SR CFG 73197
User Manual: 73197
Open the PDF directly: View PDF .
Page Count: 8
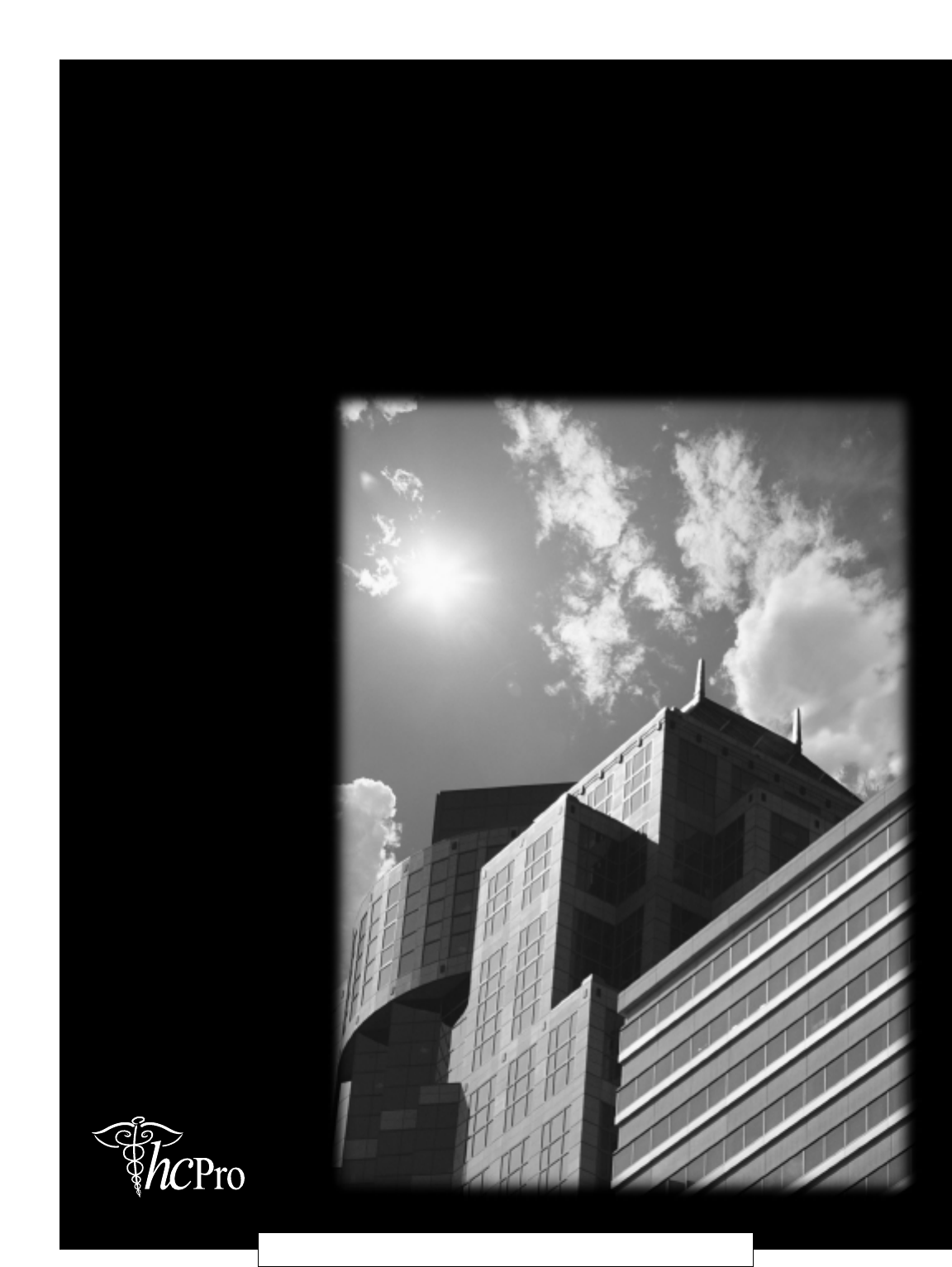
The JCAHO’s building
maintenance program:
Scoring and compliance tips
Asupplement to HCPro, Inc., publications

The JCAHO’Sbuilding maintenance program:
Scoring and compliance tips
2
Table of contents
How to succeed with your building program . . . . . . . . . . . . . . . . . . . . . . . . . . . . . . . . . . . . . . . . . . . . . . . 3
Items under the building maintenance program . . . . . . . . . . . . . . . . . . . . . . . . . . . . . . . . . . . . . . . . . . . . . 3
Crosswalk of building maintenance requirements . . . . . . . . . . . . . . . . . . . . . . . . . . . . . . . . . . . . . . . . . . . . 5
An analysis of SOC scoring benefits for hospitals . . . . . . . . . . . . . . . . . . . . . . . . . . . . . . . . . . . . . . . . . . . . 6
Take the edge offof potential penetration problems..........................................7
Inventory holes patched by colored firestopping ............................................8
Exploring the building maintenance program
The optional building maintenance program has been part of the Statement of Conditions (SOC)for hospitals
since 1999.
It’s clear today that those in charge of environment-of-care concerns at the Joint Commission on Accreditation of
Healthcare Organizations (JCAHO) are proponents of the building program because it offers advantages to hospitals
while also encouraging facilities to faithfully keep maintenance activities up to par.
With the JCAHO now switching to only unannounced surveys at accredited facilities, it’s a good time to explain the
scoring thoughts behind the building maintenance program, along with ideas about how to best comply with the
program’s intents.
We’ve culled our information from the SOC and the following experts:
§Frederick Bradley, PE, principal at FCB Engineering in Alpharetta, GA
§Mark Forstneger, spokesperson for the JCAHO
§George Mills, FASHE, CHFM, CEM, associate director of the JCAHO’s standards interpretation group, who
spoke during the American Society for Healthcare Engineering’s conference in July 2005 in Anaheim and dur-
ing an October 2005 audioconference presented by Joint Commission Resources, Inc.
§Steven MacArthur, safety consultant for The Greeley Company, a division of HCPro, Inc., in Marblehead, MA,
which also published this special report
Please contact me if you have any thoughts about this special report or ideas for futurestories.
Sincerely,
Scott Wallask
Senior Managing Editor
swallask@hcpro.com
781/639-1872, Ext. 3119
December 2005

The JCAHO’s building maintenance program:
Scoring and compliance tips
3
How to succeed with your building program
JCAHO official outlines good ideas to keep you ahead
It’s a virtual guarantee that surveyors from the Joint
Commission on Accreditation of Healthcare Organiza-
tions (JCAHO) will review the Statement of Conditions
(SOC).
Medical sites should anticipate that as surveyors look
over SOC concerns, they will ask facilities whether they
use the SOC’soptional building maintenance program,
says George Mills, FASHE, CHFM, CEM, associate
director of the JCAHO.
The building program allows facilities to correct com-
mon maintenance-related Life Safety Code® (LSC) defi-
ciencies without worrying about whether surveyors will
cite them for each problem. In exchange for this relaxed
scoring, facilities arrange scheduled, documented main-
tenance reviews for a set list of items (see the box be-
low). Facilities may choose to adopt all or some of the
items listed.
Sites must show that at least 95% of the program’s items
work properly at any given time.
Mills helped develop the idea for the building mainte-
nance program when he worked at the American
Society for Healthcare Engineering (ASHE) during the
late 1990s. The idea behind the program is to provide
relief to facilities who are trying to stay on top of small-
ticket LSC deficiencies, he says.
“It makes so much sense” to use the building mainte-
nance program, Mills says. He offers the following tips
to stay on top of the program:
3Consider adopting a policy addendum for your
building program. If your facility uses a building
maintenance program, the JCAHO would prefer to see
something in writing that formally indicates the pro-
gram’s existence, Mills says. Suggestions include a poli-
cy, memo to the safety committee, or declaration that
the building program is in use, he says.
However, the JCAHO doesn’t require a policy for the
building program, he adds.
3Make sure the program’s inspections meet the
JCAHO’s intent. When inspecting items for building
program compliance, be careful not to tap-dance
around the JCAHO’s wishes. A facilities crew member
who performs work to maintain a smoke barrier
Items under the building maintenance program
Following arethe items listed in the optional building main-
tenance program. You can find the building program in the
Statement of Conditions, Parts 3A and 3B, question 6J:
1. Do one-hour and 90-minute fire-resistance-rated assembly
doors have
• positive latches?
• self- or automatic-closing devices?
• 1/8-in. or smaller gaps between meeting edges of door
pairs?
• 3/4-in. or smaller undercuts?
2. Do linen and trash chute inlet and outlet doors have
•positive latches?
• self- or automatic-closing devices?
3. Do smoke barrier doors
• have self- or automatic-closing devices?
•prevent the spread of smoke?
4. Do corridor doors
• have positive latches?
• restrict the spread of smoke?
5. Are smoke barrier penetrations sealed properly?
6. Are corridor wall penetrations sealed properly?
7. Do lights in the means of egress work?
8. Areexit signs illuminated?
9. Arethe means of egress free from accumulation of ice
and snow?
10. Does the facility clean and maintain
• exhaust hoods?
•exhaust duct systems?
•grease-removal devices?
n
>p. 4

The JCAHO’Sbuilding maintenance program:
Scoring and compliance tips
4
Building program <p. 3
is not inspecting that barrier for compliance with the
program, Mills says.
Instead, department managers or similar folks should be
charged with inspecting the barriers for penetrations and
other problems, Mills says.
The inspections should validate whether the mainte-
nance work is appropriate, which is why the same per-
son can’t conduct both efforts simultaneously.
3If you have trouble meeting the 95% mainte-
nance rate, increase your inspections. Suppose that
asmall facility has only 10 fire doors under a building
maintenance program and that crews check those doors
once per year.
If one of those doors doesn’t latch properly, the facility
has already dropped below the required 95% rate in the
program.
Yet a larger site with 100 fire doors could also have one
door in disrepair and still make it above the 95% rate,
even though the number of deficient items is the same
in both facilities.
One way around this dilemma is to increase inspection
frequencies. For example, perform quarterly inspections
of fire doors in the small facility, Mills says.
That brings the total sample up to 40—10 doors multi-
plied by four inspections each. With increased inspec-
tions, one door out of 10 that doesn’t latch now makes it
above the 95% compliance rate in the program.
You can also choose to increase inspections of items in
specific areas, which may be prone to more abuse from
carts (e.g., doors in the dietary departments), Mills says.
3Small sample sizes shouldn’t be a detriment.
Facilities that have small sample sizes for certain items in
the building maintenance program shouldn’t shy away
from the program for that reason, Mills says.
In some cases, it’s reasonable to assume that those items
will remain in good repair.
Take kitchen hoods, for example, which fall under
grease-producing devices in the building program. A
facility might only have three hoods in the entire
building.
“So you’ve got a small number of [hoods]. How many
times are you visiting them?” Mills says. “Immediately,
you’re visiting them twice a year just to be compliant
with [NFPA codes], so that’s a denominator of six. And
if [hood maintenance] is contracted out and you make
sure the guy’s coming in there, is there really a concern
about failure rate on those particular three items? Most
likely not.”
If you run into a problem with the hoods, you could
elect to increase visual inspections of the equipment as
noted above, he adds.
3Take action if you fall below 95%. If your mainte-
nance activities don’t live up to the building program’s
required 95% rate, take one of the following two steps:
1. Fix the deficiencies as soon as possible and determine
what it will take to bring your building program back
up to acceptable levels.
2. Pull the item category in question out of the building
program until you can solve the problem. Although
the deficiency may still receive a citation on its
own, it won’t sink your entire building program,
Mills says.
n
Editor’s note: For more information about the continu-
ally challenging aspect of tracking penetrations within
the building maintenance program, see the related story
on p. 7.
Contact Senior Managing Editor Scott Wallask
Telephone:
781/639-1872, Ext. 3119
E-mail:
swallask@hcpro.com
Questions? Comments? Ideas?
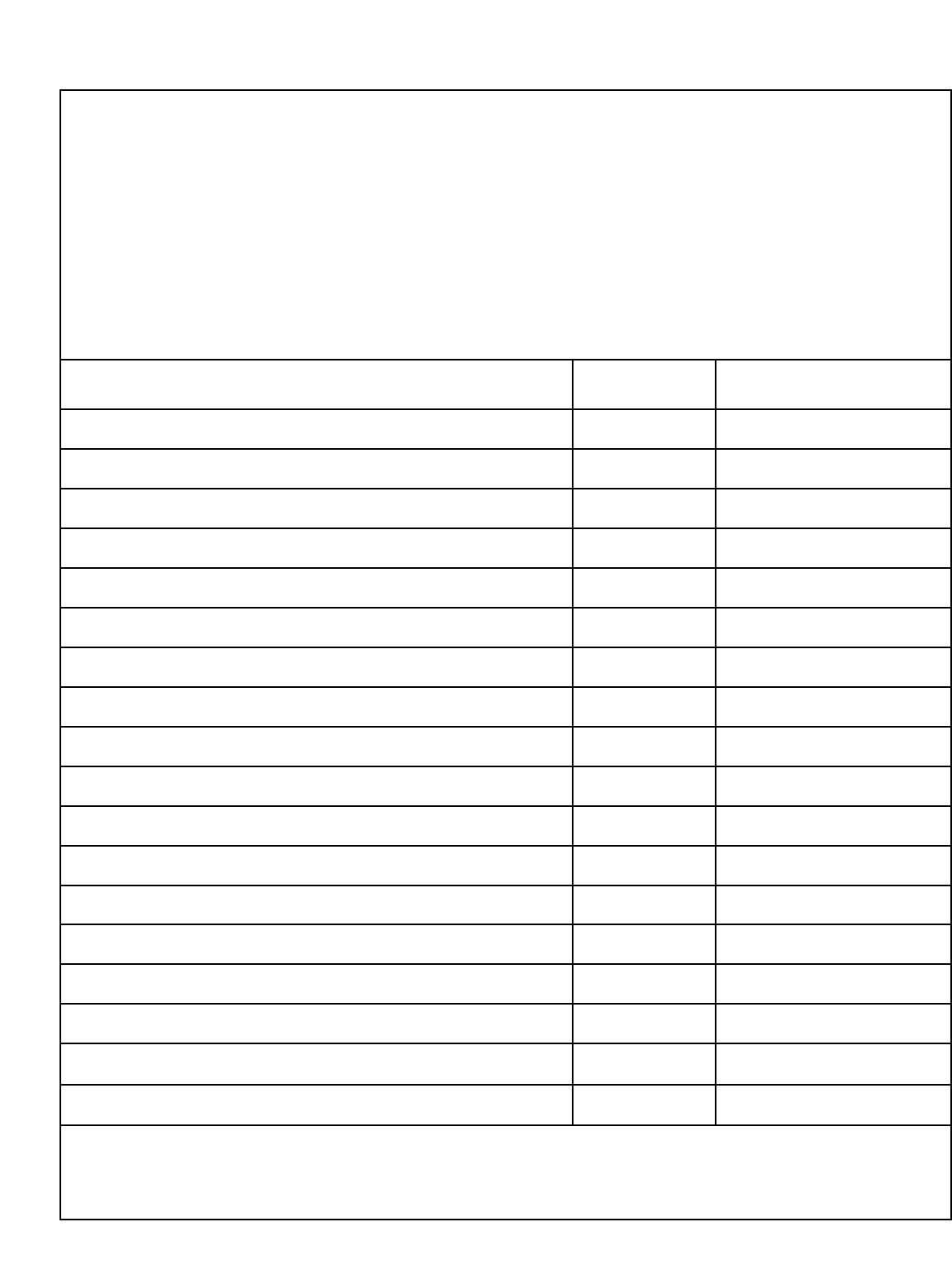
The JCAHO’s building maintenance program:
Scoring and compliance tips
5
Crosswalk of building maintenance requirements
This chart traces the items listed under the building maintenance program within the Statement of Conditions (SOC)and how
they tie into NFPA provisions.
The items in the building maintenance program receive scoring advantages when they meet a 95% compliance rate. These
items, when not included in a building maintenance program, fall under the SOC’sregularly scored questions.
Those questions in turn stem from various NFPA code requirements. This chart features NFPA references to the
•Life Safety Code (LSC), 2000 edition
• NFPA 80, Fire Doors and Fire Windows, 1999 edition
• NFPA 96, Ventilation Control and Fire Protection of Commercial Cooking Operations, 1998 edition
Building maintenance program item
Positive latches on fire-rated doors
Self-closing or automatic-closing devices on fire-rated doors
1/8-in. or smaller gaps between meeting edges of fire-rated door pairs
3/4-in. or smaller undercuts on fire-rated doors
Positive latches on linen/trash chute inlet and outlet doors
Self-closing or automatic-closing devices on linen/trash chute inlet
and outlet doors
Self-closing or automatic-closing devices on smoke barrier doors
Smoke barrier doors prevent the spread of smoke
Positive latches on corridor doors
Corridor doors restrict the spread of smoke
Properly sealed smoke barrier penetrations
Properly sealed corridor wall penetrations
Lights in the means of egress
Illuminated exit signs
Means of egress free of ice and snow
Cleaned and maintained exhaust hoods
Cleaned and maintained exhaust ducts
Cleaned and maintained grease removal devices
SOC question
1C
1C
1C
1C
4B
4B
3D
3D
2I
2I
3C
2A
5C
5K
5M
6I
6I
6I
NFPA code reference
LSC—8.2.3.2
NFPA 80—2-4.4.3
LSC—8.2.3.2.1
NFPA 80—2-4.1.2
LSC—8.2.3.2.1
NFPA80—2-3.1.7
LSC—8.2.3.2.1
NFPA80—1-11.4
LSC—8.2.3.2.3.1, 19.3.1,
and 19.5.4
LSC—8.2.3.2.3.1, 19.3.1,
and 19.5.4
LSC—19.3.7.6
LSC—8.3.4.1 and 19.3.7.6
LSC—19.3.6.3.2*
LSC—19.3.6.3.1
LSC—8.3 and 19.3.7.3
LSC—19.3.6.2.2
LSC—7.8, 7.9, and 19.2.8
LSC—7.10.5
LSC—7.1.10.1
LSC—9.2.3 and 19.3.2.6
NFPA 96—Chapter 8
LSC—9.2.3 and 19.3.2.6
NFPA 96—Chapter 8
LSC—9.2.3 and 19.3.2.6
NFPA 96—Chapter 8
*An exception under 19.3.6.3.2 allows existing roller latches to remain on corridor doors in certain situations. Effective March
13, 2006, the Joint Commission on Accreditation of Healthcare Organizations and Centers for Medicare & Medicaid Services will
override this exception and require all facilities to replace roller latches on corridor doors with positive latches.
Sources: LSC and SOC.

The JCAHO’Sbuilding maintenance program:
Scoring and compliance tips
6
An analysis of SOC scoring benefits for hospitals
Although the calculations sometimes are complex, the
final tally is clear: Hospitals that successfully use the
optional building maintenance program win a scoring
advantage from the Joint Commission on Accreditation
of Healthcare Organizations (JCAHO). Let’s look at
how this benefit occurs.
Surveyors score each item within the Statement of Con-
ditions (SOC),including the questions that allow the
building maintenance program (question 6J under Parts
3A and 3B).
But the scoring is different than the typical 0, 1, and 2
ranks you find alongside each environment of care
(EC) element of performance. In those scores, a 0
equals noncompliance with an element, 1 translates to
partial compliance, and 2 is full compliance. In turn,
those element scores work into overall EC standard
scores.
In this case, learnyour XYZs
As Mills explains it, instead of using 0, 1, and 2 scores,
the SOC items use scores of X, Y, and Z, in which
§X = 1/6 of a 0 score for standard EC.5.20 (which
requires compliance with the SOC and Life Safety
Code)
§Y=1/3 of a 0 scorefor EC.5.20
§Z=0score for EC.5.20
It takes two Xs to equal one Y score, Mills says. Six Xs
equal one Z score, which, as noted in the bullet above,
translates to a 0 score for EC.5.20.
Surveyors use a scoring grid that establishes the X and
Yscores to determine how to rate each SOC item.
Seek out the scoring tables
The tabulations areconfusing to explain, Mills says.
What makes it worse is that it’s not easy to find the
scores.
The last accreditation manual in which HCPro found
the scores was from late 2003. Now the scores are
available online through all facilities extranet connec-
tion to the JCAHO.
If you have access to that grid, you’ll see that all 10
building maintenance program entries have an X next
to them, which means that any deficiency that falls
below the 95% rate receives an X score, says Mark
Forstneger, aspokesperson for the JCAHO.
Corridor doors: A comparison
The “all X” approach to scoring the building mainte-
nance program is advantageous.
Here’s how the benefit plays out, using corridor doors
as an example.
As noted earlier, if at least 95% of your corridor doors
arein good shape, you comply with the building pro-
gram. If enough doors have deficiencies (e.g., not
latching properly) to drop you below 95%, surveyors
will score you with an X.
If you didn’t include corridor doors in a building main-
tenance program, surveyors will score those doors in
the regular SOC.In this case, corridor door latching
falls under question 2I.3 in Part 3A.
If one latch doesn’t close properly on a corridor door
because of poor maintenance, surveyors will hand you
ascoreof X under 2I.3. A second latching problem
will get you another X, for a total of two Xs or one Y.
What’s the bottom line?
In theory, if you had six latching problems for corridor
doors covered under the building maintenance program,
you might still make it above 95%, and even if you did-
n’t, you would receive one X for all of the deficiencies,
Mills says.
But if you didn’t use the building program, six latching
deficiencies under question 2I.3 result in a 0 score
under EC.5.20, which could lead to a requirement for
improvement citation.
With the building program in place, “we’regiving you
the grace by reducing the scoring,” Mills says.
In return, hospitals must show the JCAHO that they have a
process in place to oversee routine maintenance issues.
n

The JCAHO’s building maintenance program:
Scoring and compliance tips
7
Take the edge off of potential penetration problems
Strive for a successful maintenance effort, not a number-crunching exercise
Smoke barrier penetrations have always been the bane
of the building maintenance program because the Joint
Commission on Accreditation of Healthcare Organiza-
tions (JCAHO) has never offered much guidance about
how a facility should track penetrations.
Remember, facilities that use a building maintenance
program need to maintain all the
items that they’ve included in the
program at a deficiency rate of no
more than 5%.
This goal is generally easy for items
such as extinguishers and exit signs
because it’s simply a matter of establishing an inventory
and then inspecting for deficiencies, says safety consult-
ant Steven MacArthur.
However, meeting the 95% compliance rate can be a
challenge when in comes to barrier penetrations.
For example, does the 95% rate come from the total num-
ber of penetrations that a facility notes? Or is it based on
the amount of penetrations per the average barrier area?
‘Pretty darn close’ compliance
The JCAHO’s George Mills, FASHE, CHFM, CEM,
doesn’t see barrier penetration measurement as a black-
or-white issue.
Suppose that a facility has 200 smoke barriers and the
maintenance director inspects 10 barriers each week. One
week, he notes four penetrations among the 10 barriers.
That works out to a 60% rate, which is far out of compli-
ance with building program requirements, Mills says.
“On the other hand, if you hit 10 of them and one of
them had a hole in it, I’d say we’re pretty darn close” to
compliance even though the rate is still only 90%, he says.
95% rate isn’talways literal
It isn’t the JCAHO’s intent for facilities to calculate the
total surface area of their smoke barriers and then allow
5% noncompliance, Mills says.
Common sense would dictate that if a campus has
100,000 sq. ft. of smoke barriers, then the JCAHO
would never be happy if 5,000 sq. ft. of that total
were deficient, even if it still met the 95% rate, he
says.
In other words, there’s a practical approach to barrier
penetration maintenance that goes
beyond the numbers.
“You know when your program is
effective,” Mills says. “Don’t go into
the mathematics of it and do crazy
calculations. [Focus on] what’s rea-
sonable with your barriers.”
Ways to embrace barrier monitoring
Consultant Frederick Bradley, PE, has come up with
useful ideas to help facilities better track barrier main-
tenance and penetrations:
§Develop accurate drawings that clearly show the
locations of barriers. If necessary, talk to long-time
engineering employees about this issue because
they may have knowledge that others don’t about
the barriers.
§Each year, take a copy of these drawings and
check the facility for barrier penetrations.
§Provide the drawings to contractors so they know
which walls are barriers.
§Put into any construction or renovation contract
that workers must repair and properly seal any
penetrations they create.
§Make contractors submit penetration sealant data
ahead of time so the facility is familiar with the
product that will be used.
§Inspect any penetration sealing before the facility
issues final contractor payments.
“The key is the first two steps. Find out where your
smoke barriers are” and inspect them, Bradley says.
“It’s important that you establish a program for check-
ing [barriers for penetrations].”
n
There’s a practical approach to
barrier penetration maintenance
that goes beyond the numbers.

The JCAHO’Sbuilding maintenance program:
Scoring and compliance tips
8
Inventory holes patched by colored firestopping
Your building may use various firestopping materials de-
pending on the area in which crews applied them and
what vendors supplied the products.
During inspections of healthcare sites that he’s perform-
ed, safety consultant Steven MacArthur has noted
firestopping that’s white, black, red, and green in the
same facility.
Take advantage of the different looks of firestopping by
cataloging them, MacArthur says.
Digital photos make it easy
Shoot digital photos of the firestopping materials used
and note with which projects the pictures correspond.
Attach specification sheets to the photos and identify the
vendors from which you bought the firestopping prod-
ucts. Arrange the information in a binder or a chart for
easy presentation.
Not only will it help your facilities and safety employ-
ees, but surveyors and inspectors will find it an easier
way to check on your sealed penetrations, MacArthur
says.
Explain your efforts first
Often, surveyors will move on to other issues if the first
sealed penetration they check meets with their satisfac-
tion. Describe your process for tracking penetration to
surveyors before they pop a ceiling tile.
“You want to make it as easy as you can for [surveyors]
to stop looking,” he says.
You might also be able to exploit firestopping colors by
using certain hues for different departmental work. For
example, when information services runs computer and
data lines through fire walls, insist that it identify its
penetrations by using blue firestopping, MacArthur
says.
n
This special report is published by HCPro, Inc., 200 Hoods Lane, Marblehead, MA 01945. • $20 • Copyright 2006 HCPro, Inc.
All rights reserved. Printed in the USA. Except where specifically encouraged, no part of this publication may be reproduced,
in any formor by any means, without prior written consent of HCPro, Inc., or the Copyright Clearance Center at 978/750-8400. Please
notify us immediately if you have received an unauthorized copy. • For editorial comments or questions, call 781/639-1872
or fax 781/639-2982. For renewal or subscription information, call customer service at 800/650-6787, fax 800/639-8511, or e-mail:
customerservice@hcpro.com •Opinions expressed are not necessarily those of the editors. Mention of products and services does
not constitute endorsement. Advice given is general, and readers should consult professional counsel for specific legal, ethical,
or clinical questions. HCPro, Inc., is not affiliated in any way with the Joint Commission on Accreditation of Healthcare
Organizations, which owns the trademark.
01/06 SR206