MEGALUG Series 1100 Mechanical Joint Restraint For Ductile Iron Pipe Product Brochure Telephone PDX Brochure.1100
User Manual: Telephone PDX-1100 series
Open the PDF directly: View PDF .
Page Count: 6
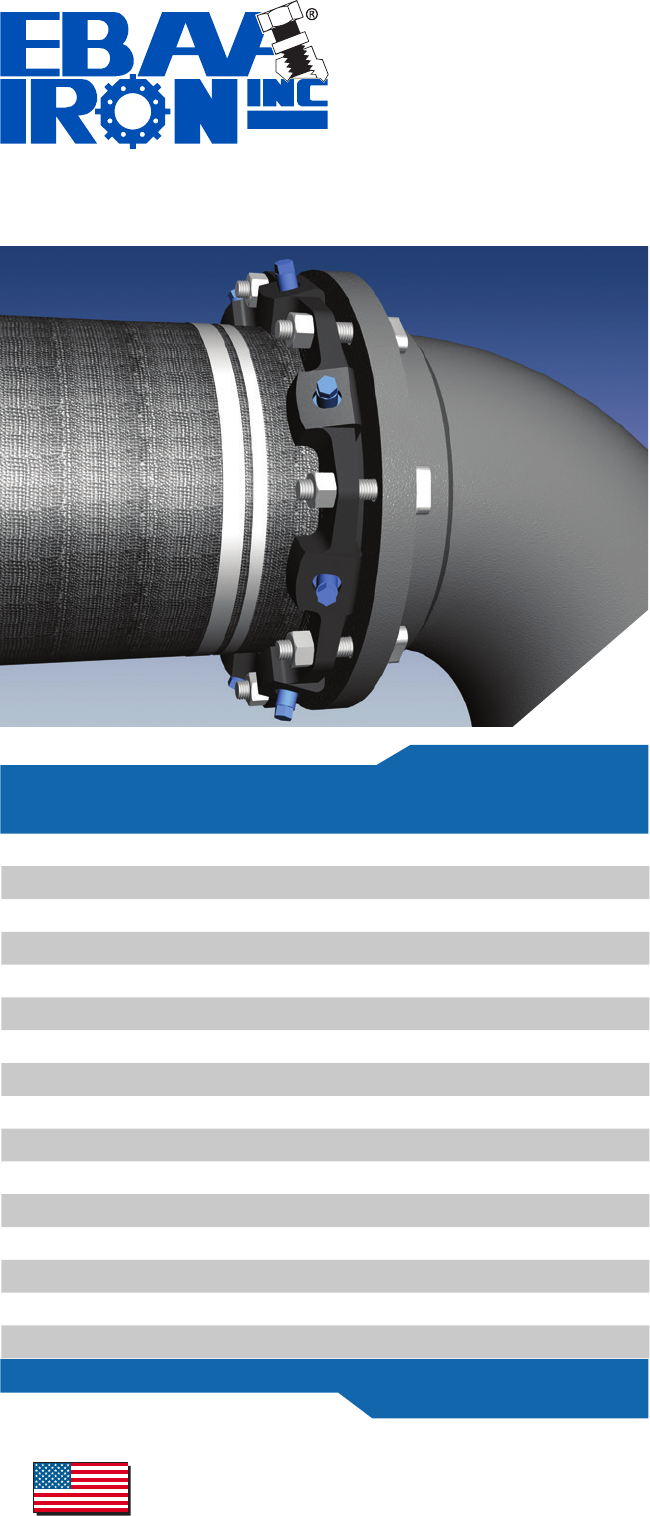
MEGALUG®
Series 1100
Mechanical Joint Restraint for Ductile Iron Pipe
Features and Applications:
• Sizes 3 inch through 54 inch
• Constructed of ASTM A536 Ductile Iron
• Torque Limiting Twist-Off Nuts
• MEGA-BOND®
Restraint Coating System
For more information on MEGA-BOND,
refer to www.ebaa.com
• The Mechanical Joint Follower Gland is
incorporated into the restraint
• Heavy Duty thick wall design
• Support Products Available:
Split repair style available 3 inch
through 48 inch.
EBAA Series 1100SD
Solid restraint harness available for
push-on pipe bells.
EBAA Series 1700
Split restraint harness available for
existing push-on bells.
EBAA Series 1100HD
• All MEGALUG and related restraint
products can be furnished as packaged
accessories complete with appropriate
restraint, gasket, lubrication, and bolt-
ing hardware
• For use on water or wastewater pipe-
lines subject to hydrostatic pressure
and tested in accordance with either
AWWA C600 or ASTM D2774
Nominal
Pipe Size
Series
Number
Shipping
Weights
Post
Assembly
Deection
Pressure
Rating
(PSI)
3 1103 6.1 3° 350
4 1104 7.7 3° 350
6 1106 11.9 3° 350
8 1108 14.8 3° 350
10 1110 23.9 3° 350
12 1112 31.2 3° 350
14 1114 48.5 2° 350
16 1116 56.4 2° 350
18 1118 63.1 1½° 250
20 1120 72.3 1½° 250
24 1124 133.1 1½° 250
30 1130 194.6 1° 250
36 1136 234.0 1° 250
42 1142 536.0 1° 250
48 1148 653.0 1° 250
54 1154 700.2 0.5° 200
NOTE: For applications or pressures other than those shown please
contact EBAA for assistance.
U.S. Patent Nos.
4092036, 4627774, 4779900, 4896903, 5544922
Made In
The USA
0218-J Copyright © 2018. EBAA Iron, Inc. All Rights Reserved.
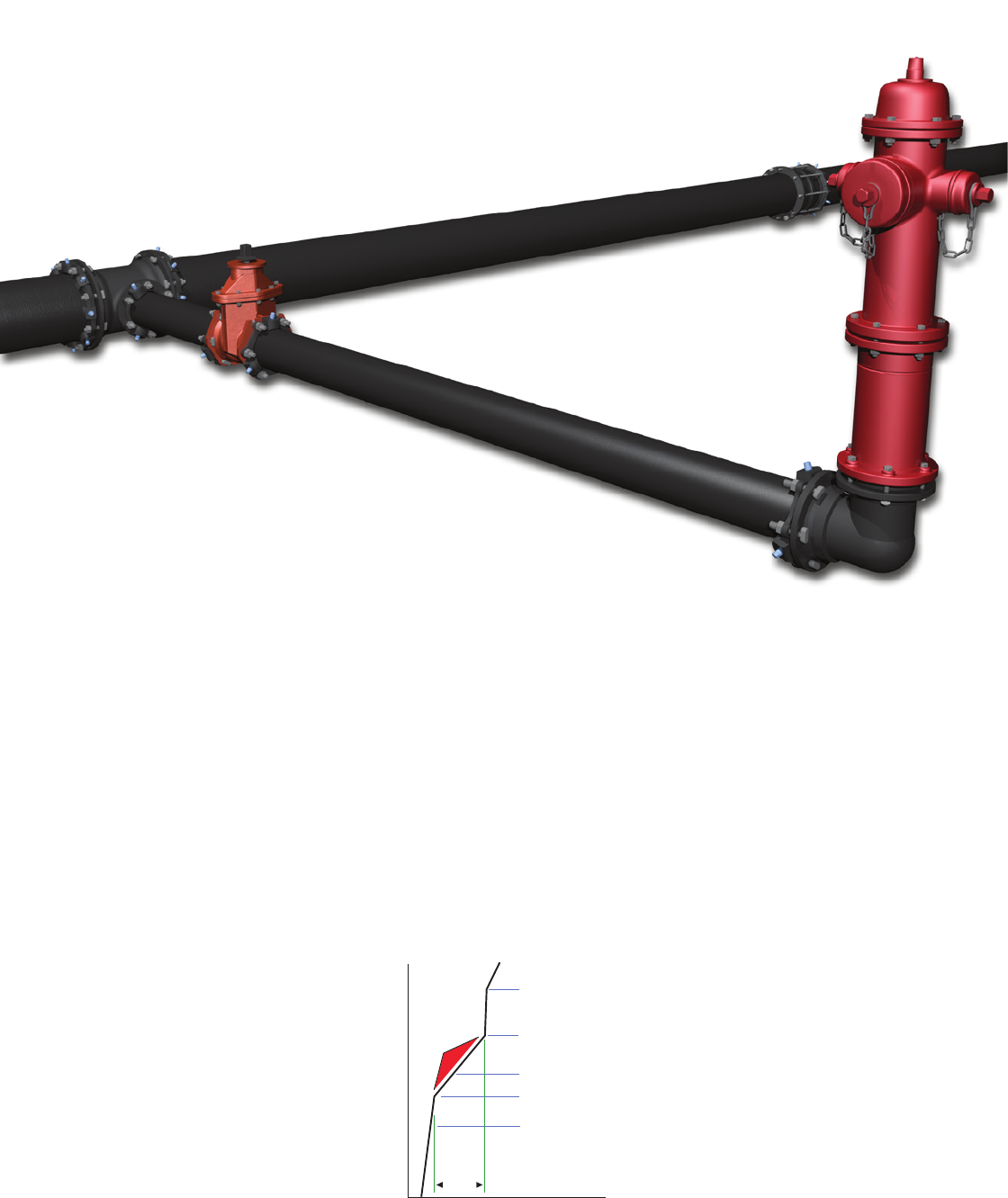
MOVEMENT
PRESURE OR EXTERNAL FORCE
Max pressure
Movement
causes
wedges to
increase
grip
Max movement
Rated pressure
Wedge movement
begins
Normal operating
pressure
RCM
Since 1984, engineers and contractors designing and installing
water and wastewater pipelines and systems have come to rely
on the EBAA Series 1100 MEGALUG Mechanical Joint Restraint
as the “Product of Preference” for effectively and economically
restraining ductile iron pipe connections above or below ground.
MEGALUG Mechanical Joint Restraints replace external re-
straints such as cumbersome concrete thrust blocks and corrod-
ible metal tie rods creating a quicker, safer and more economical
installation.
Major testing laboratories agree as the 3” through 24” sizes
are Underwriters Laboratories (UL) listed, and the 3” through 12”
sizes are Factory Mutual (FM) approved.
For use on all classes of ductile iron pipe (PC350 through
PC150 and CL56 through CL50), for practically any application
including valves, hydrants and pipe, the MEGALUG Mechanical
Joint Restraint effectively and safely performs without damage to
the pipe or cement linings.
The wedge style MEGALUG design reacts
to the amount of force acting on the joint.
When each wedge is set, the wedge teeth
penetrate the pipe’s outer surface, and
the wedge does not move on the pipe.
There is very little change in this interface
until the wedge movement begins inside
the pocket of the main casting. Once the
wedge starts moving, the formation of the
buttress begins.
This “dam” of material (the wedge
impression) is cold formed as the wedging
action continues. If the force of pressure
acting on the joint is released, the wedge
moves back to near its original position.
This engages the reserve-controlled move-
ment or “RCM”. The wedge is then ready
for another round.
After the wedge has moved to the back
of the pocket at the maximum pressure or
load, the wedge buttress are in shear. The
maximum movement is about 0.3 inch
through the thirty-six inch size and 0.4
inch for forty-two and forty-eight inch.
The RCM is available even with severe
cyclic loads. This has been tested to very
high-pressure differentials and the wedge
impressions look the same as if a single
test had been performed.
Typically, the depth of pipe wall pen-
etration, or wedge impression at around
25,000 pounds of force per wedge (200
PSI on a six inch and 150 PSI on a twelve
inch) is 0.03”. Finally, at roughly twice that
force the penetration is around 0.05” At
these high pressures, there is no affect on
the design thickness of ductile iron pipe
made according to AWWA C150. The lack
of damage to the cement lining clearly
indicates that the thrust load is primarily
longitudinal.
This ability to move in the pocket allows
for angular exibility as well as longitudi-
nal exibility.
THE MEGALUG GRIPPING WEDGE... PERFORMANCE PROVEN
MEGALUG: THE PRODUCT OF PREFERENCE SINCE 1984
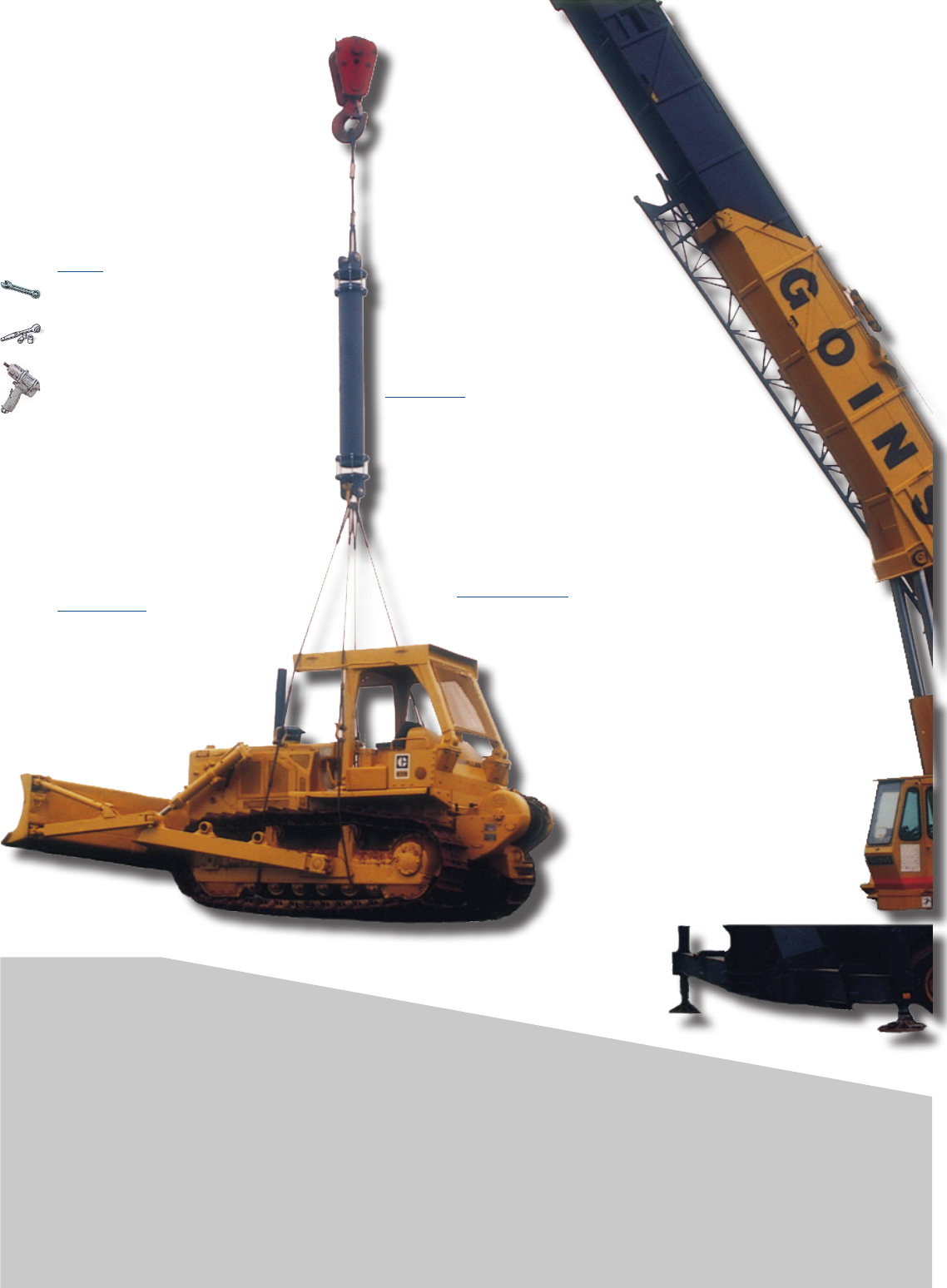
THE ORIGINAL PATENTED
GRIPPING WEDGES
Since 1964 EBAA Iron has responded
aggressively to the needs of the
water industry for better solutions
to joint restraint problems - thus the
development of the family of self
actuating MEGALUG wedge action
restraints.
TOOLS
MEGALUGS install using an ordinary
wrench (box, ratchet, or air-driven),
because the torque-limiting, twist-
off nuts automatically shear during
tightening when the proper torque
is reached. The same 1¼ wrench
used to tighten the T-bolts on the
4” through 24” sizes can be used
to tighten and shear the twist off
nuts in all sizes. If removal becomes
necessary, a 5/8 hex head remains
so the screws can be loosened, and
retightened with a torque-indicating
wrench. During removal, the wedges
are held in place by retainer clips.
DEFLECTION
The MEGALUG gripping wedges
provide resiliency to your
pipeline design. In addition
to deecting as much as
allowed by the
mechanical joint
during installation,
it can also deect
after assembly:
Sizes of 12” and below
are capable of up to 3
degrees of deection after
installation (depending on the
preset deection.)
The 14” and 16” sizes are
capable of 2 degrees deection.
The 18” through 24” sizes are
capable of 1.5 degrees deection.
The 30” through 48” sizes are capable of
1 degree deection.
The 54” size has a 0.5 degree deection.
STEEL PIPE
The 1100 Series MEGALUG can be used to restrain
3” - 8” SCH 40 or 80 steel pipe when joining to
mechanical appurtenances. It can also be used on
steel pipe in all sizes if the pipe’s outside diameter is
the same as the ductile iron pipe and its thickness is
equal to or greater than PC350 ductile iron pipe in sizes
of 16 inch and below and PC250 ductile iron pipe 18
inches and above.
CAST IRON PIPE
Grey iron pipe diameters are often larger than ductile
iron pipe diameters. The Series 1100 MEGALUG
restraint may be used with grey iron pipe having
standardized cast iron O.D. per AWWA C150 and
C151, and with pit cast Classes “A” and “B”
without modication. Use of the Series 1100
with pit cast grey iron Classes “C” and “D”
will require over sizing the MEGALUG. More
information on this is explained in detail in
“Connections Bulletin DI-1”.
MEGALUG
Takes the Load
On April 11, 1997 EBAA Iron performed a remark-
able force demonstration of their series 1100 MEGALUG Joint
Restraint. With the use of EBAA’s Series 1100 MEGALUG using a standard
mechanical joint installation on 12 inch Ductile Iron Pipe, and a 80 Ton mo-
tor crane, EBAA Iron lifted a D7 Caterpillar Track Type Tractor weighing in at
50,350 lbs. Along with this, the Series 1100 MEGALUG has been tested to over
700 PSI. Concluding that EBAA’s MEGALUGS can take the load.
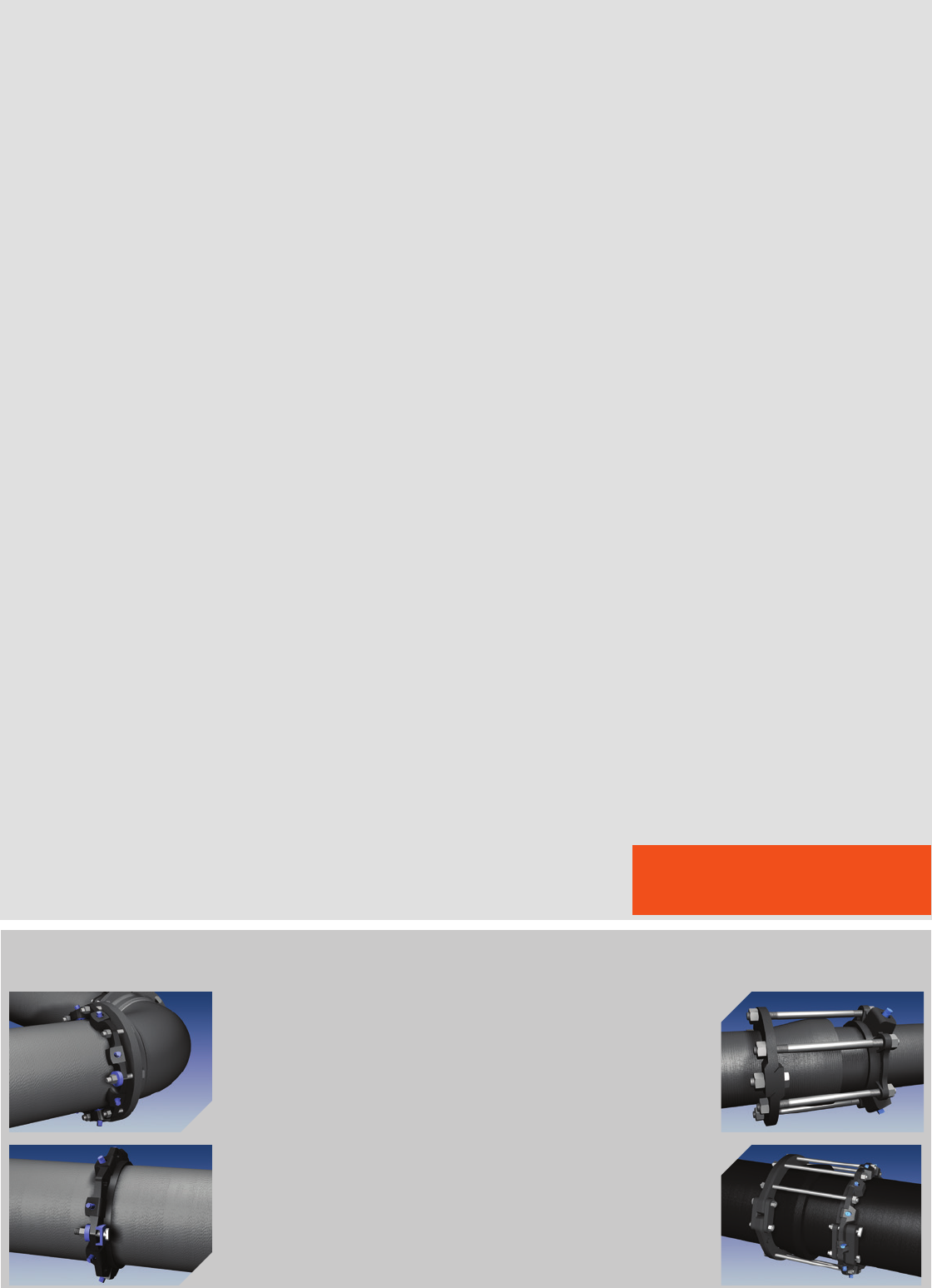
Mechanical Joint Restraint Sample Specications
(The text of the specications below can be copied pasted from www.ebaa.com/download/1100Spec.DOC)
Restraint devices for mechanical joint ttings and appurtenances conforming to either ANSI/AWWA C111/
A21.11 or ANSI/AWWA C153/A21.53, shall conform to the following:
Design
Restraint devices for nominal pipe sizes
3 inch through 54 inch shall consist of
multiple gripping wedges incorporated into
a follower gland meeting the applicable
requirements of ANSI/AWWA C110/A21.10.
The devices shall have a working pressure
rating of 350 psi for 3-16 inch, 250 psi for
18-48 inch and 200 psi for the 54 inch.
Ratings are for water pressure and must
include a minimum safety factor of 2 to 1 in
all sizes.
Material
Gland body, wedges and wedge actuating
components shall be cast from grade 65-
45-12 ductile iron material in accordance
with ASTM A536.
For applications requiring restraint 30
inch and greater, an alternate grade of
iron meeting the material requirements of
ASTM A536 is acceptable, providing the
device meets all end product performance
requirements.
Ductile iron gripping wedges shall be heat
treated within a range of 370 to 470 BHN.
Three (3) test bars shall be incrementally
poured per production shift as per
Underwriter’s Laboratory (U.L.)
Specications and ASTM A536. Testing for
tensile, yield and elongation shall be done
in accordance with ASTM E8.
Chemical and nodularity tests shall be
performed as recommended by the Ductile
Iron Society, on a per ladle basis.
Traceability
An identication number consisting of
year, day, plant and shift (YYDDD)(plant
designation)(Shift number), shall be cast
into each gland body.
All physical and chemical test results
shall be recorded such that they can be
accessed via the identication number on
the casting. These Material Traceability
Records (MTR’s) are to be made available,
in hard copy, to the purchaser that requests
such documentation and submits his gland
body identication number.
Production pieces that are too small to
accommodate individual numbering,
such as fasteners and wedges, shall be
controlled in segregate inventory until
such time as all quality control tests are
passed. These component parts may then
be released to a general inventory for nal
assembly and packaging.
All components shall be manufactured
and assembled in the United States. The
purchaser shall, with reasonable notice,
have the right to plant visitation at his/her
expense.
Installation
Mechanical joint restraint shall require
conventional tools and installation
procedures per AWWA C600, while
retaining full mechanical joint deection
during assembly as well as allowing joint
deection after assembly.
Proper actuation of the gripping wedges
shall be ensured with torque limiting twist
off nuts.
Approvals
Restraint devices shall be Listed by
Underwriters Laboratories (3” through 24”
inch size) and Approved by Factory Mutual
(3” through 12” inch size).
Mechanical joint restraint for ductile
Iron pipe shall be Megalug Series 1100
produced by EBAA Iron Inc. or approved
equal.
MEGA-BOND® Restraint Coating
System
All wedge assemblies and related parts
shall be processed through a phosphate
wash, rinse and drying operation prior
to coating application. The coating shall
consist of a minimum of two coats of liquid
thermoset epoxy coating with heat cure to
follow each coat.
All casting bodies shall be surface
pretreated with a phosphate wash, rinse
and sealer before drying. The coating shall
be electrostatically applied and heat cured.
The coating shall be a polyester based
powder to provide corrosion, impact and UV
resistance.
The coating system shall be MEGA-BOND by
EBAA Iron, Inc. or approved equal. Requests
for approved equal must submit coating
material and process details for review prior
to bid.
For more information regarding
MEGA-BOND, refer to the MEGA-BOND
brochure or visit www.ebaa.com.
Support Products
for more information concerning these products please consult the catalog or www.ebaa.com
Series 1100SD
Split MEGALUG Restraint
For Existing Mechanical Joints
Series 1100SDB
Split MEGALUG Restraint
For Mid-Span Applications
Series 1700
MEGALUG Restraint Harness
For Push-On Bell Joints
Series 1100HD
Split MEGALUG Restraint
Harness for Existing Push-On Bells
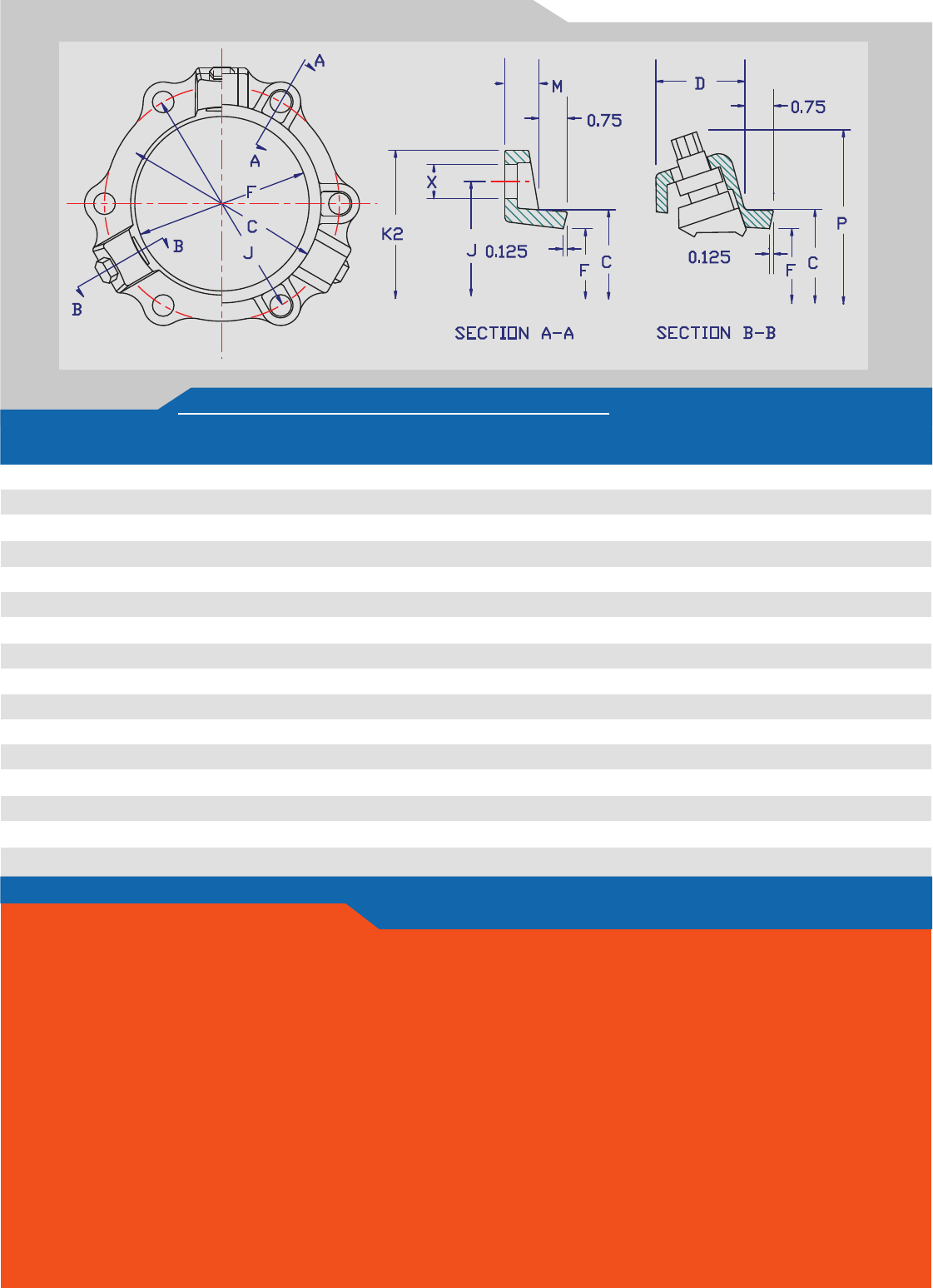
Series 1100 Submittal Reference Drawing
MADE IN USA
EBAA IRON
Nominal
Pipe Size
Series
Number
C D F M P* X J K2 Wedge
QT Y.
Bolt
QT Y.
Weight
(LBS.)
Pressure
Rating
(PSI)
31103 4.48 2.27 4.06 0.62 9.06 0.750 6.19 7.69 2 4 6.1 350
41104 5.92 2.27 4.90 0.75 9.90 0.875 7.50 9.12 2 4 7.7 350
61106 8.02 2.27 7.00 0.88 12.00 0.875 9.50 11.12 3611.9 350
81108 10.17 2.31 9.15 1.00 14.15 0.875 11.75 13.37 46 14.8 350
10 1110 12.22 2.37 11.20 1.00 16.20 0.875 14.00 15.62 6 8 23.9 350
12 1112 14.32 2.37 13.30 1.25 18.30 0.875 16.25 17.88 8 8 31.2 350
14 1114 16.40 2.69 15.44 1.50 20.94 0.875 18.75 20.25 10 10 48.5 350
16 1116 18.50 2.69 17.54 1.56 22.90 0.875 21.00 22.50 12 12 56.4 350
18 1118 20.60 2.69 19.64 1.63 25.00 0.875 23.25 24.75 12 12 63.1 250
20 1120 22.70 2.69 21.74 1.69 27.10 0.875 25.50 27.00 14 14 72.3 250
24 1124 26.90 3.20 25.94 1.81 32.64 0.875 30.00 31.50 16 16 133.1 250
30 1130 33.29 3.20 32.17 2.25 38.87 1.125 36.88 39.12 20 20 194.6 250
36 1136 39.59 3.20 38.47 2.25 45.17 1.125 43.75 46.00 24 24 234.0 250
42 1142 45.79 4.56 44.67 3.88 55.57 1.375 50.62 53.48 28 28 536.0 250
48 1148 52.09 4.56 50.97 3.88 61.87 1.375 57.50 60.36 32 32 653.0 250
54 1154 58.82 4.56 57.73 3.88 66.40 1.375 63.20 66.33 36 36 700.3 200
* With Twist-Off Nuts twisted off.
NOTE: Dimensions are in inches (±1%) and are subject to change without notice.
Important Notes
• The Series 1100 MEGALUG should not be used on plain end
ttings.
• EBAA-Seal™ Mechanical Joint Gaskets are provided with 30 inch
through 54 inch MEGALUG restraints. These are required on the above
referenced sizes to accommodate the pressure ratings and safety factors
shown.
• If encased in concrete, polyethylene wrap must be used to
prevent concrete intrusion into the wedge pocket.
• Extra length T-bolts are provided with the 42 inch, 48 inch and 54 inch
sizes to facilitate easier assembly of the mechanical joint.
• For test pressures above the rated pressures shown, contact
EBAA for recommendations, such as tandem restraint for high
pressure applications.
• All Series 1100 MEGALUG components are made of ductile iron
conforming to ASTM A536. The wedges are heat treated to a hardness
range of 370 to 470 BHN.
• If you experience the need to install the Series 1100
MEGALUG in an unconventional manner please consult our
engineering department.
• LISTINGS AND APPROVALS: Sizes 3 inch through 24 inch are listed by
Underwriters Laboratories, Inc. Category HJKF “Fittings, Retainer Type”
with a deection angle of 5 degrees (3 inch through 12 inch) and 2½
degrees (14 inch through 24 inch). The listing le number is EX2836,
Sizes 3 inch through 12 inch are Factory Mutual approved.
• The Series 1100 MEGALUG is intended for use on ductile iron pipe. The restraint can be used on grey iron pipe if the pipe is not severely
corroded and is in sound condition and has an outside diameter that can be accommodated. For more information on the use of the
MEGALUG restraint on grey iron pipe ask for Connections Bulletin DI-1.
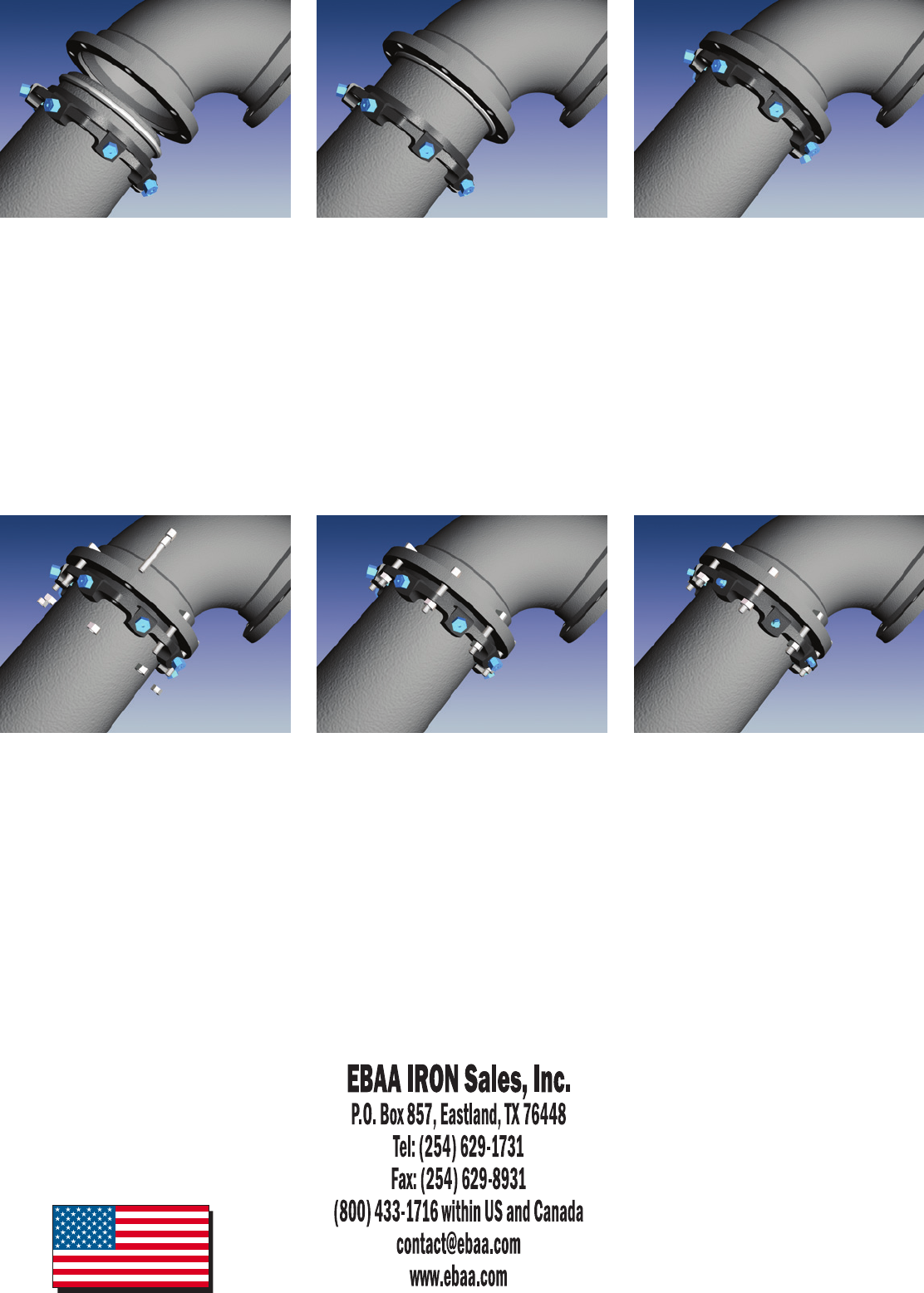
For More Information
For more information about MEGALUG restraints call
EBAA today and request
“EBAA Connections Bulletin DI-1” concerning use of
the MEGALUG restraint on grey iron pipe, or “EBAA
Connections Bulletin DI-2” covering the background
and operation of the MEGALUG system of restraint.
“Restraint Length Calculation” Software is available
for PC/Windows applications. Support documenta-
tion about the software can be found in “EBAA Con-
nections Bulletin PD-1 through PD-5”.
2. 3. 4.
4. (cont.) 5. 6.
1. The Series 1100 MEGALUG joint
restraint is designed for use on
ductile iron pipe conforming to
ANSI/AWWA C151/A21.51 (all
thickness classes) when restraining
mechanical joint pipe ttings.
2. Clean the socket and the plain
end. Lubrication and additional
cleaning should be provided by
brushing both the gasket and the
plain end with soapy water or an
approved pipe lubrication meeting
the requirement of ANSI/AWWA
C111/A21.11, just prior to slipping
the gasket onto the plain end for
joint assembly. Place the gland on
the plain end with lip extension
toward the plain end, followed by
the gasket.
NOTE: In cold weather it is
preferable to warm the gasket
to facilitate assembly of the
joint.
3. Insert the pipe into the socket and
press the gasket rmly and evenly
into the gasket recess. Keep the
joint straight during assembly.
4. Push the gland toward the socket
and center it around the pipe with
the gland lip against the gasket.
Insert bolts and hand tighten
nuts. Make deection after joint
assembly but before tightening
bolts.
7. If removal is necessary, utilize
the ⅝ inch hex heads provided. If
reassembly is required, assemble
the joint in the same manner as
above, by tightening the wedge
bolts to 90 ft-lbs. If the series 1100
restraint is removed from the pipe,
be sure that all the collar bolts and
wedges are in place before the
restraint is reassembled.
Steps 2-5 are requirements of
AWWA. AWWA Standard C600
6. Tighten the torque limiting twist
off nuts in a clockwise direction
(direction indicated by arrow
on top of nut) until all wedges
are in rm contact with the pipe
surface. Continue tightening in an
alternating manner until all of the
nuts have been twisted off.
5. Tighten the bolts to the normal
range of torque as indicated [3
inch 45-60 ft-lbs., 4-24 inch 75-
90 ft-lbs., 30-36 inch 100-120
ft-lbs., and 42, 48 and 54 inch
120-150 ftlbs.] While at all times
maintaining approximately the
same distance between the gland
and the face of the ange at all
points around the socket. This
can be accomplished by partially
tightening the bottom bolt rst,
then top bolt, next the bolts at
either side, nally the remaining
bolts. Repeat the process until all
bolts are within the appropriate
range of torque. In large sizes (30-
48 [and 54] inch), ve or more
repetitions may be required. The
use of a torque-indicating wrench
will facilitate this procedure.