Gas Boiler CE30 Domestic Heating By
User Manual: Gas Boiler
Open the PDF directly: View PDF .
Page Count: 64
- Introduction to best practice
- UK building regulations
- Boiler types
- Systems and components
- Controls
- Central Heating System Specifications (CHeSS)
- Energy efficiency
- System selection: practical issues
- Which type of boiler is most suitable?(31,43)
- What size boiler is required? (31,35)
- Where will the boiler be positioned? (31,32)
- What will be the flue terminal position and arrangement? (32,47)
- Where does the condensate drain go? (45)
- Are there any special ventilation requirements? (32,47)
- Will it be an open or sealed system? (31,43)
- What type of hot water system is most suitable?
- What type and size of heat emitters are required? (31,35)
- What controls are needed?(31,38)
- Installing central heating systems
- Commissioning and handover
- Appendix A – Notes to CHeSS 2008
- Appendix B – Definitions of boiler types
- Appendix C – Definitions of heating controls
- Appendix D – Energy efficiency checklist
- Appendix E – Heating controls: simple explanations for householders
- References

Domestic heating by gas:
boiler systems – guidance
for installers and specifiers
CE30

2Domestic heating by gas: boiler systems – guidance for installers and specifiers (2008 edition)
Contents
Introduction to best practice 1. 3
Boiler efficiency 1.1 4
Energy consumption and emissions 1.2 4
Environmental impact of gas heating 1.3 5
UK building regulations 2. 6
Introduction 2.1 6
General requirements 2.2 6
England and Wales 2.3 8
Scotland 2.4 9
Northern Ireland 2.5 9
Boiler types 13. 1
Condensing boilers 13.1 1
Regular boilers 13.2 2
Combination boilers 13.3 2
Range Cooker boilers 13.4 3
Systems and components 14. 4
Sealed and open-vented systems 14.1 4
Domestic hot water 14.2 5
Solar hot water systems 14.3 7
Passive Flue-Gas Heat Recovery 4.4 Devices
(PFGHRD) 18
Upgrading systems 14.5 8
Flue types 14.6 9
Heat emitters 24.7 1
Circulator pumps 24.8 1
Controls 25. 2
Individual controls 25.1 2
Selecting controls 25.2 6
Further control improvements 25.3 7
Central Heating System Specifications 6.
(CHeSS) 29
Energy efficiency 37. 1
Comparing boiler efficiencies 37.1 1
The Standard Assessment Procedure 37.2 2
Energy consumption and running costs 37.3 2
Carbon dioxide emissions 37.4 3
The Boiler Efficiency Database 37.5 4
Saving energy with better controls 37.6 4
System selection: practical issues 38. 6
Which type of boiler is most suitable?8.1 36
What size boiler is required? 38.2 7
Where will the boiler be positioned? 38.3 7
What will be the flue terminal position 8.4
and arrangement? 38
Where does the condensate drain go? 38.5 8
Are there any special ventilation 8.6
requirements? 39
Will it be an open or sealed system? 38.7 9
What type of hot water system is 8.8
most suitable? 39
What type and size of heat emitters are 8.9
required? 40
What controls are needed?8.10 40
Installing central heating systems 49. 1
Competent person requirements 49.1 1
Installing the boiler 49.2 1
Installing the condensate drain pipe 49.3 2
Condensate drain termination 49.4 4
Controls 49.5 7
Water treatment 49.6 8
Commissioning and handover 410. 9
Commissioning 410.1 9
Advising householders 410.2 9
Servicing 410.3 9
Appendix A – Notes to CHeSS 2008 50
Appendix B – Definitions of boiler types 53
Appendix C – Definitions of heating controls 55
Appendix D – Energy efficiency checklist 57
Appendix E – Heating controls: simple
explanations for householders 59
References 62

Domestic heating by gas: boiler systems – guidance for installers and specifiers (2008 edition) 3
Home energy use is responsible for over a quarter
of UK carbon dioxide (CO2) emissions which
contribute to climate change. To help mitigate
the effects of climate change, the Energy Saving
Trust has a range of technical solutions to help UK
housing professionals build to higher levels of energy
efficiency.
This guide is designed to help installers, specifiers
and purchasers of domestic central heating systems
to select the most suitable system for their needs.
It gives advice on how to achieve better energy
efficiency, lower running costs and reduced CO2
emissions.
This publication is particularly concerned with
the encouragement of best practice. While the
requirements for satisfying building regulations
in various parts of the UK are described, the
main purpose is to explain how to achieve better
performance through careful choice of systems and
practices.
This publication focuses on wet or hydronic central
heating systems in which the water is circulated to
heat emitters from a gas boiler. ‘Gas’ in this context
means natural gas or Liquefied Petroleum Gas
(LPG). Other guides in this series deal with systems
containing oil and solid fuel boilers.
This publication specifically addresses issues
concerning the selection of boilers, hot water storage
vessels, controls and indeed complete systems. It
brings together information on most types of boiler
currently available, the systems to which they can
be fitted and key points to consider when choosing
equipment for a particular installation. It concentrates
on the use of condensing boilers since it is no longer
acceptable to fit non-condensing boilers in most
cases for both new or replacement situations.
How to use this guide
The guide is set out as follows:
Section 2 explains the building regulations for
heating and hot water systems in different parts
of the UK.
Sections 3, 4 and 5 go into some detail about the
range of systems, boilers and controls currently
available.
Section 6 reproduces the Central Heating Systems
Specifications (CHeSS). These set out specifications
for meeting the basic efficiency levels needed
to comply with building regulations as well as
higher performance levels regarded as current
best practice. They can be used as ready-made
purchase specifications.
Section 7 focuses on the benefits to be obtained
from choosing best practice.
Section 8 covers the practical issues affecting the
selection of boilers, systems and controls.
Section 9 is concerned with proper installation,
especially with regard to the flues and drains
needed for condensing boilers, as well as the
installation of controls.
Section 10 offers guidance on commissioning
and other related issues such as servicing and
information to be provided to customers.
The appendices provide additional notes to the
CHeSS specification, together with definitions of
different boiler types and controls.
Note: the superscript numbers in brackets in the
text refer to documents listed at the end of this
guide.
Introduction to best practice1.

4Domestic heating by gas: boiler systems – guidance for installers and specifiers (2008 edition)
Introduction to best practice
Boiler efficiency 1.1
The efficiency of the boiler is the main factor in the
overall efficiency of a domestic central heating system.
This is why minimum standards of efficiency are
required by law for most boiler types. UK building
regulations requires a higher performance than the EU
Boiler Efficiency Directive(17) but best practice requires
boilers of even higher efficiency to be selected.
In turn, the efficiency of the overall system has a
major impact on running costs and the associated
CO2 emissions. Boiler efficiency depends upon:
Fuel•
Boiler type and design•
Ignition system (automatic or permanent pilot).•
Burner control (on/off, gas modulating, air/gas •
modulating)
The load on the boiler due to the weather•
Boiler and radiator sizing relative to the design •
heat load
System controls•
Flow and return temperatures•
Installation and commissioning•
System free of sludge and scale•
Regular servicing and maintenance. •
The advances in boiler technology mean that when
older boilers are replaced, substantial efficiency
improvements can be expected from newer
equipment. Manufacturers now design for maximum
efficiency consistent with durability. The greatest
energy efficiency benefits are obtained from installing
condensing boilers. These are always more efficient
than non-condensing models. It is now a requirement
of the building regulations that newly installed gas-
fired boilers should be condensing (excludes range-
cooker boilers), with a SEDBUK (Seasonal Efficiency
of a Domestic Boiler in the UK) efficiency of 86% or
more, unless exceptional circumstances apply (see
Section 2.2).
Energy consumption and emissions 1.2
Boilers consume far more energy than household
appliances. In the UK the average dwelling with
central heating uses about 23,000 kilowatt-hours
(kWh) of energy each year, of which about 85% is
for heating and hot water. To reduce fuel costs and
emissions it is important to choose the most efficient
boilers and install them in suitably designed and
controlled systems.
Figure 1: Heating and hot water as a proportion of total energy usage in homes heated by natural gas
Boiler
85%
Other
15%
Energy consumption
Boiler
67%
Other
33%
CO2 emissions
Boiler
56%
Other
44%
Relative costs
Why are condensing boilers more efficient?
A condensing boiler has a large heat exchanger
(or, in some designs, a second heat exchanger)
that extracts more heat from the flue gases. In
a non-condensing boiler, the flue gases are at
a temperature of 120-200°C. In a condensing
boiler, more heat is removed and the temperature
falls to below 100°C and as low as 50°C for
the most efficient boilers operating at reduced
boiler return temperature. The water vapour in
the gases condenses (hence the name) and the
resulting liquid has to be drained away. As the
‘flue gas’ side of the heat exchanger gets wet in
the process, it is more susceptible to corrosion. To
avoid this, it has to be constructed from corrosion-
resistant materials e.g. stainless steel or aluminium.
For more information on different boiler types (see
Section 3).

Domestic heating by gas: boiler systems – guidance for installers and specifiers (2008 edition) 5
Introduction to best practice
Environmental impact of gas heating1.3
Gas relative to other fuels
The main environmental impact of heating systems
is the emission of CO2. The CO2 emissions from
burning natural gas are low in comparison with most
other fuels, though higher than from biomass (e.g.
wood). Emissions from LPG are about 21% greater
than those from burning natural gas to give an equal
amount of heat. However, it is possible to obtain
slightly higher efficiencies from LPG boilers, so for the
same amount of useful heat output from a boiler the
CO2 emissions are approximately 18% higher.
Alternatives to gas heating
Alternatives that may have a lower environmental
impact should be considered where practicable.
Possible alternatives include wood-burning boilers,
and micro-CHP units. Micro-CHP, while burning gas,
produces electricity as a by-product that offsets the
carbon burden of central generation.
Where a gas heating system is chosen, fuel
consumption and carbon emissions can be reduced
by combining it with solar water heating (see
Section 4.3).

6Domestic heating by gas: boiler systems – guidance for installers and specifiers (2008 edition)
UK building regulations2.
Introduction2.1
This section outlines the minimum standards
for heating efficiency as set out in the building
regulations. The remainder of this guide then
concentrates on best practice – a higher standard.
The building regulations set a legal requirement to
make ‘reasonable provision… for the conservation
of fuel and power in dwellings’. However, the
approved guidance makes clear that there may well
be alternative ways of achieving compliance, and
different strategies can be adopted provided it can
be shown they are at least as good as those already
accepted as reasonable provision.
There are different building regulations* in England
and Wales, Scotland, and Northern Ireland. They
restrict the types of heating system that may be
installed in both new and existing dwellings. The
different regulations in each country are summarised
in later sections, but for details reference should
always be made to the official documents(18,19,20).
For new dwellings the general approach is to
demonstrate compliance by showing that the
carbon emissions are below a given threshold for a
particular dwelling. There are also minimum SEDBUK
efficiencies that apply to gas and LPG boilers. The
efficiency of the particular make and model of boiler
installed is used in the calculation of carbon emissions
for individual dwellings.
For existing dwellings there are minimum
requirements for boiler efficiency, hot water storage
vessels, pipe insulation, controls, and commissioning
that apply when heating systems are replaced or
modified.
In England, Wales and Northern Ireland detailed
guidance on the minimum requirements for heating
and hot water systems is given in the Domestic
Heating Compliance Guide(21). This guide was
prepared with support from industry and offers
specific information on how to achieve compliance.
In Scotland the detailed guidance is incorporated in
Technical Standards handbooks(19).
* This guide outlines the relevant building regulations in England,
Wales, Scotland and Northern Ireland. Regulations that apply in
Jersey, Guernsey and the Isle of Man are broadly similar but it is
essential to refer to official guidance.
Other parts of the regulations deal with the related
issues of the safety of heating installations and with
fuel storage. They are Part J (England and Wales),
Section 3: Environment (Scotland) and Technical
Booklet L (Northern Ireland). Requirements for sealed
(unvented) systems are in Part G (England and Wales),
Section 4: Safety (Scotland) and Technical Booklet P
(Northern Ireland).
General requirements2.2
Calculation of carbon emissions
The Government’s Standard Assessment Procedure
(SAP), see below, is used to calculate the energy
and environmental performance ratings and carbon
emissions of individual dwellings. To comply with
building regulations, a new dwelling must have carbon
emissions that do not exceed a target value. Compliance
is established by calculating a Dwelling Emission Rate
(DER) and Target Emission Rate (TER) – see box on
page 7. There are some differences in the way that DER
and TER are calculated and applied in each country, and
for more information reference should be made to the
respective regulations or standards(18,19,20).
Whilst this guide is concerned with gas-fired heating
and hot water systems, renewable energy should also
be considered. The use of technologies such as solar
water heating (see Section 4.3) will reduce the DER.
Standard Assessment Procedure (SAP)
SAP is the UK government’s procedure for the
energy rating of homes(22). The properties of a
building, such as the insulation, determine its heat
requirements, while the type of heating system
and heating fuel determine the energy use, cost
and CO2 emissions under standard occupancy
conditions.
In the latest version, SAP 2005, the rating scale is
1 to 100. This is based on the calculated cost of
space and water heating, ventilation and lighting,
less savings from any energy generated in the
building. High numbers represent better energy
performance, and a rating of 100 is reached when
the net energy consumption (over a whole year)
is zero. Ratings above 100 are possible when the
dwelling is a net exporter of energy. To comply with
building regulations all new homes must have a SAP
assessment. SAP also calculates the environmental
impact (CO2) rating, the dwelling emission rate (DER)
and the target emission rate (TER).

Domestic heating by gas: boiler systems – guidance for installers and specifiers (2008 edition) 7
UK building regulations
Boiler efficiency
SAP 2005 uses SEDBUK (Seasonal Efficiency of
Domestic Boilers in the UK) boiler efficiencies to
calculate the energy required to meet the heating
demand of the building. Only SEDBUK efficiency
figures are acceptable and the best source of this
information is the Government’s Boiler Efficiency
Database. See www.boilers.org.uk
The current minimum efficiencies for gas fired boilers
are shown in table 1.
Condensing boilers are required in most cases
except where the installation would be impractical or
excessively costly. In these cases it may be reasonable
to install a non-condensing boiler instead (see box
– condensing boiler exceptions). The procedure
is referred to as ‘Assessing the case for a non-
condensing boiler’ in England, Wales and Northern
Ireland and ‘Condensing Boiler Installation Procedure’
in Scotland.
Table 1: Minimum efficiency (SEDBUK)
requirements – UK building regulations
New
dwellings
Existing
dwellings
Regular boilers 86% 86%
Combination boilers 86% 86%
Range cooker/boilers* 75% 75%
* The cooker and boiler must have two
independently controlled burners
Environmental Impact (CO2) rating, and
Environmental Impact (CO2) band
The Environmental Impact (EI) rating is a number
representing the annual CO2 emissions, calculated as
part of the SAP procedure. Higher numbers represent
lower emissions, with 100 representing zero net
emissions. Numbers above 100 are possible if the
dwelling is a net exporter of energy. The number
range is divided into bands labelled A to G that are
intended for use on building energy certificates.
Dwelling emission rate (DER) and target
emission rate (TER)
The DER and TER are calculated as part of the
SAP procedure. The DER gives the CO2 emissions
per unit of floor area, expressed in kg/m2/year. To
comply with building regulations in England and
Wales, the DER of a new dwelling must not exceed
a target value (TER). The TER is calculated for a
notional dwelling of the same size and shape, and
varies with choice of fuel.
Condensing boiler exceptions
To determine the conditions under which a non-condensing boiler
is accepted as reasonable, an assessment of the property should be
carried out. Details are given in (19,21). There is an assessment form,
with instructions for completion, and a technical guide(23,24). Key
points include the following:
The assessment considers fuel type, dwelling type, boiler position, •
flue options, flue terminal positions and condensate drain points.
The lowest cost installation position must be found, as defined by •
the procedure.
Standardised costs and benefits are assumed, which will not be •
the same as actual costs and benefits in any particular property.
The installation position is based on the characteristics of the •
empty building, ignoring furniture and fittings as well as any
position preferred by the owner.
A simple points system determines whether the lowest cost •
installation option exceeds a fixed threshold.
The assessment form must be completed and signed by a •
competent person and a copy given to the building owner, who
should retain it as evidence an assessment has been carried out.
If confirmed by the assessment, a non-condensing boiler may •
then be installed. The assessment form may be needed as
evidence when the building is sold.
Even when an exception is allowed, a condensing boiler is •
preferable and a grant may be available to the householder to
assist with the extra installation cost.
The boiler installed, whether condensing or non-condensing, does •
not have to be installed in the position evaluated for the purpose
of the assessment.

8Domestic heating by gas: boiler systems – guidance for installers and specifiers (2008 edition)
UK building regulations
Storage vessels
Hot water storage vessels should be insulated in
accordance with BS 1566:2002(25), and the internal
heat exchanger should be sized accordingly. They
must also have a label showing type, capacity, heat
loss and performance.
There should be pumped circulation through the
primary circuit to the heat exchanger.
System circulation
Both heating and hot water domestic primary
circulation systems should have pumped circulation.
Existing semi-gravity systems should be converted to
fully pumped.
Controls
Zone controls should allow different air temperatures
to be set for living and sleeping areas (other than
in small open-plan flats and other properties where
these areas are not separated).
In most dwellings, both temperature zones can be
controlled by a single time switch or programmer
channel. However, in properties with a floor area of
more than 150m2, multiple timing zones are required
(with no zone larger than 150m2).
Separate timing control should be provided for hot
water, unless this is provided by a combi boiler.
Boiler interlock (see Section 5.1) is needed to ensure
that the boiler and pump is switched off when
neither heat nor hot water is wanted. Thermostatic
radiator valves (TRVs) alone do not provide boiler
interlock. They must be supplemented by a room
thermostat or similar device to turn off the boiler and
prevent unnecessary boiler cycling.
A bypass circuit of specified minimum length should
be provided if the boiler manufacturer’s instructions
require it, in which case it should be fitted with an
automatic bypass valve.
Pipework
Pipes should be insulated wherever they pass
outside the heated living space. In addition, all hot
water pipes connected to the hot water cylinder
(including the vent pipe and the primary flow and
return) should be insulated for at least 1m from the
connection. Pipework in unheated areas must be
insulated to meet requirements to limit heat loss.
Electrical Works
All electrical works must be carried out to BS 7671(26).
Existing buildings
New or replacement hot water storage vessels and
controls should meet the same requirements as in
new buildings.
Commissioning
Upon completion of the installation, the system
should be inspected and then brought into service
so that it operates efficiently and meets its specified
performance levels. The owner or occupier should
also be given information on the operation and
maintenance of the system. Further information on
the requirements for commissioning and handover
can be found in the Domestic Heating Compliance
Guide (England, Wales and Northern Ireland) and in
the Technical Standards handbook (Scotland).
England and Wales2.3
General
There are two Approved Documents(18) ADL1 (new
dwellings) and ADL2 (existing dwellings) that outline
basic requirements, and they are supported by more
detail given in the Domestic Heating Compliance
Guide(21).
Further information is available from the Communities
and Local Government (CLG) planning portal website
www.planningportal.gov.uk
Hot Water
Hot water storage vessels should be insulated
in accordance with BS 1566, BS 3198 or BS EN
12897(25,27,28), and the internal heat exchanger should
be sized accordingly. There should be pumped
circulation through the primary circuit to the heat
exchanger. If a thermal store is used, it should meet
the requirements of the Waterheater Manufacturers’
Association 1999 performance specification(29).
They must also have a label showing type, capacity,
heat loss and performance.
Electrical works
In addition to the requirements of BS 7671, certain
electrical works are regarded as controlled services
and should only be carried out by a competent
person and notified by the competent person
scheme to which they belong.

Domestic heating by gas: boiler systems – guidance for installers and specifiers (2008 edition) 9
UK building regulations
Commissioning
Upon completion of the installation, the system
should be inspected and then brought into service
so that it operates efficiently and meets its specified
performance levels. The owner or occupier should
also be given information on the operation and
maintenance of the system. The installer (competent
person) should provide details of the installation
to the operator of the competent person scheme
who will send a certificate to the householder and
supply any relevant information to the local authority
building control department. Alternatively installers or
their customers can use the local authority building
control route for building regulation notification for
which a charge is made.
Existing buildings
Approved document ADL2 specifies requirements
for existing buildings. There are no TER and DER
calculations required but when the work involves
the provision or upgrade to a heating or hot water
system, it must follow the requirements given in the
Domestic Heating Compliance Guide(21).
In particular, any new boiler (whether or not it
replaces an existing unit) should meet or exceed
the minimum efficiency requirements given in
table 1. Where the installation of a condensing boiler
would be impractical or excessively costly, it may
be reasonable to install a non-condensing boiler
instead (see boiler exceptions panel). Replacements
should be specified as for new systems and no
worse than 2 percentage points lower than the boiler
being replaced. Further requirements apply if the
replacement involves fuel change.
Most types of heating system are controlled services,
including central heating systems with boilers.
Alterations to controlled services or fittings require a
Building Control Notice, unless they are carried out
by a recognised competent person allowed to self-
certify the work.
Scotland 2.4
General
New dwellings must comply with the Building
(Scotland) Regulations(19) as presented in their
technical handbooks (last updated in May 2007).
Requirements for the conservation of fuel and
power are given in the domestic handbook
Section 6 (Energy). Demonstration of compliance
is based on carbon emissions. SEDBUK efficiencies
are used in the carbon emission calculations and
minimum efficiency values also apply.
Further information is available from the Scottish
Building Services Agency website (SBSA) website
www.sbsa.gov.uk
Commissioning
Upon completion of installation, systems must be
inspected, tested, and brought into service so as
to meet the specified performance and operate
efficiently. Written information on the operation and
maintenance of the system must be provided to the
occupier. A building warrant scheme is used, and it
should always be confirmed whether a warrant is
required for works involving gas-fired boilers, systems
and controls.
Existing buildings
If a central heating boiler is to be replaced in an
existing dwelling it is required to meet the minimum
SEDBUK efficiency as stated for new systems.
Where it is impractical or uneconomic to install a
condensing boiler, the dwelling may be assessed as
given in the Guide to Condensing Boiler Installation
Assessment procedure for dwellings (Scotland)(53).
Where this assessment confirms a non-condensing
boiler can be fitted it should have a minimum
SEDBUK efficiency of 78% (natural gas) or 80%
(LPG). Alternatively a back-boiler with a SEDBUK of
3 percentage points less than the above figures may
be installed.
Existing systems with semi-gravity circulation should
be converted to fully-pumped. Replacement boilers
should always be fitted with controls as required for
new systems. TRVs should be fitted on all radiators
in a new building extension, even though the heat
may be supplied from an existing boiler. Where only
part of a heating system is replaced it should be
done in such a way that the energy efficiency is not
downgraded.
Northern Ireland 2.5
General
The relevant building regulations are the Building
Regulations (Northern Ireland) 2000, and specifically
Building Regulations F3 and F4(30). These were
last amended in 2006 and call for ‘reasonable
provisions’ to be made for space heating and hot
water supply.

10 Domestic heating by gas: boiler systems – guidance for installers and specifiers (2008 edition)
UK building regulations
The installation, alteration or replacement of any
heating system must comply with the relevant
regulations. All new heating systems should be
notified to building control, and any alteration to an
existing heating system where a structural alteration
is involved. Where an existing heating system is
extended, the extension to the system must be
insulated to comply with regulation F4.
‘Technical Booklet F1: Conservation of fuel and
power’(20) gives provisions that are deemed-to-
satisfy the requirements of regulations F3 and F4.
Although it is not essential to follow Technical
Booklet F1, it is obligatory to comply with building
regulations F3 and F4.
Further information is available from the Department
of Finance and Personnel, Northern Ireland website
www.dfpni.gov.uk
Existing buildings
A new boiler (whether or not it replaces an existing
unit) should meet or exceed the minimum efficiency
requirements given in table 1 (page 7). Where
the installation of a condensing boiler would be
impractical or excessively costly, it may be reasonable
to install a non-condensing boiler instead (see
panel – condensing boiler exceptions on page 7).
Replacements should as specified for new systems
and no worse than 2 percentage points lower than the
boiler being replaced. Further requirements apply if the
replacement involves fuel change.
The technical booklets refer to the Communities
and Local Government (CLG) publication ‘Domestic
Heating Compliance Guide’(21) for requirements on
controlled services, insulation of pipes, ducts and
storage vessels.
Hot Water
Hot water storage vessels should be insulated
in accordance with BS 1566, BS 3198 or BS EN
12897(25,27,28), and the internal heat exchanger should
be sized accordingly. There should be pumped
circulation through the primary circuit to the heat
exchanger. If a thermal store is used, it should meet
the requirements of the Waterheater Manufacturers’
Association 1999 performance specification(29).
They must also show a label detailing type, capacity,
heat loss and performance.
Commissioning
Upon completion of the installation, the
system should be inspected and then brought
into service so that it operates efficiently and
meets its specified performance levels. Local
authority building control must be notified
of any gas firing, storage, installation and
commissioning works.
A building notice confirming that all fixed building
services have been commissioned by a suitably
qualified person is required and a copy given to the
district council and the dwelling owner.

Domestic heating by gas: boiler systems – guidance for installers and specifiers (2008 edition) 11
Boiler types3.
While this guide describes all types of gas-fired
boilers, it concentrates on condensing units which in
most cases must be fitted since building regulations
specify them as a minimum requirement.
Condensing boilers provide optimum performance
with low running costs and reduced CO2 emissions.
Natural gas produces the lowest CO2 emissions per
unit of heat delivered and also offers low running
costs for a wide range of dwellings. LPG boilers
are similar in design and efficiency, but the fuel is
considerably more expensive. The additional cost of
storage tanks (usually rented from the fuel supplier)
also needs to be considered.
When seeking estimates of installation costs for
LPG-fired boilers, ensure that the provision and
installation of an adequate LPG gas storage tank is
taken into account as well.
In most households, a single boiler provides both
space heating and hot water, either:
Indirectly, through a regular boiler and separate •
hot water tank (which is usually a copper cylinder
with a heating coil inside);
Or
Directly, using a combination boiler with no •
separate tank.
Condensing boilers 3.1
Condensing boilers are the only type that meet
best practice requirements and should always be
considered as first choice in any application. In the
UK all gas-fired boilers installed must be condensing
(except range cooker-boilers), with a SEDBUK
efficiency of 86% or more, unless an exception is
allowed (see Section 2.2).
Even if an exception is allowed, a condensing boiler
should always be the first choice and a grant may be
available to the householder to assist with the extra
installation cost.
Features of condensing boilers
SEDBUK efficiencies between 86% and 97% •
(with natural gas as the fuel).
Typically a new condensing gas boiler will have •
an efficiency of 90%, compared with 80% for
a new non-condensing boiler and 55-65% for
older types.
The system does not need to be designed to •
make the boiler condense all the time to achieve
improved efficiency.
Available in regular and combi models. •
Mostly wall-mounted, although some larger •
output models are floor standing.
Only room-sealed, fan-flue models available for •
domestic applications.
Most have extended flue options. •
Suitable for replacing most existing boilers (but •
not back boiler units (BBUs) in the same position).
Installation considerations for condensing boilers
They are as easy to install as non-condensing •
boilers, but need a connection from the
condensate outlet to a drain.
Can be installed in modern fully-pumped •
systems.
Oversized radiators will increase efficiency •
but good efficiency can still be obtained with
‘normally sized’ radiators.
Care is needed in siting the flue terminal due to •
the plume of water vapour usually present during
boiler operation. The plume will be visible for
much of the time the boiler is in operation.
Can employ a range of extended flue and plume •
management options, with the visible plume less
likely to be a nuisance at high levels.

12 Domestic heating by gas: boiler systems – guidance for installers and specifiers (2008 edition)
Boiler types
Regular boilers 3.2
Units that are not combination boilers (see below)
are commonly referred to as ‘regular’, or ‘heat only’
boilers. They can be wall-mounted or floor-standing.
Space heating is provided directly, but for hot water
they need to be connected to a separate hot water
storage system.
A back boiler unit (BBU) is one designed to be installed
within a fireplace (condensing BBUs are not available).
Regular boilers for sealed systems (see Section 4.1)
which have components such as pumps and
expansion vessels within their casings are known as
system boilers.
Combination boilers 3.3
Combination or combi boilers provide both space
and hot water heating directly. They are available as
instantaneous or storage types,
The most common type is the instantaneous combi
boiler (figure 3), which heats water on demand and
does not maintain a large internal store of already
heated water. These boilers are capable of providing
a continuous flow of hot water, but most provide
a lower flow rate than typical hot water storage
systems. Units with a much higher heat output (up to
40kW) have now been introduced which are capable
of much higher water flow rates.
The storage types (figure 4) include those with small
to medium stores and also CPSUs (see page 13)
which can provide very high water flow rates. Higher
water flow rates are required if there are regular
simultaneous demands for hot water, i.e. multiple
bathrooms.
Combi boilers save space because:
They are fed directly from the water main, with •
no need for a hot water storage cylinder or cold
water feed cistern.
They are usually intended for use in a sealed •
system which does not require a feed-and-
expansion cistern (allows a dry roof space).
Before selecting a combi boiler, check the
manufacturers’ instructions to ensure that the
dwelling has both satisfactory water pressure and an
adequately-sized water supply pipe. Otherwise, hot
water service may not be adequate.
Figure 2: Condensing regular boiler
drain
Space
heating
Hot
w
ater
Note: Condensate drain omitted to improve clarity
Space
heating
Hot
water
Note: Condensate drain omitted to improve clarity
Figure 3: Condensing instantaneous combi boiler
Figure 4: Condensing storage combi boiler

Domestic heating by gas: boiler systems – guidance for installers and specifiers (2008 edition) 13
Boiler types
Space heating
The power (rate of heat output) of combi boilers is
usually governed by hot water service requirements,
and often exceeds that needed for space heating.
Consequently most combi boilers are designed
with modulating burners; i.e. they reduce the firing
rate to match the lower heat output requirements
for space heating. In some cases the boiler design
heat output for space heating is lower than that for
domestic hot water.
Hot water
Factors to consider are:
The time taken for hot water to reach an •
acceptable temperature.
Hot water flow rate at the acceptable •
temperature.
How long this rate can be sustained. •
Can hot water be drawn off at more than one •
point simultaneously?
These factors will be influenced by the following:
The size of the internal hot water store. A store •
can reduce the delay in delivering hot water.
There are four different types:
Instantaneous: no internal hot water store. –
Keep-hot: small or no internal hot water –
store, keeps water within the boiler
permanently hot to reduce warm-up time
at boiler start-up (sometimes called ‘warm-
start’).
Medium store: sufficient to meet small hot –
water requirements without delay, but
insufficient for a bath.
Large store: sufficient for a bath or multiple –
simultaneous draw-off without delay.
Combined Primary Storage Units (CPSU): see –
figure 5.
Boiler power affects the rate at which hot •
water at the required temperature can
be drawn off after any internal store is
exhausted.
Boilers generally limit the hot water flow rate •
to ensure the declared temperature rise.
Combined primary storage units
CPSUs are a special category of storage combi boiler.
They include a very large store of water (a minimum
of 70 litres) designed to buffer both the hot water and
space heating requirements. The store is sufficiently
large to reduce frequent boiler cycling. CPSUs allow
radiators to warm up very quickly and are capable of
providing hot tap water at a high flow rate.
Range Cooker boilers 3.4
Some gas-fired cookers have a hot water boiler
(either integral or separate).
The latest units have two burners: one is for heating
and hot water; the other is for cooking and has
independent control. The casings of these cooker
boilers have relatively high heat loss, which can be
useful in winter but not in summer. Condensing units
are now being introduced.
Figure 5: CPSU
Space
heating
Hot
water

14 Domestic heating by gas: boiler systems – guidance for installers and specifiers (2008 edition)
Systems and components4.
Systems may either be sealed or open-vented to
prevent ingress or escape of air. In the past, most
installations were open-vented, but many are now
being replaced by sealed systems. Whether a system
is sealed or open vented makes no difference to its
energy efficiency.
Sealed and open-vented systems 4.1
Sealed
This is a popular option for new systems and
increasingly used for boiler replacements. The feed-
and-expansion cistern is replaced by an expansion
vessel incorporating a diaphragm to accommodate
variations in water volume. As the system is not
open to the atmosphere, the pressure rises with
increasing temperature, and additional safety controls
must be installed (these are often within the boiler).
The system will need a relief valve connected to
an external discharge point, which must be placed
where any discharge of hot water will be harmless.
There is no permanent connection to a water supply,
and the system may have to be topped up with
water occasionally.
As the system is not open to the atmosphere, there
is little possibility of oxygen being absorbed into the
water and, consequently, reduced risk of corrosion.
Because these systems may remove the need to
install pipes and cisterns in the roof space, they
reduce the risk of freezing.
Most combi boilers, and all system boilers, are
designed for use with sealed systems and will usually
incorporate system components, including a pump,
expansion vessel and safety controls within the boiler
case. In such cases, it must be ensured that this
integral expansion vessel has sufficient capacity to
allow for the water expansion of the whole system.
Open-vented
The majority of existing systems with a regular boiler
and an indirect hot water cylinder are open vented.
‘Open vent’ refers to the separate vent pipe which is
open to the atmosphere. The system also needs a
feed-and-expansion cistern to allow for changes in
water volume with temperature. This cistern has to be
at the highest point of the system, usually in the loft
space where it must be protected against freezing.
Expansion
vessel
Figure 6: Sealed system
Feed and
expansion cistern
Figure 7: Open system

Domestic heating by gas: boiler systems – guidance for installers and specifiers (2008 edition) 15
Systems and components
Domestic hot water 4.2
The main issues to be considered regarding domestic
hot water are:
The number of people in the dwelling. •
The number of baths/showers/taps.•
The hot water flow rate required. •
Likelihood of simultaneous hot water draw-offs. •
Availability of space for a hot water cylinder, or •
storage-combi, or CPSU.
Importance of a dry loft. •
Feasibility of solar water heating. •
Specific issues relating to combis are given in
Section 3.3.
Most existing regular boiler systems employ a
vented, indirect, hot water storage cylinder. In
households with a single bathroom, these are
typically of 117-140 litre capacity, but for larger
dwellings with more than one bathroom (and
perhaps with separate shower facilities), a larger
cylinder capacity will be required(31).
Hot water taps
Cold water taps
Cold
w
ater
main
Figure 8: Unvented hot water system
High performance cylinders contain a rapid
heating coil. This is a heat exchanger with
larger surface than normal, which reduces the
time taken to heat the water and may reduce
boiler cycling. It gives a valuable reduction in
recovery time between large draw-offs (such as
baths), and helps to increase system efficiency
(especially with older boilers). High performance
cylinders often have improved factory-applied
insulation as well.
Unvented cylinders are increasingly used in new
systems and these operate at mains pressure.
They employ an internal expansion facility or a
dedicated external expansion vessel, and do not
require a feed cistern in the loft.
Most hot water cylinders and thermal stores
are supplied with factory-applied insulation and
these should always be used in preference to
cylinders with separate jackets. Cylinders should
satisfy British Standards with regard to insulation
and heat exchanger performance.

16 Domestic heating by gas: boiler systems – guidance for installers and specifiers (2008 edition)
Systems and components
Medium-duty cylinders have inferior performance
and do not meet CHeSS basic requirements or those
of the building regulations, and so should not be
used for either new or replacement installations.
Thermal stores can be obtained that hold water
at high temperatures, heated by the boiler directly.
These are available for ‘hot water only’ or ‘hot water
and space heating’.
Mains-fed systems such as combi boilers, unvented
cylinders and thermal stores can supply hot water at
mains pressure. This is extremely beneficial when high
pressure is needed at the outlet, e.g. for showers. It
is therefore important to ensure that the incoming
water supply pressure and flow to the dwelling are
adequate and that all showers have the hot and
cold water supply at the same nominal pressure. This
eliminates the need for a shower pump.
Hot water
taps
Feed and
expansion cistern
Cold water
main
Figure 9: Thermal storage system
Table 2: Domestic hot water flow rates
System type Flow rate
Low Medium High
Instantaneous combi1,3 x x x
Storage combi2,3 x x
Thermal store3x x
Unvented storage2,3 x x
Vented storage4x x
Notes
1. Depends on boiler heat output; less satisfactory for two or more simultaneous draw-offs unless very high
heat input
2. Depends on boiler heat output and storage capacity
3. Depends on adequate mains water supply
4. Requires high level feed cistern

Domestic heating by gas: boiler systems – guidance for installers and specifiers (2008 edition) 17
Systems and components
Solar hot water systems4.3
The use of solar water heating provides the
opportunity to reduce running costs and carbon
emissions when used in conjunction with wet central
heating systems. There is now a large choice of
systems available and the technology is improving
all the time. Depending on system design a thermal
solar system can provide most of the average
dwelling domestic hot water requirement in the
summer and up 50% all the year round.
There are a range of different systems available,
but the general principle is that roof-mounted solar
collectors are heated by the sun, and the heated water
is passed to a special hot water storage cylinder. This
water is then further heated to raise the temperature, if
necessary, by the gas-fired boiler system.
Figure 10 shows a typical open vented system with
a large cylinder containing an additional solar heat
exchanger, usually referred to as twin-coil. Sealed
solar primary systems (i.e. to collectors) are commonly
used and unvented ‘twin-coil’ cylinders are also
available. The capital costs of systems are relatively
high but costs can be recouped through reduced
heating bills. When systems are being upgraded
and the hot water cylinder is being replaced,
consideration should be given to installing a larger
cylinder containing a solar heating coil. This facility will
then save cost and disruption if it is decided to install
solar heating panels at a later date.
Solar hot water systems can also be used in
conjunction with some combi boilers. However, this
should only be considered where the combi boiler
is part of an integrated solar package since systems
based on ad-hoc components may not achieve
good energy savings and boilers may not operate
correctly. When considering this option the boiler
manufacturer’s advice should always be obtained.
Separate guidance and advice on solar systems
should be sought(34,46). Also where appropriate, low
carbon supplementary heat sources such as heat
pumps or wood burning stoves can be considered.
Where these are combined with gas-fired systems,
expert advice should be sought to ensure both safety
and energy efficiency is optimised.
Controller
Solar
collector
To
boiler
Figure 10: Solar water heating system for connection to a boiler (safety controls not shown)

18 Domestic heating by gas: boiler systems – guidance for installers and specifiers (2008 edition)
Systems and components
Passive Flue-Gas Heat Recovery 4.4
Devices (PFGHRD)
A class of energy saving devices is now available
for use with certain condensing combi boilers (see
figure 11). The passive flue gas heat recovery device
(PFGHRD) uses a heat exchanger and heat store
fitted into the flue of a boiler to pre-heat domestic
hot water supply.
The cold inlet water is warmed directly from the flue
gases, and also indirectly from energy in the heat
store, whenever the boiler operates for space heating
or hot water service. The unit can also save water,
because it reduces the time during which water
delivered from an instantaneous combi is rejected
before it reaches an acceptable temperature.
Annual savings depend on the demand for both
space heating and water heating within the building.
Named products can be recognised for their energy
saving in SAP2005 assessments (using Appendix Q).
Note that these devices can only be used with boilers
specifically designed and approved to use them.
Upgrading systems 4.5
Many existing wet central heating systems are
poorly controlled and of obsolete design. Poor
design features which fail to meet current building
regulations and best practice requirements include:
Gravity circulation to the hot water cylinder, which •
results in stored water being slow to re-heat.
Lack of cylinder thermostat, resulting in excessive •
stored water temperature (risk of scalding).
Lack of room thermostat (rooms are too hot). •
Lack of TRVs, causing excessive room •
temperatures and poor system balancing.
Absence of boiler interlock, causing the boiler •
to stay hot and to cycle unnecessarily during
programmed periods.
It is important that an existing system is cleaned and
recommendations regarding the use of corrosion
inhibitor are followed when boilers are replaced and/
or systems upgraded(57). When upgrading, use the
CHeSS specifications (see Section 6).
Cold inlet
Space heating
Hot water
PFGHRD
Figure 11: PFGHRD fitted to instantaneous combi boiler

Domestic heating by gas: boiler systems – guidance for installers and specifiers (2008 edition) 19
Systems and components
Flue types 4.6
Most new boilers installed will be of the condensing
type and in most cases they will be replacing non-
condensing units. The different flue arrangements
of the existing model may affect the sitting of the
new boiler. All domestic gas condensing boilers are
room-sealed or fanned. Existing non-condensing
boiler flues can be open-flue or room sealed, natural
draught or fanned (figure 12).
New condensing boilers can have the following
flue types, straight-through-the-wall; extended
concentric or extended twin pipe (figure 13);
or extended non-balanced which is sometimes
referred to as a plume management option
(figure 14). In addition some flues offer a
directional terminal which can be used to minimise
plume nuisance. e.g. adjacent to an internal corner
(figure 15).
A
ir
inlet Fan
Room-sealed
fan flue
Secondary
air
Draught
diverter
Air
inlet
Open flue
Air
inlet
Natural draft
room-sealed flue
Figure 12: Existing flue types
Separate air intake
and flue
With concentric
termination
Vertical concentric Twin pipe
Horizontal concentric
Figure 13: Concentric flues for condensing boilers

20 Domestic heating by gas: boiler systems – guidance for installers and specifiers (2008 edition)
Systems and components
Important factors to consider when
replacing a non-condensing boiler with a
condensing unit.
New gas-fired boilers are very efficient and •
operate with comparatively low flue-gas
temperatures.
Room-sealed appliances must use flue •
systems which are certificated and supplied
as part of the boiler or specified by the boiler
manufacturer(33). Always refer to the boiler
manufacturers instructions to check what
options can be used.
The plume will be visible for much of the time •
the boiler is in use and can sometimes cause a
nuisance. For this reason, special consideration
should be given to the siting of the new flue
terminal (see Section 9.2).
A wide range of extended flues are now •
available which can be used to minimize
the possible nuisance caused from the flue
products.
Extended and vertical flues are available for •
many condensing boilers in concentric and
twin-flue configurations. In some cases these
allow flue lengths of over 30m, with a number
of bends.
A non-balanced flue, where the air intake •
and flue outlet are run to separate locations,
is available for use with some boilers. Here
the air intake can remain at low level but
the flue outlet can be directed to high level.
This is sometimes referred to as the plume
management option and can often reduce
plume nuisance in restricted locations.
Directional flue terminals, where the direction •
of the flue stream can be adjusted, are also
available for use with some boilers.
Room-sealed boilers do not require special •
provision for combustion air in that room.
Figure 14: Plume ‘management’ option
Air
inlet
Flue
outlet
Flue
outlet
or
Figure 15: Directional terminal
Flue
outlet
Air
inlet
Plan view
of boiler

Domestic heating by gas: boiler systems – guidance for installers and specifiers (2008 edition) 21
Systems and components
Heat emitters 4.7
A wide range of heat emitters are available (see table 3).
Radiators remain the most popular type and modern
versions are usually slightly smaller for an equivalent
heat output. Many modern radiators also have lower
water content, making for a faster warm-up.
The heat output of the radiators should be carefully
calculated(31,35). All radiators should be fitted with a
TRV (see CHeSS) excluding those in a room with a
controlling room thermostat.
Underfloor heating is an attractive alternative in
the right circumstances, but it needs to be installed
by specialists(36). It also requires careful control in
accordance with the manufacturer’s guidance.
Other important points regarding heat emitters
include the following.
Radiators sited under windows counteract cold •
downdraughts and so give a more comfortable
environment in the room.
Radiators should be installed close to the floor, •
preferably 100-150mm above finished floor level.
Wide, low radiators will be more effective at •
heating the room evenly than tall, narrow
designer styles.
Enclosures around radiators reduce the heat •
output.
Circulator pumps 4.8
A circulator pump must be selected with sufficient
design pressure and flow rate for the total system
resistance when operational. If the pump is
undersized or is set too low, the flow may be
inadequate to meet the manufacturer’s minimum
requirement. This will result in the boiler operating
with a larger temperature rise than intended. On the
other hand, a pump that is larger than required will
result in excessive water velocity noise as well as
unnecessary electricity consumption.
Circulator pumps are built into combi and system
boilers and it must be ensured that the pump has
adequate head and flow rate to meet the system
design.
Pumps that are installed separately (i.e. not supplied
as part of the boiler unit) and that have automatic
speed control should only be used in heating systems
with TRVs if the design of the pump and system
ensures that the minimum flow rate through the
boiler (as specified by the boiler manufacturer) is
certain to be maintained under all conditions.
Multiple pumps (one for each water circuit) may
be used as an alternative to a single pump with
motorised valves, provided that each water circuit
has a non-return valve. Advice on pump sizing can
be obtained from the British Pump Manufacturers’
Association (BPMA) website at www.bpma.org.uk
Table 3: Heat emitters
Type Comment
Panel radiator The most common type in modern housing. Available in a wide range of
outputs and sizes.
Compact radiator A radiator or convector fitted with top grille and side covers.
Column and designer radiators Available in a wide range of colours and shapes.
Low Surface Temperature (LST)
radiator
Safe option where young children or the elderly may be at risk. Limited to a
surface temperature of 43°C in order to prevent injury.
Towel rail For towel warming and will give some heat to the bathroom.
Fan convector Wall hung and kickspace units available. These provide a more rapid heating
response. They need an electrical supply and there may be some fan noise.
Underfloor heating coils Requires specialist installation and controls. May be less suitable for rooms
requiring only intermittent heating.

22 Domestic heating by gas: boiler systems – guidance for installers and specifiers (2008 edition)
Controls5.
Installing effective controls can have a major impact
on the energy consumption of heating and hot water
systems. This section describes the types of controls
now available and outlines which are most suitable
for different heating systems.
Effective controls will increase operating efficiencies,
especially when older systems are being updated.
They also provide the householder with the
opportunity to minimise energy consumption
by ensuring the right comfort temperatures are
maintained and so reducing overheating. Reducing
room temperatures will also save energy (see box).
Timed space and water heating periods will also
help to avoid excessive use of energy. Heating fuel is
expensive (gas-fired boilers typically consume 30-70
pence of fuel an hour when operating) and reducing
the firing time will make a proportionate difference to
running costs.
A good control system is one which ensures the
boiler does not operate unless there is a demand and
that only provides heat where and when it is needed
in order to achieve the required temperatures. The
selection of suitable controls plays a key part in
minimising the overall running costs of a heating or
hot water system.
Control standards must meet best practice to
maximise the efficiency of a heating system.
However, in order just to achieve the SEDBUK
efficiency claimed for a boiler, at least the basic set
of controls given in CHeSS must be installed (see
Section 6).
The cost benefit of controls should not be
underestimated. Upgrading the controls on older
heating systems can save up to 18% on energy bills,
for example when a full set of controls is fitted to a
system which previously had none. This is important,
as over 80% of the energy a householder uses in the
home is for space and hot water heating.
Individual controls5.1
This section describes the range of controls
commonly used in gas-fired systems, what they do
and why they are important.
The controls listed here are normally installed
separately from the boiler although some may be
incorporated within it. For clarity of specification,
Appendix C contains a full list of controls
including those often fitted within appliances and
gives industry-agreed definitions. Appendix E
provides simple explanations that can be given to
householders on what controls do and how they
should be used.
Further advice on controls most suitable for the
disabled, particularly with visual and dexterity
impairment, can be found in the Ricability report(37).
In the following listing, best practice controls are
noted.
Time Switch
A simple time control that will only switch one circuit.
It should be chosen so that it is easy to understand
and reset, especially when there is a change to the
householder’s domestic routine.
Programmer
This can switch two circuits separately (usually
heating and hot water). There are two basic types:
A standard programmer uses the same time •
settings for space heating and hot water.
A full programmer allows fully independent time •
setting for space and hot water heating.
Energy savings from good controls
Installing a minimum standard of controls on a •
system which previously had none can reduce
fuel consumption and CO2 emissions by 18%.
Reducing higher than necessary room •
temperatures will cut energy use. Turning
down the room thermostat by 1°C will reduce
space heating consumption by 6-10%.
An easy to use programmer that is adjusted •
to match the householder’s occupancy pattern
helps reduce wasteful heating when no one
is at home.
VAT on heating controls
Heating controls for domestic wet central heating
systems are recognized by the Government as
an energy efficiency measure. VAT is therefore
charged at a lower rate – currently 5% instead
of the full rate of 17.5%. This lower rate applies
to both equipment and installation costs, but
only when the work is carried out by an installer
registered for VAT.

Domestic heating by gas: boiler systems – guidance for installers and specifiers (2008 edition) 23
Controls
Room thermostat
A simple room temperature control. Traditional types
use expansion/contraction (e.g. bimetallic strip) to
operate a switch or relay. They usually include an
accelerator or anticipator, which is a small resistance
heater having the effect of smoothing out the
temperature cycle by preventing overshoot.
Electronic room thermostats are also available which
can react more rapidly to temperature change. Some
of the latest units include a function to control the
boiler firing frequency. These units are designed to
minimise the variations in both the boiler and room
temperature.
Wireless units that provide increased flexibility in
positioning and eliminate visible wiring are now
commonly used.
Programmable room thermostat (best practice)
This allows different temperatures to be set for
different periods of the day or week and so can
provide a good match to householder living patterns,
particularly if occupancy varies. This device also has a
‘night setback’ feature where a minimum temperature
can be maintained. Many of these models are
battery-operated and can replace a conventional
thermostat without the need for additional cabling.
Some versions also allow time control of hot water
provision. Electronic and wireless versions with extra
functions are available.
Cylinder thermostat (best practice)
A simple control of stored hot water temperature,
usually strapped to the side of the hot water cylinder.
It is commonly used with a motorised valve to
provide close control of water temperature and boiler
interlock.
Frost thermostat
A simple override control used to prevent frost
damage to the dwelling and/or boiler system. The
frost air thermostat should be fitted in a suitable
place within the dwelling to ensure a minimum
temperature is always maintained.
Pipe thermostat
Where the boiler is installed in an unheated area
such as a garage, a pipe thermostat should be fitted
to the exposed pipework. This is in addition to the
frost air thermostat and is designed to prevent the
boiler from firing unnecessarily in cold weather and
so wasting fuel. If the boiler incorporates its own frost
thermostat, a separate pipe thermostat is normally
not required.
Thermostatic radiator valve (TRV) (best practice)
TRVs are used to limit the temperature in individual
rooms. They also prevent overheating from solar and
other incidental gains. In this way, they cut down
on unnecessary consumption. Programmable units,
which can be timed to switch on and off, are also
available.
Figure 16: A programmable room thermostat offers greater flexibility in setting temperatures and times than a
standard room thermostat, producing greater savings
MorningEarly morning Afternoon
Room
temperature
EveningNight

24 Domestic heating by gas: boiler systems – guidance for installers and specifiers (2008 edition)
Controls
Thermostatic hot water temperature limit valve
These self-acting valves without motors are used to
limit hot water temperature in domestic hot water
cylinders. Some units sense primary water (boiler)
temperature, others have a separate remote sensor
for stored water temperature. Cylinder controls
should not be used with these unless they also
operate an electrical switch to provide boiler interlock.
Otherwise the boiler will cycle unnecessarily.
Motorised valve (best practice)
These control water flow from the boiler to heating
and hot water circuits. Two-port valves can also be
used to provide zone control e.g. allowing lower
temperatures to be set for sleeping areas or different
heating times. An explanation of the different types
is given in Appendix D. Multiple pumps are an
alternative to motorised valves (see Section 4.8).
Boiler interlock (best practice)
This is not a device, but rather a wiring arrangement
to prevent the boiler firing when there is no demand
for heat. The boiler is interlocked when it is switched
on and off by thermostats containing electrical
switches. All thermostats in the heating system fitted
with electrical switches should be wired in this way.
This includes room thermostats, programmable room
thermostats, cylinder thermostats and some types of
boiler energy managers. In many cases, the interlock
is also applied to the operation of the pump, although
any requirements for pump overrun stipulated by
the boiler manufacturer must be observed. Without
interlock, a boiler is likely to cycle on an off regularly,
wasting energy by keeping hot unnecessarily.
Achieving interlock depends upon the boiler type and
the controls fitted. Typical examples of boiler interlock
are as follows.
Regular boiler with one 3-port or at least •
two 2-port motorised valves. The interlock is
usually arranged so that the room or cylinder
thermostat switches the power supply to the
boiler (and sometimes the pump) through the
motorised valve end switches. In other words,
electrical power from the programmable room
thermostat (or separate programmer and room
thermostat) and the cylinder thermostat will
drive the valve motor to the open position.
Once the motor is fully open, the end switch
will close and electrical power is then passed
to the boiler and pump. Once the power to the
valve is removed (programmer off-period, or
thermostat is satisfied) the motorised valve will
close, the end switch will open and the boiler
and pump will stop.
Regular boiler with two separate pumps for heating •
and hot water. Where separate pumps are used,
advice from the manufacturer is needed in regard to
the correct use of relays, check valves, etc.
Combi boiler. This only requires a time switch •
and room thermostat (or programmable room
thermostat) connection to provide interlock as
hot water delivery is controlled directly by the
boiler. A boiler energy manager may need a
different wiring arrangement, achieving interlock
by an alternative method.
Automatic bypass valve (best practice)
This controls water flow according to the differential
pressure of the water across it. It is used to maintain
a minimum flow rate through the boiler and to limit
the circulation pressure when alternative water paths
are closed. A bypass circuit must be installed if the
boiler manufacturer requires one, or specifies that a
minimum flow rate has to be maintained while the
boiler is firing. The installed bypass circuit must then
include an automatic bypass valve, not a manual
(fixed position) valve.
The use of an automatic bypass is important where
the system includes a large number of TRVs. When
most of these are open, the automatic bypass
remains closed, allowing the full water flow to
circulate around the heating system. As the TRVs
start to close, the automatic bypass starts to open,
maintaining the appropriate water flow through the
boiler. It also helps to reduce noise in the system
caused by excess water velocity.
An automatic bypass is always preferable to a fixed
bypass. With a fixed bypass, there is a constant
flow of hot water coming out of the boiler, which is
fed directly into the return at all times. This means
that the boiler operates at a higher temperature,
reducing efficiency and restricting the amount of heat
transferred to the system.
It is very important that both automatic and fixed
bypasses are correctly adjusted. Poor adjustment will
give rise to increased boiler return temperatures and
reduced boiler efficiency.

Domestic heating by gas: boiler systems – guidance for installers and specifiers (2008 edition) 25
Controls
Particular care is required when selecting a pump
with automatic speed control for a system with
an automatic bypass. It is important to ensure that
the boiler manufacturer’s minimum recommended
water flow rate is maintained under all operating
conditions.
Boiler energy manager
These are self-contained devices which have a
number of the functions found in other individual
controls described in this section. They usually have
a number of control functions including weather or
load compensation and sometimes optimum start,
Figure 17: Boiler interlock in a system with two, 2-port valves (this shows the general logic and should not be
interpreted as an installation instruction, as the actual wiring will depend on the particular products used).
SH
Programmable room
thermostat for each
additional space
heating zone
SH motorised valve
for each additional
space heating zone
End
switch
End
switch
End
switch
Pump
Cylinder
thermostat
Programmable
room thermostat
with timing for
hot water
HW
SH
Boiler
HW
motorised
valve
230 V Neutral
SH
motorised
valve
Repeat for
each additional
heating zone
frost protection, night setback, anti-cycling control
and hot water override. Table 4 lists a range of
control functions which may be included.
Wireless controls
Wireless controls should be designed with
adequate immunity to blocking by other radio
transmissions. If not, they may become unreliable
or cease to work as nearby radio frequency bands
become increasingly used for mobile phones and
other communication services. See CHeSS Note
12 in Appendix A for more details on wireless
controls.

26 Domestic heating by gas: boiler systems – guidance for installers and specifiers (2008 edition)
Controls
Selecting controls 5.2
The minimum sets of controls consistent with building
regulation requirements and satisfactory heating system
performance are those listed as basic in the CHeSS
specification (see Section 6). However, it is recommended
that the best practice level is followed. Figures 18 and 19
show best practice regular and combi boiler systems.
Best practice – regular boilers
Programmable room thermostat with additional •
hot water timing capability.
Cylinder thermostat.•
TRVs on all radiators except in rooms with a •
room thermostat.
Automatic bypass valve.•
Boiler interlock.•
Best practice – combi boilers
Programmable room thermostat.•
TRVs on all radiators except in rooms with a •
room thermostat.
Automatic bypass valve.•
Boiler interlock.•
New systems must always be fully pumped and existing
semi-gravity systems (i.e. with gravity circulation to the
hot water cylinder) should be converted. Published boiler
efficiencies cannot be achieved unless the whole system
is fully pumped and effectively controlled.
Table 4: Control functions commonly built into boilers and control units
Compensator Reduces boiler water temperature for space heating according to internal/external air
temperature. It should increase the efficiency of condensing boilers by reducing the average
water temperature of the system.
Delayed start Reduces energy use by delaying the heating start time to after the programmed time when
the weather is mild.
Night
setback
Allows a low temperature to be maintained at night, providing improved comfort and
reduced warm-up time in the dwelling in cold weather. In this way it can reduce the risk of
hypothermia. A programmable room thermostat can fulfil this function.
PI or PID The letters stand for Proportional/Integral, or Proportional/Integral/Derivative. These control
functions can be built into room thermostats to reduce variations in room temperature.
Anti-cycling
control
Delays boiler firing in order to reduce cycling frequency, but is unlikely to produce significant
energy savings. In some circumstances consumption may be reduced, but normally at the
expense of performance or comfort. Standalone units (i.e. those not supplied as part of the
boiler) are not generally recommended as they provide little or no improvement over the basic
level of control detailed in CHeSS.
Figure 18: Best practice schematic for regular boiler systems (the
programmable room thermostat must have an additional hot water
timing capability)
Key for figures 18 to 20
Room thermostat
Programmable thermostat
Cylinder thermostat
Boiler interlock
TRVs on most radiators
Motorised valve

Domestic heating by gas: boiler systems – guidance for installers and specifiers (2008 edition) 27
Controls
Further control improvements 5.3
Zone control
CHeSS best practice and basic options already include
zone temperature control, achieved using TRVs. If
zones are to be independently time controlled as
well, it will usually be necessary to install additional
room thermostats and a two-port motorised valve (to
allow the programmer to shut off water circulation).
The wiring in such situations must be arranged so
that boiler interlock works in all zones.
Zone control is particularly beneficial in larger,
poorly insulated buildings. Building regulations in
the UK require that no zone is larger than 150m2
in floor area and each zone should be capable of
independent time and temperature control.
Systems that provide multiple zone control are now
available which allow time and temperature control of
individual rooms or multiple zones, thereby providing
more effective and efficient heat distribution in the
dwelling. Individual time and temperature control of
separate rooms can be achieved using TRVs fitted
with special heads which include on-off control linked
to a programmer (either wired or wireless).
Weather compensation
As external temperatures rise, so a weather
compensating function reduces average water
circulation temperature (see figure 21). Greatest
benefit is achieved with condensing boilers.
Figure 19: Best Practice schematic for combi systems
Mains water
Hot water
Figure 20: Zone controls
Zoned radiators
Figure 21: Weather compensation
20
16
12
8
4
0
-4
External
t
emperature (C)
Warmer
Cooler
Compensation
slope
Boiler flow temperature (C)
020406080100

28 Domestic heating by gas: boiler systems – guidance for installers and specifiers (2008 edition)
Controls
Delayed start
The user sets the timer to bring on the heating
taking account of the time it normally takes to heat
the dwelling to an acceptable temperature under
cold ambient conditions. A delayed start unit, will,
at the time of switch-on of the programmer/room
thermostat, compare the current room temperature
to that required and will then hold off the heating
if appropriate. Therefore during mild weather, as
heat-up times are reduced, energy can be saved. (See
figure 22). Room thermostats with a delayed start
function are now available.
Optimum start
The user sets the occupancy time and the required
room temperature and the control then calculates
the required pre-heat time. The approach is to
always reach the required room temperature in the
optimum time independently of outside temperature.
With optimum start controls the priority is ensuring
comfort whereas with delayed start controls the
priority is energy saving.
Integrated boiler and system controls
Control options are increasingly being offered by
both boiler and control manufacturers to provide
integrated control strategies. For example systems are
available which allow boiler flow temperature to be
closely controlled by an outside (weather) or inside
compensator. This is achieved by adjusting the firing
rate of the boiler.
Room thermostats are also available that modulate
the heat output of the boiler in response to the
gap between the measured and target room
temperature. This type of control has the potential to
reduce the boiler return temperature and so increase
the efficiency of a condensing boiler and reduce
temperature swing (above and below the target air
temperature) without excessive boiler cycling. Some
of the thermostats and boiler combinations that
use this strategy conform to ‘Open Therm’ which is
an independent protocol/specification for signalling
between separate components of a heating system.
Home automation
Whole house control systems are now available,
integrating the operation and control of a wide range
of systems and appliances. Of particular relevance for
energy efficiency is:
Time and temperature control of individual •
rooms.
Features to permit remote setting and operation •
of time switches, i.e. programmers and
thermostats.
Feedback for the householder on energy use, •
which can encourage energy efficiency.
Potential
energy savings
Earliest
normal
start
Internal
t
emperature (C)
Time (hours)
5678910
20
16
12
8
Delayed start
Typical settings
• Maximum heat up period, e.g. 6am to 8am
• Normal occupancy period, e.g. 8am to 10am
Figure 22: Delayed/optimum start function

Domestic heating by gas: boiler systems – guidance for installers and specifiers (2008 edition) 29
Central Heating System Specifications (CHeSS)6.
CHeSS provides a series of ready-made specifications
for purchasing the components that critically affect
the energy efficiency of wet central heating systems.
Following them will improve energy efficiency and
reduce carbon emissions.
Purchasers should use these specifications to ensure
their heating installations will meet best practice or
basic requirements. Installers can use them to quote
for systems of defined quality, comparable with those
of their competitors.
The main elements are reproduced in the following
tables and the explanatory notes can be found at the
end of this document. The complete specification is
available in a separate Energy Efficiency Best Practice in
Housing document(38). That publication also contains
quantified energy, carbon and cost savings for the
different specifications.
The basic specifications HR7 and HC7 are sufficient
to comply with the building regulations. The two best
practice specifications HR8 and HC8 are to be preferred
(see table below).
Central heating system specifications (Year 2008)
Basic (2008) (For notes see Appendix A)
Reference CHeSS – HR7 (2008)
Description Domestic wet central heating system with regular boiler
(natural gas, LPG, or oil) and separate hot water store.
Boiler
(see notes 5 and 6)
A regular boiler (not a combi) which has a SEDBUK efficiency of at least •
86% (bands A and B).
Hot water store EITHER
Hot water cylinder, whose heat exchanger and insulation properties both •
meet or exceed (see note 7) those of the relevant British Standards
(see Refs [7],[8]).
OR
Thermal (primary) storage system, whose insulation properties meet or •
exceed those specified in Ref [9].
Controls
(see notes 10, 11 and 12)
Full programmer•
Room thermostat•
Cylinder thermostat•
Boiler interlock (see note 13)•
TRVs on all radiators, except in rooms with a room thermostat•
Automatic bypass valve (see note 14)•
Installation See notes 1, 2, 3 and 4.
Basic (2008) (For notes see Appendix A)
Reference CHeSS – HC7 (2008)
Description Domestic wet central heating system with combi or CPSU boiler
(natural gas, LPG, or oil).
Boiler
(see notes 5 and 6)
A combi or CPSU boiler which has a SEDBUK efficiency of at least 86% •
(bands A and B).
Hot water store None, unless included within boiler.
Controls
(see notes 10, 11 and 12)
Time switch•
Room thermostat•
Boiler interlock (see note 13)•
TRVs on all radiators, except in rooms with a room thermostat•
Automatic bypass valve (see note 14)•
Installation See notes 1, 2, 3 and 4.

30 Domestic heating by gas: boiler systems – guidance for installers and specifiers (2008 edition)
Central Heating System Specifications (CHeSS)
Central Heating System Specifications (Year 2008)
Recommended best practice (2008) (For notes see Appendix A)
Reference CHeSS – HR8 (2008)
Description Domestic wet central heating system with regular boiler
(natural gas, LPG, or oil) and separate hot water store.
Boiler
(see notes 5 and 6)
A regular boiler (not a combi) which has a SEDBUK efficiency of at least •
90% (band A).
Hot water store EITHER
High-performance hot water cylinder (see note 8).•
OR
High-performance thermal (primary) storage system (see note 9).•
In suitable buildings, consideration should be given to fitting a cylinder with an
additional heat exchanger to allow for solar water heating.
Controls
(see notes 10, 11 and 12)
Programmable room thermostat, with additional timing capability for hot •
water
Cylinder thermostat•
Boiler interlock (see note 13)•
TRVs on all radiators, except in rooms with a room thermostat•
Automatic bypass valve (see note 14)•
More advanced controls, such as weather compensation, may be considered,
but at present cannot be confirmed as cost effective.
Installation See notes 1, 2, 3 and 4.
Recommended best practice (2008) (For notes see Appendix A)
Reference CHeSS – HC8 (2008)
Description Domestic wet central heating system with combi or CPSU boiler
(natural gas, LPG, or oil).
Boiler
(see notes 5 and 6)
A combi or CPSU boiler which has a SEDBUK efficiency of at least 90% •
(band A).
Hot water store None, unless included within boiler.
Controls
(see notes 10, 11 and 12)
Programmable room thermostat•
Boiler interlock (see note 13)•
TRVs on all radiators, except in rooms with a room thermostat•
Automatic bypass valve (see note 14)•
More advanced controls, such as weather compensation, may be considered,
but at present cannot be confirmed as cost effective.
Installation See notes 1, 2, 3 and 4.

Domestic heating by gas: boiler systems – guidance for installers and specifiers (2008 edition) 31
Energy efficiency7.
The information in this guide is designed to improve
the energy efficiency of dwellings. Selecting the most
energy efficient boilers suitable for the particular
application is vital. Several factors need to be
considered when choosing a boiler:
Seasonal (i.e. annual in-use) efficiency. •
Typical heating and hot water running costs for •
the dwelling(s).
Typical CO• 2 emissions for space and water
heating.
Comparing boiler efficiencies 7.1
The term ‘boiler efficiency’ needs some explanation
since there are many values that may be quoted,
and these are calculated in different ways. In any
comparison of the efficiency of alternative products,
it is essential to ensure that the same method is
being used.
The efficiency value now used in the Government’s
Standard Assessment Procedure and in the building
regulations is known by the acronym SEDBUK,
(Seasonal Efficiency of a Domestic Boiler in the UK).
SEDBUK represents the best estimate presently
available of overall seasonal in-use boiler efficiency
for space heating and hot water in UK dwellings.
It is used throughout this guide as well as in
CHeSS, the Energy Saving Trust’s ‘Energy Efficiency
Recommended’ scheme, and other programmes
designed to promote efficient boilers.
A boiler’s SEDBUK efficiency is an indicator of the
average annual boiler efficiency determined by the
amount of heat delivered to the primary (boiler
water) heating circuit. It is assumed that the boiler is
installed in a fully-pumped system which has been
correctly designed and which has adequate controls.
The claimed SEDBUK efficiency level will not be
achieved otherwise.
The SEDBUK calculation process (which can be
found in Appendix D of the SAP[22]) uses actual
boiler test data, the measurements being taken by
methods defined in European standards to meet
the requirements of the European Boiler Efficiency
Directive(39). This provides manufacturers with an
incentive to make their products as efficient as
possible.
As SEDBUK has been designed specifically for SAP
energy rating purposes, it takes account of heat
losses associated with space and water heating. It
does not, however, include surface heat losses from
any hot water store within or external to the boiler.
These are treated separately as they may provide
a small amount of useful heat to the dwelling
during the heating season. This is important when
comparing products, as stores with high heat losses
will increase annual energy consumption but do not
affect SEDBUK values.
The best source of SEDBUK figures is the Boiler
Efficiency Database (see Section 7.5). Where this is
not available, purchasers should look for this standard
form of words in manufacturers’ literature:
‘Seasonal efficiency (SEDBUK) = [x]% The value is
used in the UK Government’s Standard Assessment
Procedure (SAP) for energy rating of dwellings. The
test data from which it has been calculated have
been certified by [name and/or certification of
Notified Body].’
Energy efficiency figures calculated by other methods
may not be consistent with SEDBUK, and should be
disregarded.
Figure 23 shows typical SEDBUK efficiencies for
both new and older boilers. In practice there are
limits both to the minimum efficiency due to the
requirements of the Boiler Efficiency Directive, and to
the maximum permitted value based on theoretical
considerations.
Minimising demand
Whilst this guide aims to improve heating and hot
water systems through careful selection of boilers
and controls, it is important to remember that
other factors affect the overall energy efficiency
of the dwelling. In particular, it is essential to
minimise:
Fabric heat loss through walls, floors, roofs and •
windows.
Ventilation heat loss from windows, unused •
chimneys and cracks or gaps in the structure
of the dwelling.

32 Domestic heating by gas: boiler systems – guidance for installers and specifiers (2008 edition)
Energy efficiency
The Standard Assessment 7.2
Procedure (SAP)
Home energy ratings are designed to give an
indication of the energy efficiency of a dwelling and
so allow householders to compare different homes.
The SAP is the Government’s chosen rating system
and indicates the running costs of space and water
heating. The building regulations procedures require
all new dwellings to be assessed in this way.
The current version of SAP is SAP 2005. The ratings
are expressed on a scale of 1-100, with higher figures
representing greater efficiency and lower running
costs. Ratings above 100 are possible when the
dwelling is a net exporter of energy. The actual figure
depends on certain characteristics of the building and
its heating systems, in particular:
Building design. •
Insulation levels. •
Solar heat gains.•
Ventilation. •
Heating and hot water efficiency (SEDBUK) and •
controls.
Energy export.•
Energy consumption and running costs 7.3
Table 5 gives typical annual fuel costs for some of
the more common types of dwelling found in the
UK – both existing properties and new buildings.
Existing housing is typical of the existing housing
stock(40). New housing has the same floor areas for
comparison, but is built with insulation levels that
would satisfy the latest building regulations. The flat
is on the top floor (a top floor flat has an energy
consumption intermediate between a ground and
mid-floor flat). Hot water costs are related to a typical
number of occupants for the size of property.
Figures shown assume average UK weather
conditions (the Midlands). Consumption would be
around 3-6% lower in the south and 3-6% higher in
the north.
Typical energy consumption has been calculated
using the Building Research Establishment (BRE)
Domestic Energy Model, BREDEM-12(41). This
estimates annual domestic energy usage associated
with house design, insulation levels, local climate
and type of heating system (including efficiency
and heating usage). The model is widely used for
calculating domestic fuel running costs.
Regular (old heavyweight)
Regular (old lightweight)
Combi (old)
Back boiler
Regular
Combi
CPSU
Condensing regular
Condensing combi
Condensing CPSU
50 54 58 62 66 70 74 78 82 86 90 94
SEDBUK ranges for gas boilers
Efficiency (%)
Note: Grey sections indicate additional range of boilers with permanent pilot ignition.
Figure 23: Typical SEDBUK values for different boiler types

Domestic heating by gas: boiler systems – guidance for installers and specifiers (2008 edition) 33
Energy efficiency
Fuel costs of 1.63 and 3.71 pence per kWh are used
for natural gas and bulk LPG as given in the 2005
edition of the SAP (Table 12). These costs do not
include standing charges, maintenance or circulating
pump running costs.
Carbon dioxide emissions 7.4
Table 6 gives typical values of annual CO2 emissions
for the same types of dwelling. Carbon intensity
values are taken from SAP (2005) Table 12.
Table 5: Annual fuel (gas or LPG) costs for heating and hot water in different property types
Boiler type SEDBUK Existing housing New housing
F B T SD D F B T SD D
Gas - old boiler (heavy weight) 55% £287 £361 £383 £434 £575 £92 £116 £116 £145 £172
Gas - old boiler (light weight) 65% £243 £305 £324 £368 £486 £78 £98 £96 £123 £146
Gas - new, non-condensing 79% £200 £251 £266 £302 £400 £65 £81 £81 £101 £120
Gas - new, condensing 90% £175 £220 £234 £266 £351 £56 £71 £71 £89 £105
LPG - old boiler (heavy weight) 57% £630 £792 £840 £954 £1,262 £203 £255 £255 £318 £378
LPG - old boiler (light weight) 67% £536 £674 £715 £812 £1,074 £173 £217 £217 £271 £322
LPG - new, non-condensing 81% £443 £557 £591 £672 £888 £143 £180 £180 £224 £266
LPG - new, condensing 92% £390 £491 £521 £591 £782 £126 £158 £158 £197 £234
F Flat
B Bungalow
T Terraced
SD Semi-detached
D Detached
Table 6: CO2 emission (tonne/yr) for gas or LPG heating and hot water in different property types
Boiler type SEDBUK Existing housing New housing
F B T SD D F B T SD D
Gas - old boiler (heavy weight) 55% 3.41 4.29 4.55 5.17 6.84 1.52 1.91 1.91 2.38 2.83
Gas - old boiler (light weight) 65% 2.89 3.63 3.85 4.38 5.79 1.28 1.62 1.62 2.02 2.40
Gas - new, non-condensing 79% 2.38 2.99 3.17 3.60 4.76 1.06 1.33 1.33 1.66 1.97
Gas - new, condensing 90% 2.09 2.62 2.78 3.16 4.18 0.93 1.17 1.17 1.46 1.73
LPG - old boiler (heavy weight) 57% 3.97 4.99 5.30 6.02 7.96 1.77 2.22 2.22 2.77 3.30
LPG - old boiler (light weight) 67% 3.38 4.25 4.51 5.12 6.77 1.50 1.89 1.89 2.36 2.80
LPG - new, non-condensing 81% 2.80 3.52 3.73 4.24 5.60 1.24 1.57 1.57 1.95 2.32
LPG - new, condensing 92% 2.46 3.09 3.28 3.73 4.93 1.09 1.38 1.38 1.72 2.04
F Flat
B Bungalow
T Terraced
SD Semi-detached
D Detached

34 Domestic heating by gas: boiler systems – guidance for installers and specifiers (2008 edition)
Energy efficiency
The Boiler Efficiency Database 7.5
The Boiler Efficiency Database(42) is an independently
authenticated record of the efficiency of most
gas and oil-fired domestic boilers in the UK. Most
of the data in it can be viewed at the website
www.boilers.org.uk. Both current and obsolete boilers
are included and the database is updated regularly,
with a new edition issued each month.
For boilers currently on sale, the database
gives SEDBUK efficiency figures derived from
independently certified tests and the corresponding
efficiency band (see panel). Manufacturers send
details of their products to the database manager,
who checks that the efficiency test results have
been independently certified by an approved testing
organisation and then calculates SEDBUK figures
for the database entry. For obsolete boilers, where
certified test results may not be available, a generic
efficiency for the type of boiler concerned is quoted
instead of SEDBUK.
In addition to the database, the website also has two
interactive programs. The first is an annual fuel cost
estimator for boilers of known efficiency in different
types of housing. The second is a whole-house
boiler sizing calculator to help estimate a suitable
replacement boiler size for individual properties
where dimensions and other relevant data are
known. (See also Section 8.2).
Saving energy with better controls 7.6
It is better to replace both boiler and controls when
upgrading a heating system. However, in some
circumstances, it may be appropriate to leave an
existing boiler in place and upgrade the controls.
Table 7 shows what savings could be obtained by
fitting new controls (to CHeSS standards) to older
types of boiler.
As a simple guide to efficiency, SEDBUK values are
divided into seven bands, from A (most efficient)
to G (see panel below). The entries for each boiler
on the database give the banding which may be
used on product literature and labels, although
there is no requirement to do so.
SEDBUK range Band
90% and above A
86%-90% B
82%-86% C
78%-82% D
74%-78% E
70%-74% F
Below 70% G

Domestic heating by gas: boiler systems – guidance for installers and specifiers (2008 edition) 35
Energy efficiency
Table 7: Typical energy savings achievable by upgrading the controls on existing systems
Existing system has
the following controls:
Add the following1 for
best practice controls
Approximate
average
savings2
(% of the existing
fuel consumption)
Older boiler with gravity DHW
18
13
312
4
10
Older boiler - fully pumped4
17
10
4
9
Older combi boiler4
15
7
4
Key:
Room thermostat
Programmable thermostat
Cylinder thermostat
Boiler interlock
TRVs on most radiators
Motorised valve
1. All improved systems must include a programmable room thermostat (replaces existing room thermostat).
2. These are average savings assuming normal controls, systems and user behaviour. Actual savings may be
significantly different. The savings only apply where an older-type boiler is fitted. It is assumed that the
SEDBUK (see 7.1) is 60% for the Gravity DHW system and 68% for the fully-pumped and combi systems.
3. This option provides only a partial interlock (hot water only).
4. All improved systems should include an automatic bypass valve if a bypass circuit is necessary (see
Appendix A note 14).

36 Domestic heating by gas: boiler systems – guidance for installers and specifiers (2008 edition)
System selection: practical issues8.
When choosing which best practice system to install
the following questions should be addressed.
1. Which boiler type is most suitable?
2. What size boiler is required?
3. Where will the boiler be positioned?
4. What will be the flue terminal position and
arrangement?
5. Where does the condensate drain go?
6. Are there any special ventilation requirements?
7. Will it be an open or sealed system?
8. What type of hot water system is most suitable?
9. What type and size of heat emitters are required?
10. What controls are needed?
CHeSS (see Section 6) specifies the main components
needed to achieve best practice in wet central
heating systems, but there are many additional
aspects of the installation to consider. The following
tables outline the key points.
Which type of boiler is most suitable?8.1 (31,43)
Regular or combi? Best practice regular boilers (see CHeSS HR8) provide most flexibility in system
design. A combi (see CHeSS HC8) incorporates some system equipment which
reduces installation time.
Condensing or non-
condensing?
Condensing boilers must be installed unless an exception is allowed (see
panel in Section 2.2). Use condensing types as specified in CHeSS HR8 or HC8
only. These provide significantly higher efficiency than non-condensing types,
although they do require connection to a drain as well as particular care in
siting the flue terminal.
Instantaneous combi The maximum flow rate at the hot water tap will depend on the boiler’s heat
output and the design of the draw-off pipe. Large heat outputs units (>35kW)
are now available which give high water flowrates. Lower heat output
versions will need more time to fill a bath or provide water at an acceptable
temperature compared to storage units. Some units have a keep-hot facility
which prevents any undue delay in hot water availability. This option may
increase running costs.
Storage combi These are usually capable of a higher flow rate at the hot water tap than an
equivalent heat output instantaneous unit. The flow rate and the capability to
sustain this will depend on the volume of the store and the boiler heat input.
CPSU This type is capable of high flow rates at the tap due to its comparatively large
store. It will also warm radiators more quickly as both the space heating and
hot water are fed from this store.
Range Cooker boilers Condensing units are now becoming available.
Back Boiler Units These are not recommended as they are not currently available in condensing
versions. Back boilers are only available in open-flue models and usually include
an integral gas fire in front.
Ignition system All Condensing boilers include automatic electronic ignition. Permanent pilot
ignition (which does not meet best practice) reduces SEDBUK efficiency by
around 4%.
Large boilers For boilers with output greater than 50kW, refer to suitable publications at
www.thecarbontrust.co.uk

Domestic heating by gas: boiler systems – guidance for installers and specifiers (2008 edition) 37
System selection: practical issues
What size boiler is required? 8.2 (31,35)
Maximum load The boiler needs to be sized to meet the maximum load expected on the
system. This includes the heat used by the emitters, the hot water system and
the pipework.
New systems A full design heat loss method should be employed to identify the most
suitable boiler. A full design method is given in the CIBSE Domestic
Heating Design Guide(32) and a computer based program can be found at
www.centralheating.co.uk
Boiler replacements Size-for-size replacement is not recommended. Insulation levels may have
been improved or the original sizing may have been incorrect. Heating and
hot water requirements should be re-checked before a new boiler is chosen.
Oversizing will result in lower efficiency and unnecessary capital costs. An
interactive procedure for correctly sizing boilers up to 25kW can be found at
www.boilers.org.uk
Combis Power rating is normally determined by hot water requirements and there is
generally more than enough heat output for space heating. This should always
be checked in large and/or poorly insulated dwellings.
Where will the boiler be positioned?8.3 (31,32)
General issues
Exception: is it difficult to
install a condensing boiler?
If an exception is being considered, follow the exceptions procedure (see panel
in Section 2.2) before a boiler position is considered.
Space It has to be adequate for the boiler type (including flue pipe space).
Access It needs to be sufficient for installation, maintenance and servicing.
Flue position Can a flue be fitted easily? Is an extended horizontal or vertical flue required,
and will angled flue bends be necessary? (See Section 8.4).
Condensate drain Is there a suitable adjacent drain point? (See Section 8.5).
Location
Heated area Preferred, saves energy.
Unheated area Requires frost protection. Consider externally mounted boiler.
Understairs May require special provision for ventilation and fire resistance.
Bathroom, shower room,
sleeping room
There are regulations regarding electrical work in bath and shower rooms.
Open-flue boilers must not be installed where they can draw combustion air
from a bathroom or bedroom. Room-sealed boilers should not be installed in
sleeping areas if avoidable.
Roofspace, loft, attic The weight of the boiler, ventilation and safe access must all be taken into
account.
Fireplace Condensing back boiler units (BBU) are not currently available. Where boilers
are located inside a living space, particular consideration must be given to
the position of the flue, the air supply routes and the provision of suitable
condensate drainage.
Garage Frost protection will be required.
Basements and cellars Ensure a practical connection to a drain point is available – consider using a
condensate pump.

38 Domestic heating by gas: boiler systems – guidance for installers and specifiers (2008 edition)
System selection: practical issues
What will be the flue terminal position and arrangement? 8.4 (32,47)
Condensing boilers
Plume A plume is present most of the time that the boiler operates. Avoid terminal
positions where a plume would be directed:
Towards or across a door or window.•
Towards a frequently used area (e.g. patio, access route or car parking •
space).
Across a neighbouring dwelling or boundary.•
In close proximity to an opposite wall or surface.•
Freezing Avoid situations where:
Condensate from a terminal may drip onto a path, then freeze and cause •
a hazard.
The plume may condense then freeze, damaging a wall or surface. •
Terminal guards Usually required where terminal is less than 2m from ground level. These need
to withstand corrosive effect of condensate.
Extended flues If the plume may cause a nuisance, consider an extended vertical/horizontal
flue, plume management option, a ‘directional’ terminal or alternative boiler
position.
Where does the condensate drain go? 8.5 (45)
Boiler position Ensure the chosen drain point can be reached from the proposed boiler
position.
Drain points Condensate can be drained to:
An internal stack pipe.•
A waste pipe.•
An external drain, gully or rainwater hopper.•
A purpose-made small soakaway. •
Boiler condensate siphons Check whether the chosen boiler has a fitted condensate siphon. If not,
externally situated condensate pipework is more likely to freeze in cold
weather.
Condensate traps Check whether the chosen boiler has an internal condensate trap with a water
seal greater than 75mm. If not, an air-break and additional trap with a seal
greater than 75mm must be installed.
Pipework All pipework must have a fall of 2.5 degrees and be securely clipped. External
runs must not exceed 3m and be insulated. Pipe materials must be corrosion
resistant to condensate (not copper or steel).
Pipe sizes Where there is no manufacturer’s guidance:
Pipes in a heated area should have a nominal diameter of at least 22mm.
Externally run pipes should have a nominal diameter of at least 32mm.
Condensate pumps If gravity will not take the condensate to the drain point, e.g. if the boiler is
situated in a basement, a condensate pump will need to be considered.

Domestic heating by gas: boiler systems – guidance for installers and specifiers (2008 edition) 39
System selection: practical issues
Are there any special ventilation requirements? 8.6 (32,47)
Room sealed Room-sealed balanced-flue appliances do not require special provision for
room ventilation.
Compartment Some boilers may require purpose made ventilation when a boiler is fitted in a
compartment.
Will it be an open or sealed system?8.7 (31,43)
Sealed Commonly used in new systems, especially with combis and all system
boilers. They incorporate an expansion vessel. The system pressure rises with
temperature. The necessary additional safety controls are normally incorporated
as part of the boiler. It is important to check that this expansion vessel has
enough capacity for the whole installed system.
Open Typical of existing installations, these systems require an expansion cistern
which must be at the highest point in the system.
What type of hot water system is most suitable? 8.8
Mains fed (combis,
unvented cylinders, thermal
stores, CPSUs)
Ensure that water supply to the dwelling (both pressure and flow rate) is
adequate (with both hot and cold water running) and the mains inlet pipe is of
adequate size. The flow rate obtainable from an instantaneous combi will also
depend on its maximum heat output.
Storage systems Cylinders meeting current best practice standards use high recovery coils and
are well insulated. It is no longer permitted to install ‘medium-duty’ cylinders,
which have inferior performance. Ensure existing hot water cylinders are well
insulated. Cylinders of 117-140 litre capacity are usually adequate for smaller
households with a single bathroom(31).
Unvented storage These are mains fed and usually give a high hot water flow rate at high
pressure.
Thermal storage These are also mains fed and will provide a high hot water flow rate at high
pressure.
Vented storage This type needs a cold water cistern and will usually provide a high hot water
flow rate at low pressure.
Solar systems In suitable properties, especially those with an unobstructed south-facing roof,
solar water heating systems can make a significant contribution to the hot
water energy requirements, and save boiler fuel. A hot water cylinder with an
additional coil for connection to the solar collector system is necessary. If solar
water heating is likely to be installed in the near future, it is advisable to choose
a suitable cylinder at the time the main heating system is installed, as it will
save cost and disruption later. Separate guidance and advice on solar water
heating should be sought(34,46).

40 Domestic heating by gas: boiler systems – guidance for installers and specifiers (2008 edition)
System selection: practical issues
What type and size of heat emitters are required? 8.9 (31,35)
Heat emitter type Panel radiators offer the lowest cost option. Use Low Surface Temperature
(LST) radiators where young children or elderly are likely to be present and may
be at risk. Where underfloor systems are being considered refer to specialist
advice(36).
Size Avoid undersizing as it will result in unsatisfactory heating performance and
may give rise to reduced boiler efficiency from excessive boiler cycling. If
radiators are oversized ensure boiler controls are set to operate at suitable
temperatures. Use a full design heat loss calculation method(19). An example
can be found at www.centralheating.co.uk
When used with
condensing boilers
Increasing radiator sizes can reduce average boiler operating temperatures
and therefore increase efficiency. However, care should be exercised when
oversized radiators are installed in a room with a controlling room thermostat.
If radiators in other rooms are not similarly oversized, the controllability of the
whole system may be affected.
System upgrades The heat emitters and system should be cleaned to remove deposits and
sludge which reduce heating performance.
What controls are needed?8.10 (31,38)
Best practice Regular boilers – use a programmable room thermostat with separate timing
capability for hot water. All systems should be fully pumped, have both room
and cylinder thermostats, use motorised valves or multiple pumps, and have
separate zones for heating and hot water. They should also have TRVs, an
automatic bypass valve and a boiler interlock.
Combi boilers – use a programmable room thermostat, TRVs and boiler
interlock. Install an automatic bypass valve if the manufacturer advises that a
bypass should be fitted.
Basic The basic CHeSS specification is the minimum acceptable standard. The system
should include a full programmer (a time switch for combis). All other controls
as for best practice.
Thermostatic Radiator
Valves (TRVs)
TRVs must be installed on all radiators except in rooms with a room
thermostat. An automatic bypass valve must be installed if the manufacturer’s
instructions require one or if a minimum flow rate has to be maintained while
the boiler is firing.
Pumps Advice on pump selection is available from www.bpma.org.uk
See Section 4.8 for pumps with automatic speed control.
Systems with gravity hot
water
These must be converted to fully-pumped to comply with best practice and
building regulation requirements.
Very large dwellings These should be divided into separate zones not exceeding 150m2 in floor
area. Each zone should be capable of independent time and temperature
control.
Frost protection This should always be considered for both the dwelling and the central heating
system.
Other controls Additional controls can also be beneficial (see Section 5.3).

Domestic heating by gas: boiler systems – guidance for installers and specifiers (2008 edition) 41
Installing central heating systems9.
Competent person requirements 9.1
In England and Wales, the installation of a gas boiler
requires that details of the installation are made
available to CORGI who will send a certificate to the
householder and supply any relevant information
to the local authority building control department.
Alternatively installers or their customers can use
the local authority building control route for building
regulation notification for which a charge is made.
Businesses or self-employed persons who install
gas boilers in residential dwellings must be
registered with CORGI. Full details of requirements
regarding gas safety and CORGI registration can
be found in the Gas Safety (Installation and Use)
Regulations 1998.
Also in England and Wales all installations of
unvented hot water systems must be carried out
by a competent person who is approved by an
appropriate body.
Installing the boiler 9.2
While condensing boilers can normally be installed in
a similar location to non-condensing units, additional
factors need to be considered:
The plume from the flue terminal should not •
cause a nuisance.
There must be a drain point for the condensate. •
Where a boiler, particularly a replacement unit,
is being installed inside a dwelling it may not be
appropriate to site it in the same location. Even
where it is, extended flue options may have to be
considered as well as the practicalities of finding (and
connecting to) a suitable drain point. Where there
are particular difficulties with installing a condensing
boiler, a boiler exception can be considered (see
panel in Section 2.2). Even if an exception is allowed,
a condensing boiler should always be considered due
to increased efficiency and lower running costs.
Flue terminal position
Condensing boilers will produce a visible plume of
water vapour for a significant proportion of their
operating time. To avoid this causing a nuisance, a
vertical flue can remove the plume to a high level.
At low level, the plume may be a nuisance. Some
boilers eject flue gases horizontally in a powerful jet
which may not disperse for a considerable distance.
Some of the key minimum statutory distances from
terminals to obstacles (such as opposite walls)
are shown in figure 24. These distances are set
to maintain safe operation of the appliance but in
many cases will be insufficient to avoid nuisance and
therefore figure 24 also gives suggested minimum
distances help alleviate plume nuisance. Refer to
building regulations(47,48,49) which show all minimum
statutory distances from flue terminals.
Figure 24: Wall – Flue terminal siting
Opening
window
Pathway
Opposite
boundary
AB
C
Distances for flue terminal siting
Minimum
statutory
distances
To help
avoid plume
nuisance
A From a facing wall,
fence or property
boundary
0.6m 2.5m
B Below an openable
window
0.3m 1.0m
C From the side of a
door
0.3m 1.0m
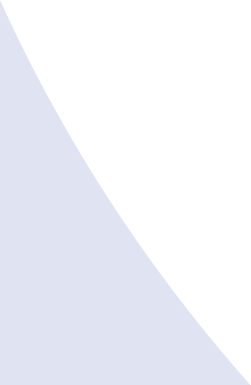
42 Domestic heating by gas: boiler systems – guidance for installers and specifiers (2008 edition)
Installing central heating systems
Refer to the condensing boiler exceptions procedure
before the boiler/flue terminal position is decided. In any
event particular care is required where it is intended to fit
a flue terminal which will be positioned less than 2.5m
from a facing wall, boundary fence or neighbouring
property. Where the plume from a terminal may cause
a nuisance, consider an extended vertical or horizontal
flue or moving the boiler to an alternative position which
may provide a more acceptable terminal position. Also
consider a ‘plume management’ option and/or using a
flue terminal in which the direction in which the jet of
flue products can be adjusted.
The plume should not cross:
A frequently used access route.•
Any frequently used area (such as a patio or car •
parking space).
A neighbouring dwelling. •
Nor should it be directed towards a window or door,
or be sited close to a facing wall or other surface.
There are also other aspects to consider when
planning the flue terminal position:
A free passage of air is needed at all times to •
aid plume dispersal, which may be difficult in
sheltered locations.
In cold weather, the condensate could cause a •
safety hazard if it freezes on pathways, or if it
results in frost damage to surfaces.
The plume could trigger infra-red security lighting •
if sited in the wrong place.
Ensure terminals do not obscure security camera •
field of vision.
The terminal guards must be able to resist •
corrosive properties of the condensate.
Condensate drain point
The amount of condensate produced by a condensing
boiler depends upon a number of factors but four litres
a day is not unusual. The liquid is slightly acidic (a pH
value of between three and six) and must be disposed
of correctly. Suitable drain points include:
An internal stack pipe. •
A waste pipe. •
An external drain or gully. •
A rainwater hopper that is part of a combined •
system (i.e. sewer carries both rainwater and foul
water).
A purpose-made small soakaway. •
Internal drain points are to be preferred as they are
less likely to become blocked by leaves, or by frozen
condensate(45).
Installing the condensate drain pipe 9.3
Condensate traps
Building regulations require a trap to be installed in
the condensate pipe from the boiler:
If this goes straight to a gully or rainwater hopper, •
a water seal of at least 38mm is required.
If connected to another waste pipe, the water •
seal must be at least 75mm to prevent foul
smells entering the dwelling.
Internal traps already fitted within the boiler may
not always satisfy the building regulations. Unless
otherwise stated by the manufacturer’s instructions,
an additional trap of either 38mm or 75mm
(depending on the proposed connection) will be
required. An air break between the traps is also
necessary (see figure 25).
Pipe runs
These should be as short as possible. If a condensate
drainpipe runs outside the dwelling, this external
run should be restricted to a maximum of 3m in
order to reduce the risk of freezing. If the boiler is
installed in an unheated space such as a garage, all
the condensate drainpipes should be regarded as
‘external’.
Pipe slope
A minimum of 2.5 degrees away from the boiler.
Bends
These should be kept to a minimum. Similarly, the
number of fittings or joints outside the dwelling
needs to be minimised in order to reduce the risk of
condensate being trapped.
Fixings
These must be sufficient to prevent sagging. A
maximum spacing of 0.5m for horizontal and 1.0m
for vertical sections is recommended.

Domestic heating by gas: boiler systems – guidance for installers and specifiers (2008 edition) 43
Installing central heating systems
Pipe sizes
Follow the boiler manufacturer’s instructions. In the
absence of such guidance:
The minimum nominal diameter for internal pipe •
runs is 22mm.
A larger diameter (at least 32mm nominal •
diameter) is required for externally run pipes to
reduce the risk of freezing.
Pipe materials
These should be resistant to the acid condensate. The
plastics used for standard wastewater plumbing systems
and cistern overflow pipes are suitable. Copper or mild
steel pipes and fittings must not be used.
Condensate siphons
Many boilers have a siphon fitted as part of the
condensate trap arrangement. This intermittently
discharges the condensate, reducing the risk
of freezing where part of the pipework runs
externally. If the boiler does not include a siphon,
avoid external pipework as far as possible. Where
necessary it should have a minimum nominal
diameter of 32mm.
Condensate pumps
These may be considered where the boiler is in the
basement or a drain point cannot be reached by
gravity. Pump manufacturers’ instructions must always
be followed.
Figure 25: Condensate trap options
Boiler
Boiler condensate water trap should
have a water seal H 38mm.
If boiler trap has a water seal of
<38mm use option C
Water seal must be > 75mm
Direct to external gulley or hopper
Option A – Boiler connected directly
to an external gulley or hopper
Boiler
Boiler condensate water
trap should have a water
seal H 75mm.
If not use option C
To another waste pipe
Option B – Boiler connected
to another waste pipe
Boiler
Water seal within boiler is insufficient
Air break
Option C – Boiler condensate
trap water is insufficient

44 Domestic heating by gas: boiler systems – guidance for installers and specifiers (2008 edition)
Installing central heating systems
Condensate drain termination 9.4
Connecting to an internal stack
This is the preferred method of connection. The stack
must be made of a material resistant to the corrosive
effect of the condensate, such as the plastics
recommended for condensate pipes.
A trap with a minimum condensate seal of 75mm
is required. The boiler may incorporate a trap of
this size, if not one will have to be fitted to the
condensate drainpipe. A visible air break is required
between this and any other trap.
For single dwellings up to three stories high, the
condensate drainpipe should discharge into the stack
at least 450mm above the invert of the tail of the bend
at the foot of the stack. If this point is not visible, then
the height should be measured from the bottom of the
lowest straight section of stack to be seen. This height
should be increased for buildings of more storeys.
The stack connection should not cause cross flow
into any other branch pipe, nor should it allow flow
from that branch into the condensate pipe. This can
be ensured by maintaining an offset between branch
pipes of at least 110mm on a 100mm diameter stack,
or 250mm on a 150mm stack.
Connecting to an external stack
In addition to the requirements detailed above,
care must be paid to reducing any risk of the drain
blocking due to the condensate freezing. The length
of pipe external to the dwelling should be kept as
short as possible and certainly less than 3m. Traps
in the drainpipe must be inside the building. In
exposed locations, the pipe should be protected with
waterproof insulation.
Connecting to an internal waste pipe
The most convenient (and most frequently used)
method of connection is via an internal discharge
branch to a kitchen sink, washing machine or
dishwasher drain. It can be connected up or down-
stream of the relevant waste trap and if practical
should be mounted onto the top of the pipe. If
connected upstream of the waste trap an air break
is necessary between this trap and the boiler’s own
trap. This is usually provided by the sink waste pipe
itself, as long as the sink has an integral overflow (see
figure 27).
Pipe slope >2.5º deg
Internal trap >75mm
>110mm (for 100mm stack)
>450mm (for up to 3 floors)
100mm Internal stack
Branch pipe
Figure 26: Condensate connection to internal stack

Domestic heating by gas: boiler systems – guidance for installers and specifiers (2008 edition) 45
Installing central heating systems
If, on the other hand, the condensate drain is
connected downstream of the sink (or other appliance)
waste trap, and the boiler does not have an integral
trap with a seal of at least 75mm, an additional trap
with that seal must be fitted. An air break must be
included between the traps (see figure 28).
In either case the trap and airbreak should be above
the level of the sink to prevent flows into the boiler
or airbreak. It is preferable to connect to a washing
machine drain rather than a kitchen sink. This reduces
the likelihood of solid waste and fats blocking or
restricting the condensate drain entry point.
Pipe slope >2.5º deg
SINK
Height above sink >100mm
Internal trap >75mm
Figure 27: Connection to an internal sink waste (upstream of sink trap)
SINK
Height above sink >100mm
Figure 28: Connection to an internal sink waste (downstream of sink trap)

46 Domestic heating by gas: boiler systems – guidance for installers and specifiers (2008 edition)
Installing central heating systems
Connecting to an external drain point
If the condensate cannot be drained via an internal
route, then direct connection to an external gully or
rainwater hopper can be considered. A rainwater
hopper must be connected to a combined system
(i.e. sewer carries both rainwater and foul water).
The open end of the pipe should be below the grid
level but above the water level in the gully or hopper.
Condensate must not be disposed of in grey water
systems.
Connecting to a small soakaway
If none of the previous solutions are possible then a
purpose made soakaway can be used. It should be
located as close as possible to the boiler but clear
of the building foundations and not in the vicinity
of other services such as gas, electricity or water
connections. The external pipework must be kept
to a minimum and not more than 3m in length. The
pipe may be taken below or above the ground level.
Figure 29 shows a suitable small soakaway design. It
should be sited around 1m away from the building
(at least 0.5m) and clear of building foundations and
other services. The size of the soakaway will depend
to a large extent on the soil conditions. Unlike the
case of a rainwater soakaway, the soil does not
have to accommodate large water volumes over
short periods. A soakaway container approximately
200mm diameter and 400mm deep will normally
be sufficient. The soakaway should be backfilled
with limestone chippings. Note that where the soil
is poorly drained, e.g. clay, this option may not be
practical.
Figure 29: Possible configuration for a condensate soakaway drain
0.5 to 1.0 m
Note: Condensate pipe can be run above or below ground
Section of plastic
drain pipe
Holes in side away
from dwelling
Ground level
Limestone
chipping fill
Bottom of pipe sealed

Domestic heating by gas: boiler systems – guidance for installers and specifiers (2008 edition) 47
Installing central heating systems
Controls9.5
There are a number of points to be considered when
installing commonly-used central heating controls.
Programmable Room Thermostat
CHeSS best practice specification
If fitted with a regular boiler, this must have a hot
water timing capability. In larger dwellings, where
separate time/temperature zones are required, only
one programmable room thermostat needs this
hot water timing capability. A programmable room
thermostat should be located in a regularly heated
area. While free movement of air is important, it
should be mounted away from draughts, internal
heat sources and direct sunlight. It should not
be fitted in a room where supplementary room
heating, e.g. electric heaters or open fires can affect
it. So do not site one in a kitchen or combined
kitchen and living room. Only install one in a main
living room if it is certain that no supplementary
heating is used there. Suitable positions would be
in the hall or a living room without supplementary
heating.
The unit should be readily accessible to the
householder, not hidden away in a cupboard or
behind furniture. It should be located at a height of
about 1.5m above floor level unless the occupants
include wheelchair users. In this instance a suitable
height in excess of 1m should be agreed with the
homeowner.
Time switch/programmer
CHeSS basic systems only
Time switches can only switch one circuit (such as
combi heating), while programmers can control two
(e.g. heating and hot water). Ensure that the unit is
suitable.
These controls should be installed where they can
be easily reached, read and altered. Do not fit them
in places inconvenient for the householder (e.g. in an
airing cupboard).
Room thermostat
CHeSS basic systems only
Installation considerations are the same as for the
programmable room thermostat.
Cylinder thermostat
CHeSS best practice specification
This control is usually strapped onto the cylinder about
one third of the way up from the base. The strap
needs to be tight to ensure good thermal contact and
be adjusted to about 60°C. If set too high, it may result
in scalding, but if too low it can increase the risk of
legionella bacteria which could result in serious health
problems.
Motorised valve
CHeSS best practice specification
The most common types of motorised valves are two
and three-port. How each will be used depends on
pipework layout and preference – as displayed in the
following examples.
Three-port valves can provide separate heating •
and hot water circuits. Most three-port units
feature a mid-position which allows shared flow.
Where there is more than one heating zone, as •
well as a hot water zone, use a separate two-
port valve for each zone.
Valves of 22mm can be used on boilers up to •
around 20kW. Beyond that, 28mm or larger
should be used.
Note: motorised valves must not be positioned in the
line of the open safety vent pipe or the feed-and-
expansion pipe.
Thermostatic Radiator Valve (TRV)
CHeSS basic and best practice specifications
TRVs must be used in systems meeting either
specification. They should be installed in all rooms
except those in which a controlling room thermostat
provides a boiler interlock. Many TRVs can be fitted
on the flow or return to the radiator and many are
bi-directional. If not, the direction of the water flow
must be taken into account when installing them.

48 Domestic heating by gas: boiler systems – guidance for installers and specifiers (2008 edition)
Installing central heating systems
Automatic bypass valve
CHeSS basic and best practice specifications
These should be used for systems meeting either
specification unless the boiler manufacturer does not
require a bypass circuit be fitted to ensure a minimum
flow rate. The valve should be installed between the
boiler primary flow and return, taking account of the
direction of flow. Ensure that the valve has adequate
flow capacity. It should be set so as to ensure
adequate flow through the boiler when all motorised
valves and/or TRVs are closed.
Frost protection
(air and pipe thermostat)
Where both air and pipe thermostats are used, the
contacts should be wired in series from a live supply*
that is not switched by a timeswitch/programmer or
thermostats. This ensures that protection is available
24 hours a day. Some boilers already include their
own frost protection, but the level of protection for
the whole dwelling needs to be considered.
* For units that require thermostats with voltage-free contacts, refer
to the manufacturer’s instructions.
Weather compensator or unit with external
sensor
The external sensor should be positioned on a north-
facing wall, away from direct sunlight and other heat
sources.
Water treatment 9.6
Effective water treatment of a central heating system
is essential to ensure continued efficient and trouble
free operation.
Key points are:
Both new and existing systems should be •
thoroughly cleaned and flushed out before a new
boiler is fitted.
A suitable corrosion inhibitor should be used •
in the boiler primary water circuit to minimise
corrosion and the formation of scale and sludge.
The water supply may require softening to •
prevent scaling of heat exchangers. This is
particularly important in the case of water heaters
which are installed in hard water areas (where
the water hardness exceeds 200 parts per million.
See BS 7593:2006(57)).
Always refer to boiler manufacturer’s instructions •
to ensure appropriate cleaning, softening and
inhibitor products are used and any special
requirements for particular models are applied.
A system with excessive hardness scale and •
sludge will not operate at optimal efficiency.
More advice is available on water treatment, the
need for it, methods and dealing with problems(56,57).
The outline setting procedure is as follows:
Once the system is commissioned and •
balanced, make a note of the selected pump
speed.
Determine the minimum flow requirement of •
the boiler (from manufacturer’s instructions).
From the pump manufacturers pump curve at •
the selected pump speed, determine available
pump head at the required minimum flow.
Using the manufacturer’s automatic bypass •
setting chart, adjust the valve setting to
correspond to the pump head at the minimum
flow.
Should persistent water velocity noise occur in the
system, gradually reduce the valve setting until the
noise is eliminated.

Domestic heating by gas: boiler systems – guidance for installers and specifiers (2008 edition) 49
Commissioning and handover10.
Commissioning 10.1
For safe and energy-efficient operation, all parts of a
new central heating and hot water system need to
be checked to ensure they are working properly. In
particular:
The boiler and system should be cleaned using a •
recognised flushing procedure (see BS 7593:2006).
A suitable corrosion inhibitor should be used in the •
boiler primary water circuit to minimise corrosion
and the formation of scale and sludge (subject to
recommendations by the boiler manufacturer).
The key system components must be checked for •
correct and safe operation.
The controls should be set to their optimum •
settings.
The customer should be instructed on how to •
operate the controls, and the importance of regularly
servicing the system needs to be made clear.
In England and Wales, a CORGI registered installer will
carry out this work and they will send details to CORGI
who will send certificates to the householder and the
local authority Building Control. Alternatively installers
or their customers can use the local authority Building
Control route for notification.
To raise the standard of the installation, commissioning
and servicing of central heating systems in the UK,
the Benchmark scheme has been introduced. It is
intended to ensure that all new boilers are both safe
and energy efficient throughout their working life.
Most new boilers will have a log book. This should be
signed by a CORGI registered installer to confirm the
boiler has been fitted and commissioned in accordance
with the manufacturer’s instructions. Householders will
be encouraged to ask the installer for this log book
and to retain it for evidence of correct installation,
commissioning and servicing of the boiler and systems.
Advising householders 10.2
Installers must instruct the householder how to set and
use the controls properly and effectively. In particular,
the operation of programmers can be difficult to
understand and homeowners will gain little or no
benefit from an incorrectly set device. In fact, they will
probably end up wasting energy.
As a bare minimum, the manufacturer’s instructions
should be left with the householder. However, it will
usually be necessary to demonstrate:
How to set the programmer clock and adjust for •
GMT and BST.
The use of the time control override function. •
How to set summer hot water only. •
How to separate space heating and domestic hot •
water time settings (regular boilers only).
How to set room and cylinder thermostats. •
How to set TRVs. •
The installer will also need to explain:
The function of room thermostats and TRVs and •
the need to set them carefully to avoid wasteful
heating. They should be altered when the needs of
the household change, and should not be treated
as on/off switches.
That the cylinder thermostat needs to be left at •
approximately 60°C, since setting it higher may
result in scalding while setting it lower can allow
the growth of legionella bacteria.
That the radiator lockshield and automatic bypass •
valve should not be adjusted once set by the
installer.
Why it is best to switch space and water heating •
off when not required.
Why it is best to turn the room thermostat down to •
frost protection levels (approximately 12°C) unless
a separate frost protection system has been fitted.
That sealed boiler systems must have adequate •
system pressure and what to do if re-pressurising
is needed.
Servicing 10.3
Users should be made aware of the importance of
regular servicing, both of the boiler and the system as
a whole. This will help maintain its safety and efficiency.
In particular, users should consider taking out a regular
service contract where a competent service engineer
(registered with CORGI) will clean and maintain the
boiler, check the operation of the system and controls,
as well as completing the record of servicing in the
Benchmark log book.
Note that homeowners in England and Wales can now
ask for a energy rating for their boiler with advice on
how to cut fuel bills, whenever an engineer makes a
regular service visit. An example of the form used in
shown in Appendix D.

50 Domestic heating by gas: boiler systems – guidance for installers and specifiers (2008 edition)
Appendix A – Notes to CHeSS 2008
CHeSS is published in full as reference(38) and part of
it is reproduced here in Section 6. The Notes below
apply to CHeSS HR7, HC7, HR8, HC8 (Year 2008).
1. Other components
The specifications list only the principal components
of a heating system affecting energy efficiency.
Other components will be required, such as
radiators, circulator pumps (see note 4), cisterns
(feed and expansion tanks), and motorised valves. All
components must be selected and sized correctly.
2. Design, installation and commissioning
Heating systems should be designed to match the
heating needs of the buildings in which they are
installed, using methods such as those described in
Ref [5]. They should be installed in accordance with
relevant safety regulations, manufacturers’ instructions,
the Benchmark scheme (see Ref [10]), building
regulations (see Refs [1], [2], [11]), the Domestic Heating
Compliance Guide (see Ref [16]), and British Standards
(see Refs [12], [13], [17], [18]). For oil boilers the OFTEC
forms CD/10 and CD/11 (or similar) for installation and
commissioning should be completed. More detailed
advice on domestic wet central heating systems is given
in the Energy Saving Trust guides (see Refs [3] and [4]),
and the CIBSE guide (see Ref [5]). Commissioning and
handover of information on operation and maintenance
is a requirement of building regulations and a suitable
commissioning certificate should be issued.
3. Water treatment
Water treatment is important as it prolongs effective
and trouble-free operation. Three types of water
treatment should be considered:
• Cleaningandflushingofthesystembeforeuse
• Corrosioninhibition
• Softeningofthewatersupplytocombiboilersfor
hot water service in hard water areas.
In each case the recommendation of the boiler
manufacturer must be followed as damage may be
caused by unsuitable treatment. For both new and
replacement systems, thorough cleaning is essential.
When a boiler is replaced it is essential to drain and
flush all old water from the system in case it contains
a corrosion inhibitor unsuitable for the new boiler.
Advice on the need for treatment and on causes of
problems is given in BS 7593 (see Ref [14]).
4. Circulator pump
Advice on pump dimensioning is available from the
BPMA (British Pump Manufacturers’ Association)
website at www.bpma.org.uk
Pumps installed separately from the boiler (not supplied
as part of the boiler unit) which have automatic speed
control should not be used in heating systems with
TRVs unless the design of the pump and system
ensures that the minimum flow rate through the boiler
(as specified by the boiler manufacturer) is certain to be
maintained under all conditions.
5. Boiler size and type
The whole house boiler sizing method for houses
and flats gives guidance on boiler size and is
available on the Energy Saving Trust website at
www.energysavingtrust.org.uk/housingbuildings/
calculators/boilersizing
A regular boiler does not have the capability to
provide domestic hot water directly, though it may do
so indirectly via a separate hot water store.
A combination (combi) boiler does have the
capability to provide domestic hot water directly, and
some models contain an internal hot water store.
A combined primary storage unit (CPSU) is a
boiler with a burner that heats a thermal store directly.
Each of these may be either a condensing or non-
condensing boiler, and condensing boilers are always
more efficient. Condensing boilers are fitted with a drain
to dispose of the liquid condensate. Building regulations
require all new gas and oil boilers to be condensing,
whether installed in new or existing housing, unless
there are exceptional circumstances that would make
the installation impractical or excessively costly. All boilers
in the CHeSS specifications HR7, HC7, HR8 and HC8 are
condensing boilers.
For further definitions of boiler types see Appendix D
of Ref [6].
6. Boiler efficiency
SEDBUK (Seasonal Efficiency of Domestic Boilers
in the UK) is the preferred measure of the
seasonal efficiency of a boiler installed in typical
domestic conditions in the UK, and is used in
SAP assessments and the building regulations.
The SEDBUK efficiency of most current and
obsolete boilers can be found on the website

Domestic heating by gas: boiler systems – guidance for installers and specifiers (2008 edition) 51
Notes to CHeSS 2008
www.boilers.org.uk. Although SEDBUK is expressed
as a percentage, an A to G scale of percentage
bands has also been defined below.
SEDBUK
Efficiency range Band
90% and above A
86% – 90% B
82% – 86% C
78% – 82% D
74% – 78% E
70% – 74% F
Below 70% G
7. Hot water cylinder (basic)
Vented cylinders shall comply with the performance
requirements of BS 1566:2002 Type P cylinders (see
Ref [7]). The performance of unvented cylinders shall
comply with BS EN 12897:2006 (see Ref [8]) or be
approved by the BBA or other equivalent body. All
cylinders must be factory insulated such that the
standing heat loss will not exceed:
1.6 x (0.2 + 0.051 V2/3) kWh per 24 hours, where V
is the capacity in litres. All cylinders shall be labelled
with the standing heat loss in kWh/24hours.
Indirect cylinders shall also be labelled with the
heat exchanger performance in kW as measured
by BS 1566: 2002 (vented) or BS EN 12897
(unvented). Where cylinder capacity (V) in litres
is less than 200, the ratio of V to heat exchanger
performance (in kW) shall not exceed 10; e.g.
a 150 litre cylinder shall have a minimum heat
exchanger performance of 15kW. Where V is 200
or above the cylinder shall have a minimum heat
exchanger performance of 20kW.
8. Hot water cylinder (high performance)
A high performance cylinder may be either vented
or unvented. The manufacturer must confirm
that the heat exchanger and insulation properties
exceed the requirements of the relevant British
Standards (see Refs [7], [8]). The standing heat loss
must not exceed: 1.28 x (0.2 + 0.051 V2/3) kWh
per 24 hours, where V is the capacity in litres. All
cylinders shall be labelled with the standing heat
loss in kWh/24hours.
High performance cylinders shall comply with
the heat exchanger performance and labelling
requirements of basic cylinders, as set out in Note 7.
Solar-compatible cylinders contain an additional heat
exchanger or other provision for connection to a solar
water heating system. They offer the opportunity to
install a solar water heating system at greatly reduced
cost and with less disruption in the future. In the case
of solar-compatible cylinders the heat exchanger
performance of the upper coil (connected to the
boiler) shall relate to the volume of water heated
by that coil; i.e. the dedicated solar volume shall be
subtracted from the total cylinder capacity for the
purposes of heat exchanger assessment.
9. Thermal store (high performance)
A high-performance thermal (primary) storage
system must have insulation properties exceeding by
at least 15% those given in the WMA Performance
Specification for Thermal Stores (see Ref [9]), and
comply with the specification in other respects. Note
that the WMA Performance Specification for Thermal
Stores is shortly to be superseded by a revised 2008
specification from the HWA (Hot Water Association).
10. Circuits and zones
Systems with regular boilers must have separately
controlled circuits to the hot water cylinder and
radiators, and both circuits must have pumped
circulation. Large properties must be divided into
zones not exceeding 150m2 floor area, so that
the operation of the heating in each zone can be
timed and temperature controlled independently.
11. Heating controls
Definitions of heating controls are given in Ref [4].
The most common are repeated below.
A time switch is an electrical switch operated by a
clock to control either space heating or hot water, or
both together but not independently.
A full programmer allows the time settings
for space heating and hot water to be fully
independent.
A room thermostat measures the air temperature
within the building and switches the space heating
on and off. A single target temperature may be set
by the user.

52 Domestic heating by gas: boiler systems – guidance for installers and specifiers (2008 edition)
Notes to CHeSS 2008
A programmable room thermostat is a
combined time switch and room thermostat that
allows the user to set different periods with different
target temperatures for space heating, usually in a
weekly cycle. Some models also allow time control of
hot water, therefore replacing a full programmer.
A cylinder thermostat measures the temperature
of the hot water cylinder and switches the water
heating on and off.
A thermostatic radiator valve (TRV) has an air
temperature sensor which is used to control the heat
output from the radiator by adjusting water flow.
12. Wireless controls
Wireless controls are susceptible to radio
transmissions and should therefore be designed
to a satisfactory level of immunity, otherwise they
may become unreliable as nearby frequency bands
become increasingly utilised by communication
services.
Compliance with the essential requirements of
the European Radio and Telecommunications
Terminal Equipment (RTTE) Directive 1999/5/EC
is insufficient, as the directive is designed only to
ensure that wireless products do not cause harmful
interference to other transmissions. It does not give
any assurance that the product has a satisfactory
level of immunity to interference from other radio
transmissions.
Consequently it is not sufficient for the manufacturer
to confirm compliance with the RTTE Directive. The
manufacturer should also confirm that the switching
range, and preferably alignment range, do not
include any frequencies below 430MHz, and that in
regard to ETSI EN 300 220-1 v1.3.1 (see Ref [15]) the
receiver classification (clause 4.1.1) is either Class 1 or
Class 2, and the device is marked in accordance with
clause 4.3.4.
13. Boiler interlock
Boiler interlock is not a physical device but an
arrangement of the system controls (room
thermostats, programmable room thermostats,
cylinder thermostats, programmers and time
switches) so as to ensure that the boiler does not fire
when there is no demand for heat.
In a system with a combi boiler this can be achieved
by fitting a room thermostat. In a system with a
regular boiler this can be achieved by correct wiring
interconnection of the room thermostat, cylinder
thermostat, and motorised valve(s). It may also be
achieved by more advanced controls, such as a boiler
energy manager. TRVs alone are not sufficient for
boiler interlock.
14. An automatic bypass valve
An automatic bypass valve controls water flow in
accordance with the water pressure across it, and
is used to maintain a minimum flow rate through
the boiler and to limit circulation pressure when
alternative water paths are closed.
A bypass circuit must be installed if the boiler
manufacturer requires one, or specifies that a
minimum flow rate has to be maintained while the
boiler is firing. The installed bypass circuit must then
include an automatic bypass valve (not a fixed-
position valve).
Care must be taken to set up the automatic bypass
valve correctly, in order to achieve the minimum flow
rate required (but not more) when alternative water
paths are closed.

Domestic heating by gas: boiler systems – guidance for installers and specifiers (2008 edition) 53
Appendix B – Definitions of boiler types
B1.1 Boiler
A gas or liquid fuelled appliance designed to provide
hot water for space heating. It may (but need not) be
designed to provide domestic hot water as well.
B1.2 Condensing boiler
A boiler designed to make use of the latent heat
released by the condensation of water vapour in the
combustion flue products. The boiler must allow the
condensate to leave the heat exchanger in liquid
form by way of a condensate drain. Condensing
may only be applied to the definitions B1.3 to B1.14
inclusive. Boilers not so designed, or without the
means to remove the condensate in liquid form, are
called ‘non-condensing’.
B1.3 Regular boiler
A boiler which does not have the capability to
provide domestic hot water directly (i.e. not a
combination boiler). It may nevertheless provide
domestic hot water indirectly via a separate hot water
storage cylinder.
B1.4 On/off regular boiler
A regular boiler without the capability to vary the fuel
burning rate whilst maintaining continuous burner
firing. This includes those with alternative burning
rates set once only at time of installation, referred to
as range rating.
B1.5 Modulating regular boiler
A regular boiler with the capability to vary the fuel
burning rate whilst maintaining continuous burner
firing.
B1.6 Combination boiler
A boiler with the capability to provide domestic hot
water directly, in some cases containing an internal
hot water store.
B1.7 Instantaneous combination boiler
A combination boiler without an internal hot water
store, or with an internal hot water store of capacity
less than 15 litres.
B1.8 On/off instantaneous combination
boiler
An instantaneous combination boiler that only has
a single fuel burning rate for space heating. This
includes appliances with alternative burning rates set
once only at time of installation, referred to as range
rating.
B1.9 Modulating instantaneous combination
boiler
An instantaneous combination boiler with the capability
to vary the fuel burning rate whilst maintaining
continuous burner firing.
B1.10 Storage combination boiler
A combination boiler with an internal hot water store
of capacity at least 15 litres but less than 70 litres, OR
a combination boiler with an internal hot water store
of capacity at least 70 litres, in which the feed to the
space heating circuit is not taken directly from the store.
If the store is at least 70 litres and the feed to the space
heating circuit is taken directly from the store, treat as a
CPSU (B1. 13 or B1. 14).
B1.11 On/off storage combination boiler
A storage combination boiler that only has a single fuel
burning rate for space heating. This includes appliances
with alternative burning rates set once only at time of
installation, referred to as range rating.
B1.12 Modulating storage combination boiler
A storage combination boiler with the capability to vary
the fuel burning rate whilst maintaining continuous
burner firing.
B1.13 On/off combined primary storage unit
(CPSU)
A single appliance designed to provide both space
heating and the production of domestic hot water, in
which there is a burner that heats a thermal store which
contains mainly primary water which is in common with
the space heating circuit. The store must have a capacity
of at least 70 litres and the feed to the space heating
circuit must be taken directly from the store. The appliance
does not have the capability to vary the fuel burning rate
whilst maintaining continuous burner firing. This includes
those with alternative burning rates set once only at time
of installation, referred to as range rating.
B1.14 Modulating combined primary storage
unit (CPSU)
A single appliance designed to provide both space
heating and the production of domestic hot water, in
which there is a burner that heats a thermal store which
contains mainly primary water which is in common
with the space heating circuit. The store must have a
capacity of at least 70 litres and the feed to the space
heating circuit must be taken directly from the store. The
appliance has the capability to vary the fuel burning rate
whilst maintaining continuous burner firing.

54 Domestic heating by gas: boiler systems – guidance for installers and specifiers (2008 edition)
Definitions of boiler types
B1. 15 Low temperature boiler
A non-condensing boiler designed as a low
temperature boiler and tested as a low temperature
boiler as prescribed by the Boiler Efficiency Directive
(i.e. the part load test was carried out at average
boiler temperature of 40°C).
B1. 16 Keep-hot facility
A facility within an instantaneous combination boiler
whereby water within the boiler may be kept hot
while there is no demand. The water is kept hot
either (i) solely by burning fuel, or (ii) by electricity, or
(iii) both by burning fuel and by electricity, though not
necessarily simultaneously.

Domestic heating by gas: boiler systems – guidance for installers and specifiers (2008 edition) 55
Appendix C – Definitions of heating controls
As given in SAP Appendix D(22) The list of definitions
has been discussed and agreed with industry
representatives, and, for completeness, includes some
controls for heating systems other than gas central
heating.
Automatic bypass valve
A valve to control water flow, operated by the water
pressure across it. It is commonly used to maintain
a minimum flow rate through a boiler and to limit
circulation pressure when alternative water paths are
closed (particularly in systems with TRVs).
Boiler anti-cycling device
A device to introduce a time delay between boiler
firing. Any energy saving is due to a reduction in
performance of the heating system. The device does
not provide boiler interlock.
Boiler auto ignition
An electrically controlled device to ignite the boiler at
the start of each firing, avoiding use of a permanent
pilot flame.
Boiler energy manager
No agreed definition, but typically a device intended
to improve boiler control using a selection of features
such as weather compensation, load compensation,
optimum start control, night setback, frost protection,
anticycling control and hot water override.
Boiler interlock
This is not a physical device but an arrangement of
the system controls so as to ensure that the boiler
does not fire when there is no demand for heat.
In a system with a combi boiler it can be achieved
by fitting a room thermostat. In a system with a
regular boiler it can be achieved by correct wiring
interconnections between the room thermostat,
cylinder thermostat, and motorised valve(s). It may
also be achieved by a suitable boiler energy manager.
Boiler modulator (air temperature)
A device, or feature within a device, to vary the fuel
burning rate of a boiler according to measured room
temperature. The boiler under control must have
modulating capability and a suitable interface for
connection.
Boiler modulator (water temperature)
A device, or feature within a device, to vary the fuel
burning rate of a boiler according to measured water
temperature. It is often fitted within the boiler casing. The
boiler under control must have modulating capability.
Boiler thermostat
A thermostat within the boiler casing to limit the
temperature of water passing through the boiler by
switching off the boiler. The target temperature may
either be fixed or set by the user.
CELECT-type electric heating control
Integrated central control system for electric storage
and panel heaters that provides programmed space
temperatures at different times of the day for a
number of separate heating zones in the dwelling. It
minimises the charge period of the storage heaters
according to the external temperature.
Cylinder thermostat
A sensing device to measure the temperature of the
hot water cylinder and switch on and off the water
heating. A single target temperature may be set by
the user.
Delayed start
A device, or feature within a device, to delay the
chosen starting time for space heating according to the
temperature measured inside or outside the building.
Frost thermostat
A device to detect low air temperature and switch on
heating to avoid frost damage, arranged to override
other controls.
Load compensator
A device, or feature within a device, which adjusts
the temperature of the water circulating through
the heating system according to the temperature
measured inside the building.
Motorised valve
A valve to control water flow, operated electrically. A
two-port motorised valve controls water flow to a
single destination. A three-port motorised valve controls
water flow to two destinations (usually for space
heating and hot water), and may be either a diverter
valve (only one outlet open at a time) or a mid-position
valve (either one, or both, outlets open at a time). The
valve movement may also open or close switches,
which are used to control the boiler and pump.

56 Domestic heating by gas: boiler systems – guidance for installers and specifiers (2008 edition)
Definitions of heating controls
Night setback
A feature of a room thermostat that allows a lower
temperature to be maintained outside the period
during which the normal room temperature is
required.
On/off-peak hot water controller
A control to switch the electrical supply to the main
immersion heater from the off-peak electricity supply.
It may also include a boost function so that some of
the stored water can also be heated using on-peak
electricity.
Optimum start
A device, or feature within a device, to adjust
the starting time for space heating according to
the temperature measured inside or outside the
building, aiming to heat the building to the required
temperature by a chosen time.
Optimum stop
A device, or feature within a device, to adjust the stop
time for space heating according to the temperature
measured inside (and possibly outside) the building,
aiming to prevent the required temperature of the
building being maintained beyond a chosen time.
Pipe thermostat
A switch governed by a sensor measuring pipe
temperature, normally used in conjunction with other
controls such as a frost thermostat.
Programmable cylinder thermostat
A combined time switch and cylinder thermostat that
allows the user to set different periods with different
target temperatures for stored hot water, usually in a
daily or weekly cycle.
Programmable room thermostat
A combined time switch and room thermostat that
allows the user to set different periods with different
target temperatures for space heating, usually in a
daily or weekly cycle.
Programmer
Two switches operated by a clock to control both
space heating and hot water. The user chooses one
or more periods, usually in a daily or weekly cycle.
A mini-programmer allows space heating and hot
water to be on together, or hot water alone, but
not heating alone. A standard programmer uses the
same time settings for space heating and hot water.
A full programmer allows the time settings for space
heating and hot water to be fully independent.
Pump modulator
A device to reduce pump power when not needed,
determined by hydraulic or temperature conditions or
firing status of the boiler.
Pump over-run
A timing device to run the heating system pump for a
short period after the boiler stops firing to discharge
very hot water from the boiler heat exchanger.
Room thermostat
A sensing device to measure the air temperature
within the building and switch on and off the space
heating. A single target temperature may be set by
the user.
Self-adaptive (or self-learning) control
A characteristic of a device (of various types) that
learns from experience by monitoring, and modifies
its subsequent behaviour accordingly.
Temperature and time zone control (or full
zone control)
A control scheme in which it is possible to select
different temperatures at different times in two (or
more) different zones.
Time switch
An electrical switch operated by a clock to control
either space heating or hot water, or both together
but not independently. The user chooses one or more
‘on’ periods, usually in a daily or weekly cycle.
Thermostatic radiator valve
A radiator valve with an air temperature sensor,
used to control the heat output from the radiator by
adjusting water flow.
Weather compensator
A device, or feature within a device, that adjusts
the temperature of the water circulating through
the heating system according to the temperature
measured outside the building.
Zone control
A control scheme in which it is possible to select
different times and/or temperatures in two (or more)
different zones.

Domestic heating by gas: boiler systems – guidance for installers and specifiers (2008 edition) 57
Appendix D – Energy efficiency checklist
Gas fired Home Heating Installations – energy efficiency checklist
This energy assessment is not a service or safety check. You should ensure your heating system is
regularly maintained and inspected by a competent heating engineer to ensure its safety and efficiency.
This is part of an initiative to help homeowners cut their fuel bills and reduce their carbon emissions.
Section 1 – Installation information
Customer Name
Installation Address
Customer Address (if different)
Date of assessment
Section 2 – Stored Hot Water Systems (if applicable)
Are the water pipes connected to the cylinder insulated? Yes No
Does the hot water cylinder have spray foam insulation or a jacket with a
thickness greater than 75mm? Yes No
Section 3 – Heating Controls
Does the system incorporate time control? Yes No
Does the system have thermostatic radiator valves (TRV)? Yes No
Does the system have room thermostat(s) and boiler interlock1?Yes No
Does the hot water cylinder have a thermostat and boiler interlock1?Yes No
1 Boiler interlock ensures the boiler and pump shuts down when heating and/or hot water are at the required temperature
Section 4 – Boiler
Manufacturer Approximate Age
Model name/number
The Energy Efficiency of your boiler
High efficiency (A-C rating) D rated E rated F rated High G rated Low G rated
Section 5 – Energy Efficiency Assessment
A brief inspection of your heating system has been carried out in accordance with recommended industry good
practice. Depending upon the outcome of this inspection there may be an opportunity for you to improve the
energy efficiency of the system, thereby reducing emissions to the environment and at the same time reducing
your fuel bills.
In any of the following cases you are strongly advised to obtain a more thorough examination of your boiler
and complete heating system by a competent heating engineer.
t *GBOZPGUIFBOTXFSTJO4FDUJPOTBOEBSFA/P
t *GUIFCPJMFSJTSBUFE%PSCFMPX
t *GUIFCPJMFSJTNPSFUIBOZFBSTPMEPSJGBDPNQMFUFFYBNJOBUJPOPGUIFEFTJHOBOEDPOEJUJPOPGZPVS
heating system has not been carried out in the last 15 years.
Name of service engineer
4JHOBUVSFPGTFSWJDFFOHJOFFS

58 Domestic heating by gas: boiler systems – guidance for installers and specifiers (2008 edition)
Energy efficiency checklist
Potential savings – all information is provided by the Energy Saving Trust
Improving your heating system and controls
Typical Annual
saving up to
(£/yr)
CO2 savings
Insulating hot water pipes connected to the hot water cylinder £10 70 kg/yr
Insulating your hot water cylinder with a jacket thicker than 75mm b 160 kg/yr
Installing heating controls £65 LHZS
Changing from a D rated boiler to an A rated boiler could save you: £54 ,HZS
Changing from an E rated boiler to an A rated boiler could save you: £77 ,HZS
Changing from an F rated boiler to an A rated boiler could save you: £104 ,HZS
Changing from a High G rated boiler to an A rated boiler could save you: £157 UPOOFTZS
Changing from a Low G rated boiler to an A rated boiler could save you: b UPOOFTZS
Other possible home improvements
Typical Annual
saving up to
(£/yr)
CO2 savings
Cavity Wall insulation £90 750 kg/yr
4PMJE8BMMJOTVMBUJPOJOUFSOBM b UPOOFTZS
4PMJE8BMMJOTVMBUJPOFYUFSOBM b UPOOFTZS
Double glazing £90 740 kg/yr
-PGUJOTVMBUJPOOFXJOTUBMMBUJPOUPBUIJDLOFTTPGNN £110 LHZS
Floor insulation £45 LHZS
Draught proofing b 155 kg/yr
Filling gaps between floor and skirting board £15 LHZS
The savings shown are approximate and are provided as an illustration only. They are based on a natural gas heated semi-detached
IPVTFXJUICFESPPNTVTJOHBHBTQSJDFPGQL8I4PNFPGUIFTBWJOHTNBEFNBZCFUBLFOJOJODSFBTFEDPNGPSU5IFBDUVBMBOOVBM
TBWJOHTXJMMWBSZEFQFOEJOHPOUIFUZQFPGBQQMJBODFTJ[FBOEBHFPGIPVTFBOEUZQFPGGVFMVTFE*GZPVJNQMFNFOUNPSFUIBOPOFPG
UIFJNQSPWFNFOUTUIFUPUBMTBWJOHTNBZCFMFTTUIBOUIFTVNPGUIFJOEJWJEVBMTBWJOHT
An Energy Performance Certificate will give you an energy rating for your home and specific recommendations and savings for your
property. Energy Performance Certificates (EPCs) are a legal requirement within a Home Information Pack for the marketed sales of
IPNFT&1$TXJMMCFSFRVJSFEGPSIPNFTXIFOSFOUFEGSPN0DUPCFS
'PSBEWJDFPOIPXUPUBLFBDUJPOBOEUPmOEPVUBCPVUPGGFSTBWBJMBCMFUPIFMQNBLFZPVSIPNFNPSFFOFSHZFGmDJFOUDBMM0800 512 012
or visit www.energysavingtrust.org.uk/myhome
5PEFUFSNJOFXIBUTJ[FCPJMFSZPVOFFEGPSZPVSIPNFWJTJUXXXTFECVLDPNBOEDMJDLPOA3FDPNNFOEFE#PJMFS4J[F#ZQSPWJEJOH
TPNFCBTJDEFUBJMTBCPVUUIFTJ[FPGZPVSIPNFZPVDBOTFFXIBUTJ[FPGCPJMFSZPVOFFE
For a more thorough inspection of your heating system you should contact a competent heating engineer with an energy efficiency
qualification.
Contact CORGI if you have any concerns about the safety of your gas appliance or to check your installer is CORGI registered on
0800 915 0485 or visit www.trustcorgi.com.
Address Details
ª$SPXO$PQZSJHIU1VCMJTIFECZUIF%FQBSUNFOUGPS$PNNVOJUJFTBOE-PDBM(PWFSONFOU0DUPCFS
1SPEVDUDPEF#%C

Domestic heating by gas: boiler systems – guidance for installers and specifiers (2008 edition) 59
Appendix E – Heating controls: simple explanations for
householders
Simple explanations of the purpose and principles
of domestic heating controls are necessary to help
householders understand them, and encourage
more effective usage. The following pages have been
written in conjunction with control manufacturers
to accompany the installation and commissioning
instructions for individual products, and are included
with heating controls that carry the Energy Saving
Recommended logo.
1. What is a room thermostat?
A room thermostat simply switches the heating
system on and off as necessary. It works by sensing
the air temperature, switching on the heating when
the air temperature falls below the thermostat
setting, and switching it off once this set temperature
has been reached.
Turning a room thermostat to a higher setting will not
make the room heat up any faster. How quickly the
room heats up depends on the design of the heating
system, for example, the size of boiler and radiators.
Neither does the setting affect how quickly the room
cools down. Turning a room thermostat to a lower
setting will result in the room being controlled at a
lower temperature, and saves energy.
The heating system will not work if a time switch or
programmer has switched it off.
The way to set and use your room thermostat is
to find the lowest temperature setting that you are
comfortable with, and then leave it alone to do its job.
The best way to do this is to set the room thermostat
to a low temperature – say 18°C – and then turn it
up by one degree each day until you are comfortable
with the temperature. You won’t have to adjust the
thermostat further. Any adjustment above this setting
will waste energy and cost you more money.
If your heating system is a boiler with radiators,
there will usually be only one room thermostat to
control the whole house. But you can have different
temperatures in individual rooms by installing
thermostatic radiator valves (TRVs) on individual
radiators. If you don’t have TRVs, you should choose
a temperature that is reasonable for the whole house.
If you do have TRVs, you can choose a slightly higher
setting to make sure that even the coldest room is
comfortable, then prevent any overheating in other
rooms by adjusting the TRVs.
Room thermostats need a free flow of air to sense
the temperature, so they must not be covered by
curtains or blocked by furniture. Nearby electric fires,
televisions, wall or table lamps may prevent the
thermostat from working properly.
2. What is a cylinder thermostat?
A cylinder thermostat switches on and off the heat
supply from the boiler to the hot-water cylinder. It
works by sensing the temperature of the water inside
the cylinder, switching on the water heating when
the temperature falls below the thermostat setting,
and switching it off once this set temperature has
been reached.
Turning a cylinder thermostat to a higher setting will
not make the water heat up any faster. How quickly
the water heats up depends on the design of the
heating system, for example, the size of boiler and
the heat exchanger inside the cylinder.
The water heating will not work if a time switch or
programmer has switched it off. And the cylinder
thermostat will not always switch the boiler off,
because the boiler sometimes needs to heat the
radiators.
Cylinder thermostats are usually fitted between one
quarter and one third of the way up the cylinder. The
cylinder thermostat will have a temperature scale
marked on it, and it should be set at between 60°C
and 65°C, then left to do its job. This temperature is
high enough to kill off harmful bacteria in the water,
but raising the temperature of the stored hot water
any higher will result in wasted energy and increase
the risk of scalding.
If you have a boiler control thermostat, it should
always be set to a higher temperature than that of
the cylinder thermostat. In most boilers, a single boiler
thermostat controls the temperature of water sent
to both the cylinder and radiators, although in some
there are two separate boiler thermostats.
3. What is a programmer?
Programmers allow you to set ‘On’ and ‘Off’ time
periods. Some models switch the central heating
and domestic hot water on and off at the same
time, while others allow the domestic hot water
and heating to come on and go off at different
times.

60 Domestic heating by gas: boiler systems – guidance for installers and specifiers (2008 edition)
Heating controls: simple explanations for householders
Set the ‘On’ and ‘Off’ time periods to suit your own
lifestyle. On some programmers you must also set
whether you want the heating and hot water to run
continuously, run under the chosen ‘On’ and ‘Off’
heating periods, or be permanently off.
The time on the programmer must be correct. Some
types have to be adjusted in spring and autumn at
the changes between Greenwich Mean Time (GMT)
and British Summer Time (BST).
You may be able to temporarily adjust the heating
programme, for example, ‘Override’, ‘Advance’ or
‘Boost’. These are explained in the manufacturer’s
instructions.
The heating will not work if the room thermostat has
switched the heating off. And, if you have a hot-
water cylinder, the water heating will not work if the
cylinder thermostat detects that the hot water has
reached the correct temperature.
4. What is a programmable room
thermostat?
A programmable room thermostat is both a
programmer and a room thermostat. A programmer
allows you to set ‘On’ and ‘Off’ time periods to suit
your own lifestyle. A room thermostat works by
sensing the air temperature, switching on the heating
when the air temperature falls below the thermostat
setting, and switching it off once this set temperature
has been reached.
So, a programmable room thermostat lets you
choose what times you want the heating to be on,
and what temperature it should reach while it is on. It
will allow you to select different temperatures in your
home at different times of the day (and days of the
week) to meet your particular needs.
Turning a programmable room thermostat to a
higher setting will not make the room heat up any
faster. How quickly the room heats up depends on
the design of the heating system, for example, the
size of boiler and radiators. Neither does the setting
affect how quickly the room cools down. Turning a
programmable room thermostat to a lower setting
will result in the room being controlled at a lower
temperature, and saves energy.
The way to set and use your programmable room
thermostat is to find the lowest temperature settings
that you are comfortable with at the different
times you have chosen, and then leave it alone to
do its job. The best way to do this is to set low
temperatures first, say 18°C, and then turn them up
by one degree each day until you are comfortable
with the temperatures. You won’t have to adjust the
thermostat further. Any adjustments above these
settings will waste energy and cost you more money.
If your heating system is a boiler with radiators,
there will usually be only one programmable
room thermostat to control the whole house. But
you can have different temperatures in individual
rooms by installing thermostatic radiator valves
(TRVs) on individual radiators. If you don’t have
TRVs, you should choose a temperature that is
reasonable for the whole house. If you do have
TRVs, you can choose a slightly higher setting
to make sure that even the coldest room is
comfortable, then prevent any overheating in other
rooms by adjusting the TRVs.
The time on the programmer must be correct. Some
types have to be adjusted in spring and autumn at
the changes between GMT and BST.
You may be able to temporarily adjust the heating
programme, for example, ‘Override’, ‘Advance’ or
‘Boost’. These are explained in the manufacturer’s
instructions.
Programmable room thermostats need a free flow
of air to sense the temperature, so they must not be
covered by curtains or blocked by furniture. Nearby
electric fires, televisions, wall or table lamps may
prevent the thermostat from working properly.
5. What is a timeswitch?
A timeswitch is an electrical switch operated by a
clock. It allows you to set ‘On’ and ‘Off’ time periods
for either central heating or hot water. It can be
arranged to control both central heating and hot
water together, but will turn them both on and off at
the same times. If you want to control both central
heating and hot water and turn them on and off
at different times, you should have a programmer
instead of a timeswitch.

Domestic heating by gas: boiler systems – guidance for installers and specifiers (2008 edition) 61
Heating controls: simple explanations for householders
Set the ‘On’ and ‘Off’ time periods to suit your own
lifestyle. On some timeswitches you can choose
whether you want the system to run continuously,
run under the chosen ‘On’ and ‘Off’ periods, or be
permanently off. You may also be able to adjust
the on and off timing temporarily, e.g. ‘Override’ or
‘Advance’. These are explained in the manufacturer’s
instructions.
The clock in the timeswitch must be set to the correct
time. Some types have to be adjusted in spring and
autumn at the changes between GMT and BST.
The heating system may have other controls
that switch it on or off. For example, the room
thermostat will switch off the heating when the
room has warmed up. And, if you have a hot water
cylinder, the cylinder thermostat will switch off the
water heating when it detects that the hot water
has reached the correct temperature.
6. What is a thermostatic radiator
valve (TRV)?
TRVs sense the air temperature around them and
regulate the flow of water through the radiator which
they are fitted to. They do not control the boiler.
They should be set at a level that gives you the
room temperature you want. These settings may
have to be different in each room, and you should
set the TRVs to suit each room and then leave
them to do their job.
Turning a TRV to a higher setting will not make
the room heat up any faster. How quickly the room
heats up depends on the boiler size and setting,
and the radiator size. Turning a TRV to a lower
setting will result in the room being controlled at a
lower temperature, and saves energy.
TRVs need a free flow of air to sense the
temperature, so they must not be covered by
curtains or blocked by furniture.
TRVs cannot turn off the boiler when the whole
house is warm. To do that, you will need a room
thermostat as well. The radiator in the room
with the room thermostat should not normally
have a TRV, but, if it does, keep the TRV on the
maximum setting and adjust the room thermostat
as explained with the instructions.

62 Domestic heating by gas: boiler systems – guidance for installers and specifiers (2008 edition)
References
References used in CHeSS (year 2008)
[1] The Building Regulations 2000. Approved
Documents L1A (New Dwellings) and L1B
(Existing Dwellings), Conservation of fuel and
power in dwellings, 2006 Edition.
[2] Section 6: Energy, Domestic Technical Handbook,
Guidance on achieving the standards set in the
Building (Scotland) Regulations 2004, Scottish
Building Standards Agency, 2007. See website
www.sbsa.gov.uk
[3] Domestic heating by gas: boiler
systems:guidance for installers and specifiers:
Energy Efficiency Best Practice in Housing (CE30).
[4] Domestic heating by oil: boiler systems:guidance
for installers and specifiers: Energy Efficiency Best
Practice in Housing (CE29).
[5] Domestic Heating Design Guide, CIBSE, 2007.
[6] The Government’s Standard Assessment
Procedure for Energy Rating of Dwellings, 2005
Edition.
[7] BS 1566:2002, Copper indirect cylinders for
domestic purposes.
[8] BS EN 12897:2006, Specification for indirectly
heated unvented hot water storage water
heaters.
[9] Waterheater Manufacturers’ Association
Performance Specification for Thermal Stores,
1999. [Shortly to be superseded by a revised
2008 specification from the HWA (Hot Water
Association)].
[10] Benchmark Code of Practice for the Installation,
Commissioning and Servicing of Central
Heating Systems (available from Heating
& Hot water Information Council, website
www.centralheating.co.uk or telephone
0845 600 2200).
[11] The Building (Amendment No. 2) Regulations
(Northern Ireland) 2006, Technical booklet F1,
Conservation of fuel and power (2006).
See website www.dfpni.gov.uk
[12] BS EN 12828:2003 Heating Systems in Buildings.
Design for water based systems.
[13] BS 7671:2001, Requirements for electrical
installations, IEE Wiring Regulations, Sixteenth
edition.
[14] BS 7593:2006, Code of Practice for Treatment
of water in domestic hot water central heating
systems.
[15] European Standard (Telecommunications
series) ETSI EN 300 220-1 v1. 3. 1 (2000-
09):Electromagnetic compatibility and Radio
spectrum Matters (ERM); Short Range Devices
(SRD);Radio equipment to be used in the
25MHz to 1000MHz frequency range with
power levels ranging up to 500 mW; Part
1:Technical characteristics and test methods.
[16] Domestic Heating Compliance Guide,
(Compliance with Approved Documents L1A:
New Dwellings and L1B: Existing Dwellings), First
Edition, Communities and Local Government.
References used elsewhere in this guide
[17] The Boiler (Efficiency) Regulations 1993, SI (1993)
No 3083, as amended by the Boiler (Efficiency)
(Amendment) Regulations 1994, SI (1994) No
3083.
[18] The Building Regulations 2000. Approved
Documents L1A (New Dwellings) and L1B
(Existing Dwellings), Conservation of fuel and
power in dwellings, 2006 Edition.
[19] Section 6: Energy, Domestic Technical
Handbook , Guidance on achieving the
standards set in the Building (Scotland)
Regulations 2004, Scottish Building Standards
Agency, 2007; See website www.sbsa.gov.uk
[20] The Building (Amendment No. 2) Regulations
(Northern Ireland) 2006, Technical booklet F1,
Conservation of fuel and power (2006).
See website www.dfpni.gov.uk
[21] Domestic Heating Compliance Guide,
(Compliance with Approved Documents L1A:
New Dwellings and L1B: Existing Dwellings), First
Edition, Communities and Local Government.
[22] The Government’s Standard Assessment
Procedure for Energy Rating of Dwellings, 2005
Edition.
[23] Guide to the Condensing Boiler Installation
Assessment Procedure for dwellings, CLG,
DEFRA April 2005.
[24] Guide to the Condensing Boiler Installation
Assessment Procedure for dwellings, SBSA.
[25] BS 1566:2002, Copper indirect cylinders for
domestic purposes.
[26] BS 7671: 2001, Requirements for electrical
installations, IEE Wiring Regulations, Sixteenth
edition.
[27] BS 3198:1981, Specification for copper hot water
storage combination units for domestic purposes
[28] BS EN 12897:2006, Specification for indirectly
heated unvented hot water storage water
heaters.

Domestic heating by gas: boiler systems – guidance for installers and specifiers (2008 edition) 63
References
[29] Waterheater Manufacturers’ Association
Performance Specification for Thermal Stores,
1999. [Shortly to be superseded by a revised
2008 specification from the HWA (Hot Water
Association)].
[30] The Building Regulations (Northern Ireland)
2000. Technical booklet F1, Conservation of fuel
and power (2006).
See website www.dfpni.gov.uk
[31] Domestic Heating Design Guide, CIBSE, May
2007.
[32] BS 5440:Part 1 and Part 2:2000, Installation of
flues and ventilation for gas appliances of rated
input not exceeding 60kW (1st, 2nd and 3rd
family gases.
[33] BS EN 483:2000 Gas-fired central heating boilers
– Type C boilers of nominal heat input not
exceeding 70kW.
[34] Solar hot water installation guide: Energy
Efficiency Best Practice Programme in Housing
CE131 [2005].
[35] BS EN 12831:2003 Heating Systems in Buildings.
Method for calculation of design heat load.
[36] Under floor Heating, Design and Installation
Guide), CIBSE, 2004.
[37] Taking Control, A Guide to buying or upgrading
central heating controls, Ricability.
See www.ricability.org.uk
[38] Central Heating System Specifications (CHeSS) –
Year 2008 (CE51).
[39] Council Directive 92/42/EEC on efficiency
requirements for new hot water boilers fired
with liquid or gaseous fuels. Official Journal of
the European Communities No L/167/17. 21 May
1992, p. 92.
[40] Domestic Energy Fact File 2006, J.I Utley
and L D Shorrock, BRE.
[41] BREDEM-12, Building Research Establishment
Report BR315. BRE, Garston, 1996.
[42] Boiler Efficiency Database: see website
www.boilers.org.uk
[43] BS EN 12828:2003 Heating Systems in Buildings.
Design for water based systems.
[44] DCLG website www.planningportal.gov.uk
See ‘Building Regulations’ then ‘Technical
guidance’ then ‘Approved documents’.
[45] BS 6798:2000 Specification for installation of
gas-fired boilers rated not exceeding
70kW net.
[46] Solar Heating, Design and Installation Guide),
CIBSE, 2007.
[47] The Building Regulations 2000. Approved
Document J, Combustion Appliances & Fuel
Storage Systems.
[48] Section 3: Environment, Domestic Technical
Handbook, Guidance on achieving the
standards set in the Building (Scotland)
Regulations 2004, Scottish Building Standards
Agency, 2007. See website www.sbsa.gov.uk
[49] SR2006 No.335 The Building (Amendment)
Regulations (Northern Ireland) 2006.
[50] BS EN 14336:2004 Heating Systems in buildings.
Installation and commissioning of water based
systems.
[51] BS 7593:2006, Code of Practice for Treatment
of water in domestic hot water central heating
systems.

CE30
This publication (including any drawings forming part of it) is intended for general guidance only and not as a substitute for the
application of professional expertise. Anyone using this publication (including any drawings forming part of it) must make their own
assessment of the suitability of its content (whether for their own purposes or those of any client or customer), and the Energy Saving
Trust cannot accept responsibility for any loss, damage or other liability resulting from such use.
All technical information was produced by BRE on behalf of the Energy Saving Trust.
CE30 © Energy Saving Trust February 2005. Revised June 2008. E&OE
Energy Saving Trust 21 Dartmouth Street London SW1H 9BP
Tel 0845 120 7799 Fax 0845 120 7789
bestpractice@est.org.uk www.energysavingtrust.org.uk/housing