marking smooth or lug
rubber tires
17. Drive-in rack overhead guard
18. Overhead guard heights
19. Tilt options
20. Work lights
21. Strobe lights
Operator visibility is
improved with:
• Low-profile sculpted
power unit
• High visibility mast
• Angled overhead guard post
and placement
• Radial design overhead guard
• Flexible side stance
Crown Drive System
Crown has applied the latest
generation AC drive system,
enhanced with Access 1 2 3
technology. The demand for
high efficiency systems that
closely match customer torque
requirements is met with this
generation control system.
Crown-manufactured, indepen-
dently controlled, AC drive
motors are specifically designed
to optimize system integration
between the traction and
braking controls.
Crown’s Access 1 2 3
technology provides optimum
performance and control by
offering a communication
interface for operators and
technicians, intelligent
coordination of lift truck
system and simplified service
with advanced diagnostics.
The Crown display is used for
easy troubleshooting, access
service history and set perfor-
mance features. A distribution
panel is conveniently located
with all test points, control
fuses and central wiring for
easy troubleshooting.
Three modes of performance
can be selected to accommo-
date operator experience or
application requirements.
Mast Type TT QUAD
9Lifting Height in 154 190 208 226 244 240 246 258 264 276
11 Free Lift Height in 20.2 32.2 38.2 44.2 50.2 33.2 36.2 39.2 42.2 45.2
14 Tilt B/F* degree 3/5 5/5 5/5 5/5 5/5 3/5 3/5 3/5 3/5 3/5
17 Mast Collapsed Height in 71.3 83.3 89.3 95.3 101.3 83.4 86.4 89.4 92.4 95.4
18 Mast Extended Height in 202 238 256 274 292 288 294 306 312 324
All values with 48" Load Backrest
*Forward Tilt limited to 2º above staging
RC 5500 Series Technical Information
e-GEN™ Braking System
Variable regenerative motor
braking is optimized and virtually
eliminates brake maintenance.
The appropriate amount of
stopping force is applied to
match operator brake input
and the current operating
conditions of the truck.
The closed loop Access 1 2 3
traction control will keep the
truck static until a travel input is
requested, even when operating
on a grade.
Automatic electric parking
brakes activate when the
operator releases the brake
pedal, a travel input has not
been requested or battery
power has been disconnected.
Steering
Load-sense hydrostatic
steering is an on-demand
system which reduces energy
consumption. Smooth, quiet
steering control with minimal
operator effort required at the
steer tiller. Steer tires rotate 182º
for maximum maneuverability.
Crown’s hydrostatic steering
system is simplified with signifi-
cantly fewer parts, thus reducing
maintenance requirements.
Hydraulics
The hydraulic system provides
continuous filtration. A pressur-
ized steel hydraulic tank reduces
oil misting and contamination.
Hydraulic attachments can be
added easily in the field.
Hydraulic manifold is mounted
on the mast reducing the number
of hoses and fittings.
Ram displacement type lift
cylinders and two double
acting tilt cylinders are
Crown-manufactured. All
rams and piston rods are
hard chrome plated to
reduce pitting and extend
cylinder packing life. O-ring
face seal fittings are used
to eliminate leaks.
Mast Assembly
Crown-manufactured mast
assembly utilizes a “flush-face”
interlocked I-beam design to
improve visibility and reduce
truck length. Roller bearing studs
are welded on both sides of the
rails for maximum strength and
roller bearings are canted to run
in the thick cross section of the
rail. Tie bars wrap around the
rails for added strength and to
resist off-center load forces.
“In-line” hose routing opens up
visibility. Cylinders are placed
to the sides to create a high
visibility design.
The mast has four points of
attachment to the truck for good
load force distribution. Two
mounting points are at the
frame, where tilt cylinders attach.
Tilt cylinders use spherical
bushings to resist off center load
distortions. Two large diameter
studs secure the mast to the
drive units.
Drive Units
Two Crown-manufactured
independent double reduction
planetary gear drives offer
27 to 1 gear reduction. The
first and second reduction
use helical gears for low noise
and efficiency. The drive unit
gears are splash lubricated in
an oil bath.
Carriage
An ITA Class II carriage is stan-
dard. An optional hook type ITA
sideshifter or other attachments
are easily added. Optional fork
lengths are available.
Other Options
1. Audible travel alarm
2. Flashing lights
Safety considerations and
dangers associated with
audible travel alarms and
flashing lights include:
• Multiple alarms and/or lights
can cause confusion.
• Workers ignore the alarms
and/or lights after day-in and
day-out exposure.
• Operator may transfer the
responsibility for “looking out”
to the pedestrians.
• Annoys operators and
pedestrians.
Other Options Available
Contact your local Crown dealer.
Dimensions and performance
data given may vary due to
manufacturing tolerances.
Performance is based on an
average size vehicle and is
affected by weight, condition of
truck, how it is equipped and
the conditions of the operating
area. Crown products and
specifications are subject to
change without notice.
Because Crown is continually improving its products,
specifications are subject to change without notice.
Crown, the Crown logo, the color beige, the
Momentum symbol, Access 1 2 3, InfoLink,
InfoPoint, e-GEN, FlexRide, Intrinsic Stability
System and Work Assist are trademarks of
Crown Equipment Corporation.
Copyright 2007-2008 Crown Equipment Corporation
SF14737 Rev. 8/08
Printed in U.S.A.
Crown Equipment Corporation
New Bremen, Ohio 45869 USA
Tel 419-629-2311
Fax 419-629-3796
crown.com
You can count on Crown to build lift trucks
designed for safe operation, but that’s
only part of the safety equation. Crown
encourages safe operating practices through
ongoing operator training, safety-focused
supervision, maintenance and a safe working
environment. Go to crown.com and view our
safety section to learn more.
C