A_37397C A 37397C
User Manual: A_37397C
Open the PDF directly: View PDF .
Page Count: 652 [warning: Documents this large are best viewed by clicking the View PDF Link!]
- Title Page
- Table of Contents
- Chapter 1 General Information
- 1-1 SCOPE OF MANUAL 1-3
- 1-2 INTRODUCTION 1-3
- 1-3 IDENTIFICATION NUMBER 1-3
- 1-4 ONLINE MANUALS 1-3
- 1-5 SYSTEM DESCRIPTION 1-3
- 1-6 MILLIMETER WAVE MEASUREMENTS 1-5
- 1-7 PRECISION COMPONENT KITS 1-5
- Model 3650 SMA/3.5 mm Calibration Kit 1-5
- Model 3651 GPCŒ7 Calibration Kit 1-6
- Model 3652 K Connector Calibration Kit 1-7
- Model 3653 Type N Calibration Kit 1-8
- Model 3654B V Connector® Calibration Kit 1-9
- Model 3656 W1 Connector Calibration Kit 1-10
- Model 3666 3.5 mm Verification Kit 1-11
- Model 3667 GPCŒ7 Verification Kit 1-12
- Model 3668 K Connector® Verification Kit 1-13
- Model 3669/3669B V Connector® Verification Kits 1-14
- 1-8 OPTIONS 1-15
- 1-9 PERFORMANCE SPECIFICATIONS 1-15
- 1-10 PREVENTIVE MAINTENANCE 1-15
- Chapter 2 Installation
- Chapter 3 Network Analyzers, A Primer
- Chapter 4 Front Panel Operation
- 4-1 INTRODUCTION 4-3
- 4-2 KEY-GROUPS 4-3
- 4-3 CALIBRATION KEY-GROUP 4-11
- 4-4 SAVE/RECALL MENU KEY 4-21
- 4-5 MEASUREMENT KEY-GROUP 4-22
- 4-6 CHANNELS KEY-GROUP 4-25
- 4-7 DISPLAY KEY-GROUP 4-26
- 4-8 ENHANCEMENT KEY-GROUP 4-30
- 4-9 HARD COPY KEY-GROUP 4-32
- 4-10 SYSTEM STATE KEY-GROUP 4-34
- 4-11 MARKERS/LIMITS KEY-GROUP 4-37
- 4-12 DISK STORAGE INTERFACE 4-41
- 4-13 COMMAND LINE 4-43
- Chapter 5 Error and Status Messages
- Chapter 6 Data Displays
- Chapter 7 Measurement Calibration
- Chapter 8 Measurements
- Chapter 9 Time Domain
- Chapter 10 AutoCal
- Chapter 11 Operational Checkout Procedures: 371XXC
- Chapter 12 Operational Checkout Procedures: 372XXC, 373XXC
- Chapter 13 Calibration Kits
- Chapter 14 Millimeter Wave System
- 14-1 INTRODUCTION 14-3
- 14-2 DESCRIPTION 14-3
- 14-3 PERFORMANCE SPECIFICATIONS 14-4
- 14-4 INSTALLATION 14-6
- 14-5 CONTROLS AND CONNECTORS 14-11
- 14-6 CALIBRATION 14-13
- 14-7 OPERATION 14-14
- Entering/ Leaving Millimeter Wave Operation 14-14
- Changing Bands/Modules While in Millimeter Wave 14-18
- Allowable Millimeter Wave Module Configurations, Measurements and Calibrations 14-18
- Effect of Default Program 14-19
- Redefinition of Band Frequency Ranges 14-20
- Use of Normal Multiple Source Mode 14-21
- Stored Setups and Calibrations 14-21
- External Source and Power Levels 14-22
- 14-8 MEASUREMENT PROCEDURE 14-23
- 14-9 REMOTE OPERATION 14-24
- 14-10 OPERATIONAL CHECKOUTŠ GENERAL 14-25
- 14-11 OPERATION CHECKOUTŠIF POWER LEVEL TEST 14-26
- 14-12 OPERATIONAL CHECKOUTŠ TRANSMISSION HIGH LEVEL NOISE TEST 14-28
- 14-13 OPERATIONAL CHECKOUTŠ REFLECTION HIGH LEVEL NOISE TEST 14-30
- Chapter 15 ME7808A Broadband Measurement System
- Appendix A Front Panel Menus
- Menu ACAL, AutoCal Menu A-12
- Menu ACAL_SETUP, AutoCal Setup Menu A-13
- Menu ACAL_S11 1 PORT, AutoCal S11 1 Port Menu A-14
- Menu ACAL_S22 1 PORT, AutoCal S22 1 Port Menu A-15
- Menu ACAL_FULL, AutoCal Full Menu A-16
- Menu ACAL_AR, AutoCal Adapter Removal Menu A-17
- Menu ACAL_UTILS, AutoCal Utilities Menu A-18
- Menu ACAL_CHAR, AutoCal Characterization Menu A-19
- Menu APPL, Applications Menu A-20
- Menu BB2, Broadband Select Menu1 A-21
- Menu BB3, Broadband Select Menu 2 A-22
- Menu BB4, Broadband Select Menu3 A-23
- Menu BW1 or CAL_BW1, Select Video Bandwidth A-24
- Menu C1, Select Calibration Data Points A-25
- Menu C2, Frequency Range of Calibration (Start/Stop) A-26
- Menu C2_CENTER, Frequency Range of Calibration (Center/Span) A-27
- Menu C2A, Insert Individual Frequencies A-28
- Menu C2C, Calibration RangeŠHarmonic Cal for Time Domain A-29
- Menu C2B, Single Point Calibration A-29
- Menu C2D, Fill Frequency Ranges A-30
- Menu C3, Confirm Calibration Parameters A-31
- Menu C3A, Confirm Calibration Parameters A-32
- Menu C3B, Confirm Calibration Parameters A-33
- Menu C3C, Confirm Calibration Parameters A-34
- Menu C3D, Confirm Calibration Parameters A-35
- Menu C3E, Confirm Calibration Parameters A-36
- Menu C3F, Confirm Calibration Parameters A-37
- Menu C3G, Confirm Calibration Parameters A-38
- Menu C3H, Confirm Calibration Parameters A-39
- Menu C3I, ConfirmCalibration Parameter 2 A-40
- Menu C3J, ConfirmCalibration Parameter 3 A-41
- Menu C4_P1/C4_P2, Select Connector Type A-42
- Menu C4A_P1/C4A_P2, Select Connector Type A-43
- Menu C4B, Select Open and Short Type A-44
- Menu C5, Select Calibration Type A-45
- Menu C5A, Select 1 Path 2 Port Calibration Type A-46
- Menu C5B, Select Transmission Freq Response Calibration Type A-46
- Menu C5C, Select Reflection Only Calibration Type A-47
- Menu C5D, Select Use of Isolation A-47
- Menu C6, Select Load Type A-48
- Menu C6A, Enter Broadband Load Impedance A-48
- Menu C6B, Enter Broadband Load Impedance A-48
- Menu C7-Series, Begin Calibration Sequence A-49
- Menu C8, Slide Load to Position X A-49
- Menu C9A, Connect Device 1, Line A-50
- Menu C9, Connect Throughline A-50
- Menu C9C, Connect Device 2, Line A-51
- Menu C9B, Connect Device 2, Line/Lowband A-51
- Menu C11, Begin Calibration A-52
- Menu C11A, Select Calibration Method A-53
- Menu C12_P1/C12_P2, Enter the Capacitance Coefficients for Open Devices A-54
- Menu C12A_P1/C12A_P2, Enter the Offset Length A-55
- Menu C13, Set Reflection Pairing Menu A-56
- Menu C13A, Set Reflection Pairing Menu A-57
- Menu C13B, Set Reflection Pairing Menu A-57
- Menu C14, Select Port X Offset Short Connecotr Type A-58
- Menu C14A, Select Port X Offset Short A-58
- Menu C15, Select Waveguide Kit to Use A-59
- Menu C15A, Enter Waveguide Parameters A-60
- Menu C15B, Enter Waveguide Parameters A-60
- Menu C15C, Select Waveguide Kit to Use A-61
- Menu C15D, Enter Waveguide Parameters A-62
- Menu C16A, Enter Microstrip Parameters A-63
- Menu C16, Select Microstrip Parameters A-63
- Menu C17, Enter Line Impedance A-64
- Menu C18, Change LRL/LRM Parameters A-64
- Menu C18A, Change LRL/LRM Parameters A-65
- Menu C18B, Change LRL/LRM ParametersŠTwo Band Calibration A-66
- Menu C19, Change LRL/LRM Parameters A-67
- Menu C20, Change Through Parameters A-68
- Menu C21A, Port X Offset Short 1 A-69
- Menu C21B, Port X Offset Short 2 A-70
- Menu C21C, Port X Offset Short 3 A-71
- Menu Cal_Completed A-72
- Menu Cal_Applied A-73
- Menu Cal_EM, Enhancement Menu for Calibration A-74
- Menu CAR1, Adapter Removal 1 A-75
- Menu CAR2, Adapter Removal 2 A-75
- Menu EXT_CAR, Adapter Removal Help Menu A-76
- Menu CAR3, Adapter Removal 3 A-77
- Menu CAR4, Adapter Removal 4 A-77
- Menu CM, Select Display Mode A-78
- Menu DE1, E/O Measurement A-79
- Menu EXT_DE1, E/O Measurement A-79
- Menu DE2, O/E Measurement A-80
- Menu EXT_DE2, O/E Measurement A-80
- Menu DE3, E/O Measurement A-81
- Menu DE3A, E/O Measurement A-81
- Menu DE4, De-embed Network A-82
- Menu DE4A, De-embed Network A-82
- Menu DE5, De-embed O/E S2P A-83
- Menu DE5A, De-embed O/E S2P A-83
- Menu DE6, Generate E/O S2P Characterization A-84
- Menu DE7, O/E Measurement A-85
- Menu DE7A, O/E Measurement A-85
- Menu DF1, Discrete Fill A-86
- Menu DF2, Insert Individual Frequencies A-87
- Menu DFLT, Default Program Selected A-88
- Menu DG1, Diagnostics 1 A-89
- Menu DG3, Diagnostics 3 A-90
- Menu DG2, Troubleshooting A-90
- Menu DSK_FD, Floppy Disk Utilities A-91
- Menu DSK_HD, Hard Disk Utilities A-92
- Menu DSK2, Select File to Read A-93
- Menu DSK3, Select File to Overwrite A-94
- Menu DSK6, Type of Files to Delete A-95
- Menu DSK7, Select File to Delete A-96
- Menu DSK8, Type of Files to Copy A-97
- Menu DSK9, Select File to Copy A-98
- Menu DSK10, Capture Tabular Data A-99
- Menu DSK11, Format Floppy Disk A-99
- Menu DSK12, Format Hard Disk A-99
- Menu EM, Enhancement Menu A-100
- Menu GC1, Swept Frequency Gain Compression A-101
- Menu EXT_GC1, Gain Compression Help Menu 1 A-102
- Menu GC2, Swept Power Gain Compression 1 A-103
- Menu EXT_GC2, Gain Compression Help Menu 2 A-104
- Menu GC3, Swept Power Gain Compression 2 A-105
- Menu EXT_GC3, Gain Compression Help Menu 3 A-106
- Menu GC4, Multiple Frequency Gain Compression 1 A-107
- Menu GC4_ABORT, Multiple Frequency Gain Compression 2 A-107
- Menu EXT_GC4, Gain Compression Help Menu 4 A-108
- Menu GC_DF2, Swept Power Frequencies A-109
- Menu EXT_GC_DF2, Gain Compression Help Menu A-110
- Menu GC_NORM, Normalize S21 A-110
- Menu GC_RCVR, Receiver Calibration A-111
- Menu GC_SU2, Swept Power Gain Compression 2 A-112
- Menu GC_SU8A, Calibrate for Linear Power A-113
- Menu GC_SU8A-ABORT, Abort Calibrate for Linear Power A-114
- Menu EXT_GC_SU8A, Gain Compression Help Menu A-115
- Menu GC_S21OPT, S21 Options A-116
- Menu GP5, Select Name A-117
- Menu GP7, Display GPIB Status A-118
- Menu GT1/CAL_GT1, Select Graph Type A-119
- Menu GT2/CAL_GT2, Select Graph Type A-120
- Menu L1, Set LimitsŠMagnitude and Phase A-121
- Menu L2, Set LimitsŠLinear Polar A-122
- Menu L3, Set LimitsŠLinear Polar/Smith Chart A-123
- Menu L4, Set LimitsŠLog Magnitude A-124
- Menu L5, Set LimitsŠPhase A-125
- Menu L6, Set LimitsŠLog Polar A-126
- Menu L7, Set LimitsŠGroup Delay A-127
- Menu L8, Set LimitsŠLinear Magnitude A-128
- Menu L9, Set LimitsŠLinear Magnitude and Phase A-129
- Menu L10, Set LimitsŠReal Values A-130
- Menu L11, Set LimitsŠImaginary Values A-131
- Menu L12, Set LimitsŠReal and Imaginary Values A-132
- Menu L13, Set LimitsŠSWR A-133
- Menu L14, Set LimitsŠPower Out A-134
- Menu LD1, Define Upper Limit Segment A-135
- Menu LD2, Define Lower Limit Segmen A-136
- Menu LF1, Set Limit FrequenciesŠLog Mag A-137
- Menu LF2, Set Limit FrequenciesŠPhase A-138
- Menu LF3, Set Limit FrequenciesŠGroup Delay A-139
- Menu LF4, Set Limit FrequenciesŠLinear Mag A-140
- Menu LF5, Set Limit FrequenciesŠSWR A-141
- Menu LF6, Set Limit FrequenciesŠReal A-142
- Menu LF7, Set Limit FrequenciesŠImaginary A-143
- Menu LF8, Set Limit FrequenciesŠPower Out A-144
- Menu LSX, Segmented Limits A-145
- Menu LTST, Test Limits A-146
- Menu M1, Set Markers A-147
- Menu M2, Select DREF Marker A-148
- Menu M3, Select Readout Marker A-149
- Menu M4, Readout Marker A-150
- Menu M5, Set DREF Marker Readout A-151
- Menu M6, Marker X All Displayed Channels A-152
- Menu M7, Search A-153
- Menu M8, Filter Parameters A-154
- Menu M8A, Filter Setup A-155
- Menu M9, Marker Readout Functions A-156
- Menu MMW1, Millimeter Wave Test Set Band A-157
- Menu MMW2, Millimeter Wave Test Set Modules A-158
- Menu MMW3, Millimeter Wave Test Set A-159
- Menu MMW4, mm Wave Band A-160
- Menu EXT_MMW4 A-161
- Menu MRG1, Merge Calibration Menu A-162
- Menu EXT_MRG1, Merge Calibration Menu A-162
- Menu MRG2, Merge Calibration Menu A-163
- Menu MRG3, Merge Calibration Menu A-163
- Menu NO1, Trace Memory Functions A-164
- Menu NO2, Select Trace Math A-165
- Menu NO3, Trace Memory Disk Functions A-165
- Menu OM1, Multiple Source Control Menu A-166
- Menu OM1A, Source Lock Polarity Menu A-167
- Menu OM2, Define Bands Menu A-168
- Menu OM3, Edit System Equations A-169
- Menu OPTNS, Select Options A-170
- Menu ORP1, Rear Panel Output Control A-171
- Menu ORP2, Select Output Mode A-172
- Menu OTS1, Test Set Configuration A-172
- Menu OTS2, Warning A-173
- Menu PC1, Select Polar Chart Mode A-174
- Menu PD1, Parameter Definition 1 A-175
- Menu PD2, Parameter Ratio A-176
- Menu PD3, Parameter Definition 2 A-177
- Menu PL1, Plot Options A-178
- Menu PL2, Select Plot Size A-179
- Menu PL3, Select Pen Colors A-180
- Menu PM1, Select Data Output Type A-181
- Menu PM2, Data Output Headers A-182
- Menu PM2A, Data Output Headers A-183
- Menu PM3, Tabular Printer Output Format A-184
- Menu PM3A, Graphical Printer Output Format A-185
- Menu PM4, Disk Output Operations A-186
- Menu PM4A, Disk File Options A-187
- Menu PM5, Printer Type, Options A-188
- Menu RCV1, Receiver Mode A-189
- Menu RCV1 _WARN, Standard Receiver Mode Warning A-189
- Menu RCV2, User Defined Receiver Mode Menu A-190
- Menu RCV2 _WARN, User Defined Receiver Mode Warning A-191
- Menu RCV3, Standard Receiver Mode Warning Menu A-192
- Menu RCV4, User Defined Receiver Mode Warning Menu A-193
- Menu RD1, Set Reference Delay A-194
- Menu RD2, Set Dielectric Constant A-195
- Menu SC, Source Configure A-196
- Menu SP, Select S Parameter A-197
- Menu SR1, Save/Recall Front Panel Information A-198
- Menu SR2, Recall or Save A-199
- Menu SR3, Save to Internal memory A-200
- Menu SS1 or CAL_SS1, Set Scaling 1 A-201
- Menu SS2 or CAL_SS2, Set Scaling 2 A-202
- Menu SS3Z/SS3Y or CAL_SS3Z/CALSS3Y, Set Scaling 3 A-203
- Menu SS4 or CAL_SS4, Set Scaling 4 A-204
- Menu SS5 or CAL_SS5, Set Scaling 5 A-205
- Menu SS6 or CAL_SS6, Set Scaling 6 A-206
- Menu SS7 or CAL_SS7, Set Scaling 7 A-207
- Menu SS8 or CAL_SS8, Set Scaling 8 A-208
- Menu SS9 or CAL_SS9, Set Scaling 9 A-209
- Menu SS10 or CAL_SS10, Set Scaling 10 A-210
- Menu SS11 or CAL_SS11, Set Scaling 11 A-211
- Menu SS12 or CAL_SS12, Set Scaling 12 A-212
- Menu SS13 or CAL_SS13, Set Scaling 13 A-213
- Menu SS14, Set Scaling 14 A-214
- Menu SU1, Sweep Setup 1 A-215
- Menu SU1_CENTER, Sweep Setup 1 A-216
- Menu SU2 or CAL_SU2, Sweep Setup 2 A-217
- Menu SU2A or CAL_SU2A, Sweep Setup 2A A-218
- Menu SU3, Single-Point Measurement Setup A-219
- Menu SU3A, Swept-Power Measurement Setup A-220
- Menu SU4, Select Function for Hold Button A-221
- Menu SU5, Frequency Marker Sweep A-222
- Menu SU6, Frequency Marker C.W. A-223
- Menu SU8 or CAL_SU8, Calibrate For Flat Test Port Power A-224
- Menu EXT_SU8 Flat Power Calibration Instructions A-225
- Menu SU9, Number of Data Points A-226
- Menu SU9A, Number of Data Points 2 A-227
- Menu TD1, Domain (Frequency/Display) A-228
- Menu TD2_LP_TIME, Lowpass Time Domain Setup A-229
- Menu TD2_LP_DIST, Lowpass Distance Display Setup A-230
- Menu TD2_BP_TIME, Bandpass Time Domain Setup A-231
- Menu TD2_BP_DIST, Bandpass Distance Display Setup A-232
- Menu TD3_BP, Bandpass Time Domain Setup A-233
- Menu TD3_LP, Lowpass Time Domain Setup A-233
- Menu TD4_TIME & TD4_DIST, Gate (Distance/Time) A-234
- Menu TD5_WINDOW, Shape A-235
- Menu TD5_GATE, Shape A-235
- Menu TD6, Set D.C. Term for Low Pass Processing A-236
- Menu TD7_TIME, Time Marker Sweep. A-237
- Menu TD7_DIST, Distance Marker Range A-238
- Menu TRIG, Triggers Measurement A-239
- Menu U1, Utility Menu A-240
- Menu U2, Display Instrument State A-241
- Menu U3, Calibration Component Utilities A-243
- Menu EXT_U3, SSLT and SSST Waveguide Parameters A-243
- Menu U4, Display Installed Calibration Components Information 1 A-244
- Menu EXT_U4, SOLT Calibration Kit Information A-245
- Menu U4A, Display Installed Calibration Components Information 2 A-246
- Menu U4B, Display Installed Calibration Components Information 3 A-247
- Menu EXT_U4B, SSLT and SSST Calibration Kit Information A-248
- Menu U5, Color Configuration A-249
- Menu U5, Color Configuration A-250
- Menu U6, Set Date/Time A-251
- Appendix B Rear Panel Connectors
- 372XXC, 373XXC Rear Panel B-4
- 371XXC Rear Panel B-4
- Pinout Diagram, GPIB and Dedicated GPIB Connectors B-6
- Pinout Diagram, Printer Connector (1 of 2) B-7
- Pinout Diagram, Printer Connector (2 of 2) B-8
- Pinout Diagram, External I/O Connector (1 of 2) B-9
- Pinout Diagram, External I/O Connector (2 of 2) B-10
- Pinout Diagram, VGA IN/OUT Connector B-11
- Pinout Diagram, Serial Port Connector B-12
- Pinout Diagram, Transfer Switch B-13
- Pinout Diagram, Port 1 Source and Port 2 Test Connectors B-14
- Pinout Diagram, Test Set Control Out Connector (Option 12) B-15
- Appendix C Performance Specifications
- Chapter 1 General Information
- Subject Index
- !
- A
- B
- C
- Cable Length Restrictions 2-5
- Cables 15-4
- CAD System 8-28
- Calibrating for a Measurement 7-9
- Calibration
- Calibration Key-Group Description 4-11 to 4-20
- Calibration Keys 4-4,4-11 to 4-20
- Calibration Kits
- Calibration Sequence 4-11
- Ch 1 Key 4-8
- Ch 2 Key 4-8
- Ch 3 Key 4-8
- Ch 4 Key 4-8
- Ch1 - Ch4 Keys 4-25
- Channel Menu Key 4-8,4-25
- Channels Key-Group 4-25
- Channels Keys 4-8
- Cleaning Connectors 13-12
- Clear/Ret Loc Key 4-9
- Connector Pin Depth 13-10
- Connector Pin Depth Tolerance 13-11
- Connectors, Cleaning 13-12
- Console and Table Setup 15-5
- Copying Data Files 4-42
- D
- Data Display
- Active Channel Selection 6-13
- Analog Instrument Status 6-12
- Control 6-13 to 6-14
- Frequency Range 6-12
- Limits 6-11
- Linear Phase 3-9
- Log Magnitude 3-9
- Markers 6-14
- Measurement Status 6-13
- Plotter Output 6-15
- Polar 3-10
- Reference Position Marker 6-12
- Scale Resolution 6-12
- Screen-Image Printout 6-15
- Smith 3-10
- S-parameter Selection 6-14
- Status 6-12
- Sweep Marker Indicator 6-13
- Tabular Printout 6-15
- Update 6-14
- Data Display Modes
- Data Display Modes and Types 6-3 to 6-6
- Data Entry Keys 4-9
- Data Plotting 4-32
- Data Points Key 4-8,4-22
- Default Parameters 8-3,8-10
- Default Program Key 4-4,4-34
- Default Settings 4-35
- Device ID Key 4-22
- Disk Files, Format 4-41
- Disk Output 6-15
- Disk Storage Interface 4-41 to 4-42
- Diskette Drive 4-7
- Display Key-Group 4-26 to 4-29
- Display Keys 4-6,4-26
- Domain Key 4-8,4-22
- Drive, External SCSI 2-4
- Dual Channel Display Mode 6-4
- Dual Channel Rectilinear Display Mode 6-8
- Dual Source Control
- Dual Source Control Measurements
- Dual Trace Overlay Display Mode 6-6
- Data Display
- E
- F
- Four Channel Display Mode 6-5
- Fourier Transform 9-3
- Frequency
- Frequency Domain 9-3,9-8,9-12
- Front Panel
- Calibration Key-Group Description 4-11 to 4-20
- Channels Key-Group Description 4-25
- Display Key-Group Description 4-26 to 4-29
- Key-Group Descriptions 4-3 to 4-10
- Markers/Limits Key-Group Description 4-37 to 4-40
- Measurement Key-Group Description 4-22 to 4-24
- Output Key-Group Description 4-32 to 4-33
- Save/Recall Key, Description 4-21
- System State Key-Group Description 4-34 to 4-36
- G
- H
- I
- K
- L
- M
- Marker
- Marker Designation 6-11
- Marker Menu Key 4-5,4-37
- Markers/Limits Key-Group 4-37 to 4-40
- Markers/Limits Keys 4-5,4-37
- ME7808A 15-3
- Measurement Calibration
- Calibration Types 7-6
- Discussion 7-3 to 7-12
- Error Modeling and Flowgraphs 7-6
- Evaluating the Calibration 7-11
- LRL/LRM Procedure 7-36 to 7-45
- Offset-Short Procedure 7-28 to 7-31
- Sliding Load, Procedure 7-13 to 7-18
- Standared (SOLT) Procedure 7-19 to 7-27
- Triple Offset-Short Procedure 7-32
- Understanding the Calibration System 7-5
- Measurement Instruments 15-3
- Measurement Key-Group Description 4-22 to 4-24
- Measurement Keys 4-8,4-22
- Measurement Status 6-13
- Measurement Uncertainty 7-3
- Measurements
- Mechanical Shock 13-11
- Menu Flow
- Menu Key 4-5,4-32
- Menu Keys 4-9
- Menus
- MHz/X1/ns/cm Key 4-9
- Microwave Load 7-13
- Millimeter Wave Measurements 1-5
- Millimeter Wave System
- Allowable Measurements and Calibrations 14-18
- Allowable Module Configurations 14-18
- Calibration 14-13
- Controls and Connectors 14-11
- Description 14-3
- Effect of Default Program 14-19
- Installation 14-6
- Measurement Capabilities 14-5
- Measurement Procedures 14-23
- Operation 14-14
- Operational Checkout-General 14-25
- Operational Checkout-High Level Noise Test 14-28,14-30
- Operational Checkout-IF Power Level Test 14-26
- Performance Specifications 14-4
- Remote Operation 14-24
- System Performance 14-4
- Test Port Characteristics 14-5
- Model 3650 Calibration Kit 13-4
- Model 3651 Calibration Kit 13-5
- Model 3652 Calibration Kit 13-6
- Model 3653 Calibration Kit 13-7
- Model 3654/3654B Calibration Kit 13-8
- Model 3656 Calibration Kit 13-9
- Multiple Source Control
- N
- O
- O/E Measurements 8-65
- Offset-Short Calibration Procedure 7-28 to 7-31
- Offset-Short Calibration Setup Menu Flow 4-14
- Open 8-27
- Operational Checkout
- Optical Application 8-62 to 8-73
- Option 2 Time Domain
- Option 2A Time Domain
- Option 4 External SCSI Drive
- Option 5 Receiver Mode
- Option Menu Key 4-7,4-30
- Options 1-15
- Output Key-Group 4-32 to 4-33
- Over Torquing Connectors 13-11
- P
- Performance Specifications 1-15
- Phasor-impulse Response 9-5
- Pin Depth 7-13
- Plotter Output 6-15
- Plotting 4-32
- Polar Display 3-10
- Port 1 Connector 4-6
- Port 1 Test Connector 4-4,4-10
- Port 2 Connector 4-6
- Port 2 Test Connector 4-5,4-10
- Precision Component Kits 1-5
- Preparation for Storage and/or Shipment 2-9
- Preparation for Use 2-3
- Printing
- Purpose 13-3
- R
- S
- S Params Key 4-6,4-26
- S2P File
- Sampler Efficiency Test 11-4,12-4
- Save/Recall Menu 4-21
- Save/Recall Menu Key 4-4
- Save/Recall Menu Key 4-21
- Scale Resolution 6-12
- Scattering Parameters 3-9
- Screen-Image Printout 6-15
- SCSI Drive, External 2-4
- Self Test 11-3,12-3
- Set Scale Key 4-6,4-26
- Setup Menu Key 4-8,4-22
- Short 8-27
- Single Channel Display Mode 6-3
- Sliding Load 7-13
- Smith Chart 8-10
- Smith Chart Display 3-10
- Source Match 7-6
- Source Module
- S-parameter 8-25
- Specifications, Performance 1-15
- Standard Calibration Setup Menu Flow 4-12
- Start Print Key 4-5,4-32
- Start Printing 4-32
- Status Display 6-12
- Stop Print Key 4-5,4-32
- Stop Printing 4-32
- Sweep Marker Indicator 6-13
- System Cabling 15-9
- System Description 1-3 to 1-4
- System GPIB Interconnection 2-6
- System State Key-Group 4-34 to 4-36
- System State Keys 4-4,4-34
- T
- Tabular Printout 6-15
- Teflon Tuning Washers 13-11
- Test Ports
- Test Set
- Test Set Module
- Time Delay
- Time Domain Measurements 9-3
- Trace Memory Key 4-6,4-27
- Trace Smooth and Average Keys 4-30
- Trace Smooth Key 4-7
- Tracking 7-6
- Transmission and Reflection Measurements 8-3
- Triple Offset Short Calibration Procedure 7-32
- TRM Calibration Setup Menu Flow 4-18
- U
- V
- W
- Z

SERIES
37XXXC
VECTOR NETWORK ANALYZER
OPERATION MANUAL
490 JARVIS DRIVE ·MORGAN HILL, CA 95037-2809 P/N: 10410-00226
REVISION: E
PRINTED: MARCH 2004
COPYRIGHT 2004 ANRITSU CO.
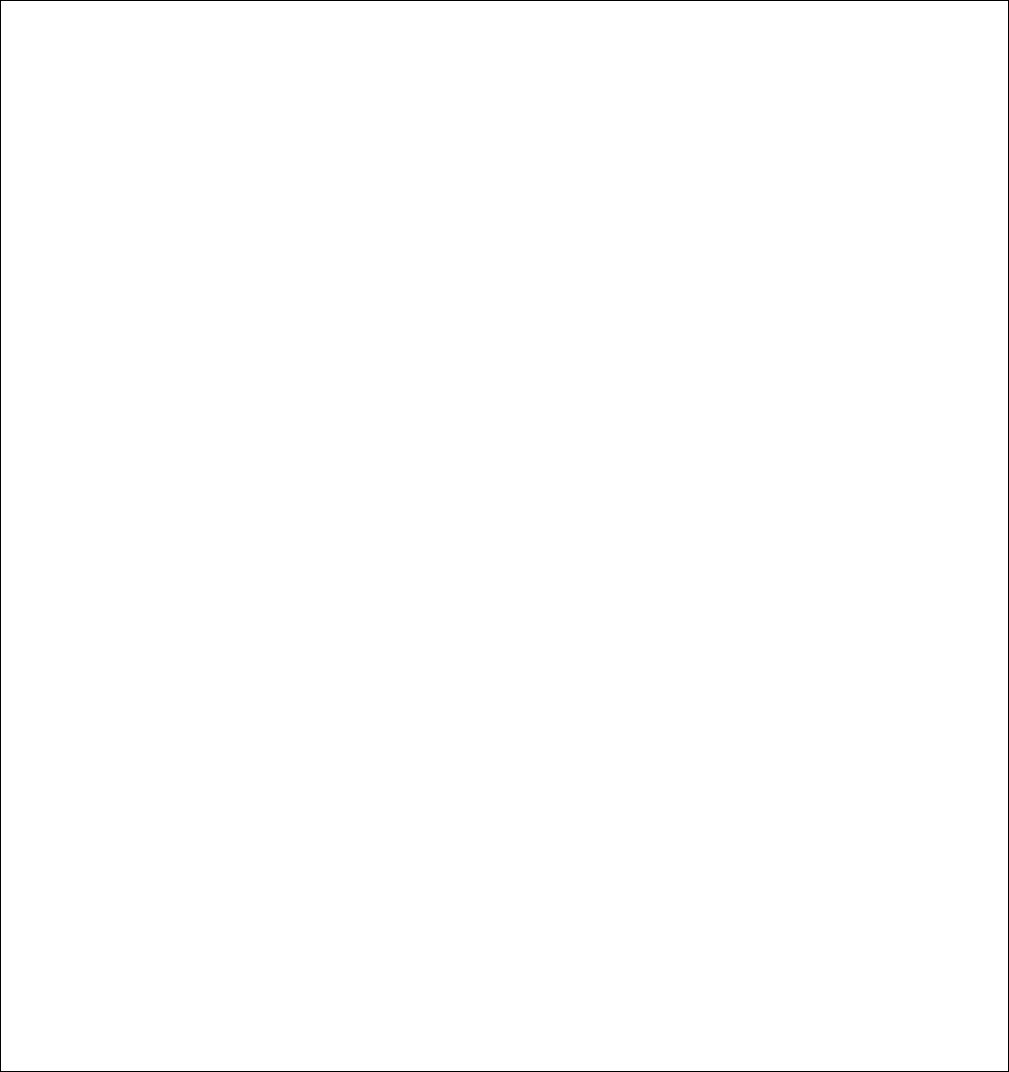
WARRANTY
The ANRITSU product(s) listed on the title page is (are) warranted against defects in materials and
workmanship for three years from the date of shipment.
ANRITSU’s obligation covers repairing or replacing products which prove to be defective during the
warranty period. Buyers shall prepay transportation charges for equipment returned to ANRITSU for
warranty repairs. Obligation is limited to the original purchaser. ANRITSU is not liable for consequential
damages.
LIMITATION OF WARRANTY
The foregoing warranty does not apply to ANRITSU connectors that have failed due to normal wear. Also,
the warranty does not apply to defects resulting from improper or inadequate maintenance by the Buyer,
unauthorized modification or misuse, or operation outside of the environmental specifications of the
product. No other warranty is expressed or implied, and the remedies provided herein are the Buyer’s sole
and exclusive remedies.
TRADEMARK ACKNOWLEDGEMENTS
V Connector and K Connector are registered trademarks of ANRITSU Company.
GPC-7 is a registered trademark of Amphenol Corporation.
ANACAT is a registered trademark of EEsof, Inc.
QuietJet and ThinkJet are registered trademarks of Hewlett-Packard Co.
Microsoft, Excel, and MS-DOS are registered trademarks of Microsoft Corporation.
Acrobat and Acrobat Reader are trademarks of Adobe Corporation.
Iomega and Zip are registered trademarks of Iomega Company.
NOTICE
ANRITSU Company has prepared this manual for use by ANRITSU Company personnel and customers as
a guide for the proper installation, operation and maintenance of ANRITSU Company equipment and
computer programs. The drawings, specifications, and information contained herein are the property of
ANRITSU Company, and any unauthorized use or disclosure of these drawings, specifications, and
information is prohibited; they shall not be reproduced, copied, or used in whole or in part as the basis for
manufacture or sale of the equipment or software programs without the prior written consent of ANRITSU
Company.
UPDATES
Updates to this manual, if any, may be downloaded from the Anritsu Internet site at:
http://www.us.anritsu.com.
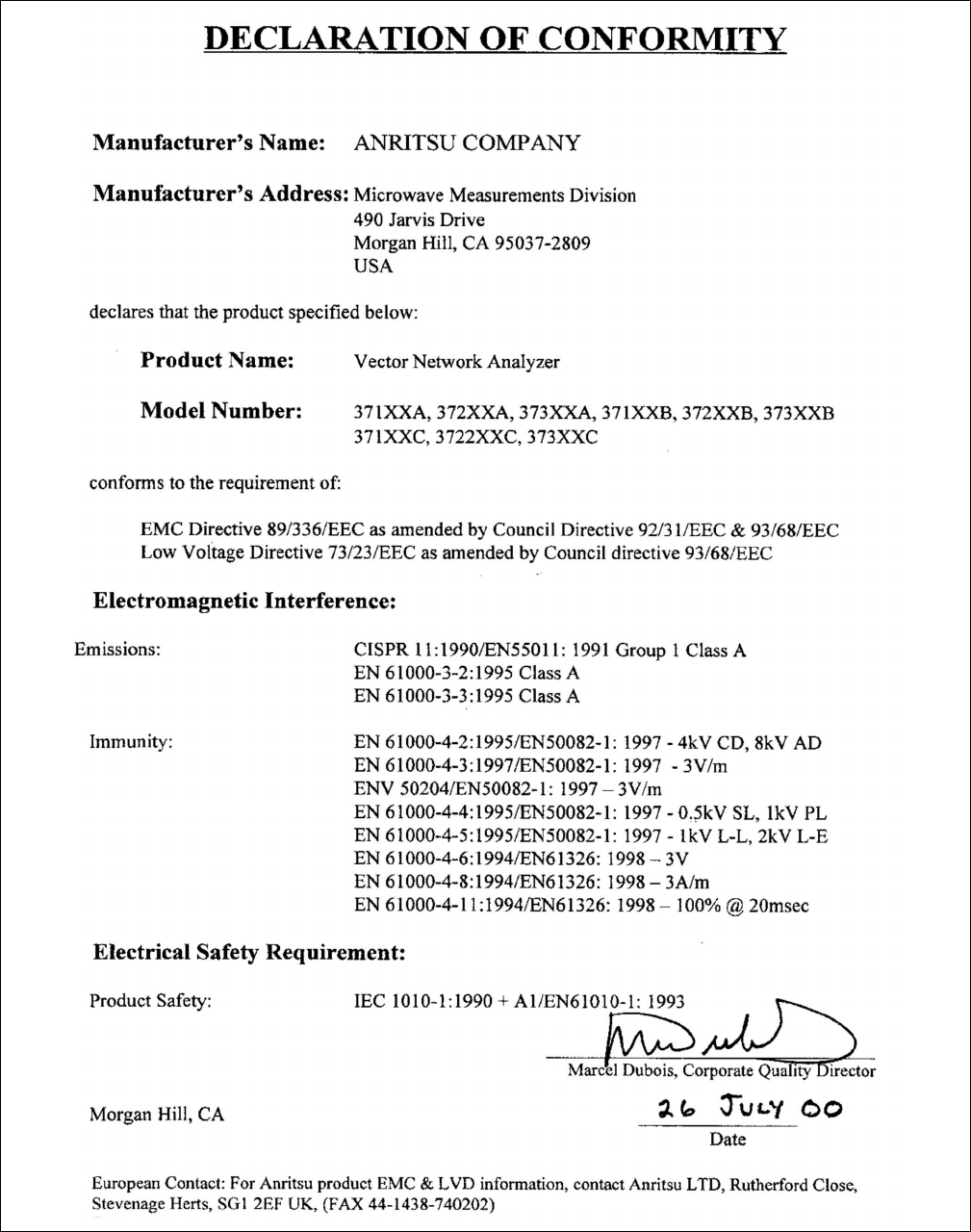
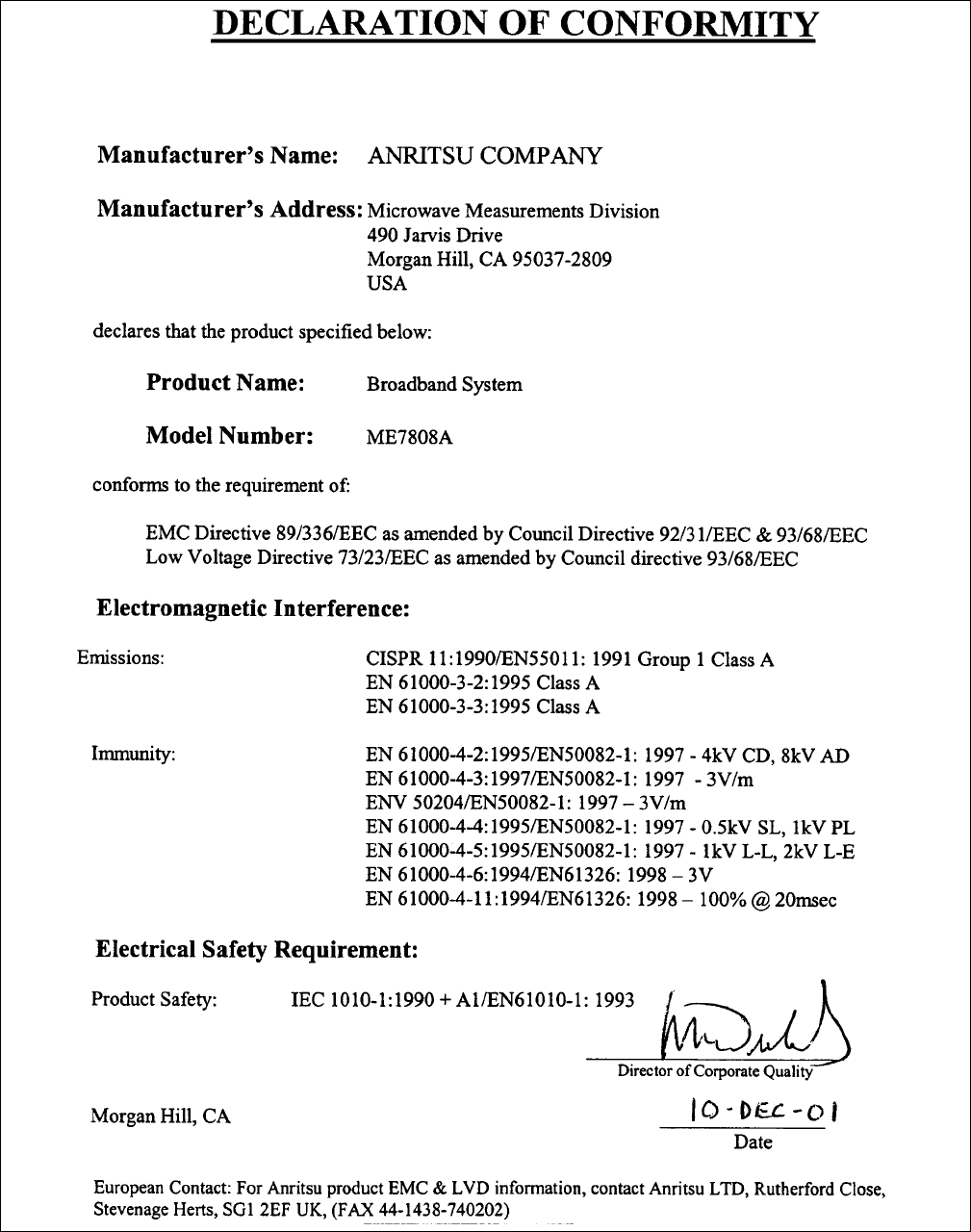
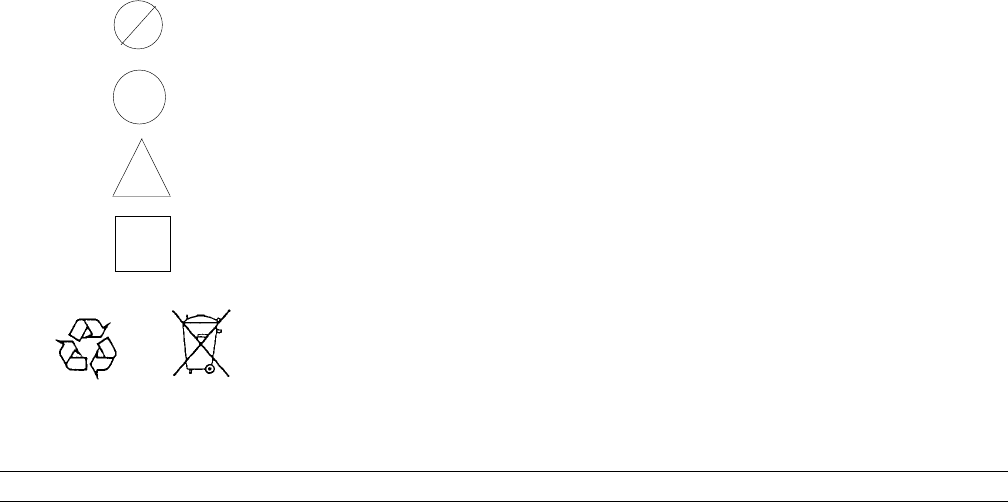
Safety Symbols
To prevent the risk of personal injury or loss related to equipment malfunction, Anritsu Company uses the
following symbols to indicate safety-related information. For your own safety, please read the information
carefully BEFORE operating the equipment.
Symbols used in manuals
DANGER This indicates a very dangerous procedure that could result in serious
injury or death if not performed properly.
WARNING This indicates a hazardous procedure that could result in serious in-
jury or death if not performed properly.
CAUTION This indicates a hazardous procedure or danger that could result in
light-to-severe injury, or loss related to equipment malfunction, if
proper precautions are not taken.
Safety Symbols Used on Equipment and in Manuals
(Some or all of the following five symbols may or may not be used on all Anritsu equipment. In addition,
there may be other labels attached to products that are not shown in the diagrams in this manual.)
The following safety symbols are used inside or on the equipment near operation locations to provide infor-
mation about safety items and operation precautions. Ensure that you clearly understand the meanings of
the symbols and take the necessary precautions BEFORE operating the equipment.
This indicates a prohibited operation. The prohibited operation is indi-
cated symbolically in or near the barred circle.
his indicates a compulsory safety precaution. The required operation is
indicated symbolically in or near the circle.
This indicates warning or caution. The contents are indicated symboli-
cally in or near the triangle.
This indicates a note. The contents are described in the box.
These indicate that the marked part should be recycled.
37XXXC OM Safety-1
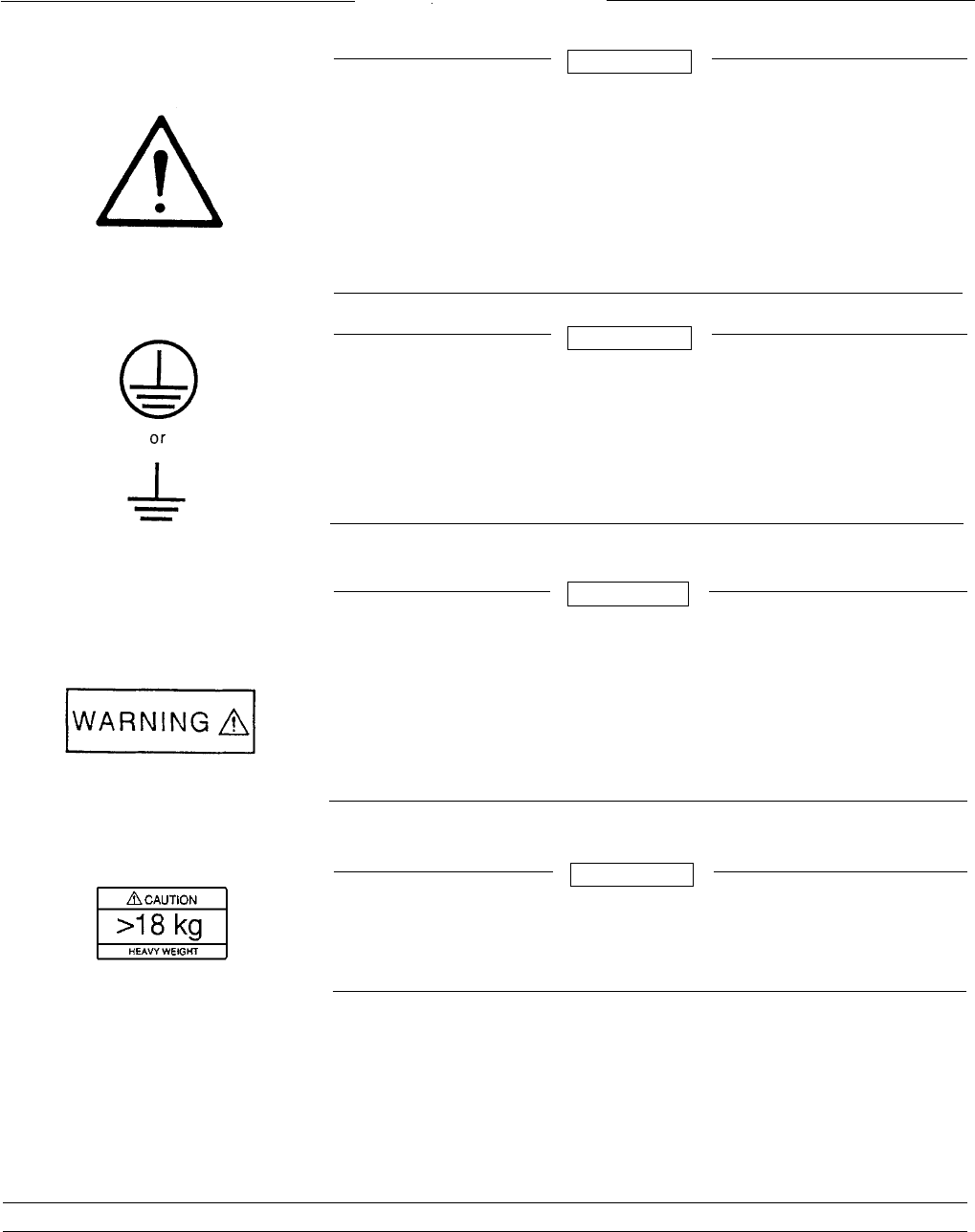
Safety-2 37XXXC OM
Always refer to the operation manual when working near locations at
which the alert mark, shown on the left, is attached. If the operation,
etc., is performed without heeding the advice in the operation manual,
there is a risk of personal injury. In addition, the equipment perfor-
mance may be reduced.
Moreover, this alert mark is sometimes used with other marks and de-
scriptions indicating other dangers.
WARNING
When supplying power to this equipment, connect the accessory 3-pin
power cord to a 3-pin grounded power outlet. If a grounded 3-pin outlet
is not available, use a conversion adapter and ground the green wire, or
connect the frame ground on the rear panel of the equipment to ground.
If power is supplied without grounding the equipment, there is a risk of
receiving a severe or fatal electric shock.
WARNING
This equipment can not be repaired by the operator. DO NOT attempt to
remove the equipment covers or to disassemble internal components.
Only qualified service technicians with a knowledge of electrical fire
and shock hazards should service this equipment. There are
high-voltage parts in this equipment presenting a risk of severe injury
or fatal electric shock to untrained personnel. In addition, there is a risk
of damage to precision components.
WARNING
Repair
For Safety
Use two or more people to lift and move this equipment, or use an
equipment cart. There is a risk of back injury, if this equipment is lifted
by one person.
WARNING
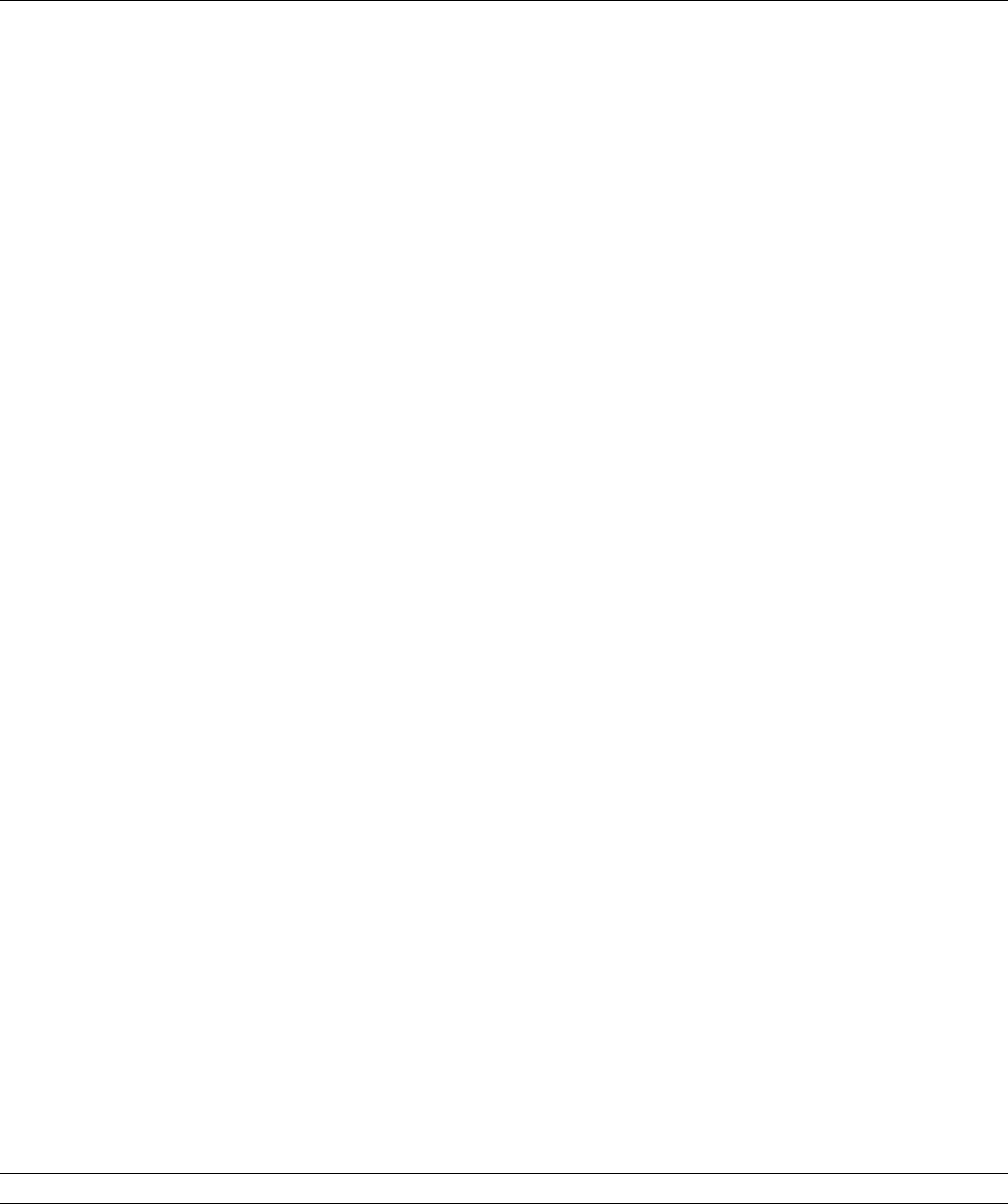
Narrative Table Of Contents
Chapter 1—General Information
This chapter provides a general description of the Anritsu Model 37XXXC Vector Network Analyzer
System and its major units: network analyzer, test set, and frequency source. It also provides de-
scriptions for the precision component kits, and equipment options. Additionally, it contains the list-
ing of recommended test equipment.
Chapter 2—Installation
This chapter provides instructions for performing an initial inspection, preparing the equipment for
use, setting up for operation over the IEEE-488.2 (GPIB) Bus, using a printer, and preparing the
units for storage and/or shipment. It also provides a listing of Anritsu Customer Service Centers.
Chapter 3—Network Analyzers, A Primer
This chapter provides an introduction to network analysis and the types of measurements that can
be made using them. It provides general and introductory description.
Chapter 4—Front Panel Operation
This chapter describes the front panel controls and provides flow diagrams for the menus called up
using the front panel controls. It contains the following sub-chapters:
·Front Panel Control-Group Descriptions
·Calibration Keys and Indicators, Detailed Description
·Save/Recall Menu Key and Menus, Key Description and Menu Flow
·Measurement Keys and Menus, Key Descriptions and Menu Flow
·Channel Keys and Menu, Key Descriptions and Menu Flow
·Display Keys and Menus, Key Descriptions and Menu Flow
·Enhancement Keys and Menus, Key Descriptions and Menu Flow
·Hard Copy Keys and Menus, Key Descriptions and Menu Flow
·System State Keys and Menus, Key Descriptions and Menu Flow
·Markers/limits Keys and Menus, Key Descriptions and Menu Flow
·Disk Storage Interface, Detailed Description
Chapter 5—Error And Status Messages
This chapter describes the type of error messages you may encounter during operation and provides a
tabular listing. This listing describes and defines the error types.
Chapter 6—Data Displays
This chapter provides a detailed description of the various data displays. It describes the graph
types, frequency markers, measurement limit lines, status displays, and data display controls.
37XXXC OM i

Chapter 7—Measurement Calibration
This chapter provides a discussion and tutorial on measurement calibration. It contains step-by-step
calibration procedures for the Standard (OSL), Offset-Short, TRM, and LRL/LRM methods. It also
has a procedure for calibrating using a sliding termination.
Chapter 8—Measurements
This chapter discusses measurements with the 37XXXC VNA. It contains sub-chapters that provide
a detailed descriptions for Transmission and Reflection, Low Level and Gain, Group Delay, Active
Device, Multiple Source Control, Adapter Removal, Gain Compression, and Receiver Mode
measurements
Chapter 9—Time Domain
This chapter describes the Option 2, Time Domain feature. It provides an operational procedure and
a flowchart of the time domain menus.
Chapter 10—AutoCal
This chapter describes the Automatic Calibrator (AutoCal) feature and provides operational informa-
tion and procedures.
Chapter 11—Operational Checkout Procedures: 371XXC
This chapter provides a procedure for operational checkout.
Chapter 12—Operational Checkout Procedures: 372XXC, 373XXC
This chapter provides a procedure for operational checkout
Chapter 13—Calibration Kits
This chapter provides a description and listing of components for the calibration kits.
Chapter 14—Millimeter Wave System
This chapter contains description, operation, and checkout procedures for the millimeter wave mea-
surement capability that can be added to the 371XXC Vector Network Analyzer.
Chapter 15—ME7808A Broadband Measurement System
This chapter contains description, operation, and checkout procedures for the optional broadband
measurement capability that can be added to the 37XXXC Vector Network Analyzer.
Appendix A—Front Panel Menus, Alphabetical Listing
This appendix shows all of the menus that are called up using the front panel controls. It provides a
replica of the menu and descriptive text for all of the various menu choices. The listing is alphabeti-
cal by the menu call letters mentioned and/or illustrated in Chapter 4.
Appendix B—Model 37XXXC VNA Rear Panel Connectors
This appendix describes the rear panel connectors. It also provides pinout listing.
Appendix C—Performance Specifications
This appendix contains the Technical Data Sheet, part number 11410-00247, which provides perfor-
mance specifications.
Subject Index
ii 37XXXC OM
Narrative Table of Contents (Continued)
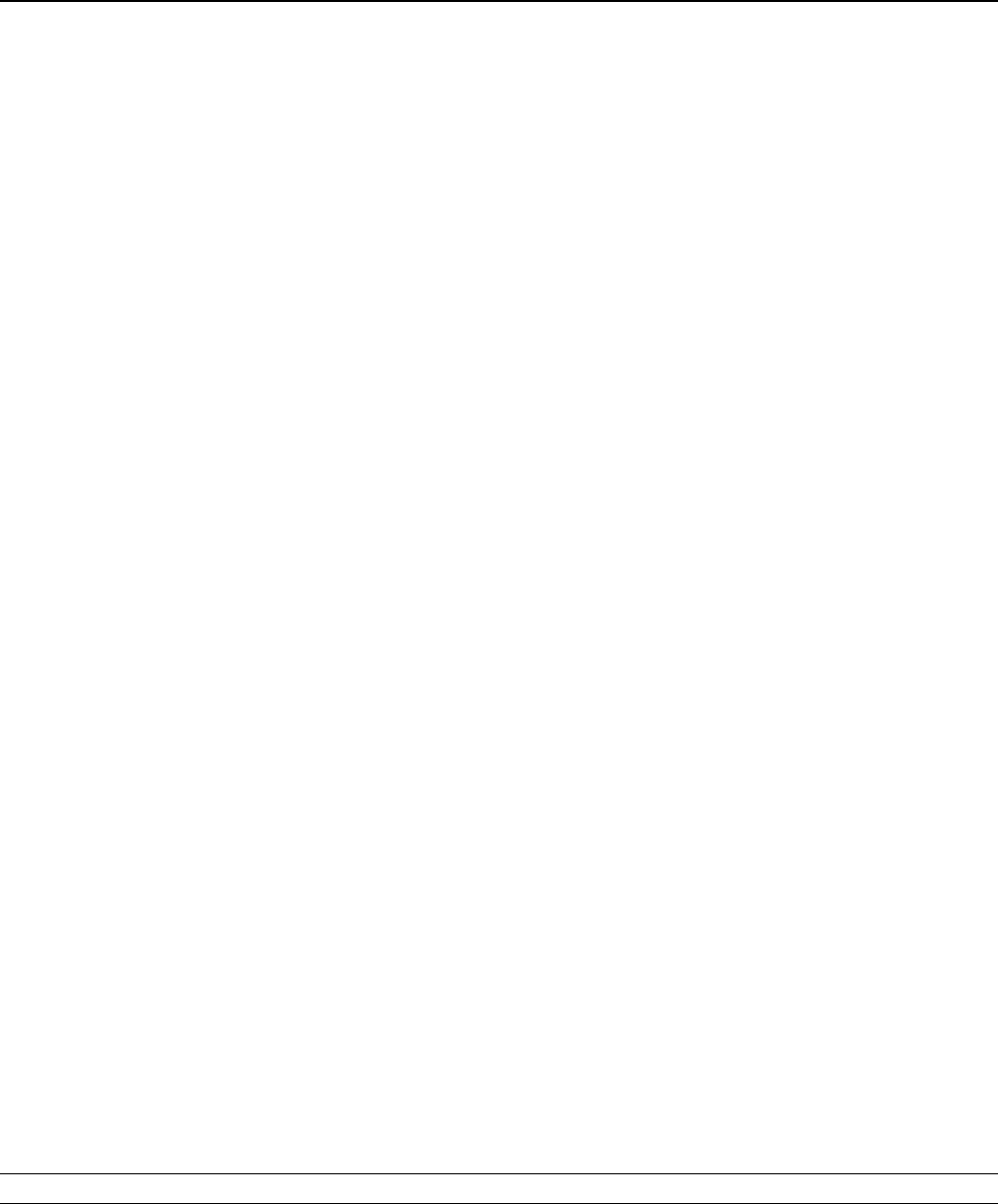
Table of Contents
Chapter 1 General Information
1-1 SCOPE OF MANUAL .................................1-3
1-2 INTRODUCTION ...................................1-3
1-3 IDENTIFICATION NUMBER.............................1-3
1-4 ONLINE MANUALS..................................1-3
1-5 SYSTEM DESCRIPTION ...............................1-3
371XXC .......................................1-4
372XXC .......................................1-4
373XXC .......................................1-4
1-6 MILLIMETER WAVE MEASUREMENTS ......................1-5
1-7 PRECISION COMPONENT KITS ..........................1-5
Model 3650 SMA/3.5 mm Calibration Kit .....................1-5
Model 3651 GPC–7 Calibration Kit ........................1-6
Model 3652 K Connector Calibration Kit .....................1-7
Model 3653 Type N Calibration Kit ........................1-8
Model 3654B V Connector® Calibration Kit....................1-9
Model 3656 W1 Connector Calibration Kit ....................1-10
Model 3666 3.5 mm Verification Kit .......................1-11
Model 3667 GPC–7 Verification Kit........................1-12
Model 3668 K Connector® Verification Kit....................1-13
Model 3669/3669B V Connector® Verification Kits ...............1-14
1-8 OPTIONS .......................................1-15
1-9 PERFORMANCE SPECIFICATIONS........................1-15
1-10 PREVENTIVE MAINTENANCE ..........................1-15
Chapter 2 Installation
2-1 INTRODUCTION ...................................2-3
2-2 INITIAL INSPECTION ................................2-3
2-3 PREPARATION FOR USE ..............................2-3
Option 4, External SCSI Drive Setup .......................2-4
37XXXC OM iii
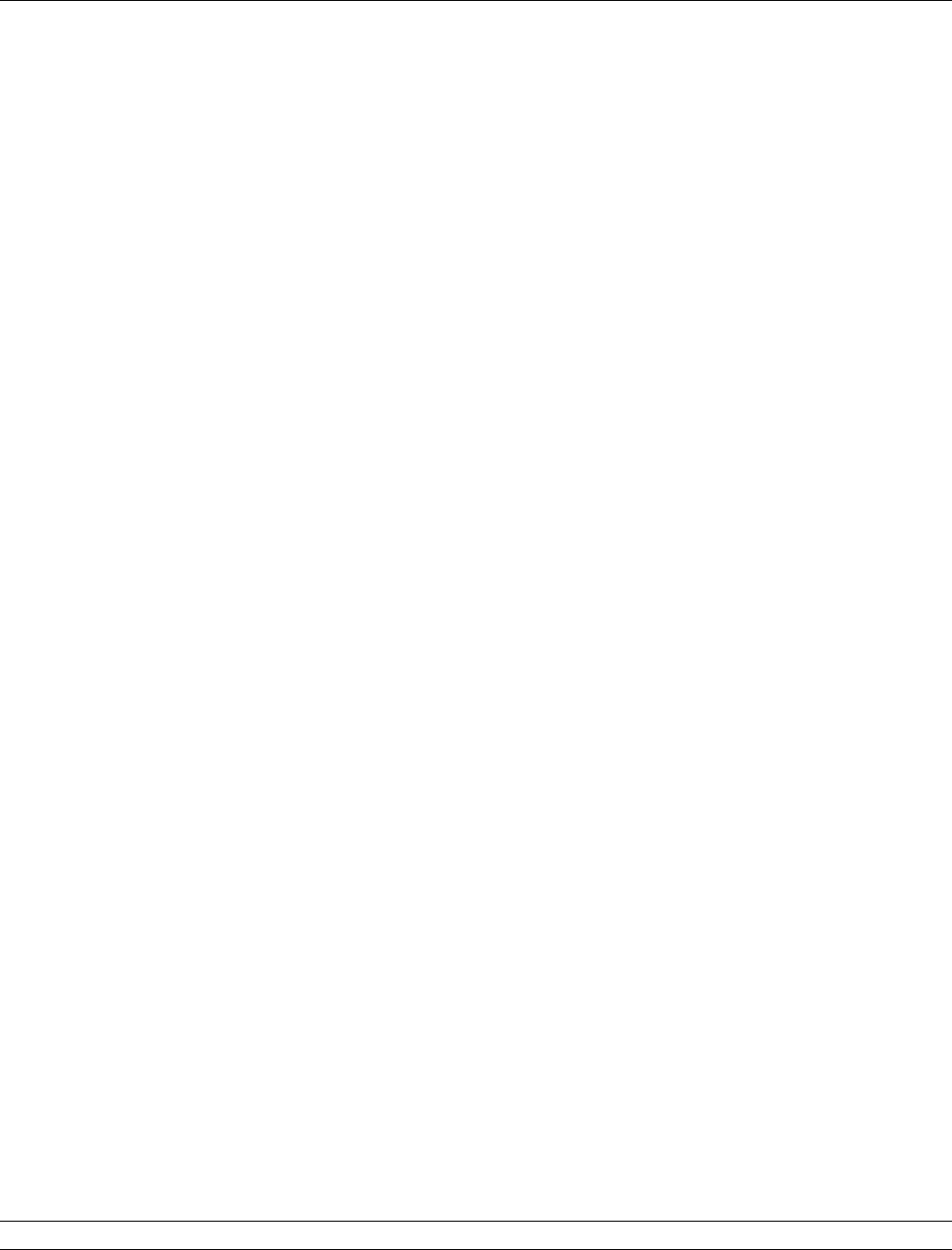
2-4 GPIB SETUP .....................................2-5
Interface Connector .................................2-5
Cable Length Restrictions .............................2-5
2-5 SYSTEM GPIB INTERCONNECTION........................2-6
GPIB Interface to an External Plotter .......................2-6
GPIB Addresses...................................2-6
2-6 EXTERNAL MONITOR CONNECTOR .......................2-6
2-7 RACK MOUNT.....................................2-6
2-8 STORAGE OR SHIPMENT ..............................2-9
Preparation for Storage...............................2-9
Preparation for Shipment..............................2-9
2-9 SERVICE CENTERS.................................2-10
Chapter 3 Network Analyzers, A Primer
3-1 INTRODUCTION ...................................3-3
3-2 GENERAL DESCRIPTION ..............................3-3
Source Module....................................3-4
Test Set Module ...................................3-4
Analyzer Module ..................................3-4
3-3 NETWORK ANALYZERS ...............................3-5
Chapter 4 Front Panel Operation
4-1 INTRODUCTION ...................................4-3
4-2 KEY-GROUPS .....................................4-3
4-3 CALIBRATION KEY-GROUP ............................4-11
4-4 SAVE/RECALL MENU KEY.............................4-21
4-5 MEASUREMENT KEY-GROUP ..........................4-22
4-6 CHANNELS KEY-GROUP..............................4-25
4-7 DISPLAY KEY-GROUP ...............................4-26
4-8 ENHANCEMENT KEY-GROUP...........................4-30
4-9 HARD COPY KEY-GROUP .............................4-32
4-10 SYSTEM STATE KEY-GROUP ...........................4-34
4-11 MARKERS/LIMITS KEY-GROUP ..........................4-37
iv 37XXXC OM
Table of Contents (Continued)
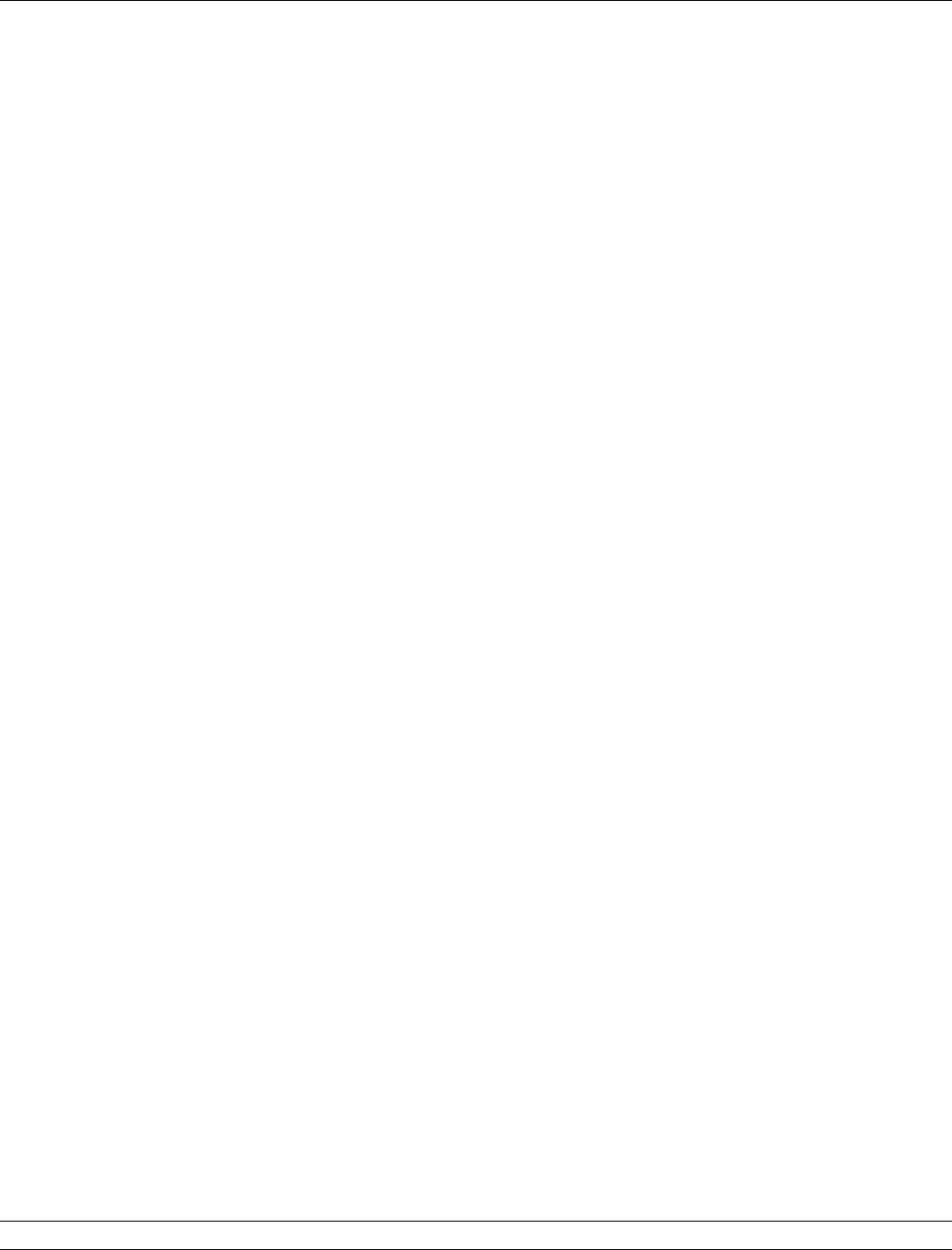
4-12 DISK STORAGE INTERFACE ...........................4-41
Disk Format ....................................4-41
Disk Files......................................4-41
Disk File Output Device..............................4-42
Formatting a Data File Disk ...........................4-42
Copying Data Files From Disk to Disk ......................4-42
Recovering From Disk Write/Read Errors ....................4-42
4-13 COMMAND LINE ..................................4-43
Create Directory ..................................4-43
List Directory ...................................4-43
Change Directory .................................4-43
Delete Files.....................................4-43
Remove Directory .................................4-44
Copy Files .....................................4-44
Conventions ....................................4-44
Chapter 5 Error and Status Messages
5-1 INTRODUCTION ...................................5-3
5-2 ERROR MESSAGES..................................5-3
Chapter 6 Data Displays
6-1 INTRODUCTION ...................................6-3
6-2 DISPLAY MODES AND TYPES ...........................6-3
Single Channel Display: Ch 1, 2, 3, 4........................6-3
Dual Channel Display: Ch 1 and 3 or Ch 2 and 4 .................6-4
Four Channel Display: Ch 1, 2, 3, 4 ........................6-5
Dual Trace Overlay .................................6-6
Graph Data Types..................................6-7
6-3 FREQUENCY MARKERS ..............................6-11
Marker Designation ................................6-11
6-4 LIMITS ........................................6-11
37XXXC OM v
Table of Contents (Continued)
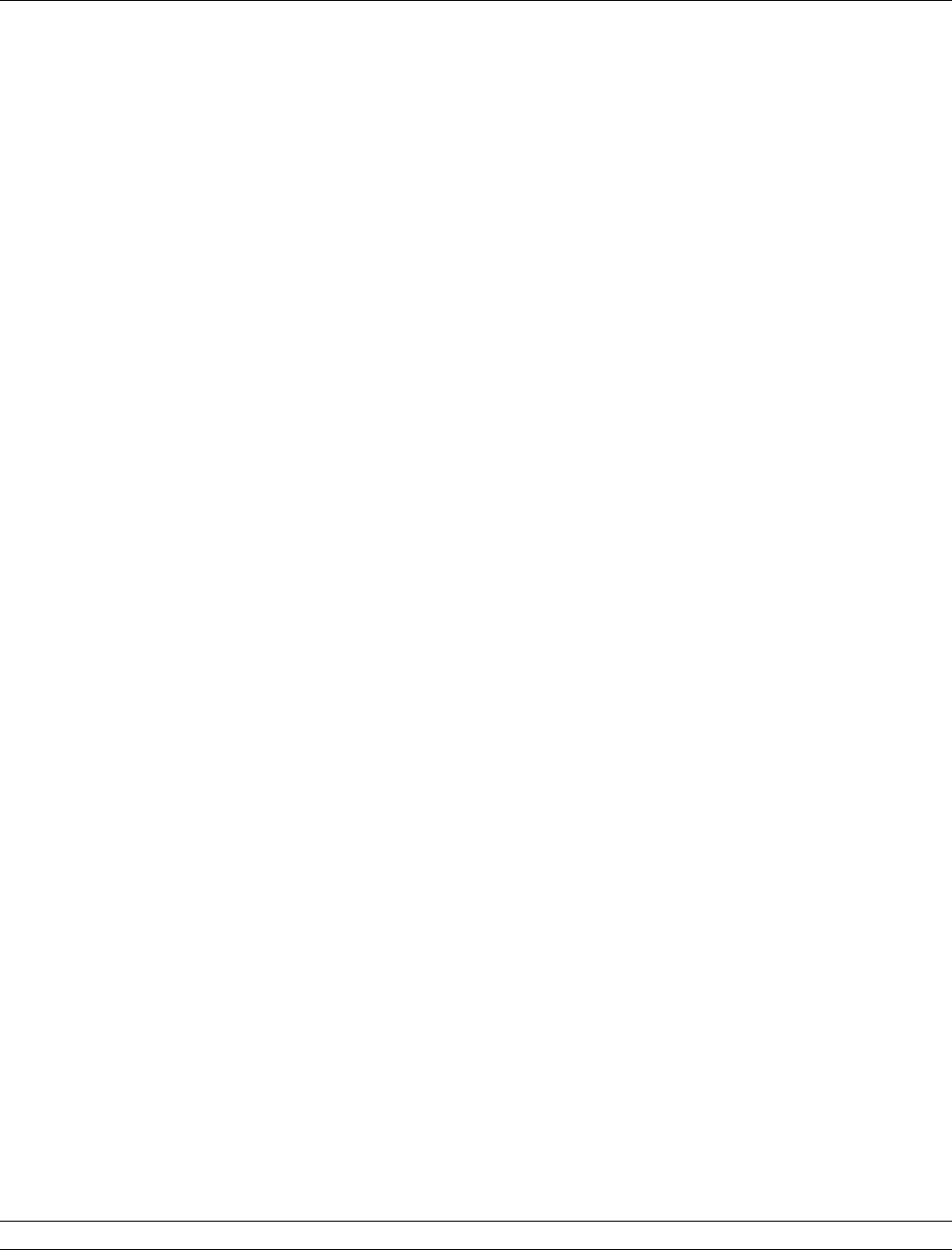
6-5 STATUS DISPLAY ..................................6-12
Reference Position Marker ............................6-12
Scale Resolution ..................................6-12
Frequency Range .................................6-12
Analog Instrument Status.............................6-12
Measurement Status ...............................6-13
Sweep Indicator Marker..............................6-13
6-6 DATA DISPLAY CONTROL .............................6-13
S-parameter Selection ...............................6-14
Data Display Update ...............................6-14
Display of Markers.................................6-14
6-7 HARD COPY AND DISK OUTPUT .........................6-15
Tabular Printout..................................6-15
Screen-Image Printout ..............................6-15
Plotter Output ...................................6-15
Disk Output ....................................6-15
Chapter 7 Measurement Calibration
7-1 INTRODUCTION ...................................7-3
7-2 DISCUSSION .....................................7-3
Establishing the Test Ports.............................7-3
Understanding the Calibration System ......................7-5
Calibrating for a Measurement ..........................7-9
Evaluating the Calibration ............................7-11
Verification Kits ..................................7-11
7-3 SLIDING TERMINATION..............................7-13
7-4 SOLT CALIBRATION ................................7-19
7-5 OFFSET-SHORT CALIBRATION (SSLT)......................7-28
7-6 TRIPLE OFFSET-SHORT CALIBRATION (SSST).................7-32
7-7 LRL/LRM CALIBRATION ..............................7-36
7-8 TRM CALIBRATION.................................7-46
7-9 MERGE CAL FILES APPLICATION ........................7-47
vi 37XXXC OM
Table of Contents (Continued)
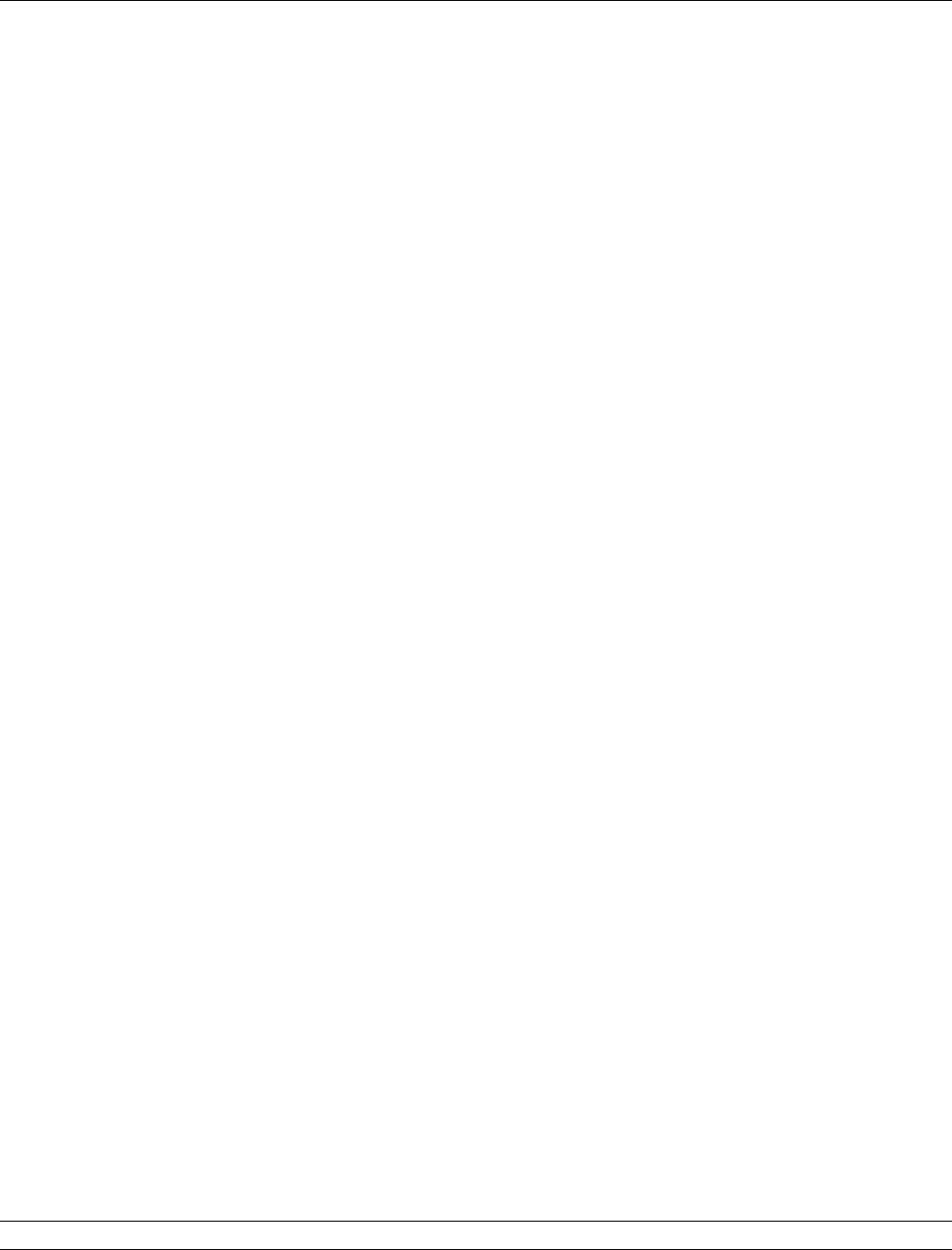
Chapter 8 Measurements
8-1 INTRODUCTION ...................................8-3
8-2 TRANSMISSION AND REFLECTION ........................8-3
8-3 LOW LEVEL AND GAIN ..............................8-12
8-4 GROUP DELAY ...................................8-20
8-5 ACTIVE DEVICE ..................................8-24
8-6 MULTIPLE SOURCE CONTROL ..........................8-29
Control Formula ..................................8-29
8-7 ADAPTER REMOVAL ................................8-34
8-8 GAIN COMPRESSION................................8-39
Power and VNAs..................................8-39
Swept Power Gain Compression .........................8-41
Swept Frequency Gain Compression .......................8-41
8-9 RECEIVER MODE ..................................8-58
Source Lock Mode .................................8-58
Tracking Mode ...................................8-58
Set-on Mode ....................................8-58
Receiver Mode Block Diagram ..........................8-59
Receiver Mode Menus ...............................8-59
Procedure, Receiver Mode Operation .......................8-59
8-10 OPTICAL APPLICATION ..............................8-62
E/O Measurements ................................8-62
O/E Measurements ................................8-65
Creating a Characterization (*.S2P) File for E/O and O/E Measurements . . . 8-71
Chapter 9 Time Domain
9-1 INTRODUCTION ...................................9-3
9-2 TIME DOMAIN MEASUREMENTS .........................9-3
9-3 OPERATING TIME DOMAIN ............................9-8
9-4 WINDOWING.....................................9-11
9-5 GATING........................................9-12
9-6 ANTI-GATING ....................................9-14
9-7 EXAMPLES, GATING AND ANTI-GATING ....................9-14
37XXXC OM vii
Table of Contents (Continued)
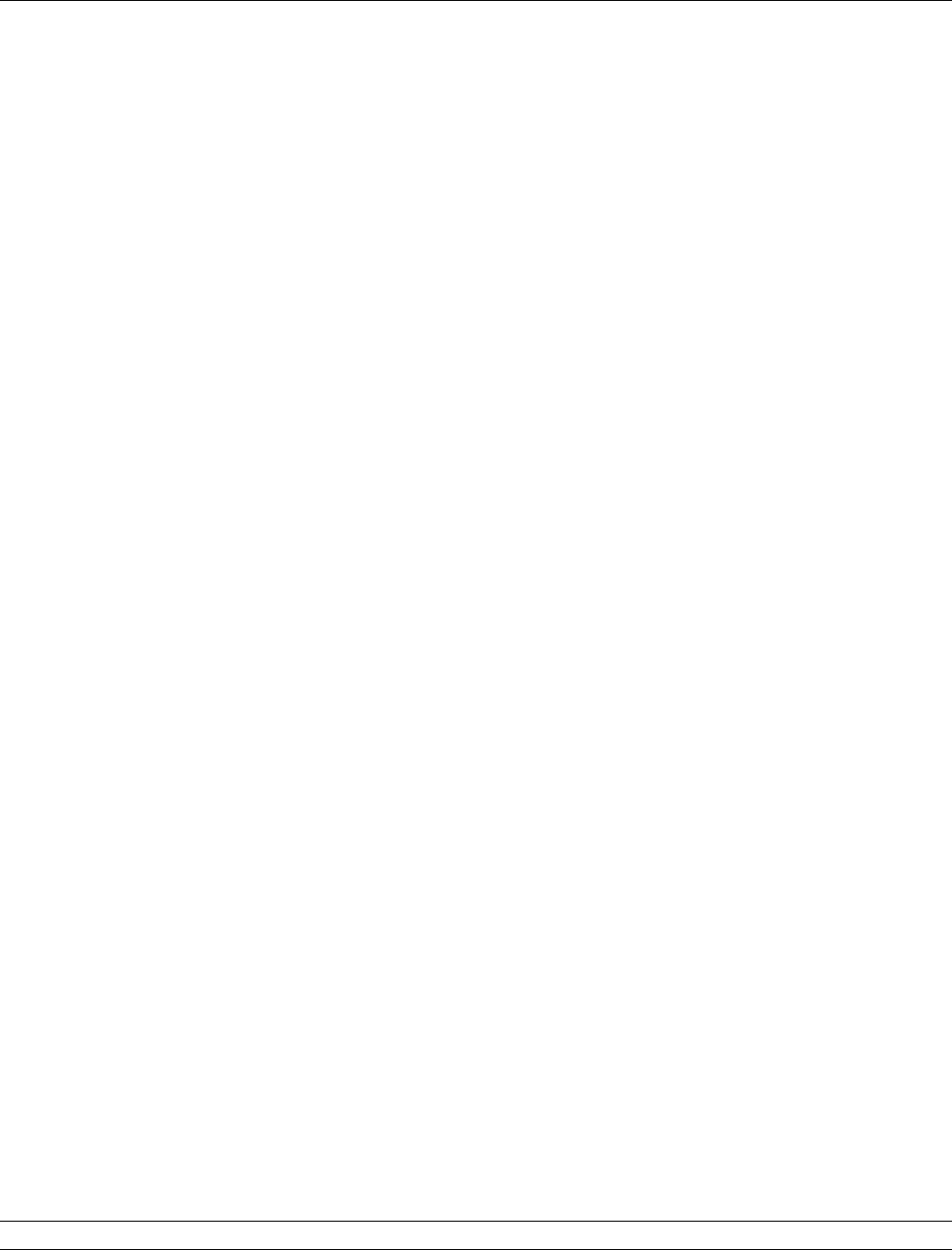
9-8 TIME DOMAIN MENUS...............................9-14
Chapter 10 AutoCal
10-1 INTRODUCTION...................................10-3
10-2 DESCRIPTION ....................................10-3
10-3 CALIBRATIONS ...................................10-4
10-4 DEFINITIONS ....................................10-4
10-5 PHYSICAL SETUP..................................10-6
10-6 CHARACTERIZATION FILES ...........................10-7
10-7 USING AUTOCAL ..................................10-9
10-8 PIN DEPTH SPECIFICATIONS ..........................10-13
10-9 AUTOCAL MENUS FLOW DIAGRAM ......................10-14
Chapter 11 Operational Checkout Procedures: 371XXC
11-1 INTRODUCTION...................................11-3
11-2 REQUIRED EQUIPMENT..............................11-3
11-3 INITIAL SETUP ...................................11-3
11-4 SELF TEST ......................................11-3
11-5 SAMPLER EFFICIENCY TEST...........................11-4
11-6 HIGH LEVEL NOISE TEST.............................11-8
Chapter 12 Operational Checkout Procedures: 372XXC, 373XXC
12-1 INTRODUCTION...................................12-3
12-2 REQUIRED EQUIPMENT..............................12-3
12-3 INITIAL SETUP ...................................12-3
12-4 SELF TEST ......................................12-3
12-5 NON-RATIO POWER ................................12-4
12-6 HIGH LEVEL NOISE TEST.............................12-6
Chapter 13 Calibration Kits
13-1 INTRODUCTION...................................13-3
13-2 PURPOSE.......................................13-3
viii 37XXXC OM
Table of Contents (Continued)
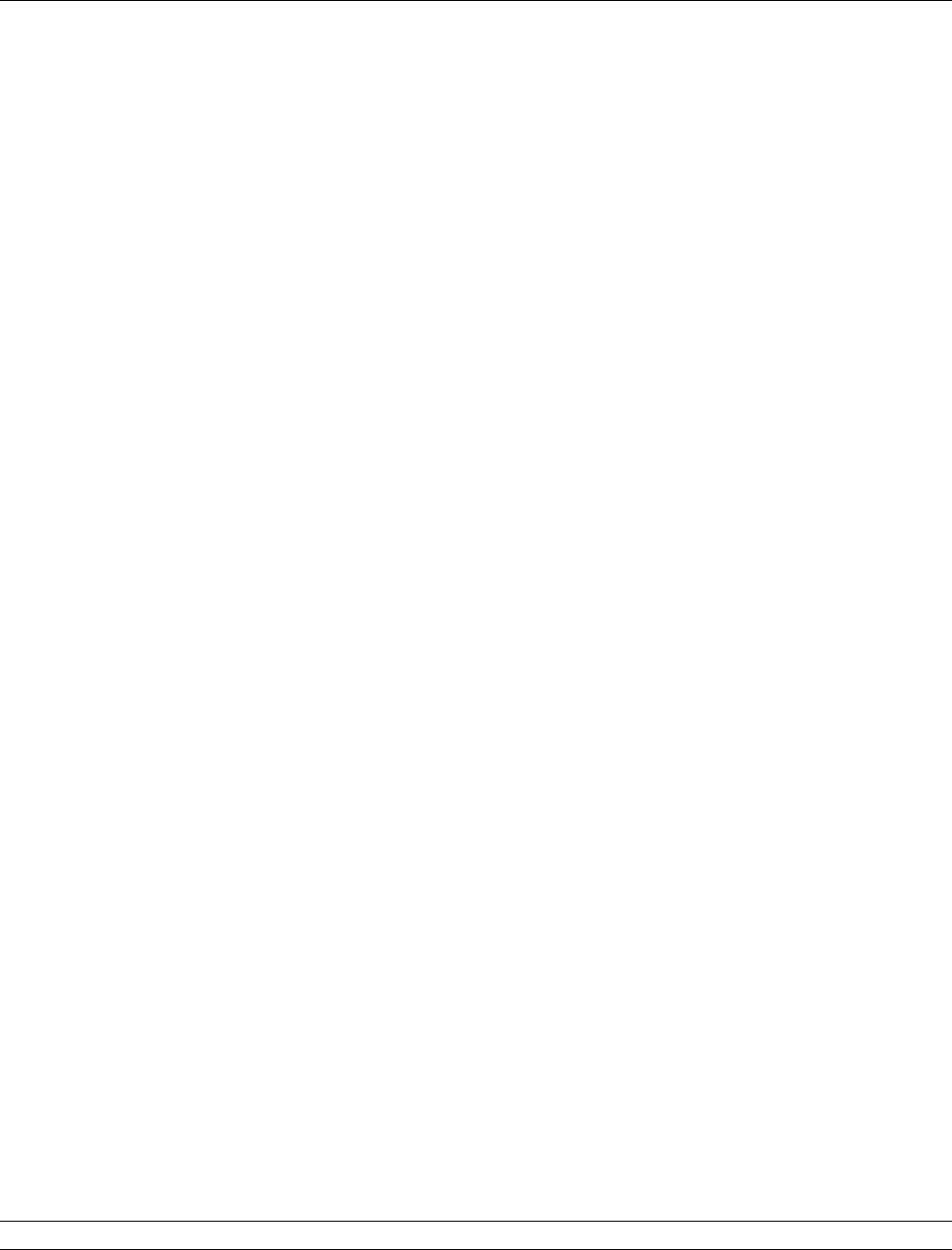
13-3 KIT CONTENTS ...................................13-3
Model 3650 Calibration Kit ............................13-4
Model 3651 Calibration Kit ............................13-5
Model 3652 Calibration Kit ............................13-6
Model 3653 Calibration Kit ............................13-7
Model 3654/ 3654B Calibration Kit ........................13-8
Model 3656 Calibration Kit ............................13-9
13-4 PRECAUTIONS ...................................13-10
Pin Depth .....................................13-10
Pin Depth Tolerance ...............................13-11
Over Torquing Connectors ............................13-11
Teflon Tuning Washers..............................13-11
Mechanical Shock ................................13-11
13-5 CLEANING INSTRUCTIONS ...........................13-12
Chapter 14 Millimeter Wave System
14-1 INTRODUCTION...................................14-3
14-2 DESCRIPTION ....................................14-3
14-3 PERFORMANCE SPECIFICATIONS........................14-4
System Performance................................14-4
Test Port Characteristics .............................14-5
Measurement Capabilities ............................14-5
14-4 INSTALLATION ...................................14-6
14-5 CONTROLS AND CONNECTORS.........................14-11
14-6 CALIBRATION ...................................14-13
14-7 OPERATION ....................................14-14
Entering/ Leaving Millimeter Wave Operation .................14-14
Changing Bands/Modules While in Millimeter Wave..............14-18
Allowable Millimeter Wave Module Configurations, Measurements and
Calibrations....................................14-18
Effect of Default Program ............................14-19
Redefinition of Band Frequency Ranges ....................14-20
Use of Normal Multiple Source Mode ......................14-21
Stored Setups and Calibrations .........................14-21
External Source and Power Levels .......................14-22
37XXXC OM ix
Table of Contents (Continued)
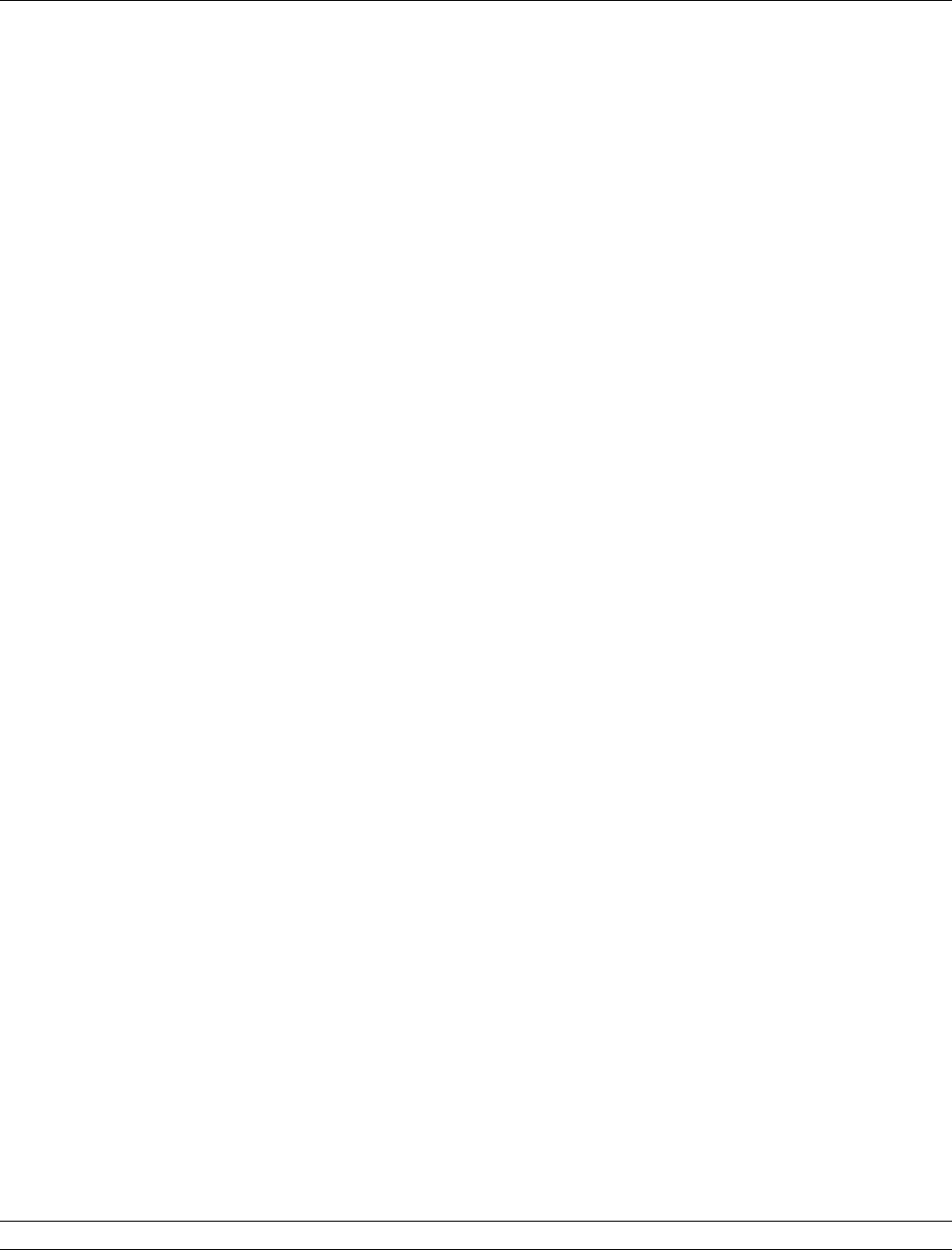
14-8 MEASUREMENT PROCEDURE..........................14-23
14-9 REMOTE OPERATION...............................14-24
14-10 OPERATIONAL CHECKOUT— GENERAL ...................14-25
14-11 OPERATION CHECKOUT—IF POWER LEVEL TEST .............14-26
14-12 OPERATIONAL CHECKOUT— TRANSMISSION HIGH LEVEL NOISE TEST14-28
14-13 OPERATIONAL CHECKOUT— REFLECTION HIGH LEVEL NOISE TEST . 14-30
Chapter 15 ME7808A Broadband Measurement System
15-1 INTRODUCTION...................................15-3
15-2 SYSTEM DESCRIPTION ..............................15-3
Measurement Instruments ............................15-3
Console and Associated Hardware ........................15-4
Cables .......................................15-4
15-3 INSTALLATION ...................................15-4
Console and Table Setup .............................15-5
Instrument Installation into Console .......................15-6
System Cabling ..................................15-9
15-4 INITIAL ELECTRICAL TESTS ..........................15-11
Millimeter Module Checkout...........................15-11
40 MHz to 65 GHz Checkout...........................15-12
15-5 WAFER PROBE STATION ............................15-13
15-6 BROADBAND MENUS, FLOW...........................15-15
15-7 BROADBAND CALIBRATION...........................15-16
Merging Calibrations...............................15-16
x 37XXXC OM
Table of Contents (Continued)
Appendix A Front Panel Menus, Alphabetical Listing
Appendix B Rear Panel Connectors
Appendix C Performance Specifications
Subject Index

Table of Contents
1-1 SCOPE OF MANUAL .................................1-3
1-2 INTRODUCTION ...................................1-3
1-3 IDENTIFICATION NUMBER.............................1-3
1-4 ONLINE MANUALS..................................1-3
1-5 SYSTEM DESCRIPTION ...............................1-3
371XXC .......................................1-4
372XXC .......................................1-4
373XXC .......................................1-4
1-6 MILLIMETER WAVE MEASUREMENTS ......................1-5
1-7 PRECISION COMPONENT KITS ..........................1-5
Model 3650 SMA/3.5 mm Calibration Kit .....................1-5
Model 3651 GPC–7 Calibration Kit ........................1-6
Model 3652 K Connector Calibration Kit .....................1-7
Model 3653 Type N Calibration Kit ........................1-8
Model 3654B V Connector® Calibration Kit....................1-9
Model 3656 W1 Connector Calibration Kit ....................1-10
Model 3666 3.5 mm Verification Kit .......................1-11
Model 3667 GPC–7 Verification Kit........................1-12
Model 3668 K Connector® Verification Kit....................1-13
Model 3669/3669B V Connector® Verification Kits ...............1-14
1-8 OPTIONS .......................................1-15
1-9 PERFORMANCE SPECIFICATIONS........................1-15
1-10 PREVENTIVE MAINTENANCE ..........................1-15
Chapter 1
General Information

Chapter 1
General Information
1-1 SCOPE OF MANUAL This manual provides general information, installation, and operating
information for the Model 37XXXC Vector Network Analyzer (VNA)
system. (Throughout this manual, the terms VNA, 37XXXC VNA, and
37XXXC will be used interchangeably to refer to the system.) It also
provides description and instructions for the Millimeter Wave System
that can be added to the 371XXC. Manual organization is shown in the
table of contents.
1-2 INTRODUCTION This section provides general information about the 37XXXC VNA sys-
tem and one or more precision-component calibration or performance
verification kits. The section also provides a listing of recommended
test equipment.
1-3 IDENTIFICATION
NUMBER All Anritsu instruments are assigned a unique six-digit ID number,
such as “940101.” This number is affixed to a decal on the rear panel of
each unit. In any correspondence with Anritsu Customer Service,
please use this number.
1-4 ONLINE MANUALS Manual updates, if any, are available on Anritsu's Internet download
page (http://www.us.anritsu.com/downloads/).
1-5 SYSTEM DESCRIPTION The 37XXXC Network Analyzer (Figure 1-1) is a single-instrument
system that contains a built-in source, test set, and analyzer. It is pro-
duced in three series—371XXC, 372XXC, and 373XXC—described be-
low. All models provide up to 1601 measurement data points, a built-in
hard-disk drive for storing and recalling front panel setups and mea-
surement and calibration data. They also provide an on-screen display
of total operational time and dates of system calibrations. They sup-
port operation over the IEEE 488.2 General Purpose Interface Bus
(GPIB).
37XXXC OM 1-3
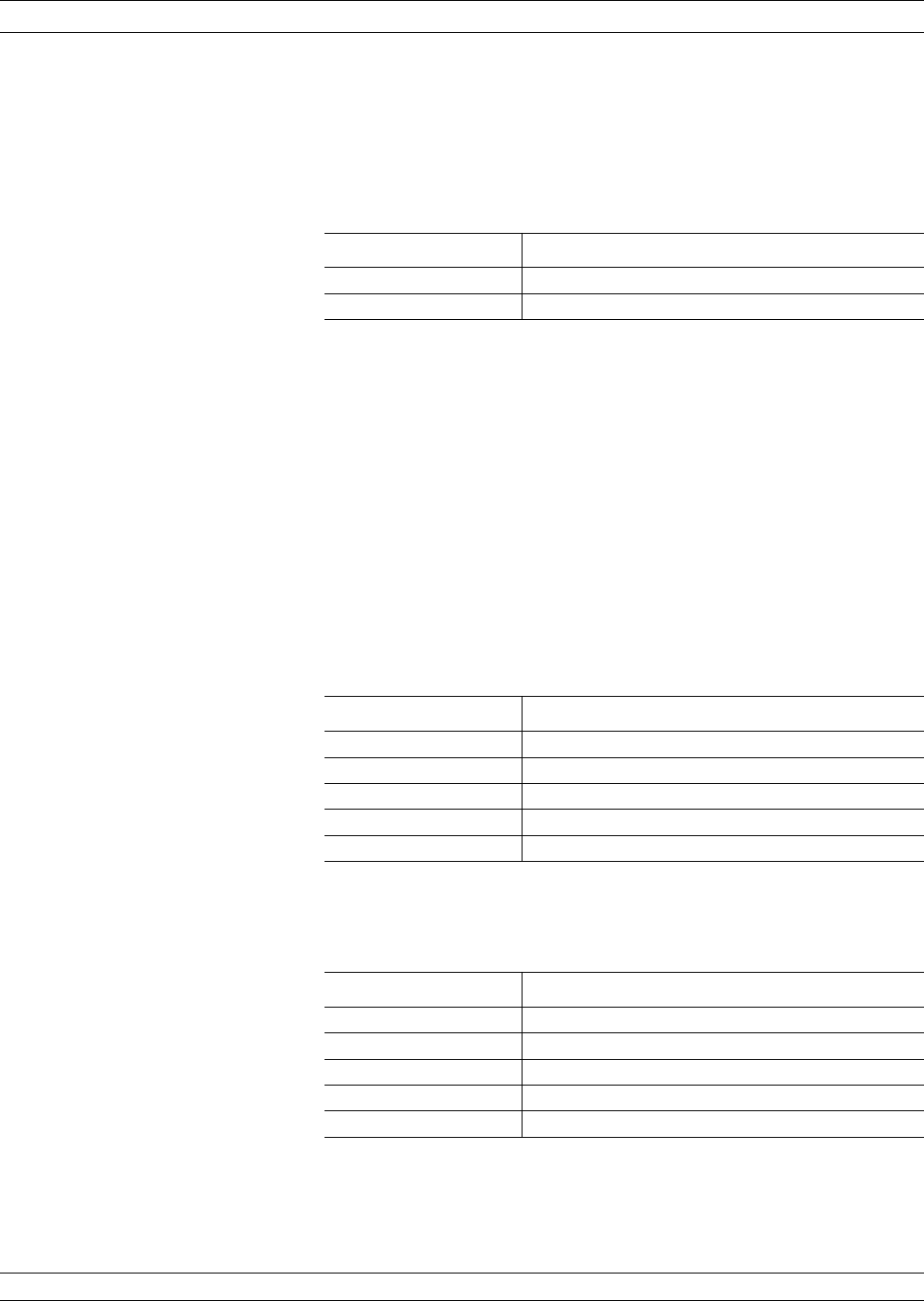
371XXC The 371XXC is a direct-receiver access (DRA) VNA consisting of two
models that cover a range from 22.5 MHz to 40 GHz. It cannot make
S-parameter measurements without the use of an external
reflectometer. See “Important Note” below.
Model Frequency Range
37147C 22.5 MHz to 20.0 GHz
37169C 22.5 MHz to 40.0 GHz
IMPORTANT NOTE
The 37100C Direct Access Receiver cannot make S-param-
eter measurements without an external reflectometer
setup. This manual describes calibration and S-parameter
measurements for 372XXC and 373XXC. Most of these
measurements can also be used with 371XXC assuming
the user understands the need for an external
reflectometer. Anritsu offers an optional reflectometer test
set that can be used. This reflectometer is described and a
drawing shown in the Technical Data Sheet provided as
Appendix C in this manual.
372XXC The 372XXC is a fully functioning VNA for making passive-device
measurements. The series offers five models that cover a range from
22.5 MHz to 65 GHz. The models are shown below:
Model Frequency Range
37225C 40.0 MHz to 13.5 GHz
37247C 40.0 MHz to 20.0 GHz
37269C 40.0 MHz to 40.0 GHz
37277C 40.0 MHz to 50.0 GHz
37297C 40.0 MHz to 65.0 GHz
373XXC The 373XXC is a fully functioning VNA for making passive- and ac-
tive-device measurements. The series offers five models that cover a
range from 22.5 MHz to 65 GHz. The models are shown below.
Model Frequency Range
37325C 40.0 MHz to 13.5 GHz
37347C 40.0 MHz to 20.0 GHz
37369C 40.0 MHz to 40.0 GHz
37377C 40.0 MHz to 50.0 GHz
37397C 40.0 MHz to 65.0 GHz
SYSTEM DESCRIPTION GENERAL INFORMATION
1-4 37XXXC OM
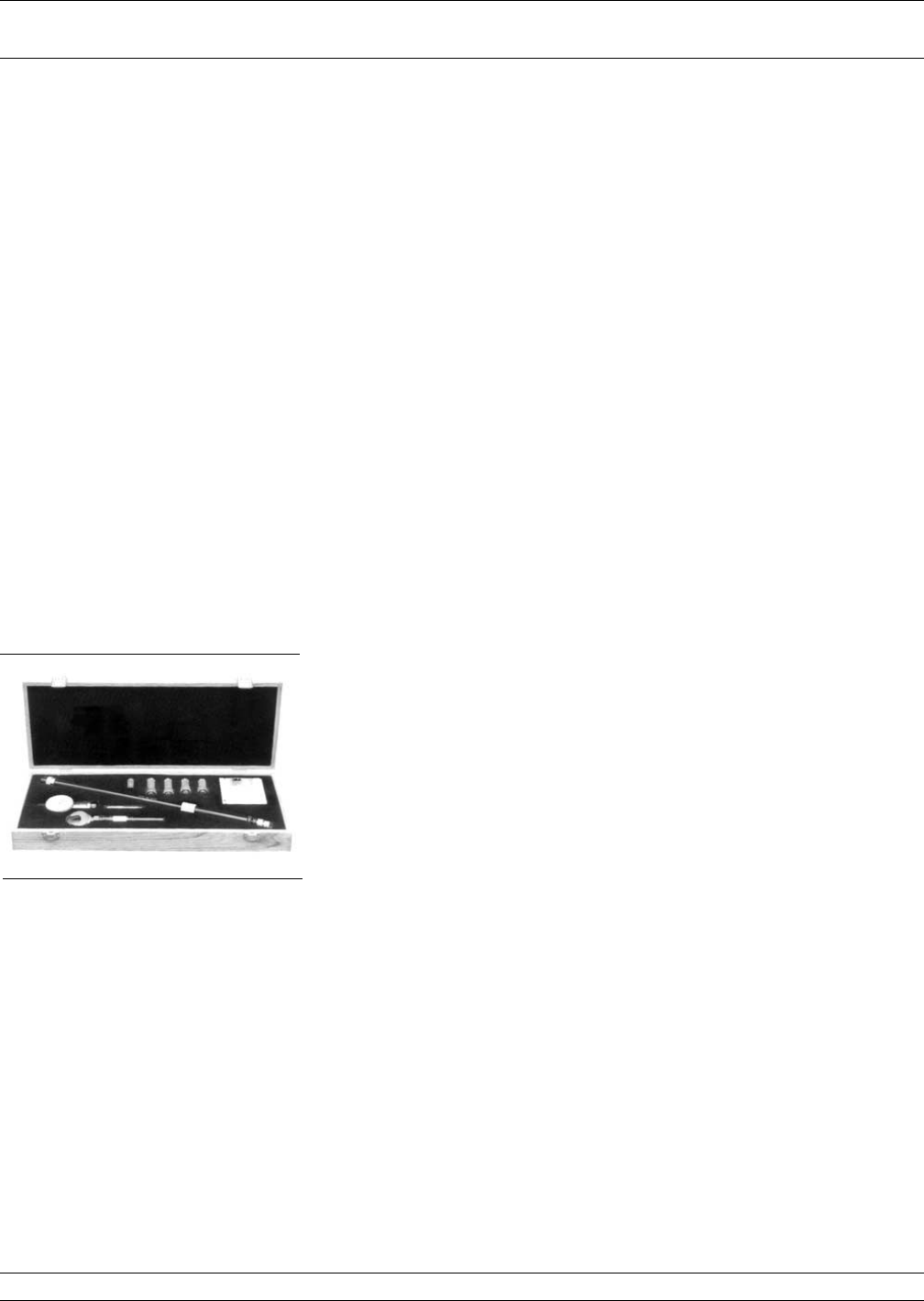
1-6 MILLIMETER WAVE
MEASUREMENTS The 371XXC can be equipped for making millimeter wave measure-
ments. A description of this measurement mode is provided in
Chapter 14.
1-7 PRECISION COMPONENT
KITS Two types of precision-component kits are available: calibration and
verification. Calibration kits contain components used to identify and
separate error sources inherent in microwave test setups. Verification
kits consist of components with characteristics traceable to the
National Institute of Standards and Technology (NIST). This type of
kit is usually kept in the metrology laboratory where it provides the
most dependable means of checking system accuracy. Each of these
kits contains a micro-floppy disk providing coefficient or measurement
data for each component. Details of these kits are described in the fol-
lowing paragraphs.
Model 3650 SMA/3.5 mm
Calibration Kit The 3650 Calibration Kit (Figure 1-2) contains all the precision
components and tools required to calibrate the 37XXXC VNA for
12-term error-corrected measurements of test devices with SMA or
3.5 mm connectors. Components are included for calibrating both male
and female test ports. The kit supports calibration with broadband
loads. The kit consists of the following components:
q23S50 Short, SMA/3.5 mm Male
q23SF50 Short, SMA/3.5 mm Female
q24S50 Open, SMA/3.5 mm Male
q24SF50 Open, SMA/3.5 mm Female
q28S50–2 Termination, SMA/3.5 mm Male, 2 ea. (dc–26.5 GHz)
q28SF50–2 Termination, SMA/3.5 mm Female, 2 ea.(dc–26.5 GHz)
q33SFSF50 Insertable, SMA/3.5 mm Female/Female, 2 ea.
q33SS50 Insertable, SMA/3.5 mm Male/Male
q33SSF50 Insertable, SMA/3.5 mm Male/Female, 2 ea.
q34AS50–2 Adapter, GPC–7 to SMA/3.5 mm Male, 2 ea.
q34ASF50-2 Adapter, GPC–7 to SMA/3.5 mm Female, 2 ea.
q01–201 Torque Wrench
q01–210 Reference Flat
q01–222 Connector Gauge
q01–223 Gauge Kit Adapter
qData Disk
Option 1: Adds 17S50 Sliding Load, SMA/3.5 mm Male; 17SF50
Sliding Load, SMA/3.5 mm Female; 01–211 Female Flush Short; and
01–212 Male Flush Short.
37XXXC OM 1-5
GENERAL INFORMATION MILLIMETER WAVE
MEASUREMENTS
Figure 1-2. Typical Model 365X
Calibration Kit
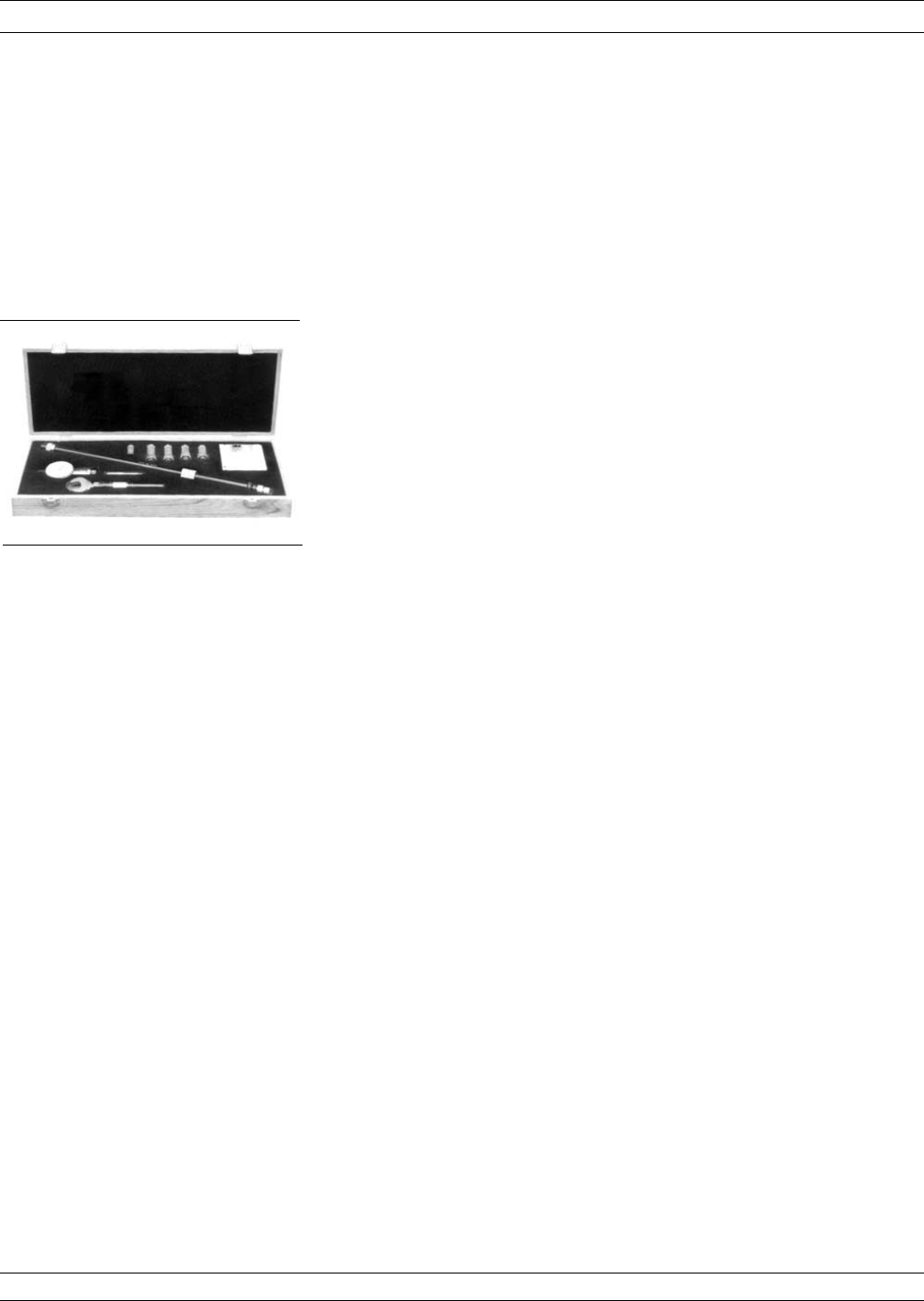
Model 3651 GPC–7
Calibration Kit The 3651 Calibration Kit (Figure 1-3) contains all the precision
components and tools required to calibrate the 37XXXC for 12-term
error-corrected measurements of test devices with GPC–7 connectors.
The kit supports calibration with broadband loads. Option 1 adds a
sliding load and a pin depth gauge.
The kit consists of the following components:
q23A50 Short, GPC–7
q24A50 Open, GPC–7
q28A50–2 Termination, GPC–7, 2 ea. (dc–18 GHz)
q01–200 Torque Wrench
q01–221 Collet Extractor Tool and Vial of Four Collets
qData Disk
Option 1 Adds:
q17A50 Sliding Load, GPC–7
q01–220 GPCP–7 Connector Gauge
q01–210 Reference Flat Model 3652 K Connector® Calibration Kit
PRECISION COMPONENT KITS GENERAL INFORMATION
1-6 37XXXC OM
Figure 1-3. Typical Model 365X
Calibration Kit
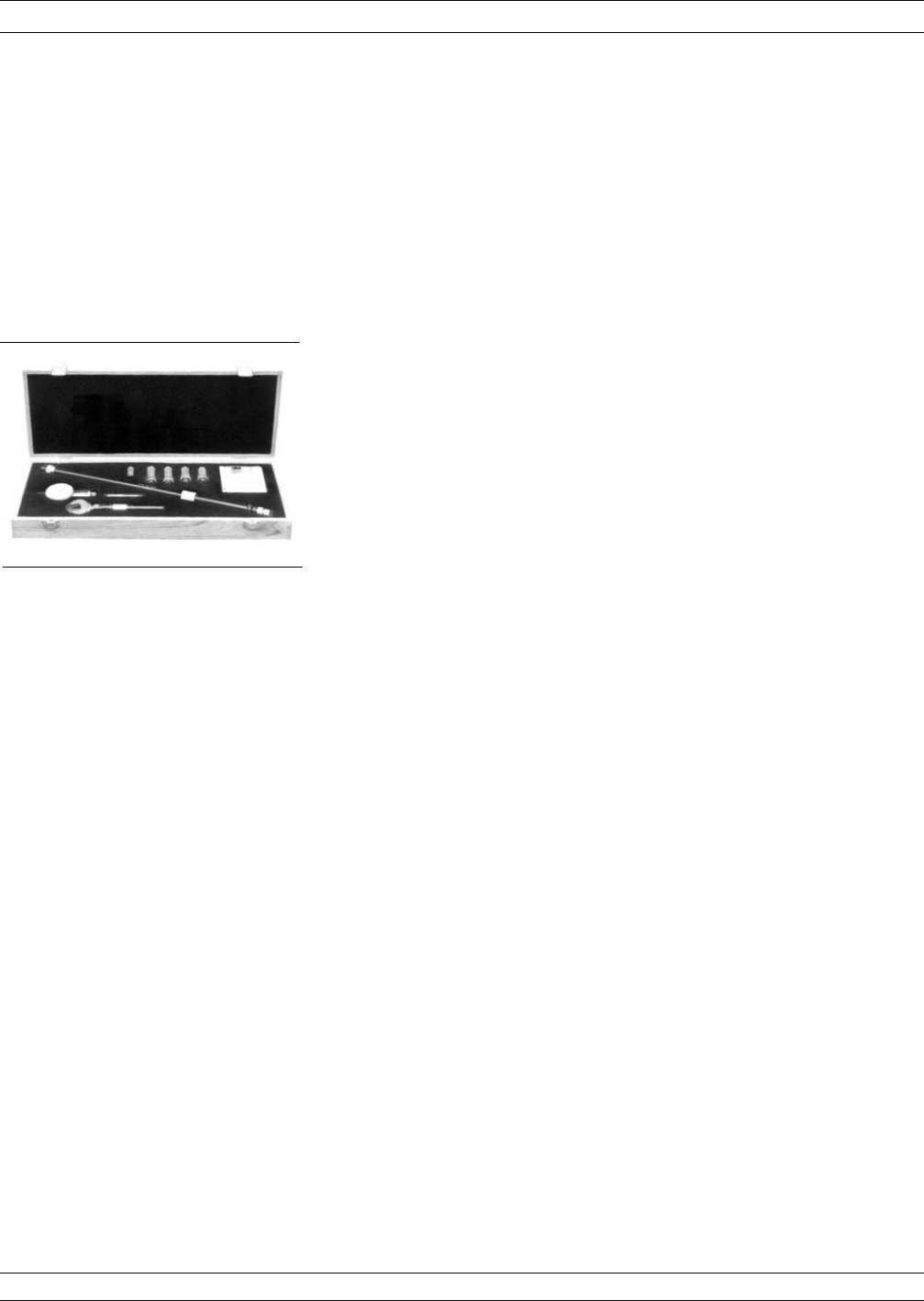
Model 3652 K Connector
Calibration Kit The 3652 Calibration Kit (Figure 1-4) contains all the precision
components and tools required to calibrate the 37XXXC for 12-term
error-corrected measurements of test devices with K Connectors.
Components are included for calibrating both male and female test
ports. The kit supports calibration with broadband loads. Option 1
adds sliding loads.
The kit consists of the following components:
q23K50 Short, K Male
q23KF50 Short, K Female
q24K50 Open, K Male
q24KF50 Open, K Female
q28K50 Termination, K Male, 2 ea. (dc–40 GHz)
q28KF50 Termination, K Female, 2 ea. (dc–40 GHz)
q33KK50 Insertable, K Male/Male
q33KFKF50 Insertable K Female/Female, 2 ea.
q33KKF50 Insertable, K Male/Female, 2 ea.
q34AK50 Adapter, GPC–7/K Male, 2 ea.
q34AKF50 Adapter, GPC–7/K Female, 2 ea.
q01–201 Torque Wrench
q01–210 Reference Flat
q01–222 Connector Gauge
q01–223 Gauge Kit Adapter
qData Disk
Option 1 Adds:
q17K50 Sliding Load, K Male
q17KF50 Sliding Load, K Female
q01–211 Female Flush Short
q01–212 Male Flush Short.
37XXXC OM 1-7
GENERAL INFORMATION PRECISION COMPONENT KITS
Figure 1-4. Typical Model 365X
Calibration Kit
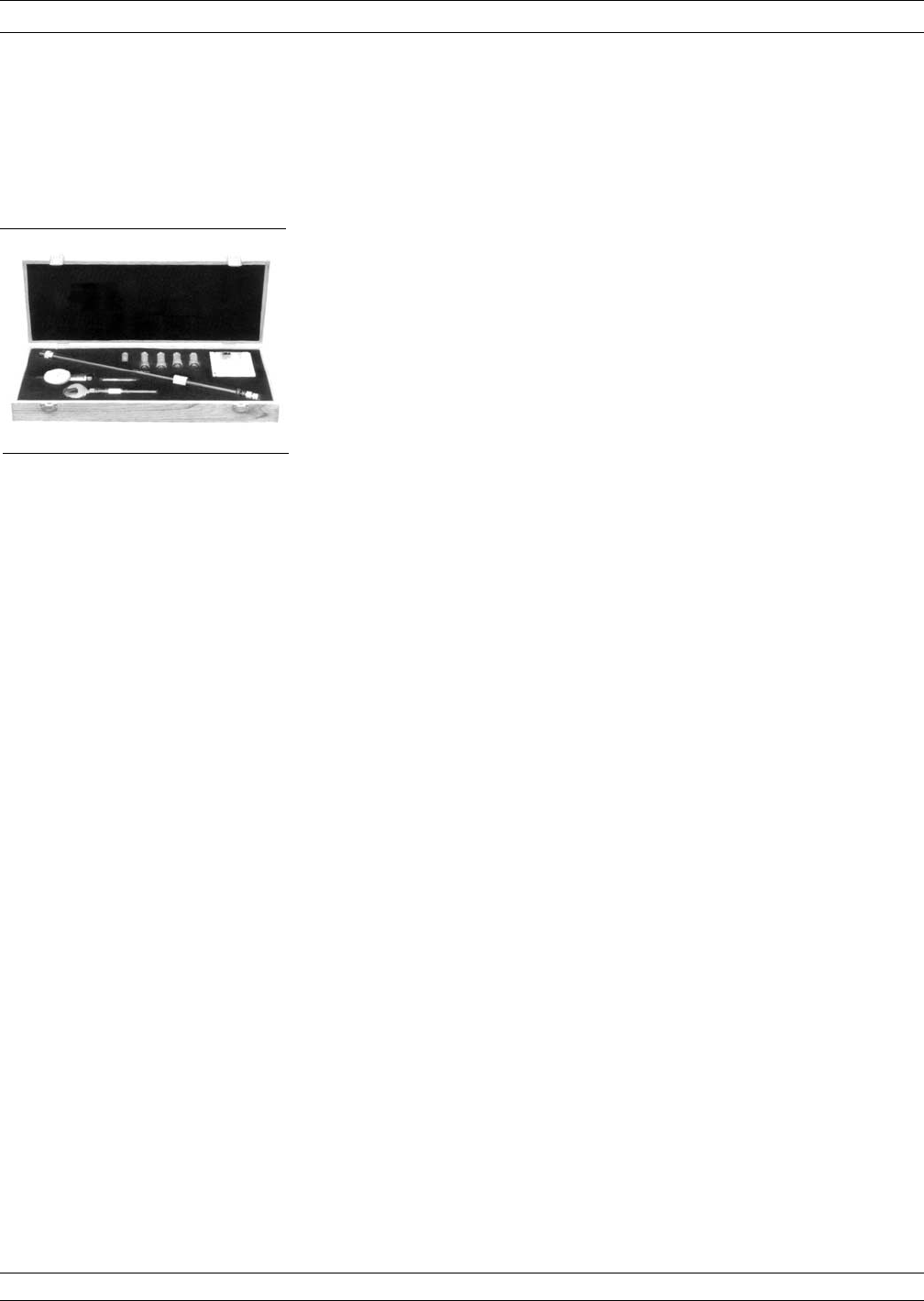
Model 3653 Type N
Calibration Kit The 3653 Calibration Kit (Figure 1-5) contains all the precision
components and tools required to calibrate the 37XXXC for 12-term
error-corrected measurements of test devices with Type N connectors.
Components are included for calibrating both male and female test
ports. The kit supports calibration with broadband loads. Option 1 for
sliding loads is not available in this calibration kit.
The kit consists of the following components:
q23N50 Short, N Male
q23NF50 Short, N Female
q24N50 Open, N Male
q24NF50 Open, N Female
q28N50–2 Termination, N Male, 2 ea. (dc–18 GHz)
q28NF50–2 Termination, N Female, 2 ea. (dc–18 GHz)
q34AN50–2 Adapter, GPC–7/N Male, 2 ea.
q34ANF50–2 Adapter, GPC–7/N Female, 2 ea.
q01–213 Type N Reference Gauge
q01–224 Type N Connector Gauge
qData Disk Model 3654B
PRECISION COMPONENT KITS GENERAL INFORMATION
1-8 37XXXC OM
Figure 1-5. Typical Model 365X
Calibration Kit
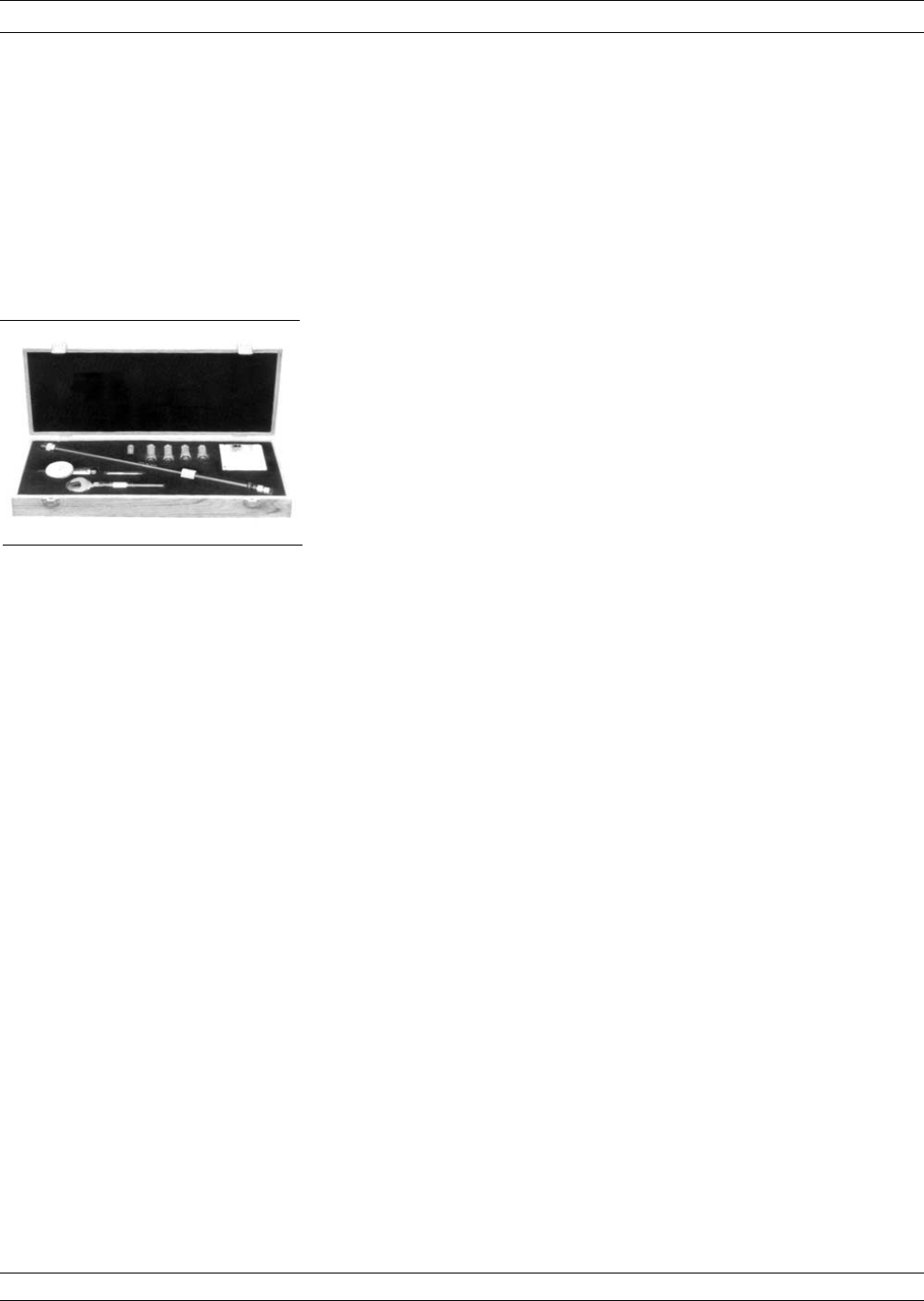
Model 3654B
V Connector® Calibration
Kit
The 3654B Calibration Kit (Figure 1-6) contains all the precision
components and tools required to calibrate the 372XXC for 12-term
error-corrected measurements of test devices with V Connectors.
Components are included for calibrating both male and female test
ports.
The kit consists of the following components:
q17VF50B Female Sliding Termination
q17V50B Male Sliding Termination
q33VVF50 Male-Female Adapter (2)
qCalibration Software, 2360-54B
q28V50B Male and 28VF50B Female Broadband Terminations
(2 ea.)
q24V50B Male and 24VF50B Female Opens
q23V50B-5.1 Male and 23VF50B-5.1 Female Shorts 5.1mm
q33VV50 Male-Male Adapter
q33VFVF50 Female-Female Adapter (2)
qConnector Thumb Wheel (4)
q01-201 Torque Wrench
q01-323 Female Adapter for Pin Gauge
q01-322 Pin Depth Gauge
q01-210 Reference Flat, 01-204 Adapter Wrench
q01-312 Male Flush Short
q01-311 Female Flush Short
37XXXC OM 1-9
GENERAL INFORMATION PRECISION COMPONENT KITS
Figure 1-6. Typical Model 365X
Calibration Kit
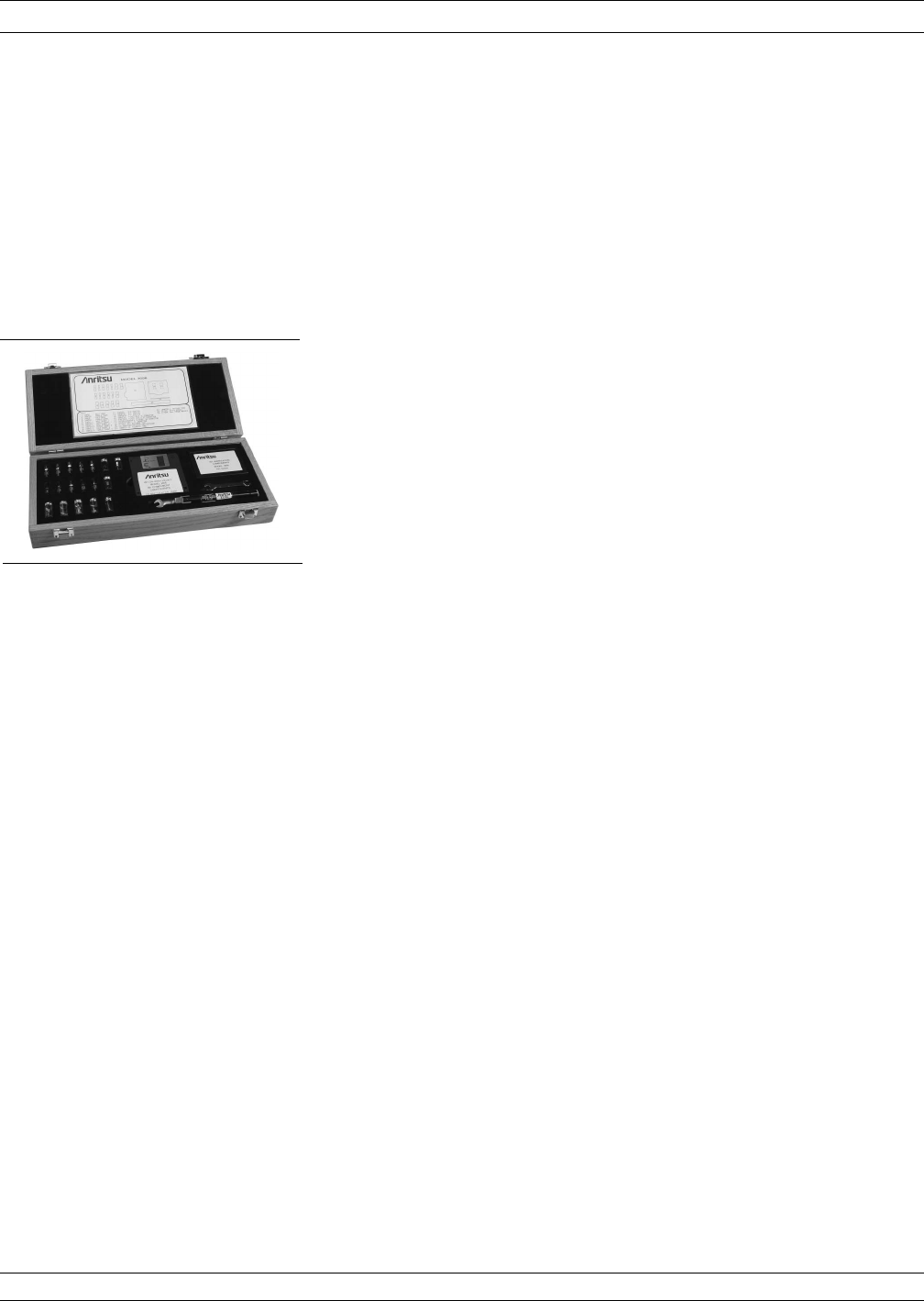
Model 3656 W1 Connector
Calibration Kit The 3656 W1 (1.0 mm) Connector Calibration Kit (Figure 1-7) consists
of precision components to calibrate the VNA to 110 GHz. The kit sup-
ports SOLT calibrations with opens, shorts, and loads to 65 GHz, and
Triple Offset short calibrations from 65 GHz to 110 GHz. The kit also
includes verification devices for determining system accuracy of the
VNA. A diskette containing factory measured test data is supplied for
comparison with customer measured data.
q23W50-1, Male Offset Short 2.02 mm
q23WF50-1, Female Offset Short 2.02 mm
q23W50-2, Male Offset Short 2.65 mm
q23WF50-2, Female Offset Short 2.65 mm
q23W50-3, Male Offset Short 3.180 mm
q23WF50-3, Female Offset Short 3.180 mm
q24W50, Male Open 1.510 mm
q24WF50, Female Open 1.930 mm
q28W50, Male Broadband Termination
q28WF50, Female Broadband Termination
q33WW50, Male-Male Adapter (1)
q33WWF50, Male-Female Adapter (1)
q33WFWF50, Female-Female Adapter (1)
q01-401, Interchangeable Adapter Fixed Female
q01-402, Interchangeable Adapter Fixed Male
q18WWF50-1, 50 Matched Thruline (Verification Device)
q18WWF50-1B, Stepped Impedance Thruline (Verification Device)
q01-504, Torque Wrench
q01-505, End Wrench
qCalibration coefficients diskette
qVerification kit diskette
1-10 37XXXC OM
PRECISION COMPONENT KITS GENERAL INFORMATION
Figure 1-7. Typical Model 3656
Calibration Kit
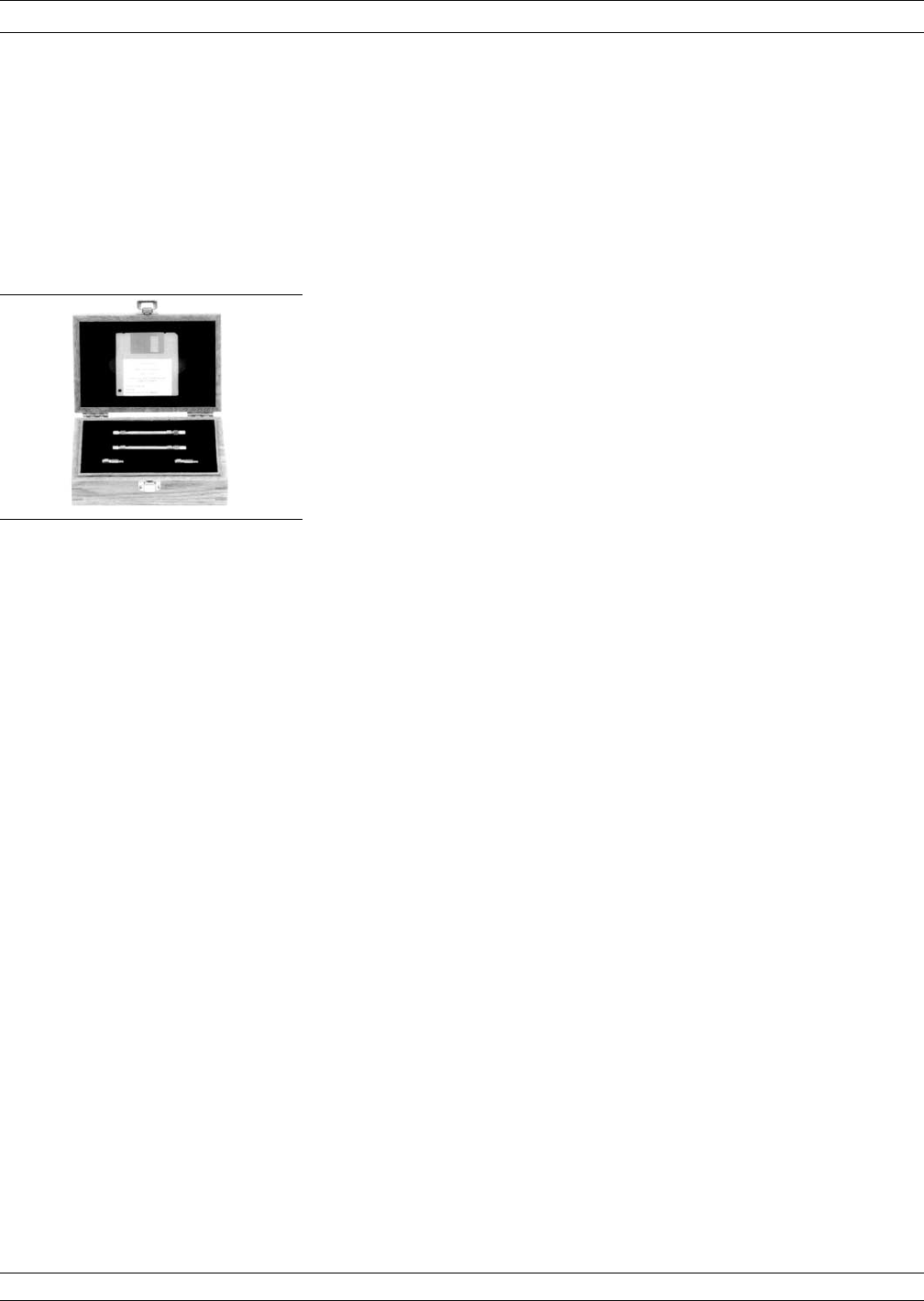
Model 3666 3.5 mm
Verification Kit The 3666 Verification Kit (Figure 1-8) contains precision 3.5 mm
components with characteristics that are traceable to the NIST. Used
primarily by the metrology laboratory, these components provide the
most dependable means of determining system accuracy. A disk
containing factory-measured test data for all components is supplied
for comparison with customer-measured data.
The 3666 consists of the following components:
q19S50–7 7.5 cm Air Line
q19S50–7B 7.5 cm Stepped Impedance Air Line (Beatty Standard)
q42S–20 20 dB Attenuator
q42S–50 50 dB Attenuator
37XXXC OM 1-11
GENERAL INFORMATION PRECISION COMPONENT KITS
Figure 1-8. Typical Model 366x
Verification Kit
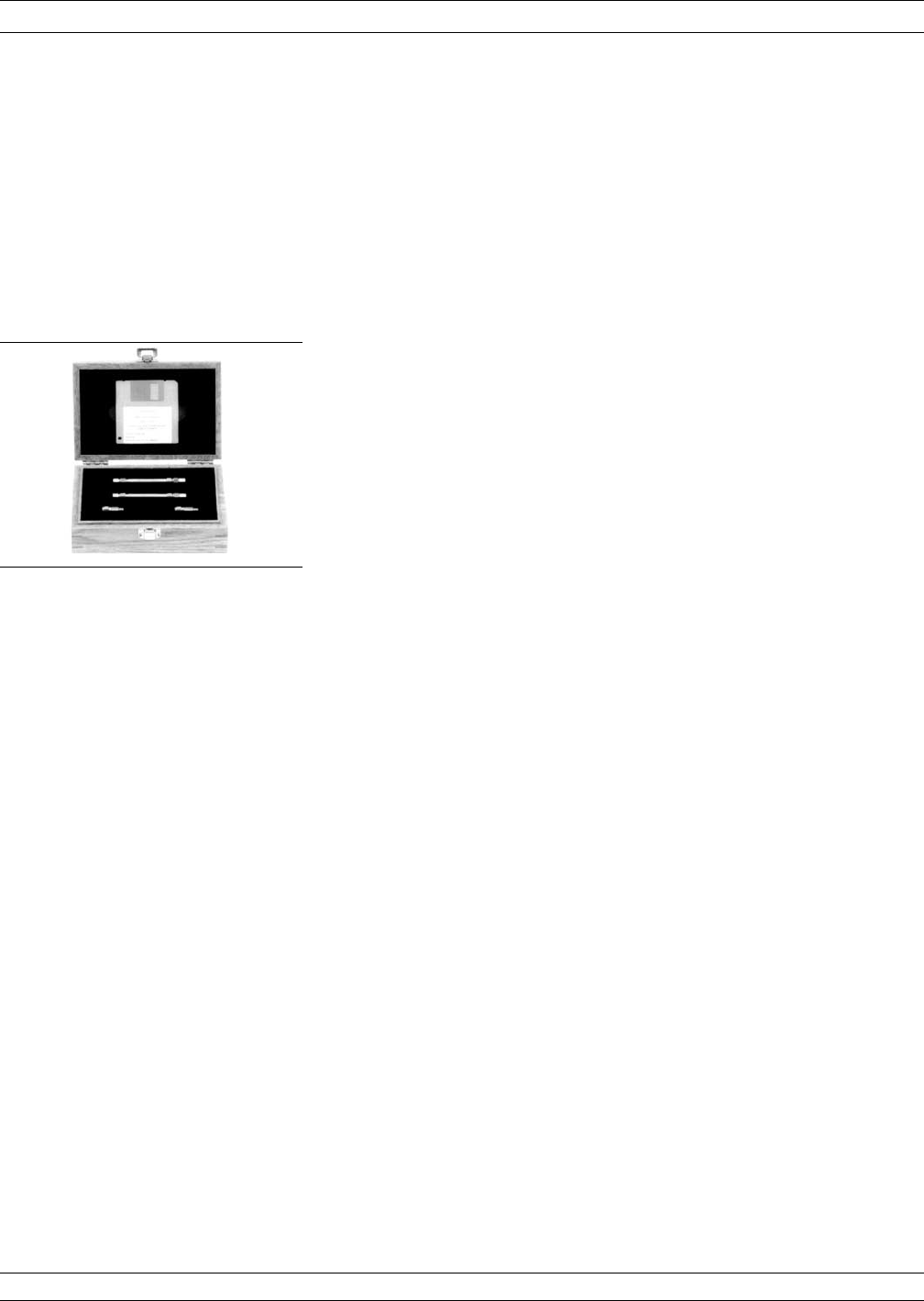
Model 3667 GPC–7
Verification Kit The 3667 Verification Kit (Figure 1-9) contains precision GPC–7
components with characteristics that are traceable to the NIST. Used
primarily by the metrology laboratory, these components provide the
most dependable means of determining system accuracy. A disk
containing factory-measured test data for each component is supplied
for comparison with customer-measured data.
The kit consists of the following components:
q18A50–10B 10 cm Stepped Impedance Air Line
(Beatty Standard)
q18A50–10 10 cm Air Line
q42A–20 20 dB Attenuator
q42A–50 50 dB Attenuator
PRECISION COMPONENT KITS GENERAL INFORMATION
1-12 37XXXC OM
Figure 1-9. Typical Model 366x
Verification Kit
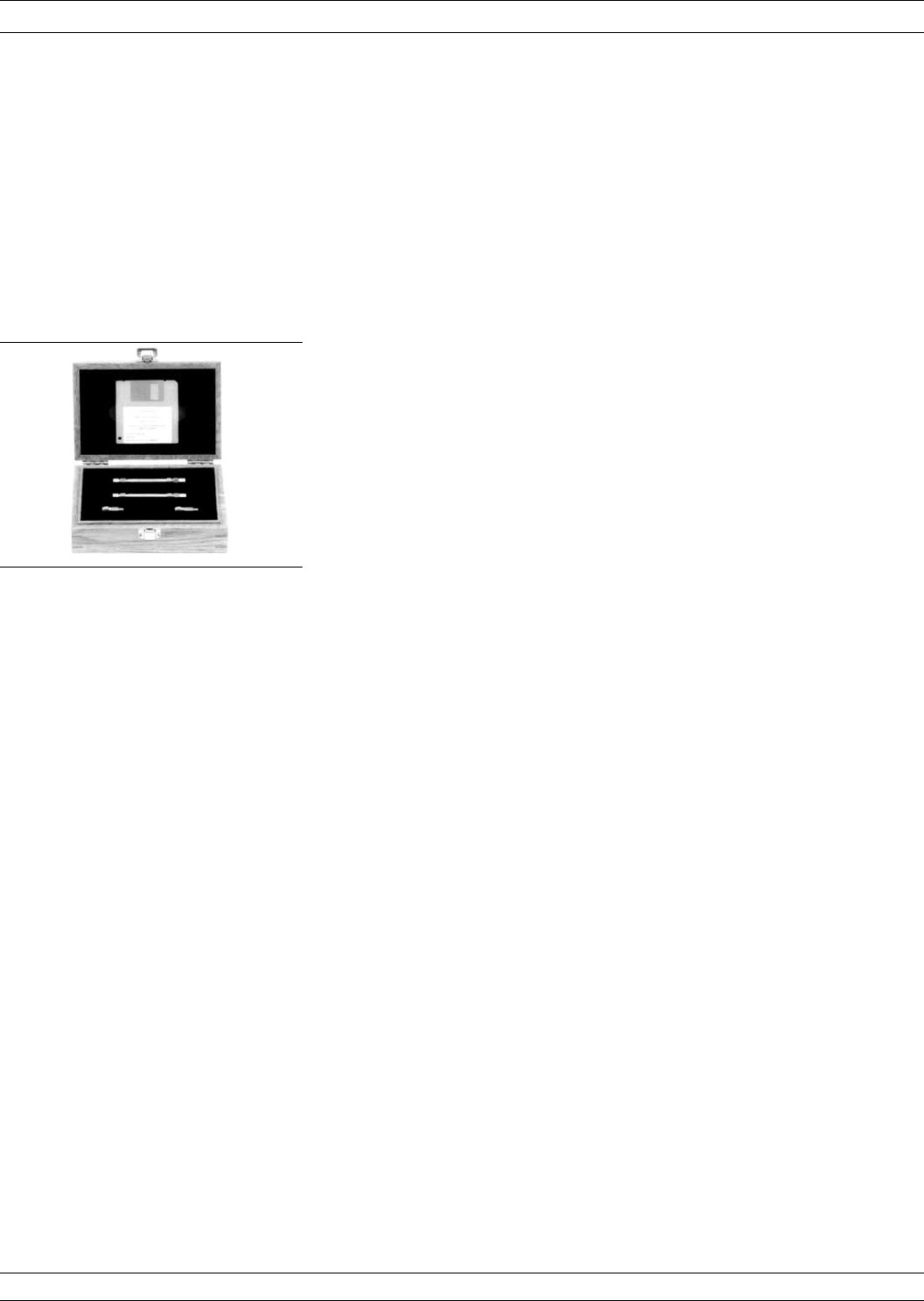
Model 3668
K Connector® Verification
Kit
The 3668 Verification Kit (Figure 1-10) contains precision K Connector
components with characteristics that are traceable to the NIST. Used
primarily by the metrology laboratory, these components provide the
most dependable means of determining system accuracy. A disk
containing factory-measured test data for each component is supplied
for comparison with customer-measured data.
The kit consists of the following components:
q19K50–7 7.5 cm Air Line
q19K50–7B 7.5 cm Stepped Impedance Air Line (Beatty Stan-
dard)
q42K–20 20 dB Attenuator
q42K–50 50 dB Attenuator
37XXXC OM 1-13
GENERAL INFORMATION PRECISION COMPONENT KITS
Figure 1-10. Typical Model 366x
Verification Kit
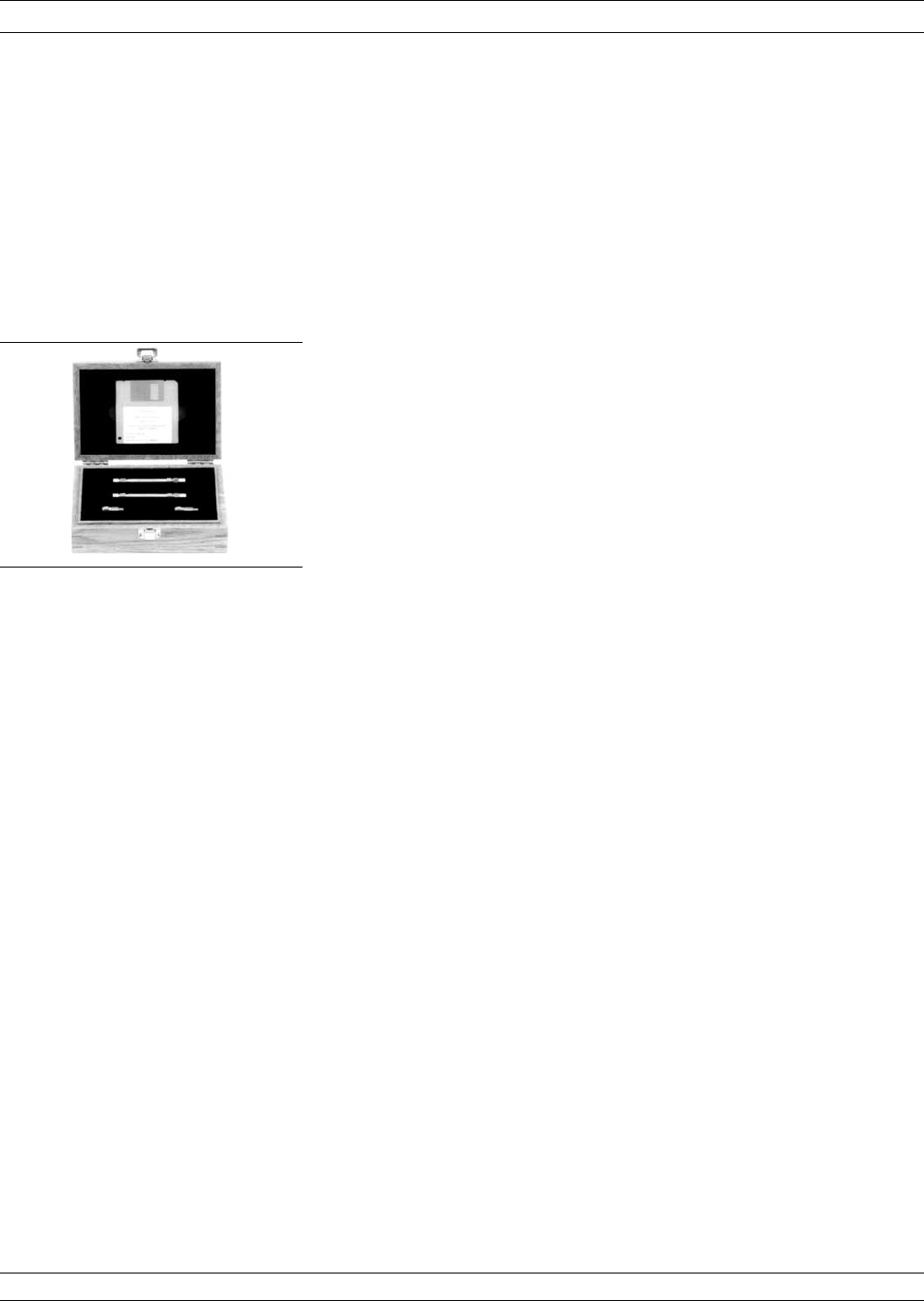
Model 3669/3669B
V Connector® Verification
Kits
The 3669 and 3669B Verification Kits (Figure 1-11) contain precision
V Connector components with characteristics that are traceable to the
NIST. Used primarily by the metrology laboratory, these components
provide the most dependable means of determining system accuracy. A
disk containing factory-measured test data for each component is
supplied for comparison with customer-measured data.
The kit consists of the following components:
q19-V50-5 5 cm Air Line
q19V50-5B 5 cm Stepped Impedance Air Line (Beatty Standard)
q42V-20 20 dB Attenuator
q42V-40 40 dB Attenuator
PRECISION COMPONENT KITS GENERAL INFORMATION
1-14 37XXXC OM
Figure 1-11. Typical Model 366x
Verification Kit
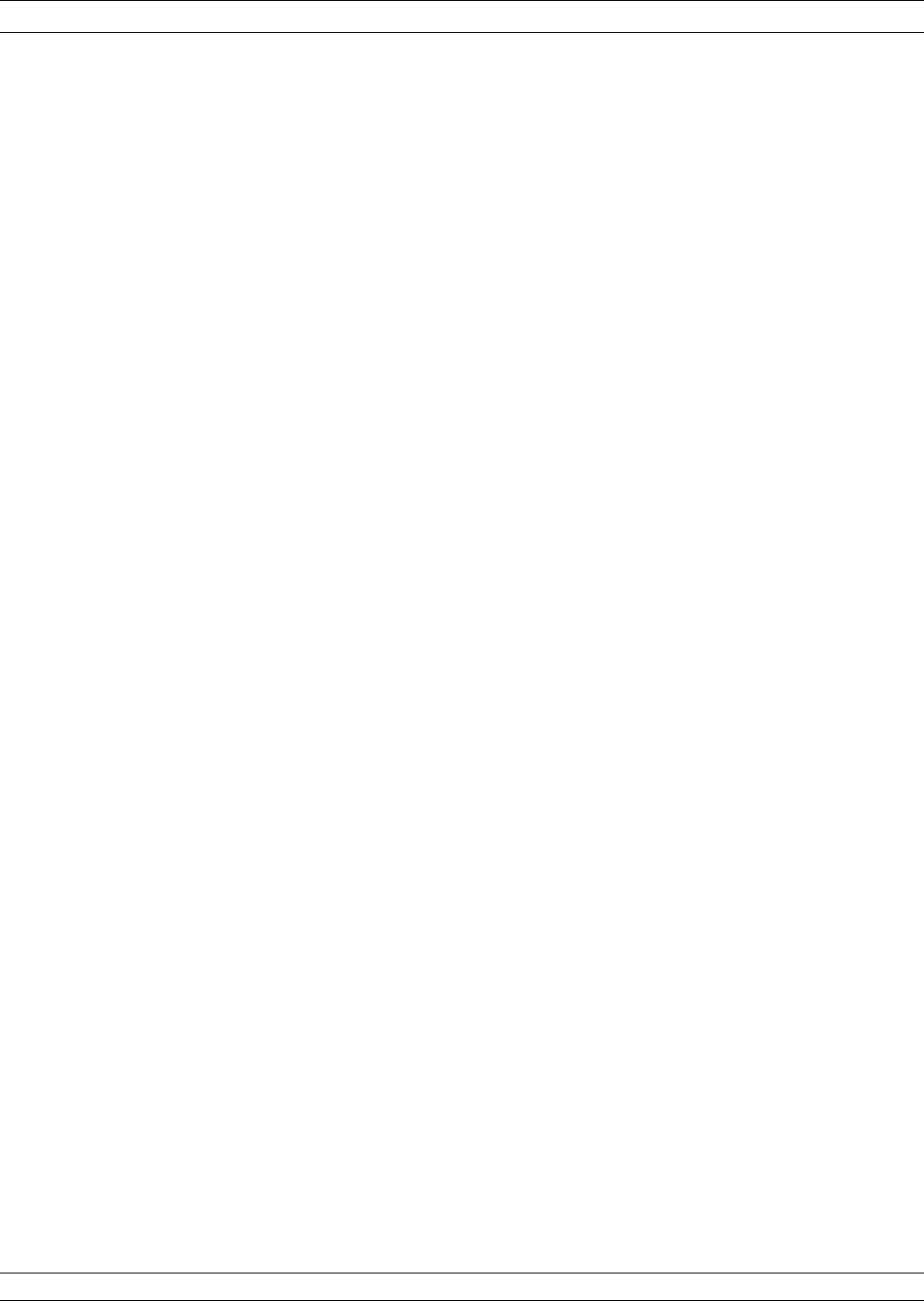
1-8 OPTIONS The following options are available:
qOption 1: Rack Mount Kit
qOption 2: Time (Distance) Domain Measurement Capability
qOption 4: External SCSI Hard Drive Interface
qOption 11: Reference Loop Extension Cables
qOption 12: Rear Panel I.F. Inputs
qOption 13: Delete source (371xxC models only)
1-9 PERFORMANCE
SPECIFICATIONS System performance specifications are provided in Appendix C.
1-10 PREVENTIVE
MAINTENANCE The 37XXXC VNA system does not require any preventive mainte-
nance.
37XXXC OM 1-15/1-16
GENERAL INFORMATION OPTIONS

Table of Contents
2-1 INTRODUCTION ...................................2-3
2-2 INITIAL INSPECTION ................................2-3
2-3 PREPARATION FOR USE ..............................2-3
Option 4, External SCSI Drive Setup .......................2-4
2-4 GPIB SETUP .....................................2-5
Interface Connector .................................2-5
Cable Length Restrictions .............................2-5
2-5 SYSTEM GPIB INTERCONNECTION........................2-6
GPIB Interface to an External Plotter .......................2-6
GPIB Addresses...................................2-6
2-6 EXTERNAL MONITOR CONNECTOR .......................2-6
2-7 RACK MOUNT.....................................2-6
2-8 STORAGE OR SHIPMENT ..............................2-9
Preparation for Storage...............................2-9
Preparation for Shipment..............................2-9
2-9 SERVICE CENTERS.................................2-10
Chapter 2
Installation
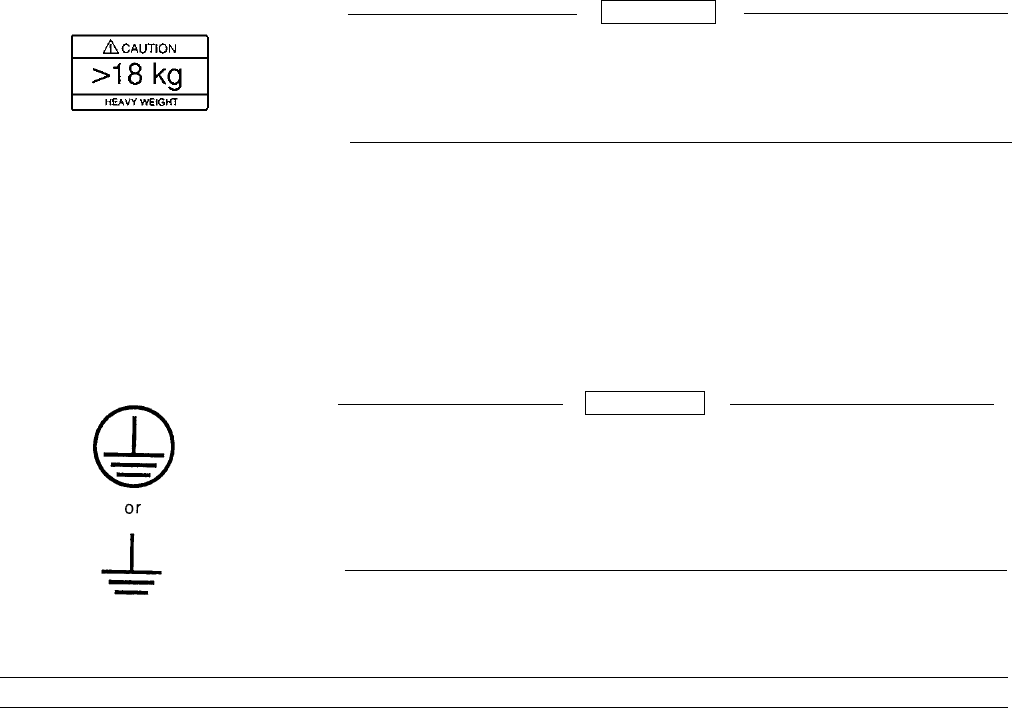
Chapter 2
Installation
2-1 INTRODUCTION This chapter provides information for the initial inspection and prepa-
ration for use of the 37XXXC Vector Network Analyzer. Information
for interfacing the 37XXXC to the IEEE-488 General Purpose Inter-
face Bus and reshipment and storage information is also included.
2-2 INITIAL INSPECTION Inspect the shipping container for damage. If the container or cushion-
ing material is damaged, retain until the contents of the shipment
have been checked against the packing list and the instrument has
been checked for mechanical and electrical operation.
If the 37XXXC is damaged mechanically, notify your local sales repre-
sentative or Anritsu Customer Service. If either the shipping container
is damaged or the cushioning material shows signs of stress, notify the
carrier as well as Anritsu. Keep the shipping materials for the car-
rier’s inspection.
2-3 PREPARATION FOR USE Except for units with Option 4 (see following page), no initial setup is
required. After unpacking, the 37XXXC is ready for use. The 37XXXC
is equipped with automatic line-power sensing, and will operate with
any of the following line voltages: 100V, 120V, 220V, 240V +5%, –10%,
48–63 Hz, 350 VA. The 37XXXC is intended for Installation Category
(Overvoltage Category) II.
37XXXC OM 2-3
Use two or more people to lift and move this equipment, or use an
equipment cart. There is a risk of back injury, if this equipment is lifted
by one person.
WARNING
When supplying power to this equipment, always use a three-wire
power cable connected to a three-wire power line outlet. If power is sup-
plied without grounding the equipment, there is a risk of receiving a se-
vere or fatal electric shock.
WARNING
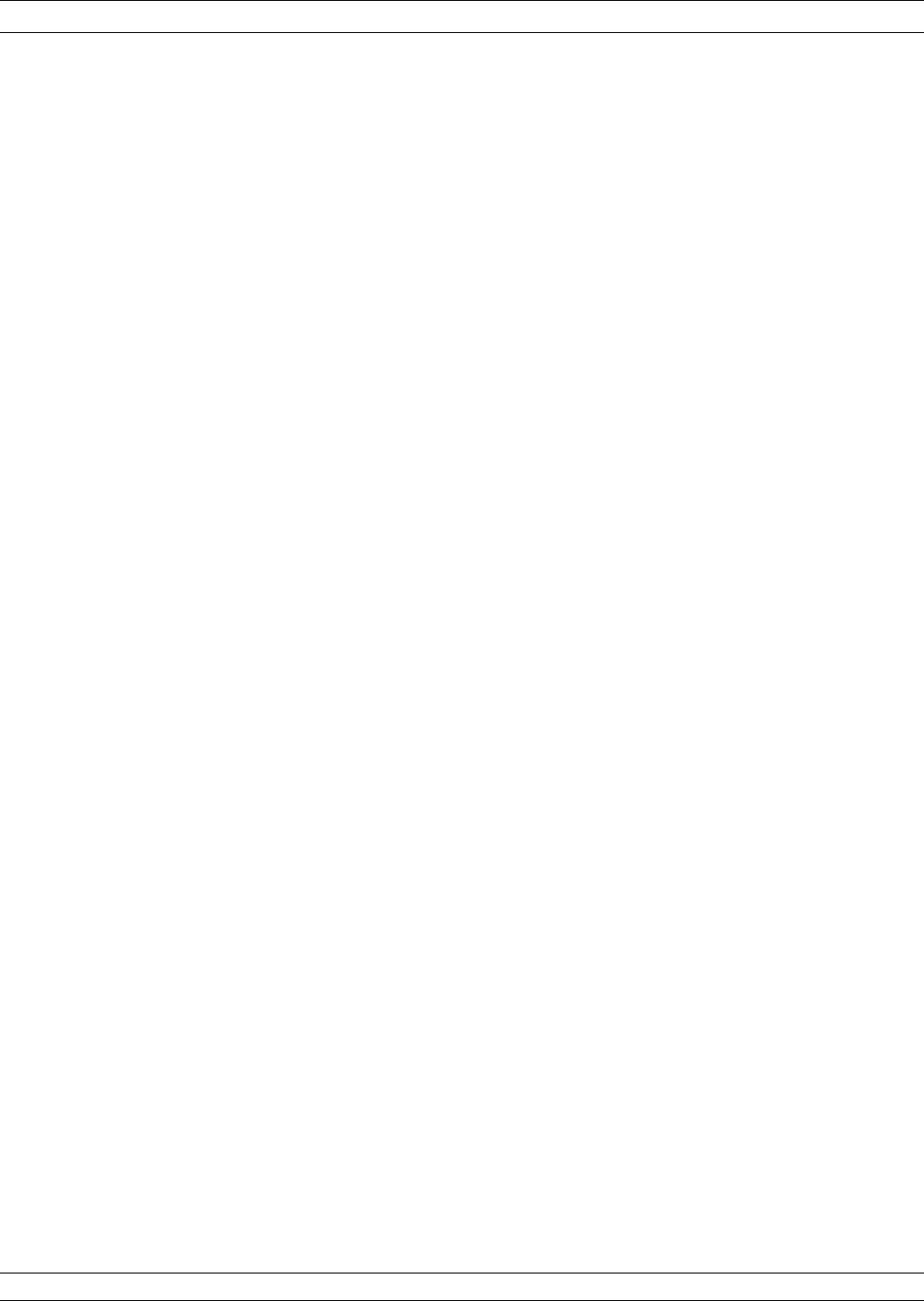
Option 4,
External SCSI Drive Setup The 37XXXC is available with an external SCSI drive interface as Op-
tion 4. This option deletes the usual internal hard disk and provides
support for the use of an external SCSI drive.
An external SCSI drive and interface cable are not included with
Option 4, but may be purchased from Anritsu. Contact your local sales
representative for information on availability and price. Compatible
drives may also be purchased from your local computer retailer.
Requirements:
qInterface: SCSI, SCSI-2
qSupported Drives: Iomega®Zip®100MB SCSI, Zip®250MB SCSI,
Jaz 1, Jaz 2 (other drives may operate, but are not guaranteed)
qConnector: Centronics 50 Male Pro Series SCSI I
(37XXXC is Female)
qSCSI ID: 5
qTerminated: Yes
System Boot:
Depending on your system configuration at the time of shipment, a
drive (and cartridge) may be included. If not, your external drive must
be connected to the 37XXXC and initialized with the system files as
described below before proceeding.
Ensure that the drive is configured correctly and powered on. If the
drive is a cartridge type, ensure that a cartridge with the system file
on it is installed. Turn on the 37XXXC and the system should boot nor-
mally. Cartridges may then be exchanged if you wish to share files.
Initializing the Drive:
A set of 37000 Basic Measurement Software floppy disks, Anritsu part
number 2300-212, is required. This 4-disk set is supplied with your
shipment. Anritsu recommends BMS version 4.01 or above when using
an external SCSI drive.
NOTE
This operation will erase all of the files on the SCSI drive.
Copy any important files before proceeding.
Step 1. Connect the external drive to the 37XXXC’s rear panel SCSI port with
the interface cable (refer to Appendix B for information on the rear
panel connectors). Ensure that the external SCSI drive is powered on
with a cartridge installed (if applicable).
Step 2. With the 37XXXC powered off, insert Disk 1 of the 37000 BMS into the
37XXXC floppy drive.
Step 3. Power up the 37XXXC and immediately press any key to view the
“Format Hard Drive” menu.
2-4 37XXXC OM
PREPARATION FOR USE INSTALLATION
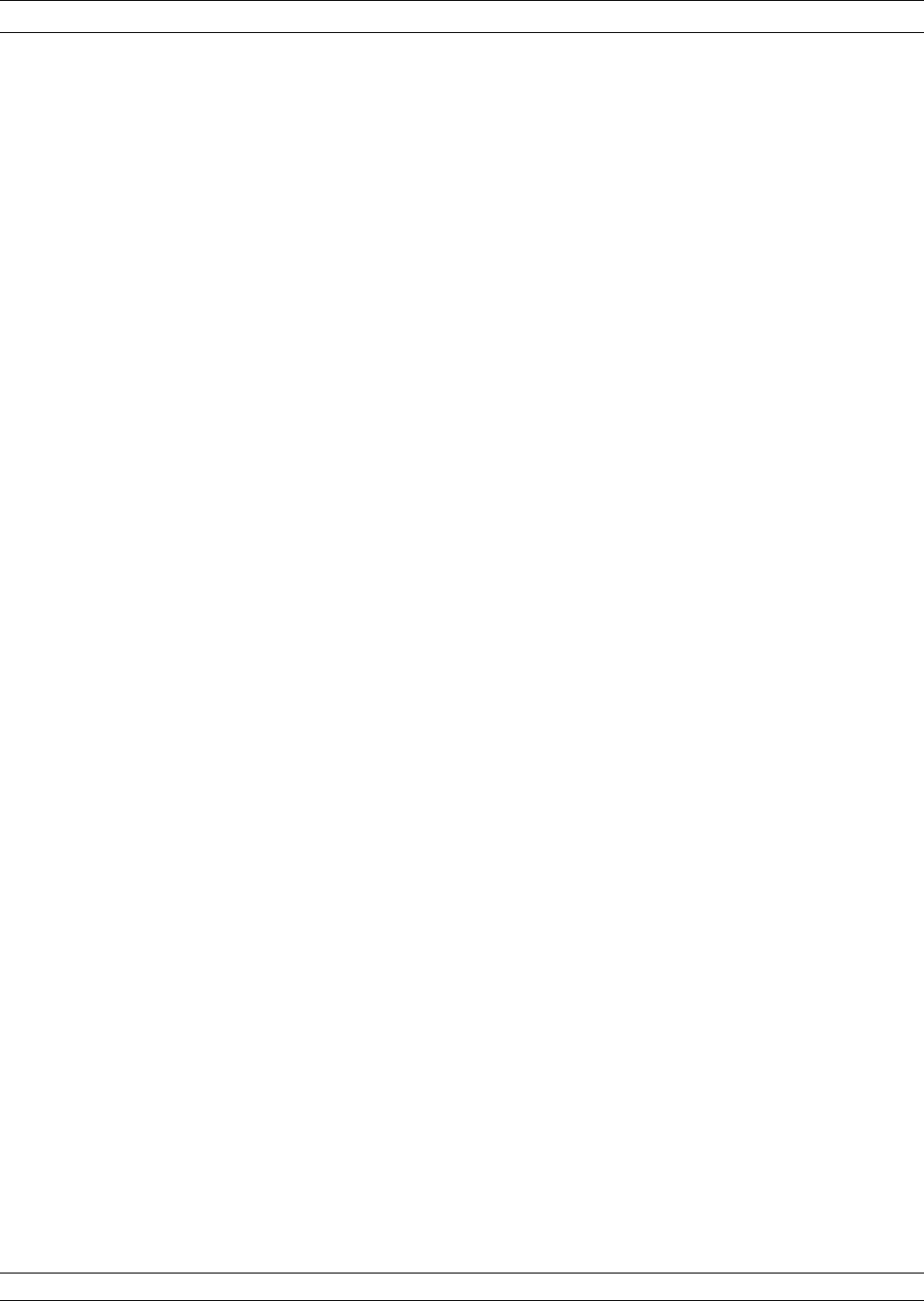
Step 4. Press 1to format the drive. Disk 1 will load automatically.
Step 5. Follow the instructions on the 37XXXC display to load the next three
disks. During this step, the system files are transferred to the SCSI
drive.
The SCSI drive initialization is now complete. The 37XXXC should
sweep with no displayed errors and is now ready to boot-up from the
external drive at power-on.
2-4 GPIB SETUP All functions of the 37XXXC (except power on/off and initialization of
the hard disk) can be controlled remotely by an external computer/con-
troller via the IEEE-488.2 GPIB. The information in this section per-
tains to interface connections and cable requirements for the rear
panel GPIB connector. Refer to the Model 37XXXC Programming Man-
ual, Anritsu Part Number 10410-00227, for information about remote
operation of the 37XXXC using the GPIB.
The 37XXXC GPIB operates with any IBM XT, AT, or PS/2 compatible
computer/controller equipped with a National Instruments
GPIB-PCII/IIA interface card and software.
Interface Connector Interface between the 37XXXC and other devices on the GPIB is via a
standard 24-wire GPIB interface cable. For proper operation, order
Anritsu part number 2100-1, -2, -4, or -5 (1, 2, 4, or 0.5 meter length)
cables through your local sales representative. This cable uses a dou-
ble-sided connector; one connector face is a plug, the other a receptacle.
These double-function connectors allow parallel connection of two or
more cables to a single instrument connector. The pin assignments for
the rear panel GPIB connector are shown in Figure B-1, located in Ap-
pendix B.
Cable Length Restrictions The GPIB system can accommodate up to 15 instruments at any one
time. To achieve design performance on the bus, proper timing and
voltage level relationships must be maintained. If either the cable
length between separate instruments or the accumulated cable length
between all instruments is too long, the data and control lines cannot
be driven properly and the system may fail to perform. Cable length
restrictions are as follows:
qNo more than 15 instruments may be installed on the bus.
qTotal accumulative cable length in meters may not exceed two
times the number of bus instruments or 20 meters—whichever is
less. NOTE
For low EMI applications, the GPIB cable should be a fully
shielded type, with well-grounded metal-shell connec-
tors. (Use Anritsu 2100-series cables.)
37XXXC OM 2-5
INSTALLATION GPIB SETUP
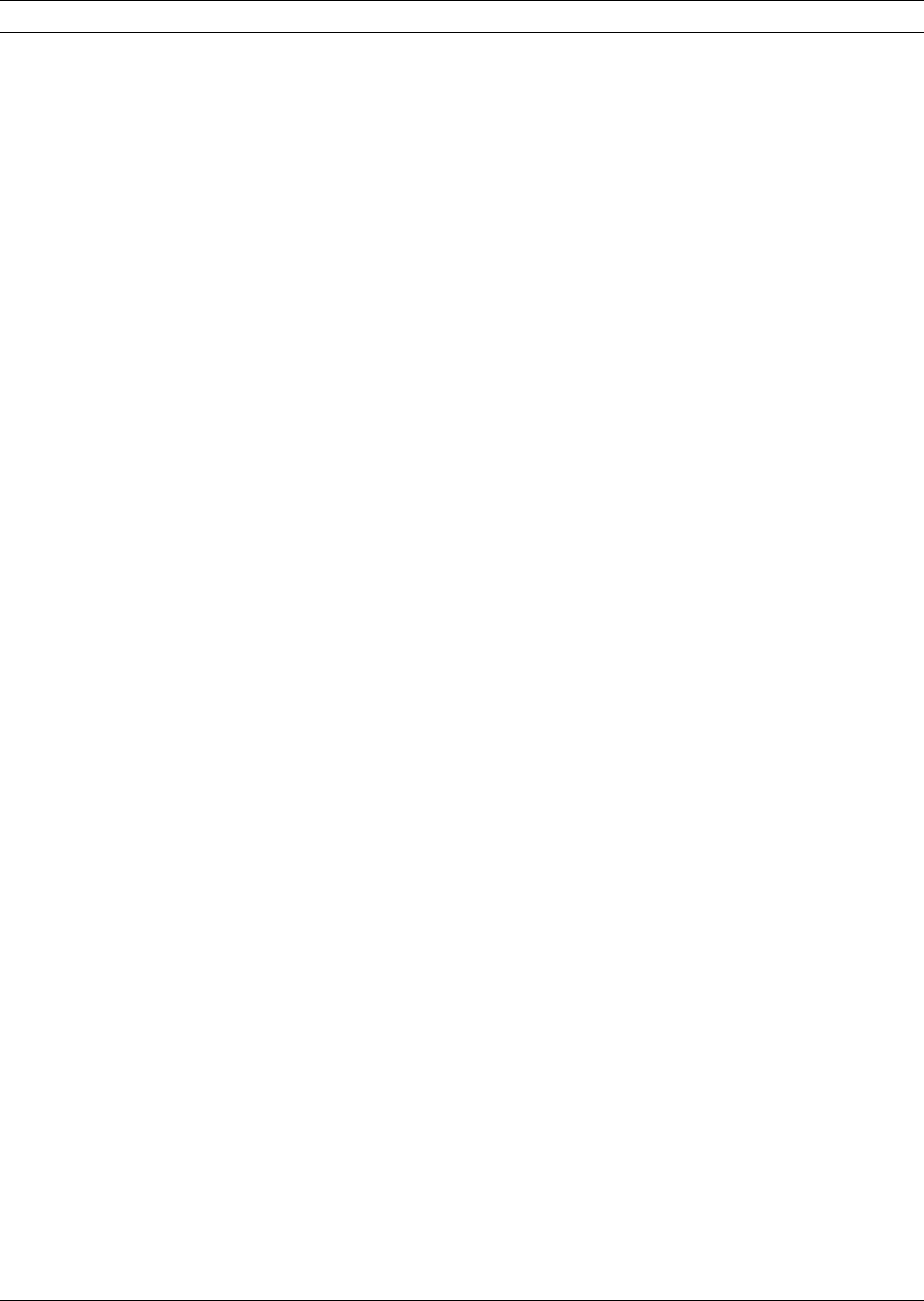
2-5 SYSTEM GPIB
INTERCONNECTION There are two rear panel GPIB IEEE-488 connectors. The IEEE 488.2
connector used to interface the 37XXXC to an external computer/ con-
troller via a standard GPIB cable. The Dedicated GPIB connector is
used to interface to plotters and a second source for multiple source
operation via a standard GPIB cable.
GPIB Interface to an
External Plotter The 37XXXC GPIB interface can be configured to control a suitable ex-
ternal plotter (refer to Chapter 6, Data Displays). In this mode of oper-
ation, the GPIB is dedicated to this application and only the 37XXXC
and the plotter are connected to the GPIB. Standard GPIB cables are
used to interconnect to the plotter.
GPIB Addresses The 37XXXC leaves the factory with the default GPIB address set to
six. This address may be changed using the GP7 menu (see Appendix
A).
2-6 EXTERNAL MONITOR
CONNECTOR The rear panel External Monitor connector allows the internal display
information of the 37XXXC to be connected to an external VGA moni-
tor (either color or monochrome). The pinout of this 15-pin Type D con-
nector is shown in Figure B-4, located in Appendix B.
2-7 RACK MOUNT To install the Option 1 Rack Mount rails, refer to the below-listed pro-
cedure.
Step 1. Disconnect the line cord and any other attachments from the instru-
ment.
Step 2. Carefully place the instrument on its top (bottom-side up) on a secure
and stable work surface.
SYSTEM GPIB INTERCONNECTION INSTALLATION
2-6 37XXXC OM
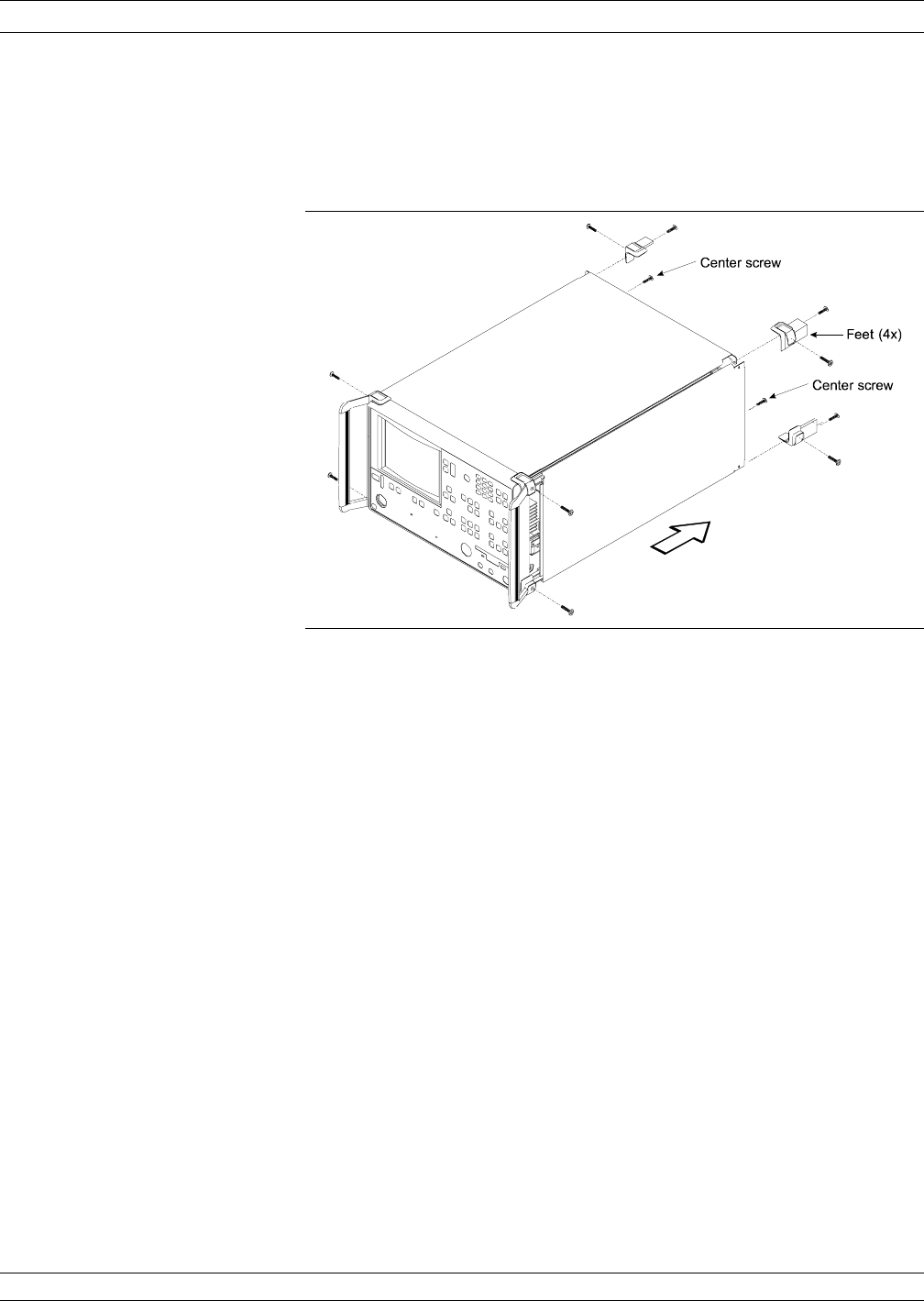
Step 3. Using a Phillips screwdriver, remove the two handles or four bumper
assemblies (and tilt bail, if installed) from the front of the unit, and
the four feet at the rear (Figure 2-1). Save the screws for later use.
NOTES
qThe green-headed screws are metric threads and must be used
only in the appropriately tapped holes
qThe feet, handles, and bumpers are not reused in this application
Step 4. Remove the center screws from the rear of the left and right side cov-
ers.
Step 5. Remove the two side carrying handle screws (if so equipped) located
under the plastic handle ends.
Step 6. Remove the left and right side covers. These side covers are not reused
in this application.
Step 7. Install the two Rack Mount Handles using the green-headed screws
removed earlier.
Refer to Figure 2-2, on the following page, for the remainder of the
assembly procedure.
37XXXC OM 2-7
INSTALLATION RACK MOUNT
Figure 2-1. Removing Cover
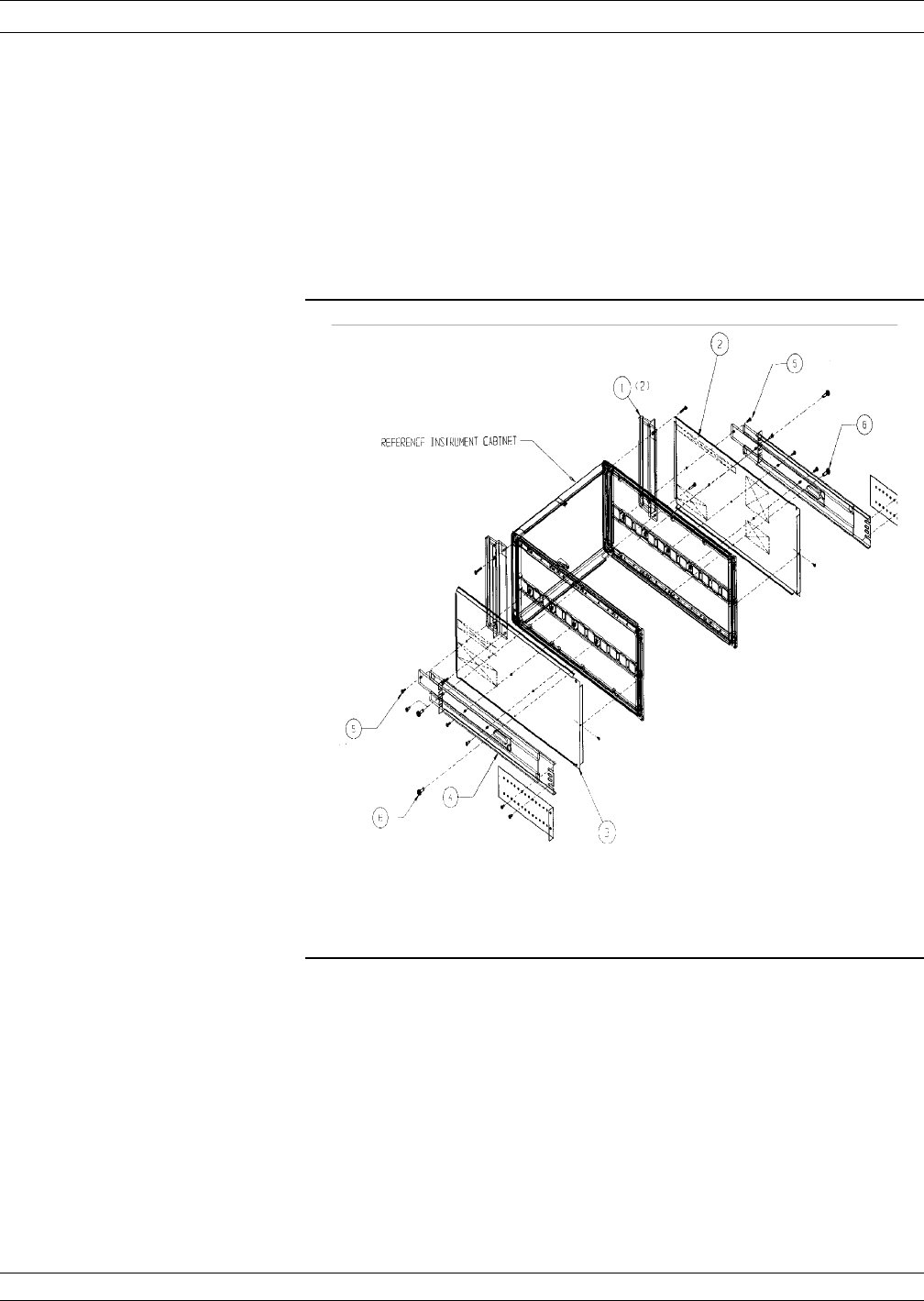
Step 8. Secure the new left cover (2) from this retrofit kit to the left side chas-
sis of the instrument by installing the two center screws (6) to the top
and bottom and the previously removed center screw at the rear of the
left cover.
Step 9. Secure the slide assembly (4) to the left cover by installing the four
mounting screws (5) to the left chassis.
Step 10. Secure the new right cover (3) from this retrofit kit to the right side
chassis of the instrument by installing the center screw (6) through
the center of the right side cover and the previously removed center
screw at the rear of the right side cover.
Step 11. Secure the slide assembly (4) to the right cover by installing the four
mounting screws (5) to the right chassis.
This completes the installation of the slide assembly.
RACK MOUNT INSTALLATION
2-8 37XXXC OM
Figure 2-2. Mounting Rails
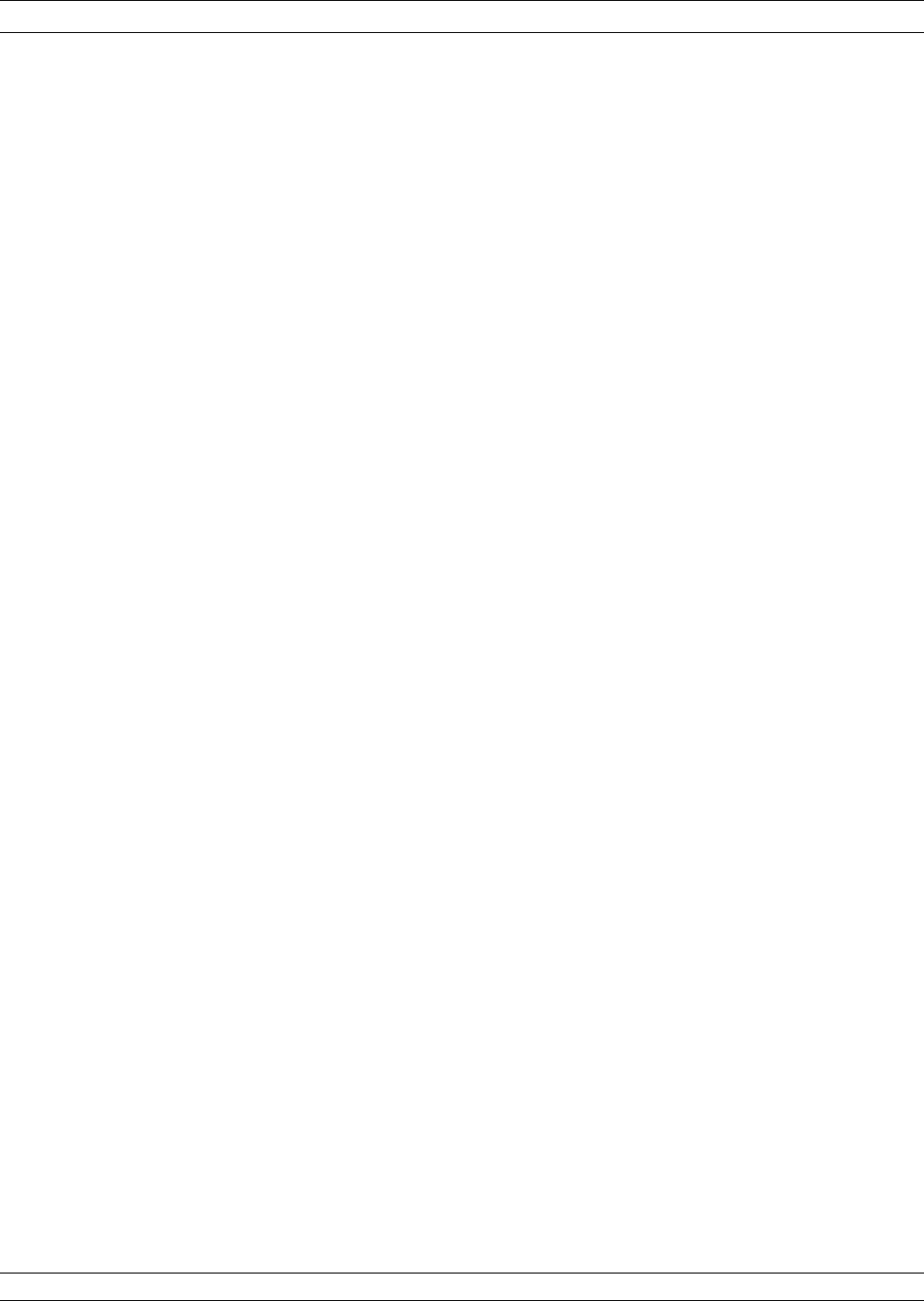
2-8 STORAGE OR SHIPMENT The following paragraphs describe the procedure for preparing the
37XXXC for storage or shipment.
Preparation for Storage Preparing the 37XXXC for storage consists of cleaning the unit, pack-
ing the inside with moisture-absorbing desiccant crystals, and storing
the unit in a temperature environment that is maintained between
–40 and +70 degrees centigrade (–40 to 156 degrees Fahrenheit).
Preparation for Shipment To provide maximum protection against damage in transit, the
37XXXC should be repackaged in the original shipping container. If
this container is no longer available and the 37XXXC is being returned
to Anritsu for repair, advise Anritsu Customer Service; they will send
a new shipping container free of charge. In the event neither of these
two options is possible, instructions for packaging and shipment are
given below.
Use a Suitable Container
Obtain a corrugated cardboard carton with a 275-pound test strength.
This carton should have inside dimensions of no less than six inches
larger than the instrument dimensions to allow for cushioning.
Protect the Instrument
Surround the instrument with polyethylene sheeting to protect the fin-
ish.
Cushion the Instrument
Cushion the instrument on all sides by tightly packing dunnage or
urethane foam between the carton and the instrument. Provide at
least three inches of dunnage on all sides.
Seal the Container
Seal the carton by using either shipping tape or an industrial stapler.
Address the Container
If the instrument is being returned to Anritsu for service, mark the
Anritsu address and your return address on the carton in one or more
prominent locations. Refer to the address of your local representative
listed in Table 2-1 on the following page.
INSTALLATION STORAGE OR SHIPMENT
37XXXC OM 2-9/2-10
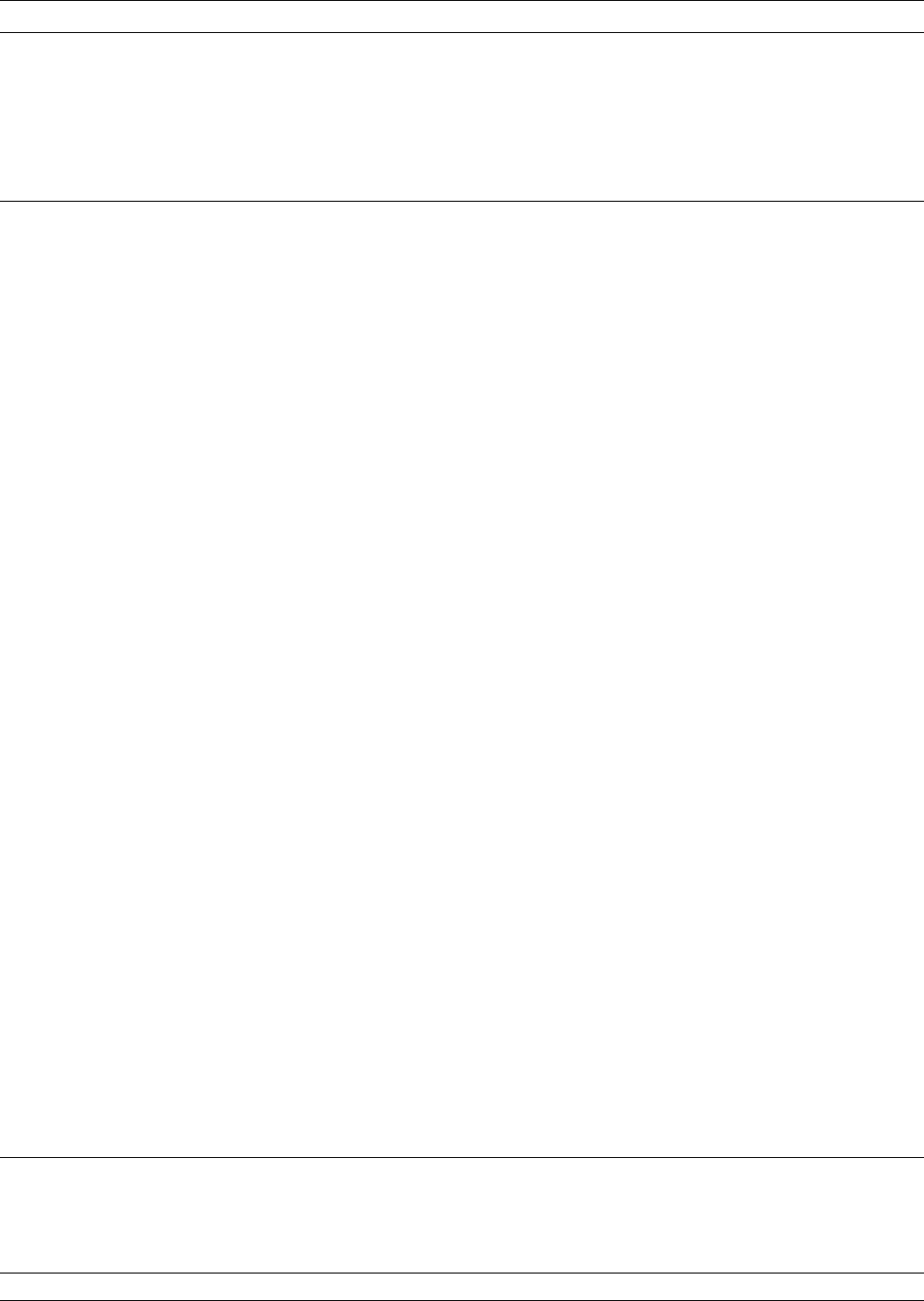
2-9 SERVICE CENTERS Table 2-1 provides a list of international service centers.
SERVICE CENTERS INSTALLATION
2-10 37XXXC OM
UNITED STATES
ANRITSU COMPANY
490 Jarvis Drive
Morgan Hill, CA 95037-2809
Telephone: (408) 776-8300
1-800-ANRITSU
FAX: 408-776-1744
FRANCE
ANRITSU S.A
9 Avenue du Quebec
Zone de Courtaboeuf
91951 Les Ulis Cedex
Telephone: 016-09-21-550
FAX: 016-44-61-065
JAPAN
ANRITSU CUSTOMER SERVICES LTD.
1800 Onna Atsugi-shi
Kanagawa-Prf. 243 Japan
Telephone: 0462-96-6688
FAX: 0462-25-8379
ANRITSU COMPANY
10 New Maple Ave., Unit 305
Pine Brook, NJ 07058
Telephone: (973) 227-8999
1-800-ANRITSU
FAX: 973-575-0092
GERMANY
ANRITSU GmbH
Grafenberger Allee 54-56
D-40237 Dusseldorf, Germany
Telephone: 0211-968550
FAX: 0211-9685555
SINGAPORE
ANRITSU (SINGAPORE) PTE LTD.
10, Hoe Chiang Road
#07-01/02 Keppel Towers
Singapore 089315
Telephone: 6-282-2400
FAX: 6-282-2533
ANRITSU COMPANY
1155 E. Collins Blvd
Richardson, TX 75081
Telephone: 1-800-ANRITSU
FAX: 972-671-1877
INDIA
MEERA AGENCIES PVT. LTD.
23 Community Centre
Zamroodpur, Kailash Colony Extension,
New Delhi, India 110 048
Phone: 011-2-6442700/6442800
FAX : 011-2-644250023
SOUTH AFRICA
ETECSA
12 Surrey Square Office Park
330 Surrey Avenue
Ferndale, Randburt, 2194
South Africa
Telephone: 011-27-11-787-7200
FAX: 011-27-11-787-0446
AUSTRALIA
ANRITSU PTY. LTD.
Unit 3, 170 Foster Road
Mt Waverley, VIC 3149
Australia
Telephone: 03-9558-8177
FAX: 03-9558-8255
ISRAEL
TECH-CENT, LTD.
4 Raul Valenberg St
Tel-Aviv 69719
Telephone: (03) 64-78-563
FAX: (03) 64-78-334
SWEDEN
ANRITSU AB
Fagelviksvagen 9A
145 84 Stockholmn, Sweden
Telephone: 08-534-70700
FAX: 08-534-707-30
BRAZIL
ANRITSU ELECTRONICA LTDA.
Praia de Botafogo, 440, Sala 2401
CEP22250-040, Rio de Janeiro, RJ, Brasil
Telephone: 021-527-6922
FAX: 021-53-71-456
ITALY
ANRITSU Sp.A
Roma Office
Via E. Vittorini, 129
00144 Roma EUR
Telephone: (06) 50-99-711
FAX: (06) 50-22-425
TAIWAN
ANRITSU CO., INC.
7F, No. 316, Section 1
NeiHu Road
Taipei, Taiwan, R.O.C.
Telephone: 886-2-8751-1816
FAX: 886-2-8751-2126
CANADA
ANRITSU INSTRUMENTS LTD.
700 Silver Seven Road, Suite 120
Kanata, Ontario K2V 1C3
Telephone: (613) 591-2003
FAX: (613) 591-1006
KOREA
ANRITSU CORPORATION LTD.
Head Office:
14F, Hyunjuk Building, 832-41
Yeoksam-Dong, Kangnam-Ku
Seoul 135-080, South Korea
Telephone: 02-553-6603
FAX: 02-553-6604
Service Center:
8F Hyunjuk Building, 832-41
Yeoksam Dong, Kangnam-Ku
Seoul, South Korea 135-080
Telephone: 02-553-6603
FAX: 02-553-6605
UNITED KINGDOM
ANRITSU LTD.
200 Capability Green
Luton, Bedfordshire
LU1 3LU, England
Telephone: 015-82-433200
FAX: 015-82-731303
CHINA
ANRITSU ELECTRONICS (SHANGHAI) CO. LTD.
2F, Rm B, 52 Section Factory Building
No. 516 Fu Te Rd (N)
Shanghai 200131 P.R. China
Telephone:21-58680226, 58680227, 58680228
FAX: 21-58680588
Table 2-1. Anritsu Service Centers

Table of Contents
3-1 INTRODUCTION ...................................3-3
3-2 GENERAL DESCRIPTION ..............................3-3
Source Module....................................3-4
Test Set Module ...................................3-4
Analyzer Module ..................................3-4
3-3 NETWORK ANALYZERS ...............................3-5
Chapter 3
Network Analyzers,
APrimer
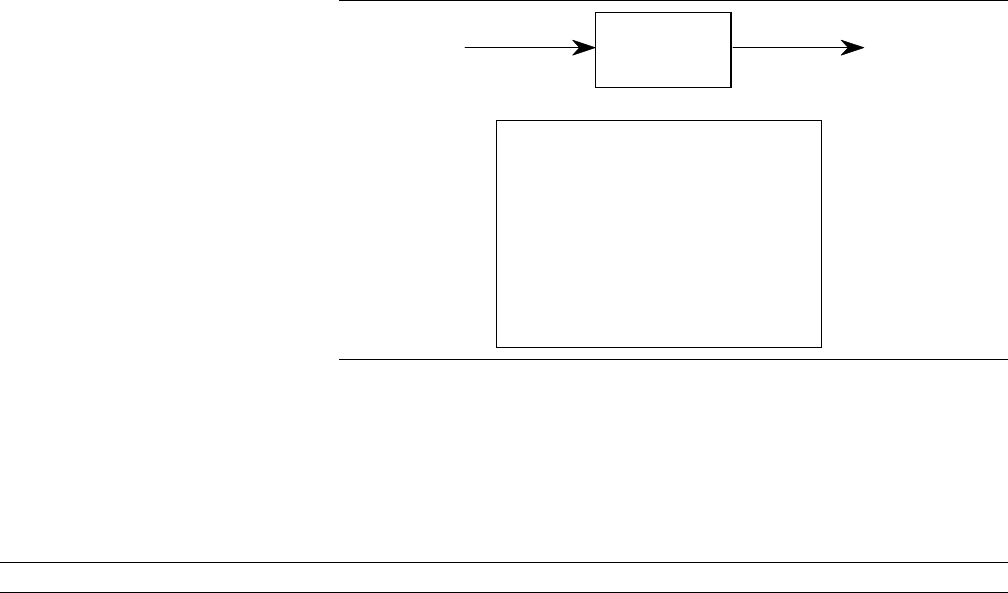
Chapter 3
Network Analyzers,
A Primer
3-1 INTRODUCTION This section provides front panel operating and measurement applica-
tion information and data. It includes discussions on the following top-
ics:
qSystem description
qGeneral discussion about network analyzers
qBasic measurements and how to make them
qError correction
qGeneral discussion on test sets
3-2 GENERAL DESCRIPTION The Model 37XXXC Vector Network Analyzer System measures the
magnitude and phase characteristics of networks, amplifiers,
attenuators, and antennas. It compares the incident signal that leaves
the analyzer with either the signal that is transmitted through the
test device or the signal that is reflected from its input. Figure 3-1 and
Figure 3-2 illustrate the types of measurements that the 37XXXC can
make.
37XXXC OM 3-3
TRANSMITTEDINCIDENT
TEST
DEVICE
Gain (dB)
Insertion Loss (dB)
Insertion Phase (degrees)
Transmission Coefficients (S12, S21)
Separation of Transmission
Components (Real and Imaginary)
Electrical Length (m)
Electrical Delay (s)
Deviation from Linear Phase (degrees)
Group Delay (s)
Figure 3-1. Transmission Measurements
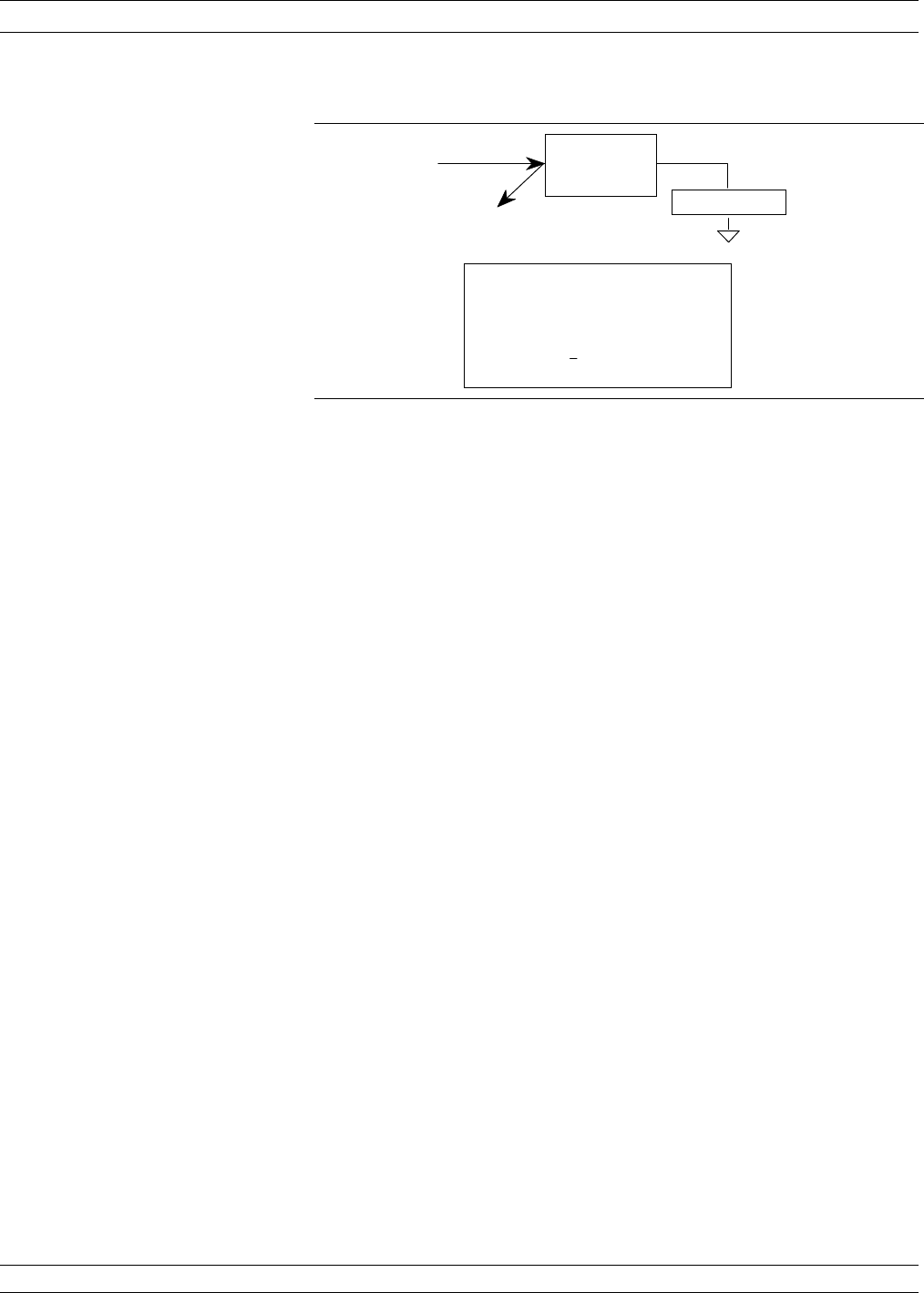
The 37XXXC is a self-contained, fully integrated measurement system
that includes an optional time domain capability. The system hard-
ware consists of the following:
qAnalyzer
qPrecision components required for calibration and performance
verification
qOptional use of Anritsu 67XXB, 68XXXA/B/C, or 69XXXA/B as a
second source
The 37XXXC internal system modules perform the following functions:
Source Module This module provides the stimulus to the device under test (DUT). The
frequency range of the source and test set modules establish the fre-
quency range of the system. The frequency stability of the source is an
important factor in the accuracy (especially phase accuracy) of the net-
work analyzer. Hence, the 37XXXC always phase locks the source to an
internal 10 MHz crystal reference.
Test Set Module The test set module routes the stimulus signal to the DUT and sam-
ples the reflected and transmitted signals. The type of connector used
is important, as is the “Auto Reversing” feature. Auto Reversing means
that it applies the stimulus signal in both the forward and reverse di-
rection. The direction is reversed automatically. This saves you from
having to reverse the test device physically to measure all four scatter-
ing parameters (S-parameters). Frequency conversion (1st and 2nd
IFs) occurs in the test set module.
Analyzer Module The analyzer module down-converts, receives, and interprets the 3rd
IF signal for phase and magnitude data. It then displays the results of
this analysis on a large, 190 mm (7-1/2 inch) diagonal color display.
This display can show all four S-parameters simultaneously. In addi-
tion to the installed display, you can also view the measurement re-
sults on an external color monitor.
GENERAL DESCRIPTION NETWORK ANALYZERS, A PRIMER
3-4 37XXXC OM
REFLECTED
INCIDENT
TERMINATION
TEST
DEVICE
Return Loss (dB)
Reflection Coefficients (S11, S22)
Reflection Coefficients vs Distance
(Fourier Transform)
Impedance (R + j X)
SWR
Figure 3-2. Reflection Measurements
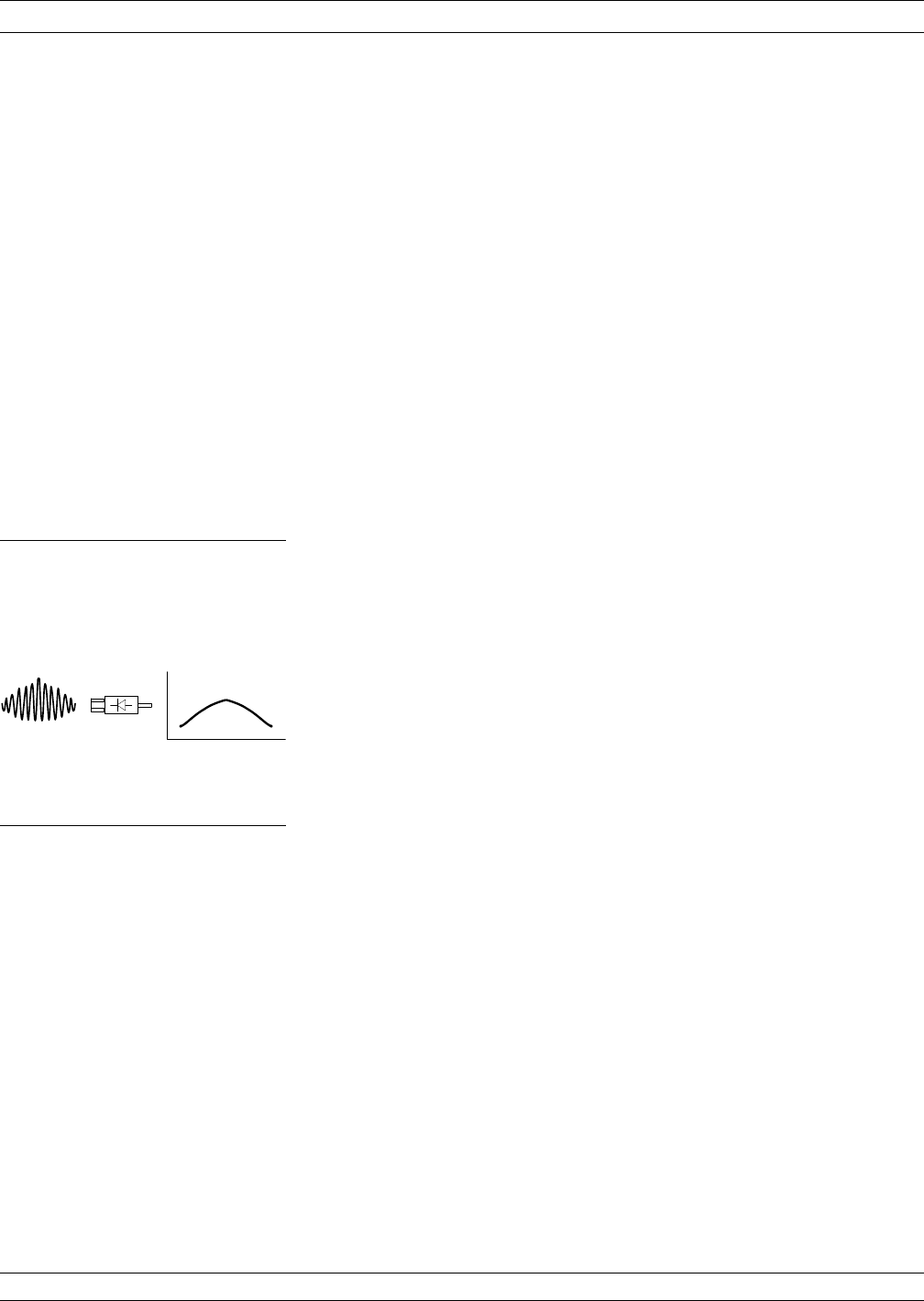
3-3 NETWORK ANALYZERS We will begin this discussion with a subject familiar to most Anritsu
customers: scalar network analysis. After showing comparisons, we
will proceed to the fundamentals of network analyzer terminology and
techniques. This discussion serves as an introduction to topics pre-
sented in greater detail later in this section. This discussion will touch
on new concepts that include the following:
qReference Delay
qS-parameters: what they are and how they are displayed
qComplex Impedance and Smith Charts
Scalar Analyzer Comparison
Network Analyzers do everything that scalar analyzers do except dis-
play absolute power. In addition, they add the ability to measure the
phase characteristics of microwave devices and allow greater dynamic
range.
If all a Network Analyzer added was the capability for measuring
phase characteristics, its usefulness would be limited. While phase
measurements are important in themselves, it is the availability of
this phase information that unlocks many new features for complex
measurements. These features include Smith Charts, Time Domain,
and Group Delay. Phase information also allows greater accuracy
through vector error correction of the measured signal.
First, let us look at scalar network analyzers (SNAs). SNAs measure
microwave signals by converting them to a DC voltage using a diode
detector (Figure 3-3). This DC voltage is proportional to the magnitude
of the incoming signal. The detection process, however, ignores any
information regarding the phase of the microwave signal.
In a network analyzer, access is needed to both the magnitude and
phase of a microwave signal. There are several different ways to per-
form the measurement. The method Anritsu employs (called Harmonic
Sampling or Harmonic Mixing) is to down-convert the signal to a lower
intermediate frequency (IF). This signal can then be measured directly
by a tuned receiver. The tuned receiver approach gives the system
greater dynamic range. The system is also much less sensitive to inter-
fering signals, including harmonics.
37XXXC OM 3-5
NETWORK ANALYZERS, A PRIMER NETWORK ANALYZERS
SCALAR NETWORK ANALYZERS
MICROWAVE
SIGNAL MICROWAVE
DETECTOR
DETECTOR
OUTPUT
VOLTAGE
DETECTOR OUTPUT VOLTAGE IS PROPORTIONAL
TO SIGNAL AMPLITUDE.
Figure 3-3. Scalar Analyzer
Detection
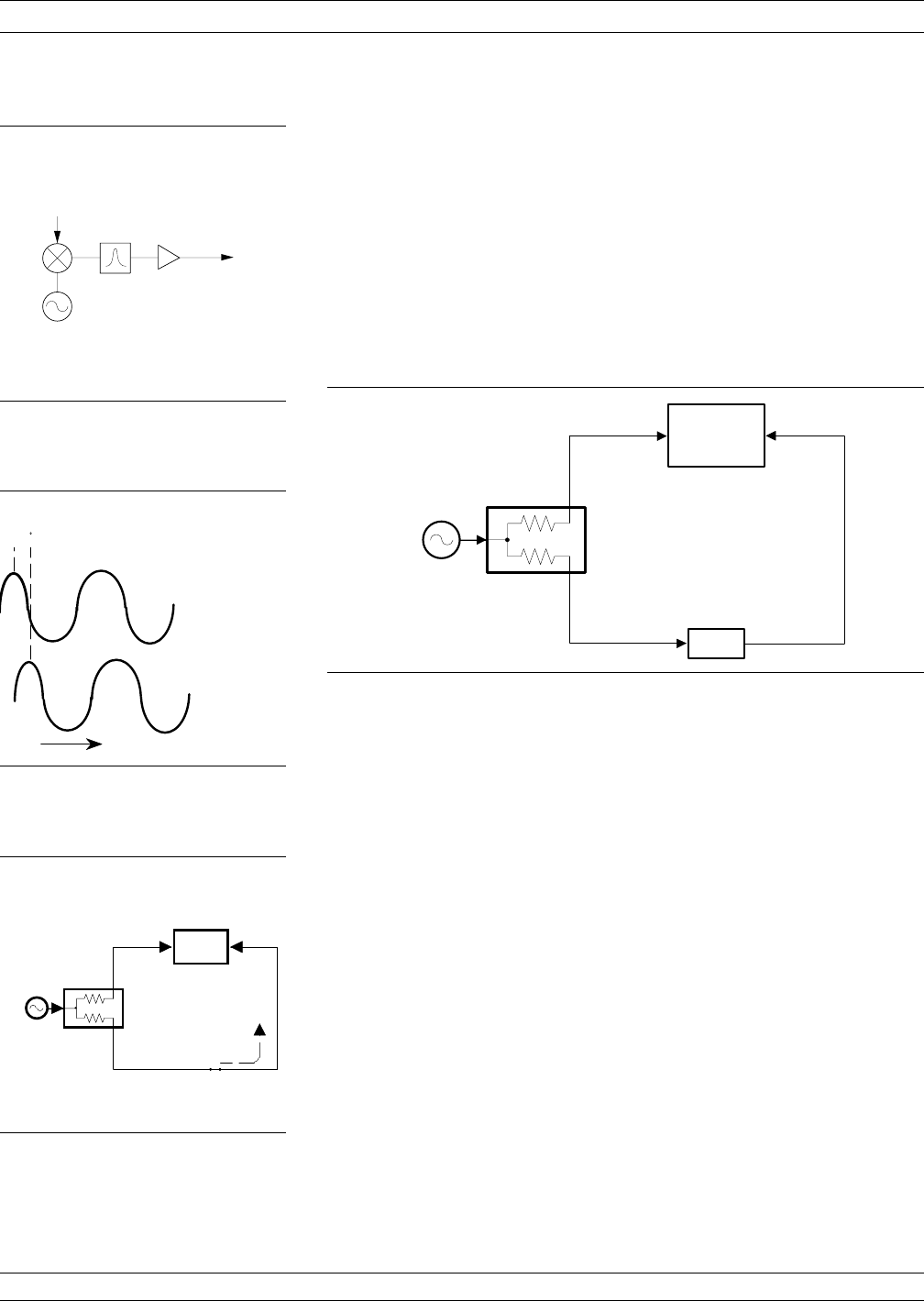
Vector Network Analyzer Basics
The network analyzer is a tuned receiver (Figure 3-4, left). The
microwave signal is down converted into the passband of the IF. To
measure the phase of this signal, we must have a reference to compare
it with. If the phase of a signal is 90 degrees, it is 90 degrees different
from the reference signal (Figure 3-5, left). The network analyzer
would read this as –90 degrees, since the test signal is delayed by 90
degrees with respect to the reference signal.
This phase reference can be obtained by splitting off some of the
microwave signal before the measurement (Figure 3-7, below).
The phase of the microwave signal after it has passed through the de-
vice under test (DUT) is then compared with the reference signal. A
network analyzer test set automatically samples the reference signal,
so no external hardware is needed.
Let us consider for a moment that you remove the DUT and substitute
a length of transmission line (Figure 3-6, left). Note that the path
length of the test signal is longer than that of the reference signal.
Now let us see how this affects our measurement.
NETWORK ANALYZERS NETWORK ANALYZERS, A PRIMER
3-6 37XXXC OM
Figure 3-4. Network Analyzer is
a Tuned Receiver
PHASE MEASUREMENT
TIME
TEST
SIGNAL
REFERENCE
SIGNAL
90
Figure 3-5. Signals with a
90 Degree Phase
Difference
REFERENCE
SIGNAL
SPLITTER
TEST
SIGNAL
MICROWAVE
SOURCE
LONGER
PATH
LENGTH
PHASE
DETECTOR
Figure 3-6. Split Signal where
a Length of Line
Replaces the DUT
A
NETWORK ANALYZER IS A TUNED RECEIVER
TUNABLE
LOCAL
OSCILLATOR
INTERMEDIATE
FREQUENCY (IF)
MICROWAVE
SIGNAL
•GREATER DYNAMIC RANGE
•LESS SENSIVITY TO INTERFERING SIGNALS
DUT
PHASE
DETECTOR
REFERENCE
SIGNAL
SPLITTER
TEST
SIGNAL
MICROWAVE
SOURCE
Figure 3-7. Splitting the Microwave Signal
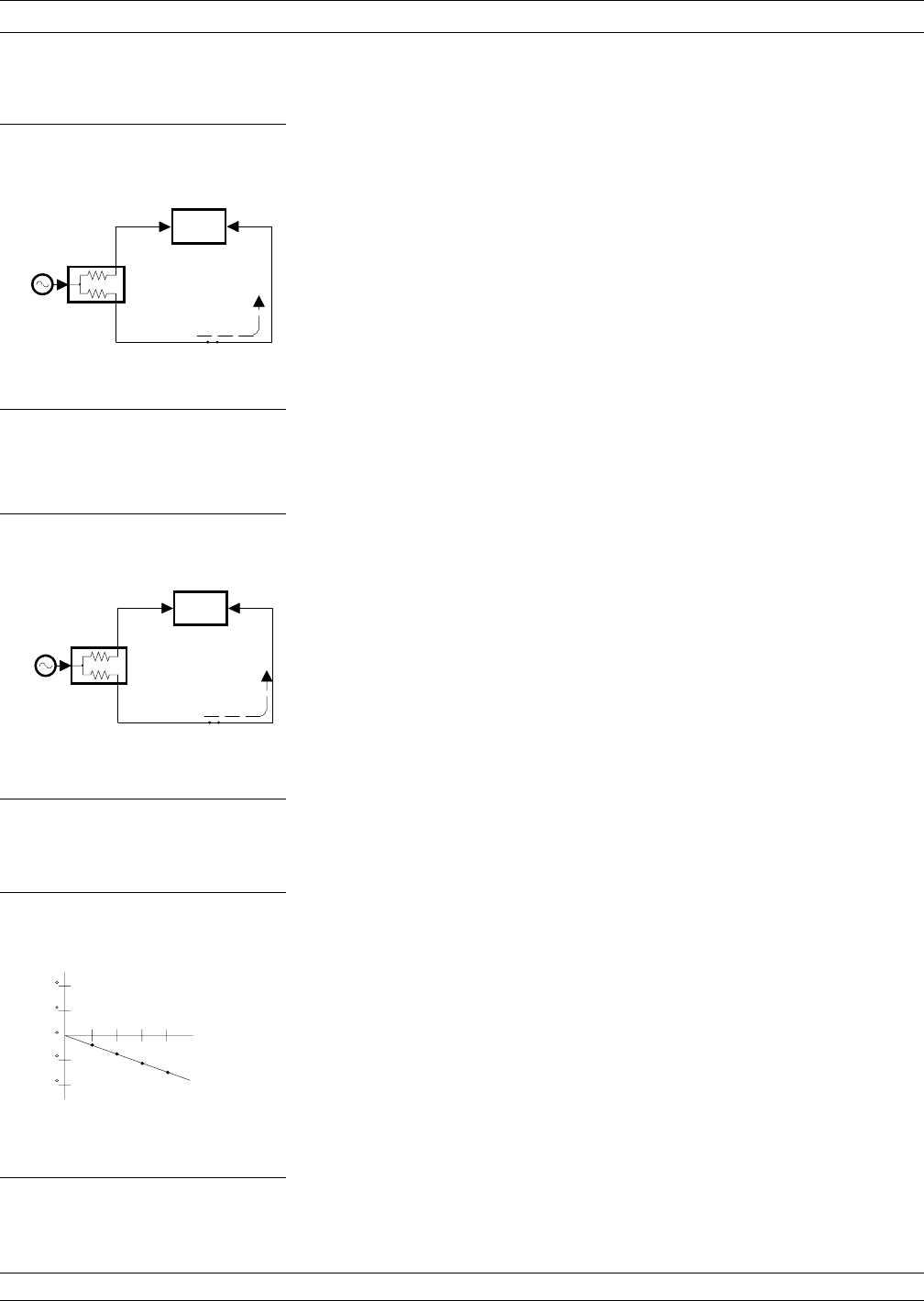
Assume that we are making a measurement at 1 GHz and that the
difference in path-length between the two signals is exactly 1
wavelength. This means that test signal is lagging the reference signal
by 360 degrees (Figure 3-8). We cannot really tell the difference
between one sine wave maxima and the next (they are all identical), so
the network analyzer would measure a phase difference of 0 degrees.
Now consider that we make this same measurement at 1.1 GHz. The
frequency is higher by 10 percent so therefore the wavelength is
shorter by 10 percent. The test signal path length is now 0.1
wavelength longer than that of the reference signal (Figure 3-9). This
test signal is:
1.1 X 360 = 396 degrees
This is 36 degrees different from the phase measurement at 1 GHz.
The network analyzer will display this phase difference as –36 de-
grees.
The test signal at 1.1 GHz is delayed by 36 degrees more than the test
signal at 1 GHz.
You can see that if the measurement frequency is 1.2 GHz, we will get
a reading of –72 degrees, –108 degrees for 1.3 GHz, etc. (Figure 3-10).
There is an electrical delay between the reference and test signals. For
this delay we will use the common industry term of reference delay.
You also may hear it called phase delay. In older network analyzers
you had to equalize the length of the reference arm with that of the
test arm to make an appropriate measurement of phase vs. frequency.
To measure phase on a DUT, we want to remove this
phase-change-vs.-frequency due to changes in the electrical length.
This will allow us to view the actual phase characteristics. These char-
acteristics may be much smaller than the phase change due to
electrical length difference.
37XXXC OM 3-7
NETWORK ANALYZERS, A PRIMER NETWORK ANALYZERS
REFERENCE
SIGNAL
SPLITTER
TEST
SIGNAL
MICROWAVE
SOURCE
PHASE
DETECTOR
LONGER BY
ONE WAVELENGTH
LENGTH (360 degrees)
Figure 3-8. Split Signal where
Path Length Differs
by Exactly One
Wavelength
REFERENCE
SIGNAL
SPLITTER
TEST
SIGNAL
MICROWAVE
SOURCE
SAME PATH
LENGTH -BUT-
WAVELENGTH
IS NOW SHORTER
1.1 WAVELENGTHS = 396 degrees
PHASE
DETECTOR
Figure 3-9. Split Signal where
Path Length is
Longer than One
+180
+90
0
-90
-180
1.1 1.2 1.3 1.4 FREQUENCY,
GHz
MEASURED PHASE
Figure 3-10. Electrical Delay
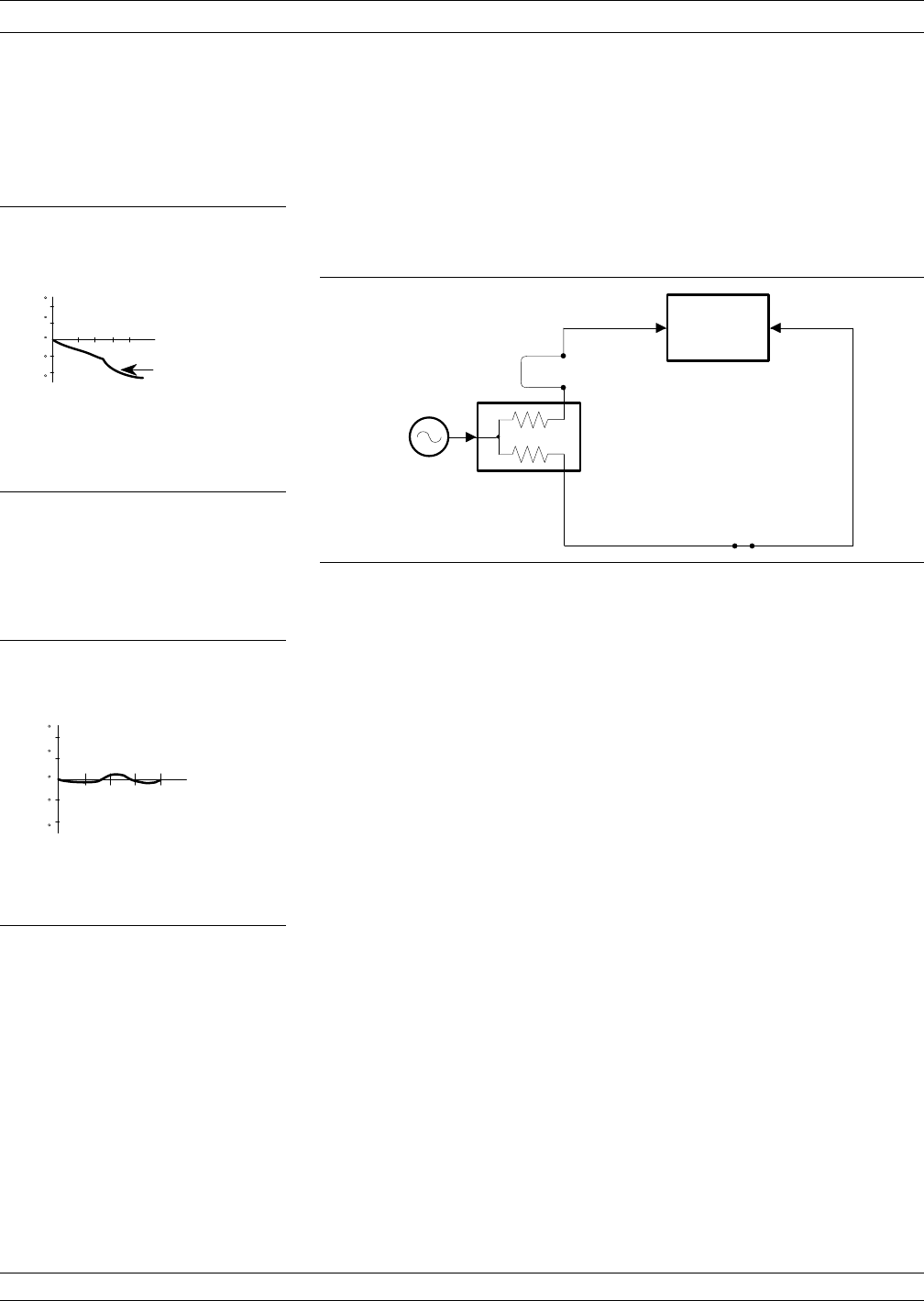
There are two ways of accomplishing this. The most obvious way is to
insert a length of line into the reference signal path to make both
paths of equal length (Figure 3-11, below). With perfect transmission
lines and a perfect splitter, we would then measure a constant phase
as we change the frequency. The problem using this approach is that
we must change the line length with each measurement setup.
Another approach is to handle the path length difference in software.
Figure 3-12 (left) displays the phase-vs.-frequency of a device. This
device has different effects on the output phase at different
frequencies. Because of these differences, we do not have a perfectly
linear phase response. We can easily detect this phase deviation by
compensating for the linear phase. The size of the phase difference
increases linearly with frequency so we can modify the phase display
to eliminate this delay.
The 37XXXC offers automatic reference delay compensation with the
push of a button. Figure 3-13 (left) shows the resultant measurement
when we compensate path length. In a system application you can
usually correct for length differences; however, the residual phase
characteristics are critical.
NETWORK ANALYZERS NETWORK ANALYZERS, A PRIMER
3-8 37XXXC OM
PHASE
DETECTOR
REFERENCE
SIGNAL
SPLITTER
TEST
SIGNAL
MICROWAVE
SOURCE
BOTH LINE
LENGTHS
NOW EQUAL
Figure 3-11. Split Signal where Paths are of Equal Length
+180
+90
0
-90
-180
1.1 1.2 1.3 1.4 FREQUENCY,
GHz
MEASURED PHASE
SUBTRACT LINEAR
PHASE FROM
MEASURED PHASE
Figure 3-12. Phase Difference
Increases Linearly
with Frequency
0
1.1
1.2
1.3 1.4 FREQUENCY,
GHz
+2
+1
-1
-2
RESULTANT PHASE
Figure 3-13. Resultant Phase
with Path
Length
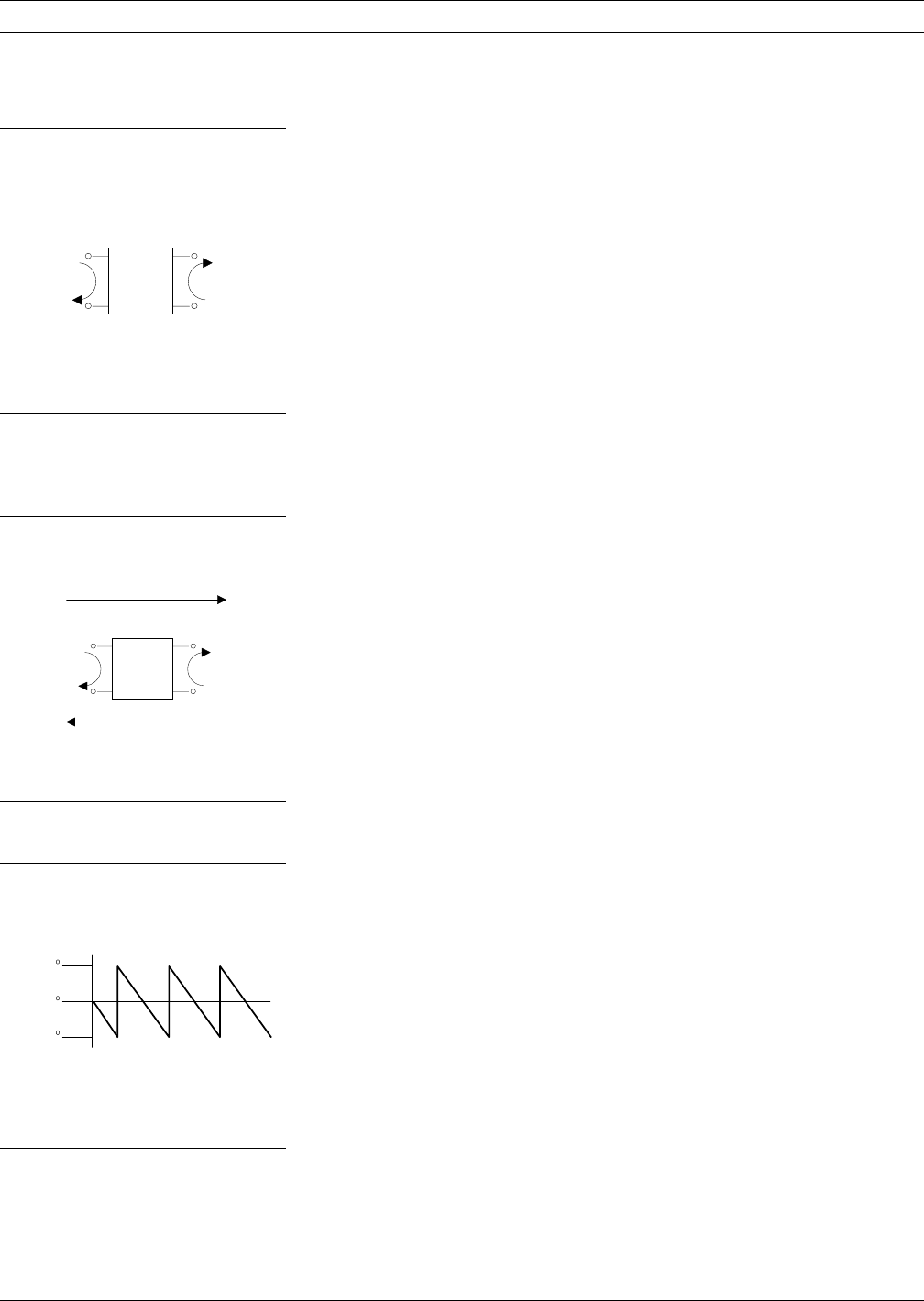
Network Analyzer Measurements
Now let us consider measuring the DUT. Consider a two port device;
that is, a device with a connector on each end. What measurements
would be of interest?
First, we could measure the reflection characteristics at either end
with the other end terminated into 50 ohms. If we designate one end
as the normal place for the input that gives a reference. We can then
define the reflection characteristics from the reference end as forward
reflection, and those from the other end as reverse reflection
(Figure 3-14).
Second, we can measure the forward and reverse transmission
characteristics. However, instead of saying “forward,” “reverse,”
“reflection,” and “transmission” all the time, we use a shorthand. That
is all that S-parameters are, a shorthand! The “S” stands for
scattering. The second number is the device port that the signal is
being injected into, while the first is the device port that the signal is
leaving. S11, therefore, is the signal being injected into port 1 relative
to the signal leaving port 1. The four scattering parameters
(Figure 3-15) are:
qS11 Forward Reflection
qS21 Forward Transmission
qS22 Reverse Reflection
qS12 Reverse Transmission
S-parameters can be displayed in many ways. An S-parameter consists
of a magnitude and a phase. We can display the magnitude in dB, just
like a scalar network analyzer. We often call this term log magnitude.
We can display phase as “linear phase” (Figure 3-16). As discussed
earlier, we can’t tell the difference between one cycle and the next.
Therefore, after going through 360 degrees we are back to where we
began. We can display the measurement from –180 to +180 degrees.
The –180 to +180 approach is more common. It keeps the display
discontinuity removed from the important 0 degree area used as the
phase reference.
37XXXC OM 3-9
NETWORK ANALYZERS, A PRIMER NETWORK ANALYZERS
FORWARD
REFLECTION REVERSE
REFLECTION
PORT 1 PORT 2
DUT
Figure 3-14. Forward and
Reverse
Measurements
S12 REVERSE TRANSMISSION
PORT 1 PORT 2
S11 FORWARD
REFLECTION S22 REVERSE
REFLECTION
S21 FORWARD TRANSMISSION
DUT
Figure 3-15. S-parameters
+180
0
-180
PHASE
FREQUENCY
Figure 3-16. Linear
Phase-with-frequen
cy Waveform
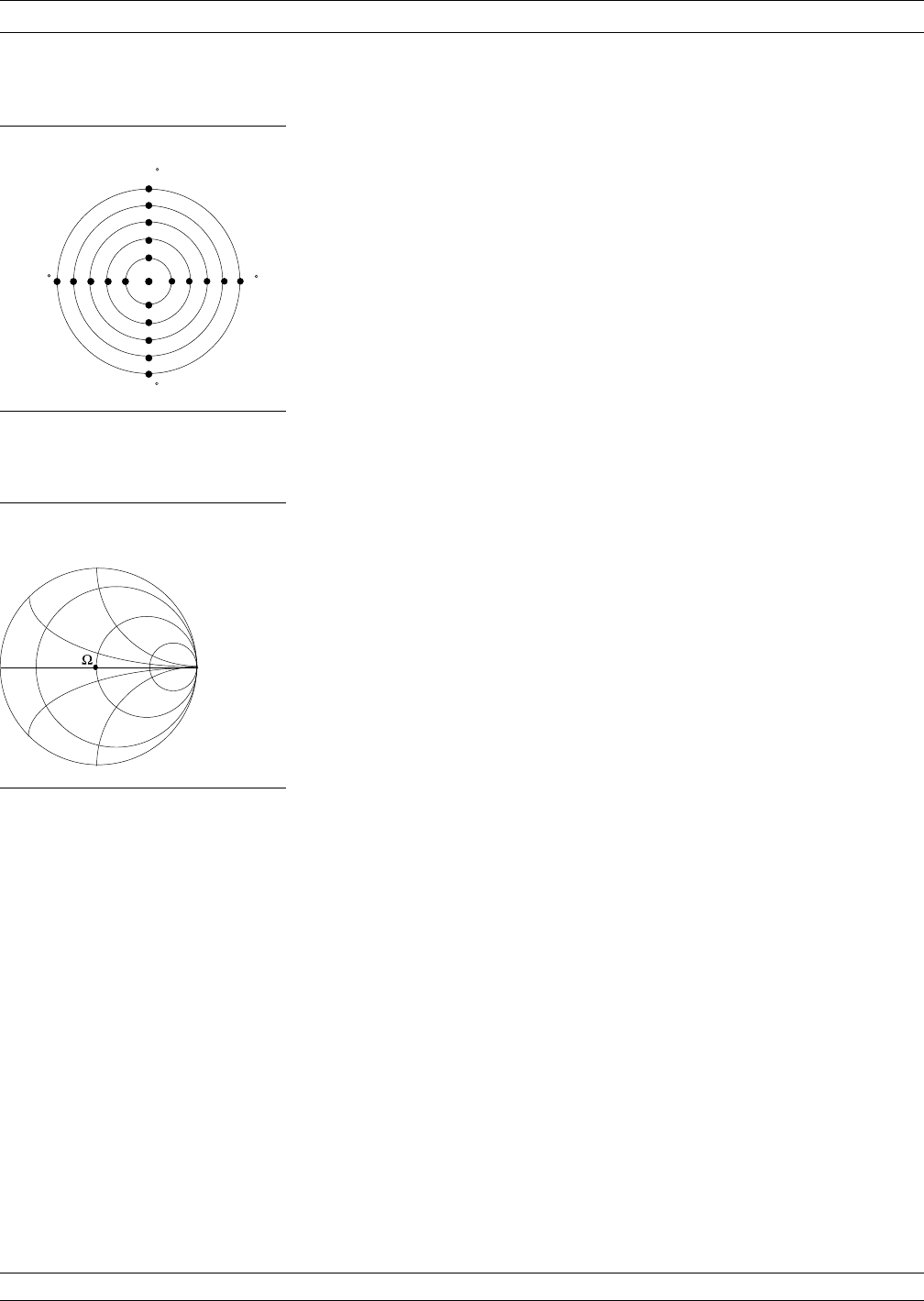
There are several ways in which all the information can be displayed
on one trace. One method is a polar display (Figure 3-17). The radial
parameter (distance from the center) is magnitude. The rotation
around the circle is phase. We sometimes use polar displays to view
transmission measurements, especially on cascaded devices (devices in
series). The transmission result is the addition of the phase and log
magnitude (dB) information of each device’s polar display.
As we have discussed, the signal reflected from a DUT has both mag-
nitude and phase. This is because the impedance of the device has
both a resistive and a reactive term of the form r+jx. We refer to the r
as the real or resistive term, while we call xthe imaginary or reactive
term. The j, which we sometimes denote as i, is an imaginary number.
It is the square root of –1. If xis positive, the impedance is inductive; if
xis negative, the impedance is capacitive.
The size and polarity of the reactive component xis important in im-
pedance matching. The best match to a complex impedance is the com-
plex conjugate. This complex-sounding term simply means an imped-
ance with the same value of rand x, but with xof opposite polarity.
This term is best analyzed using a Smith Chart (Figure 3-18), which is
a plot of rand x.
To display all the information on a single S-parameter requires one or
two traces, depending upon the format we want. A very common re-
quirement is to view forward reflection on a Smith Chart (one trace)
while observing forward transmission in Log Magnitude and Phase
(two traces). Let us see how to accomplish this in the 37XXXC.
The 37XXXC has four channels. Each channel can display a complete
S-parameter in any format on either one or two traces. All four S-pa-
rameters can be seen simultaneously in any desired format. A total of
eight traces can be viewed at the same time. While this is a lot of infor-
mation to digest, the 37XXXC’s large color display makes recognizing
and analyzing the data surprisingly easy.
NETWORK ANALYZERS NETWORK ANALYZERS, A PRIMER
3-10 37XXXC OM
-90
180
90
0
POLAR DISPLAY
Figure 3-17. Polar Display
50
INDUCTIVE
CAPACITIVE
SMITH CHART
Figure 3-18. Smith Chart
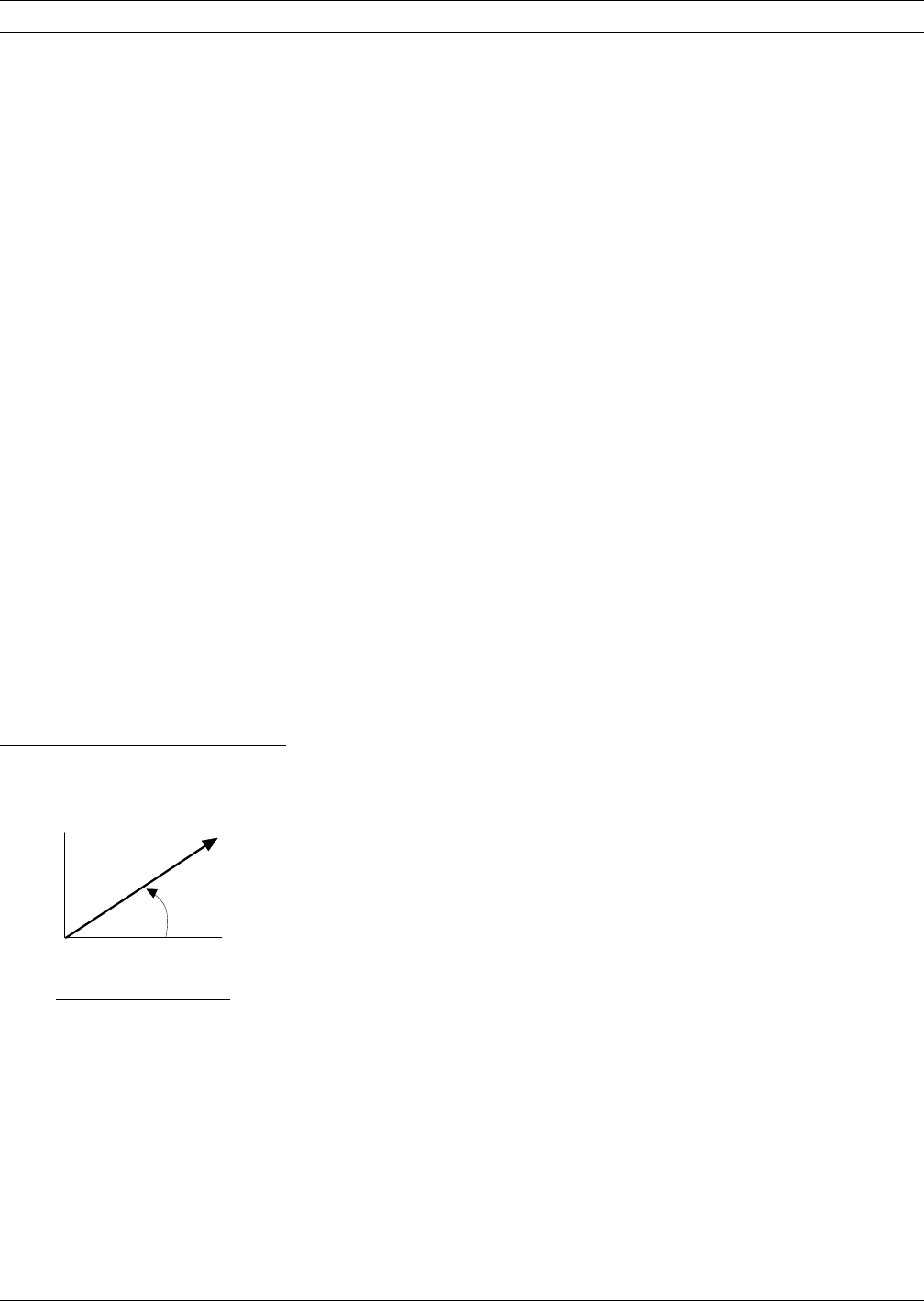
Another important parameter we can measure when phase informa-
tion is available is group delay. In linear devices, the phase change
through the DUT is linear-with-frequency. Thus, doubling the fre-
quency also doubles the phase change. An important measurement, es-
pecially for communications system users, is the rate of
change-of-phase-vs.-frequency (group delay). If the rate of
phase-change-vs.-frequency is not constant, the DUT is nonlinear. This
nonlinearity can create distortion in communications systems.
Measurement Error Correction
Since we can measure microwave signals in both magnitude and
phase, it is possible to correct for six major error terms:
qSource Test Port Match
qLoad Test Port Match
qDirectivity
qIsolation
qTransmission Frequency Response
qReflection Frequency Response
We can correct for each of these six error terms in both the forward
and reverse directions, hence the name 12-term error correction. Since
12-term error correction requires both forward and reverse measure-
ment information, the test set must be reversing. “Reversing” means
that it must be able to apply the measurement signal in either the for-
ward or reverse direction.
To accomplish this error correction, we measure the magnitude and
phase of each error signal (Figure 3-19). Magnitude and phase infor-
mation appear as a vector that is mathematically applied to the mea-
surement signal. This process is termed vector error correction.
Summary
A vector network analyzer is similar to a scalar network analyzer. The
major difference is that it adds the capability for measuring phase as
well as amplitude. With phase measurements comes scattering, or
S-parameters, which are a shorthand method for identifying forward
and reverse transmission and reflection characteristics. The ability to
measure phase introduces two new displays, polar and Smith Chart. It
also adds vector error correction to the measurement trace. With vec-
tor error correction, errors introduced by the measurement system are
compensated for and measurement uncertainty is minimized. Phase
measurements also add the capability for measuring group delay,
which is the rate of change-of-phase vs. frequency (group delay). All in
all, using a network analyzer provides for making a more complete
analysis of your test device.
NETWORK ANALYZERS, A PRIMER NETWORK ANALYZERS
37XXXC OM 3-11/3-12
VECTOR ERROR CORRECTION
THEN THE RESULTANT VECTOR IS
APPLIED MATHEMATICALLY, HENCE
MAGNITUDE AND PHASE OF
EACH ERROR SIGNAL IS MEASURED
MAG
PHASE
Figure 3-19. Magnitude and
Phase

Table of Contents
4-1 INTRODUCTION ...................................4-3
4-2 KEY-GROUPS .....................................4-3
4-3 CALIBRATION KEY-GROUP ............................4-10
4-4 SAVE/RECALL MENU KEY.............................4-21
4-5 MEASUREMENT KEY-GROUP ..........................4-22
4-6 CHANNELS KEY-GROUP..............................4-25
4-7 DISPLAY KEY-GROUP ...............................4-26
4-8 ENHANCEMENT KEY-GROUP...........................4-30
4-9 HARD COPY KEY-GROUP .............................4-32
4-10 SYSTEM STATE KEY-GROUP ...........................4-34
4-11 MARKERS/LIMITS KEY-GROUP ..........................4-37
4-12 DISK STORAGE INTERFACE ...........................4-41
Disk Format ....................................4-41
Disk Files......................................4-41
Disk File Output Device..............................4-42
Formatting a Data File Disk ...........................4-42
Copying Data Files From Disk to Disk ......................4-42
Recovering From Disk Write/Read Errors ....................4-42
4-13 COMMAND LINE ..................................4-43
Create Directory ..................................4-43
List Directory ...................................4-43
Change Directory .................................4-43
Delete Files ....................................4-43
Remove Directory .................................4-44
Copy Files .....................................4-44
Conventions ....................................4-44
Chapter 4
Front Panel Operation

Calibration
Menu
Hard Copy
Markers/Limits
System State
Local Lockout
SRQ
Listen
Tal k
Remote
GPIB
Power
Port 1
CAUTION
+30 dBm Max
40 VDC Max
Avoid Static
Discharge
9
8
76
5
4
3
2
1
10
Default
Program
Utility
Menu
Begin
Cal
Apply
Cal
Save/
Recall
Menu
Start
Print
Stop
Print
Menu
Limits
Marker
Menu
Readout
Marker
Graph
Type
Set
Scale
Auto
Scale
S
Params
Ref
Plane
Trace
Memory
Channel
Menu
Ch 1 Ch 2
Ch 3 Ch 4
Option
Menu
Video
IF BW
Avg/
Smooth
Menu
Trace
Smooth
Average
Setup
Menu
Data
Points
Hold Domain Appl
Enter
789
456
123
0.-
MHz
ns
X1
cm
GHz 103
us m
kHz
ps
10
-3
mm
Clear
Ret Loc
Measurement
Enhancement
Channels
Data Entry
Display
a
a
S
b
12
S
21
S
S
b
11 22
1
1
2
2
CAUTION
+20 dBm Max
40 VDC Max
Avoid Static
Discharge
Port 2
11 12 14 15
16
18
17
19
20
37347C Network Analyzer
40MHz - 20GHz
Port 2Port 1
Bias Input
13
Keyboard
Input Output
Figure 4-1. Model 37XXXC Front Panel
b
R F O u t
K e y b o a r d
1a1
S o u r c e L o c k
Input S o u r c e L o c k O u t p u t
a2
S o u r c e L o c k
Input
b2
R F I n I n t e r n a l S o u r c e
O u t p u t
371XXC Connector Panel
22 23 24 25 2827
21 26

Chapter 4
Front Panel Operation
4-1 INTRODUCTION This chapter describes the front panel keys, controls, and menus. The
chapter is organized into an overall description of the front panel
key-groups and detailed descriptions of individual keys within the
key-groups.
4-2 KEY-GROUPS The following pages provide descriptions of the front panel key-groups
illustrated in Figure 4-1 on the previous page.
Index 1. LCD display: Displays any or all of the four mea-
surement channels, plus menus.
Index 2. Power: Turns the 37XXXC on and off. When on, the
operating program runs a self test then recalls the
parameters and functions in effect when previously
powered down.
Index 3. GPIB Indicators:
Remote: Lights when the 37XXXC switches to re-
mote (GPIB) control. It remains lit until the unit re-
turns to local control.
Talk: Lights when you address the 37XXXC to talk
and remains lit until unaddressed.
Listen: Lights when you address the 37XXXC to lis-
ten and remains lit until unaddressed.
SRQ: Lights when the 37XXXC sends a Service Re-
quests (SRQ) to the external controller. The LED re-
mains lit until the 37XXXC receives a serial poll or
until the controller resets the SRQ function.
Local Lockout: Lights when a local lockout mes-
sage is received. The LED remains lit until the mes-
sage is rescinded. When lit, you cannot return the
37XXXC to local control via the front panel.
37XXXC OM 4-3
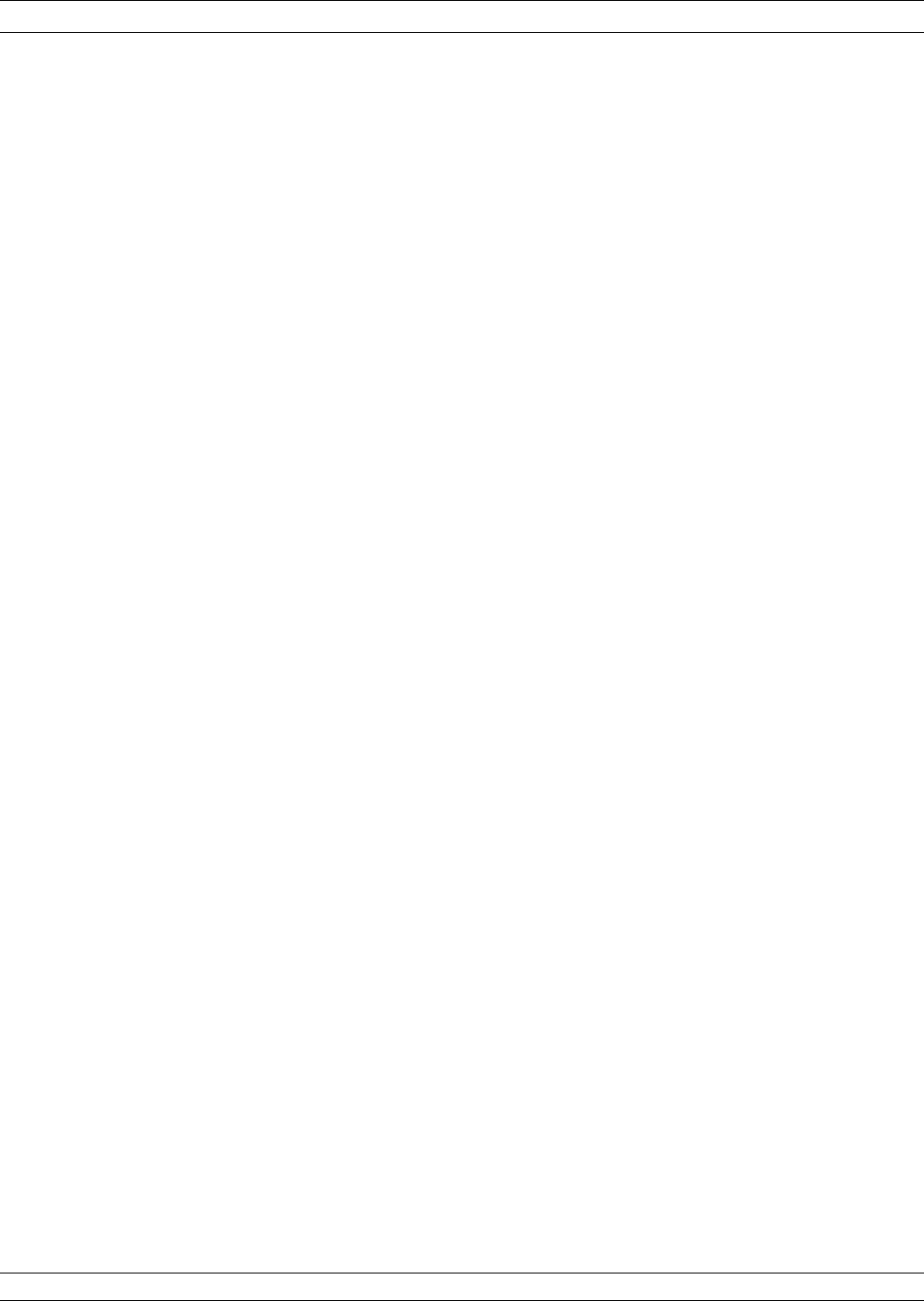
Index 4. System State Keys: (Refer to Section 4-10,
page 4-34, for details and menu flow diagrams.)
Default Program: Resets the front panel to the fac-
tory-preset state and displays Menu SU1 or SU3
(Appendix A). Pressing this key in conjunction with
the “0” or “1” key resets certain internal memories
and front panel key states (refer to Sections 4-5 and
4-10).
NOTE
Use of the Default Program key will destroy
front panel and calibration setup data, un-
less they have been saved to disk.
Utility Menu: Displays the first in a series of menus
that let you perform diskette and other utility-type
functions and operations.
Index 5. Port 1 Test Connector: Provides an input test con-
nection for the device-under-test (DUT).
Index 6. Amplifier Loop: Provides for inserting additional
amplification before the coupler.
Index 7. Calibration Keys: (Refer to Section 4-3, page 4-11,
for details and menu flow diagrams.)
Begin Cal: Calls up the first in a sequence of
menus that guide you through a measurement cali-
bration. Refer to Section 4-3 for a detailed discus-
sion of the calibration keys, indicators, and menus.
Apply Cal: Turns on and off the applied error cor-
rection and tune mode.
Index 8. Save/Recall Menu Key: Displays the first of several
menus that let you save the current calibration or
front panel setup or recall a previously saved cali-
bration or setup. Refer to Section 4-4, page 4-21, for
menu flow diagram.
KEY-GROUPS FRONT PANEL OPERATION
4-4 37XXXC OM
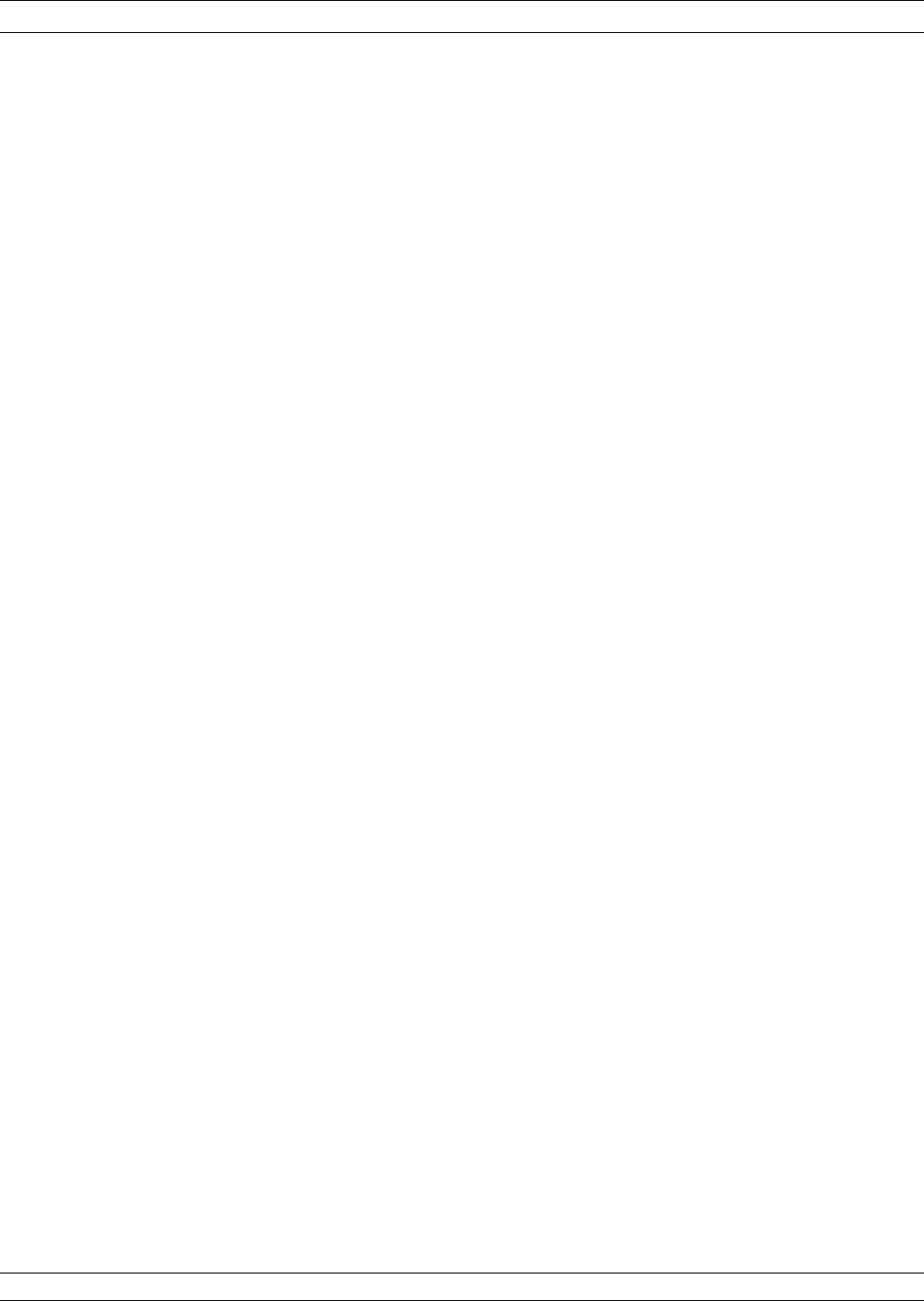
Index 9. Hard Copy Keys: (Refer to Section 4-9, page 4-32,
for details and menu flow diagrams.)
Menu: Displays option menus that let you define
what will happen each time you press the Start
Print key. The displayed menu also selects disk I/O
operations.
Start Print: Tells the printer or plotter to start out-
put based on the current selections.
Stop Print: Immediately stops printing the data,
clears the print buffer, and sends a form-feed com-
mand to the printer.
Index 10. Markers/Limits Keys: (Refer to Section 4-11,
page 4-37, for details and menu flow diagrams.)
Marker Menu: Displays the first in a series of
menus that let you set and manipulate marker fre-
quencies, times, and distances.
Readout Marker: Displays a menu that lists all of
the active markers. If no markers are active, the
marker menu is displayed.
Limits: Displays one of the menus that let you ma-
nipulate the limit lines.
Index 11. Port 2 Test Connector: Provides an input test con-
nection for the device-under-test (DUT).
37XXXC OM 4-5
FRONT PANEL OPERATION KEY-GROUPS
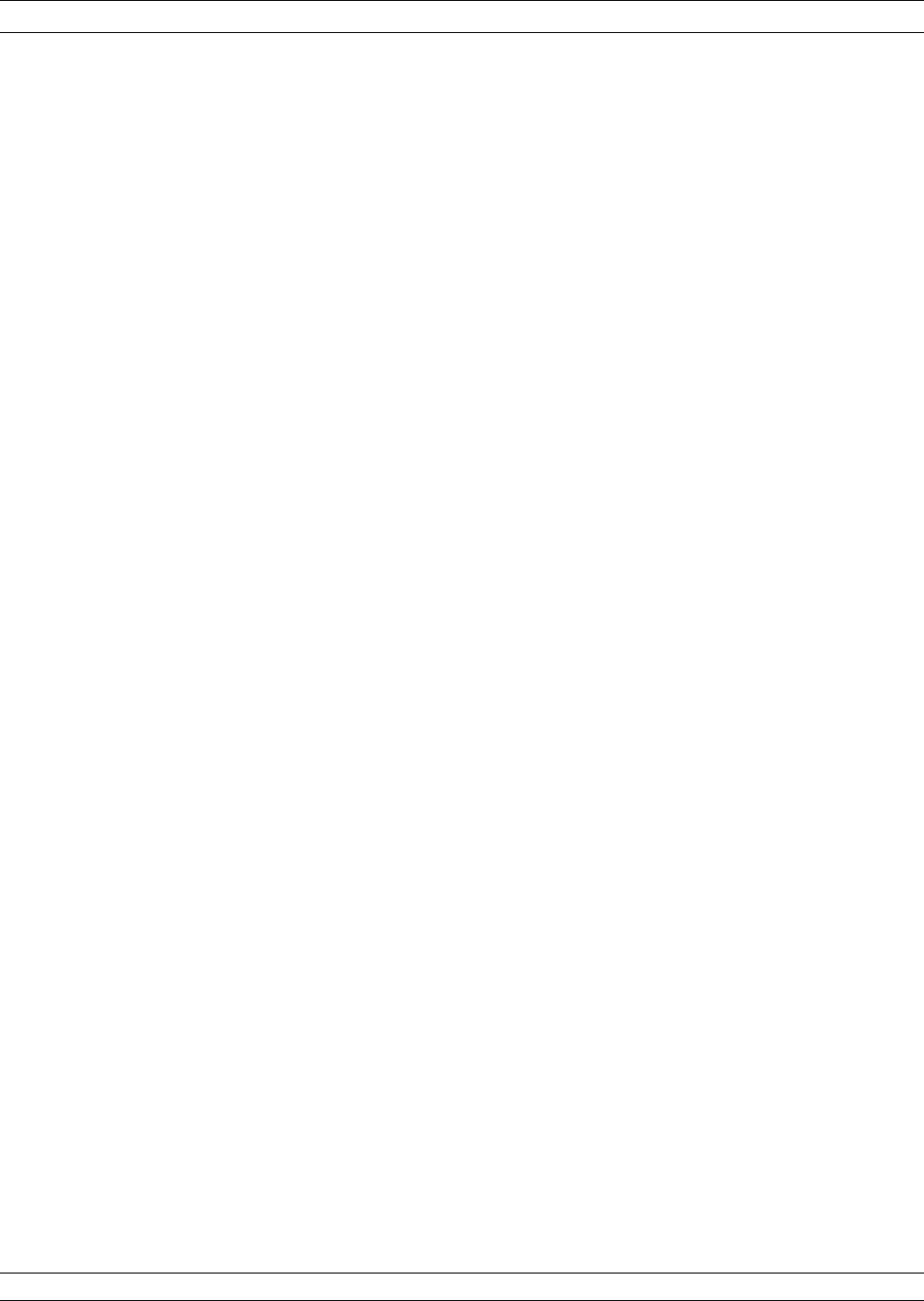
Index 12. Display Keys: (Refer to Section 4-7, page 4-26, for
details and menu flow diagrams.)
Graph Type: Displays the two menus that let you
choose the graph type for the active channel.
Set Scale: Displays the appropriate scaling menu,
based on the graph type for the active channel.
Auto Scale: Automatically scales the active chan-
nel for optimum viewing.
S Params: Displays Menu SP (Appendix A), which
lets you choose between S11, S12, S21, or S22. You
may display the same parameter on two or more
channels.
Ref Plane: Displays the first of two menus that let
you set the reference plane for the active channel in
time or distance. For a correct distance readout, you
must set the dielectric constant to the correct value.
Refer to the discussion in menu RD2 (Appendix A).
Trace Memory: Displays the menus that let you do
any of the following. (1) Store the measured data in
memory. (2) View the stored data. (3) Add, subtract,
multiply, or divide the measured data from the
stored data (normalize to the stored memory). (4)
View both the measured and the stored data simul-
taneously on the active channel. (5) Store/Recall
saved data to disk. Four memories exist—one for
each channel. This lets you normalize the data in
each channel independently. The LED on this but-
ton lights when the active channel is displaying
memory data or measurement data normalized to
memory.
Index 13. Bias Input connectors:
Port 1: Provides for supplying a bias voltage for the
Port 1 input.
Port 2: Provides for supplying a bias voltage for the
Port 2 input.
KEY-GROUPS FRONT PANEL OPERATION
4-6 37XXXC OM
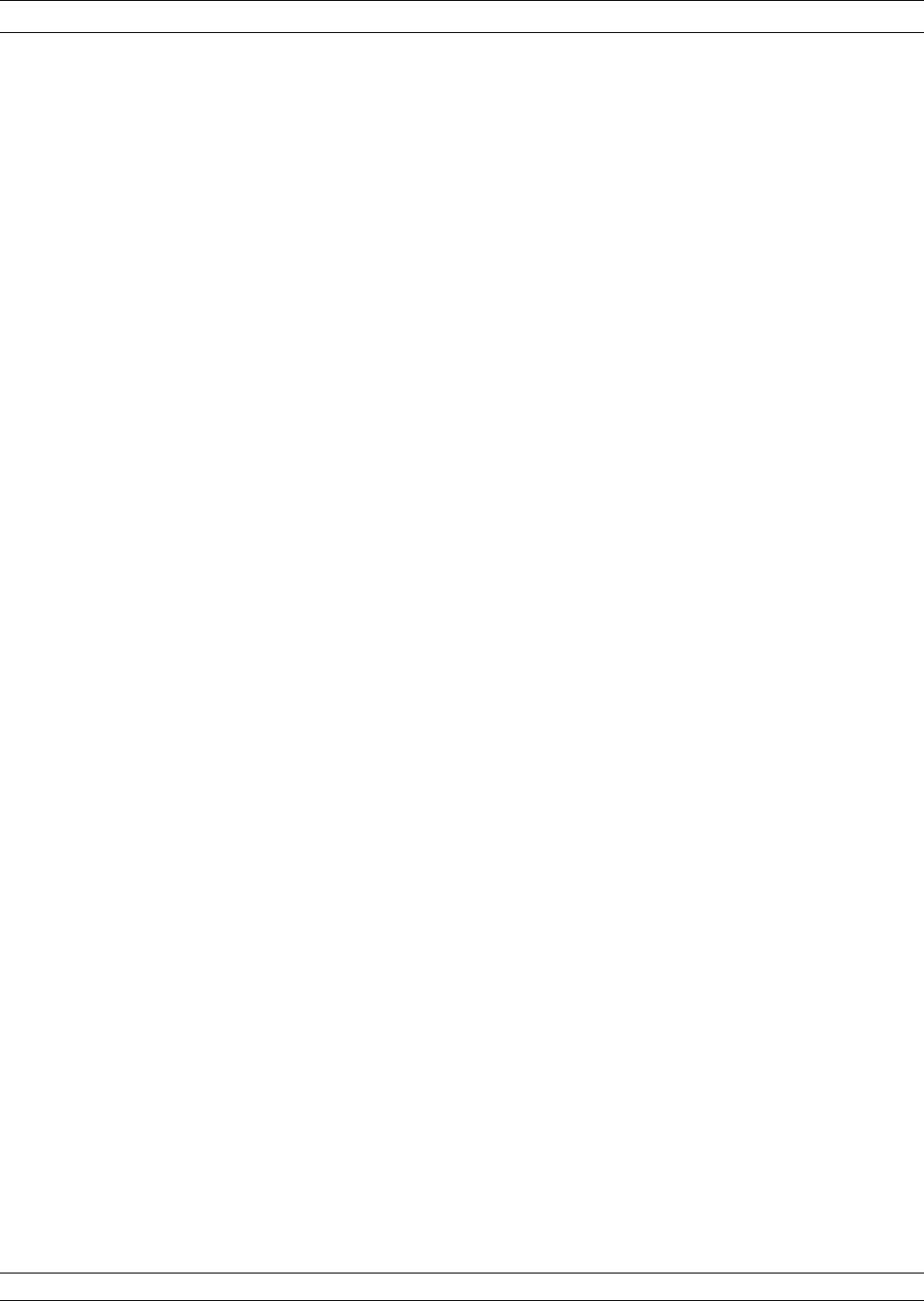
Index 14. Enhancement Keys: (Refer to Section 4-8,
page 4-30 for details and menu flow diagrams.)
Option Menu: Displays a series of menus showing
the choice of optional features.
Video IF BW: Displays a menu that lets you chose
between 10 kHz, 1 kHz, 100 Hz, or 10 Hz intermedi-
ate frequency (IF) bandwidth filters.
Avg/Smooth Menu: Displays a menu that lets you
enter values for Averaging and Smoothing.
Trace Smooth: Turns the trace smoothing function
on and off.
Average: Turns the average function on and off.
Index 15. Keyboard connector: Provides for connecting an
external IBM-AT-type keyboard. All alphanumeric
field entries can be input from this keyboard. These
inputs include Device ID, Model, Date, Operator
Identification, frequencies, filenames, as well as
comment-type entries. The analog knob and keypad
input for these entries remains active. The F1
through F12 function keys can be used to access cer-
tain key and menu functions. A template is pro-
vided. Two versions of an actual-size template are
provided in a foldout page at the end of this chapter
in the event a replacement is needed.
Index 16. Diskette Drive: Provides a drive for the 3.5-inch,
high-density (1.44 MB) floppy diskette used to store
selected front panel setups and calibrations. Refer to
Section 4-12, page 4-41, for disk storage informa-
tion.
37XXXC OM 4-7
FRONT PANEL OPERATION KEY-GROUPS
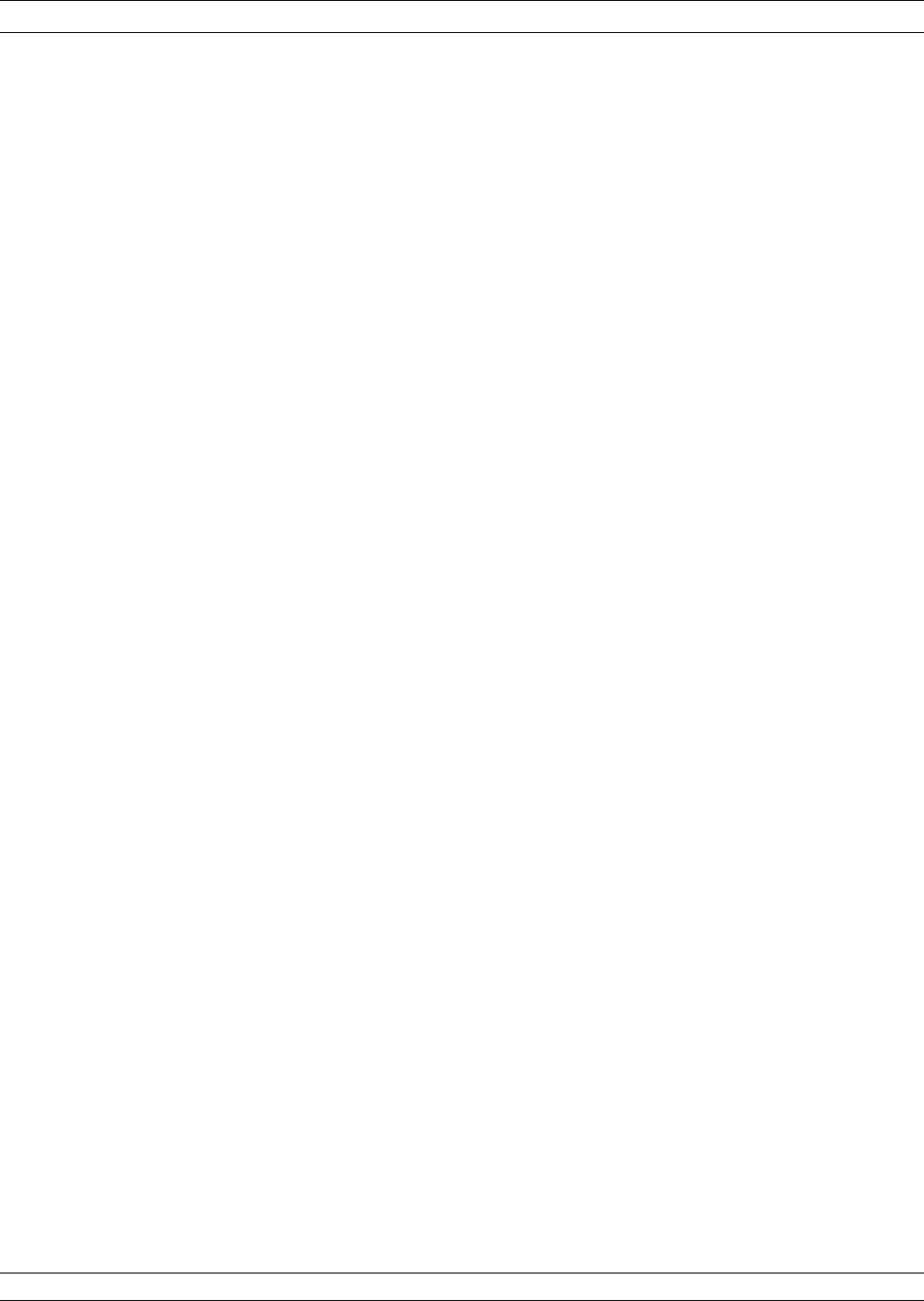
Index 17. Channels Keys: (Refer to Section 4-6, page 4-25, for
details and menu flow diagrams.)
Channel Menu: Displays a menu that lets you se-
lect the format for the number of channels dis-
played.
Ch 1: Makes Channel 1 the active channel. The ac-
tive channel is the one acted on by the keys in the
Display section. Only one channel can be active at
any one time.
Ch 2: Makes Channel 2 the active channel.
Ch 3: Makes Channel 3 the active channel.
Ch 4: Makes Channel 4 the active channel.
Index 18. Measurement Keys: (Refer to Section 4-5,
page 4-22 for details and menu flow diagrams.)
Setup Menu: Displays the first of several menus
that let you select functions affecting measure-
ments.
Data Points: Displays a menu that lets you select
between 1601, 801, 401, 201, 101, or 51 data points.
Hold: Toggles the instrument in and out of the hold
mode; or it triggers a sweep, depending on the func-
tion selected in menu SU4 (Appendix A).
Domain: Displays the first in a series of menus that
let you set the Time Domain display parameters.
(This key is only active if your 37XXXC is equipped
with the Time Domain option.)
If already in the Domain menus, pressing this
key will return to the first menu in the sequence.
If in the Domain menus and another (non-time
domain) menu is displayed by pushing a menu
key, the last displayed domain menu redisplays
when the Domain key is next pressed.
Applications Menu: Displays the first in a series of
menus that provide instructions for adapter removal
and gain compression.
KEY-GROUPS FRONT PANEL OPERATION
4-8 37XXXC OM
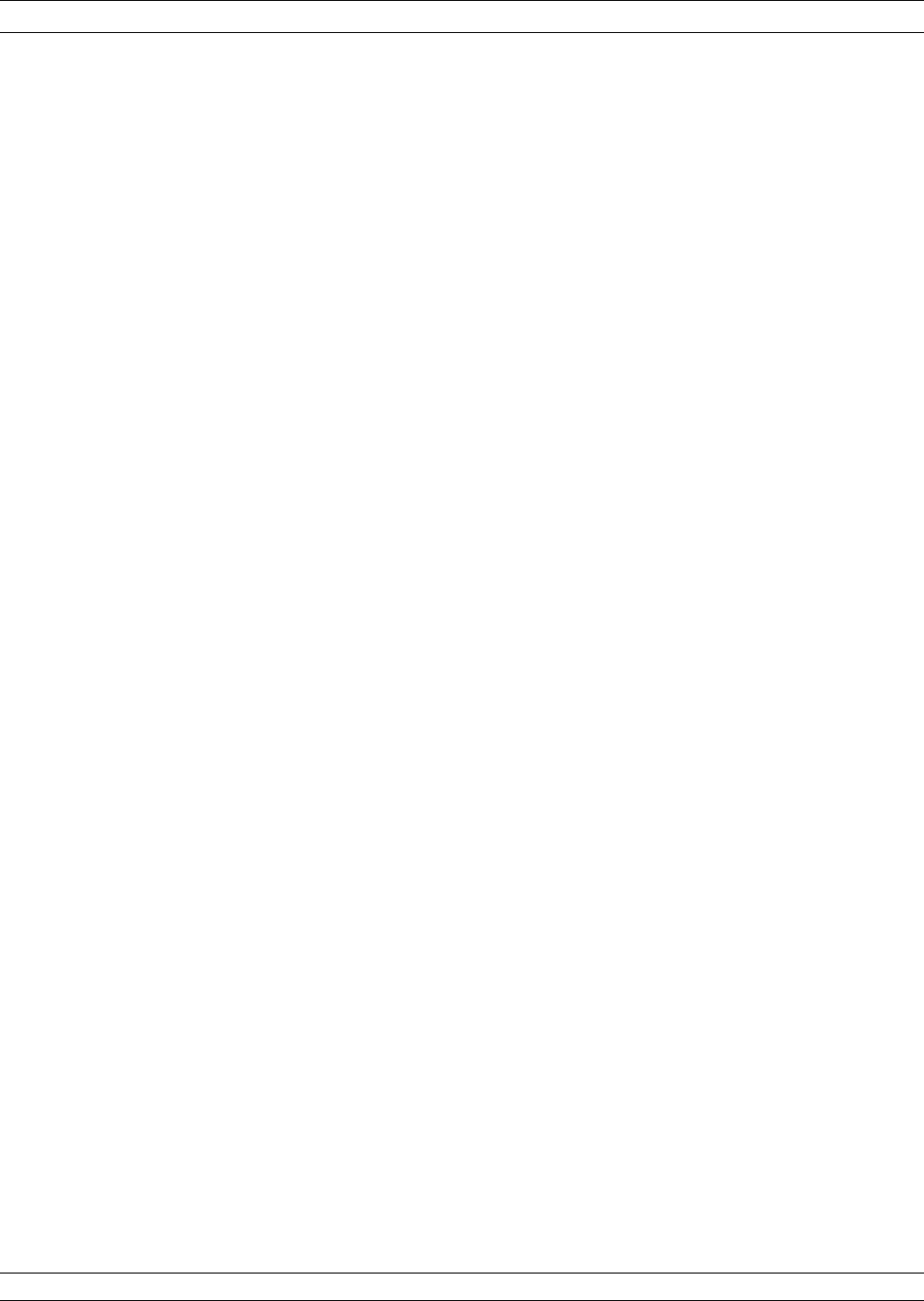
Index 19. Data Entry Keys:
Rotary Knob: Used to alter measurement values
for the active parameter (Start Frequency, Stop Fre-
quency, Offset, etc.).
Keypad: Provides for entering values for the active
parameter. The active parameter is the one to which
the menu cursor is pointing.
MHz/X1/ns/cm: Terminates a value entered on the
keypad in the units shown—that is; megahertz for
frequency, unity for dimensionless or angle entries,
nanoseconds for time, or centimeters for length.
GHz/103/ms/m: Terminates a value entered on the
keypad in the units shown—that is; gigahertz for
frequency, 1´103power for dimensionless or angle
entries, microseconds for time, or meters for length.
kHz/10-3/ps/mm: Terminates a value entered on the
keypad in the units shown—that is; kilohertz for
frequency, 1´10-3 for dimensionless or angle entries,
picoseconds for time, or millimeters for length.
a. Clear/Ret Loc: Local (Non-GPIB) Mode: (1)
The key clears entries not yet terminated by
one of the terminator keys above, which allows
the previously displayed values to redisplay. Or
(2) the key turns off the displayed menu and
expands the data area to fill the entire screen,
if you have not made any keypad entries need-
ing termination.
b. GBIB Mode: The key returns the instrument to
local (front panel) control, unless the controller
has sent a local lockout message (LLO) over
the bus.
Index 20. Menu Keys:
Arrow Keys: Moves the menu cursor up and down
to select items appearing in the menu area of the
LCD.
Enter: Implements the menu selection chosen using
the arrow keys.
37XXXC OM 4-9
FRONT PANEL OPERATION KEY-GROUPS
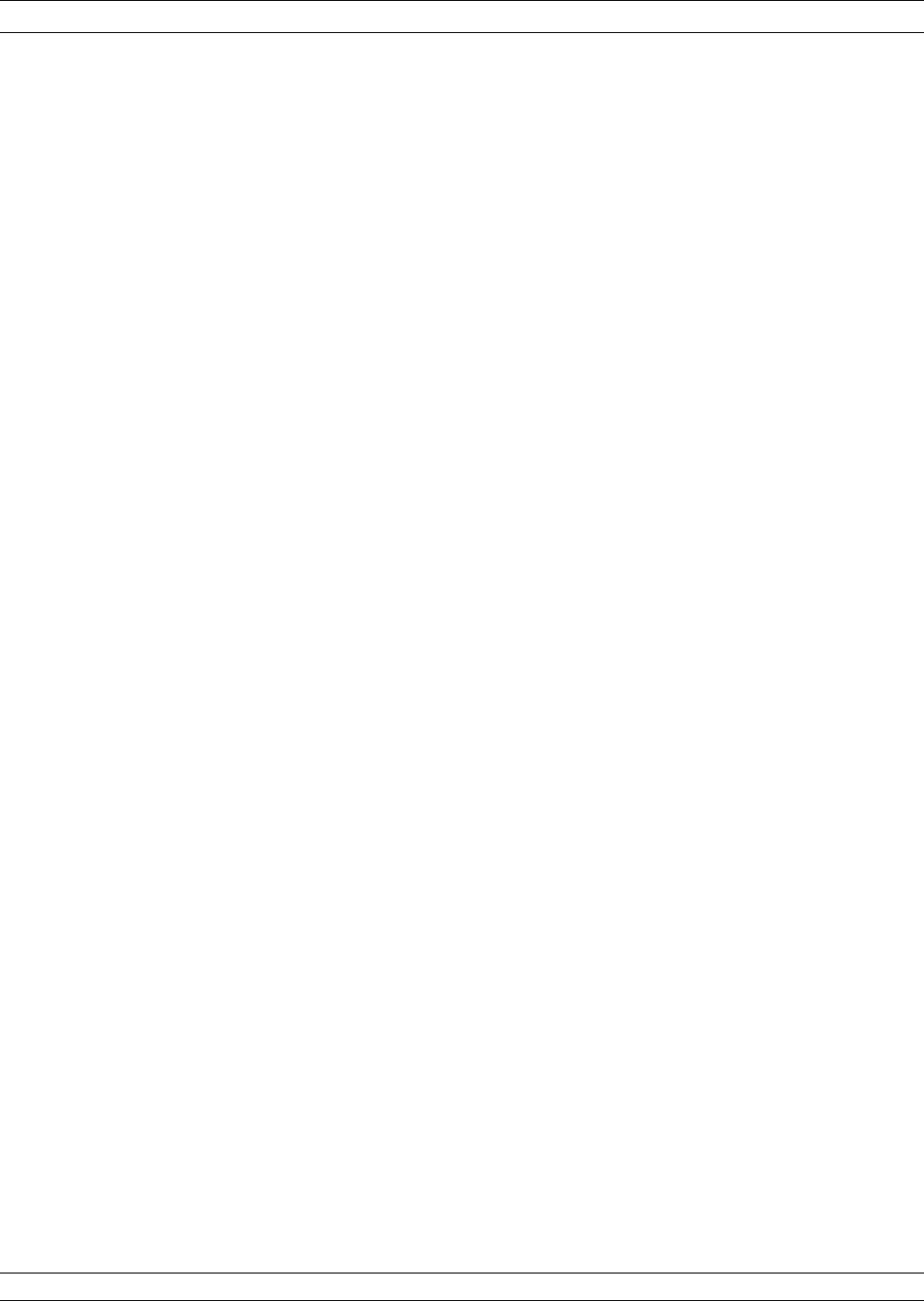
Index 21. b1 Test Connector: Provides an input test connec-
tion to the b1sampler.
Index 22. a1/Source Lock Input Connector: Provides an in-
put test connection to the a1sampler.
Index 23. Source Lock Output Connector: Provides an RF
output test connection to route the a1or a2samplers
for locking purposes.
Index 24. a2/Source Lock Input Connector: Provides an in-
put test connection to the a2sampler.
Index 25. b2Test Connector: Provides an input test connec-
tion to the b2sampler.
Index 26. RF Out Connector: Provides RF output.
Index 27. RF In Connector: Provides the means to input an
external source instead of the internal source.
Index 28. Internal Source Output Connector: Provides a loop
to insert an external source.
KEY-GROUPS FRONT PANEL OPERATION
4-10 37XXXC OM
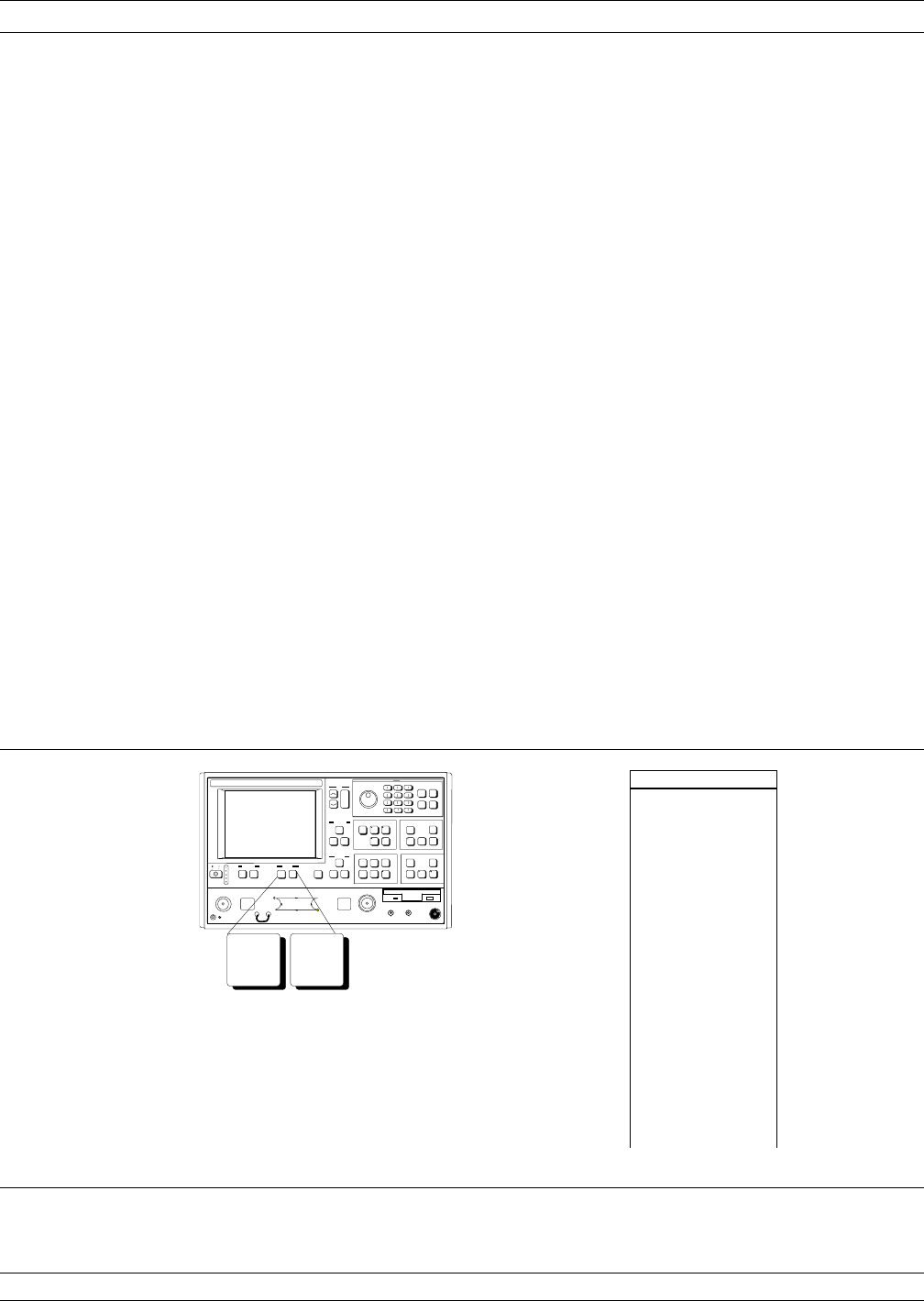
4-3 CALIBRATION
KEY-GROUP The Calibration keys (Begin Cal and Apply Cal, below) are described
below. The calibration menus are diagramed according to the method
of calibration performed: Standard, Offset-Short, TRM or LRL/LRM.
The menu sequencing is complex and looping and can be said to have
two parts: setup and calibration. The setup flow for the four calibra-
tion methods is diagramed in Figures 4-3 through 4-6. Each setup flow
chart leads to the main calibration sequence, which is diagramed in
Figure 4-6. A full description of each menu is provided in Appendix A,
where the menus are arranged in alphabetical order by call letter (C1,
C2, C3, etc).
Begin Cal Key: This key displays a menu that lets you initiate the
calibration sequence. That is, to begin a sequence of steps that corrects
for errors inherent in a measurement setup.
Apply Cal Key: This key displays a menu (below) that lets you turn
on and off the error correction that may be applied to the displayed
channel(s) using the currently valid error-correction indicator. Addi-
tionally, the menu lets you turn the tune mode on and off and change
the number of forward sweeps between reverse sweeps (or reverse
sweeps between forward sweeps).
NOTE
Pressing the Clear key while in a calibration setup or se-
quencing will let you abort the calibration and return to
the first setup menu. Pressing the Setup Menu key will do
the same, but without requesting confirmation.
37XXXC OM 4-11
FRONT PANEL OPERATION CALIBRATION KEY-GROUP
MENU CAL_APPLIED
APPLY
CALIBRATION
APPLY ON (OFF)
CALIBRATION
FULL 12-TERM
(S11, S21
S22, S12)
TUNE MODE ON (OFF)
NO. OF FWD (REV)
SWEEPS BETWEEN
REV (FWD) SWEEPS
XXXXX SWEEPS
(XXXXX REMAINING)
PRESS <APPLY CAL>
TO TURN ON/OFF
PRESS <ENTER>
TO TURN ON/OFF
Apply
Cal
Begin
Cal
Figure 4-2. Calibration Key Group Menu
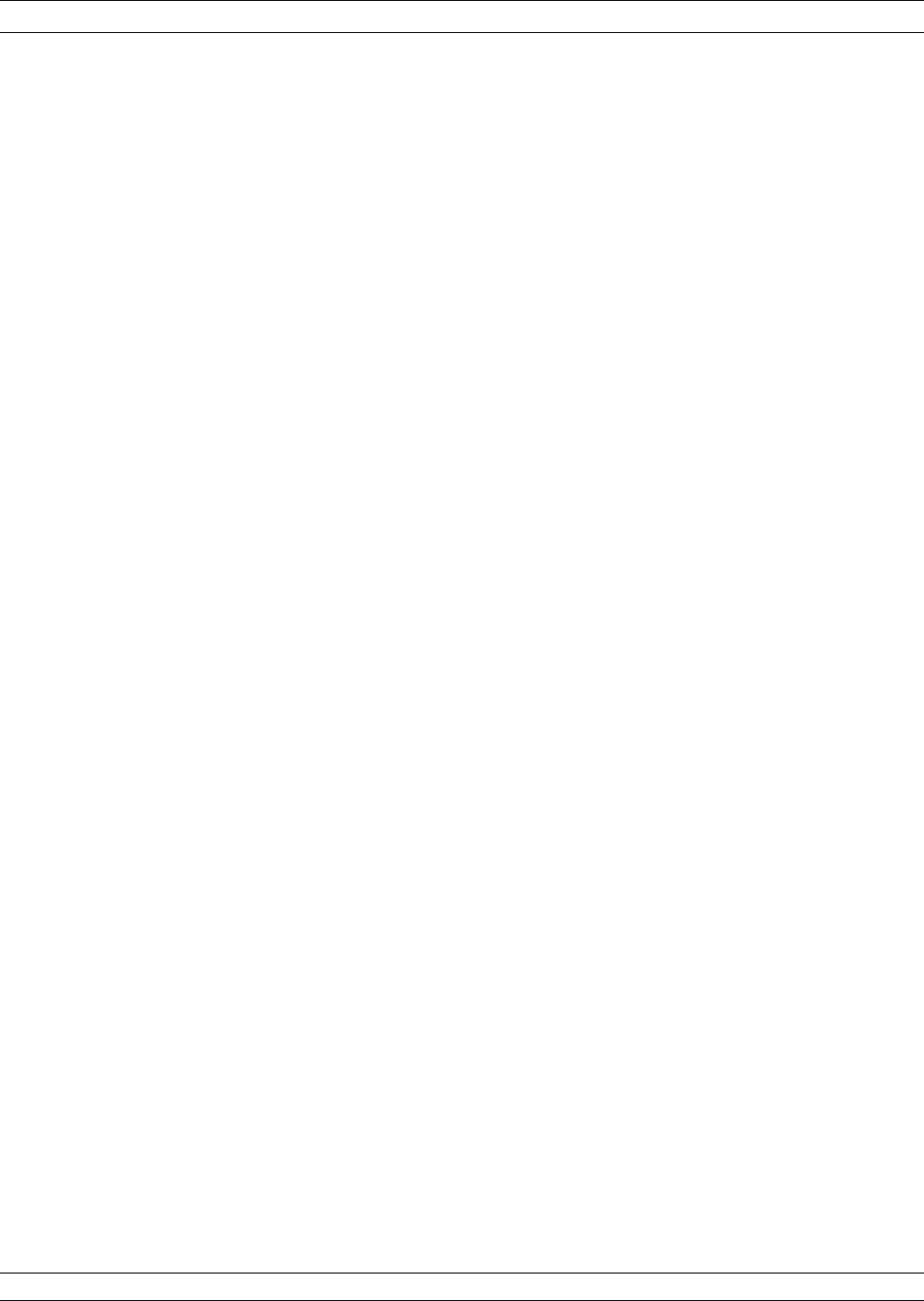
Standard Calibration Setup Flow—Description
1. Pressing the Begin Cal key calls Menu C11.
2. With one exception, the flow is from left to right in the direction of
the arrow head. The exception occurs in Menu C1, for the TIME
DOMAIN choice. Here the flow direction reverses to Menu C2C
then returns to a left-to-right flow on to Menu C3 or C3D.
3. Arrowheads that point both left and right indicate that the flow
returns to the right-most menu after a choice had been made.
4. The group of menus to the left of Menu C3 and C3D are the initial
selection set and are essentially the same for all four calibration
types: Standard, Offset-Short, TRM, and LRL/LRM.
5. The group of menus that follow Menu C3 or C3D are, for the most
part, type specific. The selection of Menu C3 or C3D depends upon
the choice made in Menu C11A: COAXIAL or MICROSTRIP. For
the Standard Calibration, the WAVEGUIDE selection in Menu
C11A is not used.
CALIBRATION KEY-GROUP FRONT PANEL OPERATION
4-12 37XXXC OM
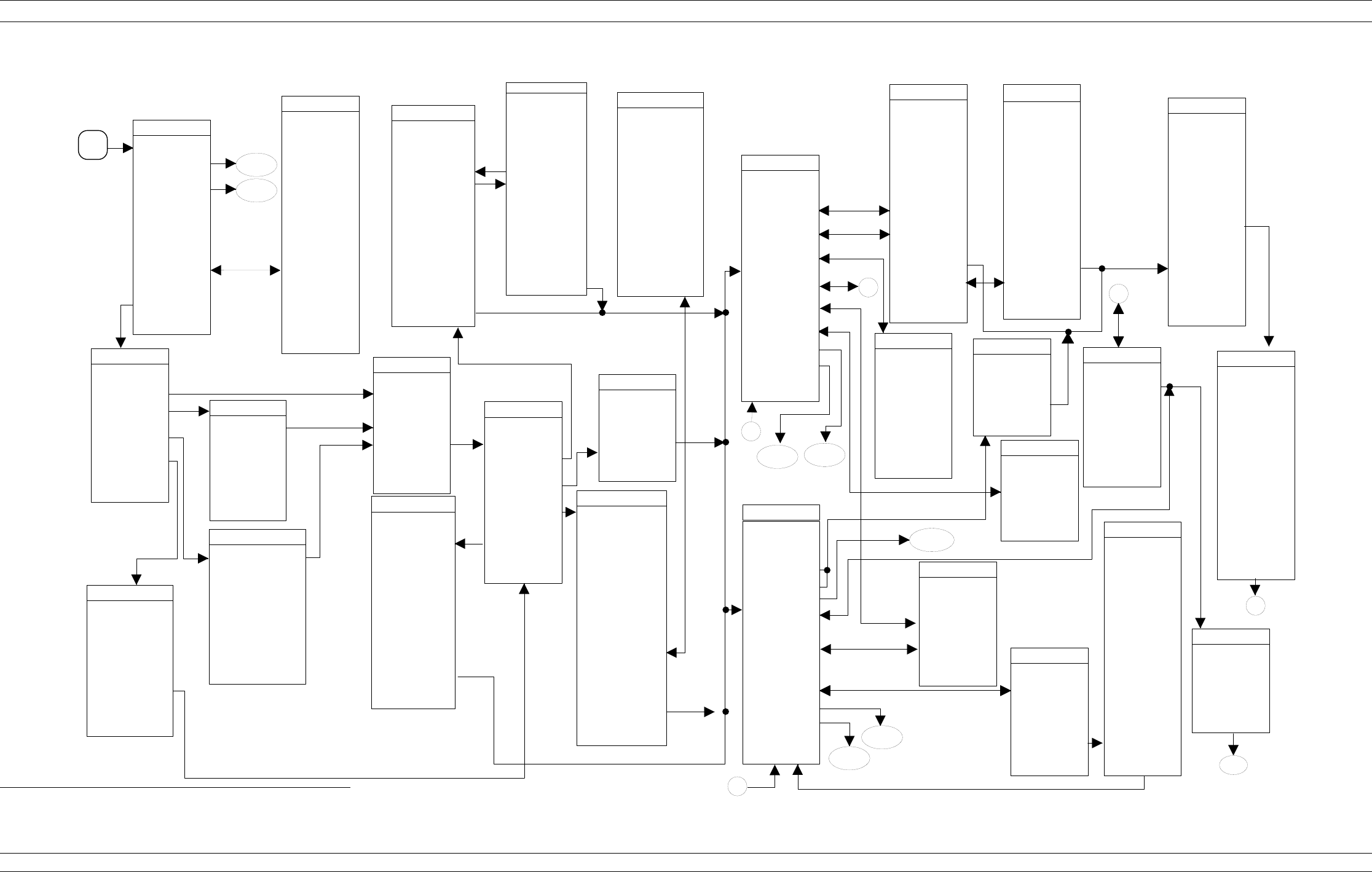
37XXXC OM 4-13
FRONT PANEL OPERATION CALIBRATION KEY-GROUP
M E N U C 1 1 A
N E X T C A L S T E P
C A L M E T H O D
L R L / L R M
C O A X I A L
W A V E G U I D E
M I C R O S T R I P
C H A N G E
C A L M E T H O D
A N D L I N E T Y P E
S O L T ( S T A N D A R D )
PRESS
< E N T E R >
T O S E L E C T
T R A N S M I S S I O N
L I N E T Y P E
M E N U C 1 7
E N T E R
R E F E R E N C E
I M P E D A N C E
P R E S S < E N T E R >
W H E N C O M P L E T E
R E F E R E N C E
I M P E D A N C E
XXX.XXX
9
B e g i n
C a l
T o C a l
S e q * *
C O A X
( S e e M e n u C 1 1 A )
M I C R O S T R I P
( S e e M e n u C 1 1 A )
M E N U C 5 D
S E L E C T U S E
O F I S O L A T I O N
I N C A L I B R A T I O N
INCLUDE
I S O L A T I O N
( S T A N D A R D )
E X C L U D E
I S O L A T I O N
P R E S S < E N T E R >
T O S E L E C T
M E N U C 5 C
P R E S S < E N T E R >
T O S E L E C T
S E L E C T
R E F L E C T I O N O N L Y
C A L I B R A T I O N T Y P E
P O R T 1 O N L Y
( S 1 1 )
P O R T 2 O N L Y
( S 2 2 )
B O T H P O R T S
( S 1 1 , S 2 2 )
S E L E C T
C A L I B R A T I O N
D A T A P O I N T S
N O R M A L
( 1 6 0 1 P O I N T S
M A X I M U M
C . W .
( 1 P O I N T )
N - D I S C R E T E
F R E Q U E N C I E S
( 2 T O 1 6 0 1
P O I N T S )
T I M E D O M A I N
( H A R M O N I C )
P R E S S < E N T E R >
T O S E L E C T
M E N U C 1
T E S T S I G N A L S
S T A R T C A L
C O N F I R M
C A L I B R A T I O N
P A R A M E T E R S
P O R T 1 C O N N
XXXXXXXX
P O R T 2 C O N N
XXXXXXXX
R E F L E C T I O N
P A I R I N G
X X X X X X
L O A D T Y P E
XXXXXXXX
T H R O U G H L I N E
P A R A M E T E R S
R E F E R E N C E
I M P E D A N C E
P R E S S < E N T E R >
T O S E L E C T
O R C H A N G E
M E N U C 3
M E N U C 6
S E L E C T
T Y P E O F L O A D
S L I D I N G L O A D
( M A Y A L S O
R E Q U I R E A
B R O A D B A N D
F I X E D L O A D )
P R E S S < E N T E R >
T O S E L E C T
B R O A D B A N D
F I X E D L O A D
M E N U C 2 B
P R E S S < E N T E R >
T O S E L E C T
S I N G L E P O I N T
C . W . C A L I B R A T I O N
C . W . F R E Q
XX.XXXXXXXX GHz
N E X T C A L S T E P
M E N U C 2 0
E N T E R
T H R O U G H L I N E
P A R A M E T E R S
O F F S E T L E N G T H
X X X X X X m m
P R E S S < E N T E R >
W H E N C O M P L E T E
T H R O U G H L I N E
I M P E D A N C E
X . X X X X
9
T o C a l
S e q * *
T o C a l
S e q * *
T o M e n u
S U 1 / S U 3 *
F U L L 1 2 - T E R M
S E L E C T
C A L I B R A T I O N T Y P E
1 P A T H
2 P O R T
T R A N S M I S S I O N
F R E Q U E N C Y
R E S P O N S E
R E F L E C T I O N
O N L Y
P R E S S < E N T E R >
T O S E L E C T
M E N U C 5
F O R W A R D P A T H
( S 1 1 , S 2 1 )
P R E S S < E N T E R >
T O S E L E C T
S E L E C T
1 P A T H 2 P O R T
C A L I B R A T I O N T Y P E
R E V E R S E P A T H
( S 2 2 , S 1 2 )
M E N U C 5 A
S E L E C T
T R A N S M I S S I O N
F R E Q R E S P O N S E
C A L I B R A T I O N T Y P E
F O R W A R D P A T H
( S 2 1 )
M E N U C 5 B
P R E S S < E N T E R >
T O S E L E C T
REVERSE PATH
( S 1 2 )
B O T H P A T H S
( S 2 1 , S 1 2 )
M E N U C 2 C
C A L I B R A T I O N
R A N G E
H A R M O N I C C A L
F O R T I M E D O M A I N
U S I N G A B O V E
S T A R T A N D S T O P
W I L L R E S U L T I N
X X X D A T A P O I N T S
XXX.XXXXXXXXX GHz
T R U E S T O P F R E Q
S T A R T ( S T E P )
XXX.XXXXXXXXX GHz
A P P R O X I M A T E S T O P
XXX.XXXXXXXXX GHz
N E X T C A L S T E P
P R E S S < E N T E R >
T O S E L E C T
M E N U C 2 D
D I S C R E T E F I L L
C L E A R A L L
P R E S S < E N T E R >
T O S E L E C T
I N P U T S T A R T ,
I N C R , P O I N T S ,
T H E N S E L E C T
" F I L L R A N G E "
S T A R T F R E Q
XXX.XXXXXXXXX GHz
I N C R E M E N T
XXX.XXXXXXXXXGHz
N U M B E R O F P T S
X X X P O I N T ( S )
S T O P F R E Q
X X X . X X X X X X X X X G H z
F I L L R A N G E
( X X X E N T E R E D )
I N D I V I D U A L
F R E Q I N S E R T
F I N I S H E D
N E X T C A L S T E P T E S T S I G N A L S
S T A R T C A L
C O N F I R M
C A L I B R A T I O N
P A R A M E T R S
P O R T 1
O P E N / S H O R T
L O A D I M P E D A N C E
X X X X X X
T H R O U G H L I N E
P A R A M E T E R S
XXXXXXXX
M I C R O S T R I P
P A R A M E T E R S
XXXXXXXXXXX
P R E S S < E N T E R >
T O S E L E C T
O R C H A N G E
M E N U C 3 D
P O R T 2
O P E N / S H O R T
R E F L E C T I O N
P A R I N G
M E N U C 4 _ P 1 o r _ P 2
S E L E C T P O R T X
C O N N E C T O R T Y P E
T Y P E N ( M )
T Y P E N ( F )
T Y P E N ( M ) 7 5 W
T Y P E N ( F ) 7 5 W
7 / 1 6 ( M )
7 / 1 6 ( F )
T N C ( M )
T N C ( F )
2 . 4 m m ( M )
2 . 4 m m ( F )
S P E C I A L ( M )
S P E C I A L ( F )
U S E R D E F I N E D
M O R E
S E L E C T P O R T X
C O N N E C T O R T Y P E
P R E S S < E N T E R >
T O S E L E C T
M E N U C 4 A _ P 1 o r _ P 2
P R E S S < E N T E R >
W H E N C O M P L E T E
O F F S E T L E N G T H
+ X X . X X X X m m
E N T E R T H E
O F F S E T L E N G T H
T E R M 4 - C 3
+ X X X . X X e - 4 5
T E R M 3 - C 2
+ X X X . X X e - 3 6
T E R M 2 - C 1
+ X X X . X X e - 2 7
T E R M 1 - C 0
+ X X . X X e - 1 5
E N T E R T H E
C A P A C I T A N C E
C O E F F I C I E N T S
P O R T X
O P E N D E V I C E
M E N U C 1 2 _ P 1 o r _ P 2
P R E S S < E N T E R >
W H E N C O M P L E T E
O F F S E T L E N G T H
X X . X X X X m m
P O R T X
S H O R T D E V I C E
E N T E R T H E
INDUCTANCE
C O E F F I C I E N T S
M E N U C 1 2 A _ P 1 o r _ P 2
M E N U C 1 6
1 0 M I L K I T
1 5 M I L K I T
2 5 M I L K I T
U S E R D E F I N E D
S E L E C T
M I C R O S T R I P
K I T T O U S E
P R E S S < E N T E R >
T O S E L E C T
M E N U C 1 6 A
E N T E R
M I C R O S T R I P
P A R A M E T E R S
P R E S S < E N T E R >
W H E N C O M P L E T E
W I D T H O F
S T R I P
XX.XXXX m m
T H I C K N E S S O F
S U B S T R A T E
XXXX.XXXX m m
S U B S T R A T E
D I E L E C T R I C
X . X X
E F F E C T I V E
D I E L E C T R I C
X .X X
( R E C O M M E N D E D
1.00)
Z c
X . X X X p
9
A
A
A o r B
B
M E N U C 2 A
P R E V I O U S M E N U
I N P U T A F R E Q ,
P R E S S < E N T E R >
T O I N S E R T
N E X T F R E Q .
XXX.XXXXXXXXX G Hz
X X X F R E Q S .
E N T E R E D ,
L A S T F R E Q W A S
X X X . X X X X X X X X X G H z
A U T O I N C R O N ( O F F )
X X X . X X X X X X X X X G H z
P R E S S < E N T E R >
T O S E L E C T
O R T U R N O N / O F F
I N S E R T
I N D I V I D U A L
F R E Q U E N C I E S
T o M e n u
C A L _ S U 2 *
T o M e n u
C A L _ S U 2 *
C A L F R E Q R A N G E
C E N T E R
XXX.XXXXXXXXX GHz
SPAN
XXX.XXXXXXXXX GHz
S E T S T A R T / S T O P
X X X D A T A P O I N T ( S )
XX.XXXXXXXXX GHz
S T E P S I Z E
M E N U C 2 _ C E N T E R
P R E S S < E N T E R >
T O S E L E C T
N U M O F D A T A P O I N T S
1 6 0 1 M A X P T S
8 0 1 M A X P T S
4 0 1 M A X P T S
2 0 1 M A X P T S
1 0 1 M A X P T S
5 1 M A X P T S
N E X T C A L S T E P
S T A R T
X X X . X X X X X X X X X G H z
X X X D A T A P O I N T S
XXX.XXXXXXXXX GHz
S T E P S I Z E
P R E S S < E N T E R >
T O S E L E C T
S T O P
X X X . X X X X X X X X X G H z
N U M O F D A T A P O I N T S
1 6 0 1 M A X P T S
8 0 1 M A X P T S
4 0 1 M A X P T S
2 0 1 M A X P T S
1 0 1 M A X P T S
5 1 M A X P T S
N E X T C A L S T E P
M E N U C 2
C A L F R E Q R A N G E
S E T C E N T E R / S P A N
T E R M 1 - L 0
- X X X X . X X e - 1 2
T E R M 2 - L 1
- X X X X . X X e - 2 4
T E R M 3 - L 2
- X X X X . X X e - 3 3
T E R M 4 - L 3
- X X X X . X X e - 4 2
E N T E R T H E
O F F S E T L E N G T H
M E N U C 6 A
B R O A D B A N D L O A D
P A R A M E T E R S
P R E S S < E N T E R >
W H E N C O M P L E T E
I M P E D A N C E
X X . X X X
9
I N D U C D A N C E
X X . X X X p H
M E N U C 1 1
B E G I N C A L I B R A T I O N
N E X T C A L S T E P
K E E P E X I S T I N G
C A L D A T A
C H A N G E C A L
M E T H O D A N D
L I N E T Y P E
P R E S S < E N T E R >
T O S E L E C T
R E P E A T
P R E V I O U S C A L
C A L M E T H O D
S T A N D A R D
T R A N S M I S S I O N
L I N E T Y P E :
XXXXXXXX
A U T O C A L
S S L T ( D O U B L E
O F F S E T S H O R T
W I T H L O A D )
S S S T ( T R I P L E
O F F S E T S H O R T )
T R M
K - C O N N ( M )
K - C O N N ( F )
V - C O N N ( M )
V - C O N N ( F )
W 1 - C O N N ( M )
W 1 - C O N N ( F )
S M A ( M )
S M A ( F )
G P C - 3 . 5 ( M )
G P C - 3 . 5 ( F )
G P C - 7
U S E R D E F I N E D
M O R E
P R E S S < E N T E R >
T O S E L E C T
O R C H A N G E
M E N U C 1 3
S E L E C T
R E F L E C T I O N
P A I R I N G
M I X E D
( O P E N - S H O R T
S H O R T - O P E N )
M A T C H E D
( O P E N - O P E N
S H O R T - S H O R T )
P R E S S < E N T E R >
T O S E L E C T
C
C
M E N U C 4 B
P R E S S < E N T E R >
T O S E L E C T
S E L E C T P O R T X
O P E N & S H O R T
S P E C I A L ( M )
S P E C I A L ( F )
U S E R D E F I N E D
T o M e n u
C 1 3 A o r B * * *
Figure 4-3. Menu Sequencing, Standard Calibration
* Setup Menu SU1/SU3 – See Figure 4-6
** Cal Seq (Calibration Sequence) – See Figure 4-5
*** Reflection Pairing Menu C13A or C13B – See Figure 4-4

SSLT and SSST (Offset-Short)
Calibration Setup Flow—Description
1. Pressing the Begin Cal key calls Menu C13.
2. With one exception, the flow is from left to right in the direction of
the arrow head. The exception occurs in Menu C1, for the TIME
DOMAIN choice. Here the flow direction reverses to Menu C2C
then returns to a left-to-right flow on to Menu C3A, C3C, or C3B.
3. Arrowheads that point both left and right indicate that the flow
returns to the right-most menu after a choice had been made.
4. The group of menus to the left of Menu C3A, C3C, or C3B are the
initial selection set and are essentially the same for all four
calibration types: Standard, Offset-Short, TRM, and LRL/LRM.
5. The group of menus that follow Menu C3A, C3C, or C3B are, for
the most part, type specific. The selection of Menu C3A, C3C, or
C3B depends upon the choice made in Menu C11A: COAXIAL,
WAVEGUIDE, or MICROSTRIP.
CALIBRATION KEY-GROUP FRONT PANEL OPERATION
4-14 37XXXC OM
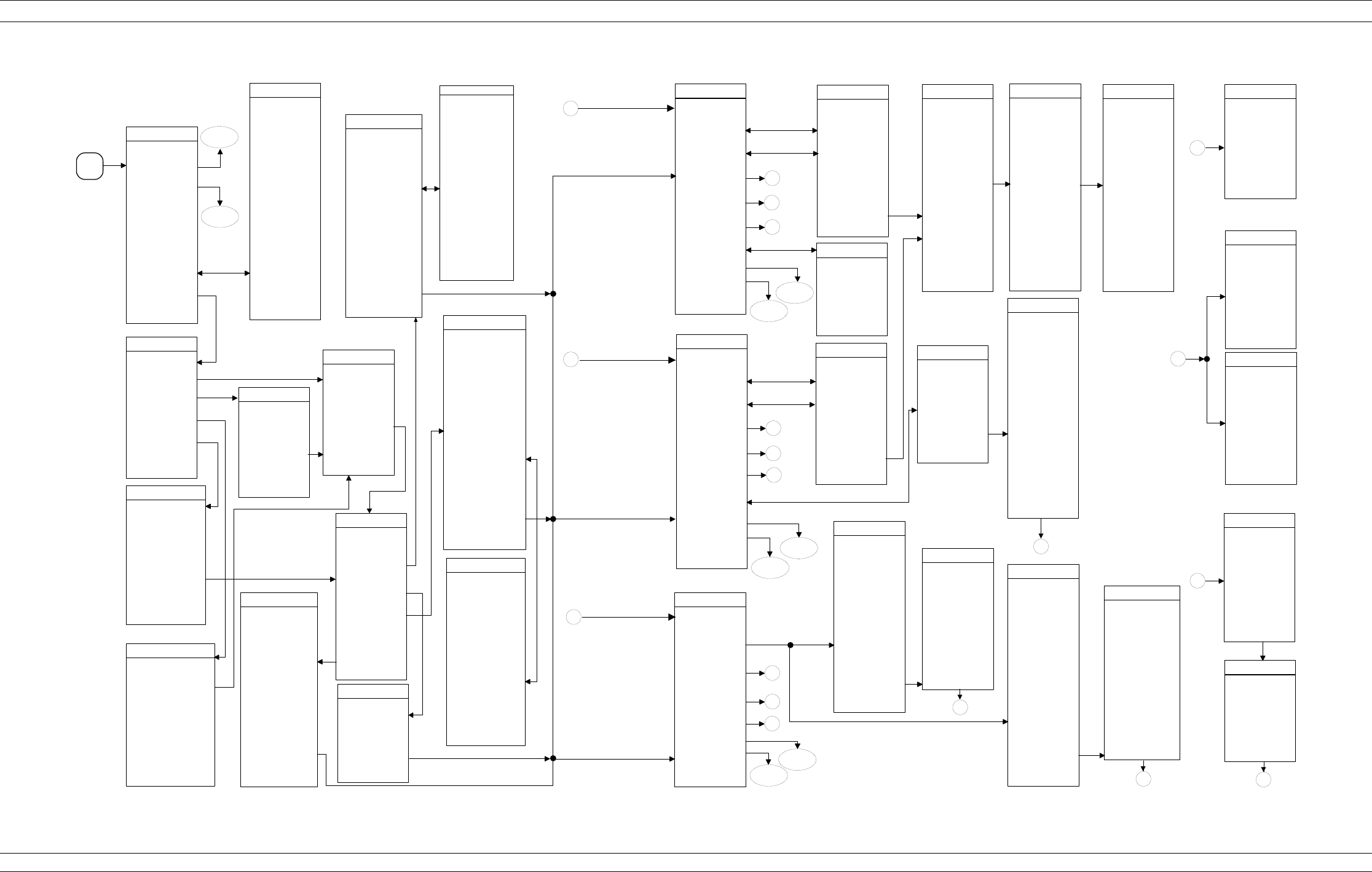
37XXXC OM 4-15
FRONT PANEL OPERATION CALIBRATION KEY-GROUP
M E N U C 1 7
E N T E R
R E F E R E N C E
I M P E D A N C E
P R E S S < E N T E R >
W H E N C O M P L E T E
R E F E R E N C E
I M P E D A N C E
X X X . X X X 9
T o C a l
S e q * *
B e g i n
C a l
T o C a l
S e q * *
M E N U C 5 D
S E L E C T U S E
O F I S O L A T I O N
I N C A L I B R A T I O N
INCLUDE
I S O L A T I O N
( S T A N D A R D )
E X C L U D E
I S O L A T I O N
P R E S S < E N T E R >
T O S E L E C T
M E N U C 5 C
P R E S S < E N T E R >
T O S E L E C T
S E L E C T
R E F L E C T I O N O N L Y
C A L I B R A T I O N T Y P E
P O R T 1 O N L Y
( S 1 1 )
P O R T 2 O N L Y
( S 2 2 )
B O T H P O R T S
( S 1 1 , S 2 2 )
S E L E C T
C A L I B R A T I O N
D A T A P O I N T S
N O R M A L
( 1 6 0 1 P O I N T S
M A X I M U M
C . W .
( 1 P O I N T )
N - D I S C R E T E
F R E Q U E N C I E S
( 2 T O 1 6 0 1
P O I N T S )
T I M E D O M A I N
( H A R M O N I C )
P R E S S < E N T E R >
T O S E L E C T
M E N U C 1
M E N U C 2 B
P R E S S < E N T E R >
T O S E L E C T
S I N G L E P O I N T
C . W . C A L I B R A T I O N
C . W . F R E Q
XX.XXXXXXXX GHz
N E X T C A L S T E P
T o M e n u
S U 1 / S U 3 *
F U L L 1 2 - T E R M
S E L E C T
C A L I B R A T I O N T Y P E
1 P A T H
2 P O R T
T R A N S M I S S I O N
F R E Q U E N C Y
RESPONSE
R E F L E C T I O N
O N L Y
P R E S S < E N T E R >
T O S E L E C T
M E N U C 5
F O R W A R D P A T H
( S 1 1 , S 2 1 )
P R E S S < E N T E R >
T O S E L E C T
S E L E C T
1 P A T H 2 P O R T
C A L I B R A T I O N T Y P E
R E V E R S E P A T H
( S 2 2 , S 1 2 )
M E N U C 5 A
S E L E C T
T R A N S M I S S I O N
F R E Q R E S P O N S E
C A L I B R A T I O N T Y P E
F O R W A R D P A T H
( S 2 1 )
M E N U C 5 B
P R E S S < E N T E R >
T O S E L E C T
REVERSE PATH
( S 1 2 )
B O T H P A T H S
( S 2 1 , S 1 2 )
M E N U C 1 5
- I N S T A L L E D K I T -
U S E R D E F I N E D
S E L E C T
W A V E G U I D E
K I T T O U S E
I D E N T I F I E R
X X X X
C U T O F F F R E Q :
XX.XXXXXXXX G Hz
S H O R T 1
X X . X X X X m m
S H O R T 2
X X . X X X X m m
U S E I N S T A L L E D
W A V E G U I D E K I T
P R E S S < E N T E R >
T O S E L E C T
M E N U C 1 6
1 0 M I L K I T
1 5 M I L K I T
2 5 M I L K I T
U S E R D E F I N E D
S E L E C T
M I C R O S T R I P
K I T T O U S E
P R E S S < E N T E R >
T O S E L E C T
T o M e n u
C A L _ S U 2 *
M E N U C 2 C
C A L I B R A T I O N
R A N G E
H A R M O N I C C A L
F O R T I M E D O M A I N
U S I N G A B O V E
S T A R T A N D S T O P
W I L L R E S U L T I N
X X X D A T A P O I N T S
X X X . X X X X X X X X X G H z
T R U E S T O P F R E Q
S T A R T ( S T E P )
XXX.XXXXXXXXX GHz
A P P R O X I M A T E S T O P
XXX.XXXXXXXXX GHz
N E X T C A L S T E P
P R E S S < E N T E R >
T O S E L E C T
M E N U C 2 A
P R E V I O U S M E N U
I N P U T A F R E Q ,
P R E S S < E N T E R >
T O I N S E R T
N E X T F R E Q .
XXX.XXXXXXXXX GHz
X X X F R E Q S .
E N T E R E D ,
L A S T F R E Q W A S
XXX.XXXXXXXXX G Hz
A U T O I N C R O N ( O F F )
XXX.XXXXXXXXX G Hz
P R E S S < E N T E R >
T O S E L E C T
O R T U R N O N / O F F
I N S E R T
I N D I V I D U A L
F R E Q U E N C I E S
M E N U C 2 D
D I S C R E T E F I L L
C L E A R A L L
P R E S S < E N T E R >
T O S E L E C T
I N P U T S T A R T ,
I N C R , P O I N T S ,
T H E N S E L E C T
" F I L L R A N G E "
S T A R T F R E Q
XXX.XXXXXXXXX GHz
I N C R E M E N T
XXX.XXXXXXXXXG Hz
N U M B E R O F P T S
X X X P O I N T ( S )
S T O P F R E Q
XXX.XXXXXXXXXG Hz
F I L L R A N G E
( X X X E N T E R E D )
I N D I V I D U A L
F R E Q I N S E R T
F I N I S H E D
N E X T C A L S T E P
M E N U C 1 5 A
E N T E R W A V E G U I D E
P A R A M E T E R S
P R E S S < E N T E R >
W H E N C O M P L E T E
W A V E G U I D E
C U T O F F F R E Q
XXX.XXXXXXXXXG Hz
O F F S E T L E N G T H
O F S H O R T 1
X . X X X X m m
O F F S E T L E N G T H
O F S H O R T 2
X . X X X X m m
C
M E N U C 1 6 A
E N T E R
M I C R O S T R I P
P A R A M E T E R S
P R E S S < E N T E R >
W H E N C O M P L E T E
W I D T H O F
S T R I P
XX.XXXX m m
T H I C K N E S S O F
S U B S T R A T E
XXXX.XXXX m m
S U B S T R A T E
D I E L E C T R I C
X . X X
E F F E C T I V E
D I E L E C T R I C
X .X X
( R E C O M M E N D E D
1.00)
Z c
X . X X X p
9
C
C A L F R E Q R A N G E
C E N T E R
XXX.XXXXXXXXX GHz
SPAN
XXX.XXXXXXXXX GHz
S E T S T A R T / S T O P
X X X D A T A P O I N T ( S )
XX.XXXXXXXXX GHz
S T E P S I Z E
M E N U C 2 _ C E N T E R
P R E S S < E N T E R >
T O S E L E C T
N U M O F D A T A P O I N T S
1 6 0 1 M A X P T S
8 0 1 M A X P T S
4 0 1 M A X P T S
2 0 1 M A X P T S
1 0 1 M A X P T S
5 1 M A X P T S
N E X T C A L S T E P
S T A R T
XXX.XXXXXXXXX G Hz
X X X D A T A P O I N T S
XXX.XXXXXXXXX GHz
S T E P S I Z E
P R E S S < E N T E R >
T O S E L E C T
S T O P
XXX.XXXXXXXXX G Hz
N U M O F D A T A P O I N T S
1 6 0 1 M A X P T S
8 0 1 M A X P T S
4 0 1 M A X P T S
2 0 1 M A X P T S
1 0 1 M A X P T S
5 1 M A X P T S
N E X T C A L S T E P
M E N U C 2
C A L F R E Q R A N G E
S E T C E N T E R / S P A N
M E N U C 1 1
B E G I N C A L I B R A T I O N
N E X T C A L S T E P
K E E P E X I S T I N G
C A L D A T A
C H A N G E C A L
M E T H O D A N D
L I N E T Y P E
P R E S S < E N T E R >
T O S E L E C T
R E P E A T
P R E V I O U S C A L
C A L M E T H O D
S T A N D A R D
T R A N S M I S S I O N
L I N E T Y P E :
XXXXXXXX
A U T O C A L
M E N U C 1 1 A
N E X T C A L S T E P
C A L M E T H O D
L R L / L R M
C O A X I A L
W A V E G U I D E
M I C R O S T R I P
C H A N G E
C A L M E T H O D
A N D L I N E T Y P E
S O L T ( S T A N D A R D )
PRESS
< E N T E R >
T O S E L E C T
T R A N S M I S S I O N
L I N E T Y P E
S S L T ( D O U B L E
O F F S E T S H O R T
W I T H L O A D )
S S S T ( T R I P L E
O F F S E T S H O R T )
T R M
A
C O A X
( S e e M e n u C 1 1 A )
M E N U C 3 A
C O N F I R M
C A L I B R A T I O N
P A R A M E T R S
P R E S S < E N T E R >
T O S E L E C T
O R C H A N G E
P O R T 1 C O N N
W 1 - C O N N ( M )
P O R T 2 C O N N
W 1 - C O N N ( M )
R E F L E C T I O N
P A I R I N G
XXXXXXXX
L O A D T Y P E
XXXXXXXX
T H R O U G H L I N E
P A R A M E T E R S
R E F E R E N C E
I M P E D A N C E
T E S T S I G N A L S
S T A R T C A L
P R E S S < E N T E R >
W H E N C O M P L E T E
M E N U C 1 4
S E L E C T P O R T X
O F F S E T S H O R T
C O N N E C O T R T Y P E
W 1 - C O N N ( M )
W 1 - C O N N ( F )
S P E C I A L A ( M )
S P E C I A L A ( F )
S P E C I A L B ( M )
S P E C I A L B ( F )
S P E C I A L C ( M )
S P E C I A L C ( F )
U S E R D E F I N E D
M E N U C 1 4 A
P R E S S < E N T E R >
W H E N C O M P L E T E
S E L E C T P O R T X
O F F S E T S H O R T
C O N N E C O T R T Y P E
S P E C I A L A ( M )
S P E C I A L A ( F )
S P E C I A L B ( M )
S P E C I A L B ( F )
S P E C I A L C ( M )
S P E C I A L C ( F )
U S E R D E F I N E D
M E N U C 2 1 A
P O R T X
O F F S E T S H O R T 1
E N T E R T H E
I N D U C T A N C E
C O E F F I C I E N T S
L 0 [ e - 1 2 H ]
+XXXX.XXXX
L 1 [ e - 2 4 H / H z ]
+XXXX.XXXX
L 2 [ e - 3 3 H / H z
2
]
+XXXX.XXXX
L 3 [ e - 4 2 H / H z
3
]
+XXXX.XXXX
E N T E R T H E
O F F S E T L E N G T H
O F F S E T L E N G T H
+XXX.XXXX m m
P R E S S < E N T E R >
W H E N C O M P L E T E
M E N U C 2 1 B
P O R T X
O F F S E T S H O R T 2
E N T E R T H E
I N D U C T A N C E
C O E F F I C I E N T S
L 0 [ e - 1 2 H ]
+XXXX.XXXX
L 1 [ e - 2 4 H / H z ]
+XXXX.XXXX
L 2 [ e - 3 3 H / H z
2
]
+XXXX.XXXX
L 3 [ e - 4 2 H / H z
3
]
+XXXX.XXXX
E N T E R T H E
O F F S E T L E N G T H
O F F S E T L E N G T H
+XXX.XXXX m m
P R E S S < E N T E R >
W H E N C O M P L E T E
M E N U C 2 1 C
P O R T X
O F F S E T S H O R T 3
E N T E R T H E
I N D U C T A N C E
C O E F F I C I E N T S
L 0 [ e - 1 2 H ]
+XXXX.XXXX
L 1 [ e - 2 4 H / H z ]
+XXXX.XXXX
L 2 [ e - 3 3 H / H z
2
]
+XXXX.XXXX
L 3 [ e - 4 2 H / H z
3
]
+XXXX.XXXX
E N T E R T H E
O F F S E T L E N G T H
O F F S E T L E N G T H
+XXX.XXXX m m
P R E S S < E N T E R >
W H E N C O M P L E T E
M E N U C 1 5 C
S E L E C T
W A V E G U I D E
K I T T O U S E
- I N S T A L L E D K I T -
I D E N T I F I E R :
XXXX
C U T O F F F R E Q :
XXX.XXXXXXXXX GHz
S H O R T 1 :
+XX.XXXX m m
S H O R T 2 :
+XX.XXXX m m
S H O R T 3 :
+XX.XXXX m m
U S E I N S T A L L E D
W A V E G U I D E K I T
U S E R D E F I N E D
P R E S S < E N T E R >
T O S E L E C T
M E N U C 1 5 D
S E L E C T
W A V E G U I D E
K I T T O U S E
W A V E G U I D E
C U T O F F F R E Q
XXX.XXXXXXXXX G Hz
O F F S E T L E N G T H
O F S H O R T 1
+ X . X X X X m m
O F F S E T L E N G T H
O F S H O R T 2
+ X . X X X X m m
O F F S E T L E N G T H
O F S H O R T 3
+ X . X X X X m m
P R E S S < E N T E R >
T O S E L E C T
C
F o r S S L T
F o r S S S T
B
M I C R O S T R I P
( S e e M e n u C 1 1 A )
M E N U C 3 C
C O N F I R M
C A L I B R A T I O N
P A R A M E T E R S
P R E S S < E N T E R >
T O S E L E C T
O R C H A N G E
P O R T 1 S H O R T S
U S E R D E F I N E D
P O R T 2 S H O R T S
U S E R D E F I N E D
R E F L E C T I O N
P A I R I N G
XXXXXX
L O A D T Y P E
XXXXXXXX
T H R O U G H L I N E
P A R A M E T E R S
M I C R O S T R I P
P A R A M E T E R S
XXXXXXXXXXX
T E S T S I G N A L S
S T A R T C A L
C
W A V E G U I D E
( S e e M e n u C 1 1 A )
M E N U C 3 B
C O N F I R M
C A L I B R A T I O N
P A R A M E T E R S
P R E S S < E N T E R >
T O S E L E C T
O R C H A N G E
W A V E G U I D E
P A R A M E T E R S
XXXXXX
R E F L E C T I O N
P A I R I N G
XXXXXX
L O A D T Y P E
XXXXXXXX
T H R O U G H L I N E
P A R A M E T E R S
T E S T S I G N A L S
S T A R T C A L
T o C a l
S e q * *
T o M e n u
C A L _ S U 2 *
T o C a l
S e q * *
T o M e n u
C A L _ S U 2 *
M E N U C 2 0
E N T E R
T H R O U G H L I N E
P A R A M E T E R S
O F F S E T L E N G T H
X X X X X X m m
P R E S S < E N T E R >
W H E N C O M P L E T E
T H R O U G H L I N E
I M P E D A N C E
X . X X X X
9
D
D
D
D
E
E
E
A
M E N U C 6 A
B R O A D B A N D L O A D
P A R A M E T E R S
P R E S S < E N T E R >
W H E N C O M P L E T E
I N D U C T A N C E
X X . X X X p H
I M P E D A N C E
X X . X X X
9
M E N U C 6
S E L E C T
T Y P E O F L O A D
S L I D I N G L O A D
( M A Y A L S O
R E Q U I R E A
B R O A D B A N D
F I X E D L O A D )
P R E S S < E N T E R >
T O S E L E C T
B R O A D B A N D
F I X E D L O A D
E
F
F
F
M E N U C 1 3 A
M I X E D
( S H O R T 1 - S H O R T 2 ,
S H O R T 2 - S H O R T 1 )
M A T C H E D
( S H O R T 1 - S H O R T 1 ,
S H O R T 2 - S H O R T 2 )
P R E S S < E N T E R >
T O S E L E C T
S E L E C T
R E F L E C T I O N
P A I R I N G
M E N U C 1 3 B
M I X E D
( S H O R T 1 - S H O R T 2 ,
S H O R T 2 - S H O R T 3 ,
S H O R T 3 - S H O R T 1 )
M A T C H E D
( S H O R T 1 - S H O R T 1 ,
S H O R T 2 - S H O R T 2 ,
S H O R T 3 - S H O R T 3 )
P R E S S < E N T E R >
T O S E L E C T
S E L E C T
R E F L E C T I O N
P A I R I N G
F
F o r S S L T
F o r S S S T
Figure 4-4. Menu Sequencing, SSLT and SSST
(Offset-Short) Calibration
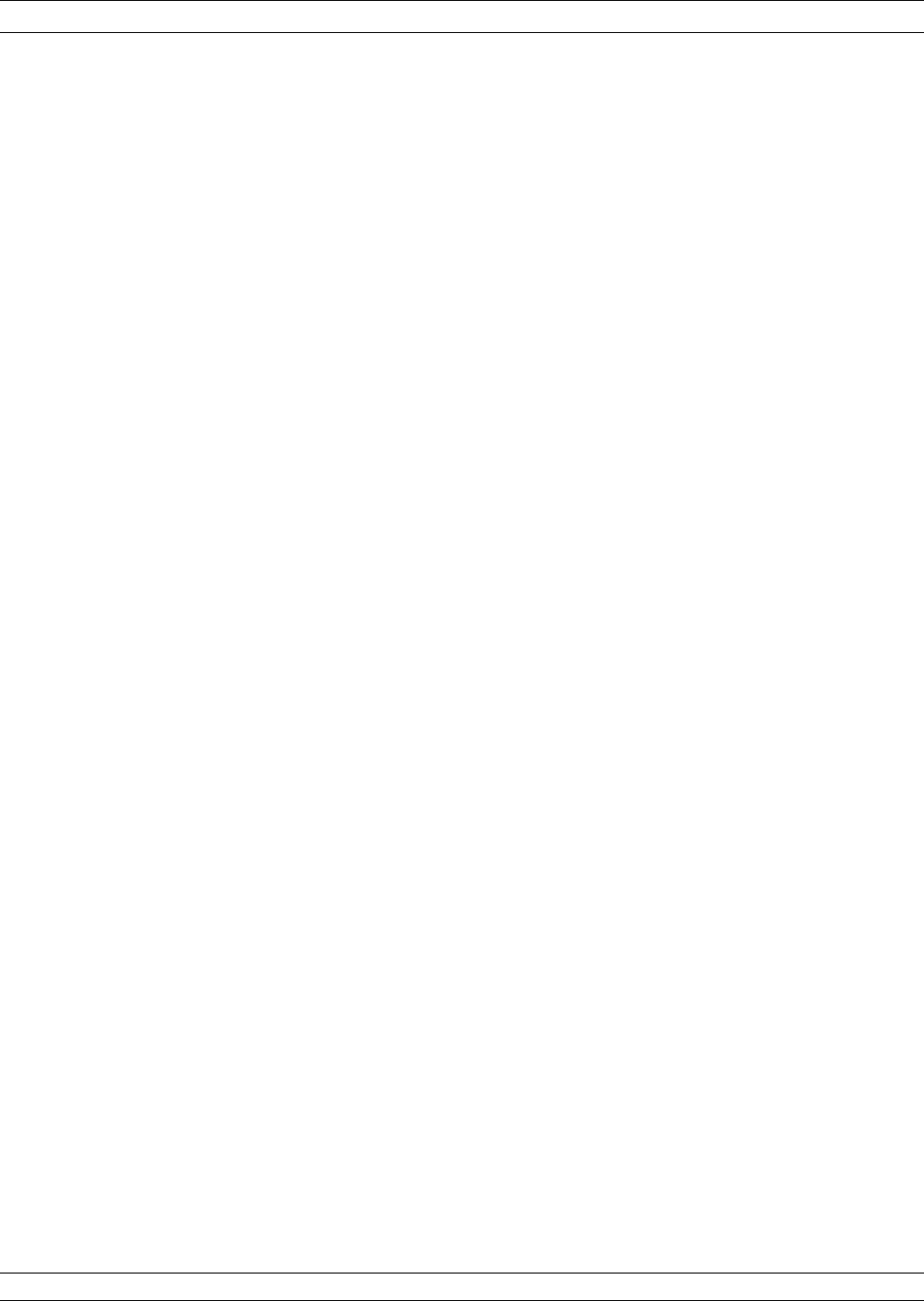
LRL/LRM Calibration Setup Flow—Description
1. Pressing the Begin Cal key calls Menu C15.
2. With one exception, the flow is from left to right in the direction of
the arrow head. The exception occurs in Menu C1, for the TIME
DOMAIN choice. Here the flow direction reverses to Menu C2C
then returns to a left-to-right flow on to Menu C3E, C3G, or C3F.
3. Arrowheads that point both left and right indicate that the flow
returns to the right-most menu after a choice had been made.
4. The group of menus to the left of Menu C3E, C3G, or C3F are the
initial selection set and are essentially the same for all four
calibration types: Standard, Offset-Short, TRM, and LRL/LRM.
5. The group of menus that follow Menu C3E, C3G, or C3F are, for
the most part, type specific. The selection of Menu C3E, C3G, or
C3F depends upon the choice made in Menu C11A: COAXIAL,
WAVEGUIDE, or MICROSTRIP.
CALIBRATION KEY-GROUP FRONT PANEL OPERATION
4-16 37XXXC OM
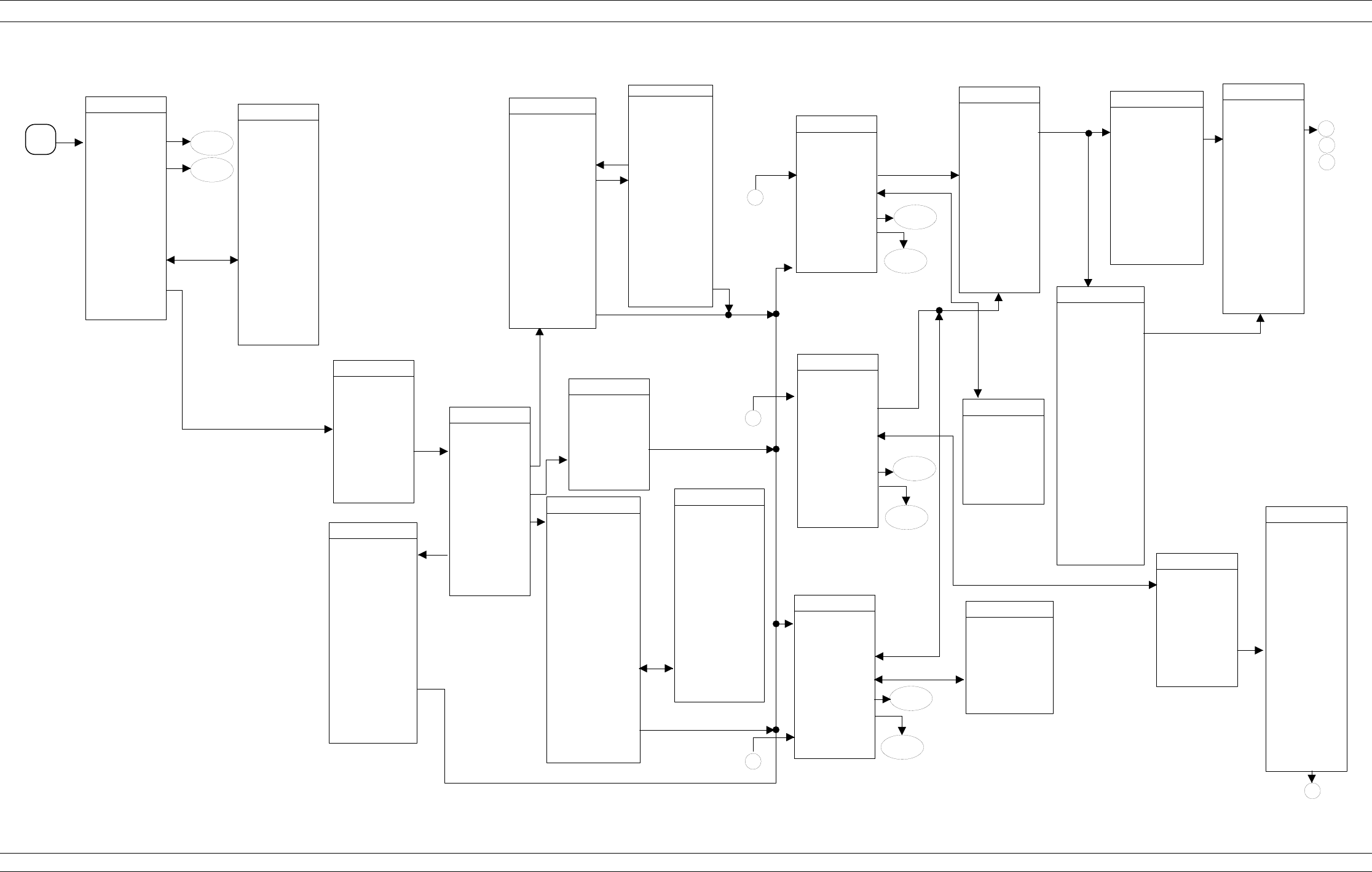
37XXXC OM 4-17
FRONT PANEL OPERATION CALIBRATION KEY-GROUP
M I C R O S T R I P
( S e e M e n u C 1 1 A )
W A V E G U I D E
( S e e M e n u C 1 1 A )
C O A X
( S e e M e n u C 1 1 A )
M E N U C 3 E
T E S T S I G N A L S
S T A R T C A L
C O N F I R M
C A L I B R A T I O N
P A R A M E T E R S
L R L / L R M
P A R A M E T E R S
R E F E R E N C E
I M P E D A N C E
P R E S S < E N T E R >
T O S E L E C T
O R C H A N G E
M E N U C 3 F
T E S T S I G N A L S
S T A R T C A L
C O N F I R M
C A L I B R A T I O N
P A R A M E T E R S
L R L / L R M
P A R A M E T E R S
P R E S S < E N T E R >
T O S E L E C T
O R C H A N G E
W A V E G U I D E
C U T O F F F R E Q
M E N U C 3 G
T E S T S I G N A L S
S T A R T C A L
C O N F I R M
C A L I B R A T I O N
P A R A M E T E R S
L R L / L R M
P A R A M E T E R S
P R E S S < E N T E R >
T O S E L E C T
O R C H A N G E
M I C R O S T R I P
P A R A M E T E R S
U S E R D E F I N E D
M E N U C 1 8
N E X T C A L S T E P
O N E B A N D
T W O B A N D S
C H A N G E L R L / L R M
P A R A M E T E R S
M I D D L E O F
L I N E 1 ( R E F )
E N D S O F
L I N E 1 ( R E F )
N U M B E R O F
B A N D S U S E D
L O C A T I O N O F
R E F E R E N C E
P L A N E S
P R E S S < E N T E R >
T O S E L E C T
O N E B A N D
T W O B A N D S
M E N U C 1 7
E N T E R
R E F E R E N C E
I M P E D A N C E
P R E S S < E N T E R >
W H E N C O M P L E T E
R E F E R E N C E
I M P E D A N C E
X X X . X X X 9
M E N U C 1 9
N E X T C A L S T E P
R E F L E C T I O N
O F F S E T L E N G T H
+ X X X . X X X m m
R E F L E C T I O N T Y P E
G R E A T E R T H A N Z o
L E S S T H A N Z o
M A T C H P A R A M E T E R S
M A T C H I M P E D A N C E
+ X X X . X X X
9
M A T C H I N D U C T A N C E
+ X X X X . X X X X p H
C H A N G E L R L / L R M
P A R A M E T E R S
P R E S S < E N T E R >
T O S E L E C T
T o C a l
S e q * *
T o C a l
S e q * *
T o C a l
S e q * *
M E N U C 1 1 A
N E X T C A L S T E P
C A L M E T H O D
O F F S E T S H O R T
L R L / L R M
C O A X I A L
W A V E G U I D E
M I C R O S T R I P
C H A N G E
C A L M E T H O D
A N D L I N E T Y P E
S T A N D A R D
( N O T U S E D F O R
W A V E G U I D E )
P R E S S
< E N T E R >
T O S E L E C T
T R A N S M I S S I O N
L I N E T Y P E
B e g i n
C a l
T o C a l
S e q * *
M E N U C 5 D
S E L E C T U S E
O F I S O L A T I O N
I N C A L I B R A T I O N
INCLUDE
I S O L A T I O N
( S T A N D A R D )
E X C L U D E
I S O L A T I O N
P R E S S < E N T E R >
T O S E L E C T
S E L E C T
C A L I B R A T I O N
D A T A P O I N T S
N O R M A L
( 1 6 0 1 P O I N T S
M A X I M U M
C . W .
( 1 P O I N T )
N - D I S C R E T E
F R E Q U E N C I E S
( 2 T O 1 6 0 1
P O I N T S )
T I M E D O M A I N
( H A R M O N I C )
P R E S S < E N T E R >
T O S E L E C T
M E N U C 1
M E N U C 2 B
P R E S S < E N T E R >
T O S E L E C T
S I N G L E P O I N T
C . W . C A L I B R A T I O N
C . W . F R E Q
XX.XXXXXXXX G Hz
N E X T C A L S T E P
T o M e n u
S U 1 / S U 3 *
M E N U C 1 5 B
W A V E G U I D E
C U T O F F F R E Q
X X X . X X X X X X X X X G H z
P R E S S < E N T E R >
W H E N C O M P L E T E
E N T E R
W A V E G U I D E
C U T O F F
F R E Q U E N C Y
M E N U C 1 6
1 0 M I L K I T
1 5 M I L K I T
2 5 M I L K I T
U S E R D E F I N E D
S E L E C T
M I C R O S T R I P
K I T T O U S E
P R E S S < E N T E R >
T O S E L E C T
M E N U C 1 6 A
E N T E R
M I C R O S T R I P
P A R A M E T E R S
P R E S S < E N T E R >
W H E N C O M P L E T E
W I D T H O F
S T R I P
XX.XXXX m m
T H I C K N E S S O F
S U B S T R A T E
XXXX.XXXX m m
S U B S T R A T E
D I E L E C T R I C
X . X X
E F F E C T I V E
D I E L E C T R I C
X .X X
( R E C O M M E N D E D
1 . 0 0 )
Z c
X . X X X p
9
T o M e n u
C A L _ S U 2 *
T o M e n u
C A L _ S U 2 *
T o M e n u
C A L _ S U 2 *
M E N U C 1 8 B
N E X T C A L S T E P
C H A N G E L R L / L R M
P A R A M E T E R S
C H A R A C T E R I Z E
C A L D E V I C E S
B R E A K P O I N T
X X X . X X X X X X X X X G H Z
P R E S S < E N T E R >
T O S E L E C T
O R S W I T C H
F R E Q A F T E R
W H I C H T H E U S E
O F D E V I C E 2
A N D D E V I C E 3
I S E X C H A N G E D
D E V I C E 1
L I N E 1 ( R E F )
X X . X X X X
D E V I C E 2
L I N E / M A T C H
X X . X X X X / L O W B A N D
D E V I C E 3
L I N E / M A T C H
X X . X X X X / H I G H B A N D
M E N U C 1 8 A
N E X T C A L S T E P
D E V I C E 1
L I N E 1 ( R E F )
X . X X X X m m
D E V I C E 2
L I N E / M A T C H
X . X X X X m m / F U L L B A N D
C H A R A C T E R I Z E
C A L D E V I C E S
C H A N G E L R L / L R M
P A R A M E T E R S
P R E S S < E N T E R >
T O S E L E C T
O R S W I T C H
B
A
C
A
B
C
B
M E N U C 2 C
C A L I B R A T I O N
R A N G E
H A R M O N I C C A L
F O R T I M E D O M A I N
U S I N G A B O V E
S T A R T A N D S T O P
W I L L R E S U L T I N
X X X D A T A P O I N T S
X X X . X X X X X X X X X G H z
T R U E S T O P F R E Q
S T A R T ( S T E P )
XXX.XXXXXXXXX G Hz
A P P R O X I M A T E S T O P
XXX.XXXXXXXXX G Hz
N E X T C A L S T E P
P R E S S < E N T E R >
T O S E L E C T
M E N U C 2 A
P R E V I O U S M E N U
I N P U T A F R E Q ,
P R E S S < E N T E R >
T O I N S E R T
N E X T F R E Q .
XXX.XXXXXXXXX G Hz
X X X F R E Q S .
E N T E R E D ,
L A S T F R E Q W A S
XXX.XXXXXXXXX GHz
A U T O I N C R O N ( O F F )
XXX.XXXXXXXXX GHz
P R E S S < E N T E R >
T O S E L E C T
O R T U R N O N / O F F
I N S E R T
I N D I V I D U A L
F R E Q U E N C I E S
M E N U C 2 D
D I S C R E T E F I L L
C L E A R A L L
P R E S S < E N T E R >
T O S E L E C T
I N P U T S T A R T ,
I N C R , P O I N T S ,
T H E N S E L E C T
" F I L L R A N G E "
S T A R T F R E Q
XXX.XXXXXXXXX G Hz
I N C R E M E N T
XXX.XXXXXXXXXGHz
N U M B E R O F P T S
X X X P O I N T ( S )
S T O P F R E Q
X X X . X X X X X X X X X G H z
F I L L R A N G E
( X X X E N T E R E D )
I N D I V I D U A L
F R E Q I N S E R T
F I N I S H E D
N E X T C A L S T E P
S T A R T
XXX.XXXXXXXXX GHz
X X X D A T A P O I N T S
XXX.XXXXXXXXX G Hz
S T E P S I Z E
P R E S S < E N T E R >
T O S E L E C T
S T O P
XXX.XXXXXXXXX GHz
N U M O F D A T A P O I N T S
1 6 0 1 M A X P T S
8 0 1 M A X P T S
4 0 1 M A X P T S
2 0 1 M A X P T S
1 0 1 M A X P T S
5 1 M A X P T S
N E X T C A L S T E P
M E N U C 2 C A L F R E Q R A N G E
C E N T E R
XXX.XXXXXXXXX G Hz
SPAN
XXX.XXXXXXXXX G Hz
S E T S T A R T / S T O P
X X X D A T A P O I N T ( S )
XX.XXXXXXXXX G Hz
S T E P S I Z E
M E N U C 2 _ C E N T E R
P R E S S < E N T E R >
T O S E L E C T
N U M O F D A T A P O I N T S
1 6 0 1 M A X P T S
8 0 1 M A X P T S
4 0 1 M A X P T S
2 0 1 M A X P T S
1 0 1 M A X P T S
5 1 M A X P T S
N E X T C A L S T E P
C A L F R E Q R A N G E
S E T C E N T E R / S P A N
M E N U C 1 1
B E G I N C A L I B R A T I O N
N E X T C A L S T E P
K E E P E X I S T I N G
C A L D A T A
C H A N G E C A L
M E T H O D A N D
L I N E T Y P E
P R E S S < E N T E R >
T O S E L E C T
R E P E A T
P R E V I O U S C A L
C A L M E T H O D
S T A N D A R D
T R A N S M I S S I O N
L I N E T Y P E :
XXXXXXXX
A U T O C A L
Figure 4-5. Menu Sequencing, LRL/LRM Calibration
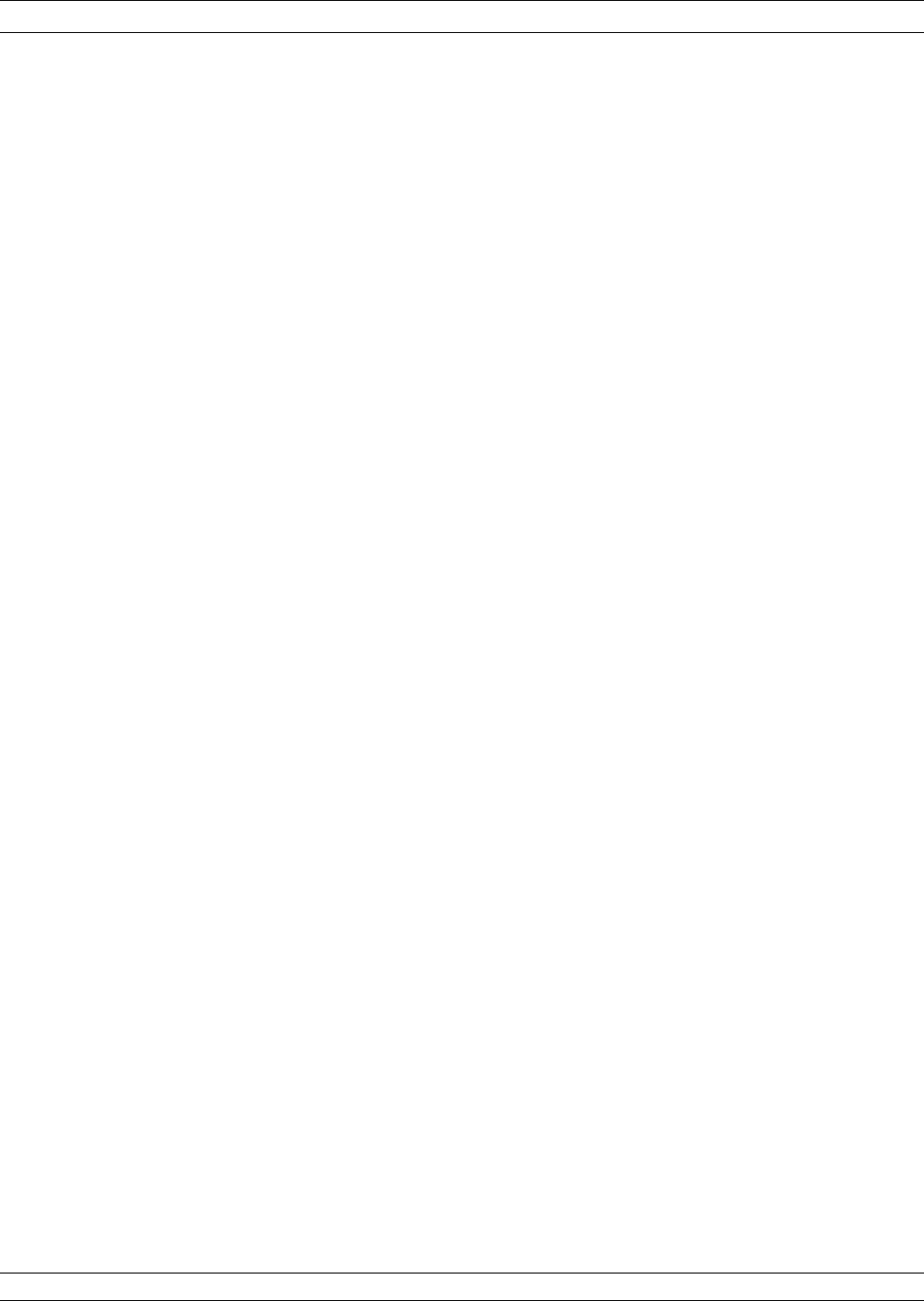
TRM Calibration Setup Flow—Description
1. Pressing the Begin Cal key calls Menu C17.
2. With one exception, the flow is from left to right in the direction of
the arrow head. The exception occurs in Menu C1, for the TIME
DOMAIN choice. Here the flow direction reverses to Menu C2C
then returns to a left-to-right flow on to Menu C3H, C3J, or C3I.
3. Arrowheads that point both left and right indicate that the flow
returns to the right-most menu after a choice had been made.
4. The group of menus to the left of Menu C3H, C3J, or C3I are the
initial selection set and are essentially the same for all four
calibration types: Standard, Offset-Short, TRM, and LRL/LRM.
5. The group of menus that follow Menu C3H, C3J, or C3I are, for the
most part, type specific. The selection of Menu C3H, C3I, or C3J
depends upon the choice made in Menu C11A: COAXIAL,
WAVEGUIDE, or MICROSTRIP.
CALIBRATION KEY-GROUP FRONT PANEL OPERATION
4-18 37XXXC OM
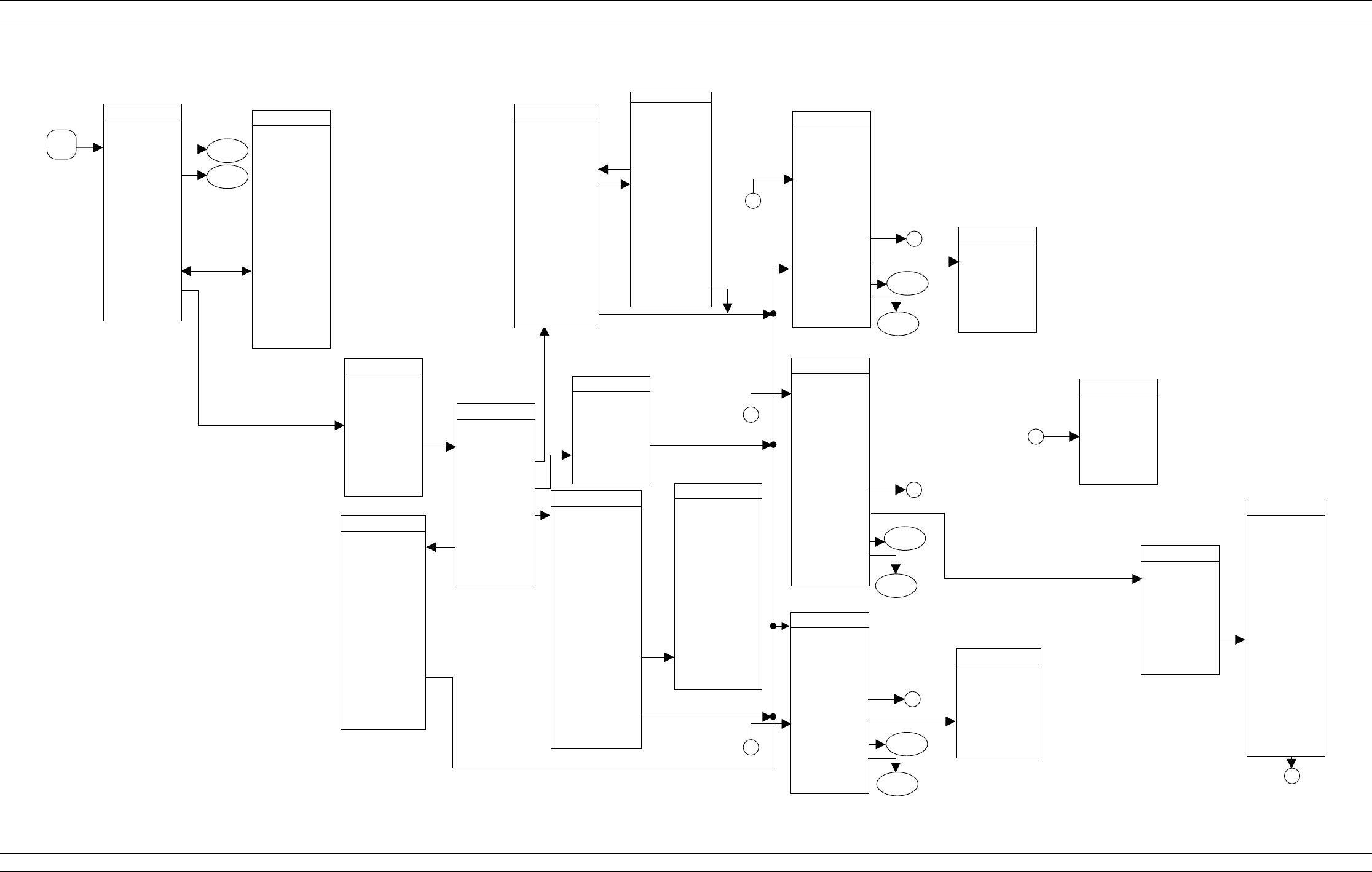
37XXXC OM 4-19
FRONT PANEL OPERATION CALIBRATION KEY-GROUP
M I C R O S T R I P
( S e e M e n u C 1 1 A )
W A V E G U I D E
( S e e M e n u C 1 1 A )
C O A X
( S e e M e n u C 1 1 A )
M E N U C 3 H
T R M R E F L E C T
O F F S E T L E N G T H
+ X X X . X X X X m m
T R M R E F L E C T T Y P E
G R E A T E R T H A N Z o
L E S S T H A N Z o
T R M M A T C H
I M P E D A N C E
R E F E R E N C E
I M P E D A N C E
T E S T S I G N A L S
S T A R T C A L
C O N F I R M
C A L I B R A T I O N
P A R A M E T E R S
P R E S S < E N T E R >
T O S E L E C T
O R C H A N G E
M E N U C 3 I
C O N F I R M
C A L I B R A T I O N
P A R A M E T E R S
P R E S S < E N T E R >
T O S E L E C T
O R C H A N G E
M E N U C 3 J
C O N F I R M
C A L I B R A T I O N
P A R A M E T E R S
T R M R E F L E C T
O F F S E T L E N G T H
+XXX.XXXX m m
T R M M A T C H
I M P E D A N C E
W A V E G U I D E
C U T O F F F R E Q
T E S T S I G N A L S
S T A R T C A L
P R E S S < E N T E R >
T O S E L E C T
O R C H A N G E
M E N U C 1 7
E N T E R
R E F E R E N C E
I M P E D A N C E
P R E S S < E N T E R >
W H E N C O M P L E T E
R E F E R E N C E
I M P E D A N C E
X X X . X X X 9
T o C a l
S e q * *
T o C a l
S e q * *
T o C a l
S e q * *
B e g i n
C a l
T o C a l
S e q * *
M E N U C 5 D
S E L E C T U S E
O F I S O L A T I O N
I N C A L I B R A T I O N
INCLUDE
I S O L A T I O N
( S T A N D A R D )
E X C L U D E
I S O L A T I O N
P R E S S < E N T E R >
T O S E L E C T
S E L E C T
C A L I B R A T I O N
D A T A P O I N T S
N O R M A L
( 1 6 0 1 P O I N T S
M A X I M U M
C . W .
( 1 P O I N T )
N - D I S C R E T E
F R E Q U E N C I E S
( 2 T O 1 6 0 1
P O I N T S )
T I M E D O M A I N
( H A R M O N I C )
P R E S S < E N T E R >
T O S E L E C T
M E N U C 1
M E N U C 2 B
P R E S S < E N T E R >
T O S E L E C T
S I N G L E P O I N T
C . W . C A L I B R A T I O N
C . W . F R E Q
XX.XXXXXXXX GHz
N E X T C A L S T E P
T o M e n u
S U 1 / S U 3 *
M E N U C 1 5 B
W A V E G U I D E
C U T O F F F R E Q
X X X . X X X X X X X X X G H z
P R E S S < E N T E R >
W H E N C O M P L E T E
E N T E R
W A V E G U I D E
C U T O F F
F R E Q U E N C Y
M E N U C 1 6
1 0 M I L K I T
1 5 M I L K I T
2 5 M I L K I T
U S E R D E F I N E D
S E L E C T
M I C R O S T R I P
K I T T O U S E
P R E S S < E N T E R >
T O S E L E C T
M E N U C 1 6 A
E N T E R
M I C R O S T R I P
P A R A M E T E R S
P R E S S < E N T E R >
W H E N C O M P L E T E
W I D T H O F
S T R I P
XX.XXXX m m
T H I C K N E S S O F
S U B S T R A T E
XXXX.XXXX m m
S U B S T R A T E
D I E L E C T R I C
X . X X
E F F E C T I V E
D I E L E C T R I C
X .X X
( R E C O M M E N D E D
1.00)
Z c
X . X X X p
9
T o M e n u
C A L _ S U 2 *
T o M e n u
C A L _ S U 2 *
T o M e n u
C A L _ S U 2 *
B
A
C
B
M E N U C 2 C
C A L I B R A T I O N
R A N G E
H A R M O N I C C A L
F O R T I M E D O M A I N
U S I N G A B O V E
S T A R T A N D S T O P
W I L L R E S U L T I N
X X X D A T A P O I N T S
X X X . X X X X X X X X X G H z
T R U E S T O P F R E Q
S T A R T ( S T E P )
XXX.XXXXXXXXX GHz
A P P R O X I M A T E S T O P
XXX.XXXXXXXXX GHz
N E X T C A L S T E P
P R E S S < E N T E R >
T O S E L E C T
M E N U C 2 A
P R E V I O U S M E N U
I N P U T A F R E Q ,
P R E S S < E N T E R >
T O I N S E R T
N E X T F R E Q .
XXX.XXXXXXXXX GHz
X X X F R E Q S .
E N T E R E D ,
L A S T F R E Q W A S
XXX.XXXXXXXXX GHz
A U T O I N C R O N ( O F F )
XXX.XXXXXXXXX GHz
P R E S S < E N T E R >
T O S E L E C T
O R T U R N O N / O F F
I N S E R T
I N D I V I D U A L
F R E Q U E N C I E S
M E N U C 2 D
D I S C R E T E F I L L
C L E A R A L L
P R E S S < E N T E R >
T O S E L E C T
I N P U T S T A R T ,
I N C R , P O I N T S ,
T H E N S E L E C T
" F I L L R A N G E "
S T A R T F R E Q
XXX.XXXXXXXXX GHz
I N C R E M E N T
XXX.XXXXXXXXXGHz
N U M B E R O F P T S
X X X P O I N T ( S )
S T O P F R E Q
X X X . X X X X X X X X X G H z
F I L L R A N G E
( X X X E N T E R E D )
I N D I V I D U A L
F R E Q I N S E R T
F I N I S H E D
N E X T C A L S T E P
S T A R T
XXX.XXXXXXXXX GHz
X X X D A T A P O I N T S
XXX.XXXXXXXXX GHz
S T E P S I Z E
P R E S S < E N T E R >
T O S E L E C T
S T O P
XXX.XXXXXXXXX GHz
N U M O F D A T A P O I N T S
1 6 0 1 M A X P T S
8 0 1 M A X P T S
4 0 1 M A X P T S
2 0 1 M A X P T S
1 0 1 M A X P T S
5 1 M A X P T S
N E X T C A L S T E P
C A L F R E Q R A N G E
C E N T E R
XXX.XXXXXXXXX GHz
SPAN
XXX.XXXXXXXXX GHz
S E T S T A R T / S T O P
X X X D A T A P O I N T ( S )
XX.XXXXXXXXX GHz
S T E P S I Z E
M E N U C 2 _ C E N T E R
P R E S S < E N T E R >
T O S E L E C T
N U M O F D A T A P O I N T S
1 6 0 1 M A X P T S
8 0 1 M A X P T S
4 0 1 M A X P T S
2 0 1 M A X P T S
1 0 1 M A X P T S
5 1 M A X P T S
N E X T C A L S T E P
C A L F R E Q R A N G E
S E T C E N T E R / S P A N
T R M R E F L E C T
O F F S E T L E N G T H
+ X X X . X X X X m m
T R M R E F L E C T T Y P E
G R E A T E R T H A N Z o
L E S S T H A N Z o
T R M M A T C H
I M P E D A N C E
M I C R O S T R I P
P A R A M E T E R S
XXXXXXXX
T E S T S I G N A L S
S T A R T C A L
M E N U C 1 1 A
N E X T C A L S T E P
C A L M E T H O D
O F F S E T S H O R T
L R L / L R M
C O A X I A L
W A V E G U I D E
M I C R O S T R I P
C H A N G E
C A L M E T H O D
A N D L I N E T Y P E
S T A N D A R D
( N O T U S E D F O R
W A V E G U I D E )
T R A N S M I S S I O N
L I N E T Y P E
P R E S S < E N T E R >
T O S E L E C T
T R M
M E N U C 2
M E N U C 1 1
B E G I N C A L I B R A T I O N
N E X T C A L S T E P
K E E P E X I S T I N G
C A L D A T A
C H A N G E C A L
M E T H O D A N D
L I N E T Y P E
P R E S S < E N T E R >
T O S E L E C T
R E P E A T
P R E V I O U S C A L
C A L M E T H O D
S T A N D A R D
T R A N S M I S S I O N
L I N E T Y P E :
XXXXXXXX
A U T O C A L
M E N U C 6 B
T R M M A T C H
P A R A M E T E R S
P R E S S < E N T E R >
W H E N C O M P L E T E
I M P E D A N C E
+ X X X . X X X
9
I N D U C T A N C E
+ X X X X . X X X X p H
D
D
D
D
Figure 4-6. Menu Sequencing, TRM Calibration
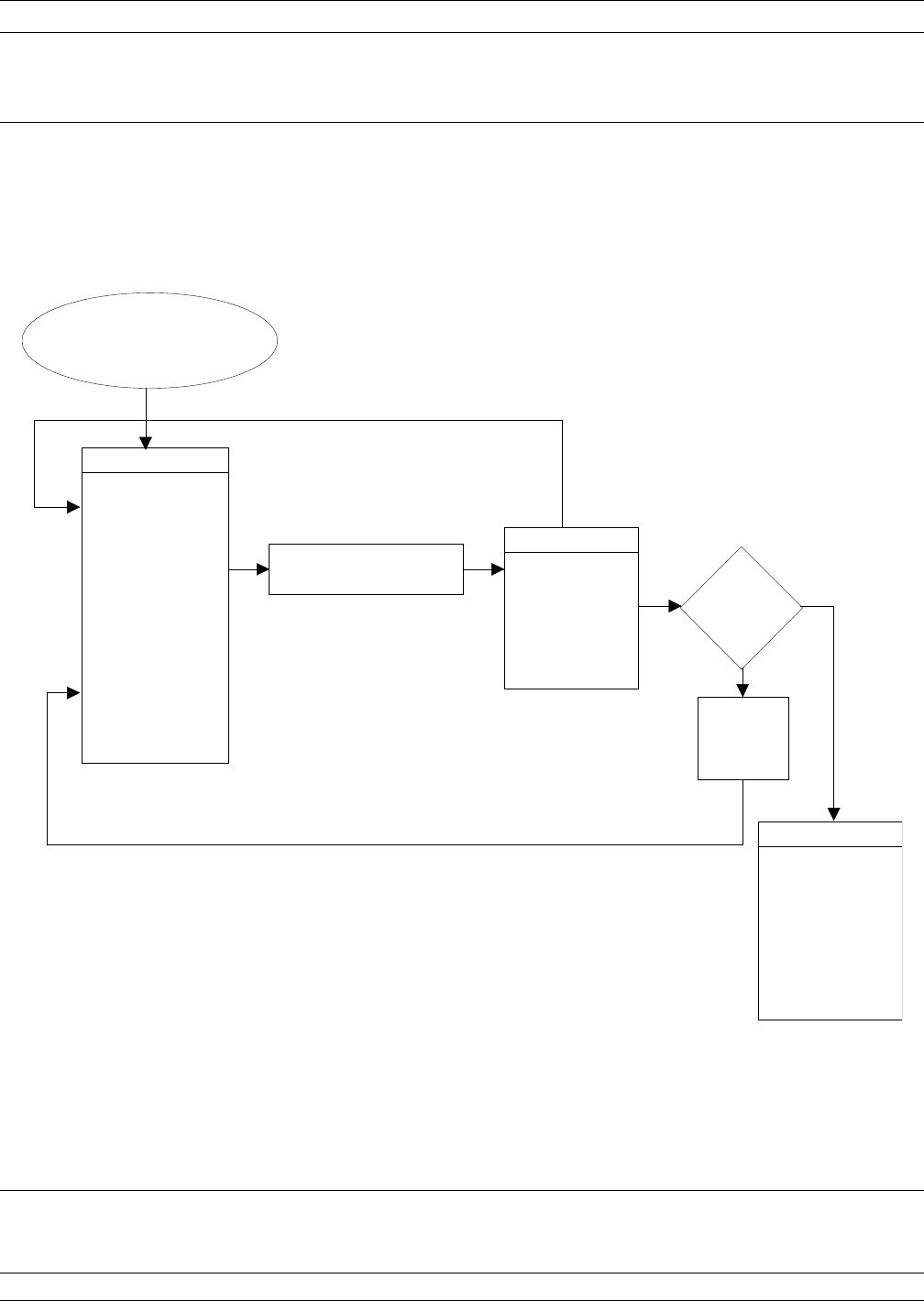
CALIBRATION KEY-GROUP FRONT PANEL OPERATION
4-20 37XXXC OM
MENU C7, C8, C9 Series
CALIBRATION
SEQUENCE
CONNECT
CALIBRATION
DEVICE(S)
PORT 1:
XXXXXXXXXXXX
PORT 2:
XXXXXXXXXXXX
PRESS <2> FOR
PORT 2 DEVICE
PRESS <ENTER>
TO MEASURE
DEVICE(S)
PRESS <1> FOR
PORT 1 DEVICE
MEASURING
MENU CAL_NEXT_DEV
CAL
DONE
GO
TO NEXT
CAL STEP
<ENTER>
YES
NO
CONNECT NEW CALIBRATION STANDARDS
C7 SERIES = REFLECTION DEVICES
C8 SERIES = SLIDING LOAD
C9 SERIES = TRANSMISSION DEVICES
*
From Standard,
Offset-Short, and
LRL/LRM Calibration
Flowcharts
MENU CAL_COMPLETED
OR
CALIBRATION
SEQUENCE
COMPLETED
PRESS
<SAVE/RECALL>
TO STORE CAL
DATA ON DISK
PRESS <ENTER>
TO PROCEED
CAL_MEAS_DEV
PRESS <ENTER>
FOR NEXT CAL
STEP
OR
PRESS <CLEAR>
TO RE-MEASURE
Figure 4-6. Calibration Sequence Menus
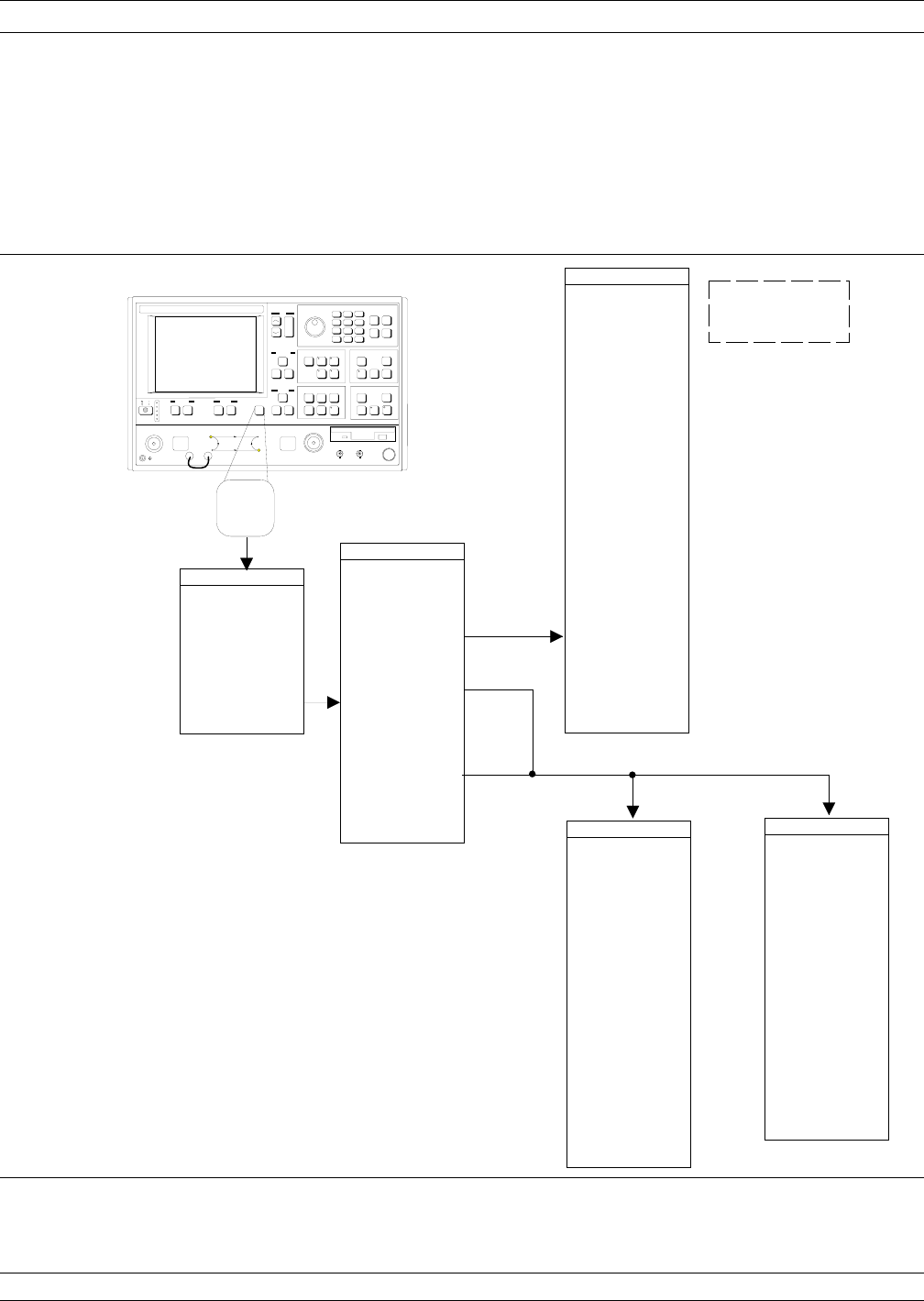
4-4 SAVE/RECALL MENU
KEY Pressing this key displays the first of a menu set (below) that lets you
save or recall control panel setups and calibration data. Full menu de-
scriptions can be found in the alphabetically ordered Appendix A un-
der the menu’s call letters (SR1, SR2, SR3, etc).
37XXXC OM 4-21
FRONT PANEL OPERATION SAVE/RECALL MENU KEY
M E N U S R 1
S A V E / R E C A L L
F R O N T P A N E L
A N D C A L D A T A
P R E S S < E N T E R >
T O S E L E C T
F U N C T I O N
S A V E
R E C A L L
M E N U S R 2
R E C A L L
( O R S A V E )
F R O N T P A N E L
S E T U P I N
I N T E R N A L M E M O R Y
P R E S S < E N T E R >
T O S E L E C T
F R O N T P A N E L
S E T U P A N D
C A L D A T A
O N H A R D D I S K
F R O N T P A N E L
S E T U P A N D
C A L D A T A
O N F L O P P Y D I S K
M E N U S R 3
M E M O R Y 1
M E M O R Y 2
M E M O R Y 3
M E M O R Y 4
S A V E F R O N T
P A N E L S E T U P T O
I N T E R N A L M E M O R Y
P R E S S < E N T E R >
T O S E L E C T
O R
USE KEYPAD
M E M O R Y 4
M E M O R Y 6
M E M O R Y 5
M E M O R Y 7
M E M O R Y 8
M E M O R Y 9
M E M O R Y 1 0
P R E V I O U S M E N U
R E C A L L F R O N T
P A N E L S E T U P F R O M
I N T E R N A L M E M O R Y .
A L T E R N A T I V E T E X T
M E N U D S K 3
F I L E 1
F I L E 2
P R E V I O U S M E N U
P R E S S < E N T E R >
T O S E L E C T
S E L E C T F I L E
T O O V E R W R I T E
C R E A T E N E W F I L E
P R E S S < 1 > F O R
P R E V I O U S P A G E
P R E S S < 2 > F O R
N E X T P A G E
F I L E 3
F I L E 4
F I L E 5
F I L E 6
F I L E 7
F I L E 8
M E N U D S K 2
F I L E 1
F I L E 2
P R E V I O U S M E N U
P R E S S < E N T E R >
T O S E L E C T
S E L E C T F I L E
T O R E A D
P R E S S < 1 > F O R
P R E V I O U S P A G E
P R E S S < 2 > F O R
N E X T P A G E
F I L E 3
F I L E 4
F I L E 5
F I L E 6
F I L E 7
F I L E 8
E i t h e r D i s k
789
456
123
0.-
S a v e /
R e c a l l
M e n u
S A V E R E C A L L
N o t e
A n a s t e r i s k ( * ) n e x t t o
a m e m o r y l o c a t i o n i n d i c a t e s
t h a t i t h a s s t o r e d d a t a .
Figure 4-7 Save/Recall Key-Group Menus
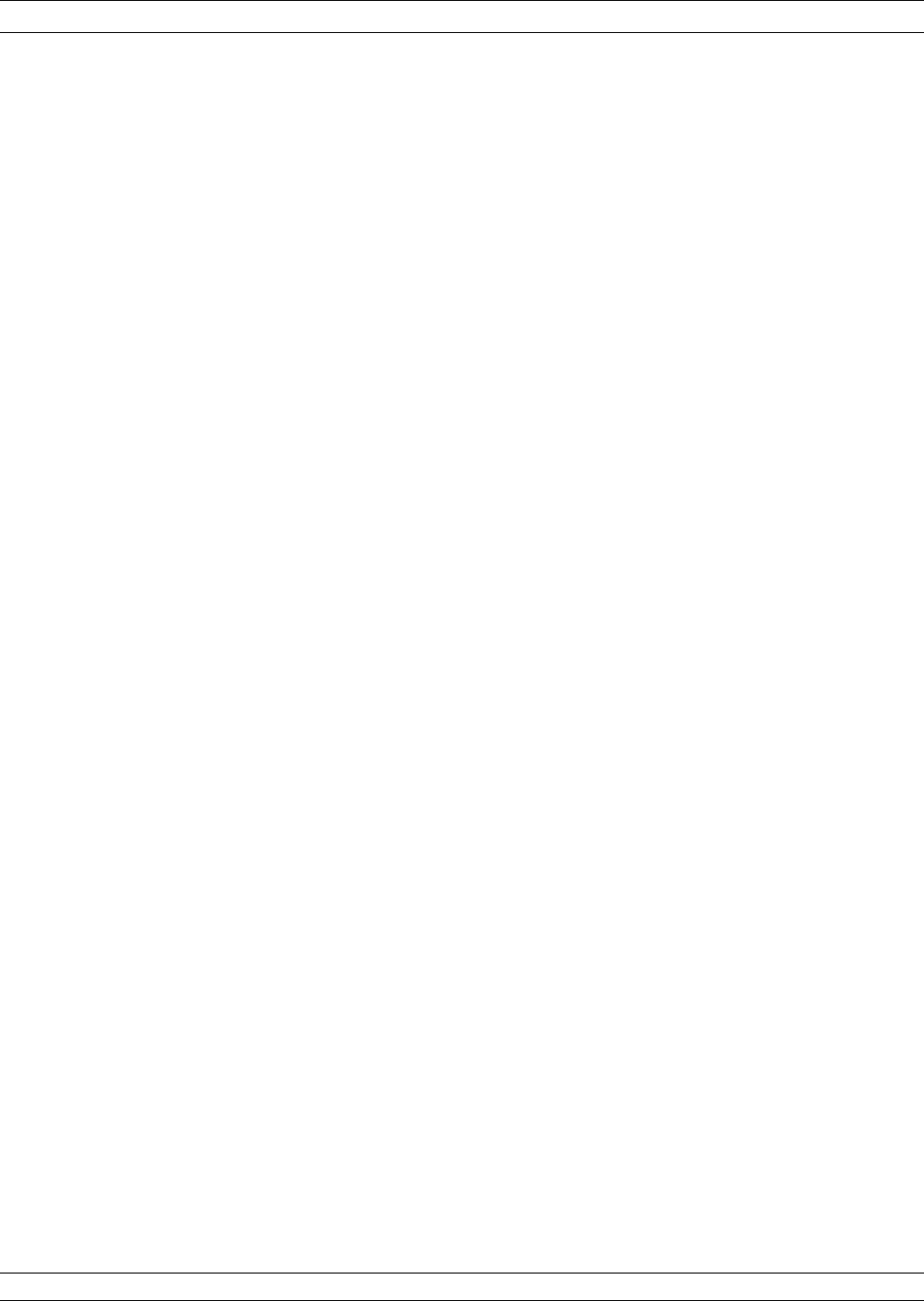
4-5 MEASUREMENT
KEY-GROUP The individual keys within the Measurement key-group are described
below. Flowcharts of the Setup Key and Data Points key menus are
shown in Figure 4-8. As described for the calibration menus, the flow
is left-to-right and the double arrowhead lines indicate that the flow
returns to the calling menu once a selection has been made. Full menu
descriptions can be found in the alphabetically ordered Appendix A
under the menu’s call letters (SU1, SU2, DF, etc).
Setup Menu Key: Pressing this key calls Sweep Setup Menu SU1 or
SU3. Depending upon which menu items you select, additional menus
may also be called.
Data Points Key: Pressing this key calls Menu SU9 or SU9A. Menu
SU9 provides for data point selection. Menu SU9A is called if the C.W.
MODE selection in Menu SU1 is on.
Hold Key: If the instrument is sweeping, pressing this key results in
an immediate halt of the sweep at the current data point. The LED on
the button lights, indicating that the Hold Mode is active.
If you restart the sweep after performing any recall-from-disk opera-
tions in the Hold Mode (sweep stopped at some data point), the sweep
restarts from the beginning. The instrument may be taken out of the
hold mode as follows:
qBy pressing the Default Program key. This causes the 37XXXC to
revert to a predefined state
qBy pressing the Begin Cal key. This causes the 37XXXC to re-
sume sweeping and begin the Calibration Menu sequence
NOTE
See the description for Menu SU4 for a discussion of the
interaction between the Hold Mode and the selection of
“Single Sweep” or “Restart Sweep.”
Domain Key: This key function is fully described in paragraph 4-2
(page 4-8). Additionally, if the Time Domain option is installed, making
a selection other than “Frequency Domain” lets you display measured
data in the time domain. It also calls a further sequence of Time Do-
main Menus. Refer to paragraph 9-2 for additional details.
Appl: Pressing this key calls a menu that lets you select the following
applications: Adapter Removal, Swept Frequency Gain Compression,
or Swept Power Gain Compression.
MEASUREMENT KEY-GROUP FRONT PANEL OPERATION
4-22 37XXXC OM
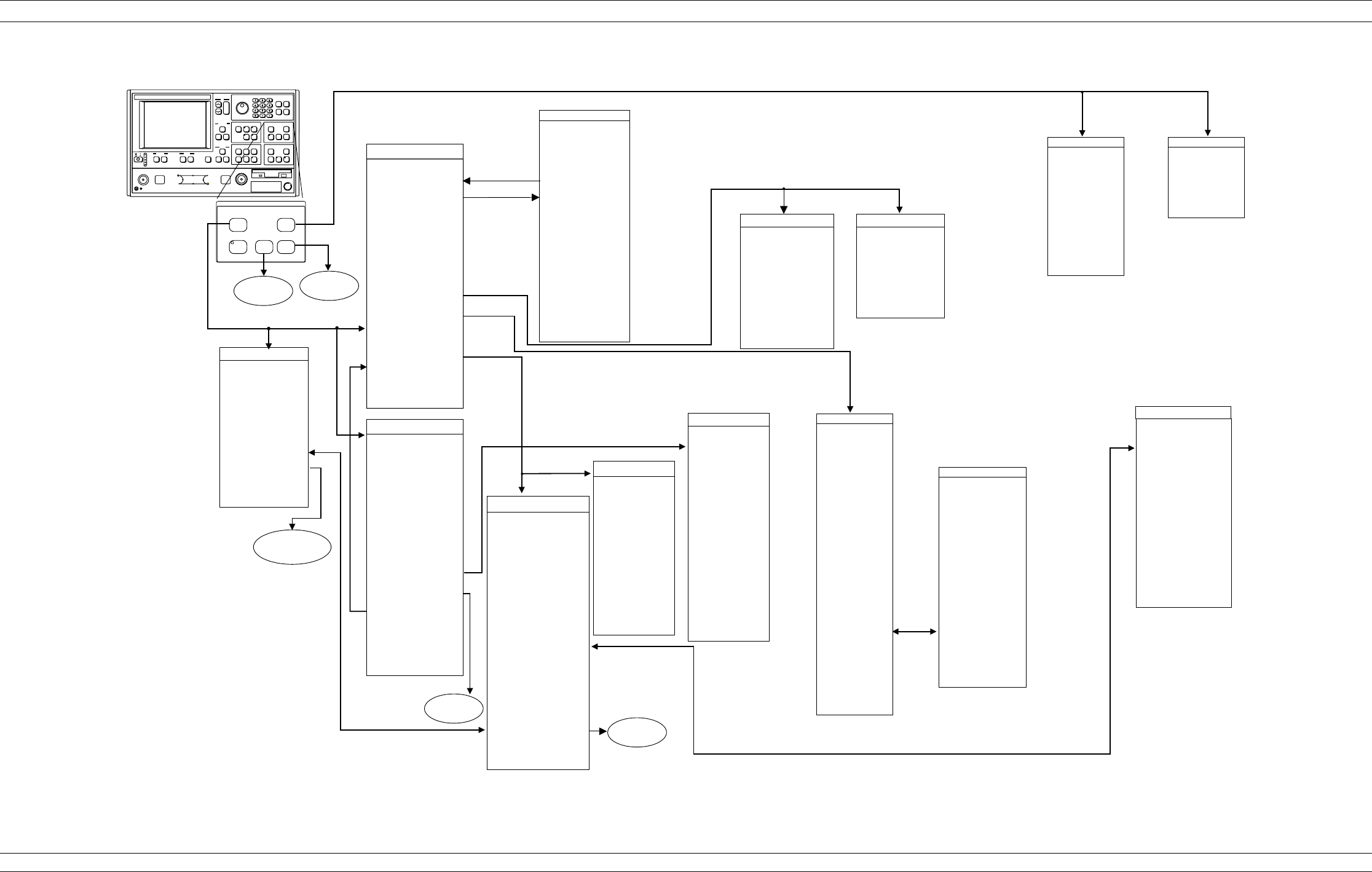
37XXXC OM 4-23
FRONT PANEL OPERATION MEASUREMENT KEY-GROUP
MENU SU8 or CAL_SU8
PREVIOUS MENU
CALIBRATE FOR
FLAT PORT POWER
FORWARD
DIRECTION ONLY
XXX POINTS
MEASURE 1 PWR
POINT EVER
XX POINTS
POWER TARGET
-XXX.X dBm
START FLAT
POWER CALIBRATION
PRESS <ENTER>
TO SELECT
MENU DF1
DISCRETE FILL
INPUT START,
INCR, POINTS,
THEN SELECT
"FILL RANGE"
START FREQ
XX.XXXX GHz
INCREMENT
X.XXXX GHz
NUMBER OF PTS
XXX POINTS
STOP FREQ
XX.XXXX
FILL RANGE
(XXX ENTERED)
INDIVIDUAL
FREQ INSERT
CLEAR ALL
FINISHED
RETURN TO SWP
Measurement
Data
Points
Hold Domain
Setup
Menu
See
Chapter 9
Menu SU1
(Destroys Calibration)
PRESS <ENTER>
TO SELECT
OR TURN ON/OFF
MENU DF2
NEXT FREQ
XX.XXXX GHz
INSERT
INDIVIDUAL
FREQUENCIES
INPUT A FREQ,
PRESS <ENTER>
TO INSERT
XXX FREQS
ENTERED
LAST FREQ WAS
XX.XXXX GHz
AUTO INCR ON (OFF)
XX.XXXX GHz
PREVIOUS MENU
MENU SU9
PRESS <ENTER>
TO SELECT
NUMBER OF
DATA POINTS
1601 MAX PTS
801 MAX PTS
401 MAX PTS
201 MAX PTS
101 MAX PTS
51 MAX PTS
MENU SU9A
NUMBER OF
DATA POINTS
POINTS DRAWN
IN CW
XXXX POINT(S)
MENU SU3
SINGLE POINT
MEASUREMENT
SETUP
C.W. FREQ
XXX.XXXXXXXXX GHz
HOLD BUTTON
FUNCTION
TEST
SIGNALS
RETURN TO
SWEEP MODE
PRESS <ENTER>
TO SELECT
MENU SU5
FREQUENCY
MARKER SWEEP
START SWEEP
MARKER (n)
XXX.XXXXXXXXX GHz
STOP SWEEP
MARKER (n)
XXX.XXXXXXXXX GHz
USE KEYPAD
TO SELECT
MARKER (1-6)
MENU SU6
FREQUENCY
MARKER C.W.
C.W FREQ
MARKER (n)
XXXX.XXXXXXXXX GHz
USE KEYPAD
TO SELECT
MARKER (1-6)
MENU SU1
SWEEP SETUP
MARKER SWEEP
DISCRETE FILL
START
XX.XXXXXX GHz
STOP
XX.XXXXXX Gz
XXX DATA POINT(S)
XX.XXXXXXXXX GHz
STEP SIZE
C.W. MODE ON (OFF)
XX.XXXXXXXXX GHZ
HOLD BUTTON
FUNCTION
TEST SIGNALS
PRESS <ENTER>
TO SELECT
OR TURN ON/OFF
SET CENTER/SPAN
SWEEP SETUP
CENTER
XXX.XXXXXXXXX GHz
SPAN
XXX.XXXXXXXXX GHz
SET START/STOP
C.W. MODE ON (OFF)
XX.XXXXXXXXX GHZ
XXXDATAPOINT(S)
XX.XXXXXXXXX GHz
STEP SIZE
MARKER SWEEP
DISCRETE FILL
HOLD BUTTON
FUNCTION
TEST SIGNALS
PRESS <ENTER>
TO SELECT
OR TURN ON/OFF
MENU SU1_CENTER
MENU SU4
HOLD/CONTINUE
HOLD/RESTART
SELECT FUNCTION
FOR
HOLD BUTTON
SINGLE SWEEP
AND HOLD
BIAS/RF HOLD
CONDITIONS
PRESS <ENTER>
TO SELECT
BIAS ON
RF ON
DUT/AUT ON (OFF)
PROTECTION
DEFAULT RESET
TURNS ON HOLD
WITH BIAS/RF
TURNED OFF
PRESS <ENTER>
TO SELECT
TURN KNOB TO
CHANGE NUMBER
OF POINTS
Appl
MENU SU3A
SWEPT POWER
SETUP
RETURN TO SWEPT
FREQUENCY MODE
PSTART
-XX.XX dBm
POWER SWEEP ON(OFF)
-XX.XX dB
HOLD BUTTON
FUNCTION
PRESS <ENTER>
TO SELECT
OR TURN ON/OFF
STEPSIZE
X.XX dB
SWEPT POWER
FREQUENCY
XXX.XXXXXXXXX GHz
PSTOP
-XX.XX dBm
SWEPT POWER
GAIN COMPRESSION
To Menu
GC 4
See
Sheet 2
MENU SU2A
TEST SIGNALS
SOURCE 1 PWR
-XX.XX dBM
PORT 1 ATTN
0 *10 dB (0 - 70)
PORT 2 ATTN
0*10 dB (0-00)
PRESS <ENTER>
TO SELECT
OR TURN ON/OFF
.
MENU SU2, SU2a, CAL_SU2
TEST SIGNALS
POWER CONTROL
XX.X dB
(0 TO -15 dB)
SOURCE 2 PWR
XX.X dBm
PORT 1 POWER
-XX.XX dBm
PORT 2 ATTN
XXX dB (0-X0)
PRESS <ENTER>
TO SELECT
CALIBRATE
FOR FLATNESS
(CAL EXISTS)
FLATNESS ON(OFF)
CORRECTION
AT XX.X dBm
PORT 1 ATTN
20 dB (0 - 70)
EXIT APPLICATION*
SOURCE 2 PWR
-XX.XX dBM
To Menu
SU1
*Exit Application appears only
when in the Swept Frequency
Gain Compression application
Figure 4-8. Measurement Key-Group Menus Menu Flow (Sheet 1 of 2)
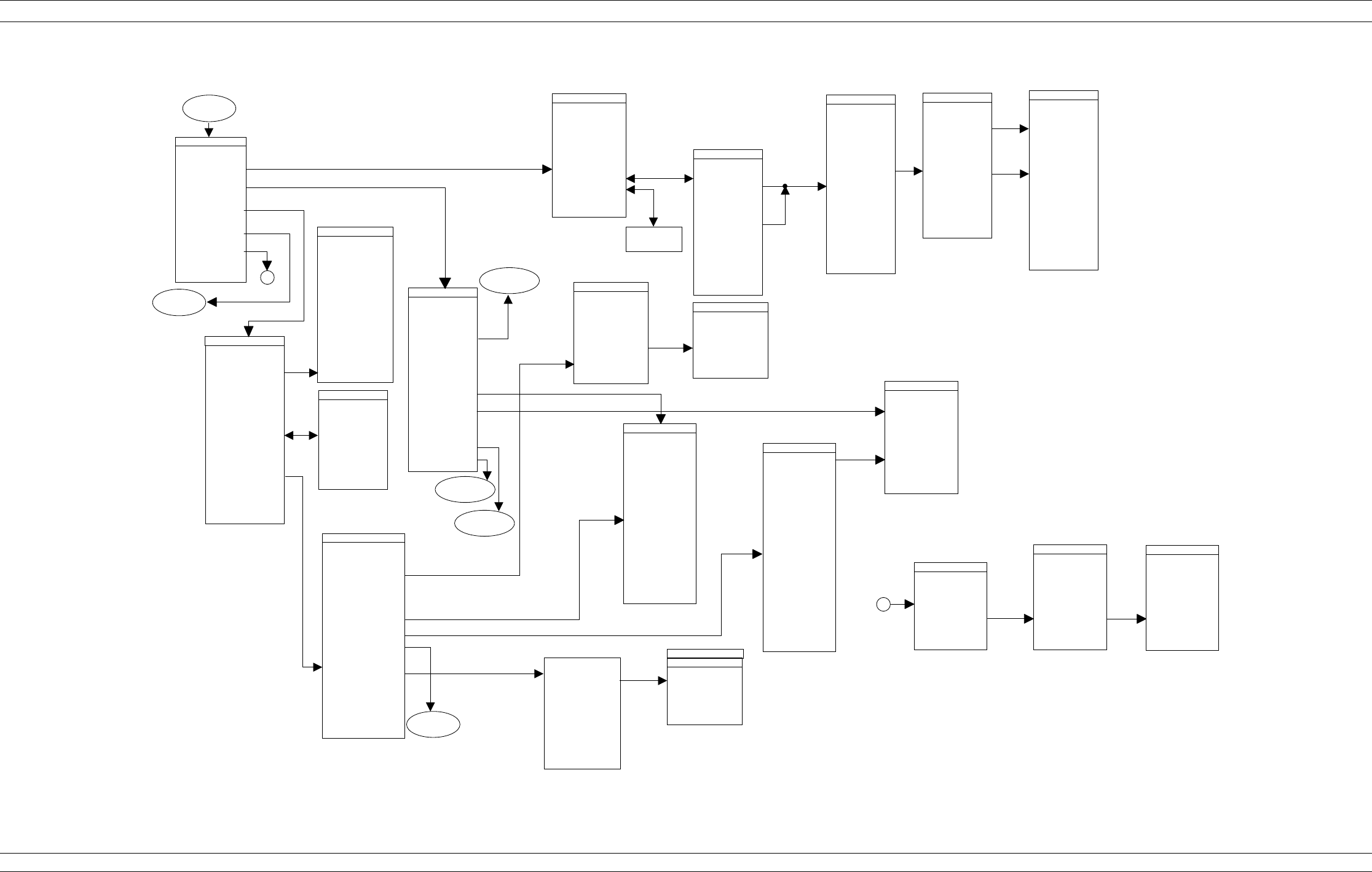
4-24 37XXXC OM
MEASUREMENT KEY-GROUP FRONT PANEL OPERATION
M E N U A P P L
P R E S S < E N T E R >
T O S E L E C T
A P P L I C A T I O N S
A D A P T E R R E M O V A L
S W E P T F R E Q U E N C Y
G A I N C O M P R E S S I O N
S W E P T P O W E R
G A I N C O M P R E S S I O N
S W E P T P O W E R
F R E Q U E N C I E S
P R E S S < E N T E R >
T O S E L E C T
M E N U G C - D F 2
S E T F R E Q U E N C I E S
S W E P T P O W E R
F R E Q U E N C Y
XXX.XXXXXXXXX G Hz
F I N I S H E D ,
R E T U R N T O P O W E R
SW EEP SETUP
I N P U T A F R E Q
P R E S S < E N T E R >
T O I N S E R T
C L E A R F R E Q N U M B E R
X X
C L E A R A L L
C A L I B R A T E F O R
L I N E A R P O W E R
P R E S S < E N T E R >
T O S E L E C T
M E N U G C - S U 8 A
F O R W A R D
D I R E C T I O N O N L Y
S T A R T L I N E A R
P O W E R C A L I B R A T I O N
P R E V I O U S M E N U
L I N E A R P O W E R
C A L I B R A T I O N
C A L I B R A T I N G F O R
L I N E A R P O W E R
P R E S S < C L E A R >
T O A B O R T
M E N U G C - S U 8 A _ A B O R T
M U L T I P L E F R E Q U E N C Y
G A I N C O M P R E S S I O N
T E S T I N G A U T
P R E S S < C L E A R >
T O A B O R T
M E N U G C 4 _ A B O R T
M E N U D S K 2
F I L E 1
F I L E 2
P R E V I O U S M E N U
P R E S S < E N T E R >
T O S E L E C T
S E L E C T F I L E
T O R E A D
P R E S S < 1 > F O R
P R E V I O U S P A G E
P R E S S < 2 > F O R
N E X T P A G E
F I L E 3
F I L E 4
F I L E 5
F I L E 6
F I L E 7
F I L E 8
E X T _ C A R 1
H E L P F I L E
F r o m
S h e e t 1
S W E P T P O W E R
G A I N C O M P R E S S I O N
P S T A R T
- X X . X X d B m
P R E S S < E N T E R >
T O S E L E C T
M E N U G C 2
S E T F R E Q U E N C I E S
S T E P S I Z E
X . X X d B
G A I N C O M P R E S S I O N
P O I N T ( M A X R E F )
X X . X X d B
M O R E
P S T O P
- X X . X X d B m
N O M I N A L O F F S E T
- X X . X X d B
A T T E N U A T I O N
S W E P T P O W E R
G A I N C O M P R E S S I O N
P R E S S < E N T E R >
T O S E L E C T
M E N U G C _ S U 2
P O R T 1 A T T N
0 * 1 0 d B ( 0 - 0 0 )
P O R T 2 A T T N
0 * 1 0 d B ( 0 - 0 0 )
P R E V I O U S M E N U
M E N U G C 3
M U L T I P L E F R E Q U E N C Y
G A I N C O M P R E S S I O N
M E N U G C 4
T E X T D A T A
T O H A R D D I S K
T E S T A U T
T E X T D A T A
T O F L O P P Y D I S K
P R E S S < E N T E R >
T O S E L E C T
S W E P T P O W E R
G A I N C O M P R E S S I O N
R E T U R N T O S W E P T
F R E Q U E N C Y M O D E
A D A P T E R R E M O V A L
P R E S S < E N T E R >
T O S E L E C T
M E N U C A R 1
1 2 - T E R M C A L S F O R
X A N D Y M U S T
E X I S T S I N T H E
C U R R E N T D I R E C T O R Y
E L E C T R I C A L L E N G T H
O F T H E A D A P T E R
+XXX.XXXX ps
H E L P
R E M O V E A D A P T E R
P R E S S < E N T E R >
T O S E L E C T
A D A P T E R R E M O V A L
R E A D C A L F I L E O F
T H E X T E S T P O R T
F R O M H A R D D I S K
( A D A P T E R O N
P O R T 2 )
M E N U C A R 2
R E A D C A L F I L E O F
T H E X T E S T P O R T
F R O M F L O P P Y D I S K
( A D A P T E R O N
P O R T 2 )
P R E S S < C L E A R >
T O A B O R T
P R E S S < E N T E R >
T O S E L E C T
A D A P T E R R E M O V A L
R E A D C A L F I L E O F
T H E Y T E S T P O R T
F R O M H A R D D I S K
( A D A P T E R O N
P O R T 1 )
M E N U C A R 3
R E A D C A L F I L E O F
T H E Y T E S T P O R T
F R O M F L O P P Y D I S K
( A D A P T E R O N
P O R T 1 )
P R E S S < C L E A R >
T O A B O R T
S U 8 A
S h e e t 1
S W E P T F R E Q U E N C Y
G A I N C O M P R E S S I O N
C A L I B R A T E
F O R F L A T N E S S
( N O C A L E X I S T S )
M E N U G C 1
N O M I N A L O F F S E T
- X X . X X d B
F L A T N E S S
C O R R E C T I O N
A T - X X . X X d B m
C A L I B R A T E
R E C E I V E R
( N O C A L E X I S T S )
N O R M A L I Z E S 2 1
( N O T S T O R E D )
G A I N C O M P R E S S I O N
P O I N T ( 0 d B R E F )
X X . X X d B
T E S T A U T
E X I T A P P L I C A T I O N
R E C E I V E R
C A L I B R A T I O N
P R E S S < E N T E R >
T O S T O R E
M E N U G C _ R C V R
C O N N E C T
T H R O U G H L I N E
BETW EEN
T E S T P O R T S
I N C L U D E A N Y
C O M P O N E N T S W I T H
A R E P A R T O F T H E
M E A S U R E M E N T P A T H
P R E S S < C L E A R >
T O A B O R T
W A I T F O R O N E
C O M P L E T E S W E E P
B E F O R E S T O R I N G
M E N U D S K 2
F I L E 1
F I L E 2
P R E V I O U S M E N U
P R E S S < E N T E R >
T O S E L E C T
S E L E C T F I L E
T O R E A D
P R E S S < 1 > F O R
P R E V I O U S P A G E
P R E S S < 2 > F O R
N E X T P A G E
F I L E 3
F I L E 4
F I L E 5
F I L E 6
F I L E 7
F I L E 8
S W E P T P O W E R
G A I N C O M P R E S S I O N
C A L I B R A T E
F O R L I N E A R I T Y
( N O C A L E X I S T S )
L I N E A R I T Y O N ( O F F )
C O R R E C T I O N
A L L T E S T T Y P E S
M U L T I P L E F R E Q U E N C Y
G A I N C O M P R E S S I O N
P R E V I O U S M E N U
P R E S S < E N T E R >
T O S E L E C T
O R T U R N O N / O F F
S U 1
S h e e t 1
S U 2 A
S h e e t 1
S U 8 A
S h e e t 1
G A I N C O M P R E S S I O N
A M / P M
R E T U R N T O S W E P T
F R E Q U E N C Y M O D E
C A L I B R A T E
R E C E I V E R
( N O C A L E X I S T S )
S 2 1 O P T I O N S
( N O T S T O R E D )
R E S U L T S I N A
D I S P L A Y T H A T I S
N O R M A I L Z E D T O T H E
A U T P E R F O R M A N C E
A T P S T A R T .
N O R M A L I Z A T I O N I S
A U T O M A T I C F O R
E A C H P O W E R S W E E P
N O R M A L I Z E S 2 1
P R E S S < E N T E R >
T O S T O R E
M E N U G C _ S 2 1 _ O P T
C O N N E C T A U T
A N D A P P L Y B I A S
D I S P L A Y S 2 1
R E S U L T S I N A
D I S P L A Y S H O W I N G
T H E V A L U E O F
S 2 1 F O R E A C H
P O W E R S W E E P
C O N N E C T T H R O U G H
W A I T F O R O N
C O M P L E T E S W E E P
B E F O R E S T O R I N G
W A I T F O R O N E
C O M P L E T E S W E E P
B E F O R E S T O R I N G
N O R M A L I Z E S 2 1
P R E S S < E N T E R >
T O S T O R E
M E N U G C _ N O R M
C O N N E C T A U T
A N D A P P L Y B I A S
P R E S S < C L E A R >
T O A B O R T
E / O M E A S U R E M E N T
O / E M E A S U R E M E N T
S e e
C h a p t e r 8
M E R G E C A L F I L E S
A
M E N U M R G 1
M E R G E C A L F I L E S
C A L F I L E S M U S T
E X I S T I N T H E
C U R R E N T D I R E C T O R Y
M E R G E C A L F I L E S
P R E S S < E N T E R >
T O S E L E C T
M E N U M R G 2
M E R G E C A L F I L E S
P R E S S < E N T E R >
T O S E L E C T
R E A D C A L F I L E 1
F R O M H A R D D I S K
R E A D C A L F I L E 1
F R O M F L O P P Y D I S K
P R E S S < C L E A R >
T O A B O R T
M E N U M R G 3
M E R G E C A L F I L E S
P R E S S < E N T E R >
T O S E L E C T
R E A D C A L F I L E 2
F R O M H A R D D I S K
R E A D C A L F I L E 2
F R O M F L O P P Y D I S K
P R E S S < C L E A R >
T O A B O R T
A
Figure 4-8. Measurement Key-Group Menus Menu Flow
(Sheet 2 of 2)
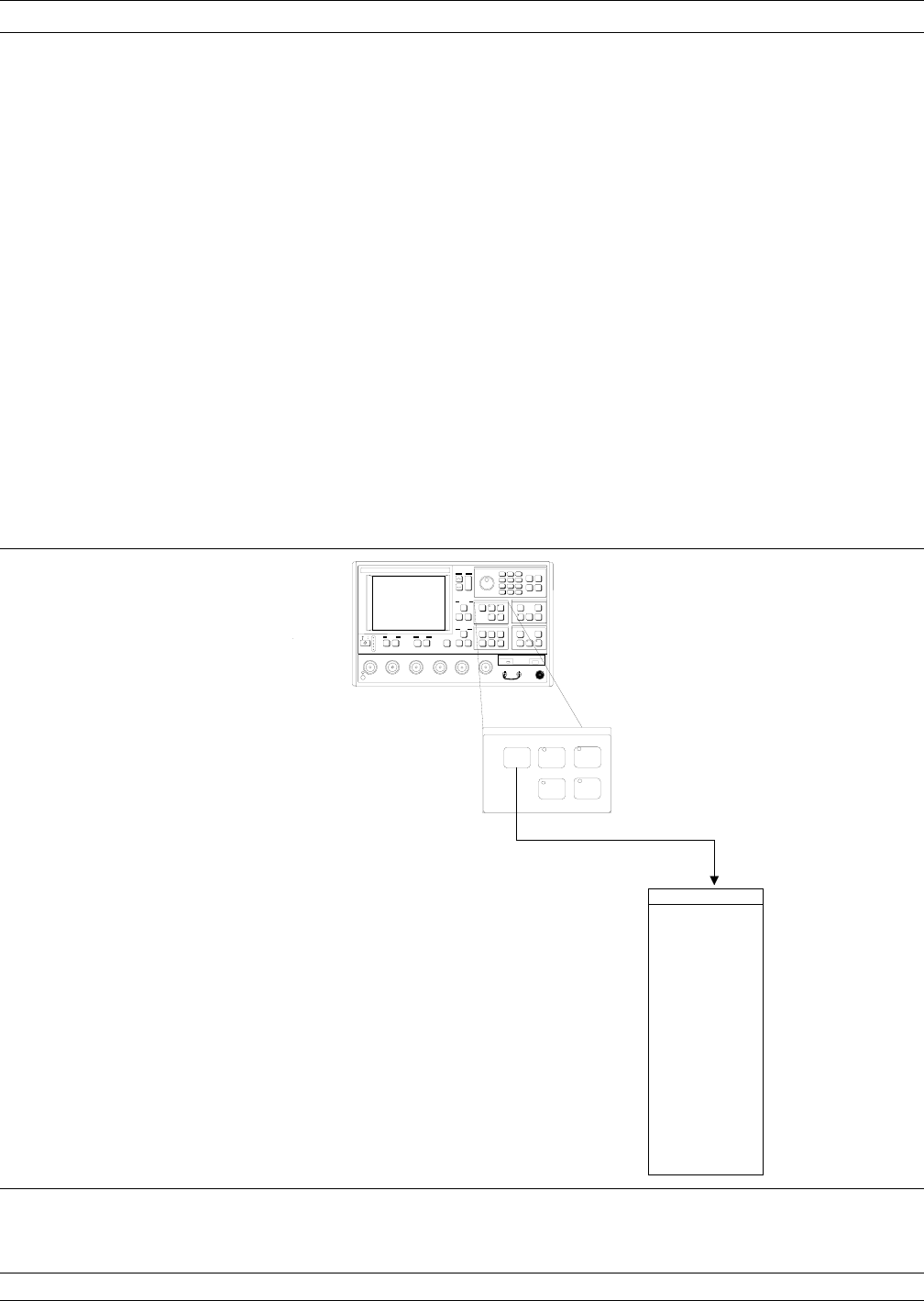
4-6 CHANNELS KEY-GROUP The individual keys within the Channels key-group are described be-
low:
Ch 1-4 Keys: These keys (below) define the active channel. One (and
only one) must always be active as indicated by the associated LED.
Pressing a button makes the indicated channel active. If channel indi-
cated by the key is already active, pressing the key has no effect.
The active channel will be the channel acted upon by the S Params,
Graph Type, Ref Plane, Trace Memory, Set Scale, Auto Scale,
Markers/Limits and Domain keys. When in the single channel display
mode, the active channel will be the one displayed.
Channel Menu: Pressing this key calls menu CM (below). Here, you
select the number of channels to be displayed. When in the single dis-
play mode, only the active channel will be displayed. Full menu de-
scription can be found in the alphabetical listing (Appendix A) under
the menu’s call letters (CM).
37XXXC OM 4-25
FRONT PANEL OPERATION CHANNELS KEY-GROUP
M E N U C M
S E L E C T
D I S P L A Y M O D E
S I N G L E
C H A N N E L
D U A L
C H A N N E L S 1 & 3
O V E R L A Y D U A L
C H A N N E L S 1 & 3
D U A L
C H A N N E L S 2 & 4
O V E R L A Y D U A L
C H A N N E L S 2 & 4
A L L F O U R
C H A N N E L S
P R E S S < E N T E R >
T O S E L E C T
C hannel
M e n u C h 1
C h 4
C h a n n e l s
7
8 9
4
56
1
23
0.
-
D a t a E n t r y
C h 2
C h 3
Figure 4-9. Channel Key-Group Menu
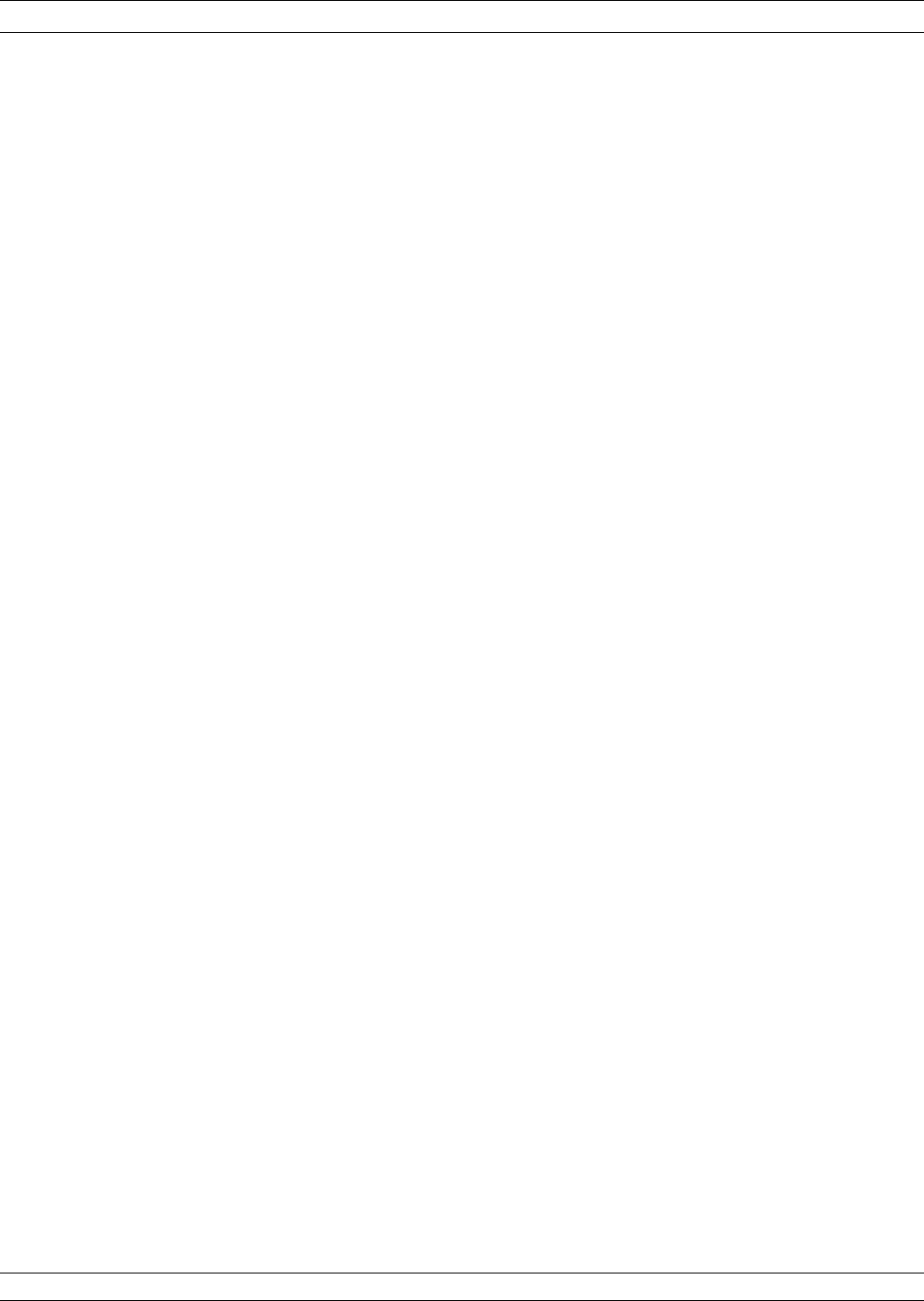
4-7 DISPLAY KEY-GROUP The individual keys within the Display key-group are described below.
Menu flow diagrams are shown in Figure 4-10. Full menu descrip-
tion(s) for menu SP and all others mentioned below can be found in
the Appendix A alphabetical listing under the menu’s call letters (SP,
GT1, RD1, etc.).
Graph Type Key: Pressing this key calls menu GT1 or GT2. These
menus let you select the type of display to appear on the active chan-
nel for the selected S-Parameter.
Set Scale Key: Pressing this key calls the appropriate scaling menu
(SS1, SS2, SS3, etc.) depending upon the graph type being displayed
on the active channel for the selected S-Parameter.
Auto Scale Key: Pressing this key autoscales the trace or traces for
the active channel. The new scaling values are then displayed on the
menu (if it is displayed) and graticule. The resolution will be selected
from the normal sequence of values you have available using the knob.
When the active channel has a Real and Imaginary type display, the
larger of the two signals will be used to autoscale both the real and
imaginary graphs. Both graphs will be displayed at the same resolu-
tion.
S Params Key: Pressing this key calls menu SP. This menu allows
you to select the S-Parameter to be displayed by the active channel for
the selected S-Parameter.
Ref Plane Key: Pressing this key calls menu RD1. This menu lets you
input the reference plane in time or distance. You do this by selecting
the appropriate menu item. For a correct distance readout, the dielec-
tric constant must be set to the correct value. This is accomplished by
selecting SET DIELECTRIC, which calls menu RD2.
DISPLAY KEY-GROUP FRONT PANEL OPERATION
4-26 37XXXC OM
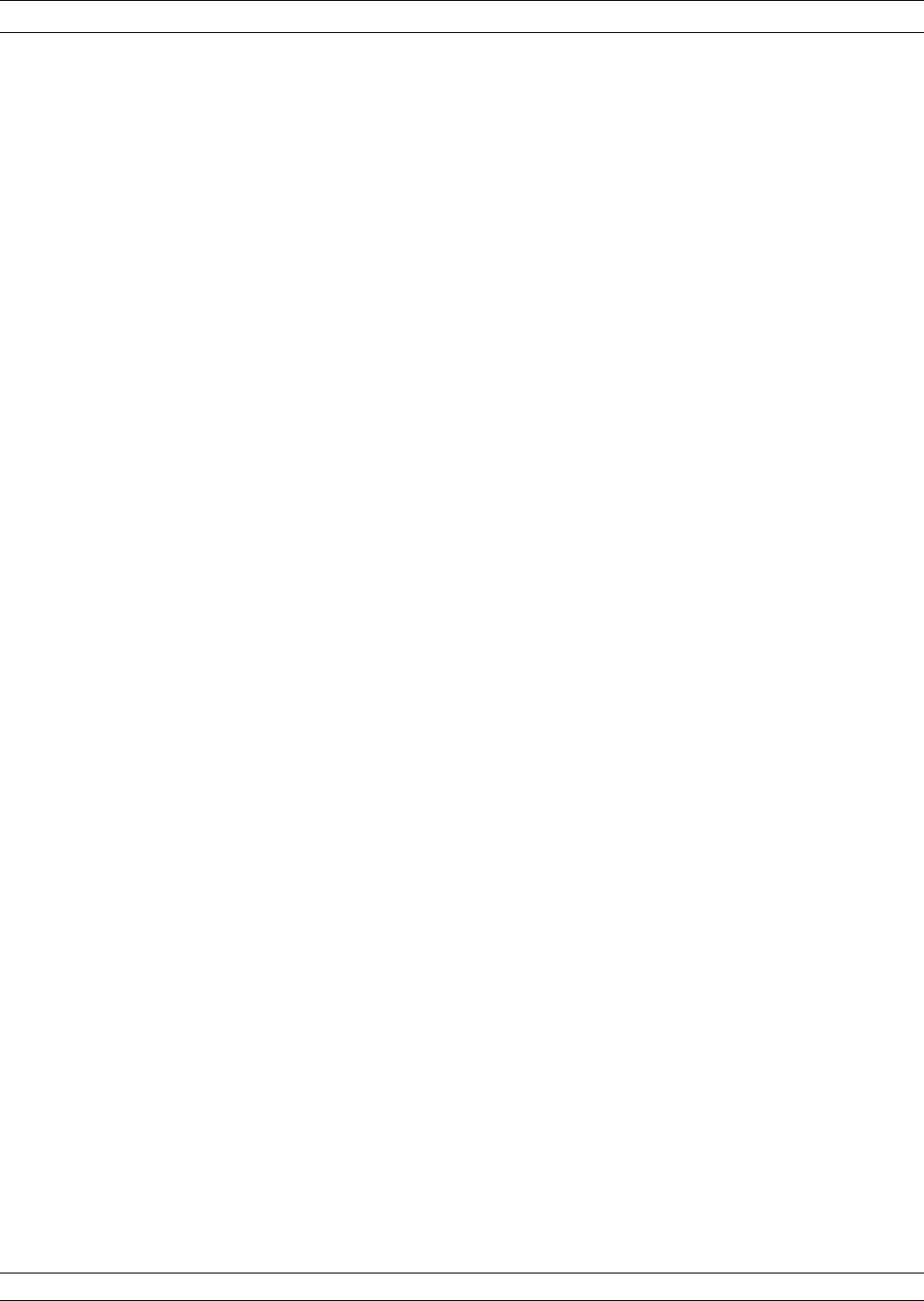
On menu RD1, selecting AUTO automatically adjusts the reference de-
lay to unwind the phase for the active channel.
The 37XXXC unwinds the phase as follows:
qFirst, it sums the phase increments between each pair of mea-
sured data points, then it takes the average “Pdelta” over the en-
tire set of points
qNext, it corrects the phase data by applying the following for-
mula:
PP NxP
correct measured delta
=-
Where P = phase
Assuming there are fewer than 360 degrees of phase rotation between
each data point, the operation described above removes any net phase
offset. The endpoints of the phase display then fall at the same phase
value.
Trace Memory Key: Pressing this key brings up menu NO1. This
menu—which relates to the active channel—allows you to store data
to memory, view memory, perform operations with the stored memory,
and view both data and memory simultaneously. Four memories exist,
one for each channel. This allows each channel to be stored and nor-
malized independent of the other channels. Data from the trace mem-
ory may be stored on the disk or recalled from it.
NOTE
Trace memory will automatically be set to VIEW DATA
(that is, turned off), if a sweep with a greater number of
points is selected while operating on a stored trace.
37XXXC OM 4-27
FRONT PANEL OPERATION DISPLAY KEY-GROUP
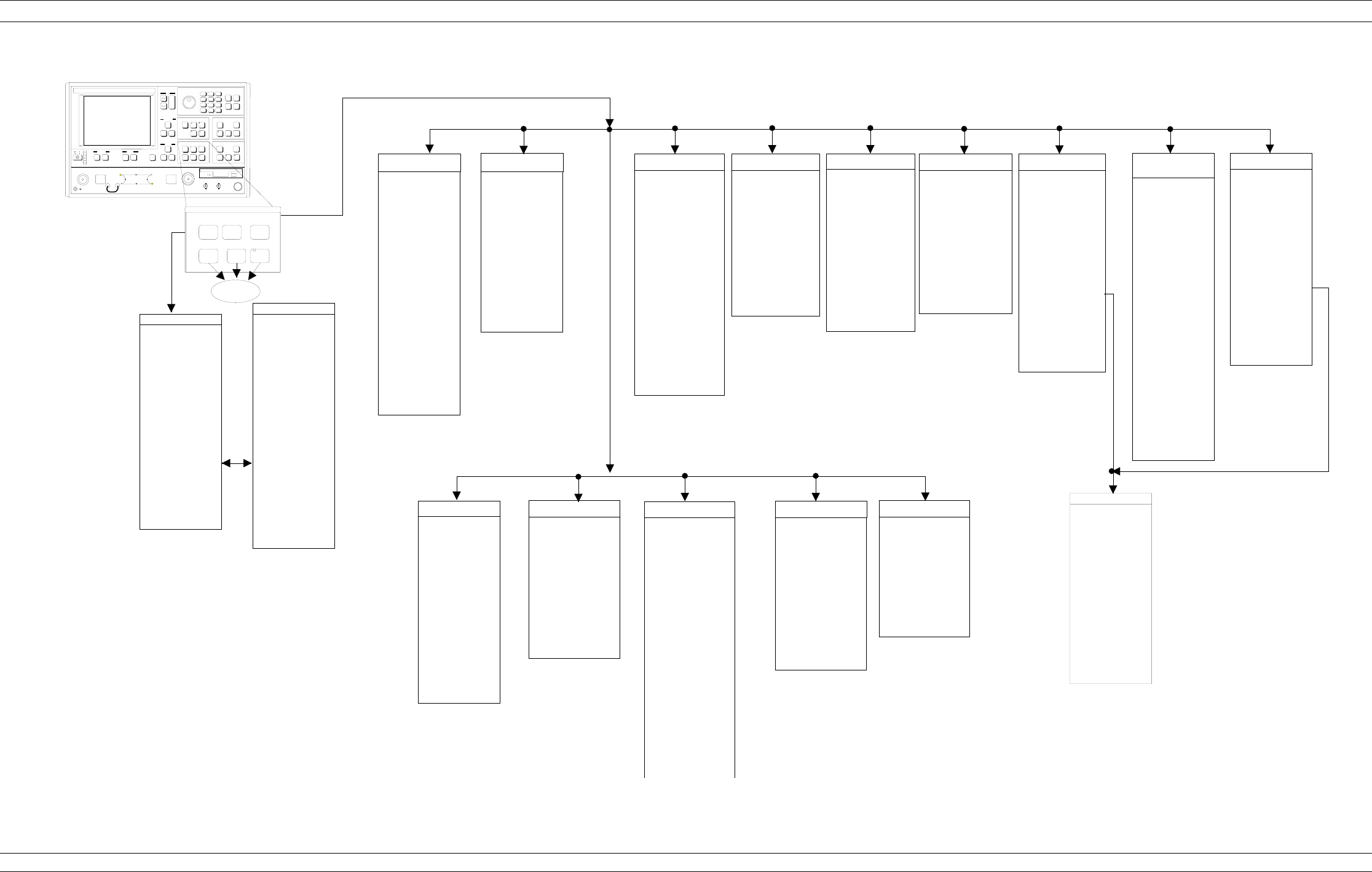
4-28 37XXXC OM
DISPLAY KEY-GROUP FRONT PANEL OPERATION
M E N U G T 2
L I N E A R P O L A R
L O G P O L A R
L I N E A R M A G
R E A L
I M A G I N A R Y
M O R E
S E L E C T
G R A P H T Y P E
L I N E A R M A G
A N D P H A S E
R E A L A N D
I M A G I N A R Y
P R E S S < E N T E R >
T O S E L E C T
S M I T H C H A R T
( A D M I T T A N C E )
S e e s h e e t 2
M E N U G T 1
PHASE
S W R
G R O U P D E L A Y
M O R E
S E L E C T
G R A P H T Y P E
L O G M A G N I T U D E
L O G M A G N I T U D E
A N D P H A S E
S M I T H C H A R T
( I M P E D A N C E )
P R E S S < E N T E R >
T O S E L E C T
M E N U S S 1
o r C A L _ S S 1
M E N U S S 4
o r C A L _ S S 4
- L I N E A R M A G -
- P H A S E -
S E T S C A L I N G
O R P R E S S
< A U T O S C A L E >
R E S O L U T I O N
X X . X X X U / D I V
R E F E R E N C E V A L U E
X X X . X X X p U
R E S O L U T I O N
X X . X X ° / D I V
R E F E R E N C E V A L U E
X X X . X X °
- L I N E A R M A G -
S E T S C A L I N G
O R P R E S S
< A U T O S C A L E >
R E S O L U T I O N
X X . X X X U / D I V
R E F E R E N C E V A L U E
X X X . X X X p U
- P H A S E -
R E S O L U T I O N
X X . X X X * / D I V
R E F E R E N C E V A L U E
X X X . X X X *
P H A S E S H I F T
X . X X °
S E T S C A L I N G
O R P R E S S
< A U T O S C A L E >
- I M A G I N A R Y -
S E T S C A L I N G
O R P R E S S
< A U T O S C A L E >
R E S O L U T I O N
X X . X X X U / D I V
R E F E R E N C E V A L U E
X X X . X X X p U
- L I N E A R P O L A R -
S E T S C A L I N G
O R P R E S S
< A U T O S C A L E >
R E S O L U T I O N
X X . X X X U / D I V
R E F E R E N C E V A L U E
X X X . X X X U
M E N U S S 9 o r
C A L _ S S 9
M E N U S S 8 o r
C A L _ S S 8
M E N U S S 5
o r C A L _ S S 5
M E N U S S 1 1
o r C A L _ S S 1 1
M E N U S S 2
o r C A L _ S S 2 M E N U S S 3 _ Z o r _ Y
o r C A L _ S S 3 _ Z o r _ Y
M E N U S S 6
o r C A L _ S S 6
R E F E R E N C E L I N E
X
- L O G M A G -
S E T S C A L I N G
O R P R E S S
< A U T O S C A L E >
- L O G P O L A R -
S E T S C A L I N G
O R P R E S S
< A U T O S C A L E >
R E S O L U T I O N
X X . X X X d B / D I V
R E F E R E N C E V A L U E
X X X . X X X d B
S E L E C T P O L A R
C H A R T M O D E
M E N U S S 7 o r C A L _ S S 7
- S W R -
S E T S C A L I N G
O R P R E S S
< A U T O S C A L E >
R E S O L U T I O N
X X . X X X U /
R E F E R E N C E V A L U E
XXX.XXX U
- R E A L -
- I M A G I N A R Y -
S E T S C A L I N G
O R P R E S S
< A U T 0 S C A L E >
R E S O L U T O N
X X . X X X U / D I V
R E F E R E N C E V A L U E
X X X . X X X p U
R E S O L U T I O N
X X . X X D E G / D I V
- R E A L -
S E T S C A L I N G
O R P R E S S
< A U T O S C A L E >
R E S O L U T I O N
X X . X X X U / D I V
M E N U S S 1 2 o r C A L _ S S 1 2 M E N U S S 1 0 o r C A L _ S S 1 0
M E N U S S 1 3 o r C A L _ S S 1 3
R E F E R E N C E V A L U E
X X X . X X X °
R E F E R E N C E V A L U E
X X X . X X X p U
- G R O U P D E L A Y -
S E T S C A L I N G
O R P R E S S
< A U T O S C A L E >
R E S O L U T I O N
X X X . X X X f s / D I V
R E F E R E N C E V A L U E
X X X . X X X f s
A P E R T U R E
X . X P E R C E N T
O F S W E E P
X X . X X
- L O G M A G -
- P H A S E -
S E T S C A L I N G
O R P R E S S
< A U T O S C A L E >
R E S O L U T I O N
X X . X X X d B / D I V
R E F E R E N C E V A L U E
X X X . X X X d B
R E F E R E N C E L I N E
X
R E S O L U T I O N
X X . X X ° / D I V
R E F E R E N C E V A L U E
X X X . X X °
P H A S E S H I F T
X . X X °
* A p p e a r s f o r C A L _ S S X X M e n u s
S E T S C A L I N G
O R P R E S S
< A U T O C A L E >
I M P E D A N C E
( A D M I T T A N C E )
- S M I T H C H A R T -
N O R M A L S M I T H
( R E F L = 1 . 0 0 0 0 0 0 0
F U L L S C A L E )
E X P A N D 1 0 d B
( R E F L = O . 3 1 6 2 2 7 8
F U L L S C A L E )
E X P E N D 2 0 d B
( R E F L = 0 . 1 0 0 0 0 0 0
F U L L S C A L E )
E X P A N D 3 0 d B
( R E F L = 0 . 0 3 1 6 2 2 8
F U L L S C A L E )
C O M P R E S S 3 d B
( R E F L = 1 . 4 1 2 5 3 7 5
F U L L S C A L E )
P R E S S < E N T E R >
T O R E S U M E C A L *
P R E S S < E N T E R >
T O R E S U M E C A L *
P R E S S < E N T E R >
T O R E S U M E C A L *
P R E S S < E N T E R >
T O R E S U M E C A L *
P R E S S < E N T E R >
T O R E S U M E C A L
*
P R E S S < E N T E R >
T O R E S U M E C A L
P R E S S < E N T E R >
T O R E S U M E C A L P R E S S < E N T E R >
T O R E S U M E C A L
P R E S S < E N T E R >
T O R E S U M E C A L
P R E S S < E N T E R >
T O S E L E C T
*
P R E S S < E N T E R >
T O S E L E C T
*
P R E S S < E N T E R >
T O R E S U M E C A L *
*
*
**
*
R E S O L U T I O N
X X . X X X d B / D I V
R E F E R E N C E V A L U E
XXX.XXX dB
M E N U P C 1
M A G N I T U D E
P H A S E
M A G N I T U D E
S W P P O S I T I O N
SET SW EEP
P O S I T I O N
B O U N D A R I E S
S T A R T A N G L E
X . X X
S T O P A N G L E
X . X X
P R E S S < E N T E R >
T O S E L E C T
7 8 9
456
123
0.-
D i s p l a y
G r a p h
T y p e
A u t o
S c a l e
S
P a r a m s
R e f
P l a n e
T r a c e
M e m o r y
S e t
S c a l e
P R E S S < E N T E R >
T O S E L E C T
A N D R E S U M E C A L
*
A N D R E S U M E C A L *
A N D R E S U M E C A L *
R E F E R E N C E L I N E
XR E F E R E N C E L I N E
X
R E F E R E N C E L I N E
XR E F E R E N C E L I N E
X
F I X E D
R E F E R E N C E L I N E
R E F E R E N C E L I N E
X
R E F E R E N C E L I N E
X
R E F E R E N C E L I N E
X
R E F E R E N C E L I N E
X
S E L E C T P O L A R
C H A R T M O D E
M A G N I T U D E ,
PHASE
F I X E D
R E F E R E N C E L I N E
M A G N I T U D E ,
P H A S E
S E L E C T P O L A R
C H A R T M O D E
R E F E R E N C E L I N E
X
R E F E R E N C E L I N E
X
R E F E R E N C E L I N E
X
P O W E R O U T
- P O W E R O U T -
S E T S C A L I N G
O R P R E S S
< A U T O S C A L E >
R E S O L U T I O N
X X . X X X U /
R E F E R E N C E V A L U E
X X X . X X X U
M E N U S S 1 4
R E F E R E N C E L I N E
X
A N D R E S U M E C A L A N D R E S U M E C A L
Figure 4-10. Display Key-Group Menus (1 of 2)
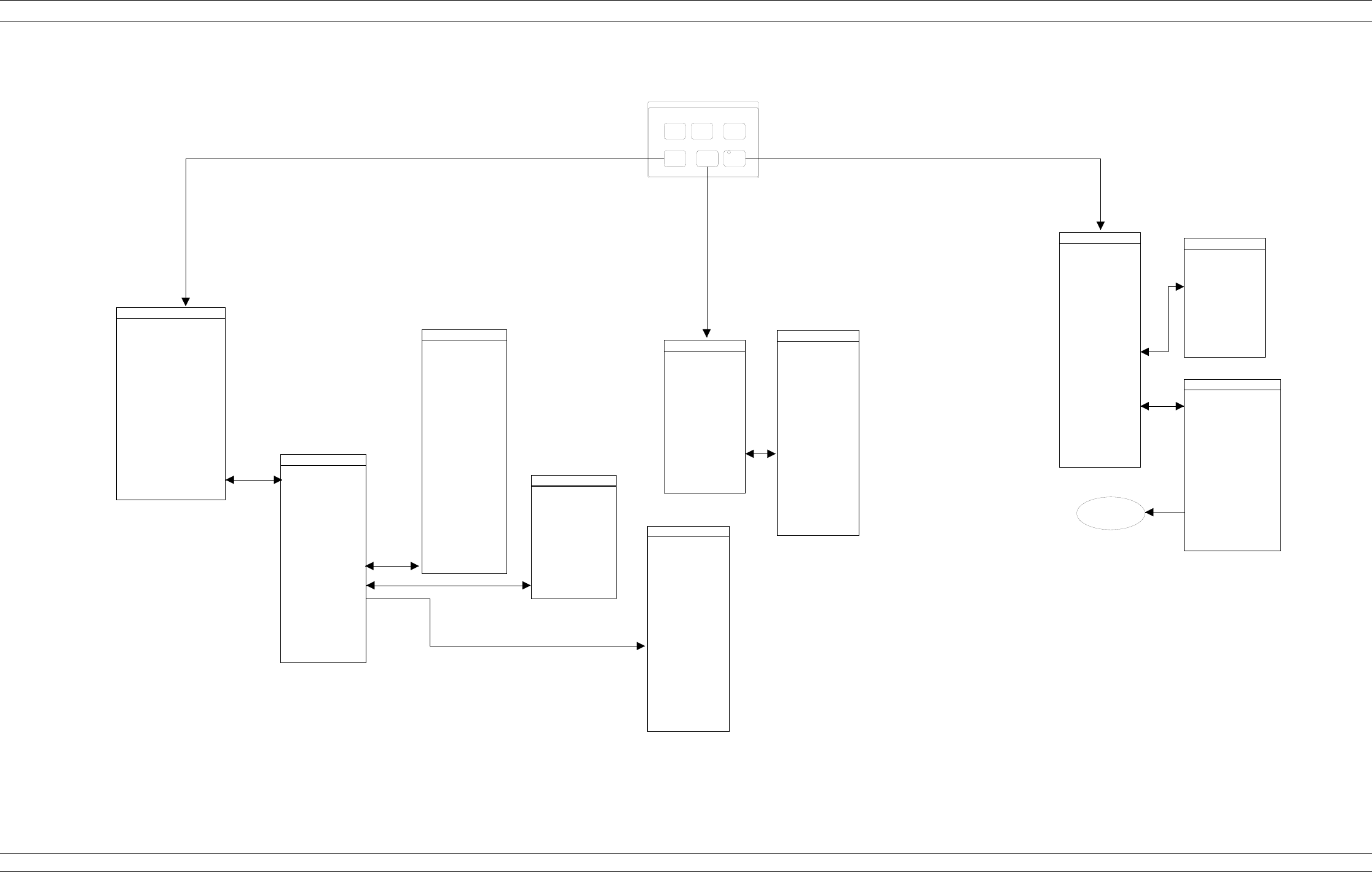
37XXXC OM 4-29
FRONT PANEL OPERATION DISPLAY KEY-GROUP
D i s p l a y
G r a p h
T y p e
S e t
S c a l e A u t o
S c a l e
M E N U R D 2
S E T
D I E L E C T R I C
C O N S T A N T
A I R
(1.000649)
P O L Y E T H Y L E N E
( 2 . 2 6 )
T E F L O N
( 2 . 1 0 )
M I C R O P O R O U S
T E F L O N
( 1 . 6 9 )
O T H E R
X X X X . X X
P R E S S < E N T E R >
T O S E L E C T
M E N U R D I
A U T O
S E T D I E L E C T R I C
X X X
S E T
R E F E R E N C E
P L A N E
D I S T A N C E
XXX.XXX m m
T I M E
X X X . X X X m s
P R E S S < E N T E R >
T O S E L E C T
M E N U N O 1
V I E W D A T A
V I E W M E M O R Y
T R A C E M E M O R Y
F U N C T I O N S
V I E W D A T A
A N D M E M O R Y
V I E W D A T A ( X )
B Y M E M O R Y
S E L E C T
T R A C E M A T H
S T O R E D A T A
T O M E M O R Y
( S T O R E D )
( N O T S T O R E D )
D I S K
O P E R A T I O N S
P R E S S < E N T E R >
T O S E L E C T
M E N U N O 2
A D D ( + )
S U B T R A C T ( - )
M U L T I P L Y ( * )
D I V I D E ( / )
S E L E C T
T R A C E M A T H
P R E S S < E N T E R >
T O S E L E C T
M E N U N O 3
C H A N N E L X
R E C A L L M E M O R Y
F R O M H A R D D I S K
T R A C E M E M O R Y
D I S K O P E R A T I O N S
P R E S S < E N T E R >
T O S E L E C T
S A V E M E M O R Y
T O H A R D D I S K
S A V E M E M O R Y
T O F L O P P Y D I S K
R E C A L L M E M O R Y
F R O M F L O P P Y D I S K
M E N U S P
S E L E C T
P A R A M E T E R
S 2 1 , F W D T R A N S
b 2 / a 1
S 1 1 , U S E R 2
b 2 / 1
S 1 2 , R E V T R A N S
b 1 / a 2
S 2 2 , R E V R E F L
b 2 / a 2
P R E S S < E N T E R >
T O S E L E C T
M E N U D S K 2 o r
D S K 3
P R E S S < 1 >
T O R E D E F I N E
S E L E C T E D P A R A M E T E R
M E N U P D 2
P A R A M E T E R R A T I O
N U M E R A T O R
a 1 ( R a )
1 ( U N I T Y )
P R E S S < E N T E R >
T O S E L E C T
P R E V I O U S M E N U
a 2 ( R b )
b 1 ( T a )
b 2 ( T b )
D E N O M I N A T O R
a 1 ( R a )
1 ( U N I T Y )
a 2 ( R b )
b 1 ( T a )
b 2 ( T b )
S E L E C T L A B E L
- - - - - - - - -
T U R N K N O B
T O I N D I C A T E
C H A R A C T E R O R
F U N C T I O N
P R E S S < E N T E R >
T O S E L E C T
N U M B E R S M A Y
A L S O B E
S E L E C T E D
U S I N G K E Y P A D
M E N U G P 5
A B C D E F G H I J K L M
N O P Q R S T U V W X Y Z
0 1 2 3 4 5 6 7 8 9 ( ) -
! # $ % & @ ^ _ ' { } ~
B K S P C L R D O N E
M E N U P D 1
P A R A M E T E R
D E F I N I T I O N
S 2 1 / U S E R 1
U S E R R A T I O
b 2 / a 1
U S E R P H A S E L O C K
a 1
P R E S S < E N T E R >
T O S E L E C T
O R S W I T C H
C H A N G E R A T I O
C H A N G E
P H A S E L O C K
C H A N G E L A B E L
P R E V I O U S M E N U
U S E R L A B E L
M E N U P D 3
a 1 ( R a )
P R E S S < E N T E R >
T O S E L E C T
P R E V I O U S M E N U
a 2 ( R b )
P A R A M E T E R
D E F I N I T I O N
P H A S E L O C K
S
P a r a m s
R e f
P l a n e
T r a c e
M e m o r y
Figure 4-10. Display Key-Group Menus (2 of 2)
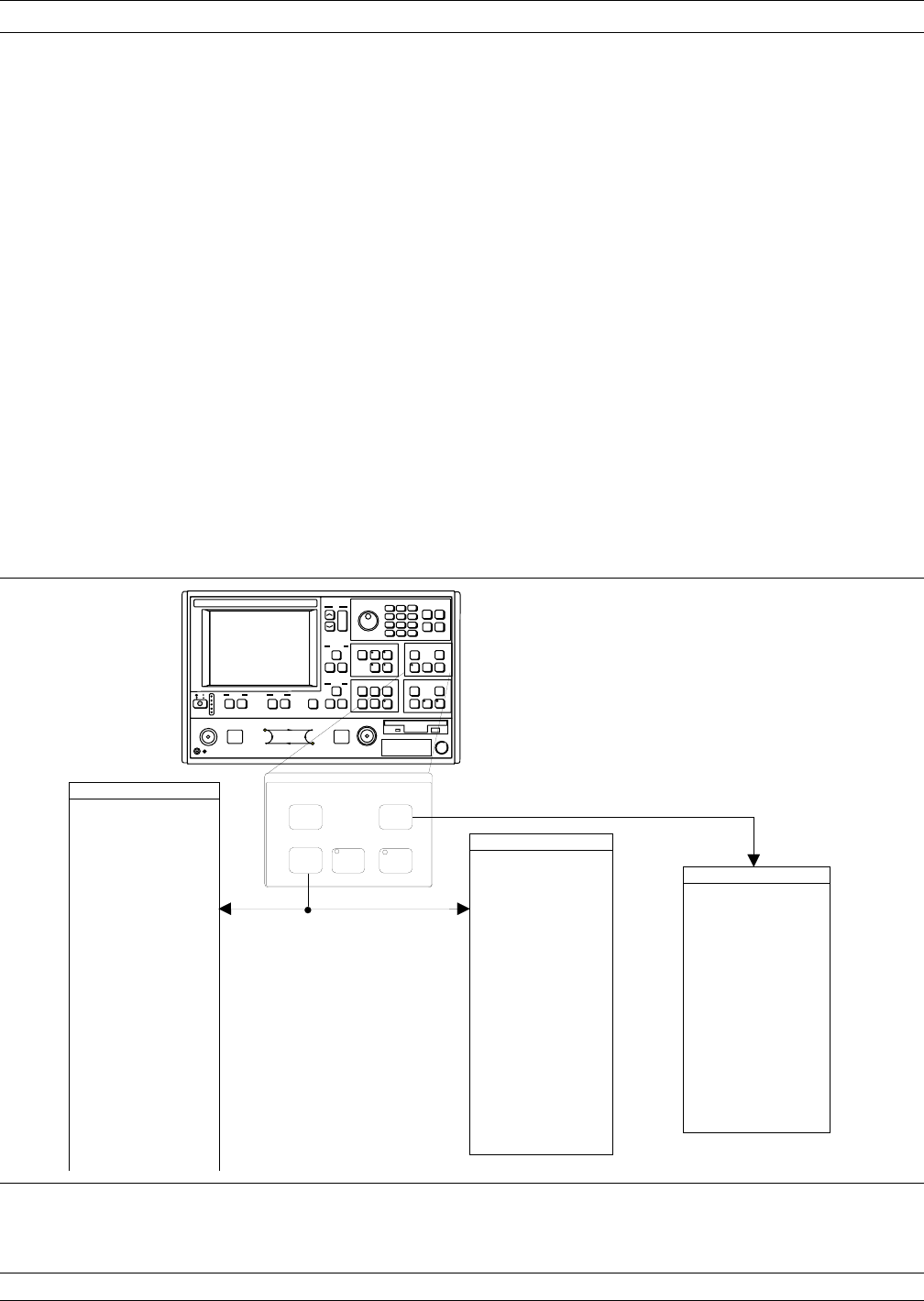
4-8 ENHANCEMENT
KEY-GROUP The individual keys within the Enhancement key-group are described
below. Full menu description(s) for menu OPTNS and all others men-
tioned below can be found in the Appendix A alphabetical listing un-
der the menu’s call letters (OPTNS, EM, CAL_BW, etc).
Option Menu Key: This key brings up the OPTNS menu. Depending
on choices selected, this menu causes other menus to appear. A menu
flow diagram for this key is shown in Figure 4-12 on the following
page.
Video IF BW Key: Pressing this produces a menu that lets you choose
between four different IF bandwidths. This menu is shown below.
Avg/Smooth Menu Key: Pressing this key brings up the EM Menu.
When pressed during the calibration sequence, it brings up the EM
Cal Menu instead. These menus are shown below.
Trace Smooth and Average Keys: The Average and Trace Smooth
keys set their respective functions on and off with the appropriate
LED indicating when the function is selected.
ENHANCEMENT KEY-GROUP FRONT PANEL OPERATION
4-30 37XXXC OM
T h i s m e n u o n l y
a p p e a r s d u r i n g
c a l i b r a t i o n .
M E N U E M
D A T A E N H A N C E M E N T
A V E R A G I N G
X X X X M E A S .
S M O O T H I N G
X . X P E R C E N T .
O F S W E E P
X X X P O I N T ( S )
M E N U B W 1 o r C A L _ B W 1
S E L E C T V I D E O
B A N D W I D T H
M A X I M U M
( 1 0 k H z )
N O R M A L
( 1 k H z )
REDUCED
( 1 0 0 H z )
M I N I M U M
( 1 0 H z )
P R E S S < E N T E R >
T O S E L E C T
M E N U C A L _ E M
D A T A E N H A N C E M E N T
E n h a n c e m e n t
O p t i o n
M e n u
V i d e o
I F B W
A v g
S m o o t h
M e n u
A v e r a g e
T r a c e
S m o o t h
A N D R E S U M E C A L *
* A p p e a r s f o r M e n u C A L _ B W 1
789
456
123
0.-
A V E R A G I N G T Y P E
P O I N T - B Y - P O I N T
SW EEP-BY-SW EEP
R E S E T A V G C O U N T
XXXX SW EEP(S)
SAM PLERS USED
PER SW EEP
X S A M P L E R S
P R E S S < E N T E R >
T O S E L E C T
PRESS
< A V G / S M O O T H M E N U >
T O R E S E T A V G C O U N T
A V E R A G I N G
X X X X M E A S .
A V E R A G I N G T Y P E
P O I N T - B Y - P O I N T
SW EEP-BY-SW EEP
R E S E T A V G C O U N T
XXXX SW EEP(S)
SAM PLERS USED
PER SW EEP
X S A M P L E R S
R E S U M E C A L
P R E S S < E N T E R >
T O S E L E C T
PRESS
< A V G / S M O O T H M E N U >
T O R E S E T A V G C O U N T
Figure 4-11. Enhancement Key-Group Menus
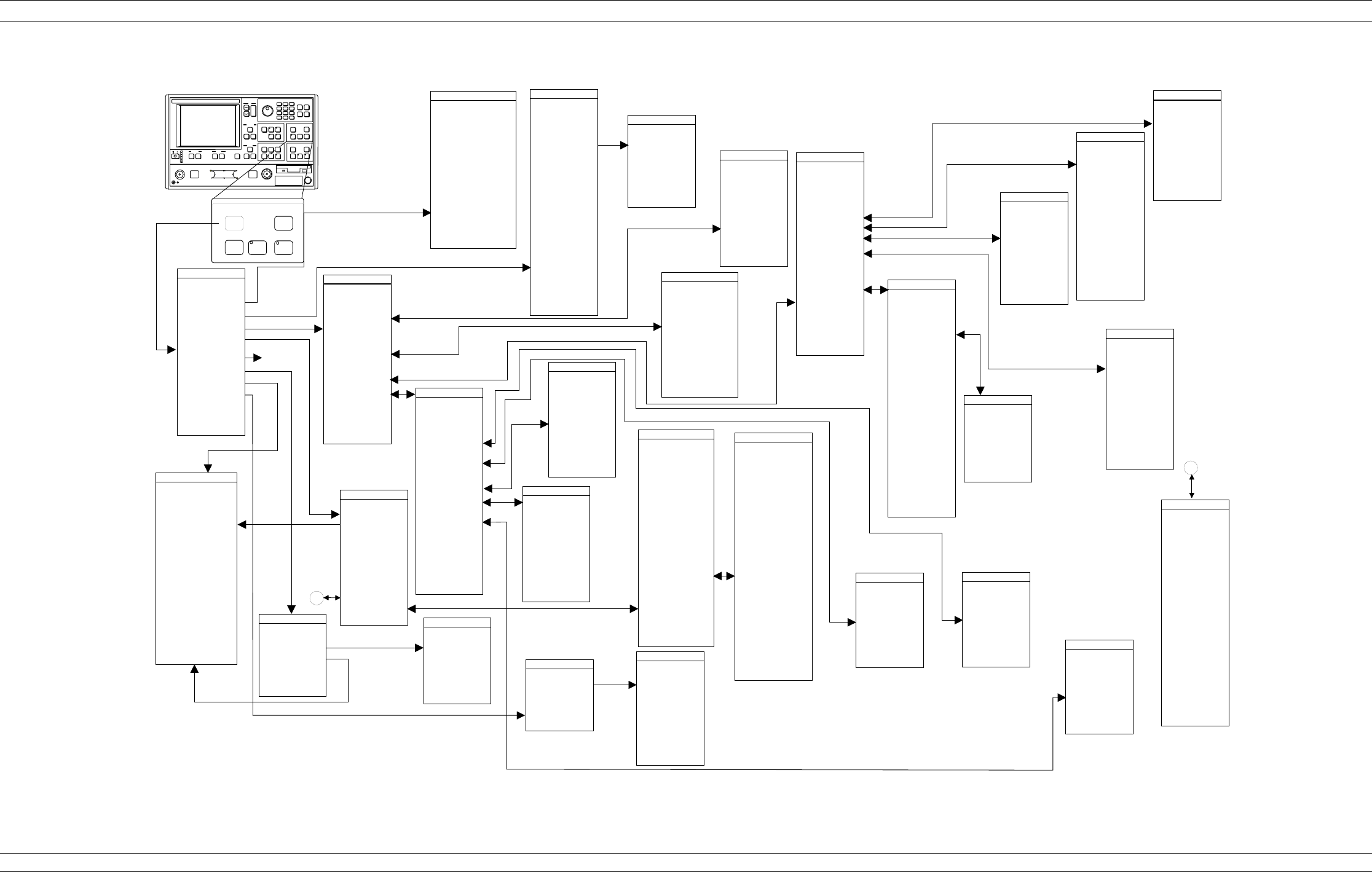
37XXXC OM 4-31
FRONT PANEL OPERATION ENHANCEMENT KEY-GROUP
H O R I Z O N T A L
V E R T I C A L
P H A S E L O C K
S E L E C T M O D E
F O R O U T P U T
P R E S S < E N T E R >
T O S E L E C T
M E N U D G 1
R E A D S E R V I C E L O G
T R O U B L E S H O O T I N G
( F O R S E R V I C E
U S E O N L Y )
P R E S S < E N T E R >
T O S E L E C T
D I A G N O S T I C S
S T A R T S E L F T E S T
I N S T A L L E D O P T I O N S
P E R I P H E R A L T E S T S
H / W C A L I B R A T I O N S
( F O R S E R V I C E
U S E O N L Y )
P R E S S < E N T E R >
T O S E L E C T
O R T U R N O N / O F F
M E N U D G 4 A
P R E V I O U S M E N U
D V M C H A N N E L
X X X X
( U N U S E D C H A N N E L )
P R E S S < E N T E R >
T O S E L E C T
M E N U D G 4
T R O U B L E S H O O T I N G
( F O R S E R V I C E
U S E O N L Y )
L O 1
L O 2
S O U R C E
N O N - R A T I O E D
P A R A M E T E R S
F I R S T I . F .
BANDPASS
M O R E
F I N I S H E D ,
R E C O V E R F R O M
T R O U B L E S H O O T I N G
E X T E R N A L
A T O D I N P U T
R E C E I V E R M O D E
S O U R C E L O C K
S E A R C H O N ( O F F )
F O R L O C K
L A T C H C O N T R O L
A D D R E S S
X X X
( U N U S E D A D D R E S S )
T R I G G E R R E A D
O U T P U T : X
T R I G G E R W R I T E
I N P U T : X
P R E S S < E N T E R >
T O S E L E C T
T R O U B L E S H O O T I N G
L O 1
P H A S E L O C K
V O L T A G E
D / A V O L T A G E
P R E V I O U S M E N U
P R E S S < E N T E R >
T O S E L E C T
M E N U D G 4 _ L O 2
M A I N P H A S E
L O C K V O L T A G E
M A I N D / A
V O L T A G E
P R E V I O U S M E N U
O F F S E T D / A
V O L T A G E
O F F S E T P H A S E
L O C K V O L T A G E
T R O U B L E S H O O T I N G
L O 2
D D S P H A S E
L O C K V O L T A G E
P R E S S < E N T E R >
T O S E L E C T
M E N U D G 4 _ S O U R C E
T R O U B L E S H O O T I N G
S O U R C E
S O U R C E L I N E A R I T Y
V O L T A G E
P O W E R O U T P U T
V O L T A G E
P R E V I O U S M E N U
P R I N T L O G
S A V E L O G
T O F L O P P Y D I S K
P R E S S < E N T E R >
T O S E L E C T
M E N U D G 2
S E R V I C E L O G
D I S P L A Y L O G
C L E A R L O G
P R E V I O U S M E N U
P R E S S < E N T E R >
T O S E L E C T
M E N U D G 5 _ S R C
P R E V I O U S M E N U
H A R D W A R E
C A L I B R A T I O N
( F O R S E R V I C E
U S E O N L Y )
S T A R T S O U R C E
F R E Q C A L I B R A T I O N
T R O U B L E S H O O T I N G
( F O R S E R V I C E
U S E O N L Y )
P R E S S < E N T E R >
T O S E L E C T
M E N U D G 5 _ A L C
P R E V I O U S M E N U
H A R D W A R E
C A L I B R A T I O N
( F O R S E R V I C E
U S E O N L Y )
S T A R T A L C
F R E Q C A L I B R A T I O N
M E N U D G 4 _ L O 1
P R E S S < E N T E R >
T O S E L E C T
M E N U D G 4 _ R C V R
T R O U B L E S H O O T I N G
R E C E I V E R M O D E
T R A C K I N G
S E T O N
S O U R C E L O C K
M E N U T R I G
M E A S U R E M E N T
P R E S S < E N T E R >
T O S E L E C T
O R T U R N O N / O F F
I N T E R N A L
E X T E R N A L
I . F . C A L I B R A T I O N
A U T O M A T I C O N ( O F F )
I . F . C A L
T R I G G E R
I . F . C A L
M E N U O R P 1
O U T P U T O N ( O F F )
R E A R P A N E L
O U T P U T C O N T R O L
S E L E C T M O D E
XXXXXXXXXX
H O R I Z O N T A L
O R P H A S E L O C K
S C A L I N G
S T A R T / L O C K a 1
X . X X X X V
S T O P / L O C K a 2
X . X X X X V
V E R T I C A L S C A L I N G
R E S O L U T I O N
1 . 0 0 0 V / D I V
R E F E R E N C E V A L U E
0 .0 0 V /D IV
P R E S S < E N T E R >
T O S E L E C T
O R T U R N O N / O F F
P R E S S < E N T E R >
T O S E L E C T
M E N U D G 4 _ I F B P
T R O U B L E S H O O T I N G
F I R S T I . F .
BANDPASS
L O 1 F R E Q U E N C Y
X X . X X X X G H z
H A R M O N I C N U M
X X X
P R E V I O U S M E N U
F I R S T I . F .
BANDPASS
E n h a n c e m e n t
V i d e o
I F B W
M E N U O M 2
D E F I N E B A N D S
B A N D F U N C T I O N S
B A N D S T A R T F R E Q
XXX.XXXXXXXXX G Hz
B A N D S T O P F R E Q
XXX.XXXXXXXXX G Hz
C L E A R A L L
D E F I N I T I O N S
S E T M U L T I P L E
S O U R C E M O D E
P R E S S < E N T E R >
T O S E L E C T
B A N D 1
D I S P L A Y E D
F R E Q R A N G E
S T O R E B A N D 1
B A N D S S T O R E D :
( XXXXXX)
E D I T S Y S T E M
E Q U A T I O N S
M E N U O M 3
S O U R C E 1
S O U R C E 2
R E C E I V E R
C . W . O N ( O F F )
P R E V I O U S M E N U
E D I T S Y S T E M
E Q U A T I O N S
E Q U A T I O N
T O E D I T
E Q U A T I O N
S U M M A R Y
M U L T I P L I E R
X X
D I V I S O R
X X
O F F S E T F R E Q
XXX.XXXXXXXXX GHz
P R E S S < E N T E R >
T O S E L E C T
CRT
F R O N T P A N E L
P R E S S < E N T E R >
T O S E L E C T
M E N U D G 3
EXTERNAL KEYBO ARD
P E R I P H E R A L T E S T S
P R I N T E R I N T E R F A C E
G P I B I N T E R F A C E
P R E V I O U S M E N U
M E N U R C V 1
U S E R D E F I N E D
S T A N D A R D
S O U R C E C O N F I G
P R E S S < E N T E R >
T O S E L E C T
R E C E I V E R M O D E
M E N U R C V 2
T R A C K I N G
S O U R C E L O C K
S E T O N
P R E S S < E N T E R >
T O S E L E C T
U S E R D E F I N E D
R E C E I V E R M O D E
M E N U D G 5
L O 1
C A L I B R A T I O N
M E N U
P R E S S < E N T E R >
T O S E L E C T
H A R D W A R E
C A L I B R A T I O N S
( F O R S E R V I C E
U S E O N L Y )
L O 2
C A L I B R A T I O N
S O U R C E F R E Q U E N C Y
C A L I B R A T I O N
S O U R C E A L C
C A L I B R A T I O N
D I S K
O P E R A T I O N S
S O U R C E L O C K
T H R E S H O L D
C A L I B R A T I O N
M E N U L O 1
S T A R T L O 1
C A L I B R A T I O N
( F O R S E R V I C E
U S E O N L Y )
P R E V I O U S M E N U
P R E S S < E N T E R >
T O S E L E C T
H A R D W A R E
C A L I B R A T I O N
S T A R T L O 2
C A L I B R A T I O N
( F O R S E R V I C E
U S E O N L Y )
P R E V I O U S M E N U
P R E S S < E N T E R >
T O S E L E C T
H A R D W A R E
C A L I B R A T I O N
M E N U S L T
S T A R T S L T
C A L I B R A T I O N
( F O R S E R V I C E
U S E O N L Y )
P R E V I O U S M E N U
P R E S S < E N T E R >
T O S E L E C T
H A R D W A R E
C A L I B R A T I O N
P R E V I O U S M E N U
M E N U S C
S O U R C E C O N F I G
P R E S S < E N T E R >
T O S E L E C T
O R T U R N O N / O F F
S O U R C E 1
A C T I V E / I N A C T I V E
S O U R C E L O C A T I O N
I N T E R N A L / E X T E R N A L
G P I B A D D R E S S
4
G P I B C O N T R O L O N ( O F F )
S O U R C E 2
A C T I V E / I N A C T I V E
S O U R C E L O C A T I O N
E X T E R N A L
G P I B A D D R E S S
5
G P I B C O N T R O L O N ( O F F )
M E N U O T S 1
M I L L I M E T E R W A V E
I N T E R N A L
P R E S S < E N T E R >
T O S E L E C T
T E S T S E T
C O N F I G U R A T I O N
M E N U O T S 2
C O N T I N U I N G
W I L L I N V A L I D A T E
CURRENT
S E T U P A N D
C A L I B R A T I O N
W A R N I N G :
P R E S S < E N T E R >
T O C O N T I N U E
I N T E R N A L
T E S T S E T
P R E S S < C L E A R >
T O A B O R T
O p t i o n
M e n u
A v g
S m o o t h
M e n u
T r a c e
S m o o t h A v e r a g e
M E N U L O 2
M E N U O R P 2
*
O r
M U L T I P L E S O U R C E
C O N T R O L
N O T E 1 : G O E S T O M E N U M M W 4 I F
3 7 3 5 A T E S T S E T I S I N S T A L L E D ( S E E C H A P T E R 1 4 )
S E E N O T E 1
789
456
123
0.-
O P T I O N S
T R I G G E R S
D I A G N O S T I C S
P R E S S < E N T E R >
T O S E L E C T
M I L L I M E T E R W A V E
B A N D D E F I N I T I O N
R E A R P A N E L
O U T P U T
R E C E I V E R M O D E
S O U R C E C O N F I G
T E S T S E T C O N F I G
M E N U O P T N S
*
R F O N [O F F ]
D U R I N G R E T R A C E
S P U R R E D U C T I O N
N O R M A L / O F F
M E N U O M 1
D E F I N E B A N D S
O F F
D E F I N E
M O R E
M U L T I P L E
S O U R C E C O N T R O L
M U L T I P L E
S O U R C E M O D E
P R E S S < E N T E R >
T O S E L E C T
S O U R C E C O N F I G
O N
M E N U O M 1 A
N O R M A L
T H E D U T C O N T A I N S
M U L T I - C O N V E R S I O N
S T A G E S , A N D
T H E P H A S E O F T H E
F I N A L O U T P U T I . F .
I S O P P O S I T E O F
N O R M A L
S O U R C E L O C K
P O L A R I T Y
S E L E C T < R E V E R S E >
S O U R C E L O C K
P O L A R I T Y I F :
REVERSE
N O R M A L P O L A R I T Y
I S D E F I N E D B Y T H E
S O U R C E 1 A N D 2
E Q U A T I O N S
I F S O U R C E 1 F R E Q
I S G R E A T E R T H A N
S O U R C E 2 F R E Q ,
T H E T H E I . F .
I S A S S U M E D T O B E
P O S I T I V E P O L A R I T Y
A N D V I C E V E R S A
A
A
B R O A D B A N D
D E F I N I T I O N
* *
* *
A p p e a r s i f O p t i o n 1 2
i n s t a l l e d
N O T E 2 : G O E S T O M E N U B B 2 I F
O P T I O N 1 2 I S I N S T A L L E D ( S E E C H A P T E R 1 5 )
S e e N O T E 2
M E A S U R E M E N T O N ( O F F )
D E L A Y
X X . X X X s e c
T R I G G E R S
Figure 4-12. Enhancement Key-Group (Options Menu Key)
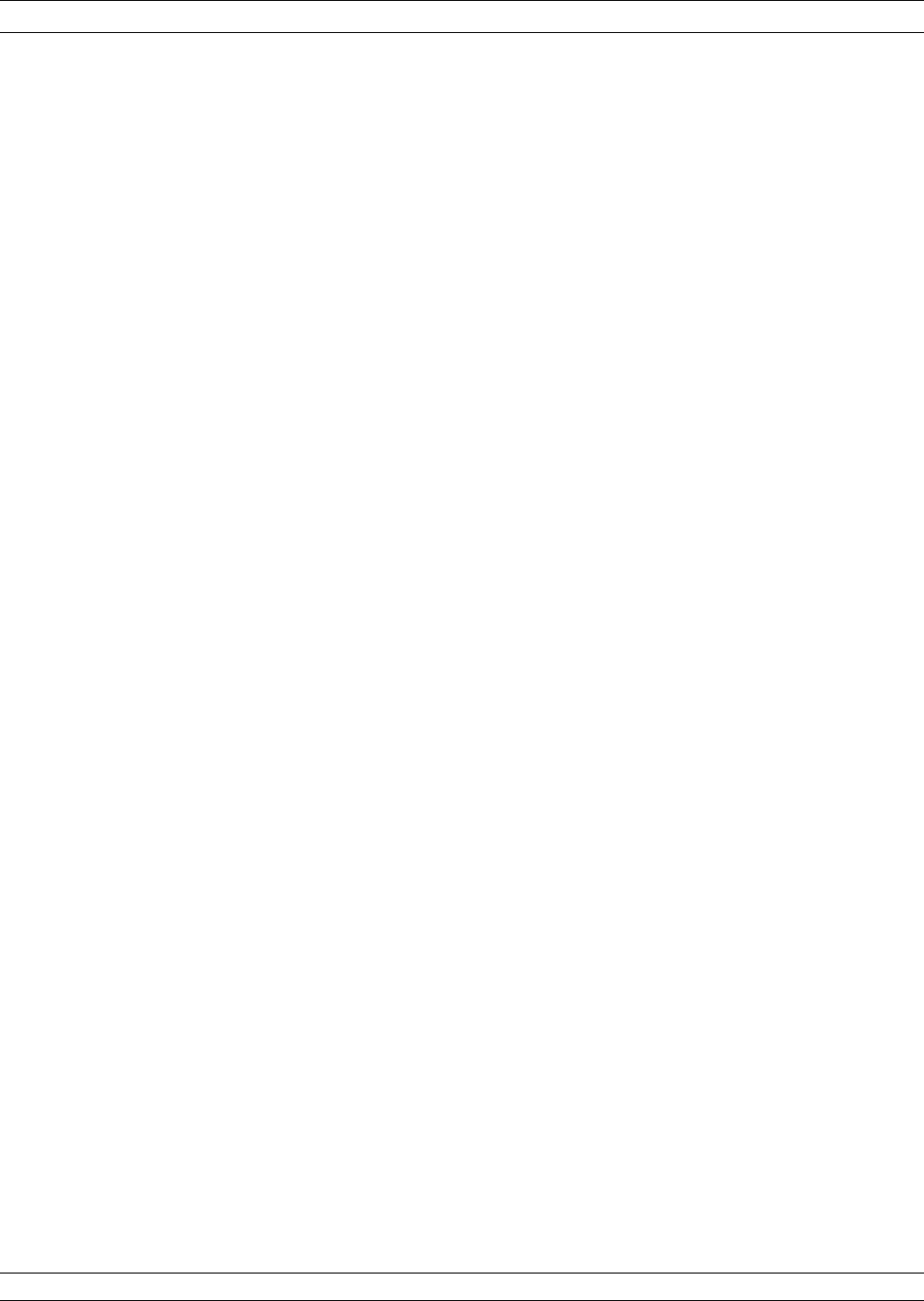
4-9 HARD COPY KEY-GROUP The individual keys within the Hard Copy key-group are described be-
low. Full descriptions for menus can be found in the alphabetical list-
ing (Appendix A) under the menu’s call letters (PM1, PM2, PM3, etc.)
Menu Key: Pressing this key brings up menu PM1. This menu allows
you to define what will happen every time you press the Start Print
key. A menu flow diagram is shown in Figure 4-13.
Start Print Key: Pressing this key starts outputting the measured
data as defined by the setup defined by the selected MENU key.
Stop Print Key: Pressing this key can result in any of the following
actions if the printer is selected:
qIf the printer is active, the key aborts the printing and sends a
form feed command to the printer. Aborting the printing clears
the print buffer
qIf the printer is not active and another form of output is active,
pressing this key aborts printing, but does not send a form feed
to the printer
Plotting Functions: The 37XXXC can plot an image of either the en-
tire screen or subsets of it. Plots can be either full size or they can be
quarter size and located in any of the four quadrants. You can select
different pens for plotting different parts of the screen. You cannot,
however, plot tabular data.
HARD COPY KEY-GROUP FRONT PANEL OPERATION
4-32 37XXXC OM
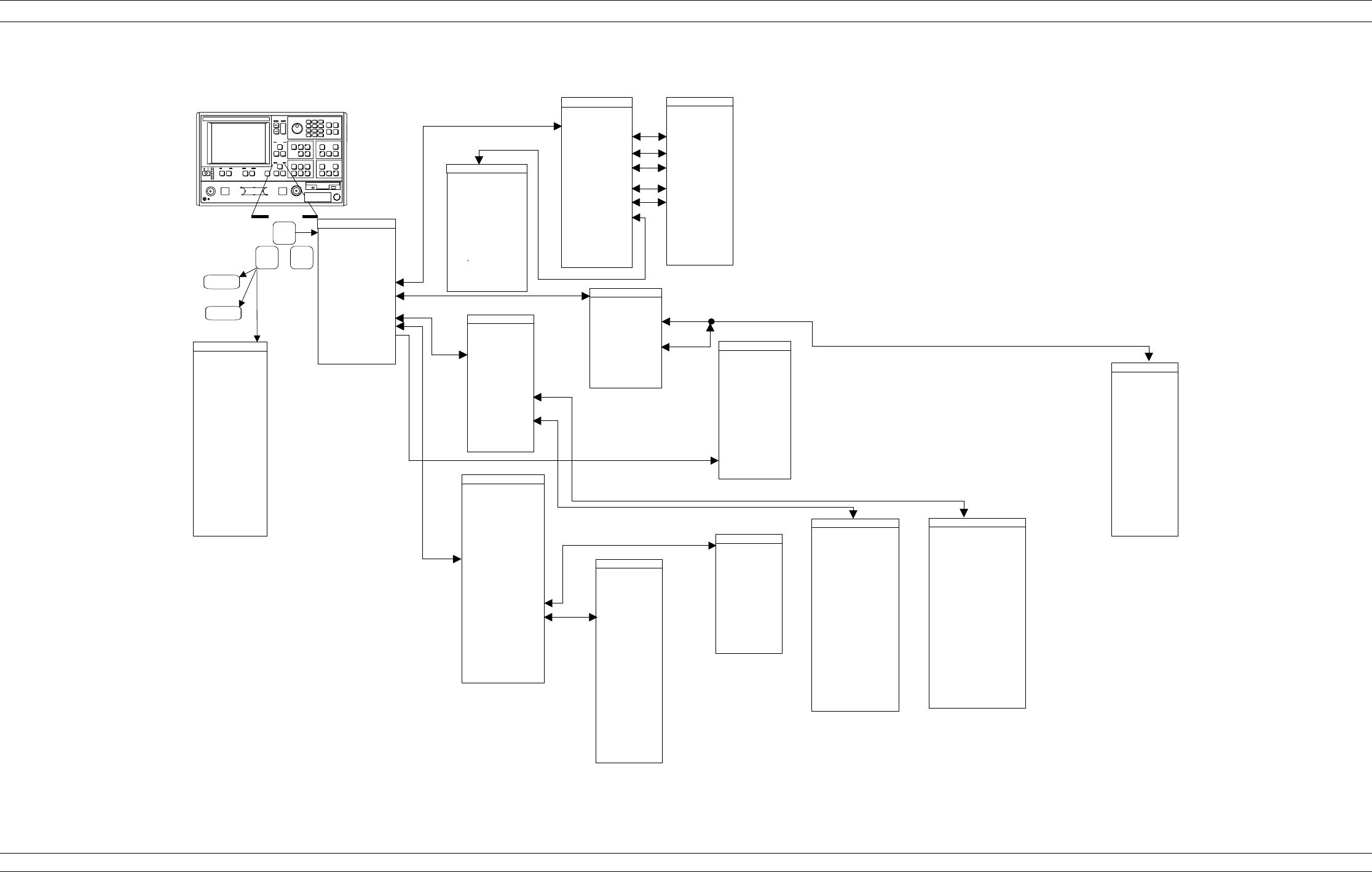
37XXXC OM 4-33
FRONT PANEL OPERATION HARD COPY KEY-GROUP
M E N U P L 3
S E L E C T
P E N C O L O R S
D A T A P E N
n
D A T A T R A C E
O V E R L A Y P E N
n
G R A T I C U L E P E N
n
M A R K E R S A N D
L I M I T S P E N
n
H E A D E R P E N
n
P E N S P E E D
1 0 0 P E R C E N T
O F M A X I M U M
P R E V I O U S M E N U
P R E S S < E N T E R >
T O S E L E C T
M E N U P M 2
D A T A O U T P U T
H E A D E R S
M O D E L O N ( O F F )
XXXXXXXXXXXX
D E V I C E I D O N ( O F F )
XXXXXXXXXXXX
D A T E O N ( O F F )
O P E R A T O R O N ( O F F )
XXXXXXXXXXXXX
P R E S S < E N T E R >
T O T U R N O N / O F F
O R
P R E S S < 1 >
T O C H A N G E
C O M M E N T O N ( O F F )
M E N U P L 1
F U L L P L O T
O B J E C T S T O P L O T
P L O T F O R M A T
P L O T S I Z E
P E N C O L O R S
P L O T O P T I O N S
P R E S S < E N T E R >
T O S E L E C T
O R T U R N O N / O F F
P L O T O R I E N T A T I O N
P O R T R A I T
L A N D S C A P E
M E N U P L 2
F U L L S I Z E
U P P E R L E F T
U P P E R R I G H T
L O W E R L E F T
L O W E R R I G H T
- Q U A R T E R
S I Z E P L O T S -
P R E S S < E N T E R >
T O S E L E C T
P L O T S I Z E
S E L E C T L A B E L
- - - - - - - - -
T U R N K N O B
T O I N D I C A T E
C H A R A C T E R O R
F U N C T I O N
P R E S S < E N T E R >
T O S E L E C T
N U M B E R S M A Y
A L S O B E
S E L E C T E D
U S I N G K E Y P A D
M E N U G P 5
A B C D E F G H I J K L M
N O P Q R S T U V W X Y Z
0 1 2 3 4 5 6 7 8 9 ( ) -
! # $ % & @ ^ _ ' { } ~
B K S P C L R D O N E
P R E S S < E N T E R >
T O S E L E C T
M E N U P M 5
P R I N T O P T I O N S
P R I N T E R T Y P E
T H I N K J E T
D E S K J E T
E P S O N
G R A P H I C A L D A T A
T A B U L A R D A T A
F O R M A T O F
P R I N T E R O U T P U T
M E N U P M 1
P R I N T E R
P L O T T E R
O U T P U T O P T I O N S
P L O T O P T I O N S
O U T P U T D E V I C E
S E T U P & O P E R A T I O N S
D I S K O P E R A T I O N S
P R E S S < E N T E R >
T O S E L E C T
P R I N T O P T I O N S
M E N U D S K 2
F I L E 1
F I L E 2
P R E V I O U S M E N U
P R E S S < E N T E R >
T O S E L E C T
S E L E C T F I L E
T O R E A D
P R E S S < 1 > F O R
P R E V I O U S P A G E
P R E S S < 2 > F O R
N E X T P A G E
F I L E 3
F I L E 4
F I L E 5
F I L E 6
F I L E 7
F I L E 8
H a r d C o p y
M e n u
S t a r t
P r i n t
S t o p
P r i n t
M E N U P M 3 A
G R A P H I C A L P R I N T E R
O U T P U T F O R M A T
P R E S S < E N T E R >
T O S E L E C T
O R T U R N O N / O F F
H E A D E R O N ( O F F )
S C R E E N A R E A
T O O U T P U T
F U L L S C R E E N
G R A P H O N L Y
P R E V I O U S M E N U
M E N U P M 3
T A B U L A R P R I N T O U T
O U T P U T F O R M A T
P R E S S < E N T E R >
T O S E L E C T
O R T U R N O N / O F F
M A R K E R D A T A O N ( O F F )
S W E E P D A T A ( O N ) ( O F F )
P R I N T D E N S I T Y
H E A D E R A N D O N ( O F F )
PAGE BREAKS
X X X P R I N T P T ( S )
O U T P U T P R I N T S
1 P O I N T E V E R Y
X X X P O I N T ( S )
T U R N K N O B T O
C H A N G E N U M B E R
O F P O I N T S
P R E V I O U S M E N U
H E A D E R O N ( O F F )
M E N U O N ( O F F )
L I M I T S O N ( O F F )
G R A T I C U L E O N ( O F F )
D A T A T R A C E S O N ( O F F )
A N D M A R K E R S
S E T U P L O G O
M E N U P M 4
H A R D C O P Y
D I S K O P E R A T I O N S
T A B U L A R D A T A
F R O M H A R D D I S K
T O P R I N T E R
P R E S S < E N T E R >
T O S E L E C T
T A B U L A R D A T A
F R O M F L O P P Y D I S K
T O P R I N T E R
P R E S S < E N T E R >
T O T U R N O N / O F F
L O G O S E T U P
L O G O O N ( O F F )
L O G O T Y P E
S T A N D A R D
M E N U P M 2 A
U S E R L O G O
I N S T A L L U S E R L O G O
F R O M F L O P P Y D I S K
F O R P R I N T E R
F O R P L O T T E R
P R E V I O U S M E N U
D I S K F I L E
S E T U P H E A D E R S
D I S K F I L E O P T I O N S
M E N U P M 4 A
D I S K F I L E O P T I O N S
P R E S S < E N T E R >
T O S E L E C T
D E S T I N A T I O N
H A R D D I S K
F L O P P Y D I S K
F O R M A T
T E X T
S 2 P
T A B U L A R D A T A
B I T M A P
H P G L
U S E < S T A R T P R I N T >
T O C A P T U R E D A T A
P r i n t
P l o t
P R E S S < E N T E R >
T O S E L E C T
M E N U D S K 3
S E L E C T F I L E
T O O V E R W R I T E
T R U E C O L O R
C O L O R O N
W H I T E B A C K G R O U N D
B I T M A P F I L E
O U T P U T O P T I O N S
B L A C K O N
W H I T E B A C K G R O U N D
O R
O R
P R E S S < 1 > F O R
P R E V I O U S P A G E
P R E S S < 2 > F O R
N E X T P A G E
C R E A T E N E W F I L E
F I L E 1
F I L E 2
F I L E 3
F I L E 4
F I L E 5
F I L E 6
F I L E 7
F I L E 8
7 8 9
456
123
0.-
Figure 4-13. Hard Copy Key-Group Menus
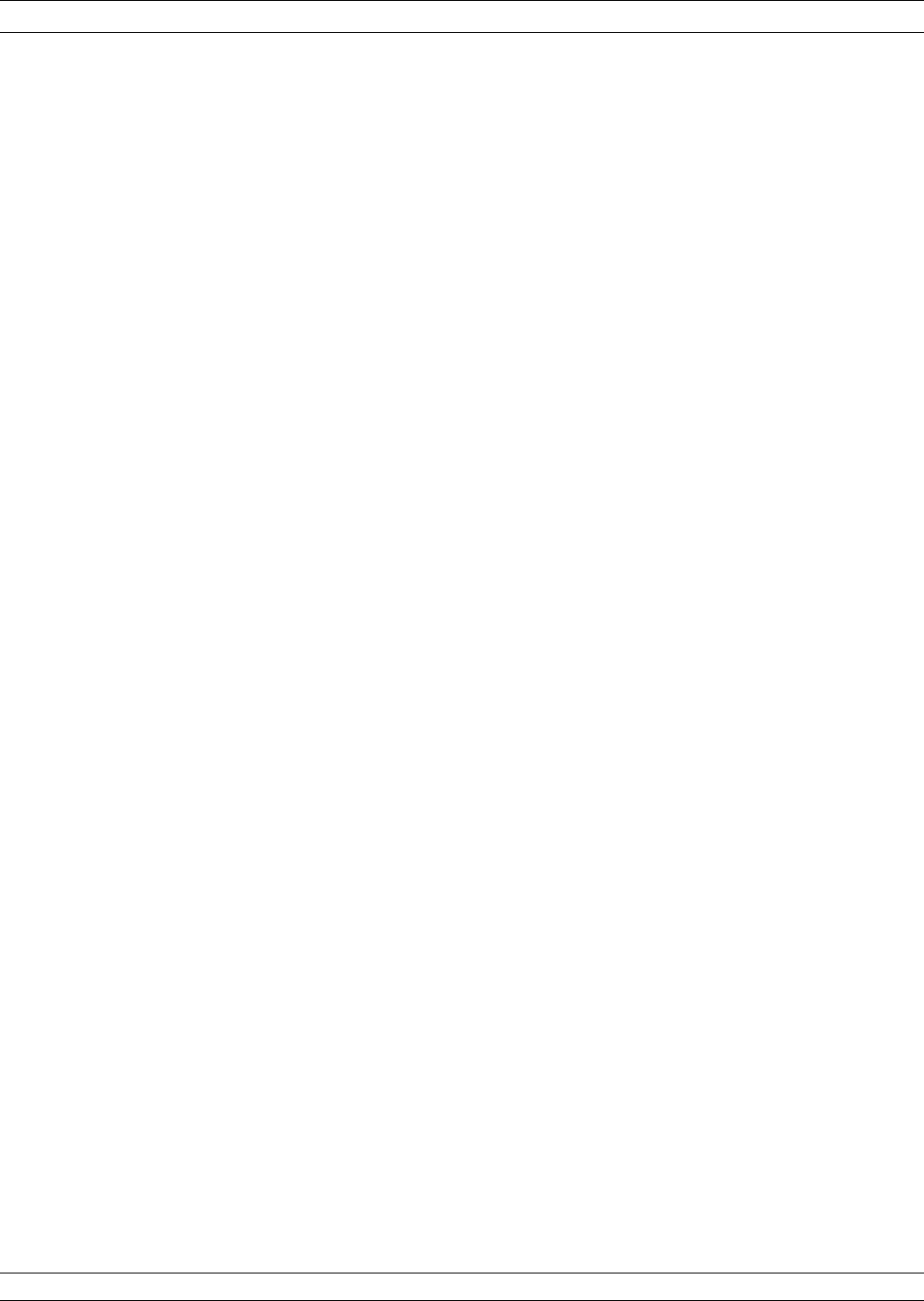
4-10 SYSTEM STATE
KEY-GROUP The individual keys within the System State key-group are described
below. The menu flow for the Utility Menu key is shown in Figure 4-14
on page 4-36. Full descriptions for menus can be found in the
alphabetical listing (Appendix 1) under the menu’s call letters (U1, U2,
U3, etc.)
Default Program Key: Pressing this key brings up the default menu.
If pressed again, it recalls the factory selected default values for the
control panel controls. The values are defined in Table 4-2 on the
following page.
Pressing this key then the 1key resets front panel key states and in-
ternal memories 1 through 4.
Pressing this key then the 0key resets front panel key states, internal
memories 1 through 10, and certain hardware settings.
NOTE
Use of this key will destroy control panel and calibration
setup data, unless they have been saved to disk.
Utility Menu Key: Pressing this key calls menu U1. This menu ac-
cesses subordinate menus to perform system, disk, and system utili-
ties. The only functions performed directly from the U1 Menu are
“Blank Frequency Information.” and “Data Drawing.”
SYSTEM STATE KEY-GROUP FRONT PANEL OPERATION
4-34 37XXXC OM
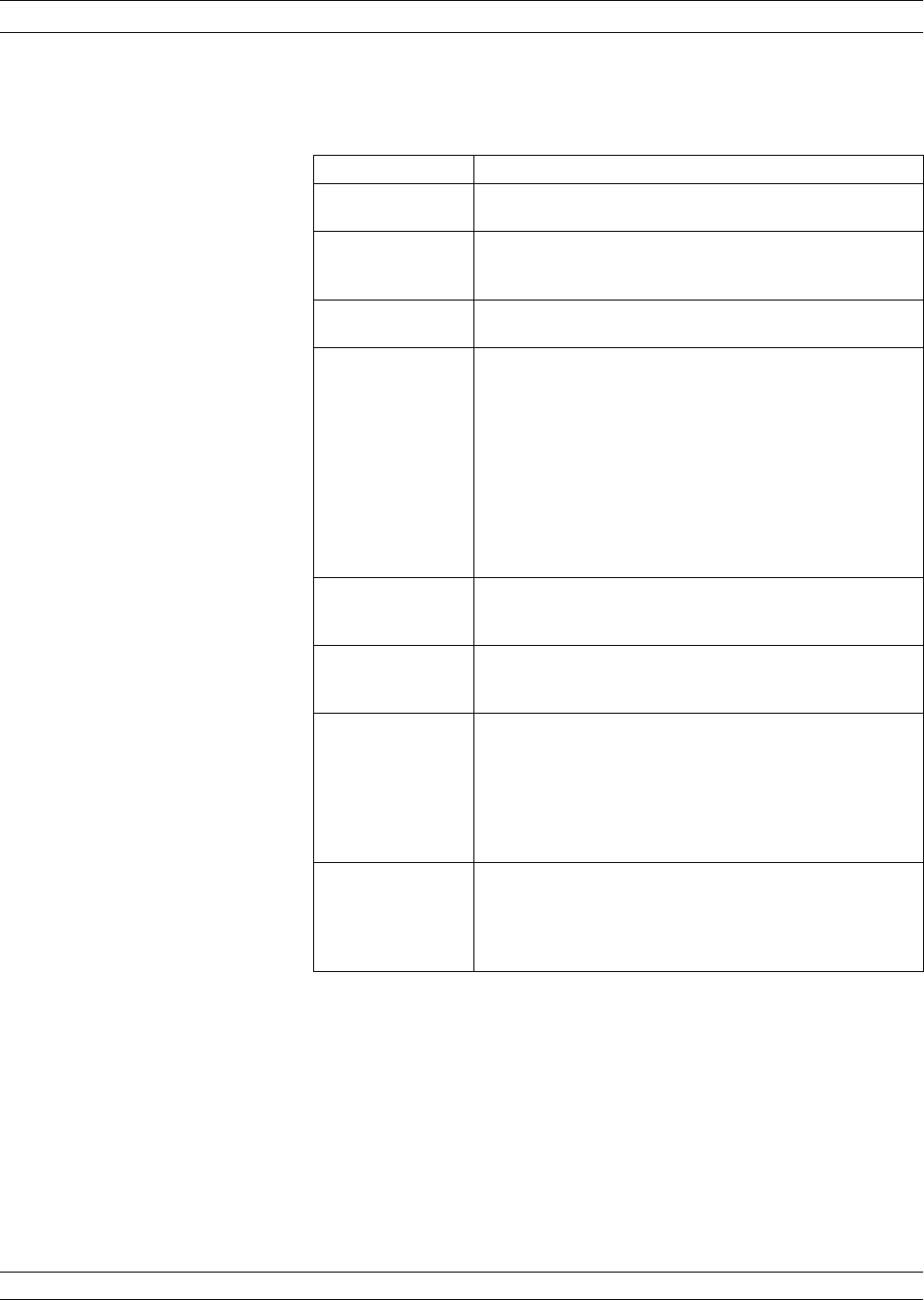
37XXXC OM 4-35
FRONT PANEL OPERATION SYSTEM STATE KEY-GROUP
Function Default Setting
Instrument
State Measurement Setup Menu Displayed
Measurement Maximum sweep range of source and test set
Source Power: Model Dependent
Resolution: Normal (401 points)
Channel Quad (four-channel) display
Channel 1 active
Display Channel 1: S11, 1:1 Smith Chart
Channel 2: S12, Log Magnitude and Phase
Channel 3: S21, Log Magnitude and Phase
Channel 4: S22, 1:1 Smith Chart
Scale: 10 dB/Division or 90/Division
Offset: 0.000dB or 0.00 degree
Reference Position: Midscale
Electrical Delay: 0.00 seconds
Dielectric: Air (1.000649)
Normalization: Off
Normalization Sets: Erased
Enhancement Video IF Bandwidth: Normal
Averaging: Off
Smoothing: Off
Calibration Correction: Off and Calibration erased
Connector: K Connector
Load: Broadband
Markers/Limits Markers On/Off: All off
Markers Enabled/Disabled: All enabled
Marker Frequency: All set to the start-sweep frequency
(or start -time distance)
DReference: Off
Limits: All set to reference position value (all off all en-
abled)
System State GPIB Addresses: Unchanged
Frequency Blanking : Disengaged,
Error(s): GPIB SRQ errors are cleared, Service Log
errors are not cleared
Measurement: Restarted
Table 4-2. Default Settings
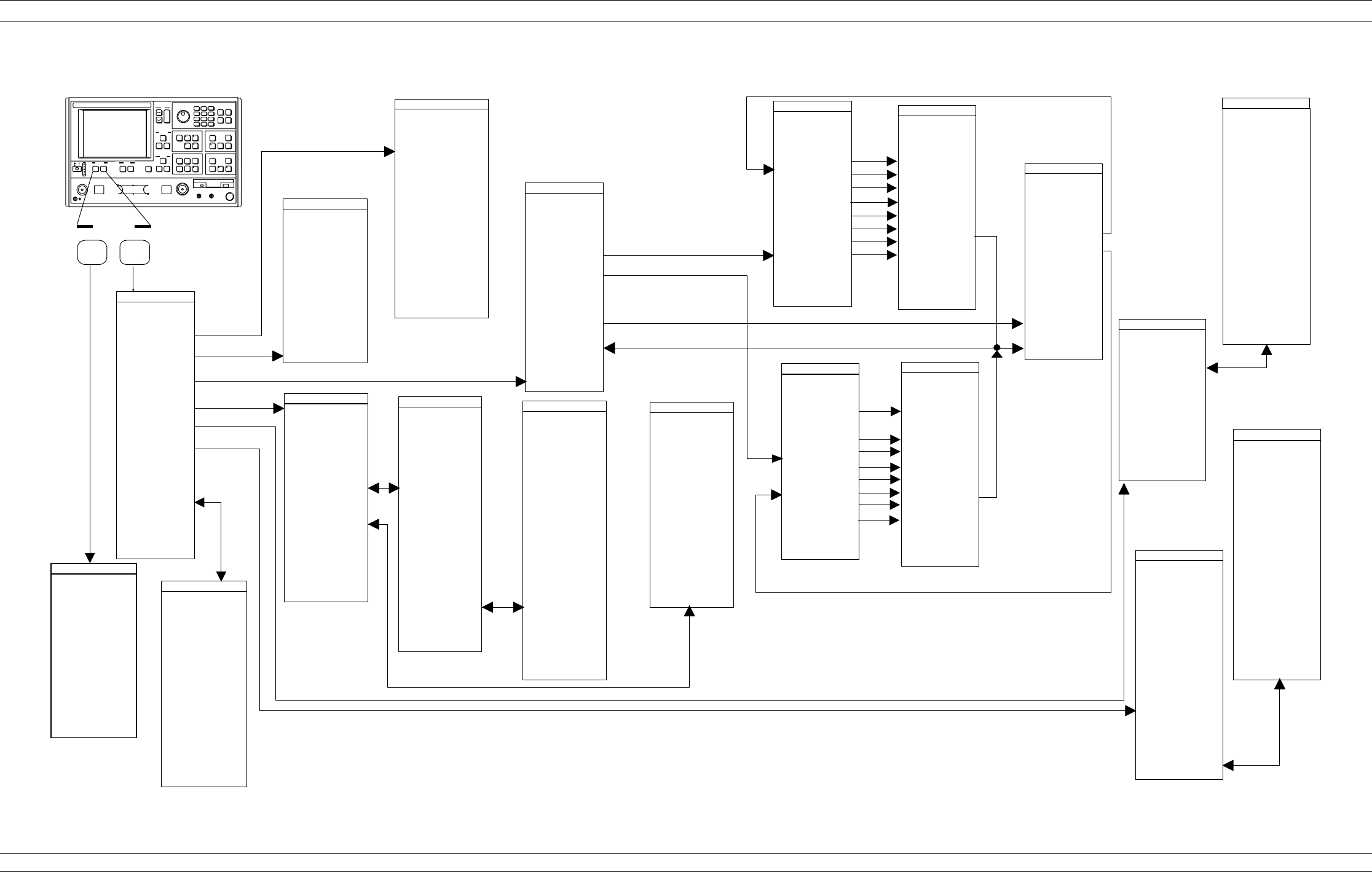
4-36 37XXXC OM
SYSTEM STATE KEY-GROUP FRONT PANEL OPERATION
S y s t e m S t a t e
D e f a u l t
P r o g r a m
U t i l i t y
M e n u
S E L E C T U T I L I T Y
F U N C T I O N O P T I O N S
G E N E R A L
D I S K U T I L I T I E S
C A L C O M P O N E N T
U T I L I T I E S
G P I B A D D R E S S E S
D I S P L A Y
I N S T R U M E N T
S T A T E P A R A M S
B L A N K I N G
F R E Q U E N C Y
I N F O R M A T I O N
C O L O R
C O N F I G U R A T I O N
P R E S S < E N T E R >
T O S E L E C T
O R T U R N O N / O F F
D A T A O N ( O F F )
D R A W I N G
M E N U U 4
D I S P L A Y I N S T A L L E D
O P E N & S H O R T
T E S T P O R T
C O N N E C T O R I N F O
P R E S S < E N T E R >
T O S E L E C T
K - C O N N ( M )
K - C O N N ( F )
V - C O N N ( M )
V - C O N N ( F )
W 1 - C O N N ( M )
W 1 - C O N N ( F )
S M A ( M )
S M A ( F )
G P C - 3 . 5 ( M )
G P C - 3 . 5 ( F )
G P C - 7
N E X T C O N N E C T O R
M O R E C O N N E C T O R S
P R E V I O U S M E N U
C A L I B R A T I O N
C O M P O N E N T
U T I L I T I E S
D I S P L A Y C O A X I A L
O P E N & S H O R T
I N F O R M A T I O N
D I S P L A Y C O A X I A L
O F F S E T S H O R T
I N F O R M A T I O N
D I S P L A Y
W A V E G U I D E
I N F O R M A T I O N
P R E S S < E N T E R >
T O S E L E C T
I N S T A L L K I T
I N F O R M A T I O N
F R O M F L O P P Y D I S K
M E N U U 3
M E N U U 2
D I S P L A Y I N S T R U M E N T
S T A T E P A R A M E T E R S
SYSTEM
C A L I B R A T I O N
M O R E C A L I B R A T I O N
P R E S S < E N T E R >
T O S E L E C T
O P E R A T I N G
C H A N N E L S 1 & 2
C H A N N E L S 3 & 4
N E X T P A R A M P A G E
M E N U D F L T
W A R N I N G
D E F A U L T
P R O G R A M
S E L E C T E D
C O N T I N U I N G
W I L L E R A S E
CURRENT
S E T U P A N D
C A L I B R A T I O N
PRESS
< D E F A U L T P R O G R A M >
T O C O N F I R M
P R E S S < C L E A R >
T O A B O R T
M E N U D S K 1 - H D
H A R D D I S K
U T I L I T I E S
D I S P L A Y
D I R E C T O R Y
D E L E T E F I L E S
C O P Y F I L E S
T 0 F L O P P Y D I S K
P R E S S < E N T E R >
T O S E L E C T
F O R M A T
H A R D D I S K
F L O P P Y D I S K
U T I L I T I E S
C O M M A N D L I N E
M E N U D S K 1 - F D
F L O P P Y D I S K
U T I L I T I E S
D I S P L A Y
D I R E C T O R Y
D E L E T E F I L E S
C O P Y F I L E S
T 0 H A R D D I S K
P R E S S < E N T E R >
T O S E L E C T
F O R M A T
F L O P P Y D I S K
H A R D D I S K
U T I L I T I E S
C O M M A N D L I N E
S E T D A T E / T I M E
M E N U U 6
S E T D A T E / T I M E
M O N T H
X X
D A Y
X X
YEAR
X X X X
H O U R
X X
M I N U T E
X X
D O N E ,
( S E T D A T E / T I M E )
P R E V I O U S M E N U
( D A T E / T I M E
N O T S E T )
P R E S S < E N T E R >
T O S E L E C T
G P I B A D D R E S S E S
I E E E 4 8 8 . 2
G P I B I N T E R F A C E
A D D R E S S
6
D E D I C A T E D
G P I B I N T E R F A C E
P L O T T E R
8
P O W E R M E T E R
2 3
F R E Q U E N C Y C O U N T E R
7
M E N U G P 7
E X T E R N A L S O U R C E 1
4
E X T E R N A L S O U R C E 2
5
M E N U D S K 7
F I L E 1
F I L E 2
P R E V I O U S M E N U
P R E S S < E N T E R >
T O S E L E C T
S E L E C T F I L E
T O D E L E T E
P R E S S < 1 > F O R
P R E V I O U S P A G E
P R E S S < 2 > F O R
N E X T P A G E
F I L E 3
F I L E 4
F I L E 5
F I L E 6
F I L E 7
F I L E 8
M E N U D S K 6
F R O N T P A N E L
S E T U P A N D
C A L D A T A
P R E V I O U S M E N U
P R E S S < E N T E R >
T O S E L E C T
T Y P E O F F I L E S
T O D E L E T E
T R A C E D A T A
T A B U L A R D A T A
T E X T D A T A
S 2 P D A T A
B I T M A P D A T A
H P G L D A T A
A L L T Y P E S ( * . * )
M E N U D S K 8
F R O N T P A N E L
S E T U P A N D
C A L D A T A
P R E V I O U S M E N U
P R E S S < E N T E R >
T O S E L E C T
T Y P E O F F I L E S
T O C O P Y
T R A C E D A T A
T A B U L A R D A T A
M E N U D S K 9
F I L E 1
F I L E 2
P R E V I O U S M E N U
P R E S S < E N T E R >
T O S E L E C T
S E L E C T F I L E
T O C O P Y
P R E S S < 1 > F O R
P R E V I O U S P A G E
P R E S S < 2 > F O R
N E X T P A G E
F I L E 3
F I L E 4
F I L E 5
F I L E 6
F I L E 7
F I L E 8
T E X T D A T A
S 2 P D A T A
B I T M A P D A T A
H P G L D A T A
A L L T Y P E S ( * . * )
M E N U U 1
789
456
123
0.-
A U T O C A L
U T I L I T I E S
M E N U A C A L _ U T I L S
A U T O C A L
C H A R A C T E R I Z A T I O N
P R E S S < E N T E R >
T O S E L E C T
A U T O C A L
U T I L I T I E S
SAVE
T O H A R D D I S K
SAVE
T O F L O P P Y D I S K
R E C A L L
F R O M H A R D D I S K
R E C A L L
F R O M F L O P P Y D I S K
M E N U A C A L _ C H A R
S W I T C H A V E R A G I N G
XXXX
P R E S S < E N T E R >
T O S E L E C T
O R S W I T C H
A U T O C A L
C H A R A C T E R I Z A T I O N
P O R T C O N F I G
L = 1 , R = 2 /
R = 1 , L - 2
N U M B E R O F A V G S
R E F L E C T I O N
XXXX
L O A D
XXXX
T H R U
XXXX
I S O L A T I O N
XXXX
S T A R T A U T O C A L
C H A R A C T E R I Z A T I O N
M E N U U 5
D A T A
XXXX
C O L O R S C H E M E S
C O L O R
C O N F I G U R A T I O N
O V E R L A Y D A T A
XXXX
M E M O R Y D A T A
XXXX
M A R K E R S & L I M I T S
XXXX
G R A T I C U L E
XXXX
A N N O T A T I O N &
M E N U T E X T
XXXX
M E N U H E A D E R S
( T I T L E S & I N F O )
X X X X
B A C K G R O U N D
X X X X
R E S E T C O L O R S
M E N U U 5 A
R E S E T C O L O R S
C O L O R S C H E M E S
N E W C O L O R S
C L A S S I C C O L O R S
I N V E R S E C O L O R S
B R I L L I A N T C O L O R S
S O F T C O L O R S
T O C U S T O M I Z E
S E L E C T A C O L O R
S C H E M E A N D / O R
M O D I F Y T H E C O L O R
C O N F I G , T H E N
S T O R E A S R E S E T
S T O R E C O L O R
C O N F I G A S R E S E T
( D E F A U L T ) C O L O R S
P R E S S < E N T E R >
T O S E L E C T
P R E V I O U S M E N U
M E N U U 4 B
T O S E L E C T
P R E S S < E N T E R >
W 1 - C O N N ( M )
W 1 - C O N N ( F )
S P E C I A L A ( M )
S P E C I A L A ( F )
S P E C I A L B ( M )
S P E C I A L B ( F )
S P E C I A L C ( M )
S P E C I A L C ( F )
N E X T C O N N E C T O R
P R E V I O U S M E N U
M E N U U 4 A
T O S E L E C T
P R E S S < E N T E R >
T Y P E N ( M )
T Y P E N ( F )
T Y P E N ( M ) 7 5
9
T Y P E N ( F ) 7 5
9
7 / 1 6 ( M )
7 / 1 6 ( F )
T N C ( M )
T N C ( F )
2 . 4 m m ( M )
2 . 4 m m ( F )
S P E C I A L ( M )
S P E C I A L ( F )
N E X T C O N N E C T O R
M O R E C O N N E C T O R
P R E V I O U S M E N U
D I S P L A Y I N S T A L L E D
O P E N & S H O R T
T E S T P O R T
C O N N E C T O R I N F O
D I S P L A Y I N S T A L L E D
O P E N & S H O R T
T E S T P O R T
C O N N E C T O R I N F O
Figure 4-14. System State Key-Group Menus
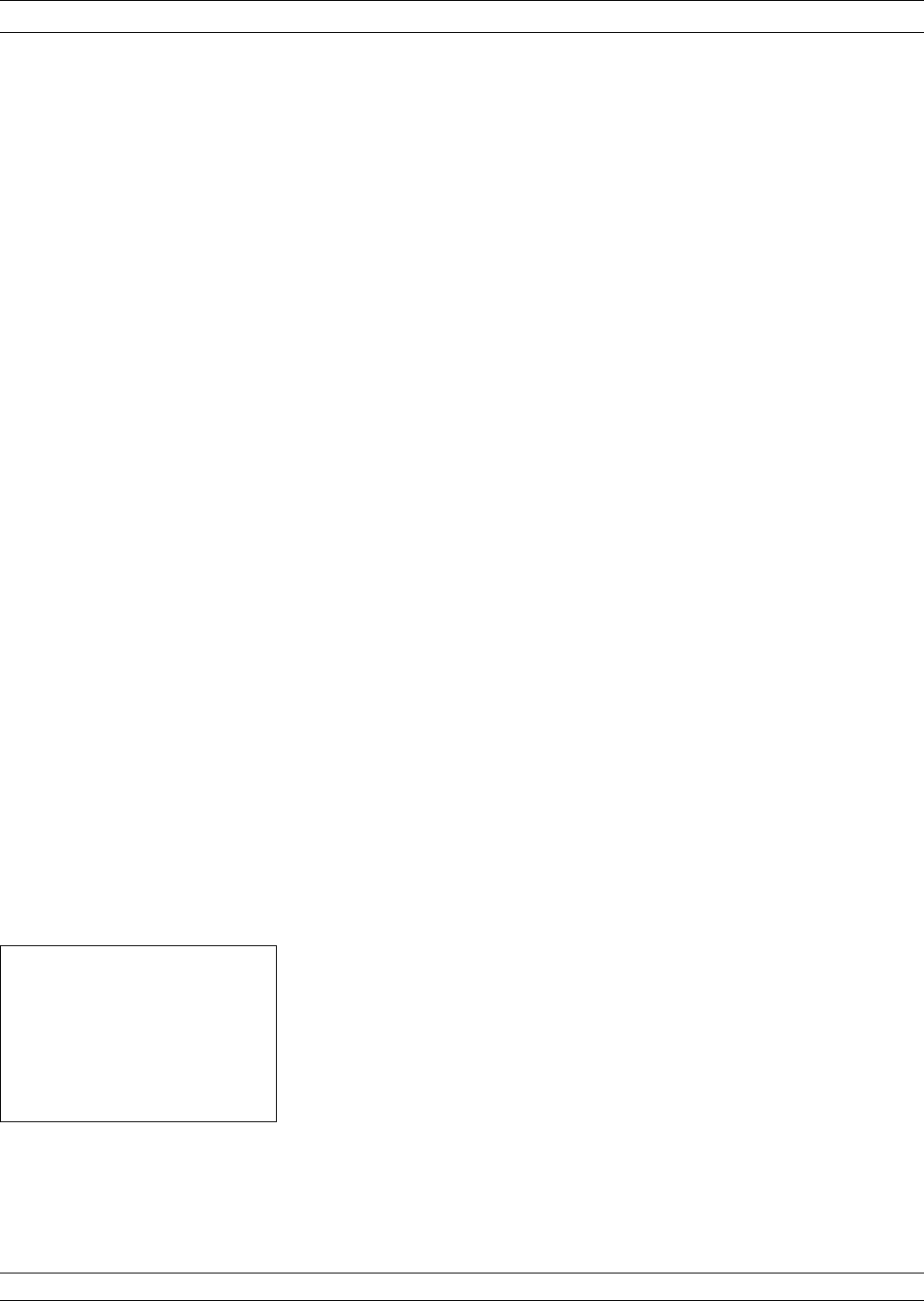
4-11 MARKERS/LIMITS
KEY-GROUP The individual keys within the Markers/Limits key-group are de-
scribed below. The menu flow for the Marker Menu key is shown in
Figure 4-15 on the following page. Full descriptions for these menus
can be found in the alphabetical listing (Appendix A) under the menu’s
call letters (M1, M2, M3, etc.)
Marker Menu Key: Pressing the Marker Menu key calls Menu M1. This
menu lets you toggle markers on and off and set marker frequencies,
times, or distances.
Readout Marker Key: Pressing this key calls different menus, depend-
ing upon front panel key selections, as described below:
qIt calls menu M1 if there are no markers available within the se-
lected frequency range
qIt calls menu M3 if no Delta ref marker has been selected
qIt calls menu M4 if the DReference mode is off and the selected
marker is in the current sweep range (or time/distance)
qIt calls menu M5 if the DReference mode and marker are both on
and the DReference marker is in the selected sweep range (or
time/distance)
qIt calls menu M6 if ACTIVE MARKER ON ALL CHANNELS has
been previously selected in menu M9
qIt calls menu M7 if SEARCH has been previously selected in
menu M9
qIt calls menu M8 if FILTER PARAMETER has been previously
selected in menu M9
Limits Key: Pressing this key calls the appropriate Limit menu based
on the graph type selected using the Graph Type key and menu.
Marker Readout Functions: This menu choice, which appears on sev-
eral marker menus, provides for several filter-related measurements.
It also allows for performing a marker-value search and for reading
the active marker value on all displayed channels.
Limit Frequency Readout Function: The 37XXXC has a
Limit-Frequency Readout function. This function allows frequency val-
ues to be read at a specified level (such as the 3 dB point) on the data
trace. This function is available for all rectilinear graph-types.
The graph-type and their menu call letters are listed below:
qLog Magnitude, Menu LF1
qPhase, Menu LF2
qGroup Delay, Menu LF3
qLinear Magnitude, Menu LF4
qSWR, Menu LF5
qReal, Menu LF6
qImaginary, Menu LF7
qPower Out, Menu LF8
37XXXC OM 4-37
FRONT PANEL OPERATION MARKERS/LIMITS KEY-GROUP
NOTE
Full menu descriptions can
be found in the alphabetical
listing (Appendix A) under the
menu call letters (LF1, LF2,
LF3, etc.)
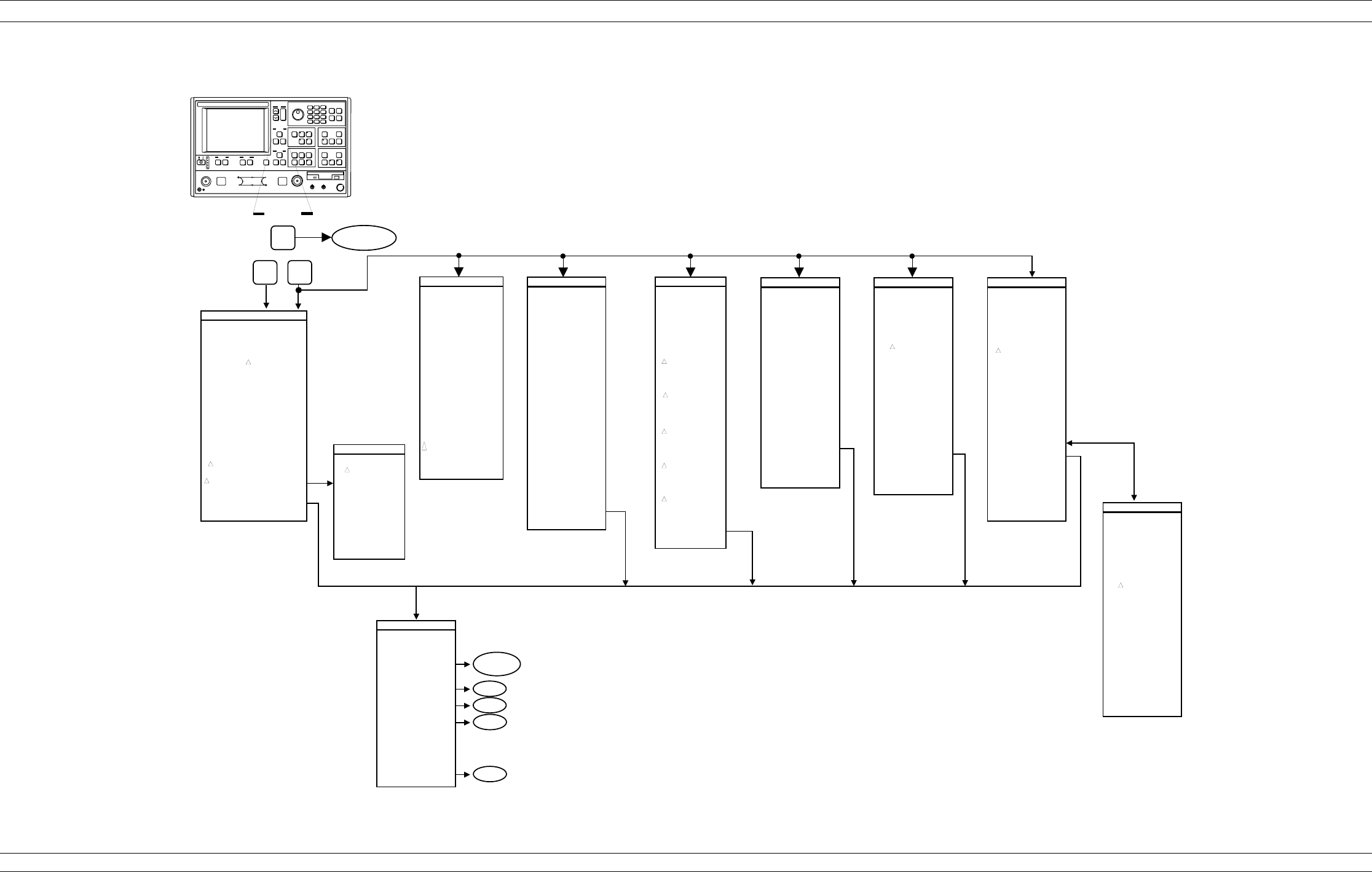
4-38 37XXXC OM
MARKERS/LIMITS KEY-GROUP FRONT PANEL OPERATION
N O T E 2 N O T E 3 N O T E 4
N O T E 2 : M e n u M 3 a p p e a r s w h e n M A R K E R S O N A C T I V E C H A N N E L h a s b e e n p r e v i o u s l y s e l e c t e d i n M e n u M 9 a n d
( 1 ) I f t h e D e l t a R e f e r e n c e m o d e i s o f f a n d t h e r e i s n o s e l e c t e d m a r k e r o r i f t h e s e l e c t e d m a r k e r i s n o t w i t h i n t h e s w e e p r a n g e .
( 2 ) I f t h e D e l t a R e f e r e n c e m o d e i s o n a n d t h e D e l t a R e f e r e n c e m a r k e r i s n o t w i t h i n t h e s w e e p r a n g e o r i f n o D e l t a R e f e r e n c e m a r k e r i s s e l e c t e d .
N O T E 3 : M e n u M 4 a p p e a r s w h e n M A R K E R S O N A C T I V E C H A N N E L h a s b e e n p r e v i o u s l y s e l e c t e d i n M e n u M 9
a n d i f t h e D e l t a R e f e r e n c e m o d e i s o f f a n d t h e s e l e c t e d m a r k e r i s w i t h i n t h e c u r r e n t s w e e p r a n g e .
N O T E 4 : M e n u M 5 a p p e a r s w h e n M A R K E R S O N A C T I V E C H A N N E L h a s b e e n p r e v i o u s l y s e l e c t e d i n M e n u M 9 a n d i f t h e D e l t a R e f e r e n c e m o d e
a n d m a r k e r a r e b o t h o n a n d t h e D e l t a R e f e r e n c e m a r k e r i s w i t h i n t h e s e l e c t e d s w e e p r a n g e .
S e e S h e e t 2
N O T E 1 : M e n u M 1 a p p e a r s i f n o m a r k e r s a r e a v a i l a b l e w i t h i n t h e s e l e c t e d f r e q u e n c y r a n g e .
M E N U M 2
M A R K E R 1
X X . X X X X X X G H z
M A R K E R 3
X X . X X X X X X G H z
M A R K E R 4
X X . X X X X X X G H z
P R E S S < E N T E R >
T O S E L E C T
S E L E C T
R E F M A R K E R
M E N U M 1
S E T M A R K E R S
M A R K E R 4 O N ( O F F )
M A R K E R 5 O N ( O F F )
R E F M O D E O N ( O F F )
M A R K E R 1 O N ( O F F )
XX.XXXXXX GHz
M A R K E R 2 R E F O N
X X . X X X X X X G H z
M A R K E R 3 O N ( O F F )
XX.XXXXXX GHz
M A R K E R 6 O N ( O F F )
XX.XXXXXX GHz
D I S P L A Y O N ( O F F )
M A R K E R S
S E L E C T
R E F M A R K E R
M a r k e r s / L i m i t s
L i m i t s
M a r k e r
M e n u
R e a d o u t
M a r k e r
M E N U M 5
M A R K E R 1
XX.XXXXXX G Hz
M A R K E R T O M A X
M A R K E R T O M I N
( 1 - 4 )
XX.XXXXX G Hz
XX.XXX dB
( X X X . X X D E G )
( 1 - 5 )
X X . X X X X X G H z
X X . X X X d B
( X X X . X X D E G )
( 1 - 6 )
X X . X X X X X G H z
X X . X X X d B
( X X X . X X D E G )
( 1 - 2 )
XX.XXXXX G Hz
XX.XXX dB
( X X X . X X ° )
M A R K E R R E A D O U T
F U N C T I O N S
( 1 - 3 )
XX.XXXXX G Hz
X X . X X X d B
( X X X . X X D E G )
M A R K E R R E A D O U T
F U N C T I O N S
N O T E 5 : M e n u M 6 a p p e a r s w h e n A C T I V E M A R K E R S O N A L L C H A N N E L S h a s b e e n p r e v i o u s l y s e l e c t e d i n M e n u M 9 .
N O T E 6 : M e n u M 7 a p p e a r s w h e n S E A R C H h a s b e e n p r e v i o u s l y s e l e c t e d i n M e n u M 9 .
N O T E 7 : M e n u M 8 a p p e a r s w h e n F I L T E R P A R A M E T E R S h a s b e e n p r e v i o u s l y s e l e c t e d i n M e n u M 9 .
N O T E 5 N O T E 6 N O T E 7
M E N U M 3 M E N U M 4
M A R K E R 1
XX.XXXXXX G Hz
XX.XXX dB
XXX.XXX DEG
M A R K E R T O M A X
M A R K E R T O M I N
2 X X . X X X X G H z
X X . X X X d B
X X . X X D E G
3 X X . X X X X G H z
X X . X X X d B
X X . X X D E G
4 X X . X X X X G H z
X X . X X X d B
X X . X X D E G
5 X X . X X X X G H z
X X . X X X d B
X X . X X D E G
6 X X . X X X X G H z
X X . X X X d B
X X . X X D E G
M A R K E R R E A D O U T
F U N C T I O N S
S E L E C T
R E A D O U T M A R K E R
M A R K E R 1
X X . X X X X X X G H z
M A R K E R 2
X X . X X X X X X G H z
M A R K E R 5
X X . X X X X X X G H z
R E F M O D E I S O N ( O F F )
P R E S S < E N T E R >
T O S E L E C T
M A R K E R 3
X X . X X X X X X G H z
M A R K E R 4
X X . X X X X X X G H z
M A R K E R 6
X X . X X X X X X G H z
M E N U M 9
M A R K E R R E A D O U T
F U N C T I O N S
M A R K E R S O N
A C T I V E C H A N N E L
A C T I V E M A R K E R S
O N A L L C H A N N E L S
S E A R C H
F I L T E R
P A R A M E T E R S
M A R K E R M O D E
C O N T I N U O U S
D I S C R E T E
S E T M A R K E R S
M e n u M 3 ,
M 4 , o r M 5
M e n u M 7
M e n u M 8
M e n u M 1
M E N U M 6
M A R K E R R E A D O U T
F U N C T I O N S
M A R K E R X
A L L D I S P L A Y E D
C H A N N E L S
C H 1 - S 1 1
XX.XXXXXXXX GHz
- X X X . X X X d B
- X X X . X X °
C H 2 - S 2 1
C H 3 - S 1 2
XX.XXXXXXXX GHz
- X X X . X X X d B
- X X X . X X °
C H 4 - S 2 2
M A R K E R T O M A X
M A R K E R T O M I N
M E N U M 7
T R A C K I N G O N ( O F F )
S E A R C H
V A L U E
- X X X . X X X d B
R E F E R E N C E
M A X I M U M V A L U E
V A L U E A T R E F E R E N C E
- X X X . X X X d B
X X . X X X X X X X X G H z
M A R K E R R E A D O U T
F U N C T I O N S
0 d B
R E F M A R K E R
P R E S S < E N T E R >
T O S E L E C T
M E N U M 8
Q
XXXX.XXX
S H A P E F A C T O R
X X X . X X X
F I L T E R P A R A M E T E R S
C E N T E R F R E Q
X X . X X X X X X X X G H z
L O S S A T R E F
- X X X . X X X d B
T R A C K I N G O N
F I L T E R S E T U P
M A R K E R R E A D O U T
F U N C T I O N S
B A N D W I D T H
- X X X . X X X d B
R E F M A R K E R
XX.XXXXXXXX GHz
P R E S S < E N T E R >
T O S E L E C T
O R T U R N O N / O F F
M E N U M 8 A
F I L T E R S E T U P
B A N D W I D T H
L O S S V A L U E
X X X . X X X D B
R E F E R E N C E
M A X I M U M V A L U E
0 D B
S H A P E F A C T O R
H I G H
XXX.XXX dB
L O W
XXX.XXX dB
R E A D O U T S
Q O F F
S H A P E O F F
F A C T O R
P R E V I O U S M E N U
R E F M A R K E R
M e n u M 6
S E A R C H L E F T
S E A R C H R I G H T
S E A R C H M R K R V A L U E S
C H 1 : - X X . X X X d B
C H 2 : - X X . X X X d B
C H 3 : - X X . X X X d B
C H 4 : - X X . X X X d B
N O T E 1
789
456
123
0.-
+ X X X . X X X X m m R E F
+ X X X . X X X d B O F F S E T
+ X X X . X X ° O F F S E T
+ X X X . X X X X m m R E F
+ X X X . X X X d B O F F S E T
+ X X X . X X ° O F F S E T
Figure 4-15. Markers Menus (1 of 3)
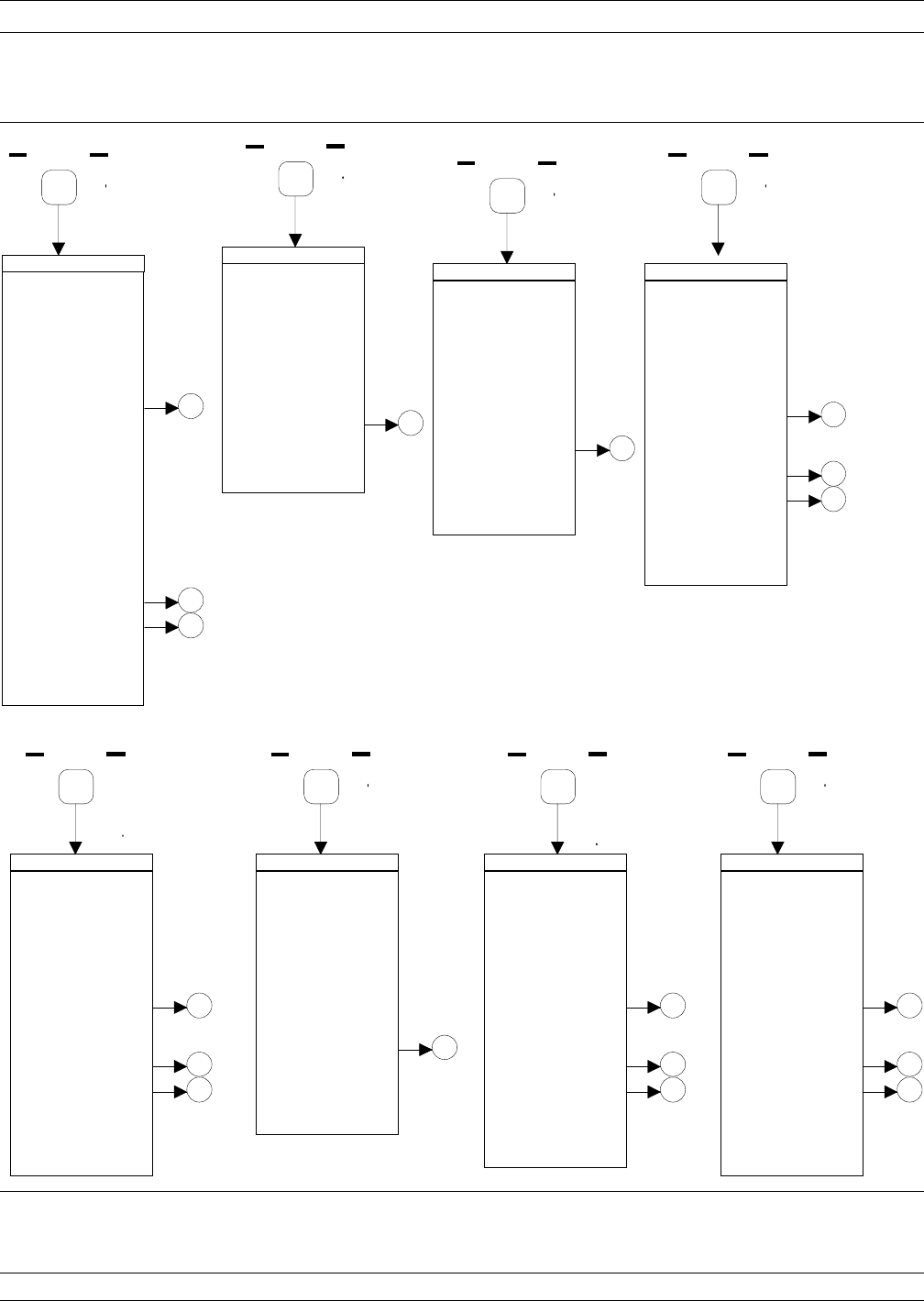
37XXXC OM 4-39
FRONT PANEL OPERATION MARKERS/LIMITS KEY-GROUP
Markers/Limits
Limits
MENU L3
PRESS <ENTER>
TO SELECT
OR TURN ON/OFF
SINGLE LIMITS
- SMITH CHART-
UPPER LIMIT ON(OFF)
XXX.XXX mV
LOWER LIMIT ON(OFF)
XXX.XXX mV
DISPLAY ON(OFF)
LIMITS
TEST LIMITS B
MENU L6
PRESS <ENTER>
TO SELECT
OR TURN ON/OFF
SINGLE LIMITS
- LOG POLAR -
UPPER LIMIT ON(OFF)
XXX.XXX dB
LOWER LIMIT ON(OFF)
XXX.XXX dB
DISPLAY ON(OFF)
LIMITS
TEST LIMITS
B
Markers/Limits
Limits
Markers/Limits
Limits
MENU L2
PRESS <ENTER>
TO SELECT
OR TURN ON/OFF
SINGLE LIMITS
- LINEAR POLAR-
UPPER LIMIT ON(OFF)
XXX.XXX mV
LOWER LIMIT ON(OFF)
XXX.XXX mV
DISPLAY ON(OFF)
LIMITS
TEST LIMITS
B
Markers/Limits
Limits
MENU L4
PRESS <ENTER>
TO SELECT
OR TURN ON/OFF
SINGLE LIMITS
- LOG MAG -
UPPER LIMIT ON(OFF)
XXX.XXX dB
LOWER LIMIT ON(OFF)
XXX.XXX dB
READOUT LIMIT
DISPLAY ON(OFF)
LIMITS
TEST LIMITS
SEGMENTED LIMITS
A
B
C
Markers/Limits
Limits
MENU L7
PRESS <ENTER>
TO SELECT
OR TURN ON/OFF
SINGLE LIMITS
- GROUP DELAY-
UPPER LIMIT ON(OFF)
XXX.XXX fs
LOWER LIMIT ON(OFF)
XXX.XXX fs
READOUT LIMIT
DISPLAY ON(OFF)
LIMITS
TEST LIMITS
SEGMENTED LIMITS
A
B
C
Markers/Limits
Limits
MENU L1
PRESS <ENTER>
TO SELECT
OR TURN ON/OFF
SINGLE LIMITS
- LOG MAG -
UPPER LIMIT ON(OFF)
XXX.XXX dB
LOWER LIMIT ON(OFF)
XXX.XXX dB
READOUT LIMIT
- PHASE -
UPPER LIMIT ON/OFF
XXX.XXX ˚
LOWER LIMIT ON(OFF)
XXX.XXX ˚
READOUT LIMIT
DISPLAY ON(OFF)
LIMITS
TEST LIMITS
SEGMENTED LIMITS
A
B
C
MENU L5
PRESS <ENTER>
TO SELECT
OR TURN ON/OFF
SINGLE LIMITS
- PHASE -
UPPER LIMIT ON/OFF
XXX.XXX ˚
LOWER LIMIT ON(OFF)
XXX.XXX ˚
READOUT LIMIT
DISPLAY ON(OFF)
LIMITS
TEST LIMITS
SEGMENTED LIMITS
A
B
C
Markers/Limits
Limits
Markers/Limits
Limits
MENU L8
PRESS <ENTER>
TO SELECT
OR TURN ON/OFF
SINGLE LIMITS
- LINEAR MAG -
UPPER LIMIT ON(OFF)
XXX.XXX pU
LOWER LIMIT ON(OFF)
XXX.XXX pU
READOUT LIMIT
DISPLAY ON(OFF)
LIMITS
TEST LIMITS
SEGMENTED LIMITS
A
B
C
Figure 4-15. Markers/Limits Key-Group Menus (2 of 3)
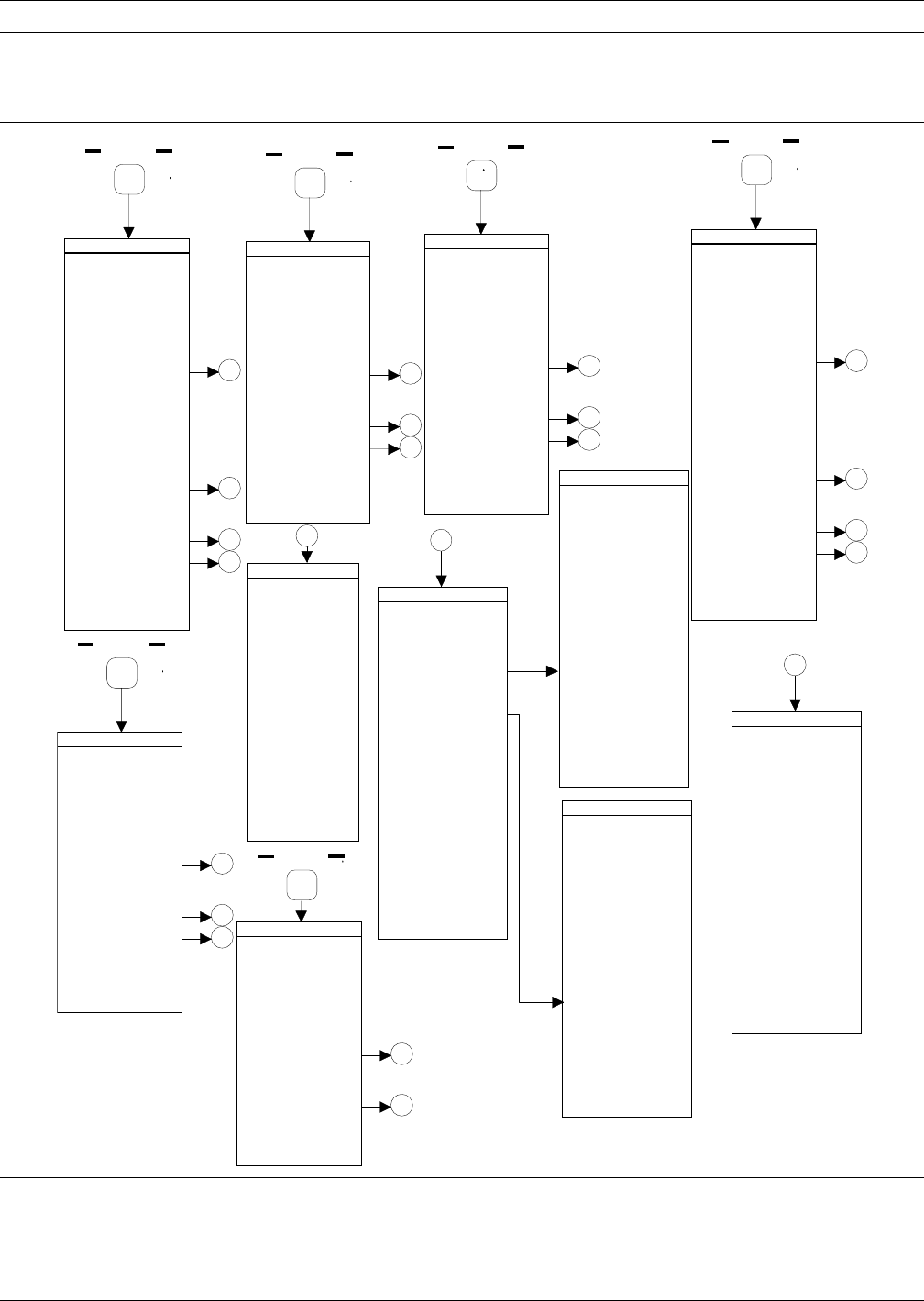
MARKERS/LIMITS KEY-GROUP FRONT PANEL OPERATION
4-40 37XXXC OM
MENU L13
PRESS <ENTER>
TO SELECT
OR TURN ON/OFF
SINGLE LIMITS
- SWR-
READOUT LIMIT
DISPLAY ON(OFF)
LIMITS
TEST LIMITS
SEGMENTED LIMITS
A
B
C
UPPER LIMIT ON(OFF)
XXX.XXX pU
LOWER LIMIT ON(OFF)
XXX.XXX pU
UPPER LIMIT ON(OFF)
XXX.XXX pU
LOWER LIMIT ON(OFF)
XXX.XXX pU
MENU L12
PRESS <ENTER>
TO SELECT
OR TURN ON/OFF
SINGLE LIMITS
- REAL -
READOUT LIMIT
- IMAGINARY -
READOUT LIMIT
DISPLAY ON(OFF)
LIMITS
TEST LIMITS
SEGMENTED LIMITS
A
B
C
LOWER LIMIT ON(OFF)
XXX.XXX pU
UPPER LIMIT ON(OFF)
XXX.XXX pU
A
Markers/Limits
Limits
Markers/Limits
Limits
MENU L9
PRESS <ENTER>
TO SELECT
OR TURN ON/OFF
SINGLE LIMITS
- LINEAR MAG -
UPPER LIMIT ON(OFF)
XXX.XXX dB
LOWER LIMIT ON(OFF)
XXX.XXX dB
READOUT LIMIT
- PHASE -
UPPER LIMIT ON/OFF
XXX.XXX ˚
LOWER LIMIT ON(OFF)
XXX.XXX ˚
READOUT LIMIT
DISPLAY ON(OFF)
LIMITS
TEST LIMITS
SEGMENTED LIMITS
B
C
A
Markers/Limits
Limits
A
B
MENU L11
PRESS <ENTER>
TO SELECT
OR TURN ON/OFF
SINGLE LIMITS
- IMAGINARY-
UPPER LIMIT ON(OFF)
XXX.XXX pU
LOWER LIMIT ON(OFF)
XXX.XXX pU
READOUT LIMIT
DISPLAY ON(OFF)
LIMITS
TEST LIMITS
SEGMENTED LIMITS
A
B
C
Markers/Limits
Limits
MENU LTST
TEST LIMITS
LIMIT ON (OFF)
TESTING
PRESS <ENTER>
TO SELECT
OR TURN ON/OFF
BEEP FOR ON (OFF)
TEST FAILURE
LIMIT TEST TTL
FAIL CONDITION
TTL LOW/TTL HIGH
CHANNEL 1 TEST
PASS (FAIL)
CHANNEL 2 TEST
PASS (FAIL)
CHANNEL 3 TEST
PASS (FAIL)
CHANNEL 4 TEST
PASS (FAIL)
MENU LD1
PRESS <ENTER>
TO SELECT
OR TURN ON/OFF
DEFINE UPPER SEGS
SEGMENT ON (OFF)
X
START POSITION
HORIZONTAL
XXX.XXXXXXXXX GHz
STOP POSITION
VERTICAL
XX.XXX dB
HORIZONTAL
XXX.XXXXXXXXX GHz
VERTICAL
XX.XXX dB
BEGIN NEXT
ATTACH NEXT
CLEAR SEGMENT
PREVIOUS MENU
MENU LD1
PRESS <ENTER>
TO SELECT
OR TURN ON/OFF
DEFINE LOWER SEGS
SEGMENT ON (OFF)
X
START POSITION
HORIZONTAL
XXX.XXXXXXXXX GHz
STOP POSITION
VERTICAL
XX.XXX dB
HORIZONTAL
XXX.XXXXXXXXX GHz
VERTICAL
XX.XXX dB
BEGIN NEXT
ATTACH NEXT
CLEAR SEGMENT
PREVIOUS MENU
C
MENU LSX
PRESS <ENTER>
TO SELECT
OR TURN ON/OFF
SEGMENTED LIMITS
XXXXXXXXX
UPPER LIMIT ON(OFF)
DEFINE UPPER
LOWER LIMIT ON(OFF)
DEFINE LOWER
SEGMENTED OFFSETS
CLEAR ALL
DISPLAY ON(OFF)
LIMITS
TEST LIMITS
SINGLE LIMITS
A
MENU LFX
READOUT LIMIT
INTERCEPTS
UPPER LIMIT (REF)
XXX.XXX xx
LOWER LIMIT
XXX.XXX xx
L IMIT DIFFERENCE
(UPPER-LOWER)
INTERCEPTS AT
LOWER LIMIT
X.XXXX GHz
X.XXXX GHz
X.XXXX GHz
X.XXXX GHz
X.XXXX GHz
X.XXXX GHz
- XXXXXXX -
∆
HORIZONTAL
XXX.XXXXXXXXX GHz
VERTICAL
XX.XXX dB
B
C
MENU L10
PRESS <ENTER>
TO SELECT
OR TURN ON/OFF
SINGLE LIMITS
- REAL -
UPPER LIMIT ON(OFF)
XXX.XXX pU
LOWER LIMIT ON(OFF)
XXX.XXX pU
READOUT LIMIT
DISPLAY ON(OFF)
LIMITS
TEST LIMITS
SEGMENTED LIMITS
A
Markers/Limits
Limits
MENU L14
PRESS <ENTER>
TO SELECT
OR TURN ON/OFF
SINGLE LIMITS
- POWER OUT--
READOUT LIMIT
DISPLAY ON(OFF)
LIMITS
TEST LIMITS
A
B
UPPER LIMIT ON(OFF)
XXX.XXX pU
LOWER LIMIT ON(OFF)
XXX.XXX pU
Markers/Limits
Limits
Figure 4-15. Markers/Limits Key-Group Menus (3 of 3)
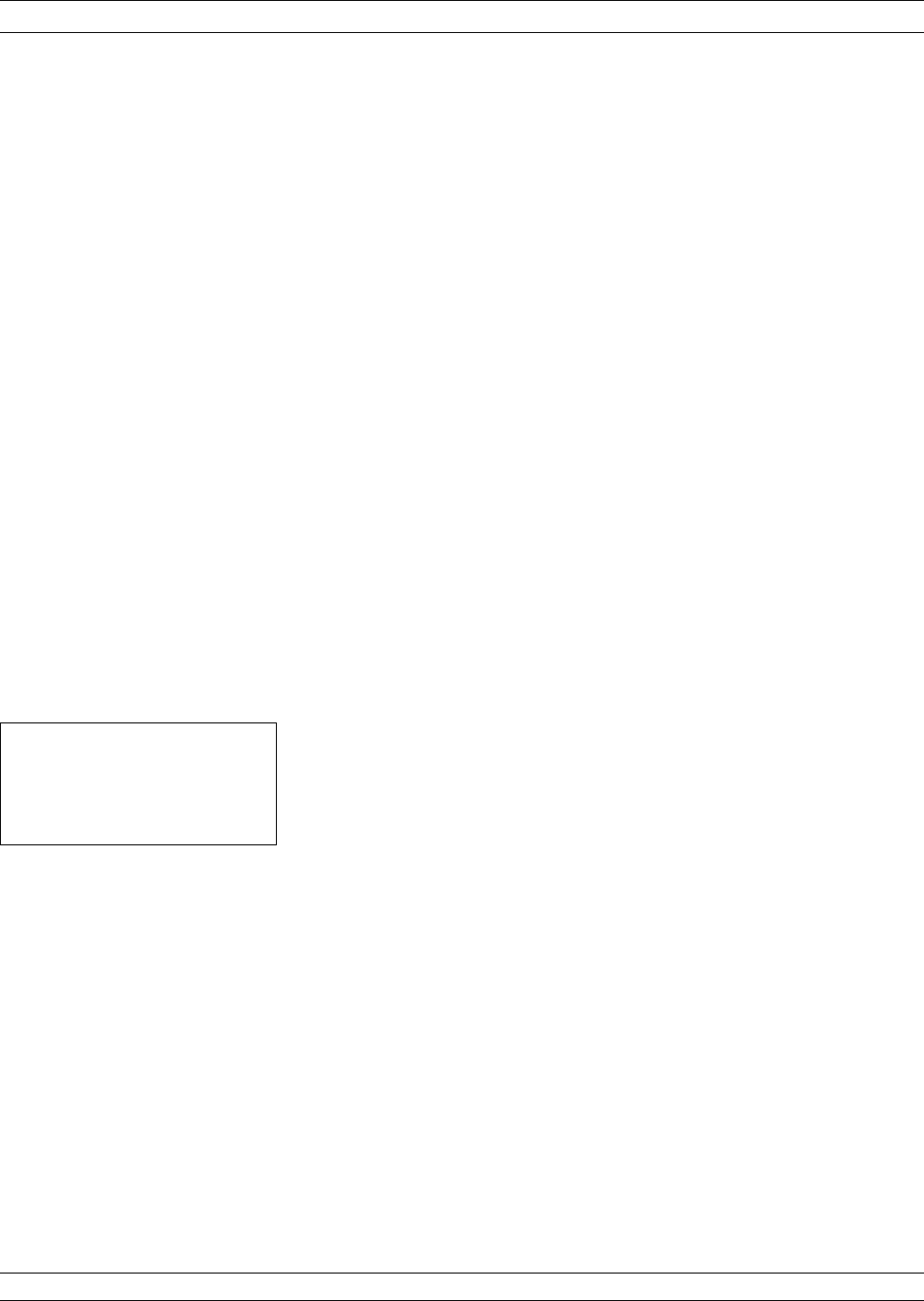
4-12 DISK STORAGE
INTERFACE The 37XXXC has two internally mounted disk drives: an 80 MB hard
disk and a 3.5 inch floppy. The format, files, and directory are compati-
ble with MS-DOS, Version 5.0 and above.
Disk Format Floppy diskettes are MS-DOS compatible and have a 1.44 MByte ca-
pacity.
Disk Files You may find any of the following file-types on the 37XXXC disk:
qProgram Files: These are binary files used to load the operating
program. They are provided on the hard drive, and a backup copy
is provided on floppy diskettes. Application programs cannot
read them
qCalibration Data Files: These are binary files used to store and
retrieve calibration and other data. Application programs cannot
read them. File size depends on calibration type
qText Files: These are tab-delimited ASCII files with the “txt” file
extension. They can be read by application programs
qS2P Parameter Data Files: These files define a 2-port file format
that includes all four S parameters. They can be read by applica-
tions programs. They have a file extension of “S2P”
qTabular Measurement Data Files: These are ASCII files used to
store actual measurement data. They can be read by applications
programs. File size depends on selected options
qTrace Memory Files: These are binary files used to store trace
data. Applications programs cannot read them. You use them to
perform trace math operations on data
qCal Kit File for Coax or Waveguide
qAutoCal Characterization file
37XXXC OM 4-41
FRONT PANEL OPERATION DISK STORAGE INTERFACE
NOTE
File names must begin with
alphabetical, not numeric
characters.
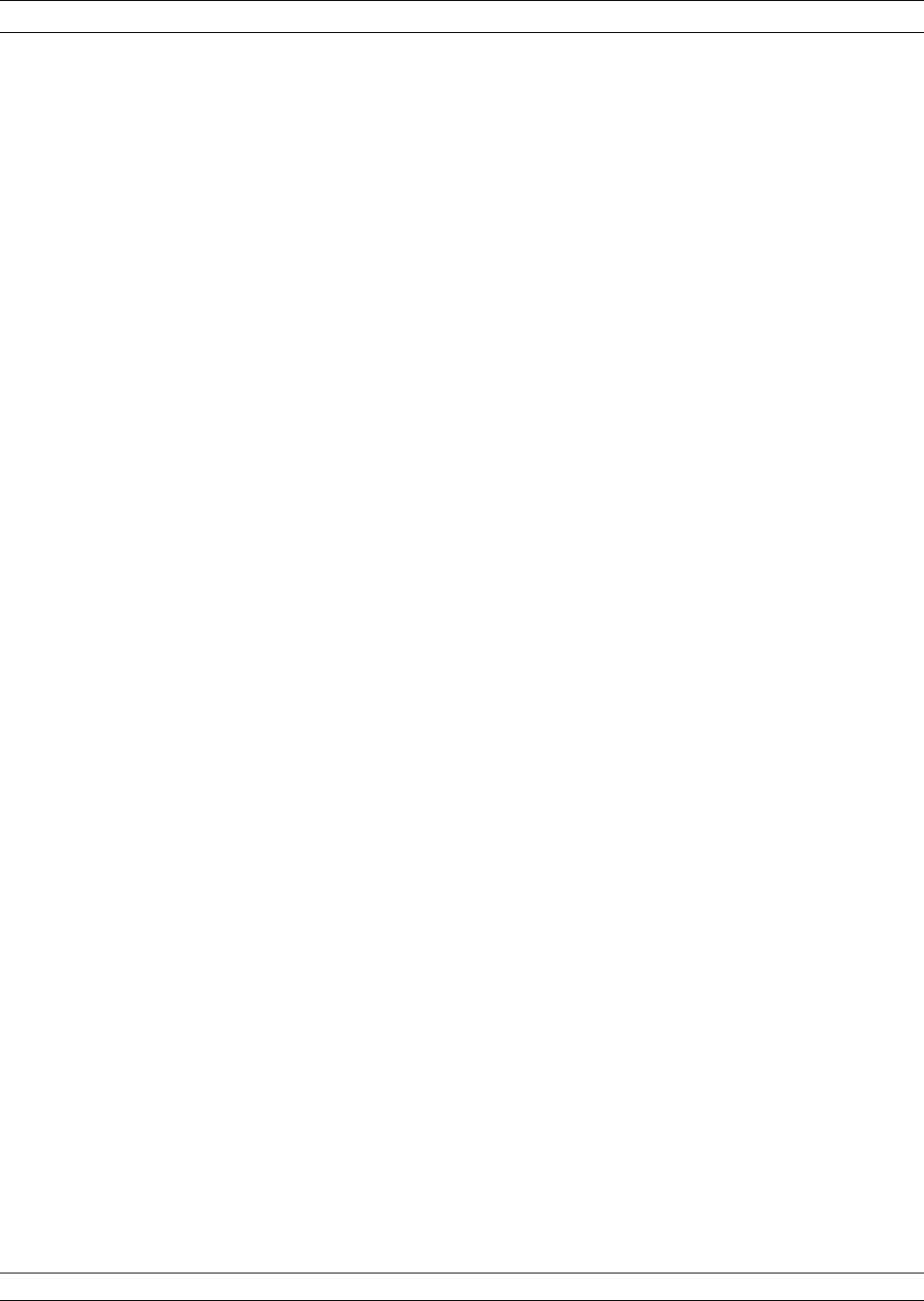
Disk File Output Device You can select the output drive destination for the disk file as either
the hard disk (C:) or the floppy drive (A:). The format of the disk file is
also selected. The default condition is text disk file to the hard disk.
You may then proceed with normal measurements. The Start Print key
may then be used at the instant you intend to capture the data. Menu
DISK 3 then appears and allows the creation of a new file or to over-
write an existing file in the current directory.
Note that the output for text and S2P files have predefined formats.
Tabular data format is configured via the Print Options (Menu PM5)
or Tabular Data (Menu PM3). Bitmap format is configured via the
Print Options (Menu PM5), Options (Menu PM5, or Graphical Data
(Menu PM3A). HPGL format is configured via the Plot Options (Menu
PL1).
You are able to direct hard copy output to the HDD or floppy, in addi-
tion to the printer and plotter. In addition to text (*.txt), S2P (*.s2p),
and tabular (*.dat) files, bitmaps (*.bmp) and HPGL (*.hgl) files are of-
fered to satisfy your desktop publishing requirements. Specifically,
color bitmaps and graphic language files can be imported into Win-
dows applications, such as Cap3700.
Formatting a Data File Disk You may format additional diskettes to hold calibration, tabular mea-
surement, and trace-memory data files. Do this using the FORMAT
DISK selection on the “Floppy Disk Utilities” menu. Using this selec-
tion will format the target disk and overwrite any existing data it con-
tains.
A format hard disk utility is provided in case of hard disk failure.
Using this feature overwrites your system software and requires boot-
ing from the backup floppy diskettes.
Copying Data Files From
Disk to Disk Use the COPY FILES selection on the “Floppy Disk Utilities” and
“Hard Disk Utilities” menus to copy data files between hard and floppy
diskettes.
Recovering From Disk
Write/Read Errors If you experience a read or write error during a disk operation, you
should:
qVerify first character of filename is alphabetical and not numeric
qVerify that the diskette has been properly formatted
qVerify that the diskette is high density (1.44 MB). Low density
(720 KB) diskettes are not supported
qVerify that the write-protect tab on the disk is engaged
qRetry the disk operation
Repeated disk errors may indicate a defective diskette and format.
DISK STORAGE INTERFACE FRONT PANEL OPERATION
4-42 37XXXC OM
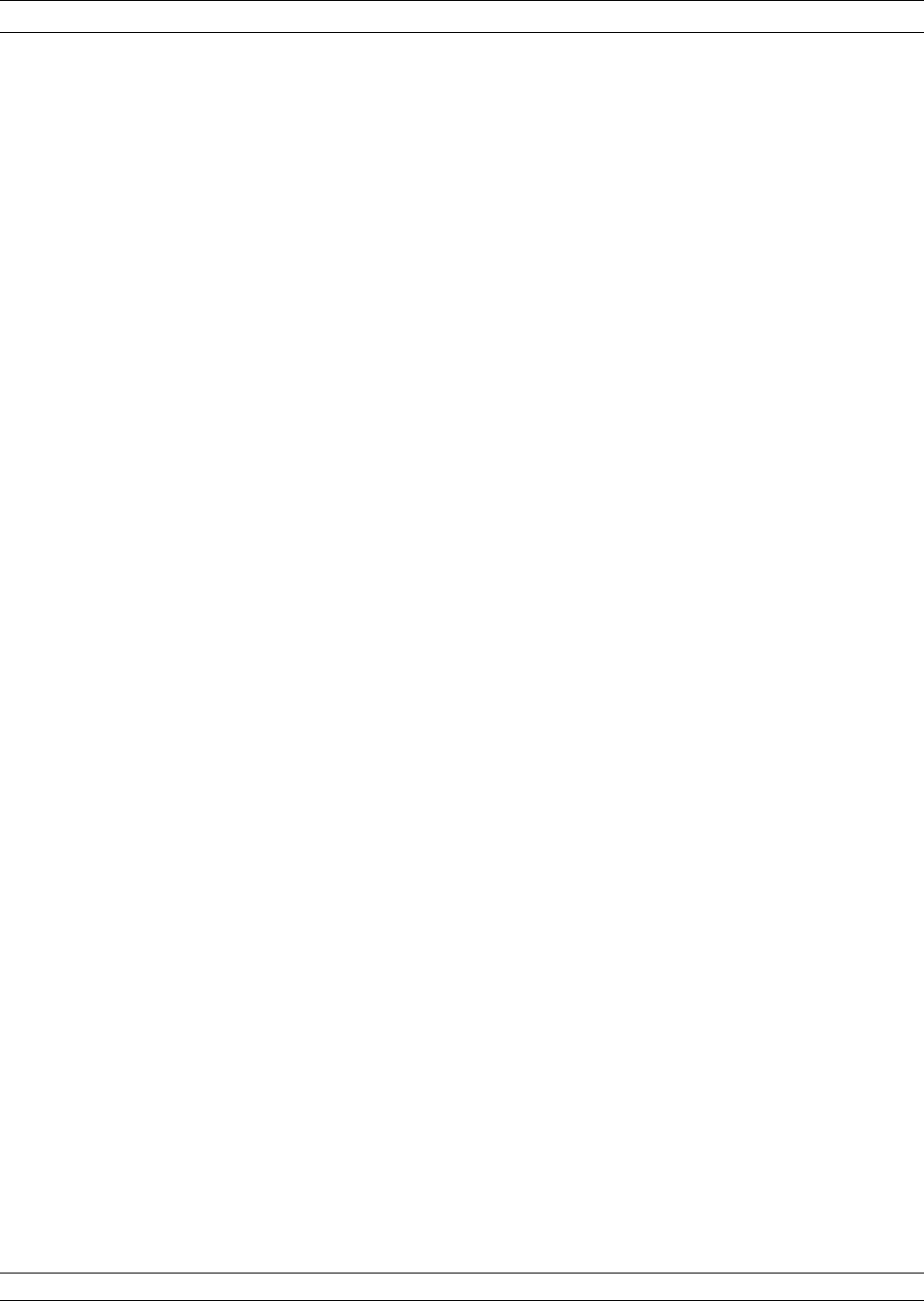
4-13 COMMAND LINE The Command Line menu choice provides several DOS compatible
commands. Command line options are:
qCREATE DIRECTORY (MD)
qLIST DIRECTORY (DIR)
qCHANGE DIRECTORY (CD)
qDELETE FILES (DEL)
qREMOVE DIRECTORY (RD)
qCOPY FILES (COPY)
These options are NOT case sensitive.
Create Directory This command is performed by: MD c:\pat-h\dir_name or
MD a:\path\dir_name. The c: is used to refer to the hard disk, and a:
is for the floppy disk.
List Directory This command is performed by “DIR” command. This may be used as
DIR c:\path or without any path specified. The syntax is:
DIR c:\path or DIR a:\path.
If c: or a: is not used, the default is the current hard disk directory. You
may use wild cards as follows:
qDIR *.cal
qDIR filter?.cal
Change Directory This command is performed by CD c:\path or CD a:\path. Both of
these options do not require a device name. The device name is re-
ferred to by c: or a:.
If you choose to do CD dir_name, this implies the current Hard disk di-
rectory.
Delete Files This command is used to delete a particular file(s) in a directory, or de-
lete the entire contents of the directory by using the wild card option.
The command line is:
qDEL filename
qDEL c:\path\filename
qDEL a:\path\*
37XXXC OM 4-43
FRONT PANEL OPERATION COMMAND LINE
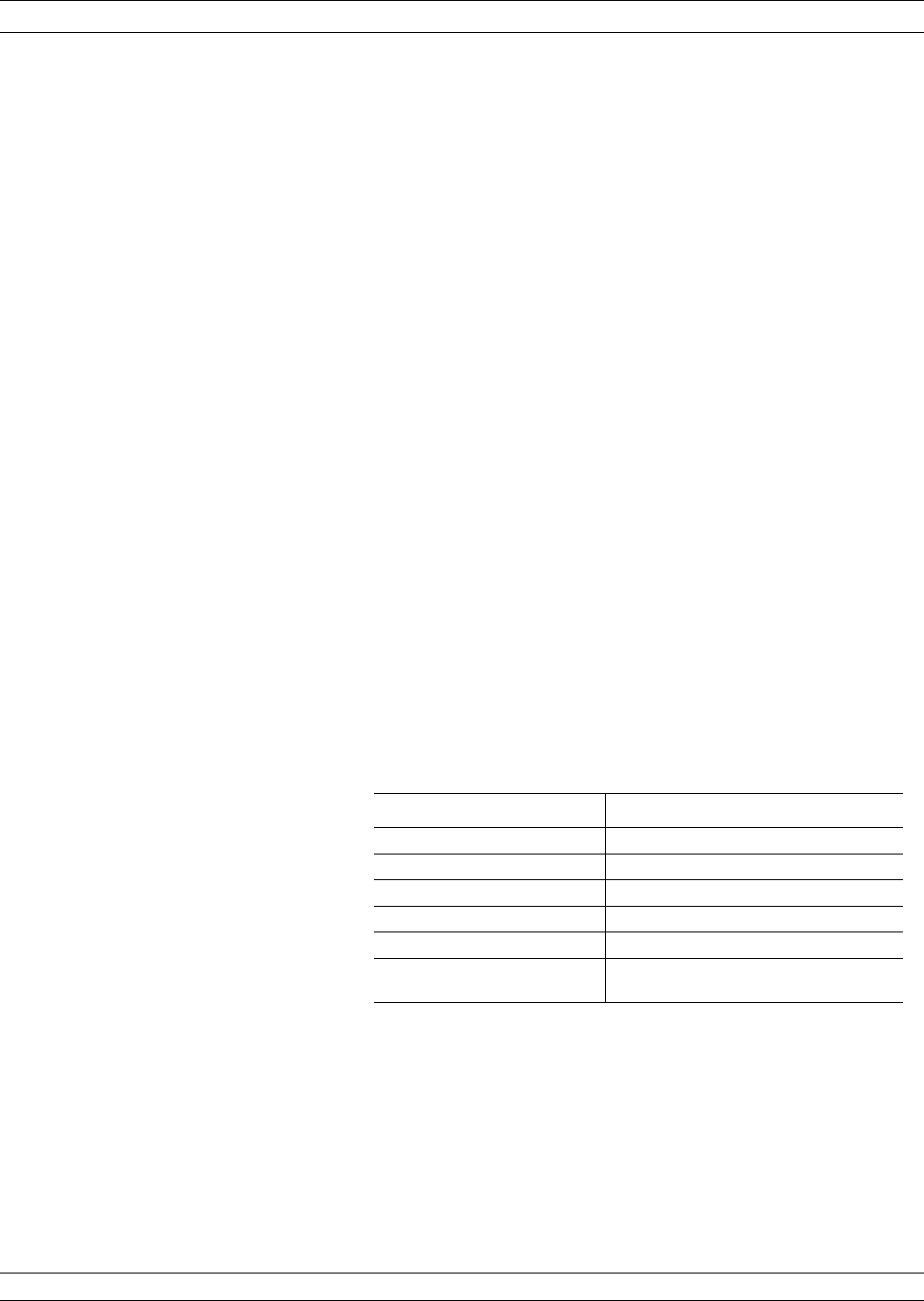
Remove Directory This command is used to delete a particular directory. The command is
only valid when the entire directory is empty:
qRD c:\path\directory
qRD a:\path\directory
Copy Files This command is performed by the command line COPY source: desti-
nation:
COPY c:\path\name a:\path\name
Any combination of the drive is allowed, except for the same directory,
and the same name.
Once the COMMAND LINE is selected, the system will prompt a one
line dialog box to allow command entry. The dialog box remains open
only for the user interface.
Conventions Be aware of the following conventions when using the Command Line
choice. There is a limitation of five sublevel directories in the 37XXXC
models:
qAny directory change will force the system to use that as the cur-
rent directory for other menus that deal with the file system. For
example, if the user changes the directory to c:\lib\junk, then
any activity for saving hard copy or calibration files will be saved
on the junk directory.
qThe default directory is the root directory.
qGPIB support: GPIB mnemonics will provide functionality for
each of the above operations. The format is shown below:
Function Path
List directory DIR “[device:/][”
Make directory MD “[device:/][path]name”
Change directory CD “[device:/][path]napath]nameme”
Delete File(s) DEL “[device:/][path]name”
Remove directory RD “[device:/][path]name”
Copy files COPY “[device:][/path/][source]”“[de-
vice:][/path/][destination]”
COMMAND LINE FRONT PANEL OPERATION
4-44 37XXXC OM
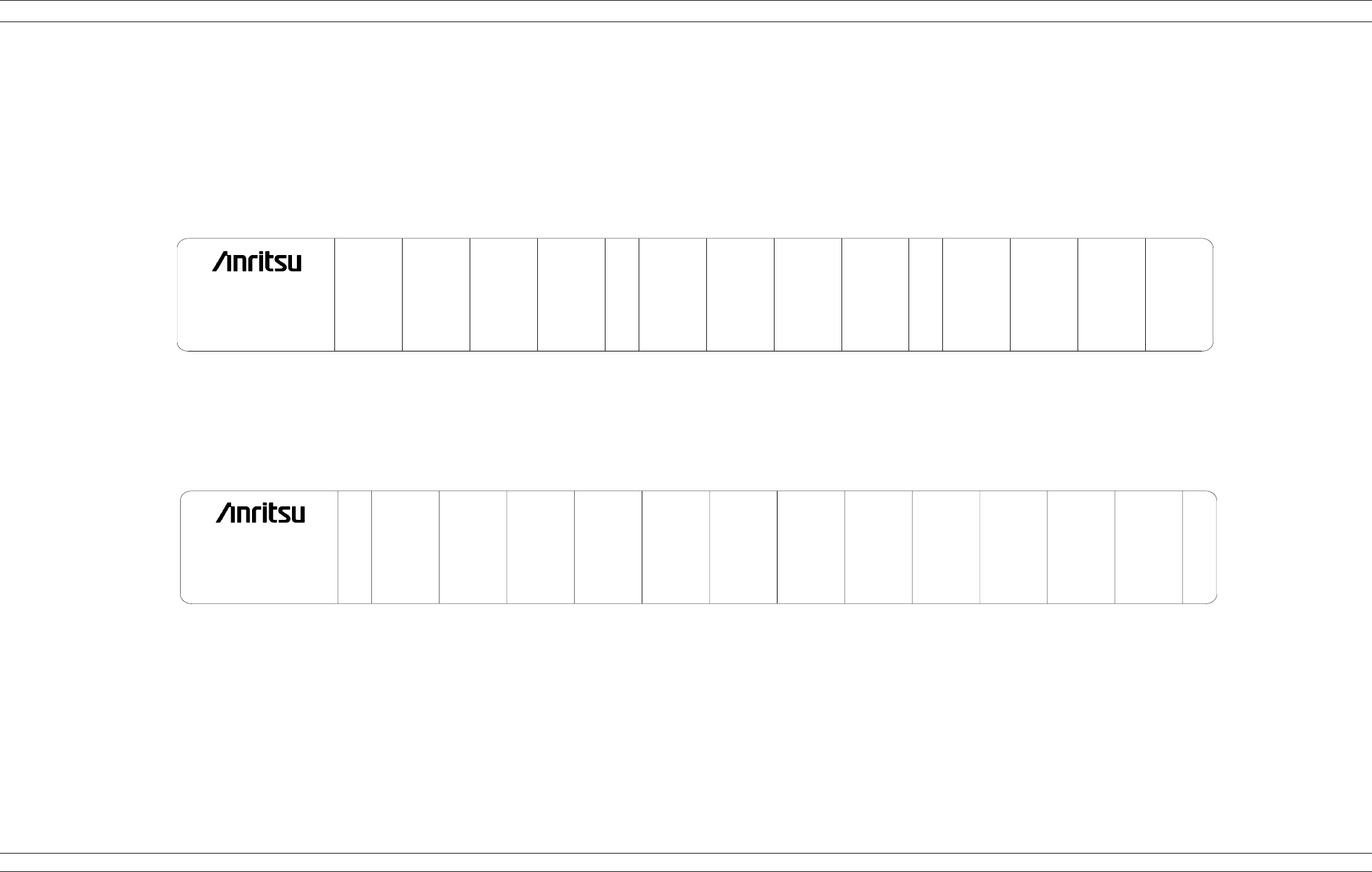
FRONT PANEL OPERATION COMMAND LINE
37XXXC OM 4-45/4-46
F2 F3 F4F1 F5 F6 F7 F8 F9 F10 F11 F12
Ctrl
Alt
Shift
Ctrl
Alt
Shift
Ch1 Ch2 Ch3 Ch4 GraphType AutoScale Auto Ref
Plane
Store Data
to Memory
Channel Menu Marker Menu Readout
Marker Limits S Params Set Scale Ref Plane Trace Memory
Avg/Smooth
Menu Trace Smooth Average Video IF BW Save Save CAL
to HDD
Save NRM
to HDD
Default
Program Utility Menu Options Menu Recall CAL
from HDD
Recall NRM
from HDD
Setup Menu Data Points Apply Cal Start Print
Stop PrintBegin CalApplicationsDomain
Save TXT
to HDD
Save S2P
to HDD
Save DAT
to HDD
Hardcopy
Menu
Command
Line
Start Print ________
Hold _____________
Print Screen, F12
Pause
Copyright (c) 1994-98 by Anritsu Company
Save TXT
to Floppy
Save S2P
to Floppy
Save DAT
to Floppy
Recall
Vector Network Analyzer
Clear/Ret Loc _____ Esc
Ctrl
Alt
Shift
Ctrl
Alt
Shift
F2 F3 F4F1 F5 F6 F7 F8 F9 F10 F11 F12
Clear/Ret Loc _____
Start Print ________
Hold _____________
Esc
Print Screen, F12
Pause Ch1 Ch2 Ch3 Ch4 GraphType AutoScale Auto Ref
Plane
Store Data
to Memory
Channel Menu Marker Menu Readout
Marker Limits S Params Set Scale Ref Plane Trace Memory
Avg/Smooth
Menu Trace Smooth Average Video IF BW Save CAL
to HDD
Save NRM
to HDD
Default
Program Utility Menu Options Menu Recall CAL
from HDD
Recall NRM
from HDD
Setup Menu Data Points Apply Cal Start Print
Stop PrintBegin CalApplicationsDomain
Save TXT
to HDD
Save S2P
to HDD
Save DAT
to HDD
Hardcopy
Menu
Command
Line
Save TXT
to Floppy
Save S2P
to Floppy
Save DAT
to Floppy
Save
Recall
Vector Network Analyzer
Copyright (c) 1994-98 by Anritsu Company
Actual-Size Keyboard Templates for 37XXXC

Table of Contents
5-1 INTRODUCTION ...................................5-3
5-2 ERROR MESSAGES..................................5-3
Chapter 5
Error and Status
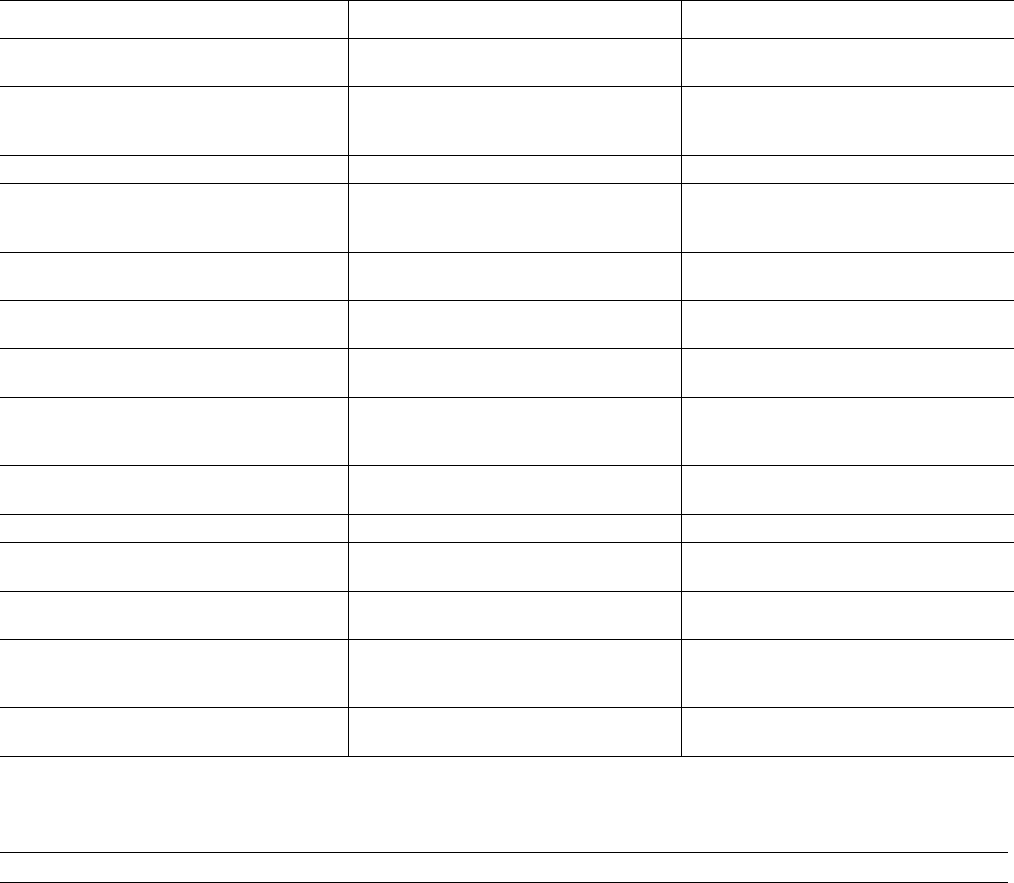
Chapter 5
Error and Status Messages
5-1 INTRODUCTION This chapter lists, describes, and provides corrective action for the er-
ror messages that point to problems that the operator can correct. Any
error messages that appear on the display but do not appear in this
chapter will require action by a qualified service representative.
5-2 ERROR MESSAGES Error messages are provided in Tables 5-1 and 5-2.
37XXXC OM 5-3
Error Message Description Corrective Action
ATTENUATOR UNAVAILABLE Option 6 Port 2 Test Step Attenuator is
not installed.
Install Option 6 Step Attenuator,
BANDS MUST SEQUENCE Frequency bands in Multiple Source
mode must sequence in a 1-2-3-4-5 or-
der.
None, no skipping is allowed.
BOTH LIMITS MUST BE ON Must have both limits activated. Turn on limits.
DIFFERENT H/W SETUP. RECALL
ABORTED
Source is different from the recalled
setup.
Reconfigure system to duplicate the
hardware setup that was used to store
the saved data.
DIFFERENT S/W VERSION, RECALL
ABORTED
Saved state not compatible with hard-
ware or software version.
Load compatible software (S/W) version
and retry.
DISCRETE FREQS LOST Change in frequency caused discrete fill
frequencies to be lost.
None.
DISPERSIVE MEDIUM, ONLY TIME
USED
Distance does not apply for dispersive
media.
None.
FREQUENCIES HAVE REACHED UPPER
LIMIT
Frequencies being defined in Multiple
Source mode have reached upper limits
of Sources.
Redefine frequencies to not exceed lim-
its of Sources.
ILLEGAL IN C.W. MODE Attempted to readout limit frequency. None, no limit lines are permitted in CW
mode.
ILLEGAL IN TIME DOMAIN Attempted to readout limit frequency None.
LOGO FILE NOT FOUND Attempted to read a non-existent logo
file from disk.
Create user-defined logo using applica-
tion on external controller.
MEAS DATA NOT AVAILABLE FOR
STORAGE
Measurement data is not available for
storage on floppy or hard disk.
None.
MEMORY LOCATION CORRUPTED Requested memory location is cor-
rupted.
None. If problem reoccurs after storing a
new setup, contact Anritsu Customer
Service.
NO BANDS ARE STORED No frequency bands have been defined
and stored.
Need to define and store frequency
bands to turn on Multiple Source mode.
Table 5-1. General Error Messages (1 of 3)
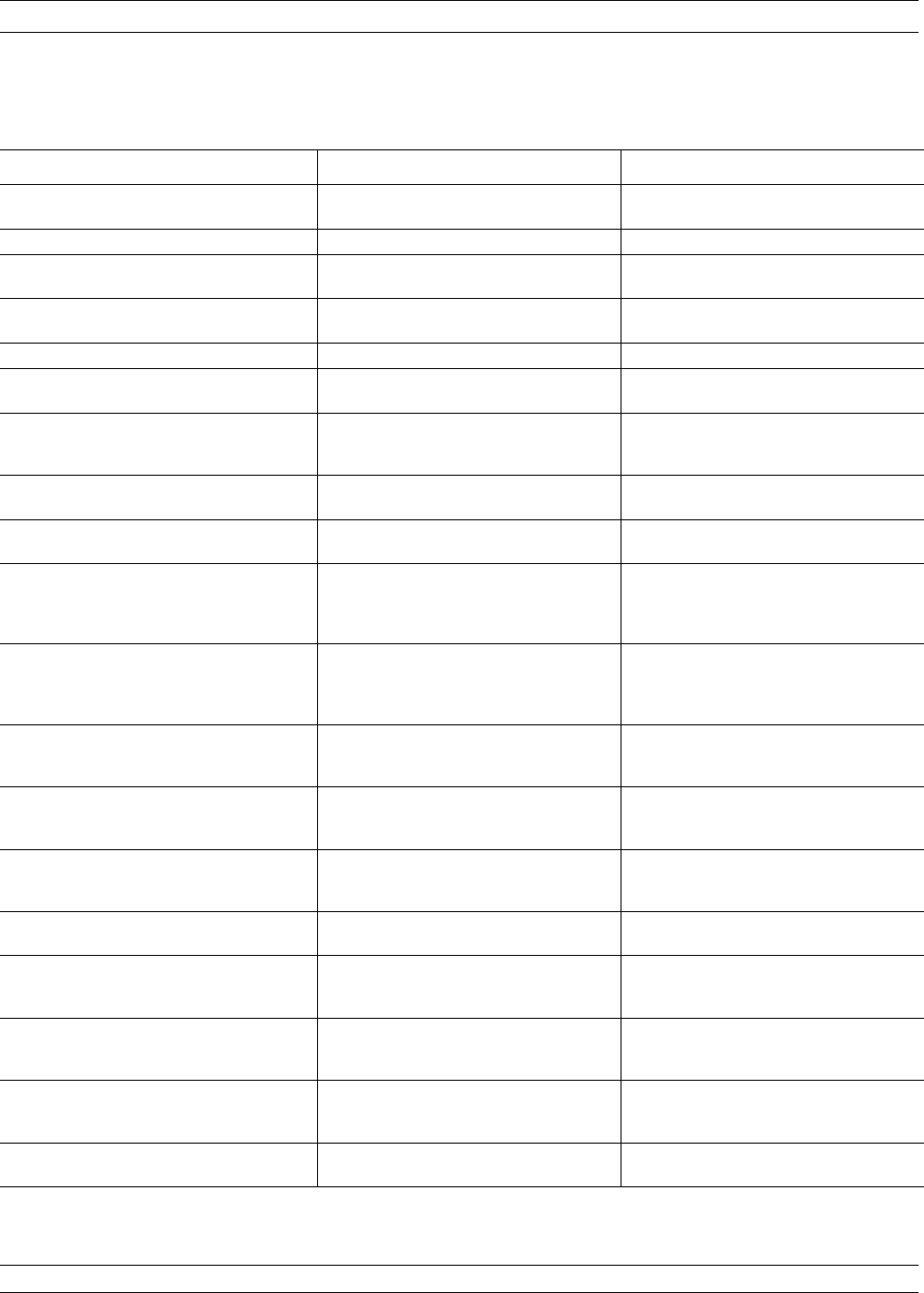
ERROR MESSAGES ERROR AND STATUS MESSAGES
5-4 37XXXC OM
Error Message Description Corrective Action
NO STORED MEMORY DATA No data is stored in floppy or hard disk
memory.
None.
OPTION NOT INSTALLED Selected an option that is not installed. None.
OUT OF CAL RANGE Entered values out of the selected cali-
bration range.
Change calibration range or re-enter val-
ues that are within the current range.
OUT OF H/W RANGE Entered value is out of the instrument’s
hardware range.
Re-enter values that are within range.
OUT OF RANGE Entered value is out of range. Re-enter values that are within range.
OUT OF RANGE, 10 PERCENT MIN Entered value is out of the instrument’s
range by greater than 10 percent.
Re-enter frequency or power value.
OUT OF RANGE, 20 PERCENT MAX Entered smoothing or group delay value
exceeds the range by greater than 20
percent.
Re-enter values that are within range, 0
to 20%.
OUT OF SWEEP RANGE Entered a frequency that is out of the in-
strument sweep range.
Re-enter frequency.
OUT OF WINDOW RANGE Attempted to set marker outside start to
stop range.
Redefine marker to be within frequency
start/stop range.
POWER OUT OF CALIBRATED RANGE Power range has been changed to be
outside the range of the active linearity
calibration. Linearity calibration is turned
off.
Perform linearity calibration over new
power range.
POWER RESTORED TO CAL RANGE Power range is outside of the linearity
calibration range when the calibration
was turned on. The power range is
changed to the calibration range.
If new power range is desired, perform
new linearity calibration over new power
range.
RECEIVER OUT OF RANGE BY EQUA-
TION
Equation defined in Multiple Source
mode places receiver frequency out of
range when attempting to store band.
Redefine frequency.
SOURCE 1 OUT OF RANGE BY EQUA-
TION
Equation defined in Multiple Source
mode places Source 1 frequency out of
range when attempting to store band.
Redefine frequency.
SOURCE 2 OUT OF RANGE BY EQUA-
TION
Equation defined in Multiple Source
mode places Source 2 frequency out of
range when attempting to store band.
Redefine frequency.
STANDARD CAL NOT VALID FOR WAVE-
GUIDE
Cannot use waveguide when calibrating
with the standard method.
Use the Offset Short method with wave-
guide.
START F FOLLOWS PREVIOUS STOP F Start frequency of current band immedi-
ately follows stop frequency of previous
band. Cannot be modified.
None.
START GREATER THAN STOP Entered start frequency is greater than
the stop frequency.
Re-enter frequency values such that the
start frequency is lower than the stop
frequency.
START MUST BE LESS THAN STOP Entered start frequency is greater than
the stop frequency.
Re-enter frequency values such that the
start frequency is lower than the stop
frequency.
STEP IS TOO LARGE Entered discrete fill step extends the
stop fill out of range.
Re-enter so that step is within range.
Table 5-1. General Error Messages (2 of 3)
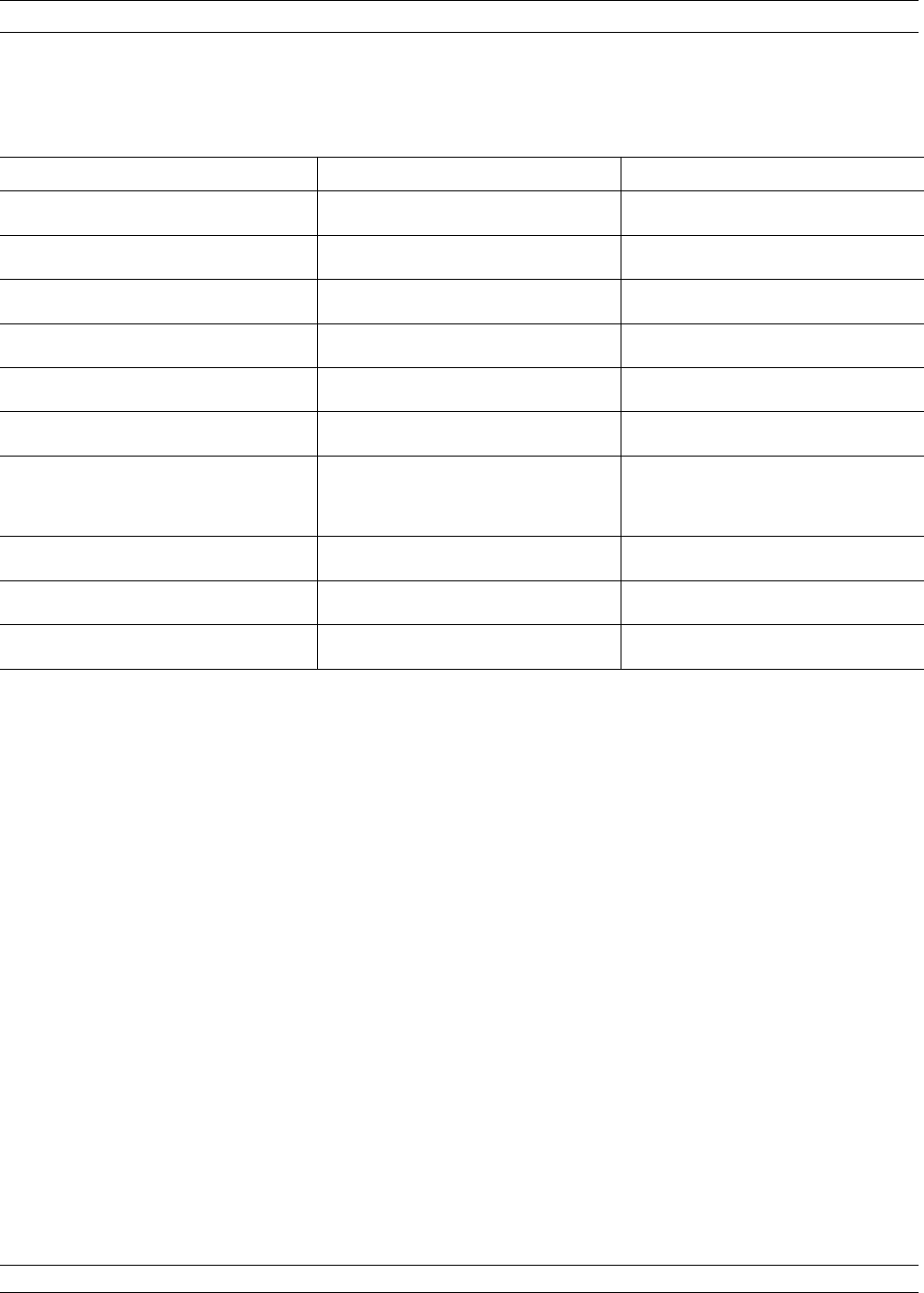
37XXXC OM 5-5
ERROR AND STATUS MESSAGES ERROR MESSAGES
Error Message Description Corrective Action
STOP IS OVER RANGE Entered value exceeds the instrument’s
stop frequency.
Re-enter stop frequency.
SYSTEM BUS ADDRESSES MUST BE
UNIQUE
GPIB address is being used by another
bus instrument.
Select a different, unique GPIB address.
SYSTEM UNCALIBRATED 37XXXC is uncalibrated for the selected
measurement values.
Perform a measurement calibration.
TOO FEW POINTS, 2 MINIMUM Entered too few discrete file points, 2 is
minimum.
Re-enter data points.
TOO MANY POINTS, 1601 MAXIMUM Entered too many discrete file points,
1601 points are the maximum allowed.
Re-enter data points.
UNDEFINED DIVIDE BY ZERO Denominator cannot be zero in equation. Make denominator a value other than
zero.
WARNING: NO GPIB CONTROL OF
SOURCE SWEEP
Neither Source power nor flat-port power
can be modified when receiver mode is
user-defined with NO Source GPIB con-
trol.
None.
WARNING: SET ON RECEIVER MODE Phase-lock setting is undefined when
VNA is Set-On Receiver mode.
None.
WARNING: SOURCE 2 DOES NOT EX-
IST
2nd, external, frequency source is not
present.
Connect frequency source.
WINDOW TOO SMALL Attempted to set start greater than or
equal to stop.
Re-enter frequency values.
Table 5-1. General Error Messages (3 of 3)
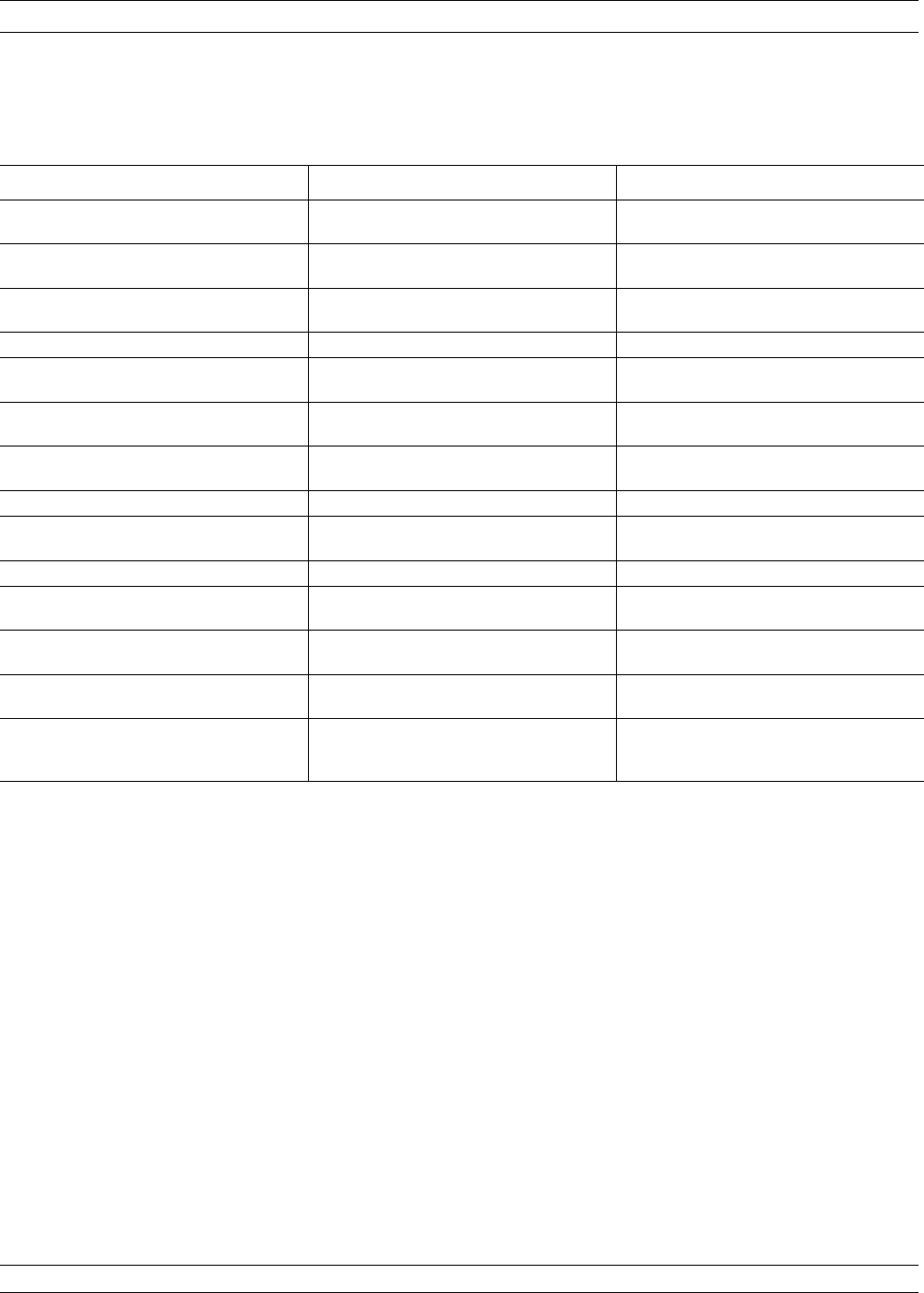
ERROR MESSAGES ERROR AND STATUS MESSAGES
5-6 37XXXC OM
Error Message Description Corrective Action
7140: FLOPPY DISK GENERAL ERROR Invalid disk media or format. Use 1.44 MB diskette and format in the
37XXXC.
7142: FLOPPY DISK READ ERROR Read error when accessing disk file. Use 1.44 MB diskette and format in the
37XXXC.
7143: DISK WRITE ERROR Error in writing to disk file. Use 1.44 MB diskette and format in the
37XXXC.
7147: FLOPPY DISK UNAVAILABLE Floppy disk is not available. Install floppy diskette or floppy disk drive.
7170: HARD DISK GENERAL ERROR General error in accessing hard disk. Retry and if still fails, reformat the hard
disk drive.
7172: HARD DISK READ ERROR Read error when accessing disk file. Retry and if still fails, reformat the hard
disk drive.
7173: HARD DISK WRITE ERROR Error in writing to disk file. Retry and if still fails, reformat the hard
disk drive.
7177: HARD DISK UNAVAILABLE Hard disk is not available. Install hard disk drive circuit board.
8140: GENERAL DISK BUFFER ERROR Out of RAM. Press the System State, Default Program
key and retry.
FILE NOT FOUND Disk file not found. None.
FLOPPY DISK HAS NO ROOM FOR
FILE
Floppy diskette is full. Delete files or install new diskette.
FLOPPY DISK NOT READY Floppy disk is not ready (or not in-
stalled.).
Install diskette in floppy drive.
FLOPPY DISK WRITE PROTECTED Write protect tab in place on floppy dis-
kette.
Remove write-protect tab.
HARD DISK HAS NO ROOM FOR FILE,
DELETE EXISTING FILES(S) TO CRE-
ATE SPACE
Hard disk is full. Delete files.
Table 5-2. Disk Error Messages

Table of Contents
6-1 INTRODUCTION ...................................6-3
6-2 DISPLAY MODES AND TYPES ...........................6-3
Single Channel Display: Ch 1, 2, 3, 4........................6-3
Dual Channel Display: Ch 1 and 3 or Ch 2 and 4 .................6-4
Four Channel Display: Ch 1, 2, 3, 4 ........................6-5
Dual Trace Overlay .................................6-6
Graph Data Types..................................6-7
6-3 FREQUENCY MARKERS ..............................6-11
Marker Designation ................................6-11
6-4 LIMITS ........................................6-11
6-5 STATUS DISPLAY ..................................6-12
Reference Position Marker ............................6-12
Scale Resolution ..................................6-12
Frequency Range .................................6-12
Analog Instrument Status.............................6-12
Measurement Status ...............................6-13
Sweep Indicator Marker..............................6-13
6-6 DATA DISPLAY CONTROL .............................6-13
S-Parameter Selection...............................6-14
Data Display Update ...............................6-14
Display of Markers.................................6-14
6-7 HARD COPY AND DISK OUTPUT .........................6-15
Tabular Printout..................................6-15
Screen-Image Printout ..............................6-15
Plotter Output ...................................6-15
Disk Output ....................................6-15
Chapter 6
Data Displays
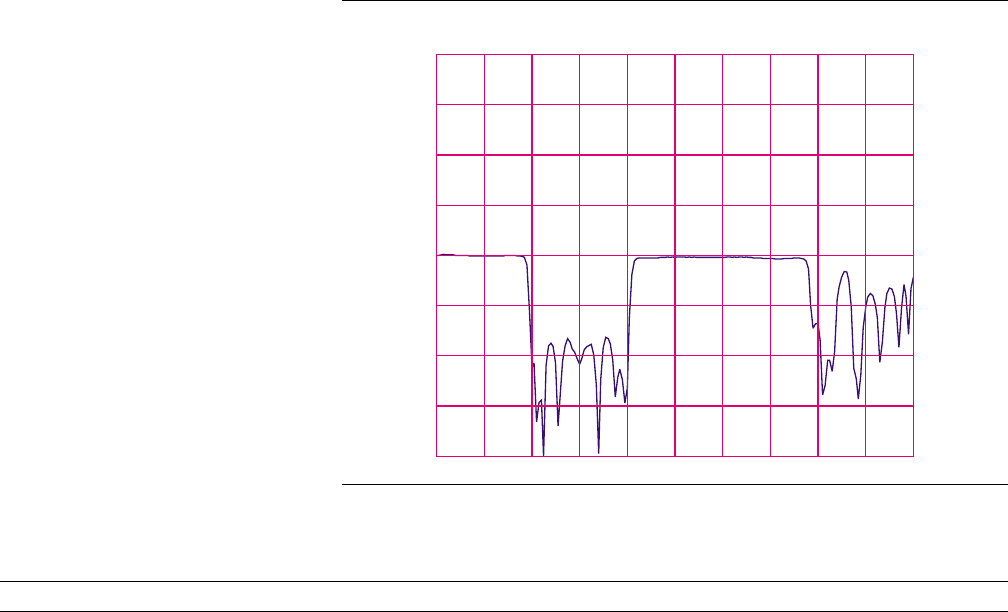
Chapter 6
Data Displays
6-1 INTRODUCTION This chapter provides discussion and examples of the various types of
data displays.
6-2 DISPLAY MODES AND
TYPES The 37XXXC displays measurement data using a “Channel Concept.”
This means that each channel can display both a different
S-Parameter and a different graph type. As you select each channel,
the graph type, scaling, reference delay, S-Parameter, etc., associated
with that channel appears on the screen. You can display the same
S-Parameter on two or more channels.
Several graph-types are possible: polar, rectilinear, or Smith chart. The
rectilinear graph-type may be magnitude, phase, magnitude and
phase, SWR, group delay, real, imaginary, and real and imaginary. The
Smith chart graph-type is specifically designed to plot complex imped-
ances.
Single Channel Display:
Ch 1, 2, 3, 4 You select this display type (Figures 6-1 and 6-2) by choosing “Single
Display” on Menu CM (Appendix A). Possible graph types are Smith,
polar, rectilinear, or dual (split) rectilinear (magnitude and phase).
37XXXC OM 6-3
GHz0.040000000 20.000000000
S11 FORWARD REFLECTION
LOG MAG. REF= 0.000 dB 10.000 dB/DIV
Figure 6-1. Single Channel Display, Log Magnitude
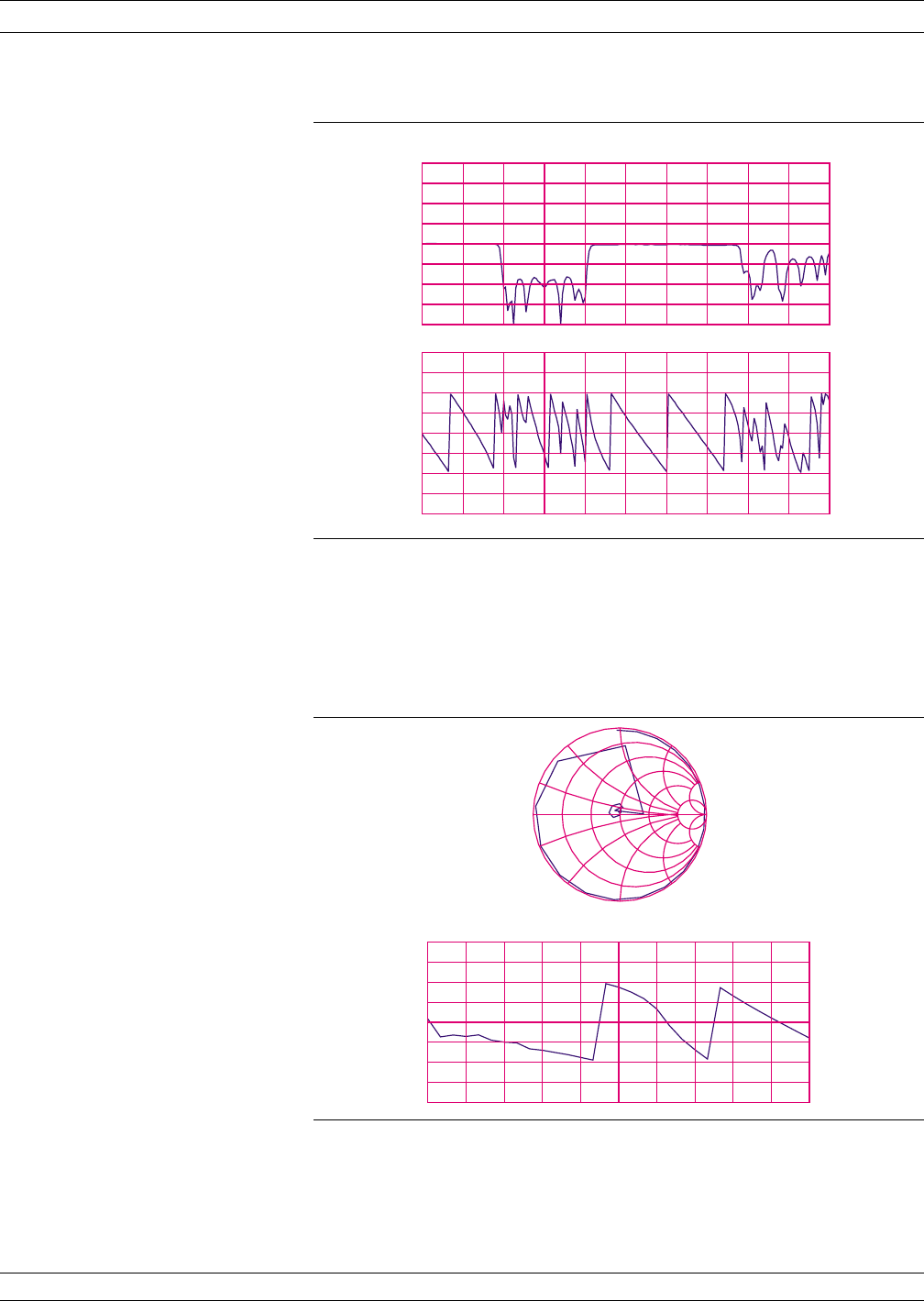
Dual Channel Display:
Ch1and3orCh2and4
If you have chosen a dual display of magnitude and phase, the affected
area of the LCD screen is subdivided into two smaller portions (Figure
6-3). You select this display type by choosing “Dual Display” in Menu
CM (Appendix A).
DISPLAY MODES AND TYPES DATA DISPLAYS
6-4 37XXXC OM
GHz0.040000000 20.000000000
S11 FORWARD REFLECTION
LOG MAG.
PHASE
REF= 0.000 dB
REF= 0.00
|
10.000 dB/DIV
90.00
|/
DIV
Figure 6-2. Single Channel Display, Magnitude and Phase
0
.2
-.2
.5
-.5
1
2
-2
5
-5
2.036000000 - 5.030000000 GHz
S11 FORWARD REFLECTION
IMPEDANCE
GHz2.036000000 5.030000000
S12 REVERSE TRANSMISSION
PHASE REF= 0.00| 90.00| /DIV
Figure 6-3. Dual Channel Display
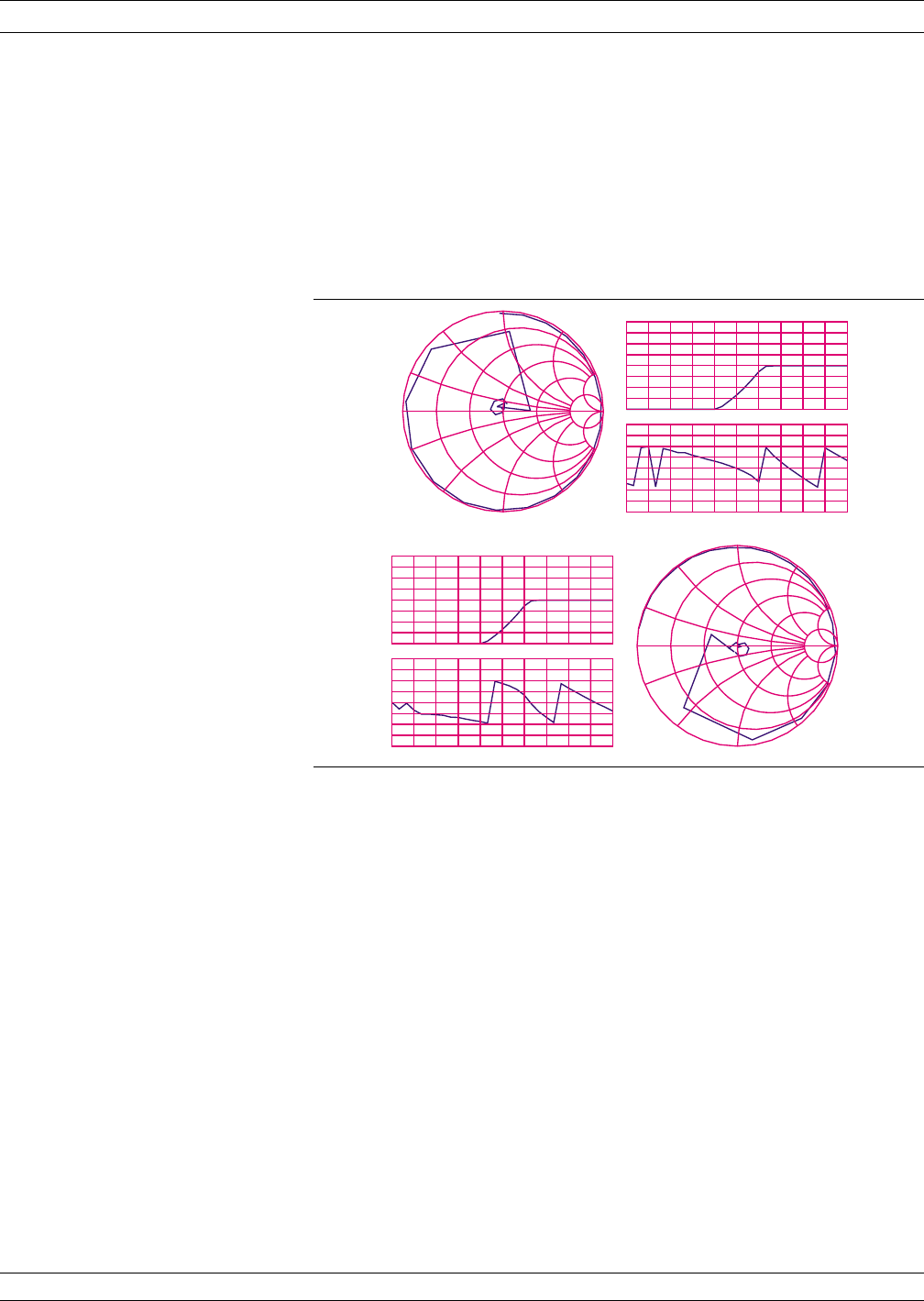
Four Channel Display:
Ch 1, 2, 3, 4 From four-to-eight graph types are displayed. In each quadrant, the
graph type can be any of the possible choices listed in the GT menu
(Appendix A). If you have chosen to display magnitude and phase on a
channel, the quadrant displaying that channel is further subdivided as
described above. You select this display type by choosing “All Four
Channels” in Menu CM. An example of a four-channel display appears
in Figure 6-4, below.
37XXXC OM 6-5
DATA DISPLAYS DISPLAY MODES AND TYPES
0
.2
-.2
.5
-.5
1
-1
2
-2
5
-5
S11
Z
GHz2.036000000 5.030000000
S21 LOGM+P
0.000 dB
0.00|
10.000 dB/DIV
90.00| /DIV
GHz2.036000000 5.030000000
S12 LOGM+P
0.000 dB
0.00|
10.000 dB/DIV
90.00| /DIV
0
.2
-.2
.5
-.5
1
-1
2
-2
5
-5
S22
Z
Figure 6-4. Four-Channel Display
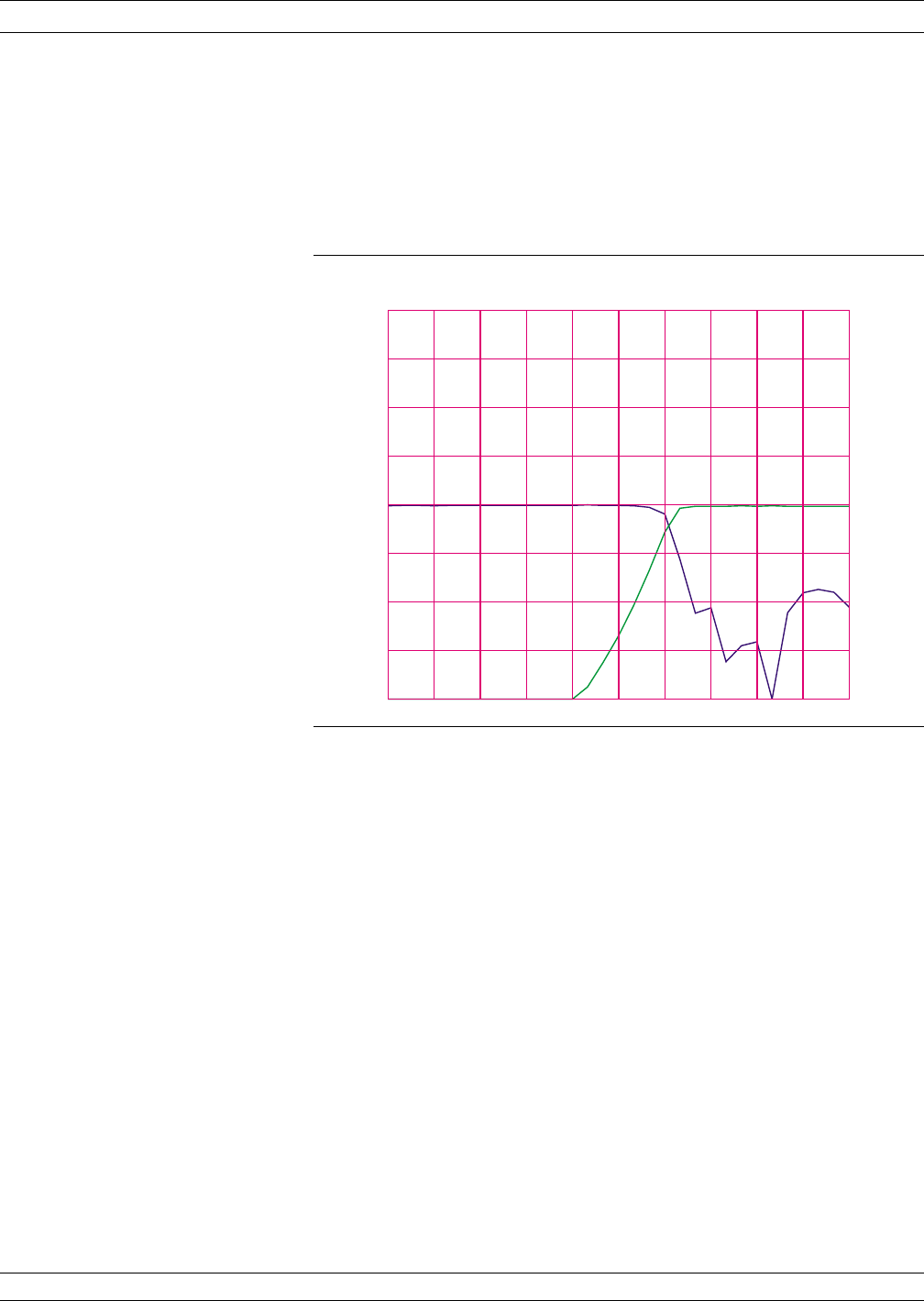
Dual Trace Overlay For rectilinear graph types, two traces can be displayed, one overlaid
(superimposed) on the other (Figure 6-5). By menu selection, the two
traces can be Channel 1 overlaid on Channel 3 or Channel 2 overlaid
on Channel 4. Each trace is in a different color. Channels 1 and 2 are
displayed in red, while Channels 3 and 4 are displayed in yellow.
DISPLAY MODES AND TYPES DATA DISPLAYS
6-6 37XXXC OM
CH1:S11 FWD REFL
LOG MAG.
REF= 0.000 dB
10.000 dB/DIV
CH3:S21 FWD TRANS
LOG MAG.
REF= 0.000 dB
10.000 dB/DIV
GHz2.036000000 5.030000000
Figure 6-5. Dual Trace Overlay
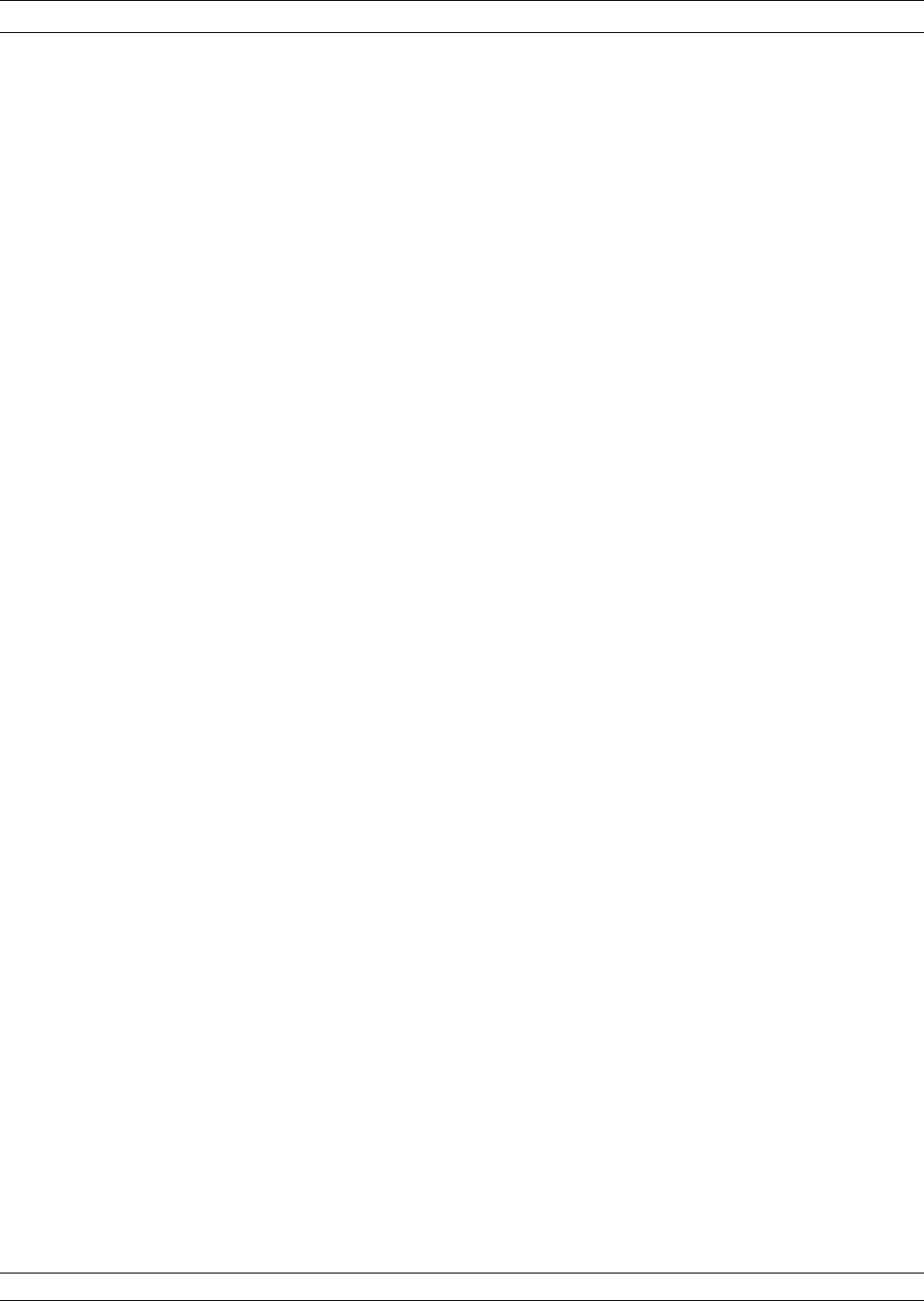
Graph Data Types The data types (real, imaginary, magnitude, phase) used in the dis-
played graph-types reflect the possible ways in which S-Parameter
data can be represented in polar, Smith, or rectilinear graphs. For ex-
ample: Complex data—that is, data in which both phase and magni-
tude are graphed—may be represented and displayed in any of the
ways described below:
qComplex Impedance—displayed on a Smith chart graph
qReal and imaginary—displayed on a real and imaginary graph
qPhase and magnitude components—displayed on a rectilinear
(Cartesian) or polar graph
qGroup delay plot—group-delay measurement units are time,
those of the associated aperture are frequency and SWR
The quantity group delay is displayed using a modified rectilin-
ear-magnitude format. In this format the vertical scale is in linear
units of time (ps-ns-ms). With one exception, the reference value and
reference line functions operate the same as they do with a normal
magnitude display. The exception is that they appear in units of time
instead of magnitude.
Examples of graph-data types are shown in Figure 6-6 through 6-11,
on the following pages.
37XXXC OM 6-7
DATA DISPLAYS DISPLAY MODES AND TYPES
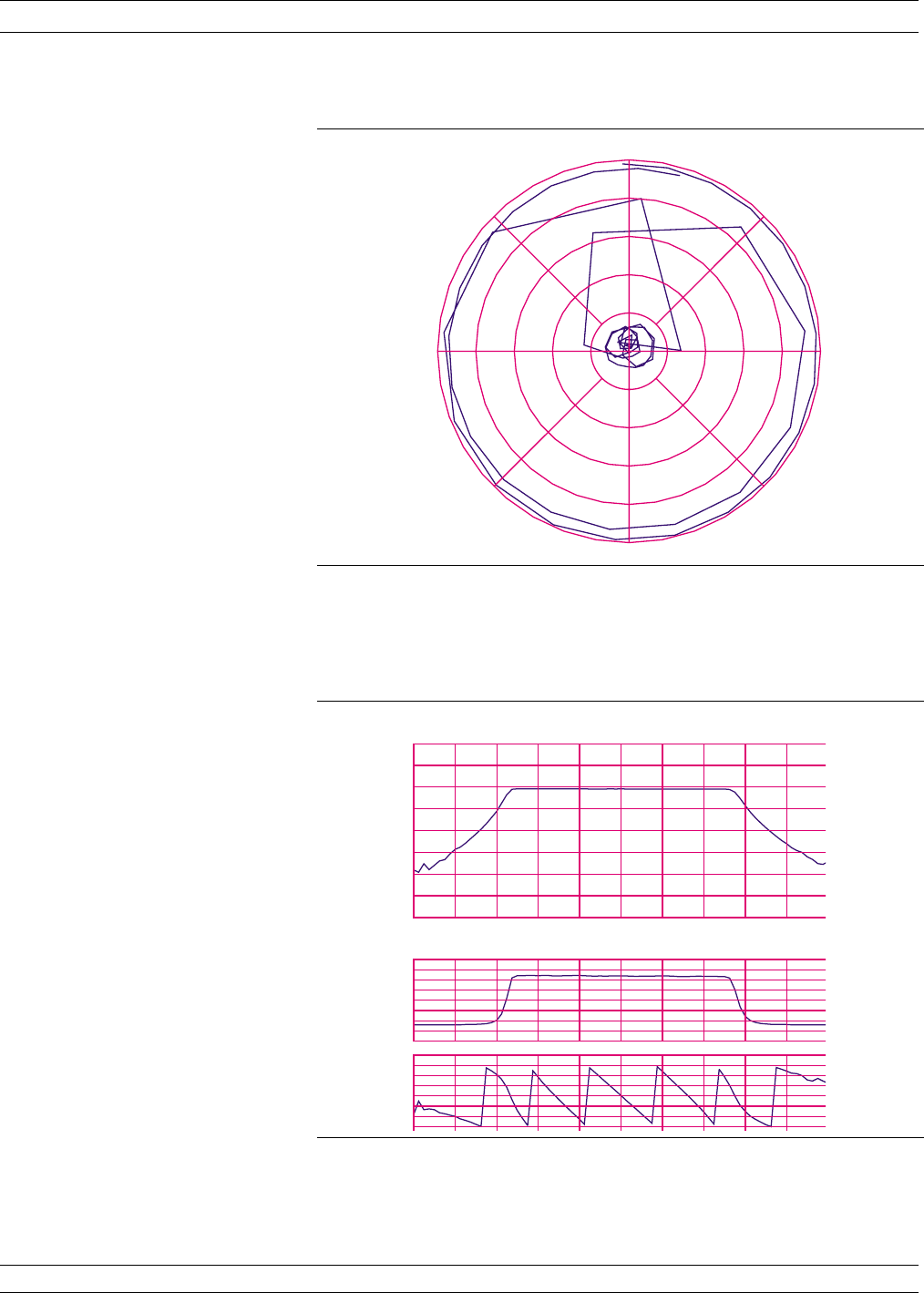
DISPLAY MODES AND TYPES DATA DISPLAYS
6-8 37XXXC OM
0
0
45
90
135
180
-135
-90
-45
S11 FWD REFL
LINEAR POLAR
REF= 1.000 U 200.000 mU/DIV
Figure 6-6. Linear Polar Graticule
GHz2.036000000 10.020000000
S21 FORWARD TRANSMISSION
LOG MAG. REF= -38.569 dB 20.000 dB/DIV
GHz2.036000000 10.020000000
S21 FORWARD TRANSMISSION
LINEAR MAG. REF= 483.588 mU 200.000 mU/DIV
Figure 6-7. Dual Channel Rectilinear Graticule
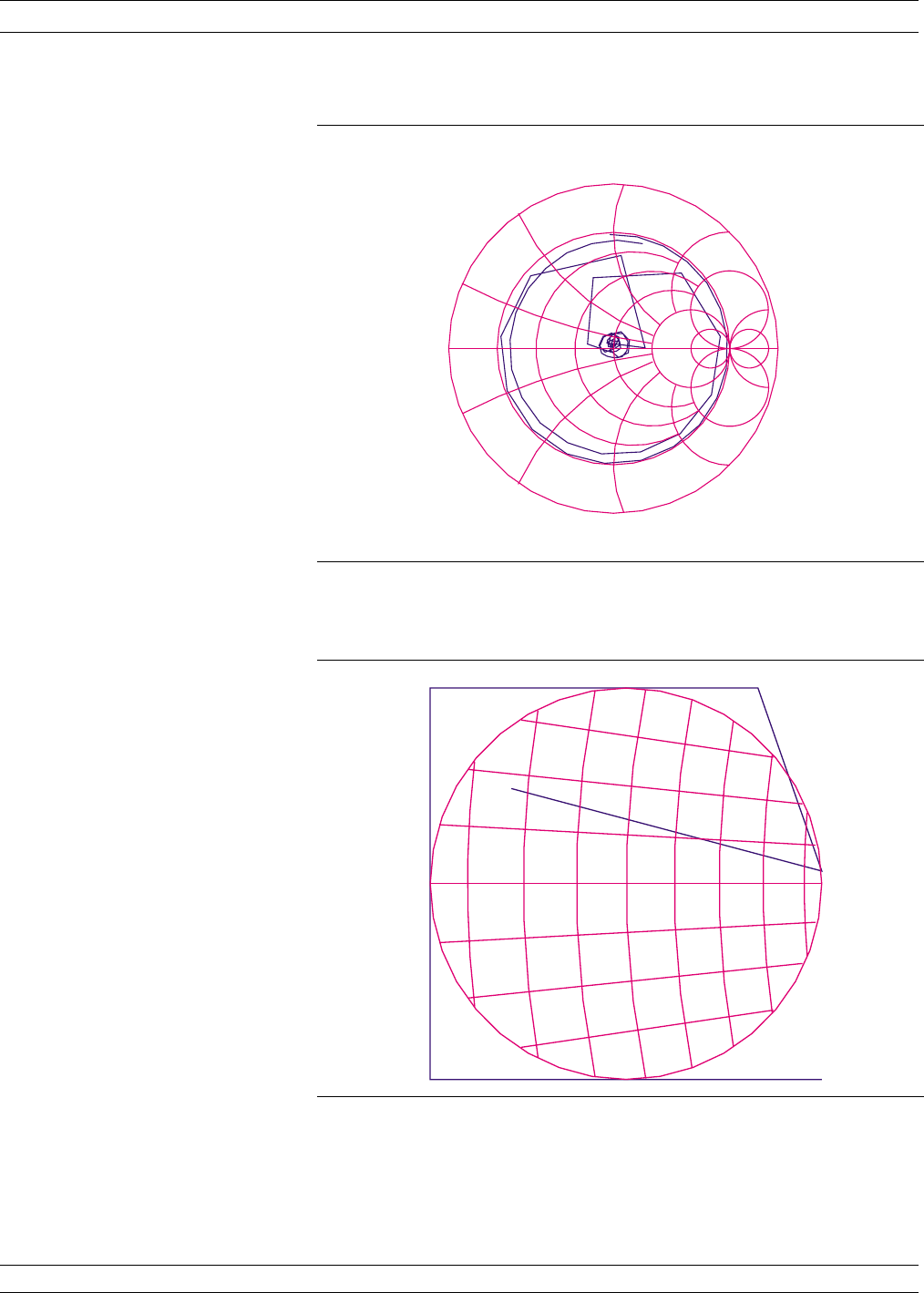
DISPLAY MODES AND TYPES DATA DISPLAYS
6-10 37XXXC OM
-.17 0 .2 .5 1 2 5 -5.8
.2
-.2
.5
-.5
1
-1
2
-2
2.036000000 - 10.020000000 GHz
S11 FORWARD REFLECTION
IMPEDANCE
Figure 6-10. 3 dB Compressed Smith Chart
.82 .85 .90 .95 1.0 1.05 1.10 1.15 1.20
.20
20
.15
-.15
.10
-.10
.05
-.05
0
S11 FORWARD REFLECTION
IMPEDANCE
Figure 6-11. 20 dB Compressed Smith Chart
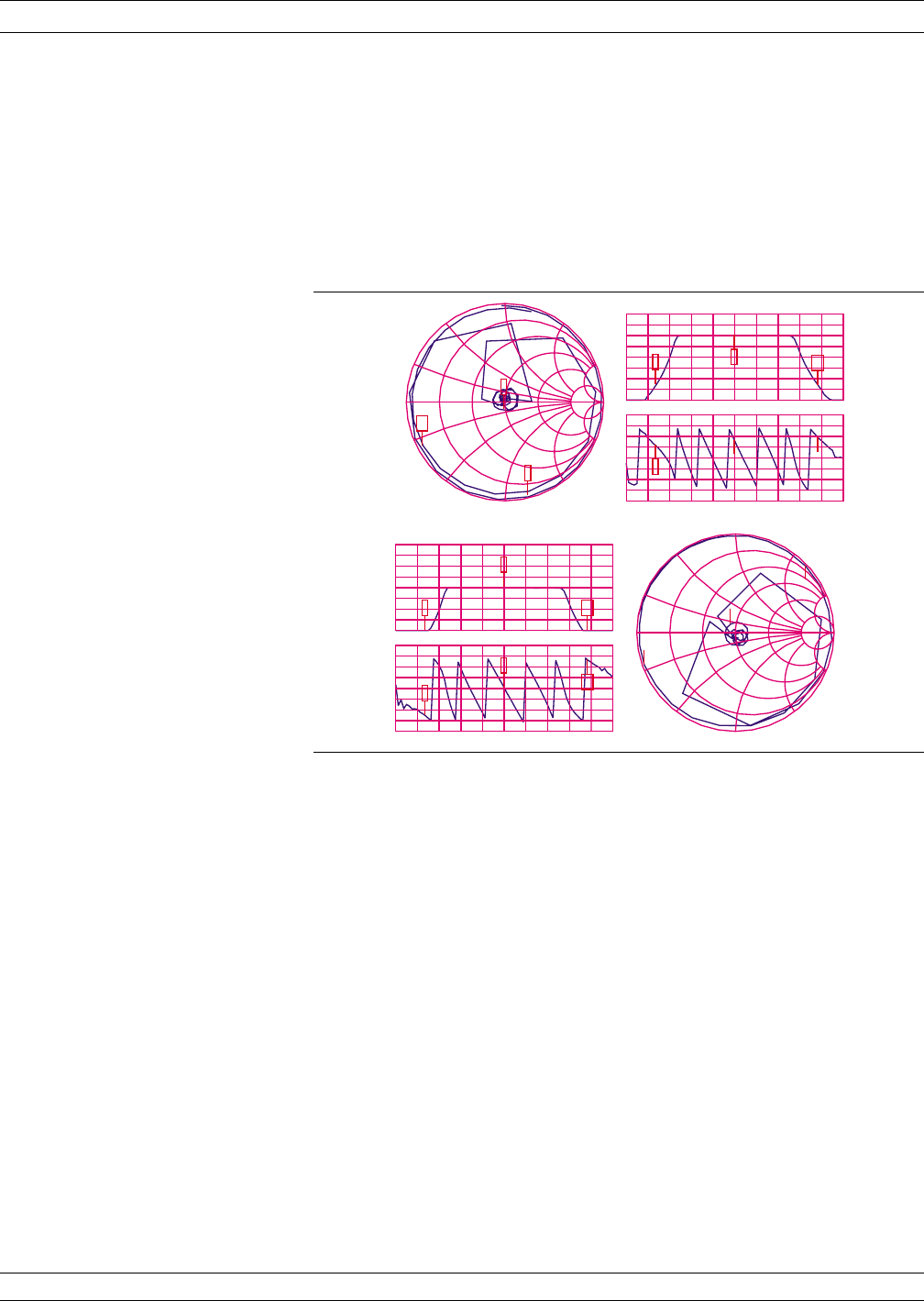
6-3 FREQUENCY MARKERS The example below shows how the 37XXXC annotates markers for the
different graph-types. Each marker is identified with its own number.
When a marker reaches the top of its graticule, it will flip over and its
number will appear below the symbol. When markers approach the
same frequency, they will overlap. Their number will appear as close to
the marker as possible without overlapping.
Marker Designation Depending on menu selection, you may designate a marker as the “ac-
tive” or the “delta reference” marker. If you choose a marker to be ac-
tive—indicated by its number being enclosed in a square box—you
may change its frequency or time (distance) (or point number in CW
Draw) with the Data Entry keypad or knob. If you have chosen it to be
the delta-reference marker, a delta symbol ( D) appears one character
space above the marker number (or one character space below a
“flipped” marker). If the marker is both active and the delta reference
marker, the number and the delta symbol appear above (below) the
marker. The delta symbol appears above (below) the number.
6-4 LIMITS Limit lines function as settable maximum and minimum indicators for
the value of displayed data. These lines are settable in the basic units
of the measurement on a channel-by-channel basis. If the display is
rescaled, the limit line(s) will move automatically and thereby main-
tain their correct value(s).
37XXXC OM 6-11
DATA DISPLAYS FREQUENCY MARKERS
0
.2
-.2
.5
-.5
1
-1
2
-2
5
-5
S11
Z
GHz2.036000000 10.020000000
S12 LOGM+P
-20.000 dB
3.91|
10.000 dB/DIV
60.00| /DIV
GHz2.036000000 10.020000000
S21 LOGM+P
0.000 dB
7.99|
10.000 dB/DIV
60.00| /DIV
0
.2
-.2
.5
-.5
1
-1
2
-2
5
-5
S22
Z
1
2
3
123
123
1
2
3
1
2
3
1
2
3
Figure 6-12. Marker Annotation
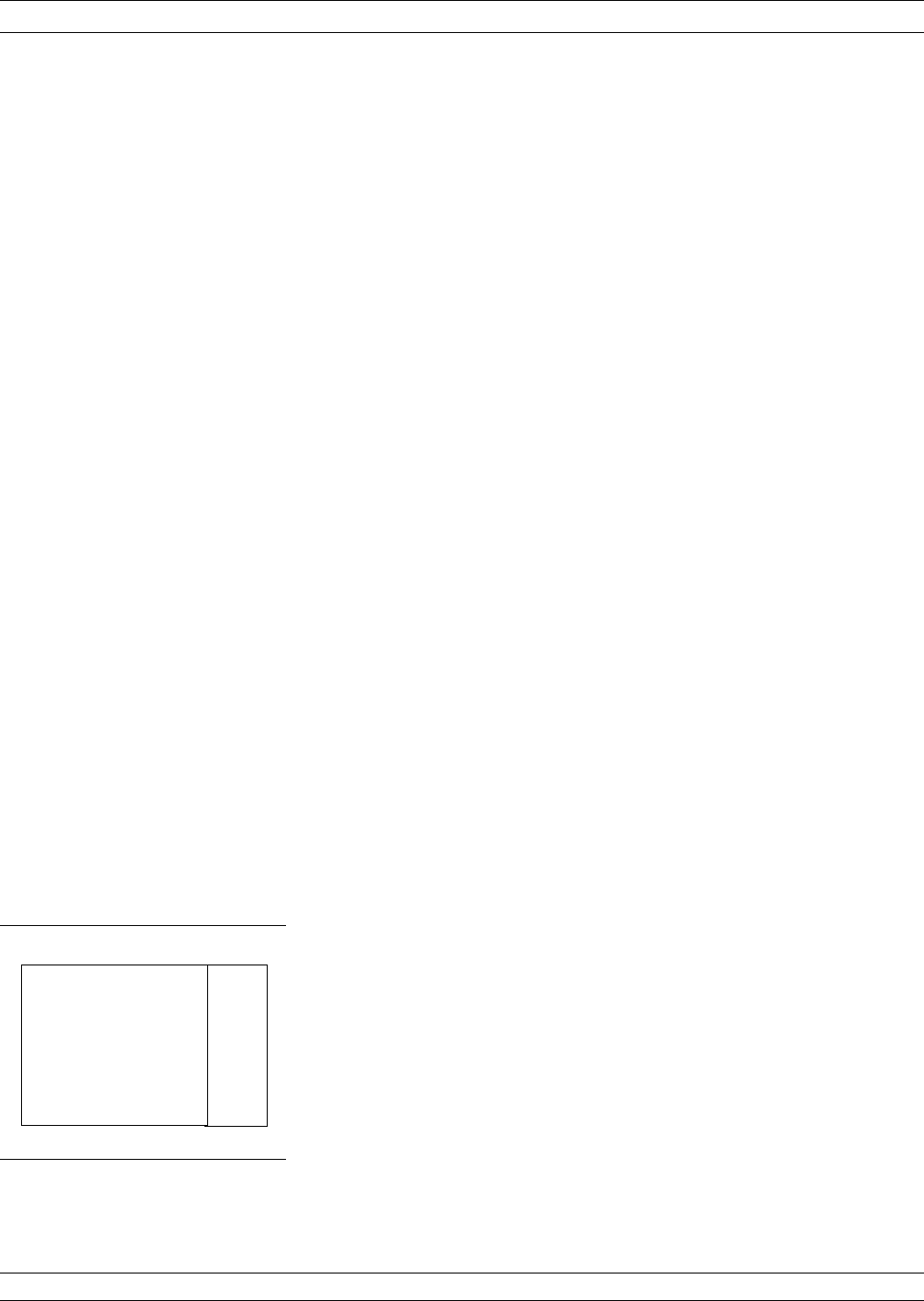
Each channel has two limit lines (four for dual displays), each of which
may take on any value. Limit lines are either horizontal lines in recti-
linear displays or concentric circles around the origin in Smith and po-
lar displays.
Each channel can produce segmented limits. They allow different up-
per and lower limit values to be set at up to ten segments across the
measurement range.
6-5 STATUS DISPLAY In addition to the graticules, data, markers, and marker annotation,
the 37XXXC displays certain instrument status information in the
data display area. This information is described below.
Reference Position Marker The Reference Position Marker indicates the location of the reference
value. It is displayed at the left edge of each rectilinear graph-type. It
consists of a green triangular symbol similar to the cursor displayed in
the menu area. You can center this symbol on one of the vertical
graticule divisions and move it up or down using the “Reference Posi-
tion” option. When you do this, the data trace moves accordingly. If you
also select the reference value option, the marker will remain station-
ary and the trace will move with the maximum allowable resolution.
When changing from a full-screen display to half- or quarter-screen
display, the marker will stay as close to the same position as possible.
Scale Resolution Each measurement display is annotated with the scale resolution. For
log-magnitude displays resolution ranges from 0.001 to 50 dB per divi-
sion. Linear displays of magnitude range from 0.001 to 50 units per di-
vision. Cartesian phase displays can range from 0.01 to 90 degrees per
division. The polar display is 45 degrees per display graticule.
Frequency Range Each measurement display is annotated with the frequency range of
the measurement.
Analog Instrument Status The 37XXXC displays analog-instrument-status messages (in red
when appropriate) in the upper right corner of the data-display area
(left). They appear at the same vertical position as line 2 of the menu
area. If more than one message appears, they stack up below that line.
STATUS DISPLAY DATA DISPLAYS
6-12 37XXXC OM
Display screen
showing the data
Menu
Area
Display
Area
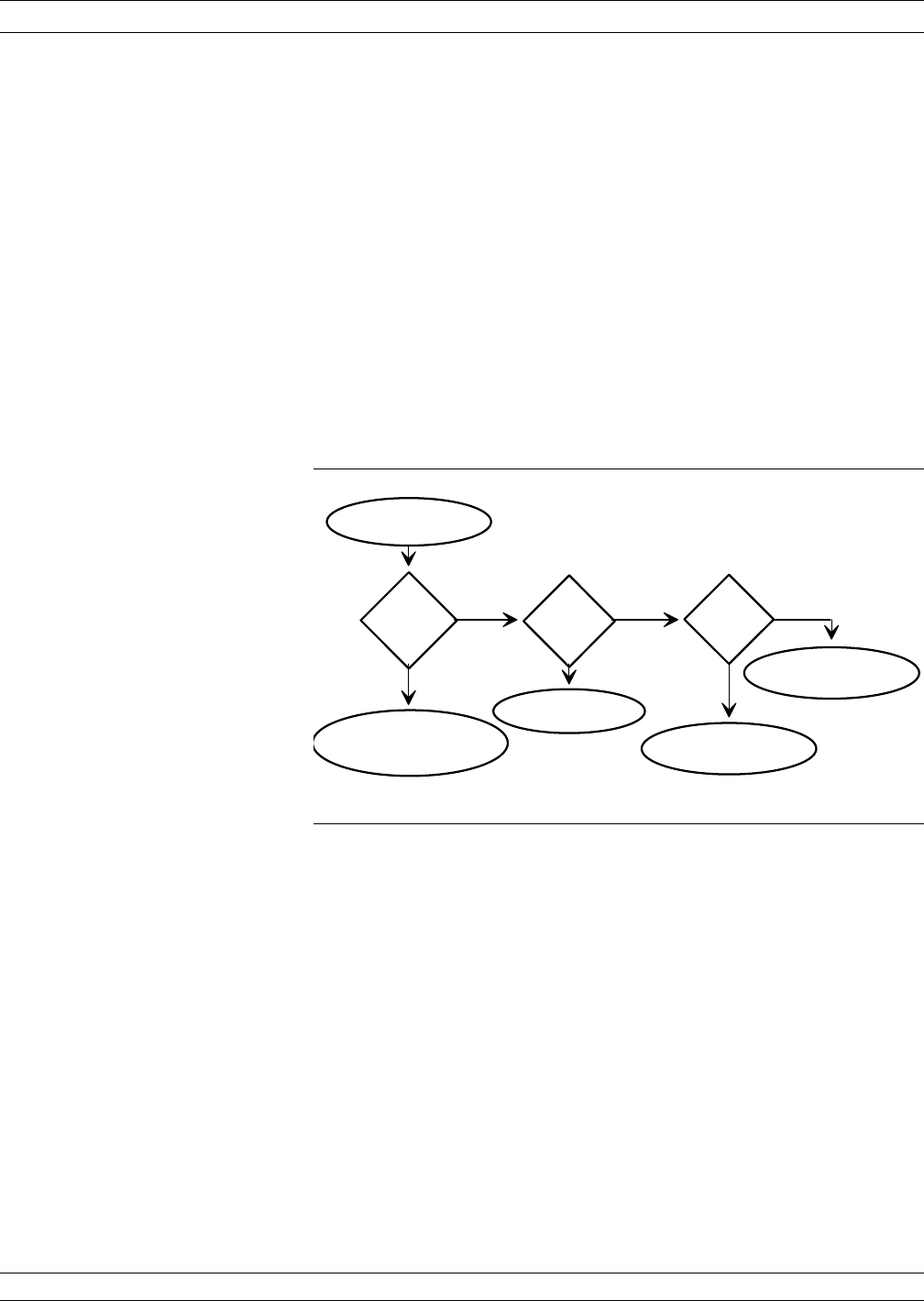
Measurement Status The 37XXXC displays measurement-status messages (in red when ap-
propriate) in the upper-right corner of the graticule (channel) to which
they apply.
Sweep Indicator Marker A blue sweep-indicator marker appears at the bottom of each dis-
played graph-type. It indicates the progress of the current sweep.
When measuring quiet data—that is, data having few or no perturba-
tions—this indicator assures that the instrument is indeed sweeping.
Its position is proportional to the number of data points measured in
the current sweep. If the sweep should stop for any reason, the posi-
tion of the indicator will stop changing until the sweep resumes.
6-6 DATA DISPLAY
CONTROL The following figure shows the algorithm that the 37XXXC uses to dis-
play the active channel.
37XXXC OM 6-13
DATA DISPLAYS DATA DISPLAY CONTROL
YES
N O
YES
YES
N O N O
DUAL
CHANNEL
D I S P L A Y E D
1 - 3 ?
C H A N G E T O D U A L 1 - 3
+ C H A N G E T O
A C T I V E C H A N N E L
C H A N G E T O D U A L 2 - 4
+ C H A N G E T O
A C T I V E C H A N N E L
S E L E C T A C T I V E C H A N N E L
( P R E S S C H 1 , C H 2 , C H 3 , C H 4 )
C H A N N E L
P R E S E N T L Y
D I S P L A Y E D
?
C O N T I N U E
D I S P L A Y I N G A C T I V E C H A N N E L
( S I N G L E , D U A L , O R F O U R - C H A N N E L
D I S P L A Y )
C H A N G E T O
A C T I V E C H A N N E L
S I N G L E
CHANNEL
D I S P L A Y E D
?
Figure 6-13. Active Channel Algorithm
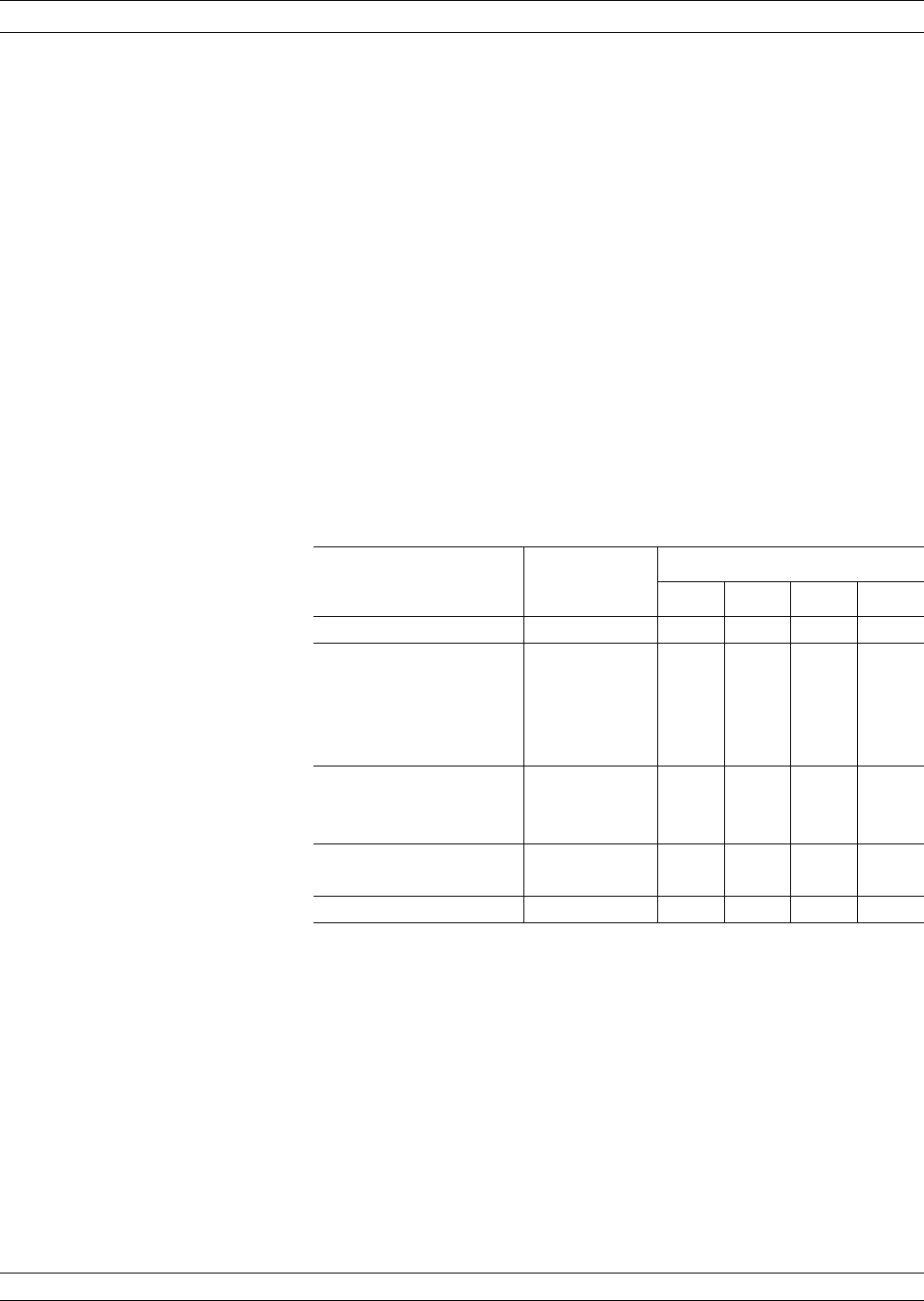
S-parameter Selection If you select a new S-parameter using Menu SP (Appendix A), it ap-
pears on the then-active channel in the same graph-type in which it
was last displayed. The following table shows the displayable S-pa-
rameters based on the correction type you have in place. If you at-
tempt to display other S-parameters, an error message appears. In
cases when there is no last-displayed S-parameter stored, the display
will default as shown. If an S-parameter is selected for which there
was no last-displayed graph-type, the display defaults to S21,S
12 Log
Magnitude and Phase and S11,S
22 Smith.
Data Display Update When you change a control panel parameter that affects the appear-
ance of the display, the entire display changes immediately to reflect
that change. For example, if you press Autoscale, the entire display
rescales immediately. You do not have to wait for the next sweep to see
the results of the change. The following parameters are supported for
this feature: Reference Delay, Offset, Scaling, Auto Scale, Auto Refer-
ence Delay, Trace Math, IF BW, and Smoothing. In the case of Aver-
aging, the sweep restarts.
If the knob is used to vary any of the above parameters, the change oc-
curs as the measurement progresses–that is, the continuing trace will
reflect the new setting(s).
When you change a marker frequency or time (distance), the readout
parameters will change. This change reflects the changes in measure-
ment data at the marker’s new frequency, using data stored from the
previous sweep.
Display of Markers Once you have selected a marker to display, it will appear on the
screen. It does not matter what resolution you have selected. When
you set a marker to another calibrated frequency and then lower the
DATA DISPLAY CONTROL DATA DISPLAYS
6-14 37XXXC OM
Correction Type Displayable
S-parameters Default Display Position
CH1 CH2 CH3 CH4
None All S11 S12 S21 S22
Frequency
Response
Reverse Transmission S12 S12
Forward Transmission S21 S21
Both S12,S
21 S12 S21
Port 1 Reflection Only S11 S11
Port 2Reflection Only S22 S22
Reflection Only, Both S11, S22 S11 S22
Forward 1-Path 2-Port S11,S
21 S11 S21
Reverse 1-Path 2-Port S12,S
22 S12 S22
12-Term All S11 S12 S21 S22
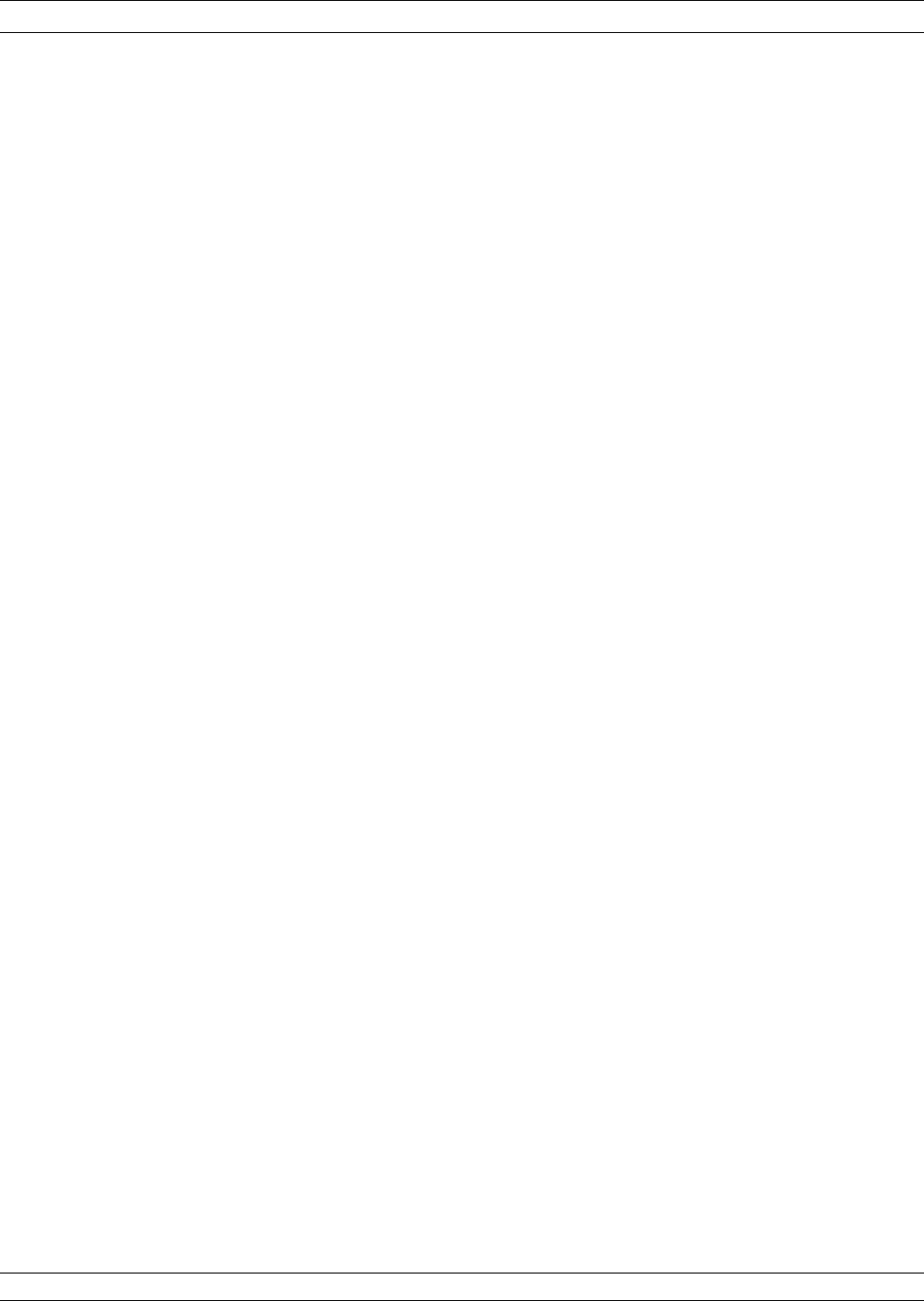
resolution, that frequency and the marker will continue to display. It
will display even if its frequency is not consistent with the data points
in the lower-resolution sweep.
6-7 HARD COPY AND DISK
OUTPUT In addition to the LCD screen, the Model 37XXXC is capable of output-
ting measured data as a:
qTabular Printout
qScreen-Image Printout
qPen Plot
qDisk Image of the Tabular Data Values
The selection and initiation of this output is controlled by the Hard
Copy keys.
Tabular Printout An example of a tabular format is shown in Figure 6-14 (page 6-16).
The tabular formats are used as follows:
qTabular Printout Format: Used when printing three or four chan-
nels.
qAlternate Data Format: Used when printing one or two channels.
In tabular printouts, the 37XXXC shifts the data columns to the left
when an S-Parameter is omitted. Leading zeroes are always sup-
pressed. The heading (Model, Device ID, Date, Operator, Page) appears
on each page.
Screen-Image Printout In a Screen-Image Printout, the exact data displayed on the screen is
dumped to the printer. The dump is in the graphics mode, on a
pixel-by-pixel basis.
Plotter Output The protocol used to control plotters is “HP-GL (Hewlett-Packard
Graphics Language). HP-GL contains a comprehensive set of vector
graphics type commands. These commands are explained in the Inter-
facing and Programming Manual for any current model
Hewlett-Packard plotter, such as the 7470A.
When the plotter is selected as the output device, it is capable of draw-
ing the graph shown on the screen or of drawing only the data trace(s).
Multiple traces may be drawn on a single sheet of paper (in different
colors, if needed).
Disk Output The 37XXXC can write-to or read-from the disk all measured data.
This data is stored as an ASCII file in the exact same format as that
shown for the tabular printout in Figure 6-14 (page 6-16). If read back
from the disk, the data is output to the printer. There, it prints as
tabular data.
37XXXC OM 6-15
DATA DISPLAYS HARD COPY AND DISK OUTPUT

Table of Contents
7-1 INTRODUCTION ...................................7-3
7-2 DISCUSSION .....................................7-3
Establishing the Test Ports.............................7-3
Understanding the Calibration System ......................7-5
Calibrating for a Measurement ..........................7-9
Evaluating the Calibration ............................7-11
Verification Kits ..................................7-11
7-3 SLIDING TERMINATION..............................7-13
7-4 SOLT CALIBRATION ................................7-19
Calibration Procedure ...............................7-19
7-5 OFFSET-SHORT CALIBRATION (SSLT)......................7-28
Calibration Procedure ...............................7-28
7-6 TRIPLE OFFSET-SHORT CALIBRATION (SSST).................7-32
Calibration Procedure ...............................7-32
7-7 LRL/LRM CALIBRATION ..............................7-36
7-8 TRM CALIBRATION.................................7-46
7-9 MERGE CAL FILES APPLICATION ........................7-47
Chapter 7
Measurement
Calibration
IMPORTANT NOTE
The 37100C Direct Access Receiver cannot make S-parameter measurements without an ex-
ternal reflectometer setup. This manual describes calibration and S-parameter measure-
ments for the 372XXC and 373XXC. Most of these measurements can also be used with the
371XXC assuming the user understands the need for an external reflectometer. Anritsu of-
fers an optional reflectometer test set that can be used. This reflectometer is described and a
drawing is shown in the Technical Data Sheet provided as Appendix C in this manual.
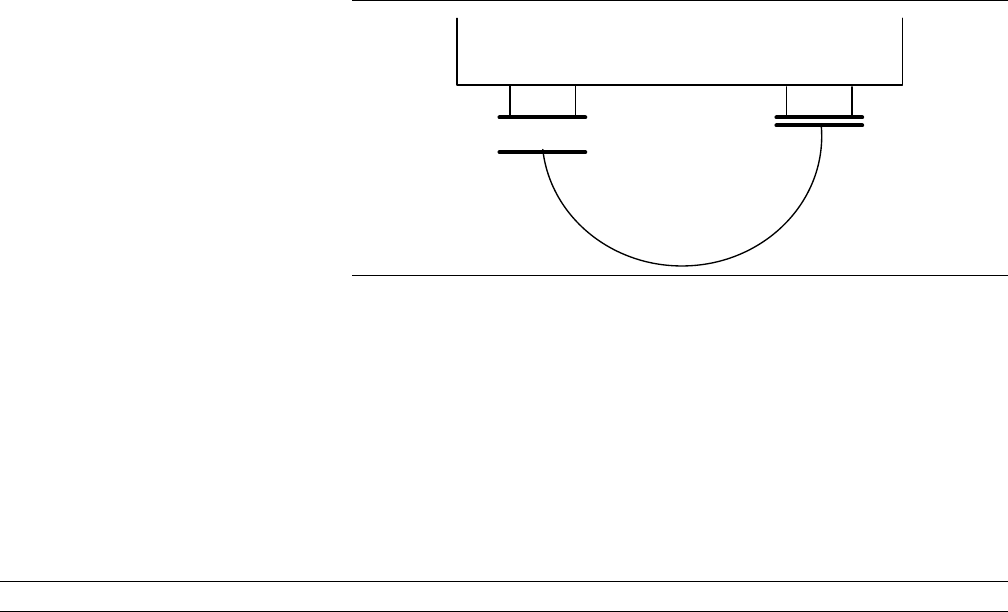
Chapter 7
Measurement Calibration
7-1 INTRODUCTION This section provides discussion and examples for performing a mea-
surement calibration. It also provides a detailed procedure for calibrat-
ing with a sliding termination.
7-2 DISCUSSION Measurements always include a degree of uncertainty due to imperfec-
tions in the measurement system. The measured value is always a
combination of the actual value plus the systematic measurement er-
rors. Calibration, as it applies to network analysis, characterizes the
systematic measurement errors and subtracts them from the mea-
sured value to obtain the actual value.
The calibration process requires that you establish the test ports, per-
form the calibration, and confirm its quality. Let us examine each of
these steps.
Establishing the Test Ports Figures 7-1 and 7-2 are two of the most common approaches used to
make measurements on two-port devices. In many cases, you may need
adapters to change between connector types (N, SMA, GPC-7, etc.) or
between genders (male [M] or female [F]).
37XXXC OM 7-3
PORT 1
PORT 2
Figure 7-1. Establishing the Test Port
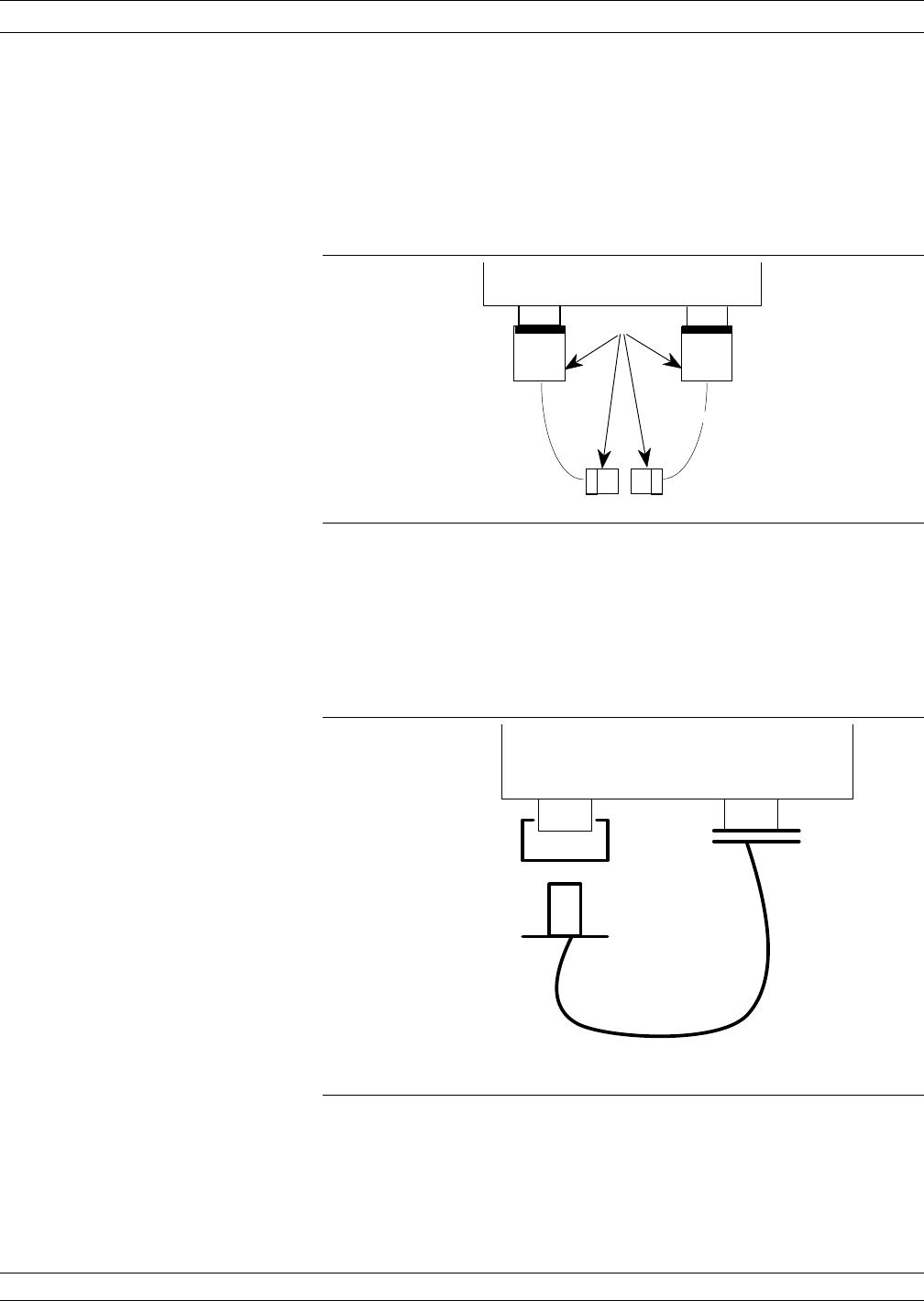
The use of cables and/or adapters does not effect the final measure-
ment result, if they were in place for the calibration process. The vec-
tor error corrections established during the calibration process elimi-
nates cable and/or adapter effects as long as the ports used are stable
and exhibit good repeatability. Figure 7-2 shows such a configuration.
Many calibration kits include adapters that are designed to have equal
phase length. These parts are called phase equal adapters (PEA).
Anritsu designs in-series adapters (e.g., K Connector M-M, M-F, F-F)
to be phase insertable when technically possible. When available, it is
good practice to use PEAs to establish test ports (Figure 7-3).
DISCUSSION MEASUREMENT CALIBRATION
7-4 37XXXC OM
PORT 1 PORT 2
ADAPTERS
Figure 7-2. Using Adapters on the Test Port
33KKF50
33KFKF50
TEST SET CONNECTOR
KM
TEST PORT 1
KM
TEST PORT 2
KF
CABLE CONNECTOR
KM
Figure 7-3. Use of PEAs to Establish Test Ports
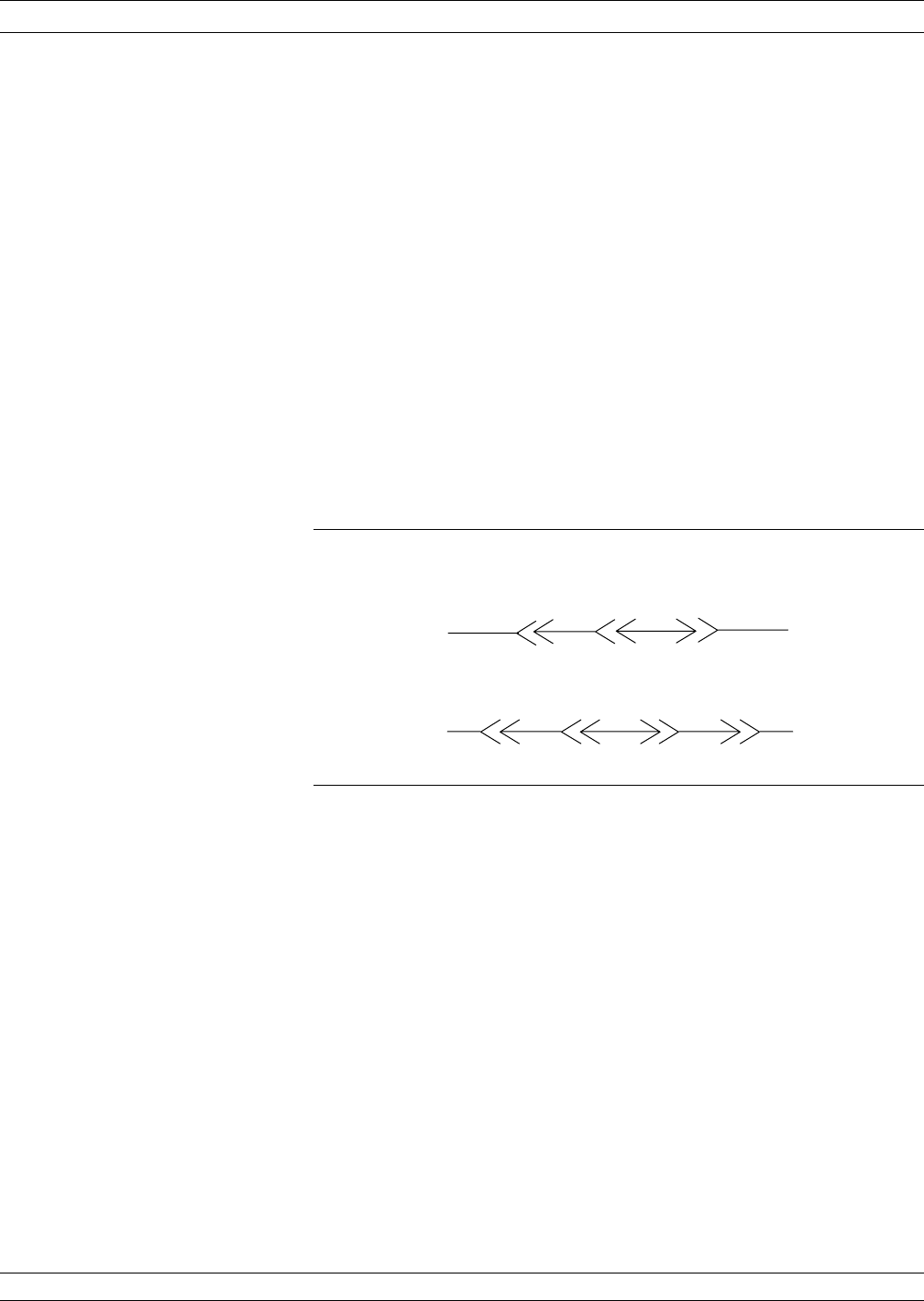
This approach offers two advantages:
qIt minimizes wear on the more expensive test set and cable con-
nectors
qIt provides a simple solution to measuring non-insertable devices
(e.g., a filter with K female input and output connectors) by
merely swapping PEAs after calibration. See Figure 7-4
NOTE
In this and other discussions, we will talk about
“insertable” and “non-insertable” devices. Insertable de-
vices have an insertable connector pair (i.e., male input
and female output connectors) and can be measured after
a through calibration. A non-insertable device has a
non-insertable pair of connectors. This would be the case if
it included female connectors on both ports or different
connector types on each port. Therefore, “non-insertables”
cannot be connected directly into the measurement path
without an adapter.
Understanding the
Calibration System Measurement errors must be reduced by a process that uses calibra-
tion standards. The standards most commonly used are Opens, Shorts,
and Z0(Characteristic Impedance) Loads. In conjunction with a
through connection, these standards can correct for the major errors in
a microwave test system. These errors are Directivity, Source Match,
Load Match, Isolation, and Frequency Tracking (reflection and trans-
mission).
Calibration also corrects for many internal system errors, such as RF
leakage, IF leakage, and system component interaction.
Random errors such as noise, temperature, connector repeatability,
DUT sensitive leakages, frequency repeatability, and calibration vari-
ables are not completely correctable. However, some of them can be
minimized by careful control. For instance: temperature effects can be
reduced by room temperature control, calibration variables can be re-
duced through improved technique and training, and frequency errors
can be virtually eliminated by the fully synthesized internal source.
37XXXC OM 7-5
MEASUREMENT CALIBRATION DISCUSSION
Calibration
Measurement
MF
PEA
USING THE PHASE-EQUAL INSERTABLE
(PEI)
FMF
MFMF MFMF
DUT
TEST
PORT TEST
PORT
TEST
PORT TEST
PORT
PEA
PEA
PEA
M
Figure 7-4. Using Phase-Equal Insertables
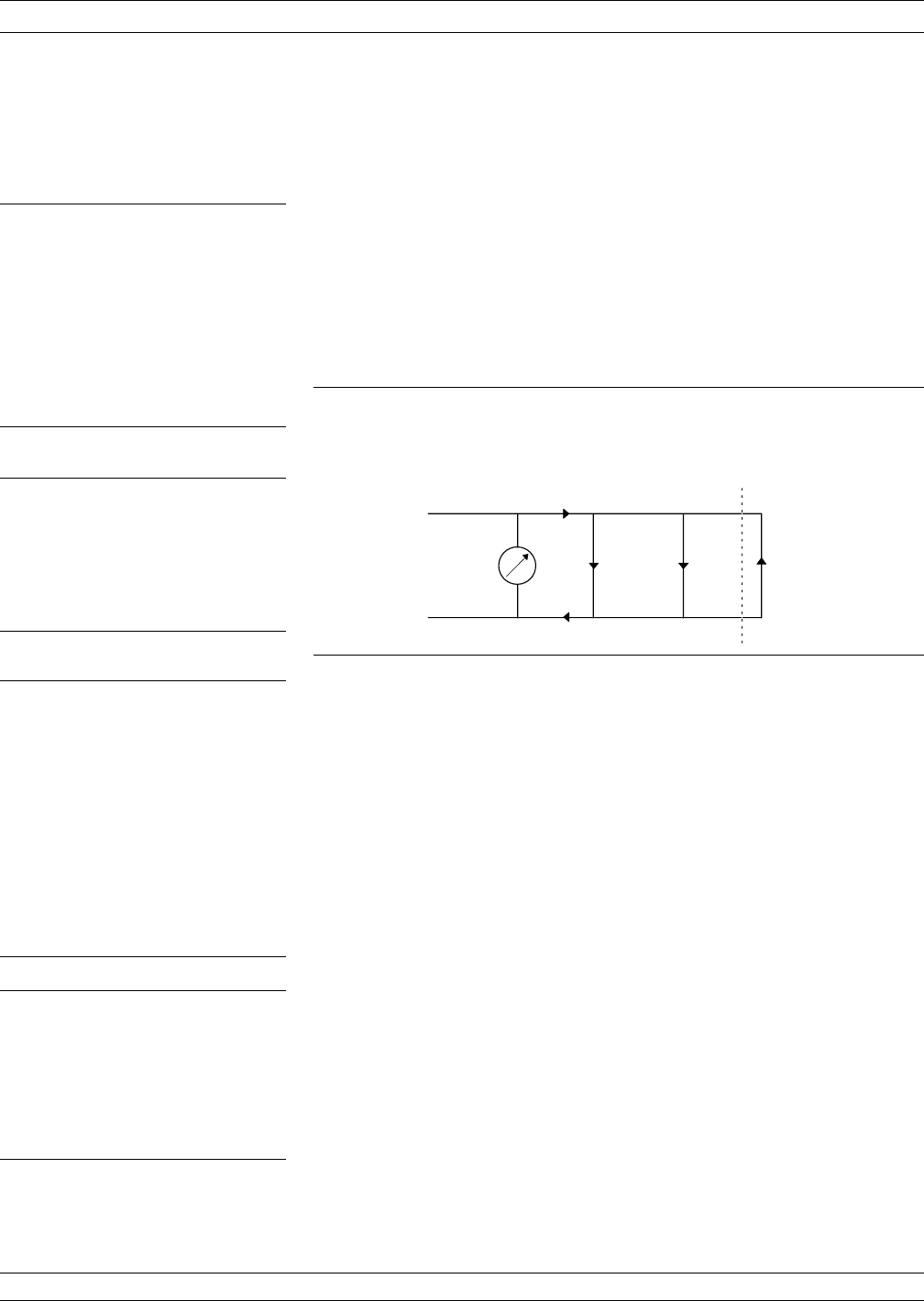
We know that adapters and cables degrade the basic directivity of the
system, but these errors are compensated by vector error correction.
In general, transmission measurement errors are source match, load
match, and tracking; while reflection measurement errors are source
match, directivity, and tracking.
Error modeling and flow graphs are techniques used to analyze the
errors in a system. Error models describe the errors, while flow graphs
show how these errors influence the system. Error models (Figure 7-5)
can become quite complex.
The 37XXXC offers a selection of calibration possibilities depending on
the user’s needs. These possibilities are as follows:
qFrequency Response
qReflection Only—1 Port
q1 Path, 2 Port
q12-Term—2 Port, Both Directions
These calibration types are described below.
Frequency Response: Corrects for one or both of the transmission error
terms associated with measurements of S21, S12, or both.
DISCUSSION MEASUREMENT CALIBRATION
7-6 37XXXC OM
INTERNAL SYSTEM ERRORS
·RF Leakage
·IF Leakage
·System Interaction
RANDOM ERRORS
·Frequency
·Repeatability
·Noise
·Connector Repeatability
·Temperature/Environmental
Changes
·Calibration Variables
ERRORS REDUCED BY CALIBRATION
·Directivity
·Source Match
·Load Match
·Frequency Sensitivity (Tracking)
·Isolation
DIRECTIVITY, SOURCE MATCH,
AND TRACKING ERRORS
DISTORTED MEASUREMENT
S
11M
E
D
S
11A
E
S
Figure 7-5. Example of Error Modeling
TRANSMISSION MEASUREMENT
ERRORS
·Source Match
·Load Match
·Tracking
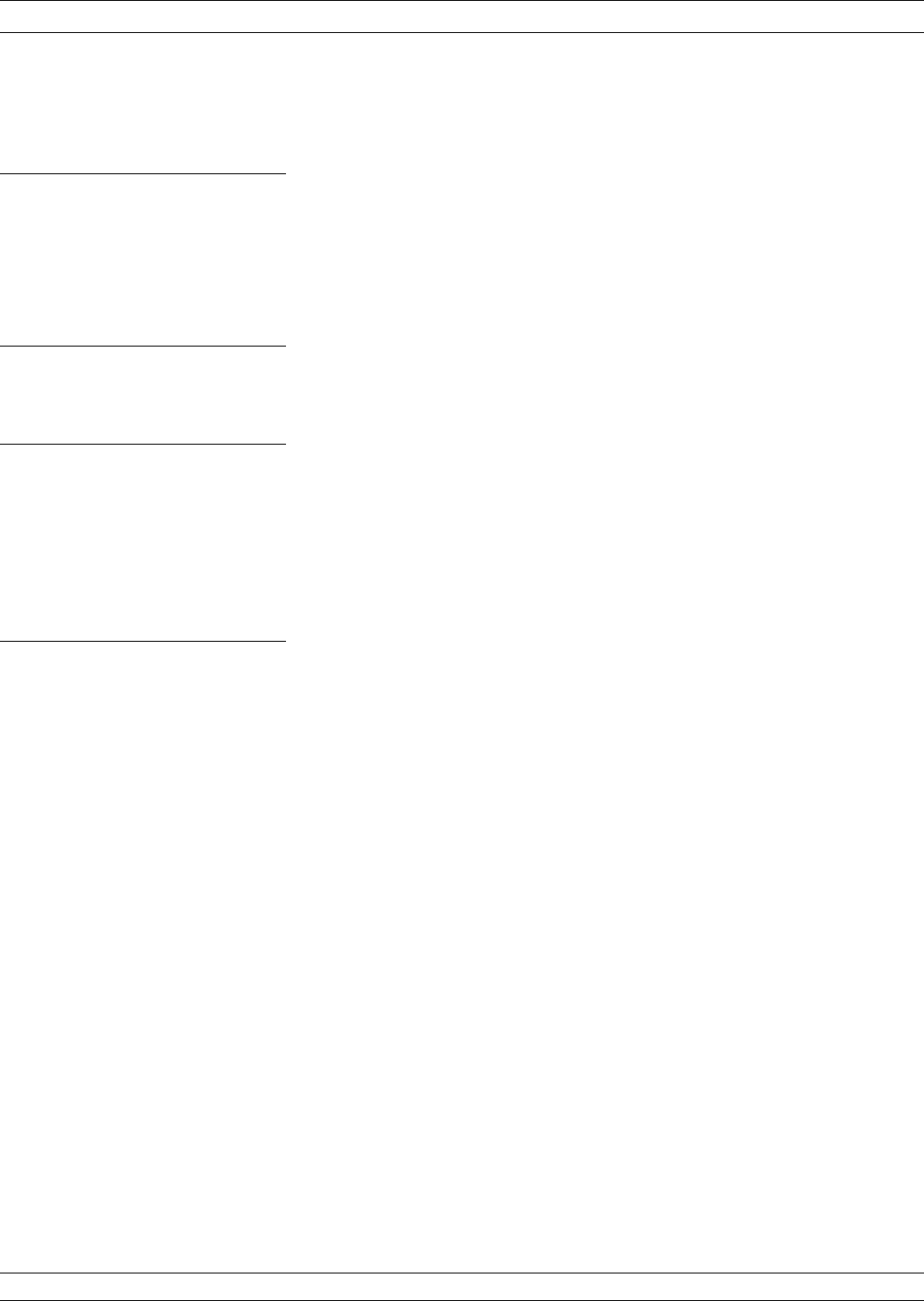
Reflection Only: Corrects for the three error terms associated with an
S11 measurement (EDF, ESF, and ERF), an S22 measurement (EDR,
ESR, and ERR), or both.
1 Path, 2 Port: Corrects for the four forward-direction error terms
(EDF, ESF, ERF, and ETF), or the four reverse-direction error terms
(EDR, ESR, ERR, and ETR).
Full 12-Term: Corrects for all twelve error terms associated with a
two-port measurement. A 12-Term error model is shown in Figure 7-6.
Measurement calibration using the 37XXXC is straightforward and
menu directed. A short time spent in preparation and preplanning will
make the process simple and routine. (Example: Adjusting the coaxial
cables used in the measurement setup such that insertion of the DUT
causes minimal flexing of these cables).
The screen prompts on the 37XXXC guide you through the calibration
process—a process that consists of connecting and disconnecting con-
nectors and moving the slide on a sliding load (if one is used).
The most critical part of the calibration process is properly seating and
torquing the connectors. Also, you will notice that the calibration takes
longer when the ports are terminated with a load. This is intentional.
It allows for more averaging during the isolation measurement.
37XXXC OM 7-7
MEASUREMENT CALIBRATION DISCUSSION
REFLECTION MEASUREMENT ERRORS
·Source Match
·Directivity
·Tracking
CALIBRATION TYPES
·Frequency Response
·Reflection Only—1 Port
·1 Path, 2 Port
·12 Term—2 Port, Both Directions
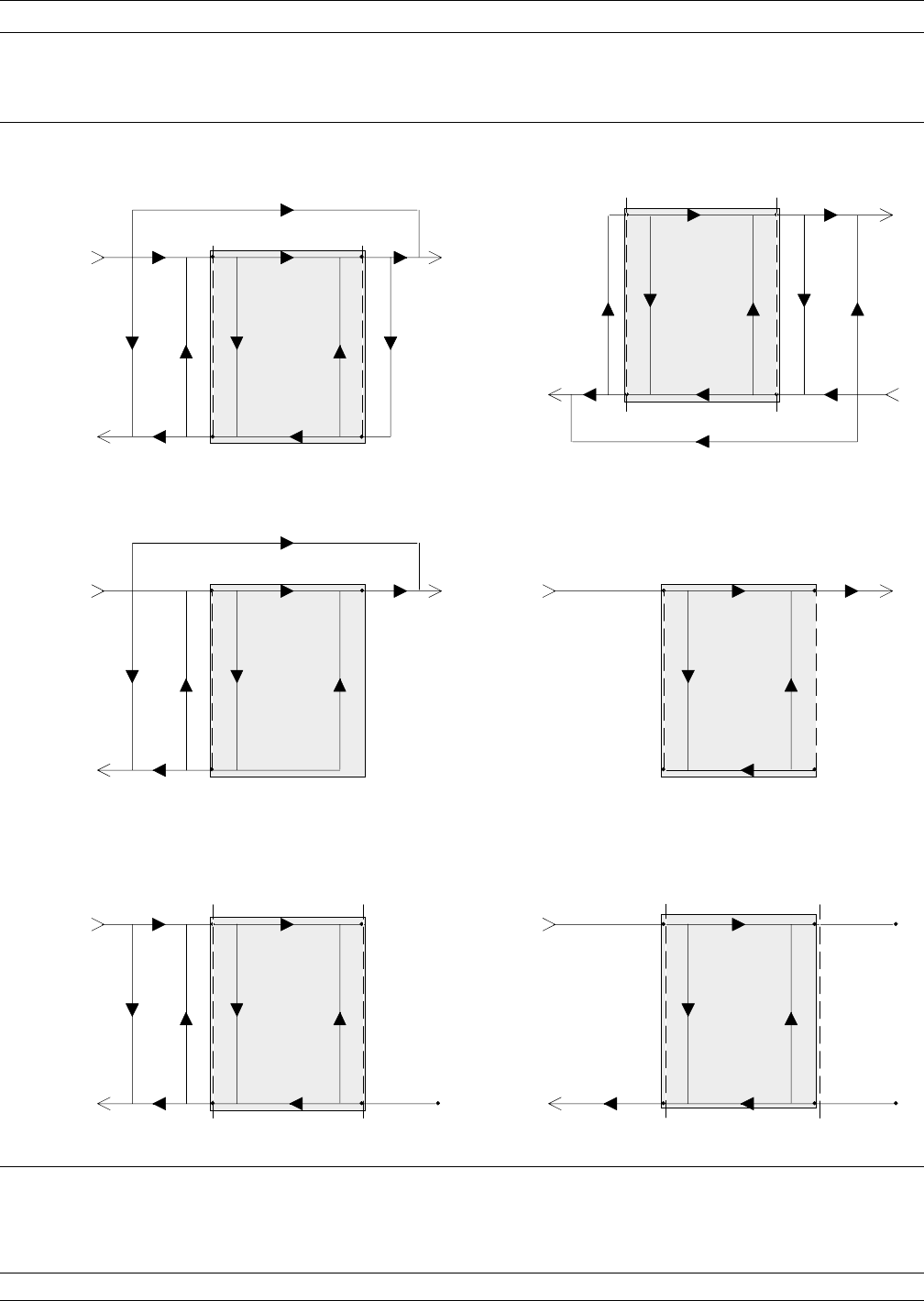
DISCUSSION MEASUREMENT CALIBRATION
7-8 37XXXC OM
PORT 1 PORT 2
RF IN
PORT 1 PORT 2
PORT 1 PORT 1
PORT 2 PORT 2
PORT 1 PORT 2 PORT 1 PORT 2
RF IN RF IN
RF IN
RF IN
DUT DUT
DUT
DUT
DUT
DUT
12 - TERM
E
LFDF
E
TF
E
TR
E
SR
E
DR
E
RF
E
S
12
S
21
S
11
LR
E
22
S
RR
E
S
21
S
21
S
21
R
S
11
S
11
S
11
S
11
S
12
DF
E
DF
E
22
S
RF
E
TF
E
TF
E
RF
E
RF
EE
XR
1
1
Forward Direction Terms Reverse Direction Terms
1 Path - 2 Port Terms
Reflection Only Terms
Frequency Response - Transmission Only Terms
Frequency Response - Reflection Only Terms
E
XF
E
SF
S
21M
E
SF
11M
S
11M
S
S
21M
S
12M
S
S
22
21
E
S
11M
SF
E
XF
Figure 7-6. Error Models
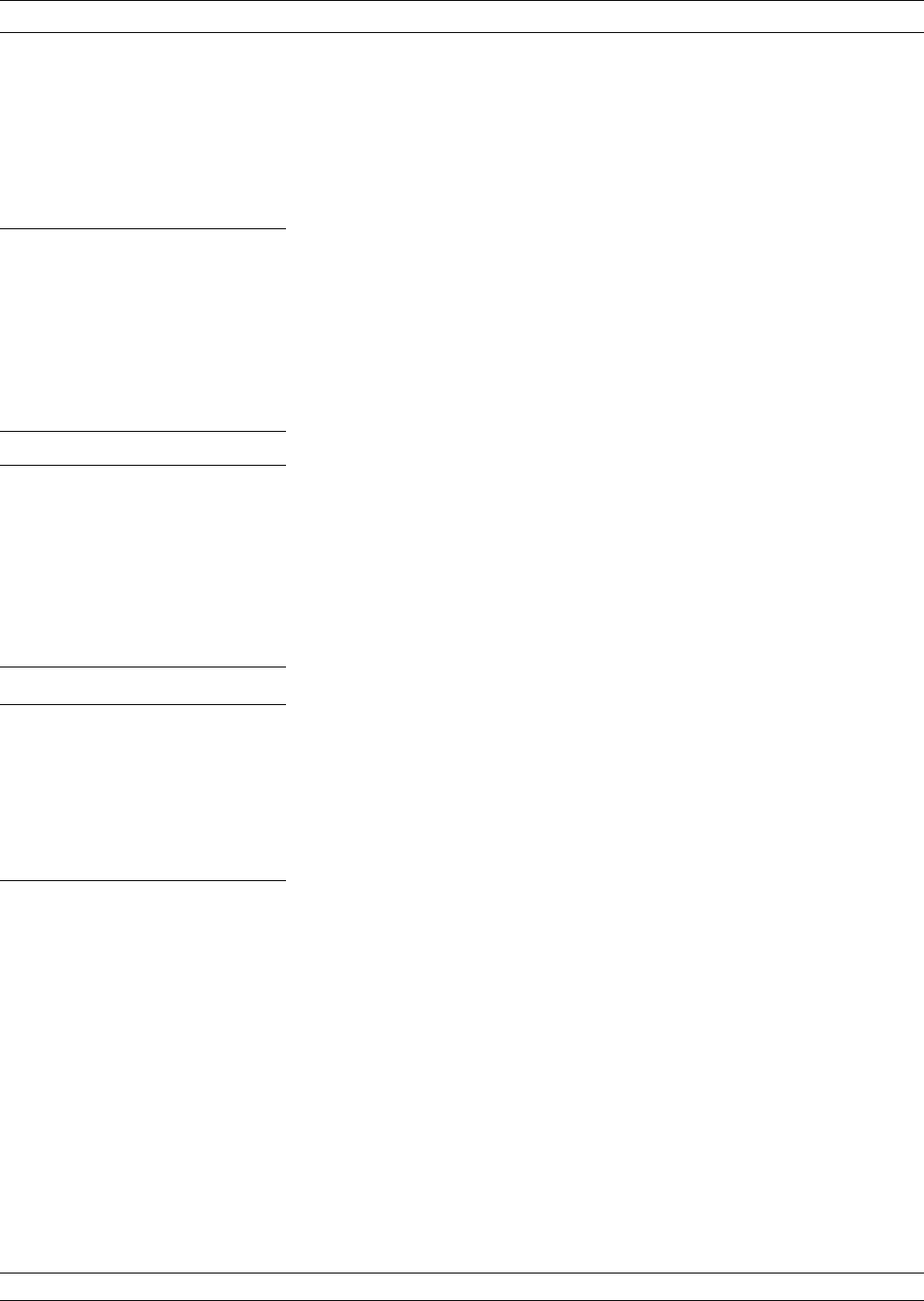
Calibrating for a
Measurement Let us assume that we want to correct for three errors in the reflection
measurement: source match, directivity, and tracking. We accomplish
this using three standards.
Shorts are the easiest to visualize. They totally reflect all of the inci-
dent RF energy output at a precise phase. The terms zero-ohms imped-
ance, voltage null, and 180° phase all define an RF Short.
Opens are similar to Shorts, but their response is more complex. The
terms voltage maximum, infinite impedance, and 0° phase all define a
perfect Open. A perfect Open, however, is only a concept. In reality
Opens always have a small fringing capacitance.
To account for the fact that the Open will not predictably reflect im-
pedance at an exact 0° phase reference, we alter its response using co-
efficients that accurately characterize the fringing capacitance. The co-
efficients are different for each coaxial line size, since each size has a
different fringing capacitance. To maximize accuracy, ensure that
these coefficients are installed prior to the calibration (Menu U3).
As Opens and Shorts provide two references for a full reflection, Z0ter-
minations provide a zero-reflection reference.
Ideal Z0terminations must consist of two parts, a perfect connector
and an infinite-length perfect transmission line that absorbs all of the
RF energy that enters it (no reflections).
Infinite length transmission lines are unwieldy at best, so you must
use less-than-ideal terminations. For calibration purposes there are
two common types: broadband loads and sliding terminations.
37XXXC OM 7-9
MEASUREMENT CALIBRATION DISCUSSION
CALIBRATING FOR A REFLECTION
MEASUREMENT USES THREE
STANDARDS:
·Short
·Open
·Termination
IDEAL TERMINATIONS
·Reflectionless
·Perfect Connector
·Infinite-Length, Dimensionally Ex-
act, Reflectionless Transmission
Line
PRACTICAL Zo TERMINATIONS
·Broadband Load
·Sliding Termination
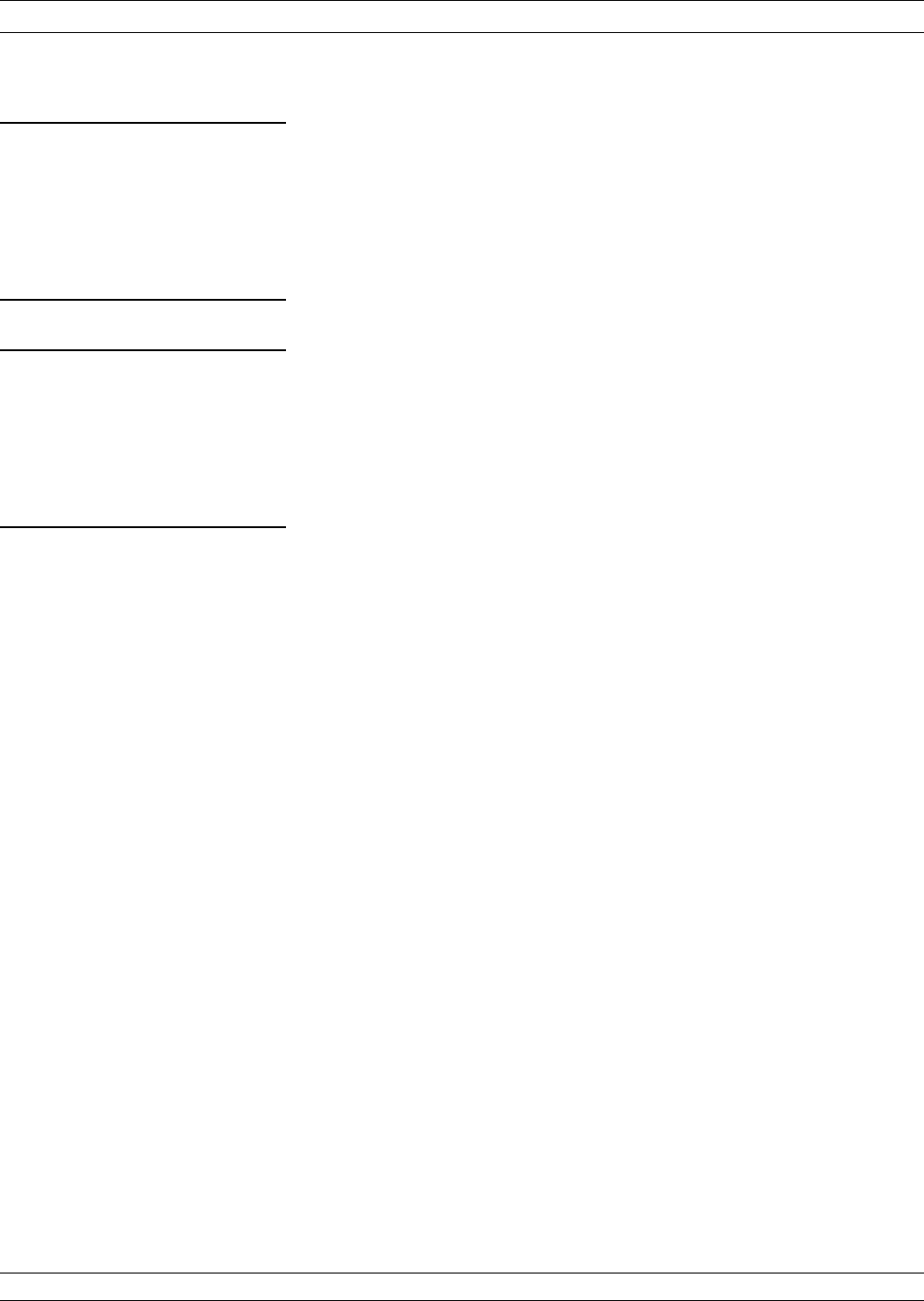
Broadband loads are widely used. An example is the Anritsu 28 Series
Termination. These terminations are easy to use as calibration tools,
and they are adequate for most applications.
Sliding Loads are the traditional vector network analyzer Z0calibra-
tion reference. They provide the best performance when the applica-
tion requires high-precision return loss measurements. Sliding loads
consist of a connector, a long section of precision transmission line, and
a microwave load that is movable within the transmission line. One
thing to remember with sliding loads is that they have a low-frequency
limit and must be used with a fixed load below this cutoff frequency
for full frequency coverage. Anritsu sliding loads cut off at 2 GHz.
(V-connector sliding loads cut off at 4 GHz).
Pin depth—the relationship between the interface positions of the
outer and center conductors—is the most critical parameter under
your control in a sliding load. An example of its criticality is that an
incorrect pin depth of 0.001 inch can cause a reflection return loss of
44 dB. And, since we are trying to calibrate to accurately measure a 40
dB return loss, correct pin depth makes a big difference!
Cables in the measurement system are another cause for concern. The
main criteria for a cable are stability and repeatability. Anritsu offers
two types of cables that meet these criteria: semi-rigid and flexible.
Our semi-rigid cables provide maximum stability with limited flexibil-
ity of movement. Our flexible cables allow more freedom of movement
and provide good phase stability.
DISCUSSION MEASUREMENT CALIBRATION
7-10 37XXXC OM
BROADBAND LOAD
·Easy to Use
·Inexpensive
·Adequate for Most Applications
SLIDING LOAD
·Connector
·Long Transmission Line
·Movable Microwave Load
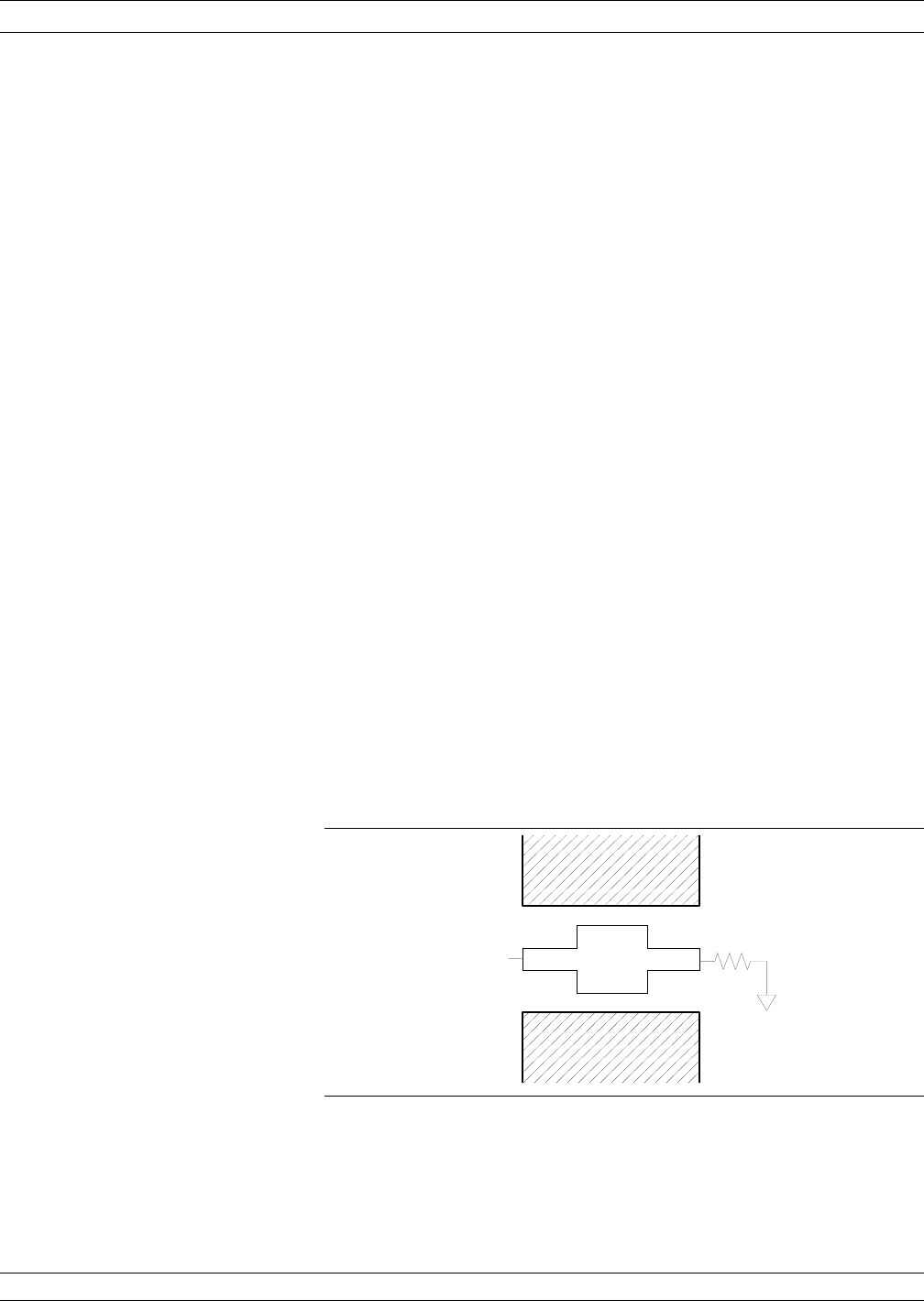
Evaluating the Calibration The 37XXXC provides an accurate representation of complex data.
However, it can only provide accuracy to the extent of the supplied cal-
ibration data. For this reason, it is necessary to periodically verify the
calibration data and the 37XXXC system performance.
Calibration verification reveals problems such as a poor contact with
one of the calibration components, improper torquing, or a test port out
of specification. Problems like these can easily occur during a calibra-
tion procedure. Anyone who has experienced one of these problems and
stored bad data—after having performed a complete calibration proce-
dure—knows the frustration it can cause. Additionally, it can be very
costly to use incorrectly taken measurement data for design or quality
assurance purposes.
The best way to confirm a calibration is to measure a precision,
known-good device and confirm its specifications.
Verification Kits Anritsu has developed several precision-component kits: for 3.5 mm
connectors, for GPC-7 connectors, K Connectorsâand V Connectorsâ.
These are, respectively, the Models 3666, 3667, and 3668 and 3669 Ver-
ification Kits.
Each of the kits contain 20 dB and 50 dB attenuators, an airline, and a
Beatty Standard. A Beatty Standard is a two-port mismatch similar to
a beadless airline. It consists of a center conductor with a discontinuity
in the middle providing the mismatch (Figure 7-7).
Typically, these verification kits will be used by calibration or metrol-
ogy labs. Each of the kits contain several precision components, all of
which have been characterized at specified frequencies. The data on
these components is stored on a disk provided with the verification kit.
37XXXC OM 7-11
MEASUREMENT CALIBRATION DISCUSSION
S
1 1
5 0
9
2 5
9
5 0
9
5 0
9
Figure 7-7. The Beatty Standard
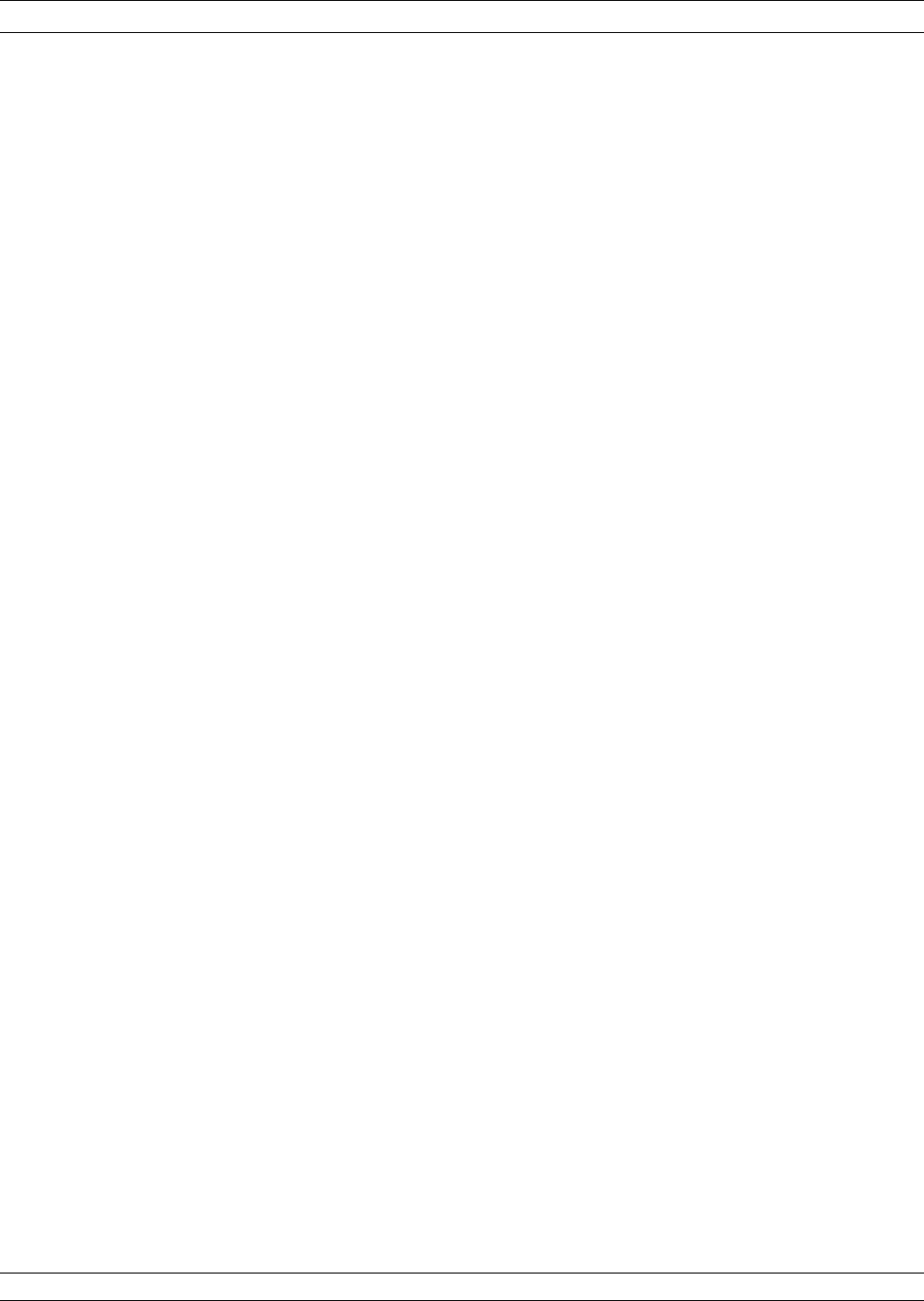
The verification of the kit components is straight forward. The compo-
nents are first measured with the 37XXXC, then they are compared
with the data recorded on the disk. If the measured data compares fa-
vorably with the recorded data (taking tolerances into consideration),
then the system is known to be operating properly and providing accu-
rate data.
There is one caution that you need to observe when using Verification
Kits. Because the verification components have been characterized,
you must handle them carefully so that you do not change their known
characteristics. Consequently, you should not have them available for
daily use. Rather, you should only use them for the accuracy verifica-
tion checks taken every 6-to-12 months (or at any other time the sys-
tem’s integrity is in doubt).
This completes the discussion on calibration. Refer to paragraph 7-3
for a procedure showing how to calibrate the sliding load.
DISCUSSION MEASUREMENT CALIBRATION
7-12 37XXXC OM
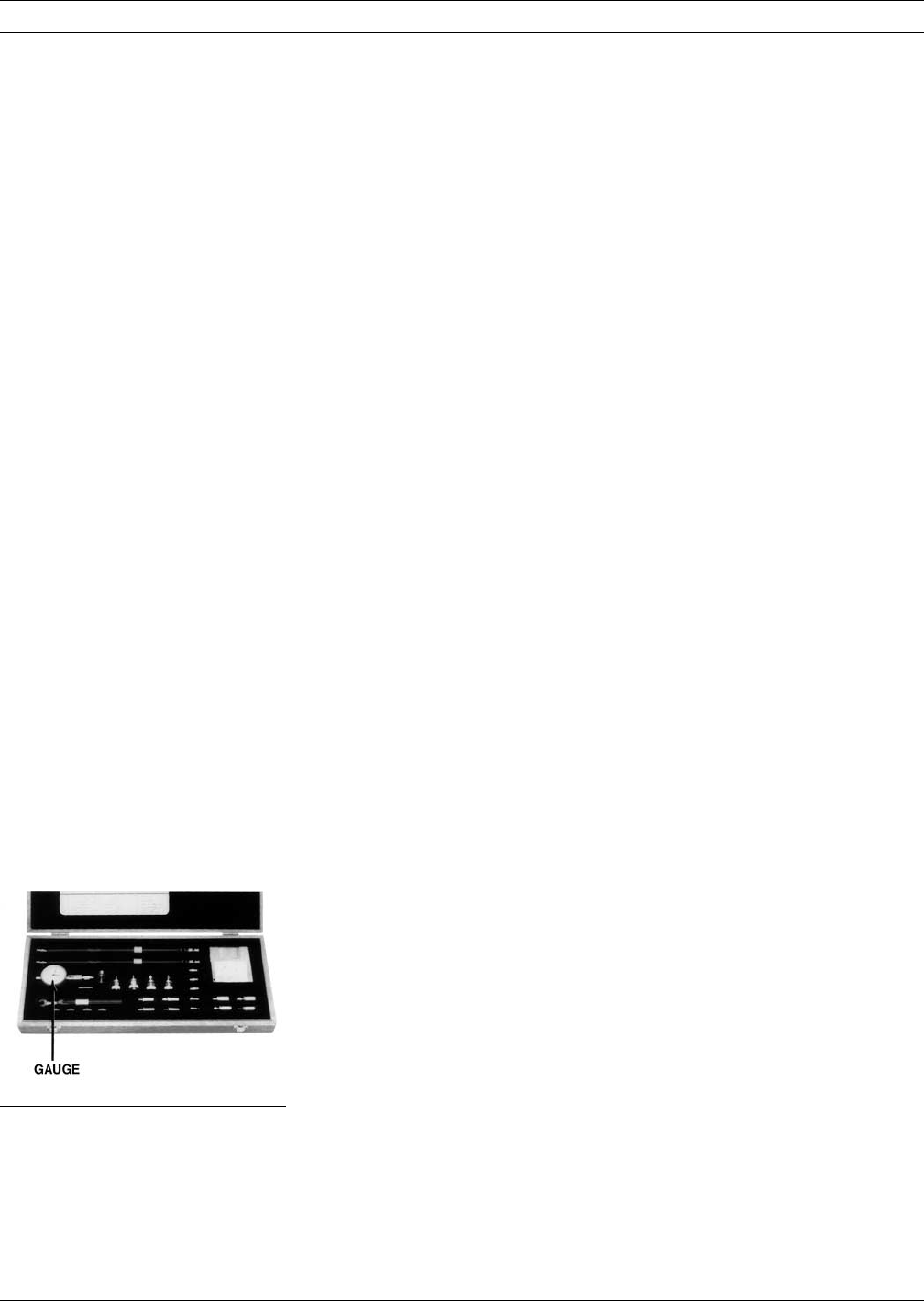
7-3 SLIDING TERMINATION Sliding terminations (loads) are the traditional Z0calibration-refer-
ence devices for vector network analyzer calibration. When correctly
used and perfectly aligned, they can be more accurate than precision
fixed loads. However, sliding terminations have a 2 GHz (4 GHz for
V-Connector sliding loads) low-frequency limit and must be used with
a fixed load for full frequency-range coverage.
Sliding terminations consist of a connector, a long section of precision
transmission line, and a microwave load that is movable within the
transmission line. Pin depth—the relationship between the interface
positions of the outer and center conductors—is the most critical pa-
rameter that you can control in a sliding termination. An example of
its criticality is that an incorrect pin depth of 0.001 inch can cause a
reflection return loss of 44 dB. Since you are usually calibrating to ac-
curately measure a greater than 40 dB return loss, correct pin depth is
essential.
Since setting an accurate pin depth is so important, this discussion
centers on describing how to set the pin depth for male and female
sliding terminations. Calibration with the sliding termination is essen-
tially the same as described below for the broadband load.
The procedure below uses the Model 3652 Calibration Kit and its
17KF50 and 17K50 Sliding Terminations. Calibration is similar for the
Model 3650 SMA/3.5mm, Model 3651 GPC-7 and Model 3654 V con-
nector kits. For the 3651, the procedure is simpler because the GPC-7
connector is genderless, there are no male and female versions.
Procedure
Step 1. Remove the Pin Depth Gauge from the kit, place it
on the bench top.
NOTE
The gauge is convertible between male and female. The
following procedure describes the zeroing process for the
female fitting. The procedure for the male fitting begins
with Step 16.
37XXXC OM 7-13
MEASUREMENT CALIBRATION SLIDING TERMINATION
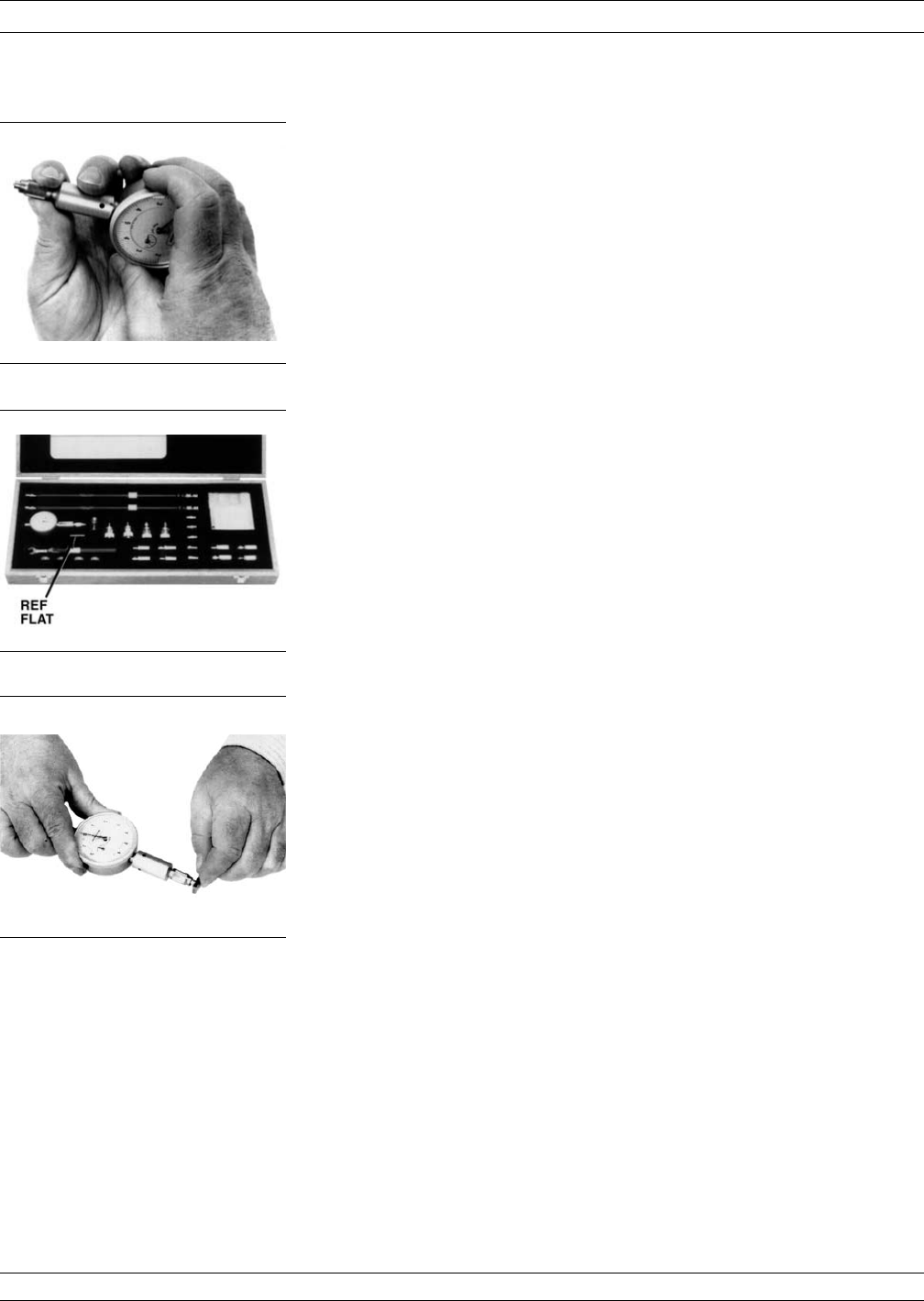
Step 2. Push the outer locking ring towards the gauge to ex-
pose the center pin.
Step 3. Take the 01-210 Ref Flat from the kit.
Step 4. While holding the gauge as shown, press the Ref
Flat firmly against the end of the exposed center
pin.
SLIDING TERMINATION MEASUREMENT CALIBRATION
7-14 37XXXC OM
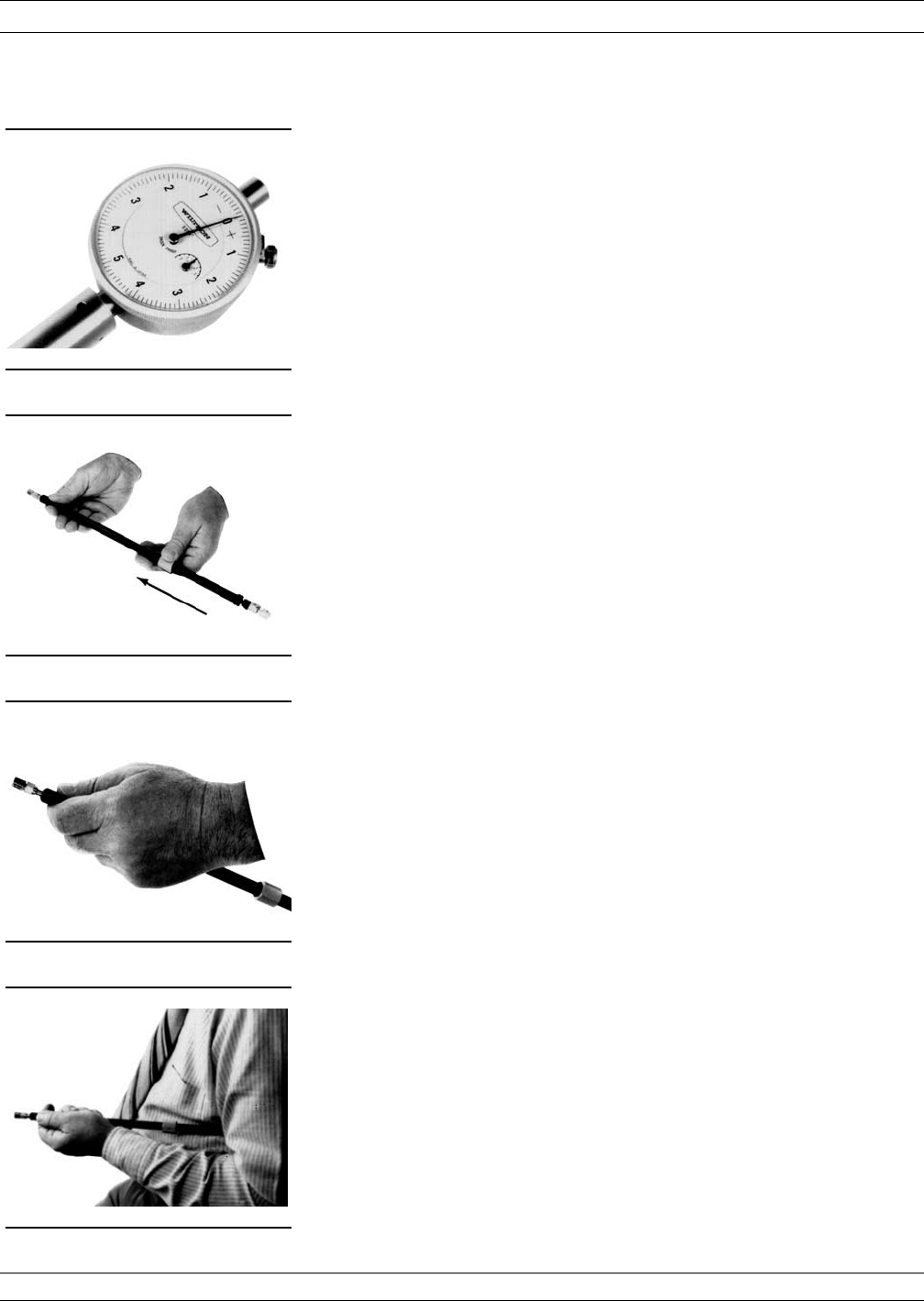
Step 5. While pressing the Ref Flat against the center pin,
check that the pointer aligns with the “0” mark. If it
does not, loosen the bezel lockscrew and rotate the
bezel to align the pointer with the “0” mark. Tighten
the bezel lock screw.
NOTE
Gently rock the Ref Flat against the center
pin to ensure that it is fully depressed and
you have accurately set the gauge for zero.
Step 6. Remove the sliding termination with the fe-
male-connector (17KF50, for this example) from the
kit, and slide the load all the way toward the end
closest to the connector.
Step 7. With either hand, pick up the sliding termination
near its connector end.
Step 8. Cup the sliding termination in your palm, and sup-
port the barrel between your body and crooked el-
bow.
37XXXC OM 7-15
MEASUREMENT CALIBRATION SLIDING TERMINATION
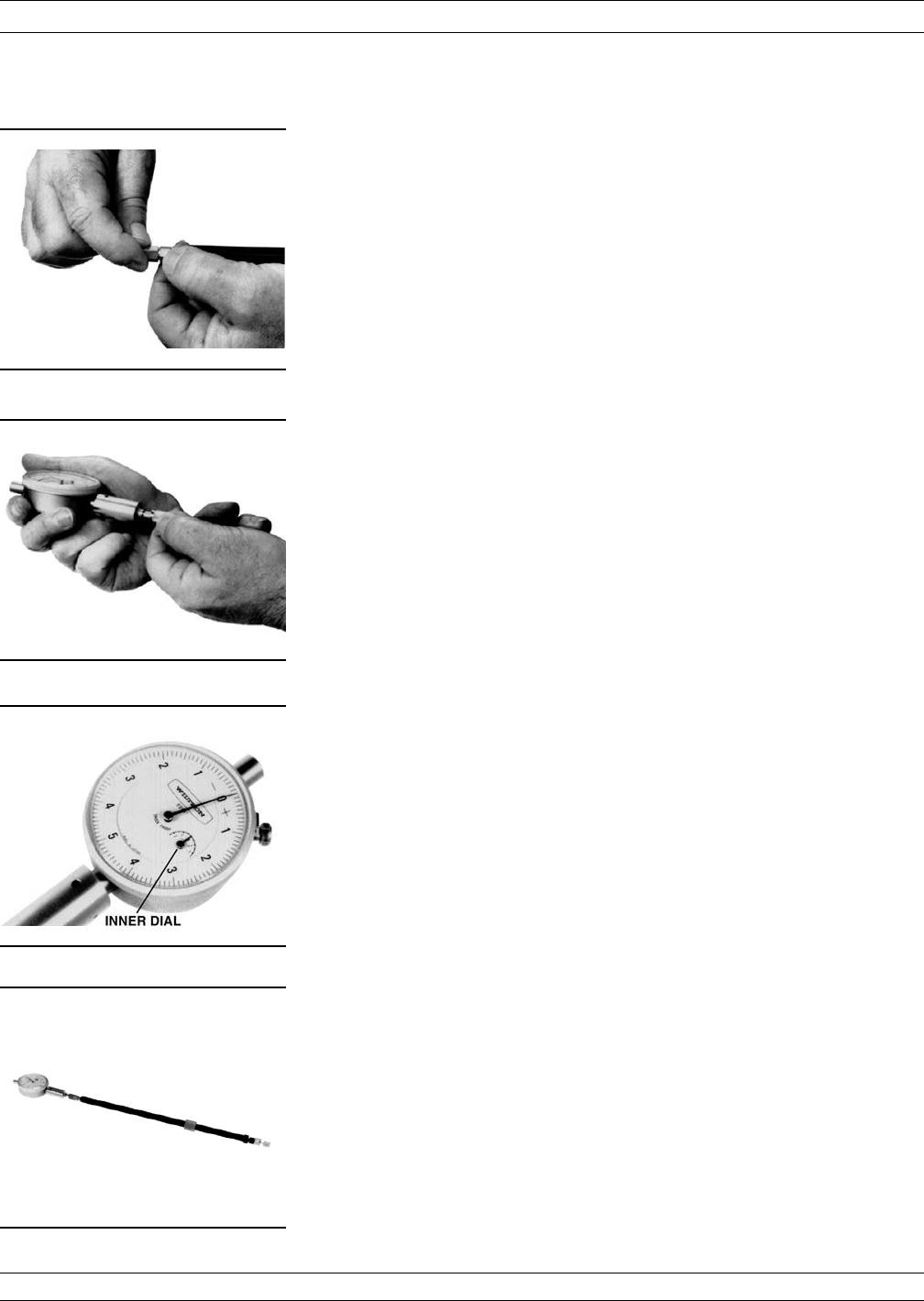
Step 9. Remove the flush short by holding its body and un-
screwing its connector.
Step 10. Install the gauge onto the end of the sliding termi-
nation.
Step 11. If the COARSE SET adjustment—which has been
set at the factory—has not moved, the inner dial on
the gauge will read “0.” If it doesn’t, perform the
Coarse Set Adjustment in Step 15.
Step 12. Place the sliding termination, with the gauge at-
tached, on the bench top.
SLIDING TERMINATION GENERAL INFORMATION
7-16 37XXXC OM
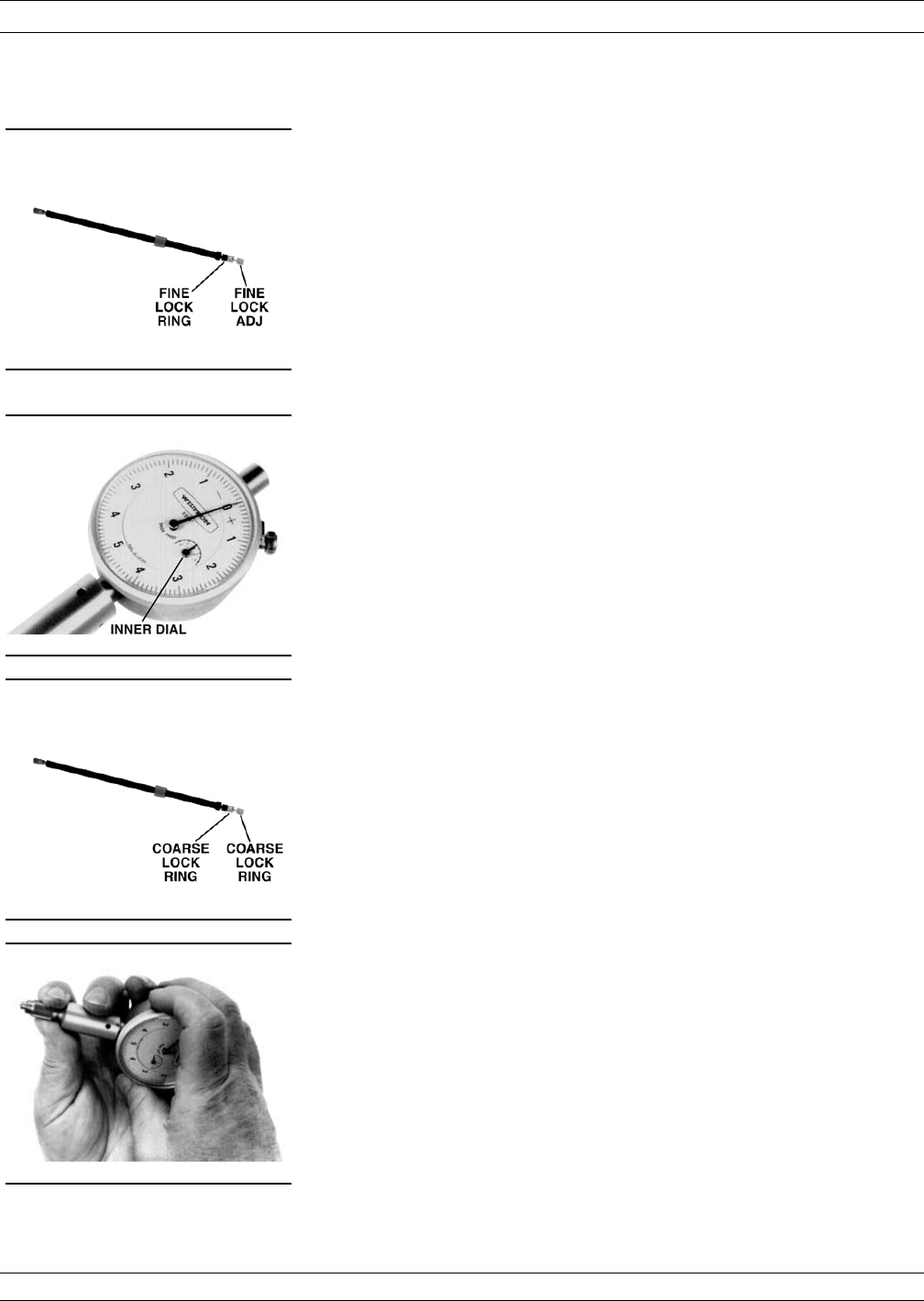
Step 13. Loosen the FINE LOCK ring and turn the FINE
ADJ ring to position the gauge pointer 2-3 small di-
visions on the “–” side of zero.
Step 14. Turn the FINE LOCK ring clockwise to both tighten
the adjustment and place the pointer exactly to “0.”
The Sliding Termination is now ready to use.
NOTES
Ensure that the inner dial reads “0.”
The following step is not normally necessary.
It needs to be done only if the adjustment
has changed since it was set at the factory.
Step 15. With the 01-211 Flush Short installed, loosen the
COARSE LOCK and gently push the COARSE SET
adjustment rod in as far as it will go. This coarsely
sets the center conductor to be flush against the at-
tached short. Return to Step 2.
Step 16. The procedure for adjusting the male-connector slid-
ing termination is essentially the same as that de-
scribed above. The only difference is that you must
install the female adapter on the end of the gauge
shaft, over the center conductor. To install this
adapter, proceed as follows:
Zero-set the gauge as described in Steps 2
through 5.
Push the outer locking ring back toward the
gauge and turn it clockwise onto the exposed
threads.
Loosen the lock ring one turn in a counterclock-
wise direction.
37XXXC OM 7-17
MEASUREMENT CALIBRATION SLIDING TERMINATION
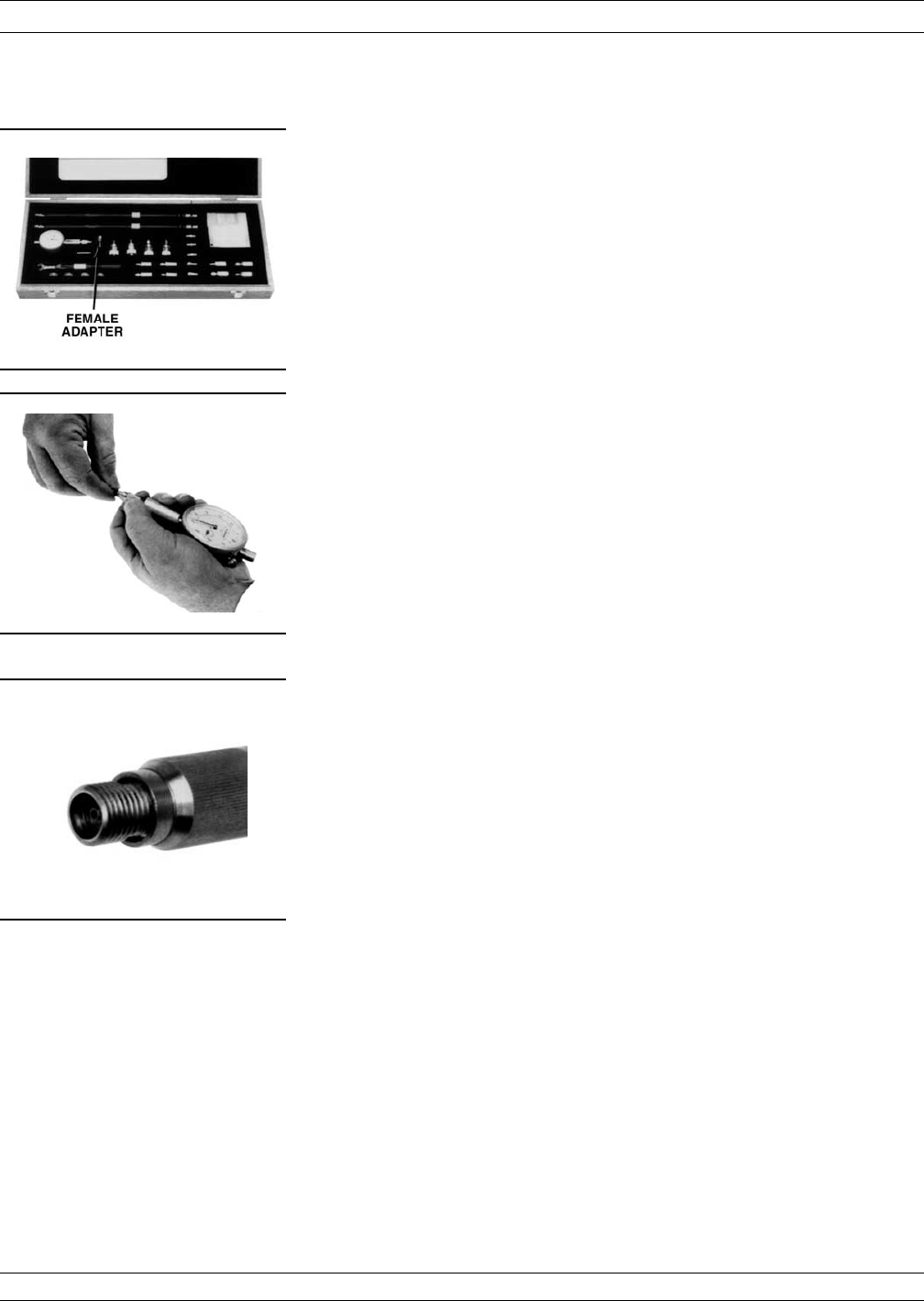
Step 17. Remove the 01-223 Female Adapter (“F ADAPTER
FOR PIN GAUGE”) from the kit.
Step 18. Install the female adapter over the center pin and
screw it into the locking ring, and tighten the outer
ring until it is snug against the housing.
Step 19. Inspect the end of the adapter, you should see no
more than two exposed threads. If so, repeat Steps 7
through 10.
Step 20. Connect the gauge to the sliding termination and
zero set the center pin using the FINE ADJ as pre-
viously described in Steps 2 through 5.
SLIDING TERMINATION GENERAL INFORMATION
7-18 37XXXC OM
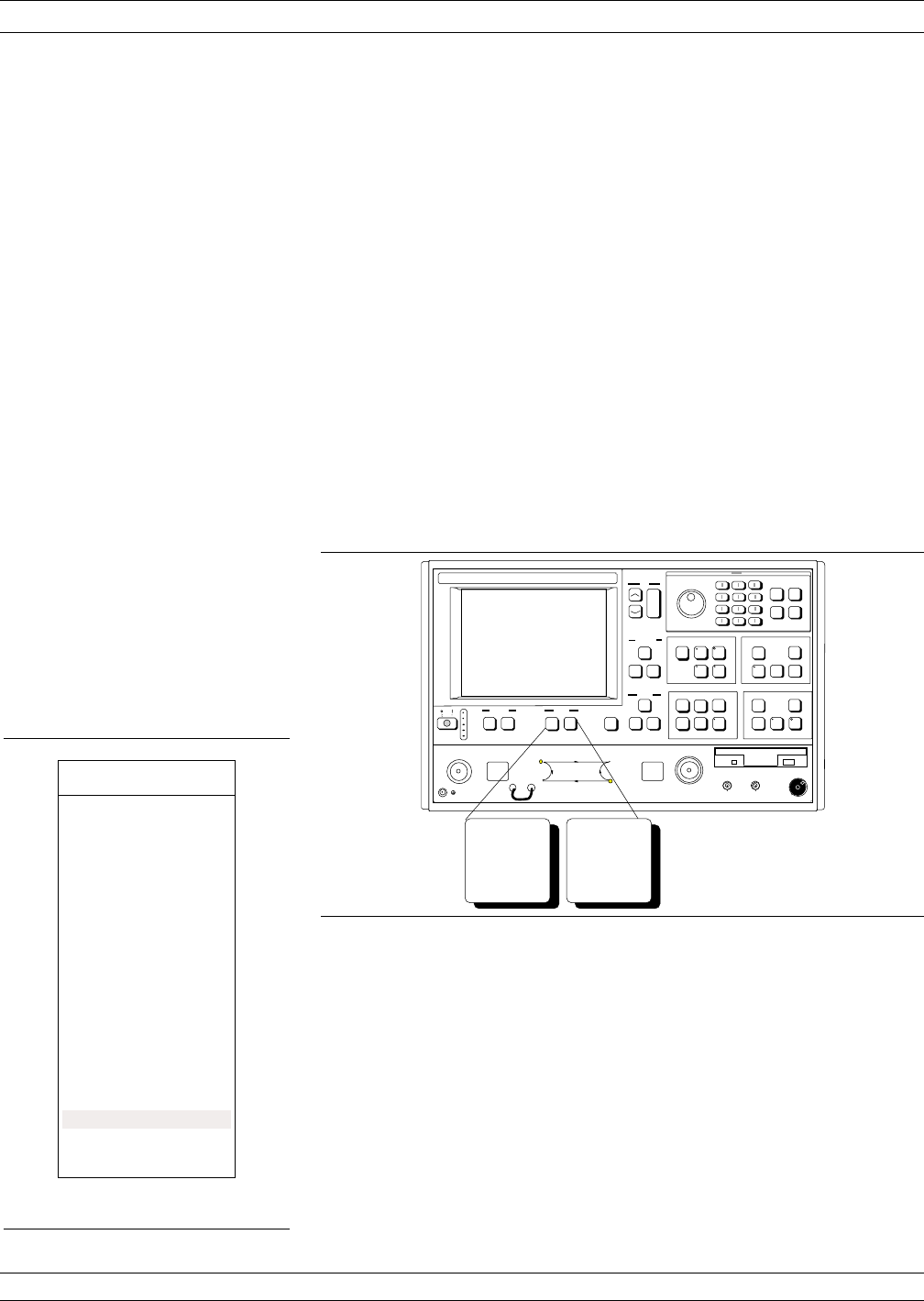
7-4 SOLT CALIBRATION The SOLT calibration for the 37XXXC Vector Network Analyzer sys-
tem uses a Short, Open, Load, and a Thru line connection to categorize
the inherent errors in the measurement system. These errors include
those caused by connectors as well as internal system errors such as
RF leakage, IF leakage, and component interaction. For maximum ac-
curacy, install the capacitive coefficients (for the open device) using
Menu U3.
NOTE
The SOLT calibration, in conjuction with the SSST calibra-
tion,are merged to create a continuous,single sweep broad-
band calibration on the ME7808A system. Refer to Chapter
15 for details about the broadband mode of operation.
Calibration Procedure A detailed, step-by-step procedure for performing a
Short-Open-Load-Throughline calibration is given below.
Step 1. Press the Begin Cal key.
Step 2. Select CHANGE CAL METHOD AND LINE
TYPE, in menu C11 (left). (This assumes SOLT and
COAXIAL are not presently shown in blue as being
selected.)
37XXXC OM 7-19
MEASUREMENT CALIBRATION SOLT CALIBRATION
Apply
Cal
Begin
Cal
MENU C11
BEGIN CALIBRATION
KEEP EXISTING
CAL DATA
REPEAT
PREVIOUS CAL
AUTOCAL
CAL METHOD
STANDARD
TRANSMISSION
LINE TYPE:
XXXXXXXX
CHANGE CAL
METHOD AND
LINE TYPE
NEXT CAL STEP
PRESS <ENTER>
TO SELECT
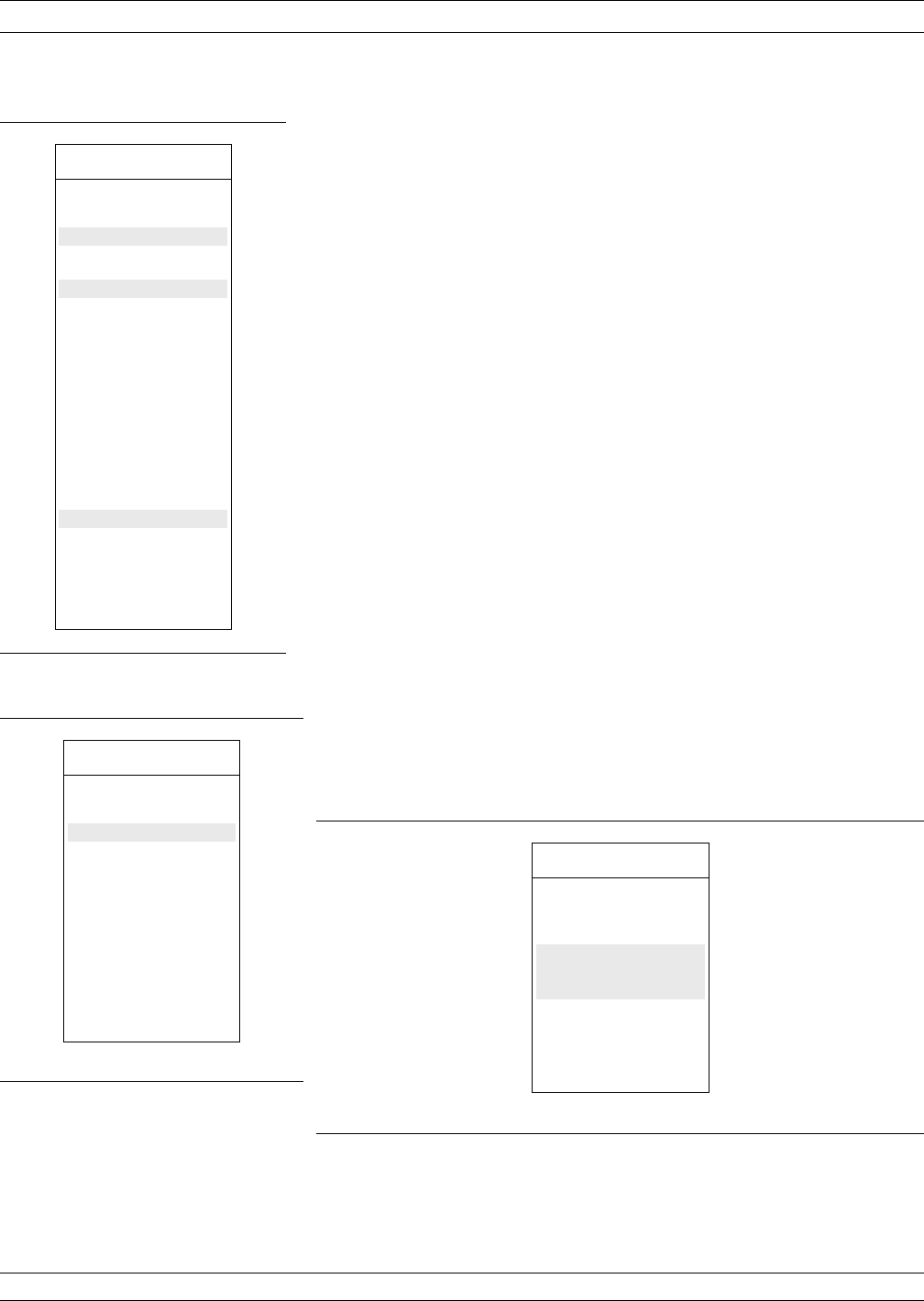
Step 3. When menu C11A (left) appears, move the cursor to
the following:
a. SOLT (STANDARD), then press the Enter key.
This selects Standard (SOLT) as the calibration
method.
b. COAXIAL, then press the Enter key. This se-
lects coaxial transmission line media.
c. NEXT CAL STEP, then press the Enter key.
This causes menu C11 to return to the screen.
Step 4. When menu C11 reappears, confirm that the SOLT
calibration method and COAXIAL line type have
been selected. Select NEXT CAL STEP and press
the Enter key to proceed. This brings up menu C5.
Step 5. Menu C5 (left) lets you select the type of calibration.
For this example, move the cursor to FULL
12-TERM and press the Enter key. This selection cal-
ibrates for all twelve error terms.
Step 6. The next menu, C5D, lets you choose whether to in-
clude or exclude the error terms associated with
leakage between measurement channels. For a nor-
mal calibration, you would choose to include these
error terms. Therefore, move the cursor to IN-
CLUDE ISOLATION ( STANDARD ) and press
the Enter key.
SOLT CALIBRATION MEASUREMENT CALIBRATION
7-20 37XXXC OM
MENU C11A
CHANGE CAL METHOD
AND LINE TYPE
NEXT CAL STEP
CAL METHOD
SOLT (STANDARD)
SSLT (DOUBLE
OFFSET SHORT
WITH LOAD)
SSST (TRIPLE
OFFSET SHORT)
LRL/LRM
TRM
TRANSMISSION
LINE TYPE
COAXIAL
WAVE GUIDE
MICROSTRIP
PRESS <ENTER>
TO SELECT
MENU C5
CALIBRATION
TYPE
FULL 12-TERM
1 PATH
2 PORT
TRANSMISSION
FREQUENCY
RESPONSE
REFLECTION
ONLY
PRESS <ENTER>
TO SELECT
MENU C5D
SELECT USE
OF ISOLATION
IN CALIBRATION
INCLUDE
ISOLATION
(STANDARD)
EXCLUDE
ISOLATION
PRESS <ENTER>
TO SELECT
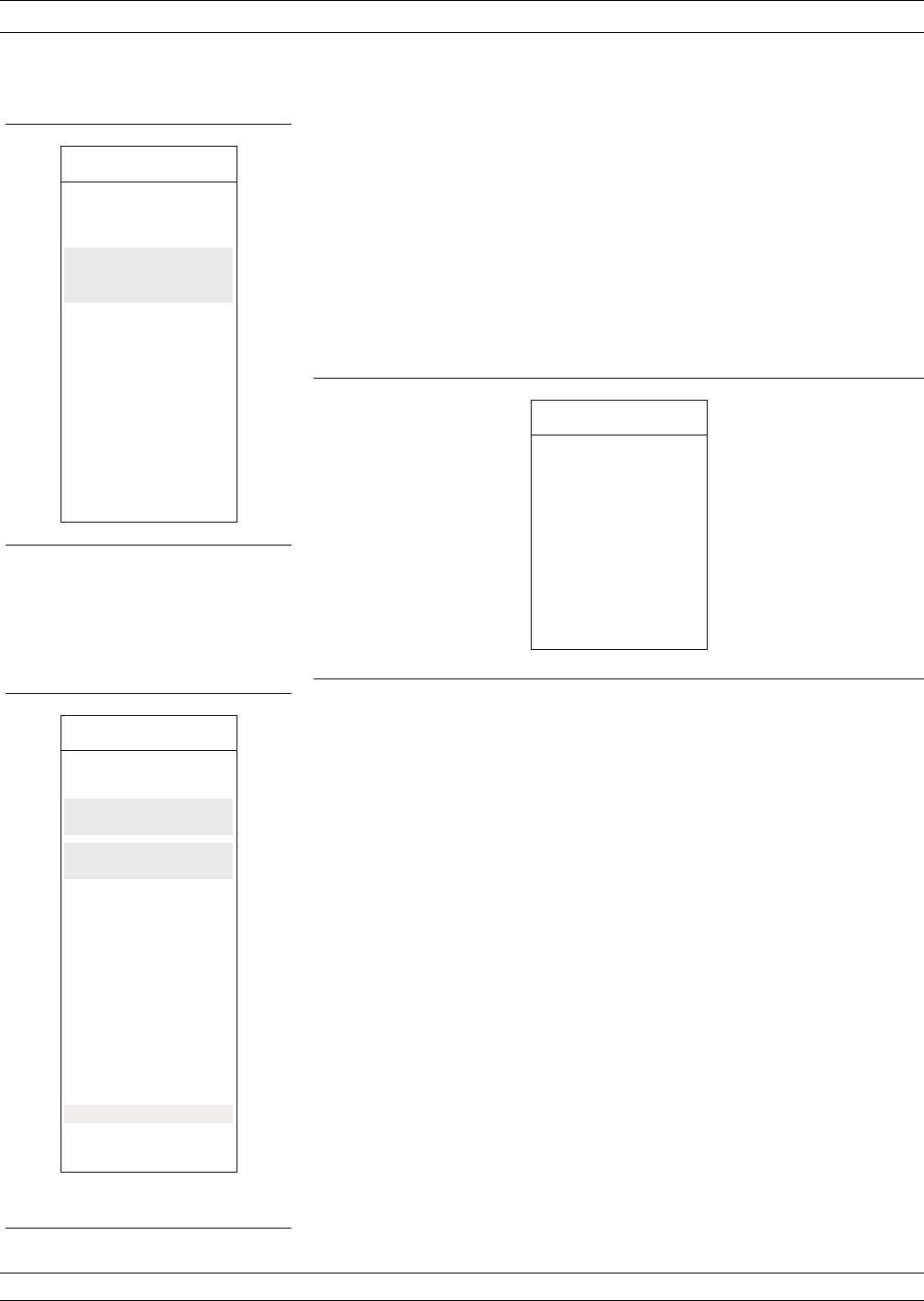
Step 7. Next, menu C1 appears. It lets you select the number
of frequency points at which calibration data is to be
taken. The choices are:
a. NORMAL: Data is taken at up to 1601 equally
spaced frequencies across the calibration fre-
quency range. Use this selection for this example.
b. C.W.: Data is taken at one point. This choice
brings up menu C2B (below) that lets you select
the single CW frequency point.
c. N-DISCRETE FREQUENCIES: This selection
lets you specify a discrete number of frequency
points, from 2 to 1601.
d. TIME DOMAIN: This selection is the calibra-
tion mode for low-pass time-domain processing.
It lets you select frequencies at integer (har-
monic) multiples of the start frequency.
Step 8. The next menu, C2 (left), lets you set your start and
stop frequencies. For this example, move the cursor
to START, press 40 on the keypad, and hit the MHz
terminator key. Perform like operations for the
STOP choice, except make entry read 20 GHz. After
setting the frequencies, select NEXT CAL STEP
and press the Enter key.
37XXXC OM 7-21
MEASUREMENT CALIBRATION SOLT CALIBRATION
MENU C1
SELECT
CALIBRATION
DATA POINTS
NORMAL
(1601 POINTS
MAXIMUM)
C.W.
(1 POINT)
N-DISCRETE
FREQUENCIES
(2 TO 1601
POINTS)
TIME DOMAIN
(HARMONIC)
PRESS <ENTER>
TO SELECT
MENU C2
FREQ RANGE OF
CALIBRATION
START
0.0400000000GHz
STOP
20.000000000 GHz
201 DATA PTS
0.099800000 GHz
STEP SIZE
MAXIMUM NUMBER
OF DATA POINTS
1601 MAX PTS
801 MAX PTS
401 MAX PTS
201 MAX PTS
101 MAX PTS
51 MAX PTS
NEXT CAL STEP
PRESS <ENTER>
TO SELECT
MENU C2B
SINGLE POINT
CALIBRATION
C.W. FREQ
XX.XXXX GHz
FINISHED
ENTRY, NEXT
CAL STEP
INPUT FREQ AND
PRESS <ENTER>
TO SELECT
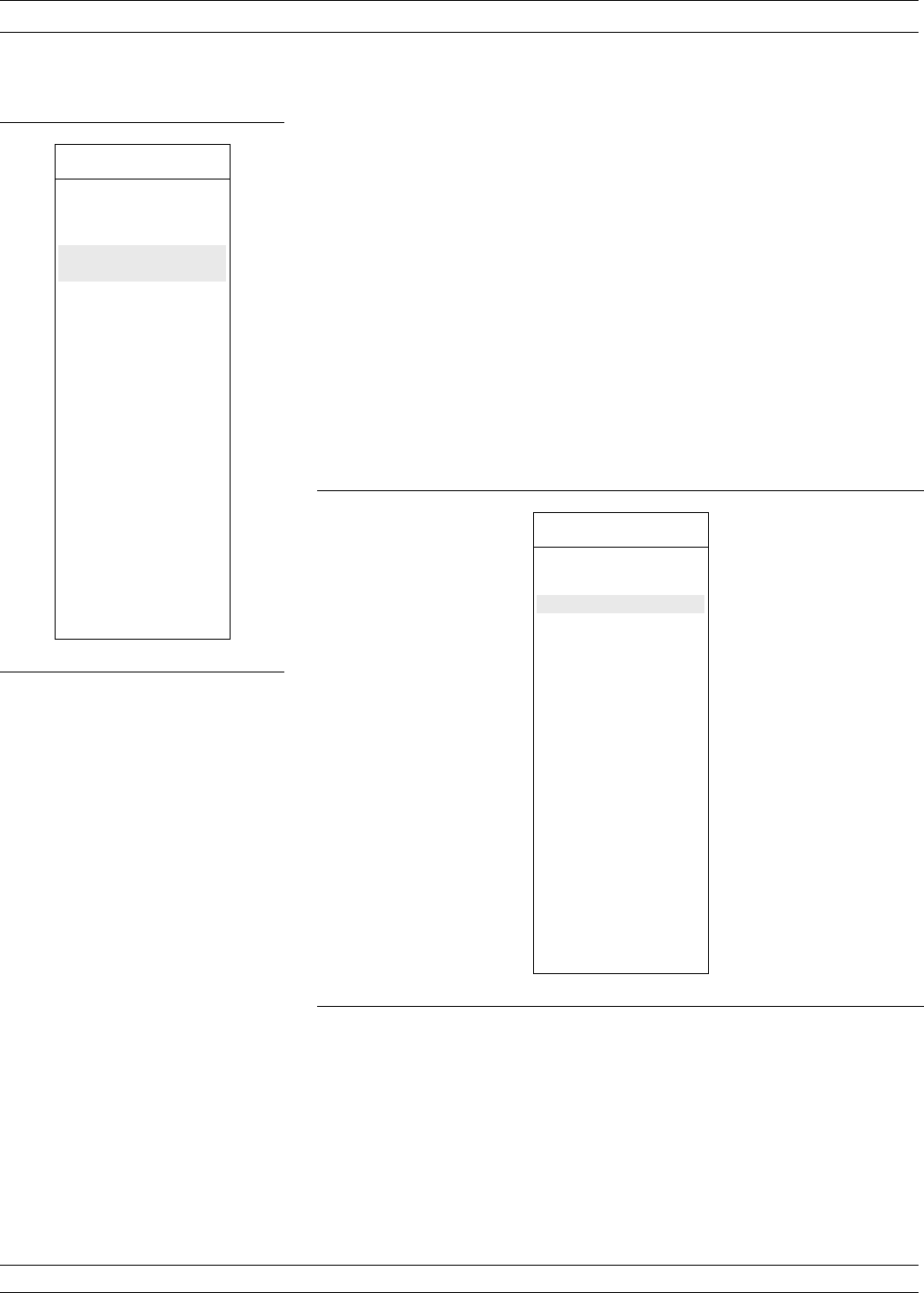
Step 9. When menu C3 (left) appears, if you want to change
any of the parameters shown in blue letters, place
the cursor on that parameter and press the Enter
key. For this example, we will change them all, start-
ing with the top one. Move the cursor to PORT 1
CONN and press the Enter key.
Step 10. In menu C4 (below), which appears next, move the
cursor to K CONN (M) and then press the Enter key.
This choice presumes that you have a K-Female con-
nector on the device-under-test (DUT). Remember, in
this menu you choose the connector type on the test
port, or the connector type that mates with the DUT
connector. When menu C3 returns, observe that K
CONN (M) is now shown in blue for the PORT 1
CONN choice.
SOLT CALIBRATION MEASUREMENT CALIBRATION
7-22 37XXXC OM
MENU C3
CONFIRM
CALIBRATION
PARAMETERS
PORT 1 CONN
K CONN (M)
PORT 2 CONN
SMA (M)
REFLECTION
PAIRING
MIXED
LOAD TYPE
SLIDING
THROUGHLINE
PARAMETERS
REFERENCE
IMPEDANCE
TEST SIGNALS
START CAL
PRESS <ENTER>
TO SELECT
OR CHANGE
MENU C4
SELECT PORT 1
CONNECTOR TYPE
K-CONN (M)
K-CONN (F)
V-CONN (M)
V-CONN (F)
W1-CONN (M)
W1-CONN (F)
SMA (M)
SMA (F)
GPC-3.5 (M)
GPC-3.5 (F)
GPC-7
USER DEFINED
MORE
PRESS <ENTER>
TO SELECT
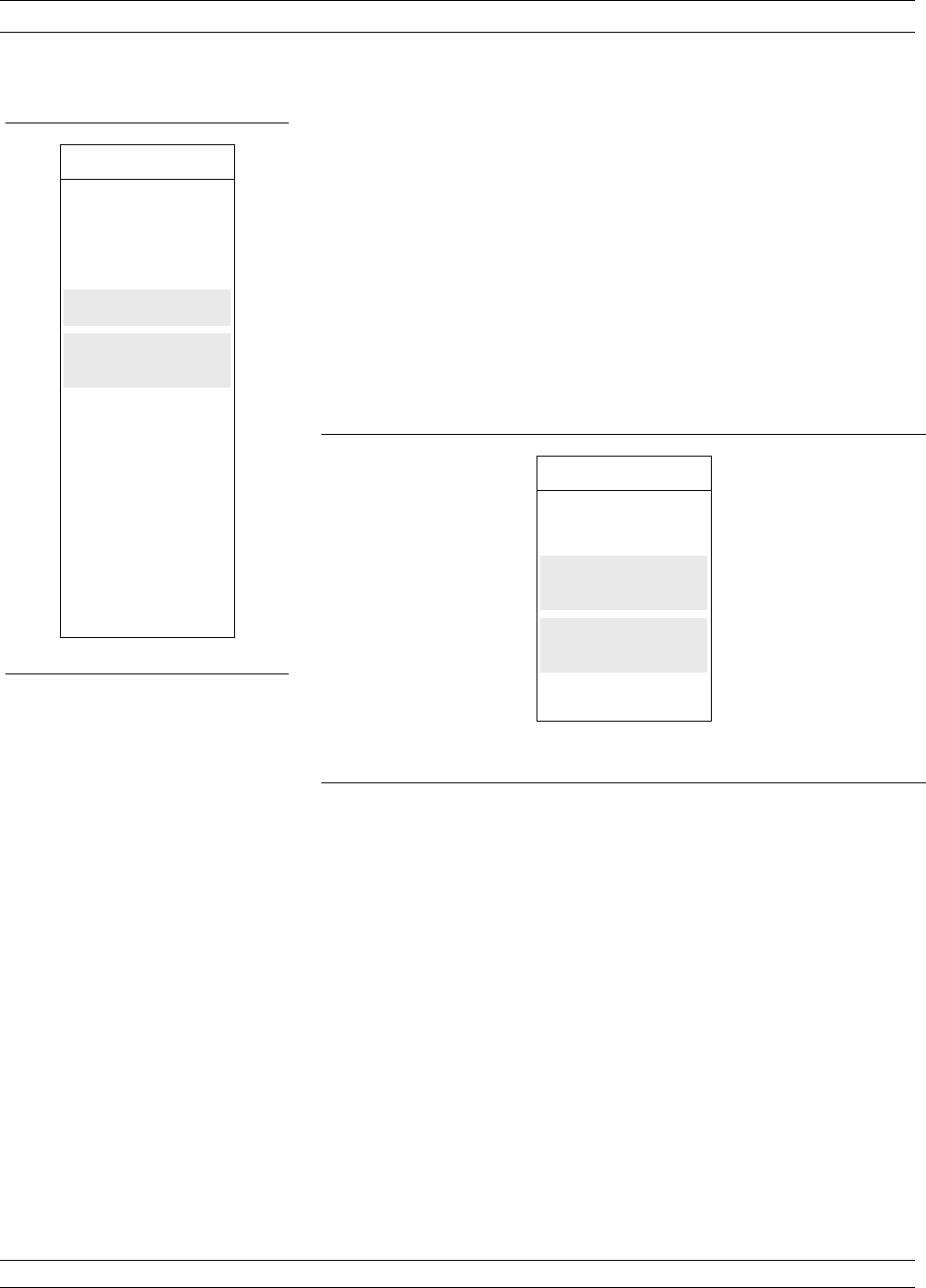
Step 11. With menu C3 (left) displayed, move the cursor to
PORT 2 CONN and press the Enter key. Following
the procedure in Step 10, select K CONN (M) for the
Port 2 connector.
Step 12. When menu C3 returns:
a. Observe that PORT 2 CONN now reflects K
CONN (M).
b. Move the cursor to REFLECTION PARING
and press the Enter key. This brings up menu
C13 (below).
Reflection Pairing lets you mix or match the
Open and Short reflection devices in the Cali-
bration Sequence menus. The MIXED choice
lets you calibrate using first an Open on one
port and a Short on the other, then a Short on
one port and an Open on the other. Conversely,
MATCHED lets you calibrate first using an
Open on both ports then using a Short on both
ports. For this example, choose MIXED and
press the Enter key.
37XXXC OM 7-23
MEASUREMENT CALIBRATION SOLT CALIBRATION
MENU C3
CONFIRM
CALIBRATION
PARAMETERS
PORT 1 CONN
K CONN (M)
PORT 2 CONN
K CONN (M)
REFLECTION
PAIRING
MIXED
LOAD TYPE
SLIDING
THROUGH
PARAMETERS
REFERENCE
IMPEDANCE
TEST SIGNALS
START CAL
PRESS <ENTER>
TO SELECT
OR CHANGE
MENU C13
SELECT
REFLECTION
PAIRING
MIXED
(OPEN–SHORT
SHORT–OPEN)
MATCHED
(OPEN–OPEN
SHORT–SHORT)
PRESS <ENTER>
TO SELECT

Step 13. When menu C3 returns:
a. Observe that REFLECTION PARING now re-
flects MIXED.
b. Move cursor to LOAD TYPE and press the En-
ter key. This brings up menu C6 (below).
This menu lets you select either of two load
types, broadband or sliding. Broadband loads
are adequate for all but the most demanding re-
flection measurements. They are easier to use
and less expensive than sliding loads. If you
choose a sliding load, refer to paragraph 7-3 for
a procedure on setting pin depth.
For this example, select BROADBAND LOAD
and press the Enter key.
c. The next menu to appear, C6A (left), prompts
you to enter an impedance value. For this exam-
ple, use the rotary knob to change the displayed
value to 50W. Alternatively, you can key in
50 ohms. That is, press 50 on the keypad and
the X1 terminator key. If the value is 1 mW, key
in .001 and press the 10–3 terminator key. Con-
versely, if the value is 1 MW, key in 1000 and
press the 103terminator key.
SOLT CALIBRATION MEASUREMENT CALIBRATION
7-24 37XXXC OM
MENU C6
SELECT
TYPE OF LOAD
BROADBAND
FIXED LOAD
SLIDING LOAD
(MAY ALSO
REQUIRE
BROADBAND
FIXED LOAD)
PRESS <ENTER>
TO SELECT
MENU C3
CONFIRM
CALIBRATION
PARAMETERS
PORT 1 CONN
TYPE N (M)
PORT 2 CONN
TYPE N (F)
REFLECTION
PARING
MIXED
LOAD TYPE
BROADBAND
THROUGH
PARAMETERS
REFERENCE
IMPEDANCE
TEST SIGNALS
START CAL
PRESS <ENTER>
TO SELECT
MENU C6A
ENTER
BROADBAND LOAD
IMPEDANCE
BROADBAND
LOAD
IMPEDANCE
50.000 W
PRESS <ENTER>
TO SELECT
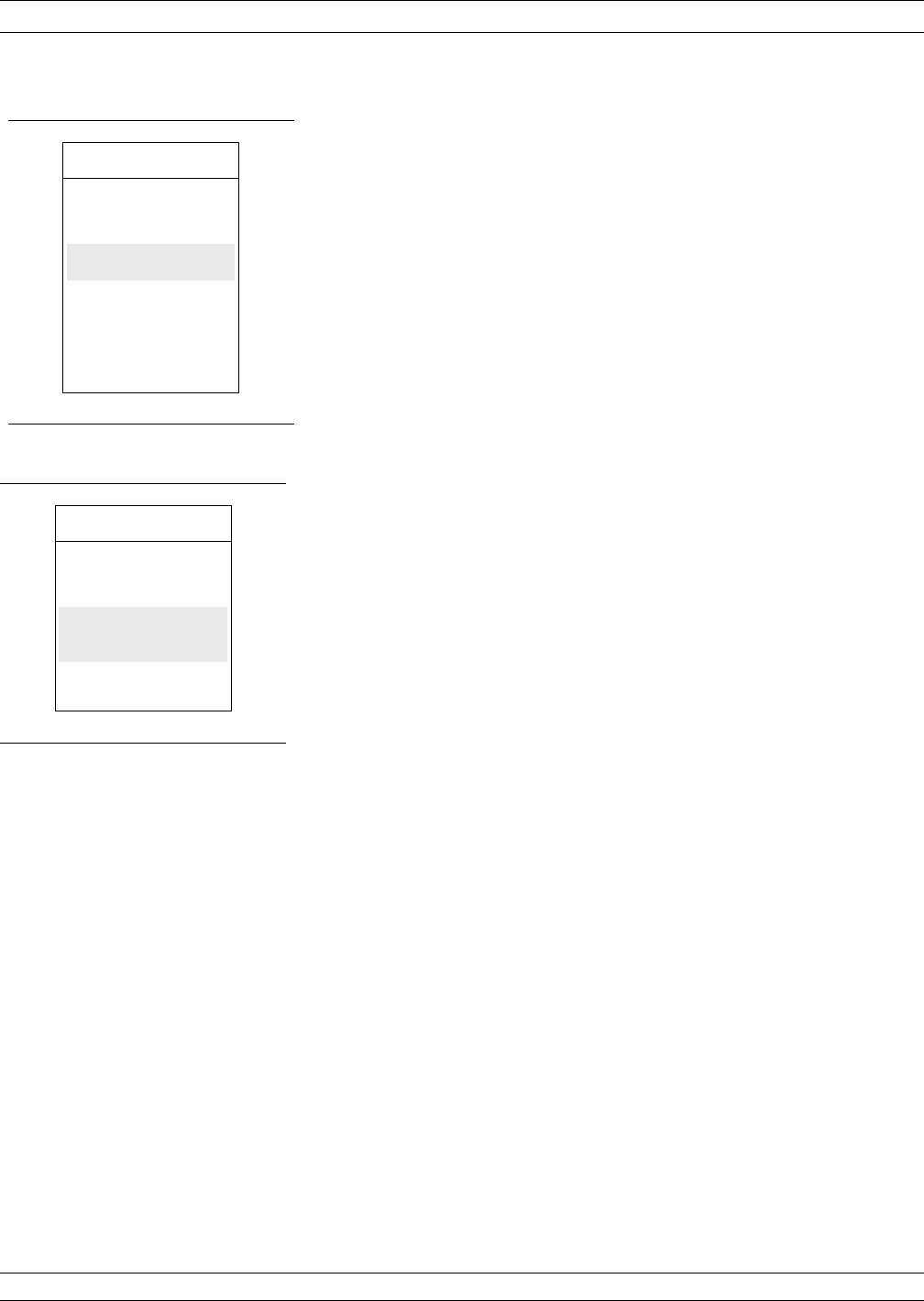
Step 14. When menu C3 again returns:
a. Observe that LOAD TYPE now shows
BROADBAND.
b. Move cursor to THROUGH PARAMETERS
and press the Enter key.
Step 15. Menu C20 (left) appears next. It lets you define the
length of the offset and the impedance of the
throughline. For this example, enter 0 mm for length
and 50 ohms for impedance.
Step 16. When menu C3 reappears, move the cursor to REF-
ERENCE IMPEDANCE and press the Enter key.
This brings up menu C17 (left).
Step 17. Move cursor to REFERENCE IMPEDANCE and
use the rotary knob to change the displayed value to
50W.
Press the Enter key when you have completed your
value entry.
37XXXC OM 7-25
MEASUREMENT CALIBRATION SOLT CALIBRATION
MENU C20
ENTER
THROUGH LINE
PARAMETERS
OFFSET LENGTH
0.0000 mm
THROUGHLINE
IMPEDANCE
50.000 W
PRESS <ENTER>
WHEN COMPLETE
MENU C17
ENTER
REFERENCE
IMPEDANCE
REFERENCE
IMPEDANCE
50.000 W
PRESS <ENTER>
WHEN COMPLETE
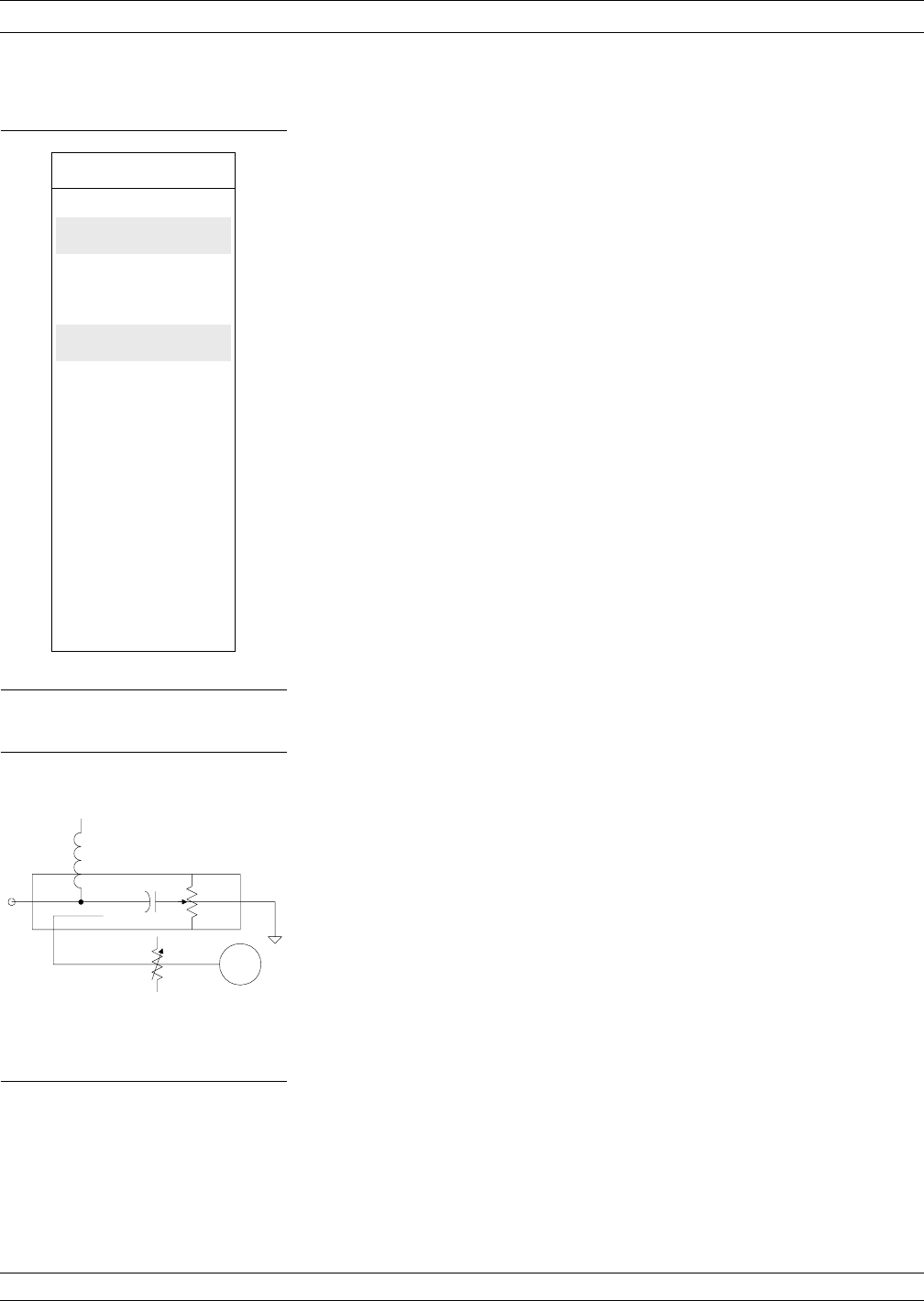
Step 18. When menu C3 returns, select TEST SIGNALS to
bring up menu SU2 (left).
Step 19. Menu SU2 lets you define the power level of the sig-
nals at the two test ports. Power delivered to the
DUT by the test set must be such that the measured
signals are well above the noise floor but below the
0.1 dB compression level of the Test Set samplers.
(Noise floor and maximum signal into Port 2 levels
are specified in Appendix C.)
For measuring high power signals, a Port 2 attenu-
ator in the forward transmission path allows up to
1 Watt of power (30 dBm) before 0.1 dB compression
occurs.
Determine the required input power level and the
expected output RF power level from the DUT.
Ideally, the Port 2 step attenuator should be set so
that the input to the test sampler (left) is less than
–10 dBm. For example, if the input to the DUT is set
for –20 dBm and the device gain is 40 dB, set the
PORT 2 ATTN menu option for 20 dB.
(If you needed to calibrate the test port for power
flatness, you would move the cursor to FLATNESS
CORRECTION and press the Enter key.)
Finally, move the cursor to PREVIOUS MENU and
press the Enter key. This returns you to menu SU1.
When you get there, press the Enter key to return to
menu C3.
SOLT CALIBRATION MEASUREMENT CALIBRATION
7-26 37XXXC OM
MENU SU2
TEST SIGNALS
POWER CONTROL
0.0 dB
(0 TO -20)
PORT 1 ATTN
20 dB (0 - 70)
PORT 1 POWER
XX.XX dBm
PORT 2 ATTN
X0 dB (0-40)
CALIBRATE
FOR FLATNESS
(CAL EXISTS)
FLATNESS
CORRECTION
AT XX.X dBm
SOURCE 2 PWR
XX.X dBm
PREVIOUS MENU
PRESS <ENTER>
TO SELECT
TB
Sample
r
0to40dB
P2
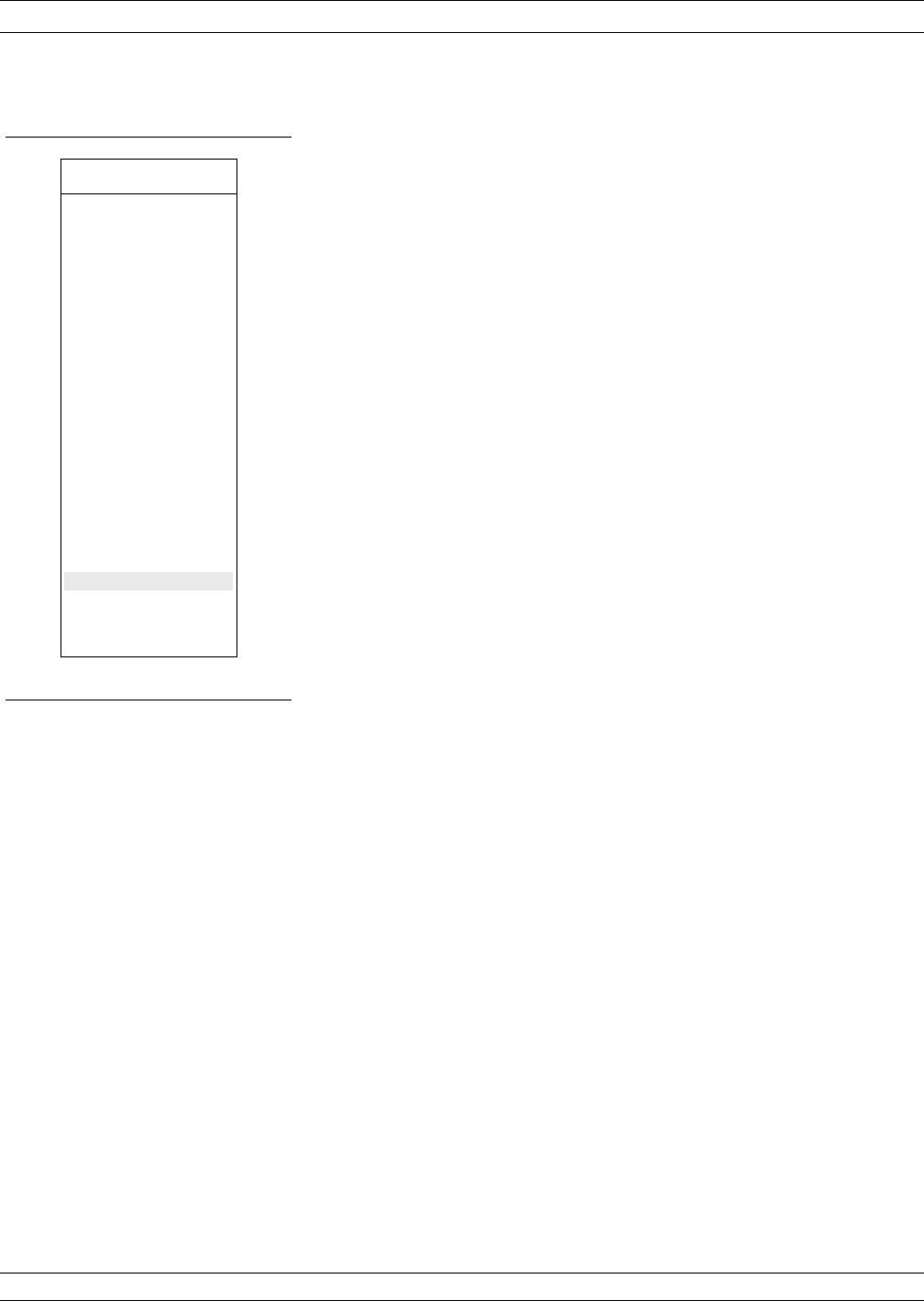
Step 20. When menu C3 reappears, select START CAL and
press the Enter key to begin the calibration proce-
dure.
Continue the calibration sequence by following the
prompts as they appear. Connect the appropriate Iso-
lation Devices, Broadband Loads, Opens, Shorts, and
Throughlines, when requested in the calibration se-
quence.
37XXXC OM 7-27
MEASUREMENT CALIBRATION SOLT CALIBRATION
MENU C3
CONFIRM
CALIBRATION
PARAMETERS
PORT 1 CONN
TYPE N (M)
PORT 2 CONN
SMA (M)
REFLECTION
PAIRING
MIXED
LOAD TYPE
SLIDING
THROUGH
PARAMETERS
REFERENCE
IMPEDANCE
TEST SIGNALS
START CAL
PRESS <ENTER>
TO SELECT
OR CHANGE
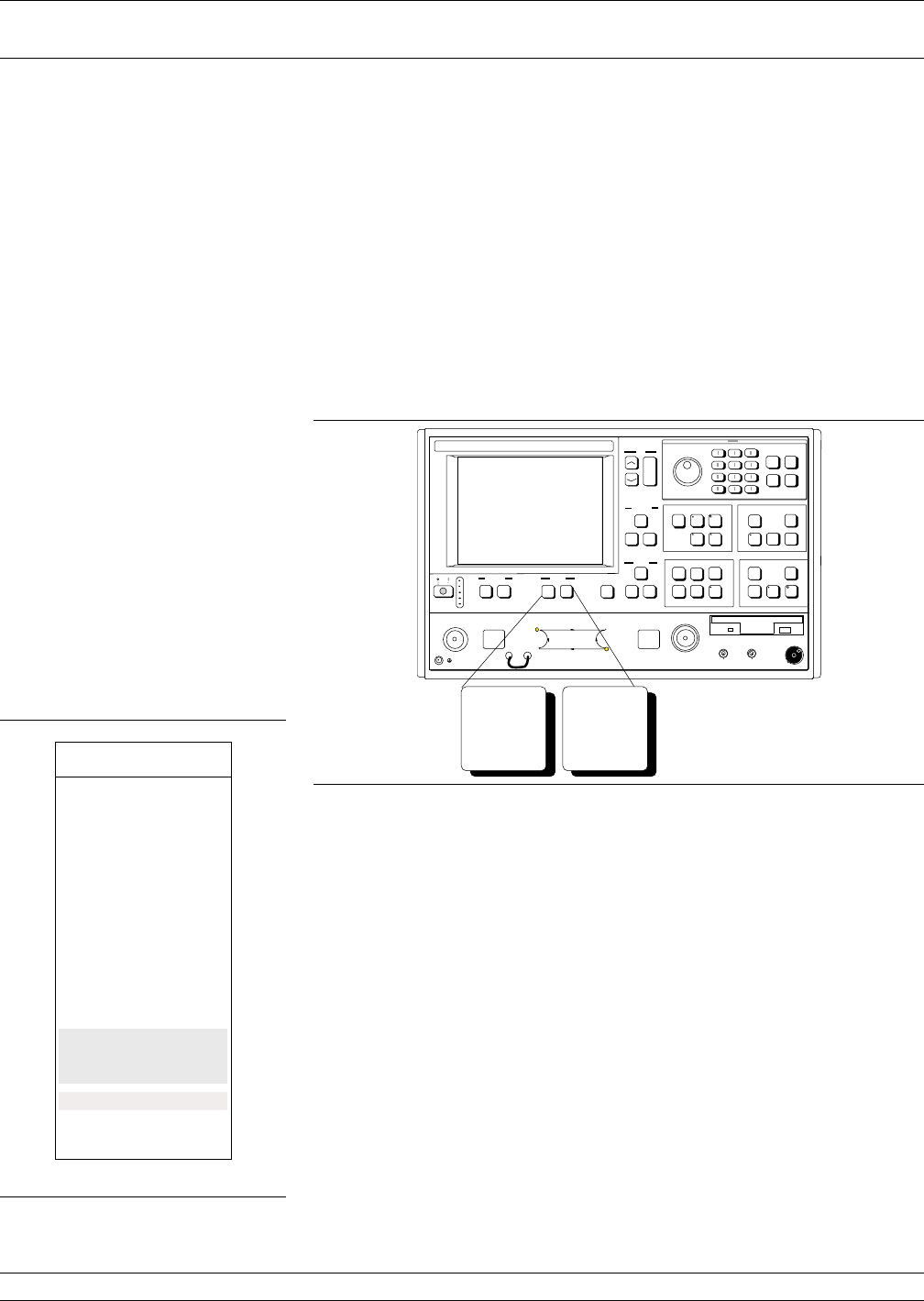
7-5 OFFSET-SHORT
CALIBRATION (SSLT) The Offset-Short calibration, now also referred to as the Double Off-
set-Short Calibration, is the standard technique for waveguide; how-
ever, this method can be used for the coaxial and microstrip line types
as well. It uses two shorts, two loads, and a thru line to categorize the
inherent errors in the waveguide measurement system. These errors
include those caused by connectors as well as internal system errors
such as RF leakage, IF leakage, and component interaction.
Calibration Procedure A detailed, step-by-step procedure for performing an Offset-Short cali-
bration for waveguide is given below.
Step 1. Press the Begin Cal key.
Step 2. Select CHANGE CAL METHOD AND LINE
TYPE, in menu C11 (left). (This assumes OFFSET
SHORT and WAVEGUIDE are not presently shown
in blue as being selected.)
OFFSET-SHORT CALIBRATION (SSLT)
MEASUREMENT CALIBRATION
7-28 37XXXC OM
Apply
Cal
Begin
Cal
MENU C11
BEGIN CALIBRATION
KEEP EXISTING
CAL DATA
REPEAT
PREVIOUS CAL
AUTOCAL
CAL METHOD
XXXXXXX
TRANSMISSION
LINE TYPE:
XXXXXXXX
CHANGE CAL
METHOD AND
LINE TYPE
NEXT CAL STEP
PRESS <ENTER>
TO SELECT
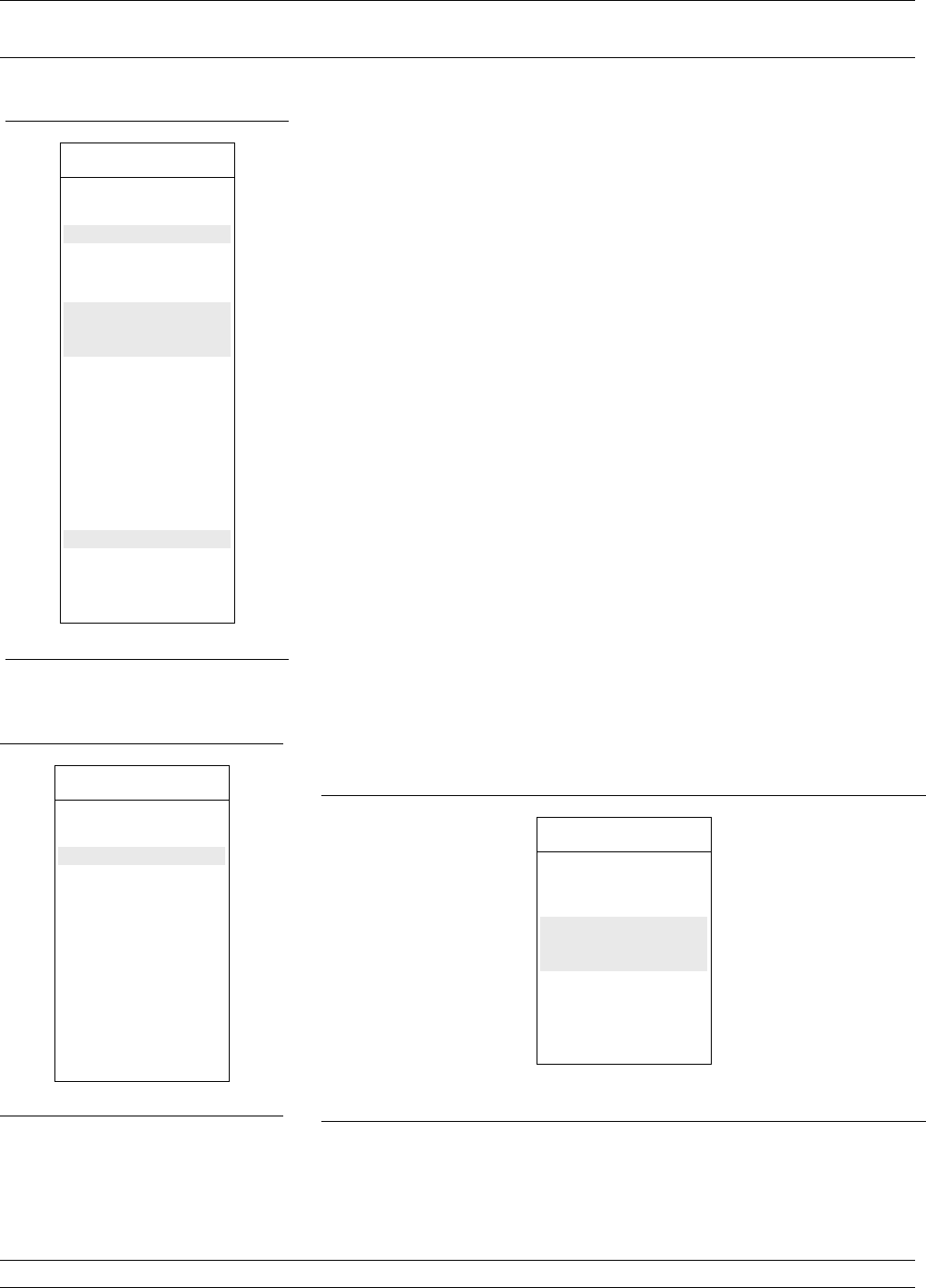
Step 3. When menu C11A (left) appears, move cursor to the
following:
a. SSLT (DOUBLE OFFSET SHORT), then
press the Enter key. This selects Offset Short as
the calibration method.
b. WAVEGUIDE, then press the Enter key. This
brings menu C5 (bottom left) to the screen.
c. NEXT CAL STEP, then press the Enter key.
This causes menu C11 to return to the screen.
Step 4. When menu C11 reappears, confirm that the OFF-
SET SHORT calibration method and WAVEGUIDE
line-type have been selected. Select NEXT CAL
STEP and press the Enter key to proceed.
Step 5. Menu C5 appears next. This menu (bottom left) lets
you select the type of calibration. For this example,
move the cursor to FULL 12-TERM and press the
Enter key.
Step 6. The next menu, C5D (below), lets you choose
whether to include or exclude the error terms associ-
ated with leakage between measurement channels.
For a normal calibration, you would choose to include
these error terms. Therefore, move the cursor to IN-
CLUDE ISOLATION (STANDARD) and press the
Enter key.
37XXXC OM 7-29
MEASUREMENT CALIBRATION OFFSET-SHORT CALIBRATION
(SSLT)
MENU C11A
CHANGE CAL METHOD
AND LINE TYPE
NEXT CAL STEP
CAL METHOD
SOLT (STANDARD)
SSLT (DOUBLE OFF-
SET SHORT WITH
LOAD)
SSST (TRIPLE
OFFSET SHORT)
LRL/LRM
TRM
TRANSMISSION
LINE TYPE
COAXIAL
WAVEGUIDE
MICROSTRIP
PRESS <ENTER>
TO SELECT
MENU C5
SELECT
CALIBRATION TYPE
FULL 12-TERM
1 PATH
2 PORT
TRANSMISSION
FREQUENCY
RESPONSE
REFLECTION
ONLY
PRESS <ENTER>
TO SELECT
MENU C5D
SELECT USE
OF ISOLATION
IN CALIBRATION
INCLUDE
ISOLATION
(STANDARD)
EXCLUDE
ISOLATION
PRESS <ENTER>
TO SELECT
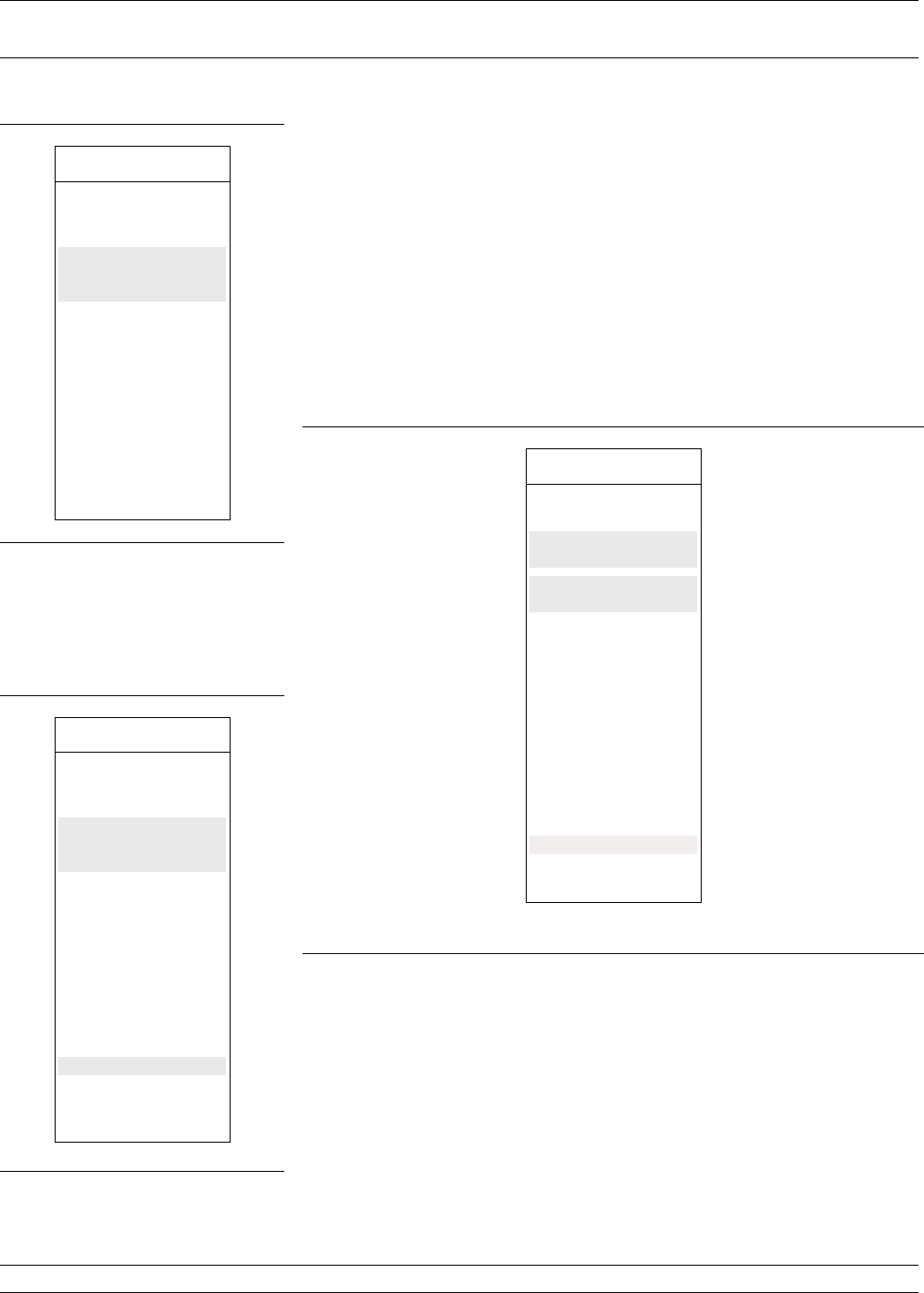
Step 7. Menu C1 (left), which appears next, lets you select
the number of frequency points at which calibration
data is to be taken. Of these choices, which were de-
scribed in paragraph 7-4, choose NORMAL (1601
POINTS MAXIMUM) for this example.
Step 8. The next menu, C2 (below), lets you set your start
and stop frequencies. For this example, move cursor
to START, press 40 on keypad, and press the MHz
terminator key. Perform like operations for the
STOP choice, except make entry read 20 GHz. After
setting the frequencies, select NEXT CAL STEP
and press the Enter key.
Step 9. When menu C3B (bottom left) appears, if you want
to change any of the parameters shown in blue let-
ters, place the cursor on that parameter and press
the Enter key. (These choices operate the same as
was described for menu C3 in paragraph 7-4.) For
this example, we change the waveguide parameters.
Move the cursor to WAVEGUIDE PARAMETERS
and press the Enter key.
OFFSET-SHORT CALIBRATION (SSLT)
MEASUREMENT CALIBRATION
7-30 37XXXC OM
MENU C1
SELECT
CALIBRATION
DATA POINTS
NORMAL
(1601 POINTS
MAXIMUM)
C.W.
(1 POINT)
N-DISCRETE
FREQUENCIES
(2 TO 1601
POINTS)
TIME DOMAIN
(HARMONIC)
PRESS <ENTER>
TO SELECT
MENU C2
FREQ RANGE OF
CALIBRATION
START
0.0400000000GHz
STOP
20.000000000 GHz
201 DATA PTS
0.099800000 GHz
STEP SIZE
MAXIMUM NUMBER
OF DATA POINTS
1601 MAX PTS
801 MAX PTS
401 MAX PTS
201 MAX PTS
101 MAX PTS
51 MAX PTS
NEXT CAL STEP
PRESS <ENTER>
TO SELECT
MENU C3B
CONFIRM
CALIBRATION
PARAMETERS
WAVEGUIDE
PARAMETERS
INSTALLED
REFLECTION
PAIRING
XXXXXXXX
LOAD TYPE
BROADBAND
THROUGH LINE
PARAMETERS
TEST SIGNALS
START CAL
PRESS <ENTER>
TO SELECT
OR CHANGE
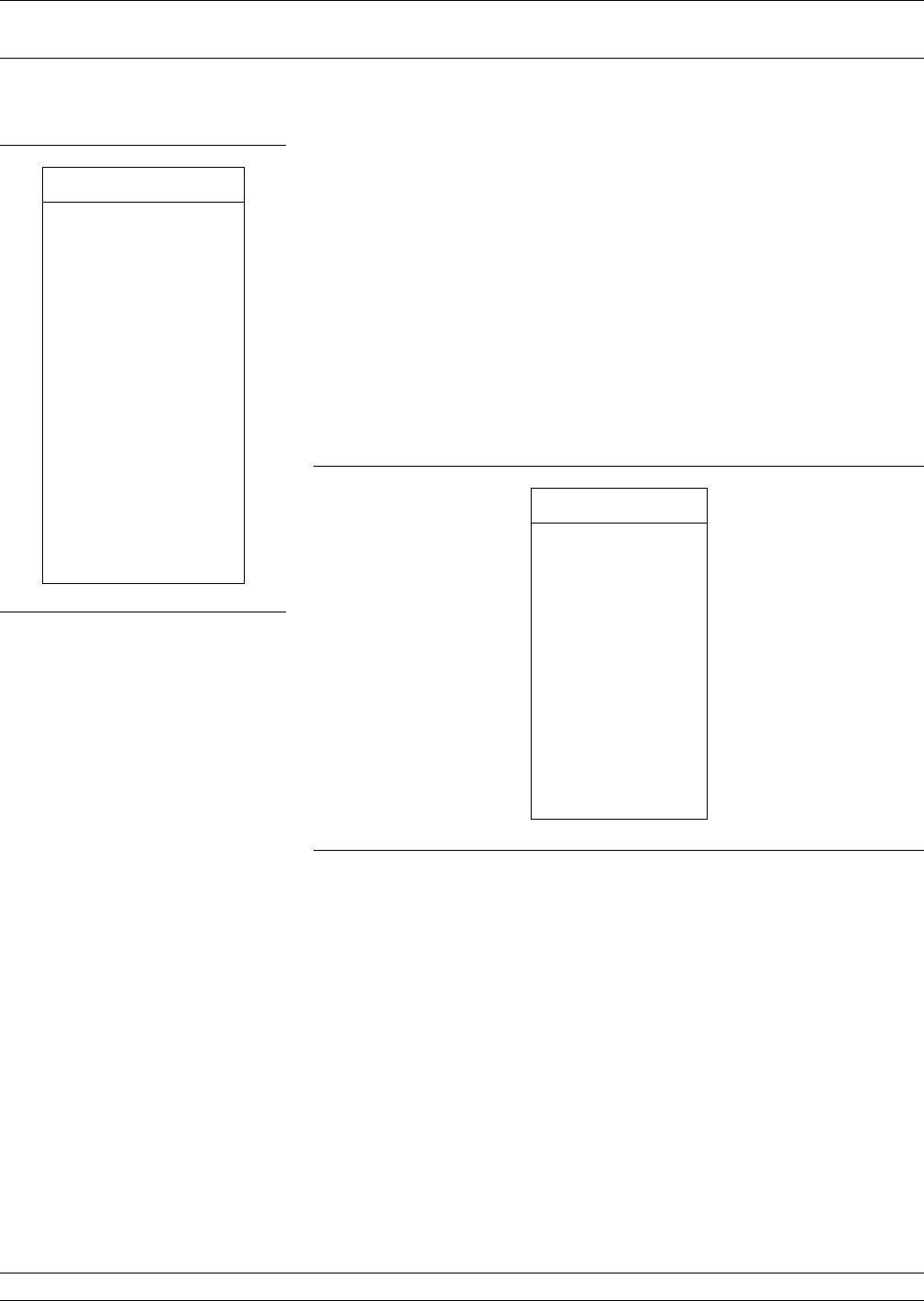
Step 10. When menu C15 (left) appears, move cursor to one of
the two available choices and press the Enter key.
These choices are described below.
a. USE INSTALLED WAVEGUIDE KIT: Se-
lecting this choice uses the values shown in blue
for IDENTIFIER, CUTOFF FREQ, SHORT 1,
and SHORT 2. Select this choice, for this exam-
ple.
b. USER DEFINED: Selecting this choice brings
up menu C15A (below), which lets you specify
waveguide parameters. After defining your
waveguide parameters, you are returned to
menu C3B.
Step 11. Continue the calibration sequence by following the
prompts as they appear. Connect the appropriate Iso-
lation Devices, Broadband Loads, Shorts, and
Throughlines, when requested in the calibration se-
quence.
37XXXC OM 7-31
MEASUREMENT CALIBRATION OFFSET-SHORT CALIBRATION
(SSLT)
MENU C15
SELECT
WAVEGUIDE
KIT TO USE
–INSTALLED KIT—
IDENTIFIER
XXXX
CUTOFF FREQ:
XXX.XXXXXXXXX GHz
SHORT 1
XX.XXXX mm
SHORT 2
XX.XXXX mm
USE INSTALLED
WAVEGUIDE KIT
USER DEFINED
PRESS <ENTER>
TO SELECT
MENU C15A
ENTER
WAVEGUIDE
PARAMETERS
WAVEGUIDE
CUTOFF FREQ:
XXX.XXXXXXXXX GHz
OFFSET LENGTH
OF SHORT 1
XX.XXXX mm
OFFSET LENGTH
OF SHORT 2
XX.XXXX mm
PRESS <ENTER>
WHEN COMPLETE
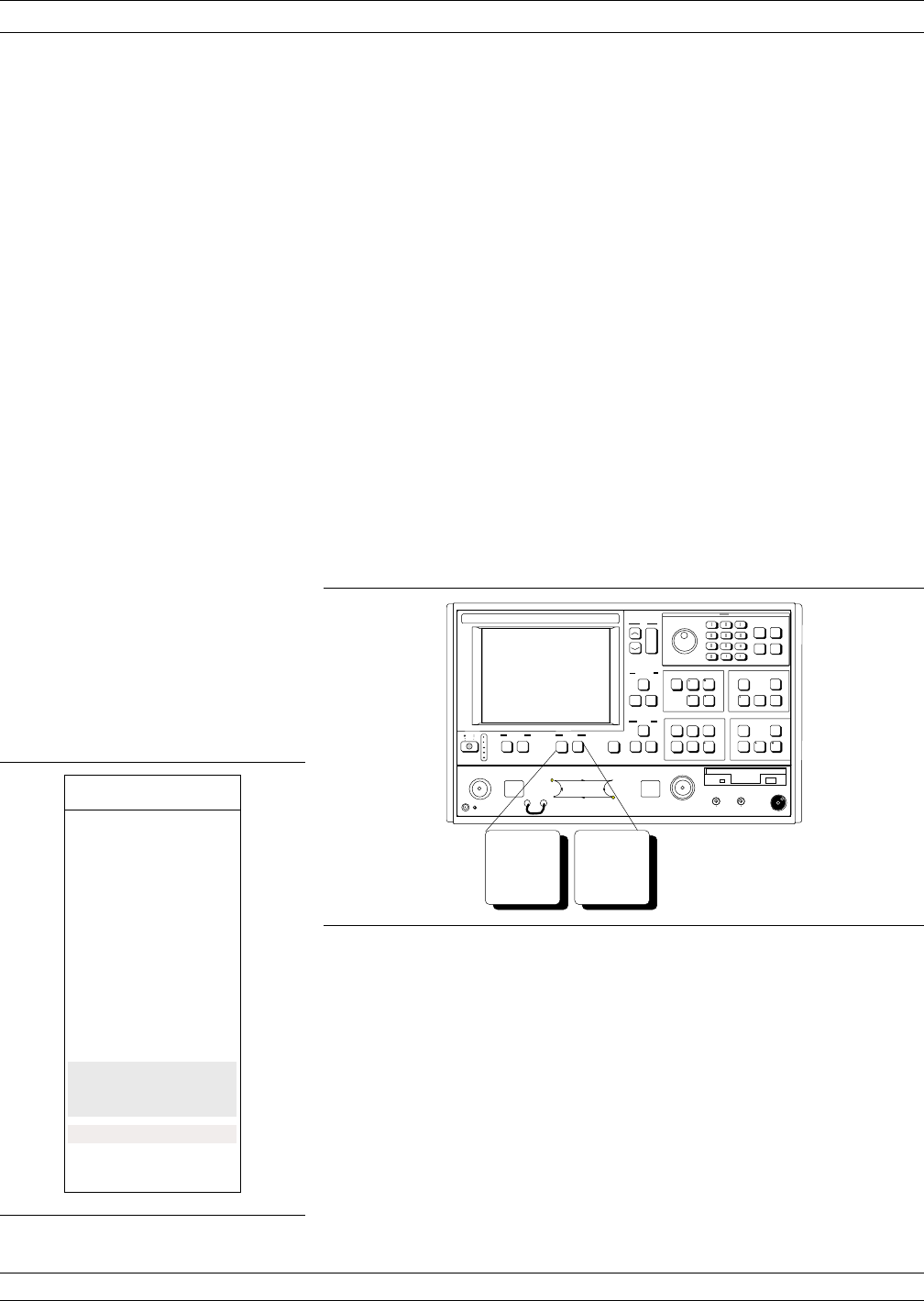
7-6 TRIPLE OFFSET-SHORT
CALIBRATION (SSST) The Triple Offset-Short calibration method can be used in coax, wave-
guide, and microstrip line types, and is most accurate when used over
narrower frequency ranges. As the name implies, this method uses
three offset-shorts to categorize the inherent errors in the measure-
ment system. These errors include those caused by connectors as well
as internal system errors such as RF leakage, IF leakage, and compo-
nent interaction.
NOTE
A continuous single sweep bradband calibration from
40 MHz to 110 GHz can be created by merging a 40 MHz to
65 GHz SOLT calibration with a 65 GHz to 110 GHz SSST
calibration.Formoreinformation,refertoSection7-9,Merge
Cal Files, and to Chapter 15 for details about the broadband
mode of operation.
Calibration Procedure A detailed, step-by-step procedure for performing a Triple Offset-Short
calibration is given below:
Step 1. Press the Begin Cal key.
Step 2. Select CHANGE CAL METHOD AND LINE
TYPE, in menu C11 (left). (This assumes that OFF-
SET SHORT and WAVEGUIDE are not presently
shown in blue as being selected.)
TRIPLE OFFSET-SHORT (SSST) MEASUREMENT CALIBRATION
7-32 37XXXC OM
MENU C11
BEGIN CALIBRATION
KEEP EXISTING
CAL DATA
REPEAT
PREVIOUS CAL
AUTOCAL
CAL METHOD
STANDARD
TRANSMISSION
LINE TYPE:
XXXXXXXX
CHANGE CAL
METHOD AND
LINE TYPE
NEXT CAL STEP
PRESS <ENTER>
TO SELECT
Apply
Cal
Begin
Cal
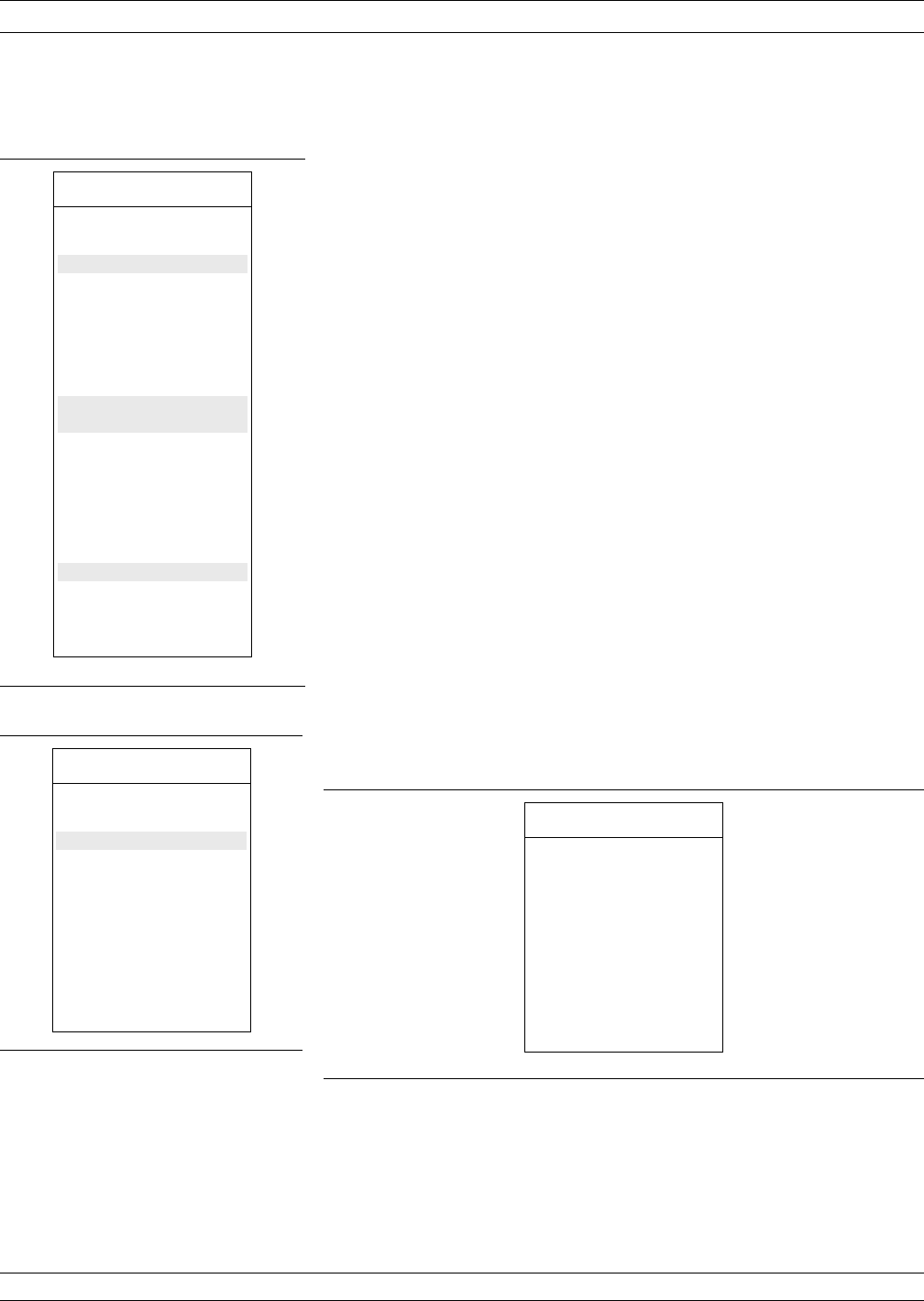
Step 3. When menu C11A (left) appears, move cursor to the
following:
a. SSST (TRIPLE OFFSET SHORT), then press
the Enter key. This selects Triple Offset-Short as
the calibration method.
b. COAXIAL, then press the Enter key. This brings
menu C5 (left) to the screen.
c. NEXT CAL STEP, then press the Enter key.
This causes menu C11 to return to the screen.
Step 4. When menu C11 reappears, confirm that the SSST
calibration method and COAXIAL line-type have
been selected. Select NEXT CAL STEP and press
the Enter key to proceed.
Step 5. Menu C5 appears next (lower left). This menu lets
you select the type of calibration. For this example,
move the cursor to FULL 12-TERM and press the
Enter key.
Step 6. The next menu, C5D (below), lets you choose
whether to include or exclude the error terms associ-
ated with leakage between measurement channels.
For a normal calibration, you would choose to include
these error terms. Therefore, move the cursor to
INCLUDE ISOLATION (STANDARD) and press
the Enter key.
37XXXC OM 7-33
MEASUREMENT CALIBRATION TRIPLE OFFSET-SHORT (SSST)
MENU C11A
CHANGE CAL METHOD
AND LINE TYPE
NEXT CAL STEP
CAL METHOD
SOLT (STANDARD)
SSLT (DOUBLE OFF-
SET SHORT WITH
LOAD)
SSST (TRIPLE OFFSET
SHORT)
LRL/LRM
TRM
TRANSMISSION
LINE TYPE
COAXIAL
WAVEGUIDE
MICROSTRIP
PRESS <ENTER>
TO SELECT
Menu C5
CALIBRATION
TYPE
FULL 12-TERM
1 PATH
2 PORT
TRANSMISSION
FREQUENCY
RESPONSE
REFLECTION ONLY
PRESS <ENTER>
TO SELECT
Menu C5D
SELECT USE
OF ISLOATION
IN CALIBRATION
INCLUDE
ISOLATION
(STANDARD)
EXCLUDE
ISOLATION
PRESS <ENTER>
TO SELECT
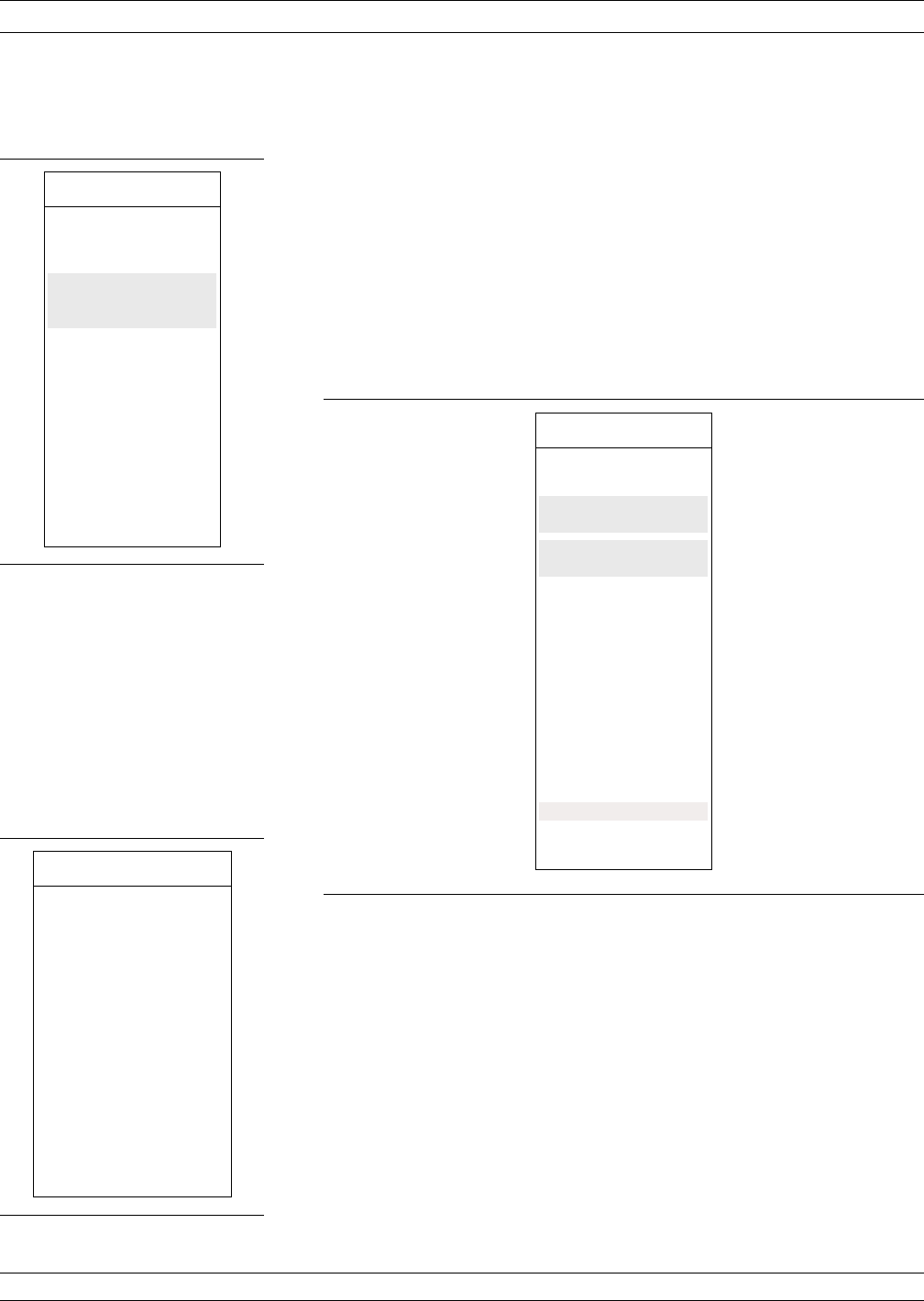
Step 7. Menu C1 appears next (left) and lets you select the
number of frequency points for which calibration
data is to be taken. Select NORMAL (1601 POINTS
MAXIMUM) (refer to Section 7-4 for a description).
Step 8. The next menu, C2 (left), lets you set your start and
stop frequencies. For this example, move the cursor
to START, press 65 on the keypad, then press the
GHz terminator key. Perform like operations for the
STOP choice, except make the entry read 110 GHz.
After setting the frequencies, select NEXT CAL
STEP and press the Enter key.
Step 9. This brings up the Menu C14 (lower left) for select-
ing the connector types on ports 1 and 2. Select the
W1-CONN connectors with the appropriate sex for a
W1 (1mm) calibration.
TRIPLE OFFSET-SHORT (SSST) MEASUREMENT CALIBRATION
7-34 37XXXC OM
MENU C2
FREQ RANGE OF
CALIBRATION
START
0.0400000000GHz
STOP
20.000000000 GHz
201 DATA PTS
0.099800000 GHz
STEP SIZE
MAXIMUM NUMBER
OF DATA POINTS
1601 MAX PTS
801 MAX PTS
401 MAX PTS
201 MAX PTS
101 MAX PTS
51 MAX PTS
NEXT CAL STEP
PRESS <ENTER>
TO SELECT
MENU C1
SELECT
CALIBRATION
DATA POINTS
NORMAL
(1601 POINTS
MAXIMUM)
C.W.
(1 POINT)
N-DISCRETE
FREQUENCIES
(2 TO 1601
POINTS)
TIME DOMAIN
(HARMONIC)
PRESS <ENTER>
TO SELECT
Menu C14
SELECT PORT n
OFFSET SHORT
CONNECTOR TYPE
W1-CONN (M)
W1-CONN (F)
SPECIAL A (M)
SPECIAL A (F)
SPECIAL B (M)
SPECIAL B (F)
SPECIAL C (M)
SPECIAL C (F)
USER DEFINED
PRESS <ENTER>
TO SELECT
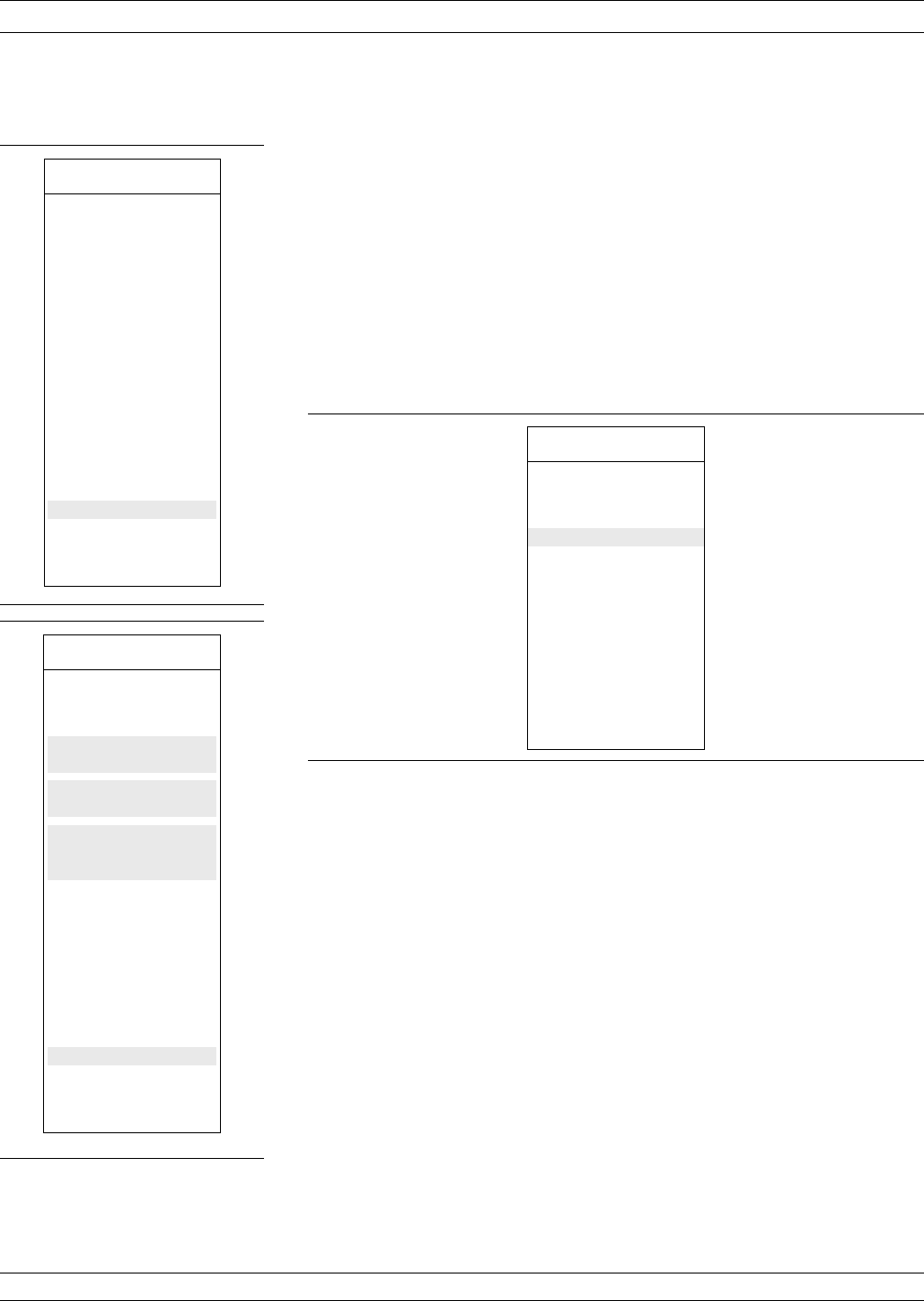
Step 10. When menu C3B (left) appears, if you want to
change any of the parameters shown in blue letters,
place the cursor on that parameter and press the En-
ter key.
Step 11. When menu C3 (lower left) returns:
a. Observe that PORT 1 CONN and
PORT 2 CONN now reflects W1 CONN (M).
b. Move the cursor to REFLECTION PARING
and press the Enter key. This brings up menu
C13 (below).
Step 12. Reflection Pairing lets you mix or match Offset Short
devices in the Calibration Sequence menus, as per
the kit available. Generally, on-wafer calibration sub-
strates have matched components; however, it is
more convenient, on a coaxial calibration, to use
MIXED pairing in the case of the same connector
types on both ports. The MIXED choice lets you cali-
brate using different offset shorts on the two ports.
Conversely, MATCHED pairing lets you calibrate in
sequence using one offset short type in each step. For
this example, choose MIXED and press the Enter
key.
Step 13. When menu C3 reappears, confirm the calibration
parameters selected for the calibration, then select
START CAL and continue the calibration sequence
by following the prompts as they appear.
Step 14. Connect the appropriate Isolation Devices, the three
Offset Shorts, and the Throughlines when requested
in the calibration sequence.
37XXXC OM 7-35
MEASUREMENT CALIBRATION TRIPLE OFFSET-SHORT (SSST)
MENU C3B
CONFIRM
CALIBRATION
PARAMETERS
WAVEGUIDE
PARAMETERS
INSTALLED
REFLECTION
PAIRING
MIXED
LOAD TYPE
BROADBAND
THROUGH LINE
PARAMETERS
TEST SIGNALS
START CAL
PRESS <ENTER>
TO SELECT
OR CHANGE
MENU C3
CONFIRM
CALIBRATION
PARAMETERS
PORT 1 CONN
W1-CONN (M)
PORT 2 CONN
W1-CONN (M)
REFLECTION
PAIRING
XXXXXXXX
LOAD TYPE
BROADBAND
THROUGH LINE
PARAMETERS
REFERENCE
IMPEDANCE
TEST SIGNALS
START CAL
PRESS <ENTER>
TO SELECT
OR CHANGE
MENU C13
SELECT
REFLECTION
PAIRING
MIXED
(SHORT1-SHORT2,
SHORT2-SHORT3,
SHORT3-SHORT1)
MATCHED
(SHORT1-SHORT1,
SHORT2-SHORT2,
SHORT3-SHORT3)
PRESS <ENTER>
TO SELECT
OR CHANGE
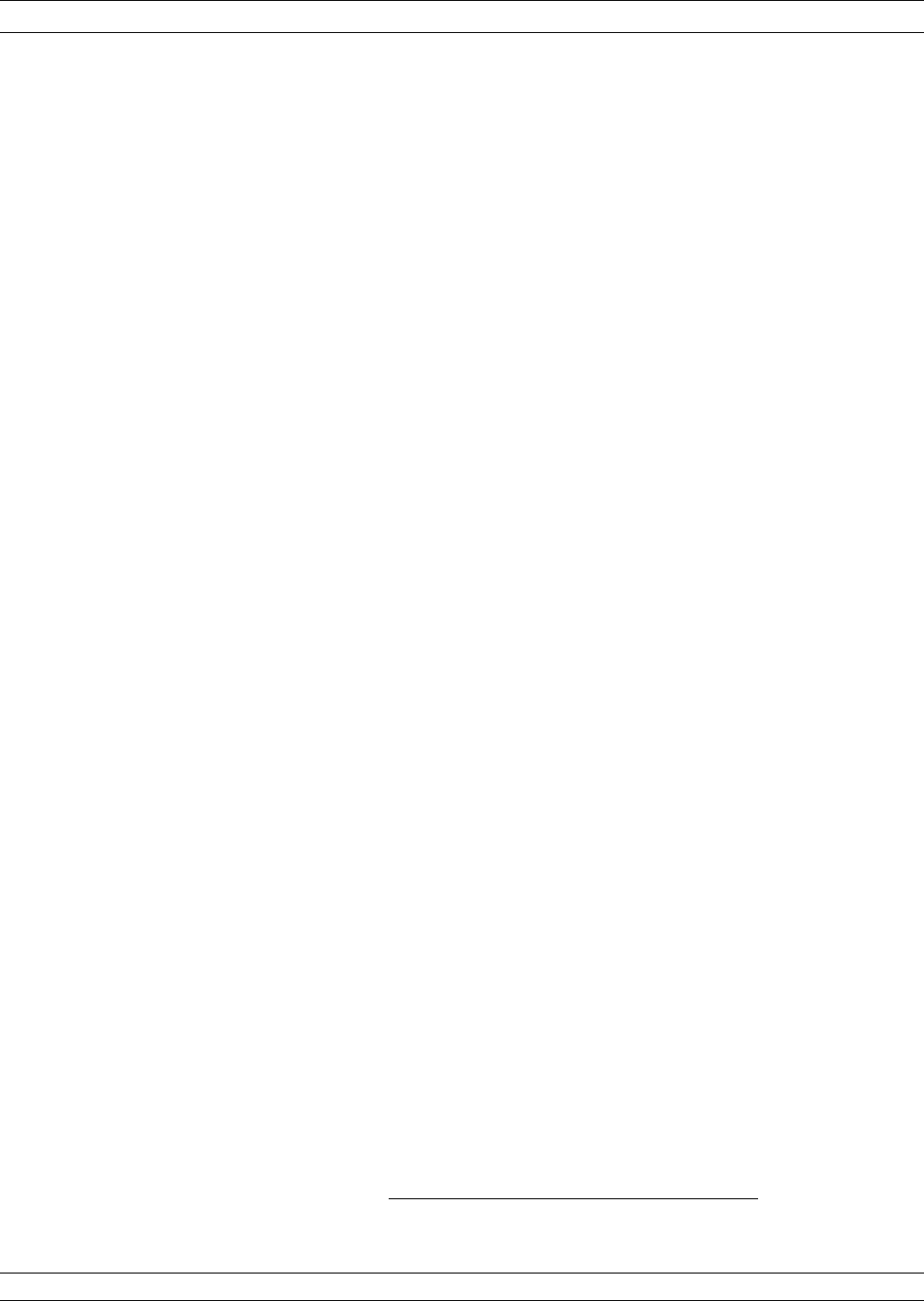
7-7 LRL/LRM CALIBRATION The LRL/LRM (line-reflect-line/line-reflect-match) calibration* feature
provides an enhanced capability for error compensation when making
measurements in coaxial, microstrip and waveguide transmission me-
dia. Instead of using the standard Open, Short, and Load, the
LRL/LRM calibration method uses two lines and a reflection or match.
The difference in length between line 1 and line 2 creates the mea-
surements necessary for the error solutions.
The LRL/LRM calibration technique uses the characteristic impedance
of a length of transmission line or a precision match as the calibration
standard. A full LRL/LRM calibration consists of two transmission line
measurements, a high reflection measurement, and an isolation mea-
surement. Using this technique full 12-term error correction can be
performed with the 37XXXC.
Three-line LRL/LRM calibration can also be selected. In a two-line
LRL measurement, the difference in length between line one and line
two is necessary for calibration but limits the frequency range to a 9:1
span. The use of three lines in the calibration extends the frequency
range to an 81:1 span. A combination of LRL and LRM can accomodate
any broadband measurement.
1. Through the use of LRL/LRM calibration and an external com-
puter, in conjunction with ANACAT software, multiple-level de-em-
bedding is possible. This calibration allows you to make semi-con-
ductor chip measurements up to 40 GHz with a single test fixture.
2. In addition, any non-coaxial transmission media, including mixed
media interconnects, can be accommodated. For example, a test de-
vice with a waveguide input and a coplanar microstrip output can
be measured. Software automatically compensates for the
microstrip dispersion.
A detailed procedure for calibrating for a measurement using the
LRL/LRM method is provided in the following pages.
LRL/LRM CALIBRATION MEASUREMENT CALIBRATION
7-36 37XXXC OM
*LRM Calibration Method of Rhode & Scharwz, Germany
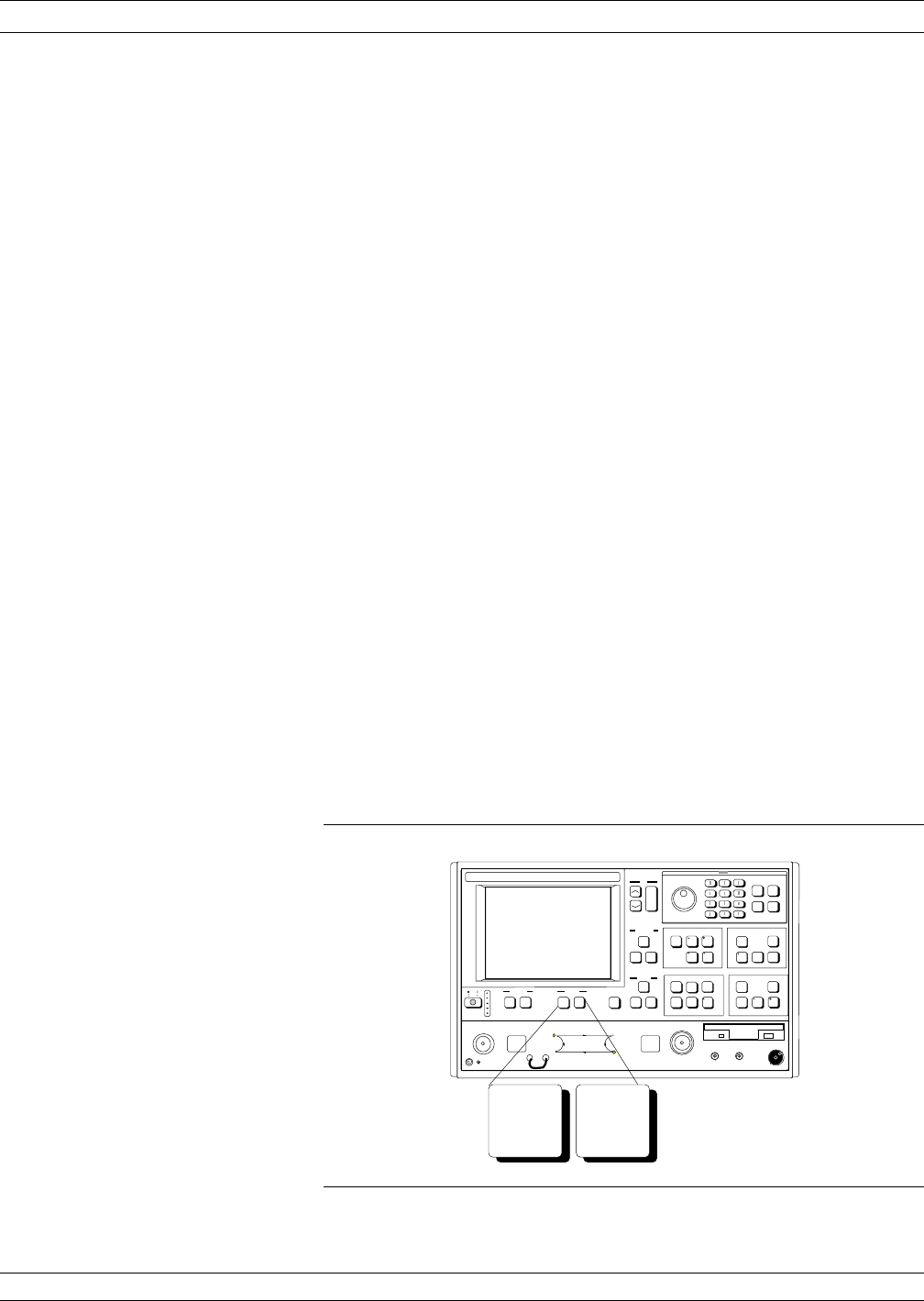
LRL/LRM Calibration
(Microstrip) Microstrip is a dispersive media. The 37XXXC applies dispersion com-
pensation during calibration for microstrip measurements. Because
the 37XXXC must know the specific microstrip parameters, during the
calibration procedure menus are available for entering the:
qwidth of the strip
qthickness of the substrate
qsubstrate dielectric constant
qeffective dielectric constant Zc
qcharacteristic impedance (reference)
When testing microstrip devices it is necessary to launch from coax to
microstrip. In production testing this launching must be temporary, so
that the device can easily be installed in and be removed from the fix-
ture. The requirement for launching to 65 GHz is met by the Anritsu
Universal Test Fixture (UTF). The UTF provides accurate, repeatable
launch to substrates from 5 to 70 mils thick, and from 0.15 to 2 inches
long. Offset connections and right angles can be configured. DC bias
probes can be mounted to the UTF to inject bias onto the substrate.
UTF calibration/verification kits are available for alumina in 10 mil,
15 mil, and 25 mil microstrip, and for 25 mil coplanar waveguide. Al-
though a UTF is not essential, the following calibration procedures
presume its use.
Step 1. Select the desired LRL line substrates from the ap-
propriate microstrip calibration kit. When called for
in the calibration sequence, mount the LRL line sub-
strates on the UTF following the procedure given in
the 3680 OMM.
Step 2. Press the Begin Cal key.
37XXXC OM 7-37
MEASUREMENT CALIBRATION LRL/LRM CALIBRATION
Apply
Cal
Begin
Cal
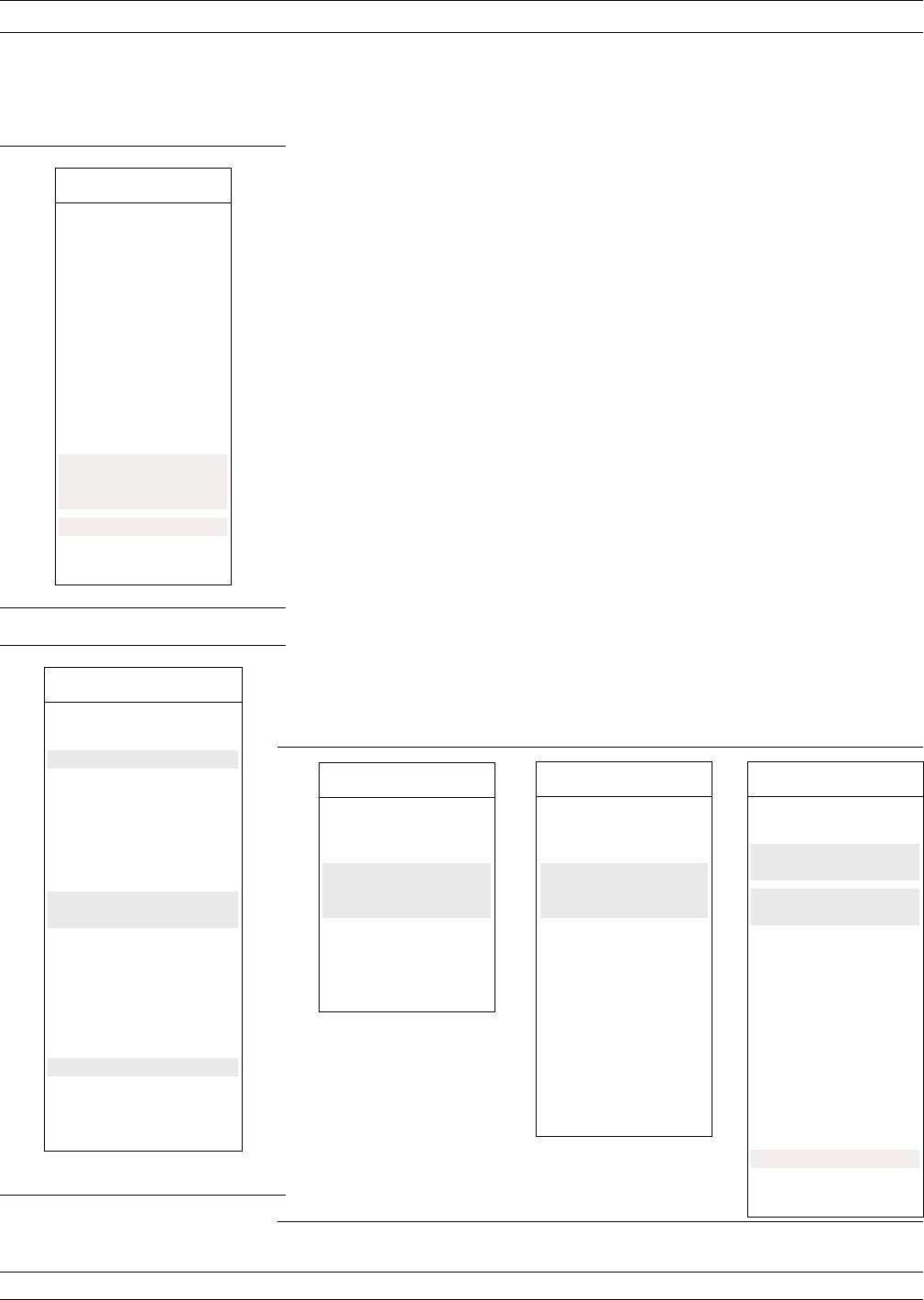
Step 3. Select CHANGE CAL METHOD AND LINE
TYPE, in menu C11 (left). (This assumes LRL and
MICROSTRIP are not presently shown in blue as be-
ing selected.)
Step 4. When menu C11A (bottom left) appears, highlight
the following selections.
a. LRL/LRM and press the Enter key.
b. MICROSTRIP and press the Enter key.
c. NEXT CAL STEP and press the Enter key.
Step 5. When menu C11 reappears, confirm that the
LRL/LRM calibration method and MICROSTRIP
line-type have been selected. Select NEXT CAL
STEP and press the Enter key to proceed.
Step 6. Continue through the calibration sequence, and
make the following selections from the menus that
appear:
INCLUDE ISOLATION (STANDARD) (Menu
C5D)
NORMAL (1601 POINTS MAXIMUM) (Menu C1)
START (Your start frequency) (Menu C2)
STOP (Your stop frequency) (Menu C2)
LRL/LRM CALIBRATION MEASUREMENT CALIBRATION
7-38 37XXXC OM
MENU C11
BEGIN CALIBRATION
KEEP EXISTING
CAL DATA
REPEAT
PREVIOUS CAL
AUTOCAL
CAL METHOD
XXXXXXXX
TRANSMISSION
LINE TYPE:
XXXXXXXX
CHANGE CAL
METHOD AND
LINE TYPE
NEXT CAL STEP
PRESS <ENTER>
TO SELECT
MENU C11A
CHANGE CAL METHOD
AND LINE TYPE
NEXT CAL STEP
CAL METHOD
SOLT (STANDARD)
SSLT (DOUBLE OFF-
SET SHORT WITH
LOAD)
SSST (TRIPLE OFFSET
SHORT)
LRL/LRM
TRM
TRANSMISSION
LINE TYPE
COAXIAL
WAVEGUIDE
MICROSTRIP
PRESS <ENTER>
TO SELECT
MENU C5D
SELECT USE
OF ISOLATION
IN CALIBRATION
INCLUDE
ISOLATION
(STANDARD)
EXCLUDE
ISOLATION
PRESS <ENTER>
TO SELECT
MENU C1
SELECT
CALIBRATION
DATA POINTS
NORMAL
(1601 POINTS
MAXIMUM)
C.W.
(1 POINT)
N-DISCRETE
FREQUENCIES
(2 TO 1601
POINTS)
TIME DOMAIN
(HARMONIC)
PRESS <ENTER>
TO SELECT
MENU C2
FREQ RANGE OF
CALIBRATION
START
0.0400000000GHz
STOP
20.000000000 GHz
201 DATA PTS
0.099800000 GHz
STEP SIZE
MAXIMUM NUMBER
OF DATA POINTS
1601 MAX PTS
801 MAX PTS
401 MAX PTS
201 MAX PTS
101 MAX PTS
51 MAX PTS
NEXT CAL STEP
PRESS <ENTER>
TO SELECT
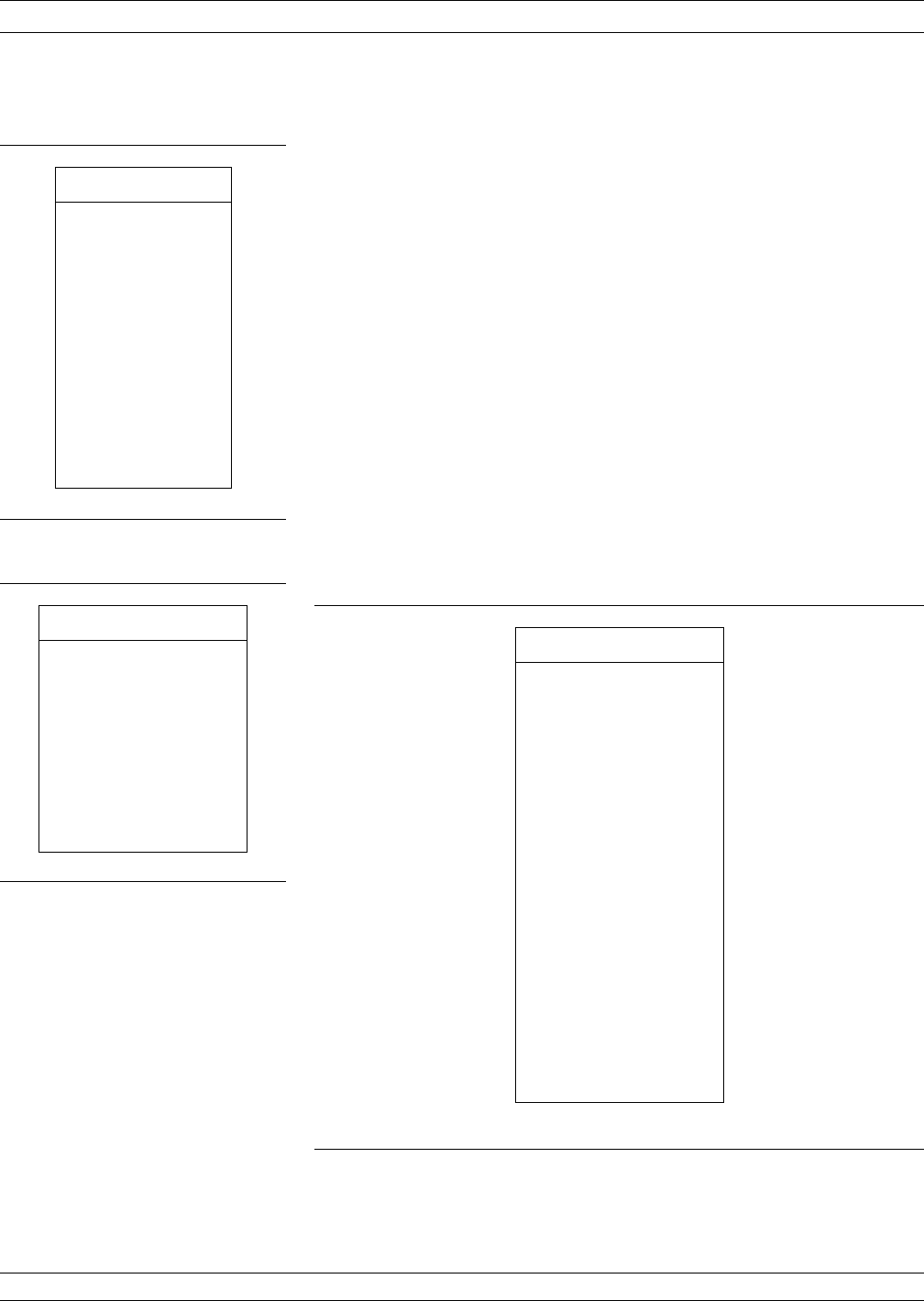
Step 7. When menu C3G appears, if you want to change
microstrip parameters to be different from those
shown in blue, place the cursor on MICROSTRIP
PARAMETERS and press the Enter key.
Step 8. When menu C16 (left) appears, move the cursor to
the Anritsu 3680 UTF calibration kit you wish to use
or to USER DEFINED; then press the Enter key.
The calibration kit selections shown in menu C16
are for the following 3680 Connection Substrate
Kits:
10 MIL KIT — 36804B-10M
15 MIL KIT — 36804B-15M
25 MIL KIT — 36804B-25M
If you choose USER DEFINED, the next menu that
appears (C16A), lets you characterize your parame-
ters. Move the cursor to each selection, key in a
value, then press the Enter key to return to menu
C16.
37XXXC OM 7-39
MEASUREMENT CALIBRATION LRL/LRM CALIBRATION
MENU C3G
CONFIRM
CALIBRATION
PARAMETERS
LRL/LRM
PARAMETERS
MICROSTRIP
PARAMETERS
USER DEFINED
TEST SIGNALS
START CAL
PRESS <ENTER>
TO SELECT
OR CHANGE
MENU C16
SELECT
MICROSTRIP
KIT TO USE
10 MIL KIT
15 MIL KIT
25 MIL KIT
USER DEFINED
PRESS <ENTER>
WHEN COMPLETE
MENU C16A
ENTER
MICROSTRIP
PARAMETERS
WIDTH OF
STRIP
XX.XXXX mm
THICKNESS OF
SUBSTRATE
XXXX.XXXX mm
Zc
XXX.XXX pW
SUBSTRATE
DIELECTRIC
XX.XX
EFFECTIVE
DIELECTRIC
XX.XX
(RECOMMENDED
0.00)
PRESS <ENTER>
WHEN COMPLETE
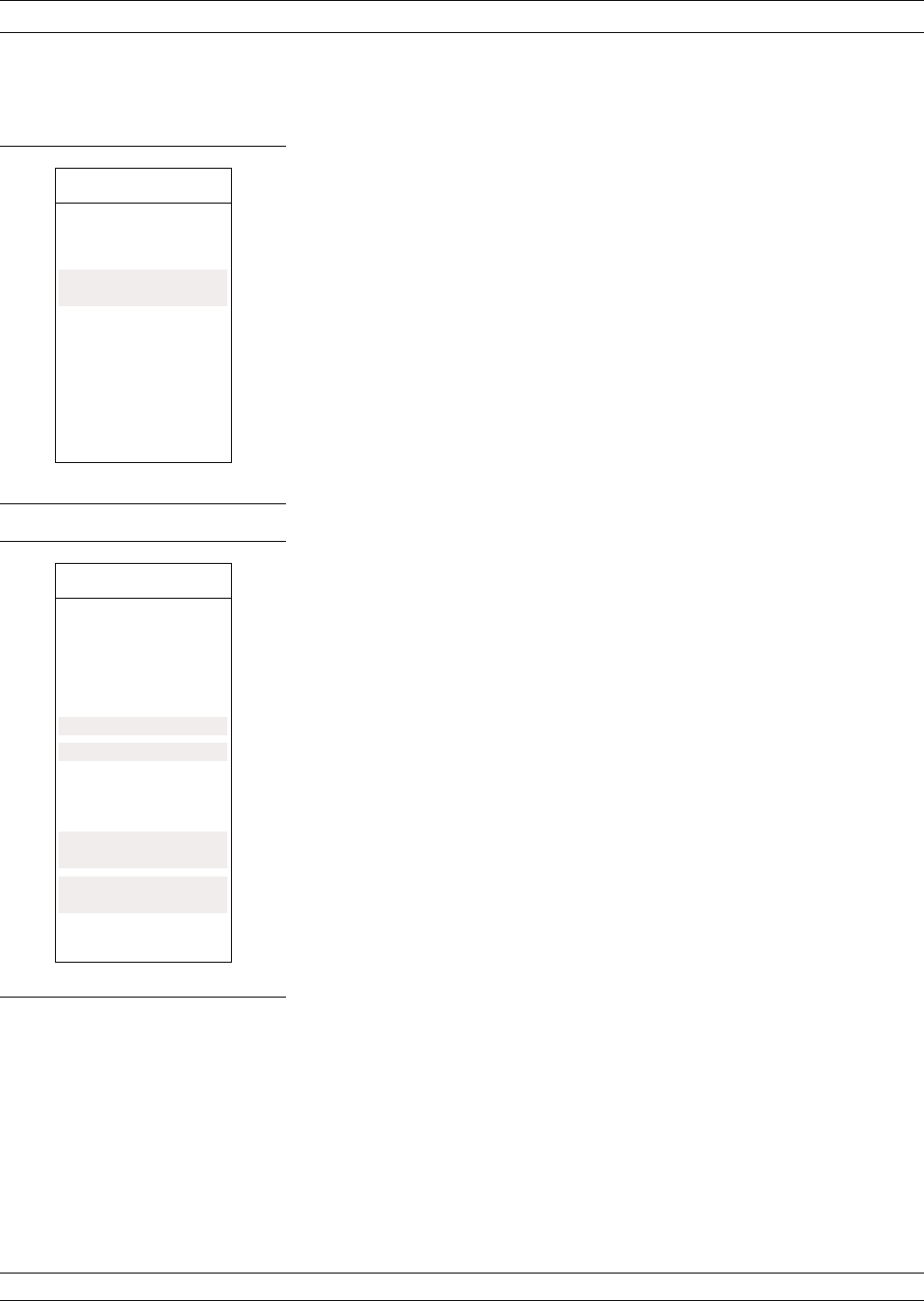
Step 9. Select LRL/LRM PARAMETERS, when menu C3G
returns.
Step 10. When menu C18 appears, you have two choices to
make: whether your calibration is to be two-line or
three-line, and where you want to have your refer-
ence plane.
a. Select the reference plane: Highlight MIDDLE
OF LINE 1 (REF) or ENDS OF LINE 1
(REF) and press the Enter key.
b. Select the type of LRL/LRM calibration: High-
light ONE BAND for a two-line calibration or
TWO BANDS for a three-line calibration.
As mentioned earlier in a two-line measurement,
the difference in length between line 1 and line 2 is
necessary for calibration, but limits the frequency
range to a 9:1 span. By using three lines in the cali-
bration, you extend the frequency range to an 81:1
span.
If you select TWO BANDS, skip to Step 12.
LRL/LRM CALIBRATION MEASUREMENT CALIBRATION
7-40 37XXXC OM
MENU C18
CHANGE LRL/LRM
PARAMETERS
NEXT CAL STEP
NUMBER OF
BANDS USED
ONE BAND
TWO BANDS
LOCATION OF
REFERENCE
PLANES
MIDDLE OF
LINE 1 (REF)
ENDS OF
LINE 1 (REF)
PRESS <ENTER>
TO SELECT
MENU C3G
CONFIRM
CALIBRATION
PARAMETERS
LRL/LRM
PARAMETERS
CHANGE
MICROSTRIP
PARAMETERS
XXXXXXXXX
START CAL
PRESS <ENTER>
TO SELECT
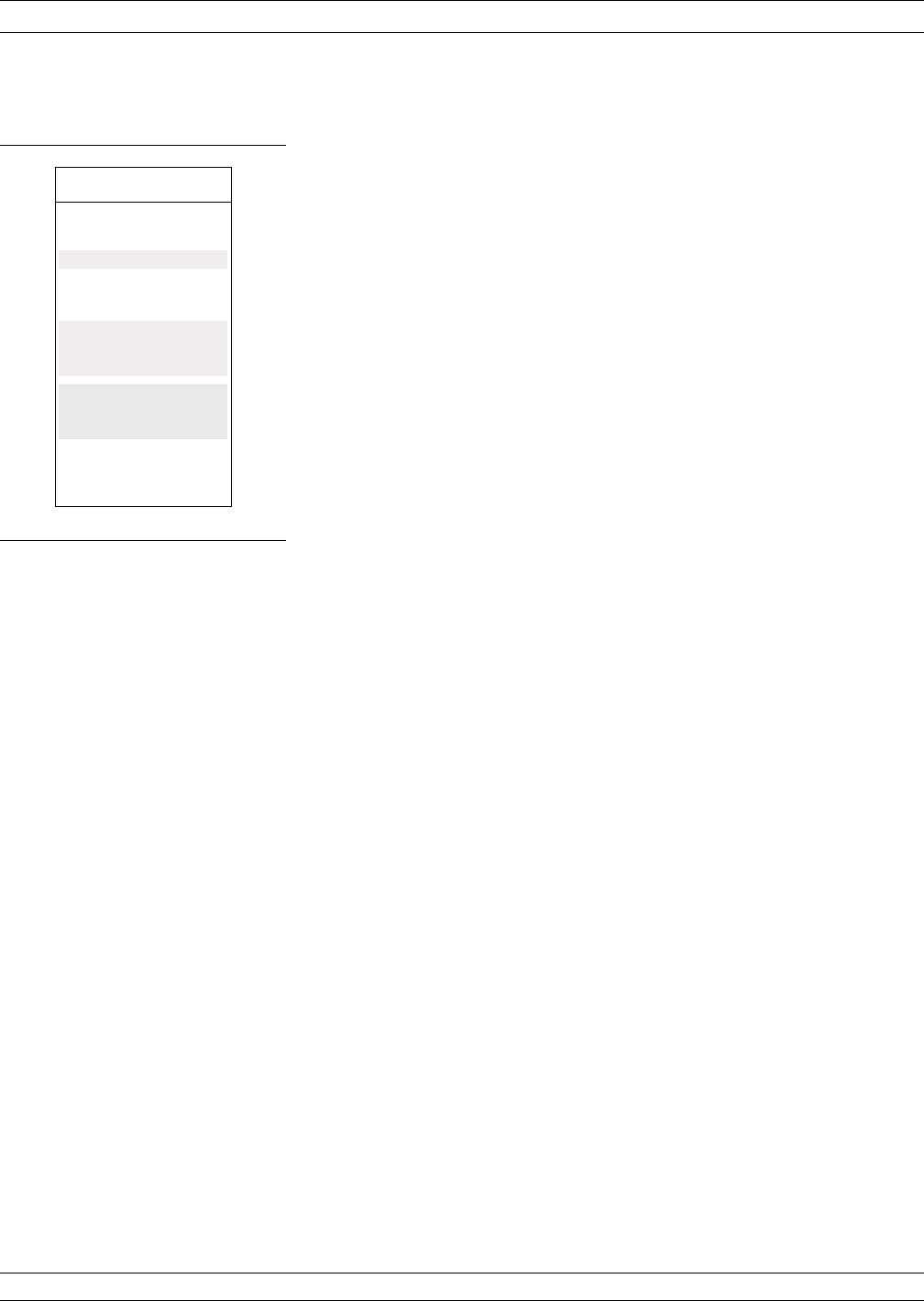
Step 11. When menu C18A (left) appears, make the following
selections (for 2-line):
a. Move the cursor to DEVICE 1 LINE 1 (REF)
and key in the value.
b. Move the cursor to DEVICE 2 LINE/MATCH.
Here you have another decision to make:
whether your calibration is to be LRL or LRM.
For this selection, the Enter key acts as a toggle.
c. If you toggle such that LINE turns red, then
key in the value for line 2. This value depends
on your frequency range.
d. If you toggle MATCH red, observe that
FULLBAND appears. This indicates that your
reflective device covers the full calibration
range.
e. When you have made both selections, move the
cursor to NEXT CAL STEP and press the Enter
key to produce the next menu. Skip to Step 13.
37XXXC OM 7-41
MEASUREMENT CALIBRATION LRL/LRM CALIBRATION
MENU C18A
CHANGE LRL/LRM
PARAMETERS
NEXT CAL STEP
CHARACTERIZE
CAL DEVICES
DEVICE 1
LINE 1 (REF)
X.XXXX mm
DEVICE 2
LINE /MATCH
X.XXXX mm
PRESS <ENTER>
TO SELECT
OR SWITCH
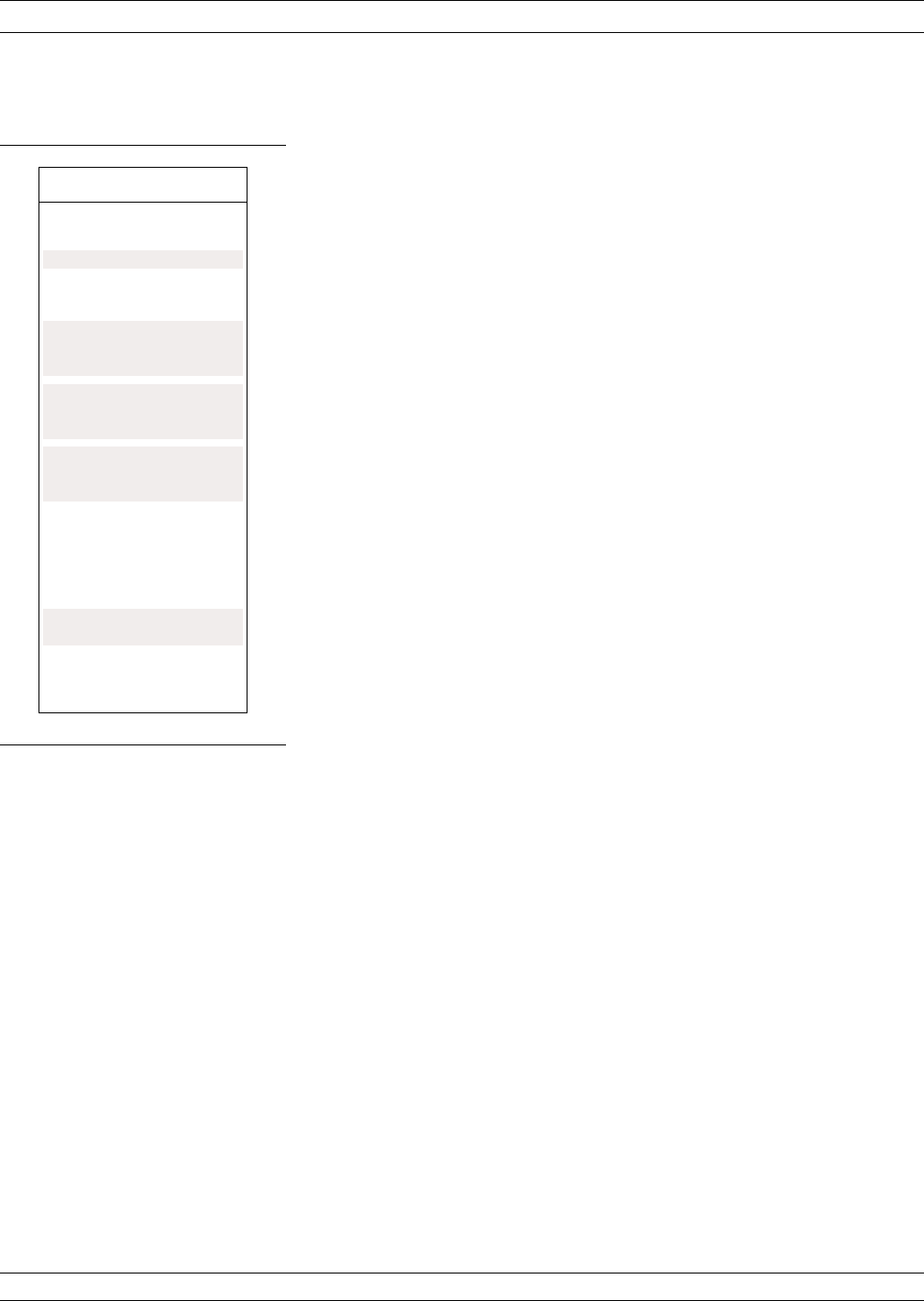
Step 12. When menu C18B (left) appears, make the following
selections (for 3-line):
a. Move the cursor to DEVICE 1 LINE 1 (REF)
and key in the value (typically 1.00 cm). Press
the Enter key to select.
b. Move the cursor to DEVICE 2 LINE/MATCH.
Both here, and for the next choice, you have an-
other decision to make: whether your calibration
is to be LRL or LRM. For this selection, the En-
ter key acts as a toggle.
c. If you toggle such that LINE turns red, then
key in the value for line 2. This value depends
on your frequency range.
d. If you toggle MATCH red, observe that
LOWBAND appears. This indicates that your
reflection device is a low-band load. This load
must have a passband such that it passes all
frequencies from the start to the breakpoint (see
below).
e. Move the cursor to DEVICE 3 LINE/MATCH.
If device 3 is a line, key in the value. If it is a
match, the term HIGHBAND will appear. This
indicates that your match is a high-band load.
This load must have a passband such that it
passes all frequencies from the breakpoint to
the stop frequency.
f. Move the cursor to BREAKPOINT and enter
your breakpoint frequency. For two-line LRL cal-
ibrations, select a breakpoint equal to the upper
frequency of the low frequency LRL line. For a
combined LRL and LRM calibration, select a
breakpoint equal to the top frequency of the cali-
bration divided by six; for instance, to cover the
frequency range 0.04 to 60 GHz, select 10 GHz
as the breakpoint.
g. When you have made all selections, move the
cursor to NEXT CAL STEP and press Enter to
produce the next menu.
LRL/LRM CALIBRATION MEASUREMENT CALIBRATION
7-42 37XXXC OM
MENU C18B
CHANGE LRL/LRM
PARAMETERS
NEXT CAL STEP
CHARACTERIZE
CAL DEVICES
DEVICE 1
LINE 1 (REF)
XX.XXXX
DEVICE 2
LINE/MATCH
XX.XXXX/LOWBAND
DEVICE 3
LINE/MATCH
XX.XXXX/HIGHBAND
FREQ AFTER
WHICH THE USE
OF DEVICE 2
AND DEVICE 3
IS EXCHANGED
BREAKPOINT
XXX.XXXXXXXXXGHZ
PRESS <ENTER>
TO SELECT
OR SWITCH
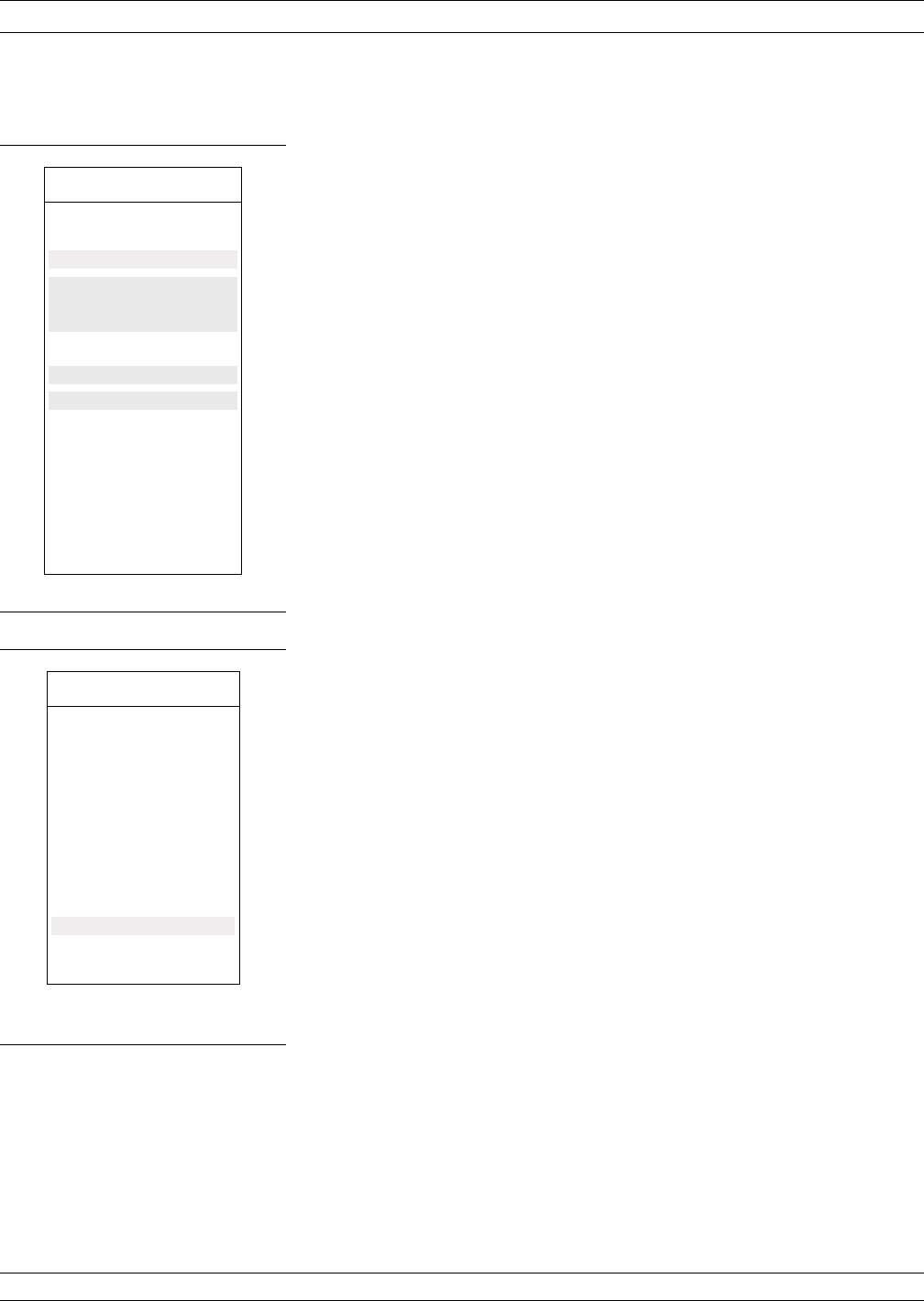
Step 13. The next menu, C19, gives you choices for your re-
flective device.
a. Move the cursor to REFLECTION OFFSET
LENGTH and key in a value (typically
0.0000 mm).
b. Move the cursor to GREATER THAN Z0or
LESS THAN Z0, depending on whether your re-
flective device is an Open or a Short. Press the
Enter key to select.
NOTE
Choose GREATER THAN Z0for an Open
and LESS THAN Z0for a Short.
c. When you complete your choices, move the cur-
sor to NEXT CAL STEP and press the Enter
key.
Step 14. When menu C3G reappears, move cursor to START
CAL and press Enter.
Step 15. Continue the calibration sequence by following the
prompts as they appear. Mount the appropriate LRL
line substrates when requested in the calibration se-
quence.
For the REFLECTIVE DEVICE and BROAD-
BAND LOAD prompts, remove all substrates from
the UTF and allow the lower jaws to short the cen-
ter conductor. Separate the connector blocks by at
least an inch. (The BROADBAND LOAD prompt
only appears if you selected to include isolation in
menu C5B.)
Step 16. Store the calibration.
37XXXC OM 7-43
MEASUREMENT CALIBRATION LRL/LRM CALIBRATION
MENU C19
CHANGE LRL/LRM
PARAMETERS
NEXT CAL STEP
REFLECTION
OFFSET LENGTH
+XXX.XXXX mm
REFLECTION TYPE
GREATER THAN Zo
LESS THAN Zo
MATCH PARAMETERS
MATCH IMPEDANCE
+XXX.XXX W
MATCH INDUCTANCE
+XXXX.XXXX pH
PRESS <ENTER>
TO SELECT
MENU C3G
CONFIRM
CALIBRATION
PARAMETERS
CHANGE
LRL/LRM
PARAMETERS
CHANGE
MICROSTRIP
PARAMETERS
XXXXXXXXX
START CAL
PRESS <ENTER>
TO SELECT
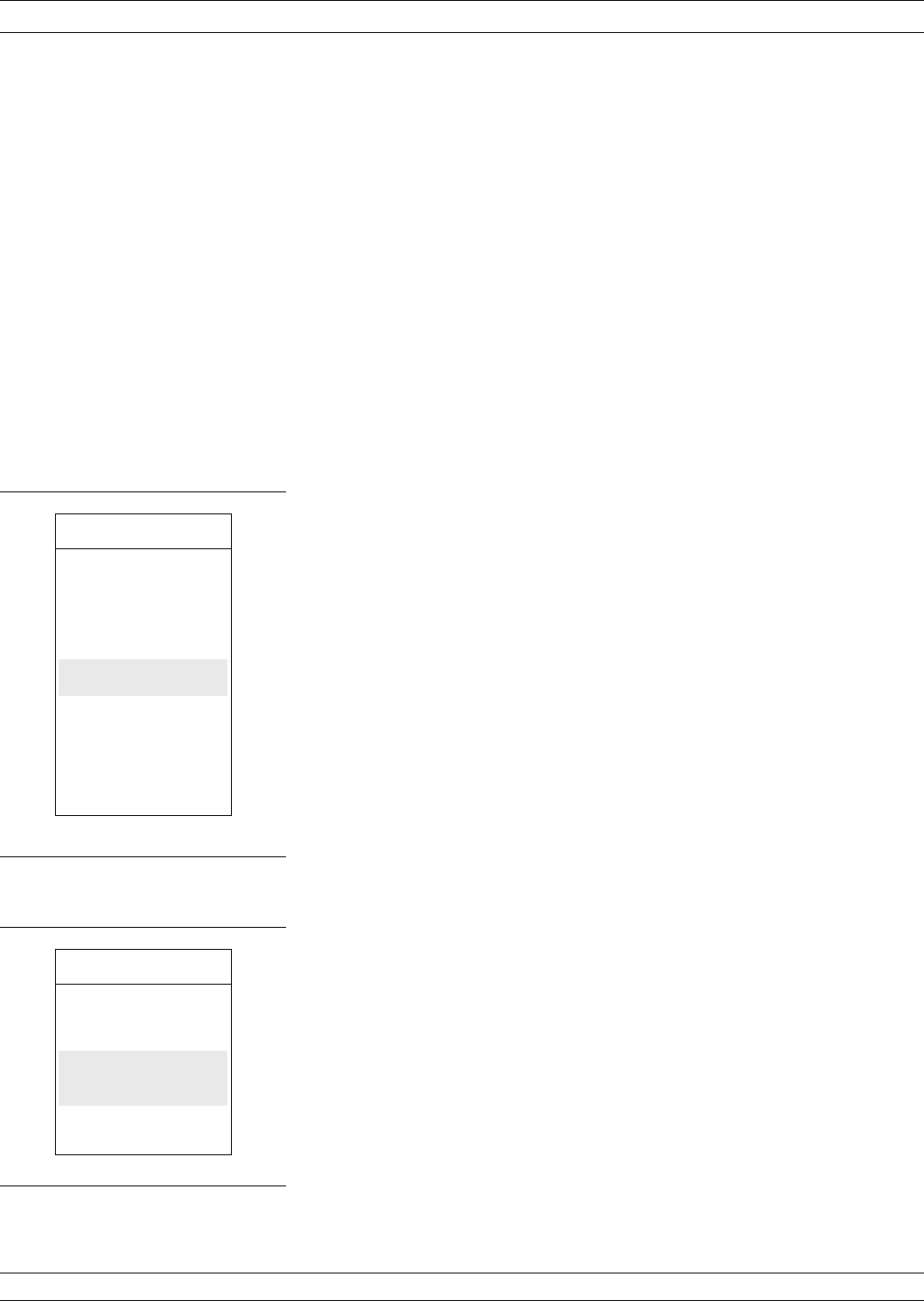
LRL/LRM Calibration
(Coaxial) An LRL cal kit is necessary to perform the coaxial calibration. Calibra-
tion kits for GPC-7 are available from Maury Microwave and Hewlett
Packard.
Two line lengths are used as the impedance standard. The calibration
frequency range is limited by the difference in the lengths of the two
lines. Their length must be different by approximately 90 degrees at
the mid-band frequency. A good calibration can be achieved over the
range of 18 degrees to 162 degrees making it possible to calibrate LRL
over a 9:1 frequency range.
LRL calibration is very sensitive to uncalibrated source match. If some
padding is placed at the test ports, the directivity and source match
will be improved. If the goal is high level measurements, then padding
should be included. If low level measurements are being performed,
then the padding must be left out.
Step 1. Same as Steps 1 through 6 in the Microstrip proce-
dure, except choose COAXIAL in menu C11A.
Step 2. When menu C3E (left) appears, if you want to
change line impedance, place cursor on REFER-
ENCE IMPEDANCE and press the Enter key.
Step 3. When menu C17 (left) appears, move cursor to REF-
ERENCE IMPEDANCE, key in the value, then
press the Enter key.
Step 4. Same as Steps 9 through 16 in the microstrip proce-
dure.
In the coaxial, three-line calibration there are fac-
tors you need to be aware of. Note that it is the line
length differences that are important to the LRL cal-
ibration, namely (L2–L1) and (L3–L1) where L1 is
the length of line 1, L2 is the length of line 2, and L3
is the length of line 3.
Longer length differences are used for longer wave-
lengths (lower frequencies). For frequencies up to
and including the breakpoint frequency, the larger
absolute value of the (L2–L1) and (L3–L1) differ-
ences is used. At frequencies above the breakpoint,
the smaller absolute value of the (L2–L1) and
(L3–L1) differences is used.
LRL/LRM CALIBRATION MEASUREMENT CALIBRATION
7-44 37XXXC OM
MENU C3E
CONFIRM
CALIBRATION
PARAMETERS
LRL/LRM
PARAMETERS
REFERENCE
IMPEDANCE
TEST SIGNALS
START CAL
PRESS <ENTER>
TO SELECT
OR CHANGE
MENU C17
ENTER
REFERENCE
IMPEDANCE
REFERENCE
IMPEDANCE
50.000 W
PRESS <ENTER>
WHEN COMPLETE
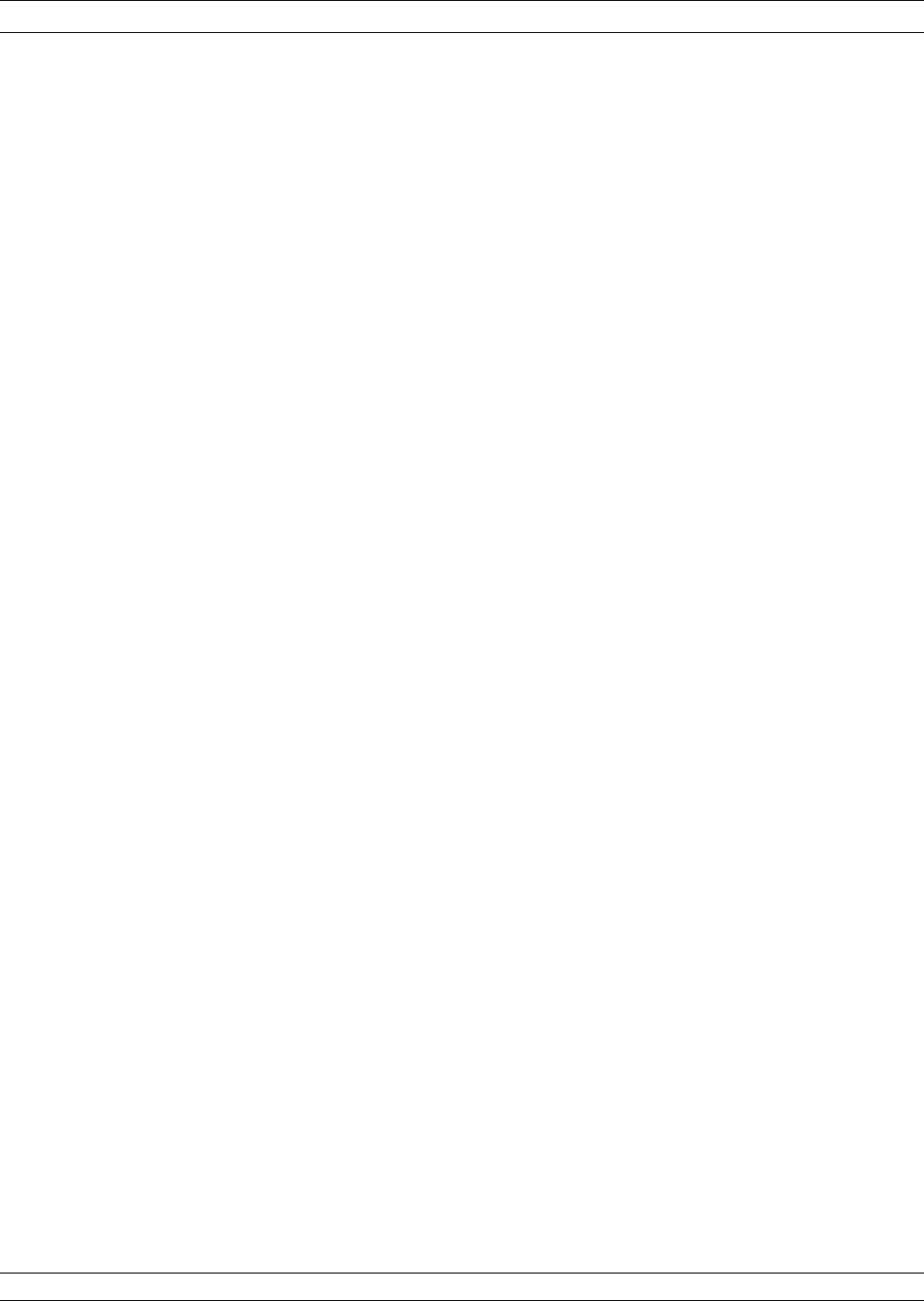
Consideration must also be given to selecting the
breakpoint frequency. Divide the frequency range to
satisfy the 9:1 rule for any given pair of lines. The
range is thus divided by the frequency breakpoint
into the intervals [f1, f2] and [f2, f3]. Based on these
intervals, next determine the appropriate length dif-
ferences; the longer difference is associated with the
lower interval [f1, f2]. Note that if the differences
are equal to each other, concurrent frequency ranges
are implied and only two lines need be used.
Select a line 1 reference (L1) around which to place
these two differences. Use any combination of posi-
tive or negative differences around line 1. The soft-
ware selects which interval is associated with either
of line 2 or line 3 by comparing the absolute values
of the differences with line 1. Data from the two
lines, which make up the larger absolute difference,
are used for the interval [f1, f2]. Data from the two
lines, which make up the smaller absolute differ-
ence, are used for the interval [f2, f3].
37XXXC OM 7-45
MEASUREMENT CALIBRATION LRL/LRM CALIBRATION
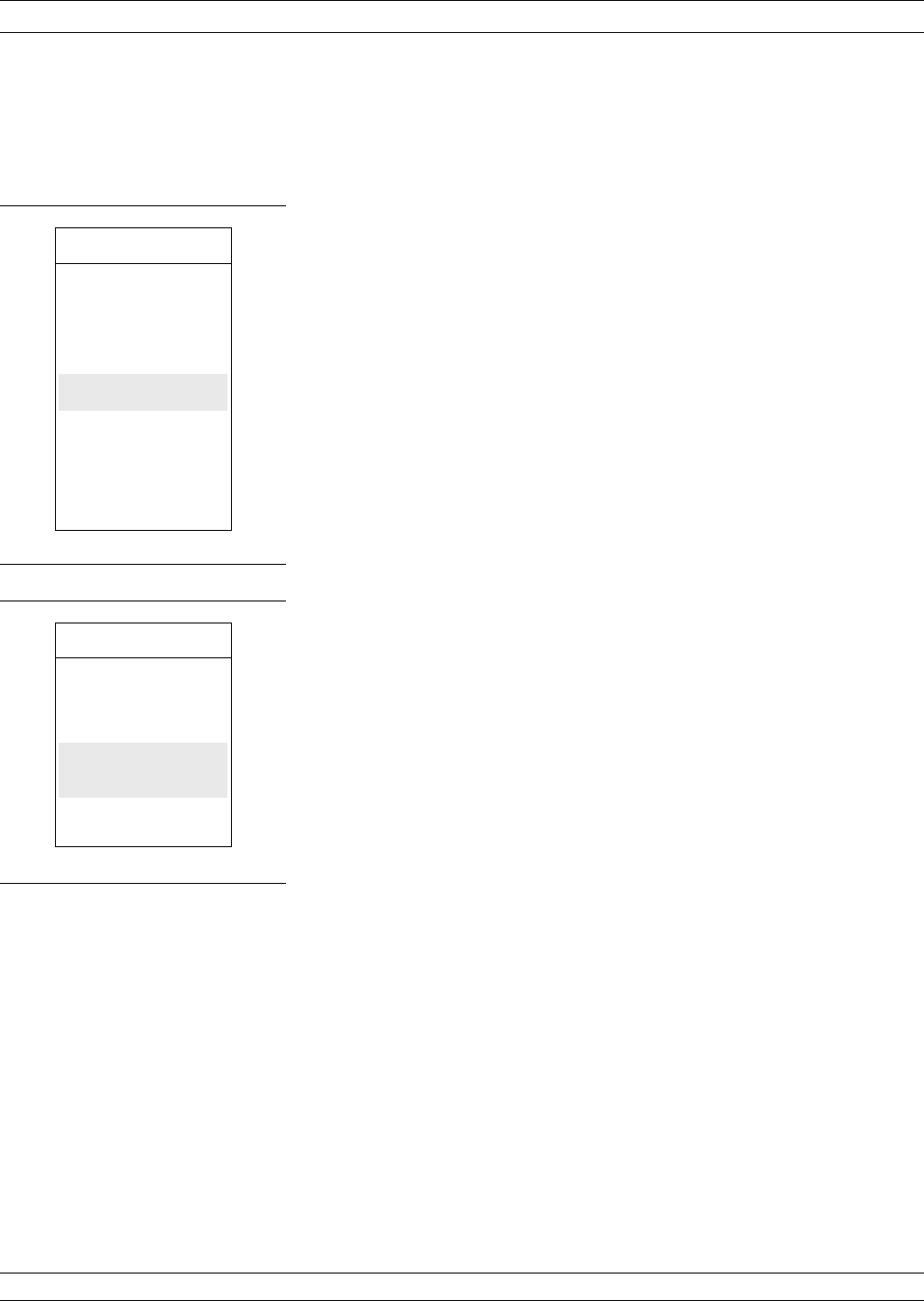
LRL/LRM Calibration
(Waveguide) The waveguide procedure is very similar to the coaxial and microstrip
procedures already described.
Step 1. Follow Steps 1 through 6 in the Microstrip proce-
dure, page 7-37, except choose WAVEGUIDE in
menu C11A.
The only difference is with menu C3F (left). For a
waveguide calibration, move the cursor to WAVE-
GUIDE CUTOFF FREQ and press Enter. This ac-
tion calls menu C15B, which lets you enter the
waveguide cutoff frequency. After doing so, you are
returned to menu C3F.
Step 2. When menu C3F reappears, place cursor on
CHANGE LRL/LRM PARAMETERS and press
the Enter key.
Step 3. Follow Steps 9 through 13, page 7-40, in the
Microstrip procedure.
7-8 TRM CALIBRATION The TRM Calibration procedure is the same as the LRL/LRM proce-
dure, previous page, except that certain parameters have been set by
default so that the calibration is simpler to perform (e.g., the L-param-
eter in the LRM calibration has been set to equal a length of 0 mm for
a through, and the R-parameter is set for a short).
TRM CALIBRATION MEASUREMENT CALIBRATION
7-46 37XXXC OM
MENU C3F
CONFIRM
CALIBRATION
PARAMETERS
LRL/LRM
PARAMETERS
WAVEGUIDE
CUTOFF FREQ
TEST SIGNALS
START CAL
PRESS <ENTER>
TO SELECT
OR CHANGE
MENU C15B
ENTER
WAVEGUIDE
CUTOFF
FREQUENCY
WAVEGUIDE
CUTOFF FREQ
XX.XXXX GHz
PRESS <ENTER>
WHEN COMPLETE
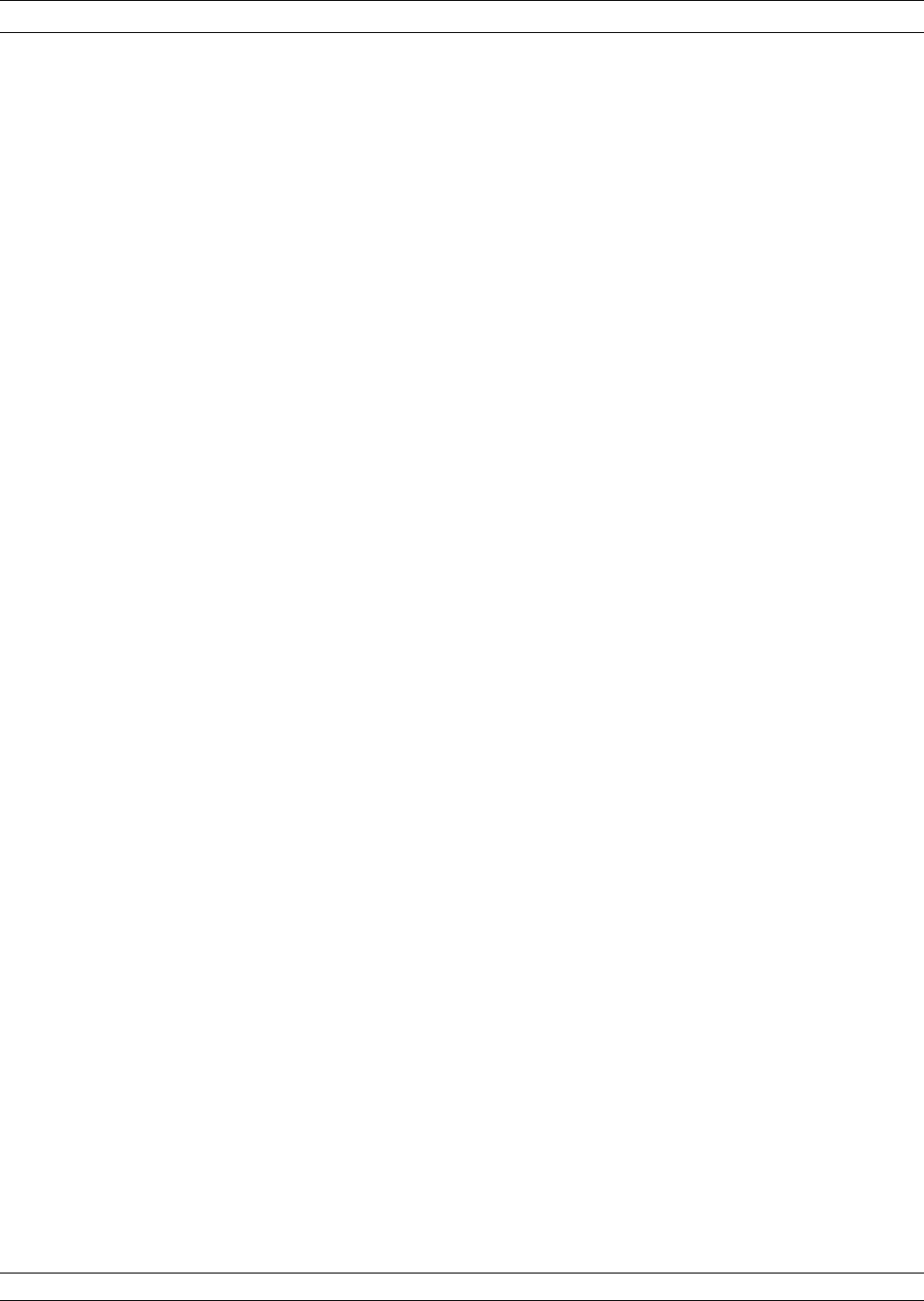
7-9 MERGE CAL FILES
APPLICATION The Merge Cal Files application allows the user to combine two cali-
brations that were performed on the VNA, but having differing fre-
quency ranges. This is of particular importance when a wide band RF
calibration cannot be performed because wide band calibration compo-
nents, such as loads and shorts, are not available. Such a case exists
when using Anritsu’s 37X97C wideband VNAs. Here, the preferred cal-
ibration method would be to perform a standard method (SOLT) coax-
ial calibration in the 0.04 to 65 GHz bands, a triple offset-short (SSST)
coaxial calibration in the 65 to 110 GHz band, then combine the cali-
brations to yield a wideband 0.04 to 110 GHz calibration that can be
saved and recalled.
The resultant calibration file setup will be the first calibration file
setup except that the frequency points and RF correction values of the
second calibration file will be intermingled with the frequency points
and RF correction values of the first.The start and stop frequencies
will be adjusted to reflect the lowest and highest frequencies in the in-
termingling. If there are frequency points in common, then the correc-
tion values of the first file will be used and that frequency and data
point in the second file will be discarded.
Both RF calibration files must be the same type, that is, full 12 Term,
1 Path 2 Port Forward, 1 Path 2 Port Reverse, etc., and the total num-
ber of frequency points of the first and second files added together can-
not exceed 1601.
In most cases, it doesn’t matter which calibration file is chosen as the
first calibration file; however, if the VNA is a 37397C used in a Broad-
band setup that crosses the 65 GHz switchpoint, it is advised that the
first calibration data be from the lower frequency band and the second
calibration data be from the higher frequency band. Additionally, if the
higher frequency band calibration starts at 65.0 GHz, the lower fre-
quency band calibration must end at 65.0 GHz. This will prevent a
spike at the 65.0 GHz band switch point.
NOTE
Refer to Appendix A, Front Panel Menus, for descriptions
of menus MRG1, EXT_MRG1, MRG2, and MRG3 that re-
late to this application.
37XXXC OM 7-47/7-48
MEASUREMENT CALIBRATION MERGE CAL FILES APPLICATION

Table of Contents
8-1 INTRODUCTION ...................................8-3
8-2 TRANSMISSION AND REFLECTION ........................8-3
8-3 LOW LEVEL AND GAIN ..............................8-12
8-4 GROUP DELAY ...................................8-20
8-5 ACTIVE DEVICE ..................................8-24
8-6 MULTIPLE SOURCE CONTROL ..........................8-29
Control Formula ..................................8-29
8-7 ADAPTER REMOVAL ................................8-34
8-8 GAIN COMPRESSION................................8-39
Power and VNAs..................................8-39
Swept Power Gain Compression .........................8-41
Swept Frequency Gain Compression .......................8-41
8-9 RECEIVER MODE ..................................8-58
Source Lock Mode .................................8-58
Tracking Mode ...................................8-58
Set-on Mode ....................................8-58
Receiver Mode Block Diagram ..........................8-59
Receiver Mode Menus ...............................8-59
Procedure, Receiver Mode Operation .......................8-59
8-10 OPTICAL APPLICATION ..............................8-62
E/O Measurements ................................8-62
O/E Measurements ................................8-65
Creating a Characterization (*.S2P) File for E/O and O/E Measurements . . . 8-71
Chapter 8
Measurements
IMPORTANT NOTE
The 37100C Direct Access Receiver cannot make S-parameter measurements without an ex-
ternal reflectometer setup. This manual describes calibration and S-parameter measure-
ments for 372XXC and 373XXC. Most of these measurements can also be used with 371XXC
assuming the user understands the need for an external reflectometer. Anritsu offers an op-
tional reflectometer test set that can be used. This reflectometer is described and a drawing
shown in the Technical Data Sheet provided as Appendix C in this manual.
NOTE ON MEASUREMENTS
With the exception of Active Device (paragraph 8-5) and Receiver Mode (paragraph 8-9), all
measurements can be made with the 373XXC and the 372XXC. They can also be made with
the 371XXC using an appropriate reflectometer, such as the optional Anritsu reflectometer
test set described in Appendix C. Active Device and Receiver Mode measurements can only
be made using the 373XXC and a 371XXC with an appropriate user-supplied reflectometer.

Chapter 8
Measurements
8-1 INTRODUCTION This section discusses typical measurements that can be made with
the Model 37XXXC Vector Network Analyzer.
8-2 TRANSMISSION AND
REFLECTION This discussion provides information on general measurement consid-
erations and transmission and reflection measurements using the
37XXXC.
Setup and Calibration
To get started, apply power to the system.
After turning on the power, allow the system to warm up for at least
60 minutes before operation.
In normal operation, the system comes on line in the state that it was
in when last turned off. If you want to return the system to its default
state, you can do so by pressing the Default Program key twice.
The default parameters provide a known starting point. For example,
they reset the start and stop frequencies for maximum sweep width,
the source control to 0 dB, and the display resolution to 401 data
points.
The Sweep Setup menu should now appear on the display (it also can
be displayed using the Setup Menu key). If you like, you can select a
new start frequency, stop frequency, or source power.
You can further reduce the power level at Ports 1 and 2 with the
built-in attenuators. Using the Reduced Test Signals option in the
Sweep Setup menu, you can change the setting of the Port 1 source at-
tenuator over a range of from 0 to 70 dB. The Port 2 test attenuator
has a range of from 0 to 40 dB (in 10 dB steps) (if Option 6 is in-
stalled).
37XXXC OM 8-3
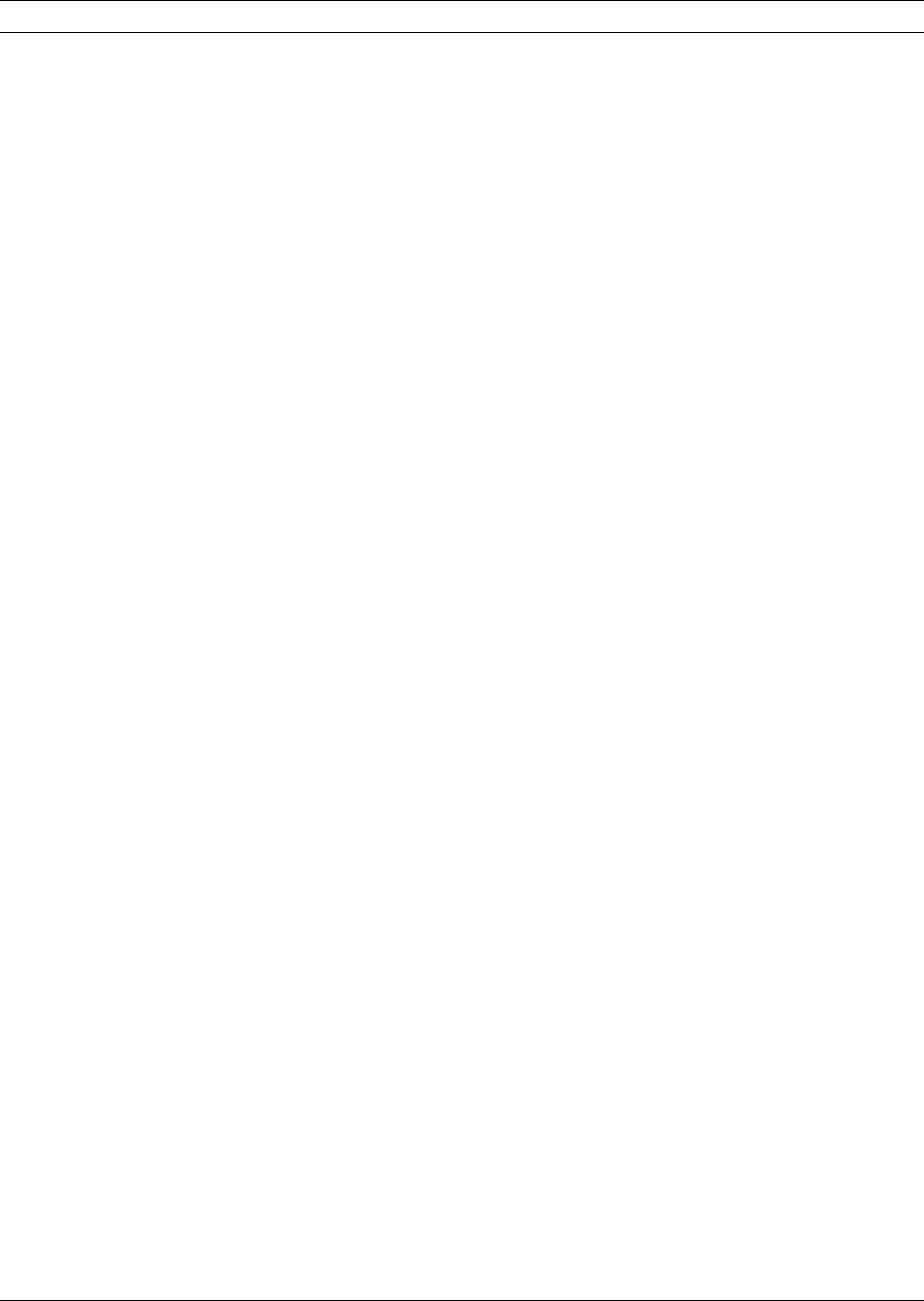
Install the calibration kit devices to the test ports as instructed by the
U3 menu. Both the capacitance coefficients for the Open and the offset
lengths for the Open and Short can be modified or defined.
Selecting the Begin Cal key starts the calibration process. The Calibra-
tion menus step you through the calibration process, as follows:
Select the type of calibration desired.
Select the frequency range of calibration. Using the Data Points key,
you can choose from 51 up to 1601 measurement data points.
When the calibration is completed, you can store the calibration data
on a disk. You are now ready to install the test device and proceed with
the measurement. At this point you have a number of measurement
options to consider such as displays, markers, limits, outputs, sweeps,
and enhancements.
You can select any of the available graph types and display them for
any calibrated parameter on any of the four channels (if a 12-term cal-
ibration was performed).
TRANSMISSION AND REFLECTION MEASUREMENTS
8-4 37XXXC OM
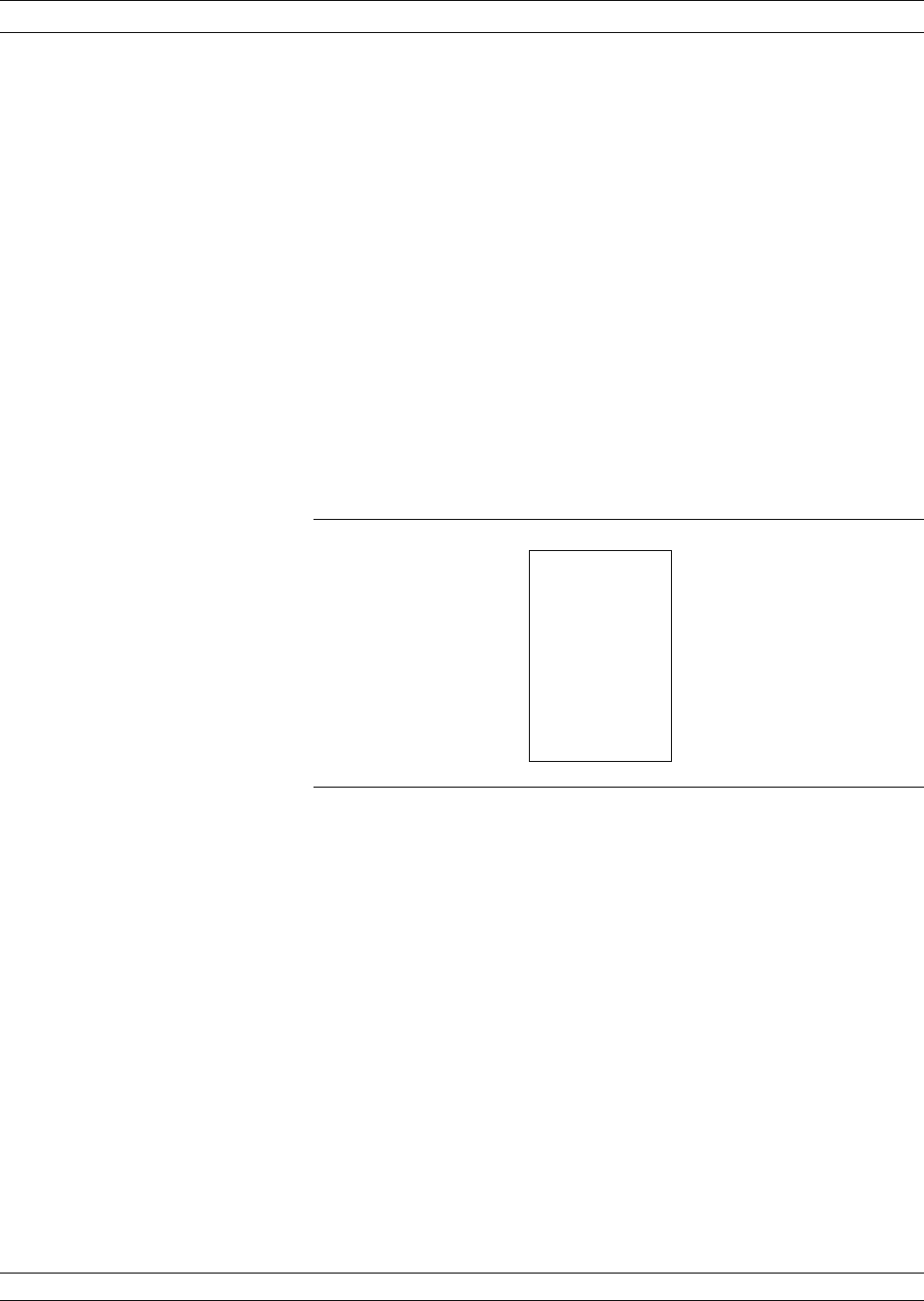
Up to six markers are available. Using the Marker Menu, you can set
the frequency of each one, you can set each one in the delta marker
mode, and you can set each marker’s level to maximum or minimum.
In some cases—such as in a production environment—limit lines are
desirable. Options within the menu called up using the Limits key, pro-
vide for one or two flat, sloped, or single-point-segmented limit lines
for each channel. These limit lines function with all of the graph types,
including Smith and admittance. The color of the limit lines (blue) dif-
fers from that of the measurement trace. This allows for easy analysis
of results.
The Hard Copy Menu key menu (Figure 8-1) gives you a choice be-
tween a printer and a colored-pen plotter. It also lets you select menus
from which you may chose from a variety of print or plot options.To
output the display, press the Start Print key. The default setting pro-
vides for a full display printout from the associated printer.
37XXXC OM 8-5
MEASUREMENTS TRANSMISSION AND REFLECTION
Figure 8-1.Output Menu
SELECT OUTPUT
DEVICE
PRINTER
PLOTTER
OUTPUT OPTIONS
SETUP OUTPUT
HEADERS
OPERATIONS
PRINT OPTIONS
PLOT OPTIONS
PRESS <ENTER>
TO SELECT
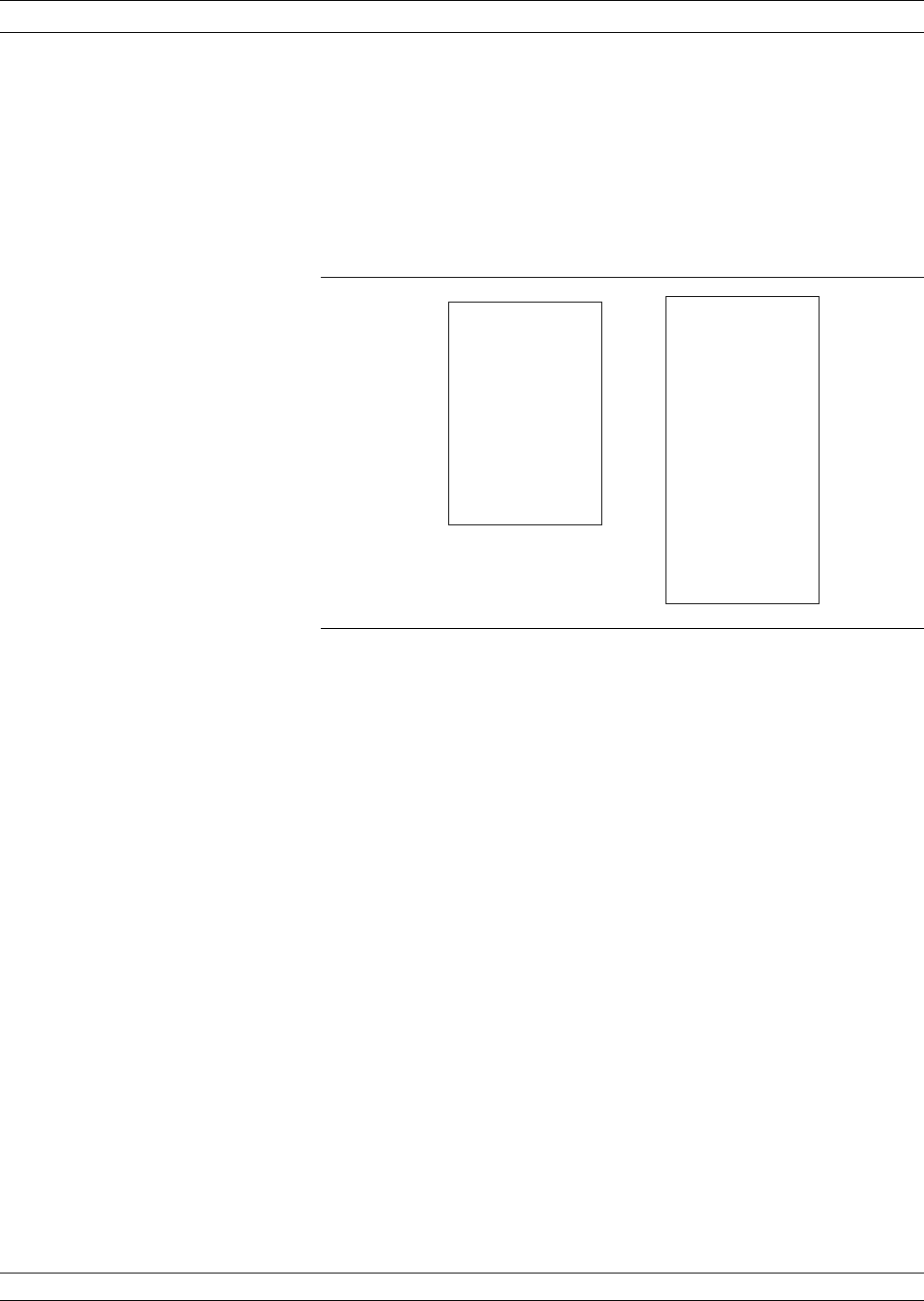
To label the output, select Setup Output Headers in the Output Menu
or press the Device ID key.
On the output to the printer, plotter, or disk. a menu then appears that
lets you specify the device name/serial number, the date, the operator’s
name, and user comments (Figure 8-2).
Sweep frequencies can be changed with the calibration applied as long
as the frequencies are between the calibration start and stop frequen-
cies.
Additionally, a marker sweep can be selected from the Setup Menu.
This allows you to sweep between any two active markers as long as
the frequency of each falls between the calibrated start and stop fre-
quencies.
Using the Data Points key, you can select the number of data points for
optimal resolution-vs-speed.
TRANSMISSION AND REFLECTION MEASUREMENTS
8-6 37XXXC OM
Figure 8-2.Label Menus
DATA OUTPUT
HEADERS
MODEL
ON
FILTER
DEVICE ID
ON
870124
DATE
ON
28-_JUNE_87
ÁOPERATOR ON
MIKE
COMMENTS
SELECT NAME
FILTER_#2—-
ABCDEFGHIJKLM
NOPQRSTUVWXYZ
0123456788-_/#
DEL CLEAR DONE
TURN KNOB
TO INDICATE
CHARACTER
OR FUNCTION
PRESS <ENTER>
TO SELECT
NUMBERS MAY
ALSO BE
SELECTED
USING KEYPAD
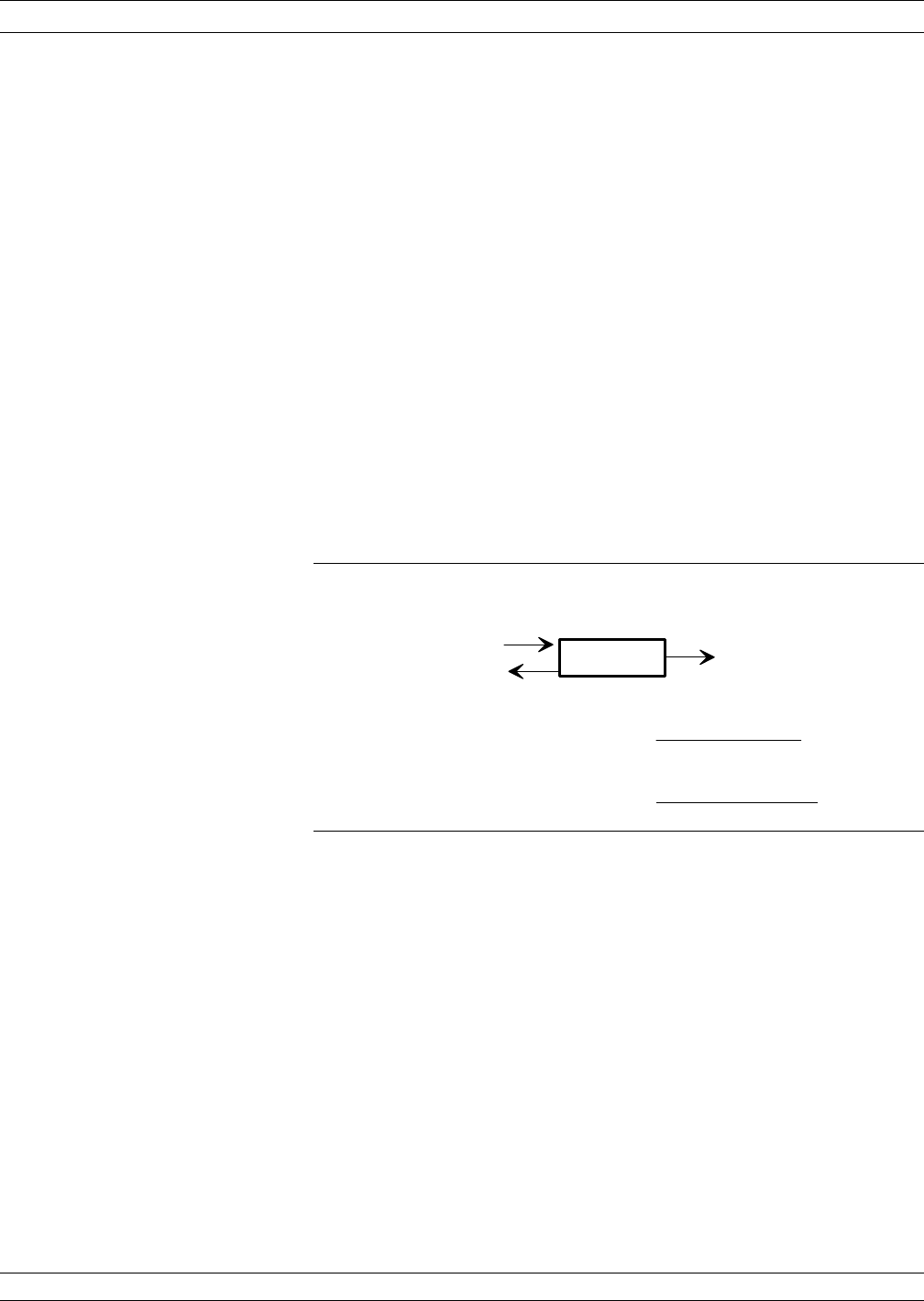
Finally, you can enhance the measurement data by reducing the IF
bandwidth and using averaging and/or smoothing.
qChange the IF bandwidth by selecting the Video IF BW key
qSet the averaging and smoothing values by selecting the
Avg/Smooth Menu key
qTurn on the averaging and smoothing using the Trace Smooth
and Average keys, which have LED’s to let you know that the en-
hancement is being applied
Measurement Discussion
Before going any further, let us take a few moments to review some ba-
sic principles of network measurements. First, we apply incident en-
ergy to the input of a test device. If the device’s input impedance dif-
fers from the measurement system’s impedance, some of that energy is
reflected. The remainder is transmitted through the device. We call the
ratio of reflected-to-incident energy the reflection coefficient. The ratio
of transmitted-to-incident energy we call the transmission coefficient
(Figure 8-3).
These ratios are complex quantities that have magnitude and phase
components. Using vector representation, the vector magnitude is the
ratio of reflected-to-incident magnitude (or transmitted-to-incident
magnitude), while the vector phase is the difference in phase between
the incident energy and the reflected/transmitted energy (Figure 8-4).
37XXXC OM 8-7
MEASUREMENTS TRANSMISSION AND REFLECTION
I N C I D E N T
E N E R G Y
R E F L E C T E D
E N E R G Y
T R A N S M I T T E D
E N E R G Y
R E F L E C T I O N C O E F F I C I E N T =
T R A N S M I S S I O N C O E F F I C I E N T =
R E F L E C T E D E N E R G Y
I N C I D E N T E N E R G Y
T R A N S M I T T E D E N E R G Y
I N C I D E N T E N E R G Y
B A S I C M E A S U R E M E N T P R I N C I P L E S
DUT
Figure 8-3. Basic Measurement Principles
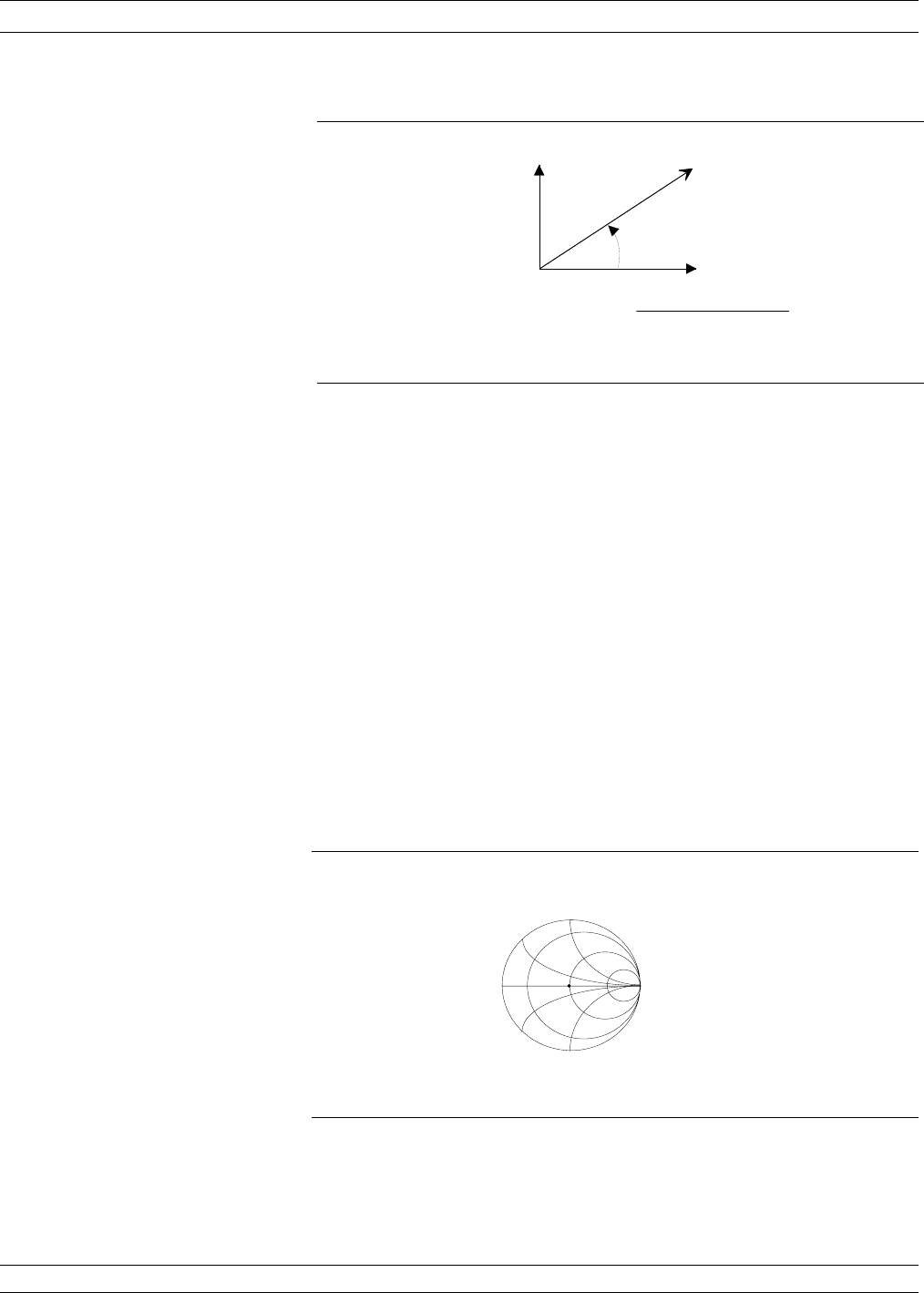
The measurement reference for the incident energy is the point at
which the device connects to the measurement system. We call this
point the reference plane. The incident energy at the reference plane is
defined as having a magnitude of 1 and a phase of 0 degrees. We estab-
lish this during the calibration.
The ratio of reflected and transmitted energy to the incident energy
can be represented by a number of different measurements and units,
as shown below.
The default display for reflection measurements is the Smith chart.
The default display for transmission measurements is the Log Magni-
tude and Phase graph.
The Smith chart is a convenient way to display device impedance and
is a useful aid for the graphical design and analysis of microwave cir-
cuits (Figure 8-18).
TRANSMISSION AND REFLECTION MEASUREMENTS
8-8 37XXXC OM
P H A S E
M A G N I T U D E
I M A G I N A R Y
R E A L
R E F L E C T I O N C O E F F I C I E N T = R E F L E C T I O N ( M A G N I T U D E )
I N C I D E N T ( M A G N I T U D E )
P H A S E = I N C I D E N T ( P H A S E ) - R E F L E C T E D ( P H A S E )
Figure 8-4. Magnitude/Phase Vector
50
INDUCTIVE
CAPACITIVE
SMITH CHART
Ω
Figure 8-5 Smith Chart Display 1
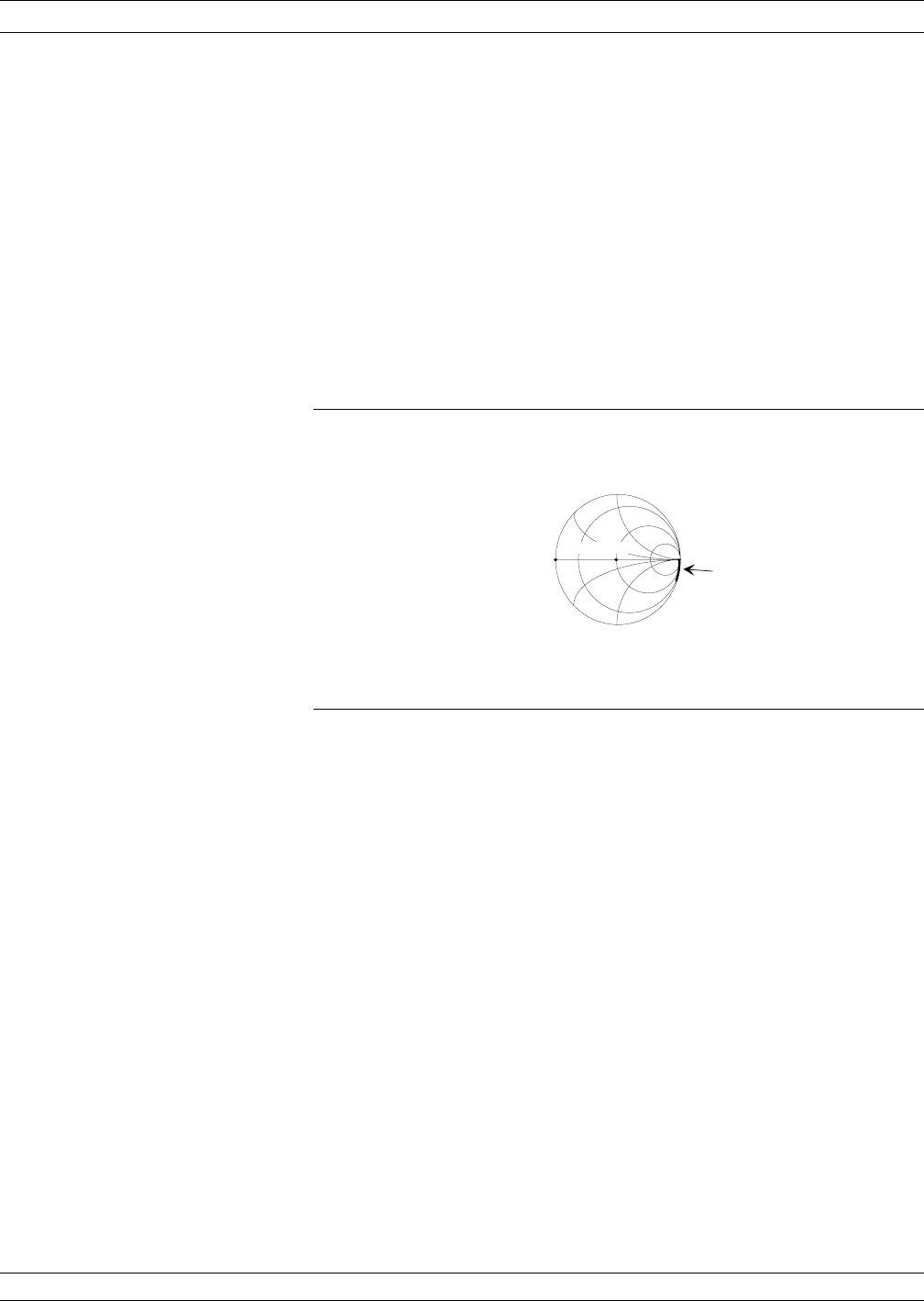
Let us assume both that our system is already calibrated and that we
have equalized the system for the test port in use. We would then
1. Connect the Short: A Short always appears as a dot at the left-most
edge of the Smith chart’s horizontal axis.
2. Connect a Termination: Now you will see another dot located at the
center (1+j0) of the chart (this assumes a 50-ohm load).
3. Connect the Open: An Open appears as an arc on the chart’s right
edge. This is due to the fringing capacitance of the Open standard
(Figure 8-6).
37XXXC OM 8-9
MEASUREMENTS TRANSMISSION AND REFLECTION
SMITH CHART
SHORT OPEN
ARC
TERMINATION
Figure 8-6. Smith Chart Display 2
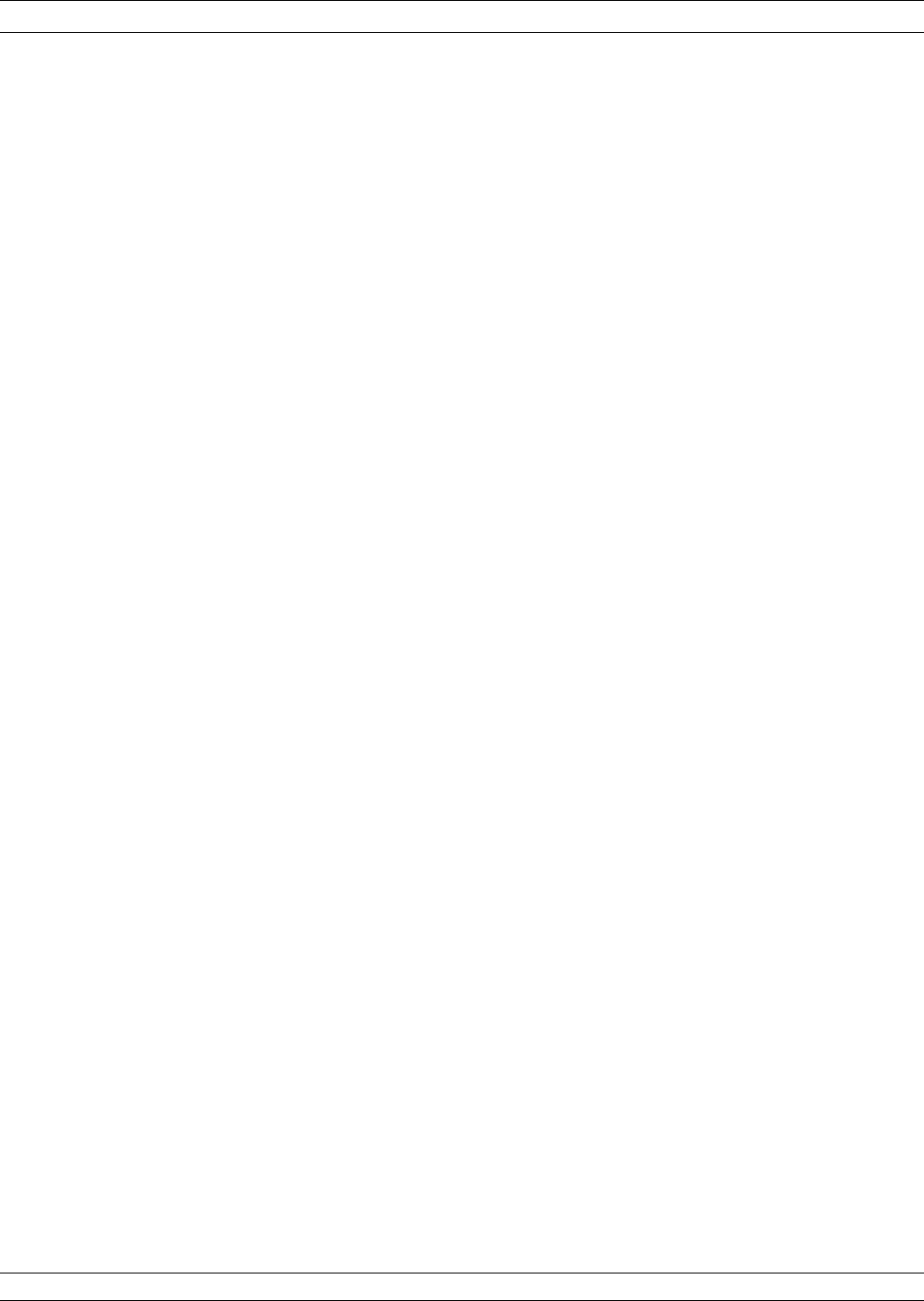
Now let’s perform a reflection measurement on a 20 dB attenuator
over the 1 to 18 GHz range.
We need to determine the setup, calibration, and measurement re-
quirements.
A known good starting point is to reset with Default Program parame-
ters. Since our measurement lies between 1 and 18 GHz, set the Start
and Stop frequencies using the Sweep Setup menu that appears on the
display following system reset.
Let’s perform a simple Reflection Only calibration, which uses an open,
a short, and a broadband load. To do this, press the Begin Cal key and
follow the directions in the menu area.
When you complete the calibration, the “CHANNEL 1 WITH S11”
Smith chart appears on the display. Now:
1. Select the Log Magnitude display and install the attenuator.
2. Select Auto Scale to optimize the display data.
3. Use Markers 1 and 2 to find the maximum and minimum imped-
ance.
TRANSMISSION AND REFLECTION MEASUREMENTS
8-10 37XXXC OM

Now let us perform a transmission measurement on the same 20 dB
attenuator over the same frequency range. We will follow the same
steps as before, but this time we will use additional features.
Once again, reset the system using the Default Program key.
In this calibration we will select the N-Discrete Frequencies menu op-
tion and step all frequencies in increments of 50 MHz.
When the calibration is complete, Channel 1 will display “S21 FOR-
WARD TRANSMISSION WITH LOG MAGNITUDE AND PHASE.”
You can use Markers 1 and 2 to find the maximum and minimum val-
ues of the attenuators insertion loss.
37XXXC OM 8-11
MEASUREMENTS TRANSMISSION AND REFLECTION
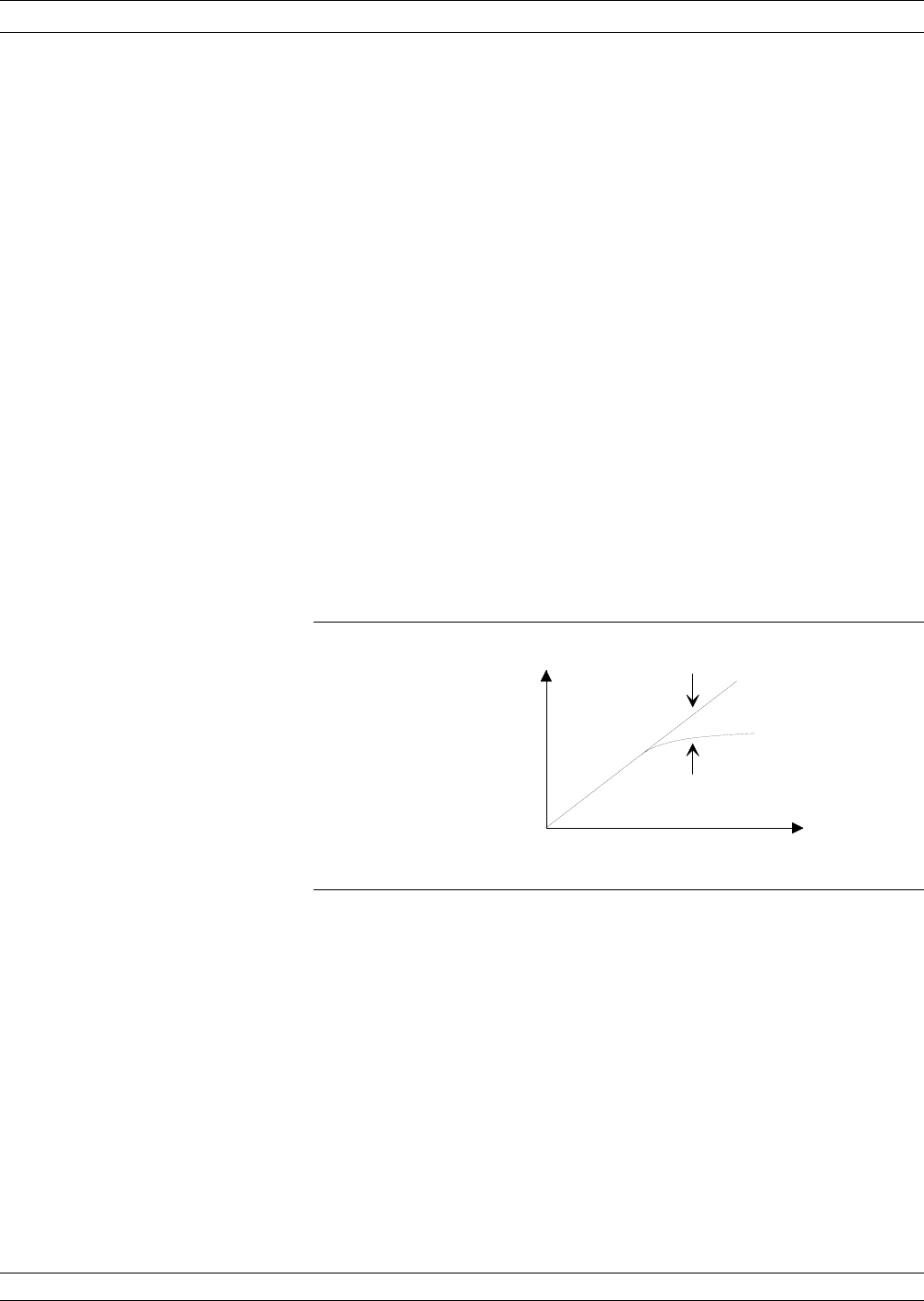
8-3 LOW LEVEL AND GAIN This discussion provides methods and techniques for making gain and
low-signal-level measurements. It is divided into 37XXXC system con-
siderations and test device considerations.
37XXXC System Considerations
The 37XXXC system is limited in its ability to test low-signal levels by
its dynamic range and signal-to-noise-power ratio. First we will dis-
cuss receiver dynamic range, which is the difference between the maxi-
mum and minimum acceptable signal levels (Receiver Dynamic Range
= Pmax – Pmin).
Receiver Dynamic Range
The dynamic range of the 37XXXC is limited by the 0.1 dB compres-
sion level of the samplers at high signal levels. It is further limited at
low signal levels by leakage signals and noise.
Figure 8-7 shows the detected output signal as a function of the power
level at the sampler. The 0.1 dB compression level is on the order of
–10 dBm. The 37XXXC is designed such that all other conversions
compress at a much greater level, which leaves the samplers as the
main source of nonlinearity.
The small signal response is limited by errors due to noise and leakage
signals. The leakage signals are both from within the 37XXXC and at
the device-under-test (DUT) connectors.
LOW LEVEL AND GAIN MEASUREMENTS
8-12 37XXXC OM
- 1 0
D E T E C T E D
P O W E R O U T P U T
( d B m )
P O W E R L E V E L A T I N P U T T O S A M P L E R
( d B m )
0 . 1 d B C O M P R E S S I O N
- 1 0
C O M P R E S S I O N L E V E L
Figure 8-7. Compression at 0.1 dB
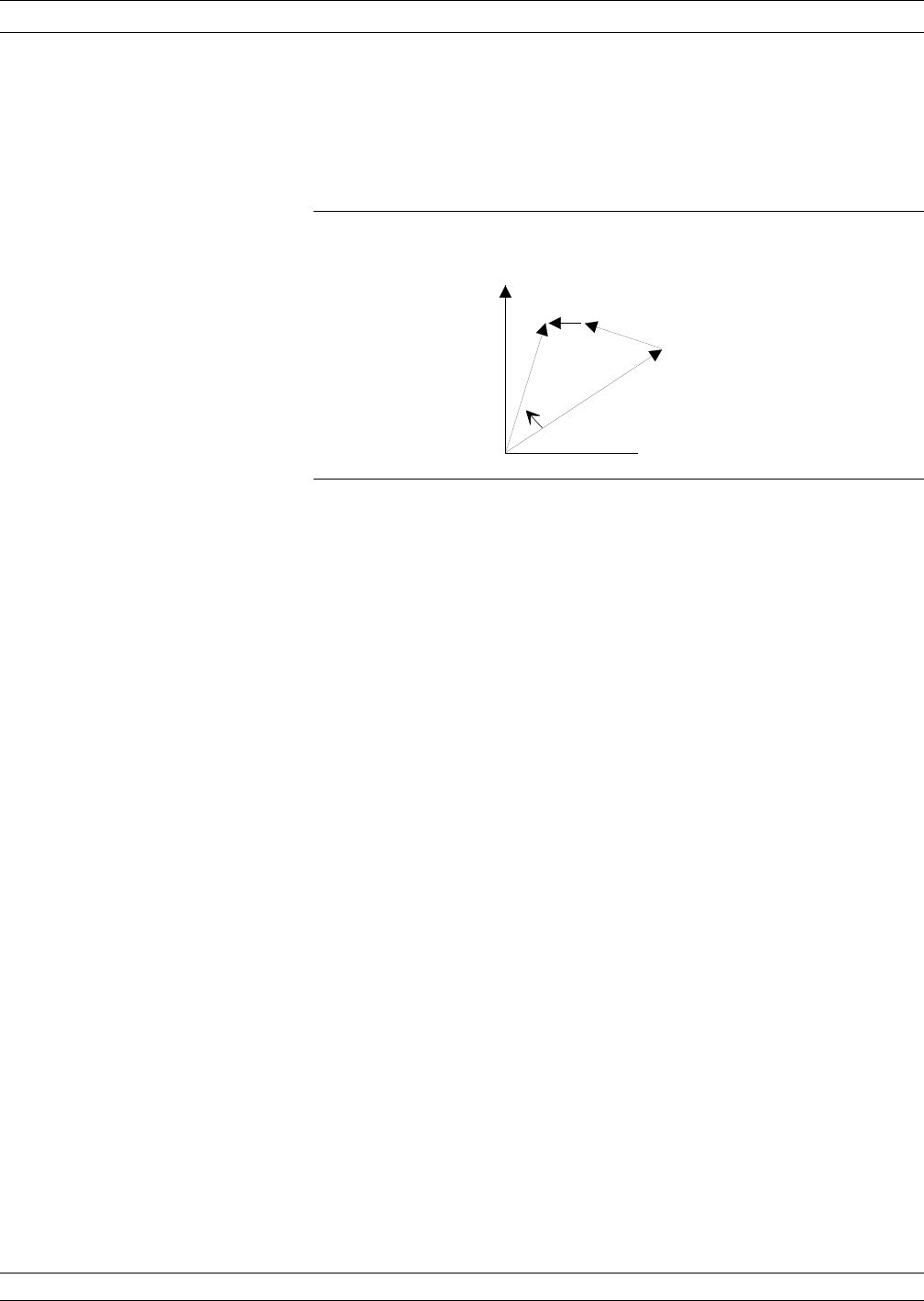
The detected signal is the vector sum of the desired signals, the noise
signals, and the leakage signals. These signals introduce an error or
uncertainty (Figure 8-8).
Some of the possible leakage paths for the 37XXXC are the transfer
switch, the frequency conversion module, and the DUT. The system
limits these leakages to greater than 100 dB. The 12-term error correc-
tion can reduce this leakage to better than 110 dB at 18 GHz and
90 dB at 40 GHz.
NOTE
We recommend using an isolation cell to decrease leakage
signals for sensitive measurements. For best results, in-
crease the default averaging value and decrease the de-
fault IF bandwidth setting during calibration and
measurement. Using higher enhancement during the mea-
surement than the calibration will not result in any accu-
racy improvements.
The DUT connectors should have internally captivated center pins.
Those connectors which use external pins to captivate the center con-
ductor should have silver loaded epoxy on the pins to reduce radiation
to better than 80 dB.
Signal-to-Noise-Power Ratio
The signal-to-noise-power ratio for each of the test or reference chan-
nels is as shown. The “signal power” is the power level of the 80 kHz
IF signal at the internal synchronous detectors, and the “noise power”
is the total power contained within the bandwidth of the bandpass fil-
ter at 80 kHz.
The uncertainty, or error, in a measurement is a function of the ampli-
tude of leakage signals and of the noise level. The uncertainty in the
measurement of magnitude and phase of the S-parameters are calcula-
ble and shown in Figures 8-9 and 8-10.
37XXXC OM 8-13
MEASUREMENTS LOW LEVEL AND GAIN
D E T E C T E D O U T P U T S I G N A L
U N C E R T A I N T Y
N O I S E S I G N A L
A C T U A L S I G N A L
R E A L
M E A S U R E D
S I G N A L
L E A K A G E O R
F A L S E S I G N A L
I
MAGI
NARY
P H A S E E R R O R
Figure 8-8. Amplitude and Phase Uncertainty
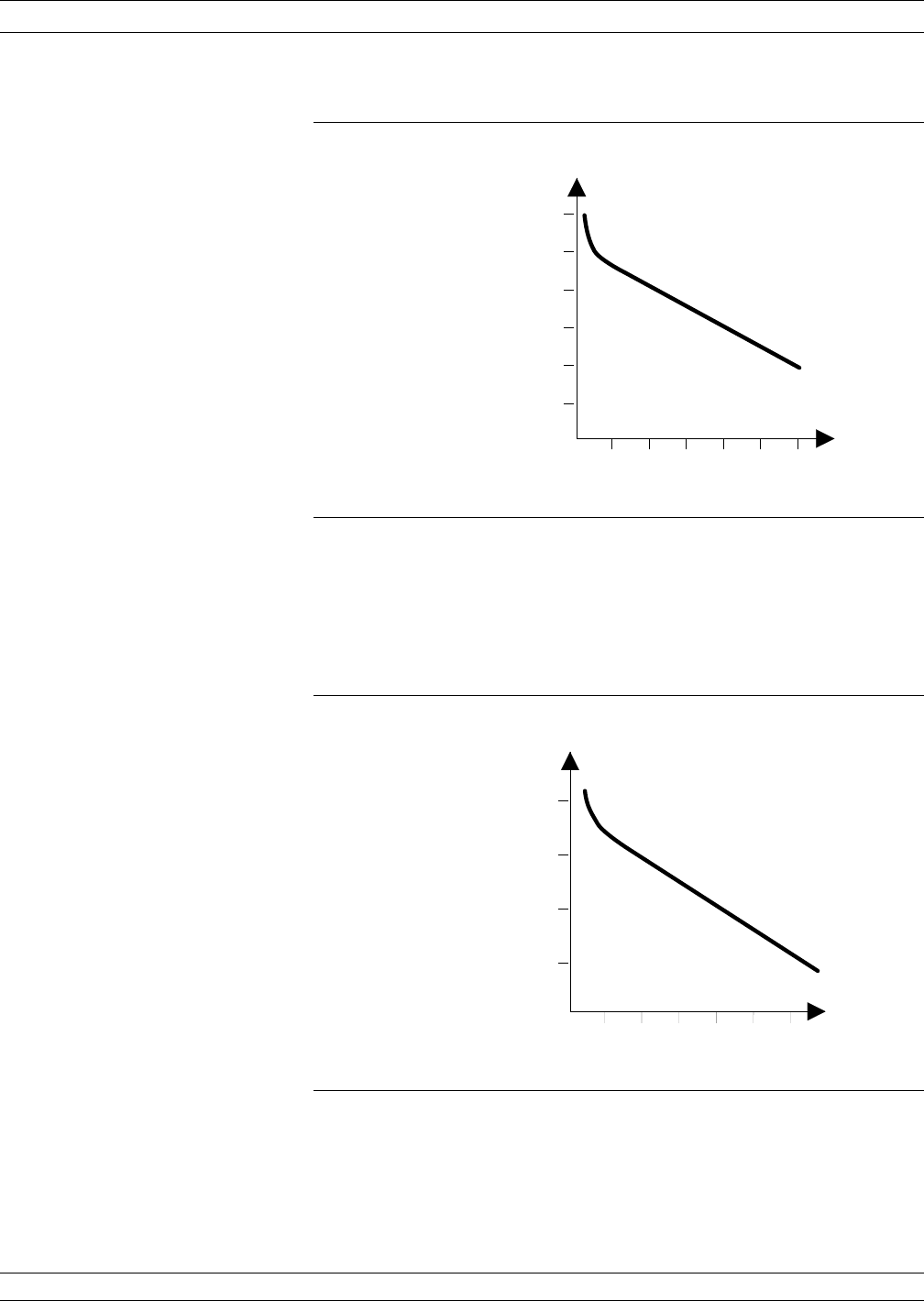
LOW LEVEL AND GAIN MEASUREMENTS
8-14 37XXXC OM
1 0 0 . 0
1 0 . 0
1 . 0
. 1
. 0 1
. 0 0 1
. 0 0 0 1
0 1 0 2 0 3 0 4 0 5 0 6 0
M A X I M U M
UNCERTAINTY
( d B m )
S I G N A L / N O I S E R A T I O
( d B )
M A X U N C E R T A I N T Y F O R M A G N I T U D E
A S A F U N C T I O N O F S / N R A T I O
Figure 8-9. The Effect of S/N Ratio On Magnitude Measurements (Noise
Only)
1 0 0 . 0
. 1
0 1 0 2 0 3 0 4 0 5 0 6 0
S I G N A L / N O I S E R A T I O
(
d B
)
1 0 . 0
1 . 0
M A X I M U M
UNCERTAINTY
( D E G R E E S )
M A X U N C E R T A I N T Y F O R P H A S E
A S A F U N C T I O N O F S / N R A T I O
Figure 8-10. The Effect of S/N Ratio On Phase Measurements (Noise Only)
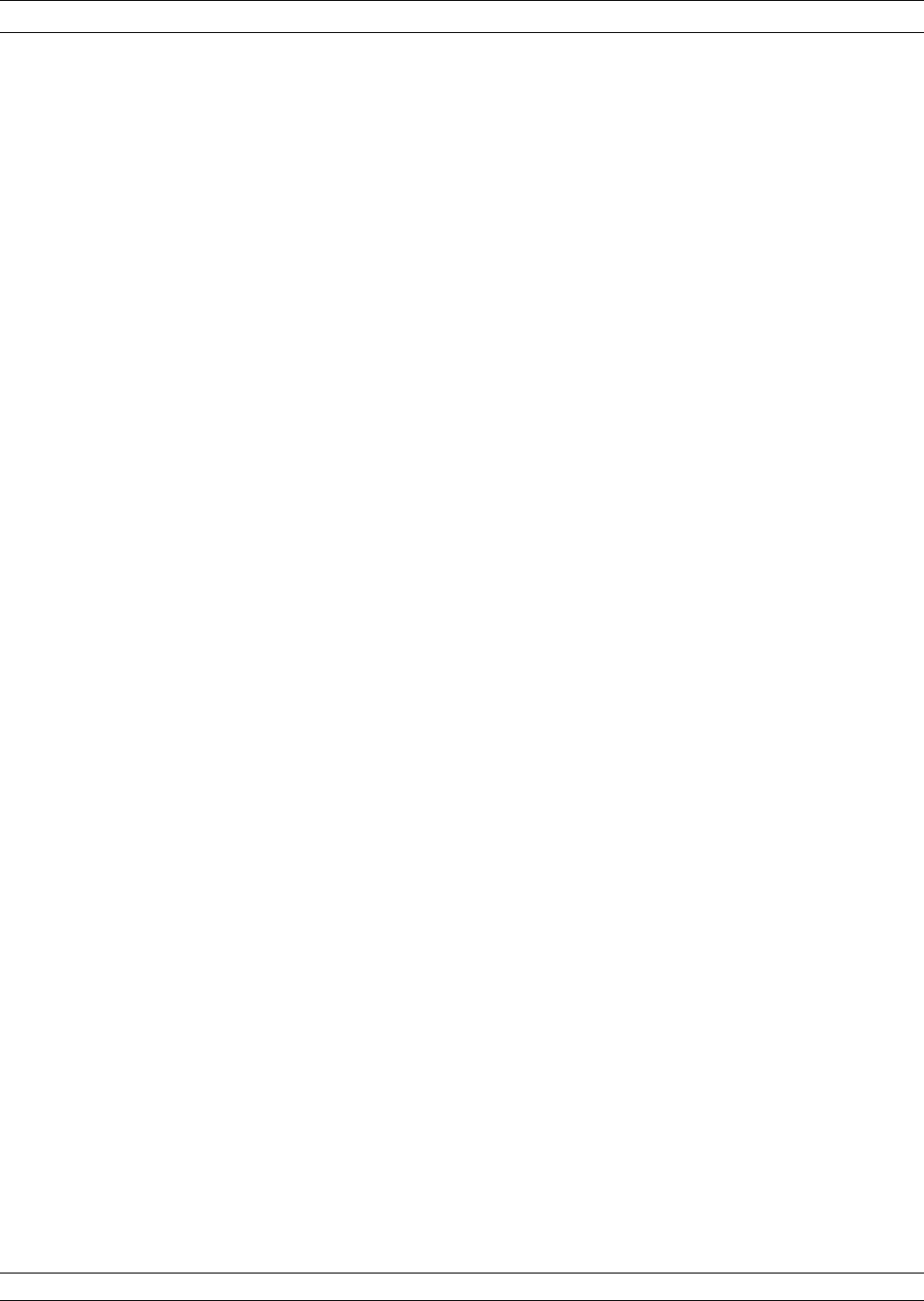
The most difficult types of measurements are those that exercise the
full dynamic range of the 37XXXC, such as filters (Figure 8-). Filter
measurements are examples of where one must observe both
low-insertion loss (in the passband) and high attenuation (in the stop
band).
There are two techniques that you can use to optimize the sig-
nal-to-noise ratio. They are (1) maximizing the RF signal level and (2)
using signal enhancement.
To maximize the RF signal level, use the default settings of the
37XXXC.
The 37XXXC provides two enhancements for improving the sig-
nal-to-noise ratio: IF bandwidth reduction and averaging.
Reducing the IF bandwidth is a primary method for enhancing accu-
racy. The 37XXXC has a choice of four bandwidths available from the
front panel: Maximum (10 kHz), Normal (1 kHz), Reduced (100 Hz),
and Minimum (10 Hz). The noise level should decrease by a factor
equal to the square root of the IF bandwidth. Using IF Bandwidth re-
duction makes for faster measurements than with the use of an equiv-
alent amount of averaging.
37XXXC OM 8-15
MEASUREMENTS LOW LEVEL AND GAIN
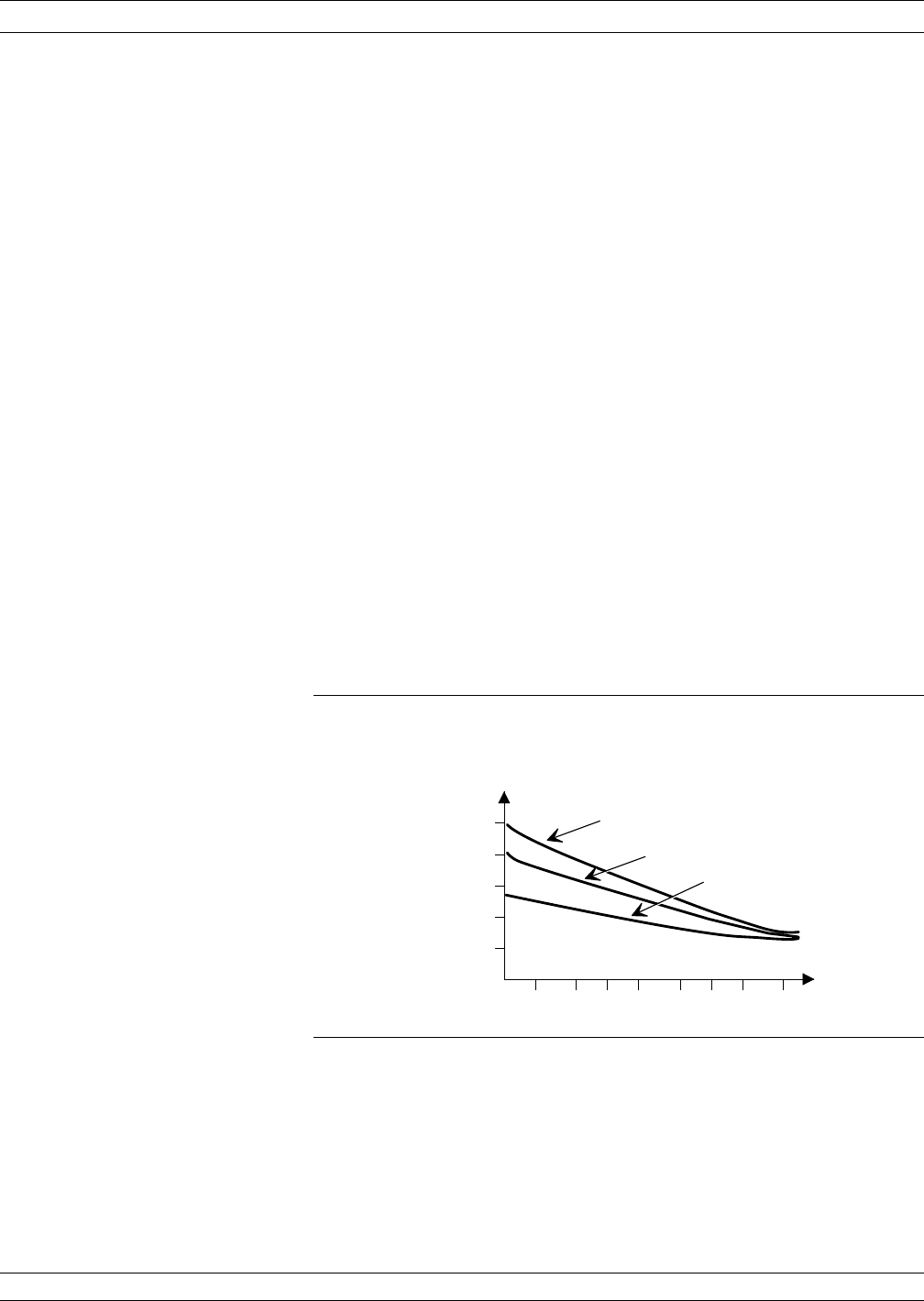
Averaging is another way to improve accuracy. The improvement is
proportional to the square root of the number of averages. Two types of
averaging are supported: Sweep-by-sweep and point-by-point.
Point-by-point averaging works by collecting multiple measurements
while at each frequency point and then averaging them together.
Sweep-by-sweep averaging works by performing multiple complete
sweeps and averaging the individual the individual frequency points
by taking data from the different sweeps. The primary difference is the
amount of time between samples at a given frequency point (short for
point-by-point, longer for sweep-by-sweep).
Sweep-by-sweep averaging may produce lower trace noise because the
averaging time is more likely to exceed the coherence time of the noise
source. The disadvantage is that any slow drift or transient response
of the device under test will be lost in the averaging process.
Sweep-by-sweep is hence less suitable for use during device tuning.
Conversely, point-by-point averaging will better preserve device tuning
response or device drift. It may, however, result in slightly elevated
trace noise (relative to sweep-by-sweep) since the measurement time
may be less than the coherence time of the noise source.
Figure 8-11 shows the measured reduction in noise due to bandwidth
and averaging.
Example: Using 1 kHz BW reduction and 10 averages, you would in-
crease the signal-to-noise ratio by 7.6 dB but would lengthen the time
required for the measurement by a factor of 4.3. This example assumes
a constant signal power.
LOW LEVEL AND GAIN MEASUREMENTS
8-16 37XXXC OM
M E A S U R E M E N T S O N A 7 0 d B A T T E N U A T O R
A L L D A T A N O R M A L I Z E D T O
A 1 k H z I F B A N D W I D T H A N D 1 A V E R A G E
R E L A T I V E
N O I S E ( d B )
N U M B E R O F A V E R A G E S
7 . 0
3 . 5
1 . 4
. 3 5
. 1 4
1 2 5 1 0 2 0 5 0 1 0 0 2 0 0 5 0 0
1 0 K H z ( I F B W )
1 K H z
1 0 0 H z
. 7
Figure 8-11. Reduction in Noise Using Averaging
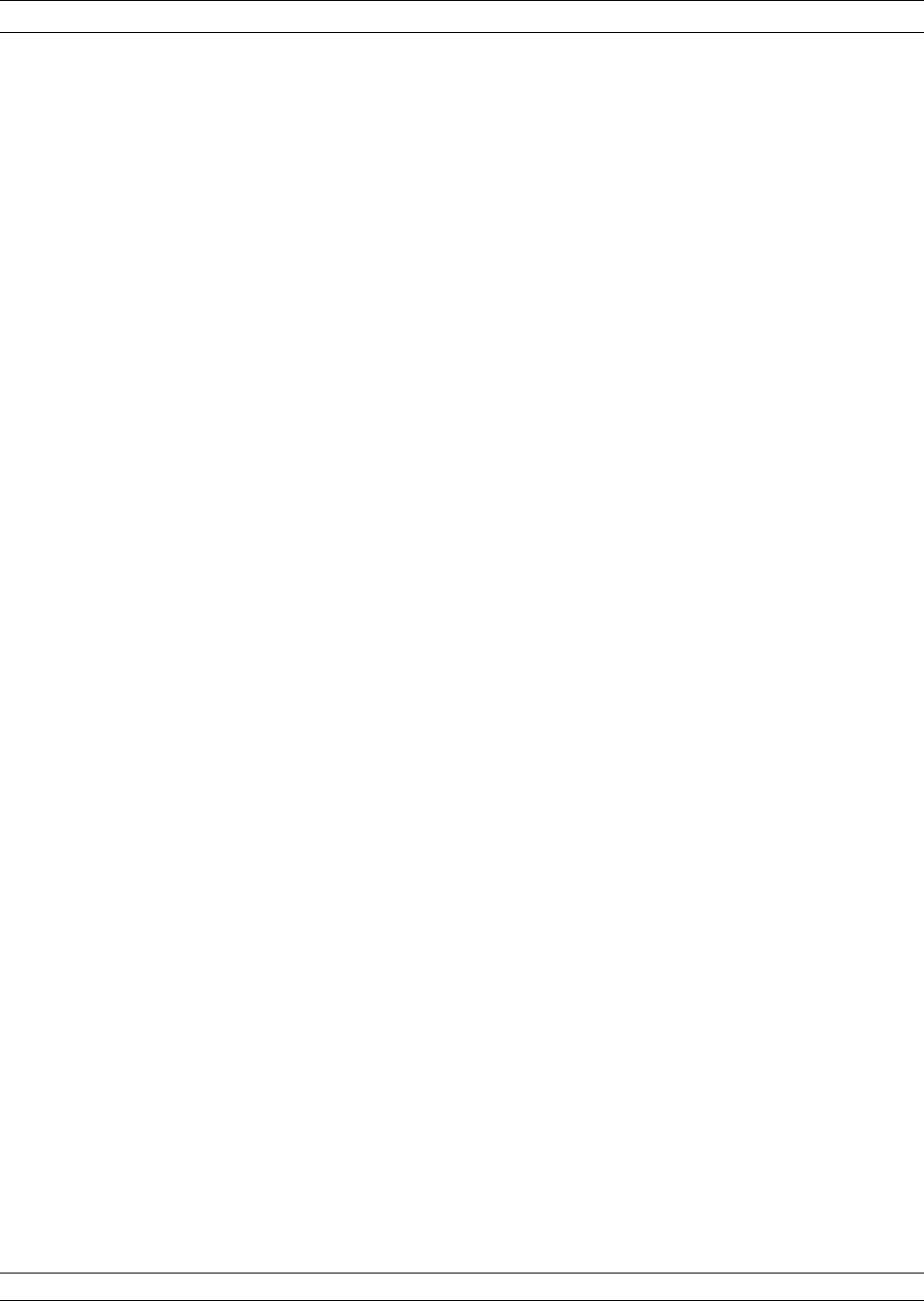
Test Device (DUT) Considerations
In order to test a device, the required input RF level and the expected
device output RF level must be determined.
The RF level at Port 1 must be set for the device input RF power level
required. Attenuation can be added in steps of 10 dB up to 70 dB using
the built-in source attenuator. Amplification can be added by removing
the front panel loop and adding an external amplifier.
Before calibration, ensure that the test setup is correct by setting the
power level and adding attenuation as needed.
37XXXC OM 8-17
MEASUREMENTS LOW LEVEL AND GAIN
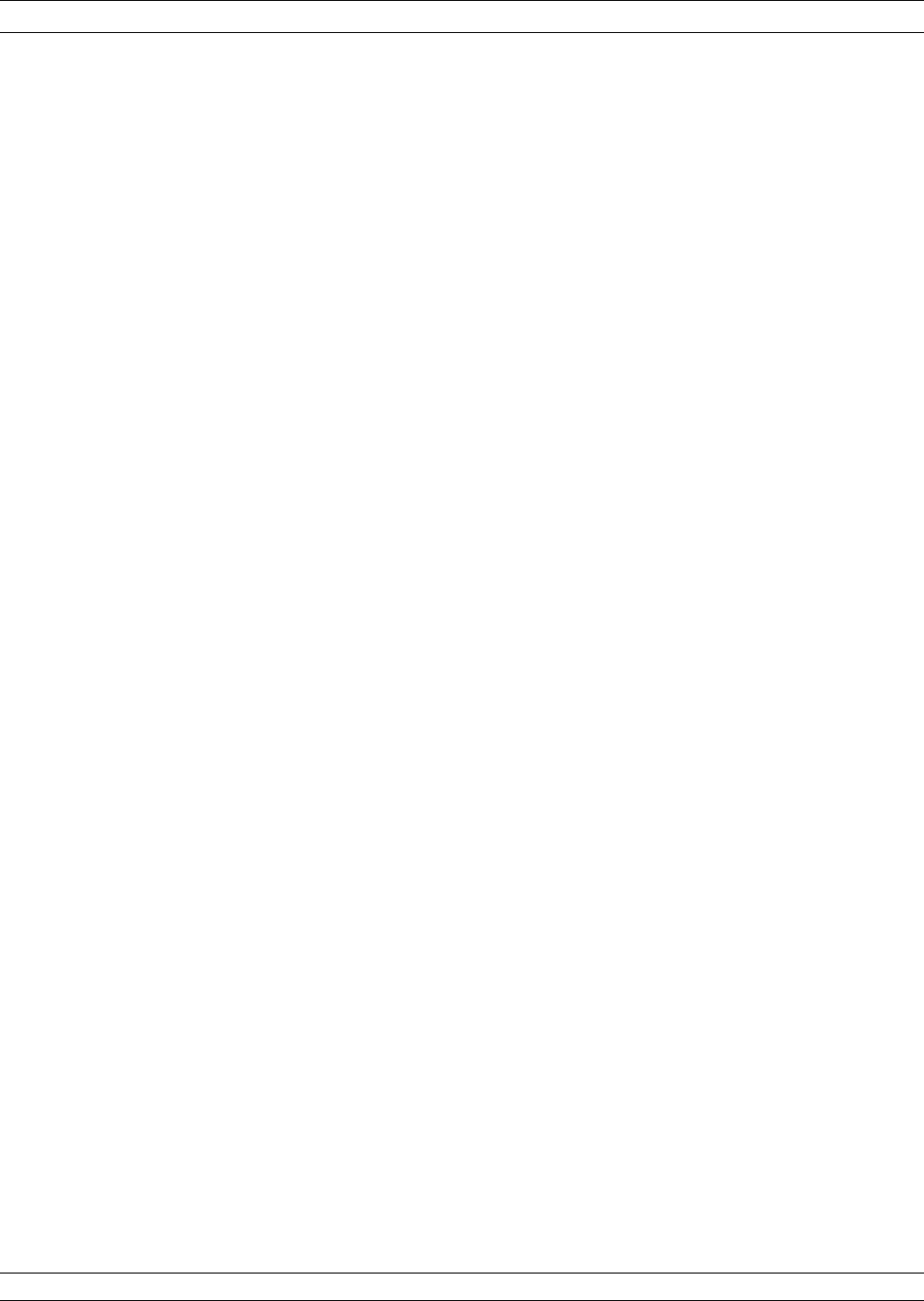
The 37XXXC uses enhancements in the calibration to ensure a wide
dynamic range. It automatically selects 1 kHz IF bandwidth and var-
ies the number of averages with the calibration device. Terminations
require the most averages.
If desired, the Video IF bandwidth and number of averages can be
specified for the calibration measurements. Using 100 averages (Avg =
100) appears to be sufficient for most measurements.
To obtain the maximum performance from the 37XXXC for measure-
ments of attenuation, you can use the capability of the N discrete fre-
quency calibration to spot check measurements in the frequency band
of interest.
LOW LEVEL AND GAIN MEASUREMENTS
8-18 37XXXC OM
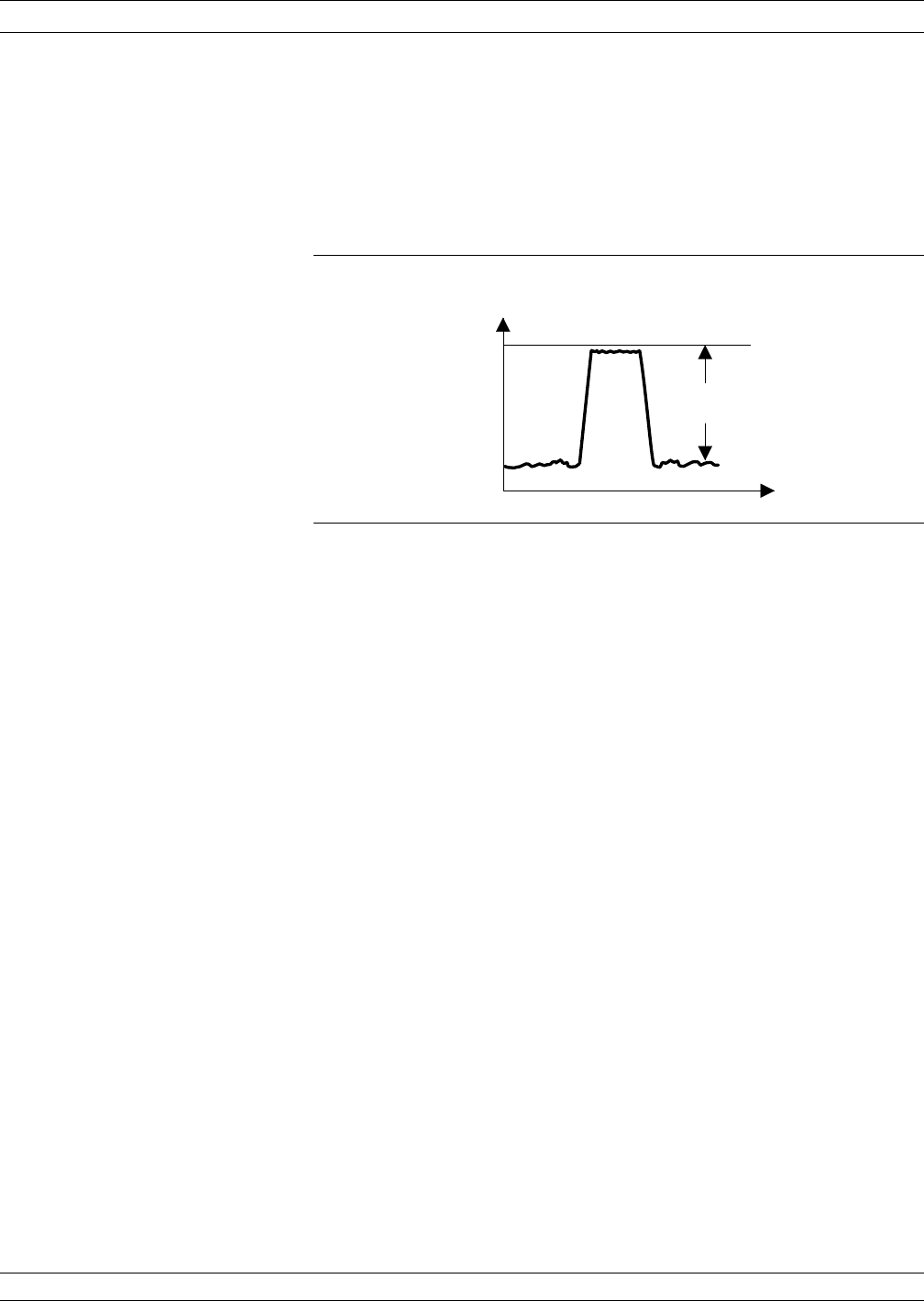
Wide Dynamic Range Device - Filter
Since you do both low-insertion-loss and high- attenuation measure-
ments simultaneously, use the maximum RF signal level and no atten-
uation. Selecting the 1 kHz Video IF BW setting and 100 averages will
likely suffice for this kind of measurement.
High Gain Device - FET
This device has a typical 15 dB gain and requires an input level of
about –30 dBm. Set the Port 1 Source Attenuator to 30 dB. Since the
device RF output level is –15 dBm (–30 dBm + 15 dB[gain] = –15 dBm)
no attenuation is needed at Port 2.
Medium Power Device - Amplifier
Measure the small signal parameters of a 10 dB gain device that re-
quires an input power level of 0 dBm. Here, Port 1 will have no attenu-
ation. The device RF output level is 10 dBm. This level equals 10 dBm
(0 dBm + 10 dB[gain] = 10 dBm) into Port 2 and will cause compres-
sion in the measurement. At least 10 dB of test attenuation will be
needed at Port 2, which will reduce the Port 2 RF level to 0 dB.
37XXXC OM 8-19
MEASUREMENTS LOW LEVEL AND GAIN
P A S S B A N D
< 1 d B
F R E Q U E N C Y
d B
B A N D P A S S F I L T E R
0 d B
S T O P B A N D
> 5 0 d B
S
2 1
Figure 8-12. Filter Measurements
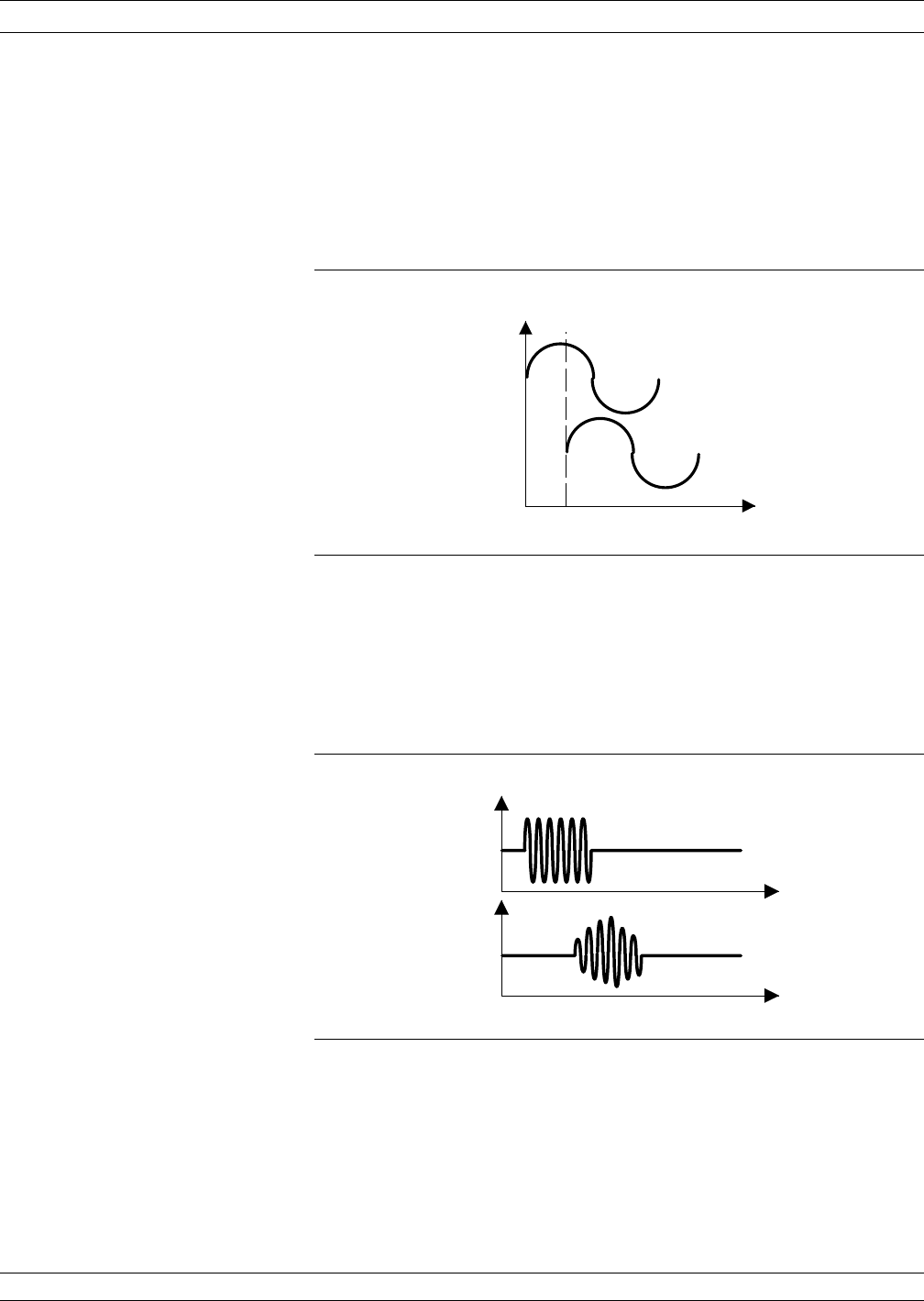
8-4 GROUP DELAY Group delay is the measure of transit time through a device at a par-
ticular frequency. Ideally, we want to measure a constant—or rela-
tively constant—transit time over frequency. The top waveform shown
in Figure 8-13 is measured at one frequency. The bottom waveform is
identical to the first, simply delayed in time.
Referring to Figure 8-14, the first waveform shown is the original
waveform. It is made up of many frequency components. After travel-
ing through a device the signal is delayed in time. Some frequencies
are delayed more than others and thus our waveform does not have ex-
actly the same shape as before.
When delay is nonlinear, as shown above, distortion occurs. By meas-
uring group delay with a network analyzer you can characterize the
distortion that occurs from a signal traveling through your test device.
GROUP DELAY MEASUREMENTS
8-20 37XXXC OM
M A G N I T U D E
T I M E
t
0
t
1
Figure 8-13. Two Waveforms Delayed in Time
I N P U T
O U T P U T
M A G N I T U D E
T I M E
Figure 8-14. Waveform with Frequency Differences
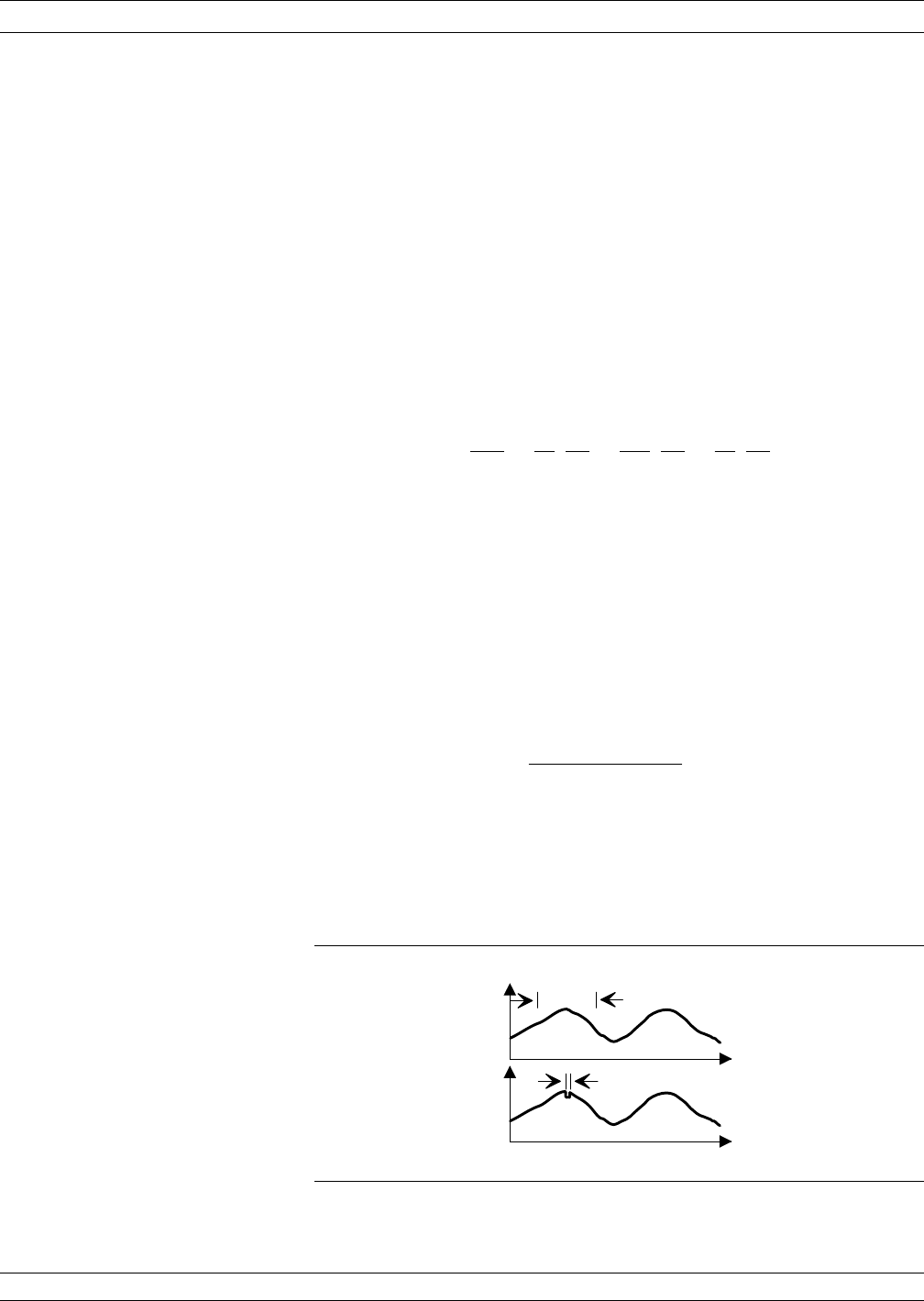
When designing components it is important to measure group delay so
that you can compensate for any distortion caused by the component.
You may be able to tune the device so as to optimize the performance
of group delay over the frequency range of interest. Outside of the
specified frequency range, the group delay may or may not be linear.
So how is group delay measured? Signals travel too fast to enable
measuring the input and output times of each frequency component.
Consequently, we must use mathematical calculations to derive the
group delay from the phase slope.
Group delay is mathematically represented by the following equations:
tq
wp
qq
p
q
=-
-=-=-=
d
dd
df d
df f
1
21
360 1
2D
D
What this equation shows is that group delay is a measure of the
change in phase with relation to the change in frequency.
The change in frequency is referred to as an aperture.
DfAperture=
To measure group delay the frequency aperture must be selected. De-
pending on the size of aperture, different levels of precision can result
for the measurement of group delay.
Aperture Frequency Range
Of Data Points
=#
A wide aperture results in a loss of fine-grain variations but gives
more sensitivity in the measurement of time delay. A small aperture
gives better frequency resolution, but at the cost of lost sensitivity.
Thus, for any comparison of group delay data you must know the aper-
ture used to make the measurement (Figure 8-15).
37XXXC OM 8-21
MEASUREMENTS GROUP DELAY
M A G N I T U D E
A P E R T U R E T O O W I D E
A P E R T U R E T O O N A R R O W
F R E Q U E N C Y
Figure 8-15. Waveforms With Aperture Differences
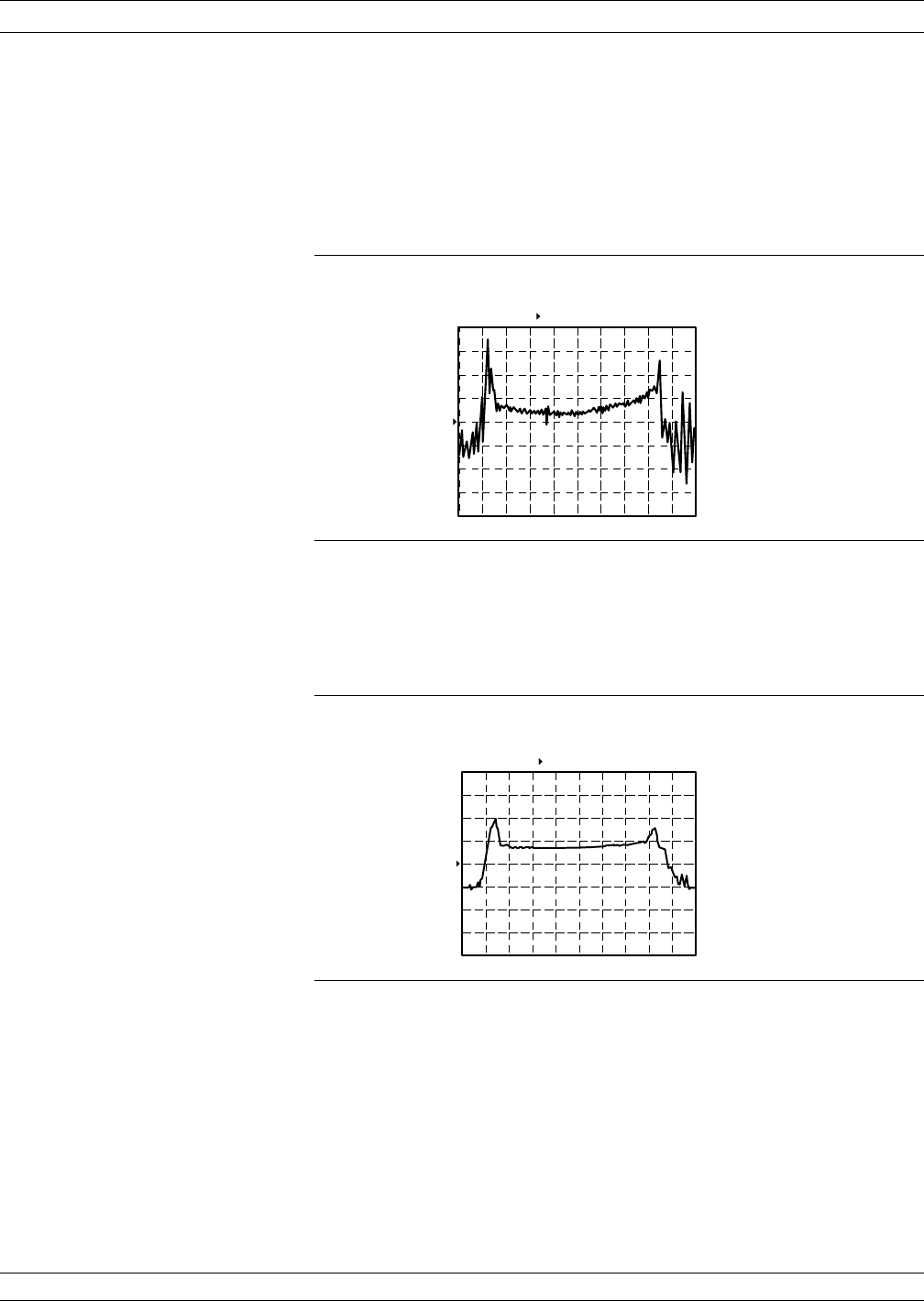
Let us take a look at a group delay measurement made on the Anritsu
37347C Vector Network Analyzer. Group delay, as a measurement op-
tion, can be found in the Graph Type menu. After selecting the option,
the VNA displays the data in a time-vs-frequency graph, or to be more
exact, a group-delay-vs-frequency graph (Figure 8-16).
The 37XXXC automatically selects the frequency spacing between
data points—that is, the aperture. Notice that this value is displayed
on the screen with the measurement (Figure 8-17).
GROUP DELAY MEASUREMENTS
8-22 37XXXC OM
S 2 1 F O R W A R D T R A N S M I S S I O N
G R O U P D E L A Y
R E F = 1 . 0 0 0 n S 6 0 0 . 0 0 0 p S / D I V
9 . 0 0 0 0
3 . 0 0 0 0 G H z
Figure 8-16. Group Delay-vs-Frequency Graph
S 2 1 F O R W A R D T R A N S M I S S I O N
G R O U P D E L A Y R E F = 1 . 0 0 0 n S 6 0 0 . 0 0 0 p S / D I V
9 . 0 0 0 0
3 . 0 0 0 0 G H z
Figure 8-17. Group Delay Screen Showing Aperture
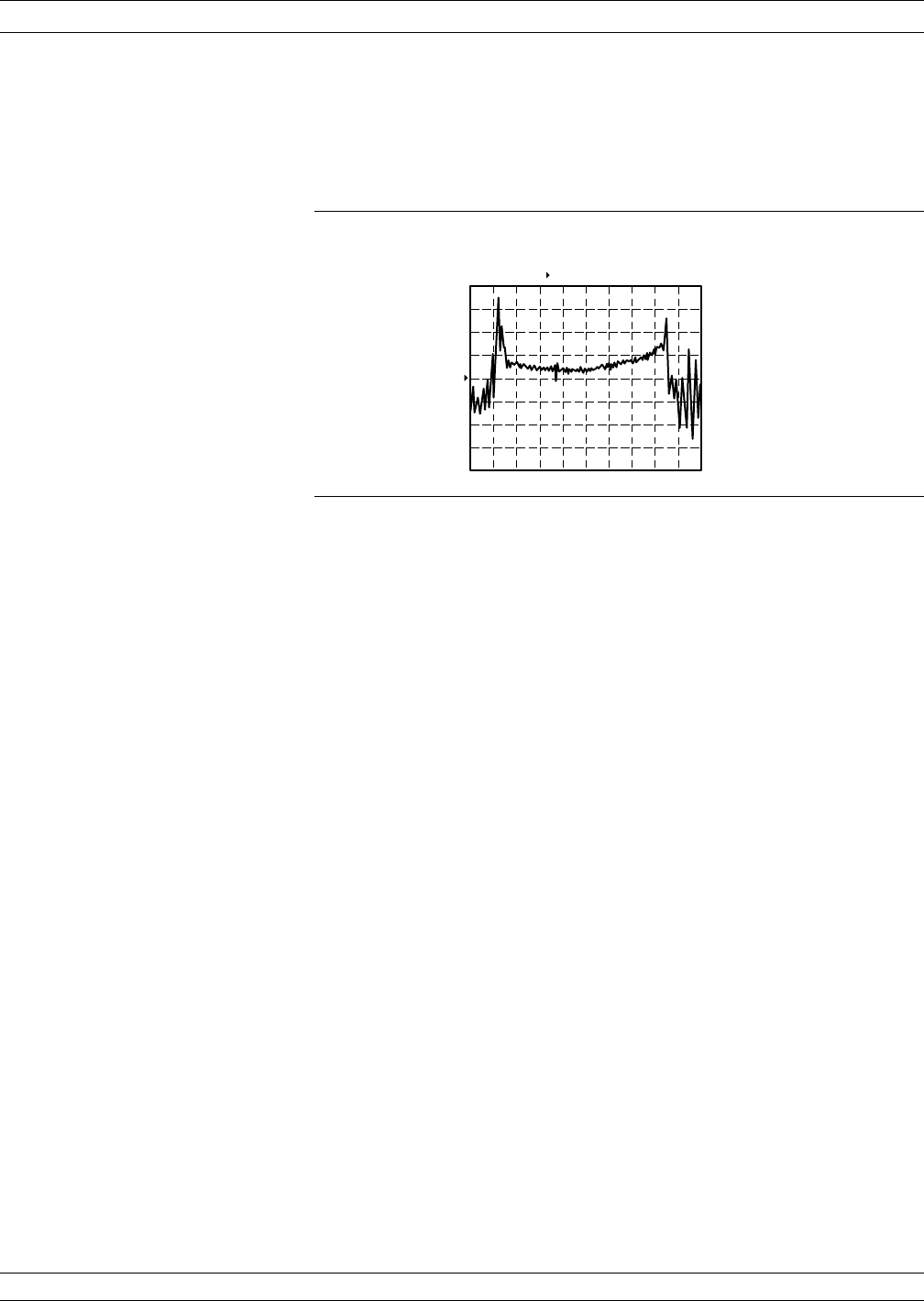
The aperture defaults to the smallest setting for the frequency range
and number of data points selected. This value is displayed in the Set
Scale key menu when measuring group delay (Figure 8-18).
Group delay applications are found throughout the microwave indus-
try, although the majority of such measurements are made in the tele-
communications area.
One occurrence of group delay that you may have experienced is with
a long-distance telephone call. Occasionally a phone call can be dis-
turbing because of the delay in time from when you speak and when
the other person responds. If there is simply a delay, then time de-
lay—or linear group delay—has occurred. But if the voices are also dis-
torted, then non-linear group delay has occurred. It is this distortion
that we must avoid. We can avoid linear group delay by measuring
group delay both during the design and development stages and dur-
ing recalibration in the field.
One final group-delay application is found in the development of com-
ponents. In this application, group delay is measured for the transit
time of a signal through the device. When time is of the essence in a
fast switching system, as in a modern computer, the travel time
through a device is critical.
37XXXC OM 8-23
MEASUREMENTS GROUP DELAY
S 2 1 F O R W A R D T R A N S M I S S I O N
G R O U P D E L A Y R E F = 1 . 0 0 0 n S 6 0 0 . 0 0 0 p S / D I V
9 . 0 0 0 0
3 . 0 0 0 0
G H z
Figure 8-18. 37XXXC Aperture
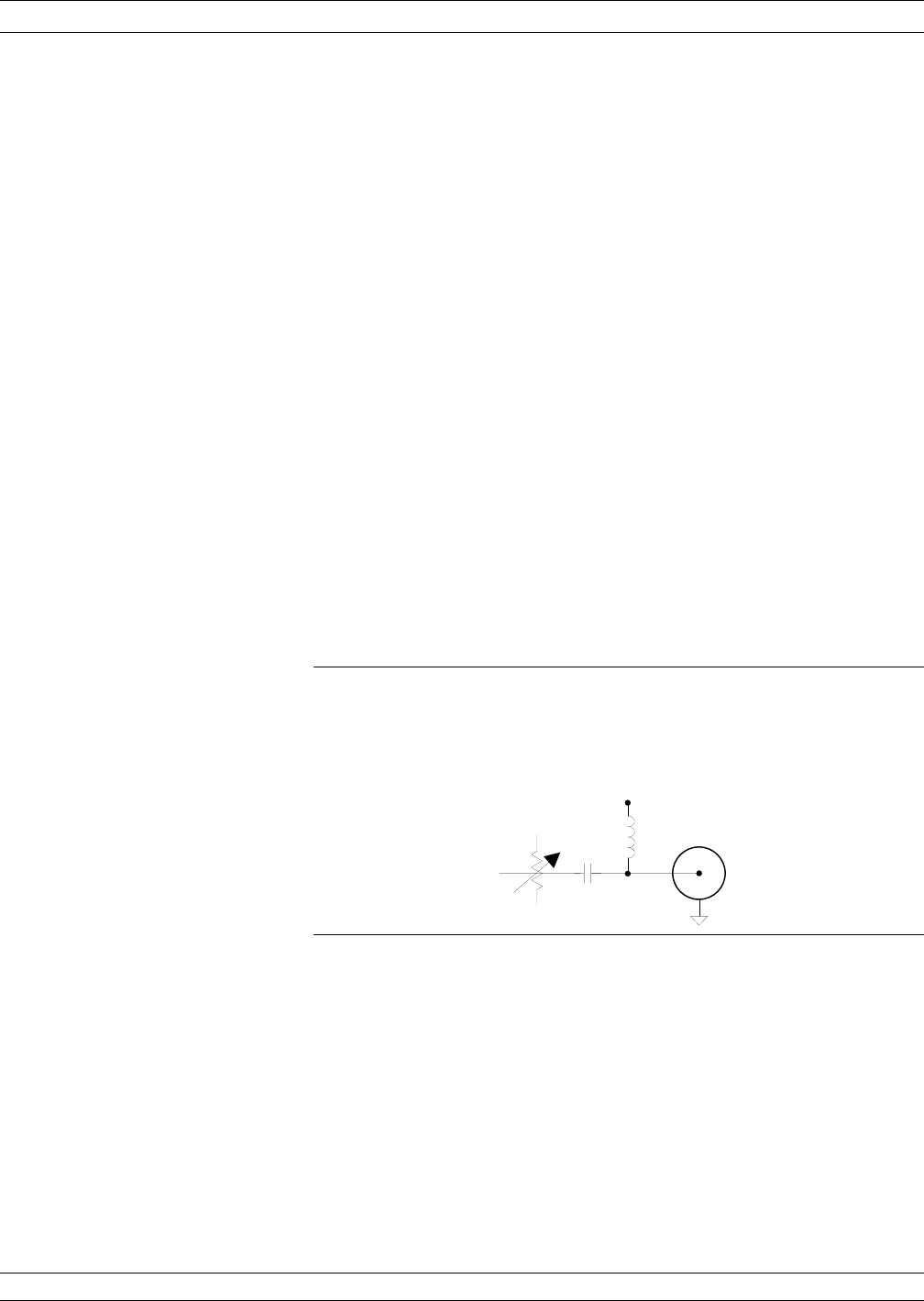
8-5 ACTIVE DEVICE Active devices are key components in microwave systems.
The measurements that are made on active devices are similar to
those made on passive devices.
Active devices come in many shapes and sizes. In most cases we are
going to have to develop a fixture in which to mount the device.
Active devices require bias voltages, and in many cases they are easily
damaged. High gain amplifiers may saturate with input signals of
–50 dBm. With active devices, we have a new set of measurement re-
quirements.
The 373XXC has been designed to help you make these types of mea-
surements. It includes one 70 dB step attenuator (60 dB for 37377C
and 37397C) used to adjust the Port 1 power level. A second 40 dB step
attenuator is also included (with Option 6) in the forward transmis-
sion path to allow measurement of high gain devices without sacrific-
ing reverse transmission and reflection measurements (S12,S
22). Bias
tees on each port are used to bias the device via the test port center
conductor. This approach to bias is useful for testing transistors; how-
ever, MMIC’s usually require bias injection at other points (Fig-
ure 8-19).
ACTIVE DEVICE MEASUREMENTS
8-24 37XXXC OM
B i a s T e e s
R F
I N
T E S T
P O R T
V
B I A S
Figure 8-19. Bias Tee
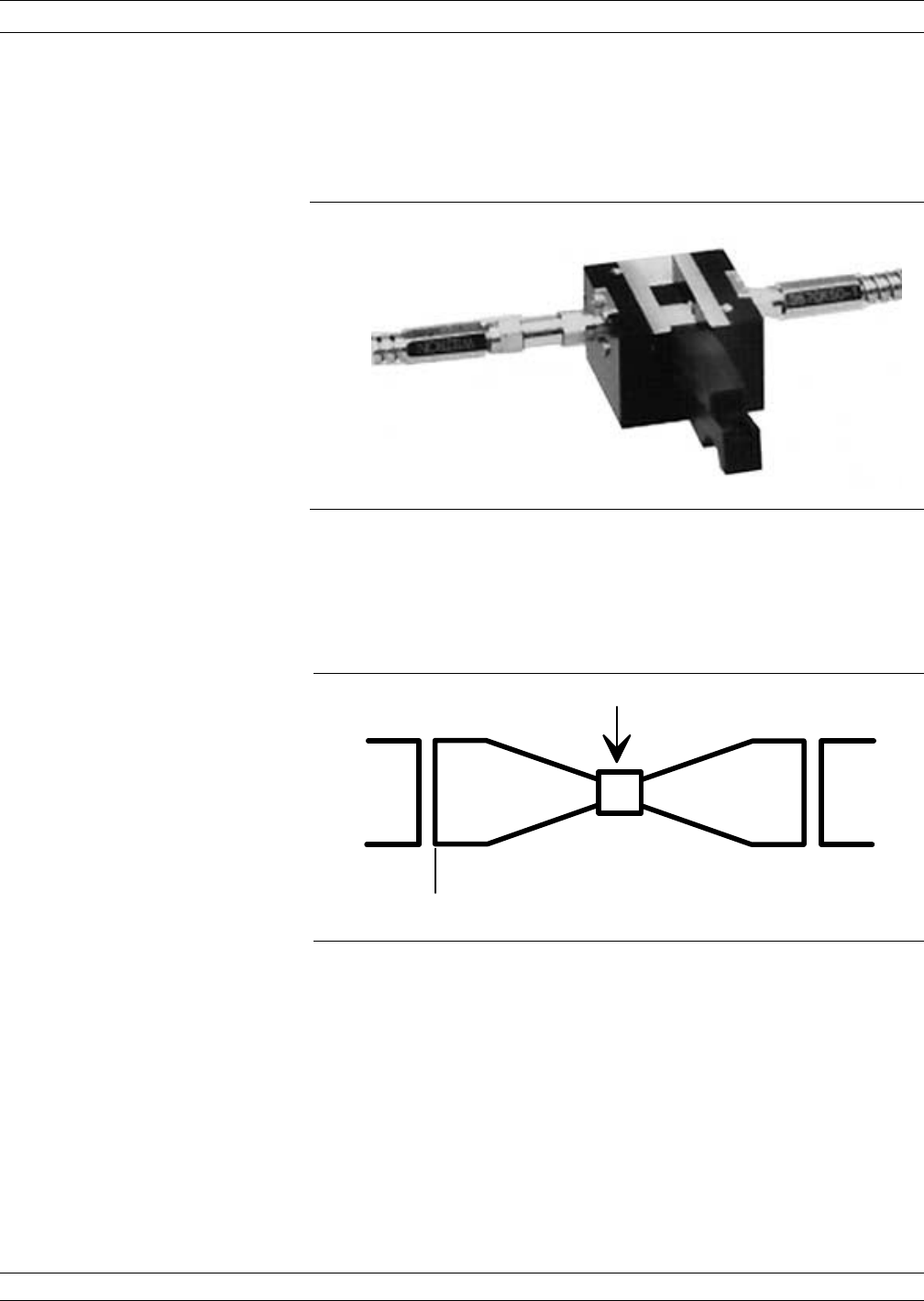
Test fixtures are necessary for mounting the device so that it can be
measured in our coaxial (or waveguide) measuring system
(Figure 8-20).
Now we have an interesting situation. While we can measure the per-
formance at the connector—which is the calibration plane—what we
really want to know is how our device performs (Figure 8-21).
You can consider the device embedded in the fixture and can measure
the S-parameters of the fixture with the device installed.
The most elementary situation is a system in which the test fixture is
electrically ideal or transparent. In this case, the solution is sim-
ple—merely move the reference plane out to the device (Figure 8-22).
37XXXC OM 8-25
MEASUREMENTS ACTIVE DEVICE
Figure 8-20. Active Device Test Fixture
F E T
G P C - 7
S
1 1 M
G P C - 7
S
1 1
Figure 8-21. View of a Test Device
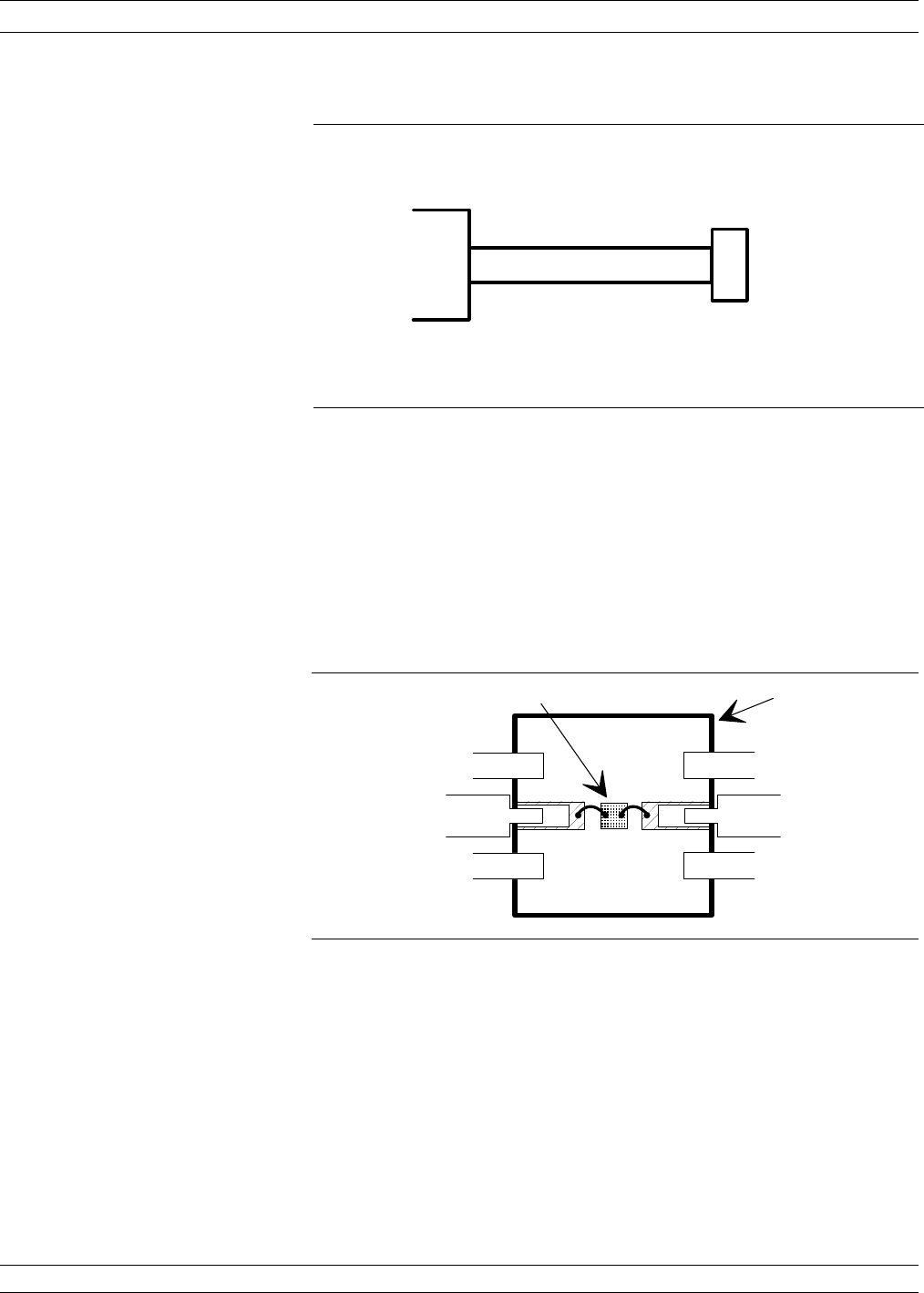
In some cases—depending on the fixture or the device being meas-
ured—this is satisfactory. But when it is not, we need to employ other
techniques.
One of the reasons that moving the reference plane out to the device
does not always work, is that the test fixture includes a transition
from coax to a structure such as microstrip, coplanar waveguide, or
stripline (Figure 8-23).
Engineers have come to grips with the general problem. However,
there is no established standard approach. Two of the more common
approaches are to calibrate the fixture as a part of the analyzer, and to
characterize the fixture and compute the desired result.
ACTIVE DEVICE MEASUREMENTS
8-26 37XXXC OM
G P C - 7 D U T
5 0 O H M L I N E
N O L O S S , R E F L E C T I O N L E S S
Figure 8-22. Simple Example of De-Embedding
G R O U N D
I N P U T
F E T
C O P L A N A R
LAUNCHER
I N P U T
G R O U N D
G R O U N D G R O U N D
C O P L A N A R
LAUNCHER
A L U M I N A
CARRIER
Figure 8-23. Coax-to-Substrate Transition
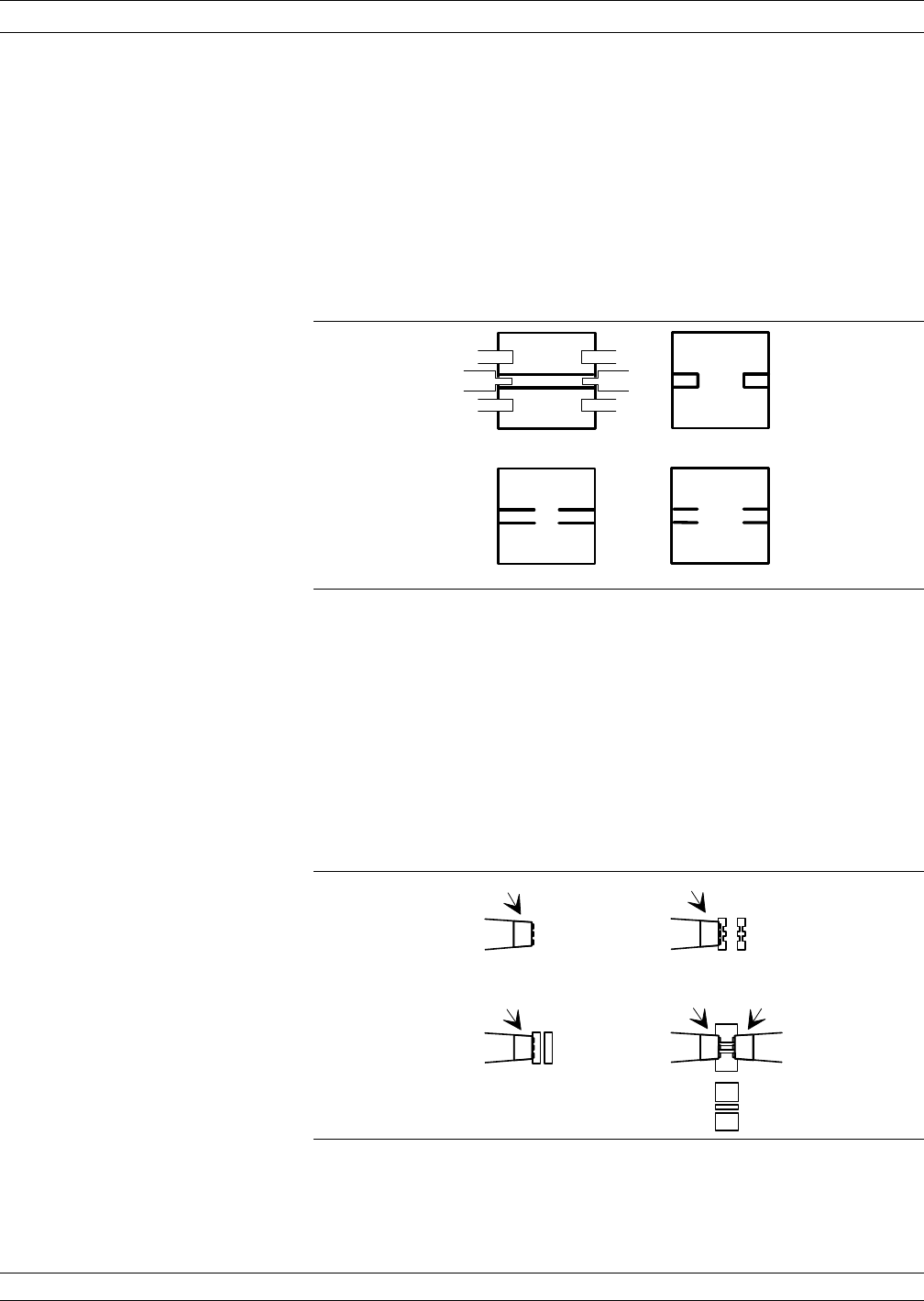
In the discussion on calibration we saw that the calibration compo-
nents establish the reference plane and determine the quality of the
measurement. If we have a good Open, Short and Z0load to place at
the end of a microstrip line, we can calibrate the system at the point of
measurement.
Figure 8-24 shows some of the special test-fixture calibration stan-
dards that are available.
These special calibration kits are far from perfect, but they are supe-
rior to our perfect transmission line assumption.
You may also have heard of the probe stations built to permit on-wafer
calibration measurements.
The Open, Short, termination approach provides three known stan-
dards that permit the analyzer to solve for three unknowns (Fig-
ure 8-25).
37XXXC OM 8-27
MEASUREMENTS ACTIVE DEVICE
T H R U L I N E
O F F S E T S H O R T
O P E N
O F F S E T S H O R T
5 0 O H M
1 8 0 / 8 2 - S C 2 4 0 / 5 2 - S C
2 4 0 / 5 2 - O C
Figure 8-24. Special Test Fixtures
5 0 O H M
T E R M I N A T I O N
S H O R T
C I R C U I T
P R O B E
5 0 O H M
T H R O U G H L I N E
P R O B E
P R O B E
1 0 0 O H M
1 0 0 O H M
P R O B E
P R O B E
O P E N C I R C U I T
( I N A I R )
Figure 8-25. Solving for Unknowns
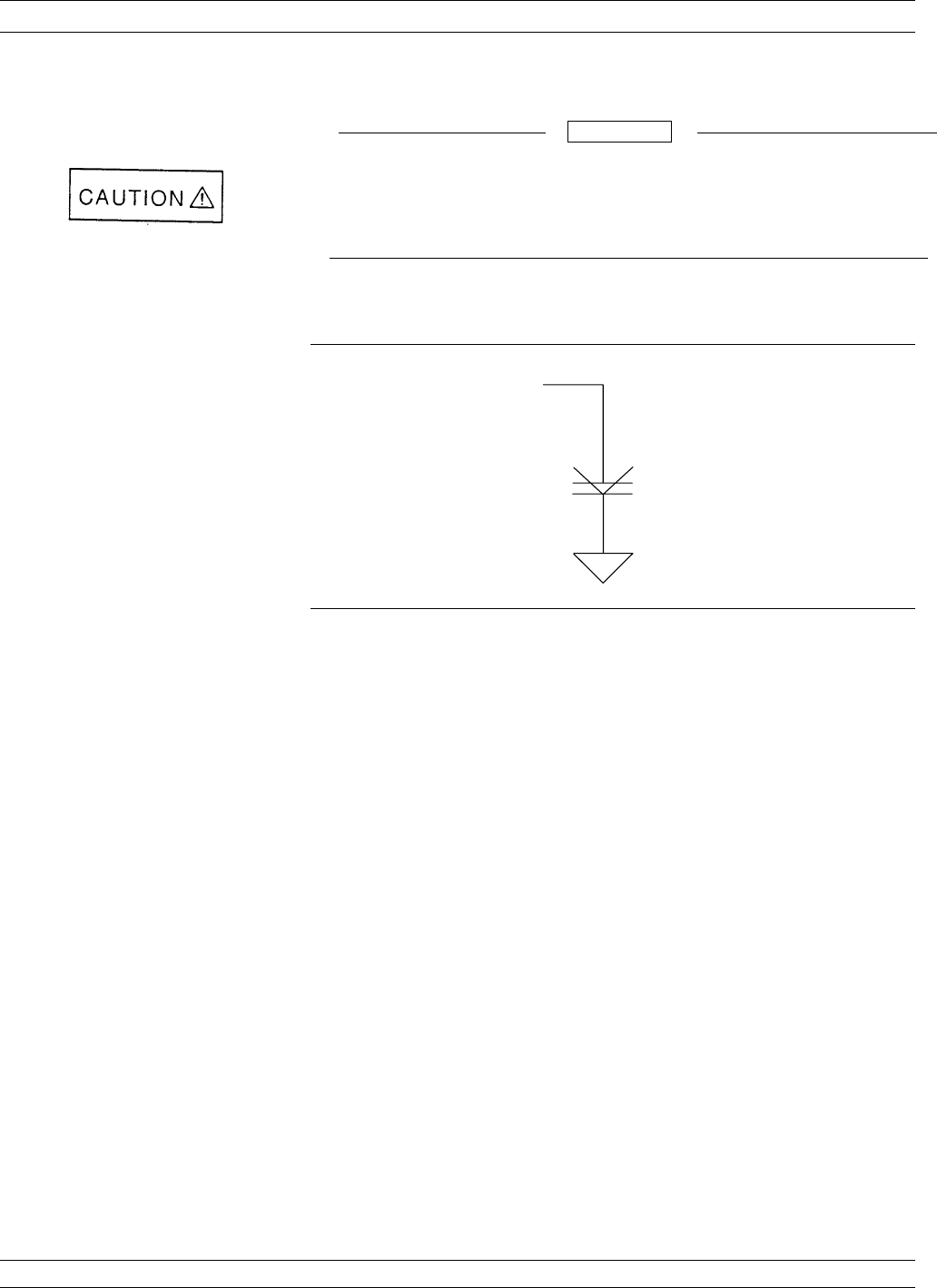
It is also possible to use three known impedances. For instance, a var-
actor with three voltages applied (Figure 8-26).
The second approach is to model the fixture. Modeling is elegant but of
limited use due to the non-ideal characteristics of the fixture. Modeling
can be accomplished in a CAD system.
In summary, there are quite a variety of approaches—all with their
own characteristic pitfalls. Engineers try to choose the most appropri-
ate technique for their application.
ACTIVE DEVICE MEASUREMENTS
8-28 37XXXC OM
C 1
C 2
C 3
C I S V A R I E D
B Y C H A N G I N G
V O L T A G E
N O T P E R F E C T E I T H E R
S P E C I A L C A L I B R A T I O N K I T S
Figure 8-26. Three Known Impedances
You should turn off or disconnect the bias supplies during the calibra-
tion, since you are using a Short as the calibration standard.
CAUTION
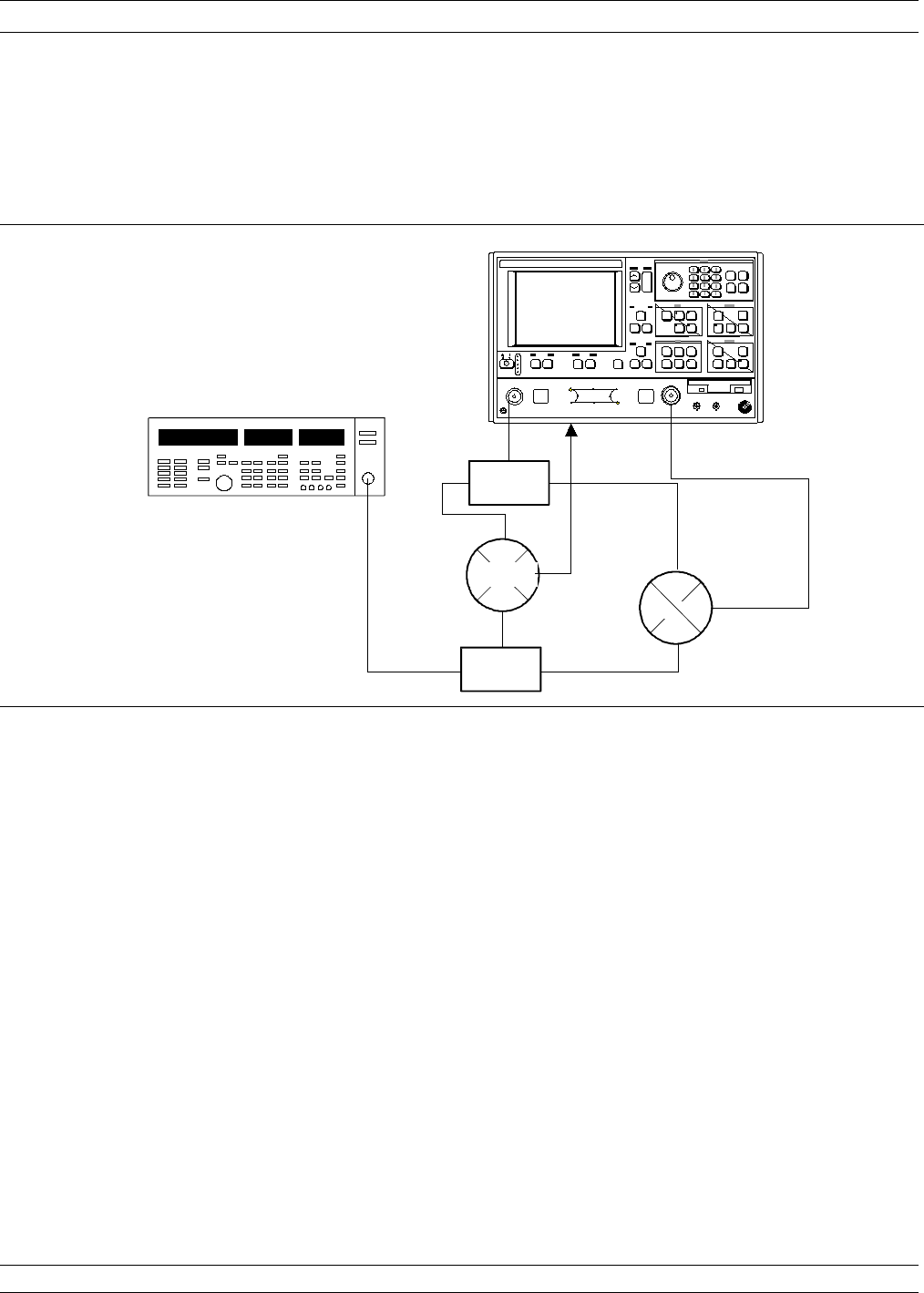
8-6 MULTIPLE SOURCE
CONTROL The Multiple Source Control mode permits independent control of the
37XXXC source, receiver, and an external Anritsu synthesizer (67XXB,
68XXXB), without the need of an external controller (Figure 8-27).
Operation in this mode requires Option 11. Removing the reference
loop lets you isolate the receiver from the source. This permits testing
of frequency converters such as mixers.
The software lets the frequency ranges and output powers of the two
sources be specified. A frequency sweep can comprise up to five sepa-
rate bands, each with independent source and receiver settings for
convenient testing of frequency translation devices such as mixers. Up
to five sub-bands (harmonics) can be tested in one sweep.
Control Formula Multiple Source control is specified as a displayed frequency range
partitioned into from one-to-five consecutive bands. For each band
Source 1, Source 2, and receiver frequencies may be interdependently
specified per the formula:
FORMULA
37XXXC OM 8-29
MEASUREMENTS MULTIPLE SOURCE CONTROL
I.F.
L.O.
R.F.
MI XER 1
372XXA VECTOR NETWORK ANALYZER
I.F.
L.O.
R.F.
MIXER 2
To
RA In
(Rear Panel)
STANDARD MIXER
PHASE-LOCK
MIXER
1. Remove loop between Reference Extension connectors
RA In and RA Out.
2. Set up equipment as shown.
3. Normalize the data trace with the standard mixer installed.
4. Subsequent mixers can be tested for magnitude
or phase match with respect to the "Standard Mixer."
POWER
DIVIDER
POWER
DIVIDER
67XXB SYNTHESIZER
Figure 8-27. Test Setup for Multiple Source Control Operation
37XXXC VNA
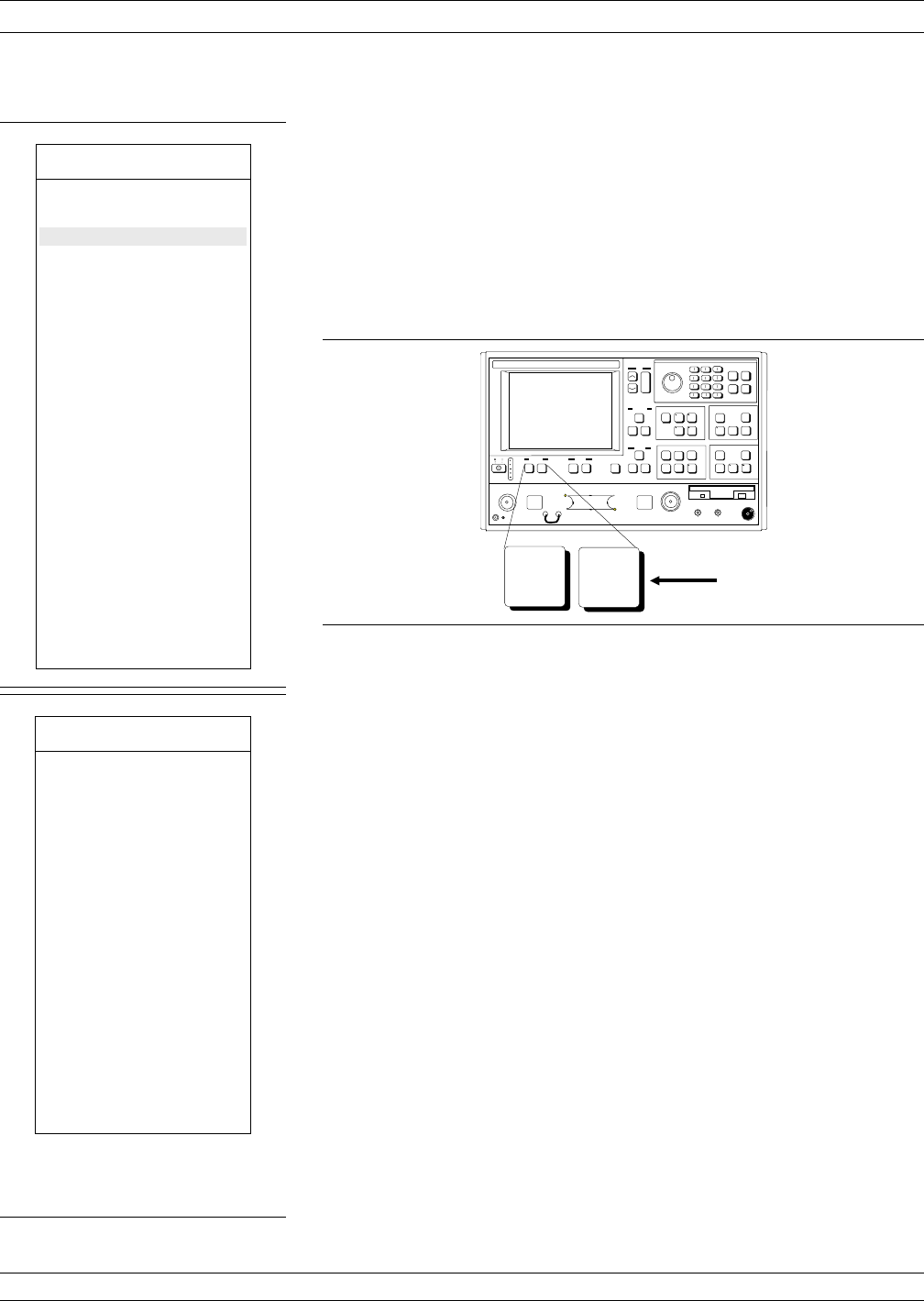
Multiple Source Control Pre-operational Setup
The two sources receive control information from the 37XXXC VNA.
The GPIB address assigned to the external source must be identical to
the address contained in the data directed to the source by the
37XXXC VNA. Assure source/VNA address compatibility as follows:
Step 1. Install Sources 1 and 2 on the Dedicated GPIB bus.
Step 2. Press the Utility Menu key.
Step 3. Move cursor to GPIB ADDRESSES and press Enter,
when menu U1 (left) appears.
Step 4. When menu GP7 (left) appears, observe that the ad-
dress number is correct. If necessary, use the keypad
to enter a new address.
MULTIPLE SOURCE CONTROL MEASUREMENTS
8-30 37XXXC OM
MENU U1
SELECT UTILITY
FUNCTION OPTIONS
GPIB ADDRESSES
DISPLAY
INSTRUMENT
STATE PARAMS
GENERAL DISK
UTILITIES
CAL COMPONENT
UTILITIES
AUTOCAL UTILITIES
COLOR
CONFIGURATION
DATA ON(OFF)
DRAWING
BLANKING
FREQUENCY
INFORMATION
SET DATA/TIME
PRESS <ENTER>
TO SELECT
OR TURN ON/OFF
MENU 7
GPIB ADDRESSES
IEEE 488.2
GPIB INTERFACE
ADDRESS
6
DEDICATED
GPIB INTERFACE
EXTERNAL SOURCE 1
4
EXTERNAL SOURCE 2
5
PLOTTER
8
POWER METER
23
FREQUENCY COUNTER
7
Default
Program Utility
Menu
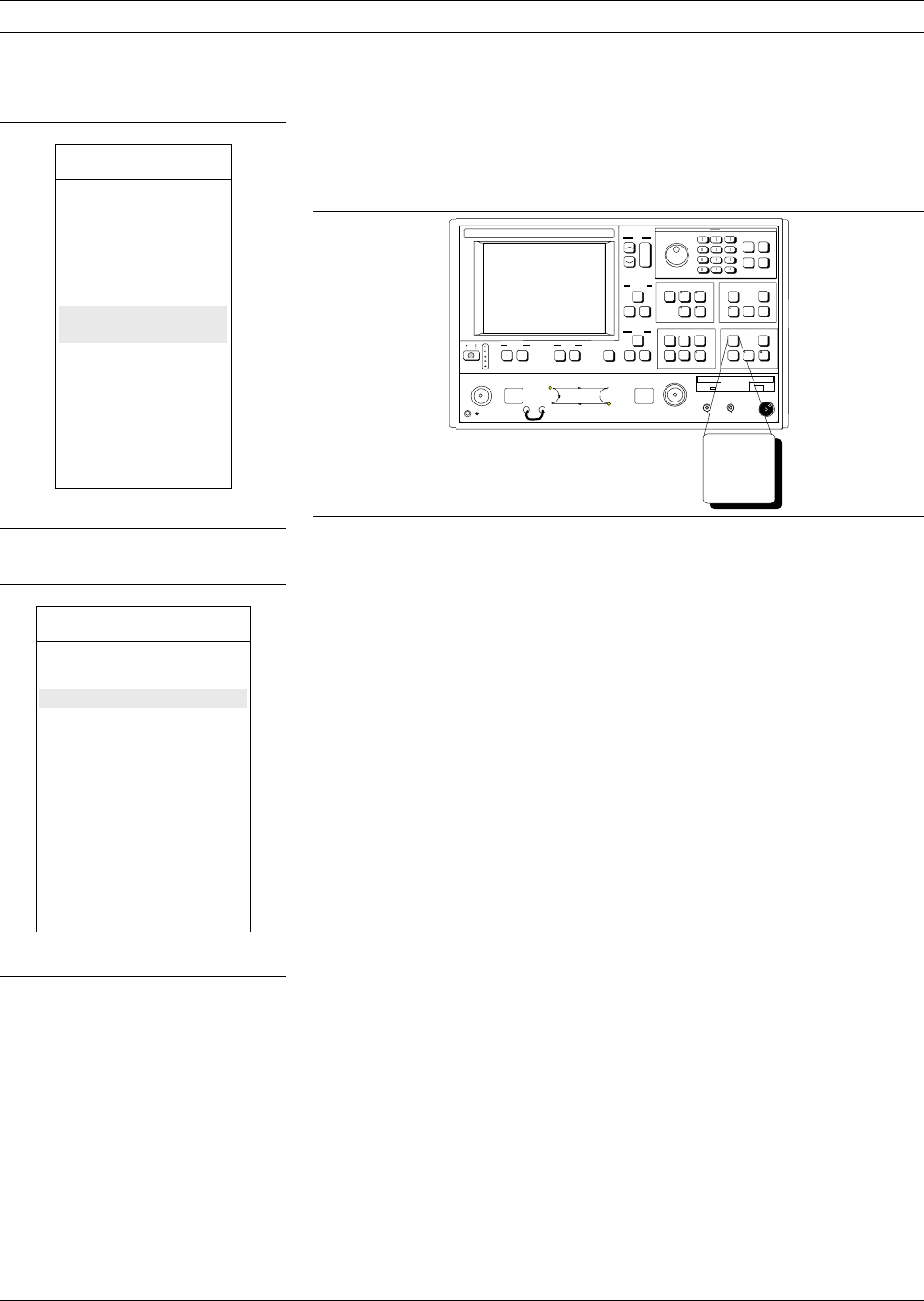
Multiple Source Control Operation
Step 5. Press the Option Menu key.
Step 6. When menu OPTIONS (left) appears, move cursor to
MULTIPLE SOURCE CONTROL and press the
Enter key.
Step 7. When menu OM1(left) appears, move cursor to DE-
FINE BANDS and press the Enter key. This brings
menu OM 1 to the screen.
37XXXC OM 8-31
MEASUREMENTS MULTIPLE SOURCE CONTROL
MENU OPTNS
OPTIONS
TRIGGERS
REAR PANEL
OUTPUT
DIAGNOSTICS
MULTIPLE SOURCE
CONTROL
RECEIVER MODE
SOURCE CONFIG
RF ON/OFF
DURING RETRACE
PRESS <ENTER>
TO SELECT
MENU OM1
MULTIPLE SOURCE
CONTROL
DEFINE BANDS
SOURCE CONFIG
MULTIPLE
SOURCE MODE
OFF
STANDBY
ON
MORE
PRESS <ENTER>
TO SELECT
Option
Menu
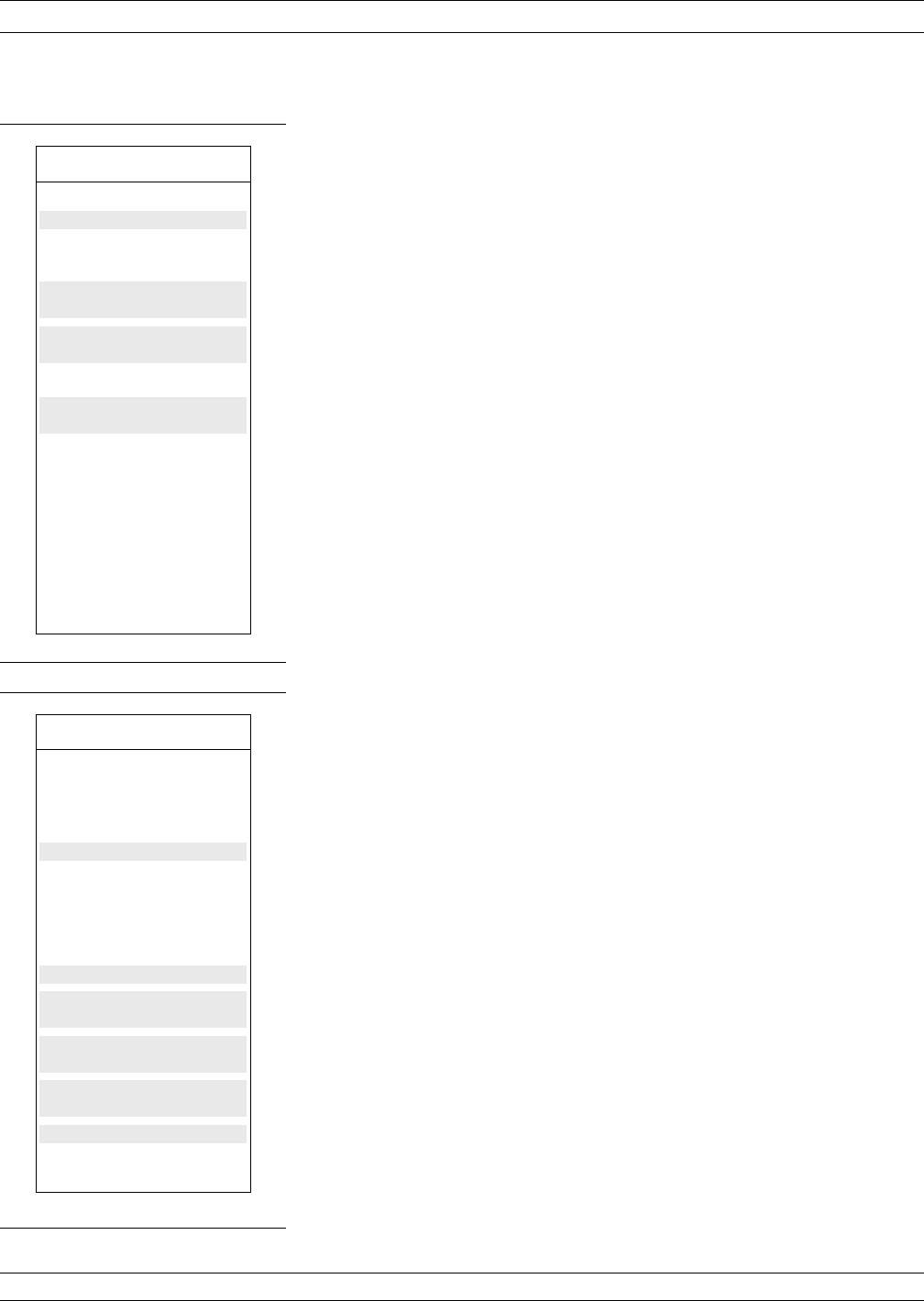
Step 8. Coincident with menu OM2 (left), the data display
area of the screen presents a chart entitled
“RANGES OF BANDS STORED.” This chart shows
the band start and band stop frequencies that have
been stored for each of five bands.
Using menu OM2, the displayed frequency range can
be divided into one to five bands.
Band 1 must start at the beginning of the frequency
range and end at either the user-specified stop fre-
quency or the end of the frequency range.
Band 2 must begin at the next point after band 1
ends and end at either the user-specified stop fre-
quency or the end of the frequency range.
Step 9. Move cursor to BAND; select BAND 1 by entering
“1” using the keypad or rotary knob.
Step 10. Move cursor to BAND START F, and use keypad or
rotary knob to enter the band 1 start frequency.
Step 11. Move cursor to BAND STOP F, and enter the
band 1 stop frequency.
Step 12. Move cursor to EDIT SYSTEM EQUATIONS and
press the Enter key.
Step 13. When menu OM3 (left) appears, select SOURCE 1.
Step 14. Move cursor to MULTIPLIER and use keypad or ro-
tary knob to enter desired multiplier for Source 1.
This is the multiplier term in the following equation:
Freq = (Multiplier/Divisor) X (F + Offset Frequency)
Step 15. Move cursor to DIVISOR and use keypad or rotary
knob to enter desired DIVISOR for source 1. This is
the divisor term given in the above equation.
Step 16. Move cursor to either OFFSET FREQUENCY, and
use keypad or rotary knob to enter desired offset fre-
quency for Source 1; or C.W., and press Enter to tog-
gle C.W. to OFF.
The Offset Frequency choice is the offset frequency
given in the above equation. The C.W. choice removes
F from the equation and places Source 1 in the CW
mode.
MULTIPLE SOURCE CONTROL MEASUREMENTS
8-32 37XXXC OM
MENU OM2
DEFINE BANDS
BAND 1
DISPLAYED
FREQ RANGE
BAND START F
XXX.XXXXXX XXX GHz
BAND STOP F
XXX.XXXXXXXXX GHz
BAND FUNCTIONS
EDIT SYSTEM
EQUATIONS
STORE BAND 1
BANDS STORED:
(12345)
CLEAR ALL
DEFINITIONS
SET MULTIPLE
SOURCE MODE
PRESS <ENTER>
TO SELECT
MENU OM3
EDIT SYSTEM
EQUATIONS
EQUATION
TO EDIT
SOURCE 1
SOURCE 2
RECEIVER
EQUATION
SUMMARY
C.W. OFF
MULTIPLIER
XX
DIVISOR
XX
OFFSET FREQ
XXX.XXXXXXXXX GHz
PREVIOUS MENU
PRESS <ENTER>
TO SELECT
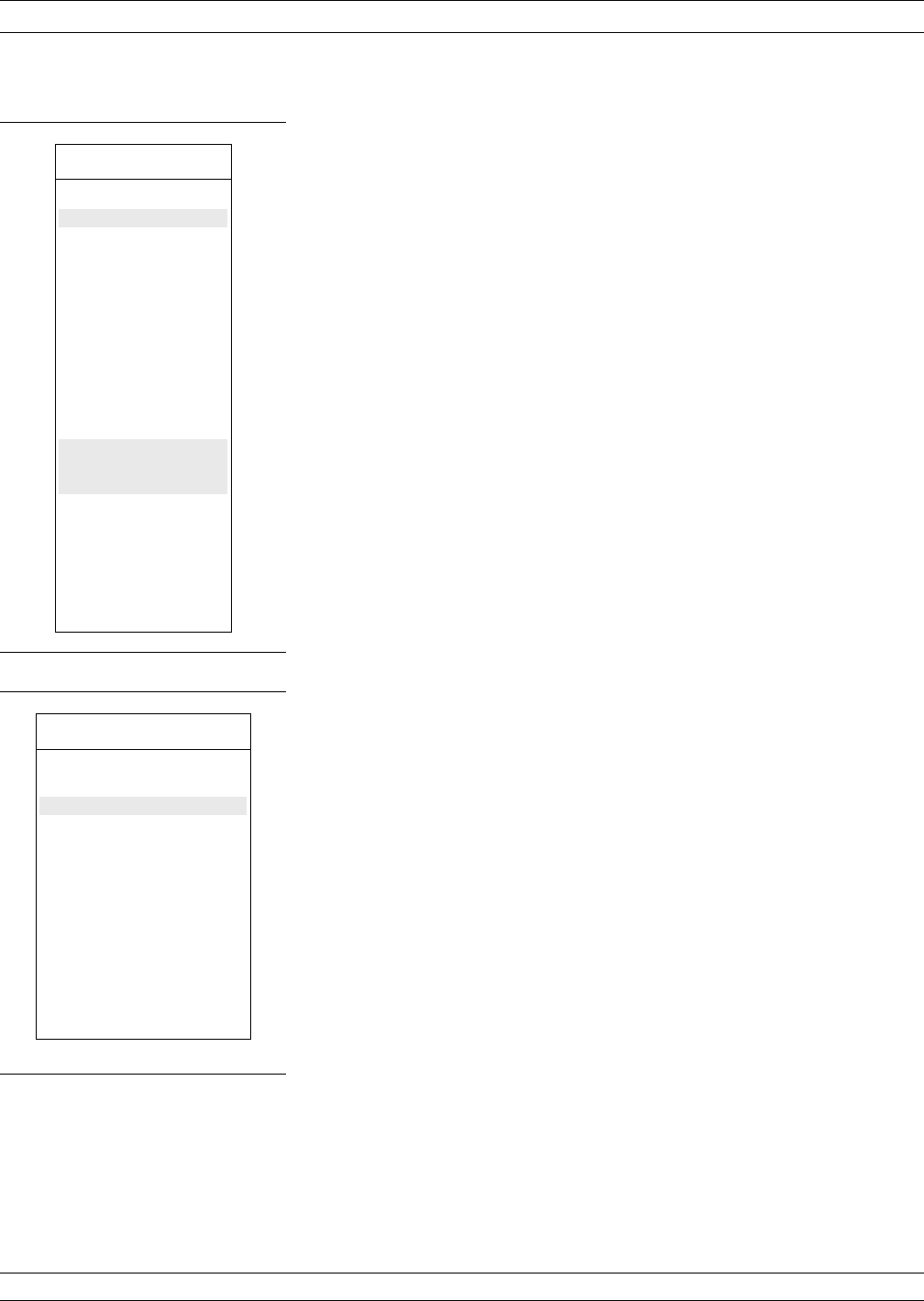
Step 17. Move the cursor to PREVIOUS MENU and press
the Enter key. This returns you to menu OM2 (left).
Step 18. Move cursor to STORE BAND 1 and press the Enter
key. This stores the band start frequency, the band
stop frequency and the Source 1, Source 2 and Re-
ceiver equations.
Step 19. Note that the BAND number has incremented to 2.
Step 20. Repeat the above steps to define the start and stop
frequencies for bands 2 through 5. Set up the system
equations for each band.
NOTE
Except for band 1, the system software constrains all start
frequencies to follow the previous band’s stop frequency.
However, while frequency bands are being defined or the
system equations are being edited, the system is automati-
cally placed in the standby mode. In this mode, frequencies
that may be entered are not supervised by the system soft-
ware; any frequency can be entered and displayed. When
the mode is switched to ON (in menu OM1, left), the sys-
tem software restricts the frequencies to band limits.
When the mode is switched to OFF, the frequencies are re-
stricted to system limits.
Source Lock Polarity: Normal/Reverse
When making frequency translated devices measurements using the
Multiple Source Control mode, enter the RF (source 1) and LO (source
2) frequencies. If the LO frequency is lower than the RF frequency, no
phase inversion is expected by the VNA. The opposite is true if the LO
frequency is higher than the RF frequency. These determinations may
be wrong if the DUT is a cascaded multiple conversion device. In that
case, determine if the final phase polarity is inverse of what is as-
sumed by the VNA, and set the Source Lock Polarity to Reverse. Fail-
ure to do so may cause the RF source to be erroneously locked at a
5 MHz offset.
37XXXC OM 8-33
MEASUREMENTS MULTIPLE SOURCE CONTROL
MENU OM2
DEFINE BANDS
BAND 2
DISPLAYED
FREQ RANGE
BAND START F
XX.XXXXXX GHz
BAND STOP F
XX.XXXXXX GHz
BAND FUNCTIONS
EDIT SYSTEM
EQUATIONS
STORE BAND 1
BANDS STORED:
( NONE )
CLEAR ALL
DEFINITIONS
SET MULTIPLE
SOURCE STATE
PRESS <ENTER>
TO SELECT
MENU OM1
MULTIPLE SOURCE
CONTROL
DEFINE BANDS
SOURCE CONFIG
MULTIPLE
SOURCE MODE
OFF
STANDBY
ON
MORE
PRESS <ENTER>
TO SELECT
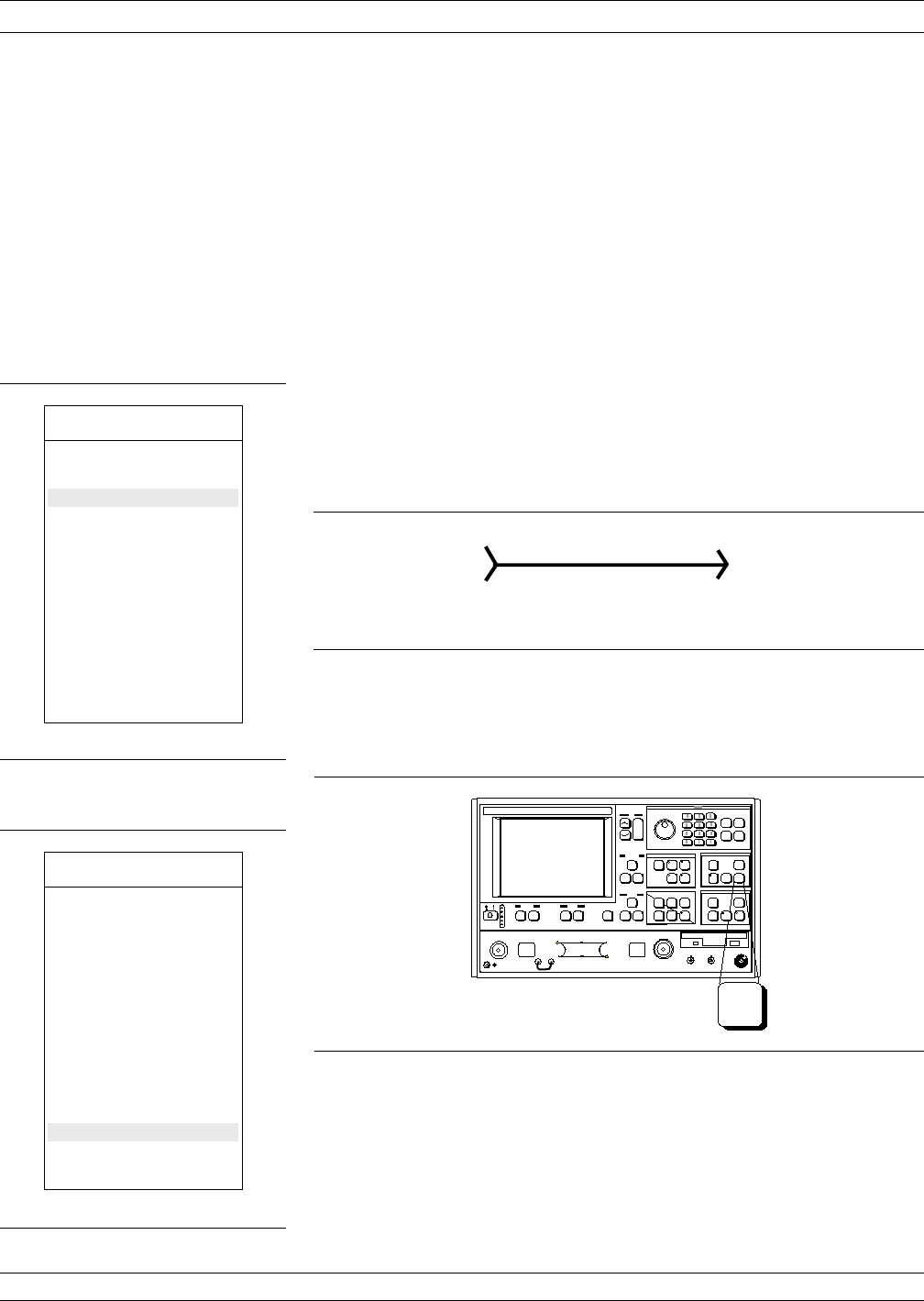
8-7 ADAPTER REMOVAL Using adapters in VNA measurement applications can introduce com-
plex errors that add to measurement uncertainty. The VNA Adapter
Removal procedure provides for adapter compensation. This on-screen,
menu-driven procedure allows the use of a through-line device or
adapter with different connector types (non-insertables) on either end
to be used for measurement calibration. The electrical effects are sub-
sequently compensated for. The Adapter Removal procedure is de-
scribed below.
NOTE
For purposes of explanation, assume that the adapter to be
used is a length of rigid coax with a type N male connector
on one end and an SMA male connector on the other end.
Further assume that the Test Port 1 connector is a type N
female and that the Test Port 2 connector is an SMA fe-
male (below).
Procedure:
Step 1. Press the Appl key (below) to display the APPLICA-
TIONS menu (top left).
Step 2. Move the cursor to ADAPTER REMOVAL and
press the Enter key.
Step 3. Select HELP in the next menu (bottom left) to pro-
duce the step-by-step procedure shown in
Figure 8-28 (next page).
ADAPTER REMOVAL MEASUREMENTS
8-34 37XXXC OM
Test Adapter
Type N Male
(X’)SMA Male
(Y’)
Electrical Length: 170 ps
MENU APPL
APPLICATIONS
ADAPTER REMOVAL
SWEPT FREQUENCY
GAIN COMPRESSION
SWEPT POWER
GAIN COMPRESSION
E/O MEASUREMENT
O/E MEASUREMENT
MERGE CAL FILES
PRESS <ENTER>
TO SELECT
MENU CAR1
ADAPTER REMOVAL
12-TERM CALS FOR
X AND Y
MUST EXIST IN THE
CURRENT DIREC-
TORY
ELECTRICAL LENGTH
OF THE ADAPTER
+XXX.XXXXX ps
REMOVE ADAPTER
HELP
PRESS <ENTER>
TO SELECT
Appl
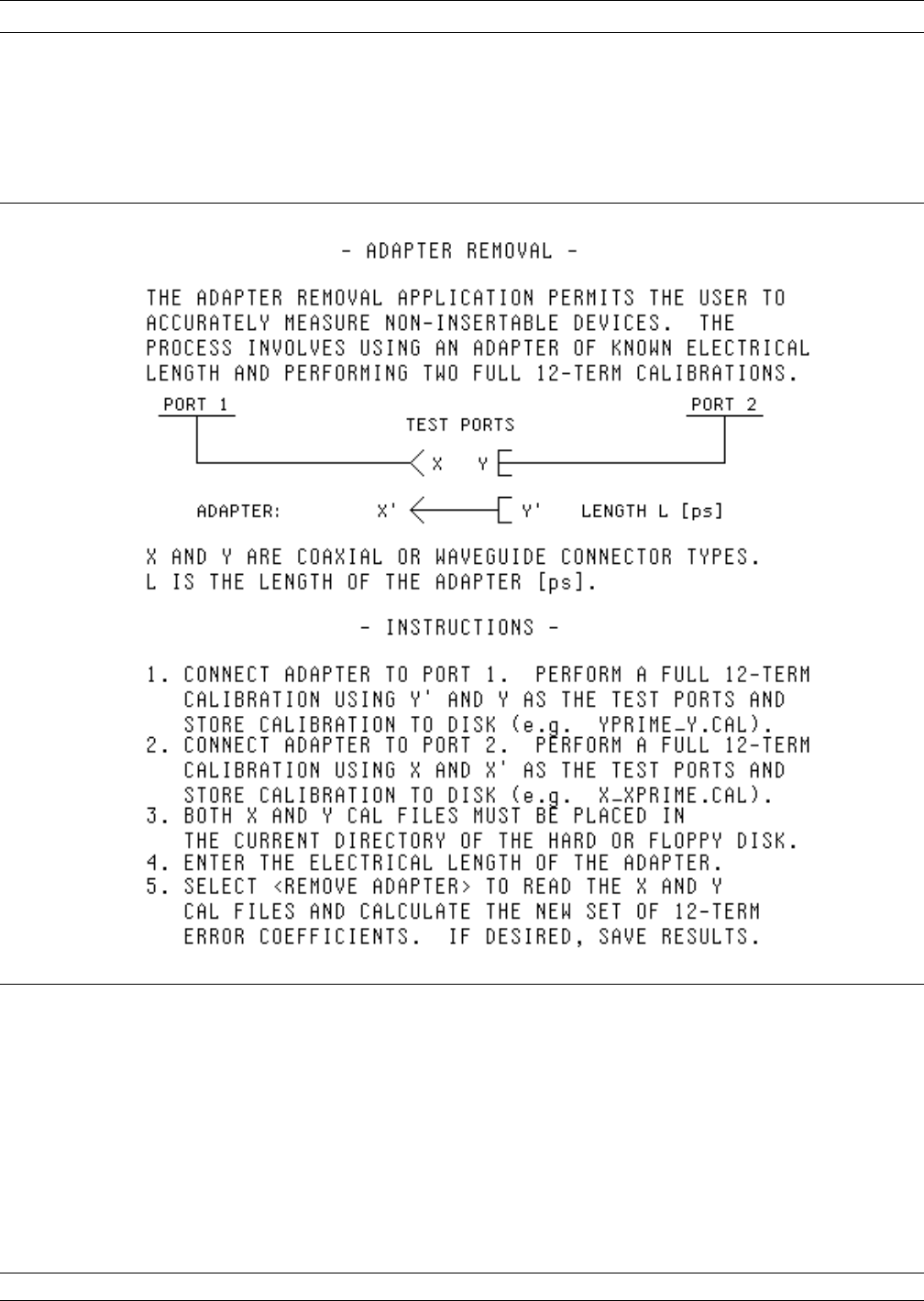
Step 4. Follow the on-line procedure and connect the
Adapter’s N male connector (X’) to the N female con-
nector on the VNA’s Test Port 1.
37XXXC OM 8-35
MEASUREMENTS ADAPTER REMOVAL
Figure 8-28. Adapter Removal Help Screen
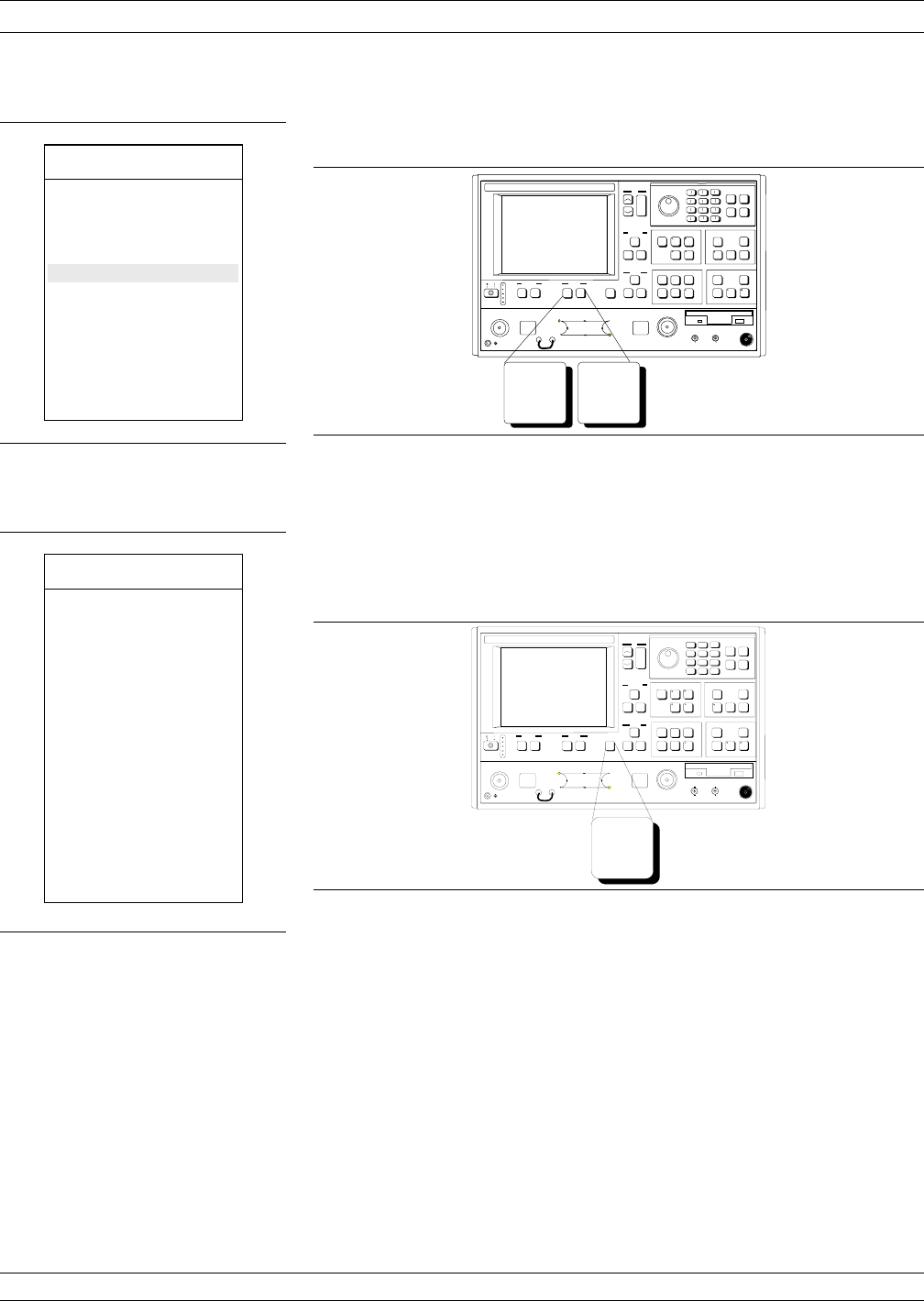
Step 5. Press the Begin Cal key (below).
Step 6. Follow the menu prompts and choose to perform a
full 12-term calibration. Use the Adapter’s SMA
male connector (Y') as Test Port 1 and the VNA’s Test
Port 2 connector as Test Port Y (Figure 8-27).
Step 7. Press the Save/Recall Menu key (below).
Step 8. Choose SAVE from the displayed menu (top left).
Step 9. Choose the appropriate hard or floppy disk location,
based on individual preference (Menu SR2, bottom
left).
Step 10. When prompted, select CREATE NEW FILE and en-
ter a conventional DOS filename, such as YP-
RIME_Y.CAL. (Store this file in the current direc-
tory.)
Step 11. Now connect the Adapter’s SMA male end to the
VNA’s Test Port 2 SMA female connector.
ADAPTER REMOVAL MEASUREMENTS
8-36 37XXXC OM
7 8 9
456
123
0.-
D a ta E n t r y
S a v e /
R e c a l l
M e n u
MENU SR1
SAVE/RECALL
FRONT PANEL
AND CAL DATA
SAVE
RECALL
SET UP OUTPUT
HEADERS
PRESS <ENTER>
TO SELECT
FUNCTION
MENU SR2
SAVE
FRONT PANEL
SETUP IN
INTERNAL MEMORY
FRONT PANEL
SETUP AND
CAL DATA
ON HARD DISK
FRONT PANEL
SETUP AND
CAL DATA
ON FLOPPY DISK
PRESS <ENTER>
TO SELECT
Apply
Cal
Begin
Cal

Step 12. Press the Begin Cal key again.
Step 13. Follow the menu prompts; again choose to perform a
full 12-term calibration. Now use the Adapter’s Type
N male connector (X’) as Test Port 2. Use the VNA’s
Test Port 1 connector as Test Port X.
Step 14. Save the calibration as described in Steps 7 and 8,
above. Give this file a unique filename, such as
X_XPRIME.CAL. (Store this file in the current direc-
tory.)
Step 15. Press the Appl key and chose ADAPTER RE-
MOVAL to return to Menu CAR1 (top left).
Step 16. Enter the electrical length of the Adapter (170 ps for
the test adapter) in the appropriate place in Menu
CAR1.
NOTE
Electrical length does not have to be precise.
Plus or minus 5 ps is adequate for this pro-
cedure.
Step 17. Move the cursor to REMOVE ADAPTER, and press
the Enter key.
Step 18. Move the cursor to the appropriate READ CAL
FILE OF THE X TEST PORT . . . , depending on
where the calibration data is stored (hard or floppy
disk). Press the Enter key.
NOTE
At this juncture, the “X” calibration file is
marked for reading, but not actually read.
Both the “X” and “Y” files will be read into
the VNA together in the next step.
37XXXC OM 8-37
MEASUREMENTS ADAPTER REMOVAL
MENU CAR1
ADAPTER REMOVAL
12-TERM CALS FOR
X AND Y
MUST EXIST IN THE
CURRENT DIREC-
TORY
ELECTRICAL LENGTH
OF THE ADAPTER
+170.0000 ps
REMOVE ADAPTER
HELP
PRESS <ENTER>
TO SELECT
MENU CAR2
ADAPTER REMOVAL
READ CAL FILE OF
THE X TEST PORT
FROM HARD DISK
(ADAPTER ON
PORT 2)
READ CAL FILE OF
THE X TEST PORT
FROM FLOPPY DISK
(ADAPTER ON
PORT 2)
PRESS <ENTER>
TO SELECT
PRESS <CLEAR>
TO ABORT
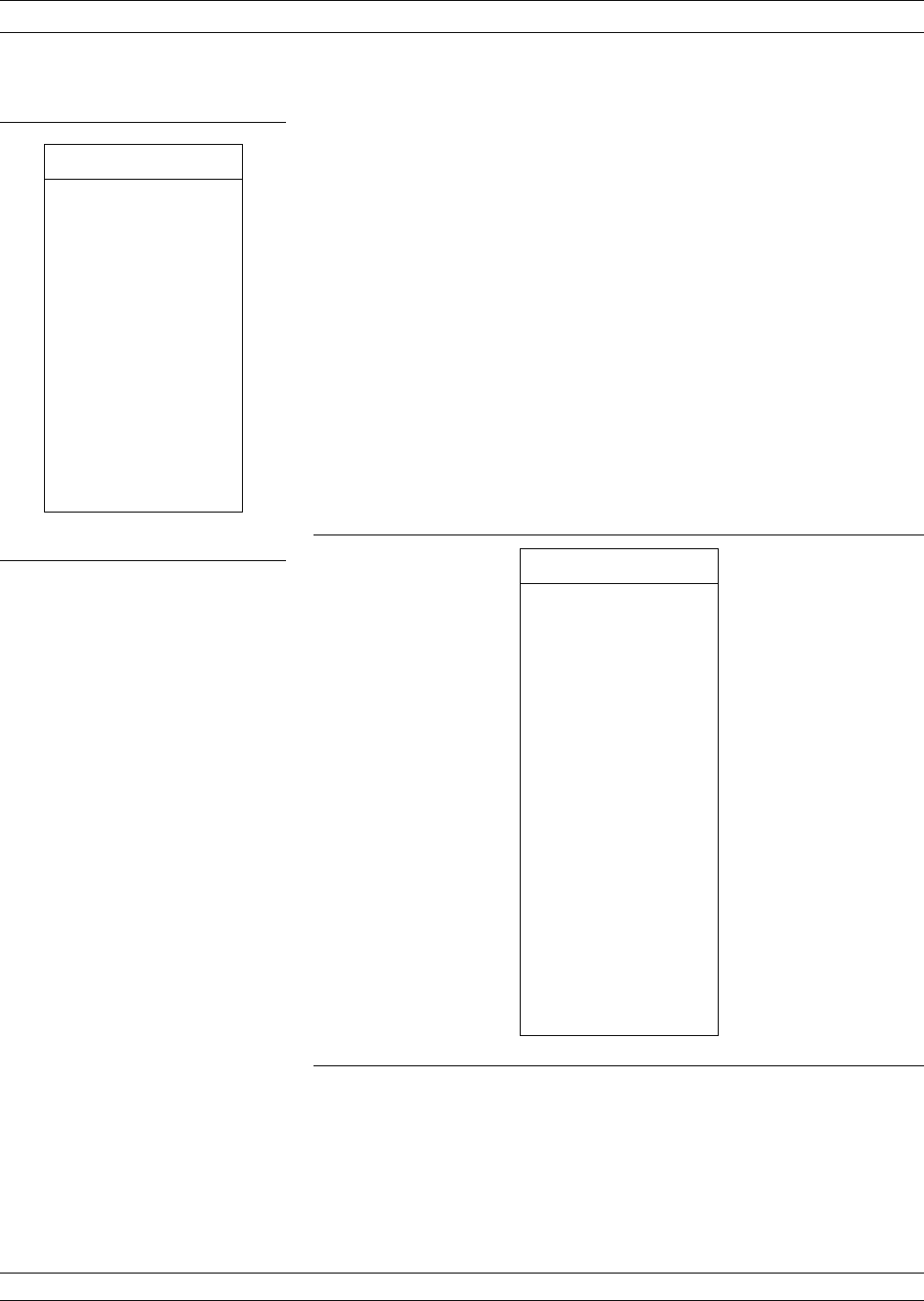
Step 19. Move the cursor to the appropriate READ CAL
FILE OF THE Y TEST PORT. . . choice (top left).
Press the Enter key.
Step 20. Observe that the text READING . . . FROM DISK
appears in the menu area.
Step 21. When the file has finished reading, the procedure is
complete and the program returns to the SWEEP
SETUP menu (below).
If the adapter is still connected, the display will
show the S-parameters of the adapter. Any device to
be measured with that same connector configuration
will be measured in an absolute sense.
Also, you may wish to store the resulting Adapter
Removal calibration for later use.
ADAPTER REMOVAL MEASUREMENTS
8-38 37XXXC OM
MENU CAR3
ADAPTER REMOVAL
READ CAL FILE OF
THE Y TEST PORT
FROM HARD DISK
(ADAPTER ON
PORT 2)
READ CAL FILE OF
THE Y TEST PORT
FROM FLOPPY DISK
(ADAPTER ON
PORT 2)
PRESS <ENTER>
TO SELECT
PRESS <CLEAR>
TO ABORT
MENU SU1
SWEEP SETUP
START
XX.XXXXXXXXX GHz
STOP
XX.XXXXXXXXX GHz
SET CENTER/SPAN
XXX DATA POINT(S)
XX.XXXXXXXXX GHz
STEP SIZE
C.W. MODE ON (OFF)
XX.XXXXXXXXX GHz
MARKER SWEEP
DISCRETE FILL
HOLD BUTTON
FUNCTION
TEST SIGNALS
PRESS <ENTER>
TO SELECT
OR TURN/OFF
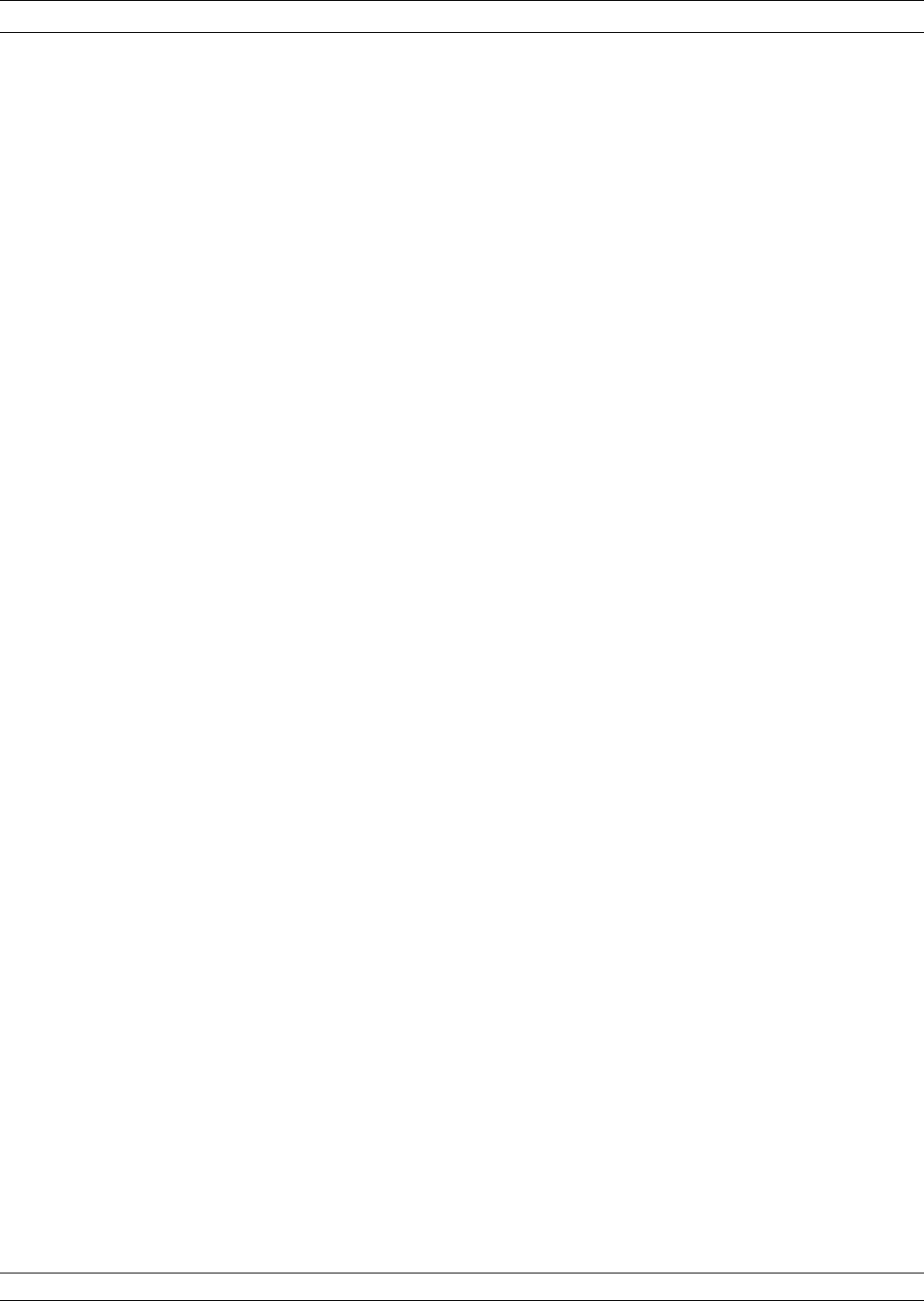
8-8 GAIN COMPRESSION There are a number of ways to measure Gain Compression. With a
VNA two approaches are possible: Swept Frequency Gain Compression
(SFGC) and Swept Power Gain Compression (SPGC). The 37XXXC of-
fers a very straightforward approach to each of these measurements.
It is normally desirable to make S-parameter measurements in the
linear operating region of an amplifier and then observe Compression
or amplitude-modulation/phase-modulation (AM/PM) characteristics
by increasing the input power to drive the amplifier into it's nonlinear
region. The characteristics of the amplifier-under-test (AUT) dictate
the operating power levels required for the tests. Prior to making
measurements on a specific amplifier the user must determine the de-
sired operating levels. A recommended level for linear region operation
is:
P = PG – Gain – 15dB (PGC=Nominal l dB compression of the AUT)
The actual level is constrained by the power available from the VNA
and the built in 70 dB step attenuator. (In the case of the 37XXXC,
available power is easily supplemented by the addition of an external
amplifier/attenuator combination.) Power input to Port 2 must also be
considered as the test should not drive the VNA into nonlinear opera-
tion. Typical specifications show 0.1dB compression at a VNA receiver
input level of –10 dBm. The receiver signal is derived through a 13 dB
coupler from the Port 2 signal. The 37XXXC also includes a 40 dB step
attenuator in this path that enables linear operation with input sig-
nals as high as 30 dBm (1 watt), the maximum signal level that should
be input to Port 2. Higher power levels can be measured by attenuat-
ing the signal prior to Port 2.
A typical power configuration example that will also be used through-
out this section is included in Figure 8-28. A 10 dB pad has been used
at both Port 1 and Port 2 to minimize mismatch errors.
Power and VNAs It is necessary to measure absolute power to deter-
mine Gain Compression. VNA receiver channels are
typically down-converters and do not measure
power directly. They are, however, linear so that an
accurate power calibration at one level will result in
a receiver channel that will accurately indicate
power in dBm.
The 37XXXC firmware supports calibration with the
following power meters: Anritsu ML2430A, HP437B,
HP438, and Gigatronics 8541C/8542C. These meters
differ in the way they handle sensor efficiency (con-
sult the power meter manual), and the 37XXXC
does expect to receive corrected data from the power
meter.
37XXXC OM 8-39
MEASUREMENTS GAIN COMPRESSION
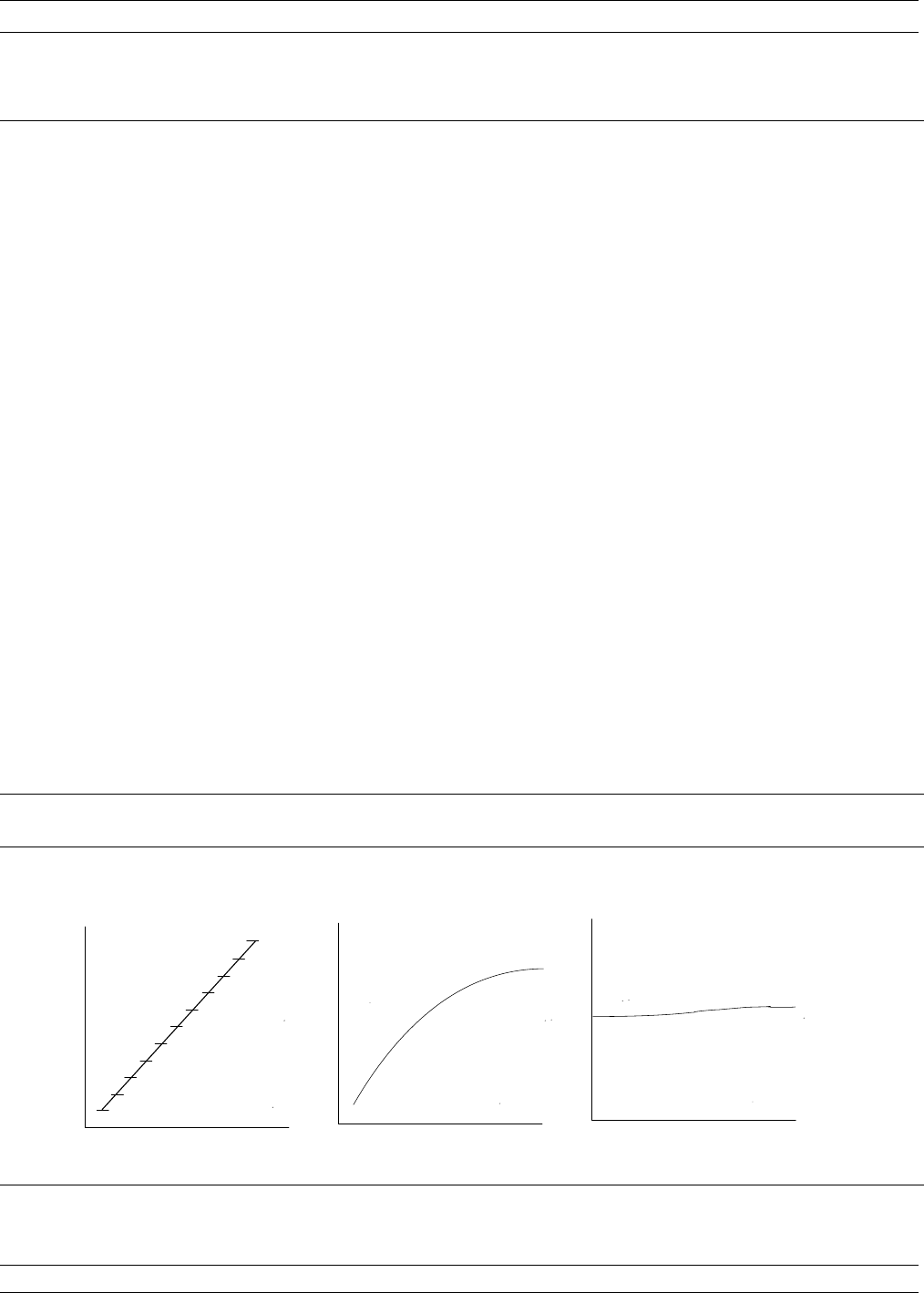
GAIN COMPRESSION MEASUREMENTS
8-40 37XXXC OM
Gain Compression Power Configuration
Amplifier Specifications:
Frequency Range: 8 to 12 GHz
Gain 25 dB nominal
1 dB Gain Compres-
sion (GC) 12 dBm minimum
Gain Compression Formula: P = 12 – 25 – 15 = –28 dBm
37369C Setup
Default Power: –7 dBm
Power Control: –8 dB
Port 1 Attenuator: 0 dB
External Port 1 Attenuator: 10 dB
The above setting result in
Port 1 Power: –25 dBm
Maximum Amplifier Output @15 dBm
Coupler Loss: @13 dB
Port 2 Attenuator: 10 dB
Figure 8-28. Gain Compression Measurement Plan (Example)
Output
Power
Input Power
Phase
Input Power
Input
Power
Time
Pstart
Pstop
Figure 8-29. Power In (Pi) versus Power Out (Po) Graphical Example
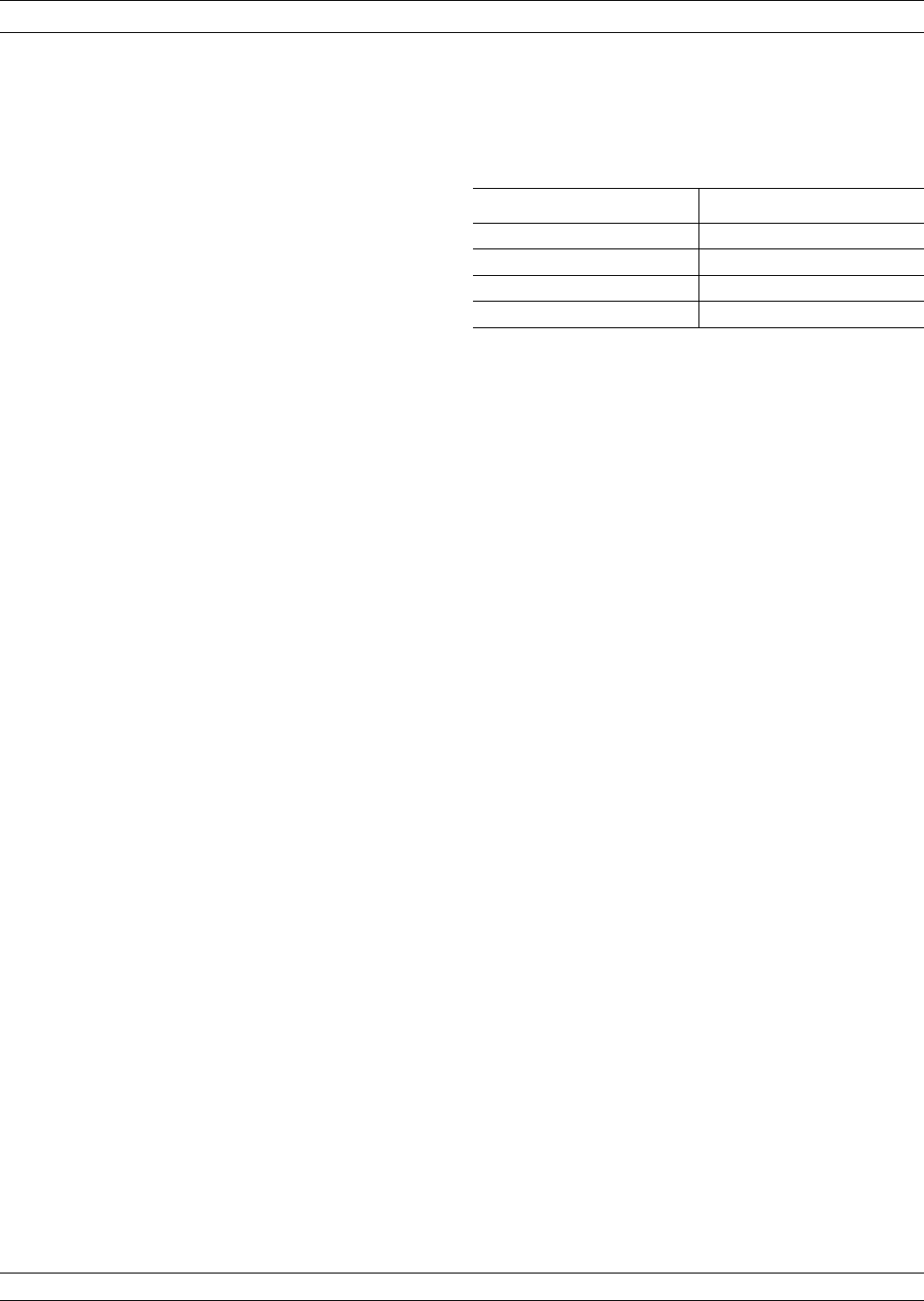
Errors can result if the proper correction factor is
not applied by the power meter, as shown below.
Correction Factor (%) Error (dB)
1 0.043
3 0.128
5 0.212
10 0.414
It is desirable to set the power control at or near the
minimum (this varies from -20 to -30 dB, depending
upon model) when establishing P, as this provides
the full ALC range for a power sweep.
The vector error correction available in VNAs is de-
pendent upon ratioed S-parameter measurements.
Power is measured using a single, unratioed chan-
nel; therefore, when power is being measured error
correction is turned off.
Swept Power Gain
Compression A swept power test is done at a CW frequency. The
input power will be increased with a step sweep
starting at Pstart and ending at Pstop. The step in-
crement is also user defined. This lets you observe
the conventional Po vs. Pi presentation or a display
of Phase vs. Pi. Figure 8-29 (previous page) illus-
trates this process. The SPGC process is imple-
mented in the 37XXXC by following the procedure
that begins on page 8-43. The test setup required for
this procedure is shown in Figure 8-30 (page 8-42).
Swept Frequency Gain
Compression This is a manual procedure that provides a normal-
ized amplifier response as a function of frequency at
Pstart and manually increases the input power
while observing the decrease in gain as the ampli-
fier goes into compression. This lets you easily ob-
serve the most critical compression frequency of a
broadband amplifier. The SFGC process is imple-
mented in the 37XXXC by following the procedure
that begins on page 8-52. The test setup required for
this procedure is shown in Figure 8-30 (following
page).
37XXXC OM 8-41
MEASUREMENTS GAIN COMPRESSION
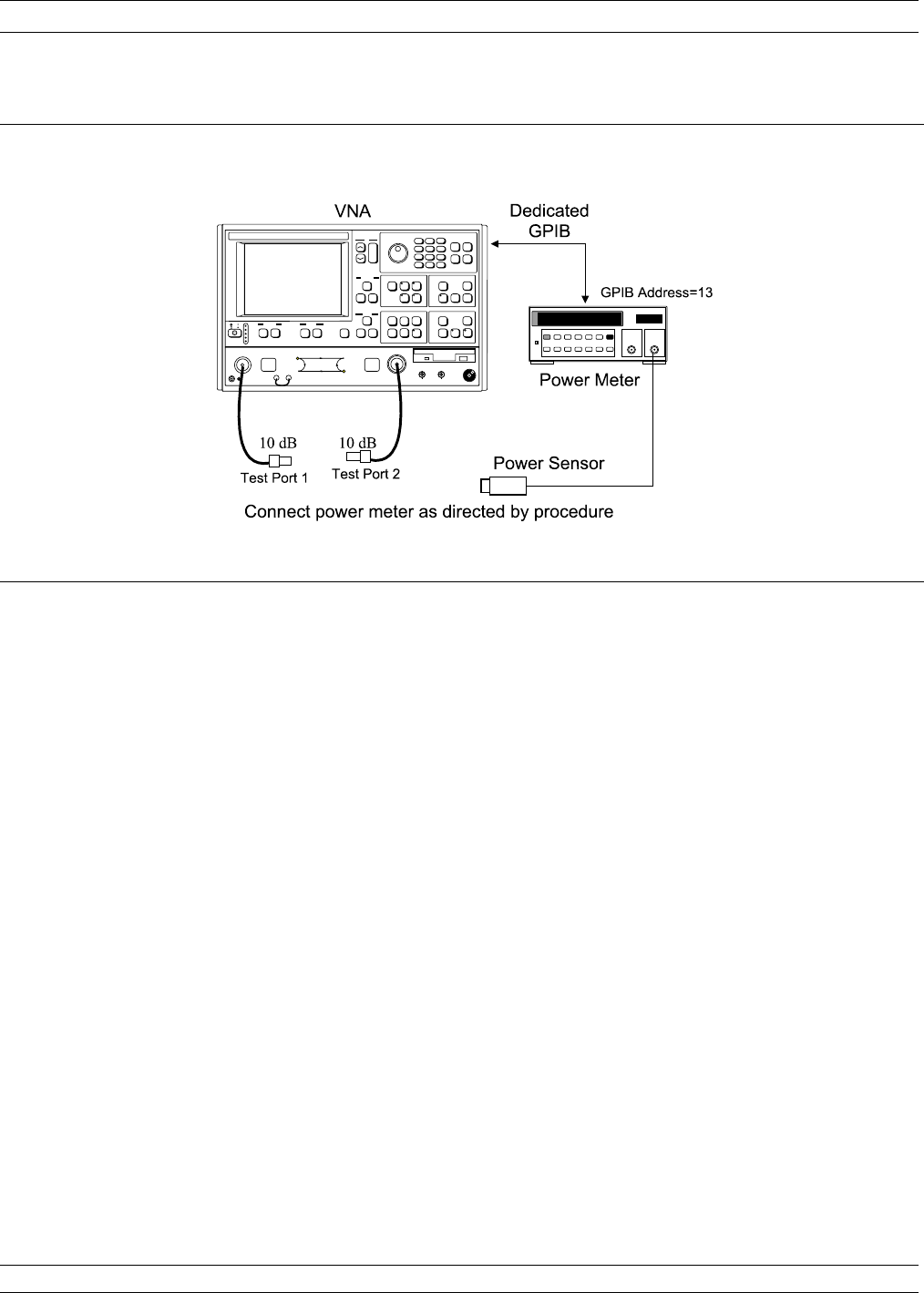
GAIN COMPRESSION MEASUREMENTS
8-42 37XXXC OM
789
456
123
0.-
Figure 8-30. Test Setup for Gain Compression Measurements
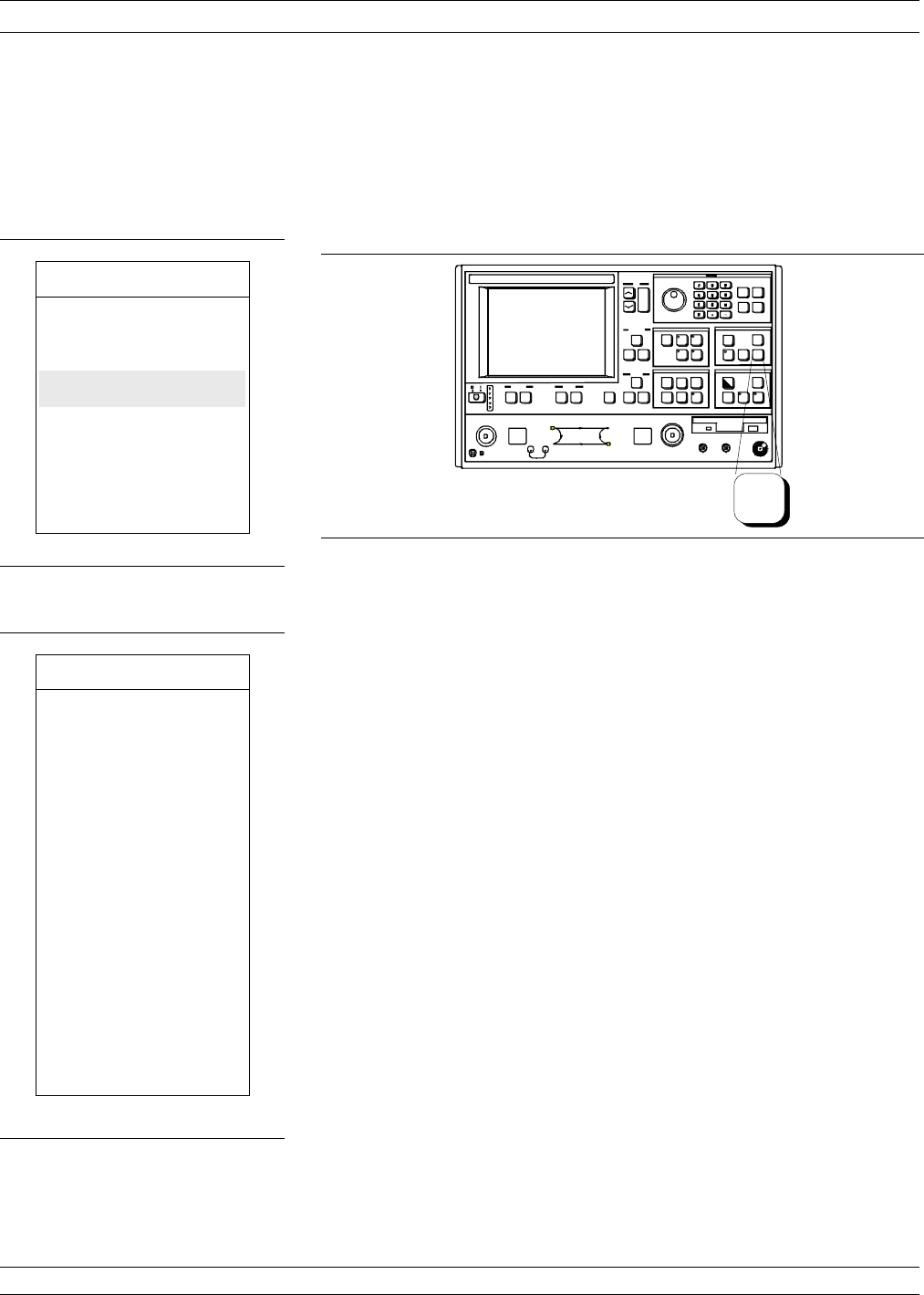
Swept Power Gain Compression Measurement
The following procedures describes the Swept Power Gain Compres-
sion Measurement.
Step 1. Press the Appl key.
NOTE
A 12-Term S-parameter calibration is not
necessary for gain compression calibration
and measurement. If such a calibration is in
place, it will be disabled during the gain
compression operation.
Step 2. Move cursor to SWEPT POWER GAIN COM-
PRESSION and press Enter, when menu APPL (top
left) appears.
Step 3. When menu GC2 (bottom left) appears, follow the di-
rections that appear adjacent to the menu, as de-
scribed below:
Move cursor to SET FREQUENCIES, press Enter
and select from 1 to 10 frequencies.
Enter the frequency value, press a terminator key (e.g.
GHz/103/ms/m), then Enter to add the frequency to the
list.
NOTE
The number of frequencies and step size,
that is entered later, directly affect the time
required for Linear Power Calibration, in a
later step.
37XXXC OM 8-43
MEASUREMENTS GAIN COMPRESSION
MENU APPL
ADAPTER REMOVAL
SWEPT FREQUENCY
GAIN COMPRESSION
SWEPT POWER
GAIN COMPRESSION
E/O MEASUREMENTS
O/E MEASUREMENTS
MERGE CAL FILES
PRESS <ENTER>
TO SELECT
MENU GC2
SWEPT POWER
GAIN COMPRESSION
SET FREQUENCIES
PSTART
–25.00 dBm
PSTOP
–5.00 dBm
STEP SIZE
1.00 dB
ATTENUATION
GAIN COMPRESSION
POINT (MAX REF)
1.00 dB
NOMINAL OFFSET
0.00 dB
MORE
PRESS <ENTER>
TO SELECT
Appl
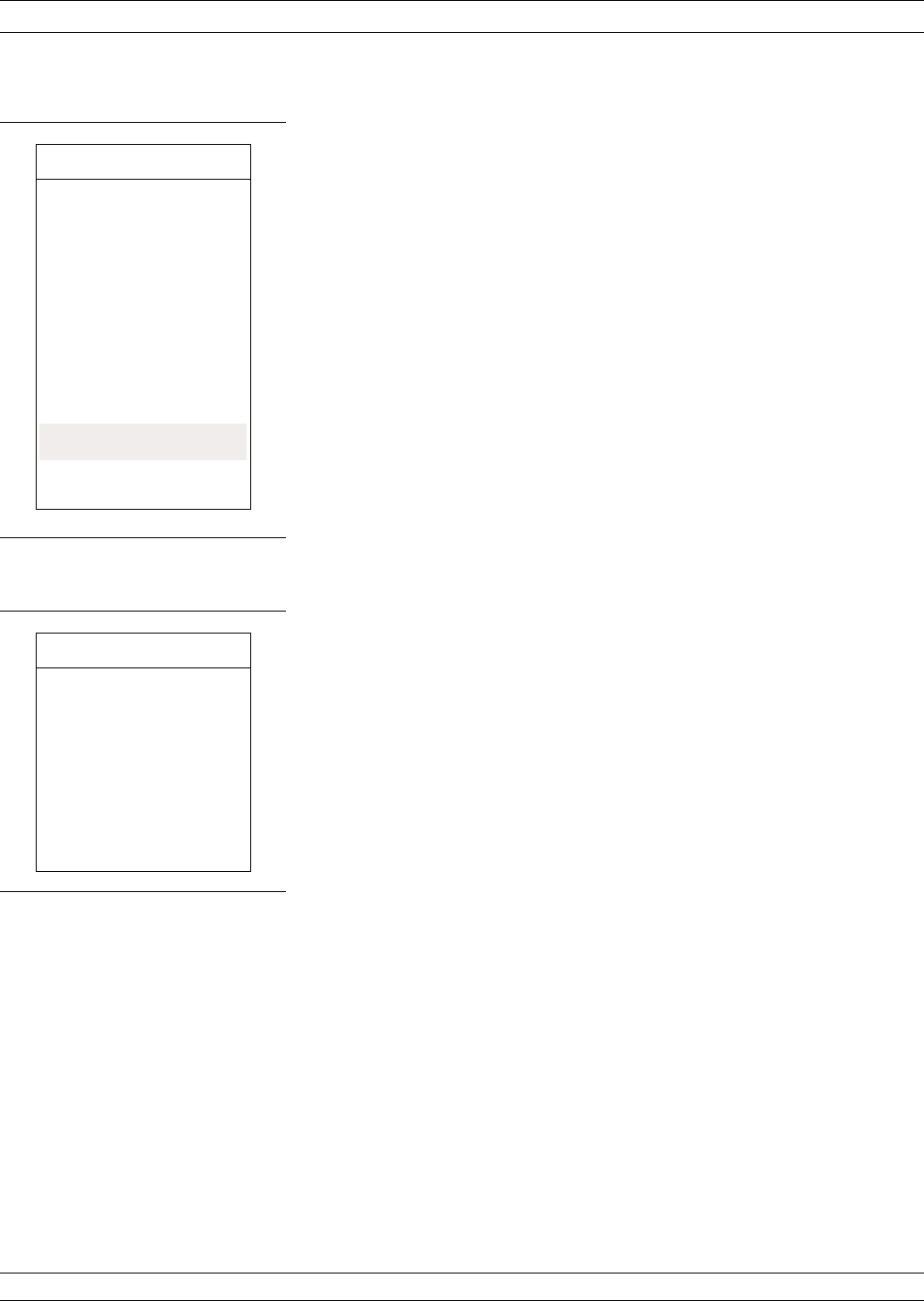
Move cursor to FINISHED, RETURN TO POWER
SWEEP SETUP and press Enter.
Move cursor to P START (previous page), set per
power plan (Figure 8-28), and press Enter.
Move cursor to PSTOP(previous page), set per
power plan, and press Enter.
Move cursor to STEP SIZE (previous page), enter a
value, and press Enter.
The 1 dB default value is reasonable. This value,
along with the number of frequencies entered in a
previous step, directly affect the time required for Lin-
ear Power Calibration, in a later step.
Move cursor to ATTENUATION (previous page) and
press Enter. Set power values (bottom left) per power
plan. Move cursor to PREVIOUS MENU and press
Enter when finished.
Move cursor to GAIN COMPRESSION (previous
page), enter the desired value (1 dB is typical), and
press Enter.
Move cursor to NOMINAL OFFSET (previous
page), enter the value of any external device(s) con-
nected between the front panel Input and Output con-
nectors. Press Enter when done. In the example use
-10 dB.
A setting of 0.00 dB is normal when no external de-
vices are connected.
Move cursor to MORE (previous page) and press En-
ter to proceed to the next menu (GC3) (next page).
GAIN COMPRESSION MEASUREMENTS
8-44 37XXXC OM
MENU GC_DF2
SWEPT POWER
FREQUENCIES
INPUT A FREQ,
PRESS <ENTER>
TO INSERT
SWEPT POWER
FREQUENCY
12.000000000 GHz
CLEAR FREQ NUMBER
1
CLEAR ALL
FINISHED, RETURN TO
POWER SWEEP SETUP
PRESS <ENTER>
TO SELECT
MENU GC_DF2
SWEPT POWER
GAIN COMPRESSION
PORT 1 ATTN
0*10 dB (0 - 70)
PORT 2 ATTN
2*10 dB (0 - 40)
PREVIOUS MENU
PRESS <ENTER>
TO SELECT
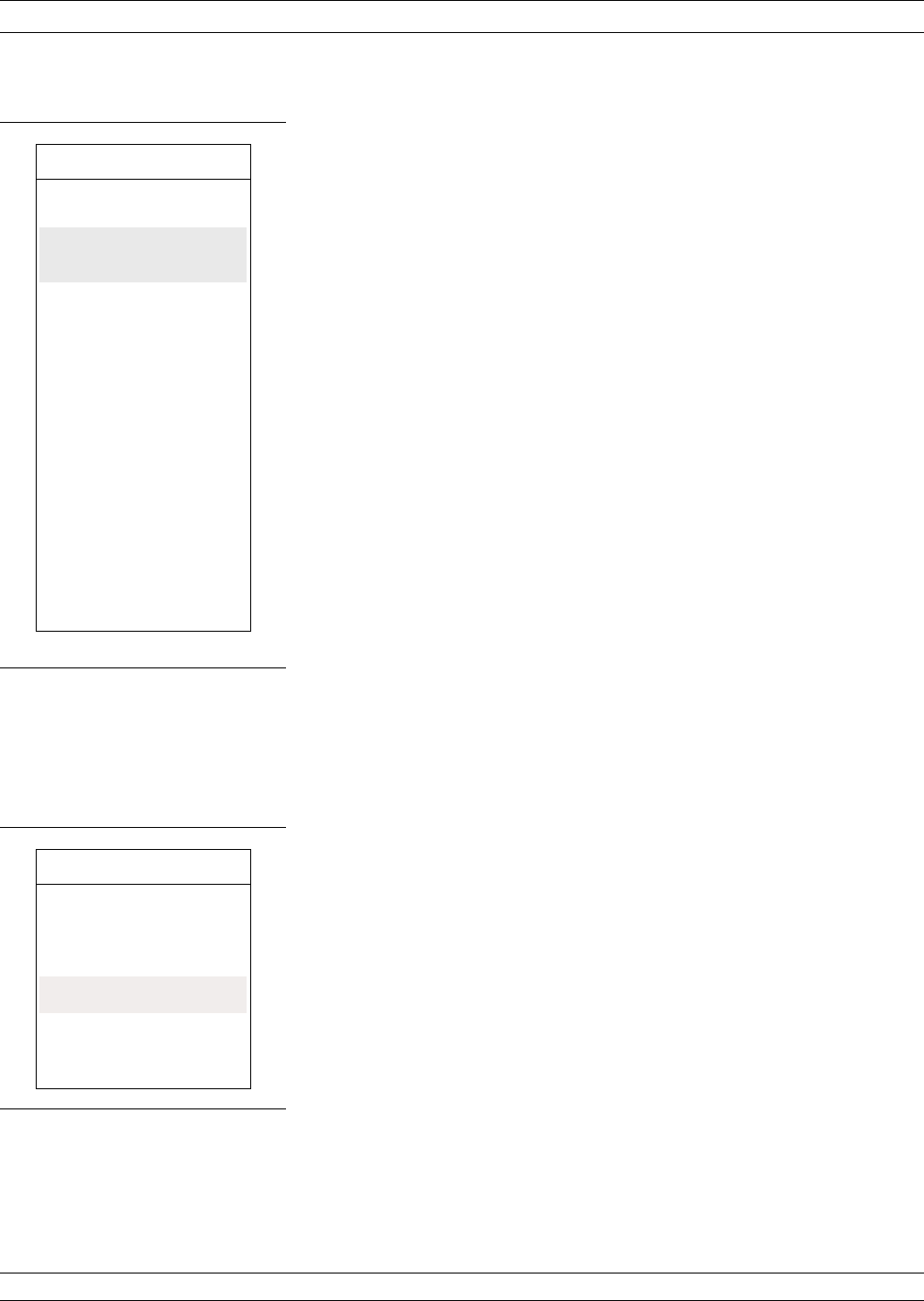
Step 4. Move the cursor to CALIBRATE FOR LINEARITY,
press Enter, and follow the instructions that (1) ap-
pear adjacent to the follow-on menu and (2) are de-
scribed below.
If a calibration already exists, the menu choice will indi-
cate CAL EXIST in blue letters.
NOTE
This step is not required for a successful
gain compression measurement; however,
linearizing the power from Port 1 (which is
what this step does) provides increased ac-
curacy.
Prepare the power meter as described in the
following instructions:
a. Preset, zero, and calibrate the power meter.
b. Set power meter offset, if required.
c. Connect the power meter to the dedicated gpib
interface and the power sensor to the test port.
d. Select <START LINEAR POWER CALIBRA-
TION>.
Connect the power sensor to Test Port 1.
With START LINEAR POWER CALIBRATION
highlighted (bottom left), press Enter to begin the cal-
ibration.
Step 5. Observe LINEARITY CORRECTION choice (top
left). If a linearity correction has been performed, it
will indicate ON in blue letters.
Step 6. Move cursor to CALIBRATE RECEIVER and fol-
low the instructions, as follows:
Connect a through line between Test Port 1 and Test
Port 2.Be sure to include all components that are
part of the measurement path.
37XXXC OM 8-45
MEASUREMENTS GAIN COMPRESSION
MENU GC3
SWEPT POWER
GAIN COMPRESSION
CALIBRATE
FOR LINEARITY
([NO] CAL EXIST)
LINEARITY ON [OFF]
CORRECTION
CALIBRATE
RECEIVER
([NO] CAL EXISTS)
S21 OPTIONS
([NOT] STORED)
AUT TEST TYPES
GAIN COMPRESSION
AM/PM
MULTIPLE FREQ
GAIN COMPRESSION
RETURN TO SWEPT
FREQUENCY MODE
PREVIOUS MENU
MENU GC_SU8A
CALIBRATE FOR
LINEAR POWER
FORWARD
DIRECTION ONLY
START LINEAR
POWER CALIBRATION
PREVIOUS MENU
PRESS <ENTER>
TO SELECT
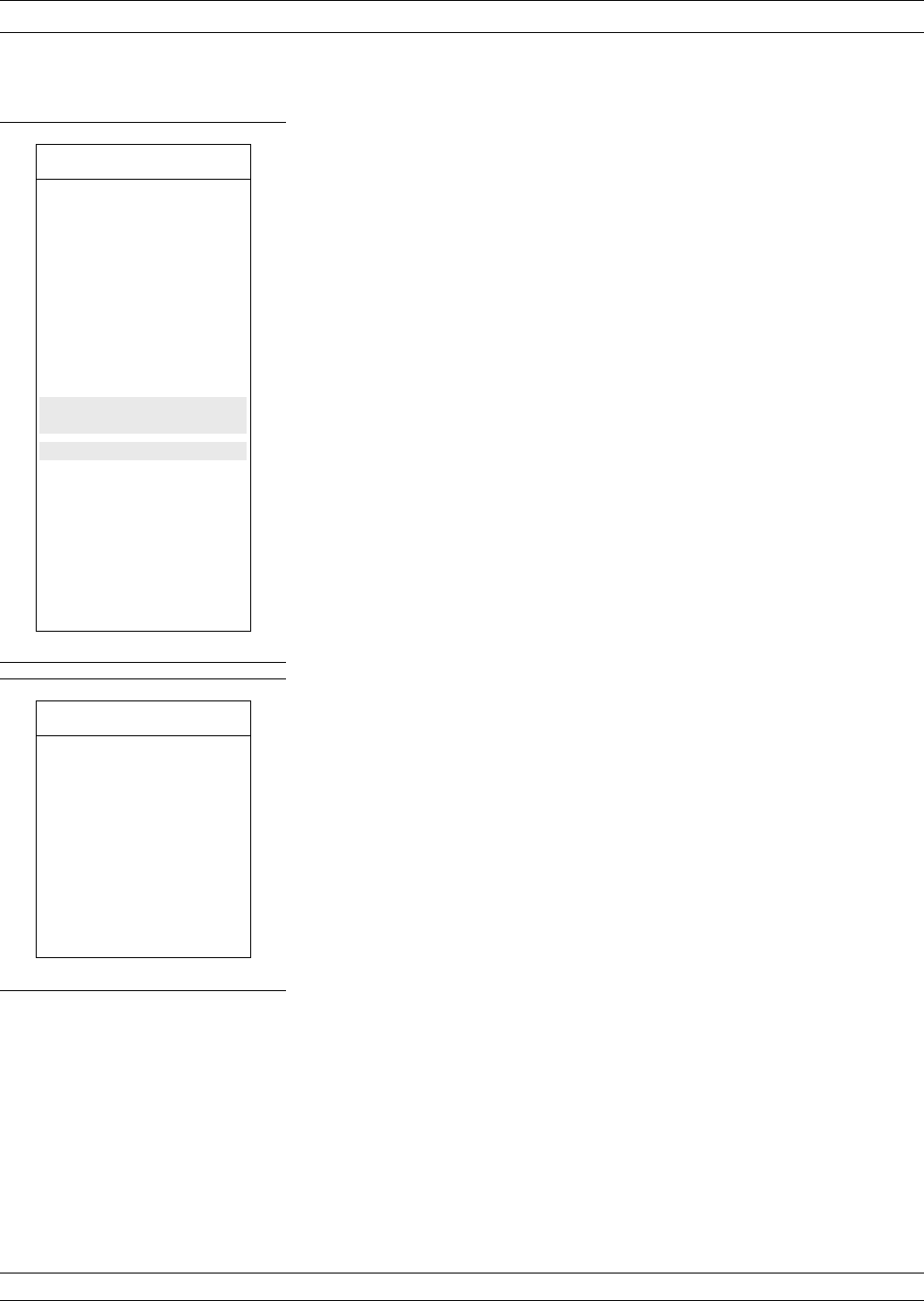
Wait until one complete sweep has completed, then
press Enter to store the calibration.
NOTE
It is likely that the trace will be off screen at
the bottom of the display. If so, press Autos-
cale to obtain a discernable trace. If this
trace shows vertical instability, then do the
following:
1. Press Video IF BW and select REDUCED
(100 Hz) from the menu.
2. Press Avg/Smooth Menu and select AVER-
AGING 100 MEAS. PER POINT from the
menu.
3. Press Average to turn averaging on.
Step 7. Press Appl to return to the gain compression menu
set, and follow the prompts to return to Menu GC3.
Repeat Step 6.
Step 8. Move the cursor to S21 OPTIONS (top left), select
NORMALIZE S21 in the next menu (not shown),
then NORMALIZE S21 again (bottom left); then
press Enter and follow the menu instructions:
Remove the through line and connect the ampli-
fier-under-test (AUT) between Port 1 and Port 2.
Apply bias to the AUT.
Wait until one complete sweep has completed, then
press Enter to store the normalization measurement.
Step 9. Move the cursor to the desired test and pressEnter.
The steps that follow presume that gain compression
has been selected.
8-46 37XXXC OM
GAIN COMPRESSION MEASUREMENTS
MENU GC_NORM
NORMALIZE S21
CONNECT AUT
AND APPLY BIAS .
WAIT FOR ONE
COMPLETE SWEEP
BEFORE STORING
PRESS <ENTER>
TO STORE
PRESS <CLEAR>
TO ABORT
MENU GC3
SWEPT POWER
GAIN COMPRESSION
CALIBRATE
FOR LINEARITY
([NO] CAL EXIST)
LINEARITY ON [OFF]
CORRECTION
CALIBRATE
RECEIVER
([NO] CAL EXISTS)
S21 OPTIONS
([NOT] STORED)
AUT TEST TYPES
GAIN COMPRESSION
AM/PM
MULTIPLE FREQ
GAIN COMPRESSION
RETURN TO SWEPT
FREQUENCY MODE
PREVIOUS MENU
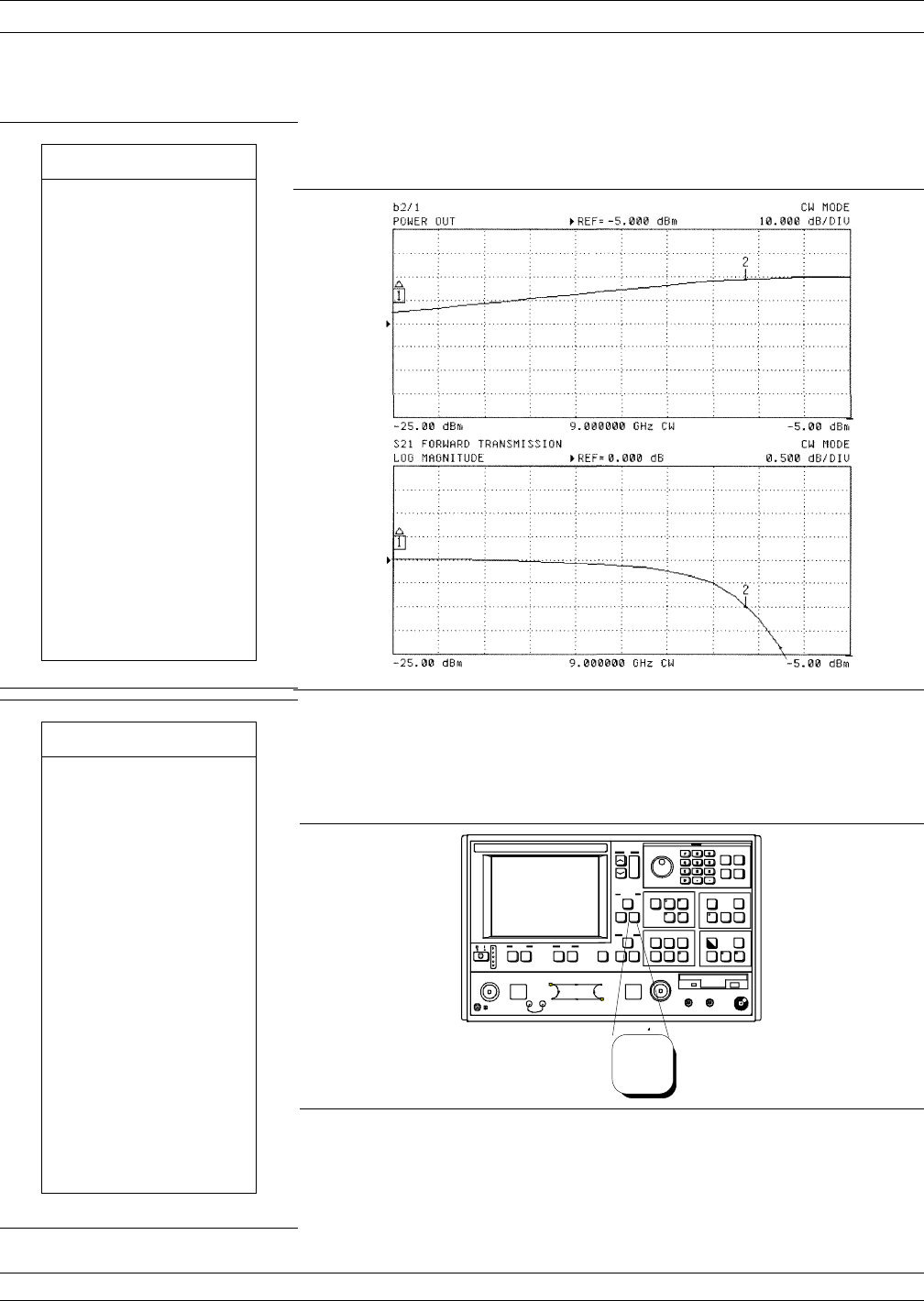
Step 10. Observe that the SWEPT POWER SETUP menu and
the dual-trace display resembles that shown below.
Step 11. Press Readout Marker (below) for a display of gain
compression at the marker frequency.
Step 12. Observe the readout marker values from the dis-
played menu (left).
37XXXC OM 8-47
MEASUREMENTS GAIN COMPRESSION
Readout
Marker
MENU M7
SEARCH
VALUE
–1.000dB
REFERENCE
MAXIMUM VALUE
DREF MARKER
0dB
VALUE AT REFERENCE
–0.000 dB
SEARCH LEFT
SEARCH RIGHT
–9.56 dBm
SEARCH MRKR VALUES
CH1: 13.753dBm
CH2:
CH3: –1.000 dB
CH4:
TRACKING ON
MARKER READOUT
FUNCTIONS
MENU SU3A
SWEPT POWER
SETUP
SWEPT POWER
FREQUENCY
9.000000000 GHz
PSTART
–25.00 dBm
PSTOP
–5.00 dBm
STEP SIZE
1.00 dB
POWER SWEEP ON
HOLD BUTTON
FUNCTION
MULTIPLE FREQ
GAIN COMPRESSION
RETURN TO SWEPT
FREQUENCY MODE
PRESS <ENTER>
TO SELECT
OR TURN ON/OFF
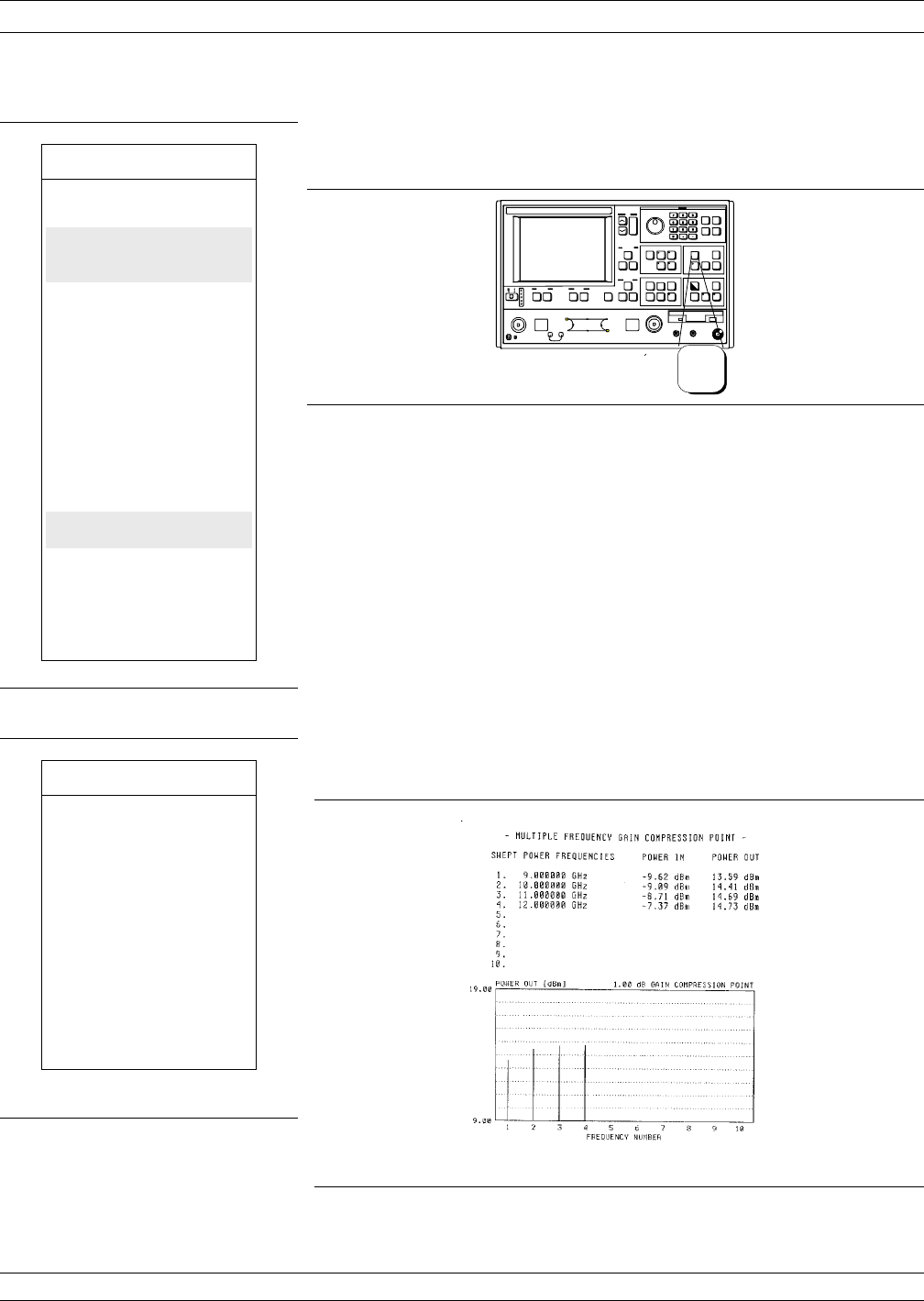
Step 13. Press Setup Menu (below) to return to SWEPT
POWER SETUP menu.
Step 14. Move cursor to SWEPT POWER FREQUENCY
(top left), select the next frequency from the SET
FREQUENCY list, and press Enter.
Step 15. Repeat Steps 11 through 13.
Step 16. Repeat Steps 14 and 15 until all frequencies have
been observed.
Step 17. To examine the phase performance for a swept input
power, AM/PM should be selected. This leads to the
two channel display (Channels 2 and 4) with Chan-
nel 4 active shown below. The sweep mode is contin-
uous to facilitate tuning, Markers are set to the
DReference mode on the active channel.
GAIN COMPRESSION MEASUREMENTS
8-48 37XXXC OM
MENU
CH2-21
REFERENCE PLANE
0.0000mm
MARKER 1
-25.00 dBm
MARKER TO MAX
MARKER TO MIN
D(1-2)
-15.44 dBm
4.17°
MARKER READOUT
FUNCTIONS
Setup
Menu
MENU SU3A
SWEPT POWER
SETUP
SWEPT POWER
FREQUENCY
9.000000000 GHz
PSTART
–25.00 dBm
PSTOP
–5.00 dBm
STEP SIZE
1.00 dB
POWER SWEEP ON
HOLD BUTTON
FUNCTION
MULTIPLE FREQ
GAIN COMPRESSION
RETURN TO SWEPT
FREQUENCY MODE
PRESS <ENTER>
TO SELECT
OR TURN ON/OFF
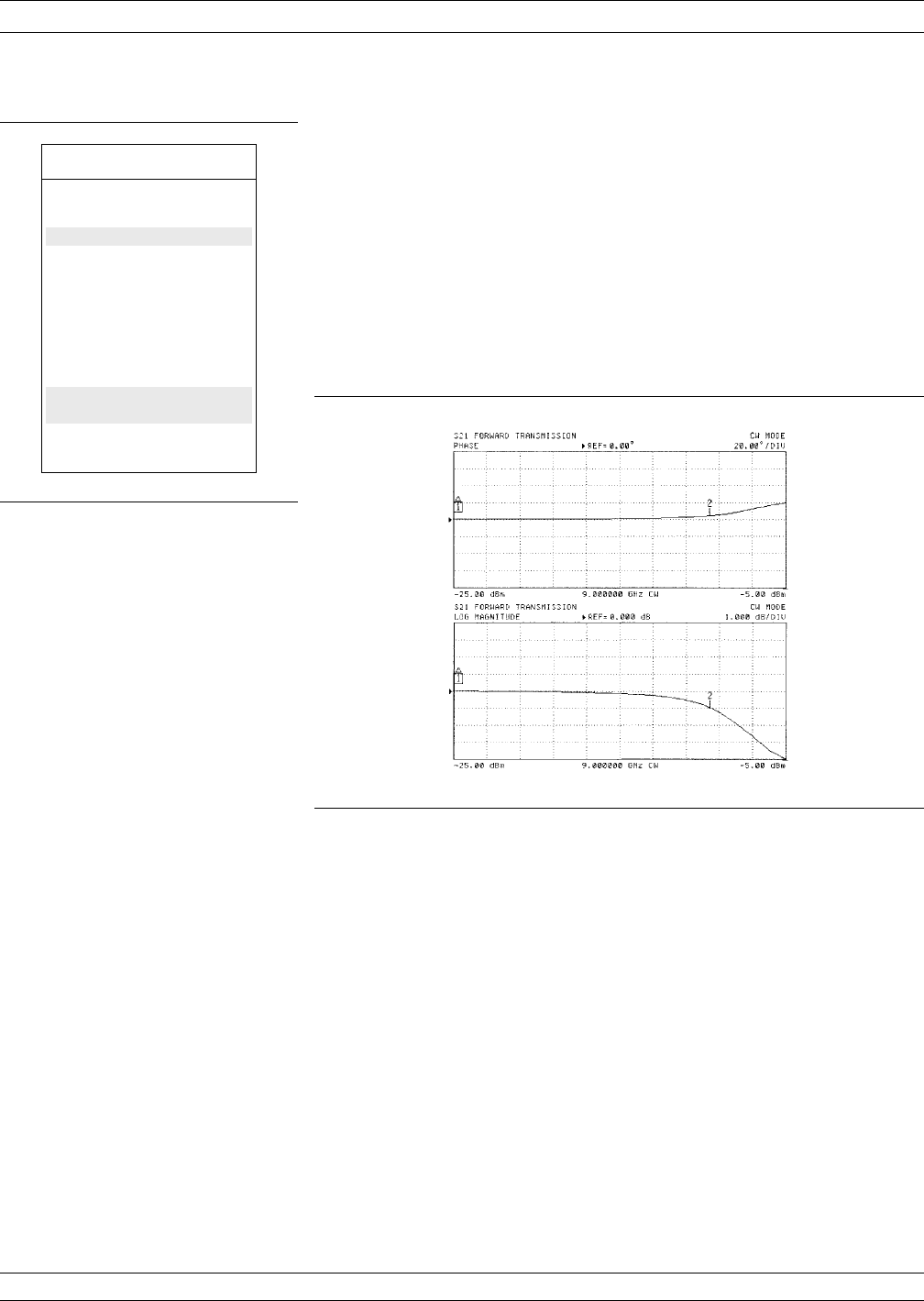
Step 18. Repeat Steps 13 through 16 until all desired fre-
quencies have been observed.
Step 19. If desired, a multiple frequency gain compression
display can be obtained by selecting MULTIPLE
FREQUENCY GAIN COMPRESSION (left) and
pressing Enter.
Step 20. Move cursor to TEST AUT (top left) and press Enter.
Step 21. Observe that the Multiple Frequency Gain Compres-
sion display resembles that shown below.
Step 22. Make desired selection from menu to copy text and
data to hard or floppy disk (top left).
Step 23. The power linearity calibration, receiver calibration,
and DUT normalized data exists in volatile memory.
At this time, the data can be stored for subsequent
recall using the SAVE function.
NOTE
It is prudent to save this calibration; other-
wise, it will be destroyed if you move any-
where in the program except between this
calibration and the S-parameters menu.
37XXXC OM 8-49
MEASUREMENTS GAIN COMPRESSION
MENU GC4
MULTIPLE FREQUENCY
GAIN COMPRESSION
TEST AUT
TEXT DATA
TO HARD DISK
TEXT DATA
TO FLOPPY DISK
SWEPT POWER
GAIN COMPRESSION
RETURN TO SWEPT
FREQUENCY MODE
PRESS <ENTER>
TO SELECT
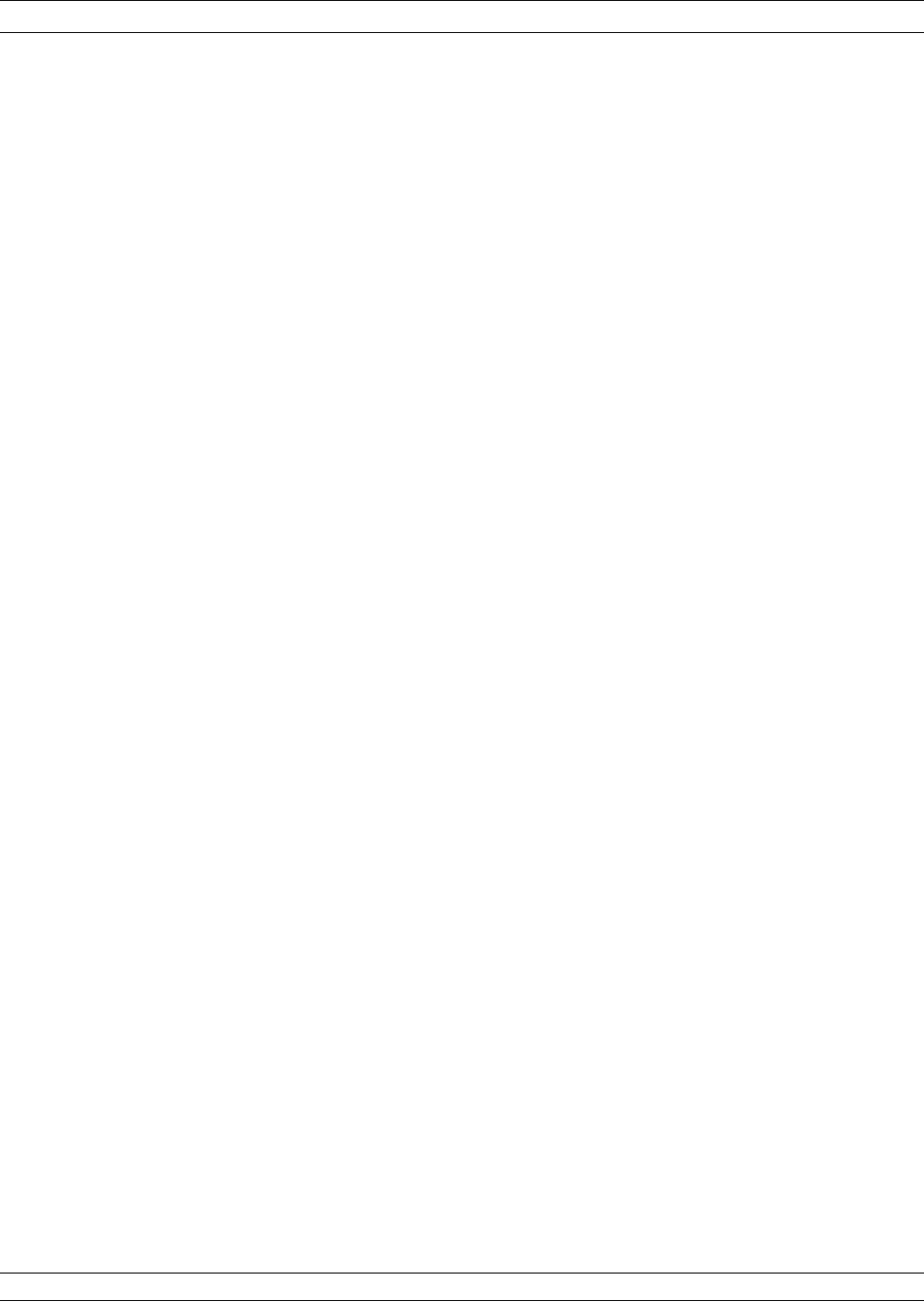
Step 24. Move cursor to RETURN TO SWEPT FRE-
QUENCY MODE and press Enter to exit the gain
compression mode.
NOTE
When exiting the Swept Frequency Power Gain Compres-
sion mode, the DUT should be turned off, unless the user
has selected the proper attenuator settings for standard
swept frequency (S-parameter) operation.
GAIN COMPRESSION MEASUREMENTS
8-50 37XXXC OM
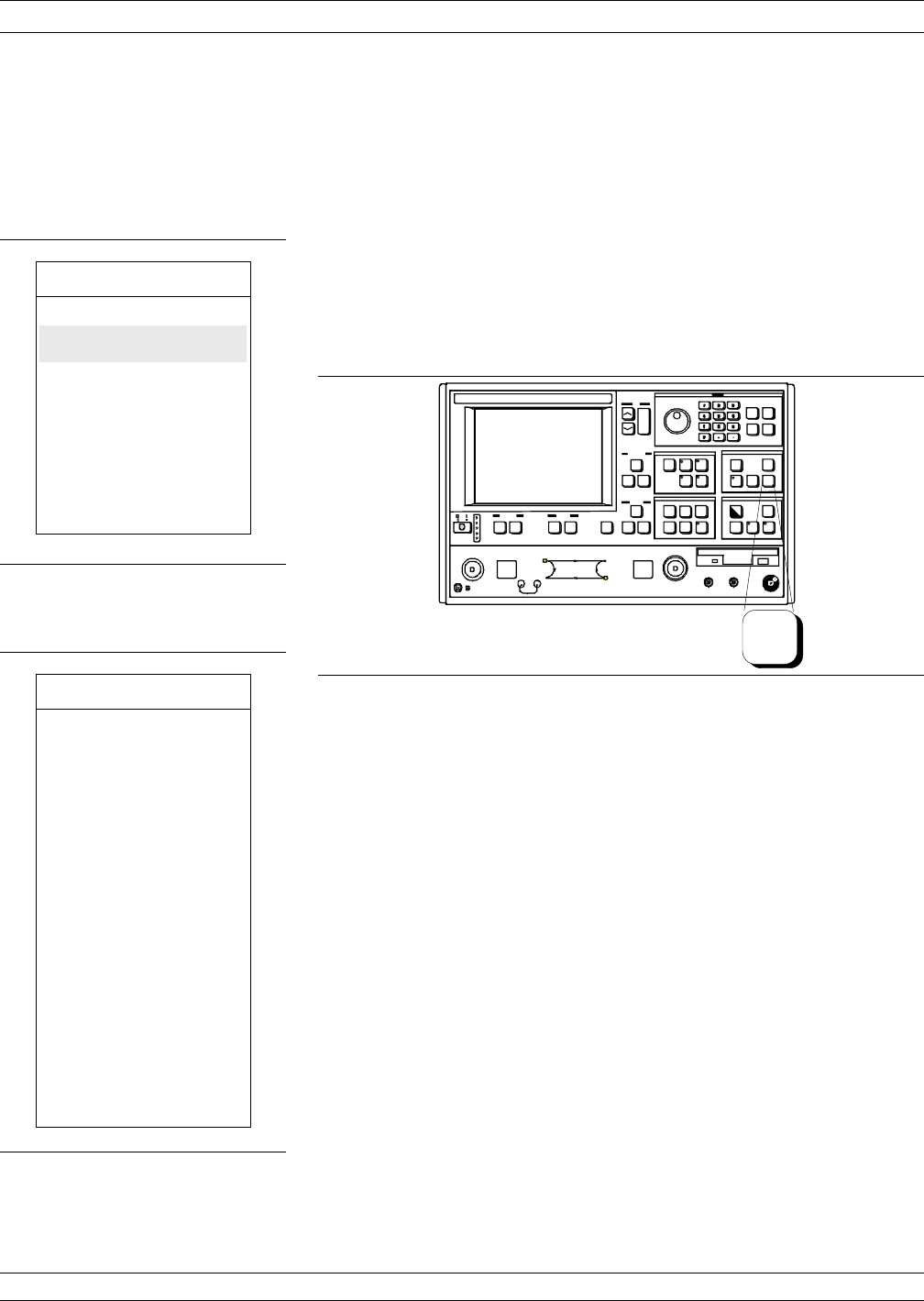
Swept Frequency Gain Compression Measurement
The following procedure describes the Swept Frequency Gain Com-
pression Measurement.
Preliminary: Refer to Figure 8-28 and set the Power Control and Port
1 Attenuator for the values shown in the power plan for the example,
or in the power plan constructed for measurement of a test device.
These power plan values should also be used in the S-parameter cali-
bration that may be performed using the Begin Cal key and menus.
Step 1. Press the Appl key.
Step 2. Move cursor to SWEPT FREQUENCY GAIN
COMPRESSION and press Enter, when menu
APPL (top left) appears.
Step 3. When menu GC3 (bottom left) appears, follow the di-
rections that appear adjacent to the menu, as de-
scribed below:
Move the cursor to NOMINAL OFFSET, enter the
value of any external device(s) connected between
the front panel Input and Output connectors. Press
the Enter key when done.
Optionally, move the cursor to CALIBRATE FOR
FLATNESS, press Enter and follow the instruction
menu as described on the following page.
If a calibration already exists, the menu choice will
indicate CAL EXIST in blue letters.
37XXXC OM 8-51
MEASUREMENTS GAIN COMPRESSION
MENU APPL
ADAPTER REMOVAL
SWEPT FREQUENCY
GAIN COMPRESSION
SWEPT POWER
GAIN COMPRESSION
E/O MEASUREMENTS
O/E MEASUREMENTS
MERGE CAL FILES
PRESS <ENTER>
TO SELECT
MENU GC3
SWEPT FREQUENCY
GAIN COMPRESSION
NOMINAL OFFSET
0.00 dB
CALIBRATE
FOR FLATNESS
(N0 CAL EXISTS)
FLATNESS OFF
CORRECTION
CALIBRATE
RECEIVER
[NO CAL EXISTS)
NORMALIZE S21
(NOT STORED)
GAIN COMPRESSION
POINT (0 dB REF)
1.00 dB
TEST AUT
EXIT APPLICATION
Appl
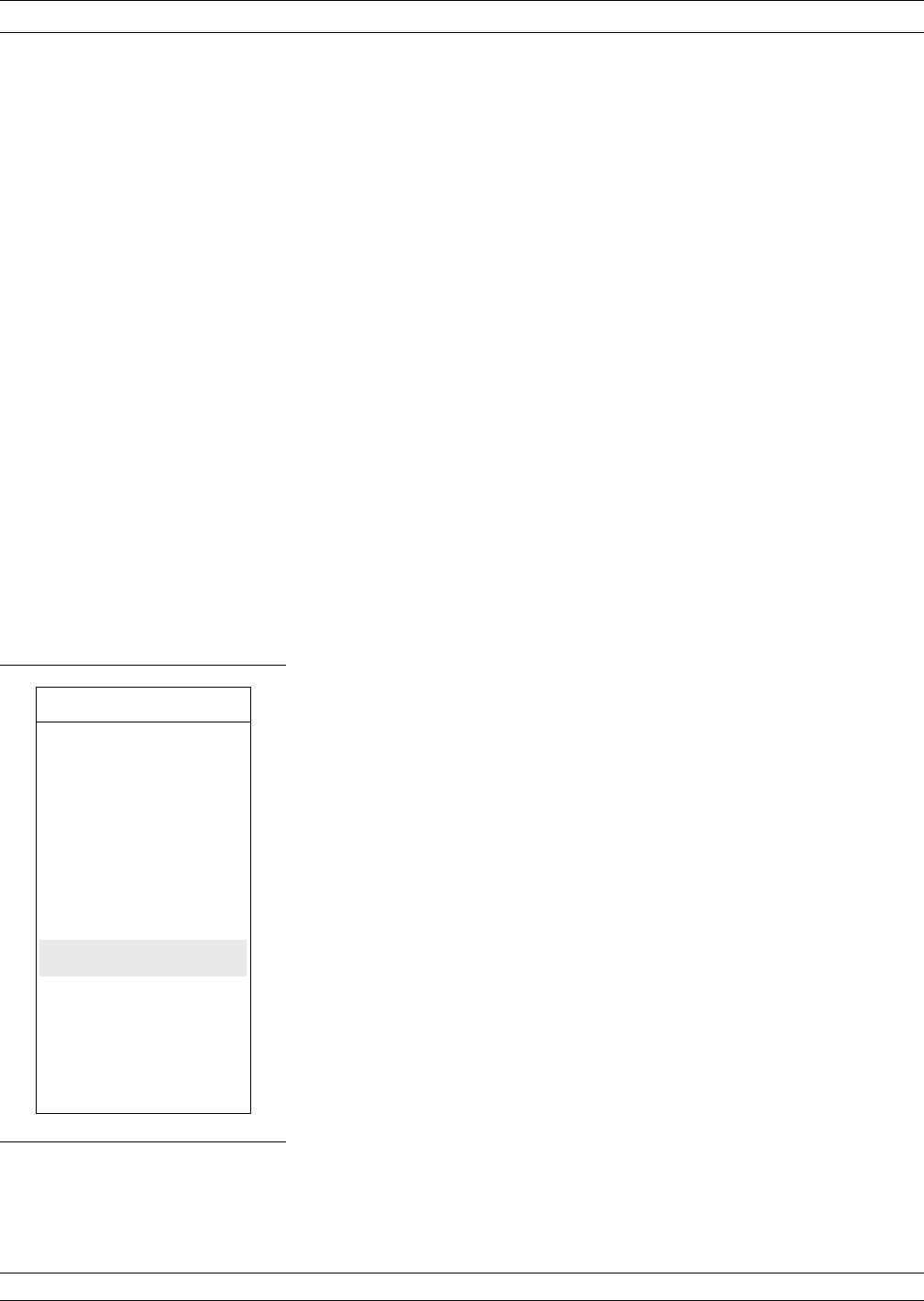
NOTE
This step is not required for a successful
gain compression measurement; however,
calibrating the power from Port 1 (which is
what this step does) provides increased ac-
curacy.
Prepare the power meter as described in the follow-
ing instructions:
a. Preset, zero, and calibrate the power meter.
b. Set power meter offset, if required.
c. Connect the power meter to the dedicated GPIB
interface and the power sensor to the test port.
d. Select <START LINEAR POWER CALIBRA-
TION>.
Connect the power sensor to Port 1.
Set the number of power calibration points.
If, in a previous menu, data points had been set to
401 points, entering 8 provides 50 power points
(every 8th point); entering 4 provides 100 power
point (every 4th point)s, and entering 1 provides 401
power points. The VNA interpolates between power
calibration frequencies.
Enter a POWER TARGET value.
Make this value the same as resulting Port 1 power
value shown in Figure 8-28 (page 8-40). –25 dBm for
the example.
With START FLAT POWER CALIBRATION high-
lighted (bottom left), press Enter to begin the calibra-
tion.
NOTE
When the above calibration finishes, the
source power will have been accurately cali-
brated. In the next step, this power calibra-
tion will be transferred via the through line
to the receiver.
GAIN COMPRESSION MEASUREMENTS
8-52 37XXXC OM
MENU GC_SU8A
CALIBRATE FOR
FLAT PORT POWER
FORWARD
DIRECTION ONLY
101 POINTS
MEASURE 1 PWR
POINT EVERY
1 POINT(S)
POWER TARGET
–25.00 dBm
START FLAT
POWER CALIBRATION
PREVIOUS MENU
PRESS <ENTER>
TO SELECT
TURN KNOW TO
CHANGE NUMBER
OF POINTS
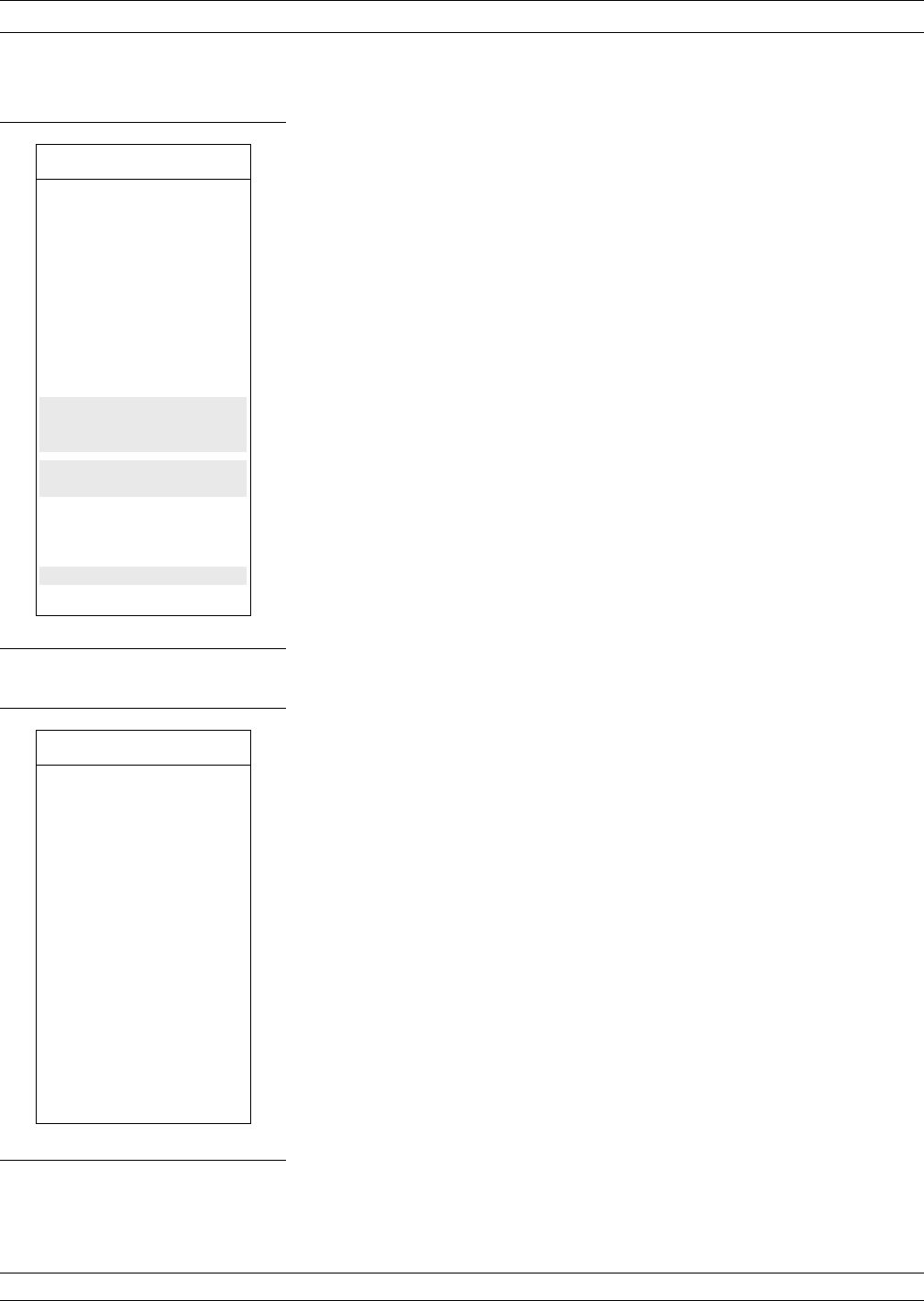
Step 4. Move cursor to CALIBRATE RECEIVER and fol-
low the instructions, as follows:
Connect a through line between Test Port 1 and Test
Port 2. Be sure to include all components that are
part of the measurement path.
Wait until one complete sweep has completed, then
press Enter to store the calibration.
NOTE
It is likely that the trace will be off screen at
the bottom of the display. If so, press
Autoscale to obtain a discernable trace. If
this trace shows vertical instability,
·Press Video IF BW and select REDUCED
(100 Hz) from the menu
·Press Avg/Smooth Menu and select AV-
ERAGING 100 MEAS. PER POINT
from the menu
·Press Average to turn averaging on
Step 5. Press Appl to return to the gain compression menu,
and follow the prompts to return to Menu GC1. Re-
peat Step 4.
Step 6. Move the cursor to NORMALIZE S21 (top left),
press Enter, and follow the menu instructions (bot-
tom left):
Remove the through line and connect the amplifier-
under-test (AUT) between Port 1 and Port 2.
Apply bias to the AUT.
Wait until one complete sweep has completed, then
press Enter to store the normalization measurement.
Step 7. Move the cursor to TEST AUT (top left) and press
Enter.
37XXXC OM 8-53
MEASUREMENTS GAIN COMPRESSION
MENU GC1
SWEPT FREQUENCY
GAIN COMPRESSION
NOMINAL OFFSET
-10.00 dB
CALIBRATE
FOR FLATNESS
(]CAL EXISTS)
FLATNESS
CORRECTION
AT -25.00 dBm
CALIBRATE
RECEIVER
(CAL EXISTS)
NORMALIZE S21
([NOT]STORED)
GAIN COMPRESSION
POINT (0 dB REF)
1.00 dB
TEST AUT
EXIT APPLICATION
MENU GC_SU8A
RECEIVER
CALIBRATION
CONNECT
THROUGHLINE
BETWEEN
TEST PORTS
INCLUDE ANY
COMPONENTS WHICH
ARE PART OF THE
MEASUREMENT PATH
WAIT FOR ONE
COMPLETE SWEEP
BEFORE STORING
PRESS <ENTER>
TO STORE
PRESS <CLEAR>
TO ABORT
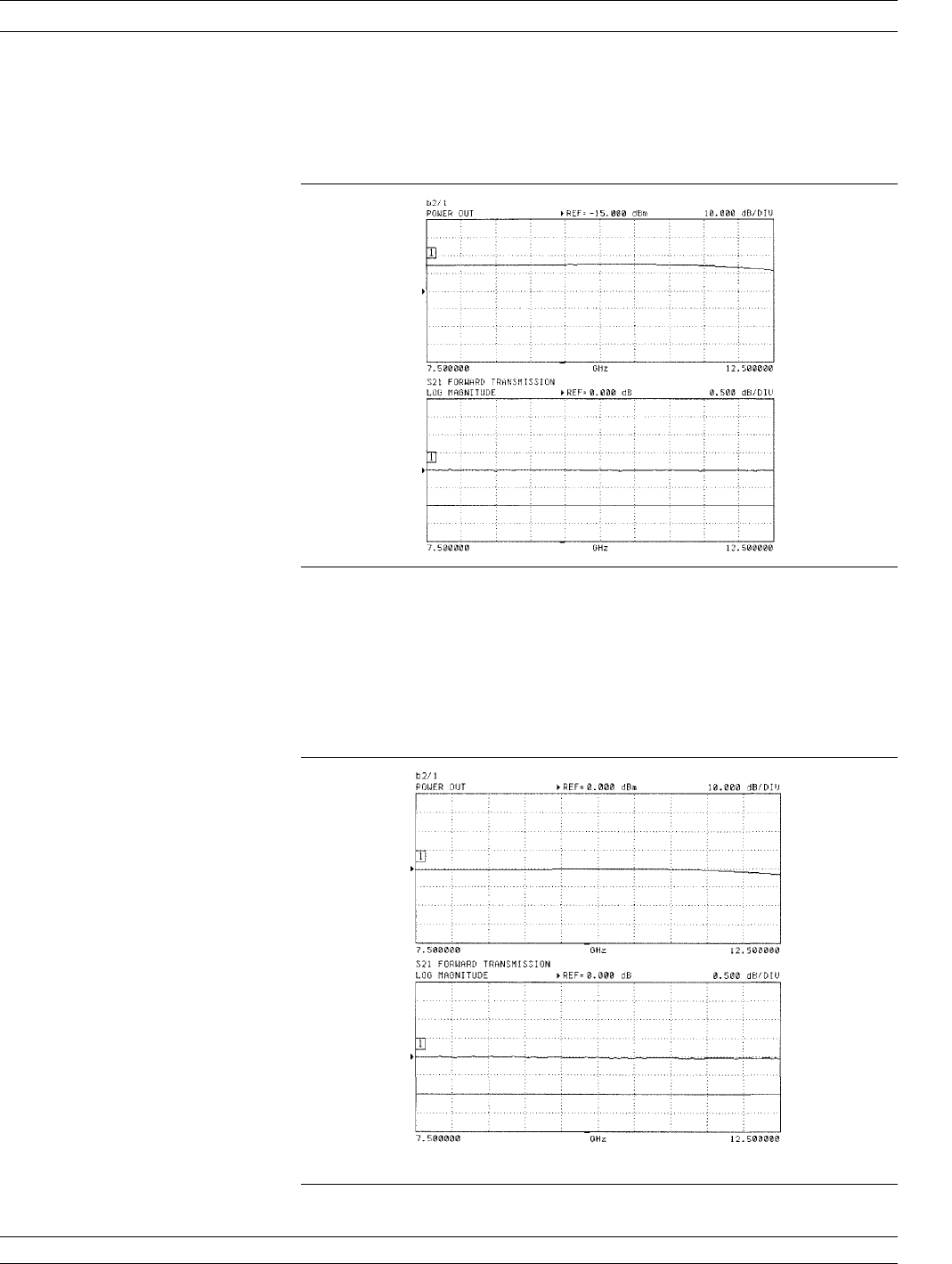
Step 8. Observe that the dual-trace display resembles that
shown below.
Step 9. Note that the top display (Channel 1), shows the
power out from the AUT. For the example test device,
the nominal output power is about 0 dBm with the
input at –25 dBm. To better evaluate this device,
turn on markers and set the Channel 1 reference to
0 dB, as shown below.
GAIN COMPRESSION MEASUREMENTS
8-54 37XXXC OM
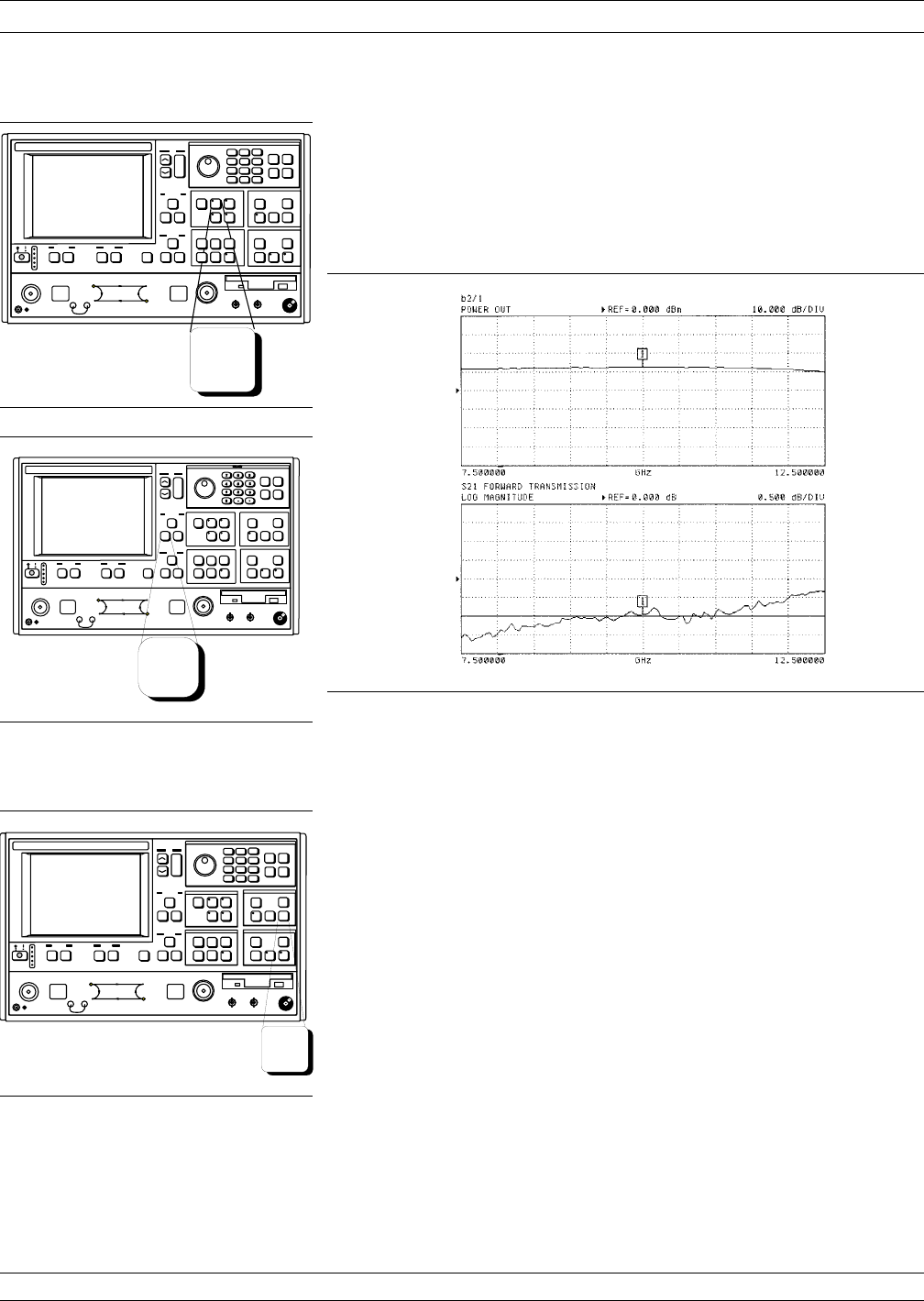
Step 10. Press the Ch1 key (top left) to make channel 1 active.
Step 11. Press the Marker Menu key (middle left), turn on
marker 1, and position it to a desired point on the
trace (below). (Press the Readout Marker key for fre-
quency and amplitude information.)
Step 12. Press the Appl key to return to the TEST SIGNALS
menu (Menu SU2, next page).
37XXXC OM 8-55
MEASUREMENTS GAIN COMPRESSION
789
456
123
0.-
D a t a E n t r y
C h 1
Marker
Menu
789
456
123
0.-
D a t a E n t r y
A p p l
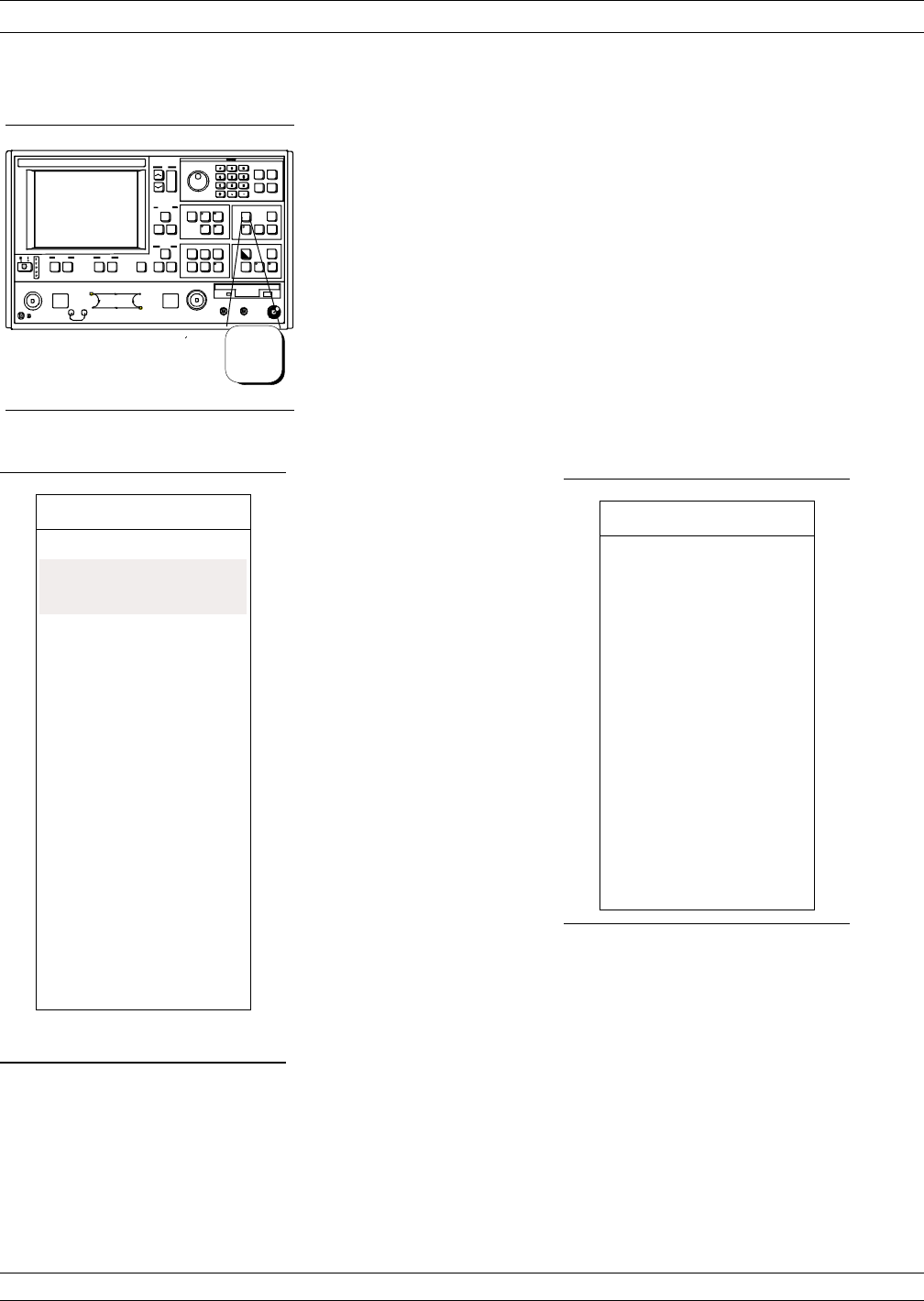
Step 13. Press the Setup Menu key (top left), select POWER
CONTROL (bottom left) and increase the value
while observing compression in channel 3 (S21).
NOTE
The rotary knob or the keypad can be used
to set the POWER CONTROL value. In us-
ing the rotary knob, the displayed value
does not change in real time with movement
of the control. Change occurs after the rota-
tion of the knob is complete.
Step 14. Press the Marker Menu key again, and observe the
displayed Ch 3 trace and the marker values from the
displayed menu (below).
Step 15. The power linearity calibration, receiver calibration,
and DUT normalized data exists in volatile memory.
At this time, the data can be stored for subsequent
recall using the SAVE function.
NOTE
It is prudent to save this calibration; other-
wise, it will be destroyed if you move any-
where in the program except between this
calibration and the S-parameters menu.
GAIN COMPRESSION MEASUREMENTS
8-56 37XXXC OM
Setup
Menu
MENU SU2
MARKER 1
ALL DISPLAYED
CHANNELS
CH1-S11 USER
10.000000 GHz
12.06 dBm
CH 2 - S12
CH 3 - S21
10.000000 GHz
-0.992 dB
CH 4 - S21
MARKER TO MAX
MARKER TO MIN
MARKER READOUT
FUNCTIONS
PRESS <ENTER>
TO SELECT
MENU SU2
TEST SIGNALS
POWER CONTROL
5.47 dB
0TO–20.00 dB
PORT 1 ATTN
0*10dB(0–70)
PORT 1 POWER
–1.53 dBm
PORT 2 ATTN
0*10dB(0–40)
CALIBRATE
FOR FLATNESS
(CAL EXISTS)
FLATNESS
CORRECTION
AT –11.53 dBm
PORT 2 POWER
0.00 dBm
EXIT APPLICATION
PRESS <ENTER>
TO SELECT
OR TURN ON/OFF
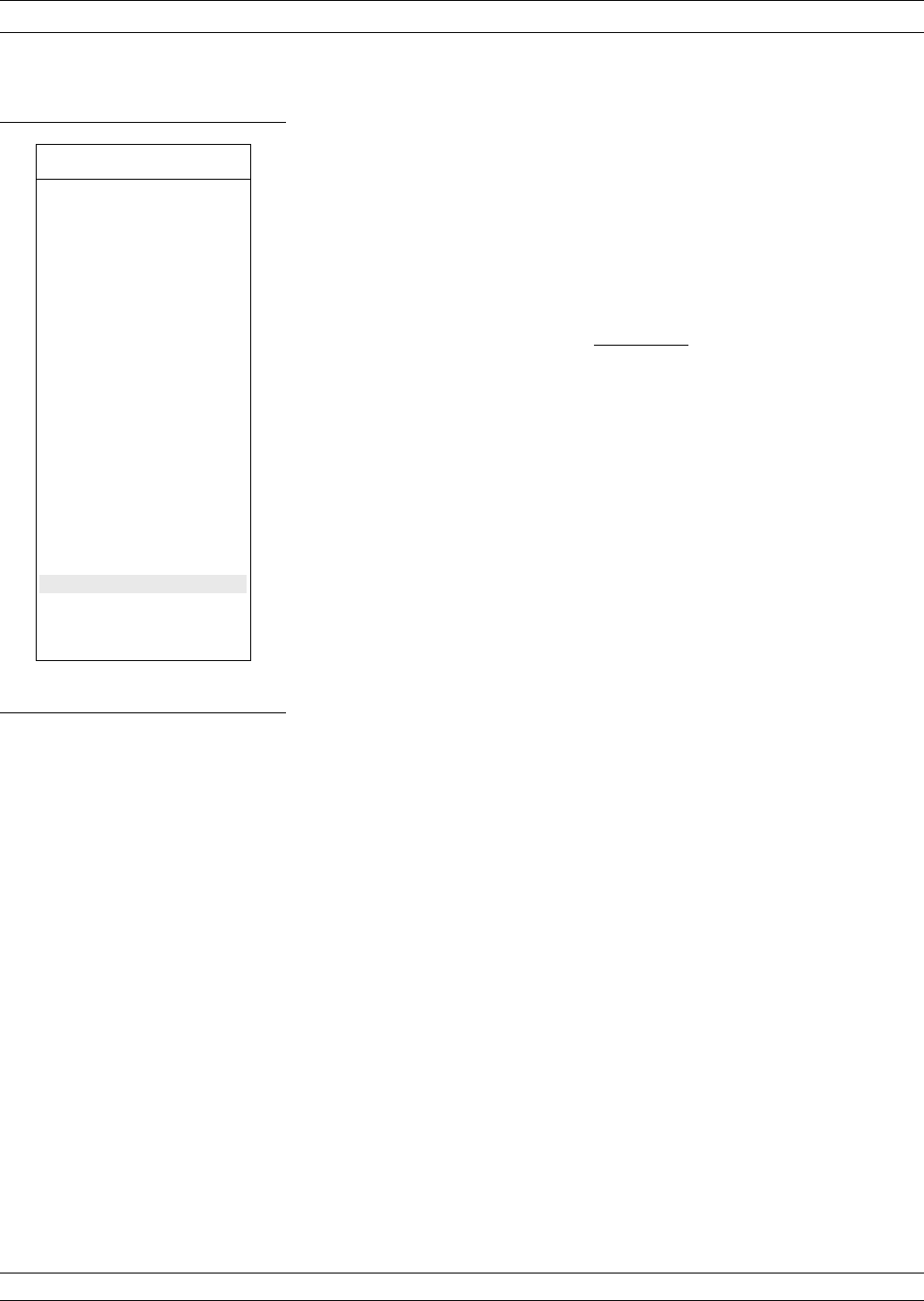
Step 16. Move cursor to RETURN TO SWEPT
FREQUENCY MODE and press Enter to exit the
gain compression mode.
Step 17. Press the Appl key to return to the TEST SIGNALS
menu (left), highlight EXIT APPLICATION and
press Enter to exit the gain compression measure-
ment area.
CAUTION
When exiting the Swept Frequency Power Gain Compres-
sion mode, the DUT should be turned off, unless the user
has selected the proper attenuator settings for standard
swept frequency (S-parameter) operation.
37XXXC OM 8-57
MEASUREMENTS GAIN COMPRESSION
MENU SU2
TEST SIGNALS
POWER CONTROL
5.47 dB
0TO–20.00 dB
PORT 1 ATTN
0*10dB(0–70)
PORT 1 POWER
–1.53 dBm
PORT 2 ATTN
0*10dB(0–40)
CALIBRATE
FOR FLATNESS
(CAL EXISTS)
FLATNESS
CORRECTION
AT –11.53 dBm
PORT 2 POWER
0.00 dBm
EXIT APPLICATION
PRESS <ENTER>
TO SELECT
OR TURN ON/OFF
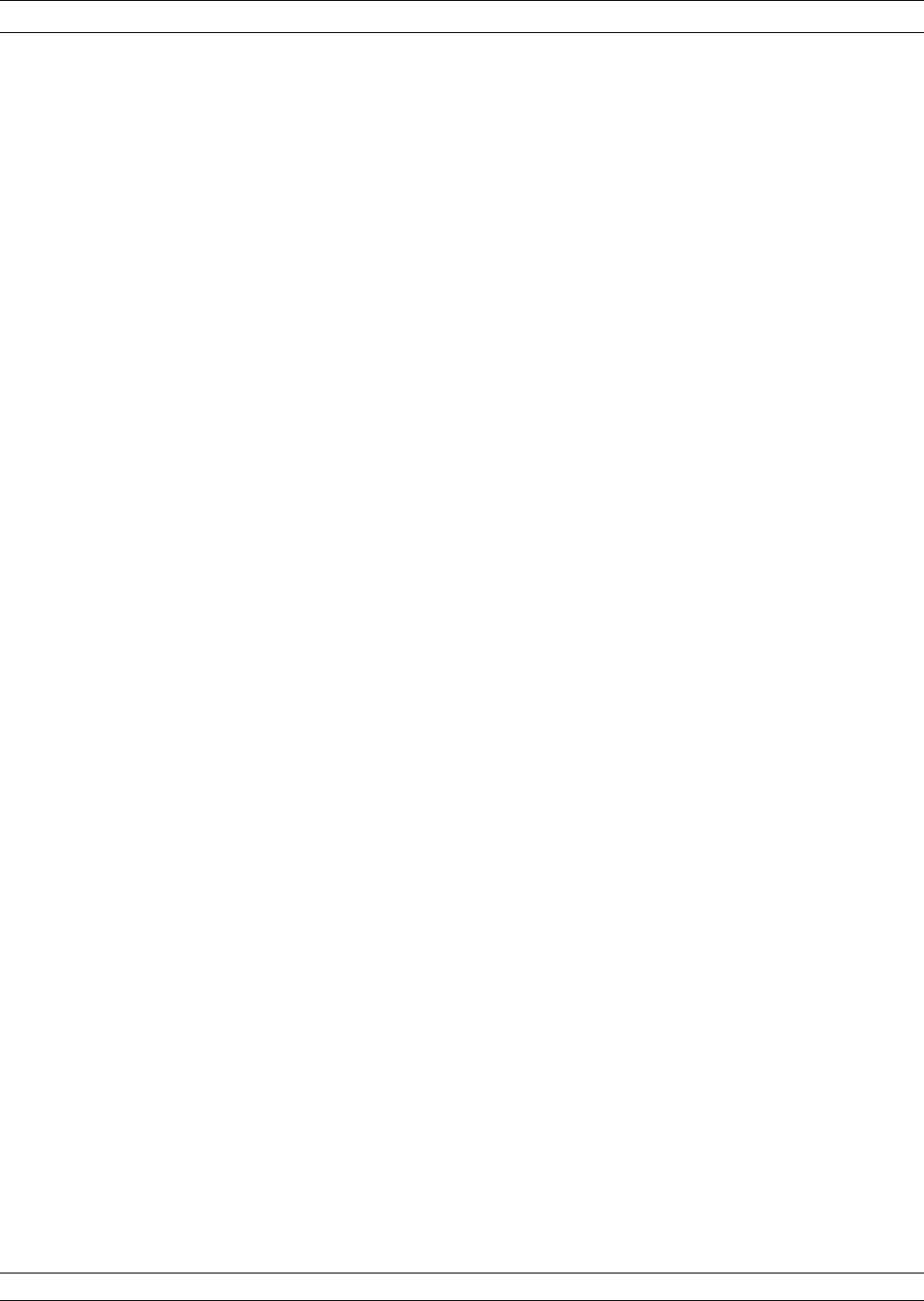
8-9 RECEIVER MODE The Receiver Mode provides three distinct modes of operation:
qSweep/Source Lock mode, phase locks the internal source
qSynthesizer/Tracking mode, lets the receiver track a 67XXB,
68XXXB, or 69XXXA synthesizer
qSet-On mode, lets the VNA operate as a tuned receiver
Source Lock Mode The Source Lock mode enables the 37XXXC to phase lock to its inter-
nal source.
Tracking Mode In the Tracking Mode, the 37XXXC steers its second local oscillator
frequency and phase signal so as to phase-lock itself to the reference
signal. Typically the source is a synthesizer, since it must be accurate
to better than ±10 MHz for the 37XXXC to achieve lock. Due to the in-
herent resolution of the 37XXXC, frequency resolution is limited to 1
kHz intervals. If Option 3 is installed frequency resolution is limited to
1 Hz.
For receive frequencies outside the indicated test set range, the use of
external mixers and a synthesizer is required. Dual Source Control is
required in this case.
Set-on Mode In the Set-On mode, the source lock circuitry of the 37XXXC is com-
pletely by-passed. Reference signals are no longer necessary for system
operation. This allows all of the 37XXXC samplers to operate over
their full dynamic range. As a result, the source and the 37XXXC must
be locked to the same 10 MHz time base, otherwise coherent detection
is not possible. Only synthesized sources may be used in this mode.
Dual source control is required.
Due to the inherent resolution of the 37XXXC local oscillators, fre-
quency resolution is limited to 1 kHz intervals over the frequency
range of the VNA. If Option 3 is installed, frequency resolution is lim-
ited to 1 Hz.
RECEIVER MODE MEASUREMENTS
8-58 37XXXC OM
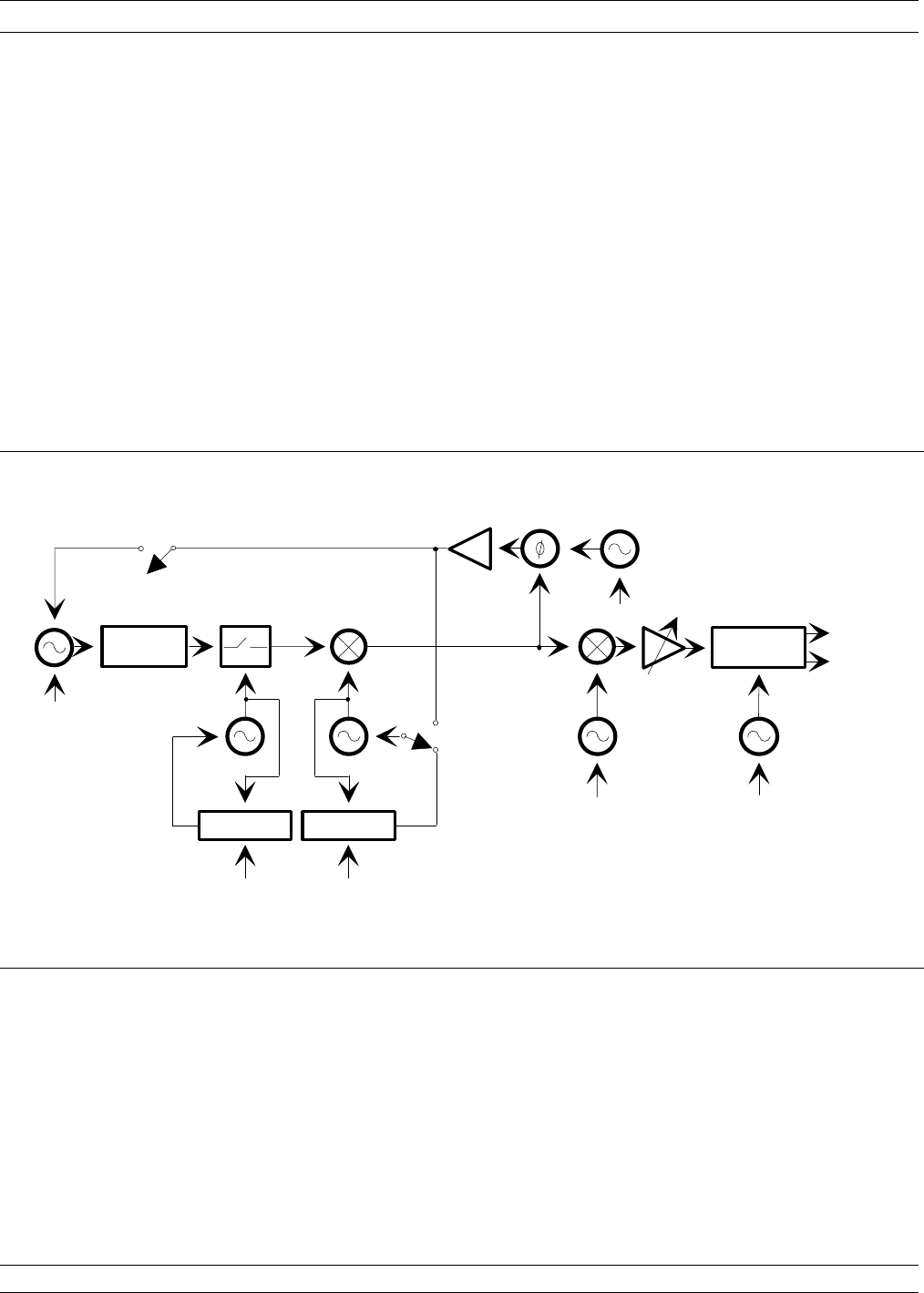
Receiver Mode Block
Diagram The block diagram shown in Figure 8-31 shows how the system is con-
figured for all of the possible modes of operation. With the switches set
as shown, the system operates in the Set-On mode. LO1 and LO2 are
pre-set to allow only a prescribed signal to be detected by the synchro-
nous detector. With the switch in SOURCE LOCK position the system
is operating in the internal source-lock mode. With the switch in the
TRACKING position, the system is in the synthesizer tracking mode.
Receiver Mode Menus The menus associated with the Receiver Mode are described in the al-
phabetical listing (Appendix A) under their call sign: RCV1, RCV2,
RCV3, etc.
Procedure, Receiver Mode
Operation A detailed procedure for operation using the Receiver Mode option is
provided in the following pages.
37XXXC OM 8-59
MEASUREMENTS RECEIVER MODE
SOURCE LOCK ANALOG LOCK SIGNAL
SAMPLER
1ST L.O. 2ND L.O.
TRACKING
SET ON
10 MHz
(SYNTHESIZER) TRACKING
SOURCE LOCK/
SET ON
10 MHz
10 MHz
10 MHz
REAL
IMAGINARY
2.5 MHz
3RD L.O.
2.42 MHz 4TH L.O.
80 KHz
10 MHz 10 MHz
SYNCHRONOUS
DETECTOR
PLLPLL
RF MEASURE
CIRCUIT
Figure 8-31. 37XXXC Phase Lock Modes
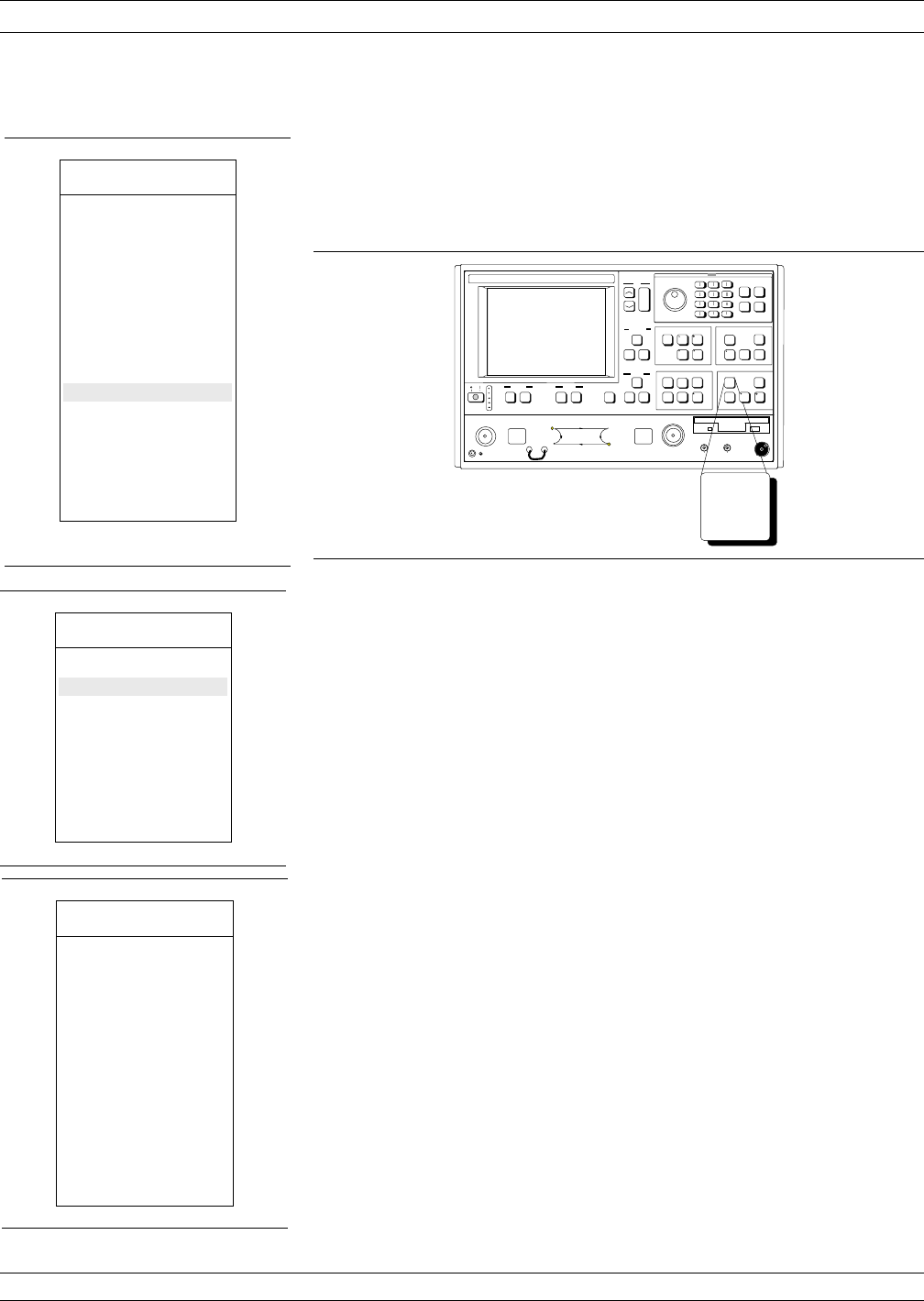
Operating Procedure, Receiver Mode
The three operational modes that comprise the Receiver Mode can be
set up as follows:
Step 1. Press the Option Menu key (below).
Step 2. When menu OPTNS (top left) appears, select RE-
CEIVER MODE.
Step 3. When menu RCV1 (middle left) appears, select ei-
ther STANDARD (Step 4) or USER DEFINED
(Step 5). Your selection depends on the application.
Step 4. The Standard mode uses the Source Lock mode for
operation with the internal source. The user has no
control over selections within the Standard Mode.
Because entering the standard mode from the User
Defined Mode erases the current stored calibration
data, a warning menu (RCV3, bottom left) appears
when STANDARD is selected. Press Enter to enter
into the Standard mode or press Clear to abort.
NOTE
Spur Reduction: Normal/OFF: Spur Reduction Off may be
selected when making non-ratioed measurements or using
the Set-On Receiver mode. Under those measurement con-
ditions, it may reduce high level noise. In normal
S-parameter measurement mode, Spur Reduction should
remain “Normal,” as the noise level is not affected.
RECEIVER MODE MEASUREMENTS
8-60 37XXXC OM
Option
Menu
MENU RCV3
STANDARD
RECEIVER MODE
WARNING:
CONTINUING
MAY INVALIDATE
CURRENT
SETUP AND
CALIBRATION
PRESS <ENTER>
TO CONTINUE
PRESS <CLEAR>
TO ABORT
MENU RCV1
RECEIVER MODE
STANDARD
USER DEFINED
SOURCE CONFIG
SPUR REDUCTION
NORMAL/OFF
PRESS <ENTER>
TO SELECT
MENU OPTNS
OPTIONS
TRIGGERS
REAR PANEL
OUTPUT
DIAGNOSTICS
MULTIPLE
SOURCE
CONTROL
RECEIVER MODE
SOURCE CONFIG
RF ON/OFF
DURING RETRACE
PRESS <ENTER>
TO SELECT
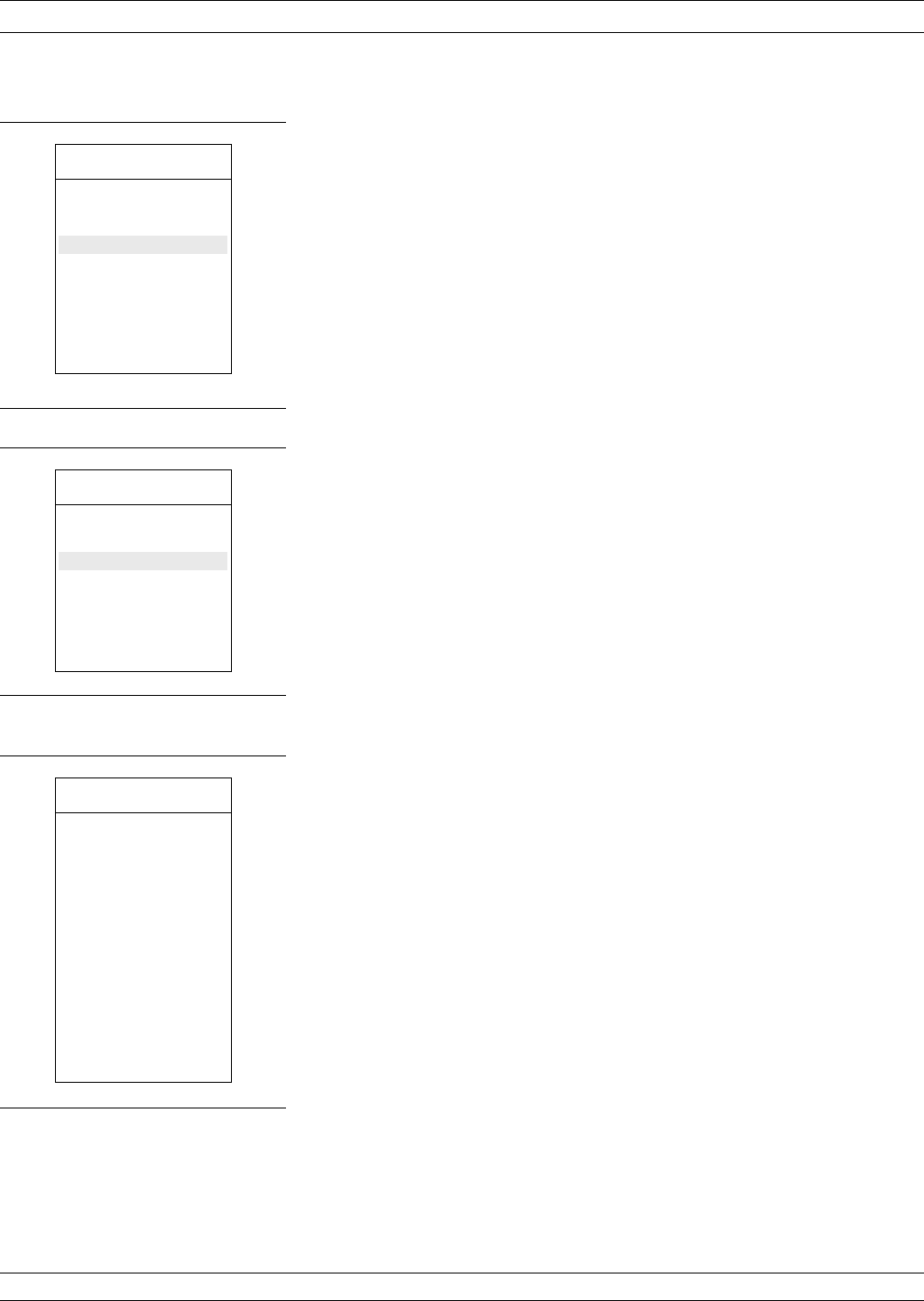
Step 5. Selecting USER DEFINED RECEIVER MODE in
menu RCV1 brings menu RCV 2 to the screen. When
menu RCV 2 appears, the last mode selected is high-
lighted in red. The default selection is SOURCE
LOCK.
Source Lock, Tracking or Set-On modes can be se-
lected from this menu. When a mode is selected, in-
formation about that mode is displayed on the
screen. This information describes the mode and the
capabilities required of the RF source.
MEASUREMENTS RECEIVER MODE
37XXXC OM 8-61
MENU RCV1
RECEIVER MODE
STANDARD
USER DEFINED
SOURCE CONFIG
SPUR REDUCTION
NORMAL/OFF
PRESS <ENTER>
TO SELECT
MENU RCV2
USER DEFINED
RECEIVER MODE
SOURCE LOCK
TRACKING
SET ON
PRESS ENTER
TO SELECT
MENU RCV4
USER DEFINED
RECEIVER MODE
WARNING:
CONTINUING
MAY INVALIDATE
CURRENT
SETUP AND
CALIBRATION
PRESS <ENTER>
TO CONTINUE
PRESS <CLEAR>
TO ABORT
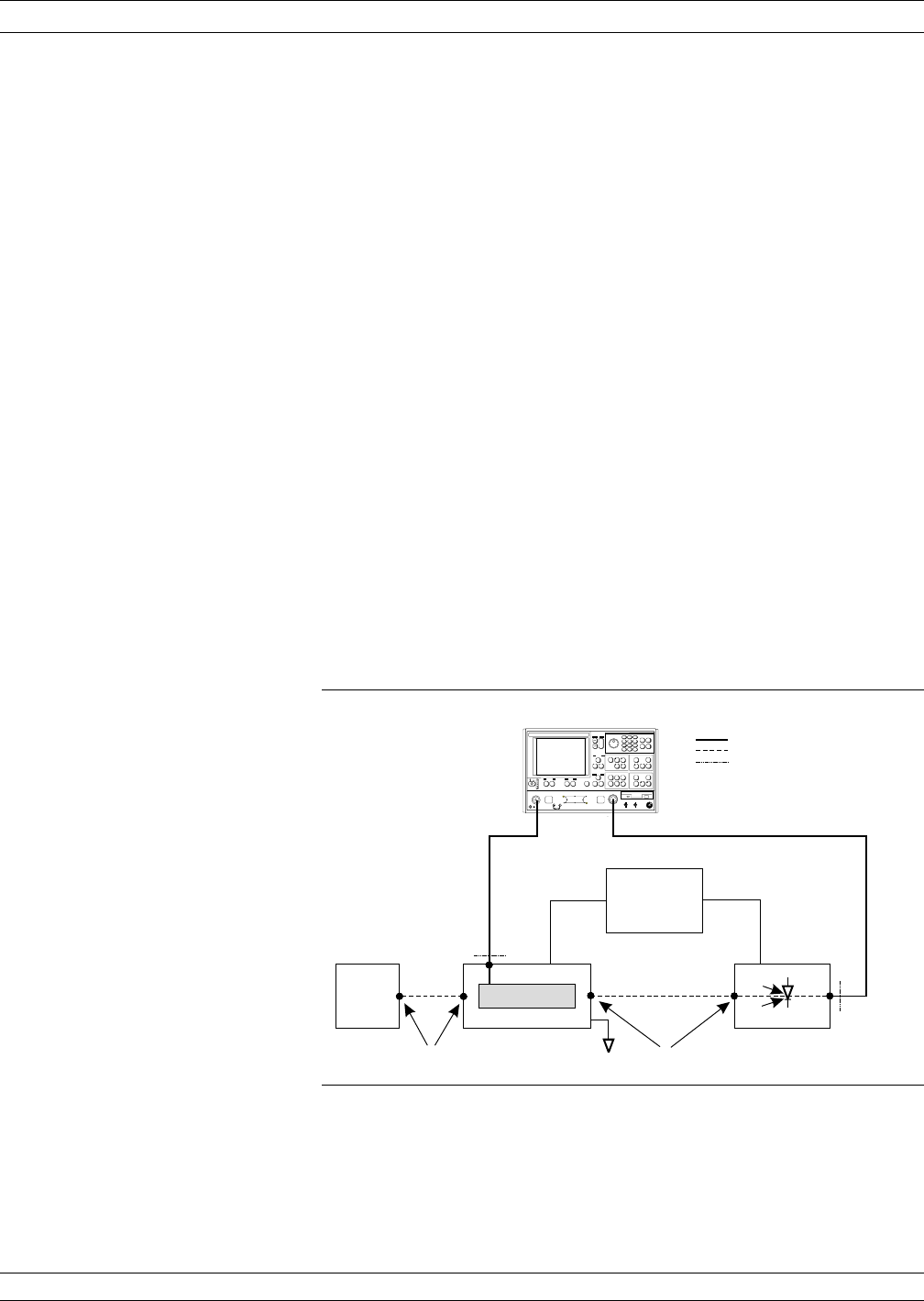
8-10 OPTICAL
APPLICATION Optical applications are divided into two measurement categories,
electro-optical (E/O) and opto-electrical (O/E).
E/O measurements can be performed with the 372XXC/373XXC series
VNAs using the built-in E/O measurement application. On-screen
menu-driven procedures guide you through the set-up and calibration
required for E/O measurements of optical modulators such as band-
width, flatness, and group delay.
O/E measurements of a photo-diode or photo-receiver can be per-
formed with the 372XXC/373XXC series VNAs by using the built-in
O/E measurement application. On-screen-menu-driven procedures
guide you through the set-up and calibration required for O/E mea-
surements such as bandwidth, flatness, and group delay.
E/O Measurements Optical modulators modulate digital data signals over a light wave
carrier and send it over fiber optic networks. Since a VNA is only capa-
ble of generating and measuring electrical signals, a laser source is re-
quired to provide optical input to the modulator DUT and a photo-di-
ode/photo-receiver is required to convert the modulator output back to
an electrical signal that can be measured by the VNA. The MN4765A
(65 GHz characterized photo-diode) is used with the following proce-
dure. The equipment set up for an E/O measurement is shown in Fig-
ure 8-32, below.
The E/O measurement application de-embeds the response of the
photo-diode/photo-receiver transfer standard from a 12-term calibra-
tion to enable measurements of a modulator DUT.
OPTICAL APPLICATION MEASUREMENTS
8-62 37XXXC OM
789
456
123
0.-
DataEntry
Laser
Modulator
(DUT)
Photo-diode
(Transfer Standard)
Power
Supply
372XXC/373XXC
FC/PC FC/PC
Bias
(3Vto5V)
Bias
(3Vto5V)
Optical Fiber Connectors
FC/PC: Flat Fiber Surface (White)
Microwave Signal
Optical Signal
12-term Calibration Reference Plane
s
Figure 8-32. E/O Measurement Setup
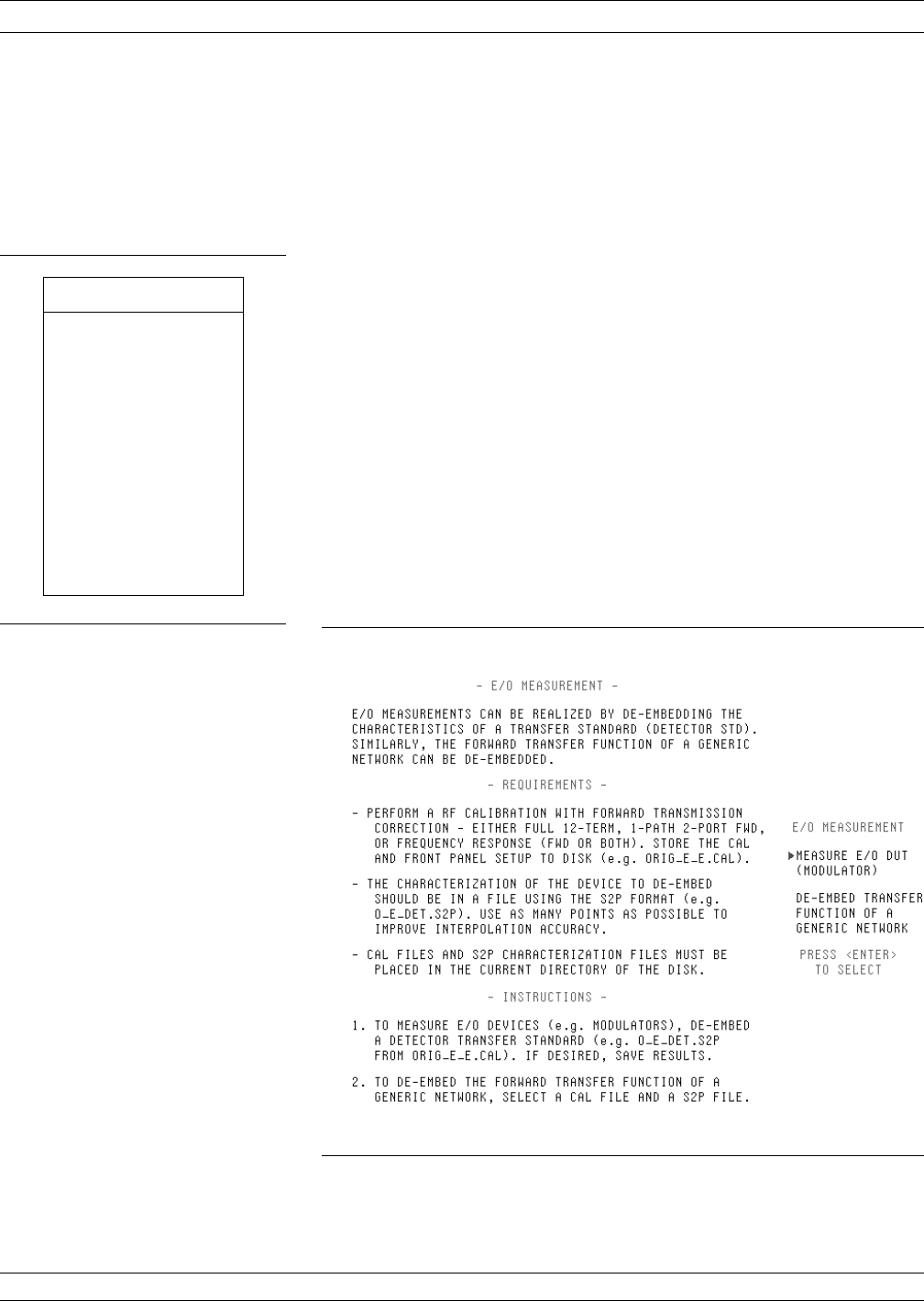
E/O Measurement Procedure
The following procedure will explain ways of using the MN4765A
photo-diode to make an E/O measurement of a modulator DUT. The
same set up can be used for a user characterized photo-diode as well.
Step 1. Set-up the measurement as shown in Figure 8-32.
Step 2. Perform a 12-term calibration on the VNA over the
frequency range of interest with reference planes at
the DUT input and the photo-diode output. (Refer to
section 7-4 for the 12-term calibration steps.)
Step 3. Press Save/Recall to save the calibration and set-up
to the hard disk or a floppy disk.
Step 4. Press the APPL key to display the applications menu
(left).
Step 5. Move the cursor to E/O MEASUREMENT and press
Enter.
This brings up the step-by-step procedure, Fig-
ure 8-33, for making the measurement.
37XXXC OM 8-63
MEASUREMENTS OPTICAL APPLICATION
MENU APPL
APPLICATIONS
ADAPTER REMOVAL
SWEPT FREQUENCY
GAIN COMPRESSION
SWEPT POWER
GAIN COMPRESSION
E/O MEASUREMENT
O/E MEASUREMENT
MERGE CAL FILES
PRESS <ENTER>
TO SELECT
Figure 8-33. E/O Measurement Menu
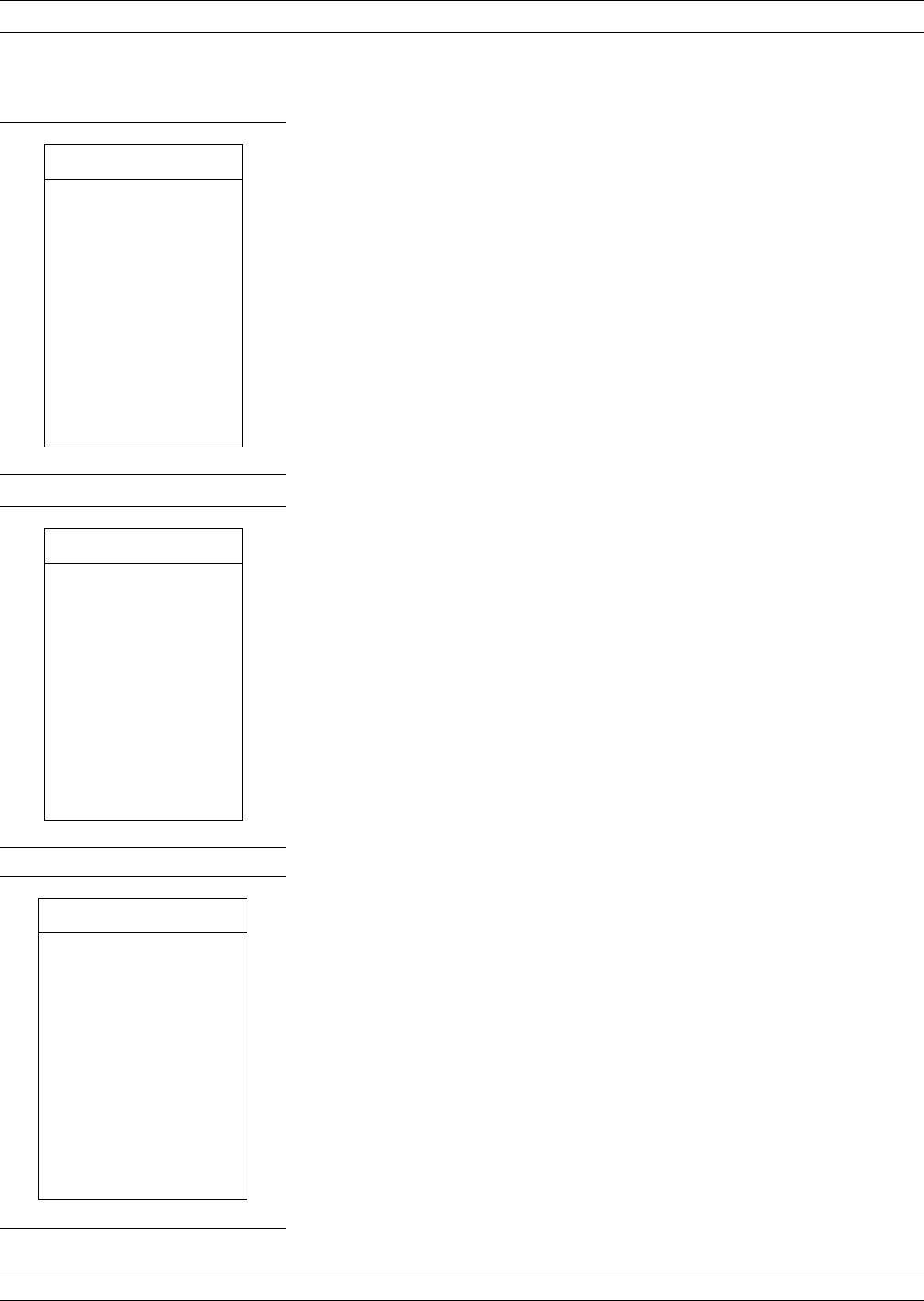
Step 6. Press Enter to select MEASURE E/O DUT (MODU-
LATOR).
This brings up MENU DE3 (top left).
Step 7. Select READ CALIBRATION FILE FROM HARD
DISK or READ CALIBRATION FILE FROM
FLOPPY DISK depending on where the 12-term cali-
bration was saved in Step 3.
This bring up MENU DSK2 (middle left).
Step 8. Select the calibration file and press Enter.
Step 9. Read the S2P file (characterization data file) for the
photo-diode transfer standard. This will de-embed
the photo-diode for an E/O measurement (MENU
DE3A, bottom left).
NOTE
If an S2P file is not available, it can be gen-
erated from the characterization data pro-
vided by the vendor. This is explained on
page 8-71.
The VNA now displays the measurement of the mod-
OPTICAL APPLICATION MEASUREMENTS
8-64 37XXXC OM
MENU DE3
E/O MEASUREMENT
ORIGINAL CAL FILE
WITH FWD TRANS
CORRECTION
READ CAL FILE
FROM HARD DISK
READ CAL FILE
FROM FLOPPY DISK
PRESS <ENTER>
TO SELECT
PRESS <CLEAR>
TO ABORT
MENU DSK2
SELECT FILE
TO READ
TESTCAL CAL
PREVIOUS MENU
PRESS <ENTER>
TO SELECT
PRESS <1> FOR
PREVIOUS PAGE
PRESS <2> FOR
NEXT PAGE
MENU DE3A
E/O MEASUREMENT
TRANSFER STANDARD
TO BE DE-EMBEDDED
(DETECTOR STD)
READ S2P FILE
FROM HARD DISK
READ S2P FILE
FROM FLOPPY DISK
PRESS <ENTER>
TO SELECT
PRESS <CLEAR>
TO ABORT
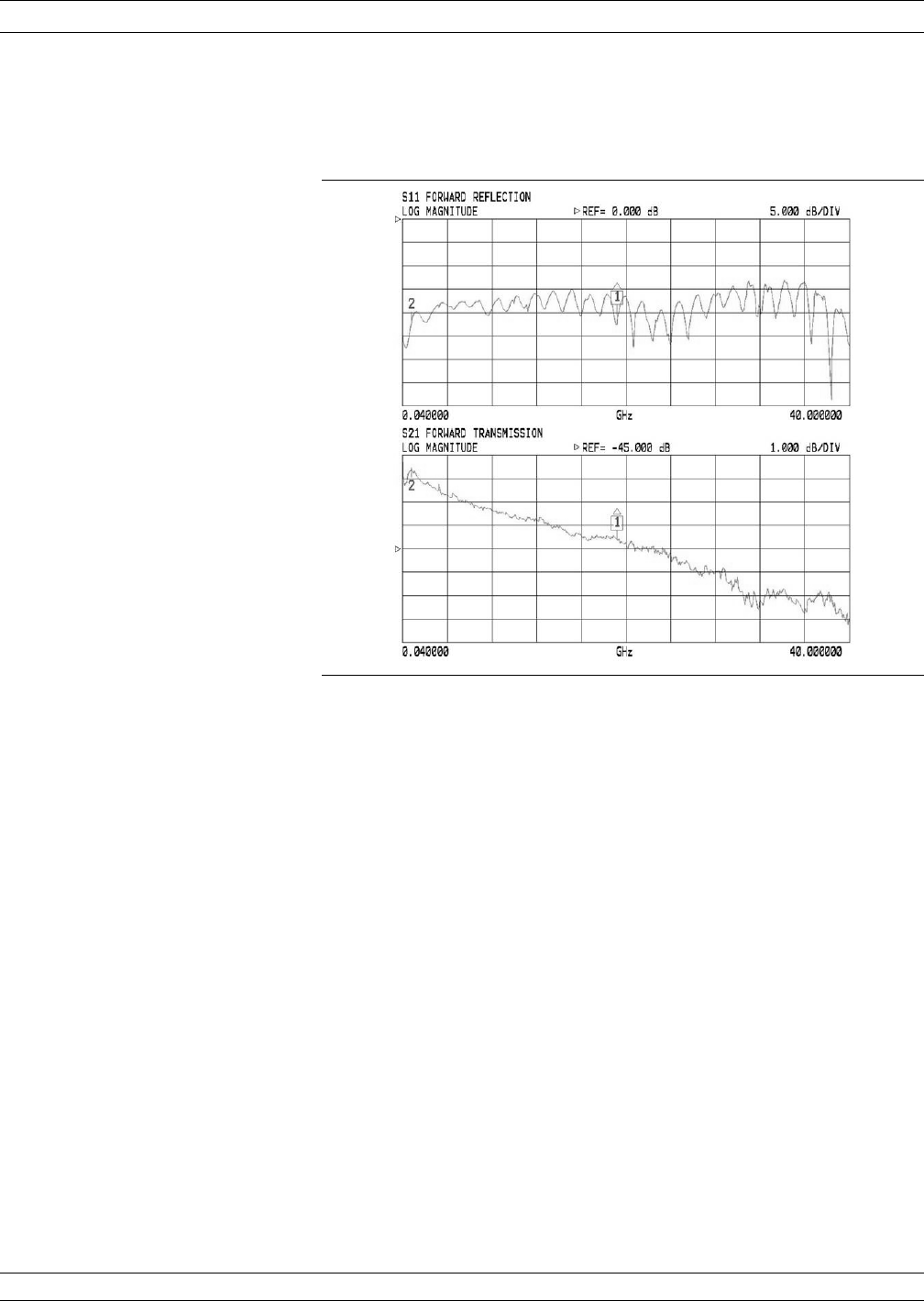
ulator DUT. An example measurement of a 40 Gb/s
NRZ modulator is shown below.
Step 10. Press SAVE/RECALL and save this de-embedded cali-
bration to the hard disk or the floppy disk.
Note that the S11 graph displays the electrical return loss (port
match) of the modulator and S21 represents the transfer function of
the modulator. The bandwidth of the modulator can be calculated from
the S21 data by setting the delta markers or using the marker search
function to find the 3 dB change in magnitude. The 3 dB bandwidth of
the modulator measured in this example is 24 GHz.
O/E Measurements Photo-diodes/photo-receivers convert an optical signal into an electri-
cal signal. Bandwidth measurements can be made on a photo-di-
ode/photo-receiver by stimulating its input with a modulated optical
source and measuring the output signal. A laser and a characterized
37XXXC OM 8-65
MEASUREMENTS OPTICAL APPLICATION
Figure 8-34. E/O Measurement of a 40 Gb/s NRZ Modulator
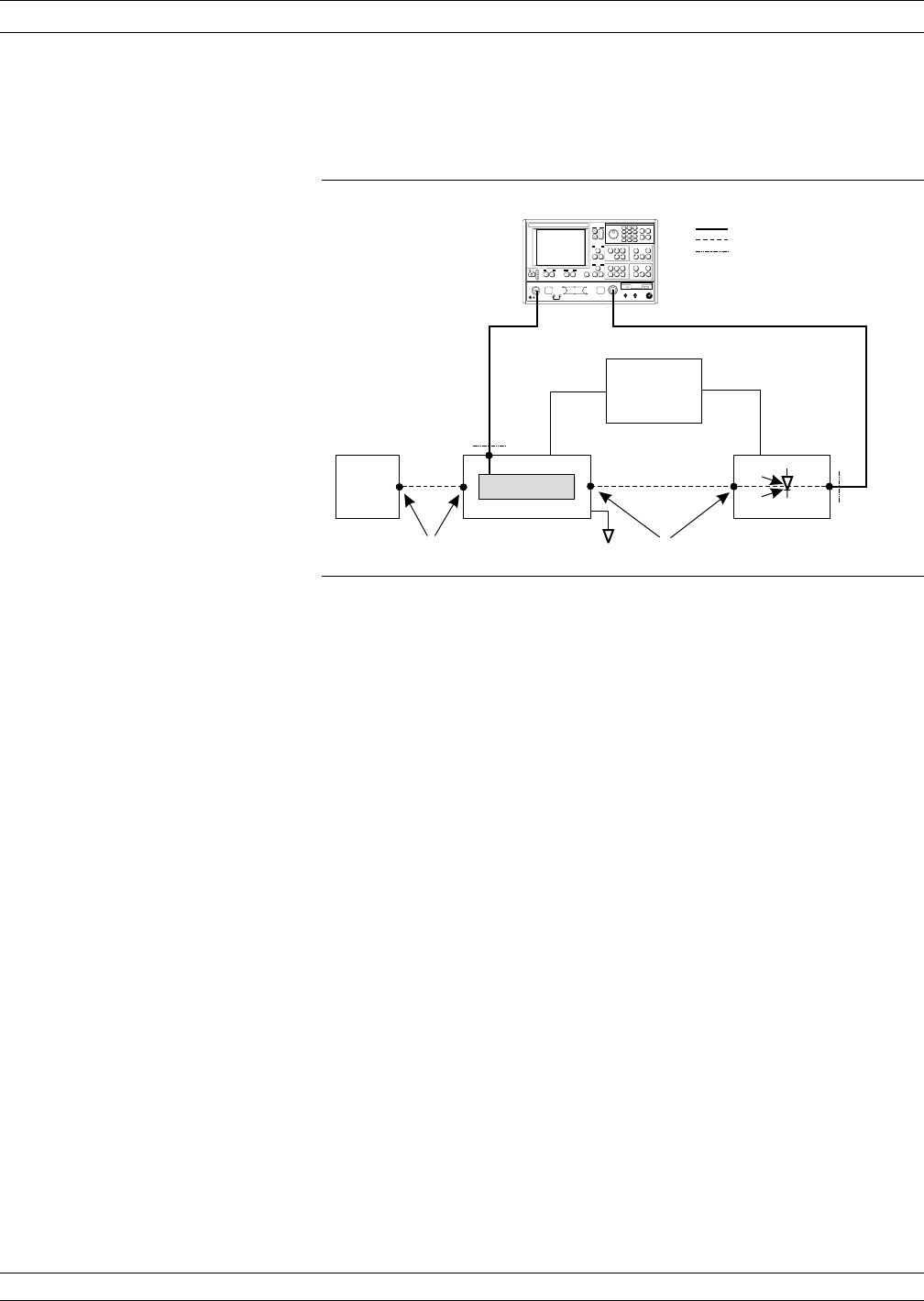
modulator are required, in addition to the VNA, to make O/E measure-
ments. See Figure 8-35, below, for the equipment set-up.
The O/E measurement application de-embeds the response of the mod-
ulator transfer standard from a 12-term calibration to enable mea-
surements of the photo-diode DUT.
O/E Measurement Procedure
The following procedure will explain ways of obtaining characteriza-
tion data for a modulator and then how to use it to make an O/E mea-
surement of a photo-receiver.
Step 1. Set-up the measurement as shown in Figure 8-35,
above.
Step 2. Perform a 12-term calibration on the VNA over the
frequency range of interest with reference planes at
the modulator input and the photo-receiver DUT
output. (Refer to section 7-4 for the 12-term calibra-
tion steps.)
Step 3. Press Save/Recall to save the calibration and set up
to the hard disk or a floppy disk.
OPTICAL APPLICATION MEASUREMENTS
8-66 37XXXC OM
789
456
123
0.-
DataEntry
Laser
Modulator
(Transfer Standard)
Photo-diode
(DUT)
Power
Supply
372XXC/373XXC
FC/PC FC/PC
Bias
(3Vto5V)
Bias
(3Vto5V)
Optical Fiber Connectors
FC/PC: Flat Fiber Surface (White)
Microwave Signal
Optical Signal
12-term Calibration Reference Plane
s
Figure 8-35. O/E Measurement Set-up
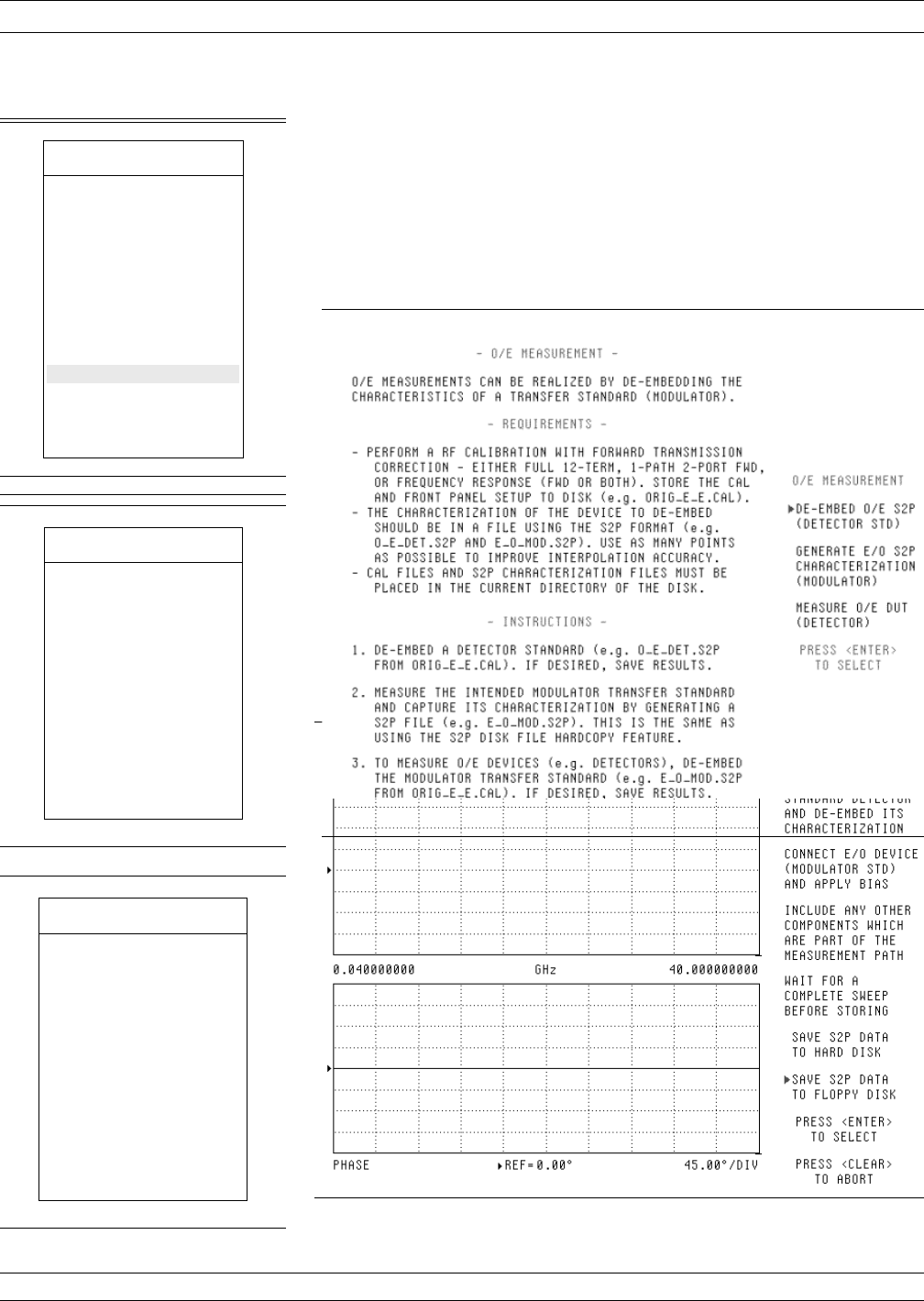
Step 4. Press the APPL key to display the applications menu
(left).
Step 5. Move the cursor to O/E MEASUREMENT and press
Enter.
This brings up the step-by-step procedure for making
the measurement as shown in Figure 8-37, below.
37XXXC OM 8-67
MEASUREMENTS OPTICAL APPLICATION
MENU DSK2
SELECT FILE
TO READ
TESTCAL CAL
PREVIOUS MENU
PRESS <ENTER>
TO SELECT
PRESS <1> FOR
PREVIOUS PAGE
PRESS <2> FOR
NEXT PAGE
MENU DE5A
DE-EMBED E/O S2P
TRANSFER STANDARD
TO BE DE-EMBEDDED
(DETECTOR STD)
READ S2P FILE
FROM HARD DISK
READ S2P FILE
FROM FLOPPY DISK
PRESS <ENTER>
TO SELECT
PRESS <CLEAR>
TO ABORT Figure 8-36. Generate E/O S2P Characterization Menu
Figure 8-37. O/E Measurement Menu
MENU APPL
APPLICATIONS
ADAPTER REMOVAL
SWEPT FREQUENCY
GAIN COMPRESSION
SWEPT POWER
GAIN COMPRESSION
E/O MEASUREMENT
O/E MEASUREMENT
MERGE CAL FILES
PRESS <ENTER>
TO SELECT
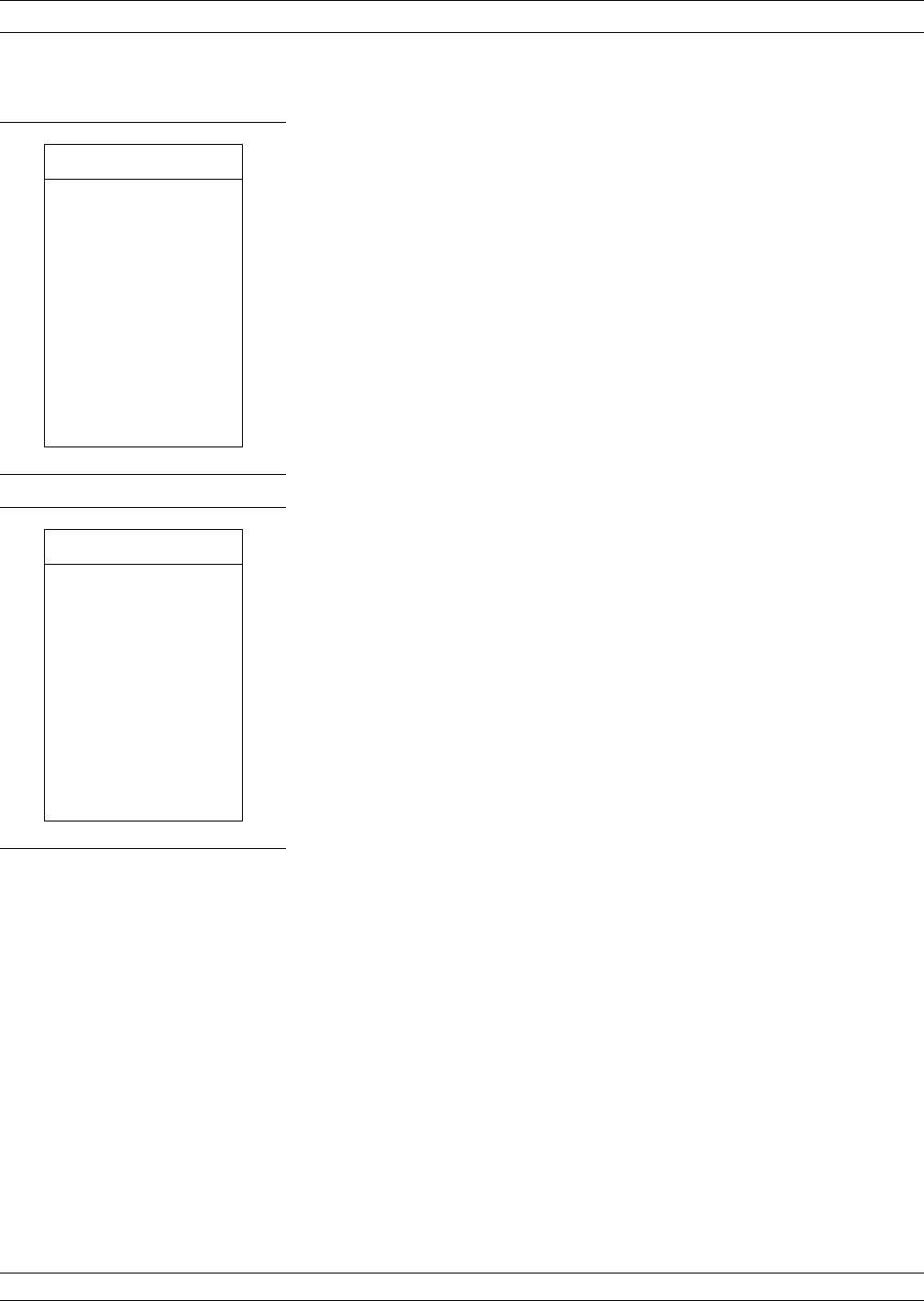
The measurement of the photo-receiver DUT relies
on a characterized modulator standard. If a charac-
terized modulator is not available, an S2P file can be
created by using a characterized photo-diode and
de-embedding it from the 12-term calibration per-
formed in Step 2.
Step 6. With the measurement set-up as shown in Fig-
ure 8-35, select DE-EMBED O/E S2P (DETECTOR
STD).
This brings up MENU DE5 (top left).
Step 7. Select READ CALIBRATION FILE FROM HARD
DISK or READ CALIBRATION FILE FROM
FLOPPY DISK depending on where the 12-term cali-
bration was saved in Step 3.
This brings up MENU DSK2 (middle left).
Step 8. Select the calibration file and press Enter.
Step 9. Select READ THE S2P FILE FROM HARD DISK or
READ THE S2P FILE FROM FLOPPY DISK
(MENU DE5A, bottom left). This is the characteriza-
tion data file for the photo-diode transfer standard.
This will de-embed the photo-diode for an O/E mea-
surement.
Step 10. Move the cursor to GENERATE E/O S2P CHARAC-
TERIZATION (MODULATOR STD) and press Enter.
This will generate an S2P characterization file for
the modulator and opens the menu shown in Fig-
ure 8-36, below.
Once the modulator characterization S2P file has
been generated, it can be used as a transfer standard
for the photo-receiver DUT measurement.
After the characterization file has been saved, the
OPTICAL APPLICATION MEASUREMENTS
8-68 37XXXC OM
MENU DE7
O/E MEASUREMENT
ORIGINAL CAL FILE
WITH FWD TRANS
CORRECTION
READ CAL FILE
FROM HARD DISK
READ CAL FILE
FROM FLOPPY DISK
PRESS <ENTER>
TO SELECT
PRESS <CLEAR>
TO ABORT
MENU DSK2
SELECT FILE
TO READ
TESTCAL CAL
PREVIOUS MENU
PRESS <ENTER>
TO SELECT
PRESS <1> FOR
PREVIOUS PAGE
PRESS <2> FOR
NEXT PAGE
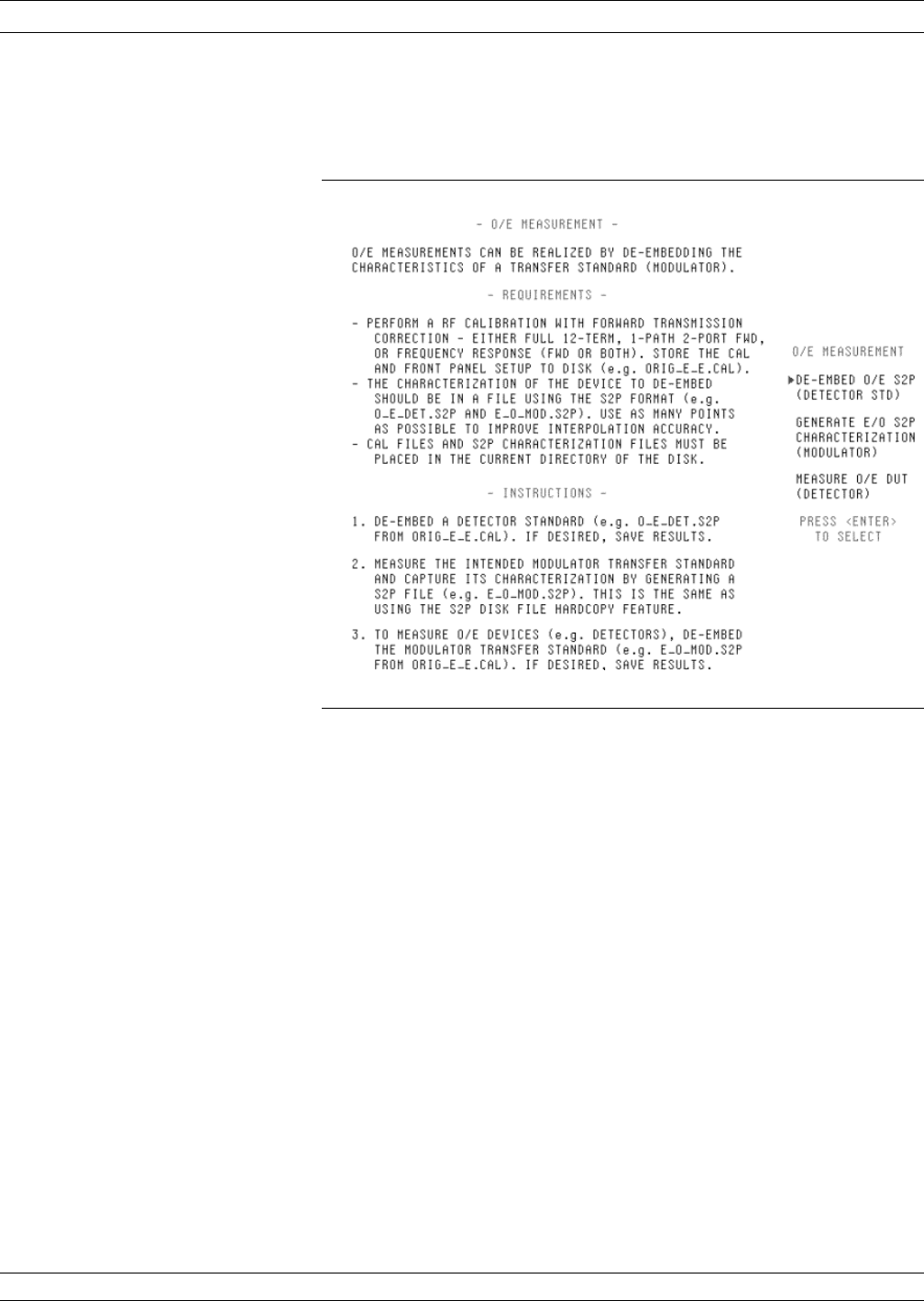
VNA returns to the O/E measurement menu shown
in Figure 8-38, below.
Step 11. Move the cursor to MEASURE O/E DUT (DETEC-
TOR) and press Enter.
This brings up MENU DE7 (top left).
Step 12. Select READ CALIBRATION FILE FROM HARD
DISK or READ CALIBRATION FILE FROM
FLOPPY DISK depending on where the original
12-term calibration was saved in Step 3.
This brings up MENU DSK2 (lower left).
37XXXC OM 8-69
MEASUREMENTS OPTICAL APPLICATION
Figure 8-38. O/E Measurement Menu
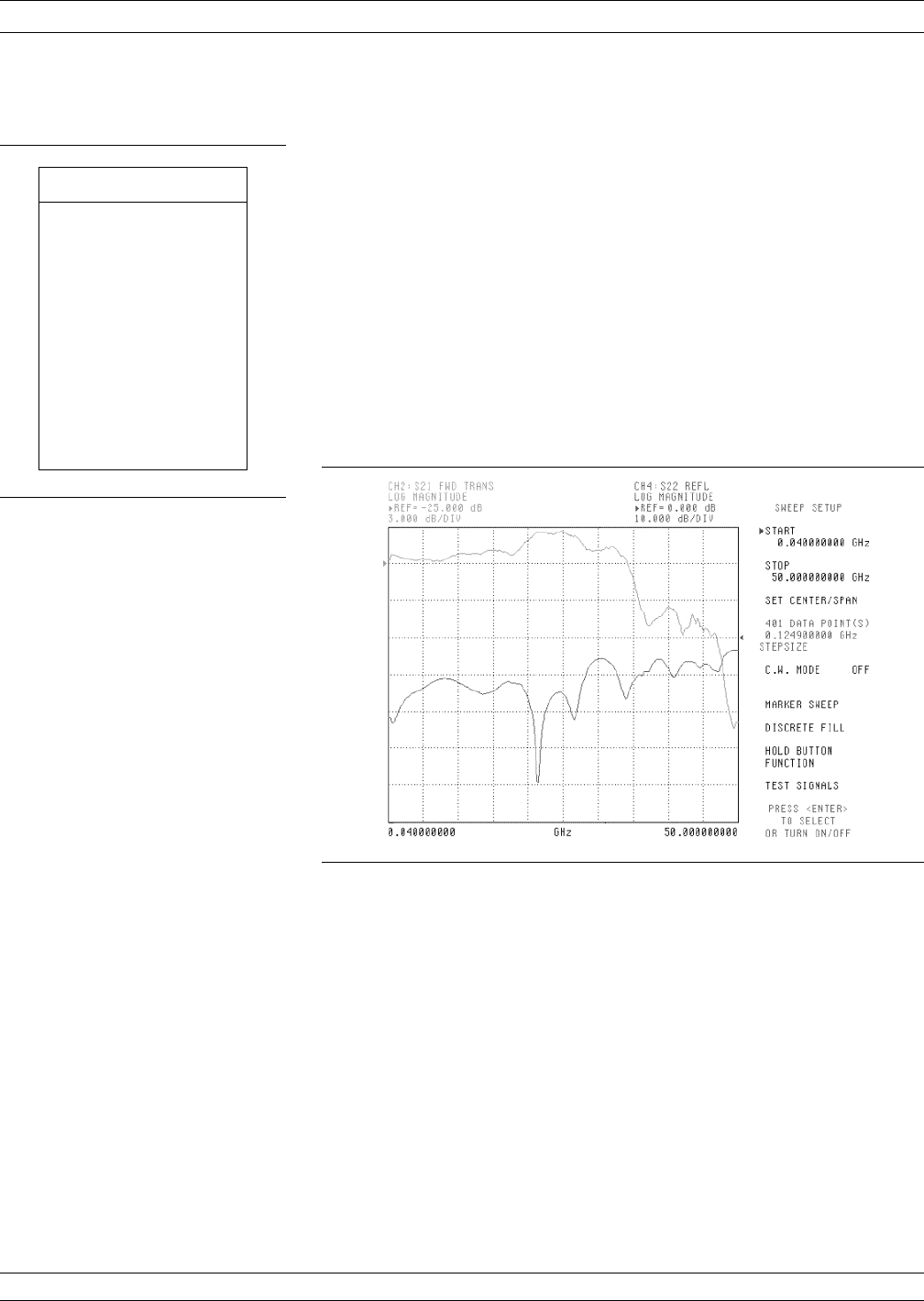
Step 13. Read the S2P file for the modulator that was gener-
ated in Step 10 from the hard drive or floppy drive
(MENU DE7A, bottom left). This will de-embed the
modulator response from the set-up for an O/E mea-
surement.
NOTE
If an S2P file is not available, it can be gen-
erated from the characterization data pro-
vided by the vendor. This is explained on
page 8-71.
An O/E measurement of a photo-receiver is shown below. The S21
measurement represents the transfer function of the photo-receiver
and S22 represents the electrical return loss.
OPTICAL APPLICATION MEASUREMENTS
8-70 37XXXC OM
Figure 8-39. O/E Measurement of a Photo-receiver
MENU DE7A
O/E MEASUREMENT
TRANSFER STANDARD
TO BE DE-EMBEDDED
(MODULATOR)
READ S2P FILE
FROM HARD DISK
READ S2P FILE
FROM FLOPPY DISK
PRESS <ENTER>
TO SELECT
PRESS <CLEAR>
TO ABORT
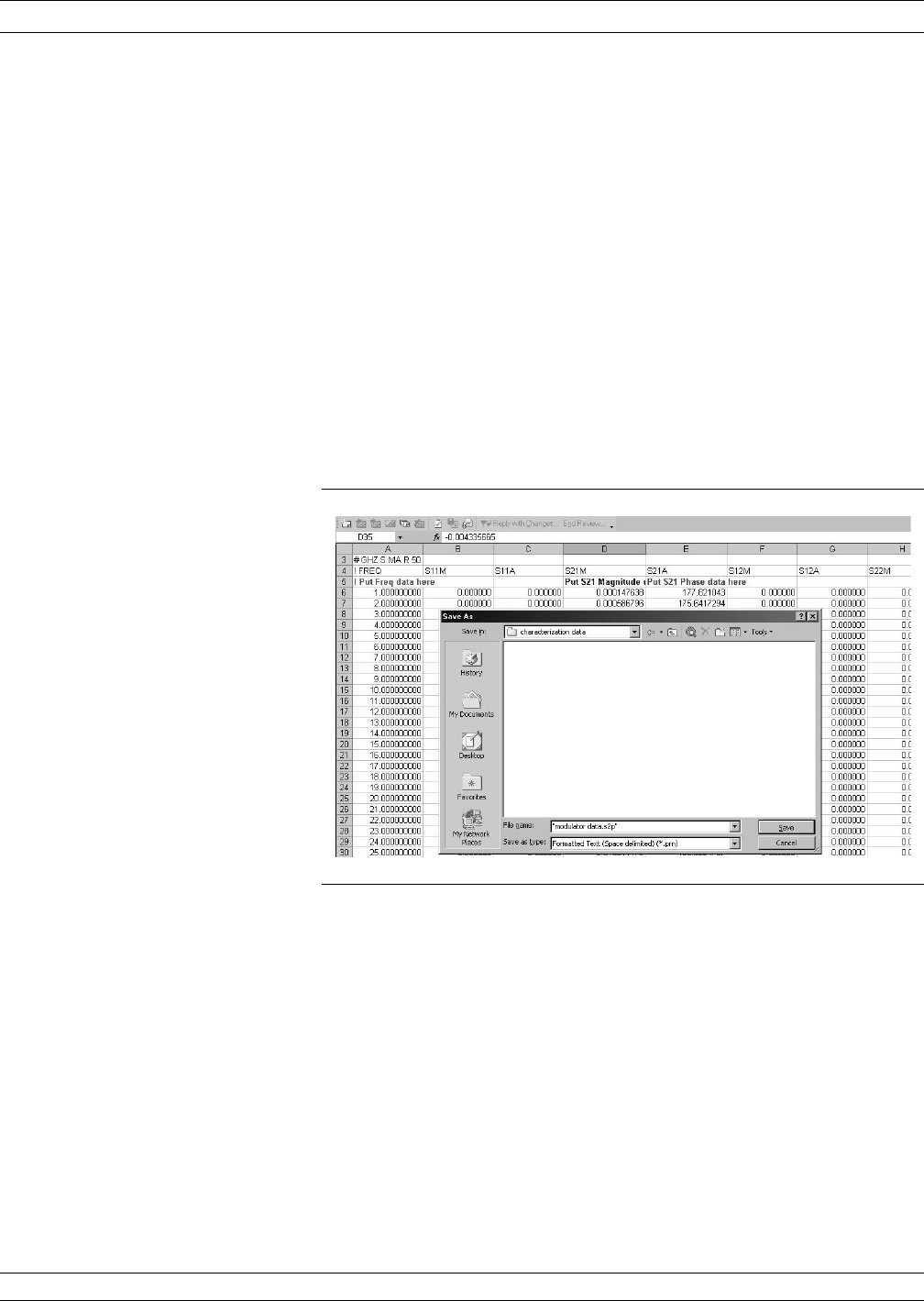
Creating a Characterization
(*.S2P) File for E/O and O/E
Measurements
This section guides you through the process of creating an S2P file
from vendor supplied characterization data. The S2P file can then be
read into the VNA for de-embedding the response of the transfer stan-
dard used for either a modulator or photo-diode.
Microsoft Excel is the recommended application for creating and stor-
ing the S2P file containing the characterization data. A sample S2P
file is available for reference (contact Anritsu MMD Customer Service
for a copy).
The file format is the standard S2P format that includes the four S-pa-
rameters (see the section below for details on the S2P format). The
transfer function data supplied by the vendor should be copied into the
columns designated for S21 data and the frequencies into the FREQ
column. Once the data has been entered, the file should be saved as an
S2P file (as shown below).
S2P File Format
S2P data files are ASCII text files in which data appears line by line,
one line per data point, in increasing order of frequency. Each line of
data consists of a frequency value and one or more pairs of values for
the magnitude and phase of each S-parameter at that frequency.
Values are separated by one or more spaces, tabs, or commands. Com-
ments are preceded by an exclamation mark (!). Comments can appear
on separate lines or after the data on any line.
37XXXC OM 8-71
MEASUREMENTS OPTICAL APPLICATION
Figure 8-40. Saving the S2P File in Excel
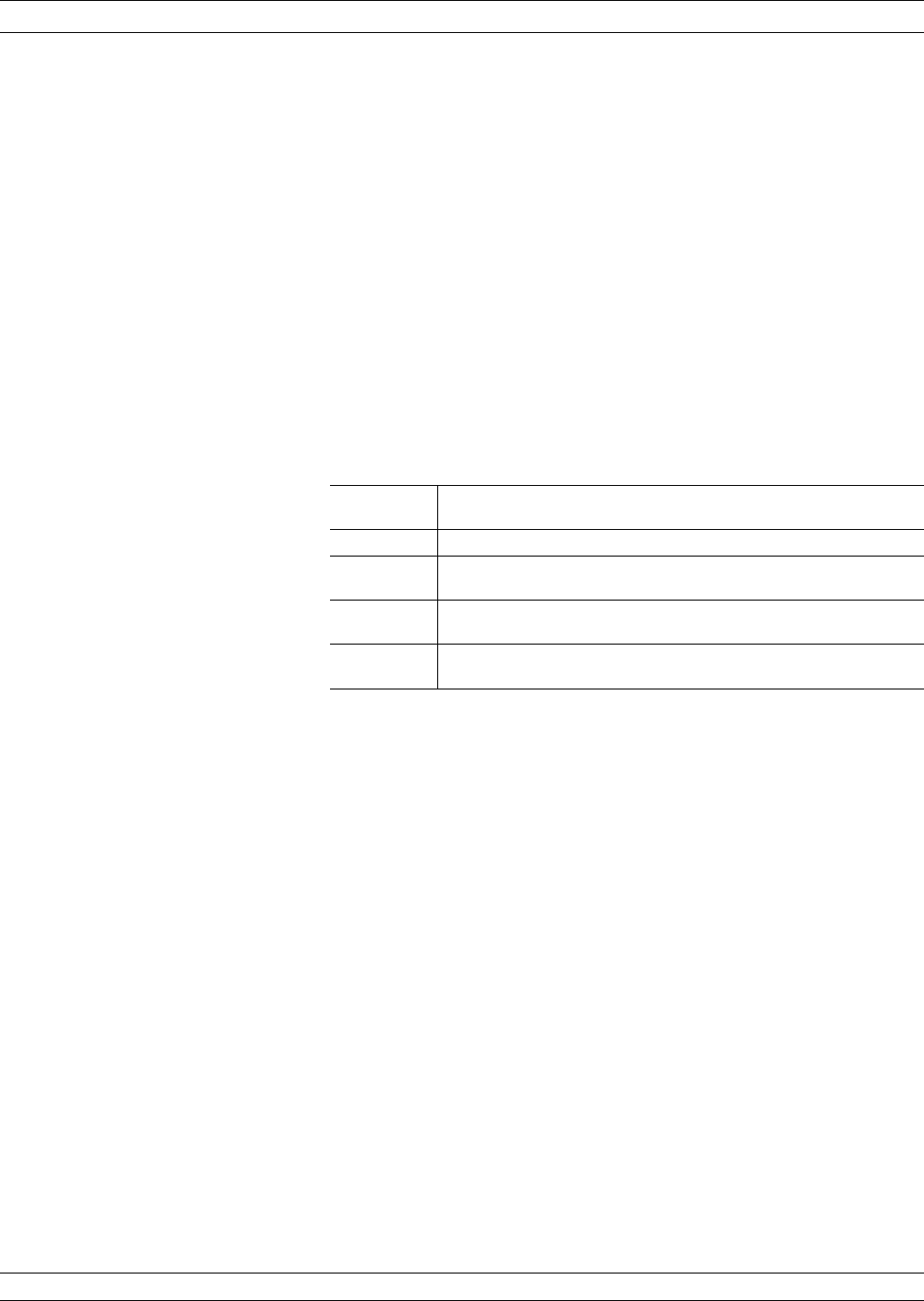
The standard S2P file format consists of:
qOption Lines
qData Lines
qComments
The option line contains the specifications of the data, for example, the
frequency units, the normalizing impedance, and the measured param-
eter (S, Y, Z, etc.)
The option line format is:
# <frequency unit> <parameter> <format> <Rn>
where:
# The delimiter that tells the program you are specifying these param-
eters
frequency unit The set of units desired (GHz, MHz, KHz, Hz)
parameter The parameter desired (S, Y or Z for S1P components; S, Y, Z, G, or
H for S2P components; S for S3P or S4P components)
format The format desired (DB for dB-angle, MA for magnitude-angle, or RI
for real-imaginary)
R n The reference resistance in ohms, where n is a positive number of
ohms (the real impedance to which the parameters are normalized)
The default option line for a component data files is:
#GHZSMAR50
For Y-parameters with real imaginary data, the option line header will
change to:
#GHzYRIR50
The data lines contain the data of interest. Data for all four S-parame-
ters will be listed on a single line for a particular frequency point. The
format is:
Frequency S11 S21 S12 S22
Data Line Examples:
Frequency S11 (magnitude) S11 (angle)
0.040000000 1.426492E-04 18.642
0.139900000 2.840961E-03 22.262
OPTICAL APPLICATION MEASUREMENTS
8-72 37XXXC OM
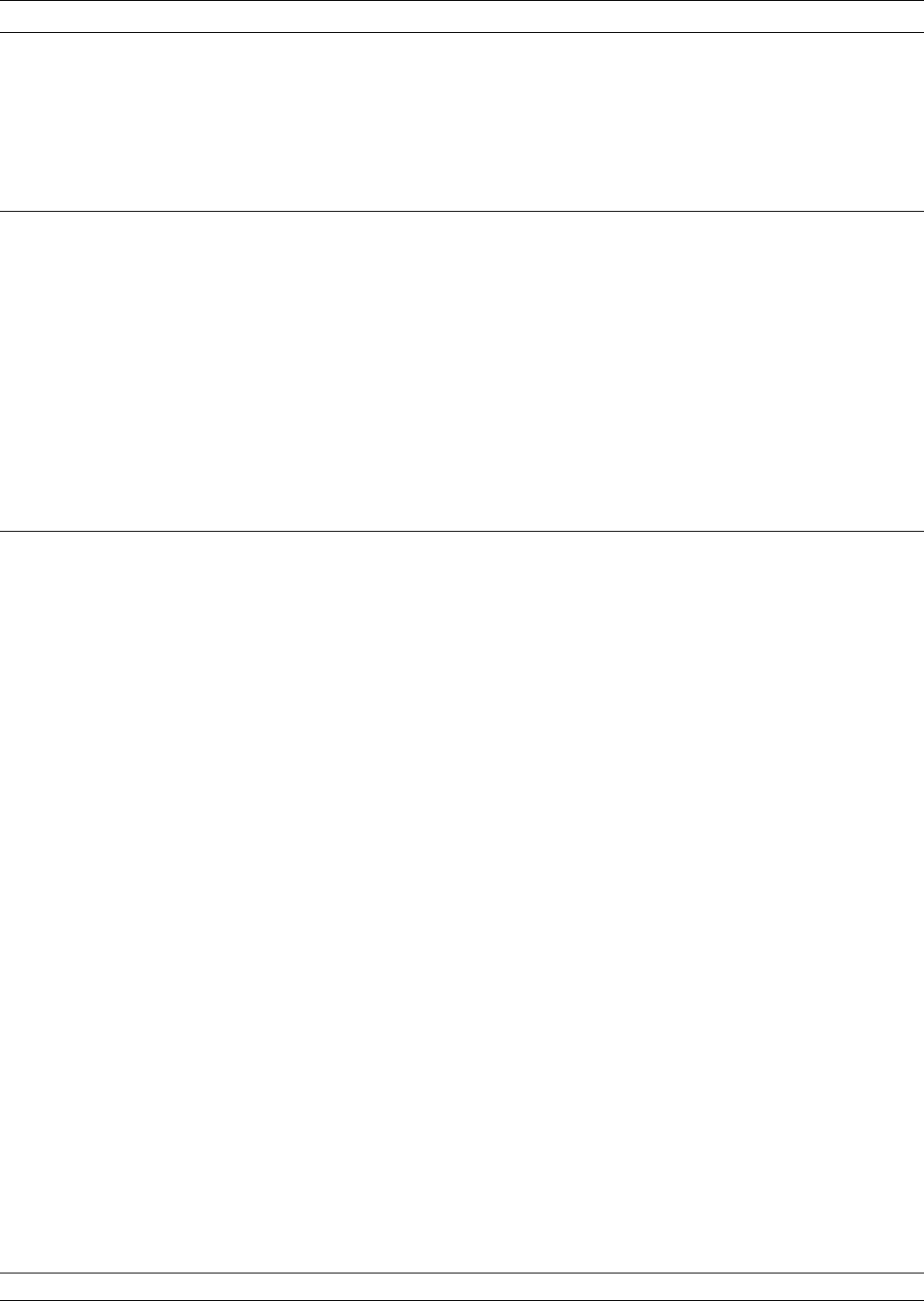
Finally, the comment lines begin with an exclamation point“!.”They
can be inserted at any point in an S2P file and are ignored by the ap-
plication program. An S2P file example appears below.
37XXXC OM 8-73/8-74
MEASUREMENTS OPTICAL APPLICATION
! Anritsu Company
! DATE 04/11/2002 13:16 PAGE 1
! Photo-diode receiver characterization –NRZ-40G
# GHz S MA R 50.00
!FREQ S11M S11A S21M S21A S12M S12A S22M S22A
0.040000000 1.426492E-04 18.642 3.008963E-04 87.040 1.618370E-04 27.317 2.708149E-04 129.056
0.139900000 2.840961E-03 22.262 6.185992E-03 -114.026 2.539190E-03 125.940 5.977178E-03 -7.691
0.239800000 3.072268E-03 97.851 7.423908E-03 109.019 3.147963E-03 -88.205 7.634960E-03 -75.071
0.339700000 1.887820E-02 81.836 3.814256E-02 -135.753 1.632677E-02 -27.669 3.348942E-02 117.818
0.439600000 2.173782E-02 142.412 4.595363E-02 72.973 1.962434E-02 107.429 3.946349E-02 40.979
0.539500000 2.634556E-02 -62.971 5.206176E-02 31.589 2.257828E-02 -22.787 4.638838E-02 70.663
0.639400000 3.060178E-02 -103.325 6.416773E-02 120.463 2.732290E-02 5.656 5.685493E-02 -124.645
Figure 8-41. S2P File Example

Table of Contents
9-1 INTRODUCTION ...................................9-3
9-2 TIME DOMAIN MEASUREMENTS .........................9-3
9-3 OPERATING TIME DOMAIN ............................9-8
9-4 WINDOWING.....................................9-11
9-5 GATING........................................9-12
9-6 ANTI-GATING ....................................9-14
9-7 EXAMPLES, GATING AND ANTI-GATING ....................9-14
9-8 TIME DOMAIN MENUS...............................9-14
Chapter 9
Time Domain

Chapter 9
Time Domain
9-1 INTRODUCTION This chapter describes the optional Time Domain feature.
9-2 TIME DOMAIN
MEASUREMENTS The Option 2, Time Domain feature provides a useful measurement
tool for determining the location of impedance discontinuities. Some
typical applications are identifying and analyzing circuit elements, iso-
lating and analyzing a desired response, locating faults in cables, and
measuring antennas.
The relationship between the frequency-domain response and the
time-domain response of a network is described mathematically by the
Fourier transform.
The 37XXXC makes measurements in the frequency domain then cal-
culates the inverse Fourier transform to give the time-domain re-
sponse. The time-domain response is displayed as a function of time
(or distance). This computational technique benefits from the wide dy-
namic range and the error correction of the frequency-domain data.
Let us examine the time-domain capabilities. Two measurement
modes are available: lowpass and bandpass.
We use the lowpass mode with devices that have a dc or low-frequency
response. In the lowpass mode two responses to the device-under-test
(DUT) are available: impulse or step response.
The frequencies used for the test must be harmonically related (inte-
ger multiples) to the start frequency. The simplest way to calculate
this relationship is to divide the highest frequency in the calibration
by 1600 (the default number-of-points available); this is the start fre-
quency. For example, if the highest frequency is 40 GHz, the calculated
start frequency is 0.025 GHz (40/1600). If the highest frequency is 65
GHz, the calculated start frequency is 0.040625 GHz (65/1600).
37XXXC OM 9-3
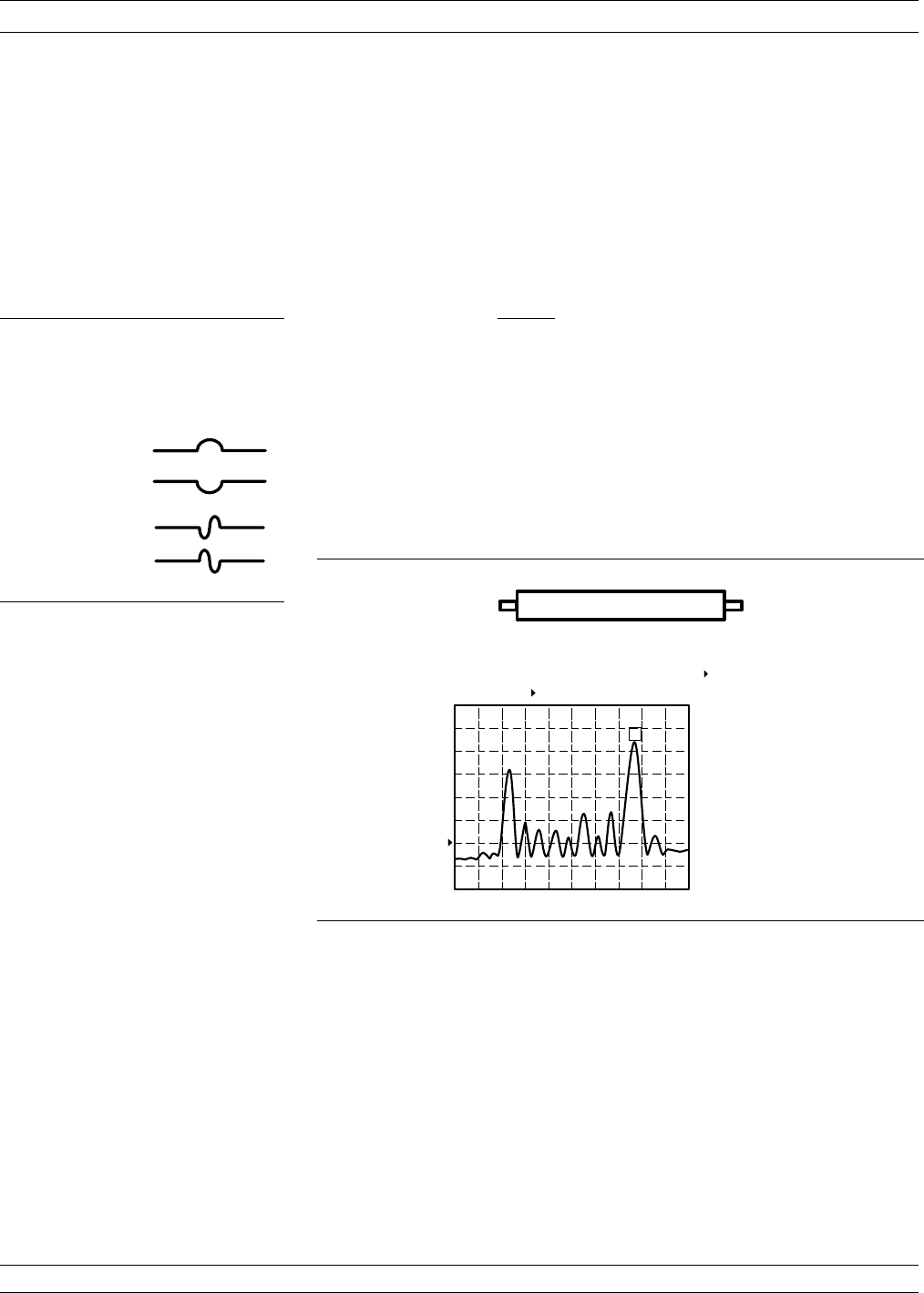
The lowpass impulse response displays the location of discontinuities
as well as information useful in determining the impedance (R, L, or
C) of each discontinuity.
The impulse response is a peak that goes positive for R>Z0and nega-
tive for R<Z0. The height of the response is equal to the reflection coef-
ficient:
r= -
+
RZ
RZ
0
0
The impulse response for a shunt capacitance is a negative-then-
positive peak and for a series inductance is a positive-then-negative
peak (Figure 9-1).
An example of using an impulse response is a circuit impedance analy-
sis. With an impulse response we can observe the circuit response of a
passive device, such as a multi-element step attenuator (Figure 9-2),
and make final, realtime adjustments during the test.
In the above example, the connectors at each end have been gated out
(page 9-12), which lets you better observe the internal circuit response.
Each displayed marker has been manually set to the peak of the re-
sponse at each adjustable circuit element. In this way, the data display
lets you make the adjustment in realtime, while the marker menu
shows the magnitude of the response at each marker.
TIME DOMAIN MEASUREMENTS TIME DOMAIN
9-4 37XXXC OM
C I R C U I T E L E M E N T S
R > Z
O
S H U N T C
S E R I E S L
I M P E D A N C E
O
R < Z
L o w p a s s I m p u l s e R e s p o n s e
1 1
S R E A L
Figure 9-1. Lowpass Impulse
Response
0.000ps
700.000ps
S 1 1 F O R W A R D R E F L E C T I O N
L I N E A R M A G .
R E F = 5 . 0 0 0 m U
7 . 0 0 0 m U / D I V
L P w / G
6 1 5 2 . 5 1 4 p s
2 7 . 5 3 4 m U
2 4 6 5 . 3 6 3 p s
1 5 . 6 2 4 m U
3 3 7 5 . 4 1 9 p s
1 5 . 0 2 0 m U
4 2 9 3 . 2 9 6 p s
9 . 5 9 3 m U
5 1 9 5 . 5 3 1 p s
1 1 . 6 2 4 m U
M A R K E R T O M A X
M A R K E R T O M I N
M A R K E R 1
5 1 2 . 2 9 1 p s
3 6 . 8 9 0 m U
C H 1 - S 1 1
00.000 ps diy
S T E P A T T E N U A T O R
1
4
6
2
3
5
Figure 9-2. Example of Lowpass Impulse Response
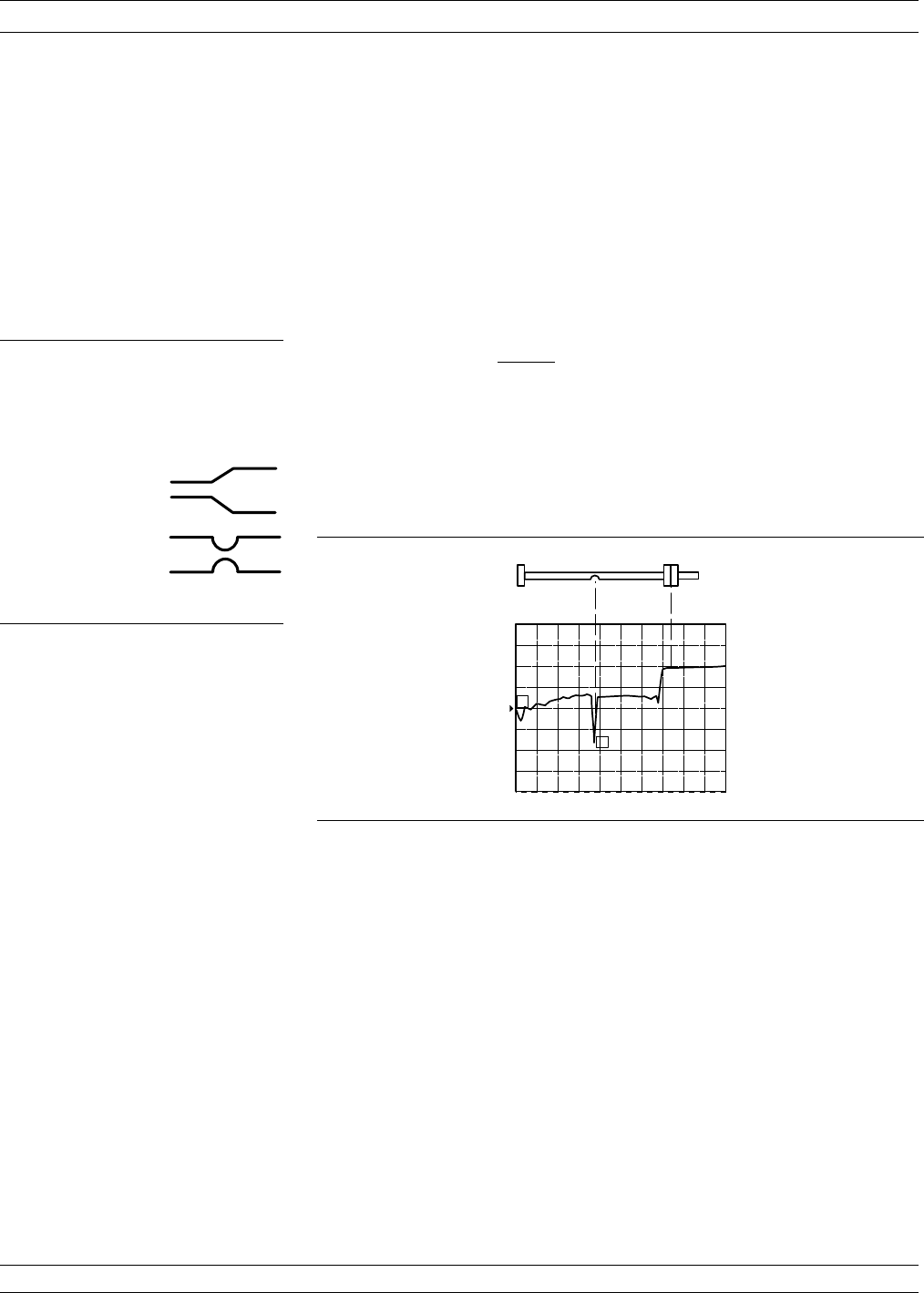
The lowpass step response displays the location of discontinuities as
well as information useful in determining the impedance (R, L, or C) of
each discontinuity. If you are familiar with time-domain reflectometry
(TDR) you may feel more comfortable with step response, as the dis-
plays are similar.
The lowpass step response for a resistive impedance is a positive level
shift for R>Z0and a negative level shift for R<Z0. The height of the re-
sponse is equal to the reflection coefficient
r= -
+
RZ
RZ
0
0
The step response for a shunt capacitance is a negative peak, and for a
series inductance it is a positive peak (Figure 9-3).
An example of using the lowpass step response is cable-fault location.
In the frequency domain a cable with a fault exhibits a much worse
match than a good cable. Using lowpass step response, both the loca-
tion of the discontinuity and the information about its type are avail-
able (Figure 9-4).
In the above example, the dip in the display shows the shunt-
capacitive response caused by a crimp in the cable. The response at the
end of the cable shows the step-up that is typical of an open (Figure
9-3, left).
The 37XXXC bandpass mode gives the response of the DUT to an
RF-burst stimulus. Two types of response are available: impulse and
phasor-impulse. An advantage of the bandpass mode is that any fre-
quency range can be used. Use this mode with devices that do not have
a dc or low-frequency path.
37XXXC OM 9-5
TIME DOMAIN TIME DOMAIN MEASUREMENTS
C I R C U I T E L E M E N T S
R > Z
O
S H U N T C
S E R I E S L
I M P E D A N C E
O
R < Z
1 1
S R E A L
L o w p a s s S t e p R e s p o n s e
Figure 9-3. Lowpass Step
Response
4 0 . 0 0 0 c m
0 . 0 0 0 m m
1
3
CABLE
2
O P E N
Figure 9-4. Example of Lowpass Step Response
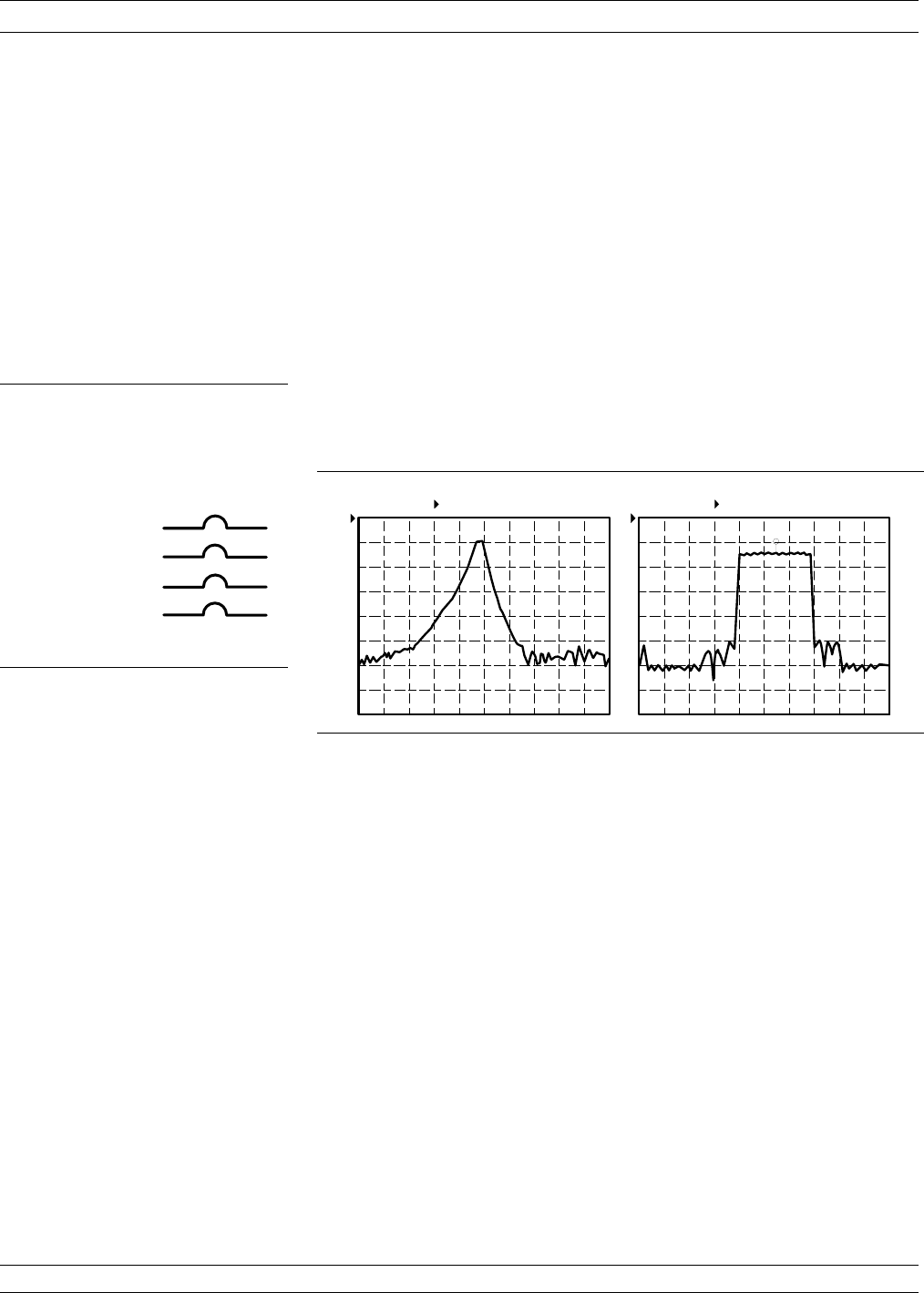
Use the bandpass-impulse response to show the location of a disconti-
nuity in time or distance, as indicated by changes in its magnitude.
Unlike the lowpass mode, no information as to the type of the disconti-
nuity is available. A typical use for this mode is to measure de-
vices—such as, filters, waveguide, high-pass networks, bandpass net-
works—where a low-frequency response is not available.
The bandpass-impulse response for various impedance discontinuities
is shown in Figure 9-5. As we can see, no information about the type of
discontinuity is available.
An example of using the bandpass-impulse response, is the pulse
height, ringing, and pulse envelope of a bandpass filter (Figure
9-6).Use the phasor-impulse response with bandpass response to de-
termine the type of an isolated impedance discontinuity.
After the bandpass-impulse response has been isolated, the phasor-im-
pulse response for a resistive-impedance-level change is a peak that
goes positive (R>Z0) for the real part of S11 and negative for R<Z0. The
imaginary part remains relatively constant. In each case the peak is
proportional to the reflection coefficient. The phasor-impulse response
for a shunt capacitance is a negative-going peak in the imaginary part
of S11. For a series inductance, it is a positive going peak (Figure 9-7).
TIME DOMAIN MEASUREMENTS TIME DOMAIN
9-6 37XXXC OM
C I R C U I T E L E M E N T S
R > Z
O
S H U N T C
S E R I E S L
I M P E D A N C E
B a n d p a s s I m p u l s e R e s p o n s e
O
R < Z
1 1
S L O G M A G N I T U D E
Figure 9-5. Bandpass Impulse
Response
L O G M A G .
0 . 5 0 0 0 G H z 4 . 0 0 0 0
R E F = 2 0 . 0 0 0 d B 2 0 . 0 0 0 d B / D I V L O G M A G .
0 . 5 0 0 0 G H z 4 . 0 0 0 0
1 0 . 0 0 0 d B / D I VR E F = 3 0 . 0 0 0 d B
B P w /G
S 2 1 F O R W A R D T R A N S M I S S I O N S 2 1 F O R W A R D T R A N S M I S S I O N
Figure 9-6. Example of Bandpass-Impulse Response
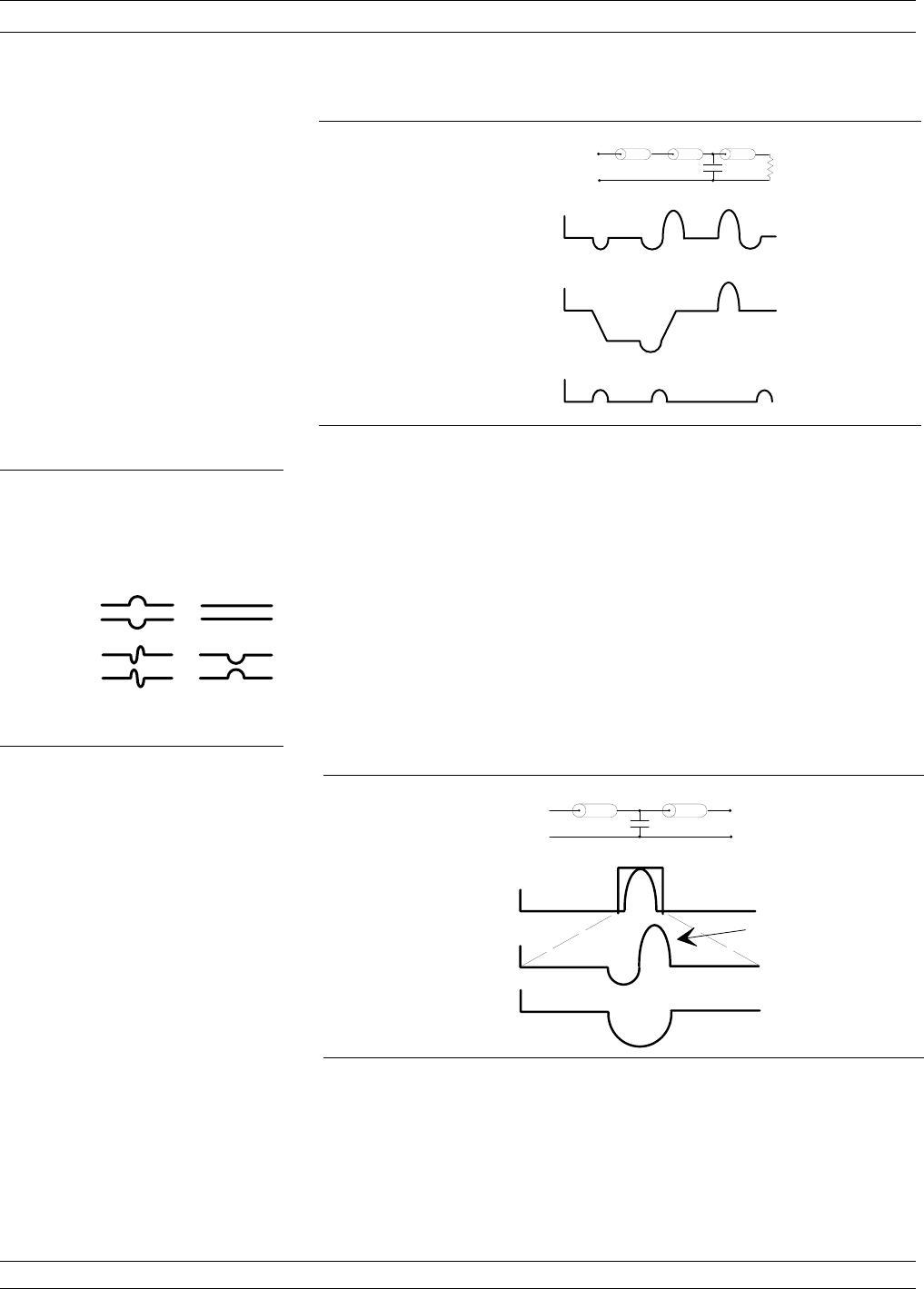
Next, let us look at a complex circuit. A resistive impedance change
R<Z0and a shunt capacitance and series inductance. These impedance
changes are shown in the time domain for the lowpass-impulse re-
sponse, lowpass-step response, and bandpass-impulse response (Figure
9-8).
The 37XXXC processes bandpass-impulse-response data to obtain
phasor-impulse response. This becomes most advantageous where both
a reactive reflection and an impedance change occur at the same loca-
tion. The real part of the time-domain response shows the location of
impedance level changes, while the imaginary part shows the type of
reactive discontinuity. Phasor-impulse response displays one disconti-
nuity at a time (Figure 9-9).
37XXXC OM 9-7
TIME DOMAIN TIME DOMAIN MEASUREMENTS
R E A L S 1 1
M A G N I T U D E S 1 1
R E A L S 1 1
5 c m1 0 c m
1 0 c m
5 0
9
2 0
9
5 0
9
L O W P A S S
R E S P O N S E
L O W P A S S
R E S P O N S E
BANDPASS
R E S P O N S E
Figure 9-7. Complex Impedances
C I R C U I T E L E M E N T S
B a n d p a s s - P h a s o r I m p u l s e R e s p o n s e
R > Z
O
S H U N T C
S E R I E S L
I M P E D A N C E
1 1
R E A L S
I M A G I N A R Y S
1 1
O
R < Z
Figure 9-8. Bandpass Phasor
Response
M A G N I T U D E
R E A L
I M A G I N A R Y
S P A N
B A N D P A S S
C
5 c m 10 cm
2 0
9
5 0
9
I M P U L S E
P H A S O R
Figure 9-9. Phasor-Impulse Response Data
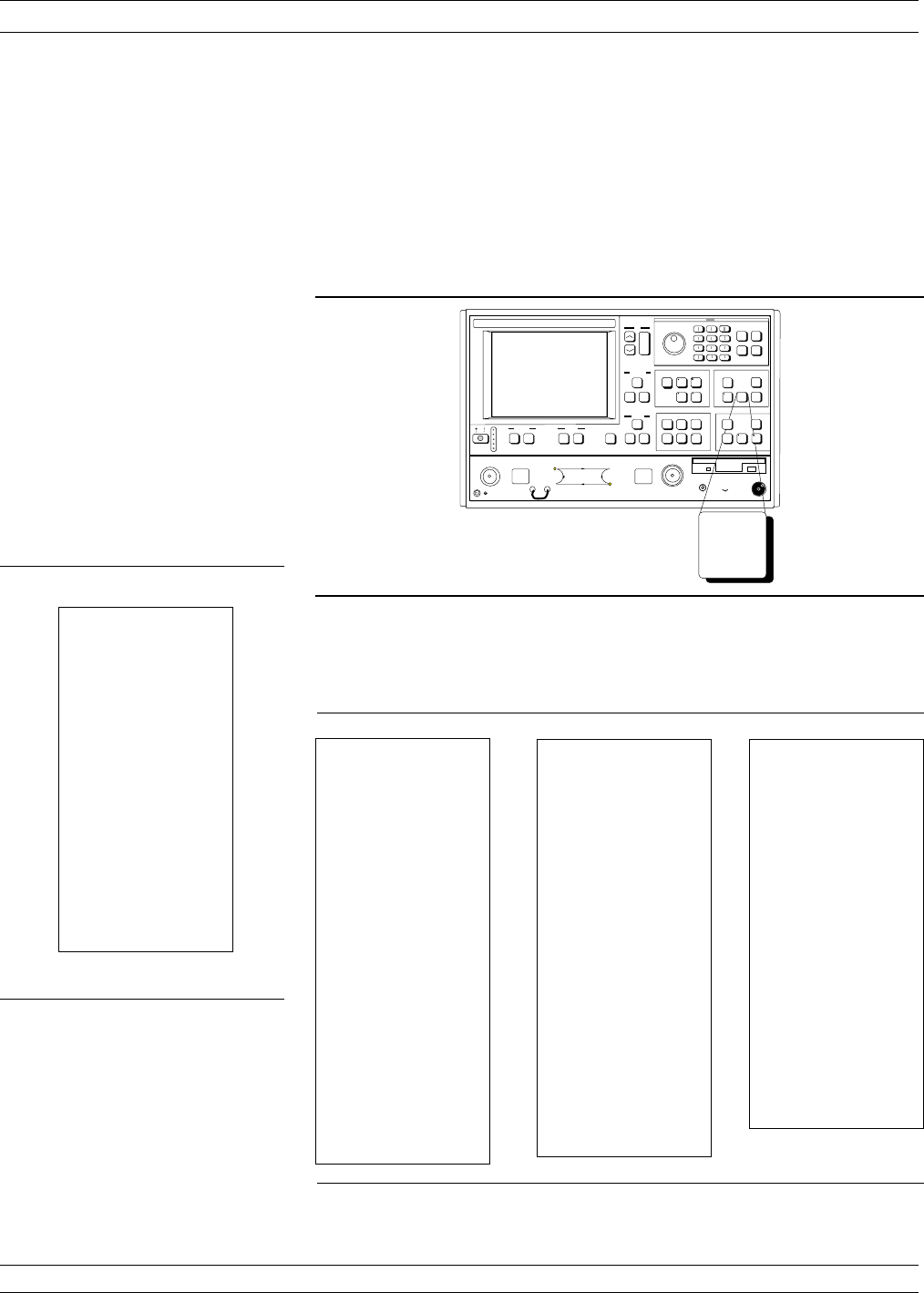
9-3 OPERATING TIME
DOMAIN To operate in the time domain mode, press the Domain key (below). A
domain menu (Figure 9-10) lets you select the frequency- or time-do-
main modes by simple cursor selection. The 37XXXC defaults to the
frequency domain.
Select time or distance for the horizontal axis. The 37XXXC defaults to
time axis.
NOTE
If you select distance, be sure to set the dielectric constant
in the Reference Delay menu (Figure 9-11).
OPERATING TIME DOMAIN TIME DOMAIN
9-8 37XXXC OM
Figure 9-10. Domain Menu
DOMAIN
FREQUENCY
FREQUENCY
WITH TIME
GATE
TIME
LOWPASS MODE
TIME
BANDPASS
MODE
DISPLAY
TIME/DISTANCE
SET RANGE
SET GATE
GATE ON/OFF
HELP
PRESS <ENTER>
TO SELECT
OR SWITCH
DOMAIN
FREQUENCY
FREQUENCY
WITH TIME
GATE
TIME
LOWPASS MODE
TIME
BANDPASS
MODE
DISPLAY
TIME/DISTANCE
SET RANGE
SET GATE
GATE ON/OFF
HELP
PRESS <ENTER>
TO SELECT
OR SWITCH
DOMAIN
FREQUENCY
FREQUENCY
WITH TIME
GATE
TIME
LOWPASS MODE
TIME
BANDPASS MODE
DISPLAY
TIME/DISTANCE
SET RANGE
SET GATE
GATE ON/OFF
HELP
PRESS <ENTER>
TO SELECT
OR SWITCH
Figure 9-11. Reference Delay
Menu
SET
DIELECTRIC
CONSTANT
AIR
(1.000649)
POLYETHYLENE
(2.26)
TEFLON
(2.10)
MICROPOROUS
TEFLON
(1.69)
OTHER
XXXX.XX
PRESS <ENTER>
TO SELECT
Domain
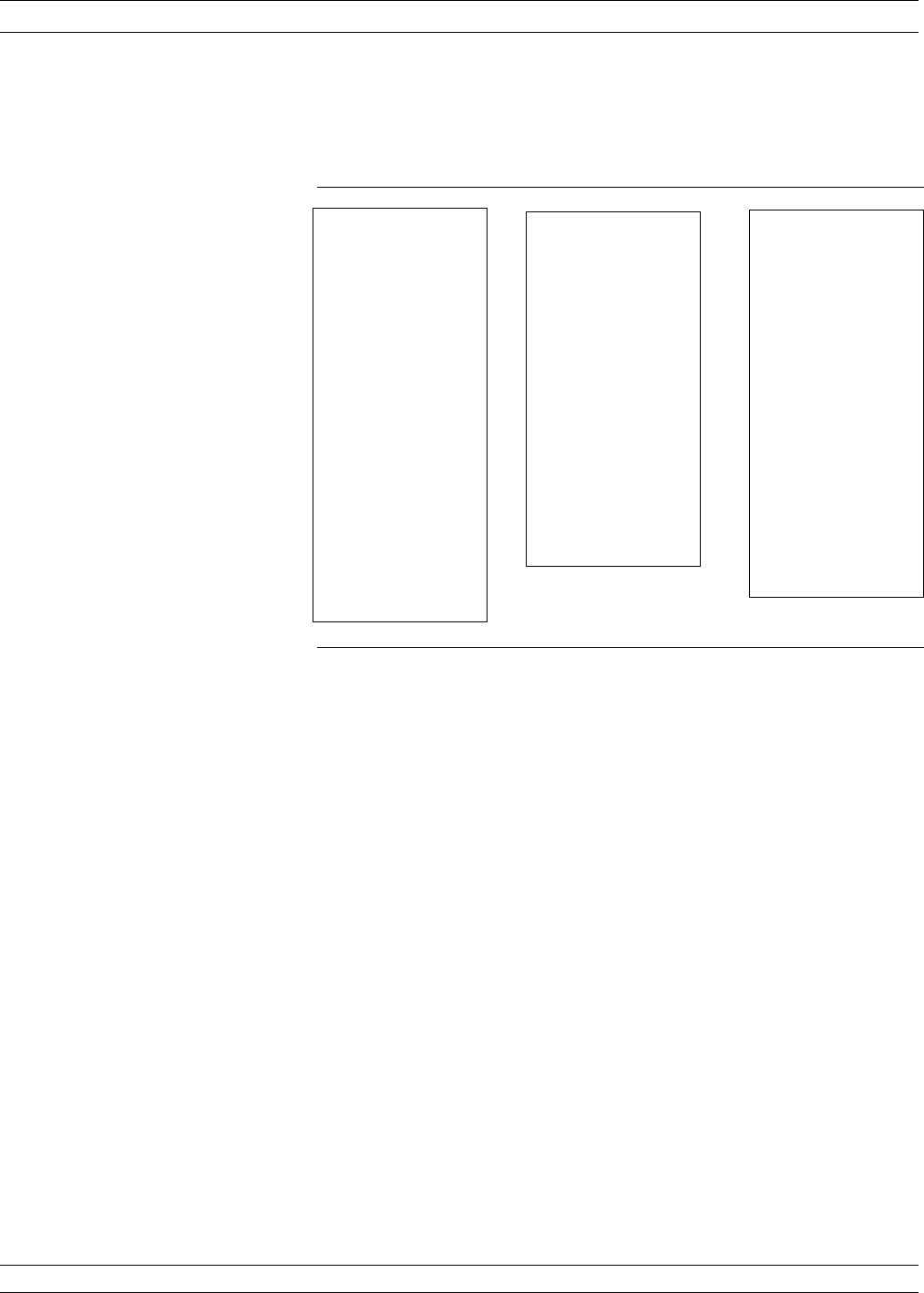
Select SET RANGE and use the START/STOP or GATE/SPAN selec-
tions to set the range (Figure 9-12).
For the lowpass mode select either IMPULSE or STEP Response and
set the DC term. The 37XXXCdefaults to the IMPULSE Response and
the AUTO EXTRAPOLATE mode for the DC term (Figure 9-13).
NOTE
The bandpass mode displays Bandpass Impulse Response
unless we select Phasor Impulse Response.
37XXXC OM 9-9
TIME DOMAIN OPERATING TIME DOMAIN
Figure 9-12. Set Range Menu
LOWPASS TIME
DOMAIN SETUP
START
XXX.XXX ps
STOP
XXX.XXX ps
CENTER
XXX.XXX ps
SPAN
XXX.XXX ps
MARKER RANGE
RESPONSE
IMPULSE/STEP
MORE
PRESS <ENTER>
TO SELECT
DOMAIN
FREQUENCY
FREQUENCY
WITH TIME
GATE
TIME
LOWPASS
MODE
TIME
BANDPASS
MODE
DISPLAY
TIME/DISTANCE
SET RANGE
SET GATE
GATE ON/OFF
HELP
PRESS <ENTER>
TO SELECT
OR SWITCH
BANDPASS TIME
DOMAIN SETUP
START
XXX.XXX ps
STOP
XXX.XXX ps
CENTER
XXX.XXX ps
SPAN
XXX.XXX ps
MARKER RANGE
PHASOR ON/OFF
IMPULSE
HELP - PHASOR
IMPULSE
MORE
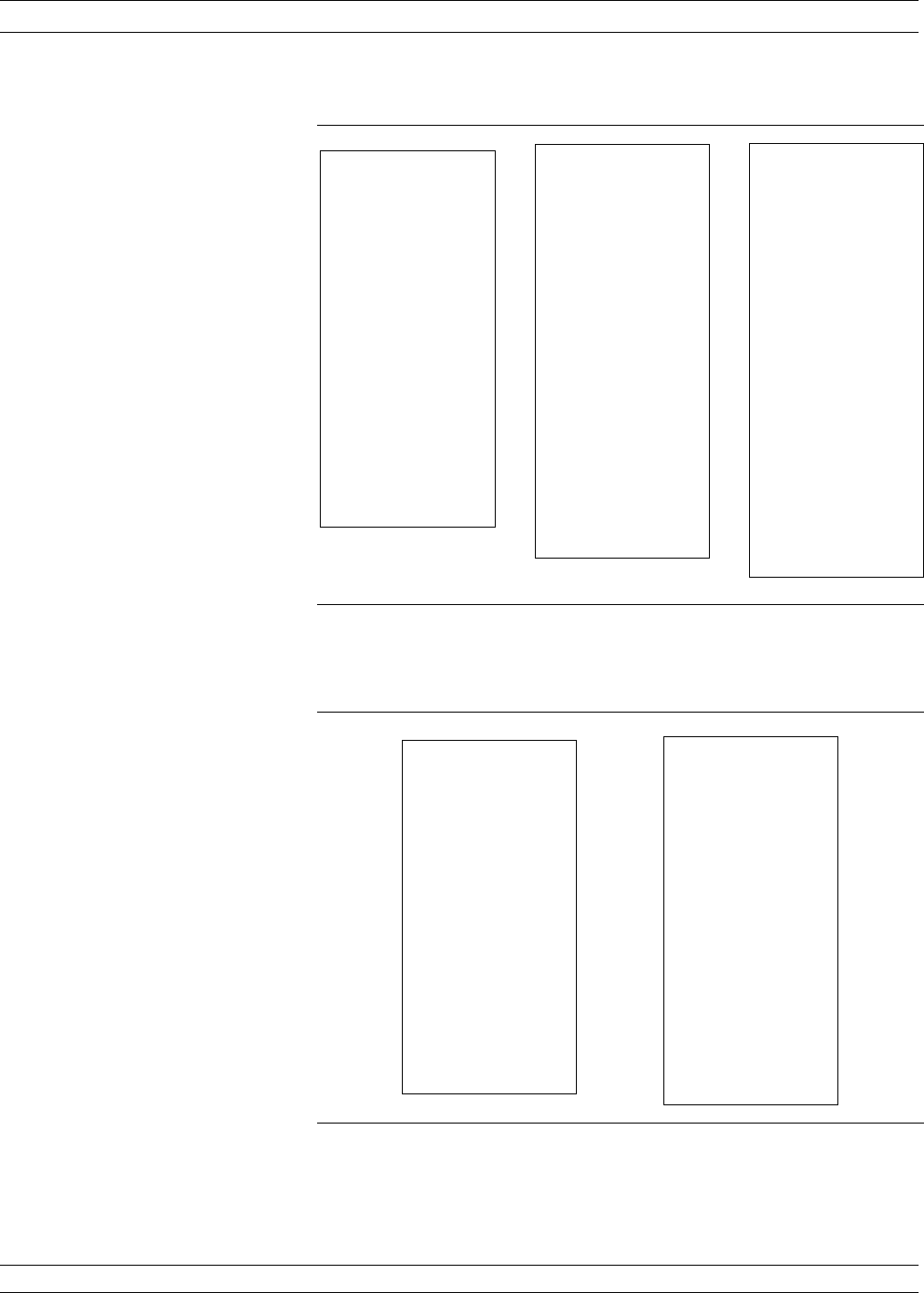
The Marker Range menu allows us to zoom in and display the range
between two selected markers (Figure 9-14).
OPERATING TIME DOMAIN TIME DOMAIN
9-10 37XXXC OM
Figure 9-13. Response Menus
SET D.C. TERM
FOR LOWPASS
PROCESSING
AUTO
EXTRAPOLATE
LINE
IMPEDANCE
OPEN
SHORT
OTHER
–XXX.XXX #
ABOVE VALUE
REPRESENTS A
REFLECTION
COEFF. OF
XX.XXX mU
PREVIOUS MENU
PRESS <ENTER>
TO SELECT
LOWPASS TIME
DOMAIN SETUP
START
XXX.XXX ps
STOP
XXX.XXX ps
CENTER
XXX.XXX ps
SPAN
XXX.XXX ps
MARKER RANGE
RESPONSE
IMPULSE/STEP
MORE
PRESS <ENTER>
TO SELECT
BANDPASS TIME
DOMAIN SETUP
START
XXX.XXX ps
STOP
XXX.XXX ps
CENTER
XXX.XXX ps
SPAN
XXX.XXX ps
MARKER RANGE
PHASOR ON/OFF
IMPULSE
HELP-PHASOR
IMPULSE
MORE
PRESS <ENTER>
TO SELECT
Figure 9-14. Marker Range Menus
TIME
MARKER SWEEP
START TIME
MARKER ( )
XXX.XXX nS
STOP TIME
MARKER ( )
XXX.XXX nS
RESTORE
ORIGINAL
RANGE
PREVIOUS MENU
USE KEYPAD
TO CHOOSE
MARKER (1 - 6)
OR
PRESS <ENTER>
TO SELECT
LOWPASS TIME
DOMAIN SETUP
START
XXX.XXX ps
STOP
XXX.XXX ps
CENTER
XXX.XXX ps
SPAN
XXX.XXX ps
MARKER RANGE
RESPONSE
IMPULSE/STEP
MORE
PRESS <ENTER>
TO SELECT
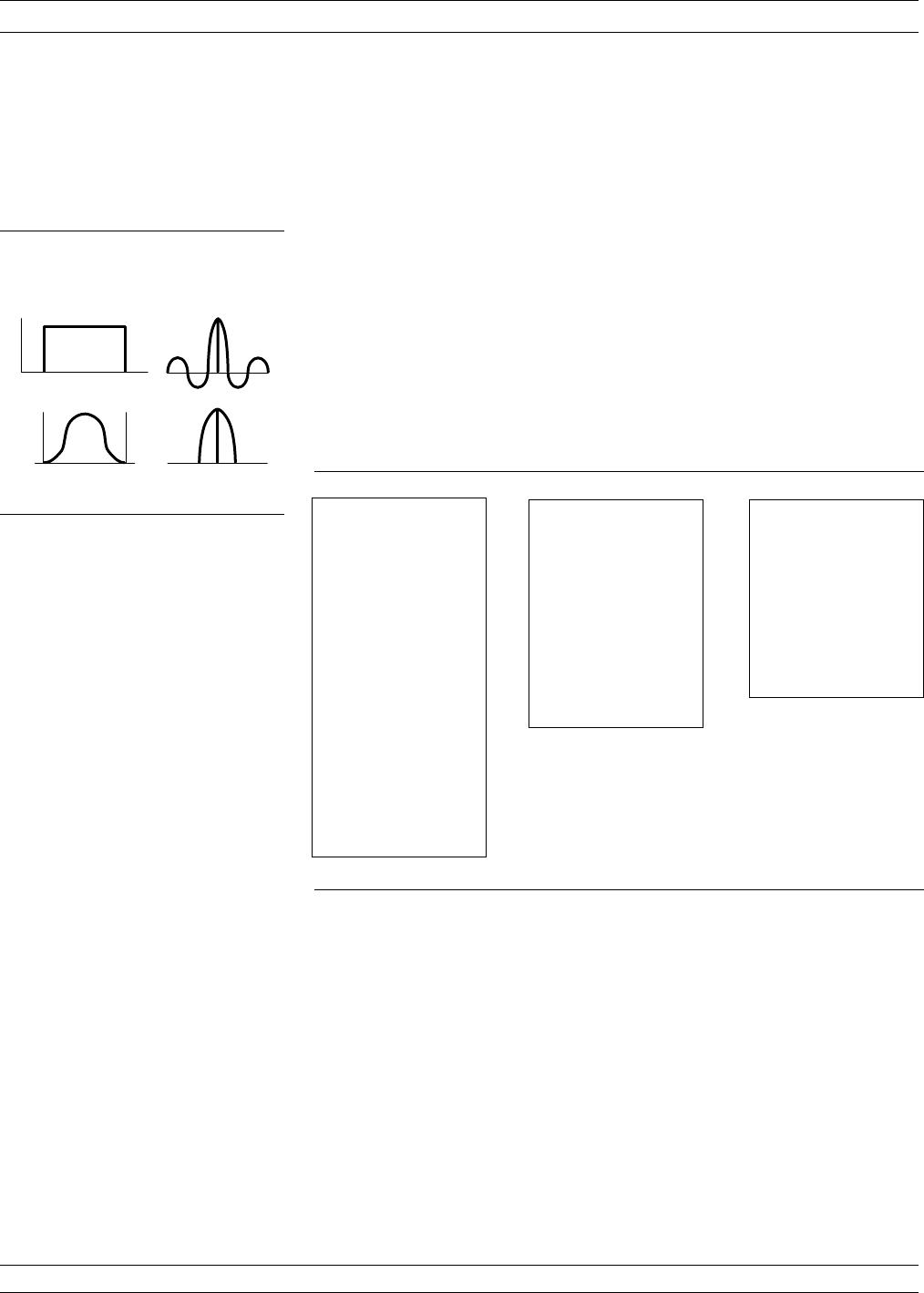
9-4 WINDOWING Windowing is a frequency filter that we apply to the frequency-domain
data when we convert it to time-domain data. This filtering rolls off
the abrupt transition at F1 and F2. This effectively produces a time-
domain response with lower sidelobes. Windowing allows a limited de-
gree of control over the pulse shape, trading off ringing (sidelobes) for
pulse width (Figure 9-15).
We select windowing from the Time Domain Setup menu. Four differ-
ent windows are available: RECTANGLE, NOMINAL, LOW
SIDELOBE, and MINIMUM SIDELOBE. The RECTANGLE option
provides the narrowest pulse width, while the MINIMUM SIDELOBE
option provides the least ringing (fewest sidelobes). The 37XXXC de-
faults to the NOMINAL option, which is acceptable for most measure-
ments. Windowing menus are shown in Figure 9-16.
37XXXC OM 9-11
TIME DOMAIN WINDOWING
F R E Q U E N C Y D O M A I N T I M E D O M A I N
1 - T E R M W I N D O W
2 - T E R M W I N D O W
W I N D O W I N G
F 1
N O T E : W i d e r b u t n o r i n g i n g
F 2
Figure 9-15. Windowing
Figure 9-16. Window Shape Menus
LOWPASS TIME
DOMAIN SETUP
SET WINDOW
NOMINAL
SET GATE
SET D.C. TERM
XXX.XXX
PREVIOUS MENU
PRESS <ENTER>
TO SELECT
LOWPASS TIME
DOMAIN SETUP
START
XXX.XXX ps
STOP
XXX.XXX ps
CENTER
XXX.XXX ps
SPAN
XXX.XXX ps
MARKER RANGE
RESPONSE
IMPULSE/STEP
MORE
PRESS <ENTER>
TO SELECT
SHAPE
RECTANGULAR
NOMINAL
LOW SIDELOBE
MIN SIDELOBE
HELP
PRESS <ENTER>
TO SELECT
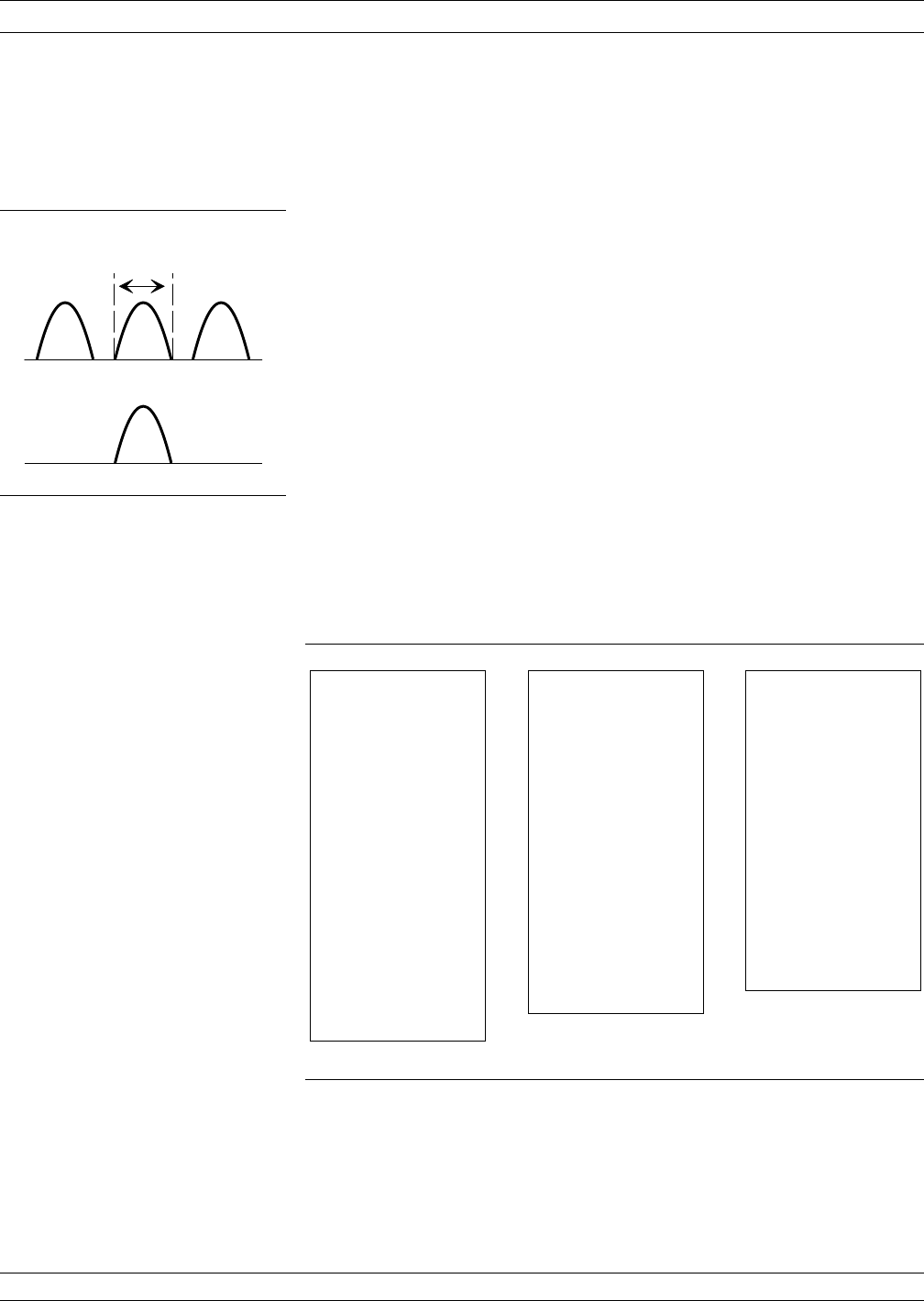
9-5 GATING Gating is a time filter that allows for removing unwanted time-domain
responses by gating the desired response. We can view the isolated re-
sponse in both time domain—and in the frequency domain—using the
FREQUENCY WITH TIME GATE selection (Figure 9-17).
There are four different gate shapes available: MINIMUM, NOMI-
NAL, WIDE, and MAXIMUM (Figure 9-18). The 37XXXC defaults to
the NOMINAL gate. To specify a different shape simply enter the Gate
menu and select the desired gating shape. The MINIMUM has the
sharpest rolloff and some frequency domain ripple, while MAXIMUM
has the least rolloff and best residual ripple. Figures 9-18A through
9-18D, on the next page, show gating shapes.
The combinations of gate/window shapes will be restricted. For the
MINIMUM gate shape, the LOW and MIN SIDELOBE window shape
will not be allowed. For the NOMINAL gate shape, the MIN SIDE-
LOBE window will not be allowed. If the user has set the window
shape to MIN or LOW SIDELOBE and changes the-gate shape to
MINIMUM, the window will be reset to NOMINAL. If the user has set
the window to MIN SIDELOBE and changes the gate shape to NOMI-
NAL, the window will be reset to LOW SIDELOBE. Gate shapes will
be adjusted in a similar manner.
GATING TIME DOMAIN
9-12 37XXXC OM
G A T E
D I S T A N C E
G A T E A P P L I E D
G A T I N G
Figure 9-17. Gating
Figure 9-18. Gating Menus
LOWPASS TIME
DOMAIN SETUP
SET WINDOW
NOMINAL
SET GATE
SET DC TERM
XXX.XXX
PREVIOUS MENU
PRESS <ENTER>
TO SELECT
LOWPASS TIME
DOMAIN SETUP
START
XXX.XXX ps
STOP
XXX.XXX ps
CENTER
XXX.XXX ps
SPAN
XXX.XXX ps
MARKER RANGE
RESPONSE
IMPULSE/STEP
MORE
PRESS <ENTER>
TO SELECT
SELECT GATE
SHAPE
MINIMUM
NOMINAL
WIDE
MAXIMUM
HELP
PRESS <ENTER>
TO SELECT
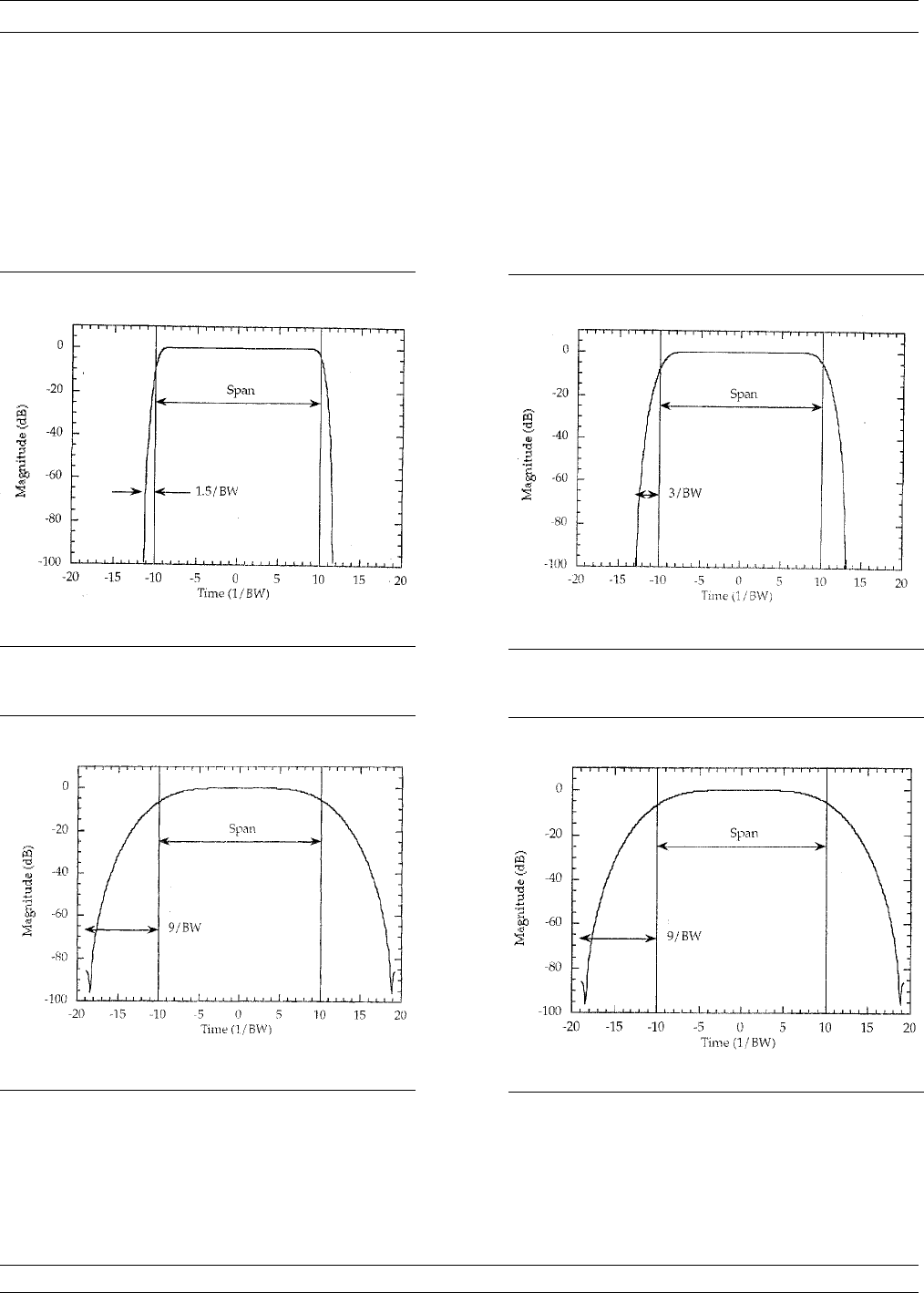
37XXXC OM 9-13
TIME DOMAIN GATING
An informational message will be displayed in the data area when the
window or gate shape reset in this way. The message will last two
sweeps and will say:
“GATE SHAPE ADJUSTED” or “WINDOW SHAPE ADJUSTED”
depending on which was changed by the software.
Figure 9-18A. Minimum Gate Shape Figure 9-18B. Nominal Gate Shape
Figure 9-18C. Wide Gate Shape Figure 9-18D. Maximum Gate Shape
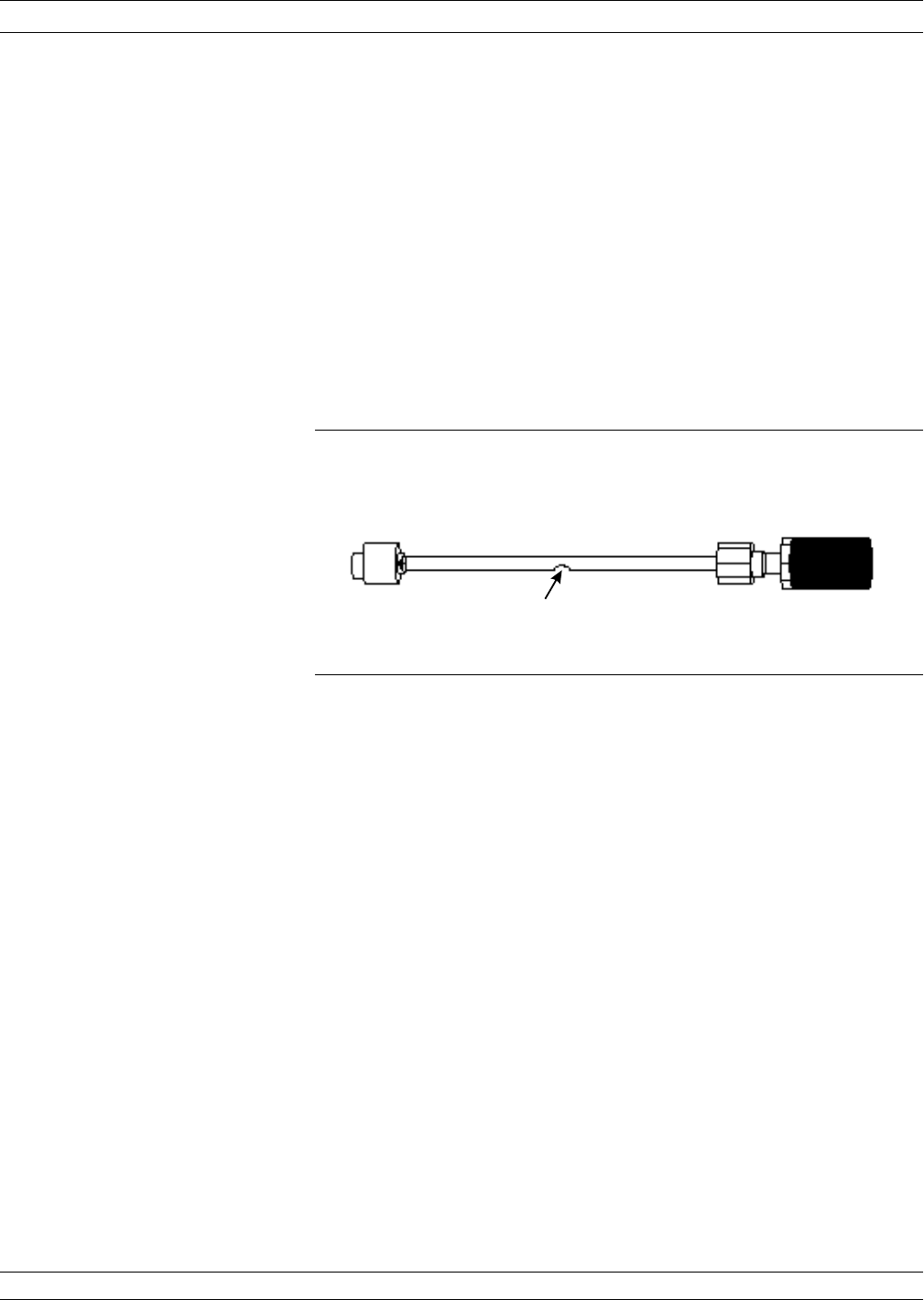
9-6 ANTI-GATING Anti-gating is the opposite of gating. Whereby, gating provides for re-
moving all but the desired response, anti-gating displays all but the
desired response. To provide anti-gating, gate in the normal manner,
except use a minus value for the SPAN width.
9-7 EXAMPLES, GATING
AND ANTI-GATING Examples of anti-gating are shown in Figures 9-19 through 9-24. The
figures, all captured from an actual VNA display, show a sequence of
measurements using gating and anti-gating to enhance measurement
technique and accuracy. The examples use a dented length of semi-
rigid cable having a connector on one end and a connector-DUT on the
other end, as shown below. The DUT has a smoothly varying 15 dB re-
turn loss.
9-8 TIME DOMAIN MENUS A flow diagram of the menus associated with the Time Domain Option
is shown in foldout Figure 9-25. The menu choices are described in Ap-
pendix A. They appear in alphabetical order by their call letters: TD1,
TD2, TD2dl, etc.
ANTI-GATING TIME DOMAIN
9-14 37XXXC OM
Connector
Dent
15 dB
DUT
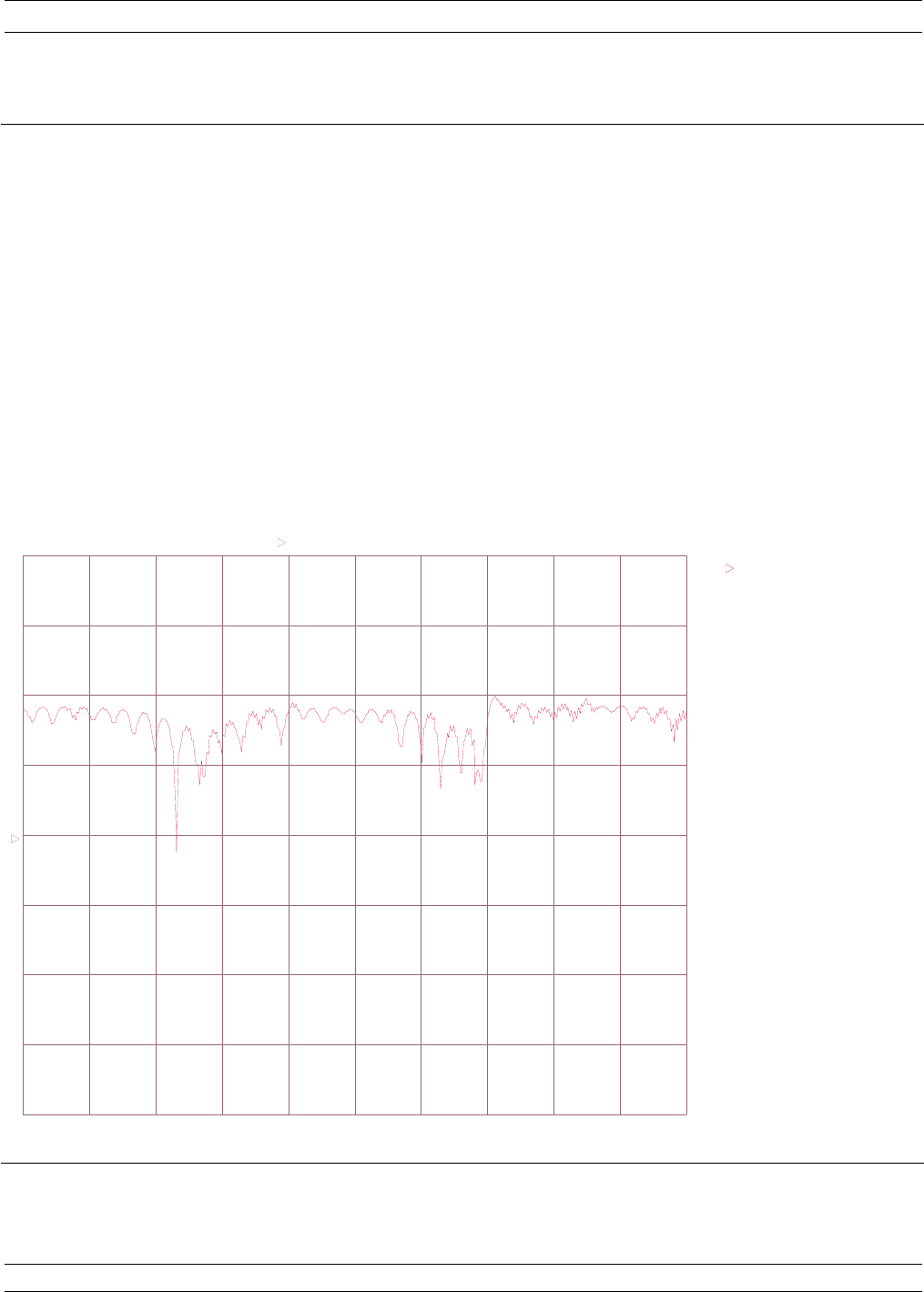
37XXXC OM 9-15
TIME DOMAIN TIME DOMAIN MENUS
37369A
MODEL: DATE: 03/27/96 15:10
DEVICE: OPERATOR:
START: 4.000000000 GHz GATE START: ERROR CORR: REFL PORT1
STOP: 40.000000000 GHz GATE STOP: AVERAGING: 1 PT
STEP: 0.090000000 GHz GATE: IF BNDWDTH: 1 KHz
WINDOW:
FREQUENCY
TIME
FREQUENCY
WITH TIME GATE
TIME
LOWPASSMODE
TIME
BANDPASSMODE
DISPLAY
/ DISTANCE
SET RANGE
SET GATE
GATE OFF
HELP
GHz4.000000000 40.000000000
S11 FORWARDREFLECTION
LOG MAGNITUDE REF= -40.000 dB 20.000 dB/DIV
DOMAIN
SETUP
PRESS <ENTER>
TO SELECT
OR SWITCH
Figure 9-19. Frequency Domain Trace of Test Cable—Gating Off
37369A

TIME DOMAIN MENUS TIME DOMAIN
9-16 37XXXC OM
37369A
MODEL: DATE: 03/27/96 15:12
DEVICE: OPERATOR:
START: 4.000000000 GHz GATE START: 315.0000 ps ERROR CORR: REFL PORT1
STOP: 40.000000000 GHz GATE STOP: 165.0000 ps AVERAGING: 1 PT
STEP: 0.090000000 GHz GATE: NOMINAL IF BNDWDTH: 1 KHz
WINDOW: NOMINAL
MARKER3
240.0000 ps
MARKERTO MAX
MARKERTO MIN
MARKERREADOUT
FUNCTIONS
-500.0000 ps 1.5000 ns
BPS11 FORWARDREFLECTION
LOG MAGNITUDE REF= -40.000 dB 20.000 dB/DIV
CH 1 - S11
REFERENCEPLANE
0.0000 mm
0.0000 ps
705.0000 ps
-16.260 dB
-29.255 dB
-18.001 dB
1
2
1
2
3
Figure 9-20. Time Domain Trace of Test Cable—Gating Off
Connector interface with
VNA Dent DUT Interface
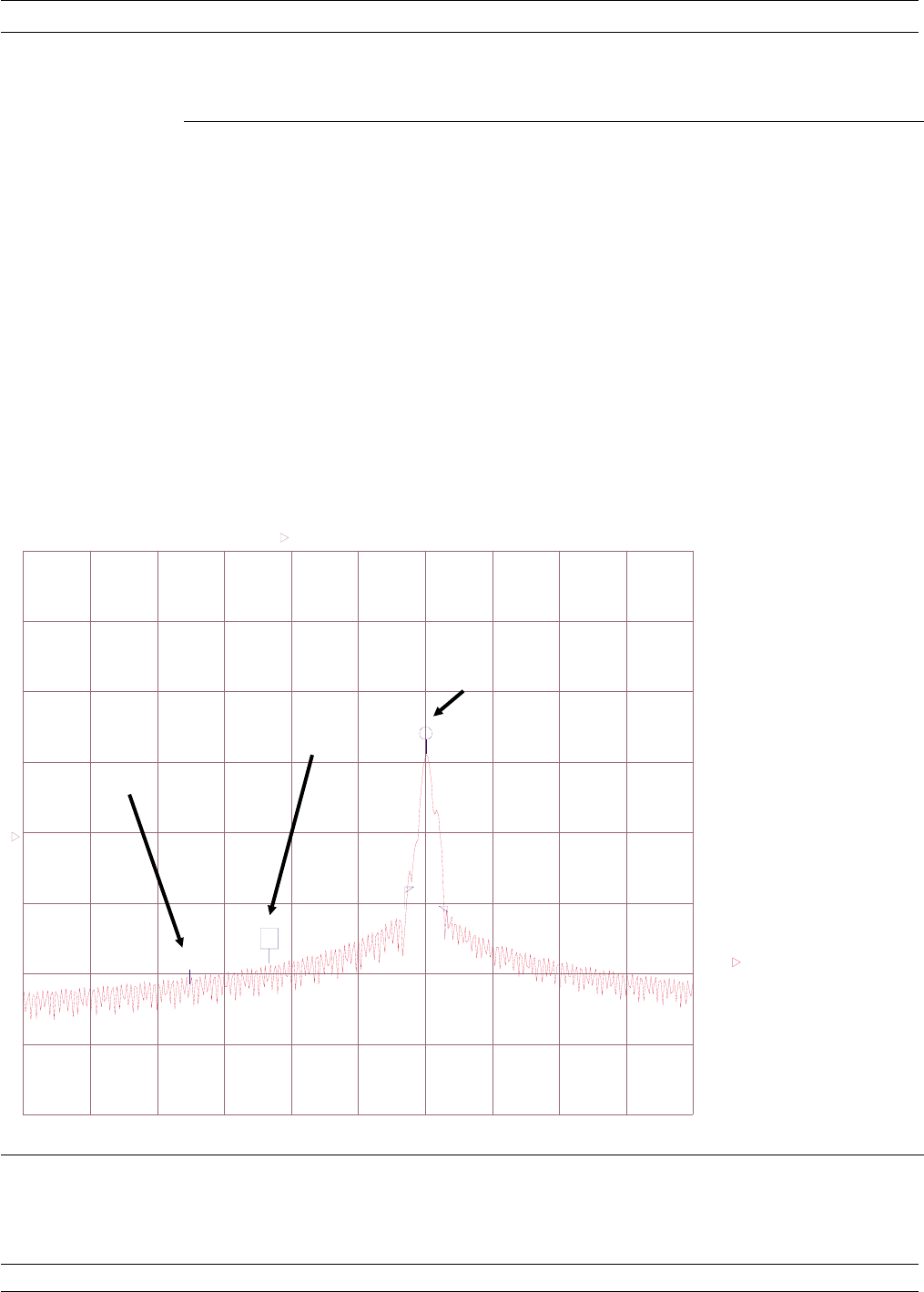
37XXXC OM 9-17
TIME DOMAIN TIME DOMAIN MENUS
37369A
MODEL: DATE: 03/27/96 15:14
DEVICE: OPERATOR:
START: 4.000000000 GHz GATE START: 642.5000 ps ERROR CORR: REFL PORT1
STOP: 40.000000000 GHz GATE STOP: 767.5000 ps AVERAGING: 1 PT
STEP: 0.090000000 GHz GATE: NOMINAL IF BNDWDTH: 1 KHz
WINDOW: NOMINAL
ON
START
642.5000 ps
STOP
767.5000 ps
CENTER
705.0000 ps
SPAN
125.0000 ps
GATE SHAPE
GATE
SET RANGE
-500.0000 ps 1.5000 ns
BP w/GATES11 FORWARDREFLECTION
LOG MAGNITUDE REF= -40.000 dB 20.000 dB/DIV
GATE
NOMINAL
PRESS <ENTER>
TO SELECT
1
2
3
Figure 9-21. Time Domain Trace of Test Cable—Gating On and Positioned Over DUT Interface Discontinuity.
Connector interface with VNA
removed by gating
DUT Interface
gated for display
Dent removed
by gating
Flag
Flag
Note that gating is turned on and span is set to cover the
discontinuity (125 ps down line from connection with VNA).
Further note that the gating flags point inward.
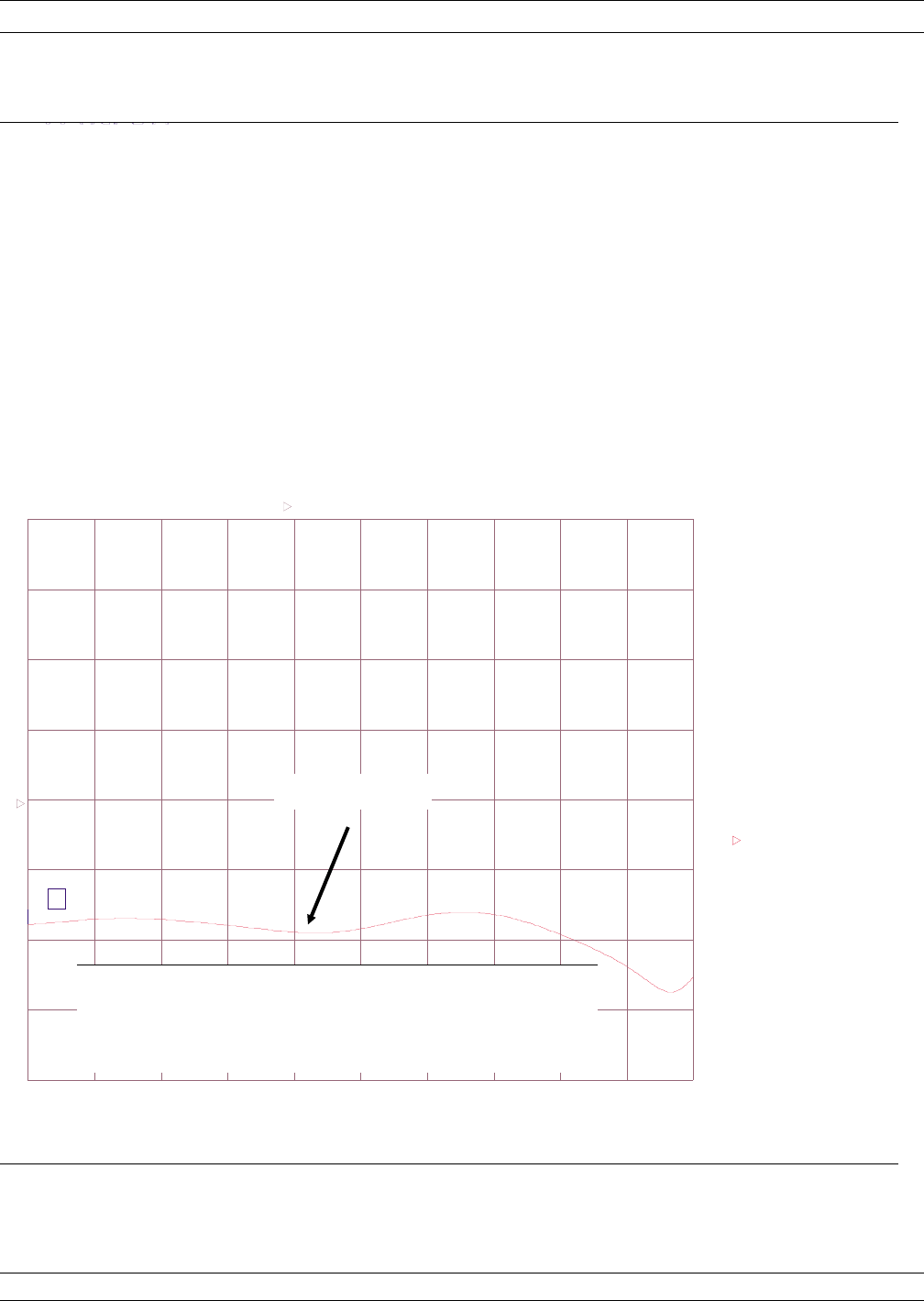
TIME DOMAIN MENUS TIME DOMAIN
9-18 37XXXC OM
37369A
MODEL: DATE: 03/27/96 15:16
DEVICE: OPERATOR:
START: 4.000000000 GHz GATE START: 642.5000 ps ERROR CORR: REFL PORT
1
STOP: 40.000000000 GHz GATE STOP: 767.5000 ps AVERAGING: 1 PT
STEP: 0.090000000 GHz GATE: NOMINAL IF BNDWDTH: 1 KHz
WINDOW: NOMINAL
RESOLUTION
10.000 dB/DIV
REFERENCEVALU
E
0.000 dB
REFERENCELINE
4
GHz4.000000000 40.000000000
FGTS11 FORWARDREFLECTION
LOG MAGNITUDE REF= 0.000 dB 10.000 dB/DIV
SET SCALING
OR PRESS
<AUTOSCALE>
-LOG MAG-
12 3
Figure 9-22. Frequency Domain Trace of DUT
DUT Interface
enlarged for evaluation
Note that the reference value is 0 dB and the resolution is
10 db per division. These values are optimum for viewing
the smoothly varying return loss characteristics of the DUT
interface - approximately 15 dB
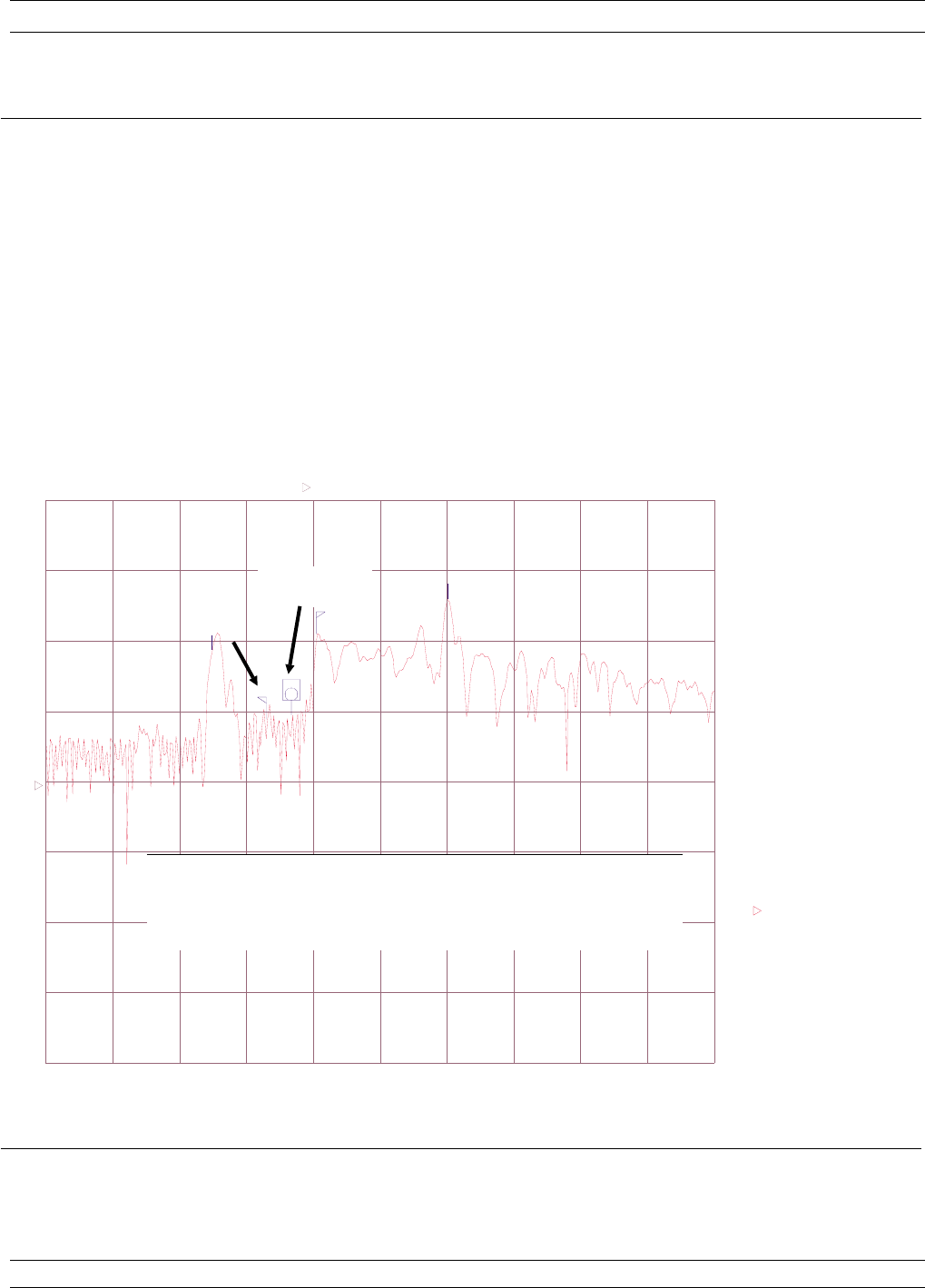
37XXXC OM 9-19
TIME DOMAIN TIME DOMAIN MENUS
37369A
MODEL: DATE: 03/27/96 15:19
DEVICE: OPERATOR:
START: 4.000000000 GHz GATE START: 315.0000 ps ERROR CORR: REFL PORT
1
STOP: 40.000000000 GHz GATE STOP: 165.0000 ps AVERAGING: 1 PT
STEP: 0.090000000 GHz GATE: NOMINAL IF BNDWDTH: 1 KHz
WINDOW: NOMINAL
O
START
315.0000 ps
STOP
165.0000 ps
CENTER
240.0000 ps
SPAN
-150.0000 ps
GATE SHAPE
GATE
SET RANGE
-500.0000 ps 1.5000 ns
BP w/GATES11 FORWARDREFLECTION
LOG MAGNITUDE REF= -87.348 dB 20.000 dB/DIV
GATE
NOMINAL
PRESS <ENTER>
TO SELECT
1
2
3
Figure 9-23. Time Domain Trace of Test Cable—Gating On and Positioned Over Dent (Cable Fault)
Interface Discontinuity.
Flag Flag
Dent removed
by anti-gating
Note that anti-gating is turned on by changing the polarity of
the SPAN to negative and changing its value to cover the dent.
Also, note that the flags point outward.
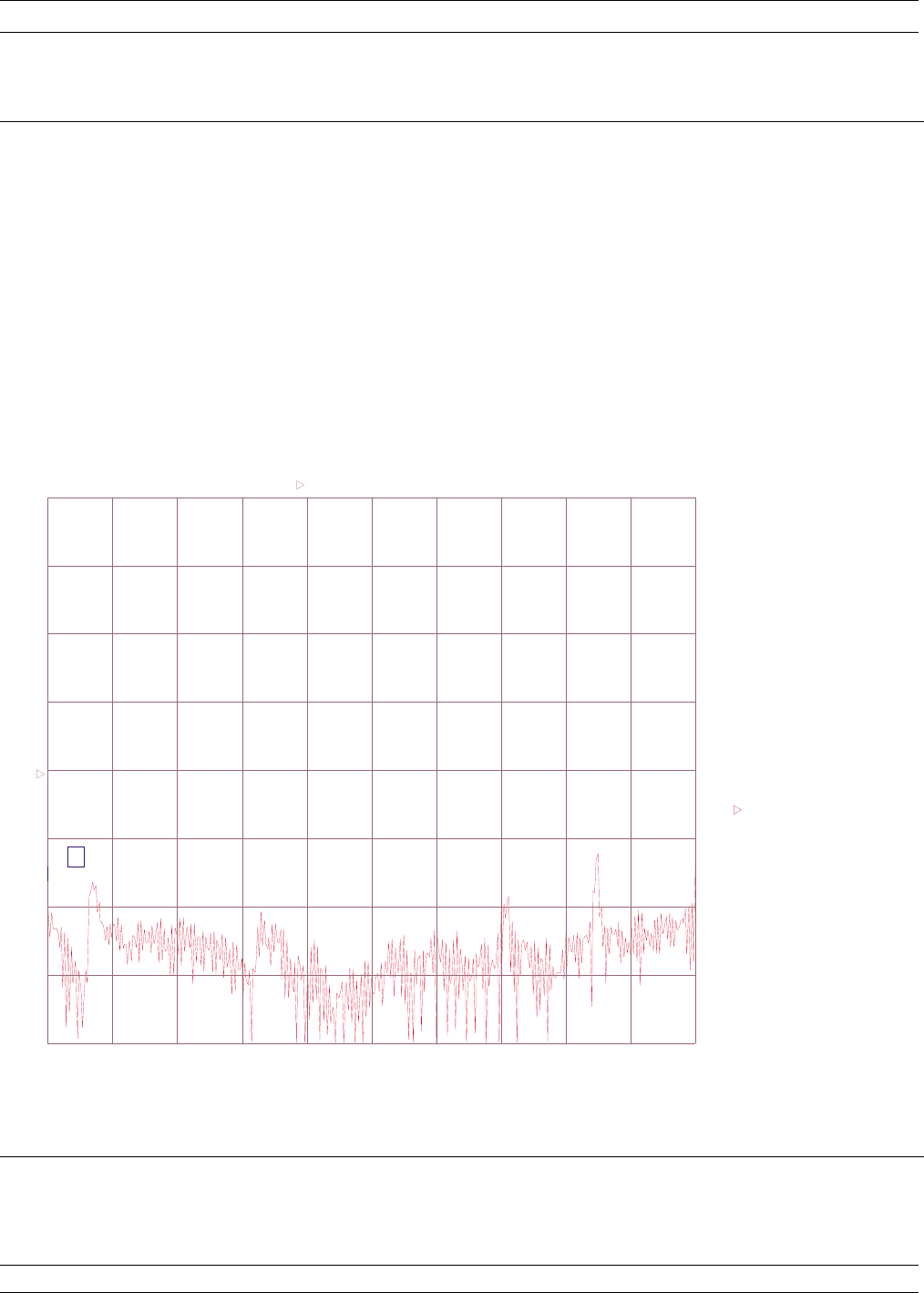
TIME DOMAIN MENUS TIME DOMAIN
9-20 37XXXC OM
37369A
MODEL: DATE: 03/27/96 15:23
DEVICE: OPERATOR:
START: 4.000000000 GHz GATE START: 340.0000 ps ERROR CORR: REFL PORT1
STOP: 40.000000000 GHz GATE STOP: 140.0000 ps AVERAGING: 1 PT
STEP: 0.090000000 GHz GATE: NOMINAL IF BNDWDTH: 1 KHz
WINDOW: NOMINAL
RESOLUTION
10.000 dB/DIV
REFERENCEVALUE
0.000 dB
REFERENCELINE
4
GHz4.000000000 40.000000000
FGTS11 FORWARDREFLECTION
LOG MAGNITUDE REF= 0.000 dB 10.000 dB/DIV
SET SCALING
OR PRESS
<AUTOSCALE>
-LOG MAG-
12 3
Figure 9-24. Frequency Domain Trace of Test Cable—Gating On
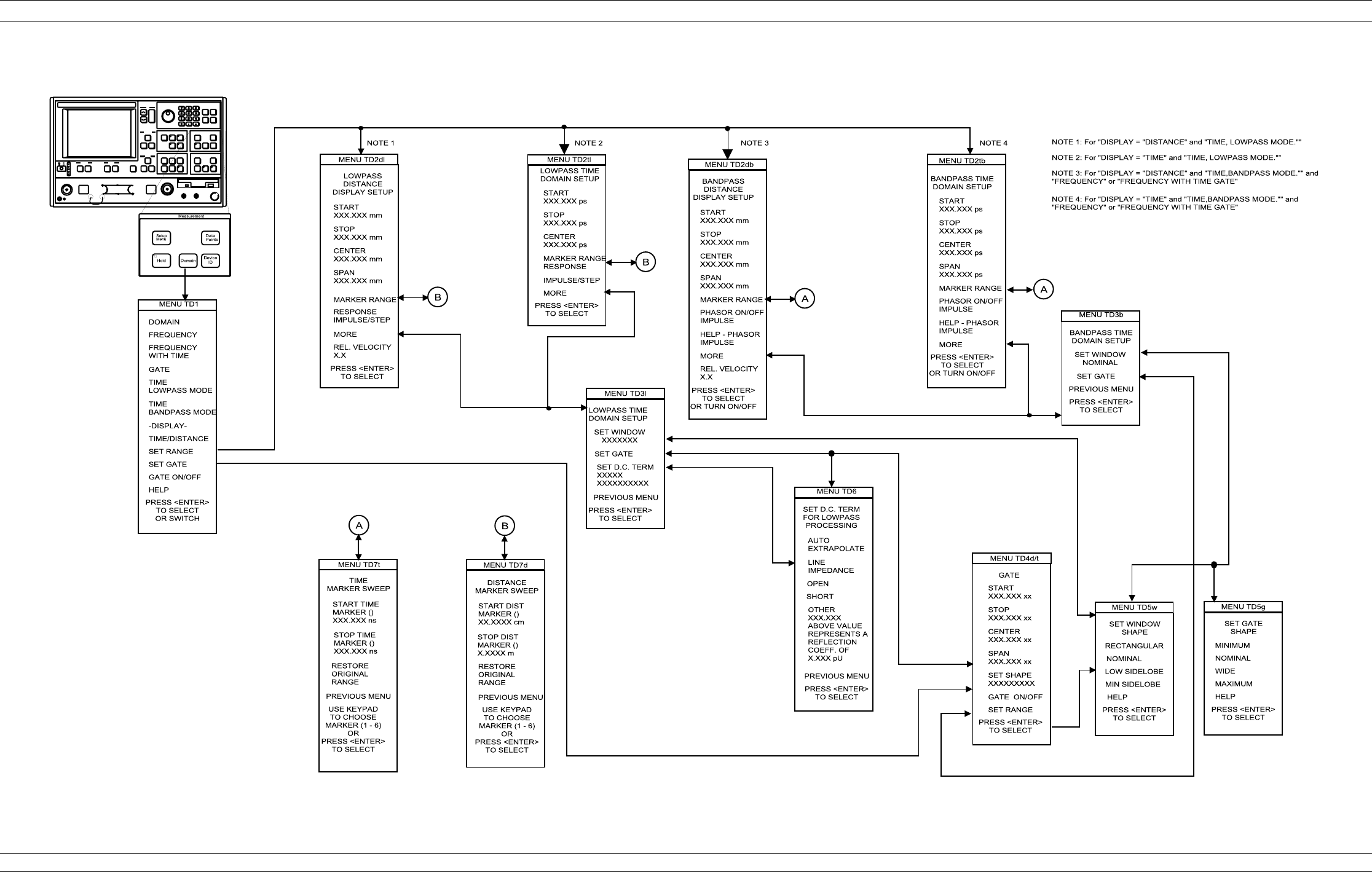
37XXXC OM 9-21/9-22
TIME DOMAIN MENU FLOWCHART
Figure 9-25. Time Domain Menu Flow

Table of Contents
10-1 INTRODUCTION...................................10-3
10-2 DESCRIPTION ....................................10-3
10-3 CALIBRATIONS ...................................10-4
10-4 DEFINITION .....................................10-4
10-5 PHYSICAL SETUP..................................10-6
10-6 CHARACTERIZATION FILES ...........................10-7
10-7 USING AUTOCAL ..................................10-9
10-8 PIN DEPTH SPECIFICATIONS ..........................10-13
10-9 AUTOCAL MENUS FLOW DIAGRAM ......................10-14
Chapter 10
AutoCal
IMPORTANT NOTE
The 37100C Direct Access Receiver cannot make S-parameter measurements without an ex-
ternal reflectometer setup. This manual describes calibration and S-parameter measure-
ments for 372XXC and 373XXC. Most of these measurements can also be used with the
371XXC assuming the user understands the need for an external reflectometer.
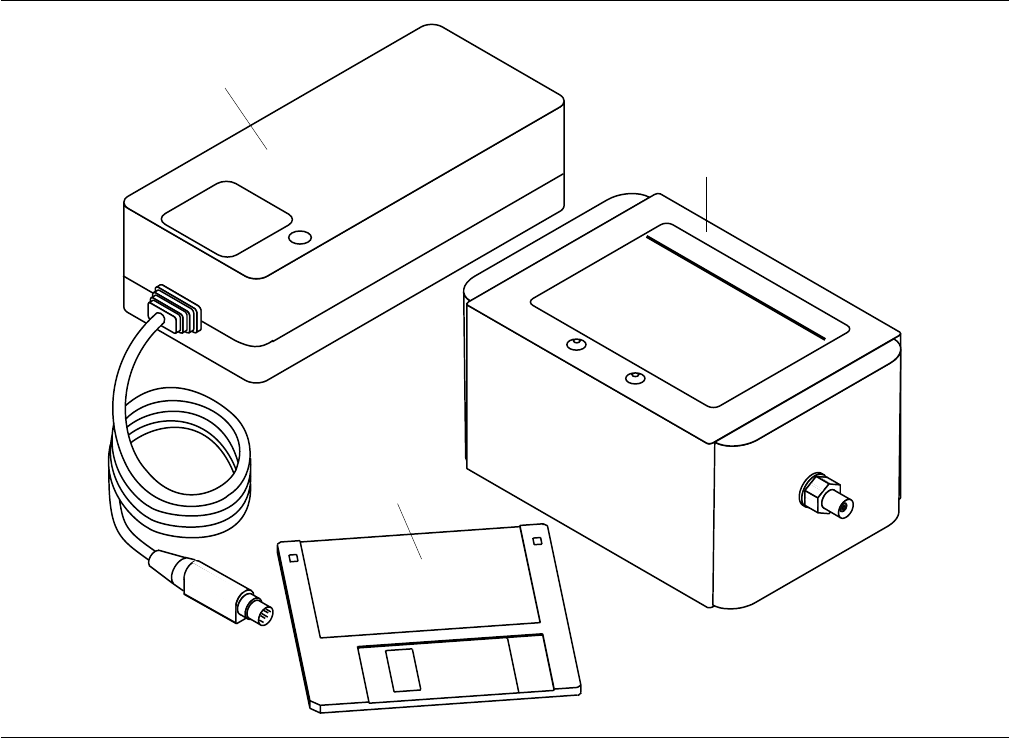
AUTOCAL MODULE 36581KKF
40 MHz - 20 GHz
LEFT RIGHT
Power Operate
Figure 10-1. AutoCal Module, Power Supply, and Calibration Coefficients Disk
Power Supply
AutoCal
Calibration Coefficients
Disk
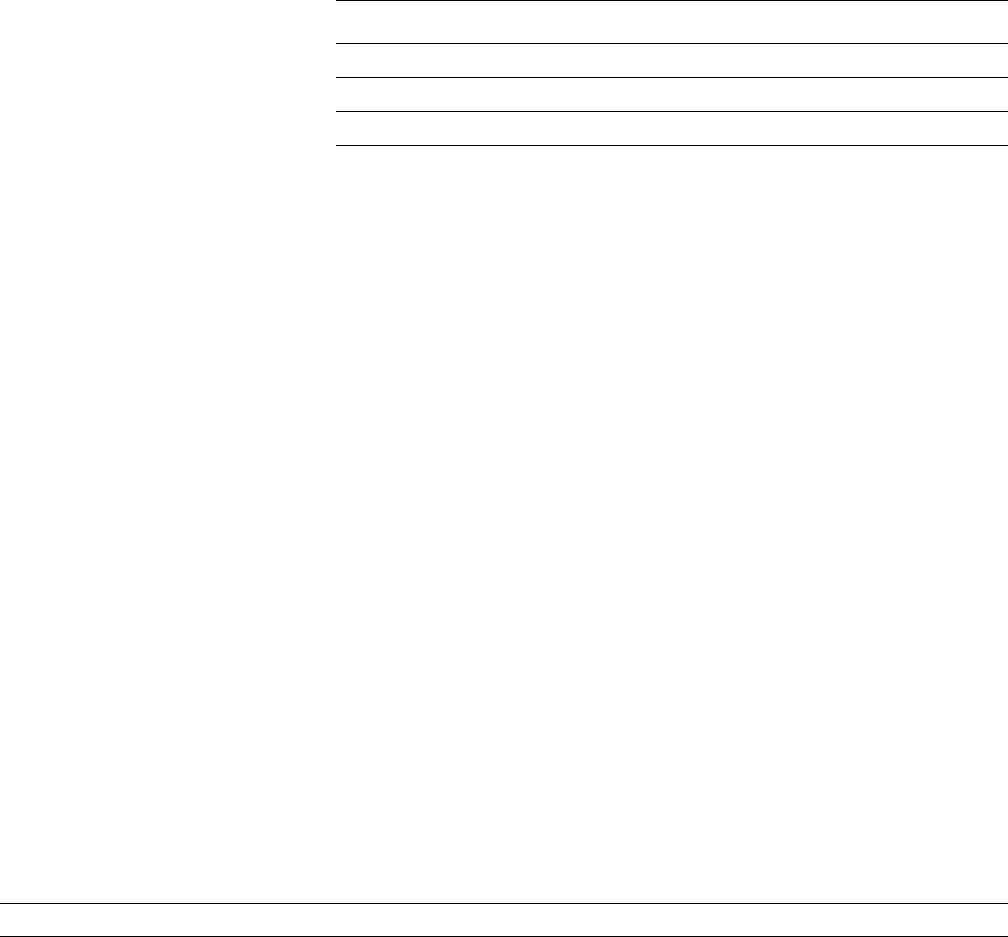
Chapter 10
AutoCal
10-1 INTRODUCTION This chapter provides a general description of the AutoCal calibrators,
including specifications, setup, and the use of the associated software
and on-line documentation. This series has three models, as shown be-
low. Throughout this manual, the term AutoCal will refer to the series.
Individual models will be referred to by model number. Figure 10-1
shows the AutoCal module and all of its attaching parts.
Model Switch Freq. Range Connector
36581NNF Electronic 40MHz-18 GHz N (Male)-N(Fem)
36581KKF Electronic 40MHz-20 GHz K(Male)-K(Fem)
36582KKF Mechanical 40MHz-40 GHz K(Male)-K(Fem)
10-2 DESCRIPTION The AutoCal module provides an automatic system for fast, repeatable
high-quality calibrations of a Vector Network Analyzer (VNA). The
AutoCal module is connected between the VNA's test ports 1 and 2 to
perform the calibration. Refer to Figure 10-2 for a diagram of the
AutoCal connections.
The electronic AutoCal modules use solid state electronic switches to
exchange the internal calibration standards. Note that these units
have a lower frequency limit (18 and 20 GHz). The mechanical module
uses electro-mechanical actuators to exchange the standards and has
the highest frequency limit, but has a small non-repeatability error.
The mechanical module contains internal standards used to measure
port isolation; the electronic module does NOT contain isolation stan-
dards and requires a manual operation to perform this measurement.
A standard serial RS-232 interface cable is used to connect the
AutoCal module to the 37XXXC. Power is supplied by a connecting ca-
ble from a universal power supply (+5V, +15V, –15V for the electronic
modules; +5V, +24V for the mechanical modules). A power on-off
switch is not provided.
Test Port Cable Converters (Anritsu series 36583) are used during and
after the calibration process to establish the desired test port connec-
tor type and sex.
37XXXC OM 10-3
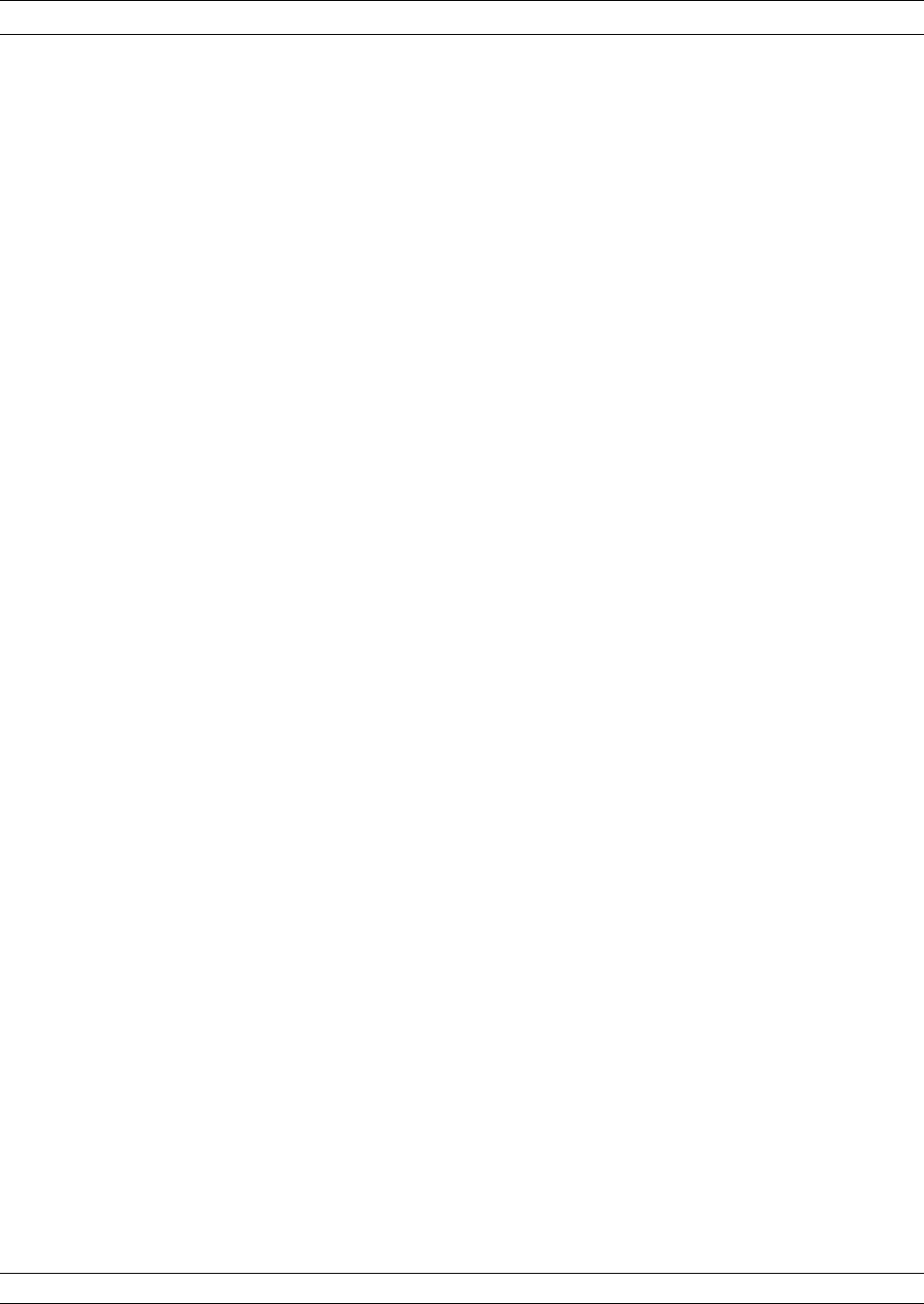
10-3 CALIBRATIONS Four types of calibration can be performed using AutoCal:
One-Port: S11 1-Port and S22 1-Port are 1-port calibrations per-
formed on the indicated port of the VNA and are equivalent to the tra-
ditional Open-Short-Load calibrations.
Full 2-Port: This type is equivalent to the traditional
Open-Short-Load-Thru (OSLT) calibration.
Thru Update: This type is a new form of calibration which is used to
update an existing 12-term calibration in the VNA. This calibration
could have been performed using any method of calibration which
yields 12 terms (LRL, LRM, AutoCal, or OSLT). Due to cable move-
ment and aging, the calibration may have degraded over time. The
Thru Update refreshes the calibration by measuring a Thru connec-
tion and updating the Transmission Tracking and Load Match calibra-
tion coefficients.
Adapter Removal: This calibration measures the characteristics of
male-male or female-female test port cables for subsequent measure-
ment of non-insertable devices. An adapter is required for this calibra-
tion. Adapter Removal requires two calibration procedures in order to
calculate the parameters and electrical length of the adapter.
10-4 DEFINITIONS The following terms are used in explaining the calibration procedure
using the AutoCal module:
Thru: Athru is a connection of the two test ports. Two kinds of thru
connections are defined for the AutoCal calibration: (1) a Calibrator
thru is an internal path through the calibrator. (2) a True thru is a di-
rect cable connection between the test ports, with no intervening con-
nectors. The calibrator thru is not as accurate as a true thru, so the
you have the option during a calibration to use the more accurate
method, if necessary.
Switch Averaging: The mechanical AutoCal module uses electro-me-
chanical switches to select calibration standards. These switches have
a small amount of non-repeatability (typically less than –55 dB). For
most calibrations, this is more than adequate because it is below con-
nector repeatability error. If desired, you can choose to reduce the ef-
fect of this non-repeatability in the mechanical module by using
Switch Averaging, which causes additional calibration measurements.
By setting a Switch Averaging factor larger than 1, switch repeatabil-
ity error will be reduced. The tradeoff is that calibration time will be
proportionally increased.
CALIBRATIONS AUTOCAL
10-4 37XXXC OM
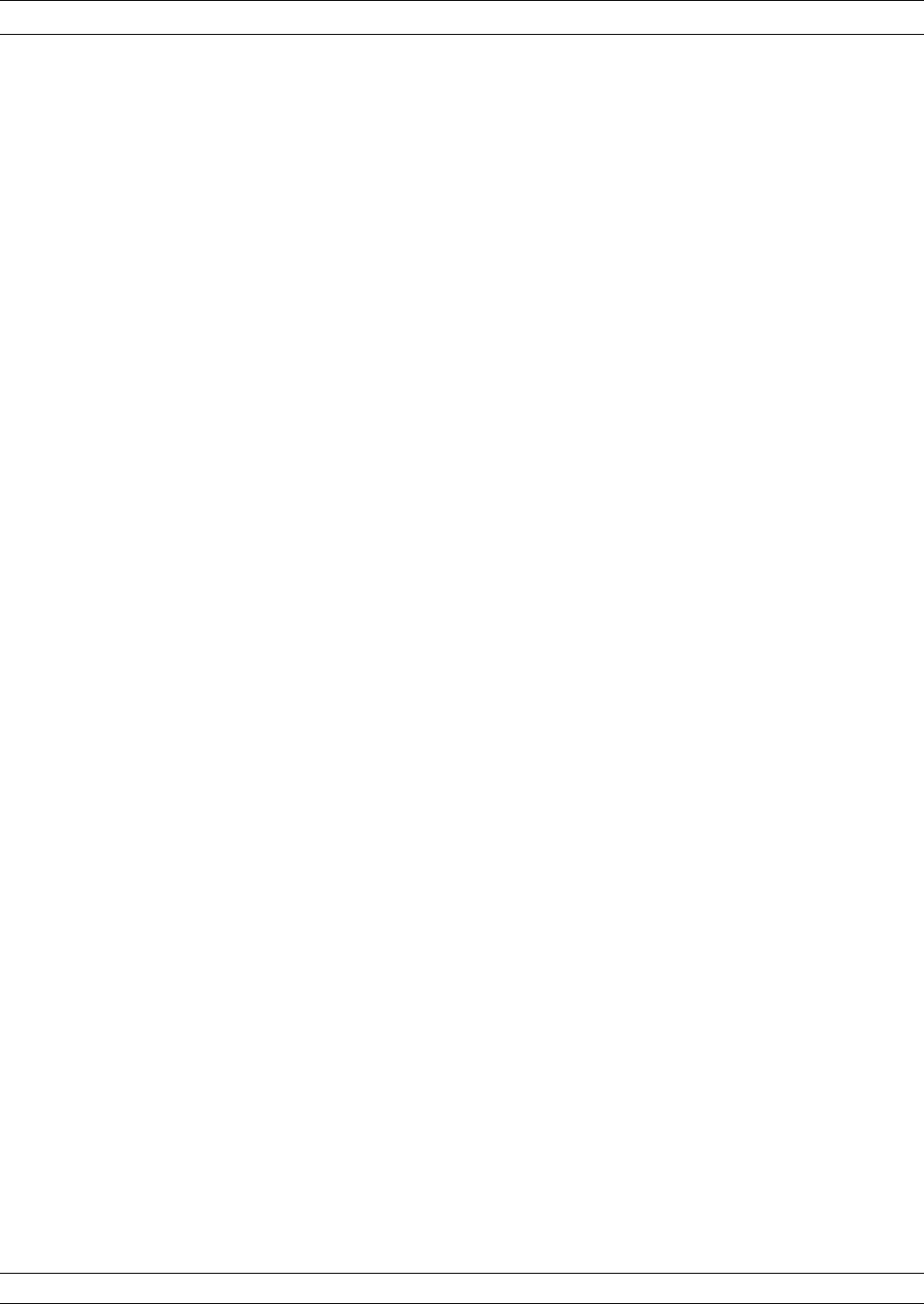
Isolation: For certain measurements which require accurate S21 or
S12 readings for very small values of those parameters, an isolation
step is required to characterize the leakage of the VNA and test setup.
The isolation step can be performed automatically as part of a “Full
2-Port” calibration when using the mechanical module. The isolation
step requires a manual operation for the electronic module. In order to
achieve high accuracy for the characterization of the leakage, a high
averaging factor is needed.
VNA Measurement Averaging Factor: This is the number of
measurements taken at a given data point (frequency) and may be
adjusted to meet the measurement requirements. The average of all
the measurements will become the measured data. For example, if 256
averages is selected, each data point is measured 256 times and the
average of these measurements is displayed, then the VNA moves to
the next data point.
VNA Video IF Bandwidth: The bandwidth of the receiver may be
changed to enhance the measurement accuracy or, conversely, to
increase the measurement speed. Selecting the minimum IF
bandwidth results in the greatest accuracy for low-signal-level
measurements and the slowest measurement speed. Selecting the
maximum IF bandwidth results in the greatest measurement speed
and reduced accuracy on low-signal-level measurements.This can be
set by using the Video IF BW key and selecting the desired IFBW.
Characterization File: Each calibrator module has a file containing
data which characterizes each standard in the calibrator. This file also
contains information (identification number, start and stop frequen-
cies) concerning the capabilities of the calibrator. Each characteriza-
tion file has the extension “.acd.” When modules are changed, you
must install the appropriate new characterization file. This file can be
installed using the Utility key (AutoCal Utilities) to recall the charac-
terization file from a disk. In addition, each AutoCal module can be
re-characterized using the VNA. A valid 12-term calibration must be
active, which is used to characterize the standards within the module.
37XXXC OM 10-5
AUTOCAL DEFINITIONS
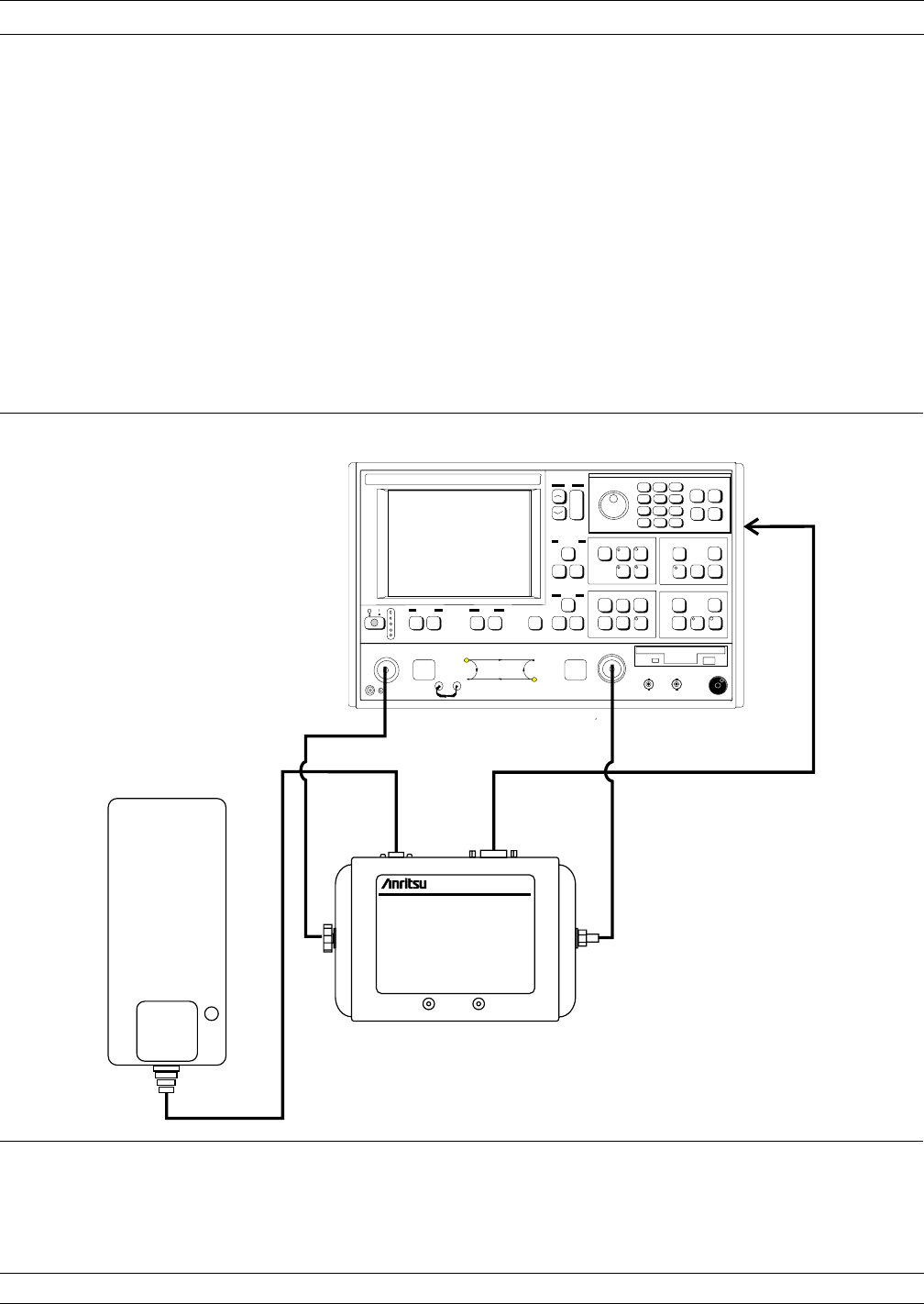
10-5 PHYSICAL SETUP See Figure 10-2 for an illustration of the connections necessary to per-
form an automatic calibration using the AutoCal module. Note that
the connection is very simple. Different power cable connectors are
used with the mechanical modules and the electronic modules to pre-
vent connecting the wrong power supply in error.
There is no on-off switch. When power is connected to the AutoCal
module, the LED labeled POWER should come on immediately. The
second LED, labeled OPERATE, should come on in about five minutes,
after the internal temperature control oven has stabilized. The
internal temperature is held within a 5 oC window.
PHYSICAL SETUP AUTOCAL
10-6 37XXXC OM
789
456
123
0.-
Data E ntry
AUTOCAL MODULE 36581KKF
40 MHz - 20 GHz
LEFT RIGHT
Power Operate
AUTOCAL
AUTOCAL
POWER
SUPPLY
37XXX
C
SERIAL
PORT
SERIAL
CABLE
Figure 10-2. AutoCal Equipment Setup
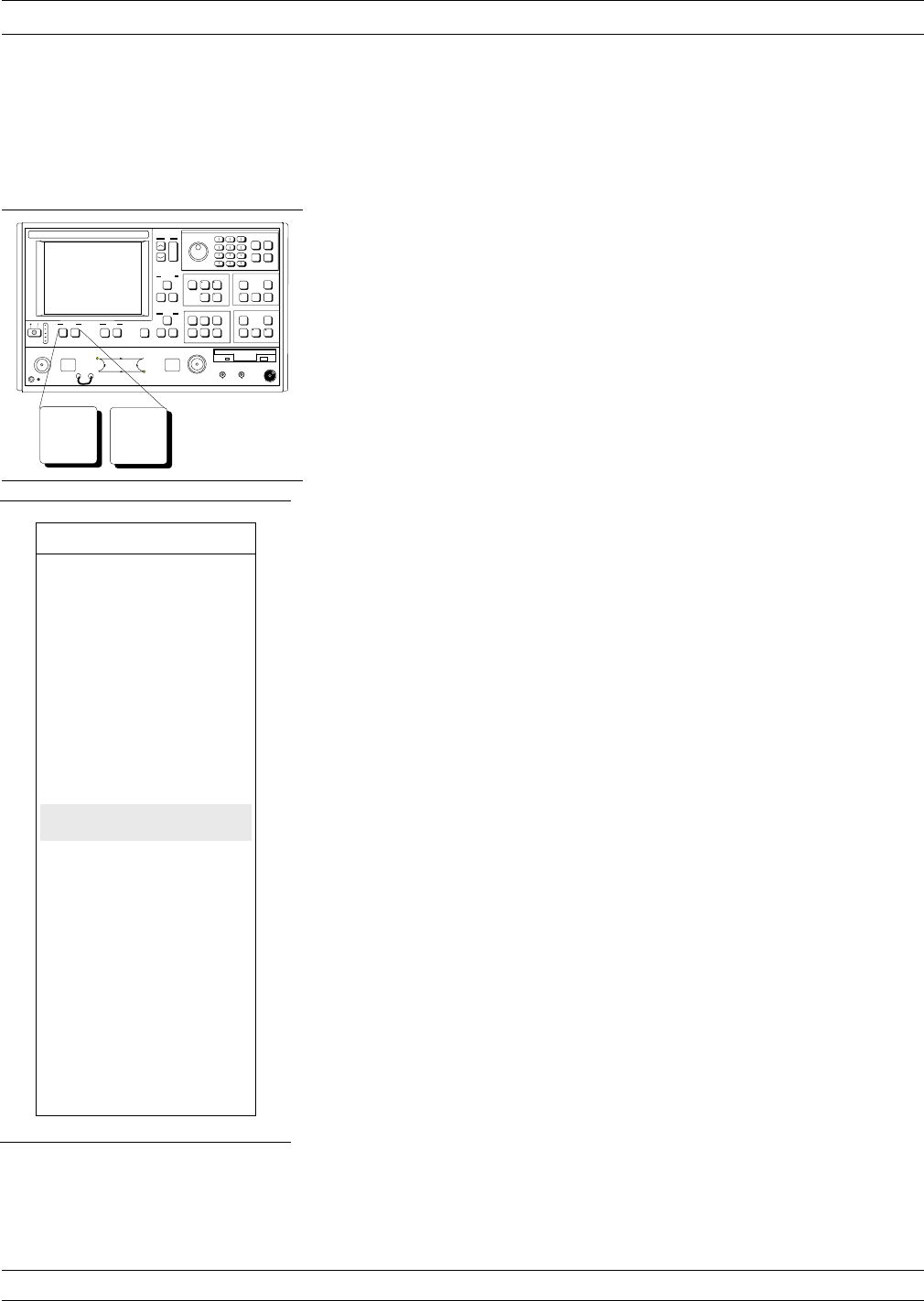
10-6 CHARACTERIZATION
FILES Before performing an AutoCal on a 37XXXC, the Characterization File
for the AutoCal Module has to be loaded. This file may be recalled
from the floppy disk accompanying the Module. It may also be recalled
from one generated using the user's specialized manual calibration.
Insert the AutoCal Module Characterization Disk into the floppy drive.
Press the Utility Menu key (left), then select the following menu options,
in turn: AUTOCAL UTILITIES, RECALL FROM FLOPPY DISK.
Select the file “Lxxxxxx.ACD“.
If a copy of the Characterization File is in the hard-disk, you can recall
it by choosing RECALL FROM HARD DISK instead. Select the
same file “Lxxxxxx.ACD”.
NOTE
The “xxxxxx” in the above paragraphs correspond to the
serial number of the AutoCal module.
Should you desire to re-characterize the module, which is recom-
mended every six months of usage, perform the following procedure:
Step 1. Using a 365x or 375x Calibration Kit, perform a
12-Term calibration over the desired frequency range
of characterization, but within the range of the
AutoCal module and the VNA.
NOTE
Any calibration method may be used (Stan-
dard, Offset Short, LRL/LRM, or TRM)
along with either the Coaxial or Waveguide
line types.
Step 2. Upon completion of the calibration, press the Utility
Menu key.
37XXXC OM 10-7
AUTOCAL CHARACTERIZATION FILES
Default
Program Utility
Menu
MENU UTIL
SELECT UTILITY
FUNCTION OPTIONS
GPIB ADDRESSES
DISPLAY
INSTRUMENT
STATE PARAMS
GENERAL DISK
UTILITIES
CAL COMPONENT
UTILITIES
AUTOCAL
UTILITIES
COLOR
CONFIGURATION
DATA ON (OFF)
DRAWING
BLANKING
FREQUENCY
INFORMATION
SET DATE/TIME
PRESS <ENTER>
TO SELECT
OR TURN ON/OFF
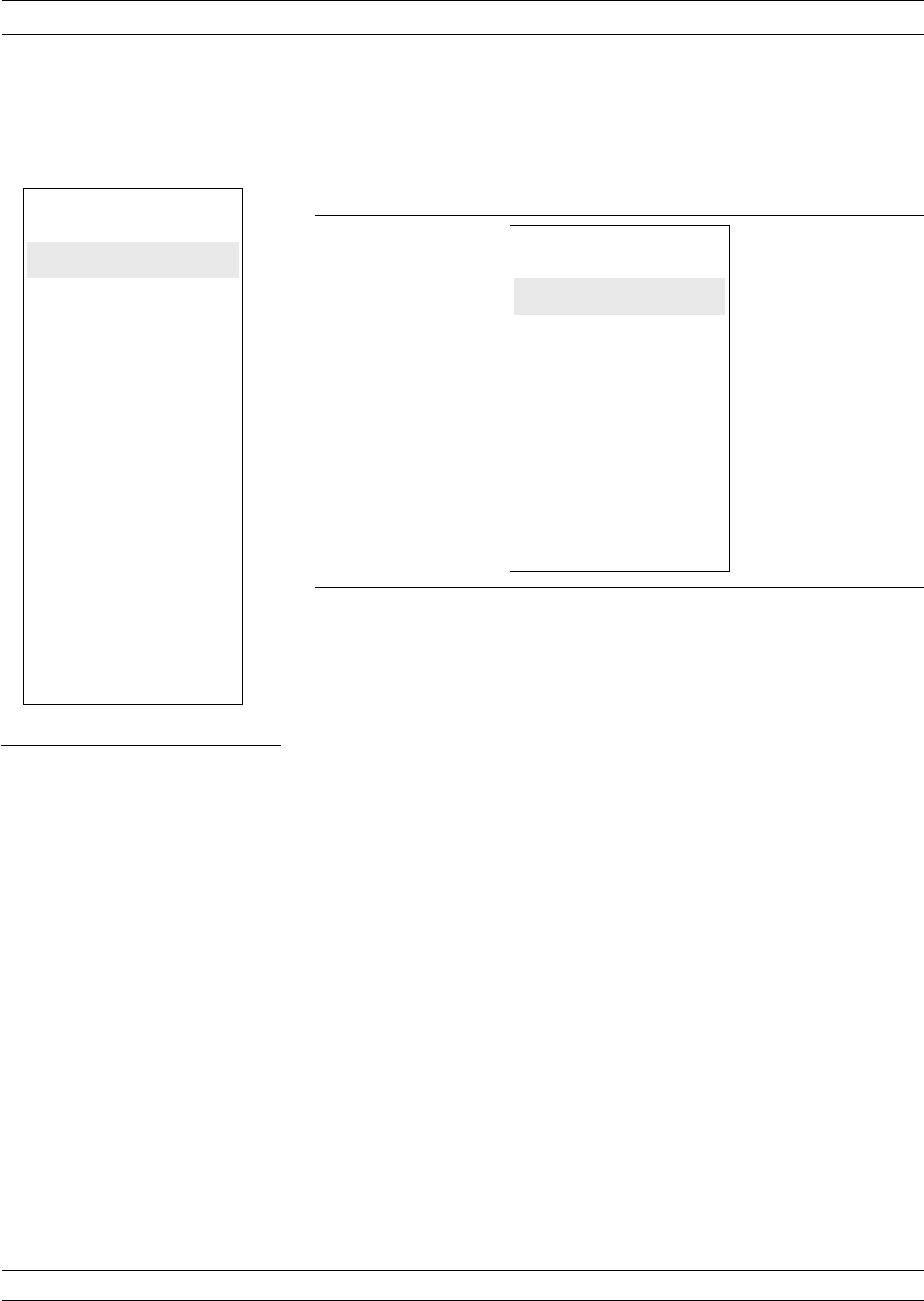
Step 3. Select AUTOCAL UTILITIES then AUTOCAL
CHARACTERIZATION, from the next menu to ap-
pear.
Step 4. Select an appropriate amount of SWITCH AVER-
AGING (recommend 4 for the electronic modules,
and 16 for the electro-mechanical modules).
Step 5. Ensure the Module Configuration is correct (L=1,
R=2 or R=1, L=2).
Step 6. If desired, you may change the amount of averaging
during characterization of each standard, by enter-
ing the NUMBER OF AVERAGES.
Step 7. Ensure the Autocal Module is connected between the
Test Ports, power is applied, and the serial cable is
connected to the VNA. Verify that both the “Power”
and “Operate” LED’s are ON.
Step 8. Select START AUTOCAL CHARACTERIZATION.
The VNA will proceed through a characterization of
the attached Autocal Module.
Step 9. When the calibration is complete, press the Save/Re-
call key.
Step 10. Select SAVE then FRONT PANEL SETUP AND
CAL DATA TO HARD DISK (middle and bottom
left).
CHARACTERIZATION FILES AUTOCAL
10-8 37XXXC OM
AUTOCAL
CHARACTERIZATION
SWITCH AVERAGING
XXXX
PORT CONFIG
L=1, R=2
R=1, L=2
NUMBER OF
AVERAGES
REFLECTION
XXXX
LOAD
XXXX
THRU
XXXX
ISOLATION
XXXX
START AUTOCAL
CHARACTERIZATION
PRESS <ENTER>
TO SELECT
OR SWITCH
AUTOCAL
UTILITIES
AUTOCAL
CHARACTERIZATION
SAVE
TO HARD DISK
SAVE
TO FLOPPY DISK
RECALL
FROM HARD DISK
RECALL
FROM FLOPPY DISK
PRESS <ENTER>
TO SELECT
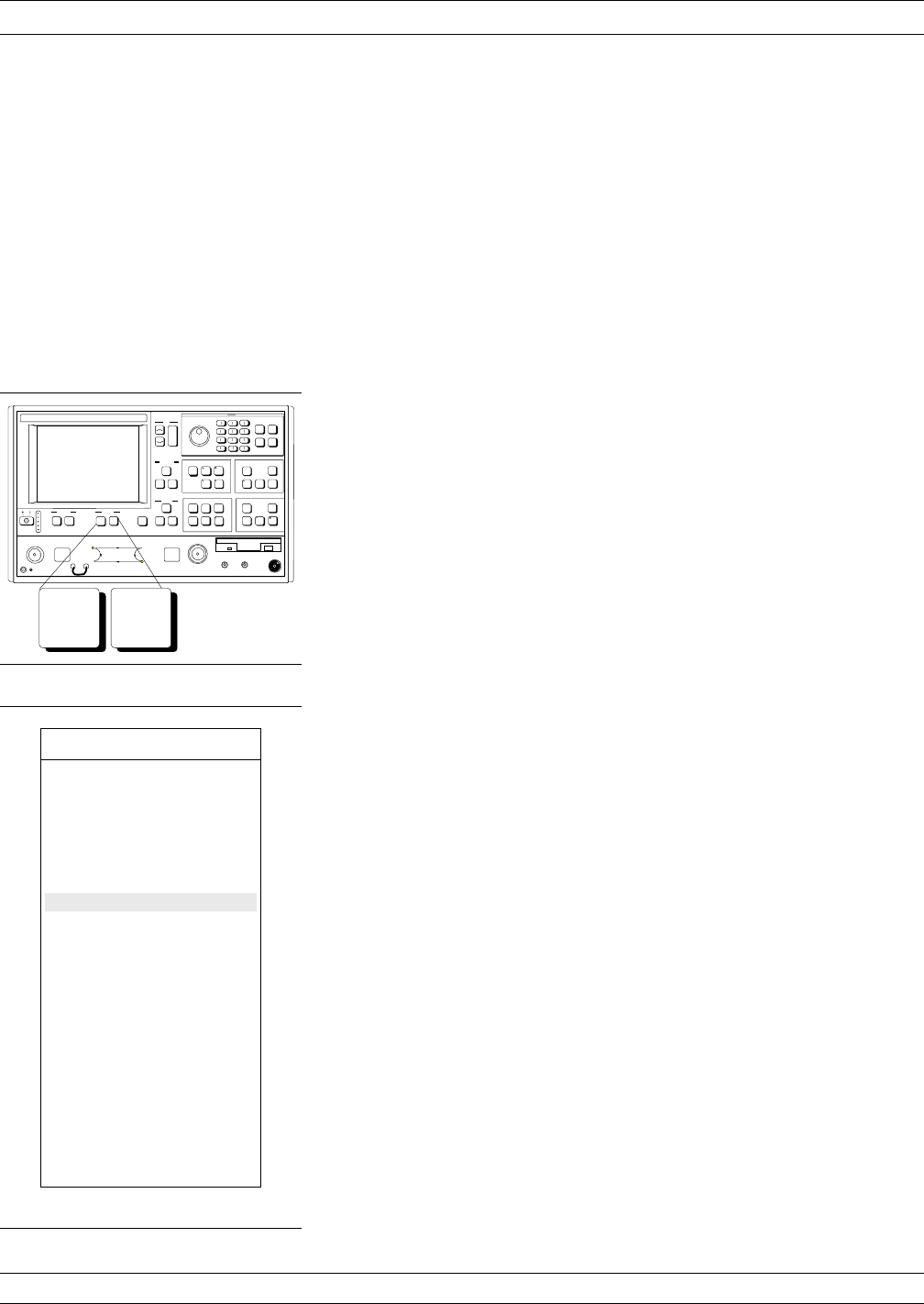
Step 11. Select a file or CREATE NEW FILE and press En-
ter.
If you are creating a new file, enter the filename and
select DONE when finished.
10-7 USING AUTOCAL An example procedure for using the AutoCal module is given below.
This example assumes a frequency range of 40 MHz to 40 GHz, a
power level of -7 dBm, and use of a Series 36582 AutoCal module.
Step 1. Press the Begin Cal key (top left).
Step 2. Select AUTOCAL from the displayed menu (C11,
left).
37XXXC OM 10-9
AUTOCAL USING AUTOCAL
Apply
Cal
Begin
Cal
MENU C11
BEGIN CALIBRATION
KEEP EXISTING
CAL DATA
REPEAT
PREVIOUS CAL
AUTOCAL
CAL METHOD
XXXXXXXXX
TRANSMISSION
LINE TYPE:
XXXXXXXXX
CHANGE CAL
METHOD AND
LINE TYPE
NEXT CAL STEP
PRESS <ENTER>
TO SELECT
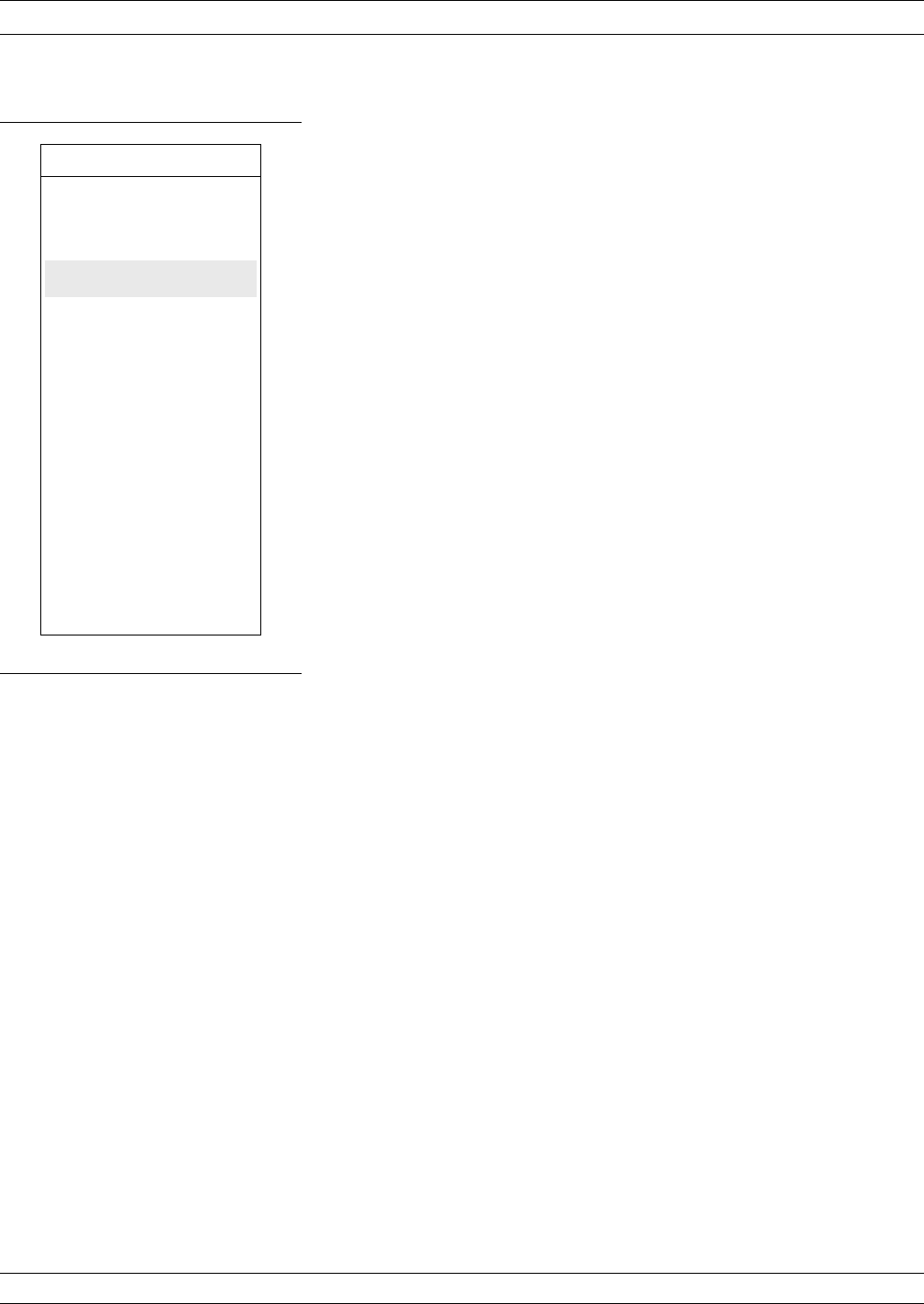
Step 3. The selections in the next menu to appear, MENU
ACAL, will depend on current instrument conditions,
as follows:
a. THRU UPDATE lets you update the Thru cali-
bration of an active 12-term Calibration. This
updates the transmission frequency response
and load match coefficients.
b. START AUTOCAL lets you start a calibration
using the current setup.
c. CHANGE AUTOCAL SETUP lets you set up a
new calibration, which is what we will do for
this example. This example also assumes that
you have selected the transmission medium and,
if waveguide, identified the cutoff frequency.
USING AUTOCAL AUTOCAL
10-10 37XXXC OM
MENU ACAL
AUTOCAL
AUTOCAL TYPE:
XXXXXXXX
CHANGE
AUTOCAL SETUP
START AUTOCAL
THRU UPDATE
CONNECT THROUGH
LINE BETWEEN
PORTS 1 AND 2
NUMBER OF AVGS
XXX
START THRU UPDATE
USE PREVIOUS
AUTOCAL SETUP
PRESS <ENTER>
TO SELECT
OR SWITCH
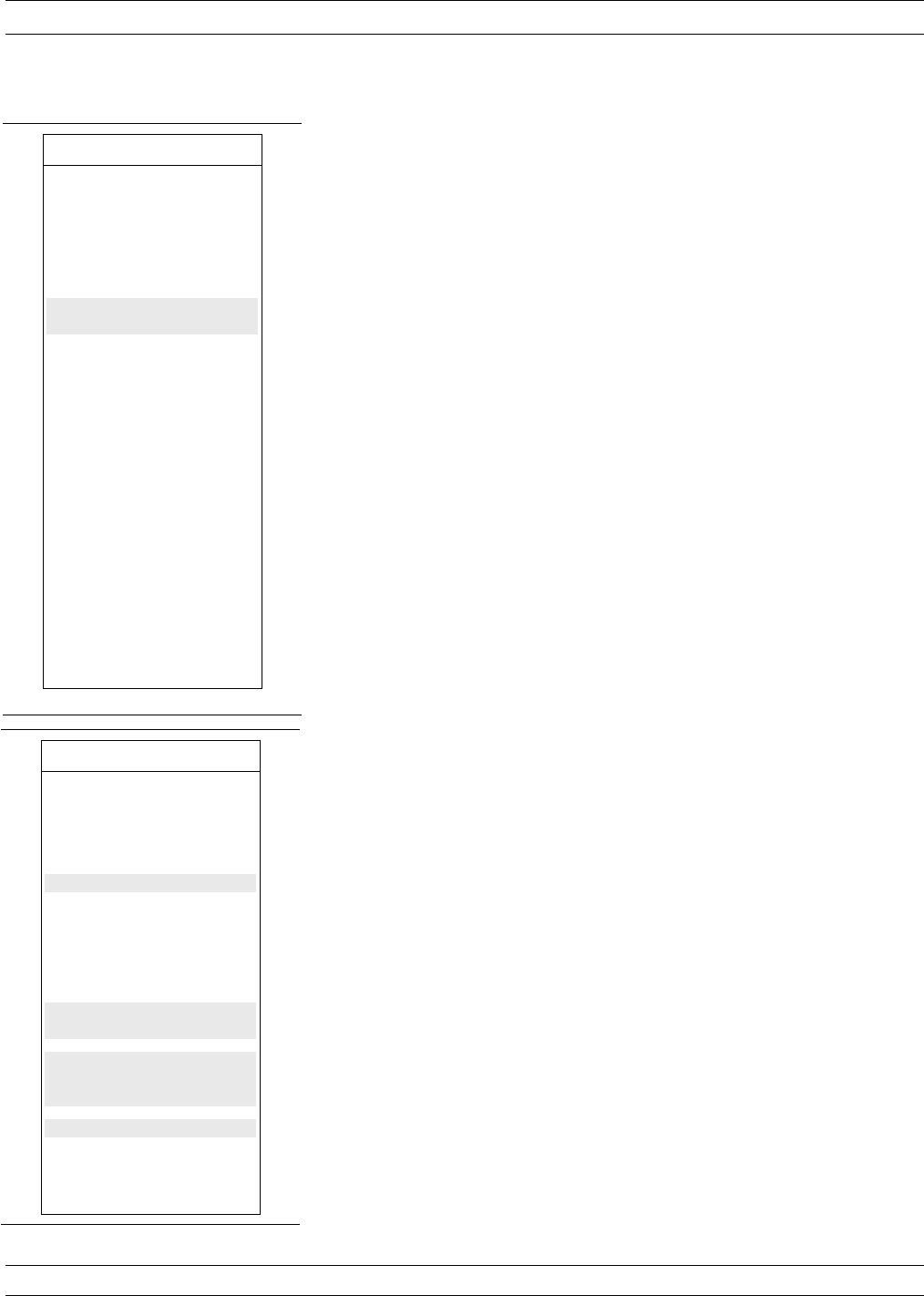
Step 4. Select CHANGE AUTOCAL SETUP. This causes
MENU ACAL_SETUP (left) to appear.
Step 5. Enter a SWITCH AVERAGING value of 8.
To improve the effect of switch repeatability error
with the 36582 series (mechanical switch), you can
change the switch averaging. Note, however, that
switch averaging will have no affect on the 36581 se-
ries (electronic switch).
Step 6. Select FULL 2 PORT. This displays a menu (MENU
ACAL_FULL) that lets you set up the calibration
(bottom left).
You could have also selected S11 1-PORT, S22
1-PORT,orADAPTER REMOVAL. The last of
these lets you remove the effects of an adapter used
in the calibration.
Step 7. Select the PORT CONFIG setting that matches the
physical setup (R-1, L=2 or L=1, R=2).
It is critical to ensure the correct module orientation
is established. Each side (left and right) of the mod-
ule is labeled.
Step 8. Select the THRU TYPE to be either CALIBRATOR
or TRUE.
By default, the CALIBRATOR (internal) thru stan-
dard is used for the Thru Calibration. The transmis-
sion response of the calibration may be improved by
selecting the TRUE thru standard. This will result
in an added manual step.
Step 9. Observe that OMIT is shown for the ISOLATION
AVERAGING.
Isolation may be omitted (default). You may also se-
lect DEFAULT to use the default value during the
isolation step. You may also use your own AVER-
AGING FACTOR. Including isolation involves a
manual step for the 36581 models.
Step 10. Ensure the AutoCal module is properly connected
between Ports 1 and 2, then select START
AUTOCAL.
37XXXC OM 10-11
AUTOCAL USING AUTOCAL
MENU ACAL_SETUP
AUTOCAL SETUP
LINE TYPE
COAXIAL/WAVEGUIDE
WAVEGUIDE CUTOFF
XX.XXXXXX GHz
SWITCH AVERAGING
8
NUMBER OF AVGS
REFLECTION
XXXX
LOAD
XXXX
THRU
XXXX
ISOLATION
XXXX
AUTOCAL TYPE
SII 1 PORT
S22 1 PORT
FULL 2 PORT
ADAPTER REMOVAL
MENU ACAL_FULL
AUTOCAL
FULL 2-PORT
ISOLATION
AVERAGING
OMIT
DEFAULT
AVERAGING
FACTOR
XXXX
THRU TYPE
CALIBRATOR/TRUE
PORT CONFIG
L=1, R=2
R=1, L=2
START AUTOCAL
PRESS <ENTER>
TO SELECT
OR SWITCH
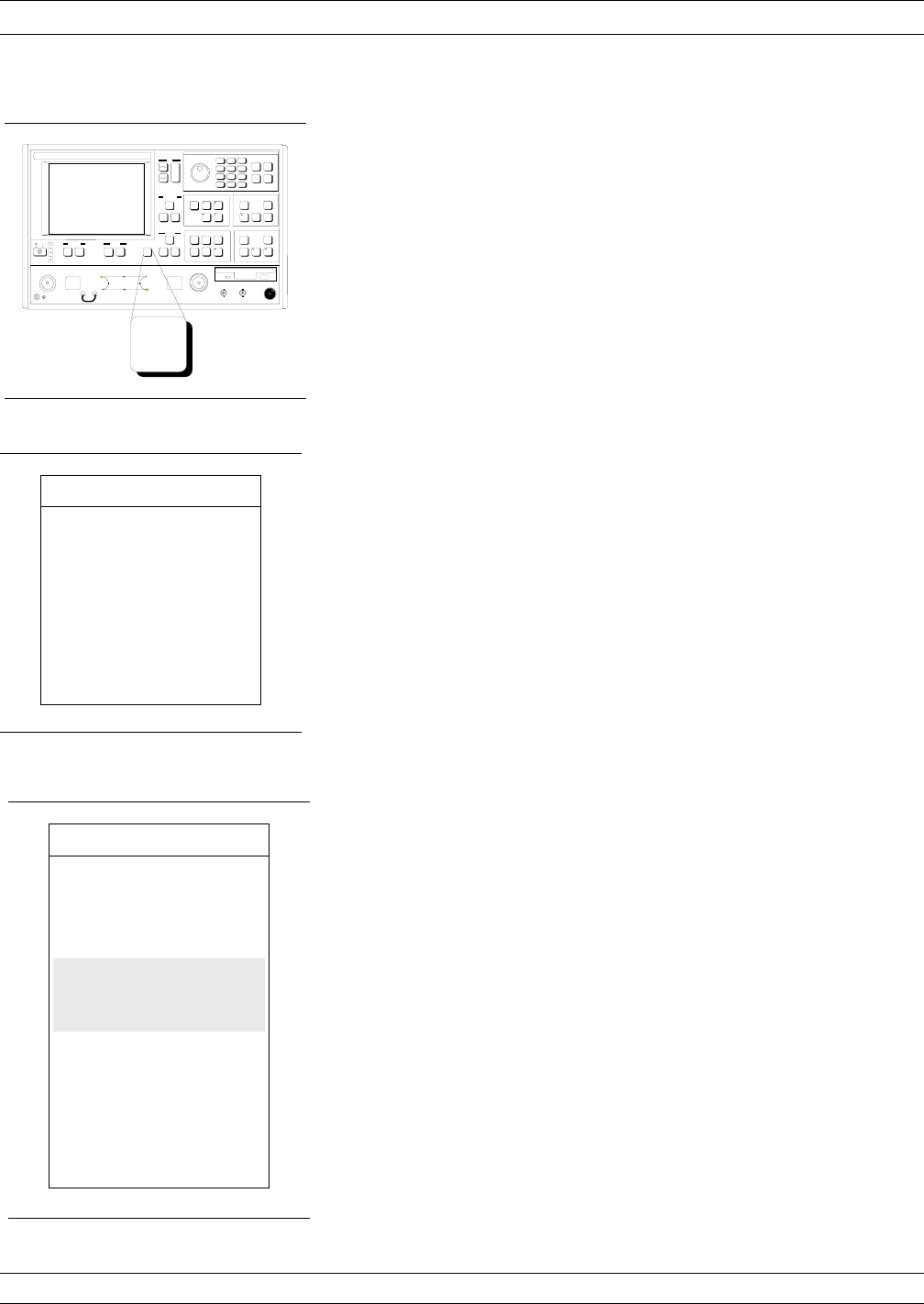
Follow the on-screen instructions and do not disturb
the setup during the calibration. Please note that
you should not start a calibration until both LED's
on the AutoCal module are lit. This will ensure accu-
rate calibration of the VNA.
Step 11. When the calibration is complete, press the Save/Re-
call key.
Step 12. Select SAVE then FRONT PANEL SETUP AND
CAL DATA TO HARD DISK (middle and bottom
left).
Step 13. Select a file or CREATE NEW FILE and press En-
ter.
If you are creating a new file, enter the filename and
select DONE when finished.
10-12 37XXXC OM
USING AUTOCAL AUTOCAL
7 8 9
456
123
0.-
D a t a E n t r y
S a v e /
R e c a l l
M e n u
MENU SR2
SAVE
FRONT PANEL
SETUP IN
INTERNAL MEMORY
FRONT PANEL
SETUP AND
CAL DATA
TO HARD DISK
FRONT PANEL
SETUP AND
CAL DATA
TO FLOPPY
DISK
PRESS <ENTER>
TO SELECT
MENU SR1
SAVE/RECALL
FRONT PANEL
AND CAL DATA
SAVE
RECALL
PRESS <ENTER>
TO SELECT
FUNCTION
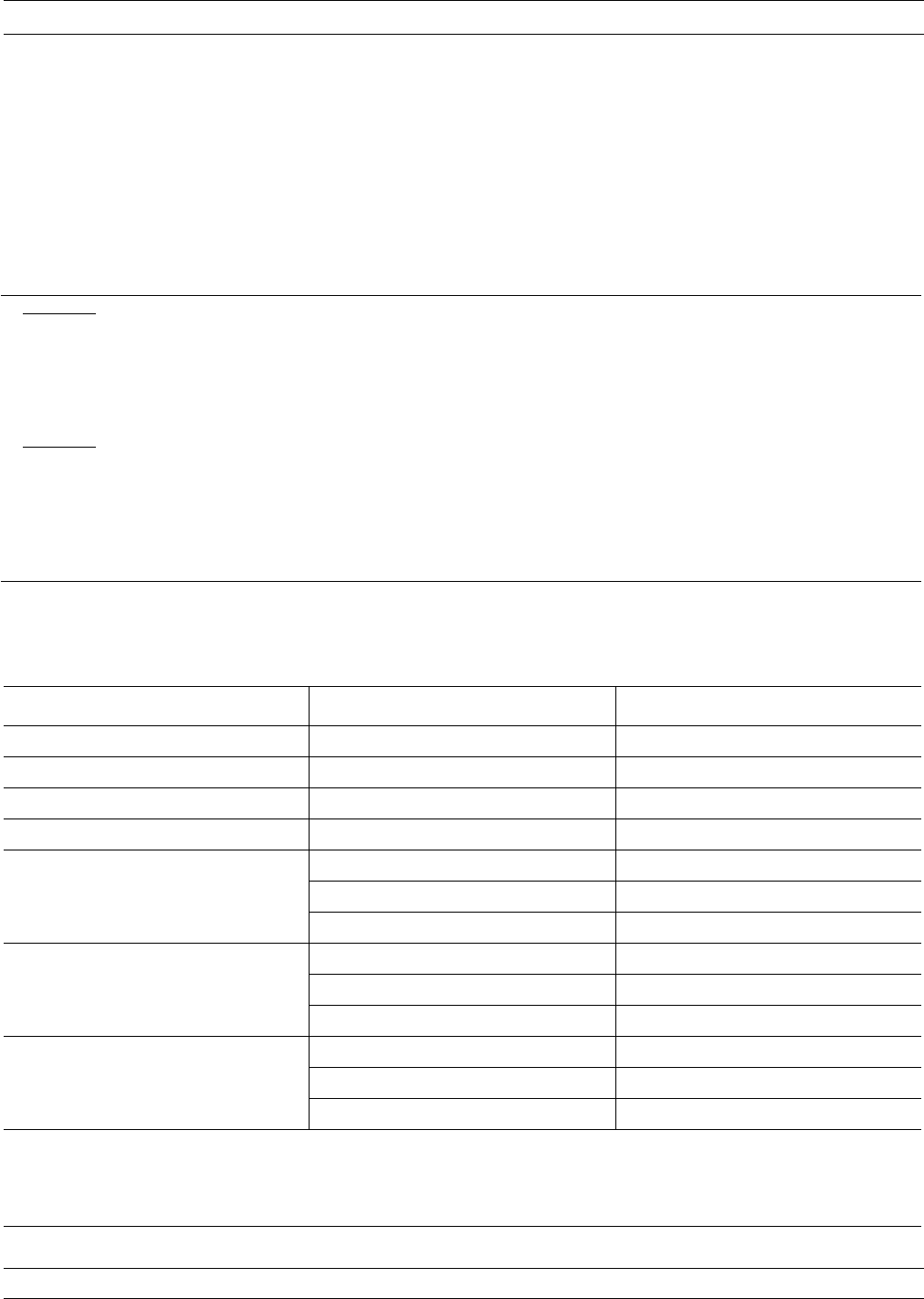
10-8 PIN DEPTH
SPECIFICATIONS The depth of the center pin on connectors is a critical specification,
which if not met, can cause damage to mating connectors. Table 10-1
provides pin depth examples and Table 10-2 provides pin-depth speci-
fications for associated AutoCal connectors.
37XXXC OM 10-13
AUTOCAL PIN DEPTH SPECIFICATIONS
Example 1:
FEMALE MASTER GAUGE BLOCK (protrusion)
Desired nominal value: 0.2070
Case1 Actual value of master gauge 0.2071 (protrusions 0.0001 more than desired)
Gauge should be set to indicate: +0.0001
Case2 Actual value of master gauge 0.2069 (protrusions 0.0001 less than desired)
Gauge should be set to indicate: -0.0001
Example 2:
MALE MASTER GAUGE BLOCK (cavity)
Desired nominal value: 0.2070
Case1 Actual value of master gauge 0.2071 (cavity 0.0001 deeper than desired)
Gauge should be set to indicate: -0.0001
Case2 Actual value of master gauge 0.2069 (cavity 0.0001 shallower than desired)
Gauge should be set to indicate: +0.0001
Table 10-1. Checking Connector Pin Depth (Example)
Device Connector Pin Depth (inches)
3658XXX K-Female +0.0000 to -0.005
3658XXX K-Male +0.0000 to -0.005
3658XXX N-Female *[0.207](+0.000, -0.005)
3658XXX K-Female *[0.207](+0.000, -0.005)
32K50
32KF50
K-Male (cable side) **Negative Indication
K-Female +0.0000 to -0.0005
K-Male (DUT side) +0.0000 to -0.0005
32L50
32LF50
K-Male (cable side) **Negative Indication
3.5mm-Female (DUT side) +0.006 to -0.008
3.5mm-Male (DUT side) +0.006 to -0.008
32S50
32SF50
K-Male (cable side) **Negative Indication
SMA-Female (DUT side) +0.0005 to -0.0015
SMA-Male (DUT side) +0.0005 to -0.0015
*Gauging Type N Connectors: The actual value of a Type N master gauge block will always vary to some degree from the desired nomi-
nal value. The recorded measured value of the master gauge must be observed when calibrating the Pin Depth Gauge to the desired
nominal value. Although the AutoCal Module Pin Depths are not critical, this information may be helpful in the measurement of Type N
mating components. Examples are shown in Table 10-1, on the preceding page.
Table 10-2. AutoCal Module Connector Pin Depth Specifications

10-9 AUTOCAL MENUS
FLOW DIAGRAM A flow diagram for the AutoCal menus is provided in Figure 10-3.
AUTOCAL MENUS FLOW DIAGRAM AUTOCAL
10-14 37XXXC OM
Menu ACAL_SETUP
LINE TYPE
COAXIAL/WAVEGUIDE
AUTOCAL SETUP
WAVEGUIDE CUTOFF
XX.XXXXXX GHz
SWITCH AVERAGING
XXXX
AUTOCAL TYPE
S11 1 PORT
S22 1 PORT
FULL 2 PORT
ADAPTER REMOVAL
NUMBER OF AVGS
REFLECTION
XXXX
LOAD
XXXX
THRU
XXXX
ISOLATION
XXXX
Menu C11
BEGIN CALIBRATION
KEEP EXISTING
CAL DATA
REPEAT PREVIOUS
CAL
AUTOCAL
CAL METHOD
XXXXXXXX
TRANSMISSION
LINE TYPE:
XXXXXXXX
CHANGE CAL
METHOD AND
LINE TYPE
NEXT CAL STEP
PRESS <ENTER>
TO SELECT
Menu ACAL
AUTOCAL
AUTOCAL TYPE
XXXXXXXX
CHANGE
AUTOCAL SETUP
START AUTOCAL
NUMBER OF AVGS
XXX
START THRU UPDATE
THRU UPDATE
CONNECT THROUGH
LINE BETWEEN
PORTS 1 AND 2
PRESS <ENTER>
TO SELECT
OR SWITCH
Menu ACAL_S11
AUTOCAL
S11 1 PORT
PORT 1
CONNECTION
LEFT/RIGHT
START AUTOCAL
TEST SIGNALS
PRESS <ENTER>
TO SELECT
OR SWITCH
Menu ACAL_S22
AUTOCAL
S22 1 PORT
PORT 1
CONNECTION
LEFT/RIGHT
START AUTOCAL
PRESS <ENTER>
TO SELECT
OR SWITCH
Menu ACAL_FULL
AUTOCAL
FULL 2 PORT
ISOLATION
AVERAGING
OMIT
DEFAULT
AVERAGING
FACTOR
XXXX
THRU TYPE
CALIBRATOR/TRUE
PORT CONFIG
L=1, R=2
R=1, L=2
START AUTOCAL
PRESS <ENTER>
TO SELECT
OR SWITCH
Begin
Cal
Cal Sequence
Menus,
Page 4-18
Cal Sequence
Menus,
Page 4-18
Menu ACAL_AR
AUTOCAL
ADAPTER REMOVAL
ISOLATION
AVERAGING
OMIT
DEFAULT
AVERAGING
FACTOR
XXXX
PORT CONFIG
ADAPT&L=1, R=2
L=1, ADAPT&R=2
ADAPT&R=1, L=2
R=1, ADAPT&L=2
START AUTOCAL
PRESS <ENTER>
TO SELECT
OR SWITCH
Menu U1
UTILITY
GPIB ADDRESSES
DISPLAY
INSTRUMENT
PARAMETERS
GENERAL
DISK UTILITIES
CAL COMPONENT
UTILITIES
AUTOCAL
UTILITIES
COLOR
CONFIGURATION
DATA ON(OFF)
DRAWING
BLANK(ING)
FREQUENCY
INFORMATION
SET DATE/TIME
PRESS <ENTER>
TO SELECT
OR TURN ON/OFF
Utility
Menu
Cal Sequence
Menus,
Page 4-18
Menu ACAL_UTIL
Menu ACAL_CHAR
AUTOCAL
UTILITIES
AUTOCAL
CHARACTERIZATION
AUTOCAL
CHARACTERIZATION
SWITCH AVERAGING
XXXX
SAVE
TO HARD DISK
PORT CONFIG
L=1, R=2
R=1, L=2K
RECALL
FROM HARD DISK
RECALL
FROM FLOPPY DISK
SAVE
TO FLOPPY DISK
PRESS <ENTER>
TO SELECT
PRESS <ENTER>
TO SELECT
OR SWITCH
START AUTOCAL
CHARACTERIZATION
NUMBER OF AVGS
REFLECTION
XXXX
LOAD
XXXX
THRU
XXXX
ISOLATION
XXXX
TEST SIGNALS
TEST SIGNALS
TEST SIGNALS
Figure 10-3. AutoCal Menus Flow Diagram

Table of Contents
11-1 INTRODUCTION...................................11-3
11-2 REQUIRED EQUIPMENT..............................11-3
11-3 INITIAL SETUP ...................................11-3
11-4 SELF TEST ......................................11-3
11-5 SAMPLER EFFICIENCY TEST...........................11-4
11-6 HIGH LEVEL NOISE TEST.............................11-8
Chapter 11
Operational Checkout
Procedures: 371XXC
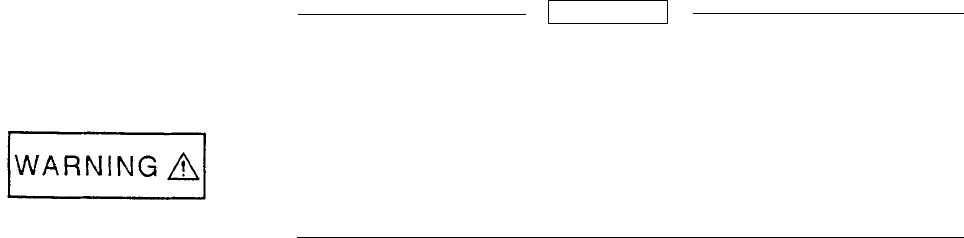
This equipment can not be repaired by the operator. DO NOT attempt to
remove the equipment covers or to disassemble internal components.
Only qualified service technicians with a knowledge of electrical fire
and shock hazards should service this equipment. There are
high-voltage parts in this equipment presenting a risk of severe injury
or fatal electric shock to untrained personnel. In addition, there is a risk
of damage to precision components.
WARNING
Repair
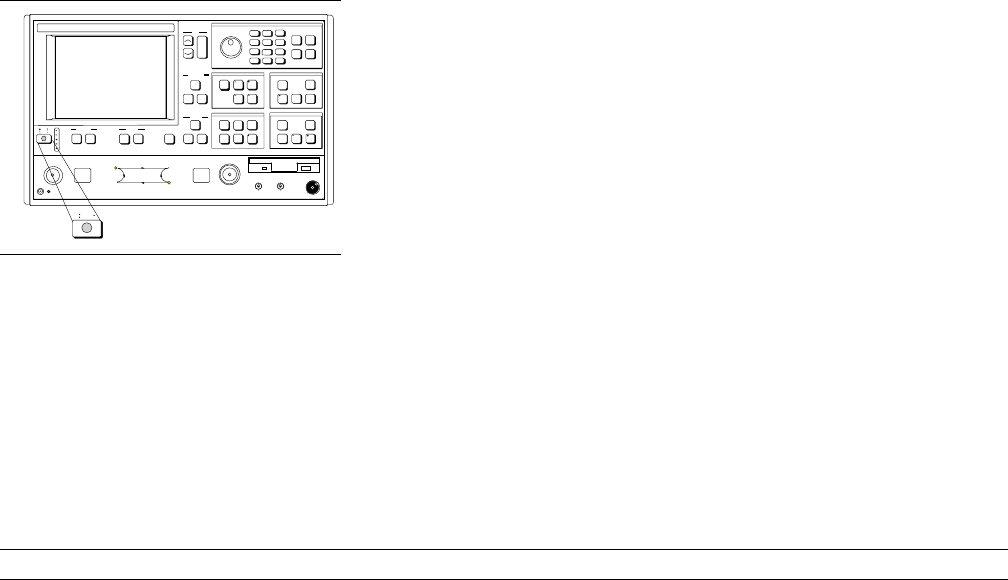
Chapter 11
Operational Checkout
Procedures: 371XXC
11-1 INTRODUCTION This chapter provides quick operational checkout procedures that may
be used by incoming inspectors to ensure that the Model 371XXC Vec-
tor Network Analyzer is operational. This is a quick-check procedure.
For the full performance verification procedure, refer to the Series
371XXC Maintenance Manual, Anritsu Part Number 10410-00228.
11-2 REQUIRED
EQUIPMENT Cable/Attenuator Kits, Anritsu Part Number ND45331 and ND45332.
They consist of the following:
qAttenuators: 43KC-10 (1), 43KC-3 (1)
qCable Assemblies: B18265-276 (1), B18265-277 (1),
B18625-278 (2)
qPower Splitter D17900* or K241C (2).
*D17900 can be substituted with Anritsu K241C.
11-3 INITIAL SETUP Before starting the performance tests, press the Power key (left) to On.
NOTE
Allow the system to warm up for at least 60 minutes to en-
sure operation to performance specifications.
11-4 SELF TEST Perform an instrument self test to ensure that the 371XXC is operat-
ing properly. To start a self test, Press the Option Menu key and make
the menu choices shown in Figure 11-1.
Note that a semi-rigid cable must be connected between front panel
connectors Source Lock Output and a1.
37XXXC OM 11-3
Power
-
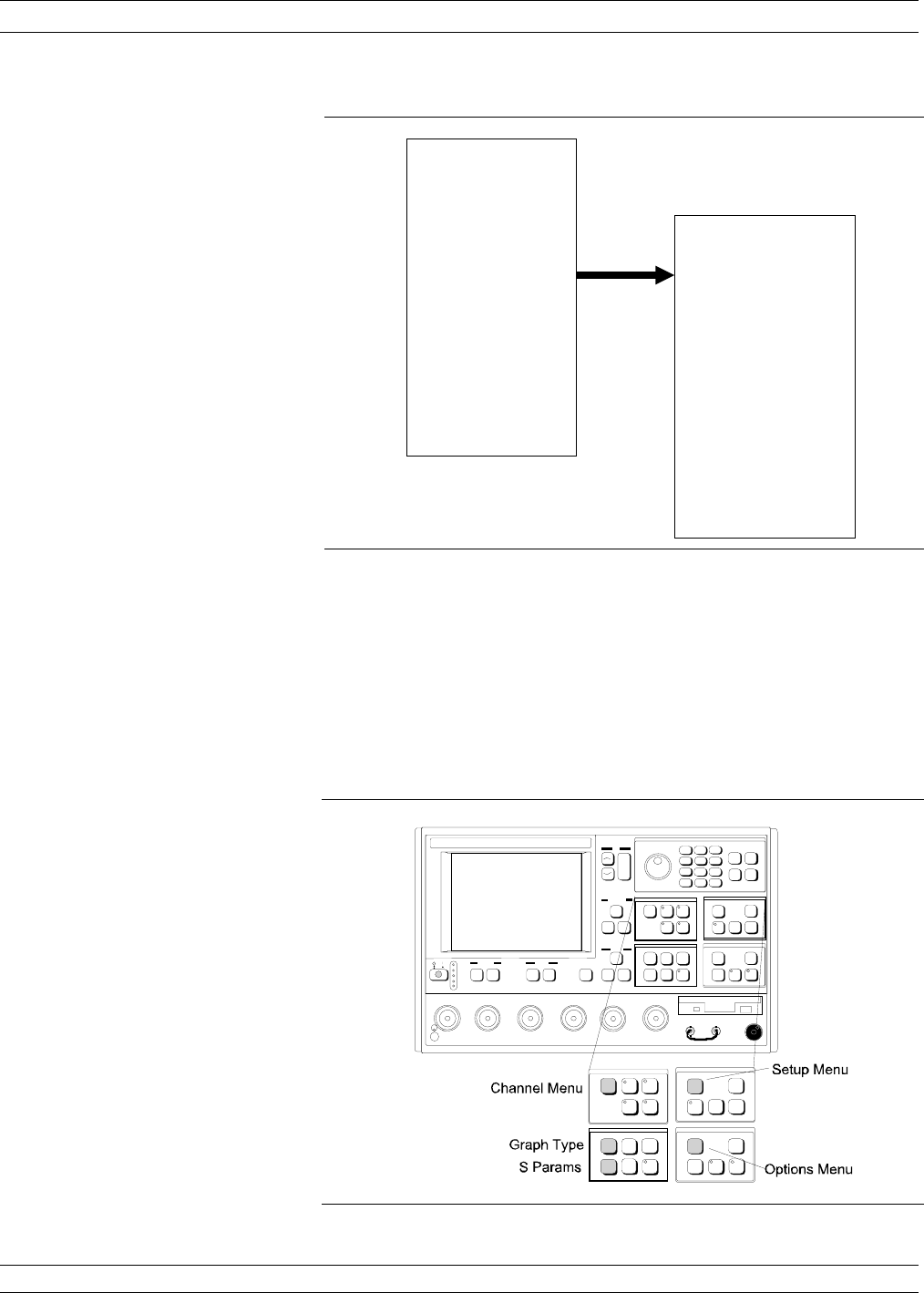
11-5 SAMPLER EFFICIENCY
TEST This test verifies that each individual receiver channel operates prop-
erly. Measurement calibration of the system is not required for this
test.
This test requires that you press specified front panel keys and make
choices from the displayed menu(s). The keys used in this test are
shown below:
SAMPLER EFFICIENCY TEST OPERATIONAL CHECKOUT
11-4 37XXXC OM
789
456
123
0.-
Data Entry
Figure 11-1. Performing a Self Test
OPTIONS
TRIGGERS
REAR PANEL
OUTPUT
DIAGNOSTICS
MULTIPLE SOURCE
CONTROL
RECEIVER MODE
SOURCE CONFIG
PRESS < ENTER>
TO SELECT
DIAGNOSTICS
START SELF TEST
READ SERVICE LOG
INSTALLED OPTIONS
PERIPHERAL TESTS
TROUBLESHOOTING
(FOR SERVICE
USE ONLY)
H/W CALIBRATIONS
(FOR SERVICE
USE ONLY)
PRESS < Enter>
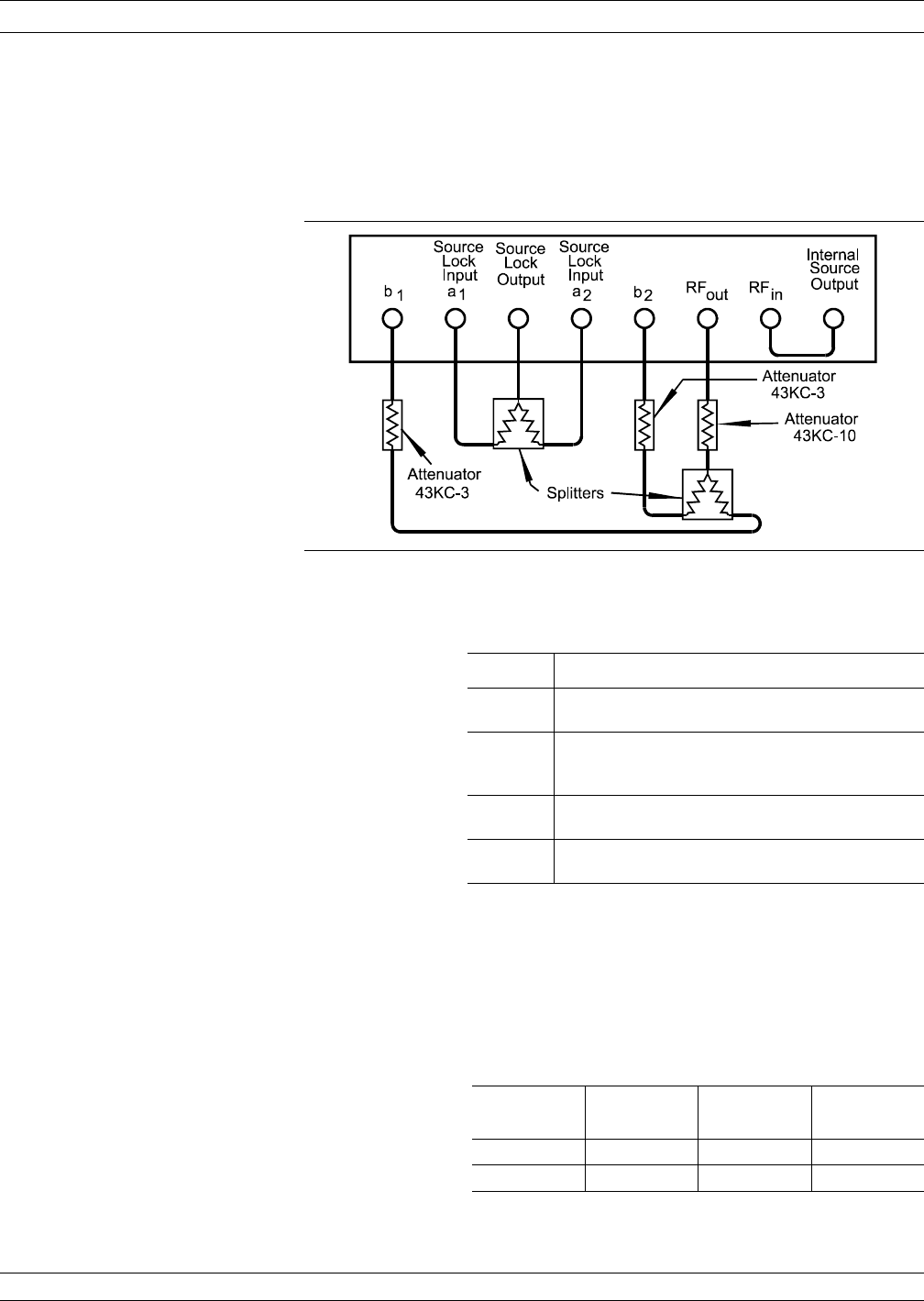
Test Setup Set up the 371XXC as described below.
Step 1. Connect Test Fixtures ND45331 and ND45332 to
371XXC (as shown below).
Step 2. Reset the 371XXC using the Default Program key.
Step 3. Set up the 371XXC as shown in the table below.
Test Procedure Perform test as described below.
Step 1. Observe the sweep indicators and allow at least one
complete sweep to occur on all four channels.
Step 2. Verify that the maximum-value to minimum-value
amplitude slope (Figure 11-3, page 11-7) meets the
specifications shown below.
37XXXC OM 11-5
OPERATIONAL CHECKOUT SAMPLER EFFICIENCY TEST
Key Menu Choice
Options
Menu
Non-Ratioed Parameters, see Figure 11-2 (follow-
ing page)
Setup
Menu
START: 1 GHz
STOP: Table 11-1 (previous page), High-End Fre-
quency
Channel
Menu
FOUR CHANNELS
Graph
Type
LOG MAGNITUDE
(All channels)
Model High-End
Frequency Reference
Channel Slope Test Channels
Slope
37147C 20 GHz â10 dB â12 dB
37169C 40 GHz â12 dB â14 dB
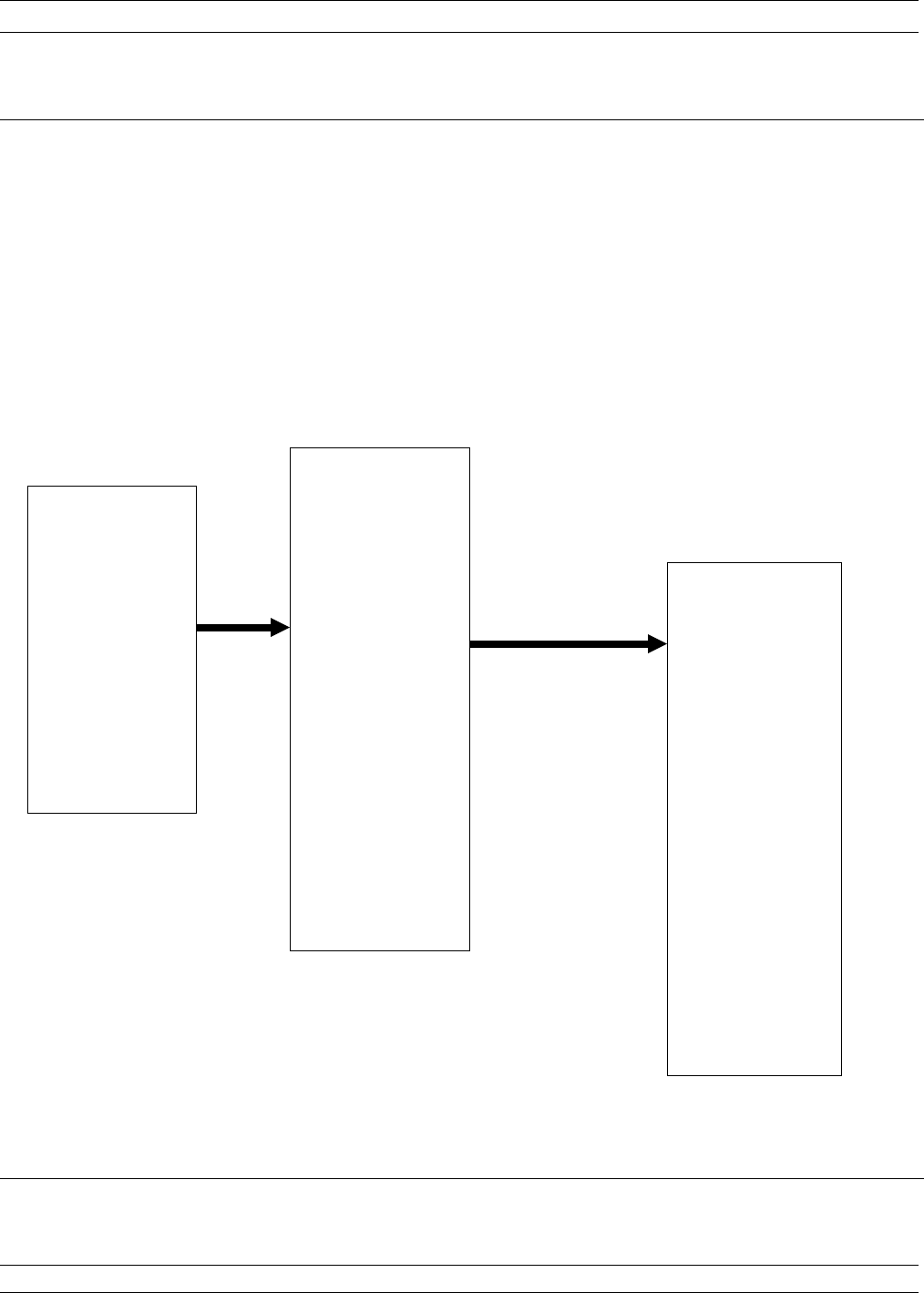
SAMPLER EFFICIENCY TEST OPERATIONAL CHECKOUT
11-6 37XXXC OM
Step 1. Press the OPTION MENU key.
Step 2. Make menu choices as shown below.
Step 3. Press SETUP MENU key; set the start frequency to 1 GHz.
Figure 11-2. Redefining Selected Parameter Automatically for Sampler Efficiency Testing
OPTIONS
TRIGGERS
REAR PANEL
OUTPUT
DIAGNOSTICS
MULTIPLE SOURCE
CONTROL
RECEIVER MODE
SOURCE CONFIG
PRESS < ENTER>
TO SELECT
DIAGNOSTICS
START SELF TEST
READ SERVICE LOG
INSTALLED OPTIONS
PERIPHERAL TESTS
TROUBLESHOOTING
(FOR SERVICE
USE ONLY)
H/W CALIBRATIONS
(FOR SERVICE
USE ONLY)
PRESS < ENTER>
TO SELECT
TROUBLESHOOTING
(FOR SERVICE
USE ONLY)
NON-RATIOED
PARAMETERS
LO1
LO2
SOURCE
FIRST I.F.
BANDPASS
EXTERNAL A2
INPUT
MORE
FINISHED,
RECOVER FROM
TROUBLESHOOTING
PRESS < ENTER>
TO SELECT
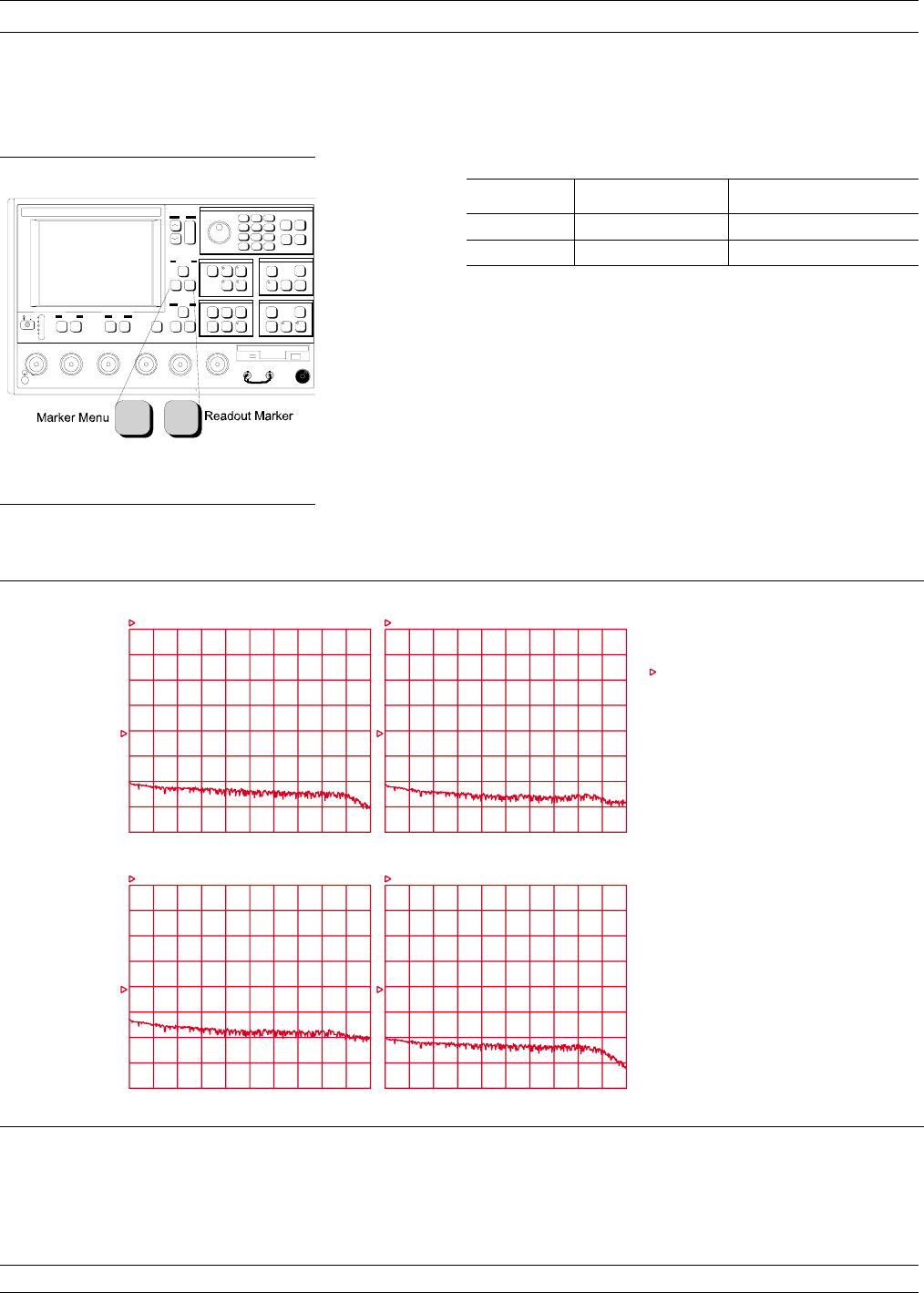
Step 3. Verify that the minimum amplitude meets the speci-
fications shown below.
NOTE
Use the Marker Menu and Readout Marker keys (left) and
menus to obtain precise frequency and amplitude values.
37XXXC OM 11-7
OPERATIONAL CHECKOUT SAMPLER EFFICIENCY TEST
789
456
123
0.-
Data Entry
TS: NON-RATIOEDPARAMETERS TS: NON-RATIOEDPARAMETERS
TS: NON-RATIOEDPARAMETERS TS: NON-RATIOEDPARAMETERS
START
1
1
.
.
0
0
0
0
0
0
0
0
0
0
0
0
0
0
0
0
0
0
GHz
STOP
GHz
SET CENTER/SPAN
C.W. MODE OFF
MARKERSWEEP
DISCRETE FILL
HOLD BUTTON
FUNCTION
TEST SIGNALS
GHz1.000000000 40.000000000
REF-A L
O
GMAG.
0.000 dB 10.000 dB/DIV
GHz1.000000000 40.000000000
TST-A L
O
GMAG.
0.000 dB 10.000 dB/DIV
GHz1.000000000 40.000000000
TST-B LOGMAG.
0.000 dB 10.000 dB/DIV
GHz1.000000000 40.000000000
REF-B LOGMAG.
0.000 dB 10.000 dB/DIV
SWEEPSETUP
401 DATA POINT(S)
STEPSIZE
0.097500000 GHz
PRESS <ENTER>
TO SELECT
OR TURN ON/OFF
Figure 11-3. Sampler Efficiency Test Waveforms
Model Test Channels Reference Channel
37147C –26 –28
37169C –38 –36
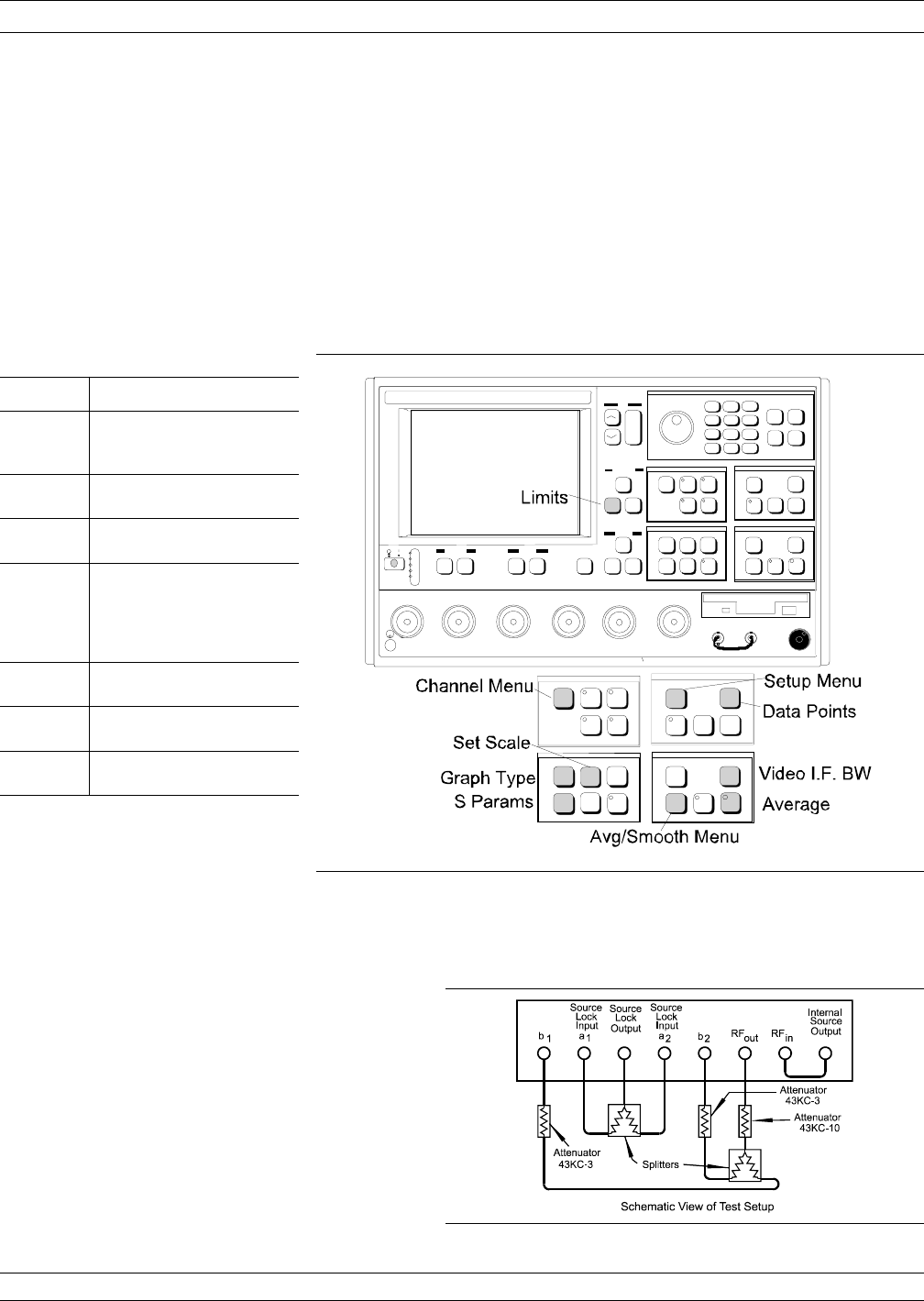
11-6 HIGH LEVEL NOISE
TEST The following test verifies that the high-level signal noise in the
371XXC will not significantly affect the accuracy of subsequent mea-
surements. Calibration of the system is not required for this test.
This test requires that you press specified front panel keys and make
choices from the displayed menu(s). The keys used in this test are
highlighted below.
Test Procedure Setup the 371XXC as described in the table at the left.
Step 1. Reset the 371XXC using the Default Program key.
Step 2. Connect the ND45331 and ND45332 test fixtures to
the 371XXC (see the figure below).
HIGH LEVEL NOISE TEST OPERATIONAL CHECKOUT
11-8 37XXXC OM
Key Menu Choice
Setup
Menu
START: 40 MHz
STOP: High-end fre-
quency
Channel
Menu
DUAL CHANNELS 1-3
Graph
Type
LOG MAGNITUDE
(Both channels)
Set
Scale
RESOLUTION:
0.020 dB/DIV
REF VALUE:
0.0 dB
(Both channels)
S-Params Channel 1 –S12
Channel 3 –S21
Data
Points
201
Video
IF BW
NORMAL (1 kHz)
789
456
123
0.-
Data E ntry
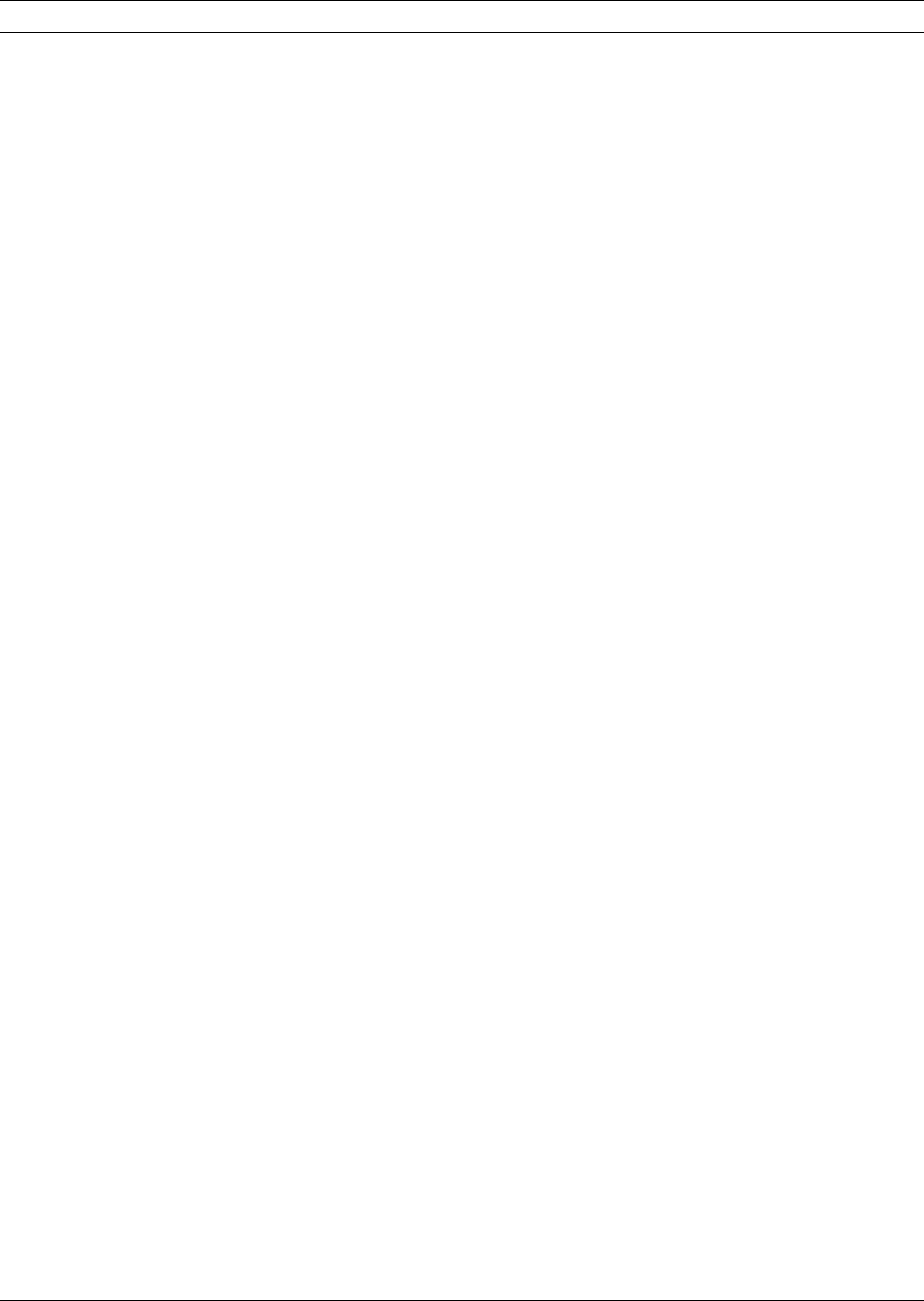
Step 3. Press the Ch1key.
Step 4. Press the Trace Memory key.
Step 5. Choose VIEW DATA from the menu and press the
Enter key.
Step 6. While observing the sweep indicators, allow at least
two complete sweeps to occur.
Step 7. Choose STORE DATA TO MEMORY from the
menu and press the Enter key.
Step 8. Choose VIEW DATA / MEMORY from menu and
press the Enter key.
Step 9. While observing the sweep indicators, allow at least
two complete sweeps to occur.
Step 10. Verify that the peak-to-peak High Level Noise falls
within the area between the two limit lines
(Figure 11-4, following page).
Step 11. Press the Ch3key.
Step 12. Repeat Steps 4 through 9 for Channel 3.
37XXXC OM 11-9
OPERATIONAL CHECKOUT HIGH LEVEL NOISE TEST
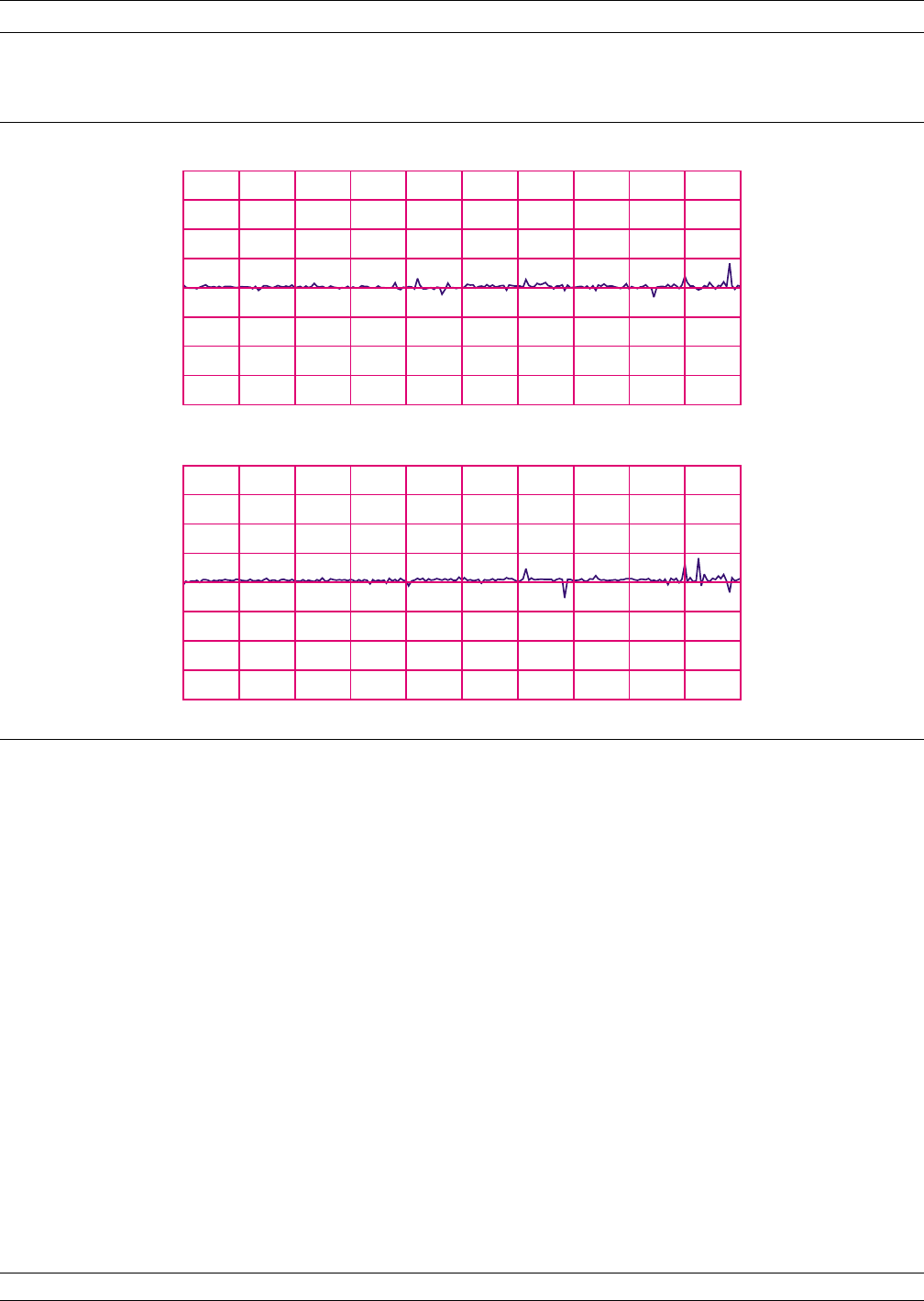
HIGH LEVEL NOISE TEST OPERATIONAL CHECKOUT
11-10 37XXXC OM
GHz0.040000000 20.000000000
S12 REVERSE TRANSMISSION
LOG MAG. REF= 0.000 dB 0.020 dB/DIV
GHz0.040000000 20.000000000
S21 FORWARD TRANSMISSION
LOG MAG. REF= 0.000 dB 0.020 dB/DIV
Figure 11-4. High Level Noise Test Waveform

Table of Contents
12-1 INTRODUCTION...................................12-3
12-2 REQUIRED EQUIPMENT..............................12-3
12-3 INITIAL SETUP ...................................12-3
12-4 SELF TEST ......................................12-3
12-5 NON-RATIO POWER ................................12-4
12-6 HIGH LEVEL NOISE TEST.............................12-6
Chapter 12
Operational Checkout
Procedures: 372XXC, 373XXC
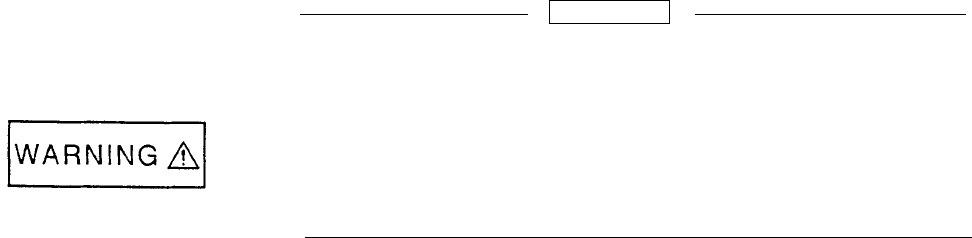
This equipment can not be repaired by the operator. DO NOT attempt to
remove the equipment covers or to disassemble internal components.
Only qualified service technicians with a knowledge of electrical fire
and shock hazards should service this equipment. There are
high-voltage parts in this equipment presenting a risk of severe injury
or fatal electric shock to untrained personnel. In addition, there is a risk
of damage to precision components.
WARNING
Repair
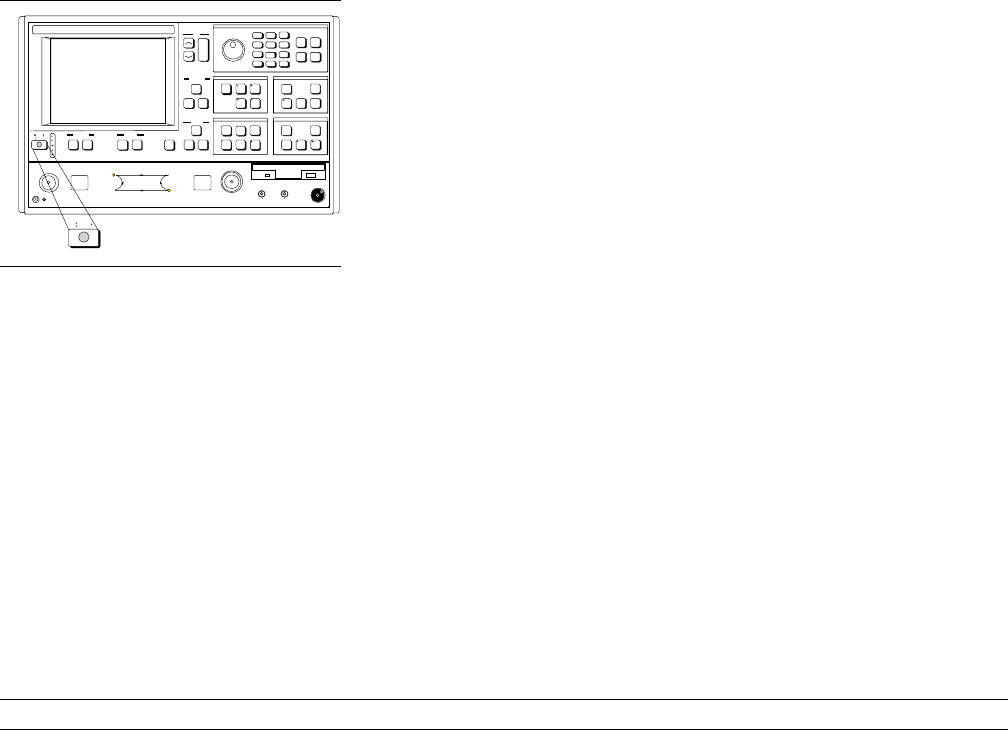
Chapter 12
Operational Checkout
Procedures: 372XXC, 373XXC
12-1 INTRODUCTION This chapter provides quick operational checkout procedures that may
be used by incoming inspectors to ensure that the Model 37XXXC Vec-
tor Network Analyzer is operational. This is a quick-check procedure.
For the full performance verification procedure, refer to the Series
37XXXC Maintenance Manual, Anritsu Part Number 10410-00228.
12-2 REQUIRED
EQUIPMENT The following equipment is required for the procedures in this chapter:
qFlexible microwave cable (through line)
qShort
12-3 INITIAL SETUP Before starting the performance tests, press the Power key (left) to On.
NOTE
Allow the system to warm up for at least 60 minutes to en-
sure operation to performance specifications.
12-4 SELF TEST Perform an instrument self test to ensure that the VNA is operating
properly. To start a self test, Press the Option Menu key and make the
menu choices shown in Figure 12-1.
37XXXC OM 12-3
Power
-
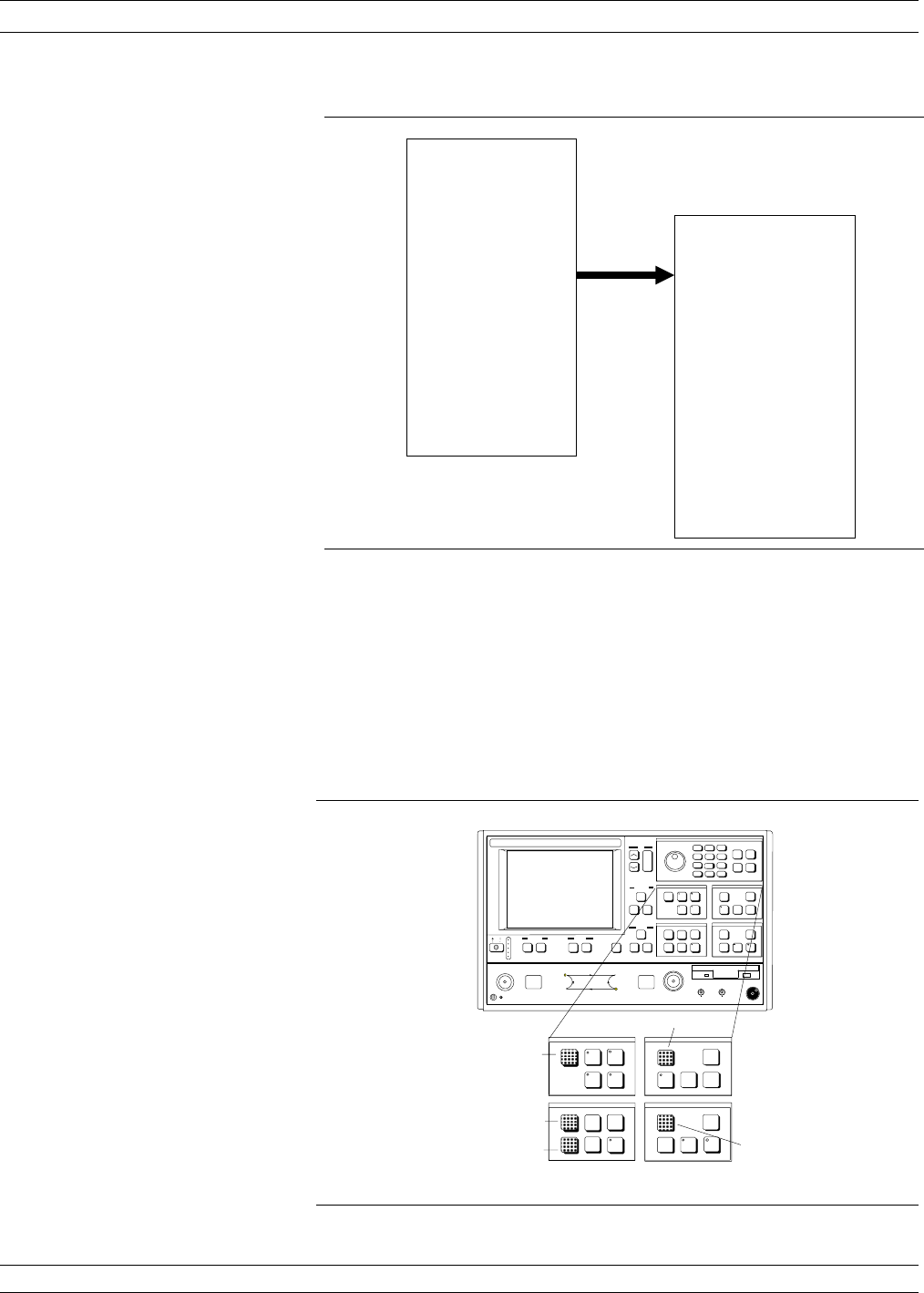
12-5 NON-RATIO POWER This test verifies that each individual receiver channel operates prop-
erly. Measurement calibration of the system is not required for this
test.
This test requires that you press specified front panel keys and make
choices from the displayed menu(s). The keys used in this test are
shown below.
NON-RATIO POWER OPERATIONAL CHECKOUT
12-4 37XXXC OM
Figure 12-1. Performing a Self Test
OPTIONS
TRIGGERS
REAR PANEL
OUTPUT
DIAGNOSTICS
MULTIPLE SOURCE
CONTROL
RECEIVER MODE
SOURCE CONFIG
PRESS < ENTER>
TO SELECT
DIAGNOSTICS
START SELF TEST
READ SERVICE LOG
INSTALLED OPTIONS
PERIPHERAL TESTS
TROUBLESHOOTING
(FOR SERVICE
USE ONLY)
H/W CALIBRATIONS
(FOR SERVICE
USE ONLY)
PRESS < Enter>
Channel Menu
Graph Type
S Params
Setup Menu
Option Menu
-
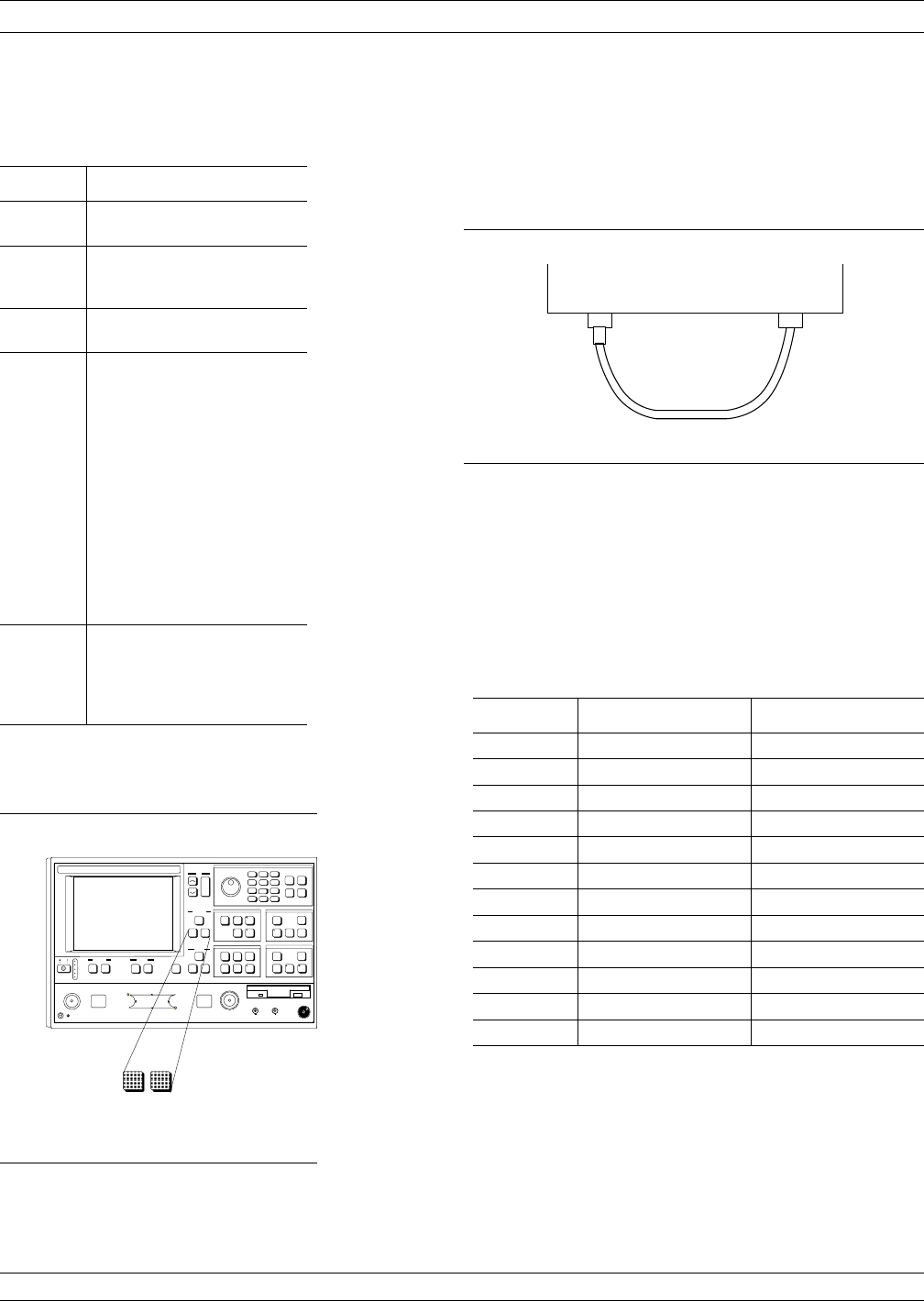
Test Procedure Perform test as described below.
Step 1. Connect Test Ports 1 and 2 together using a
high-quality through line (below).
Step 2. Reset the VNA using the Default Program key.
Step 3. Set up the VNA as shown in table at left.
Step 4. Observe the sweep indicators and allow at least one
complete sweep to occur on all four channels.
Step 5. Verify that the minimum amplitude meets the speci-
fications shown below.
Model Test Channel Reference Channel
37217C >-28 dB >-35 dB
37317C >-28 dB >-35 dB
37225C >-25 dB >-34 dB
37325C >-30 dB >-32 dB
37247C >-26 dB >-35 dB
37347C >-31 dB >-33 dB
37269C >-40 dB >-40 dB
37369C >-34 dB >-34 dB
37277C >-45 dB >-45 dB
37377C >-45 dB >-45 dB
37297C >-60 dB >-55 dB
37397C >-60 dB >-55 dB
NOTE
Use the Marker Menu and Readout Marker keys ( left) and
menus to obtain precise frequency and amplitude values.
37XXXC OM 12-5
OPERATIONAL CHECKOUT NON-RATIO POWER
PORT 1 PORT 2
TEST PORT 1
TEST PORT 2
Key Menu Choice
Options
Menu
Non-Ratioed Parameters,
see Figure 11-2
Setup
Menu
START: 1 GHz
STOP: High-End Fre-
quency
Channel
Menu
FOUR CHANNELS
Graph
Type
LOG MAGNITUDE
(All channels)
S-PARAMS USER 1: (Channel 3)
Parameter: Ra/1
Phase Lock: Ra
USER 2: (Channel 1)
Parameter: Ta/1
Phase Lock: Ra
USER 3: (Channel 2)
Parameter: Tb/1
Phase Lock: Ra
USER 4: (Channel 4)
Parameter: Rb/1
Phase Lock: Rb
SET
SCALE
RESOLUTION:
20 dB/DIV
REF VALUE:
0dB
(All four channels)
-
Marker Menu Readout Marker
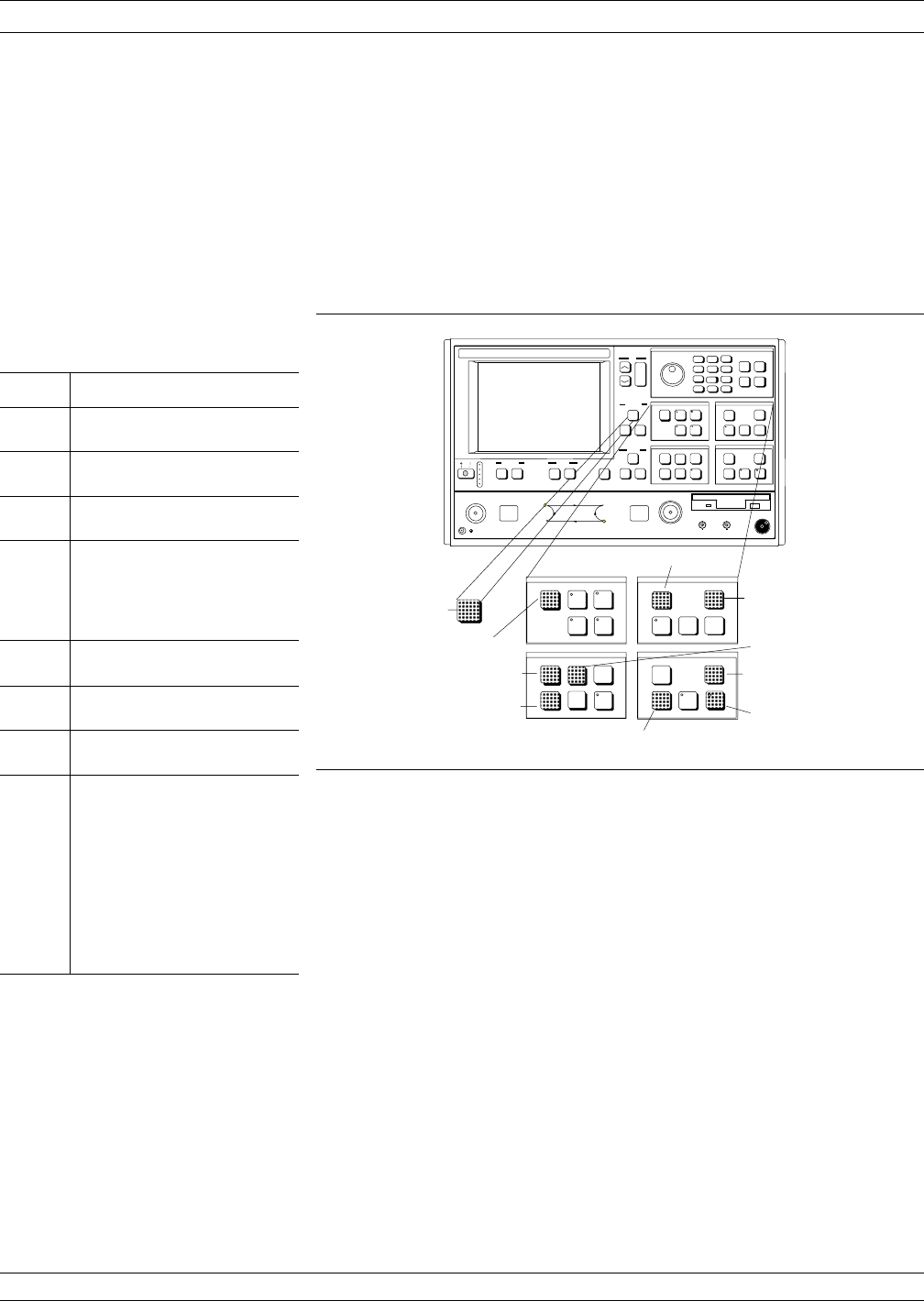
12-6 HIGH LEVEL NOISE
TEST The following test verifies that the high-level signal noise in the VNA
will not significantly affect the accuracy of subsequent measurements.
Calibration of the system is not required for this test.
This test requires that you press specified front panel keys and make
choices from the displayed menu(s). The keys used in this test are
highlighted below.
Setup the VNA as described in the table at the left.
HIGH LEVEL NOISE TEST OPERATIONAL CHECKOUT
12-6 37XXXC OM
Key Menu Choice
Setup
Menu
START: 40 MHz
STOP: High-end frequency
Channel
Menu
DUAL CHANNELS 1-3
Graph
Type
LOG MAGNITUDE
(Both channels)
Set
Scale
RESOLUTION:
0.020 dB/DIV
REF VALUE:
0.0 dB
(Both channels)
S-Params Channel 1 –S12
Channel3–S
21
Data
Points
201
Video
IF BW
NORMAL (1 kHz)
Limits UPPER LIMIT ON
0.015 if less than 40 GHz
0.04 if 40 GHz
0.14 if above 40 GHz
LOWER LIMIT ON
-0.015 if less than 40 GHz
-0.04 if 40 GHz
-0.14 if above 40 GHz
DISPLAY LIMITS ON
Channel Menu
Graph Type
S Params
Setup Menu
Video I.F. BW
Data Points
Average
Avg/Smooth Menu
Set Scale
Limits
-
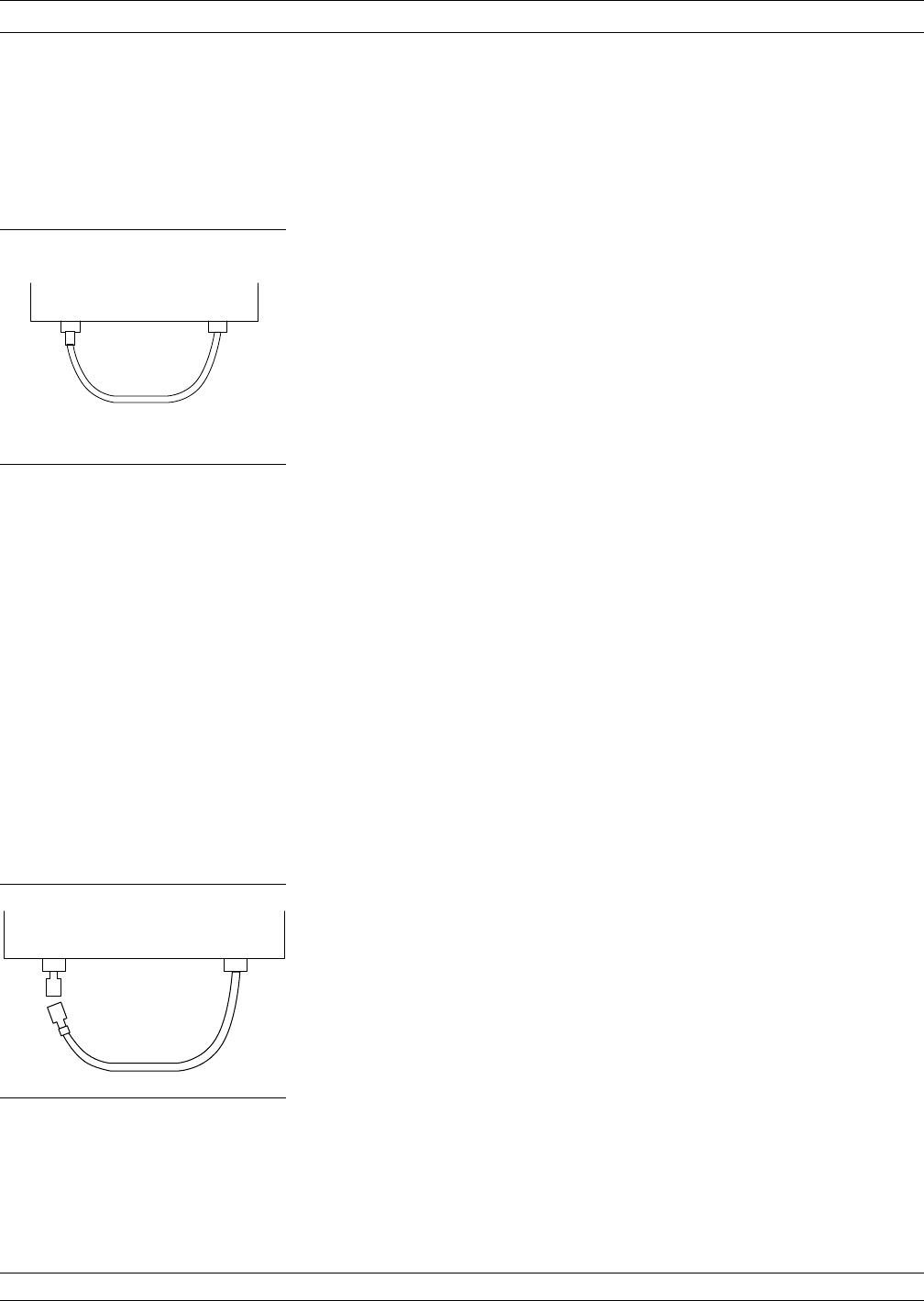
Perform the test as described below:
Step 1. Reset the VNA using the Default Program key.
Step 2. Connect Test Port 1 and Test Port 2 (top left) to-
gether.
Step 3. Press the Ch1key.
Step 4. Press the Trace Memory key.
Step 5. Choose VIEW DATA from the menu and press the En-
ter key.
Step 6. While observing the sweep indicators, allow at least
two complete sweeps to occur.
Step 7. Choose STORE DATA TO MEMORY from the menu
and press the Enter key.
Step 8. Choose VIEW DATA / MEMORY from the menu and
press the Enter key.
Step 9. While observing the sweep indicators, allow at least
two complete sweeps to occur.
Step 10. Verify that the peak-to-peak High Level Noise falls
within the area between the two limit lines
(Figure 12-2, following page).
Step 11. Press the Ch3key.
Step 12. Repeat Steps 4 through 9 for channel 3.
Step 13. Press the S Params key; set Ch 1 for S11 and Ch 3 for
S22.
Step 14. Connect a Short to Test Port 1 and an Open to Test
Port 2 (left).
Step 15. Repeat Steps 2 through 9.
37XXXC OM 12-7
OPERATIONAL CHECKOUT HIGH LEVEL NOISE TEST
PORT 1 PORT 2
TEST PORT 1
TEST PORT 2
PORT 1 PORT 2
SHORT
OPEN
TEST
PORT 1
TEST
PORT 2
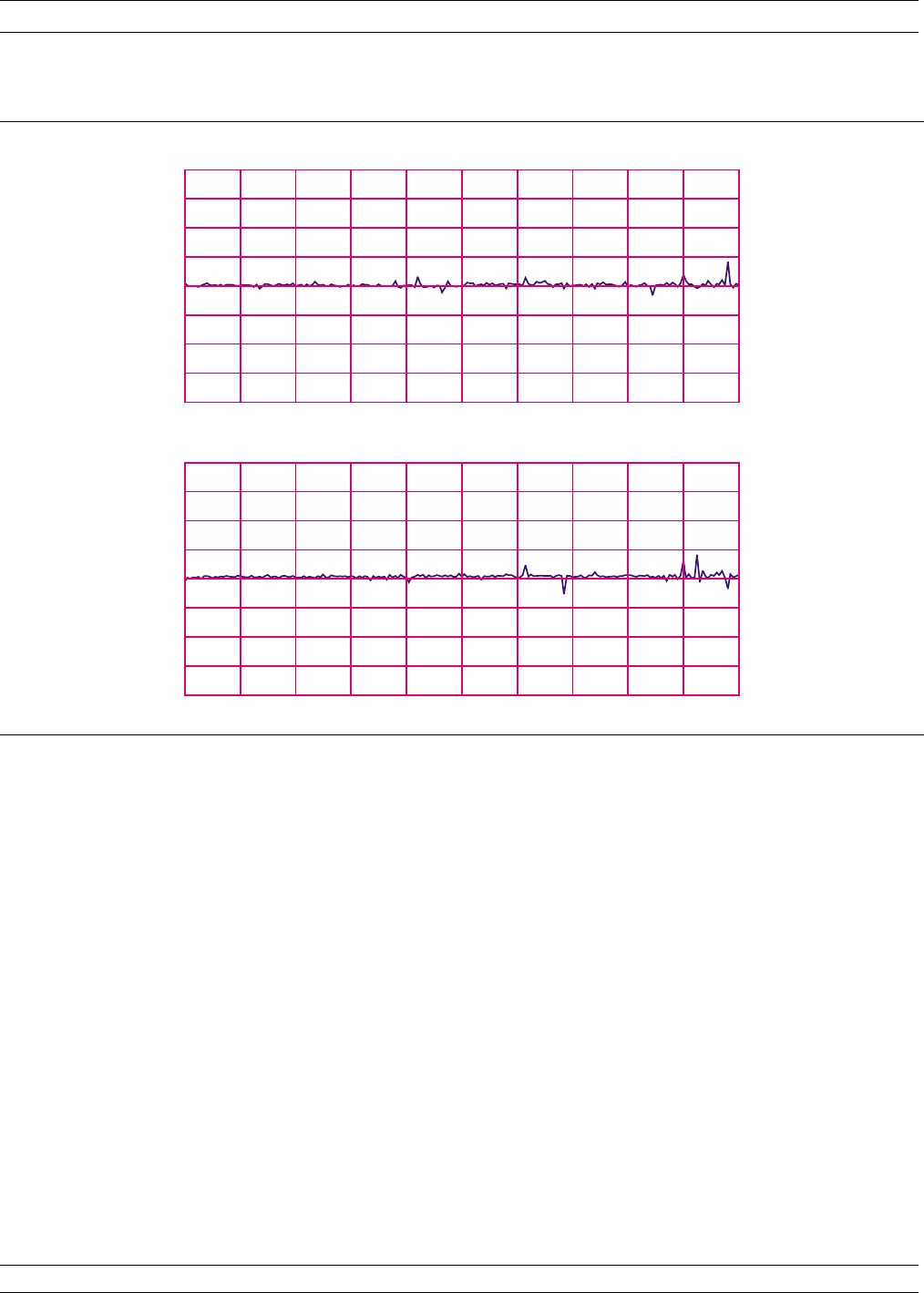
HIGH LEVEL NOISE TEST OPERATIONAL CHECKOUT
12-8 37XXXC OM
GHz0.040000000 20.000000000
S12 REVERSE TRANSMISSION
LOG MAG. REF= 0.000 dB 0.020 dB/DIV
GHz0.040000000 20.000000000
S21 FORWARD TRANSMISSION
LOG MAG. REF= 0.000 dB 0.020 dB/DIV
Figure 12-2. High Level Noise Test Waveform

Table of Contents
13-1 INTRODUCTION...................................13-3
13-2 PURPOSE.......................................13-3
13-3 KIT CONTENTS ...................................13-3
Model 3650 Calibration Kit ............................13-4
Model 3651 Calibration Kit ............................13-5
Model 3652 Calibration Kit ............................13-6
Model 3653 Calibration Kit ............................13-7
Model 3654/ 3654B Calibration Kit ........................13-8
Model 3656 Calibration Kit ............................13-9
13-4 PRECAUTIONS ...................................13-10
Pin Depth .....................................13-10
Pin Depth Tolerance ...............................13-11
Over Torquing Connectors ............................13-11
Teflon Tuning Washers..............................13-11
Mechanical Shock ................................13-11
13-5 CLEANING INSTRUCTIONS ...........................13-12
Chapter 13
Calibration Kits

Chapter 13
Calibration Kits
13-1 INTRODUCTION This chapter provides illustrations and contents for the Models 3650,
3651, 3652, 3653, 3654/3654B, 36550 and 36552 Calibration Kits.
13-2 PURPOSE The calibration kits contain all of the precision components and tools
required to calibrate the 37XXXC Vector Network Analyzer System for
a 12-term error-corrected measurement.
13-3 KIT CONTENTS The contents and illustrations of the calibration kits are listed on the
following pages.
37XXXC OM 13-3
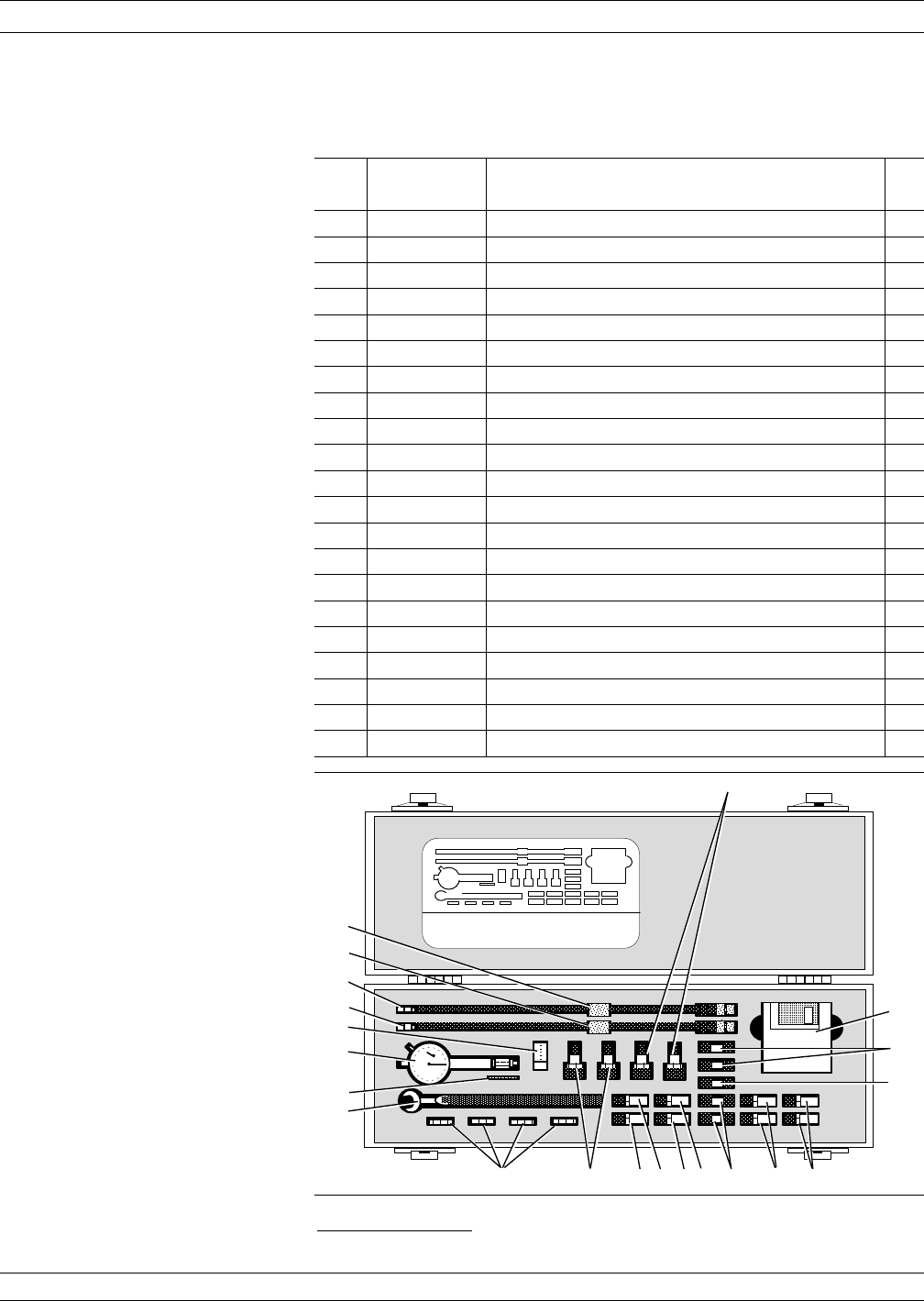
Model 3650 Calibration Kit
KIT CONTENTS CALIBRATION KITS
13-4 37XXXC OM
* Phase Equal Adapters
Index Anritsu Part
Number Description Qty.
1 01-212 Female Flush Short (Option 1) 1
2 01-211 Male Flush Short (Option 1) 1
3 17SF50 Female Sliding Termination 1
4 17S50 Male Sliding Termination (Option 1) 1
5 34ASF50-2 Female Adapter 2
6 Calibration Software Diskette 1
7 33FSF50 Female-Female Adapter 2
8 33SS50 Male-Male Adapter* 1
9 28S50-2 Male Termination 2
10 28SF50-2 Broadband Female Termination 2
11 33SSF50 Male-Female Adapter* 2
12 24S50 Male Open 1
13 23SF50 Female Open 1
14 23S50 Male Short 1
15 23SF50 Female Short 1
16 34AS50-2 Male Adapter 2
17 Connector Thumb Wheel 4
18 01-201 Torque Wrench 1
19 01-210 Reference Flat 1
20 01-222 Pin Depth Gauge 1
21 01-223 Pin Depth Gauge 1
Table 13-1. Model 3650 (SMA/3.5 mm) Calibration Kit Contents
WILTRON
MODEL 3650
21
22
8
7
6
19
18
17 16 131215 14 11 9
3
1
2
4
5
10
*
*
*
Figure 13-1. Model 3650 (SMA/3.5 mm) Calibration Kit Components
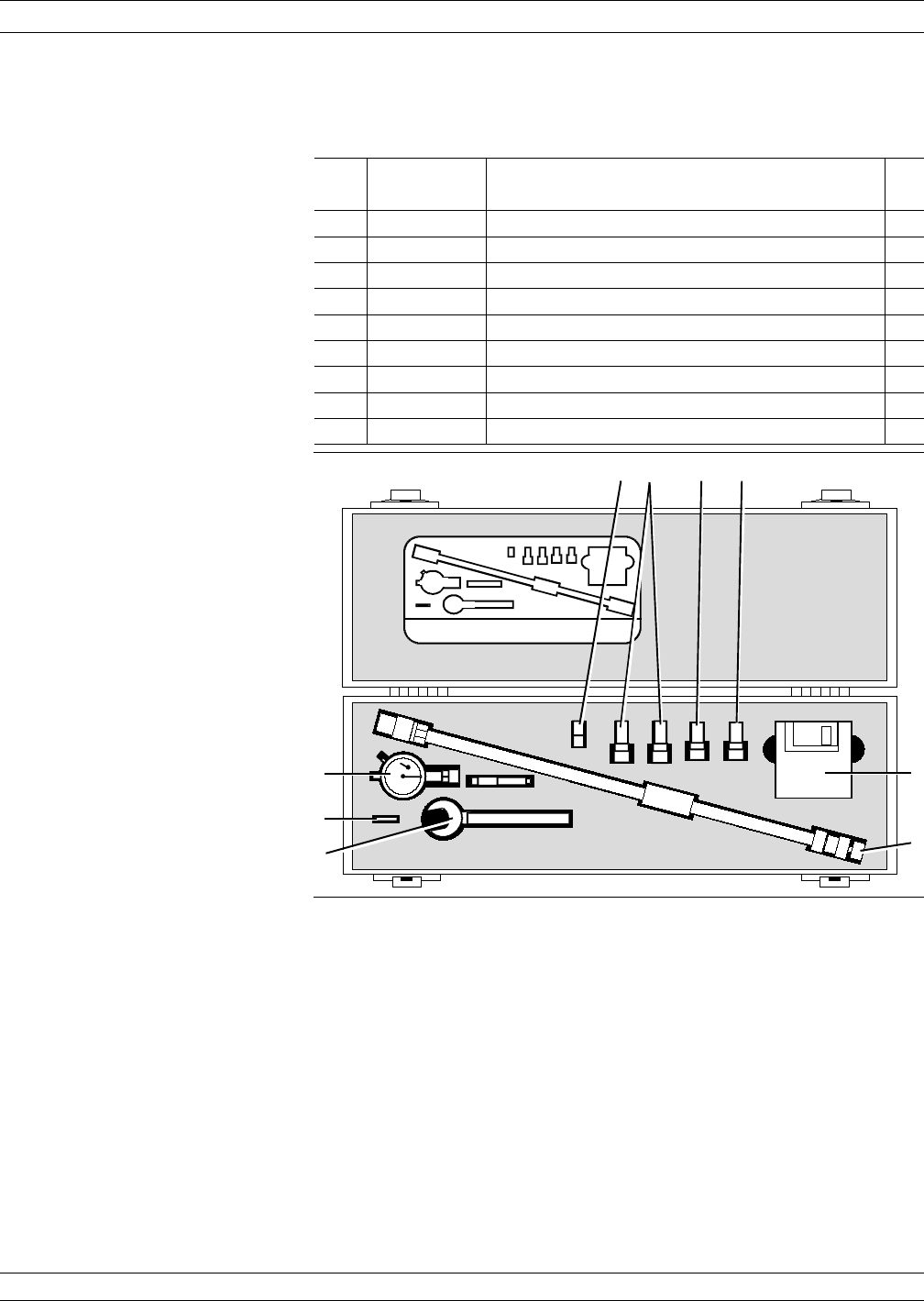
Model 3651 Calibration Kit
37XXXC OM 13-5
CALIBRATION KITS KIT CONTENTS
Index Anritsu Part
Number Description Qty.
1 01-221 Collet and Extractor Tool 1
2 28A50-2 Broadband Termination 2
3 24A50 Open 1
4 23A50 Short 1
5 Calibration Software Diskettet 1
6 17A50 Sliding Termination (Option 1) 1
7 01-200 Torque Wrench 1
8 01-210 Reference Flat 1
9 01-220 Pin Depth Gauge 1
Table 13-2. Model 3651 (GPC-7) Calibration Kit Contents
WILTRON MODEL 3651
12 3 4
5
6
7
8
9
Figure 13-2. Model 3651 (GPC-7) Calibration Kit Components
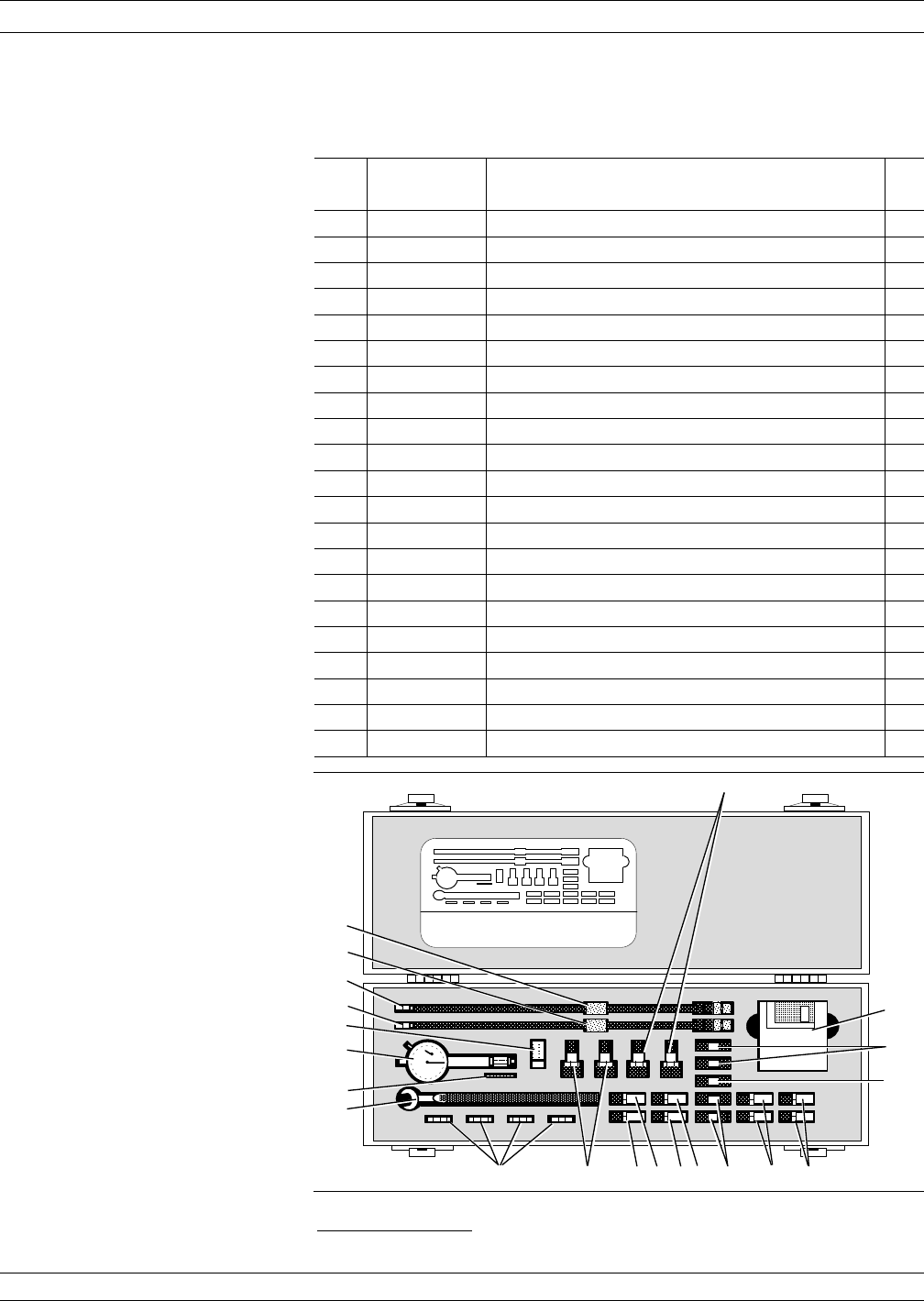
Model 3652 Calibration Kit
KIT CONTENTS CALIBRATION KITS
13-6 37XXXC OM
Index Anritsu Part
Number Description Qty.
1 01-212 Female Flush Short (Option 1) 1
2 01-211 Male Flush Short (Option 1) 1
3 17KF50 Female Sliding Termination 1
4 17K50 Male Sliding Termination (Option 1) 1
5 34AKF50-2 Female Adapter 2
6 Calibration Software Diskette 1
7 33FKF50 Female-Female Adapter 2
8 33KK50 Male-Male Adapter* 1
9 28K50-2 Male Termination 2
10 28KF50-2 Broadband Female Termination 2
11 33KKF50 Male-Female Adapter* 2
12 24K50 Male Open 1
13 23KF50 Female Open 1
14 23K50 Male Short 1
15 23KF50 Female Short 1
16 34AK50-2 Male Adapter 2
17 Connector Thumb Wheel 4
18 01-201 Torque Wrench 1
19 01-210 Reference Flat 1
20 01-222 Pin Depth Gauge 1
21 01-223 Pin Depth Gauge 1
Table 13-3. Model 3652 (K-Connector) Calibration Kit Contents
WILTRON
MODEL 3652
21
22
8
7
6
19
18
17 16 131215 14 11 9
3
1
2
4
5
10
*
*
*
Figure 13-3. Model 3652 (K-Connector) Calibration Kit Components
* Phase Equal Adapters
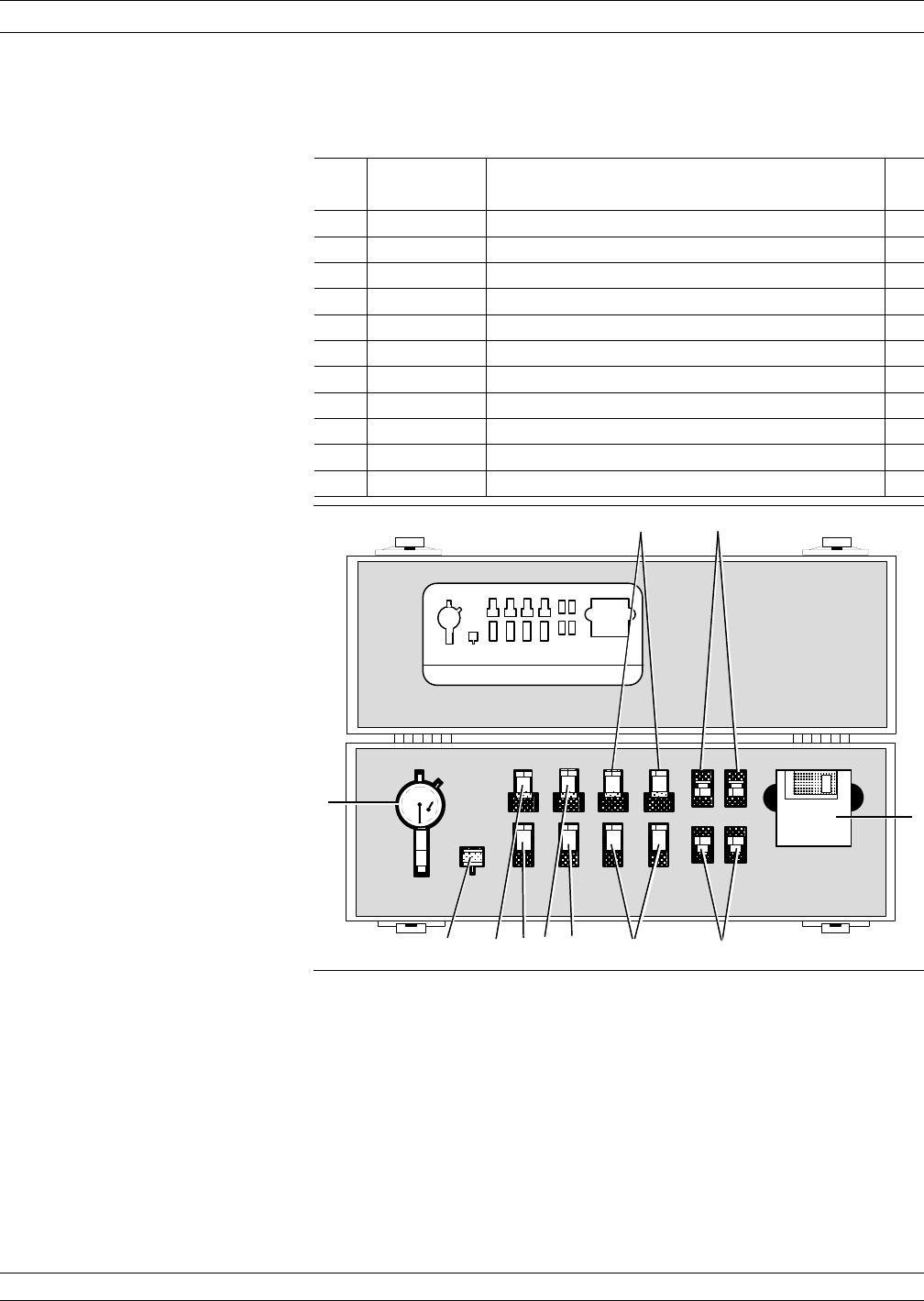
Model 3653 Calibration Kit
37XXXC OM 13-7
CALIBRATION KITS KIT CONTENTS
Index Anritsu Part
Number Description Qty.
1 28N50-2 Broadband Male Termination 2
2 34AN50-2 Male Adapter 2
3 Calibration Software Diskette 1
4 34ANF50-2 Female Adapter 2
5 28NF50-2B Braodband Female Termination 2
6 24NF50 Female Open 1
7 24N50 Male Open 1
8 23NF50 Female Short 1
9 23N50 Male Short 1
10 01-213 Reference Gauge 1
11 01-224 Pin Depth Gauge 1
Table 13-4. Model 3653 (Type N) Calibration Kit Contents
W I L T R O N M O D E L 3 6 5 3
1 1
1 0 9 8 7 6 5 4
3
21
Figure 13-4. Model 3653 (Type N) Calibration Kit Components
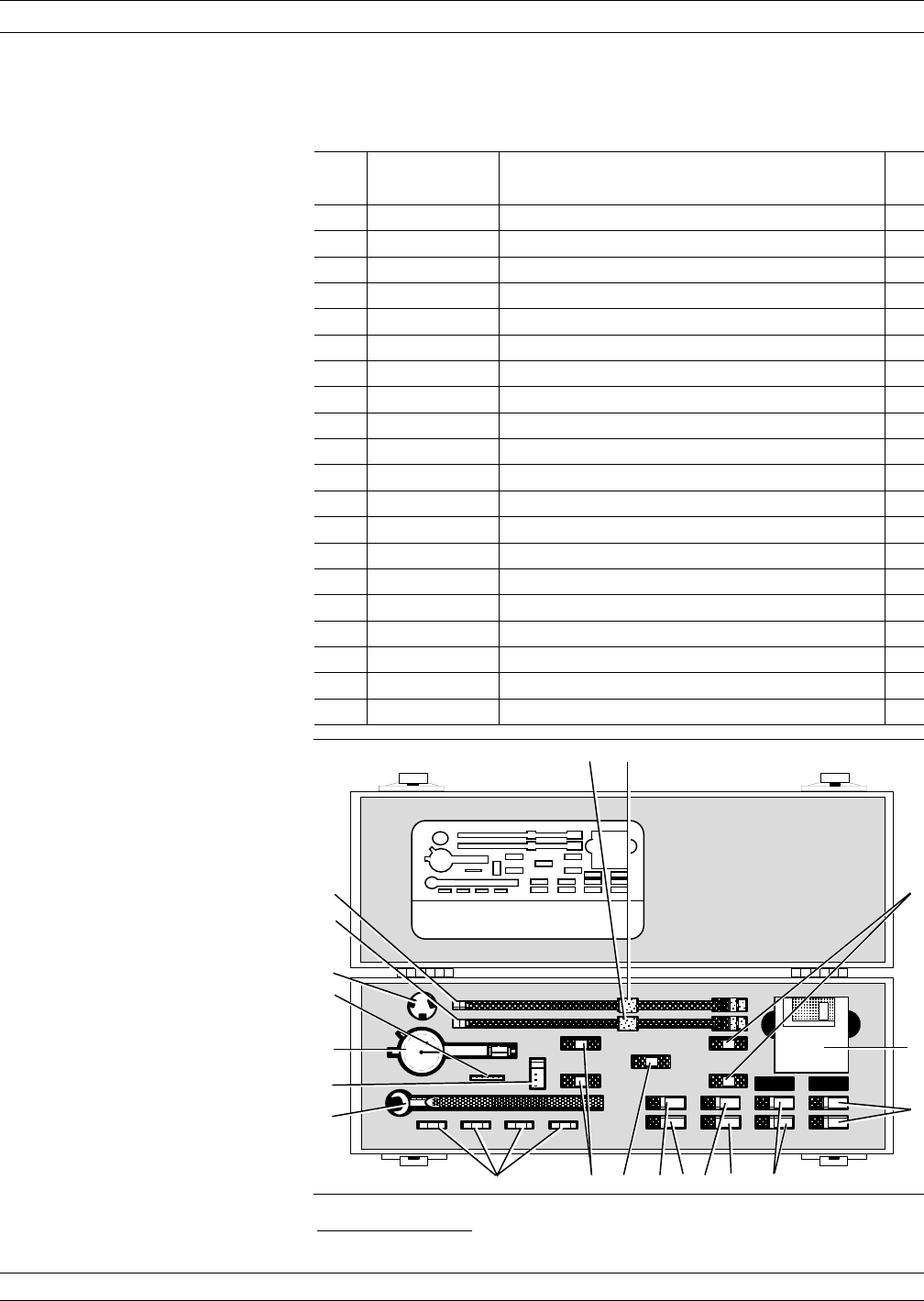
Model 3654/ 3654B
Calibration Kit
KIT CONTENTS CALIBRATION KITS
13-8 37XXXC OM
* Phase Equal Adapters
Index Anritsu Part
Number Description Qty.
1 17VF50B Female Sliding Termination 1
2 17V50B Male Sliding Termination 1
3 33VVF50 Male-Female Adapter 2
4 2360-54B Calibration Software Diskette 1
5 28V50B Male Broadband Termination 2
6 28VF50B Female Broadband Termination 2
7 24V50B Male Open 1
8 24VF50B Female Open 1
9 23V50B-5.1 Male Short, 5.1 mm 1
10 23VF50B-5.1 Female Short, 5.1 mm 1
11 33VV50 Male-Male Adapter 1
12 33VFVF50 Female-Female Adapter 2
13 Connector Thumb Wheel 4
14 01-201 Torque Wrench 1
15 01-323 Female Adapter For Pin Gauge 1
16 01-322 Pin Depth Gauge 1
17 01-210 Reference Flat 1
18 01-204 Adapter Wrench 1
19 01-312 Male Flush Short 1
20 01-311 Female Flush Short 1
Table 13-5. Model 3654 (V-Connector) Calibration Kit Contents
W I L T R O N
M O D E L 3 6 5 4
2 0
1 9
1 8
1 7
1 6
1 5
1 4
1 3 1 2 1 1 1 0 9 8 7 6
5
4
3
21
Figure 13-5. Model 3654 (V-Connector) Calibration Kit Components
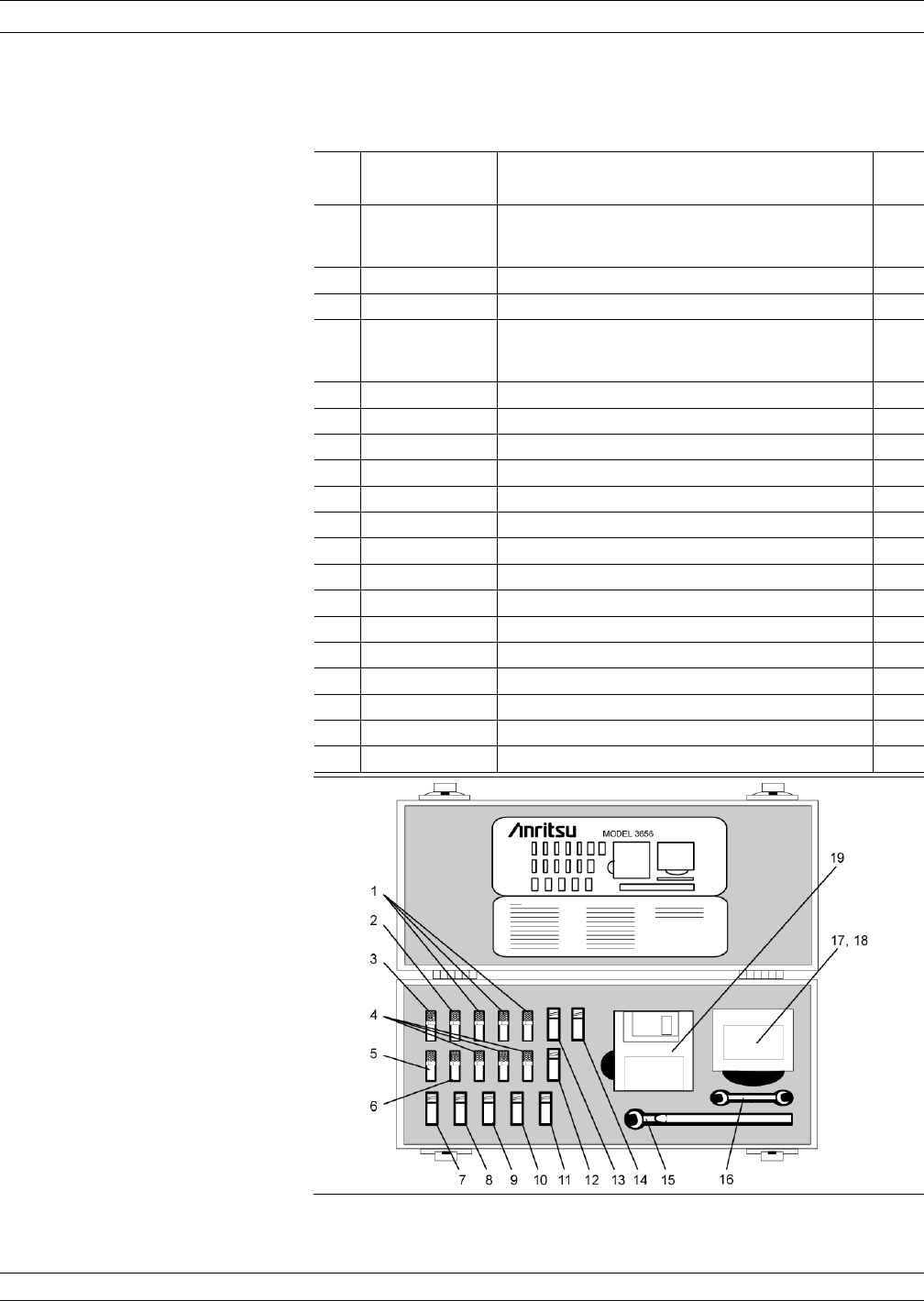
Model 3656 Calibration Kit
37XXXC OM 13-9
CALIBRATION KITS KIT CONTENTS
Figure 13-6. Model 3656 (W1-Connector) Calibration Kit Components
Index Anritsu
Part Number Description Qty.
1 23W50-1
23W50-2
23W50-3
Male Offset Short 1 (2.02 mm)
Male Offset Short 2 (2.65 mm)
Male Offset Short 3 (3.180 mm)
1
1
1
2 24W50 Male Open (1.510 mm) 1
3 28W50 Male Broadband Termination 1
4 23WF50-1
23WF50-2
23WF50-3
Female Offset Short 1 (2.02 mm)
Female Offset Short 2 (2.65 mm)
Female Offset Short 3 (3.180 mm)
1
1
1
5 28WF50 Female Broadband Termination 1
6 24WF50 Female Open (1.930 mm) 1
7 33WSC50 Fixed Male SC Connector 1
8 33WFSC50 Fixed Female SC Connector 1
9 Interchangeable Sliders, SC Connectors 1
10 Locking Keys, SC Connectors 1
11 01-402 Interchangeable Adapter Fixed Male 1
12 33WWF50 Male-Female Adapter 1
13 33WW50 Male-Male Adapter 1
14 33WFWF50 Female-Female Adapter 1
15 01-504 6 mm Torque Wrench 1
16 01-505 6x7 mm End Wrench 1
17 18-WWF50-1B Stepped Impedance Thruline (Verification Device) 1
18 18-WWF50-1 50WMatched Thruline (Verification Device) 1
19 Calibration/Verification Software
Table 13-6. Model 3656 (W1-Connector) Calibration Kit Contents
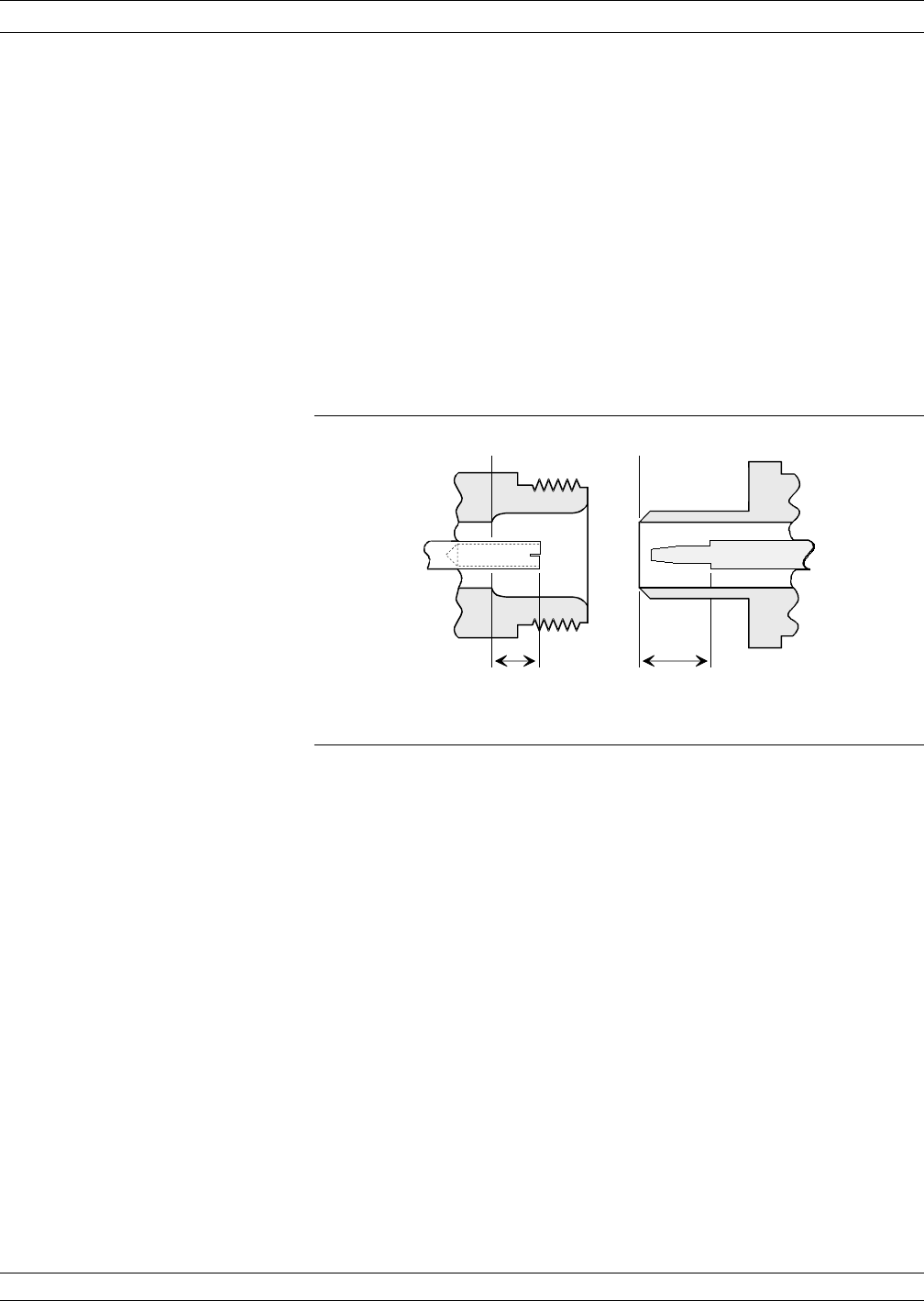
13-4 PRECAUTIONS The following are precautionary notes related to the use of connectors.
For specific information on setting pin depths on sliding terminations,
refer to the 37XXXC Operation Manual, Chapter 7.
Pin Depth Before mating, measure the pin depth (Figure 13-7) of the device that
will mate with the RF component, using an Anritsu Pin Depth Gauge
or equivalent (Figure 13-8). Based on RF components returned for re-
pair, destructive pin depth of mating connectors is the major cause of
failure in the field. When an RF component is mated with a connector
having a destructive pin depth, damage will likely occur to the RF
component connector. (A destructive pin depth has a center pin that is
too long in respect to the connector’s reference plane.)
PRECAUTIONS CALIBRATION KITS
13-10 37XXXC OM
REFERENCE
PLANE
MALE
PIN
DEPTH
(INCHES)
REFERENCE
PLANE
FEMALE
PIN
DEPTH
(INCHES)
Figure 13-7. N-Connector Pin Depth
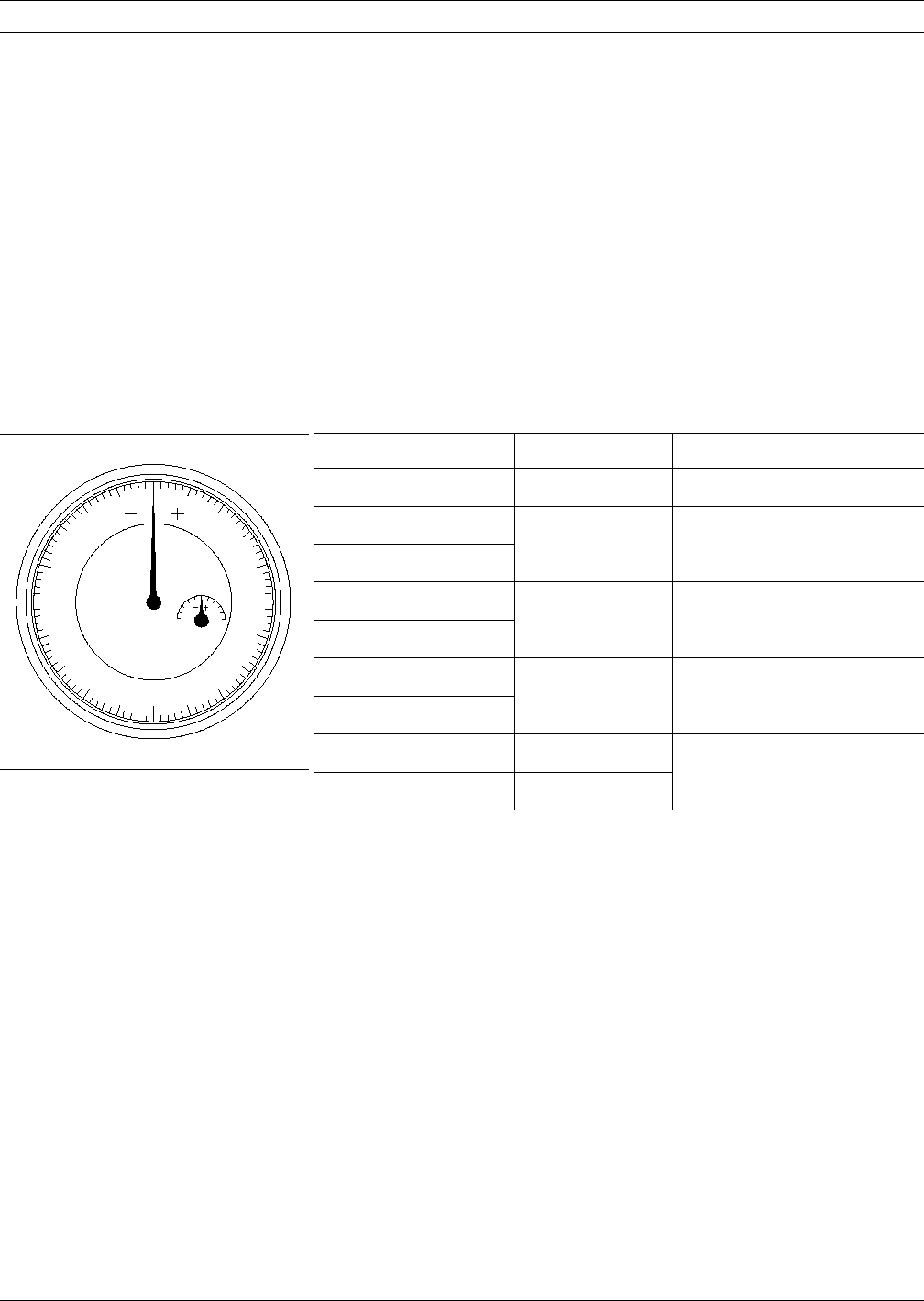
Pin Depth Tolerance The center pin of RF component connectors has a precision tolerance
measured in mils (1/1000 inch). Connectors on test devices that mate
with RF components may not be precision types and may not have the
proper depth. They must be measured before mating to ensure suit-
ability. When gauging pin depth, if the test device connector measures
out of tolerance (Table 13-7) in the “+” region of the gauge
(Figure 13-8), the center pin is too long. Mating under this condition
will likely damage the termination connector. On the other hand, if the
test device connector measures out of tolerance in the “–” region, the
center pin is too short. While this will not cause any damage, it will re-
sult in a poor connection and a consequent degradation in perfor-
mance.
Over Torquing Connectors Over torquing connectors is destructive; it may damage the connector
center pin. Finger-tight is usually sufficient, especially on Type N con-
nectors. Never use pliers to tighten connectors.
Teflon Tuning Washers The center conductor on most RF components contains a small teflon
tuning washer located near the point of mating (interface). This
washer compensates for minor impedance discontinuities at the inter-
face. The washer’s location is critical to the RF component’s perfor-
mance. Do not disturb it.
Mechanical Shock RF components are designed to withstand years of normal bench han-
dling. However, do not drop or otherwise treat them roughly. They are
laboratory-quality devices, and like other such devices, they require
careful handling.
37XXXC OM 13-11
CALIBRATION KITS PRECAUTIONS
Port/Connector Type Pin Depth (mils) Anritsu Gauge Setting
GPC 7 +0.000 to –0.003 Same as pin depth
N Male .207 +0.003
-0.003 Same as pin depth
N Female
WSMA Male –0.0025
–0.0035 Same as pin depth
WSMA Male
K Male +0.000 to –0.003 Same as pin depth
K Female
V Male +0.000 to –0.001 Same as pin depth
V Female +0.000 to –0.001
Table 13-7. Pin Depth Tolerances
0
1
2
3
45
1
2
3
4
2
11
2
Figure 13-8. Pin Depth Gauge
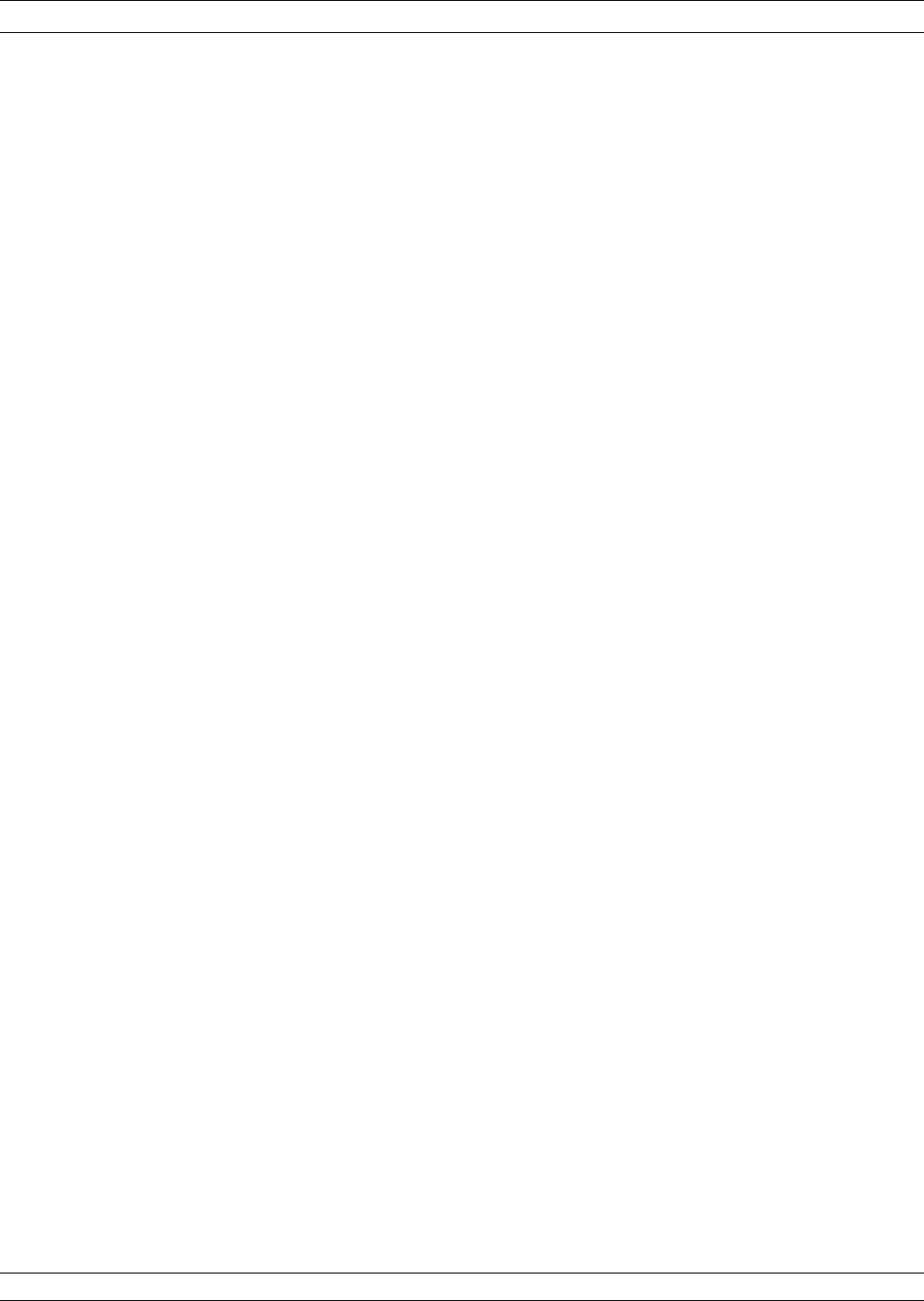
13-5 CLEANING
INSTRUCTIONS Connector interfaces—especially the outer conductors on the GPC 7
and SMA connectors—should be kept clean and free of dirt and other
debris.
Denatured alcohol applied with a cotton swab applicator is recom-
mended for cleaning connector interfaces.
NOTE
Most cotton swabs are too large to fit in the smaller con-
nector types. It is necessary to remove most of the cotton
and then twist the remaining cotton tight. Be sure that the
remaining cotton does not get stuck in the connector.
The following are some important tips on cleaning connectors:
qUse only denatured alcohol as a solvent
qAlways use an appropriate size of cotton swab
qGently move the cotton swab around the center conductor
qNever put lateral pressure on the connector’s center pin
qVerify that no cotton or other foreign material remains in the
connector after cleaning
qOnly dampen the cotton swab. Do NOT saturate it
qCompressed air can be used to remove foreign particles and to
dry the connector
qVerify that the center pin has not been bent or damaged
Figure 13-9, following page, illustrates how to clean connectors.
CLEANING INSTRUCTIONS CALIBRATION KITS
13-12 37XXXC OM
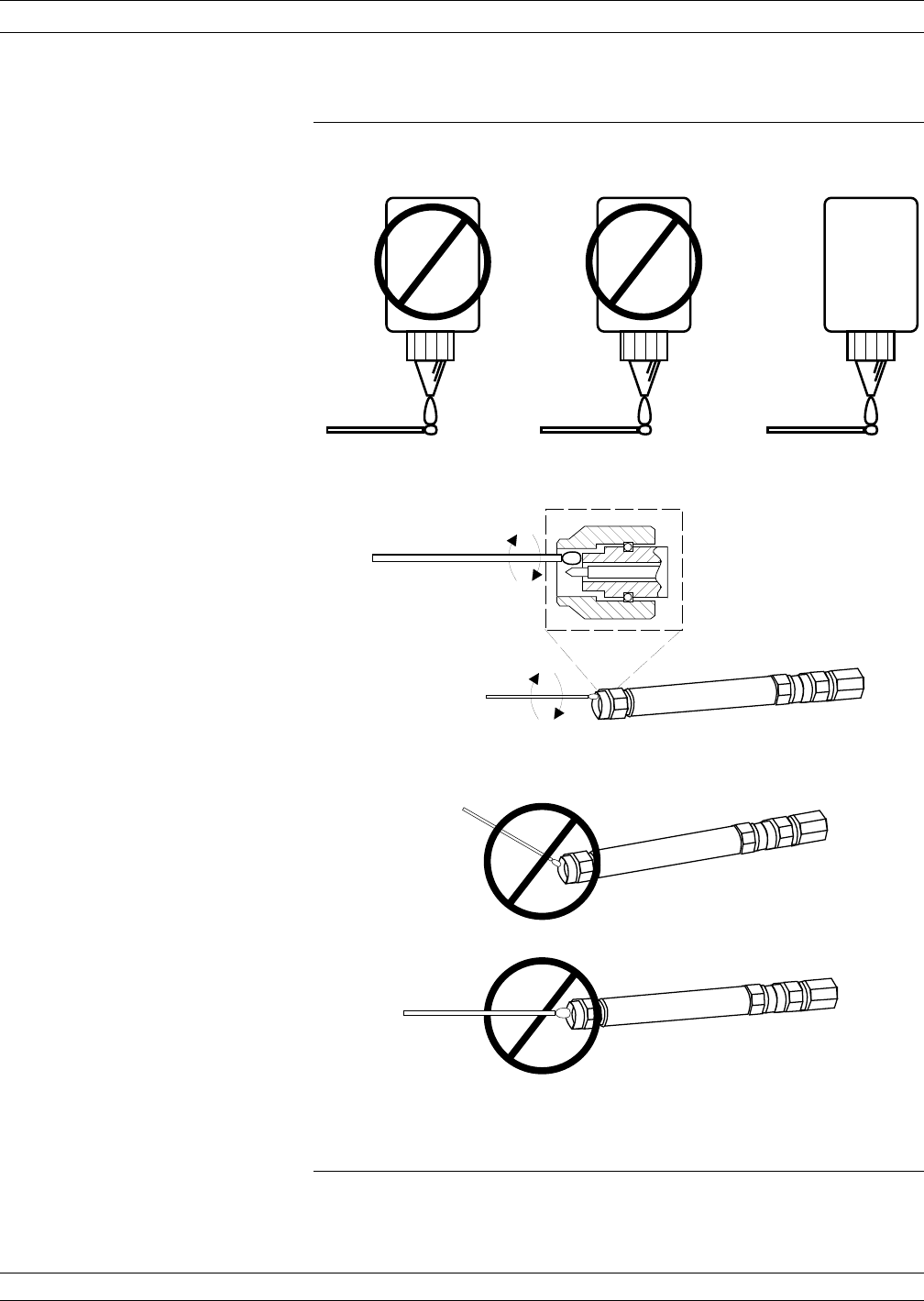
37XXXC OM 13-13/13-14
CALIBRATION KITS CLEANING INSTRUCTIONS
D o N O T u s e I n d u s t r i a l S o l v e n t s o r W a t e r o n c o n n e c t o r . U s e o n l y D e n a t u r e d A l c o h o l .
U s e o n l y d e n a t u r e d a l c o h o l a n d t h e p r o p e r s i z e o f c o t t o n s w a b . G e n t l y r o t a t e t h e s w a
b
a r o u n d t h e c e n t e r p i n b e i n g c a r e f u l n o t t o s t r e s s o r b e n d t h e p i n o r y o u w i l l d a m a g e
t h e c o n n e c t o r .
D o N O T p u t c o t t o n s w a b s i n a t a n a n g l e , o r y o u w i l l d a m a g e t h e c o n n e c t o r s .
D o N O T u s e t o o l a r g e o f c o t t o n s w a b , o r y o u w i l l d a m a g e t h e c o n n e c t o r s .
D E N A T U R E D
A L C O H O L
W A T E R
I N D U S T R I A L
S O L V E N T S
Figure 13-9. How to Clean Connectors

Table of Contents
14-1 INTRODUCTION...................................14-3
14-2 DESCRIPTION ....................................14-3
14-3 PERFORMANCE SPECIFICATIONS........................14-4
System Performance................................14-4
Test Port Characteristics .............................14-5
Measurement Capabilities ............................14-5
14-4 INSTALLATION ...................................14-6
14-5 CONTROLS AND CONNECTORS.........................14-11
14-6 CALIBRATION ...................................14-13
14-7 OPERATION ....................................14-14
Entering/ Leaving Millimeter Wave Operation .................14-14
Changing Bands/Modules While in Millimeter Wave..............14-18
Allowable Millimeter Wave Module Configurations, Measurements and
Calibrations....................................14-18
Effect of Default Program ............................14-19
Redefinition of Band Frequency Ranges ....................14-20
Use of Normal Multiple Source Mode ......................14-21
Stored Setups and Calibrations .........................14-21
External Source and Power Levels .......................14-22
14-8 MEASUREMENT PROCEDURE..........................14-23
14-9 REMOTE OPERATION...............................14-24
14-10 OPERATIONAL CHECKOUT— GENERAL ...................14-25
14-11 OPERATION CHECKOUT—IF POWER LEVEL TEST .............14-26
14-12 OPERATIONAL CHECKOUT— TRANSMISSION HIGH LEVEL NOISE TEST14-28
14-13 OPERATIONAL CHECKOUT— REFLECTION HIGH LEVEL NOISE TEST . 14-30
Chapter 14
Millimeter Wave
System

Chapter 14
Millimeter Wave System
14-1 INTRODUCTION This chapter describes the 371XXC Millimeter Wave System, its opera-
tion, and its measurement capabilities. For information on ME7808A
Broadband System, refer to Chapter 15.
14-2 DESCRIPTION The 371XXC Millimeter Wave System (371XXCmm) consists of a
37147C or 37169C VNA, two 680XXCor MG369XA Frequency Synthe-
sizers, and a 3735B Millimeter Test Set having two 374X Millimeter
Wave Modules. There are 14 different 374X modules available (below)
to accommodate different measurement types and frequency ranges.
q3741A-Q 33 to 50 GHz Transmission Module
q3741A-V 50 to 75 GHz Transmission Module
q3741A-E 60 to 90 GHz Transmission Module
q3741A-EE56 to 94 GHz Transmission Module
q3741A-W 75 to 110 GHz Transmission Module
q3741A-EW 65 to 110 GHz Transmission Module
q3741A-F 90 to 140 GHz Transmission Module
q3740A-Q 33 to 50 GHz Transmission/Reflection Module
q3740A-V 50 to 75 GHz Transmission/Reflection Module
q3740A-E 60 to 90 GHz Transmission/Reflection Module
q3740A-EE 56 to 94 GHz Transmission/Reflection Module
q3740A-W 75 to 110 GHz Transmission/Reflection Module
q3740A-EW 65 to 110 GHz Transmission/Reflection Module
q3740A-F 90 to 140 GHz Transmission/Reflection Module
37XXXC OM 14-3
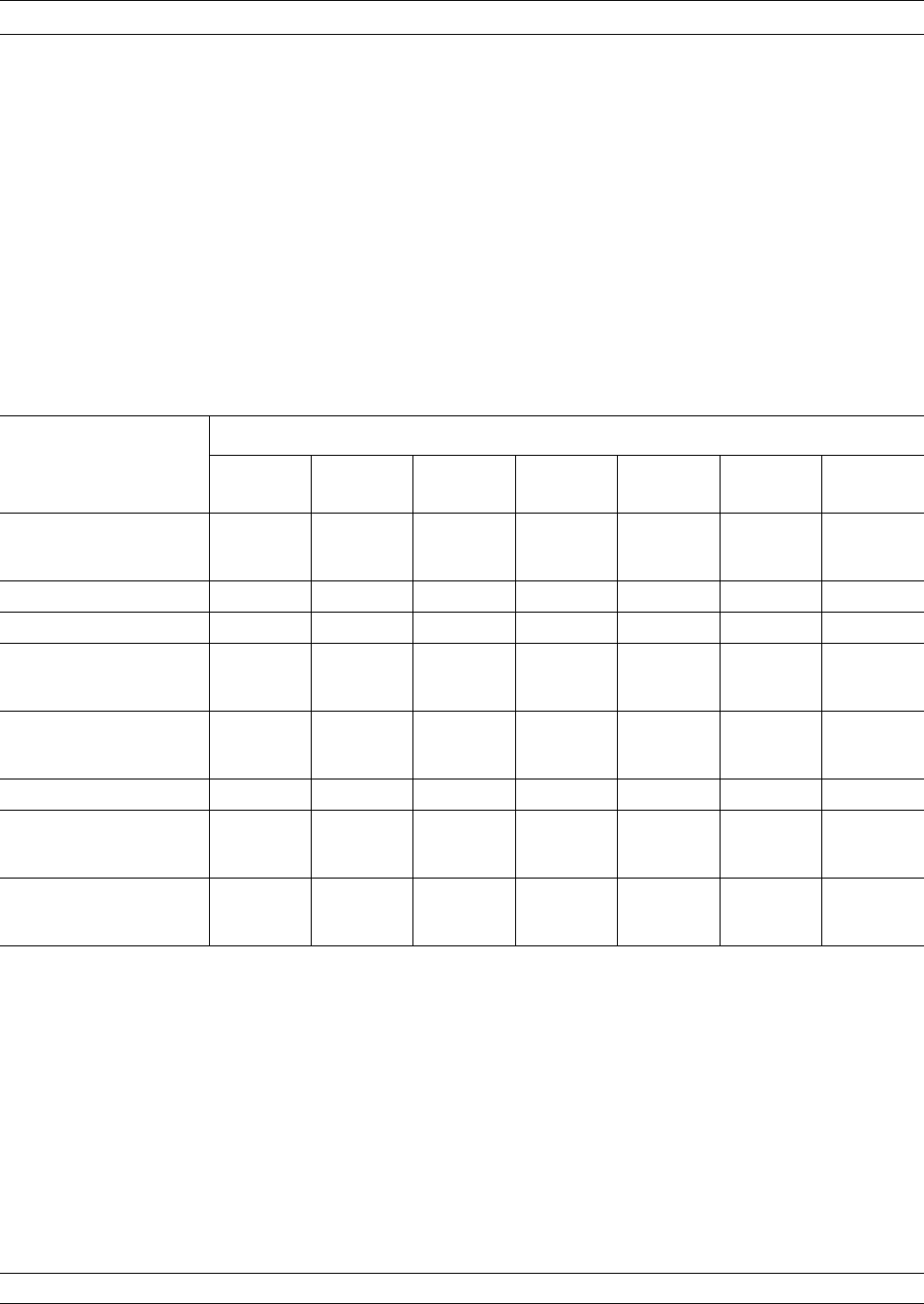
14-3 PERFORMANCE
SPECIFICATIONS Performance specifications are given below in Table 14-1.
System Performance “Receiver Dynamic Range” is defined as the ratio of the maximum sig-
nal level at Port 2 for 0.1 dB compression to the noise floor at Port 2.
"System Dynamic Range" is defined as the ratio of the power incident
on Port 2 in a through line connection (reference) to the noise floor at
Port 2 (forward measurements only). The "Noise Floor" is the maxi-
mum measured signal with the test ports terminated using 10 Hz IF
bandwidth and 512 averages.
PERFORMANCE SPECIFICATIONS MILLIMETER WAVE
14-4 37XXXC OM
Specification
Model
Q Band
(WR-22) V Band
(WR-15) E Band
(WR-12) Extended
E Band W Band
(WR-10) Extended
W Band F Band
(WR-8)
Frequency Range (GHz) 33–50 50–75 60–90
56–60
60–85
85–94
75–100
100–110
65–75
75–100
100–110
90–115
115–140
Frequency Resolution 3Hz 3Hz 6Hz 6Hz 6Hz 6Hz 6Hz
Max Signal Into Port 2 +10 dBm +8 dBm +8 dBm +8 dBm +6 dBm +6 dBm +4 dBm
Noise Floor –93 dBm –90 dBm –90 dBm
–85 dBm
–90 dBm
–76 dBm
–90 dBm
–90 dBm
–90 dBm
–89 dBm
–87 dBm
–88 dBm
–87 dBm
Receiver Dynamic Range 103 dB 98 dB 98 dB
93 dB
98 dB
84 dB
96 dB
96 dB
96 dB
95 dB
93 dB
92 dB
91 dB
High Level Noise (typical) 0.02 dB 0.05 dB 0.06 dB 0.08 dB 0.06 dB 0.08 dB 0.08 dB
Power Out (typical) +7 dBm +7 dBm +6 dBm
+5 dBm
+6 dBm
+4 dBm
+5 dBm
+2 dBm
–5 dBm
+5 dBm
+2 dBm
–3 dBm
–7 dBm
System Dynamic Range 100 dB 97 dB 96 dB
90 dB
96 dB
80 dB
95 dB
92 dB
85 dB
94 dB
89 dB
85 dB
80 dB
Table 14-1. Performance Specifications, Millimeter Wave Modules
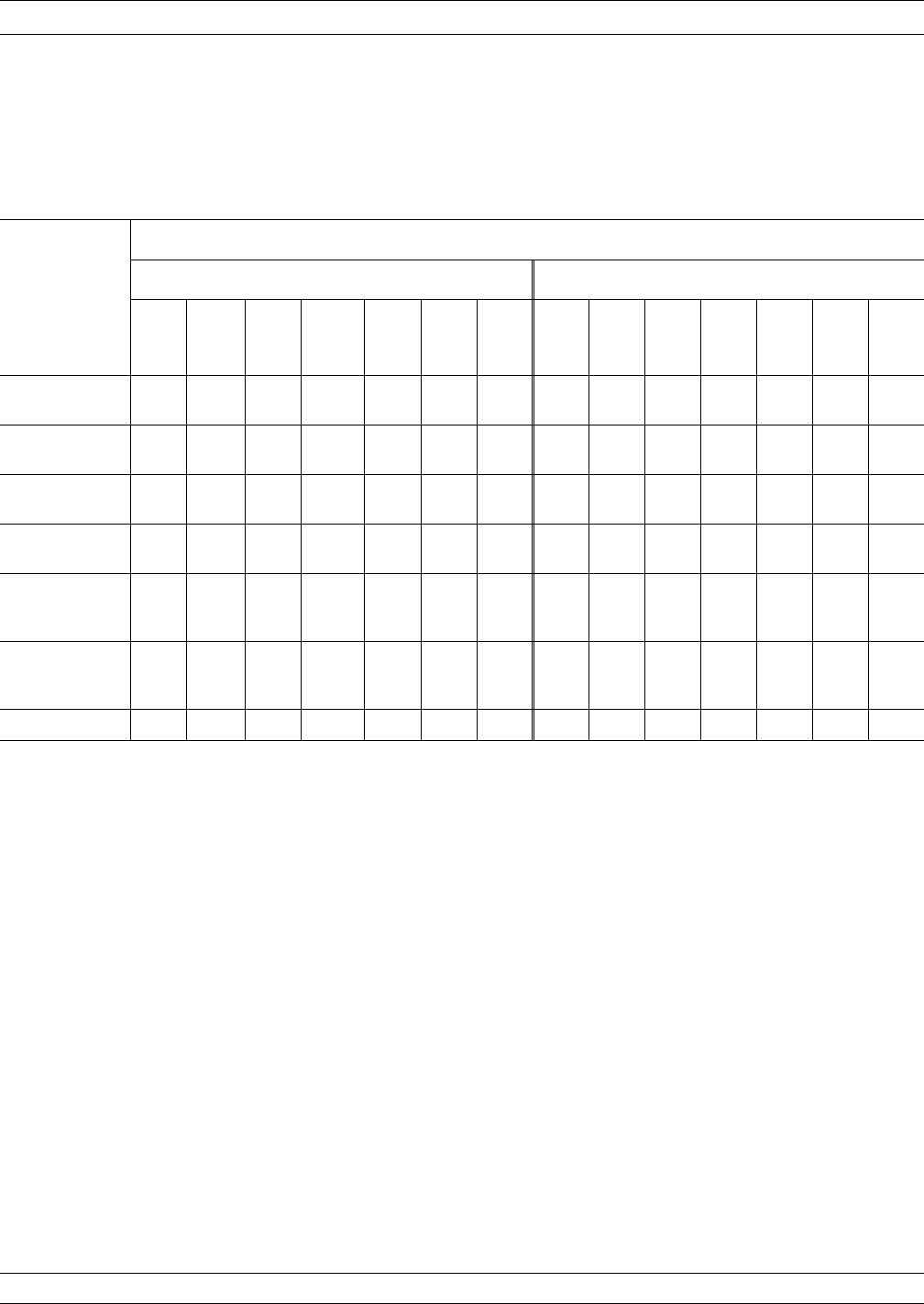
Test Port Characteristics Test port characteristics for the waveguide connector used on the vari-
ous modules are given in Table 14-2.
Measurement Capabilities Measurement capabilities are the same as the standard 371XXC. That
is: Four Channels, Standard S-parameters as well as User Defined Pa-
rameters, Auto-Reversing, Data Points 1601, 801, 201, 51, N Discrete,
and CW (see Appendix D).
NOTE
When a 371XXC is configured as a Millimeter Wave Sys-
tem, the frequency range is extended per the specifications
of the Millimeter Wave Modules and the system will be
limited to operate with only two external sources. That is,
the internal source is removed or disabled.
37XXXC OM 14-5
MILLIMETER WAVE PERFORMANCE SPECIFICATIONS
Specification
Waveguide Designation
Offset Short Calibration LRL Calibration
WR-22 WR-15 WR-
12 WR-12
Ext. WR-
10 WR-10
Ext. WR-
8WR-22 WR-15 WR-
12 WR-
12
Ext.
WR-
10 WR-
10
Ext.
WR-
8
Frequency
(GHz) 33–50 50–75 60–90 56–94 75–110 65–110 90–14
033–50 50–75 60–90 56–94 75–110 65–110 90–14
0
Directivity
(dB) >46 >46 >46 >44 >46 >40 >43 >46 >46 >46 >44 >46 >40 >43
Source
Match (dB) >45 >37 >36 >33 >36 >30 >32 >46 >46 >46 >43 >46 >40 >41
Load Match
(dB) >46 >46 >46 >44 >46 >40 >43 >46 >46 >46 >44 >46 >40 >43
Reflection
Frequency
Tracking (dB)
±0.010 ±0.030 ±0.040 ±0.080 ±0.040 ±0.080 ±0.060 ±0.02 ±0.02 ±0.02 ±0.06 ±0.02 ±0.06 ±0.04
Transmission
Frequency
Tracking (dB)
±0.010 ±0.060 ±0.060 ±0.100 ±0.070 ±0.100 ±0.100 ±0.02 ±0.02 ±0.02 ±0.06 ±0.02 ±0.06 ±0.04
Isolation (dB) >100 >90 >90 >80 >90 >80 >80 >100 >90 >90 >80 >90 >80 >80
Table 14-2. Test Port Characteristics
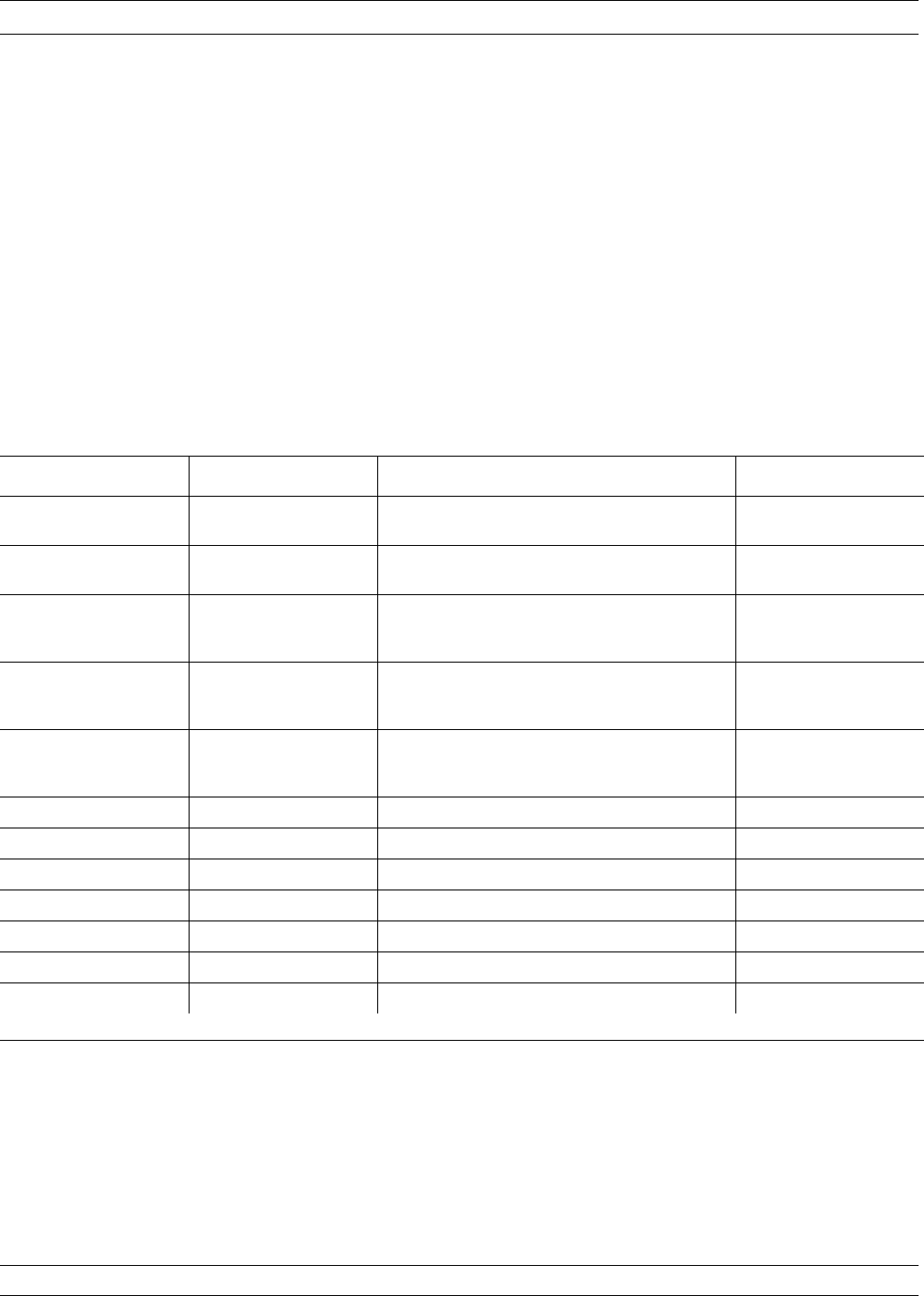
14-4 INSTALLATION The Millimeter Wave System requires interconnections between the
371XXC Vector Network Analyzer, 3735B Test Set, and two 680XXCor
MG369XA Frequency Synthesizers. Installation in the optional
3700C3 System Console is shown in Figure 14-1. Interconnections be-
tween the various units would be the same in any other rack-mount
installation. Installation procedures for the optional 3700C3 con-
sole-mounted system and for the standard bench top system are de-
scribed below.
3700C3 System Console
The following procedure describes installation in the 3700C3 System
Console. Table 14-3 lists the accessory kit contents.
INSTALLATION MILLIMETER WAVE
14-6 37XXXC OM
Anritsu Part Number Description Function Quantity
B46743 Ribbon Cable Assem-
bly
Interconnects transfer switch on VNA and test set 1
ND46618 Rigid Cable Assembly U-shaped cable that connect between front panel
connectors on VNA and test set
4
C34429-7 Rigid Cable Assembly Connects between RF Output connector on VNA
and RF Output connector on 681XXB frequency
source
1
C34429-8 Rigid Cable Assembly Connects between LO (local oscillator) connector
on VNA and RF Output connector on 681XXB
frequency source
1
2100-2 GPIB interconnect ca-
ble
Connects between Dedicated GPIB connectors
on VNA rear panel and Dedicated GPIB connec-
tor on 681XXB rear panel
2
* Power Cord AC line cord 4
2000-292 Mat, static Provides static protection for work surface 1
783-163 Wrist Strap Provides static discharge path for user 1
900-223 Screw, Pan 8
900-354 Washer, #1 2
900-396 Washer, #1 8
900-821 Screw, Special 20
Table 14-3. 3700C3 System Console Accessory Kit Contents
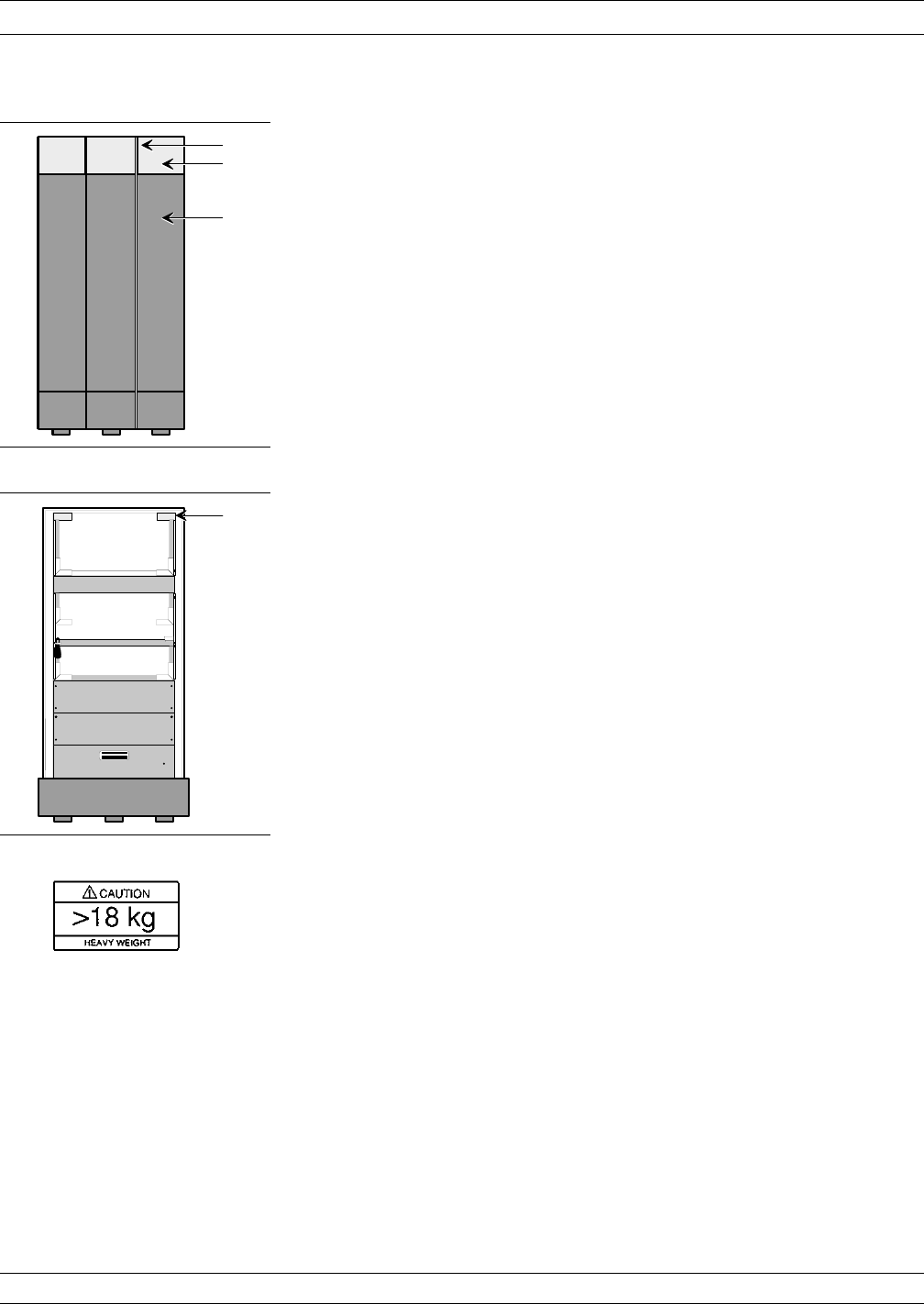
Step 1. Remove the console from its shipping container (top
left), as follows:
a. Cut the bands (1).
b. Lift off the top (2).
c. Remove the cardboard sleeve (3) by pulling
straight up and away.
d. Remove the packing materials.
e. Remove the writing surface from atop the con-
sole and set it aside. You will be directed to com-
plete its assembly in a later step.
Step 2. Remove the console from the shipping pallet (bottom
left), as follows:
a. Insert two lengths of lumber through the top
opening in the console (4).
b. With a person stationed on the front side and
another on the back side, use the lumber to lift
the console off and away from the pallet.
Alternatively, you can tilt the console on its back, be-
ing careful not to scratch the paint, and remove the
pallet.
NOTE
The empty console weights 65.9 kg (145 lb). We recom-
mend employing two or more people to lift it off of the
shipping pallet.
37XXXC OM 14-7
MILLIMETER WAVE INSTALLATION
4
2
3
1
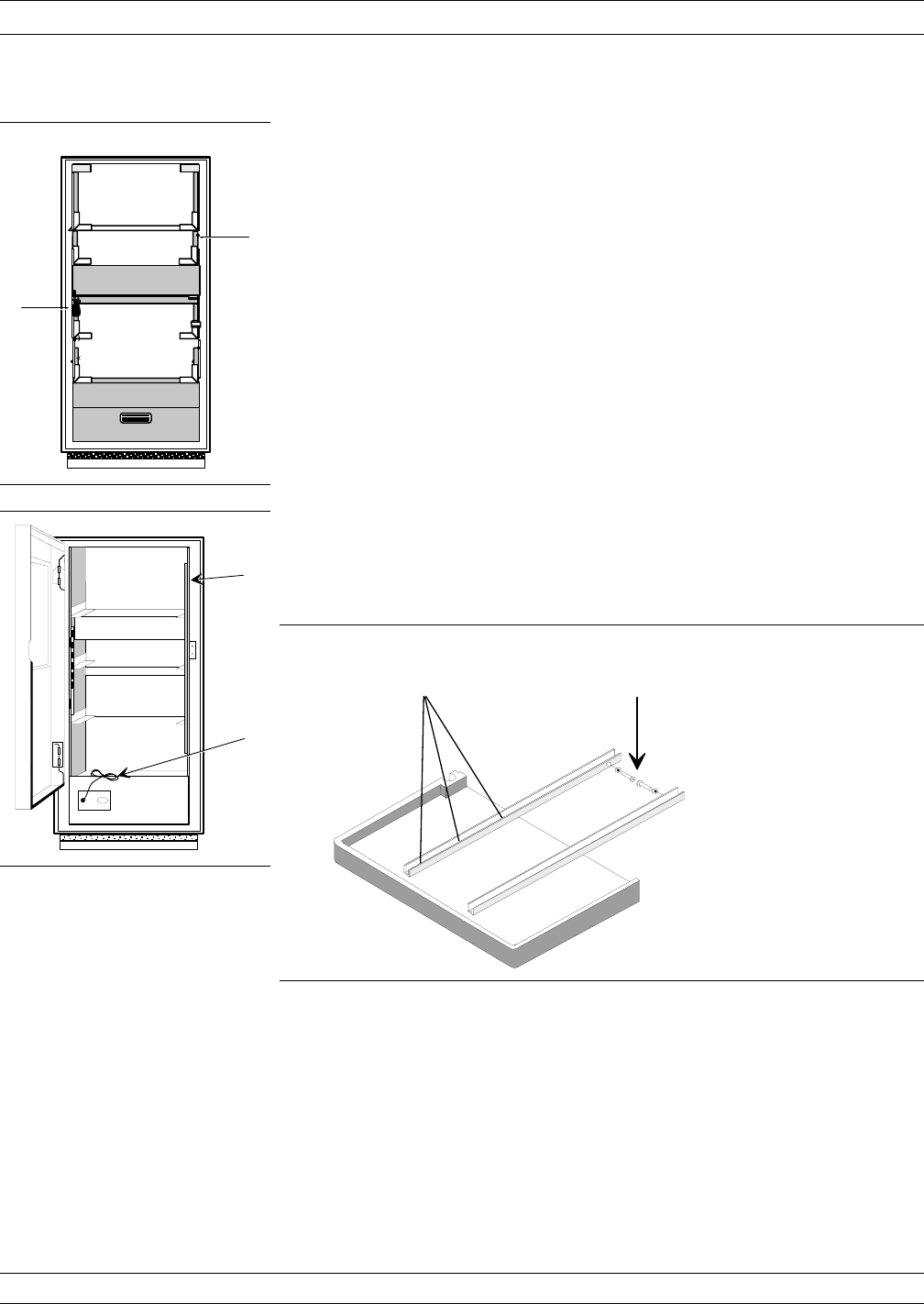
Step 3. Prepare the front of the console (top left) for installa-
tion of the equipment, as follows:
Cut the tie wrap from the Wrist Strap/Table Mat
ground port (6), bring it out through the opening
above panel (7), and let it hang free and out of the
way.
Step 4. Prepare the rear of the console (bottom left) for in-
stallation of the equipment, as follows:
a. Open the rear door, cut the tie wraps from the
writing-surface rails (8), and remove the rails
from the console.
b. Cut the tie wrap from the Line Cord (9), and un-
coil the cord.
Step 5. Prepare the Writing Surface by attaching the two
rails as shown below, using the 10-32 x 1-inch screws
and #10 split-lock washers supplied in the attach-
ing-parts kit.
NOTE
In the next step, install the 680XXC that contains
Option 15 (High Power Option) as the top Source. For
WR-8 F-Band installation, the bottom Source is the
68067C or MG369XA with Option 15.
Step 6. Install the 371XXC VNA, 3735B Test Set, and two
680XXCor MG369XA Frequency Synthesizers in the
console, as shown in Figure 14-1. Secure with screws
900-821 (Table 14-3).
INSTALLATION MILLIMETER WAVE
14-8 37XXXC OM
1 0 - 3 2 x 1 / 2 I N C H
# 1 0 L O C K W A S H E R
# 1 0 F L A T W A S H E R
I N S T A L L I N T W O P L A C E S A F T E R
P L A C I N G T H E W R I T I N G S U R F A C E
I N T O T H E C O N S O L E .
1 0 - 3 2 x 1 / 2 I N C H
# 1 0 L O C K W A S H E R
I N S T A L L I N 6 P L A C E S
6
7
8
9
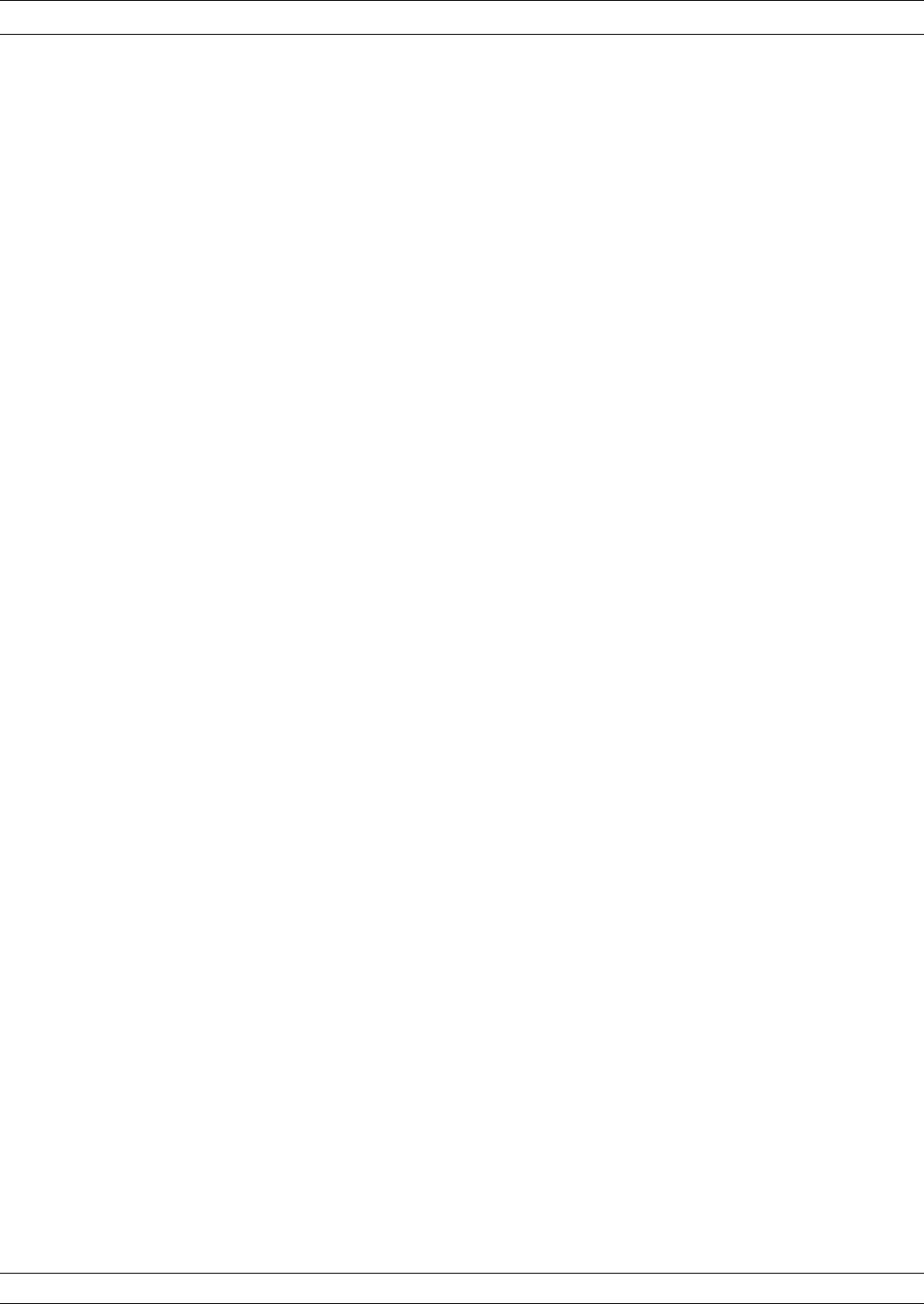
Step 7. From the rear, connect cables as described below (see
Figure 14-1 for illustration):
a. Ribbon cable between Transfer Switch connec-
tors on VNA and test set
b. 2100-2 cable between Dedicated GPIB on VNA
and Dedicated GPIB on frequency source #1
(top)
c. 2100-2 between Dedicated GPIB on VNA and
Dedicated GPIB on frequency source #2 (bottom)
d. From the front, connect the four U-shaped
semirigid cables (ND46618) between connector
b1, a1, a2, and b2 on VNA and test set
e. Connect cable ND46620 between RF Input on
VNA and RF Output on 680XXCor MG369XA #2
(bottom source)
f. Connect cable ND46621 between the LO Input
on the VNA and the RF Output on the
680XXCor MG369XA #1 (top source)
Step 8. Secure the Writing Surface rails to the tapped hole
in each rail guide. Use two 10-32x1/2-inch screws,
two #10 split-lock washers, and two #10 flat washers
from the attaching parts kit.
Step 9. Install the static mat on the work surface and con-
nect the wrist strap.
Step 10. Lay the appropriate Transmission/Reflection Module
(3740 Series), or Transmission Only Module
(3741 Series), or one of each, on the work surface
with the test port connectors facing each other.
NOTE
The system will function with a single Transmission/Re-
flection Module, and it can be connected to either Port 1
Module or Port 2 Module connector pad. The normal con-
figuration, however, uses a Transmission/Reflection Mod-
ule connected to the Port 1 Module connector pad and a
Transmission Only Module connected to the Port 2 Module
connector pad.
37XXXC OM 14-9
MILLIMETER WAVE INSTALLATION
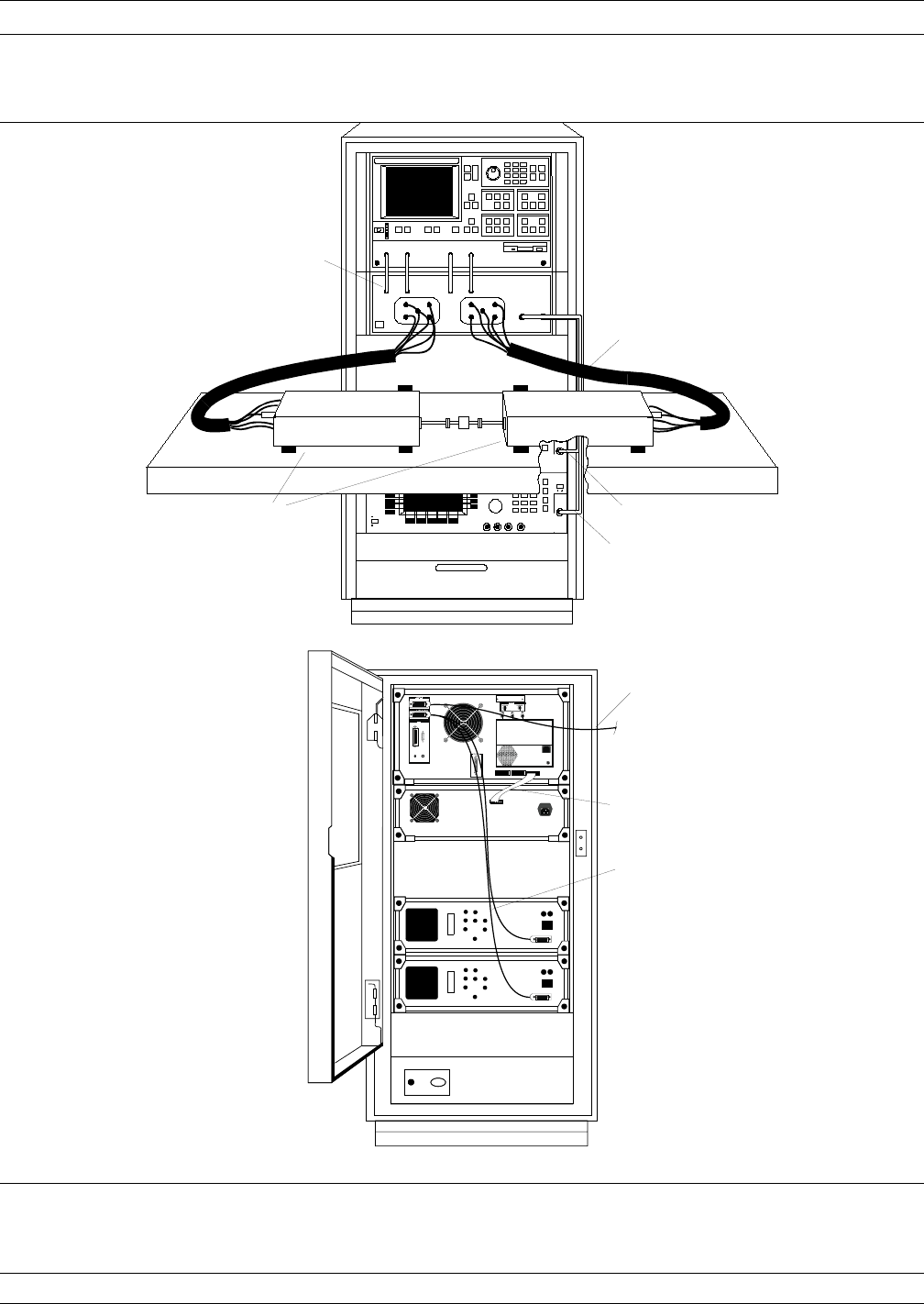
INSTALLATION MILLIMETER WAVE
14-10 37XXXC OM
Figure 14-1. Millimeter Wave System Equipment Installation
RF
Output
RF
Output
47958
(2 PLACES)
ND46618
(4 PLACES)
DUT
MILLIMETER
WAVE MODULE
ND46620
ND46621
GPIB CABLE
2100-X
B46743
2100-2
(2 PLACES)
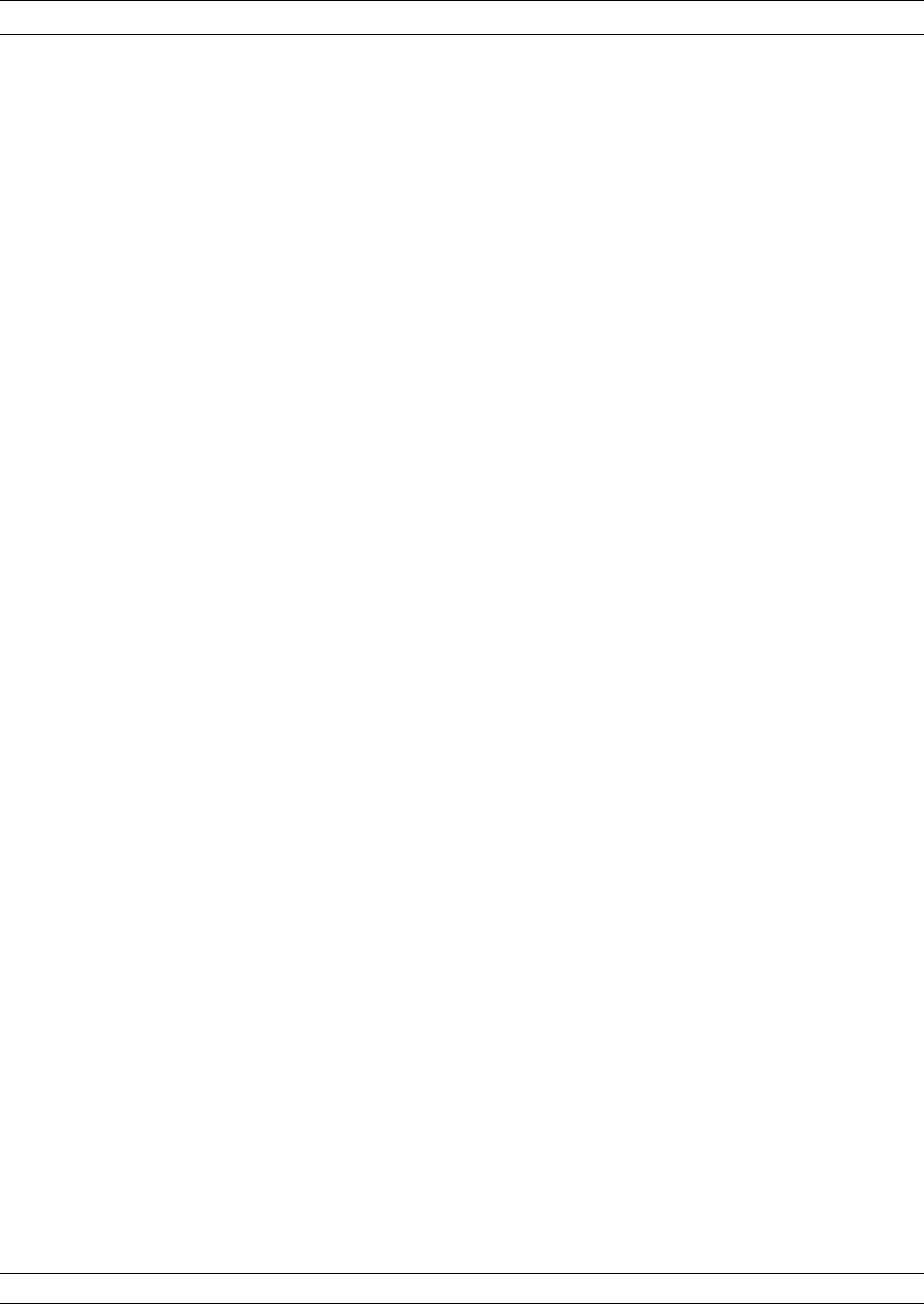
Step 11. Place one of the grey cable harnesses between the
Port 1 Module connector pad and the Transmis-
sion/Reflection Module. Connect the named connec-
tors on each end with their like-named counterparts
on the module and the test set.
Step 12. Place the other grey cable harness between the
Port 2 Module connector pad and the Transmission
Only Module. Connect the named connectors on each
end with their like-named counterparts on the mod-
ule and the test set.
Bench Top System
The following procedure describes how to arrange and interconnect the
system instruments in a benchtop configuration.
Step 13. Arrange the instruments in a stack as they are in
the console; that is, from top to bottom: VNA, test
set, source #1, source #2.
Step 14. Interconnect the instruments as described in Step 3
of the 3700C3 procedure.
Step 15. Interconnect the module(s) as described in Steps 9
through 11 of the 3700C3 procedure.
14-5 CONTROLS AND
CONNECTORS Figure 14-2 (following page) shows the front and rear panel connectors
and describes each one for the 3735B Test Set and 3740 and 3741
Modules.
37XXXC OM 14-11
MILLIMETER WAVE CONTROLS AND CONNECTORS

CONTROLS AND CONNECTORS MILLIMETER WAVE
14-12 37XXXC OM
Figure 14-2. 3735B Front and Rear Panel Connectors and Module Connectors
1. REF IF: Provides reference IF from DUT.
2. RF: Provides RF power to DUT.
3. Power: Provides input power connection.
4. LO: Provides local oscillator signal for DUT.
5. TEST IF. Provides test IF from DUT.
6. Test Port 1 or 2: Provide test port interface with DUT.
Module Connectors
1. b1: Provides an input test connection to the b1sampler.
2. a1: Provides an input test connection to the a1sampler
3. a2: Provides an input test connection to the a2sampler.
4. b2: Provides an input test connection to the b2sampler.
5. LO Input. Provides local oscillator input for source lock-
ing.
6. RF Input. Provides RF input connection for test set.
7. Port 2 Module Connector Pad: Connectors provide con-
nections for REF IF, RF, Power, LO, and TEST IF with exter-
nal test module.
8. Port 1 Module Connector Pad: Connectors provide con-
nections for REF IF, RF, Power, LO, and TEST IF with exter-
nal test module.
9. Power: Turns line power on and off .
10. 37100C Interface: Provides signals to and from 371XXC
VNA.
Test Set Connectors
Power
Port 1 Module Port 2 Module
RF Input LO Input
b1
RF RF
TEST
IF
TEST
IF
REF
IN
REF
IN
Power Power
LO LO
a2
a1b2
3735B Millimiter
Test Set
1
9
234
8 7 65
WARNING
NO OPERATOR SERVICE-
ABLE PARTS INSIDE
REFER SERVICING TO
QUALIFIED PERSONNEL
CAUTION
CAUTION
FOR CONTINUED FIRE
DO NOT OPERATE
WITH POWER CORD
UNGROUNDED
PROTECTION REPLACE
ONLY WITH SPECIFIED
TYPE AND RATED FUSE
MADE IN USA
SN 000001
37100C Interface
10
REF IF RF POWER LO TEST IF
125
4
36
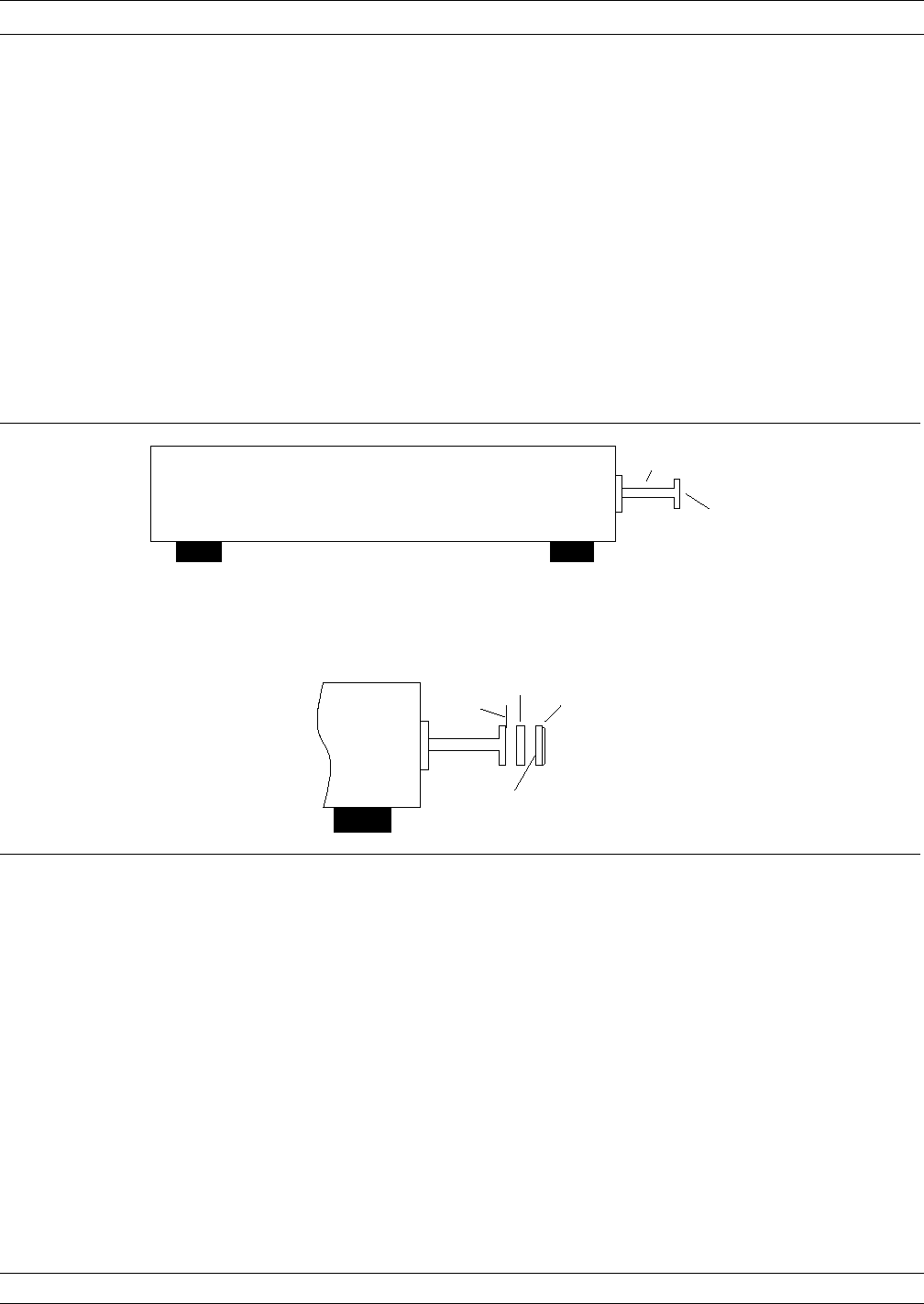
14-6 CALIBRATION Calibration for millimeter wave measurements is accomplished using
a waveguide offset-short method. Anritsu provides the Series 3655X,
3655X-1, 3755X, and 3755X-1 Calibration Kits, which contain all re-
quired precision calibration components. For optimum calibration and
measurement results, the following apply to modules that are not pro-
vided with precision waveguide extensions. (Refer to Figure 14-3, be-
low, for a supporting illustration.)
qUse the precision waveguide extension from the calibration kit to
connect to the waveguide module
qDuring calibration connect the highly polished (non-beveled) side
of the short toward the module
37XXXC OM 14-13
MILLIMETER WAVE CALIBRATION
Waveguide Extension
from Calibration Kit
New reference
plane
Beveled side
Highly Polished
Side
SHORT
OFFSET
Reference
Plane
MODULE
MODULE
Figure 14-3. Waveguide Connections for Optimum Measurement and Calibration Results
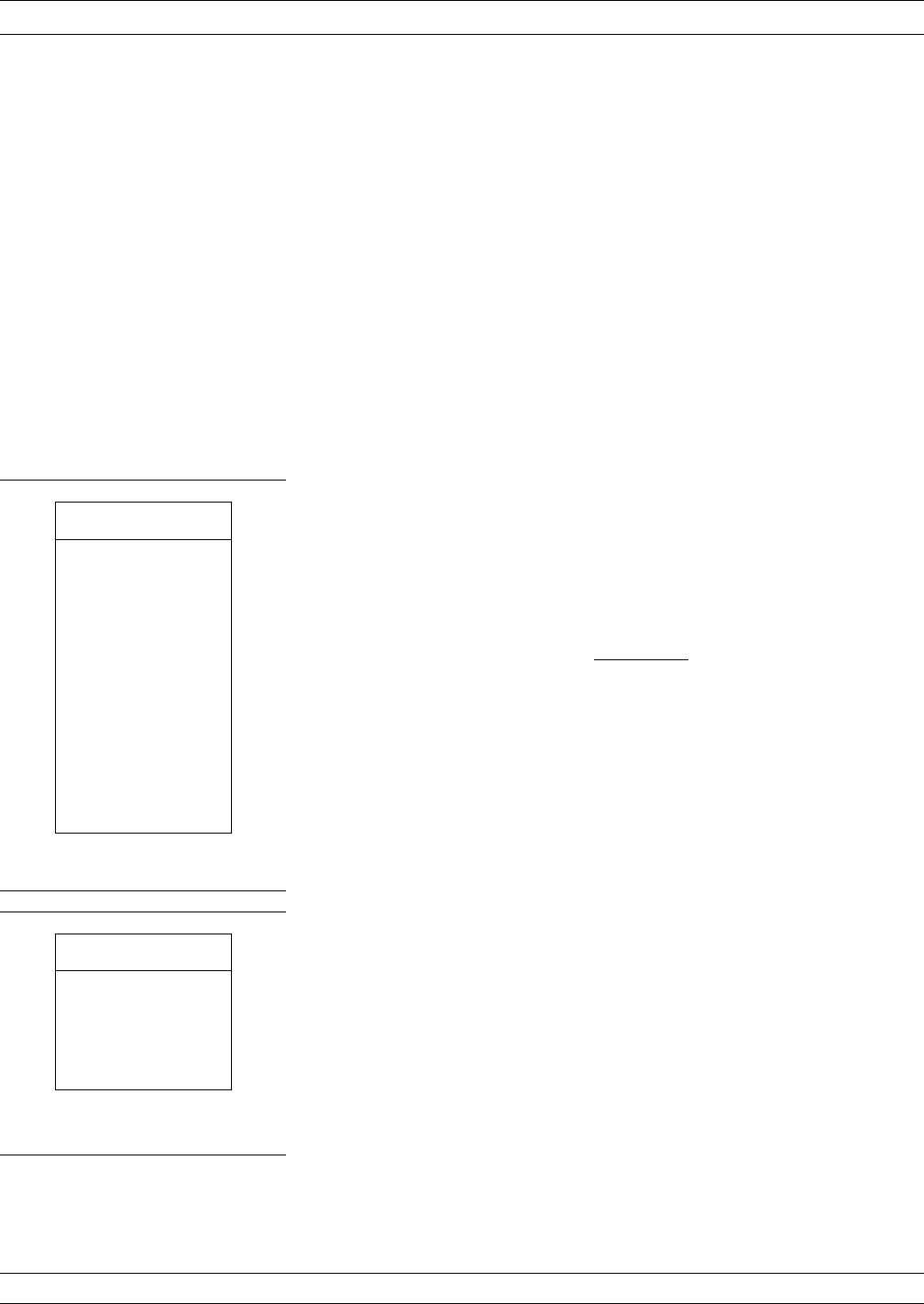
14-7 OPERATION The 371XXC Millimeter Wave System is menu driven and the millime-
ter wave operation is entered into via the Enhancement Key-Group’s
Options Menu key. Selecting Millimeter Wave BAND DEFINITION
in that menu provides for defining measurement parameters; selecting
TEST SET CONFIG provides for configuring the 3735B Test Set pa-
rameters (Figure 14-4, next page).
The menu options shown in Figure 14-4, Millimeter Wave System
Menu Flow, are described in Appendix A, along with all of the other
371XXC menus. Additional operating instructions are provided below.
Entering/ Leaving Millimeter
Wave Operation Before entering the Millimeter Wave mode, users should have com-
pleted all of the steps in the “Installation” section of this manual. The
system should be ready for operation, with all connections properly
made to the Millimeter Wave test set, modules, and frequency synthe-
sizers. The system should then be powered up, and the procedure be-
low followed.
NOTE
Until the Millimeter Wave configuration is activated, the
system will not operate and it will fail to lock.
CAUTION
The transition to or from Millimeter Wave operation is a
major setup change that does NOT preserve the previous
setup. All current set up and RF calibration information
will be lost on entering or leaving the Millimeter Wave
mode configuration. If the existing setup needs to be saved,
this should be done before the system is reconfigured for
Millimeter Wave mode operation.
When the millimeter wave band is selected, the system automatically
reconfigures itself to measure at that frequency range. The lower and
upper limits of the displayed sweep frequencies will change to the
band selected. The frequency resolution changes to account for multi-
plier factors. However, users will (1) have access to the multiple source
control definitions and (2) be able to change the sweep frequencies as
desired.
Procedure
The first step is to press the Options button on the front panel. This
brings up the Menu OPTNS (top left). Select TEST SET CONFIG. This
causes the Menu OTS1 (bottom left) to appear.
OPERATION MILLIMETER WAVE
14-14 37XXXC OM
MENU OPTNS
OPTIONS
TRIGGERS
REAR PANEL
OUTPUT
Millimeter Wave
BAND DEFINITION
RECEIVER MODE
SOURCE CONFIG
TEST SET CONFIG
MENU OTS1
TEST SET
CONFIGURATION
INTERNAL
MILLIMETER WAVE
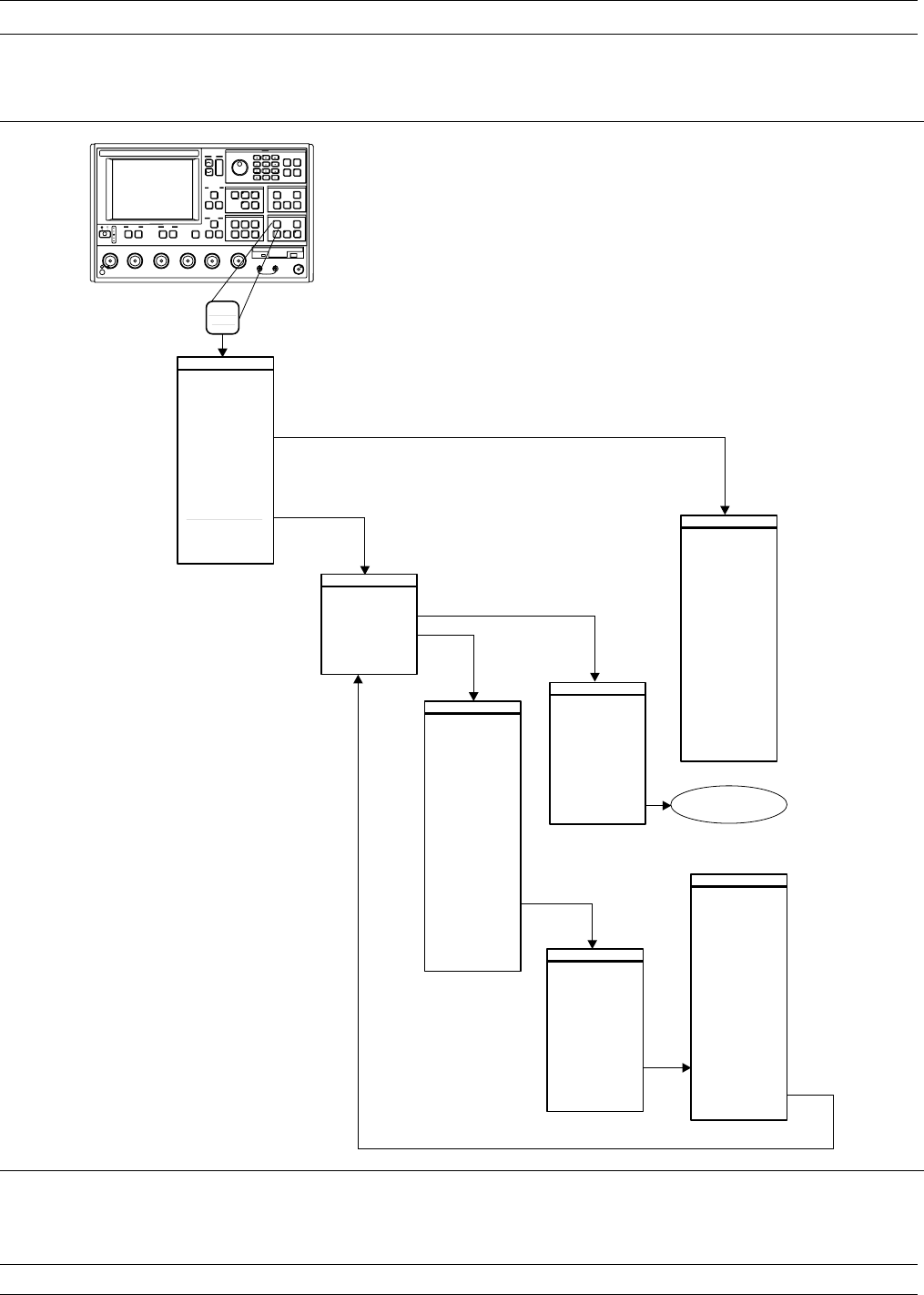
37XXXC OM 14-15
MILLIMETER WAVE OPERATION
Option
Menu
MENU OPTNS
REAR PANEL
OUTPUT
DIAGNOSTICS
MILLIMETER WAVE
BAND DEFINITION
PLOT OPTIONS
OPTIONS
RECEIVER MODE
TO SELECT
PRESS <ENTER>
SOURCE CONFIG
TEST SET CONFIG MENU MMW4
BAND START FREQ
XX.XXXXXX
Mm WAVE BAND
RECEIVER
SOURCE 2
SOURCE 1
C.W. ON/OFF
MULTIPLIER
XXX
DIVISOR
XXX
OFFSET FREQ
XXXXXXXX
DEFAULT EQUATIONS
ACCEPT EQUATIONS
EQUATION TO EDIT
EQUATION SUMMARY
XX.XXXXXX
BAND STOP FREQ
MENU MMW1
MENU MMW2
MILLIMETER WAVE
TEST SET BAND
MILLIMETER WAVE
TEST SET MODULES
WR-22
(33 - 50 GHz)
PORT 1 MODULE
3740/3741/NONE
PORT 1 MODULE
3740/3741/NONE
WR-15
(50 - 75 GHz)
PORT 2 MODULE
3740/3741/NONE
PORT 2 MODULE
3740/3741/NONE
ACCEPT CONFIG
WR-12
(60 - 90 GHz)
WR-10
(75 - 110 GHz)
(56 - 94 GHz)
WR-12 EXTENDED
(65 - 110 GHz)
WR-10 EXTENDED
90- 140 GHz)
WR-8
MENU OTS1
INTERNAL
MILLIMETER WAVE
TEST SET
CONFIGURATION
PRESS <ENTER>
TO SELECT
MENU OTS2
MENU MMW3
WARNING
CONTINUING
WILL INVALIDATE
CURRENT
SETUP AND
CALIBRATION
WARNING
CONTINUING
WILL INVALIDATE
CURRENT
SETUP AND
CALIBRATION
TEST SET
CONFIGURATION
TEST SET
CONFIGURATION
mm WAVE BAND:
XXXXXXXXXX
TO SELECT
TO SELECT
PRESS <ENTER>
PRESS <ENTER>
PRESS <ENTER>
TO SELECT
PRESS <ENTER>
TO SELECT
PRESS <CLEAR>
TO ABORT
PRESS <CLEAR>
TO ABORT
TO MENU SU1/SU2
Figure 14-4. Millimeter Wave System Menu Flow
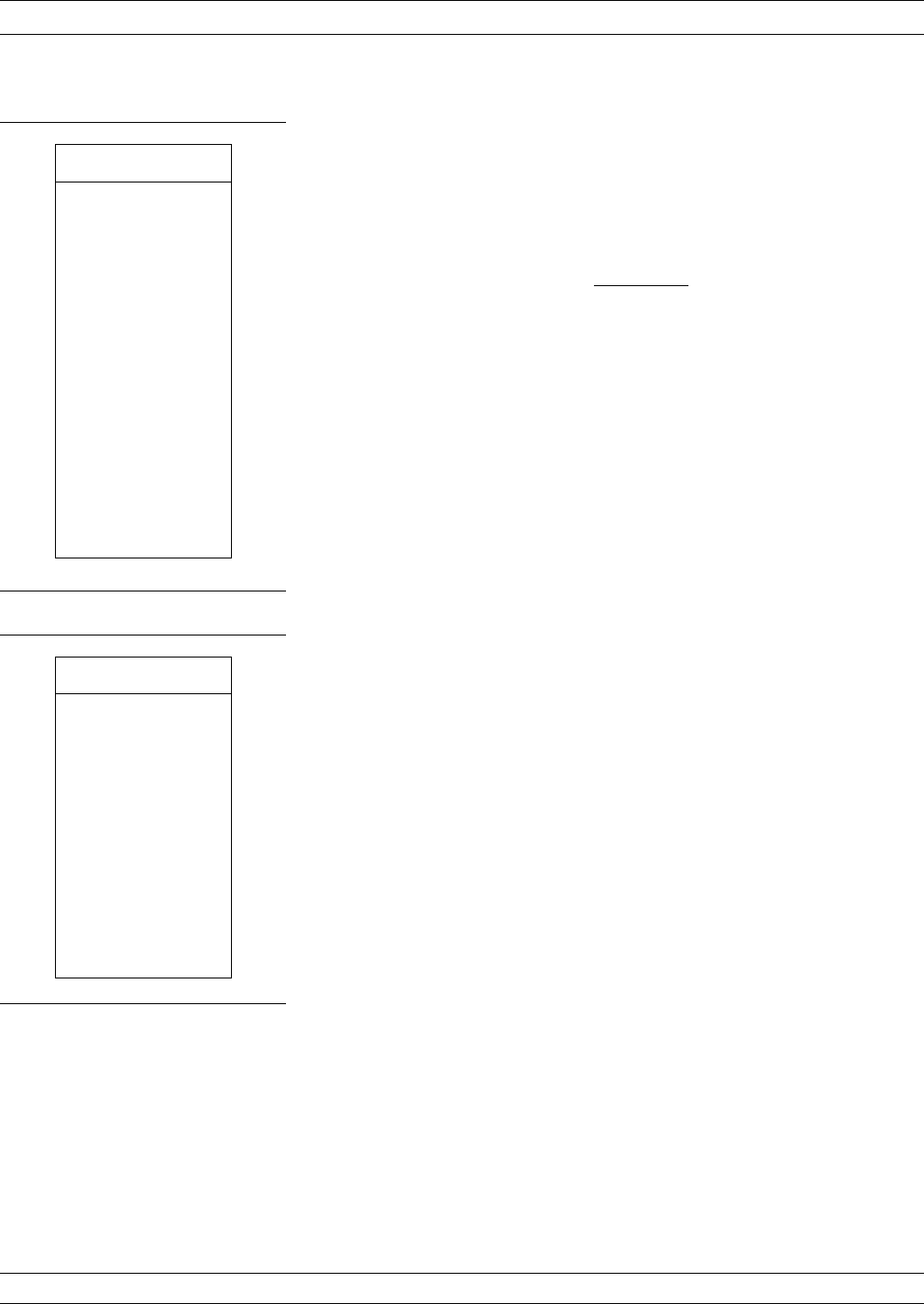
If the system is not already configured for Millimeter Wave operation,
select Millimeter Wave to call the MMW1 (top left).
In menu MMW1, select the millimeter wave band for which modules
have been installed.
CAUTION
A band other than the one for which hardware is installed
can be selected. In this case, the system may appear to op-
erate normally, but it will not make accurate measure-
ments.
Upon completing the selection in the Menu MMW1, Menu MMW2
(bottom left), appears.
OPERATION MILLIMETER WAVE
14-16 37XXXC OM
MENU MMW2
MILLIMETER WAVE
TEST SET MODULES
PORT 1 MODULE
3740/41/42/NONE
PORT 2 MODULE
3740/41/42/NONE
ACCEPT CONFIG
PRESS <ENTER>
TO SELECT
PRESS <CLEAR>
TO ABORT
MENU MMW1
MILLIMETER WAVE
TEST SET BAND
WR-22
(33 - 50 GHz)
WR-15
(50 - 75 GHz)
WR-12
(60 - 90 GHz)
WR-12 EXTENDED
(56 - 94 GHz)
WR-10
(75 - 110 GHz)
WR-10 EXTENDED
(65 - 110 GHz)
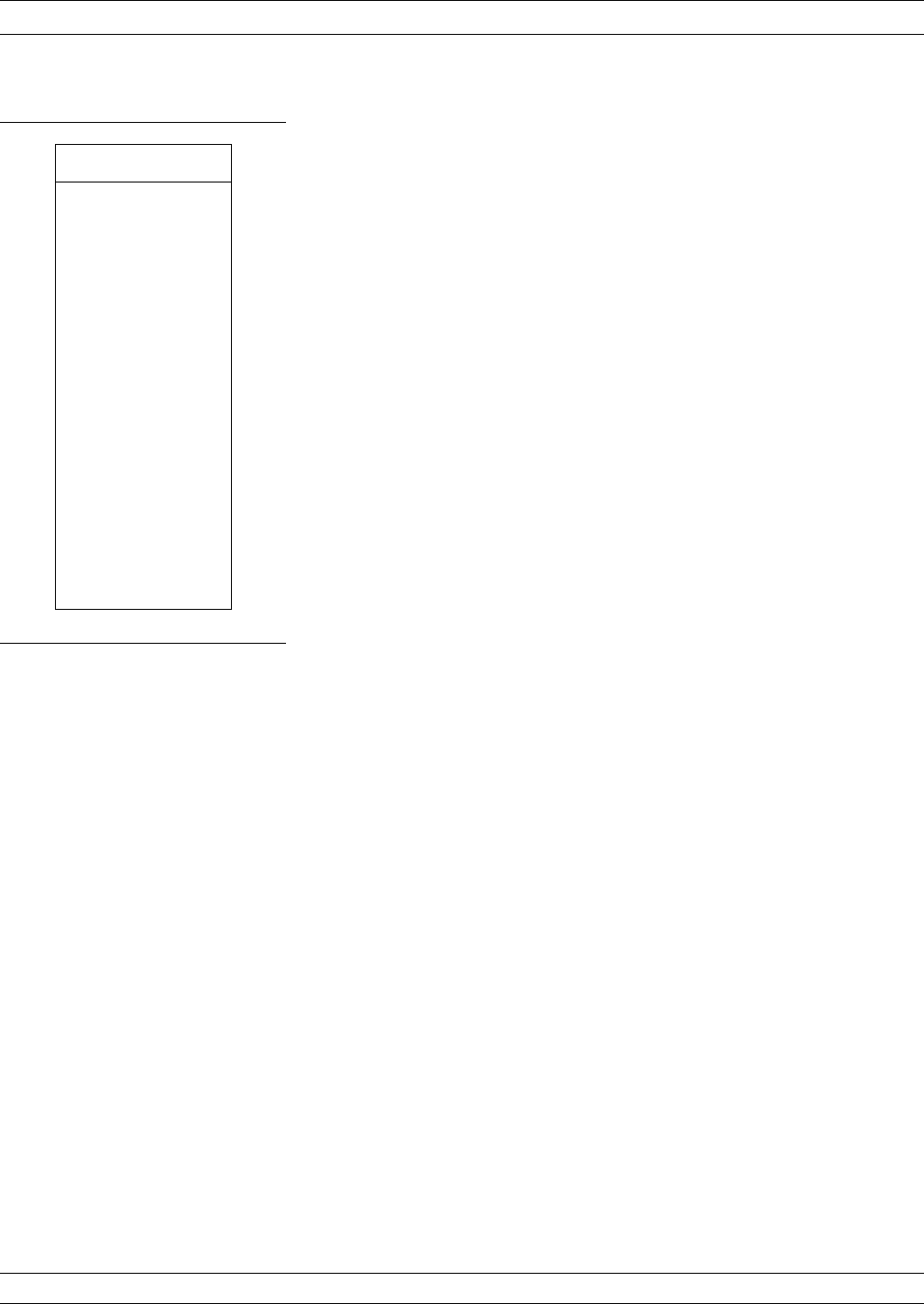
In this menu, select which module is Transmission-Reflection and
which is Transmission Only. Do this carefully, as an incorrect selection
causes the wrong S-parameters to be displayed. Once the selection is
made in this menu, MMW3 (left) appears.
At this point, users have one last opportunity to abort the change in
configuration, by pressing the Clear key. If the Enter key is pressed, the
old configuration is lost. The system is reconfigured for millimeter
wave operation.
37XXXC OM 14-17
MILLIMETER WAVE OPERATION
MENU MMW3
TEST SET
CONFIGURATION
mmWAVE BAND
XXXXXXXX
PORT 1 MODULE
3740
PORT 2 MODULE
3740
WARNING
CONTINIUING
MAY INVALIDATE
CURRENT
SETUP AND
CALIBRATION
PRESS <ENTER>
TO SELECT
PRESS <CLEAR>
TO ABORT
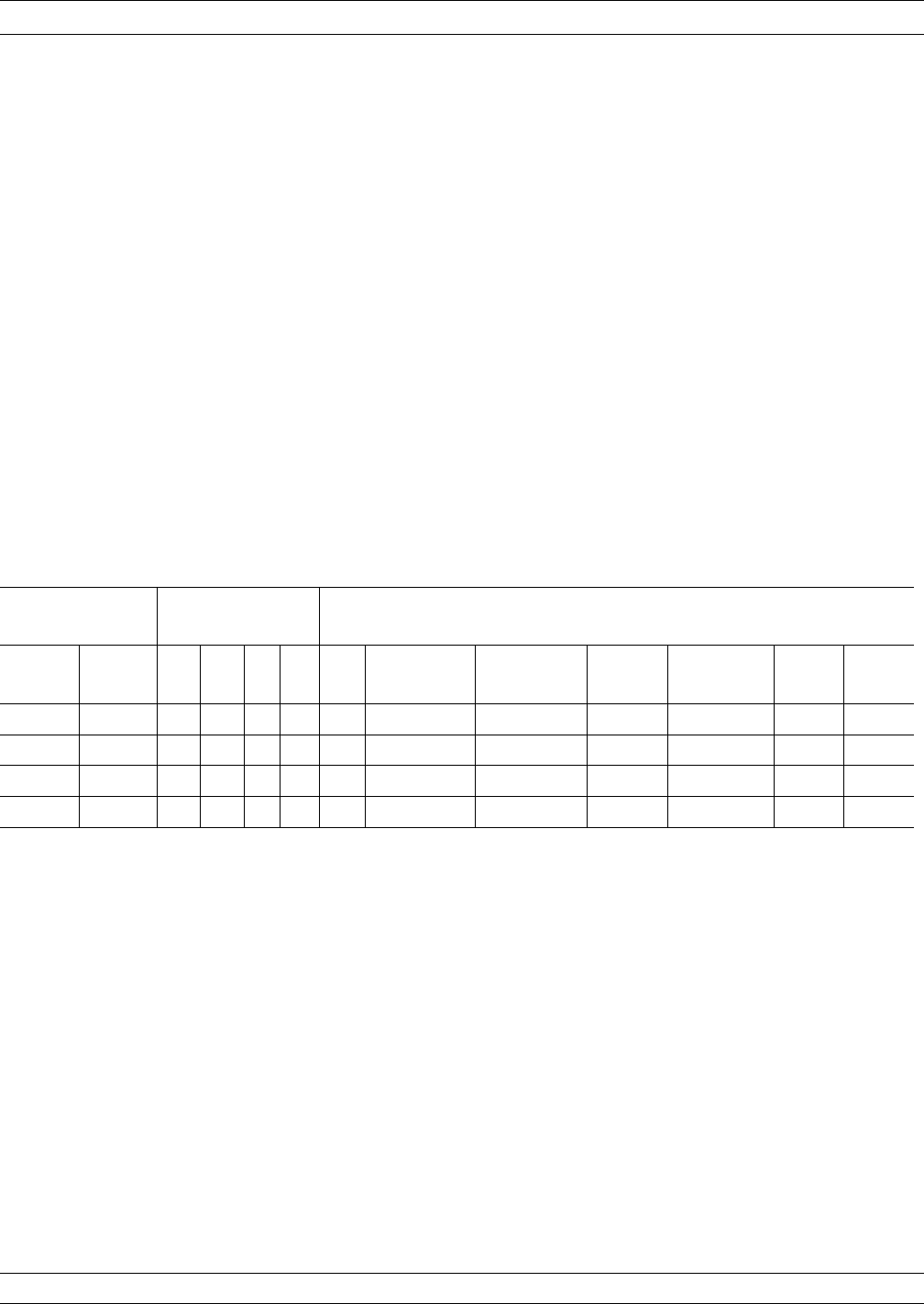
Changing Bands/Modules
While in Millimeter Wave The effect of changing millimeter wave bands while in Millimeter
Wave mode operation will be to (1) change the sweep frequency range
to the default range for the new band and (2) delete any current RF
calibrations. Therefore, the Caution on page 14-15 applies. Actually, it
is unlikely that any calibration would be valid if the modules are
changed. (This is because of manufacturing variations from module to
module.)
To configure the system for a different band or for one or more differ-
ent modules, follow the exact same steps as described on pages 14-13
through 14-16, except that only the new band or module types are
changed.
Allowable Millimeter Wave
Module Configurations,
Measurements and
Calibrations
The S-parameter measurements and RF calibrations allowed are a
function of the type of millimeter wave module users have selected in
Menu MMW2. Note that one could actually have only one module and
still make reflection-only measurements. The criteria in Table 14-4 ap-
plies.
OPERATION MILLIMETER WAVE
14-18 37XXXC OM
MMW
Modules Allowed
S-parameters Allowed RF Calibrations
Port 1 Port 2 S11 S12 S21 S22 12
Term Forward
1 Path 2 Port Reverse
1 Path 2 Port Reflection
P1 Reflection
P2 Forward
Trans Reverse
Trans
3740 3740 X X X X X X X X X X X
3740 3741 X X X X X
3741 3740 X X X X X
3741 3740 b1/1 b2/1 b2/1 b1/1 X X X
Table 14-4. Calibration Criteria
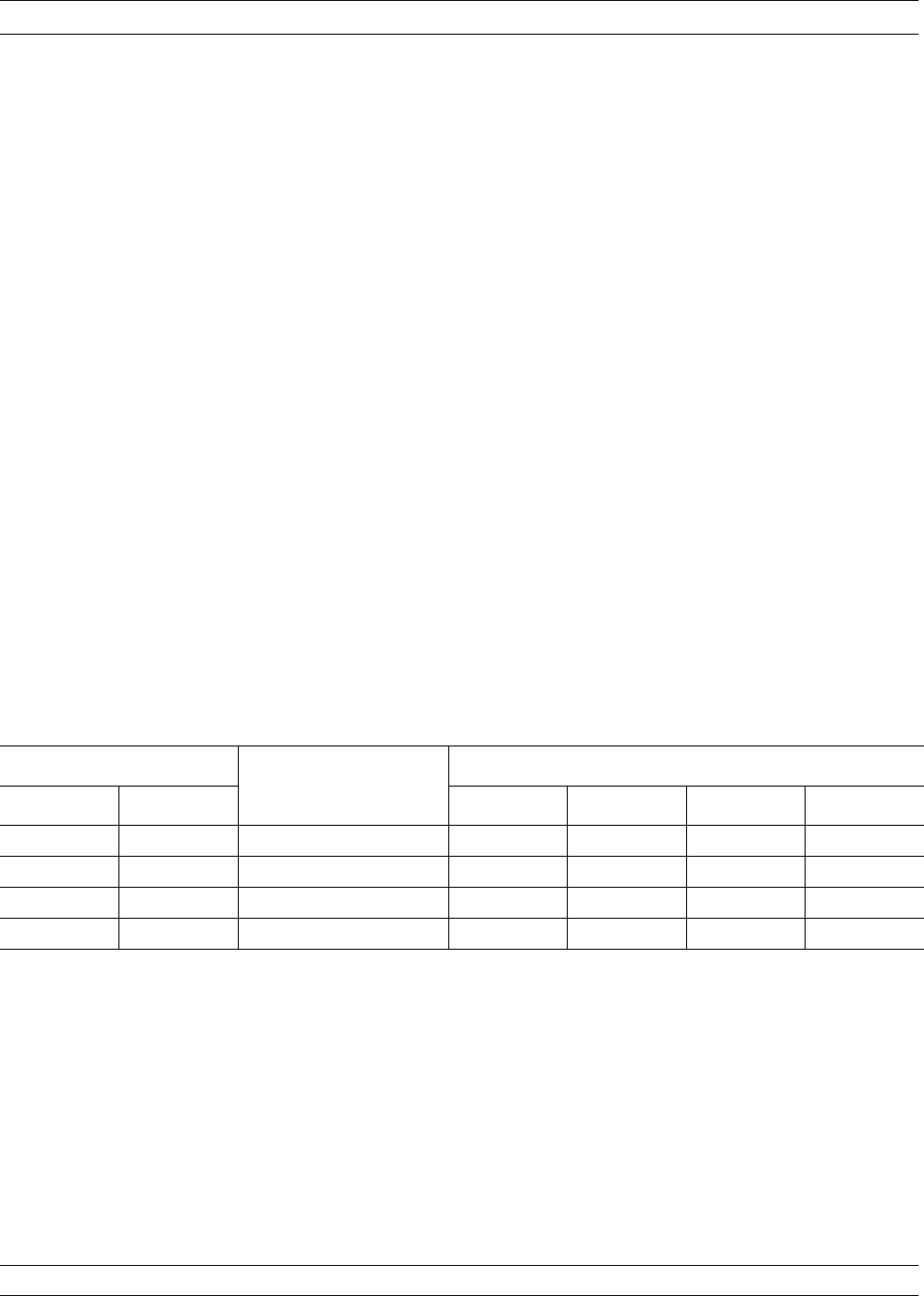
Effect of Default Program Because the system is reconfigured for Millimeter Wave mode opera-
tion, the effects of performing a “Default Program” are somewhat dif-
ferent. Performing a default program operation, either from the front
panel or via the GPIB will have the following results:
qPressing the Default Program key twice:
The Millimeter Wave operating band, its associated frequency
range, multipliers, and millimeter wave module types will re-
main unchanged. If the frequency range has been modified from
the default values for the band, the modified values will remain
in force. The current sweep range will be set to the band fre-
quency range. This is consistent with other similar setup param-
eters, such as GPIB addresses
qPressing the Default Program key, then the 1data entry key:
Except for clearing the internal setup memories, the effect will be
the same as for pressing the Default Program key twice
qPressing the Default Program key, then the 0data entry key:
The system resets to its default, non-millimeter wave configura-
tion; that is, internal source active, no multiple source equations,
normal default system frequency range, and internal test set con-
figuration. If the “delete source” option is active, the system will
attempt to use an external source for source 1
The restrictions stated in the above “Allowable Microwave Modules
Configurations, Measurements, and Calibrations” paragraph (previous
page) will impact the display resulting from a “Default - Default” ac-
tion. S-parameters displayed will be as indicated above, while the
channel configuration will be as shown in Table 14-5.
37XXXC OM 14-19
MILLIMETER WAVE OPERATION
MMW Modules Default Channel
Configuration S-parameters Assigned
Port 1 Port 2 Ch 1 Ch 2 Ch 3 Ch 4
3740 3740 All Four Channels S11 S12 S21 S22
3740 3741 Dual, Channels 1 and 3 S11 S21 S21 S11
3741 3740 Dual, Channels 2 and 4 S22 S12 S12 S22
3741 3741 All Four Channels b1/1 b2/1 b2/1 b1/1
Note: In the case of two 3741’s, the system will be put into SET ON mode. If users provide a phase-lock signal, they may set the
“user-defined”receiver mode to TRACKING.
Table 14-5. Channel Configuration
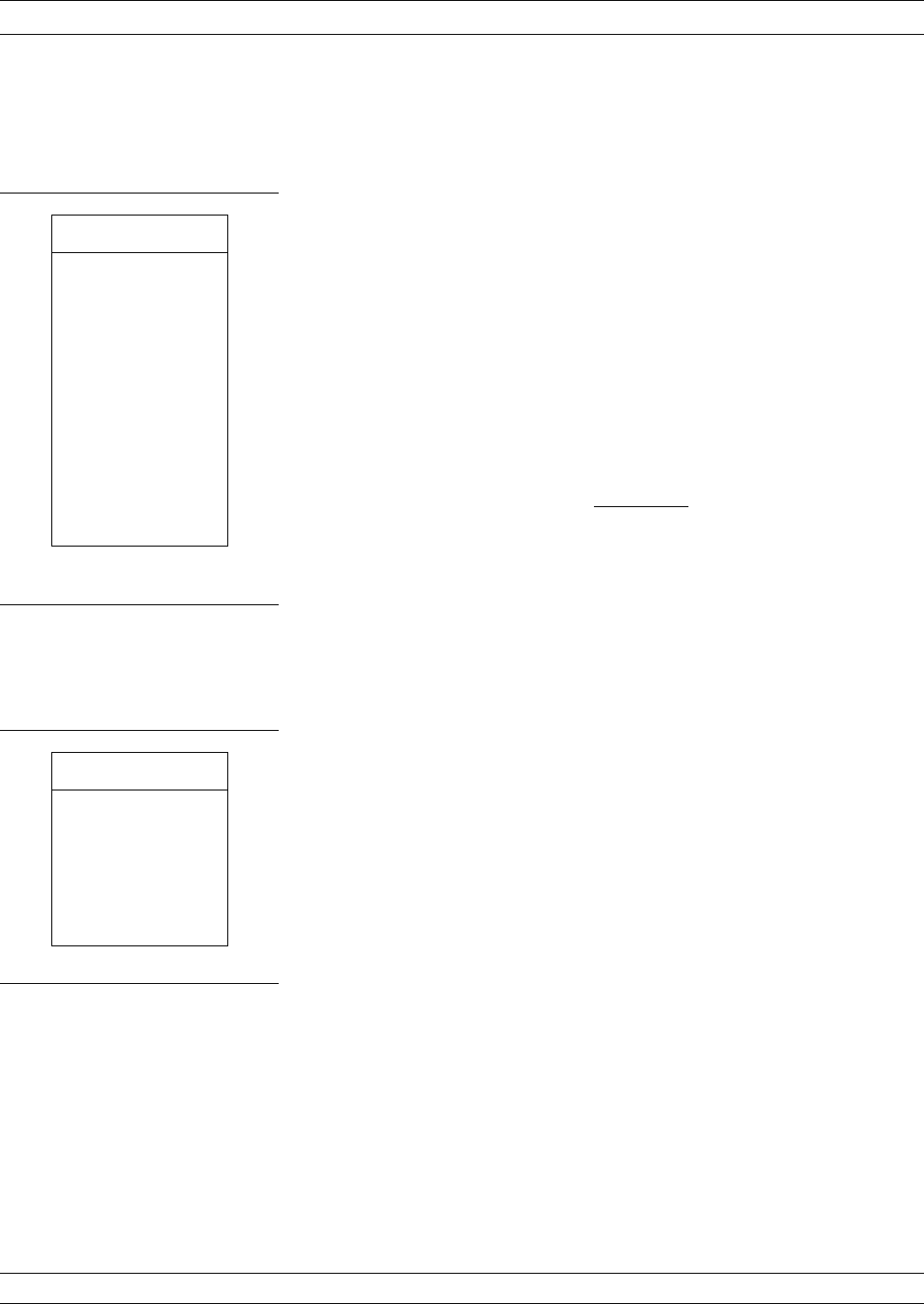
Redefinition of Band
Frequency Ranges It is possible to modify the Millimeter Wave band equations to a range
different than the default range for the band currently installed. This
is done by pressing the Options key to display Menu OPTNS (top left).
In this menu, select Millimeter Wave BAND DEFINITION and
cause Menu MMW4 (bottom left) to appear.
The receiver equation or either of the sources may be edited. New val-
ues for the multiplier, the divisor, or the offset may be entered. To ap-
ply the selections, select ACCEPT EQUATIONS. Or select DE-
FAULT EQUATIONS to return selections or edits to the standard
default values.
The EXT_MILLIMETER WAVE 4 menu (Figure 14-5) appears next to
Menu Millimeter Wave 4 to provide the current or proposed band in-
formation.
CAUTION
It is possible for the equations to be set to values that may
prevent normal operation of the system, due to excessive
frequency range beyond the capabilities of the system
hardware. The only way of restoring the system to its
known default settings is by selecting DEFAULT EQUA-
TIONS then ACCEPT EQUATIONS in Menu MMW 4.
Using the DEFAULT-DEFAULT method will not reset
the equations.
If the frequency range of a millimeter wave band is changed to a range
where some or all of the frequencies are outside of the default range
for that band, or if the frequency multipliers are altered, the change
will be allowed, but upon selecting ACCEPT EQUATIONS in Menu
MMW4, a warning message will be issued in the data area: “CAU-
TION: NON-STD BAND DEFINITION.” If the frequency range of a
Millimeter Wave band is changed to a range that is a subset of the de-
fault range for that band, no warning message will be issued.
OPERATION MILLIMETER WAVE
14-20 37XXXC OM
MENU MMW4
mmWAVE BAND
BAND START FREQ
65.000000
BAND STOP FREQ
110.000000
MENU OPTNS
OPTIONS
TRIGGERS
REAR PANEL
OUTPUT
Millimeter Wave
BAND DEFINITION
RECEIVER MODE
SOURCE CONFIG
TEST SET CONFIG
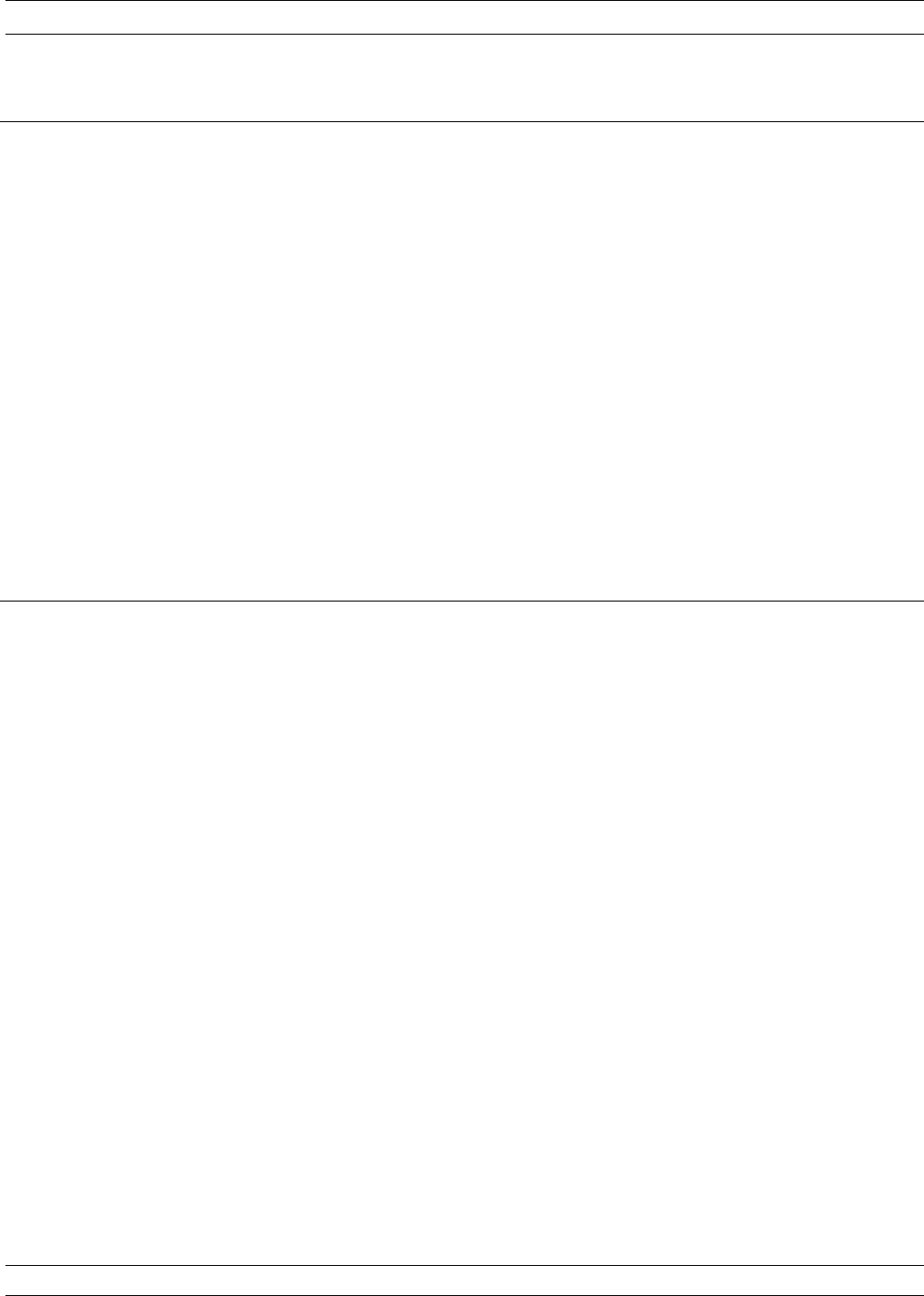
Use of Normal Multiple
Source Mode While the millimeter wave feature is active, the normal multiple
source mode will not be available. Access to the Menus OM0 through
OM2 will not be allowed. If the system is in multiple source mode
when switched to millimeter wave, all multiple source information will
be lost, and the unit will return to normal (single source) operation
when millimeter wave operation is ended. In Millimeter Wave mode,
users may change the default values of the current waveguide band
frequency range, multipliers, and offset (CW-IF) frequency, by using
Menu MMW4.
Stored Setups and
Calibrations The Millimeter Wave band definition and module information is stored
with a stored setup in internal memory, and with the setup and RF
CAL on disk. When a setup is recalled, first the band and module
types will be compared with the current settings. If different, the setup
will be rejected, and a message “ABORTED: HARDWARE DIFFER-
ENT” will be posted. If the hardware settings are compatible, the fre-
quency range of the stored setup will be compared with the current
system low and high frequency limits, in case the user has employed a
customized-band definition. If the recalled setup is within the current
frequency range of the system, it will be recalled with no warn-
ing—even if the current range is customized. If the recalled setup is
outside the normal frequency range, or if it has changed equations
(been customized) it will be recalled. However, a time-out warning
message will be issued in the data area: “CAUTION: NON-STD BAND
DEFINITION.”
37XXXC OM 14-21
MILLIMETER WAVE OPERATION
- MILLIMETER WAVE BAND DEFINITION SUMMARY -
BAND FREQUENCY RANGE
BAND START F
BAND STOP F
XXX,XXXXXX XXX
XXX.XXXXXX XXX
FREQUENCY = (MULTIPLIER/DIVISOR)*F+OFFSET FREQ)
SOURCE1=(1/8)*(F–0.270000 GHz)
SOURCE 2 = (1/ 6) * (F + 0.000000 GHz)
RECEIVER = (1/ 1) * (0.270000 GHz C.W.)
- NOTES -
1. SELECT <DEFAULT EQUATIONS> TO OVERWRITE DEFINITION
WITH VALUES SUITABLE FOR THE MILLIMETER WAVE BAND.
2. SELECT <ACCEPT EQUATIONS> TO CONFIRM ANY CHANGES.
3. PERFORMANCE SPECIFICATIONS ARE VALID ONLY WHILE
USING THE DEFAULT EQUATIONS OVER THE DEFAULT BAND
FREQUENCY RANGE.
4. DEVIATING FROM THE DEFAULT MAY CAUSE LOCK FAILURES.
Figure 14-5. Menu EXT_MMW4
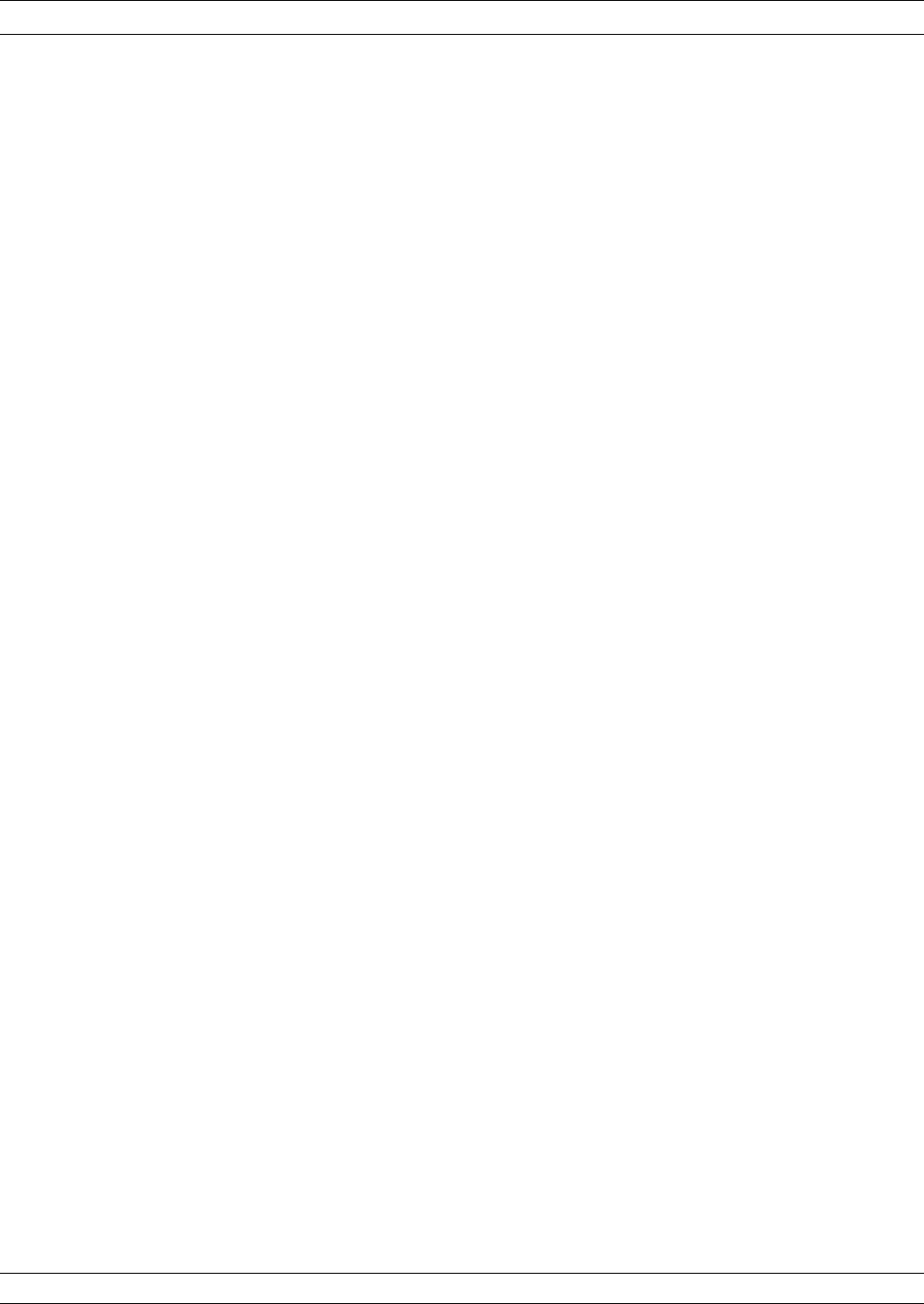
External Source and Power
Levels When MILLIMETER WAVE has been selected in Menu OTS1, the
system checks for the existence of two external sources. If either
source is not connected and operating, a warning message is posted to
the screen. On entering Millimeter Wave mode operation, the system
will automatically be configured to use the two external sources. The
Millimeter Wave mode will not function properly with low
source-power levels. Therefore, on entering this mode the source-power
levels will be adjusted to a predefined level. However the Source
Config and Test Signals menus will still be available to users, to
change power settings and source configuration if so desired.
OPERATION MILLIMETER WAVE
14-22 37XXXC OM
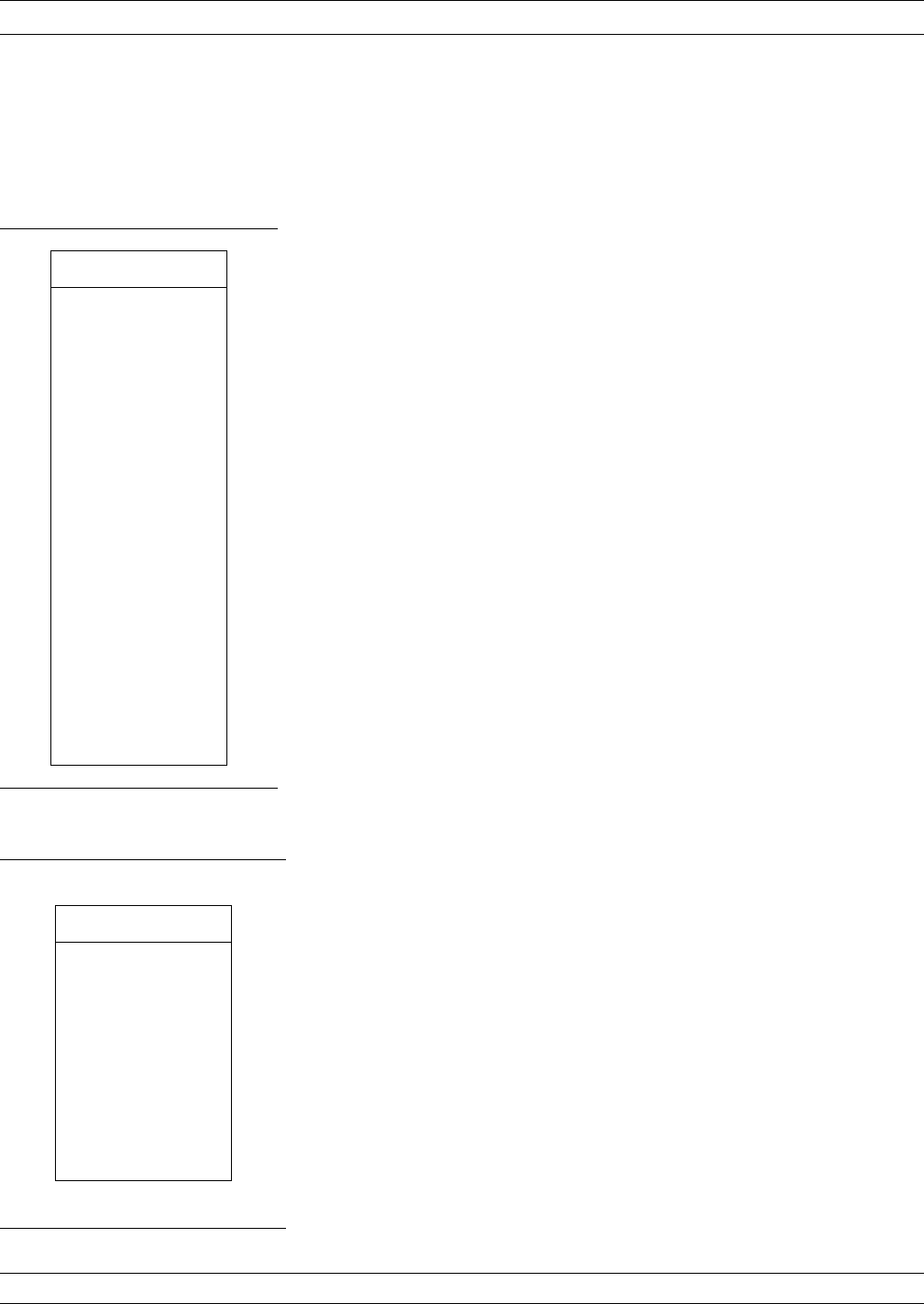
14-8 MEASUREMENT
PROCEDURE The measurement of a Device Under Test (DUT) using the Millimeter
Wave mode is quite similar to one using a coaxial measurement tech-
nique. However, due to the more complex nature of the Millimeter
Wave System equipment, additional care must be taken to ensure that
everything is set up properly. Depending upon the type of measure-
ment being performed, the setup may vary. The following is a descrip-
tion of a typical measurement procedure for a passive two-port DUT.
Step 1. Verify Correct Band Definition
Use Menu MMW1 (top left) to examine the current
millimeter wave band selection, and Menu MMW2
(bottom left) to examine the current module selec-
tions to be sure that they match the installed hard-
ware. Examine MenuMMW4 (next page) to verify
that the band equations are set correctly. If there is
any doubt whether the setting are correct, use the
DEFAULT EQUATIONS selection to reset them.
Step 2. Verify Correct Setup for the System
The safest way to do this is to press the Default key
twice. This returns the system to the proper fre-
quency range and power settings for the current mil-
limeter wave hardware configuration. It is very im-
portant that the RF sources be set to the correct
power levels. Set Source 1 (LO) to +17 dBm and
Source 2 (RF) to +13 dBm.
Step 3. Perform and Verify an RF Calibration
The system may now be calibrated using an appro-
priate Anritsu Calibration Kit. Be sure to load the
calibration kit information from the provided floppy
disk into the instrument first. The default calibra-
tion type is Offset-Short, but an LRL/LRM calibra-
tion may also be used. See Chapters 4 and 7 for help
with RF Calibration details. Consult Table 14-4 for
limitations on which calibrations may be performed
as a function of the module types installed.
Step 4. Attach the DUT
Use the calibrated torque wrench provided with the
Calibration Kit to tighten the waveguide flange re-
taining screws on the DUT. This results in more re-
producible measurements.
Step 5. Select the S-parameter(s) and Graph Type(s) to Be
Used for the Measurement
The selection may be limited due to the types of mil-
limeter wave modules installed. Consult Table 14-4
on page 14-18 for further information.
37XXXC OM 14-23
MILLIMETER WAVE MEASUREMENT PROCEDURE
MENU MMW1
MILLIMETER WAVE
TEST SET BAND
WR-22
(33 - 50 GHz)
WR-15
(50 - 75 GHz)
WR-12
(60 - 90 GHz)
WR-12 EXTENDED
(56 - 94 GHz)
WR-10
(75 - 110 GHz)
WR-10 EXTENDED
(65 - 110 GHz)
WR-8
(90 - 140 GHz)
PRESS <ENTER>
TO SELECT
MENU MMW2
MILLIMETER WAVE
TEST SET MODULES
PORT 1 MODULE
3740/3741/NONE
PORT 2 MODULE
3740/3741/NONE
ACCEPT CONFIG
PRESS <ENTER>
TO SELECT
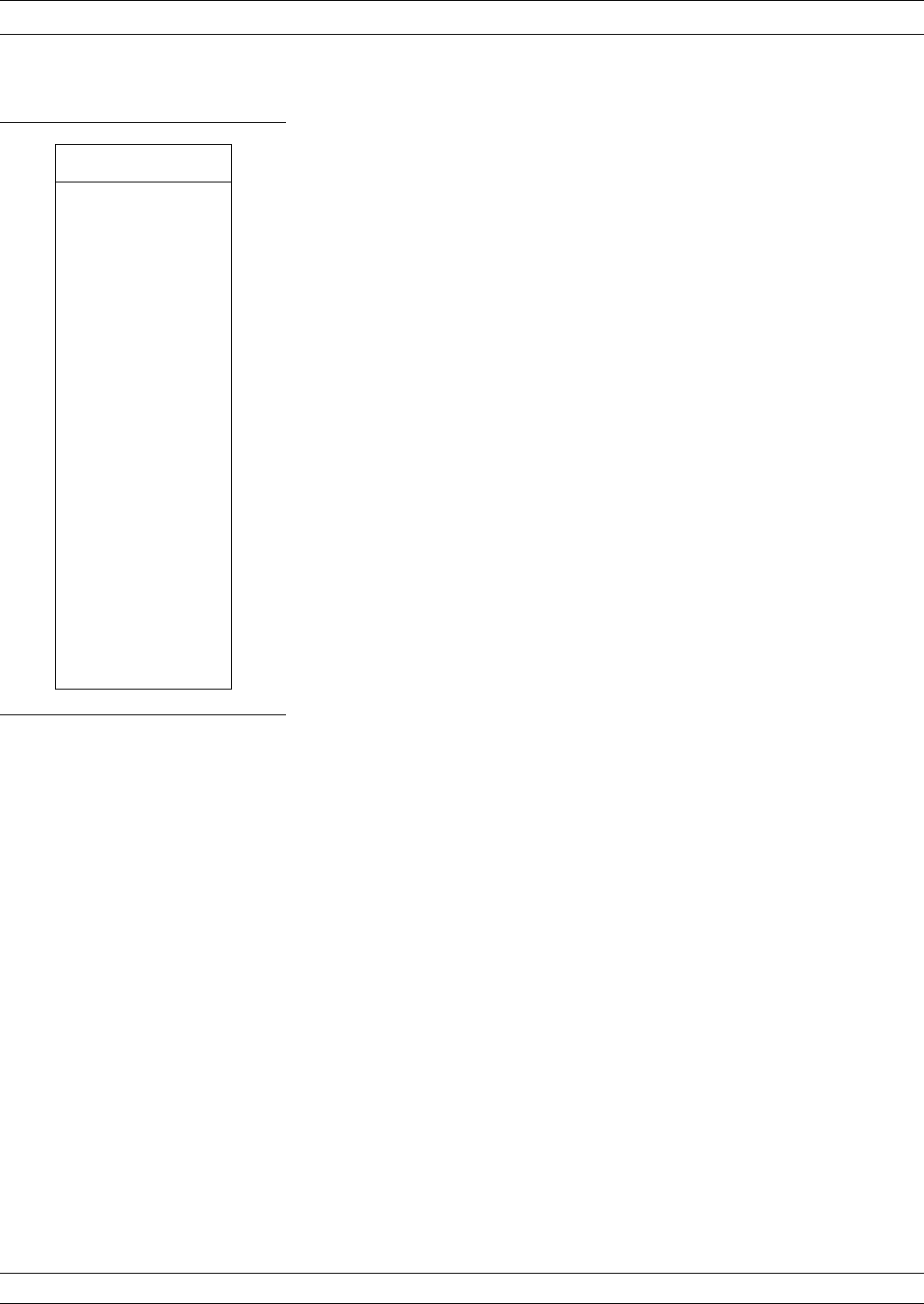
Step 6. Set the Display Scale
This may be done most quickly by selecting each ac-
tive channel, and pressing the Autoscale key. The
scale and reference values may then be set to a de-
sired value using the appropriate SET SCALE menu
for the graph type selected.
Step 7. Observe the Measured Data
It should not vary from sweep to sweep, and should
be within the range expected for the type of mea-
surement. Re-check tightness of the flange retaining
screws if data appears abnormal.
Step 8. Save the Calibration and Setup On the Hard Disk
Press the Save/Recall key to initiate the saving of
the current setup. An instrument setup in the milli-
meter wave configuration may be saved exactly like
any other VNA setup and RF calibration.
NOTE
Anritsu strongly recommends that any setup and calibra-
tion used for measurement be saved.
14-9 REMOTE OPERATION All functions of the 371XXCmm can be controlled remotely, via the
IEEE 488 Bus (GPIB). The remote operation and controlling com-
mands are provided in the 37XXX Programming Manual
(PN: 10410-00200).
OPERATIONAL CHECKOUT MILLIMETER WAVE
14-24 37XXXC OM
MENU MMW4
mmWAVE BAND
BAND START FREQ
65.000000
BAND STOP FREQ
110.000000
EQUATION TO EDIT
SOURCE 1
SOURCE 2
RECEIVER
EQUATION SUMMARY
CW OFF
MULTIPLIER
1
DIVISOR
8
DEFAULT EQUATIONS
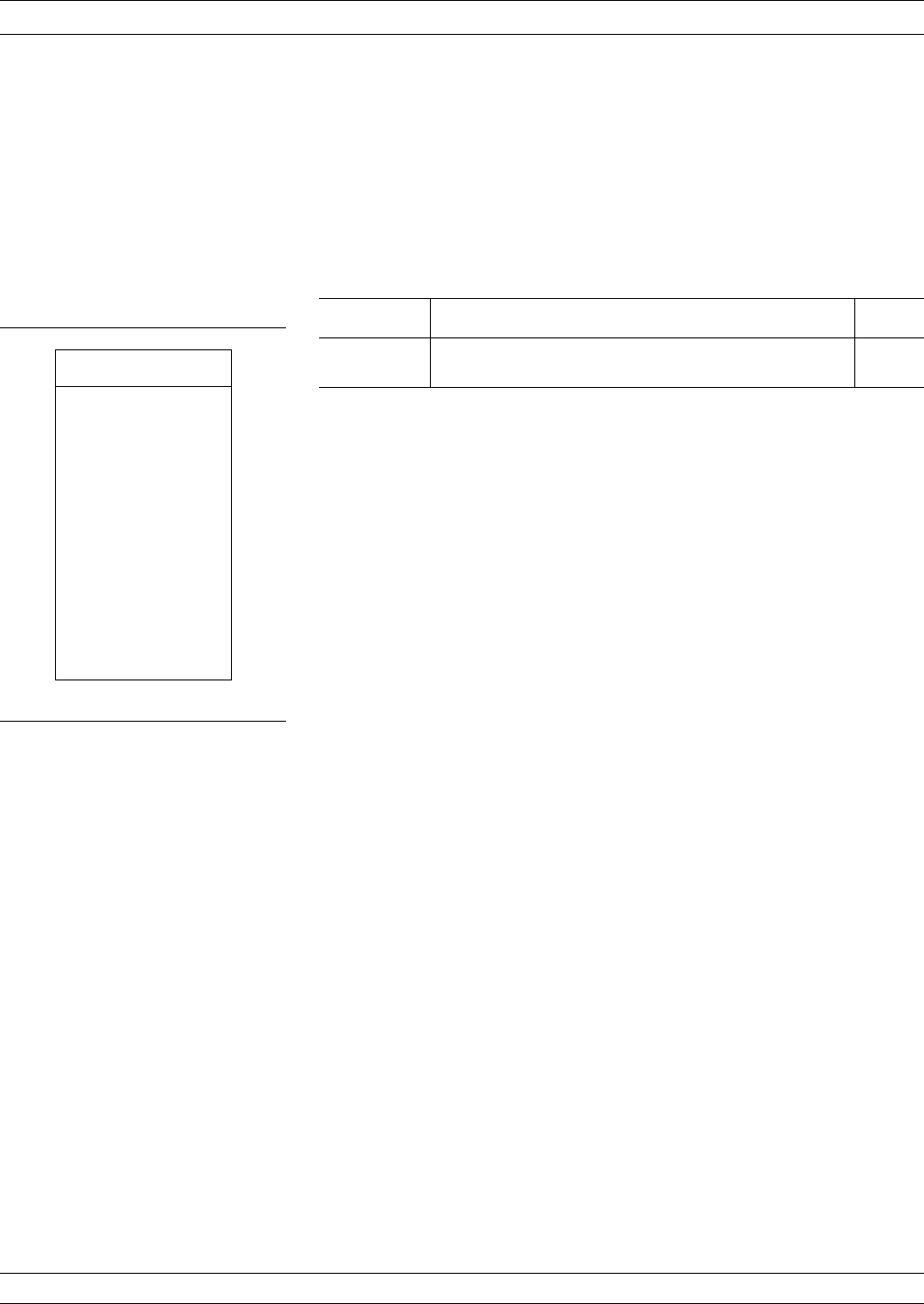
14-10 OPERATIONAL
CHECKOUT—
GENERAL
The Operational Checkout subsection provides for checking that the
371XXC Millimeter Wave System is functioning properly.
Required Equipment
The following equipment is required to perform the verification tests.
Model Description Quantity
Anritsu
3655 Series
Waveguide Calibration Kit, with Option 1: Sliding Termination 1
Step 1. Remove the silver straight waveguide sections from
the modules, if installed.
Step 2. Install the precision-straight waveguide sections
that are contained in the calibration kit on the wave-
guide output connector of each millimeter module.
NOTE
These waveguide sections (test port adapters) use high
precision flanges to improve connection repeatability and
calibration quality. They must be used to ensure specified
system performance.
Step 3. Apply power to both system Sources and allow them
to complete self test.
Step 4. Apply power to the network analyzer.
Step 5. Press the Option Menu key, select TEST SET
CONFIG to configure the system for the types of
millimeter modules used.
Step 6. Allow the system to warm up for at least 60 minutes
to ensure operation to performance specifications.
37XXXC OM 14-25
MILLIMETER WAVE OPERATIONAL CHECKOUT
MENU OPTNS
OPTIONS
TRIGGERS
REAR PANEL
OUTPUT
Millimeter Wave
BAND DEFINITION
RECEIVER MODE
SOURCE CONFIG
TEST SET CONFIG
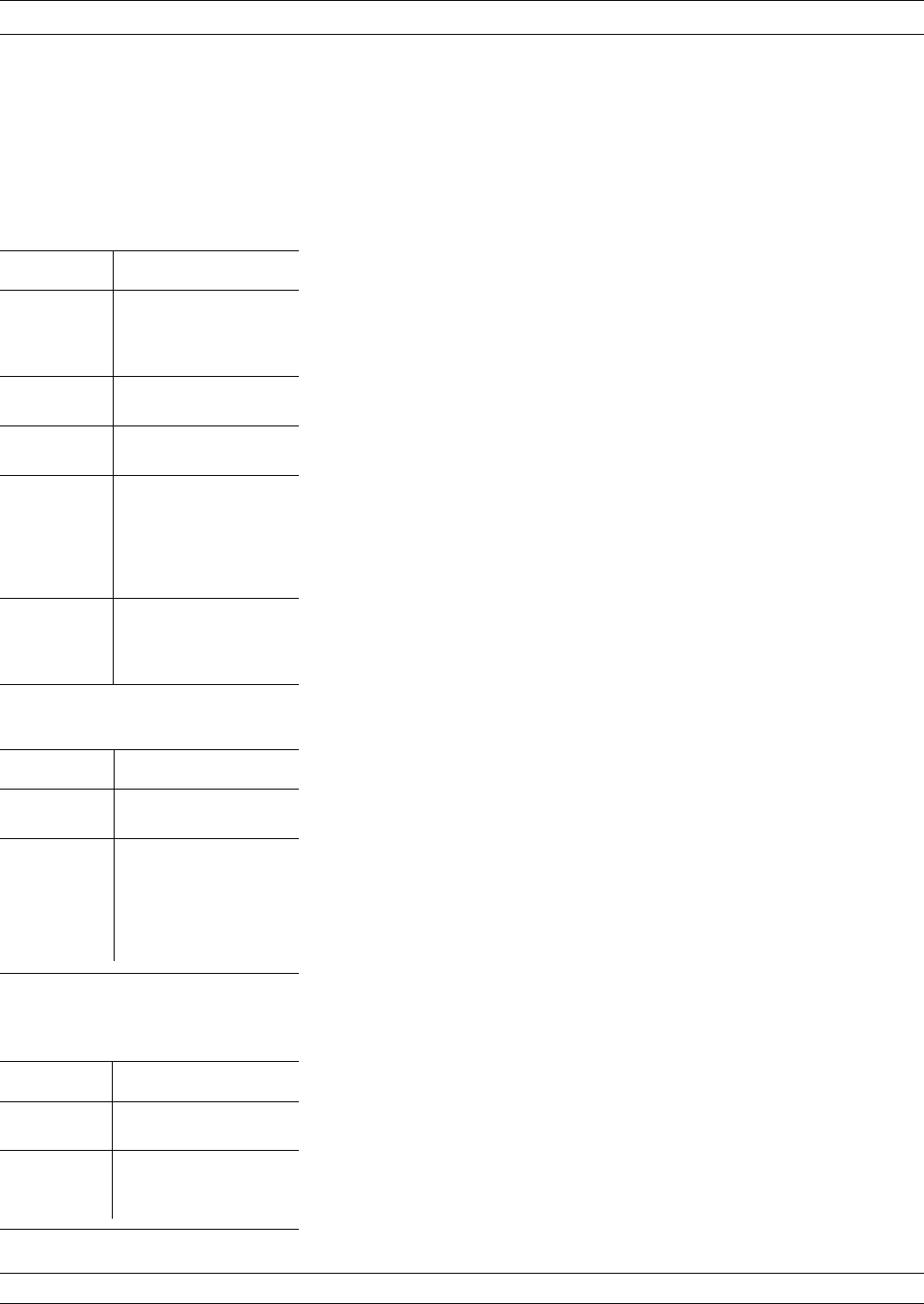
14-11 OPERATION
CHECKOUT—IF
POWER LEVEL TEST
This test verifies that each individual receiver channel operates prop-
erly. Measurement calibration of the system is not required for this
test.
Test Setup
Set up test equipment as described below.
Step 1. Install a flush short on the output of the 3740A-X
module connected to Port 1.
Step 2. Set up the network analyzer controls as shown at
left.
NOTE
For 3741A Series, use limit settings for
b1/1 (b2/1).
Test Procedure
The test procedure is described below.
Step 3. Observe sweep indicator and allow at least one com-
plete sweep to occur.
Step 4. Verify that the measurement traces fall within the
limit lines (Table 14-6).
Step 5. If the second module connected to Port 2 is also a
Model 3740A-X Transmission/Reflection module,
change the setup to that shown at the top left and
perform Step 4. Otherwise, skip to Step 7.
Step 6. Install a flush short to the output of the 3740A-X
module on Port 2.
Step 7. Verify that the measurement traces fall within the
limit lines.
Step 8. If the second module to be tested is a Model
3741A-X, connect the two modules together and
change the setup to that shown at the bottom left.
Step 9. Verify that the measurement trace falls within the
limit lines.
OPERATIONAL CHECKOUT MILLIMETER WAVE
14-26 37XXXC OM
Key Menu Choice
SETUP
MENU
START: Low-end Fre-
quency
STOP: High-end Fre-
quency
CHANNEL
MENU
DUAL CHANNELS
1&3
GRAPH
TYPE
LOG MAGNITUDE
(both channels)
S-PARAMS Channel 1
User Ratio: a1/1
User Phase Lock: a1
Channel 3
User Ratio: b1/1
User Phase Lock: a1
SET
SCALE
RESOLUTION: 10.0
dB/DIV
REF VALUE: -10.0 dB
(both channels)
Key Menu Choice
CHANNEL
MENU
DUAL CHANNELS
2&4
S-PARAMS Channel 2
User Ratio: a2/1
User Phase Lock: a2
Channel 4
User Ratio: b2/1
User Phase Lock: a2
Key Menu Choice
CHANNEL
MENU
SINGLE CHANNEL
S-PARAMS Channel 3
User Ratio: b2/1
User Phase Lock: a1
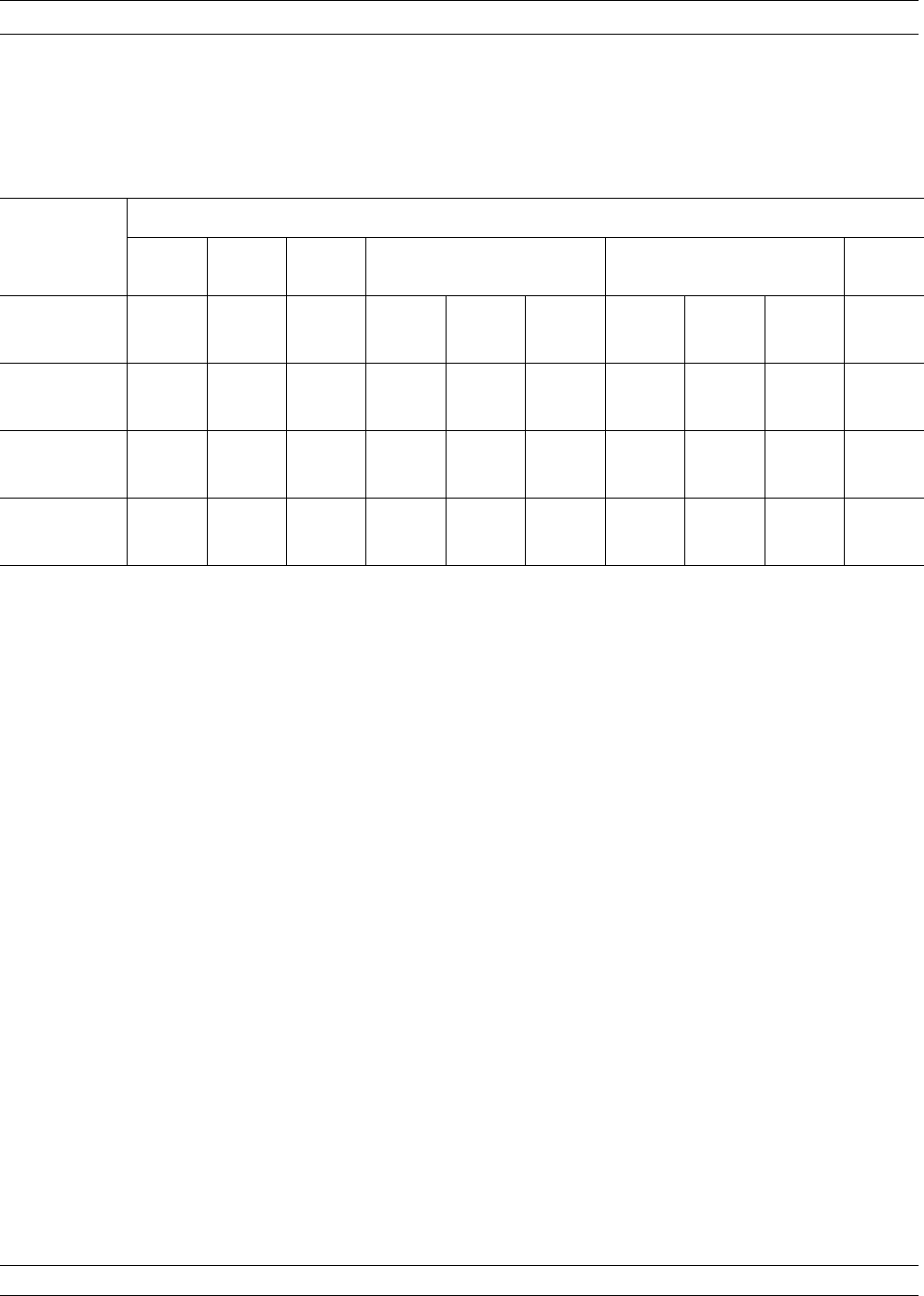
37XXXC OM 14-27
MILLIMETER WAVE OPERATIONAL CHECKOUT
Limit
Type Model and Frequency Range (GHz)
3740A-Q
33-50 3740A-V
50-75 3740A-E
60-90 3740A-EE
56-60 60-85 85-94 3740A-W and 3740A-EW
65-75 75-100 100-110 3740A-F
90-140
a1/1 (a2/1)
UPPER
LIMIT dB
–5–5–5–5–5–5–5–5–5–5
a1/1 (a2/1)
LOWER
LIMIT dB
–29 –27 –29 –34 –29 –39 –39 –24 –34 –39
b1/1 (b2/1)
UPPER
LIMIT dB
–2–2–2–2–2–2–2–2–2–2
b1/1 (b2/1)
LOWERLIMI
TdB
–26 –24 –26 –31 –26 –36 –36 –21 –31 –36
Table 14-6. Limit Line Settings
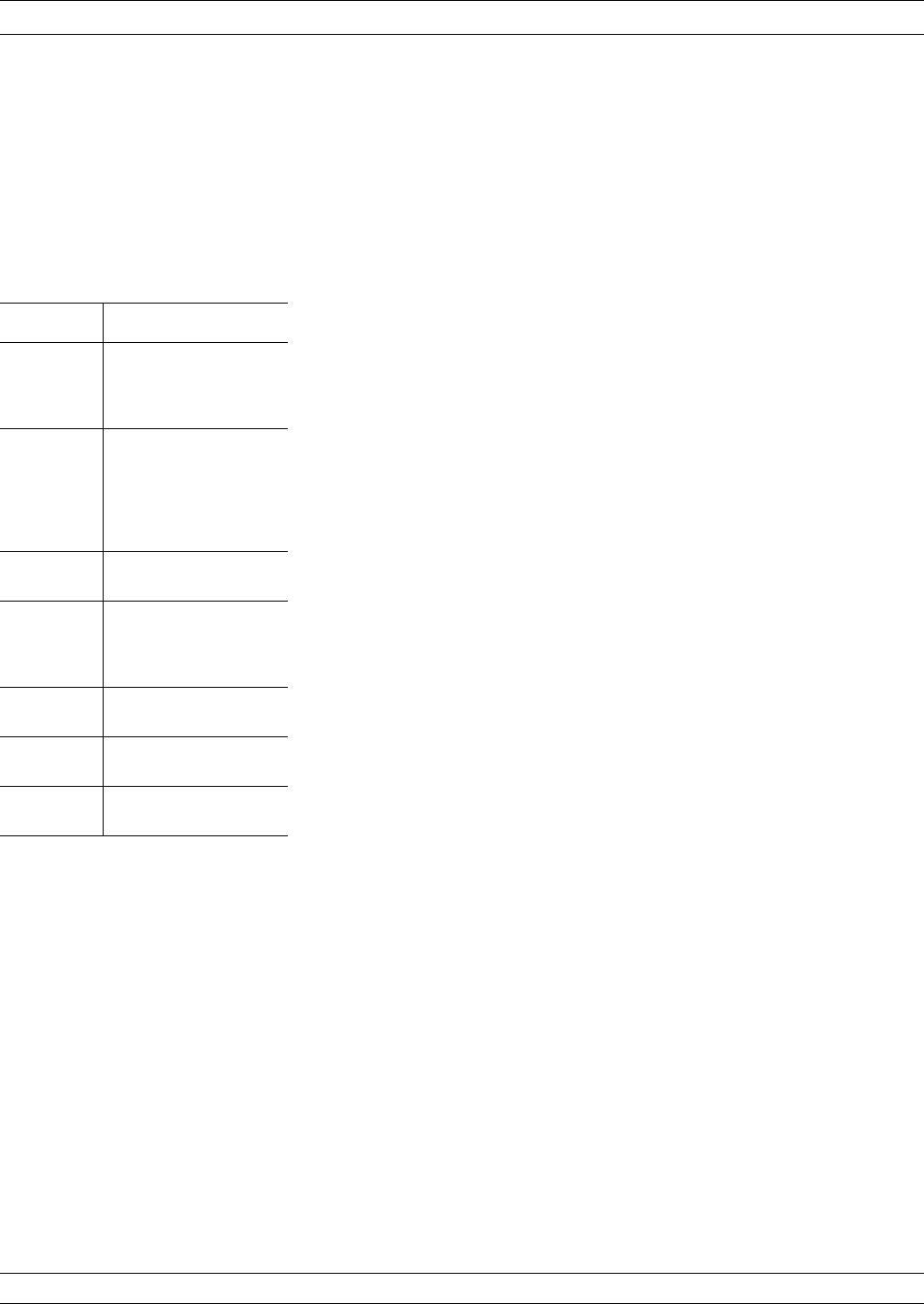
14-12 OPERATIONAL
CHECKOUT—
TRANSMISSION
HIGH LEVEL NOISE
TEST
The following test verifies that the transmission high-level noise in the
371XXC Millimeter VNA System will not significantly affect the accu-
racy of subsequent measurements. High-level noise is the random
noise that exists in the 371XXC Millimeter VNA System. Because it is
non-systematic, it cannot be accurately predicted or measured. Thus, it
cannot be removed using conventional error-correction techniques.
Measurement calibration is not required for this test.
NOTE
This test is not applicable if you are only using a single
3740A-X module on Port 1.
Test Setup
Set up the 371XXC Millimeter VNA System controls as shown at left.
Test Procedure
The test procedure is described below.
Step 1. Connect the two modules together.
Step 2. If using two 3740A-X’s, press the Ch 1 key and per-
form Steps 3 through 9. Otherwise, go to Step 10.
Step 3. Press the Trace Memory key.
OPERATIONAL CHECKOUT MILLIMETER WAVE
14-28 37XXXC OM
Key Menu Choice
SETUP
MENU
START: Low-end
Frequency
STOP: High-end
Frequency
CHAN-
NEL
MENU
DUAL CHANNELS 1
&3
(two 3740A-X’s)
SINGLE CHANNEL 3
(one 3740A-X and
one 3741A-X)
GRAPH
TYPE
LOG MAGNITUDE
(both channels)
SET
SCALE
RESOLUTION: 0.050
dB/DIV
REF VALUE: 0.0 dB
(both channels)
S-PARA
MS
Channel 1 S12
Channel 3 S21
DATA
POINT
401
VIDEO IF
BW
1 KHz
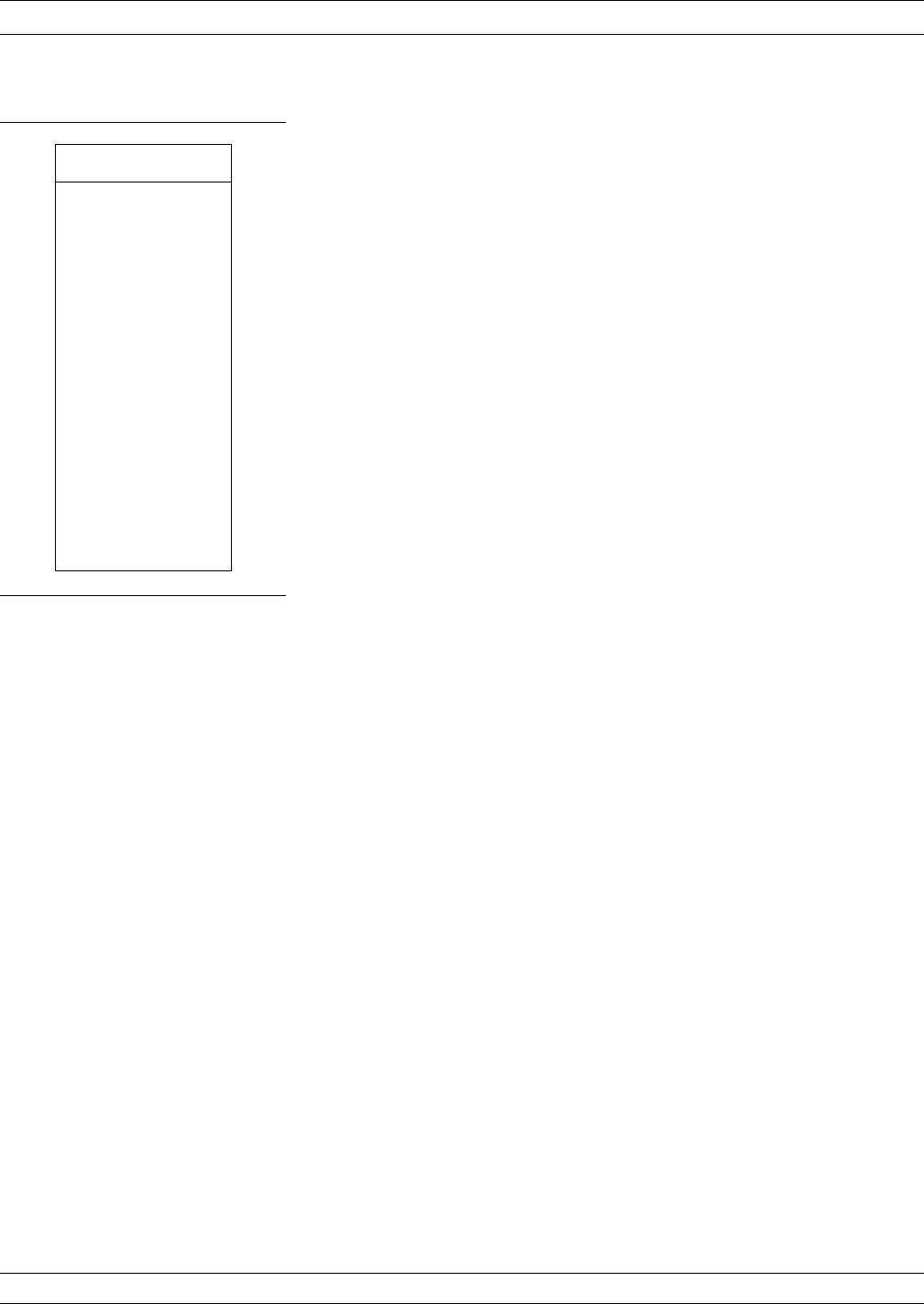
Step 4. Choose VIEW DATA from the menu (left) and press
the Enter key.
Step 5. While observing the sweep indicator, allow at least
two complete sweeps to occur. (One complete sweep if
using single channel display.)
Step 6. Choose STORE DATA TO MEMORY from menu
and press the Enter key.
Step 7. Choose VIEW DATA / MEMORY from the menu
and press the Enter key.
Step 8. While observing the sweep indicator, allow at least
two complete sweeps to occur. (One complete sweep if
using single channel display.)
Step 9. Verify that the peak-to-peak High Level Noise falls
within the area between the two limit lines.
NOTE
Displayed data is only valid for the first few
sweeps.
Step 10. Press the Ch3key.
Step 11. Repeat Steps 4 through 9 for channel 3.
37XXXC OM 14-29
MILLIMETER WAVE OPERATIONAL CHECKOUT
MENU NO1
TRACE MEMORY
FUNCTIONS
VIEW DATA
VIEW MEMORY
VIEW DATA
AND MEMORY
VIEW DATA (/)
MEMORY
SELECT
TRACE MATH
STORE DATA
TO MEMORY
DISK
OPERATIONS
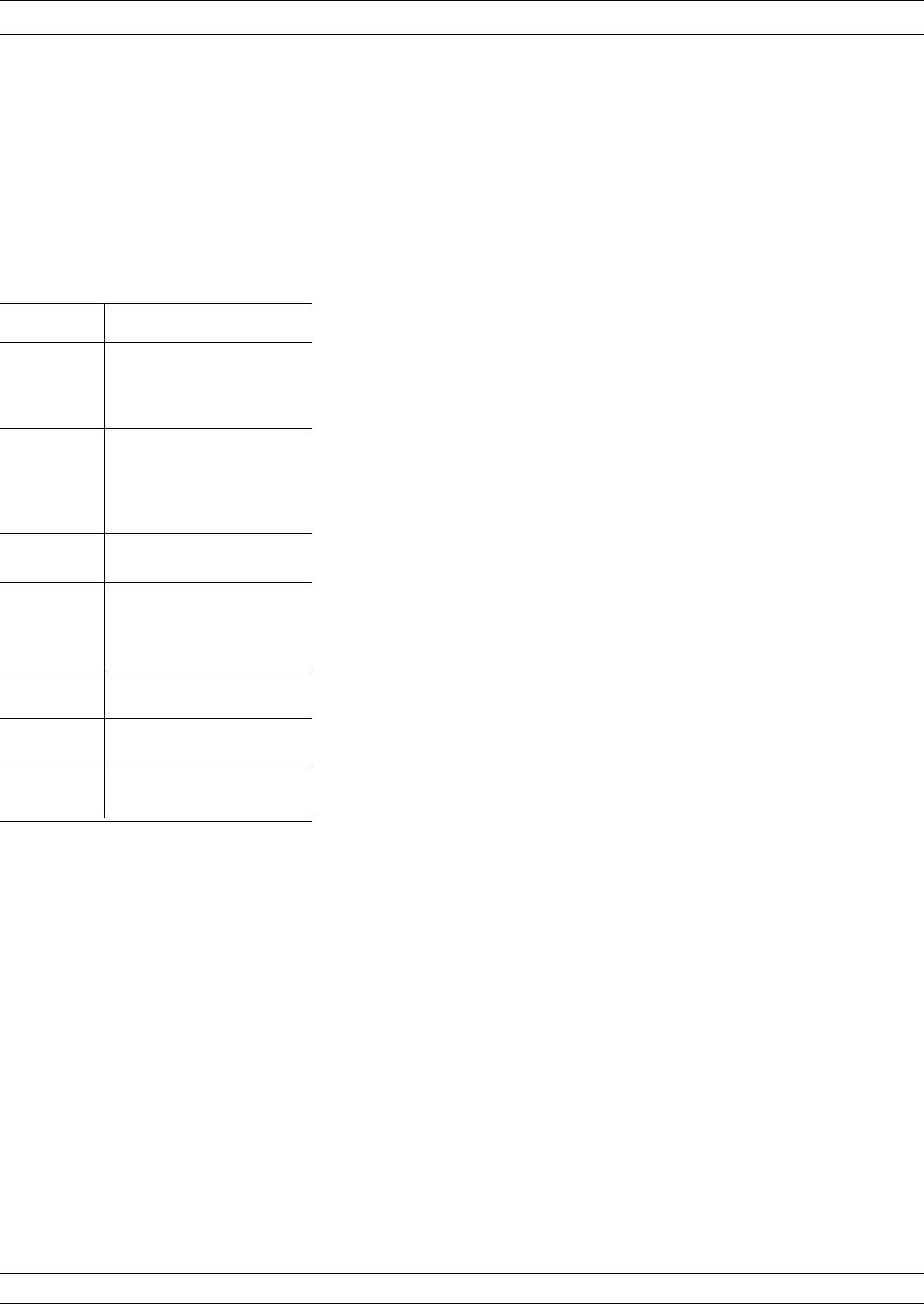
14-13 OPERATIONAL
CHECKOUT—
REFLECTION HIGH
LEVEL NOISE TEST
The following test verifies that the reflection high-level noise in the
371XXC Millimeter VNA System will not significantly affect the accu-
racy of subsequent measurements. High-level noise is the random
noise that exists in the 371XXC Millimeter VNA System. Because it is
non-systematic, it cannot be accurately predicted or measured. Thus, it
cannot be removed using conventional error-correction techniques.
Measurement calibration is not required for this test.
Test Setup
Set up the 371XXC Millimeter VNA System controls as shown at left.
Test Procedure
The test procedure is described below:
Step 1. Attach the flush short to the waveguide port on the
3740A-X on Port 1 (and Port 2, if two are used); leave
the waveguide port on 3741A-X unterminated.
Step 2. Press the CH1key.
Step 3. Press the Trace Memory key.
OPERATIONAL CHECKOUT MILLIMETER WAVE
14-30 37XXXC OM
Key Menu Choice
SETUP
MENU
START: Low-end Fre-
quency
STOP: High-end Fre-
quency
CHAN-
NEL
MENU
DUAL CHANNELS1&3
(two 3740A-X’s)
SINGLE CHANNEL 3
(one 3740A-X and one
3741A-X)
GRAPH
TYPE
LOG MAGNITUDE (both
channels)
SET
SCALE
RESOLUTION: 0.050
dB/DIV
REF VALUE: 0.0 dB
(both channels)
S-PARA
MS
Channel 1 S11
Channel 3 S22
DATA
POINT
401
VIDEO IF
BW
1 KHz
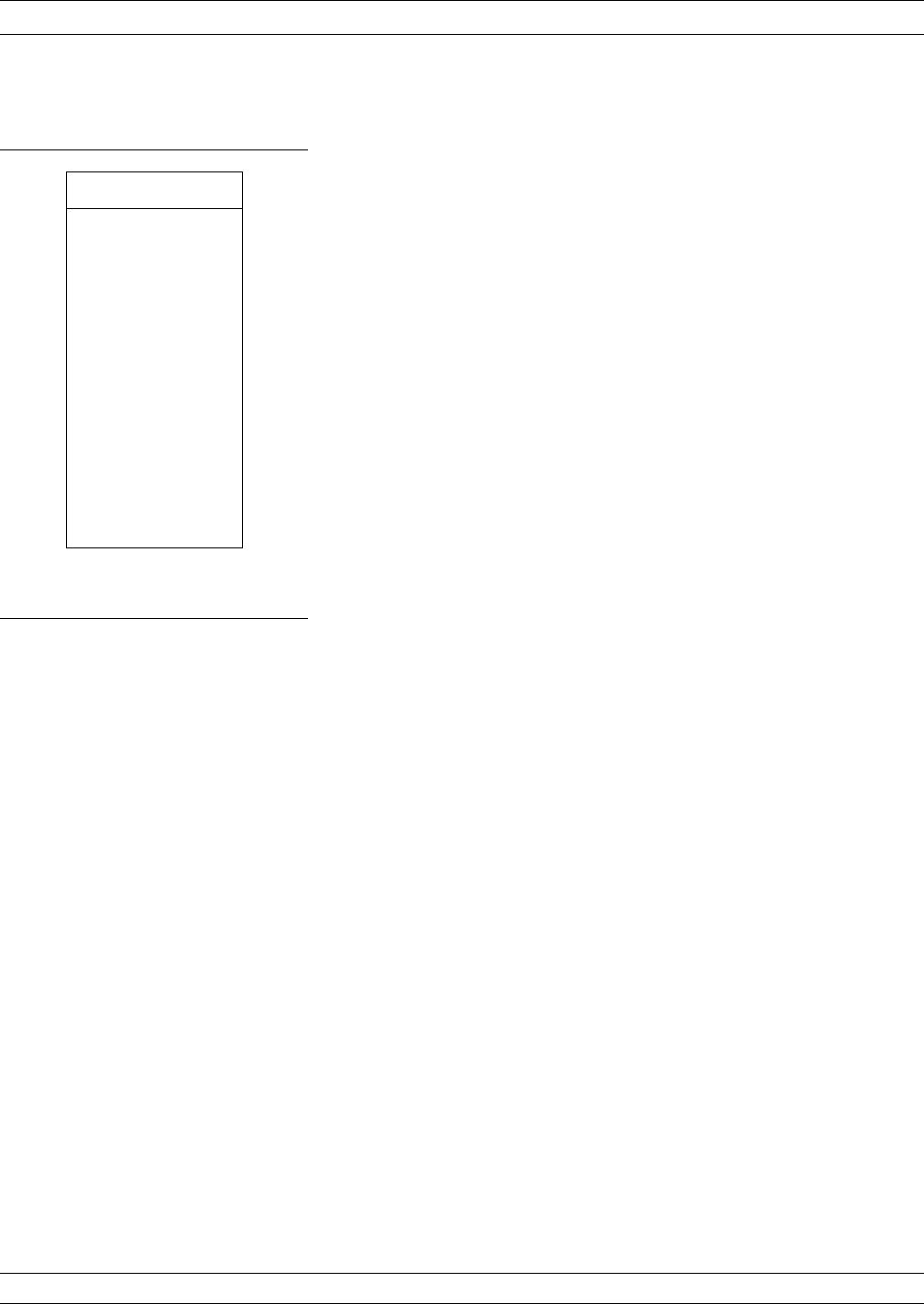
Step 4. Choose VIEW DATA from the menu (left) and press
the Enter key.
Step 5. While observing the sweep indicator, allow at least
two complete sweeps to occur. (One complete sweep if
using single channel display.)
Step 6. Choose STORE DATA TO MEMORY from the
menu and press the Enter key.
Step 7. Choose VIEW DATA (/) MEMORY from the menu
and press the Enter key.
Step 8. While observing sweep indicator, allow at least two
complete sweeps to occur. (One complete sweep if us-
ing single channel display.)
Step 9. Verify that the peak-to-peak High Level Noise falls
within the area between the two limit lines.
NOTE
Displayed data is only valid for the first few
sweeps.
Step 10. If two 3740A-X’s are used, press the Ch3key and re-
peat Steps 4 through 9 for channel 3.
MILLIMETER WAVE OPERATIONAL CHECKOUT
37XXXC OM 14-31/14-32
MENU NO1
TRACE MEMORY
FUNCTIONS
VIEW DATA
VIEW MEMORY
VIEW DATA
AND MEMORY
VIEW DATA (/)
MEMORY
SELECT
TRACE MATH
STORE DATA
TO MEMORY

Chapter 15
ME7808A Broadband
Measurement System
Table of Contents
15-1 INTRODUCTION...................................15-3
15-2 SYSTEM DESCRIPTION ..............................15-3
Measurement Instruments ............................15-3
Console and Associated Hardware ........................15-4
Cables .......................................15-4
15-3 INSTALLATION ...................................15-4
Console and Table Setup .............................15-5
Instrument Installation into Console .......................15-6
System Cabling ..................................15-9
15-4 INITIAL ELECTRICAL TESTS ..........................15-11
Millimeter Module Checkout...........................15-11
40 MHz to 65 GHz Checkout...........................15-12
15-5 WAFER PROBE STATION ............................15-13
15-6 BROADBAND MENUS, FLOW...........................15-15
15-7 BROADBAND CALIBRATION...........................15-16
Merging Calibrations...............................15-16

Chapter 15
ME7808A Broadband
Measurement System
15-1 INTRODUCTION This chapter describes the ME7808A Broadband Measurement System
and the broadband mode of operation (40 MHz to 110 GHz). For other
setup modes, refer to Chapter 14 (Millimeter Wave System), or other
pertinent chapters in this manual. Model 3742A-EW modules (65 to
110 GHz) are assumed to be installed on the system, even though
other modules are available.
The W1 Calibration Kit (P/N 3656) is designed for the purpose of per-
forming coaxial calibrations with the ME7808A Vector Network Ana-
lyzer up to 110 GHz. The calibration kit comprises of Open, Short, and
Load standards to enable two sets of calibrations—a Short Open Load
Thru (SOLT) calibration from 40 MHz to 65 GHz, and a Triple Offset
Short (SSST) calibration from 65 to 110 GHz (refer to Chapter 7, Mea-
surement Calibration for these calibration procedures). The ME7808A
firmware supports concatenation to allow merging of the two calibra-
tions for broadband corrected measurements from 40 MHz to 110 GHz
(discussed later in this chapter). In addition, the calibration kit in-
cludes fixed and interchangeable adapters, which may be used as test
port connector savers. The interchangeable adapters have one fixed
end and one interchangeable end that can be changed to a male or fe-
male for non-insertable device measurements.
15-2 SYSTEM DESCRIPTION The ME7808A Broadband system is normally composed of the follow-
ing Anritsu instruments and accessories (your system may vary de-
pending on your application):
Measurement Instruments
q37397C Vector Network Analyzer with Option 12
q68037C or MG3692A Synthesized Signal Generator with
Option 15A
q68037C or MG3692A Synthesized Signal Generator
(no options necessary)
q3738A Millimeter Test Set
q3742A-EW Millimeter Module (quantity 2)
q57215 (left) and 57216 (right) Coupler (quantity 1)
37XXXC OM 15-3
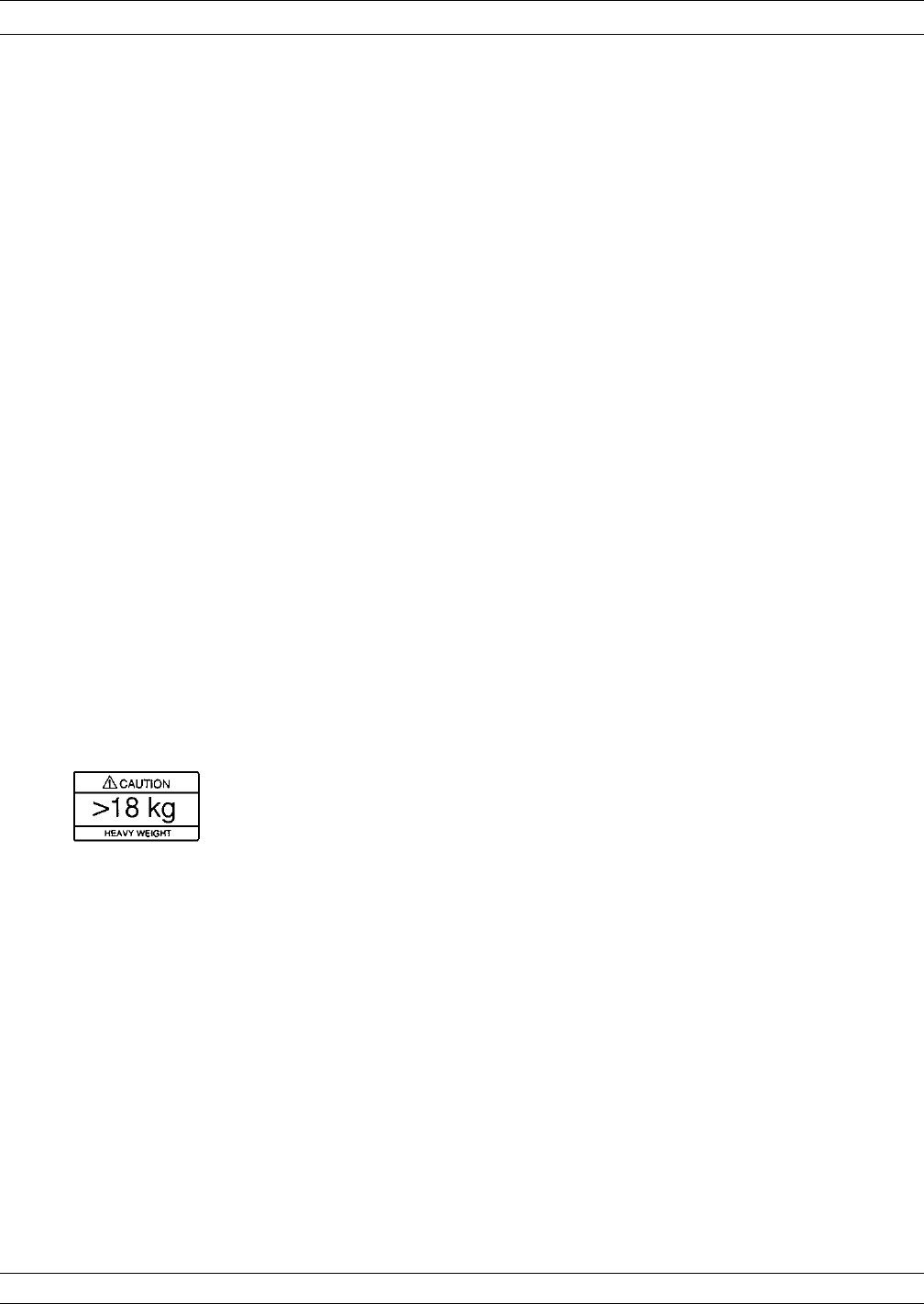
Console and Associated
Hardware
qConsole
qTable
qMounting rails for Table (quantity 2)
qStatic Dissipative Mat for Table
qWrist Strap
Cables
qRigid RF Cable (Upper synthesizer to 3738A)
qRigid RF Cable (Lower synthesizer to 3738A)
qCable Assembly (3742A to 3738A front panel) (quantity 2)
qCable Assembly (3738A rear panel to VNA rear panel) (quan-
tity 1)
qFlexible RF Cable (coupler to VNA) (quantity 2)
qGPIB Cable (VNA to Synthesizer) (quantity 2)
qPower Cord (quantity 4)
15-3 INSTALLATION This section describes installation and system check-out without mak-
ing use of a wafer-probe test station. For instructions on installation of
the wafer probe test station, refer to paragraph 15-5.
IMPORTANT NOTES
·The empty console weighs approximately 66kg
(145 pounds). Use two people to remove the console from
the pallet.
·Many of the instruments are quite heavy and require
two people to lift them.
·Instruments should be loaded into the bottom sections of
the console first, to prevent tipping of the console.
·The VNA instrument has fragile RF cables connected to
both the front and rear panels. Be careful not to bend
these cables when handling the instrument.
·If the synthesizers are not installed precisely as de-
scribed below, the system will be non-functional.
·We suggest using an 8 in/lb torque wrench to tighten
SMA connectors (available in most Anritsu VNA Cali-
bration kits) Do not tighten any connectors over 8 in/lbs.
INSTALLATION BROADBAND SYSTEM
15-4 37XXXC OM
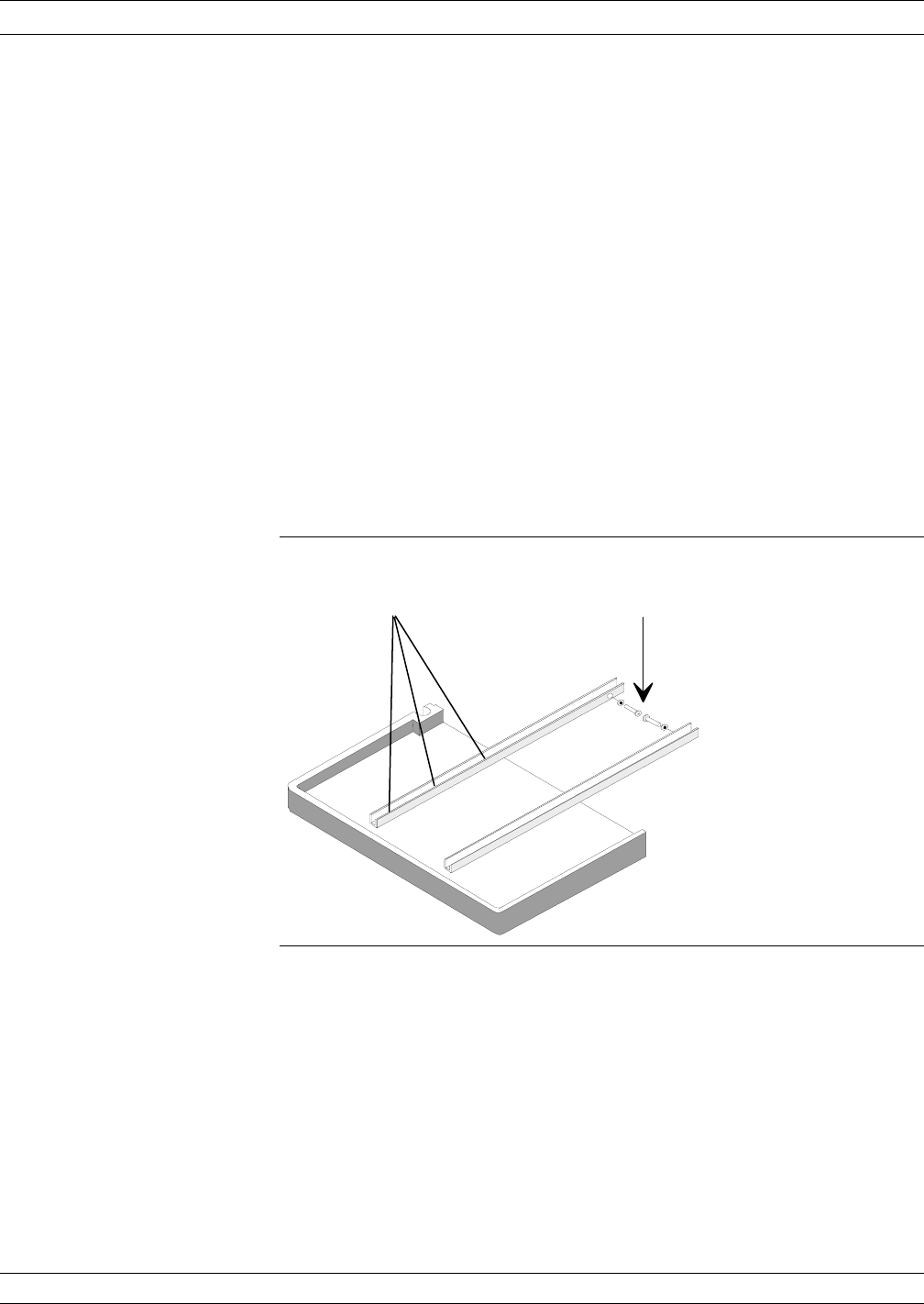
Console and Table Setup Set up the console and table as described below.
Step 1. Remove the shipping container and all packaging
and accessories from around the console. Set the ta-
ble aside. Instructions for table installation appear
later.
Step 2. Lift or roll the console off the pallet (to lift: insert
two sections of lumber through the console top and
lift it, using one person on each side).
Step 3. Cut the tie wraps which are securing the table
mounting rails at the console rear door. Cut the tie
wraps which are securing the power cords and wrist
strap ground wire.
Step 4. Attach the mounting rails to the table as shown in
Figure 15-1.
37XXXC OM 15-5
BROADBAND SYSTEM INSTALLATION
1 0 - 3 2 x 1 / 2 I N C H
# 1 0 L O C K W A S H E R
# 1 0 F L A T W A S H E R
I N S T A L L I N T W O P L A C E S A F T E R
P L A C I N G T H E W R I T I N G S U R F A C E
I N T O T H E C O N S O L E .
1 0 - 3 2 x 1 / 2 I N C H
# 1 0 L O C K W A S H E R
I N S T A L L I N 6 P L A C E S
Figure 15-1. Console Table
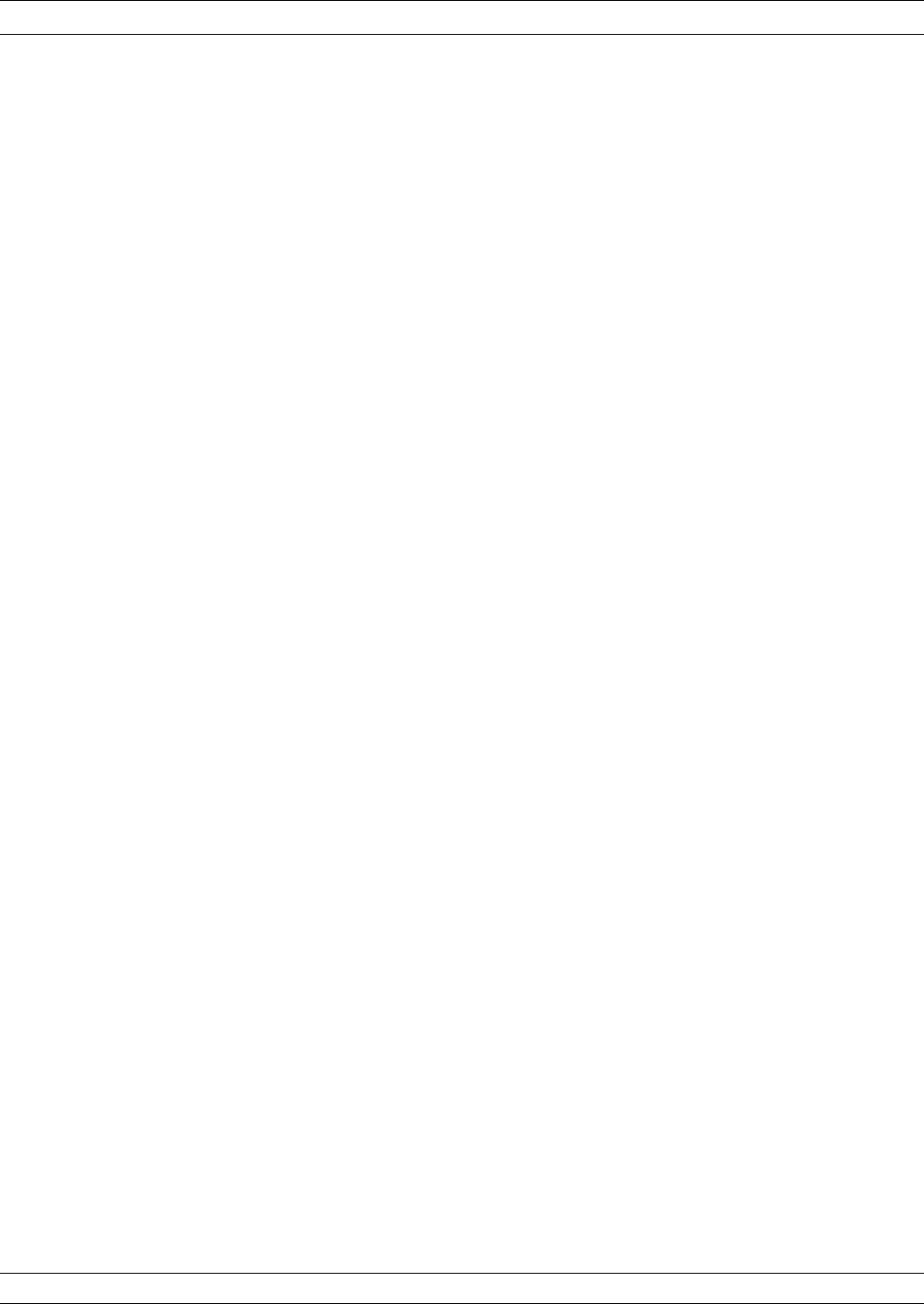
Instrument Installation
into Console Refer to Figures 15-2, 15-3, and 15-4 for installation of major instru-
ments and cables.
Step 1. Check the rear panel serial number labels of the syn-
thesizers. The instrument without Option 15 belongs
in the bottom compartment (“RF” synthesizer).
Step 2. Install the synthesizer with Option 15 in the second
opening from the bottom.
Step 3. Install the VNA into the top compartment. Ensure
the three small RF cables are installed onto the front
and rear panels (one in front, and two in back).
Step 4. Install the 3738A Test Set into the compartment be-
low the VNA.
Step 5. Secure all instruments in the console using the
screws provided.
Step 6. On the left front of the console, move the black
ground wire away from the guide of the table-mount-
ing rail, and install the table by sliding the table
rails into the guides.
Step 7. Secure the table rails at the rear of the console using
the screws provided.
INSTALLATION BROADBAND SYSTEM
15-6 37XXXC OM
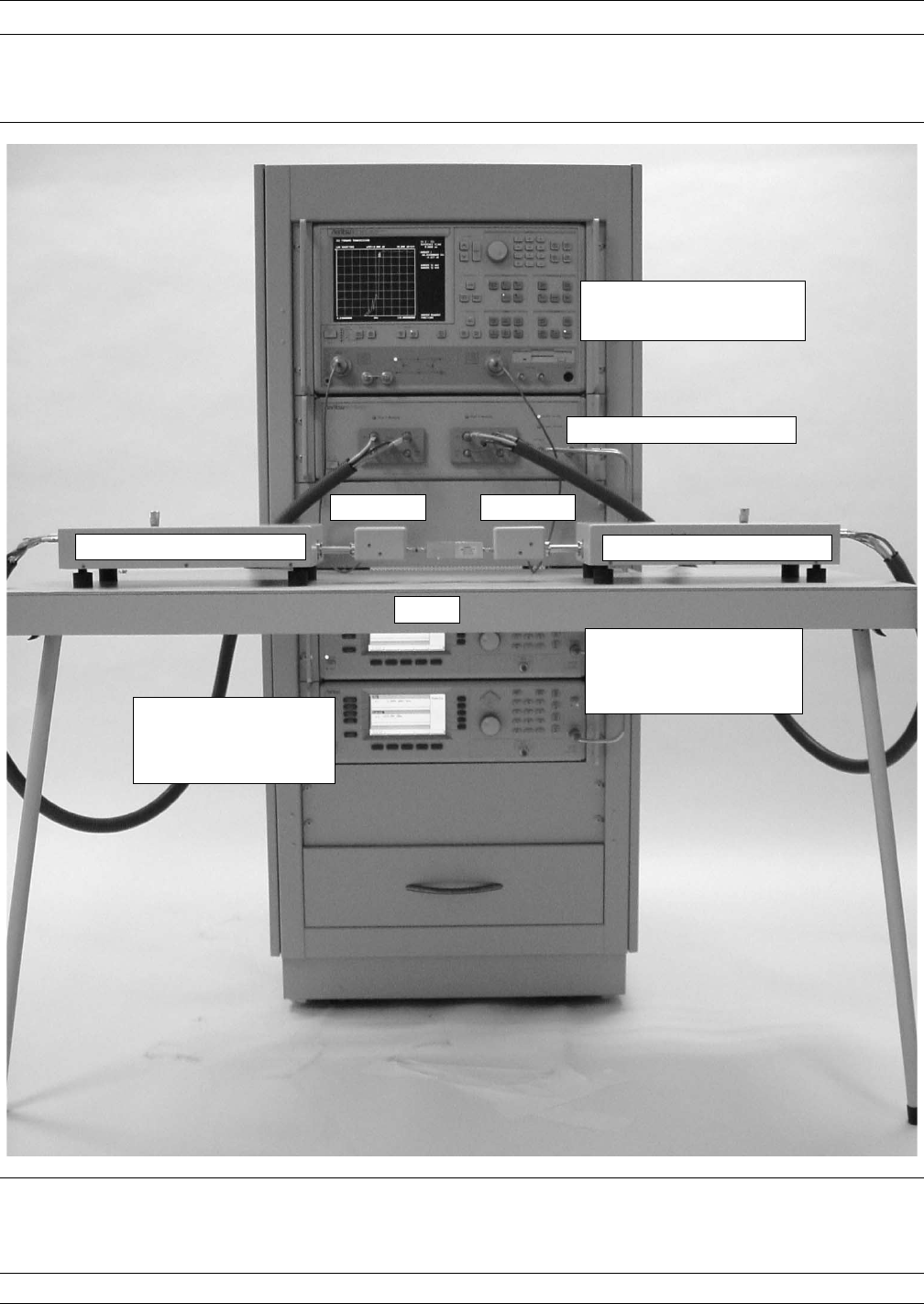
37XXXC OM 15-7
BROADBAND SYSTEM INSTALLATION
68037C or MG3692A
Synthesized Signal Generator
Not Option 15
GPIB Address: 5
68037C or MG3692A
Synthesized Signal Generator
Option 15
GPIB Address: 4
37397C Vector Network
Analyzer with Option 12
Table
Coupler Coupler
3742A-EW Millimeter Module
3738A Millimeter Test Set
3742A-EW Millimeter Module
Figure 15-2. ME7808A Console Showing Major Components
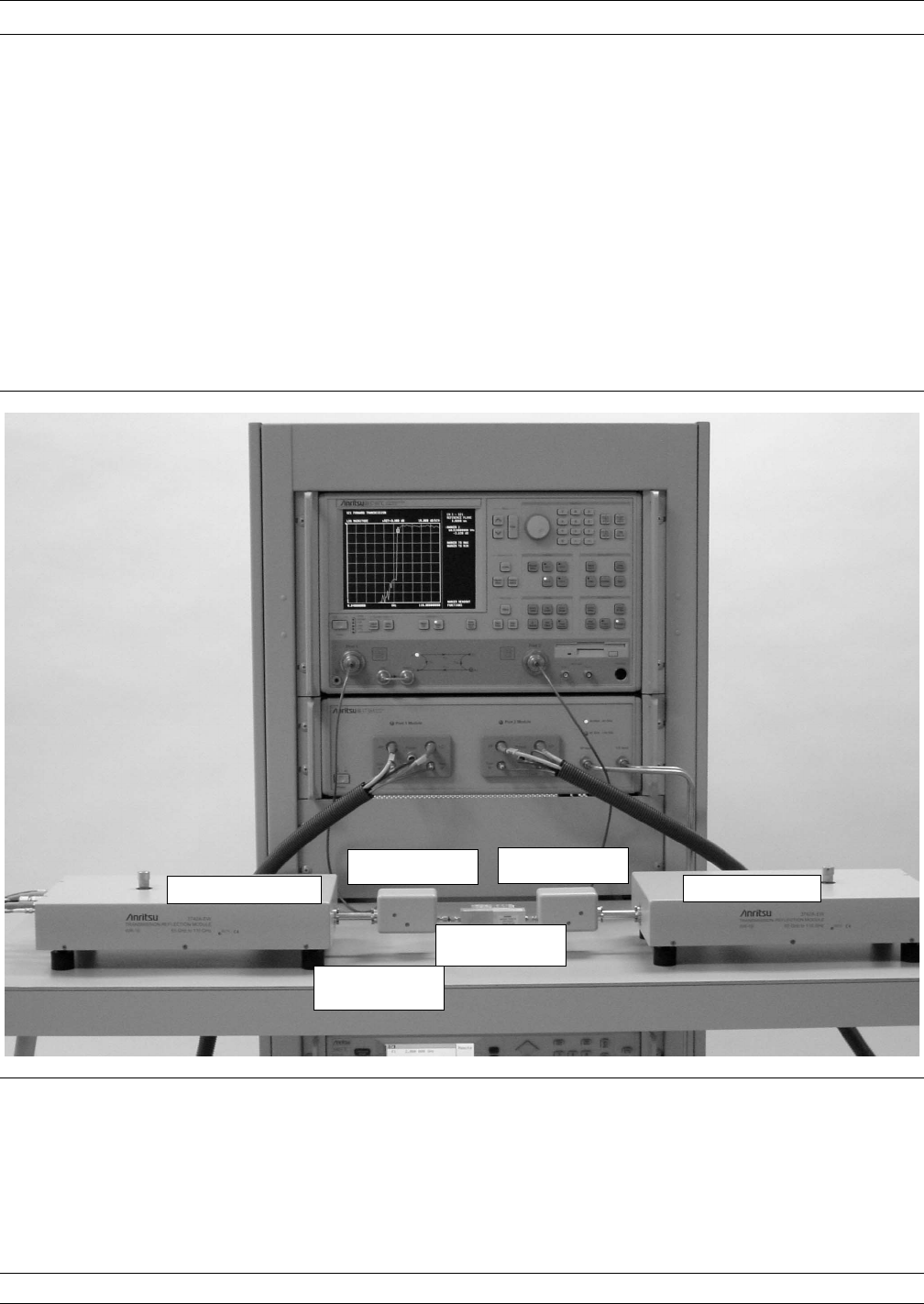
Step 8. Lay the static-safe mat on the table and attach the
ground cable.
Step 9. Unpack the 3742A-EW modules and set them on the
table. Do not attach the couplers to the module test
ports - they will not be tested at this time. (To test
the couplers requires a W1 (1 mm) Male-Male
adapter for mating of Port 1 to Port 2, or a full instal-
lation on a wafer probe station.)
INSTALLATION BROADBAND SYSTEM
15-8 37XXXC OM
Coupler (Do not
install, initially)
3742A-EW Module
Devices Under
Test (DUT)
Grounded,
Static-safe mat
3742A-EW Module
Coupler (Do not
install, initially)
Figure 15-3. ME7808A Console Showing Table and Module Setup
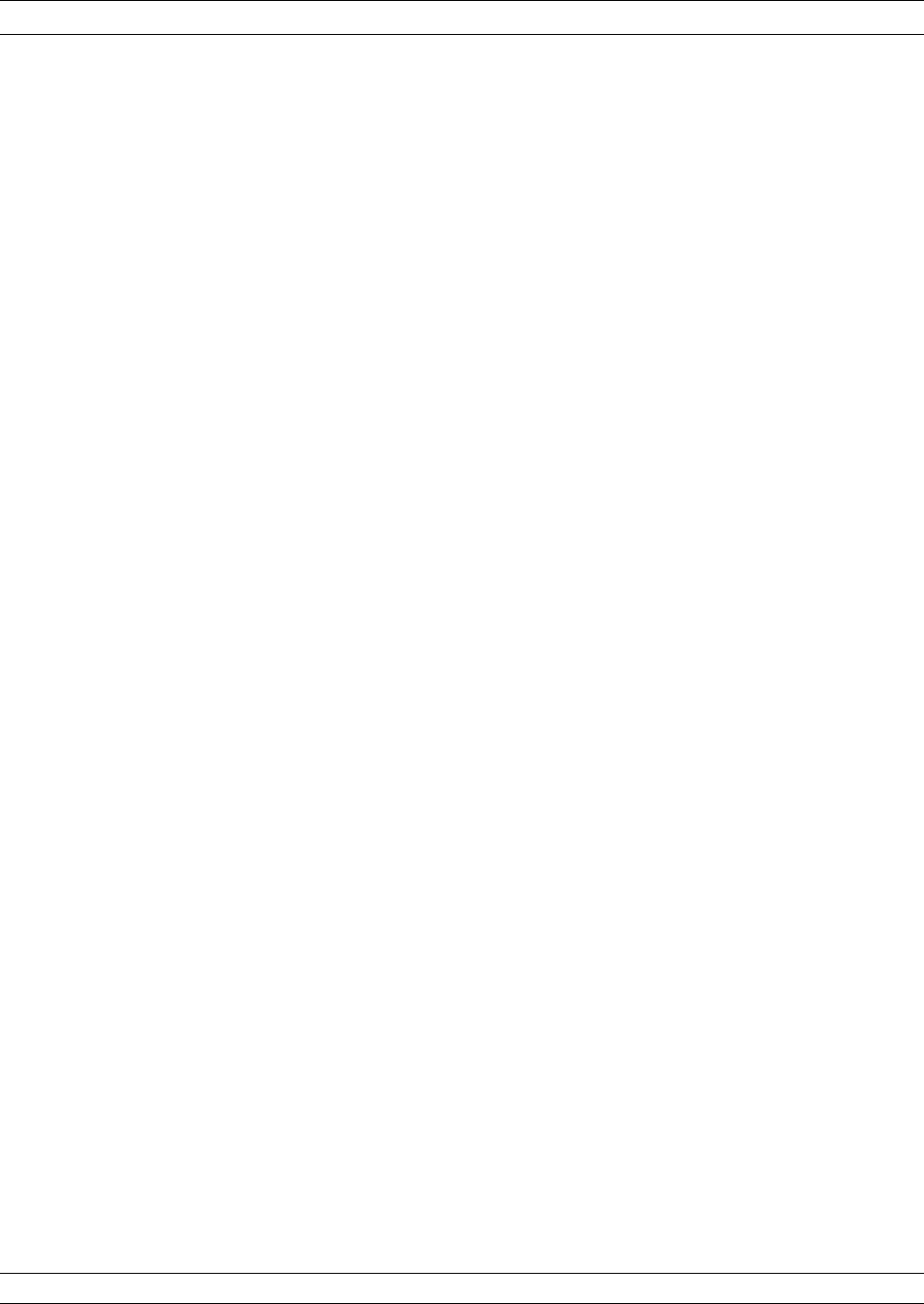
System Cabling Connect ME7808A system cables as described below and shown in Fig-
ure 15-4 on the following page.
Step 1. From the front, connect the rigid RF cable between
the upper synthesizer and the 3738A LO IN connec-
tor. Ensure the connectors are seated correctly and
tightened securely.
Step 2. From the front, connect the rigid RF cable between
the bottom synthesizer and the 3738A RF IN connec-
tor. Ensure the connectors are seated correctly and
tightened securely.
Step 3. From the front, install the two RF cable sets between
the 3738A and the 3742A-EW modules. Connect ex-
actly as the labels indicate.
Step 4. From the rear, unscrew the four small
chain-mounted terminations from on VNA (let them
hang loose) and install the Cable Set. Connect indi-
vidual cables as indicated on the labels .
Step 5. Connect one GPIB cable from the lower (Dedicated)
GPIB connector of the VNA to the upper synthesizer.
Connect the second GPIB cable between the two syn-
thesizers.
Step 6. Insert the power cords into all 4 instruments and
turn all the instruments on.
Step 7. Ensure that the two synthesizers' GPIB addresses
are set correctly. The top unit should be set to ad-
dress 4 and the bottom unit should be set to
address 5. This can be verified or changed by press-
ing SYSTEM |CONFIG |GPIB ADDRESS and en-
tering the appropriate GPIB address.
37XXXC OM 15-9
BROADBAND SYSTEM INSTALLATION
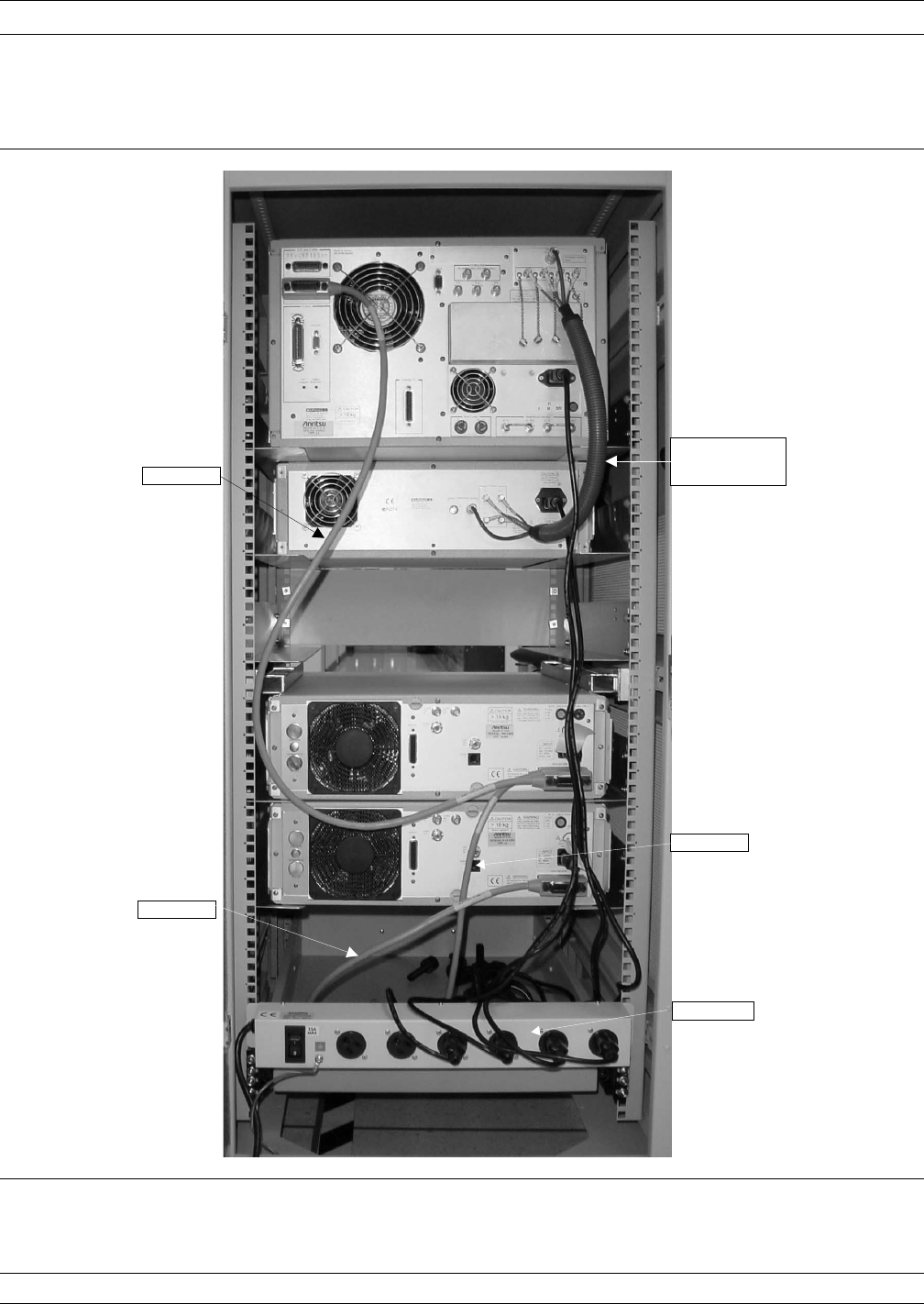
INSTALLATION BROADBAND SYSTEM
15-10 37XXXC OM
Cable Set.
Install individual
cables as marked
GPIB Cable
GPIB Cable
GPIB Cable
Power Cords
Figure 15-4. ME7808A Console Rear Panel Cabling
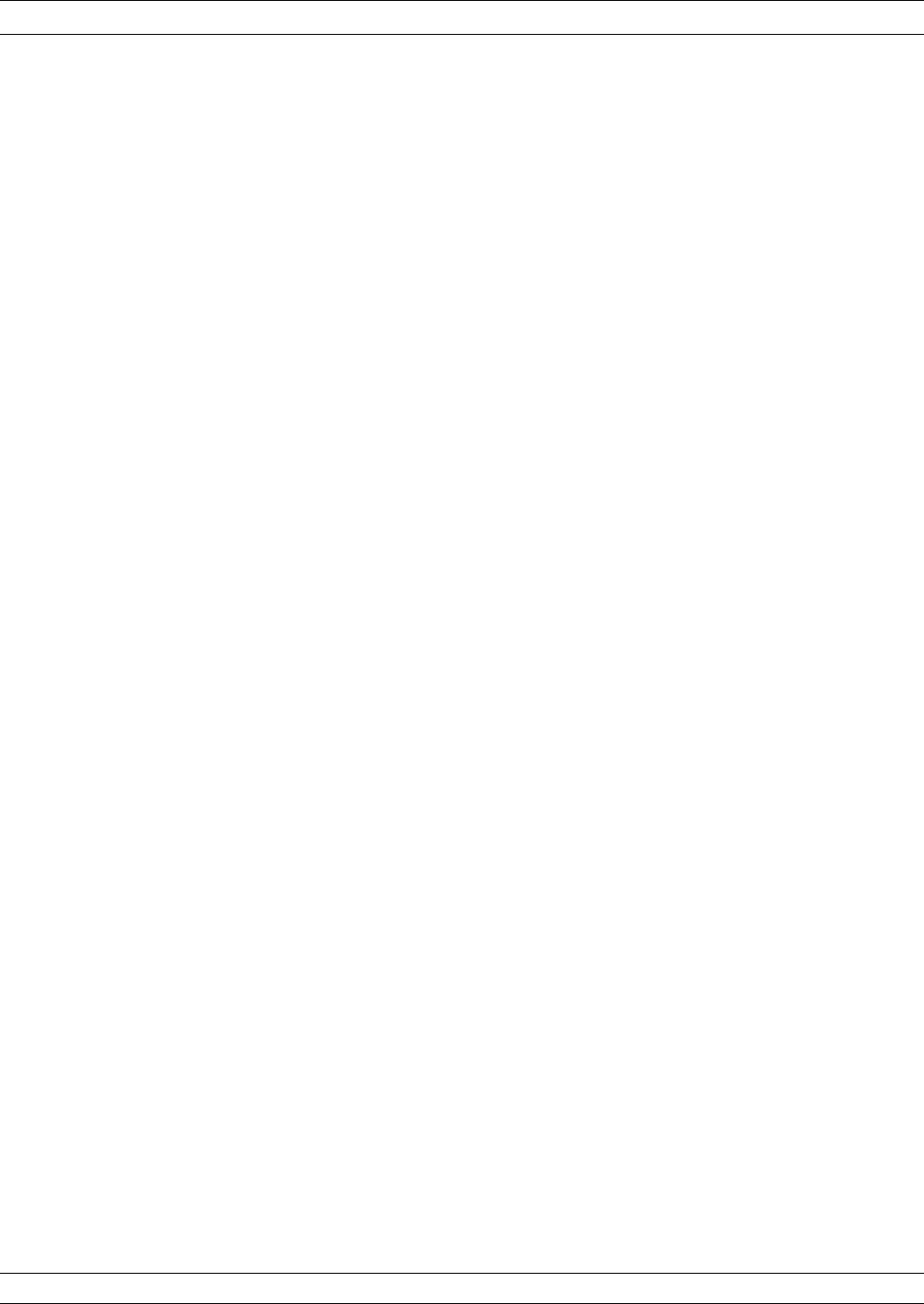
15-4 INITIAL ELECTRICAL
TESTS Perform electrical tests as described below:
Millimeter Module Checkout Check out the Millimeter Modules as described below:
Step 1. Ensure the VNA displays “Self-Test Passed”. If
self-test fails, contact your Anritsu Representative.
Step 2. To put the system into the “Millimeter” mode, press
the OPTION MENU key, and select TEST SET
CONFIG / MILLIMETER WAVE, then press
<ENTER>. Select the correct WR modules for your
system.
Step 3. Connect the Port 1 and Port 2 3742A-EW waveguide
test ports tightly together.
Step 4. If error messages appear, or the system does not
sweep:
·Look for error messages displayed on the
synthesizers’ front panels (“ovn cold” is not an
error)
·Double-check all cable connections
·Verify the synthesizers’ GPIB addresses are set cor-
rectly
·Verify the power control verniers on top of the
3742A-EW modules are set to maximum power
(fully CW)
Step 5. Ensure the system is set to default settings (Press
DEFAULT PROGRAM two times to reset the sys-
tem).
Step 6. Set the VNA display as follows:
a. Press CHANNEL MENU and select
SINGLE CHANNEL
b. Press CH3
c. Press GRAPH TYPE and select LOG MAGNITUDE
Step 7. Ensure the display is similar to Figure 15-5 (next
page).
Step 8. Press CH2.
Step 9. Press GRAPH TYPE and select LOG MAGNITUDE.
37XXXC OM 15-11
BROADBAND SYSTEM INITIAL ELECTRICAL TESTS
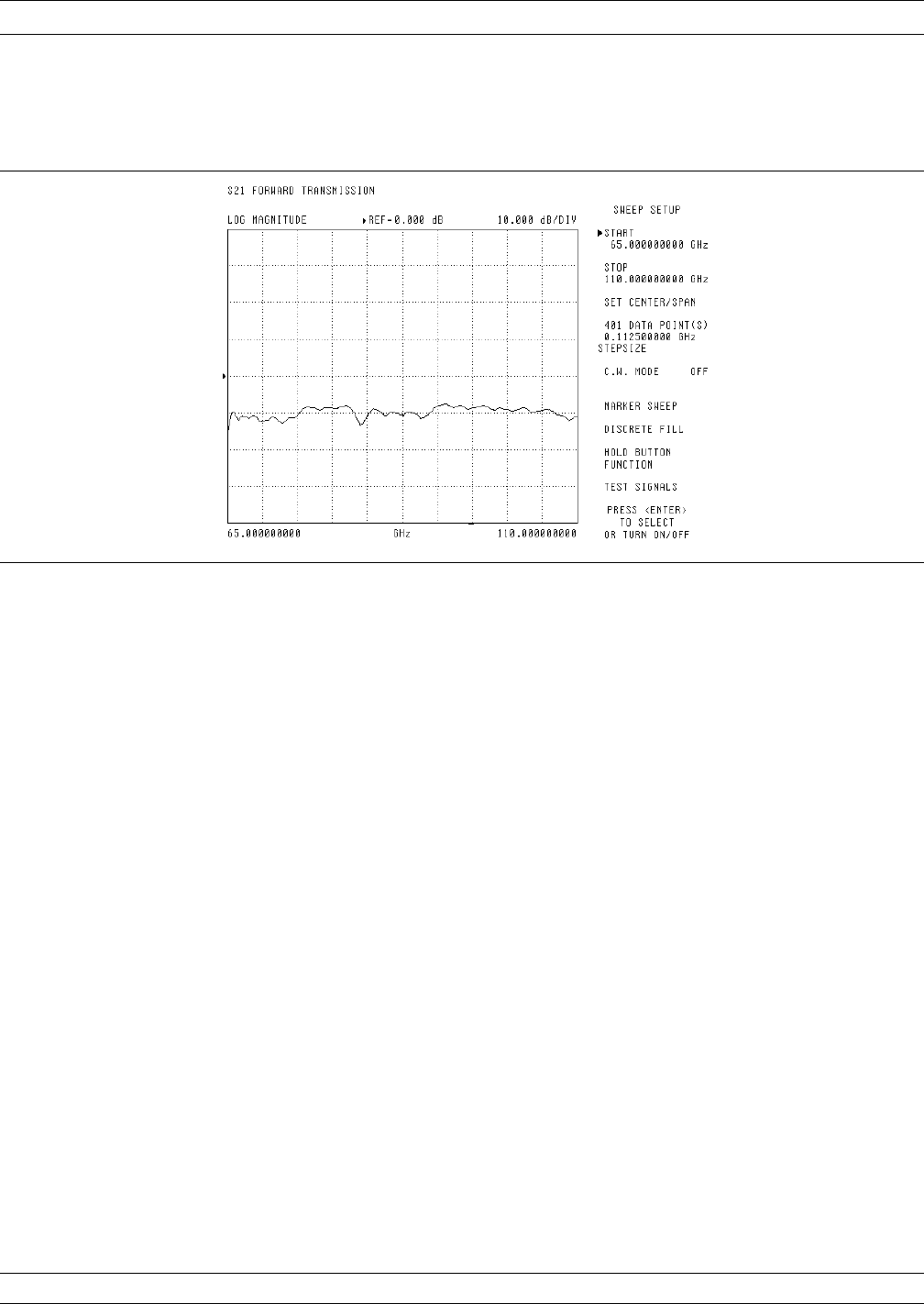
Step 10. Ensure the display resembles Figure 15-5.
40 MHz to 65 GHz Checkout Checkout the 40 MHz to 65 GHz range as described below.
Step 1. Install a throughline between the test ports on the
VNA.
Step 2. Disconnect the cables from the rear panel of the
VNA that connect to the Test Set. Install the four
small terminations, which are hanging from the
chains, to the VNA.
Step 3. Press the OPTION MENU key and select TEST SET
CONFIG / INTERNAL.
Step 4. View single channel S21 and S12 as described above
and verify that the traces are similar in appearance
to Figure 15-6 on the following page.
INITIAL ELECTRICAL TESTS BROADBAND SYSTEM
15-12 37XXXC OM
Figure 15-5. Normal S21 Display of MM Module Uncalibrated Transmission
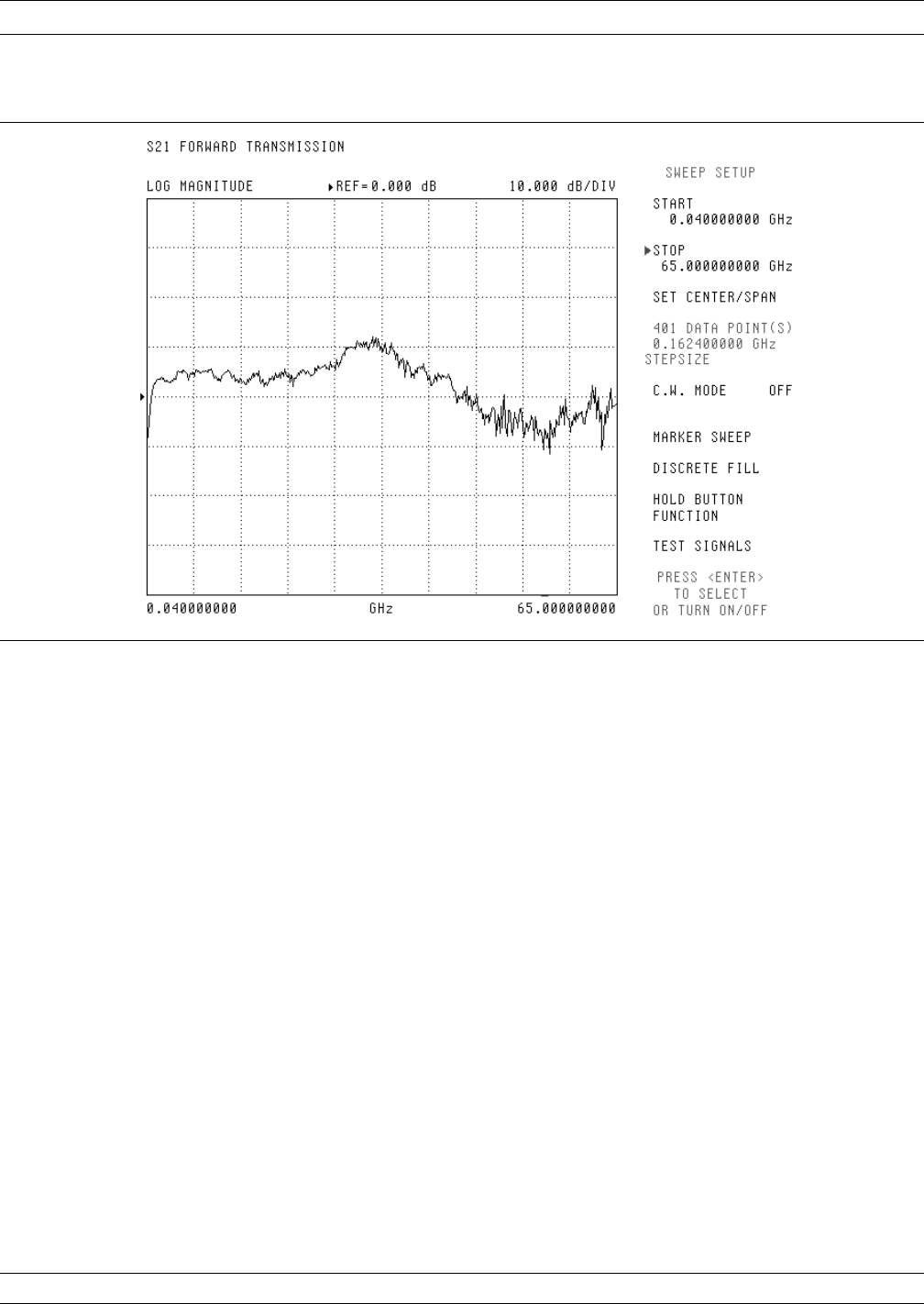
The preliminary checkout is complete. (Coupler operation can be
checked using the wafer probe station).
You are now ready to install the system to the wafer probe station or
configure it to your needs. To activate the full 40 GHz to 110 GHz
sweep, press the OPTION MENU key, and select BROADBAND.
15-5 WAFER PROBE
STATION The ME7808A VNA can be integrated with any standard probe station
(manual or semi-automatic) for making on-wafer measurements of ac-
tive or passive components to 110 GHz. However, there are some con-
siderations for set-up that will ensure accurate and repeatable mea-
surements.
Figure 15-7 (following page) shows integration of the ME7808A VNA
with a probe station. The primary connection is from the W1 (1.00
mm) coaxial output on the multiplexing coupler to the wafer probes. If
losses through the probes and cables are excessive, the result can be a
poor calibration. Therefore, it is recommended that the distance be-
tween the couplers and the probes be kept as small as possible. This
can be achieved by mounting the millimeter wave modules
(3742A-EW) on top of the positioners, as shown in the following figure.
37XXXC OM 15-13
BROADBAND SYSTEM WAFER PROBE STATION
Figure 15-6. S21 or S12 Forward Transmission
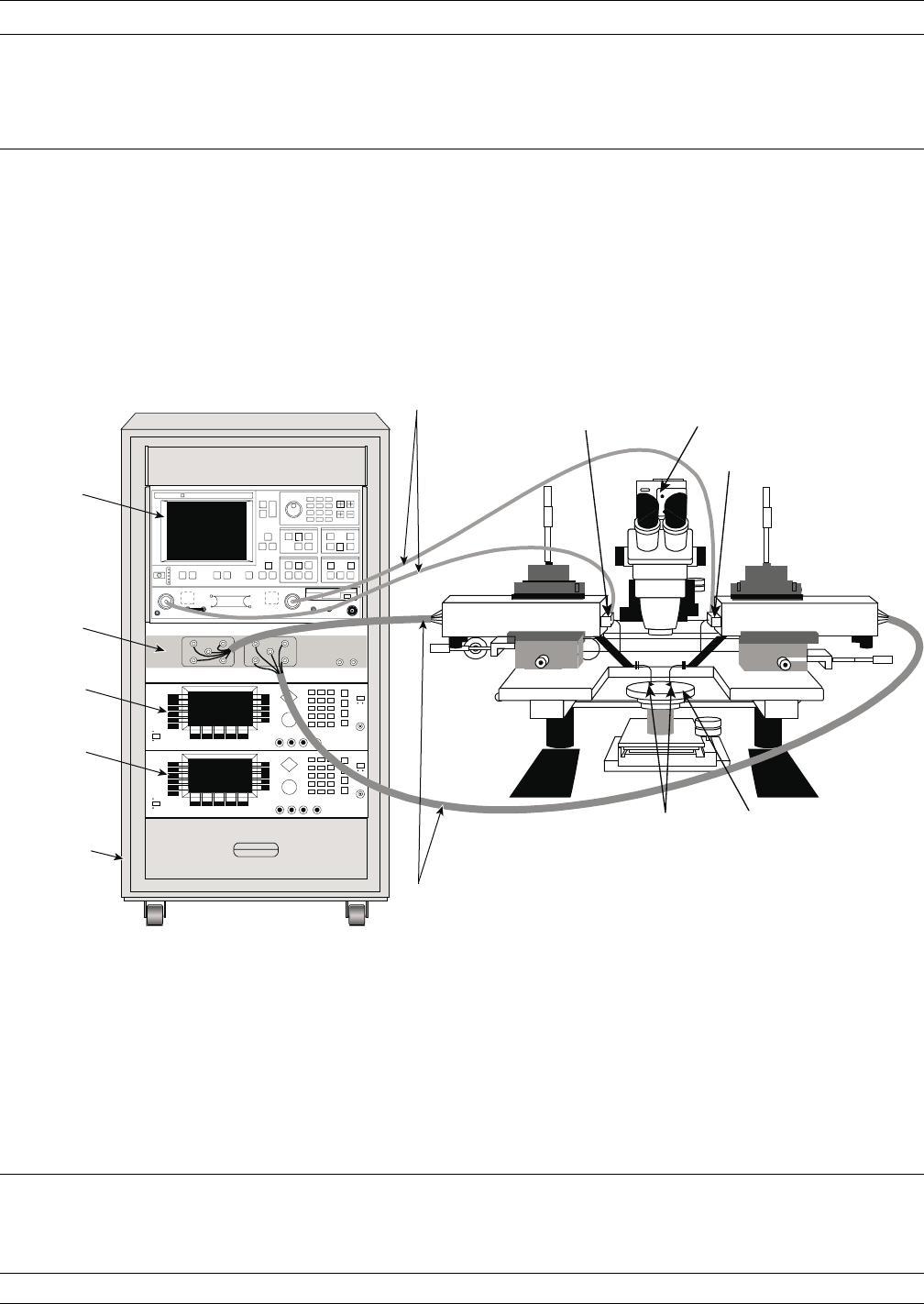
WAFER PROBE STATION BROADBAND SYSTEM
15-14 37XXXC OM
Note: The probe station is positioned in front of the equipment
rack such that the 65 GHz flex cables from the VNA are kept
equal and as short as possible in length.
110 GHz Probes HF Chuck
1.5m Cable
3700C3
68037C
(w/o Option15)
GPIB Address 5
68037C
(w/Option15)
GPIB Address 4
3738A
37397C
(W/Option 12)
0.7m Flex Cables
Coupler Scope
Coupler
3742A-EW
3742A-EW
Positioner Positioner
Table 15-7. Probe Station Interconnection
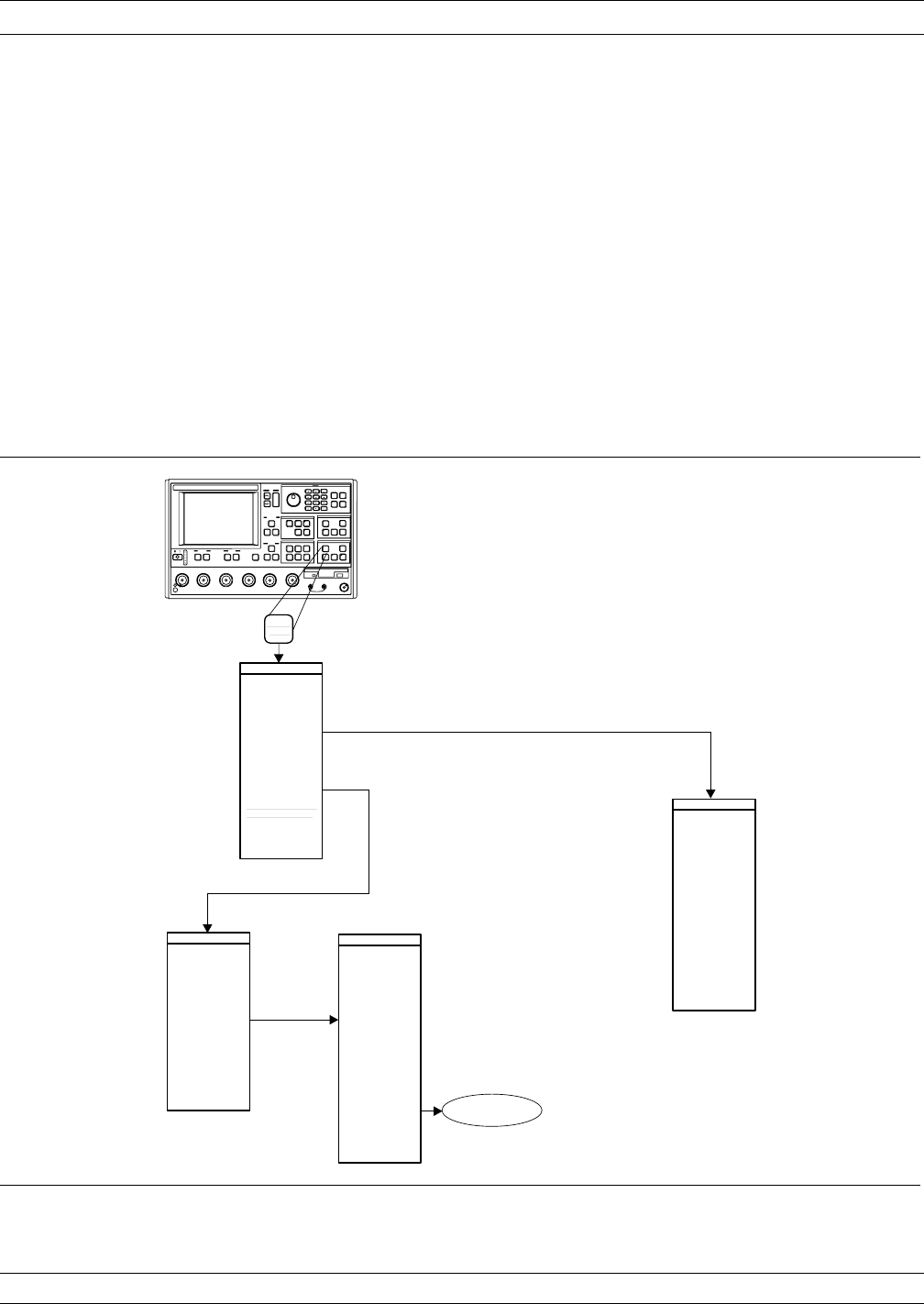
This results in increased output power and hence, enhanced system
dynamic range. This concern also applies for the V-connector cables
that connect the 37397C VNA to the multiplexing couplers. Placing the
probe station directly in front of the ME7808A can minimize these ca-
ble lengths. Note that the probe station is shown on the side of the
rack simply for clarity purposes.
For more information on wafer probe station integration, please con-
tact Anritsu at 1-800-ANRITSU.
15-6 BROADBAND MENUS,
FLOW The menus associated with the broadband system are shown in Fig-
ure 15-8.
37XXXC OM 15-15
BROADBAND SYSTEM BROADBAND MENUS, FLOW
Option
Menu
MENU OPTNS
MENU BB2 MENU BB3
REAR PANEL
OUTPUT
DIAGNOSTICS
BROADBAND
DEFINITION
OPTIONS
RECEIVER MODE
TO SELECT
PRESS <ENTER>
PRESS <ENTER>
TO SELECT
PRESS <CLEAR>
TO ABORT
SOURCE CONFIG
TEST SET CONFIG
RF ON/OFF
DURING RETRACE
MENU BB4
BROADBAND BAND 2
BAND 2 START FREQ
65.000000000 GHz
BAND 2 ST0PT FREQ
110.000000000 GHz
DEFAULT RANGE
ACCEPT RANGE
TO MENU SU1/SU2
BROADBAND
TEST SET MODULES
PORT 1 MODULE
3740/41/42/NONE
3740/41/42/NONE
PORT 2 MODULE
ACCEPT CONFIG
PRESS <ENTER>
TO SELECT
OR SWITCH
PRESS <CLEAR>
TO ABORT
PRESS <CLEAR>
TO ABORT
BROADBAND
TEST SET
BROADBAND BAND 2
WR10 EXTENDED
PORT 1 MODULE
3742
PORT 2 MODULE
3742
WARNING
CONTINUING
MAY INVALIDATE
CURRENT
SETUP AND
CALIBRATION
PRESS <ENTER>
TO CONTINUE
Table 15-8. Broadband System Menu Flow
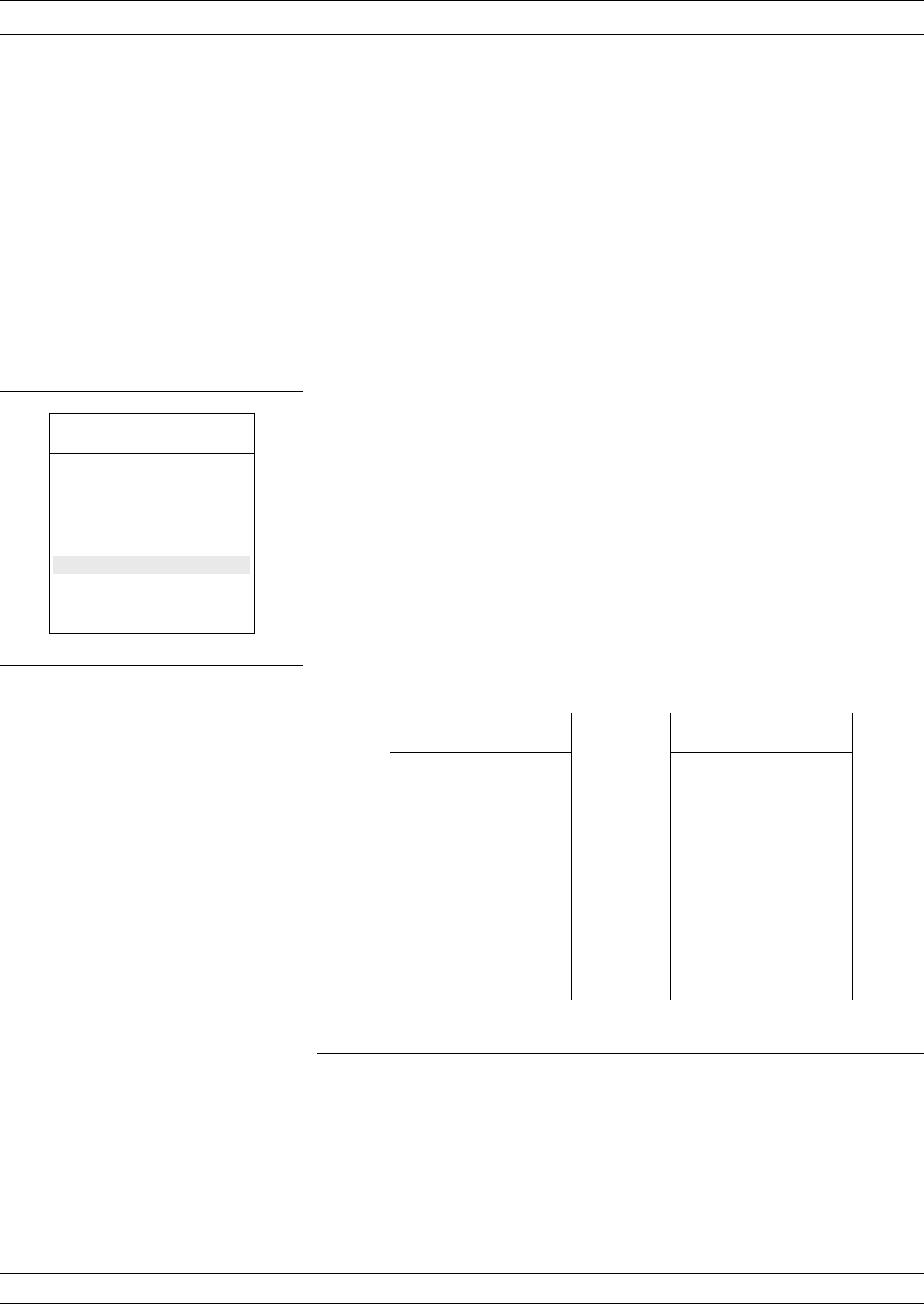
15-7 BROADBAND
CALIBRATION Once the SOLT and SSST calibrations have been performed and saved,
they can be merged for a continuous, single sweep broadband calibra-
tion. (Refer to Chapter 7, Measurement Calibration for SOLT and
SSST calibration procedures.)
Merging Calibrations Merge the calibrations as follows:
Step 1. Open the applications menu by pressing the APPL
key.
Step 2. Select MERGE CAL FILES to open menu MRG1 (left).
Step 3. Select MERGE CAL FILES again to open menu
MRG2 (below left).
Step 4. Select READ CAL FILE 1 FROM HARD DISK or READ
CAL FILE 1 FROM FLOPPY DISK to select the SOLT
calibration file.
Step 5. After loading the SOLT cal file, select READ CAL
FILE 2 FROM HARD DISK or READ CAL FILE 2
FROM FLOPPY DISK from menu MRG3 (below right)
and select the SSST calibration file. This step
merges the calibration files together.
Step 6. The system is now ready for calibrated measure-
ments over the 40 MHz to 110 GHz frequency range.
BROADBAND CALIBRATION BROADBAND SYSTEM
15-16 37XXXC OM
MENU MRG1
MERGE CAL FILES
CAL FILES MUST
EXIST IN THE
CURRENT DIRECTORY
MERGE CAL FILES
PRESS <ENTER>
TO SELECT
MENU MRG2 MENU MRG3
MERGE CAL FILES MERGE CAL FILES
READ CAL FILE 1
FROM HARD DISK
READ CAL FILE 2
FROM HARD DISK
READ CAL FILE 1
FROM FLOPPY
DISK
READ CAL FILE 2
FROM FLOPPY
DISK
PRESS <ENTER>
TO SELECT
PRESS <ENTER>
TO SELECT
PRESS <CLEAR>
TO ABORT
PRESS <CLEAR>
TO ABORT
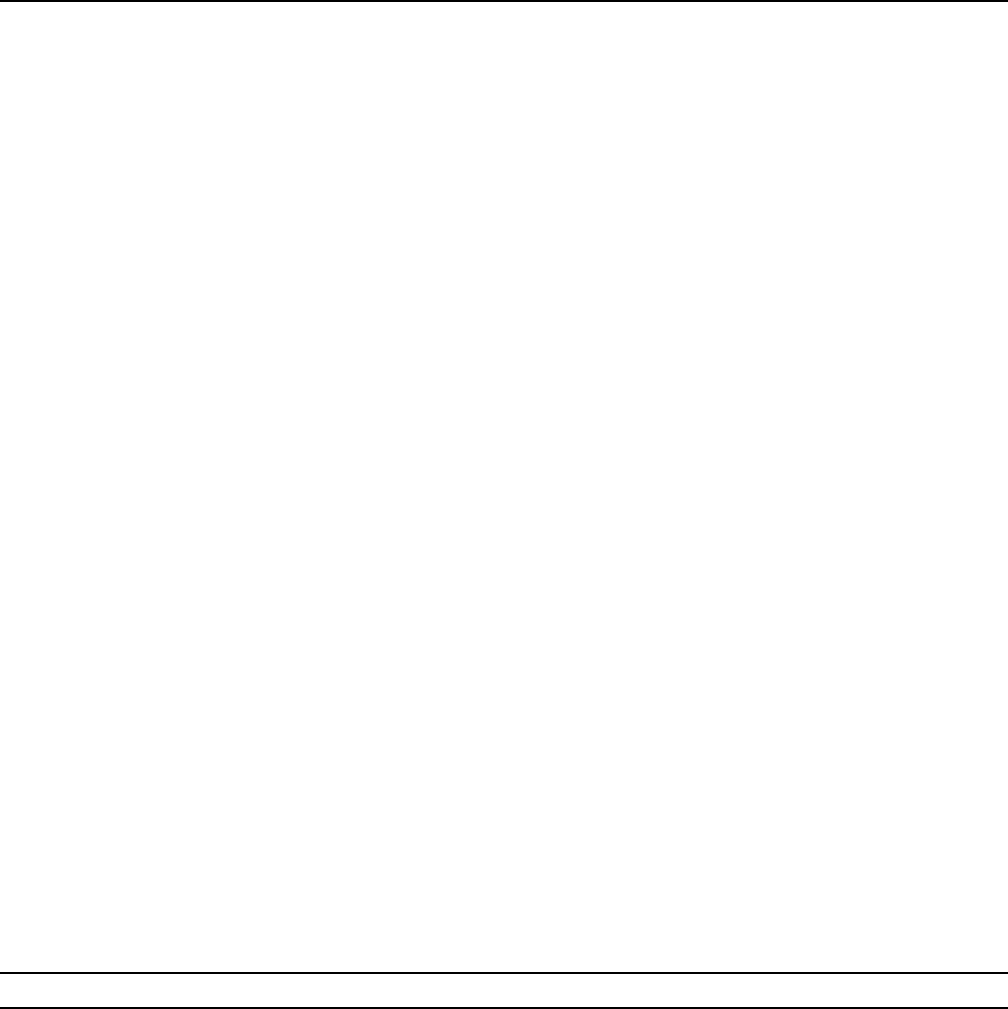
Contents
Menu ACAL, AutoCal Menu...........................A-12
Menu ACAL_SETUP, AutoCal Setup Menu ..................A-13
Menu ACAL_S11 1 PORT, AutoCal S11 1 Port Menu .............A-14
Menu ACAL_S22 1 PORT, AutoCal S22 1 Port Menu .............A-15
Menu ACAL_FULL, AutoCal Full Menu ....................A-16
Menu ACAL_AR, AutoCal Adapter Removal Menu ..............A-17
Menu ACAL_UTILS, AutoCal Utilities Menu .................A-18
Menu ACAL_CHAR, AutoCal Characterization Menu.............A-19
Menu APPL, Applications Menu ........................A-20
Menu BB2, Broadband Select Menu1......................A-21
Menu BB3, Broadband Select Menu 2 .....................A-22
Menu BB4, Broadband Select Menu3......................A-23
Menu BW1 or CAL_BW1, Select Video Bandwidth ..............A-24
Menu C1, Select Calibration Data Points....................A-25
Menu C2, Frequency Range of Calibration (Start/Stop) ............A-26
Menu C2_CENTER, Frequency Range of Calibration (Center/Span) .....A-27
Menu C2A, Insert Individual Frequencies ...................A-28
Menu C2C, Calibration Range—Harmonic Cal for Time Domain .......A-29
Menu C2B, Single Point Calibration ......................A-29
Menu C2D, Fill Frequency Ranges .......................A-30
Menu C3, Confirm Calibration Parameters...................A-31
Menu C3A, Confirm Calibration Parameters..................A-32
Menu C3B, Confirm Calibration Parameters..................A-33
Menu C3C, Confirm Calibration Parameters..................A-34
37XXXC OM A-1
Appendix A
Front Panel Menus,
Alphabetical Listing
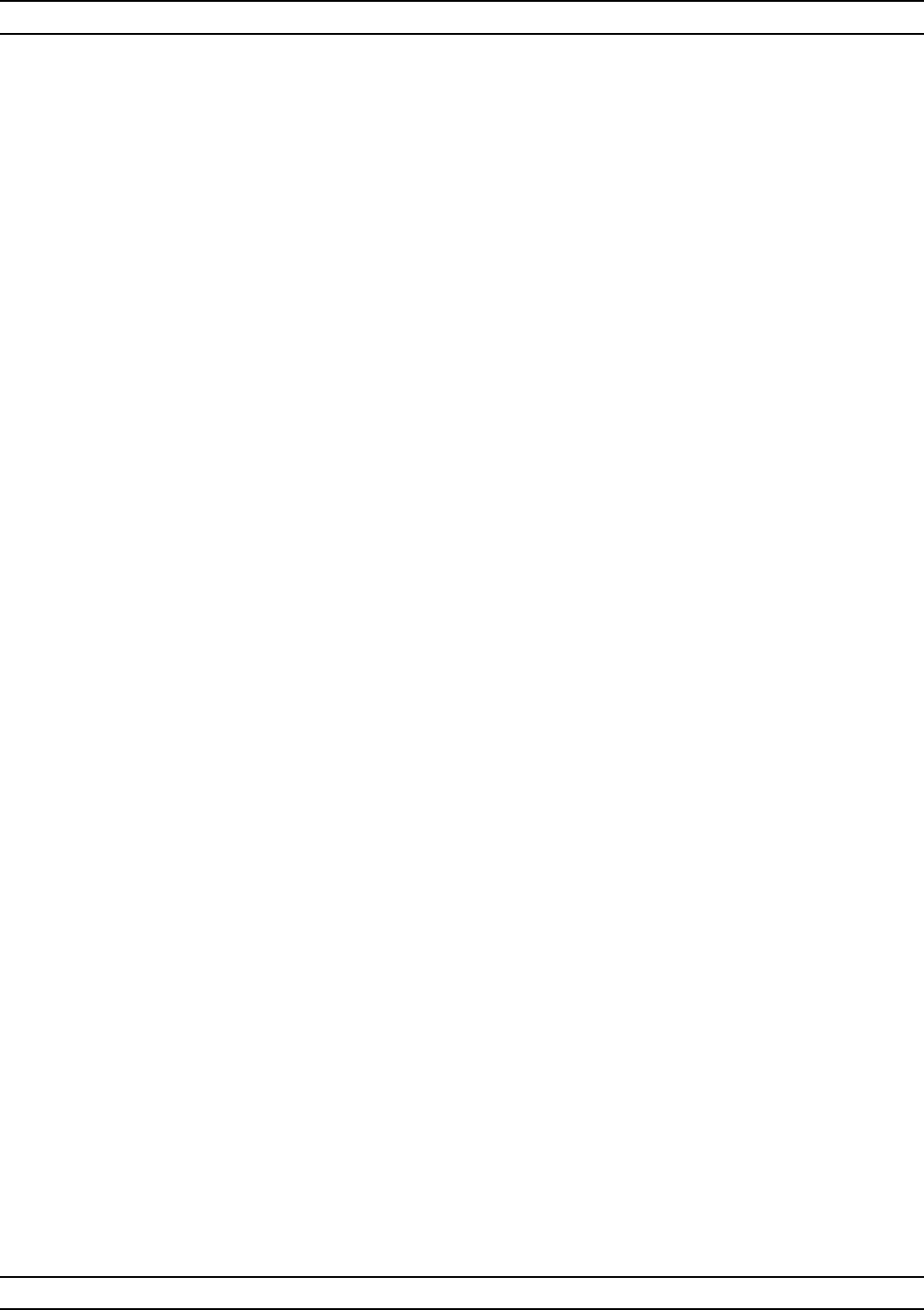
Menu C3D, Confirm Calibration Parameters..................A-35
Menu C3E, Confirm Calibration Parameters..................A-36
Menu C3F, Confirm Calibration Parameters ..................A-37
Menu C3G, Confirm Calibration Parameters..................A-38
Menu C3H, Confirm Calibration Parameters..................A-39
Menu C3I, ConfirmCalibration Parameter 2 ..................A-40
Menu C3J, ConfirmCalibration Parameter 3 ..................A-41
Menu C4_P1/C4_P2, Select Connector Type ..................A-42
Menu C4A_P1/C4A_P2, Select Connector Type ................A-43
Menu C4B, Select Open and Short Type ....................A-44
Menu C5, Select Calibration Type .......................A-45
Menu C5A, Select 1 Path 2 Port Calibration Type ...............A-46
Menu C5B, Select Transmission Freq Response Calibration Type ......A-46
Menu C5C, Select Reflection Only Calibration Type..............A-47
Menu C5D, Select Use of Isolation .......................A-47
Menu C6, Select Load Type ...........................A-48
Menu C6A, Enter Broadband Load Impedance.................A-48
Menu C6B, Enter Broadband Load Impedance.................A-48
Menu C7-Series, Begin Calibration Sequence .................A-49
Menu C8, Slide Load to Position X .......................A-49
Menu C9A, Connect Device 1, Line .......................A-50
Menu C9, Connect Throughline .........................A-50
Menu C9C, Connect Device 2, Line .......................A-51
Menu C9B, Connect Device 2, Line/Lowband..................A-51
Menu C11, Begin Calibration ..........................A-52
Menu C11A, Select Calibration Method ....................A-53
Menu C12_P1/C12_P2, Enter the Capacitance Coefficients for Open Devices A-54
Menu C12A_P1/C12A_P2, Enter the Offset Length ..............A-55
Menu C13, Set Reflection Pairing Menu ....................A-56
Menu C13A, Set Reflection Pairing Menu ...................A-57
Menu C13B, Set Reflection Pairing Menu ...................A-57
Menu C14, Select Port X Offset Short Connecotr Type.............A-58
Menu C14A, Select Port X Offset Short.....................A-58
A-2 37XXXC OM
CONTENTS ALPHABETICAL LISTING
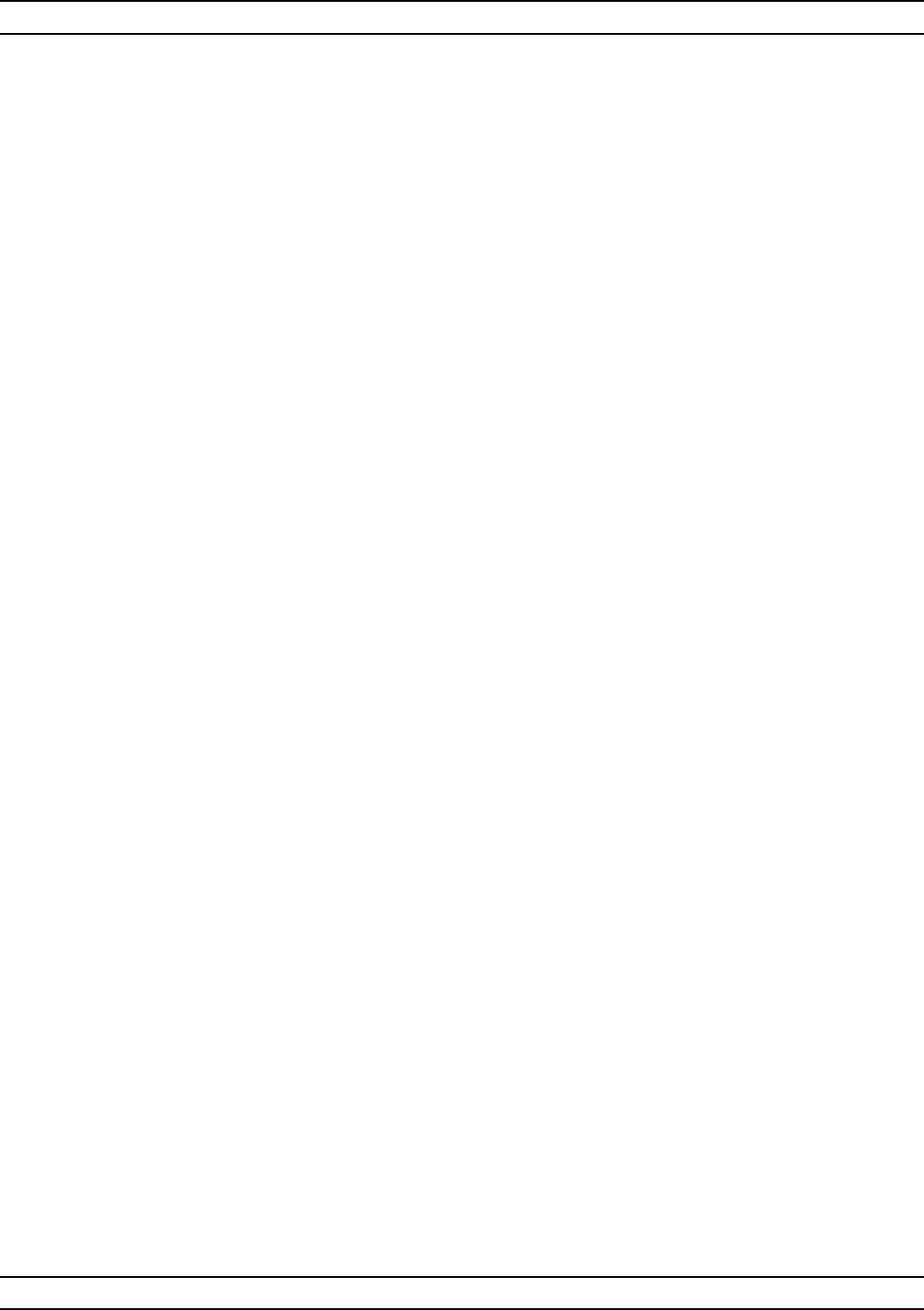
Menu C15, Select Waveguide Kit to Use ....................A-59
Menu C15A, Enter Waveguide Parameters...................A-60
Menu C15B, Enter Waveguide Parameters...................A-60
Menu C15C, Select Waveguide Kit to Use ...................A-61
Menu C15D, Enter Waveguide Parameters...................A-62
Menu C16A, Enter Microstrip Parameters ...................A-63
Menu C16, Select Microstrip Parameters....................A-63
Menu C17, Enter Line Impedance .......................A-64
Menu C18, Change LRL/LRM Parameters ...................A-64
Menu C18A, Change LRL/LRM Parameters ..................A-65
Menu C18B, Change LRL/LRM Parameters—Two Band Calibration.....A-66
Menu C19, Change LRL/LRM Parameters ...................A-67
Menu C20, Change Through Parameters ....................A-68
Menu C21A, Port X Offset Short 1 .......................A-69
Menu C21B, Port X Offset Short 2 .......................A-70
Menu C21C, Port X Offset Short 3 .......................A-71
Menu Cal_Completed ..............................A-72
Menu Cal_Applied ................................A-73
Menu Cal_EM, Enhancement Menu for Calibration ..............A-74
Menu CAR1, Adapter Removal 1 ........................A-75
Menu CAR2, Adapter Removal 2 ........................A-75
Menu EXT_CAR, Adapter Removal Help Menu ................A-76
Menu CAR3, Adapter Removal 3 ........................A-77
Menu CAR4, Adapter Removal 4 ........................A-77
Menu CM, Select Display Mode .........................A-78
Menu DE1, E/O Measurement .........................A-79
Menu EXT_DE1, E/O Measurement ......................A-79
Menu DE2, O/E Measurement .........................A-80
Menu EXT_DE2, O/E Measurement ......................A-80
Menu DE3, E/O Measurement .........................A-81
Menu DE3A, E/O Measurement.........................A-81
Menu DE4, De-embed Network .........................A-82
Menu DE4A, De-embed Network ........................A-82
ALPHABETICAL LISTING CONTENTS
37XXXC OM A-3
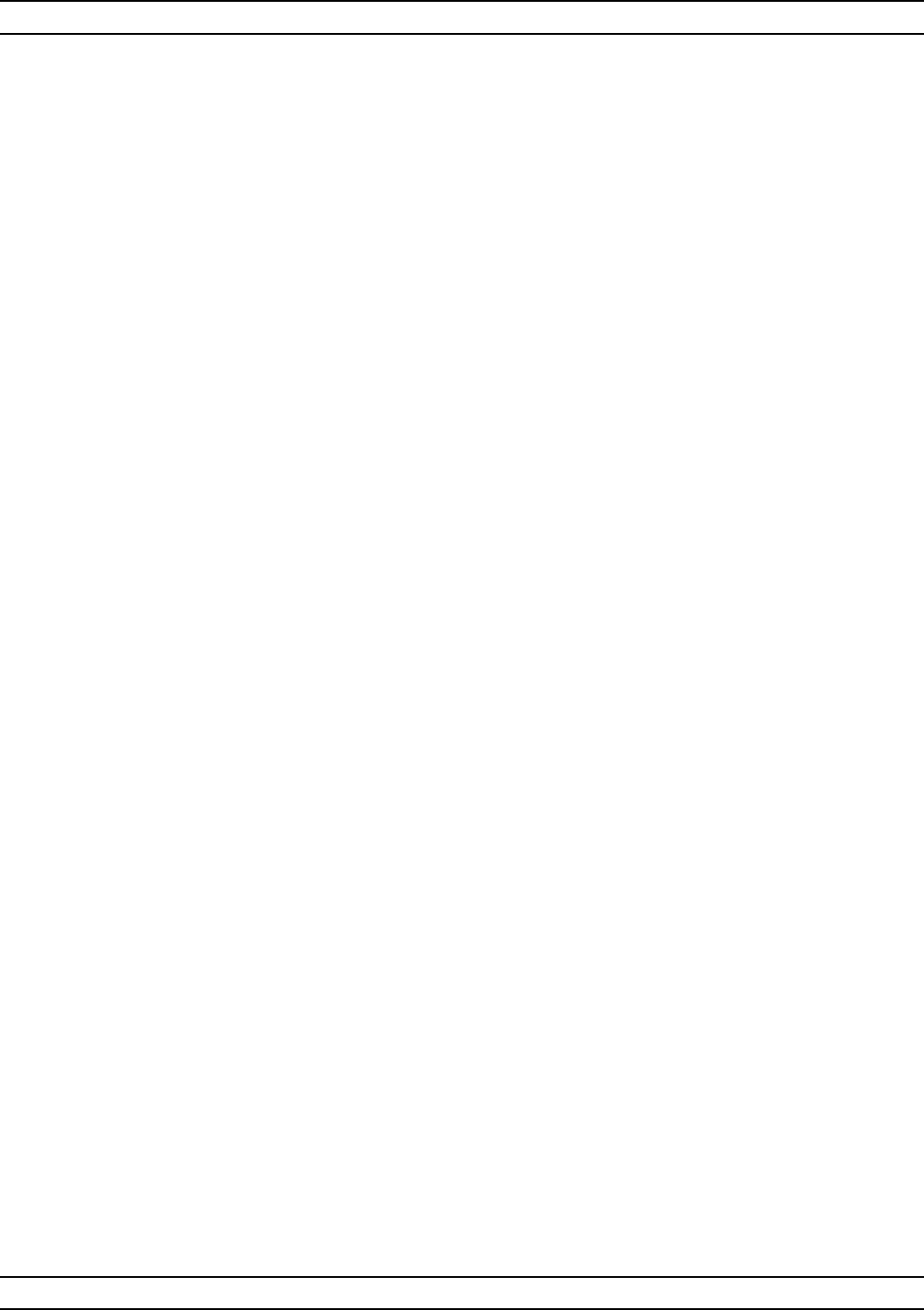
Menu DE5, De-embed O/E S2P .........................A-83
Menu DE5A, De-embed O/E S2P ........................A-83
Menu DE6, Generate E/O S2P Characterization................A-84
Menu DE7, O/E Measurement .........................A-85
Menu DE7A, O/E Measurement.........................A-85
Menu DF1, Discrete Fill .............................A-86
Menu DF2, Insert Individual Frequencies ...................A-87
Menu DFLT, Default Program Selected.....................A-88
Menu DG1, Diagnostics 1 ............................A-89
Menu DG3, Diagnostics 3 ............................A-90
Menu DG2, Troubleshooting...........................A-90
Menu DSK_FD, Floppy Disk Utilities......................A-91
Menu DSK_HD, Hard Disk Utilities ......................A-92
Menu DSK2, Select File to Read ........................A-93
Menu DSK3, Select File to Overwrite......................A-94
Menu DSK6, Type of Files to Delete ......................A-95
Menu DSK7, Select File to Delete........................A-96
Menu DSK8, Type of Files to Copy .......................A-97
Menu DSK9, Select File to Copy ........................A-98
Menu DSK10, Capture Tabular Data ......................A-99
Menu DSK11, Format Floppy Disk .......................A-99
Menu DSK12, Format Hard Disk ........................A-99
Menu EM, Enhancement Menu ........................A-100
Menu GC1, Swept Frequency Gain Compression ...............A-101
Menu EXT_GC1, Gain Compression Help Menu 1 ..............A-102
Menu GC2, Swept Power Gain Compression 1 ................A-103
Menu EXT_GC2, Gain Compression Help Menu 2 ..............A-104
Menu GC3, Swept Power Gain Compression 2 ................A-105
Menu EXT_GC3, Gain Compression Help Menu 3 ..............A-106
Menu GC4, Multiple Frequency Gain Compression 1 ............A-107
Menu GC4_ABORT, Multiple Frequency Gain Compression 2........A-107
Menu EXT_GC4, Gain Compression Help Menu 4 ..............A-108
Menu GC_DF2, Swept Power Frequencies ..................A-109
A-4 37XXXC OM
CONTENTS ALPHABETICAL LISTING
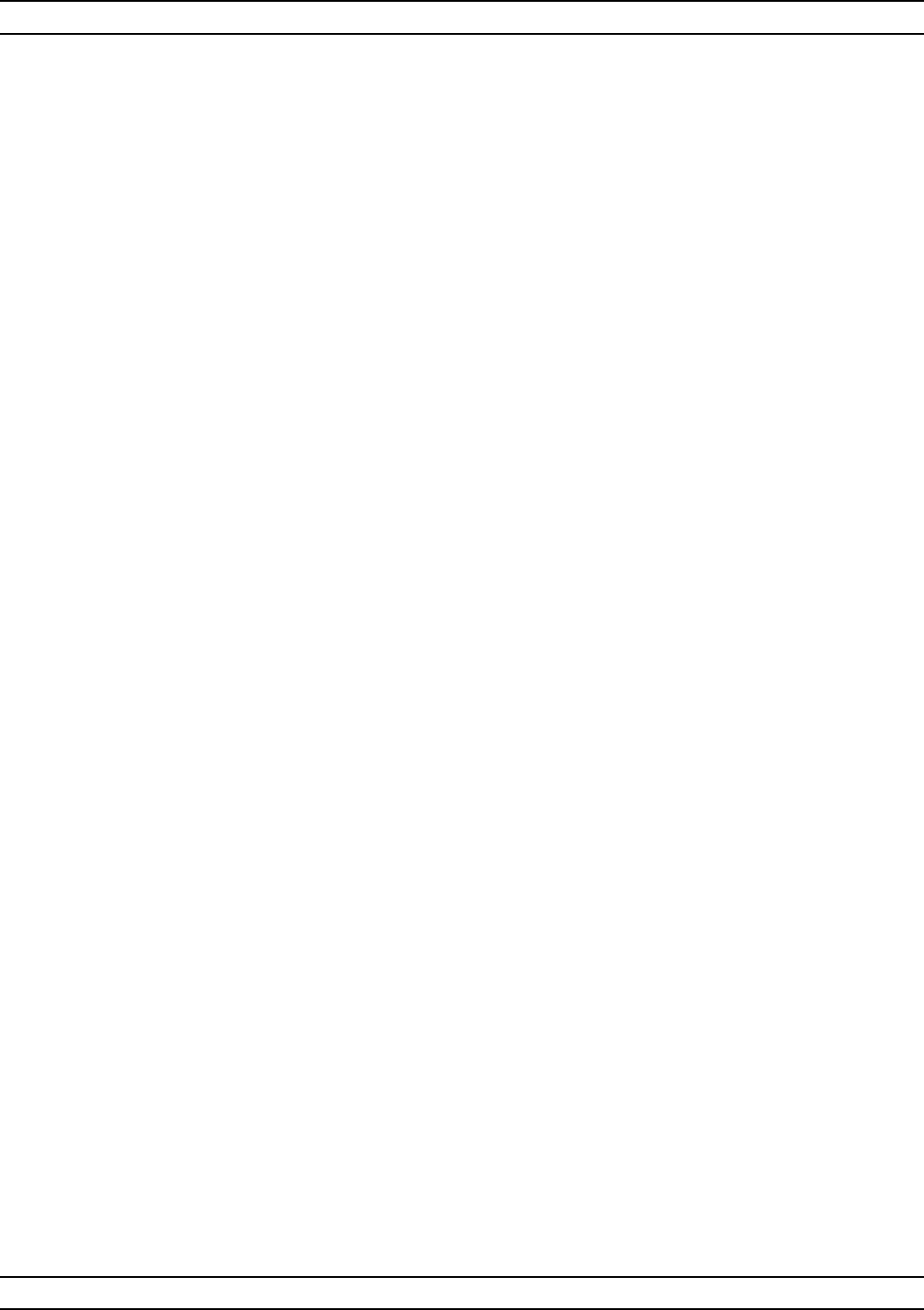
Menu EXT_GC_DF2, Gain Compression Help Menu ............A-110
Menu GC_NORM, Normalize S21 .......................A-110
Menu GC_RCVR, Receiver Calibration ....................A-111
Menu GC_SU2, Swept Power Gain Compression 2 ..............A-112
Menu GC_SU8A, Calibrate for Linear Power .................A-113
Menu GC_SU8A-ABORT, Abort Calibrate for Linear Power .........A-114
Menu EXT_GC_SU8A, Gain Compression Help Menu ............A-115
Menu GC_S21OPT, S21 Options ........................A-116
Menu GP5, Select Name ............................A-117
Menu GP7, Display GPIB Status .......................A-118
Menu GT1/CAL_GT1, Select Graph Type ...................A-119
Menu GT2/CAL_GT2, Select Graph Type ...................A-120
Menu L1, Set Limits—Magnitude and Phase .................A-121
Menu L2, Set Limits—Linear Polar ......................A-122
Menu L3, Set Limits—Linear Polar/Smith Chart...............A-123
Menu L4, Set Limits—Log Magnitude.....................A-124
Menu L5, Set Limits—Phase..........................A-125
Menu L6, Set Limits—Log Polar........................A-126
Menu L7, Set Limits—Group Delay ......................A-127
Menu L8, Set Limits—Linear Magnitude ...................A-128
Menu L9, Set Limits—Linear Magnitude and Phase ............A-129
Menu L10, Set Limits—Real Values......................A-130
Menu L11, Set Limits—Imaginary Values ..................A-131
Menu L12, Set Limits—Real and Imaginary Values .............A-132
Menu L13, Set Limits—SWR .........................A-133
Menu L14, Set Limits—Power Out ......................A-134
Menu LD1, Define Upper Limit Segment ...................A-135
Menu LD2, Define Lower Limit Segmen ...................A-136
Menu LF1, Set Limit Frequencies—Log Mag .................A-137
Menu LF2, Set Limit Frequencies—Phase ..................A-138
Menu LF3, Set Limit Frequencies—Group Delay...............A-139
Menu LF4, Set Limit Frequencies—Linear Mag ...............A-140
Menu LF5, Set Limit Frequencies—SWR ...................A-141
ALPHABETICAL LISTING CONTENTS
37XXXC OM A-5
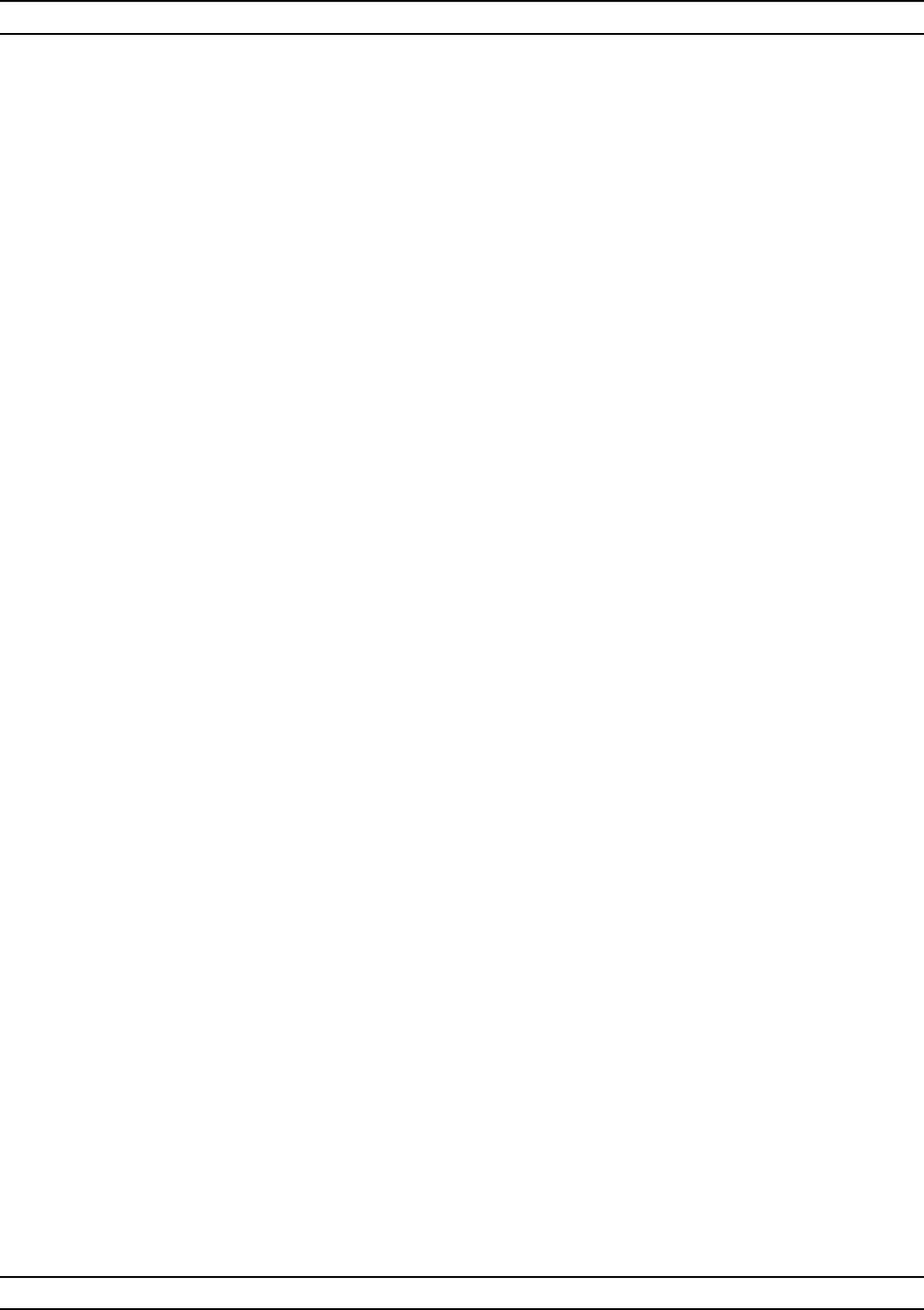
Menu LF6, Set Limit Frequencies—Real ...................A-142
Menu LF7, Set Limit Frequencies—Imaginary ................A-143
Menu LF8, Set Limit Frequencies—Power Out ................A-144
Menu LSX, Segmented Limits .........................A-145
Menu LTST, Test Limits ............................A-146
Menu M1, Set Markers ............................A-147
Menu M2, Select DREF Marker ........................A-148
Menu M3, Select Readout Marker .......................A-149
Menu M4, Readout Marker ..........................A-150
Menu M5, Set DREF Marker Readout.....................A-151
Menu M6, Marker X All Displayed Channels .................A-152
Menu M7, Search ................................A-153
Menu M8, Filter Parameters..........................A-154
Menu M8A, Filter Setup ............................A-155
Menu M9, Marker Readout Functions.....................A-156
Menu MMW1, Millimeter Wave Test Set Band ................A-157
Menu MMW2, Millimeter Wave Test Set Modules ..............A-158
Menu MMW3, Millimeter Wave Test Set ...................A-159
Menu MMW4, mm Wave Band.........................A-160
Menu EXT_MMW4 ...............................A-161
Menu MRG1, Merge Calibration Menu ....................A-162
Menu EXT_MRG1, Merge Calibration Menu .................A-162
Menu MRG2, Merge Calibration Menu ....................A-163
Menu MRG3, Merge Calibration Menu ....................A-163
Menu NO1, Trace Memory Functions .....................A-164
Menu NO2, Select Trace Math.........................A-165
Menu NO3, Trace Memory Disk Functions ..................A-165
Menu OM1, Multiple Source Control Menu ..................A-166
Menu OM1A, Source Lock Polarity Menu ...................A-167
Menu OM2, Define Bands Menu........................A-168
Menu OM3, Edit System Equations ......................A-169
Menu OPTNS, Select Options .........................A-170
Menu ORP1, Rear Panel Output Control ...................A-171
A-6 37XXXC OM
CONTENTS ALPHABETICAL LISTING
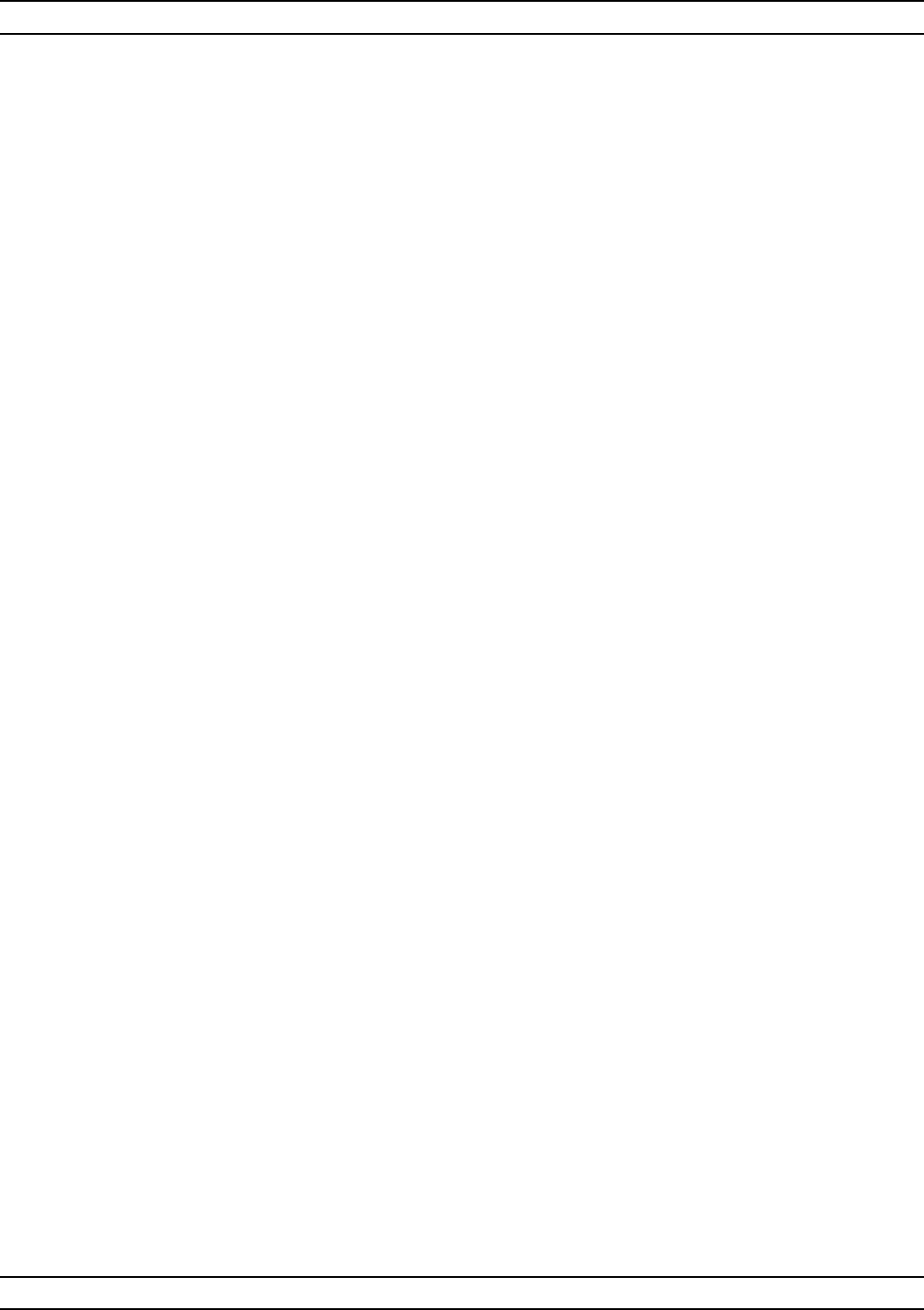
Menu ORP2, Select Output Mode .......................A-172
Menu OTS1, Test Set Configuration......................A-172
Menu OTS2, Warning .............................A-173
Menu PC1, Select Polar Chart Mode......................A-174
Menu PD1, Parameter Definition 1 ......................A-175
Menu PD2, Parameter Ratio ..........................A-176
Menu PD3, Parameter Definition 2 ......................A-177
Menu PL1, Plot Options ............................A-178
Menu PL2, Select Plot Size...........................A-179
Menu PL3, Select Pen Colors..........................A-180
Menu PM1, Select Data Output Type .....................A-181
Menu PM2, Data Output Headers.......................A-182
Menu PM2A, Data Output Headers ......................A-183
Menu PM3, Tabular Printer Output Format .................A-184
Menu PM3A, Graphical Printer Output Format ...............A-185
Menu PM4, Disk Output Operations .....................A-186
Menu PM4A, Disk File Options ........................A-187
Menu PM5, Printer Type, Options.......................A-188
Menu RCV1, Receiver Mode ..........................A-189
Menu RCV1_WARN, Standard Receiver Mode Warning ...........A-189
Menu RCV2, User Defined Receiver Mode Menu ...............A-190
Menu RCV2_WARN, User Defined Receiver Mode Warning .........A-191
Menu RCV3, Standard Receiver Mode Warning Menu ............A-192
Menu RCV4, User Defined Receiver Mode Warning Menu ..........A-193
Menu RD1, Set Reference Delay ........................A-194
Menu RD2, Set Dielectric Constant ......................A-195
Menu SC, Source Configure ..........................A-196
Menu SP, Select S Parameter .........................A-197
Menu SR1, Save/Recall Front Panel Information ...............A-198
Menu SR2, Recall or Save ...........................A-199
Menu SR3, Save to Internal memory .....................A-200
Menu SS1 or CAL_SS1, Set Scaling 1 .....................A-201
Menu SS2 or CAL_SS2, Set Scaling 2 .....................A-202
ALPHABETICAL LISTING CONTENTS
37XXXC OM A-7
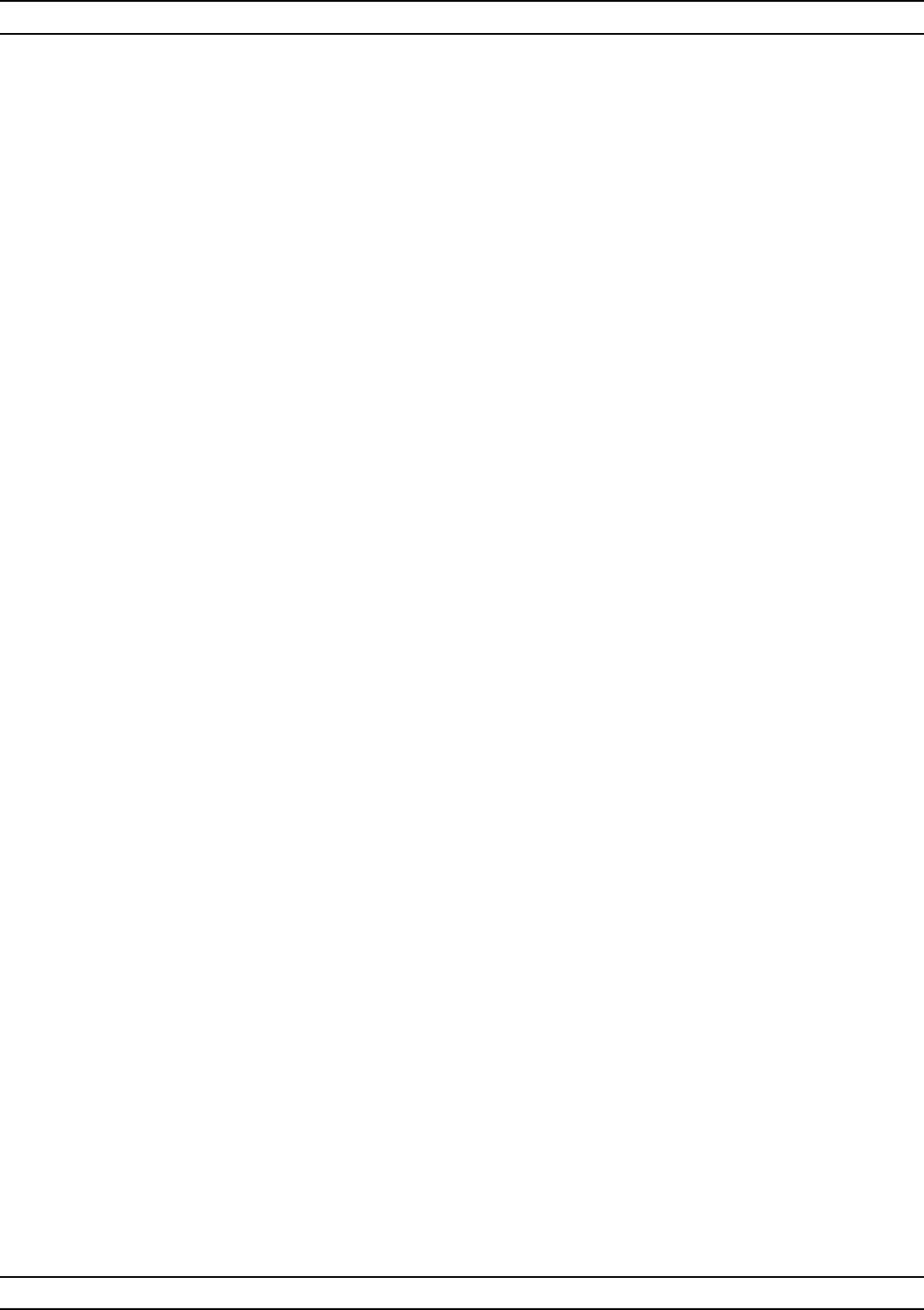
Menu SS3Z/SS3Y or CAL_SS3Z/CALSS3Y, Set Scaling 3 ..........A-203
Menu SS4 or CAL_SS4, Set Scaling 4 .....................A-204
Menu SS5 or CAL_SS5, Set Scaling 5 .....................A-205
Menu SS6 or CAL_SS6, Set Scaling 6 .....................A-206
Menu SS7 or CAL_SS7, Set Scaling 7 .....................A-207
Menu SS8 or CAL_SS8, Set Scaling 8 .....................A-208
Menu SS9 or CAL_SS9, Set Scaling 9 .....................A-209
Menu SS10 or CAL_SS10, Set Scaling 10 ...................A-210
Menu SS11 or CAL_SS11, Set Scaling 11 ...................A-211
Menu SS12 or CAL_SS12, Set Scaling 12 ...................A-212
Menu SS13 or CAL_SS13, Set Scaling 13 ...................A-213
Menu SS14, Set Scaling 14...........................A-214
Menu SU1, Sweep Setup 1 ...........................A-215
Menu SU1_CENTER, Sweep Setup 1 .....................A-216
Menu SU2 or CAL_SU2, Sweep Setup 2....................A-217
Menu SU2A or CAL_SU2A, Sweep Setup 2A .................A-218
Menu SU3, Single-Point Measurement Setup ................A-219
Menu SU3A, Swept-Power Measurement Setup ...............A-220
Menu SU4, Select Function for Hold Button .................A-221
Menu SU5, Frequency Marker Sweep.....................A-222
Menu SU6, Frequency Marker C.W. ......................A-223
Menu SU8 or CAL_SU8, Calibrate For Flat Test Port Power.........A-224
Menu EXT_SU8 Flat Power Calibration Instructions ............A-225
Menu SU9, Number of Data Points ......................A-226
Menu SU9A, Number of Data Points 2 ....................A-227
Menu TD1, Domain (Frequency/Display) ...................A-228
Menu TD2_LP_TIME, Lowpass Time Domain Setup ............A-229
Menu TD2_LP_DIST, Lowpass Distance Display Setup ...........A-230
Menu TD2_BP_TIME, Bandpass Time Domain Setup ............A-231
Menu TD2_BP_DIST, Bandpass Distance Display Setup ..........A-232
Menu TD3_BP, Bandpass Time Domain Setup ................A-233
Menu TD3_LP, Lowpass Time Domain Setup ................A-233
Menu TD4_TIME & TD4_DIST, Gate (Distance/Time) ...........A-234
A-8 37XXXC OM
CONTENTS ALPHABETICAL LISTING
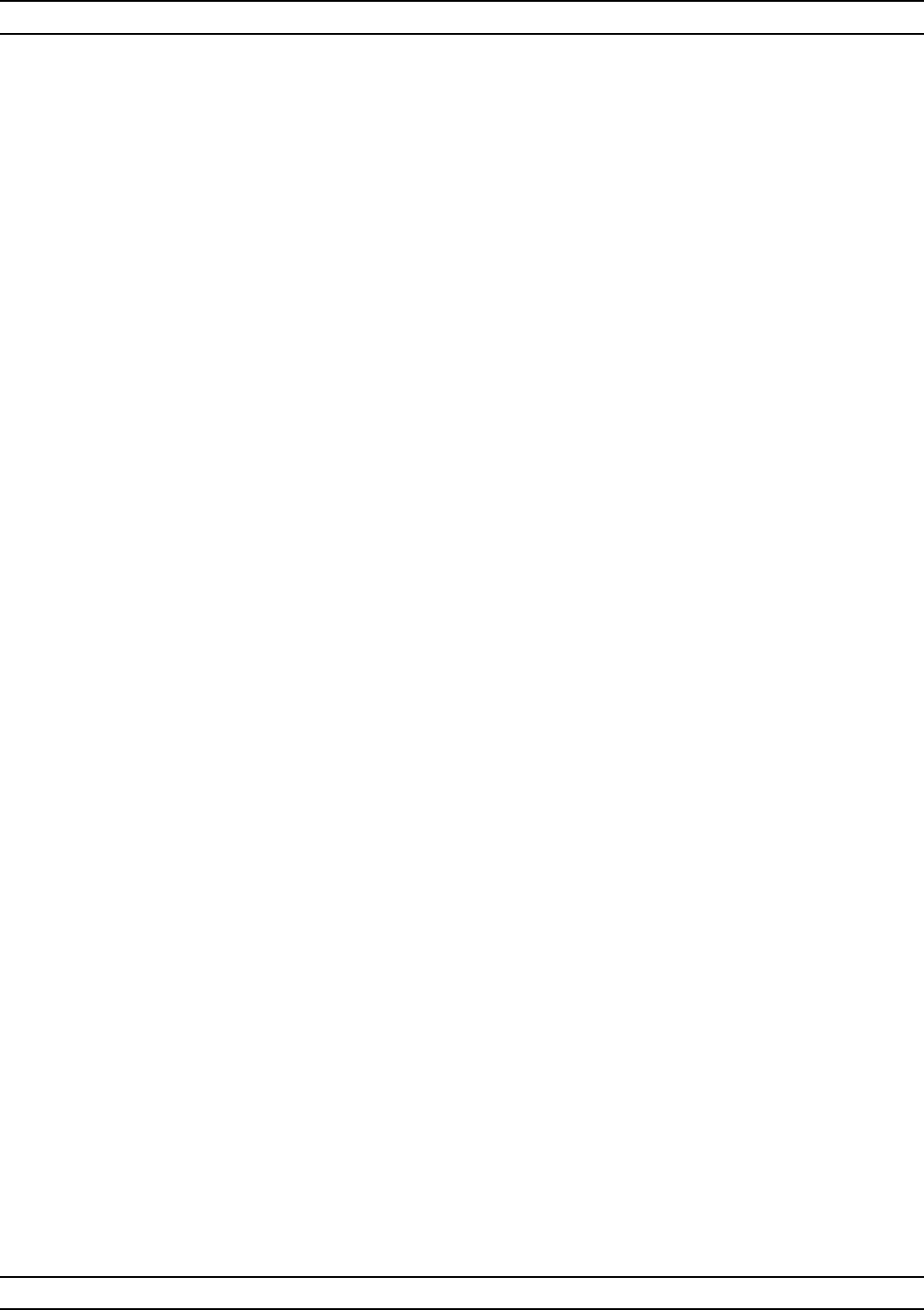
Menu TD5_WINDOW, Shape .........................A-235
Menu TD5_GATE, Shape............................A-235
Menu TD6, Set D.C. Term for Low Pass Processing .............A-236
Menu TD7_TIME, Time Marker Sweep. ...................A-237
Menu TD7_DIST, Distance Marker Range ..................A-238
Menu TRIG, Triggers Measurement......................A-239
Menu U1, Utility Menu.............................A-240
Menu U2, Display Instrument State......................A-241
Menu U3, Calibration Component Utilities ..................A-243
Menu EXT_U3, SSLT and SSST Waveguide Parameters...........A-243
Menu U4, Display Installed Calibration Components Information 1 ....A-244
Menu EXT_U4, SOLT Calibration Kit Information..............A-245
Menu U4A, Display Installed Calibration Components Information 2 . . . A-246
Menu U4B, Display Installed Calibration Components Information 3....A-247
Menu EXT_U4B, SSLT and SSST Calibration Kit Information .......A-248
Menu U5, Color Configuration.........................A-249
Menu U5, Color Configuration.........................A-250
Menu U6, Set Date/Time ............................A-251
372XXC, 373XXC Rear Panel...........................B-4
371XXC Rear Panel ................................B-4
Pinout Diagram, GPIB and Dedicated GPIB Connectors ............B-6
Pinout Diagram, Printer Connector (1 of 2) ...................B-7
Pinout Diagram, Printer Connector (2 of 2) ...................B-8
Pinout Diagram, External I/O Connector (1 of 2) ................B-9
Pinout Diagram, External I/O Connector (2 of 2)................B-10
Pinout Diagram, VGA IN/OUT Connector ...................B-11
Pinout Diagram, Serial Port Connector ....................B-12
Pinout Diagram, Transfer Switch .......................B-13
Pinout Diagram, Port 1 Source and Port 2 Test Connectors .........B-14
Pinout Diagram, Test Set Control Out Connector (Option 12) ........B-15
ALPHABETICAL LISTING CONTENTS
37XXXC OM A-9/A-10

Appendix A
Front Panel Menus,
Alphabetical Listing
A-1 INTRODUCTION This appendix provides descriptions for all menu choices. Menus are
arranged in alphabetical order by their name (C1, SU2, DSK1, etc.).
A-2 MENUS A listing of all of the menus contained in this appendix is provided in
the contents section at the beginning of this appendix. This listing
gives the menu's call sign, name, and page number.
37XXXC OM A-11
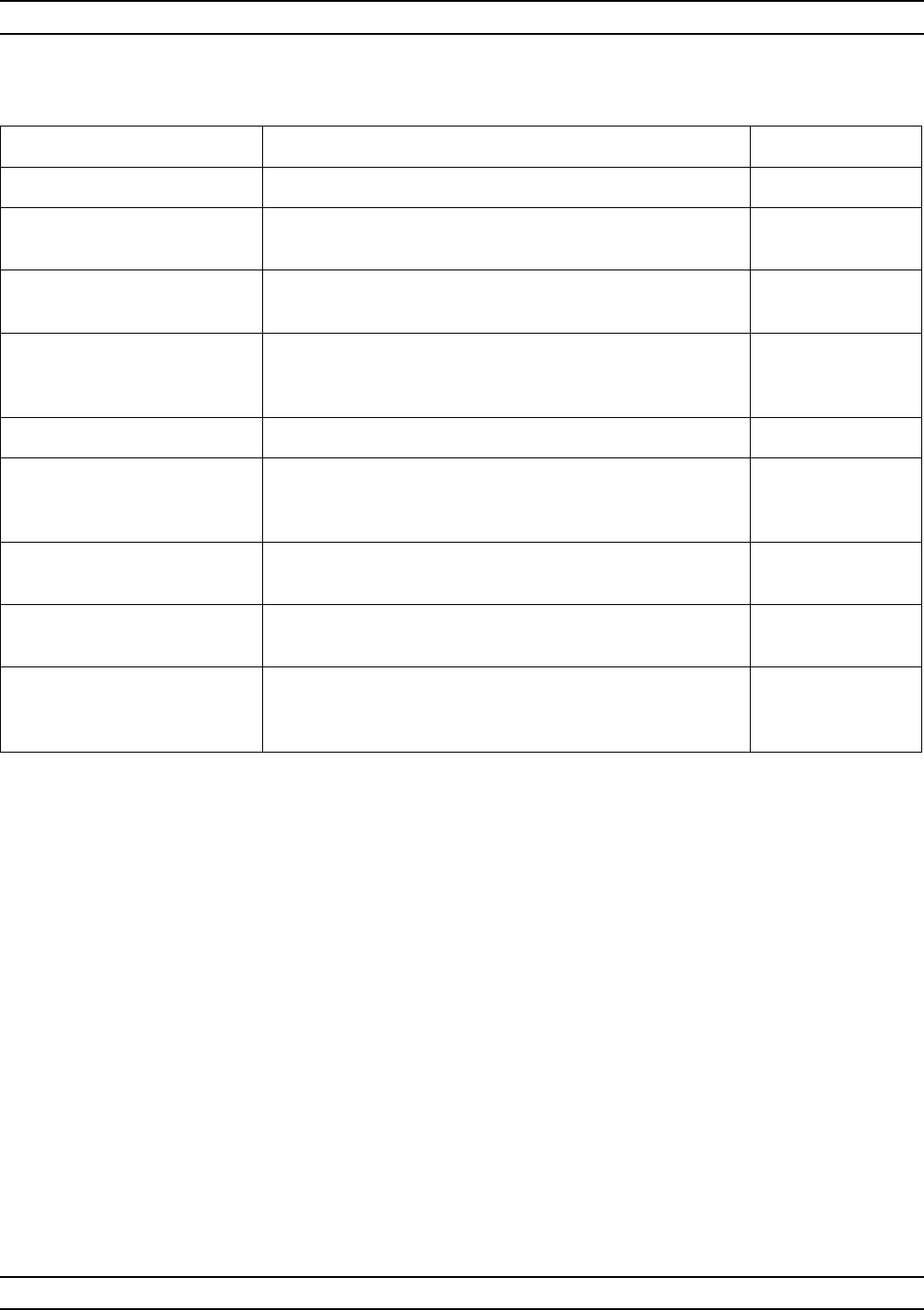
A-12 37XXXC OM
A ALPHABETICAL LISTING
MENU DESCRIPTION GPIB COMMAND
AUTOCAL None
AUTOCAL TYPE
XXXXXXXX Indicates the current type of AutoCal setup. ACF2P?
CHANGE
AUTOCAL SETUP Calls menu ACAL_SETUP, which lets you change the
AutoCal setup. None
START AUTOCAL Calls menu CAL_SEQ, which starts the AutoCal
calibration sequencing immediately using the current
AutoCal setup.
None
THRU UPDATE None
CONNECT THROUGH
LINE BETWEEN
PORTS 1 AND 2
Instruction for connecting the AutoCal to the VNA for Thru
Update. None
NUMBER OF AVGS
XXX Enter the number of averages to be used during the Thru
Update process (default 4 averages). ACTUAVG;
ACTUAVG?
START THRU UPDATE Calls menu CAL_SEQ, which starts the Thru calibration
update. BEGTU
PRESS <ENTER>
TO SELECT
OR SWITCH
Press the Enter key to select or switch. None
Menu ACAL, AutoCal Menu
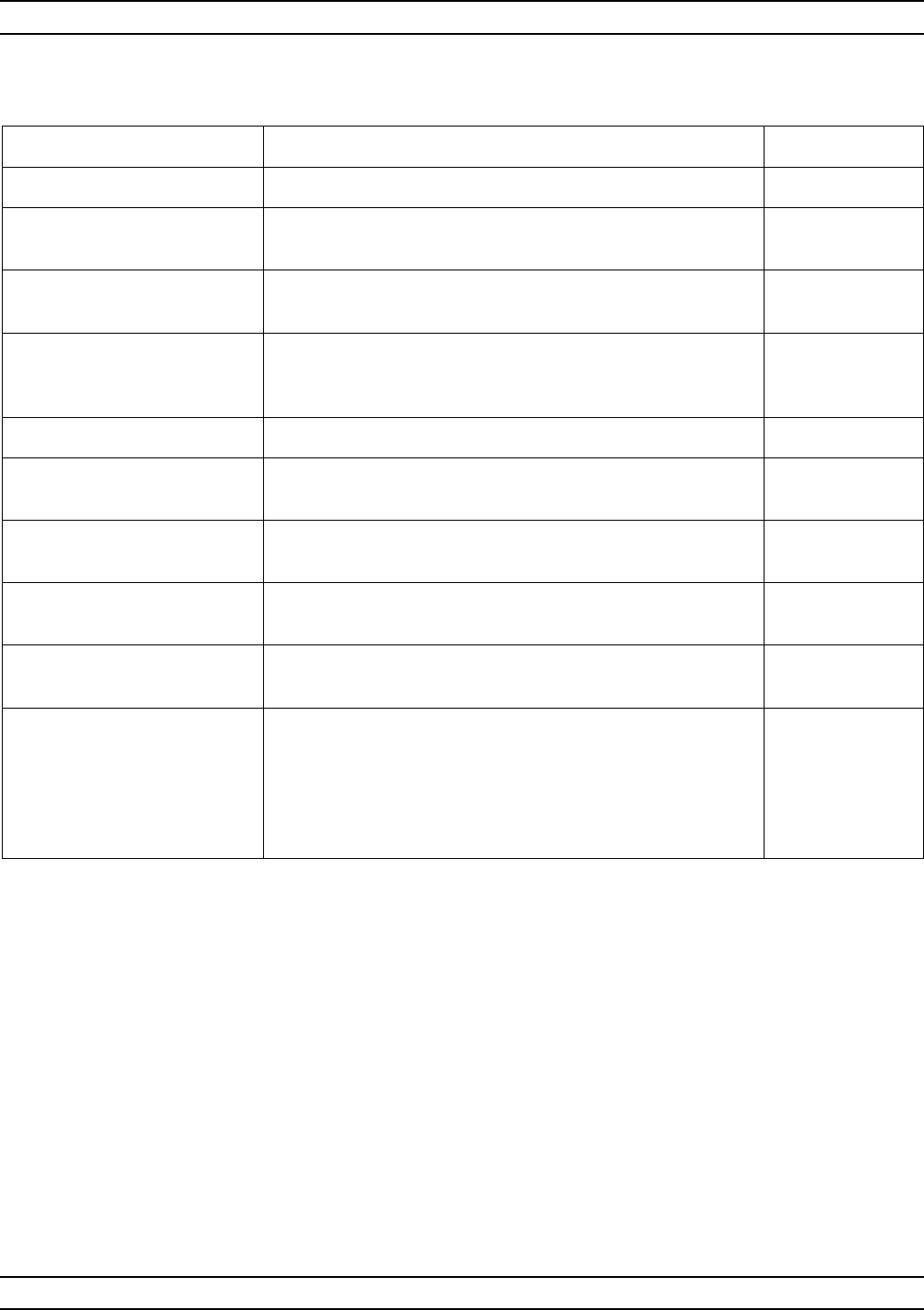
37XXXC OM A-13
ALPHABETICAL LISTING A
MENU DESCRIPTION GPIB COMMAND
AUTOCAL SETUP None
LINE TYPE
COAXIAL/WAVEGUIDE Switch between the line type used with the AutoCal
module. LTC; LTW; LTX?
WAVEGUIDE CUTOFF
XX.XXXXXX GHz Enter the Waveguide Cutoff frequency if the Waveguide
Line Type is selected. WCO; WCO?
SWITCH AVERAGING
XXXX Enter an appropriate amount of SWITCH AVERAGING
(recommend 4 for the electronic modules, and 16 for the
electromechanical modules).
ACSW; ACSW?
NUMBER OF AVGS None
REFLECTION
XXXX Enter the number of averages to be used with the reflection
standards in the AutoCal module (default 10 averages). ACRFL; ACRFL?
LOAD
XXXX Enter the number of averages to be used with the load
standard in the AutoCal module (default 10 averages). ACLO; ACLO?
THRU
XXXX Enter the number of averages to be used with the thru
standard (default 4 averages). ACTU; ACTU?
ISOLATION
XXXX Enter the number of averages to be used with the isolation
standard in the AutoCal module (default 32 averages). ACISO; ACISO?;
ACIAF?; ACIAX?
AUTOCAL TYPES
S11 1 PORT
S22 1 PORT
FULL 2 PORT
ADAPTER REMOVAL
Select the type of AutoCal calibration to perform.
Calls menu ACAL_S11, for more setup.
Calls menu ACAL_S22, for more setup.
Calls menu ACAL_FULL, for more setup.
Calls menu ACAL_AR, for more setup.
ACS11; ACX?
ACS22; ACX?
ACSF2P; ACX?
ACADR; ACX?
Menu ACAL_SETUP, AutoCal Setup Menu
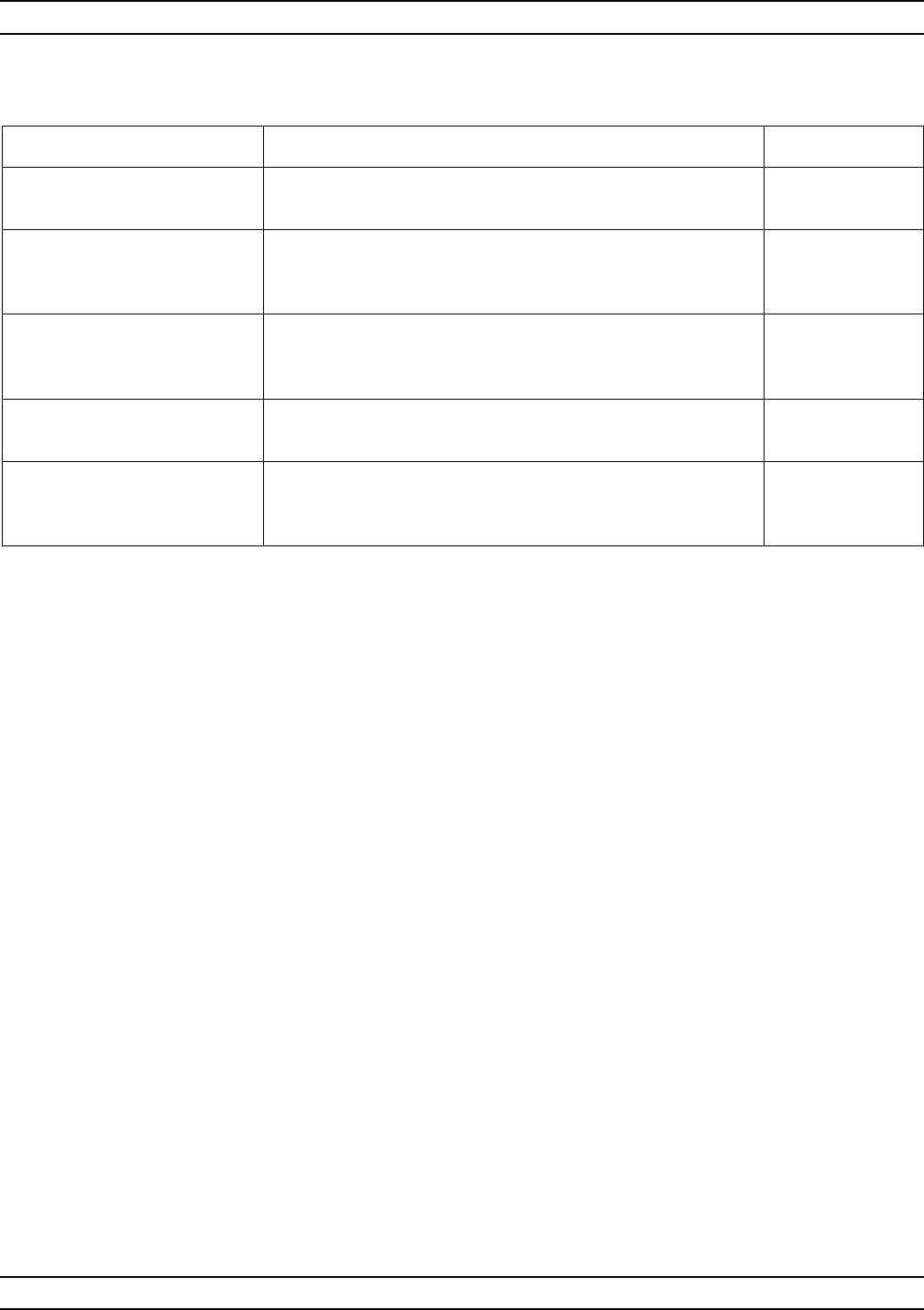
A-14 37XXXC OM
A ALPHABETICAL LISTING
MENU DESCRIPTION GPIB COMMAND
AUTOCAL
S11 1 PORT None
PORT 1
CONNECTION
LEFT/RIGHT
Switch between the side of the AutoCal module which is
connected to Port 1 (default LEFT). ACL1R2; ACR1L2
TEST SIGNALS Calls menu CAL_SU2, which lets you enter calibrate Flat
Test Port Power or change source power(s) and attenuator
settings.
None
START AUTOCAL Calls menu CAL_SEQ, which starts the AutoCal calibration
sequencing. None
PRESS <ENTER>
TO SELECT
OR SWITCH
Press the Enter key to select or switch. None
Menu ACAL_S11 1 PORT, AutoCal S11 1 Port Menu
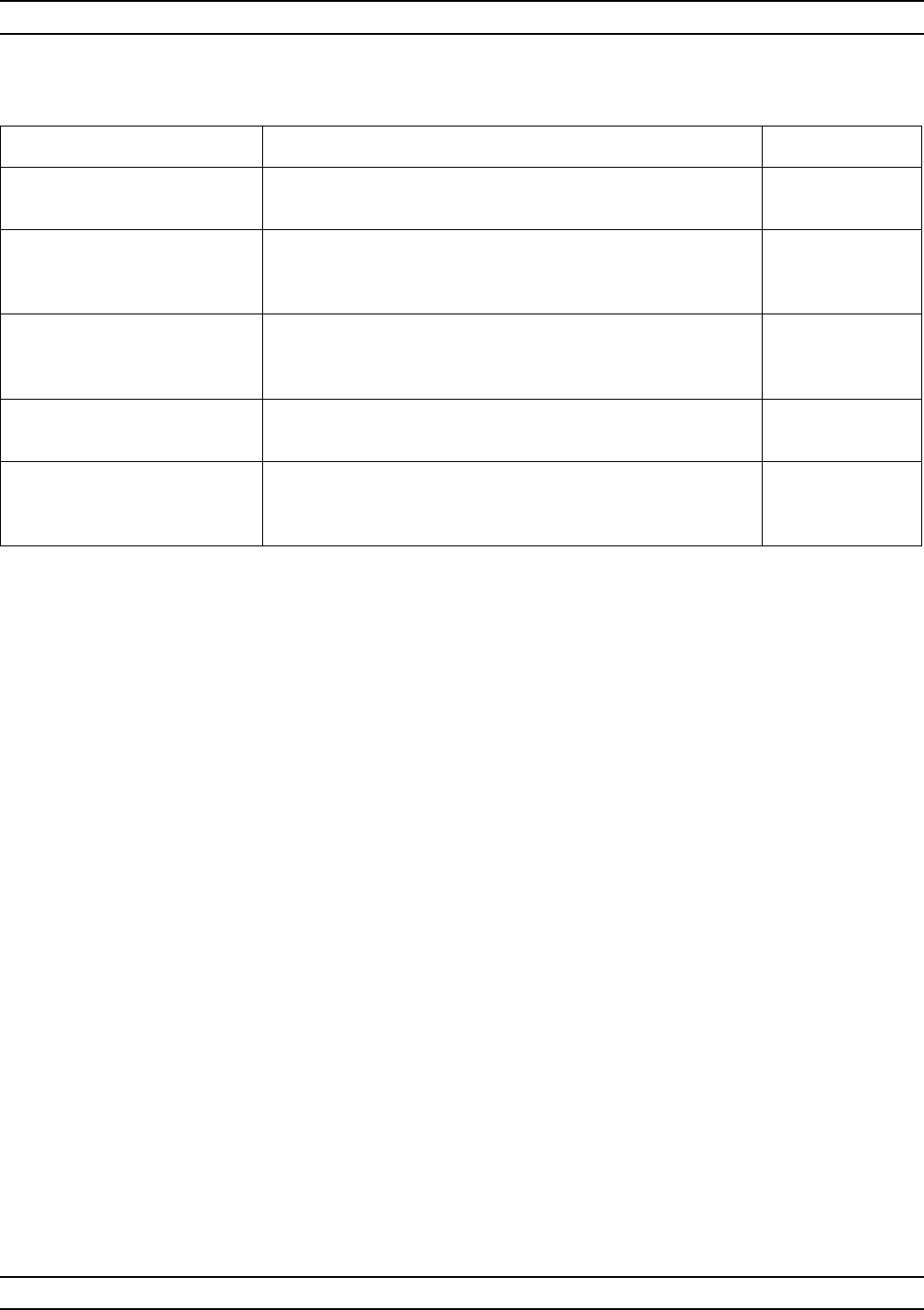
37XXXC OM A-15
ALPHABETICAL LISTING A
MENU DESCRIPTION GPIB COMMAND
AUTOCAL
S22 1 PORT None
PORT 2
CONNECTION
LEFT/RIGHT
Switch between the side of the AutoCal module which is
connected to Port 2 (default RIGHT). ACR1L2; ACL1R2
TEST SIGNALS Calls menu CAL_SU2, which lets you enter calibrate Flat
Test Port Power or change source power(s) and attenuator
settings.
None
START AUTOCAL Calls menu CAL_SEQ, which starts the AutoCal calibration
sequencing. None
PRESS <ENTER>
TO SELECT
OR SWITCH
Press the Enter key to select or switch. None
Menu ACAL_S22 1 PORT, AutoCal S22 1 Port Menu
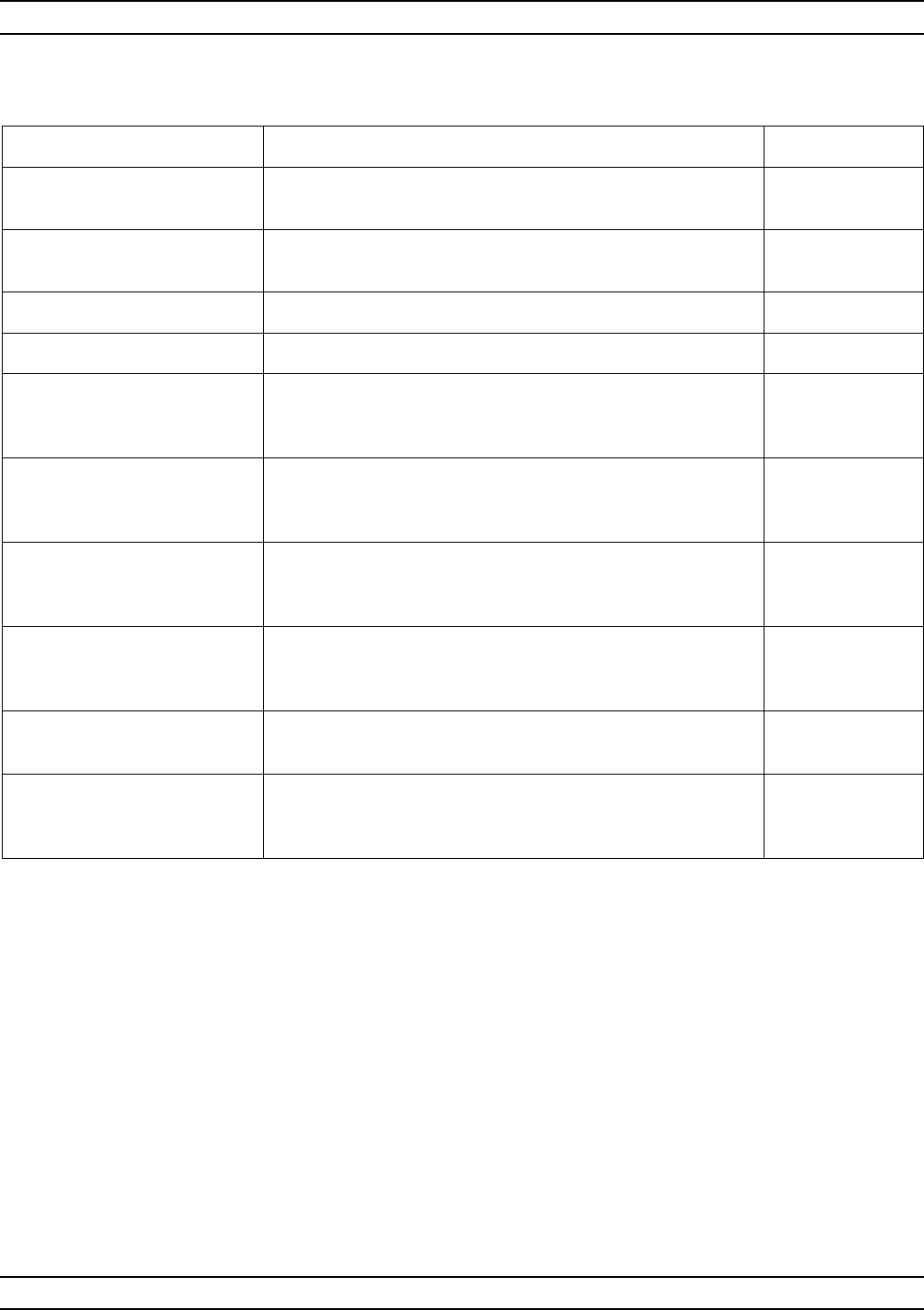
A-16 37XXXC OM
A ALPHABETICAL LISTING
MENU DESCRIPTION GPIB COMMAND
AUTOCAL
FULL 2 PORTS None
ISOLATION
AVERAGING None
OMIT Select to omit the isolation step. ACOMIT
DEFAULT Select to use the Default value during the isolation step. ACDEF
AVERAGING
FACTOR
XXXX
Select for user defined averaging factor during the isolation
step. ACIAF; ACIAF?
THRU TYPE
CALIBRATION/TRUE Switch between the Thru in the AutoCal module
(CALIBRATOR) and your own port-to-port Thru (TRUE) to
be use in the Thru Update (default CALIBRATOR).
ACF2TT;
ACF2TC;
ACF2TX?
PORT CONFIG
L=1, R=2
R=1, L=2
Switch between the side of the AutoCal module which is
connected to Port 1 and Port 2 (default LEFT connected to
Port 1, RIGHT connected to Port 2).
ACL1R2; ACRIL2
TEST SIGNALS Calls menu CAL_SU2, which lets you enter calibrate Flat
Test Port Power or change source power(s) and attenuator
settings.
None
START AUTOCAL Calls menu CAL_SEQ, which starts the AutoCal calibration
sequencing. None
PRESS <ENTER>
TO SELECT
OR SWITCH
Press the Enter key to select or switch. None
Menu ACAL_FULL, AutoCal Full Menu
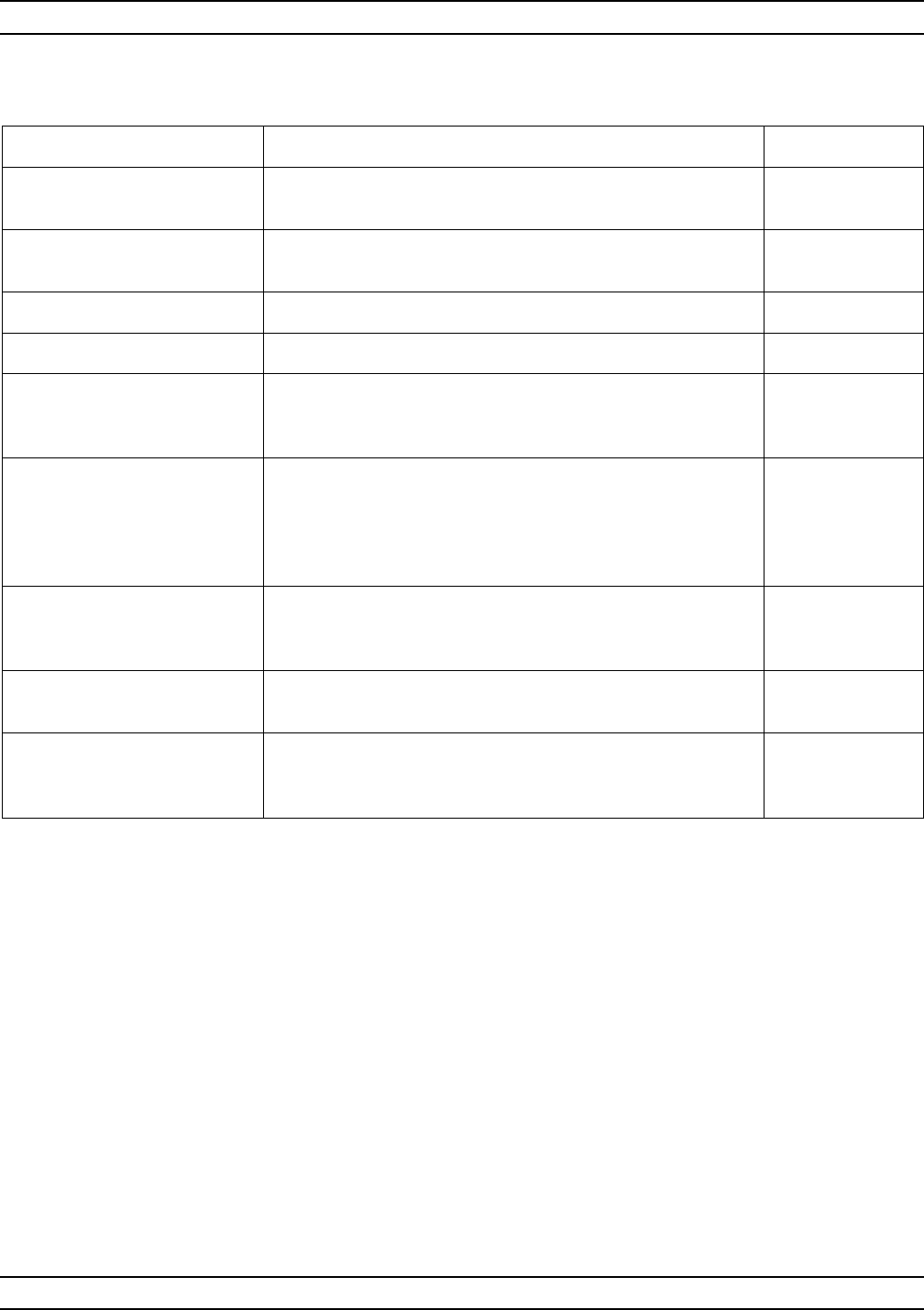
37XXXC OM A-17
ALPHABETICAL LISTING A
MENU DESCRIPTION GPIB COMMAND
AUTOCAL
ADAPTER REMOVAL None
ISOLATION
AVERAGING None
OMIT Select to omit the isolation step. ACOMIT
DEFAULT Select to use the Default value during the isolation step. ACDEF
AVERAGING
FACTOR
XXXX
Select for user defined averaging factor during the isolation
step. ACIAF
PORT CONFIG
ADAPT & L=1, R=2
L=1, ADAPT&R=2
ADAPT&R=1, L=2
R=1, ADAPT & L=2
Switch between the side of the AutoCal module and
adapter which is connected to Port 1 and Port 2 (default
LEFT connected to Adapter which is then connected to
Port 1, RIGHT connected to Port 2).
ACAL1R2;
ACL1AR2;
ACAR1L2;
ACR1AL2;
ACARP?
TEST SIGNALS Calls menu CAL_SU2, which lets you enter calibrate Flat
Test Port Power or change source power(s) and attenuator
settings.
None
START AUTOCAL Calls menu CAL_SEQ, which starts the AutoCal calibration
sequencing. None
PRESS <ENTER>
TO SELECT
OR SWITCH
Press the Enter key to select or switch. None
Menu ACAL_AR, AutoCal Adapter Removal Menu
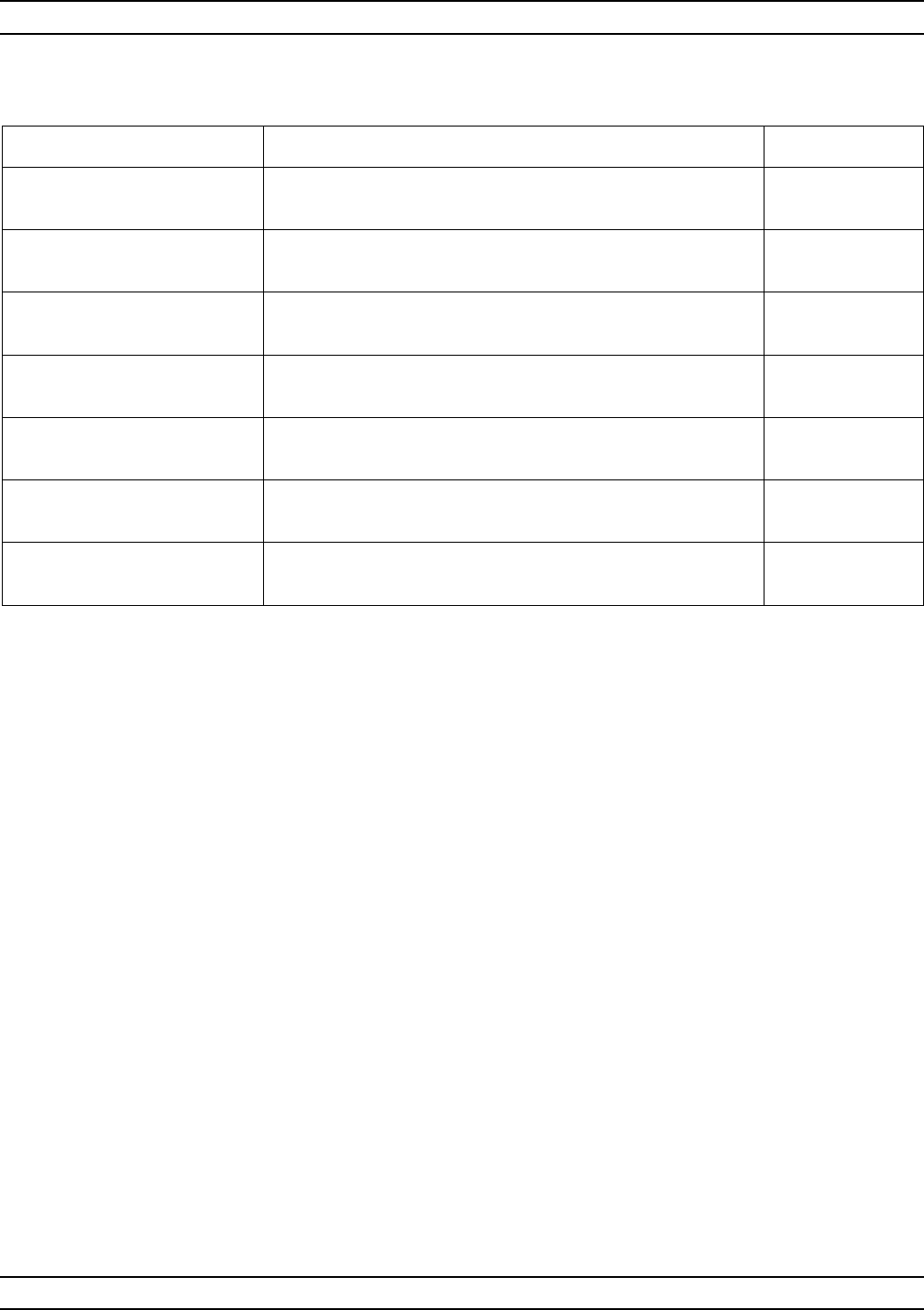
A-18 37XXXC OM
A ALPHABETICAL LISTING
MENU DESCRIPTION GPIB COMMAND
AUTOCAL
UTILITIES None
AUTOCAL
CHARACTERIZATION Calls menu ACAL_CHAR, which lets you set
characterization values. None
SAVE
TO HARD DISK Saves file to the hard disk. SAVE
SAVE
TO FLOPPY DISK Saves file to the floppy disk. SAVE
RECALL
FROM HARD DISK Recalls a file from the hard disk. RECALL
RECALL
FROM FLOPPY DISK Recalls a file from the floppy disk. RECALL
PRESS <ENTER>
TO SELECT Press the Enter key to select. None
Menu ACAL_UTILS, AutoCal Utilities Menu
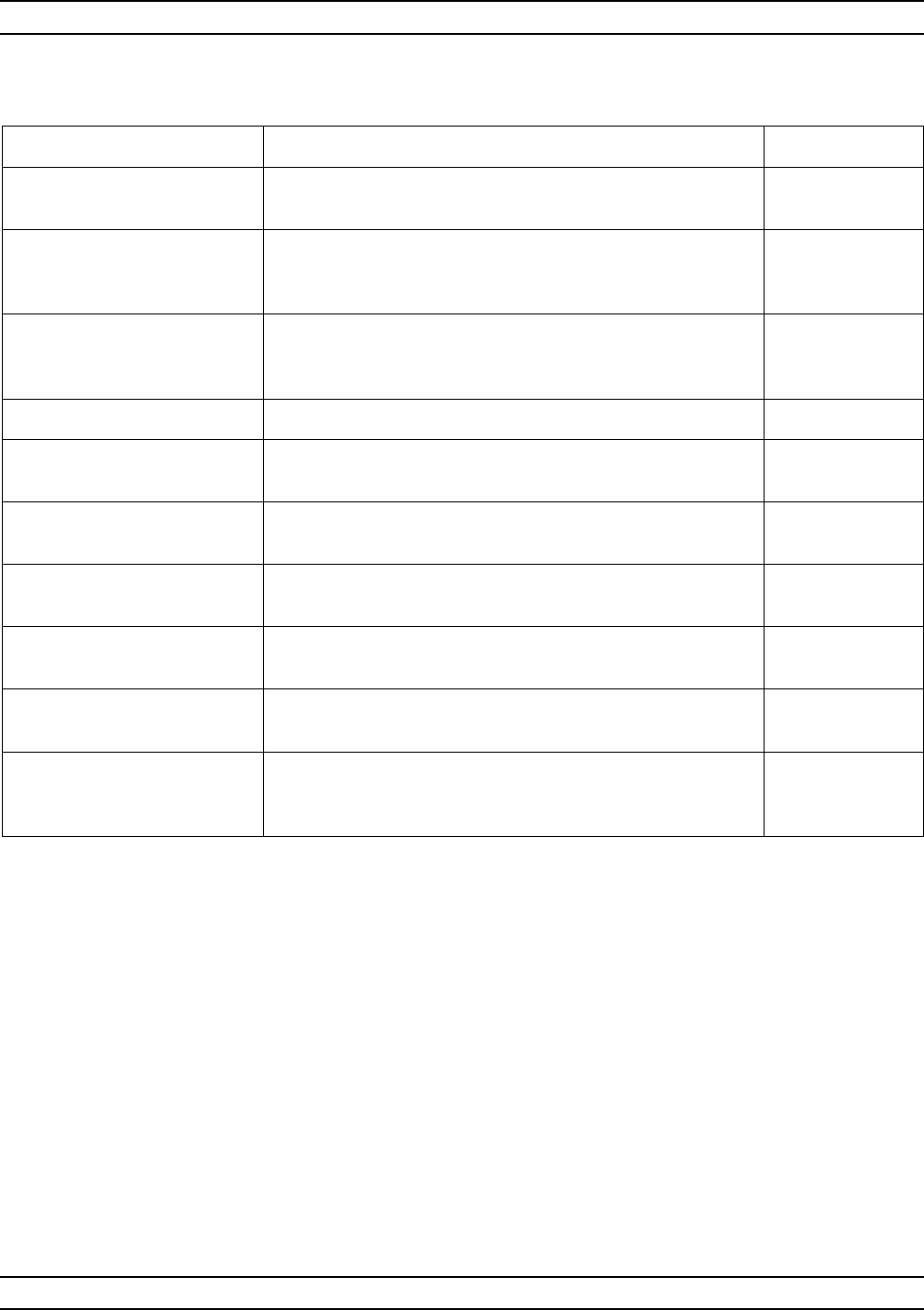
37XXXC OM A-19
ALPHABETICAL LISTING A
MENU DESCRIPTION GPIB COMMAND
AUTOCAL
CHARACTERIZATION None
SWITCH AVERAGING
XXXX Enter an appropriate amount of SWITCH AVERAGING
(recommend 4 for the electronic modules, and 16 for the
electromechanical modules).
ACSW; ACSW?
PORT CONFIG
L=1, R=2
R=1, L=2
Switch between the side of the AutoCal module which is
connected to Port 1 and Port 2 (default LEFT connected to
Port 1, RIGHT connected to Port 2).
ACL1R2;
ACR1L2;
ACARP?
NUMBER OF AVGS None
REFLECTION
XXXX Enter the number of averages to be used with the reflection
standards in the AutoCal module (default 10 averages). ACRFL; ACRFL?
LOAD
XXXX Enter the number of averages to be used with the load
standard in the AutoCal module (default 10 averages). ACLO; ACLO?
THRU
XXXX Enter the number of averages to be used with the thru
standard (default 4 averages). ACTUAVG;
ACTUAVG?
ISOLATION
XXXX Enter the number of averages to be used with the isolation
standard in the AutoCal module (default 32 averages). ACISO; ACISO?
START AUTOCAL
CHARACTERIZATION Calls menu CAL_SEQ, which starts the AutoCal
characterization sequencing. None
PRESS <ENTER>
TO SELECT
OR SWITCH
Press the Enter key to select or switch. None
Menu ACAL_CHAR, AutoCal Characterization Menu
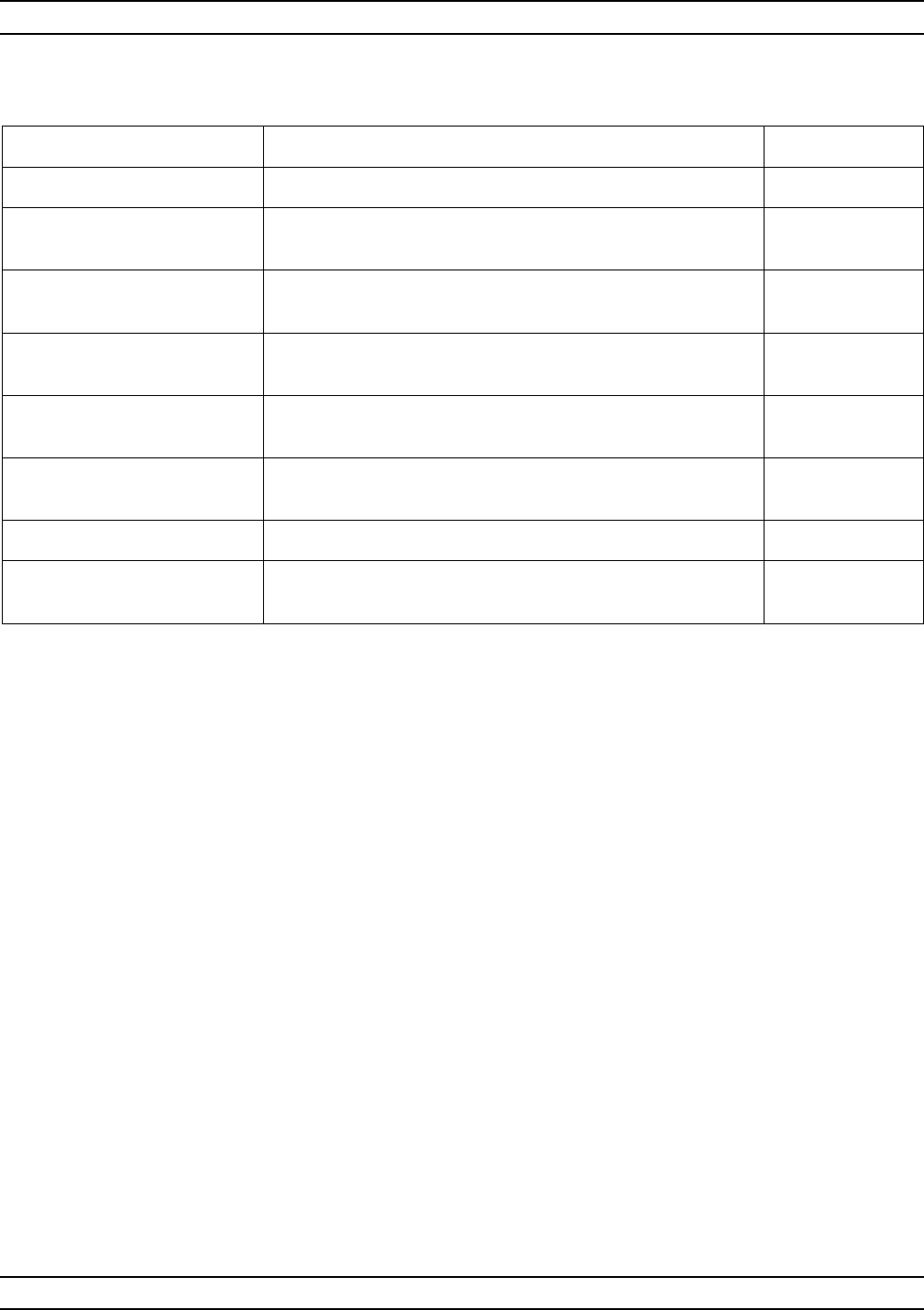
A-20 37XXXC OM
A ALPHABETICAL LISTING
MENU DESCRIPTION GPIB COMMAND
APPLICATIONS None
ADAPTER REMOVAL Calls menu CAR1, which provides options for removing an
adapter. None
SWEPT FREQUENCY
GAIN COMPRESSION Calls menu GC1, which provides options for gain
compression. None
SWEPT POWER
GAIN COMPRESSION Calls menu GC2, which provides options for gain
compression. None
E/O MEASUREMENT Calls menu DE1 and EXT_DE1, which provide information
and options for the E/O measurement application. None
O/E MEASUREMENT Calls menu DE2 and EXT_DE2, which provide information
and options for the O/E measurement application. None
MERGE CAL FILES Calls menu MRG1. None
PRESS <ENTER>
TO SELECT Pressing the ENTER key implements your selection. None
Menu APPL, Applications Menu
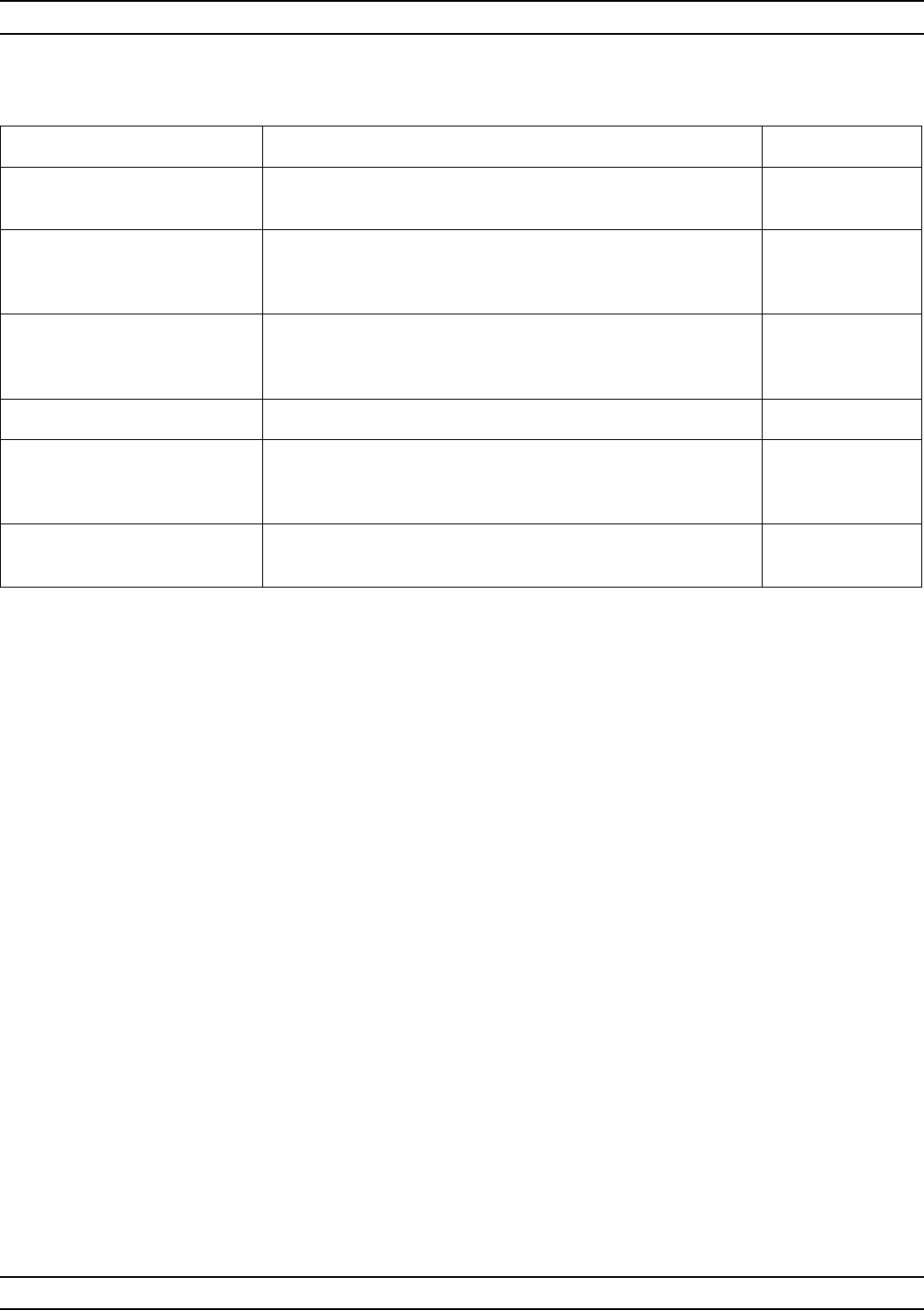
37XXXC OM A-21
ALPHABETICAL LISTING B
MENU DESCRIPTION GPIB COMMAND
BROADBAND
TEST SET MODULES BDMM
PORT 1 MODULE
3740/41/42/NONE Switch selection for port 1 module. The 3742 is standard
for Broadband systems. P1MMT; P1MMR;
P1MMA;P1MMN;
P1MMX?
PORT 2 MODULE
3740/41/42/NONE Switch selection for port 2 module. The 3742 is standard
for Broadband systems. P2MMT; P2MMR;
P2MMA;P2MMN;
P2MMX?
ACCEPT CONFIG Calls menu BB3. None
PRESS <ENTER>
TO SELECT
OR SWITCH
Press the Enter key to select or switch. None
PRESS <CLEAR>
TO ABORT Press the Clear key to abort the selection. None
Menu BB2, Broadband Select Menu1
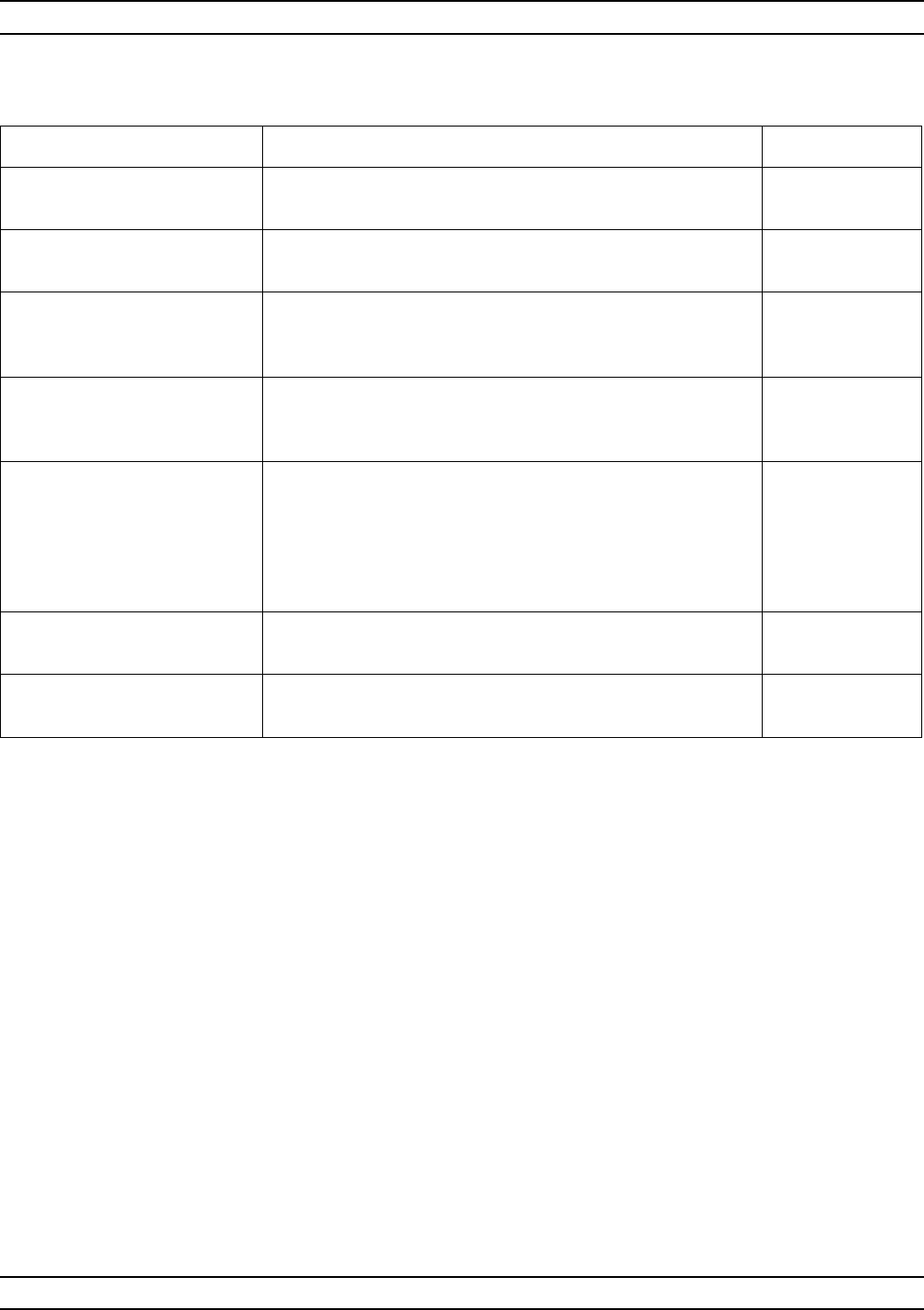
A-22 37XXXC OM
B ALPHABETICAL LISTING
MENU DESCRIPTION GPIB COMMAND
BROADBAND
TEST SET SELBB
BROADBAND BAND 2
WR10 EXTENDED Provides information for selections made in menu BB2
(previous menu). None
PORT 1 MODULE
3742 P1MMT; P1MMR;
P1MMA;P1MMN;
P1MMX?
PORT 2 MODULE
3742 P2MMT; P2MMR;
P2MMA;P2MMN;
P2MMX?
WARNING
CONTINUING
MAY INVALIDATE
CURRENT
SETUP AND
CALIBRATION
None
PRESS <ENTER>
TO CONTINUE Implements your broadband selection and calls menu SU1
or SU3. None
PRESS <CLEAR>
TO ABORT Pressing the Clear key aborts your broadband system
selection and calls menu OST1. None
Menu BB3, Broadband Select Menu 2
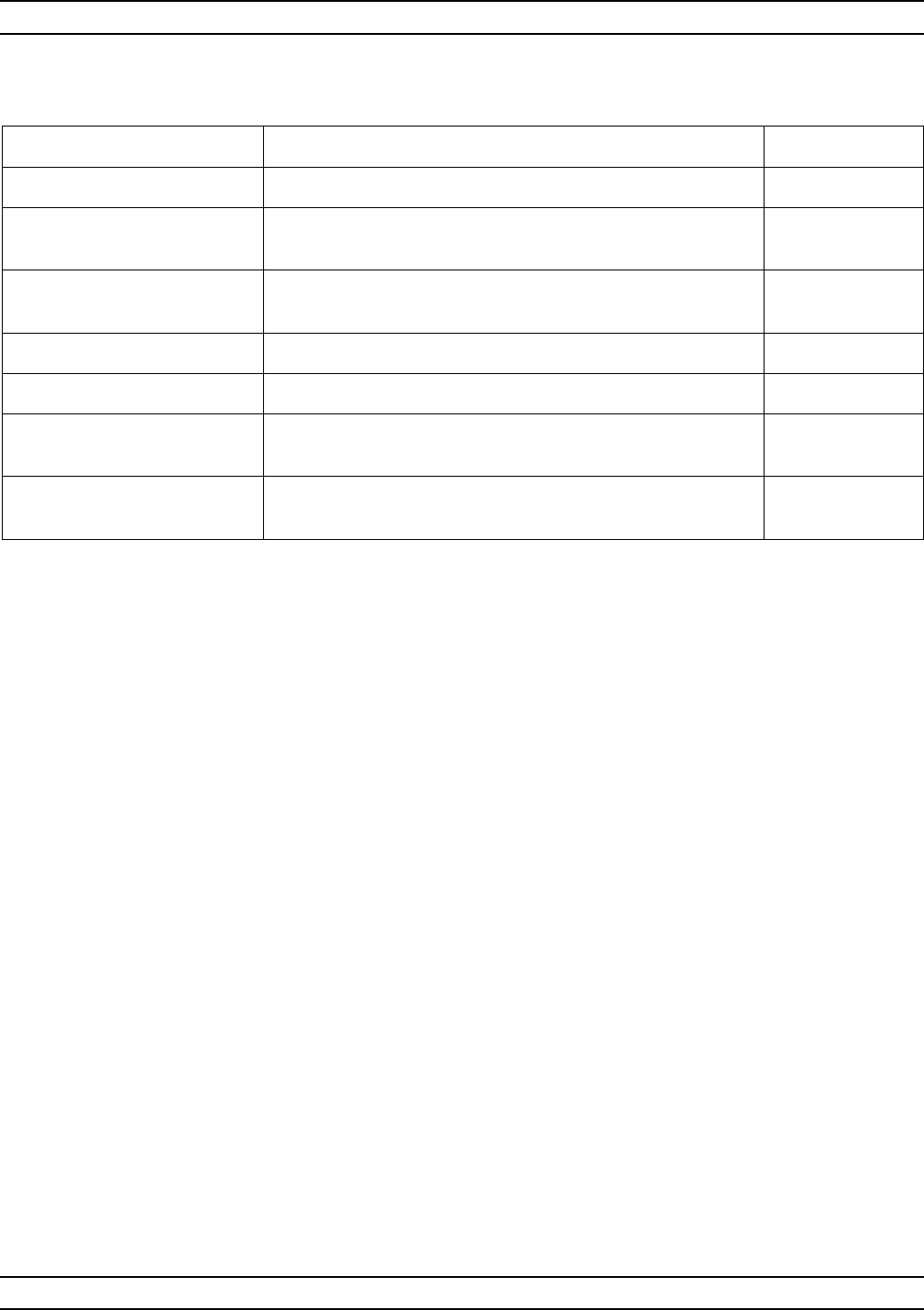
37XXXC OM A-23
ALPHABETICAL LISTING B
MENU DESCRIPTION GPIB COMMAND
BROADBAND BAND 2 None
BAND 2 START FREQ
65.000000000 GHz Displays the band 2 start frequency (fixed value). BST?
BAND 2 STOP FREQ
110.000000000 GHz Displays the band 2 stop frequency. BSP; BSP?
DEFAULT RANGE Restores the broadband band 2 frequency range to default. None
ACCEPT RANGE Accepts the new broadband band 2 frequency range. SVBMM
PRESS <ENTER>
TO SELECT Implements your broadband selection. None
PRESS <CLEAR>
TO ABORT Aborts your broadband selection and calls menu SU1 or
SU3. None
Menu BB4, Broadband Select Menu3
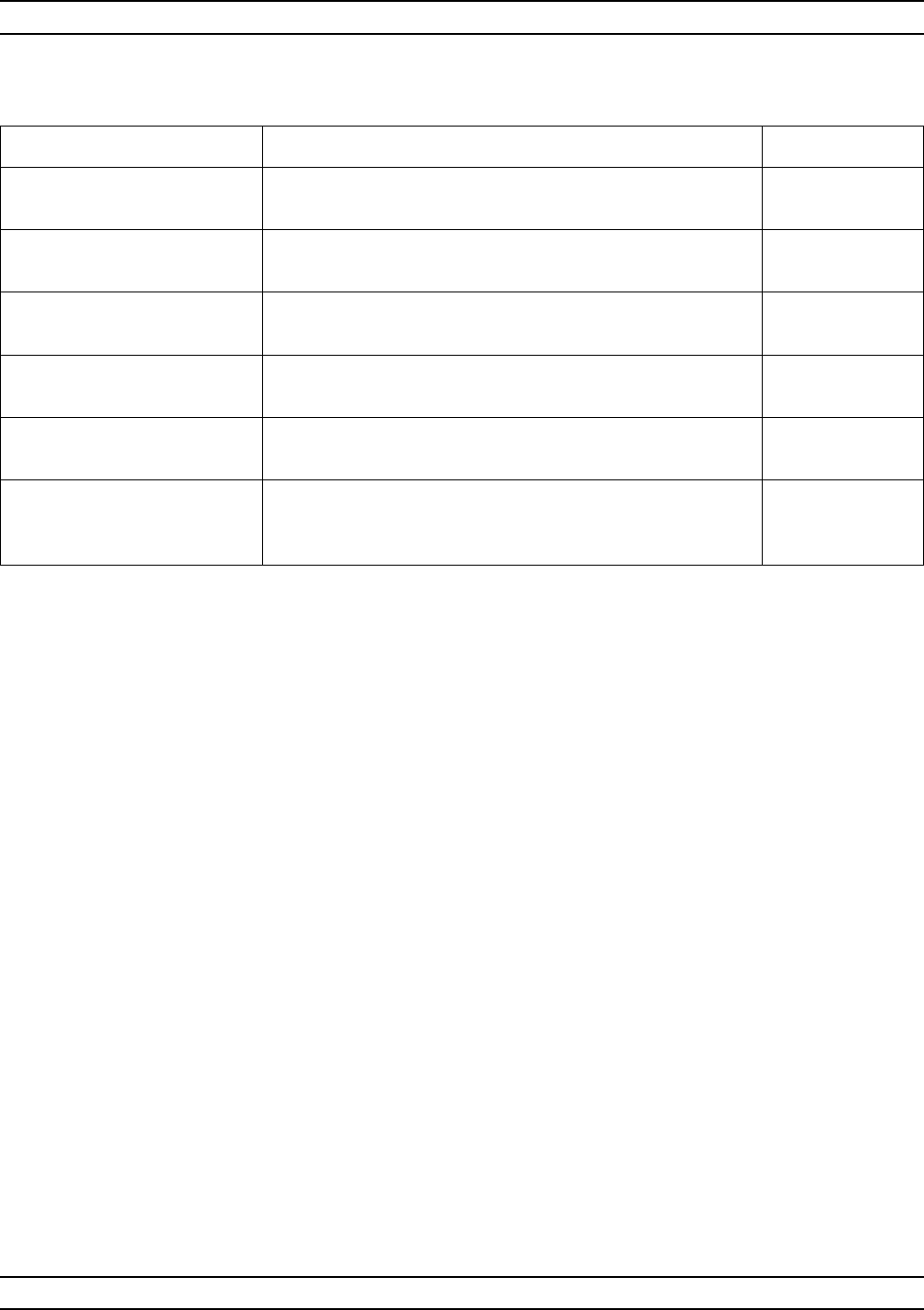
A-24 37XXXC OM
B ALPHABETICAL LISTING
MENU DESCRIPTION GPIB COMMAND
SELECT VIDEO
BANDWIDTH None
MAXIMUM
(10 kHz) Selects video bandwidth to be 10 kHz. IF4; IFX?
NORMAL
(1 kHz) Selects video bandwidth to be 1 kHz. IF3; IFN; IFX?
REDUCED
(100 Hz) Selects video bandwidth to be 100 Hz. IF2; IFR; IFX?
MINIMUM
(10 Hz) Selects video bandwidth to be 10 Hz. IF1; IFM; IFX?
PRESS <ENTER>
TO SELECT
AND RESUME CAL
Pressing the ENTER key implements your selection. The
“AND RESUME CAL” text appears when menu is accessed
during calibration.
None
Menu BW1 or CAL_BW1, Select Video Bandwidth
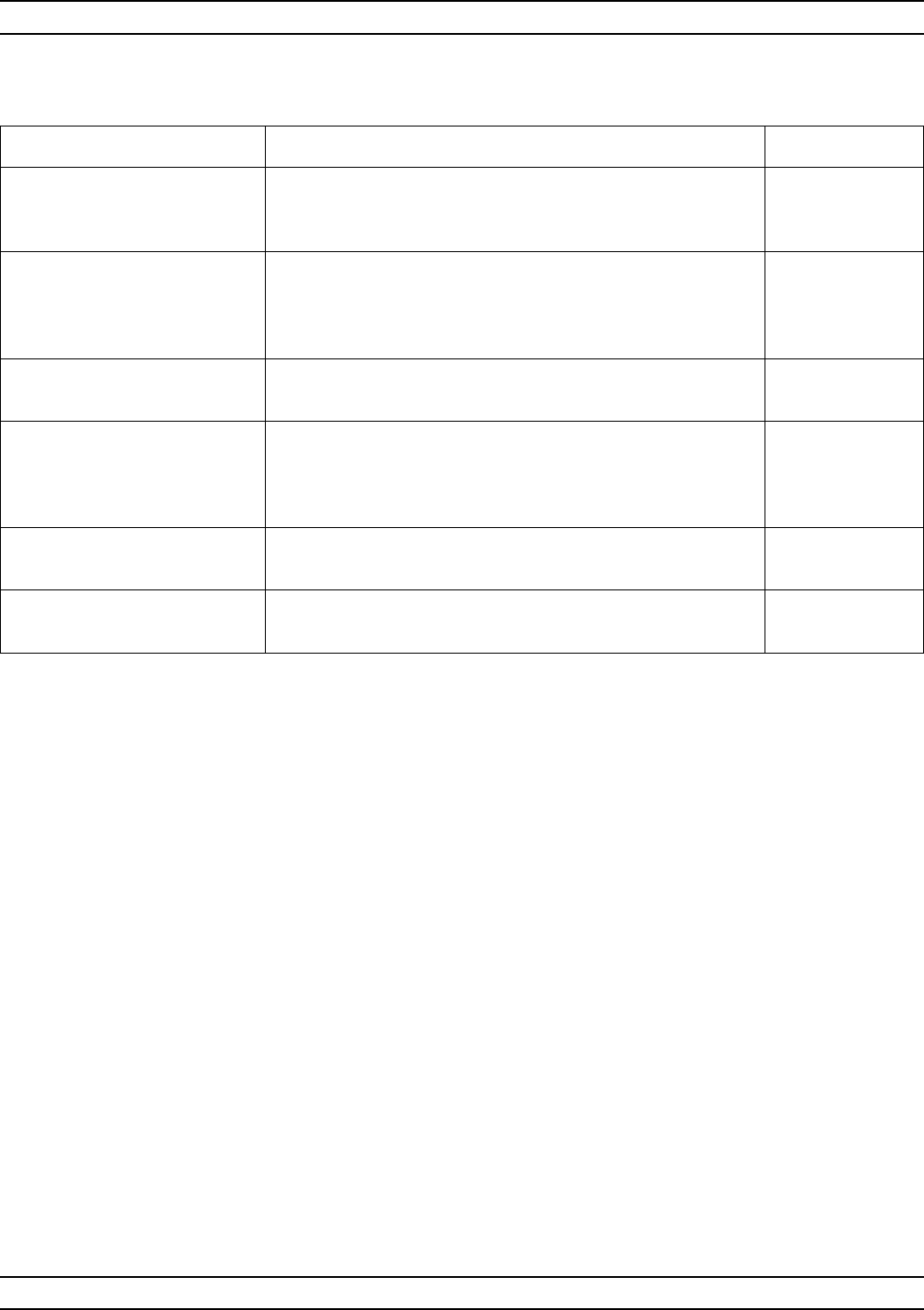
37XXXC OM A-25
ALPHABETICAL LISTING C
MENU DESCRIPTION GPIB COMMAND
SELECT
CALIBRATION
DATA POINTS
None
NORMAL
(1601 POINTS
MAXIMUM)
Selects the standard calibration from a start to a stop
frequency that provides for up to 1601 equally spaced
(except the last) points of data for the defined frequency
range.
NOC
C.W.
(1 POINT) Selects the single frequency (C.W.) calibration sequence
that provides for 1 data point at a selected frequency. CWC
N-DISCRETE
FREQUENCIES
(2 TO 1601
POINTS)
Selects the discrete frequency calibration mode that lets
you input a list of 2 to 1601 individual data point
frequencies.
DFC
TIME DOMAIN
(HARMONIC) Selects the calibration mode for low-pass time-domain
processing. TDC
PRESS <ENTER>
TO SELECT Pressing the ENTER key implements your selection. None
Menu C1, Select Calibration Data Points
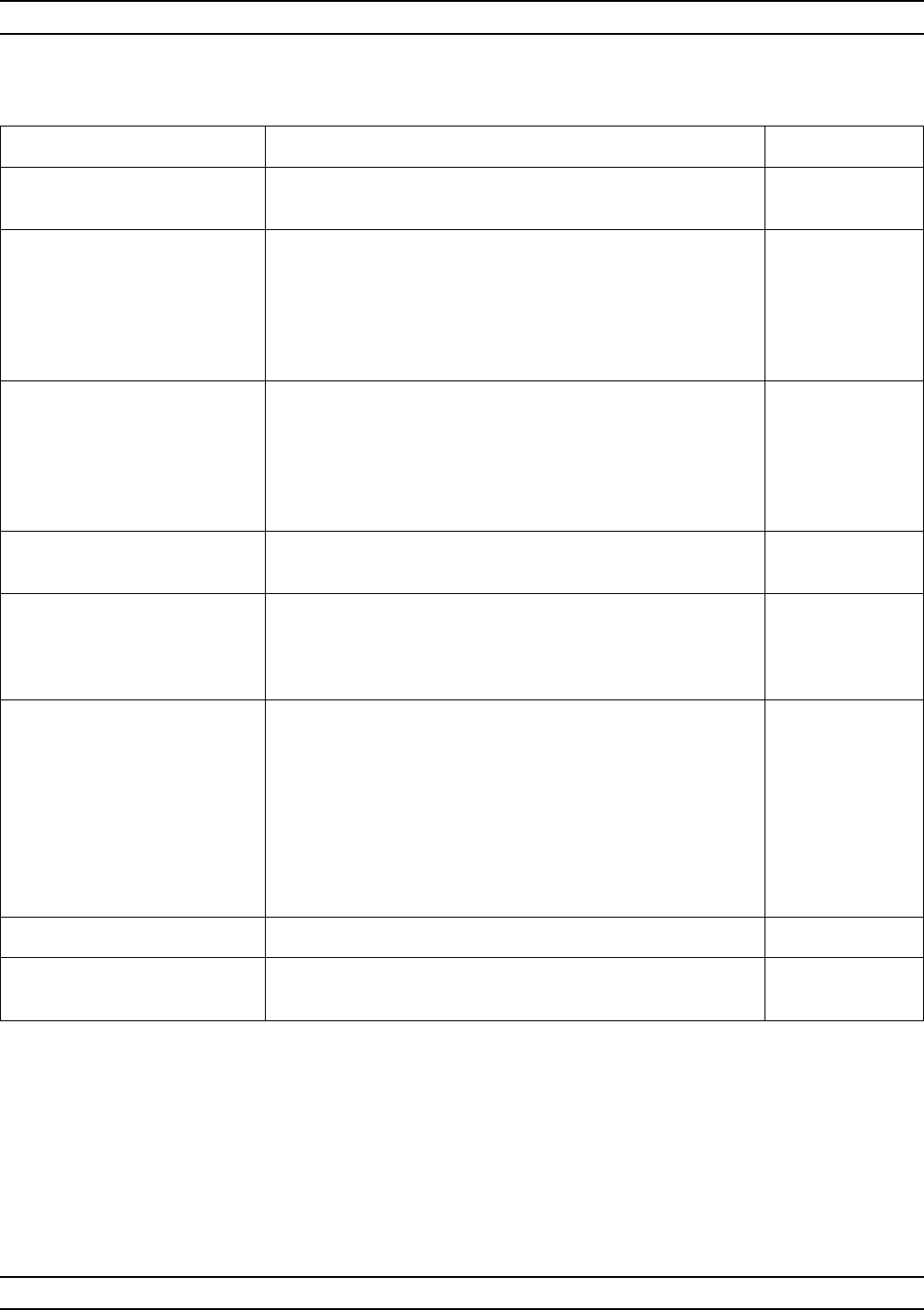
A-26 37XXXC OM
C ALPHABETICAL LISTING
MENU DESCRIPTION GPIB COMMAND
FREQUENCY RANGE
OF CALIBRATION None
START
XXX.XXXXXXXXXGHz Enter the sweep-start frequency for calibration. If you
desire, you can change this frequency for your
measurement when you reach menu SU1, which follows
the final calibration menu. The only restriction is that your
start measurement frequency be greater than or equal to
your start calibration frequency.
SRT; SRT?
STOP
XXX.XXXXXXXXX GHz Enter the sweep-stop frequency for calibration. Like the
start frequency, this too can be changed for your
measurement. The stop frequency must be lower than or
equal to your stop calibration frequency. In other words,
your measurement frequency span must be equal to or
smaller than your calibration frequency span.
STP; STP?
SET CENTER/SPAN Calls menu C2_CENTER, which lets you enter a center
frequency and span range. CNTR; SPAN
XXX DATA POINTS
XXX.XXXXXXXXXGHz
STEPSIZE
The program automatically sets the step size, based on the
selected start and stop frequencies. The step size will be
the smallest possible (largest number of points up to a
maximum of 1601), based on the chosen frequency span.
ONP
MAXIMUM NUMBER
OF DATA POINT(S)
1601 MAX PTS
801 MAX PTS
401 MAX PTS
201 MAX PTS
101 MAX PTS
51 MAX PTS
NP1601
NP801
NP401
NP201
NP101
NP51
NEXT CAL STEP Displays the next menu in the calibration sequence. None
PRESS <ENTER>
TO SELECT Pressing the ENTER key implements your menu selection. None
Menu C2, Frequency Range of Calibration (Start/Stop)
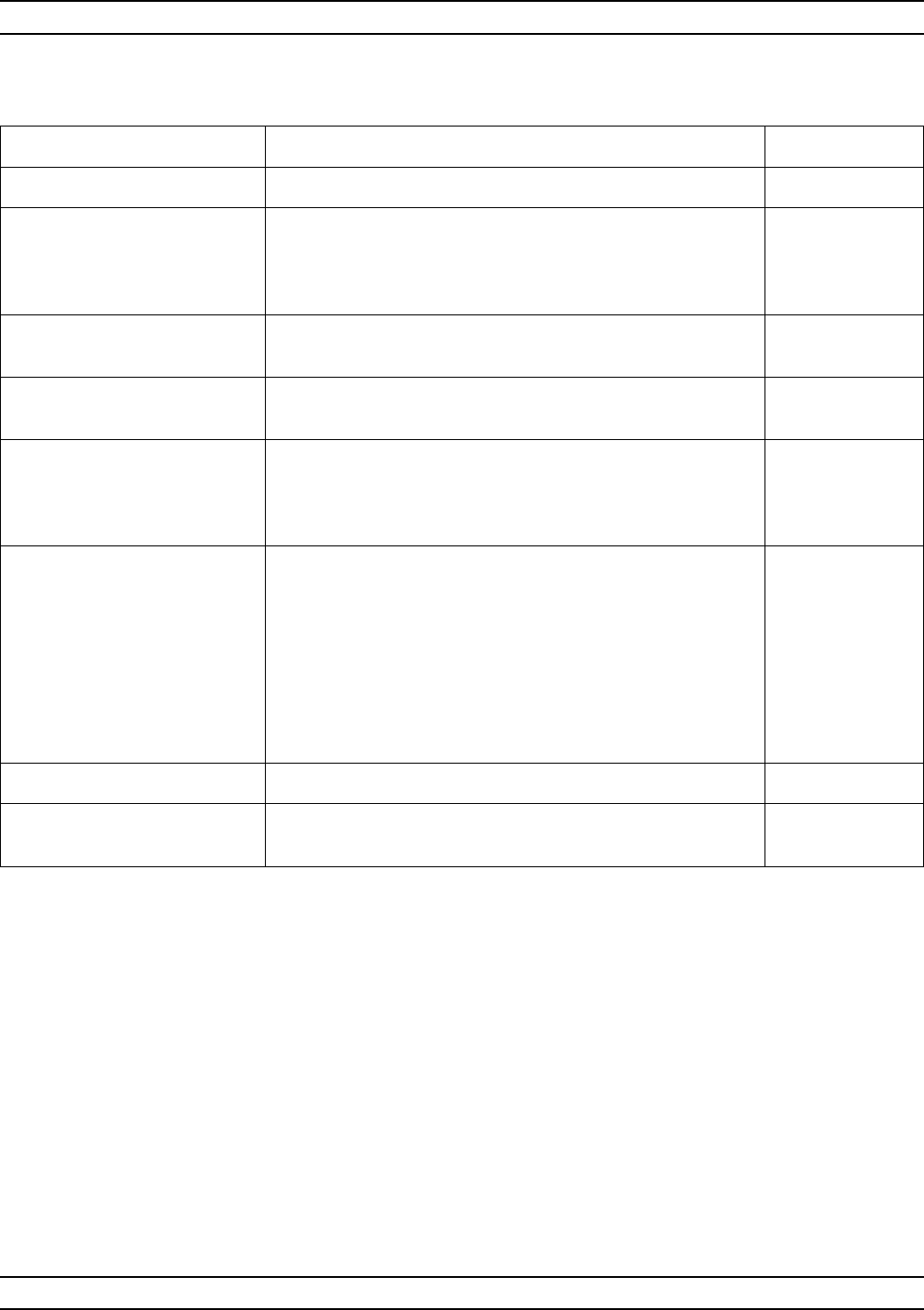
37XXXC OM A-27
ALPHABETICAL LISTING C
MENU DESCRIPTION GPIB COMMAND
CAL FREQ RANGE None
CENTER
XXX.XXXXXXXXXGHz Enter the center frequency for calibration. If you desire, you
can change this frequency for your measurement when you
reach menu SU1_CENTER, which follows the final
calibration menu.
CNTR; CNTR?
SPAN
XXX.XXXXXXXXX GHz Enter the span width for calibration. Like the start
frequency, this too can be changed for your measurement. SPAN; SPAN?
SET START/STOP Calls menu C2, which lets you enter a start and stop
frequency. SRT; STP
XXX DATA POINTS
XXX.XXXXXXXXXGHz
STEPSIZE
The program automatically sets the step size, based on the
selected center and span frequencies. The step size will be
the smallest possible (largest number of points up to a
maximum of 1601), based on the chosen frequency span.
ONP
MAXIMUM NUMBER
OF DATA POINT(S)
1601 MAX PTS
801 MAX PTS
401 MAX PTS
201 MAX PTS
101 MAX PTS
51 MAX PTS
NP1601
NP801
NP401
NP201
NP101
NP51
NEXT CAL STEP Displays the next menu in the calibration sequence. None
PRESS <ENTER>
TO SELECT Pressing the ENTER key implements your menu selection. None
Menu C2_CENTER, Frequency Range of Calibration (Center/Span)
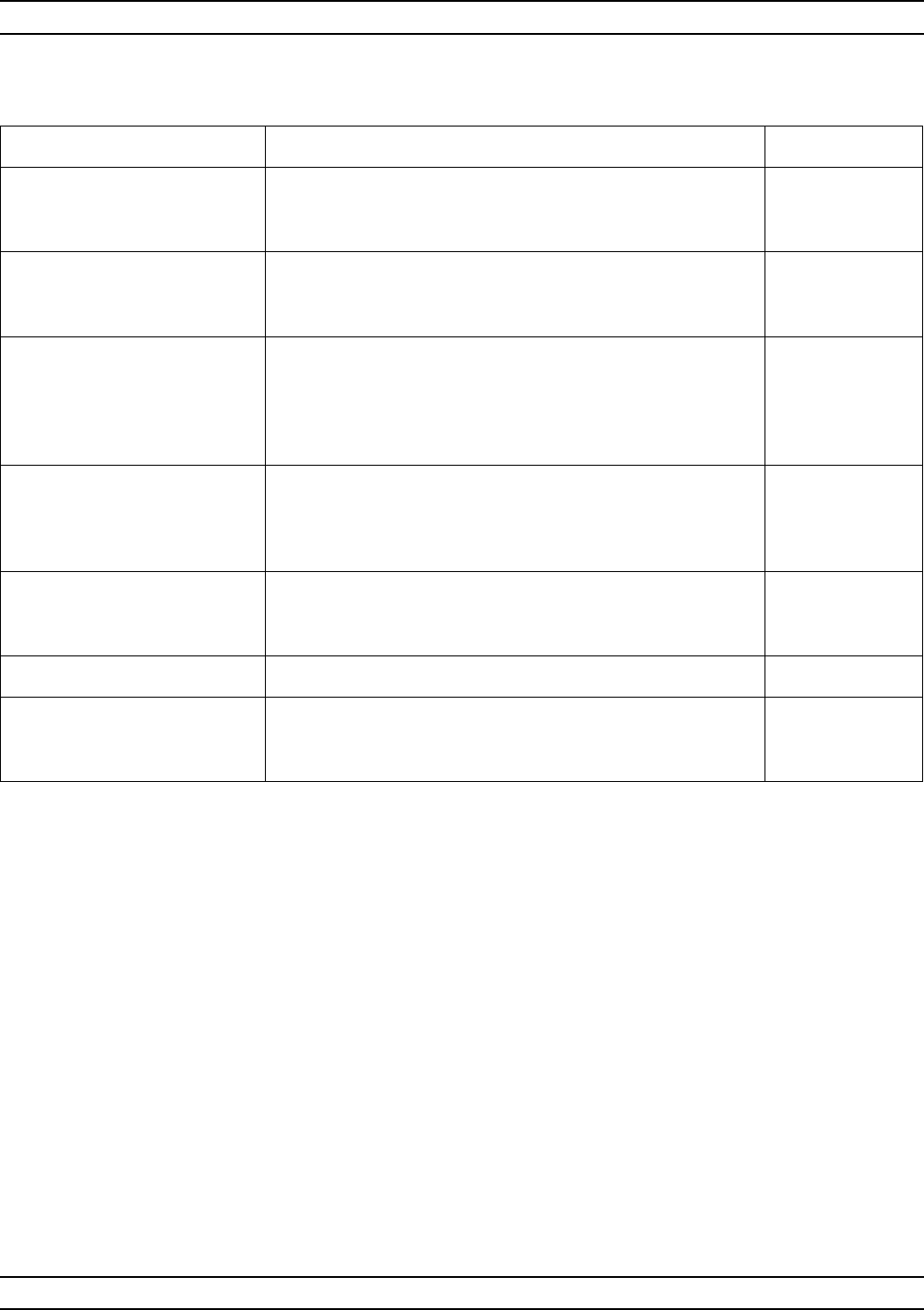
A-28 37XXXC OM
C ALPHABETICAL LISTING
MENU DESCRIPTION GPIB COMMAND
INSERT
INDIVIDUAL
FREQUENCIES
None
INPUT A FREQ,
PRESS <ENTER>
TO INSERT
DFQ
NEXT FREQ.
XXX.XXXXXXXXXGHz Move the cursor here and enter the next frequency for
which you wish calibration data taken. If the AUTO INCR
option is ON, pressing Enter automatically increments the
calibration frequency by the interval in GHz that appears
below the option.
None
XXXX FREQS.
ENTERED,
LAST FREQ WAS
XXX.XXXXXXXXXGHz
Shows the number of frequencies that you have entered
and reports the value of the last frequency entered. None
AUTO INCR ON (OFF)
XXX.XXXXXXXXXGHz Move the cursor here and press ENTER to switch the
Auto-Increment mode on or off. If AUTO INCR is on, you
may enter the frequency spacing.
None
PREVIOUS MENU Calls menu C2D. None
PRESS <ENTER>
TO SELECT
OR TURN ON/OFF
Pressing Enter will cause actions as described above. None
Menu C2A, Insert Individual Frequencies
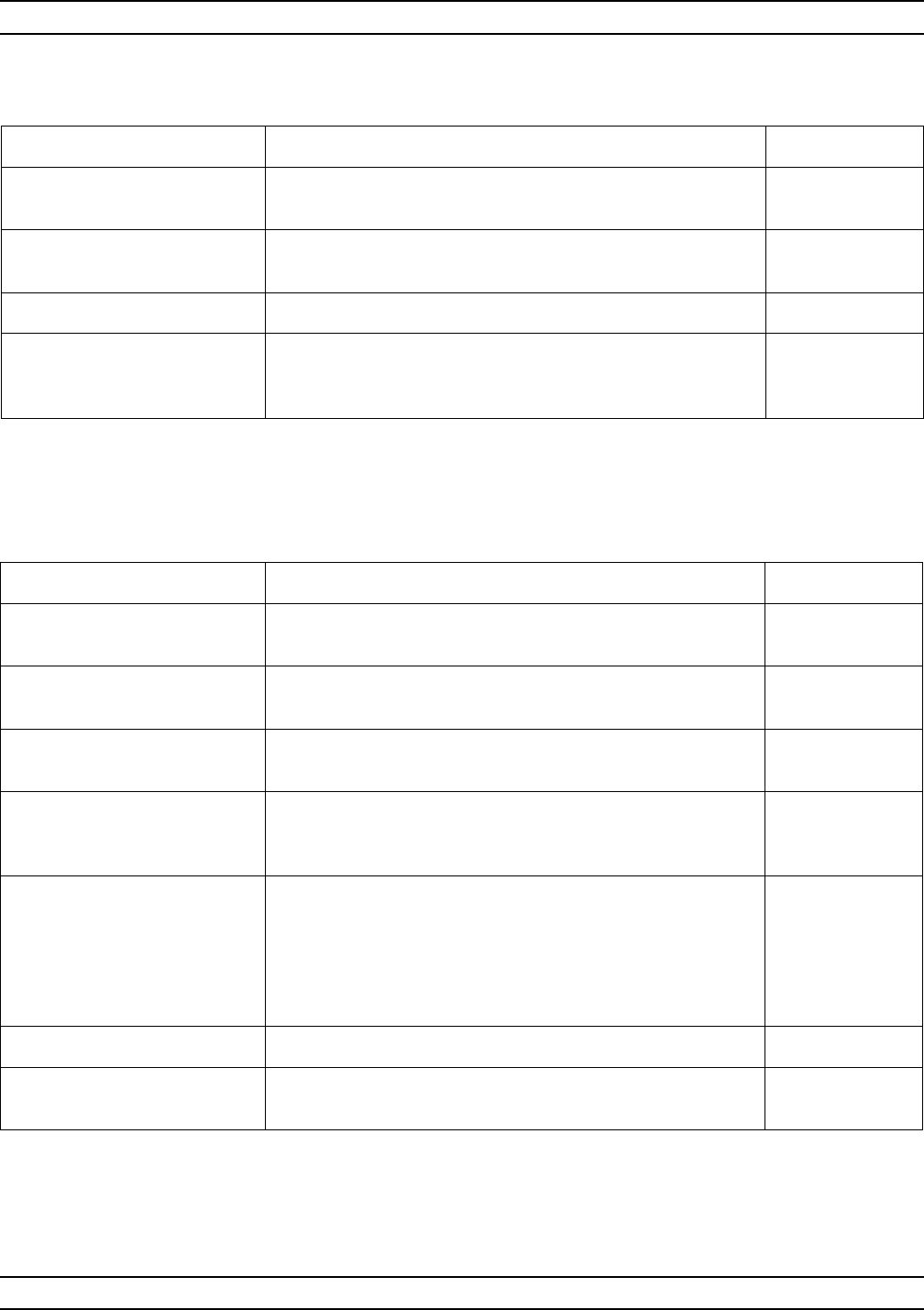
37XXXC OM A-29
ALPHABETICAL LISTING C
MENU DESCRIPTION GPIB COMMAND
CALIBRATION
RANGE None
HARMONIC CAL
FOR TIME DOMAIN None
START (STEP)
XXX.XXXXXXXXXGHz Move cursor here to enter the desired start frequency. This
frequency also will be used as the frequency increment. SRT; SRT?
APPROXIMATE STOP
XXX.XXXXXXXXX GHz Move the cursor here to enter the approximate desired stop
frequency. The frequency will be adjusted to the nearest
harmonic multiple of the start frequency.
APRXSTP?
USING ABOVE
START AND STOP
WILL RESULT IN
XXX DATA POINTS
XXX.XXXXXXXXX GHz
TRUE STOP FREQ
The program automatically indicates the number of data
points and the true (harmonic) stop frequency. ONP; STP?
NEXT CAL STEP Move the cursor here and press Enter when finished. None
PRESS <ENTER>
TO SELECT Pressing the Enter key implements your menu selection. None
Menu C2C, Calibration Range—Harmonic Cal for Time Domain
MENU DESCRIPTION GPIB COMMAND
SINGLE POINT
C.W. CALIBRATION None
C.W. FREQ
XXX.XXXXXXXXXGHz Move cursor here and enter the frequency for which
calibration is to be done. CWF; CWF?
NEXT CAL STEP Move cursor here and press ENTER when finished. None
PRESS <ENTER>
TO SELECT Pressing the Enter key implements your menu selection. None
Menu C2B, Single Point Calibration
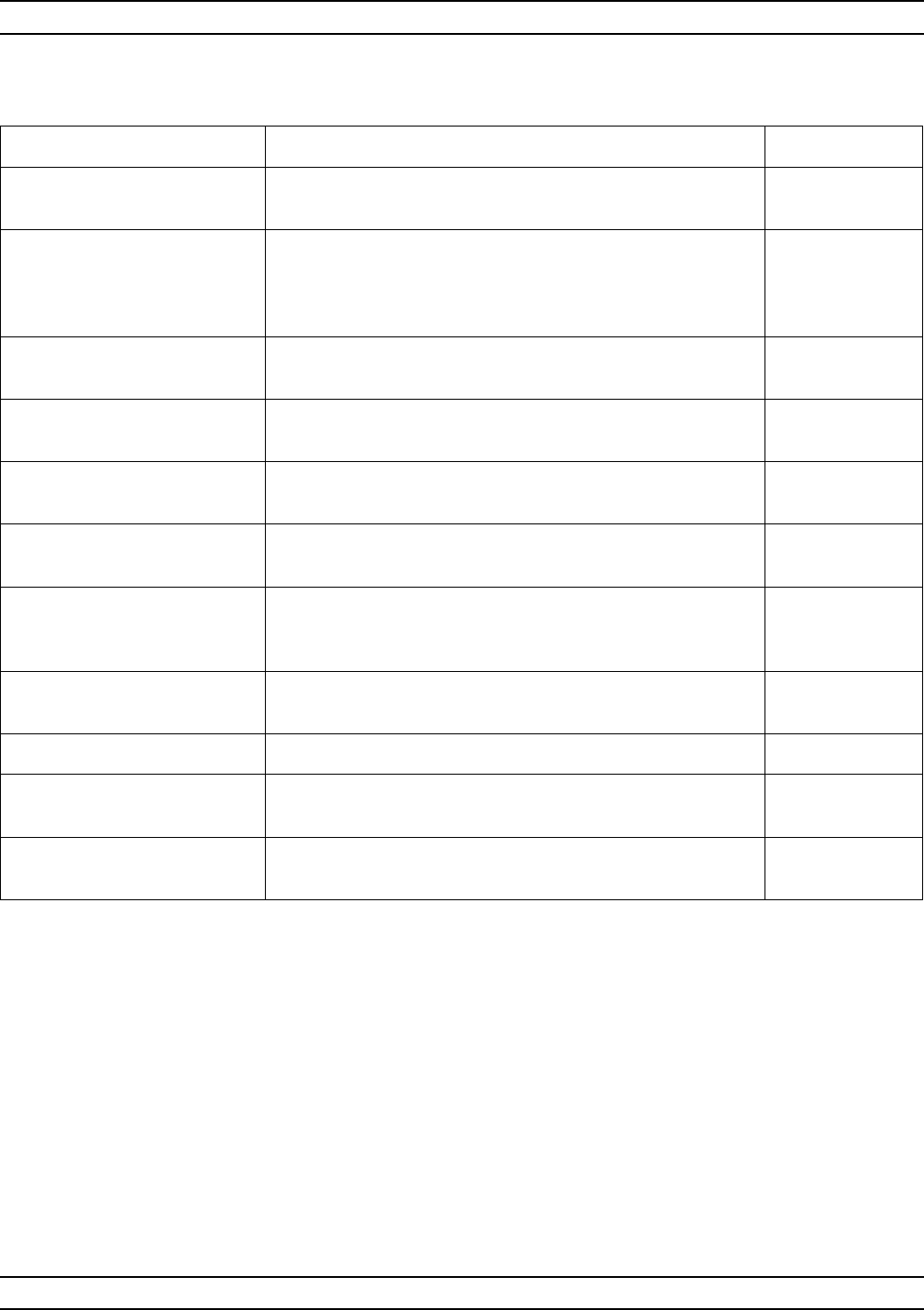
A-30 37XXXC OM
C ALPHABETICAL LISTING
MENU DESCRIPTION GPIB COMMAND
DISCRETE FILL None
INPUT START,
INCR, POINTS,
THEN SELECT
“FILL RANGE”
This menu is used to create one or more ranges of discrete
equally spaced frequency points for calibration. None
START FREQ
XXX.XXXXXXXXX GHz Enter the first frequency of the range. FRS; FRS?
INCREMENT
XXX.XXXXXXXXX GHz Enter the increment (step size) between one frequency and
the next. FRI; FRI
NUMBER OF PTS
XXXX POINT(S) Enter the number of frequency points in the range. FRP; FRP?
STOP FREQ
XXX.XXXXXXXXX GHz Enter the stop frequency, in GHz. None
FILL RANGE
( XXXX ENTERED) Moving the cursor here and pressing ENTER fills the range
and shows the number of frequencies selected (in
NUMBER OF PTS above).
FIL
INDIVIDUAL
FREQ INSERT Calls menu C2A, which allows you to set the individual
frequencies. DFQ
CLEAR ALL Clears all entries displayed above. FRC
FINISHED
NEXT CAL STEP Calls menu C3, the next menu in the calibration sequence. None
PRESS <ENTER>
TO SELECT Pressing the Enter key implements your menu selection. None
Menu C2D, Fill Frequency Ranges
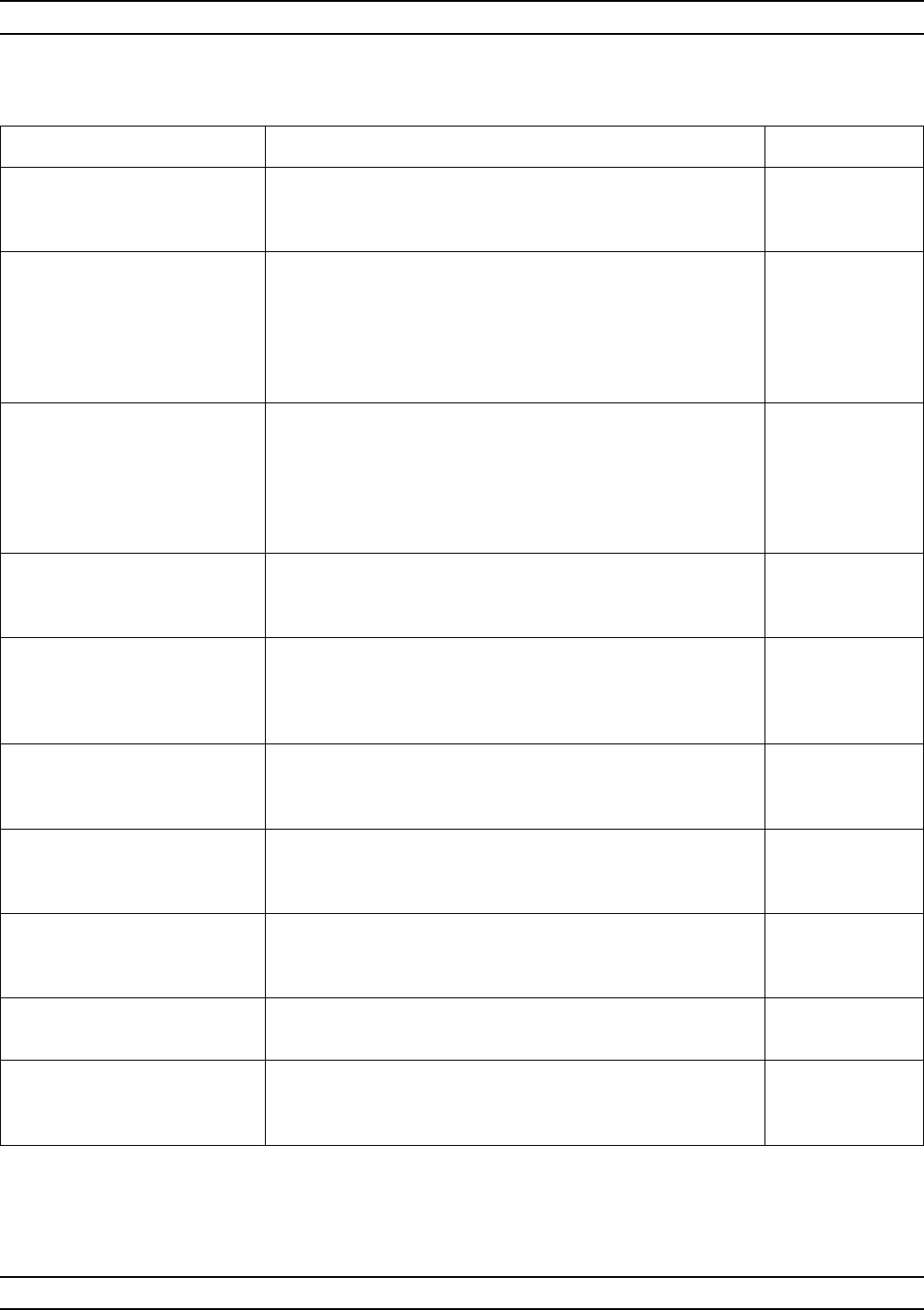
37XXXC OM A-31
ALPHABETICAL LISTING C
MENU DESCRIPTION GPIB COMMAND
CONFIRM
CALIBRATION
PARAMETERS
Used for SOST method and coaxial line type. None
PORT 1 CONN
XXXXXXXX Calls menu C4_P1 or C4A_P1, which displays the Port 1
test port connector type to be used during OSL calibration.
This should agree with the connector type that both your
calibration components and the test device mate with.
Move cursor here and press Enter to display menu used to
change connector type.
None
PORT 2 CONN
XXXXXXXX Calls menu C4_P2 or C4A_P2, which displays the Port 2
test port connector type to be used during OSL calibration.
This should agree with the connector type that both your
calibration components and the test device mate with.
Move cursor here and press Enter to display menu used to
change connector type.
None
REFLECTION
PAIRING
XXXXXX
Calls menu C13, which lets you select the pairing (mixed or
matched) for the types of reflection devices (open/short)
that you will use on Ports 1 and 2 for calibration.
None
LOAD TYPE
XXXXXXXX Calls menu C6, which displays type of load selected for
calibration—broadband fixed or sliding. Move cursor here
and press ENTER to display menu used to change load
type.
None
THROUGH LINE
PARAMETERS Calls menu C20, which lets you enter throughline
parameters—including offset length and loss equation
coefficients.
None
REFERENCE
IMPEDANCE Calls menu C17, which lets you choose the reference
impedance value (1 mW to1kW) for the devices connected
to Ports 1 and 2 for calibration. Default value is 50W.
None
TEST SIGNALS Calls menu CAL_SU2, which lets you enter calibrate Flat
Test Port Power or change source power(s) and attenuator
settings.
None
START CAL Starts the standard (OSL) calibration sequence using
coaxial standards. BEG
PRESS <ENTER>
TO SELECT
OR CHANGE
Pressing the Enter key implements your menu selection. None
Menu C3, Confirm Calibration Parameters
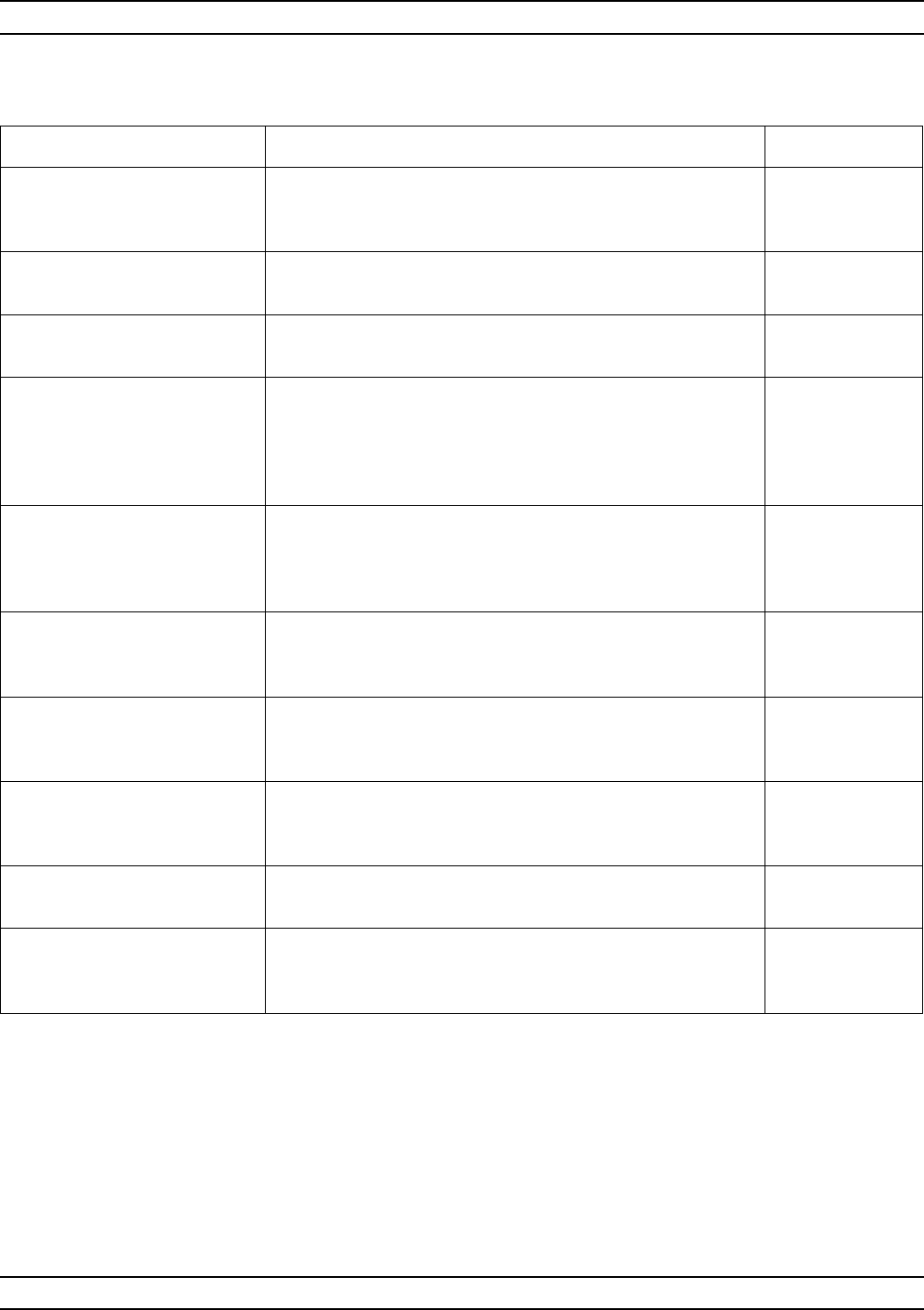
A-32 37XXXC OM
C ALPHABETICAL LISTING
MENU DESCRIPTION GPIB COMMAND
CONFIRM
CALIBRATION
PARAMETERS
Used for Offset-Short method and coaxial line type. None
PORT 1 CONN
W1-CONN (M) Calls menu C14 to select a connector offset short kit for
Port1. None
PORT 2 CONN
W1-CONN (M) Calls menu C14 to select a connector offset short kit for
Port2. None
REFLECTION
PAIRING
XXXXXXXX
Calls menu C13A for a SSLT calibration or calls
menu C13B for a SSST calibration, which lets you select
the pairing (mixed or matched) for the types of reflection
devices (open/short) that you will use on Ports 1 and 2 for
calibration.
None
LOAD TYPE
XXXXXXXX Calls menu C6, which displays type of load selected for
calibration—broadband, fixed, or sliding. Move cursor here
and press Enter to display the menu used to change the
load type.
None
THROUGH LINE
PARAMETERS Calls menu C20, which lets you enter throughline
parameters—including offset length and loss equation
coefficients.
None
REFERENCE
IMPEDANCE Calls menu C15, which lets you choose the reference
impedance value (1 mW to1MW) for the devices connected
to Ports 1 and 2 for calibration. Default value is 50W.
None
TEST SIGNALS Calls menu CAL_SU2, which lets you enter calibrate Flat
Test Port Power or change source power(s) and attenuator
settings.
None
START CAL Starts the offset-short calibration sequence using coaxial
standards. BEG
PRESS <ENTER>
TO SELECT
OR CHANGE
Pressing the Enter key implements your menu selection. None
Menu C3A, Confirm Calibration Parameters
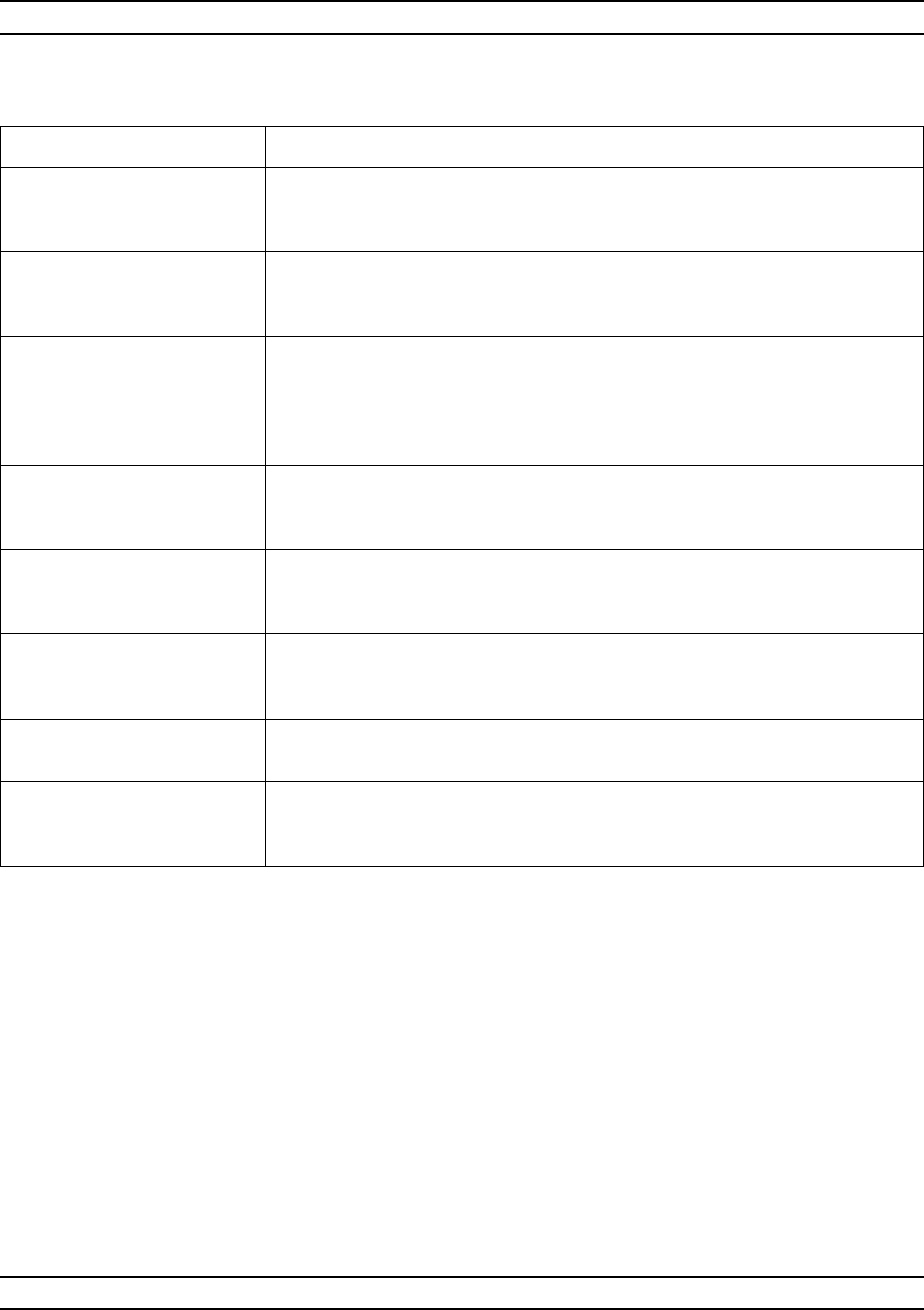
37XXXC OM A-33
ALPHABETICAL LISTING C
MENU DESCRIPTION GPIB COMMAND
CONFIRM
CALIBRATION
PARAMETERS
Used for Offset-Short method and waveguide line type. None
WAVEGUIDE
PARAMETERS
XXXXXX
Calls menu C15, which lets you enter waveguide
parameters. None
REFLECTION
PAIRING
XXXXXX
Calls menu C13A for a SSLT calibration or calls
menu C13B for a SSST calibration, which lets you select
the pairing (mixed or matched) for the types of reflection
devices (open/short) that you will use on Ports 1 and 2 for
calibration.
None
LOAD TYPE
XXXXXXXX Calls menu C6, which displays type of load selected for
calibration—broadband fixed or sliding. Load type does not
appear for the SSST method.
None
THROUGH LINE
PARAMETERS Calls menu C20, which lets you enter throughline
parameters—including offset length and loss equation
coefficients.
None
TEST SIGNALS Calls menu CAL_SU2, which lets you calibrate Flat Test
Port Power or change source power(s) and attenuator
settings.
None
START CAL Starts the offset-short calibration sequence using
waveguide standards. BEG
PRESS <ENTER>
TO SELECT
OR CHANGE
Pressing the Enter key implements your menu selection. None
Menu C3B, Confirm Calibration Parameters

A-34 37XXXC OM
C ALPHABETICAL LISTING
MENU DESCRIPTION GPIB COMMAND
CONFIRM
CALIBRATION
PARAMETERS
Used for Offset-Short method and microstrip line type. None
PORT 1 SHORTS
USER DEFINED Calls menu C14A to select an offset short kit for Port 1. None
PORT 2 SHORTS
USER DEFINED Calls menu C14A to select an offset short kit for Port 2. None
REFLECTION
PAIRING
XXXXXX
Calls menu C13A for a SSLT calibration or calls
menu C13B for a SSST calibration, which lets you select
the pairing (mixed or matched) for the types of reflection
devices (open/short) that you will use on Ports 1 and 2 for
calibration.
None
LOAD
IMPEDANCES Calls menu C6A, which lets you select an impedance type
and/or enter an impedance value. None
THROUGH LINE
PARAMETERS Calls menu C20, which lets you enter throughline
parameters—including offset length and loss equation
coefficients.
None
MICROSTRIP
PARAMETERS
XXXXXXXXXXX
Calls menu C16, which lets you change microstrip
parameters. None
TEST SIGNALS Calls menu CAL_SU2, which lets you enter calibrate Flat
Test Port Power or change source power(s) and attenuator
settings.
None
START CAL Starts the offset-short calibration sequence using microstrip
standards. BEG
PRESS <ENTER>
TO SELECT
OR CHANGE
Pressing the Enter key implements your menu selection. None
Menu C3C, Confirm Calibration Parameters
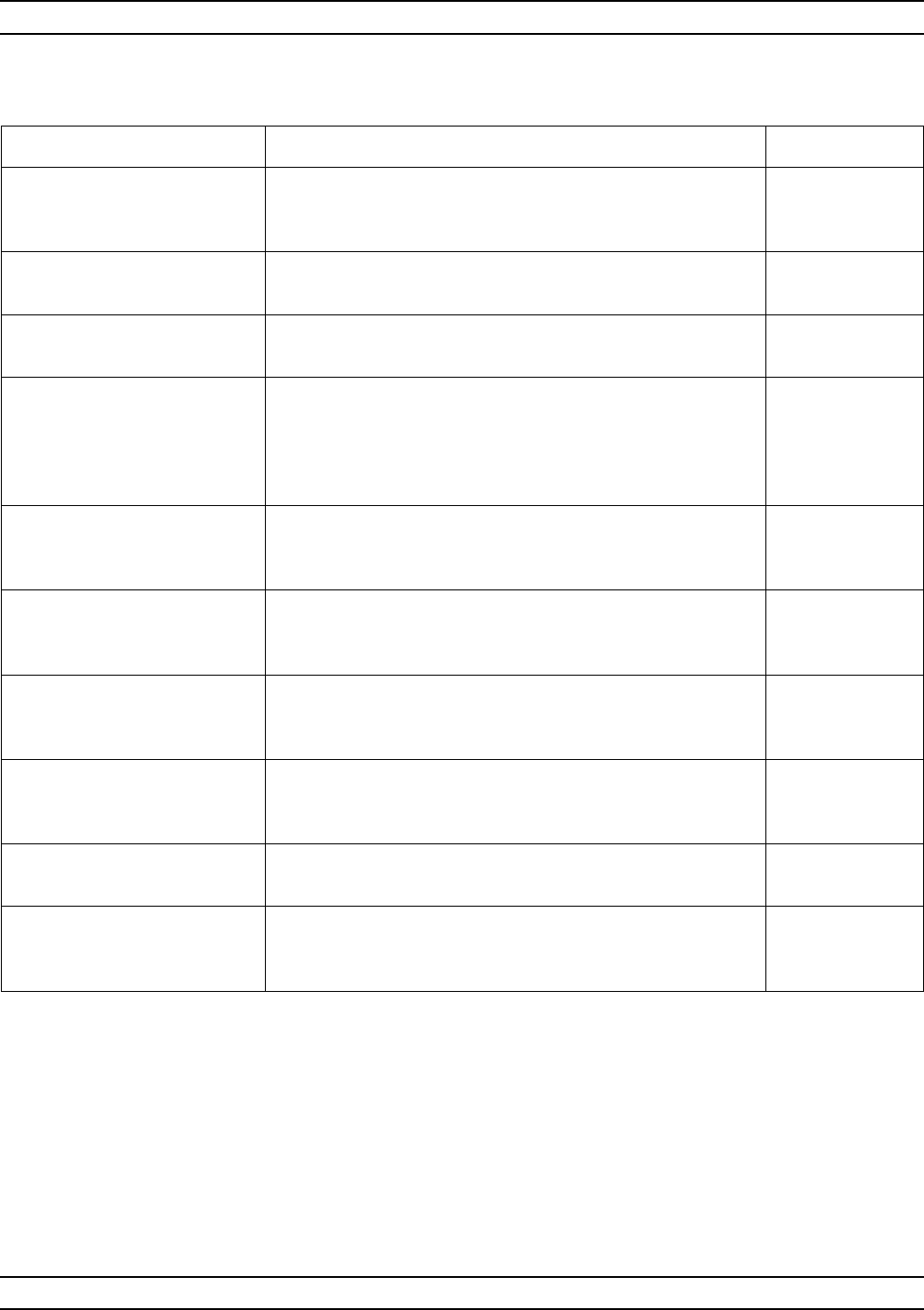
37XXXC OM A-35
ALPHABETICAL LISTING C
MENU DESCRIPTION GPIB COMMAND
CONFIRM
CALIBRATION
PARAMETERS
Used for SOLT method and microstrip line type. None
PORT 1 OPEN/SHORT
XXXXXXXX Calls menu C4B, which is used to select an offset short kit
for Port 1. None
PORT 2 OPEN/SHORT
XXXXXXXX Calls menu C4B, which is used to select an offset short kit
for Port 2. None
REFLECTION
PAIRING
XXXXXXXX
Calls menu C13A for a SSLT calibration or calls
menu C13B for a SSST calibration, which lets you select
the pairing (mixed or matched) for the types of reflection
devices (open/short) that you will use on Ports 1 and 2 for
calibration.
None
LOAD
IMPEDANCE
XXXXXXXX
Calls menu C6A, which lets you select an impedance type
and/or enter an impedance value. None
THROUGH LINE
PARAMETERS
XXXXXXXX
Calls menu C20, which lets you enter throughline
parameters—including offset length and loss equation
coefficients.
None
MICROSTRIP
PARAMETERS
XXXXXXXX
Calls menu C16, which lets you change microstrip
parameters. None
TEST SIGNALS Calls menu CAL_SU2, which lets you enter calibrate Flat
Test Port Power or change source power(s) and attenuator
settings.
None
START CAL Starts the standard calibration sequence using microstrip
standards. BEG
PRESS <ENTER>
TO SELECT
OR CHANGE
Pressing the Enter key implements your menu selection. None
Menu C3D, Confirm Calibration Parameters
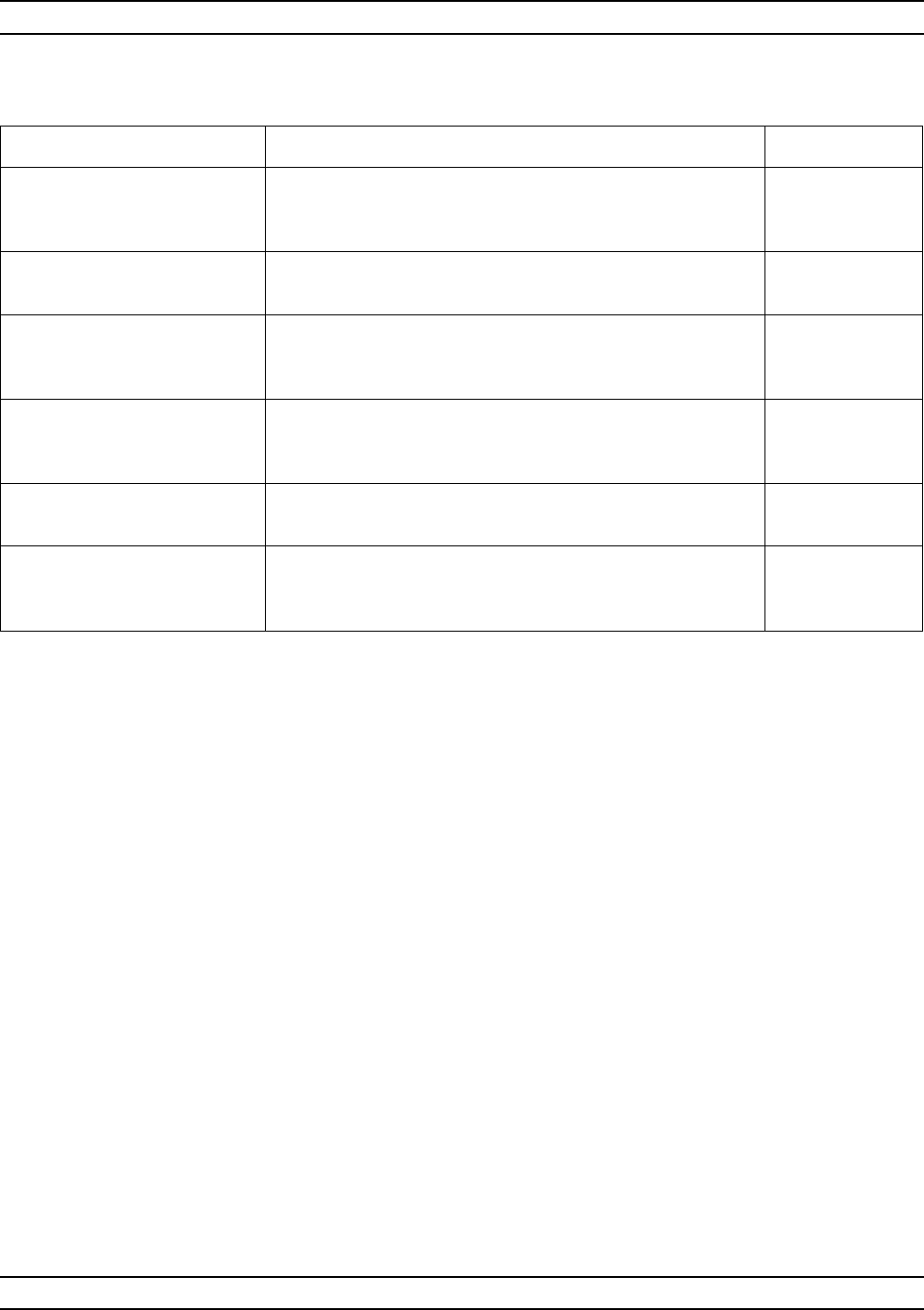
A-36 37XXXC OM
C ALPHABETICAL LISTING
MENU DESCRIPTION GPIB COMMAND
CONFIRM
CALIBRATION
PARAMETERS
Used for LRL/LRM method, coaxial line type. None
LRL/LRM
PARAMETERS Calls menu C18, which lets you change LRL/LRM
parameters. None
REFERENCE
IMPEDANCE Calls menu C17, which lets you change the reference
impedance of the coaxial line standard to other than 50
ohms (default).
None
TEST SIGNALS Calls menu CAL_SU2, which lets you enter calibrate Flat
Test Port Power or change source power(s) and attenuator
settings.
None
START CAL Starts the LRL/LRM calibration sequence using coaxial
standards. BEG
PRESS <ENTER>
TO SELECT
OR CHANGE
Pressing the Enter key implements your menu selection. None
Menu C3E, Confirm Calibration Parameters
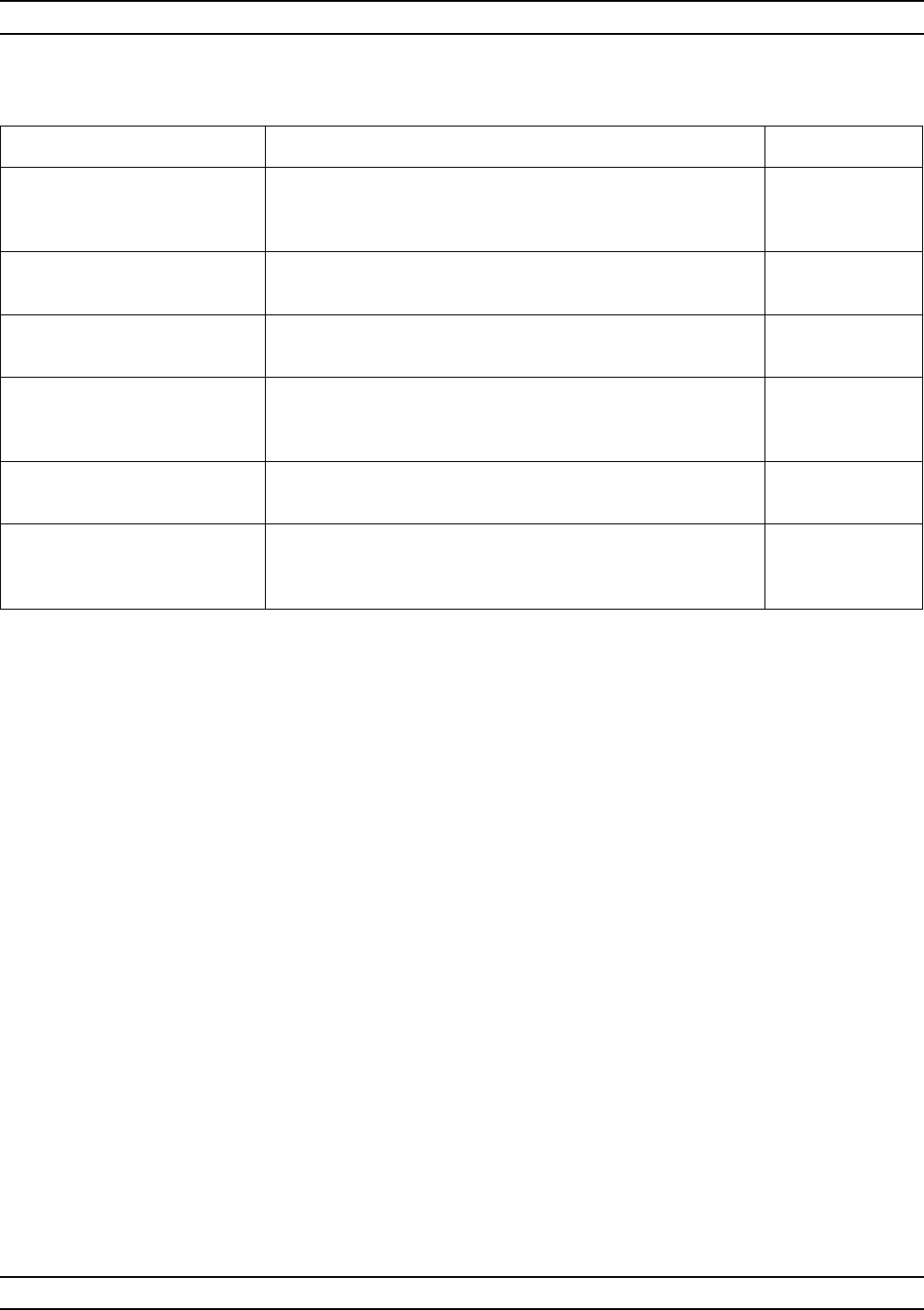
37XXXC OM A-37
ALPHABETICAL LISTING C
MENU DESCRIPTION GPIB COMMAND
CONFIRM
CALIBRATION
PARAMETERS
Used for LRL/LRM method, waveguide line type. None
LRL/LRM
PARAMETERS Calls menu C18, which lets you change LRL/LRM
parameters. None
WAVEGUIDE
CUTOFF FREQ Calls menu 15B, which lets you enter a waveguide cutoff
frequency. None
TEST SIGNALS Calls menu CAL_SU2, which lets you enter calibrate Flat
Test Port Power or change source power(s) and attenuator
settings.
None
START CAL Starts the LRL/LRM calibration sequence using waveguide
standards. BEG
PRESS <ENTER>
TO SELECT
OR CHANGE
Pressing the Enter key implements your menu selection. None
Menu C3F, Confirm Calibration Parameters
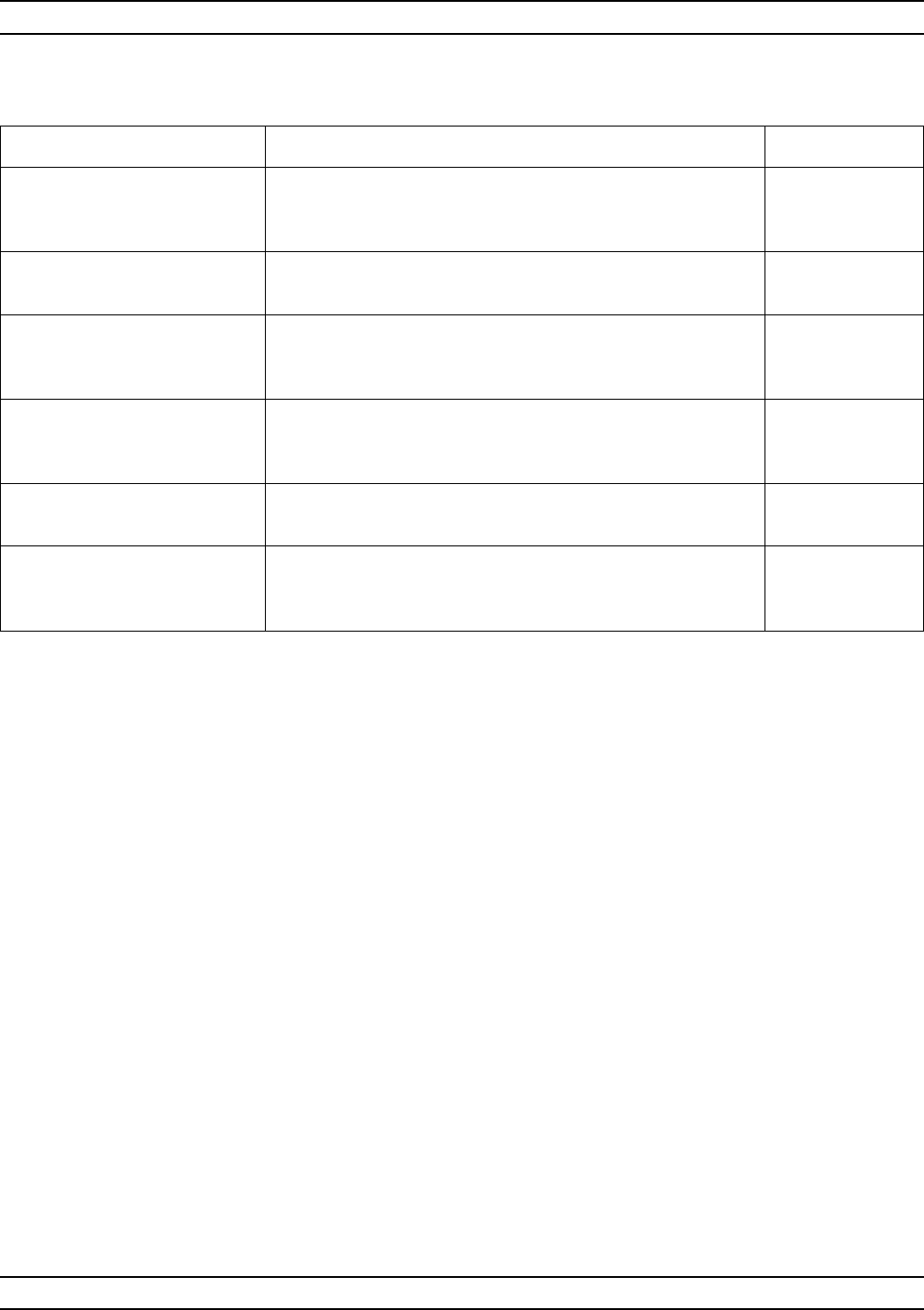
A-38 37XXXC OM
C ALPHABETICAL LISTING
MENU DESCRIPTION GPIB COMMAND
CONFIRM
CALIBRATION
PARAMETERS
Used for LRL/LRM method, microstrip line type. None
LRL/LRM
PARAMETERS Calls menu C18, which lets you change LRL/LRM
parameters. None
MICROSTRIP
PARAMETERS
USER DEFINED
Calls menu C16, which lets you change microstrip
parameters. None
TEST SIGNALS Calls menu CAL_SU2, which lets you enter calibrate Flat
Test Port Power or change source power(s) and attenuator
settings.
None
START CAL Starts the LRL/LRM calibration sequence using microstrip
standards. BEG
PRESS <ENTER>
TO SELECT
OR CHANGE
Pressing the Enter key implements your menu selection. None
Menu C3G, Confirm Calibration Parameters
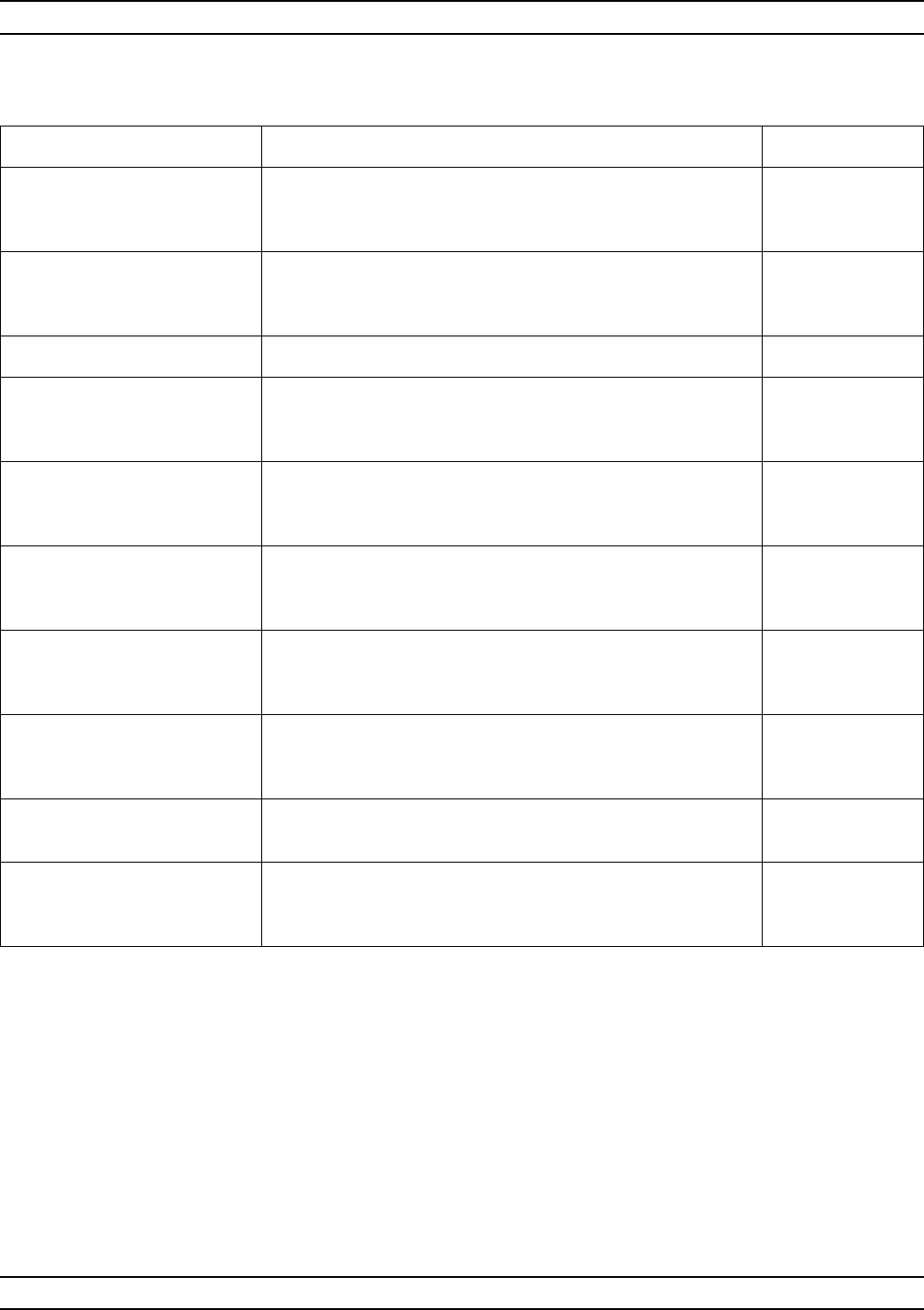
37XXXC OM A-39
ALPHABETICAL LISTING C
MENU DESCRIPTION GPIB COMMAND
CONFIRM
CALIBRATION
PARAMETERS
None
TRM REFLECT
OFFSET LENGTH
+XXX.XXX mmX
Enter the offset length of the TRM reflection. TOL; TOL?; ROL;
ROL?
TRM REFLECT TYPE None
GREATER THAN Zo Specifies the reflection to have an impedance value greater
than the reference impedance (Z0). This is typically an open
device.
RGZ; RXZ?
LESS THAN Zo Selects the reflection to have an impedance value less than
the reference impedance (Z0). This is typically a short
device.
RLZ; RXZ?
TRM MATCH
IMPEDANCE Calls menu C6B, which lets you change the match
impedance of the coaxial line standard to other than 50 W
(default).
None
REFERENCE
IMPEDANCE Calls menu C17, which lets you change the reference
impedance of the coaxial line standard to other than 50 W
(default).
None
TEST SIGNALS Calls menu CAL_SU2, which lets you enter calibrate Flat
Test Port Power or change source power(s) and attenuator
settings.
None
START CAL Starts the standard calibration sequence using microstrip
standards. BEG
PRESS <ENTER>
TO SELECT
OR CHANGE
Pressing the Enter key implements your menu selection. None
Menu C3H, Confirm Calibration Parameters
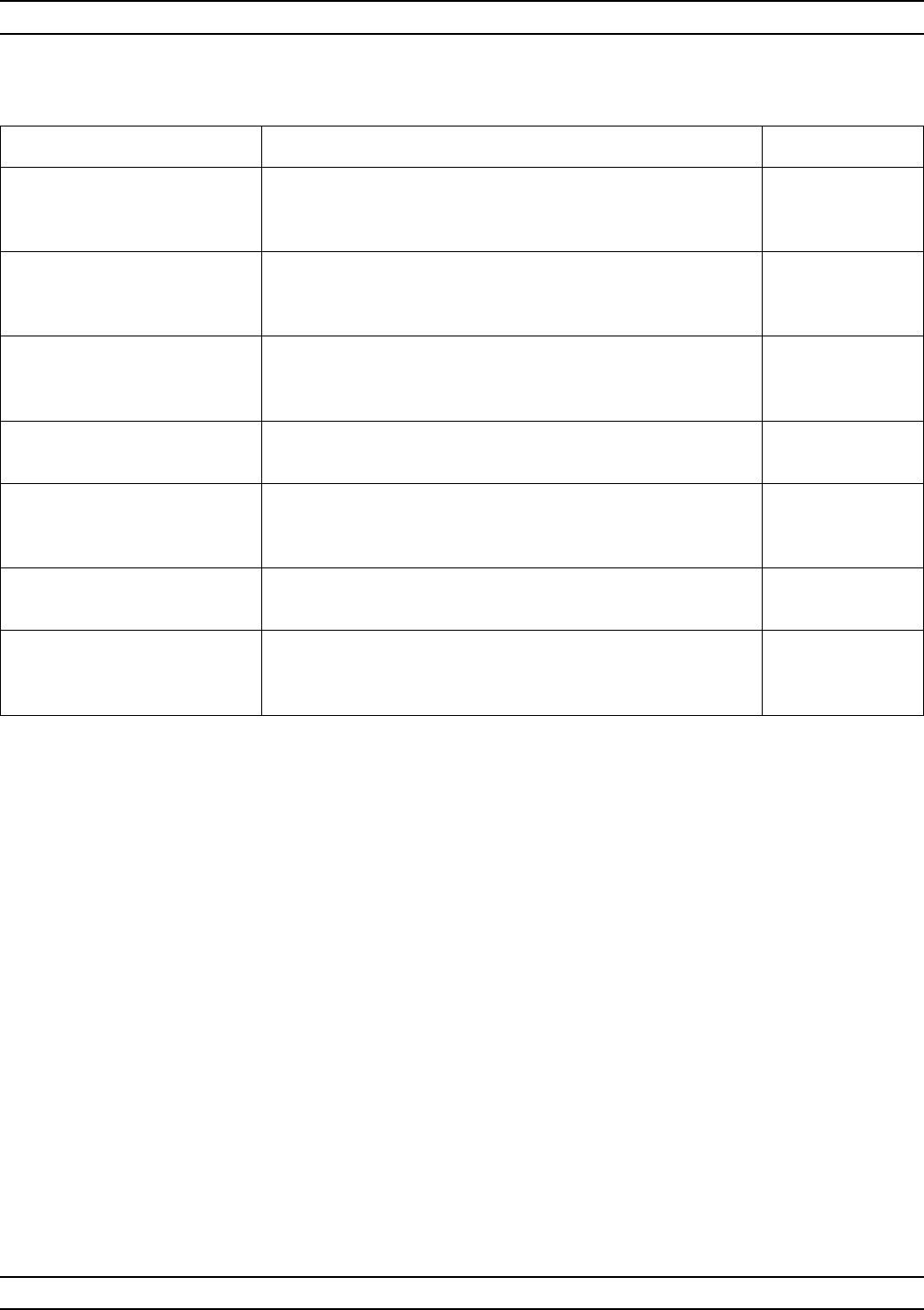
A-40 37XXXC OM
C ALPHABETICAL LISTING
MENU DESCRIPTION GPIB COMMAND
CONFIRM
CALIBRATION
PARAMETERS
None
TRM REFLECT
OFFSET LENGTH
+XXX.XXX mmX
Enter the offset length of the TRM reflection. TOL; TOL?; ROL;
ROL?
TRM MATCH
IMPEDANCE Calls menu C6B, which lets you change the match
impedance of the coaxial line standard to other than 50 W
(default).
None
WAVEGUIDE
CUTOFF FREQ Calls menu 15B, which lets you enter a waveguide cutoff
frequency. None
TEST SIGNALS Calls menu CAL_SU2, which lets you enter calibrate Flat
Test Port Power or change source power(s) and attenuator
settings.
None
START CAL Starts the standard calibration sequence using microstrip
standards. BEG
PRESS <ENTER>
TO SELECT
OR CHANGE
Pressing the Enter key implements your menu selection. None
Menu C3I, ConfirmCalibration Parameter 2
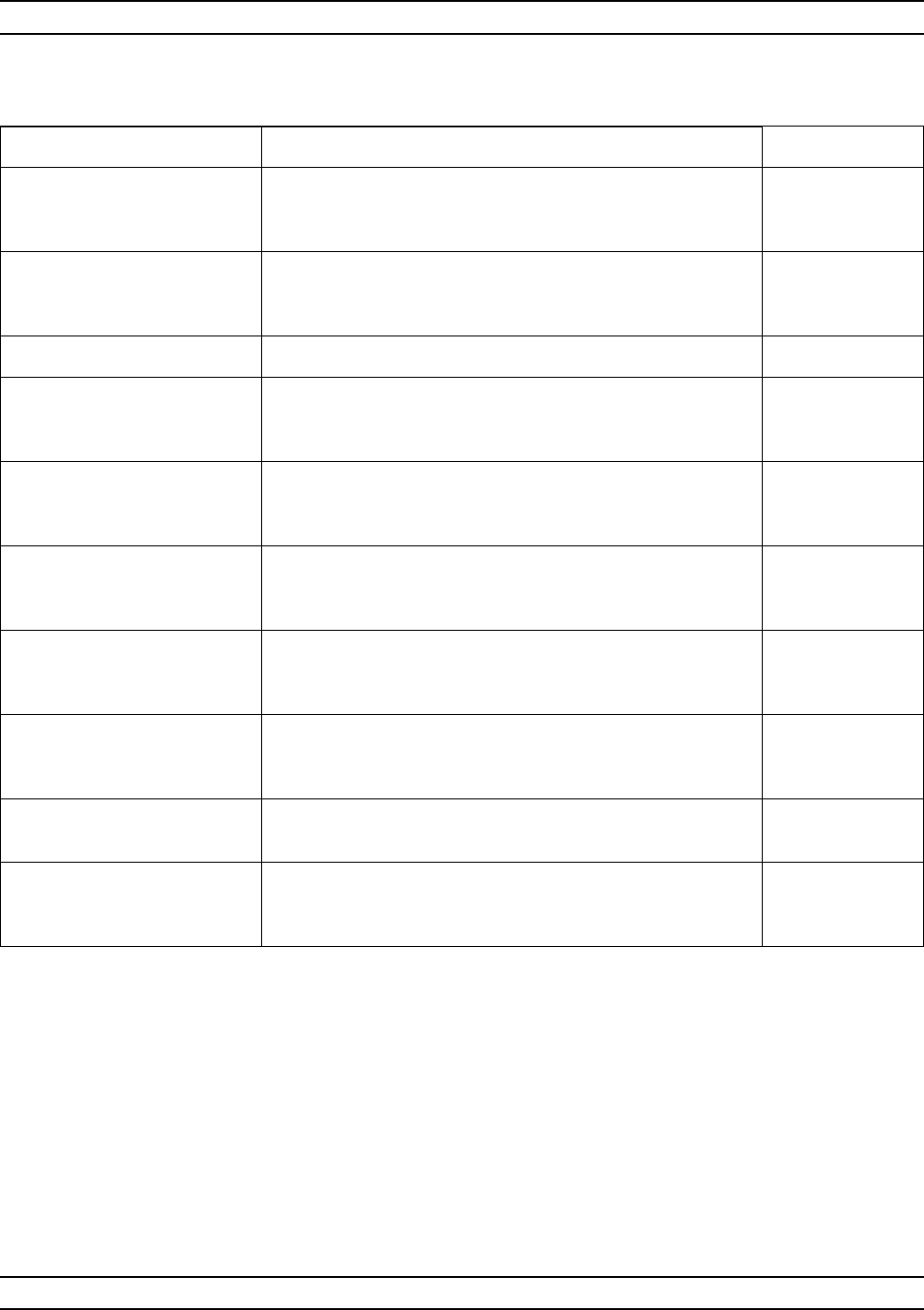
37XXXC OM A-41
ALPHABETICAL LISTING C
MENU DESCRIPTION GPIB COMMAND
CONFIRM
CALIBRATION
PARAMETERS
None
TRM REFLECT
OFFSET LENGTH
+XXX.XXX mmX
Enter the offset length of the TRM reflection. TOL; TOL?; ROL;
ROL?
TRM REFLECT TYPE None
GREATER THN Zo Specifies the reflection to have an impedance value greater
than the reference impedance (Z0).This is typically an open
device.
RGZ; RXZ?
LESS THAN Zo Selects the reflection to have an impedance value less than
the reference impedance (Z0). This is typically a short
device.
RLZ; RXZ?
TRM MATCH
IMPEDANCE Calls menu C6B, which lets you change the match
impedance of the coaxial line standard to other than 50 W
(default).
None
MICROSTRIP
PARAMETERS
XXXXXXX
Calls menu C16 or 16A, which lets you change microstrip
parameters. None
TEST SIGNALS Calls menu CAL_SU2, which lets you enter calibrate Flat
Test Port Power or change source power(s) and attenuator
settings.
None
START CAL Starts the standard calibration sequence using microstrip
standards. BEG
PRESS <ENTER>
TO SELECT
OR CHANGE
Pressing the Enter key implements your menu selection. None
Menu C3J, ConfirmCalibration Parameter 3
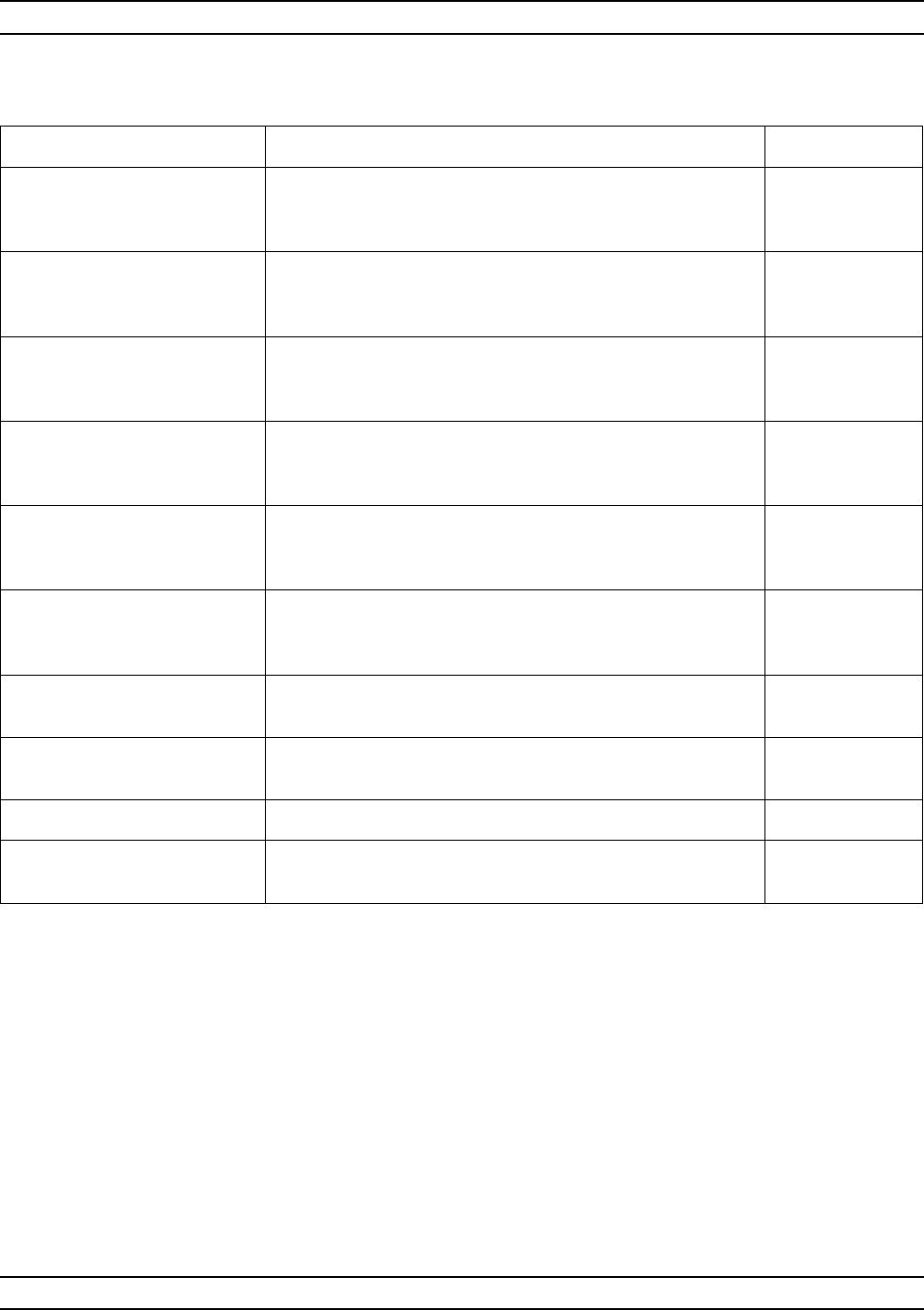
A-42 37XXXC OM
C ALPHABETICAL LISTING
MENU DESCRIPTION GPIB COMMAND
SELECT PORT X
CONNECTOR TYPE Applies the four capacitance-coefficient values to the Open
and offset length to the Short. The data appears in the
display area of the screen.
None
K-CONN (M)
K-CONN (F)
Select for K-CONN (M) connector on Port X.
Select for K-CONN (F) connector on Port X.
CMK; P1C?;P2C?
CFK; P1C?;P2C?
V-CONN (M)
V-CONN (F)
Select for V-CONN (M) connector on Port X.
Select for V-CONN (F) connector on Port X.
CMV; P1C?;P2C?
CFV; P1C?;P2C?
W1-CONN (M)
W1-CONN (F)
Select for W1-CONN (M) connector on Port X.
Select for W1-CONN (F) connector on Port X.
CM1; P1C?;P2C?
CF1; P1C?;P2C?
SMA (M)
SMA (F)
Select for SMA (M) connector on Port X.
Select for SMA (F) connector on Port X.
CMS; P1C?;P2C?
CFS; P1C?;P2C?
GPC-3.5 (M)
GPC-3.5 (F)
Select for GPC-3.5 (M) connector on Port X.
Select for GPC-3.5 (F) connector on Port X.
CM3; P1C?;P2C?
CF3; P1C?;P2C?
GPC-7 Select for GPC-7 connector on Port X. CNG; P1C?;P2C?
USER DEFINED Calls menu C12, which lets you specify the connector
coefficients. None
MORE Calls menu C4A for additional connector types. None
PRESS <ENTER>
TO SELECT Pressing the Enter key implements your menu selection. None
Menu C4_P1/C4_P2, Select Connector Type
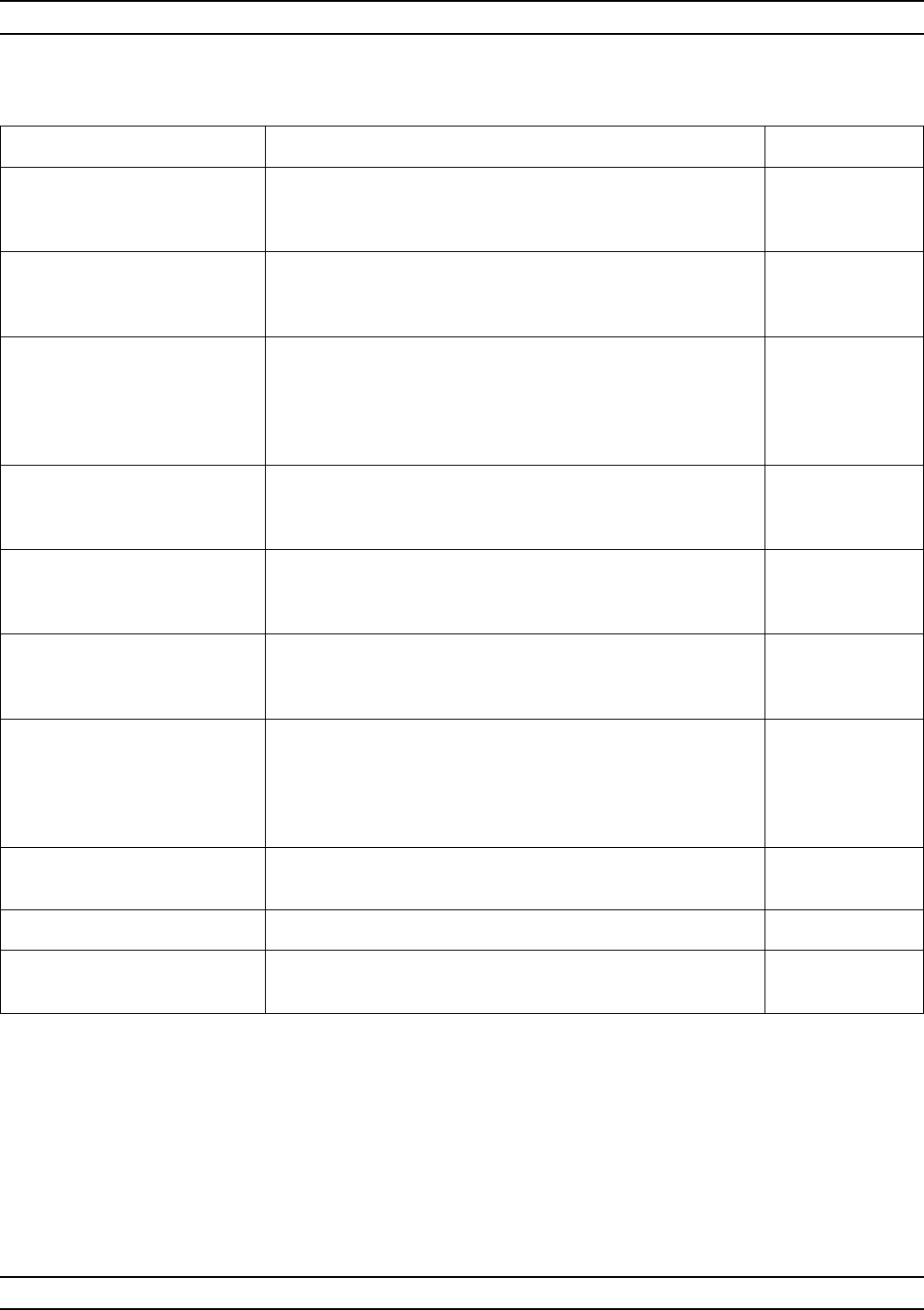
37XXXC OM A-43
ALPHABETICAL LISTING C
MENU DESCRIPTION GPIB COMMAND
SELECT PORT X
CONNECTOR TYPE Applies the four capacitance-coefficient values to the Open
and offset length to the Short. The data appears in the
display area of the screen.
None
TYPE N (M)
TYPE N (F)
Select for TYPE N (M) connector on Port X.
Select for TYPE N (F) connector on Port X.
CMN; P1C?;P2C?
CFN; P1C?;P2C?
TYPE N (M) 75W
TYPE N (F) 75W
Select for Type N (M) 75Wconnector on Port X.
Select for Type N (F) 75Wconnector on Port X.
CMN75; P1C?;
P2C?
CFN75;
P1C?;P2C?
7/16 (M)
7/16 (F)
Select for 7/16 (M) connector on Port X.
Select for 7/16 (F) connector on Port X.
CM7; P1C?;P2C?
CF7; P1C?;P2C?
TNC (M)
TNC (F)
Select for TNC (M) connector on Port X.
Select for TNC (F) connector on Port X.
CMC; P1C?;P2C?
CFC; P1C?;P2C?
2.4 mm (M)
2.4 mm(F)
Select for 2.4 mm (M) connector on Port X.
Select for 2.5 mm (F) connector on Port X.
CM2; P1C?;P2C?
CF2; P1C?;P2C?
SPECIAL (M)
SPECIAL (F)
Select for Special (M) connector on Port X.
Select for Special (F) connector on Port X.
CMSP;
P1C?;P2C?
CFSP;
P1C?;P2C?
USER DEFINED Calls menu C12, which lets you specify the connector
coefficients. None
MORE Calls additional connector types to screen. None
PRESS <ENTER>
WHEN COMPLETE Pressing the Enter key implements your menu selection. None
Menu C4A_P1/C4A_P2, Select Connector Type
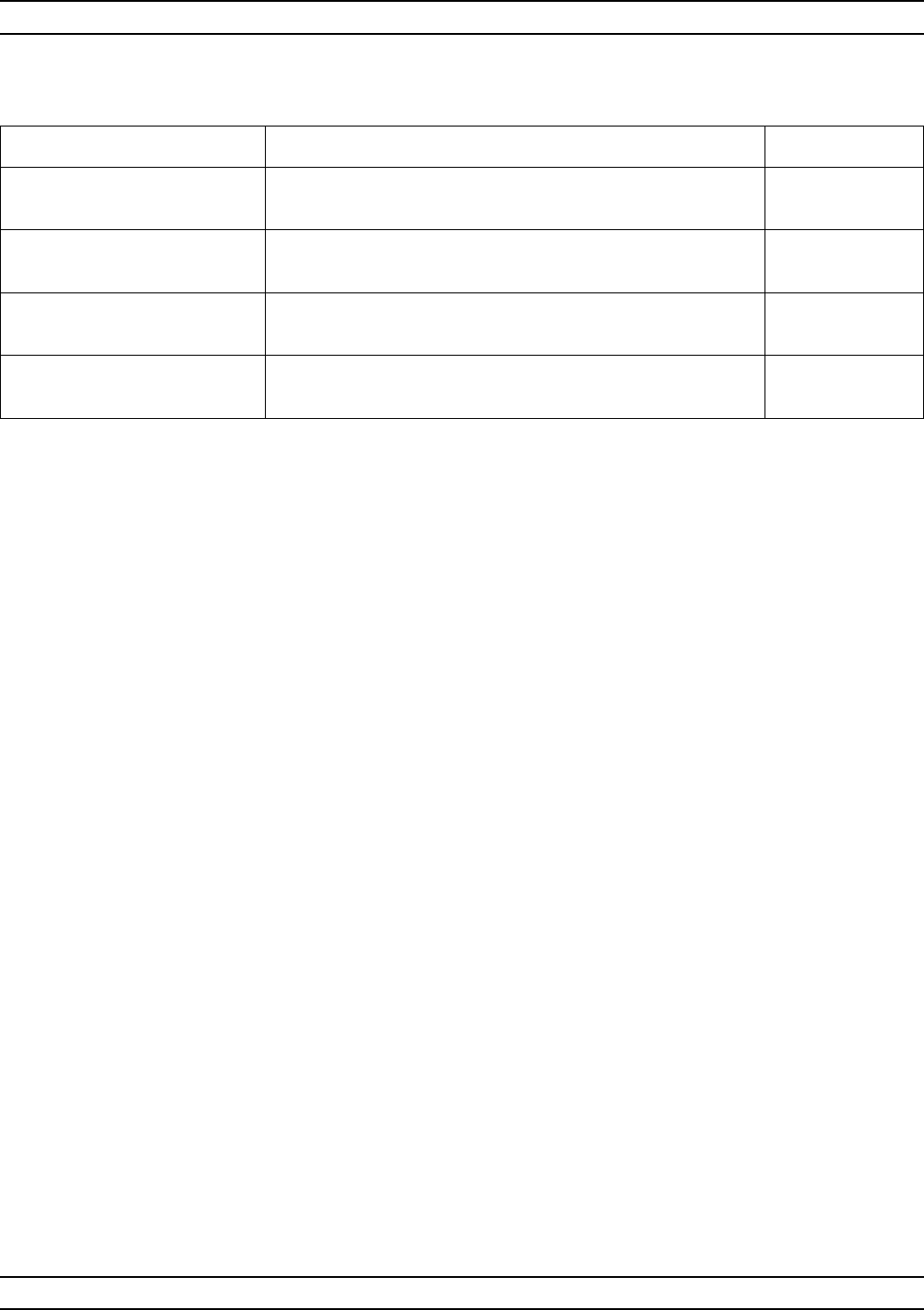
A-44 37XXXC OM
C ALPHABETICAL LISTING
MENU DESCRIPTION GPIB COMMAND
SELECT PORT X
OPEN & SHORT None
SPECIAL (M)
SPECIAL (F) C12
USER DEFINED Calls menu C12, which lets you specify the connector
coefficients. None
PRESS <ENTER>
TO SELECT Pressing the Enter key implements your menu selection. None
Menu C4B, Select Open and Short Type
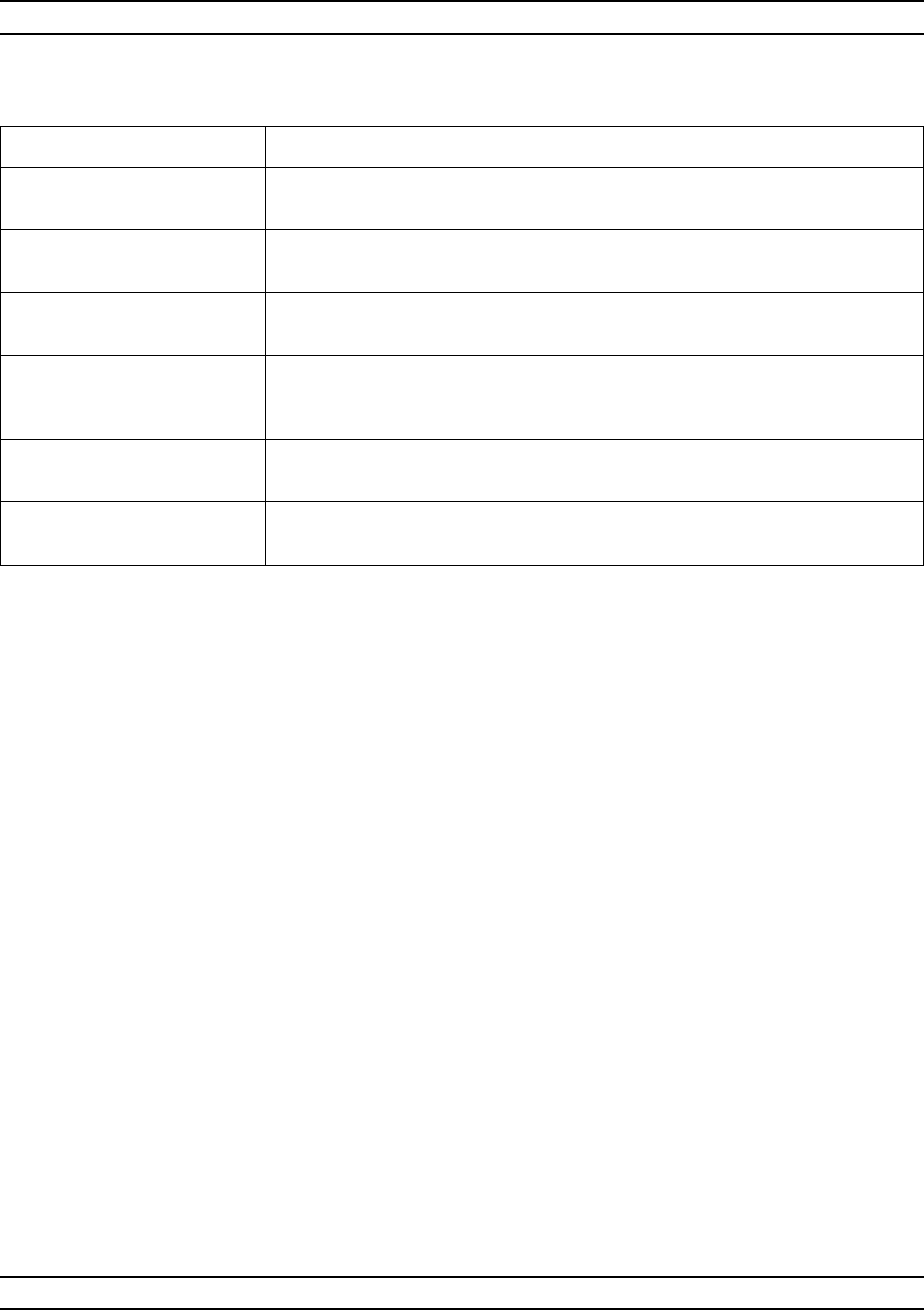
37XXXC OM A-45
ALPHABETICAL LISTING C
MENU DESCRIPTION GPIB COMMAND
SELECT
CALIBRATION TYPE None
FULL 12-TERM Select calibration using all 12 error terms EDF, ESF, ERF,
ETF, ELF, (EXF), EDR, ESR, ERR, ETR, FLR, (EXR). C12
1 PATH
2 PORT Calls menu C5A, which lets select a correction for forward-
or reverse-direction error terms. None
TRANSMISSION
FREQUENCY
RESPONSE
Calls menu C5B, which lets select a correction for
frequency response error terms. None
REFLECTION
ONLY Calls menu C5C, which lets select a correction for
reflection-only error terms. None
PRESS <ENTER>
TO SELECT Pressing the Enter key implements your menu selection. None
Menu C5, Select Calibration Type
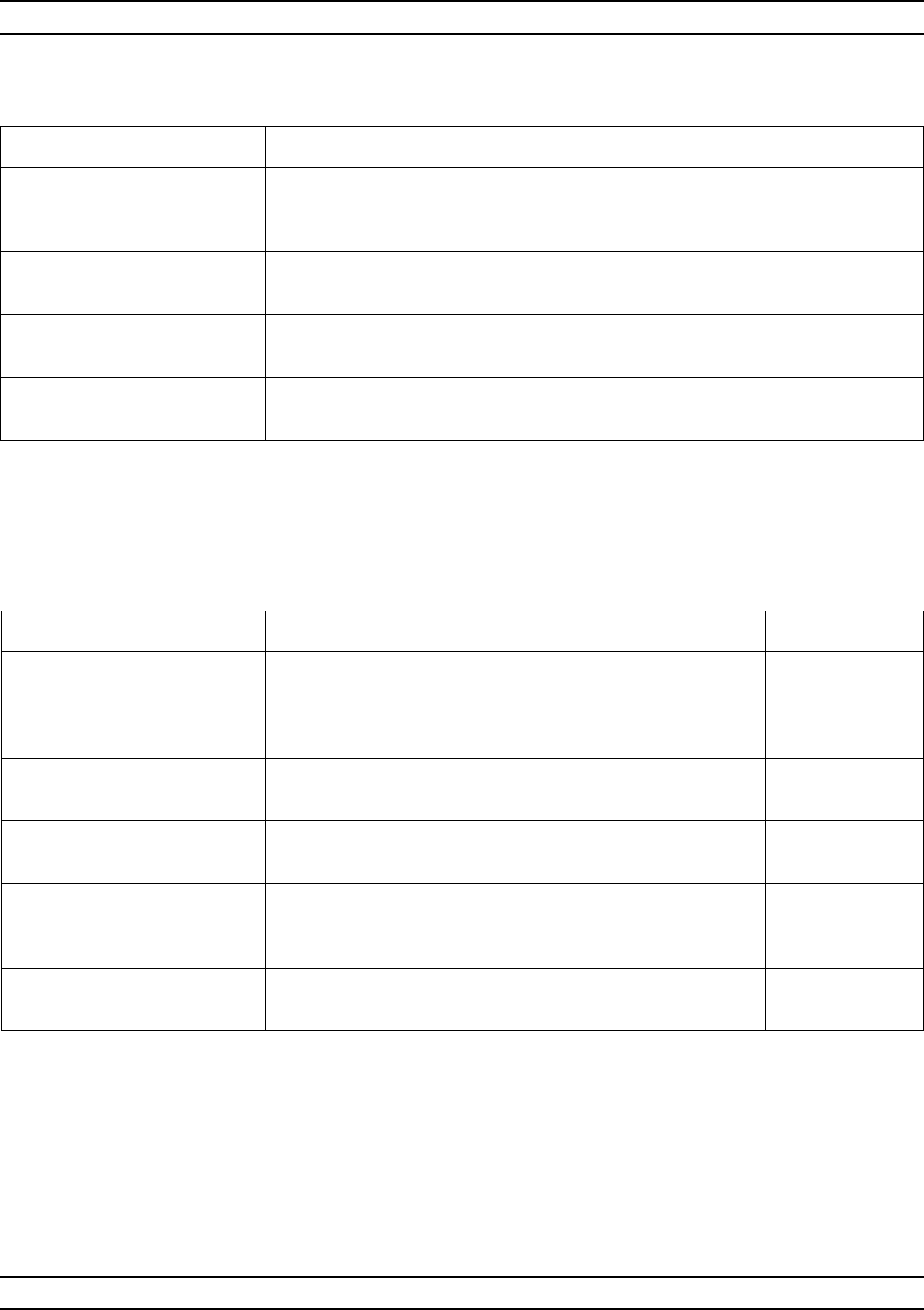
A-46 37XXXC OM
C ALPHABETICAL LISTING
MENU DESCRIPTION GPIB COMMAND
SELECT
1 PATH 2 PORT
CALIBRATION TYPE
None
FORWARD PATH
(S11, S21) For the calibration-correction of the forward transmission
and reflection error term, ETF, EDF, ESF, ERF, (EXF). C8T
REVERSE PATH
(S12, S22) For the calibration-correction of the reverse transmission
and reflection error term, EDR, ESR, ERR, ETR, (EXR). C8R
PRESS <ENTER>
TO SELECT Pressing the Enter key implements your selection. None
Menu C5A, Select 1 Path 2 Port Calibration Type
MENU DESCRIPTION GPIB COMMAND
SELECT
TRANSMISSION
FREQ RESPONSE
CALIBRATION TYPE
None
FORWARD PATH
(S21) For the calibration-correction of the forward transmission
frequency-response error term, ETF. (EXF). CFT; CXX?
REVERSE PATH
(S12) For the calibration-correction of the reverse
transmission-frequency-response error term, ETR, (EXR). CRT; CXX?
BOTH PATHS
(S21, S12) For the calibration-correction of the forward and reverse
transmission-frequency-response error terms ETF, ETR,
(EXF, EXR).
CBT; CXX?
PRESS <ENTER>
TO SELECT Pressing the Enter key implements your menu selection. None
Menu C5B, Select Transmission Freq Response Calibration Type
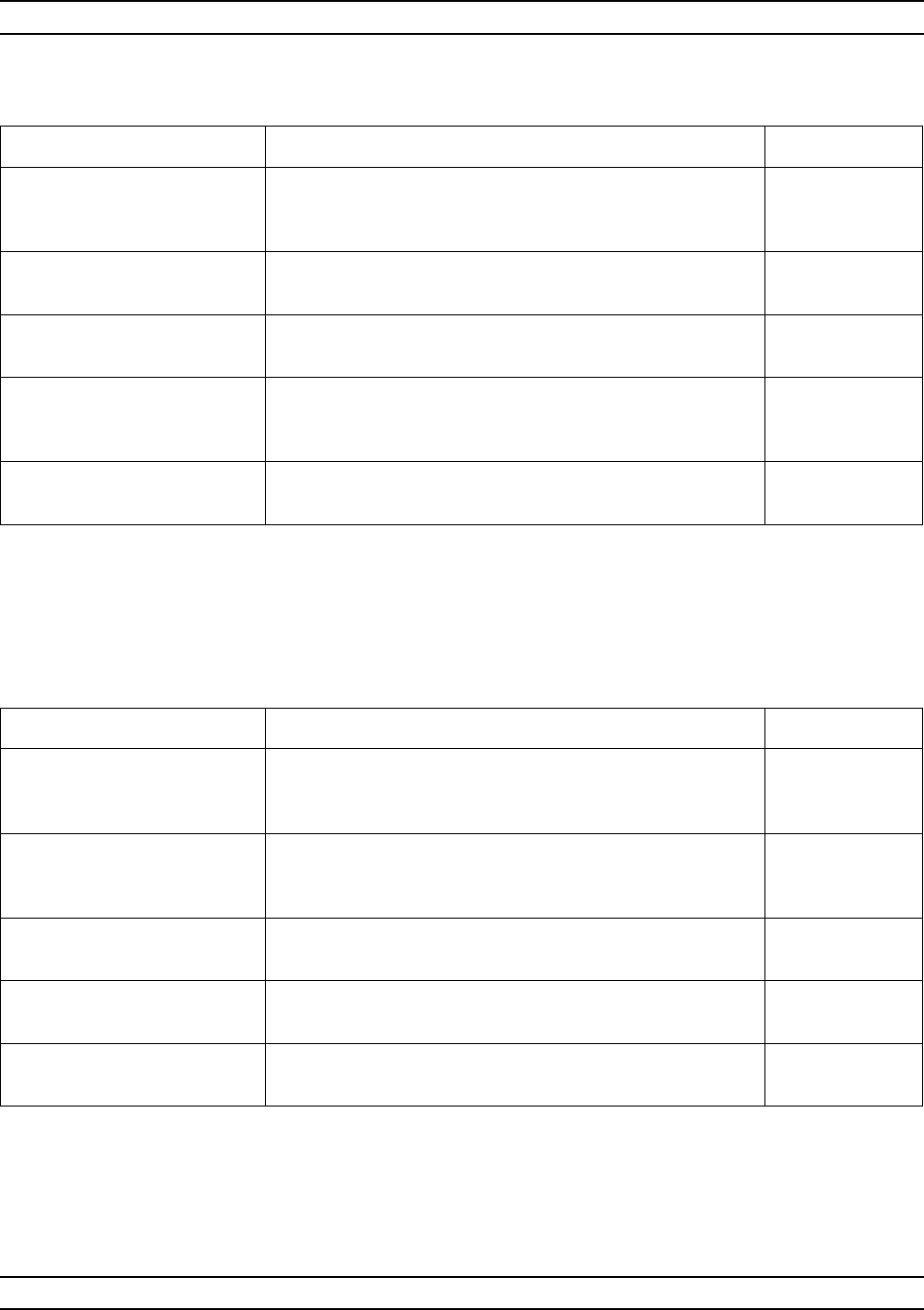
37XXXC OM A-47
ALPHABETICAL LISTING C
MENU DESCRIPTION GPIB COMMAND
SELECT
REFLECTION ONLY
CALIBRATION TYPE
None
PORT 1 ONLY
(S11) For the calibration-correction of the forward reflection-only
error terms EDF, ESF, ERF. CRF; CXX?
PORT 2 ONLY
(S22) For the calibration-correction of the reverse reflection-only
error terms EDR, ESR, ERR. CRR; CXX?
BOTH PORTS
(S11, S22) For the calibration-correction of the forward and reverse
reflection-only error terms EDF, ESF, ERF, EDR, ESR,
ERR.
CRB; CXX?
PRESS <ENTER>
TO SELECT Pressing the Enter key implements your menu selection. None
Menu C5C, Select Reflection Only Calibration Type
MENU DESCRIPTION GPIB COMMAND
SELECT USE
OF ISOLATION
IN CALIBRATION
None
INCLUDE
ISOLATION
(STANDARD)
Includes isolation term(s). ISN; ISX?
EXCLUDE
ISOLATION Excludes isolation term(s). ISF; ISX?
PRESS <ENTER>
TO SELECT Pressing the Enter key implements your menu selection. None
PRESS <ENTER>
TO SELECT Pressing the ENTER key implements your selection.
Menu C5D, Select Use of Isolation
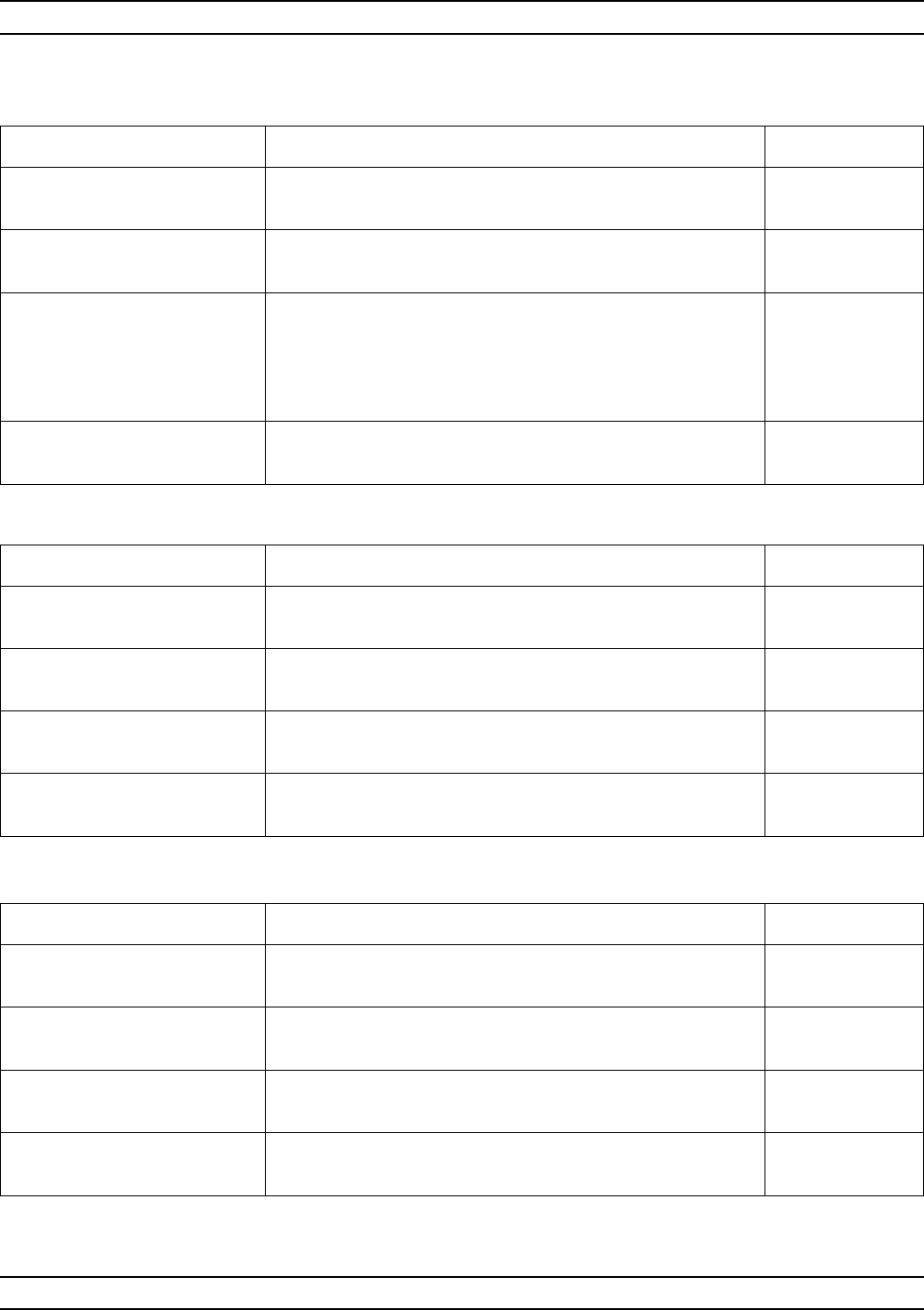
A-48 37XXXC OM
C ALPHABETICAL LISTING
MENU DESCRIPTION GPIB COMMAND
SELECT
TYPE OF LOAD None
BROADBAND
FIXED LOAD Selects calibration based on the broadband load being
used, then calls menu C6A. BBL; BBX?
SLIDING LOAD
(MAY ALSO
REQUIRE
BROADBAND
FIXED LOAD)
Selects calibration based on the sliding load being used. If
your low-end frequency is below 2 GHz (4 GHz for V
Connector), a fixed broadband load is also required.
SLD; BBX?
PRESS <ENTER>
TO SELECT Pressing the Enter key implements your menu selection. None
Menu C6, Select Load Type
MENU DESCRIPTION GPIB COMMAND
BROADBAND LOAD
PARAMETERS None
IMPEDANCE
XX.XXX W
Enter the impedance of the load. BBZ; BBZ?
INDUCTANCE
XX.XXX pH Enter the inductance of the load. BBZL; BBZL?
PRESS <ENTER>
WHEN COMPLETE Pressing the Enter key implements your menu selection. None
Menu C6A, Enter Broadband Load Impedance
MENU DESCRIPTION GPIB COMMAND
TRM MATCH
PARAMETERS None
IMPEDANCE
XX.XXX W
Allows entry of the impedance (defaults to 50.000 W). BBZ; BBZ?
INDUCTANCE
XX.XXX pH Allows entry of the inductance (defaults to 0.00 pH). BBZL; BBZL?
PRESS <ENTER>
WHEN COMPLETE Pressing the Enter key implements your menu selection. None
Menu C6B, Enter Broadband Load Impedance
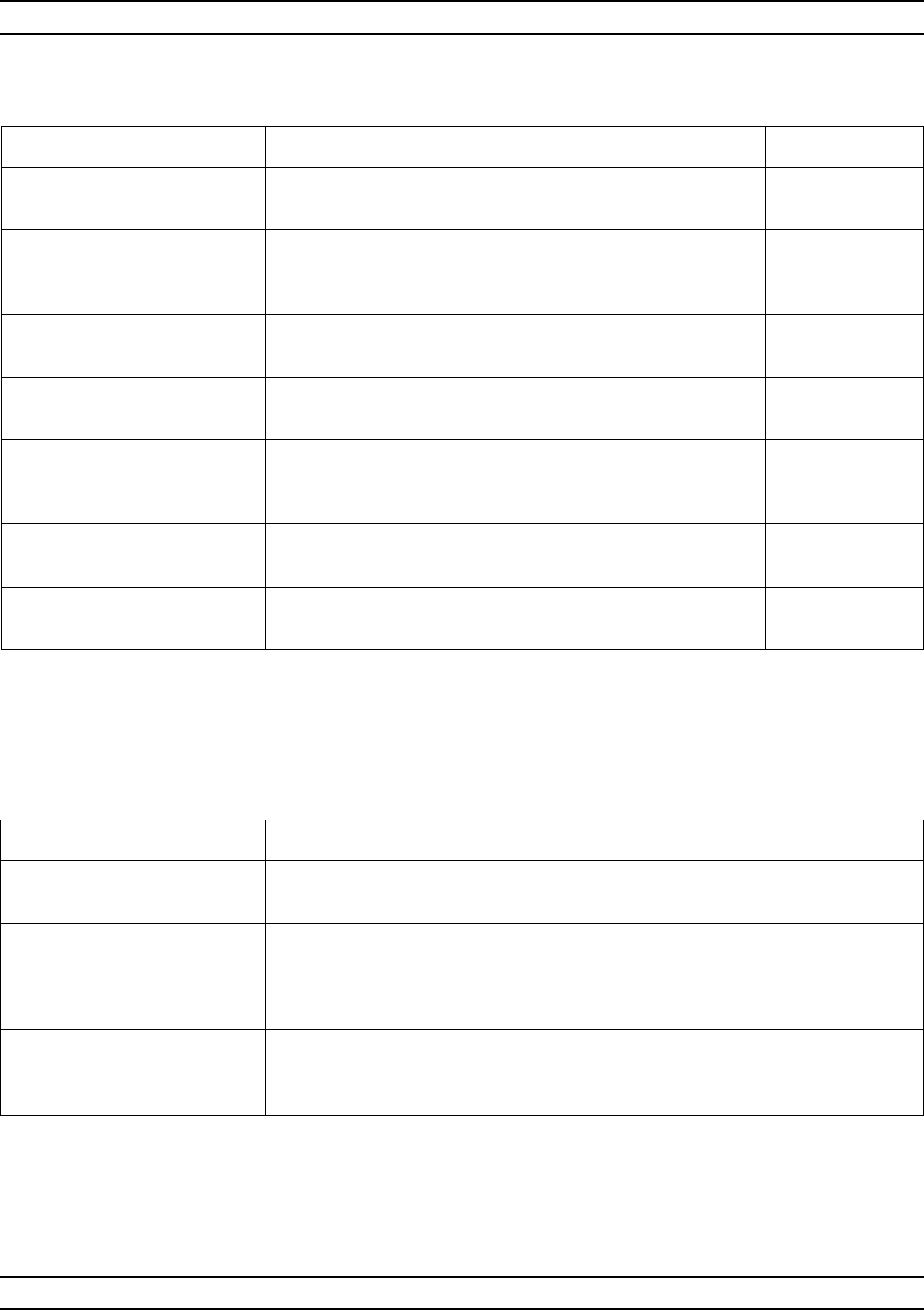
37XXXC OM A-49
ALPHABETICAL LISTING C
MENU DESCRIPTION GPIB COMMAND
CALIBRATION
SEQUENCE None
CONNECT
CALIBRATION
DEVICE(S)
None
PORT 1:
XXXXXXXXXXXX Connect the required component to Port 1. None
PORT 2:
XXXXXXXXXXXX Connect the required component to Port 2. None
PRESS <ENTER>
TO MEASURE
DEVICE(S)
Pressing the Enter key sequentially measures the devices
connected to Ports 1 and 2, beginning with Port 1. None
PRESS <1> FOR
PORT 1 DEVICE Pressing the 1 key, on the keypad, measures the device
connected to Port 1. None
PRESS <2> FOR
PORT 2 DEVICE Pressing the 2 key, on the keypad, measures the device
connected to Port 2. None
Menu C7-Series, Begin Calibration Sequence
MENU DESCRIPTION GPIB COMMAND
CALIBRATION
SEQUENCE None
SLIDE LOAD
TO POSITION X Slide the load to the next position, then press the Enter
key. Moving the slide to six different positions provides
sufficient data for the program to accurately calculate the
effective directivity of the system.
None
PRESS <ENTER>
TO MEASURE
DEVICE (S)
Pressing the Enter key begins the measurement. None
Menu C8, Slide Load to Position X
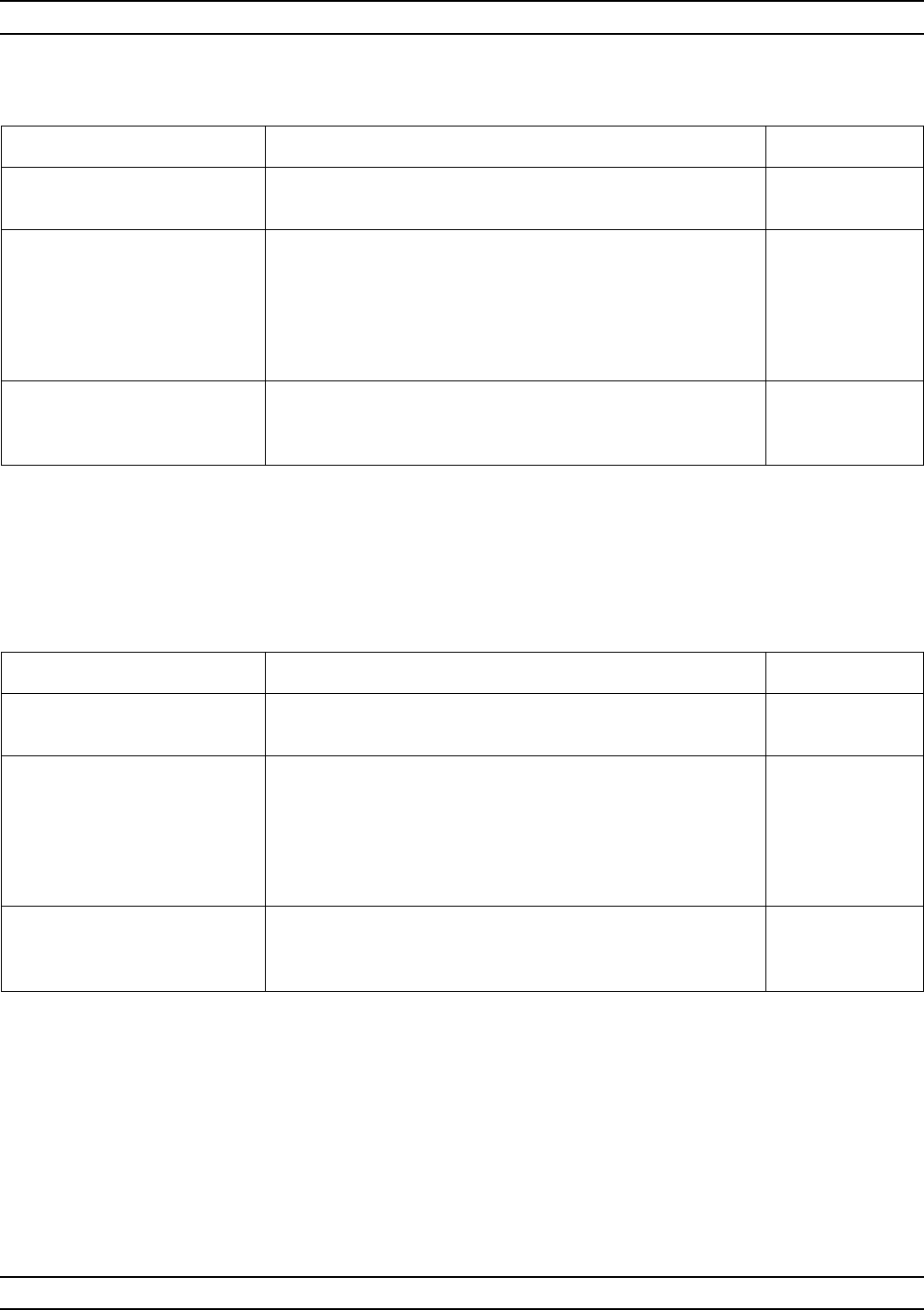
A-50 37XXXC OM
C ALPHABETICAL LISTING
MENU DESCRIPTION GPIB COMMAND
CALIBRATION
SEQUENCE None
CONNECT
DEVICE 1
LINE 1 (REF)
XXXXX
BETWEEN
TEST PORTS
Prompts you to connect reference line 1 between test
ports. None
PRESS <ENTER>
TO MEASURE
DEVICE(S)
Pressing the Enter key begins the measurement. None
Menu C9A, Connect Device 1, Line
MENU DESCRIPTION GPIB COMMAND
CALIBRATION
SEQUENCE None
CONNECT
THROUGHLINE
XXXXX
BETWEEN
TEST PORTS
Connect Ports 1 and 2 together using the Throughline
standard (zero or non-zero length). None
PRESS <ENTER>
TO MEASURE
DEVICE(S)
Pressing the Enter key begins the measurement. None
Menu C9, Connect Throughline
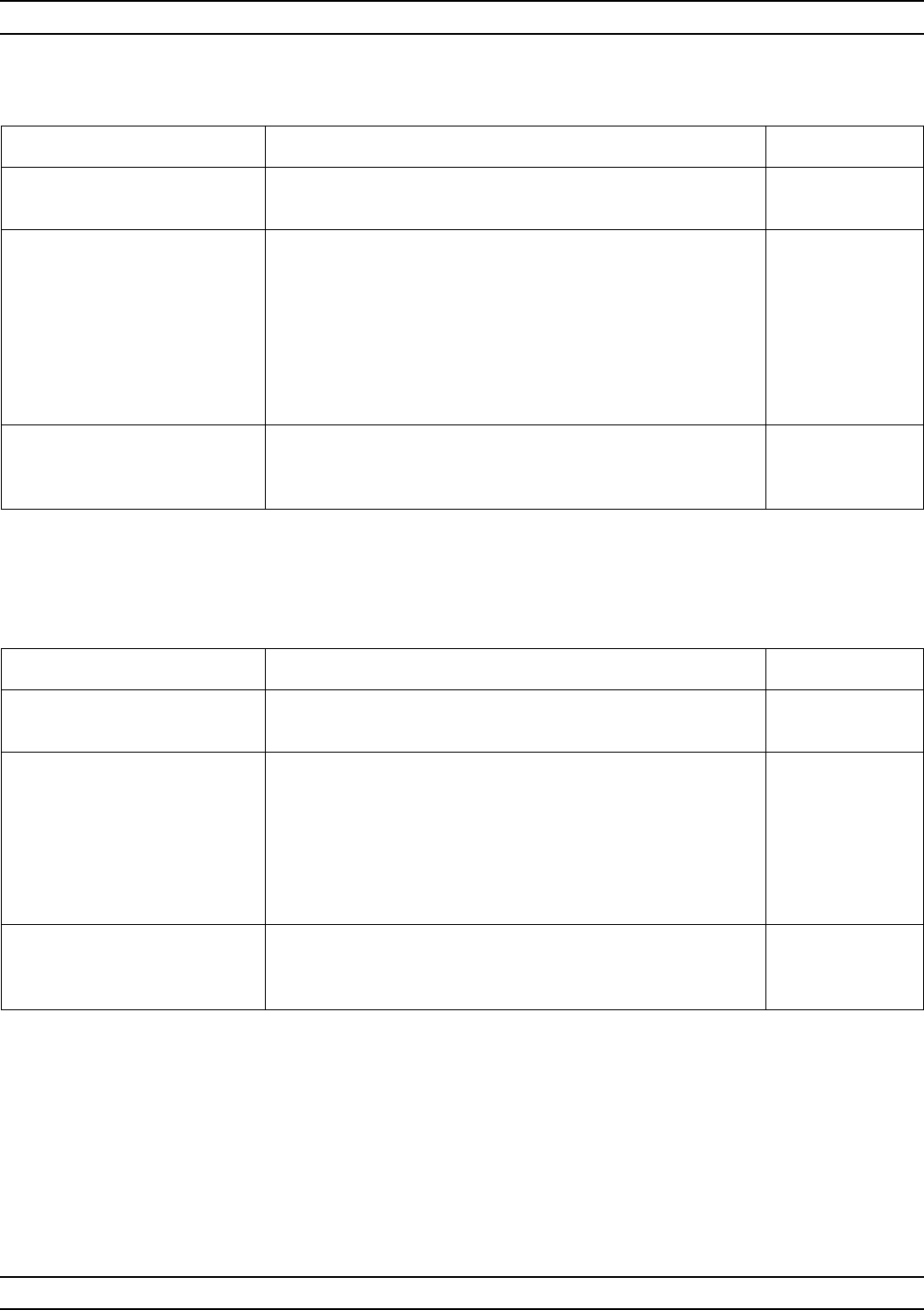
37XXXC OM A-51
ALPHABETICAL LISTING C
MENU DESCRIPTION GPIB COMMAND
CALIBRATION
SEQUENCE None
CONNECT
DEVICE 2
LINE
XXXXX
BETWEEN
TEST PORTS
Prompts you to connect the second line standard between
the test ports. None
PRESS <ENTER>
TO MEASURE
DEVICE(S)
Pressing the Enter key begins the measurement. None
Menu C9C, Connect Device 2, Line
MENU DESCRIPTION GPIB COMMAND
CALIBRATION
SEQUENCE None
CONNECT
DEVICE 2
LINE/
LOWBAND
MATCHES
BETWEEN
TEST PORTS
Connect device 2 between the test ports. This will be a
LINE for LRL measurements or LOWBAND MATCHES for
LRM measurements.
None
PRESS <ENTER>
TO MEASURE
DEVICE(S)
Pressing the Enter key begins the measurement. None
Menu C9B, Connect Device 2, Line/Lowband
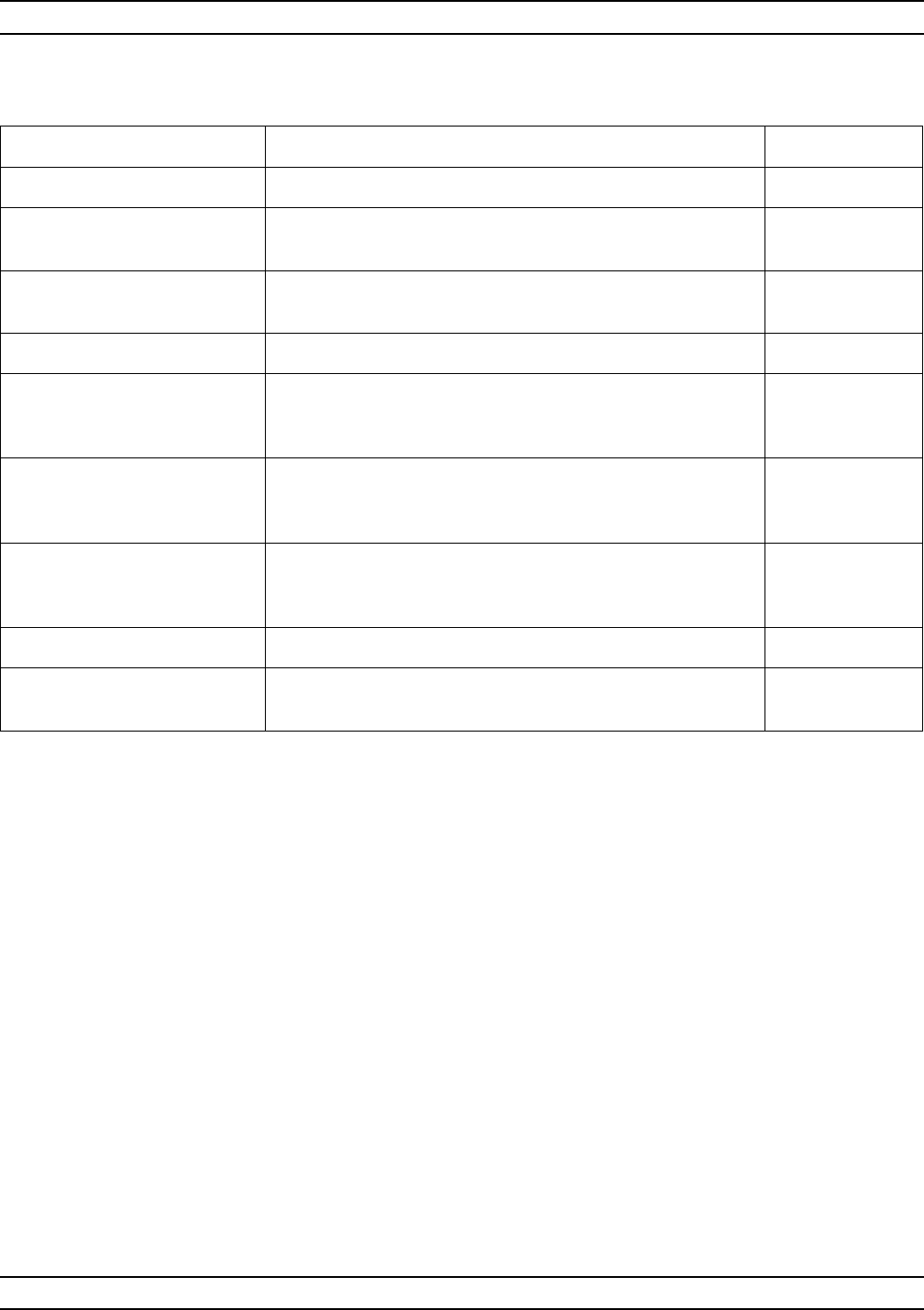
A-52 37XXXC OM
C ALPHABETICAL LISTING
MENU DESCRIPTION GPIB COMMAND
BEGIN CALIBRATION None
KEEP EXISTING
CAL DATA Keep existing calibration data. KEC
REPEAT
PREVIOUS CAL Repeats the previous calibration. RPC
AUTOCAL Calls menu ACAL, which lets you choose AutoCal settings. None
CAL METHOD
XXXXXXX Displays the calibration method that you have
selected—standard,
offset short or LRL/LRM.
CMX?
TRANSMISSION
LINE TYPE:
XXXXXXXX
Indicates type of transmission line currently selected, e. g.
coaxial,
waveguide, microstrip.
LTX?
CHANGE CAL
METHOD AND
LINE TYPE
Calls menu C11A, which allows you to change calibration
method and transmission line type. None
NEXT CAL STEP Selects the next calibration step. None
PRESS <ENTER>
TO SELECT Pressing the Enter key implements your menu selection. None
Menu C11, Begin Calibration
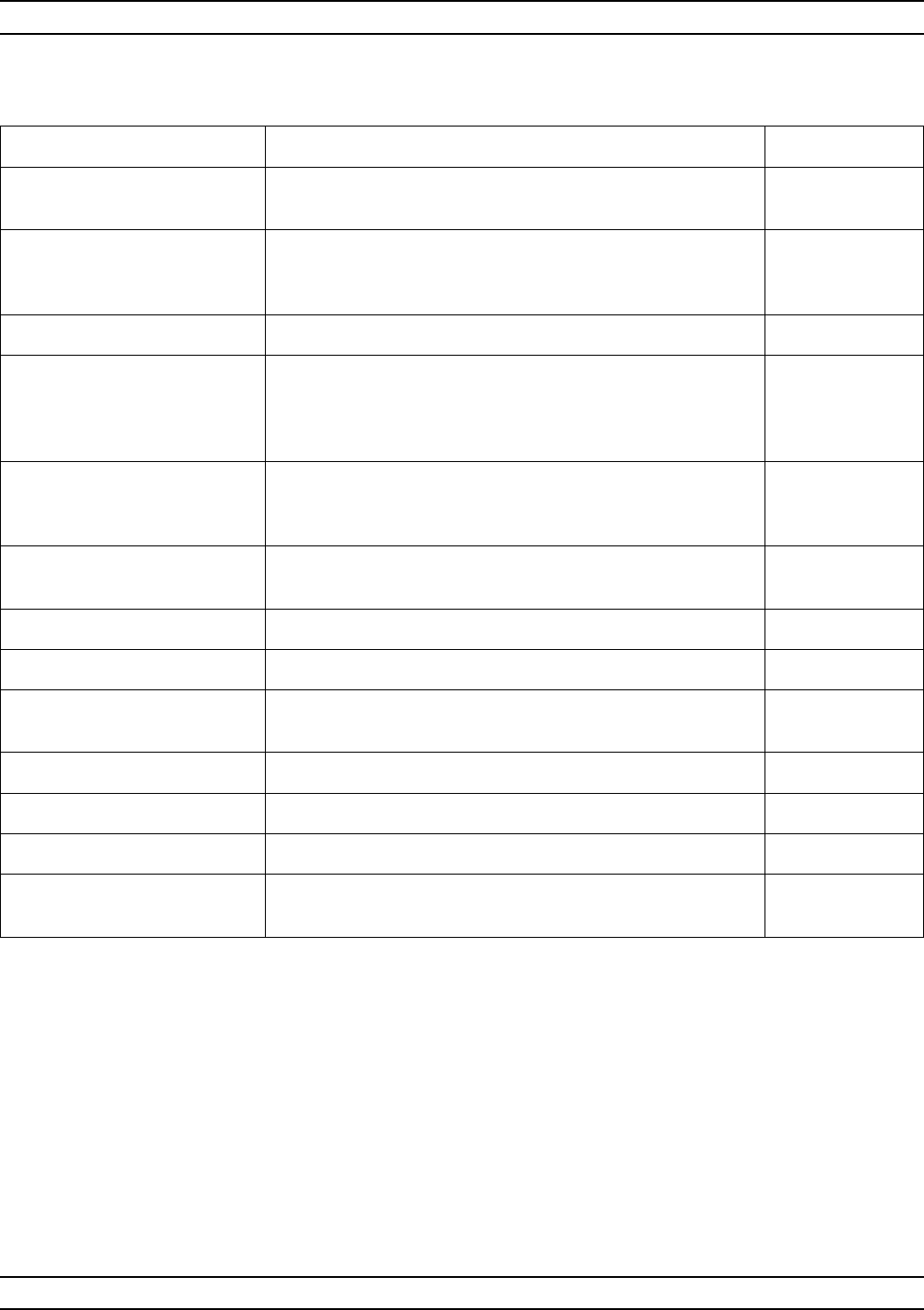
37XXXC OM A-53
ALPHABETICAL LISTING C
MENU DESCRIPTION GPIB COMMAND
CHANGE CAL METHOD
AND LINE TYPE None
NEXT CAL STEP Select next calibration step. Must move cursor to here after
making below selections. Pressing the Enter key then
moves you to the next step.
None
CAL METHOD None
(SOLT) STANDARD This option and the ones below allow you to select the
method (procedure) to be used to calibrate. This method is
independent of the calibration type, which may be 12-term,
reflection only, etc.
SCM; CMX?
SSLT (DOUBLE
OFFSET SHORT
WITH LOAD)
Selects the double offset short calibration method. OCM; CMX?
SSST (TRIPLE
OFFSET SHORT) Selects the triple offset short calibration method. OC3M; CMX?
LRL/LRM Selects LRL or LRM method. LCM; CMX?
TRM Selects TRM method. TCM; CMX?
TRANSMISSION
LINE TYPE None
COAXIAL Selects coaxial cable as the transmission line type. LTC; LTX?
WAVEGUIDE Selects waveguide as the transmission line type. LTW; LTX?
MICROSTRIP Selects microstrip as the transmission line type. LTU; LTX?
PRESS <ENTER>
TO SELECT Pressing the Enter key implements your menu selection. None
Menu C11A, Select Calibration Method
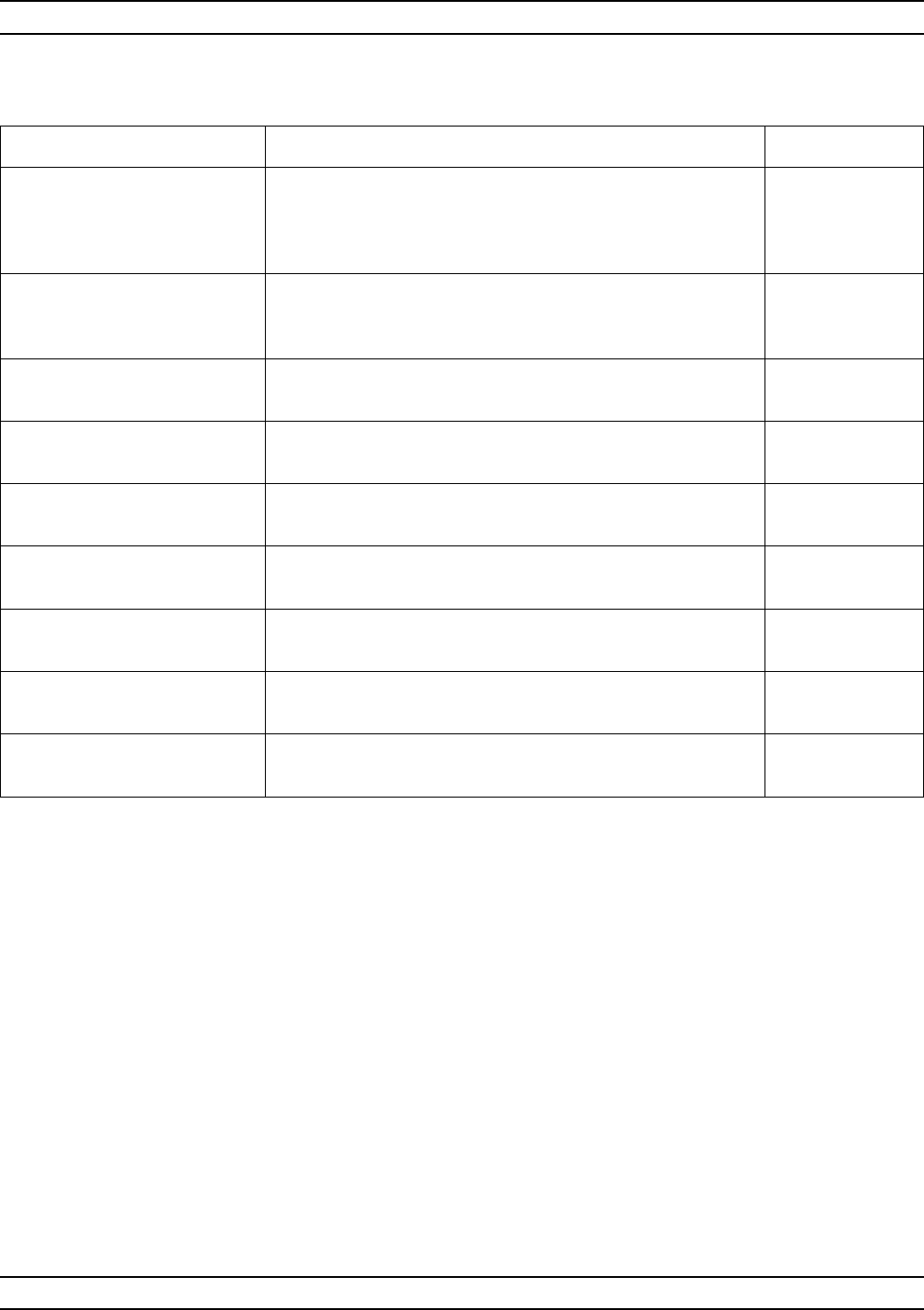
A-54 37XXXC OM
C ALPHABETICAL LISTING
MENU DESCRIPTION GPIB COMMAND
PORT X
OPEN DEVICE Enter the capacitance-coefficient values needed to correct
for your Open device. The capacitive phase shift of the
Open is characterized by the equation: COpen =C
O+(C
1x
f)+(C
2xf
2)+(C
3xf
3)
None
ENTER THE
CAPACITANCE
COEFFICIENTS
None
TERM 1-C0
±XX.XXe- 15 Enter the term 1 coefficient value (x 10–15 F). CC0; CC0?
TERM 2-C1
±XXX.XXe-27 Enter the term 2 coefficient value (x 10–27 F/Hz). CC1; CC1?
TERM 3-C2
±XXX.XXe-36 Enter the term 3 coefficient value (x 10–36 F/Hz2). CC2; CC2?
TERM 4-C3
±XXX.XXe-45 Enter the term 4 coefficient value (x 10–45 F/Hz3). CC3; CC3?
ENTER THE
OFFSET LENGTH Enter the length of the offset. COO
OFFSET LENGTH
±XX.XXXX mm Select to enter and display offset length of Open. COO?
PRESS <ENTER>
WHEN COMPLETE Pressing the Enter key calls C12A_P1/C12A_P2. None
Menu C12_P1/C12_P2, Enter the Capacitance Coefficients for Open Devices
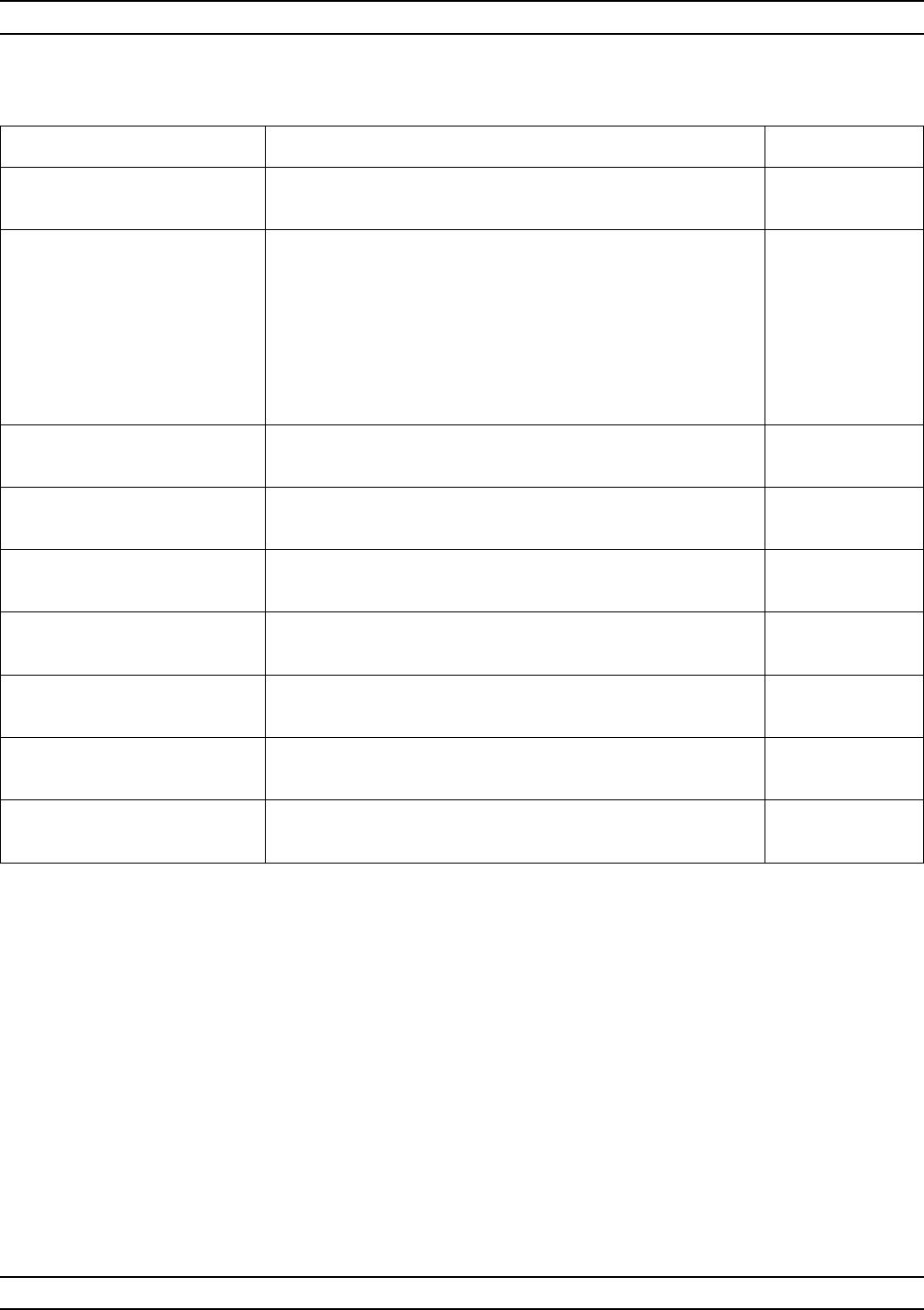
37XXXC OM A-55
ALPHABETICAL LISTING C
MENU DESCRIPTION GPIB COMMAND
PORT X
SHORT DEVICE None
ENTER THE
INDUCTANCE
COEFFICIENTS
Provide inductance term entries for the short device such
that the frequency dependent inductance is L(w) = L0 + (L1
* f) + (L2 * f^2) + (L3 * f^3). These values default to zero.
They are used in the standard calibration method in
combination with the coaxial and microstrip line types.
They are not used in the offset short and LRL/LRM
calibration methods. The calibration kits provided by
ANRITSU are not to support these terms.
None
TERM1-L0
-XXXX.XX e-12 Enter the term 1 value. CL0; CL0?
TERM2-L1
-XXXX.XX e-24 Enter the term 2 value. CL1; CL1?
TERM3-L2
-XXXX.XX e-33 Enter the term 3 value. CL2; CL2?
TERM4-L3
-XXXX.XX e-42 Enter the term 4 value. CL3; CL3?
ENTER THE
OFFSET LENGTH Enter the length of the offset device. COS
OFFSET LENGTH
-XXX.XXXX mm Displays the offset length value. COS?
PRESS <ENTER>
WHEN COMPLETE Pressing the Enter key implements your menu selection. None
Menu C12A_P1/C12A_P2, Enter the Offset Length
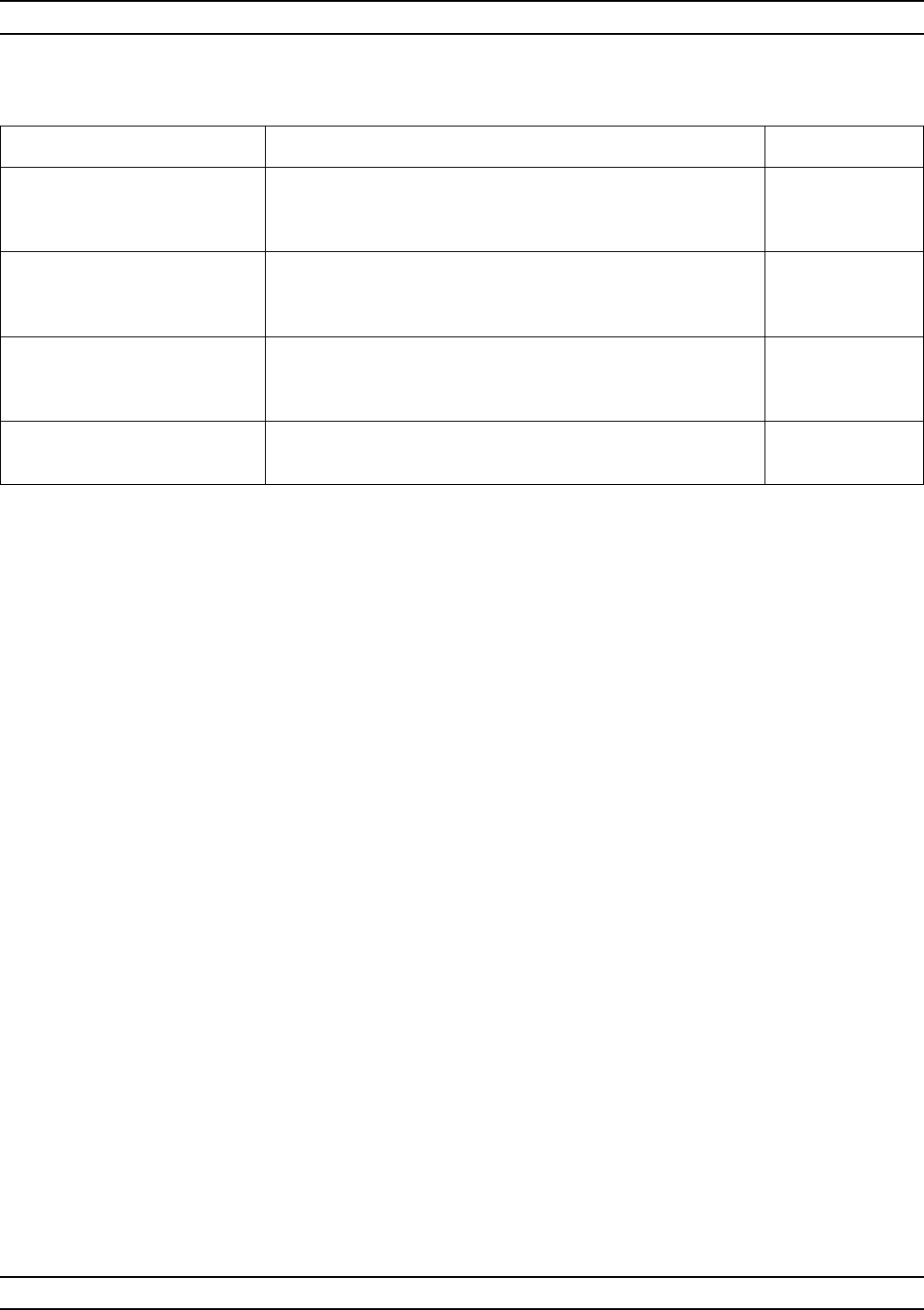
A-56 37XXXC OM
C ALPHABETICAL LISTING
MENU DESCRIPTION GPIB COMMAND
SET
REFLECTION
PAIRING
None
MIXED
(OPEN–SHORT
SHORT–OPEN)
Selects different reflection devices (open/short or
short/open) to be connected to Ports 1 and 2 for the
calibration sequencing.
MIX, MIX?
MATCHED
(OPEN–OPEN
SHORT–SHORT)
Selects the same type of reflection device (open/open or
short/short) to be connected to Ports 1 and 2 for the
calibration sequencing.
MAT, MIX?
PRESS <ENTER>
TO SELECT Pressing the Enter key implements your menu selection. None
Menu C13, Set Reflection Pairing Menu
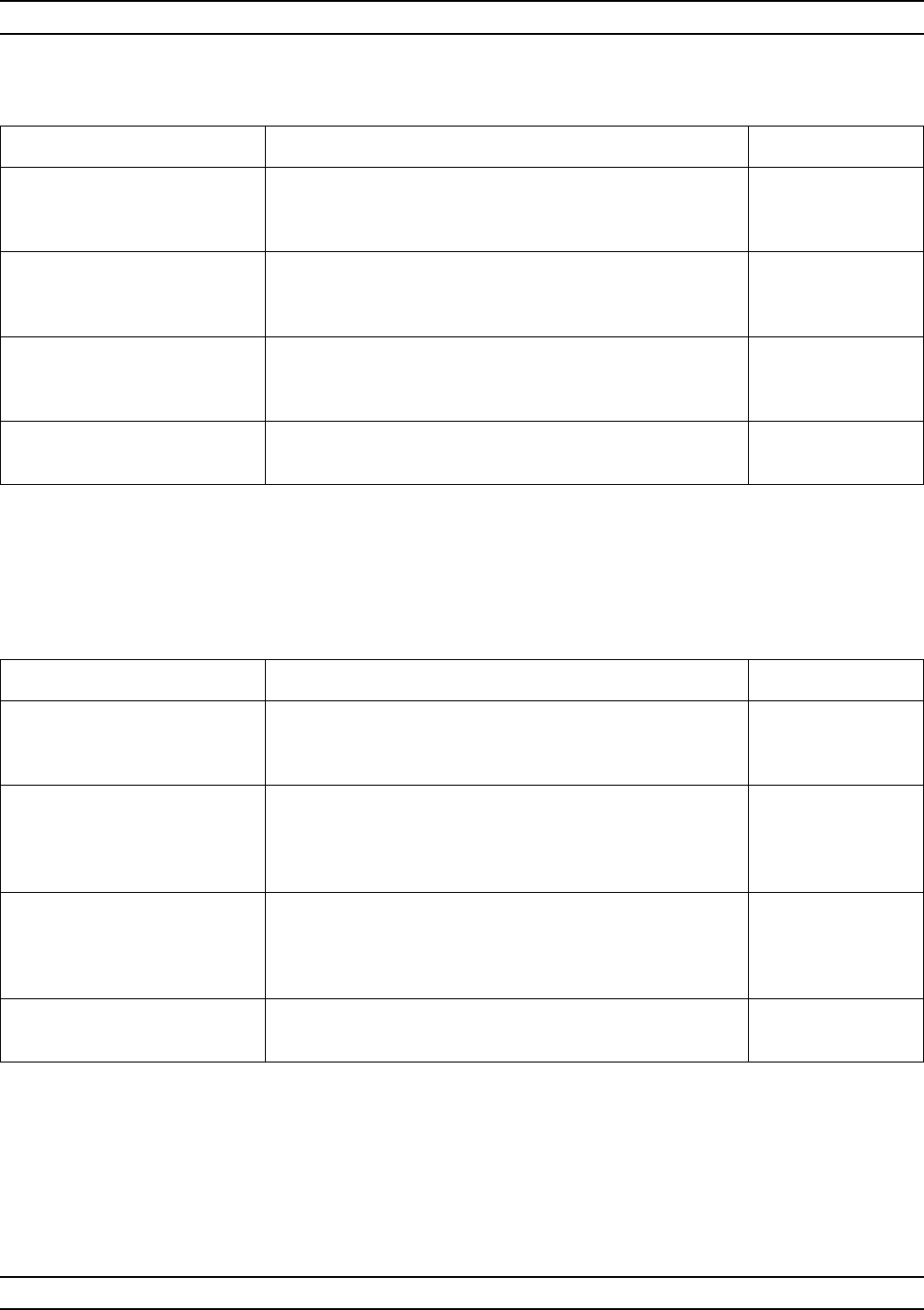
37XXXC OM A-57
ALPHABETICAL LISTING C
MENU DESCRIPTION GPIB COMMAND
SELECT
REFLECTION
PAIRING
None
MIXED
(SHORT1-SHORT2,
SHORT2-SHORT1)
Selects mixed reflection pairing. MIX
MATCHED
(SHORT1-SHORT1,
SHORT2-SHORT2)
Selects matched reflection pairing. MAT
PRESS <ENTER>
TO SELECT Pressing the Enter key implements your menu selection. None
Menu C13A, Set Reflection Pairing Menu
MENU DESCRIPTION GPIB COMMAND
SELECT
REFLECTION
PAIRING
None
MIXED
(SHORT1-SHORT2,
SHORT2-SHORT3,
SHORT3-SHORT1)
Selects mixed reflection pairing. MIX
MATCHED
(SHORT1-SHORT1,
SHORT2-SHORT2,
SHORT3-SHORT3)
Selects matched reflection pairing. MAT
PRESS <ENTER>
TO SELECT Pressing the Enter key implements your menu selection. None
Menu C13B, Set Reflection Pairing Menu
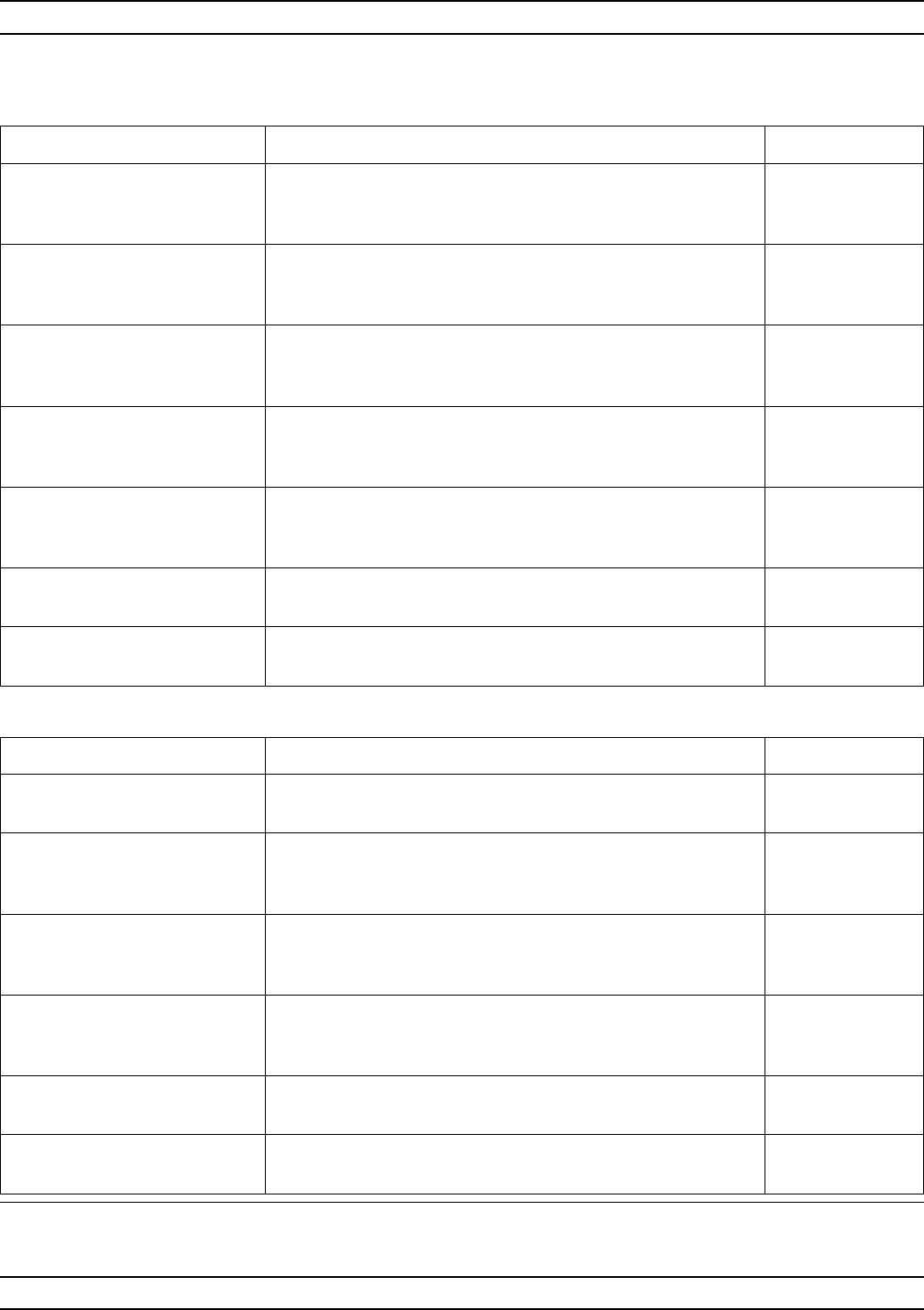
A-58 37XXXC OM
C ALPHABETICAL LISTING
MENU DESCRIPTION GPIB COMMAND
SELECT PORT X
OFFSET SHORT
CONNECOTR TYPE
Used with the coaxial line type. None
W1-CONN (M)
W1-CONN (F) Selects W1(M) connector (kit) type on Port X.
Selects W1 (F) connector (kit) type on Port X. CM1
CF1
P1C?; P2C?
SPECIAL A (M)
SPECIAL A (F) Selects Special A (M) connector (kit) type on Port X.
Selects Special A (F) connector (kit) type on Port X. CMSPA
CFSPA
P1C?; P2C?
SPECIAL B (M)
SPECIAL B (F) Selects Special B (M) connector (kit) type on Port X.
Selects Special B (F) connector (kit) type on Port X. CMSPB
CFSPB
P1C?; P2C?
SPECIAL C (M)
SPECIAL C (F) Selects Special C (M) connector (kit) type on Port X.
Selects Special C (F) connector (kit) type on Port X. CMSPC
CFSPC
P1C?; P2C?
USER DEFINED Calls menu C21A, C21B, then C21C, which allows you to
define the inductance coefficients and offset length values.
PRESS <ENTER>
WHEN COMPLETE Pressing the Enter key implements your menu selection. None
Menu C14, Select Port X Offset Short Connecotr Type
MENU DESCRIPTION GPIB COMMAND
SELECT PORT X
OFFSET SHORT Used with the microstrip line type. None
SPECIAL A (M)
SPECIAL A (F) Selects Special A (M) connector (kit) type on Port X.
Selects Special A (F) connector (kit) type on Port X. CMSPA
CFSPA
P1C?; P2C?
SPECIAL B (M)
SPECIAL B (F) Selects Special B (M) connector (kit) type on Port X.
Selects Special B (F) connector (kit) type on Port X. CMSPB
CFSPB
P1C?; P2C?
SPECIAL C (M)
SPECIAL C (F) Selects Special C (M) connector (kit) type on Port X.
Selects Special C (F) connector (kit) type on Port X. CMSPC
CFSPC
P1C?; P2C?
USER DEFINED Calls menus C21A, C21B, then C21C, which allows you to
define the inductance coefficients and offset length values.
PRESS <ENTER>
WHEN COMPLETE Pressing the Enter key implements your menu selection. None
Menu C14A, Select Port X Offset Short
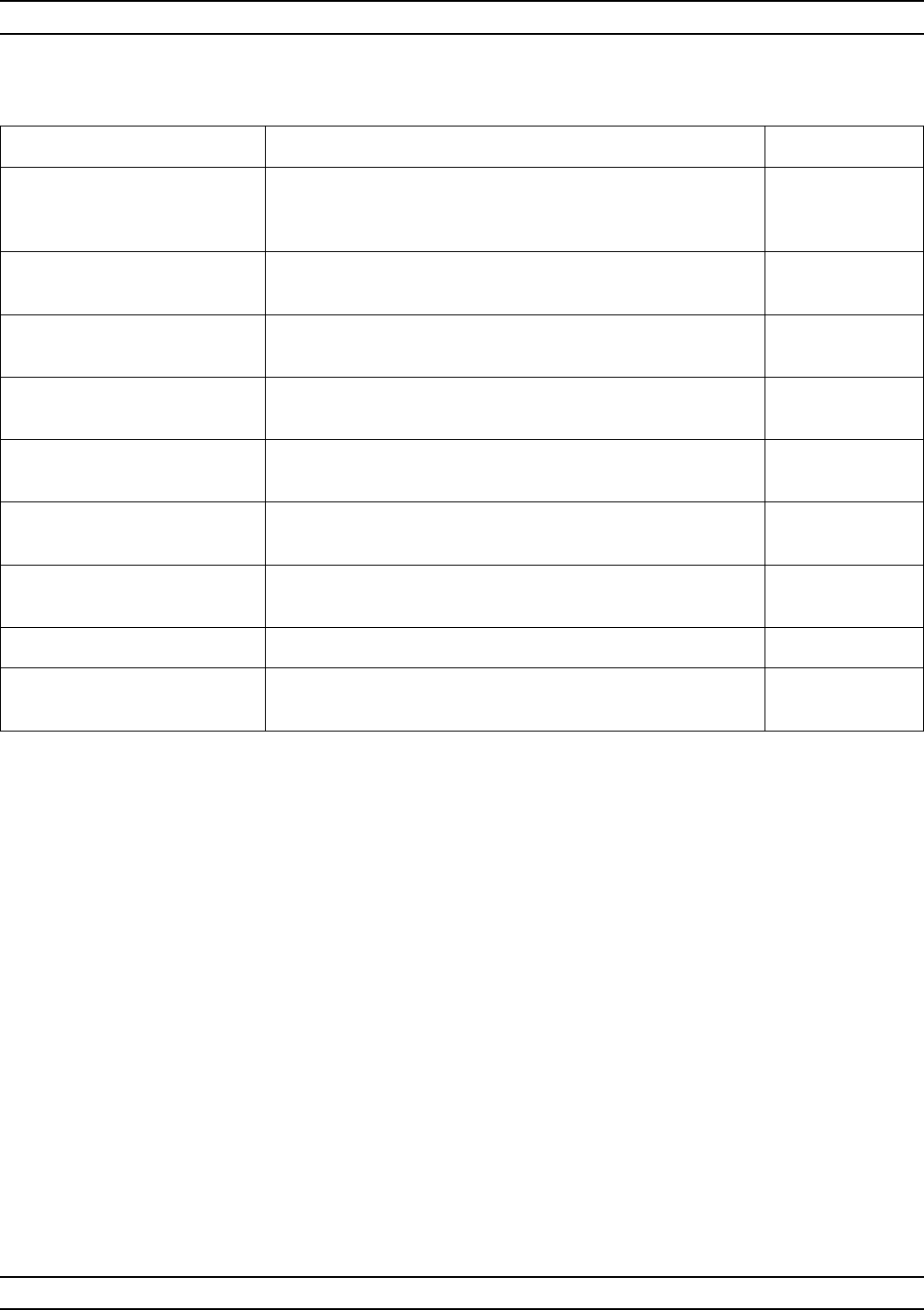
37XXXC OM A-59
ALPHABETICAL LISTING C
MENU DESCRIPTION GPIB COMMAND
SELECT
WAVEGUIDE
KIT TO USE
None
-INSTALLED KIT- The lines below indicate the characteristics of the installed
waveguide calibration kit, if applicable. None
IDENTIFIER
XXXX Displays the type of waveguide used. WGSER?
CUTOFF FREQ:
XXX.XXXXXXXXX GHz Displays the cutoff frequency of the waveguide. WGCUTOFF?
SHORT 1
XX.XXXXmm Displays the offset length of the first calibration short. WGSHOFF1?
SHORT 2
XX.XXXXmm Displays the offset length of the second calibration short. WGSHOFF2?
USE INSTALLED
WAVEGUIDE KIT Move the cursor to this line and press Enter to use the
displayed kit. WK1; WKX?
USER DEFINED Calls menu C15A, which lets you modify the parameters. None
PRESS <ENTER>
TO SELECT Pressing the Enter key implements your menu selection. None
Menu C15, Select Waveguide Kit to Use
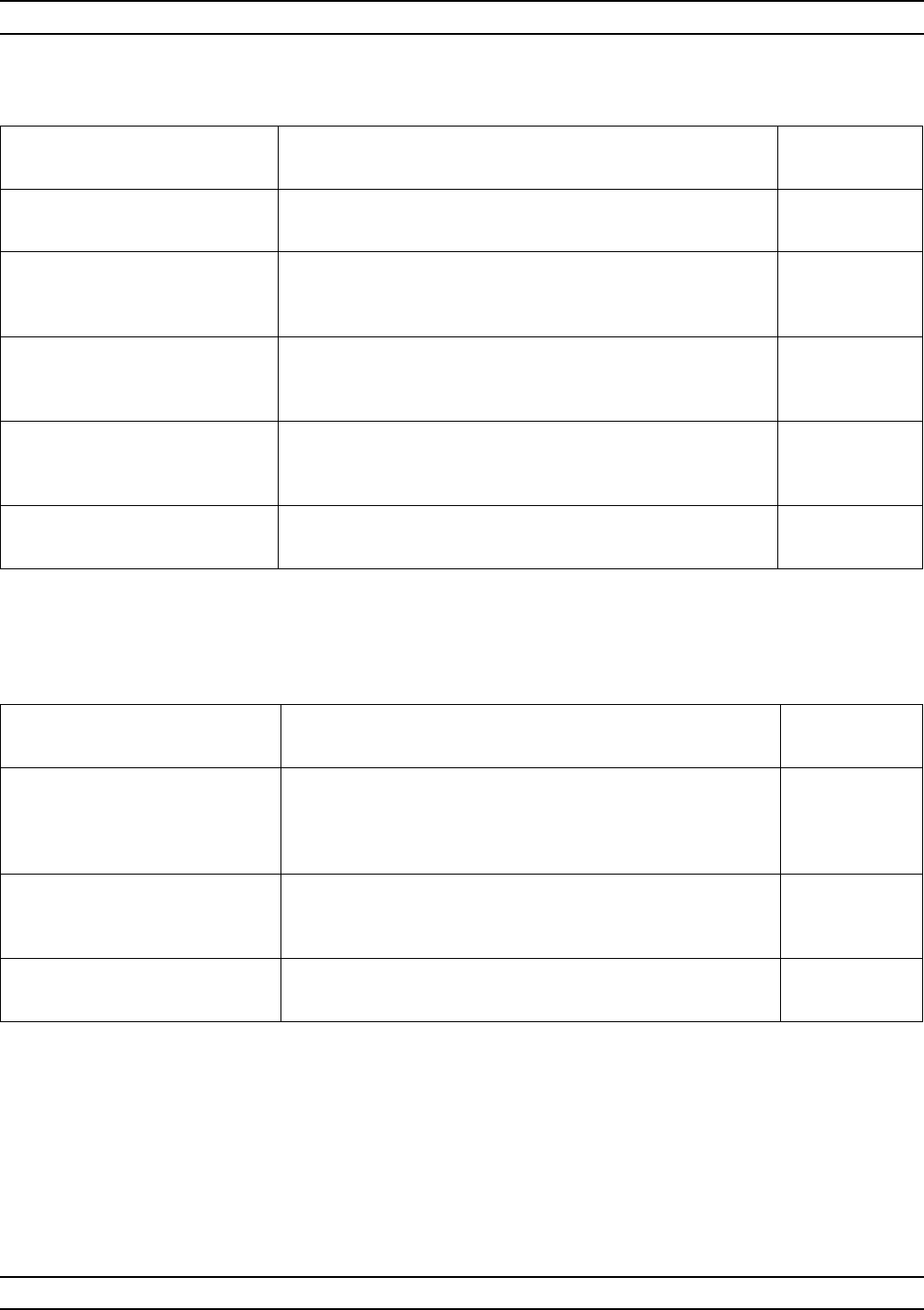
A-60 37XXXC OM
C ALPHABETICAL LISTING
MENU DESCRIPTION GPIB COM-
MAND
ENTER WAVEGUIDE
PARAMETERS None
WAVEGUIDE
CUTOFF FREQ
XXX.XXXXXXXXX GHz
Calls menu C15B that allows you to enter waveguide cutoff
frequency. None
OFFSET LENGTH
OF SHORT 1
X.XXXX mm
Move the cursor to this line and enter the offset length of
Short 1. WSH1; WSH1?
OFFSET LENGTH
OF SHORT 2
X.XXXX mm
Move the cursor to this line and enter the offset length of
Short 2. WSH2; WSH2?
PRESS <ENTER>
WHEN COMPLETE Pressing the Enter key implements your menu selection. None
Menu C15A, Enter Waveguide Parameters
MENU DESCRIPTION GPIB COM-
MAND
ENTER
WAVEGUIDE
CUTOFF
FREQUENCY
None
WAVEGUIDE
CUTOFF FREQ
XXX.XXXXXXXXX GHz
Enter waveguide cutoff frequency. WCO; WCO?
PRESS <ENTER>
WHEN COMPLETE Pressing the Enter key implements your menu selection. None
Menu C15B, Enter Waveguide Parameters
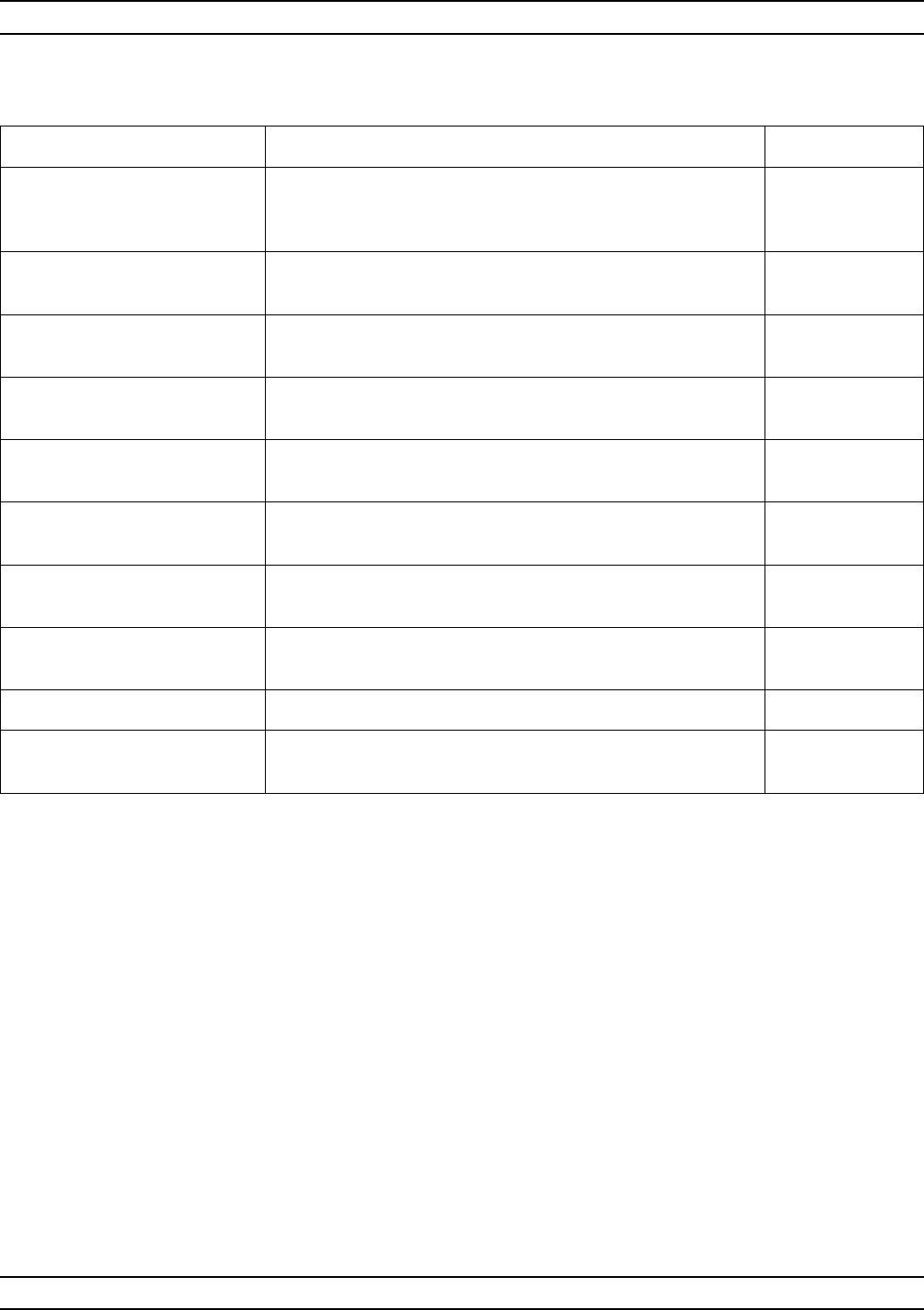
37XXXC OM A-61
ALPHABETICAL LISTING C
MENU DESCRIPTION GPIB COMMAND
SELECT
WAVEGUIDE
KIT TO USE
Used for the SSST calibration method. None
INSTALLED KIT The lines below indicate the characteristics of the installed
waveguide calibration kit, if applicable. None
IDENTIFIER:
XXXXXXXX Displays the type of waveguide used. WGSER?
CUTOFF FREQ:
XXX.XXXXXXXXX GHz Displays the cutoff frequency of the waveguide. WGCUTOFF?
SHORT 1:
+XX.XXXX mm Displays the offset length of the first calibration short. WGSHOFF1?
SHORT 2:
+XX.XXXX mm Displays the offset length of the second calibration short. WGSHOFF2?
SHORT 3:
+XX.XXXX mm Displays the offset length of the third calibration short. WGSHOFF3?
USE INSTALLED
WAVEGUIDE KIT Move the cursor to this line and press Enter to use the
displayed kit. WK1; WKX?
USER DEFINED Calls menu C15C, which lets you modify the parameters. None
PRESS <ENTER>
TO SELECT Pressing the Enter key implements your menu selection. None
Menu C15C, Select Waveguide Kit to Use
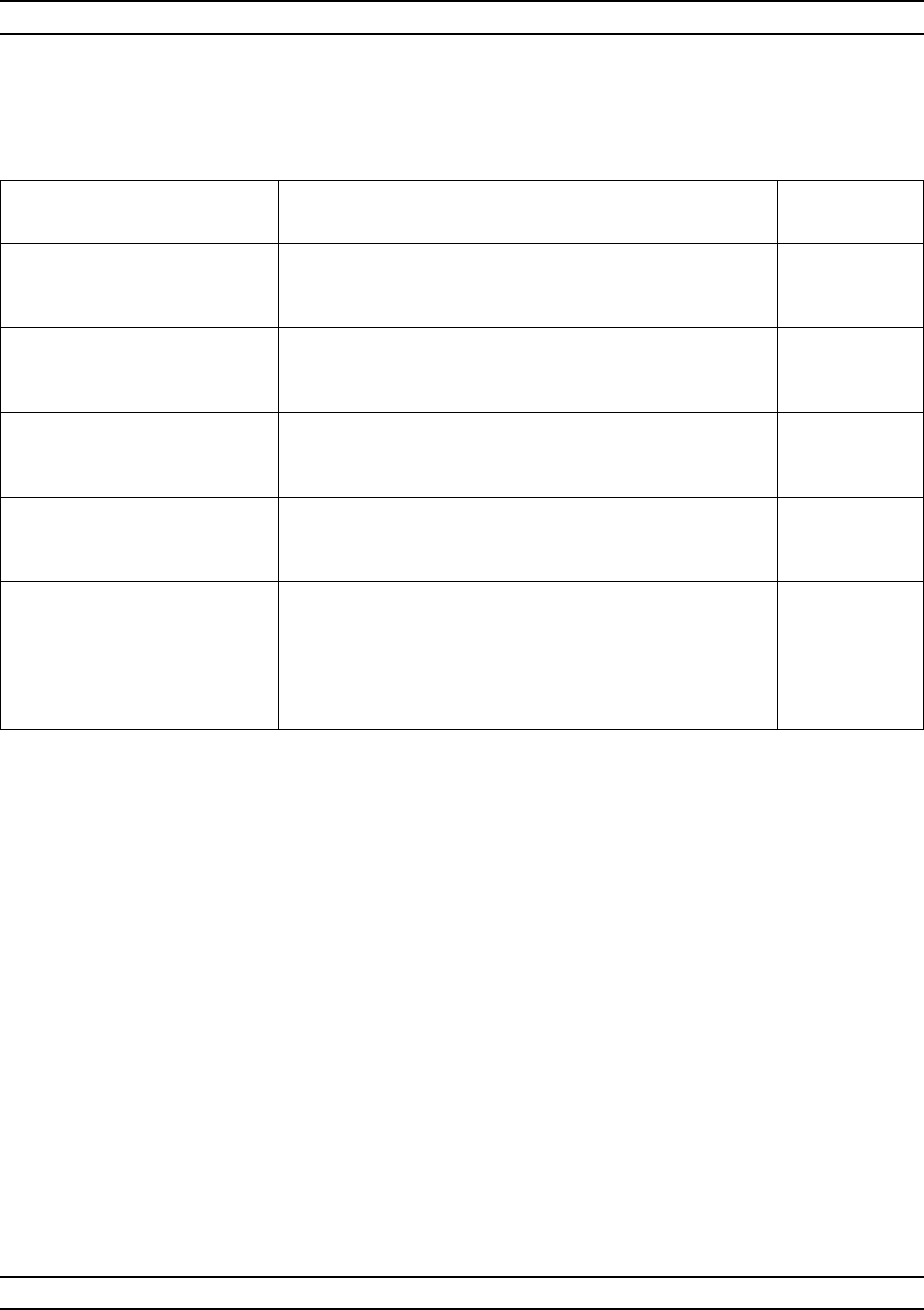
A-62 37XXXC OM
C ALPHABETICAL LISTING
MENU DESCRIPTION GPIB COM-
MAND
ENTER
WAVEGUIDE
PARAMETERS
Used for the SSST calibration method. None
WAVEGUIDE
CUTOFF FREQ
XXX.XXXXXXXXX GHz
Calls menu C15B that allows you to enter waveguide cutoff
frequency. None
OFFSET LENGTH
OF SHORT 1
+XXX.XXXX mm
Move the cursor to this line and enter the offset length of
Short 1. WSH1; WSH1?
OFFSET LENGTH
OF SHORT 2
+XXX.XXXX mm
Move the cursor to this line and enter the offset length of
Short 2. WSH2; WSH2?
OFFSET LENGTH
OF SHORT 3
+XXX.XXXX mm
Move the cursor to this line and enter the offset length of
Short 3. WSH3; WSH3?
PRESS <ENTER>
WHEN COMPLETE Pressing the Enter key implements your menu selection. None
Menu C15D, Enter Waveguide Parameters
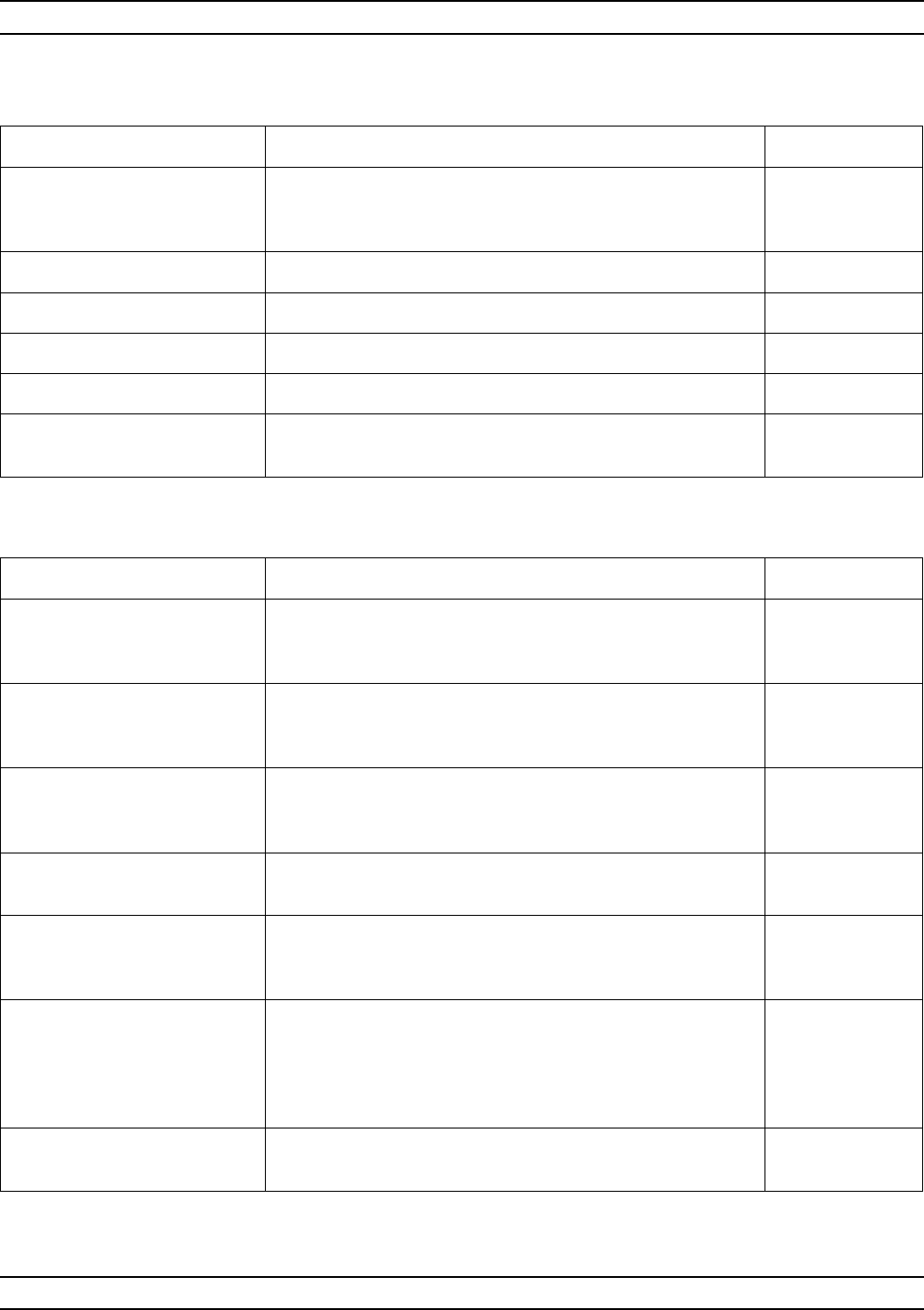
37XXXC OM A-63
ALPHABETICAL LISTING C
MENU DESCRIPTION GPIB COMMAND
ENTER
MICROSTRIP
PARAMETERS
None
WIDTH OF
STRIP
XX.XXXX mm
Move the cursor to this line and enter the width of the
microstrip you are using. USW; USW?
THICKNESS OF
SUBSTRATE
XXXX.XXXX mm
Move the cursor to this line and enter the thickness of the
substrate
you are using.
SBT; SBT?
Zc
XXX.XXX W
Move the cursor to this line and enter the characteristic
impedance of the microstrip. USZ; USZ?
SUBSTRATE
DIELECTRIC
XX.XX
Move the cursor to this line and enter the relative dielectric
constant of the substrate you are using. SBD; SBD?
EFFECTIVE
DIELECTRIC
XX.XX
(RECOMMENDED
1.00)
Move the cursor to this line and enter the effective
dielectric constant of the microstrip. A recommended value
will also be displayed.
USE; USE?
PRESS <ENTER>
WHEN COMPLETE Pressing the Enter key implements your menu selection. None
Menu C16A, Enter Microstrip Parameters
MENU DESCRIPTION GPIB COMMAND
SELECT
MICROSTRIP
KIT TO USE
None
10 MIL KIT Selects parameters for 10 mil UTF kit. U10; UTFX?
15 MIL KIT Selects parameters for 15 mil UTF kit. U15; UTFX?
25 MIL KIT Selects parameters for 25 mil UTF kit. U25; UTFX?
USER DEFINED Calls menu C16A, which lets you modify the parameters. None
PRESS <ENTER>
TO SELECT Pressing the Enter key implements your menu selection. None
Menu C16, Select Microstrip Parameters
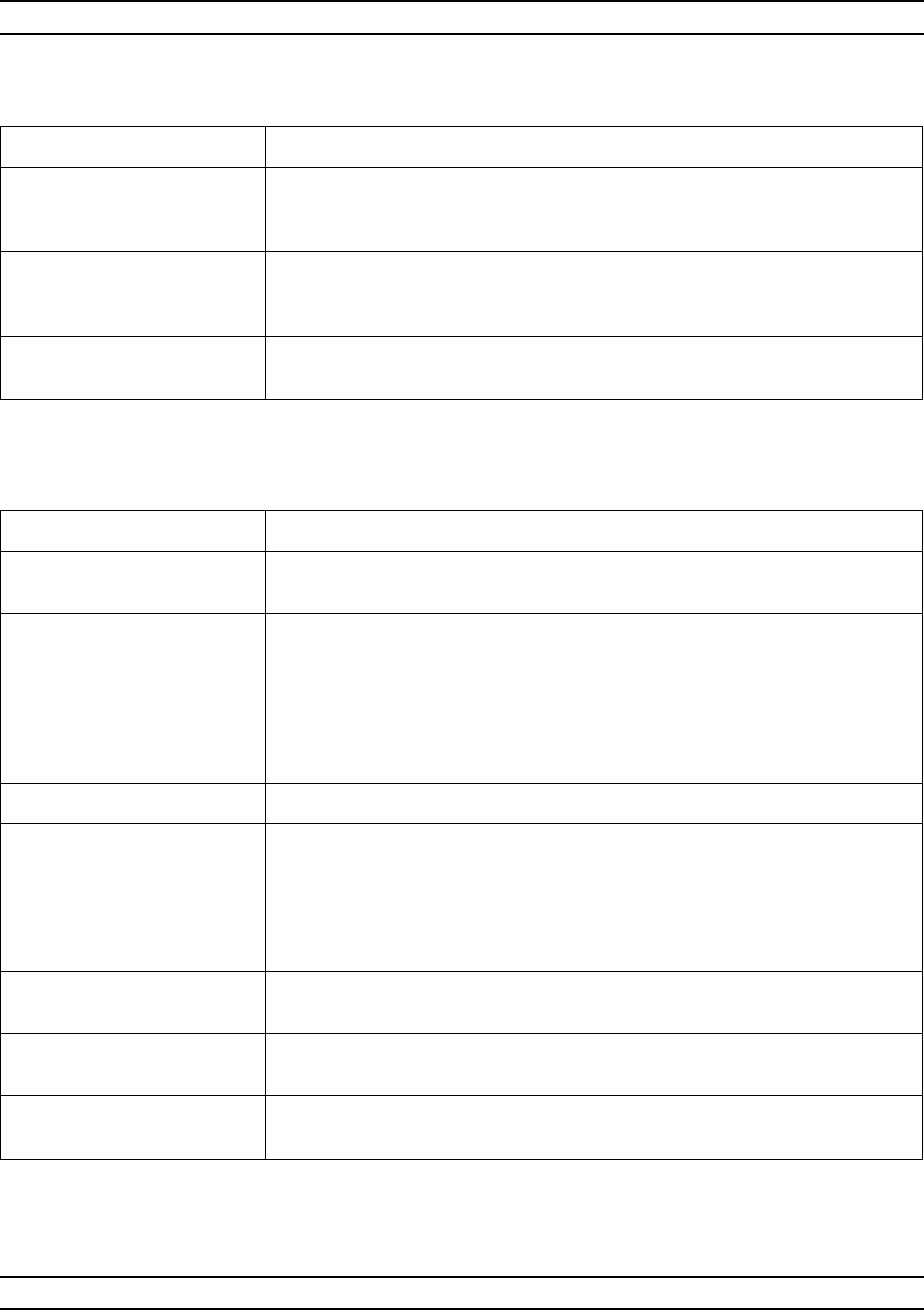
A-64 37XXXC OM
C ALPHABETICAL LISTING
MENU DESCRIPTION GPIB COMMAND
ENTER
REFERENCE
IMPEDANCE
None
REFERENCE
IMPEDANCE
XXX.XXXW
Enter the reference impedance (Z0) of the coaxial reference
line standard. LLZ; LLZ?
PRESS <ENTER>
WHEN COMPLETE Pressing the Enter key implements your menu selection. None
Menu C17, Enter Line Impedance
MENU DESCRIPTION GPIB COMMAND
CHANGE LRL/LRM
PARAMETERS None
NEXT CAL STEP Selects next calibration step. Must move cursor to here
after making below selections. Pressing the Enter key then
moves you to the next step. Calls menu C18A for one band
or C18B for two bands.
None
NUMBER OF
BANDS USED None
ONE BAND Selects a one-band LRL or LRM calibration. LR2; LRX?
TWO BANDS Selects a two-band LRL or LRM calibration (that is, a
three-line LRL or concatenated LRL and LRM calibrations). LR3; LRX?
LOCATION OF
REFERENCE
PLANES
None
MIDDLE OF
LINE 1 (REF) Select reference planes to be at middle of line 1. RM1; RMX?
ENDS OF
LINE 1 (REF) Select reference planes to be at end of line 1. RRP; RMX?
PRESS <ENTER>
TO SELECT Pressing the Enter key implements your menu selection. None
Menu C18, Change LRL/LRM Parameters
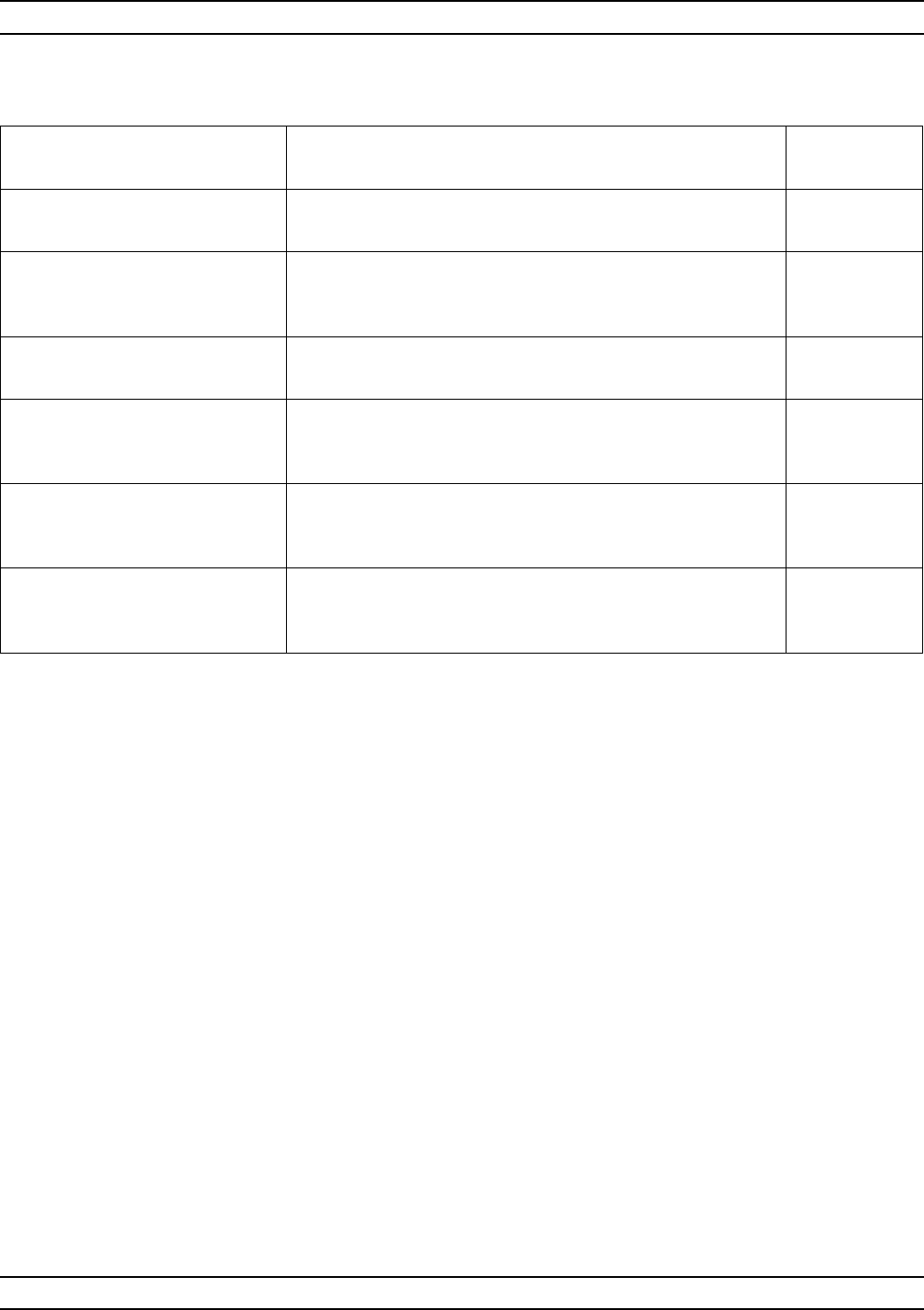
37XXXC OM A-65
ALPHABETICAL LISTING C
MENU DESCRIPTION GPIB COM-
MAND
CHANGE LRL/LRM
PARAMETERS None
NEXT CAL STEP Selects next calibration step. Must move cursor to here
after making below selections. Pressing the Enter key then
moves you to the next step. Calls menu C19.
None
CHARACTERIZE
CAL DEVICES None
DEVICE 1
LINE 1 (REF)
X.XXXX mm
Enter length of line 1. LL1; LL1?
DEVICE 2
LINE /MATCH
X.XXXX mm/FULLBAND
Select device 2—LINE or MATCH; if line is selected, enter
length. LL2; LM2;
LX2?
PRESS <ENTER>
TO SELECT
OR SWITCH
Press Enter to select. If DEVICE 2 is chosen, pressing the
Enter key toggles between LINE and MATCH. None
Menu C18A, Change LRL/LRM Parameters
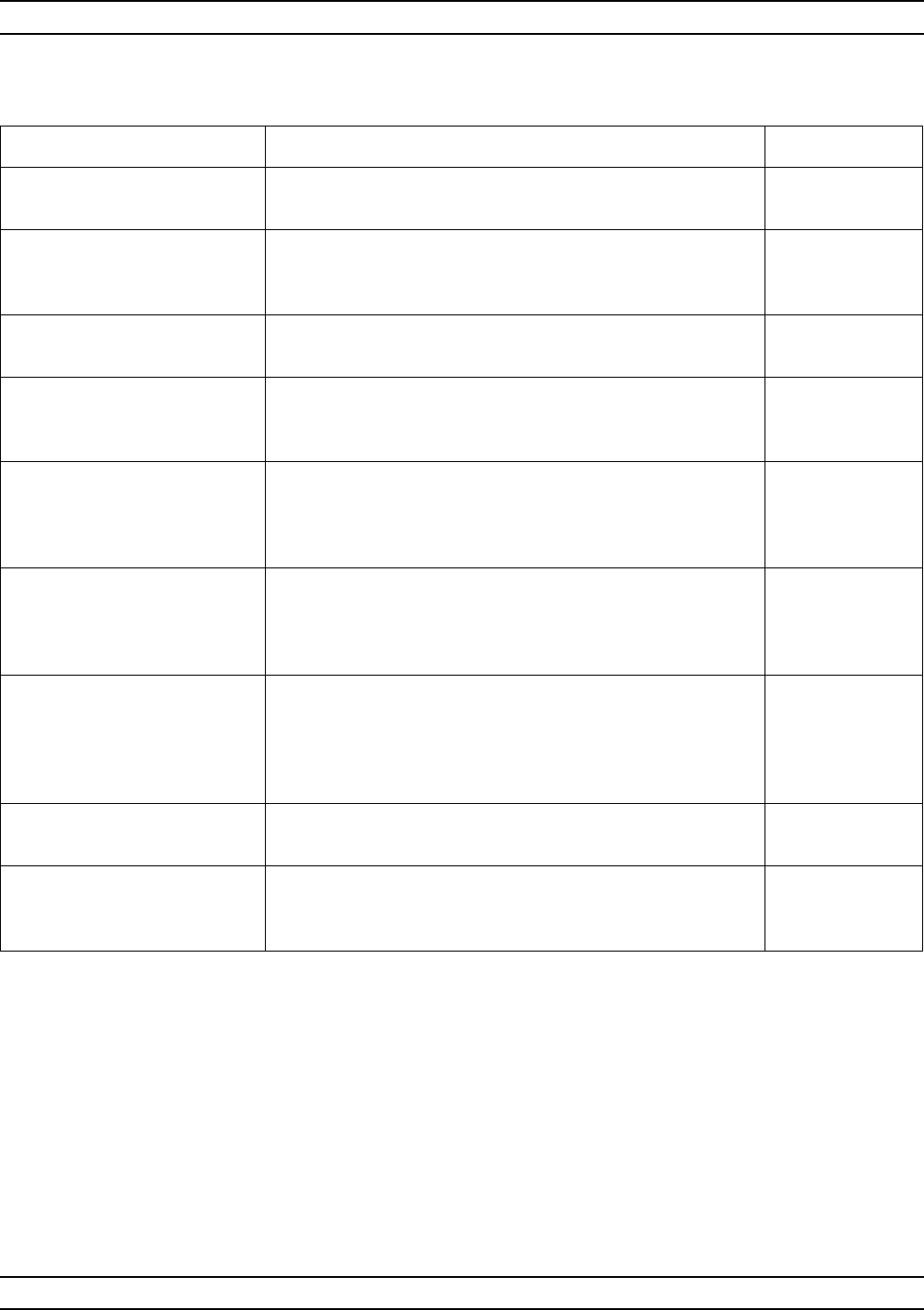
A-66 37XXXC OM
C ALPHABETICAL LISTING
MENU DESCRIPTION GPIB COMMAND
CHANGE LRL/LRM
PARAMETERS None
NEXT CAL STEP Selects next calibration step. Must move cursor to here
after making below selections. Pressing the Enter key then
moves you to the next step. Calls menu C19.
None
CHARACTERIZE
CAL DEVICES None
DEVICE 1
LINE 1 (REF)
XX.XXXX
Enter length of line 1. LL1; LL1?
DEVICE 2
LINE/MATCH
XX.XXXX/LOWBAND
Press Enter to toggle between LINE and MATCH. If LINE is
selected, enter line length. If match is selected, LOWBAND
is displayed. This indicates that device 2 is the lowband
match.
LL2; LL2?; LM2;
LX2?
DEVICE 3
LINE/MATCH
XX.XXXX/HIGHBAND
Press Enter to toggle between LINE and MATCH. If LINE is
selected, enter line length. If match is selected, HIGHBAND
is displayed. This indicates that device 3 is the high band
match.
LL3; LL3?; LM3;
LX3?
FREQ AFTER
WHICH THE USE
OF DEVICE 2
AND DEVICE 3
IS EXCHANGED
None
BREAKPOINT
XXX.XXXXXXXXXGHZ Enter breakpoint frequency: end of band 1, beginning of
band 2. BPF; BPF?
PRESS <ENTER>
TO SELECT
OR SWITCH
Pressing the Enter key implements your menu selection. None
Menu C18B, Change LRL/LRM Parameters—Two Band Calibration
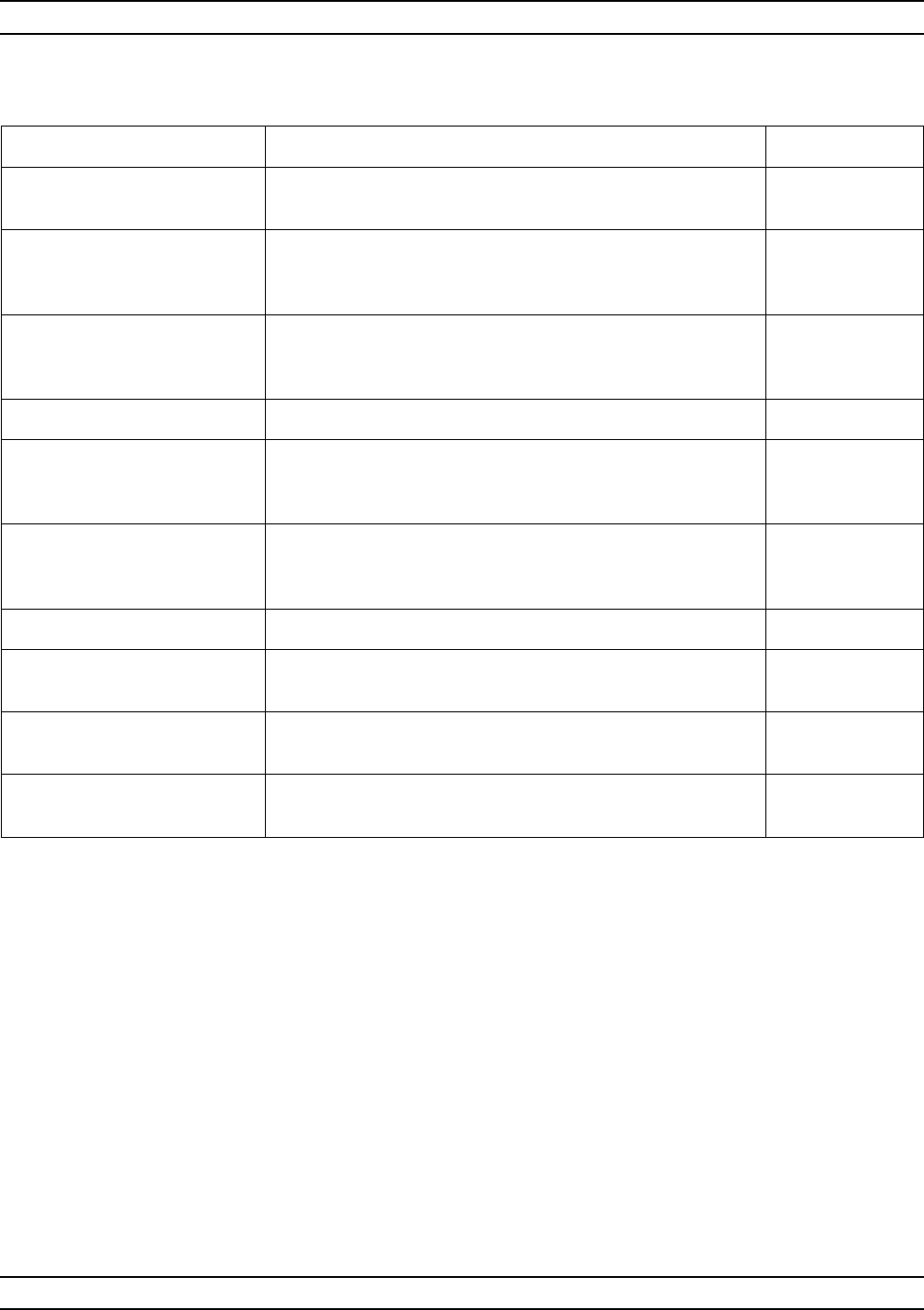
37XXXC OM A-67
ALPHABETICAL LISTING C
MENU DESCRIPTION GPIB COMMAND
CHANGE LRL/LRM
PARAMETERS None
NEXT CAL STEP Moves to the next calibration step. Must move cursor to
here after making below selections. Pressing the Enter key
then moves you to the next step.
None
REFLECTION
OFFSET LENGTH
+XXX.XXXX mm
Enter the offset length of the reflective device. None
REFLECTION TYPE ROL; ROL?
GREATER THAN Zo Specifies the reflection to have an impedance value greater
than the reference impedance (Z0). This is typically an open
device.
RGZ; RXZ?
LESS THAN Zo Selects the reflection to have an impedance value less than
the reference impedance (Z0). This is typically a short
device.
RLZ; RXZ
MATCH PARAMETERS
MATCH IMPEDANCE
+XXX.XXX W
Allows entry of the impedance (defaults to 50.000 W). LMZ; LMZ?
MATCH INDUCTANCE
+XXXX.XXXX pH Allows entry of the inductance (defaults to 0.00 e-12). LMZL; LMZL?
PRESS <ENTER>
TO SELECT Pressing the Enter key implements the selection. None
Menu C19, Change LRL/LRM Parameters
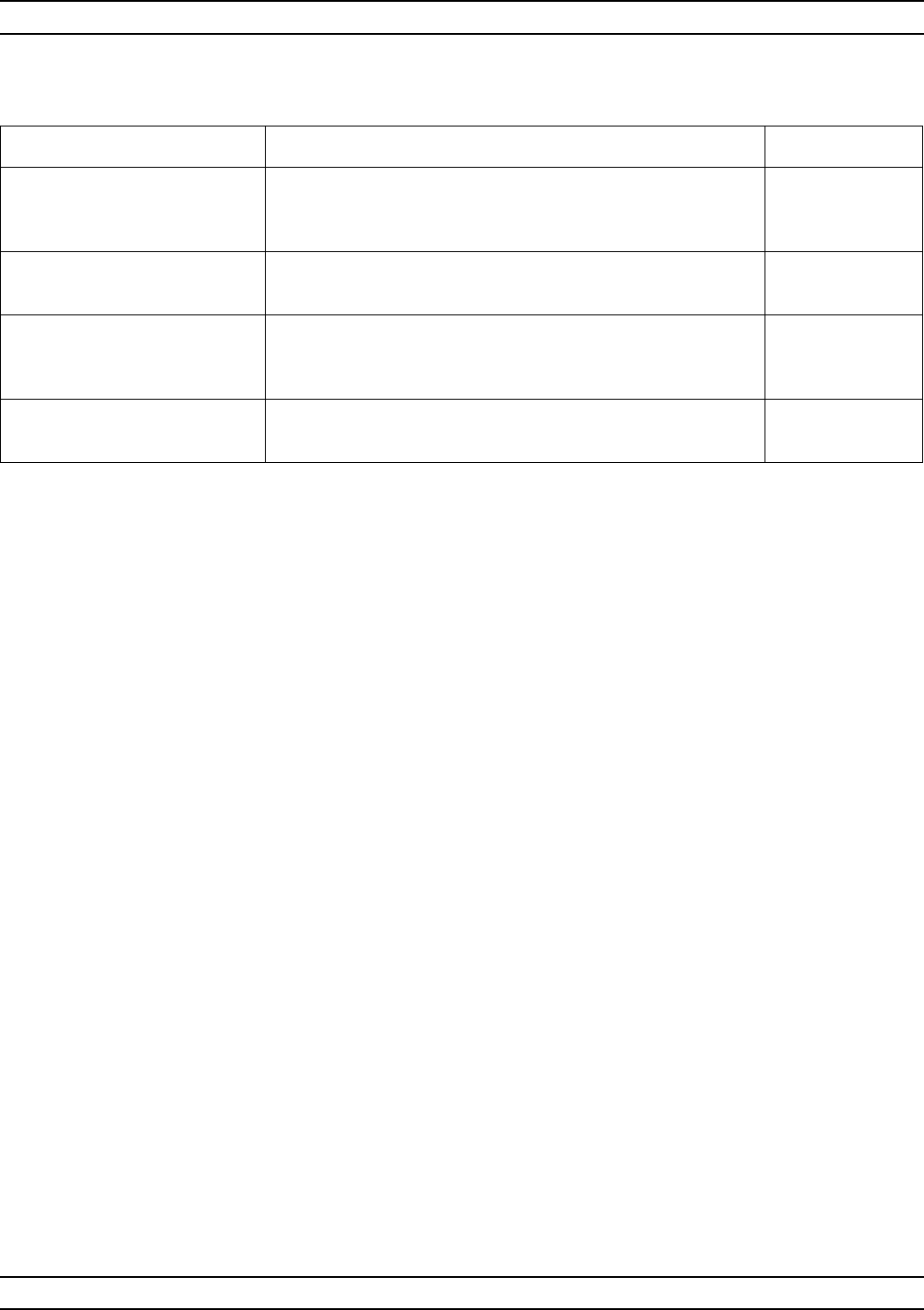
A-68 37XXXC OM
C ALPHABETICAL LISTING
MENU DESCRIPTION GPIB COMMAND
ENTER
THROUGH LINE
PARAMETERS
None
OFFSET LENGTH
X.XXXX mm Enter offset length of through-line device. TOL; TOL?
THROUGHLINE
IMPEDANCE
X.XXXX W
Enter the impedance of the through-line device. TLZ; TLZ?
PRESS <ENTER>
WHEN COMPLETE Pressing the Enter key brings the next calibration menu. None
Menu C20, Change Through Parameters
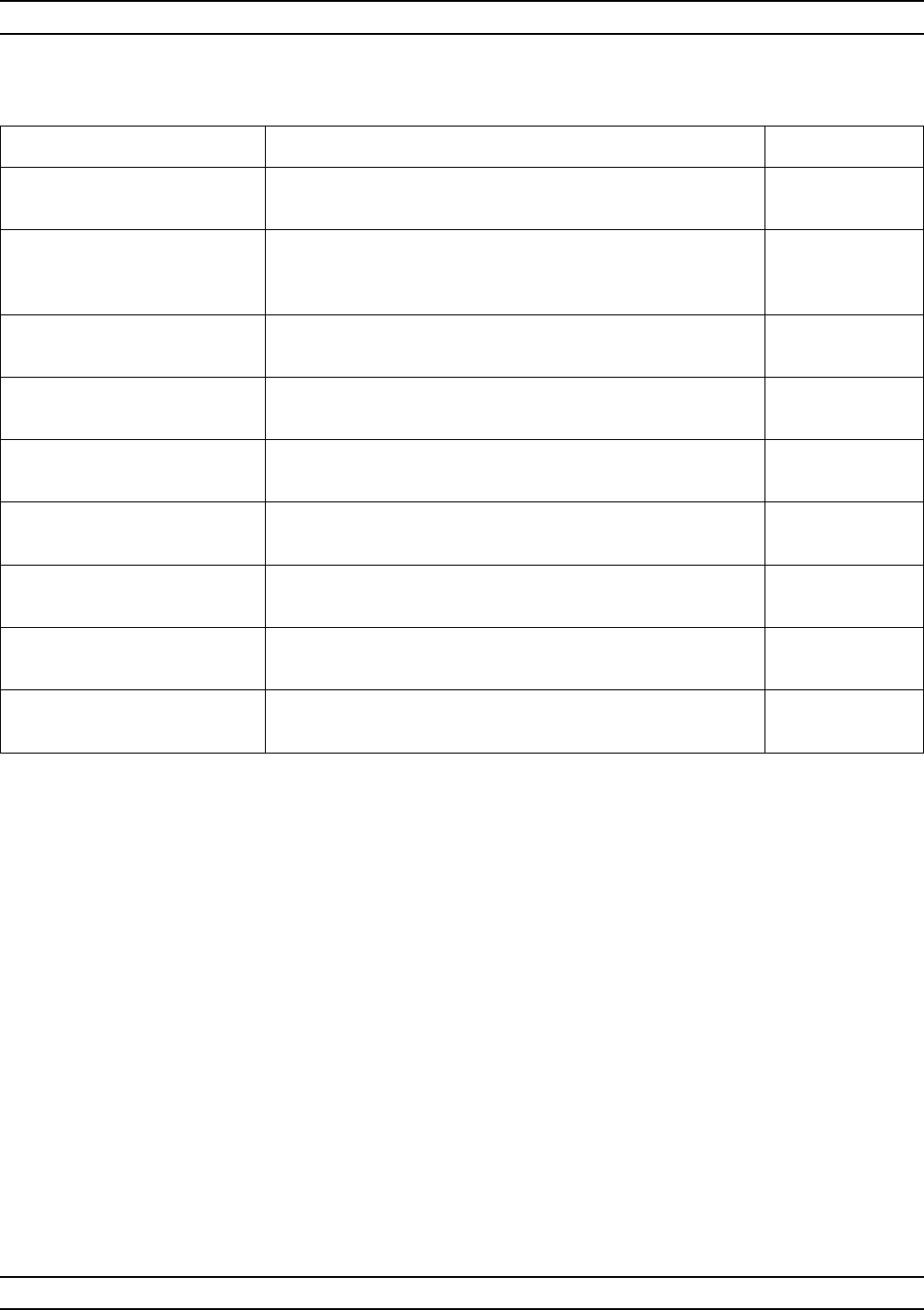
37XXXC OM A-69
ALPHABETICAL LISTING C
MENU DESCRIPTION GPIB COMMAND
PORT X
OFFSET SHORT 1 None
ENTER THE
INDUCTANCE
COEFFICIENTS
L0 [e-12 H]
+XXXX.XXXX Enter the inductance coeficients of the offset short. None
L1 [e-24 H/Hz]
+XXXX.XXXX Enter the inductance coeficients of the offset short. None
L2 [e-33 H/Hz2]
+XXXX.XXXX Enter the inductance coeficients of the offset short. None
L3 [e-42 H/Hz3]
+XXXX.XXXX Enter the inductance coeficients of the offset short. None
ENTER THE
OFFSET LENGTH
OFFSET LENGTH
+XXX.XXXX mm Enter the offset length of the offset short. None
PRESS <ENTER>
WHEN COMPLETE Pressing the Enter key calls menu C21B. None
Menu C21A, Port X Offset Short 1
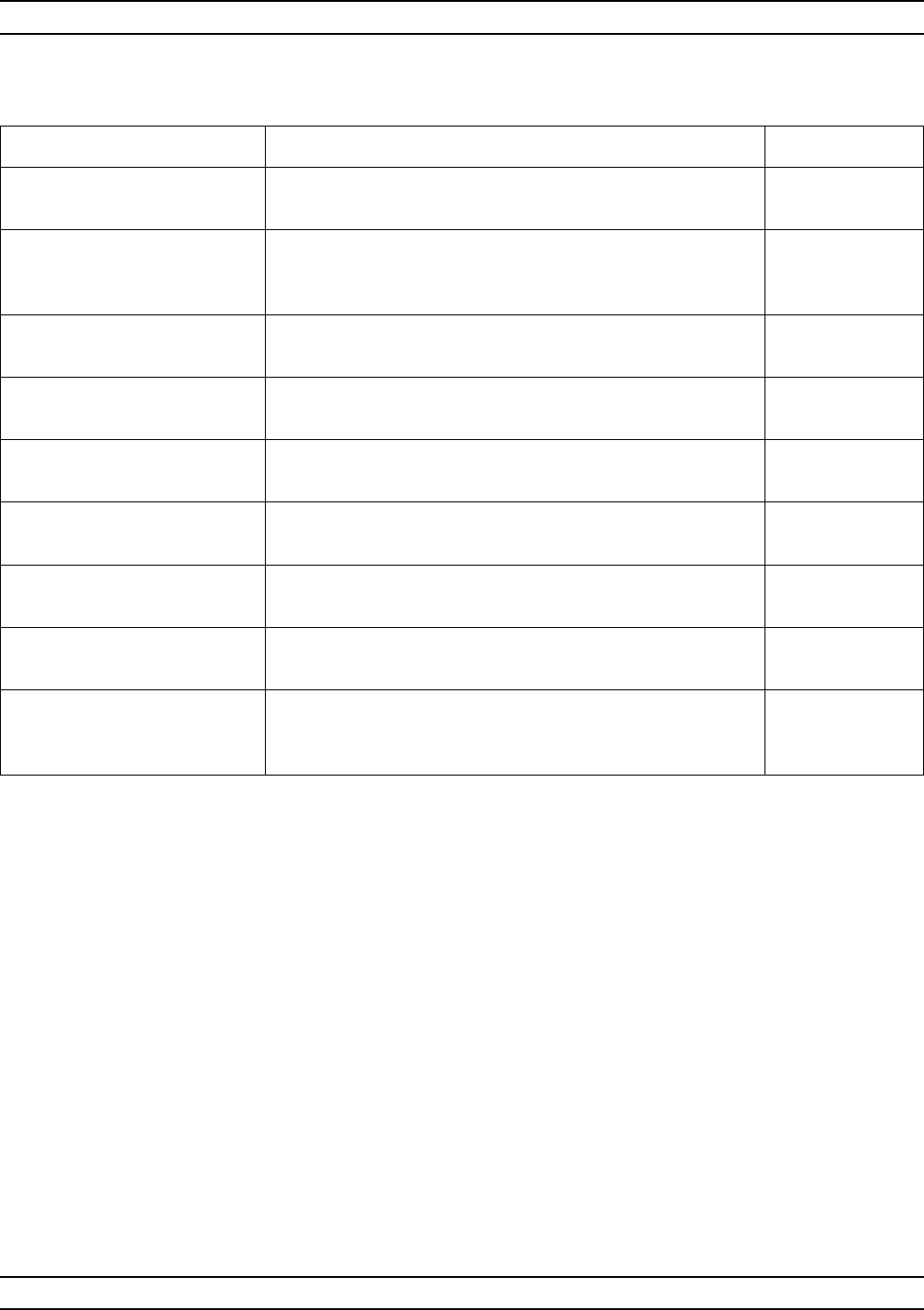
A-70 37XXXC OM
C ALPHABETICAL LISTING
MENU DESCRIPTION GPIB COMMAND
PORT X
OFFSET SHORT 2 None
ENTER THE
INDUCTANCE
COEFFICIENTS
L0 [e-12 H]
+XXXX.XXXX Enter the inductance coeficients of the offset short. None
L1 [e-24 H/Hz]
+XXXX.XXXX Enter the inductance coeficients of the offset short. None
L2 [e-33 H/Hz2]
+XXXX.XXXX Enter the inductance coeficients of the offset short. None
L3 [e-42 H/Hz3]
+XXXX.XXXX Enter the inductance coeficients of the offset short. None
ENTER THE
OFFSET LENGTH
OFFSET LENGTH
+XXX.XXXX mm Enter the offset length of the offset short. None
PRESS <ENTER>
WHEN COMPLETE Pressing the Enter key calls menu C3X, for a SSLT
calibration method, or menu C21B, for a SSST calibration
method.
None
Menu C21B, Port X Offset Short 2
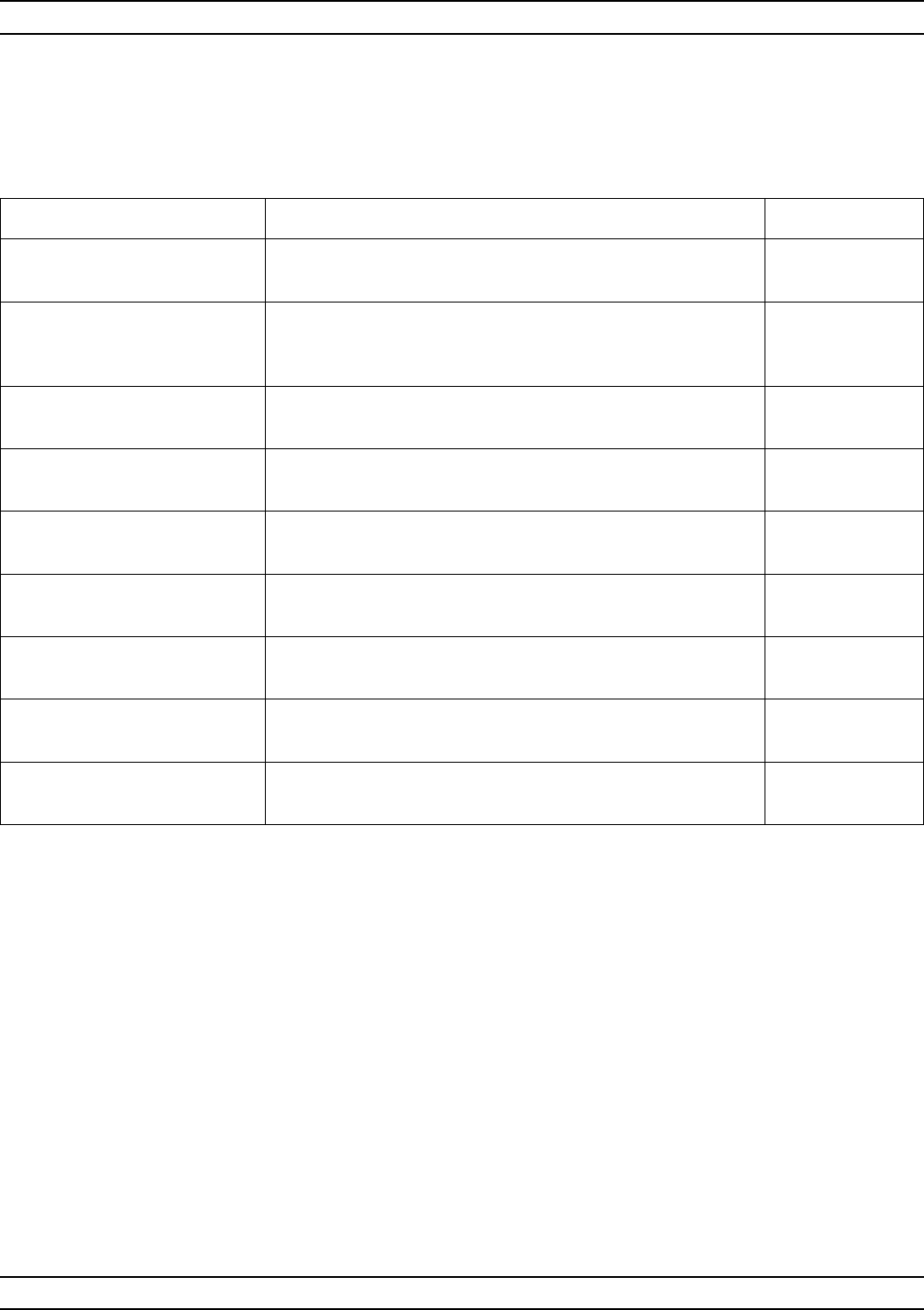
37XXXC OM A-71
ALPHABETICAL LISTING C
MENU DESCRIPTION GPIB COMMAND
PORT X
OFFSET SHORT 3 None
ENTER THE
INDUCTANCE
COEFFICIENTS
L0 [e-12 H]
+XXXX.XXXX Enter the inductance coeficients of the offset short. None
L1 [e-24 H/Hz]
+XXXX.XXXX Enter the inductance coeficients of the offset short. None
L2 [e-33 H/Hz2]
+XXXX.XXXX Enter the inductance coeficients of the offset short. None
L3 [e-42 H/Hz3]
+XXXX.XXXX Enter the inductance coeficients of the offset short. None
ENTER THE
OFFSET LENGTH
OFFSET LENGTH
+XXX.XXXX mm Enter the offset length of the offset short. None
PRESS <ENTER>
WHEN COMPLETE Pressing the Enter key calls menu C3X. None
Menu C21C, Port X Offset Short 3
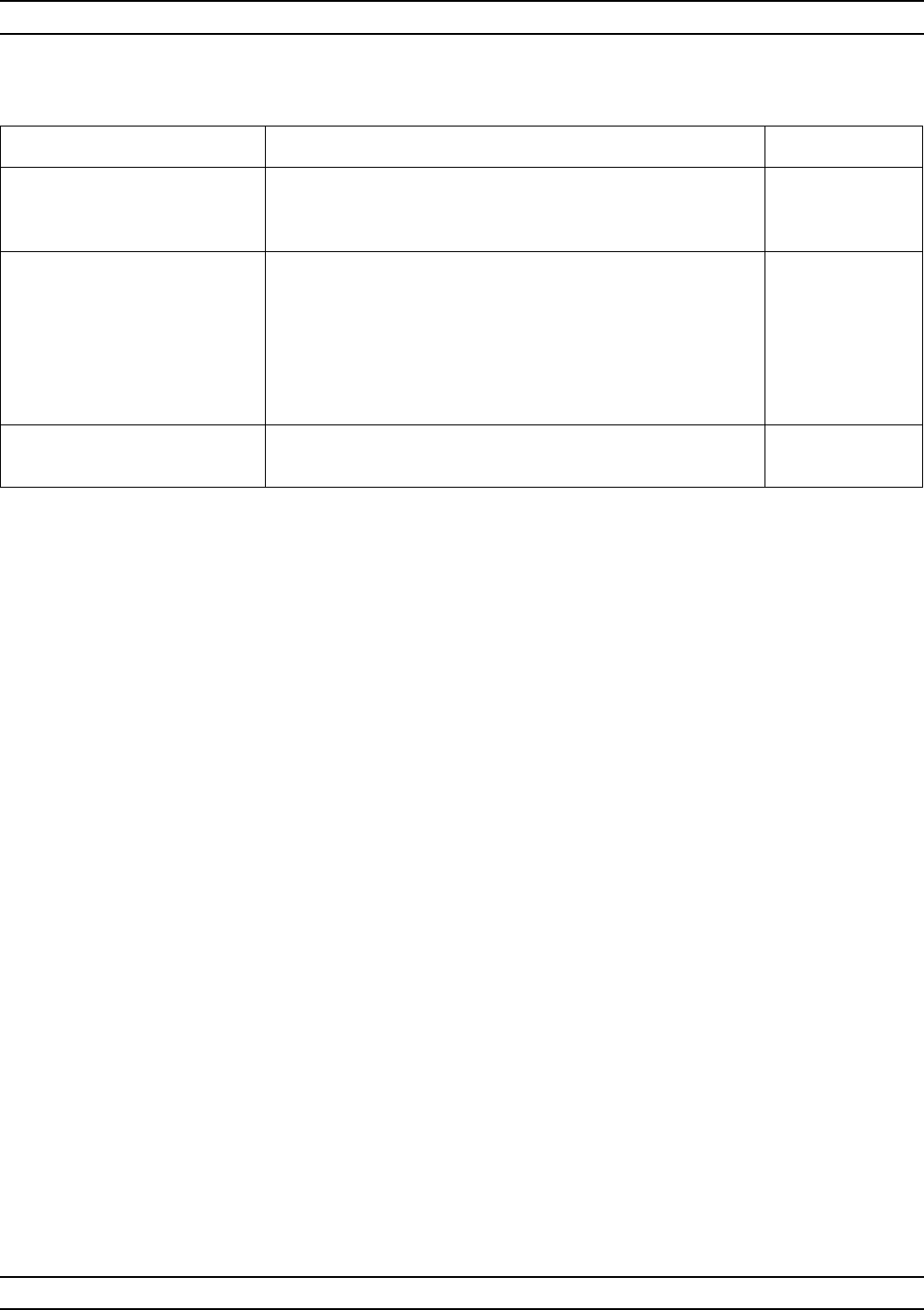
A-72 37XXXC OM
C ALPHABETICAL LISTING
MENU DESCRIPTION GPIB COMMAND
CALIBRATION
SEQUENCE
COMPLETED
None
PRESS
<SAVE/RECALL>
TO STORE CAL
DATA ON DISK
OR
Pressing the SAVE/RECALL MENU Key displays menu SR,
which lets you save your calibration data onto a disk or
recall previously saved calibration data from a disk. While
this menu provides a convenient point at which to save the
calibration data, it is not the only point allowed. You can
use the SAVE/RECALL MENU key at any point in the
measurement program.
None
PRESS <ENTER>
TO PROCEED Pressing the Enter key implements your menu selection. None
Menu Cal_Completed
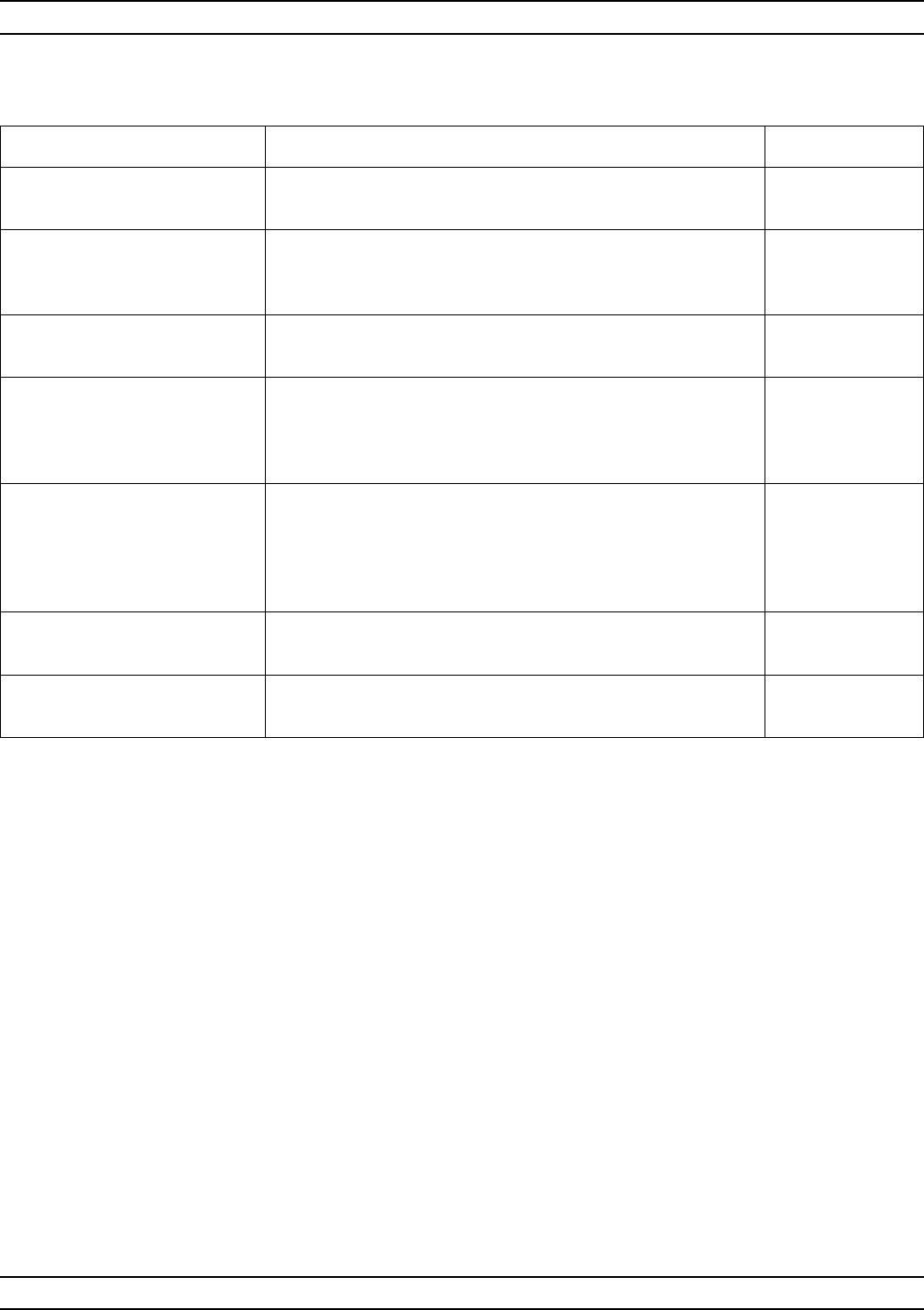
37XXXC OM A-73
ALPHABETICAL LISTING C
MENU DESCRIPTION GPIB COMMAND
APPLY
CALIBRATION None
FULL 12-TERM
(S11, S21
S22, S12)
Reflects the type of calibration presently stored in internal
memory.
APPLY ON (OFF)
CALIBRATION Turns calibration on or off. CON; COF;
CON?
TUNE MODE ON (OFF) For applied Full 12-Term calibration only. When turned off,
the ratio of forward to reverse sweeps is set to the normal
1:1.When turned on, you can set the ratio of forward
sweeps to reverse sweep from 1:1 to 10,000:1 (below).
None
NO. OF FWD (REV)
SWEEPS BETWEEN
REV (FWD) SWEEPS
XXXXX SWEEPS
(XXXXX REMAINING)
Lets you enter a value for the number of forward (or
reverse) sweeps. Alternatively, this option displays the
number of forward sweep (or reverse) remaining before a
reverse sweep will occur.
None
PRESS <APPLY CAL>
TO TURN ON/OFF Press the Apply Cal key to apply the stored calibration. None
PRESS <ENTER>
TO TURN ON/OFF Press the Enter key to turn selected mode on/off. None
Menu Cal_Applied
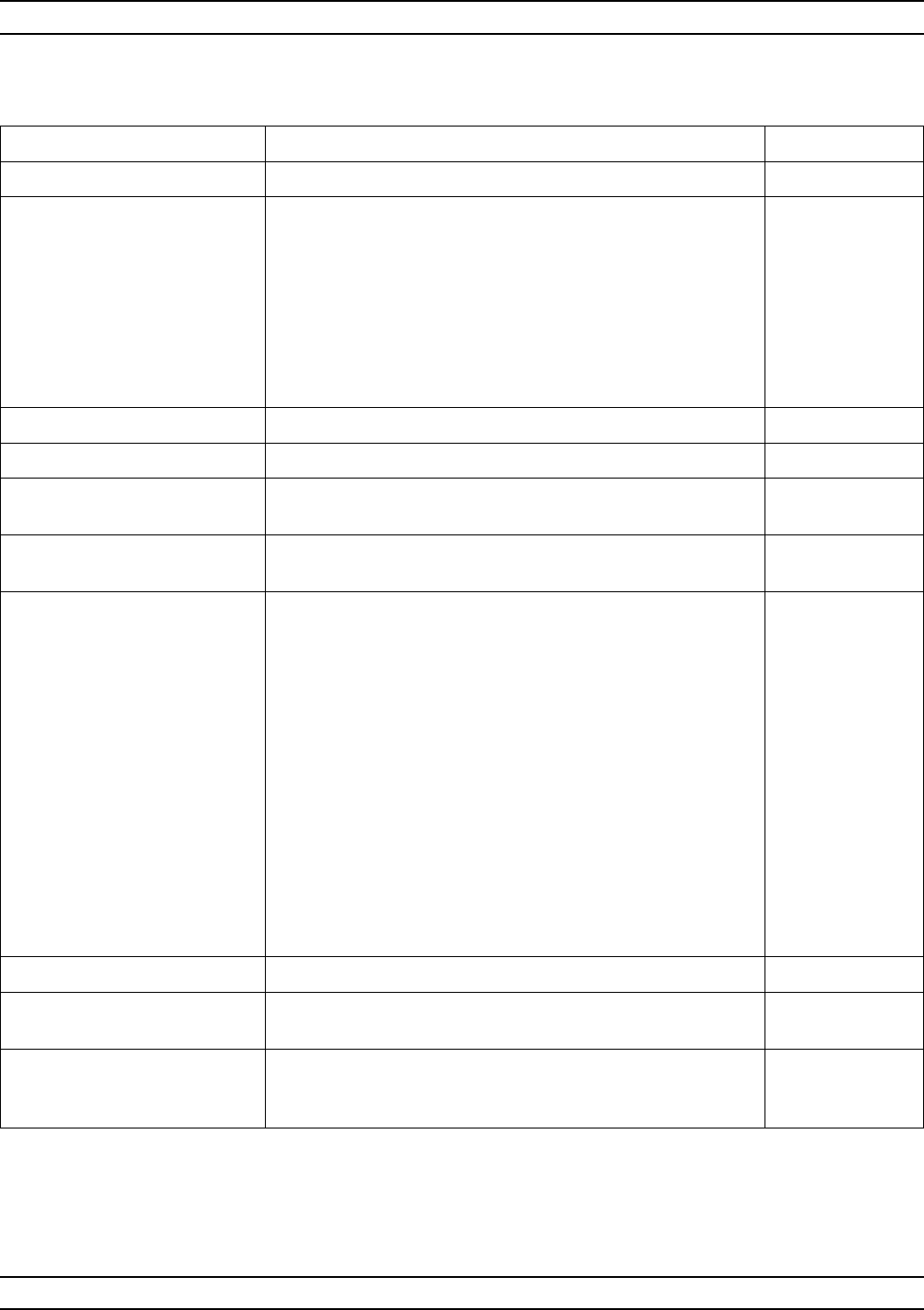
C ALPHABETICAL LISTING
A-74 37XXXC OM
MENU DESCRIPTION GPIB COMMAND
DATA ENHANCEMENT None
AVERAGING
XXXX MEAS. Averages the measured data over time, as follows:
1. The sweep stops at the first frequency point and takes a
number of readings, based on the selected number of
points.
2. The program averages the readings and writes the
average value for that frequency point in the displayed
graph.
3. The sweep then advances to the next sequential
frequency point and repeats the process.
AVG; AVG?
AVERAGING TYPE
POINT-BY-POINT Averages the point-by-point up to the number of averages. PTAVG; SWAVG?
SWEEP-BY-SWEEP Averages the sweep-by-sweep up to the number of
averages. SWAVG;
SWAVG?
RESET AVG COUNT
XXXX SWEEP(S) Zeroes the counter used for sweep averaging. RSTAVG
SAMPLERS USED
PER SWEEP
X SAMPLERS
In the normal mode of operation, three samplers are used
per forward or reverse sweep; two test samplers and a
reference sampler. This results in both transmission and
reflection parameters simultaneously.
When a device such as a filter with a deep reject-band is
measured, having both test samplers on reduces the
measurement dynamic range. A higher noise floor in the
reject band of the filter is observed. Selecting two samplers
per sweep turns off one of the test samplers. This
eliminates channel interaction and thereby improves the
dynamic range.
The drawbacks of using two sampler per sweep are a
doubling of measurement time, as two complete
one-direction sweeps are needed for both transmission and
reflection parameters.
SAMP2; SAMP3;
SAMP?
RESUME CAL
PRESS <ENTER>
TO SELECT Pressing the Enter key implements your menu selection
and returns you to the calibration setup or sequence. None
PRESS
<AVG/SMOOTH MENU>
TO RESET AVG COUNT
Menu Cal_EM, Enhancement Menu for Calibration
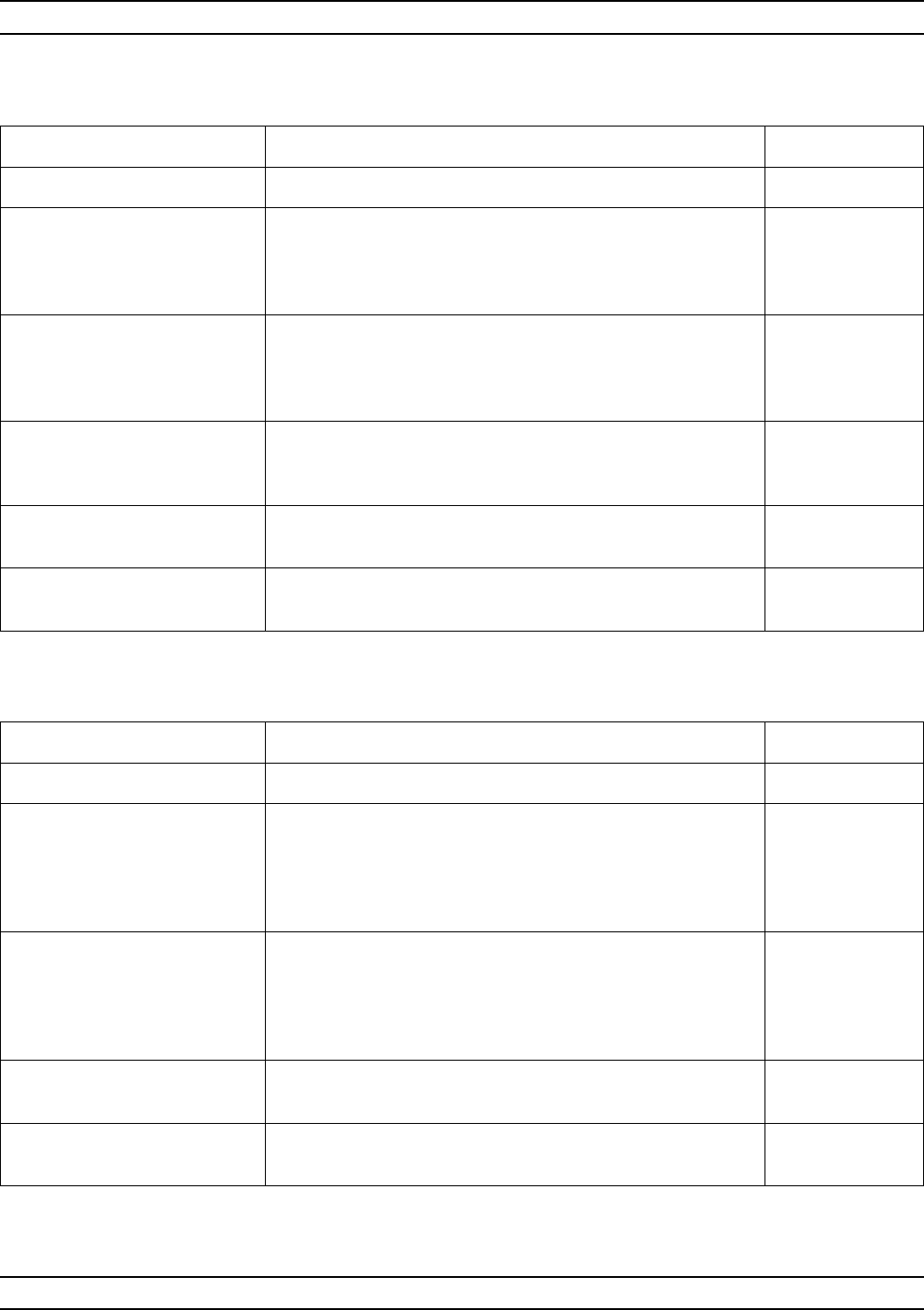
37XXXC OM A-75
ALPHABETICAL LISTING C
MENU DESCRIPTION GPIB COMMAND
ADAPTER REMOVAL None
12-TERM CALS FOR
X AND Y MUST
EXIST IN THE
CURRENT DIRECTORY
None
ELECTRICAL LENGTH
OF THE ADAPTER
+XXX.XXXX ps
Displays the electrical length of the adapter. The value of
the electrical length is used when the two calibrations are
merged. It has the same range as the time delay for
reference plane extension and a default value of 0.0000 ps.
ADPL; ADPL?
REMOVE ADAPTER Calls menu CAR2, which leads you through the reading of
the Y’-Y and X-X’ calibration files and the computation of
the new 12-term error coefficients.
None
HELP Calls menu EXT_CAR, which provides help text for using
this feature. None
PRESS <ENTER>
TO SELECT Pressing the Enter key implements the selection. None
Menu CAR1, Adapter Removal 1
MENU DESCRIPTION GPIB COMMAND
ADAPTER REMOVAL None
READ CAL FILE OF
X TEST PORT
FROM HARD DISK
(ADAPTER ON
PORT 2)
Calls menu DSK2, which provides instructions. None
READ CAL FILE OF
X TEST PORT
FROM FLOPPY DISK
(ADAPTER ON
PORT 2)
Calls menu DSK2, which provides instructions. None
PRESS <ENTER>
TO SELECT Pressing the Enter key implements the selection. None
PRESS <CLEAR>
TO ABORT Pressing the Clear key aborts the selection. None
Menu CAR2, Adapter Removal 2
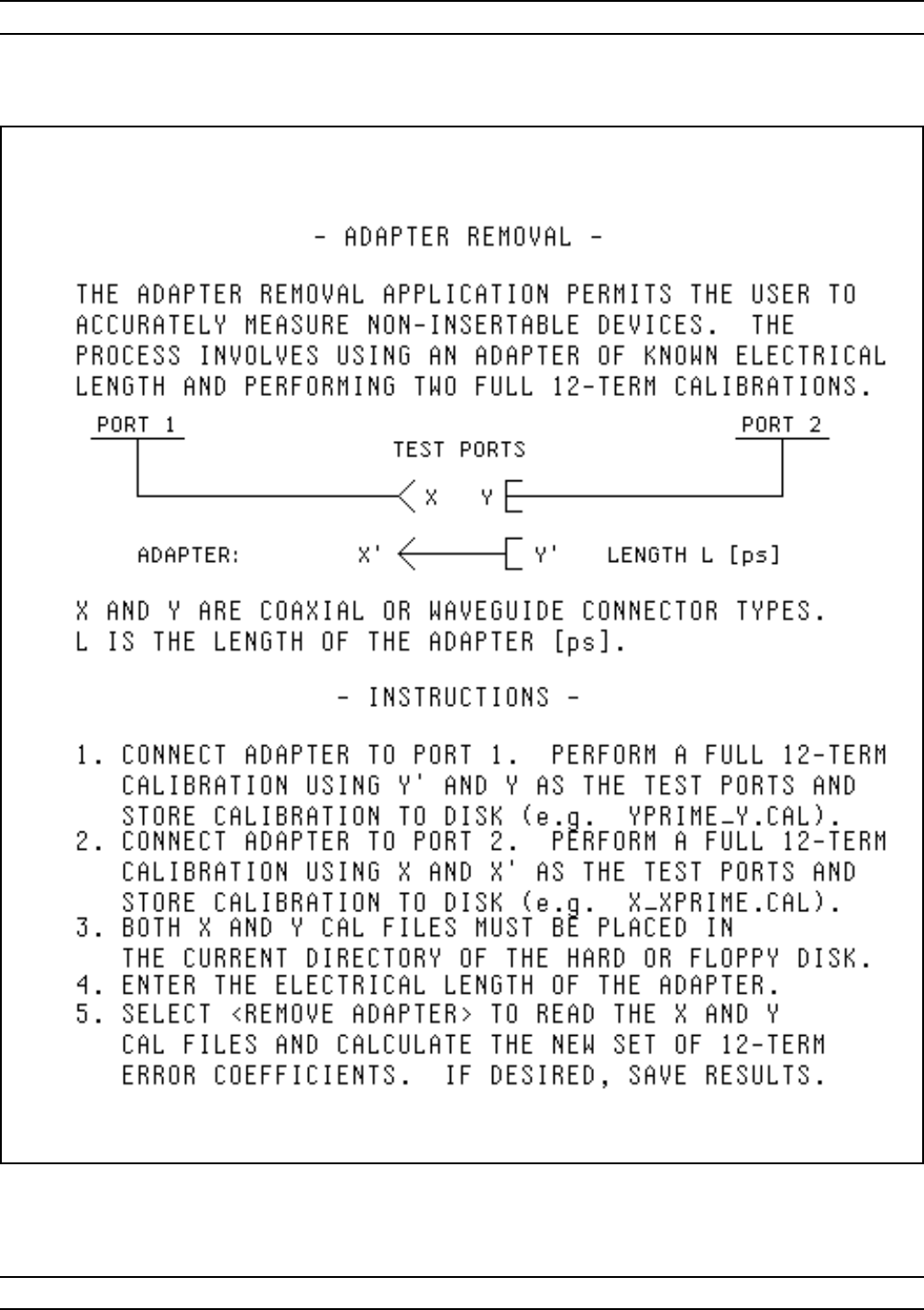
A-76 37XXXC OM
C ALPHABETICAL LISTING
Menu EXT_CAR, Adapter Removal Help Menu
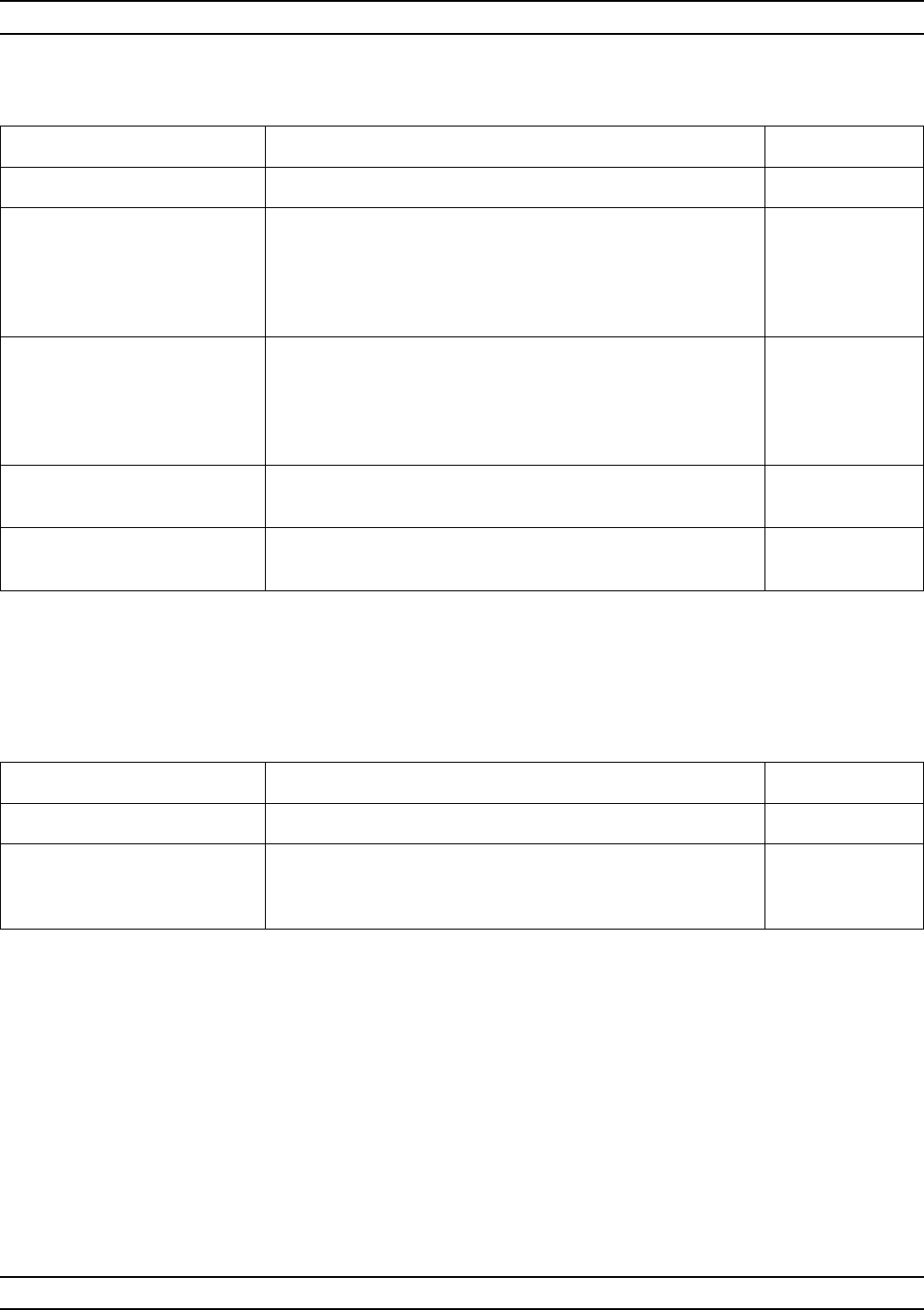
37XXXC OM A-77
ALPHABETICAL LISTING C
MENU DESCRIPTION GPIB COMMAND
ADAPTER REMOVAL None
READ CAL FILE OF
THE Y TEST PORT
FROM HARD DISK
(ADAPTER ON
PORT 1)
Calls menu DSK2, which provides instructions. None
READ CAL FILE OF
THE Y TEST PORT
FROM FLOPPY DISK
(ADAPTER ON
PORT 1)
Calls menu DSK2, which provides instructions. None
PRESS <ENTER>
TO SELECT Pressing the Enter key implements the selection. None
PRESS <CLEAR>
TO ABORT Pressing the Clear key aborts the selection. None
Menu CAR3, Adapter Removal 3
MENU DESCRIPTION GPIB COMMAND
ADAPTER REMOVAL None
COMPUTING NEW
12-TERM ERROR
COEFFICIENTS
Information text. None
Menu CAR4, Adapter Removal 4
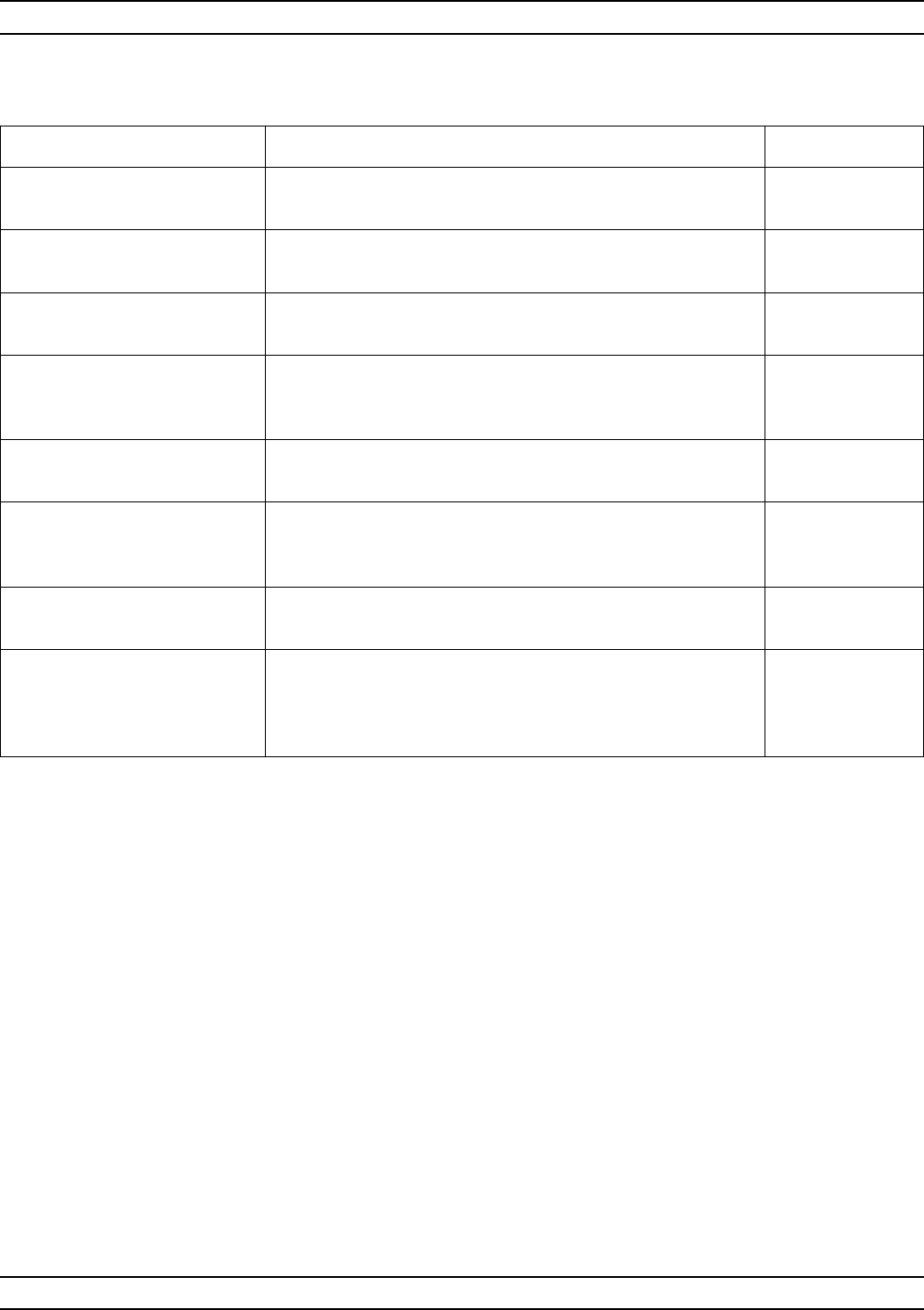
A-78 37XXXC OM
C ALPHABETICAL LISTING
MENU DESCRIPTION GPIB COMMAND
SELECT
DISPLAY MODE None
SINGLE
CHANNEL Selects a single channel for display. You select the type of
display in menu GT1 or GT2. DSP; DSP?
DUAL
CHANNELS1&3 Selects Channels 1 and 3 for display. You select the type of
display in menu GT1 or GT2. D13
OVERLAY DUAL
CHANNELS1&3 Lets you simultaneously view the Channel 1 data
superimposed over the Channel 3 data on a single display.
Channel 1 trace displays in red and Channel 3 in yellow.
T13
DUAL
CHANNELS2&4 Selects Channels 2 and 4 for display. You select the type of
display in menu GT1 or GT2. D24
OVERLAY DUAL
CHANNELS2&4 Lets you simultaneously view the Channel 2 data
superimposed over the Channel 4 data on a single display.
Channel 2 trace displays in red and Channel 4 in yellow.
T24
ALL FOUR
CHANNELS Selects all four channels for display. You select the type of
display in menu GT1 or GT2. D14
PRESS <ENTER>
TO SELECT Pressing the Enter key implements your menu selection.
The menu remains on the screen until another menu is
selected for display or until the CLEAR/RET LOC key is
pressed.
None
Menu CM, Select Display Mode
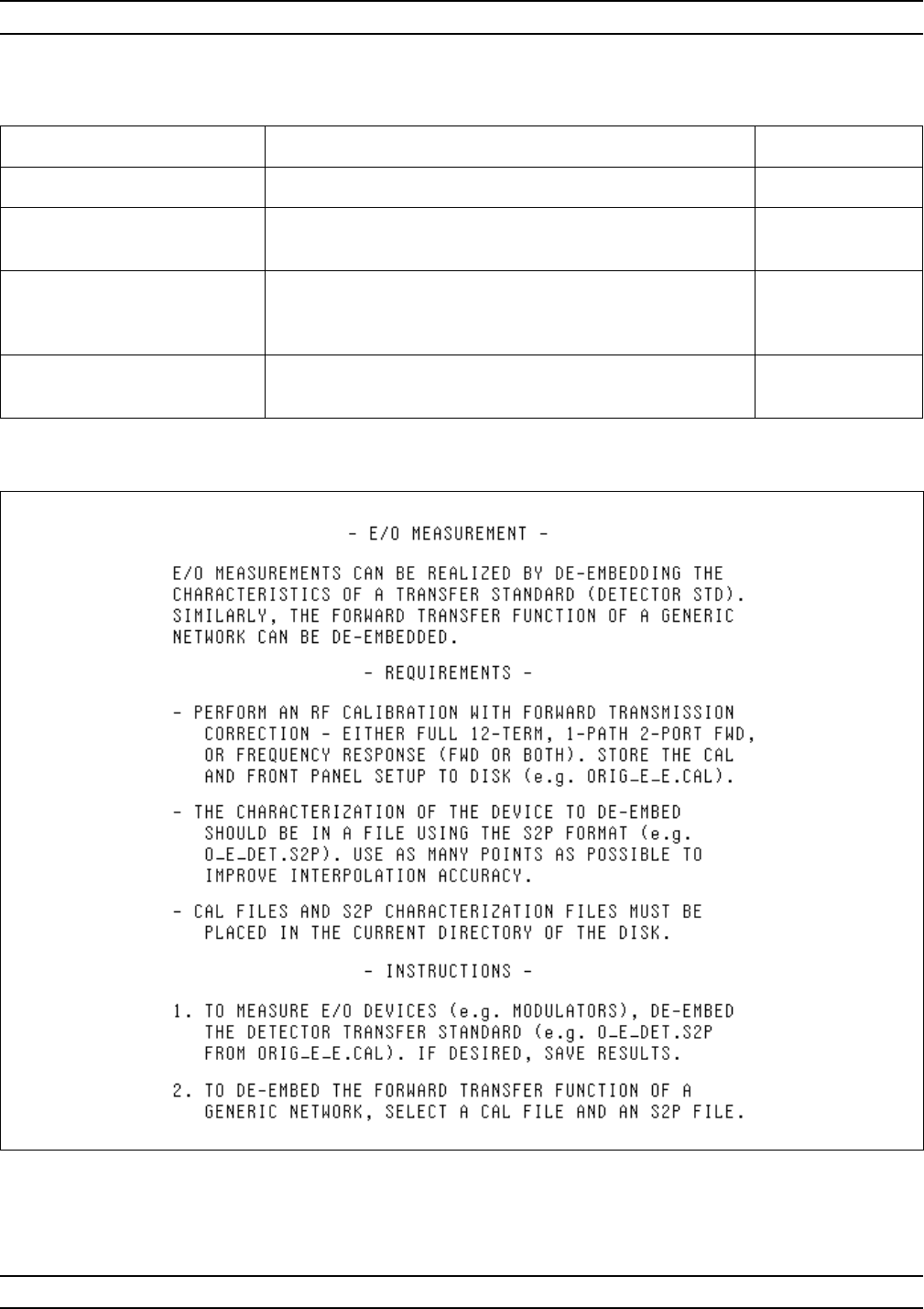
37XXXC OM A-79
ALPHABETICAL LISTING D
MENU DESCRIPTION GPIB COMMAND
E/O MEASUREMENT None
MEASURE E/O DUT
(MODULATOR) This menu selection calls menu DE3, then DE3A. IODF or LDODF
DE-EMBED TRANSFER
FUNCTION OF A
GENERIC NETWORK
This menu selection calls menu DE4, then DE4A. IODF or LDODF
PRESS <ENTER>
TO SELECT Pressing the Enter key implements your menu selection. None
Menu DE1, E/O Measurement
Menu EXT_DE1, E/O Measurement
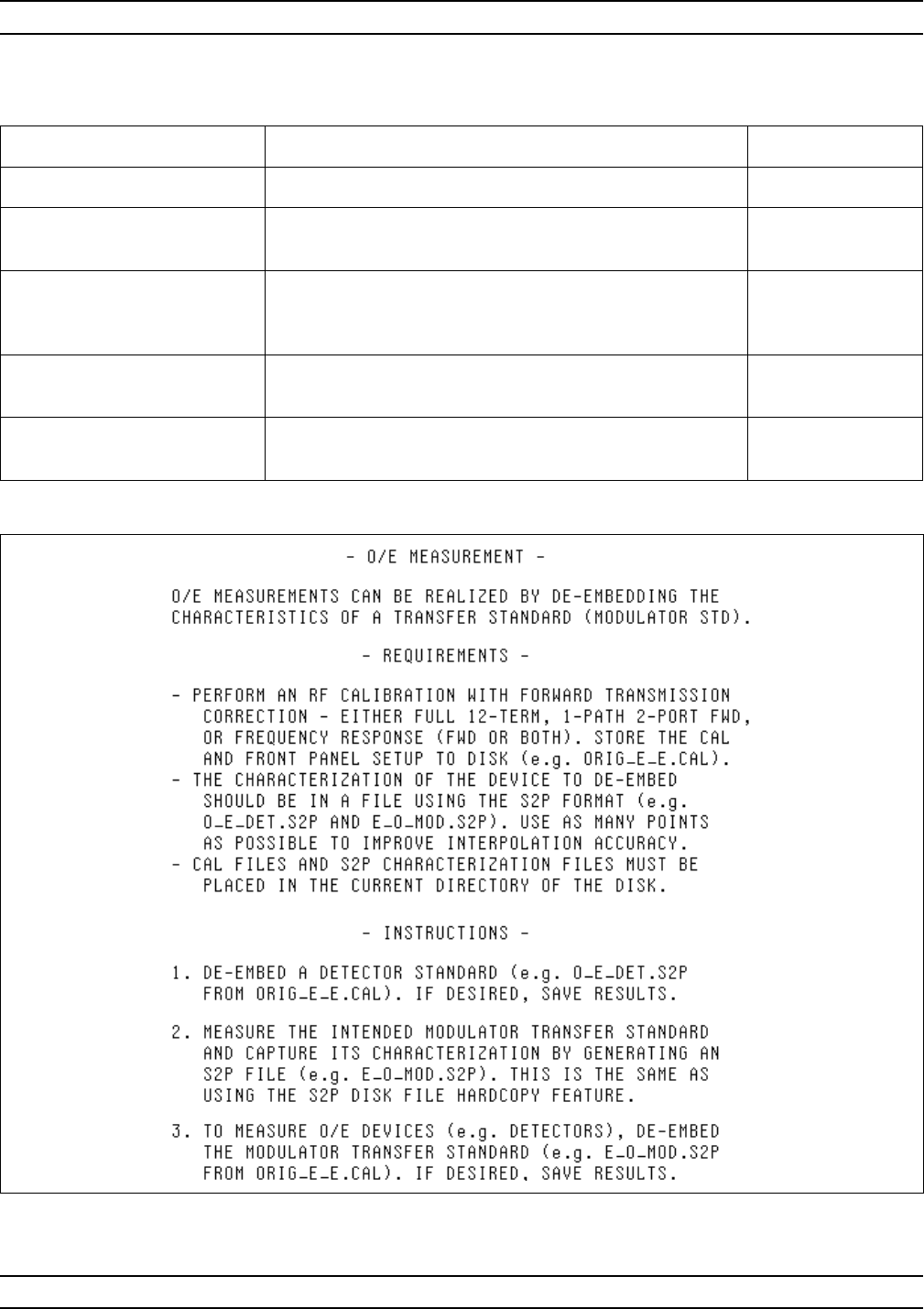
A-80 37XXXC OM
D ALPHABETICAL LISTING
MENU DESCRIPTION GPIB COMMAND
O/E MEASUREMENT None
DE-EMBED O/E S2P
(DETECTOR STD) This menu selection calls menu DE5, then DE5A. IODF or LDODF
GENERATE E/O S2P
CHARACTERIZATION
(MODULATOR)
This menu selection calls menu DE6. None
MEASURE O/E DUT
(DETECTOR) This menu selection calls menu DE7, then DE7A. IODF or LDODF
PRESS <ENTER>
TO SELECT Pressing the Enter key implements your menu selection. None
Menu DE2, O/E Measurement
Menu EXT_DE2, O/E Measurement
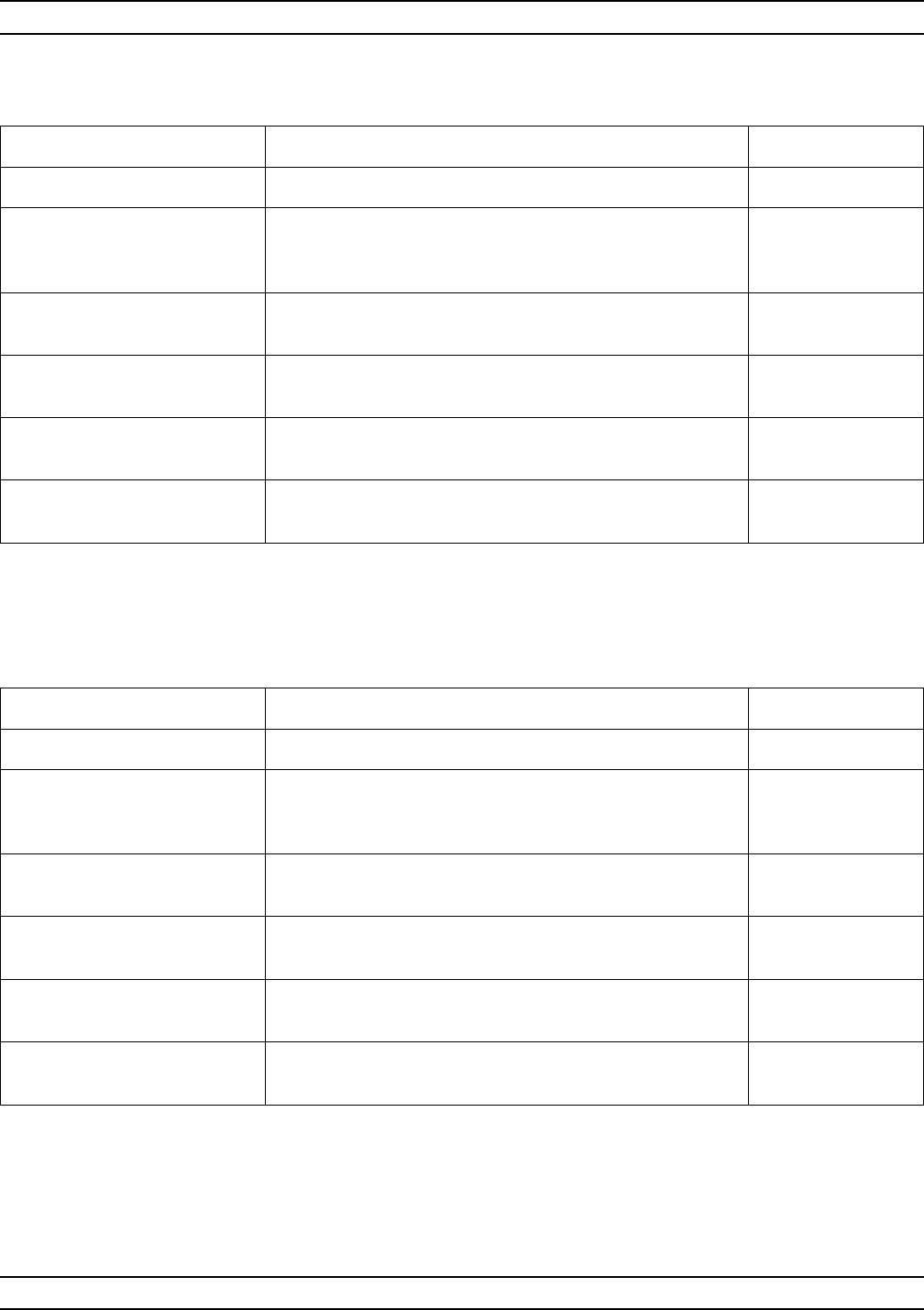
37XXXC OM A-81
ALPHABETICAL LISTING D
MENU DESCRIPTION GPIB COMMAND
E/O MEASUREMENT None
ORIGINAL CAL FILE
WITH FWD TRANS
CORRECTION
READ CAL FILE
FROM HARD DISK This menu selection calls menu DSK2 for *.CAL files on
the hard disk drive. None
READ CAL FILE
FROM FLOPPY DISK This menu selection calls menu DSK2 for *.CAL files on
the floppy disk drive. None
PRESS <ENTER>
TO SELECT Pressing the Enter key implements your menu selection. None
PRESS <CLEAR>
TO ABORT Pressing the Clear key aborts your this menu selection
and calls menu DE1. None
Menu DE3, E/O Measurement
MENU DESCRIPTION GPIB COMMAND
E/O MEASUREMENT None
TRANSFER STANDARD
TO BE DE-EMBEDED
(DETECTOR STD)
READ S2P FILE
FROM HARD DISK This menu selection calls menu DSK2 for *.S2P files on
the hard disk drive. None
READ S2P FILE
FROM FLOPPY DISK This menu selection calls menu DSK2 for *.S2P files on
the floppy disk drive. None
PRESS <ENTER>
TO SELECT Pressing the Enter key implements your menu selection. None
PRESS <CLEAR>
TO ABORT Pressing the Clear key aborts this menu selection and
calls menu DE1. None
Menu DE3A, E/O Measurement
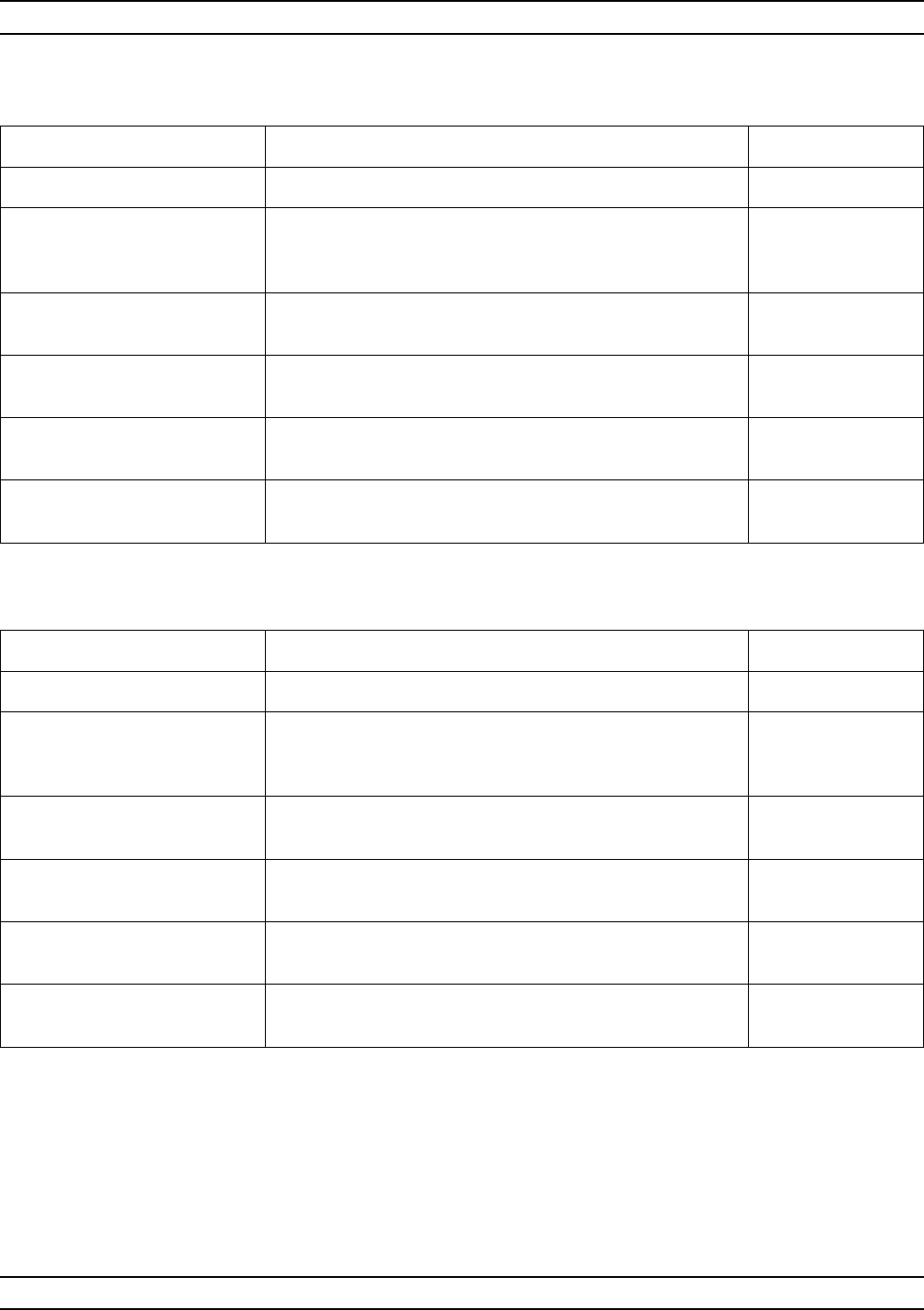
A-82 37XXXC OM
D ALPHABETICAL LISTING
MENU DESCRIPTION GPIB COMMAND
DE-EMBED NETWORK None
ORIGINAL CAL FILE
WITH FWD TRANS
CORRECTION
READ CAL FILE
FROM HARD DISK This menu selection calls menu DSK2 for *.CAL files on
the hard disk drive. None
READ CAL FILE
FROM FLOPPY DISK This menu selection calls menu DSK2 for *.CAL files on
the floppy disk drive. None
PRESS <ENTER>
TO SELECT Pressing the Enter key implements your menu selection. None
PRESS <CLEAR>
TO ABORT Pressing the Clear key aborts this menu selection and
calls menu DE1. None
Menu DE4, De-embed Network
MENU DESCRIPTION GPIB COMMAND
DE-EMBED NETWORK None
TRANSFER FUNCTION
TO BE DE-EMBEDED
(GENERIC NETWORK)
READ S2P FILE
FROM HARD DISK This menu selection calls menu DSK2 for *.S2P files on
the hard disk drive. None
READ S2P FILE
FROM FLOPPY DISK This menu selection calls menu DSK2 for *.S2P files on
the floppy disk drive. None
PRESS <ENTER>
TO SELECT Pressing the Enter key implements your menu selection. None
PRESS <CLEAR>
TO ABORT Pressing the Clear key aborts this menu selection and
calls menu DE1. None
Menu DE4A, De-embed Network
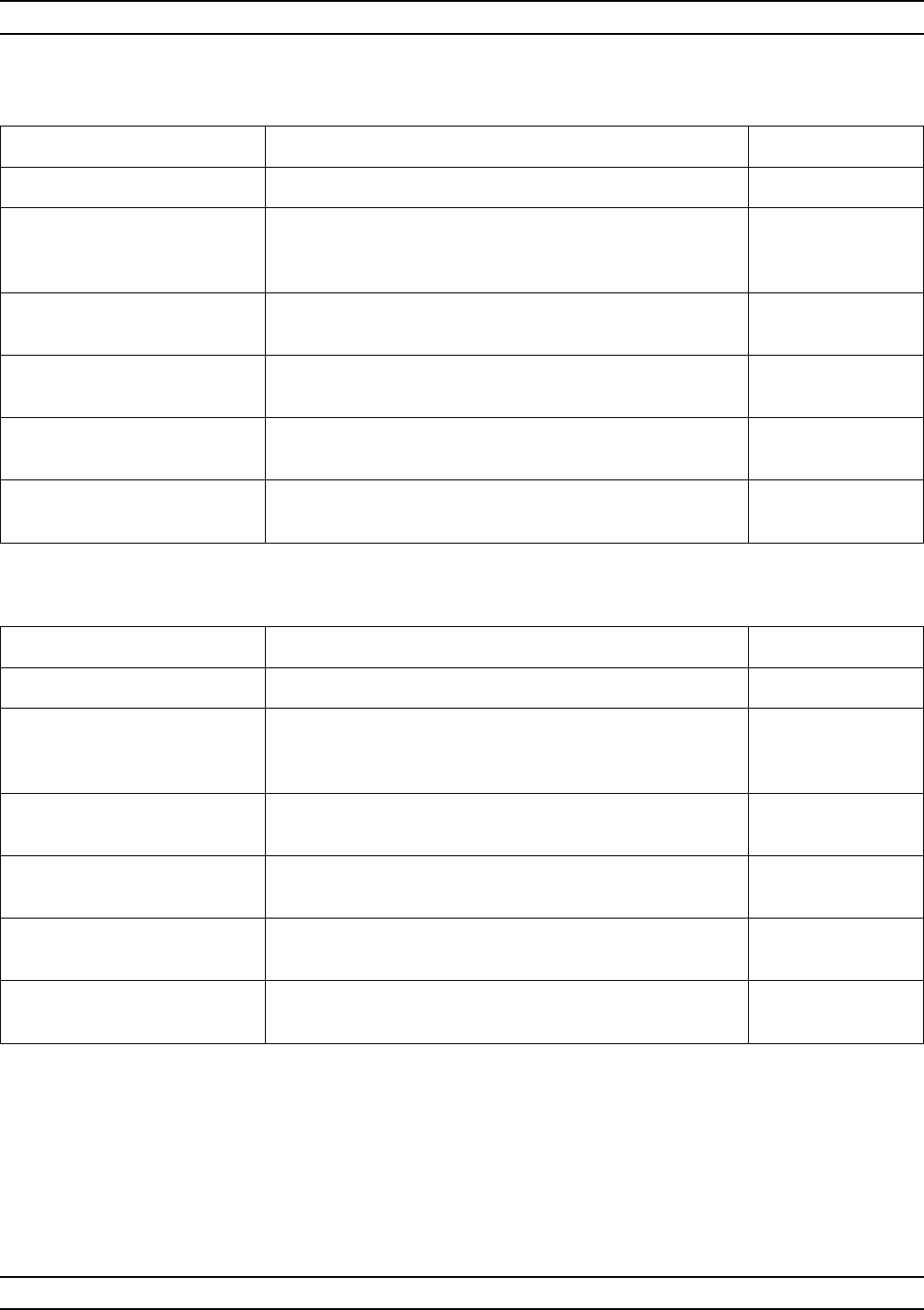
37XXXC OM A-83
ALPHABETICAL LISTING D
MENU DESCRIPTION GPIB COMMAND
DE-EMBED O/E S2P None
ORIGINAL CAL FILE
WITH FWD TRANS
CORRECTION
READ CAL FILE
FROM HARD DISK This menu selection calls menu DSK2 for *.CAL files on
the hard disk drive. None
READ CAL FILE
FROM FLOPPY DISK This menu selection calls menu DSK2 for *.CAL files on
the floppy disk drive. None
PRESS <ENTER>
TO SELECT Pressing the Enter key implements your menu selection. None
PRESS <CLEAR>
TO ABORT Pressing the Clear key aborts this menu selection and
calls menu DE2. None
Menu DE5, De-embed O/E S2P
MENU DESCRIPTION GPIB COMMAND
DE-EMBED O/E S2P None
TRANSFER STANDARD
TO BE DE-EMBEDED
(DETECTOR STANDARD)
READ S2P FILE
FROM HARD DISK This menu selection calls menu DSK2 for *.S2P files on
the hard disk drive. None
READ S2P FILE
FROM FLOPPY DISK This menu selection calls menu DSK2 for *.S2P files on
the floppy disk drive. None
PRESS <ENTER>
TO SELECT Pressing the Enter key implements your menu selection. None
PRESS <CLEAR>
TO ABORT Pressing the Clear key aborts this menu selection and
calls menu DE2. None
Menu DE5A, De-embed O/E S2P
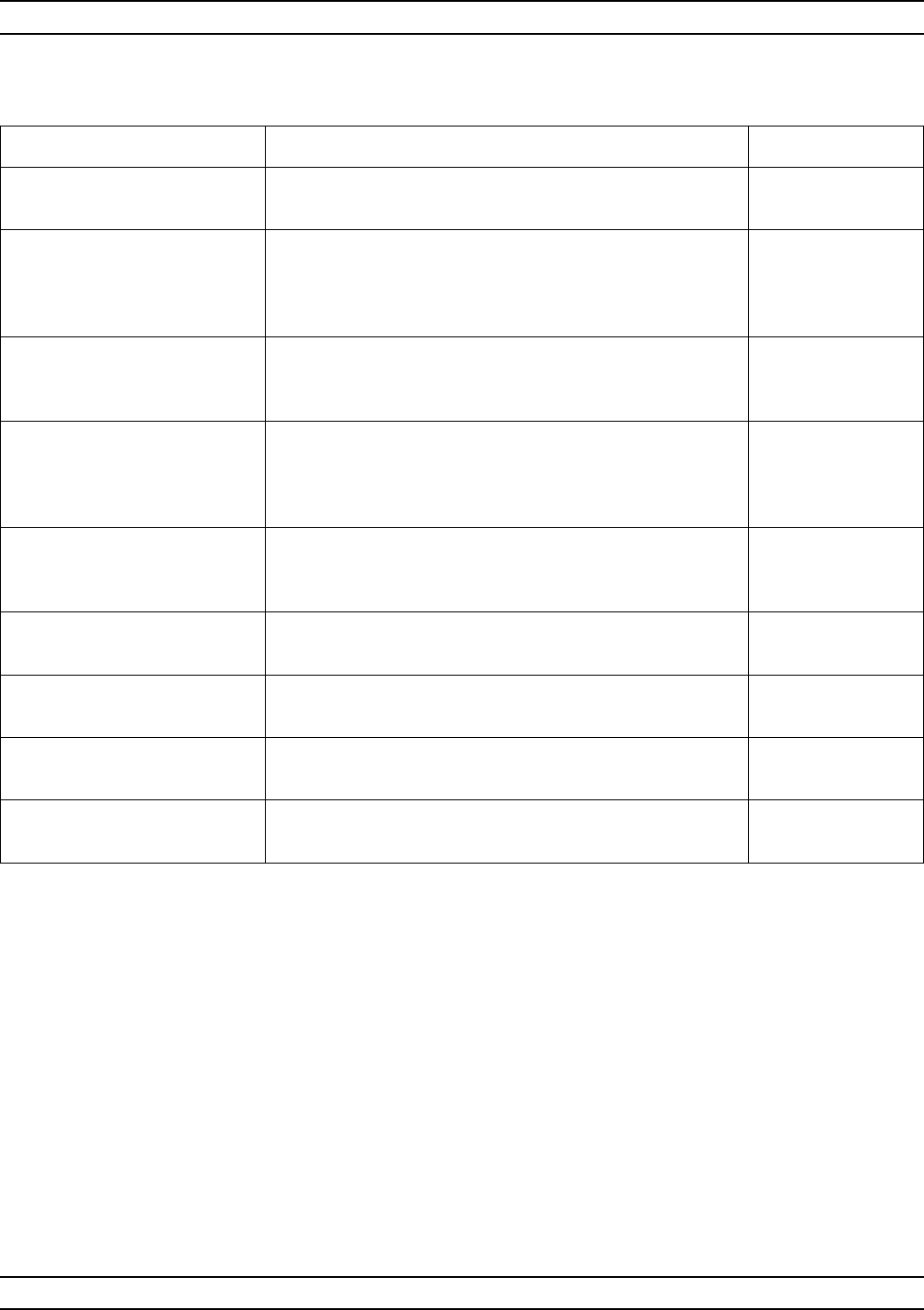
A-84 37XXXC OM
D ALPHABETICAL LISTING
MENU DESCRIPTION GPIB COMMAND
GENERATE E/O S2P
CHARACTERIZATION None
CONNECT TRANSFER
STANDARD DETECTOR
AND DE-EMBED ITS
CHARACTERIZATION
CONNECT E/O DEVICE
(MODULATOR) AND
APPLY BIAS
INCLUDE ANY OTHER
COMPONENTS WHICH
ARE PART OF THE
MEASUREMENT PATH
WAIT FOR A
COMPLETE SWEEP
BEFORE STORING
SAVE S2P DATA
TO HARD DISK This menu selection calls menu DSK3 for *.S2P files on
the hard disk drive. SAVE
SAVE S2P DATA
TO FLOPPY DISK This menu selection calls menu DSK3 for *.S2P files on
the floppy disk drive. SAVE
PRESS <ENTER>
TO SELECT Pressing the Enter key implements your menu selection. None
PRESS <CLEAR>
TO ABORT Pressing the Clear key aborts this menu selection and
calls menu DE2. None
Menu DE6, Generate E/O S2P Characterization
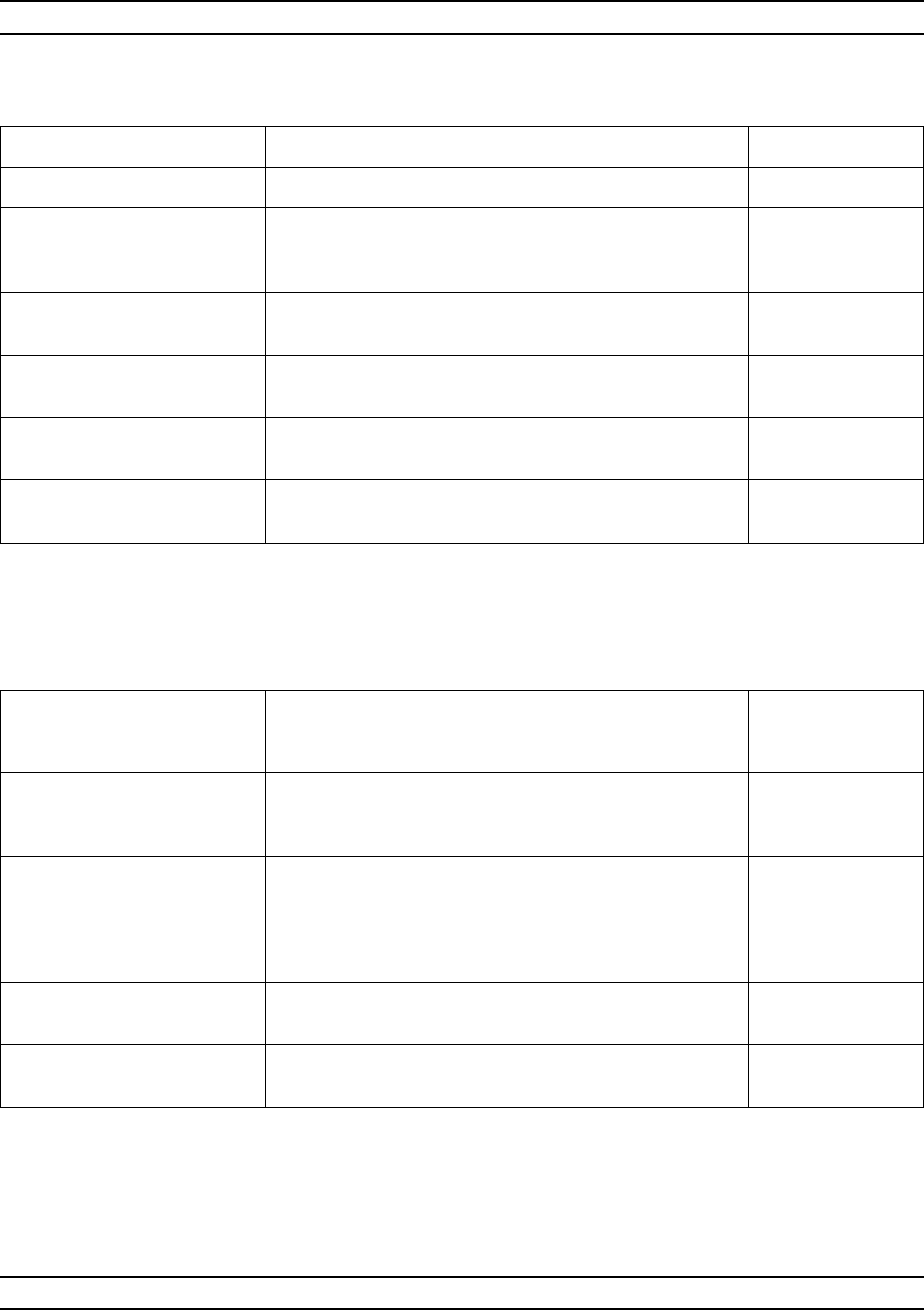
37XXXC OM A-85
ALPHABETICAL LISTING D
MENU DESCRIPTION GPIB COMMAND
O/E MEASUREMENT None
ORIGINAL CAL FILE
WITH FWD TRANS
CORRECTION
READ CAL FILE
FROM HARD DISK This menu selection calls menu DSK2 for *.CAL files on
the hard disk drive. None
READ CAL FILE
FROM FLOPPY DISK This menu selection calls menu DSK2 for *.CAL files on
the floppy disk drive. None
PRESS <ENTER>
TO SELECT Pressing the Enter key implements your menu selection. None
PRESS <CLEAR>
TO ABORT Pressing the Clear key aborts this menu selection and
calls menu DE2. None
Menu DE7, O/E Measurement
MENU DESCRIPTION GPIB COMMAND
O/E MEASUREMENT None
TRANSFER STANDARD
TO BE DE-EMBEDED
(MODULATOR)
READ S2P FILE
FROM HARD DISK This menu selection calls menu DSK2 for *.S2P files on
the hard disk drive. None
READ S2P FILE
FROM FLOPPY DISK This menu selection calls menu DSK2 for *.S2P files on
the floppy disk drive. None
PRESS <ENTER>
TO SELECT Pressing the Enter key implements your menu selection. None
PRESS <CLEAR>
TO ABORT Pressing the Clear key aborts this menu selection and
calls menu DE2. None
Menu DE7A, O/E Measurement
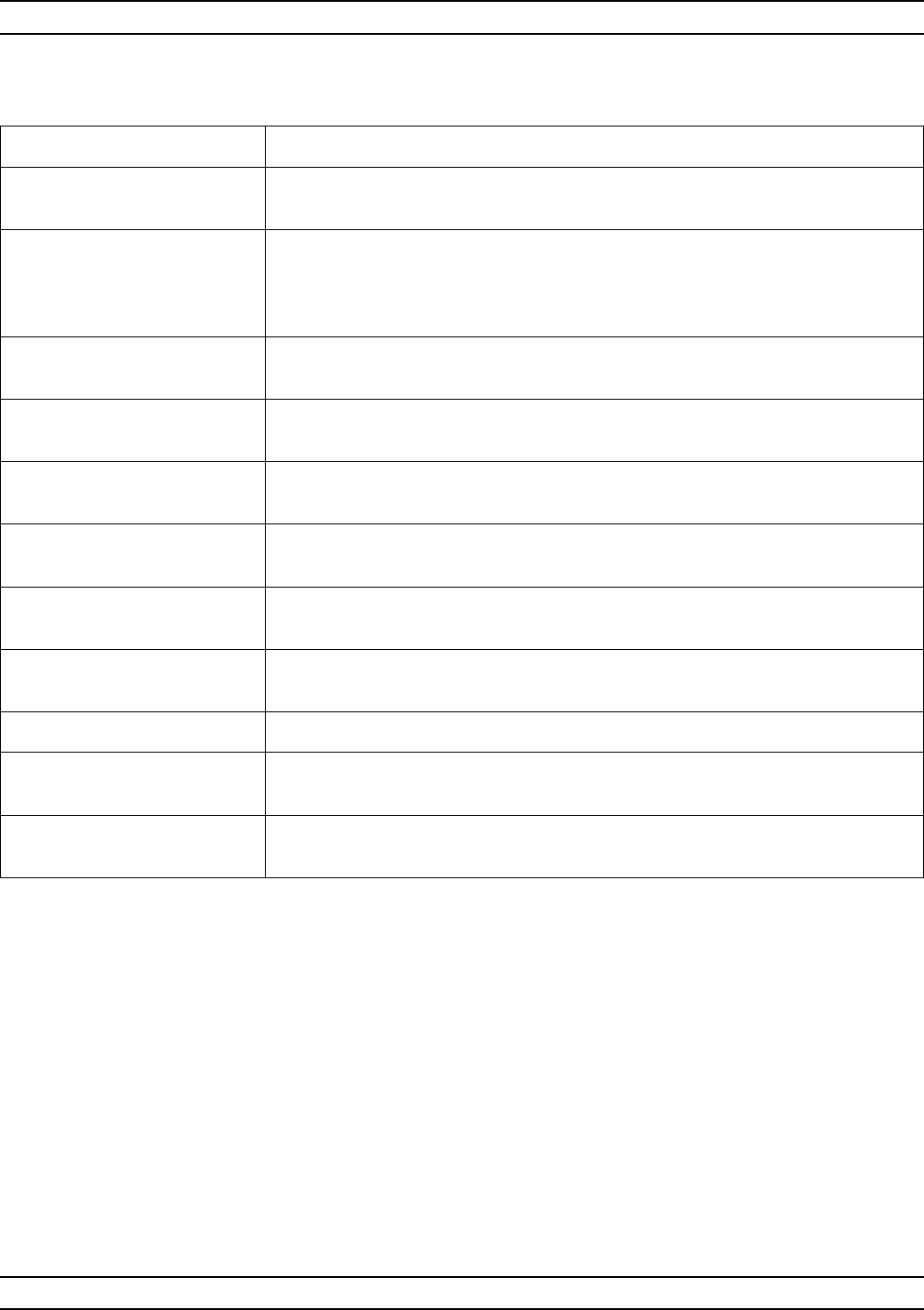
A-86 37XXXC OM
D ALPHABETICAL LISTING
MENU DESCRIPTION
DISCRETE FILL
INPUT START,
INCR, POINTS,
THEN SELECT
“FILL RANGE”
This menu is used to create one or more ranges of discrete equally spaced
frequency points.
START FREQ
XXX.XXXXXXXXX GHz Enter the first frequency of the range.
INCREMENT
XXX.XXXXXXXXX GHz Enter the increment (step size) between one frequency and the next.
NUMBER OF PTS
XXXX POINT(S) Enter the number of frequency points in the range.
STOP FREQ
XXX.XXXXXXXXX GHz Enter the stop frequency, in GHz.
FILL RANGE
( XXXX ENTERED) Moving the cursor here and pressing Enter fills the range and shows the
number of frequencies selected (in NUM OF PTS above).
INDIVIDUAL
FREQ INSERT Calls menu DF2, which allows you to set the individual frequencies.
CLEAR ALL Clears all entries displayed above.
FINISHED
RETURN TO SWP Closes this menu.
PRESS <ENTER>
TO SELECT Pressing the Enter key implements your menu selection.
Menu DF1, Discrete Fill
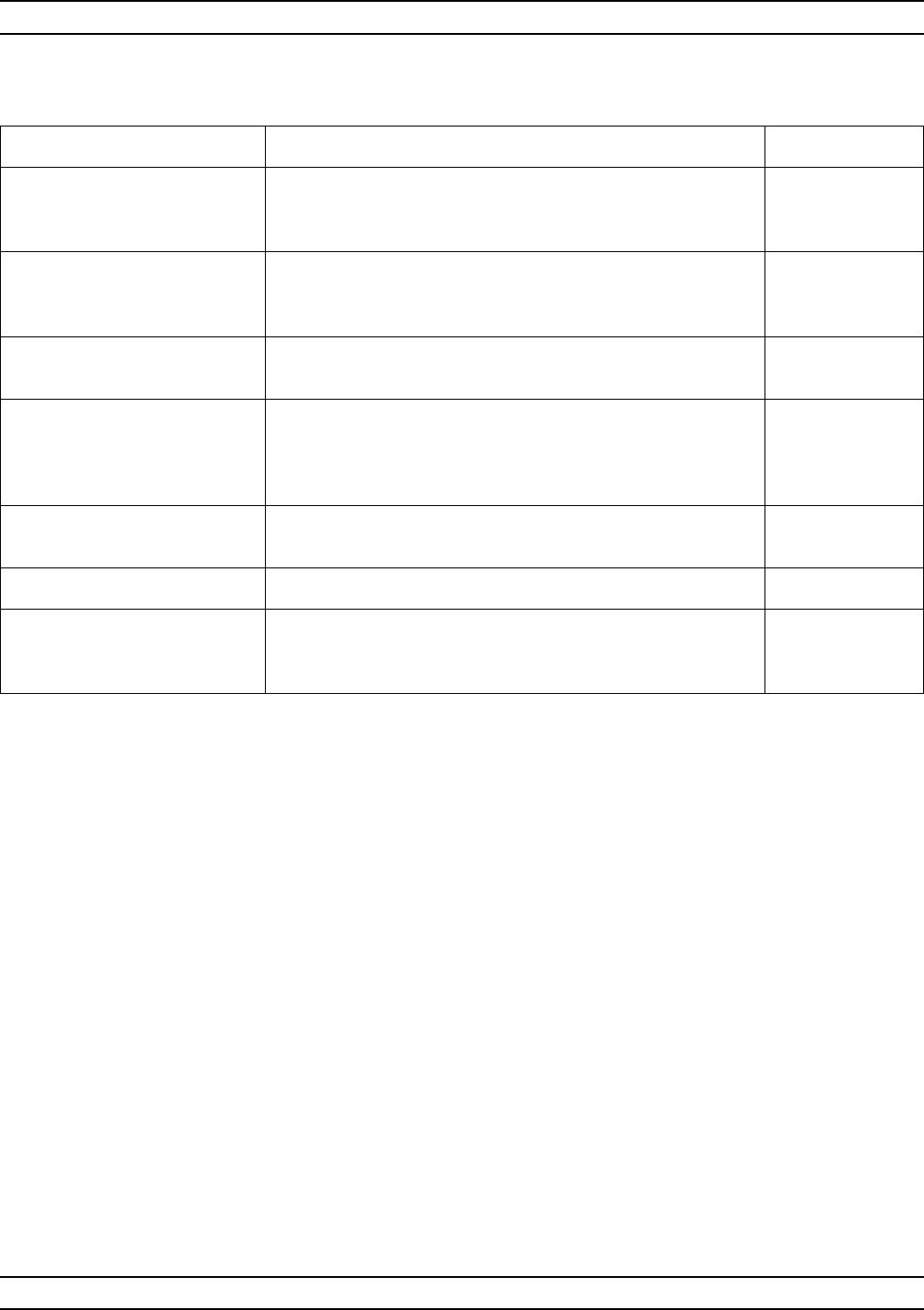
37XXXC OM A-87
ALPHABETICAL LISTING D
MENU DESCRIPTION GPIB COMMAND
INSERT
INDIVIDUAL
FREQUENCIES
None
INPUT A FREQ,
PRESS <ENTER>
TO INSERT
Enter the start frequency, increment frequency, and number
of points; then select the FILL RANGE menu option, below. None
NEXT FREQ
XXX.XXXXXXXXX GHz Enter the sweep start frequency, in GHz. None
XXXX FREQS
ENTERED
LAST FREQ WAS
XXX.XXXXXXXXX GHz
Enter the frequency, in GHz, by which you want to
increment the start frequency. None
AUTO INCR ON (OFF)
XXX.XXXXXXXXX GHz Enter the number of points. None
PREVIOUS MENU Returns to the previous menu. None
PRESS <ENTER>
THEN SELECT
OR TURN ON/OFF
Press the Enter key to implements your menu selection or
to turn a selection on or off. None
Menu DF2, Insert Individual Frequencies
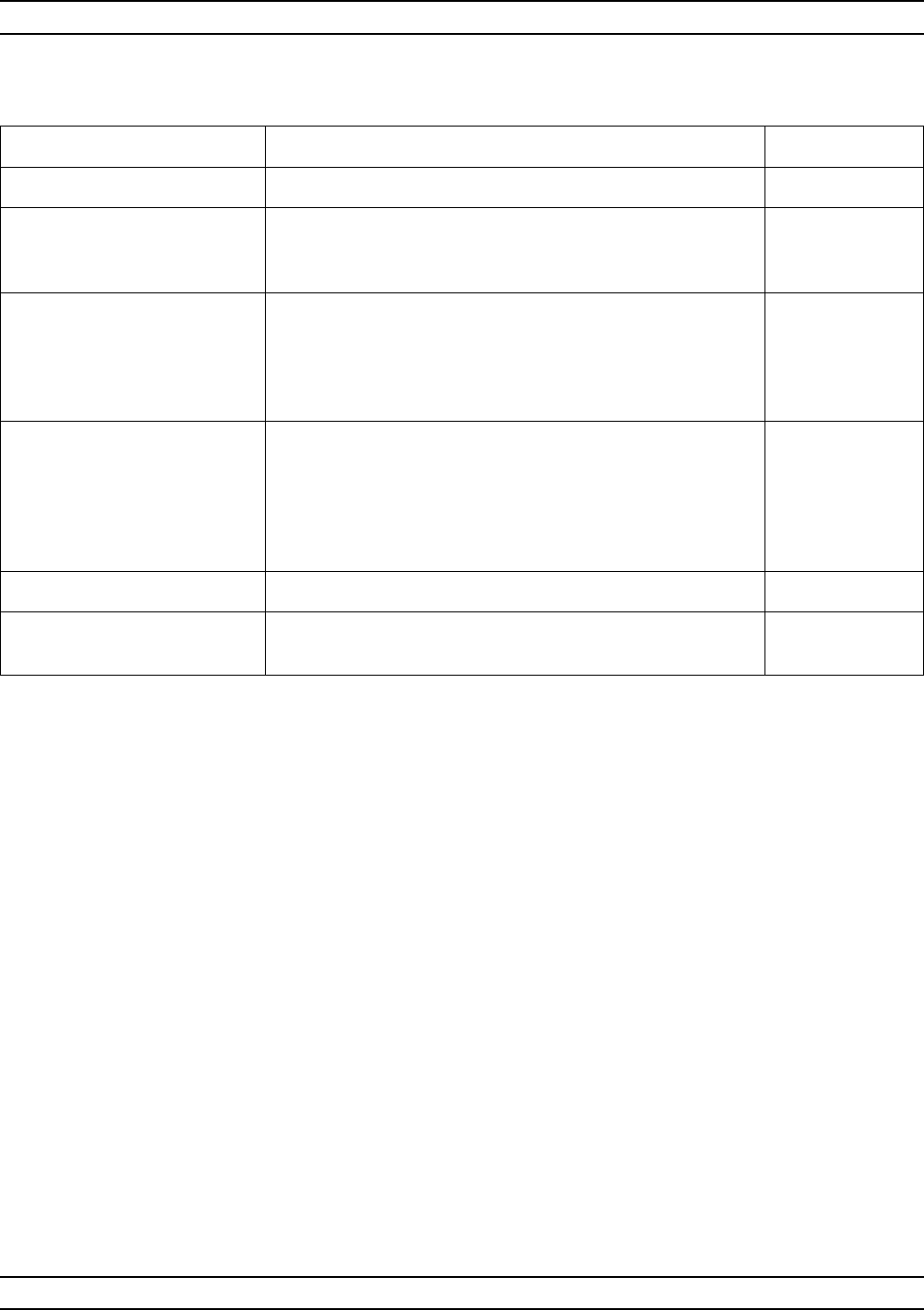
A-88 37XXXC OM
D ALPHABETICAL LISTING
MENU DESCRIPTION GPIB COMMAND
WARNING None
DEFAULT
PROGRAM
SELECTED
CONTINUING
WILL ERASE
CURRENT
SETUP AND
CALIBRATION
PRESS
<DEFAULT PRGM>
TO CONFIRM
Pressing the DEFAULT PROGRAM key a second time
resets the 360 VNA to its default settings. Press the
DEFAULT PROGRAM key, the “0” key, then the DEFAULT
PROGRAM key again clears all internal memories. This
keying method can be used to clear memories of data used
for classified operations.
OR
PRESS <CLEAR>
TO ABORT Pressing the CLEAR key implements your menu selection.
Menu DFLT, Default Program Selected
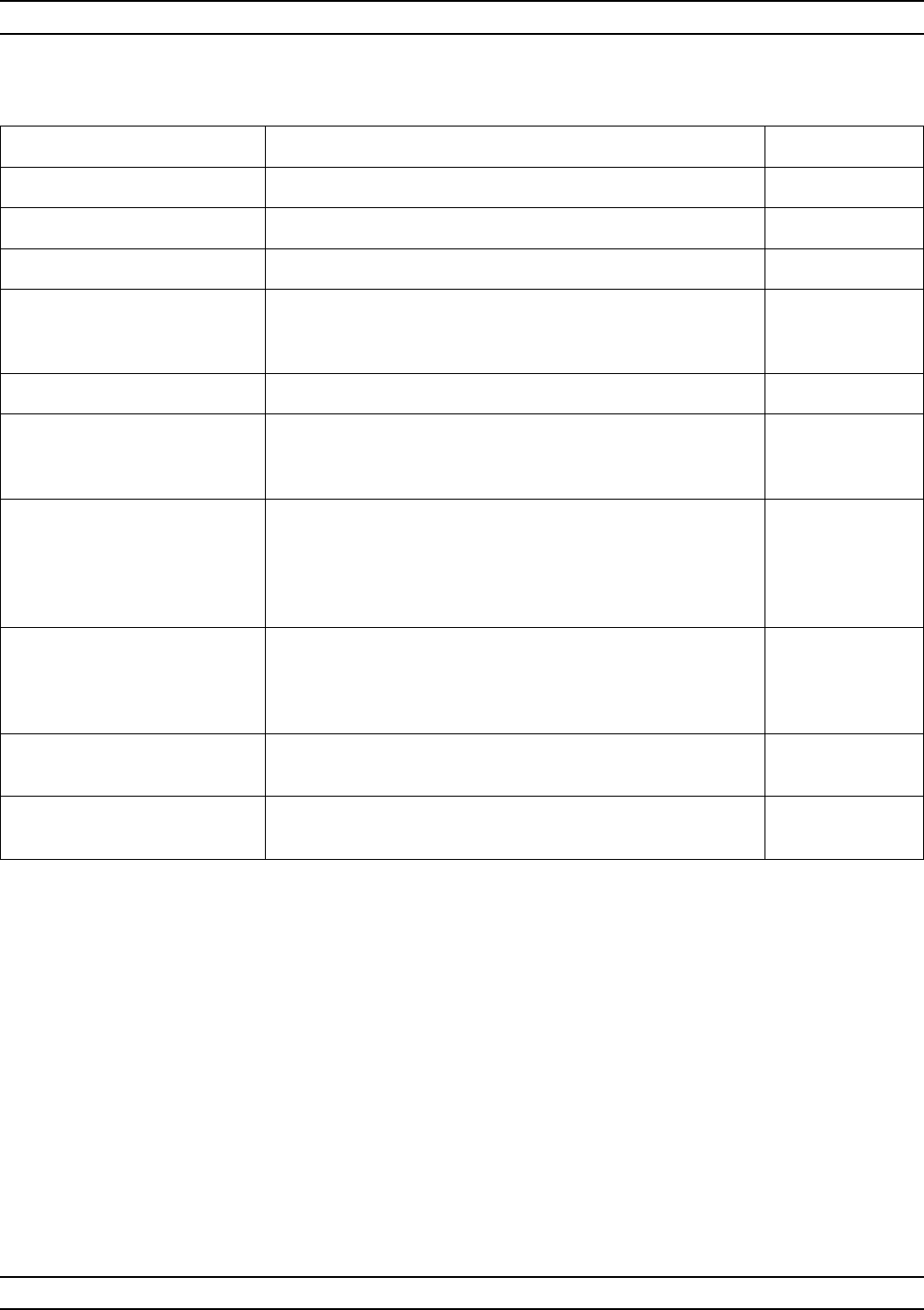
37XXXC OM A-89
ALPHABETICAL LISTING D
MENU DESCRIPTION GPIB COMMAND
DIAGNOSTICS None
START SELF TEST Starts a self test of the 37XXXC. TST; *TST?
INSTALLED OPTIONS Displays the fitted options. *OPT?
PERIPHERAL TESTS Calls menu DG3, which provides tests for peripherals such
as the LCD, front panel, external keyboard, printer and
GPIB interfaces.
None
SERVICE FUNCTIONS
READ SERVICE LOG
(FOR SERVICE
USE ONLY)
Calls menu DG2, which gives you options for using the
Service Log. None
TROUBLESHOOTING
(FOR SERVICE
USE ONLY)
Calls menu DG4, which provides options for
troubleshooting the 37XXXC hardware. This menu is
intended for use by a qualified service technician. Refer to
the Model 37XXXC Maintenance Manual for additional
information.
None
H/W CALIBRATIONS
(FOR SERVICE
USE ONLY)
Calls menu DG5, which provides for invoking calibration
routines for use by a qualified service technician. Refer to
the Model 37XXXC Maintenance Manual for additional
information.
None
AUTOCAL ASSURANCE Calls Menu ACAL_ASSUR, which provides for performing
AutoCal assurance routines. None
PRESS <ENTER>
TO SELECT Pressing the Enter key implements your menu selection. None
Menu DG1, Diagnostics 1
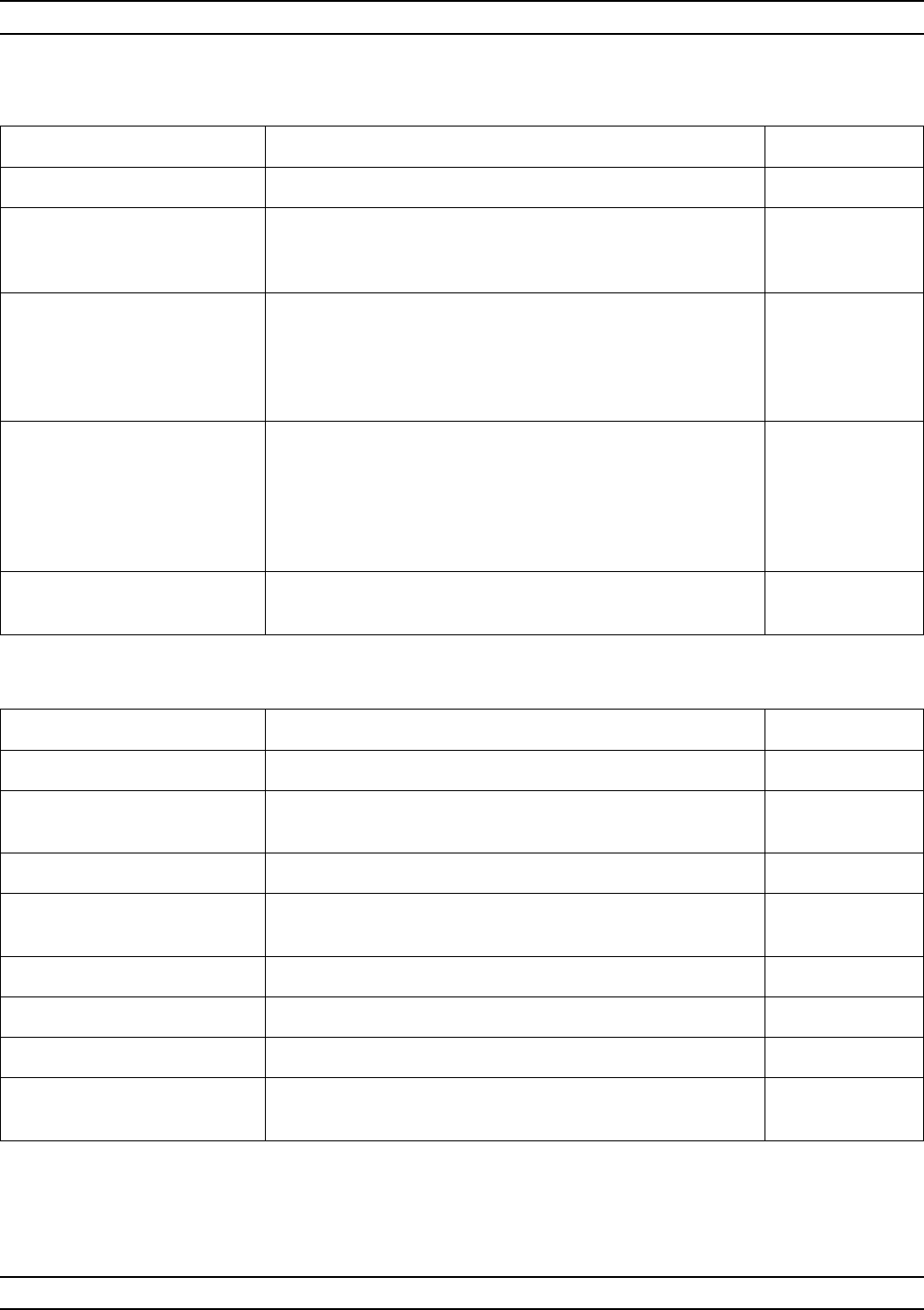
A-90 37XXXC OM
D ALPHABETICAL LISTING
MENU DESCRIPTION GPIB COMMAND
PERIPHERAL TESTS None
DISPLAY Provides a graphic display for evaluating screen colors and
linearity.
FRONT PANEL Provides for testing the front panel keys.
EXTERNAL
KEYBOARD Provides for testing the external keyboard connected to the
Keyboard connector on the front panel.
PRINTER INTERFACE Provides for testing the printer interface.
GPIB INTERFACE Provides for testing the GPIB interface.
PREVIOUS MENU Returns to menu DG1. None
PRESS <ENTER>
TO SELECT Pressing the Enter key implements your menu selection. None
Menu DG3, Diagnostics 3
MENU DESCRIPTION GPIB COMMAND
WARNING None
DEFAULT
PROGRAM
SELECTED
CONTINUING
WILL ERASE
CURRENT
SETUP AND
CALIBRATION
PRESS
<DEFAULT PROGRAM>
TO CONFIRM
Pressing the DEFAULT PROGRAM key a second time
resets the VNA to its default settings. Press the DEFAULT
PROGRAM key, the “0” key, then the DEFAULT
PROGRAM key again clears all internal memories. This
keying method can be used to clear memories of data used
for classified operations.
PRESS <CLEAR>
TO ABORT Pressing the CLEAR key implements your menu selection.
Menu DG2, Troubleshooting
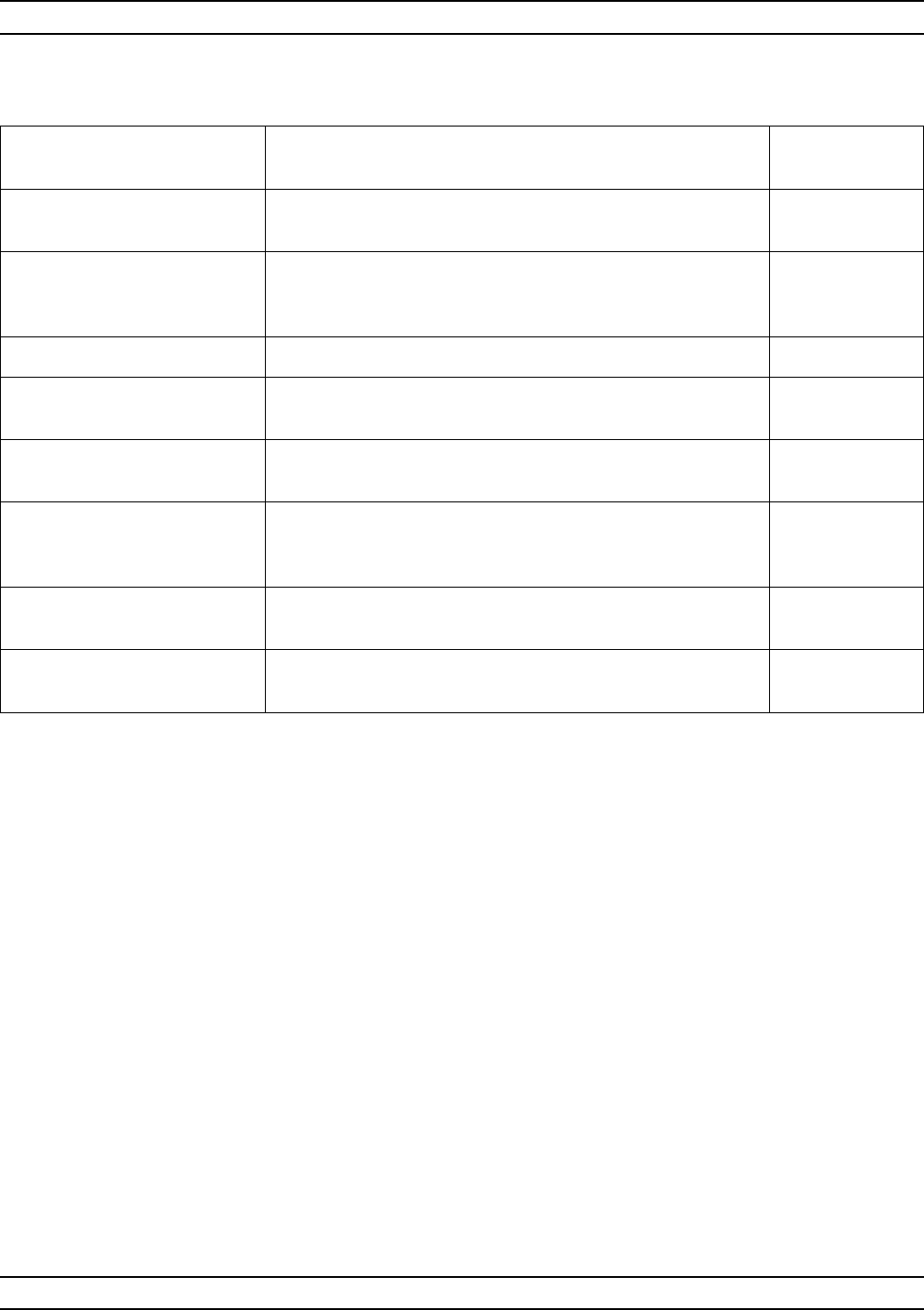
37XXXC OM A-91
ALPHABETICAL LISTING D
MENU DESCRIPTION GPIB COM-
MAND
FLOPPY DISK
UTILITIES None
DISPLAY
DIRECTORY Directory displays in the screen’s data area. Press <1> for
previous page, <2> for next page, <0> for first page, and
<3> for last page.
DIR
DELETE FILES Calls DSK6, which lets you delete data files. None
COPY FILES
TO HARD DISK Calls DSK8, which lets you copy files to the hard disk. None
FORMAT
FLOPPY DISK Formats the floppy disk. INT
COMMAND LINE Prompts a one-line dialog box that allows you to enter a
command. The dialog box remains open only for the user
interface.
None
HARD DISK
UTILITIES Calls DSK1-HD, which provides hard disk utilities. None
PRESS <ENTER>
TO SELECT Pressing Enter implements your menu selection. You will be
returned to the previous menu when your selection is made. None
Menu DSK_FD, Floppy Disk Utilities
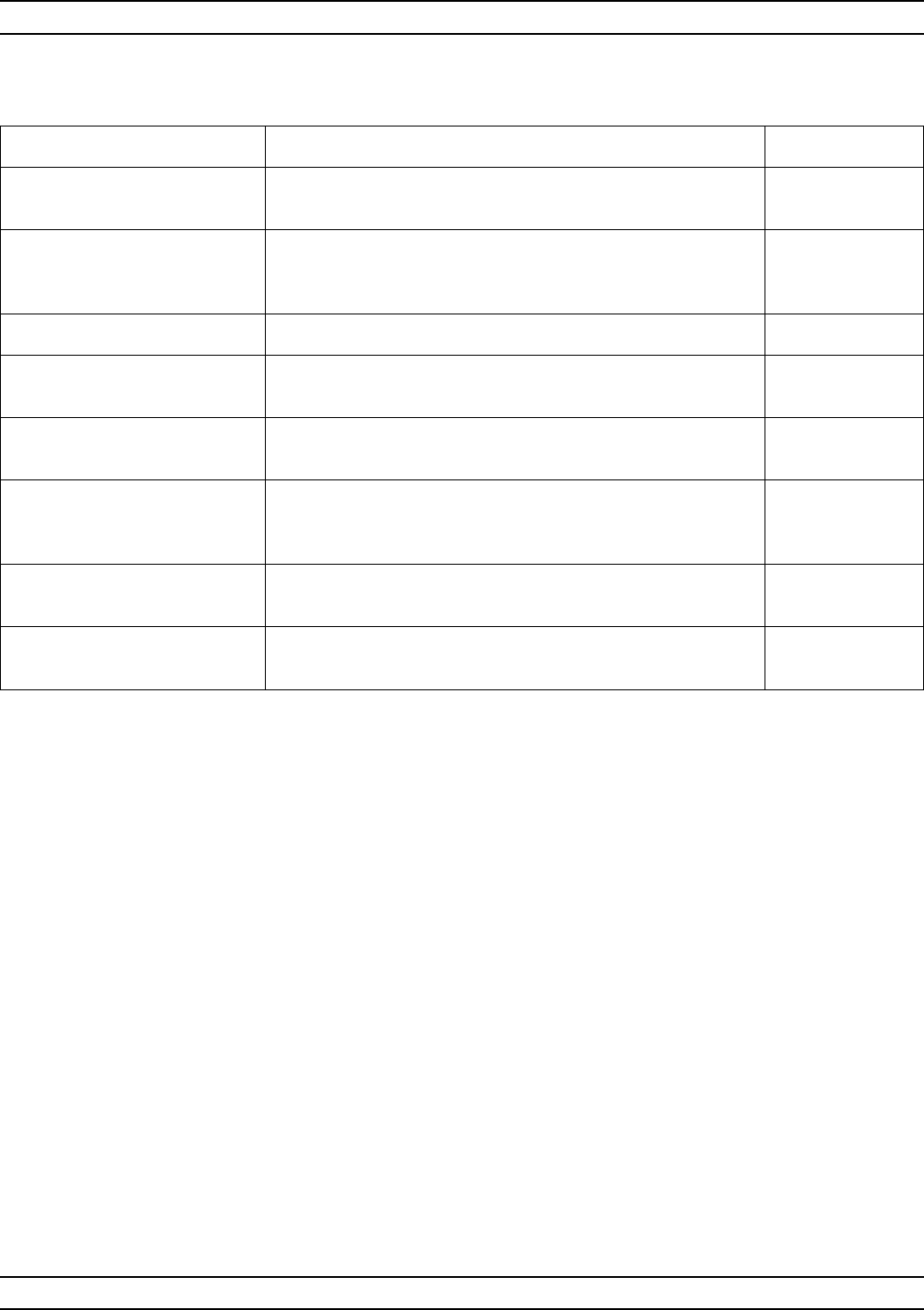
A-92 37XXXC OM
D ALPHABETICAL LISTING
MENU DESCRIPTION GPIB COMMAND
HARD DISK
UTILITIES None
DISPLAY
DIRECTORY Directory displays in the screen’s data area. Press <1> for
previous page, <2> for next page, <0> for first page, and
<3> for last page.
DIR
DELETE FILES Calls DSK6, which lets you delete data files. None
COPY FILES
TO FLOPPY DISK Calls DSK8, which lets you copy files to the floppy disk. None
FORMAT
HARD DISK Formats the hard disk. None
COMMAND LINE Prompts a one-line dialog box that allows you to enter a
command. The dialog box remains open only for the user
interface.
None
FLOPPY DISK
UTILITIES Calls DSK1-FD, which provides floppy disk utilities. None
PRESS <ENTER>
TO SELECT Pressing the Enter key implements your menu selection. None
Menu DSK_HD, Hard Disk Utilities
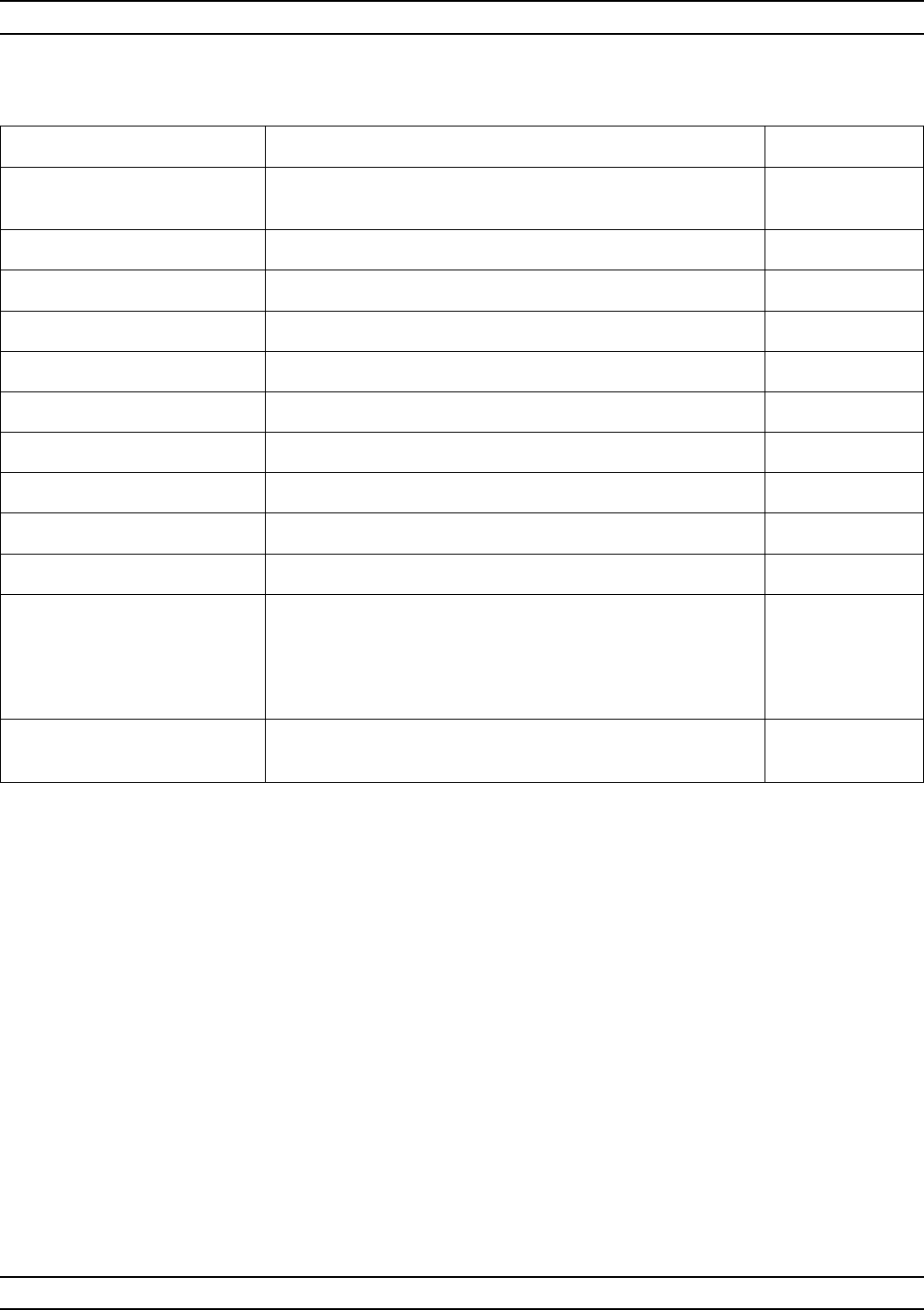
37XXXC OM A-93
ALPHABETICAL LISTING D
MENU DESCRIPTION GPIB COMMAND
SELECT FILE
TO READ None
FILE 1 Displays the data stored in file number 1.
FILE 2 Displays the data stored in file number 2.
FILE 3 Displays the data stored in file number 3.
FILE 4 Displays the data stored in file number 4.
FILE 5 Displays the data stored in file number 5.
FILE 6 Displays the data stored in file number 6.
FILE 7 Displays the data stored in file number 7.
FILE 8 Displays the data stored in file number 8.
PREVIOUS MENU Returns to the previous menu. None
PRESS <ENTER>
TO SELECT Pressing the Enter key implements your menu selection. None
PRESS <1> FOR
PREVIOUS PAGE Pressing the “1" key on the keypad returns to the previous
page.
PRESS <2>
FOR NEXT PAGE Pressing the “2" key on the keypad produces the next
page. None
Menu DSK2, Select File to Read
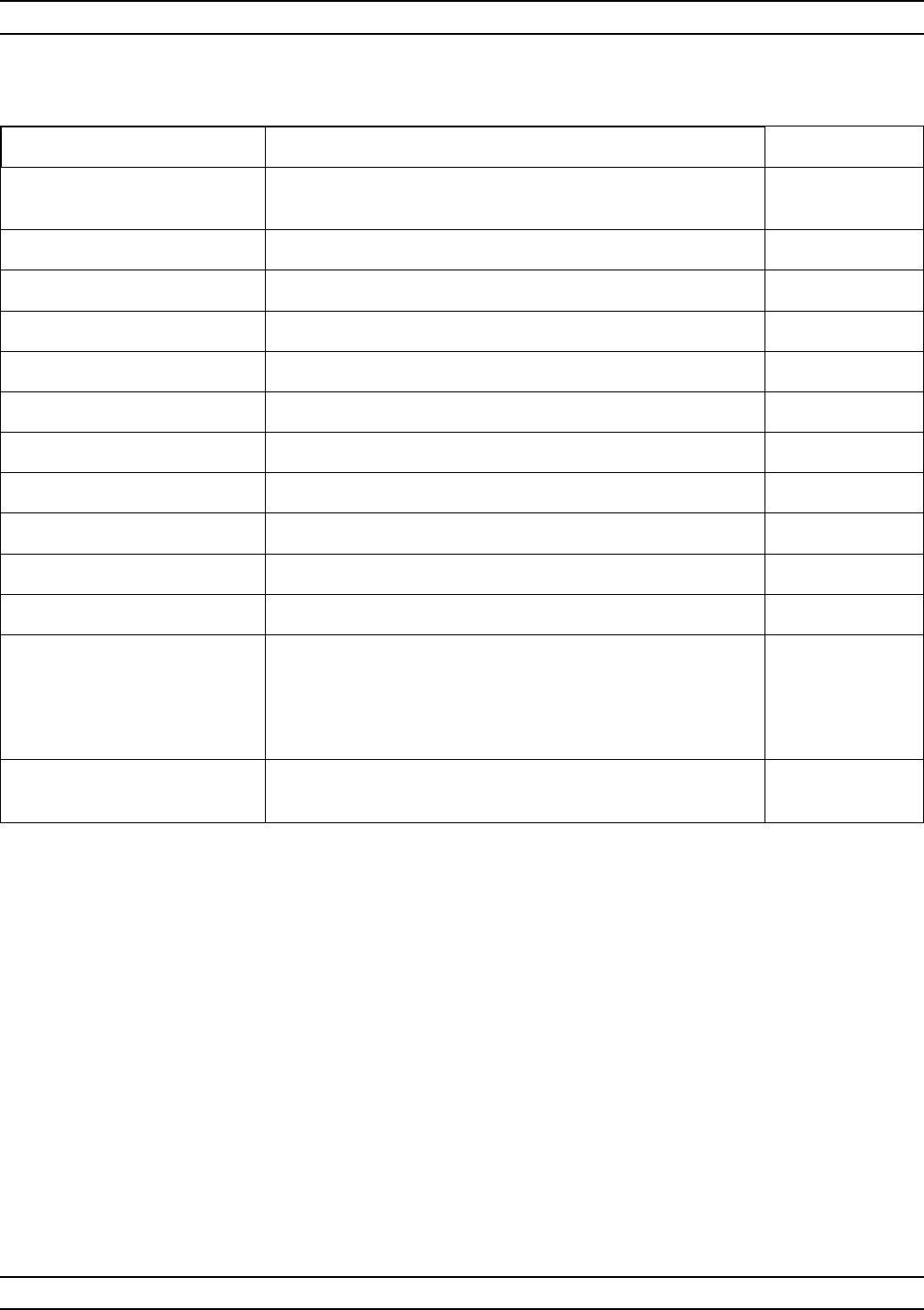
A-94 37XXXC OM
D ALPHABETICAL LISTING
MENU DESCRIPTION GPIB COMMAND
SELECT FILE
TO OVERWRITE None
CREATE NEW FILE
FILE 1 Select file number 1 to be overwritten with new data.
FILE 2 Select file number 2 to be overwritten with new data.
FILE 3 Select file number 3 to be overwritten with new data.
FILE 4 Select file number 4 to be overwritten with new data.
FILE 5 Select file number 5 to be overwritten with new data.
FILE 6 Select file number 6 to be overwritten with new data.
FILE 7 Select file number 7 to be overwritten with new data.
FILE 8 Select file number 8 to be overwritten with new data.
PREVIOUS MENU Returns to the previous menu. None
PRESS <ENTER>
TO SELECT Pressing the Enter key implements your menu selection. None
PRESS <1> FOR
PREVIOUS PAGE Pressing the “1" key on the keypad returns to the previous
page.
PRESS <2>
FOR NEXT PAGE Pressing the “2" key on the keypad produces the next
page. None
Menu DSK3, Select File to Overwrite
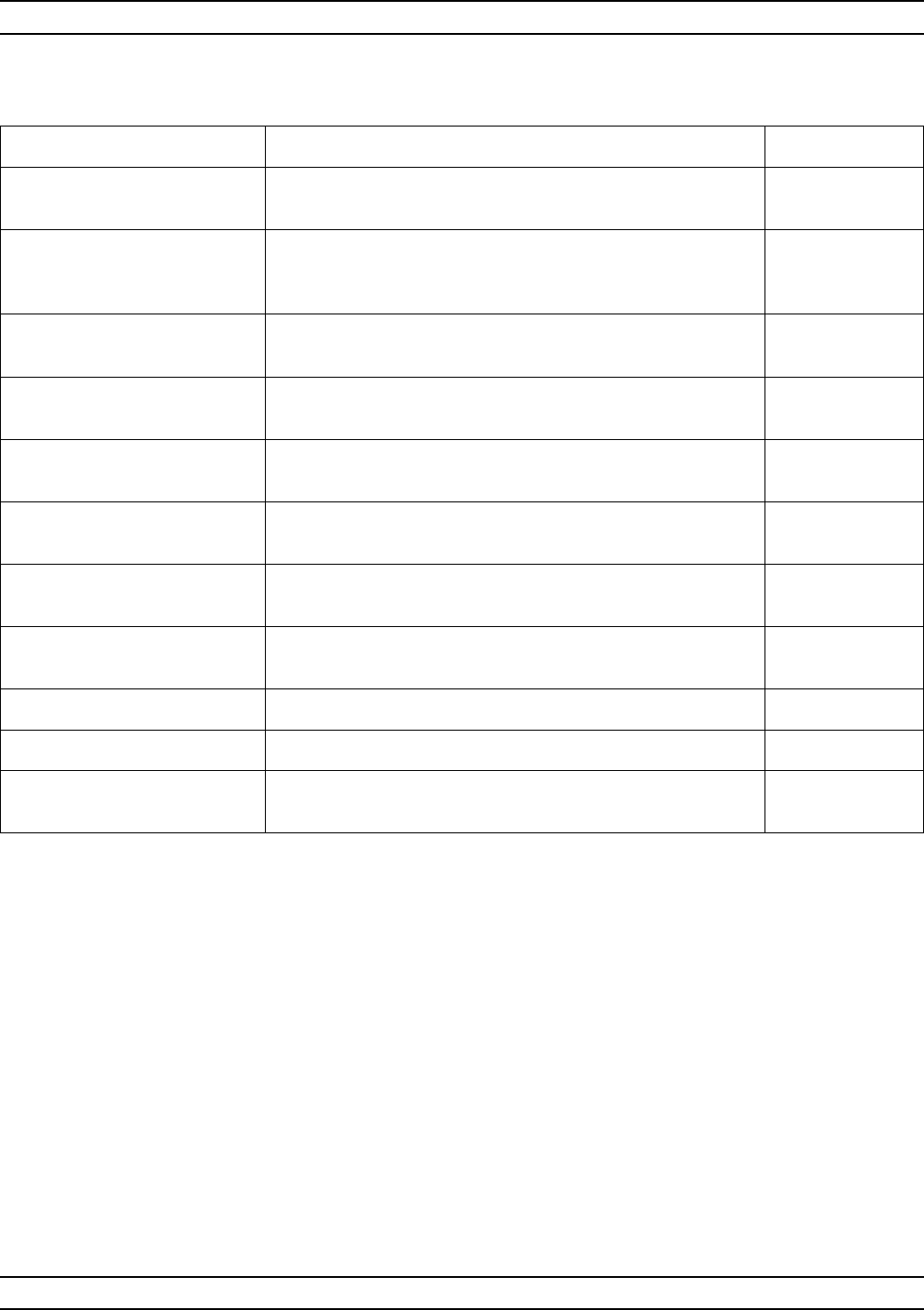
37XXXC OM A-95
ALPHABETICAL LISTING D
MENU DESCRIPTION GPIB COMMAND
TYPE OF FILES
TO DELETE None
FRONT PANEL
SETUP AND
CAL DATA
Calls menu DSK7, which provides a list of front panel and
calibration data file. None
TRACE DATA Calls menu DSK7, which provides a list of trace data files
to delete. None
TABULAR DATA Calls menu DSK7, which provides a list of tabular data files
to delete. None
TEXT DATA Calls menu DSK7, which provides a list of text files to
delete. None
S2P DATA Calls menu DSK7, which provides a list of S2P data files to
delete. None
BITMAP DATA Calls menu DSK7, which provides a list of bitmap files to
delete. None
HPGL DATA Calls menu DSK7, which provides a list of HPGL files to
delete. None
ALL TYPES (*.*) Calls menu DSK7, which provides a list of all file types. None
PREVIOUS MENU Returns to the previous menu. None
PRESS <ENTER>
TO SELECT Pressing the Enter key implements your menu selection. None
Menu DSK6, Type of Files to Delete
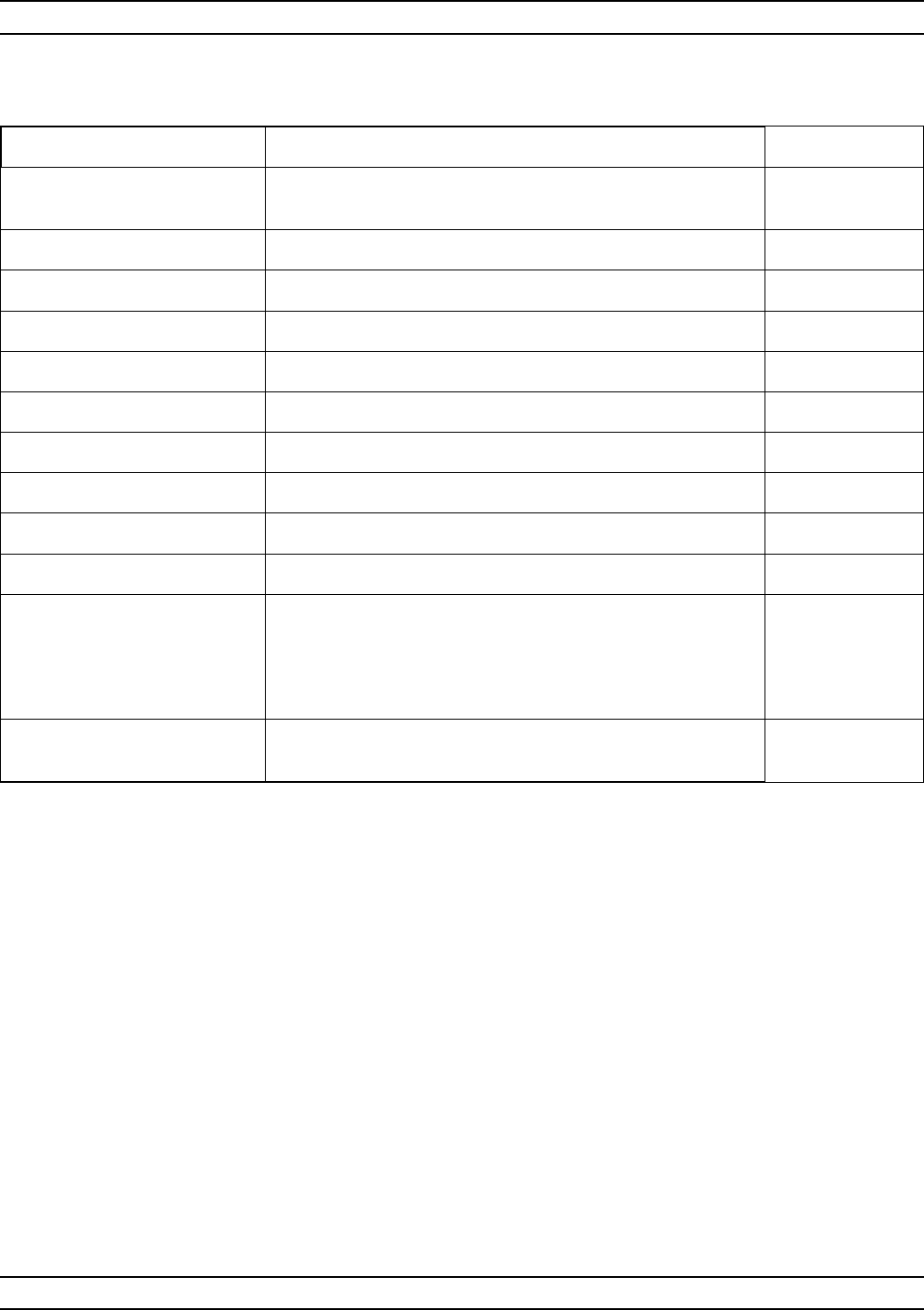
A-96 37XXXC OM
D ALPHABETICAL LISTING
MENU DESCRIPTION GPIB COMMAND
SELECT FILE
TO DELETE None
FILE 1 Selects file number 1 data to be deleted.
FILE 2 Selects file number 2 data to be deleted.
FILE 3 Selects file number 3 data to be deleted.
FILE 4 Selects file number 4 data to be deleted.
FILE 5 Selects file number 5 data to be deleted.
FILE 6 Selects file number 6 data to be deleted.
FILE 7 Selects file number 7 data to be deleted.
FILE 8 Selects file number 8 data to be deleted.
PREVIOUS MENU Returns to the previous menu. None
PRESS <ENTER>
TO SELECT Pressing the Enter key implements your menu selection. None
PRESS <1> FOR
PREVIOUS PAGE Pressing the “1" key on the keypad returns to the previous
page.
PRESS <2>
FOR NEXT PAGE Pressing the “2" key on the keypad produces the next
page. None
Menu DSK7, Select File to Delete
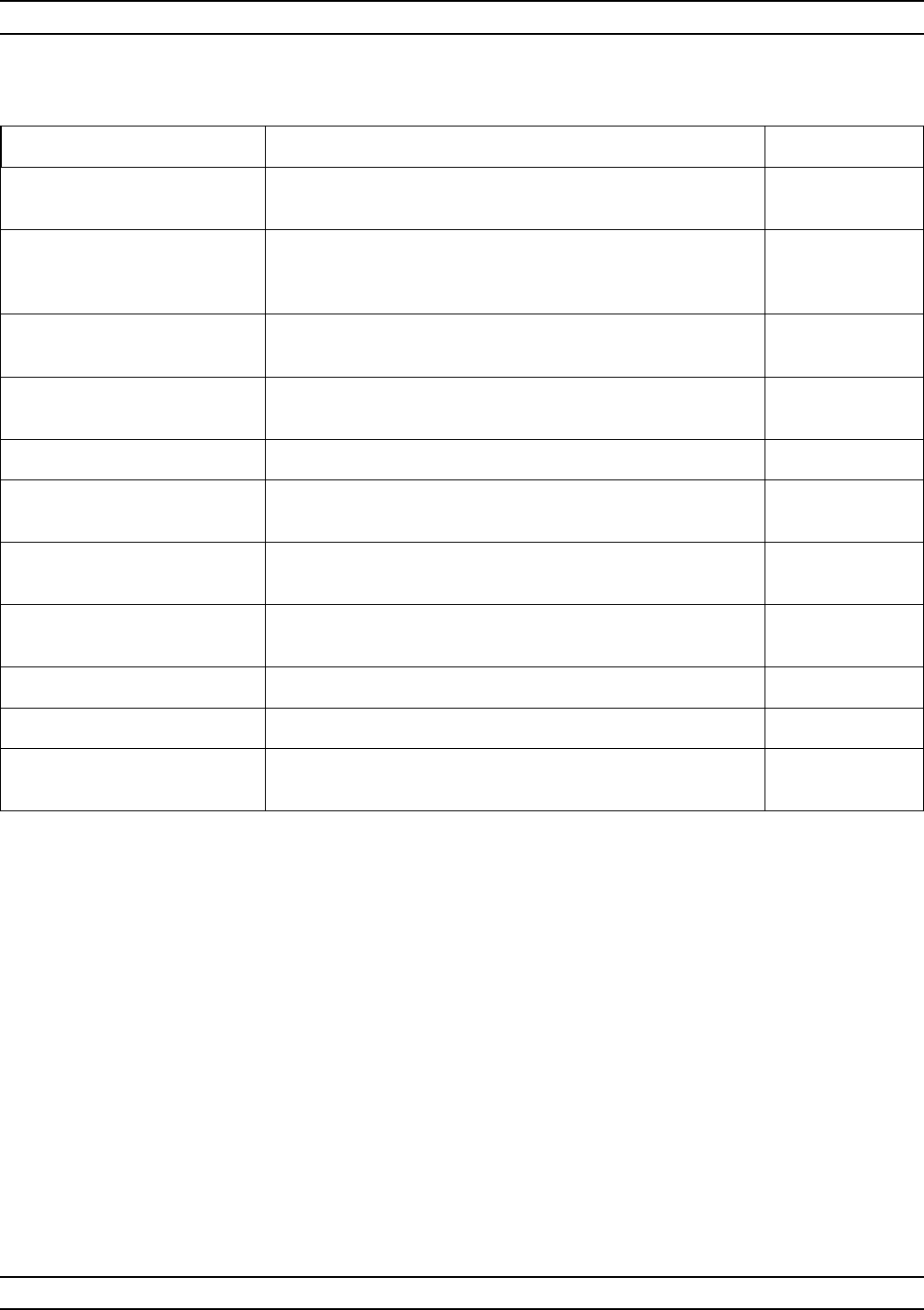
37XXXC OM A-97
ALPHABETICAL LISTING D
MENU DESCRIPTION GPIB COMMAND
TYPE OF FILES
TO COPY None
FRONT PANEL
SETUP AND
CAL DATA
Calls menu DSK9, which provides a list of front panel and
calibration data file. None
TRACE DATA Calls menu DSK9, which provides a list of trace data files
to copy. None
TABULAR DATA Calls menu DSK9, which provides a list of tabular data files
to copy. None
TEXT DATA Calls menu DSK9, which provides a list of text files to copy. None
S2P DATA Calls menu DSK9, which provides a list of S2P files to
copy. None
BITMAP DATA Calls menu DSK9, which provides a list of bitmap files to
copy. None
HPGL DATA Calls menu DSK9, which provides a list of HPGL files to
copy. None
ALL TYPES (*.*) Calls menu DSK9, which provides a list of all file types. None
PREVIOUS MENU Returns to the previous menu. None
PRESS <ENTER>
TO SELECT Pressing the Enter key implements your menu selection. None
Menu DSK8, Type of Files to Copy
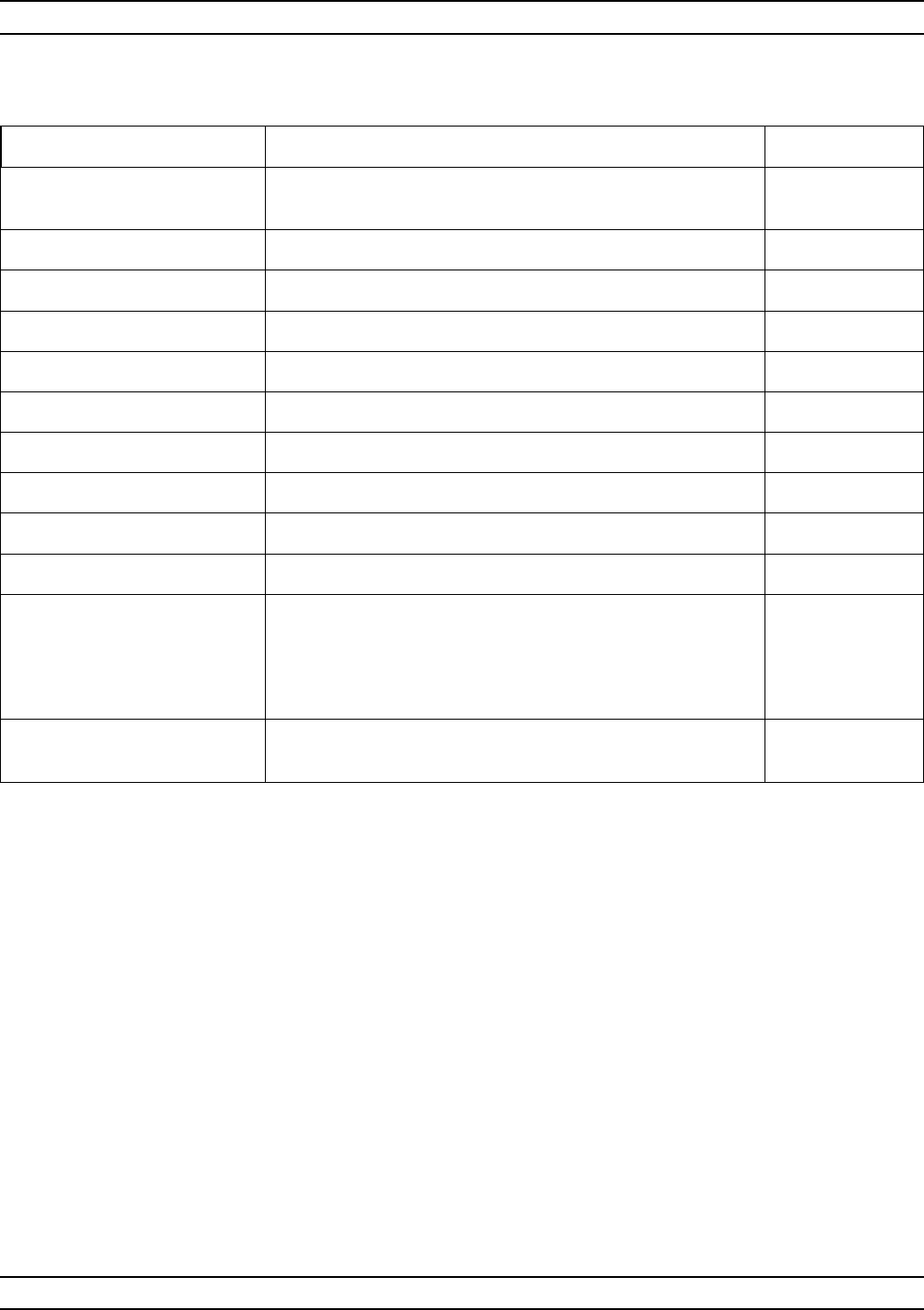
A-98 37XXXC OM
D ALPHABETICAL LISTING
MENU DESCRIPTION GPIB COMMAND
SELECT FILE
TO COPY None
FILE 1 Selects file number 1 data to be copied. COPY
FILE 2 Selects file number 2 data to be copied. COPY
FILE 3 Selects file number 3 data to be copied. COPY
FILE 4 Selects file number 4 data to be copied. COPY
FILE 5 Selects file number 5 data to be copied. COPY
FILE 6 Selects file number 6 data to be copied. COPY
FILE 7 Selects file number 7 data to be copied. COPY
FILE 8 Selects file number 8 data to be copied. COPY
PREVIOUS MENU Returns to the previous menu. None
PRESS <ENTER>
TO SELECT Pressing the Enter key implements your menu selection. None
PRESS <1> FOR
PREVIOUS PAGE Pressing the “1" key on the keypad returns to the previous
page.
PRESS <2>
FOR NEXT PAGE Pressing the “2" key on the keypad produces the next
page. None
Menu DSK9, Select File to Copy
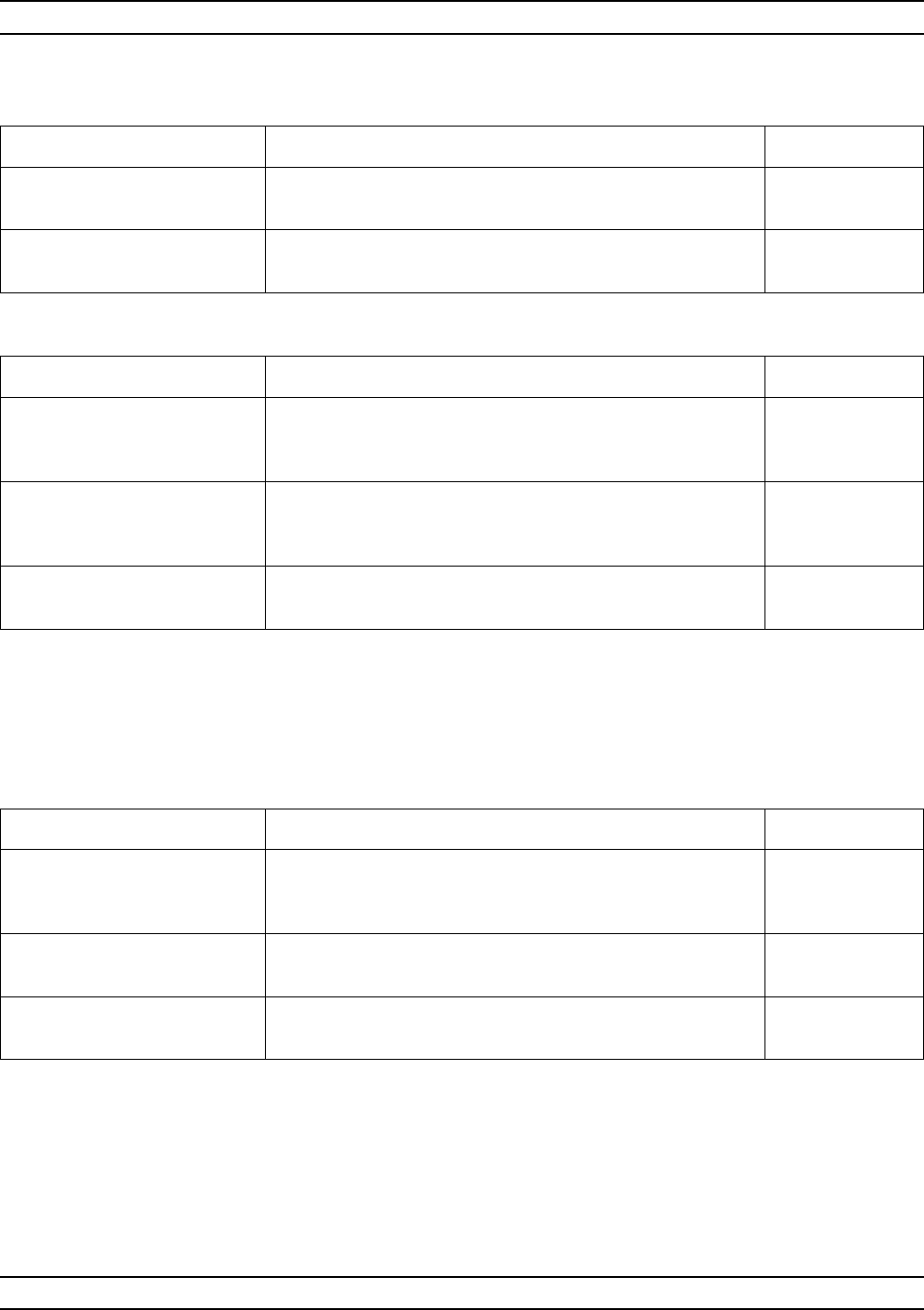
37XXXC OM A-99
ALPHABETICAL LISTING D
MENU DESCRIPTION GPIB COMMAND
CAPTURE
TABULAR DATA Captures the tabular data to a file when the Enter key is
pressed. None
PRESS <ENTER>
TO CONTINUE Pressing the Enter key implements your menu selection. None
Menu DSK10, Capture Tabular Data
MENU DESCRIPTION GPIB COMMAND
CAUTION: ALL
FLOPPY DISK DATA
WILL BE ERASED
None
INSERT DISK
TO FORMAT Ensure that you have the correct floppy diskette for
formatting, then press the Enter key to begin the formatting
process.
None
PRESS <ENTER>
TO CONTINUE Pressing the Enter key implements your menu selection. None
Menu DSK11, Format Floppy Disk
MENU DESCRIPTION GPIB COMMAND
CAUTION: ALL
HARD DISK DATA
WILL BE ERASED
None
ASSUME HARD DISK READY
TO FORMAT Assumes that the hard disk is ready to be formatted; press
the Enter key to begin the formatting process. None
PRESS <ENTER>
TO CONTINUE Pressing the Enter key implements your menu selection. None
Menu DSK12, Format Hard Disk

A-100 37XXXC OM
E ALPHABETICAL LISTING
MENU DESCRIPTION GPIB COMMAND
DATA ENHANCEMENT None
AVERAGING
XXXX MEAS. Averages the measured data over time, as follows:
1. The sweep stops at the first frequency point and takes a
number of readings, based on the selected number of
points.
2. The program averages the readings and writes the
average value for that frequency point in the displayed
graph.
3. The sweep then advances to the next sequential
frequency point and repeats the process.
AVG; AVG?
AVERAGING TYPE
POINT-BY-POINT Averages the point-by-point up to the number of averages. PTAVG; SWAVG?
SWEEP-BY-SWEEP Averages the sweep-by-sweep up to the number of
sweeps. SWAVG;
SWAVG?
RESET AVG COUNT
XXXX SWEEP(S) Zeros the counter used for sweep averaging RSTAVG
SMOOTHING
XX.XX PERCENT
OF SWEEP
XXX POINT(S)
Smooths the measured data over frequency, as follows:
1. The program divides the overall sweep into smaller
segments, based on the selected percent-of-span. (Refer to
Section 4-4 and Figure 4-23 for a description and example
of smoothing.)
2. It takes a data reading at each frequency point within
that percent-of-span segment.
3. It averages the readings with a raised Hamming window
and writes that magnitude value at the mid-frequency point
of the segment in the displayed graph or Smith chart.
4. It then advances the percent-of-span segment to
encompass the next sequential group of frequency points
and repeats the process.
The displayed number of points represents the number of
points for a given percent of sweep and is based on the
max data points, and the sweep start and stop.
SON; SON?;
SOF; SOF?
SAMPLERS USED
PER SWEEP
X SAMPLERS
Sets the number of samplers used per sweep. SAMP2; SAMP3;
SAMP?
PRESS <ENTER>
TO SELECT Pressing the Enter key implements your menu selection. None
PRESS
<AVG/SMOOTH MENU>
TO RESET AVG COUNT
Menu EM, Enhancement Menu
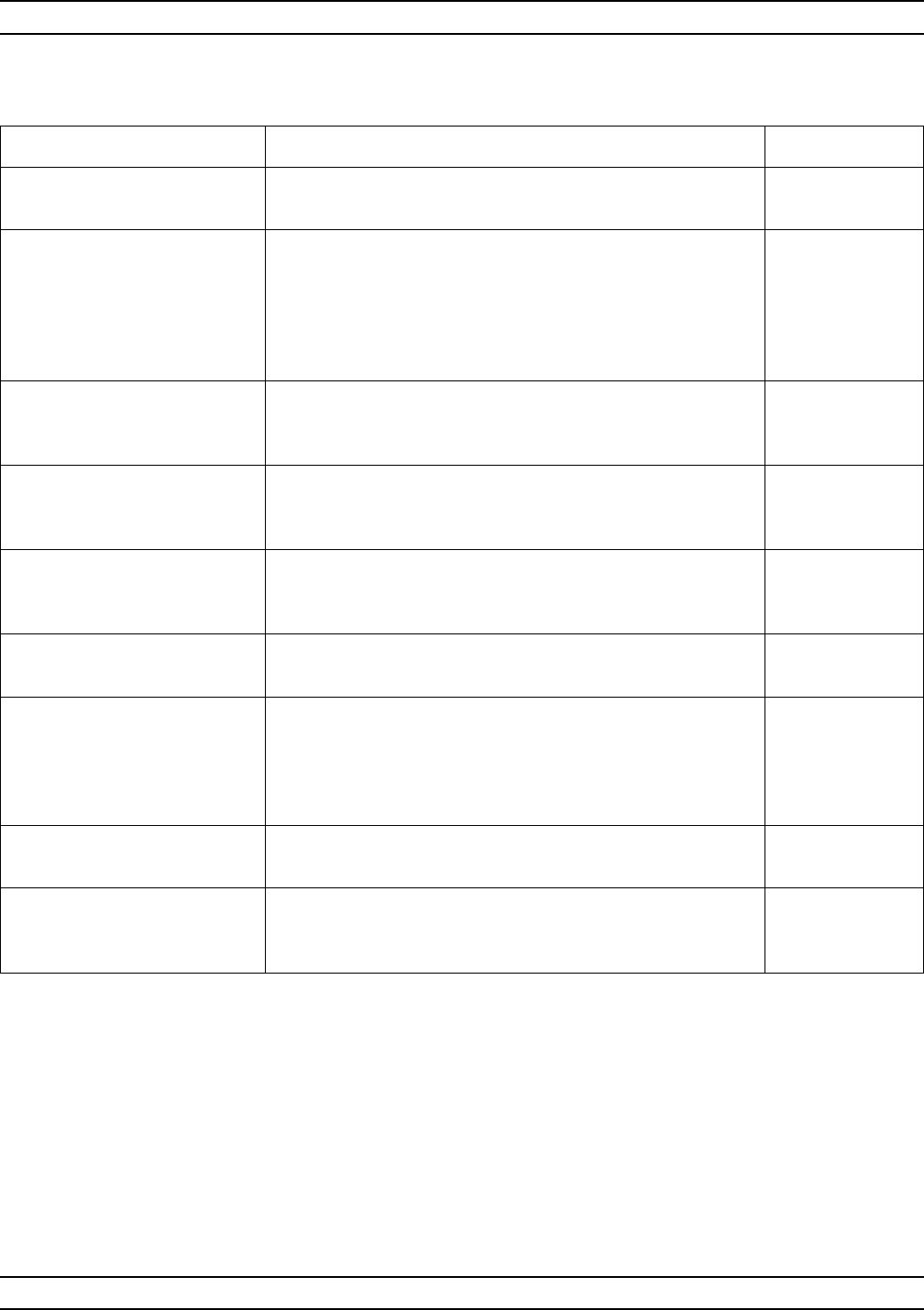
37XXXC OM A-101
ALPHABETICAL LISTING G
MENU DESCRIPTION GPIB COMMAND
SWEPT FREQUENCY
GAIN COMPRESSION None
NOMINAL OFFSET
-XX.XX dB Shows gain of nominal offset. This value is the approximate
gain (or loss) of the external devices preceding the AUT
(amplifier under test). Specifically, the gain of the amplifier
and attenuator combination. This value is used whenever
flat test port power is turned OFF (while still existing) to
prevent an unexpected jump in the power to the AUT.
NOFST?
CALIBRATE
FOR FLATNESS
(NO CAL EXISTS)
Calls menu GC_SU8, which provides calibration options. None
FLATNESS
CORRECTION
AT -XX.XX dBm
Shows value of the flatness correction. FPX?
CALIBRATE
RECEIVER
(NO CAL EXISTS)
Calls menu GC_RCVR, which provides calibration options. None
NORMALIZE S21
(NOT STORED) Calls menu GC_NORM. None
GAIN COMPRESSION
POINT (0 dB REF)
XX.XX dB
This option is used with marker search functions. Value
has a range from 0.05 to 9.99 dB and a default value of
1.00 dB. The search value is [negative] the gain
compression point value. The reference is based on
(maximum) with tracking ON.
GCMP; GCMP?
TEST AUT Closes the extended menu and displays the dual channels
1 & 3, with channel 3 active. None
EXIT APPLICATION Exits the gain compression application and returns to
S-parameter measurements. It restores the measurement
setup.
None
Menu GC1, Swept Frequency Gain Compression
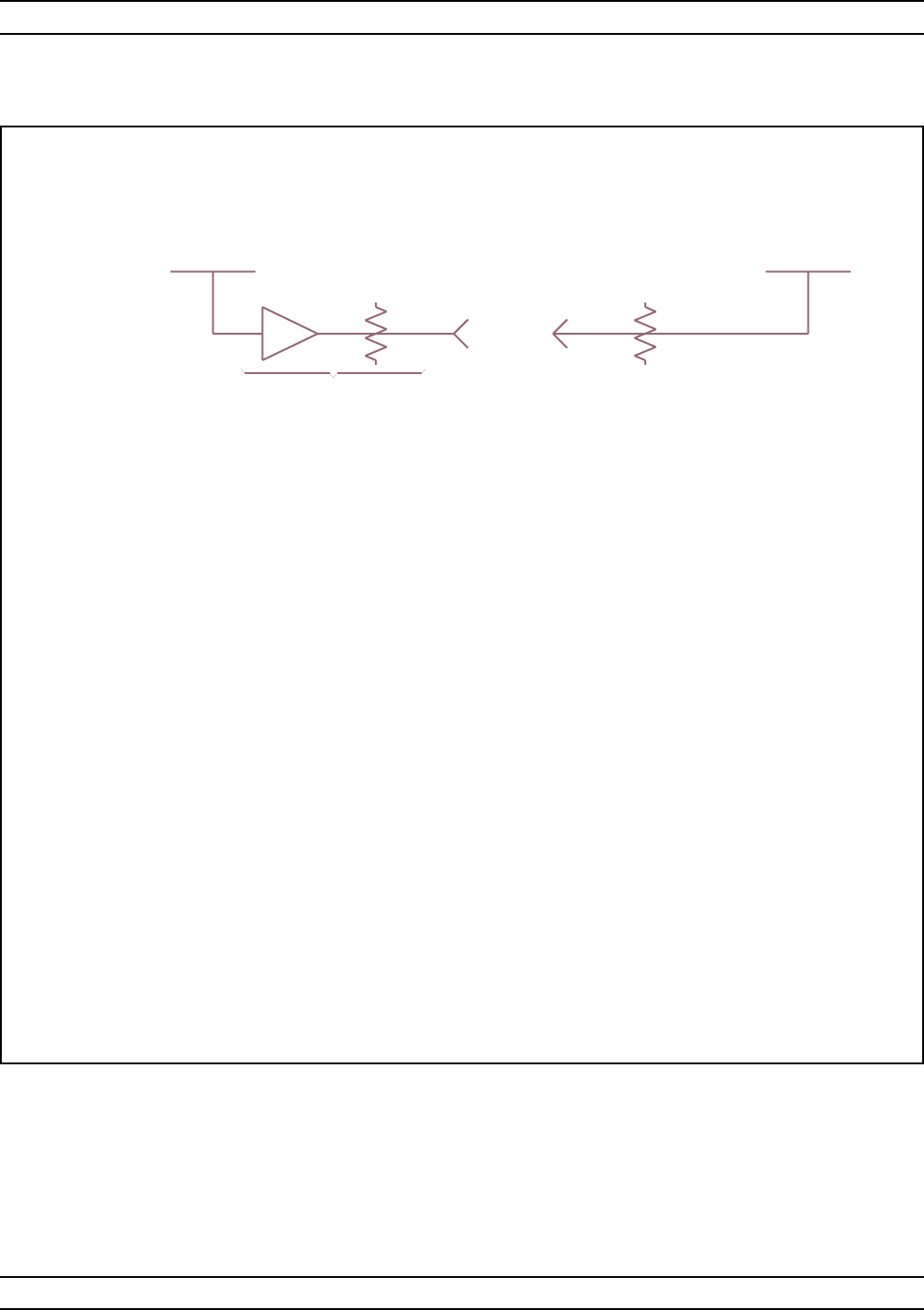
A-102 37XXXC OM
G ALPHABETICAL LISTING
1. TEST PORT 1 POWER SHOULD BE APPROXIMATELY=
AUT(x dB compression spec) - AUT(gain) - 15 dB
2. PORT 2 INPUT POWER SHOULD BE LESS THAN 0dBm
(UNLESS OPTION 6 IS INSTALLED).
3.NOMINAL OFFSET =APPROXIMATE GAIN (ORL
OSS)
OF EXTERNALDEVICES PRECEDINGTHE AUT.
4. DEFAULT DISPLAY IS DUAL CHANNEL1-3 IN WHICH
CHANNEL1 = b2/1 [dBm] AND CHANNEL3 = S21.
1. AFTER THE AUT IS CONNECTED,NORMALIZES21.
2. INDICATE THE GAIN COMPRESSION POINT VALUE
(
xdB
)
AND SELECT <TEST AUT>.
3. INCREASE TEST PORT 1 POWER UNTIL A 1 dB (or x dB)
DECREASE INS21 IS OBSERVED.
PORT1 PORT2
AMP ATTN TEST PORTS ATTN
12
NOMINAL OFFSET
- SWEPTFREQUENCY GAIN COMPRESSION-
- CALIBRATION INSTRUCTIONS -
- MEASUREMENTINSTRUCTIONS -
Menu EXT_GC1, Gain Compression Help Menu 1
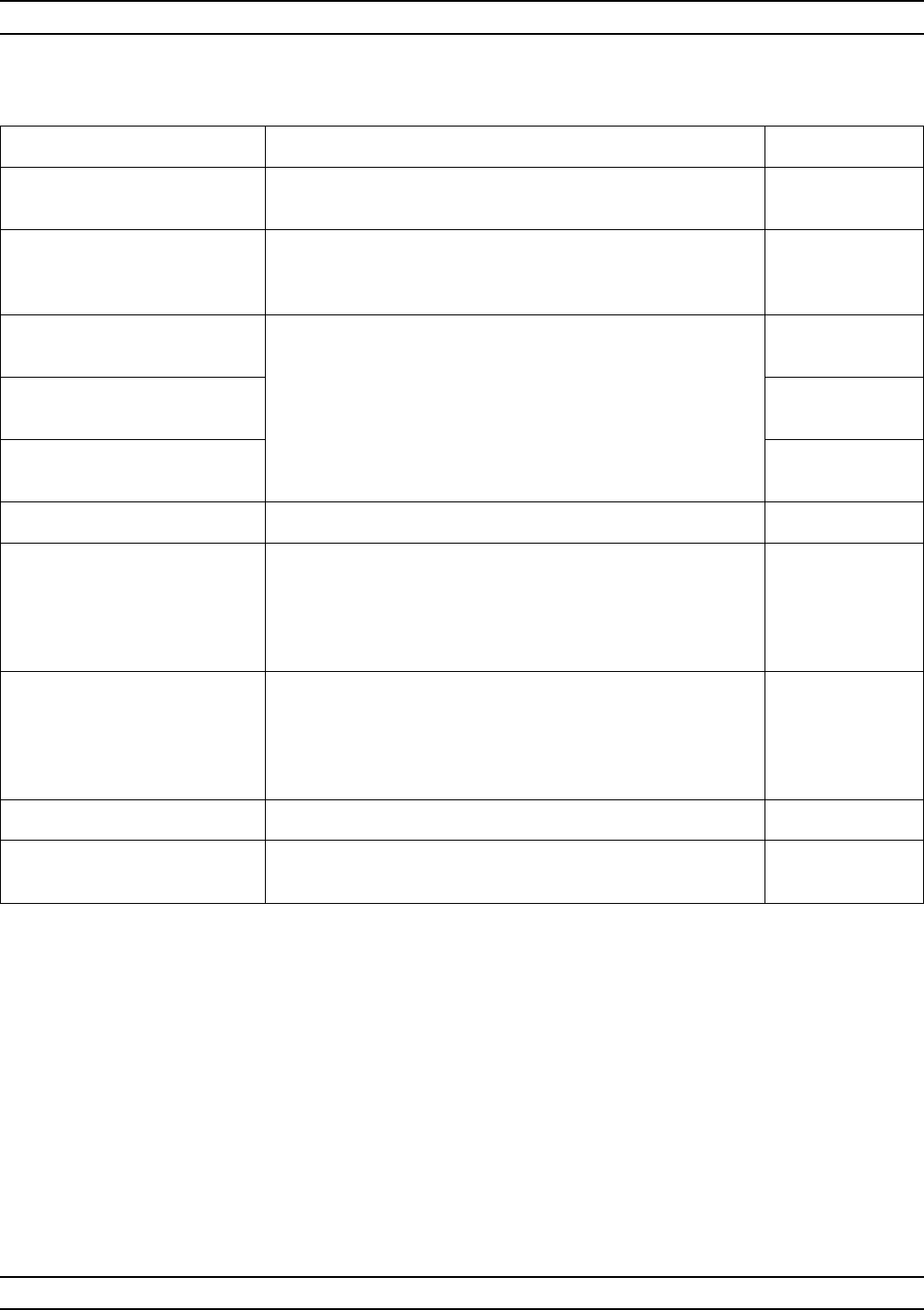
37XXXC OM A-103
ALPHABETICAL LISTING G
MENU DESCRIPTION GPIB COMMAND
SWEPT POWER
GAIN COMPRESSION None
SET FREQUENCIES Calls menu GC_DF2, with it extended menu
EXT_GC_DF2. There the you may enter from 1 to 10
discrete frequencies to be used by the application.
None
PSTART
-XX.XX dBm Defines the power sweep. The start and stop are limited
by the actual power control range of the internal source.
The stepsize resolution is limited to 0.05 dB.
PSTRT; PSTRT?
PSTOP
-XX.XX dBm PSTOP; PSTOP?
STEPSIZE
X.XX dB PSTEP; PSTEP?
ATTENUATION Calls menu GC_SU2, which lets you set attenuation values. None
GAIN COMPRESSION
POINT (MAX REF)
XX.XX dB
This option is used with marker search functions. Value
has a range from 0.05 to 9.99 dB and a default value of
1.00 dB. The search value is [negative] the gain
compression point value. The reference is based on
(maximum) with tracking ON.
GCMP
NOMINAL OFFSET
-XX.XX dB This value is the approximate gain (or loss) of the external
devices preceding the AUT. Specifically, the gain of the
amplifier and attenuator combination. This value is used
whenever power linearity is turned OFF (while still existing)
to prevent an unexpected jump in the power to the AUT.
NOFST; NOFST?
MORE Calls menu GC3, with is companion menu EXT_CG3. None
PRESS <ENTER>
TO SELECT Pressing the Enter key implements your menu selection. None
Menu GC2, Swept Power Gain Compression 1
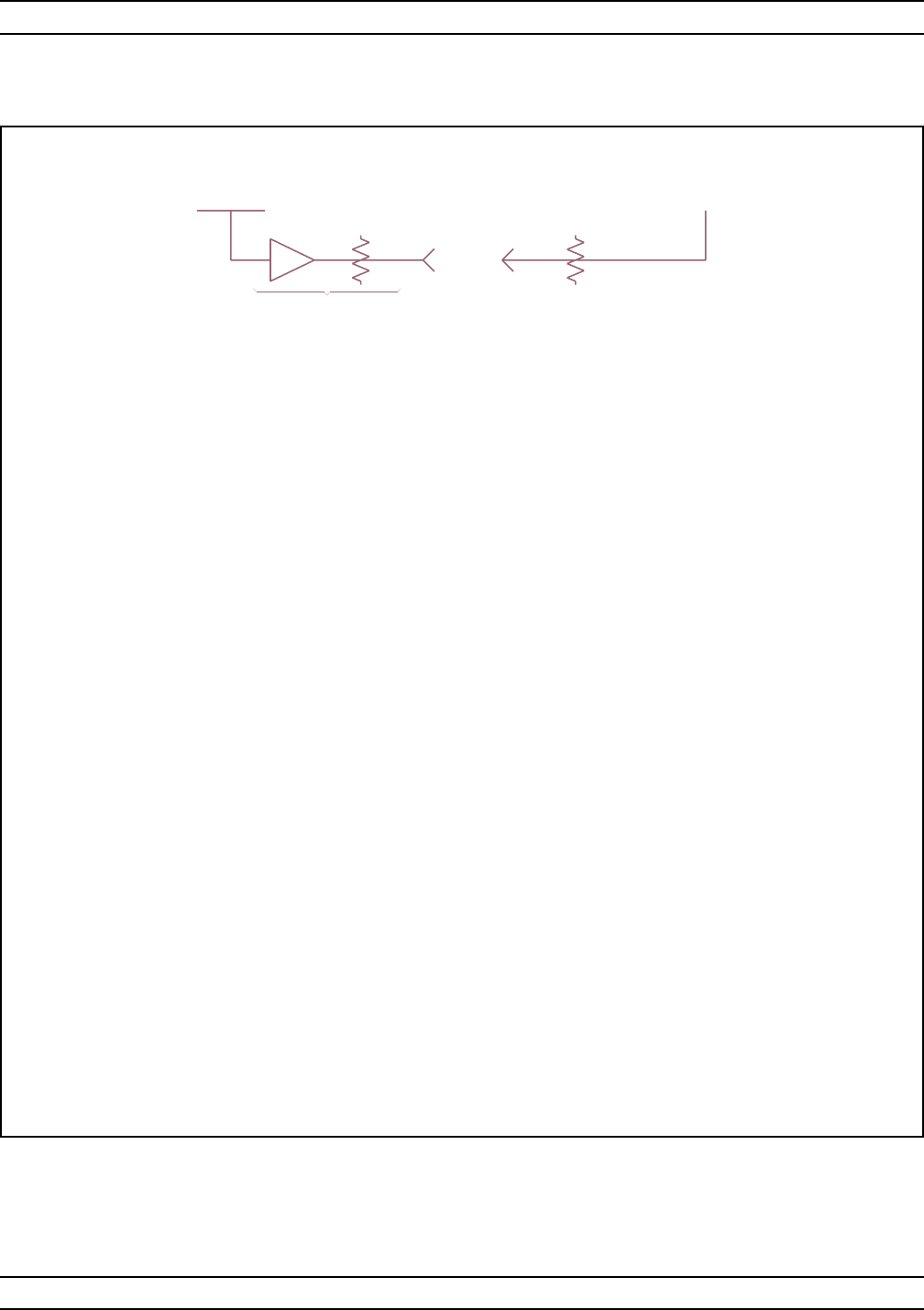
A-104 37XXXC OM
G ALPHABETICAL LISTING
- SWEPT POWER GAIN COMPRESSION -
- CALIBRATION INSTRUCTIONS -
1. SET FREQUENCIES (FROM 1 TO 10 FREQS ALLOWED).
2. P START POWER SHOULD BE APPROXIMATELY =
AUT (x dB compression spec) -AUT (gain) -15 dB.
3. P STOP SHOULD BE 20 dB HIGHER THAN P START.
4. PORT 2 INPUT POWER SHOULD BE LESS THAN 0 dB
(UNLESS OPTION 6 IS INSTALLED).
5. INDICATE THE GAIN COMPRESSION POINT VALUE (x dB).
6. NOMINAL OFFSET = APPROXIMATE GAIN (OR LOSS)
OF EXTERNAL DEVICES PRECEDING THE AUT.
Menu EXT_GC2, Gain Compression Help Menu 2
P
O
RT1 P
O
RT2
AMP ATTN TEST PORTS ATTN
12
NOMINAL OFFSET
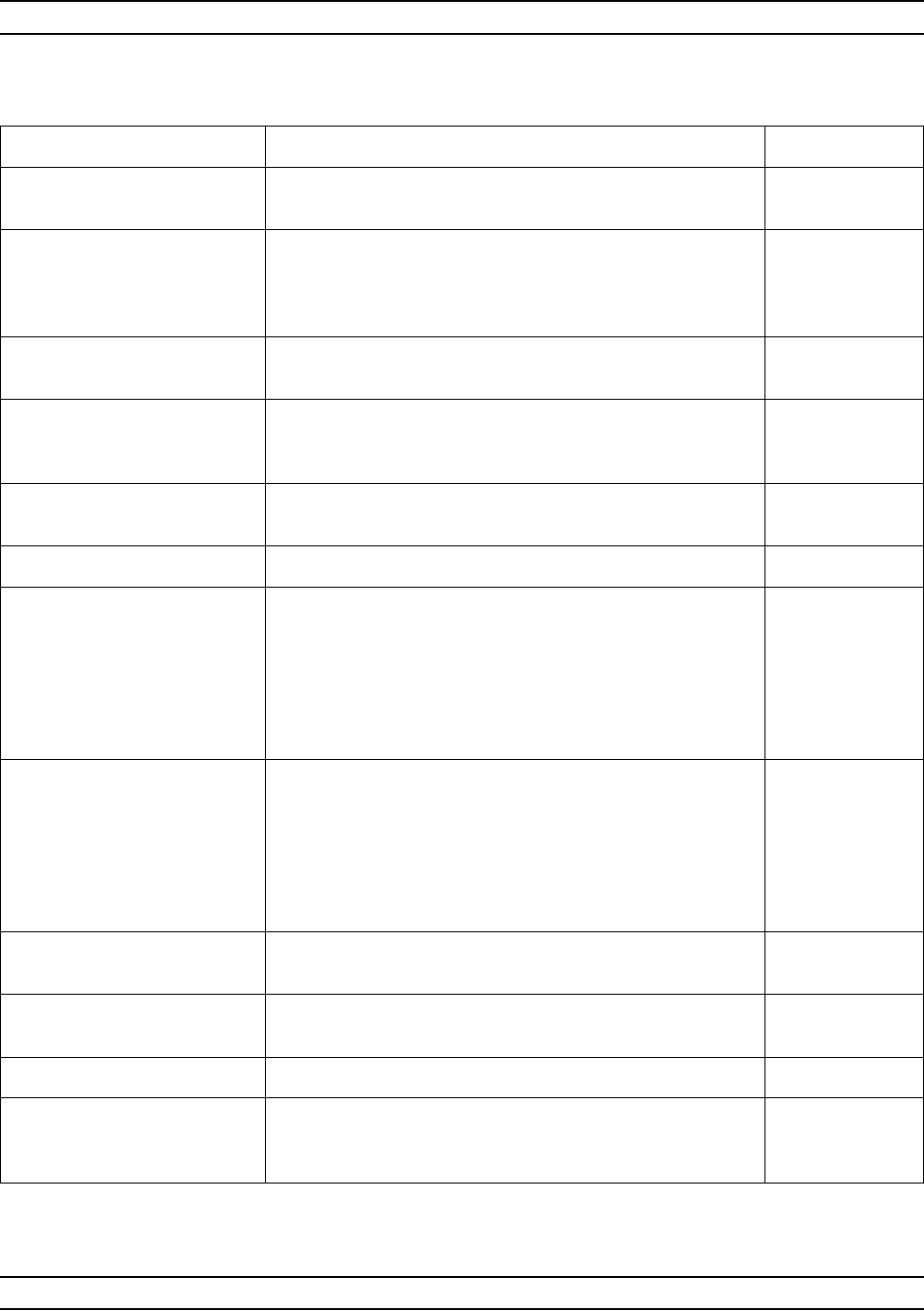
37XXXC OM A-105
ALPHABETICAL LISTING G
MENU DESCRIPTION GPIB COMMAND
SWEPT POWER
GAIN COMPRESSION None
CALIBRATE
FOR LINEARITY
(NO CAL EXISTS)
Calls menu GC_SU8A with extended menu EXT_GC_SU8A
and menu GC_SU8A_ABORT. Upon a successful power
linearity calibration, menu GC2 reappears with (CAL
EXISTS) and linearity correction ON.
None
LINEARITY ON (OFF)
CORRECTION Toggles the linearity correction on and off. PSWC0;
PSWC1;PSWCX?
CALIBRATE
RECEIVER
(NO CAL EXISTS)
Calls menu GC_RCVR. None
S21 OPTIONS
(NOT STORED) Calls menu GC_S21OPT. None
AUT TEST TYPES None
GAIN COMPRESSION Closes the extended menu and displays the dual channels
1 & 3, with channel 3 active. Up to this point, the system is
sweeping frequencies. Once <Test AUT> is pressed, the
power sweep mode is turned ON and the system goes into
single sweep and hold. One power sweep at the current
power freq is done and the system goes into hold with Bias
and RF ON. Pressing the Hold key will restart the sweep.
CALR
AM/PM Closes the extended menuand displays dual channel2&4,
with Channel 4 becoming active.The power sweep mode is
activated and the VNA goes into continuous sweep. The
power sweeps at the current power frequency; the marker
function is turned off, but markers remain. Channel 2
displays S21 on a Phase graph and Channel 4 displays
S21 on a Log Magnitude graph.
SPAMPMT
MULTIPLE FREQ
GAIN COMPRESSION Calls menu GC4. None
RETURN TO SWEPT
FREQUENCY MODE Returns program to the swept frequency operational mode. None
PREVIOUS MENU Returns to previous menu. None
PRESS <ENTER>
TO SELECT
OR TURN ON/OFF
Pressing the Enter key implements your menu selection. None
Menu GC3, Swept Power Gain Compression 2
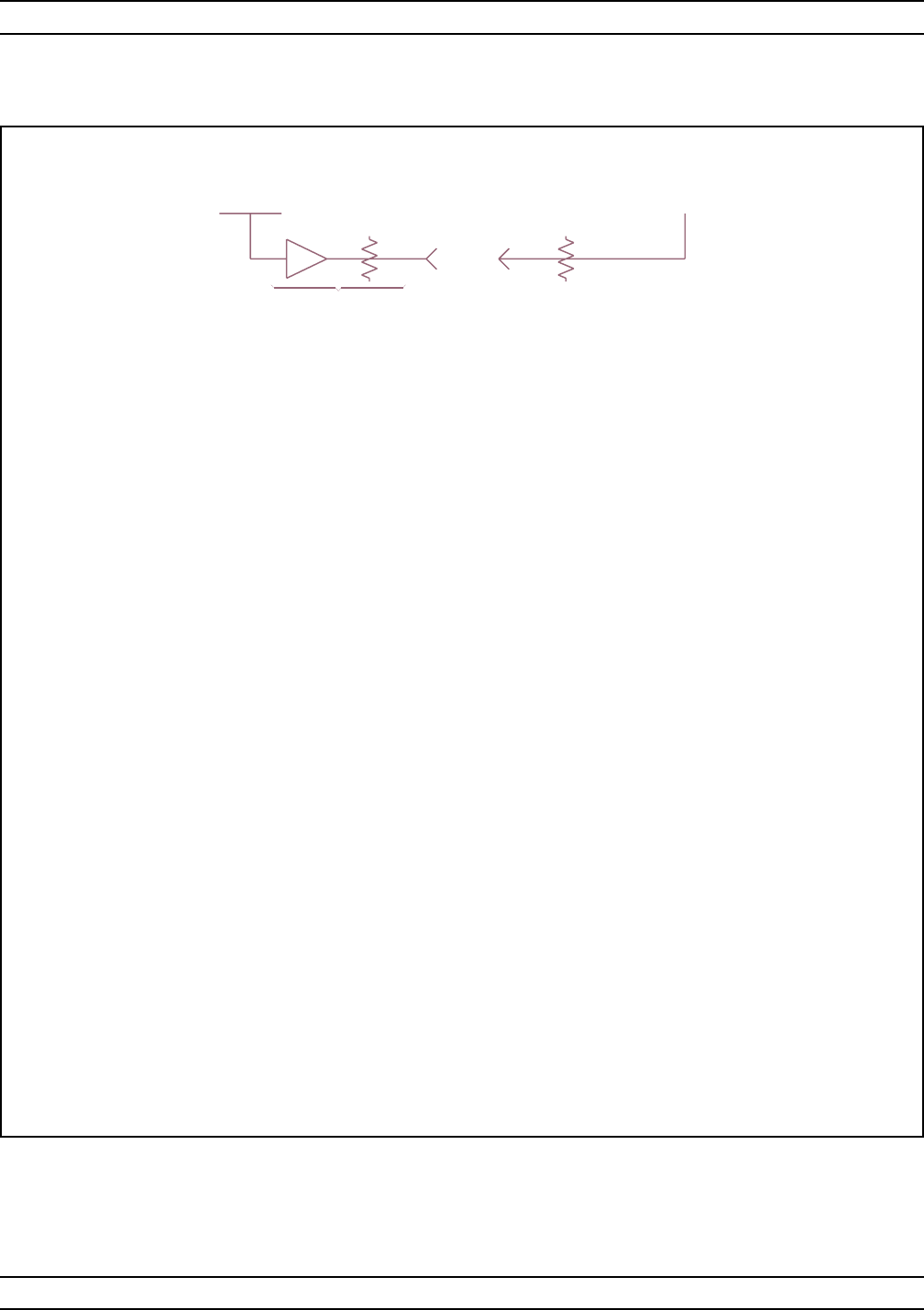
A-106 37XXXC OM
G ALPHABETICAL LISTING
- SWEPT POWER GAIN COMPRESSION -
- CALIBRATION INSTRUCTIONS -
7. LINEARITY CALIBRATION IMPROVES ACCURACY.
8. RECEIVER CALIBRATION IS DONE AT P STOP.
NORMALIZE S21 AND DISPLAY S21 ARE IS DONE AT P START.
9. DEFAULT DISPLAY IS DUAL CHANNEL 1-3 IN WHICH
CHANNEL 1 = b2/1 [dBm] AND CHANNEL 3 = S21
-MEASUREMENT INSTRUCTIONS-
1. SELECT THE DESIRED S21 OPTION.
2. SELECT <GAIN COMPRESSION> OR <AM/PM> AUT TEST.
3. MARKERS CAN BE USED TO LOCATE THE 1 dB (or x dB)
COMPRESSION POINT. CHANGE THE POWER FREQUENCY TO
MEASURE EACH OF THE OTHER POWER SWEEPS.
4. SELECT <MULTIPLE FREQ GAIN COMPRESSION> TO TEST
THE AUT AT ALL THE SWEPT POWER FREQUENCIES. THE
RESULTS ARE COMPUTED UNDER THE ASSUMPTION THAT
P OUTPUT AT P START IS IN THE AUT’S LINEAR REGION.
Menu EXT_GC3, Gain Compression Help Menu 3
P
O
RT1 P
O
RT2
AMP ATTN TEST PORTS ATTN
12
NOMINAL OFFSET
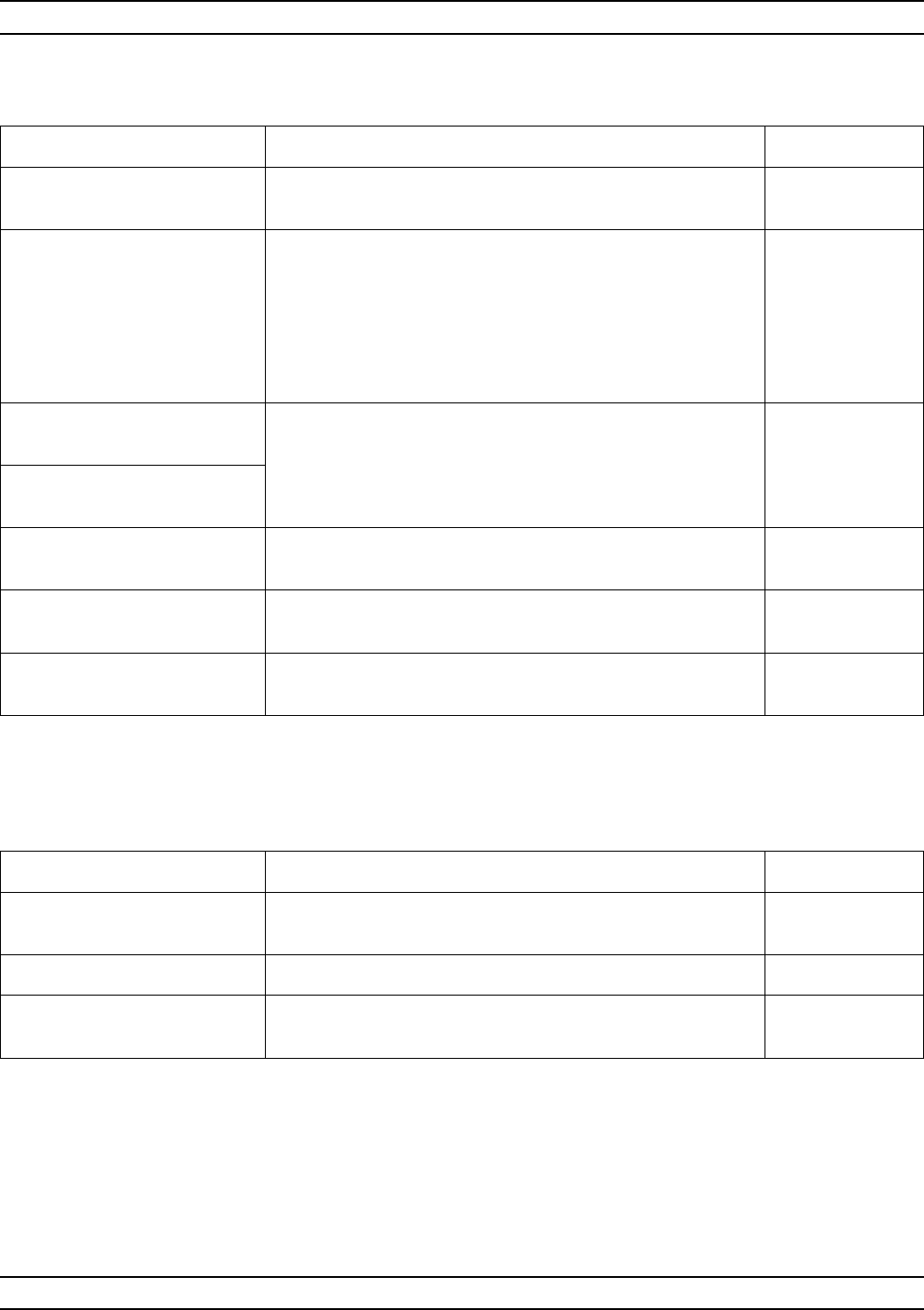
37XXXC OM A-107
ALPHABETICAL LISTING G
MENU DESCRIPTION GPIB COMMAND
MULTIPLE FREQUENCY
GAIN COMPRESSION None
TEST AUT Calls menu GC4_ABORT; and it turns on the power sweep
mode and conducts a power sweep at each of the swept
power frequencies. The gain compression points are
computed under the assumption that P Output at P Start is
in the AUT's linear region. The frequency, power in, and
power out values are listed in a table. The power out
versus frequency number is displayed in on a graph..
None
TEXT DATA
TO HARD DISK When either Text Data to Hard Disk or Text Data to Floppy
Disk are selected, the appropriate disk save file menu
DSKx is displayed and the table is captured and recorded
in a text file.
None
TEXT DATA
TO FLOPPY DISK
SWEPT POWER
GAIN COMPRESSION Calls menu CG3, which let you perform a Swept Power
Gain Compression measurement. None
RETURN TO SWEPT
FREQUENCY MODE None
PRESS <ENTER>
TO SELECT Pressing the Enter key implements your menu selection. None
Menu GC4, Multiple Frequency Gain Compression 1
MENU DESCRIPTION GPIB COMMAND
MULTIPLE FREQUENCY
GAIN COMPRESSION None
TESTING AUT None
PRESS <CLEAR>
TO ABORT Pressing the Clear key aborts the Multiple Frequency Gain
Compression. None
Menu GC4_ABORT, Multiple Frequency Gain Compression 2
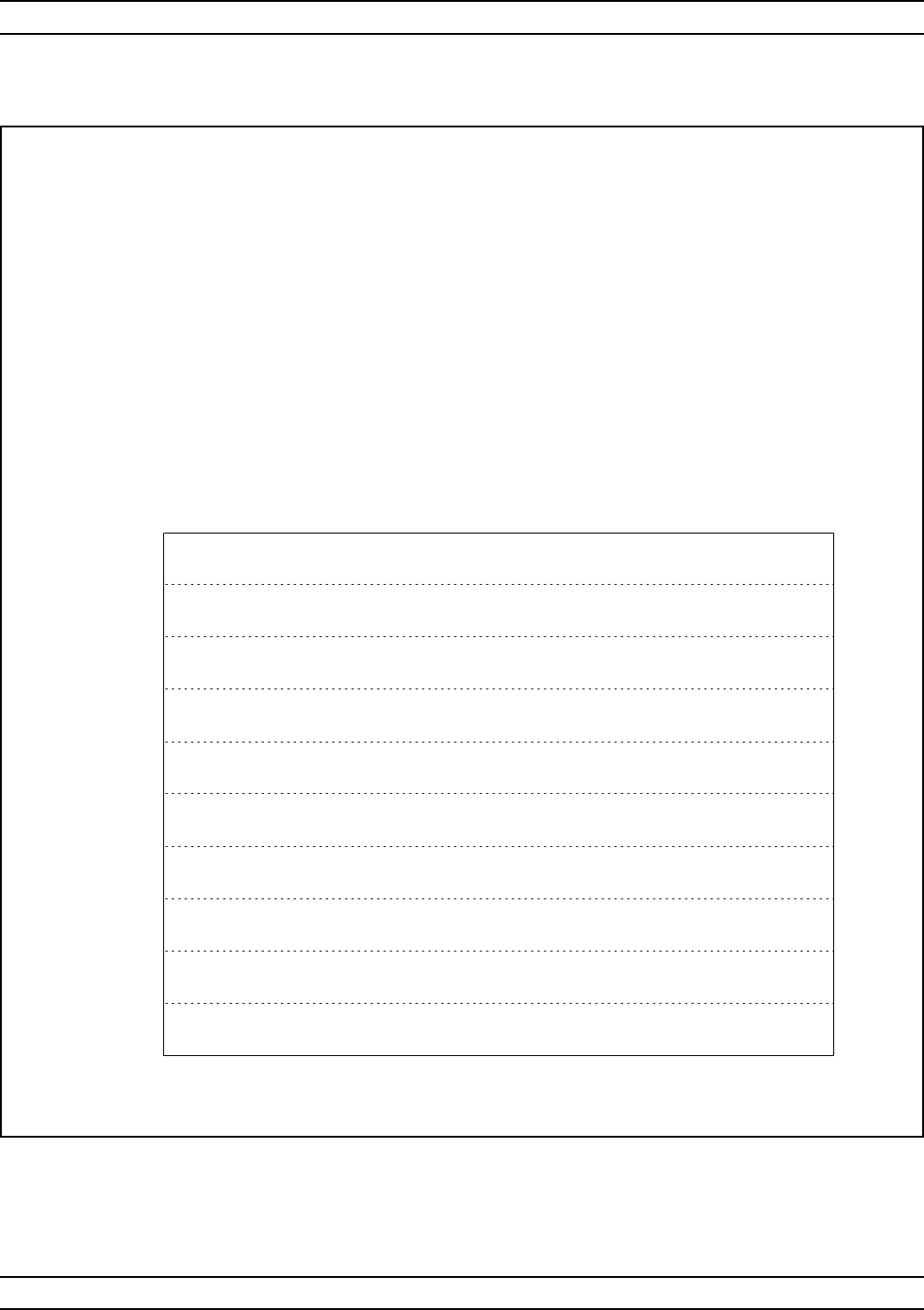
A-108 37XXXC OM
G ALPHABETICAL LISTING
- MULTIPLE FREQUENCY GAIN COMPRESSION POINT -
SWEPT POWER FREQUENCIES POWER IN POWER OUT
1. XXX.XXXXXXXXX GHz -XX.XX dBm -XX.XX dBm
2. XXX.XXXXXXXXX GHz -XX.XX dBm -XX.XX dBm
3. XXX.XXXXXXXXX GHz -XX.XX dBm -XX.XX dBm
4. XXX.XXXXXXXXX GHz -XX.XX dBm -XX.XX dBm
5. XXX.XXXXXXXXX GHz -XX.XX dBm -XX.XX dBm
6. XXX.XXXXXXXXX GHz -XX.XX dBm -XX.XX dBm
7. XXX.XXXXXXXXX GHz -XX.XX dBm -XX.XX dBm
8. XXX.XXXXXXXXX GHz -XX.XX dBm -XX.XX dBm
9. XXX.XXXXXXXXX GHz -XX.XX dBm -XX.XX dBm
Menu EXT_GC4, Gain Compression Help Menu 4
12 345678910
-XX.XX
-XX.XX
POWER OUT [dBm] 1.00 dB GAIN COMPRESSION POINT
FREQUENCY NUMBER
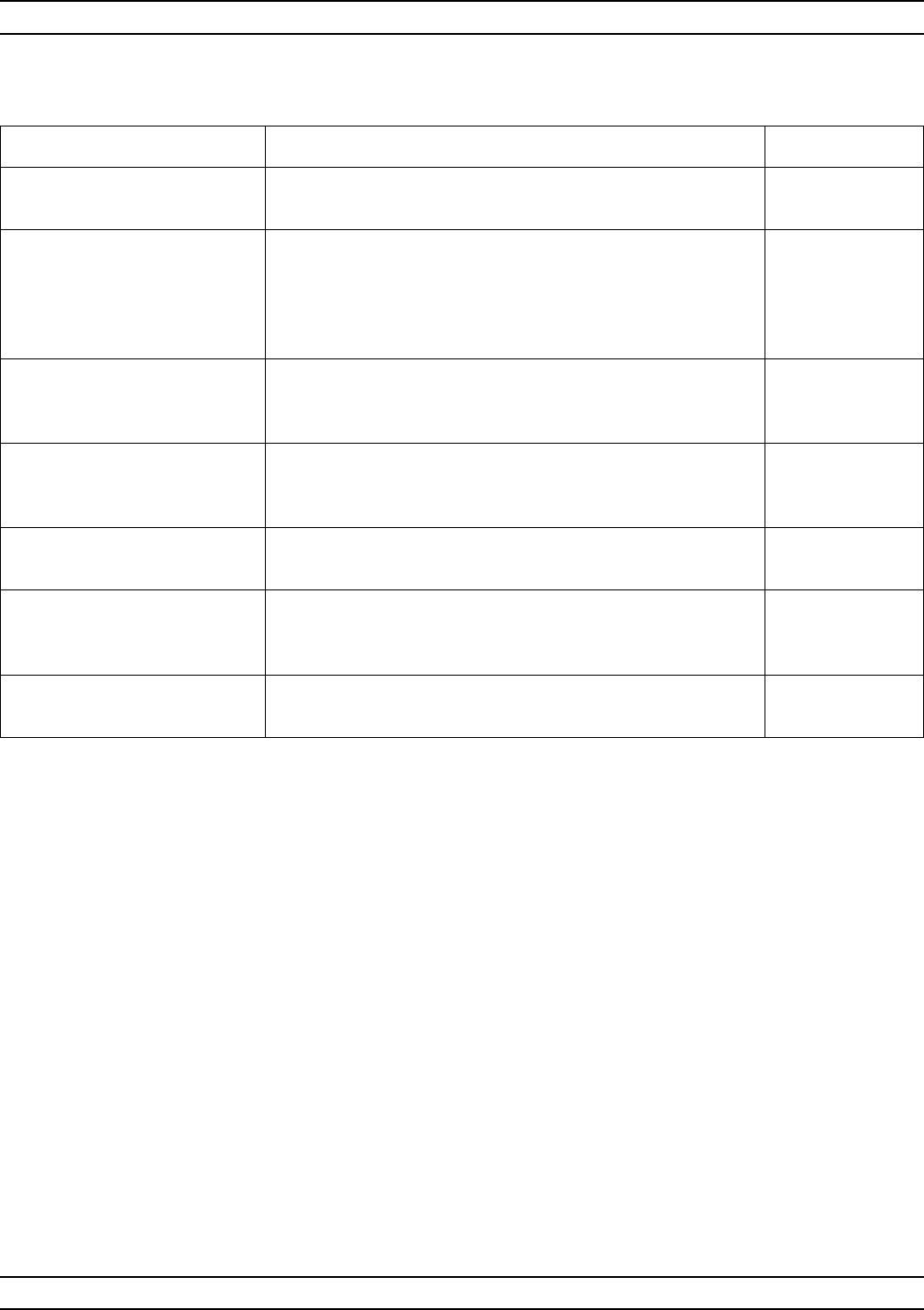
37XXXC OM A-109
ALPHABETICAL LISTING G
MENU DESCRIPTION GPIB COMMAND
SWEPT POWER
FREQUENCIES None
INPUT A FREQ,
PRESS <ENTER>
TO INSERT
This menu performs in a similar manner to the menu DF2,
Insert Individual Frequencies. The list is updated and kept
in ascending order. Any frequencies which are added or
deleted force a resorting of the list. The user can enter
from 1 to 10 swept power frequencies.
None
SWEPT POWER
FREQUENCY
XXX.XXXXXXXXX GHz
Enter the swept power frequencies using the keypad or
knob. Press <ENTER> to insert into the swept power
frequency list
CLEAR FREQ NUMBER
XX Enter the number of the frequency to remove from the list
using the keypad or knob. Press <ENTER> to remove the
selection from the list.
CLEAR ALL Press <ENTER> to remove all the frequencies from the
swept power frequency list.
FINISHED,
RETURN TO POWER
SWEEP SETUP
After the swept power frequency list is entered, this returns
to menu GC2. None
PRESS <ENTER>
TO SELECT Pressing the Enter key implements your menu selection. None
Menu GC_DF2, Swept Power Frequencies
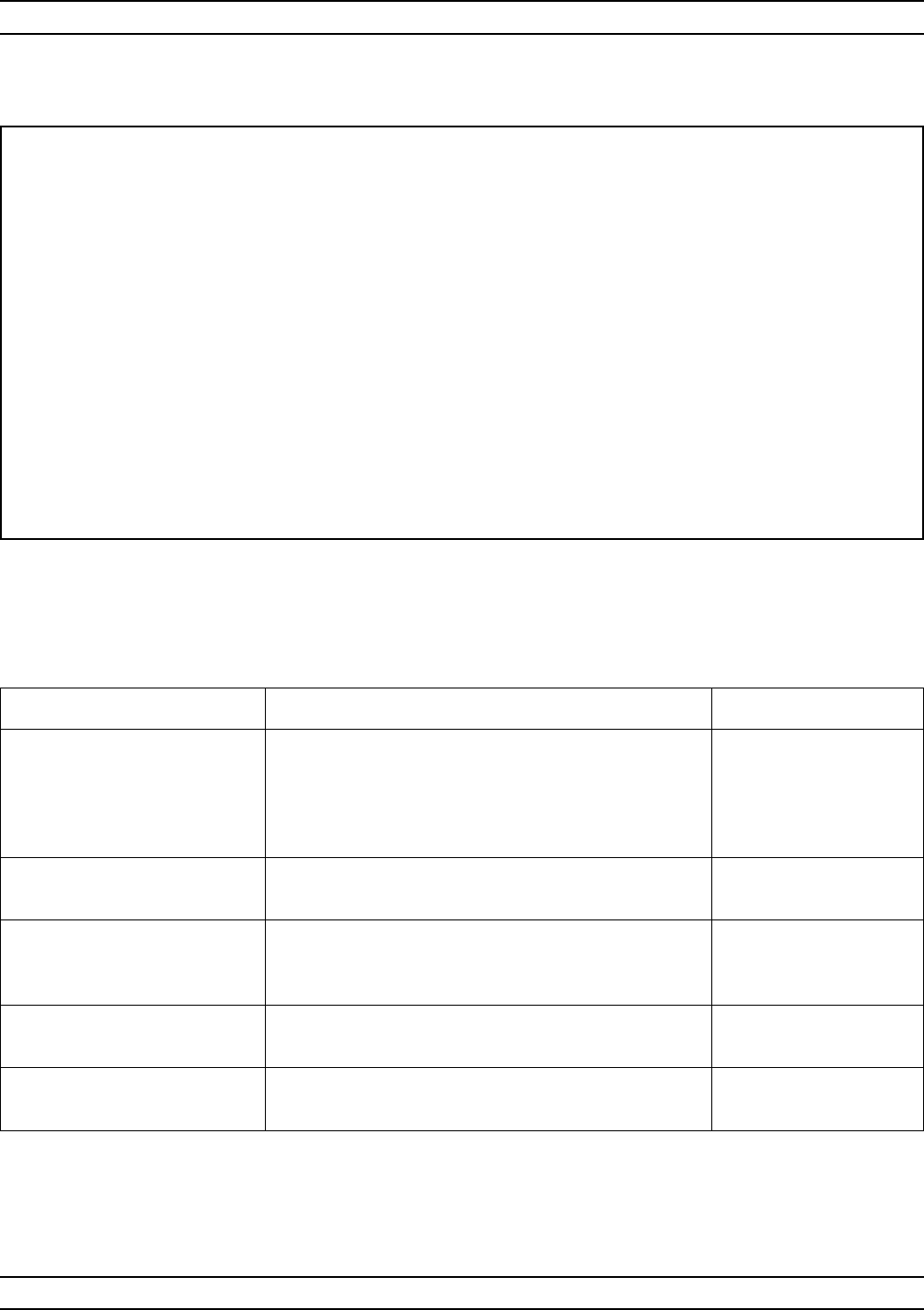
A-110 37XXXC OM
G ALPHABETICAL LISTING
- MULTIPLE FREQUENCY GAIN COMPRESSION -
SWEPT POWER FREQUENCIES
1. XXX.XXXXXXXXX GHz
2. XXX.XXXXXXXXX GHz
3. XXX.XXXXXXXXX GHz
4. XXX.XXXXXXXXX GHz
5. XXX.XXXXXXXXX GHz
6. XXX.XXXXXXXXX GHz
7. XXX.XXXXXXXXX GHz
8. XXX.XXXXXXXXX GHz
9. XXX.XXXXXXXXX GHz
10. XXX.XXXXXXXXX GHz
Menu EXT_GC_DF2, Gain Compression Help Menu
MENU DESCRIPTION GPIB COMMAND
NORMALIZE S21 This menu lets you see if you have a good
connection of the throughline before capturing the
data by pressing <Enter>. The calibration may be
aborted by pressing <Clear>. In both cases, menu
GC1 or GC3 is displayed.
NRMS21
SPS21?
CONNECT AUT
AND APPLY BIAS
WAIT FOR ONE
COMPLETE SWEEP
BEFORE STORING
PRESS <ENTER>
TO STORE Pressing the Enter key stores the Normalized S21
calibration.
PRESS <CLEAR>
TO ABORT Pressing the Clear key aborts the Normalized S21
calibation.
Menu GC_NORM, Normalize S21
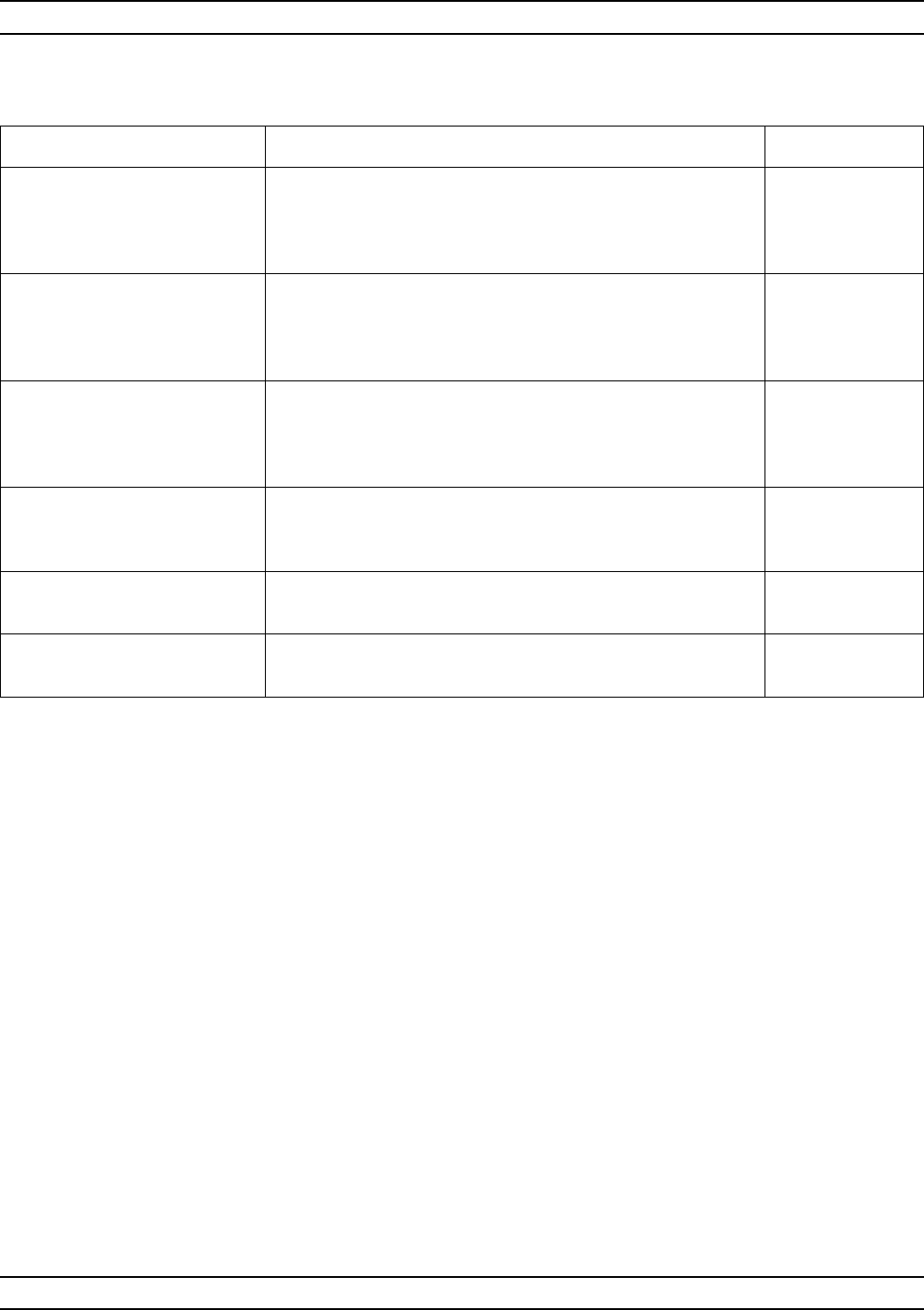
37XXXC OM A-111
ALPHABETICAL LISTING G
MENU DESCRIPTION GPIB COMMAND
RECEIVER
CALIBRATION This menu lets you see if you have a good connection of
the throughline before capturing the data by pressing
<Enter>. The calibration may be aborted by pressing
<Clear>. In both cases, menu GC1 or GC2 is displayed.
None
CONNECT
THROUGHLINE
BETWEEN
TEST PORTS
None
INCLUDE ANY
COMPONENTS WHICH
ARE PART OF THE
MEASUREMENT PATH
None
WAIT FOR ONE
COMPLETE SWEEP
BEFORE STORING
CALR
PRESS <ENTER>
TO STORE Pressing the Enter key stores the receiver calibration. None
PRESS <CLEAR>
TO ABORT Pressing the Clear key aborts the Receiver calibation. None
Menu GC_RCVR, Receiver Calibration
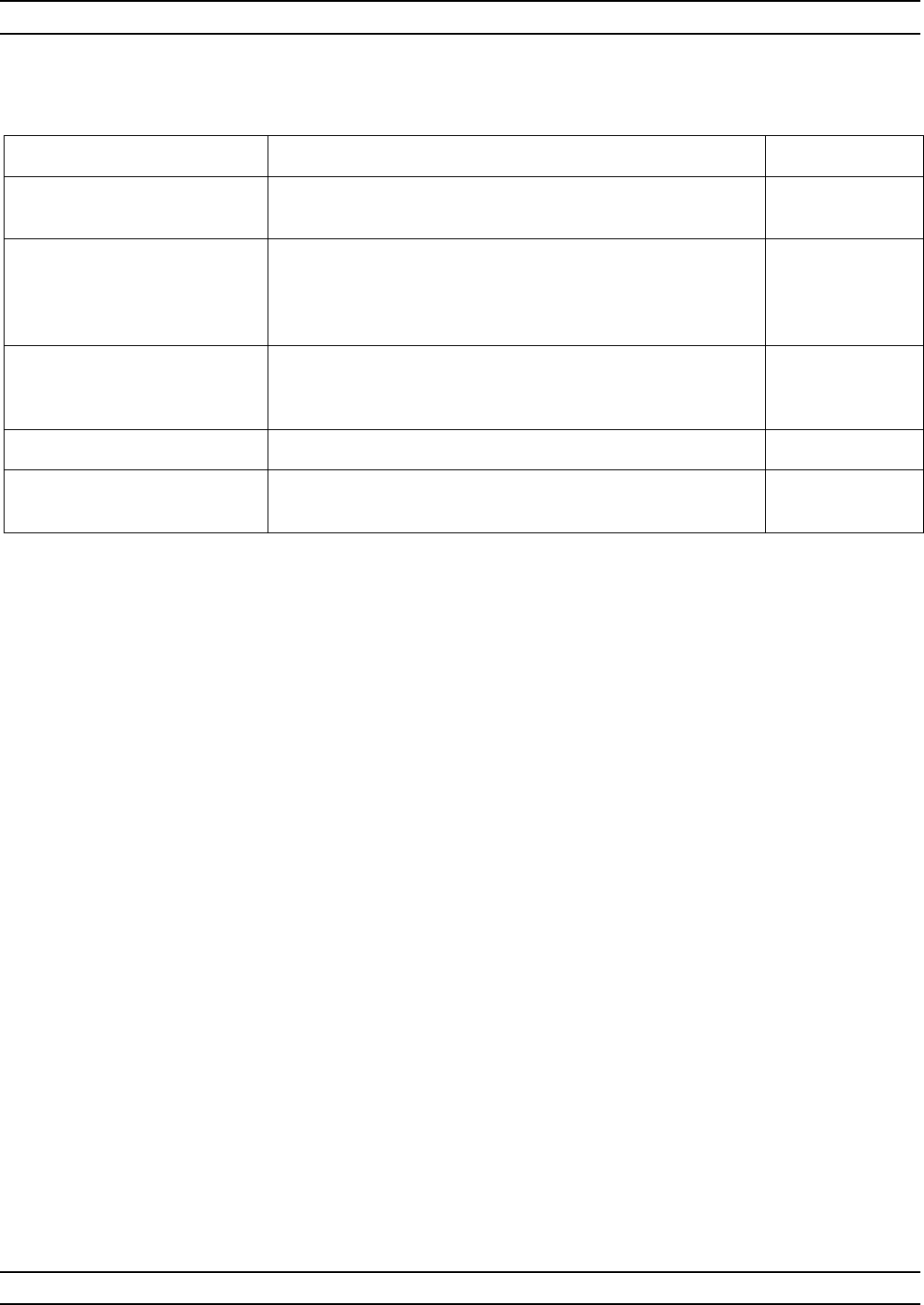
A-112 37XXXC OM
G ALPHABETICAL LISTING
MENU DESCRIPTION GPIB COMMAND
SWEPT POWER
GAIN COMPRESSION None
PORT 1 ATTN
0*10 dB (0 - 70) Attenuates the microwave source power at port 1 from 0 to
70 dB, in 10 dB steps. The power is attenuated before
being applied to Port 1 for a forward transmission or
reflection test (S21 or S11, respectively).
SA1; SA1?
PORT 2 ATTN
0*10 dB (0 - 40) Attenuates from 0 to 40 dB (10 dB steps) the microwave
power being input to Port 2 from the device-under-test
(DUT).
TA; TA2?
PREVIOUS MENU Returns to the previous menu. None
PRESS <ENTER>
TO SELECT Pressing the Enter key implements your menu selection. None
Menu GC_SU2, Swept Power Gain Compression 2
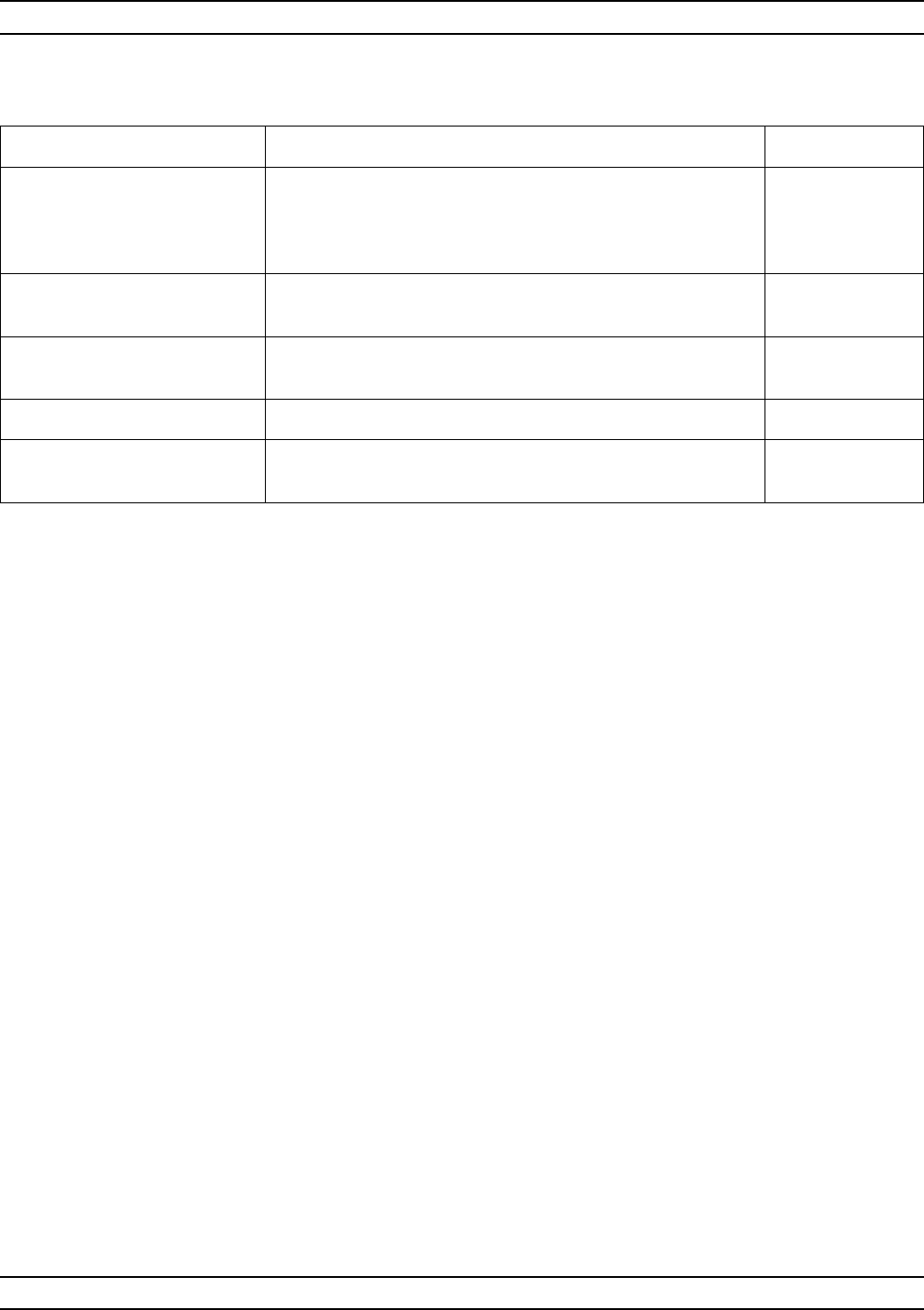
37XXXC OM A-113
ALPHABETICAL LISTING G
MENU DESCRIPTION GPIB COMMAND
CALIBRATE FOR
LINEAR POWER The power linearity calibration is done for each of the
swept power frequencies across the power sweep range.
The resolution of the calibration points is 0.25 dB. The
maximum will be equal to the power sweep step size.
None
FORWARD
DIRECTION ONLY The Linear Power Calibration is only done in the forward
direction. None
START LINEAR
POWER CALIBRATION Starts the linear power calibration. PSWC
PREVIOUS MENU Returns to previous menu. None
PRESS <ENTER>
TO SELECT Pressing the Enter key implements your menu selection. None
Menu GC_SU8A, Calibrate for Linear Power
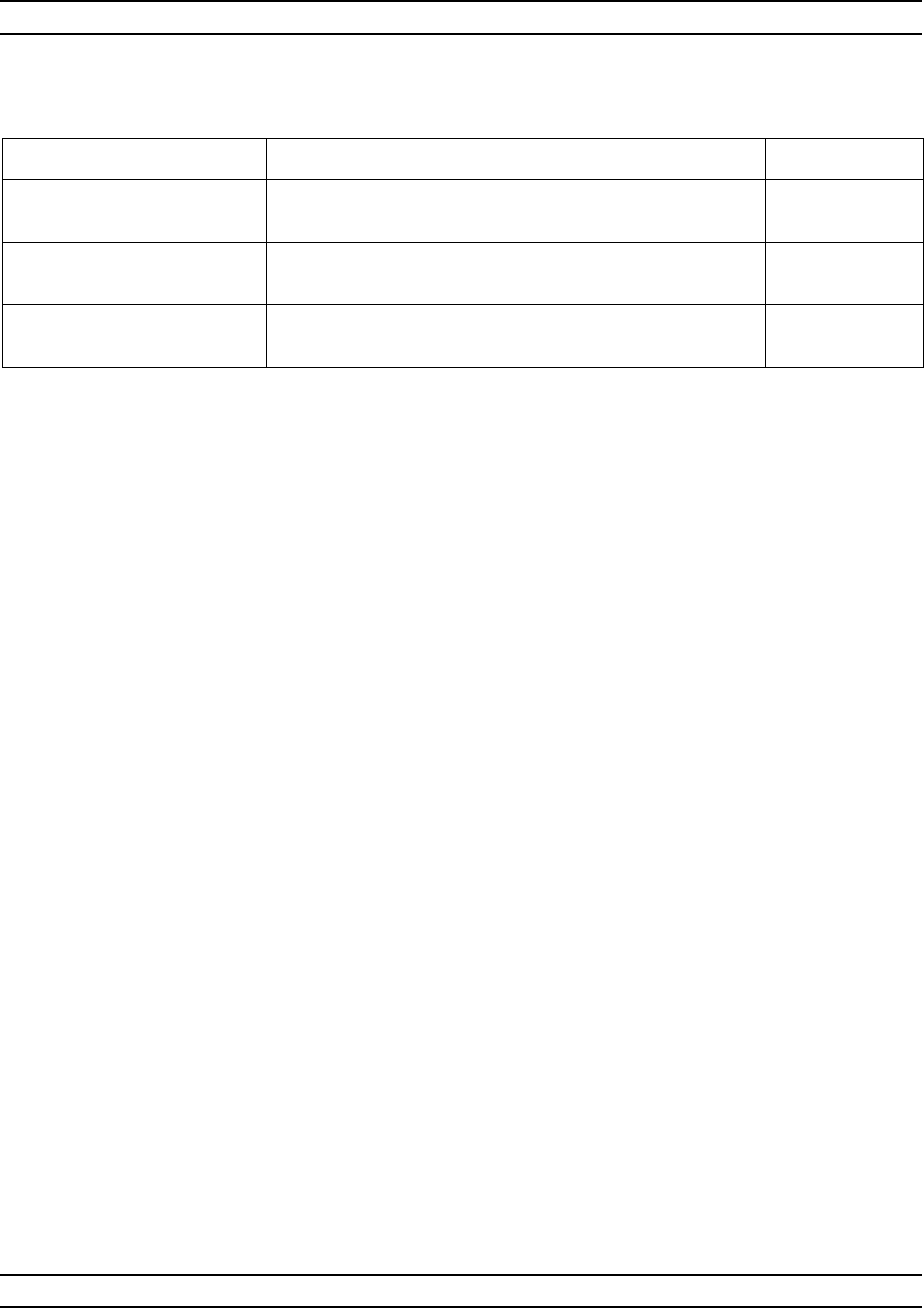
A-114 37XXXC OM
G ALPHABETICAL LISTING
MENU DESCRIPTION GPIB COMMAND
LINEAR POWER
CALIBRATION None
CALIBRATING FOR
LINEAR POWER... None
PRESS <CLEAR>
TO ABORT Pressing the Clear key aborts the Linear Power Calibration. None
Menu GC_SU8A-ABORT, Abort Calibrate for Linear Power
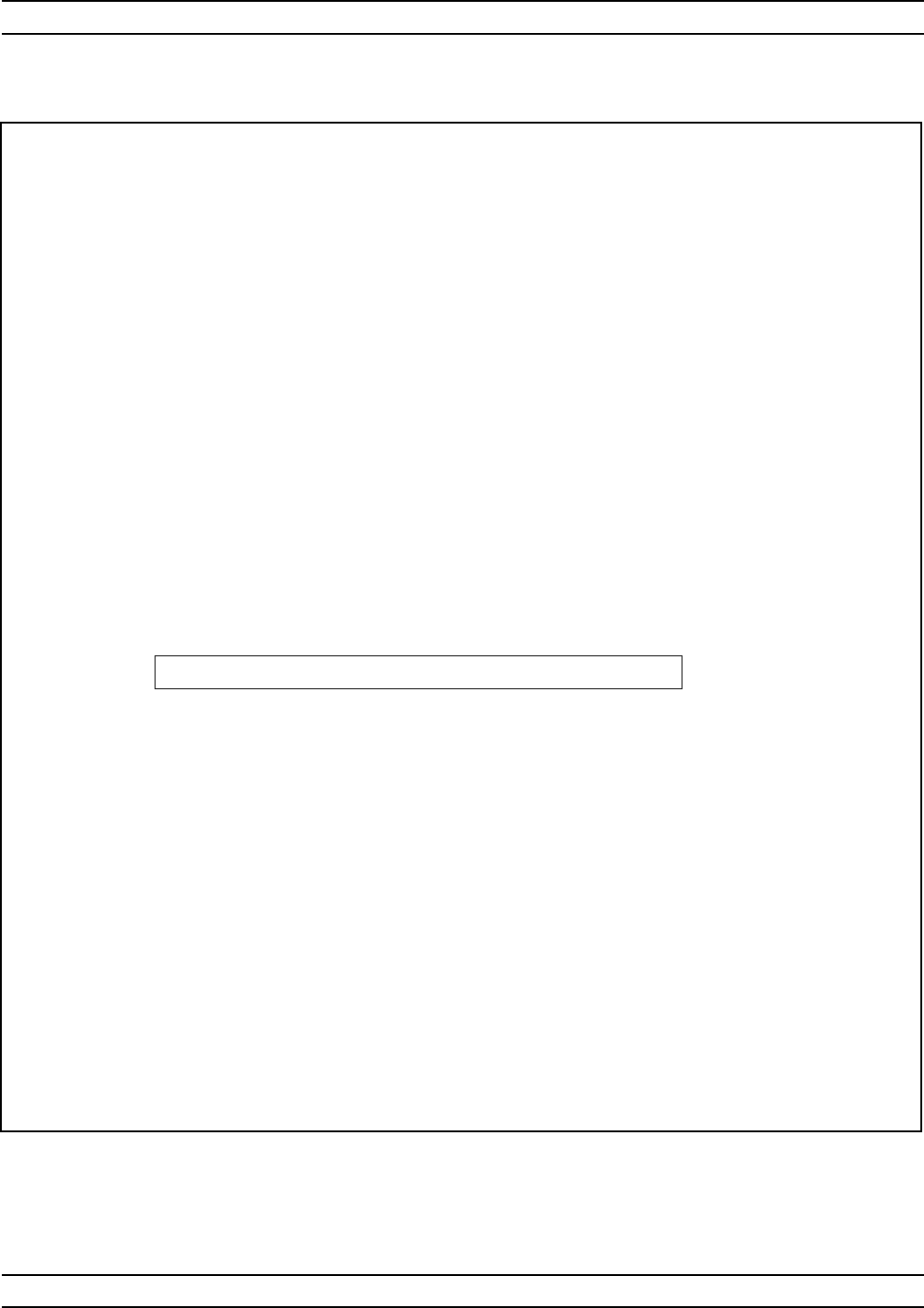
37XXXC OM A-115
ALPHABETICAL LISTING G
- LINEAR POWER CALIBRATION -
- CALIBRATION INSTRUCTIONS -
LINEAR POWER CALIBRATION ADJUSTS THE SOURCE OUTPUT
POWER FOR EACH POWER FREQUENCY POINT ACROSS THE POWER
SWEEP RANGE TO PROVIDE A LINEAR POWER LEVEL AT THE
TEST PORT (FORWARD DIRECTION ONLY).
- INSTRUCTIONS -
1. PRESET, ZERO, AND CALIBRATE THE POWER METER.
2. CREATE AND ACTIVATE THE POWER METER'S CAL
FACTOR LIST FOR THE POWER SENSOR BEING USED.
3. CONNECT THE POWER METER TO THE DEDICATED GPIB
INTERFACE AND THE POWER SENSOR TO THE TEST PORT.
4. SELECT <START LINEAR POWER CALIBRATION>.
Menu EXT_GC_SU8A, Gain Compression Help Menu
XXX.X
%
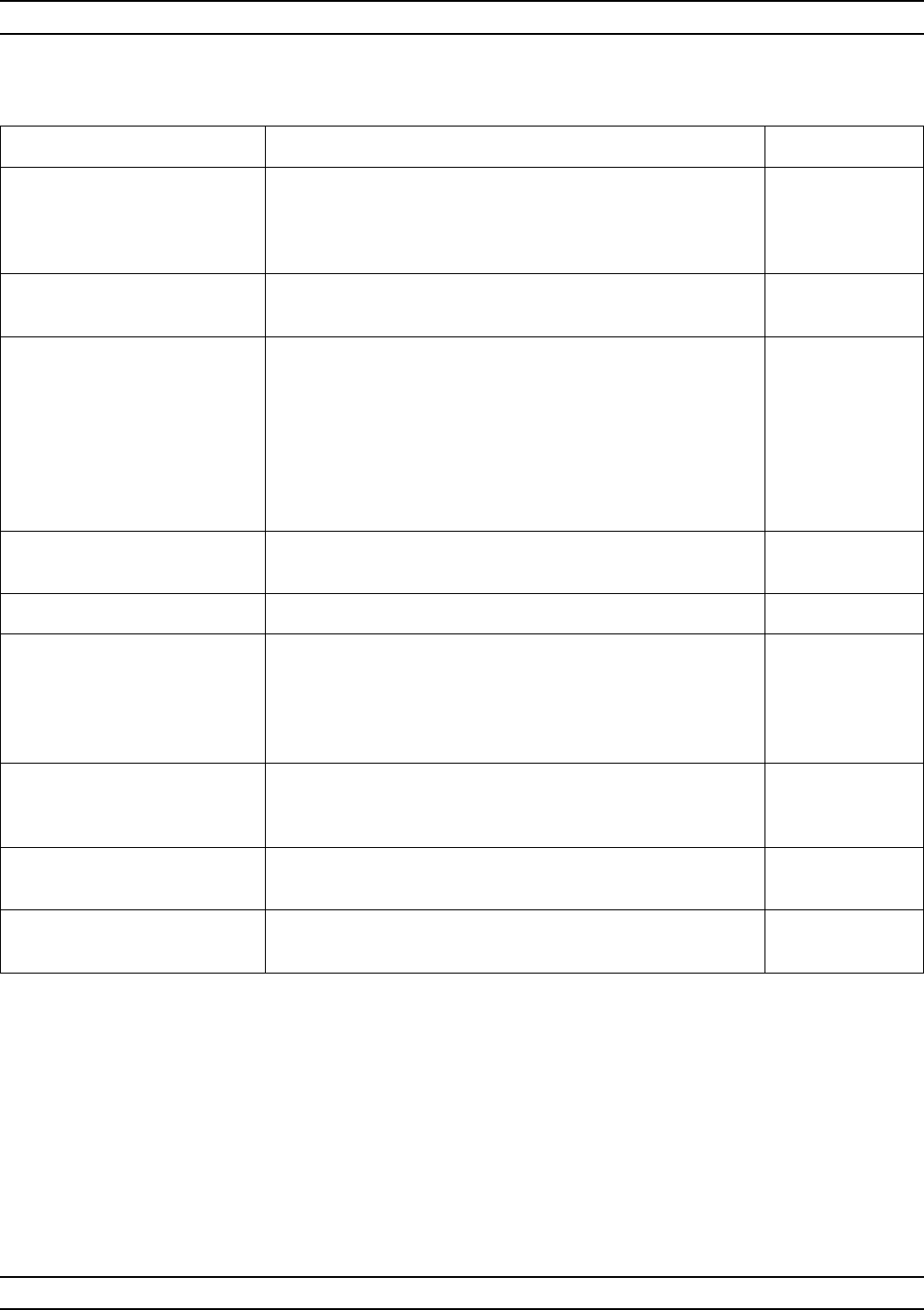
A-116 37XXXC OM
G ALPHABETICAL LISTING
MENU DESCRIPTION GPIB COMMAND
NORMALIZE S21 This menu lets you see if you have a good connection of
the throughline before capturing the data by pressing
<Enter>. The calibration may be aborted by pressing
<Clear>. In both cases, menu GC1 or GC3 is displayed.
NRMS21
DSPS21?
CONNECT AUT
AND APPLY BIAS None
RESULTS IN A
DISPLAY THAT IS
NORMALIZED TO THE
AUT PERFORMANCE
ATPSTART.
NORMALIZATION IS
AUTOMATIC FOR
EACH POWER SWEEP
None
DISPLAY S21 DSPS21
DSPS21?
CONNECT THROUGH None
RESULTS IN A
DISPLAY SHOWING
THE VALUE OF
S21 FOR EACH
POWER SWEEP
None
WAIT FOR ONE
COMPLETE SWEEP
BEFORE STORING
NRMS
CONNECT AUT
AND APPLY BIAS None
PRESS <CLEAR>
TO ABORT Pressing the Clear key aborts the Normalized S21
calibation. None
Menu GC_S21OPT, S21 Options
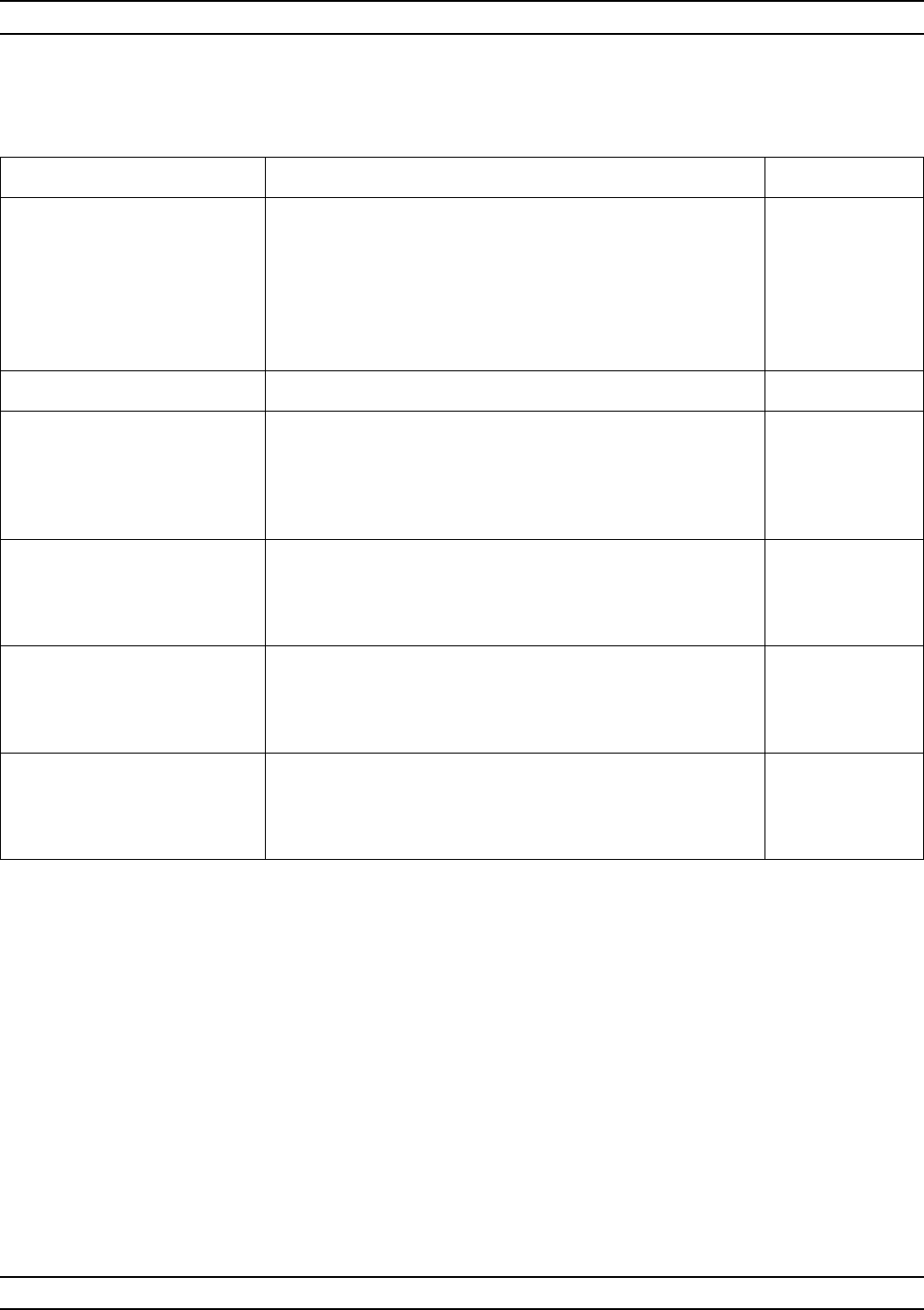
37XXXC OM A-117
ALPHABETICAL LISTING G
MENU DESCRIPTION GPIB COMMAND
SELECT LABEL
---------
ABCDEFGHIJKLM
NOPQRSTUVWXYZ
0123456789()-
!#$%&'@^_'{}~
Name your file using the rotary knob to select letters,
numbers, or both. A letter or number turns red to indicate
that the letter/number has been chosen for selection.
Pressing the Enter key selects the letter or number. the
name you spell out displays in the area below “SELECT
NAME.” You are allowed up to eight characters for a file
name and twelve characters for a label.
None
*?:\.SP Forkeyboard command line entry. None
BKSP CLR DONE Selecting “BKSP” deletes the last letter in the name
displayed above.
Selecting “CLR” deletes the entire name.
Selecting “DONE” signals that you have finished writing the
name.
None
TURN KNOB
TO INDICATE
CHARACTER OR
FUNCTION
Use the rotary knob to indicate the letter or number you
wish to select.
You can use the up-arrow and down-arrow keys to move
between rows.
None
PRESS <ENTER>
TO SELECT Pressing the Enter key implements your menu selection.
The menu remains on the screen until another menu is
selected for display or until the CLEAR/RET LOC key is
pressed.
None
NUMBERS MAY
ALSO BE
SELECTED
USING KEYPAD
You may also select numbers and decimals using the
keypad. None
Menu GP5, Select Name
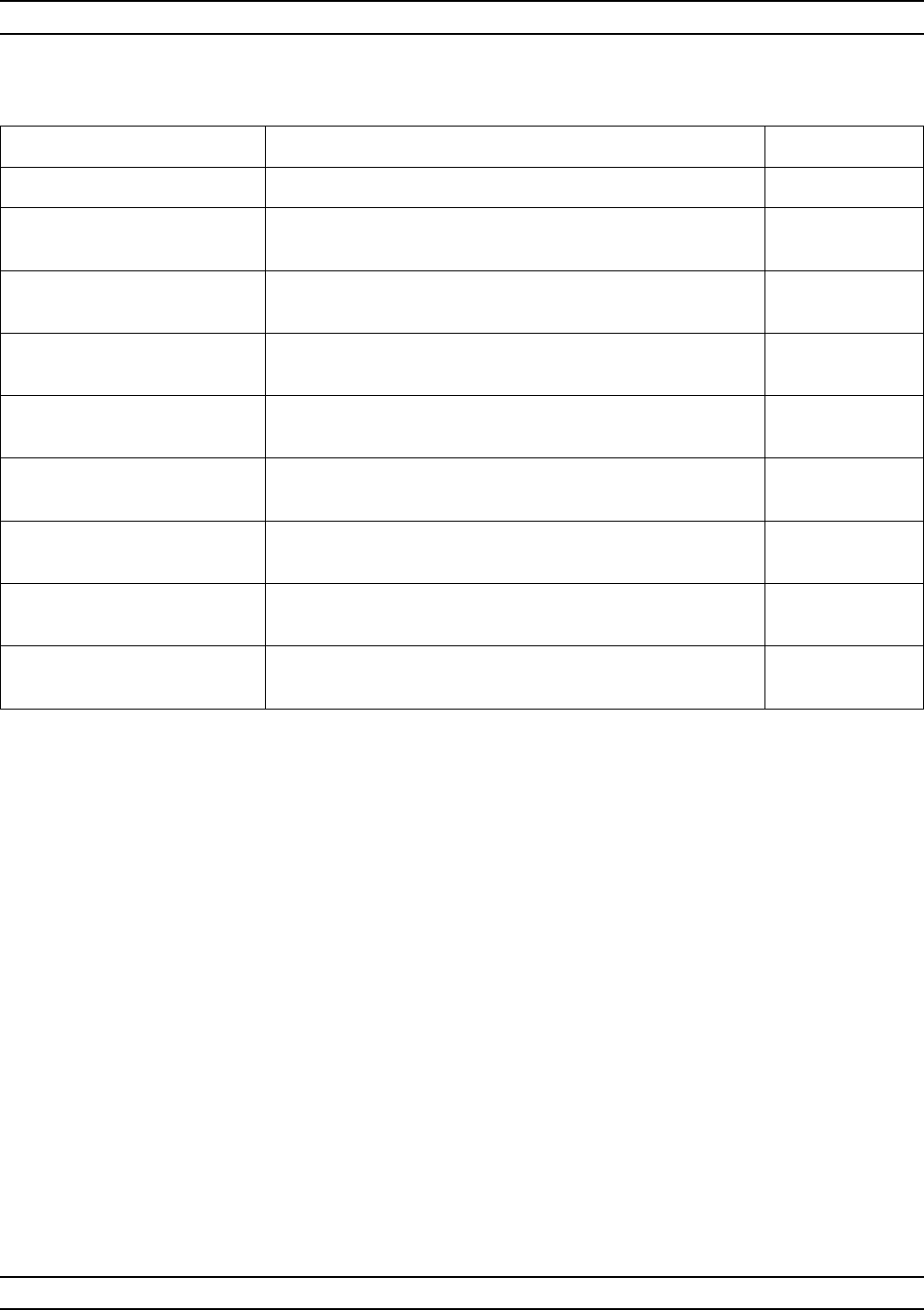
A-118 37XXXC OM
G ALPHABETICAL LISTING
MENU DESCRIPTION GPIB COMMAND
GPIB ADDRESSES None
IEEE 488.2
GPIB INTERFACE None
ADDRESS:
6Selects the GPIB address for the 37XXXC analyzer. The
default address is 6. ADDGP;
ADDGP?
DEDICATED
GPIB INTERFACE None
EXTERNAL SOURCE 1
4Selects the address for external source 1. The default
address is 4. SRC1ADD;
SRC1ADD?
EXTERNAL SOURCE 2
5Selects the address for external source 2. The default
address is 5. SRC2ADD;
SRC2ADD?
PLOTTER
8Selects the address for a compatible plotter. The default
address is 8. ADDPLT;
ADDPLT?
POWER METER
13 Selects the address for a compatible power meter. The
default address is 13. ADDPM;
ADDPM?
FREQUENCY COUNTER
7Selects the address for an external frequency counter. The
default address is 7. ADDFC; ADDFC?
Menu GP7, Display GPIB Status
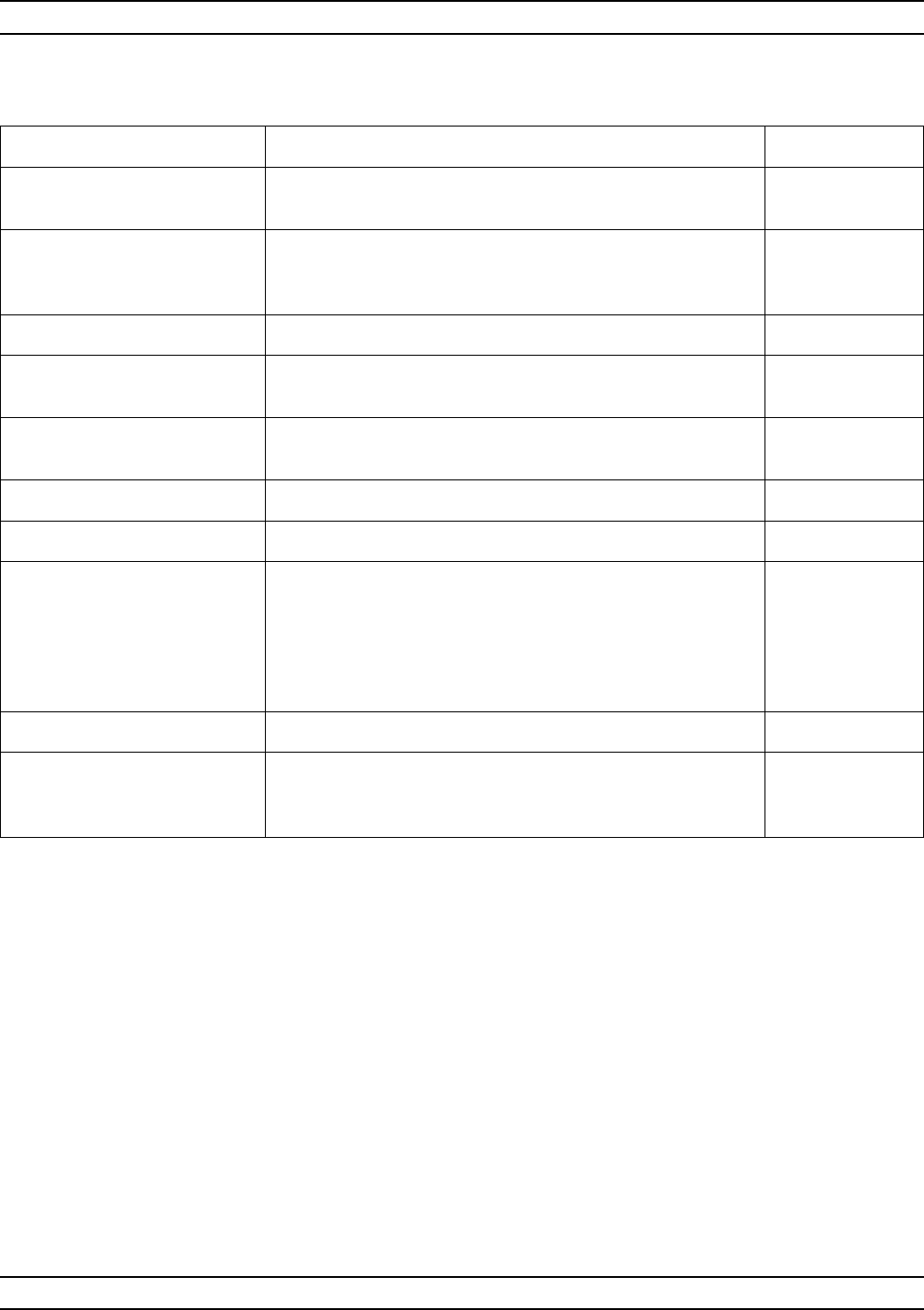
37XXXC OM A-119
ALPHABETICAL LISTING G
MENU DESCRIPTION GPIB COMMAND
SELECT
GRAPH TYPE None
LOG MAGNITUDE Selects a log magnitude graph for display on the active
channel's selected S-parameter. The active channel is
indicated by its key (CH1, CH2, CH3, CH4) being lit.
MAG
PHASE Selects a phase graph for display on the active channel. PHA
LOG MAGNITUDE
AND PHASE Selects log magnitude and phase graphs for display on the
active channel. MPH
SMITH CHART
(IMPEDANCE) Selects a Smith chart for display on the active channel. SMI; SME; SMC
SWR Selects an SWR display for the active channel. SWR
GROUP DELAY Selects a Group Delay display for the active channel. DLA
POWER OUT Provides for measuring output power. The measurement of
output power is accomplished by using the b2 (or Tb)
measured value normalized to the power supplied to the
AUT at Test Port 1. While the b2 parameter is the most
meaningful for this graph type, you may use any other
parameter.
POW
MORE Calls additional graph type selections on menu GT2. None
PRESS <ENTER>
TO SELECT
AND RESUME CAL
Pressing the Enter key implements your menu selection
(and resumes the calibration from where it left off, if in the
calibration mode).
None
Menu GT1/CAL_GT1, Select Graph Type
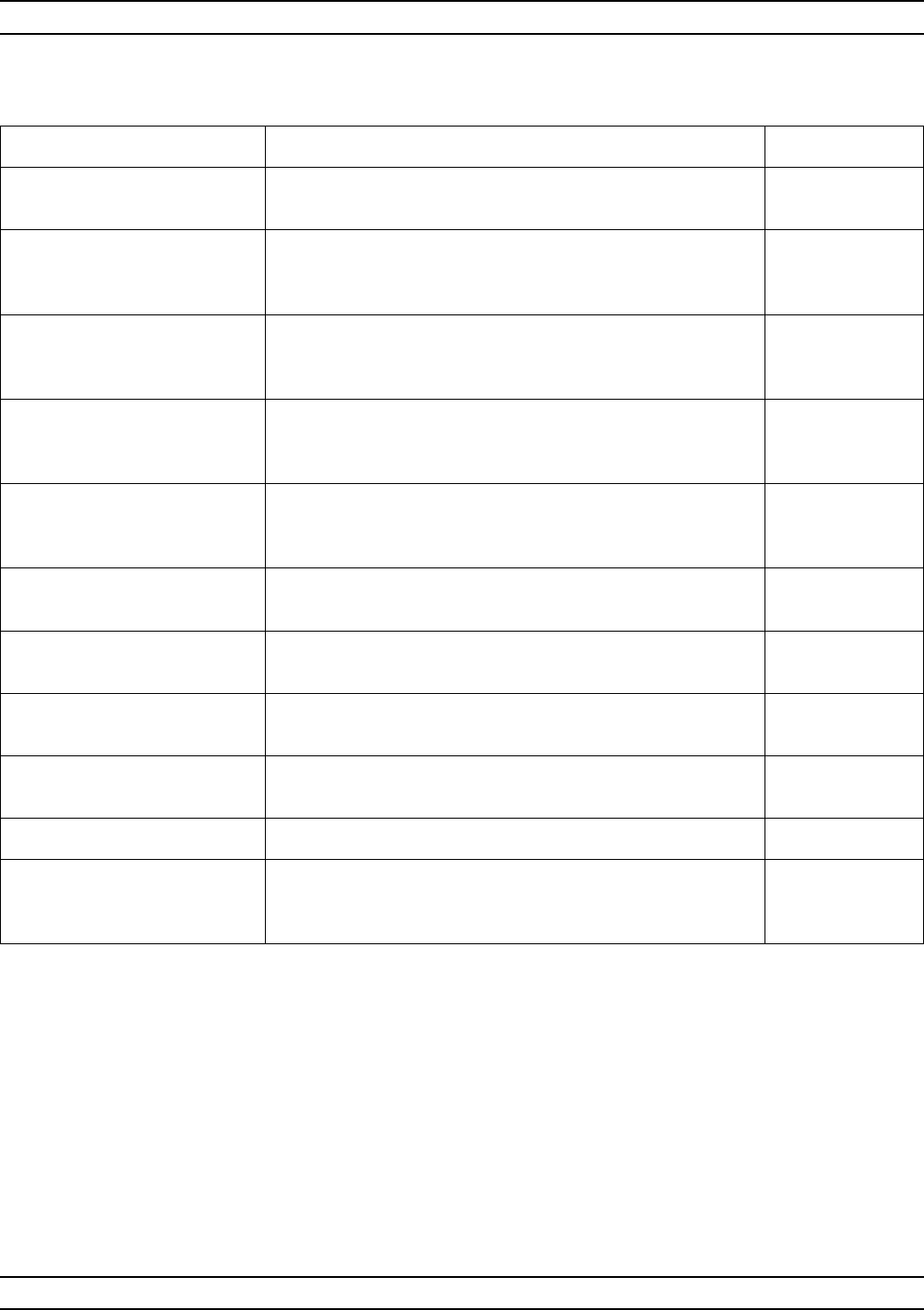
A-120 37XXXC OM
G ALPHABETICAL LISTING
MENU DESCRIPTION GPIB COMMAND
SELECT
GRAPH TYPE None
SMITH CHART
(ADMITTANCE) Selects an Admittance Smith chart for display on the active
channel's
S-parameter.
ISM; ISE; ISC
LINEAR POLAR Selects a Linear Polar graph for display on the active
channel's
S-parameter.
PLR
LOG POLAR Selects a Log Polar graph for display on the active
channel's
S-parameter.
PLG
LINEAR MAG Selects a Linear Magnitude graph for display on the active
channel's
S-parameter.
LIN
LINEAR MAG
AND PHASE Selects Linear Magnitude and Phase graphs for display on
the active channel's S-parameter. LPH
REAL Selects Real data for display on the active channel's
s-parameter. REL
IMAGINARY Selects Imaginary data for display on the active channel's
s-parameter. IMG
REAL AND
IMAGINARY Selects both Real and Imaginary data for display on the
active channel's S-parameter. RIM
MORE Calls additional graph type selections. None
PRESS <ENTER>
TO SELECT
AND RESUME CAL
Pressing the Enter key implements your menu selection
(and resumes the calibration from where it left off, if in the
calibration mode).
None
Menu GT2/CAL_GT2, Select Graph Type
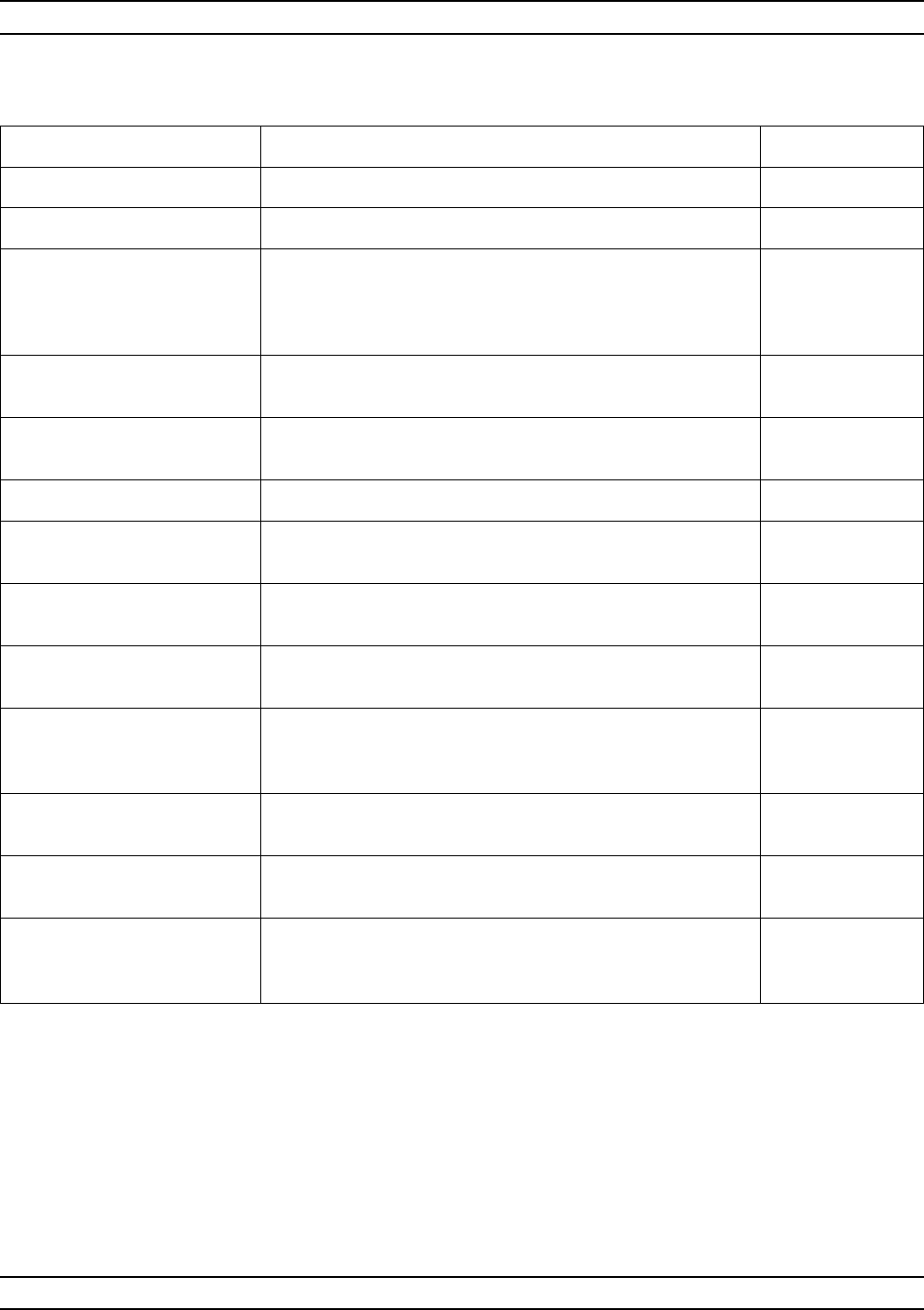
37XXXC OM A-121
ALPHABETICAL LISTING L
MENU DESCRIPTION GPIB COMMAND
SINGLE LIMITS None
—LOG MAG— None
UPPER LIMIT ON (OFF)
XXX.XXX dB Turns the Upper Limit line on or off for the active channel.
For your convenience, the arbitrarily set limit lines allow
you to delineate a go/no go line on your Log Mag display
beyond which the measured values are unacceptable.
UPL0; UPL1;
UPLX?
LOWER LIMIT ON(OFF)
XXX.XXX dB Turns the Lower Limit line on or off for the active channel
on your Log Mag display. LOL0; LOL1;
LOLX?
READOUT LIMIT Calls menu LF1, which shows points where the current
S-parameter intercepts the lower limit. None
–PHASE– None
UPPER LIMIT ON (OFF)
XXX.XXX°
Turns the Upper Limit line on or off for the active channel
on your Phase display. UPL0; UPL1;
UPLX?
LOWER LIMIT ON(OFF)
XXX.XXX °
Turns the Lower Limit line on or off for the active channel
on your Phase display. LOL0; LOL1;
LOLX?
READOUT LIMIT Calls menu LF2, which shows points where the current
S-parameter intercepts the lower limit. None
DISPLAY ON (OFF)
LIMITS Enables both limit lines for the active channel on both the
Log-
Mag and Phase graphs.
LON; LOF; LON?
TEST LIMITS Calls menu LTST, which provides choices for testing the
limits. None
SEGMENTED LIMITS Calls a menu in the LS series (LSX), which lets you set
segmented limit lines. None
PRESS <ENTER>
TO SELECT
OR TURN ON/OFF
Pressing the Enter key implements your menu selection. None
Menu L1, Set Limits—Magnitude and Phase
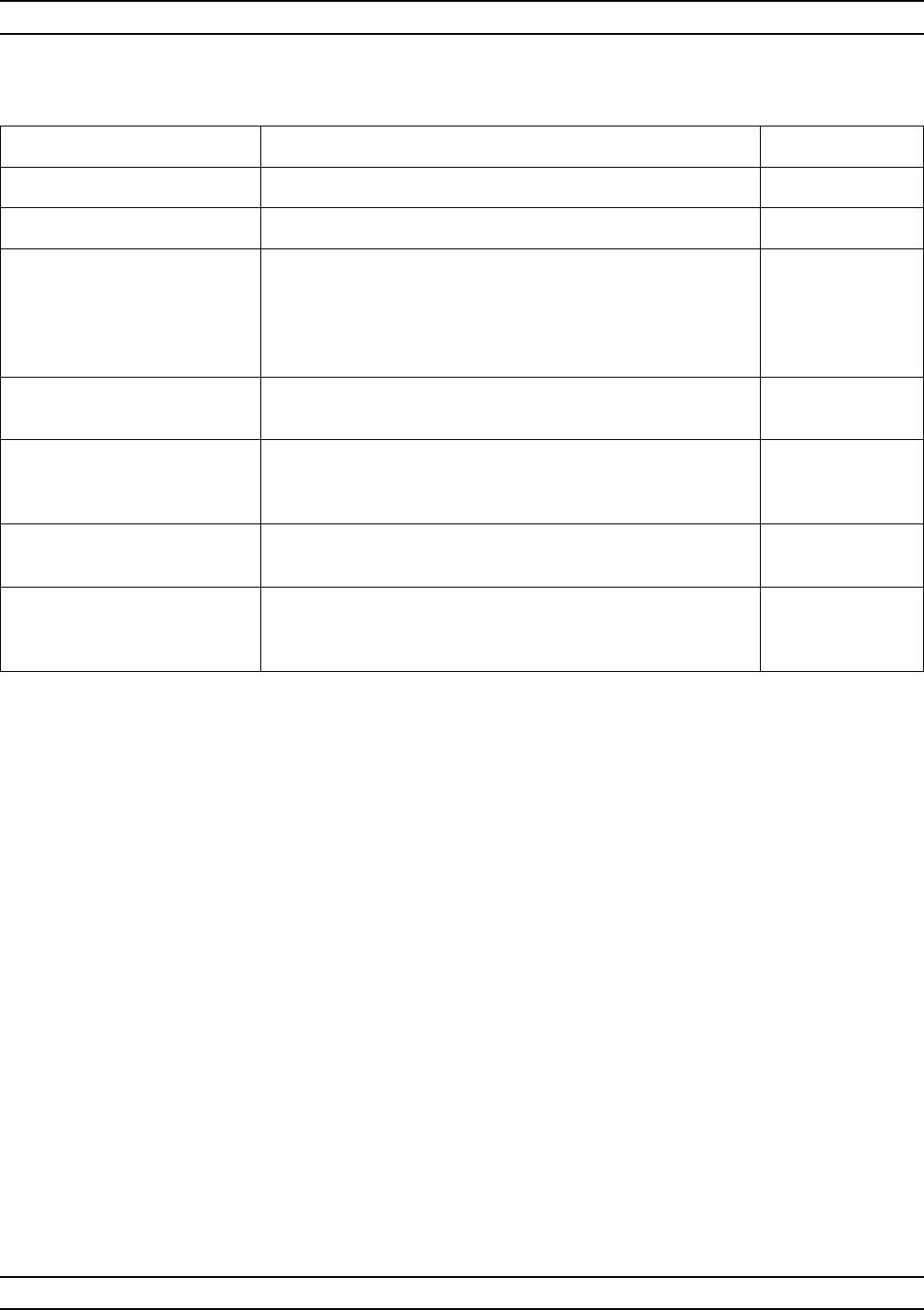
A-122 37XXXC OM
L ALPHABETICAL LISTING
MENU DESCRIPTION GPIB COMMAND
SINGLE LIMITS None
–LINEAR POLAR– None
UPPER LIMIT ON (OFF)
XXX.XXX mU Turns the Upper Limit line on or off for the active channel.
For your convenience, the arbitrarily set limit lines allow
you to delineate a go/no go line on your Linear Polar
display beyond which the measured values are
unacceptable.
UPL0; UPL1;
UPLX?
LOWER LIMIT ON(OFF)
XXX.XXX mU Turns the Lower Limit line on or off for the active channel
on your Linear Polar display. LOL0; LOL1;
LOLX?
DISPLAY ON (OFF)
LIMITS Enables both previously set limit lines to appear for the
active
channel on your polar display.
LON; LOF; LON?
TEST LIMITS Calls menu LTST, which provides choices for testing the
limits. None
PRESS <ENTER>
TO SELECT
OR TURN ON/OFF
Pressing the Enter key implements your menu selection. None
Menu L2, Set Limits—Linear Polar
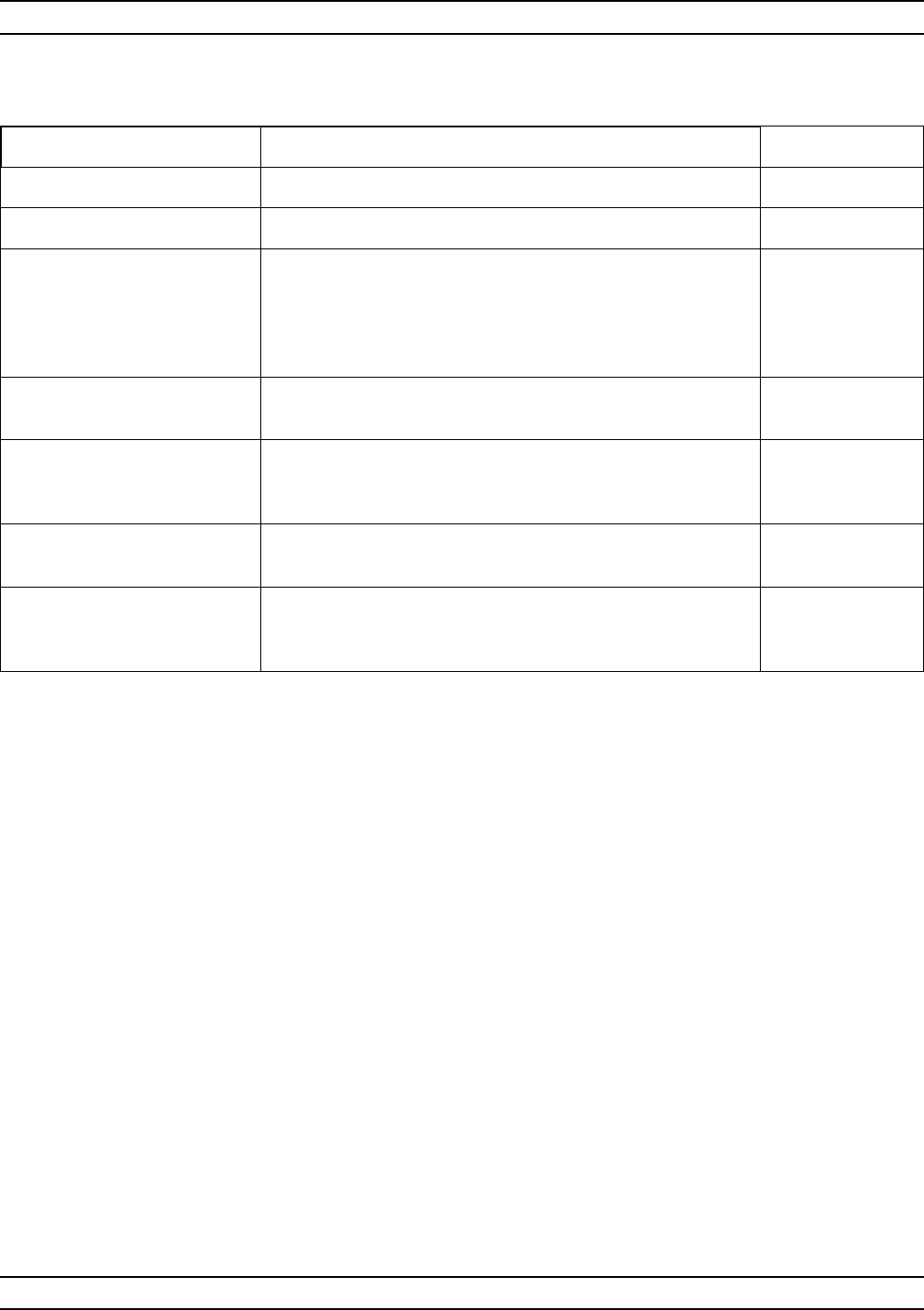
37XXXC OM A-123
ALPHABETICAL LISTING L
MENU DESCRIPTION GPIB COMMAND
SINGLE LIMITS None
–SMITH CHART– None
UPPER LIMIT ON (OFF)
XXX.XXX mU Turns the Upper Limit line on or off for the active channel.
For your convenience, the arbitrarily set limit lines allow
you to delineate a go/no go line on your Smith Chart
display beyond which the measured values are
unacceptable.
UPL0; UPL1;
UPLX?
LOWER LIMIT ON(OFF)
XXX.XXX mU Turns the Lower Limit line on or off for the active channel
on your Smith Chart. LOL0; LOL1;
LOLX?
DISPLAY ON (OFF)
LIMITS Enables both previously set limit lines to appear for the
active
channel on your Smith Chart.
LON; LOF; LON?
TEST LIMITS Calls menu LTST, which provides choices for testing the
limits. None
PRESS <ENTER>
TO SELECT
OR TURN ON/OFF
Pressing the Enter key implements your menu selection. None
Menu L3, Set Limits—Linear Polar/Smith Chart
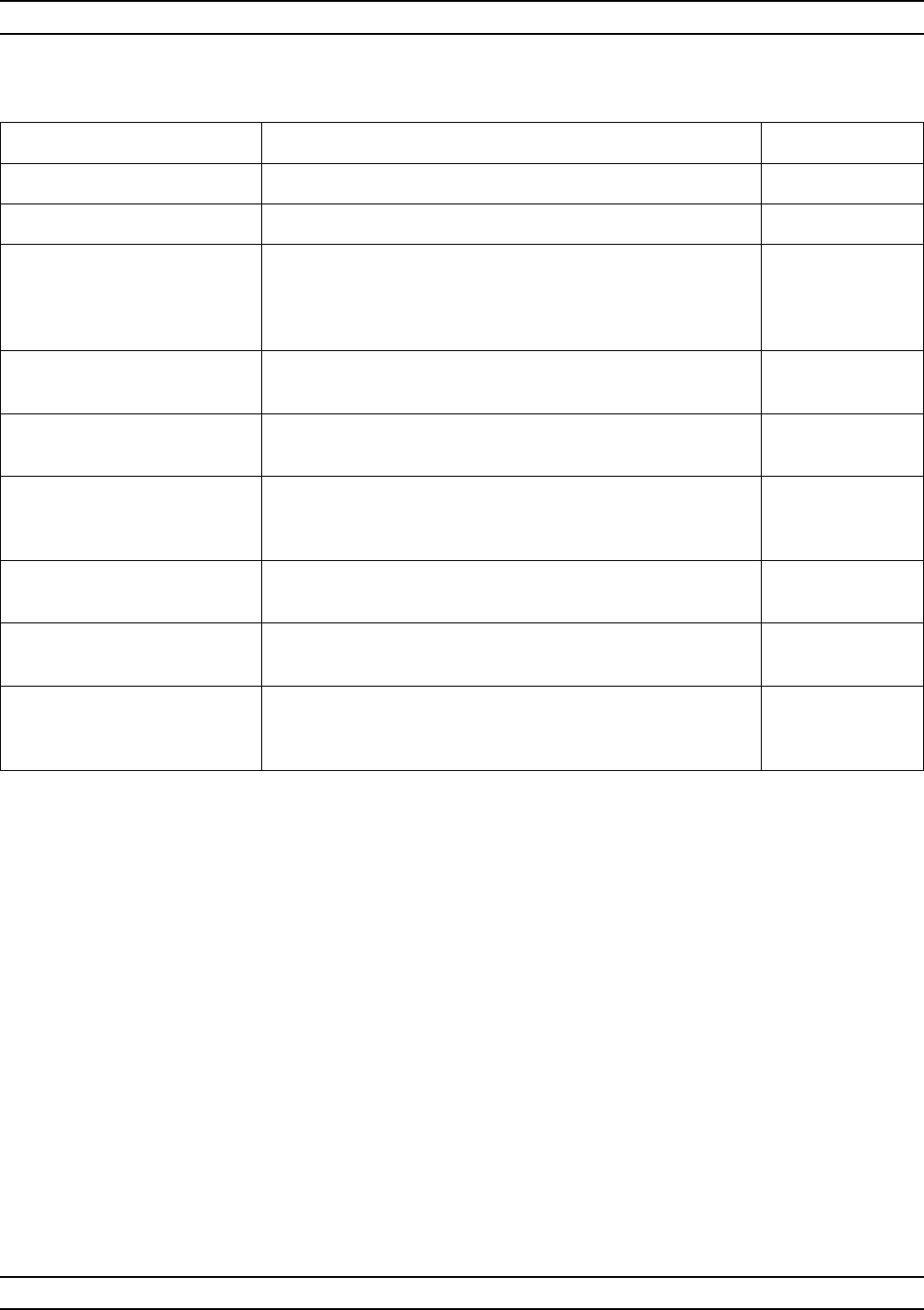
A-124 37XXXC OM
L ALPHABETICAL LISTING
MENU DESCRIPTION GPIB COMMAND
SINGLE LIMITS None
–LOG MAG– None
UPPER LIMIT ON (OFF)
XXX.XXX dB Turns the Upper Limit line on or off for the active channel.
For your convenience, the arbitrarily set limit lines allow
you to delineate a go/no go line on your Log Mag display
beyond which the measured values are unacceptable.
UPL0; UPL1;
UPLX?
LOWER LIMIT ON(OFF)
XXX.XXX dB Turns the Lower Limit line on or off for the active channel
on your Log Mag display. LOL0; LOL1;
LOLX?
READOUT LIMIT Calls menu LF1, which shows points where the current
S-parameter intercepts the lower limit. None
DISPLAY ON (OFF)
LIMITS Enables both previously set limit lines to appear for the
active
channel on your Log Mag display.
LON; LOF; LON?
TEST LIMITS Calls menu LTST, which provides choices for testing the
limits. None
SEGMENTED LIMITS Calls a menu in the LS series (LSX), which lets you set
segmented limit lines. None
PRESS <ENTER>
TO SELECT
OR TURN ON/OFF
Pressing the Enter key implements your menu selection. None
Menu L4, Set Limits—Log Magnitude
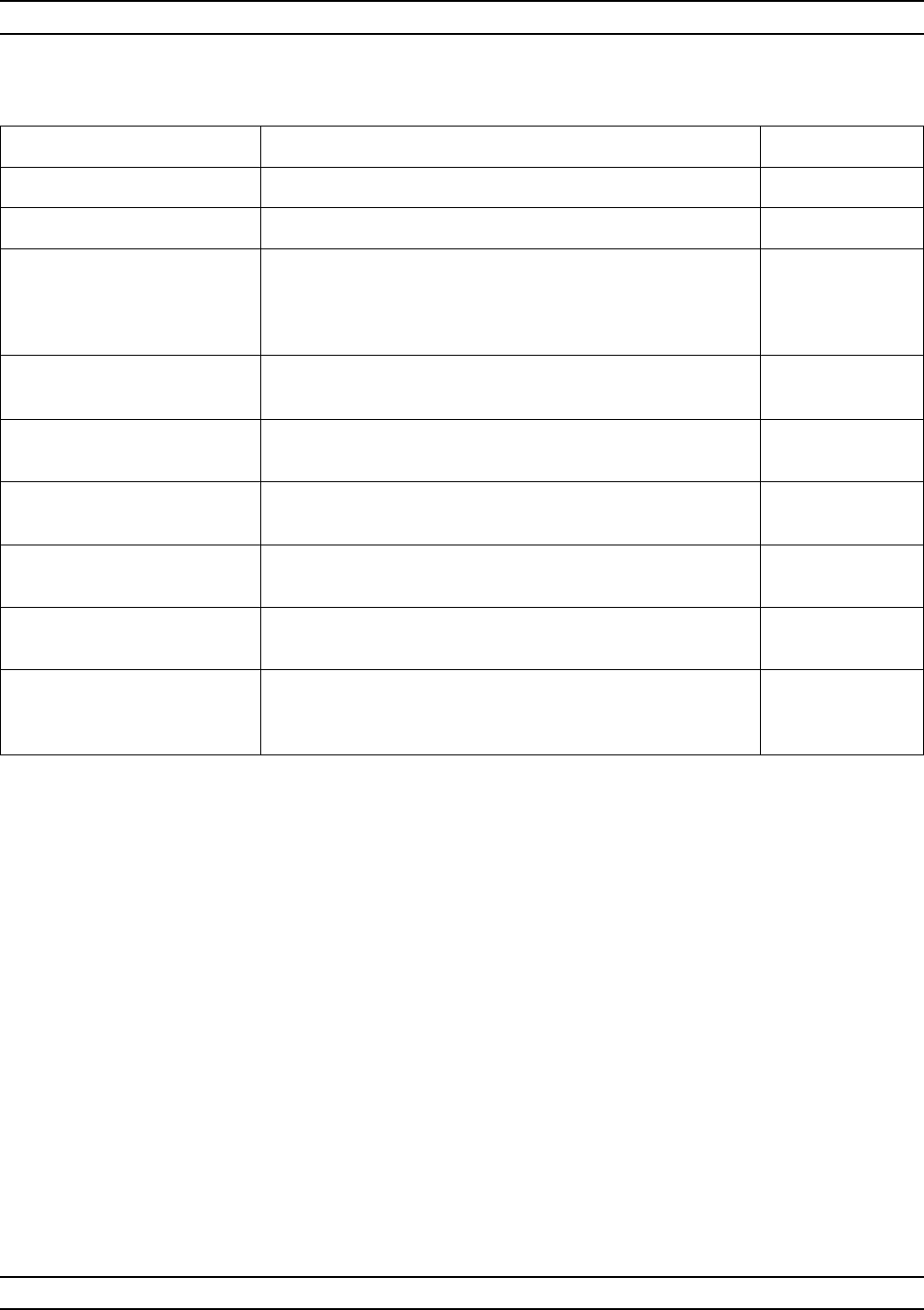
37XXXC OM A-125
ALPHABETICAL LISTING L
MENU DESCRIPTION GPIB COMMAND
SINGLE LIMITS None
–PHASE– None
UPPER LIMIT ON (OFF)
XXX.XXX °
Turns the Upper Limit line on or off for the active channel.
For your convenience, the arbitrarily set limit lines allow
you to delineate a go/no go line on your Phase display
beyond which the measured values are unacceptable.
UPL0; UPL1;
UPLX?
LOWER LIMIT ON(OFF)
XXX.XXX °
Turns the Lower Limit line on or off for the active channel
on your Phase display. LOL0; LOL1;
LOLX?
READOUT LIMIT Calls menu LF1, which shows points where the current
S-parameter intercepts the lower limit. None
DISPLAY ON (OFF)
LIMITS Enables both limit lines for the active channel on a phase
graph. LON; LOF; LON?
TEST LIMITS Calls menu LTST, which provides choices for testing the
limits. None
SEGMENTED LIMITS Calls a menu in the LS series (LSX), which lets you set
segmented limit lines. None
PRESS <ENTER>
TO SELECT
OR TURN ON/OFF
Pressing the Enter key implements your menu selection. None
Menu L5, Set Limits—Phase
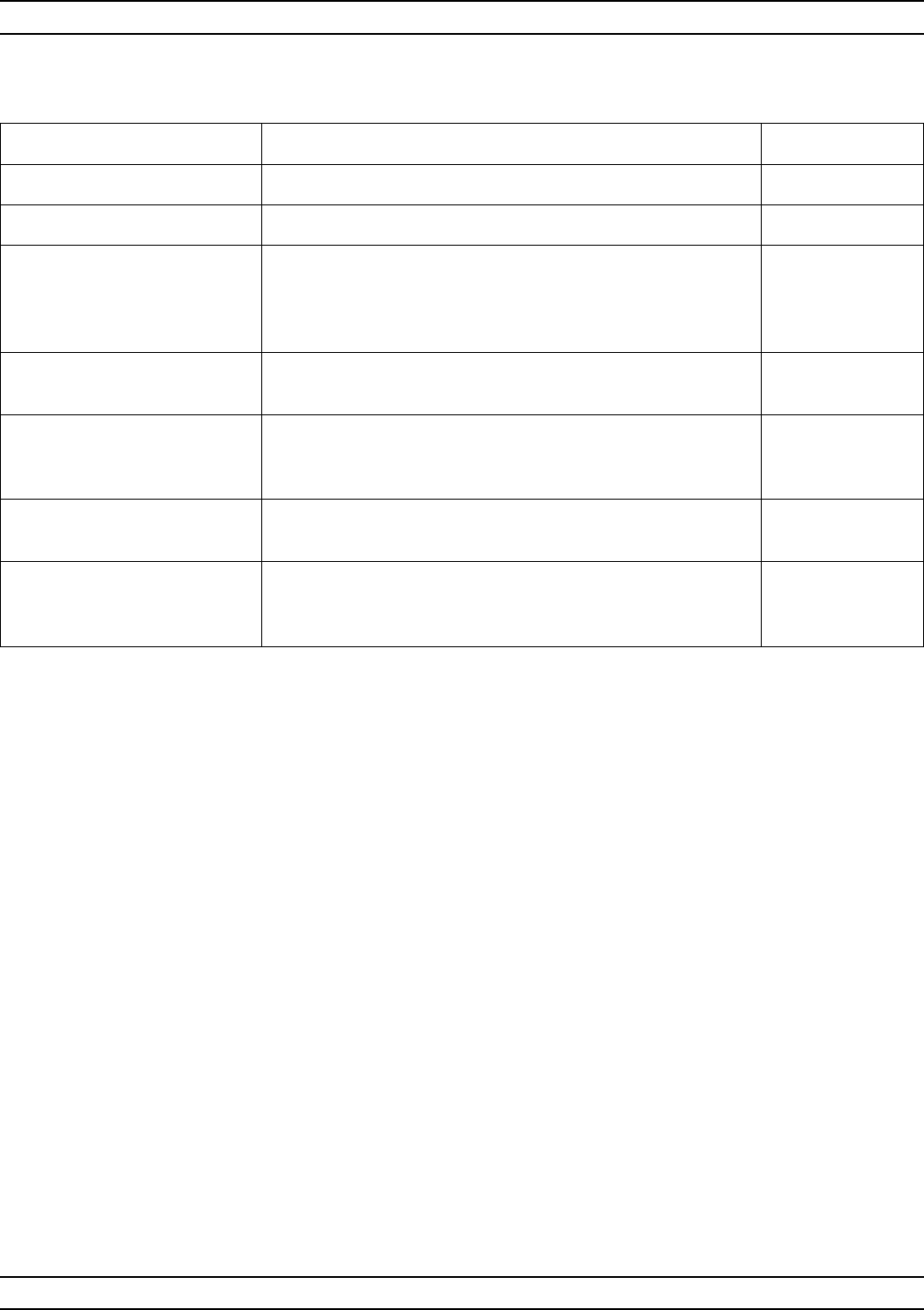
A-126 37XXXC OM
L ALPHABETICAL LISTING
MENU DESCRIPTION GPIB COMMAND
SINGLE LIMITS None
–LOG POLAR– None
UPPER LIMIT ON (OFF)
XXX.XXX dB Turns the Upper Limit line on or off for the active channel.
For your convenience, the arbitrarily set limit lines allow
you to delineate a go/no go line on your Log Polar display
beyond which the measured values are unacceptable.
UPL0; UPL1;
UPLX?
LOWER LIMIT ON(OFF)
XXX.XXX dB Turns the Lower Limit line on or off for the active channel
on your Log Polar display. LOL0; LOL1;
LOLX?
DISPLAY ON (OFF)
LIMITS Enables both previously set limit lines to appear for the
active
channel on your Log Polar display.
LON; LOF; LON?
TEST LIMITS Calls menu LTST, which provides choices for testing the
limits. None
PRESS <ENTER>
TO SELECT
OR TURN ON/OFF
Pressing the Enter key implements your menu selection. None
Menu L6, Set Limits—Log Polar

37XXXC OM A-127
ALPHABETICAL LISTING L
MENU DESCRIPTION GPIB COMMAND
SINGLE LIMITS None
–GROUP DELAY– None
UPPER LIMIT ON (OFF)
XXX.XXX fs Turns the Upper Limit line on or off for the active channel.
For your convenience, the arbitrarily set limit lines allow
you to delineate a go/no go line on your Group Delay
display beyond which the measured values are
unacceptable.
UPL0; UPL1;
UPLX?
LOWER LIMIT ON(OFF)
XXX.XXX fs Turns the Lower Limit line on or off for the active channel
on your Group Delay display. LOL0; LOL1;
LOLX?
READOUT LIMIT Calls menu LF1, which shows points where the current
S-parameter intercepts the lower limit. None
DISPLAY ON (OFF)
LIMITS Enables both previously set limit lines to appear for the
active
channel on your Group Delay display.
LON; LOF; LON?
TEST LIMITS Calls menu LTST, which provides choices for testing the
limits. None
SEGMENTED LIMITS Calls a menu in the LS series (LSX), which lets you set
segmented limit lines. None
PRESS <ENTER>
TO SELECT
OR TURN ON/OFF
Pressing the Enter key implements your menu selection. None
Menu L7, Set Limits—Group Delay
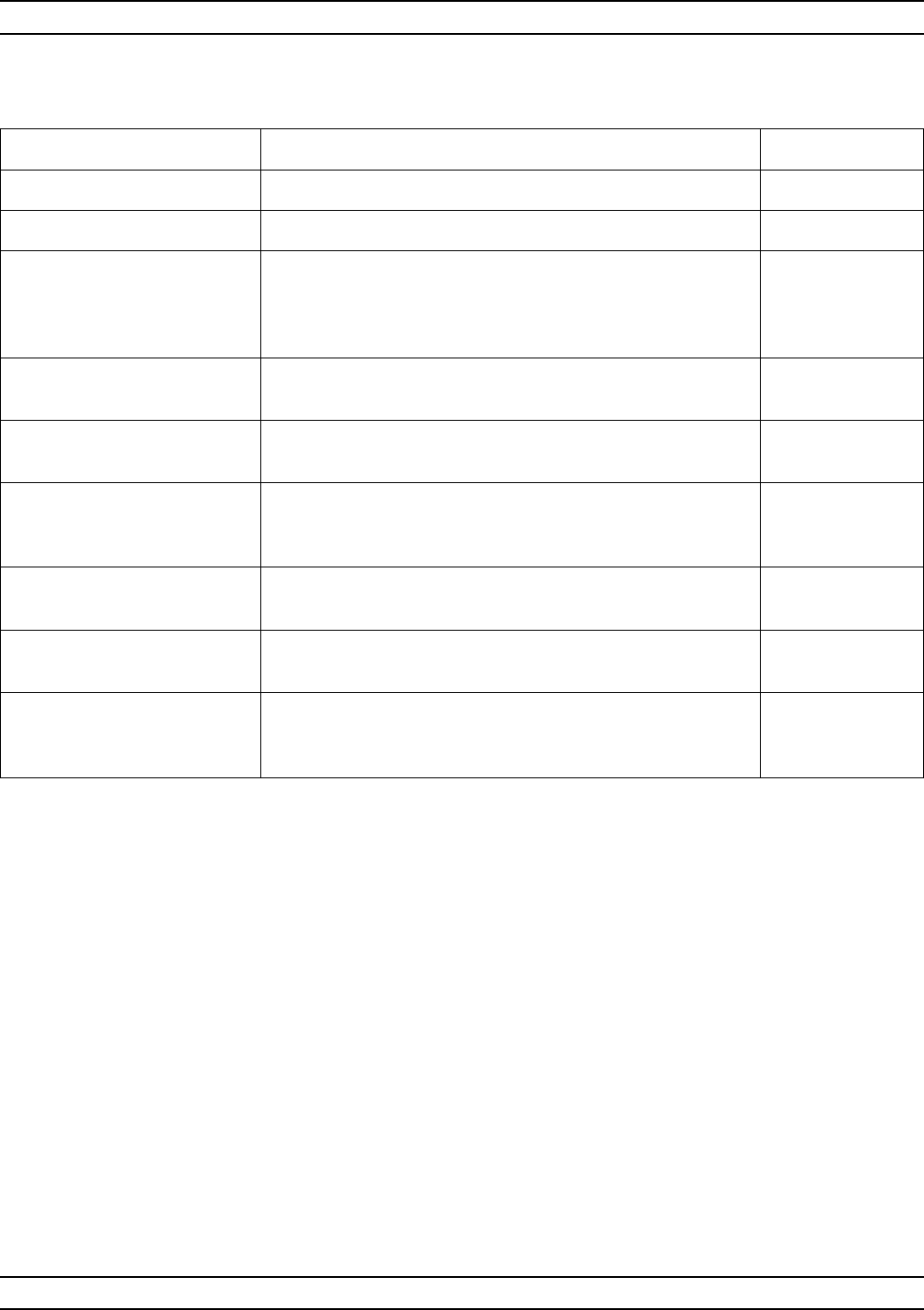
A-128 37XXXC OM
L ALPHABETICAL LISTING
MENU DESCRIPTION GPIB COMMAND
SINGLE LIMITS None
–LINEAR MAG– None
UPPER LIMIT ON (OFF)
XXX.XXX pU Turns the Upper Limit line on or off for the active channel.
For your convenience, the arbitrarily set limit lines allow
you to delineate a go/no go line on your Linear Mag display
beyond which the measured values are unacceptable.
UPL0; UPL1;
UPLX?
LOWER LIMIT ON(OFF)
XXX.XXX pU Turns the Lower Limit line on or off for the active channel
on your Linear Mag display. LOL0; LOL1;
LOLX?
READOUT LIMIT Calls menu LF1, which shows points where the current
S-parameter intercepts the lower limit. None
DISPLAY ON (OFF)
LIMITS Enables both previously set limit lines to appear for the
active
channel on your Linear Mag display.
LON; LOF; LON?
TEST LIMITS Calls menu LTST, which provides choices for testing the
limits. None
SEGMENTED LIMITS Calls a menu in the LS series (LSX), which lets you set
segmented limit lines. None
PRESS <ENTER>
TO SELECT
OR TURN ON/OFF
Pressing the Enter key implements your menu selection. None
Menu L8, Set Limits—Linear Magnitude
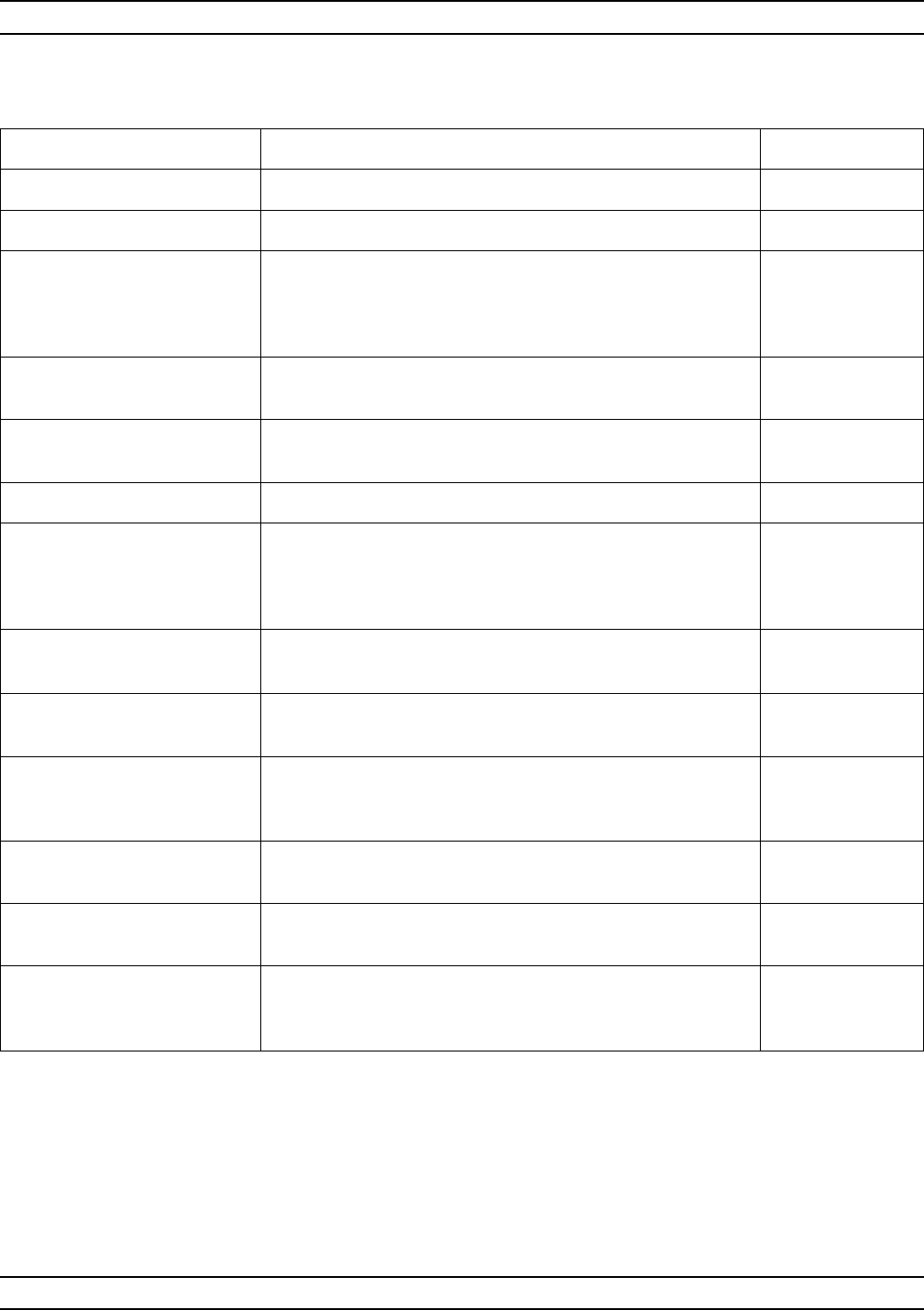
37XXXC OM A-129
ALPHABETICAL LISTING L
MENU DESCRIPTION GPIB COMMAND
SINGLE LIMITS None
–LINEAR MAG– None
UPPER LIMIT ON (OFF)
XXX.XXX pU Turns the Upper Limit line on or off for the active channel.
For your convenience, the arbitrarily set limit lines allow
you to delineate a go/no go line on your Linear Mag display
beyond which the measured values are unacceptable.
UPL0; UPL1;
UPLX?
LOWER LIMIT ON(OFF)
XXX.XXX pU Turns the Lower Limit line on or off for the active channel
on your Linear Mag display. LOL0; LOL1;
LOLX?
READOUT LIMIT Calls menu LF4, which shows points where the current
S-parameter intercepts the lower limit. None
-PHASE- None
UPPER LIMIT ON (OFF)
XXX.XXX °
Turns the Upper Limit line on or off for the active channel.
For your convenience, the arbitrarily set limit lines allow
you to delineate a go/no go line on your polar display
beyond which the measured values are unacceptable.
UPL0; UPL1;
UPLX?
LOWER LIMIT ON(OFF)
XXX.XXX °
Turns the Lower Limit line on or off for the active channel
on your Phase display. LOL0; LOL1;
LOLX?
READOUT LIMIT Calls menu LF2, which shows points where the current
S-parameter intercepts the lower limit. None
DISPLAY ON (OFF)
LIMITS Enables both previously set limit lines to appear for the
active
channel on your Phase display.
LON; LOF; LON?
TEST LIMITS Calls menu LTST, which provides choices for testing the
limits. None
SEGMENTED LIMITS Calls a menu in the LS series (LSX), which lets you set
segmented limit lines. None
PRESS <ENTER>
TO SELECT
OR TURN ON/OFF
Pressing the Enter key implements your menu selection. None
Menu L9, Set Limits—Linear Magnitude and Phase
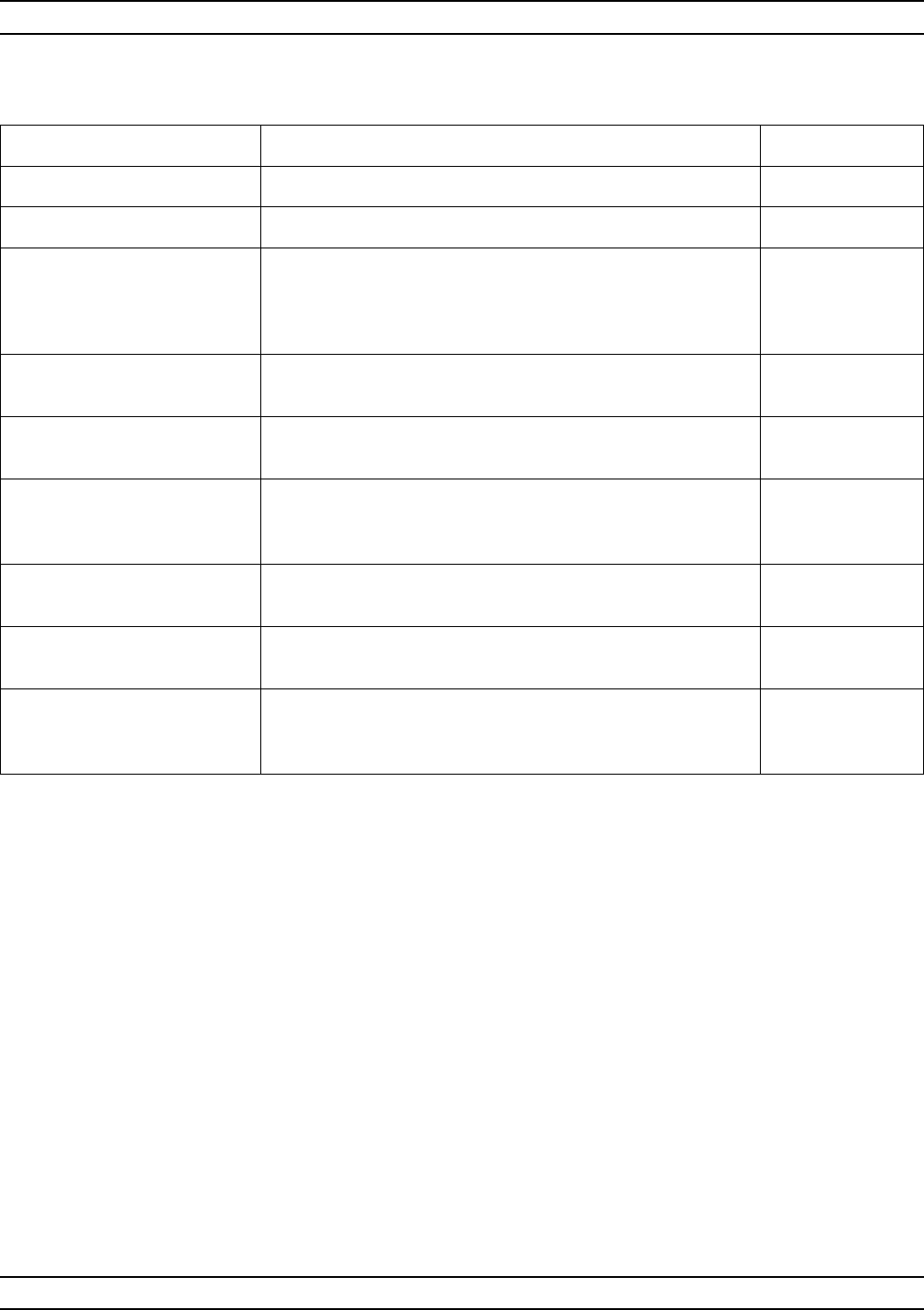
A-130 37XXXC OM
L ALPHABETICAL LISTING
MENU DESCRIPTION GPIB COMMAND
SINGLE LIMITS None
–REAL– None
UPPER LIMIT ON (OFF)
XXX.XXX pU Turns the Upper Limit line on or off for the active channel.
For your convenience, the arbitrarily set limit lines allow
you to delineate a go/no go line on your Real display
beyond which the measured values are unacceptable.
UPL0; UPL1;
UPLX?
LOWER LIMIT ON(OFF)
XXX.XXX pU Turns the Lower Limit line on or off for the active channel
on your Real display. LOL0; LOL1;
LOLX?
READOUT LIMIT Calls menu LF6, which shows points where the current
S-parameter intercepts the lower limit. None
DISPLAY ON (OFF)
LIMITS Enables both previously set limit lines to appear for the
active
channel on your Real values display.
LON; LOF; LON?
TEST LIMITS Calls menu LTST, which provides choices for testing the
limits. None
SEGMENTED LIMITS Calls a menu in the LS series (LSX), which lets you set
segmented limit lines. None
PRESS <ENTER>
TO SELECT
OR TURN ON/OFF
Pressing the Enter key implements your menu selection. None
Menu L10, Set Limits—Real Values
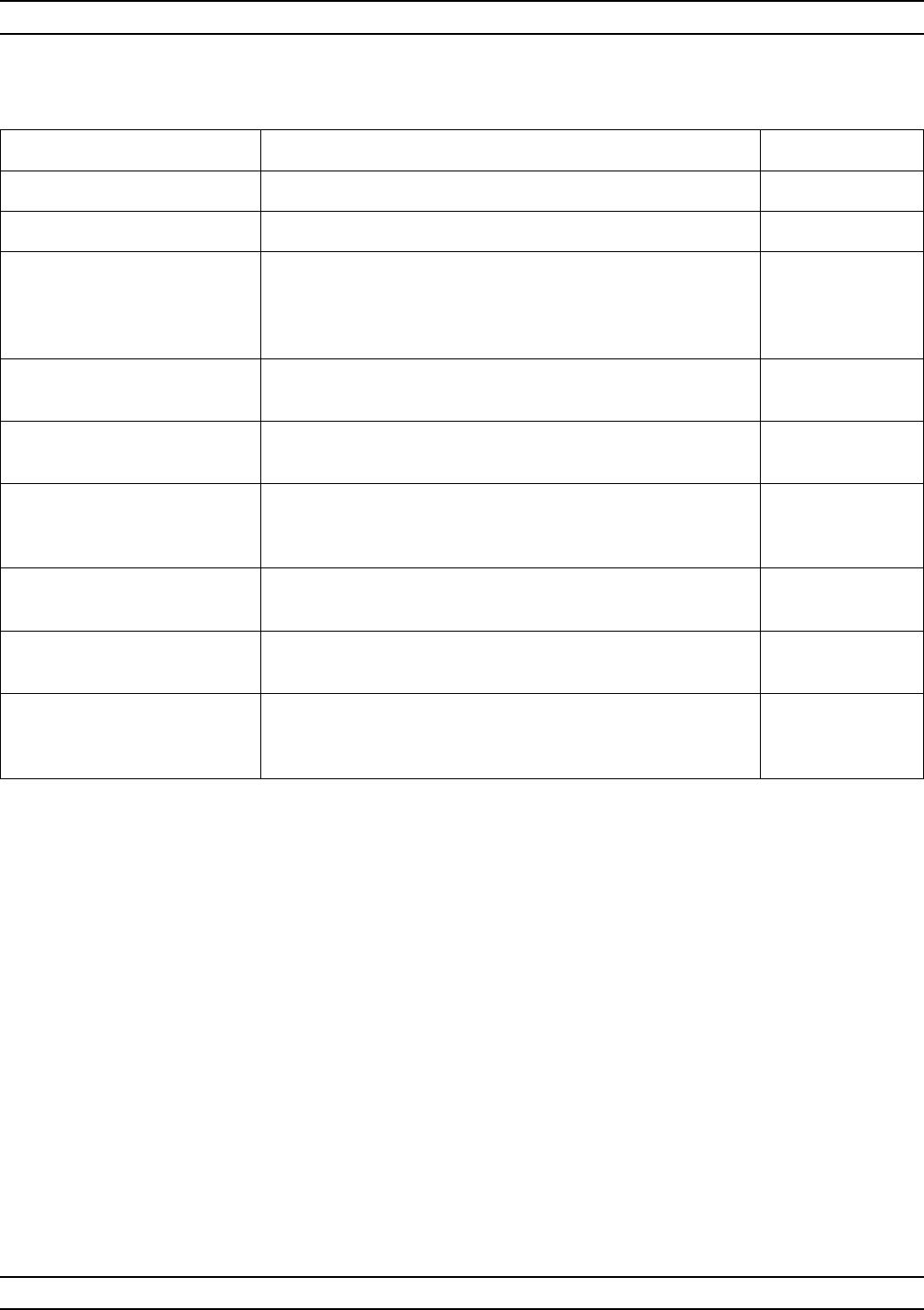
37XXXC OM A-131
ALPHABETICAL LISTING L
MENU DESCRIPTION GPIB COMMAND
SINGLE LIMITS None
–IMAGINARY– None
UPPER LIMIT ON (OFF)
XXX.XXX pU Turns the Upper Limit line on or off for the active channel.
For your convenience, the arbitrarily set limit lines allow
you to delineate a go/no go line on your Imaginary display
beyond which the measured values are unacceptable.
UPL0; UPL1;
UPLX?
LOWER LIMIT ON(OFF)
XXX.XXX pU Turns the Lower Limit line on or off for the active channel
on your Imaginary display. LOL0; LOL1;
LOLX?
READOUT LIMIT Calls menu LF7, which shows points where the current
S-parameter intercepts the lower limit. None
DISPLAY ON (OFF)
LIMITS Enables both previously set limit lines to appear for the
active
channel on your Imaginary values display.
LON; LOF; LON?
TEST LIMITS Calls menu LTST, which provides choices for testing the
limits. None
SEGMENTED LIMITS Calls a menu in the LS series (LSX), which lets you set
segmented limit lines. None
PRESS <ENTER>
TO SELECT
OR TURN ON/OFF
Pressing the Enter key implements your menu selection. None
Menu L11, Set Limits—Imaginary Values
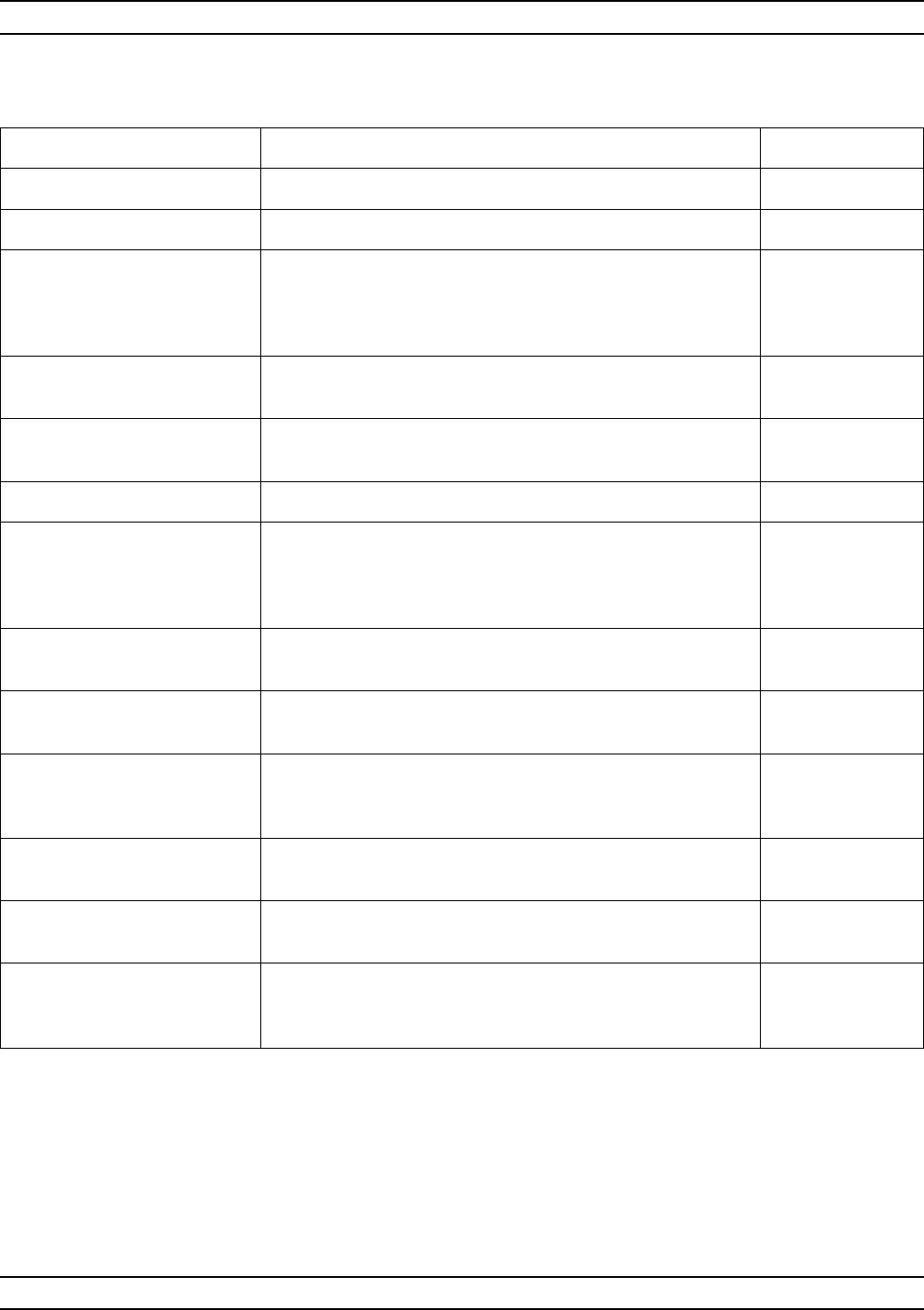
A-132 37XXXC OM
L ALPHABETICAL LISTING
MENU DESCRIPTION GPIB COMMAND
SINGLE LIMITS None
–REAL– None
UPPER LIMIT ON (OFF)
XXX.XXX pU Turns the Upper Limit line on or off for the active channel.
For your convenience, the arbitrarily set limit lines allow
you to delineate a go/no go line on your Real display
beyond which the measured values are unacceptable.
UPL0; UPL1;
UPLX?
LOWER LIMIT ON(OFF)
XXX.XXX pU Turns the Lower Limit line on or off for the active channel
on your Real display. LOL0; LOL1;
LOLX?
READOUT LIMIT Calls menu LF6, which shows points where the current
S-parameter intercepts the lower limit. None
–IMAGINARY– None
UPPER LIMIT ON (OFF)
XXX.XXX pU Turns the Upper Limit line on or off for the active channel.
For your convenience, the arbitrarily set limit lines allow
you to delineate a go/no go line on your Imaginary display
beyond which the measured values are unacceptable.
UPL0; UPL1;
UPLX?
LOWER LIMIT ON(OFF)
XXX.XXX pU Turns the Lower Limit line on or off for the active channel
on your Imaginary display. LOL0; LOL1;
LOLX?
READOUT LIMIT Displays menu LF7, which shows points where the current
S-parameter intercepts the lower limit. None
DISPLAY ON (OFF)
LIMITS Enables both previously set limit lines to appear for the
active
channel on your Imaginary values display.
LON; LOF; LON?
TEST LIMITS Calls menu LTST, which provides choices for testing the
limits. None
SEGMENTED LIMITS Calls a menu in the LS series (LSX), which lets you set
segmented limit lines. None
PRESS
TO SELECT
OR TURN ON/OFF
Pressing the Enter key implements your menu selection. None
Menu L12, Set Limits—Real and Imaginary Values
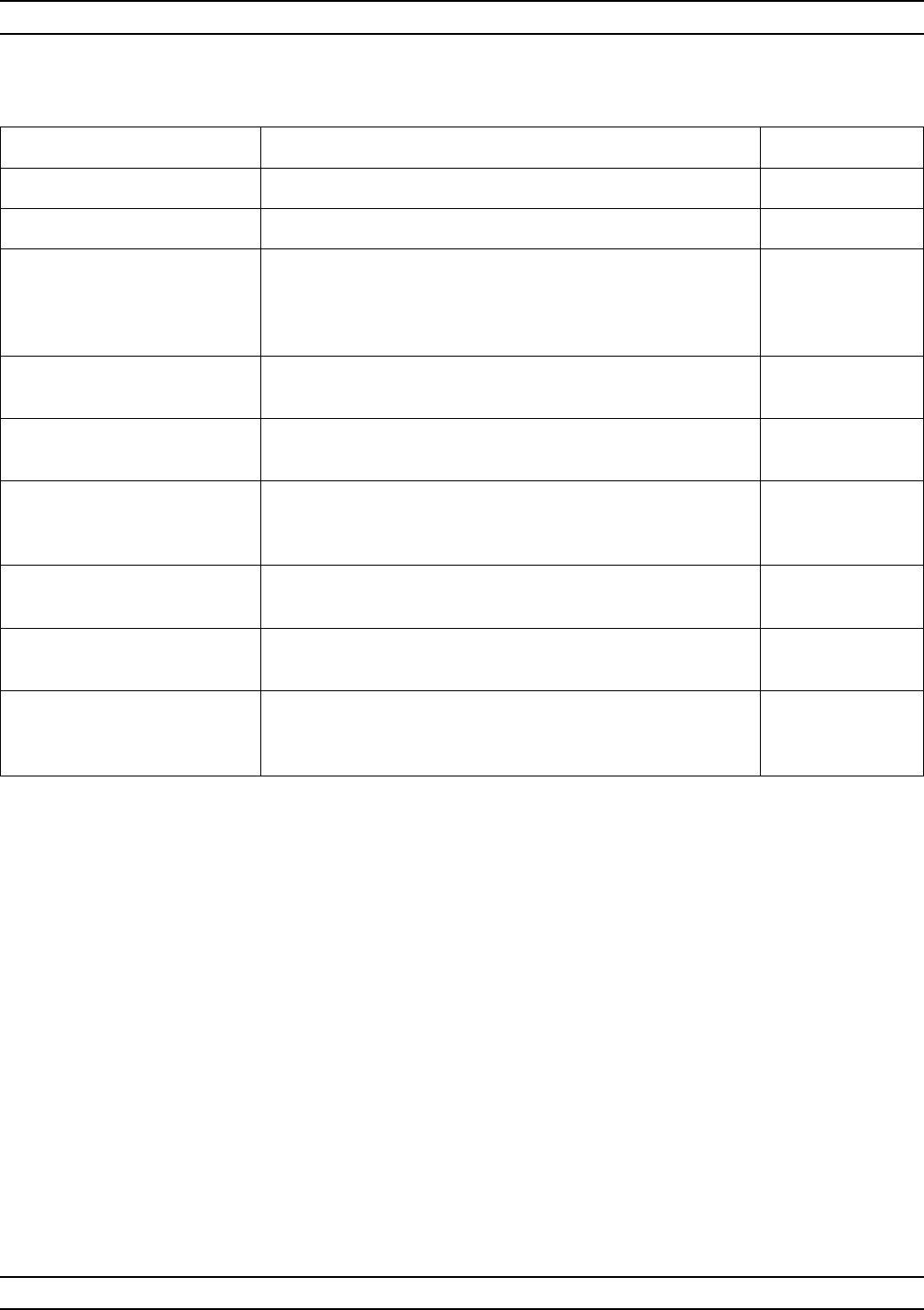
37XXXC OM A-133
ALPHABETICAL LISTING L
MENU DESCRIPTION GPIB COMMAND
SINGLE LIMITS None
–SWR— None
UPPER LIMIT ON (OFF)
XXX.XXX pU Turns the Upper Limit line on or off for the active channel.
For your convenience, the arbitrarily set limit lines allow
you to delineate a go/no go line on your SWR display
beyond which the measured values are unacceptable.
UPL0; UPL1;
UPLX?
LOWER LIMIT ON(OFF)
XXX.XXX pU Turns the Lower Limit line on or off for the active channel
on your SWR display. LOL0; LOL1;
LOLX?
READOUT LIMIT Calls menu LF5, which shows points where the current
S-parameter intercepts the lower limit. None
DISPLAY ON (OFF)
LIMITS Enables both previously set limit lines to appear for the
active
channel.
LON; LOF; LON?
TEST LIMITS Calls menu LTST, which provides choices for testing the
limits. None
SEGMENTED LIMITS Calls a menu in the LS series (LSX), which lets you set
segmented limit lines. None
PRESS <ENTER>
TO SELECT
OR TURN ON/OFF
Pressing the Enter key implements your menu selection. None
Menu L13, Set Limits—SWR
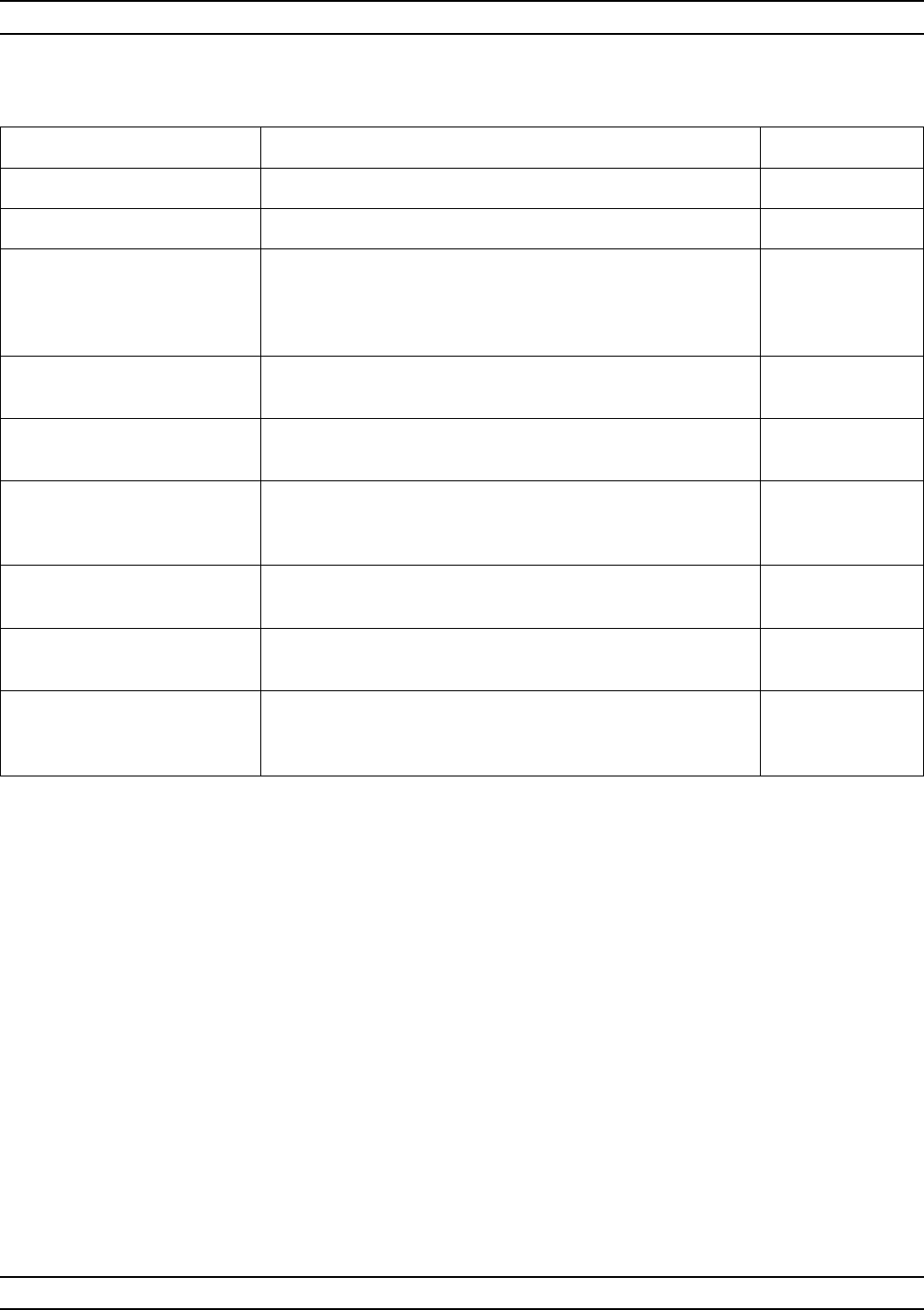
A-134 37XXXC OM
L ALPHABETICAL LISTING
MENU DESCRIPTION GPIB COMMAND
SINGLE LIMITS None
–POWER OUT— None
UPPER LIMIT ON (OFF)
XXX.XXX dBm Turns the Upper Limit line on or off for the active channel.
For your convenience, the arbitrarily set limit lines allow
you to delineate a go/no go line on your power display
beyond which the measured values are unacceptable.
UPL0; UPL1;
UPLX?
LOWER LIMIT ON(OFF)
XXX.XXX dBm Turns the Lower Limit line on or off for the active channel
on your power display. LOL0; LOL1;
LOLX?
READOUT LIMIT Calls menu LF5, which shows points where the current
S-parameter intercepts the lower limit. None
DISPLAY ON (OFF)
LIMITS Enables both previously set limit lines to appear for the
active
channel.
LON; LOF; LON?
TEST LIMITS Calls menu LTST, which provides choices for testing the
limits. None
SEGMENTED LIMITS Calls a menu in the LS series (LSX), which lets you set
segmented limit lines. None
PRESS <ENTER>
TO SELECT
OR TURN ON/OFF
Pressing the Enter key implements your menu selection. None
Menu L14, Set Limits—Power Out
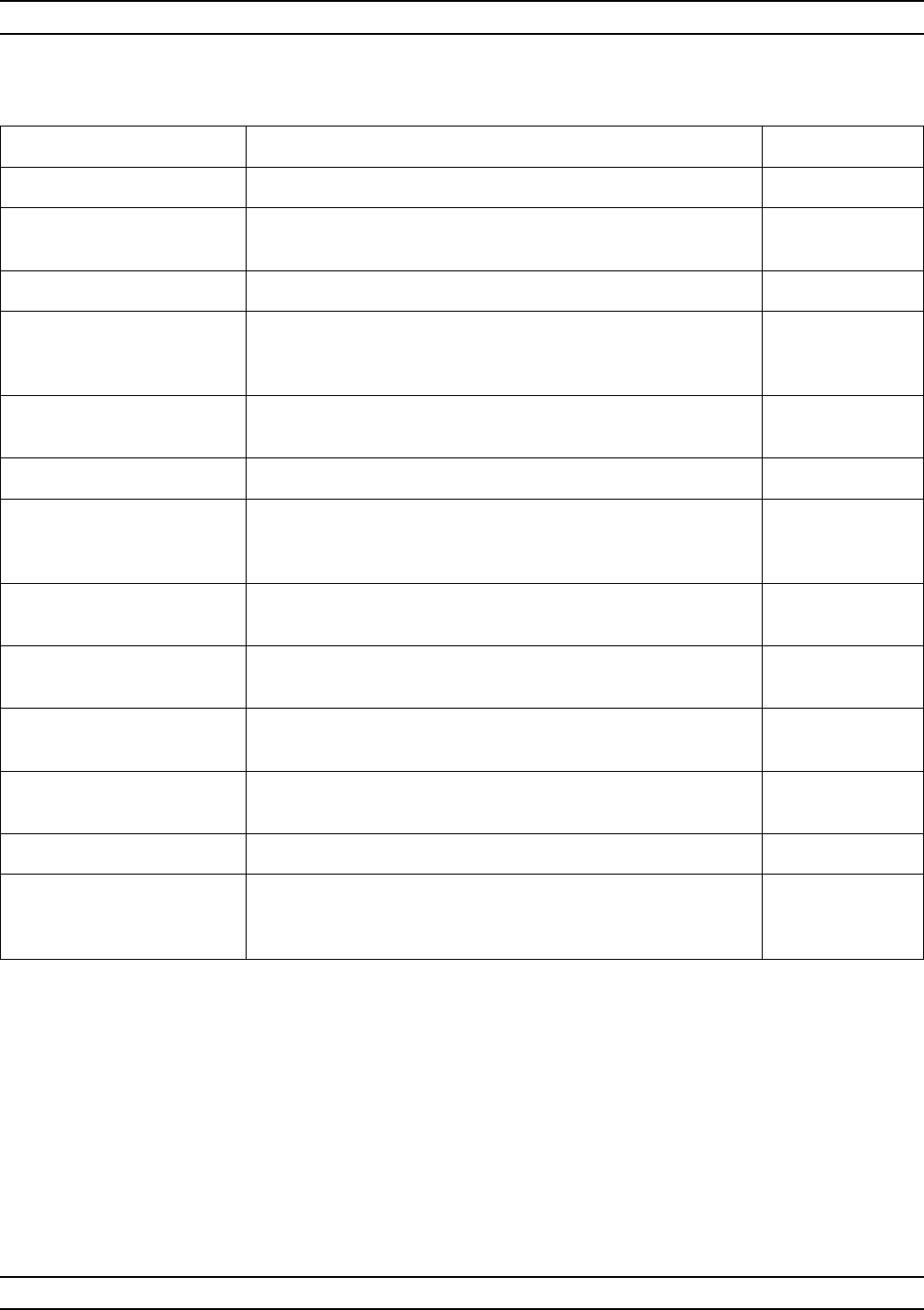
37XXXC OM A-135
ALPHABETICAL LISTING L
MENU DESCRIPTION GPIB COMMAND
DEFINE UPPER SEGS Define the upper limit segment. None
SEGMENT ON (OFF)
XEnter the segment number that you want to define, and turn
it on or off. US1 - US10;
USX?
START POSITION None
HORIZONTAL
XXX.XXXXXXXXX
GHz
Enter the start horizontal value in GHz, seconds, meter, or
points (domain dependent). STH; STH?
VERTICAL
XX.XXXXX dB Enter the start vertical value in dB, degrees, units, or
seconds (graph-type dependent). STV; STV?
STOP POSITION None
HORIZONTAL
XXX.XXXXXXXXX
GHz
Enter the stop horizontal value in GHz, seconds, meter, or
points (domain dependent). STH; STH?
VERTICAL
XX.XXXXX dB Enter the stop vertical value in dB, degrees, units, or
seconds (graph-type dependent). STV; STV?
BEGIN NEXT Turns the next segment on and sets its start and stop
postions to the previous segment’s stop position. BEGN
ATTACH NEXT Turns the next segment on and sets its start postions to the
previous segment’s stop position. ATTN
CLEAR SEGMENT Turns the current segment-to-define off and sets its start
equal to its stop. CAS
PREVIOUS MENU Returns to the previous menu. None
PRESS <ENTER>
TO SELECT
OR TURN ON/OFF
Pressing the Enter key implements your menu selection. None
Menu LD1, Define Upper Limit Segment
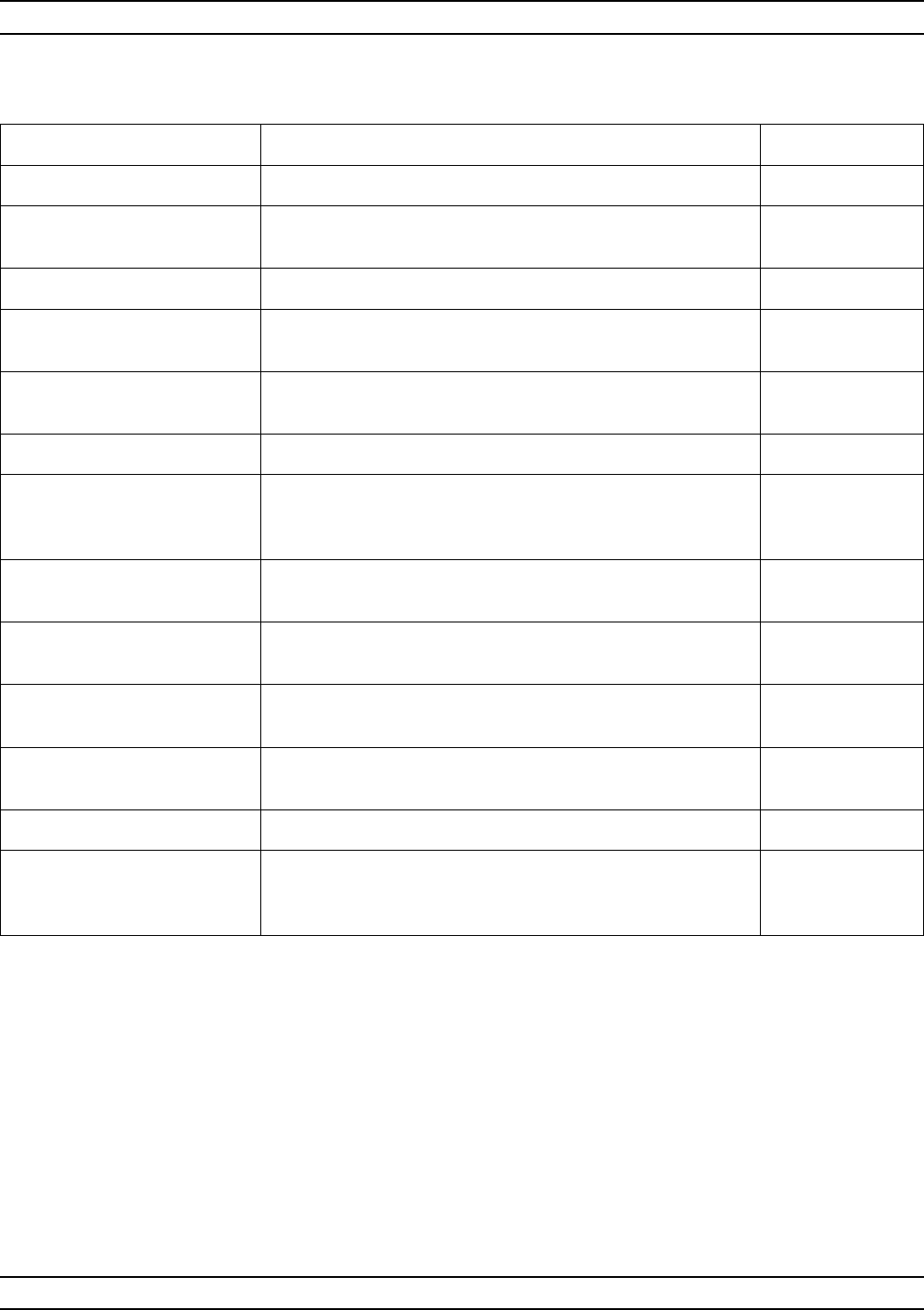
A-136 37XXXC OM
L ALPHABETICAL LISTING
MENU DESCRIPTION GPIB COMMAND
DEFINE LOWER SEGS Define the upper limit segment. None
SEGMENT ON (OFF)
XEnter the segment number that you want to define, and
turn it on or off. LS1 - LS10; LSX?
START POSITION None
HORIZONTAL
XXX.XXXXXXXXX GHz Enter the start horizontal value in GHz, seconds, meter, or
points (domain dependent). STH; STH?
VERTICAL
XX.XXXXX dB Enter the start vertical value in dB, degrees, units, or
seconds (graph-type dependent). STV; STV?
STOP POSITION None
HORIZONTAL
XXX.XXXXXXXXX
GHz
Enter the stop horizontal value in GHz, seconds, meter, or
points (domain dependent). STH; STH?
VERTICAL
XX.XXXXX dB Enter the stop vertical value in dB, degrees, units, or
seconds (graph-type dependent). STV; STV?
BEGIN NEXT Turns the next segment on and sets its start and stop
postions to the previous segment’s stop position.
ATTACH NEXT Turns the next segment on and sets its start postions to the
previous segment’s stop position.
CLEAR SEGMENT Turns the current segment-to-define off and sets its start
equal to its stop. CAS
PREVIOUS MENU Returns to the previous menu. None
PRESS <ENTER>
TO SELECT
OR TURN ON/OFF
Pressing the Enter key implements your menu selection. None
Menu LD2, Define Lower Limit Segmen
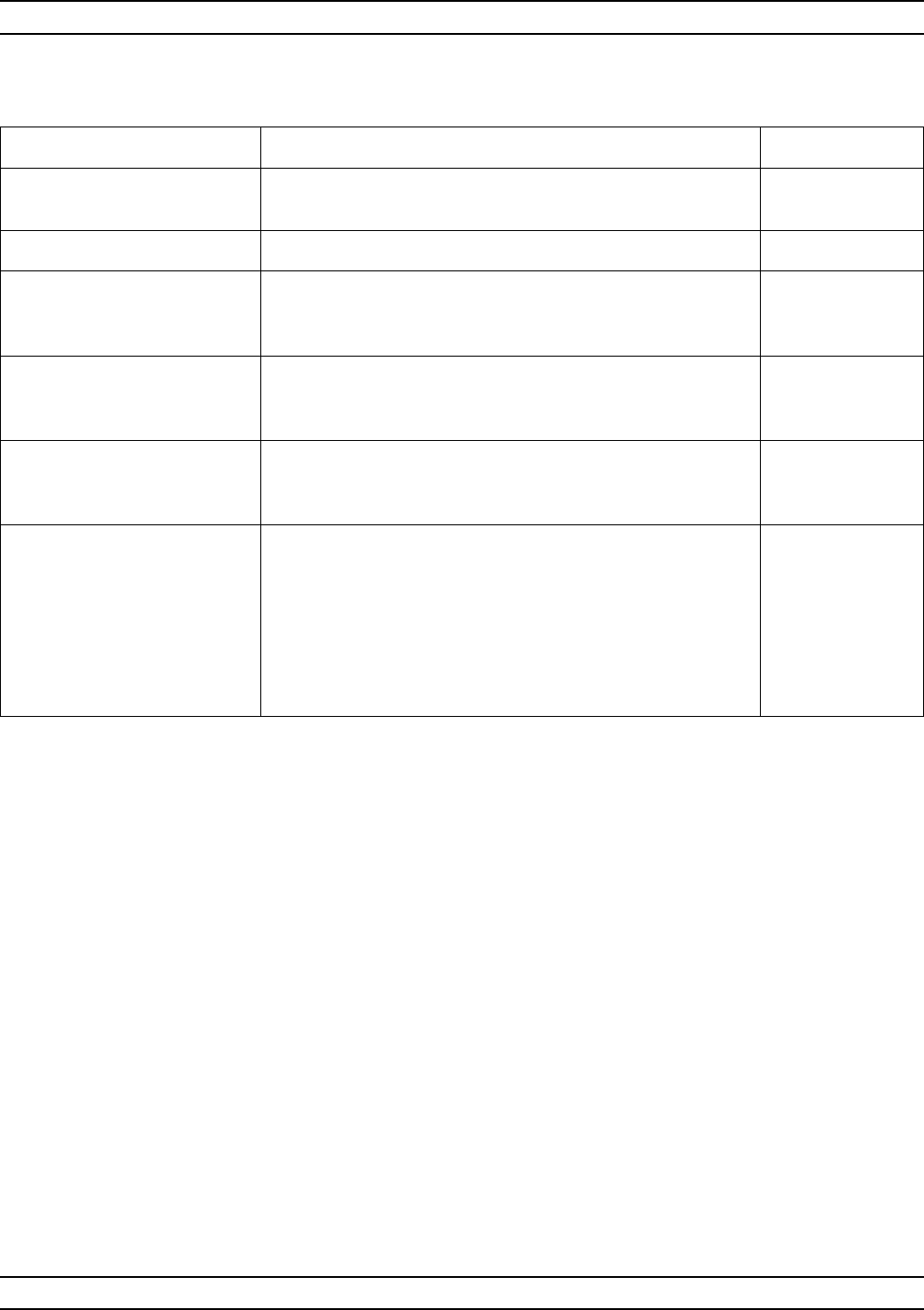
37XXXC OM A-137
ALPHABETICAL LISTING L
MENU DESCRIPTION GPIB COMMAND
READOUT LIMIT
INTERCEPTS None
–LOG MAG— None
UPPER LIMIT (REF)
XXX.XXX dB Lets you set the UPPER LIMIT (REF) limit line. Changing
this value also moves the lower limit line by the LIMIT
DIFFERENCE amount.
LUP; LUP?; LUP2;
LUP2?
LOWER LIMITdB
XXX.XXX dB Lets you set the LOWER LIMIT dB limit line. Changing this
value also changes the LIMIT DIFFERENCE amount
relative to the UPPER LIMIT (REF) value.
LLO; LLO?; LLO2;
LLO2?
LIMIT DIFFERENCE
(UPPER-LOWER)
XXX.XXX dB
Lets you set the LIMIT DIFFERENCE amount. Changing
this value also changes the lower limit value relative to the
UPPER LIMIT (REF) value.
LFD; LFD?; LFD2;
LFD2?
INTERCEPTS AT
LOWER LIMIT Displays at which frequencies the data intercepts the lower
limit. May be interpolated. None
XXX.XXXXXXXXX GHz
XXX.XXXXXXXXX GHz
XXX.XXXXXXXXX GHz
XXX.XXXXXXXXX GHz
XXX.XXXXXXXXX GHz
Menu LF1, Set Limit Frequencies—Log Mag
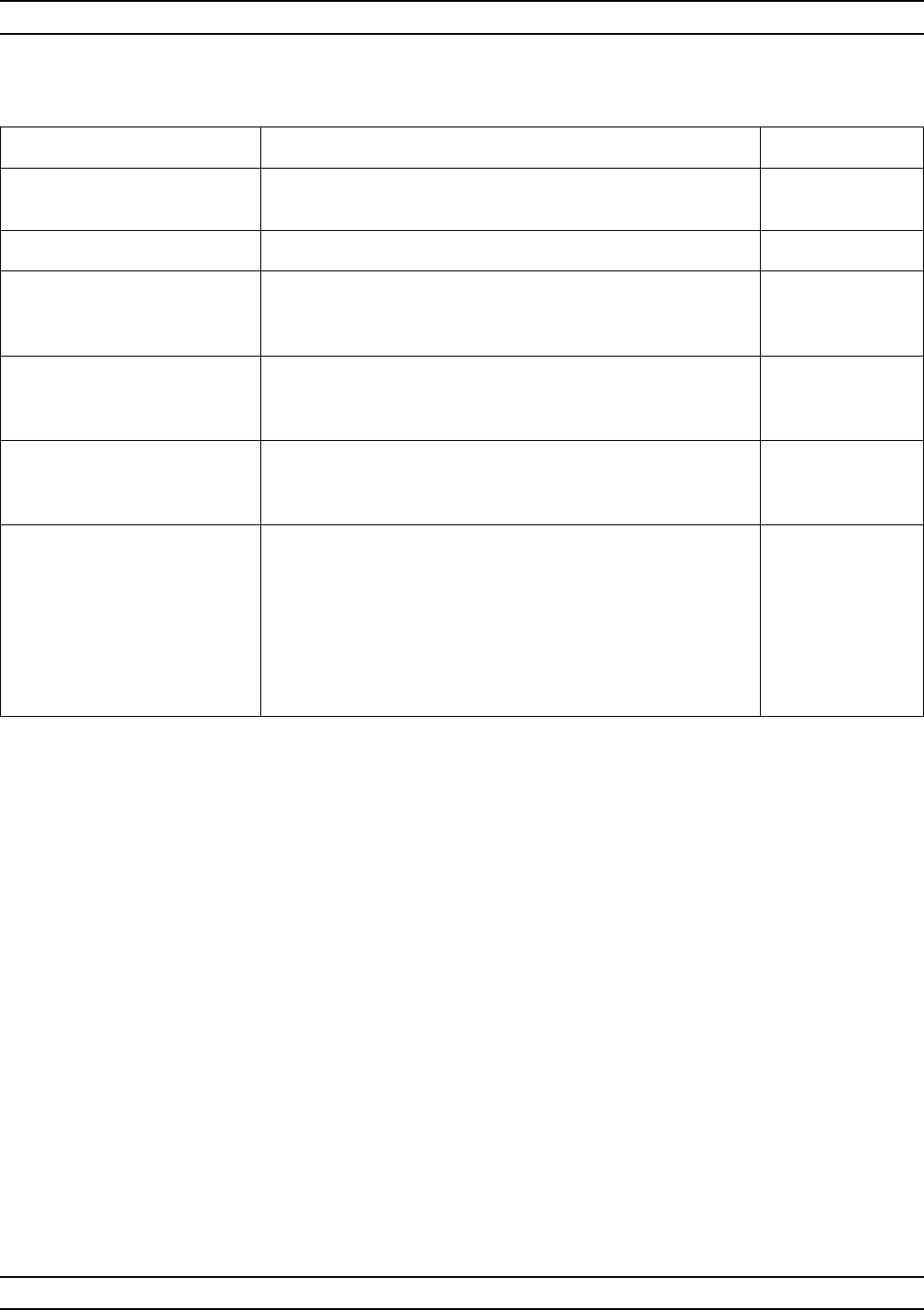
A-138 37XXXC OM
L ALPHABETICAL LISTING
MENU DESCRIPTION GPIB COMMAND
READOUT LIMIT
INTERCEPTS None
–PHASE— None
UPPER LIMIT (REF)
XXX.XXX °
Lets you set the UPPER LIMIT (REF) limit line. Changing
this value also moves the lower limit line by the LIMIT
DIFFERENCE amount.
LUP; LUP?; LUP2;
LUP2?
LOWER LIMITdB
XXX.XXX °
Lets you set the LOWER LIMIT dB limit line. Changing this
value also changes the LIMIT DIFFERENCE amount
relative to the UPPER LIMIT (REF) value.
LLO; LLO?; LLO2;
LLO2?
LIMIT DIFFERENCE
(UPPER-LOWER) Lets you set the LIMIT DIFFERENCE amount. Changing
this value also changes the lower limit value relative to the
UPPER LIMIT (REF) value.
LFD; LFD?; LFD2;
LFD2?
INTERCEPTS AT
LOWER LIMIT Displays at which frequencies the data intercepts the lower
limit. May be interpolated. None
XXX.XXXXXXXXX GHz
XXX.XXXXXXXXX GHz
XXX.XXXXXXXXX GHz
XXX.XXXXXXXXX GHz
XXX.XXXXXXXXX GHz
Menu LF2, Set Limit Frequencies—Phase
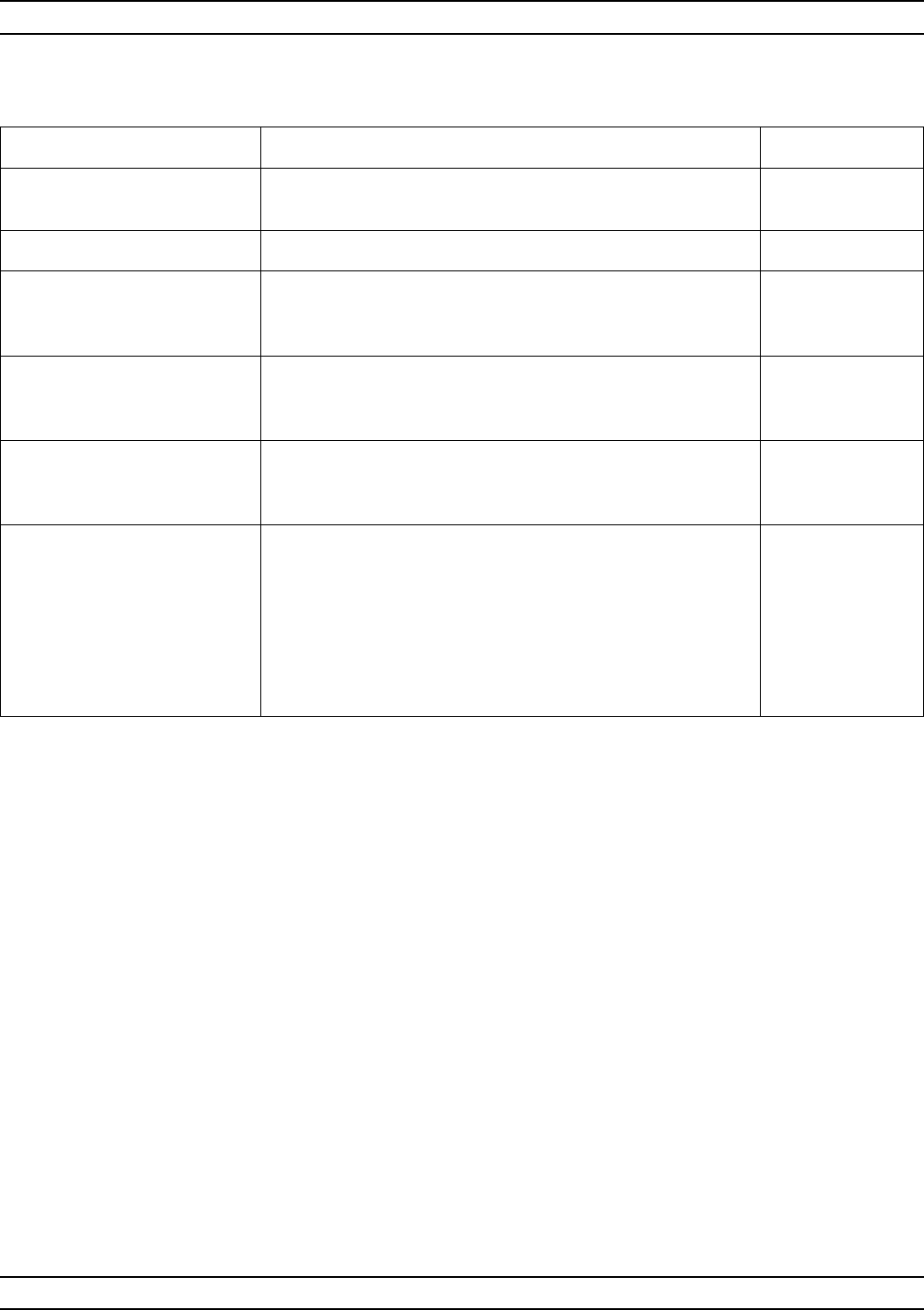
37XXXC OM A-139
ALPHABETICAL LISTING L
MENU DESCRIPTION GPIB COMMAND
READOUT LIMIT
INTERCEPTS None
–GROUP DELAY— None
UPPER LIMIT (REF)
XXX.XXX fs Lets you set the UPPER LIMIT (REF) limit line. Changing
this value also moves the lower limit line by the LIMIT
DIFFERENCE amount.
LUP; LUP?; LUP2;
LUP2?
LOWER LIMIT
XXX.XXX fs Lets you set the LOWER LIMIT dB limit line. Changing this
value also changes the LIMIT DIFFERENCE amount
relative to the UPPER LIMIT (REF) value.
LLO; LLO?; LLO2;
LLO2?
LIMIT DIFFERENCE
(UPPER-LOWER) Lets you set the LIMIT DIFFERENCE amount. Changing
this value also changes the lower limit value relative to the
UPPER LIMIT (REF) value.
LFD; LFD?; LFD2;
LFD2?
INTERCEPTS AT
LOWER LIMIT Displays at which frequencies the data intercepts the lower
limit. May be interpolated. None
XXX.XXXXXXXXX GHz
XXX.XXXXXXXXX GHz
XXX.XXXXXXXXX GHz
XXX.XXXXXXXXX GHz
XXX.XXXXXXXXX GHz
Menu LF3, Set Limit Frequencies—Group Delay
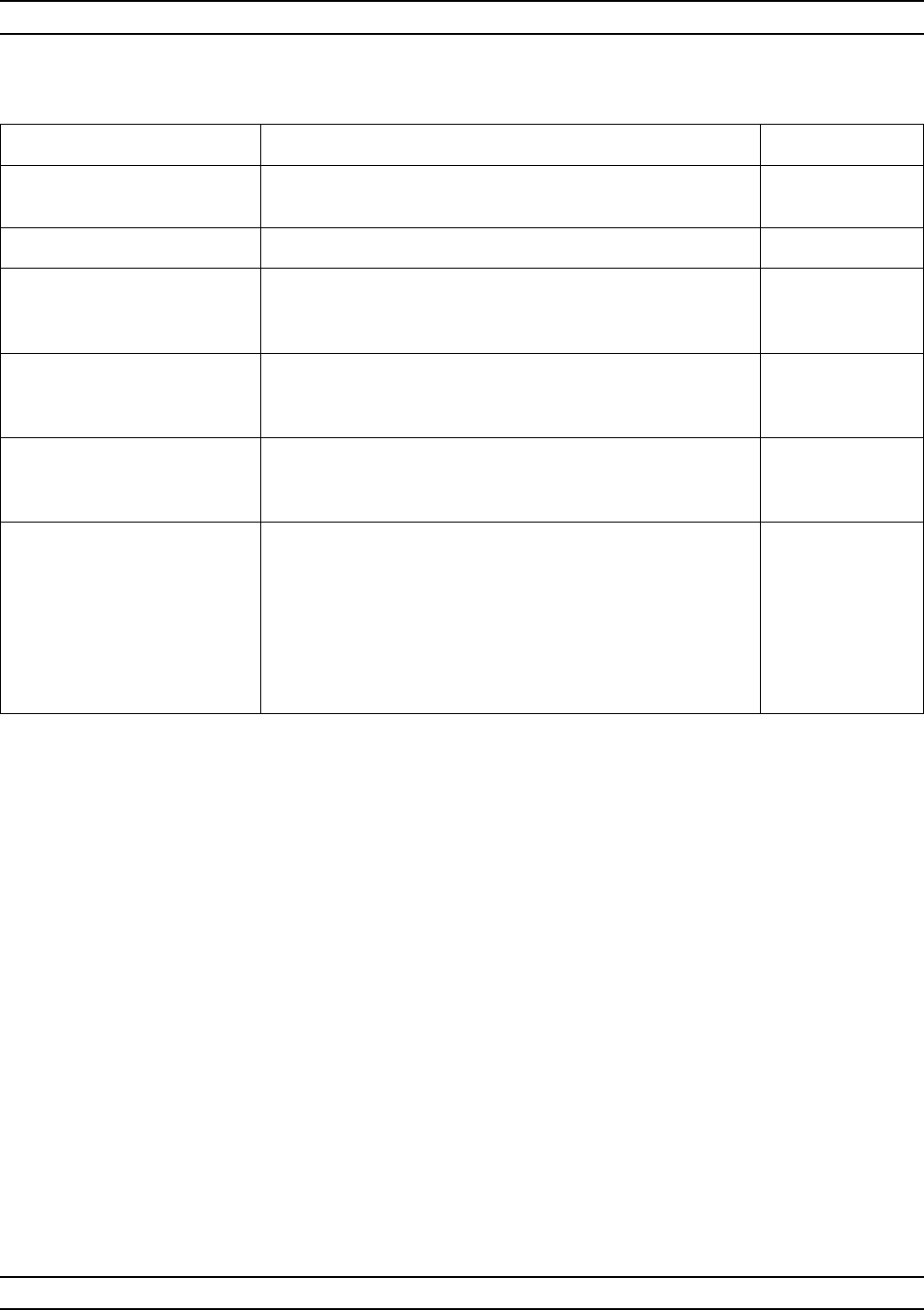
A-140 37XXXC OM
L ALPHABETICAL LISTING
MENU DESCRIPTION GPIB COMMAND
READOUT LIMIT
INTERCEPTS None
–LINEAR MAG— None
UPPER LIMIT (REF)
XXX.XXX pU Lets you set the UPPER LIMIT (REF) limit line. Changing
this value also moves the lower limit line by the LIMIT
DIFFERENCE amount.
LUP; LUP?; LUP2;
LUP2?
LOWER LIMIT
XXX.XXX pU Lets you set the LOWER LIMIT dB limit line. Changing this
value also changes the LIMIT DIFFERENCE amount
relative to the UPPER LIMIT (REF) value.
LLO; LLO?; LLO2;
LLO2?
LIMIT DIFFERENCE
(UPPER-LOWER)
XXX.XXX pU
Lets you set the LIMIT DIFFERENCE amount. Changing
this value also changes the lower limit value relative to the
UPPER LIMIT (REF) value.
LFD; LFD?; LFD2;
LFD2?
INTERCEPTS AT
LOWER LIMIT Displays at which frequencies the data intercepts the lower
limit. May be interpolated. None
XXX.XXXXXXXXX GHz
XXX.XXXXXXXXX GHz
XXX.XXXXXXXXX GHz
XXX.XXXXXXXXX GHz
XXX.XXXXXXXXX GHz
Menu LF4, Set Limit Frequencies—Linear Mag
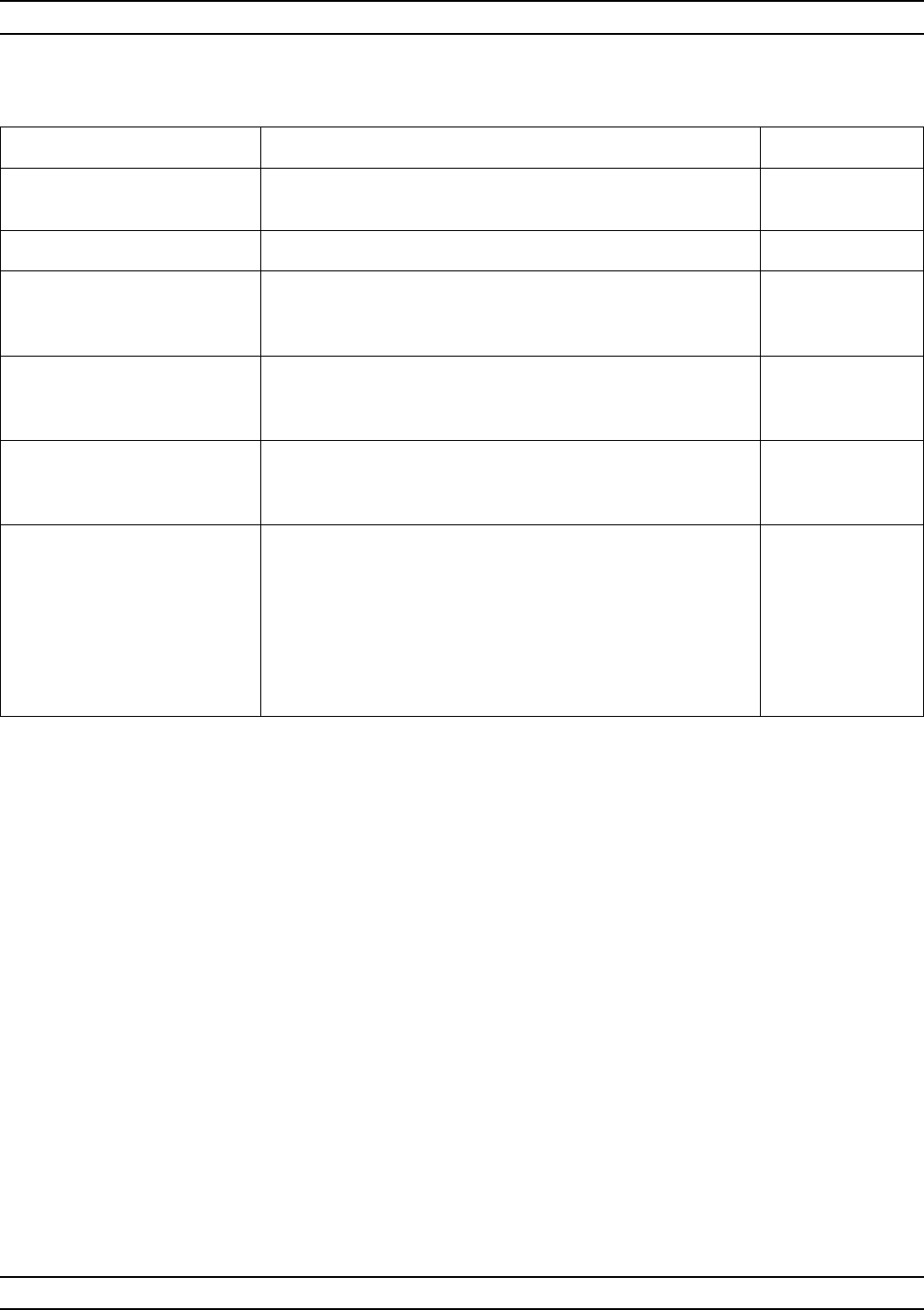
37XXXC OM A-141
ALPHABETICAL LISTING L
MENU DESCRIPTION GPIB COMMAND
SET LIMIT
FREQUENCIES None
–SWR— None
UPPER LIMIT (REF)
XXX.XXX pU Lets you set the UPPER LIMIT (REF) limit line. Changing
this value also moves the lower limit line by the LIMIT
DIFFERENCE amount.
LUP; LUP?; LUP2;
LUP2?
LOWER LIMIT
XXX.XXX pU Lets you set the LOWER LIMIT dB limit line. Changing this
value also changes the LIMIT DIFFERENCE amount
relative to the UPPER LIMIT (REF) value.
LLO; LLO?; LLO2;
LLO2?
LIMIT DIFFERENCE
(UPPER-LOWER)
XXX.XXX pU
Lets you set the LIMIT DIFFERENCE amount. Changing
this value also changes the lower limit value relative to the
UPPER LIMIT (REF) value.
LFD; LFD?; LFD2;
LFD2?
INTERCEPTS AT
LOWER LIMIT Displays at which frequencies the data intercepts the lower
limit. May be interpolated. None
XXX.XXXXXXXXX GHz
XXX.XXXXXXXXX GHz
XXX.XXXXXXXXX GHz
XXX.XXXXXXXXX GHz
XXX.XXXXXXXXX GHz
Menu LF5, Set Limit Frequencies—SWR
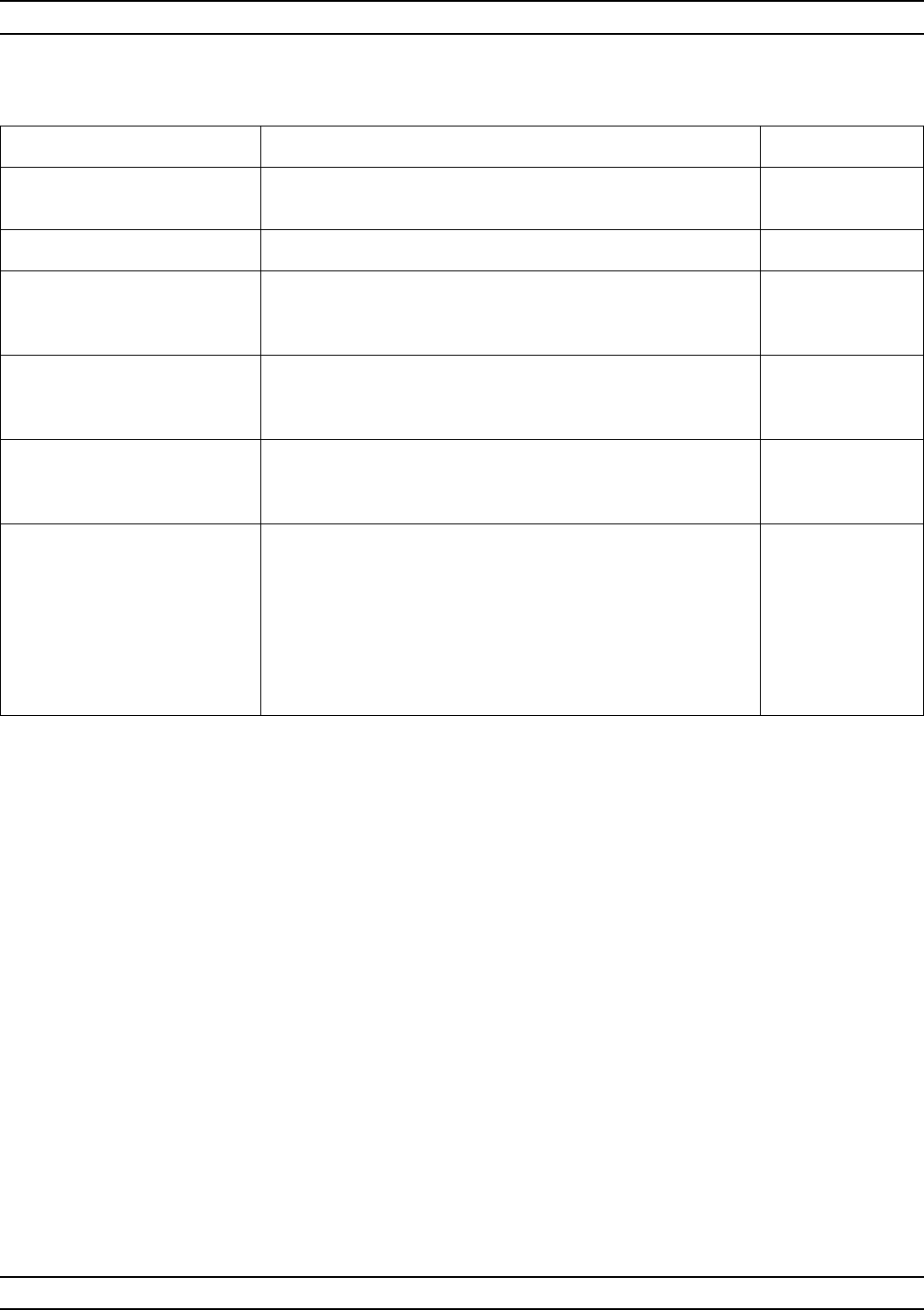
A-142 37XXXC OM
L ALPHABETICAL LISTING
MENU DESCRIPTION GPIB COMMAND
SET LIMIT
FREQUENCIES None
–REAL— None
UPPER LIMIT (REF)
XXX.XXX pU Lets you set the UPPER LIMIT (REF) limit line. Changing
this value also moves the lower limit line by the LIMIT
DIFFERENCE amount.
LUP; LUP?; LUP2;
LUP2?
LOWER LIMIT
XXX.XXX pU Lets you set the LOWER LIMIT dB limit line. Changing this
value also changes the LIMIT DIFFERENCE amount
relative to the UPPER LIMIT (REF) value.
LLO; LLO?; LLO2;
LLO2?
LIMIT DIFFERENCE
(UPPER-LOWER) Lets you set the LIMIT DIFFERENCE amount. Changing
this value also changes the lower limit value relative to the
UPPER LIMIT (REF) value.
LFD; LFD?; LFD2;
LFD2?
INTERCEPTS AT
LOWER LIMIT Displays at which frequencies the data intercepts the lower
limit. May be interpolated. None
XXX.XXXXXXXXX GHz
XXX.XXXXXXXXX GHz
XXX.XXXXXXXXX GHz
XXX.XXXXXXXXX GHz
XXX.XXXXXXXXX GHz
Menu LF6, Set Limit Frequencies—Real
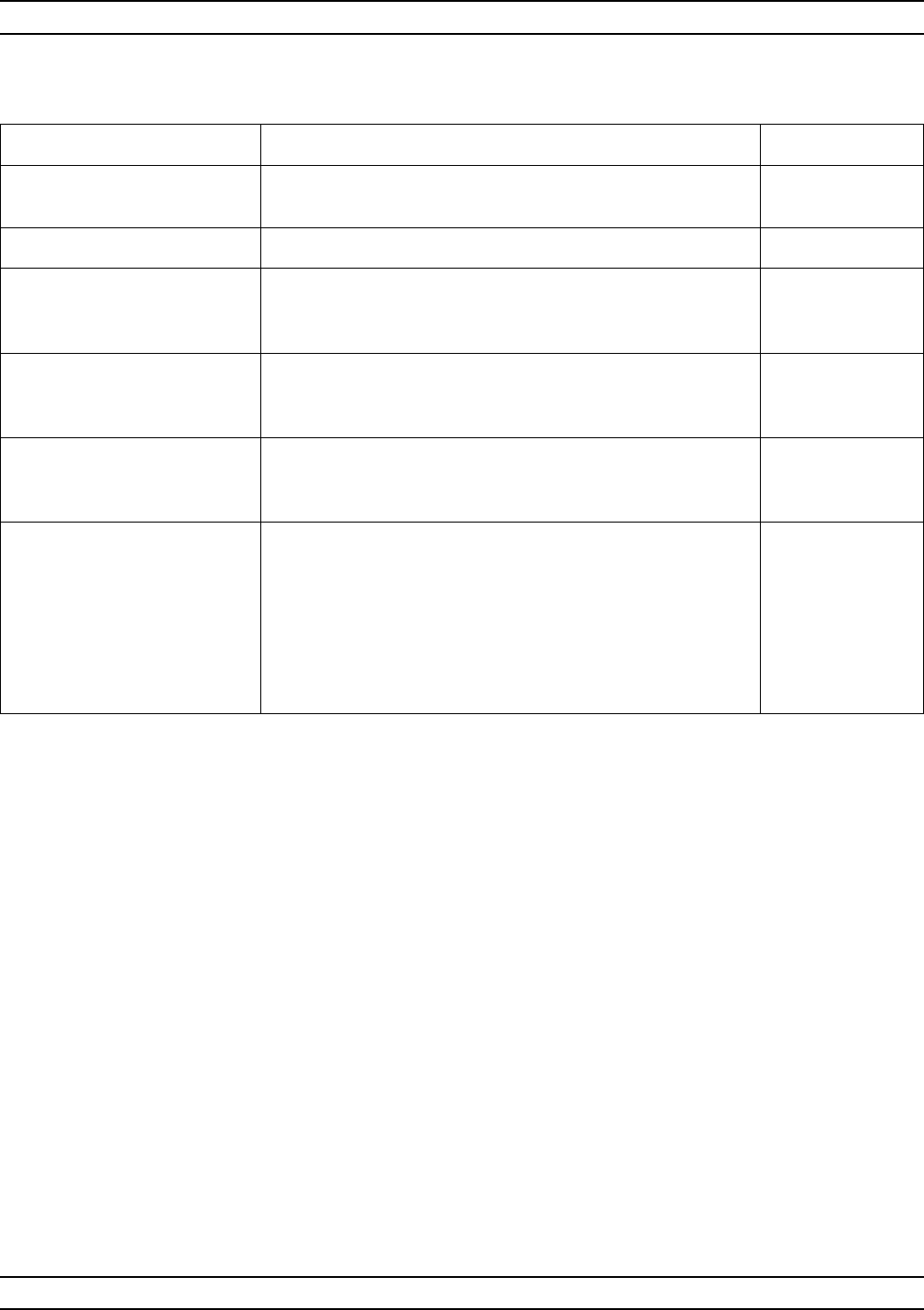
37XXXC OM A-143
ALPHABETICAL LISTING L
MENU DESCRIPTION GPIB COMMAND
SET LIMIT
FREQUENCIES None
–IMAGINARY— None
UPPER LIMIT (REF)
XXX.XXX pU Lets you set the UPPER LIMIT (REF) limit line. Changing
this value also moves the lower limit line by the LIMIT
DIFFERENCE amount.
LUP; LUP?; LUP2;
LUP2?
LOWER LIMIT
XXX.XXX pU Lets you set the LOWER LIMIT dB limit line. Changing this
value also changes the LIMIT DIFFERENCE amount
relative to the UPPER LIMIT (REF) value.
LLO; LLO?; LLO2;
LLO2?
LIMIT DIFFERENCE
(UPPER-LOWER) Lets you set the LIMIT DIFFERENCE amount. Changing
this value also changes the lower limit value relative to the
UPPER LIMIT (REF) value.
LFD; LFD?; LFD2;
LFD2?
INTERCEPTS AT
LOWER LIMIT Displays at which frequencies the data intercepts the lower
limit. May be interpolated. None
XXX.XXXXXXXXX GHz
XXX.XXXXXXXXX GHz
XXX.XXXXXXXXX GHz
XXX.XXXXXXXXX GHz
XXX.XXXXXXXXX GHz
Menu LF7, Set Limit Frequencies—Imaginary
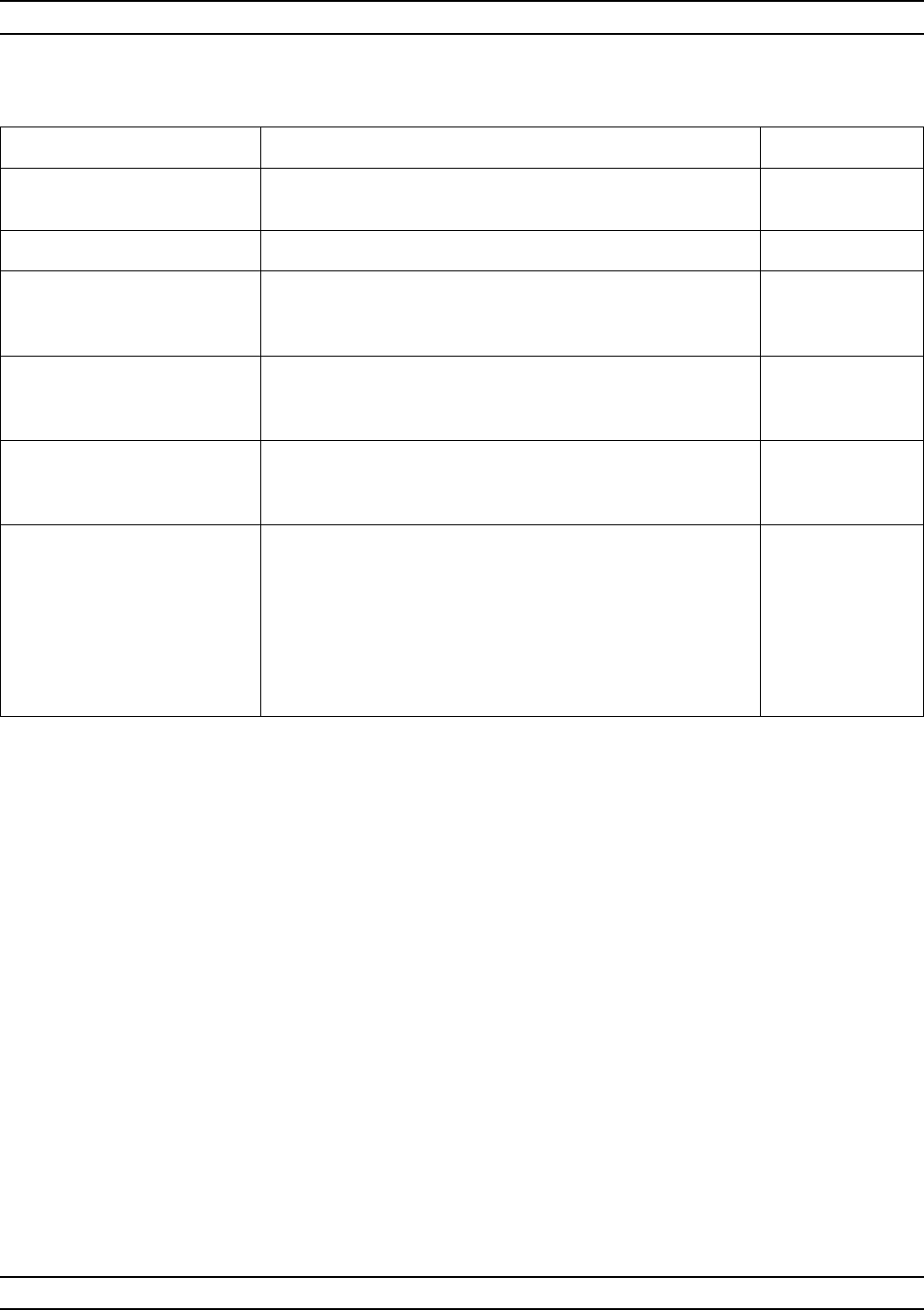
A-144 37XXXC OM
L ALPHABETICAL LISTING
MENU DESCRIPTION GPIB COMMAND
READOUT LIMIT
INTERCEPTS None
–POWER OUT— None
UPPER LIMIT (REF)
XXX.XXX dBm Lets you set the UPPER LIMIT (REF) limit line. Changing
this value also moves the lower limit line by the LIMIT
DIFFERENCE amount.
LUP; LUP?; LUP2;
LUP2?
LOWER LIMIT
XXX.XXX dBm Lets you set the LOWER LIMIT dB limit line. Changing this
value also changes the LIMIT DIFFERENCE amount
relative to the UPPER LIMIT (REF) value.
LLO; LLO?; LLO2;
LLO2?
LIMIT DIFFERENCE
(UPPER-LOWER)
XXX.XXX dBm
Lets you set the LIMIT DIFFERENCE amount. Changing
this value also changes the lower limit value relative to the
UPPER LIMIT (REF) value.
LFD; LFD?; LFD2;
LFD2?
INTERCEPTS AT
LOWER LIMIT Displays at which frequencies the data intercepts the lower
limit. May be interpolated. None
XXX.XXXXXXXXX GHz
XXX.XXXXXXXXX GHz
XXX.XXXXXXXXX GHz
XXX.XXXXXXXXX GHz
XXX.XXXXXXXXX GHz
Menu LF8, Set Limit Frequencies—Power Out
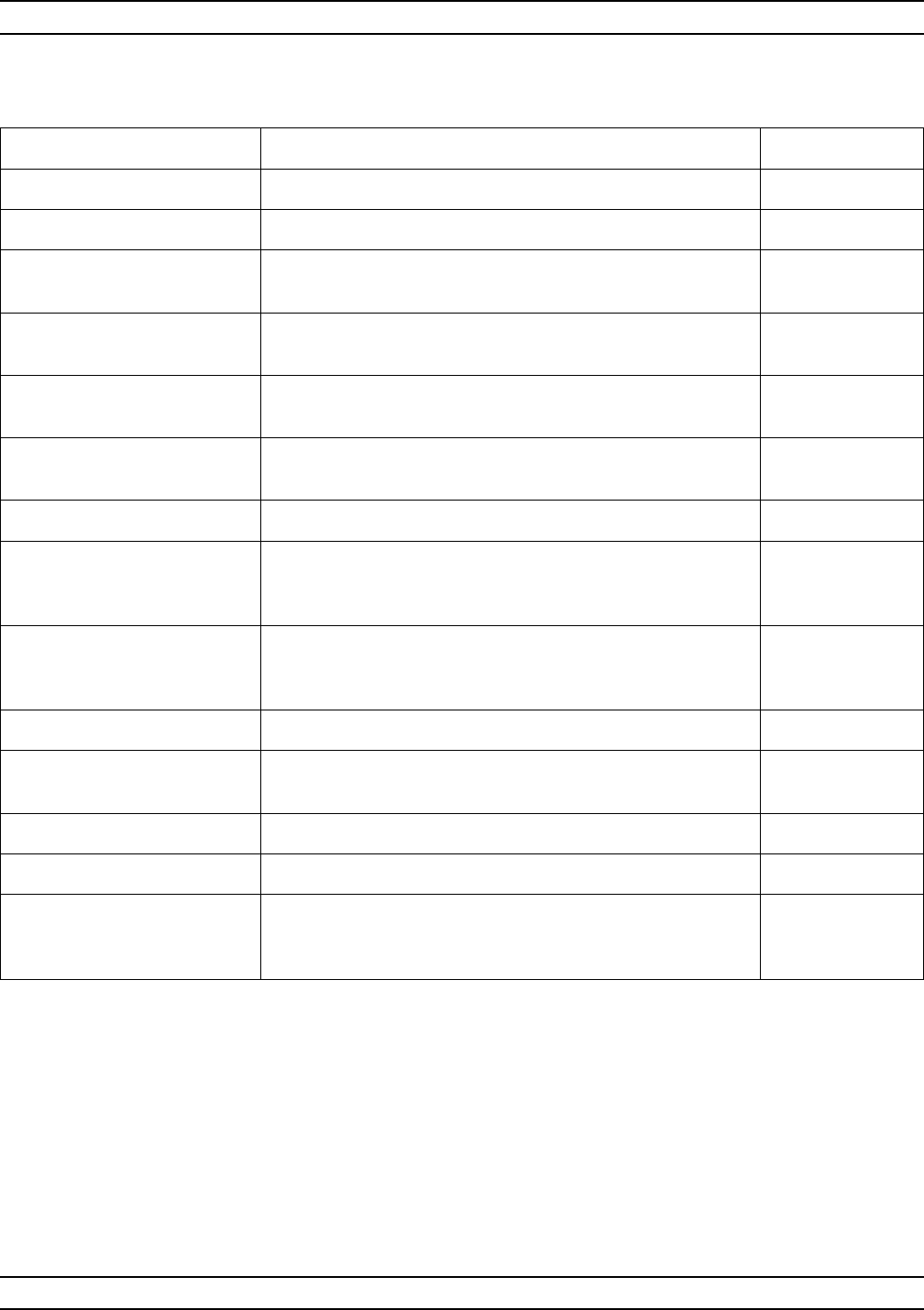
37XXXC OM A-145
ALPHABETICAL LISTING L
MENU DESCRIPTION GPIB COMMAND
SEGMENTED LIMITS None
–XXXXXXX— Displays the currently active channel’s graph type. None
UPPER LIMIT ON(OFF) Turns the Upper Limit line on or off for the active channel. SLU1; SLU0;
SLUX?
DEFINE UPPER Calls menu LD1, which lets you define an upper segment
value. None
LOWER LIMIT ON(OFF) Turns the Lower Limit line on or off for the active channel. SLL1; SLL0;
SLLX?
DEFINE LOWER Calls menu LD2, which lets you define a lower segment
value. None
SEGMENTED OFFSETS None
HORIZONTAL
XXXX GHz Enter the horizontal offset to be applied to all of the
channel’s segmented limits, in GHz, seconds, meters, or
points (domain dependent).
SLH; SLH?
VERTICAL
XXXX dB Enter the vertical offset to be applied to all of the channel’s
segmented limits, in dB, degrees, units, or seconds
(graph-type dependent).
SLV; SLV?
CLEAR ALL Clears all segments. SLC
DISPLAY ON (OFF)
LIMITS Toggle between on and off to display the active channel’s
limits. LON; LOF; LON?
TEST LIMITS Calls menu LTST, which lets test for limits. None
SINGLE LIMITS Returns to the appropriate single limits menu. None
PRESS <ENTER>
TO SELECT
OR TURN ON/OFF
Pressing the Enter key implements your menu selection. None
Menu LSX, Segmented Limits
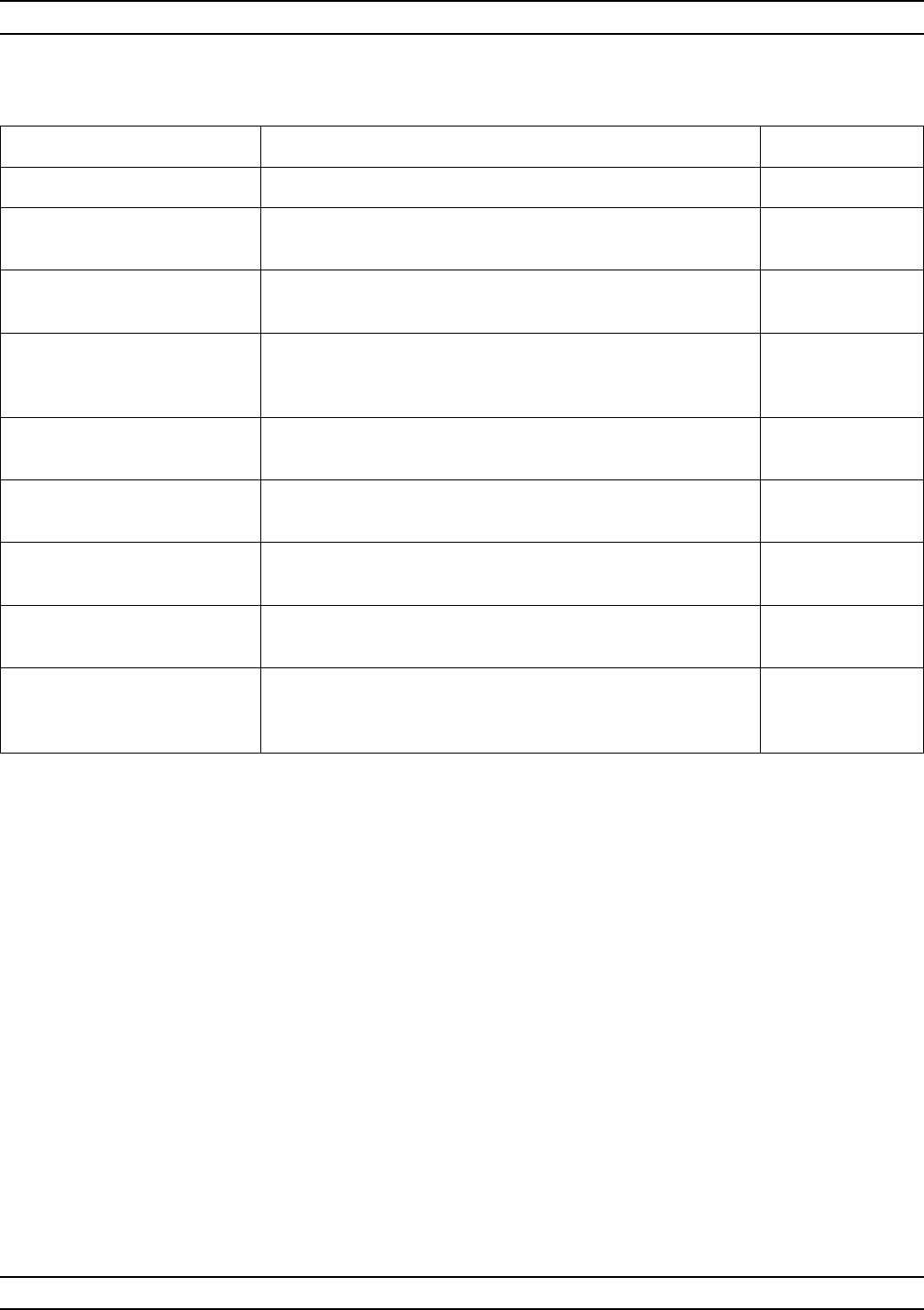
A-146 37XXXC OM
L ALPHABETICAL LISTING
MENU DESCRIPTION GPIB COMMAND
TEST LIMITS None
LIMIT ON (OFF)
TESTING Turns limit testing for all displayed channels on or off. LON; LOF; LON?
BEEP FOR ON (OFF)
TEST FAILURE Turns beeper on or off when limit test fails. LB0; LB1; LBX?
LIMIT TEST TTL
FAIL CONDITION
TTL LOW/TTL HIGH
Selects between a TTL high or TTL low to indicate that the
limit test has failed. LVH; LVL; LVX?
CHANNEL 1 TEST
PASS (FAIL) Displays result of Channel 1 limit test.
CHANNEL 2 TEST
PASS (FAIL) Displays result of Channel 2 limit test.
CHANNEL 3 TEST
PASS (FAIL) Displays result of Channel 3 limit test.
CHANNEL 4 TEST
PASS (FAIL) Displays result of Channel 4 limit test.
PRESS <ENTER>
TO SELECT
OR TURN ON/OFF
Pressing the Enter key implements your menu selection. None
Menu LTST, Test Limits
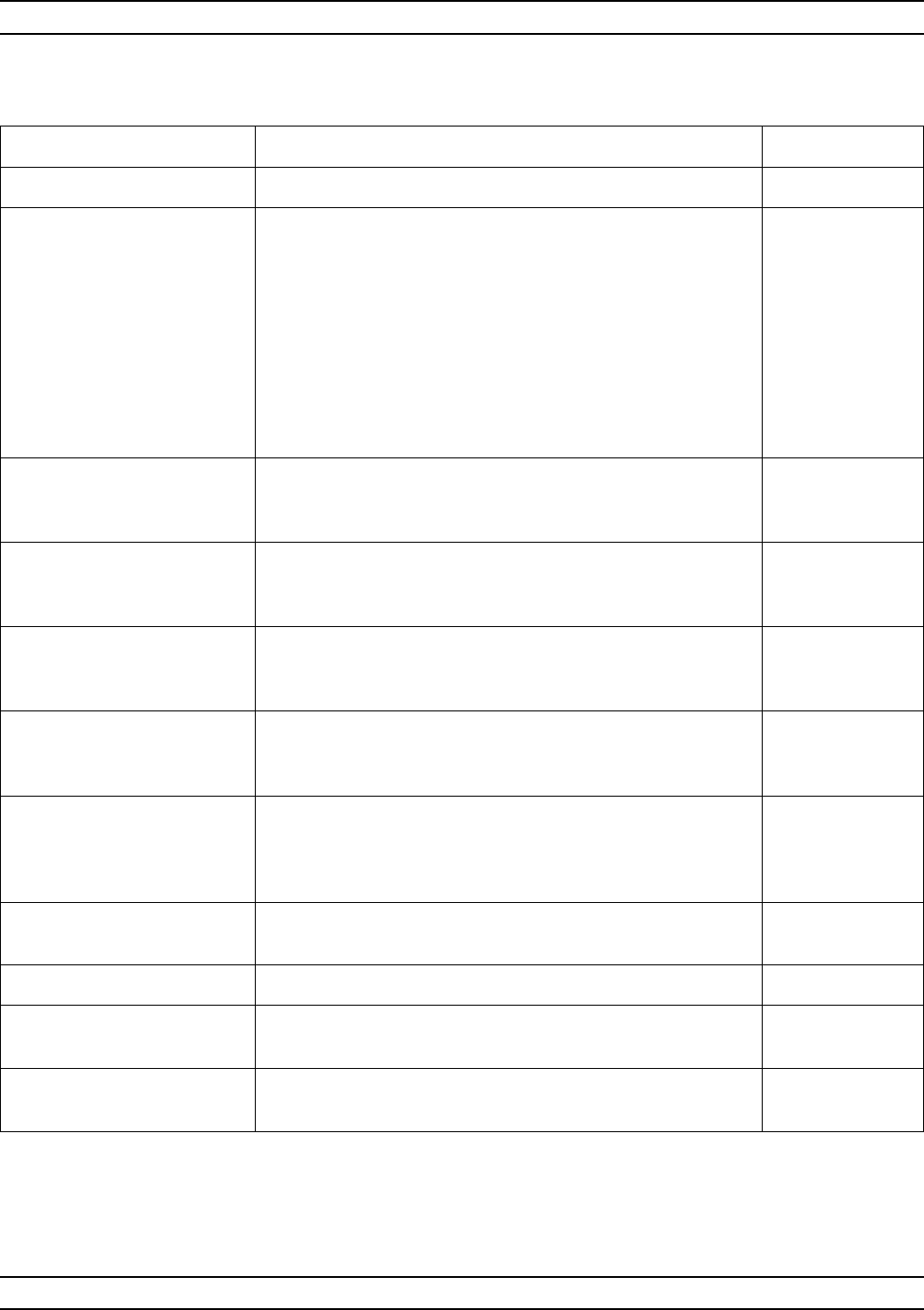
37XXXC OM A-147
ALPHABETICAL LISTING M
MENU DESCRIPTION GPIB COMMAND
SET MARKERS None
MARKER 1 ON (OFF)
XXX.XXXXXXXXX GHz Turns Marker 1 on or off (activates or deactivates). When
on (active), the frequency, time, or distance may be set
using the keypad or
rotary knob.
NOTE: In this text, markers are referred to as being active
and as being selected. Any marker that has been turned on
and assigned a frequency is considered to be selected. The
marker to which the cursor presently points is considered to
be active. The active marker is the only one for which you
can change the frequency.
MR1; MR1?; MK1
MK1?; OM1; MO1
MARKER 2 DREF ON (OFF)
XXX.XXXXXXXXX GHz Turns Marker 2 on or off (activates or deactivates). When
on (active), the frequency, time, or distance may be set
using the keypad or rotary knob.
MR2; MR2?; MK2
MK2?; OM2; MO2
MARKER 3 ON (OFF)
XXX.XXXXXXXXX GHz Turns Marker 3 on or off (activates or deactivates). When
on (active), the frequency, time, or distance may be set
using the keypad or rotary knob.
MR31; MR3?;
MK3 MK3?; OM3;
MO3
MARKER 4 ON (OFF)
XXX.XXXXXXXXX GHz Turns Marker 4 on or off (activates or deactivates). When
on (active), the frequency, time, or distance may be set
using the keypad or rotary knob.
MR4; MR4?; MK4
MK4?; OM4; MO4
MARKER 5 ON (OFF)
XXX.XXXXXXXXX GHz Turns Marker 5 on or off (activates or deactivates). When
on (active), the frequency, time, or distance may be set
using the keypad or rotary knob.
MR5; MR5?; MK5
MK5?; OM5; MO5
MARKER 6 ON (OFF)
XXX.XXXXXXX GHz Turns Marker 6 on or off (activates or deactivates). When
on (active), the frequency, time, or distance may be set
using the keypad or
rotary knob.
MR6; MR6?; MK6
MK6?; OM6; MO6
DISPLAY ON (OFF)
MARKERS Displays selected markers. MON; MON?;
MOF
DREF MODE ON (OFF) Selects the DREF Mode to be on or off. DRF; DRO; DRO?
SELECT
DREF MARKER Calls menu M2, which lets you select the DREF Marker. None
READOUT MARKER
FUNCTIONS Calls menu M9, which lets you select readout marker
parameters. None
Menu M1, Set Markers

A-148 37XXXC OM
M ALPHABETICAL LISTING
MENU DESCRIPTION GPIB COMMAND
SELECT
DREF MARKER None
MARKER 1
XXX.XXXXXXXXX GHz Marker 1 only appears if it has been activated in menu M1.
Placing the cursor on Marker 1 and pressing the Enter key
here selects it as the DREF marker. The DREF marker is
the one from which the other active markers are compared
and their difference frequency measured and displayed in
menu M3. The marker frequency may be set using the
keypad or rotary knob.
DR1; DRX?
MARKER 3
XXX.XXXXXXXXX GHz Same as above, but for Marker 3. This display is
representative if Markers 1, 3, and 4 are selected. Markers
2, 5, and 6 would also show, if they had been selected.
DR3; DRX?
MARKER 4
XXX.XXXXXXXXXGHz Same as above, but for Marker 4 DR4; DRX?
PRESS <ENTER>
TO SELECT Pressing the Enter key implements your menu selection. None
Menu M2, Select DREF Marker
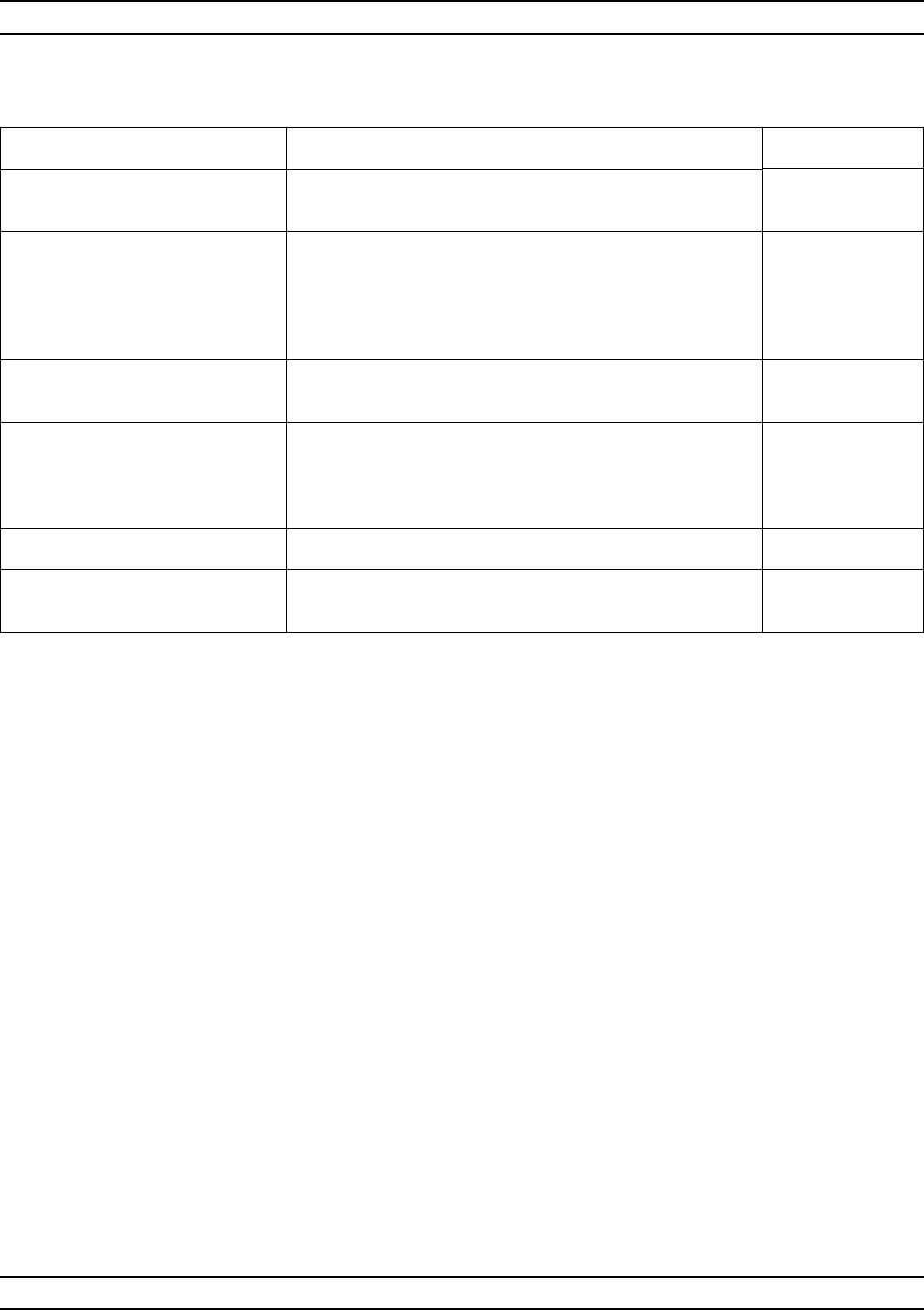
37XXXC OM A-149
ALPHABETICAL LISTING M
MENU DESCRIPTION GPIB COMMAND
SELECT
READOUT MARKER None
MARKER 1
XXX.XXXXXXXXX GHz Displays the frequency and S-Parameter value(s) of
Marker 1 on all displayed graphs and Smith Charts. The
frequency of Marker 1 also displays here. If Marker 1
was activated in menu M2 as the REF marker, REF
appears as shown for Marker M5 below.
DR1; DRX?
MARKER 2
XXX.XXXXXXXXX GHz Same as above, but for Marker 2. DR2; DRX?
MARKER 5
XXX.XXXXXXXXX GHz Same as above, but for Marker 5 This display is
representative if Markers 1, 2, and 5 are selected.
Markers 3, 4, and 6 would also show, if they had been
selected.
DR5; DRX?
DREF MODE IS ON (OFF) Indicates the status of the DREF mode. DRO; DRO?
PRESS <ENTER>
TO SELECT Pressing the Enter key implements your menu selection. None
Menu M3, Select Readout Marker
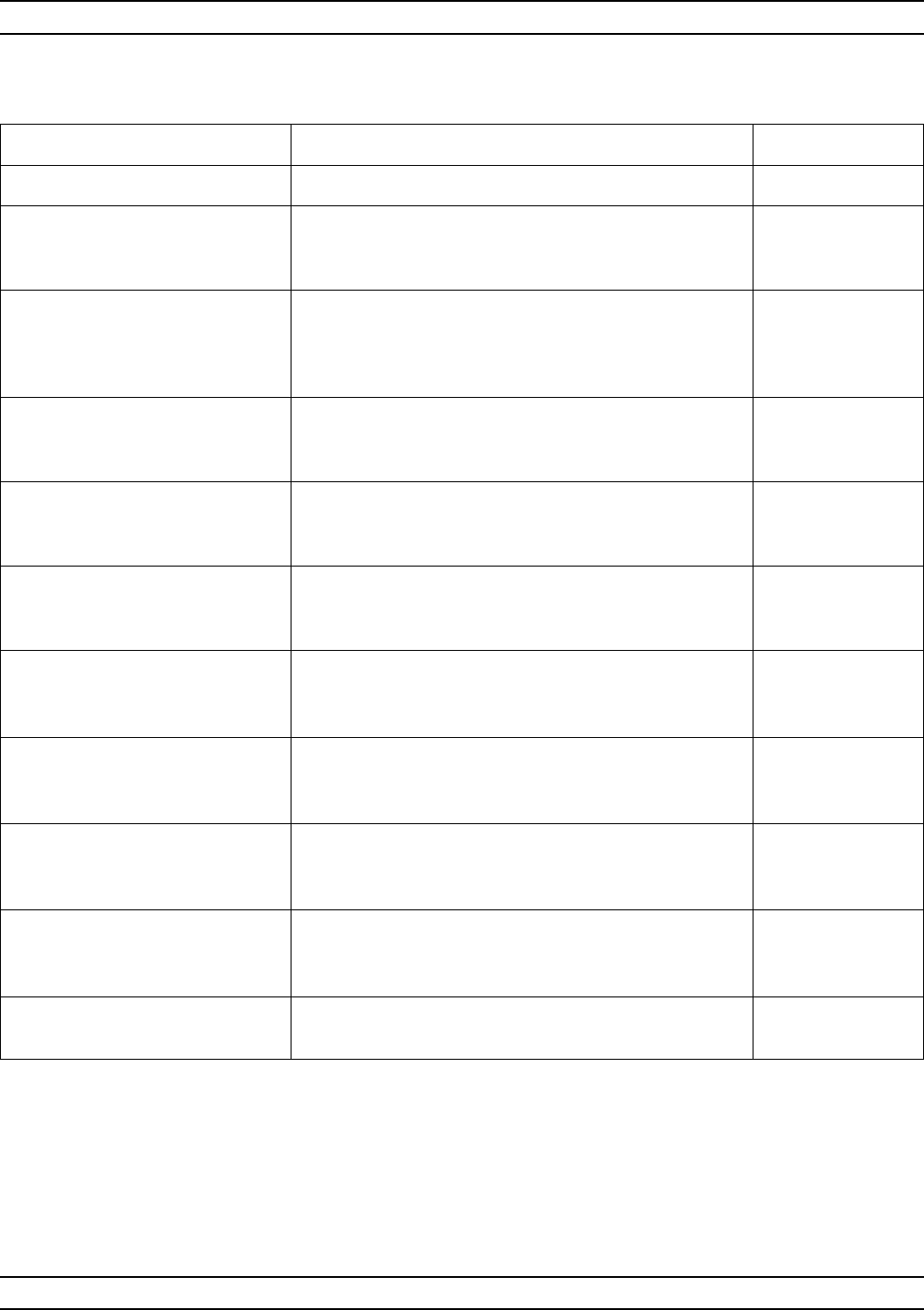
A-150 37XXXC OM
M ALPHABETICAL LISTING
MENU DESCRIPTION GPIB COMMAND
CH1—S11,USER Selects channel for readout None
+XXX.XXXX mm REF
+XXX.XXX dB OFFSET
+XXX.XX °OFFSET
The constant offset for the channel is displayed. None
MARKER X
XXX.XXXXXXXXX GHz
XX.XXX dB
XXX.XXX °
The selected marker—that is, the one to which the
cursor points in menu M1—and its frequency, time, or
distance display here. This could be any one of the six
available markers: Marker 1 through Marker 6.
MR1; MR1? MK1;
MK1? OM1
MARKER TO MAX Causes the active marker to go to the frequency with
the greatest
S-Parameter value on the active channel.
MMX
MARKER TO MIN Causes the selected marker to go to the frequency
with the smallest
S-Parameter value on the active channel.
MMN
2 XXX.XXXXXXXXX GHz
XX.XXX dB
XXX.XXX °
Displays the frequency, magnitude, and phase of the
active
S-Parameter at marker 2, if the marker is enabled.
MR2; MR2? MK2;
MK2? OM2
3 XXX.XXXXXXXXX GHz
XX.XXX dB
XXX.XXX °
Displays the frequency, magnitude, and phase of the
active
S-Parameter at marker 3, if the marker is enabled.
MR3; MR3? MK3;
MK3? OM3
4 XXX.XXXXXXXXX GHz
XX.XXX dB
XXX.XXX °
Displays the frequency, magnitude, and phase of the
active
S-Parameter at marker 4, if the marker is enabled.
MR4; MR4? MK4;
MK4? OM4
5 XXX.XXXXXXXXX GHz
XX.XXX dB
XXX.XXX °
Displays the frequency, magnitude, and phase of the
active
S-Parameter at marker 5, if the marker is enabled.
MR5; MR5? MK5;
MK5? OM5
6 XXX.XXXXXXXXX GHz
XX.XXX dB
XXX.XXX °
Displays the frequency, magnitude, and phase of the
active
S-Parameter at marker 6, if the marker is enabled.
MR6; MR6? MK6;
MK6? OM6
MARKER READOUT
FUNCTIONS Calls menu M9, which lets you select readout marker
parameters. None
Menu M4, Readout Marker
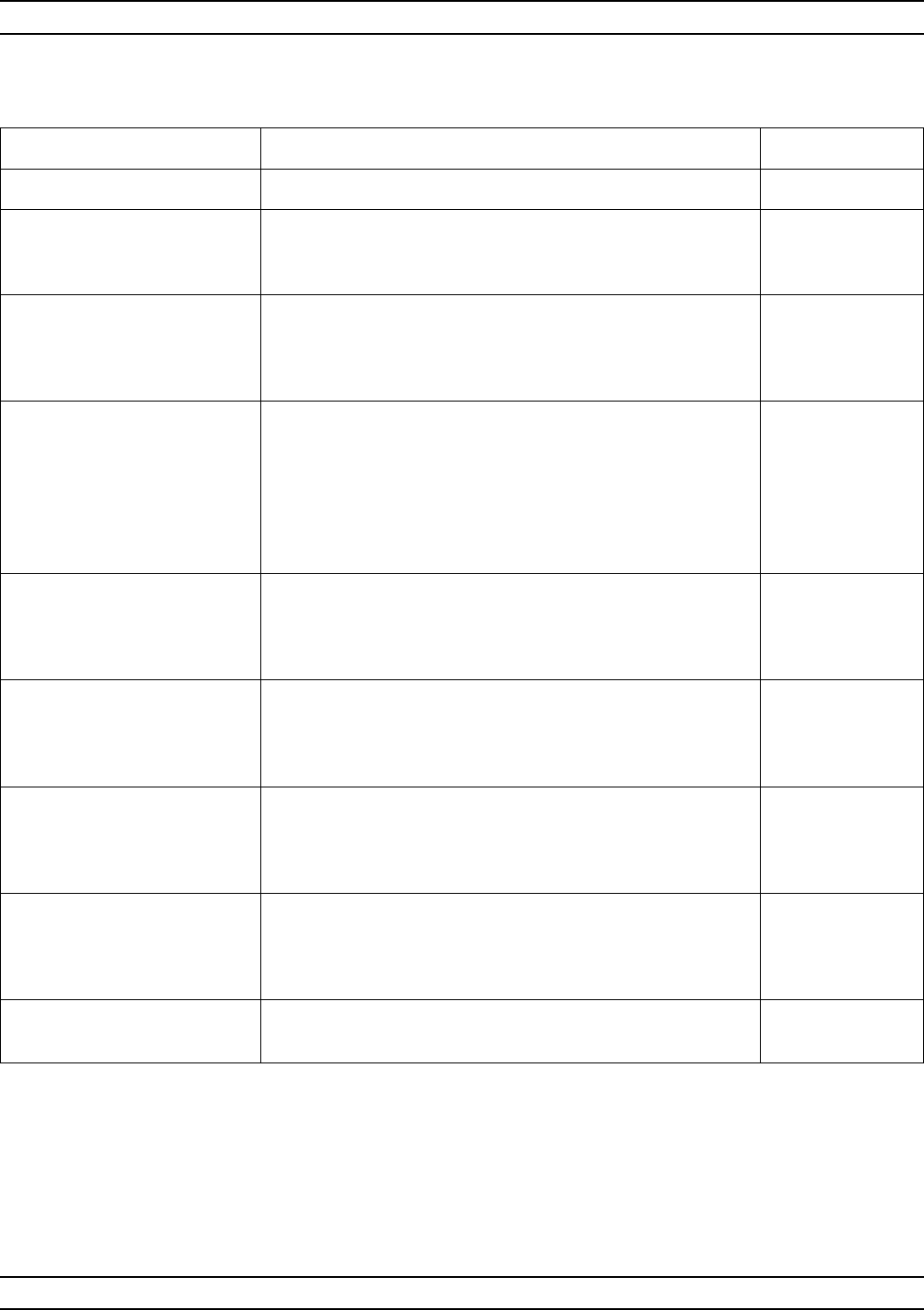
37XXXC OM A-151
ALPHABETICAL LISTING M
MENU DESCRIPTION GPIB COMMAND
CH1—S11,USER None
+XXX.XXXX mm REF
+XXX.XXX dB OFFSET
+XXX.XX °OFFSET
The constant offset for the channel is displayed. MK1? - MK6?
MARKER X
XXX.XXXXXXXXX GHz
MARKER TO MAX
MARKER TO MIN
The selected marker—that is, the one to which the cursor
points in menu M1—and its frequency, time, or distance
display here. This could be any one of the six available
markers: Marker 1 through Marker 6.
D(1-2)
XXX.XXXXXXXXX GHz
XX.XXX dB
XXX.XXX°
The marker numbers of the REF marker and the next
lowest-numbered selected marker appear between the
parentheses. This example assumes Marker 1 as the Ref
marker and Marker 2 as the next lowest-numbered selected
marker. The lines below display the difference frequency,
(or time/distance ) and trace value(s) between these two
markers on the active channel.
D(1-3)
XXX.XXXXXXXXX GHz
XX.XXX dB
XXX.XXX°
Same as above, except Marker 3 is the next
lowest-numbered selected marker.
D(1-4)
XXX.XXXXXXXXX GHz
XX.XXX dB
XXX.XXX°
Same as above, except Marker 4 is the next
lowest-numbered selected marker.
D(1-5)
XXX.XXXXXXXXX GHz
XX.XXX dB
XXX.XXX°
Same as above, except Marker 5 is the next
lowest-numbered selected marker.
D(1-6)
XXX.XXXXXXXXX GHz
XX.XXX dB
XXX.XXX°
Same as above, except Marker 6 is the next
lowest-numbered selected marker.
MARKER READOUT
FUNCTIONS Calls menu M9, which lets you select readout marker
parameters. None
Menu M5, Set DREF Marker Readout
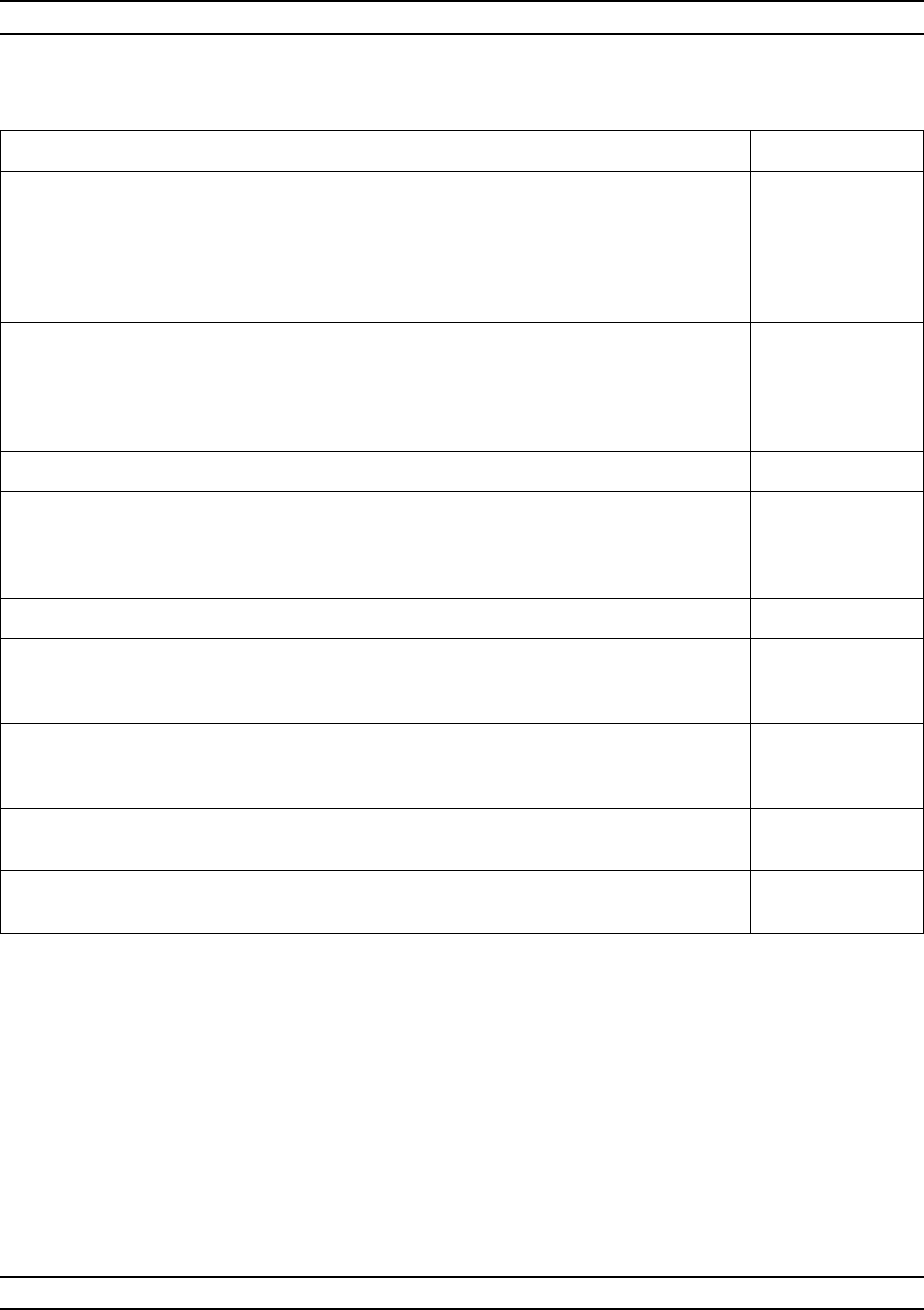
A-152 37XXXC OM
M ALPHABETICAL LISTING
MENU DESCRIPTION GPIB COMMAND
MARKER X
ALL DISPLAYED
CHANNELS
Displays the active marker number. For each channel
being displayed, the channel, S-Parameter, frequency,
time, distance or point number, and the current
readout value for the marker is shown (below). No
marker information is provided for channels that arer
not displayed .
None
CH1—S11
XX.XXXXXXXXX GHz
–XXX.XXX dB
–XXX.XX °
Displays the measured value for the active marker on
all channels currently being displayed. You can set the
marker on the active channel in this menu. The active
channel is displayed in GREEN; when not active it is
displayed in BLUE.
OAM1
CH 2 — S21 See above. OAM2
CH 3 — S12
XX.XXXXXXXXX GHz
–XXX.XXX dB
–XXX.XX °
See above. OAM3
CH 4 — S22 See above. OAM4
MARKER TO MAX Causes the active marker to go to the frequency with
the greatest
S-Parameter value on the active channel.
MMX
MARKER TO MIN Causes the selected marker to go to the frequency
with the smallest
S-Parameter value on the active channel.
MMN
MARKER READOUT
FUNCTIONS Calls menu M9, which lets you select readout marker
parameters. None
PRESS <ENTER>
TO SELECT Pressing the Enter key implements menu selection. None
Menu M6, Marker X All Displayed Channels
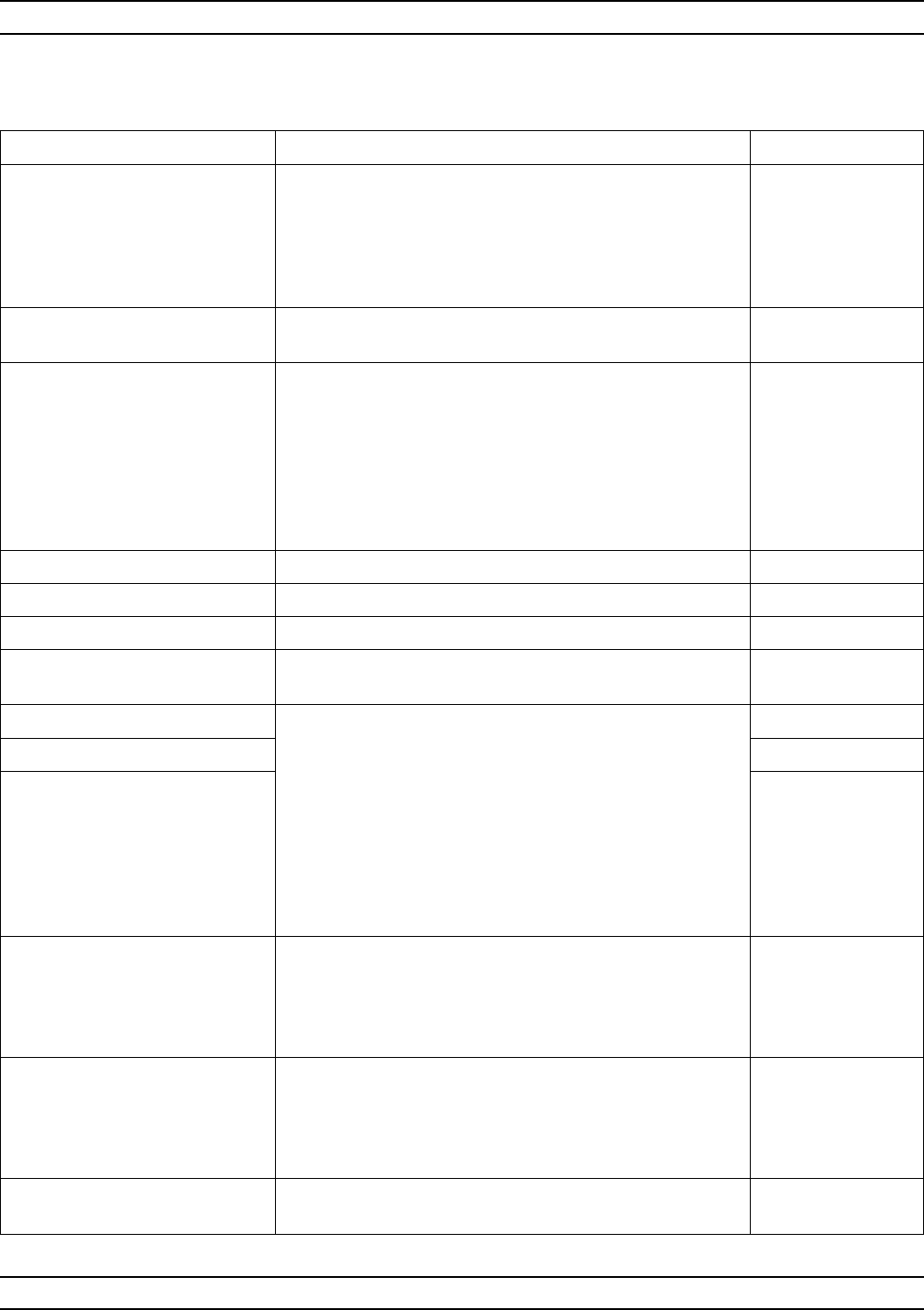
37XXXC OM A-153
ALPHABETICAL LISTING M
MENU DESCRIPTION GPIB COMMAND
SEARCH This menu provides control and readout for the marker
search function. When this function is selected, the
graph type for the active channel is automatically set to
LOG MAGNITUDE (other graph types are not allowed),
and taken out of time domain low pass or band pass
display. Frequency with time gate display is allowed.
SRCH
VALUE
–XXX.XXX dB Target search value. A value from -999.999 to 999.999
dB may be entered. SRCH
REFERENCE These menu choices let you enter the reference value
for the search. The reference may be:
-Graticule “0 dB”
-Position of Delta Ref. Marker (Marker 1 is used as the
DRef Marker)
-Maximum value in Passband (default selection). Marker
1 is used to
indicate maximum.
None
MAXIMUM VALUE Selects maximum value as the reference. MMX
DREF MARKER Selects DRef Marker (Marker 1) as the reference. DR1-DR6; DRX?
0 dB Selects 0 dB as the reference. MSR0; MSRX?
VALUE AT REFERENCE
–XXX.XXX dB Displays the difference between the reference value and
0 dB. OM1
SEARCH LEFT Goes to the next data point that is left (or right) of the
search marker (Marker 2) and whose value is equal to
VALUE plus the reference. If “TRACKING” is ON,
Marker 2 will search both left and right, and go to the
closest point whose value is equal to VALUE plus
reference. If there is no such point, the message
“VALUE NOT FOUND” is displayed in the data area.
Otherwise the marker goes to that coordinate and the
readout (under the search direction) is updated to reflect
that frequency.
MKSL
SEARCH RIGHT MKSR
XX.XXXXXXXXX GHz
SEARCH MRKR VALUES CH1:
XX.XXX dB
CH2: XX.XXX dB
CH3: XX.XXX dB
CH4: XX.XXX dB
None
TRACKING ON (OFF) When ON the active marker will change its frequency
value after every sweep to maintain the user entered
loss value. When OFF the marker stays at the same
frequency and reads out the magnitude value at that
frequency, except when a search is triggered.
MARKER READOUT
FUNCTIONS Calls Menu M9, which lets you select readout marker
parameters.
Menu M7, Search
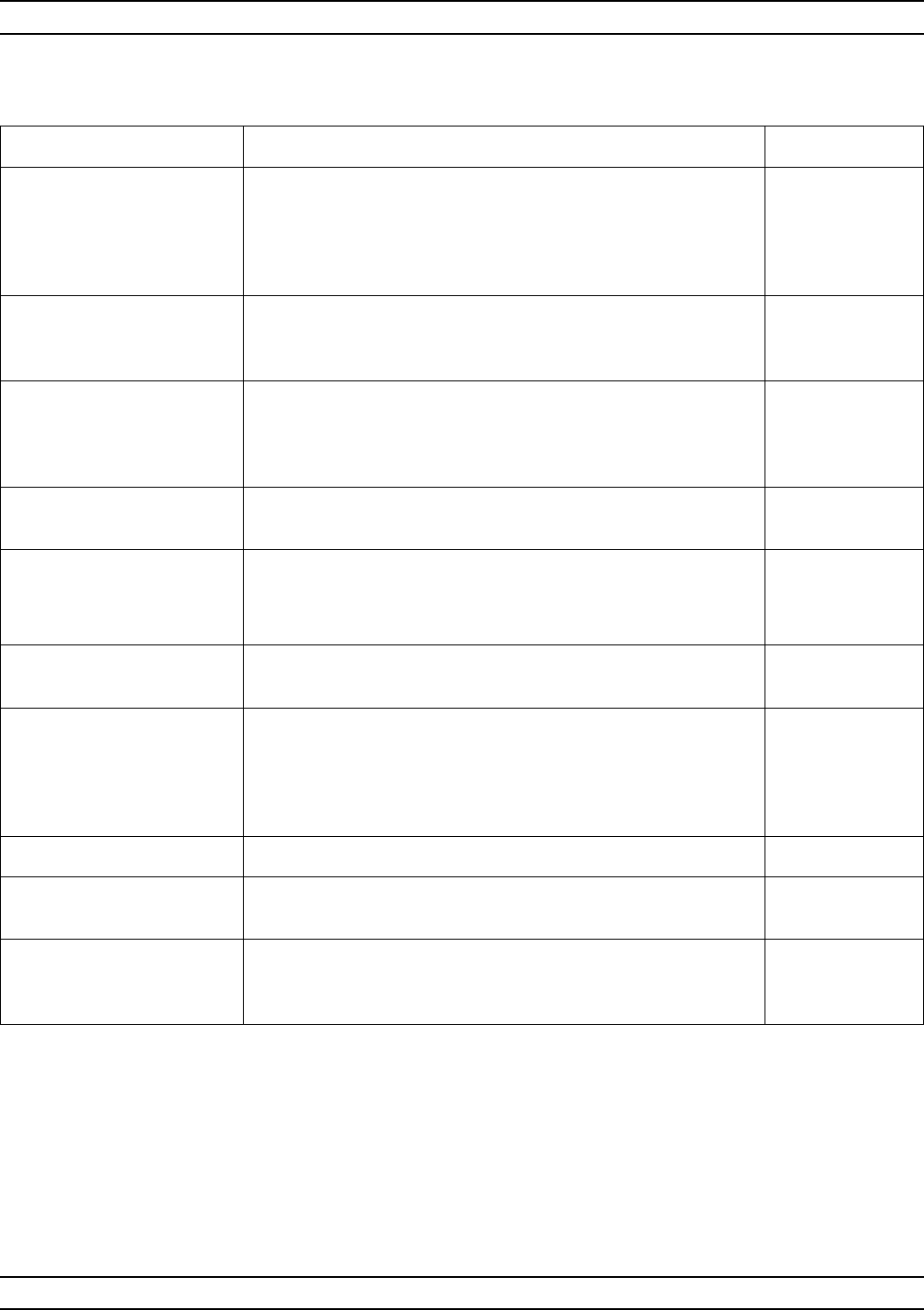
A-154 37XXXC OM
M ALPHABETICAL LISTING
MENU DESCRIPTION GPIB COMMAND
FILTER
PARAMETERS Provides the readouts for the filter measurement functions, as
well as some selections. When this function is selected, the
graph type for the active channel is automatically set to LOG
MAGNITUDE, and taken out of time domain low pass or band
pass display. Frequency with time gate display is allowed.
None
CENTER FREQ
XX.XXXXXXXXX GHz Displays the value of Marker 2. Marker 1 displays the
reference value (maximum filter response, or its set value if
delta ref).
FLTC
BANDWIDTH
XXX.XXX dB
DREF MARKER
XX.XXXXXXXXX GHz
Displays the difference between Markers 3 and 4. FLTBW?
LOSS AT REF
–XXX.XXX dB Displays the difference between the reference value and 0
dB. FLTL?
Q
XX.XXX Displays the Q value.
NOTE: “Q” and “SHAPE FACTOR” are not displayed if they
are toggled OFF in menu M8A.
FLTQ?
SHAPE FACTOR
X.XXX Displays the Shape Factor value. FLTS?
TRACKING ON (OFF) When ON the active marker will change its frequency value
after every sweep to maintain the user entered loss value.
When OFF the marker stays at the same frequency and reads
out the magnitude value at that frequency, except when a
search is triggered.
MKT1; MKT0;
MKTX?
FILTER SETUP Calls menu M8A, which lets you set filter parameters. None
MARKER READOUT
FUNCTIONS Calls menu M9, which lets you select readout marker
parameters. None
PRESS <ENTER>
TO SELECT
OR TURN ON/OFF
Pressing the Enter key implements menu selection, or toggles
selected option on or off. None
Menu M8, Filter Parameters
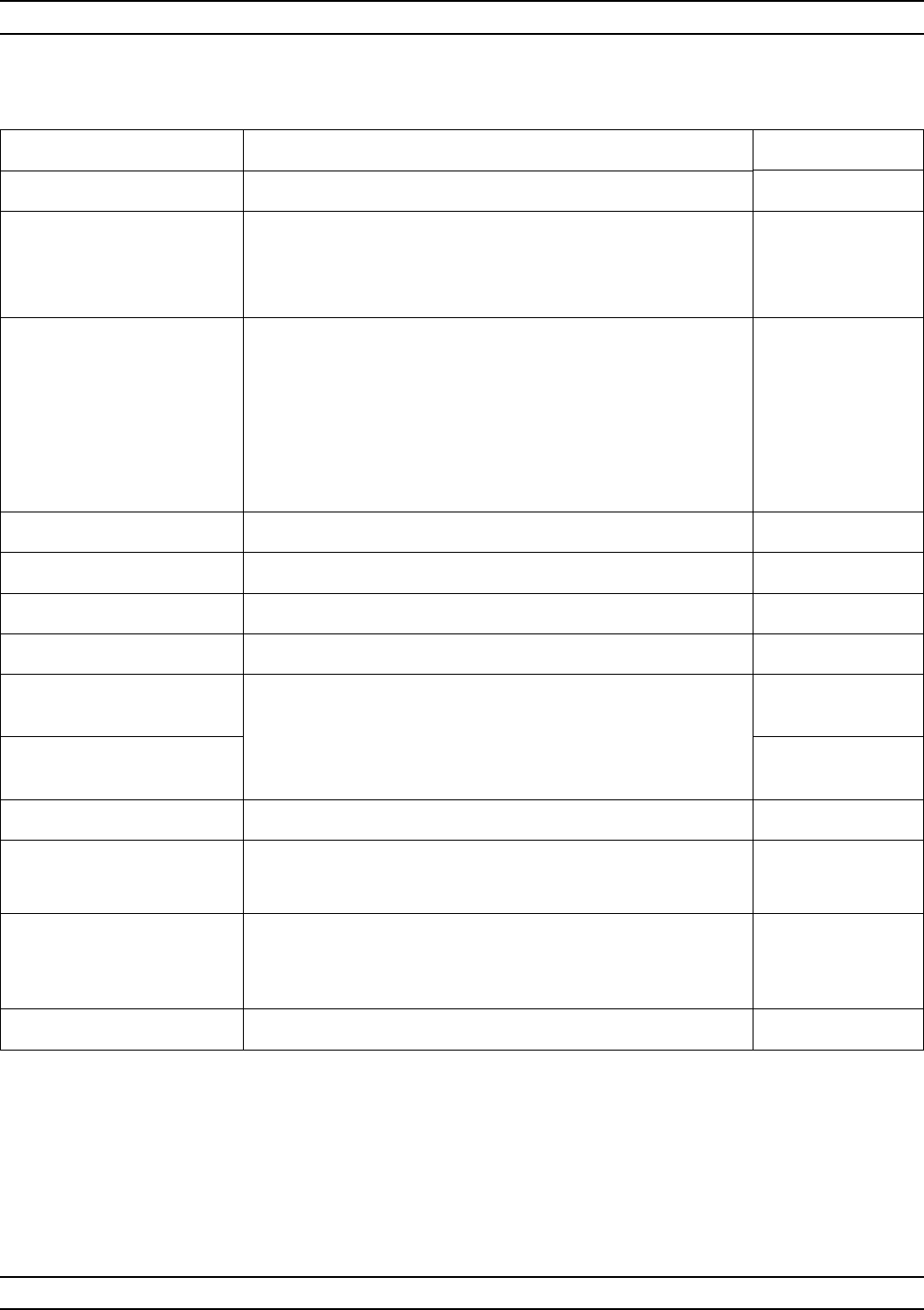
37XXXC OM A-155
ALPHABETICAL LISTING M
MENU DESCRIPTION GPIB COMMAND
FILTER SETUP None
BANDWIDTH
LOSS VALUE
XXX.XXX dB
A “loss” is a positive number. A value of 0 to 999.999 dB
may be entered. The search value for bandwidth will be
REF minus (-) LOSS. By default, the loss value is set to 3
dB.
BWLS; BWL3;
BWLS?
REFERENCE These menu choices let you enter the reference value for
the search. The reference may be:
-Graticule “0 dB”.
-Position of Delta Ref. Marker. (Marker 1 is used as the D
Ref Marker).
-Maximum value in Passband (default selection). Marker 1 is
used to
indicate maximum.
None
MAXIMUM VALUE Selects maximum value as the reference. MMX
DREF MARKER Selects DRef Marker (Marker 1) as the reference. MMN
0 dB Selects 0 dB as the reference. MSR0; MSRX?
SHAPE FACTOR
HIGH
XXX.XXX dB Enter high and low values for the Shape Factor. The LOW
entry must be less than the HIGH entry. A value of 0 to
999.999 dB may be entered. The defaults are +6 dB for the
HIGH, and +60 dB for the LOW value.
MSFH; MSFH?
LOW
XXX.XXX dB MSFL; MSFL?
READOUTS None
Q ON (OFF) Toggles Q on or off.
NOTE: “Q” is not displayed in menu M8, if it is toggled OFF.
DSQ1; DSQ0;
DSQX?
SHAPE ON (OFF)
FACTOR Toggles the Shape Factor on or off.
NOTE: “SHAPE FACTOR” is not displayed in menu M8, if it
is toggled OFF.
DSF1; DSF0;
DSFX?
PREVIOUS MENU Returns to the M8 menu.
Menu M8A, Filter Setup
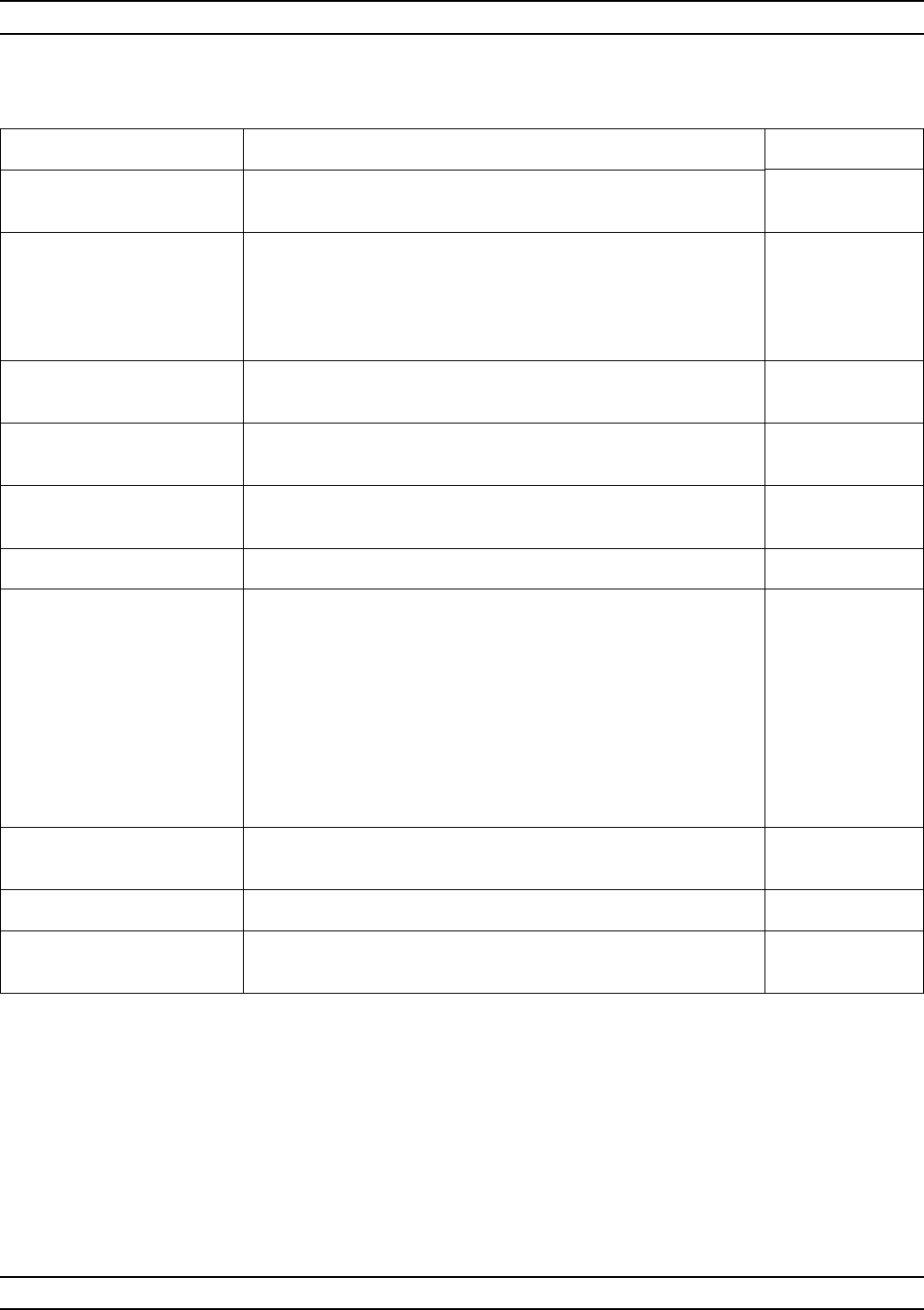
A-156 37XXXC OM
M ALPHABETICAL LISTING
MENU DESCRIPTION GPIB COMMAND
MARKER READOUT
FUNCTIONS None
MARKERS ON
ACTIVE CHANNEL Calls menu M3 directly — or causes it to be displayed when
the Readout Marker key is pressed — if there is no active
marker. Or to it calls or causes menu M4 to be displayed if
there is an active marker. If in delta reference mod, menu M5
is displayed.
None
ACTIVE MARKERS
ON ALL CHANNELS Calls menu M6 directly —or causes it to be displayed when
the Readout Marker key is pressed. None
SEARCH Calls menu M7 directly —or causes it to be displayed when
the Readout Marker key is pressed. None
FILTER
PARAMETERS Calls menu M8 directly —or causes it to be displayed when
the Readout Marker key is pressed. None
MARKER MODE None
CONTINUOUS Marker values are interpolated between data points,
Interpolated markers are allowed only when the horizontal
axis of the display is FREQUENCY. Interpolated markers are
not allowed in CW, Time Domain, or Power Sweep. If a
channel has been set to interpolated markers and the sweep
is changed to CW or Power Sweep, the markers will
automatically revert to normal mode (DISCRETE). Time
Domain will ignore CONTINUOUS mode. Interpolated markers
are allowed in any graph type, as long as the sweep is by
frequency.
MKRC; MKRX?
DISCRETE Markers are displayed only at actual measured data point
values. MKRD; MKRX?
SET MARKERS Calls menu M1, which lets you set marker parameters. None
PRESS <ENTER>
TO SELECT Pressing the Enter key implements menu selection. None
Menu M9, Marker Readout Functions
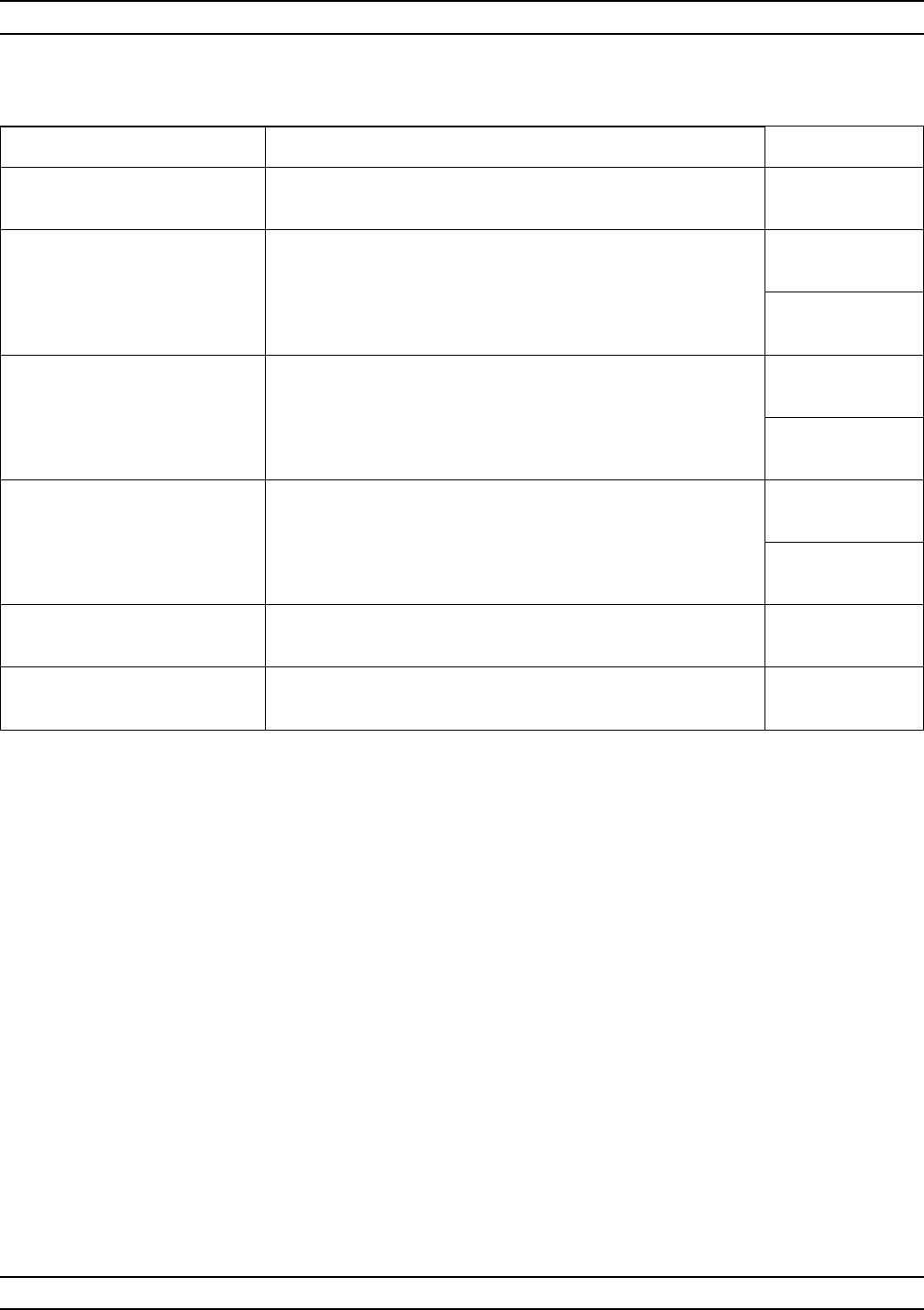
37XXXC OM A-157
ALPHABETICAL LISTING M
MENU DESCRIPTION GPIB COMMAND
MILLIMETER WAVE
TEST SET BAND None
WR-22
(33 - 50 GHz) Selects WR-22 (33 - 50 GHz) waveguide for use with
millimeter wave system. Q22
WR-15
(50 - 75 GHz) Selects WR-15 (50 - 75 GHz) waveguide for use with
millimeter wave system. V15
WR-12
(60 - 90 GHz) Selects WR-12 (60 - 90 GHz) waveguide for use with
millimeter wave system. E12
WR-12 EXTENDED
(56 - 94 GHz) Selects WR-12 Extended band (56 - 94 GHz) waveguide
for use with millimeter wave system. E12E
WR-10
(75 - 110 GHz) Selects WR-10 (75 - 110 GHz) waveguide for use with
millimeter wave system. W10
WR-10 EXTENDED
(65 - 110 GHz) Selects WR-10 Extended band (65 - 110 GHz) waveguide
for use with millimeter wave system. W10E
PRESS <ENTER>
TO SELECT Pressing the Enter key implements your menu selection
and takes you to menu MMW2. None
PRESS <CLEAR>
TO ABORT Pressing the Clear key aborts your millimeter wave system
selection and calls menu OST1. None
Menu MMW1, Millimeter Wave Test Set Band
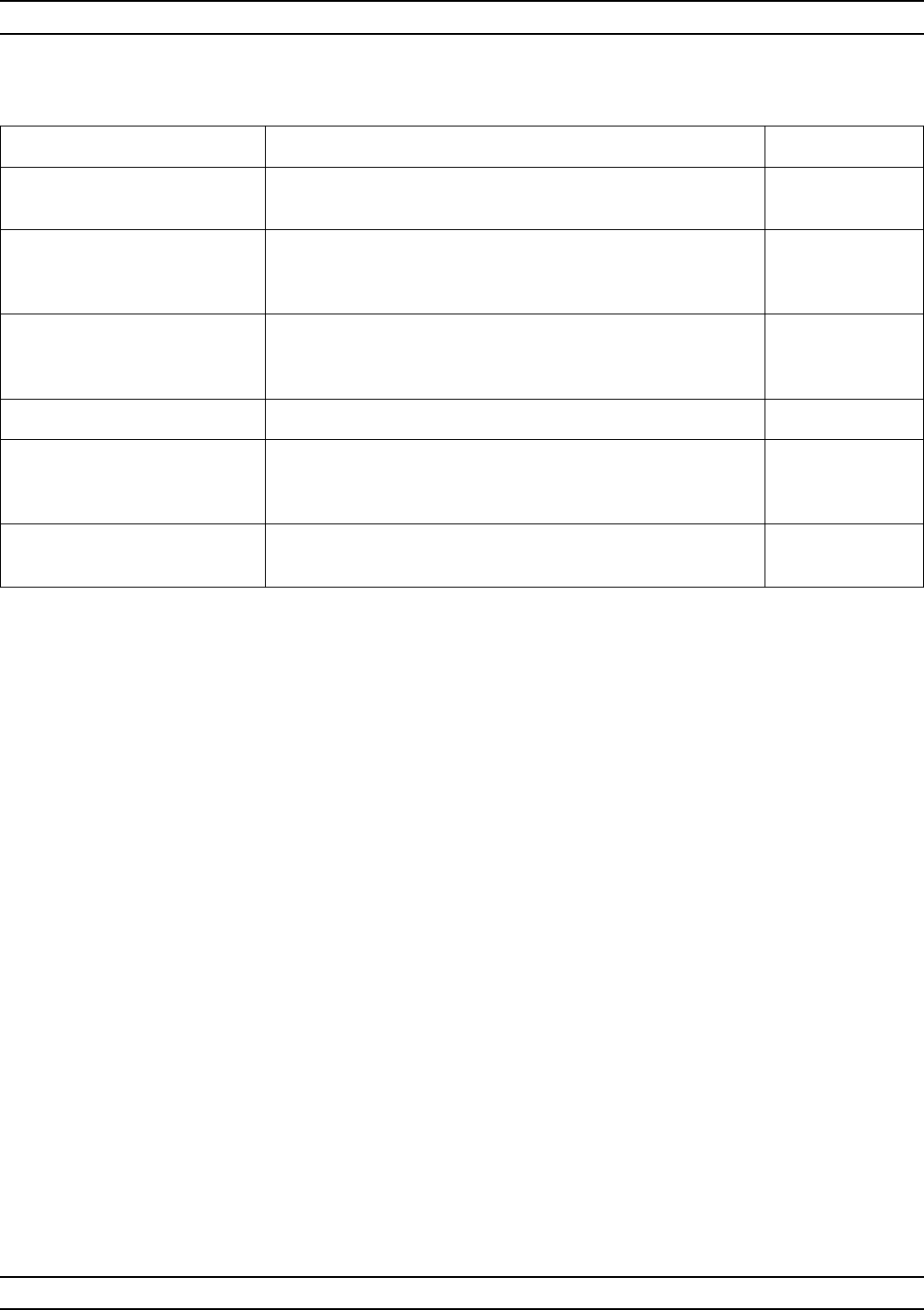
A-158 37XXXC OM
M ALPHABETICAL LISTING
MENU DESCRIPTION GPIB COMMAND
MILLIMETER WAVE
TEST SET MODULES None
PORT 1 MODULE
3740/3741/None Switch selection for Port 1 Module. P1MMN; P1MMR;
P1MMNT;
P1MMX?
PORT 2 MODULE
3740/3741/None Switch selection for Port 2 Module. P2MMN; P2MMR;
P2MMNT;
P2MMX?
ACCEPT CONFIG Accepts the selected configuration and calls menu MMW3. None
PRESS <ENTER>
TO SELECT
OR SWITCH
Pressing the Enter key implements your menu selection, None
PRESS <CLEAR>
TO ABORT Pressing the Clear key aborts your millimeter wave system
selection and calls menu OST1. None
Menu MMW2, Millimeter Wave Test Set Modules
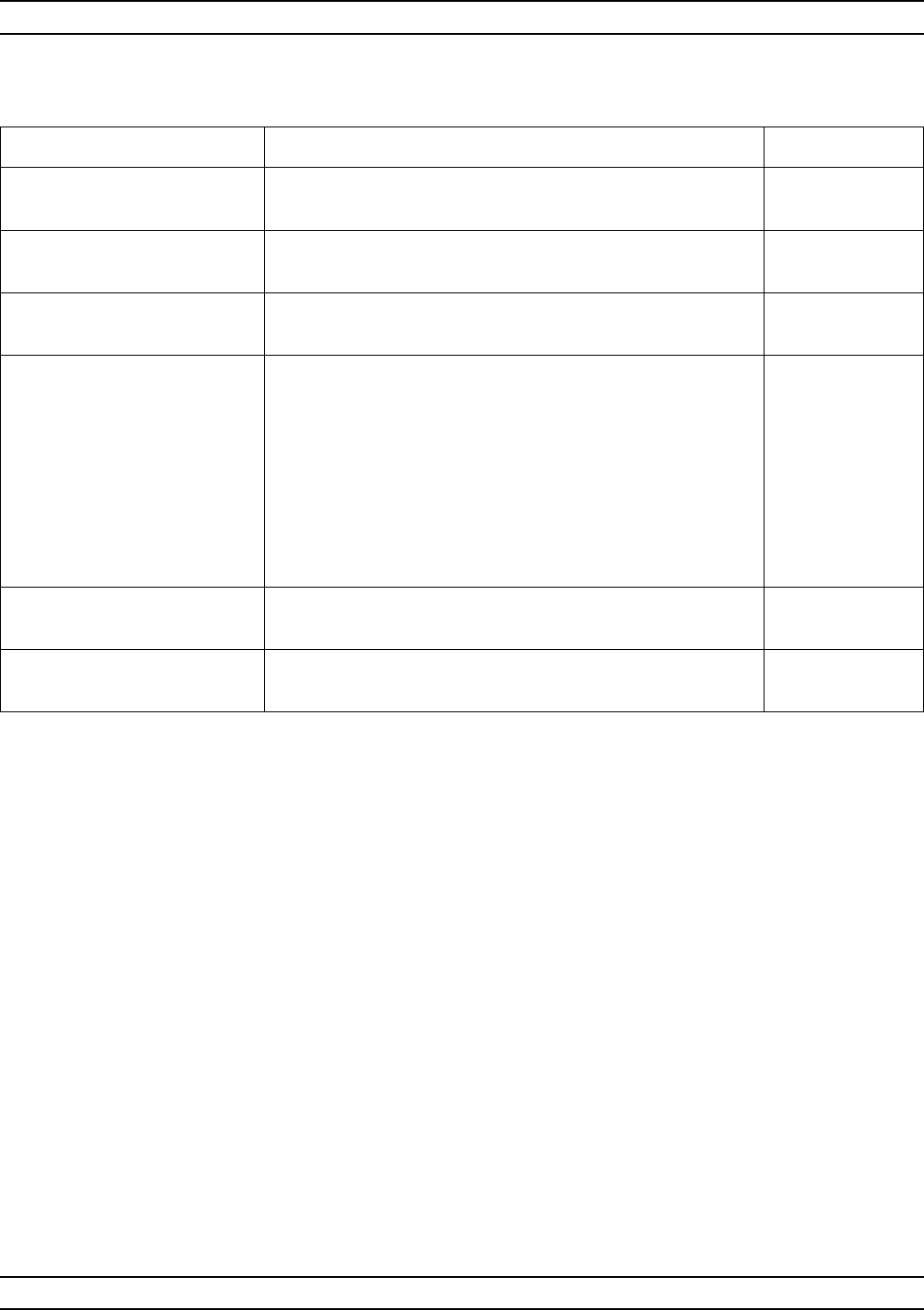
37XXXC OM A-159
ALPHABETICAL LISTING M
MENU DESCRIPTION GPIB COMMAND
MILLIMETER WAVE
TEST SET None
mm WAVE BAND:
XXXXXXXXXXX Provides information for selections made in menu MMW2
(previous menu). None
PORT 1 MODULE
XXXXXXXXXXX P1MMX?
PORT 2 MODULE
XXXXXXXXXXX P2MMX?
WARNING:
CONTINUING
MAY INVALIDATE
CURRENT
SETUP AND
CALIBRATION
PRESS <ENTER>
TO SELECT Pressing the Enter key implements your millimeter wave
selection and calls menu SU1 or SU3. None
PRESS <CLEAR>
TO ABORT Pressing the Clear key aborts your millimeter wave system
selection and calls menu OST1. None
Menu MMW3, Millimeter Wave Test Set
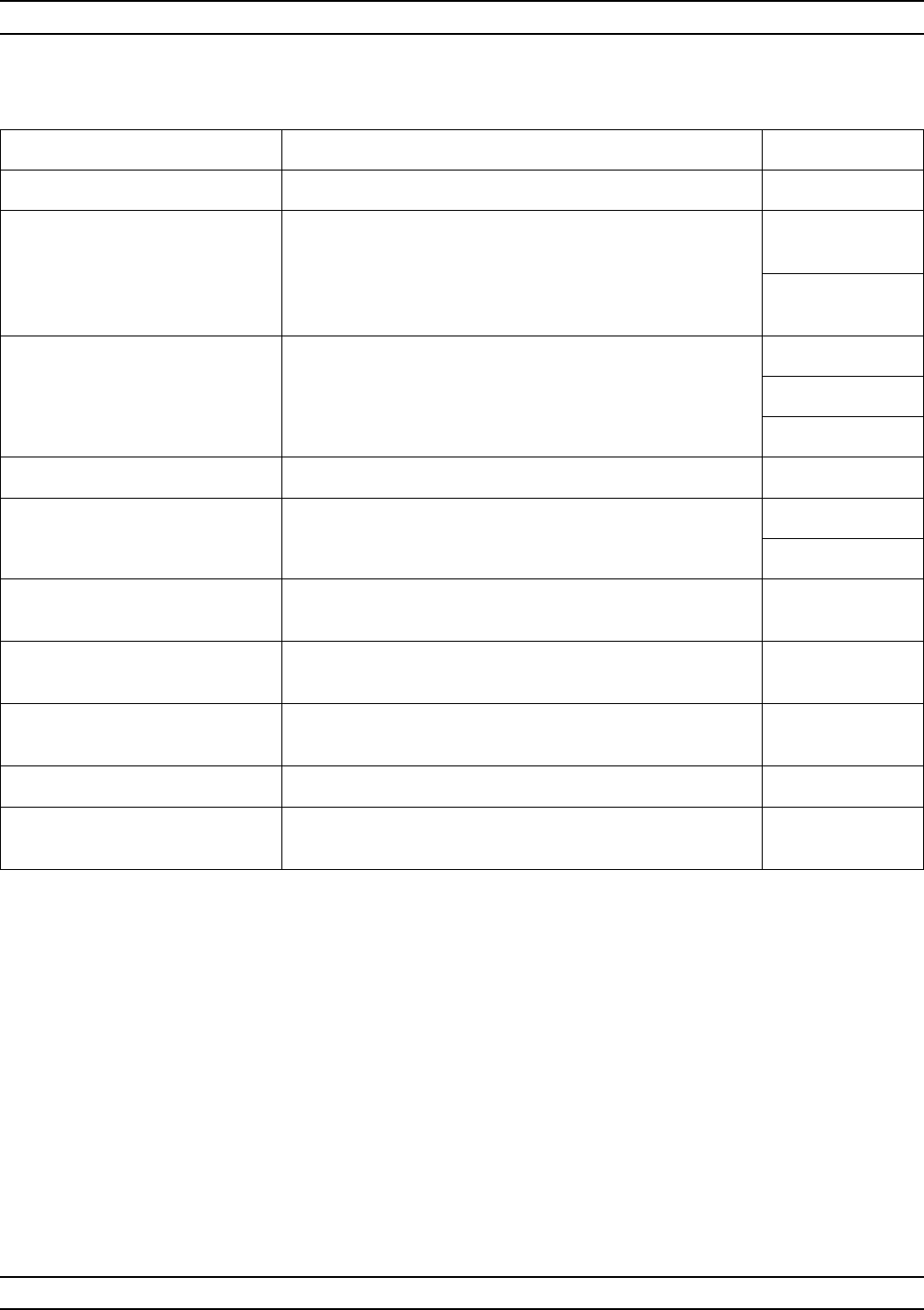
A-160 37XXXC OM
M ALPHABETICAL LISTING
MENU DESCRIPTION GPIB COMMAND
mm WAVE BAND None
BAND START FREQ
XXXXXXXXXXX Displays the start frequency of the millimeter wave band.
BAND STOP FREQ
XXXXXXXXXXX Displays the stopfrequency of the millimeter wave band.
EQUATION TO EDIT
SOURCE 1 Selects source 1 frequency equation for change.
SOURCE 2 Selects source 2 frequency equation for change.
RECEIVER Selects receiver frequency equation for change.
EQUATION SUMMARY
C.W. ON/OFF Toggles frequency term (F) in equation ON or OFF.
MULTIPLIER
XXX Enables changing multiplier term of frequency equation
via key pad or rotary knob.
DIVISOR
XXX Enables changing divisor term frequency equation via
key pad or rotary knob.
OFFSET FREQ
XXXXXXXX Enables changing offset frequency term frequency
equation via key pad or rotary knob.
DEFAULT EQUATIONS Pressing the Enter key implements your menu selection. None
ACCEPT EQUATIONS Pressing the Clear key aborts your millimeter wave
selection and calls menu SU1 or SU3. None
Menu MMW4, mm Wave Band
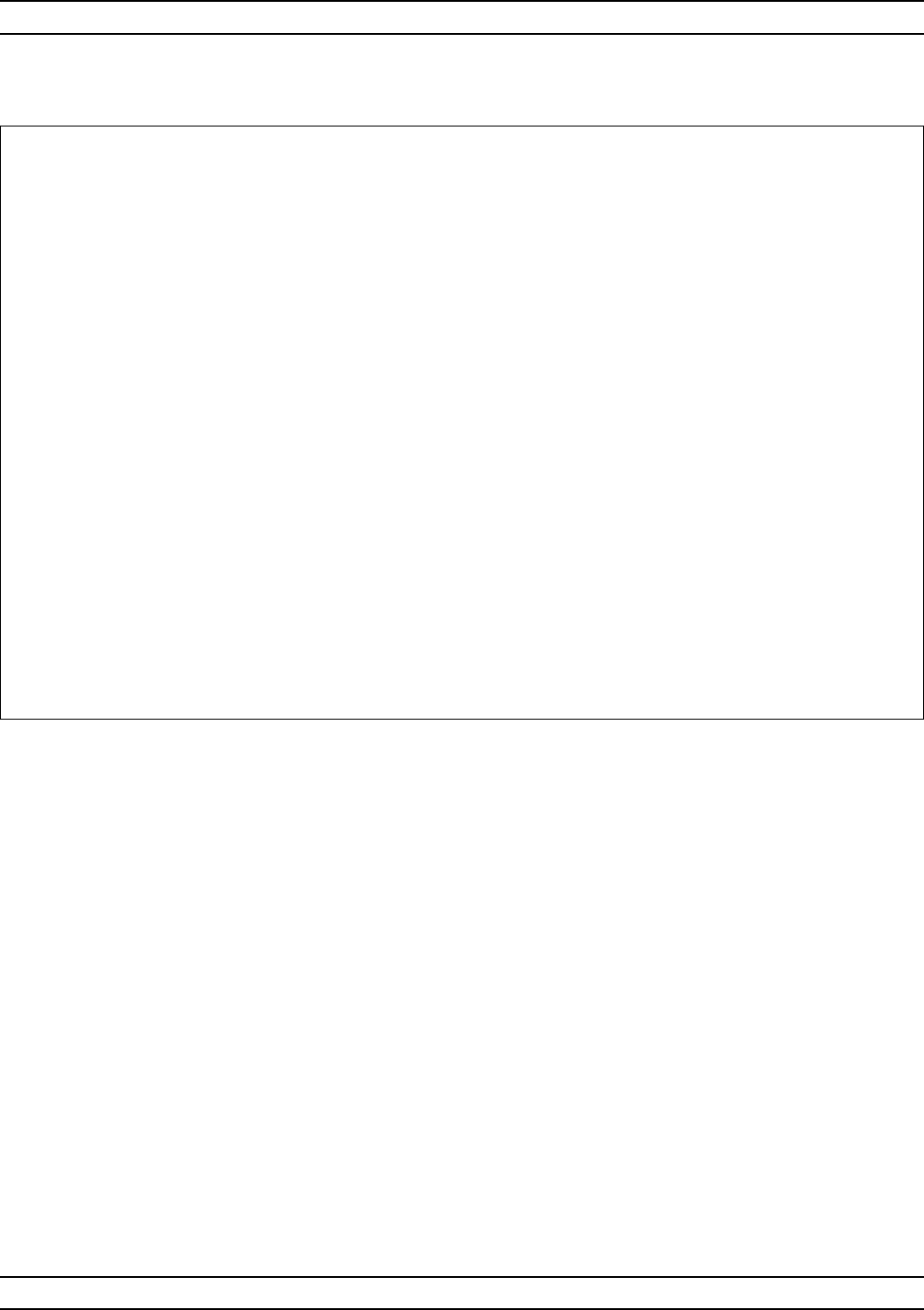
37XXXC OM A-161
ALPHABETICAL LISTING M
- MILLIMETER WAVE BAND DEFINITION SUMMARY -
BAND FREQUENCY RANGE
BAND START FBAND STOP F
XXX.XXXXXX XXXXXX.XXXXXX XXX
FREQUENCY = (MULTIPLIER/DIVISOR)*F+OFFSET FREQ)
SOURCE 1 = (1/ 6) * (F – 0.270000 GHz)
SOURCE 2 = (1/ 8) * (F+ 0.000000 GHz)
RECEIVER = (1/ 1) * (0.270000 GHz C.W.)
- NOTES -
1. SELECT <DEFAULT EQUATIONS> TO OVERWRITE DEFINITION
WITH VALUES SUITABLE FOR THE MILLIMETER WAVE BAND.
2. SELECT <ACCEPT EQUATIONS> TO CONFIRM ANY CHANGES.
3. PERFORMANCE SPECIFICATIONS ARE VALID ONLY WHILE
USING THE DEFAULT EQUATIONS OVER THE DEFAULT BAND
FREQUENCY RANGE.
4. DEVIATING FROM THE DEFAULT MAY CAUSE LOCK FAILURES.
PRESS <ENTER> TO SELECT, PRESS <CLEAR> TO ABORT
Menu EXT_MMW4
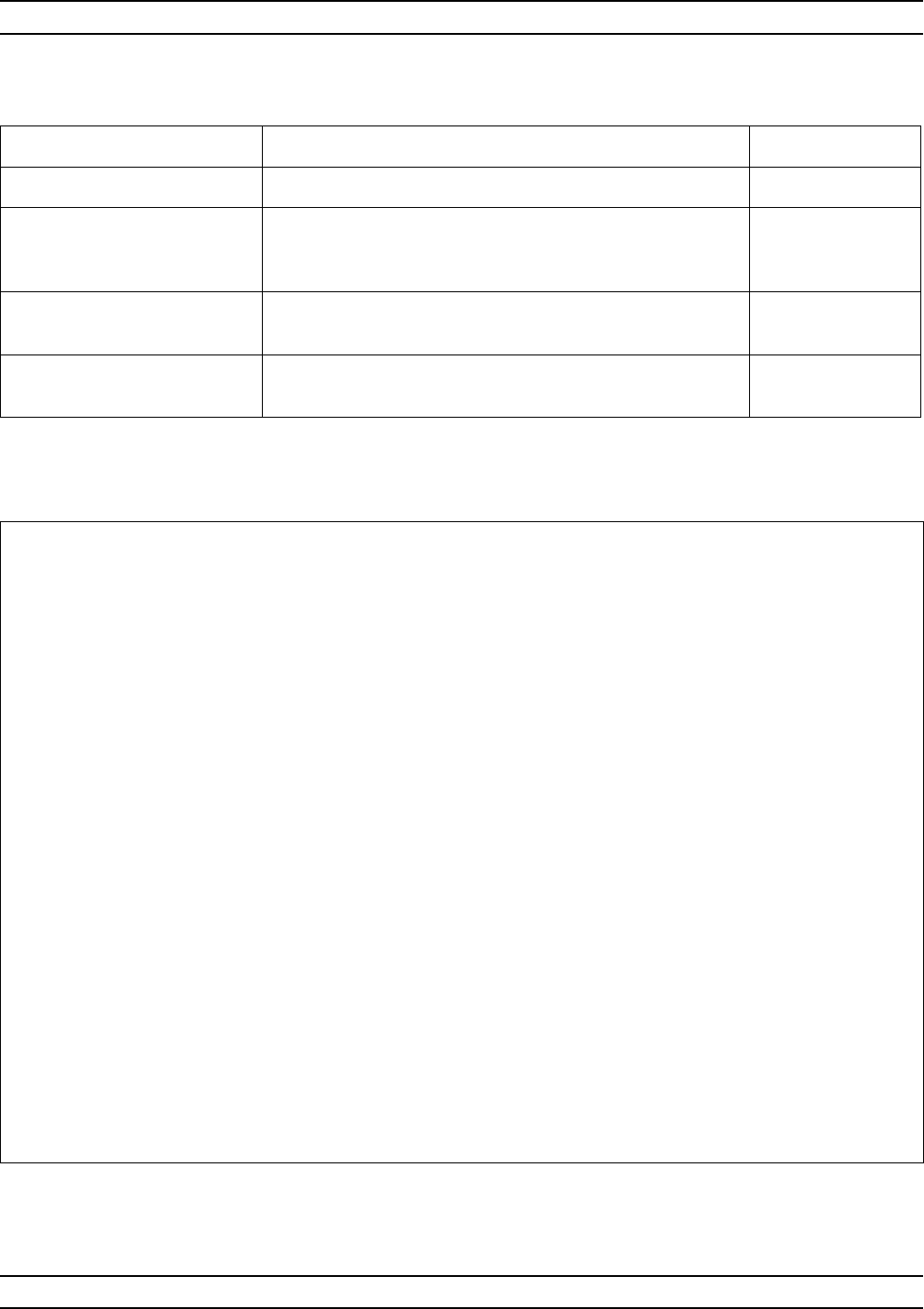
A-162 37XXXC OM
M ALPHABETICAL LISTING
MENU DESCRIPTION GPIB COMMAND
MERGE CAL FILES None
CAL FILES MUST
EXIST IN THE
CURRENT DIRECTORY
None
MERGE CAL FILES Calls menu MRG2, then menu MRG3 to select the
calibration files. LDMCF, IMCF
PRESS <ENTER>
TO SELECT Pressing the Enter key implements your menu selection. None
Menu MRG1, Merge Calibration Menu
- MERGE CALIBRATION FILES -
RF CALIBRATIONS USING DIFFERENT METHODS AND AT
DIFFERENT FREQUENCIES CAN BE MERGED USING CAL FILES.
- REQUIREMENTS -
- PERFORM TWO RF CALIBRATIONS USING THE SAME CAL TYPE
AND STORE EACH CAL AND FRONT PANEL SETUP TO DISK
(e.g. CALFILE1.CAL AND CALFILE2.CAL).
- CAL FIES MUST BE PLACED IN THE CURRENT DIRECTOY
OF THE HARD OR FLOPPY DISK.
- THE COMBINED FREQ LIST CANNOT EXCEED 1601 POINTS.
- INSTRUCTIONS -
1. SELECT <MERGE CAL FILES> TO READ THE FIRST AND
SECOND CAL FILES FROM DISK (E.G. CALFILE1.CAL AND
CALFILE2.CAL, REPECTIVELY).
2. THE FREQUENCY LISTS AND MATCHING CORRECTIONTERMS
ARE COMBINED. FOR FREQUENCIES WHICH COINCIDE,
THE TERMS FROM THE FIRST CAL FILE ARE USED. THE
FRONT PANEL SETUP FROM THE FIRST CAL FILE IS USED,
EXCEPT THAT THE START AND STOP FREQS ARE ADJUSTED
TO INCLUDETHE ENTIRE RANGE. THE DATA POINT TYPE
IS CHANGED TO MATCH THE RESULTING FREQUENCY LIST
(I.E. NORMAL, N-DISCRETE, TIME DOMAIN HARMINIC).
IF DESIRED, SAVE RESULTS.
Menu EXT_MRG1, Merge Calibration Menu
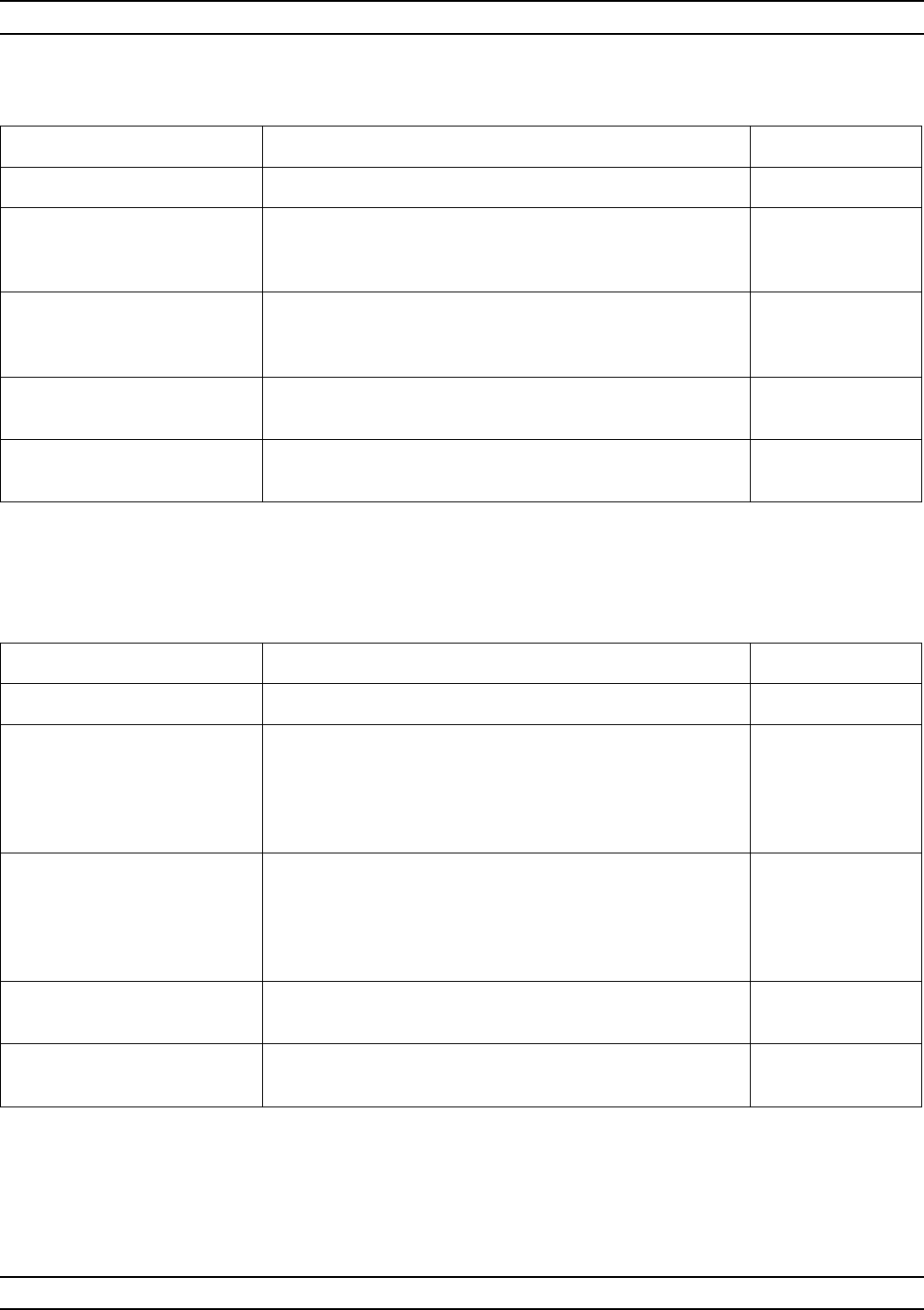
37XXXC OM A-163
ALPHABETICAL LISTING M
MENU DESCRIPTION GPIB COMMAND
MERGE CAL FILES LDMCF, IMCF
READ CAL FILE 1
FROM HARD DISK Calls menu DSK2 to read the CAL file 1 in the current
directory of the hard disk. Completion of the file read
takes the user to menu MRG3.
None
READ CAL FILE 1
FROM FLOPPY DISK Calls menu DSK2 to read the CAL file 1 in the current
directory of the floppy disk. Completion of the file read
takes the user to menu MRG3.
None
PRESS <ENTER>
TO SELECT Pressing the Enter key implements your menu selection. None
PRESS <CLEAR>
TO ABORT Pressing the Clear key aborts this menu selection and
returns to menu MRG1. None
Menu MRG2, Merge Calibration Menu
MENU DESCRIPTION GPIB COMMAND
MERGE CAL FILES LDMCF, IMCF
READ CAL FILE 2
FROM HARD DISK Calls menu DSK2 to read the CAL file 2 in the current
directory of the hard disk. Completion of the file read
starts the merge of the calibration terms. Finishing the
merge recalls the front panel setup of the CAL file 1 and
displays the setup menu.
None
READ CAL FILE 2
FROM FLOPPY DISK Calls menu DSK2 to read the CAL file 2 in the current
directory of the floppy disk. Completion of the file read
starts the merge of the calibration terms. Finishing the
merge recalls the front panel setup of the CAL file 1 and
displays the setup menu.
None
PRESS <ENTER>
TO SELECT Pressing the Enter key implements your menu selection. None
PRESS <CLEAR>
TO ABORT Pressing the Clear key aborts this menu selection and
returns to menu MRG1. None
Menu MRG3, Merge Calibration Menu
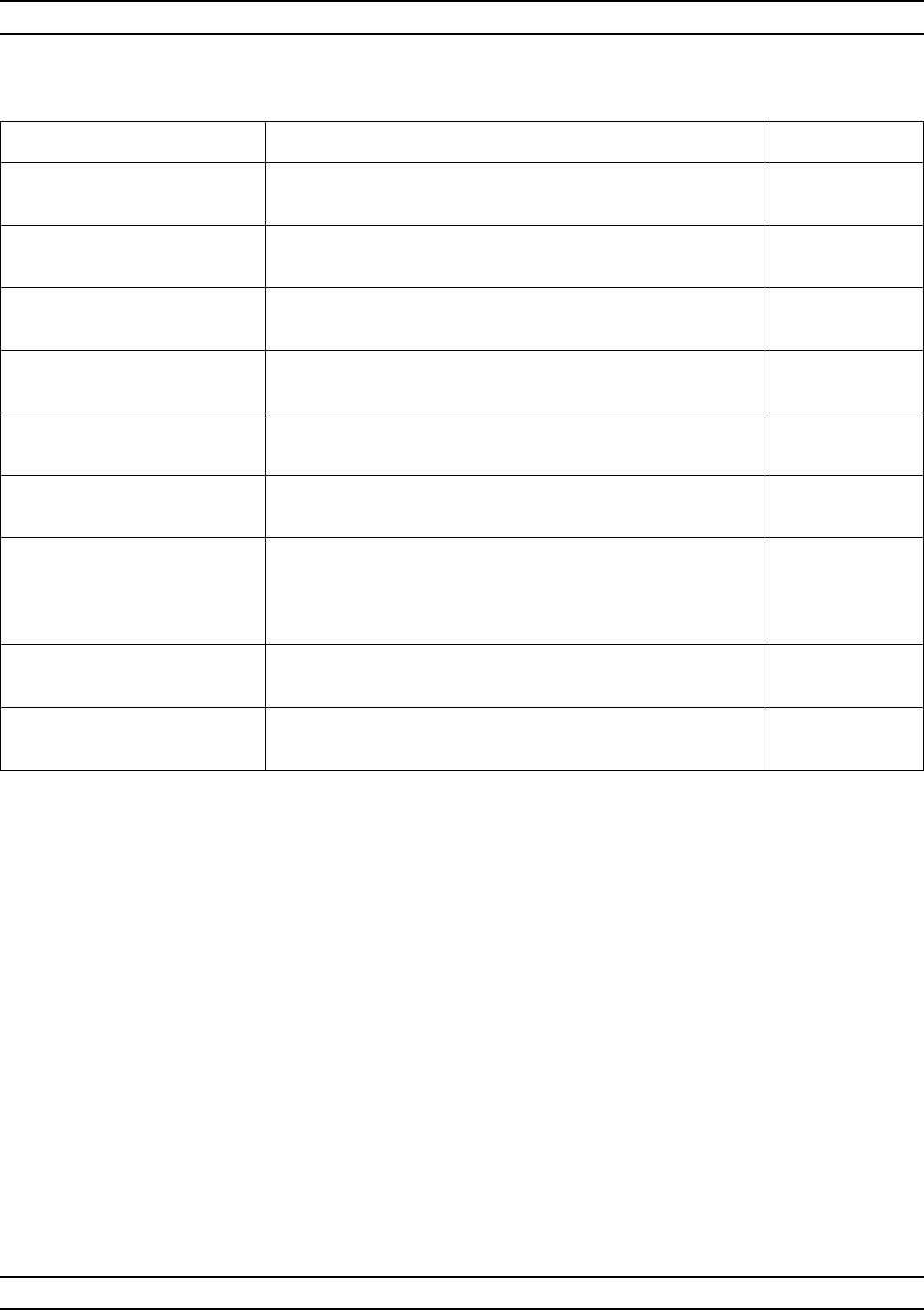
A-164 37XXXC OM
N ALPHABETICAL LISTING
MENU DESCRIPTION GPIB COMMAND
TRACE MEMORY
FUNCTIONS None
VIEW DATA Displays measured data; that is, the data presently being
taken. DAT; DAT?
VIEW MEMORY Displays stored data; that is, data that was previously taken
and stored in memory. MEM
VIEW DATA
AND MEMORY Displays measured data superimposed over stored data. DTM
VIEW DATA (/)
MEMORY Displays measured data combined with stored data using
selected math. DNM
SELECT
TRACE MATH Calls menu NO2 for selection of the type of math operation
to be performed. None
STORE DATA
TO MEMORY
(STORED)
(NOT STORED)
Stores the measured data to internal memory. STD
DISK
OPERATIONS Brings up menu NO3, which allows data to be stored to or
recalled from the disk. None
PRESS <ENTER>
TO SELECT Pressing the Enter key implements your menu selection. None
Menu NO1, Trace Memory Functions
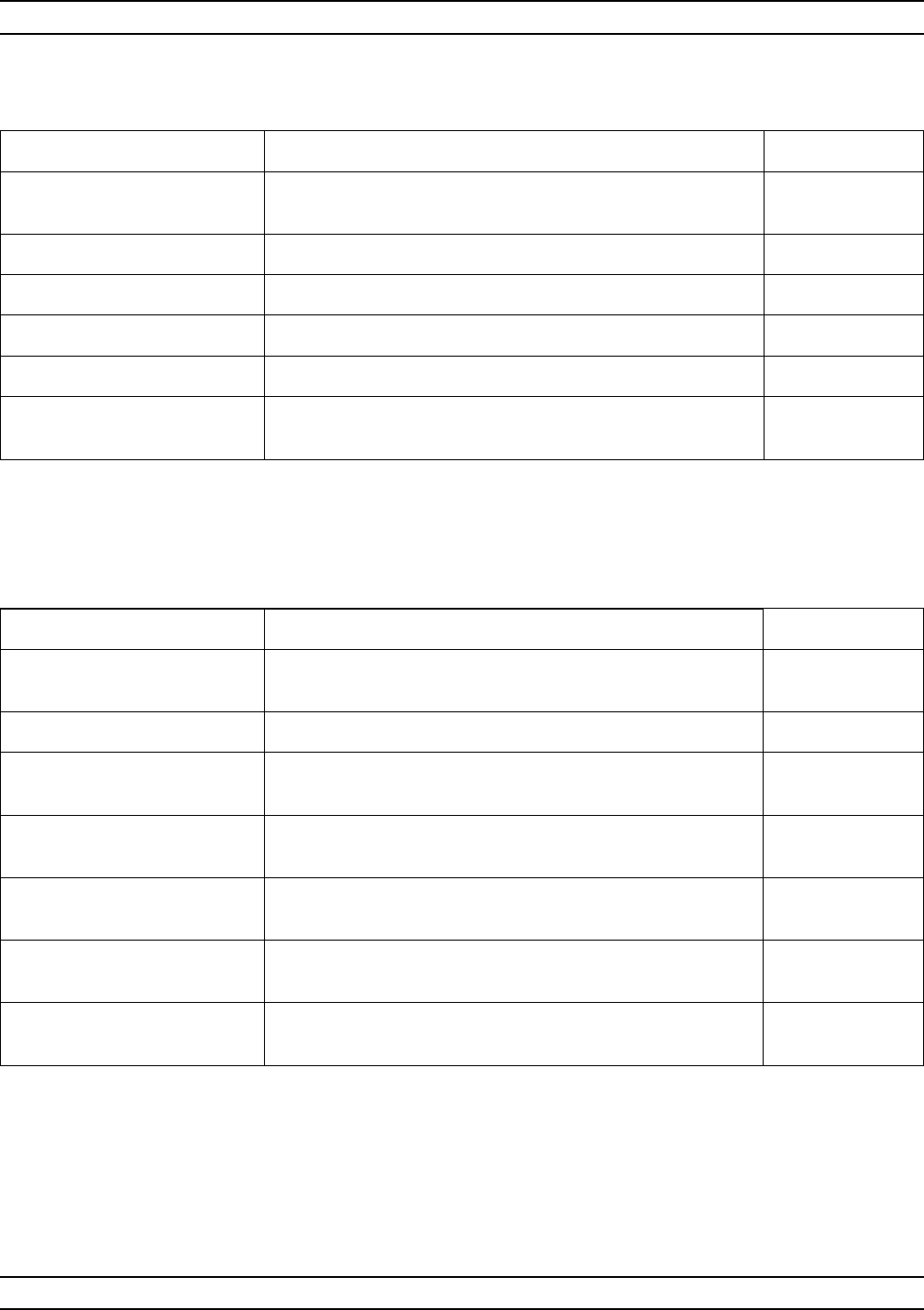
37XXXC OM A-165
ALPHABETICAL LISTING N
MENU DESCRIPTION GPIB COMMAND
SELECT
TRACE MATH None
ADD (+ ) Selects DATA + MEMORY as the math function. ADD
SUBTRACT (–) Selects DATA – MEMORY as the math function. MIN
MULTIPLY (*) Selects DATA X MEMORY as the math function. MUL
DIVIDE (/) Selects DATA MEMORY as the math function. DIV
PRESS <ENTER>
TO SELECT Pressing the Enter key implements your menu selection.
The menu returns to the NO1 menu. None
Menu NO2, Select Trace Math
MENU DESCRIPTION GPIB COMMAND
TRACE MEMORY
DISK OPERATIONS None
CHANNEL X Indicates the channel to be used (active channel). CH1-CH4; CHX?
SAVE MEMORY
TO HARD DISK Calls menu DSK3, which lets you save memory to the hard
disk. None
SAVE MEMORY
TO FLOPPY DISK Calls menu DSK3, which lets you save memory to the
floppy disk. None
RECALL MEMORY
FROM HARD DISK Calls menu DSK2, which lets you recall memory from the
hard disk. None
RECALL MEMORY
FROM FLOPPY DISK Calls menu DSK2, which lets you recall memory from the
floppy disk. None
PRESS <ENTER>
TO SELECT Pressing the Enter key implements your menu selection. None
Menu NO3, Trace Memory Disk Functions
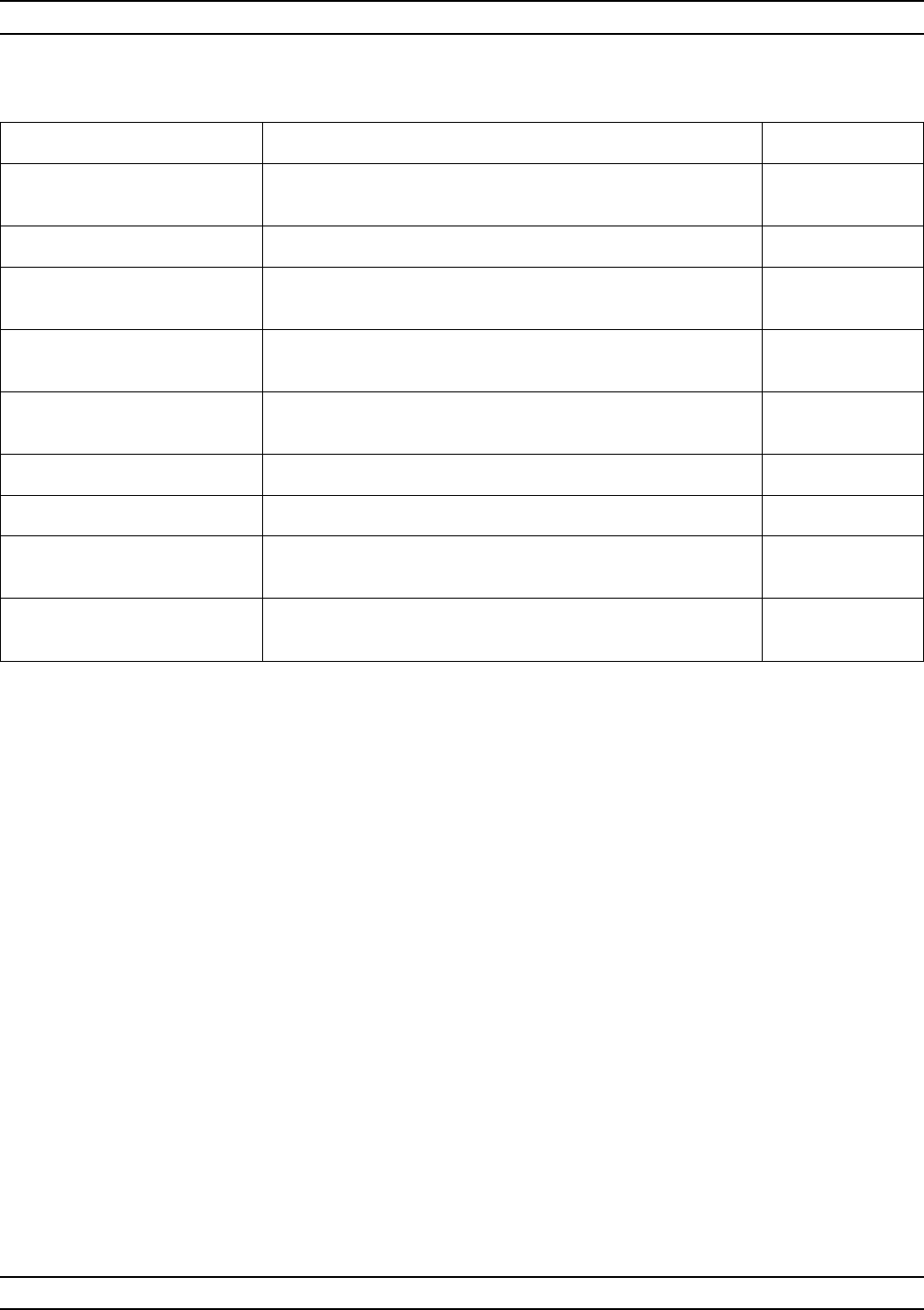
A-166 37XXXC OM
O ALPHABETICAL LISTING
MENU DESCRIPTION GPIB COMMAND
MULTIPLE
SOURCE CONTROL None
DEFINE BANDS Calls menu OM1, which lets you define a frequency band. None
SOURCE CONFIG Calls menu SC, which lets you configure the frequency
source. None
MULTIPLE
SOURCE MODE None
OFF Turns multiple source operating mode off placing 37XXXC
VNA in normal operating mode. MS0
DEFINE None
ON Sets multiple source mode to ON. MS1
MORE Calls menu OM1A, which lets you select source-lock
polarity. None
PRESS <ENTER>
TO SELECT Pressing the Enter key implements your menu selection. None
Menu OM1, Multiple Source Control Menu
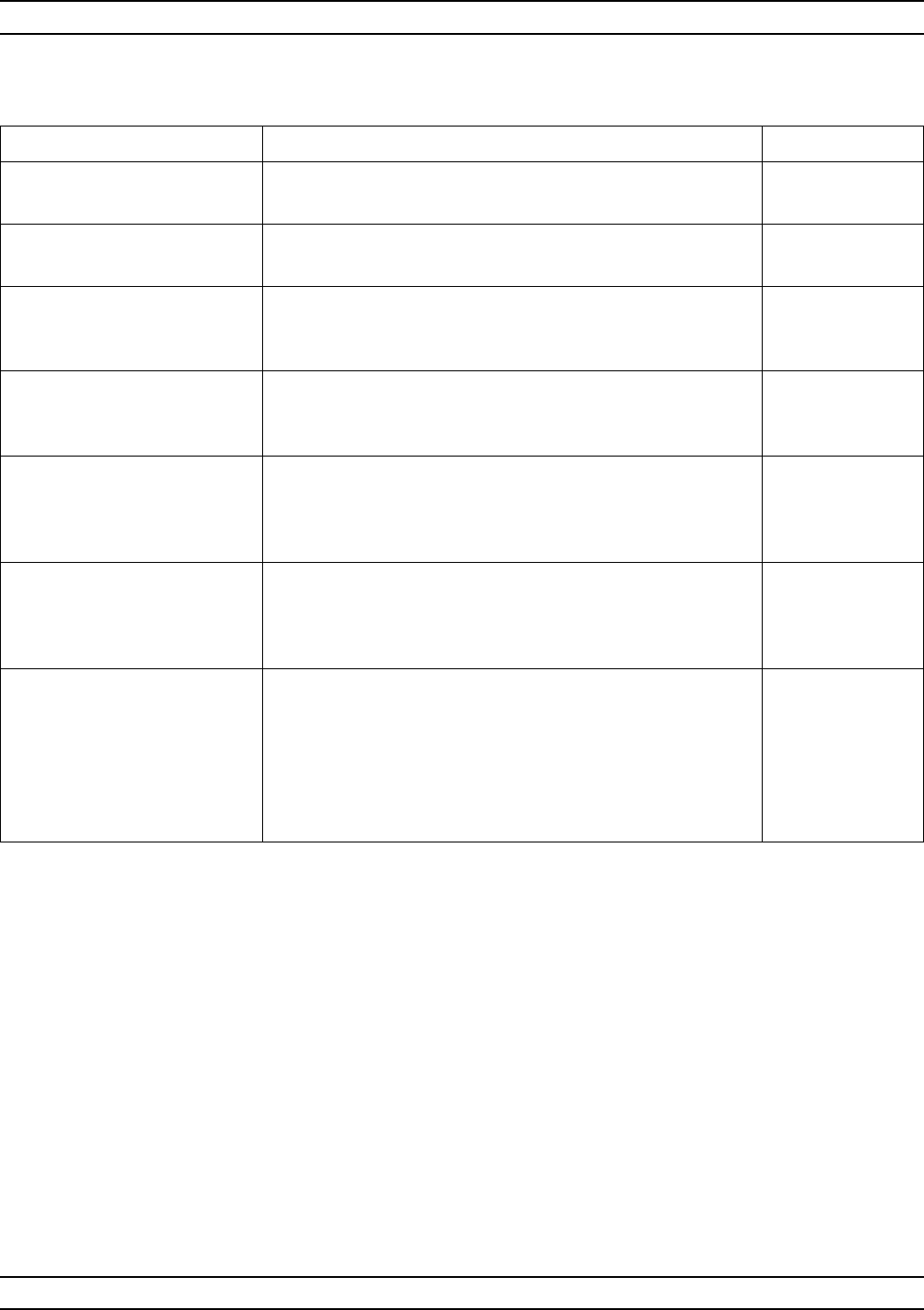
37XXXC OM A-167
ALPHABETICAL LISTING O
MENU DESCRIPTION GPIB COMMAND
SOURCE LOCK
POLARITY None
NORMAL
REVERSE Calls menu OM1, which lets you define a frequency band. None
SELECT <REVERSE>
SOURCE LOCK
POLARITY IF
None
THE DUT CONTAINS
MULTI-CONVERSION
STAGES, AND
None
THE PHASE OF THE
FINAL OUTPUT I.F.
IS OPPOSITE OF
NORMAL
None
NORMAL POLARITY
IS DEFINED BY THE
SOURCE 1 AND 2
EQUATIONS
None
IF SOURCE 1 FREQ
IS GREATER THAN
SOURCE 2 FREQ
THEN THE I.F.
IS ASSUMED TO BE
POSITIVE POLARITY
AND VICE VERSA
None
Menu OM1A, Source Lock Polarity Menu
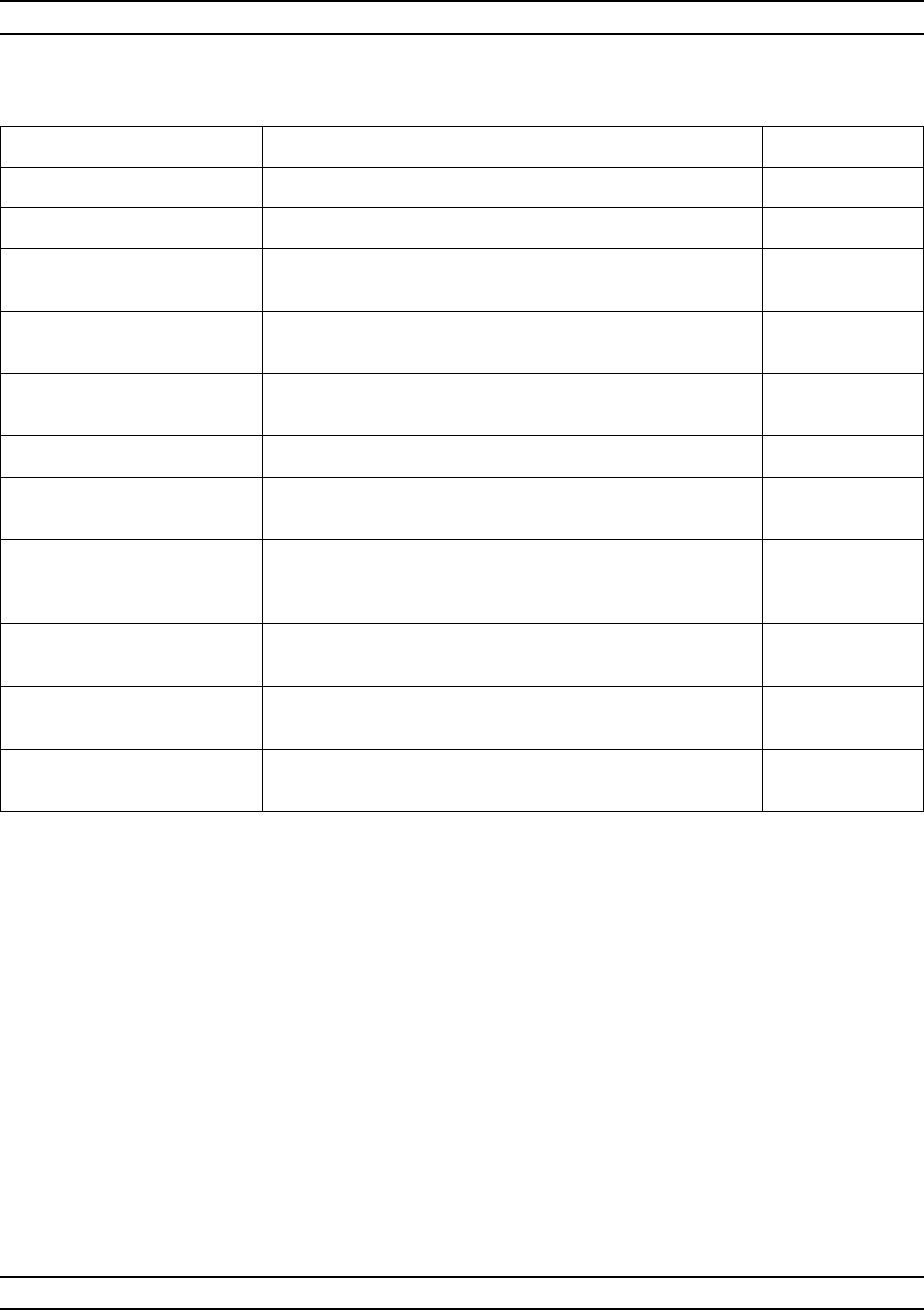
A-168 37XXXC OM
O ALPHABETICAL LISTING
MENU DESCRIPTION GPIB COMMAND
DEFINE BANDS None
BAND 1 Displays the band number being defined. BD1-BD5
DISPLAYED
FREQ RANGE None
BAND START FREQ
XX.XXXXXX GHz Displays the start frequency for the band. BST; BST?
BAND STOP FREQ
XX.XXXXXX GHz Displays the stop frequency for the band. BSP; BSP?
BAND FUNCTIONS None
EDIT SYSTEM
EQUATIONS Calls menu OM3, which lets you edit system equations. None
STORE BAND 1
BANDS STORED:
(12345)
Indicates the band that will be stored and, within the
parenthesis, indicates the bands that have been stored. SVBMM
CLEAR ALL
DEFINITIONS Clears all the band definitions that may have been
previously stored. CLB; CLBMM
SET MULTIPLE
SOURCE STATE Selects Multiple Source Control menu OM0. None
PRESS <ENTER>
TO SELECT Pressing the Enter key implements your menu selection. None
Menu OM2, Define Bands Menu
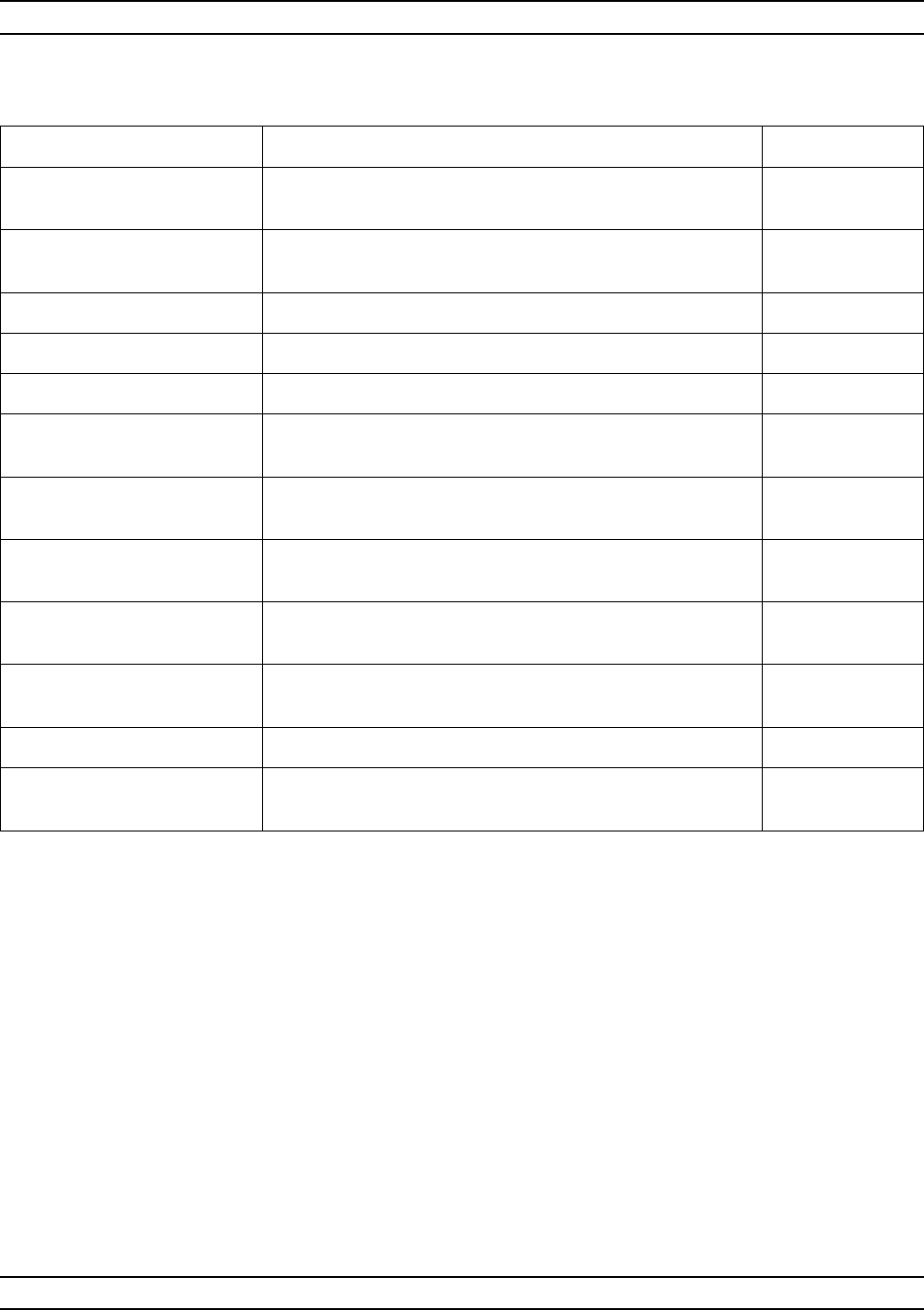
37XXXC OM A-169
ALPHABETICAL LISTING O
MENU DESCRIPTION GPIB COMMAND
EDIT SYSTEM
EQUATIONS None
EQUATION
TO EDIT None
SOURCE 1 Selects source 1 frequency equation for change. ED1
SOURCE 2 Selects source 2 frequency equation for change. ED2
RECEIVER Selects receiver frequency equation for change. EDR
EQUATION
SUMMARY None
C.W. ON (OFF) Toggles frequency term (F) in equation ON or OFF. ESW; ECW;
EXW?
MULTIPLIER
XX Enables changing multiplier term of frequency equation via
key pad or rotary knob. EML
DIVISOR
XX Enables changing divisor term frequency equation via key
pad or rotary knob. EDV
OFFSET FREQ
XXX.XXXXXXXXX GHz Enables changing offset frequency term frequency equation
via key pad or rotary knob. EOS; EOS?
PREVIOUS MENU Recalls menu OM1. None
PRESS <ENTER>
TO SELECT Pressing the Enter key implements your menu selection.
Menu OM3, Edit System Equations
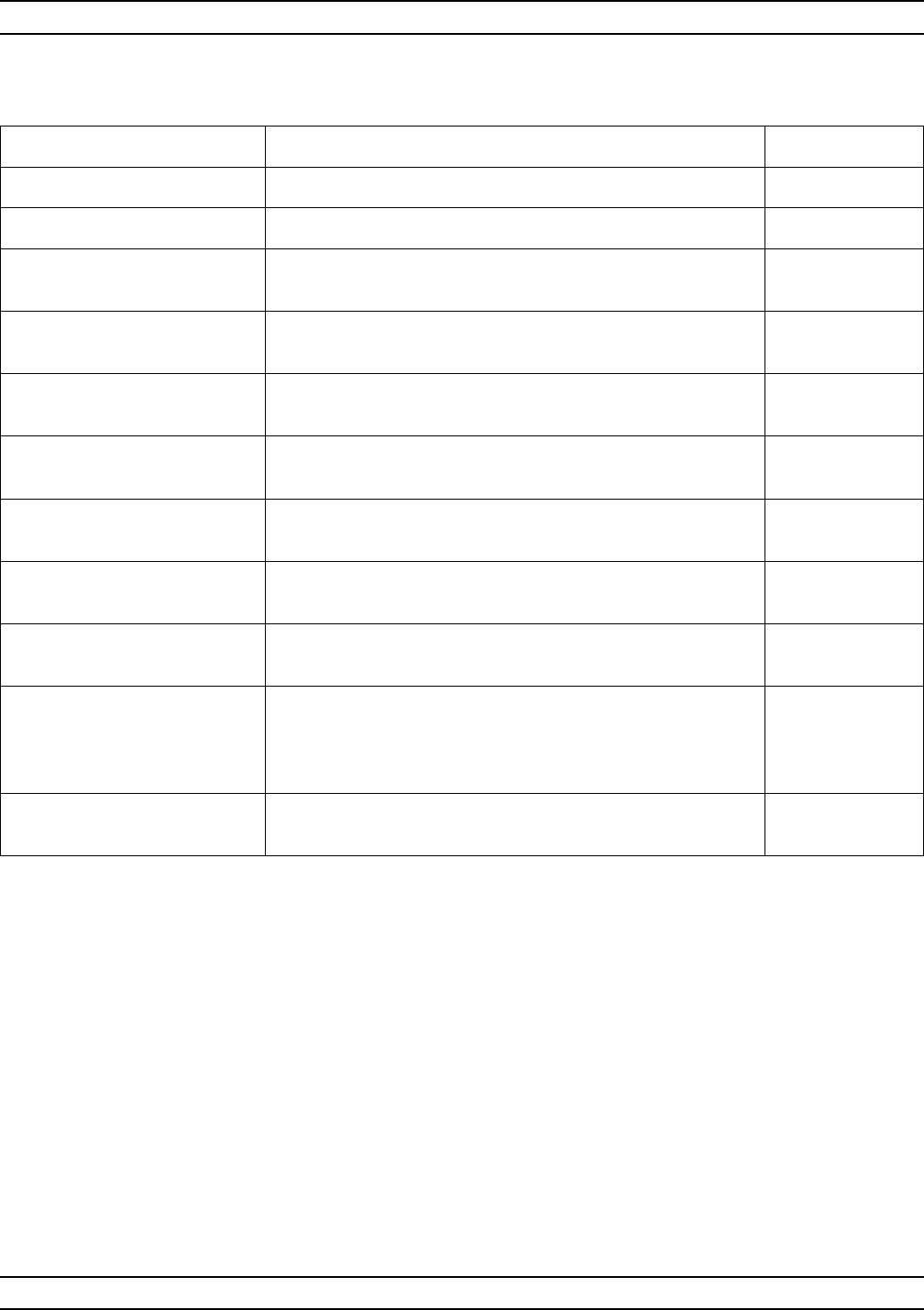
A-170 37XXXC OM
O ALPHABETICAL LISTING
MENU DESCRIPTION GPIB COMMAND
OPTIONS None
TRIGGERS Calls menu TRIG, which lets you define trigger source. None
REAR PANEL
OUTPUT Calls menu ORP1, which lets you select an output for the
rear panel AUX I/O connector. None
DIAGNOSTICS Calls menu DG1, which lets you implement system
diagonistics. None
MULTIPLE SOURCE
CONTROL Calls menu OM1, which lets you use and define multiple
sources. None
BROADBAND
DEFINITION If the Broadband Test Is selected, this option appears in
place of Multiple Source Control. It calls menu BB4. BDMM
MILLIMETER WAVE
BAND DEFINITION If unit is a 371XXC, this selection calls menu MMW4. NEED
RECEIVER MODE Calls menu RCV1, which gives you Receiver Mode control
options. None
SOURCE CONFIG Calls menu SC, which lets you configure the frequency
source. None
RF ON/OFF
DURING RETRACE Turns RF during retrace and switch points ON or OFF. The
user must keep the sweep range small, preferably below 2
GHz. Avoid including any switch points where RF would be
blanked for delays due to hardware settling.
RT0; RT1; RTX?
PRESS <ENTER>
TO SELECT Pressing the Enter key implements your menu selection. None
Menu OPTNS, Select Options
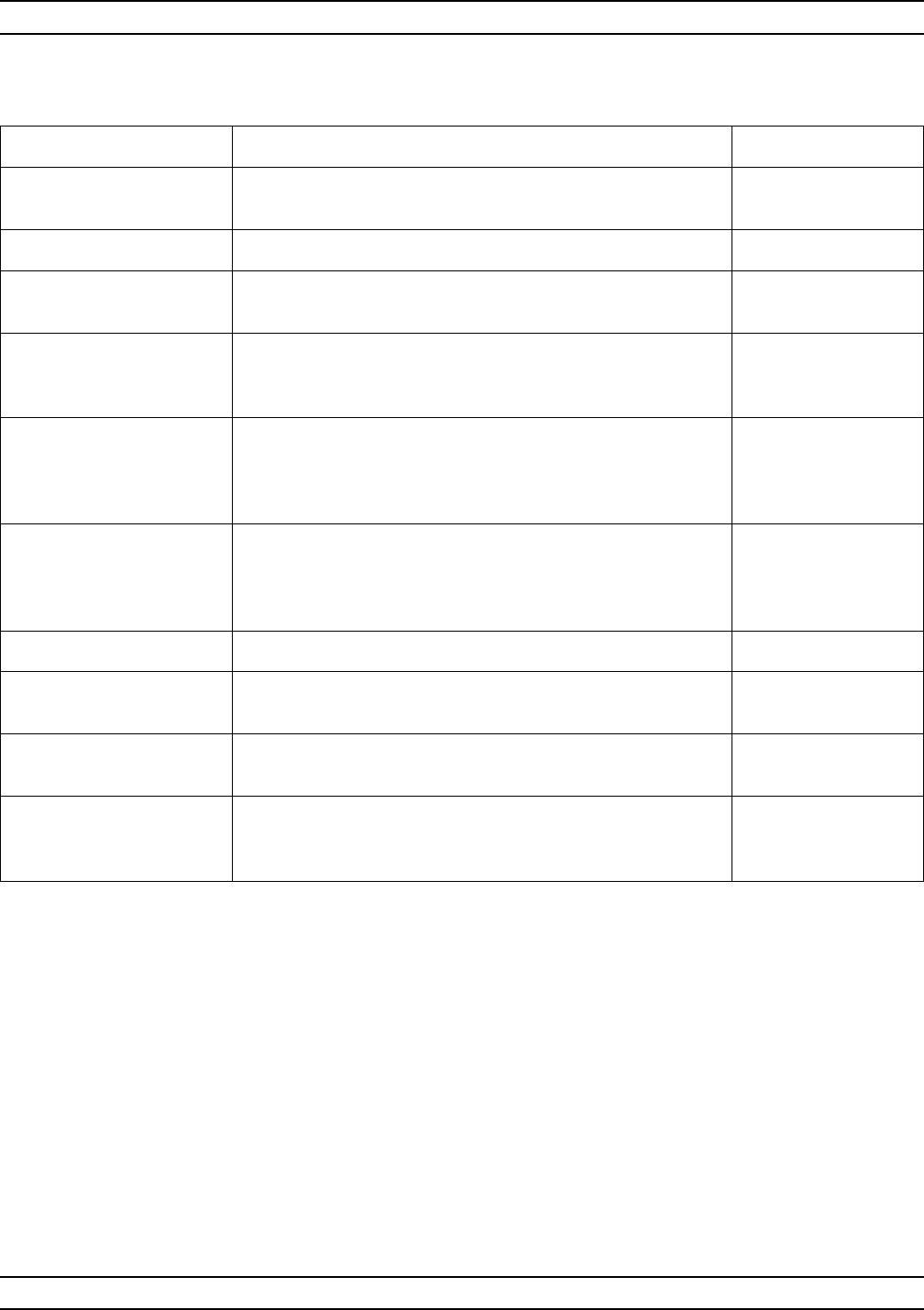
37XXXC OM A-171
ALPHABETICAL LISTING O
MENU DESCRIPTION GPIB COMMAND
REAR PANEL
OUTPUT CONTROL None
OUTPUT ON (OFF) Turns the rear panel ANALOG OUT output on or off. RV1; RV0; RV1?
SELECT MODE
XXXXXXXXXX Calls menu ORP2, which lets you select an output mode. None
HORIZONTAL
OR PHASE LOCK
SCALING
None
START/LOCK a1
X.XXXX V Lets you enter a voltage for the start/lock frequency. Value
will be a frequency start voltage if SELECT MODE choice
is HORIZONTAL. It will be a phase-lock voltage if SELECT
MODE choice is PHASELOCK.
VST; VST?
STOP/LOCK a2
X.XXXX V Lets you enter a voltage for the start/lock frequency. Value
will be a frequency stop voltage if SELECT MODE choice
is HORIZONTAL. It will be a phase-lock voltage if SELECT
MODE choice is PHASELOCK.
VSP; VSP?
VERTICAL SCALING None
RESOLUTION
1.000 V/DIV Shows fixed value for VERTICAL mode. SCL; SCL?; SCL2;
SCL2?
REFERENCE VALUE
0.000 V/DIV Shows fixed value for VERTICAL mode. OFF; OFF?; OFF2;
OFF2?
PRESS <ENTER>
TO SELECT
OR TURN ON/OFF
Pressing the Enter key implements your menu selection. None
Menu ORP1, Rear Panel Output Control
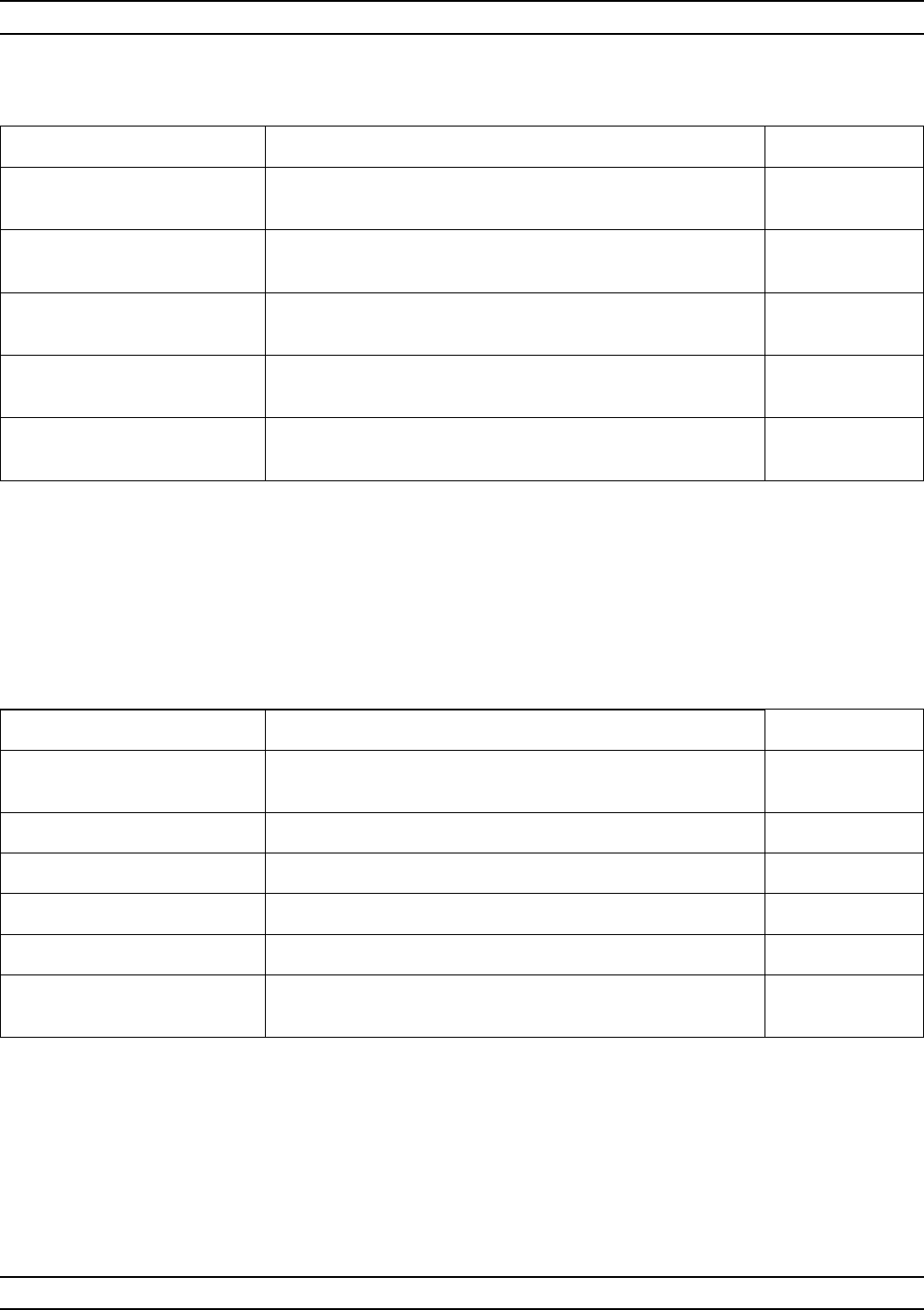
A-172 37XXXC OM
O ALPHABETICAL LISTING
MENU DESCRIPTION GPIB COMMAND
SELECT MODE
FOR OUTPUT None
HORIZONTAL Pressing Enter key selects horizontal drive for external
chart recorder connected to ANALOG OUT connector. RVH; RVX?
VERTICAL Pressing Enter key selects vertical drive for external chart
recorder connected to ANALOG OUT connector. RVV; RVX?
PHASE LOCK Pressing Enter key selects phase-lock for external chart
recorder connected to ANALOG OUT connector. RVL; RVX?
PRESS <ENTER>
TO SELECT Pressing the Enter key implements your menu selection. None
Menu ORP2, Select Output Mode
MENU DESCRIPTION GPIB COMMAND
TEST SET
CONFIGURATION None
INTERNAL Calls menu OTS2. SELINT; SELXX?
S-PARAMETER Calls menu OTS3. SELSP; SELXX?
MILLIMETER WAVE Calls menu MMW1. SELMM; SELXX?
BROADBAND Calls menu BB2. SELBB; SELXX?
PRESS <ENTER>
TO SELECT Pressing the Enter key implements your menu selection.
Menu OTS1, Test Set Configuration
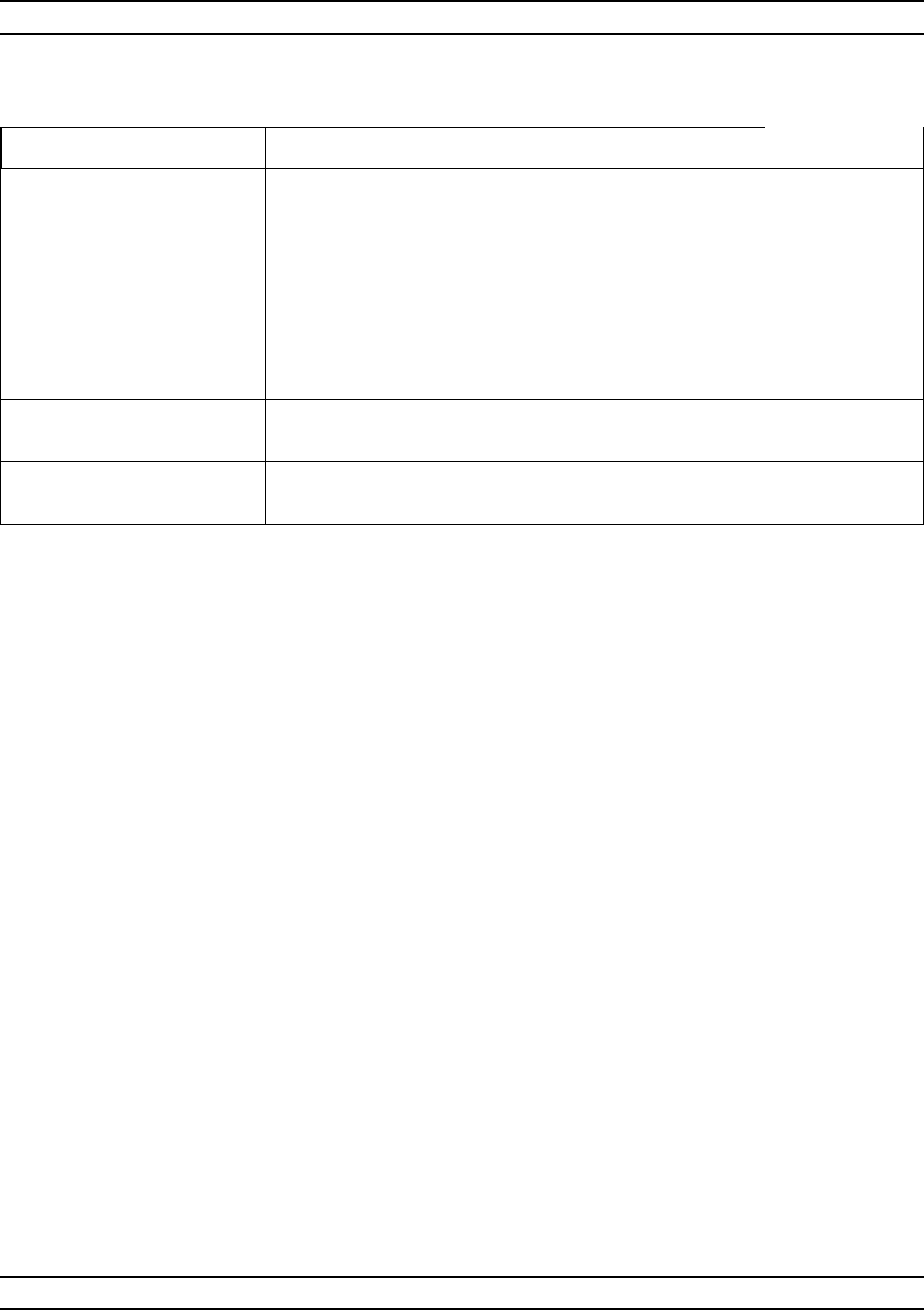
37XXXC OM A-173
ALPHABETICAL LISTING O
MENU DESCRIPTION GPIB COMMAND
INTERNAL
TEST SET None
WARNING:
CONTINUING
WILL INVALIDATE
CURRENT
SETUP AND
CALIBRATION
PRESS <ENTER>
TO SELECT Pressing the Enter key implements internal test set
configuration. None
PRESS <CLEAR>
TO ABORT Pressing the Clear key aborts internal test set
configuration. None
Menu OTS2, Warning
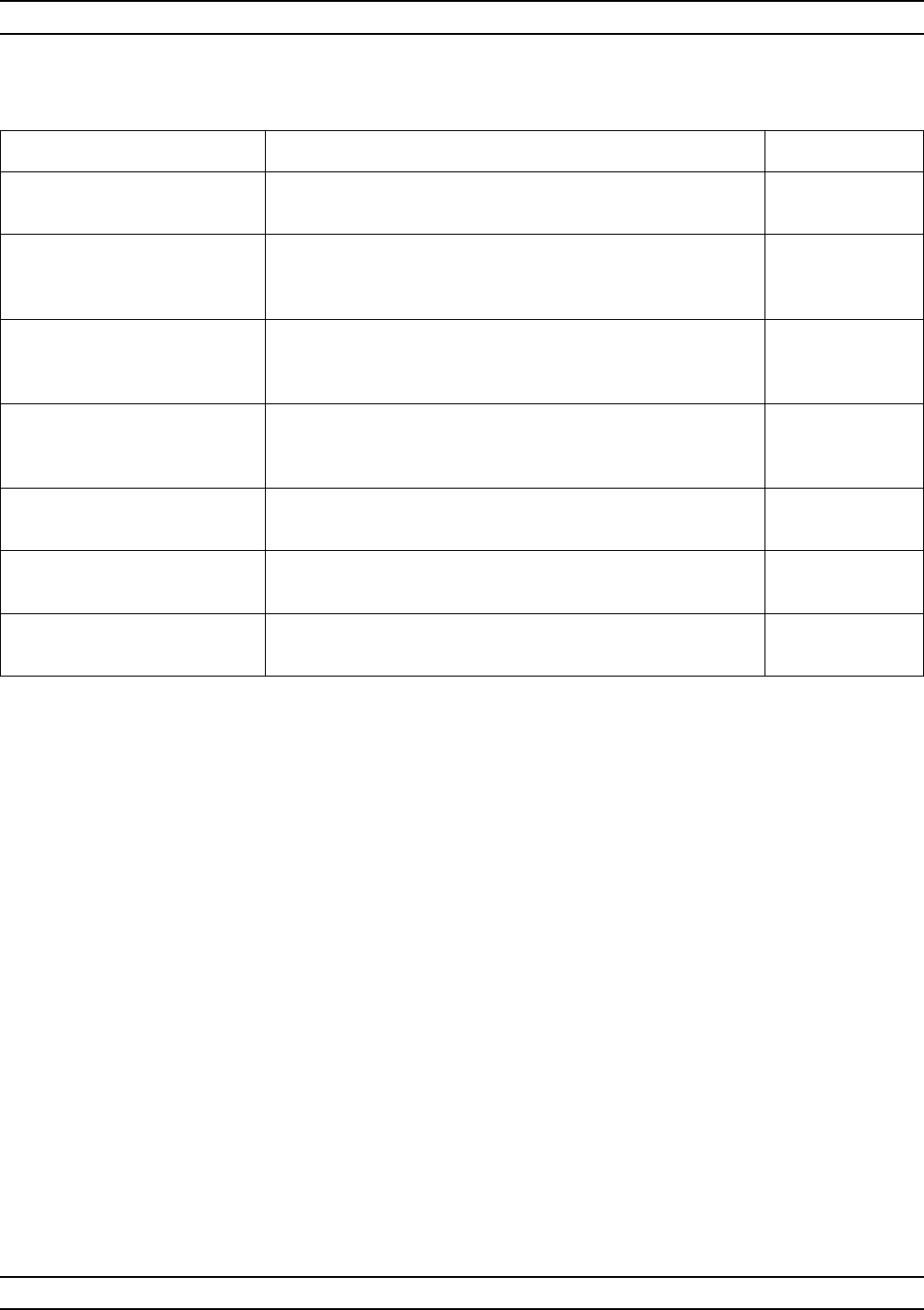
A-174 37XXXC OM
P ALPHABETICAL LISTING
MENU DESCRIPTION GPIB COMMAND
SELECT POLAR
CHART MODE None
MAGNITUDE,
PHASE Selects Polar Chart Display to show magnitude and phase
for the full frequency range—from start frequency to stop
frequency.
PCP
MAGNITUDE,
SWP POSITION Selects Polar Chart Display to show magnitude information
only for the phase data that falls between the start and stop
angles selected below.
PCS
SET SWEEP
POSITION
BOUNDARIES
Sets the start and stop angles for the data display. AST; ASP
START ANGLE
X.XX°
AST; AST?
STOP ANGLE
X.XX°
ASP; ASP?
PRESS <ENTER>
TO SELECT Pressing the Enter key implements your menu selection. None
Menu PC1, Select Polar Chart Mode
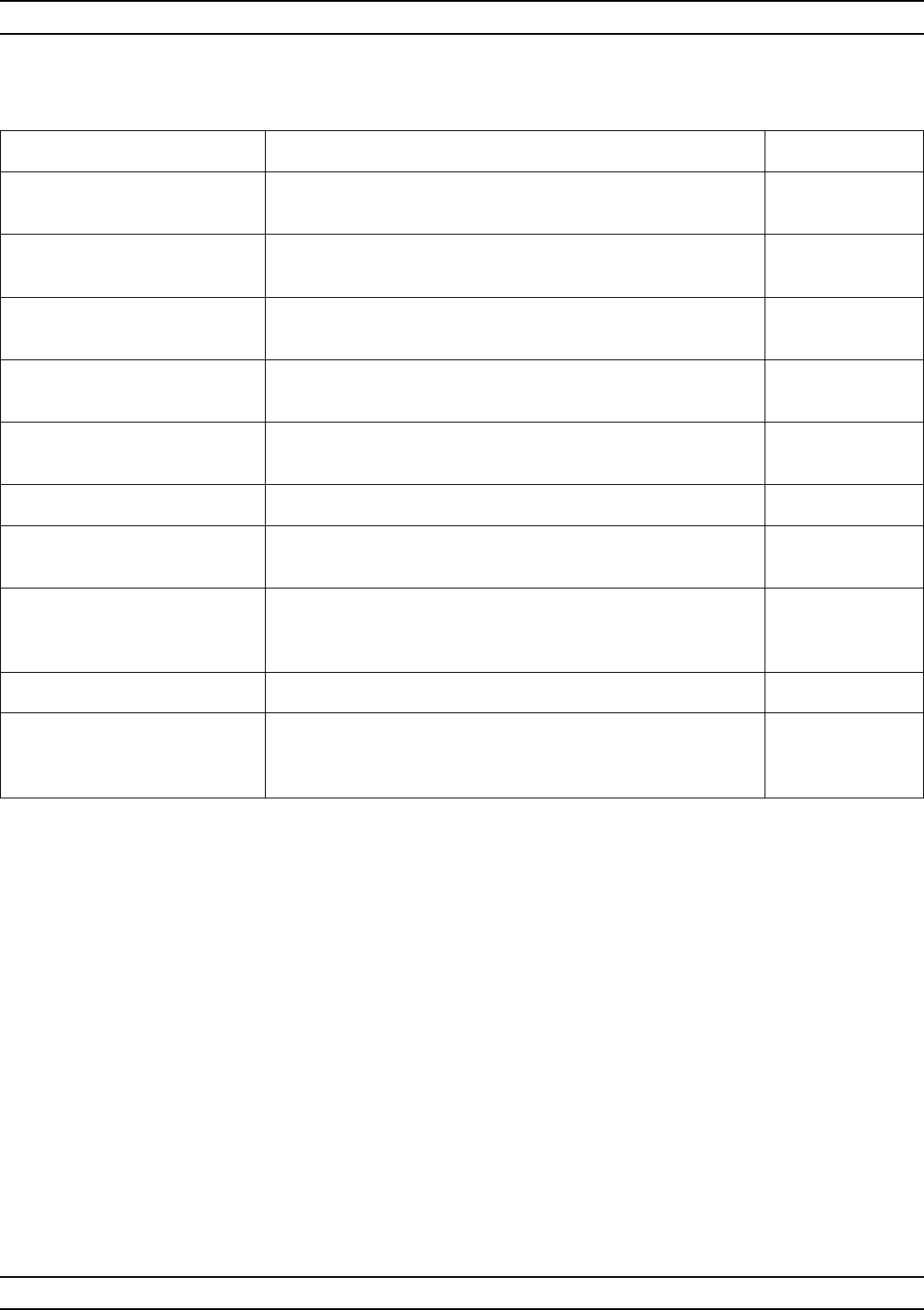
37XXXC OM A-175
ALPHABETICAL LISTING P
MENU DESCRIPTION GPIB COMMAND
PARAMETER
DEFINITION None
S21/USER 1 Lets you choose between displaying a pre-defined
S-Parameter or a user-defined parameter. USR1-USR4
RATIO
b2 / a1 Displays the parameters chosen as numerator and
denominator. DA1; DA2; DB1;
DB2; DR1
PHASE LOCK
a1 Displays the phase-lock parameter. NA1; NA2; NB1;
NB2; NU1
USER LABEL:
MY S11 Displays the name of the user-defined parameter. USL; USL?
CHANGE RATIO Calls menu PD2, which lets you change the ratio. None
CHANGE
PHASE LOCK None
CHANGE LABEL Calls menu GP5, which lets you name your newly defined
parameter. The label appears at the top of the graph-type
display and under the word “LABEL” in the menu.
None
PREVIOUS MENU Returns to the previous menu, SP. None
PRESS <ENTER>
TO SELECT
OR SWITCH
Pressing the ENTER key implements your menu selection. None
Menu PD1, Parameter Definition 1
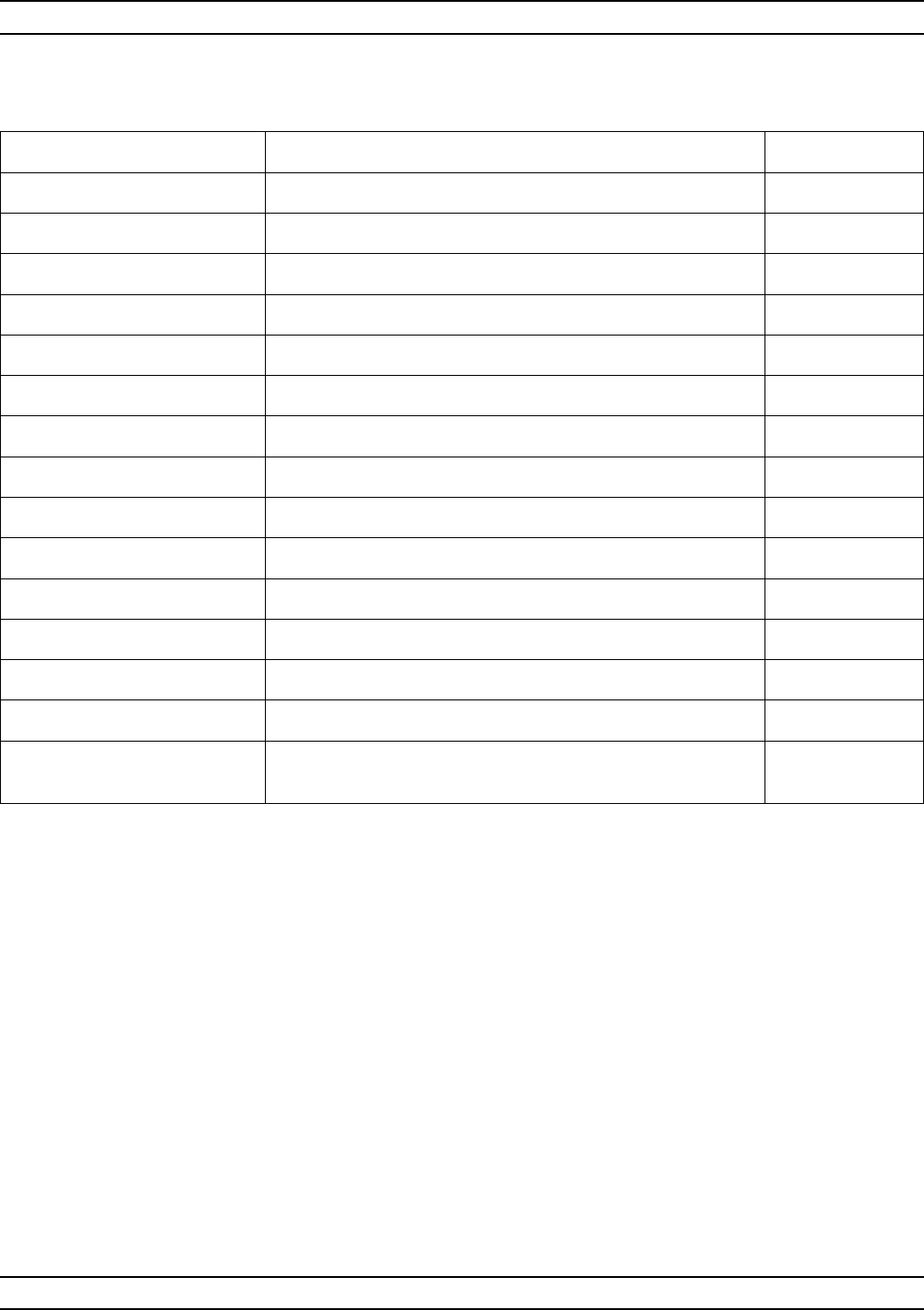
A-176 37XXXC OM
P ALPHABETICAL LISTING
MENU DESCRIPTION GPIB COMMAND
PARAMETER RATIO None
NUMERATOR None
a1 Selects a1 as the numerator. NA1
a2 Selects a2 as the numerator. NA2
b1 Selects b1 as the numerator. NB1
b2 Selects b2 as the numerator. NB2
1 (UNITY) Selects the numerator to be 1 (unity). NU1
DENOMINATOR None
a1 Selects a1 as the demoniator. DA1
a2 Selects a2 as the demoniator. DA2
b1 Selects b1 as the demoniator. DB1
b2 Selects b2 as the demoniator. DB2
1 (UNITY) Selects the numerator to be 1 (unity). DE1
PREVIOUS MENU Returns you to menu PD1. None
PRESS <ENTER>
TO SELECT Pressing the ENTER key implements your menu selection. None
Menu PD2, Parameter Ratio
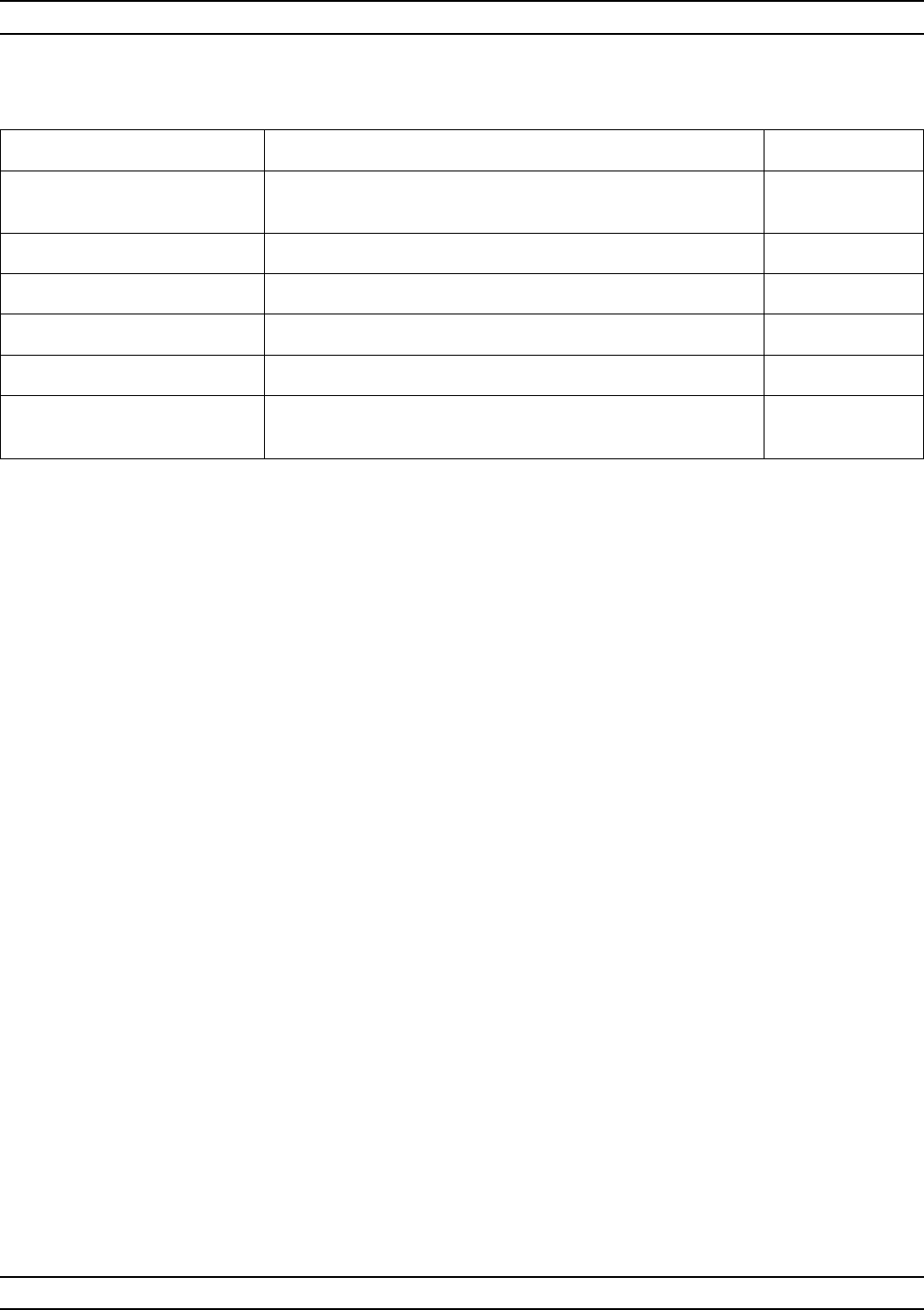
37XXXC OM A-177
ALPHABETICAL LISTING P
MENU DESCRIPTION GPIB COMMAND
PARAMETER
DEFINITION None
PHASE LOCK None
a1 (Ra) Selects a1. None
a2 (Rb) Selects a2. None
PREVIOUS MENU Returns you to menu PD1. None
PRESS <ENTER>
TO SELECT Pressing the ENTER key implements your menu selection. None
Menu PD3, Parameter Definition 2
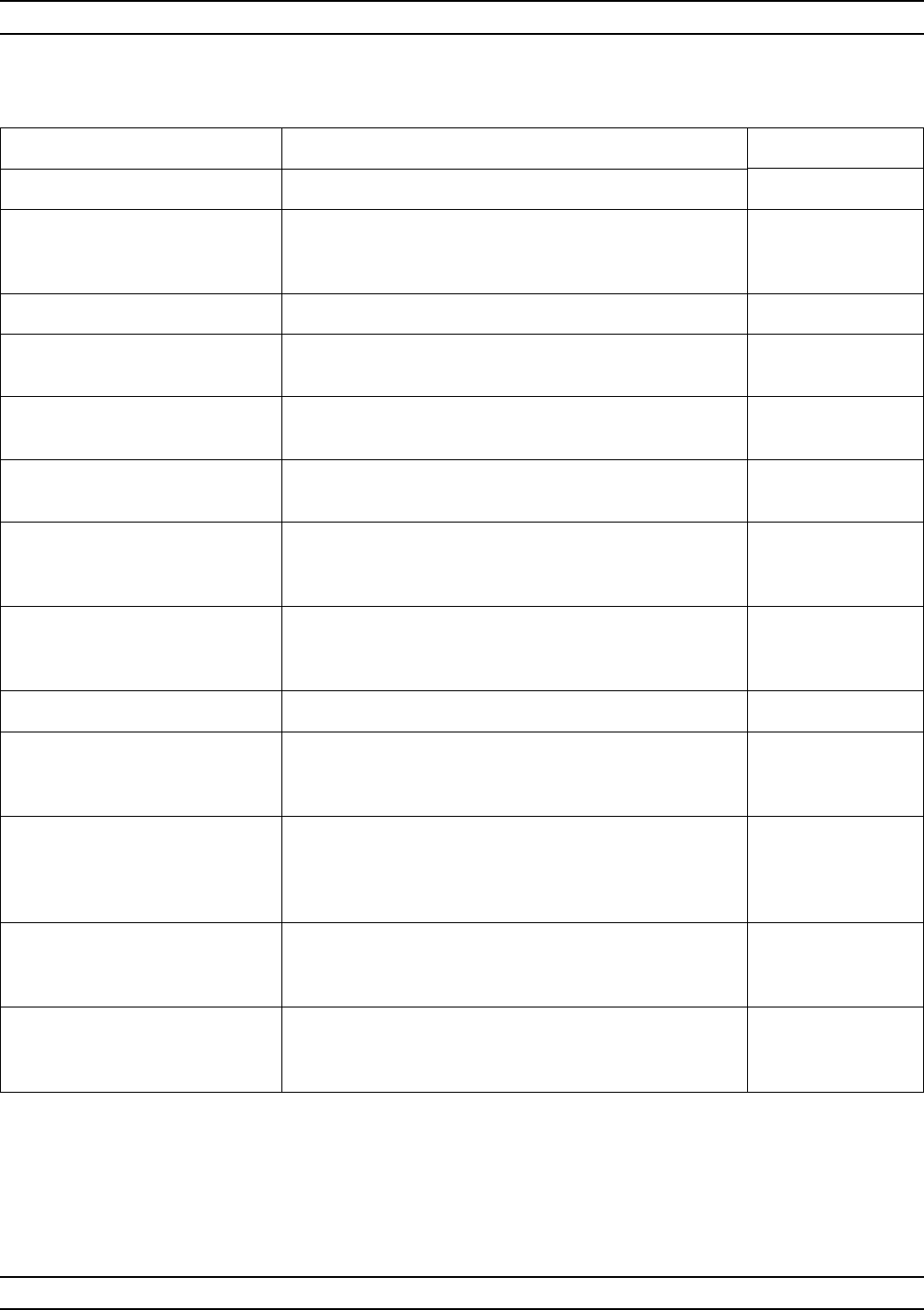
A-178 37XXXC OM
P ALPHABETICAL LISTING
MENU DESCRIPTION GPIB COMMAND
PLOT OPTIONS None
FULL PLOT The plotter will plot everything displayed on the screen
(data traces, graticule, menu text) when START PRINT
is pressed.
PFS
OPTIONS TO PLOT None
HEADER ON (OFF) The plot will include an information header if this option
is on and START PRINT is pressed. PLH; PLD
MENU ON (OFF) The plot will include the menu text if this option is on
and START PRINT is pressed. PMN
LIMITS ON (OFF) The plot will include any limit lines if this option is on
and START PRINT is pressed. PLM; PLD
GRATICULE ON (OFF) The plot will include the graticule and annotation if this
option is on and START PRINT is pressed. The plotter
plots the graticule.
PGT; PLD
DATA TRACE(S) ON(OFF)
AND MARKERS The plot will include the data and any marker that are
present if this option is on and START PRINT is
pressed. The plotter plots the graticule.
PLT; PLD
PLOT FORMAT None
PLOT SIZE Calls menu PL2, which lets you select the size and
location of
the plot.
None
PEN COLORS Calls menu PL3, which lets you select pen colors for
the various elements of the plot: graticule, data traces,
menu text and header. Also lets you select the relative
pen speed.
None
PLOT ORIENTATION
PORTRAIT
LANDSCAPE
Select the orientation for your plot, either portrait or
landscape. PORT; PLO?
LAND; PLO?
PRESS <ENTER>
TO SELECT
OR TURN ON/OFF
Pressing the Enter key implements your menu
selection. None
Menu PL1, Plot Options
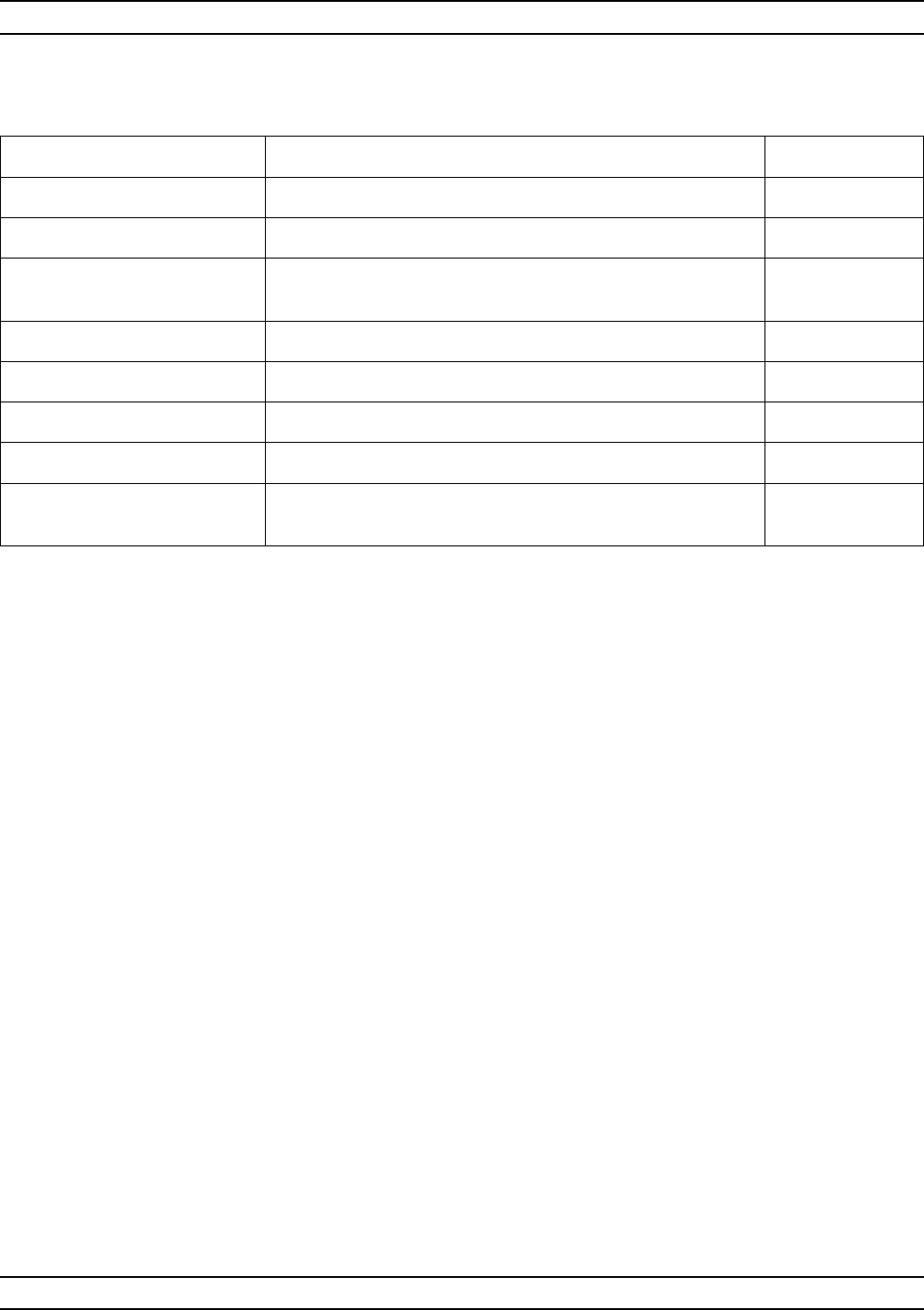
37XXXC OM A-179
ALPHABETICAL LISTING P
MENU DESCRIPTION GPIB COMMAND
PLOT SIZE None
FULL SIZE Selects a full size (page) plot. PFL
–QUARTER
SIZE PLOTS– None
UPPER LEFT Selects a quarter-size plot, upper-left quadrant. PTL
UPPER RIGHT Selects a quarter-size plot, upper-right quadrant. PTR
LOWER LEFT Selects a quarter-size plot, lower-left quadrant. PBL
LOWER RIGHT Selects a quarter-size plot, lower-right quadrant. PBR
PRESS <ENTER>
TO SELECT Pressing the Enter key implements your menu selection. None
Menu PL2, Select Plot Size
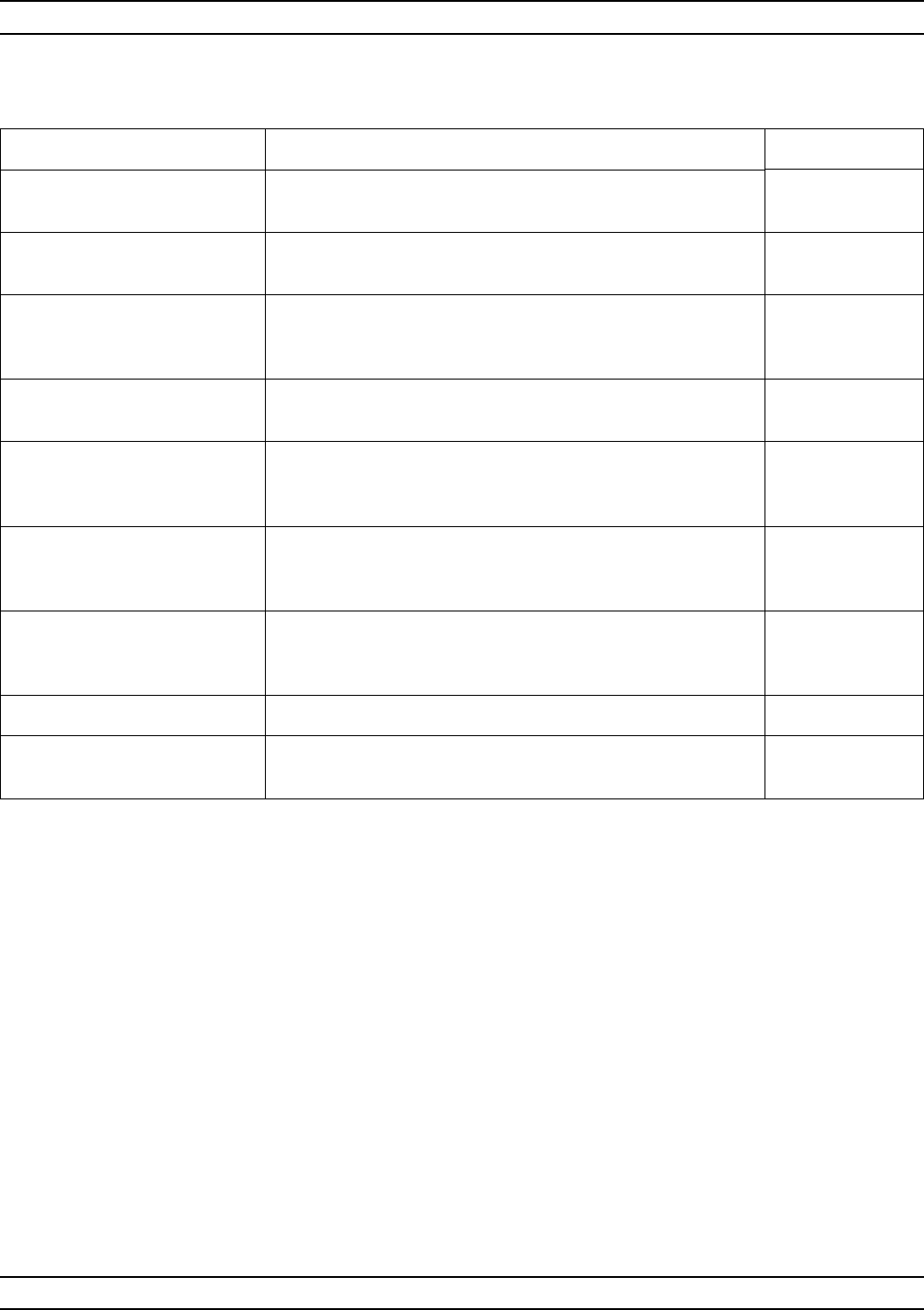
A-180 37XXXC OM
P ALPHABETICAL LISTING
MENU DESCRIPTION GPIB COMMAND
SELECT
PEN COLORS None
DATA PEN
nSelects the color in which the data will be plotted. The
number of the pen displays where the “n” is shown. DPN
DATA TRACE
OVERLAY PEN
n
Selects the color in which the 2nd trace in a dual trace
overlay plot will be plotted. The number of the pen displays
where the “n” is shown.
TPN
GRATICULE PEN
nSelects the color in which the graticule will be plotted. The
number of the pen displays where the “n” is shown. GPN; GPN?
MARKERS AND
LIMITS PEN
n
Selects the color in which the markers and limits will be
plotted. The number of the pen displays where the “n” is
shown.
MPN; MPN?
HEADER PEN
nSelects the color in which the header information will be
plotted. The number of the pen displays where the “n” is
shown.
HPN; HPN?
PEN SPEED
100 PERCENT
OF MAXIMUM
Selects the pen’s speed as a percentage of the plotter’s
maximum speed. (Used to optimize plots on transparencies
or with worn pens.)
SPD; SPD?
PREVIOUS MENU Recalls menu PL1. None
PRESS <ENTER>
TO SELECT Pressing the Enter key implements your menu selection. None
Menu PL3, Select Pen Colors
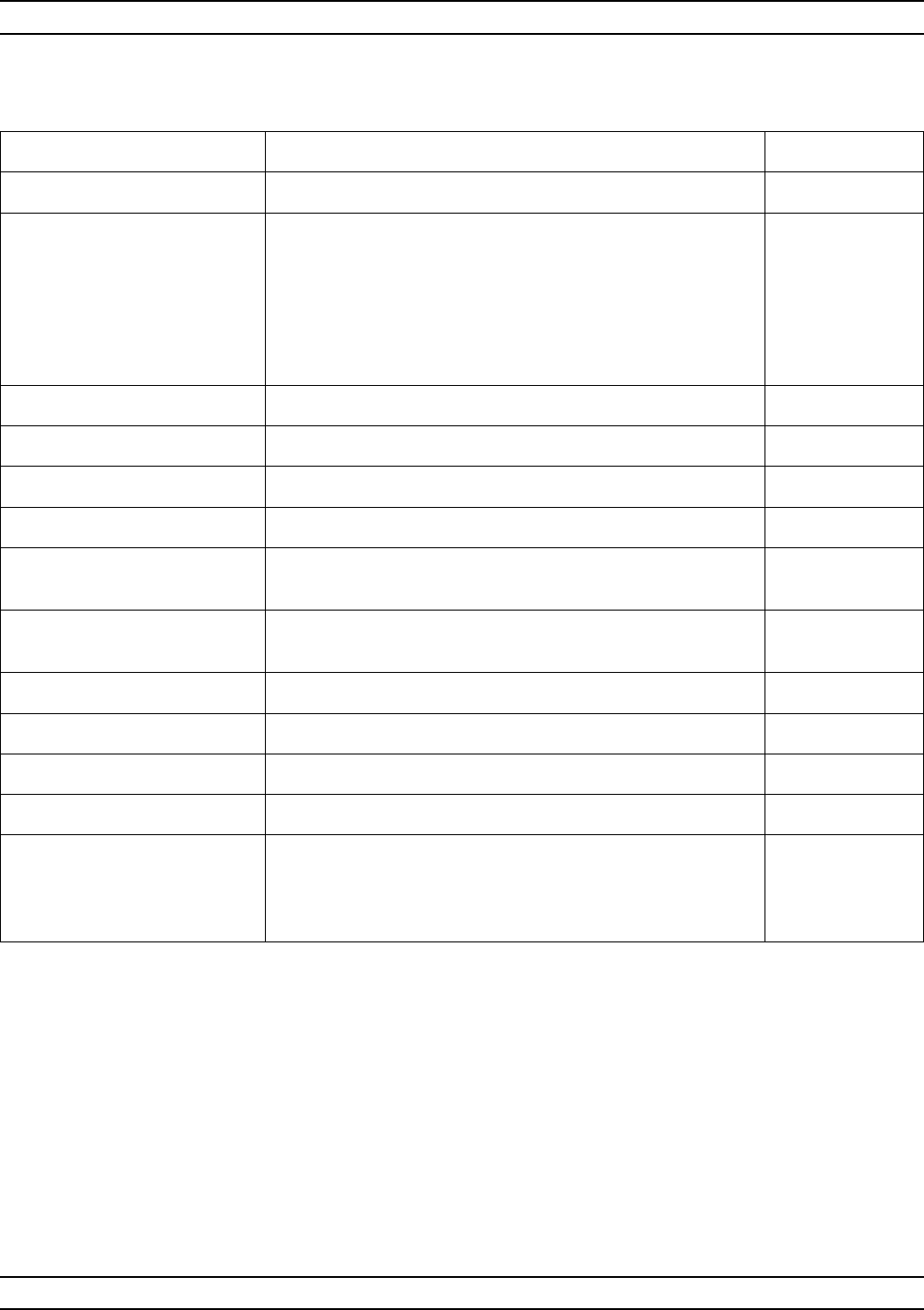
37XXXC OM A-181
ALPHABETICAL LISTING P
MENU DESCRIPTION GPIB COMMAND
HARD COPY None
OUTPUT DEVICE Allows hard copy output to be directed to the HDD or
floppy, in addition to the printer and plotter. In addition to
text (*.txt), S2P (*.s2p), and tabular (*.dat) files, bitmaps
(*.bmp) and HPGL (*.hgl) files are offered to satisfy desktop
publishing requirements. Specifically, color bitmaps and
graphic language files can be imported into Windows
applications, such as Cap3700.
None
PRINTER Selects the printer as your output device. None
PLOTTER Selects the plotter as your output device. None
DISK FILE Selects a disk file as your output device. None
SETUP & OPERATIONS None
SETUP HEADERS Calls menu PM2, which lets you define the output header
information. None
DISK OPERATIONS Calls menu PM4, which lets you store/recall tabular data
to/from disk. None
OUTPUT OPTIONS None
PRINT OPTIONS Calls menu PM5. None
PLOT OPTIONS Calls menu PL1. None
DISK FILE OPTIONS Calls menu PM4A. None
PRESS <ENTER>
TO SELECT Pressing the ENTER key implements your menu selection.
The menu remains on the screen until another menu is
selected for display or until the CLEAR/RET LOC key is
pressed.
None
Menu PM1, Select Data Output Type
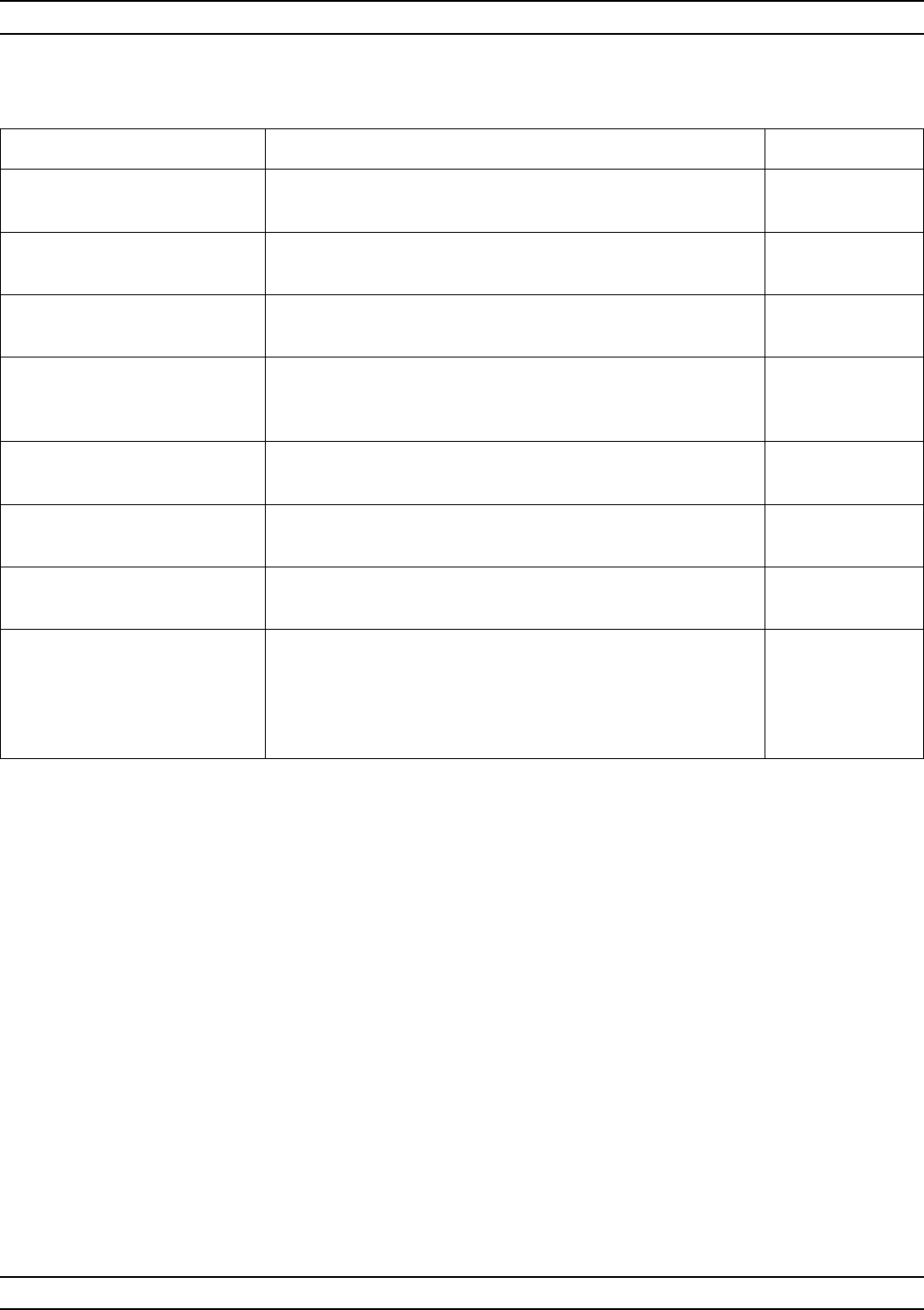
A-182 37XXXC OM
P ALPHABETICAL LISTING
MENU DESCRIPTION GPIB COMMAND
DATA OUTPUT
HEADERS None
MODEL ON (OFF)
XXXXXXXXXXXX Selecting <1> displays menu GP5, which lets you select
the letters and/or numbers in your model identifier. LMS; LMS?
DEVICE ID ON (OFF)
XXXXXXXXXXXX Selecting <1> displays menu GP5, which lets you select
the letters and/or numbers in your Device I.D. identifier. LID; LID?
OPERATOR ON (OFF)
XXXXXXXXXXXX Selecting <1> displays menu GP5, which lets you select
the letters
identifying the operator.
LNM; LNM?
COMMENT ON (OFF)
XXXXXXXXXXXX Selecting <1> displays menu GP5, which lets you enter a
comment. LOC; LOC?
DATE ON (OFF) Displays system date and time. Can be set in menu U6. LDT1; LDT0
SETUP LOGO Selecting <1> displays menu PM2A which lets you select
any of three logo options. None
PRESS <ENTER>
TO TURN ON/OFF
PRESS < 1 >
TO CHANGE
Pressing the Enter key selects between menu selections.
Pressing the CLEAR/RET LOC key lets you change the
between ON and OFF states.
Pressing <1> lets you enter the desired label in menu GP5.
None
Menu PM2, Data Output Headers
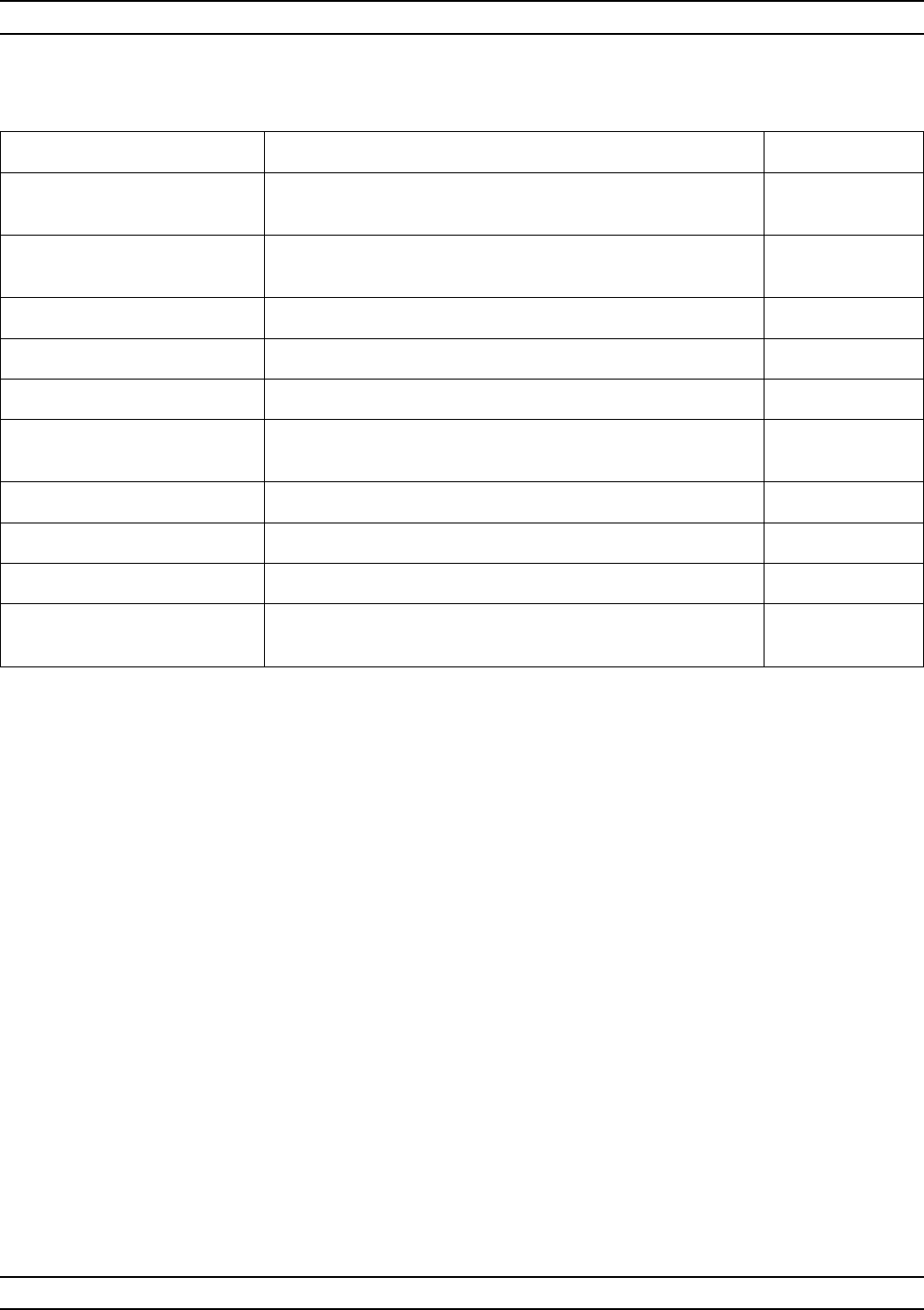
37XXXC OM A-183
ALPHABETICAL LISTING P
MENU DESCRIPTION GPIB COMMAND
LOGO SETUP Lets you turn off the Anritsu logo and select a user-define
logo. None
LOGO ON (OFF) Turns the logo on and off. LOGO1; LOGO0;
LOGOX?
LOGO TYPE Lets you define the logo type. None
STANDARD Causes the standard logo to be displayed. LOGOS
USER LOGO Lets users display their own log. LOGOU
INSTALL USER LOGO FROM
FLOPPY DISK None
FOR PRINTER Lets you define logo for printing. None
FOR PLOTTER Lets you define logo for plotting. None
PREVIOUS MENU Returns to previous menu. None
PRESS <ENTER>
TO SELECT Pressing the Enter key selects between menu selections. None
Menu PM2A, Data Output Headers
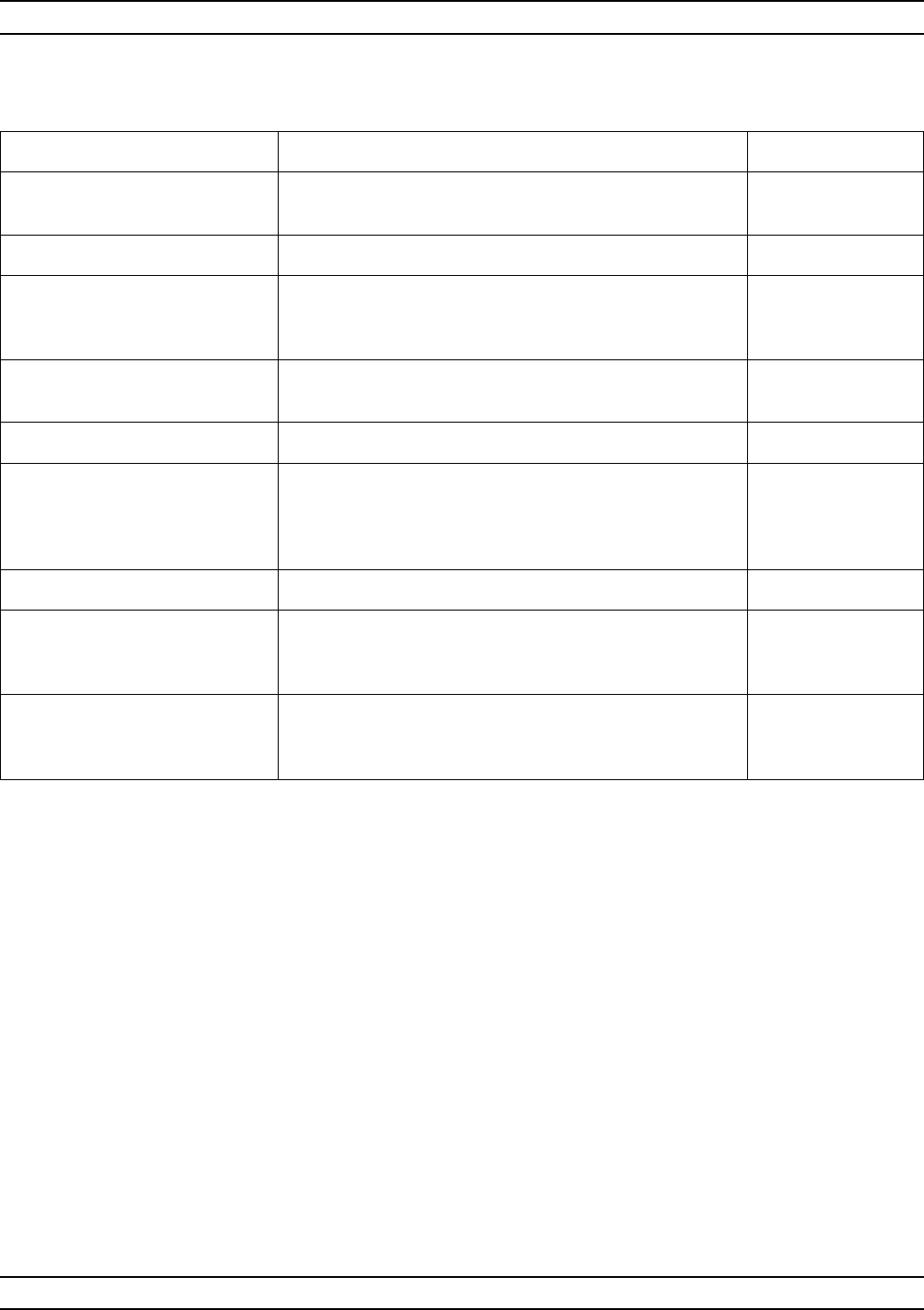
A-184 37XXXC OM
P ALPHABETICAL LISTING
MENU DESCRIPTION GPIB COMMAND
TABULAR PRINTER
OUTPUT FORMAT None
MARKER DATA ON (OFF) Provides for printing marker data. PMK; PMT
SWEEP DATA ON (OFF) Provides for printing sweep data. If you choose to print
the sweep data, you can then choose how may points
of the total sweep to print.
PTB; PMT
HEADER AND ON (OFF)
PAGE BREAKS Provides for printing header and page-break data. HD0; HD1; HDX?
PRINT DENSITY None
XXX PRINT PT(S)
OUTPUT PRINTS
1 POINT EVERY
XXX POINT(S)
Outputs one point every X points. Use the rotary knob
to select total number of points to output. Skipping
points will reduce the total number of printed points.
PT0-PT9
PREVIOUS MENU Returns to menu PM5. None
PRESS <ENTER>
TO SELECT
OR TURN ON/OFF
Pressing the Enter key selects between menu
selections. Pressing the CLEAR/RET LOC key lets you
change the between ON and OFF states.
None
TURN KNOB TO
CHANGE NUMBER
OF POINTS
None
Menu PM3, Tabular Printer Output Format
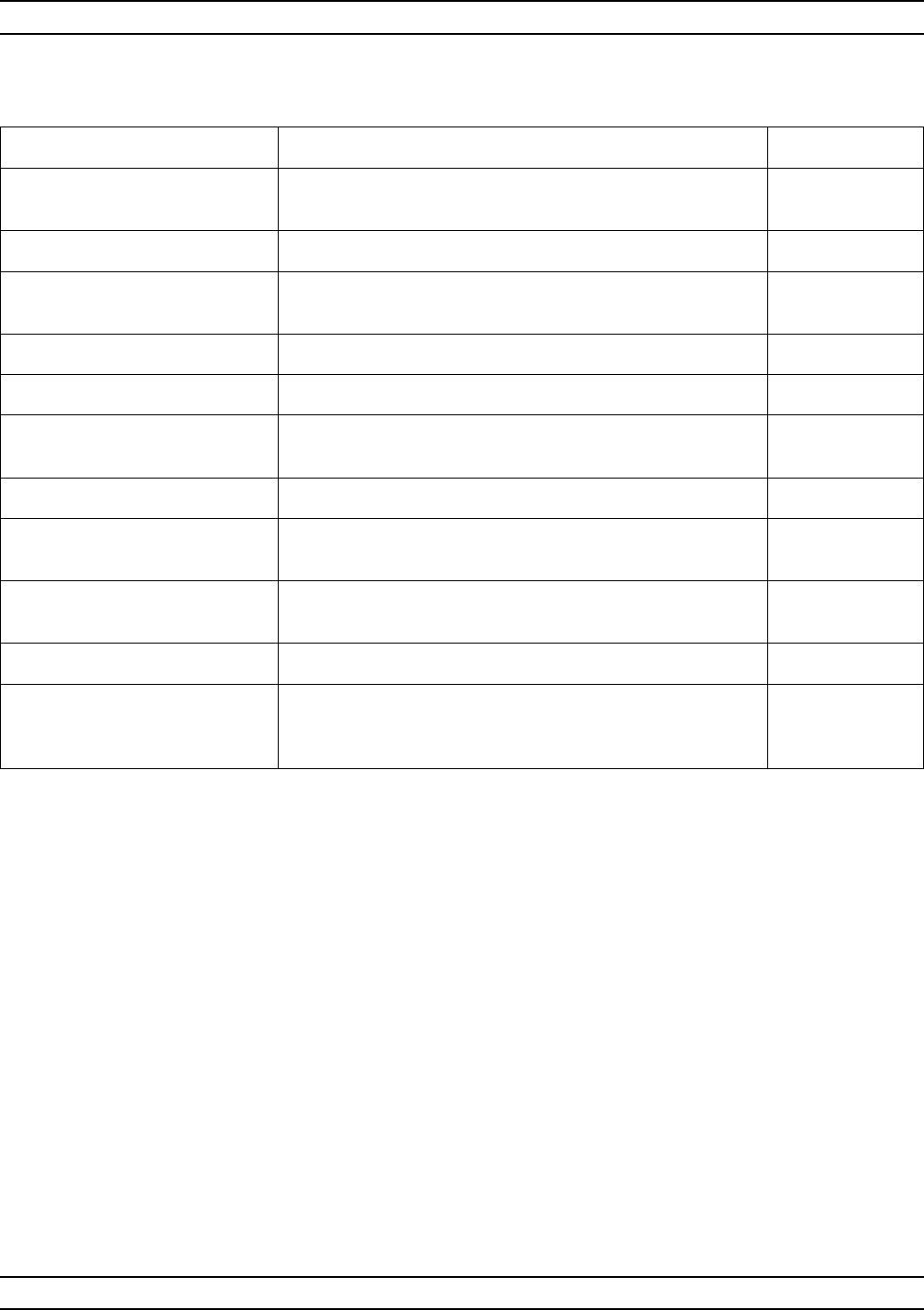
37XXXC OM A-185
ALPHABETICAL LISTING P
MENU DESCRIPTION GPIB COMMAND
GRAPHICAL PRINTER
OUTPUT FORMAT None
HEADER ON (OFF) Provides for printing header data. HD1; HD0; HDX?
SCREEN AREA
TO OUTPUT None
FULL SCREEN Prints the full-screen data, including the menus. PFS
GRAPH ONLY Prints only the graph or Smith chart. PGR
BITMAP FILE
OUTPUT OPTIONS None
TRUE COLOR Configures the bitmap disk-file format as true color. BMPT
COLOR ON
WHITE BACKGROUND Configures the bitmap disk-file format to be color on a
white background. BMPC
BLACK ON
WHITE BACKGROUND Configures the bitmap disk-file format to be black on a
white background. BMPB
PREVIOUS MENU Returns to menu PM5. None
PRESS <ENTER>
TO SELECT
OR TURN ON/OFF
Pressing the Enter key selects between menu selections.
Pressing the <ENTER> key lets you change the between
ON and OFF states.
None
Menu PM3A, Graphical Printer Output Format
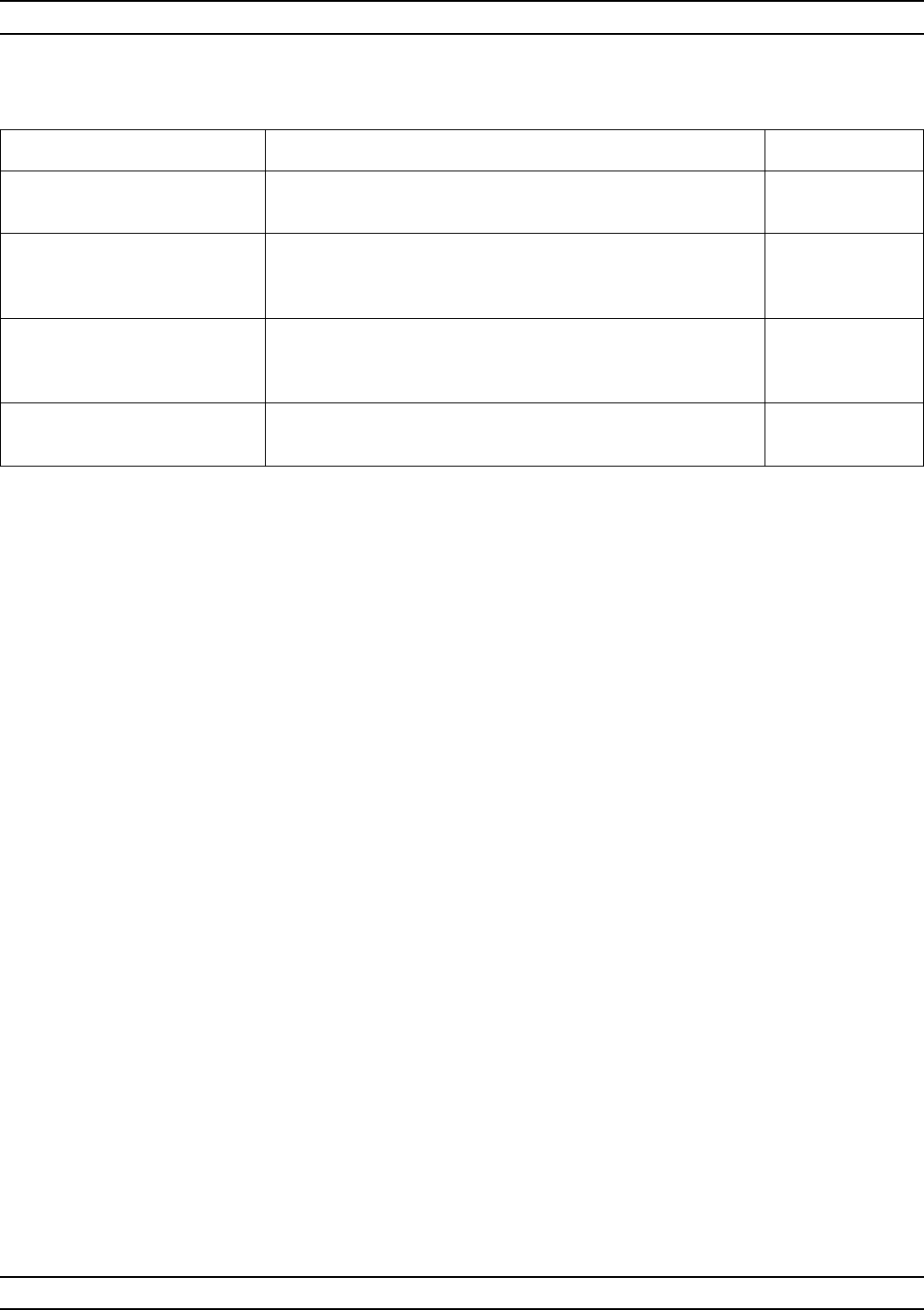
A-186 37XXXC OM
P ALPHABETICAL LISTING
MENU DESCRIPTION GPIB COMMAND
OUTPUT
DISK OPERATIONS None
TABULAR DATA
FROM HARD DISK
TO PRINTER
Calls DSK2 for selection of a measurement data file to be
output to the printer. None
TABULAR DATA
FROM FLOPPY DISK
TO PRINTER
Calls DSK2 for selection of a measurement data file to be
output to the printer. None
PRESS <ENTER>
TO SELECT Pressing the Enter key implements your menu selection. None
Menu PM4, Disk Output Operations
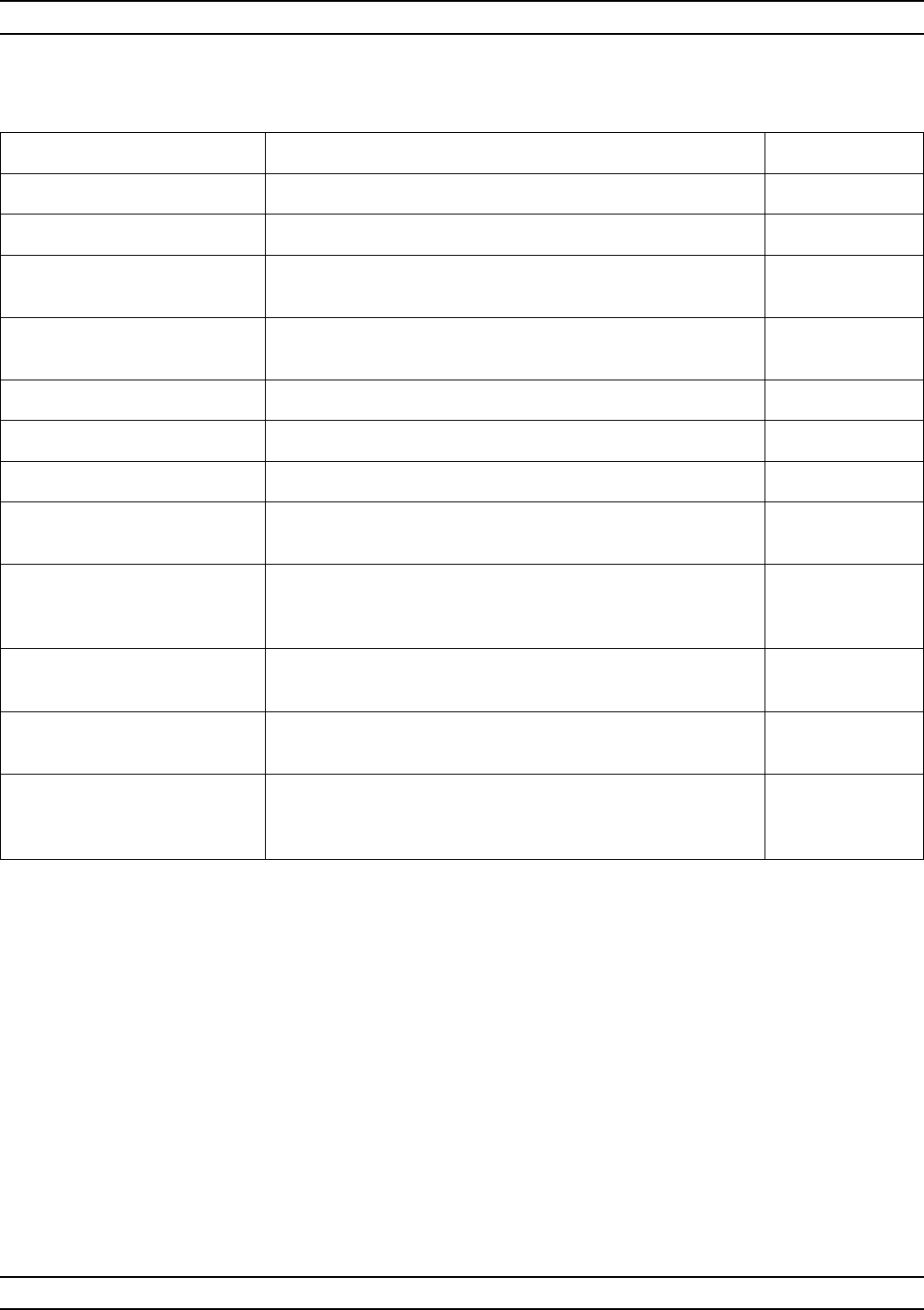
37XXXC OM A-187
ALPHABETICAL LISTING P
MENU DESCRIPTION GPIB COMMAND
DISK FILE OPTIONS None
DESTINATION None
HARD DISK Selects the output drive destination for the disk file to the
hard disk (C:). None
FLOPPY DISK Selects the output drive destination for the disk file to the
floppy disk (A:). None
FORMAT None
TEXT Text format, predefined. SAVE “*.TXT”
S2P S2P format, predefined. SAVE “*.SP2”
TABULAR DATA Tabular data format is configured via the Print Options
(Menu PM5) or Tabular Data (Menu PM3). SAVE “*.DAT”
BITMAP Bitmap format is configured via the Print Options (Menu
PM5), Options (Menu PM5, or Graphical Data (Menu
PM3A).
SAVE “*.BMP”
HPGL HPGL format is configured via the Plot Options (Menu
PL1). SAVE “*.HGL”
PRESS <ENTER>
TO SELECT Pressing the Enter key implements your menu selection. None
USE <START PRINT>
TO CAPTURE DATA Press the Start Print key at the moment data is to be
captured. This calls menu DSK3 to create a new file or
overwrite an existing file in the current directory.
None
Menu PM4A, Disk File Options
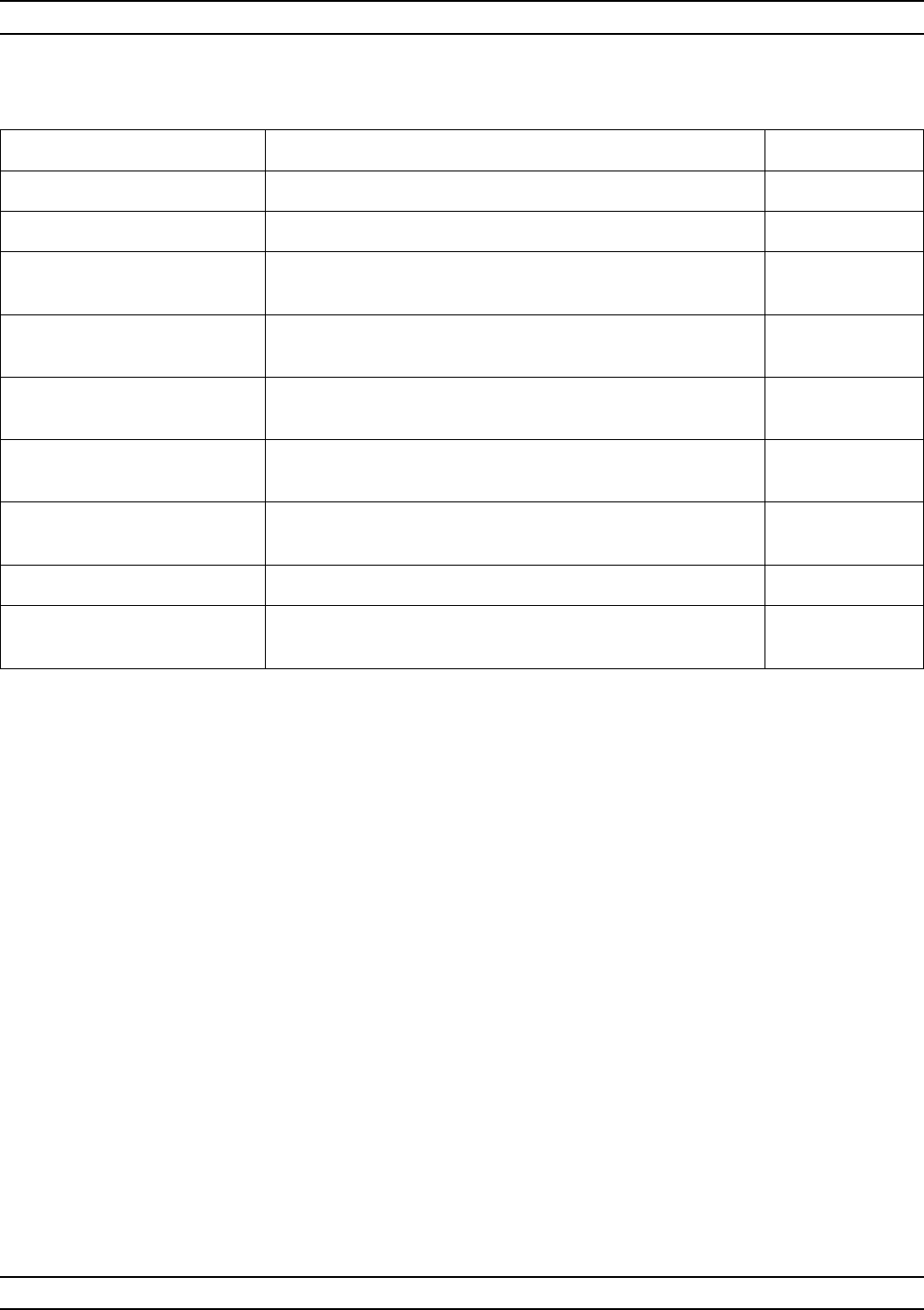
A-188 37XXXC OM
P ALPHABETICAL LISTING
MENU DESCRIPTION GPIB COMMAND
PRINT OPTIONS None
PRINTER TYPE None
THINKJET Select when HP QuietJet or HP ThinkJet is connected to
37XXXC VNA. None
DESKJET Select when HP DeskJet (B/W) or HP LaserJet II and III
series is connected to 37XXXC VNA. None
EPSON Select when Epson FX, Epson MX, or Epson 9-pin
compatible is connected to 37XXXC VNA. None
FORMAT OF
PRINTER OUTPUT None
GRAPHICAL DATA Prints only the graph or Smith chart, including any and all
data it contains. None
TABULAR DATA Prints a tabulation of the measured data None
PRESS <ENTER>
TO SELECT Pressing the Enter key implements your menu selection. None
Menu PM5, Printer Type, Options
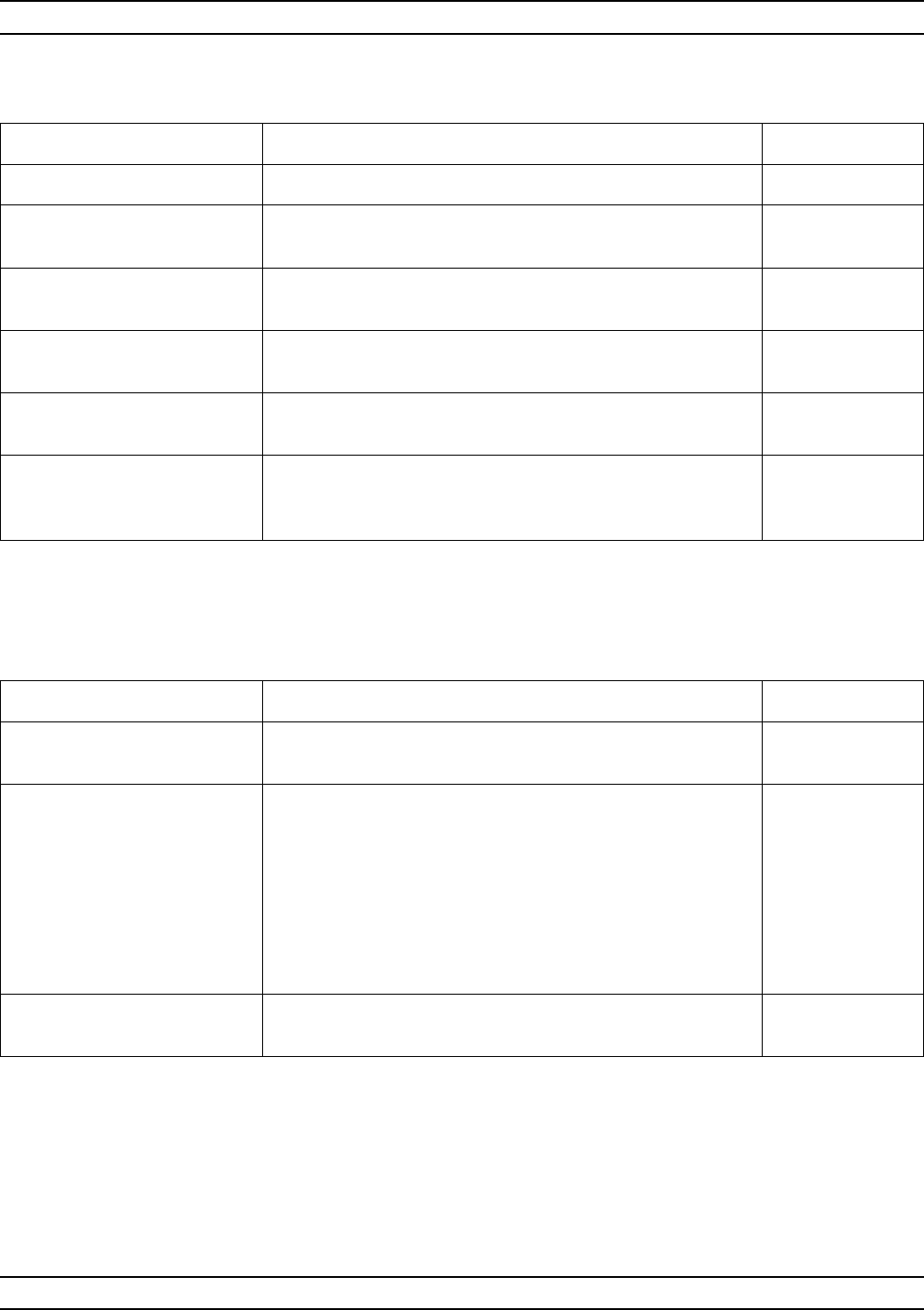
37XXXC OM A-189
ALPHABETICAL LISTING R
MENU DESCRIPTION GPIB COMMAND
RECEIVER MODE None
STANDARD Selects STANDARD mode (RECEIVER mode is not
activated). SDR; SDR?
USER DEFINED Calls menu RCV2, which lets you define rEceiver Mode
parameters. None
SOURCE CONFIG Calls menu SC, which lets you configure the frequency
source. None
SPUR REDUCTION
NORMAL/OFF Switches between NORMAL and OFF for hardware spur
reduction. Hardware control may not be available. SPR1; SPR0;
SPRX?
PRESS <ENTER>
TO SELECT
OR SWITCH
Pressing the ENTER key implements or switches your
menu selection. None
Menu RCV1, Receiver Mode
MENU DESCRIPTION GPIB COMMAND
STANDARD
RECEIVER MODE None
WARNING: None
CONTINUING
MAY INVALIDATE
CURRENT SETUP
AND CALIBRATION
PRESS <ENTER>
TO CONTINUE Pressing the ENTER key implements your menu selection.
PRESS <CLEAR>
TO ABORT Pressing the CLEAR key aborts the Receiver Mode. None
Menu RCV1_WARN, Standard Receiver Mode Warning
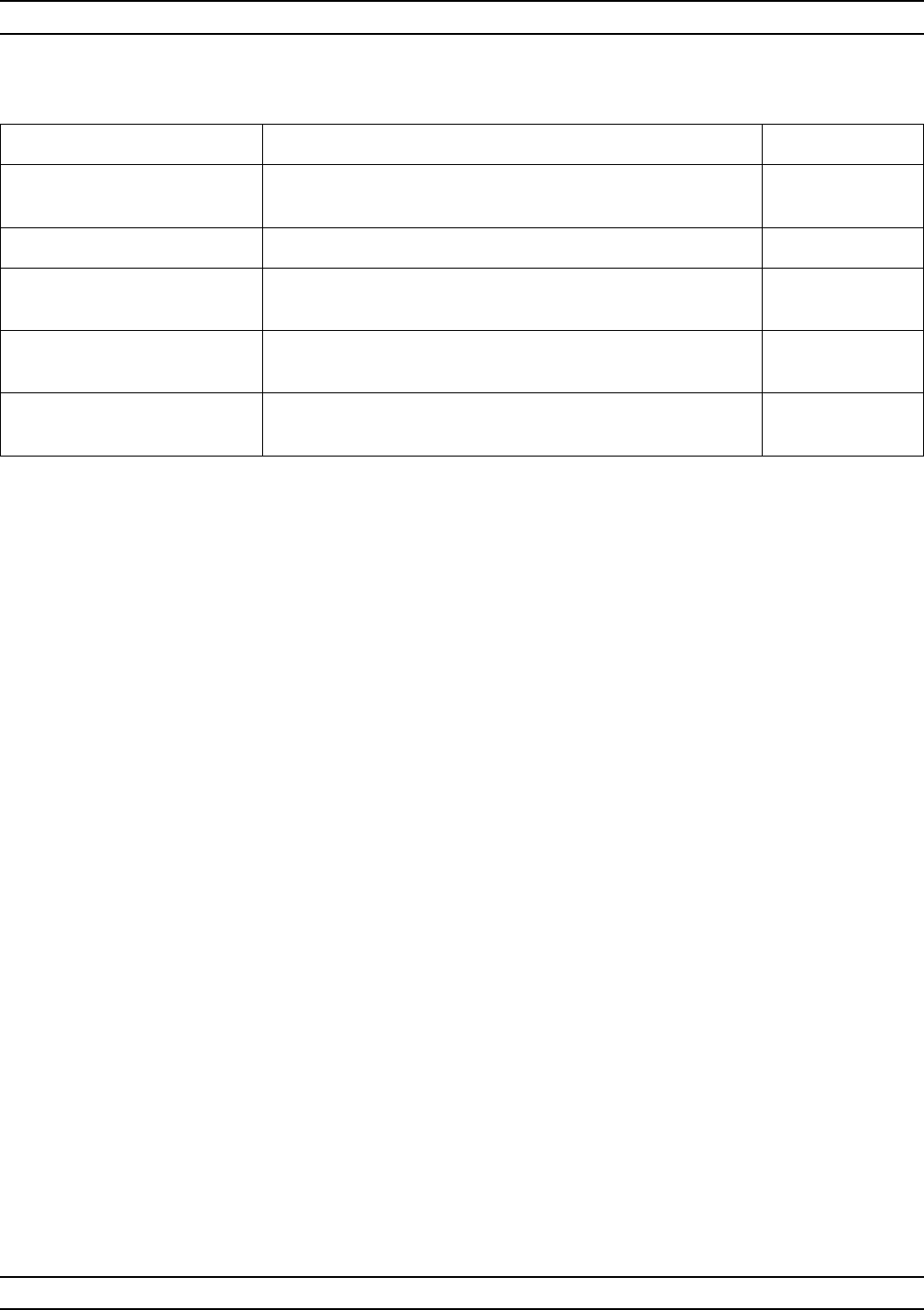
A-190 37XXXC OM
R ALPHABETICAL LISTING
MENU DESCRIPTION GPIB COMMAND
USER DEFINED
RECEIVER MODE None
SOURCE LOCK Phase locks sources having phase control reference inputs. SL1
TRACKING Phase locks 37XXXC receivers to a known frequency
source. TK1
SET ON Disables source lock circuitry, local oscillators are phase
locked to the 37XXXC internal crystal reference oscillator. ST1
PRESS ENTER
TO SELECT Pressing the Enter key implements your menu selection or
turns GPIB control on or off. None
Menu RCV2, User Defined Receiver Mode Menu
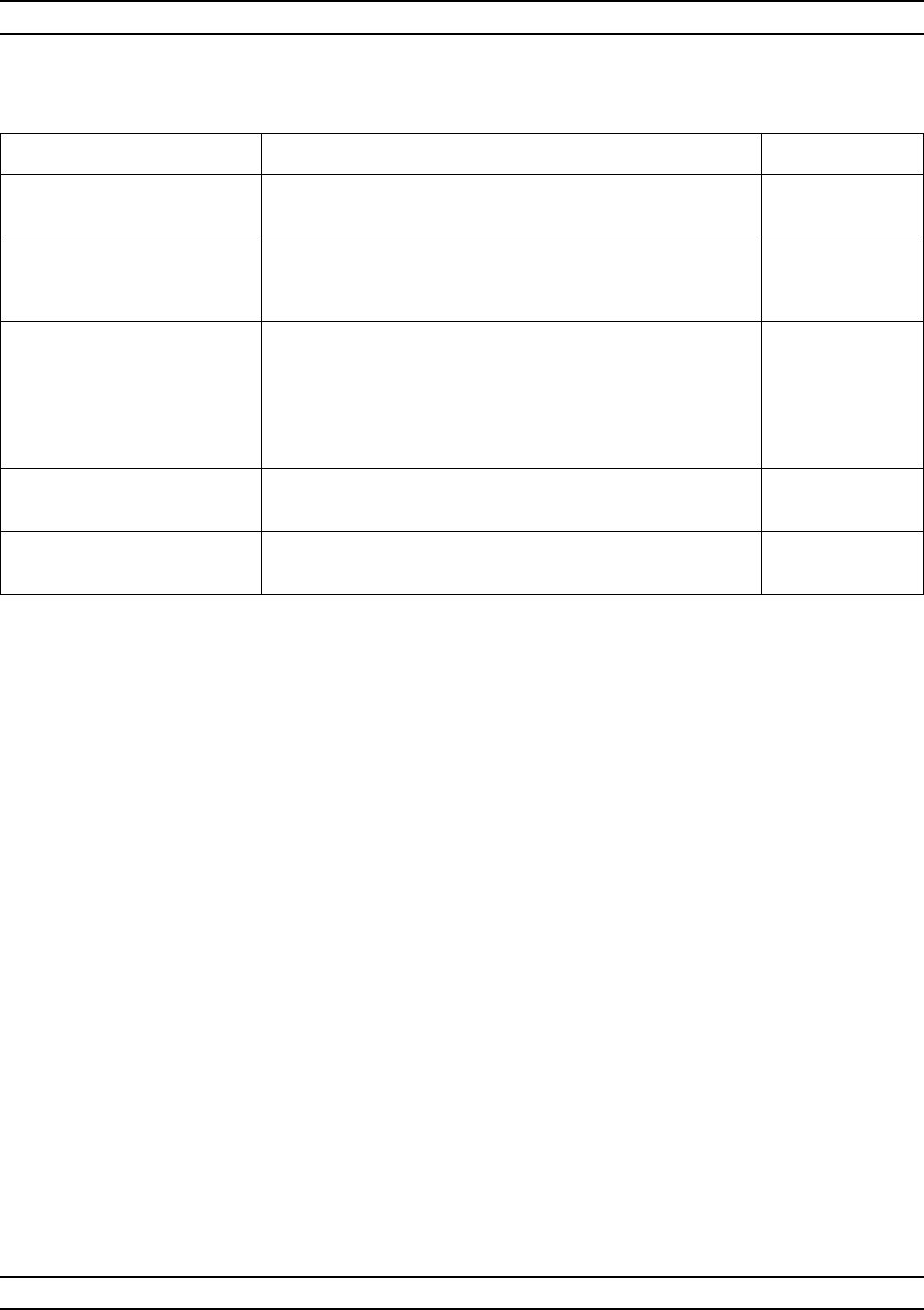
37XXXC OM A-191
ALPHABETICAL LISTING R
MENU DESCRIPTION GPIB COMMAND
USER DEFINED
RECEIVER MODE None
SET ON
WITH
GPIB CONTROL
(Warning could also read “SOURCE LOCK,” “TRACKING,”
or “WITHOUT” instead of “SET ON”). None
WARNING: None
CONTINUING
MAY INVALIDATE
CURRENT SETUP
AND CALIBRATION
PRESS <ENTER>
TO CONTINUE Pressing the ENTER key implements your menu selection. None
PRESS <CLEAR>
TO ABORT Pressing the CLEAR key aborts the Receiver Mode. None
Menu RCV2_WARN, User Defined Receiver Mode Warning
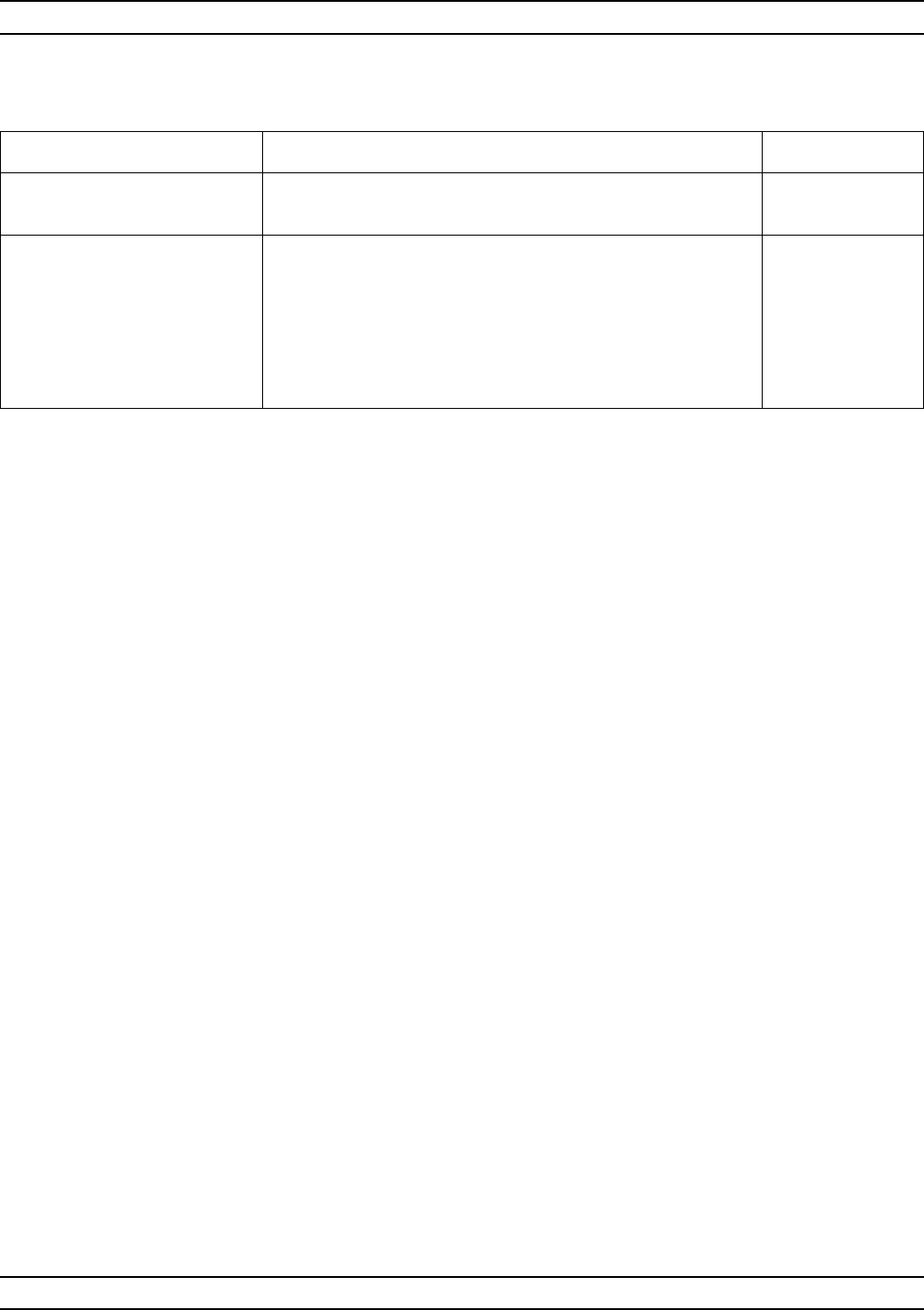
A-192 37XXXC OM
R ALPHABETICAL LISTING
MENU DESCRIPTION GPIB COMMAND
STANDARD
RECEIVER MODE Indicates that Standard Receiver mode has been selected. None
WARNING:
CONTINUING
WILL ERASE
CURRENT
SETUP AND
CALIBRATION
Indicates that continuing (by pressing the Enter key) will
erase current setup and calibration stored in the VNA. None
Menu RCV3, Standard Receiver Mode Warning Menu
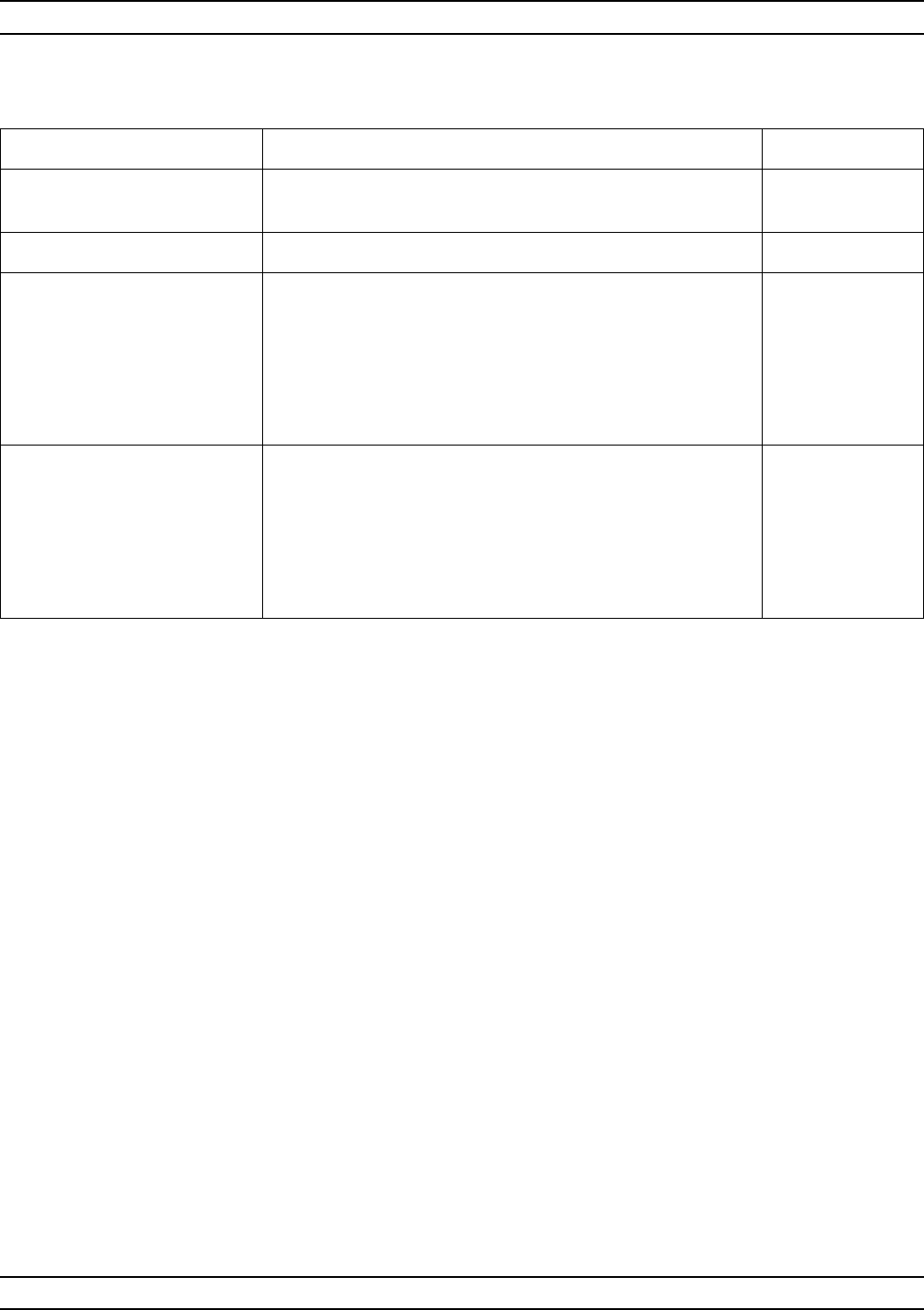
37XXXC OM A-193
ALPHABETICAL LISTING R
MENU DESCRIPTION GPIB COMMAND
USER DEFINED
RECEIVER MODE None
XXXXXXXX Indicates selected mode
WARNING:
CONTINUING
WILL ERASE
CURRENT
SETUP AND
CALIBRATION
Indicates that continuing (by pressing the Enter key) will
erase current setup and calibration stored in theVNA. None
PRESS <ENTER>
TO CONTINUE
OR
PRESS <CLEAR>
TO ABORT
Pressing Enter key implements selected mode.
Pressing the CLEAR key aborts the selected mode; current
setup and calibration data stored in the VNA is preserved.
None
Menu RCV4, User Defined Receiver Mode Warning Menu
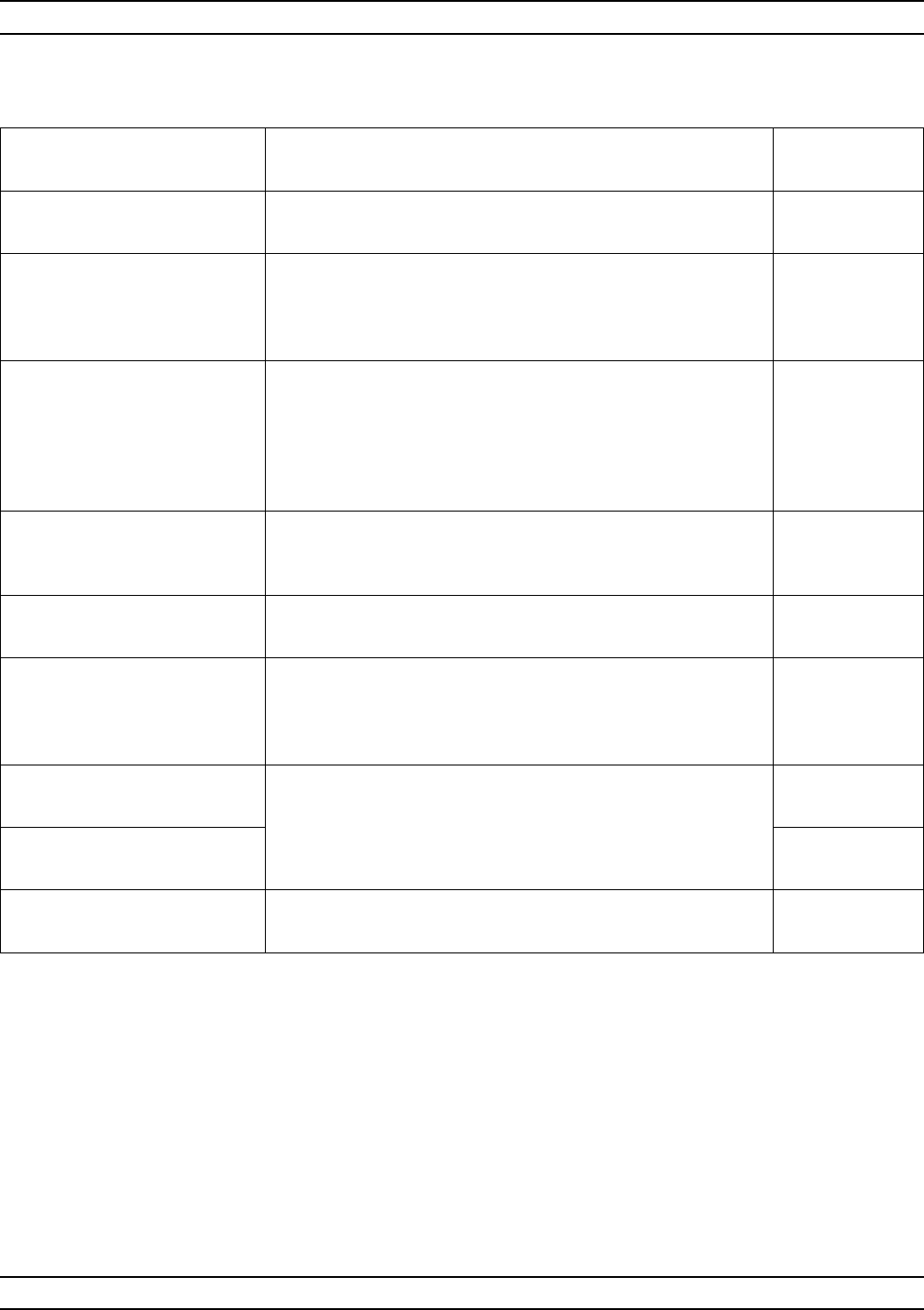
A-194 37XXXC OM
R ALPHABETICAL LISTING
MENU DESCRIPTION GPIB COM-
MAND
REFERENCE
PLANE None
AUTO Automatically sets the reference delay so that the
cumulative phase shift is zero. This selection unwinds the
phase in a Smith chart display or reduces the phase
revolutions in a rectilinear display to less than one.
RDA
DISTANCE
XXX.XXXX mm Electrically repositions the measurement reference plane, as
displayed on the active channel, by a distance value entered
in millimeters. This selection lets you compensate for the
phase reversals inherent in a length of transmission line
connected between the test set’s Port 1 connector and the
device-under-test (DUT).
RDD; RDD?
TIME
XXX.XXXX ms Electrically repositions the measurement reference plane by
a distance value that corresponds to the time in
milliseconds.
RDT; RDT?
SET DIELECTRIC
XXX Displays menu RD2, which lets you enter a value for the
dielectric constant of your transmission line. DIE
CONSTANT OFFSET Lets the user apply a constant offset vector to the channel
data. A constant magnitude and phase can be applied to the
data just after the reference plane is applied. The constant
offset is independent of frequency and media dispersion.
MAGNITUDE
+XXX.XXX dB The magnitude is entered in dB and the phase in degrees.
These values are combined into a vector where the magnitude
is converted from Log to Linear. The channel data is then
vector multiplied by this vector.
MOSET;
MOSET?
PHASE
+XXX.XXX°
POSET;
POSET?
PRESS <ENTER>
TO SELECT Pressing the Enter key implements your menu selection. None
Menu RD1, Set Reference Delay
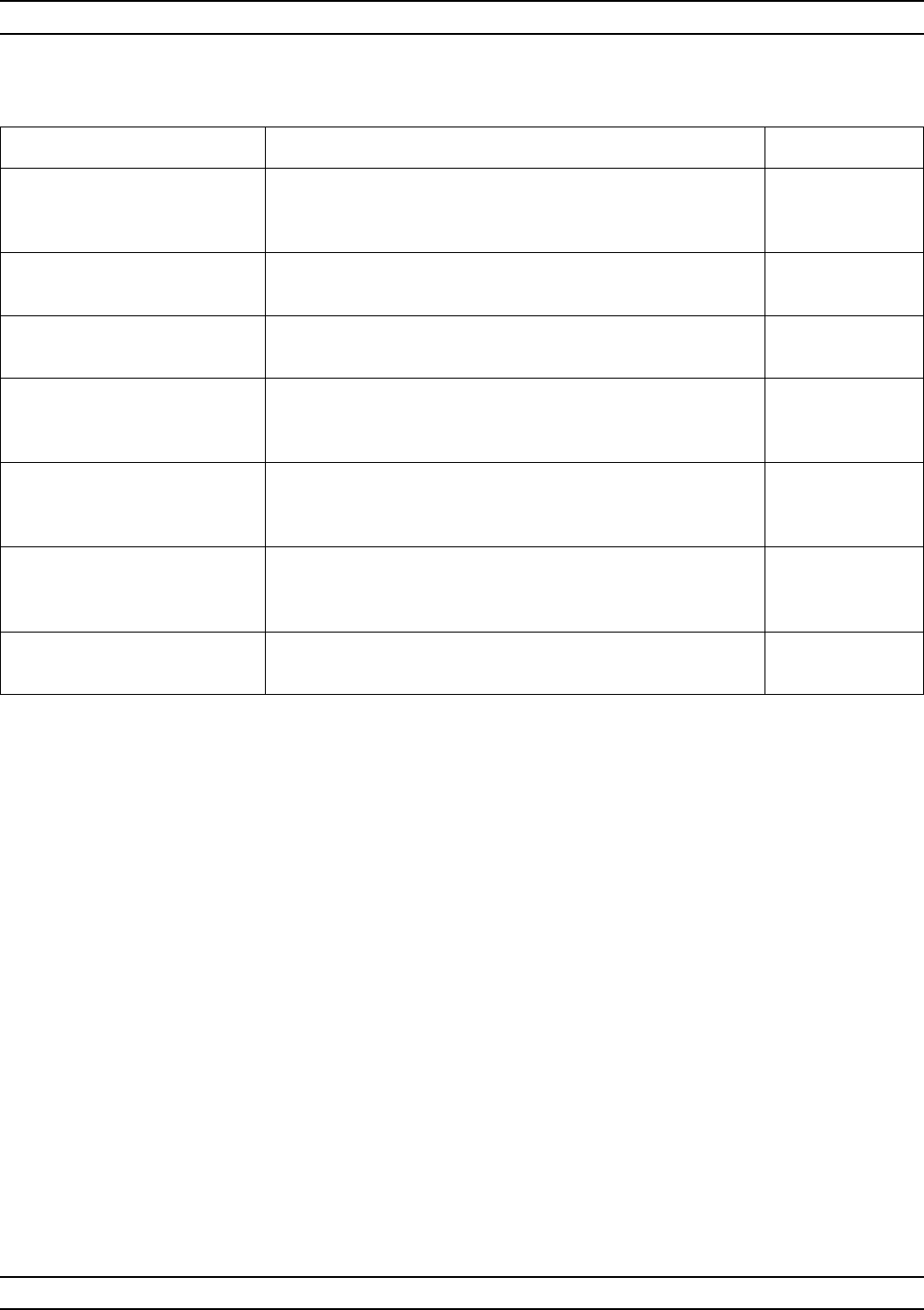
37XXXC OM A-195
ALPHABETICAL LISTING R
MENU DESCRIPTION GPIB COMMAND
SET
DIELECTRIC
CONSTANT
None
AIR
(1.000649) Calculates reference delay based on dielectric constant of
air (1.000649). DIA
POLYETHYLENE
(2.26) Calculates reference delay based on the dielectric constant
of polyethylene (2.26). DIP
TEFLON
(2.10) Calculates reference delay based on the dielectric constant
of
teflon (2.1).
DIT
MICROPOROUS
TEFLON
(1.69)
Calculates reference delay based on the dielectric constant
of microporous teflon (1.69). DIM
OTHER
XXXX.XX Calculates reference delay based on the value you enter.
Terminate your entry using any terminator and select with
the Enter key.
DIE
PRESS <ENTER>
TO SELECT Pressing the Enter key implements your menu selection
and returns you to the RD1 menu. None
Menu RD2, Set Dielectric Constant
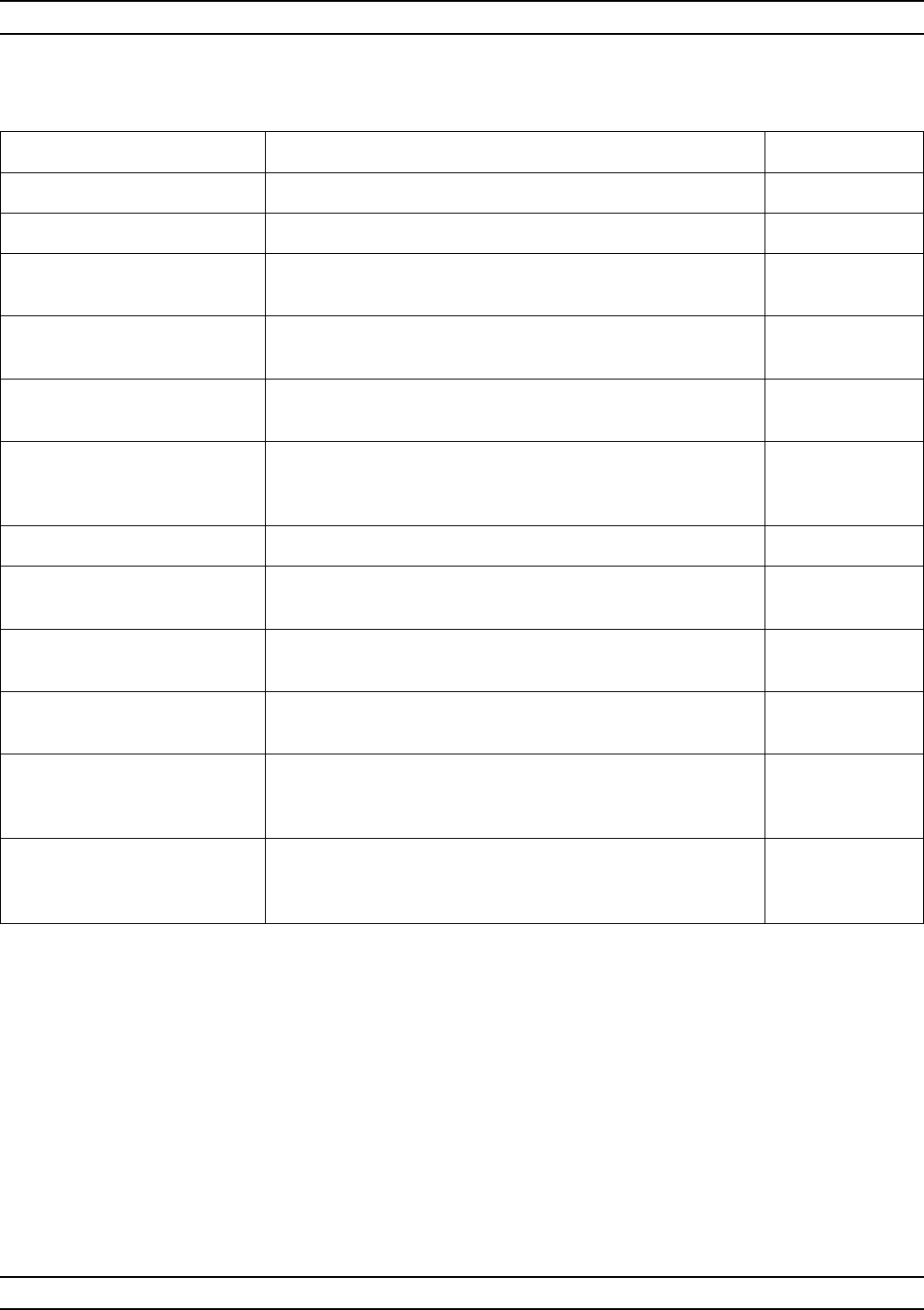
A-196 37XXXC OM
S ALPHABETICAL LISTING
MENU DESCRIPTION GPIB COMMAND
SOURCE CONFIG None
SOURCE 1 None
ACTIVE/ INACTIVE Enables and disables the internal source. SRC1AC;
SRC1AC?
SOURCE LOCATION
INTERNAL / EXTERNAL Changes location of source 1 from internal to external
(NOT CURRENTLY SUPPORTED). None
GPIB ADDRESS
4Changes GPIB address of external source 1. SRC1ADD;
SRC1ADD?
GPIB CONTROL ON (OFF) Disables GPIB control of external source 1. SRC1G1;
SRC1G0;
SRC1GX?
SOURCE 2
ACTIVE/ INACTIVE Enables and disables the external source 2. SRC2AC;
SRC2AC?
SOURCE LOCATION
EXTERNAL None
GPIB ADDRESS
54 Changes GPIB address of external source 2. SRC2ADD;
SRC2ADD?
GPIB CONTROL ON (OFF) Disables GPIB control of external source 2. SRC2G1;
SRC2G0;
SRC2GX?
PRESS <ENTER>
TO SELECT
OR TURN ON/OFF
Pressing the Enter key implements your menu selection.
Menu SC, Source Configure
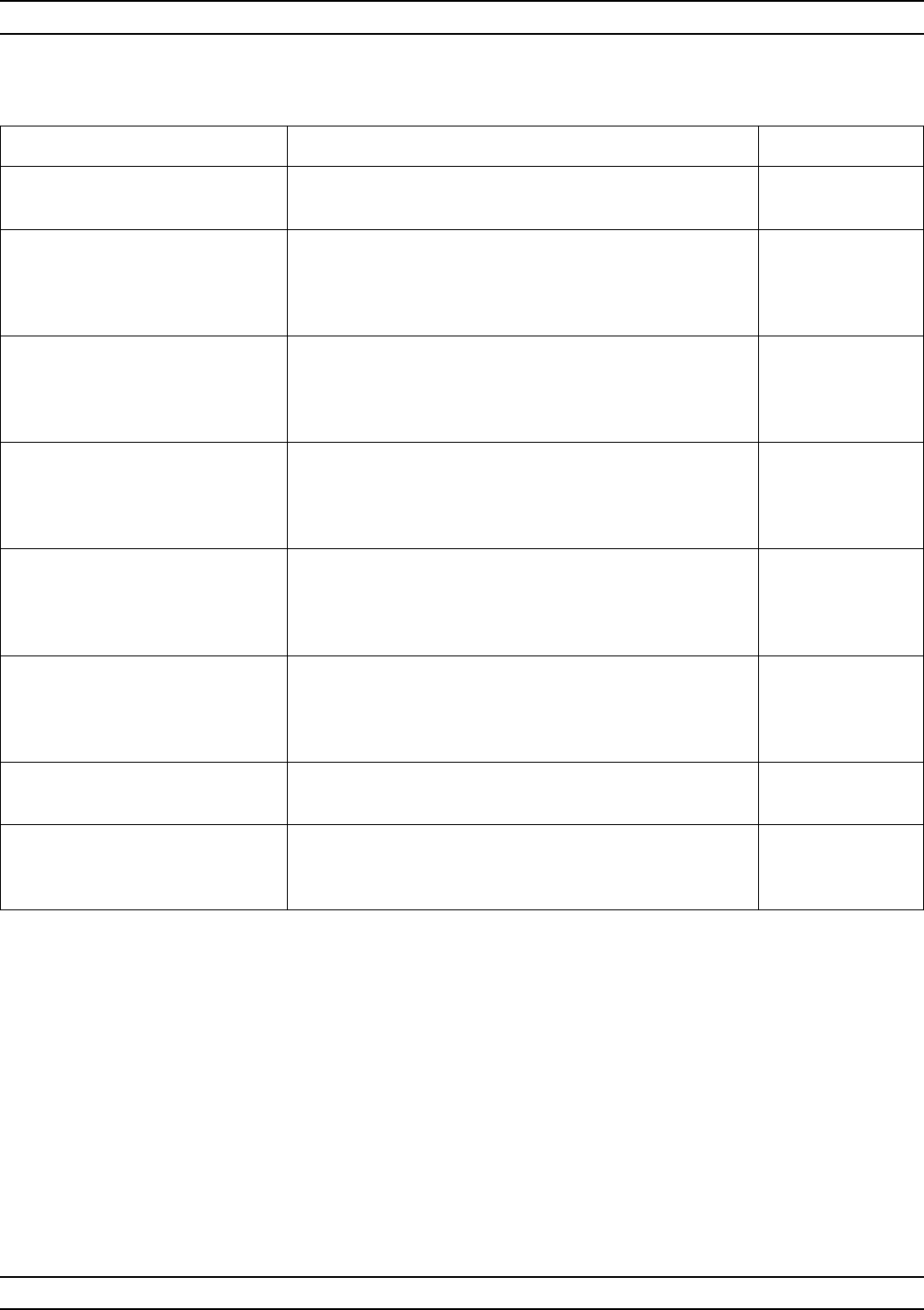
37XXXC OM A-197
ALPHABETICAL LISTING S
MENU DESCRIPTION GPIB COMMAND
SELECT
PARAMETER None
S21, FWD TRANS
b2/a1 Selects the S21 parameter to be displayed on the active
channel
The parameter can be displayed in any of the available
formats.
S21
S11, USER 2
b2 / 1 Selects the S11 parameter to be displayed on the active
channel.
The parameter can be displayed in any of the available
formats.
S11
S12, REV TRANS
b1/a2 Selects the S12 parameter to be displayed on the active
channel.
The parameter can be displayed in any of the available
formats.
S12
S22, REV REFL
b2/a2 Selects the S22 parameter to be displayed on the active
channel.
The parameter can be displayed in any of the available
formats.
S22
EXT ANALOG IN Switches from a S-parameter or user-defined parameter
to an external analog input. This is measured from the
rear panel Ext Anlg In connector input. The values may
be seen on the Real graph type where 1 Unit=1Volt.
EANAIN
PRESS <ENTER>
TO SELECT Pressing the Enter key implements your menu selection. None
PRESS <1>
TO REDEFINE
SELECTED PARAMETER
Calls menu PD1, which lets you redefine the selected
parameter. None
Menu SP, Select S Parameter
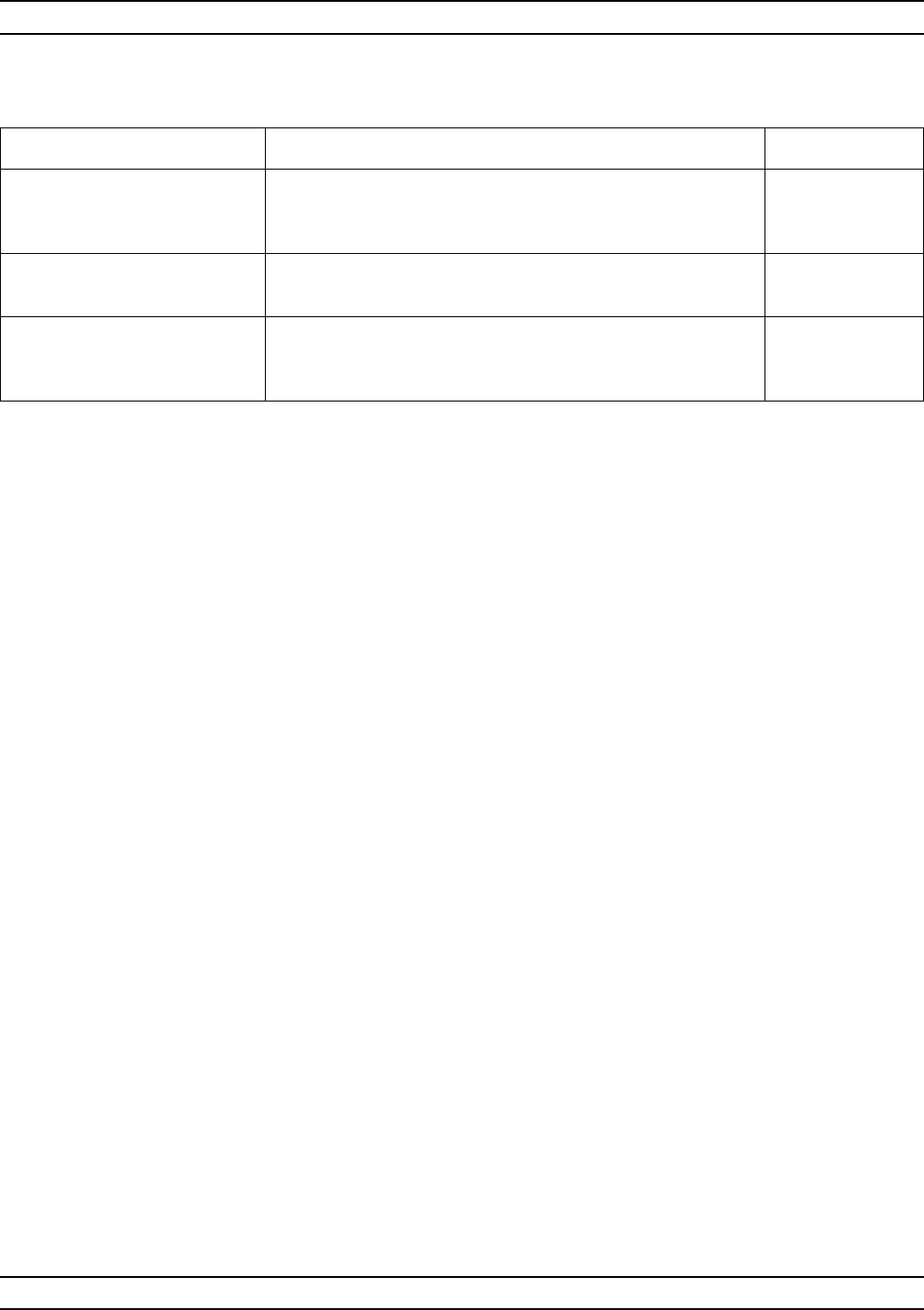
A-198 37XXXC OM
S ALPHABETICAL LISTING
MENU DESCRIPTION GPIB COMMAND
SAVE/RECALL
FRONT PANEL
AND CAL DATA
None
SAVE
RECALL Calls menu SR2, which asks you to select a storage
location—internal memory or disk. None
PRESS <ENTER>
TO SELECT
FUNCTION
Pressing the Enter key implements your selection. None
Menu SR1, Save/Recall Front Panel Information
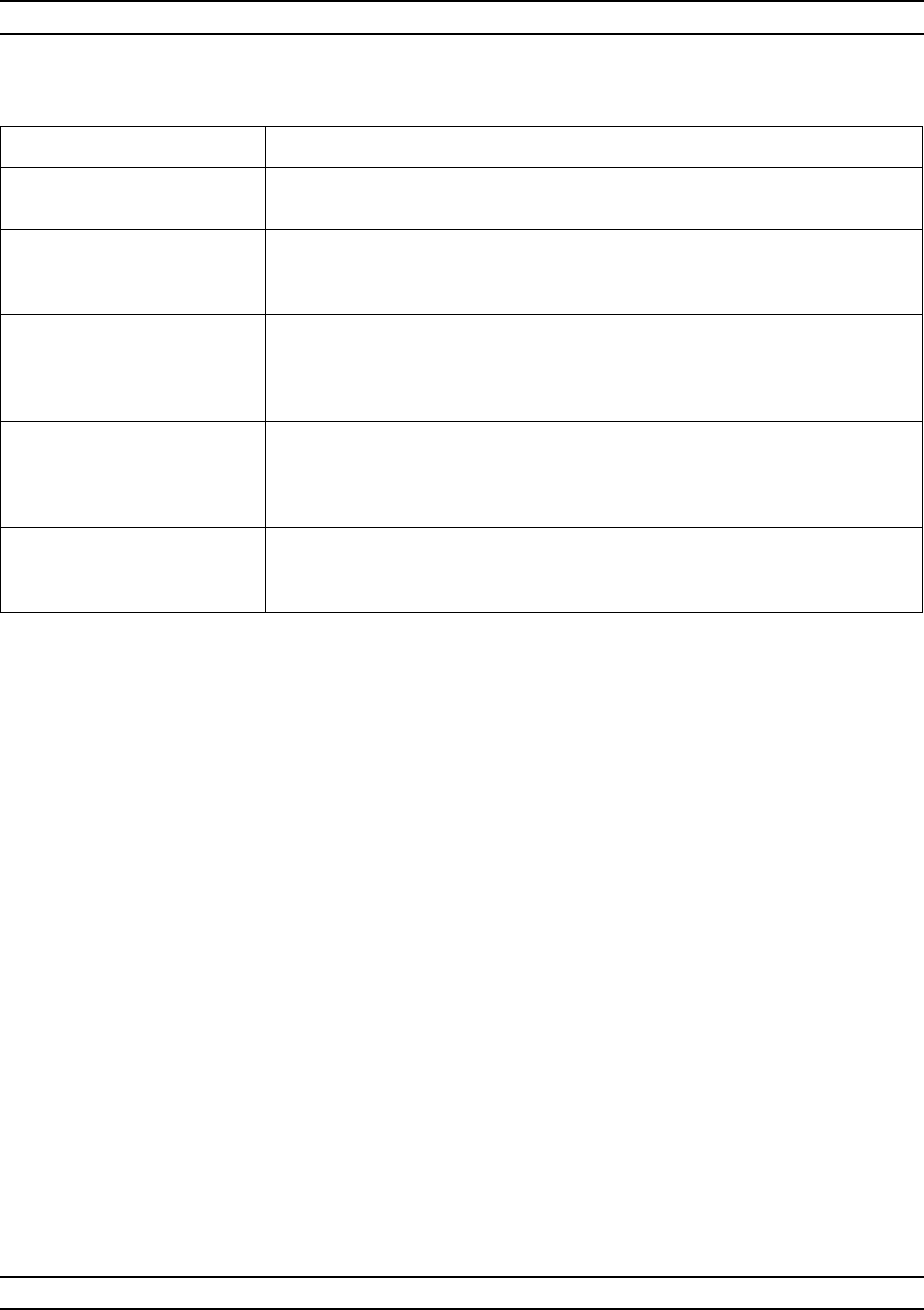
37XXXC OM A-199
ALPHABETICAL LISTING S
MENU DESCRIPTION GPIB COMMAND
RECALL
(OR SAVE) None
FRONT PANEL
SETUP IN
INTERNAL MEMORY
Calls menu SR3, which lets you save the front panel setup
into or recall it from internal memory. None
FRONT PANEL
SETUP AND
CAL DATA
ON HARD DISK
Calls menu DKS2 or DSK3, which let you recall or save to
hard disk memory. None
FRONT PANEL
SETUP AND
CAL DATA
ON FLOPPY DISK
Calls menu DKS2 or DSK3, which let you recall or save to
floppy disk memory. None
PRESS <ENTER>
TO SELECT Pressing the Enter key implements your selection. The
menu remains on the screen until another menu is selected
for display or until the Clear/Ret Loc key is pressed.
None
Menu SR2, Recall or Save
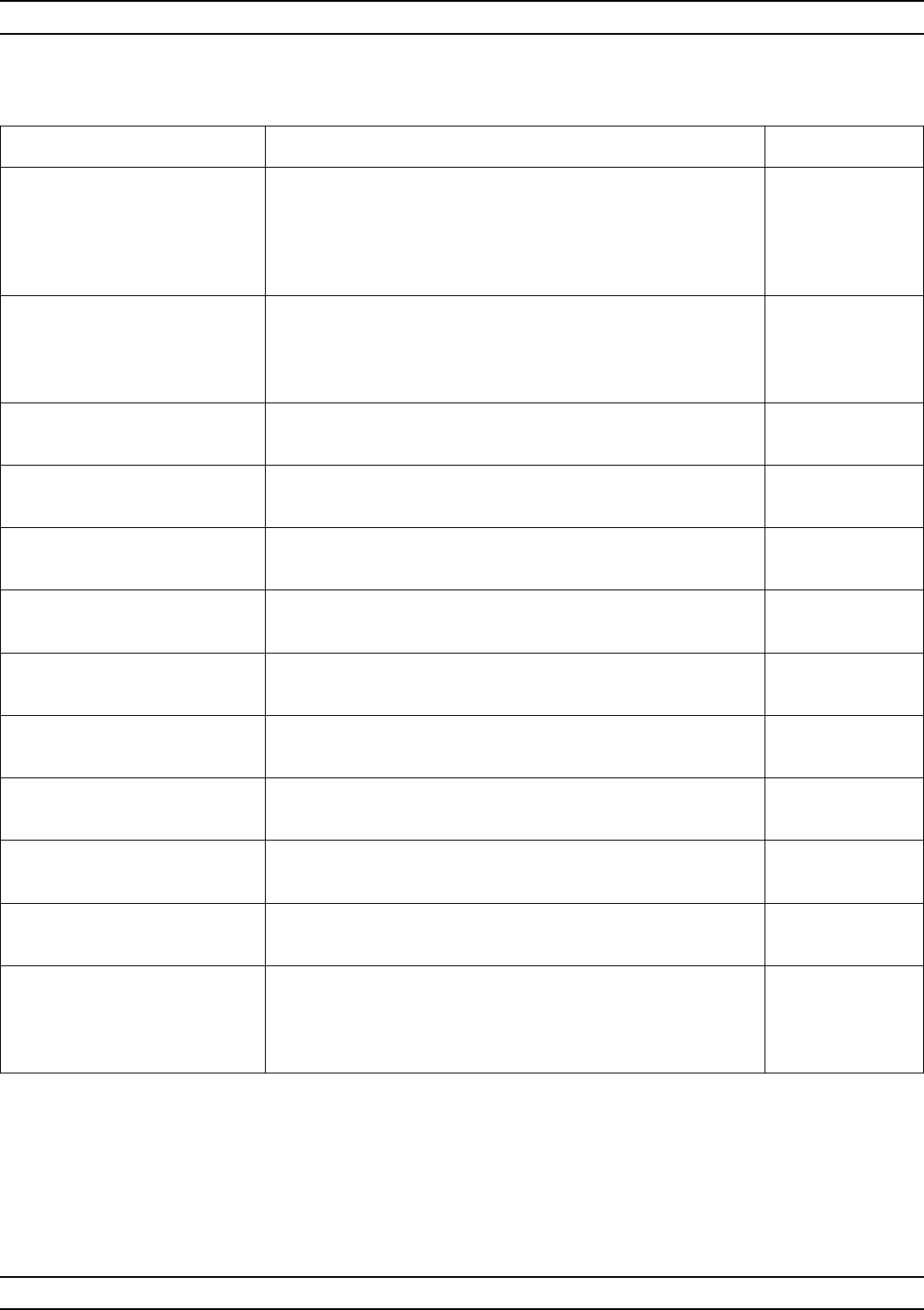
A-200 37XXXC OM
S ALPHABETICAL LISTING
MENU DESCRIPTION GPIB COMMAND
SAVE FRONT
PANEL SETUP TO
(RECALL FRONT
PANEL SETUP FROM)
INTERNAL MEMORY
None
MEMORY 1* Causes the current front panel setup to be saved to
memory location 1. If an asterisk appears beside the
selection, the memory is full. Select a different memory
location.
SV1; RC1
MEMORY 2 Same as above, except the setup saves to memory
location 2. SV2; RC2
MEMORY 3 Same as above, except the setup saves to memory
location 3. SV3; RC3
MEMORY 4* Same as above, except the setup saves to memory
location 4. SV4; RC4
MEMORY 5* Same as above, except the setup saves to memory
location 5. SV5; RC5
MEMORY 6 Same as above, except the setup saves to memory
location 6. SV6; RC6
MEMORY 7 Same as above, except the setup saves to memory
location 7. SV7; RC7
MEMORY 8 Same as above, except the setup saves to memory
location 8. SV8; RC8
MEMORY 9 Same as above, except the setup saves to memory
location 9. SV9; RC9
MEMORY 10 Same as above, except the setup saves to memory
location 10. SV10; RC10
PRESS <ENTER>
TO SELECT
OR
USE KEYPAD
Pressing the Enter key implements your menu selection. None
Menu SR3, Save to Internal memory
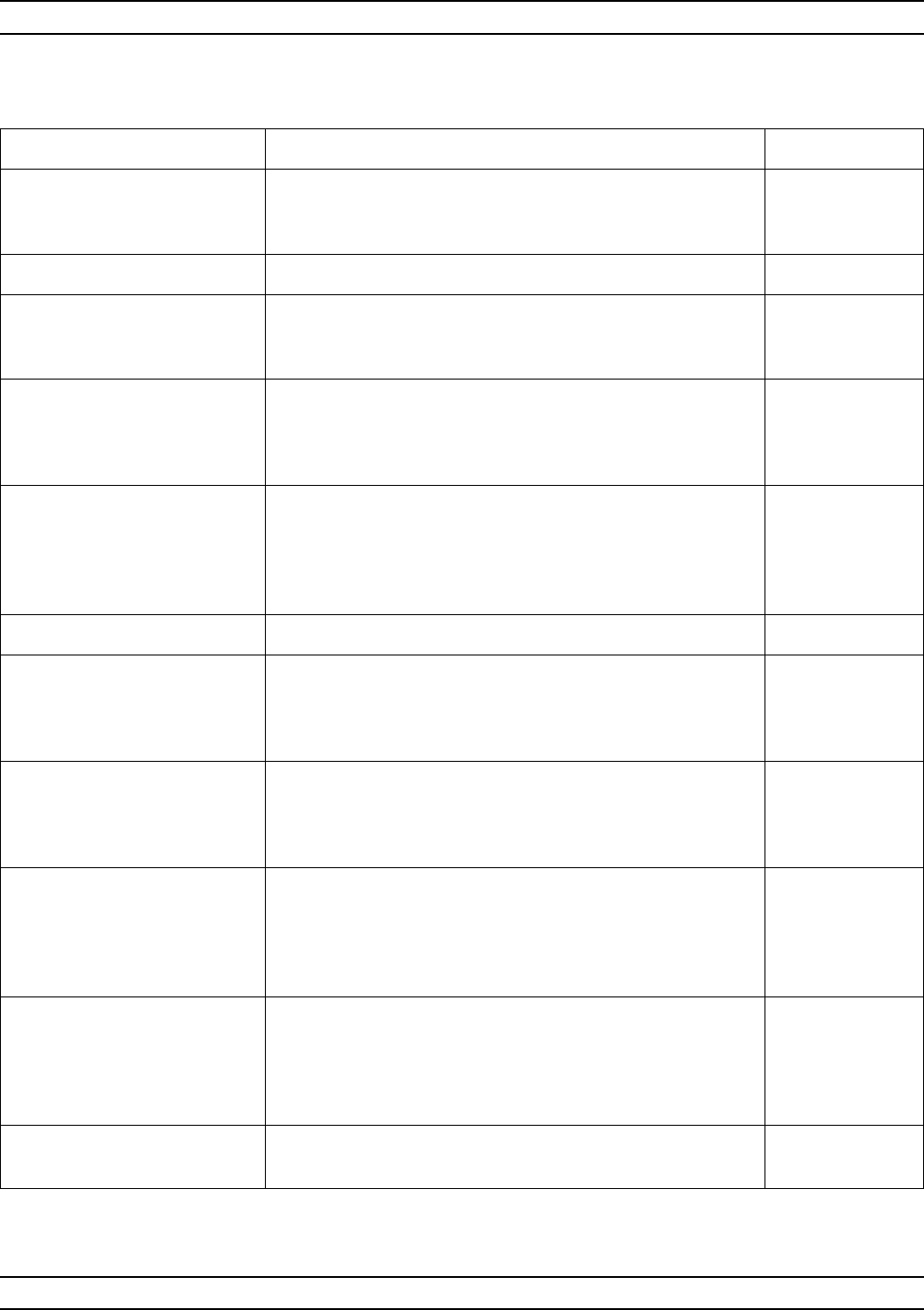
37XXXC OM A-201
ALPHABETICAL LISTING S
MENU DESCRIPTION GPIB COMMAND
SET SCALING
OR PRESS
<AUTOSCALE>
None
–LOG MAG– None
RESOLUTION
XX.XXX dB/DIV Sets the resolution for the vertical axis of the active
channel’s displayed graph. Resolution can by set
incrementally using the keypad or rotary knob.
SCL; SCL?;
SCL2; SCL2?
REFERENCE VALUE
XXX.XXX dB Sets the value at the reference line for the active channel
amplitude measurement on the log-magnitude graph. The
value can be set in increments of 0.001 dB using the
keypad or rotary knob.
OFF; OFF?
OFF2; OFF2?
REFERENCE LINE
XSets the reference line for the active channel’s amplitude
measurement on the log-magnitude graph. This is the line
about which the amplitude expands with different resolution
values. The reference line can be set to any vertical
division using the rotary knob.
REF; REF?;
REF2; REF2?
–PHASE– None
RESOLUTION
XX.XX °/DIV
Sets the resolution for the vertical axis of the active
channel’s displayed phase graph. Resolution can by set
incrementally using
the keypad or rotary knob.
SCL; SCL?;
SCL2; SCL2?
REFERENCE VALUE
XXX.XX °
Sets the value at the reference line for the active channel
amplitude measurement on the phase graph. The value
can be set in increments of 0.001 dB using the keypad or
rotary knob.
OFF; OFF?
OFF2; OFF2?
REFERENCE LINE
XSets the reference line for the active channel’s phase
measurement on the phase graph. This is the line about
which the phase expands with different resolution values.
The reference line can be set to any vertical division using
the rotary knob.
REF; REF?;
REF2; REF2?
PHASE SHIFT
X.XX °
Sets the value by which the active channel’s phase
measurement is shifted on the phase graph. The shift can
be set in increments of 0.01 degrees using the keypad or
rotary knob. This is useful when phase data is near the 180
degree rollover value.
PHO; PHO?
PRESS <ENTER>
TO RESUME CAL On the CAL_SS1 menu, pressing the Enter key returns you
to the calibration setup or sequence. None
Menu SS1 or CAL_SS1, Set Scaling 1
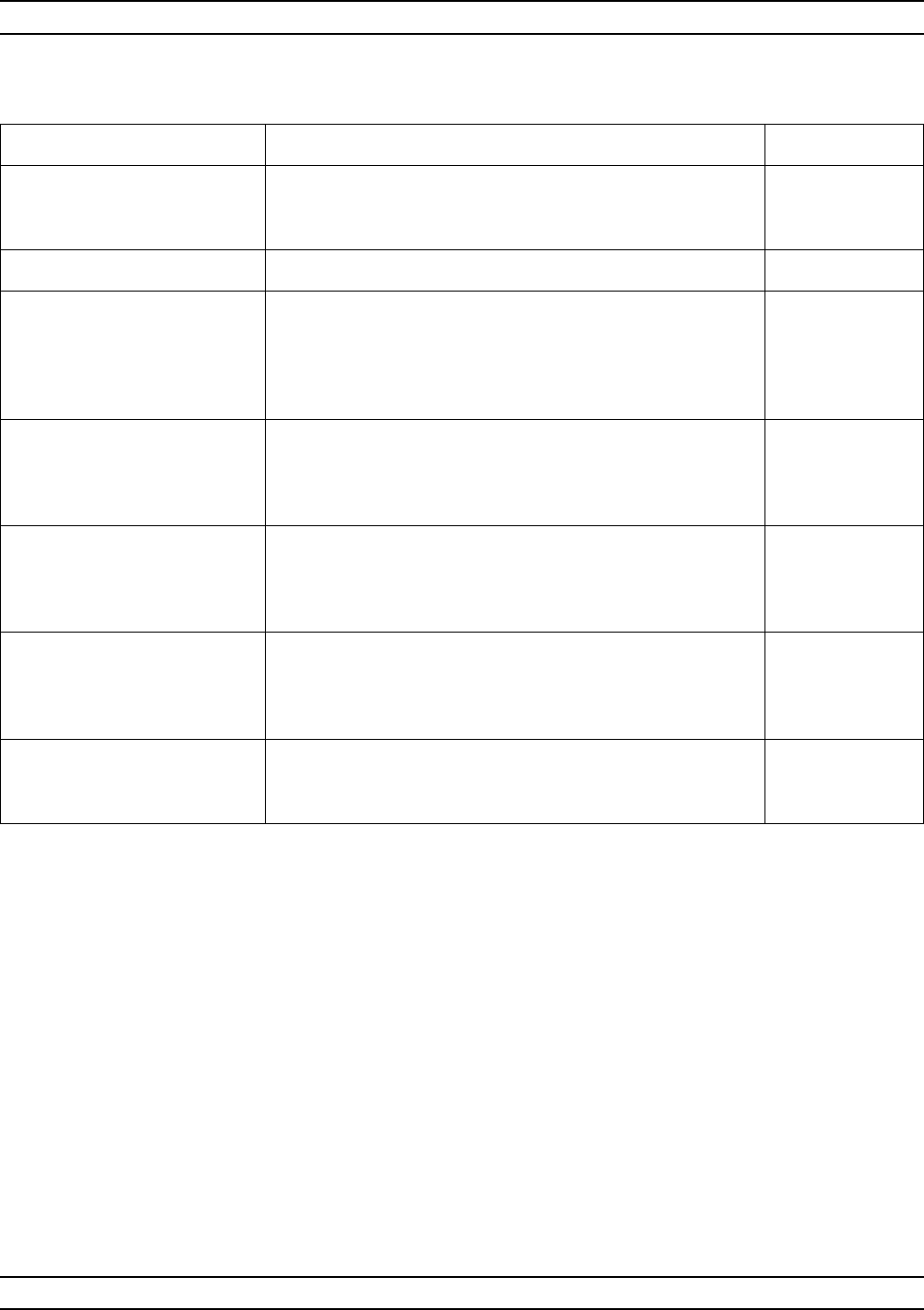
A-202 37XXXC OM
S ALPHABETICAL LISTING
MENU DESCRIPTION GPIB COMMAND
SET SCALING
OR PRESS
<AUTOSCALE>
None
–LINEAR POLAR– None
RESOLUTION
XX.XXX U/DIV Sets the resolution for the vertical axis of the active
channel’s displayed graph. Resolution can by set
incrementally using the keypad or rotary knob. The center
is fixed at 0 units; therefore, changing the resolution also
changes the reference value and vice versa
SCL; SCL?;
SCL2; SCL2?
REFERENCE VALUE
XXX.XXX U Sets the value at the reference line for the active channel
amplitude measurement on the displayed graph. The value
can be set in increments of 0.001 U using the keypad or
rotary knob.
OFF; OFF?
OFF2; OFF2?
FIXED
REFERENCE LINE Sets the reference line for the active channel’s amplitude
measurement. This is the line about which the amplitude
expands with different resolution values. The reference line
can be set to any vertical division using the rotary knob.
REF; REF?;
REF2; REF2?
SELECT POLAR
CHART MODE
MAGNITUDE
PHASE
Calls menu PC1, which lets you define the phase angles
between which your polar chart will display data. None
PRESS <ENTER>
TO SELECT
AND RESUME CAL
Pressing the Enter key implements your menu selection
and resumes the calibration from where it left off, if in the
calibration mode.
None
Menu SS2 or CAL_SS2, Set Scaling 2
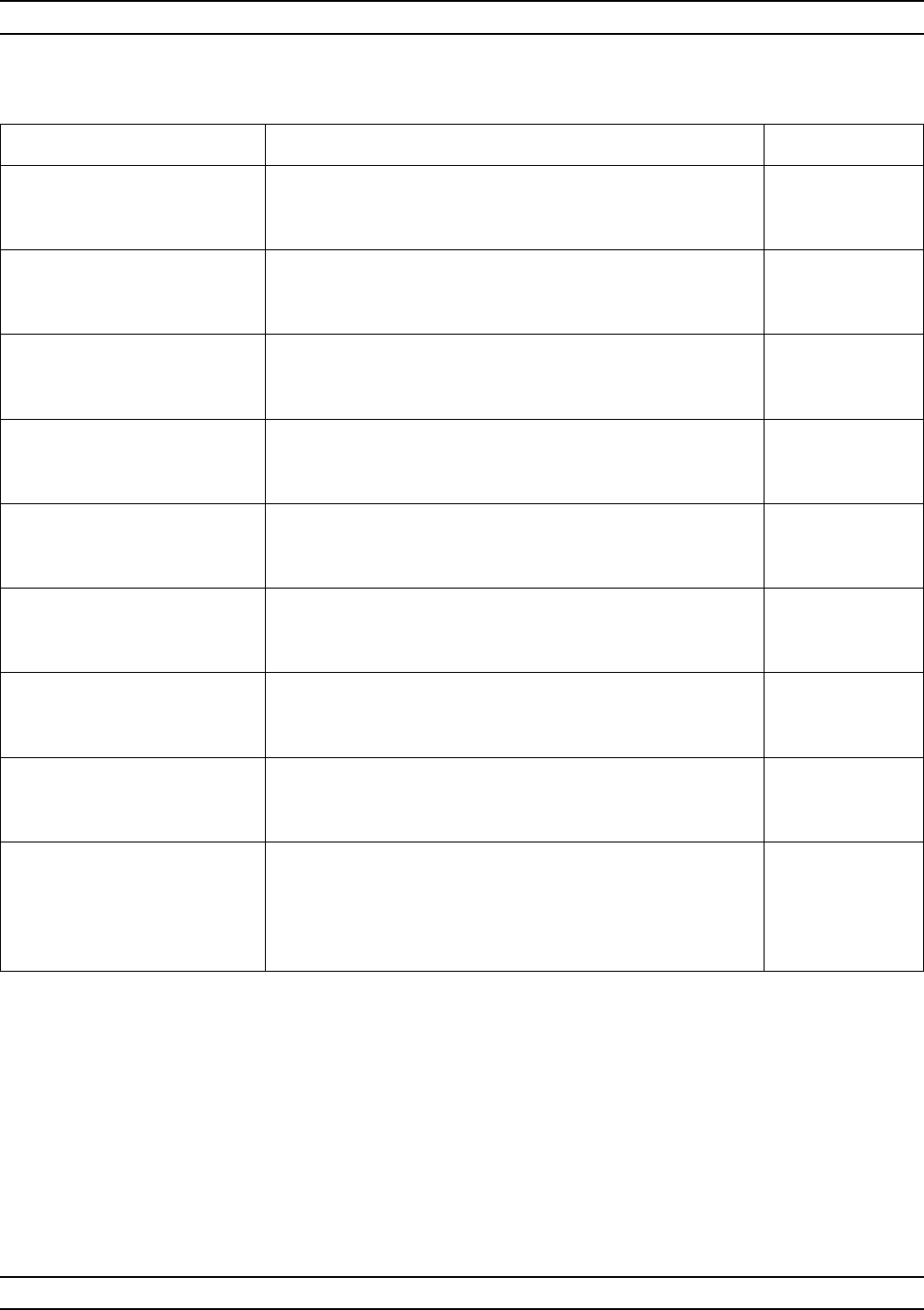
37XXXC OM A-203
ALPHABETICAL LISTING S
MENU DESCRIPTION GPIB COMMAND
SET SCALING
OR PRESS
<AUTOSCALE>
None
IMPEDANCE
(ADMITTANCE)
SMITH CHART
Scales an Impedance Smith chart for display in the active
channel. SMI; ISM
NORMAL SMITH
(REFL = 1.0000000
FULL SCALE)
Selects a normal Smith chart for display in the active
channel. SMI; ISM
EXPAND 10 dB
(REFL = 0.3162278
FULL SCALE)
Selects a 10 dB expansion of the Smith chart being
displayed for the active channel. SME10DB;
ISM10DB
EXPAND 20 dB
(REFL = 0.1000000
FULL SCALE)
Selects a 20 dB expansion of the Smith chart being
displayed for the active channel. SME20DB;
ISM20DB
EXPAND 30 dB
(REFL = 0.0316228
FULL SCALE)
Selects a 30 dB expansion of the Smith chart being
displayed for the active channel. SME30DB;
ISM30DB
COMPRESS 3 dB
(REFL =1.425375
FULL SCALE)
Selectsa3dBcompression of the Smith chart being
displayed for the active channel. SMC3DB;
ISM3DB
PRESS <ENTER>
TO SELECT
AND RESUME CAL
On the CAL_SS3Z or Y menu, pressing the Enter key
returns you to the calibration setup or sequence. None
PRESS <ENTER>
TO SELECT Pressing the ENTER key implements your menu selection
and resumes the calibration from where it left off, if in the
calibration mode.. The menu remains on the screen until
another menu is selected for display or until the
CLEAR/RET LOC key is pressed.
None
Menu SS3Z/SS3Y or CAL_SS3Z/CALSS3Y, Set Scaling 3
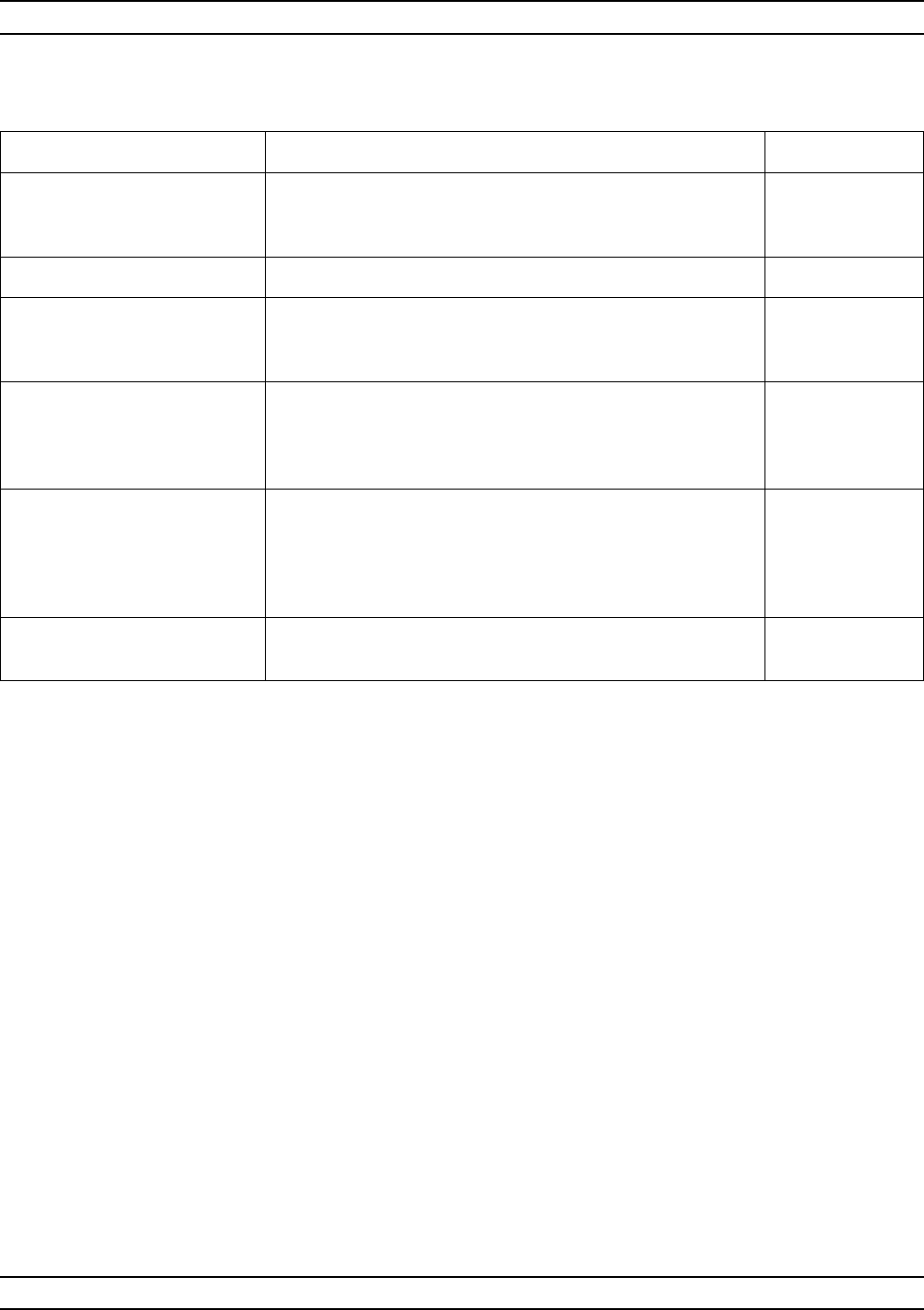
A-204 37XXXC OM
S ALPHABETICAL LISTING
MENU DESCRIPTION GPIB COMMAND
SET SCALING
OR PRESS
<AUTOSCALE>
None
–LOG MAG– None
RESOLUTION
XX.XXX dB/DIV Sets the resolution for the vertical axis of the active
channel’s displayed graph. Resolution can by set
incrementally using the keypad or rotary knob.
SCL; SCL?;
SCL2; SCL2?
REFERENCE VALUE
XXX.XXX dB Sets the value at the reference line for the active channel
amplitude measurement on the displayed graph. The value
can be set in increments of 0.001 dB using the keypad or
rotary knob.
OFF; OFF?
OFF2; OFF2?
REFERENCE LINE
XSets the reference line for the active channel’s amplitude
measurement on the log-magnitude graph. This is the line
about which the amplitude expands with different resolution
values. The reference line can be set to any vertical
division using the rotary knob.
REF; REF?;
REF2; REF2?
PRESS <ENTER>
TO RESUME CAL On the CAL_SS4 menu, pressing the Enter key returns you
to the calibration setup or sequence. None
Menu SS4 or CAL_SS4, Set Scaling 4
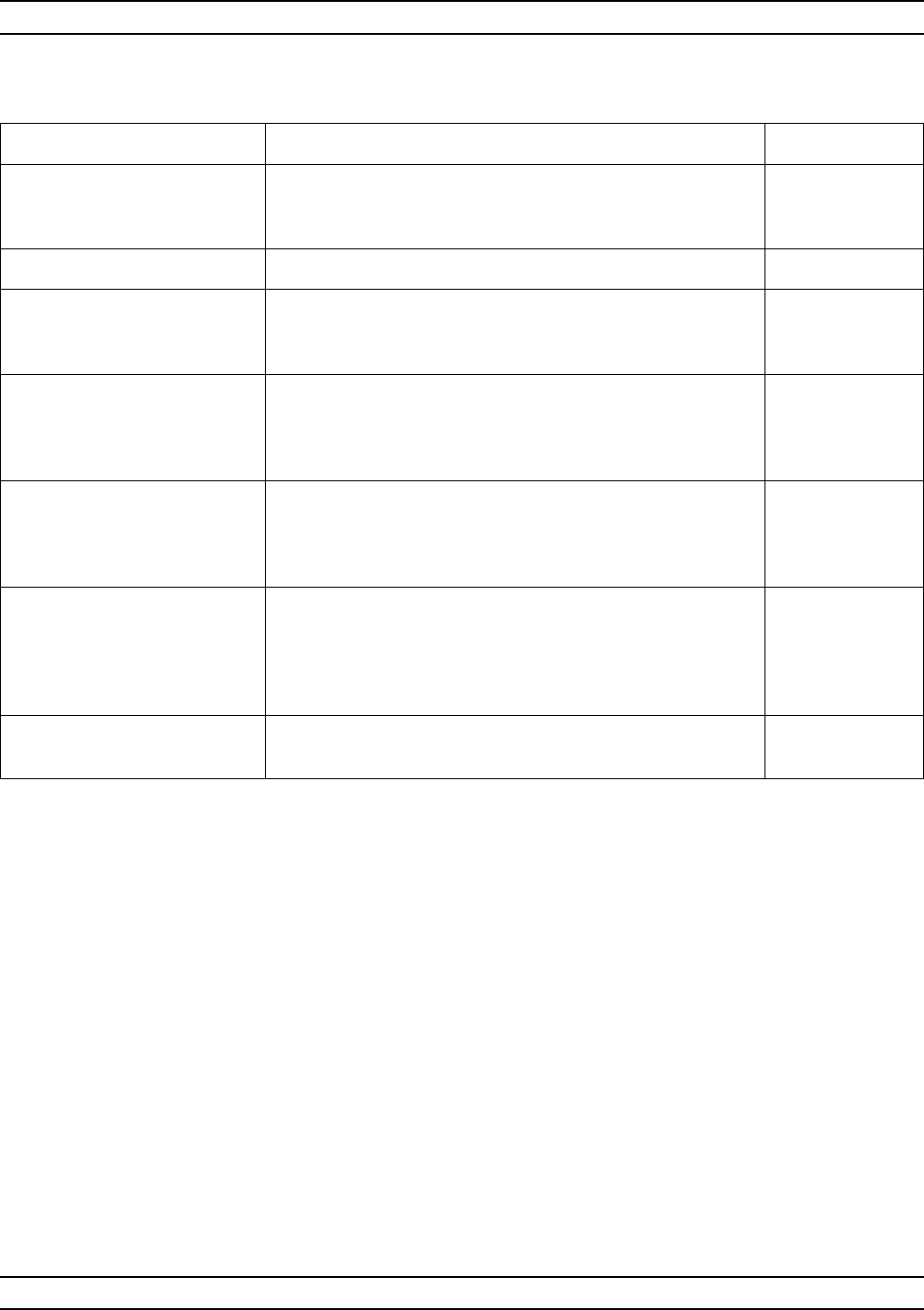
37XXXC OM A-205
ALPHABETICAL LISTING S
MENU DESCRIPTION GPIB COMMAND
SET SCALING
OR PRESS
<AUTOSCALE>
None
–PHASE– None
RESOLUTION
XX.XXX °/DIV Sets the resolution for the vertical axis of the active
channel’s displayed graph. Resolution can by set
incrementally using the keypad or rotary knob.
SCL; SCL?;
SCL2; SCL2?
REFERENCE VALUE
XXX.XXX °
Sets the value at the reference line for the active channel
amplitude measurement on the displayed graph. The value
can be set in increments of 0.01 ousing the keypad or
rotary knob.
OFF; OFF?
OFF2; OFF2?
REFERENCE LINE
XSets the reference line for the active channel’s amplitude
measurement. This is the line about which the amplitude
expands with different resolution values. The reference line
can be set to any vertical division using the rotary knob.
REF; REF?;
REF2; REF2?
PHASE SHIFT
X.XX °
Sets the value by which the active channel’s phase
measurement is shifted on the phase graph. The shift can
be set in increments of 0.01 degrees using the keypad or
rotary knob. This is useful when phase data is near the 180
degree rollover value.
PHO; PHO?
PRESS <ENTER>
TO RESUME CAL On the CAL_SS5 menu, pressing the Enter key returns you
to the calibration setup or sequence. v
Menu SS5 or CAL_SS5, Set Scaling 5
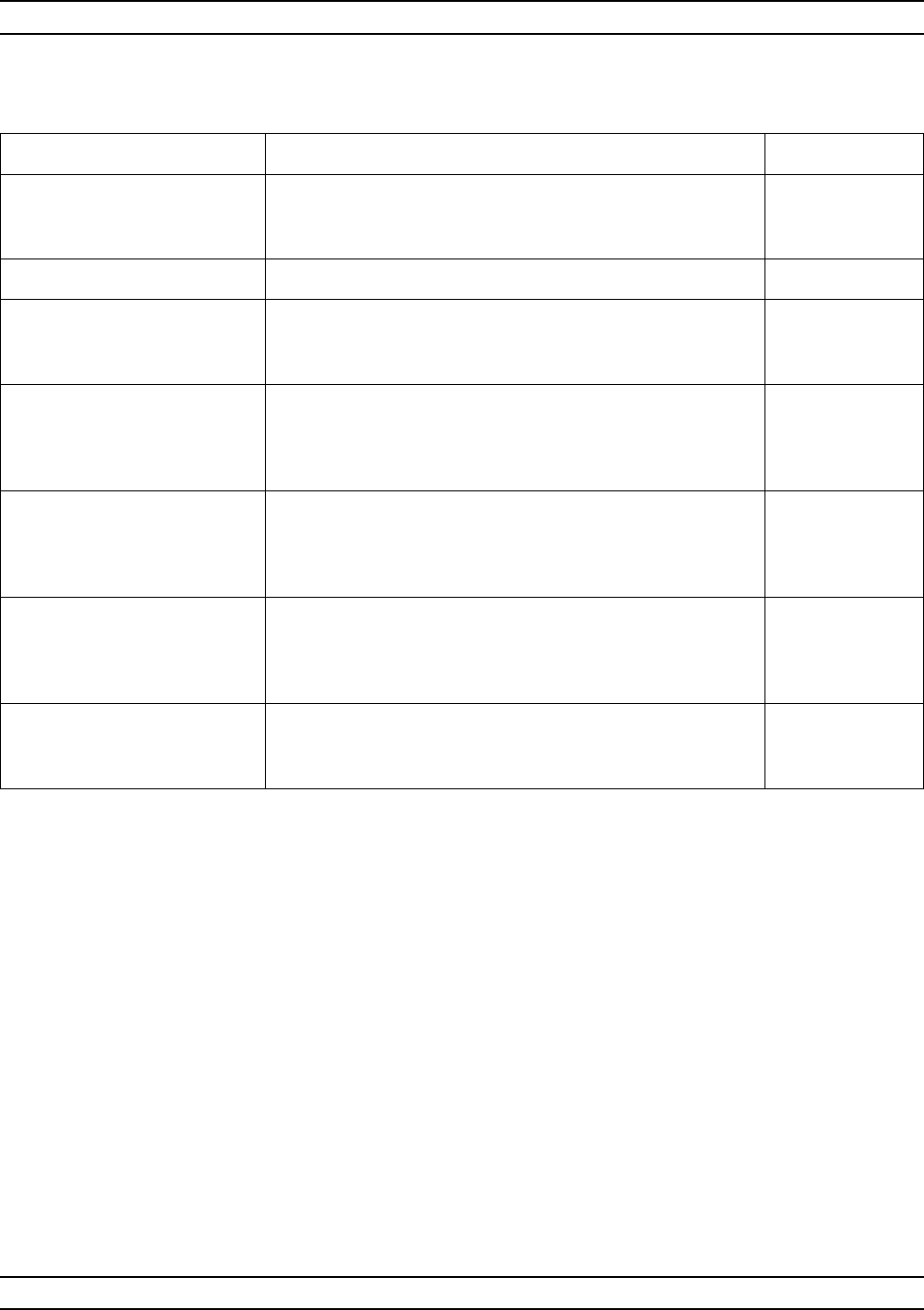
A-206 37XXXC OM
S ALPHABETICAL LISTING
MENU DESCRIPTION GPIB COMMAND
SET SCALING
OR PRESS
<AUTOSCALE>
None
–LOG POLAR– None
RESOLUTION
XX.XXX dB/DIV Sets the resolution for the vertical axis of the active
channel’s displayed graph. Resolution can by set
incrementally using the keypad or rotary knob.
SCL; SCL?;
SCL2; SCL2?
REFERENCE VALUE
XXX.XXX dB Sets the value at the reference line for the active channel
amplitude measurement on the displayed graph. The value
can be set in increments of 0.001 dB using the keypad or
rotary knob.
OFF; OFF?
OFF2; OFF2?
FIXED
REFERENCE LINE Sets the reference line for the active channel’s amplitude
measurement. This is the line about which the amplitude
expands with different resolution values. The reference line
can be set to any vertical division using the rotary knob.
REF; REF?;
REF2; REF2?
SELECT POLAR
CHART MODE
MAGNITUDE
PHASE
Calls menu PC1, which lets you define the phase angles
between which your polar chart will display data. None
PRESS <ENTER>
TO SELECT
AND RESUME CAL
Pressing the Enter key implements your menu selection
and resumes the calibration from where it left off, if in the
calibration mode.
None
Menu SS6 or CAL_SS6, Set Scaling 6
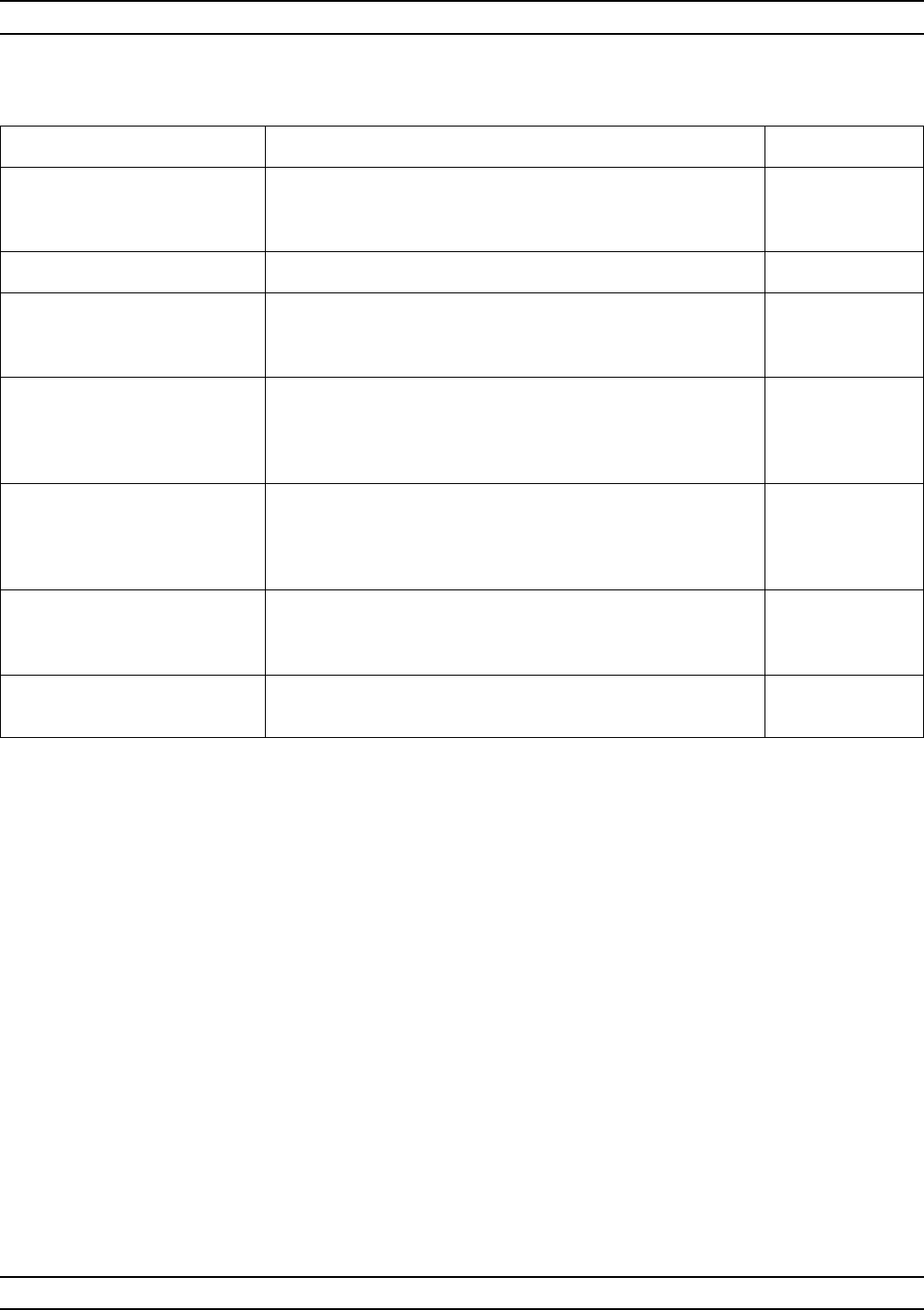
37XXXC OM A-207
ALPHABETICAL LISTING S
MENU DESCRIPTION GPIB COMMAND
SET SCALING
OR PRESS
<AUTOSCALE>
None
–GROUP DELAY– None
RESOLUTION
XX.XXX fs/DIV Sets the resolution for the vertical axis of the active
channel’s displayed graph. Resolution can by set
incrementally using the keypad or rotary knob.
SCL; SCL?;
SCL2; SCL2?
REF VALUE
XXX.XXX fs Sets the value at the reference line for the active channel
amplitude measurement on the displayed graph. The value
can be set in increments of 0.0001 s using the keypad or
rotary knob.
OFF; OFF?
OFF2; OFF2?
REFERENCE LINE
XSets the reference line for the active channel’s amplitude
measurement. This is the line about which the amplitude
expands with different resolution values. The reference line
can be set to any vertical division using the rotary knob.
REF; REF?;
REF2; REF2?
APERTURE
X.X PERCENT
OF SWEEP
Sets and displays the percent of frequency span over
which group delay is calculated. APR; APR?
PRESS <ENTER>
TO RESUME CAL On the CAL_SS7 menu, pressing the Enter key returns you
to the calibration setup or sequence. None
Menu SS7 or CAL_SS7, Set Scaling 7
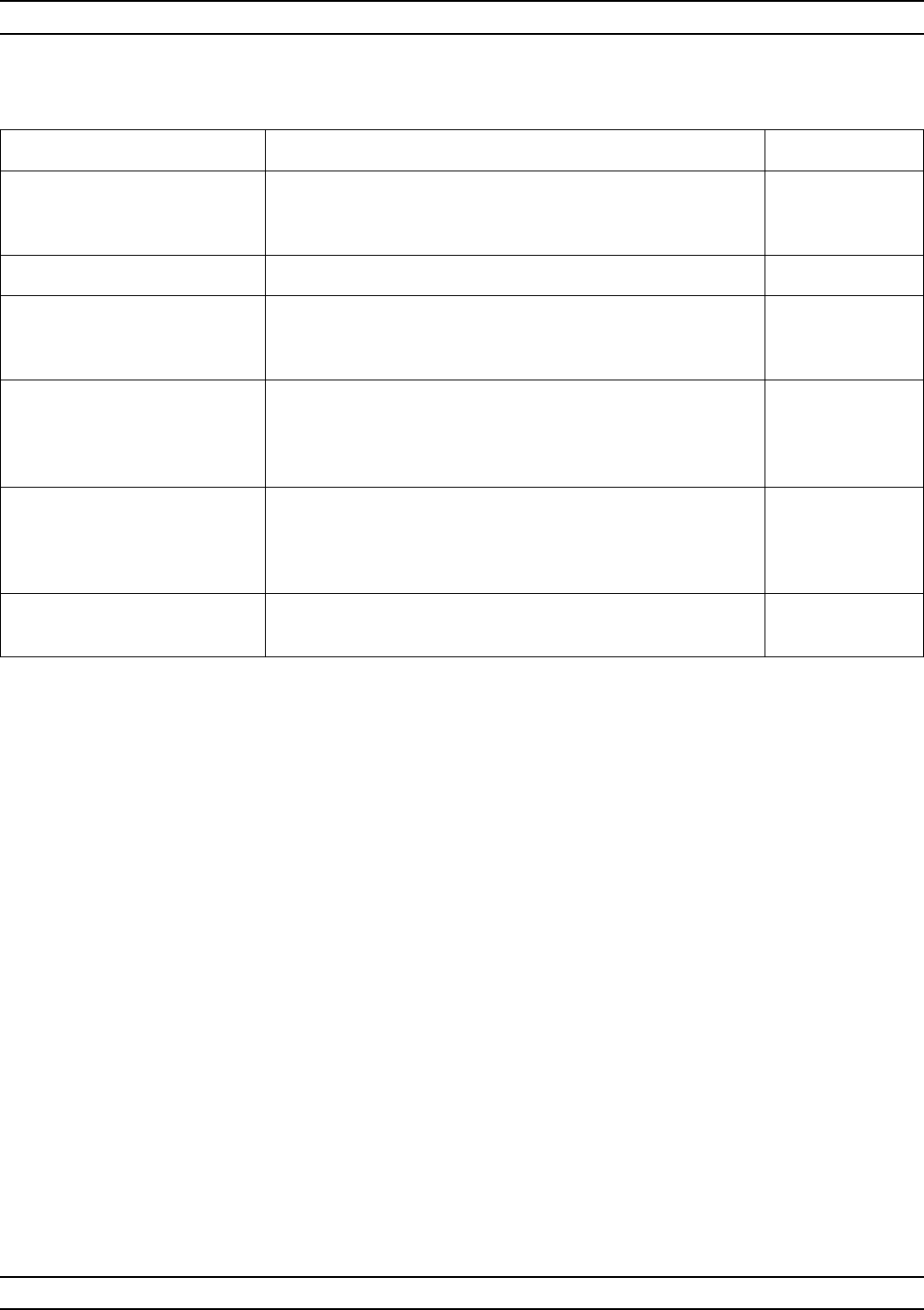
A-208 37XXXC OM
S ALPHABETICAL LISTING
MENU DESCRIPTION GPIB COMMAND
SET SCALING
OR PRESS
<AUTOSCALE>
None
–LINEAR MAG– None
RESOLUTION
XX.XXX U/DIV Sets the resolution for the vertical axis of the active
channel’s displayed graph. Resolution can by set
incrementally using the keypad or rotary knob.
SCL; SCL?;
SCL2; SCL2?
REFERENCE VALUE
XXX.XXX pU Sets the value at the reference line for the active channel
amplitude measurement on the displayed graph. The value
can be set in increments of 0.001 U using the keypad or
rotary knob.
OFF; OFF?
OFF2; OFF2?
REFERENCE LINE
XSets the reference line for the active channel’s amplitude
measurement. This is the line about which the amplitude
expands with different resolution values. The reference line
can be set to any vertical division using the rotary knob.
REF; REF?;
REF2; REF2?
PRESS <ENTER>
TO RESUME CAL On the CAL_SS8 menu, pressing the Enter key returns you
to the calibration setup or sequence. None
Menu SS8 or CAL_SS8, Set Scaling 8
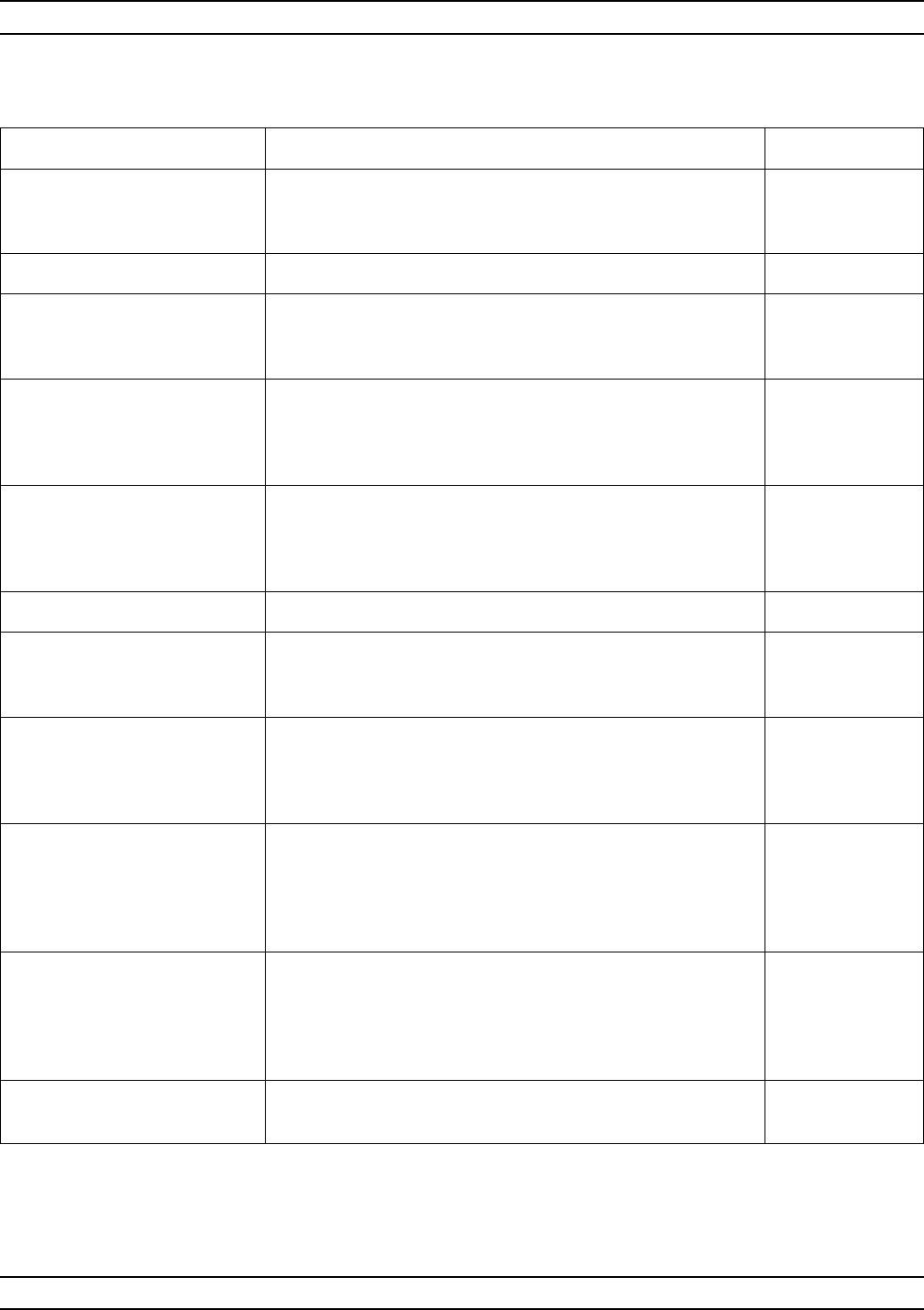
37XXXC OM A-209
ALPHABETICAL LISTING S
MENU DESCRIPTION GPIB COMMAND
SET SCALING
OR PRESS
<AUTOSCALE>
None
–LINEAR MAG– None
RESOLUTION
XX.XXX U/DIV Sets the resolution for the vertical axis of the active
channel’s displayed graph. Resolution can by set
incrementally using the keypad or rotary knob.
SCL; SCL?;
SCL2; SCL2?
REFERENCE VALUE
XXX.XXX pU Sets the value at the reference line for the active channel
amplitude measurement on the displayed graph. The value
can be set in increments of 0.001 U using the keypad or
rotary knob.
OFF; OFF?
OFF2; OFF2?
REFERENCE LINE
XSets the reference line for the active channel’s amplitude
measurement. This is the line about which the amplitude
expands with different resolution values. The reference line
can be set to any vertical division using the rotary knob.
REF; REF?;
REF2; REF2?
–PHASE– None
RESOLUTION
XX.XX °/DIV Sets the resolution for the vertical axis of the active
channel’s displayed phase graph. Resolution can by set
incrementally using the keypad or rotary knob.
SCL; SCL?;
SCL2; SCL2?
REF VALUE
XXX.XX °
Sets the value by which the active channel’s phase
measurement is offset on the phase graph. The offset can
be set in increments of 0.01 degrees using the keypad or
rotary knob.
OFF; OFF?
OFF2; OFF2?
REFERENCE LINE
XSets the reference line for the active channel’s phase
measurement
on the phase graph. This is the line about which the phase
expands with different resolution values. The reference line
can be set to any vertical division using the rotary knob.
REF; REF?;
REF2; REF2?
PHASE SHIFT
X.XX °
Sets the value by which the active channel’s phase
measurement is shifted on the phase graph. The shift can
be set in increments of 0.01 degrees using the keypad or
rotary knob. This is useful when phase data is near the 180
degree rollover value.
PHO; PHO?
PRESS <ENTER>
TO RESUME CAL On the CAL_SS9 menu, pressing the Enter key returns you
to the calibration setup or sequence. None
Menu SS9 or CAL_SS9, Set Scaling 9
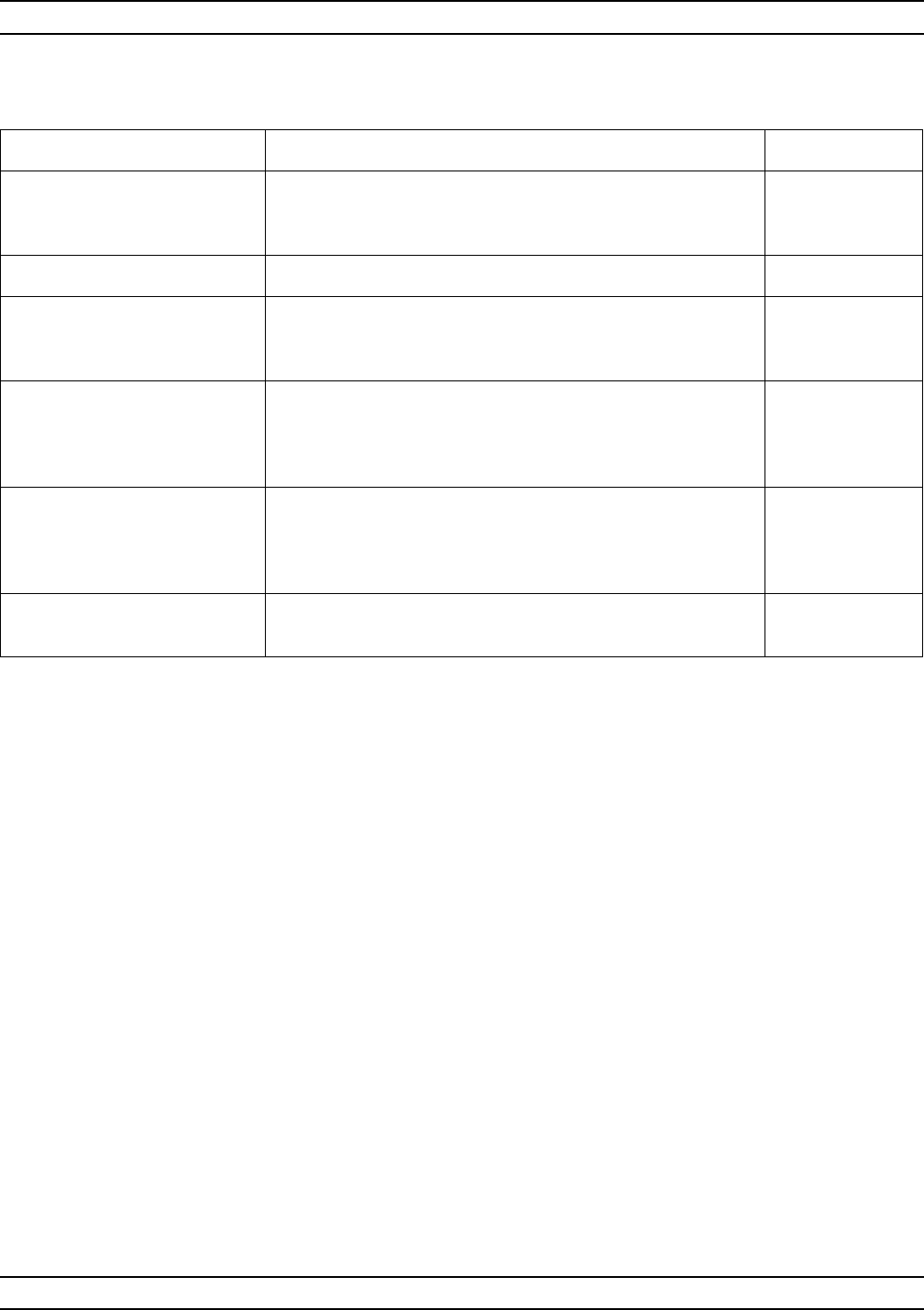
A-210 37XXXC OM
S ALPHABETICAL LISTING
MENU DESCRIPTION GPIB COMMAND
SET SCALING
OR PRESS
<AUTOSCALE>
None
–REAL– None
RESOLUTION
XX.XXX U/DIV Sets the resolution for the vertical axis of the active
channel’s displayed graph. Resolution can by set
incrementally using the keypad or rotary knob.
SCL; SCL?;
SCL2; SCL2?
REFERENCE VALUE
XXX.XXX pU Sets the value at the reference line for the active channel
amplitude measurement on the displayed graph. The value
can be set in increments of 0.001 U using the keypad or
rotary knob.
OFF; OFF?
OFF2; OFF2?
REFERENCE LINE
XSets the reference line for the active channel’s amplitude
measurement. This is the line about which the amplitude
expands with different resolution values. The reference line
can be set to any vertical division using the rotary knob.
REF; REF?;
REF2; REF2?
PRESS <ENTER>
TO RESUME CAL On the CAL_SS10 menu, pressing the Enter key returns
you to the calibration setup or sequence. None
Menu SS10 or CAL_SS10, Set Scaling 10
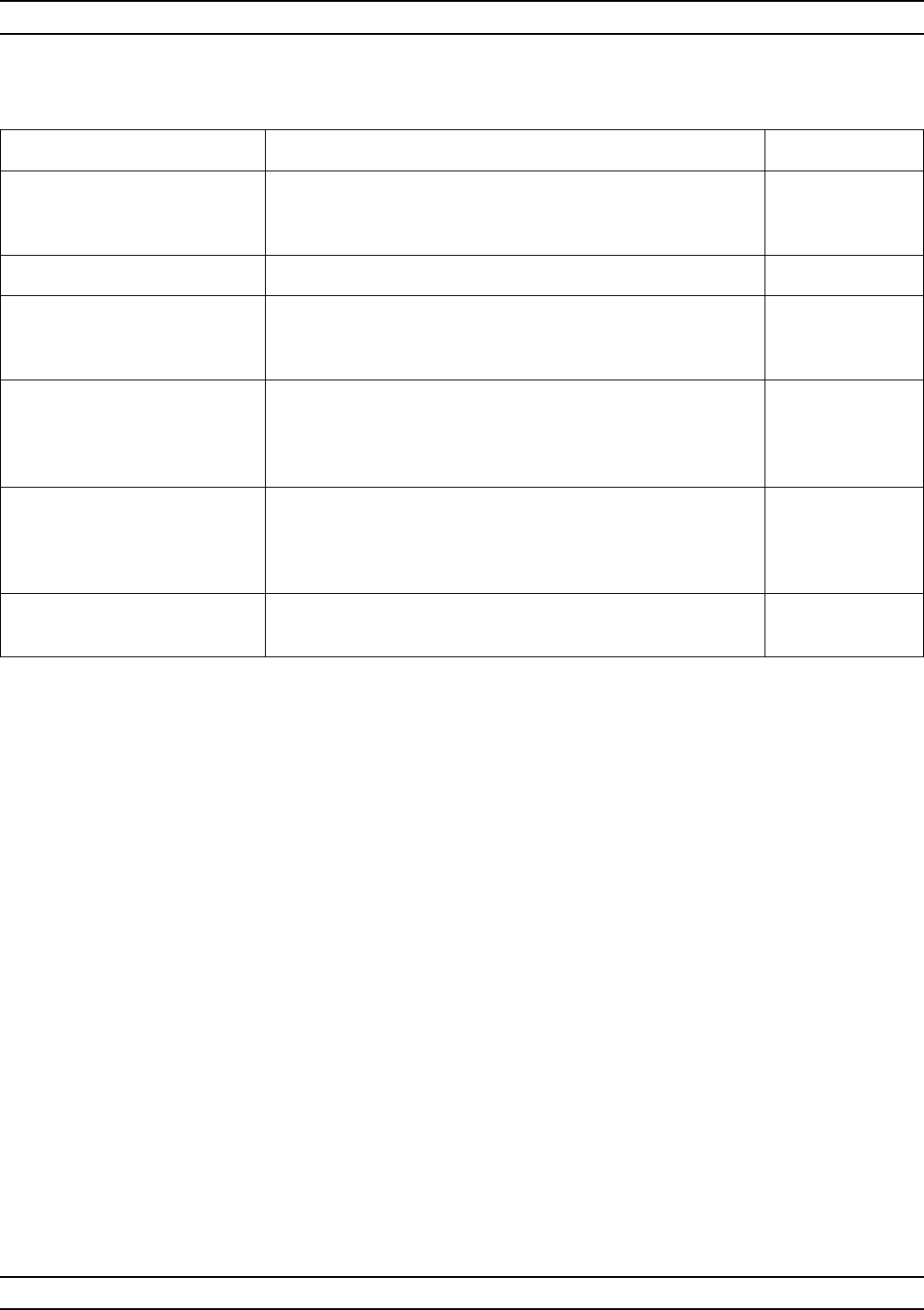
37XXXC OM A-211
ALPHABETICAL LISTING S
MENU DESCRIPTION GPIB COMMAND
SET SCALING
OR PRESS
<AUTOSCALE>
None
–IMAGINARY– None
RESOLUTION
XX.XXX U/DIV Sets the resolution for the vertical axis of the active
channel’s displayed graph. Resolution can by set
incrementally using the keypad or rotary knob.
SCL; SCL?;
SCL2; SCL2?
REFERENCE VALUE
XXX.XXX pU Sets the value at the reference line for the active channel
amplitude measurement on the displayed graph. The value
can be set in increments of 0.001 U using the keypad or
rotary knob.
OFF; OFF?
OFF2; OFF2?
REFERENCE LINE
XSets the reference line for the active channel’s amplitude
measurement. This is the line about which the amplitude
expands with different resolution values. The reference line
can be set to any vertical division using the rotary knob.
REF; REF?;
REF2; REF2?
PRESS <ENTER>
TO RESUME CAL On the CAL_SS11 menu, pressing the Enter key returns
you to the calibration setup or sequence. None
Menu SS11 or CAL_SS11, Set Scaling 11
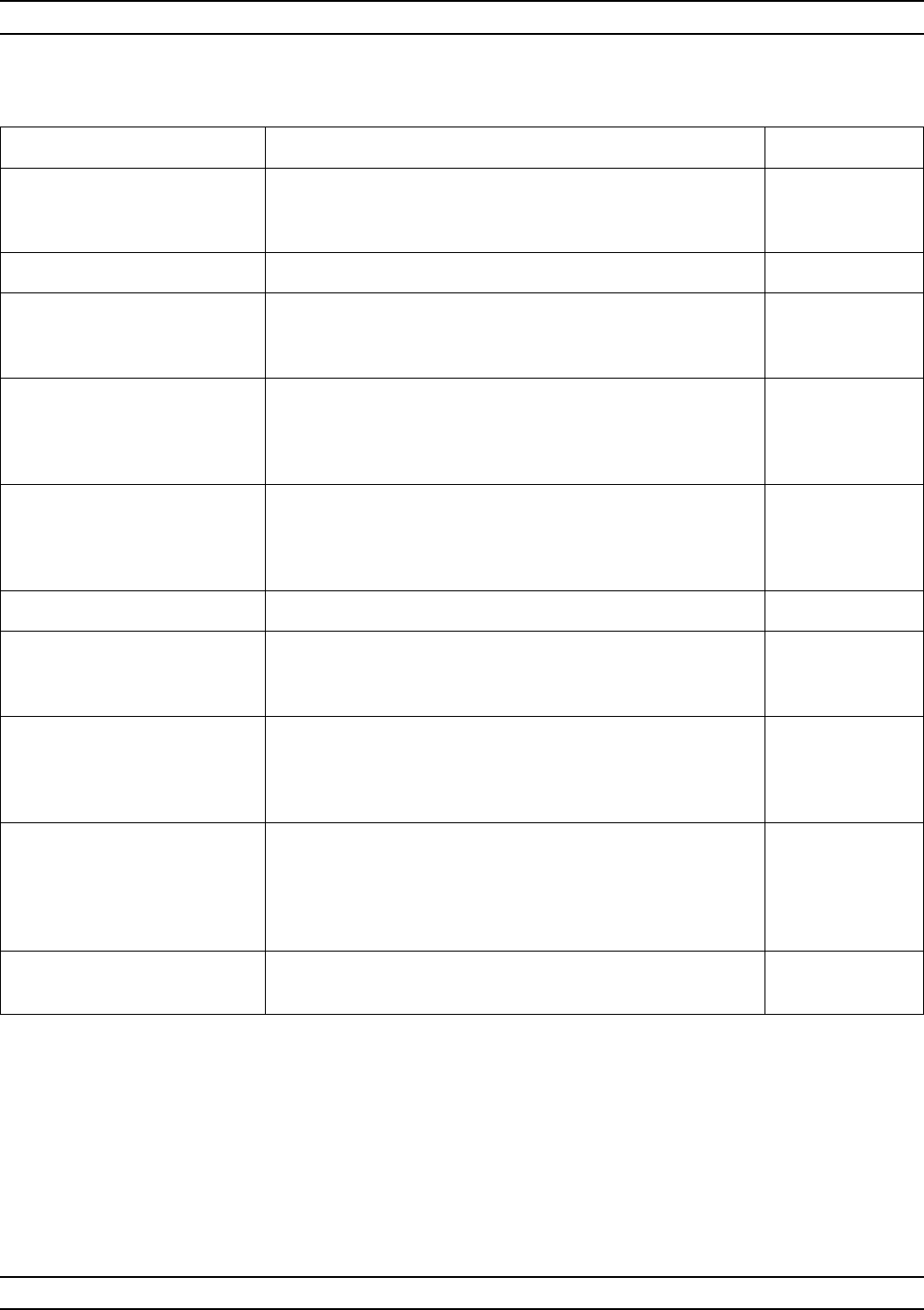
A-212 37XXXC OM
S ALPHABETICAL LISTING
MENU DESCRIPTION GPIB COMMAND
SET SCALING
OR PRESS
<AUTOSCALE>
None
–REAL– None
RESOLUTION
XX.XXX U/DIV Sets the resolution for the vertical axis of the active
channel’s displayed graph. Resolution can by set
incrementally using the keypad or rotary knob.
SCL; SCL?;
SCL2; SCL2?
REFERENCE VALUE
XXX.XXX pU Sets the value at the reference line for the active channel
amplitude measurement on the displayed graph. The value
can be set in increments of 0.001 U using the keypad or
rotary knob.
OFF; OFF?
OFF2; OFF2?
REFERENCE LINE
XSets the reference line for the active channel’s amplitude
measurement. This is the line about which the amplitude
expands with different resolution values. The reference line
can be set to any vertical division using the rotary knob.
REF; REF?;
REF2; REF2?
–IMAGINARY– None
RESOLUTION
XX.XX °/DIV Sets the resolution for the vertical axis of the active
channel’s displayed graph. Resolution can by set
incrementally using the keypad or rotary knob.
SCL; SCL?;
SCL2; SCL2?
REFERENCE VALUE
XXX.XX °
Sets the value by which the active channel’s phase
measurement is offset on the phase graph. The offset can
be set in increments of 0.01 degrees using the keypad or
rotary knob.
OFF; OFF?
OFF2; OFF2?
REFERENCE LINE
XSets the reference line for the active channel’s phase
measurement on the phase graph. This is the line about
which the phase expands with different resolution values.
The reference line can be set to any vertical division using
the rotary knob.
REF; REF?;
REF2; REF2?
PRESS <ENTER>
TO RESUME CAL On the CAL_SS12 menu, pressing the Enter key returns
you to the calibration setup or sequence. None
Menu SS12 or CAL_SS12, Set Scaling 12
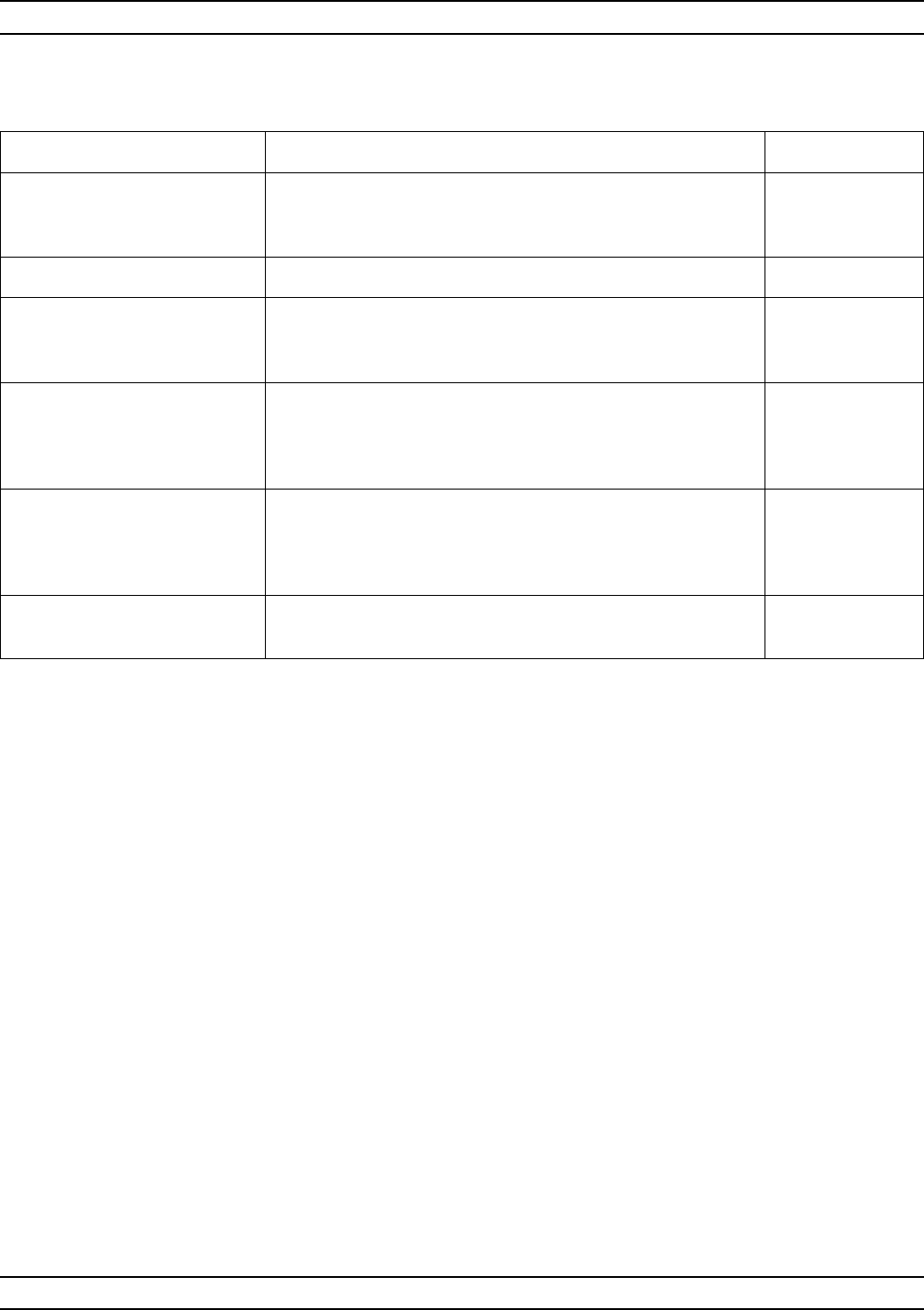
37XXXC OM A-213
ALPHABETICAL LISTING S
MENU DESCRIPTION GPIB COMMAND
SET SCALING
OR PRESS
<AUTOSCALE>
None
–SWR– None
RESOLUTION
XX.XXX U /DIV Sets the resolution for the vertical axis of the active
channel’s displayed graph. Resolution can by set
incrementally using the keypad or rotary knob.
SCL; SCL?;
SCL2; SCL2?
REFERENCE VALUE
XXX.XXX U Sets the value at the reference line for the active channel
amplitude measurement on the displayed graph. The value
can be set in increments of 0.001 U using the keypad or
rotary knob.
OFF; OFF?
OFF2; OFF2?
REFERENCE LINE
XSets the reference line for the active channel’s amplitude
measurement. This is the line about which the amplitude
expands with different resolution values. The reference line
can be set to any vertical division using the rotary knob.
REF; REF?;
REF2; REF2?
PRESS <ENTER>
TO RESUME CAL On the CAL_SS13 menu, pressing the Enter key returns
you to the calibration setup or sequence. None
Menu SS13 or CAL_SS13, Set Scaling 13
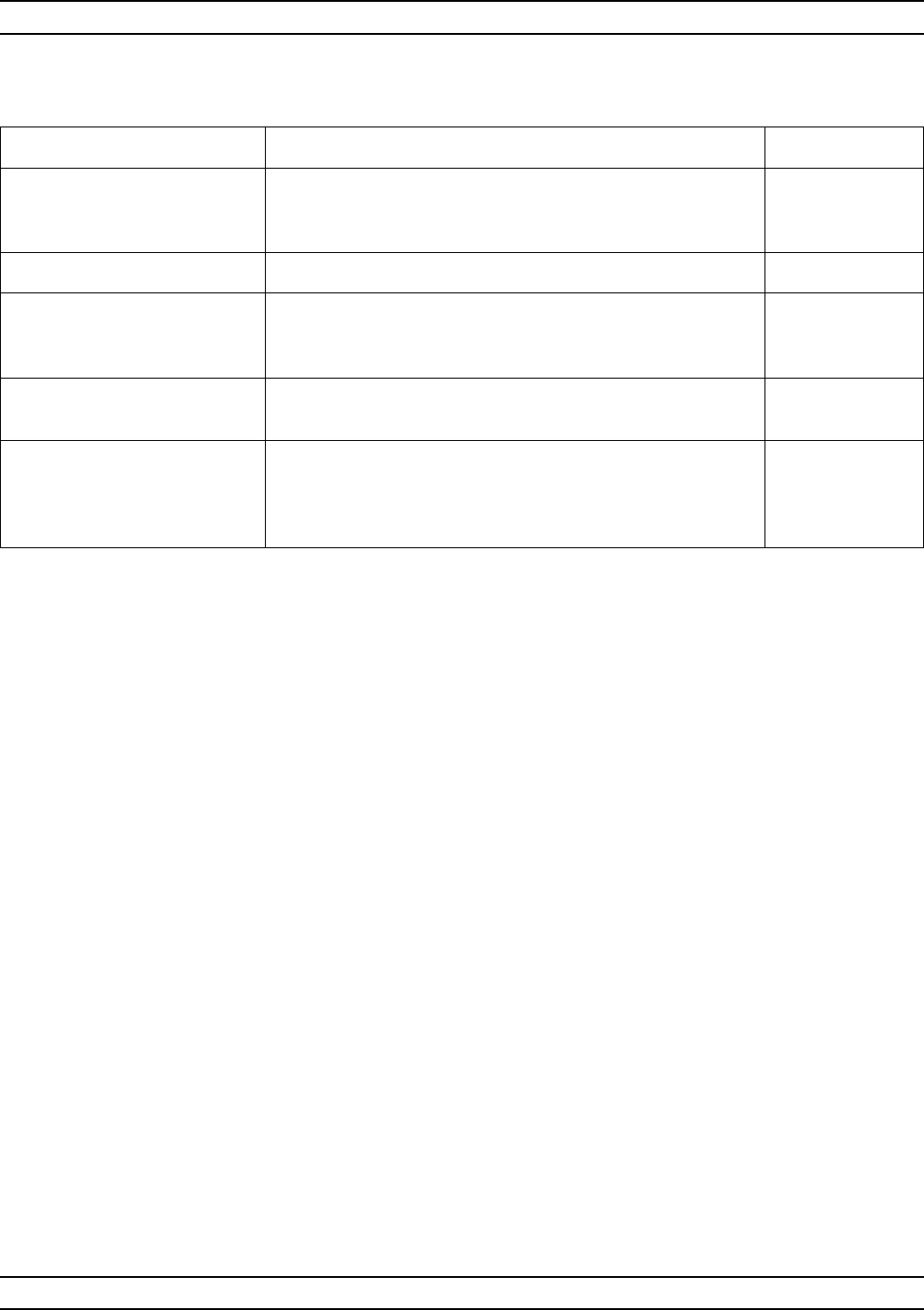
A-214 37XXXC OM
S ALPHABETICAL LISTING
MENU DESCRIPTION GPIB COMMAND
SET SCALING
OR PRESS
<AUTOSCALE>
None
–POWER OUT– None
RESOLUTION
XX.XXX dB/DIV Sets the resolution for the vertical axis of the active
channel’s displayed graph. Resolution can by set
incrementally using the keypad or rotary knob.
SCL; SCL?;
SCL2; SCL2?
REFERENCE VALUE
XXX.XXX dBm Sets the value at the reference line for the active channel
amplitude measurement on the displayed graph. OFF; OFF?
OFF2; OFF2?
REFERENCE LINE
XSets the reference line for the active channel’s amplitude
measurement. This is the line about which the amplitude
expands with different resolution values. The reference line
can be set to any vertical division using the rotary knob.
REF; REF?;
REF2; REF2?
Menu SS14, Set Scaling 14
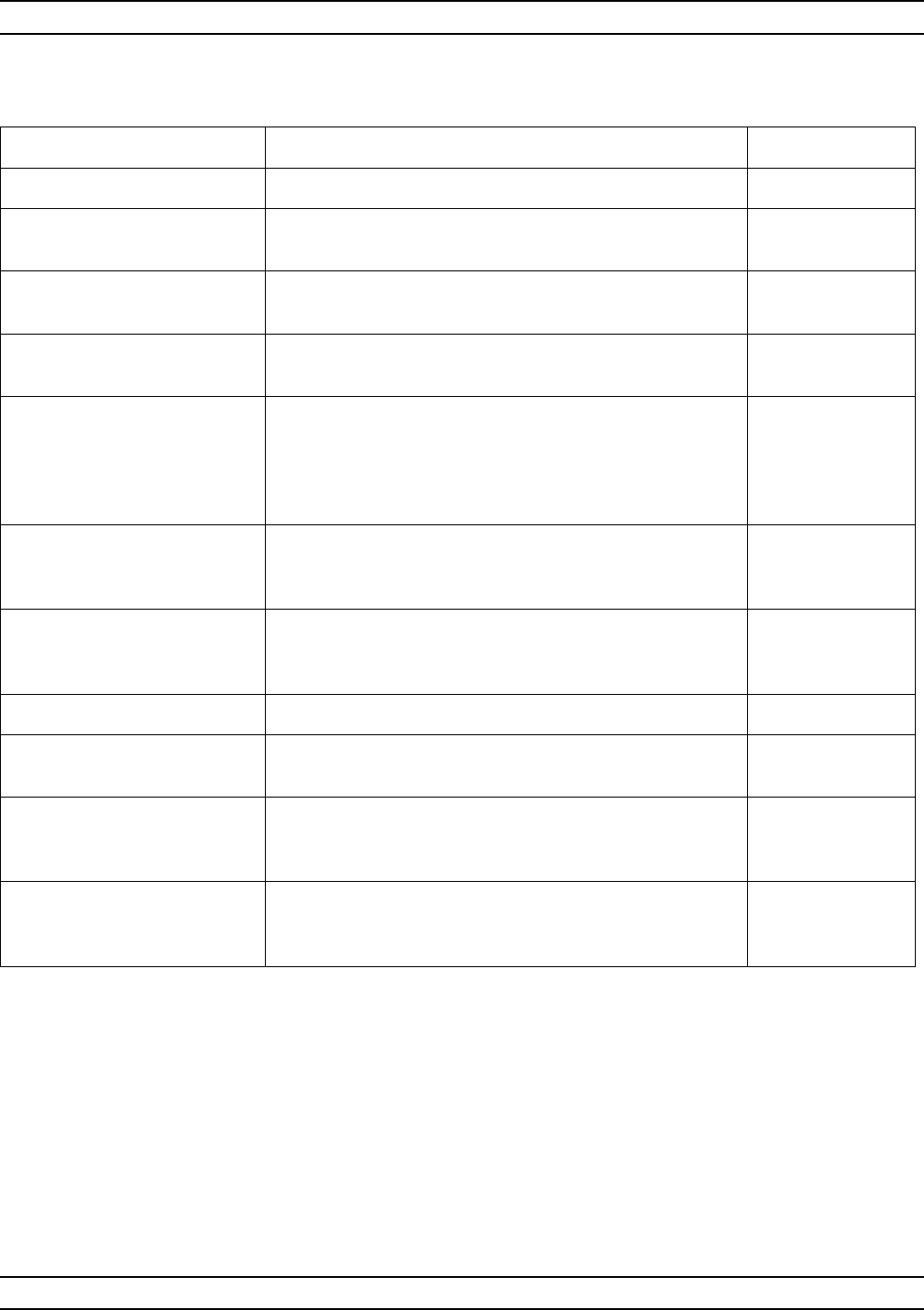
37XXXC OM A-215
ALPHABETICAL LISTING S
MENU DESCRIPTION GPIB COMMAND
SWEEP SETUP None
START
XXX.XXXXXXXXX GHz Enter the sweep-start frequency in GHz. The start
frequency must be lower than the stop frequency. SRT
STOP
XXX.XXXXXXXXX GHz Enter the sweep-stop frequency in GHz. The stop
frequency must be higher than the start frequency. STP
SET CENTER/SPAN Calls menu SU1_CENTER, which lets you set values for
center frequency and span width. None
XXX DATA POINTS
XXX.XXXXXXXXX GHz
STEPSIZE
Displays the number of frequency points and the spacing
between points for the start and stop frequencies
selected above. The number of points shown provides
the finest frequency resolution possible, based on your
Data Points key menu selection.
None
C.W. MODE ON (OFF)
XXX.XXXXXXXXX GHZ Move cursor here and press Enter to enable the CW
mode. Enter CW frequency for measurements. CWF; CWON;
CWON?; SWP;
SWP?
MARKER SWEEP Move cursor here and press Enter to set the start and
stop frequencies (menu SU5) of the CW frequency
(menu SU6) to the values of any marker.
None
DISCRETE FILL Calls the Discrete Fill menu (menu DF1). None
HOLD BUTTON
FUNCTION Calls menu SU4, which lets you set the action of the
HOLD key. None
TEST SIGNALS Calls menu SU2, which lets you set the source power
and the values for the attenuators in the 37XXXC. It also
provides entry into the Flat Test Port Power calibration.
None
PRESS <ENTER>
TO SELECT
OR TURN ON/OFF
Pressing the ENTER key implements your menu
selection. None
Menu SU1, Sweep Setup 1
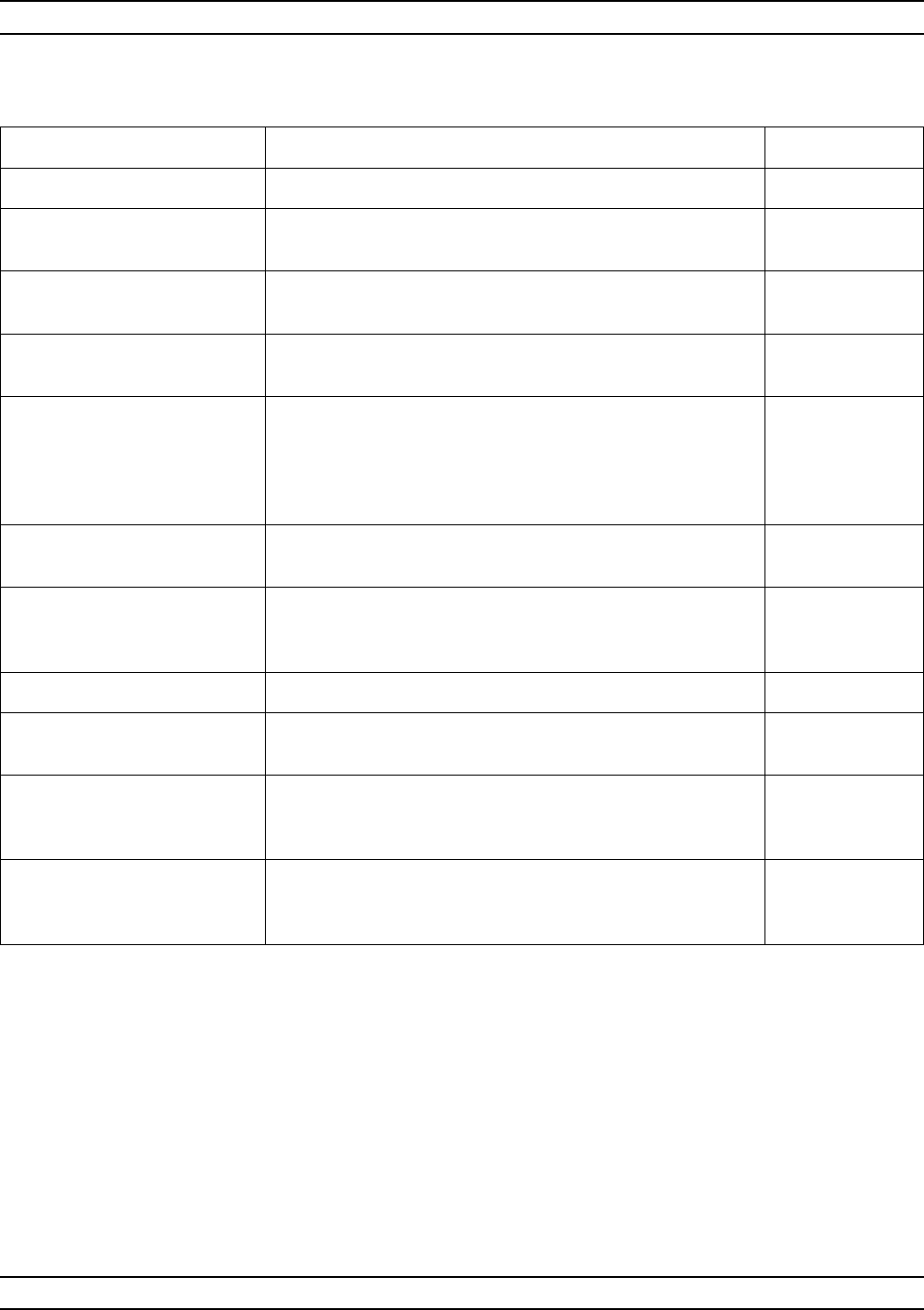
A-216 37XXXC OM
S ALPHABETICAL LISTING
MENU DESCRIPTION GPIB COMMAND
SWEEP SETUP None
CENTER
XXX.XXXXXXXXX GHz Enter the center frequency in GHz. CNTR; CNTR?
SPAN
XXX.XXXXXXXXX GHz Enter the span frequency in GHz. SPAN; SPAN?
SET START/STOP Calls menu SU1, which lets you set values for start and
stop frequencies. None
XXX DATA POINT(S)
XXX.XXXXXXXXX GHz
STEPSIZE
Displays the number of frequency points and the spacing
between points for the center and span frequencies
selected above. The number of points shown provides the
finest frequency resolution possible, based on your Data
Points key menu selection.
None
C.W. MODE ON (OFF)
XXX.XXXXXXXXX GHZ Move cursor here and press Enter to enable the CW mode.
Enter CW frequency for measurements. CWF; CWON;
SWP; CWON?
MARKER SWEEP Move cursor here and press Enter to set the start and stop
frequencies (menu SU5) of the CW frequency (menu SU6)
to the values of any marker.
None
DISCRETE FILL Calls the Discrete Fill menu (menu DF1). None
HOLD BUTTON
FUNCTION Calls menu SU4, which lets you set the action of the HOLD
key. None
TEST SIGNALS Calls menu SU2, which lets you set the source power and
the values for the attenuators in the 37XXXC. It also
provides entry into the Flat Test Port Power calibration.
None
PRESS <ENTER>
TO SELECT
OR TURN ON/OFF
Pressing the ENTER key implements your menu selection. None
Menu SU1_CENTER, Sweep Setup 1
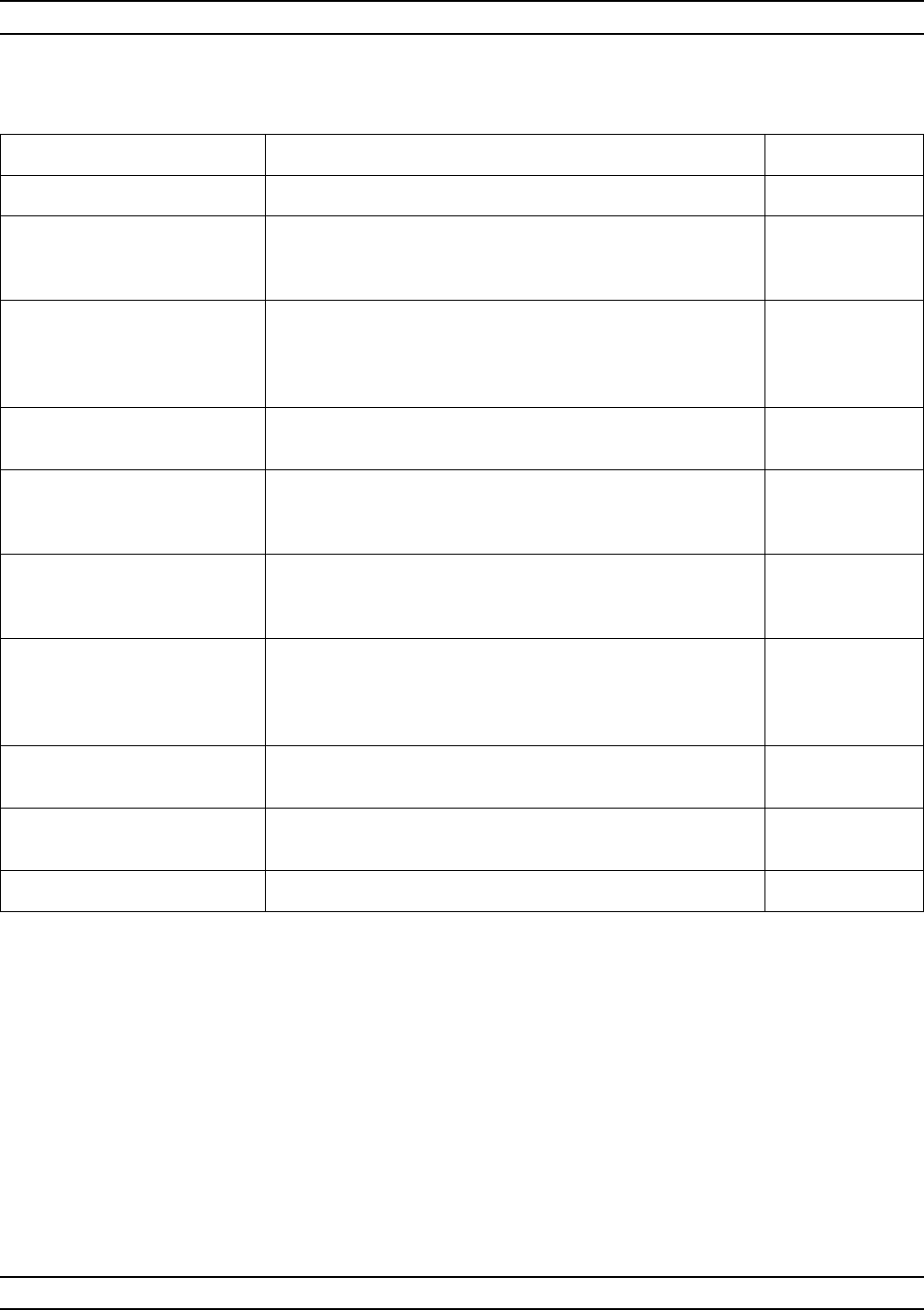
37XXXC OM A-217
ALPHABETICAL LISTING S
MENU DESCRIPTION GPIB COMMAND
TEST SIGNALS None
POWER CONTROL
+XX.X dB
0 TO -15.0 dB)
Enter the delta-power level for the Port 1 output in dB. PWR; PWR?
PORT 1 ATTN
XX10 dB (0 - 70) Attenuates the microwave source power at port 1 from 0 to
70 dB, in 10 dB steps. The power is attenuated before
being applied to Port 1 for a forward transmission or
reflection test (S21 or S11, respectively).
SA1; SA1?
PORT 1 POWER
-XX.XX dBM Displays the Port 1 power, in dBm. PIP?
PORT 2 ATTN
XX10 dB (0-X0) Attenuates from 0 to 40 dB (10 dB steps) the microwave
power being input to Port 2 from the device-under-test
(DUT).
TA2; TA2?
CALIBRATE
FOR FLATNESS
(CAL EXISTS)
None
FLATNESS ON(OFF)
CORRECTION
AT XX.X dBm
Calls menu SU8 or CAL_SU8, depending on whether valid
Flat Test Port Power calibration data exists. Both of these
menus provide selection control for the Flat Test Port
Power feature.
FP0; FP1; FPX?
EXT SOURCE 1 PWR
-XX.XX dBm Enter the power level, in dBm, of the 1st, external
frequency source. PWR1; PWR1?
EXT SOURCE 2 PWR
-XX.XX dBm Enter the power level, in dBm, of the 2nd, external
frequency source. PW2; PW2?
PREVIOUS MENU Returns to the previous menu. None
Menu SU2 or CAL_SU2, Sweep Setup 2
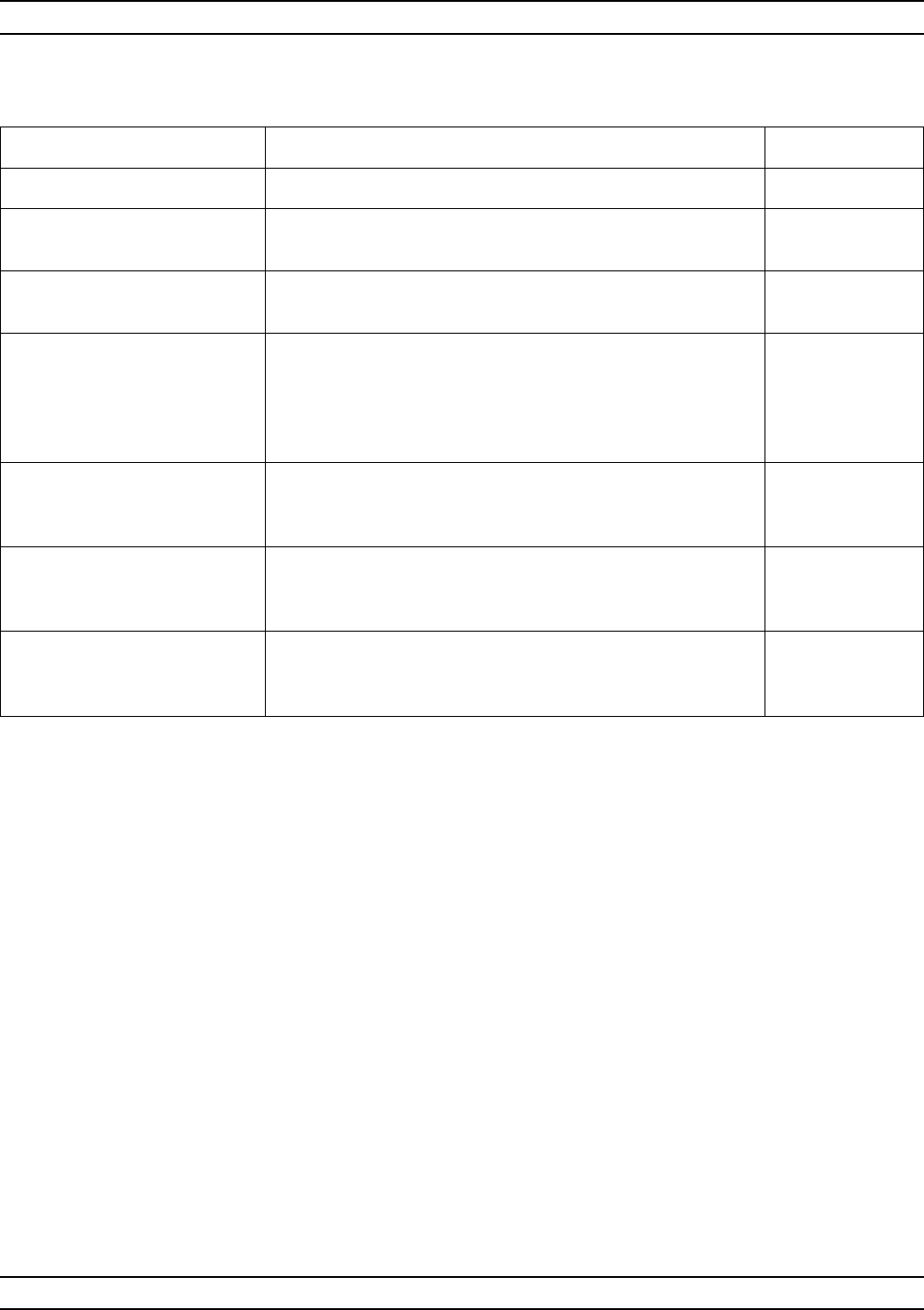
A-218 37XXXC OM
S ALPHABETICAL LISTING
MENU DESCRIPTION GPIB COMMAND
TEST SIGNALS None
EXT SOURCE 1 PWR
+XX.XX dBm Enter and display the power level, in dBm, of the 1st
external frequency source. PWR1; PWR1?
EXT SOURCE 2 PWR
+XX.XX dBm Enter and display the power level, in dBm, of the 2nd,
external frequency source. PW2; PW2?
PORT 1 ATTN
0*10dB(0-70) Attenuates the microwave source power at port 1 from 0 to
70 dB, in 10 dB steps. The power is attenuated before
being applied to Port 1 for a forward transmission or
reflection test (S21 or S11, respectively).
(NO STEP ATTENUATOR IN MODEL 372XXC)
SA1; SA1?
PORT 2 ATTN
0*10dB(0-00) Attenuates from 0 to 40 dB (10 dB steps) the microwave
power being input to Port 2 from the device-under-test
(DUT).
TA2; TA2?
PREVIOUS MENU Returns you to the previous menu. (RESUME CAL may be
used instead of PREVIOUS MENU, when accessed during
a calibration.)
None
PRESS <ENTER>
TO SELECT
OR TURN ON/OFF
Pressing the Enter key implements your menu selection. None
Menu SU2A or CAL_SU2A, Sweep Setup 2A
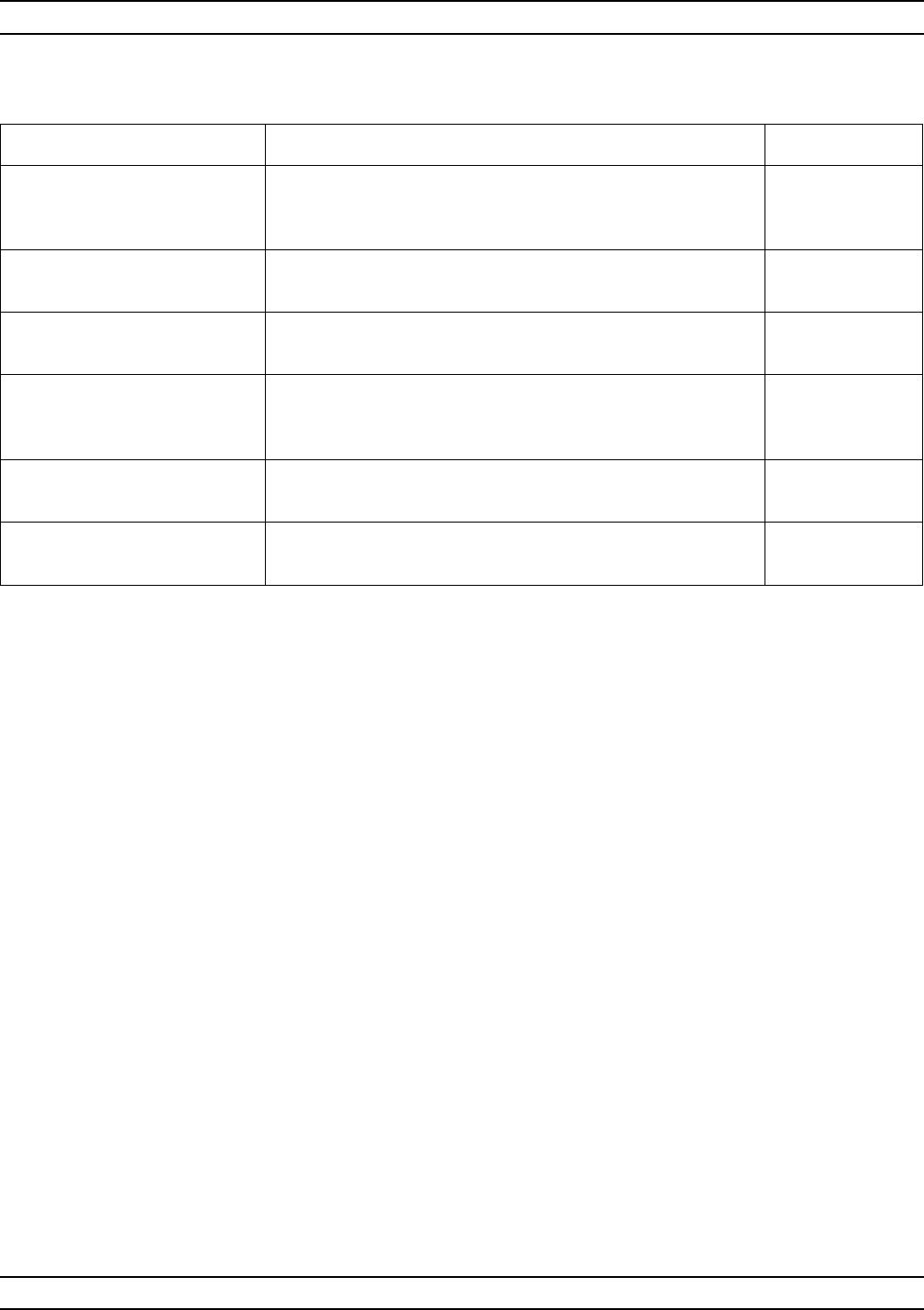
37XXXC OM A-219
ALPHABETICAL LISTING S
MENU DESCRIPTION GPIB COMMAND
SINGLE POINT
MEASUREMENT
SETUP
None
C.W. FREQ
XXX.XXXXXXXXX GHz Enter the measurement frequency in GHz for continuous
wave (CW) operation. CWF; CWF?
HOLD BUTTON
FUNCTION Calls menu SU4, which lets you set the action of the HOLD
key. None
TEST
SIGNALS Calls menu SU2, which lets you set values for the source
power and attenuators. It also provides entry into the Flat
Test Port Power calibration.
None
RETURN TO
SWEEP MODE Move cursor here and press Enter to return to the F1-F2
sweep mode (Menu SU1). None
PRESS <ENTER>
TO SELECT Pressing the Enter key implements your menu selection. None
Menu SU3, Single-Point Measurement Setup
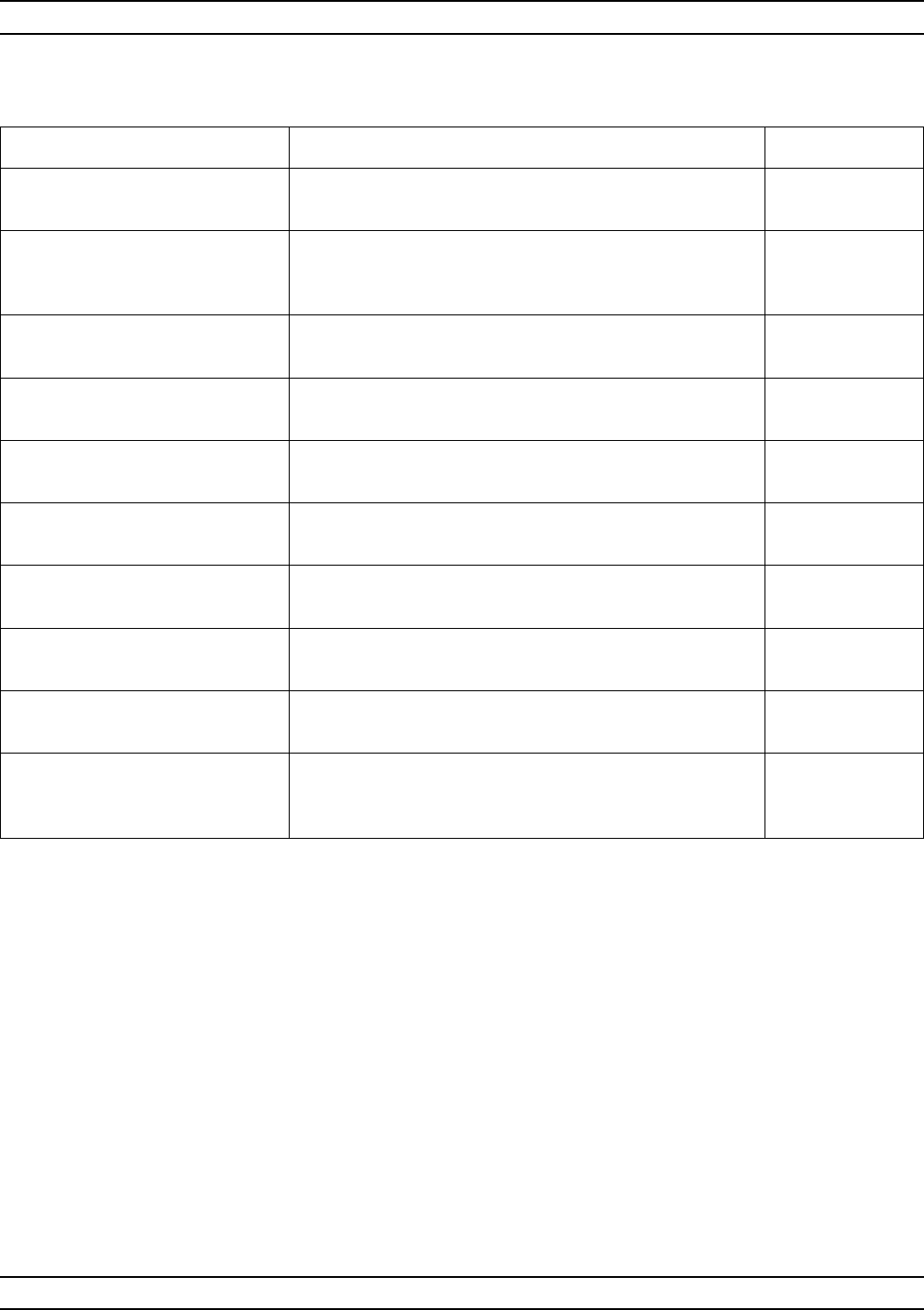
A-220 37XXXC OM
S ALPHABETICAL LISTING
MENU DESCRIPTION GPIB COMMAND
SWEPT POWER
SETUP None
SWEPT POWER
FREQUENCY
XXX.XXXXXXXXX GHz
Enter the swept-power frequency in GHz. None
PSTART
-XX.XX dBm Displays the start power value in dBm. PSTRT; PSTRT?
PSTOP
-XX.XX dBm Displays the stop power value in dBm. PSTOP; PSTOP?
STEPSIZE
-XX.XX dB Displays the power step size value in dB. PSTEP; PSTEP?
POWER SWEEP ON(OFF)
-XX.XX dBm Turns power sweep on or off. PSWP1; PSWP0;
PSWPX?
HOLD BUTTON
FUNCTION Calls menu SU4. None
SWEPT POWER
GAIN COMPRESSION Calls menu GC3 and extended menu EXT_GC3. None
RETURN TO SWEPT
FREQUENCY MODE Calls menu SU1. None
PRESS <ENTER>
TO SELECT
OR TURN ON/OFF
Pressing the Enter key implements your menu selection. None
Menu SU3A, Swept-Power Measurement Setup
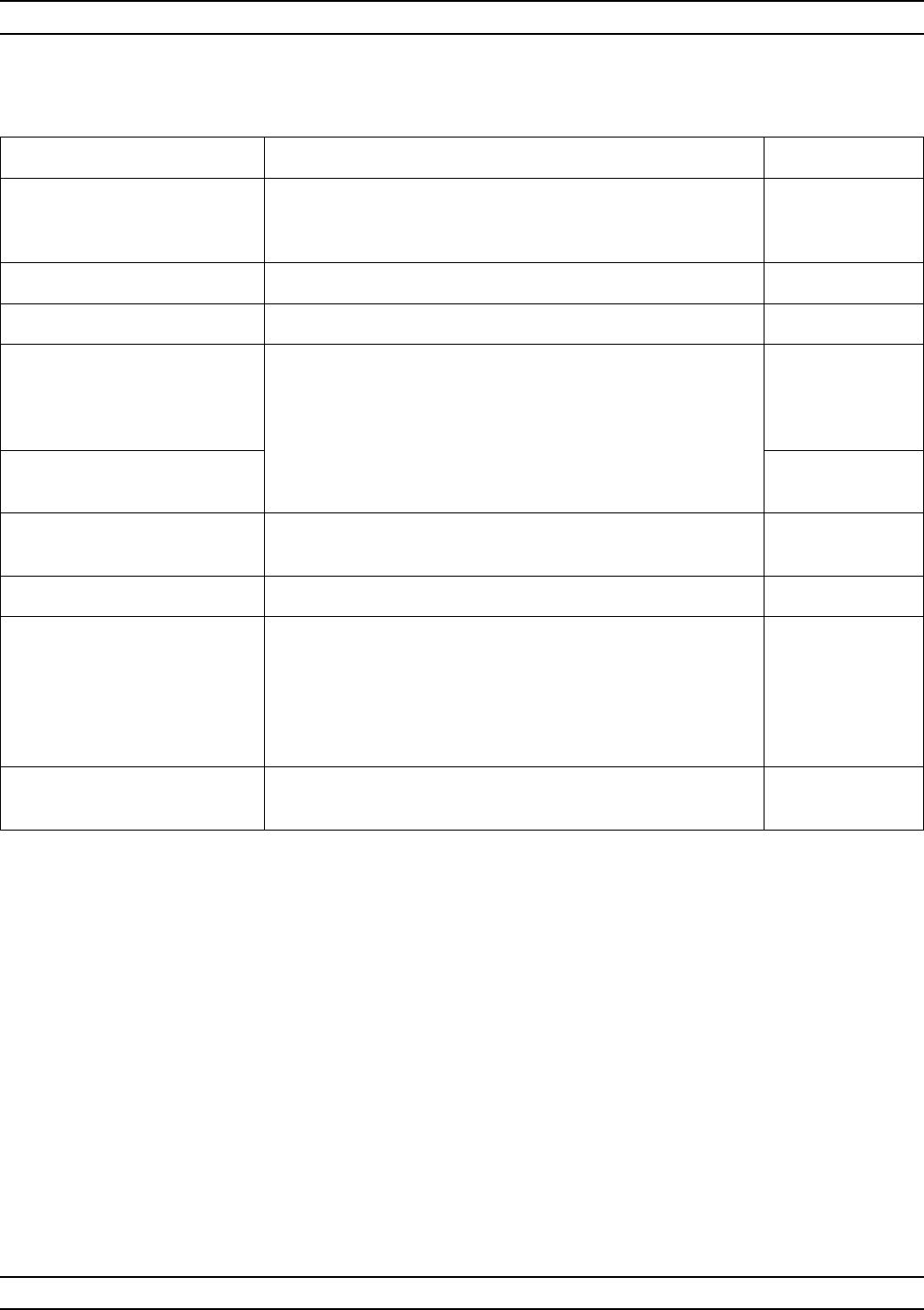
37XXXC OM A-221
ALPHABETICAL LISTING S
MENU DESCRIPTION GPIB COMMAND
SELECT
FUNCTION FOR
HOLD BUTTON
None
HOLD/CONTINUE Causes the hold key (button) to stop and start the sweep. HLD/CTN; HLD?
HOLD/RESTART Causes the hold key to stop and restart the sweep. None
SINGLE SWEEP
AND HOLD Causes the hold key to trigger a single sweep and hold
when finished. (Two sweeps, one from Port 1 to 2 and
another from Port 2 to 1, are accomplished for a 12-Term
measurement.)
HLD; TRS
BIAS/RF HOLD
CONDITIONS
BIAS ON (OFF) Select bias to be on or off (test sets having bias input only)
while system is in hold. BH1; BH0; BHX?
RF ON (OFF) Selects RF to be on or off while system is in hold. RH1; RH0; RHX?
DUT/AUT ON (OFF)
PROTECTION
DEFAULT RESET
TURNS ON HOLD
WITH BIAS/RF
TURNED OFF
When on, a default reset places the system in hold with RF
and bias turned off. This choice is initialized to OFF when
the software version changes or after a Default Program
key press, so that the system comes up in the sweep
mode.
PRESS <ENTER>
TO SELECT Pressing the Enter key implements your menu selection. None
Menu SU4, Select Function for Hold Button
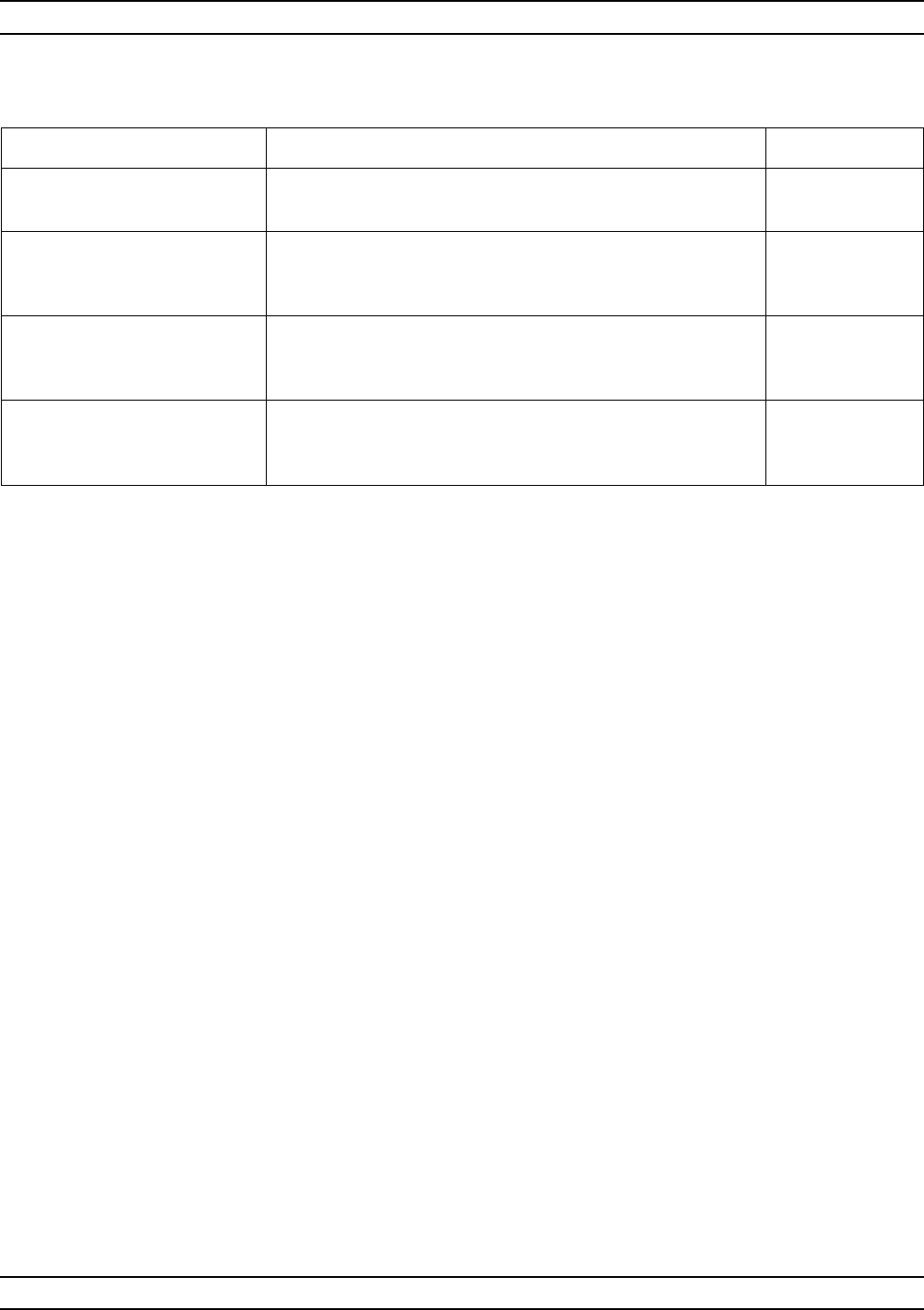
A-222 37XXXC OM
S ALPHABETICAL LISTING
MENU DESCRIPTION GPIB COMMAND
FREQUENCY
MARKER SWEEP None
START SWEEP
MARKER (X)
XXX.XXXXXXXXX GHz
Pressing a number on the keypad causes the associated
marker to be the start frequency of the sweep. M1S-M6S
STOP SWEEP
MARKER (X)
XXX.XXXXXXXXX GHz
Pressing a number on the keypad causes the associated
marker to be the stop frequency of the sweep. M1E-M6E
USE KEYPAD
TO SELECT
MARKER (1-6)
Use the keypad to select markers 1, 2, 3, 4, 5, or 6. None
Menu SU5, Frequency Marker Sweep
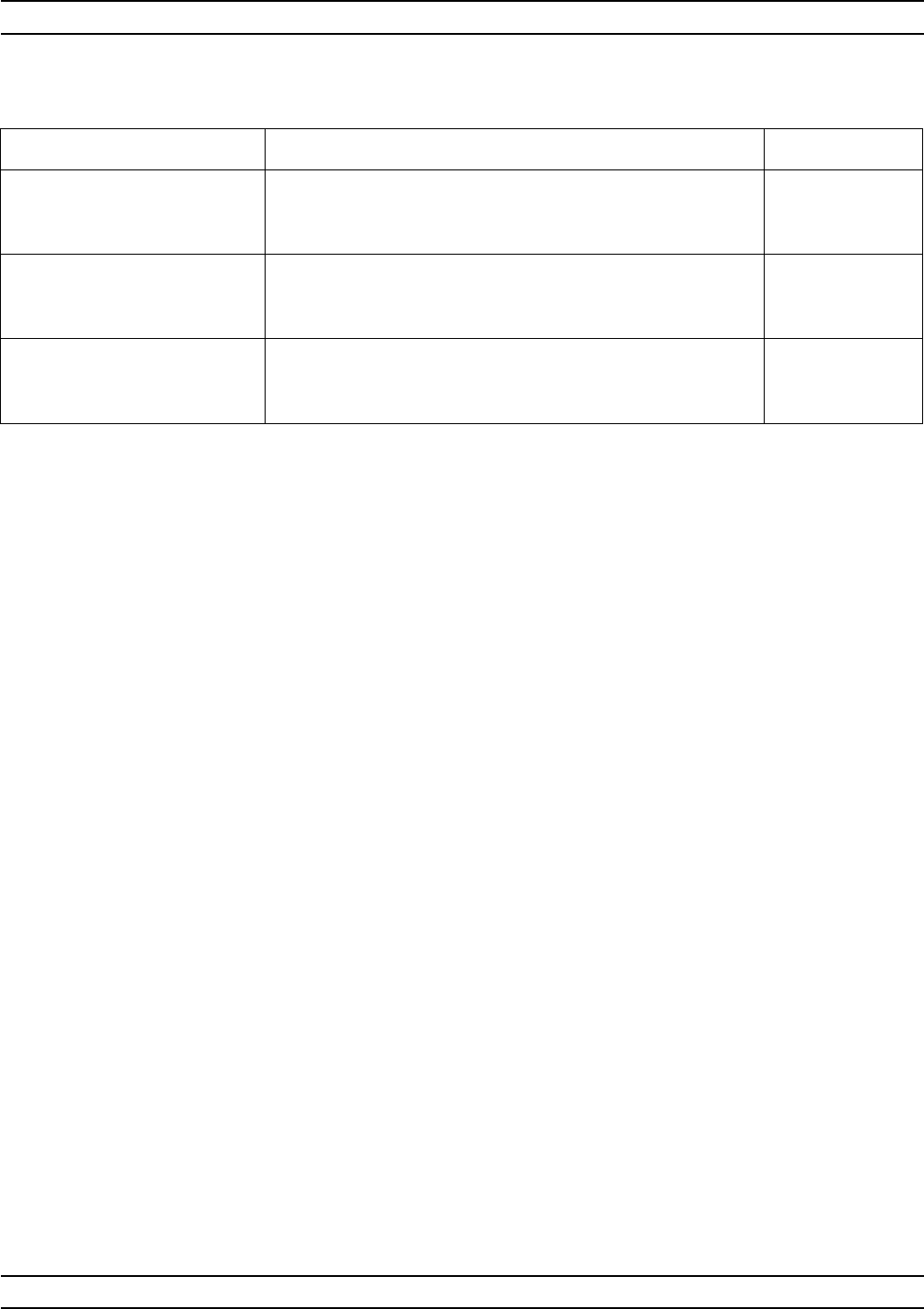
37XXXC OM A-223
ALPHABETICAL LISTING S
MENU DESCRIPTION GPIB COMMAND
FREQUENCY
MARKER C.W. None
C.W FREQ
MARKER (X)
XXX.XXXXXXXXX GHz
Pressing a number on the keypad causes the associated
marker to be the C.W. frequency. M1C-M6C
USE KEYPAD
TO SELECT
MARKER (1-6)
Use the keypad to select markers 1, 2, 3, 4, 5, or 6. None
Menu SU6, Frequency Marker C.W.
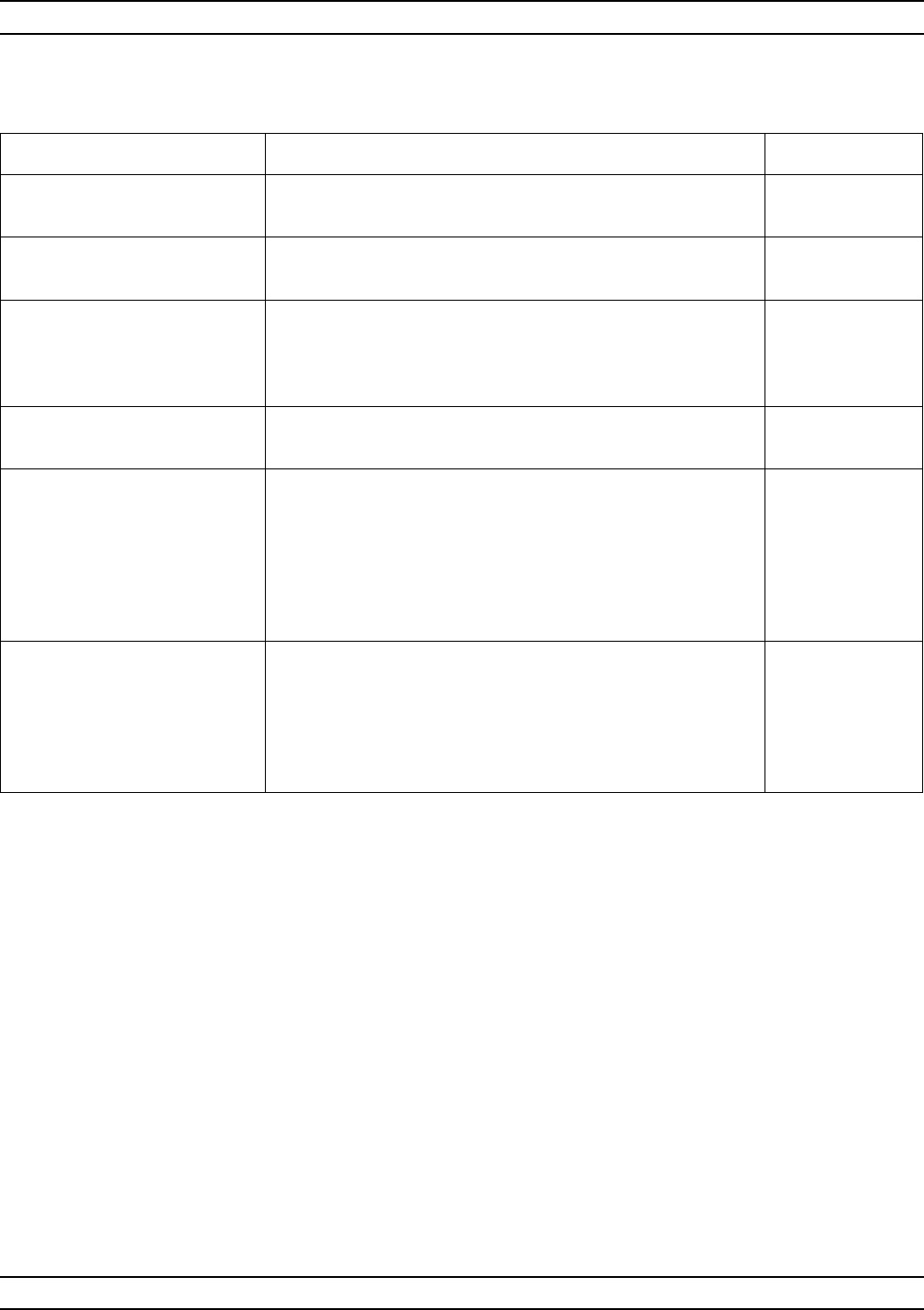
A-224 37XXXC OM
S ALPHABETICAL LISTING
MENU DESCRIPTION GPIB COMMAND
CALIBRATE FOR
FLAT PORT POWER None
FORWARD
DIRECTION ONLY None
XXX POINTS
MEASURE 1 PWR
POINT EVERY
XX POINT(S)
Displays the number of power points (0 – 50) to be skipped
during the power sweep. The points not measured are
interpolated to provide a flat sweep.
PTS; PTS?
POWER TARGET
-XXX.X dBm Lets users set a flat output-power value (power target). The
VNA defaults to Port 1 power. PTP; PTP?
START FLAT
POWER CALIBRATION Begins the calibration. If calibration is successful, you are
returned to menu SU8. If the calibration unsuccessful due
to a fatal error (Source or power meter inoperable or not
connected), this menus remains displayed. At any time,
you can abort the calibration by pressing the DEFAULT
PROGRAM or CLEAR/RET LOC keys. All other keys are
locked out.
SFC
PRESS <ENTER>
TO SELECT
TURN KNOB TO
CHANGE NUMBER
OF POINTS
Pressing the Enter key implements your menu selection or
turns the function on/off. None
Menu SU8 or CAL_SU8, Calibrate For Flat Test Port Power
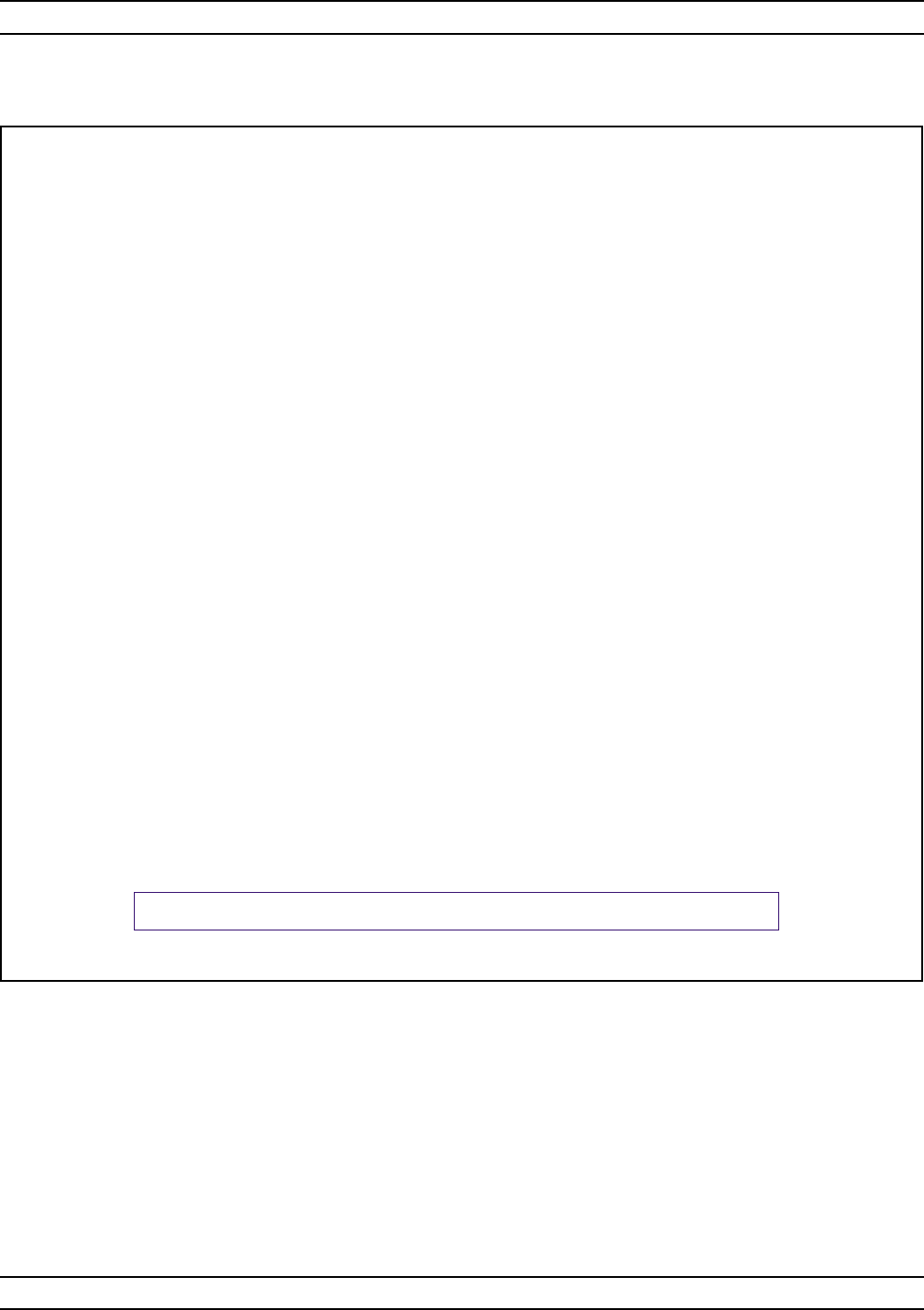
37XXXC OM A-225
ALPHABETICAL LISTING S
FLAT POWERCALIBRATION ADJUSTS THE SOURCE
OUTPUTPOWERAT EACH MEASUREMENTPOINT ACROSS
A FREQUENCYSPAN TO PROVIDE A CONSTANTPOWER
LEVEL AT THE TEST PORT (FORWARDDIRECTION ONLY).
1. PRESET, ZERO, AND CALIBRATE THE POWERMETER.
2. CREATE AND ACTIVATE THE POWERMETER'S CAL
FACTOR LIST FOR THE POWERSENSORBEING USED.
3. CONNECTTHE POWERMETERTO THE DEDICATED GPIB
INTERFACE AND THE POWERSENSORTO THE TEST PORT.
4. SELECT <START FLAT POWERCALIBRATION>.
- FLAT POWERCALIBRATION -
- INSTRUCTIONS -
000.0
%
Menu EXT_SU8 Flat Power Calibration Instructions
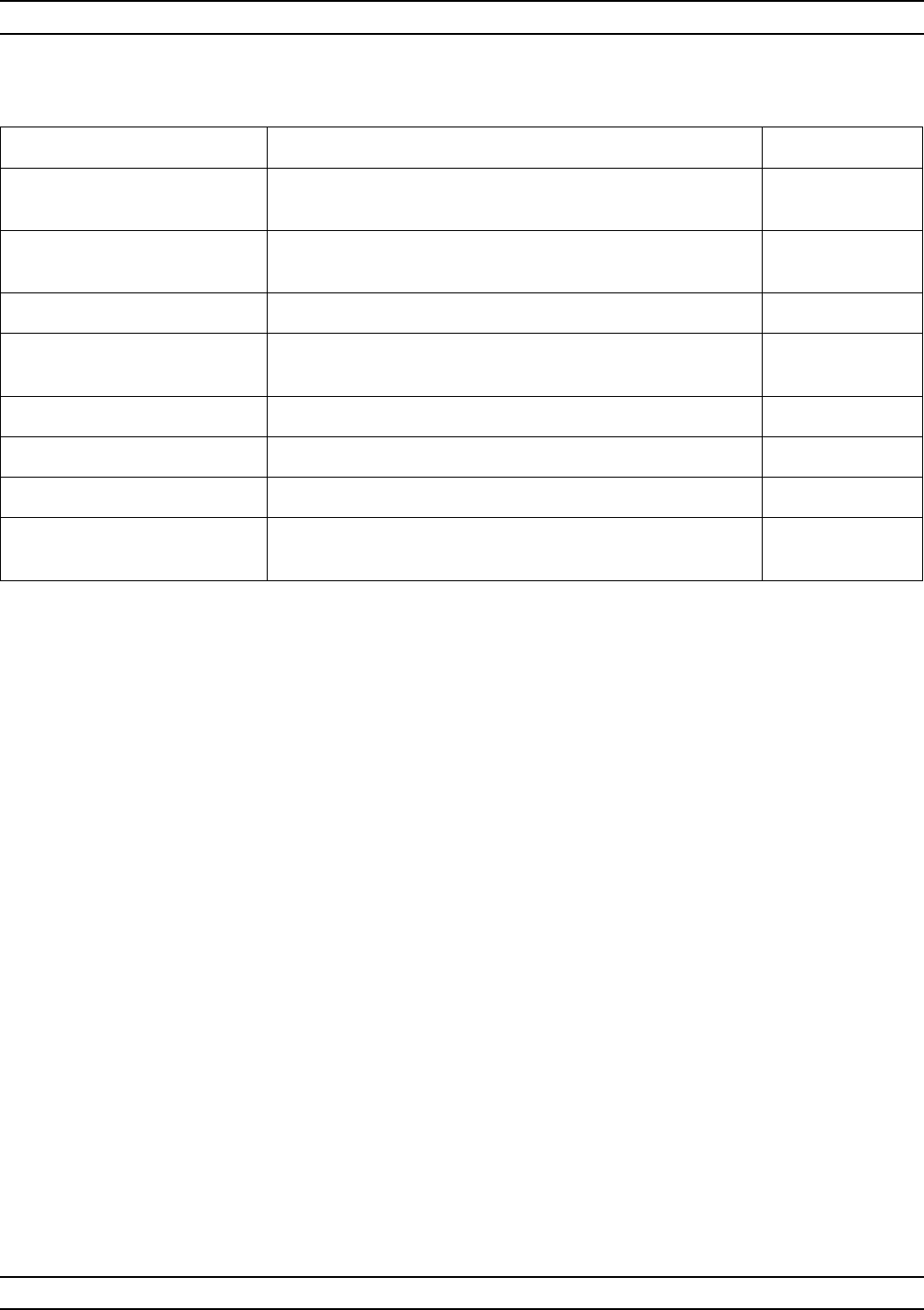
A-226 37XXXC OM
S ALPHABETICAL LISTING
MENU DESCRIPTION GPIB COMMAND
NUMBER OF
DATA POINTS None
1601 MAX PTS Selects measurement data points to be 1601. NP1601; FHI;
ONP
801 MAX PTS Selects measurement data points to be 801. NP801; ONP
401 MAX PTS Selects measurement data points to be 401. NP401; ONP;
FME
201 MAX PTS Selects measurement data points to be 201. NP101; ONP
101 MAX PTS Selects measurement data points to be 101. NP101; ONP
51 MAX PTS Selects measurement data points to be 51. NP51; ONP
PRESS <ENTER>
TO SELECT Pressing the Enter key implements you selection. None
Menu SU9, Number of Data Points
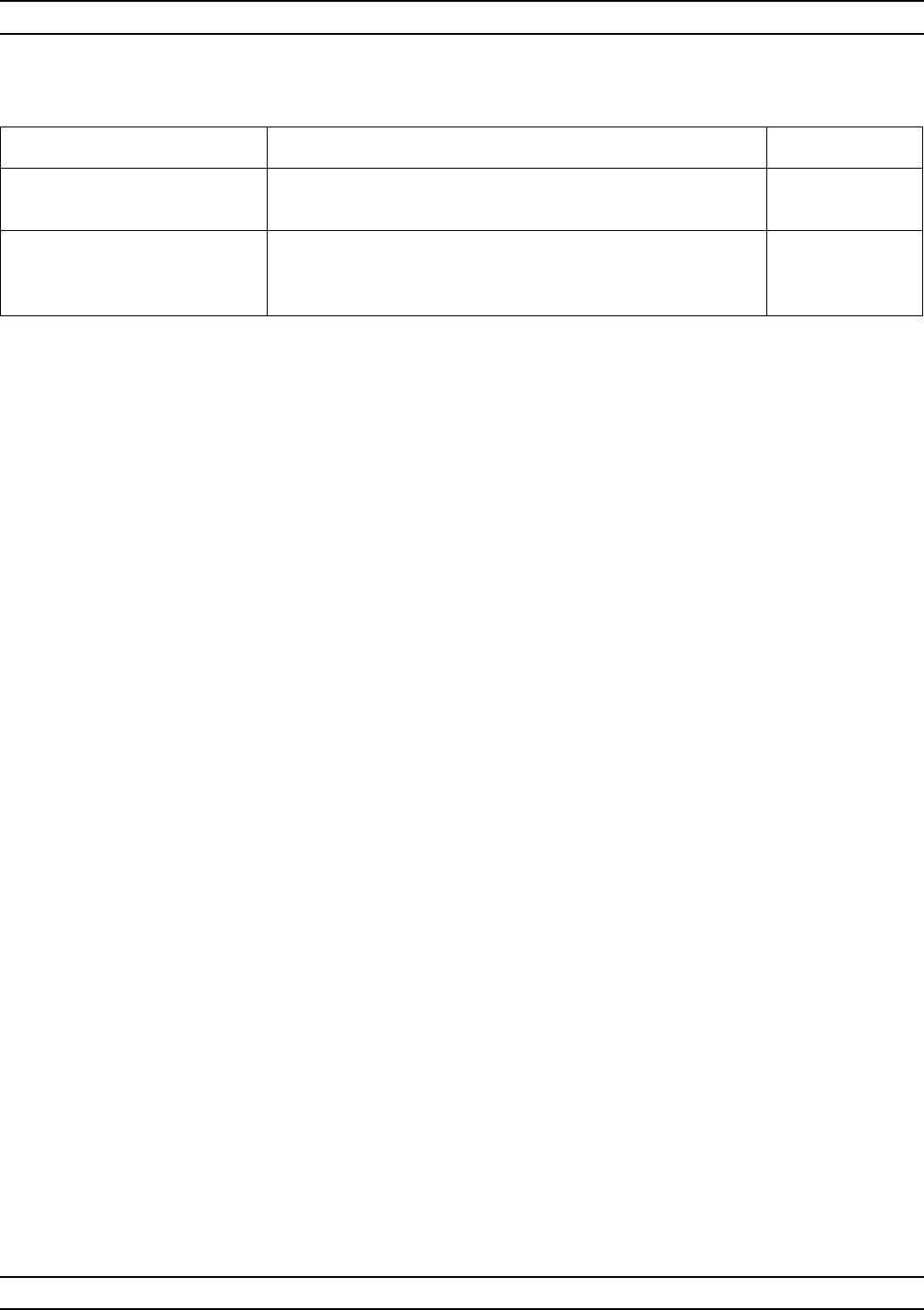
37XXXC OM A-227
ALPHABETICAL LISTING S
MENU DESCRIPTION GPIB COMMAND
NUMBER OF
DATA POINTS None
POINTS DRAWN
IN C.W.
XXXX POINT(S)
Displays the number of data point, when in the CW mode.
This number can be between 1 and 1601. CWP; CWP?
Menu SU9A, Number of Data Points 2
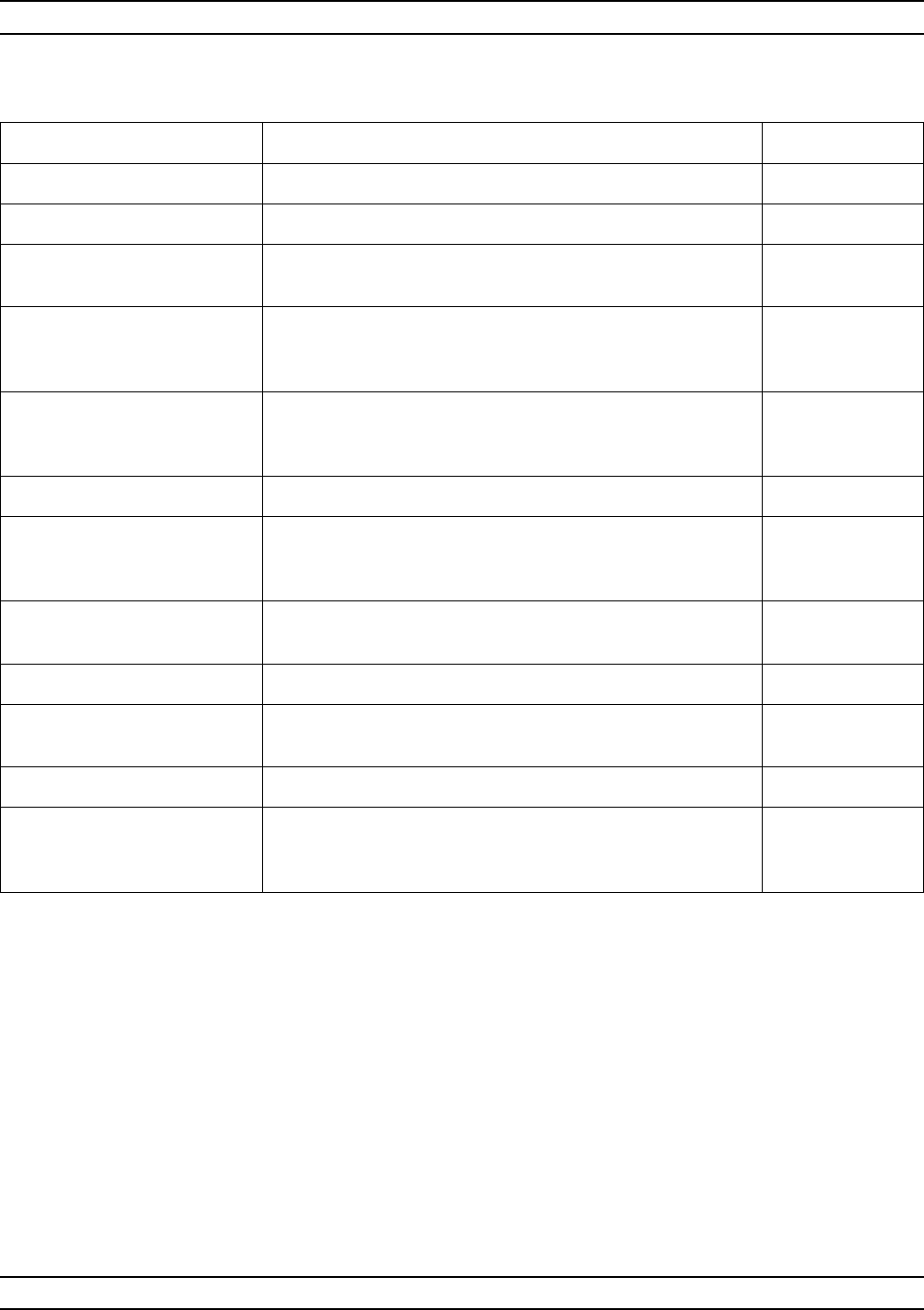
A-228 37XXXC OM
T ALPHABETICAL LISTING
MENU DESCRIPTION GPIB COMMAND
DOMAIN None
FREQUENCY Displays the data in normal frequency domain format.
FREQUENCY
WITH TIME GATE Displays the data in the frequency domain after a specific
time range has been sampled by the gate function. FGT
TIME
LOWPASS MODE Displays the data in the time (distance) domain, using true
lowpass processing. Data must be taken using a harmonic
series calibration and sweep in order to use this mode.
TLP
TIME
BANDPASS MODE Displays the data in the time (distance) domain using
bandpass processing. Any data sweep range using normal
calibration can be used.
TBP; TDX?
–SETUP– None
DISPLAY
TIME/DISTANCE Switches the mode of display between time and distance.
This does not affect the actual displayed data, but only the
annotation.
TDDIST; TDTIME
SET RANGE Calls a menu that lets you set the range and other display
parameters. None
SET GATE Calls a menu that lets you set the gate parameters. None
GATE ON/OFF/DISP Switches the gate on or off each time Enter is pressed. GON/GOF/GDS;
GOF?
HELP Displays an informational help menu. None
PRESS <ENTER>
TO SELECT
OR SWITCH
Pressing the Enter key implements your menu selection. None
Menu TD1, Domain (Frequency/Display)
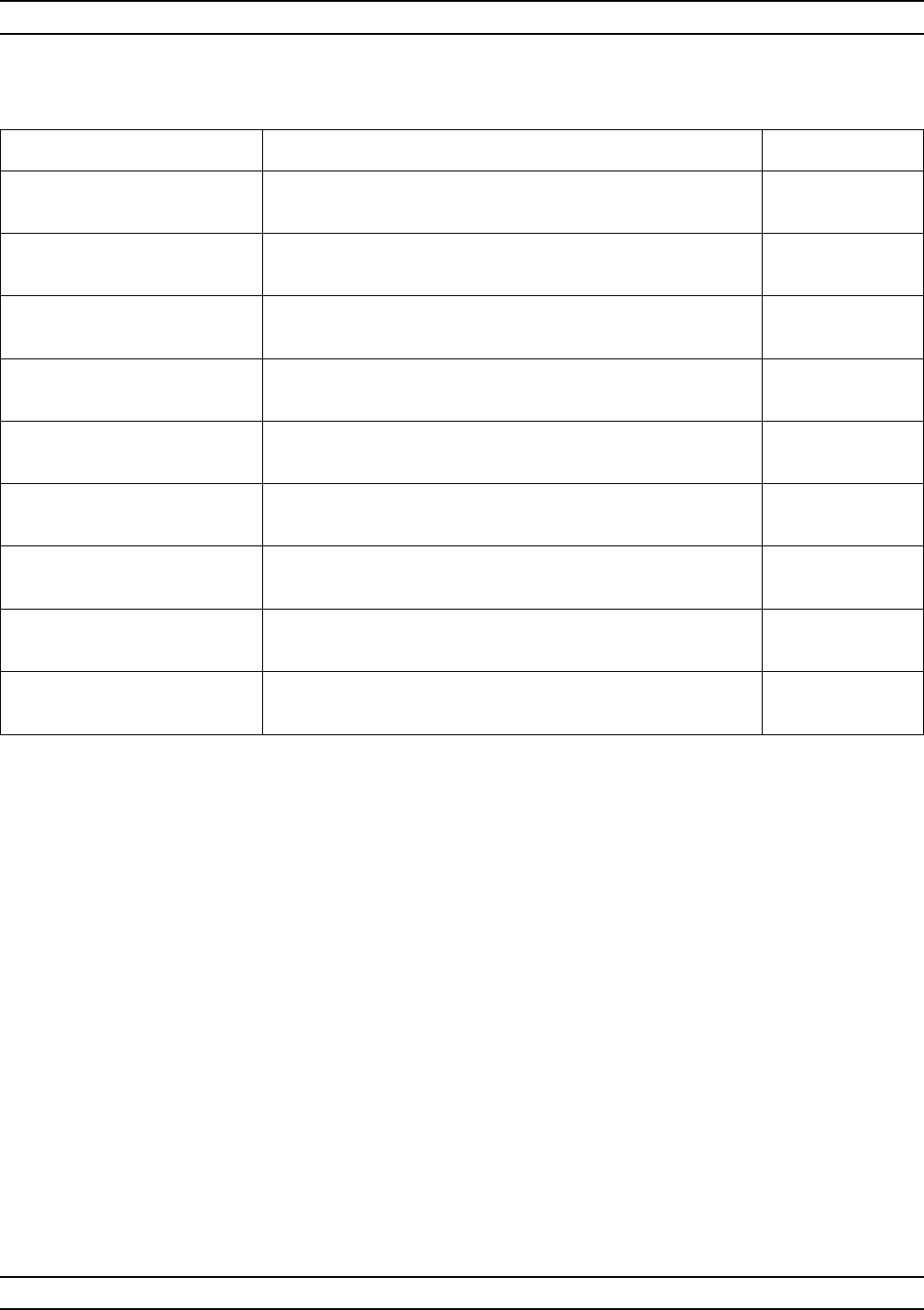
37XXXC OM A-229
ALPHABETICAL LISTING T
MENU DESCRIPTION GPIB COMMAND
LOWPASS TIME
DOMAIN SETUP None
START
XXX.XXX ps Sets the start time of the display. GST; GST?
STOP
XXX.XXX ps Sets the stop time of the display.. GSP; GSP?
CENTER
XXX.XXX ps Sets the center time of the display. GCT; GCT?
SPAN
XXX.XXX ps Sets the span (Stop - Start) of the display. GSN; GSN?
MARKER RANGE Calls a menu that lets you set the display to a range
determined by two of the markers. None
RESPONSE
IMPULSE/STEP Switches between Impulse and Step response each time
Enter is pressed. LPI/LPS; LPSX?
MORE Calls a menu that contains additional selections for display
setup. None
PRESS <ENTER>
TO SELECT Pressing the Enter key implements your menu selection. None
Menu TD2_LP_TIME, Lowpass Time Domain Setup
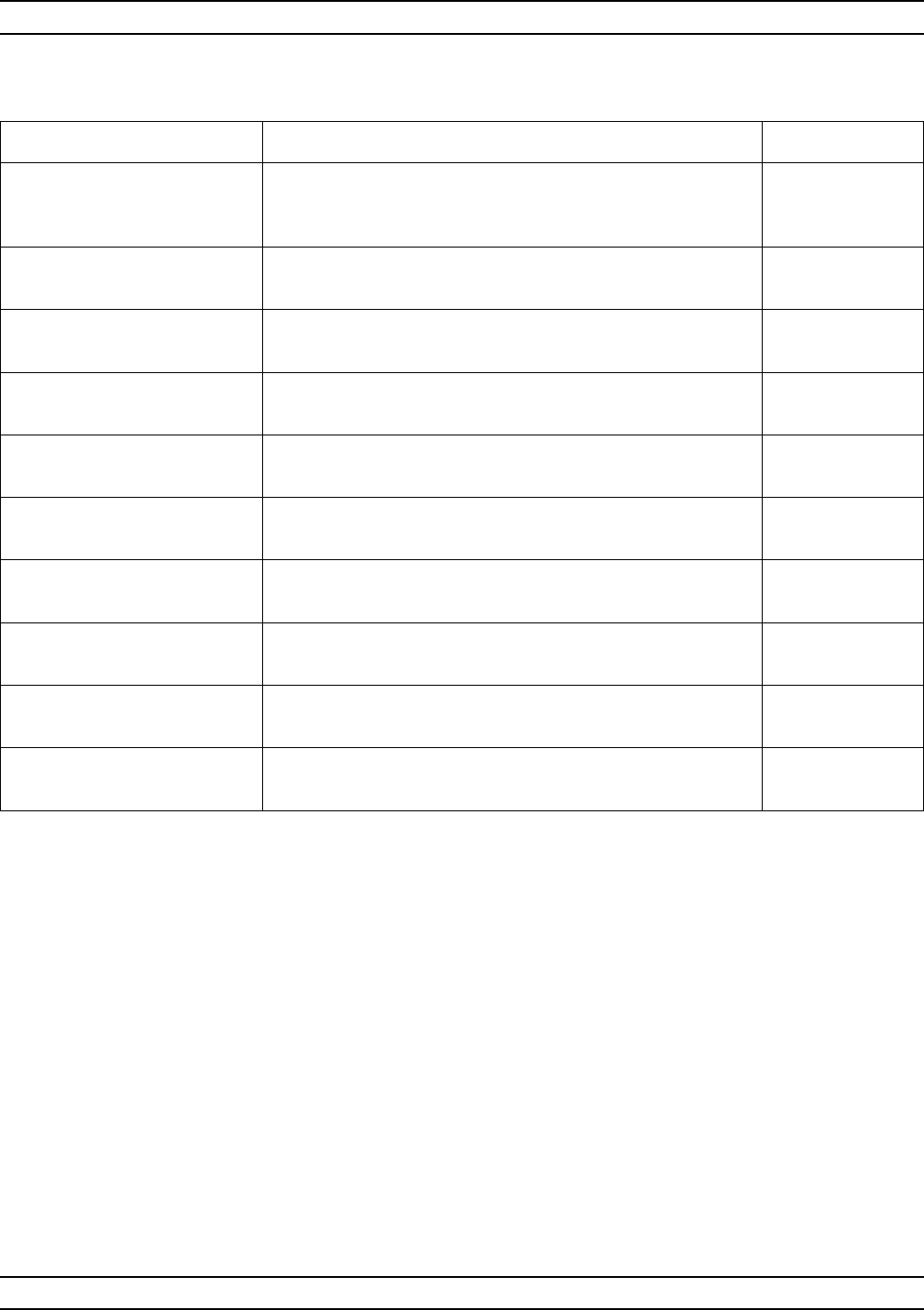
A-230 37XXXC OM
T ALPHABETICAL LISTING
MENU DESCRIPTION GPIB COMMAND
LOWPASS
DISTANCE
DISPLAY SETUP
None
START
XXX.XXX mm Sets the start time of the display. GST; GST?
STOP
XXX.XXX mm Sets the stop time of the display. GSP; GSP?
CENTER
XXX.XXX mm Sets the center time of the display. GCT; GCT?
SPAN
XXX.XXX mm Sets the span (Stop - Start) of the display. GSN; GSN?
MARKER RANGE Calls a menu that lets you set the display to a range
determined by two of the markers. None
RESPONSE
IMPULSE/STEP Switches between Impulse and Step response each time
Enter is pressed. LPI/LPS; LPSX?
MORE Calls a menu that contains additional selections for display
setup. None
RELATIVE VELOCITY
X.X Indicates the relative velocity of light, as set by the
dielectric constant in menu RD2. None
PRESS <ENTER>
TO SELECT Pressing the Enter key implements your menu selection. None
Menu TD2_LP_DIST, Lowpass Distance Display Setup
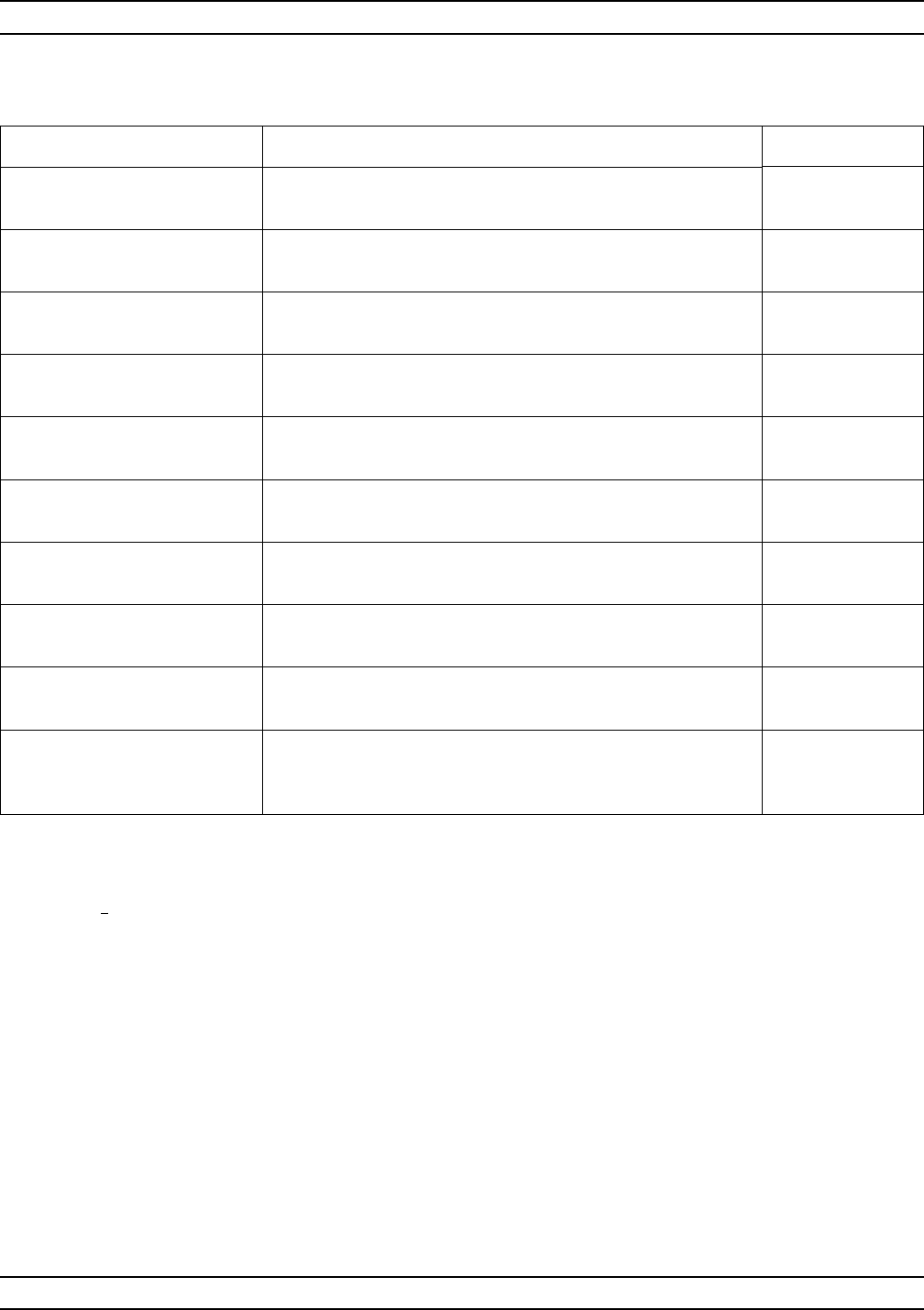
37XXXC OM A-231
ALPHABETICAL LISTING T
MENU DESCRIPTION GPIB COMMAND
BANDPASS TIME
DOMAIN SETUP None
START
XXX.XXX ps Sets the start time of the display. ZST; ZST?
STOP
XXX.XXX ps Sets the stop time of the display. ZSP; ZSP?
CENTER
XXX.XXX ps Sets the center time of the display. ZCT; ZCT?
SPAN
XXX.XXX ps Sets the span (Stop - Start) of the display. ZSN; ZSN?
MARKER RANGE Calls a menu that lets you set the display to a range
determined by two of the markers. None
PHASOR ON/OFF
IMPULSE Switches Phasor Impulse processing on or off each time
Enter is pressed. TDPI1; TDPI0;
TDPIX?
HELP – PHASOR
IMPULSE Displays an informational help menu. None
MORE Calls a menu that contains additional selections for display
setup. None
PRESS <ENTER>
TO SELECT
OR TURN ON/OFF
Pressing the Enter key implements your menu selection. None
Menu TD2_BP_TIME, Bandpass Time Domain Setup
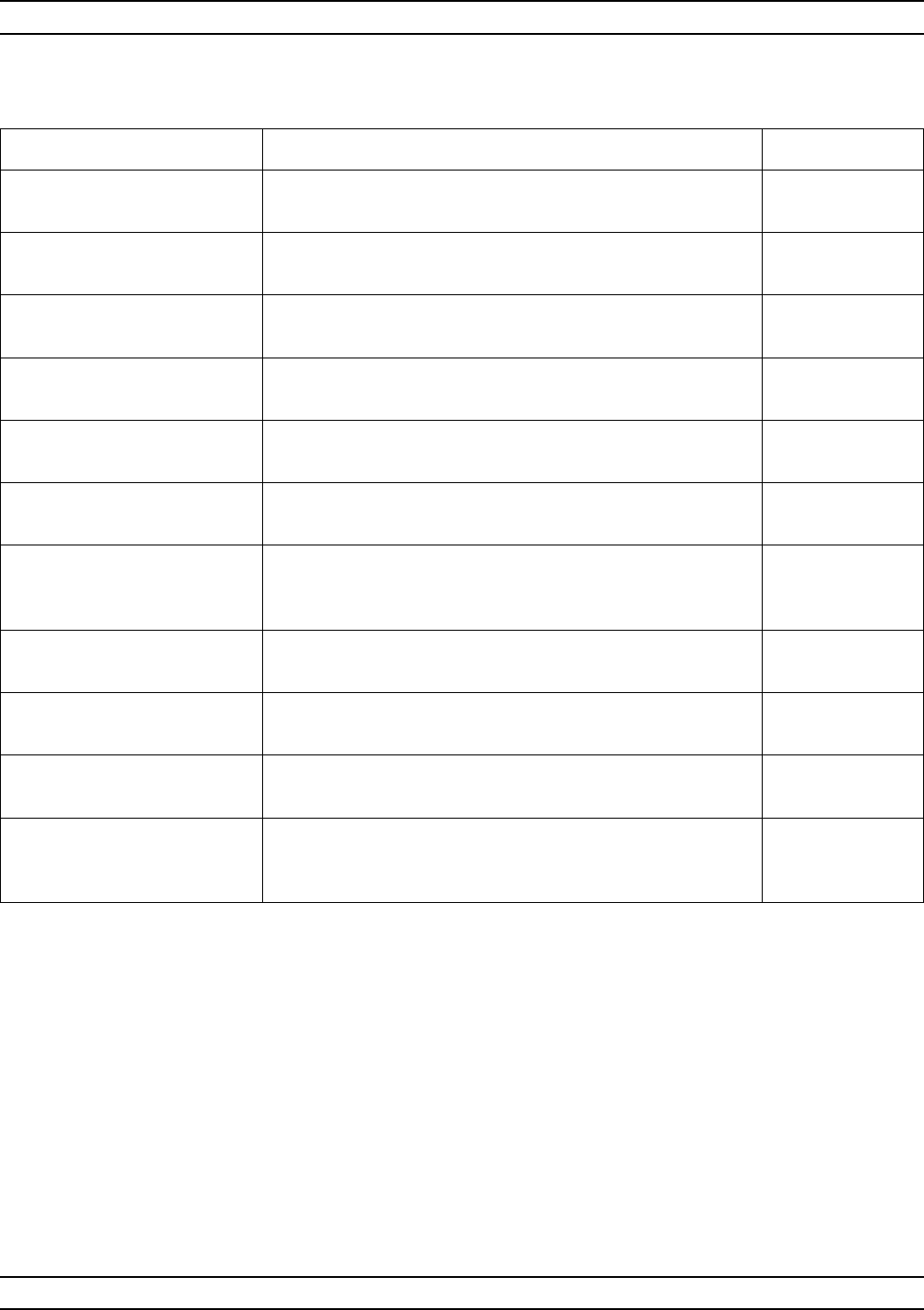
A-232 37XXXC OM
T ALPHABETICAL LISTING
MENU DESCRIPTION GPIB COMMAND
BANDPASS DISTANCE
DISPLAY SETUP None
START
XXX.XXX mm Sets the start time of the display. ZST; ZST?
STOP
XXX.XXX mm Sets the stop time of the display. ZSP; ZSP?
CENTER
XXX.XXX mm Sets the center time of the display. ZCT; ZCT?
SPAN
XXX.XXX mm Sets the span (Stop - Start) of the display. ZSN; ZSN?
MARKER RANGE Calls a menu that lets you set the display to a range
determined by two of the markers. None
PHASOR ON/OFF
IMPULSE Switches Phasor Impulse processing on or off each time
Enter is pressed. TDPI1; TDPI0;
TDPIX?
HELP – PHASOR
IMPULSE Displays an informational help menu. None
MORE Calls a menu that contains additional selections for display
setup. None
RELATIVE VELOCITY
X.X Indicates the relative velocity of light, as set by the
dielectric constant in menu RD2. None
PRESS <ENTER>
TO SELECT
OR TURN ON/OFF
Pressing the Enter key implements your menu selection. None
Menu TD2_BP_DIST, Bandpass Distance Display Setup
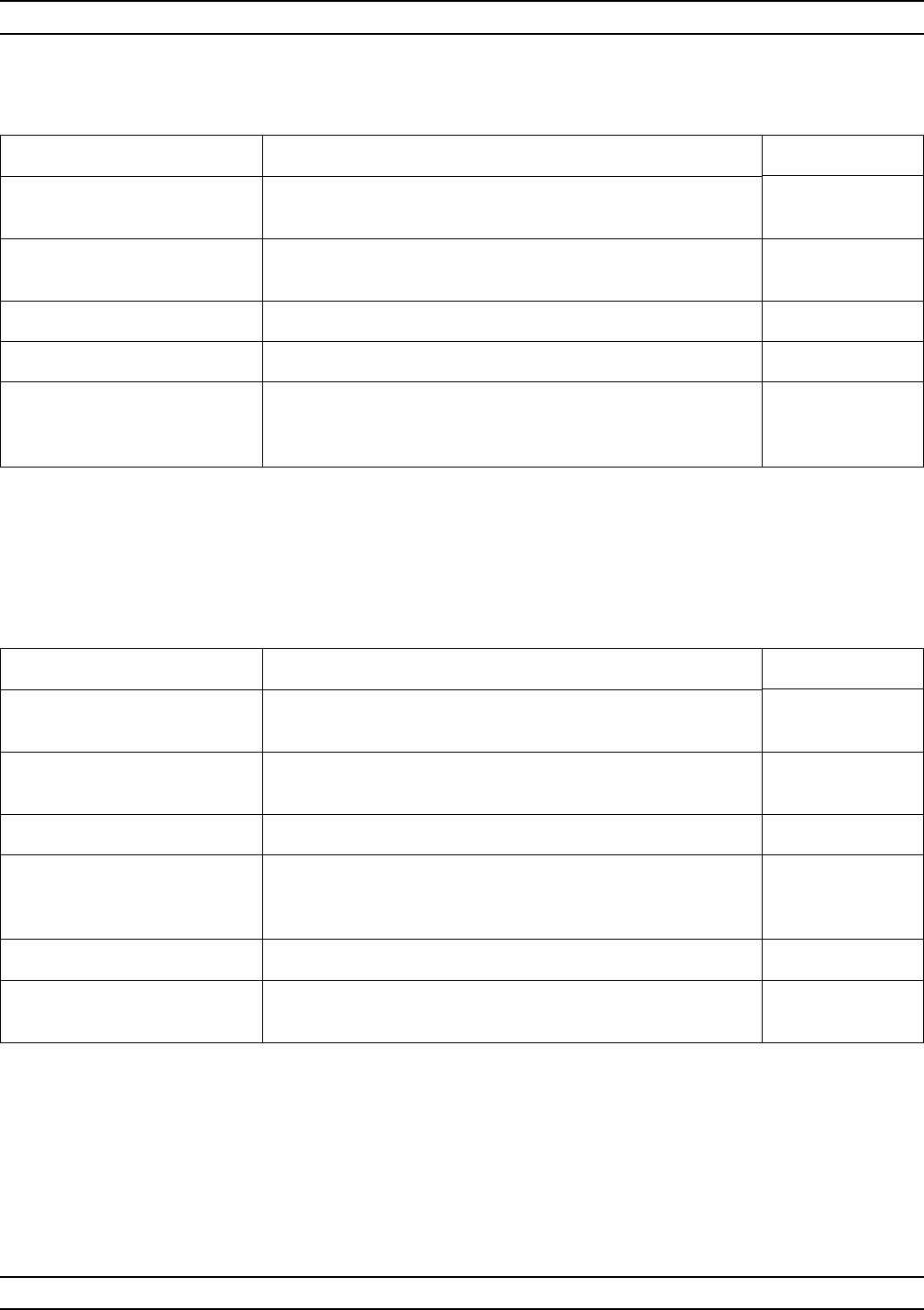
37XXXC OM A-233
ALPHABETICAL LISTING T
MENU DESCRIPTION GPIB COMMAND
BANDPASS TIME
DOMAIN SETUP None
WINDOW SHAPE
NOMINAL Calls a menu that lets you change the window type. None
SET GATE Calls a menu that lets you set the gate parameters. None
PREVIOUS MENU Returns you to the previous menu. None
PRESS <ENTER>
TO SELECT Pressing the Enter key implements your menu selection. None
Menu TD3_BP, Bandpass Time Domain Setup
MENU DESCRIPTION GPIB COMMAND
LOWPASS TIME
DOMAIN SETUP None
WINDOW SHAPE
NOMINAL Calls a menu that lets you change the window type. None
SET GATE Calls a menu that lets you set the gate. None
D.C. TERM
XXXXX
XXXXXXXXXX
Calls a menu that lets you set the D.C. term for lowpass
processing. None
PREVIOUS MENU Returns you to the previous menu. None
PRESS <ENTER>
TO SELECT Pressing the Enter key implements your menu selection. None
Menu TD3_LP, Lowpass Time Domain Setup
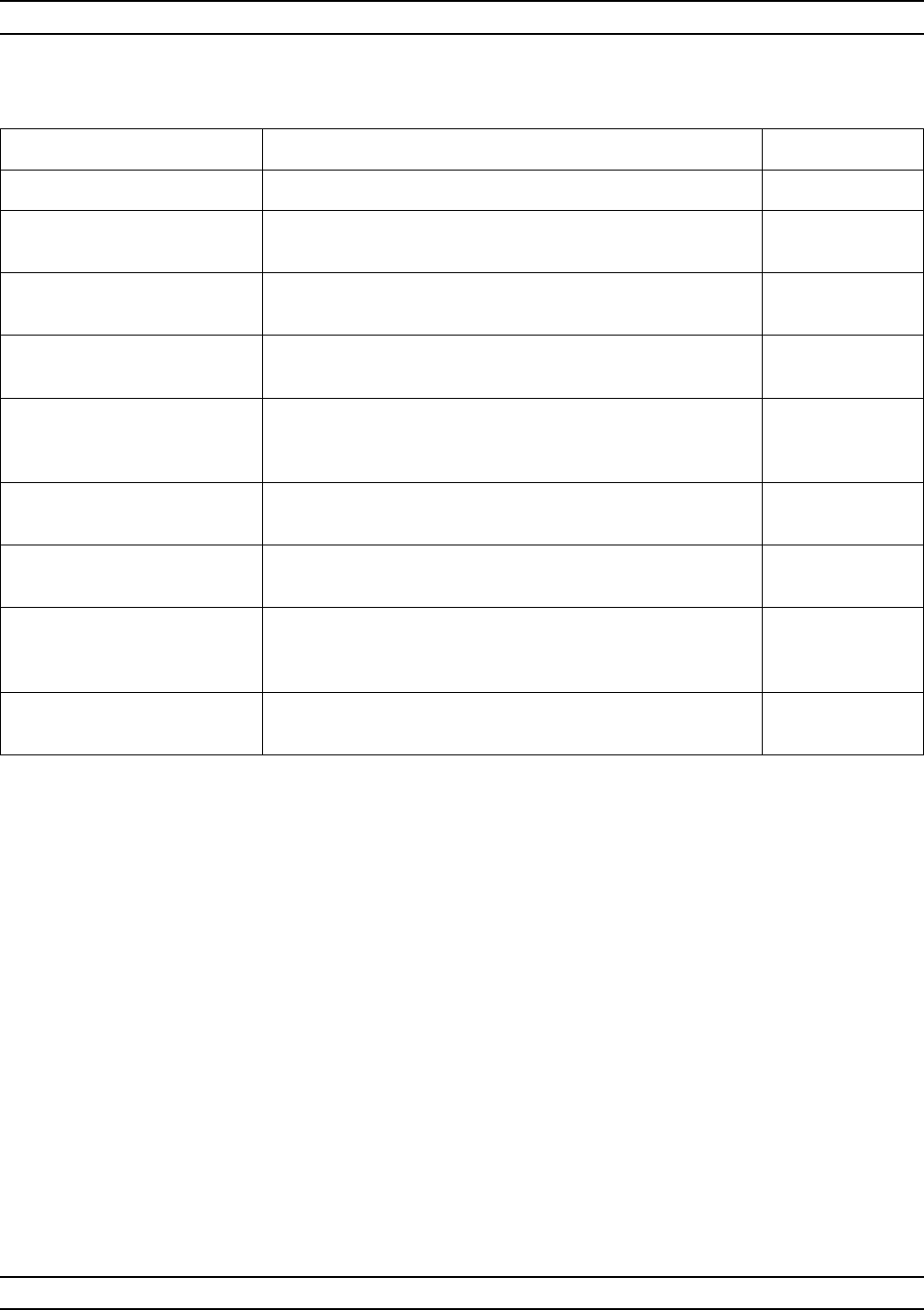
A-234 37XXXC OM
T ALPHABETICAL LISTING
MENU DESCRIPTION GPIB COMMAND
GATE None
START
XXX.XXX xx Sets the start time of the gate. GST; GST?
STOP
XXX.XXX xx Sets the stop time of the gate. GSP; GSP?
CENTER
XXX.XXX xx Sets the center time of the gate. GCT; GCT?
SPAN
XXX.XXX xx Sets the span (Stop - Start) of the gate. Also, provides for
an anti-gate if a negative value is entered. Refer to Chapter
9, paragraphs 9-6 and 9-7 for additional information.
GSN; GSN?
SET SHAPE
XXXXXXXXX Calls a menu that lets you set the shape of the gate. None
GATE ON/OFF/DISP Switches the gate on or off each time Enter is pressed. GON/GOF/GDS;
GOF?
SET RANGE Takes you back to menu TD2_XX_XXXX (LP_TIME,
LP_DIST, BP_TIME, BP_DIST), depending on the type of
measurement you selected in menu TD1.
None
PRESS <ENTER>
TO SELECT Pressing the Enter key implements your menu selection. None
Menu TD4_TIME & TD4_DIST, Gate (Distance/Time)
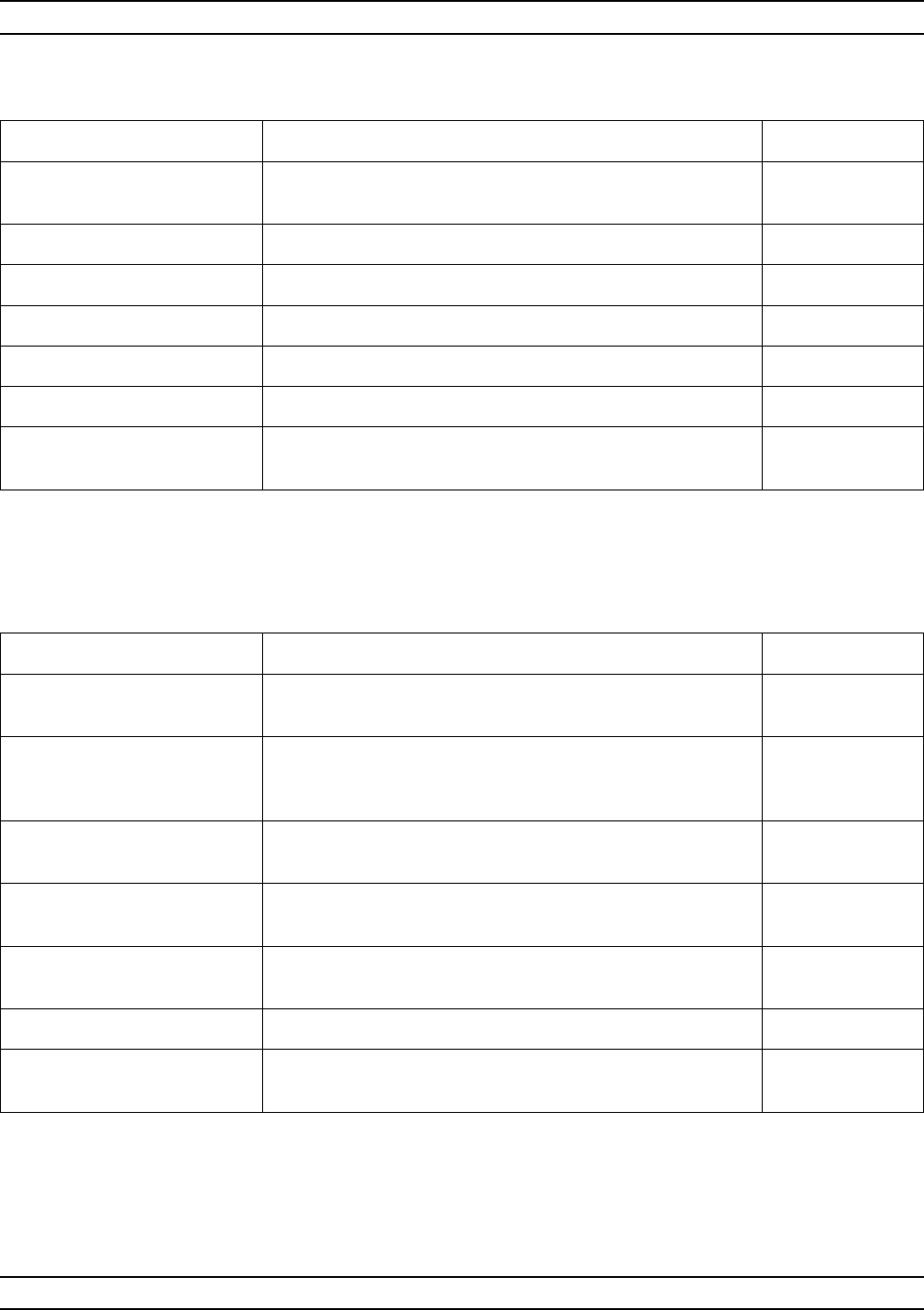
37XXXC OM A-235
ALPHABETICAL LISTING T
MENU DESCRIPTION GPIB COMMAND
SELECT
WINDOW SHAPE None
RECTANGULAR Selects a Rectangular (one-term) shape. WRT
NOMINAL Selects a two-term Hamming shape. WNM
LOW SIDELOBE Selects a three-term Blackman-Harris shape. WLS
MIN SIDELOBE Selects a four-term Blackman-Harris shape. WMS
HELP Displays an informational help menu. None
PRESS <ENTER>
TO SELECT Pressing the Enter key implements your menu selection. None
Menu TD5_WINDOW, Shape
MENU DESCRIPTION GPIB COMMAND
SELECT
GATE SHAPE None
MINIMUM Selects minimum shape. Sharpest rolloff, some frequency
domain ripple. Not allowed with low or minimum sidelobe
window.
GRT
NOMINAL Selects a nomimal shape. Good results in most
applications. Not allowed with minimum sidelobe window. GNM
WIDE Selects wide shape. Gradual rolloff and better residual
ripple.
MAXIMUM Selects a maximum shape. Least rolloff and best residual
ripple.
HELP Displays an informational help menu. None
PRESS <ENTER>
TO SELECT Pressing the Enter key implements your menu selection. None
Menu TD5_GATE, Shape
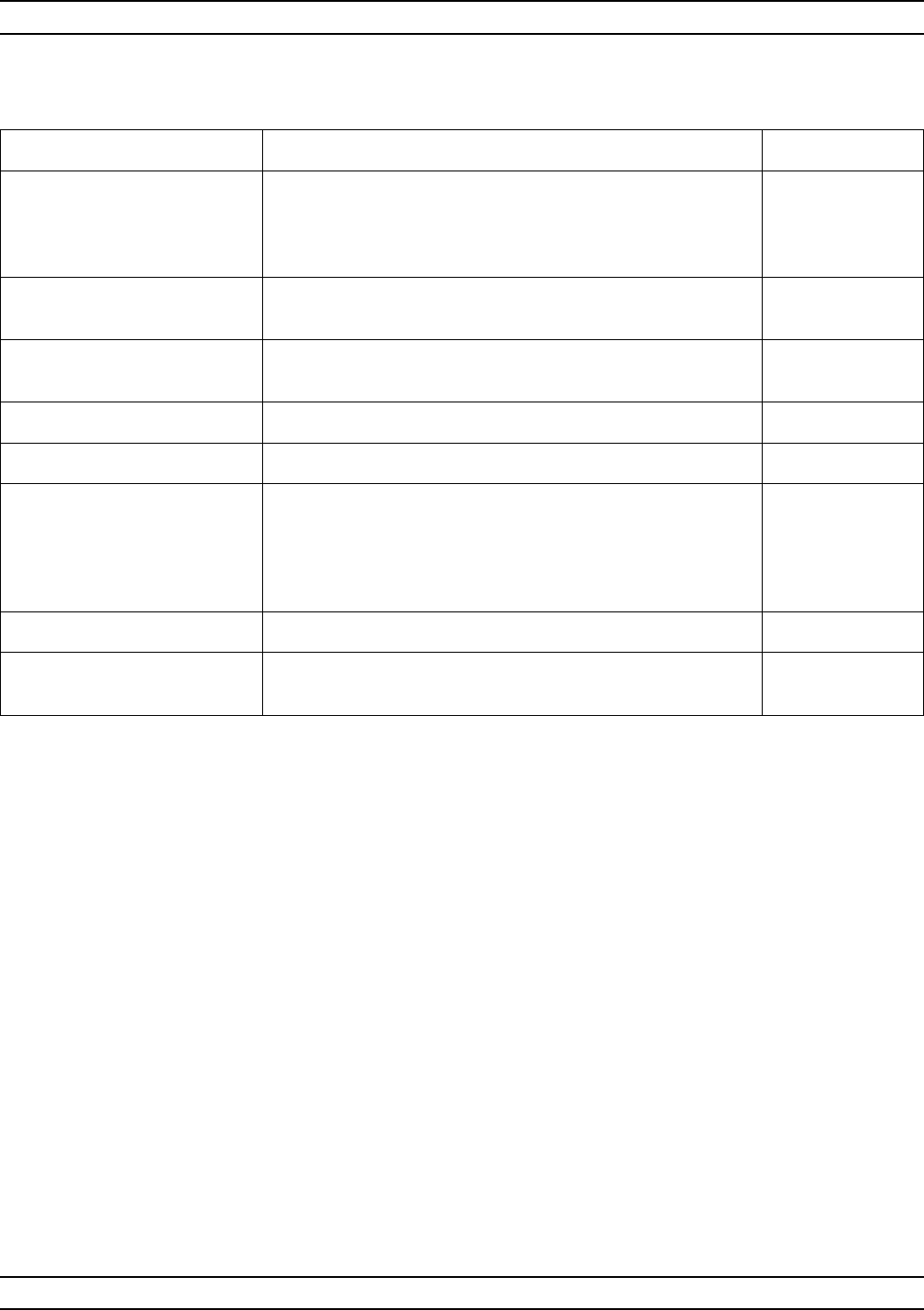
A-236 37XXXC OM
T ALPHABETICAL LISTING
MENU DESCRIPTION GPIB COMMAND
SET D.C. TERM FOR
LOWPASS PROCESSING Since it is impossible to measure the true D.C. term
required for lowpass processing, a value must be
estimated. This menu allows a choice between five different
selections for this value.
None
AUTO
EXTRAPOLATE Sets the D.C. term to a value determined by extrapolating
the data points near the zero frequency. DCA; DCX?
LINE
IMPEDANCE Sets the D.C. term to the characteristic impedance of the
transmission medium (Z0). DCZ
OPEN Sets the D.C. term to correspond to an open circuit. DCO
SHORT Sets the D.C. term to correspond to a short circuit. DCS
OTHER
XXX.XXX
(REFLECTION
COEFFICIENT
X.XXX pU)
Sets the D.C. term to the value entered. DCV; DCV?
DCX?
PREVIOUS MENU Returns you to the previous menu. None
PRESS <ENTER>
TO SELECT Pressing the Enter key implements your menu selection. None
Menu TD6, Set D.C. Term for Low Pass Processing
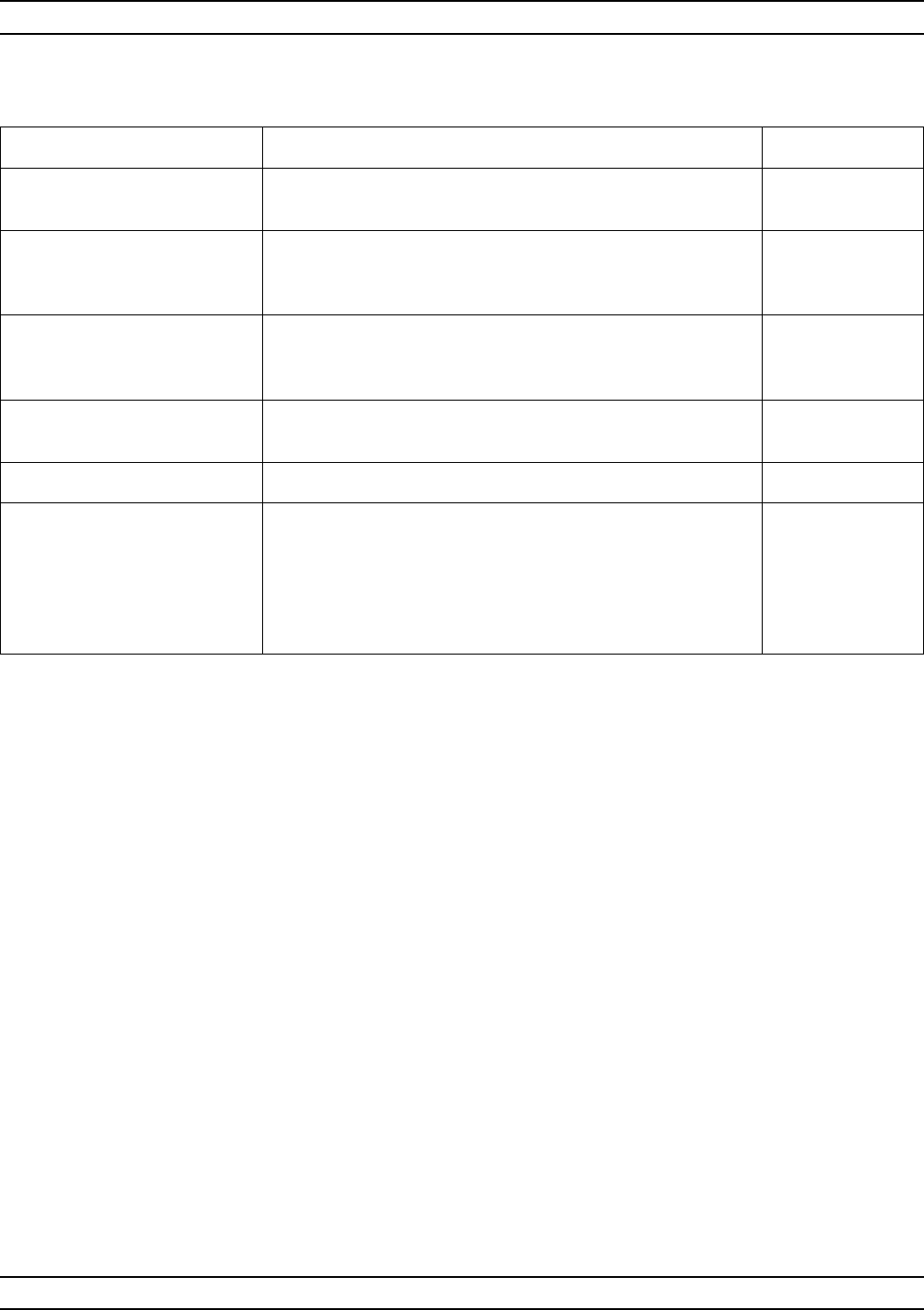
37XXXC OM A-237
ALPHABETICAL LISTING T
MENU DESCRIPTION GPIB COMMAND
TIME
MARKER SWEEP None
START TIME
MARKER ( )
XXX.XXX ns
Sets the start time to the value of the selected marker. M1S-M6S
STOP TIME
MARKER ( )
XXX.XXX ns
Sets the stop time to the value of the selected marker. M1E-M6E
RESTORE
ORIGINAL RANGE Returns the display to the original time range that was in
effect before the marker range was selected. MRR
PREVIOUS MENU Returns you to the previous menu. None
USE KEYPAD
TO CHOOSE
MARKER (1 - 6)
PRESS <ENTER>
TO SELECT
Select marker number from keypad.
Pressing the Enter key implements your menu selection.
None
Menu TD7_TIME, Time Marker Sweep.
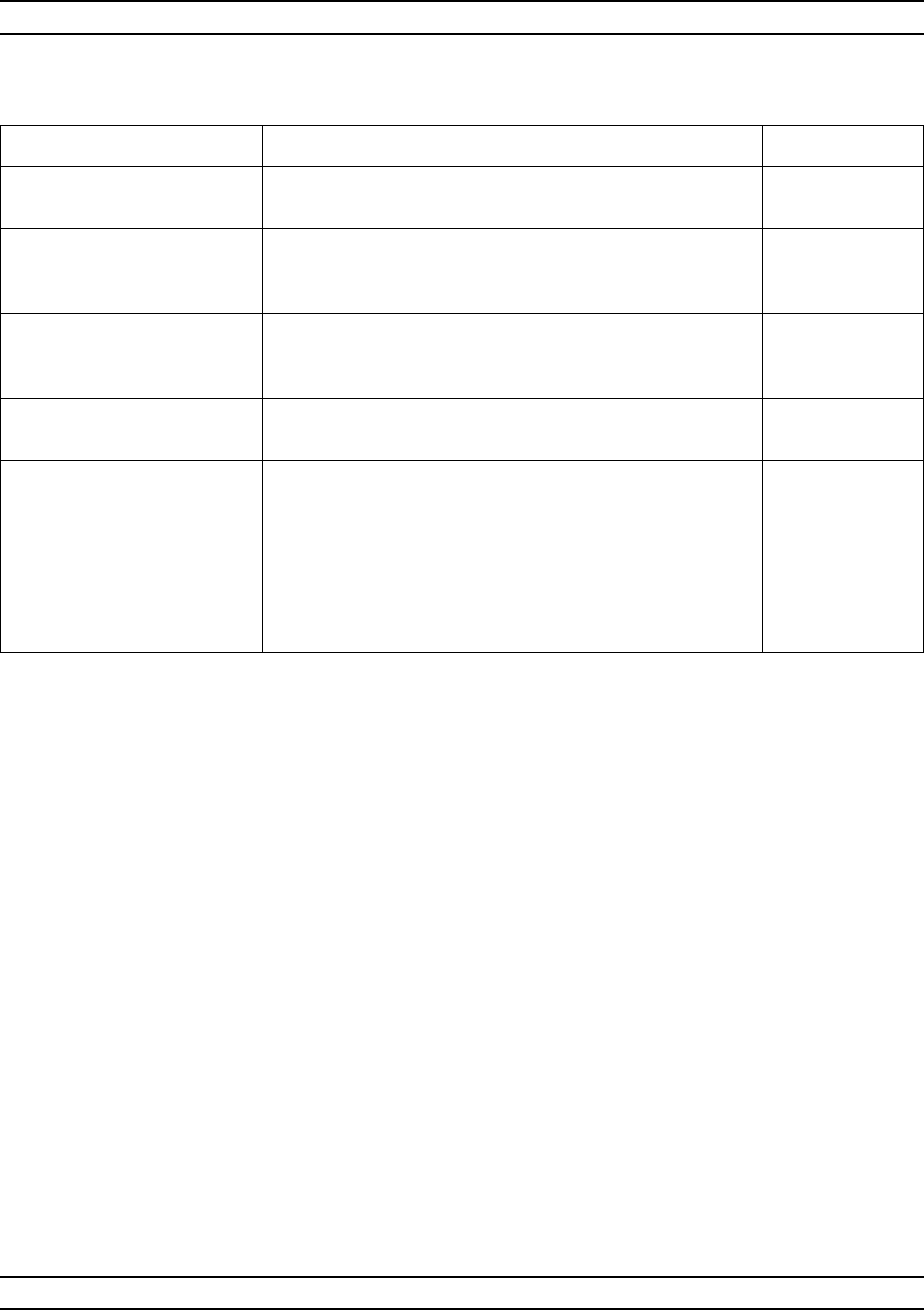
A-238 37XXXC OM
T ALPHABETICAL LISTING
MENU DESCRIPTION GPIB COMMAND
DISTANCE
MARKER SWEEP None
START DIST
MARKER ( )
XX.XXXX cm
Sets the start time to the value of the selected marker. M1S-M6S
STOP DIST
MARKER ( )
X.XXXX m
Sets the stop time to the value of the selected marker. M1E-M6E
RESTORE
ORIGINAL RANGE Returns the display to the original time range that was in
effect before the marker range was selected. MRR
PREVIOUS MENU Returns you to the previous menu. None
USE KEYPAD
TO CHOOSE
MARKER (1 - 6)
PRESS <ENTER>
TO SELECT
Select marker number from keypad.
Pressing the Enter key implements your menu selection.
None
Menu TD7_DIST, Distance Marker Range
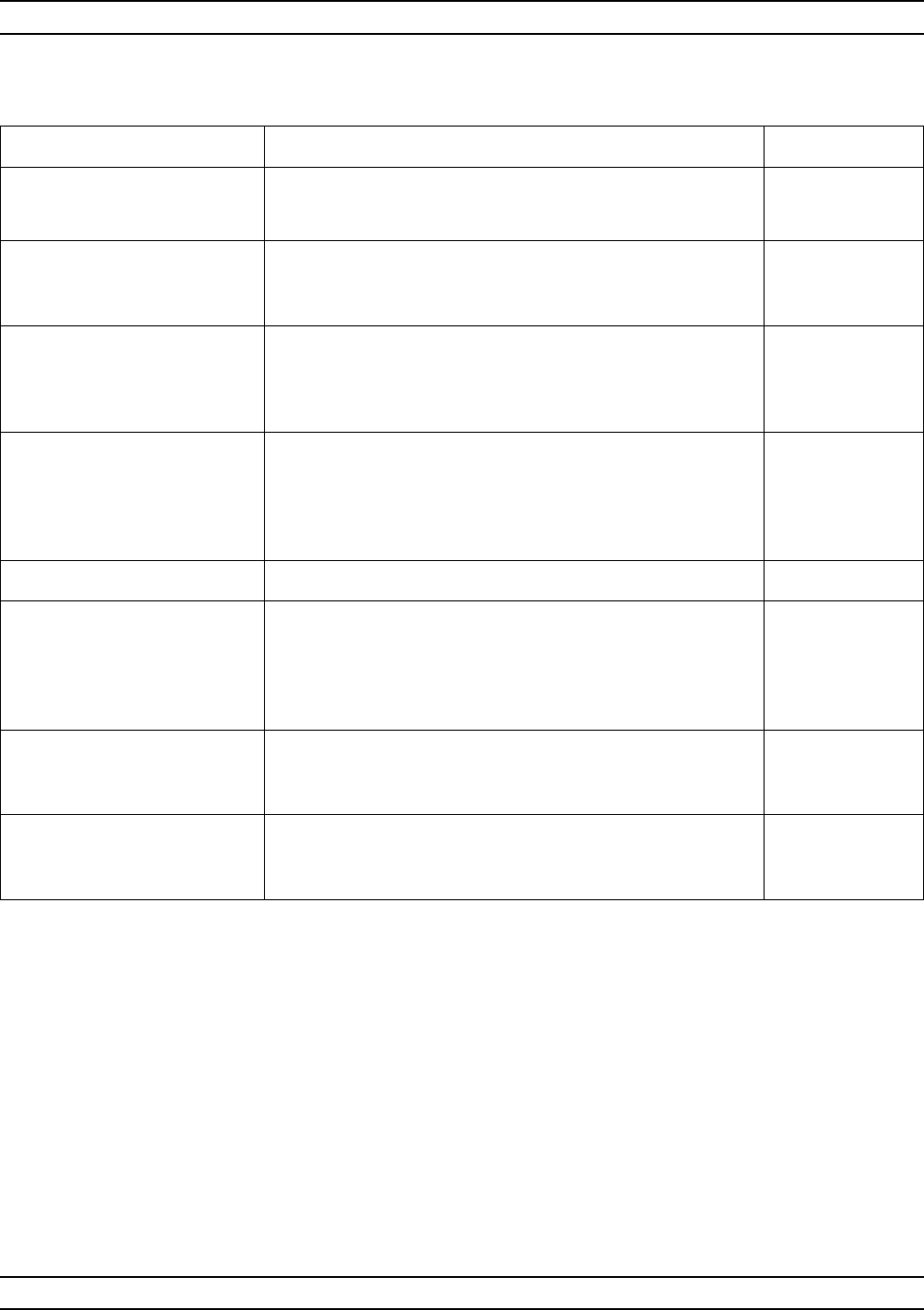
37XXXC OM A-239
ALPHABETICAL LISTING T
MENU DESCRIPTION GPIB COMMAND
TRIGGERS
MEASUREMENT
None
INTERNAL Internally triggers a point-by-point measurement. Choosing
this option always turns AUTOMATIC I.F. CALIBRATION
off.
TIN; TXX?
EXTERNAL Provides for externally triggering a point-by-point
measurement via the rear panel External Trigger connector.
Choosing this option always turns AUTOMATIC I.F.
CALIBRATION off.
TEX; TXX?
MEASUREMENT ON (OFF)
DELAY
XX.XXX sec
Toggles a measurement delay on or off. If toggled on, the
delay time is displayed for user entry. Allowed values range
from positive 0.1 to 99999.9 ms.
MEASDLY0;
MEASDLY1;
MEASDLYX?;
MEASDLY;
MEASDLY?
I.F. CALIBRATION None
AUTOMATIC ON (OFF)
I.F. CAL Turns on or off the timer for I.F. calibration. The timer
automatically triggers an I.F. calibration at regular intervals
for internal hardware calibrations. If can be set on or off
when in either INTERNAL or EXTERNAL trigger
measuement mode.
HC1; HC0; HCX?
TRIGGER
I.F. CAL Immediately triggers an I.F. calibration, which calibrates the
internal hardware. A “CALIBRATING IF...” message is
displayed.
HCT
PRESS <ENTER>
TO SELECT
OR TURN ON/OFF
Pressing the Enter key implements your menu selection. None
Menu TRIG, Triggers Measurement
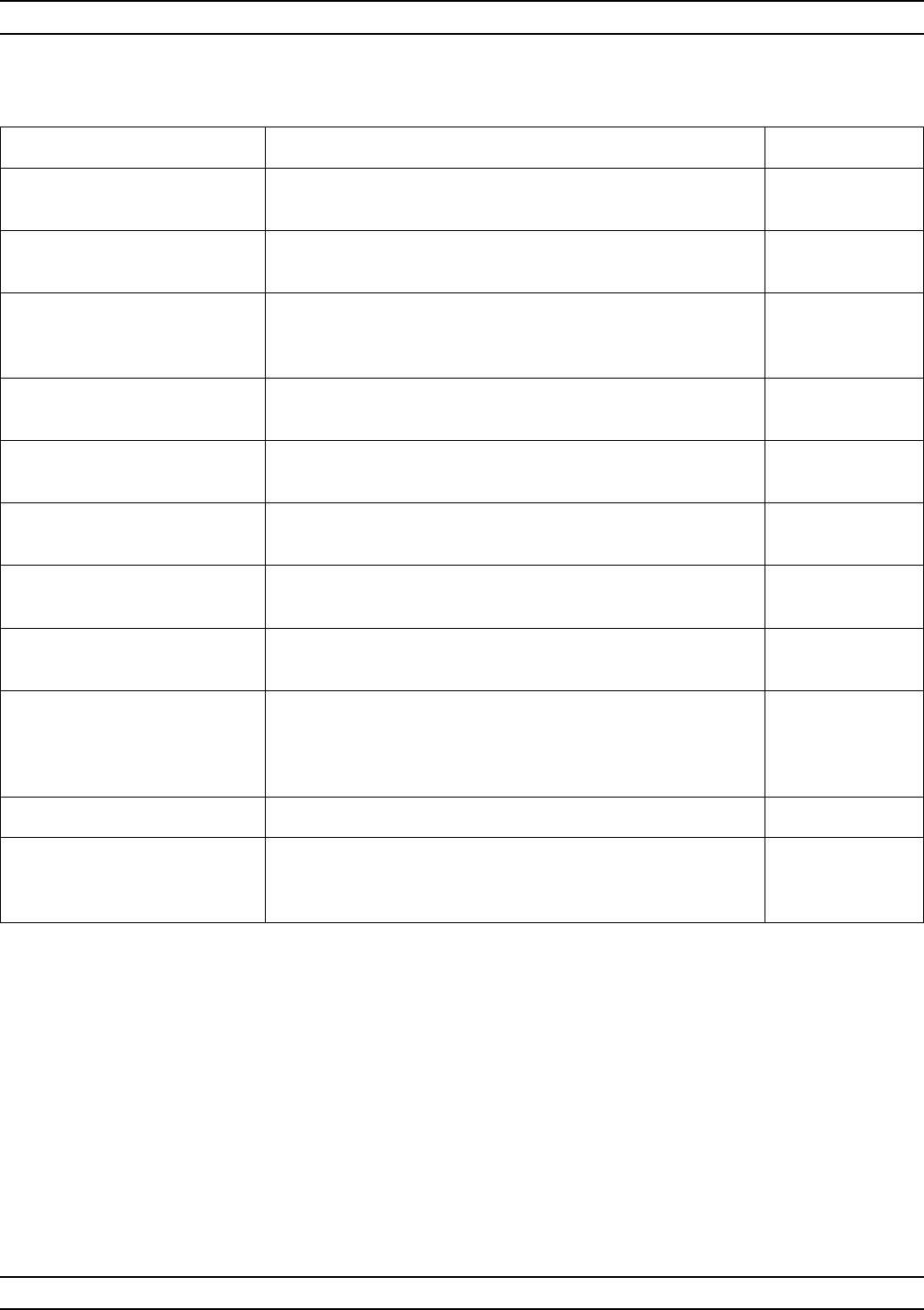
A-240 37XXXC OM
U ALPHABETICAL LISTING
MENU DESCRIPTION GPIB COMMAND
SELECT UTILITY
FUNCTION OPTIONS None
GPIB ADDRESSES Calls menu GP7, which displays the current GPIB
addresses of the various dedicated instruments. None
DISPLAY
INSTRUMENT
STATE PARAMS
Calls menu U2, which lets you display the various
instrument state parameters. None
GENERAL DISK
UTILITIES Calls menu DSK1-FD, which lets you select between
several disk utilities. None
CAL COMPONENT
UTILITIES Calls menu U3, which lets you select between several
calibration-component utilities. None
AUTOCAL
UTILITIES Calls menu ACAL_UTIL, which lets you select various
AutoCal utilities. None
COLOR
CONFIGURATION Calls menu U5, which lets you configure the screen colors. None
DATA ON (OFF)
DRAWING Turns data drawing on or off for all channels. DD1; DD0; DD1?
BLANKING
FREQUENCY
INFORMATION
Blanks all frequency-identifier information from the 37XXXC
displays, if such information is presently being displayed.
Hides the frequency value with X’s, such as
XXX.XXXXXXXXX GHz.
FOF; FON; FOX?
SET DATE/TIME Lets users set the date and time. None
PRESS <ENTER>
TO SELECT
OR TURN ON/OFF
Pressing the Enter key implements your menu selection. None
Menu U1, Utility Menu
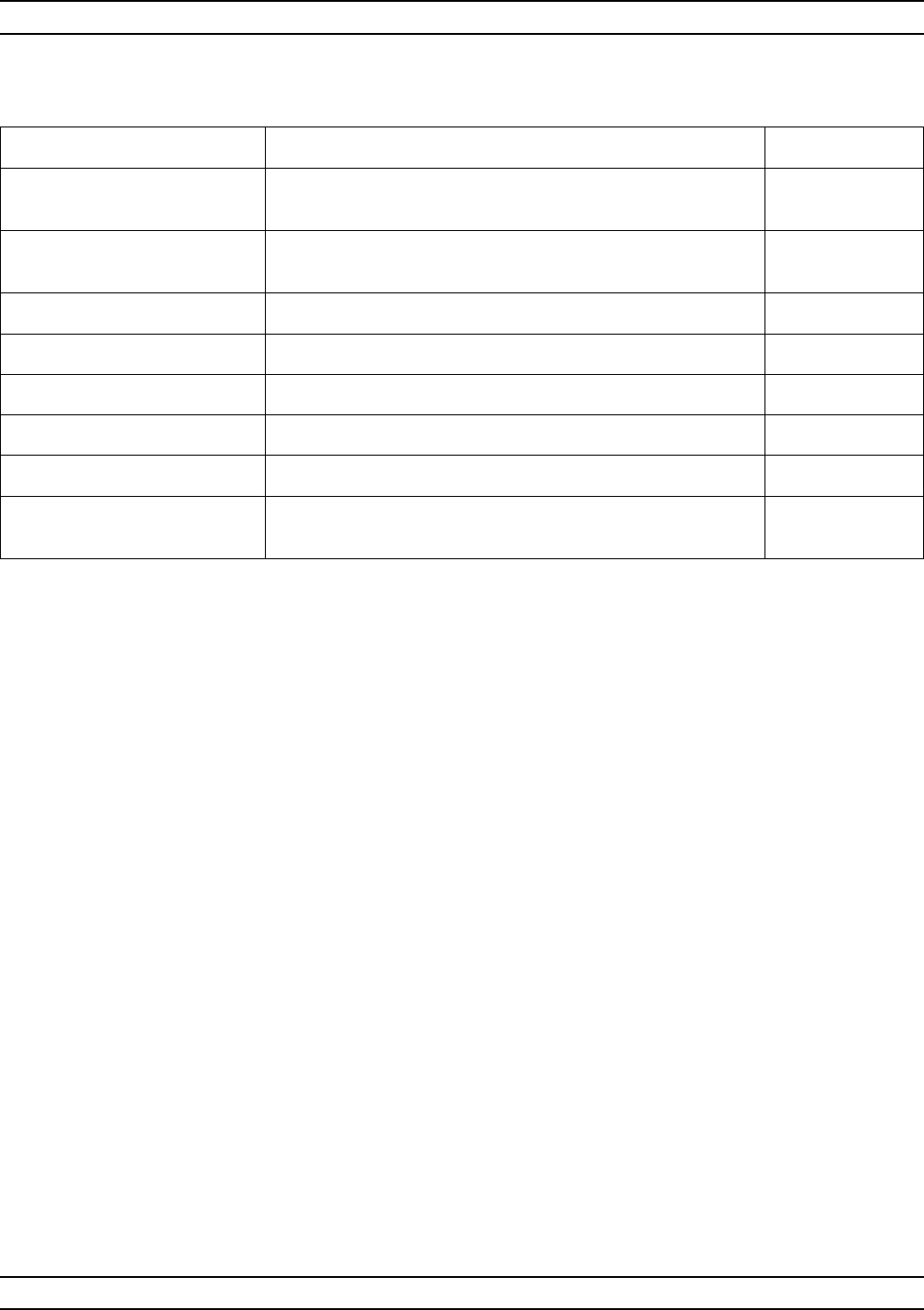
37XXXC OM A-241
ALPHABETICAL LISTING U
MENU DESCRIPTION GPIB COMMAND
DISPLAY INSTRUMENT
STATE PARAMETERS None
SYSTEM Displays all of the system parameters (Readout Text for
U2, on the following pages). DGS
CALIBRATION Displays the calibration parameters. DCP
OPERATING Displays the global operating parameters. DFP
CHANNEL 1 & 2 Displays the Channel 1-2 operating parameters. DC1
CHANNEL 3 & 4 Displays the Channel 3-4 operating parameters. DC3
NEXT PARAM PAGE Alternately displays Readout Text U3 a through e.
PRESS <ENTER>
TO SELECT Pressing the Enter key implements your menu selection. None
Menu U2, Display Instrument State
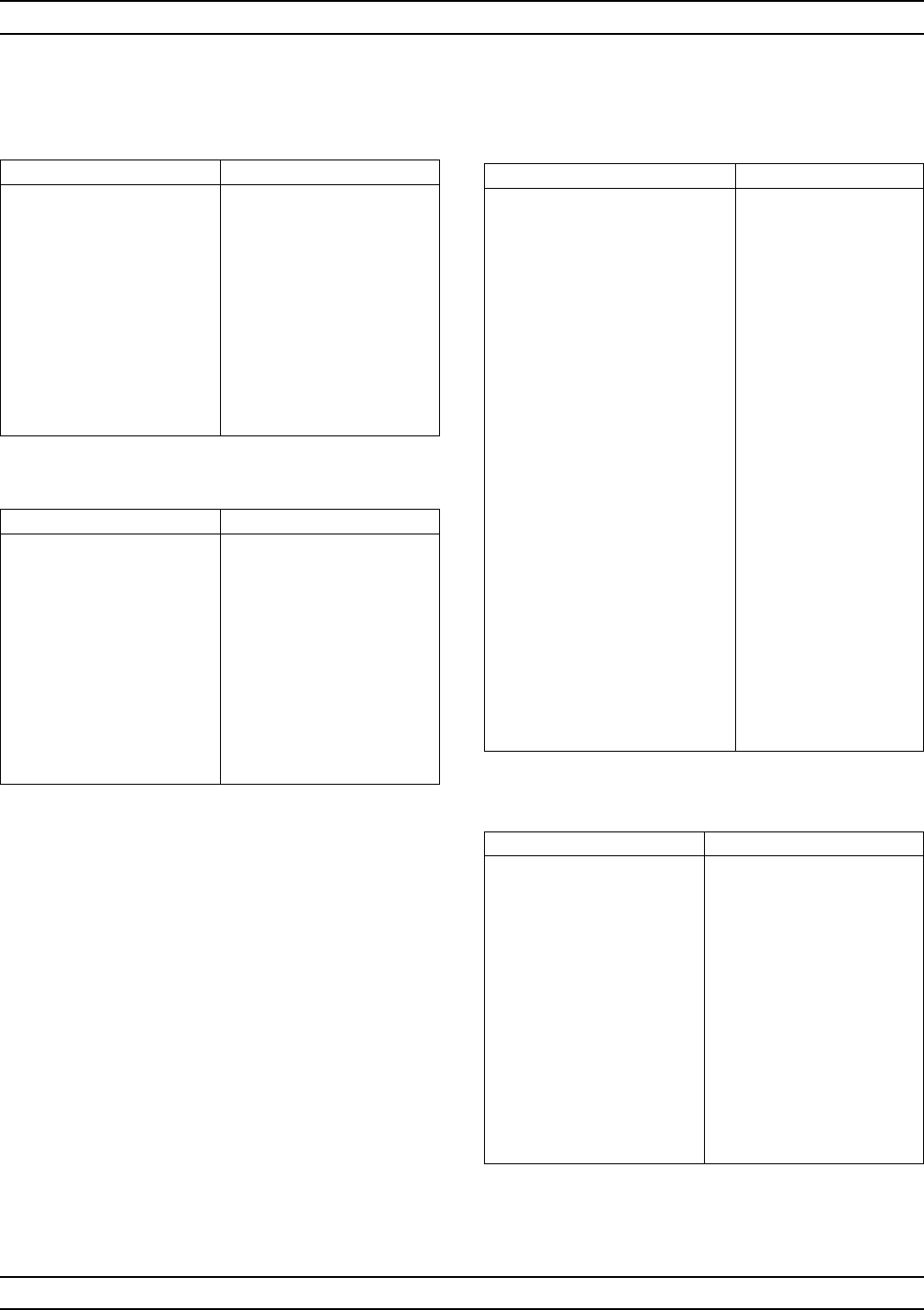
A-242 37XXXC OM
U ALPHABETICAL LISTING
Parameter Display Format
Number of Points
Power Control
Port 1 Attenuation
Porft 2 Attenuation
Source 2 Power
xx.x dB
xx.x dB
xx.x dB
xx.x dB
Reference Impedance
Averaging
Smoothing
xx.xxx W
xxx Meas. per point
Off/On
x.x percent of sweep
Off/On
Readout Text U2, Global Operating Parameters
Parameter Display Format
Model
Serial Number
Software Version
Options
xxxxxxxx
xxx
xxxxxxxx
xxxxxxxx
IEEE 488.2 GPIB Interface
Address
Enable Registers
Service Request
Standard Event Status
Parallel Poll
Extended Event Status
Limits Testing Status
xx
xx
xx
Dedicated GPIB Interface
External Source 1 Address
External Source 2 Address
Plotter Address
Power Meter Address
Frequency Counter
xxxxx
xxxxx
xxxxx
xxxxx
xxxxx
Measurement Trigger
Automatic I.F. Calibration xxxxxx
xxxxxxx
Diagnostic Mode
Troubleshooting
Receiver Mode
Search for Lock
xxx
xxxxxxxxxxxx
xxx
Readout Text U2, System Parameters
Parameter Display Format
Number of Points
Power Control
Port 1 Attenuation
Porft 2 Attenuation
Source 2 Power
xx.x dB
xx.x dB
xx.x dB
xx.x dB
Reference Impedance
Averaging
Smoothing
xx.xxx W
xxx Meas. per point
Off/On
x.x percent of sweep
Off/On
Readout Text U2, Channel Parameters
Parameter Display Format
Cal Method
Line Type Medium
Cal Type
xxxxxxxx
xxxxxxxx
xxxxxxxx
Number of Points
Start Freq
Stop Freq
xxxxxxxx
xxxxxxxx
xxxxxxxx
Power Control
Port 1 Attenuator
Port 2 Attenuator
Source 2 Power
xx.x dB
xx.x dB
xx.x dB
xx.x dB
Load Type
Through Offset xxxxxxxx
xxxxxxxx
Readout Text U2, Calibration Parameters
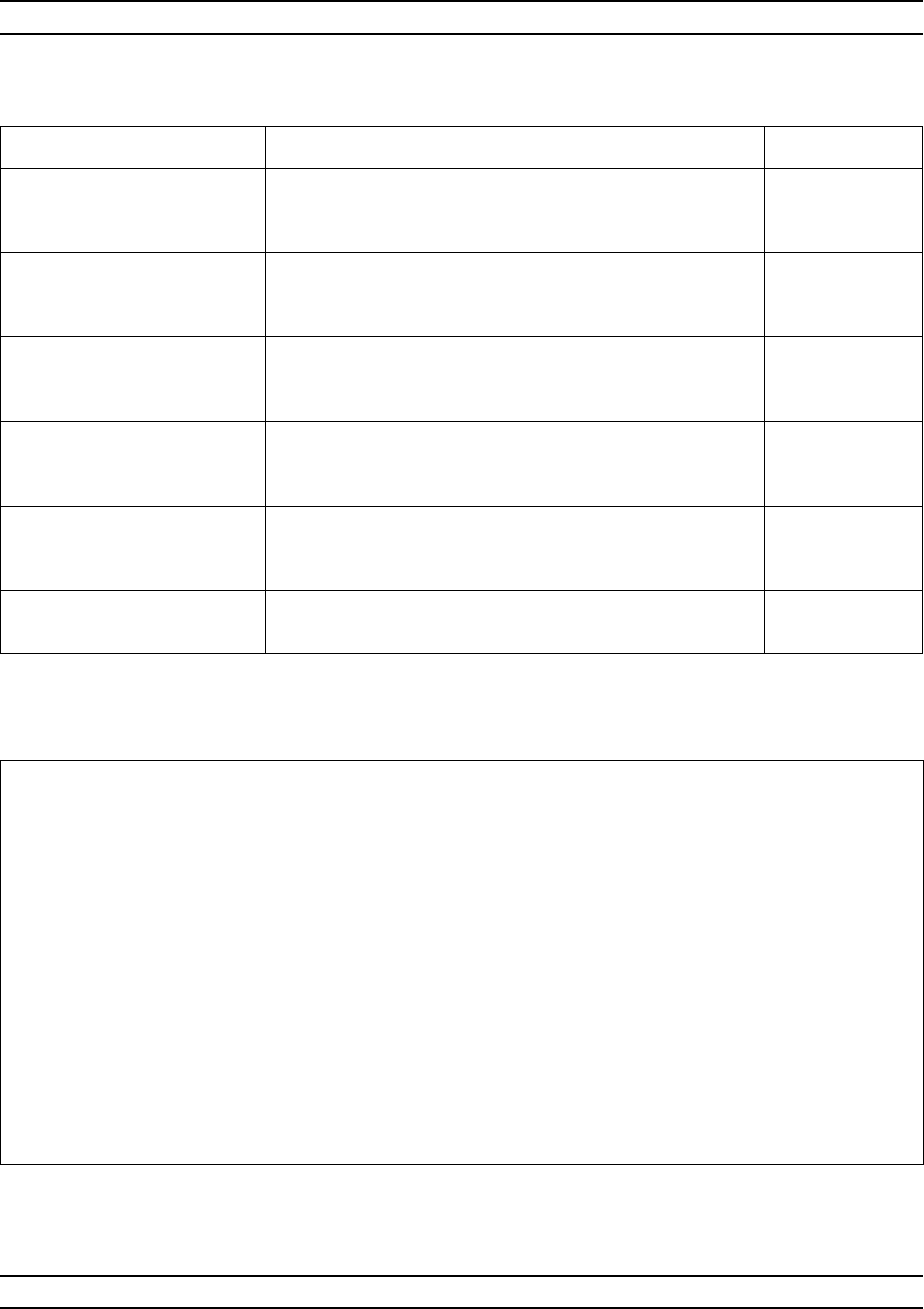
37XXXC OM A-243
ALPHABETICAL LISTING U
MENU DESCRIPTION GPIB COMMAND
CALIBRATION
COMPONENT
UTILITIES
None
INSTALL KIT
INFORMATION
FROM FLOPPY DISK
Reads into memory the coefficient data from the
calibration-components disk supplied with the calibration
kits.
LKT
DISPLAY COAXIAL
OPEN & SHORT
INFORMATION
Calls menu U4 and U4A, which lets you display the
connector information for the various coaxial connectors
supported.
None
DISPLAY COAXIAL
OFFSET SHORT
INFORMATION
Calls menu U4B, which lets you display the connector
information for the various coaxial connectors supported. None
DISPLAY
WAVEGUIDE
INFORMATION
Displays the waveguide information loaded from the floppy
diskette. DWG
PRESS <ENTER>
TO SELECT Pressing the Enter key implements your menu selection. None
Menu U3, Calibration Component Utilities
SSLT AND SSST WAVEGUIDE PARAMETERS
IDENTIFIER NOT INSTALLED
CUTOFF FREQUENCY XXX.XXXXXX GHz
OFFSET LENGTH OF SHORT 1 +XXX.XXXX mm
OFFSET LENGTH OF SHORT 2 +XXX.XXXX mm
OFFSET LENGTH OF SHORT 3 +XXX.XXXX mm
Menu EXT_U3, SSLT and SSST Waveguide Parameters
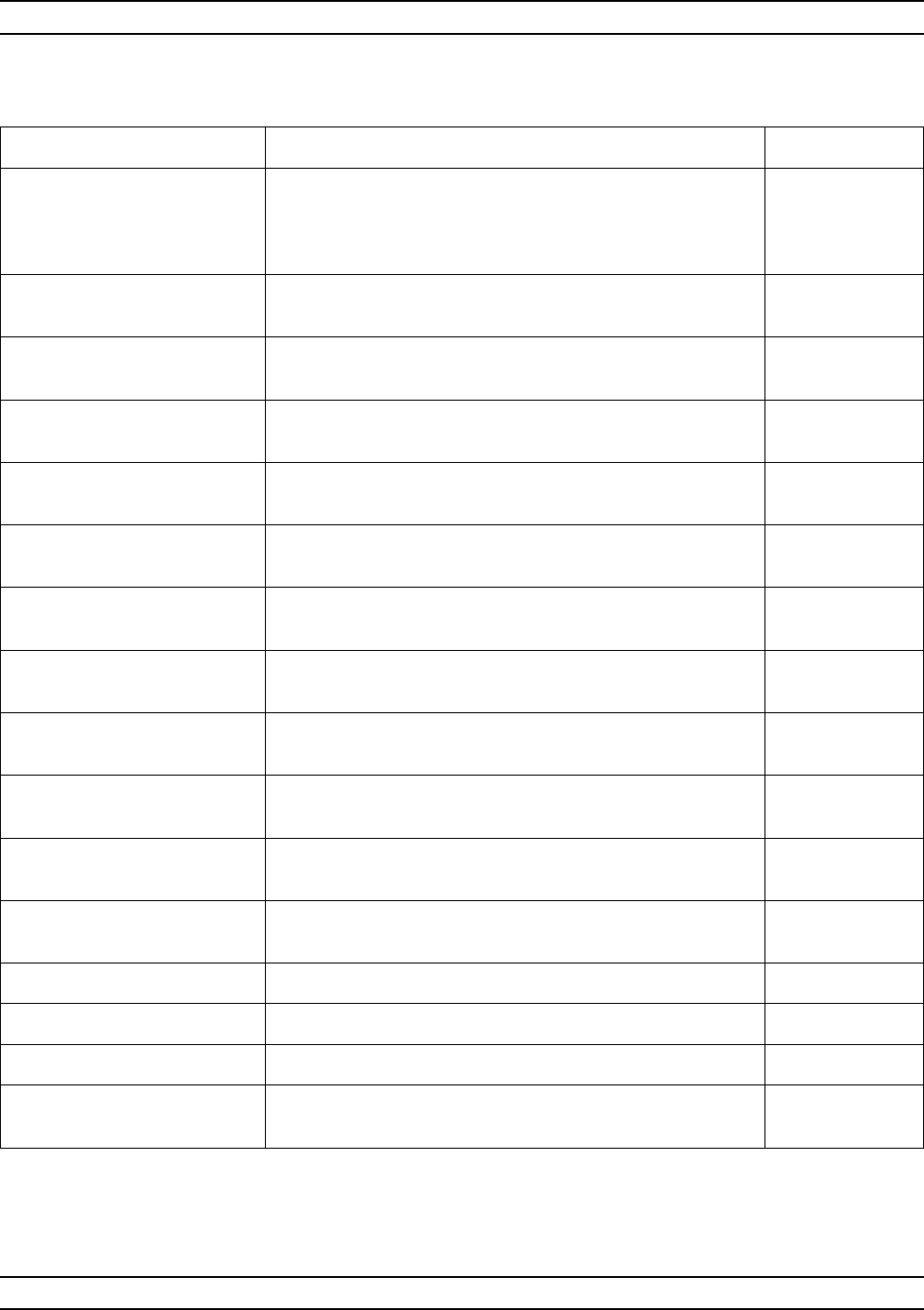
A-244 37XXXC OM
U ALPHABETICAL LISTING
MENU DESCRIPTION GPIB COMMAND
DISPLAY INSTALLED
OPEN & SHORT
TEST PORT
CONNECTOR INFO
This menu lets you view coefficient data on components.
The data appears in the display area of the screen (See
readout text on next page).
None
K – CONN (M) Select to display coefficient data for the K Connector male
components. DMK
K – CONN (F) Select to display coefficient data for the K Connector
female male components. DFK
V-CONN (M) Select to display coefficient data for the V Connector male
components. DMV
V-CONN (F) Select to display coefficient data for the V Connector
female components. DFV
W1-CONN (M) Select to display coefficient data for the W1 Connector
male components. DM1
W1-CONN (F) Select to display coefficient data for the W1 Connector
female components. DF1
SMA (M) Select to display coefficient data for the SMA male
components. DMS
SMA (F) Select to display coefficient data for the SMA female
components. DFS
GPC - 3.5 (M) Select to display coefficient data for the GPC-3.5 male
components. DM3
GPC - 3.5 (F) Select to display coefficient data for the GPC-3.5 female
components. DF3
GPC - 7 Select to display coefficient data for the sexless GPC-7
components. DG7
NEXT CONNECTOR Cycles through selections SMA (M) to GPC 7. None
MORE CONNECTORS Calls up menu U4A and lets you select more connectors. None
PREVIOUS MENU Displays menu U3. None
PRESS <ENTER>
TO SELECT Pressing the Enter key implements your menu selection. None
Menu U4, Display Installed Calibration Components Information 1
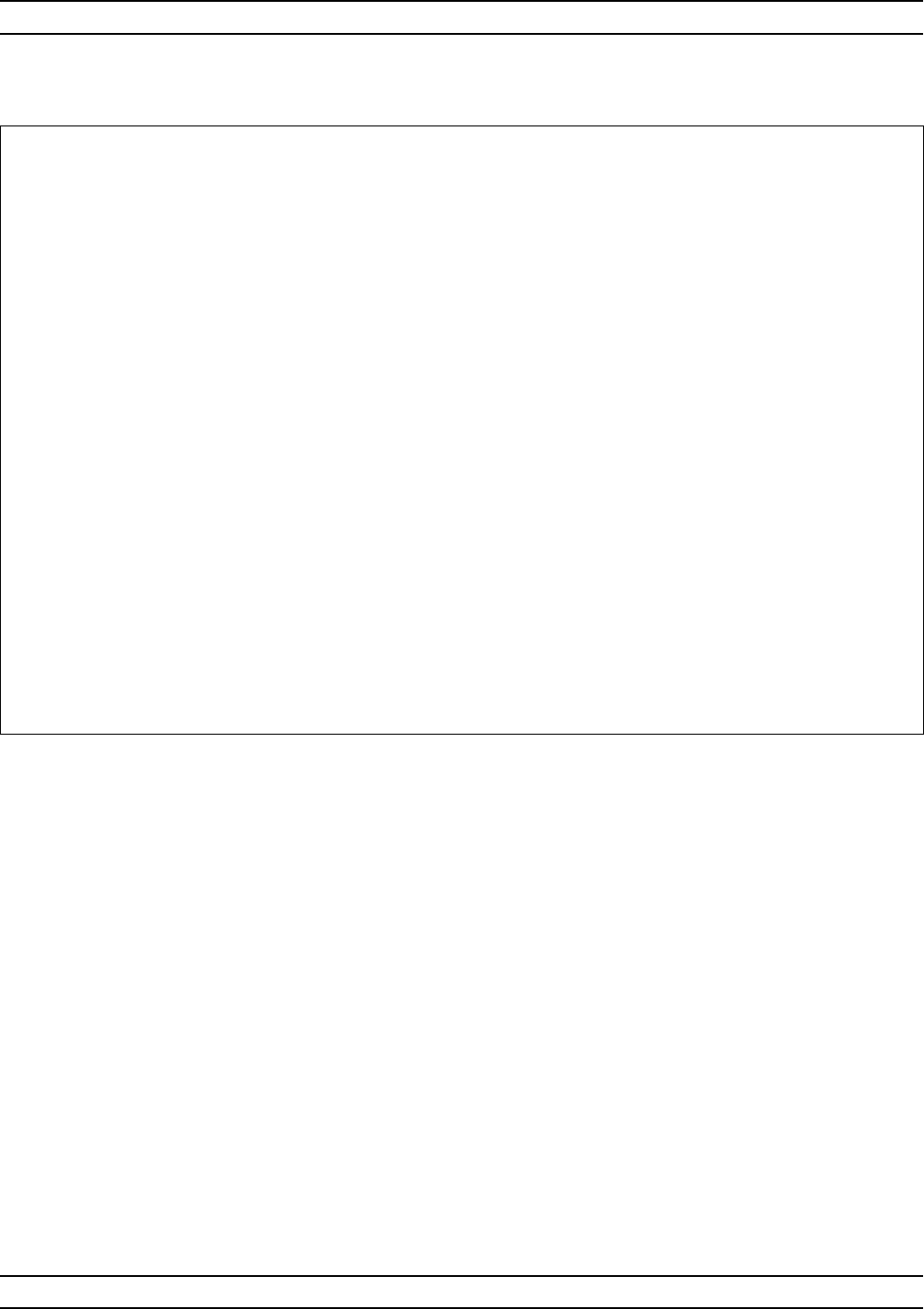
37XXXC OM A-245
ALPHABETICAL LISTING U
SOLT CALIBRATION KIT
TEST PORT: W1-CONN (MALE)
CALIBRATION COMPONENTS: W1-CONN (FEMALE)
OPEN DEVICE
C0 [e-15 F] +XXXX.XXXX
C1 [e-27 F/Hz] +XXXX.XXXX
C2 [e-36 F/Hz2] +XXXX.XXXX
C3 [e-45 F/Hz3] +XXXX.XXXX
OFFSET LENGTH +XXX.XXXX mm
SERIAL NUMBER “NNNNNN”
SHORT DEVICE
L0 [e-12 H] +XXXX.XXXX
L1 [e-24 H/Hz] +XXXX.XXXX
L2 [e-33 H/Hz2] +XXXX.XXXX
L3 [e-42 H/Hz3] +XXXX.XXXX
OFFSET LENGTH +XXX.XXXX mm
SERIAL NUMBER “NNNNNN”
Menu EXT_U4, SOLT Calibration Kit Information
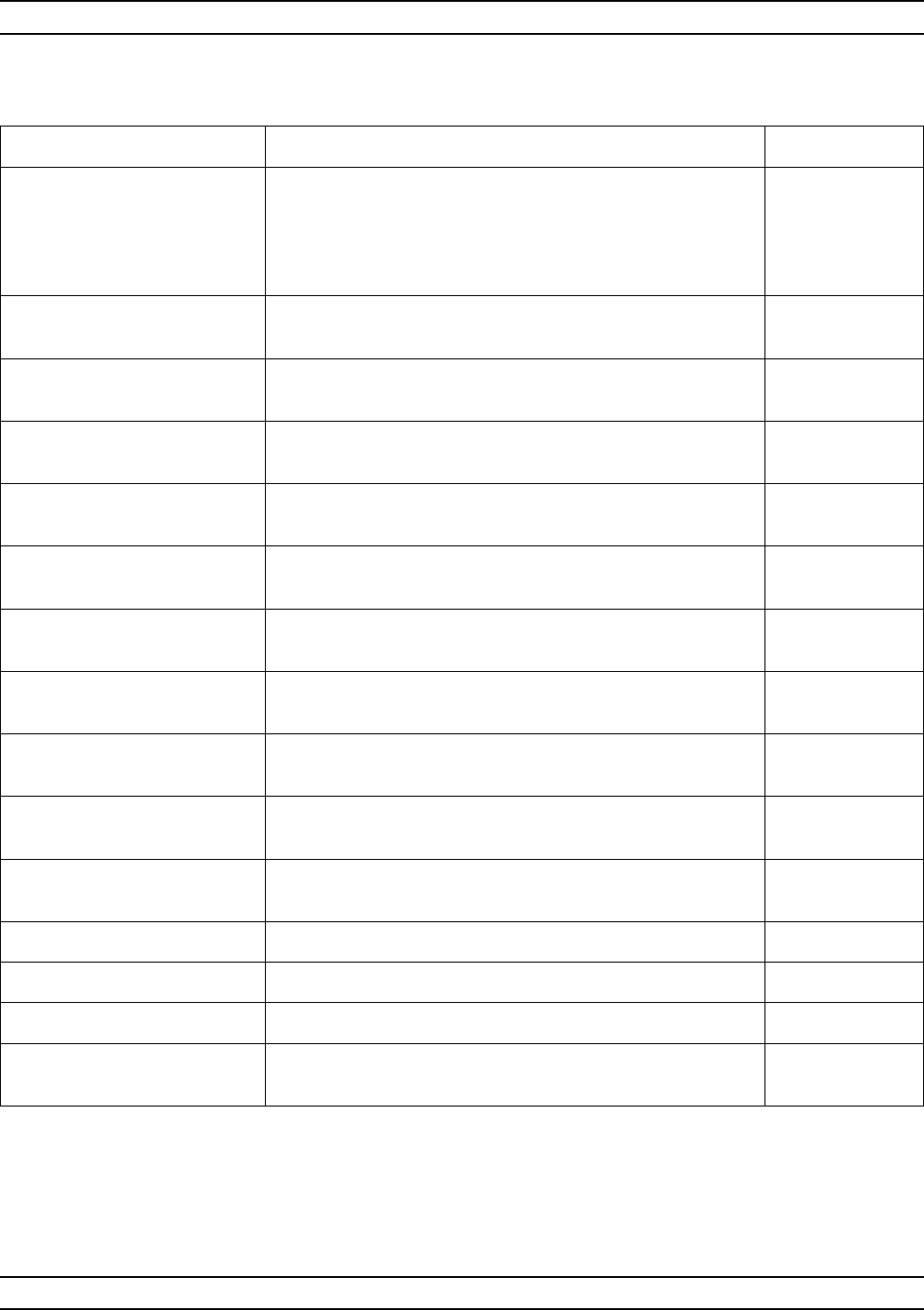
A-246 37XXXC OM
U ALPHABETICAL LISTING
MENU DESCRIPTION GPIB COMMAND
DISPLAY
INSTALLED
CALIBRATION
COMPONENT
INFORMATION
This menu lets you view coefficient data for connectors.
The data appears in the display area of the screen. None
TYPE N (M) Select to display coefficient data for the Type N male
components. DMN
TYPE N (F) Select to display coefficient data for the Type N female
components. DFN
TYPE N (M) 75WSelect to display coefficient data for the Type N male 75W
components. DMN75
TYPE N (F) 75WSelect to display coefficient data for the Type N female 75W
components. DFN75
7/16 (M) Select to display coefficient data for the 7/16 male
components. DM7
7/16 (F) Select to display coefficient data for the 7/16 female male
components. DF7
TNC (M) Select to display coefficient data for the TNC male
components. DMT
TNC (F) Select to display coefficient data for the TNC female male
components. DFT
2.4 mm (M) Select to display coefficient data for the 2.4 mm male
components. DM2
2.4 mm (F) Select to display coefficient data for the 2.4 mm female
components. DF2
NEXT CONNECTOR Cycles through selections V Connector to SPECIAL. None
MORE CONNECTORS Calls up menu U4A and lets you select more connectors. None
PREVIOUS MENU Returns you to menu U3. None
PRESS <ENTER>
TO SELECT Pressing the Enter key implements your menu selection. None
Menu U4A, Display Installed Calibration Components Information 2
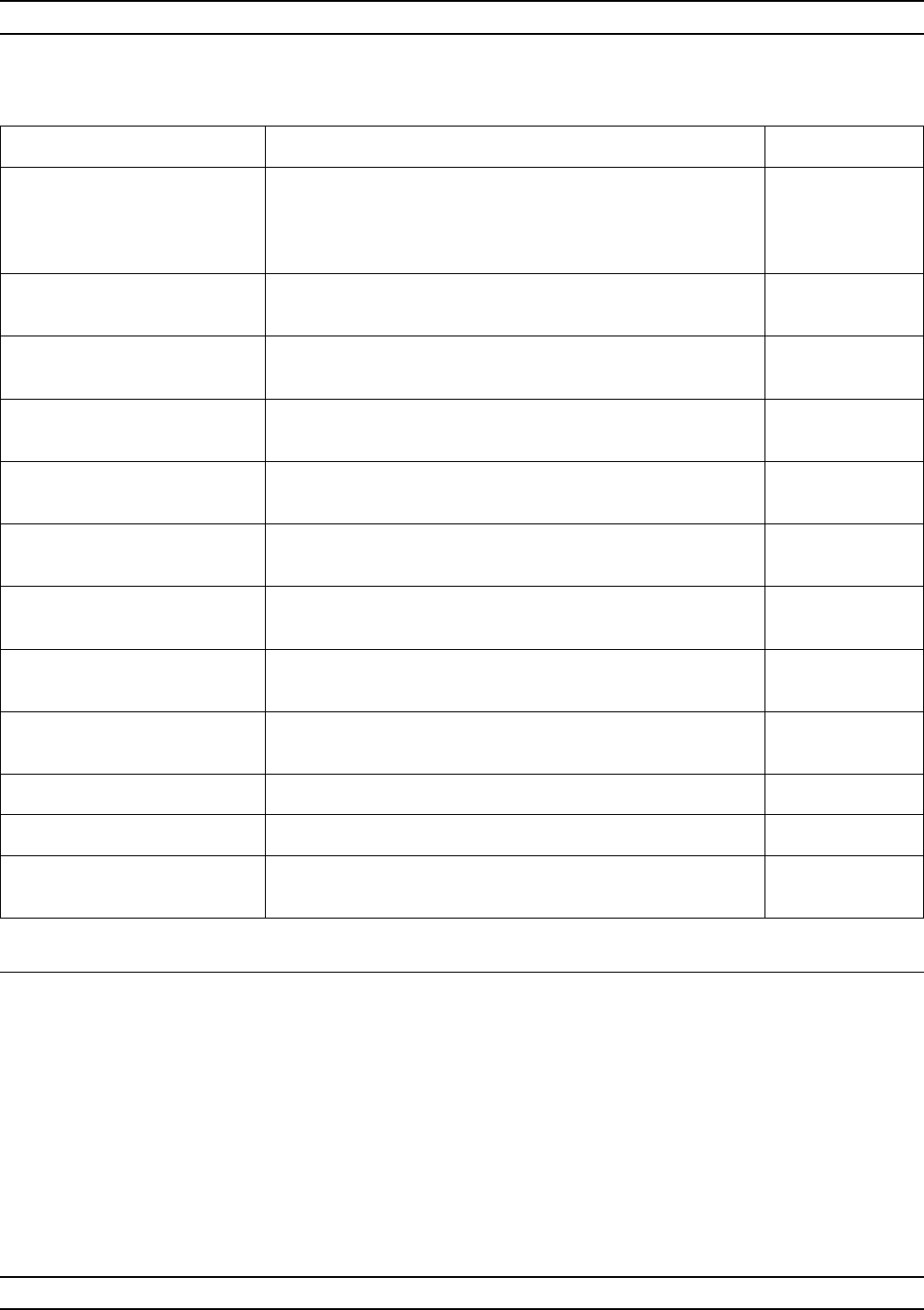
37XXXC OM A-247
ALPHABETICAL LISTING U
MENU DESCRIPTION GPIB COMMAND
DISPLAY INSTALLED
OFFSET SHORT
TEST PORT
CONNECTOR INFO
This menu lets you view coefficient data for connectors.
The data appears in the display area of the screen. None
W1-CONN (M) Select to display coefficient data for the W1 Connector
male components. DOM1
W1-CONN (F) Select to display coefficient data for the W1 Connector
female components. DOF1
SPECIAL A (M) Select to display coefficient data for special A male
components. DOASM
SPECIAL A (F) Select to display coefficient data for special A female
components. DOASF
SPECIAL B (M) Select to display coefficient data for special B male
components. DOBSM
SPECIAL B (F) Select to display coefficient data for special B female
components. DOBSF
SPECIAL C (M) Select to display coefficient data for special C male
components. DOCSM
SPECIAL C (F) Select to display coefficient data for special C female
components. DOCSF
NEXT CONNECTOR Cycles through selections W Connector to SPECIAL. None
PREVIOUS MENU Returns you to menu U3. None
PRESS <ENTER>
TO SELECT Pressing the Enter key implements your menu selection. None
Menu U4B, Display Installed Calibration Components Information 3
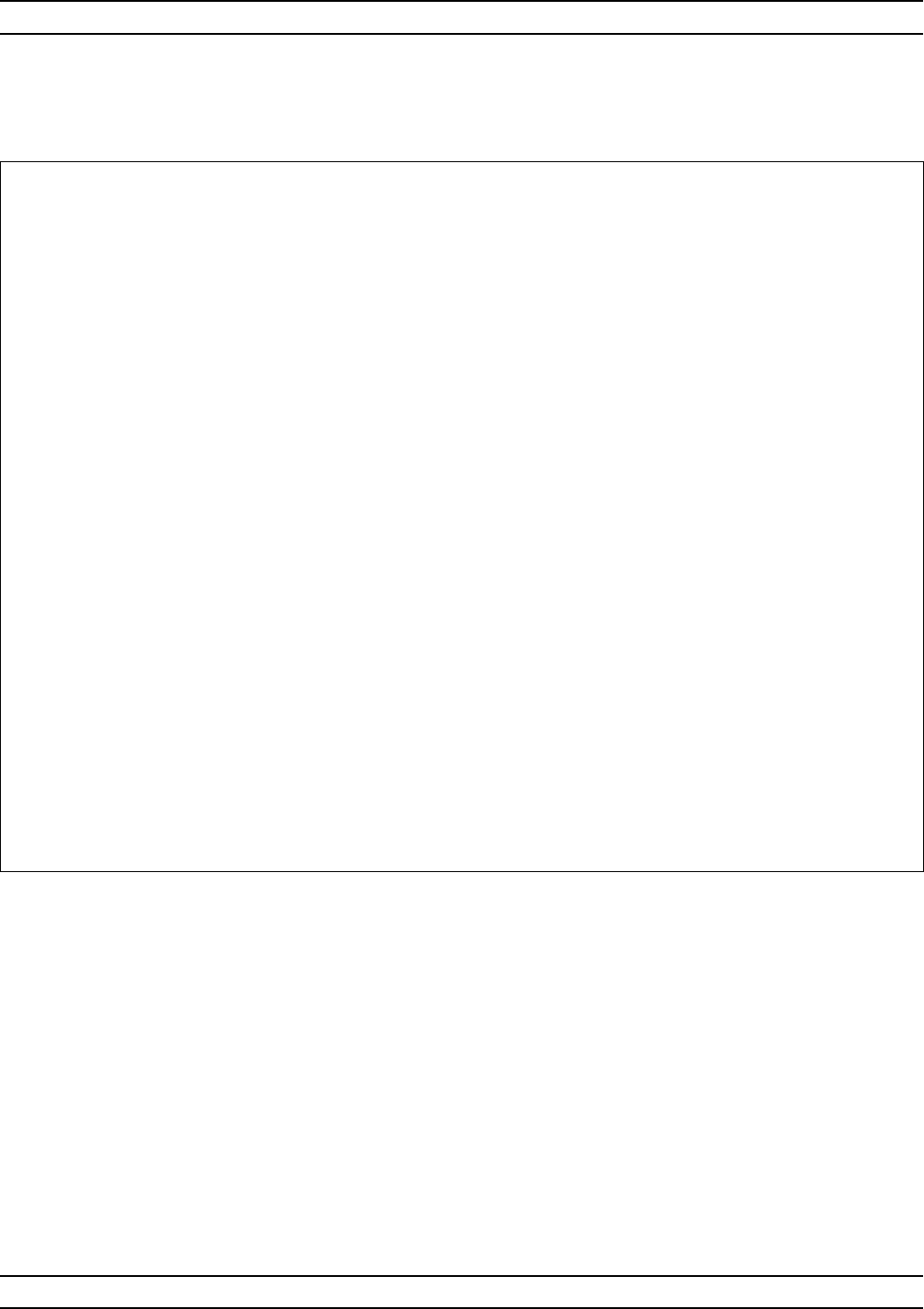
A-248 37XXXC OM
U ALPHABETICAL LISTING
SSLT AND SSST CALIBRATION KIT
TEST PORT: W1-CONN (MALE)
CALIBRATION COMPONENTS: W1-CONN (FEMALE)
OFFSET SHORT 1 DEVICE
L0 [e-12 H] +XXXX.XXXX
L1 [e-24 H/Hz] +XXXX.XXXX
L2 [e-33 H/Hz2] +XXXX.XXXX
L3 [e-42 H/Hz3] +XXXX.XXXX
OFFSET LENGTH +XXX.XXXX mm
SERIAL NUMBER “NNNNNN”
OFFSET SHORT 2 DEVICE
L0 [e-12 H] +XXXX.XXXX
L1 [e-24 H/Hz] +XXXX.XXXX
L2 [e-33 H/Hz2] +XXXX.XXXX
L3 [e-42 H/Hz3] +XXXX.XXXX
OFFSET LENGTH +XXX.XXXX mm
SERIAL NUMBER “NNNNNN”
OFFSET SHORT 3 DEVICE
L0 [e-12 H] +XXXX.XXXX
L1 [e-24 H/Hz] +XXXX.XXXX
L2 [e-33 H/Hz2] +XXXX.XXXX
L3 [e-42 H/Hz3] +XXXX.XXXX
OFFSET LENGTH +XXX.XXXX mm
SERIAL NUMBER “NNNNNN”
Menu EXT_U4B, SSLT and SSST Calibration Kit Information
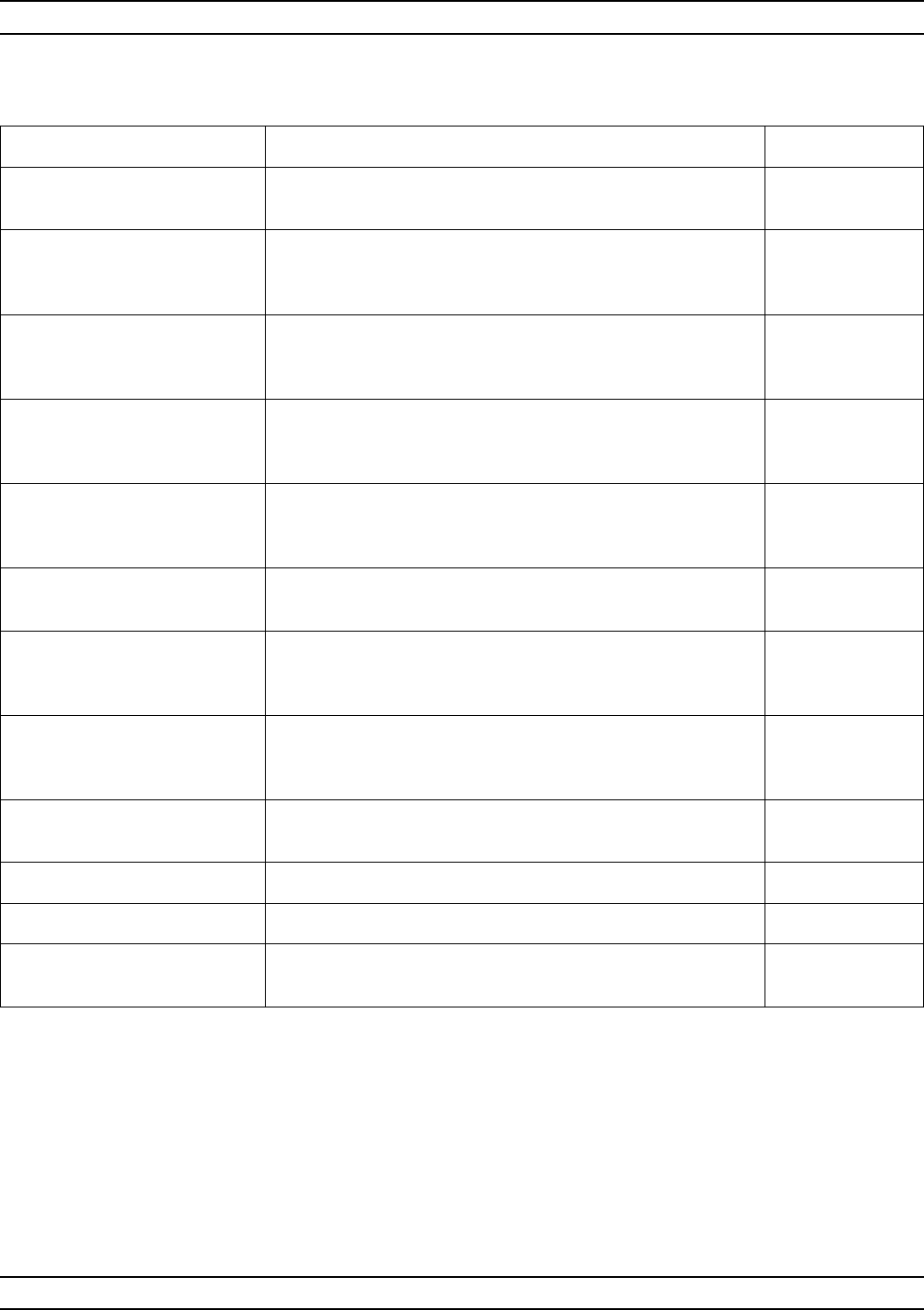
37XXXC OM A-249
ALPHABETICAL LISTING U
MENU DESCRIPTION GPIB COMMAND
COLOR
CONFIGURATION None
DATA
10 RED Sets the color for the data drawn on the display. Use rotary
knob to cycle between the available colors. Default color is
shown.
DATCOL;
DATCOL?
OVERLAY DATA
15 YELLOW Sets the color for the overlay data drawn on the display.
Use rotary knob to cycle between the available colors.
Default color is shown.
LAYCOL;
LAYCOL?
MEMORY DATA
24 GREEN Sets the color for the memory data drawn on the display.
Use rotary knob to cycle between the available colors.
Default color is shown.
TRCCOL;
TRCCOL?
MARKERS
AND LIMITS
32 CYAN
Sets the color for the markers and limits drawn on the
display. Use rotary knob to cycle between the available
colors. Default color is shown.
MKRCOL;
MKRCOL?
GRATICULE
24 GREEN Sets the color for the display graticule. Use rotary knob to
cycle between the available colors. Default color is shown. GRTCOL;
GRTCOL?
ANNOTATION
AND MENU TEXT
24 GREEN
Sets the color for the annotation and menu text. Use rotary
knob to cycle between the available colors. Default color is
shown.
ANNCOL;
ANNCOL?
MENU HEADERS
(TITLES & INFO)
32 CYAN
Sets the color for the menu headers and information. Use
rotary knob to cycle between the available colors. Default
color is shown.
MNUCOL;
MNUCOL?
BACKGROUND
0 BLANK Sets the color for the background. Use rotary knob to cycle
between the available colors. Default color is shown. BCKCOL;
BCKCOL?
RESET COLORS Resets colors to the default values. RSTCOL
COLOR SCHEMES Calls menu U5A None
PRESS <ENTER>
TO SELECT Pressing the Enter key implements your menu selection. None
Menu U5, Color Configuration
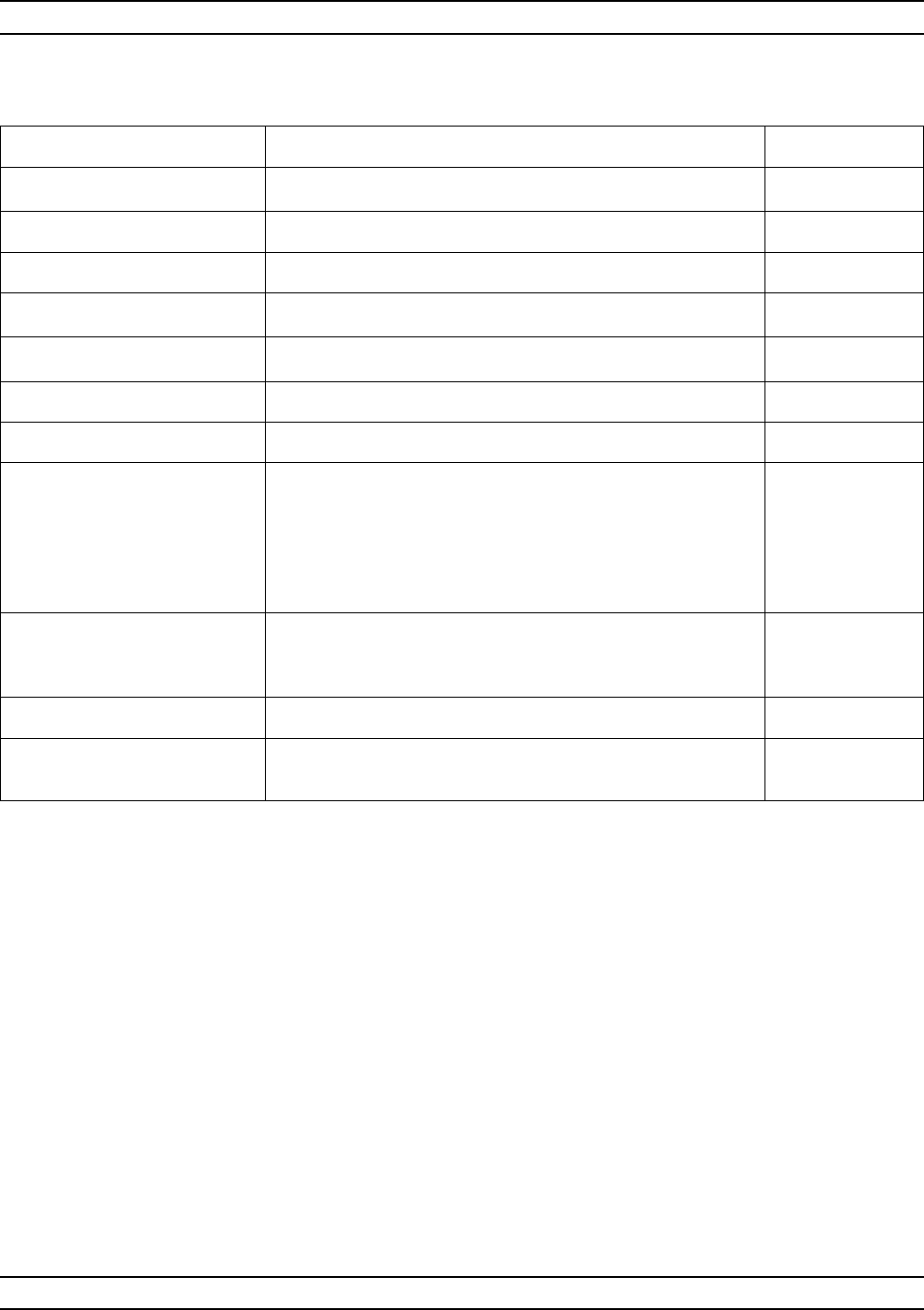
A-250 37XXXC OM
U ALPHABETICAL LISTING
MENU DESCRIPTION GPIB COMMAND
COLOR SCHEMES The user can select various color configurations by choosing between
predetermined schemes
RESET COLORS Loads the current color configuration with the reset (default) colors RSTCOL
NEW COLORS Loads the color configuration with the new colors for the "C" models. NEWCO
CLASSIC COLORS Loads the color configuration with the classic colors used in past mod-
els. CLASS
INVERSE COLORS Loads the color configuration with the colors pre-defined for a white
background. INVER
BRILLIANT COLORS Loads the color configuration with a pre-defined color set. BRILL
SOFT COLORS Loads the color configuration with a pre-defined color set. SOFTCO
TO CUSTOMIZE,
SELECT A COLOR
SCHEME AND/OR
MODIFY THE COLOR
CONFIG, THEN
STORE AS RESET
The user may also store the current color configuration as the reset
colors used in <default>. Only <default-0> will restore the colors to the
CLASSIC or NEW (“C” Models) setup.
None
STORE COLOR
CONFIG AS RESET
(DEFAULT) COLORS
Stores the current color configuration as the reset colors used in <de-
fault> and as the reset color scheme. STOCO
PREVIOUS MENU Returns you to menu U3. None
PRESS <ENTER>
TO SELECT Pressing the Enter key implements your menu selection. None
Menu U5, Color Configuration

37XXXC OM A-251/A-252
ALPHABETICAL LISTING U
MENU DESCRIPTION GPIB COMMAND
SET DATE/TIME None
YEAR
XXXX Sets the year. DATE; DATE?
MONTH
XX Sets the month. DATE; DATE?
DAY
XX Sets the day. DATE; DATE?
HOUR
XX Sets the hour. TIME; TIME?
MINUTE
XX Sets the minute. TIME; TIME?
DONE,
(SET DATE/TIME) Prompts to set a new time. None
PREVIOUS MENU
(DATE/TIME
NOT SET)
Returns to the previous menu. None
PRESS <ENTER>
TO SELECT Pressing the Enter key implements your menu selection. None
Menu U6, Set Date/Time

Table of Contents
B-1 INTRODUCTION ..............................B-3
B-2 REAR PANEL ................................B-3
B-3 CONNECTOR PINOUT DIAGRAMS....................B-3
Appendix B
Rear Panel Connectors

Appendix B
Rear Panel Connectors
B-1 INTRODUCTION This appendix provides descriptions and pinout diagrams for the
37XXXC rear panel connectors .
B-2 REAR PANEL The 37XXXC rear panel connectors are described if Figures B-1 and
B-2 on page B-2 and B-3.
B-3 CONNECTOR PINOUT
DIAGRAMS Figures B-3 through B-10 provide pinout diagrams for the rear panel
connectors.
37XXXC OM B-3
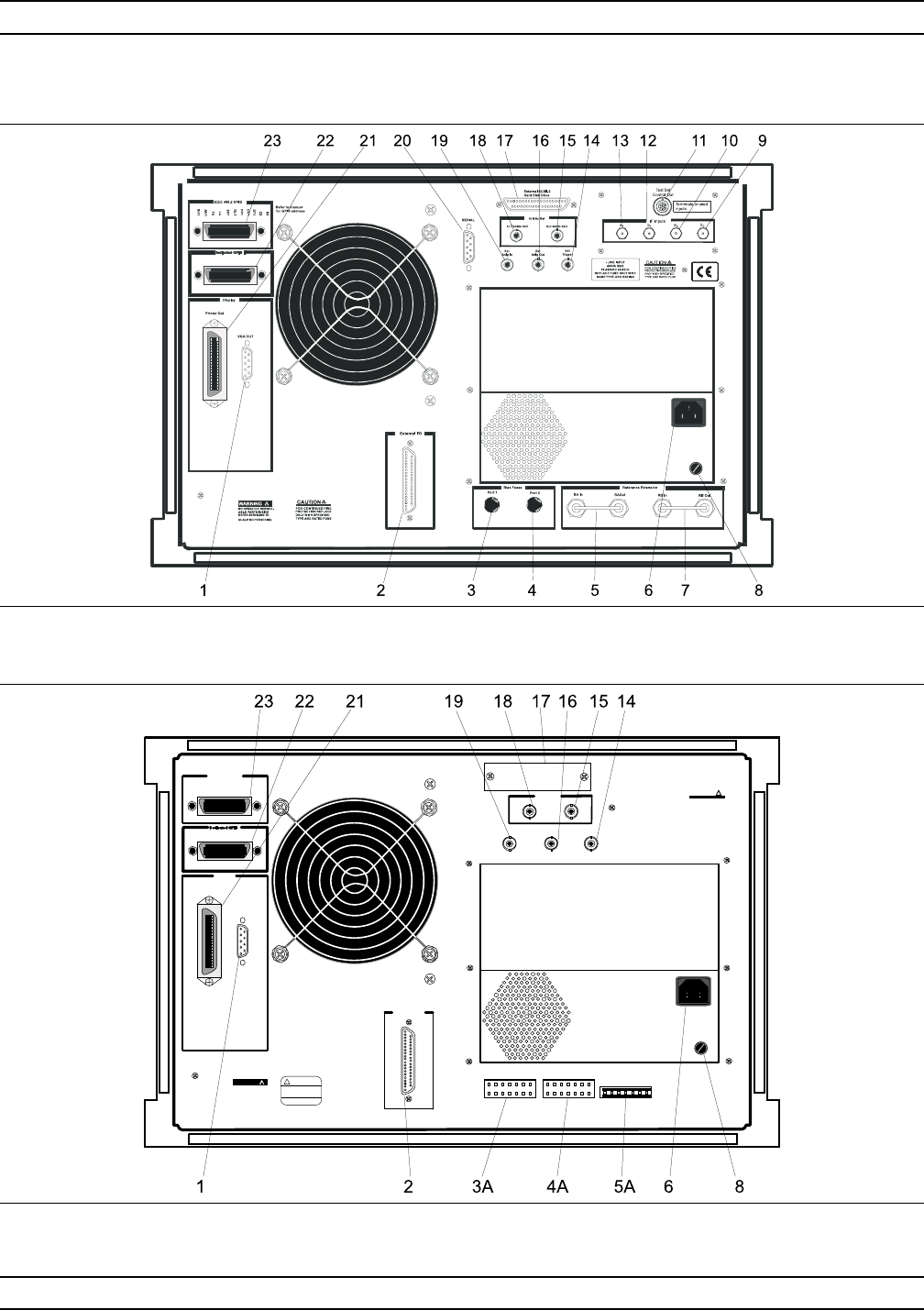
B-4 37XXXC OM
REAP PANEL DRAWINGS REAR PANEL CONNECTORS
Figure B-1. 372XXC, 373XXC Rear Panel
External I/ O
Display
IEEE 488.2 GPIB
10 MHz Ref
Ext
Trigger
Ext
AnlgIn
SAME TYPE AND RATING
85-264VAC 48-63Hz
FORCONTI NUED FIRE
PROTECTIO N REPLACE
ONLY WITH SPECIFIED
TYPE AND RATED FUS E
540VA MAX
VGAO UT
Printer O ut
WARNING
NO O PERATO RSERVICE-
ABLE PARTS I NSIDE
REFER SERVI CING TO
QUALI FI ED PERSO NNEL
CAUTI O N
SH1
AH1
T6
L4
SR1
RL1
PP1
DC1
DT1
C0
E2
Refer to manual
for GPIBaddress
1n ±5dBm50WOut0dBm50
W
Ext
Anl g O ut
!
REPLACE FUSE ONLY WITH
!CAUTION
>18kg
HEA VYWEI G HT
Port 1
Source Atten Port 2
Test Atten Transfer
Sw itch
Figure B-2. 371XXC Rear Panel
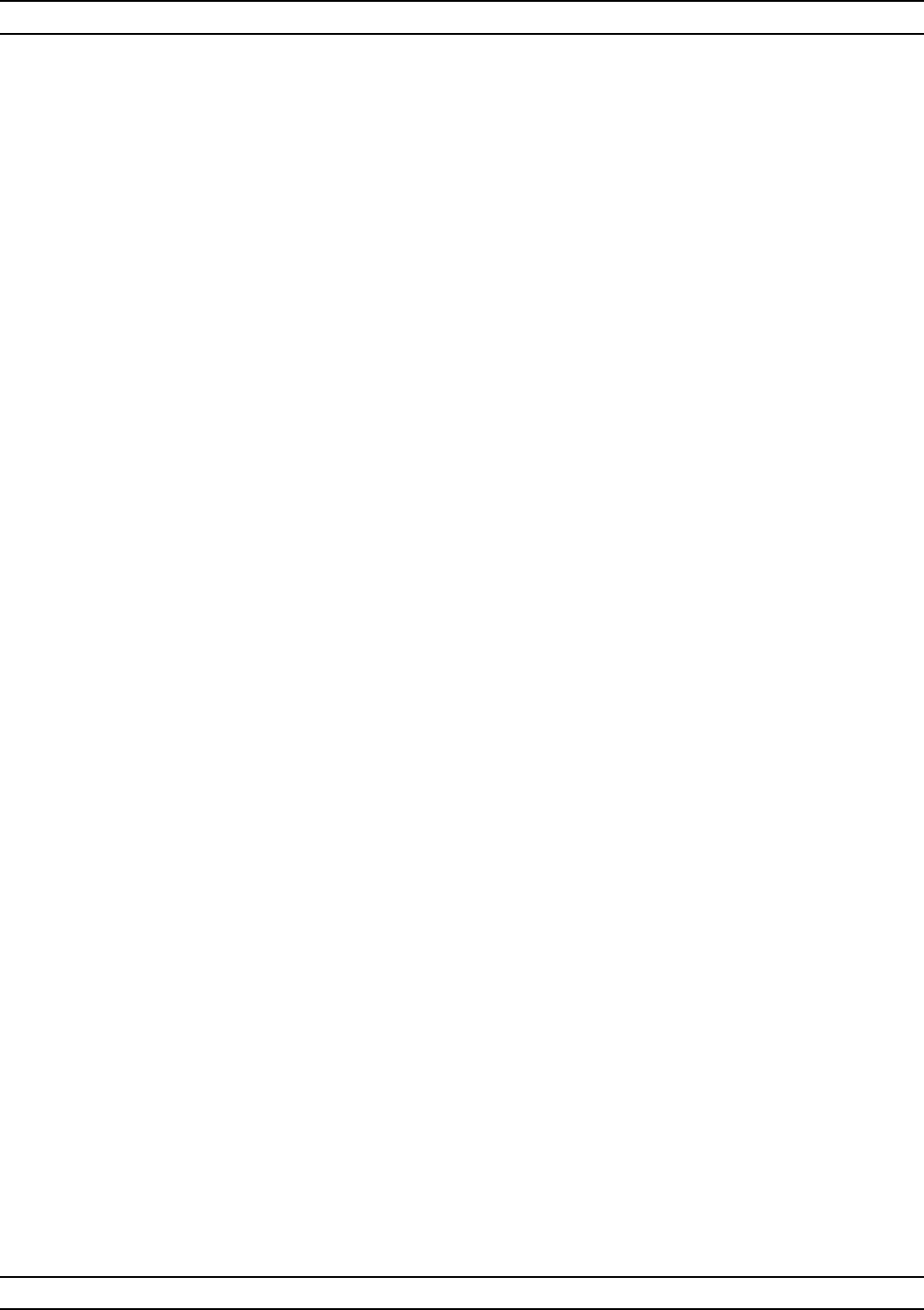
37XXXC OM B-5
REAR PANEL CONNECTORS CONNECTOR DESCRIPTIONS
1. VGA OUT: 15-pin connector provides VGA output of
37XXXC video display. Figure B-6 provides a pinout dia-
gram.
2. External I/O: Provide I/O access for Channel 1 through 4
limit and Port 1 and 2 bias voltages. Figure B-5 provides a
pinout diagram.
3. Bias Fuses, Port 1: Fuse, 0.5A, 3AG, 250V, provides pro-
tection for external bias being applied to the active device
connected to test port 1 without disturbing the accuracy of
the 37XXXC measurement.
3A. Port 1 Source Atten: Provide signal drive for an external
attenuator. Control is provided via the Test Signals menu,
which is accessed using the Setup Menu front panel key (re-
fer to Chapter 4). Refer to Figure B-9 for a pinout diagram.
4. Bias Fuses, Port 2: Fuse, 0.5A, 3AG, 250V, provides pro-
tection for external bias being applied to the active device
connected to test port 2 without disturbing the accuracy of
the 37XXXC measurement.
4A. Port 2 Test Atten: Same as for Port 1 Source Atten control
(Index 3A, above).
5. Reference Extension, a1 In to a1 Out: Loop allows ex-
ternal reference to be used as a receiver. This provides for
custom-defined user parameters with any combination of
channels.
5A. Transfer Switch: Provide signal drive for an external
ANRITSU transfer switch. Refer to Figure B- for a pinout dia-
gram.
6. Line Voltage Input: Three-prong ac plug that provides in-
put for the input-line power. The line voltage must be be-
tween 85 and 264 Vac rms, 43 to 63 Hz.
7. Reference Extension, b1 In to b1 Out: Loop allows at-
tenuation to be added to prevent damage to the b1 sampler
(when an amplifier is connected to the front panel loop).
8. Line Fuse: 3 AG fuse cartridge that protects for an input
overcurrent condition. The fuse is slow blow, 8A, 250V.
9. (Option 12) b2: IF input from 3738A Broadband Test Set.
SMA connector that should be terminated (on chain) when
not in use.
10. (Option 12) a2: IF input from 3738A Broadband Test Set.
SMA connector that should be terminated (on chain) when
not in use.
11. (Option 12) Test Set Control Out: Provides control for
3738A Broadband Test Set. Figure B-10 provides a pinout di-
agram. TTL levels.
12. (Option 12) b1: IF input from 3738A Broadband Test Set.
SMA connector that should be terminated (on chain) when
not in use.
13. (Option 12) a1: IF input from 3738A Broadband Test Set.
SMA connector that should be terminated (on chain) when
not in use.
14. External Trigger: Allows an external TTL signal to sync
the 37XXXC measurements; 10 kWinput impedance, BNC
female.
15. 10 MHz Ref OUT 0dBm 50W:BNC connector that allows
the internal 10 MHz reference to be used to phase lock an
external counter or other measuring instrument. Level is typi-
cally 0 dBm into 50Wimpedance.
16. External Anlg Out: Provides up to a ±10V signal for use in
driving an external plotter or antenna (CW draw).
17. External SCSI-2 Hard Disk Drive: Provides for connect-
ing an external SCSI-2 hard disk drive (Option 4).
18. 10 MHz Ref IN 0dBm 50W: BNC connector that allows an
external 10 MHz signal (–5 to +5 dBm) to be used as the fre-
quency reference for phase locking the source frequency.
50Wimpedance.
19. Ext Anlg In: Provides input to the A5 A/D Converter PCB.
BNC connector allows an external dc voltage to be mea-
sured by the internal analog-to-digital converter circuit.
20. Serial: Provides control for AutoCal module. Figure B-7
provides a pinout diagram.
21. Printer Out: 36-pin connector that provides a parallel in-
terface to the companion printer. Figure B-4 describes the
signal lines and shows the connector pinout.
22. Dedicated GPIB: IEEE 488 standard 24-pin connector
that allows the 37XXXC to remotely control a 2nd frequency
source, an external plotter, analyzer, or other peripheral.
Figure B-3 provides a pinout diagram.
23. IEEE 488.2 GPIB: IEEE 488 standard 24-pin connector
that provides for remotely controlling the 37XXXC from an
external computer/controller via the IEEE-488 bus (GPIB).
Figure B-3 provides a pinout diagram.
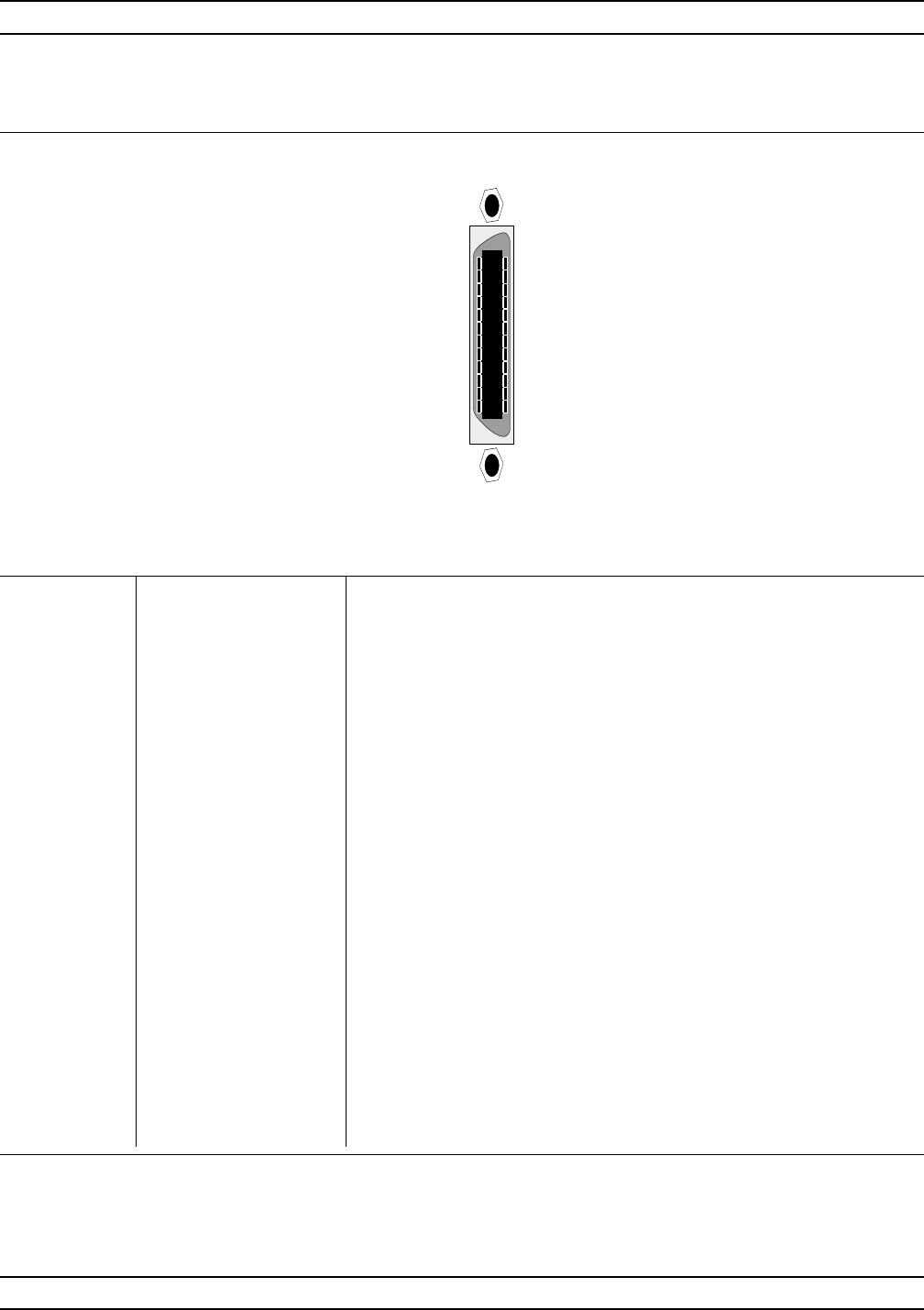
B-6 37XXXC OM
CONNECTOR PINOUT DIAGRAMS REAR PANEL CONNECTORS
12
11
10
9
8
7
6
5
4
3
2
1
24
23
22
21
20
19
18
17
16
15
14
13
Pinout Diagram
PIN NAME DESCRIPTION
1-4 DIO 1 through DIO 4 Data Input/Output. Bits are HIGH with the data is logical 0 and LOW when the data is
logical 1.
5 EOI End Or Identify. A low-true state indicates that the last byte of a multibyte message
has been placed on the line.
6 DAV Data Valid. A low-true state indicates that the talker has (1) sensed that NRFD is
LOW, (2) placed a byte of data on the bus, and (3) waited an appropriate length of
time for the data to settle.
7 NRFD Not Ready For Data. A high-true state indicates that valid data has not yet been ac-
cepted by a listener.
8 NDAC Not Data Accepted. A high-false state indicates that the current data byte has been
accepted for internal processing by a listener.
9 IFC Interface Clear. A low-true state places all bus instruments in a known state—such
as, unaddressed to talk, unaddressed to listen, and service request idle.
10 SRQ Service Request. A low-true state indicates that a bus instrument needs service from
the controller.
11 ATN Attention. A low-true state enables the controller to respond to both it’s own lis-
ten/talk address and to appropriate interface messages — such as, device clear and
serial poll.
12 Shield Chassis ground.
13-16 DIO 5 through DIO 8 Data Input/Output. Bits are high with the data is logical 0 and LOW when the data is
logical 1.
17 REN Remote Enable. A low-true state enables bus instruments to be operated remotely,
when addressed.
18-
24 GND Logic ground.
Figure B-3. Pinout Diagram, GPIB and Dedicated GPIB Connectors
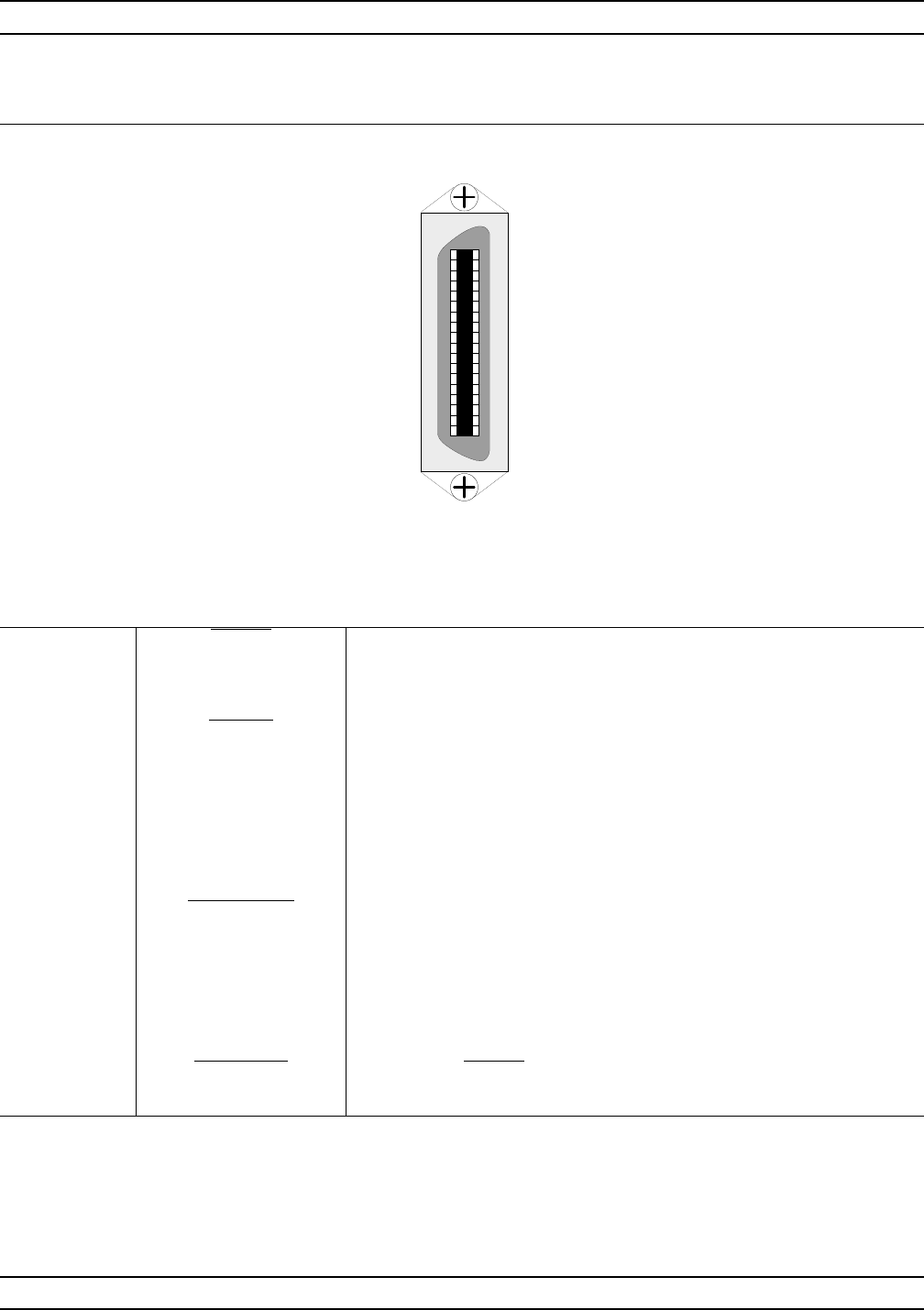
37XXXC OM B-7
REAR PANEL CONNECTORS CONNECTOR PINOUT DIAGRAMS
! $
! #
! "
! !
!
!
!
'
&
%
$
#
"
!
'
&
%
$
#
"
!
'
&
%
$
#
"
!
Pinout Diagram
PIN NAME DESCRIPTION
1 STROBE Printer Strobe. A low-true pulse that tells the printer valid data has been placed on
the bus.
2-9 DATA1 through DATA8 Data Lines. Bits are HIGH when the data is logical 1 and LOW when the data is a
logical 0.
10 ACK NLG Printer Acknowledgement. A low-true (it varies from printer to printer) pulse sent
back by the printer to acknowledge that the data has been accepted and the printer
is ready to accept more data.
11 BUSY Printer Busy. High-true level sent by the printer to indicate that it is not available.
This line is HIGH at the following times: (1) During data entry. (2) While printing. (3)
When off-line. (4) When a printer-error has been signaled.
12 PE Printer Error. High-true level sent by the printer to indicate that it is out of paper.
13 SLCT Select. A high-true logic level.
14 AUTO FEED XT Automatic Paper Feed. A low-true level that tells the printer to feed the paper auto-
matically.
15 NC No Connection.
16 OV Logic GND Level.
17 CHASSIS GND Chassis ground, which is isolated from logic ground.
18 NC No Connection.
19 STROBE RTN Return line for STROBE signal.
20-27 DATA RTN Return lines for DATA1 through DATA8 lines.
Figure B-4. Pinout Diagram, Printer Connector (1 of 2)
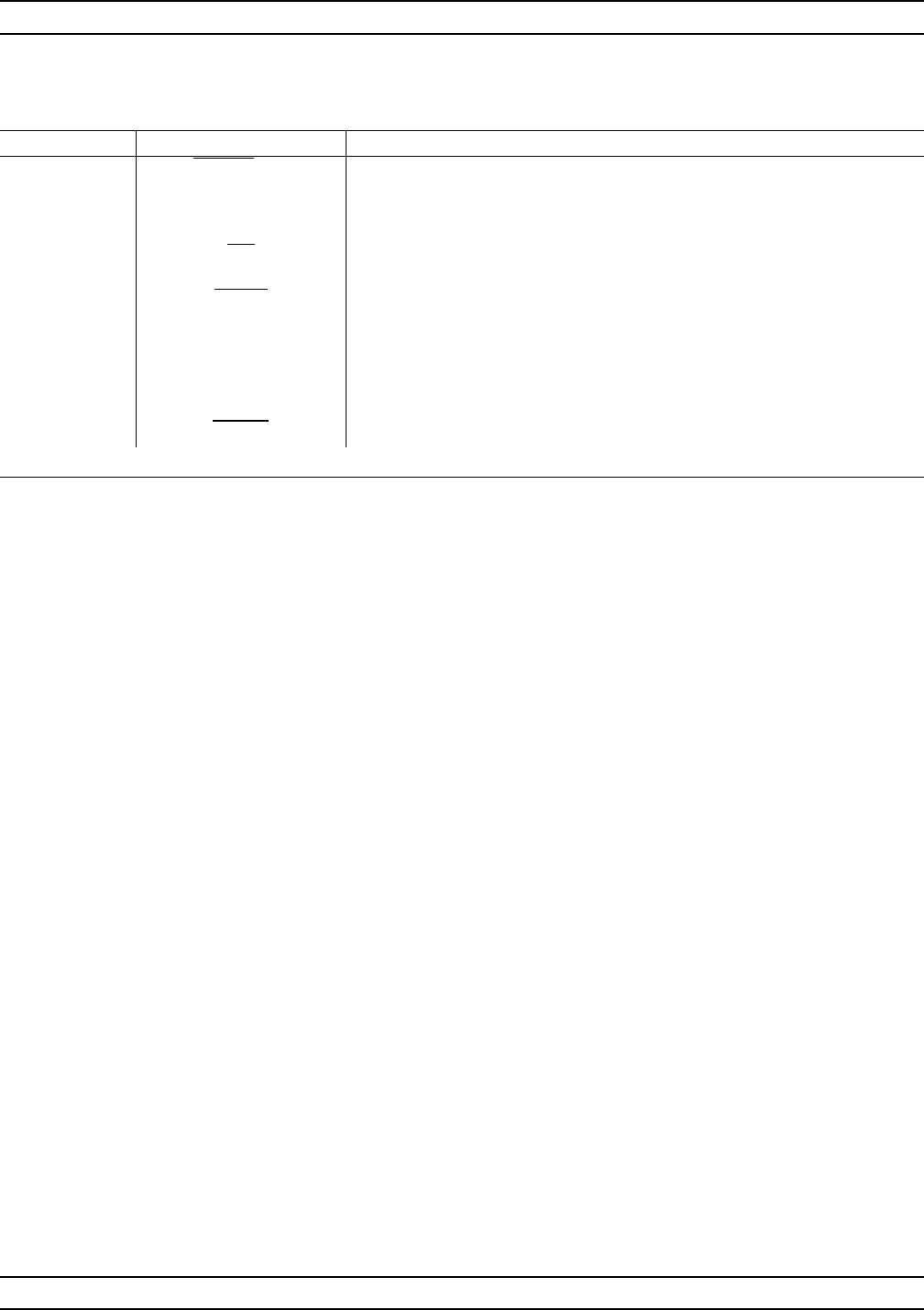
B-8 37XXXC OM
CONNECTOR PINOUT DIAGRAMS REAR PANEL CONNECTORS
PIN NAME DESCRIPTION
28 ACKNLG RTN Return line for ACKNLG signal.
29 BUSY RTN Return line for BUSY signal.
30 PE RTN Return line for PE signal.
31 INIT Printer Initial State. A low-true pulse that tells the printer to assume its initial state
and clear its print buffer.
32 ERROR Printer Error. A low-true signal that indicates the printer is (1) out of paper, (2)
off-line, or (3) in an error state.
33 GND Ground level.
34 NC No Connection.
35 +5V +5V dc level.
36 SLCT IN Printer Select Input. A low-true level that permits the printer to accept data.
Figure B-4. Pinout Diagram, Printer Connector (2 of 2)
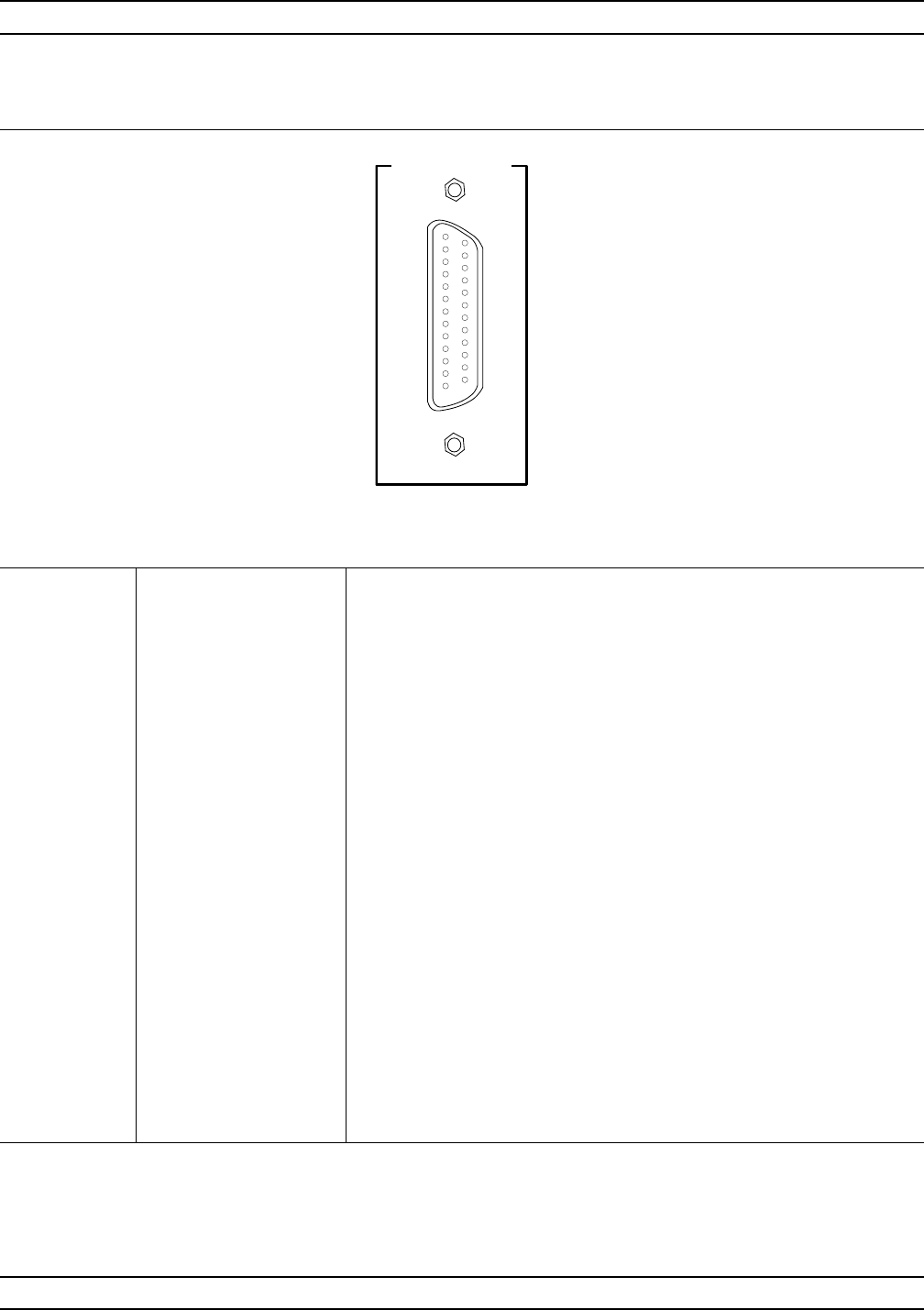
37XXXC OM B-9
REAR PANEL CONNECTORS CONNECTOR PINOUT DIAGRAMS
External I/O
1
2
3
4
5
6
7
8
9
10
11
12
13
14
15
16
17
18
19
20
21
22
23
24
25
Pinout Diagram
PIN NAME DESCRIPTION
1 Channel 1 Limit Signal indicating results of Channel 1 limit testing. User selectable TTL-high = Fail or
TTL-low = Fail.
2 Limit 1 Rtn Return for the Channel 1 limit signal
3 Channel 2 Limit Signal indicating results of Channel 2 limit testing. User selectable TTL-high = Fail or
TTL-low = Fail.
4 Limit 2 Rtn Return for the Channel 1 limit signal
5 Channel 3 Limit Signal indicating results of Channel 3 limit testing. User selectable TTL-high = Fail or
TTL-low = Fail.
6 Limit 3 Rtn Return for the Channel 3 limit signal
7 Channel 4Limit Signal indicating results of Channel 4 limit testing. User selectable TTL-high = Fail or
TTL-low = Fail. Pins 7 is also used as the TTL handshake for external trigger mode.
TTL-high = VNA has compeleted a measurement and is ready for another trigger
8 Limit 4 Rtn Return for the Channel 4 limit signal or VNA measurement complete signal. Pin 8 is
also the return for pin 7.
9 Limit Fail Signal indicating failure in any channel limit testing. User selectable TTL-high = Fail
or TTL-low = Fail.
10 Spare
11 Spare
12 Limit Fail Rtn Return for the Limit Fail signal
13 Spare
14 Spare
15 Ext Dig In Allows an external signal to sync the 37XXXC measurements; TTL level
16 Dig In Rtn Return for External Dig In signal
Figure B-5. Pinout Diagram, External I/O Connector (1 of 2)
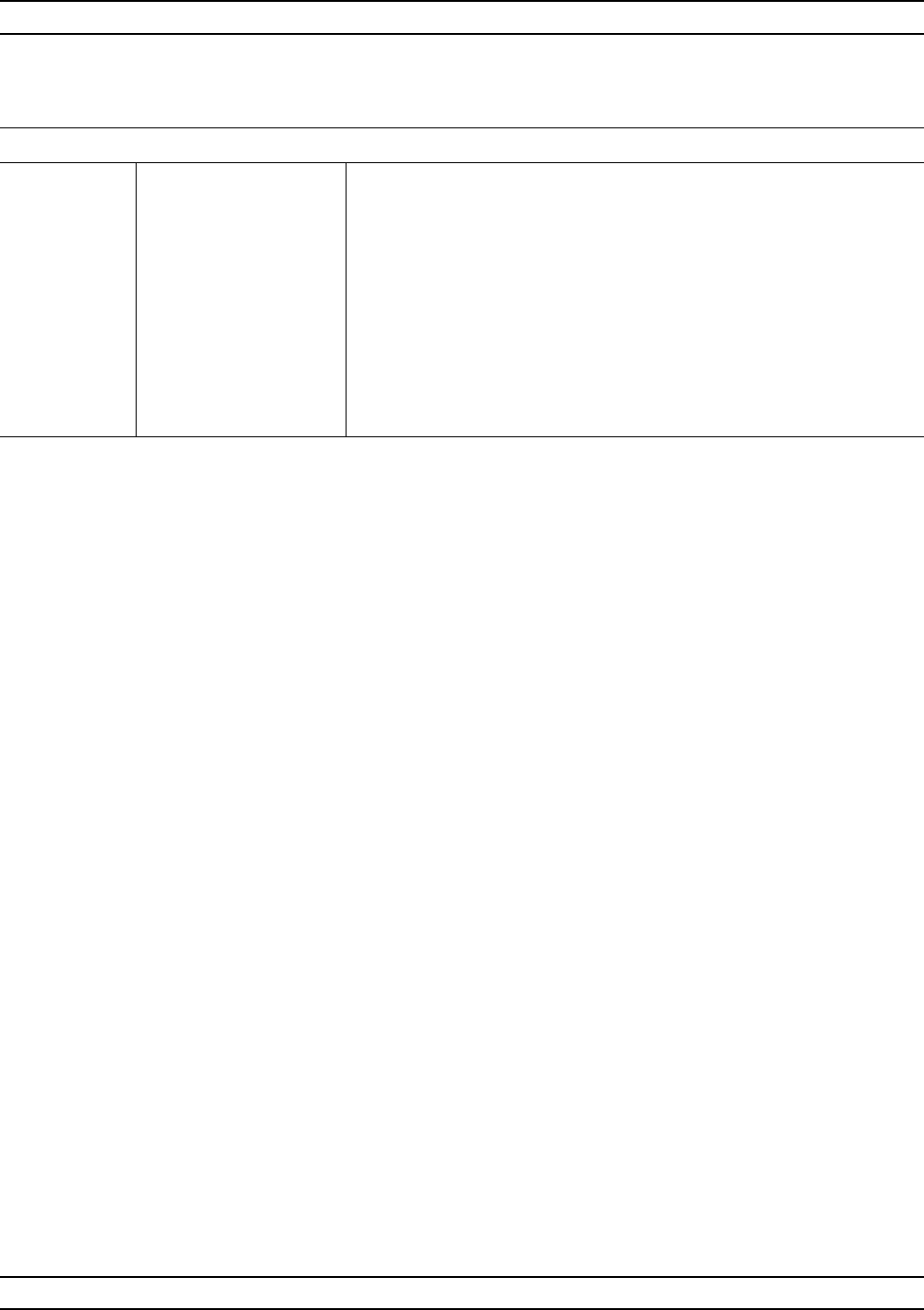
B-10 37XXXC OM
CONNECTOR PINOUT DIAGRAMS REAR PANEL CONNECTORS
PIN NAME DESCRIPTION
17 Ext Ana Out Provides an up-to-±10V signal for use in driving an external plotter or antenna (CW
draw).
18 Ana Out Rtn Return for Ext Ana Out signal
19 Spare
20 Spare
21 Spare
22 Gnd 1 Return for Port 1 Bias.
23 Port 1 Bias Provides for applying an external bias to the active device connected to test port 1.
24 Port 2 Bias Provides for applying an external bias to the active device connected to test port 2.
25 Gnd 2 Return for Port 2 Bias.
Figure B-5. Pinout Diagram, External I/O Connector (2 of 2)
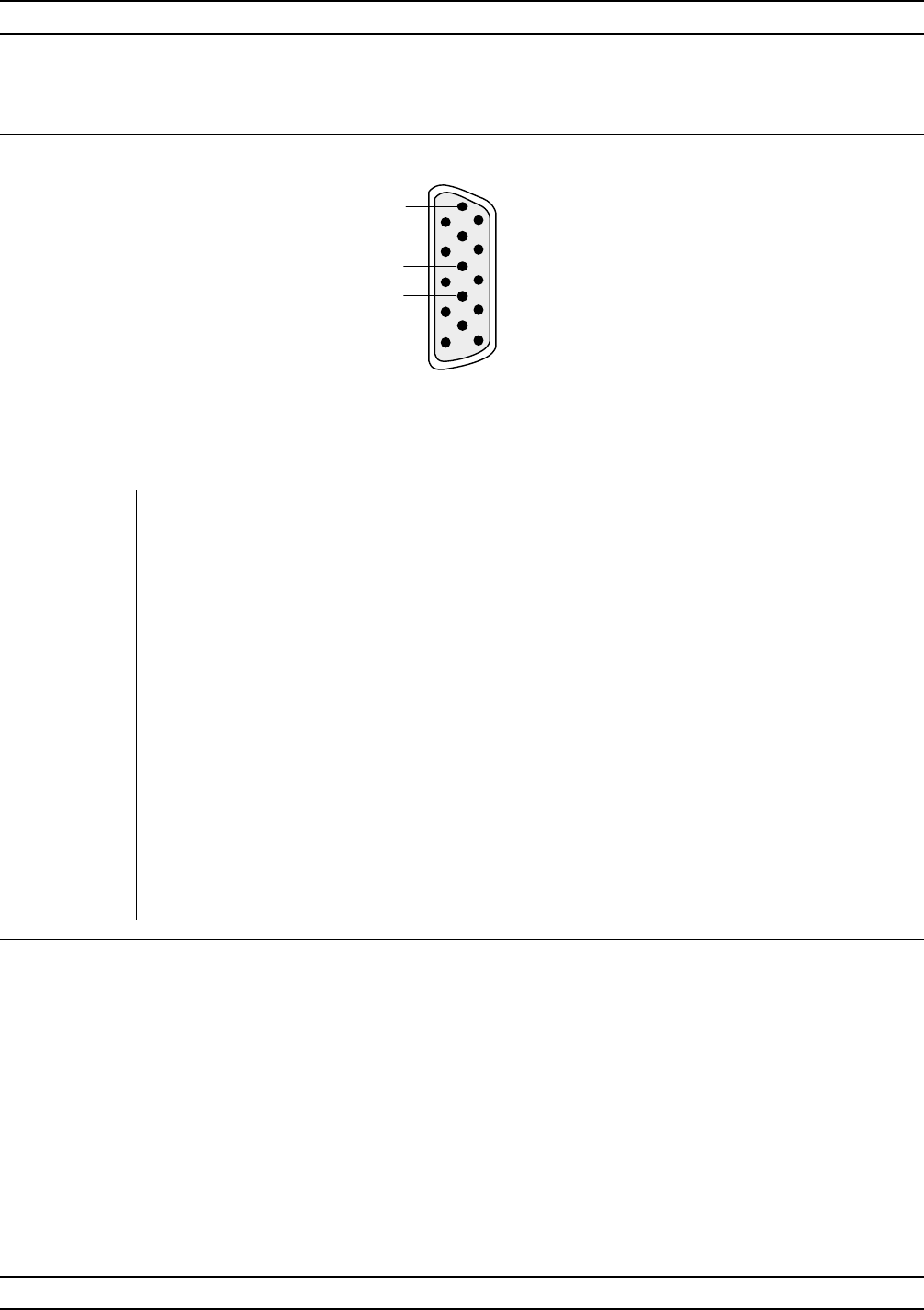
37XXXC OM B-11
REAR PANEL CONNECTORS CONNECTOR PINOUT DIAGRAMS
10
9
8
7
6
15
14
13
12
11
5
4
3
2
1
PIN NAME DESCRIPTION
1 Red Red signal
2 Green Green signal
3 Blue Blue signal
4 Not Used
5 Not Used
6 Red Return Red return
7 Green Return Green return
8 Blue Return Blue return
9 Not Used
10 Digital Ground Sync ground
11 Not Used
12 Not Used
13 Hsync Horizontal sync
14 Vsync Vertical sync
15 Not Used
Figure B-6. Pinout Diagram, VGA IN/OUT Connector
Pinout Diagram
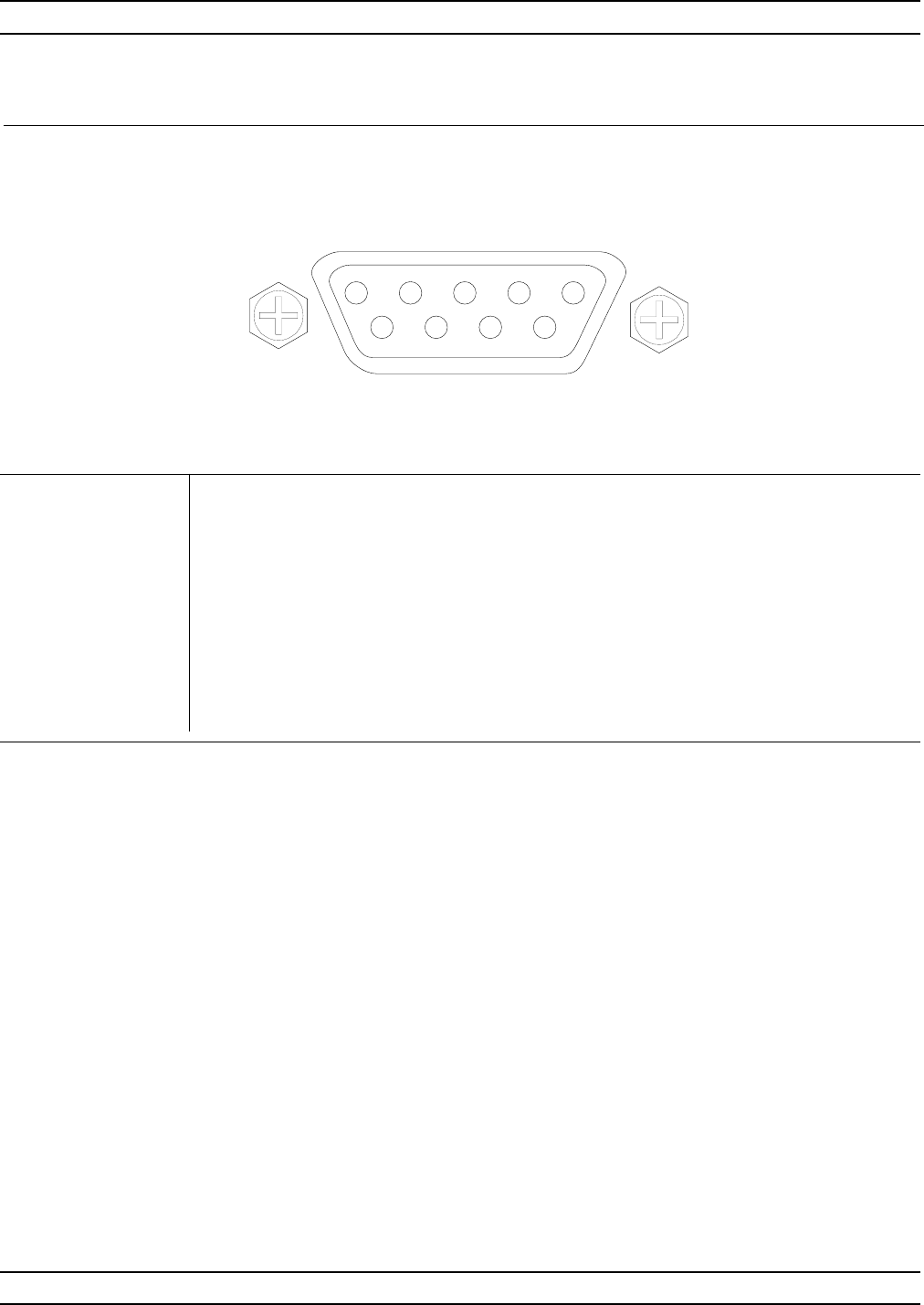
B-12 37XXXC OM
CONNECTOR PINOUT DIAGRAMS REAR PANEL CONNECTORS
1
6
5
9
PIN DESCRIPTION
1CD
2 RXD
3 TXD
4 DTR
5 N.C.
6 N.C.
7RTS
8 CTS
9 N.C.
Figure B-7. Pinout Diagram, Serial Port Connector
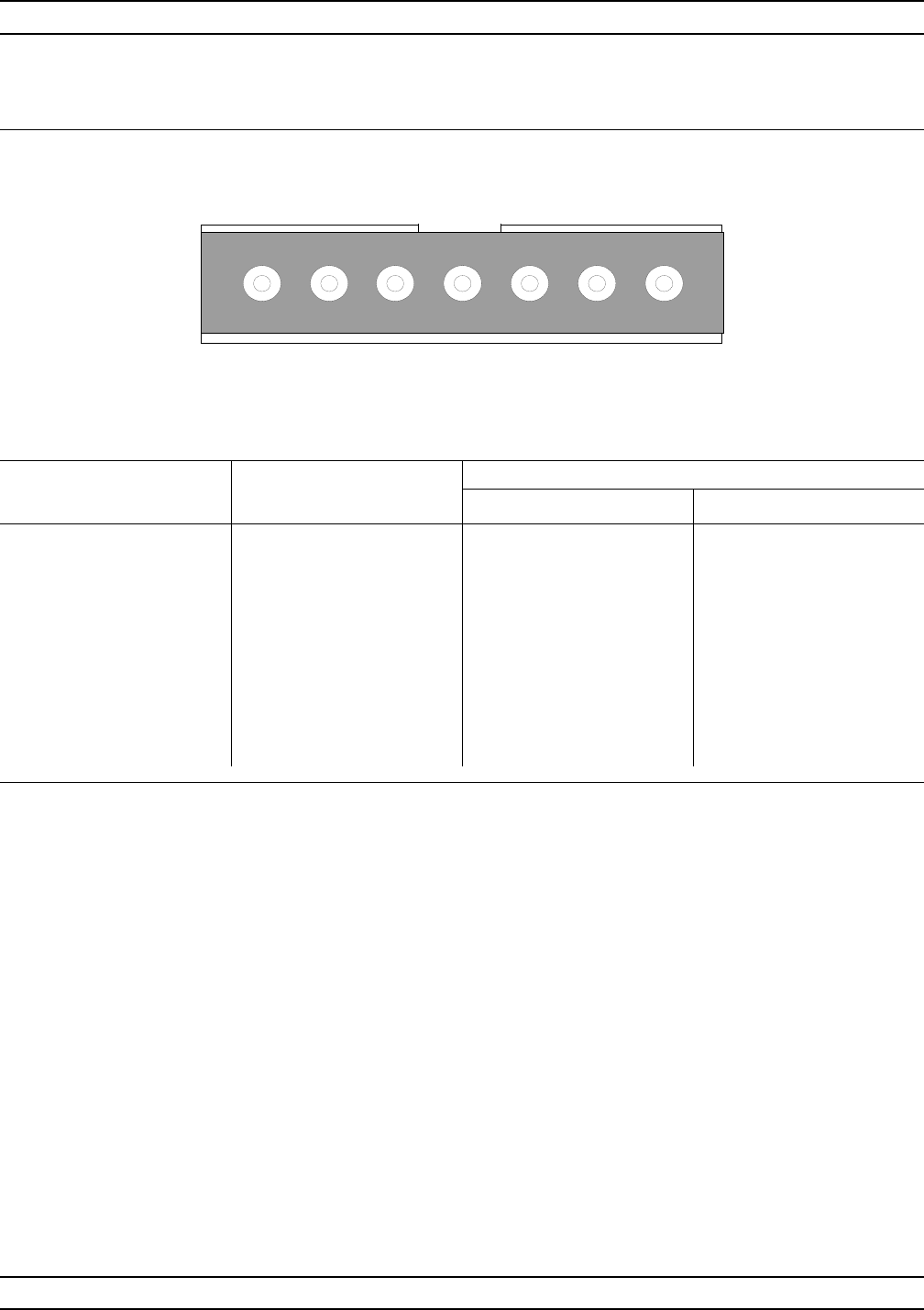
37XXXC OM B-13
REAR PANEL CONNECTORS CONNECTOR PINOUT DIAGRAMS
PIN CONTROL CONTROL VOLTAGE
FORWARD REVERSE
1 NCNCNC
2 Switch, Fwd Direction –13.7 +4.5
3 Switch, Rev Direction +4.5 –13.7
4 Switch, Fwd Direction 0 +4.0
5 Switch, Rev Direction +4.0 0
6 NCNCNC
7 Bias –4.9 –4.9
Figure B-8. Pinout Diagram, Transfer Switch
1
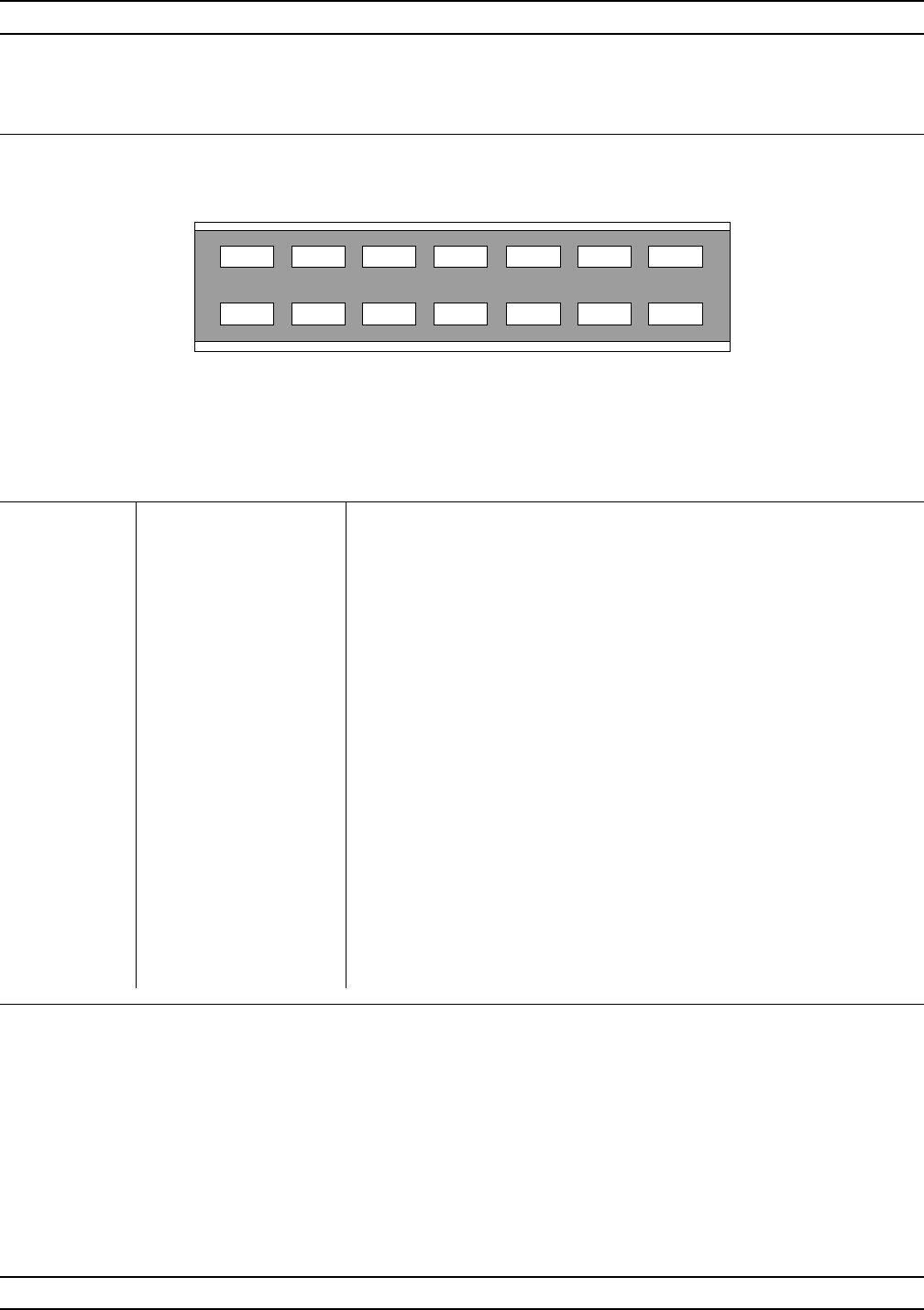
B-14 37XXXC OM
CONNECTOR PINOUT DIAGRAMS REAR PANEL CONNECTORS
PIN NAME DESCRIPTION
1 Not Used
2 10dBIN Switch 1, Position 2 (On)
3 40dBOUT Switch 3, Position 2 (Off)
4 Not Used
5 20dBIN Switch 2, Position 2 (On)
6 +24 Vdc +24 Vdc
7 Not Used
8 Not Used
9 40dBIN Switch 3, Position 2 (On)
10 Not Used
11 20 dB OUT Switch 2, Position 1 (Off)
12 Not Used
13 10 dB OUT Switch 1, Position 1 (Off)
14 Not Used
Figure B-9. Pinout Diagram, Port 1 Source and Port 2 Test Connectors
1
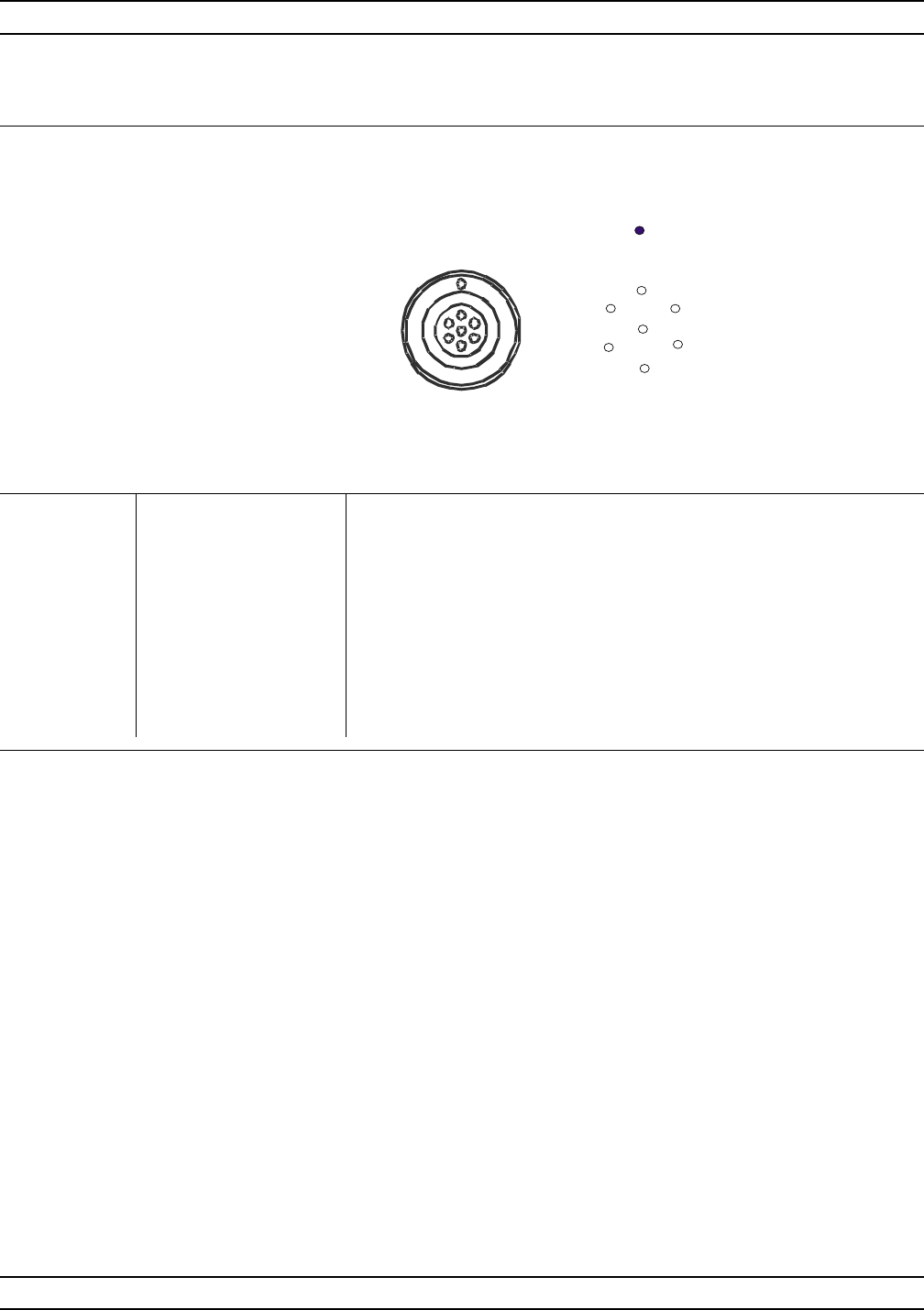
37XXXC OM B-15/B-16
REAR PANEL CONNECTORS CONNECTOR PINOUT DIAGRAMS
PIN NAME DESCRIPTION
1 Ground Ground return
2 N/C No connection
3 H Coax/L mm HIGH <65 GHz, LOW >65 GHz
4 N/C No connection
5 L Reverse LOW reverse sweep, HIGH forward sweep
6 N/C No connection
7 L Forward LOW forward sweep, HIGH reverse sweep
Figure B-10. Pinout Diagram, Test Set Control Out Connector (Option 12)
Test Set
Control Out
1
2
3
4
5
6
7
Appendix C
Performance Specifications
This appendix contains a copy of the 37100C/37200C/37300C Vector
Network Analyzers Technical Data Sheet, Anritsu Part Number
11410-00247.
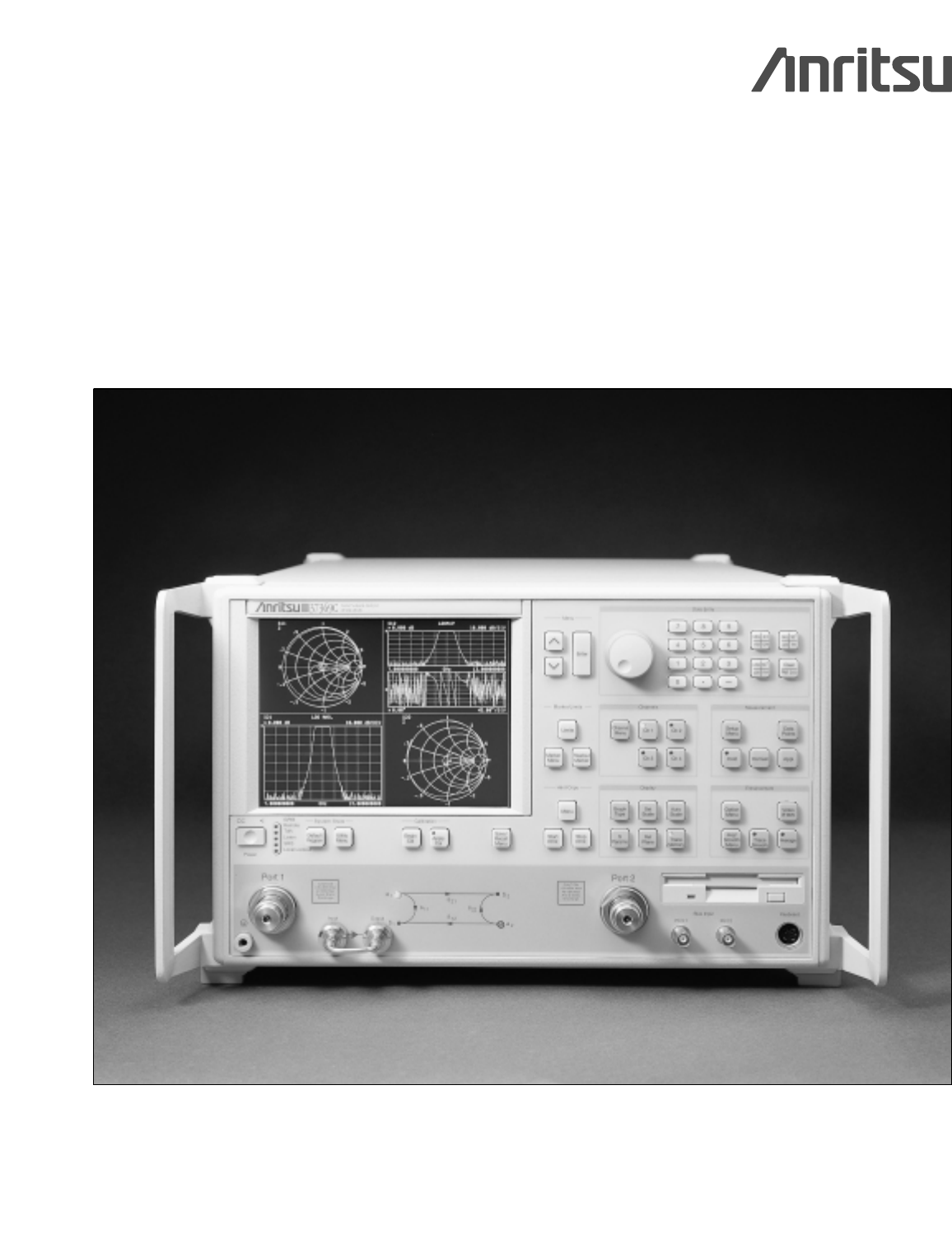
37100C/37200C/37300C
Vector Network Analyzers
Technical Data Sheet
Vector Network Analysis up to 65 GHz
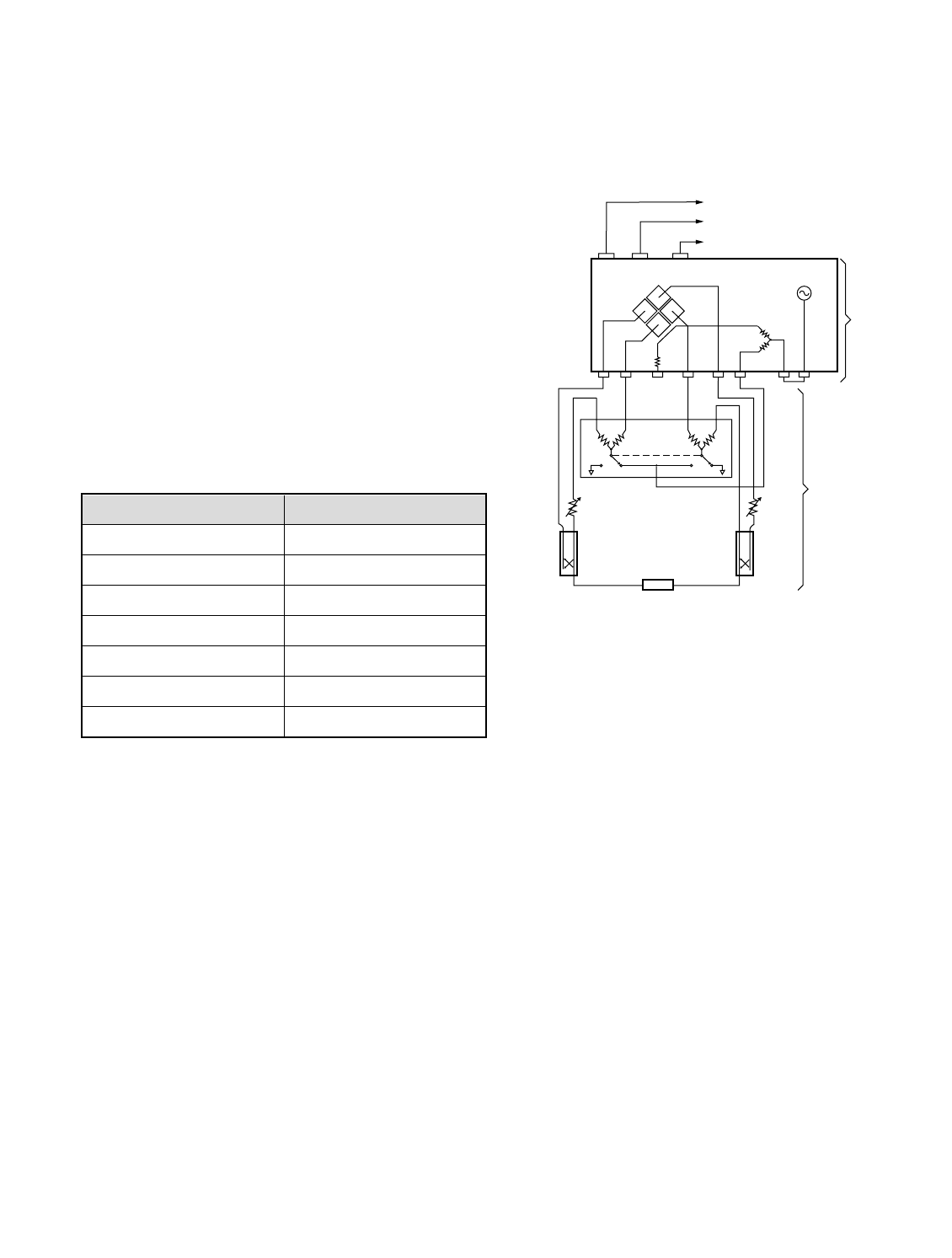
SYSTEM DESCRIPTION
The Lightning 37200C/37300C Vector Network Analyzers (VNAs)
are high performance tools designed to make fast and accurate S-
parameter measurements of active and passive devices across the
22.5 MHz to 65 GHz range.These network analyzers integrate a
synthesized source, S-parameter test set and tuned receiver into a
single compact package that is ideal for bench-top testing.
The Lightning 37100C VNAs are configured as Direct-Access
Receivers for antenna, frequency conversion, and multiple output
device measurements. These network analyzers consist of
a synthesized source and tuned receiver in a single compact unit,
with direct access provided to all four receiver samplers via the front
panel. The 37100C offers the ultimate flexibility to meet most
receiver measurement needs, while maintaining the ability to
measure all four S-parameters with the addition of a reflectometer
setup at the front end of the receiver.
Specifications for the 37100C/37200C/37300C models are detailed
on the following pages.
High throughput measurements are achieved in each model
through the use of fast, 12-term error corrected sweeps, fast GPIB
data transfers and an intuitive user interface. All measurement
results are displayed on a large LCD color display or on an external
VGA monitor.
For maximum productivity, the VNAs include as standard features:
✓Fast Sweeping Synthesized Source
✓Auto Reversing Test Set (37200C/37300C models only)
✓Solid-State Transfer Switch (37200C/37300C models only)
✓Four Independent Display Channels
✓Multiple Source Control of Two External Sources
✓Four Channel Receiver
✓Internal Hard and Floppy Disk Drives
✓LRL/LRM Calibration
✓Adapter Removal Calibrations
✓Fast Measurement Throughput via GPIB
✓Built-In AutoCal®Control
Each of the network analyzers is designed for easy upgradeability.
Any version of the 37000C VNA can be upgraded to accommodate
new capabilities or additional frequency ranges by ordering the
appropriate upgrade kit. 37100C to 37200C or 37200C to 37300C
upgrades are also supported.
SYSTEM PERFORMANCE
Dynamic Range:
The tables on the next page provide two definitions of dynamic
range:
"Receiver Dynamic Range" is defined as the difference between the
maximum signal level at Port 2 (or at any sampler input: a1, a2, b1,
or b2for a 37100C) for 0.1 dB compression and the noise floor.
"System Dynamic Range" is defined as the difference between the
power incident on Port 2 in a through line connection and the noise
floor.
In preparing the tables, 10 Hz IF bandwidth and 512 averages were
used in calibration and measurement.
High Level Noise (typical): <0.04 dB and <0.5 degrees peak-
to-peak variation in a 1 kHz IF bandwidth up to 20 GHz,
<0.08 dB and <1.0 degrees peak-to-peak variation up to 40 GHz,
<0.25 dB and <2.5 degrees peak-to-peak variation up to 65 GHz.
Model Numbers
2
A Reflectometer test set is available as a special option for the 37100C.
It contains the transfer switch, both attenuators and couplers. It also
offers two bias tees and a front panel amplifier loop for active device
testing. As compared to a 37300C VNA, the output power and hence the
dynamic range are degraded by 10 dB typically.
to Transfer Switch
to Test Attenuator
to Source Attenuator
Internal
Source
Out*
RF
In
37100C
Direct-
Access
Receiver
Configuration
*Not provided
*on Opt. 13,
*Delete Source option.
Source
Lock
Out
b1b2
a2
a1RF
Out
Splitter
6 dB
Samplers Source*
Transfer
Switch
Drive
Test
Attenuator
Drive
Source
Attenuator
Drive
3 dB
Transfer Switch
DUT
Typical
Reflectometer
Setup
Source
Attenuator Test
Attenuator
Frequency Range
37225C, 37325C 40 MHz to 13.5 GHz
37147C 22.5 MHz to 20 GHz
37247C, 37347C 40 MHz to 20 GHz
37169C 22.5 MHz to 40 GHz
37269C, 37369C 40 MHz to 40 GHz
37277C, 37377C 40 MHz to 50 GHz
37297C, 37397C 40 MHz to 65 GHz
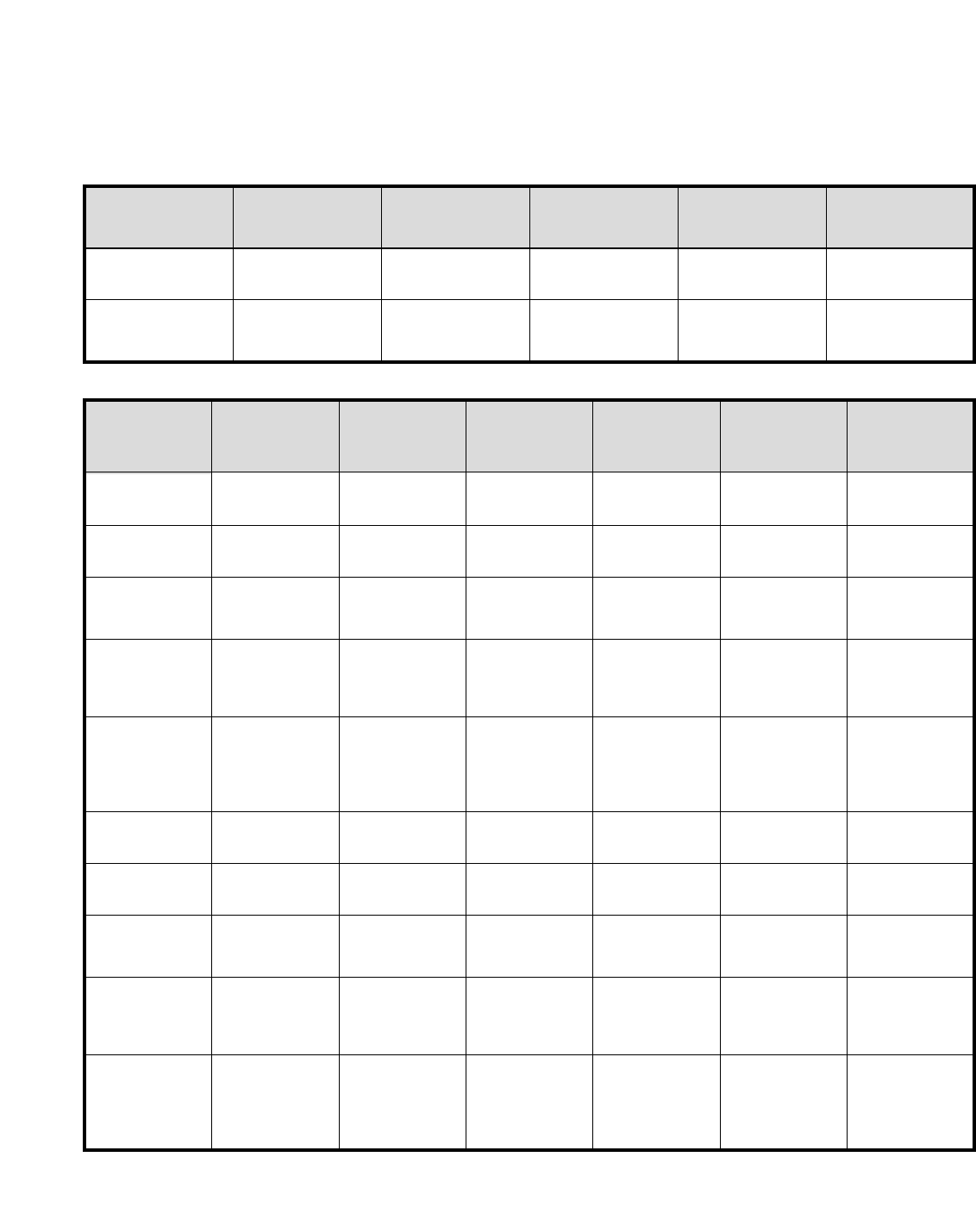
Dynamic Range (37100C)
Dynamic Range (37200C/37300C)
37369C
37347C
37377C
77
110
95
88
85
75
3
Model Numbers
Frequency (GHz)
37147C
0.0225
2
20
37169C
0.0225
2
20
40
-18
Model Frequency
(GHz)
37147C 0.0225
2
20
37169C
0.0225
2
20
40
-18
-12
-12
-15
-18
-12
-12
Maximum Signal
Into ax,b
x
(dBm)
-122
-106
-103
-100
-122
-106
-103
Noise Floor
(dBm)
104
94
91
85
104
94
91
Receiver Dynamic
Range (dB)
10
8
3
-3
10
8
5
Source Power
(dBm,Typical)
Model Frequency
(GHz)
Max. Signal
Into
Port 2 (dBm)
Noise Floor
(dBm) Receiver Dynamic
Range (dB)
37225C 0.04
2
13.5
+20
+3
+3
-70
-98
-98
90
101
101
Port 1 Power
(dBm,
Typical)
0
0
0
0
0
0
0
0
-5
-15
System Dynamic
Range (dB)*
70
98
98
70
98
96
70
98
90
78
37247C 0.04
2
20
+20
+3
+3
-70
-98
-96
90
101
99
37269C
0.04
2
20
40
+20
+3
+3
+3
-70
-98
-95
-93
90
101
98
96
0
+5
-2
-7
-2
77
110
95
88
85
37277C
0.04
2
20
40
50
+20
+3
+3
+3
+3
-77
-105
-97
-95
-87
97
108
100
98
90
0
+5
-2
-7
-2
-2
37397C
+30
+30
+30
+30
+30
+30
-77
-105
-97
-95
-87
-77
107
135
127
125
117
107
0
+5
-2
-7
-2
-2
77
110
95
88
85
75
37297C
0.04
2
20
40
50
65
+20
+3
+3
+3
+3
+3
-77
-105
-97
-95
-87
-77
97
108
100
98
90
80
*System Dynamic Range is based on the typical Port 1 power and specified noise floor at the indicated frequency range.
37325C 0.04
2
13.5
+5
+5
+5
70
98
96
0.04
2
20
+30
+30
+30
-65
-93
-91
95
123
121
+5
+5
+5
+30
+30
+30
-65
-93
-93
95
123
123
0
+5
0
-7
70
98
90
76
0.04
2
20
40
+30
+30
+30
+30
-65
-93
-90
-83
95
123
120
113
0
+5
-2
-7
-2
77
110
95
88
85
+30
+30
+30
+30
+30
-77
-105
-97
-95
-87
107
135
127
125
117
0.04
2
20
40
50
65
0.04
2
20
40
50
70
98
98
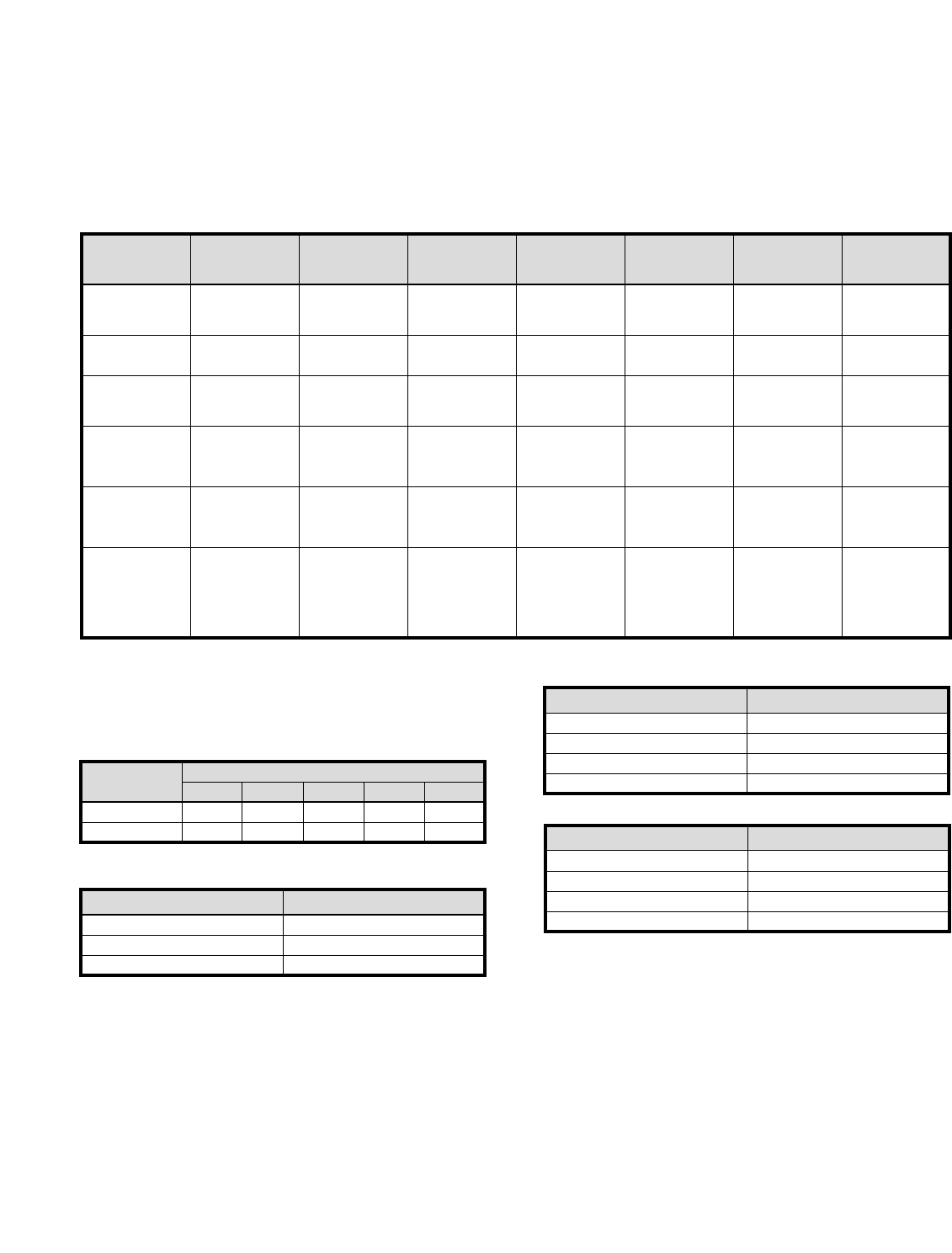
Measurement Throughput: Measurement times are based on
a single 40 MHz to 20 GHz sweep with 10 kHz IF bandwidth (no
averages) after a full 12-term calibration. Sweep times include
retrace and band switch times.
Measurement Time (ms) vs. Data Points (typical)
Measurement Time vs. Sweep Mode for 101 Data Points
(typical)
Measurement Time vs. IF BW for 101 Data Points (typical)
Measurement Time vs. Span for 101 Data Points (typical)
4
Test Port Characteristics
The specifications in the table below apply when the proper Model 34U Universal Test Port Adapters are connected, with or without phase equal
insertables, to the test set ports and calibrated with the appropriate calibration kit at 23 ± 3°C using the OSL calibration method with a sliding load
to achieve 12-term error correction (90 min. warm-up time is recommended).
Calibration
Type
Data Points
1 Port (3 Term) 3000920
2 Port (12 Term)
75
300092060
31601
350270
340
401
250
10151
IF Bandwidth Time (ms)
10 kHz 180
1 kHz 270
100 Hz 1100
10 Hz 7300
Sweep Mode Time (ms)
Linear 350
List 350
CW 190
Frequency Span Time (ms)
40 MHz to 65 GHz 900
20 GHz to 40 GHz 340
10 GHz to 11 GHz 220
40 MHz to 40 GHz 450
Connector Frequency
(GHz) Directivity
(dB)
Source
Match
(dB)
Load
Match
(dB)
Reflection
Frequency
Tracking (dB)
GPC-7 0.0225
2
18
>52
>52
>52
>44
>44
>42
>52
>52
>52
±0.003
±0.003
±0.004
GPC-7 LRL
Calibration 2
8>60
>60 >60
>60 >60
>60 ±0.001
±0.001
N-Type* 0.0225
2
18
>46
>44
>40
>36
>36
>32
>46
>44
>40
±0.004
±0.004
±0.005
3.5mm
0.0225
2
20
26.5
>44
>44
>44
>44
>40
>40
>38
>34
>44
>44
>44
>44
±0.005
±0.005
±0.006
±0.006
K
0.0225
2
20
40
>42
>42
>42
>38
>40
>40
>38
>34
>42
>42
>42
>38
±0.005
±0.005
±0.006
±0.006
V
0.04
2
20
40
50
65
>40
>40
>40
>36
>34
>34
>36
>36
>36
>32
>30
>28
>40
>40
>40
>36
>34
>34
±0.050
±0.050
±0.060
±0.060
±0.080
±0.100
Transmission
Frequency
Tracking (dB)
±0.004
±0.004
±0.012
±0.001
±0.001
±0.004
±0.004
±0.012
±0.030
±0.030
±0.050
±0.070
±0.030
±0.050
±0.070
±0.080
±0.030
±0.050
±0.070
±0.080
±0.100
±0.120
Isolation
(dB)
>105
>115
>112
>115
>112
>105
>115
>112
>105
>115
>110
>102
>105
>115
>110
>100
>105
>115
>110
>100
>90
>80
*Standard OSL calibration, sliding load not required.
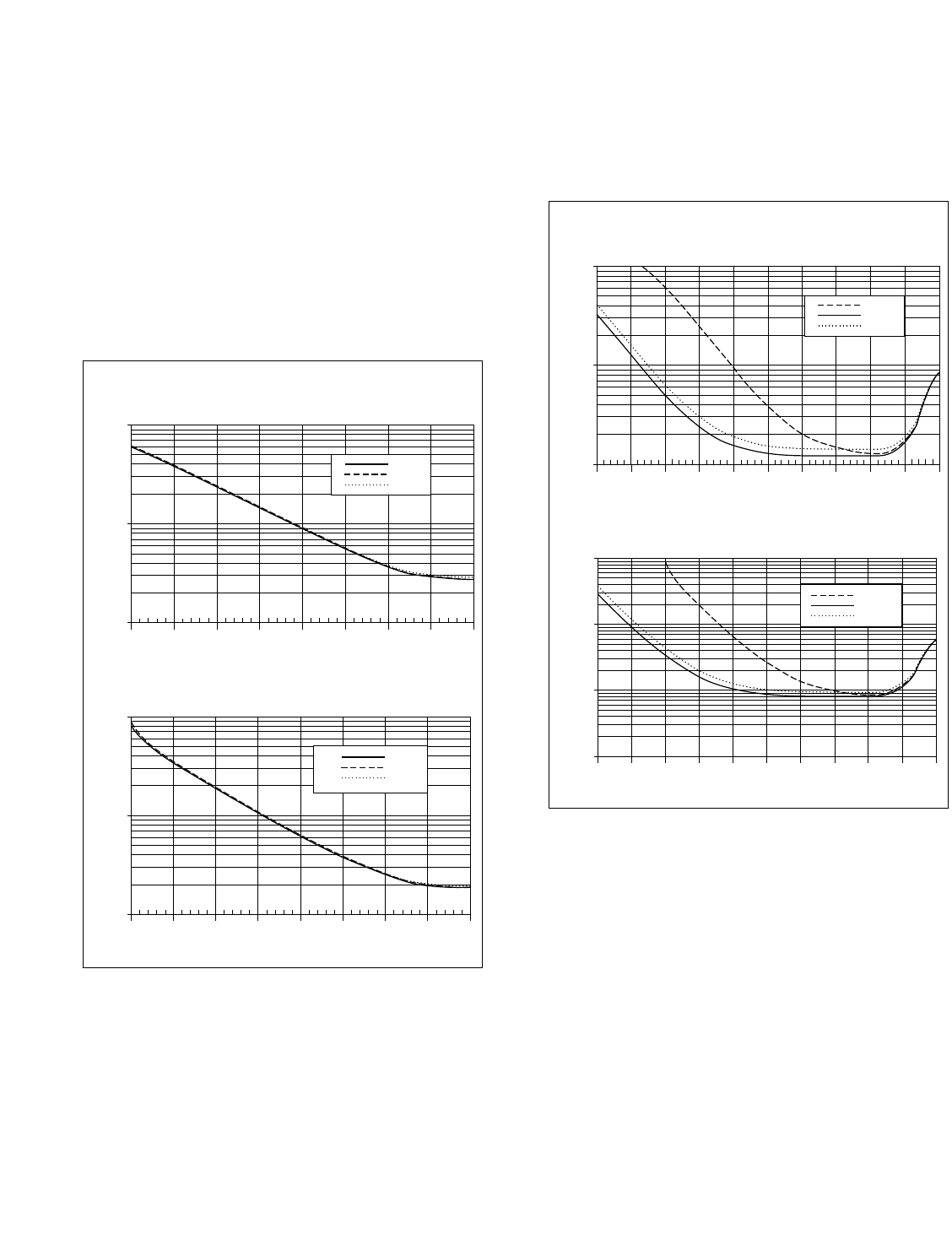
MEASUREMENT UNCERTAINTY
The following graphs give measurement uncertainty after 12-Term
vector error correction.The errors are worst case contributions of
residual directivity, load and source match, frequency response,
isolation, network analyzer dynamic accuracy, and connector
repeatability. In preparing the following graphs, 10 Hz IF bandwidth
and averaging of 512 points were used. Changes in the IF
bandwidth or averaging can result in variations at low levels.
Models 37x47C Series (K-Connectors)
Reflection Measurements:
Models 37x47C Series (K-Connectors)
Transmission Measurements:
Device S21 (dB)
Uncertainty (dB)
Transmission Magnitude Uncertainty
37x47C/3652/Transmission Only
10
1
.1
-70 -60 -50 -40 -30 -20 -10 0 10-80-90
40 MHz
2 GHz
20 GHz
40 MHz
2 GHz
20 GHz
Transmission Phase Uncertainty
37x47C/3652/Transmission Only
Uncertainty (Degrees)
100
10
1
.1
Device S21 (dB)
-90 -80 -70 -60 -50 -40 -30 -20 -10 0 10
Reflection Magnitude Uncertainty
37x47C/3652/Reflection Only
Uncertainty (dB)
10
1
.1
-40 -35 -30 -25 -20 -15 -10 -5 0
2 GHz
40 MHz
20 GHz
Reflection Phase Uncertainty
37x47C/3652/Reflection Only
Device S11 (dB)
Device S11 (dB)
Uncertainty (Degrees)
100
10
1
-40 -35 -30 -25 -20 -15 -10 -5 0
2 GHz
40 MHz
20 GHz
5
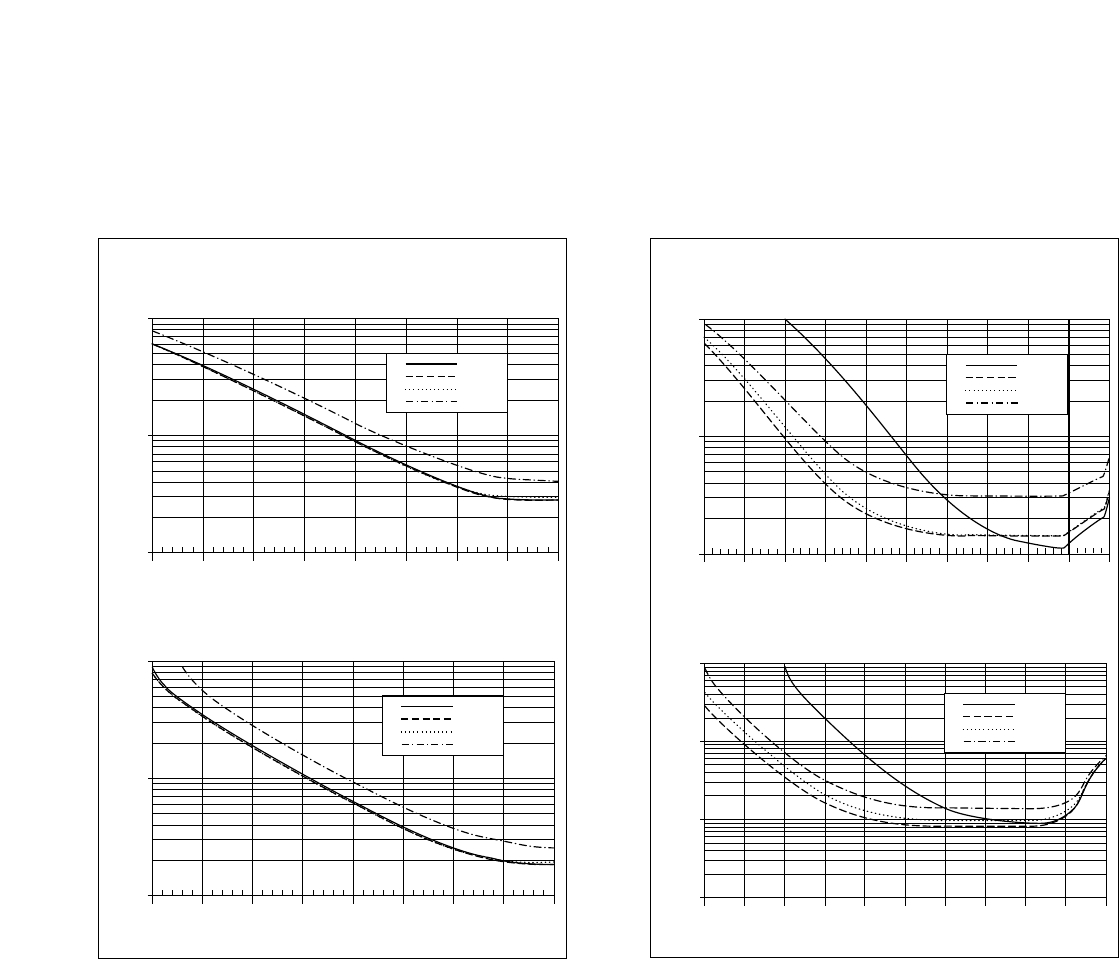
Models 37x69C Series (K-Connectors)
Reflection Measurements:
Models 37x69C Series (K-Connectors)
Transmission Measurements:
Device S21 (dB)
Uncertainty (dB)
Transmission Magnitude Uncertainty
37x69C/3652/Transmission Only
10
1
.1
-70 -60 -50 -40 -30 -20 -10 0 10-80-90
40 MHz
2 GHz
20 GHz
40 GHz
Transmission Phase Uncertainty
37x69C/3652/Transmission Only
Uncertainty (Degrees)
100
10
1
.1
Device S21 (dB)
-90 -80 -70 -60 -50 -40 -30 -20 -10 0 10
40 MHz
2 GHz
20 GHz
40 GHz
Reflection Magnitude Uncertainty
37x69C/3652/Reflection Only
Device S11 (dB)
Uncertainty (dB)
10
1
.1
-40 -35 -30 -25 -20 -15 -10 -5 0
40 MHz
2 GHz
20 GHz
40 GHz
Reflection Phase Uncertainty
37x69C/3652/Reflection Only
Device S11 (dB)
Uncertainty (Degrees)
100
10
1
-40 -35 -30 -25 -20 -15 -10 -5 0
40 MHz
2 GHz
20 GHz
40 GHz
6
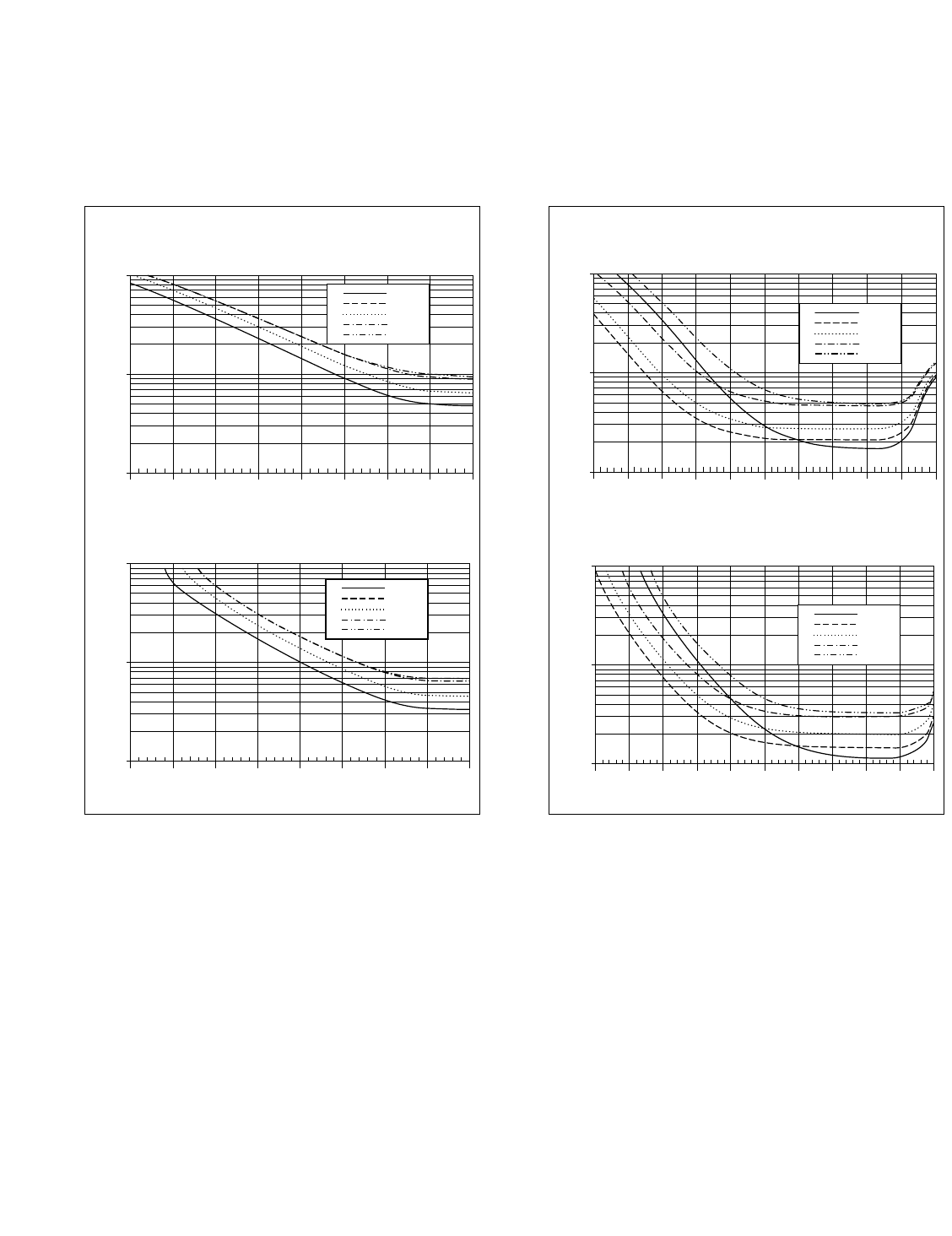
7
Model 37x77C and 37x97C (V-Connectors)
Reflection Measurements:
Model 37x77C and 37x97C (V-Connectors)
Transmission Measurements:
Device S21 (dB)
Uncertainty (dB)
Transmission Magnitude Uncertainty
37x97C/3654B/Transmission Only
10
1
.1
-70 -60 -50 -40 -30 -20 -10 0 10-80-90
40 MHz
20 GHz
40 GHz
50 GHz
65 GHz
100
10
1
Device S21 (dB)
-40-50-60-70-80-90 -30 -20 -10 0 10
Transmission Phase Uncertainty
37x97C/3654B/Transmission Only
40 MHz
20 GHz
40 GHz
50 GHz
65 GHz
Uncertainty (Degrees)
Reflection Magnitude Uncertainty
37x97C/3654B/Reflection Only
Device S11 (dB)
Uncertainty (dB)
10
1
.1
-40 -35 -30 -25 -20 -15 -10 -5 0
40 MHz
20 GHz
40 GHz
50 GHz
65 GHz
Reflection Phase Uncertainty
37x97C/3654B/Reflection Only
Device S11 (dB)
Uncertainty (Degrees)
100
10
1
-40 -35 -30 -25 -20 -15 -10 -5 0
40 MHz
20 GHz
40 GHz
50 GHz
65 GHz
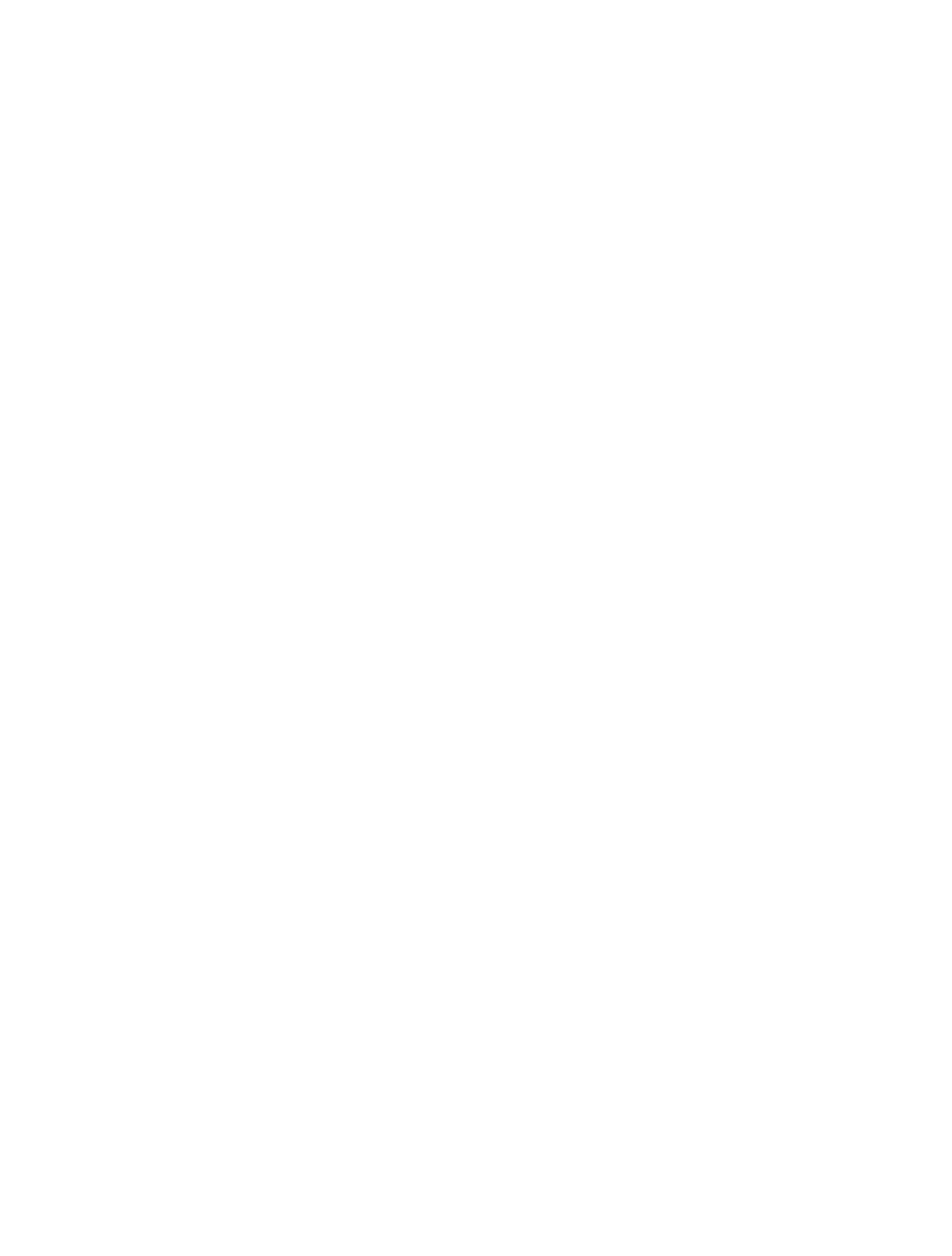
8
MEASUREMENT CAPABILITIES
Number of Channels: Four independent measurement
channels.
Parameters: S11, S21, S22, S12, or user defined combinations
of a1, a2, b1, and b2. All measurements are made without the need
to manually reverse the test device. For the 37100C models, a
reflectometer setup at the front end of the receiver is required for
S-measurements (See diagram on page 2).
Measurement Frequency Range: Frequency range of the
measurement can be narrowed within the calibration range without
recalibration. CW mode permits single frequency measurements,
also without recalibration.
Domains: Frequency Domain, CW Draw, and optional High
Speed Time (Distance) Domain.
Formats: Log Magnitude, Phase, Log Magnitude and Phase,
Smith Chart (Impedance), Smith Chart (Admittance), Linear Polar,
Log Polar, Group Delay, Linear Magnitude, Linear Magnitude and
Phase, Real, Imaginary, Real and Imaginary, SWR and Power.
Data Points: 1601 maximum. Data points can be switched to
a value of 801, 401, 201, 101 or 51 points without recalibration
(if 1601 points were used in the calibration). In addition, the system
accepts an arbitrary set of N discrete data points where
2≤N≤1601. CW mode permits selection of a single data
point without recalibration.
Reference Plane: Can be entered in time or in distance
(when the dielectric constant is entered). Automatic reference plane
feature adds the correct electrical length (delay) compensation at
the push of a button. Software compensation for the electrical
length difference between reference and test is always accurate
and stable since measurement frequencies are always synthesized.
In addition, the system compensates reference phase delay for
dispersive transmission media, such as waveguide and microstrip.
Markers: Six independent markers can be used to read out
measurement data. In delta-reference mode, any one marker can
be selected as the reference for the other five. Markers can be
directed automatically to the minimum or maximum of a data trace.
Enhanced Markers: Marker search for a level or bandwidth,
displaying an active marker for each channel, and discrete or
continuous (interpolated) markers.
Marker Sweep: Sweeps upward in frequency between any two
markers. Recalibration is not required during the marker sweep.
Limit Lines: Either single or segmented limit lines can be
displayed. Two limit lines are available for each trace.
Single Limit Readouts: Interpolation algorithm determines the
exact intersection frequencies of test data and limit lines.
Segmented Limits: A total of 20 segments (10 upper and 10
lower) can be generated per data trace. Complete segmented
traces can be offset in both frequency and amplitude.
Test Limits: Both single and segmented limits can be used for
PASS/FAIL testing. The active channel's PASS or FAIL status is
indicated on the display after each sweep. In addition, PASS/FAIL
status is output through the rear panel I/O connector as selectable
TTL levels (PASS=0V, FAIL=+5V or PASS=+5V, FAIL=0V).
Tune Mode: Tune Mode optimizes sweep speed in tuning
applications by updating forward S-parameters more frequently
than reverse ones. This mode allows the user to select the ratio of
forward sweeps to reverse sweeps after a full 12-term calibration.
The ratio of forward sweeps to reverse sweeps can be set
anywhere between 1:1 and 10,000:1.
Data Averaging: 1 to 4096 averages can be selected. A front-
panel button turns data averaging on/off, and an LED indicates
when averaging is active.
Video IF Bandwidth: Front panel button selects four levels of
video IF bandwidth: MAXIMUM (10 kHz), NORMAL (1 kHz),
REDUCED (100 Hz) and MINIMUM (10 Hz).
Trace Smoothing: Computes an average over a percentage
range of the data trace. The percentage of trace to be smoothed
can be selected from 0 to 20%. Front-panel button turns smoothing
on/off, and an LED indicates when smoothing is active.
Group Delay Aperture: Defined as the frequency span over
which the phase change is computed at a given frequency point.
The aperture can be changed without recalibration. The minimum
aperture is the frequency range divided by the number of points in
calibration and can be increased to 20% of the frequency range
without recalibration. The frequency width of the aperture and the
percent of the frequency range are displayed automatically.
Group Delay Range: The maximum delay range is limited to
measuring no more than +180°of phase change within the aperture
set by the number of frequency points. A frequency step size of 100
kHz corresponds to 10 ms.
DISPLAY CAPABILITIES
Measurement Channels: Four independent channels are
available to display any S-parameter or user defined parameter, in
any format, with up to two traces per channel for a maximum of
eight traces simultaneously. A single channel, two channels (1 and
3, or 2 and 4), or all four channels can be displayed simultaneously.
Channels 1 and 3, or channels 2 and 4 can be overlaid.
Display: Color LCD, 8.5" diagonal.
Display Colors: The color of data traces, memory, text, markers
and limit lines are all user definable.
Trace Overlay: Displays two data traces on the active channel's
graticule simultaneously.
Trace Memory: A separate memory for each channel can be
used to store measurement data for later display or subtraction,
addition, multiplication or division with current measurement data.
Scale Resolution (minimum per division):
Log Magnitude: 0.001 dB Linear Magnitude: 1 pU
Phase: 0.01°Group Delay: 0.001 ps
Time: 0.001 ms Distance: 0.1 µm
SWR: 1 pU Power: 0.01 dB
Autoscale: Automatically sets Resolution and Offset to fully
display measurement data.
Reference Position: Can be set at any graticule line.
Annotation: Type of measurement, vertical and horizontal scale
resolution, start/stop or center/span frequencies, and reference
position.
Blank Frequency Information: Blanking function removes all
references to frequencies on the display. Frequency references can
only be restored through a system reset or GPIB command.
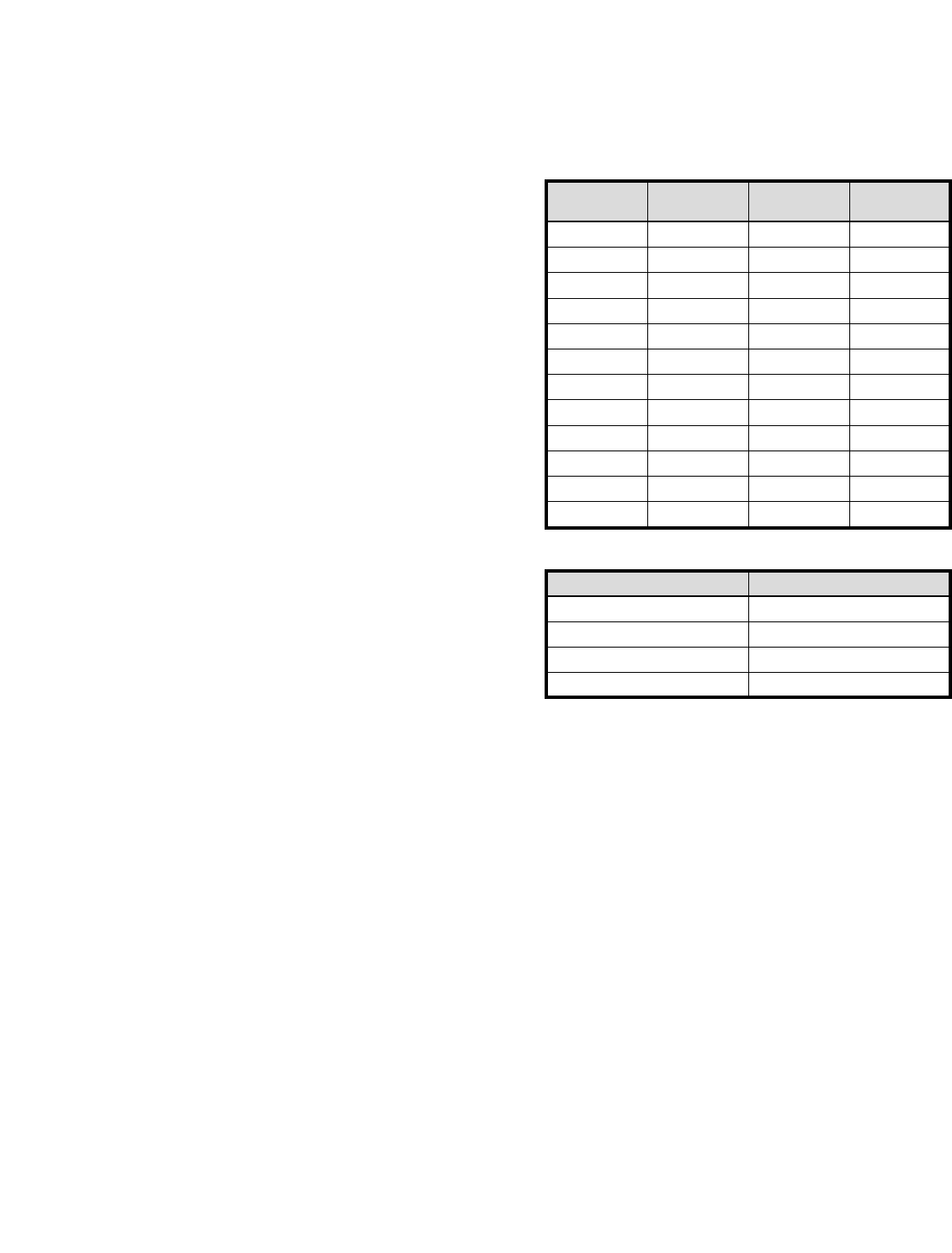
SIGNAL SOURCE CAPABILITIES
Frequency Resolution: 1 kHz (standard on all models)
Frequency Stability:
Aging: <1 x 10-9/day
Stability: <5 x 10-9 over 0˚ to +55˚C range
Source Power Level: The source power (dBm) may be set from
the front panel menu or via GPIB. Check the graphs and tables on
the following pages for the range.
In addition, on 37300C models, the port 1 power may be attenuated
in 10 dB steps, using the internal 70 dB (60 dB for 37377C and
37397C) step attenuator. Similarly, high input signals into port 2, not
exceeding 1 watt, can be attenuated up to 40 dB, using the internal
port 2 step attenuator.
Power Accuracy: ±0.5 dB at 2 GHz at default power
Power Meter Correction: The 37000C offers a user-selectable
feature that corrects for test port power variations and slope (on
Port 1) using an external power meter. Power meter correction is
available at a user-selectable power level, if it is within the power
adjustment range of the internal source. Once the test port power
has been flattened, its level may be changed within the remaining
power adjustment range of the signal source.
Set-On Receiver Mode: The 37300C can be configured to
measure the relative harmonic level of test devices with Set-On
Receiver Mode capability. The 37300C's unique phase locking
scheme allows it to operate as a tuned receiver by locking all of its
local oscillators to its internal crystal reference oscillator. Set-On
Receiver Mode capability significantly increases the versatility of
the 37300C VNA in applications that check for harmonics, intermod-
ulation products, and signals of known frequency.
Multiple Source Control Capability: Multiple Source Control
capability allows a user to independently control the frequencies of
two sources and the receiver without the need for an external
controller. The frequency ranges and output powers of the two
sources may be specified. A frequency sweep may be comprised of
up to five separate bands, each with independent source and
receiver settings, for convenient testing of frequency translation
devices such as mixers. Up to five sub-bands may be tested in one
sweep. This feature enables users to easily test mixers, up/down
converters, multipliers, and other frequency conversion devices.
Source #1: The 37000's internal source, or any of the
68XXXC, 69XXXB, 6700B or MG369XA
synthesizers
Source #2: Any of the 68XXXC, 69XXXB, 6700B or
MG369XA synthesizers
Sweep Type: Linear, CW, Marker, or N-Discrete point sweep
Spurious Response (Harmonics):
15 dBc (37277C, 37297C, 37325C, 37347C, 37369C,
37377C, 37397C) at maximum rated power
35 dBc (all other models) at maximum rated power
Spurious Response (Nonharmonics):
35 dBc at maximum rated power
Phase Noise:
>60 dBc/Hz at 10 kHz offset and 20 GHz center frequency
Power Range*
Power Flatness
*Control Power for 37x25C, and 37x47C can be set to +10 dB but is not
guaranteed. Similarly Control Power on the 37x69C, 37x77C, and 37x97C
can be set to +20 dB but not guaranteed. Complete Control Power range
also not guaranteed over temperature.
j9 Frequency Range (GHz)
9
0.0225 to 13.5 ±1.5
13.5 to 20 ±2.0
20 to 40 ±3.0
40 to 65 ±5.0
Model Rated
Power (dBm) Minimum
Power (dBm) Resolution
(dB)
37147C +5 -15 0.05
37169C -3 -23 0.05
37225C 0-20 0.05
37247C 0-20 0.05
37269C -15 -27 0.05
37277C -7 -27 0.05
37297C -7 -19 0.05
37325C +5 -90 0.05
37347C +5 -90 0.05
37369C -7 -97 0.05
37377C -7 -87 0.05
37397C -7 -79 0.05
Flatness (dB)
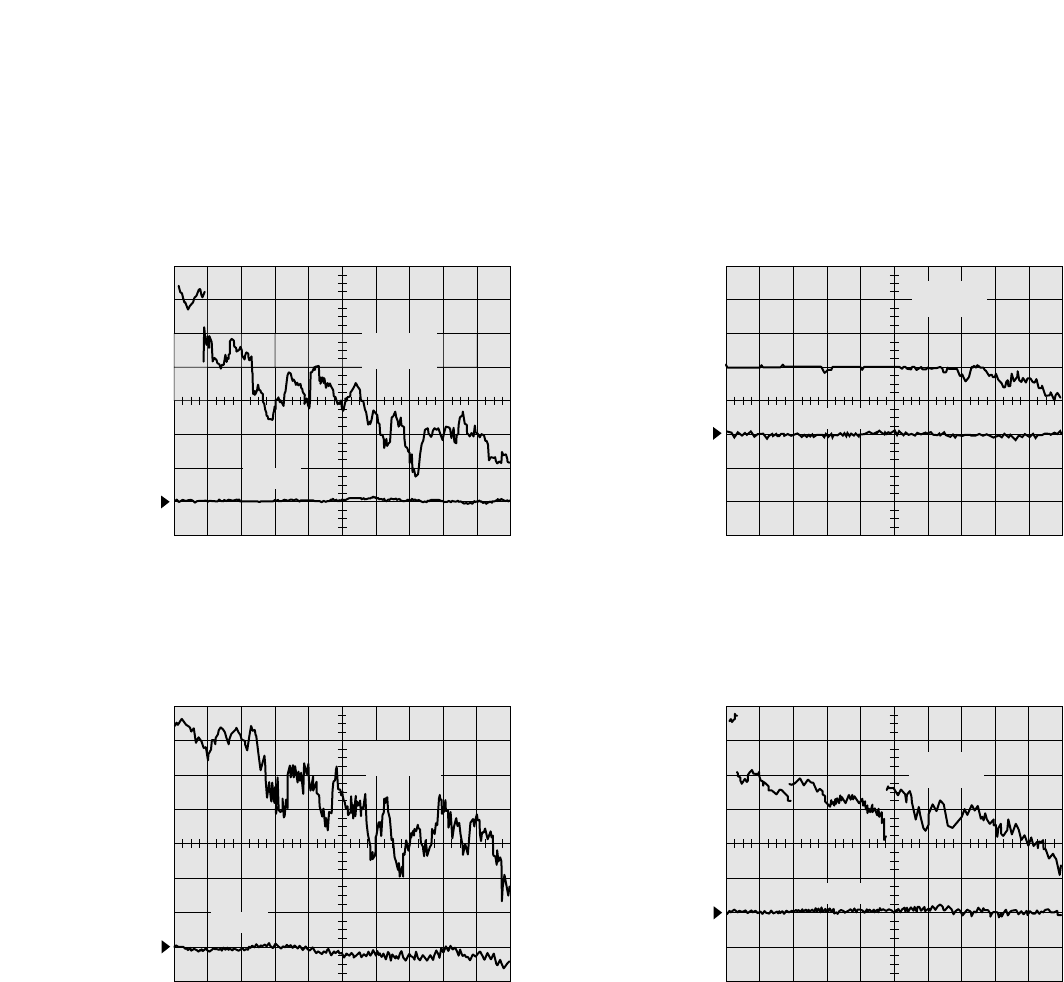
10
LOG MAG 5dB/DIV
Ref= 0dBm
40 MHz 20 GHz
Default
Available
Power
Model 37225C and 37247C Source Power
LOG MAG Ref= -15dBm 5dB/DIV
40 MHz 40 GHz
Model 37269C Source Power
Available
Power
Default
LOG MAG 2dB/DIV
Ref= 5dBm
22.5 MHz 20 GHz
Default
Available
Power
Model 37147C Source Power
LOG MAG Ref= -3dBm 2dB/DIV
22.5 MHz 40 GHz
Model 37169C Source Power
Available
Power
Default
Available Source Power
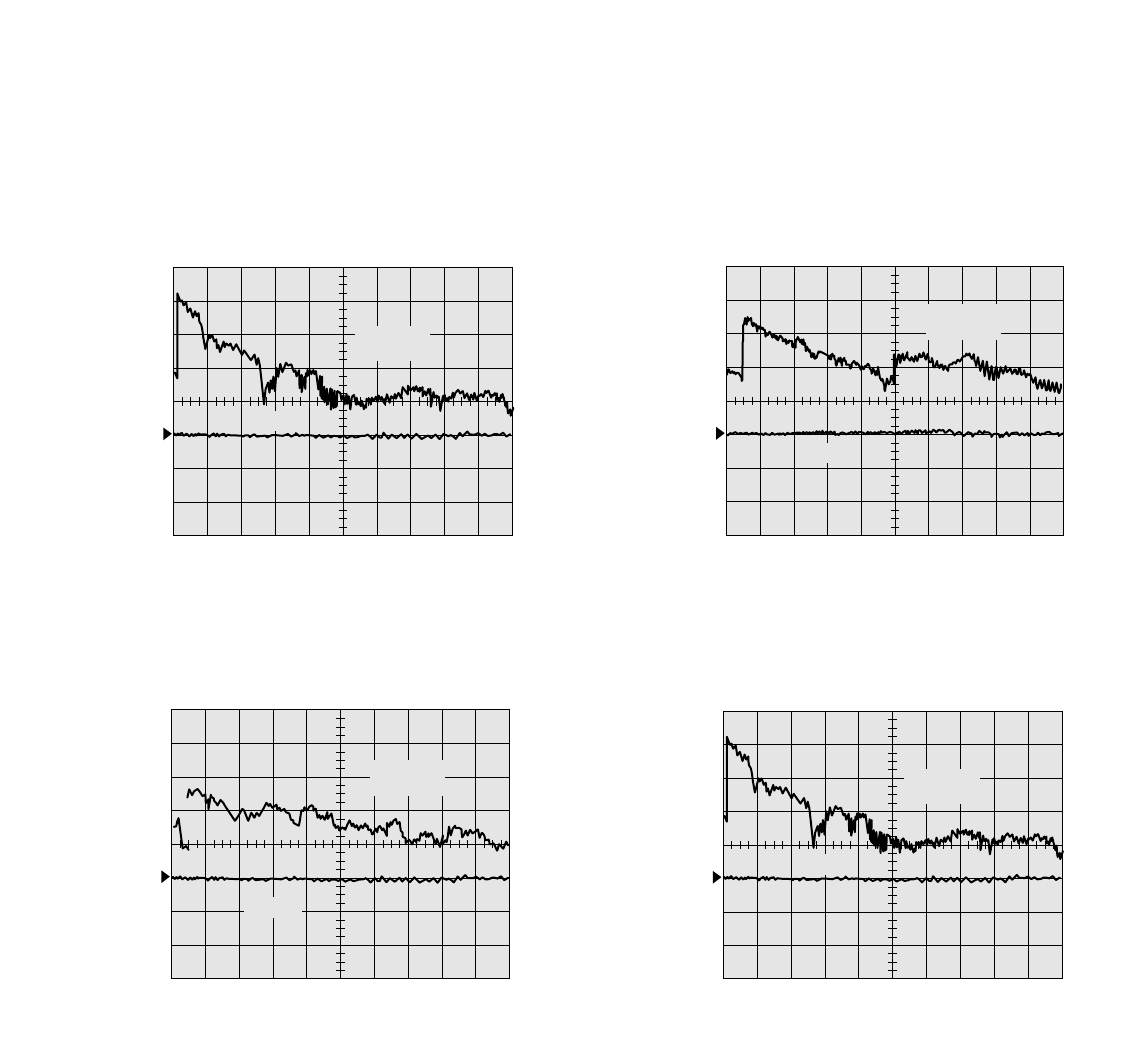
11
Model 37325C and 37347C Source Power
40 MHz 20 GHz
LOG MAG 5dB/DIV
Ref= 5dBm
Available
Power
Default
40 MHz 40 GHz
Model 37369C Source Power
LOG MAG 5dB/DIV
Ref= -7dBm
Available
Power
Default
40 MHz 65 GHz
Model 37377C and 37397C Source Power
LOG MAG 5dB/DIV
Ref= -7dBm
Available
Power
Default
Available Source Power
40 MHz 65 GHz
Model 37277C and 37297C Source Power
LOG MAG 5dB/DIV
Ref= -7dBm
Available
Power
Default
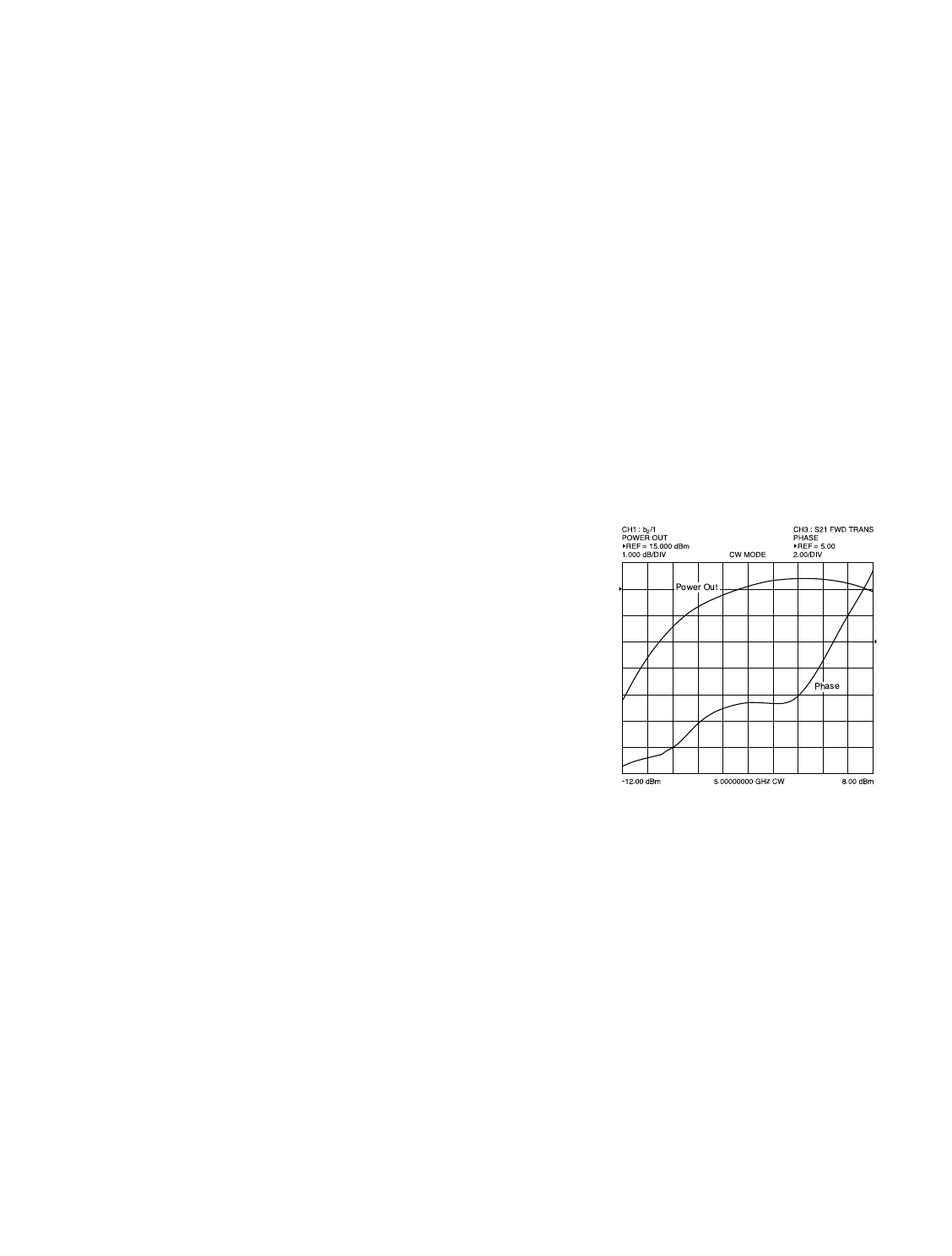
12
VECTOR ERROR CORRECTION
There are five built-in methods of calibration:
1) Open-Short-Load-Thru (OSLT): This calibration
method uses short circuits, open circuits, and terminations
(fixed or sliding).
2) Offset-Short (waveguide): This calibration method uses
short circuits and terminations.
3) LRL/LRM: The Line-Reflect-Line (LRL) or Line-Reflect-
Match (LRM) calibration uses transmission lines and a
reflective device or termination (LRM).
4) TRM: The Thru-Reflect-Match calibration uses short circuits
and fixed termination.
5) AutoCal®:This calibration method uses an automatic
calibrator module.
There are four vector error correction models available for calibration:
1) Full 12-Term
2) One Path/Two Port
3) Frequency Response
4) Reflection Only
Full 12-Term can be used for all models that automatically reverse
the test signal. The front-panel display indicates the type of
calibration stored in memory. A front-panel button selects whether
calibration is to be applied, and an LED lights when error correction
data is being applied.
Calibration Sequence: Prompts the user to connect the
appropriate calibration standard to Port 1 and/or Port 2. Calibration
standards may be measured simultaneously or one at a time.
Calibration Standards: For coaxial calibrations the user
selects SMA, 3.5 mm, GPC-7, Type N, 2.4 mm, TNC, K,
V connector or special type from the calibration menu. Use of fixed
or sliding loads can be selected for each connector type. User
defined calibration standards allow for entry of open capacitance,
load and short inductances, load impedance, and reflection
standard offset lengths.
Reference Impedance: It is possible to modify the reference
impedance of the measurement to other than 50Ω(but not 0).
AutoCal®:The VNA can internally control an external AutoCal
module to perform a 2-port OSLT calibration. AutoCal is a single
two port calibration module with built-in, switched, and charac-
terized OSLT standards. AutoCal provides quick, reliable, and
accurate calibrations that exceed the performance of a standard
broadband load OSLT calibration.
LRL/LRM Calibration: The LRL calibration technique uses the
characteristic impedance of a length of transmission line as the
calibration standard. A full LRL calibration consists merely of two
transmission line measurements, a high reflection measurement,
and an isolation measurement. The LRM calibration technique is a
variation of the LRL technique that utilizes a precision termination
rather than a second length of transmission line. A third optional
standard, either Line or Match, may be measured in order to extend
the frequency range of the calibration.This extended calibration
range is achieved by mathematically concatenating either two LRL,
two LRM, or one LRL and one LRM calibration(s). Using these
techniques, full 12-Term error correction can be performed on the
37000C models.
Adapter Removal Calibration: Built-in Adapter Removal
application software accurately characterizes and "removes" any
adapter used during calibration that will not be used for subsequent
device measurements. This technique allows for accurate
measurement of non-insertable devices.
Dispersion Compensation: Selectable as Coaxial (non-
dispersive), Waveguide, or Microstrip (dispersive).
GAIN COMPRESSION MEASUREMENT
CAPABILITY (37300C models only)
The 37300C simplifies amplifier Gain Compression and AM/PM
measurements. Once an appropriate power and frequency
schedule is selected, a power meter calibration, at a set level, will
calibrate the linear VNA receiver channels, to accurately measure
power in dBm.The 37300C supports the Anritsu, Giga-tronics, and
Agilent power meters. To measure power, b2/1, a user defined
parameter, is automatically selected.
Swept Power Gain Compression: The 37300C will display
traditional Power out vs. Power in or Phase vs. Power in, at one of
up to 10 selectable frequencies. A separate screen will easily show
Power out and Power in at 1 dB, or selected level Gain
Compression, for all entered frequencies (See figure below).
Swept Frequency Gain Compression: Once Gain is
measured at the starting power, the user increments Power in,
observing Normalized Gain vs. Frequency. This aids in analyzing
the most critical compression frequencies of a broadband amplifier.
Power Out and Phase performance as a function of Input Power at
a CW frequency.
HIGH SPEED TIME (DISTANCE) DOMAIN
MEASUREMENT CAPABILITY (OPTION 2)
Option 2A, High Speed Time (Distance) Domain software allows
the conversion of reflection or transmission measurements from
the frequency domain to the time domain. Measured S-parameter
data is converted to the time domain by application of a Fast
Fourier Transform (FFT) using the Chirp Z-Transform technique.
Prior to conversion, any one of several selectable windowing
functions may be applied. Once the data is converted to the time
domain, a gating function may be applied to select the data of
interest. The processed data may then be displayed in the time
domain with display start and stop times selected by the user or
in the distance domain with display start and stop distance selected
by the user. The data may also be converted back to the frequency
domain with a time gate to view the frequency response of the
gated data.
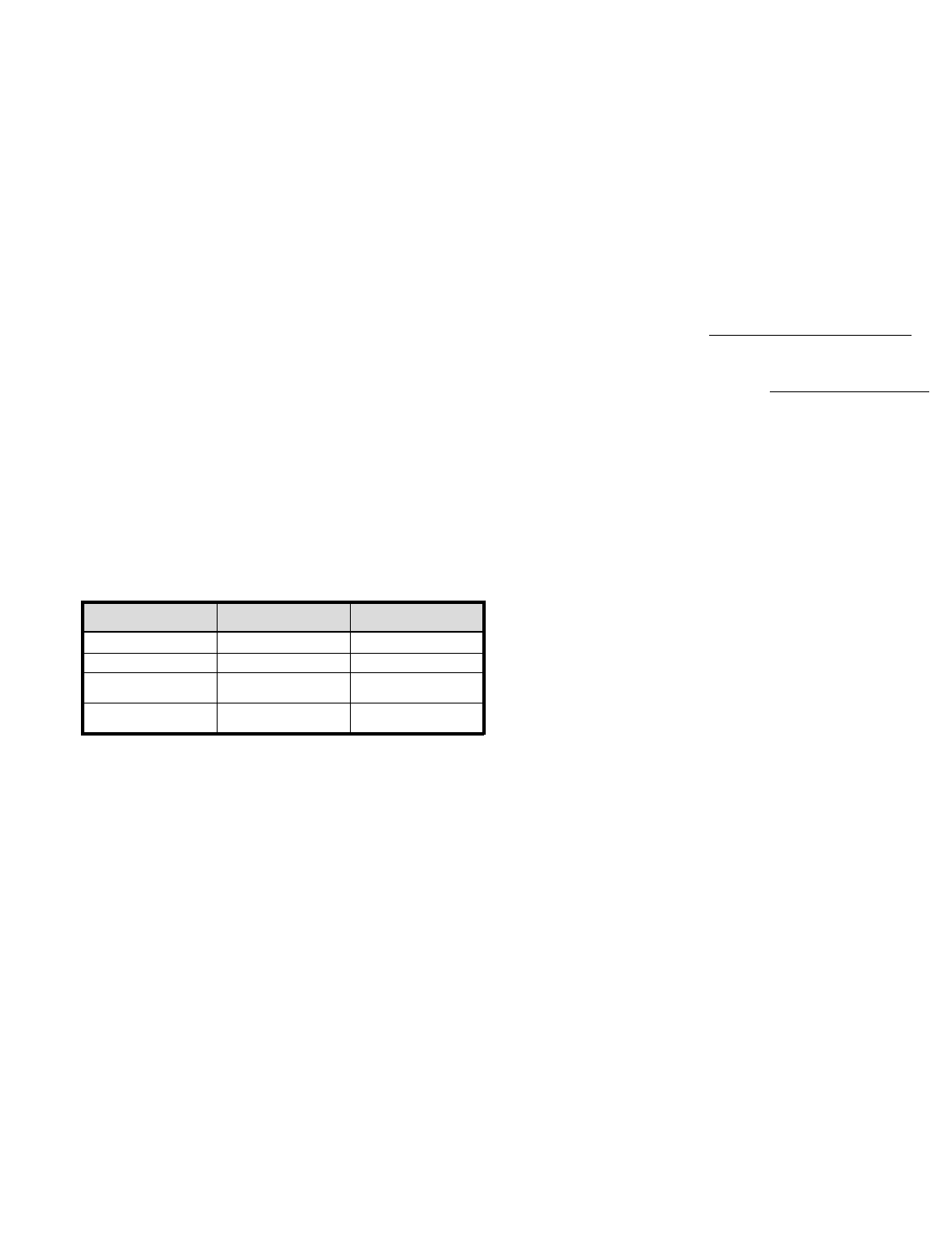
13
Lowpass Mode: This mode displays a response equivalent to
the classic "TDR" (Time Domain Reflectometer) response of the
device under test. Lowpass response may be displayed in either
the impulse or step mode.This type of processing requires a sweep
over a harmonic series of frequencies and an extrapolated or user-
entered DC value.
Bandpass Mode: This mode displays a response equivalent to
the time response of the device under test to a band limited
impulse.This type of processing may be used with any arbitrary
frequency sweep range, limited only by the test set range or device
under test response.
Phasor Impulse Mode: This mode displays a response similar
to the Lowpass impulse response, using data taken over an
arbitrary (band limited) sweep range. Detailed information, similar
to that contained in the lowpass impulse response may be used to
identify the nature of impedance discontinuities in the device under
test. Now, with Phasor Impulse, it is possible to characterize
complex impedances on band-limited devices.
Windowing: Any one of four window functions may be applied to
the initial frequency data, to counteract the effects of processing
data with a finite bandwidth. These windows provide a range of
trade offs of main lobe width versus sidelobe level (ringing). The
general type of function used is the Blackman-Harris window with
the number of terms being varied from one to four. Typical
performance follows:
Gating: A selective gating function may be applied to the time
domain data to remove unwanted responses, either in a pass-band
or reject-band (mask). This gating function may be chosen as the
convolution of any of the above window types with a rectangular
gate of user defined position and width. The gate may be specified
by entering start and stop times or center and span. The gated data
may be displayed in the time domain, or converted back to the
frequency domain.
Time Domain Display: Data processed to time domain may
be displayed as a function of time or as a function of distance,
provided the dielectric constant of the transmission media is
entered correctly. In the case of dispersive media such as
waveguide or microstrip, the true distance to a discontinuity is
displayed in the distance mode. The time display may be set to any
arbitrary range by specifying either the start and stop times or the
center time and span. The unaliased (non-repeating) time range is
given by the formula:
Number of Frequency Data Points
Unaliased Range (ns) = Frequency Sweep Range (GHz)
The resolution is given by the formula:
Main Lobe Width (null−null) in ns = kW
Freq. Sweep Range (GHz)
where kW is two times the number of window terms
(for example, four for a two-term window)
For a 40 GHz sweep range with 1601 data points, the unaliased
range is 40.025 nanoseconds. For a 65 GHz sweep with 1601 data
points, the unaliased range is 24.646 nanoseconds.
Frequency with Time Gate: Data that has been converted to
time domain and selected by the application of gating function may
be converted back to the frequency domain. This allows the display
of the frequency response of a single element contained in the
device under test. Frequency response accuracy is a function of
window and gate type, and gate width. For a full reflection,
minimum gate and window accuracy is within 0.2 dB of the
ungated response over a 40 GHz range.
ELECTRO-OPTICAL
MEASUREMENT CAPABILITY
(standard on all 37200/37300 models)
The 37200C/37300C series incorporated a de-embedding function
that simplifies VNA calibration when measuring E/O and O/E
devices. Characterize the transfer function, group delay, and return
loss of optical modulators (E/O) and photo-receivers (O/E) using
the built-in application.
E/O Measurements: The application menus guide the user
through the entire calibration and setup. A characterized photo-
diode (O/E) reference and a laser source are required to complete
the test setup. The internal VNA application de-embeds the
response of the photo-diode reference to allow direct measurement
of the bandwidth and return loss of the modulator.
O/E Measurements: Photo-receiver measurements can be
made by characterizing a modulator first and then using it as a
transfer standard for the O/E measurement. The internal application
de-embeds the response of the modulator to allow characterization
of the photo-receiver.
Type of Window
(Number of Terms) First Side Lobe
Relative to Peak
Rectangle (1) -13 dB
Nominal-Hamming (2) -43 dB
Low Side Lobe,
Blackman-Harris (3) -67 dB
Minimum Side Lobe,
Blackman-Harris (4) -92 dB 2.7W
2.1W
1.8W
1.2W
Impulse Width1
1W(Bin Width) = 1/2∆f sweep width.
Example. When ∆f = 40 MHz to 40 GHz, W = 12.5 ps
When ∆f = 40 MHz to 65 GHz, W = 7.7 ps
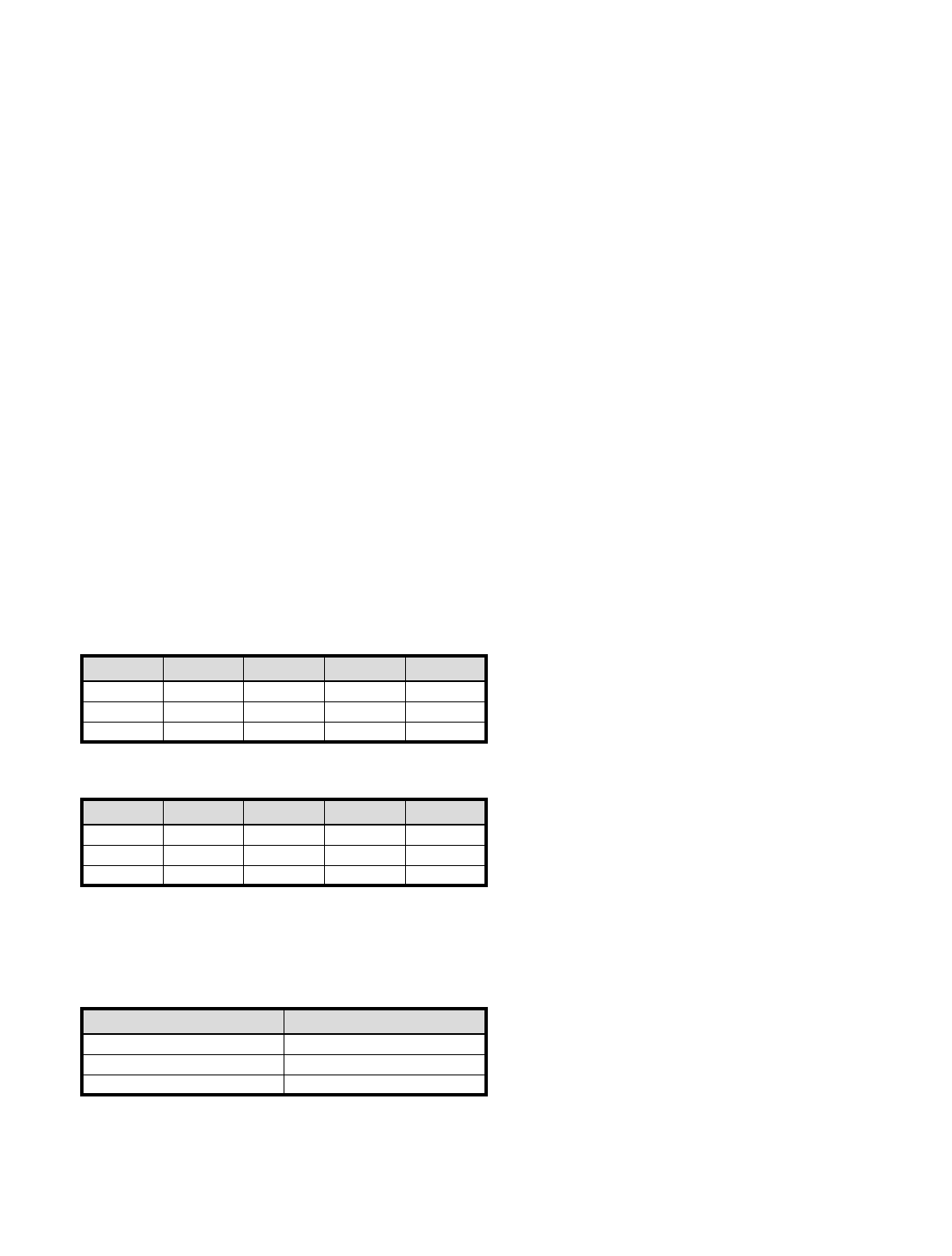
14
GPIB
GPIB INTERFACES: 2 Ports, system GPIB and dedicated
GPIB
System GPIB (IEEE-488.2): Connects to an external
controller for use in remote programming of the network
analyzer. Address can be set from the front panel and can
range from 1 to 30.
Dedicated GPIB: Connects to external peripherals for
network analyzer controlled operations (e.g., GPIB plotters,
frequency counters, frequency synthesizers and power meters).
Interface Function Codes: SH1, AH1, T6, TE0, L4, LE0, SR1,
RL1, PP1, DT1, DC0, and C0.
GPIB Data Transfer Formats: ASCII, 32-bit floating point, or
64-bit floating point. 32-bit and 64-bit floating point data can be
transferred with LSB or MSB first.
GPIB Data Transfer Speed (with or without cal):
150 kbyte/sec
GPIB Data Throughput Time: Throughput measurements for
both tables were made as follows: start the timer, trigger a sweep,
wait for a full sweep, transfer data across the GPIB and stop the
timer. Data throughput times are shown separately for
measurements made without calibration and with full two-port,
12-Term calibration. Measurement conditions: 40 MHz to 20 GHz
sweep, single channel, log magnitude display, 10 kHz IF bandwidth,
and output final data.
Throughput Times (ms) without Correction (typical)
Throughput Times (ms) with 12-Term Correction (typical)
Fast CW Operation: Fast CW is an ideal mode of operation for
rapid data taking over GPIB. To achieve a fast measurement rate
the display is not updated and only the raw S-parameter or user-
defined parameter of the active channel is measured.
Fast CW Typical Performance
Internal Buffer Data Collection: Internal Buffer Data
Collection is provided to allow saving active channel measurement
data from multiple sweeps without having to synchronize and
collect data at the end of each sweep. The 37000C can store up to
50,000 data point measurements, each consisting of two (real and
imaginary) IEEE 754 4-byte floating point numbers. GPIB transfer
speed for the 50,000 data points is typically 2.2 seconds.
STORAGE
Internal Memory: Ten front panel states (no calibration) can be
stored and recalled from non-volatile memory locations. The current
front panel setup is automatically stored in non-volatile memory at
instrument power-down.When power is applied, the instrument
returns to its last front panel setup.
Internal Hard Disk Drive: 340 MB mininum, used to store and
recall measurement and calibration data and front-panel setups. All
files are MS-DOS®compatible. File names can be 1 to 8 characters
long, and must begin with a character, not a number. Extensions
are automatically assigned.
External SCSI Interface: Option 4 deletes the internal hard
disk drive, and adds a SCSI Interface connector to the rear panel
for connecting a SCSI-2 formatted hard disk drive.
Internal Floppy Disk Drive: A 3.5-inch diskette drive with
1.44 Mbytes formatted capacity is used to load measurement
programs and to store and recall measurement and calibration
data and front-panel setups. Measurement data can be stored in
text, S2P or bitmap format. All files are MS-DOS compatible.
File names can be 1 to 8 characters long and must begin with a
character, not a number. Extensions are automatically assigned.
Measurement Data: 102.8 kbytes per 1601 point S-parameter
data file.
Calibration Data: 187.3 kbytes per 1601 point S-parameter
data file (12-Term cal plus setup).
Trace Memory File: 12.8 kbytes per 1601 point channel.
HARD COPY
Printer: A menu selects full screen, graphical, tabular data, and
printer type. The number of data points of tabular data can be
selected as well as data at markers only. Compatible with most
HP and Epson printers with parallel (Centronics) interfaces.
GPIB Plotter: The 37000 is compatible with most HP and
Tektronix plotters. A menu selects plotting of full or user-selected
portions of graphical data.The plotter is connected to the dedicated
GPIB bus.
Performance: After selecting the Start Print button, front panel
operation and measurement capability is restored to the user within
two seconds.
Data Format 3 Points* 101 Points 401 Points 1601 Points
32 Bit 150 500 1200 3600
64 Bit 150 500 1200 3600
ASCII 150 600 1500 4400
3 Points* 101 Points 401 Points 1601 Points
190 950 2300 6900
190 950 2300 6900
190 1000 2500 7400
*3 data point sweeps taken at 2, 4, and 6 GHz
Trigger Mode Measurement Speed (ms/point)
GPIB 1.5
External TTL 1.2
Internal 0.8
Data Format
32 Bit
64 Bit
ASCII
*3 data point sweeps taken at 2, 4, and 6 GHz
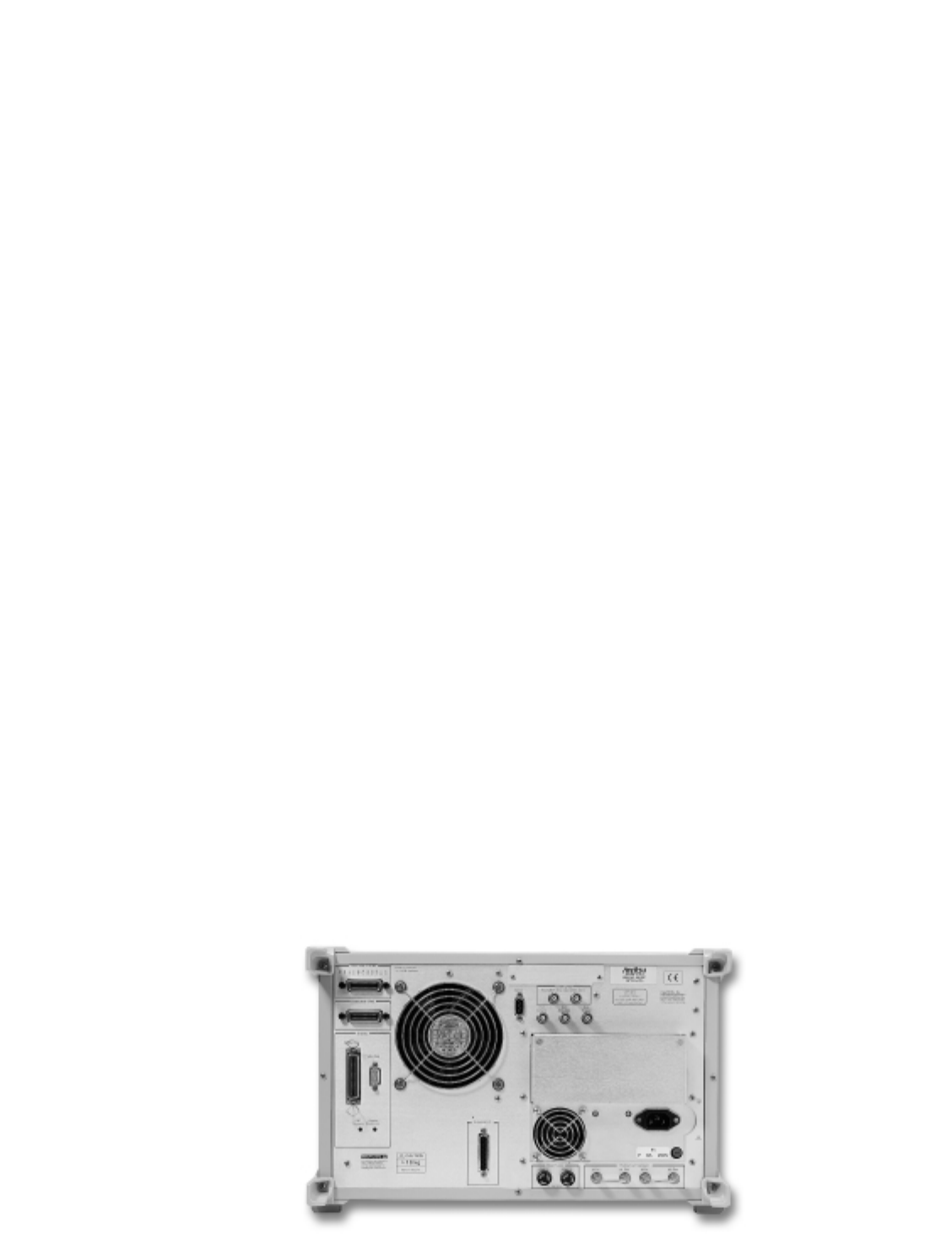
15
INTERFACES
37000C Front Panel Connectors and Controls:
Keyboard Input: An IBM-AT compatible keyboard can be
connected to the front panel for navigating through front panel
menus, annotation of data files and display labels, printing
displays and pausing instrument sweeps.
Test Ports (37200C and 37300C): Universal K male test
ports are standard on all models except for the >40 GHz models
which have Universal V male test ports as standard. For
additional configurations check Test Port Converters (Option 7).
Bias Inputs, Port 1 and 2 (37300C): 0.5 amps maximum
through BNC connectors.
Source Input Loop (37100C): Provides external source
input capability, replacing the internal source.
RF Output (37100C): K, female, provides source RF output.
a1,a
2,b
1,b
2Inputs (37100C): K, female, provide inputs to
the samplers.
Source Lock Output (37100C): Provides a sample of the
internal source, at -9 dB (typical) relative to the internal source
power.
Port 1 Amplifier Loop (37300C): Provides access to
insert an external amplifier, ahead of the port 1 coupler or
bridge, to increase port 1 power output, up to +30 dBm
(1 watt) maximum.
37000C Rear Panel Connectors and Controls:
PRINTER OUT: Centronics interface for an external printer.
VGA OUT: Provides VGA output of 37000C video display.
SERIAL: 9-Pin male DSUB connector. Provides RS-232 serial
port control for an AutoCal®module (3658 series).
10 MHz REF IN: Connects to external reference frequency
standard, 10 MHz, +5 to -5 dBm, 50Ω, BNC female.
10 MHz REF OUT: Connects to internal reference frequency
standard, 10 MHz, 0 dBm, 50Ω, BNC female.
EXT ANALOG OUT: -10V to +10V with 5 mV resolution,
varying in proportion to user-selected data (e.g., frequency,
amplitude). BNC female.
EXT ANALOG IN: ±50 volt input for displaying external
signals on the LCD. BNC female.
LINE SELECTION: Power supply automatically senses
100V, 120V, 220V or 240V lines.
EXTERNAL TRIGGER: External TTL triggering for 37000C
measurement. 10 kΩinput impedance, BNC female.
REFERENCE EXTENSION: The 37300C provides access
to the a1and b1samplers as standard. The 37200C provides
access to a1as an option. K female connectors are used,
except for >40 GHz models where V female connectors
are used.
EXTERNAL SCSI: Provides SCSI-2 connector for
connection of an external SCSI hard disk drive (Option 4).
EXTERNAL I/O: 25-pin DSUB connector.
LIMITS PASS/FAIL: Selectable TTL levels (Pass=0V,
Fail=+5V or Pass=+5V, Fail=0V. Additionally, 0 volts
(all displayed channels pass) or +5V (any one of four displayed
channels fail) output pass/fail status (1 line).
PORT 1 SOURCE ATTENUATOR (37100C): Drive signal
for a source external programmable step attenuator.
PORT 2 TEST ATTENUATOR (37100C): Drive signal for
a test external programmable step attenuator.
TRANSFER SWITCH (37100C): Drive signal for an
external transfer switch.
GENERAL
Power Requirements: 85-240 volts, 48-63 Hz,
540 VA maximum
Dimensions: 267 H x 432 W x 585 D mm
(10.5 H x 17 W x 23 D in.)
Weight: 27 kg (60 lb)-(2-man lift required)
Storage Temperature Range: -40°C to +75°C
Operating Temperature Range: 0°C to +50°C
Relative Humidity: 5% to 95% at +40°C
EMI: Meets the emissions and immunity requirements of
EN55011/1991 Class A/CISPR-11 Class A
EN50082-1/1993
IEC 801-2/1984 (4 kV CD, 8 kV AD)
IEC 1000-4-3/1995 (3 V/m, 80-1000 MHz)
IEC 801-4/1988 (500V SL, 1000V PL)
IEC 1000-4-5/1995 (2 kV L-E, 1 kV L-L)
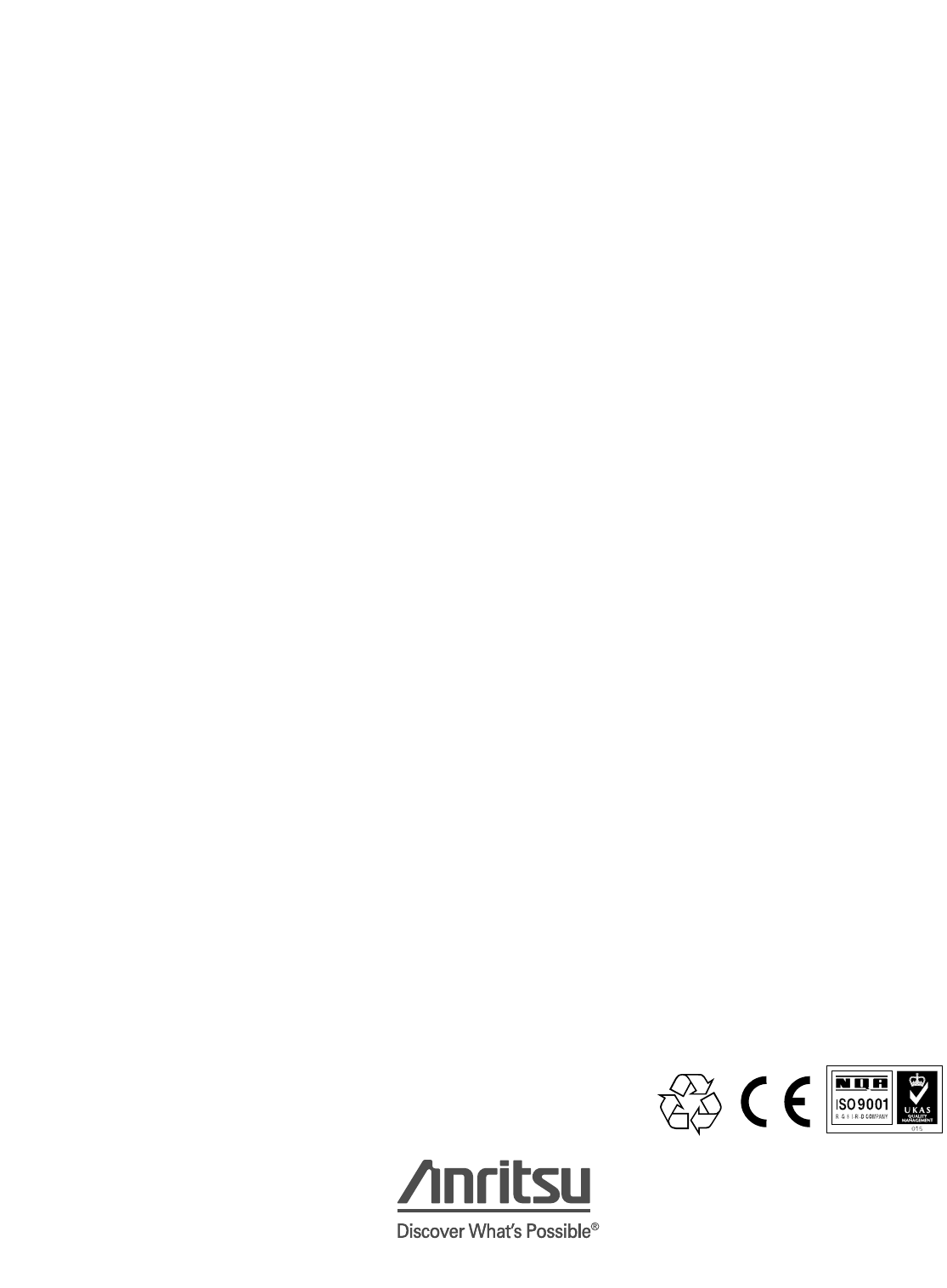
©Anritsu January 2003; Rev: C 11410-00247
Data subject to change without notice 37100C/37200C/37300C Vector Network Analyzers Technical Data Sheet
Microwave Measurements Division •490 Jarvis Drive •Morgan Hill, CA 95037-2809
http://www.us.anritsu.com • FAX (408) 778-0239
Sales Centers:
United States (800) ANRITSU
Canada (800) ANRITSU
South America 55 (21) 286-9141
Sales Centers:
Europe 44 (0) 1582 433433
Japan 81 (03) 3446-1111
Asia-Pacific 65-2822400
LRL/LRM-Calibration method of Rohde & Schwarz, Germany
GPC
−
7 is a registered trademark of Amphenol Corporation.
K Connector and V Connector are registered trademarks of Anritsu Company.
AutoCal is a registered trademark of Anritsu Company.
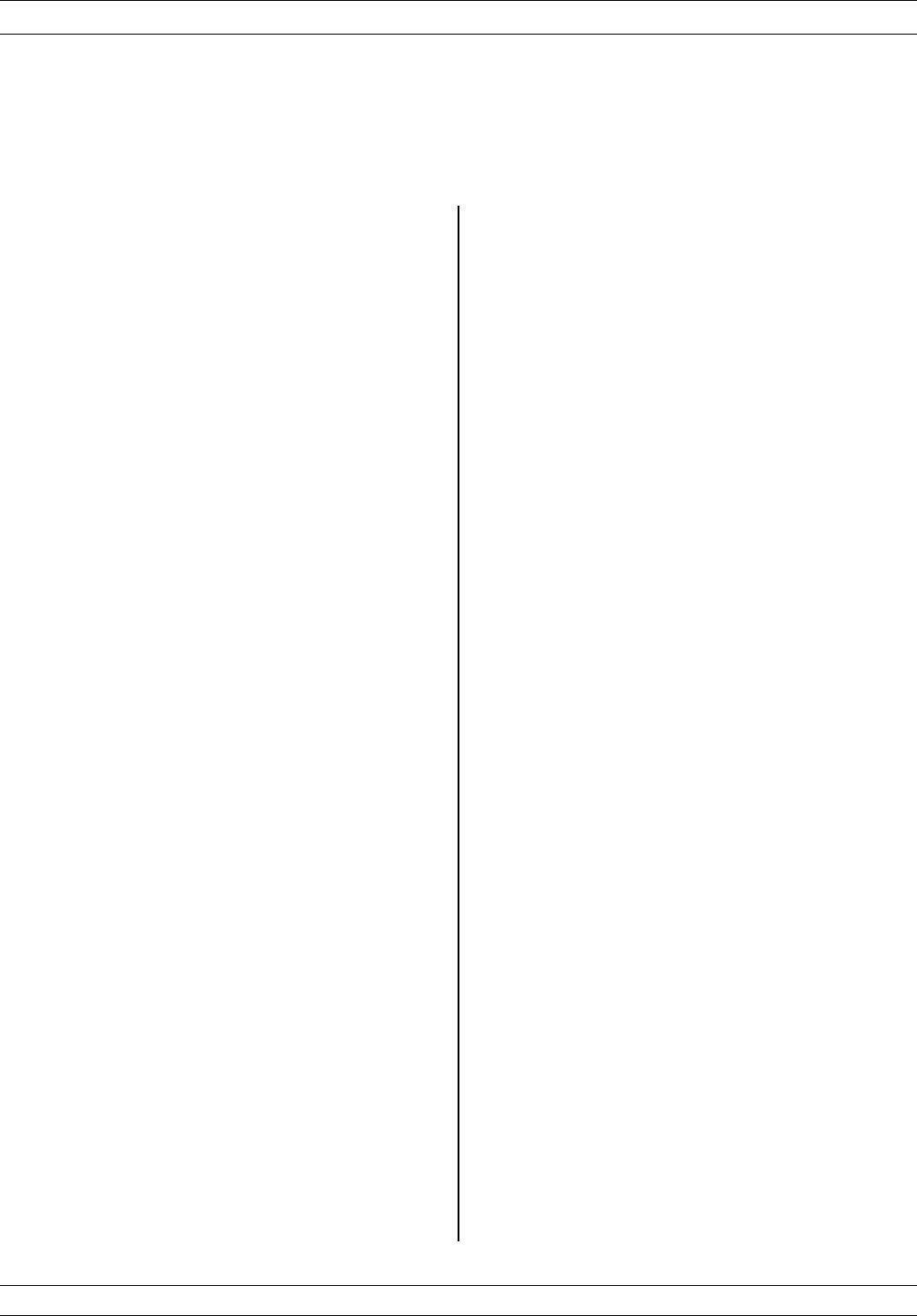
Subject Index
#
3 dB Compressed Smith Chart Display Mode . 6-10
3735B Connectors ...............14-12
40 MHz to 65 GHz Checkout .........15-12
A
Active Channel Selection ............6-13
Active Device Measurements......8-24 to 8-28
Discussion ..............8-24 to 8-28
Adapter Removal Measurements
Discussion ..............8-34 to 8-38
Address, GPIB ..................2-6
Analog Instrument Status ...........6-12
Analyzer Module .................3-4
Apply Cal Key ................4-4,4-11
Arrow Key.....................4-9
Autoscale Key ................4-6,4-26
Average Key ...................4-7
Avg/Smooth Key .................4-7
Avg/Smooth Menu Key .............4-30
B
Bandpass Impulse Response ...........9-5
Beatty Standard.................1-11
Begin Cal Key ................4-4,4-11
Bias Input Connectors ...........4-6,4-10
Broadband Calibration ............15-16
Merging Calibrations ............15-16
Broadband Measurement System .......15-3
Broadband Menus, Flow............15-15
C
Cable Length Restrictions ............2-5
Cables ......................15-4
CAD System ...................8-28
Calibrating for a Measurement .........7-9
Calibration
See Measurement Calibration
Calibration Key-Group Description . . 4-11 to 4-20
Calibration Keys ..........4-4,4-11 to 4-20
Calibration Kits
3650 ......................1-5
3651 ......................1-6
3652 ......................1-7
3653 ...................1-8to1-9
3656 ......................1-10
Contents ...................13-3
Model 3650 ..................13-4
Model 3651 ..................13-5
Model 3652 ..................13-6
Model 3653 ..................13-7
Model 3654/3654B ..............13-8
Model 3656 ..................13-9
Purpose ....................13-3
Calibration Sequence ..............4-11
Ch1Key .....................4-8
Ch2Key .....................4-8
Ch3Key .....................4-8
Ch4Key .....................4-8
Ch1 - Ch4 Keys .................4-25
Channel Menu Key .............4-8,4-25
Channels Key-Group ..............4-25
Channels Keys ..................4-8
Cleaning Connectors..............13-12
Clear/Ret Loc Key ................4-9
Connector Pin Depth..............13-10
Connector Pin Depth Tolerance ........13-11
Connectors, Cleaning .............13-12
Console and Table Setup ............15-5
Copying Data Files ...............4-42
D
Data Display
Active Channel Selection...........6-13
Analog Instrument Status ..........6-12
Control ................6-13 to 6-14
Frequency Range ...............6-12
Limits .....................6-11
Linear Phase..................3-9
Log Magnitude.................3-9
Markers....................6-14
Measurement Status .............6-13
Plotter Output ................6-15
Polar .....................3-10
Reference Position Marker..........6-12
Scale Resolution ...............6-12
SUBJECT INDEX # TO D
37XXXC OM Index-1
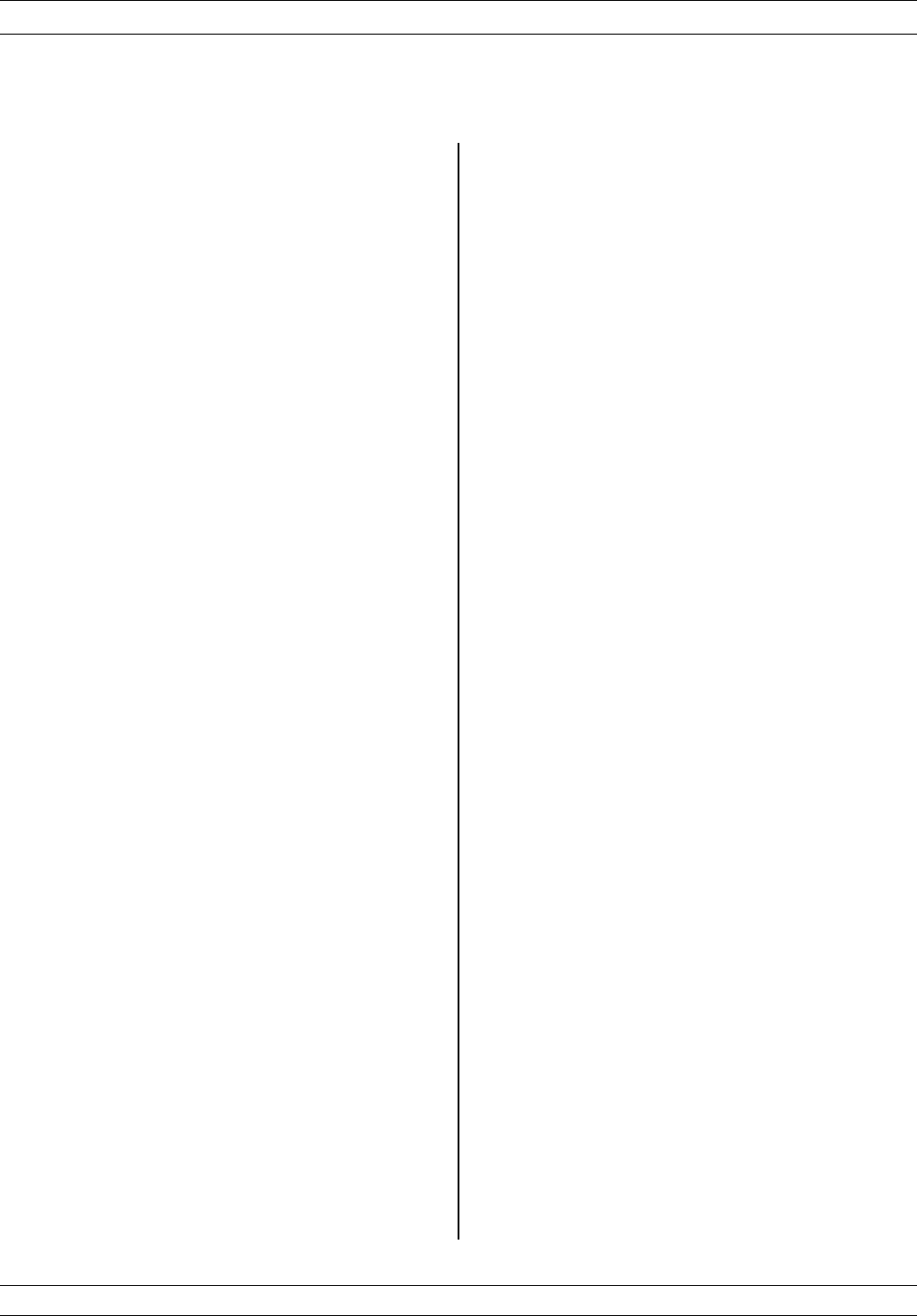
Screen-Image Printout ............6-15
Smith .....................3-10
S-parameter Selection ............6-14
Status .....................6-12
Sweep Marker Indicator ...........6-13
Tabular Printout ...............6-15
Update ....................6-14
Data Display Modes
3 dB Compressed Smith Chart .......6-10
Dual Channel .................6-4
Dual Channel Rectilinear Graticule .....6-8
Dual Trace Overlay ..............6-6
Four Channel .................6-5
Graph Data Types ...............6-7
Linear Polar Graticule.............6-8
Log Polar Graticule ..............6-9
Marker Designation .............6-11
Normal Smith Chart..............6-9
Single Channel.................6-3
Data Display Modes and Types ......6-3to6-6
Data Entry Keys .................4-9
Data Plotting ..................4-32
Data Points Key...............4-8,4-22
Default Parameters .............8-3,8-10
Default Program Key ............4-4,4-34
Default Settings .................4-35
Device ID Key ..................4-22
Disk Files, Format ...............4-41
Disk Output ...................6-15
Disk Storage Interface .........4-41 to 4-42
Diskette Drive ..................4-7
Display Key-Group ...........4-26 to 4-29
Display Keys.................4-6,4-26
Domain Key .................4-8,4-22
Drive, External SCSI...............2-4
Dual Channel Display Mode ...........6-4
Dual Channel Rectilinear Display Mode ....6-8
Dual Source Control
Pre-operational Setup ............8-30
Dual Source Control Measurements
Discussion ..............8-29 to 8-33
Dual Trace Overlay Display Mode........6-6
E
E/O Measurements ...............8-62
Equipment Setup...............8-62
Measurement Procedure ...........8-63
Enhancement Keys .............4-7,4-30
Enter Key .....................4-9
Error Messages ..................5-3
Error Modeling and Flowgraphs.........7-6
Error Terms
Description ..................3-11
Evaluating the Calibration ...........7-11
External Monitor Connector ...........2-6
External SCSI Drive, Setup ...........2-4
F
Four Channel Display Mode ...........6-5
Fourier Transform ................9-3
Frequency
Range .....................6-12
Frequency Domain ...........9-3,9-8,9-12
Front Panel
Calibration Key-Group Description . 4-11 to 4-20
Channels Key-Group Description ......4-25
Display Key-Group Description . . . 4-26 to 4-29
Key-Group Descriptions........4-3to4-10
Markers/Limits Key-Group Description . 4-37 to
4-40
Measurement Key-Group Description4-22 to 4-24
Output Key-Group Description . . . 4-32 to 4-33
Save/Recall Key, Description ........4-21
System State Key-Group Description 4-34 to 4-36
G
Gain Compression
Swep Power Gain Compression Measurement
........................8-43
Swept Frequency Measurement .......8-51
Gain Compression Measurements
Discussion ..............8-39 to 8-57
Gating ......................9-12
General Description ............3-3to3-4
GHz/10E+3/Ms/m Key ..............4-9
GPIB
Indicators ...................4-3
GPIB Addresses .................2-6
GPIB Interface to External Plotter .......2-6
GPIB Setup and Interconnection ........2-5
Graph Data Types ................6-7
Graph Type Key...............4-6,4-26
Group Delay
Applications..................8-23
Discussion ..................8-20
Index-2 37XXXC OM
E TO G SUBJECT INDEX
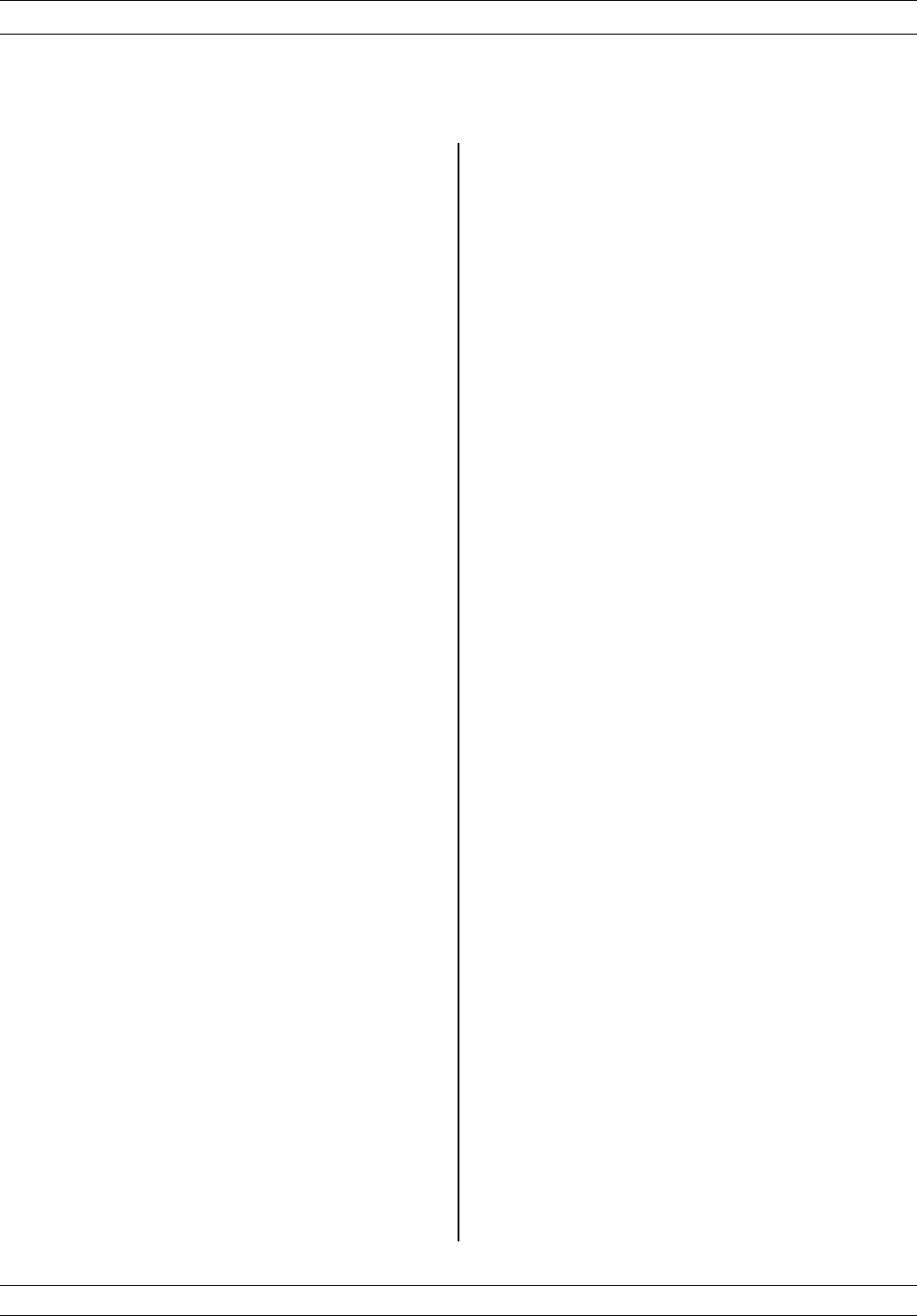
Equation ...................8-21
Frequency Aperture .............8-21
Group Delay Measurements ......8-20 to 8-23
H
Hard Copy
Plotter Output ................6-15
Screen-Image Printout ............6-15
Tabular Printout ...............6-15
Hard Copy and Disk Output ..........6-15
Hard Copy Keys...............4-5,4-32
High Level Noise Test
Test Procedure ................12-7
Test Setup ..................11-8
High Level Noises Test ..........11-8,12-6
Hold Key...................4-8,4-22
I
Identification Number ..............1-3
Impulse Response.................9-4
Initial Inspection .................2-3
Initial Setup ................11-3,12-3
Insertables ....................7-5
Instrument Installation into Console .....15-6
Interface
Connectors ...................2-5
Disk Storage .............4-41 to 4-42
Introduction ................11-3,12-3
K
Keyboard Connector ...............4-7
Keypad ......................4-9
Keys
Calibration ..............4-11 to 4-20
Channel Key-Group .............4-25
Display Key-Group..........4-26 to 4-29
Markers/Limits............4-37 to 4-40
Markers/Limits Key-Group .....4-37 to 4-40
Measurement Key-Group ......4-22 to 4-25
Output Key-Group ..........4-32 to 4-33
Save/Recall Menu ..............4-21
System State .............4-34 to 4-36
System State Key-Group.......4-34 to 4-36
kHz/10E-3/ps/mm Key ..............4-9
Kit Contents...................13-3
L
Limit Frequency Readout Function ......4-37
Limits ......................6-11
Limits Key..................4-5,4-37
Linear Polar Graticule Display Mode ......6-8
Load Match ....................7-6
Log Magnitude Display..............3-9
Log Polar Graticule Display Mode........6-9
LRL/LRM Calibration Procedure
Coaxial ....................7-44
General ................7-36 to 7-45
Microstrip...................7-37
Waveguide ..................7-46
LRL/LRM Calibration Setup Menu Flow . . . 4-16
M
Marker
Display of ...................6-14
Reference Position ..............6-12
Marker Designation...............6-11
Marker Menu Key..............4-5,4-37
Markers/Limits Key-Group.......4-37 to 4-40
Markers/Limits Keys ............4-5,4-37
ME7808A ....................15-3
Measurement Calibration
Calibration Types ...............7-6
Discussion ...............7-3to7-12
Error Modeling and Flowgraphs .......7-6
Evaluating the Calibration .........7-11
LRL/LRM Procedure .........7-36 to 7-45
Offset-Short Procedure........7-28 to 7-31
Sliding Load, Procedure .......7-13 to 7-18
Standared (SOLT) Procedure ....7-19 to 7-27
Triple Offset-Short Procedure ........7-32
Understanding the Calibration System ...7-5
Measurement Instruments ...........15-3
Measurement Key-Group Description . 4-22 to 4-24
Measurement Keys .............4-8,4-22
Measurement Status ..............6-13
Measurement Uncertainty ............7-3
Measurements
Active Device .............8-24 to 8-28
Adapter Removal...........8-34 to 8-38
Dual Source Control .........8-29 to 8-33
Gain Compression ..........8-39 to 8-57
Group Delay .............8-20 to 8-23
Receiver Mode ............8-58 to 8-61
SUBJECT INDEX H TO M
37XXXC OM Index-3

Time Domain..................9-3
Transmission and Reflection .....8-3to8-11
Mechanical Shock ...............13-11
Menu Flow
Calibration Key-Group Menus . . . 4-11 to 4-20
MARKER MENU Key ............4-37
Save/Recall Key................4-21
Menu Key ..................4-5,4-32
Menu Keys ....................4-9
Menus
Channels Key-Group .............4-25
Display Key-Group..........4-26 to 4-29
Markers/Limits Key-Group .....4-37 to 4-40
Measurement Key-Group ......4-22 to 4-24
Output Key-Group ..........4-32 to 4-33
System State Key-Group.......4-34 to 4-36
MHz/X1/ns/cm Key ................4-9
Microwave Load .................7-13
Millimeter Wave Measurements.........1-5
Millimeter Wave System
Allowable Measurements and Calibrations 14-18
Allowable Module Configurations .....14-18
Calibration .................14-13
Controls and Connectors ..........14-11
Description ..................14-3
Effect of Default Program .........14-19
Installation ..................14-6
Measurement Capabilities..........14-5
Measurement Procedures..........14-23
Operation ..................14-14
Operational Checkout-General.......14-25
Operational Checkout-High Level Noise Test
....................14-28,14-30
Operational Checkout-IF Power Level Test 14-26
Performance Specifications .........14-4
Remote Operation..............14-24
System Performance .............14-4
Test Port Characteristics ..........14-5
Model 3650 Calibration Kit...........13-4
Model 3651 Calibration Kit...........13-5
Model 3652 Calibration Kit...........13-6
Model 3653 Calibration Kit...........13-7
Model 3654/3654B Calibration Kit .......13-8
Model 3656 Calibration Kit...........13-9
Multiple Source Control
Control Formula ...............8-29
Operation ...................8-31
N
Network Analyzers ...............7-13
Basics......................3-6
Description...................1-3
Error Correction ...............3-11
Measurements .................3-9
Options ....................1-15
Primer .................3-5to3-11
Non-insertables..................7-5
Normal Smith Chart Display Mode .......6-9
O
O/E Measurements ...............8-65
Equipment Setup...............8-66
Measurement Procedure ...........8-66
Offset-Short Calibration Procedure . . 7-28 to 7-31
Offset-Short Calibration Setup Menu Flow . . 4-14
Open .......................8-27
Operational Checkout
High Level Noise Test .........11-8,12-6
Initial Setup...............11-3,12-3
Required Test Equipment .......11-3,12-3
Sampler Efficiency Test ........11-4,12-4
Self Test .................11-3,12-3
Optical Application ...........8-62 to 8-73
E/O Measurements..............8-62
O/E Measurements..............8-65
Option 2 Time Domain
Menus.................9-14 to 9-20
Option 2A Time Domain
Gating ................9-12 to 9-13
Gating Example ...............9-14
Operating ...................9-8
Windowing ..................9-11
Option 4 External SCSI Drive
Requirements .................2-4
Setup ......................2-4
Option 5 Receiver Mode
Menus.....................8-59
Operating Procedure .............8-60
Operation ...................8-59
Set--On Mode .................8-58
Sweeper Source Lock Mode .........8-58
Option Menu Key ..............4-7,4-30
Options......................1-15
Output Key-Group ...........4-32 to 4-33
Over Torquing Connectors...........13-11
Index-4 37XXXC OM
N TO O SUBJECT INDEX
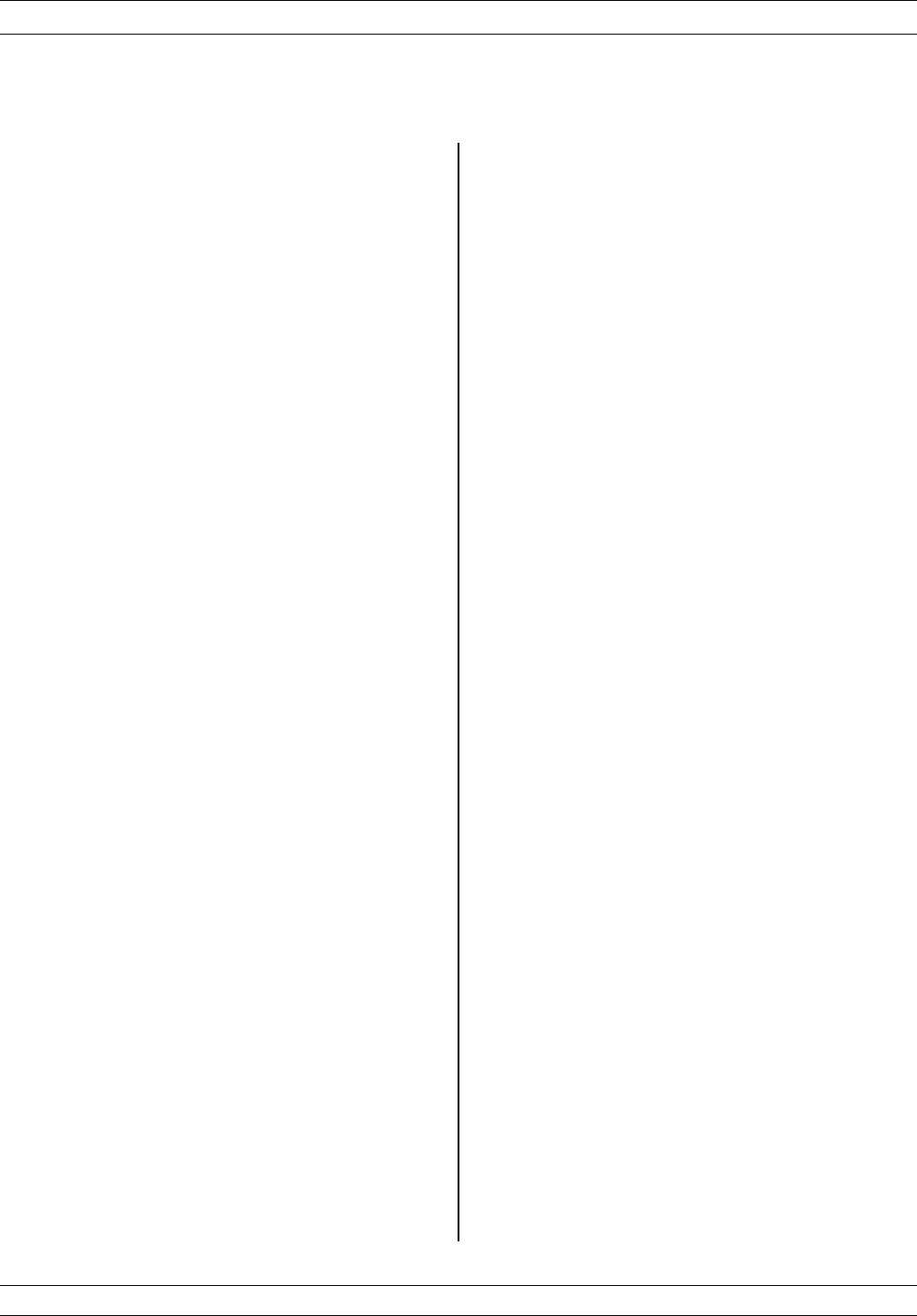
P
Performance Specifications ...........1-15
Phasor-impulse Response ............9-5
Pin Depth ....................7-13
Plotter Output..................6-15
Plotting .....................4-32
Polar Display ..................3-10
Port 1 Connector .................4-6
Port 1 Test Connector............4-4,4-10
Port 2 Connector .................4-6
Port 2 Test Connector............4-5,4-10
Precision Component Kits ............1-5
Preparation for Storage and/or Shipment ....2-9
Preparation for Use................2-3
Printing
Stop/Start...................4-32
Purpose .....................13-3
R
Readout Marker key ...............4-5
Readout Marker Key ..............4-37
Receiver Mode Measurements .....8-58 to 8-61
Operating Procedure .............8-60
Recovering, Disk Write/Read Errors ......4-42
Ref Plane Key ................4-6,4-26
Reference Flat ..................7-15
Reference Position Marker ...........6-12
Rotary Knob....................4-9
S
S Params Key ................4-6,4-26
S2P File
Comment Line ................8-73
Creating....................8-71
Data Line ...................8-72
Example....................8-73
File Format ..................8-71
Option Line ..................8-72
Sampler Efficiency Test ..........11-4,12-4
Test Procedure ................11-5
Test Setup................11-5,12-5
Save/Recall Menu ................4-21
Save/Recall Menu Key ..............4-4
Save/Recall Menu Key .............4-21
Scale Resolution.................6-12
Scattering Parameters ..............3-9
Screen-Image Printout .............6-15
SCSI Drive, External...............2-4
Self Test ..................11-3,12-3
Set Scale Key ................4-6,4-26
Setup Menu Key...............4-8,4-22
Short .......................8-27
Single Channel Display Mode ..........6-3
Sliding Load ...................7-13
17K50, 17KF50 ................1-7
17S50, 17SF50 .................1-5
Pin Depth ...................7-13
Used in Calibraton...............7-5
Smith Chart ...................8-10
3 dB Compressed ...............6-10
Measurement Discussion ...........8-8
Normal .....................6-9
Smith Chart Display ..............3-10
Source Match ...................7-6
Source Module
General.....................3-4
S-parameter ...................8-25
Description...............3-9to3-10
General.....................3-9
Selection, Display of .............6-14
Specifications, Performance ..........1-15
Standard Calibration Setup Menu Flow ....4-12
Start Print Key ...............4-5,4-32
Start Printing ..................4-32
Status Display..................6-12
Stop Print Key................4-5,4-32
Stop Printing ..................4-32
Sweep Marker Indicator ............6-13
System Cabling .................15-9
System Description ............1-3to1-4
System GPIB Interconnection ..........2-6
System State Key-Group ........4-34 to 4-36
System State Keys .............4-4,4-34
T
Tabular Printout ................6-15
Teflon Tuning Washers ............13-11
Test Ports
Establishing, Discussion ...........7-3
Test Set
Reversing ...................3-11
Test Set Module
General.....................3-4
SUBJECT INDEX P TO T
37XXXC OM Index-5
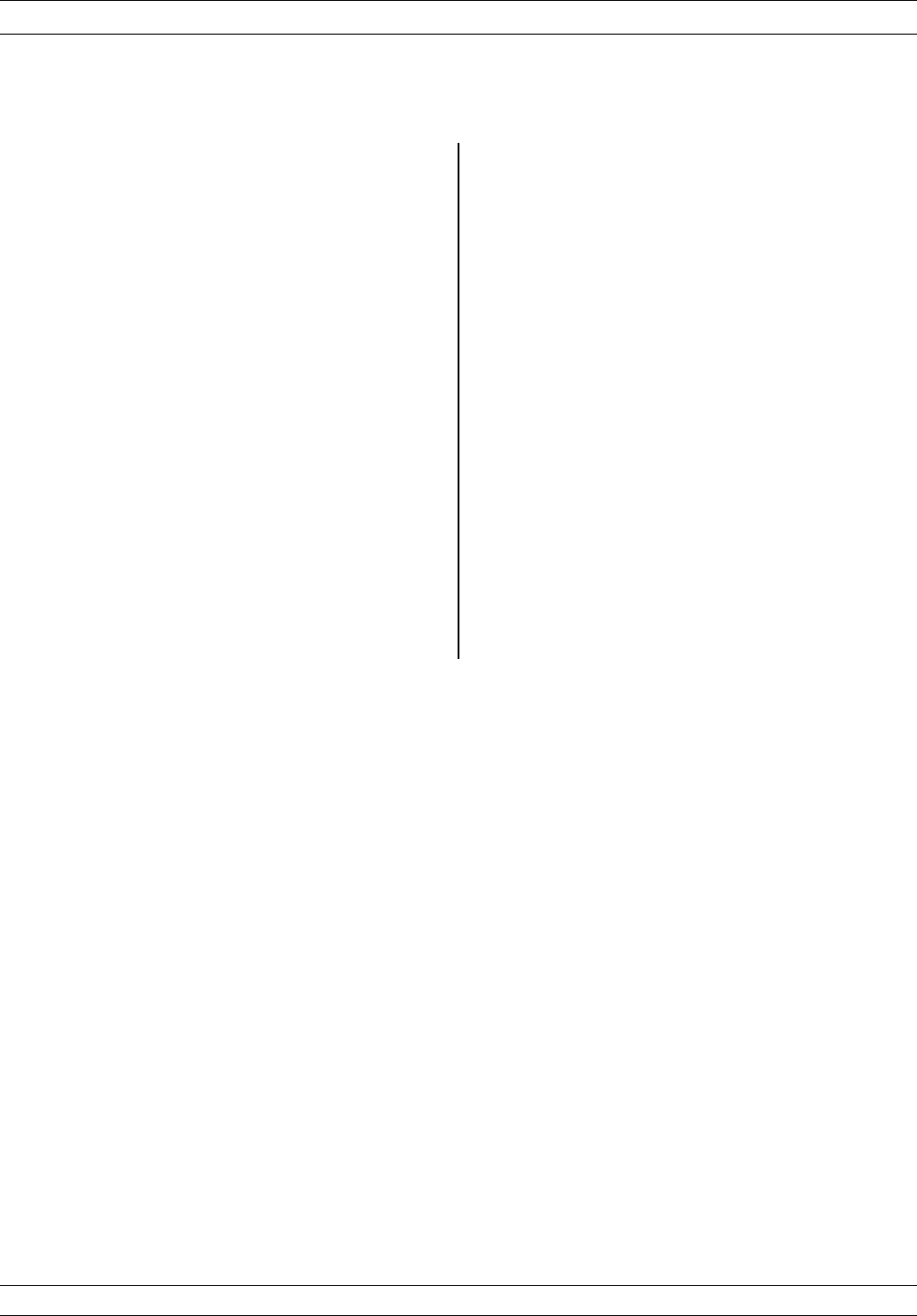
Time Delay
Linear.....................8-21
Time Domain Measurements ..........9-3
Trace Memory Key .............4-6,4-27
Trace Smooth and Average Keys ........4-30
Trace Smooth Key ................4-7
Tracking......................7-6
Transmission and Reflection Measurements . . 8-3
Discussion ...................8-7
General.................8-3to8-11
Setup and Calibration .............8-3
Smith Chart ..................8-8
Triple Offset Short Calibration Procedure . . . 7-32
TRM Calibration Setup Menu Flow ......4-18
U
Using Connectors
Mechanical Shock ..............13-11
Over Torquing................13-11
Pin Depth ..................13-10
Pin Depth Tolerance ............13-11
Teflon Tuning Washers ...........13-11
Utility Menu Key ..............4-4,4-34
V
Verification Kit
3666 ......................1-11
3668..................1-13 to 1-14
Used in Calibration..............7-11
Video IF BW Key ..............4-7,4-30
W
Wafer Probe Station .........15-13 to 15-14
Windowing....................9-11
Z
Zo Load .....................8-27
Zo Reference...................7-13
Index-6 37XXXC OM
U TO Z SUBJECT INDEX