TKA 9110 UC Coffeemaker Training Program 1508953563Bosch WTA 35 WTL 54 Dryer
User Manual: BOSCH AXXIS WTL5410UC pdf | FreeUserManuals.com
Open the PDF directly: View PDF .
Page Count: 64
- WTA 35 & WTL 54Dryer Training Program
- WTA 35 & WTL 54 Training Program
- Features and Benefits
- Product Description
- Warranty (1)
- Warranty (2)
- Warranty -- Serial # Label
- Installation -- Reprint of Installation Instructions (1)
- Installation -- Reprint of Installation Instructions (2)
- Installation -- Reprint of Installation Instructions (3)
- Installation -- Reprint of Installation Instructions (4)
- Installation -- Reprint of Installation Instructions (5)
- Operation -- Fascia Panels
- Operation -- Controls
- Operation -- Cleaning Lint Filter
- Operation -- Cleaning WTL 54 Heat Exchanger (Condenser)
- Disassembly -- Top Panel
- Disassembly -- Fascia Panel
- Disassembly -- Rear Panel (for Drum and Rear Access)
- Disassembly -- Front Panel (1) (for Drum and Front Access)
- Disassembly -- Front Panel (2) (for Drum and Front Access)
- Disassembly -- Side Panels (for Drum and Right Side Access)
- Disassembly -- Frame (1)
- Disassembly -- Frame (2)
- Disassembly -- Drum (1)
- Disassembly -- Drum (2)
- Disassembly -- Drum (3), Rear Bearing
- Disassembly -- WTA 35 Drum Drive Motor
- Disassembly -- WTL 54 Drain Pump & Drum Motor (1)
- Disassembly -- WTL 54 Drain Pump & Drum Motor (2)
- Disassembly -- WTL 54 Drain Pump & Drum Motor (3)
- Disassembly -- WTL 54 Drain Pump & Drum Motor (4)
- Disassembly -- WTL 54 Drain Pump & Drum Motor (5)
- Disassembly -- WTL 54 Drain Pump & Drum Motor (5)
- Reassembly -- Rear Main Drum Bearing (1)
- Reassembly -- Rear Main Drum Bearing (2)
- Reassembly -- Fan, Hi-Limit & NTC R2
- Reassembly -- Control Module Wire Harnesses
- Reassembly -- Drum Interior Light
- Reassembly -- Terminal Box
- WTA 35/WTL 54 Circuit Diagram
- WTA 35 /WTL 54 Wiring Diagram
- WTA 35 & WTL 54 Service Tips -- Ratings
- WTA 35 Service Tips -- Drum Drive Motor
- WTL 54 Service Tips -- Drum Drive Motor
- WTL 54 Service Tips -- Pump Motor
- WTA 35 & WTL 54 Service Tips -- NTC R2, Hi-Limit & Heater
- WTA 3500/3510 UC/13 Service Tips -- Timed Dry
- WTA 35 Service Tips -- Whistling Dryers
- WTA/WTL Service Tips -- Test Program (1)
- WTA/WTL Service Tips -- Test Program (2)
- WTA/WTL Service Tips -- Test Program (3)
- WTA/WTL Service Tips -- Test Program (4)
- WTA/WTL Service Tips -- Test Program (5)
- WTA 35 & WTL 54 Service Tips -- Troubleshooting of Minor Faults (Customer Self-Help 1)
- WTA 35 & WTL 54 Service Tips -- Troubleshooting of Minor Faults (Customer Self-Help 2)
- WTA 35 & WTL 54 Service Tips -- Resistance Measurements from Control Module (1)
- WTA 35 & WTL 54 Service Tips -- Resistance Measurements from Control Module (2)
- WTA 35 & WTL 54 Service Tips -- Troubleshooting (1)
- WTA 35 & WTL 54 Service Tips -- Troubleshooting (2)
- WTA 35 & WTL 54 Service Tips -- Troubleshooting (3)
- WTA 35 & WTL 54 Service Tips -- Dryer Operation (1): Moisture Sensing
- WTA 35 & WTL 54 Service Tips -- Dryer Operation (2): NTC Locations
- WTA 35 & WTL 54 Service Tips -- Dryer Operation (3): Preventing Overheating
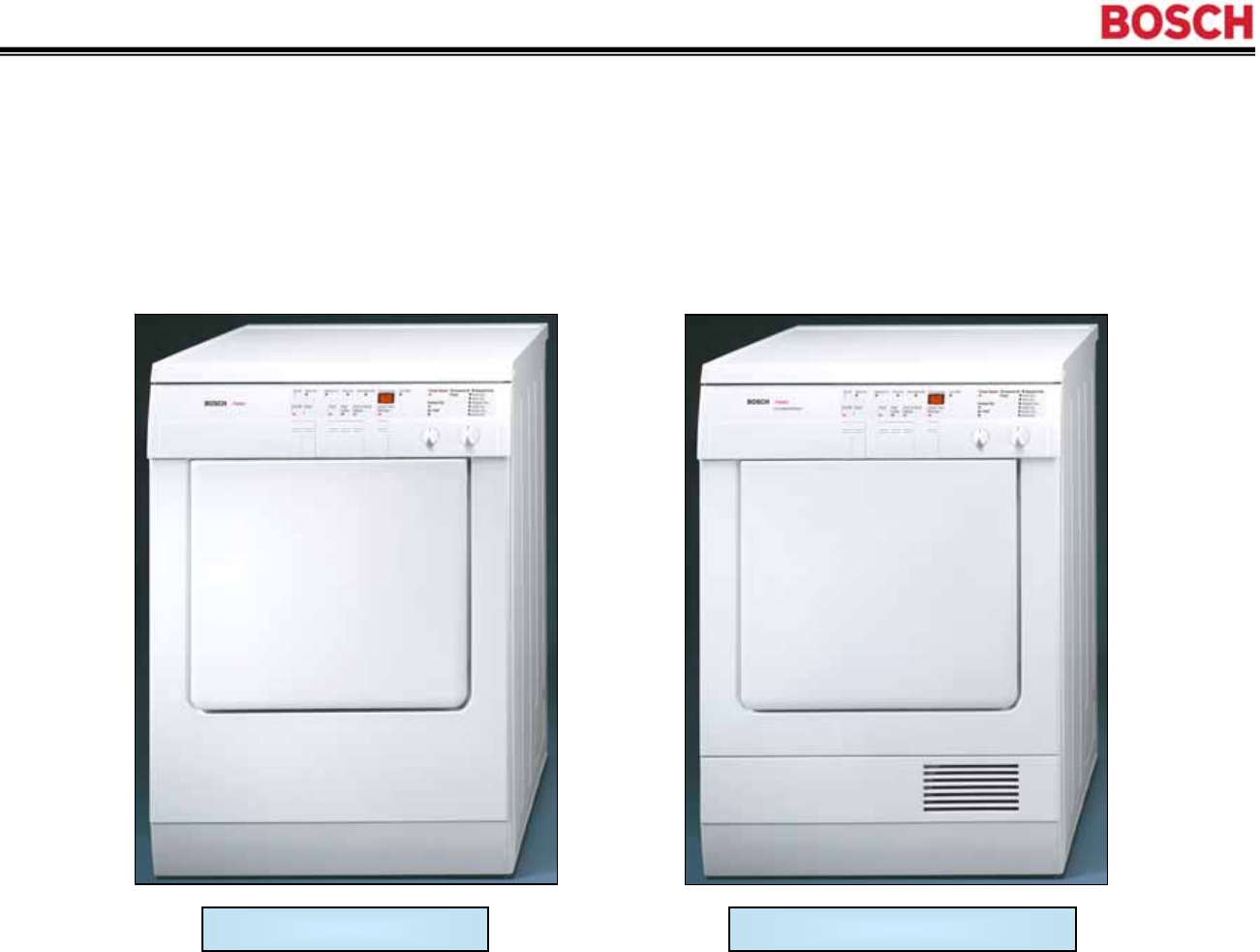
1st Edition/Revision 3 (4/11/03)
1
702_58300000141665_ara_en_a
WTA 35 & WTL 54
WTA 35 & WTL 54
Dryer Training Program
Dryer Training Program
Vented model - WTA3510UC Condensation model - WTL5410UC

1st Edition/Revision 3 (4/11/03)
2
702_58300000141665_ara_en_a
WTA 35 & WTL 54 Training Program
WTA 35 & WTL 54 Training Program
•
•Features and Benefits
Features and Benefits
•
•Product Description
Product Description
•
•Warranty
Warranty
•
•Installation
Installation
•
•Operation
Operation
•
•Disassembly
Disassembly
•
•Reassembly
Reassembly
•
•Wiring Diagram
Wiring Diagram
•
•Service Tips
Service Tips

1st Edition/Revision 3 (4/11/03)
3
702_58300000141665_ara_en_a
•
•Anti
Anti-
-crease feature
crease feature
•
•Smooth stainless steel drum
Smooth stainless steel drum -
-won
won’
’t rust & is
t rust & is
gentle to clothes
gentle to clothes
•
•Auto
Auto-
-dry with 2 digital moisture sensors and 3
dry with 2 digital moisture sensors and 3
temperature sensors
temperature sensors
•
•Moisture and temperature sensors automatically
Moisture and temperature sensors automatically
determine when laundry is dry, preventing over
determine when laundry is dry, preventing over-
-
drying and damaging clothing.
drying and damaging clothing.
•
•Regular/Cotton
Regular/Cotton -
-6 settings
6 settings
•
•Permanent Press
Permanent Press -
-5 settings
5 settings
•
•Reverse tumble action
Reverse tumble action
•
•Spanish and French fascia inserts (WTA
Spanish and French fascia inserts (WTA
3510/WTL 5410)
3510/WTL 5410)
•
•UL listed (U.S. & Canada)
UL listed (U.S. & Canada)
Features and Benefits
Features and Benefits

1st Edition/Revision 3 (4/11/03)
4
702_58300000141665_ara_en_a
•
•Electronic
Electronic Duotronic
Duotronic controls
controls
•
•Regular/Cotton
Regular/Cotton,
, Permanent Press
Permanent Press,
,
Delicates
Delicates &
& Air fluff
Air fluff settings
settings
•
•Stainless steel drum
Stainless steel drum
•
•Anti
Anti-
-Crease
Crease feature
feature
•
•Extra
Extra-
-fine lint screen
fine lint screen
•
•Digital and LED displays
Digital and LED displays
•
•Adjustable end of cycle signal
Adjustable end of cycle signal
•
•Terminal box with 30A cord and outlet
Terminal box with 30A cord and outlet
for 15A washer cord
for 15A washer cord
•
•Interior drum light
Interior drum light
•
•Vented (WTA 35) and condensation
Vented (WTA 35) and condensation
(WTL 54) versions
(WTL 54) versions
•
•UL listed (U.S. & Canada)
UL listed (U.S. & Canada)
Product Description
Product Description
Digital &
LED displays
Electronic
controls
Auto or timed dry settings
Interior
drum light
Easily accessible
extra-fine lint
screen
Vented &
condensation
versions

1st Edition/Revision 3 (4/11/03)
5
702_58300000141665_ara_en_a
Bosch Dryers and Dryers Limited Lifetime Warranty
Statement of Limited Warranty
The warranties provided by BSH Home Appliances ("Bosch") in this Statement of
Warranties apply only to Bosch clothes dryers and dryers sold to the first using
purchaser by Bosch or its authorized dealers, retailers or service centers in the United
States or Canada. The Warranties provided herein are not transferable, and take place
from date of installation.
1 Year Full Limited Warranty
Bosch will repair or replace, free of charge, any component part that proves defective
under conditions of normal home use, labor and shipping costs included. Warranty
repair service must be performed by an authorized Bosch Service Center.
2 Year Limited Warranty
Bosch will provide replacement parts, free of charge, for any component part that proves
defective under conditions of normal home use, shipping costs included.
Warranty (1)
Warranty (1)

1st Edition/Revision 3 (4/11/03)
6
702_58300000141665_ara_en_a
Warranty (2)
Warranty (2)
5 Year Limited Warranty On Electronics
Bosch will repair or replace, free of charge, any microprocessor or printed circuit
board that proves defective under conditions of normal home use for a period of
five years from the date of original installation, labor charges excluded.
5 Year Limited Warranty On Motor
Bosch will repair or replace, free of charge, any pump or component part of the
pump that proves defective under conditions of normal home use for a period of
five years from the date of original installation, labor charges excluded.
5 Year Limited Warranty On Cabinet Rust-Through
Bosch will replace any cabinet part, free of charge, if that cabinet part should rust
through under conditions of normal home use, labor charges excluded.
Lifetime Limited Warranty Against Stainless Steel Rust-Through
Bosch will replace your clothes dryer or dryer, free of charge, with the same
model or a current model that is equivalent or better in functionality if the drum
should rust through under conditions of normal home use, labor charges excluded.
For location of nearest repair depot call 1
For location of nearest repair depot call 1-
-800
800-
-944
944-
-2904 from 5:00 AM
2904 from 5:00 AM -
-5:00 PM
5:00 PM
M
M-
-F (Pacific time)
F (Pacific time)

1st Edition/Revision 3 (4/11/03)
7
702_58300000141665_ara_en_a
Warranty
Warranty --
-- Serial # Label
Serial # Label
The serial # label, located on the rear of the dryer (on the right
side), shows necessary warranty information.
•Model # - “WTA3500UC/13”.
•Serial # - “FD 8104”. To find when the product type
was built, add 20 to the 1st two digits to get the year
(81 + 20 = 101 Æproduct type was built in 2001).
The last two digits show the month (04 = April).
Serial #
label
Factory serial # - Can convert
factory serial # to FD # for
warranty use. 1st 2 digits show
factory # (47 = Nauen), 3rd digit
shows year (1 = 2001), 4th & 5th
digits show month built (04 =
April). So, serial # starting with
“47104…0008397” = dryer built @
Nauen with FD 8104 30108.
NOTE:There is another label
on the inside of the door, but it
doesn’t show the serial #.

1st Edition/Revision 3 (4/11/03)
8
702_58300000141665_ara_en_a
Installation
Installation --
-- Reprint of Installation Instructions (1)
Reprint of Installation Instructions (1)
NOTE:Be sure to follow
all national & local codes.
NOTE:Dryers must be grounded
to reduce the risk of shock should
any malfunctions occur.
NOTE:Use 4” metal duct (flexible or rigid) with these
dryers. Do not use non-metal duct.

1st Edition/Revision 3 (4/11/03)
9
702_58300000141665_ara_en_a
HINT:Washers and dryers are both rated 15A @ 240VAC. Washers have
15A cords and plugs provided. Dryers have 30A cords provided to handle the
power requirements when washers are plugged into the dryer terminal boxes.
Installation
Installation --
-- Reprint of Installation Instructions (2)
Reprint of Installation Instructions (2)
Don’t install dryers
in closets with solid
wooden doors as
dryers must have
make-up air.
Dryers must be
installed on level,
solidly constructed
floors.

1st Edition/Revision 3 (4/11/03)
10
702_58300000141665_ara_en_a
Installation
Installation --
-- Reprint of Installation Instructions (3)
Reprint of Installation Instructions (3)
HINT:Don’t exceed
maximum duct lengths
shown in Table 1.
HINT:Use as few
elbows as possible.

1st Edition/Revision 3 (4/11/03)
11
702_58300000141665_ara_en_a
Installation
Installation --
-- Reprint of Installation Instructions (4)
Reprint of Installation Instructions (4)
HINT:The dryer uses a
NEMA 10-30P 240V,
30A, 4-wire plug, which
mates to a NEMA 10-
30R outlet (receptacle).
CAUTION:When moving
a dryer, screw in the feet
(leveling legs) first so they
won’t be damaged.
4-wire connection
CAUTION:Dryers must
be grounded to reduce
the risk of shock.

1st Edition/Revision 3 (4/11/03)
12
702_58300000141665_ara_en_a
CAUTION:When moving a dryer, screw in the feet
(leveling legs) first so they won’t be damaged.
Installation
Installation --
-- Reprint of Installation Instructions (5)
Reprint of Installation Instructions (5)

1st Edition/Revision 3 (4/11/03)
13
702_58300000141665_ara_en_a
Operation
Operation --
-- Fascia Panels
Fascia Panels
WTA 3510UC
WTL 5410UC

1st Edition/Revision 3 (4/11/03)
14
702_58300000141665_ara_en_a
Operation
Operation --
-- Controls
Controls
Both have Regular/Cotton,
Permanent Press, Timed
Dry, Heated Dry, Air Fluff
& Delicates settings.
WTL 5410UC
WTA 3510UC
Timed Cycles
Selector knob Auto-Cycles Selector knob
Digital Display
Timed Cycles
Selector knob

1st Edition/Revision 3 (4/11/03)
15
702_58300000141665_ara_en_a
Lint Filter
The lint filter should be cleaned after each use or If the Lint Filter light becomes illuminated and the
buzzer sounds during operation of the dryer:
1. Immediately stop the dryer by depressing the On/Off button.
2. Depress the Door button and open the door.
3. Remove the filter.
4. Clean the filter.
5. Replace the filter.
6. Let the dryer cool down.
7. Close the door.
8. Press the Start button to restart the dryer.
Operation
Operation --
-- Cleaning Lint Filter
Cleaning Lint Filter

1st Edition/Revision 3 (4/11/03)
16
702_58300000141665_ara_en_a
Heat Exchanger (WTL 54 models only)
The heat exchanger should be cleaned 3–4 times a year; more often if used frequently. To clean the heat exchanger:
1. With the dryer turned off and disconnected from the electrical supply. Disconnect the power cord by grasping the
plug, not the cord.
2. Depress the Door button and open the door.
3. Press the button for opening the heat exchanger/inlet panel, as shown in Figure 6.
4. Open the panel fully.
5. Turn the retainers on each side of the heat exchanger towards each other, in the direction of the arrows as shown
in Figure 7.
6. Remove the heat exchanger by slowly pulling it forward and out of the dryer.
7. Clean the heat exchanger thoroughly with water. Allow the water to run freely through the heat exchanger. See
Figure 8.
8. Allow heat exchanger to dry thoroughly before reinserting into the dryer.
9. Once the heat exchanger is completely dry, reinsert it into the dryer. The handle must be underneath the heat
exchanger. Turn the retainers back to their original position.
10. Close the heat exchanger/inlet panel by pressing firmly on both the upper left and right hand sides, as shown in
Figure 9, until it snaps into place.
Note: The dryer door can only be closed if the heat exchanger/inlet panel is properly closed and locked in place.
Operation
Operation --
-- Cleaning WTL 54 Heat Exchanger (Condenser)
Cleaning WTL 54 Heat Exchanger (Condenser)

1st Edition/Revision 3 (4/11/03)
17
702_58300000141665_ara_en_a
Disassembly
Disassembly --
-- Top Panel
Top Panel
To remove top panel to access control module & frame (for
disassembly):
•cCarefully pry out plastic covers over screw on each front side of
dryer cover. Then, remove each T-20 Torx screw (total of 2).
•d(Optional) Carefully remove two rear clips from cover by
removing T-20 Torx screws.
•eWhen front screws are removed, tilt front of top cover up, then
lift white plastic top cover off of dryer.
•fTo gain access to top of dryer, remove metal top cover by
removing seven (7) T-20 Torx screws. Don’t forget to remove
screws in two white plastic bumpers on front corners.
•NOTE: Wiring diagram is contained in a clear plastic sleeve on
the metal top cover.
1
2
234
4

1st Edition/Revision 3 (4/11/03)
18
702_58300000141665_ara_en_a
Disassembly
Disassembly --
-- Fascia Panel
Fascia Panel
To remove fascia panel to access display module &
frame (for disassembly), carefully pry panel toward front
of dryer and lift panel up. Don’t break plastic tabs.
NOTE:Also need
to separate wire
harness & door
latch cable from
front panel &
display module.

1st Edition/Revision 3 (4/11/03)
19
702_58300000141665_ara_en_a
Disassembly
Disassembly --
-- Rear Panel (for Drum and
Rear Panel (for Drum and
Rear Access)
Rear Access)
To remove rear panel
to access heater,
NTC R2, Hi-Limit
safety cutout, fan &
drum rear bearing),
remove 12 screws.
Heater cover with ratings
To remove heater,
remove heater cover,
then remove two (2)
screws at top of heater
assembly and one (1)
screw at wire harness.
NOTE:Heaters cycle
on and off as needed
to keep temperatures
at appropriate levels.

1st Edition/Revision 3 (4/11/03)
20
702_58300000141665_ara_en_a
Disassembly
Disassembly --
-- Front Panel (1) (for Drum and
Front Panel (1) (for Drum and
Front Access)
Front Access)
Removing door hinges Removing front panel screws HINT:Remove front panel to
access drum, display module,
R3 NTC & door latch.
To remove front panel, remove three (3) T-20
Torx screws @ top of panel and five (5) T-20
Torx screws around door face frame. See red
dots for screw locations.
.
.
.
.
..
..
HINT:Carefully pry out white
cap to access T-20 Torx
screw underneath door.

1st Edition/Revision 3 (4/11/03)
21
702_58300000141665_ara_en_a
Disassembly
Disassembly --
-- Front Panel (2) (for Drum and
Front Panel (2) (for Drum and
Front Access)
Front Access)
Removing
door latch
HINT:Remove door latch and disconnect
NTC R3 wire harness before removing
door face frame (from front panel).
The door face frame
lifts up and out with
the NTC attached --
disconnect the NTC
connector.
NTC R3 in bottom of door face frame HINT:To remove door
latch from front panel,
remove two (2) T-10
Torx screws.

1st Edition/Revision 3 (4/11/03)
22
702_58300000141665_ara_en_a
Disassembly
Disassembly --
-- Side Panels (for Drum and
Side Panels (for Drum and
Right Side Access)
Right Side Access)
To remove side panels to
access drum & drive
motor:
• Remove four (4) T-20
Torx panel screws from
rear of dryer.
• Remove one (1) T-20
Torx screw from top front
of dryer.
• Then carefully lift panels
up and out.
Unscrewing
side panel
screws Removing
side panels
HINT:Remove right side panel to
access drum drive motor, belts/pulleys,
heater connector & motor capacitor.

1st Edition/Revision 3 (4/11/03)
23
702_58300000141665_ara_en_a
Disassembly
Disassembly --
-- Frame (1)
Frame (1)
To access the drum, the frame must be partially disassembled.
2
TO DISASSEMBLE FRAME (to access
drum):
•cRemove top, fascia & side panels (with
door).
•dRemove drum drive belt.
• See next page for rest of procedure.
1To remove
inner frame,
lift it up and
out.
1
Frame with fascia, front & side panels removed.
To remove belt,
remove motor
tensioning spring,
then slide belt off
of front of drum.

1st Edition/Revision 3 (4/11/03)
24
702_58300000141665_ara_en_a
Disassembly
Disassembly --
-- Frame (2)
Frame (2)
TO DISASSEMBLE FRAME to
access drum (continued):
•eAfter the side panels have
been removed, remove one (1)
long T-20 Torx screw from the
front of the base on each side
(total of 2 screws).
•fRemove front frame rail
screws from front of dryer.
•gRemove front frame screws
from top of dryer.
5
4
3

1st Edition/Revision 3 (4/11/03)
25
702_58300000141665_ara_en_a
Disassembly
Disassembly --
-- Drum (1)
Drum (1)
REMOVING DRUM FROM FRAME:
• If not done already, disconnect wire harnesses hindering
removing drum and place them out of the way. Leave the
control module (with wire harnesses) mounted to the side
frame.
• Lift out front panel from frame.
• Remove front frame rails.

1st Edition/Revision 3 (4/11/03)
26
702_58300000141665_ara_en_a
Disassembly
Disassembly --
-- Drum (2)
Drum (2)
REMOVING DRUM FROM FRAME (continued):
• If not done already, remove heater (rear) cover to access rear
drum bearing.
• Unscrew main nut on rear bearing to release drum from frame.
• Carefully lift drum out from frame.
HINT:Use a 13mm socket or wrench on
the main nut on the rear of the drum.

1st Edition/Revision 3 (4/11/03)
27
702_58300000141665_ara_en_a
Disassembly
Disassembly --
-- Drum (3), Rear Bearing
Drum (3), Rear Bearing
HINT:Some older WTA
3500 & WTL 5400 dryers
may have rear bearings
without a copper plate &
carbon brush (which were
added to enhance electrical
ground connections). If so,
the rear bearing should be
replaced with kit # 183897.

1st Edition/Revision 3 (4/11/03)
28
702_58300000141665_ara_en_a
To disassemble drum drive motor:
• Remove heater cover on rear of dryer.
Remove right side panel.
• Release belt tension spring and small belt.
• Using a 13mm wrench or socket on fan blade
and an adjustable wrench on pulley, loosen and
remove fan blade from motor shaft.
• Remove (“horseshoe”) drum motor clamp by
removing two screws.
• Remove belt tensioning mount by removing two
screws.
• Disconnect terminal connector from motor.
• Remove motor from dryer.
Disassembly
Disassembly --
-- WTA 35
WTA 35 Drum Drive Motor
Drum Drive Motor

1st Edition/Revision 3 (4/11/03)
29
702_58300000141665_ara_en_a
Disassembly
Disassembly --
-- WTL 54 Drain Pump & Drum Motor (1)
WTL 54 Drain Pump & Drum Motor (1)
Remove rear cover & right side panel
Push latch to unhook spring.
HINT:Carefully remove rear
cover to avoid damaging
gasket. Bring a # 167651
gasket for any WTL 54 repair
in case gasket gets damaged.
WTA 35
shown
WTA 35
shown WTA 35
shown

1st Edition/Revision 3 (4/11/03)
30
702_58300000141665_ara_en_a
Disconnect drain pump wires Slide drive belt off pulley Pull out motor clamp
Drum motor clamp removed Remove spring holder Unscrew pump cover screw
Disassembly
Disassembly --
-- WTL 54 Drain Pump & Drum Motor (2)
WTL 54 Drain Pump & Drum Motor (2)

1st Edition/Revision 3 (4/11/03)
31
702_58300000141665_ara_en_a
Disconnect hose Remove pump cover Disconnect motor wires Remove drain pump
Remove float Remove rear fan (13mm socket) Remove front insulation
Disassembly
Disassembly --
-- WTL 54 Drain Pump & Drum Motor (3)
WTL 54 Drain Pump & Drum Motor (3)

1st Edition/Revision 3 (4/11/03)
32
702_58300000141665_ara_en_a
Remove front fan cover (twist ccw), then remove front fan (while holding motor shaft)
Remove pulley assy. by removing (2) T-20 Torx screws
Disassembly
Disassembly --
-- WTL 54 Drain Pump & Drum Motor (4)
WTL 54 Drain Pump & Drum Motor (4)

1st Edition/Revision 3 (4/11/03)
33
702_58300000141665_ara_en_a
Exposed drum drive motor Remove drum motor
Disassembled drum drive motor You’re done!!
Disassembly
Disassembly --
-- WTL 54 Drain Pump & Drum Motor (5)
WTL 54 Drain Pump & Drum Motor (5)
HINT:Without removing drum, pulley
assy. screws access is tight. Use a
ratcheting screwdriver for tight locations.
HINT:If necessary, pry out motors
carefully (using wood or a tool
which won’t damage the dryer).
Push drum drive motor
toward rear of dryer.

1st Edition/Revision 3 (4/11/03)
34
702_58300000141665_ara_en_a
…and that’s all
there is to taking
apart the dryers!
To disassemble WTL 54 drain pump (quick guide):
• Remove right side panel.
• Remove wire harness from pump.
• Release belt tension.
• Remove spring holder & drum motor clamp.
• Remove black drain hose.
• Remove motor cover, being careful to not to damage water
level microswitch.
• Remove drain pump motor and float assembly from dryer.
You da man!
Drain motor
Float
Motor
cover
Drain hose
Disassembly
Disassembly --
-- WTL 54 Drain Pump & Drum Motor (5)
WTL 54 Drain Pump & Drum Motor (5)

1st Edition/Revision 3 (4/11/03)
35
702_58300000141665_ara_en_a
Reassembly
Reassembly --
-- Rear Main Drum Bearing (1)
Rear Main Drum Bearing (1)
HINT: Make sure rear
bearing nut is tight -- if
not, dryer can squeal
when drum turns.

1st Edition/Revision 3 (4/11/03)
36
702_58300000141665_ara_en_a
Reassembly
Reassembly --
-- Rear Main Drum Bearing (2)
Rear Main Drum Bearing (2)
HINT:Some older WTA
3500 & WTL 5400 dryers
may have rear bearings
without a copper plate &
carbon brush (which were
added to enhance electrical
ground connections). If so,
the rear bearing should be
replaced with kit # 183897.
HINT: Rear bearing kit #
183897 includes a copper
plate & carbon brush to
enhance electrical ground
connections.
Rear bearing kit # 183897.

1st Edition/Revision 3 (4/11/03)
37
702_58300000141665_ara_en_a
Reassembly
Reassembly --
-- Fan, Hi
Fan, Hi-
-Limit & NTC R2
Limit & NTC R2
Heater plug
Resetting
Hi-Limit
HINT: If fan nut
won’t tighten down
adequately, install
a lockwasher.
NOTE: Hi-Limit (high
temp cutout), located
on heater housing,
trips @ 212ºF (WTA
35) or 248ºF (WTL
54). To reset Hi-Limit,
press red button.
NTC R2 (on top of
heater housing)
HINT: On WTL 54
condensation dryers,
make sure the rear
seal is installed
properly to avoid any
moisture leaking.
Always bring a gasket
when doing any WTL
54 repairs.

1st Edition/Revision 3 (4/11/03)
38
702_58300000141665_ara_en_a
Reassembly
Reassembly --
-- Control Module Wire Harnesses
Control Module Wire Harnesses
OK
Wrong
HINT: Make sure there
is no gap between the
orange and pink
connectors.
NOTE: If the orange
connector isn’t reattached
properly, the E3 heater
won’t come on.

1st Edition/Revision 3 (4/11/03)
39
702_58300000141665_ara_en_a
Reassembly
Reassembly --
-- Drum Interior Light
Drum Interior Light
2
3
4 5
6
Remove fascia panel (with display module) to access light,
taking care not to damage panel plastic tabs (photos 1-3).
Remove light cover (located above
door panel next to On/Off & Door
switch assembly).
Pull out light socket (with connectors) and change light bulb.
1
I’ve seen
the light!
Plastic
tabs

1st Edition/Revision 3 (4/11/03)
40
702_58300000141665_ara_en_a
Reassembly
Reassembly --
-- Terminal Box
Terminal Box
NOTE: Fuse holders for SC-15 15A fuses
aren’t available and must be bought locally.

1st Edition/Revision 3 (4/11/03)
41
702_58300000141665_ara_en_a
WTA 35/WTL 54 Circuit Diagram
WTA 35/WTL 54 Circuit Diagram
(WTL 5400 UC & 5410UC)
HINT:“Mains” is the
European term for
“power”.
HINT:This circuit
diagram is used for
WTA 3500UC, WTA
3510UC, WTL 5400UC
& WTL 5410UC dryers.
NOTE:Heaters cycle
on and off as needed
to keep temperatures
at appropriate levels.

1st Edition/Revision 3 (4/11/03)
42
702_58300000141665_ara_en_a
HINT:“Mains” is the
European term for
“power”.
WTA 35 /WTL 54 Wiring Diagram
WTA 35 /WTL 54 Wiring Diagram
(WTL 5400UC & WTL 5410UC)
HINT:This wiring
diagram is used for
WTA 3500UC, WTA
3510UC, WTL 5400UC
& WTL 5410UC dryers.
NOTE:Heaters cycle on and off as needed to keep
temperatures at appropriate levels.

1st Edition/Revision 3 (4/11/03)
43
702_58300000141665_ara_en_a
WTA 35 & WTL 54 Service Tips
WTA 35 & WTL 54 Service Tips --
-- Ratings
Ratings
• Rated 240VAC, 15A, 60 Hz (uses 13A max.).
• Uses 15A type SC-15 fuses (for washer & dryer).
• Uses NEMA 14-30P 240V, 30A, 4-wire plug, which
mates to a NEMA 14-30R outlet. Can use NEMA 10-30P
3-wire cord (bought locally) if needed to match NEMA
10-30R outlet.
• WTL 54 max. drain hose length = 15’ (180”) & max.
drain hose height = 3-1/2’ (43”).
• WTA 3510 & WTL 5410 dryers are similar to WTA 3500
& WTL 5400 dryers (except for enhanced fascia styling &
Spanish/French fascia inserts).
• Output with clean lint filter = 112 cfm. (with dirty lint
filter = 83 cfm).
• UL listed (U.S. & Canada)
HINT:This service training
manual can be used to service
WTA 3500 & WTL 5400 dryers.

1st Edition/Revision 3 (4/11/03)
44
702_58300000141665_ara_en_a
WTA 35 Service Tips
WTA 35 Service Tips --
-- Drum Drive Motor
Drum Drive Motor
Replacing drive belt
HINT:Remove right side panel to access drum drive motor,
belts/pulleys, heater connector & motor capacitor. WTA 35WTL 54

1st Edition/Revision 3 (4/11/03)
45
702_58300000141665_ara_en_a
WTL 54 Service Tips
WTL 54 Service Tips --
-- Drum Drive Motor
Drum Drive Motor
HINT:Remove right side panel to access drum drive motor,
belts/pulleys, heater connector & motor capacitor.
Drum drive motors on WTL 54 condensation dryers
are different and are installed differently than WTA 35
vented dryers to avoid water leaking, provide space
for the drain pump and provide a condenser fan.
CAUTION:When installing WTL 54 drum drive motors, be
careful to not damage cover seal to prevent water leakage.
Motor
capacitor
Motor connector plugs

1st Edition/Revision 3 (4/11/03)
46
702_58300000141665_ara_en_a
WTL 54 Service Tips
WTL 54 Service Tips --
-- Pump Motor
Pump Motor
HINT:Remove right side panel to
access pump motor.
WTL 54 condensation dryers have drain
pumps to eliminate the condensed water.
Drain hose connection
on right rear of dryer.
HINT:Pump motor resistance
measurement is ~ 110 - 136Ω.

1st Edition/Revision 3 (4/11/03)
47
702_58300000141665_ara_en_a
WTA 35 & WTL 54 Service Tips
WTA 35 & WTL 54 Service Tips --
-- NTC
NTC
R2, Hi
R2, Hi-
-Limit & Heater
Limit & Heater
Resetting
Hi-Limit
HINT:Hi-Limit (safety cutout) trips @:
• 100ºC (212ºF) for WTA 35
• 120ºC (248ºF) for WTL 54
Hi-Limit
NTC R2
Top of heater housing
E2 = 800W @ 240V (draws ~ 3A)
E3 = 1900W @ 240V (draws ~ 7A)
Hi-Limit
HINT:NTC R2 reads ~ 21 kΩ@ room temperature.
HINT:Measure heater E3 between terminals 8& 5
and heater E2 between terminals 8& 7. If resistance
= ∞, reset Hi-Limit thermostat and remeasure.
Heater cover with ratings
NOTE:Heaters cycle on and off as needed
to keep temperatures at appropriate levels.

1st Edition/Revision 3 (4/11/03)
48
702_58300000141665_ara_en_a
WTA 3500/3510 UC/13 Service Tips
WTA 3500/3510 UC/13 Service Tips --
--
Timed Dry
Timed Dry
NOTE:WTA 3500 UC/04,
UC/08 & UC/10 dryers used
control module # 265677, which
provided full heating during
Timed Dry.
NOTE:WTA 3500 & WTA 3510
UC/13 dryers use control module #
481590, which provides reduced
heating during Timed Dry to meet
Canadian energy requirements.
WTA 3500/3510 UC/13 vented dryers have Timed Dry cycles which use
less energy than WTA 3500 UC/04 - UC/10 dryers (to meet Canadian
energy requirements). These dryers can take longer to dry laundry during
Timed Dry. This doesn’t affect WTL 54 condensation dryers -- they do not
have a reduced heat output during Timed Dry cycles.
The Timed Dry cycles are intended for drying delicates
and hand washables. When drying cotton and
permanent press fabrics, Auto-cycles (i.e. sensor
controlled drying) should be used. Using Auto-cycles,
WTA 3500/3510 UC/13 vented dryers heat to full
capacity and sense when clothes are dry, drying clothes
quickly and safely.

1st Edition/Revision 3 (4/11/03)
49
702_58300000141665_ara_en_a
WTA 35 Service Tips
WTA 35 Service Tips --
-- Whistling Dryers
Whistling Dryers
HINT:Use silicone caulk to fasten
vent covers whenever installing or
repairing WTA 35 vented dryers.
WTA 3500/3510 vented dryers can
occasionally whistle if one or more of
the vent covers has worked loose or
wasn’t installed securely.
To eliminate whistling from WTA 35 vented
dryers, reattach vent covers to dryers with
silicone caulk. Use a non-adhesive type
which will allow vent covers to be moved at a
later date.

1st Edition/Revision 3 (4/11/03)
50
702_58300000141665_ara_en_a
WTA/WTL Service Tips
WTA/WTL Service Tips --
-- Test Program (1)
Test Program (1)
WTA 35 & WTL 54 dryers have test programs enabling them to self-
diagnose problems, including listing the last fault code.
To enter/exit test program for WTA 35 & WTL 54 dryers:
♦Rotate Auto-cycle and Timed cycle knobs to Off position.
♦Push and hold Start and Delicate buttons at the same time, then turn dryer on by pushing On/Off button. After pushing
On/Off button, keep holding Start and Delicate buttons until Start light flashes rapidly. Dryer is now in the test program.
♦Lights will flash for drying faults -- fault shown will be the last fault code on the dryer (see fault chart on next page).
♦When test program has been entered:
♦Start light flashes rapidly.
♦Select individual parts to test by rotating Auto-cycle knob as shown on next page.
♦Don’t rotate Auto-cycle knob or push any button while individual tests are being run (so tests won’t stop).
♦Once part to test has been selected, start test by pushing Start button. Start light will stay on continually while tests
are running. Push Start button again to end any test. Tests have finished once Start light flashes rapidly again.
♦To exit test program, push Start button (while Start light flashes rapidly).
NOTE:Fault displayed
will be 1st fault that
occurred since last time
dryer was turned on.
Timed cycle
knob Auto-cycle
knob

1st Edition/Revision 3 (4/11/03)
51
702_58300000141665_ara_en_a
Test parts individually as follows:
♦Indicating lights & digital display – To start test, rotate Auto-cycle knob to Regular/Cotton Extra Dry, then push Start button. To
end test, rotate Auto-cycle knob out of Regular/Cotton Extra Dry position.
Cycle buttons & selector switches – To start test, rotate Auto-cycle knob to Regular/Cotton Very Dry, then push Start button. To
end test, push Start button again (since test doesn’t end).
♦Pump, motor, heater & NTC’s –To start test, rotate Auto-cycle knob to Regular/Cotton Regular Dry, then push Start button. Test
ends automatically.
♦Sensor conductance – To start test, rotate Auto-cycle knob to Regular/Cotton Light Dry, then push Start button. To end test, push
Start button again (since test doesn’t end).
WTA/WTL Service Tips
WTA/WTL Service Tips --
-- Test Program (2)
Test Program (2)
Fault Possible Causes Flashing Lights Digital Display
Drying time too long Control module failed.
Moisture sensor(s) failed.
Hi-Limit (“overheat”) thermostat tripped and failed to
reset.
Water level switch failed (WTL 54 only).
Supply voltage too low.
Overheating Control module failed.
Heater failed.
R3 NTC failed (short or open circuited) NTC # R3 failed.
R2 NTC failed (short or open circuited) NTC # R2 failed.
Condensed water not pumped out
(WTL 54 condensation models only)
Pump failed. E1
A
nti-Crease/
End
Extra Dry
Damp Dry
Regular Dry

1st Edition/Revision 3 (4/11/03)
52
702_58300000141665_ara_en_a
SELECTOR
KNOB KNOB PROGRAMS KNOB
POSITION LIGHTS
Drying Damp
Dry Regular
Dry Extra
Dry Anti-
Crease/End
Off
Regular/Cotton Extra Dry On
Regular/Cotton Very Dry On
Regular/Cotton Regular Dry On
Regular/Cotton Light Dry On
Regular/Cotton Econo Dry On
Regular/Cotton Damp Dry On On
Permanent Press Econo Dry On On
Permanent Press Light Dry On On
Permanent Press Regular Dry On On
Permanent Press Very Dry On On
Program
Selector
Knob
NOTE: Red
Regular/
Cotton Very
Dry lights stay
lit during this
test no matter
what program
selector
position is
chosen – no
other Regular/
Cotton or
Permanent
Press lights
comes on.
Permanent Press Extra Dry On On
Timed cycle Heated Dry On On
Timed cycle On On
Timed cycle On On
Timed Cycle
Knob
NOTE:
program
selector knob
MUST be
straight up for
tests to run.
Timed cycle Air Fluff On On
WTA/WTL Service Tips
WTA/WTL Service Tips --
-- Test Program (3)
Test Program (3)
Cycle Buttons &
Selector
Switches Test
Chart
NOTES:
• Pushing "START" button
after test has ended will
repeat it.
• Door can be opened (if
desired) during this test.
•Delicates, End of Cycle
Signal and Cycle Time
Minutes lights stay lit
whenever button underneath
them is pushed and held.
• Digital display does not
come on during this test.

1st Edition/Revision 3 (4/11/03)
53
702_58300000141665_ara_en_a
WTA/WTL Service Tips
WTA/WTL Service Tips --
-- Test Program (4)
Test Program (4)
To exit test program (from any test), turn unit off by pressing "ON/OFF" button.
Pump, motor, heater & NTC’s Test Sequence Chart
TEST ORDER & TIME (SECONDS) NOTES
START 15 5 2 5 29 END
PART
TESTED
3 5 5 2 5 1 5 1 5 1 5 1 5
Pump START
OF
TEST
END
OF
TEST
For WTL 54
condensation
dryer only
Motor –
right
rotation
Motor –
off
Motor –
left
rotation
During 29
second drum
reversing cycle,
drum runs for 5
seconds on / 1
second off –
check drum
rotation with
door open.
Heater
(E2) Feel for heat
with door open.
Heater
(E3) Feel for heat
with door open.
NOTES:
• Test ends
automatically.
Pushing Start
button after test
has ended will
repeat it.
• Opening door
stops test –
closing door
resumes test.
To check if
drum is turning
and if heat is
coming out of
drum, run test
with door open
by tripping door
latch (by gently
pushing it with a
screwdriver).

1st Edition/Revision 3 (4/11/03)
54
702_58300000141665_ara_en_a
LIGHTS SHOWING CONDUCTANCE OF MOISTURE SENSORS
Test "Drying" light "Damp Dry" light Comments
No fault
Drum empty –sensors and drum not connected
Fault – short circuit
No fault
Drum empty – with sensors and drum connected
HINT: Remove top panel and jumper between copper
braids (to "brushes" touching outside of drum). Fault – open circuit or
circuit resistance is too high
Drying
Drying
Damp Dry
Damp Dry
Damp Dry
Damp Dry
Drying
Drying
WTA/WTL Service Tips
WTA/WTL Service Tips --
-- Test Program (5)
Test Program (5)
Sensor Conductance Test
HINTS:
• Tests can be run with door closed. Opening door during testing stops the test.
• To run 2nd test with sensors and drum connected, remove top panel and connect jumper
to copper braids (for two "brushes" touching outside of drum).
•Drum must be empty during these tests – damp clothes in drum will give wrong results.
• Lights won't flash during this test.
To exit test program (from
any test), turn unit off by
pressing "ON/OFF" button.
HINT:Using the test program can cut down repair
times & eliminate repeat calls from misdiagnosing
problems. The pump, motor, heaters, NTC’s and
moisture sensor conductance tests are more helpful
than the buttons, knobs, lights and display tests.

1st Edition/Revision 3 (4/11/03)
55
702_58300000141665_ara_en_a
WTA 35 & WTL 54 Service Tips
WTA 35 & WTL 54 Service Tips --
--
Troubleshooting of Minor Faults
Troubleshooting of Minor Faults (Customer Self
(Customer Self-
-Help 1)
Help 1)
SELF-HELP
Dryers may exhibit problems that are unrelated to a malfunction of the dryer itself. The following table may serve to answer your
question about a problem you are having without having to call a serviceman.
PROBLEM POSSIBLE CAUSE
‘‘On/Off’’ Indicator light does not come on. • The ‘‘On/Off’’ button has not been depressed.
• A fuse may have blown or a circuit breaker tripped. Replace fuse or reset
circuit breaker at your fuse box/breaker box.
• The plug is not correctly or only loosely inserted into the receptacle.
Dryer does not start. • Cycle has not been selected.
• “Start” button has not been depressed.
• Door is not closed properly.
• Room temperature is below 32 °F (0 °C)
• If necessary, switch the machine off and wait 5 seconds before switching it
on again. Select the cycle again and depress “Start”.
Cycle is interrupted and ‘‘Lint Filter’’ light is
illuminated and buzzer sounds.
• Clean Lint Filter as described in section titled CARE and CLEANING.
• (WTA models) Check exhaust vent to see if it is blocked or too long.
• (WTL models) Clean heat exchanger as described in section titled CARE and
CLEANING.
• (WTL models) Check air inlet to make sure it is not blocked.
Cycle is interrupted, buzzer sounds, one or
several cycle indicators are flashing. Indicates faulty operation:
• Clean the Lint Filter, check the exhaust duct length (WTA models),
• Switch the dryer off, wait for it to cool down and then restart.
Drying level not reached or drying time too
long.
• Clean the Moisture sensors in the drum as described in section titled CARE
and CLEANING.
• If there is a power failure for an extended period the cycle must be restarted.

1st Edition/Revision 3 (4/11/03)
56
702_58300000141665_ara_en_a
WTA 35 & WTL 54 Service Tips
WTA 35 & WTL 54 Service Tips --
--
Troubleshooting of Minor Faults
Troubleshooting of Minor Faults (Customer Self
(Customer Self-
-Help 2)
Help 2)
PROBLEM POSSIBLE CAUSE
The laundry is not dry even though the highest drying
level has been selected.
• The drum is too full.
• The laundry was too wet when placed in the dryer.
• The room is not adequately ventilated. Make sure there is an adequate
supply of fresh air.
• The lint filter is blocked and should be cleaned.
• (WTA models) The exhaust vent is blocked or too long.
• (WTL models) The air inlet is blocked.
Drum light does not work • “On/Off” button has not been pressed.
• Bulb has failed. For safety reasons the bulb must only be replaced by an
authorized service agent.
Following items apply only to the WTL (Condensation Electric Dryer) models
Cycle is interrupted and ‘‘E1’’ appears in display • Condensate hose is blocked in some way. Turn off dryer and check hose.
Humidity level in room increases greatly • The room is not adequately ventilated. Make sure there is an adequate
supply of fresh air.
• Check air inlet to see if it is blocked.
• The heat exchanger was removed but not replaced.

1st Edition/Revision 3 (4/11/03)
57
702_58300000141665_ara_en_a
WTA 35 & WTL 54 Service Tips
WTA 35 & WTL 54 Service Tips --
--
Resistance Measurements from Control Module (1)
Resistance Measurements from Control Module (1)
Disconnect & measure 2-pin
connector (not shown) to measure
drain pump (WTL 54 models).
Pump should read ~ 110 - 136 Ω
WARNING!
Unplug dryer
before making
any resistance
measurements.
2
2
1
1
Disconnect & measure pink
2-pin connector to measure
heater E2 (800W). Heater
E2 should read 71 - 76 Ω.
Disconnect & measure pin 2(top)
of orange 2-pin connector & pin 1
(bottom) of pink 2-pin connector to
measure heater E3 (1900W).
Heater E3 should read 27 - 31 Ω.
WTA 3510
model shown

1st Edition/Revision 3 (4/11/03)
58
702_58300000141665_ara_en_a
WTA 35 & WTL 54 Service Tips
WTA 35 & WTL 54 Service Tips --
--
Resistance Measurements from Control Module (2)
Resistance Measurements from Control Module (2)
WARNING! Unplug dryer before making any resistance measurements.
Disconnect & measure yellow 3-pin connector to measure
drum motor (with fan). Motor should read (pin 1 is at bottom):
• Pins 1-2: 19 - 25 Ω(WTL 54)
• Pins 1-2: 25 - 29 Ω(WTA 35)
• Pins 1-3: 18 - 23 Ω(WTL 54)
• Pins 1-3: 25 - 30 Ω(WTA 35)
1
1
Disconnect & measure white 2-pin
connector to measure NTC R2 (@
heaters). NTC R2 should read 18 - 22 kΩ.
Disconnect & measure white 3-
pin connector between pins 1-3
(pin 1 is at left) to measure NTC
R3 (@ door frame). NTC R3
should read 9 - 11 kΩ.
1
1
WTA 3510
model shown

1st Edition/Revision 3 (4/11/03)
59
702_58300000141665_ara_en_a
WTA 35 & WTL 54 Service Tips
WTA 35 & WTL 54 Service Tips --
--
Troubleshooting (1)
Troubleshooting (1)
WARNING! Unplug dryer before starting any repairs.
Fault code Problem Possible Cause Solution
Damp Dry
light flashes
NTC # R3 (@ bearing
shield) failed
NOTE: When viewing wiring
diagram, see NTC # R3.
NTC (temperature sensor)
failed.
Check voltage at and wiring to NTC. Turn
off dryer, measure NTC resistance and
replace faulty NTC.
NOTE: NTC resistances:
9 – 11 kΩ @ 59ºF – 221ºF
Regular Dry
light flashes
NTC # R2 (@ heaters)
failed
NOTE: When viewing wiring
diagram, see NTC # R2.
NTC (temperature sensor)
failed.
Check voltage at and wiring to NTC. Turn
off dryer, measure NTC resistance and
replace faulty NTC.
NOTE: NTC resistances:
18 – 22 kΩ @ 59ºF – 392ºF
Extra Dry
light flashes
Heater (dryer
overheated)
Lint filter blocked. Clean lint filter.
Vent is blocked or vent
hose is too long (WTA 35).
Clean vent and vent hose. If vent hose is
too long, shorten hose.
Dryer is overloaded with
laundry.
Empty clothes from dryer.
Fan impeller has loosened. Tighten fan impeller. If fan impeller cannot
be tightened, replace it.

1st Edition/Revision 3 (4/11/03)
60
702_58300000141665_ara_en_a
WTA 35 & WTL 54 Service Tips
WTA 35 & WTL 54 Service Tips --
--
Troubleshooting (2)
Troubleshooting (2)
WARNING! Unplug dryer before starting any repairs.
Fault code Problem Possible Cause Solution
Extra Dry
light flashes
Heater (dryer
overheated)
Heater failed. Check voltage at and wiring to heater. Turn off
dryer, measure heater resistance and replace faulty
heater.
(continued) NOTE: Heater resistances:
62 – 67 Ω (800W - E2 on wiring diagram)
25 – 29 Ω (1900W – E3 on wiring diagram)
Drum motor failed
(or drum drive
belt has broken).
Check voltage at and wiring to drum motor. Turn off
dryer, measure motor resistance and replace faulty
motor. If drum drive belt has broken or is
excessively worn, replace it.
NOTE: Drum motor resistances (see wiring diagram):
19 – 25 Ω (between points X2.2-X2.3 for WTL 54)
18 – 23 Ω (between points X2.2-X2.4 for WTL 54)
25 – 29 Ω (between points X2.2-X2.3 for WTA 35)
25 – 30 Ω (between points X2.2-X2.4 for WTA 35)
Anti-
Crease/End
light flashes
Drying time too
long
Control module
failed.
Check voltage at and wiring to module. Turn off
dryer, and replace faulty module.

1st Edition/Revision 3 (4/11/03)
61
702_58300000141665_ara_en_a
WTA 35 & WTL 54 Service Tips
WTA 35 & WTL 54 Service Tips --
--
Troubleshooting (3)
Troubleshooting (3)
WARNING! Unplug dryer before starting any repairs.
Fault code Problem Possible Cause Solution
Anti-Crease/End
light flashes
(continued)
Moisture sensor(s)
failed.
Run moisture sensor conductance test. Check voltage
at and wiring to sensors. Turn off dryer and replace
faulty sensor(s).
Water level switch
failed (WTL 54 only).
Hi-Limit ("overheat")
thermostat tripped
and failed to reset.
Supply voltage too
low.
Check voltage at and wiring to Hi-Limit. Turn off dryer,
measure Hi-Limit resistance and replace faulty Hi-Limit.
Reset Hi-Limit 1st. If still no heat, check voltage at and
wiring to Hi-Limit. Turn off dryer, measure Hi-Limit
resistance and replace faulty Hi-Limit.
NOTE: Hi-Limit trips @ 248ºF (WTL 54) or 212ºF (WTA 35).
Have customer upgrade power system to provide
consistent voltage to dryer during heating (need min.
198V).
E1 Pump failed
(WTL 5400
condensation
dryer only)
Pump failed. Check voltage at and wiring to pump. Turn off dryer,
measure pump resistance (110 – 136 Ω) and replace
faulty pump.
--- Dryer won't run
or indicator
lights won't
come on (no
power to dryer)
Dryer not turned on.
No power to dryer.
Dryer fuse has
blown.
Turn "on/off" switch on.
Check customer circuit breaker, fuse box or power
connections.
Unscrew holder cap & replace fuse (15A, type SC-15).

1st Edition/Revision 3 (4/11/03)
62
702_58300000141665_ara_en_a
WTA 35 & WTL 54 Service Tips
WTA 35 & WTL 54 Service Tips --
--
Dryer Operation (1): Moisture Sensing
Dryer Operation (1): Moisture Sensing
The control module continually measures the conductivity of wet
clothing (by measuring the voltage between the two sensors).
When the voltage
matches the one
required by the
customer dryness
setting, the dryer
stops.
Sliding contacts
(brushes) contact
the inner and outer
drums to give the
voltage readings.
(ground)

1st Edition/Revision 3 (4/11/03)
63
702_58300000141665_ara_en_a
WTA 35 & WTL 54 Service Tips
WTA 35 & WTL 54 Service Tips --
--
Dryer Operation (2): NTC Locations
Dryer Operation (2): NTC Locations
Two NTC sensors measure
the air temperature to
prevent overheating.
•NTC R2 -- Measures the
air temperature in front of
the heater.
•NTC R3 -- Measures the
air temperature at the dryer
door.
Hi-Limit
NTC R2
Top of heater housing
NTC R3 in bottom of door face frame
HINT:Keeping lint filter &
vent hoses clean of lint will
keep NTC’s from tripping
unnecessarily.

1st Edition/Revision 3 (4/11/03)
64
702_58300000141665_ara_en_a
WTA 35 & WTL 54 Service Tips
WTA 35 & WTL 54 Service Tips --
--
Dryer Operation (3): Preventing Overheating
Dryer Operation (3): Preventing Overheating
The control module continually measures drying temperatures and
turns off heaters as needed to lower temperatures to proper levels.
The control module
drops the heat setting
down one level
whenever overheating
occurs and whenever
the drum rotates
counterclockwise.
• From 3(heater E2
+ E3) to 2(heater
E3 only)
• From 2(heater E3
only) to 0(off -no
heat).
Temp.
E2 + E3
E3 only
Off
Lowering temperature during drum ccw rotation
Correcting temperature overshoot
Temp.
NOTE:Heaters cycle on and off as
needed to keep temperatures at
appropriate levels.