03_foreword 2003 Polaris Trail Boss 330 Service Manual Part III
User Manual: 2003 Polaris Trail Boss 330 Service Manual part III
Open the PDF directly: View PDF .
Page Count: 71

FINAL DRIVE
7.2
WHEEL, HUB, AND SPINDLE
TORQUE TABLE
Item Specification
Front Wheel Nuts 20 Ft. Lbs. (27 Nm)
Rear Wheel Nuts 50 Ft. Lbs. (68 Nm)
Front Spindle Nut 40 Ft. Lbs. (54 Nm)
Rear Hub Retaining Nut 80 Ft. Lbs. (109 Nm)
NOTE: Refer to exploded views and text for torque
values of other fasteners
CAUTION: Locking nuts and bolts with preapplied
locking agent must be replaced if removed. The
self-locking properties of the nut or bolt are reduced
or destroyed during removal.
FRONT HUB
DISASSEMBLY/INSPECTION
1. Elevate front end and safely support machine
under footrest / frame area.
CAUTION: Serious injury may result if machine tips
or falls. Be sure machine is secure before beginning
this service procedure. Wear eye protection when
removing bearings and seals.
2. Check bearings for side play by grasping tire /
wheel firmly (top and bottom) and checking for
movement. It should rotate smoothly without
binding or rough spots.
3. Remove wheel nuts and wheel.
4. Remove the two brake caliper bolts and the brake
caliper.
5. Remove hub cap, cotter pin, front spindle nut, and
washer.
6. Rotate each bearing by hand and check for
smooth rotation. Visually inspect bearing for
moisture, dirt, or corrosion. Replace bearing if
moisture, dirt, corrosion, or roughness is evident.
7. Place a shop towel on hub to protect surface.
Carefully pry seal out of hub.

FINAL DRIVE
7.3
8. Using a brass drift, tap bearing spacer to one side
to expose inner bearing race. Drive bearing out
using a drift through opposite side of hub and
discard.
Tap spacer to side
9. Remove spacer and drive other bearing out and
discard.
10. Clean hub and spacer thoroughly.
11. Inspect spacer for wear or damage. Measure
length of spacer and replace if worn beyond
service limit or if ends are rounded.
Bearing Spacer Length:
Service Limit: 2.1850²(5.55 cm)
FRONT HUB ASSEMBLY
Seal
Hub assembly view
1. Drive or press one new bearing into hub using a
1.180 (46 mm) bearing driver.
CAUTION: Do not drive on the inner race of the
bearing.
Premium All-Season Grease
(PN 2871322) (3 oz. Tube)
(PN 2871423) (14 oz. Tube)
2. Coat bearing spacer with grease and install into
hub. Drive or press the other bearing into hub until
seated against spacer.

FINAL DRIVE
7.4
3. Install seal into hub (with numbers facing out) until
flush with end of seal bore.
Seal
FRONT HUB INSTALLATION
1. Inspect spindle seal and bearing surface for wear
or damage.
Inspect and Grease
2. Apply grease to spindle.
3. Install hub on spindle.
4. Apply grease to washer and install with domed
side facing out.
Out
Cone
Washer
5. Install spindle nut and tighten to specification.
2x4SpindleNutTorque:
40 ft. lbs. (55.0 Nm)
6. Install a new cotter pin. Tighten nut slightly if
necessary to align cotter pin holes.
7. Rotate wheel and check for smooth operation.
Bend both ends of cotter pin around end of
spindle in different directions.
8. Lightly grease a new O-ring and install on hub
cap. Install hub cap.
9. Rotate hub. It should rotate smoothly without
binding or rough spots or side play.
10. Install brake caliper using new bolts. Tighten
bolts to specified torque.
Caliper Mounting Bolt Torque
18 ft. lbs. (25 Nm)
11. Install wheel and wheel nuts and tighten evenly in
a cross pattern to specified torque.
Flange Nuts:
Flat side against
wheel
Front Wheel Nut Torque
20 ft. lbs. (27 Nm)

Hub
Brake Disc
Spindle
Strut Housing
Seal
Bearing
Bearing
Wheel Nut
Spacer
Washer
(domed side out)
Nut
40 ft. lbs.
(55.3 Nm)
Cotter Pin
O-Ring
Hub Cap
18 ft. lbs. (24.9 Nm)
Use new bolts with pre-applied
locking agent.
FINAL DRIVE
7.5
FRONT HUB EXPLODED VIEW

FINAL DRIVE
7.6
CONCENTRIC SWINGARM
REAR AXLE REMOVAL
1. Securely support rear of machine with rear wheels
off the floor. Remove rear wheels and hubs.
2. Remove drive chain.
3. Remove snap ring (A), lock sleeve (B) and foam
seal (C) from axle.
A
B
C
4. Remove sprocket hub nut (D).
D
5. Remove the two rear brake caliper bolts. Remove
the rear brake caliper.
Remove Rear Caliper
6. Support rear caliper with wire or a tie strap. Do not
hang caliper by brake line.
Support Caliper from Frame
7. Slide axle assembly out left side.

FINAL DRIVE
7.7
CONCENTRIC SWINGARM
REAR AXLE DISASSEMBLY
1. Remove rear axle. (See Page 7.6)
2. Remove snap ring, collar, and foam seal.
3. Remove nut, brake disc assembly, and stop ring.
Stop Ring
Disc Hub
Grooveinspline
Nut
Threads
Splines
CONCENTRIC SWINGARM
REAR AXLE ASSEMBLY
1. Installstopringingrooveonleftsideofaxle.
Stop Ring
Disc Hub
Grooveinspline
NOTE: Left side of axle is identified by the small
groove in the middle of the spline.
2. Install disc hub assembly on axle. Be sure hub
covers stop ring. Install disc in soft jawed vise.
Apply Never Seize to threads, install left axle nut
and tighten to 120 ft. lbs (166 Nm). Keep
tightening nut until flat aligns with flat on brake
hub.
Stop ring
Axle Nut (Disc Side) Torque:
120 ft. lbs. (166 Nm)
3. Lubricate spacer and new O-ring. Install on axle.

FINAL DRIVE
7.8
4. Install foam seal and axle nut lock sleeve with
taper toward nut. Install snap ring to retain the
lock sleeve.
Foam Seal
Lock Sleeve
(Tapered side toward nut)
Snap Ring
CONCENTRIC SWINGARM
REAR AXLE INSTALLATION
1. Install axle from left to right.
O--Ring on axle between
sprocket hub and bearing
2. Lubricate and install a new O-ring on right side of
axle. Slide new O-ring against RH axle bearing
seal. Apply grease to sealing area on inside of
sprocket hub and slide sprocket hub assembly
onto the axle. Seat the hub against O-ring and
bearing.
3. Apply Never Seize to threads of axle and install nut.
Tighten nut with wrench to approximately 8-10 ft.
lbs. (11-14 Nm). Align flat of nut with flat on hub.
Axle must rotate smoothly without binding. If axle
binds the nut is too tight. If axle movement (up and
down or side to side) is detected, axle is too loose.
Axle Nut (Sprocket Side) Torque:
8-10 ft. lbs. (11-14 Nm)
4. Install foam seal (C) and slide lock sleeve (B) onto
hub and install lock sleeve with taper inward.
Install snap ring (A).
A
B
C
5. Install brake caliper and drive chain. Adjust drive
chain (refer to Maintenance Chapter 2 for
procedure). Torque eccentric pinch bolts to 30 ft.
lbs. (41 Nm) on models without a trailer hitch, or
40 ft. lbs. (55 Nm) on models with a trailer hitch.
Verify proper chain adjustment after torquing
eccentric.
6. Torque brake caliper mounting bolts to 18 ft. lbs.
(25 Nm).
7. Apply Never Seize to axle splines and install rear
wheel hubs. Torque center hub nut to 80 ft. lbs.
(109 Nm) and install a new cotter pin. Torque
wheel nuts to 50 ft. lbs. (68 Nm).
8. Lubricate eccentric housing through grease fitting
with Polaris Premium All Season Grease until
grease is purged on each side of eccentric.

FINAL DRIVE
7.9
CONCENTRIC SWINGARM REAR AXLE EXPLODED VIEW
Snap Ring
Lock Collar
Left Axle Nut (120 ft. lbs.)(163 Nm)
Brake Disc
Disc Hub
Stop Ring
Seal Sleeve
O-Ring
Seal Bearing
Bearing Race
Eccentric Housing
Grease Fitting
Axle
Bearing Race
Bearing Seal
O-Ring
Sprocket Hub
Foam Seal
Axle Nut
Lock Collar
Snap Ring
Caliper Mount, Upper
Caliper Mount, Lower
Caliper
Left side of axle identified
by groove in spline
10-12 ft.lbs. (14-17 Nm)
18 ft. lbs.
(25 Nm)
Torque: 80 ft. lbs.
(110 Nm)
Torque: 50 ft. lbs.
(69 Nm)
Foam Seal

FINAL DRIVE
7.10
CONCENTRIC SWINGARM
REAR HOUSING REMOVAL
1. Remove rear axle. (See Page 7.6)
2. Remove sprocket hub. Note sealing O-ring
between sprocket hub and bearing.
3. Remove brake caliper mounting bracket from the
rear housing.
Lower Mount
Bracket
Upper Mounting
Bracket
Brake Disc
Guard
Rear Housing
Mount Bolts
4. Remove brake caliper mount bushing from the
upper mounting bracket. NOTE: Flange inward
as shown.
Upper Mounting
Bracket
Rear Housing
Caliper Mount
Bushing
5. Remove the rear housing from the swingarm.
REAR HOUSING
DISASSEMBLY/BEARING
SERVICE
1. Remove seals from housing.
Seal Bearing
Bearing Race
Seal
2. Remove bearings.
3. Drive bearing race out from opposite sides.
4. Inspect housing for cracks or wear. Replace if
damaged.
REAR HOUSING
ASSEMBLY/BEARING
SERVICE
1. Drive in new bearing race with brass drift.
2. Lubricate and install new tapered bearings.
3. Lubricate and install new seals.

FINAL DRIVE
7.11
CONCENTRIC SWINGARM
REAR HOUSING
INSTALLATION
1. Place brake caliper pivot bushing on stud with
flange inward as shown.
Upper Mounting
Bracket
Rear Housing
Caliper Mount
Bushing
2. Loosely assemble upper and lower brake caliper
mount. Do not tighten at this time.
Lower Mount
Bracket
Upper Mounting
Bracket
Brake Disc
Guard
Rear Housing
Mount Bolts
3. Install rear axle. (See Page 7.8)
4. Fill housing with grease until grease purges from
both seals.

FINAL DRIVE
7.12
NOTES

8
TRANSMISSION
8.1
CHAPTER 8
TRANSMISSION SERVICE
Special Tools 8.2............................
Torque Specifications 8.2.....................
Transmission Remove/Install 8.2..............
Transmission Disassembly 8.2--8.5................
Transmission Assembly 8.6-8.7...................
Troubleshooting 8.7..........................
Transmission Exploded View 8.7--8.8..............

TRANSMISSION
8.2
SPECIAL TOOLS
PART NUMBER TOOL
DESCRIPTION
2871710 10” Center
Distance Tool
TORQUE SPECIFICATIONS
Item Specification
Transmission Case
Bolts
12 ft. lbs. (16.6 Nm)
Bell Crank Nut 12 ft. lbs. (16.6 Nm)
Transmission Drain
Plug
14 ft. lbs. (19.3 Nm)
Transmission Mounting
Bolts
25 ft. lbs. (34.5 Nm)
Swing Arm Pivot Bolts
(Concentric Swingarm)
150 ft. lbs. (207.5 Nm)
LUBRICATION
Refer to maintenance section for transmission
lubricant type and capacity.
TRANSMISSION REMOVAL
1. Remove seat, cab and air box.
2. Remove right side heat and reservoir bracket.
3. Remove PVT outer cover, both drive and driven
clutch, and inner PVT cover (refer to Clutch
Chapter 6).
4. Remove rear PVT bracket.
5. Remove carburetor.
6. Disconnect harness from gear position switch.
7. Remove drive chain and sprocket.
8. Remove mounting bolts and brackets as shown.
9. Remove through-bolt from bottom of
transmission.
10. Remove transmission from right side of frame.
TRANSMISSION
INSTALLATION
1. Reverse removal steps to install transmission.
NOTE: Install the Center Distance Tool (PN 2871710)
on engine and transmission input shaft before
tightening transmission mounting bolts. Align
clutches as outlined in Clutch Chapter 6.
TRANSMISSION
DISASSEMBLY
1. Remove gear position switch.
CAUTION:
If switch is not removed prior to disassembly, switch
damage will result.
2. Place bellcrank in neutral position.
3. Remove sprocket retaining clip and sprocket.
4. Remove the transmission cover bolts.
5. With a soft face hammer tap on the (3) cover
bosses and carefully remove the cover.
Remove Switch
Tap with soft
face hammer
(3 places)
6. Remove detent plug, washer, spring and shifting
bullet.
NOTE: Shifting bullet has a radiused end making it
directional.

TRANSMISSION
8.3
7. Using a wrench on the nut of the bellcrank, turn in
a clockwise direction to assist with removal of
shift assembly and drive gear.
8. Remove shift assembly and gear as an assembly.
NOTE: Direction of shift fork.
9. Inspect shift fork surface for wear or damage.
Replace if necessary.
10. Remove shift fork guide pin.
11. Mark orientation of bellcrank to the shift fork shaft.
12. Remove bellcrank. Use a small puller if
necessary.

TRANSMISSION
8.4
13. Remove snap ring and washer. Pull down and
rotate shift fork shaft back and forth to remove.
14. Inspect shift fork shaft O-ring. Replace if
necessary. Lubricate O-ring to ease in
reassembly and to protect O-ring during
assembly.
15. Remove input shaft bearing.
16. Inspect gears for galling and wear on teeth and
bearing surface. Replace if necessary.
17. Remove bearing from other end of input shaft.
Remove two snap rings and gear.

TRANSMISSION
8.5
18. Inspect gear bushing. Replace if half of teflon
surface is gone.
19. Inspect output shaft gear, sprocket and bearing.
Replace if necessary.
NO
Output Shaft
Gear
Sprocket
Bearing
20. Stretch chain tight on a flat surface and measure
the length of 8 pitches in a minimum of three
places on chain. Replace chain if measurement
is longer than 3.0904I.
Chain Stretch Limit
8 pitch length = 3.0904IMaximum
Measure
8 pitches
TRANSMISSION ASSEMBLY
1. Assemble input shaft assembly.
NOTE: Install bearings with numbers and letters
facing out so they can be read after assembly.
Sprocket cogs face the dog gear.
NOTE: Input gear cogs face inward on input shaft.
Input Shaft
Bushing
Sprocket
Dog Gear
Input Gear
Thrust Washer
2. Assemble output shaft with sprocket, gear and
bearing if they were disassembled.
3. Assemble output shaft assembly with chain to the
input shaft assembly.
4. Install shift shaft, driven sprocket and gear into
the case.

TRANSMISSION
8.6
5. Install shift fork.
6. Insert fork guide pin.
7. Prior to reinstalling the cover make sure the
mating cover surfaces are clean and dry. Apply
Crankcase Sealant (PN 2871557) to mating
surfaces.
8. Reinstall cover and torque bolts in a criss-cross
pattern in 3 steps to 18 ft. lbs. (25 Nm).
9. Install drain plug with a new sealing washer.
Torquedrainplugto14ft.lbs.(19Nm).
10. Insert shifting bullet with tip in position as shown.
Insert spring and plug. Torque plug to 14 ft. lbs.
(19 Nm).
11. Install transmission and add Polaris Premium
Synthetic Gear Case Lubricant (PN 2871477)in
the recommended amount. Refer to Maintenance
Chapter 2.
12. Install gear indicator switch. Apply Loctitet242
(PN 2871949) to threads of switch screws and
torque to 13-16 in. lbs. (1.5-1.9 Nm).

TRANSMISSION
8.7
TROUBLESHOOTING
CHECKLIST
Check the following items when shifting difficulty is
encountered.
SIdle speed adjustment
STransmission oil type/quality
STransmission torque stop
adjustment
SDrive belt deflection
SLoose fasteners on rod ends
SLoose fasteners on shifter
SWorn rod ends, clevis pins, or pivot
arm bushings
SLinkage rod adjustment and rod end
positioning
S*Worn, broken or damaged internal
transmission components
*NOTE: To determine if shifting difficulty or problem
is caused by an internal transmission problem, isolate
the transmission by disconnecting linkage rods from
transmission bellcranks. Manually select each gear
range at the transmission bellcrank, and test ride
vehicle. If it functions properly, the problem is outside
the transmission.
If transmission problem remains, disassemble
transmission and inspect all gear dogs for wear
(rounding), damage. Inspect all bearings for wear.
TRANSMISSION EXPLODED VIEW
NOTE: See next page for exploded view of transmission.
Ref. Qty Description Ref.Qty Description
1Asm., Gearcase 24. 1Washer
1. 2Bearing 25. 1 Plug, Detent, Extension
2. 1Ring, Retaining 26. 1Dipstick
3. 1Washer, Thrust 27. 2 Seal
4. 1 Sprocket, 19T 28. 1 Tube, Vent
5. 1Washer, Thrust 29. 1 Gearcase, RH
6. 1Dog, Engagement, High/Reverse 30. 2Pipe, Knock
7. 1Shaft, Input 31. 1 Shaft, Shift
8. 1Gear, 21T 32. 2 Fork, Shift
9. 1Bushing 33. 1 Gearcase, LH
10. 1Washer 34. 1 Decal, Switch
11. 2Snap Ring 35. 9 Screw
12. 2 Bearing 36. 1 Screw
13. 1Nut, FLEXLOC 37. 1 Nut
14. 1Washer 38. 1 Plug, Torque Stop
15. 1Bellcrank, HLR 39. 1 Bushing, Pivot
16. 1Ring, Retaining 40. 1 Washer
17. 1Washer 41. 1 Chain, Silent, 60P, 11W
18. 1O--Ring 42. 1 Sprocket, 51T
19. 1Shaft, Shift 43. 1Shaft, Output
20. 1Switch 44. 1 Gear, 64T
21. 4Screw
22. 1Bullet, Shifting
23. 1Spring, Compression

123456
78
910 11 12
13
14
15
16
17
18
19
20
21
22
23
24
25
26
27
28
29
27
30
31 32 33 34 35
36
37
38
39
40
41 42
43
44
1
12
TRANSMISSION
8.8
TRANSMISSION EXPLODED VIEW

9
BRAKES
9.1
CHAPTER 9
BRAKES
Specifications/Torques 9.2..............
Special Tools 9.3......................
Brake System Service Notes 9.3........
Brake Noise Troubleshooting 9.3........
Hydraulic Brake System Operation 9.4...
Brake System Main Components 9.5.....
Dual Hydraulic Caliper Bleeding 9.5......
Fluid Replacement/Bleeding Procedure 9.6-9.7
Master Cylinder Disassembly 9.7........
Master Cylinder Installation 9.8..........
Front Pad Removal 9.9--9.10.................
Front Pad Assembly 9.10-9.11................
Front Disc Inspection 9.11...............
Front Disc Removal/Replacement 9.11-9.12....
Front Caliper Removal 9.12..............
Front Caliper Disassembly 9.12-9.13..........
Front Caliper Inspection 9.13-9.14.............
Front Caliper Assembly 9.14.............
Front Caliper Installation 9.15............
Front Caliper Exploded View 9.16.........
Rear Pad Removal 9.17.................
Rear Pad Installation 9.17-9.18...............
Rear Caliper Removal/Inspection 9.18-9.19.....
Rear Caliper Assembly 9.19-9.20.............
Rear Disc Inspection 9.20...............
Troubleshooting 9.21....................
Rear Caliper Exploded View 9.22.........

BRAKES
9.2
SPECIFICATIONS
Front Brake Caliper
Item Standard Service Limit
Brake Pad Thickness .298 ±.0073²/7.56±.185 mm .150²/3.81mm
Brake Disc Thickness .150-.165²/ 3.810-4.191 mm .140²/ 3.556 mm
Brake Disc Thickness Variance Between
Measurements
-.002²/ .051 mm
Brake Disc Runout -.020²/.50mm
Rear Brake Caliper
Item Standard Service Limit
Brake Pad Thickness .270 ±.005²/6.85±.127 mm .150²/3.81mm
Brake Disc Thickness .177--.188²/ 4.49--4.77 mm .167²/ 4.242 mm
Brake Disc Thickness Variance Between
Measurements
-.002²/ .051 mm
Brake Disc Runout -.010²/.25mm
Master Cylinder I.D. .750²
TORQUE SPECIFICATIONS
Item Torque
(ft. lbs. except where noted*)
Torque
(Nm)
Front Caliper Mounting Bolts 18.0 25
Rear Caliper Mounting Bolts 28 38
Master Cylinder Mounting Bolts *25 in. lbs. 3.0
Master Cylinder Reservoir
Cover Bolt
*5 in. lbs. .56
Brake Line Banjo Bolt 15.0 21
Front Brake Disc 18.0 25
Front Wheel Mounting Nuts 20.0 28
NOTE: Refer to the tightening procedures in this chapter when torquing the bolts. Some special procedures are
used when torquing certain bolts and fasteners.

BRAKES
9.3
SPECIAL TOOLS
PART NUMBER TOOL
DESCRIPTION
2870975 Mity Vac
Pressure Test Tool
BRAKE SYSTEM SERVICE
NOTES
Disc brake systems are light weight, low
maintenance, and perform well in the conditions ATVs
routinely encounter. There are a few things to
remember when replacing disc brake pads or
performing brake system service to ensure proper
system function and maximum pad service life.
GOptional pads are available to suit
conditions in your area. Select a pad to fit
riding style and environment.
GDo not over-fill the master cylinder fluid
reservoirs.
GMake sure the brake levers return freely
and completely.
GAdjust stop pin on front caliper after pad
service.
GCheck and adjust master cylinder
reservoir fluid levels after pad service.
GMake sure atmospheric vent on reservoirs
are unobstructed.
GTest for brake drag after any brake system
service and investigate cause if brake
drag is evident.
GMake sure caliper moves freely on guide
pins.
GInspect caliper piston seals for foreign
material that could prevent caliper pistons
from returning freely.
GPerform a brake burnishing procedure
after installing new pads to maximize
service life.
BRAKE NOISE
TROUBLESHOOTING
NOTE: 2003 Model Trailblazer ATVs are equipped
with anti--squeek brake pads, but in some extreme
cases brake noise may occur.
Dirt or dust buildup on the brake pads and disc is the
most common cause of brake noise (squeal caused by
vibration). If cleaning does not reduce the occurrence
of brake noise, PermatextDisc Brake Quiet (PN
2872113) can be applied to the back of the pads. Follow
directions on the package. This will keep pads in
contact with caliper piston(s) to reduce the chance of
squeaks caused by dirt or dust. See table below.
Brake Noise Troubleshooting
Possible Cause Remedy
Dirt, dust, or imbedded material on pads or disc Spray disc and pads with a non-flammable aerosol
brake cleaner. Remove pads and/or disc hub to clean
imbedded material from disc or pads.
Pad(s) dragging on disc (noise or premature pad wear)
Improper adjustment
Insufficient lever or pedal clearance
Master cylinder reservoir overfilled
Master cylinder compensating port restricted
Master cylinder piston not returning completely
Caliper piston(s) not returning
Operator error (riding the brake / park brake
applied)
Adjust pad stop (front calipers)
Check position of controls & switches.
Set to proper level
Clean compensating port
Inspect. Repair as necessary
Clean piston(s) seal
Educate operator
Loose wheel hub or bearings Check wheel and hub for abnormal movement.
Brake disc warped or excessively worn Replace disc
Brake disc misaligned or loose Inspect and repair as necessary
Noise is from other source (chain, axle, hub, disc or
wheel)
If noise does not change when brake is applied check
other sources. Inspect and repair as necessary
Wrong pad for conditions Change to a softer or harder pad

BRAKES
9.4
HYDRAULIC BRAKE SYSTEM OPERATION
AB
C
D
E
F
Must be clear to allow
proper diaphragm
movement
Compensating port compensates
for temperature changes by allowing
fluid back to master cylinder
Moveable
Brake Pad G
Typical Hydraulic Brake System
The Polaris brake system consists of the following components or assemblies: brake lever; master cylinder;
hydraulic hose; brake calipers (slave cylinder); brake pads; and brake discs, which are secured to the drive line.
When the hand activated brake lever (A) is applied it contacts a piston (B) within the master cylinder. As the
master cylinder piston moves inward it closes a small opening (compensating port) (C) within the cylinder and
starts to build pressure within the brake system. As the pressure within the system is increased, the piston (D)
located in the brake caliper moves outward and applies pressure to the moveable brake pad. This pad contacts
the brake disc and moves the caliper in its floating bracket, pulling the stationary side pad into the brake disc.
The resulting friction reduces brake disc and vehicle speed. As the lever pressure is increased, the braking affect
is also increased.
The friction applied to the brake pads will cause the pads to wear. As these pads wear, the piston within the caliper
moves further outward and becomes self adjusting. Fluid from the reservoir fills the additional area created when
the caliper piston moves outward.
Brake fluid level is critical to proper system operation. Too little fluid will allow air to enter the system and cause
the brakes to feel spongy. Too much fluid could cause brakes to drag due to fluid expansion.
Located within the master cylinder is the compensating port (C) which is opened and closed by the master cylinder
piston assembly. The port is open when the lever is released and the master cylinder piston is outward. As the
temperature within the hydraulic system changes, this port compensates for fluid expansion (heated fluid) or
contraction (cooled fluid). During system service, be sure this port is open. Due to the high temperatures created
within the system during heavy braking, it is very important that the master cylinder reservoir have adequate space
to allow for fluid expansion. Never overfill the reservoir! Fill to 1/4²-5/16²(.64 - .80 cm) from top of the cylinder.
This system also incorporates a diaphragm (E) as part of the cover gasket; and a vent port (F) located between
the gasket and the cover. The combination diaphragm and vent allow for the air above the fluid to equalize
pressure as the fluid expands or contracts. Make sure the vent is open and allowed to function. If the reservoir
is over filled or the diaphragm vent is plugged the expanding fluid may build pressure in the brake system leading
to brake failure.
When servicing Polaris ATV brake systems use only Polaris DOT 3 High Temperature Brake Fluid (PN 2870990).
Polaris brake fluid is sold in 5.5 oz. bottles. WARNING: Once a bottle is opened, use what is necessary and
discard the rest in accordance with local laws. Do not store or use a partial bottle of brake fluid. Brake fluid is
hygroscopic, meaning it rapidly absorbs moisture. This causes the boiling temperature of the brake fluid to drop,
which can lead to early brake fade and the possibility of serious injury.

BRAKES
9.5
BRAKE SYSTEM MAIN COMPONENTS
MASTER CYLINDER
CROSS FITTING
BRAKE SWITCH
RIGHT BRAKE
LEFT BRAKE
CALIPER
CALIPER
TOP VIEW
REAR BRAKE
RESERVOIR
REAR BRAKE
CALIPER
DUAL HYDRAULIC CALIPER
BLEEDING
Hand
Brake Line
Foot
Brake Line
Hand Brake Bleed
Fitting
Foot Brake
Bleed Screw
DH CALIPER TOP VIEW
Piston
Seals
Sealing “O” Rings
Pad
Spacer
This caliper is a stepped piston design, with two
independent hydraulic systems contained in the same
caliper body. The caliper piston is T-shaped, which
allows both left and right hand brake to use the same
caliper piston, but remain separated by seals. The left
hand brake system applies hydraulic pressure to both
front calipers and only the outer diameter of the rear
caliper piston. The right hand brake applies pressure
to the inner portion of the rear caliper piston. Because
the left and right hand brake hydraulic systems are
separate, there are also two bleed screws -- one for
the outer fluid chamber (left hand brake), and one for
the inner fluid chamber (right hand brake). The basic
procedure for bleeding the brake system is the same
as outlined on Page 9.6 - 9.7; however, each system
must be bled separately.
Inner Bleed Screw
Hand Brake
Outer Bleed Screw
Auxiliary Brake
A
B

BRAKES
9.6
-- The upper most (inner) bleed screw and brake line (A)
is for the left hand brake system.
-- The lower (outer) bleed screw and brake line (B) is
for the auxiliary brake system.
FLUID
REPLACEMENT/BLEEDING
PROCEDURE
NOTE: When bleeding the brakes or replacing the
fluid always start with the caliper farthest from the
master cylinder.
CAUTION:
Always wear safety glasses.
CAUTION:
Brake fluid will damage finished surfaces. Do not
allow brake fluid to come in contact with finished
surfaces.
BRAKE BLEEDING - FLUID
CHANGE
NOTE: This procedure should be used to change
fluid or bleed brakes during regular maintenance.
B
A
D
C
1. Clean reservoir cover thoroughly.
2. Remove screws, cover, and diaphragm (C) from
reservoir.
3. Inspect vent slots (A) in cover and remove any
debris or blockage.
4. If changing fluid, remove old fluid from reservoir
with a Mity Vact(PN 2870975)orsimilartool.
NOTE: Do not remove brake lever when reservoir
fluid level is low.
MAX
5. Add brake fluid to the upper level mark on
reservoir.
Polaris DOT 3 Brake Fluid
(PN 2870990)
Hand brake bleeder screw
Auxiliary brake bleeder screw
Hand Brake Line
Aux. Brake
Line
Forward
DH Caliper
6. Begin bleeding procedure with the caliper that is
farthest from the master cylinder. Install a box
end wrench on caliper bleeder screw. Attach a
clean, clear hose to fitting and place the other end
in a clean container. Be sure the hose fits tightly
on fitting.
NOTE: Fluid may be forced from compensation port
(B) when brake lever is pumped. Place diaphragm (C)
in reservoir to prevent spills. Do not install cover.
Refer to Illustration on page 9.4.
7. Slowly pump brake lever (D) until pressure builds
and holds.
8. While maintaining lever pressure, open bleeder
screw. Close bleeder screw and release brake
lever. NOTE: Do not release lever before bleeder
screw is tight or air may be drawn into caliper.

BRAKES
9.7
9. Repeat procedure until clean fluid appears in
bleeder hose and all air has been purged. Add
fluid as necessary to maintain level in reservoir.
CAUTION:
Maintain at least 1/2²(1.27 cm) of brake fluid in the
reservoir to prevent air from entering the master
cylinder.
10. Tighten bleeder screw securely and remove
bleeder hose.
11. Repeat procedure Steps 5-9 for the remaining
caliper(s).
12. Add brake fluid to the proper level.
Master Cylinder Fluid Level:
MAX level inside reservoir
Sight glass must look dark, if sight
glass is clear, fluid level is too low
13. Install diaphragm, cover, and screws. Torque the
screws to 5 in.lbs. (0.56 Nm).
Reservoir Cover Torque -
5 in. lbs. (0.56 Nm)
14. Field test machine at low speed before putting
into service. Check for proper braking action and
lever reserve. With lever firmly applied, lever
reserve should be no less than 1/2²(1.3 cm) from
handlebar.
15. Check brake system for fluid leaks and inspect all
hoses and lines for wear or abrasion. Replace
hose if wear or abrasion is found.
MASTER CYLINDER
DISASSEMBLY
1. Clean master cylinder and reservoir assembly.
Make sure you have a clean work area to
disassemble brake components.
2. Place a shop towel under brake line connection at
master cylinder. Loosen banjo bolt; remove bolt
and sealing washers.
CAUTION:
Brake fluid will damage finished surfaces. Do not
allow brake fluid to come in contact with finished
surfaces.

BRAKES
9.8
3. Remove master cylinder from handlebars.
Banjo Bolt
Master Cylinder
Piston Assy
Cover
Diaphragm
Sight Glass
Brake Lines
Master Cylinder Assembly
MASTER CYLINDER
INSTALLATION
Master cylinders are not rebuildable. The
complete master cylinder must be replaced.
When replacing the brake master cylinder assembly,
use the correct assembly. There are different brake
master cylinders for the different Polaris ATV models.
Refer to your parts manual or guide for the correct
parts.
1. Install master cylinder on handlebars. Torque
mounting bolts to 25 in. lbs. (3 Nm). Torque the
inside bolt first as indicated in the illustration.
25 in. lbs. (3 Nm)
Torque Outer Bolt First
5in.lbs.
(0.56 Nm)
NOTE: To speed up the brake bleeding procedure the
master cylinder can be purged of air before brake line
is attached. Fill with DOT3 Brake Fluid (PN 2870990)
and pump lever slowly two to three times with finger
over the outlet end to purge master cylinder of air.
2. Place new sealing washers on each side of banjo
line.
Brake Line
Banjo Bolt
Sealing Washers
Torque to 15 ft.lbs.
(21 Nm)
Master Cylinder Mounting Bolt
Torque 25 in. lbs. (3 Nm)
Brake Line Banjo Bolt Torque
15 ft. lbs. (21 Nm)
3. Install brake line on master cylinder hand tight.
4. Fill reservoir with DOT3 Brake Fluid (PN
2870990).

BRAKES
9.9
Polaris DOT 3 Brake Fluid
(PN 2870990)
5. Follow bleeding procedure on Pages 9.6-9.7.
Check all connections for leaks and repair if
necessary.
FRONT PAD REMOVAL
1. Elevate and support front of machine.
CAUTION:
Use care when supporting vehicle so that it does
not tip or fall. Severe injury may occur if machine
tips or falls.
2. Remove the front wheel. Loosen pad adjuster
screw 2-3 turns.
3. Remove caliper from mounting bracket.
4. Push caliper piston into caliper bore slowly using
a C-clamp or locking pliers with pads installed.
NOTE: Brake fluid will be forced through
compensating port into master cylinder fluid reservoir
when piston is pushed back into caliper. Remove
excess fluid from reservoir as required.
5. Push mounting bracket inward and slip outer
brake pad past edge. Remove inner pad.

BRAKES
9.10
6. Measure the thickness of the pad material.
Replace pads if worn beyond the service limit.
Measure
Thickness
Front Brake Pad Thickness
New .298²/7.6 mm
Service Limit .180²/4.0mm
FRONT PAD ASSEMBLY
1. Lubricate mounting bracket pins with a light film of
Polaris Premium All Season Grease, and install
rubber dust boots.
Polaris Premium All Season Grease
(PN 2871423)
2. Compress mounting bracket and make sure dust
boots are fully seated. Install pads with friction
material facing each other. Be sure pads and disc
are free of dirt or grease.
3. Install caliper on hub strut, and torque mounting
bolts.
18 ft. lbs. (25 Nm)
Front Caliper Mounting Bolts
Torque: 18 ft. lbs. (25Nm)
4. Slowly pump the brake lever until pressure has
been built up. Maintain at least 1/2²(12.7 mm) of
brake fluid in the reservoir to prevent air from
entering the brake system.

BRAKES
9.11
5. Install the adjuster screw and turn clockwise until
stationary pad contacts disc, then back off 1/2
turn (counterclockwise).
6. Verify fluid level in reservoir is up to MAX line
inside reservoir and install reservoir cap.
Master Cylinder Fluid
Up to MAX line inside reservoir
7. Install wheels and torque wheel nuts.
Front Wheel Nut Torque
20 ft. lbs. (27 Nm)
BRAKE BURNISHING
PROCEDURE
It is required that a burnishing procedure be
performed after installation of new brake pads to
extend service life and reduce noise.
Start machine and slowly increase speed to 30 mph.
Gradually apply brakes to stop machine. Allow pads
and disc to cool sufficiently during the procedure. Do
not allow pads or disc to become hot or warpage may
result. Repeat this procedure 10 times.
FRONT DISC INSPECTION
1. Visually inspect the brake disc for nicks,
scratches, or damage.
2. Measure the disc thickness at eight different
points around the pad contact surface using a
0-1²micrometer. Replace disc if worn beyond
service limit.
Brake Disc Thickness
Service Limit .140²/ 3.556 mm
New .150--.165²(3.81--4.19 mm)
Brake Disc Thickness Variance
Service Limit: .002²(.051 mm)
difference between measurements.
3. Mount dial indicator as shown to measure disc
runout. Slowly rotate the disc and read total
runout on the dial indicator. Replace the disc if
runout exceeds specifications.
Brake Disc Runout
Service Limit .010²(.50 mm)
FRONT BRAKE DISC
REMOVAL / REPLACEMENT
NOTE: To reduce the possibility of warpage, try
removing the brake disc mounting bolts before
applying heat to the bolts.

BRAKES
9.12
1. Apply heat to the hub in the area of the brake disc
mounting bolts to soften the bolt locking agent.
18 ft. lbs. (25 Nm)
new bolts have
pre-applied
locking agent.
2. Remove bolts and disc.
3. Clean mating surface of disc and hub.
4. Install disc on hub.
5. Install new bolts and tighten to specified torque.
Front Brake Disc Mounting Bolt Torque
18 ft. lbs. (25 Nm)
CAUTION: Always use new brake disc mounting
bolts. The bolts have a pre-applied locking agent
which is destroyed upon removal.
FRONT CALIPER REMOVAL
CAUTION:
Use care when supporting vehicle so that it does
not tip or fall. Severe injury may occur if machine
tips or falls.
1. Remove brake pads. See Page 9.9.
2. Using a line wrench, loosen and remove brake
line to caliper. Place a container under caliper to
catch fluid draining from brake line.
3. Remove brake caliper and drain fluid into
container. Do not reuse brake fluid.
FRONT CALIPER
DISASSEMBLY
1. Remove brake pad adjuster screw.
2. Push upper pad retainer pin inward and slip brake
pads past edge.

BRAKES
9.13
3. Remove mounting bracket, pin assembly and
dust boot.
Remove
Mounting Bracket
4. Remove piston, dust seal and piston seal.
5. Clean the caliper body, piston, and retaining
bracket with brake cleaner or alcohol.
NOTE: Be sure to clean seal grooves in caliper body.
Clean Components
FRONT CALIPER
INSPECTION
1. Inspect caliper body for nicks, scratches or wear.
Measure bore size and compare to specifications.
Replace if damage is evident or if worn beyond
service limit.
Front Caliper Piston Bore I.D.
Std. 1.191-1.192²(30.25-30.28 mm)
Service Limit 1.193²(30.30 mm)
2. Inspect piston for nicks, scratches, wear or
damage. Measure diameter and replace if
damaged or worn beyond service limit.

BRAKES
9.14
3. Inspect the brake disc and pads as outlined for
brake pad replacement this section. See Pages
9.10--9.11.
FRONT CALIPER REASSEMBLY
1. Install new O-rings (A) in the caliper body (B). Be
sure groove is clean and free of residue or brakes
may drag upon assembly.
A
B
C
D
2. Coat piston with clean Polaris DOT 3 Brake Fluid
(C). Install piston (D) with a twisting motion while
pushing inward. Piston should slide in and out of
bore smoothly, with light resistance.
3. Lubricate the mounting bracket pins with Polaris
Premium All Season Grease, and install the
rubber dust seal boots.
Polaris Premium All Season Grease
(PN 2871423)
4. Compress the mounting bracket and make sure
the dust seals are fully seated. Install the pads as
shown on Page 9.10. Clean the disc and pads
with brake parts cleaner or denatured alcohol to
remove any dirt, oil or grease.

BRAKES
9.15
FRONT CALIPER
INSTALLATION
1. Install caliper on hub strut, and torque mounting
bolts.
18 ft. lbs. (25 Nm)
Front Caliper Mounting Bolt Torque
18 ft. lbs. (25 Nm)
2. Install brake line and tighten securely with a line
wrench.
3. Install the adjuster screw and turn until stationary
pad contacts disc, then back off 1/2 turn.
4. Follow brake bleeding procedure outlined on
Pages 9.6-9.7.
5. Install wheels and torque wheel nuts to
specification.
Front Wheel Nut Torque
20 ft. lbs. (27 Nm).

BRAKES
9.16
FRONT BRAKE CALIPER
EXPLODED VIEW
Caliper Mount
Piston
Bushing Boot
Square
O--Rings
Socket Set Screw
Boot Bushing
Brake Pads
Caliper Assembly
Bleeder Screw
35--60 IN. LBS.
(4--6.5 NM)
APPLY POLARIS ALL
PURPOSE GREASE
APPLY POLARIS DOT 3 BRAKE
FLUID TO COMPONENT
3
3
3

BRAKES
9.17
REAR BRAKE PAD REMOVAL
1. Remove caliper mounting bolts and lift caliper off
of disc.
Support Caliper from Frame
NOTE: When removing caliper, be careful not to
damage brake line. Support caliper so as not to kink
or bend brake line.
2. With pads installed, push the caliper pistons into
their bores .
NOTE: Brake fluid will be forced through
compensating port into master cylinder fluid reservoir
when piston is pushed back into caliper. Remove
excess fluid from reservoir as required.
Spacer
Retaining Pin
3. Remove brake pad retaining pin, and pad spacer.
NOTE: This is a spring pin, do not spread apart
farther than necessary to remove it.
4. Measure the thickness of the pad material.
Replace pads if worn beyond the service limit.
Measure
Thickness
Rear Brake Pad Thickness
New .298 ±.005²(6.85 .127 mm 0
Service Limit .150²(3.81 mm)
REAR BRAKE PAD
INSTALLATION
Spacer
Retaining Pin
1. Install new pads in caliper body. Be sure to put
aluminum spacer between pads. Install retainer.
2. Torque mounting bolts to specified torque.
DH Brake Caliper Mounting
Bolts Torque:
28 ft. lbs. (38 Nm)
3. Slowly pump the brake levers until pressure has
been built up. Maintain at least 1/2²(12.7 mm) of
brake fluid in the reservoir to prevent air from
entering the master cylinder.

BRAKES
9.18
Auxiliary Brake Master Cylinder
Fluid Level
Between MIN and MAX lines
4. It is recommended that a burnishing procedure be
performed after installation of new brake pads to
extend service life and reduce noise. Start
machine and slowly increase speed to 30 mph.
Gradually apply brakes to stop machine. Repeat
procedure 10 times.
REAR CALIPER
REMOVAL/INSPECTION
1. Clean caliper area before removal.
Remove inner
and outer
brake lines
2. Using a wrench, remove left hand brake (outer)
and right hand brake (inner) lines. Place a
container to catch brake fluid draining from brake
lines.
3. Remove the caliper and pads from the caliper.
Spacer
Retaining Pin
4. Remove Allen head screw and separate caliper
halves and remove pistons with piston pliers.
5. Remove O-rings and clean O-ring grooves.
6. Clean disc, caliper body, and pistons with brake
cleaner or alcohol.
7. Remove square-rings. Clean square-ring grooves.
8. Clean disc, caliper body, and piston with brake
cleaner or alcohol.
9. Inspect caliper piston bores for scratches, severe
corrosion, or galling and replace if necessary.

BRAKES
9.19
10. Inspect surface of caliper piston for nicks,
scratches, or damage and replace if necessary.
REAR CALIPER ASSEMBLY
O-Rings
Piston Seals
1. Install new square-rings on piston. Be sure
square-ring grooves are thoroughly cleaned of all
residue, or piston may bind in bore. Apply brake
fluid to piston and install carefully with a twisting
motion to ease assembly. Install dust seal on
piston before fully seating piston.
2. Install new O-rings in caliper halves.
3. Carefully assemble caliper body, making sure
O-rings are properly positioned in groove. Apply
LocTitet242 (PN 2871949) to the allen head
screw and torque body screw evenly to 18 ft. lbs.
(25 Nm).
Caliper Halves Bolt Torque:
18 ft. lbs. (25 Nm)
4. Install brake pads in caliper body with friction
material facing each other. If equipped with a pad
spacer, install the spacer between the pads.
Install retaining pin through outer pad, pad spacer
and inner pad.
5. Install caliper and torque mounting bolts.
28 ft. lbs. (38 Nm)
Caliper Mounting Bolt Torque
28 ft. lbs. (38 Nm)

BRAKES
9.20
6. Install brake lines and tighten to specified torque.
Hand Brake Line
Auxiliary Brake
Line
Banjo Bolt Torque
15 ft. lbs. (21 Nm)
7. Follow bleeding procedure outlined on Pages
9.6--9.7 of this section and refer to system
overview and illustration on Page 9.5.
8. Field test unit for proper braking action before
putting into service. Inspect for fluid leaks and
firm brakes. Make sure the brake is not dragging
when lever is released. If the brake drags,
re-check assembly and installation.
REAR BRAKE DISC
INSPECTION
1. Visually inspect disc for scoring, scratches, or
gouges. Replace the disc if any deep scratches
are evident.
Measure
Thickness
Rear Brake
Disc
2. Usea0-1²micrometer and measure disc
thickness at 8 different points around perimeter of
disc. Replace disc if worn beyond service limit.
Brake Disc Thickness
Service Limit .167²(4.242 mm)
New .177-.188²(4.496-4.750 mm)
Brake Disc Thickness Variance
Service Limit 002²(.051 mm)
difference between measurements
3. Mount dial indicator and measure disc runout.
Replace the disc if runout exceeds specifications.
Brake Disc Runout
Service Limit .010²(.25 mm)

BRAKES
9.21
TROUBLESHOOTING
Brakes Squeal
GDirty/contaminated friction pads
GImproper alignment
GWorn disc
GWorn disc splines
Poor Brake Performance
GAir in system
GWater in system (brake fluid
contaminated)
GCaliper/disc misaligned
GCaliper dirty or damaged
GBrake line damaged or lining
ruptured
GWorn disc and/or friction pads
GIncorrectly adjusted lever
GIncorrectly adjusted stationary pad
GWorn or damaged master cylinder or
components
GImproper clearance between lever
and switch
Lever Vibration
GDisc damaged
GDisc worn (runout or thickness
variance exceeds service limit)
GCaliper Overheats (Brakes Drag)
GCompensating port plugged
GPad clearance set incorrectly
GAuxiliary brake pedal incorrectly
adjusted
GBrake lever or pedal binding or
unable to return fully
GParking brake left on
GResidue build up under caliper seals
GOperator riding brakes
Brakes Lock
GAlignment of caliper to disc.

BRAKES
9.22
DH (REAR AXLE MOUNTED) CALIPER/MASTER CYLINDER
Spacer
Torque
28 ft. lbs.
(38 Nm)
DH
Caliper
Auxiliary
Brake Pads
Hand Brake Line
Auxiliary Brake Line
Auxiliary
Brake Bleed
Hand Brake
Bleed
Torque
15 ft. lbs.
(20.7 Nm)
Torque
18 ft. lbs.
(24.8 Nm)
To r si o n
Spring
Auxiliary Brake
Reservoir
Auxiliary Brake
Master Cylinder
Torque
8 ft. lbs.
(11 Nm)
15 ft. lbs.
(20 Nm)

10
ELECTRICAL
10.1
CHAPTER 10
ELECTRICAL
Special Tools and Electrical Service Notes 10.2.....
Timing Check Procedure 10.2.....................
Transmission Gear Position Switch Testing 10.3.....
Speed Limiter System/Troubleshooting 10.3-10.5........
Oil Cooler Fan Circuit Operation 10.6..............
Thermistor / Fan Control Testing 10.6..............
Fan Motor Current Draw Test 10.6.................
Electronic Throttle Control System Operation 10.7...
Flywheel Identification -- DC/CDI Operation 10.8.....
ES32PF 200 Watt Alternator, Exploded View 10.9....
Ignition System Testing 10.10......................
Ignition System Troubleshooting 10.11..............
Cranking Output Tests 10.11.......................
Charging System Testing 10.12-10.14.....................
Battery Service 10.14-10.17.............................
Headlight/Tail Light Service 10.18-10.19...................
Starter System Testing 10.20.......................
Starter System Troubleshooting 10.21...............
Starter Motor Service 10.21-10.23........................
Starter Drive 10.24................................
Wiring Diagram 10.25.............................

ELECTRICAL
10.2
SPECIAL TOOLS
PART NUMBER TOOL
DESCRIPTION
PV--43568 Fluke77 Digital
Multimeter
2870836 Battery
Hydrometer
2870630 Timing Light
8712100 or 8712500 Tachometer
ELECTRICAL SERVICE
NOTES
Keep the following notes in mind when diagnosing an
electrical problem.
GRefer to wiring diagram for stator and
electrical component resistance
specifications.
GWhen measuring resistance of a
component that has a low resistance
value (under10 Ohms), remember to
subtract meter lead resistance from
the reading. Connect the leads
together and record the resistance.
The resistance of the component is
equal to tested value minus the lead
resistance.
GBecome familiar with the operation of
your meter. Be sure leads are in the
proper jack for the test being
performed (i.e. 10A jack for current
readings). Refer to the Owner’s
manual included with your meter for
more information.
GVoltage, amperage, and resistance
values included in this manual are
obtained with a Fluket77 Digital
Multimeter (PV--43568).This
meter is acceptable for use when
diagnosing electrical problems.
Readings obtained with other
meters may differ.
GPay attention to the prefix on the
multimeter reading (K, M, etc.) and
the position of the decimal point.
GFor resistance readings, isolate the
component to be tested. Disconnect
it from the wiring harness or power
supply.
TIMING CHECK
PROCEDURES
1. The ignition timing check hole is in the starter
recoil/magneto housing. Remove the check plug.
NOTE: The ignition timing marks are stamped on the
outside of the flywheel. Ignition timing must be
inspected with the engine at room temperature (68°F
/20°C).
2. With the transmission in neutral, start the engine
and set engine speed to 5000 +/- 200 RPM.
3. Direct the timing light at the ignition timing check
hole and check the ignition timing. NOTE: Do not
allow the engine to warm up. The timing will retard
approximately 2°when the engine is warm.
Flywheel
Rotation 32
Timing
Pointer
30°±2°BTDC@5000RPM
28
Stator Adjustment
Stator Adjustment
If the ignition timing is not within the specified range,
adjust the stator plate position as described below.
1. Remove the magneto housing.
2. Remove the flywheel.
3. Loosen the stator plate screws and adjust the
stator plate position. NOTE: Moving the stator
plate clockwise retards (delays) the ignition
timing. Moving the plate counterclockwise
advances it.
Advance
Retard

ELECTRICAL
10.3
GEAR POSITION INDICATOR
SWITCH TEST
Switch Continuity Table
High Range
Neutral
Reverse
FF
FF
DCB A
FF
High/Neutral/Reverse Switch
H/N/RSwitch
GRN/
LIMITER SPECIFICATIONS
NOTE: The part number is printed on some late
model LR modules. Whenever possible, use part
number to identify the module. Modules may have
same “LR” I.D. number, with different part numbers,
terminals, and internal function.
Speed Limiter
Module LR
ID Number
Part number is printed
on module
LIMITER SPECIFICATIONS
(Refer to parts manual or microfiche for part num-
ber and application.)
PART NO. TYPE FUNCTION / LIMIT RPM
4010137 LR44-3 Reverse Limit - 3500
NOTES

ELECTRICAL
10.4
REVERSE LIMIT SYSTEM
RPM Signal Gray/Orange
Reverse Gear Signal
Y/R
Blk
Gry/Or
LR44--3
Gry/Or
Blk
Y/R
Engine Stop Signal
RPM Signal
Transmission
Switch
Reverse speed limit
module sends signal
(ground) to CDI to
eliminate spark at
3500 (approx.) in re-
verse.
Under Front cover

NO REVERSE SPEED LIMIT
(LR44--3 Limit Module)
N
Y
REVERSE LAMP
ON?
APPLY PARKING BRAKE. START ENGINE.
SHIFT TO REVERSE GEAR
TEST GEAR POSITION INDICA-
TOR SWITCH AND INDICATOR
LAMP
Y
3V-9V AC AT
IDLE?
NTEST WIRING
NTEST VOLTAGE REGULATOR AND
CHARGING SYSTEM
MEASURE DC VOLTS ON
GRY/OR WIRE. TO GROUND
AT LR MODULE
MEASURE AC VOLTS ON
Y/R WIRE. AT LR MODULE
TO GROUND
Y
DISCONNECT BLACK
WIRE FROM LR MOD-
ULE AND CONNECT TO
GROUND.
ENGINE STOP?
NTEST WIRING / TEST CDI (BLACK
WIRE)
Y
REPLACE LIMITER MODULE
12 VOLTS
DC?
ELECTRICAL
10.5
REVERSE SPEED LIMIT SYSTEM

ELECTRICAL
10.6
OIL COOLER FAN CONTROL
Battery Voltage
OIL COOLER FAN CIRCUIT
Hot light and fan “on” with leads connected
Electronic
Module
GThermistor resistance decreases as
temperature increases
GBoth fan and hot light should be on with
thermistor leads shorted together
(low resistance)
GFan blade should rotate drawing air in
through cooler (blowing on engine)
THERMISTOR -- RESISTANCE VS.
TEMPERATURE
Tempera-
ture
Resist-
ance ±
20%
Fan ON/
OFF
Hot Light
ON/OFF
77°F(25°
C)
100KWFan OFF
240°F
(116°C)
3.5KWFan OFF
260°F
(127°C)
2.5KWFan ON
290°F
(143°C)
1.6KWFan ON Hot Light
ON/OFF
THERMISTOR / FAN
CONTROL TEST
GTurn ON and engine stop switch to RUN.
GTest voltage on R/W wire to ground -
R/W wire should have 12 Volts DC
(battery voltage)
GShort thermistor leads together - fan
and hot light ON? (If not, test hot
light, fan motor and circuit)
GDisconnect thermistor wires and test the
resistance of the thermistor (refer to
temperature/resistance table).
Replace thermistor if out of specified
range.
GReplace the module and test system.
FAN MOTOR CURRENT
DRAW TEST
Connect ammeter leads
between exposed
Orange/Black terminals at
fan connection.
Connect only the Red/White
terminals at fan connection.
A current draw test will provide a good indication of fan
motor condition. A worn or damaged fan motor will
draw more current, which causes a reduction in blade
speed and reduced cooling.
1. Turn key to off.
2. Disconnect the thermistor.
3. Reconnect fan motor connector to place a DC
ammeter in series as shown in the Illustration.
4. Be sure fan blade is free to rotate.
5. Turn ignition key and engine stop switch to “ON”
position. Read the current draw on ammeter with
fan running.
6. If the fan motor draws more than 6.5 Amps,
replace the motor.

ELECTRICAL
10.7
ELECTRONIC THROTTLE
CONTROL (ETC) SWITCH
(COMPOSITE THROTTLE
HOUSING)
The Electronic Throttle Control (ETC) system is
designed to stop the engine of an ATV in the event of
a mechanical problem with the throttle mechanism.
The ETC switch is mounted independently of the
throttle actuator lever inside the throttle block
assembly. This is a normally closed switch, and is
held in the open position (contacts are separated as
shown in Illustration 1) by throttle cable tension. The
contacts are “open” in normal operation regardless of
throttle lever position. In the event of a mechanical
problem in the throttle mechanism (cable tension is
lost), the switch contacts close, connecting the CDI
black wire to ground, preventing ignition spark. This
is the same as turning the key or engine stop switch
“OFF”.
Test the ETC switch at the harness connector. NOTE:
Adjust throttle cable freeplay (ETC switch) and make
sure throttle mechanism is functioning properly before
testing the switch. Refer to Maintenance Chapter 2
for cable adjustment procedure.
ETC OPERATION TEST
1. Remove throttle block cover by carefully
releasing all tabs around edge of cover.
2. Place transmission in neutral and apply parking
brake.
3. Start engine and open throttle lever slightly until
engine RPM is just above idle speed.
4. Hold throttle cable with fingers at point “A” as
shown below and release throttle lever. If the
ETC system is functioning properly, the engine
will lose spark and stop.
Switch contacts are open
during normal operation
A
ETC switch contacts are
closed in fault condition
(throttle cable slack).
Electronic Throttle Control (ETC) Switch
(Composite Throttle Housing)
Brn
Blk
Brn
Illustration 1

ELECTRICAL
10.8
FLYWHEEL IDENTIFICATION
A
Flywheel Identification Stamp Location
The flywheel can be identified by the stamp mark in location A. Refer to “I.D.” location in chart below. Do not
use the cast mark to determine flywheel application.
2003 Engine Application Type Cast Stamp Comment I.D. Stamp
Magnum ES32PFE10 N/A N/A N/A 200W N/A
330 -- DC/CDI IGNITION
The Trail Boss 330 has incorporated into it’s design a
DC/CDI ignition system.
Some of the advantages of DC ignition are:
0Stronger, more consistent spark at low
rpm for better performance
0Easier starts
0Simpler component design for ease
trouble shooting and maintenence
Operation Overview:
The DC/CDI system relies on battery power for ignition.
Instead of generating DC voltage via magnetic
induction, a 12 volt DC current is supplied directly to the
CDI unit from the battery.
At the CDI, 12 volt DC current charges an internal
capacitor to build up the initial ignition charge. A small
A/C signal from the Trigger (Pulse) coil closes a
thyristor (located in the CDI) at a point
pre--determined in the crankshaft rotation by magnets
on the flywheel’s outer diameter. This signal releases
the electrical charge which saturates the coil for
ignition. DC/CDI systems have the ability to ignite
with as little as 6 volts of power.
Maximum Timing 330 Trail Boss
NOTE:
DC/CDI systems and compo-
nents are not interchangeable
with any other system.

ELECTRICAL
10.9
COMPONENTS OF ES32PF / 200 WATT ALTERNATOR
battery charge Coils
Flywheel and
Ring Gear Casting.
Refer to Page 10.8 for
identification.
Resistor
Cap
CDI Box
Stator Plate
Pulse Coil (Trigger)
Air Gap: .016-.030²
(.4-.75mm)
Meter
WIgnition Coil
Primary
Winding
.3 W
Ignition Kill
Wire
(Black)
Coil Lead
Secondary Coil
Check coil mount to verify
ground to engine (0-.2 )W
Refer To Wiring Diagrams For
Specified Stator Coil Resistance
Magnetic
Switch
Meter
10.5KW
W
Note: DC/CDI components are not compatible with any other type of ignition
12 Volt DC
Supply Wire
(Red)
520W
W
Meter

ELECTRICAL
10.10
IGNITION SYSTEM TESTING
Whenever troubleshooting an electrical problem you should first check all terminal connections to be sure they
are clean and tight. Also be sure that colors match when wires are connected. Use the following pages as a guide
for troubleshooting. The resistance values are also given on the specification pages.
Condition: No Spark or intermittent spark
Disconnect the black wire at the CDI module to
isolate the ignition from the kill system, but
verify the CDI has a good ground (brown) for
operation.
Does it have spark?
-Test the ignition switch, engine stop
switch, and speed limiter circuit for
shorts to ground.
-Check connectors for moisture,
wire color matching or corrosion.
Disconnect the pulse (trigger) coil connector from
the CDI module. Measure the resistance of the
trigger coil (520W). Refer to the exploded view on
Page 10.9 or the wiring schematic for meter con-
nections and specifications. Compare results to
the specifications on the exploded views.
Is it within specification?
Inspect connectors, wiring and
grounds to the component in ques-
tion. Replace the component if a
wiring problem cannot be found.
Yes
No
Yes
Yes
No
Check coil ground connection between engine and coil
mount using an ohmmeter. The coil mount should
have good continuity to ground on the engine (0-.2 W).
Verify 12 Volt DC power is present on the red wire to CDI. Replace Spark Plug.
Disconnect and check the secondary coil. Resis-
tance values should be:
Primary Side - Primary Wire Tab to Ground
(on coil mount or engine): .3 to .5 Ohms
Secondary Side High Tension Wire to engine
ground- Cap installed - 11,300W
Cap removed - 6300W
Are these values within specs?
Replace the ignition coil.
No
Yes
If all of the above tests are within specifications, and all grounds, connections, and wire color coding
have been inspected, perform voltage output tests on following page or replace the CDI module.
Clean coil mounting area.
Repair ground wire connections.
No

ELECTRICAL
10.11
IGNITION SYSTEM
TROUBLESHOOTING
No Spark, Weak or Intermittent Spark
0No12 volt power or ground to CDI
0Spark plug gap incorrect
0Fouled spark plug
0Faulty spark plug cap or poor
connection to high tension lead
0Related wiring loose, disconnected,
shorted, or corroded
0Engine Stop switch or ignition switch
faulty
0ETC switch misadjusted or faulty
0Poor ignition coil ground (e.g. coil
mount loose or corroded)
0Faulty stator (measure resistance of
all ignition related windings)
0Incorrect wiring (inspect color coding
in connectors etc)
0Faulty ignition coil winding (measure
resistance of primary and
secondary)
0Worn magneto (RH) end Crankshaft
bearings
0Sheared flywheel key
0Flywheel loose or damaged
0Excessive crankshaft runout on
magneto (RH) end - should not
exceed .005²
0Faulty CDI module
CRANKING OUTPUT TEST
WITH PEAK READING
VOLTMETER
The following peak voltage tests will measure the
amount of output directly from each component. A
peak reading voltmeter must be used to perform the
tests. A variety of peak reading adaptors are
commercially available for use with the FlukeZ77
Digital Multimeter (PV--43568), which will allow peak
voltage tests to be performed accurately. Follow the
directions provided with the adaptor. All
measurements are indicated in DC Volts. Readings
obtained without a peak reading adaptor will be
significantly different.
Test output from the CDI and pulse (trigger) coil and
compare to the table. The following measurements
are obtained when cranking the engine with the
electric starter, spark plug installed. The starter
system must be in good condition and the battery fully
charged.
200 Watt 4 Stroke DC/CDI Ignition
Test Connect
Meter Wires
To:
Reading
(Without Peak
Reading Volt
meter)
CDI Output Yellow Blue
and Ground
20 DCV
Pulse (Trigger) Yellow/Red
and
Yellow
3.3 DCV
CDI OUTPUT TEST USING
PEAK READING ADAPTOR
Re-connect all CDI wires to stator wires. Disconnect
CDI module wire from ignition coil primary terminal.
Connect one meter lead to engine ground and the
other to the ignition coil primary wire leading from the
CDI module. Set meter to read DC Volts. Crank
engine and check output of CDI wire to coil.
Reconnect CDI wire to coil.
Output w/ Peak output tester
130 DCV
Average Output w/ Digital Voltmeter
20 DCV

ELECTRICAL
10.12
CHARGING SYSTEM TESTING
Whenever charging system problems are suspected, proceed with the following system checks:
Check for owner modification, and
discuss operating habits. The battery
will continually discharge if operated
below the “Break Even” RPM. Con-
tinued problems would call for battery
inspection.
Disconnect the Yellow/Red, Yellow, and Yel-
low/Brn (if applicable) wires from the regula-
tor/rectifier. Using a multitester, perform an
Alternator Output (AC amp) test.See
test procedure on Page 10.13 for proce-
dure.
Is output above 5 amps?
Inspect the wiring harness be-
tween the panel and the stator for
damage. If no damage is found,
remove the recoil and flywheel.
Inspect the flywheel magnets, sta-
tor coils and stator wire harness
for damage. Repair or replace
any damaged components.
Reconnect the alternator wires. Note: Red
wire must be connected to harness. Battery
voltage must be present on red wire terminal
on harness side of voltage regulator connector.
Is it?
Check regulator/rectifier connections
and ground, battery connections, cir-
cuit breaker and connecting wires.
Repair or replace faulty wiring or
components.
If all of the previous tests indicate a
good condition, but the charging voltage
does not rise above battery voltage at the
connector or terminal board, replace the
voltage regulator.
No
Yes
No
Yes
Perform system “Break Even Amperage”
test outlined on Page 10.13.
Does charging occur as specified?
Using a multitester set on D.C. volts, mea-
sure the battery open circuit voltage (See
Page 10.15). It should be 12.4 volts or
more. Is it?
Remove the battery and properly ser-
vice. Reinstall the fully charged battery
or a fully charged shop battery.
With the transmission in neutral, start the
engine and increase RPM to between 3000
and 4000. Read battery voltage with the
multitester. Readings should be between
13.0 and 14.6 V D.C.
Are they?
No
Yes
No
Yes Check Key off Current Draw
No
Meter Setting: AC Amps
Meter Setting: DC Amps
Meter Setting: DC Volts
Meter Setting: DC Volts
Yes
Refer to Page 10.13.

ELECTRICAL
10.13
CURRENT DRAW - KEY OFF
CAUTION: Do not connect or disconnect the battery
cable or ammeter with the engine running. Damage
will occur to light bulbs and speed limiter.
Connect an ammeter in series with the negative
battery cable. Check for current draw with the key off.
If the draw is excessive, loads should be
disconnected from the system one by one until the
draw is eliminated. Check component wiring as well
as the component for partial shorts to ground to
eliminate the draw.
Current Draw - Key Off:
Maximum of .02 DCA (20 mA)
CHARGING SYSTEM “BREAK
EVEN” TEST
CAUTION: Do not connect or disconnect the battery
cable or ammeter with the engine running.
CAUTION: Never use the electric starter with the
ammeter connected, as damage to the meter or meter
fuse may result. Do not run test for extended period
of time. Do not run test with high amperage
accessories.
The “break even” point of the charging system is the
point at which the alternator overcomes all system
loads (lights, etc.) and begins to charge the battery.
Depending on battery condition and system load, the
break even point may vary slightly. The battery should
be fully charged before performing this test.
GConnect an ammeter (set to DC amps)
in series between the negative
battery cable and terminal.
Do not use electric start.
--+
YB14A
Current Drain Inspection
Key Off
Less Than 9 mA
GConnect a tachometer according to
manufacturer’s instructions.
GWith engine off and the key and kill
switch in the ON position, the
ammeter should read negative amps
(battery discharge). Reverse meter
leads if a positive reading is
indicated.
GShift transmission into neutral. Start
engine with recoil only.
GIncrease engine RPM while observing
ammeter and tachometer.
GNote RPM at which the battery starts to
charge (ammeter indication is
positive).
GWith lights and other electrical load off,
this should occur at approximately
1500 RPM or lower.
GTurn the lights on and lock parking brake
to keep brake light on.
GRepeat test, observing ammeter and
tachometer. With lights on, charging
should occur at or below 2000 RPM.
ALTERNATOR OUTPUT TEST
(AC AMP)
This test measures AC amperage from the alternator.
CAUTION: This test simulates a “full load” on the
alternator. Do not perform this test longer than required
to obtain a reading or the alternator stator windings may
overheat. Do not exceed idle rpm during this test.
To Calculate Available Alternator Output
150W
12V
=12.5 Amps
I=P
E
I = Current in Amps
P = Power in Watts
E = Electromotive Force (Volts)
Alternator Current Output:
Minimum of 7 AC Amps
GMaximum alternator output will be
indicated on the meter. It is not
necessary to increase engine RPM
above idle.
GPlace the red lead on the tester in the
10A jack.

ELECTRICAL
10.14
GTurn the selector dial to the AC amps
(Aµ) position.
GConnect the meter leads to the Yellow
and Yellow/Red wires leading from
the alternator.
GStart the engine and let it idle. Reading
should be a minimum of 7A at idle.
BATTERY SERVICE
WARNING
Battery electrolyte is poisonous. It contains
sulfuric acid. Serious burns can result from
contact with skin, eyes or clothing. Antidote:
Internal: Drink large quantities of water or milk.
Follow with milk of magnesia, beaten egg, or
vegetable oil. Call physician immediately.
Eyes: Flush with water for 15 minutes and get
prompt medical attention.
Batteries produce explosive gases. Keep
sparks, flame, cigarettes, etc. away. Ventilate
when charging or using in an enclosed space.
Always shield eyes when working near batteries.
KEEP OUT OF REACH OF CHILDREN
WARNING: The gases given off by a battery are
explosive. Any spark or open flame near a battery can
cause an explosion which will spray battery acid on
anyone close to it. If battery acid gets on anyone,
wash the affected area with large quantities of cool
water and seek immediate medical attention.
The battery is located under the left rear fender.
BATTERY TERMINALS/BOLTS
Use Polaris corrosion resistant Dielectric Grease (PN
2871329) on battery bolts. See Battery Installation on
Page 10.15.
MAINTENANCE--FREE
BATTERY INSPECTION
NOTE: All 2003 Trail Boss ATV batteries are
Maintenance--Free design and construction. All
Maintenance--Free batteries are fully charged and
tested at the factory before installation. Expected
shelf life is 6--8 months depending on storage
conditions. As a general rule before placing the
battery into service, check the battery condition
and charge accordingly .
New Batteries: Batteries must be fully charged
before use or battery life can be reduced by
10-30% of full potential.Charge battery for 3--5
hours at a current equivalent of 1/10 of the
battery’s rated amp/hour capacity (i.e. 12amp hr
x .10 = 1.2 amp charging). Do not use the
alternator to charge a new battery.
Maintenance--Free batteries are permanently
sealed at the time of manufacture. The use of
lead--calcium and AGM technology instead of
lead--antimony allows the battery acid to be fully
absorbed. For this reason, a Maintenance--Free
battery case is dark and the cell caps are not
removable, since there is no need to check
electrolyte level.
NEVER attempt to add electrolyte or water to a
Maintenance--Free battery. Doing so will damage
the case and shorten the life of the battery. Refer
to the Battery Maintenance Video (PN 9917987) for
proper instruction on servicing Maintenance--Free
batteries.
To service a Maintenance--Free battery:
1. Remove battery from the vehicle
2. Test battery with a voltage meter or load tester to
determine battery condition. This will determine
the length of time required to charge the battery to
full capacity. Refer to capacity table on Page
10.15.
3. Charge battery at 1/10 of its amp/hour rating.
Example: 1/10 of 12 amp battery = 1.2 amp
charge rate.
CONVENTIONAL LEAD--ACID
BATTERY INSPECTION
Maintain
between upper
and lower level
marks
NOTE: Use these procedures ONLY if the
Maintenance- Free battery has been replaced
with a Conventional Lead- acid type.
1. Inspect the battery fluid level. When the battery
fluid nears the lower level, the battery should be
removed and distilled water should be added to
the upper level line.

ELECTRICAL
10.15
To remove the battery:
1. Disconnect holder strap and remove cover.
2. Disconnect battery negative (-) (black) cable first,
followed by the positive (+) (red) cable.
CAUTION
Whenever removing or reinstalling the battery,
disconnect the negative (black) cable first and
reinstall the negative cable last!
To activate a NEW conventional lead/acid battery:
1. Remove vent plug and battery cell caps.
2. Fill battery with electrolyte to upper level marks on
case.
3. Set battery aside and allow it to cool and stabilize
for 30 minutes.
4. Add electrolyte to bring level back to upper level
mark on case. NOTE: This is the last time that
electrolyte should be added. If the level becomes
low after this point, add only distilled water.
5. Charge battery at 1/10 of its amp/hour rating.
Example: 1/10 of 14 amp battery = 1.4 amp
To charge an existing conventional lead/acid
battery:
1. Disconnect the vent hose.
2. Remove the battery.
3. Remove the filler caps and add distilled water only
as needed to bring each cell to the proper level.
Do not overfill the battery.
To refill use only distilled water. Tap water
contains minerals which are harmful to a battery.
4. Reinstall the battery caps.
5. Charge battery at 1/10 of its amp/hour rating.
Example: 1/10 of 14 amp battery = 1.4 amp
6. Reinstall the battery after testing.
BATTERY INSTALLATION
1. Clean battery cables and terminals with a stiff wire
brush. Corrosion can be removed using a solution
of one cup water and one tablespoon baking soda.
Rinse will with clean water and dry thoroughly.
2. Reinstall battery, attaching positive (+) (red) cable
first and then the negative (-) (black) cable. Coat
terminals and bolt threads with Dielectric Grease
(PN 2871329).
3. (Conventional Lead/Acid Batteries Only) Install
clear battery vent tube from vehicle to battery vent.
WARNING: Vent tube must be free from
obstructions and kinks and securely installed. If not,
battery gases could accumulate and cause an
explosion. Vent should be routed away from frame
and body to prevent contact with electrolyte. Avoid
skin contact with battery electrolyte, severe burns
could result. If electrolyte contacts the vehicle
frame, corrosion will occur.
4. Route cables so they are tucked away in front and
behind battery.
5. Reinstall battery cover and holder strap.
Do not run the engine with the battery
disconnected. Electrical components can become
damaged.
BATTERY TESTING
Whenever a service complaint is related to either the
starting or charging systems, the battery should be
checked first.
Following are three tests which can easily be made on
a battery to determine its condition: OCV Test,
Specific Gravity Test (Conventional Lead--acid
batteries only) and Load Test.
OCV - OPEN CIRCUIT
VOLTAGE TEST
Battery voltage should be checked with a digital
multitester. Readings of 12.6 volts or less require
further battery testing and charging. See charts and
Load Test on Page 10.16.
NOTE: Lead-acid battery electrolyte levels should be
kept between the low and full marks. If the battery is
stored or used in a partially charged condition, or with
low electrolyte levels, crystal sulfation will form on the
plates, reducing the efficiency and service life of the
battery.

ELECTRICAL
10.16
SPECIFIC GRAVITY TEST
NOTE: This test is for Conventional Lead--acid
batteries only. Maintenance--Free batteries cannot be
opened.
A tool such as a Battery Hydrometer (PN 2870836)
can be used to measure electrolyte strength or
specific gravity. As the battery goes through the
charge/discharge cycle, the electrolyte goes from a
heavy (more acidic) state at full charge to a light (more
water) state when discharged. The hydrometer can
measure state of charge and differences between
cells in a multi-cell battery. Readings of 1.270 or
greater should be observed in a fully charged battery.
Differences of more than .025 between the lowest and
highest cell readings indicate a need to replace the
battery.
Detail A
1.10
1.15
1.20
1.25
1.30
Battery Hydrometer (PN 2870876)
OPEN CIRCUIT VOLTAGE
State of
charge
Conventional
Lead-acid
Maintenance
Free
100%
Charged
75% Charged
50% Charged
25% Charged
0% Charged
12.60V
12.40V
12.10V
11.90V
less than
11.80V
12.70V
12.50V
12.20V
12.0V
less than
11.9V
SPECIFIC GRAVITY
State of
charge*
Conventional
lead-acid
Maintenance
Free
100%
Charged
75% Charged
50% Charged
25% Charged
0% Charged
1.265
1.210
1.160
1.120
less than
1.100
n/a
*At80_FNOTE: Subtract .01 from the specific gravity
reading when testing. At 40_F, add .01 to the specific
gravity.
LOAD TEST
CAUTION: Remove spark plug high tension leads and
connect securely to engine ground before proceeding.
NOTE: This test can only be performed on engines with
electric starters. This test cannot be performed with an
engine or starting system that is not working properly.
A battery may indicate a full charge condition in the OCV
test and the specific gravity test, but still may not have
the storage capacity necessary to properly function in
the electrical system. For this reason, a battery capacity
or load test should be conducted whenever poor battery
performance is encountered. To perform this test, hook
a multitester to the battery in the same manner as was
done in the OCV test. The reading should be 12.6 volts
or greater. Engage the electric starter and view the
registered battery voltage while cranking the engine.
Continue the test for 15 seconds. During this cranking
period, the observed voltage should not drop below 9.5
volts. If the beginning voltage is 12.6 volts or higher and
the cranking voltage drops below 9.5 volts during the
test, replace the battery.
OFF SEASON STORAGE
To prevent battery damage during extended periods
of non-use, the following basic battery maintenance
items must be performed:
GRemove the battery from the machine and
wash the case and battery tray with a mild
solution of baking soda and water. Rinse
with fresh water after cleaning. NOTE:
Do not get any baking soda into the
battery or the acid will be neutralized.
GUsing a wire brush, remove any corrosion
from the cables and terminals.
GMake sure that the electrolyte is at the
proper level. Add distilled water if
necessary.
GCharge at a rate no greater than 1/10 of the
battery’s amp/hr capacity until the
electrolyte’s specific gravity reaches
1.270 (12.7 volts) or greater.
GStore the battery either in the machine with
the cables disconnected or place the
batter on a piece of wood and store in a
cool place.
CHARGING PROCEDURE
Charge the battery with a charger no larger than 1/10
of the battery’s amp/hr rating for as many hours as
needed to raise the specific gravity to 1.270 or greater.

ELECTRICAL
10.17
NOTE: Stored batteries lose their charge at the rate
of 1% per day. They should be recharged to a full
charge every 30 to 60 days during a non-use period.
If the battery is stored during the winter months the
electrolyte will freeze at a higher temperature as the
battery discharges. The chart at below indicates
freezing points by specific gravity.
Electrolyte Freezing Points
Specific Gravity
of Electrolyte
Freezing
Point
1.265 -75°F
1.225 -35°F
1.200 -17°F
1.150 +5°F
1.100 +18°F
1.050 +27°F
1. Install battery in vehicle with positive terminal
toward the front. Coat threads of battery bolt with
a corrosion resistant dielectric grease.
Dielectric Grease
(PN 2871329)
WARNING: To avoid the possibility of explosion,
connect positive (red) cable first and negative (black)
cable last.
2. Connect battery cables.
3. After connecting the battery cables, install the cover
on the battery and attach the hold down strap.
4. (Conventional Lead--acid batteries only) Install
clear battery vent tube from vehicle to battery vent.
WARNING: Vent tube must be free from
obstructions and kinks and securely installed. If not,
battery gases could accumulate and cause an
explosion. Vent should be routed away from frame
and body to prevent contact with electrolyte. Avoid
skin contact with battery electrolyte, severe burns
could result. If electrolyte contacts the vehicle
frame, corrosion will occur.
5. Route cables so they are tucked away in front and
behind battery.
HEADLIGHT ADJUSTMENT
The headlight beam can be adjusted up and down and
side to side.
1. Place the vehicle on a level surface with the
headlight approximately 25’ (7.6 m) from a wall.
25’ (7.6 m)
Lamp Center Height
2²(5.1 cm)
2. Measure the distance from the floor to the center
of the headlight and make a mark on the wall at
the same height.
3. Shift transmission to neutral, start the engine and
turn the headlight switch to high beam.
4. Observe headlight aim. The most intense part of
the headlight beam should be aimed 2²(5.1 cm)
below the mark placed on the wall in Step 2.
NOTE: Rider weight must be included on the
seat. For machines with separate low beam
lights, the drop should be 8²(20.3 cm) in 25’.
5. Adjust beam to desired position by moving
headlight.
HEADLIGHT LAMP
REPLACEMENT
NOTE: Allow lamp to cool before proceeding. Do not
touch a halogen lamp with bare fingers. Oil from your
skin leaves a residue, causing a hot spot which will
shorten the life of the lamp. Hold the bulb by the base
only.
Headlight Assembly Removal
1. Carefully unsnap the electrical harness from the
back of the headlight assembly and remove the
harness.
2. Remove the screws and nuts from the sides of the
headlight assembly.
3. Remove the headlight assembly.

ELECTRICAL
10.18
Headlamp Replacement
1. With the headlight assembly in place, unsnap the
electrical harness from the back the headlight
assembly.
2. Turn and pull out the connector on the back of the
headlight assembly. Gently pull the bulb out and
replace with the new bulb. Snap the harness back
into place.
TAILLIGHT/BRAKELIGHT
LAMP REPLACEMENT
If the taillight/brakelight does not work the lamp may
need to be replaced.
1. From the rear of the taillight remove two screws
holding lens cover in place and remove lens
cover.
Lens Cover
Bulb
2. Remove lamp and replace it with recommended
lamp. Apply Dielectric Grease (PN 2871329).
3. Reinstall the lens cover removed in Step 1.
4. Test the taillight/brakelight to see that it’s working.
POD ASSEMBLY REMOVAL /
INDICATOR LAMP
REPLACEMENT
1. Remove the two screw covers (A) and screws
from the pod assembly (B).
A
B
C
2. Disconnect indicator light panel from harness, by
lifting the retaining latch from the wire connector.
NOTE: The indicator panel (C) does not have to be
remove from the pod to replace an indicator light.
3. To remove defective light: Use a small
screwdriver and turn light holder a quarter turn,
pull light holder out with a needle nose pliers or
equivalent. Replace with new holder and bulb
assembly and reassemble pod.
Rear view of indicator lamp panel
1/4 Turn
4. Reverse the above steps for installation.

ELECTRICAL
10.19
HEADLAMP SWITCH
Follow procedure, Headlight Lamp Replacement, on
Page 10.17--10.18 to access connector. Probe the
headlamp plug wires (Brown, Green, Yellow) at back
of connector. Turn headlight on. Test for battery
voltage across the connections.
Check continuity across pins of the left handle bar
switch assembly. See illustration below.
Continuity
R/W Grn
Off
On FF
NEUTRAL LIGHT CIRCUIT
OPERATION
Power is supplied to the transmission switch from the
Red/White wire when the key and engine stop switch
are on. When neutral is selected, power flows through
the switch to the Green/White wire, through the lamp
and to ground via the Brown wire.
If the light is not on when neutral is selected, check the
bulb. If the bulb is good, check the wiring,
transmission switches, and lamp socket ground path.
BRAKE LIGHT SWITCH
1. Remove front cover.
2. Disconnect wire harness from switch.
3. Connect an ohmmeter across switch contacts.
Reading should be infinite (∞).
4. Apply brake at handlebar lever and check for
continuity between switch contacts. Replace
switch if there is no continuity or greater than .5
ohms resistance when the brake is applied with
slight pressure.
NOTES

ELECTRICAL
10.20
STARTER SYSTEM TESTING
Condition: Starter fails to turn motor. NOTE: Make sure engine crankshaft is free to turn before proceeding with
dynamic testing of starter system. A digital multitester must be used for this test.
With the tester on the VDC position, place the tes-
ter’s black lead on the battery negative and the red
lead on the battery positive.
Reading should be 12.4 volts or greater.
Remove battery and properly service.
Install fully charged shop battery to continue
test.
Disconnect White/Red engagement coil wire from
the starter solenoid. Connect tester black wire to
battery ground. Connect red tester lead to White/
Red harness wire at solenoid. Turn on ignition
switch and depress the starter button. Tester
should read battery voltage.
Check voltage on both sides of circuit
breaker, ignition switch/engine stop switch
and starter button. The voltage on both
sides should be the same. NOTE: The igni-
tion switch and engine stop switch must be
on and the starter button depressed. Re-
place the defective component.
Reconnect the solenoid. Connect the tester black
lead to the battery positive and the red lead to the
solenoid end of the battery-to-solenoid wire. De-
press starter button. Reading should be less than
.1 V D.C.
Clean the battery-to-solenoid cable ends or
replace the cable.
Connect the black tester lead to solenoid end of
battery-to-solenoid cable. Connect red tester lead
to solenoid end of solenoid-to-starter cable. De-
press starter button. Reading should be less than
.1 V D.C.
Replace the starter solenoid.
Connect the black tester lead to the solenoid end of
the solenoid-to-starter cable. Connect the red tester
lead to the starter end of the same cable. Depress
the starter button. The reading should be less than
.1 V D.C.
Clean the solenoid-to-starter cable ends or
replace the cable.
No
Yes
No
No
Yes
No
Yes
If all of these indicate a good condition, yet the starter still fails to turn, the
starter must be removed for static testing and inspection.
No
Yes
Test starter solenoid coil by connecting an ohmmeter between the solenoid
red wire and the solenoid mounting plate. Resistance should be 3.4W.
Check solenoid ground path by measuring resistance between mounting
plate and battery negative terminal (-).
Voltage Drop Testing
See Page 10.21 for instructions.
Yes

ELECTRICAL
10.21
STARTER SYSTEM
TROUBLESHOOTING
Starter Motor Does Not Turn
GBattery discharged - low specific gravity
GLoose or faulty battery cables or corroded
connections (see Voltage Drop Tests)
GRelated wiring loose, disconnected, or
corroded
GPoor ground connections at battery cable,
starter motor or starter solenoid (see
Voltage Drop Tests)
GFaulty starter button
GFaulty ignition switch (Do other systems
function?)
GFaulty starter solenoid or starter motor.
GEngine problem - seized or binding (Can
engine be rotated easily with recoil
starter?)
Starter Motor Turns Over Slowly
GBattery discharged - low specific gravity
GExcessive circuit resistance - poor
connections (see Voltage Drop Test
below)
GEngine problem - seized or binding (Can
engine be rotated easily with recoil
starter?)
GFaulty or worn brushes in starter motor
GAutomatic compression release inoperative
Starter Motor Turns - Engine Does Not Rotate
GFaulty starter drive
GFaulty starter drive gears or starter motor
gear
GFaulty flywheel gear or loose flywheel
VOLTAGE DROP TEST
The Voltage Drop Test is used to test for bad
connections. When performing the test, you are
testing the amount of voltage drop through the
connection. A poor or corroded connection will
appear as a high voltage reading. Voltage shown on
the meter when testing connections should not
exceed .1 VDC per connection or component.
To perform the test, place the meter on DC volts and
place the meter leads across the connection to be
tested. Refer to the chart on next page to perform
voltage drop tests on the starter system.
Voltage should not exceed:
1 DC volts per connection
STARTER MOTOR
DISASSEMBLY
NOTE: Use electrical contact cleaner to clean starter
motor parts. Some solvents may leave a residue or
damage internal parts and insulation.
1. Note the alignment marks on both ends of the
starter motor casing. These marks must align
during reassembly.
2. Remove the two bolts, washers, and sealing
O-Rings. Inspect O-Rings and replace if damaged.

ELECTRICAL
10.22
3. Remove brush terminal end of housing while
holding other two sections together.
4. Remove shims from armature shaft. NOTE: All
shims must be replaced during reassembly.
BRUSH
INSPECTION/REPLACEMENT
Brush Set
1. Using a digital multitester, measure the
resistance between the cable terminal and the
insulated brush. The reading should be .3 ohms
or less. Measure the resistance between the
cable terminal and brush housing. Make sure the
brush is not touching the case. The reading
should be infinite.
2. Remove nut, flat washer, large phenolic washer,
two small phenolic washers, and O-Ring from
brush terminal. Inspect the O-Ring and replace if
damaged.
Brush Length
5/16²(.8 cm)
Brush Length Service Limit:
5/16²(.8 cm)
3. Remove brush plate and brushes. Measure
length of brushes and replace if worn past the
service limit. Replace springs if they are
discolored or have inadequate tension.
4. Inspect surface of commutator for wear or
discoloration. See Steps 3-6 of armature testing
on Page 10.23.
5. Install a new carbon brush assembly in the brush
housing. NOTE: Be sure that the terminal bolt
insulating washer is properly seated in the
housing, and the tab on the brush plate engages
the notch in the brush plate housing.
6. Place a wrap of electrical tape on the threads of
the terminal bolt to prevent O-Ring damage
during reinstallation.
7. Install the O-Ring over the bolt. Make sure the
O-ring is fully seated.
8. Remove the electrical tape and reinstall the two
small phenolic washers, the large phenolic
washer, flat washer, and nut.

ELECTRICAL
10.23
ARMATURE TESTING
1. Remove armature from starter casing. Note
order of shims on drive end for reassembly.
2. Inspect surface of commutator. Replace if
excessively worn or damaged.
3. Using a digital multitester, measure the
resistance between each of the commutator
segments. The reading should be .3 ohms or
less.
4. Measure the resistance between each
commutator segment and the armature shaft.
The reading should be infinite (no continuity).
5. Check commutator bars for discoloration. Bars
discolored in pairs indicate shorted coils,
requiring replacement of the starter motor.
6. Place armature in a growler. Turn growler on and
position a hacksaw blade or feeler gauge
lengthwise 1/8²(.3 cm) above armature coil
laminates. Rotate armature 360°. If hacksaw
blade is drawn to armature on any pole, the
armature is shorted and must be replaced.
STARTER ASSEMBLY
1. Place armature in field magnet casing.
2. Place shims on drive end of armature shaft with
phenolic washer outermost on shaft. Engage
tabs of stationary washer in drive end housing,
holding it in place with a light film of grease.
3. Install case sealing O-Ring. Make sure O-Ring is
in good condition and not twisted on the case.
Lubricate needle bearing and oil seal with a light
film of grease, and install housing, aligning marks.
4. Install O-Ring on other end of field magnet casing.
Make sure it is in good condition and not twisted
on the case.
5. Align casing marks and install housing, pushing
back brushes while installing shaft in bushing.
6. Reinstall starter motor housing bolts.
Make sure O-Rings are in good condition and
seated in groove.
7. Inspect permanent magnets in starter housing.
Make sure they are not cracked or separated from
housing.
CAUTION: Use care when handling starter housing.
Do not drop or strike the housing as magnet damage
is possible. If magnets are damaged, starter must be
replaced.

ELECTRICAL
10.24
STARTER DRIVE
Pinion Gear - Anti Kick-out Shoe, Garter
Spring Replacement
If the garter spring is damaged, the overrun clutch
may fail to return properly. The replacement spring is
(PN 7042039). Use either of the following methods to
remove and install a new garter spring.
Starter Motor Exploded View
O-ring
Rear Brkt Assy
Armature
SetBoltAssy
Washer
Washer Set
Rubber Rings
Weight Spring
Return Spring
Carbon
Brush
Set
1. Screw the overrun clutch out to the engaged
position on the pinion shaft assembly. Use a
small piece of wire with the end bent in a hook and
pick the old spring out of its channel. Slide it off
the end of the shaft. Slide the new spring over the
overrun clutch and into the spring groove. Make
sure that the spring is positioned between the
shoe alignment pins and the back flange of the
anti kick-out shoes.
2. Remove the lock ring, end washer, spring
retainers and clutch return spring. Screw the
overrun clutch off the end of the pinion shaft.
Remove the old spring and install a new one.
Lightly grease the pinion shaft and reinstall the
clutch, spring, retainers, end washer and lock ring
in the reverse order. Make sure the end washer is
positioned properly so that it will hold the lock ring
in its groove.
Polaris Premium Starter Drive Grease
(PN 2871460)
NOTES
A
A-Arm Replacement, 5.6
Air Filter Cleaning, 2.15
Air Filter Service, 2.15
Alternator Output Test, 10.13
Alternator, Exploded View, 10.9
B
Battery Charging, 10.16
Battery Installation, 10.15
Battery Maintenance, 2.13
Battery Service, 10.14, 10.16
Battery Terminal Bolts, 10.14
Battery Testing, 10.15
Battery, Off Season Storage, 10.16
Body Assembly Exploded View, 5.2
Brake Bleeding, 9.6
Brake Bleeding/Fluid Change, 9.11
Brake Caliper Assembly, Rear, 9.19
Brake Caliper Disassembly, Front, 9.12
Brake Caliper Exploded View, Front, 9.16
Brake Caliper Exploded View, Rear, 9.22
Brake Caliper Inspection, Front, 9.13
Brake Caliper Installation, Front, 9.15
Brake Caliper Removal, Front, 9.12
Brake Caliper Removal, Rear, 9.18
Brake Disc Inspection, Front, 9.11
Brake Disc Inspection, Rear, 9.20
Brake Disc Removal/Replacement, Front, 9.11
Brake Fluid Change, 9.6
Brake Fluid Level, 2.23
Brake Hose/Fitting Inspection, 2.23
Brake Light Switch Testing, 10.19
Brake Noise, 9.3
Brake Pad Application, 9.3
Brake Pad Assembly, Front, 9.10
Brake Pad Inspection, 2.23
Brake Pad Installation, Rear, 9.17
Brake Pad Removal, Front, 9.9
Brake Pad Removal, Rear, 9.17
Brake System Inspection, 2.23
Brake System Main Components, 9.5
Brake System Operation, 9.4
Brake System Service Notes, 9.3
Brake, Auxiliary, Hydraulic, 2.23
Brakelight Lamp Replacement, 10.18
C
Cam Chain Drive Sprocket Installation, 3.34
Cam Chain Tensioner Inspection, 3.11
Cam Chain Tensioner Installation, 3.41
Cam Chain Tensioner Removal, 3.11
Cam Chain/Camshaft Installation, 3.37
Cam Chain/Tensioner Blade, 3.27
Camber & Caster, 2.21
Camshaft Inspection, 3.14
Camshaft Removal, 3.13, 3.14
Camshaft Timing, 3.37, 3.38, 3.39, 3.40
Carburetor Assembly, 4.10
Carburetor Disassembly, 4.8
Carburetor Exploded View, BST34, 4.2
Carburetor Float Bowl Draining, 2.12
Carburetor Float Height Adjustment, 4.11
Carburetor Float System, 4.8
Carburetor Fuel Level Testing, 4.12
Carburetor Inspection, 4.9, 4.10
Carburetor Main System, 4.8
Carburetor Needle and Seat Testing, 4.11
Carburetor Operation, 4.6
Carburetor Pilot System, 4.7
Carburetor Starter System, 4.7
Carburetor System Function, 4.6
CDI Output Test, 10.11
Charging System Break Even Test, 10.13
Charging System Testing, 10.12, 10.13
Choke Adjustment, 2.10
Clutch Alignment, 6.15
Clutch Offset, 6.16
Combustion Chamber, 3.18
Compression Release Installation, 3.14
Compression Release Removal/Inspection, 3.14
Compression Test, 2.13
Concentric Swing Arm Installation, 5.8
Concentric Swing Arm Removal, 5.7
Connecting Rod Bearing Clearance Inspection,
3.31
Connecting Rod Bearing Inspection, 3.31
Connecting Rod Installation, 3.33
Controls Inspection, 2.27
Conversion Table, 1.10
Cover/Panel Removal, 5.5
Crankcase Assembly, 3.34
Crankcase Bearing Inspection, 3.31
Crankcase Bearing Installation, 3.32
Crankcase Disassembly, 3.25
Crankcase Inspection, 3.32
Crankcase Oil Strainer Inspection, 3.34
Crankcase Separation, 3.29
Cranking Output Test, 10.11
Crankshaft Bearing Inspection, 3.31
Crankshaft End Play Adjustment, 3.32
Crankshaft End Play Inspection, 3.32
Crankshaft Inspection, 3.30
Crankshaft Installation, 3.34
Crankshaft Removal/Inspection, 3.29
Cylinder Head Assembly, 3.21, 3.22
Cylinder Head Disassembly, 3.16
Cylinder Head Inspection, 3.15
Cylinder Head Installation, 3.36
Cylinder Head Reconditioning, 3.18
Cylinder Head Removal, 3.15
Cylinder Head Warpage, 3.16
Cylinder Honing, 3.6
Cylinder Inspection, 3.23, 3.24
Cylinder Installation, 3.36
Cylinder Removal, 3.22
D
Decal Replacement, 5.12
Decimal Equivalents, 1.9
Draining Recoil Housing, 2.16
Drive Belt Removal/Inspection, 6.14
Drive Belt Tension, 6.13
Drive Chain Adjustment, 2.24
Drive Chain Inspection, 2.24
Drive Clutch Assembly, 6.12
Drive Clutch Bushing Service, 6.16, 6.17, 6.18
Drive Clutch Disassembly, 6.10, 6.11, 6.12
Drive Clutch Exploded View, 6.7
Drive Clutch Inspection, 6.10
Drive Clutch Operation, 6.2
Drive Sprocket Removal/Inspection, 3.27
Driven Clutch Assembly, 6.20
Driven Clutch Bushing Service, 6.21, 6.22
Driven Clutch Disassembly, 6.19
Driven Clutch Operation, 6.2, 6.3
Dual Hydraulic Caliper Bleeding, 9.5
E
Electrical Service Notes, 10.2
Engine Accessible Components, 3.5
Engine Assembly, 3.32, 3.33, 3.34, 3.35, 3.36,
3.37, 3.38, 3.39, 3.40, 3.41, 3.42
Engine Bottom End Disassembly, 3.22, 3.23,
3.24, 3.25, 3.26, 3.27, 3.28, 3.29, 3.31
Engine Break in Period, 3.6
Engine Designation Numbers, 1.2
Engine Exploded View , ES32PF, 3.10
Engine Installation Notes, 3.6
Engine Lubrication, 3.7
Engine Mounts, 2.13
Engine Oil Check, 2.17
Engine Removal, 3.5
Engine Serial Number Location, 1.2
Engine Service Data, 3.2, 3.3
Engine to Frame Ground, 2.15
Engine Top End Disassembly, 3.11, 3.12, 3.13,
3.14, 3.15, 3.16, 3.17
ETC Switch Adjustment, 2.11
ETC Switch Testing, 10.7
Exhaust System, Maintenance, 2.22
Exhaust Valve Adjustment, 2.19
F
Fan Control Circuit, 10.6
Fan Motor Current Draw Test, 10.6
Fastener Torque, 2.13
Flywheel Identification, 10.8
Flywheel Installation, 3.42
Flywheel Removal/Inspection, 3.26
Frame, Nuts, Bolts, Fasteners, 2.28
Front Hub Assembly, 7.3
Front Hub Disassembly, 7.2
Front Hub Exploded View, 7.5
Front Hub Installation, 7.4
FrontStrutAssembly,AWD,5.9
Front Strut Ball Joint Replacement, 5.10
Front Strut Weldment Replacement, 5.10
Fuel Filter Maintenance, 2.12
Fuel Pump Exploded View, 4.3
Fuel Pump Service, 4.12
Fuel System, 2.12
Fuel Tank Assembly, Exploded View, 4.4
G
Gear Position Switch Test, 10.3
Glossary of Terms, 1.11
H
Headlamp Replacement, 10.18
Headlamp Switch Testing, 10.19
Headlight Adjustment , 10.17
Headlight Assembly Removal, 10.17
Headlight Lamp Replacement, 10.17
Honing to Oversize, 3.6, 3.7
I
Idle Speed Adjustment, 2.11
Ignition System Testing, 10.10
Ignition Timing, 2.14
Indicator Lamp Replacement, 10.18
Intake Valve Adjustment, 2.19
J
Jetting Guidelines, 4.5
K
Keys, Replacement, 1.4
L
Load Test, 10.16
Lubricants, 2.4
Lubricants, Recommended, 2.5
Lubrication Chart, 2.6
Lubrication Charts, 2.5
Lubrication, Transmission, 2.8, 8.2
M
Machine Dimensions, 1.5
Maintenance Chart, Periodic, 2.2, 2.3
Master Cylinder Disassembly, 9.7
Master Cylinder Installation, 9.8
Model & Serial Number Location, 1.2
Model Identification, 1.2
Model Specifications, 1.6, 1.7
N
Neutral Light Testing, 10.19
O
Oil & Filter Change--Magnum 500, 2.18
Oil Cooler Assembly, 3.8
Oil Filter Installation, 3.35
Oil Flow, ES32PF, 3.9
Oil Pressure Test, 3.7
Oil Pump Assembly, 3.29
Oil Pump Installation, 3.34
Oil Pump Removal/Inspection, 3.28
P
Paint Codes, 1.8
Pilot Screw Adjustment, 2.10
Piston Identification, 3.5
Piston Inspection, 3.24
Piston Installation, 3.35
Piston Removal, 3.23
Piston Ring Installation, 3.35
Piston Ring Installed Gap, 3.25
Pod Assembly Removal, 10.18
Pre Ride Inspection, 2.3
Pressure Relief Valve, 3.28
Pressure Relief Valve Installation, 3.34
Publication Numbers, 1.8
PVT Assembly, 6.6
PVT Disassembly, 6.5
PVT Drying, 2.17, 6.3
PVT Maintenance, 6.3
PVT Operation, 6.2
PVT Overheating, 6.4
PVT System Sealing/Ducting Components, 6.7
PVT Troubleshooting, 6.23, 6.24
R
Rear Axle Assembly, 7.7
Rear Axle Assembly, Exploded View, 7.9
Rear Axle Disassembly, 7.7
Rear Axle Installation, 7.8
Rear Axle Removal, 7.6
Rear Housing Bearing Service, 7.10
Rear Housing Installation, 7.11
Rear Housing Removal, 7.10
Recoil Assembly, 3.44
Recoil Disassembly/Inspection, 3.42
Recoil Draining, 2.16
Reverse Limit System, 10.4, 10.5
Rocker Arm/Shaft Inspection, 3.12
Rocker Shaft/Rocker Arm Assembly Installation,
3.42
Troubleshooting, Transmission, 8.7
S
Sediment Tube, Maintenance, 2.16
Shift Linkage Adjustment, 2.9
Shift Weights, 6.9
Side Panel Removal, 5.5
Spark Plug Maintenance, 2.14
Special Tools, 2.7, 3.4, 4.5, 6.2, 8.2, 9.3, 10.2
Specific Gravity Test, 10.16
Specifications, Brake, 9.2
Specifications, Drive Clutch Spring, 6.8
Specifications, Speed Limiter, 10.3
Specifications, Torque, Brakes, 9.2
Specifications, Torque, Engine, 3.4
Specifications, Torque, Final Drive, 7.2
Specifications, Torque, PVT, 6.2
Specifications, Torque, Standard, 1.8
Specifications, Torque, Suspension, 5.4
Specifications, Torque, Transmission, 8.2
Spider Removal, 6.11
Sprocket Inspection, 2.24
Starter Assembly, 10.23
Starter Disassembly, 10.21
Starter Drive, 10.24
Starter Drive Installation, 3.42
Starter Drive Removal/Inspection, 3.26
Starter Motor Armature Testing, 10.23
Starter Motor Brush Inspection/Replacement,
10.22
Starter System Test, 10.20
Stator Installation, 3.41
Stator Removal/Inspection, 3.26
Steering Assembly, Exploded View, 4x4, 5.3
Steering Maintenance, 2.20
Steering Post Assembly, 5.12
Suspension Preload Adjustment, 2.26
Suspension Special Tools, 5.4
Suspension, Front, Inspection, 2.26
Suspension, Rear, Inspection, 2.26
T
Taillight Lamp Replacement, 10.18
Tap Drill Chart, 1.9
Tensioner Blade Installation, 3.35
Thermistor Testing, 10.6
Throttle Cable Adjustment, 2.11
Throttle Operation, 2.10, 2.11
Tie Rod Inspection, 2.20
Timing Check Procedures, 10.2
Tire Inspection, 2.28
Tire Pressure, 2.28
Tire Tread Depth, 2.28
Toe Alignment, 2.21, 2.22
Torque Patterns, Engine, 3.4
Torque Stop Adjustment, 2.8
Trailboss, 2003, Model, 1.3
Transmission Assembly, 8.5
Transmission Disassembly, 8.2
Transmission Exploded View, 8.7, 8.8
Transmission I.D. Location, 1.2
Transmission Installation, 8.2
Transmission Linkage Adjustment, 2.9
Transmission Removal, 8.2
Troubleshooting, Brakes, 9.21
Troubleshooting, Engine, 3.45, 3.46
Troubleshooting, Fuel System/Carb, 4.13
Troubleshooting, Ignition System, 10.11
Troubleshooting, Spark Plug, 3.45
Troubleshooting, Starter System, 10.21
V
Valve Clearance, 2.19
Valve Guide Removal/Installation, 3.18
Valve Inspection, 3.17
Valve Seal Testing, 3.22
Valve Seat Inspection, 3.18
Valve Seat Reconditioning, 3.18, 3.19, 3.20
VIN Identification, 1.2
Voltage Drop Test, 10.21
Voltage Test Open Circuit, 10.15
W
Wheel Inspection, 2.27
Wheel Installation, 2.27
Wheel Removal Front or Rear, 2.27
Wiring Diagram, 2002, Trail Boss 325, 10.29
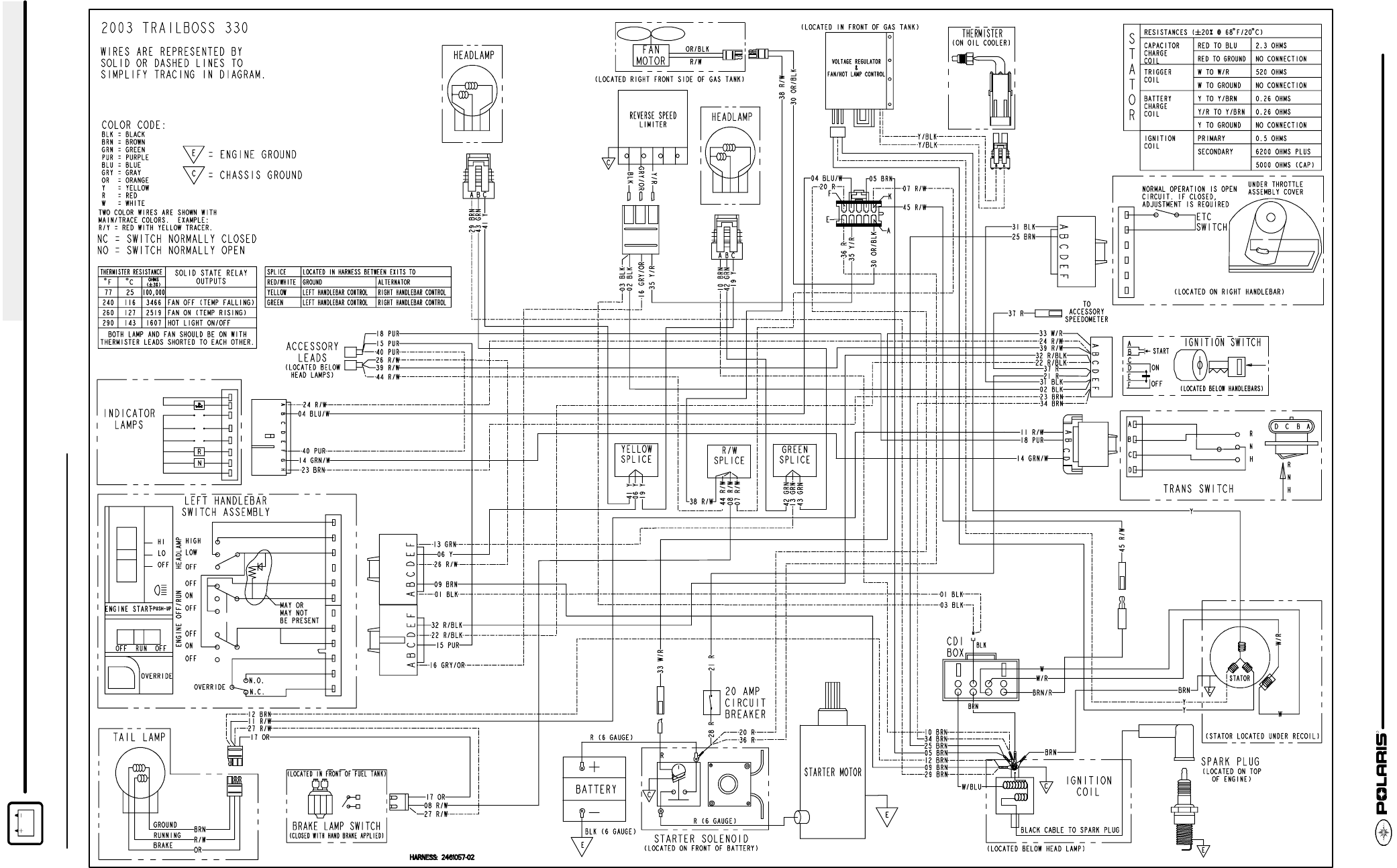
ELECTRICAL
10.25
WIRING DIAGRAM 2003 TRAILBOSS 330