DION 9102 SERIES 904 DION9102SERIES
User Manual: 9102
Open the PDF directly: View PDF .
Page Count: 7
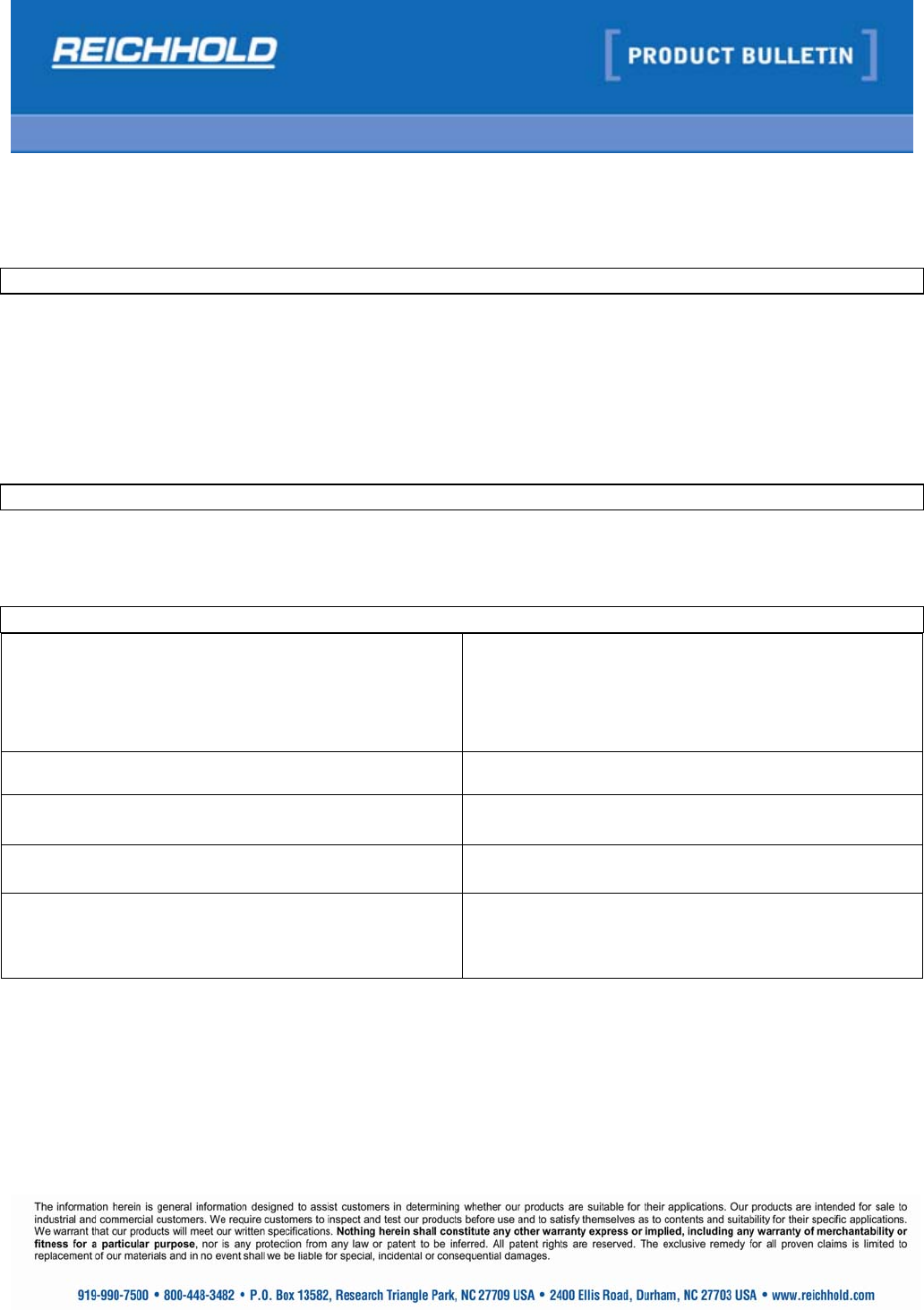
Ma
y
2007
DION
®
9102 SERIES
Bisphenol-Epoxy Vinyl Ester Resins
DESCRIPTION
The DION® 9102 series are special versions of the DION 9100 series of bisphenol-epoxy vinyl ester resin. They
provide a reduced viscosity and improved curing at low promoter levels for enhanced performance in filament
winding operations, while maintaining the mechanical properties and corrosion-resistance of the DION 9100
series.
DION 9102-00 is unique, because it is Certified to NSF/ANSI 61 for use in domestic and commercial potable
water applications in both piping and tanks.
APPLICATION
• Can be used in hand lay-up, spray-up and filament winding applications. Adapts to most other methods of
fabrication with no additional modifications.
FEATURES BENEFITS
• Premium epoxy vinyl ester polymer
• DION® 9102-00 version is Certified by NSF
International to NSF/ANSI Standard 61, Drinking
Water System Components
• Stabilized resin system
• Very good high-temperature stability
• Resistance to a wide variety of corrosive
environments
• Tough, crack and stress-fatigue resistant laminates
• Low Viscosity • Can be used in potable (drinking) water
applications
• Manufactured using statistical process control in
ISO-9002 certified plants
• Extended shelf life
• Improved glass fiber wet-out
● Compositional components listed under FDA
177.2420, Title 21
• Consistent batch-to-batch performance
● Extendible gel time to several hours at ambient
temperature without affecting the cure
• Excellent for use in vacuum infusion and Cured-In-
Place Pipe (CIPP) applications that require
extended working time at ambient temperatures
(Lateral Lining & Point Repair)
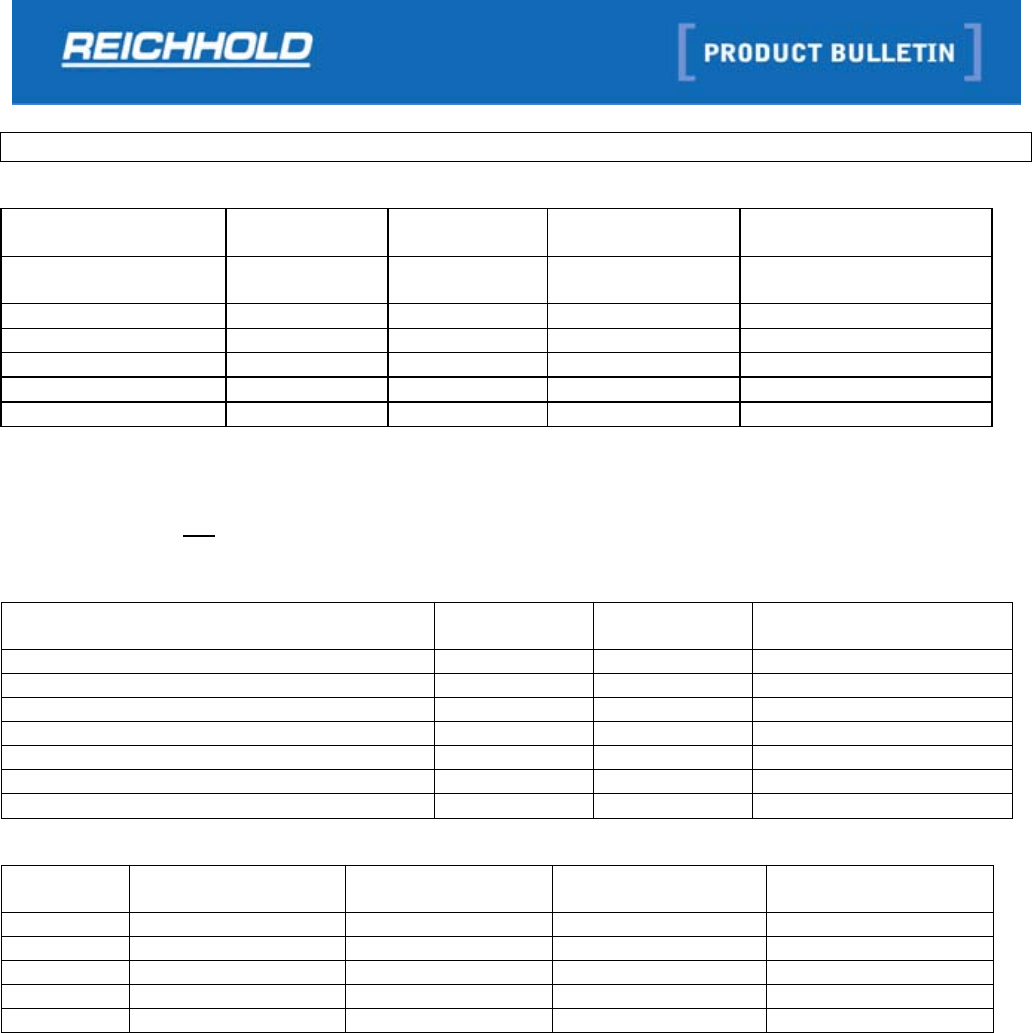
DION® SERIES
Page 2
TYPICAL PROPERTIES
PHYSICAL DATA IN LIQUID FORM AT 77°F
Version Viscosity,
CPS
Gel Time,
minutes*
Specific Gravity Shelf Life, Min.
DION 9102-00**
NSF/ANSI 61 Certified
230 unpromoted 1.04 6 months
DION 9102-05 190 unpromoted 1.05 6 months
DION 9102-10 230 unpromoted 1.05 3 months
DION 9102-20 230 unpromoted 1.05 6 months
DION 9102-30 700 unpromoted --- 3 months
DION 9102-40 180 unpromoted 1.05 6 months
Seta Closed Cup Flash Point of all DION 9102 resins is 31.6°C (89°F)
* See Page 3 for specific initiator and promotion addition tables for NSF/ANSI 61 applications. See Page 4 for initiator and promoter
addition tables for all other applications.
** DION 9102-00 is the only version in this series Certified by NSF International to the NSF/ANSI 61 Standard for use in potable
water. It can also be used for non-NSF applications.
TYPICAL MECHANICAL PROPERTIES
Properties at 77°F
Unit 1/8” Clear
Casting
Test Method
Barcol Hardness, Model 934-1 - 35 ASTM D 2583
Flexural Strength psi 23000 ASTM D 790
Flexural Modulus, x106 psi 0.50 ASTM D 790
Tensile Strength psi 11600 ASTM D 638
Tensile Modulus, x106 psi 0.46 ASTM D 638
Tensile Elongation (at break) % 5.2 ASTM D 638
Heat Deflection Temperature (HDT) °F 220 ASTM D 648
TYPICAL LAMINATE PROPERTIES AT ELEVATED TEMPERATURES
Temp
(°F)
Tensile Strength
(psi)
Tensile Modulus
(x106, psi)
Flexural Strength
(psi)
Flexural Modulus
(x106, psi)
77 19200 1.70 32800 1.17
150 22100 1.70 33100 1.12
200 22700 1.39 25700 0.83
250 14600 0.80 3000 0.37
300 9900 0.80
Laminate Construction: V-M-M-WR-M-WR-M-M V = 1 ply of 10 mil C-glass veil
Glass Content: 42% M = 1 ply of 1.5 oz/ft.2 of chopped strand mat
Thickness: 0.250 inches WR = 1 ply of 24 oz/yd.2 of woven roving
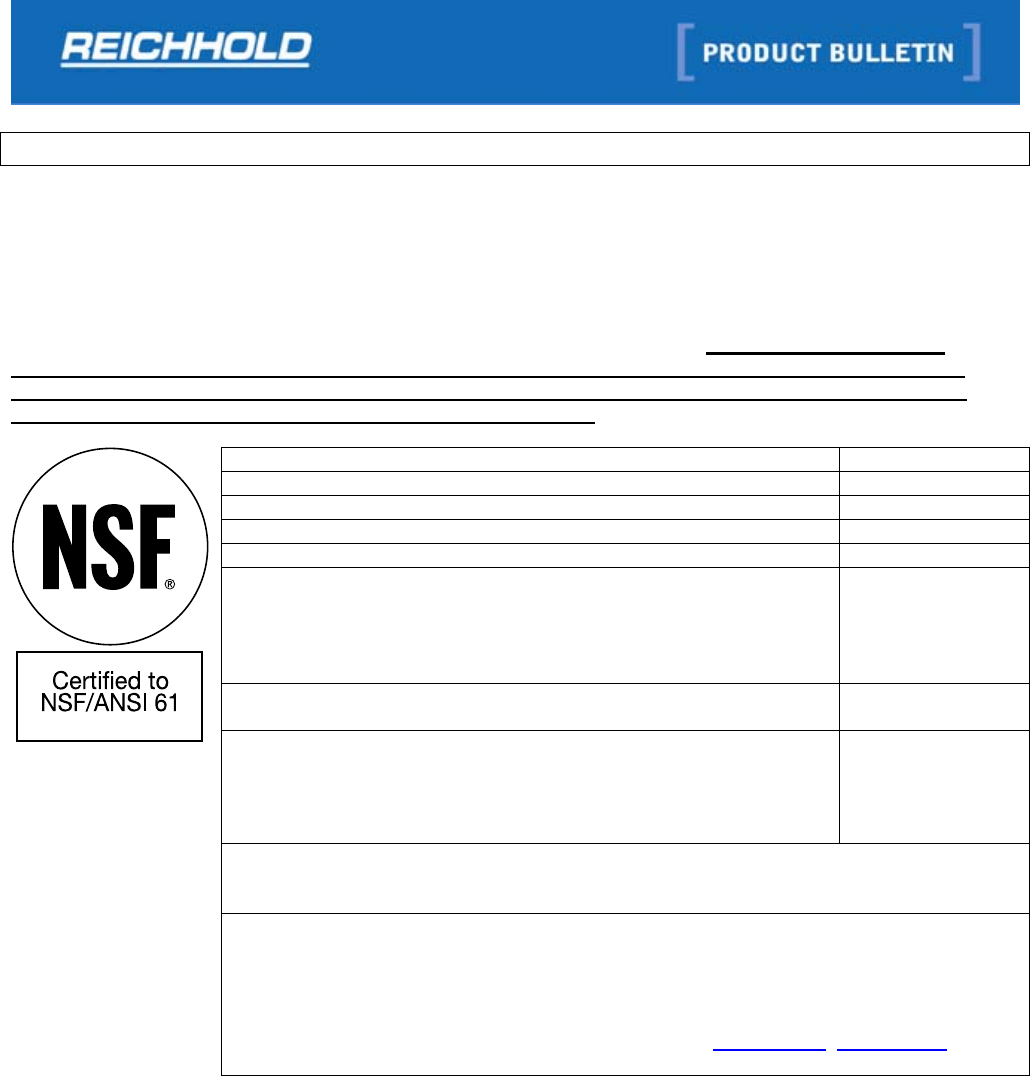
DION® SERIES
Page 3
DION9102-00 COATING SYSTEM CERTIFIED BY NSF INTERNATIONAL
REQUIREMENTS FOR USE OF DION 9102-00 IN A COATING SYSTEM CERTIFIED BY NSF TO ANSI/NSF
STANDARD 61, DRINKING WATER SYSTEM COMPONENTS.
DION 9102-00 is recommended as a coating system in potable water tanks (>=150 gal) and piping (>=1/2”
diameter) at ambient temperature
In potable water applications, the following are required of the coating system. Additional, non-specified
chemical components or designated components that are utilized outside the percentage limitations
specified below, constitutes non-compliance with the NSF Certified DION ® 9102-00 Coating System.
Strict adherence to components and percentages is required.
COMPONENT Percentage
DION 9102-00 97.9% - 98.85%
MEKP by Norac (Norox MEKP-925) or Witco (HiPoint 90) 1% - 1.5%
Cobalt Napthenate 6% by OMG Americas, Inc. 0.1% - 0.4%
Dimethylaniline (DMA) by Aceto Corporation or Aarti Industries Ltd. 0.05% - 0.2%
50/50 Blend of Styrene & Paraffin Wax (for topcoating of air
inhibited regions only).
Paraffin Wax by Amoco Oil Company Eskar Wax R-35
Styrene by Amoco, Arco, Chevron, GE, Shell Chemical, Sterling
Chemicals, Lyondell Chemical, Huntsman Chemical Corp.
0.0 -1.0%
Amorphous Fumed Silica (for topcoating) by Cabot Corp.(Cab-O-
Sil TS-720) or Nippon Aerosil Co., Ltd. (Aerosil R-972) 0.0 -2.0%
Owens Corning Fiberglass C-veil
1 Ply (Veil
Thickness –
Nominal 10 mils)
Cure time shall be 2 – 100 hours at ambient temperature with a postcure of 4 hours at
160oF, followed by 2 hours at 180oF. Equipment must be washed with a non-ionic
detergent solution after postcure and rinsed with potable water.
The DION 9102-00 Coating System is Certified by NSF International to the requirements
of NSF/ANSI Standard 61: Drinking Water System Components-Health Effects. This
certification is non-transferable. Certain jurisdictions may require certain end products to
be coated with an NSF Certified coating system, while other jurisdictions may require
certain end products to be Certified to NSF 61. If you would like information regarding
NSF Certification, please contact NSF International at info@nsf.org; www.nsf.org; or at
1-800-NSF-MARK.
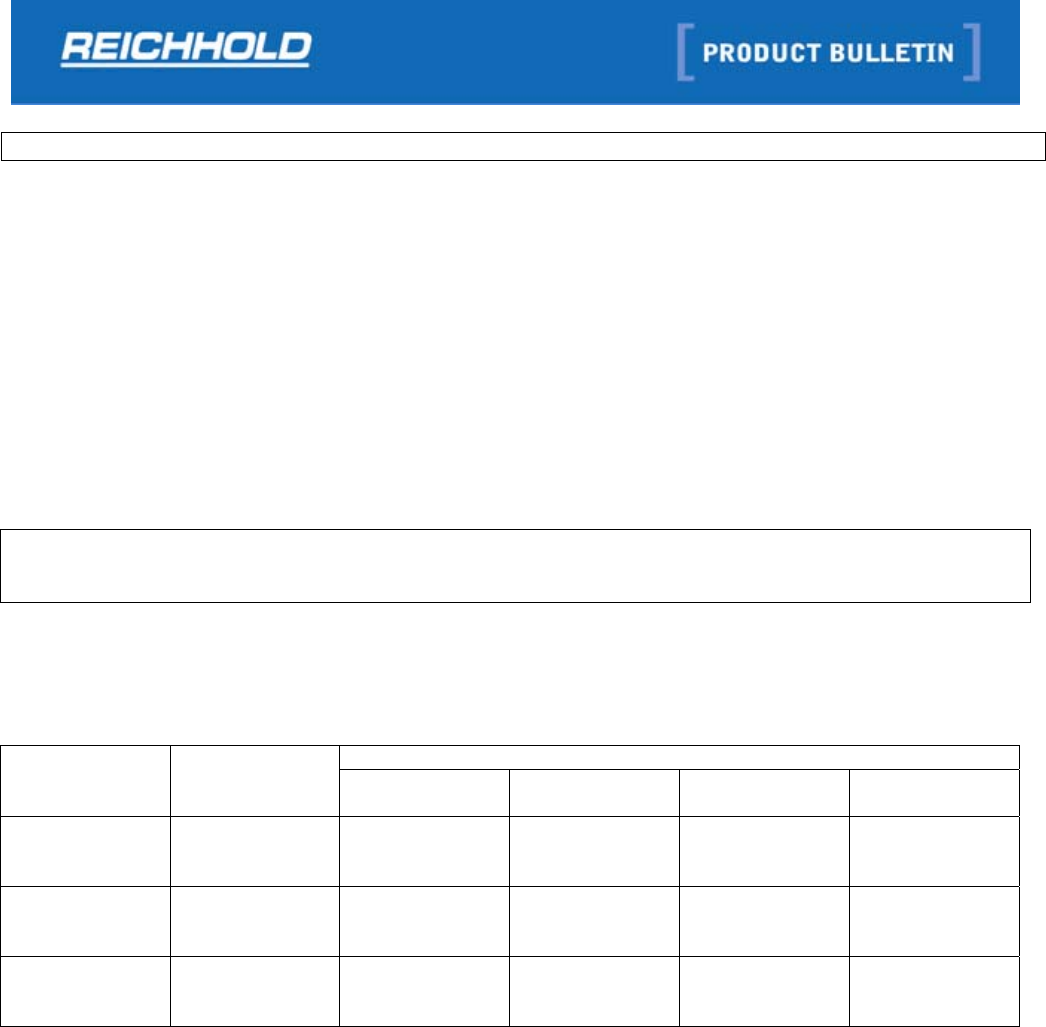
DION® SERIES
Page 4
DION 9102 CURING
The DION 9102 products are unpromoted vinyl ester resins for use with cobalt naphthenate, or octoate, and an
aniline accelerator which responds well to MEKP catalyst systems. Other catalysts work as well, but should be
thoroughly evaluated prior to use. These resins however, are sensitive to low temperatures and care must be
taken to avoid less than minimum stated quantities of MEKP type catalysts.
At temperatures below 60°F, it may be necessary to add dimethylaniline in incremental amounts of 0.05 phr to
increase gel and cure profiles. For applications at high ambient temperatures (80-90°F) the MEKP catalyst levels
must still be maintained above the minimum recommendation to achieve optimum cure. In order to lengthen gel
times at these temperatures, it is suggested that the MEKP catalyst be maintained at 1.25 phr and the gel time be
adjusted with additions of tert-butyl catechol solution (TBC-10) or low levels of 2,4 pentanedione (PDO).
The DION 9102 products can also be effectively cured using a benzyl peroxide (BPO) / dimethylaniline (DMA)
system. Note: BPO/DMA systems are not authorized for use in NSF/ANSI 61 situations.
GUIDELINES FOR DION 9102 SERIES RESINS ● INITIATOR AND PROMOTER ADDITIONS
(NOT TO BE USED IN NSF/ANSI 61 APPLICATIONS – REFER TO PAGE 3 FOR REQUIREMENTS IN THESE
APPLICATIONS)
Add cobalt naphthenate and dimethyl aniline in quantities shown to achieve working life at the temperature
indicated. Resin gel time will drift slightly if allowed to stand overnight. Readjust with additional DMA.
Guidelines for catalyst and promoter additions at various ambient temperatures:
Ambient Gel Time, minutes
Temperature
(°F)
Additive
(phr)1 10 20 30 60
55-65
6% cobalt2
DMA
HiPoint 903
-
-
-
0.4
0.10
1.5
0.3
0.05
1.25
0.2
0.05
1.25
70-80
6% cobalt
DMA
HiPoint 90
0.4
0.10
1.5
0.3
0.05
1.25
0.2
0.05
1.25
0.1
0.05
1.00
85-95
6% cobalt
DMA
HiPoint 90
0.3
0.05
1.25
0.2
0.05
1.25
0.1
0.05
1.00
0.1
0.00
1.00
1 phr = Parts per hundred resin.
2 Caution: Excessive cobalt can inhibit cure and degrade corrosion resistance. Do not use more than 0.5% of
cobalt 6% or 0.25% of cobalt 12%. If using cobalt octoate (12%), use half of the amount indicated in the chart
for cobalt 6%.
3 Witco HiPoint™90 or equivalent. HiPoint 90, Lucidol™ DHD-9 and Trigonox™ 239A have proven to be
particularly well suited for curing DION vinyl ester resins. Trigonox 239A has been shown to reduce or eliminate
foaming upon initiator addition, but may not adapt to the above cure grids. Other brands of MEKP have also
been used successfully. A thorough evaluation of initiator characteristics is suggested prior to fabrication to
satisfy user’s expectations.
WARNING: CARE MUST BE TAKEN TO AVOID DIRECT MIXING OF ANY ORGANIC PEROXIDE WITH
METAL SOAPS, AMINE OR ANY OTHER POLYMERIZATION ACCELERATOR OR
PROMOTER, AS VIOLENT DECOMPOSITION WILL RESULT!
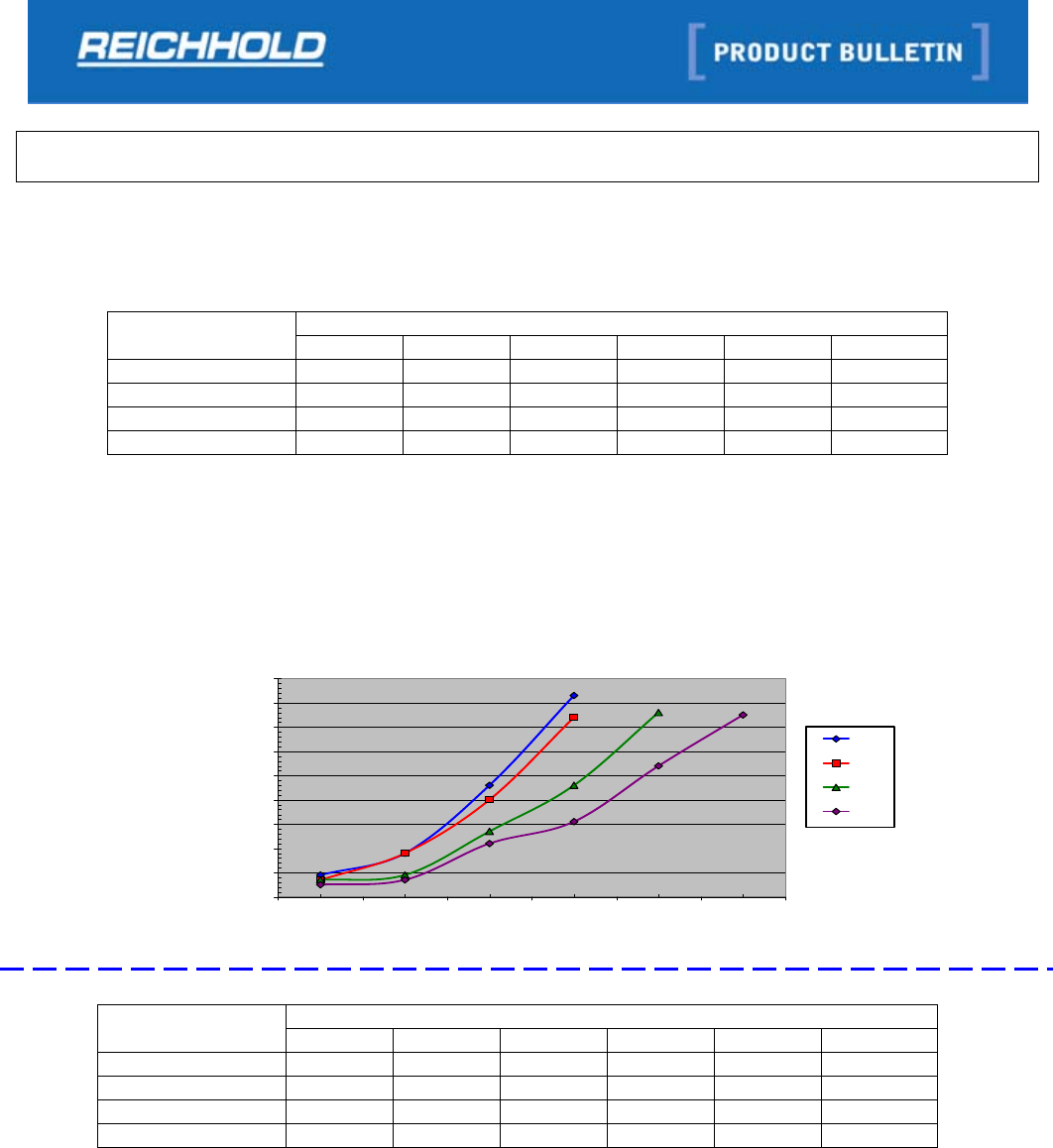
DION® SERIES
Page 5
EXTENDED AMBIENT CURING TIME WITH DION 9102 USING 2,4 - PENTANEDIONE (PDO)
(NOT FOR NSF/ANSI APPLICATIONS)
Due of the unique manner in which vinyl ester resins reacts when small amounts of 2,4-Pentanedione (PDO) are
added, it is possible to extend the ambient temperature gel time of these resins without greatly affecting their peak
exotherm and gel-to-peak profile. The following charts and graphs show ambient gel time data for various levels
of 2,4-PDO at different temperatures.
1 phr = Parts per hundred resin
2 Gel Times are listed in the format Hours:Minutes
3 Resin was promoted using 0.4% cobalt 6% (by weight) and 0.05% DMA (by weight). The initiator used for this
chart was Norac MEKP-925H at 1.25% (by weight).
DION® 9102 Extended Ambient Temperature Gel
Time with Norac MEKP-925H
0
50
100
150
200
250
300
350
400
450
0 0.05 0.1 0.15 0.2 0.225
2,4-Pentanedione Addition, %
Gel Time, Minutes
65°F
70°F
75°F
80°F
Ambient 2,4- PDO Addition, phr1
Temperature (°F) 0.0 0.05 0.1 0.15 0.2 0.225
65 00:452,3 00:90 3:50 6:55 -- --
70 00:35 00:90 3:20 6:10 -- --
75 00:35 00:45 2:15 3:50 6:20 --
80 00:25 00:35 1:50 2:35 4:30 6:15
Ambient 2,4- PDO Addition, phr1
Temperature (°F) 0.0 0.2 0.4 0.5 0.7 0.9
65 1:102,3 4:00 7:30 -- -- --
70 1:05 2:55 5:40 6:35 -- --
75 00:50 2:10 4:10 4:40 6:10 --
80 00:40 1:30 2:45 3:25 4:35 5:354
1 phr = Parts per hundred resin
2 Gel Times are listed in the format Hours:Minutes
3 Resin was promoted using 0.4% cobalt 6% (by weight) and 0.05% DMA (by weight). The initiator used for this
chart was Norac 46727 CHP at 1.25% (by weight).
4 Other gel tests were run using higher levels of 2,4-PDO. Results indicate that gel time will not lengthen
significantly beyond the 0.9% level. The 2,4-PDO may actually begin to act as a promoter or plasticizer.
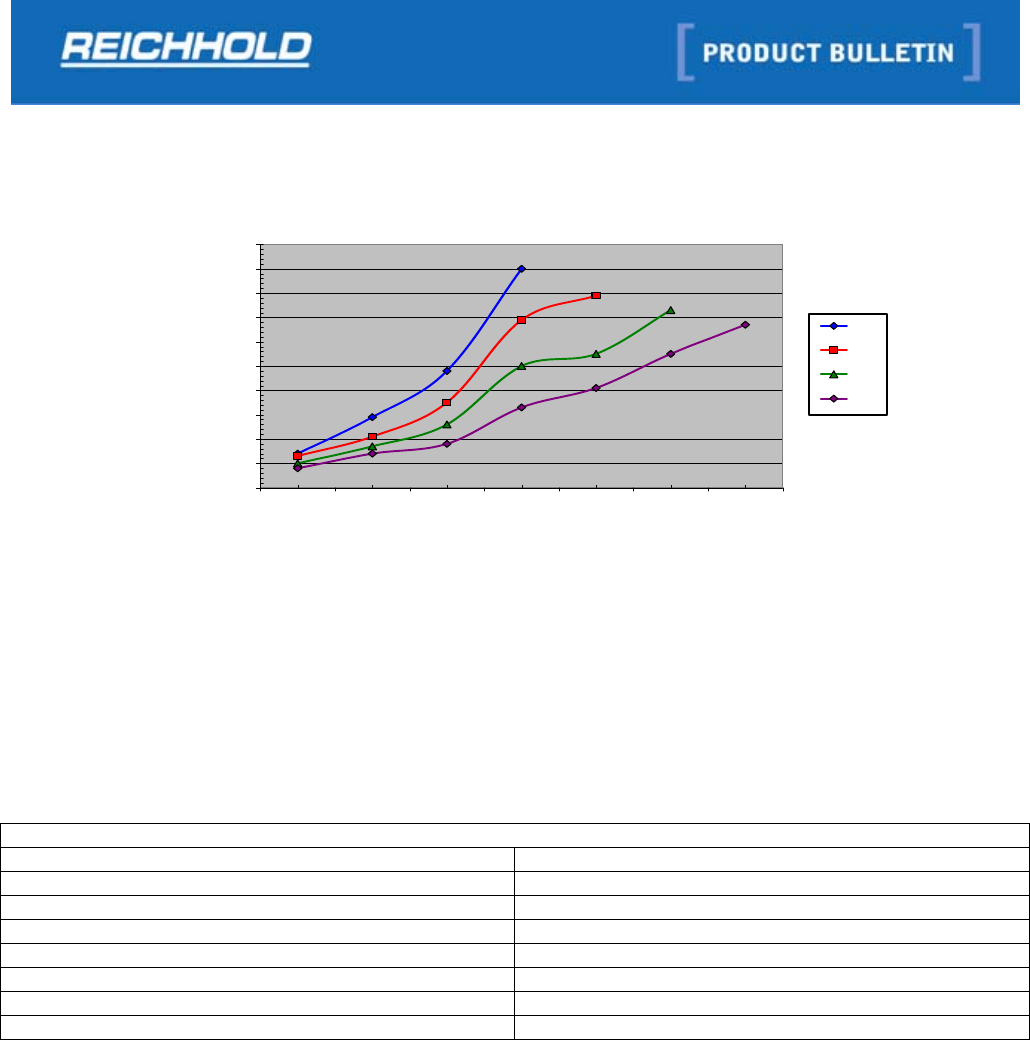
DION® SERIES
Page 6
DION® 9102 Extended Ambient Temperature Gel
Time with Norac 46727 CHP
0
50
100
150
200
250
300
350
400
450
500
0 0.1 0.2 0.4 0.5 0.7 0.9
2,4-Pentanedione Addition, %
Gel Time, Minutes
65°F
70°F
75°F
80°F
DION 9102 PARAFFINATED TOPCOATS
Even fully cured resin of a non-mold sided surface can demonstrate some tackiness due to air inhibition. Surface
cure may be improved by incorporating a paraffin wax into the resin to be used in the final ply. Alternatively, a
wax modified resin can be added as a protective topcoat once the laminate has hardened. These topcoated
surfaces will negatively influence secondary bonding. Grinding and additional surface preparation will
become necessary to enhance the success of the bond.
SUGGESTED TOPCOAT FORMULATION (Not for NSF Applications)
COMPONENT PARTS
DION 9102-00 100.0
10% paraffin wax solution in styrene 5.0
DMA (dimethylaniline) 0.2
6% cobalt naphthenate 0.4
Tween® 20 or 80 0.3
Fumed silica thixotrope* 1.5
HiPoint 90 or DHD-9 initiator 1.3
Approximate gel time, minutes; 15
* Use in sodium hypochlorite environments will result in decreased chemical resistance. We suggest this be omitted from the
formulation in those situations. Hydrophobic grades of fumed silica are suggested for vinyl ester resins.
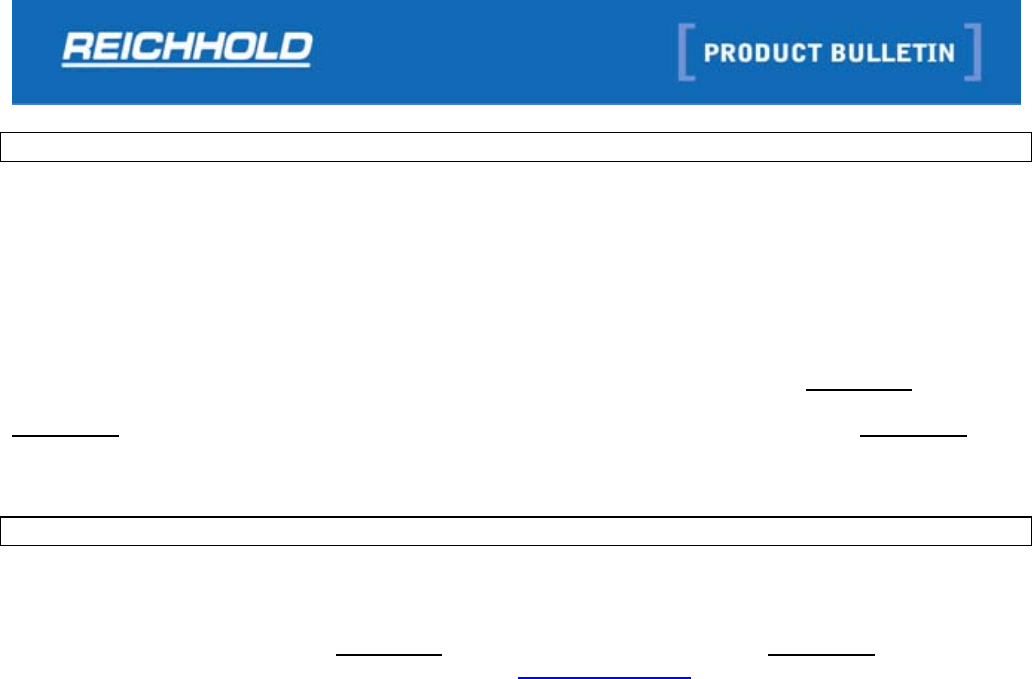
DION® SERIES
Page 7
STORAGE
These DION 9102 products are available in non-returnable 55-gallon metal drums (400 lb.net) or 40,000-44,000-
lb. tank trucks.
To ensure maximum stability and maintain optimum resin properties, resins should be stored in closed containers
at temperatures below 75°F (25°C) and away from heat sources and sunlight. All storage areas and containers
should conform to local fire and building codes. Drum stock should be stored away from all sources of flame or
combustion. Inventory levels should be kept to a reasonable minimum with first-in, first-out stock rotation.
Additional information on handling and storing unsaturated polyester resins is available in REICHHOLD’s
application bulletin “Bulk Storage and Handling of Unsaturated Polyester Resins". For information on other
REICHHOLD resin products and systems, contact your local Sales Representative or Authorized REICHHOLD
Distributor.
SAFETY
READ AND UNDERSTAND THE MATERIAL SAFETY DATA SHEET BEFORE WORKING WITH THIS PRODUCT
Obtain a copy of the Material Safety Data Sheet (MSDS) on this product prior to use. Material Safety Data
Sheets are available from your local REICHHOLD Sales Representative or Authorized REICHHOLD Distributor. In
addition, Material Safety Data Sheets can be obtained at www.reichhold.com .Such information should be
requested from suppliers of all other products and components and understood prior to working with their
materials.