Elemental Mercury OSHA ID 140 1677
User Manual: 1677
Open the PDF directly: View PDF .
Page Count: 2
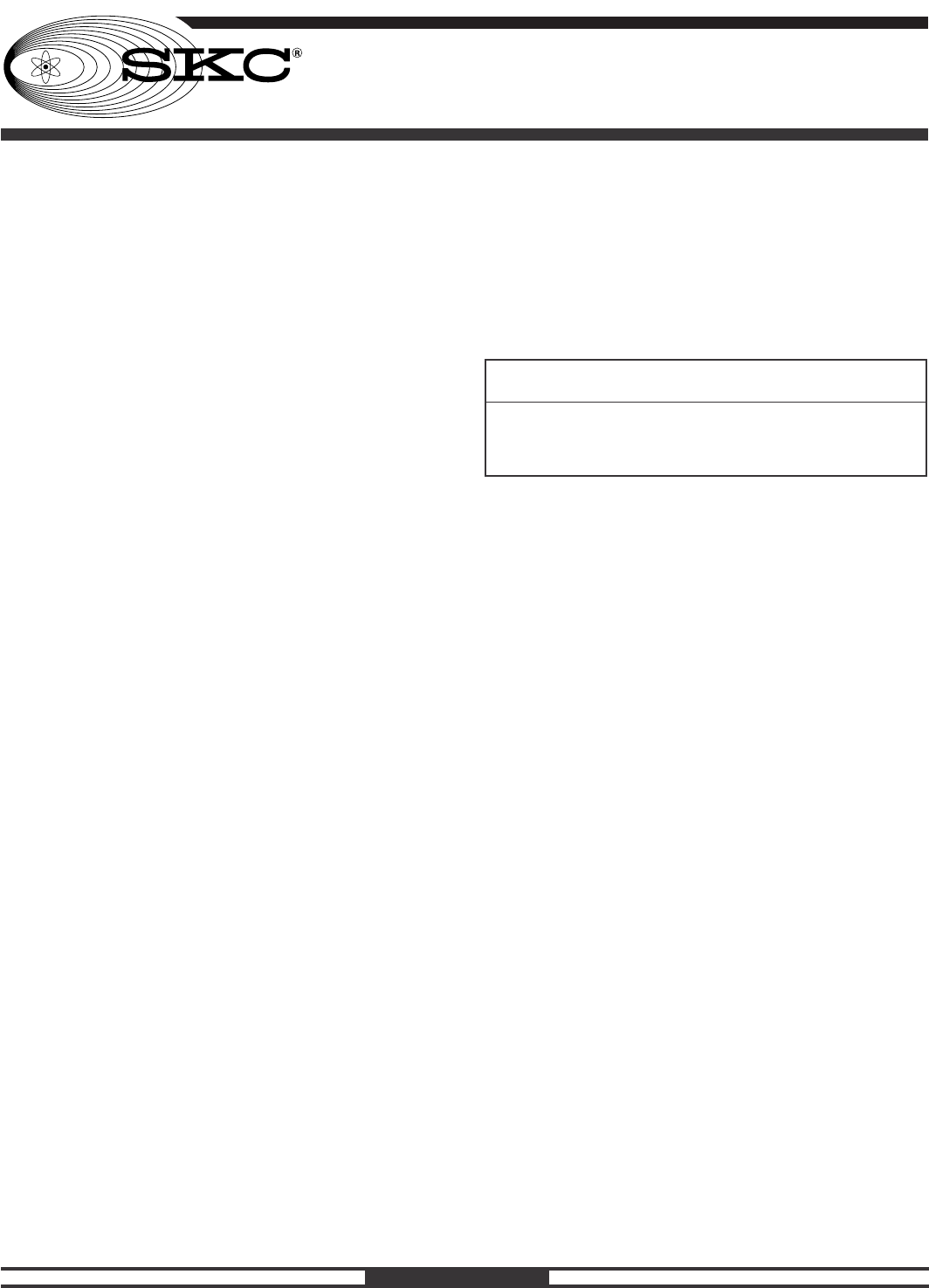
Chemical Fact File®
SKC Inc. 724-941-9701 SKC South 434-352-7149 SKC Gulf Coast 281-859-8050 SKC West 714-992-2780
www.skcinc.com
Required Equipment:
Active Method
1. An Air Sampling Pump capable of sampling at the recom-
mended flow rate with the sampling medium in line, such as:
• SKC 210 Series Pocket Pump® Sampler with Tube Holder
222-3-1
• SKC AirChek®2000 Sampler with Constant Pressure
Controller Cat. No. 224-26-CPC, Low Flow Holder Cat. No.
224-26-01, and Protective Cover Cat. No. 224-29A
• SKC AirChek 52 Sampler with Constant Pressure Controller
Cat. No. 224-26-CPC, Low Flow Holder Cat. No. 224-26-01,
and Protective Cover Cat. No. 224-29A
• SKC Universal XR Series Sampler with Low Flow Holder
Cat. No. 224-26-01 and Protective Tube Cover 224-29A
2. An Airflow Calibrator, such as:
• SKC UltraFlo® Calibrator Cat. No. 709
• DryCal® DC-Lite Flowmeter Cat. No. 717-01
3. SKC Sorbent Tube Cat. No. 226-17-1A†
Passive Method
1. SKC Passive Sampler Sorbent Capsules Cat. No. 520-02A
2. SKC Reusable Capsule Holder Cat. No. 520-03
Optional Equipment:
1. SKC Tube Breaker Cat. No. 222-3-50
2. SKC Preloaded Filter Cassette Cat. No. 225-3-01 (used in
the active method as a prefilter to capture particulate mercury)
3. SKC Collar Clip and Cable Tie Cat. No. 225-13-6 (for use
with sorbent tube-prefilter assembly)
SKC Application Guides:
1. Sampling Train - Sorbent Sample Tubes, #1168
2. Calibrating a Pump Using a Film Flowmeter, #1163
3. Calibrating a Pump Using an Electronic Calibrator, #1366
4. Prefilter and Sorbent Tube Sampling, #1164
Active Method Passive Method
Parameter TWA* TWA*
Flow Rate 200 ml/min 20 ml/min
Sample Time 8 hrs 8 hrs
Air Volume 100 L 10 L
OSHA PEL 0.1 mg/m30.1 mg/m3
(*Per 09/03/1996 OSHA Letter of Interpretation re: Standard 1910.1000 Table Z-2)
Sampling and Analysis:
Active Sampling
1. To set up a sorbent tube sampling train, break open both
ends of a sorbent tube using the optional SKC sorbent tube
breaker. Insert the sorbent tube into the rubber sleeve of the
adjustable low flow holder or tube holder. The arrow on the
sorbent tube indicates airflow and should point toward the tube
holder and the pump. In the absence of an arrow, insert the end
of the tube with the smallest sorbent section (backup section) into
the tube holder. Connect the loose end of the flexible tubing to the
inlet of a Constant Pressure Controller (CPC) if required by the
pump for low flow sampling. Use tubing to connect the outlet of
the tube or CPC to the pump inlet.
Request SKC Application
Guide #1168 for more information on preparing sorbent tube
sampling trains.
Prefilter Option:
The prefilter should be added to the sampling
train in the following situations:
a. Sampling in workplaces that contain both chlorine and
mercury.
b. Sampling to determine compliance to the OSHA PEL for
total mercury
c. Sampling in an atmosphere where particulate mercury
compounds may present a problem.
d. When the sorbent in the sorbent tube has migrated into
the tube's glass wool plug prior to sampling
To set up a sorbent tube sampling train with prefilter, insert the
opened sorbent tube into the adjustable low flow holder as
directed above. Remove the plugs from a loaded filter cassette.
Use a short length of Teflon® tubing to connect the inlet of the
sorbent tube to the outlet of the filter cassette. Use a representa-
tive filter cassette during calibration. The recommended flow rate
remains at 200 ml/min with the prefilter-sorbent tube assembly.
Request SKC Application Guide #1164 for more information on
preparing a prefilter and sorbent tube sampling train.
Elemental Mercury — OSHA ID-140
Publication 1677 Issue 0501
This method provides adequate sensitivity (qualitative detection limit 0.01
µ
g* and quantitative detection limit 0.02
µ
g*) for measuring
workplace atmospheric concentrations of elemental mercury. It offers the choice of collecting samples passively on a lightweight,
economical dosimeter or actively on a sorbent tube. The passive dosimeter and sorbent tube each collect mercury vapor only. The
sorbent tube may be used with a prefilter to collect both vapor and particulate mercury and can be used to determine compliance with
the OSHA PEL of 0.1 mg/m3 (TWA) as total mercury (vapor + particulate).
*Detection limits can vary depending on the background of the sorbent.
†SKC proprietary sorbent; performance comparable to Hydrar® and Hopcalite.
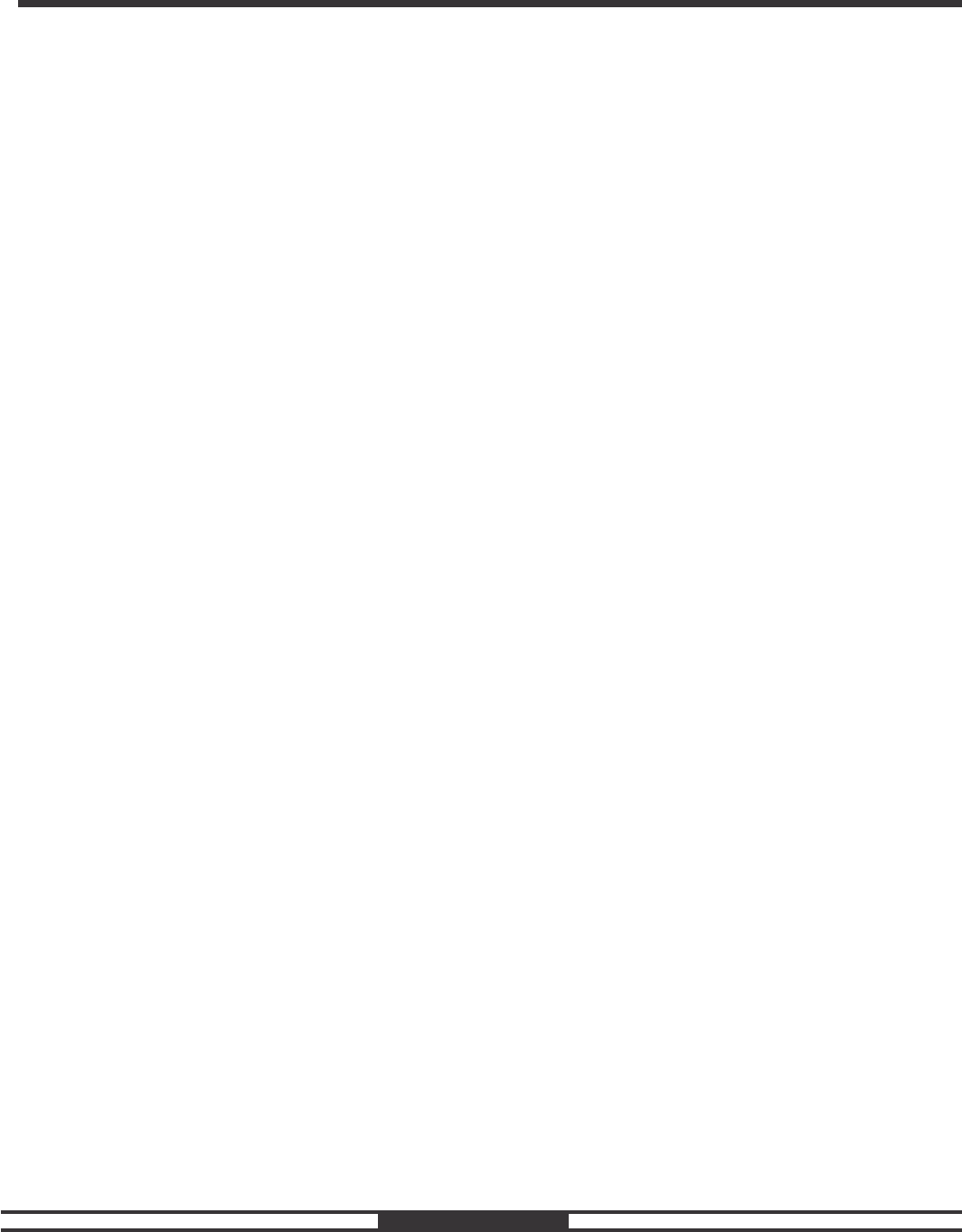
SKC Inc. 724-941-9701 SKC South 434-352-7149 SKC Gulf Coast 281-859-8050 SKC West 714-992-2780
www.skcinc.com
Elemental Mercury — OSHA ID-140
2. For calibrating the pump, use the sampling train described
above except connect the sorbent tube inlet to the calibrator with
a piece of flexible tubing. When using a prefilter, connect the inlet
of the filter cassette to the calibrator. Use representative media.
Calibrate the pump flow rate to the rate specified in the method.
When calibration has been completed, remove representative
media, cap it with the end caps provided, and save it for
recalibration at the end of sampling.
Request SKC Application
Guide #1366 or #1163 for more information on calibrating a
pump.
3. For sampling, set up a sampling train as above except use a
new sorbent tube and do not break off the ends of the sorbent
tube until ready to sample. The larger section of sorbent should
be positioned away from the pump. Place the protective cover
over the sorbent tube. Attach the clip on the protective cover to a
worker's clothing near the breathing zone and the pump to the
worker's belt. The sorbent tube should remain in a vertical
position during sampling. Turn on the pump.
If using a prefilter, use Teflon tubing to attach a new filter cassette
to the inlet of the sorbent tube. Do not unplug the cassette inlet
until ready to sample. Loop the cassette through a cable tie and
use the collar clip to attach the cassette to the worker's clothing in
the breathing zone. Turn on the pump.
4. Sample at the recommended flow rate for the recommended
period of time.
5. At the end of the sampling period, turn off the pump and note
the ending time. Remove the media, seal it with the end caps
provided, and record pertinent sampling information.
6. Verify pump flow rate with the representative sampling media
in line to confirm that the flow rate has not changed by more than
5%.
Passive Sampling
1. Remove the back cover with a screwdriver or coin.
2. Remove the sorbent capsule from the pouch, and place it in
the sampler housing with the mesh side facing toward the front of
the sampler (area with diffusion holes). Keep the pouch in a safe
place free from mercury contamination.
3. Place a clean foam disk in the back cover. Fit the back cover
into the sampler housing.
4. Record name, date, and start time on the label included with
the replacement sorbent capsules, and place it on the back of the
sampler. Note other pertinent sampling information.
5. Using the clip, attach sampler to worker's clothing near
breathing zone.
6. To begin sampling, remove the front sealing cap. Retain the
cap in a safe place that is free from contamination. The recom-
mended sampling time is four to eight hours.
7. When sampling is complete, replace the sealing cap and
record the finish time on the label. Note other pertinent sampling
information.
Submitting Samples:
1. Submit several field blanks from the same lot number as the
media used as this sorbent does have a mercury background.
Field blanks should be subjected to exactly the same handling as
the samples (open, seal, and transport) except that no air is
drawn through them.
2. Pack samples (tubes and cassettes sealed with caps and
passive sorbent capsules in pouch), used passive dosimeter
housings, field blanks, and all pertinent sampling information
securely for shipment to a laboratory for analysis.
Storage:
Sorbent Tubes:
Sorbent should be analyzed within 30 days of
sampling.
Passive Samplers:
Sorbent should be analyzed within 30 days of
sampling. Do not store sorbent capsules or capsule holders in
contaminated areas.
Analyzing Method:
Cold vapor-atomic absorption spectrophotometry (AAS)
Copyright 2004
Publication 1677 Issue 0501
Notice: This publication is intended for general information only and should not be used as a substitute for reviewing applicable government regulations, equipment operating instructions, or legal standards. The information
contained in this document should not be construed as legal advice or opinion nor as a final authority on legal or regulatory procedures.