ANYCUBIC Mega Manual English 20170809
ANYCUBIC_Mega_Manual_English_20170809
User Manual:
Open the PDF directly: View PDF .
Page Count: 39
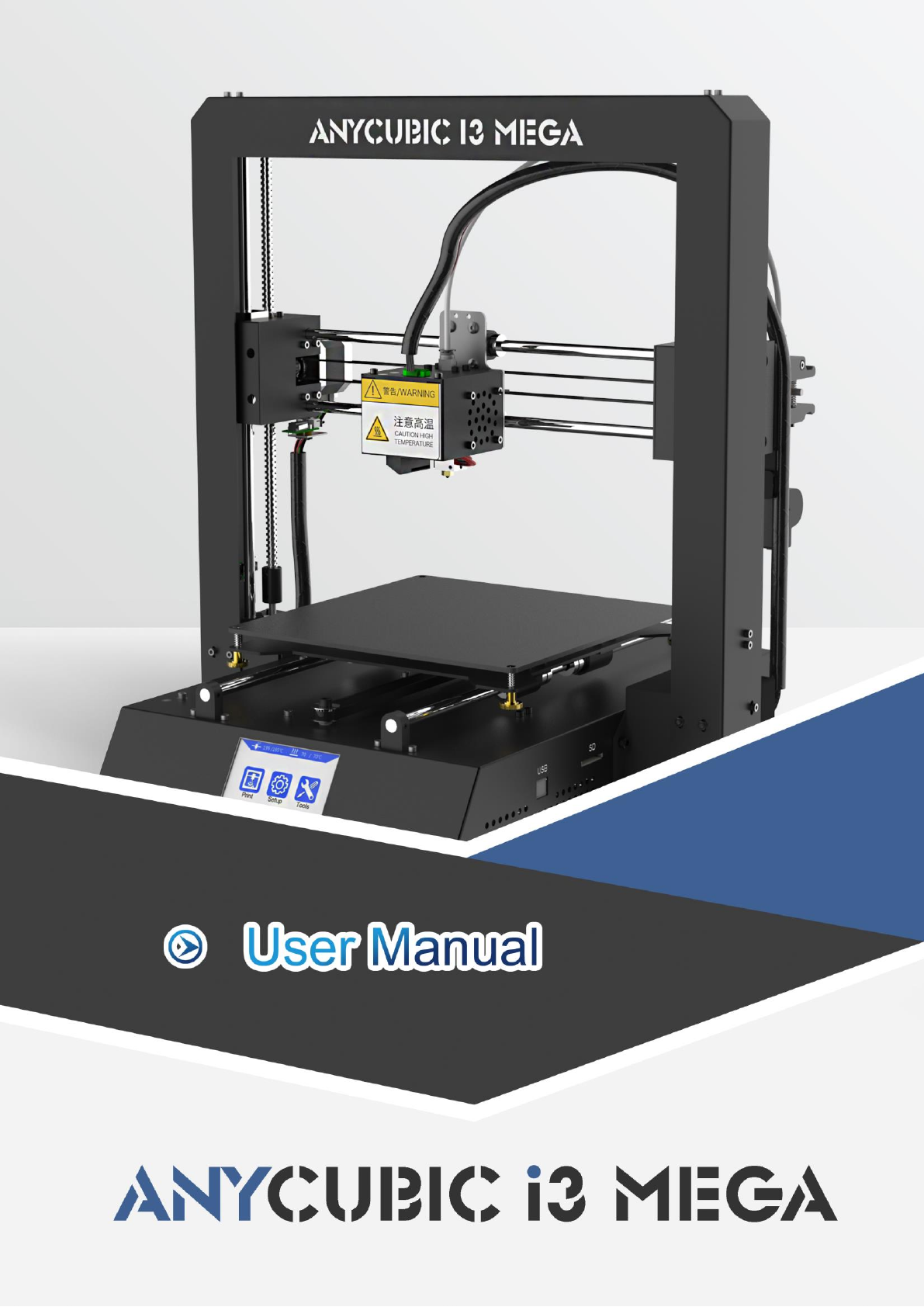


Thank you for choosing ANYcUBIC products.
Please read the user manual carefully.
Please visit www.anycubic3d.com for more information.
Email us on support@anycubic3d.com or james@anycubic3d.com for
technical support.
If you experience any issues with this product, or the performance is not what you
had expected, please contact us first. We are here to solve any problems for you.
Team ANYcUBIC
www.anycubic3d.com
Facebook group
Youtube channel

Safety Instructions
Please carefully read the safety instructions before get started.
ANYcUBIC 3D printer generates high temperature. Do not reach inside of the
printer during operation. Allow time for the printer to cool down after printing.
Contact with extruded materials may cause burns. Wait for printed objects to cool
before removing them from the build platform.
ANYcUBIC 3D printer includes moving parts that can cause injury.
Vapors or fumes may be irritating at operating temperature. Always use the
ANYcUBIC 3D printer in an open, well ventilated area.
Be cautious when using the scraper. Never direct the scraper towards your hand.
ANYcUBIC 3D printer MUST NOT be exposed to water or rain.
ANYcUBIC 3D printer is designed to be used within ambient temperature ranging
8ºC-40ºC, and humidity ranging 20%-50%. Working outside those limits may
result in low quality printing.
It is recommended to use protection glasses when cleaning/sanding the printed
models to avoid small particles contacting eyes.
In case of emergency, immediately turn off the ANYcUBIC 3D printer and contact
us or consult for professional advice.
Never leave the ANYcUBIC 3D printer unattended during operation.。

Contents
1. Product overview ......................................................................................................... 1
2. Part list ............................................................................................................................ 4
3. Assembly instruction .................................................................................................. 5
4. Leveling ........................................................................................................................... 9
5. Software installation ................................................................................................ 15
5.1 Driver installation .............................................................................................. 15
5.2 Cura Installation ................................................................................................ 17
6. Printing .......................................................................................................................... 26
7. Manual filament change ......................................................................................... 28
8. Resume from outage ................................................................................................ 29
9. Trouble shooting ........................................................................................................ 32

Technical Specification
Printing
Technology: FDM (Fused Deposition Modeling)
Build Size: 210×210×205 (mm3)
Layer Resolution: 0.05-0.3 mm
Positioning Accuracy: X/Y 0.0125mm,Z 0.002mm
Extruder Quantity: Single
Nozzle/Filament Diameter: 0.4 mm/1.75mm
Print Speed: 20~100mm/s (suggested 60mm/s)
Travel Speed: 100mm/s
Supported Materials: PLA, ABS, HIPS, Wood
Temperature
Ambient Operating Temperature: 8°C - 40°C
Operational Extruder Temperature: max 260°C
Operational Print Bed Temperature: max 110°C
Software
Slicer Software: Cura
Software Input Formats: .STL, .OBJ, .DAE, .AMF
Software Output Formats: GCode
Connectivity: SD card; USB port(expert users only)
Electrical
Input rating: 110V/220V AC, 50/60Hz
Working Voltage: 12V DC
Physical Dimensions
Printer Dimensions: 405mm×410mm×453mm
Net Weight: ~11kg

1
1. Product overview
⑹
⑻
⑴
⑵
⑷
⑸
⑿
⒀
⑾
⑼
⑽
⑺
⒁
⒂
(22)
⒃
⑴Frame ⑵Print head ⑶Hotend cooling fan ⑷Nozzle ⑸Model cooling fan ⑹Base ⑺X smooth
rods ⑻X end stop ⑼Print platform ⑽Y smooth rods ⑾Touch screen ⑿Filament spool ⒀Spool
holder ⒁Z smooth rods ⒂Z lead screw ⒃X motor ⒄Z adjustable nut ⒅Z end stop ⒆Y end stop ⒇
Z motors (21)Teflon tubing (22) Extruder (23) Filament sensor
(21)
⒆
⒇
⒅
⑶
(23)
⒄

2
Home menu
Print: enter the print list
Setup: enter the setup menu
Tools: enter the tools menu
(Other information: ①nozzle temperature ②heated bed temperature ③printer status)
Print
Print: print the selected files in SD card
Resume: Resume from outage (only valid for offline print via SD card)
(Other information: ①Page up and down ②Refresh the list ③Return to the home menu)
Setup
En/中: Change language (English/Chinese)
Menu Directory
Home Menu
Print
Tools
Setup

3
Temp: Enter the menu to adjust ① E0 (hotend) Temp (170-260°C) ②Bed Temp (0-120°C)
Motor: Disable all motors (only valid when machine is not printing)
Status: Enter the sub-menu with Print/Pause/Resume icon (only valid for offline print)
(Other information: ①Files ②Print Rate ③Time ④Progress ⑤E0 Temp ⑥Bed Temp ⑦
coordinates for X/Y/Z axis ⑧Return to previous menu)
Speed: Enter the menu to adjust ①Fan speed (0-100) ②Print Rate (50-999)
Return: Return to Home Menu
Tools
Home: ①Home X ②Home Y ③Home Z ④Home All ⑤Return (only valid when machine is not
printing)
Axis: ① Home all axis ②Move X/Y/Z axis by 0.1/1/10 ③Speed mode for axis move
Low/Medium/High (only valid when machine is not printing)
Preheat: ①Preheat PLA ②Preheat ABS (only valid when machine is not printing)
(Other information: ①E0 Temp ②Bed Temp)
Cooling: Cut off the power of hotend and heated bed (only valid when machine is not printing)
Filament: ①Filament In ②Filament Remove (will automatically heating to 200°C for filament in
or remove) ③ Stop (only valid when on print job)
Reset: Popup window to decide if reboot the mainboard
More: Enter the next page of Tools sub-menu
TP: Touch panel alignment(click on the cue points)
Help: Basic description of the Menu
Info: Information about the product
Return: Return to Home Menu

4
2. Packing list
Tool kit
M5*8 screws
SD card
SD Card reader
ANYcUBIC 3D printer
Gloves
Power cord
Tweezer
Spool holder
PLA filament (Random color)
USB cable
Extra hotend
Scraper
Plier

5
3. Assembly instruction
Step 1. Unpack and take out the printer and accessories.
Wear gloves because the smooth rods and lead screw may be greased in factory.
Step 2. Follow ① ② ③ in Fig. 1. Carefully lift the base to fit into the frame and fix them by
8 pieces of M5*8mm hex cap screws. The screw locations are indicated by red
squares in ③. The screws can be installed in diagonal order and can be tightened
after all screws installed in place.
Figure 1
Frame
Base
①
②
③

6
Step 3. Wiring
(1) Fig.2, select the correct voltage mode according to your local voltage ratings
(110V/220V). The switch is inside the bottom left of the base and 220V is default.
Allan keys can be used to move the switch inside.
(2) There are 3 ports with different color (Red/Green/Black) at the bottom right side of
the base, and there are 3 different color cable connectors respectively. Accordingly,
insert those connectors to the ports by the same color, as shown in Fig. 3.
> Make sure the connectors are well inserted, and no pins are bent inside.
> Wrong or loose connection would lead to malfunction of the machine.
(Figure 3)
(Figure 2)

7
(3) Fig. 4, customers may notice there is a ring of zip tie attached just below the plastic
ring of the quick connector. Do not cut it off.
Only cut this zip tie when swapping or repairing the hotend.
Step 4. Spool holder and filament sensor
(1) Assemble the spool holder as shown in Fig. 5, and tighten 4 pairs of screw and nuts
at the lower 4 corner. (Customers may firstly peel off the protective cover on the
acrylic plates)
(Figure 5)
(Figure 4)
Plastic ring
Zip tie
Do not cut

8
(2) As shown in Fig.6, manually install the filament spool to the spool holder. Pass the
filament through the filament sensor. Insert the filament into the extruder and Teflon
tubing, but do not fully reach it into the hotend (until preheat the hotend later).
Figure 6
> Only insert filament into the hotend after “Preheat” it later.
> It is suggested to cut off the bent tip of the filament, and rotate the filament if
feels any resistance during installation.
> It is important to make sure there is no tied or tangle on the spool.
① Extruder
② Filament sensor
Press
Insert filament in
Turn this holder out and hook the
filament sensor on by magnets
on the holder by magnets

9
4. Leveling
It is essential to level the platform for 3D printer. Please follow procedures below:
Step 1. Check and ensure all wirings are OK. Connect the machine to the power outlet
by power cord. Switch on the machine.
Step 2. As shown in Fig. 7, on Home Menu, click “Tools”-->“Home”-->“Home
All”.
(Figure 7)
Step 3. As shown in Fig. 8, return to the “Home Menu”, click “Setup”-->“Motor” to
disable the motors so the motors/axis could be moved freely.
(Figure 8)

10
Step 4. Put a piece of paper onto the print platform, and then manually move the print head
and platform back and forth to let the print head travel to the 4 corners and center
one by one (①→②→③→④→⑤), as shown in Fig.9. (Avoid nozzle rub against the
platform directly without the paper in-between)
(Figure 9)
Step 5. When nozzle has been moved to corner ①, manually adjust (tighten or loose) the
corresponding nut underneath the print platform.
The purpose is to adjust the distance between nozzle and print platform to about
a piece of paper thin (~0.1-0.2mm). Therefore, when just feel the drag resistance as
pulling the paper, it means good leveling for this particular corner.
(Note: “just feel the drag resistance” means the paper can be moved, but with resistance)
Please do so to the rest of corners and center area. Perform double check to ensure
the results, and check the corners in diagonal order: ①→③, ②→④.
①
A4 paper
Nozzle
Nut
②
③
④
⑤

11
Step 6. Ideally, after the 4 corners are leveled, the center should be spontaneously leveled,
and you may proceed to do a test print on the platform. (see details in Step 7)
However, please be mindful that in some cases, the platform may not be perfectly
flat (concave or convex) due to many factors in manufacture and usage.
ANYCUBIC promise that the flatness of the print platform is in the range of 0~0.2mm
variation, means every piece of the platforms has been tested by a 0.2mm feeler
gauge (**both sides of the platform have been respectively laid on a flat marble table and
the 0.2mm feeler gauge could not be inserted in-between the platform and marble table).
There will be more details for the fine adjustment of the leveling in Step 8.
Step 7. Test print: insert the SD card (back side facing up) into the SD card slot at the base.
Click on the Home Menu “Print” to enter the file list (Fig. 10). There is a printable
test file included -- “owl_pair” (author: etotheipi, www.thingiverse.com).
(Figure 10)
Single click on “owl_pair”, and click “Print”. The machine will be automatically
heating the platform and nozzle before printing.
Now, as the temperature rises, please manually insert the filament through
the Teflon tubing all the way into the hotend. (Refer to previous Fig.6)
The filament should flow through when temperature reaching to over
~180-190°C, otherwise the filament has not been inserted properly.

12
Customers may use tweezers to carefully remove the extruded filament at the
nozzle tip before printing.
Step 8. There might be 3 kinds of results for the first layer of the test prints (Fig. 11).
(Figure 11)
In case of “nozzle too close” or “nozzle too high”(Fig. 11 A or C), please click
Nozzle too high
A
B
C
Nozzle too close
Lack of extrusion
Proper nozzle height
Good extrusion and adhesion
Poor adhesion
√
x
x

13
“Stop” on the screen, raise the nozzle (click “Tools”-->“Axis”-->“10”on +Z
column), and manually fine tune the corresponding nuts under the platform.
Particularly, when “nozzle too high” slowly loosen the corresponding nuts
underneath the platform by half circle, while “nozzle too close”, slowly tighten
the corresponding nuts underneath by half circle. After that, clean the platform with
scraper, and run test file again to verify.
It may need adjustment for few times until satisfying results such as Fig. 11 B.
Supplements to leveling:
In some rare cases, after “Home All”, the nozzle can be still much lower than the
platform, even after fully tighten the 4 nuts underneath. On the opposite, sometimes the
nozzle is still too high from the platform, even after fully loosen the 4 nuts underneath.
How to solve this:
(1) Raise the nozzle by click “Tools”-->“Axis”-->“10”on +Z column, adjust the
4 nuts under the platform, let the height in-between the support plate and the
heated bed is ~15mm for all the 4 corners.
(2) As shown in Fig. 13, at both ends of X axis, there is a Z adjustable nut. The lower
tip of Z adjustable nut can trigger the Z end stop when Home (going down), and
~15mm
~15mm
(Figure 12)

14
‘tell’ the machine Z axis is getting to zero and stop moving.
(3) Therefore, tighten Z adjustable nut by
X
mm if nozzle is lower than the platform
(
X
is defined by how much the nozzle is under the platform), while loosen it by
Y
mm if
nozzle is too high from the platform (
Y
is defined by how much the nozzle is above the
platform). It may need adjustment for few times.
(4) Click “Tools”-->“Home”-->“Home all” to verify the results. After this, please
level the platform again from Step 3.
Tighten or loosen it
Z adjustable nut
(Figure 13)
(Figure 14)

15
5. Software installation
There are two operation mode for ANYCUBIC Mega 3D printer, print offline (via SD card)
and print online (controlled by PC via USB). Print offline: After leveling the platform,
insert SD card, click “Print” at the Home menu and select a file (gcode file) to print.
Print online: Install CP2102 driver to bridging PC and machine, and install Cura to
control the machine via USB.
Generally, it is suggested to use Print offline to minimize the noisy signal via USB. The
preparation steps for Print Online are shown as below.
5.1 Driver installation
ANYCUBIC Mega 3D printer uses CP2102 chip for communication. So, it is necessary to
install CP2102 driver so the printer could be recognized by PC.
Firstly, power on the machine and connect it to PC via USB cable.
CP2102 driver is copied in the SD card. “Files_Engish_Mega”--->
“Driver_CP2102”. There are two versions, Windows and Mac version.
For Windows, specifically, “CP210xVCPInstaller_x64” is for 64 bit system and
“CP210xVCPInstaller_x86” is for 32 bit system.
Here we take Windows 7-64 bit PC system for example, while there is
“Installation for Mac PC” in SD card for those who use Mac system.
On PC, right click on “Computer”--->“Properties”---->“Device Manger”, and

16
then follow the steps in Fig. 15 below.
(Figure 15)
After successfully installation, a COM
x
would appear in the Ports of Device Manager,
x
is
random (as here is COM3), customers will have their own COMx depends on their PC.
This COMx port will be used for communication between the printer and PC later.
Not installed
Right click and
choose update
Find the directory
of CP2102
\Desktop\Mega\ Files_Engish_Mega\Driver_CP2102\win
Click
COM3 appears in
Ports
①
②
③
④
⑤
⑥

17
If the PC has been installed CP2102 driver before, then there should be a COMx in
Ports of Device manager already.
Sometimes, even the driver is not installed properly, it may still show an abnormal
COM
x
in Ports, please just uninstall the COM
x
and try to install the driver again.
5.2 Cura Installation
ANYCUBIC Mega 3D printer reads Gcode file and prints. It is necessary to convert 3D files
(such as stl file) into Gcode files for machine to recognize. Software that convert 3D files
into Gcode files is called slicing software. Cura_15.04.6 is used for example here.
Location of Cura: SD card--->“Files_Engish_Mega”--->“Cura”--->“Windows”.
Double click “Cura_15.04.6”, and follow the procedures as shown in Fig. 16:
(Figure 16)
①
②
③
④

18
Next, before start Cura for the first time, there will be more settings about the language
and machine types, as show in Fig. 17.
(Figure 17)
Upon finish, open Cura for the first time, there might be a default robot model appears,
customers may click “File”--->“Clear platform” to delete it.
①
②
③
④

19
5.2.1 Load 3D model into Cura
(1) Clear the platform by clicking “File”--->“Clear platform”
(2) Load 3D files onto the platform by “File”--->“Load model file…”. Files with extension
such as “STL”, “OBJ”, “DAE” and “AMF” can be loaded.
Model in grey means it is outside of the printable area and needs to be moved or scaled to fit in.
5.2.2 Manipulate 3D model in Cura
(1) Zoom in/out: scroll the mouse wheel
(2) Change viewing angle: right click the model, hold on and move the mouse
(3) Position change: left click on the model, hold on and drag the model to move.
(4) Rotate: single left click on the model and several icons will appear at the bottom left
of the window (Fig. 18). Click the rotate button, 3 circles will surround the model. Rotate
the model by moving the circle lines.
Lay flat: it is very impartant to ensure the flat portion of the model is well
attached to the platform. So, please use Lay Flat option everytime after rotating
the model, as it will minimize the adhesion issues during printing. (Fig. 18)
Reset: click it to return the model to the original orientation.
(Figure 18)
Lay flat
Reset

20
(5) Scale: to uniformly scale the model along X/Y/Z dimensions. To disable uniform
scaling, click the lock in the lower section of the scaling window. (Fig. 19)
(Figure 19)
(6) View mode (Fig. 20): to view the model in different ways and helps to spotting issues
before print starts. Such as “Layers” mode: to view the toolpath of the print head to
check if there are skipped layers or gaps.
(Figure 20)
Scroll at layers mode
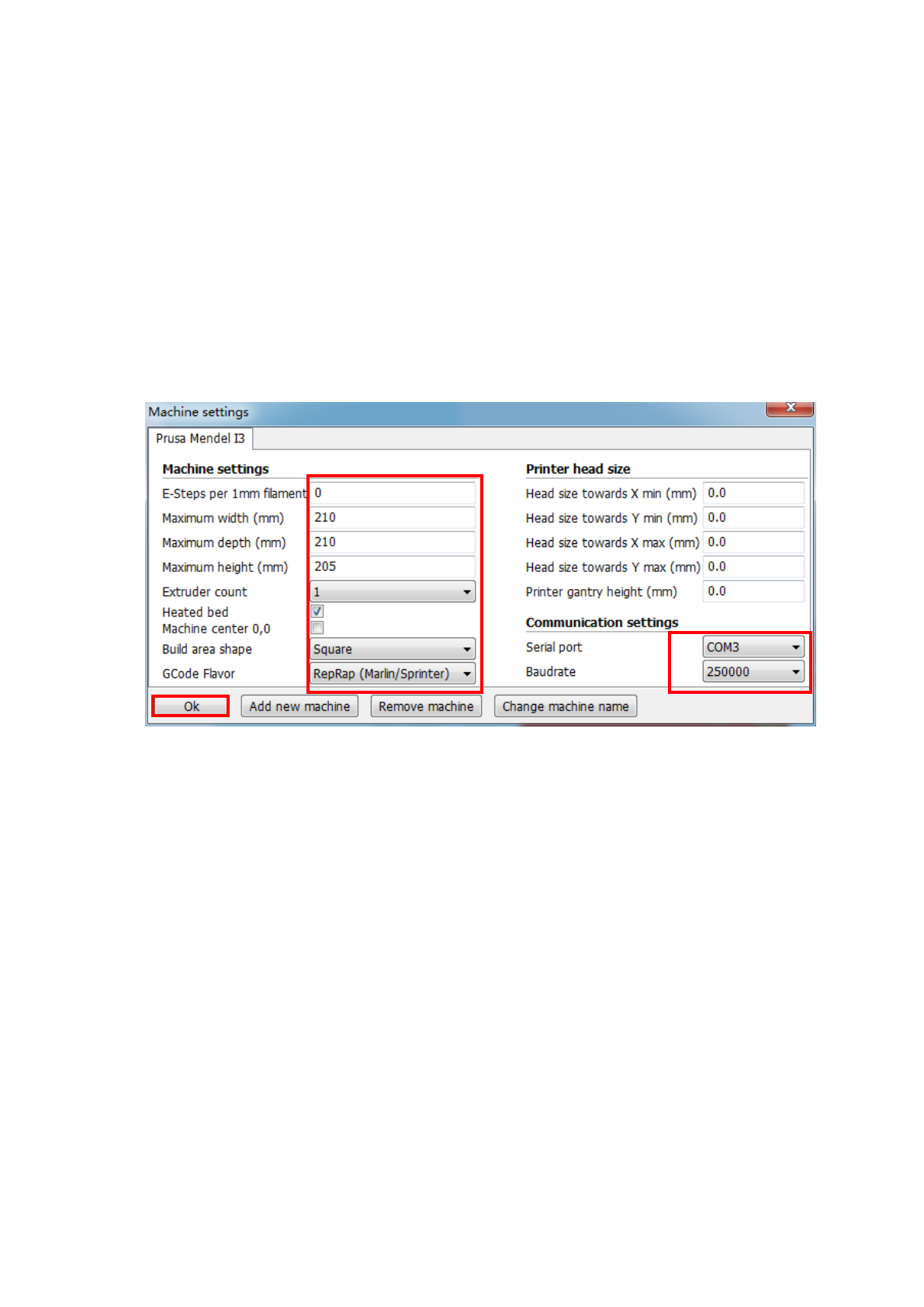
21
5.2.3 Cura settings
(1) Machine settings
Refer to Fig. 21, click “Machine”--->“Machine settings” to input those suggested
parameters into the corresponding column. Please choose the Serial Port (COM) as
shown in your PC→Device Manager→Port (refer to Fig. 15 ⑥, customers may have a
different COM
x
other than the example COM3), and set the Baudrate to 250000. Those
two parameters are essential for Cura to connect to the printer.
(Figure 21)
(2) Basic and Advanced options
Suggested “Basic” and “Advanced” setting are shown in Fig. 22. Stay the mouse
upon each box and there will be explanation for it.
Those parameters are suggested for ANYCUBIC Mega 3D printer to print ANYCUBIC PLA
filament. Generally, those settings are also compatible with other brand of PLA, but
customers may need to fine tune the parameters to get the best results, for example,
customers could try different ‘printing temperature’ based on the suggestion from a
particular filament supplier. Especially, in order to get a good adhesion for the first layer,
the ‘Bottom layer speed’ should not be too fast (20mm/s suggested).

22
(Figure 22)
(3) Plugins
*It is recommended for new user to leave the plugins as default (i.e. no plugins enabled).
Plugins are custom settings which will active at specific point during printing. There are
two pre-loaded plugins with Cura: Pause at height and Tweak At Z. More plugins can be
found via: http://wiki.ultimaker.com/Category:CuraPlugin
As shown in Fig. 23, to enable one of the plugins, such as Pause at height, first click it
and then click the drop-down arrow to enter the setting interface.
“Pause at height” will allow the printing to pause at a specified height, as well as
where the print head would move to and how much filament to retract to prevent
extruded filament blobs. So, customers could do filament change during printing.

23
“Tweak at Z” would allow custom changes at specified Z height. Customers may
decide the Z height or layer counts at which to make a change. Then there are more
settings for how you would like to change, such as temperature, fan speed and print
speed. Fine tune those for specific model would produce better results.
If wish to delete the plugins, stay mouse at the edge, hold the left button and drag
mouse to show the Delete icon.
(Figure 23)
(4) Start/End-GCode
As shown in Fig. 24, custom Gcode allows for complex automatic printer movements
and operations. By adding custom Gcode into the start or end of the Gcode file,
customer could change how it prints. A detailed list of Gcode commands can be found
via: http://reprap.org/wiki/G-code
There will be explanation later about how to add command to start-gcode to achieve
the function of resume from outage.
Stay mouse here and drag
to show the delete button
Delete

24
(Figure 24)
5.2.4 Print online by Cura
After parameter settings, customer can print online by Cura with USB connection.
Click “File”--->“Print…” enter the printing popup window (Fig. 25). (If a simplified
version of printing window appears, please click “File” --->“Preferences…” to choose the
‘Pronterface UI’ in the “Printing window type” drop-down menu)
Click “Print” icon when it is available after auto connect with the printer. Then the
temperature would rise and it will start to print when reaching to the target temperature.

25
Use tweezers to carefully get rid of the pre-extruded filament.
Note: If it fails to connect the printer in the popup “Printing window” (in a case that the
“Print” icon is gray and unavailable), check with the COMx or Baudrate in “Machine
settings”, and re-open the printing window to proceed.
(Figure 25)
5.2.5 Save GCode in Cura
In Cura, click “File”--->“Save GCode…” to save the file to a desired directory. And it
is highly recommended to save the Gcode in a SD card for printing offline.
Re-open the Gcode file again in Cura to confirm that all slices of the model have
been included by check it in the “Layers view” (refer to previous Fig. 20).
The file name should only contain English letters, underscore and space. File
name contains special characters could not be recognized by the printer.
Approx printing time

26
6. Printing
Here shows the steps of printing offline (via SD card), print online please refer to 5.2.4.
1. Click “Tools”-->“Preheat”-->“Preheat PLA (for example)”, Fig. 26.
2. After the pre-heat is finished, please click on Home screen “Tools”-->“Filament”-->
“Filament in”(Fig. 27). The extruder motor will start to feed the filament into the
hotend. There might be some excessive filament melt through the nozzle at high
temperature, use tweezers to carefully remove it from the nozzle tip before print.
3. Insert the SD card into the SD card slot at the base. On Home Menu, Click “Print” to
enter the files list. Click a exist file (e.g. “owl_pair”), and click “Print”(Fig. 28). The
machine will be sequentially heating the heated bed and nozzle and then print.
①
②
(Figure 28)
(Figure 27)
(Figure 26)

27
4. Upon finishing, the print head and heated bed will be automatically cooling down. Only
remove the printed object from the heated bed when it is cooled completely. Pull the
print platform to the front side, and use scraper to carefully remove the object as shown
in Fig. 29. Never direct scarper to your hands.
Please be mindful that the nozzle and heated bed are still hot after operation.
(Figure 29)
5. ANYCUBIC Mega 3D printer equipped with ANYCUBIC Ultra-base (a novel print platform)
which could be used for very long time without adding any masking tape, “hair spray”
or glue stick. Customers only have to clean it by alcohol or similar after every few prints.
Suggested nozzle (print) temperature for PLA: 190-210°C, ABS: 230-240°C,
Bed temperature for PLA: 60°C, ABS: 80-100°C. (it is suggested to disable
the model cooling fan for ABS in Advanced settings of Cura)
After operation, do not immediately switch off the printer. Only turn it off after
the nozzle cools to room temperature, because the heat sink still needs fan for
cooling to minimize the risk of nozzle clogging.

28
7. Manual filament change
1. Feed the filament: click via the Home menu: “Tools”-->“Preheat”-->“Preheat PLA
(for example)”. After it reaches to the target temperature, press down the handle at
the extruder as shown in Fig. 30, and manually push the filament through the Teflon
tubing till the hotend and there should be filament melt through the nozzle.
Make sure the filament passes through the filament sensor first before reaching
into the extruder.
For easier feed in the filament, it is suggested to cut off the bent tip before insert.
2. Remove the filament: at the Home menu, click “Tools”-->“Preheat”-->“Preheat
PLA (for example)”. After it reaches to the target temperature, press down the
handle at the extruder as shown in Fig. 30, manually push in the filament firstly until
seeing the filament melt through the nozzle, then quickly draw out the filament. The
purpose of pushing in the filament is to minimize the risk of nozzle clogging.
(Figure 30)
Press
Manually insert or draw out
①
②

29
8. Resume from outage
ANYCUBIC Mega 3D printer allows resume print job after accidently power loss.
*This function only valid when print offline (via SD card only).
1. As shown in Fig. 31, in slicing software (i.e. Cura), it is required to place the model at the
rear of platform. Because during “Resume from outage”, machine will home first and
could touch/interfere with the unfinished object if the model was placed in the front
area (Fig. 32).
(Figure 31)
(Figure 32)
Rear area
Zero (Home position)
Front
Rear
OK
No

30
2. For the first time of using this function, customers are required to add “G5” to the
start.gcode, as shown in Fig. 33. Then, save the model as Gcode file to the SD card by
“File”--->“Save GCode…”.
3. Insert the SD card (back side facing up) into the SD card slot at base. Print the just saved
file (i.e.“owl_pair”). The machine will automatically heating on and print.
During this printing, if there is an accident power loss, the print will stop immediately.
But after power comes back, customers could just choose the unfinished file and click
“Resume” (Fig. 34). Machine will home first and continuing on the unfinished object.
(Figure 34)
Highlight
Type G5
①
②
(Figure 33)

31
Note:
In order to get smooth surface, use tweezers to carefully remove the excessive
filament at nozzle before continuing print upon the last point.
Do not move Z axis after power off otherwise resume will be invalid.
ANYCUBIC Mega 3D printer supports resume from outage only when print offline
This function is developed based on Cura. We could not guarantee this function
compatible with other slicing software.
Due to the differences of filaments, temperature, extrusion, etc…we could not
guarantee a perfect surface at the point of “Resume from outage”, especially
for small object.

32
9. Trouble shooting
1. Motor shaking or abnormal sound
① The corresponding end stop could not be triggered when Home, check the
wirings, and inspect any obstacles by manually moving the corresponding axis
② The motor cable are not connected properly, check each connection and then
inspect the cable routing for any faults
2. File not printing or SD card failure
① Remove the SD card and insert into PC. Open the Gcode files using text editor
(eg. Notepad), and inspect if Gcode is readable or not. If files contains of multiple
“ÿÿÿ” symbol, then file has been corrupted. Try reformatting the SD card to
FAT32 format and reloading the Gcode file
② SD card is not readable, ensure file name does not contain special characters or
Change SD card
③ Touch screen freeze, reboot the machine and try again
3. No extrusion or extrusion motor knocking
① Ensure that the nozzle temperature has been set to match the filament
② Filament tangled on spool
③ Not enough cooling for the hotend
④ Nozzle clogged please try to replace it or clean it
⑤ Teflon tubing has been tangled, squeezed or bent
4. Filament leaking
Nozzle or throat tube is tightened properly, try to fix/change it after cooling
5. No sticking to the bed
① Print too fast at the bottom layer speed, reduce it to ~20mm/s
② Ensure that the print platform is clean (use alcohol if necessary)

33
③ Check if the bed is proper leveled
④ add a brim or raft to the model in slicing software
⑤ Check the bed temperature matches the filament
6. Warping/curling of the printed object
① Check the bed temperature matches the filament
② Check the infill % of the Gcode. The higher the infill, the more likely to warp
③ add a brim or raft to the model in slicing software.
7. Layer shifting
① Print head moving too fast, slow down the print speed.
② Check X/Y belt and the driving wheel and ensure they are properly installed.
③ Grease the rods and check all nuts and bolts remain tightened.
8. Freezing screen
① Inspect if the touch screen has been pressed by the metal frame at the edge
② Check if screen has cracks, if so, please contact us at support@anycubic3d.com
9. T0 sensor abnormal
① Check the wiring of the hotend and ensure a good connection
② Check if there is any pins bent inside the connector
10. Print head move abnormal
① Check if choosing the right machine type in slicing software
② Check if any plugins in the slicing software
11. Print stopped halfway
① Check if the Gcode file is corrupted
② Delete plugins in the Gcode file
③ Use print offline mode (SD card) instead of print online via USB