ESR 1338 Gypsum Association
User Manual: 1338
Open the PDF directly: View PDF .
Page Count: 6
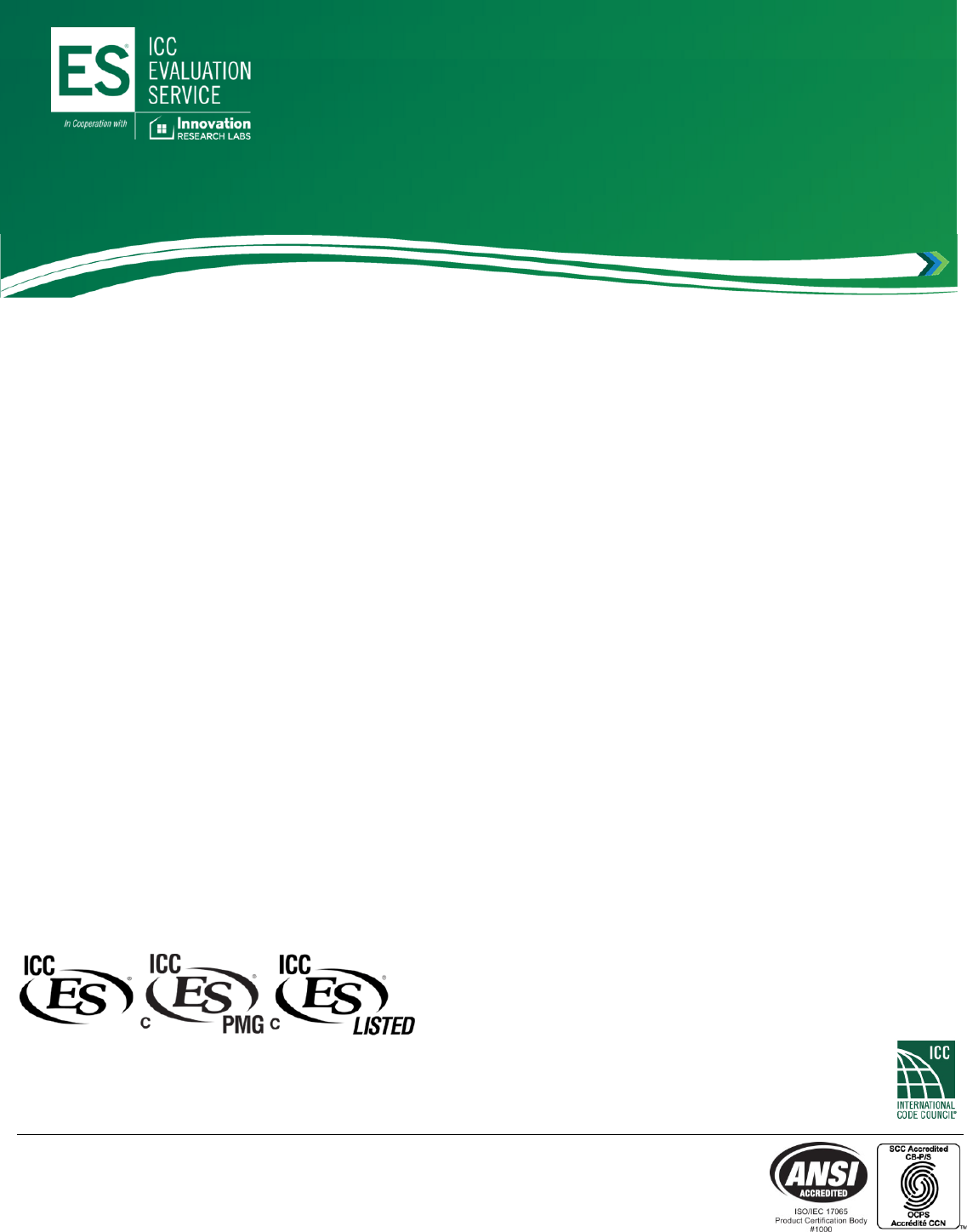
ASubsidiaryof
0
000
MostWidelyAcceptedandTrusted
ICC‐ESEvaluationRe
p
ort ESR‐1338
Reissued02/2018
Thisreportissubjecttorenewal02/2019.
ICC‐ES|(800)423‐6587|(562)699‐0543|www.icc‐es.org
ICC-ES Evaluation Reports are not to be construed as representing aesthetics or any other attributes not
specifically addressed, nor are they to be construed as an endorsement of the subject of the report or a
recommendation for its use. There is no warranty by ICC Evaluation Service, LLC, express or implied, as
to any finding or other matter in this report, or as to any product covered by the report.
Copyright
©
2018ICCEvaluationService,LLC.Allrightsreserved.
“2014RecipientofPrestigiousWesternStatesSeismicPolicyCouncil
(WSSPC)AwardinExcellence”
DIVISION:090000—FINISHES
SECTION:092116—GYPSUMBOARDASSEMBLIES
SECTION:092116.23—GYPSUMBOARDSHAFTWALLASSEMBLIES
SECTION:092116.33—GYPSUMBOARDSEPARATIONWALLASSEMBLIES
REPORTHOLDER:
GYPSUMASSOCIATION
962WAYNEAVENUE,SUITE620
SILVERSPRING,MARYLAND20910
EVALUATIONSUBJECT:
GYPSUMWALLANDCEILINGASSEMBLIESAND
GYPSUMBOARDINTERIORANDEXTERIORAPPLICATIONS
LookforthetrustedmarksofConformity!
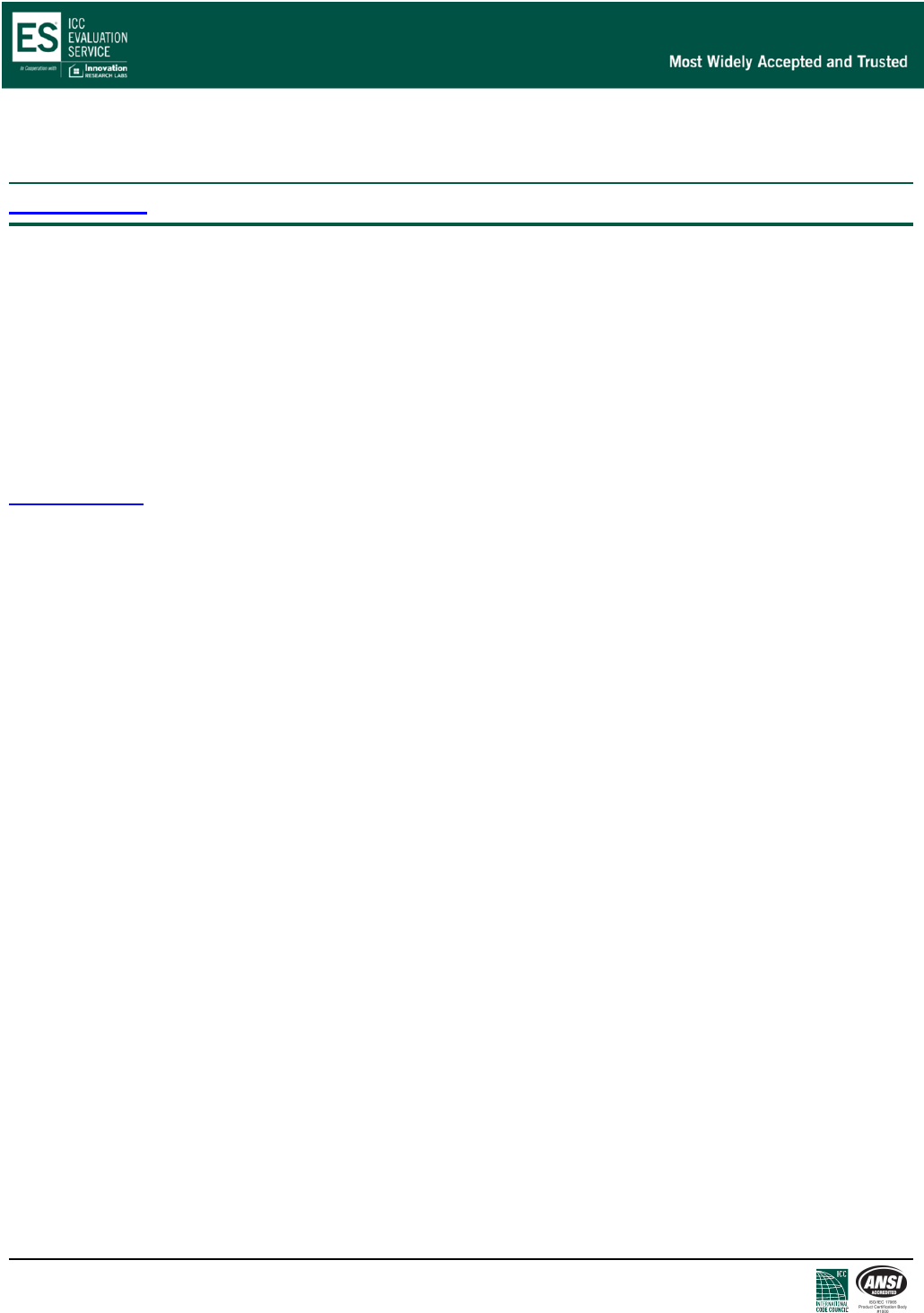
ICC-ES Evaluation Reports are not to be construed as representing aesthetics or any other attributes not specifically addressed, nor are they to be construed
as an endorsement of the subject of the report or a recommendation for its use. There is no warranty by ICC Evaluation Service, LLC, express or implied, as
to any finding or other matter in this report, or as to any product covered by the report.
Copyright © 2018 ICC Evaluation Service, LLC. All rights reserved. Page 1 of 5
ICC-ES Evaluation Report ESR-1338
Reissued February 2018
This report is subject to renewal February 2019.
www.icc-es.org | (800) 423-6587 | (562) 699-0543 A Subsidiary of the International Code Council
®
DIVISION: 09 00 00—FINISHES
Section: 09 21 16—Gypsum Board Assemblies
Section: 09 21 16.23—Gypsum Board Shaft Wall
Assemblies
Section: 09 21 16.33—Gypsum Board Area Separation
Wall Assemblies
REPORT HOLDER:
GYPSUM ASSOCIATION
962 WAYNE AVENUE, SUITE 620
SILVER SPRING, MARYLAND 20910
(301) 277-8686
www.gypsum.org
EVALUATION SUBJECT:
GYPSUM WALL AND CEILING ASSEMBLIES AND
GYPSUM BOARD INTERIOR AND EXTERIOR
APPLICATIONS
1.0 EVALUATION SCOPE
Compliance with the following codes:
2018, 2015, 2012 and 2009 International Building
Code
®
(IBC)
2018, 2015, 2012 and 2009 International Residential
Code
®
(IRC)
2013 Abu Dhabi International Building Code (ADIBC)
†
†
The ADIBC is based on the 2009 IBC. 2009 IBC code sections referenced
in this report are the same sections in the ADIBC.
Properties evaluated:
Interior finish
Fire-resistance
Sound control
Structural
Thermal barrier
Exterior finish
2.0 USES
This evaluation report recognizes gypsum products for
specific interior and exterior applications, and also
recognizes various load-bearing and nonload-bearing fire-
resistance-rated wall, floor-ceiling and roof-ceiling gypsum
board assemblies. Some assemblies also provide sound
transmission control. Structural evaluation is limited to
transverse loading.
3.0 DESCRIPTION
The gypsum products and fire-resistance-rated wall, floor-
ceiling and roof-ceiling assemblies must conform to
Section 4.0 of this report using materials as described
below. Gypsum boards must comply with ASTM C1396-
14a for use under the 2018 IBC and IRC.
3.1 Water-resistant Gypsum Backing Board:
The backing board must conform to ASTM C1396.
3.2 Gypsum Wallboard:
The wallboard must conform to ASTM C1396.
3.3 Exterior Gypsum Soffit Board:
The soffit board must conform to ASTM C1396.
3.4 Gypsum Sheathing Board:
The sheathing board must conform to ASTM C1396.
3.5 Gypsum Backing Board, Core Board and Gypsum
Shaftliner Board:
The backing, core board and shaftliner must conform to
ASTM C1396.
3.6 Gypsum Base for Veneer Plasters:
The gypsum base must conform to ASTM C1396.
3.7 Gypsum Ceiling Board:
The ceiling board must conform to ASTM C1396.
3.8 Screws:
Type S, Type W and Type G screws specified for the
assemblies described in this report must comply with
ASTM C1002 or ASTM C954.
4.0 INSTALLATION
4.1 General:
Installation of the gypsum board wall and ceiling
assemblies and interior and exterior applications as
described below must comply with this report and the
Gypsum Association’s published installation instructions.
The Gypsum Association’s published installation
instructions must be available at the jobsite at all times
during installation.
The gypsum products recognized in this report must be
assembled and installed in accordance with IBC Section
2508.1 or IRC Section R702.3.1, as applicable. Gypsum
board must not be used in areas subject to continuous high
humidity, such as saunas, steam rooms, gang shower
rooms or indoor pools.

ESR-1338 | Most Widely Accepted and Trusted Page 2 of 5
4.2 Fire-resistance-rated Wall, Floor-ceiling and Roof-
ceiling Gypsum Board Assemblies:
4.2.1 General Fire-resistance-rated Design Information:
a. The axial design stress of the wood studs used in fire-
resistive construction must be reduced to 0.78Fʹc,
calculated in accordance with Section 3.6 of the
ANSI/AWC National Design Specification (NDS) for
Wood Construction 2018 edition for the 2018 IBC,
2015 edition for the 2015 IBC, 2012 edition for the
2012 IBC and 2005 for the 2009 IBC, with the
maximum design stress not greater than 78 percent of
the calculated allowable stress with studs having a
slenderness ratio, le/d, of 33.
b. When gypsum board is used in fire-resistive
floor/ceiling, roof/ceiling, or wall assemblies, the board
thickness, type of gypsum board, and construction of
the assembly must comply with Chapter 7 of the IBC;
Section R302 of the IRC; the Gypsum Association
Fire Resistance Design Manual, GA-600, 21st Edition
for the 2018 IBC, 20th Edition for the 2015 IBC or
19th Edition for the 2012 and 2009 IBC; or current
ICC-ES evaluation reports. The Gypsum Association
Fire Resistance Design Manual GA-600 (21st Edition),
although not specifically listed as a reference
standard in the 2009, 2012, or 2015 IBC, is an
acceptable alternative to the 19th and 20th Editions
when approved by the code official.
c. Except where otherwise noted in this report, any of
the gypsum boards listed in Section 3.0, of the same
size, thickness, and core type specified, may be used.
The gypsum base for veneer plasters must be
covered with minimum 1/16-inch-thick (1.6 mm)
gypsum veneer plaster.
4.2.2 Fire-resistance-rated Assemblies: Generic fire-
resistance-rated systems (those not designated as
proprietary in the listing), as listed in the Gypsum
Association Fire Resistance Design Manual, GA-600, 21st
Edition for the 2018 IBC, 20th Edition for the 2015 IBC, or
19th edition for the 2012 and 2009 IBC, are recognized for
use. The Gypsum Association Fire Resistance Design
Manual GA-600 (21st Edition), although not specifically
listed as a reference standard in the 2009, 2012, or
2015 IBC, is an acceptable alternative to the 19th and 20th
Editions, when approved by the code official.
4.2.2.1 Two-hour Gypsum Board Solid Partition for
Shaft Enclosure: The assembly is similar to Item 9-1.1 of
Table 721.1(2) of the 2018, 2015 and 2012 IBC (Item 9-1.1
of Table 720.1(2) of the 2009 IBC), except that the gypsum
shaftliner is first installed onto 2-by-2-inch (51 by 51 mm)
steel floor and ceiling runners using Type S screws spaced
12 inches (305 mm) on center. The runners must be
anchored at 24 inches (610 mm) on center, using
approved fasteners. Two layers of 1/2-inch-thick (12.7 mm),
Type X gypsum board installed with long edges parallel to
wrapped coreboard edges are laminated to one side of the
coreboard. All vertical joints must be offset at least
3 inches (76 mm).
The assembly may also be constructed with four layers
of 1/2-inch-thick (12.7 mm), Type X gypsum board,
laminated together, with the joints of each layer offset at
least 3 inches (76 mm) from the adjoining layers. The
laminating compound must comply with ASTM C475 or be
an approved powder setting–type compound. The first
layer is attached to the 2-by-2-inch (51 by 51 mm) steel
floor and ceiling angle runners using one 7/8-inch-long
(22 mm), Type S screw at each corner. The second layer
is then fully laminated to the first layer and screw-attached
to the runners using 115/16-inch-long (49.2 mm), Type S
screws spaced 12 inches (305 mm) on center. The third
layer is laminated in the same manner as the second layer,
and is further attached using 11/2-inch-long (38 mm), Type
G screws spaced 24 inches (610 mm) on center along the
edges and along the center, and held back 21/2 inches
(63.5 mm) from the top and bottom edges. The fourth layer
is fully laminated, with all of the vertical joints being offset.
4.2.2.2 One-hour Gypsum Board Partition with Wood
Framing: The framing consists of nominal 2-by-4 wood
studs spaced 16 inches (406 mm) on center, with blocking
of the same size at midheight. Each side of the wall is
covered with a single layer of 5/8-inch-thick (15.9 mm),
Type X gypsum board applied either perpendicular to or
parallel to the framing. The gypsum board is attached to
the framing using No. 6 by 11/4-inch-long (31.7 mm),
buglehead, Type W screws spaced 8 inches (203 mm) on
center along end joints and 12 inches (305 mm) on center
in the field. Screws are placed no closer than 1/2 inch
(12.7 mm) to end or edge joints. Vertical joints are
staggered 16 inches (406 mm) on center, and horizontal
joints are staggered 12 inches (305 mm) on center on each
side. The joints are taped with joint tape and covered with
two coats of joint compound. Screw heads are covered
with joint compound.
4.2.2.3 One-hour Gypsum Board Staggered-stud
Bearing Partition: The framing consists of two rows of
nominal 2-by-3 wood studs spaced at 16 inches (406 mm)
on center or nominal 2-by-4 wood studs spaced at
24 inches (610 mm) on center, with blocking of the same
size at midheight. Studs in opposite rows are staggered
8 inches (203 mm) or 12 inches (305 mm) on center, and
the rows are spaced a minimum of 1 inch (25.4 mm) apart.
The plates for each row may be of the same size and
material, or common plates may be used for the two rows.
The exterior face of each row is then covered with
5/8-inch-thick (15.9 mm), Type X gypsum board applied
horizontally or vertically using 6d cement-coated cooler
nails at 7 inches (178 mm) on center, with end joints on
nailing members. Fire-blocks, when required, may be of
mineral wool batts, 2 inches (51 mm) thick in the
intervening spaces between the two rows of studs, or
1/2-inch-thick (12.7 mm) gypsum board. Where nominally
2-by-3 studs are used, they must be stress-graded lumber
as set forth in Table 4C of the supplement of the NDS.
4.2.2.4 One-hour Gypsum Board Floor-ceiling or
Roof-ceiling Assembly with Wood Framing: The ceiling
construction is identical to assembly FC5406 in the
Gypsum Association Fire Resistance Design Manual.
Alternate framing consists of lower chords of trussed
rafters, or pitched or flat trusses spaced a maximum of
24 inches (610 mm) on center. Alternate fasteners, having
the same spacing as the screws, are 17/8-inch-long
(47.6 mm), 6d, cooler, box or wallboard nails for the base
ply, and 23/8-inch-long (60 mm), 8d, cooler, box or
wallboard nails for the face ply. Type G screws, 11/2 inches
(38 mm) long, are still required at the end joints of the
gypsum board face layer.
4.2.2.5 One-hour Gypsum Board Roof-ceiling
Assembly with Steel Framing: The assembly consists of
steel roof framing with roof purlins spaced and designed to
support a noncombustible ceiling grid to which is attached
double 5/8-inch-thick (15.9 mm), Type X gypsum board.
Cold-rolled steel main runner channels at 4 feet (1219 mm)
on center, with size and hanger support complying with
Section 2506.2.1 of the IBC, are hung from the steel
framing. Number 25 gage, 7/8-inch-deep (22 mm), rigid
cross-furring channels are spaced 24 inches (610 mm) on

ESR-1338 | Most Widely Accepted and Trusted Page 3 of 5
center. Furring channels are wire-tied to the runner
channels using loops of No. 16 gage wire. The base layer
of 5/8-inch-thick (15.9 mm), Type X gypsum board is
applied at right angles to the furring channels using
1-inch-long (25.4 mm), Type S screws spaced at 24 inches
(610 mm) on center. The face layer of 5/8-inch-thick
(15.9 mm), Type X gypsum board is applied at right angles
to the furring channels, using 15/8-inch-long (41.3 mm),
Type S screws spaced at 12 inches (305 mm) on center at
joints, driven through the base layer and into the
intermediate furring channels. Face layer joints are offset
24 inches (610 mm) from the base layer joints. One-and-
one-half-inch-long (38 mm), Type G screws, placed
2 inches (51 mm) from either side of the face layer end
joints, are also installed at 12 inches (305 mm) on center.
The addition of insulation to the assembly is permitted,
provided a minimum plenum space of 10 inches (254 mm)
is maintained between the underside of the insulation and
the gypsum panel.
4.2.2.6 Two-hour Gypsum Board Bearing Wall with
Minimum STC (Sound Transmission Class) 50 Sound
Rating: The construction consists of nominally 2-by-4
wood studs spaced 16 inches (406 mm) on center, faced
on each side with two layers of 5/8-inch-thick (15.9 mm),
Type X gypsum board. On one side, the gypsum board is
fastened directly to the studs as specified for interior
partitions in Item 14-1.5 of Table 721.1(2) of the 2018,
2015 and 2012 IBC (Item 14-1.5 of Table 720.1(2) of the
2009 IBC); on the other side, resilient furring channels
spaced 24 inches (610 mm) on center are applied
horizontally over the wood studs and are attached using 6d
common or 11/4-inch (31.7 mm) wallboard nails or
1-inch-long (25.4 mm), Type W or Type S screws. The
5/8-inch-thick (15.9 mm), Type X gypsum board is applied
horizontally and is attached along longitudinal edges to the
furring channels using 1-inch-long (25.4 mm), Type S
screws spaced 12 inches (305 mm) on center. Six-inch-
wide (152 mm) strips of gypsum board are installed behind
unsupported vertical butt joints and are attached at the
ends and along the length of the strips using Type G,
11/2-inch-long (38 mm) screws spaced 12 inches (305 mm)
on center. A face layer of 5/8-inch-thick (15.9 mm), Type X
gypsum board is applied with joints staggered from the
base layer joints and secured to the resilient furring
channels using 15/8-inch-long (41.3 mm), Type S screws
spaced 12 inches (305 mm) on center. With this partition, a
minimum STC rating of 50 is attained. When desired, glass
fiber or mineral wool insulation may be installed in the stud
cavities.
4.2.3 Alternate Fire-resistance-rated Construction:
4.2.3.1 Alternate Suspended Ceiling Construction:
Gypsum board ceilings directly attached to steel framing as
set forth in Table 721.1(3) of the 2018, 2015 and 2012 IBC
(Table 720.1(3) of the 2009 IBC) may be suspended by
means of 11/2-inch (38 mm), cold-rolled steel, main runner
channels, spaced 48 inches (1219 mm) on center, that are
suspended with No. 8, SWG galvanized wire hangers
spaced 48 inches (1219 mm) on center. Furring channels
are placed perpendicular to the cold-rolled steel main
runner channels and are secured thereto using No. 18,
SWG galvanized wire ties (double strand); the gypsum
board is then installed in the manner required for direct
attachment.
4.2.3.2 Alternate Gypsum Board Fasteners: Screws,
either Type W or Type S, depending on the framing
member, may be used in lieu of nails in fire-resistance-
rated assemblies described in this report or described in
Tables 721.1(2) and 721.1(3) of the 2018, 2015 and 2012
IBC (Tables 720.1(2) and 720.1(3) of the 2009 IBC),
provided the screw penetration into the framing member is
equivalent to the nail penetration, the screw spacing is the
same as the nail spacing, and the cross-sectional area of
the screws is equal to that of the specified nails.
4.2.3.3 Joint Treatment: For the fire-resistive assemblies
in this report, taping and finishing of joints and fasteners is
permitted to be omitted in the following cases:
a. Where there is square-edge gypsum board or tongue-
and-groove-edge (V-edge) gypsum backing board or
gypsum sheathing.
b. In single-layer applications on wood-framed
assemblies where joints fall over framing members.
c. On inner layers and outer layers of multiple-layer
wood-framed or steel-framed assemblies, where the
joints of adjacent layers are offset from each other.
4.3 Sound Control Systems:
Generic sound control systems, as listed in the Gypsum
Association Fire Resistance Design Manual, GA-600 21st
Edition for the 2018 IBC, 20th Edition for the 2015 IBC, or
19th edition for the 2012 and 2009 IBC, are recognized for
use. The Gypsum Association Fire Resistance Design
Manual GA-600 (21st Edition), although not specifically
listed as a reference standard in the 2009, 2012, or 2015
IBC, is an acceptable alternative to the 19th and 20th
Editions when approved by the code official. Partition
systems must be sealed at perimeter and around cut-outs
using beads of non-hardening caulking compound, except
that tape and joint compound are permitted to be used in
lieu of caulking above the top plate in wood-framed
systems. Where carpet and pad are specified for the IIC
sound rating shown in the manual, the carpet must be a
44-ounce (1492 g/m2) wool carpet with a 40-ounce (1356
g/m2) hair pad.
Except where otherwise noted in this report, any of the
gypsum boards listed in Section 3.0, of the same size,
thickness, and core type specified, may be used.
4.4 Allowable Partition Heights:
4.4.1 Gypsum Board or Veneer Base: To comply with
2018 IBC Section 1607.15 (2015 and 2012 IBC Section
1607.14 and 2009 IBC Section 1607.13) and Table 1604.3
of the 2018, 2015 and 2012 IBC, Section 1607.13 and
Table 1604.3 of the 2009 IBC, the allowable height limits of
non-bearing partitions are as follows:
Partitions utilizing No. 25 gage [minimum 0.0179 inch
(0.454 mm) uncoated base-metal thickness] steel channel
studs conforming to ASTM C645 must have maximum
heights as set forth in a current ICC-ES evaluation report.
Mechanical fastening of intermediate studs to the track is
not required unless this is specified in the evaluation
report.
4.5 Joint Treatment at Areas to Receive Tile:
Gypsum board joints, including those at all angle
intersections, which are under areas to receive tile or wall
panels, must be treated with joint compound and tape, but
must not be finish-coated. All cut edges and openings
around pipes and fixtures must be treated with an
approved, water-resistant, flexible compound or caulk.
Areas to be tiled that are covered with a joint compound
must be skim-coated with bedding adhesive. The bedding
adhesive for ceramic tile must conform to ANSI A136.1 for
Organic Adhesives for Installation of Ceramic Tile, Type I.
4.6 Exterior Surfaces:
4.6.1 Exterior Ceiling Surfaces:

ESR-1338 | Most Widely Accepted and Trusted Page 4 of 5
4.6.1.1 Location: Exterior gypsum soffit board may be
used as a ceiling finish at exterior locations such as
carports, open porches, walkways, soffits and similar
installations that are horizontal or inclined downward away
from the building. Gypsum wallboard is permitted for use
as a ceiling finish at exterior horizontal applications not
exposed to the weather as defined by Chapter 2 of the
2018 and 2015 IBC (Section 2502 of the 2012 and 2009
IBC), or Section R702.3.5 of the IRC.
4.6.1.2 Framing: Maximum spacing of framing members
must be 16 inches (406 mm) on center when supporting
1/2-inch-thick (12.7 mm) board, and must be 24 inches
(610 mm) on center when supporting 5/8-inch-thick
(15.9 mm) board. Gypsum board applications
perpendicular to framing members must comply with
ASTM C840 (IBC), or Table R702.3.5 of the IRC.
4.6.1.3 Joints: In ceiling areas having long runs, the
maximum spacing of expansion joints must be 30 feet
(9.144 m). A 1/4-inch (6.4 mm) clearance joint is required
between gypsum board and adjacent walls, fascia, beams
or columns. Fascia boards must extend downward past the
ceiling board surface a minimum of 1/4 inch (6.4 mm).
Exterior gypsum soffit board or gypsum wallboard joints
and fastener heads must be provided with joint treatment.
An alternate joint treatment is batten strips.
4.6.1.4 Surface Treatment: The exterior gypsum soffit
board and the gypsum wallboard as allowed by the
applicable code must have one of the following surface
treatments applied at the jobsite:
a. One coat of latex exterior paint applied over an oil-
base primer.
b. Two coats of an oil- or alkyd-based exterior paint.
4.7 Thermal Barrier:
Regular gypsum board, a minimum of 1/2-inch (12.7 mm)
thick, is permitted to be used as a thermal barrier in
accordance with Sections 2603.4 or 2603.5.2 of the IBC or
Section R316.4 of the IRC. The gypsum board must be
attached in such a manner that it will remain in place for
15 minutes of fire exposure. For walls constructed of wood
framing, attachment of the gypsum board in accordance
with ASTM C840 (IBC), or IRC Section R702.3.5, is
permitted. For other construction, attachment of the
gypsum wallboard must comply with a specific ICC-ES
evaluation report, or the method of attachment must be
qualified by testing in accordance with FM 4880, UL 1040,
NFPA 286 or UL 1715 (IBC and IRC).
4.8 Shear Walls:
Table 1 shows maximum allowable shear values for
gypsum board shearwalls. Gypsum board must be applied
either horizontally or vertically on nominally 2-by-4 (50 by
102 mm) wood studs. Additionally, Section 2505 of the IBC
or R602.10 of the IRC is applicable.
5.0 CONDITIONS OF USE
The gypsum board wall and ceiling assemblies and interior
and exterior applications described in this report comply
with, or are suitable alternatives to what is specified in,
those codes listed in Section 1.0 of this report, subject to
the following conditions:
5.1 Installation must comply with this report, the Gypsum
Association’s published installation instructions and
the applicable code. In the event of a conflict between
the Gypsum Association’s published installation
instructions and this report, this report governs.
5.2 Partition construction and heights are as set forth in
this report. Indicated stud spacings are maximums.
Stud sizes (depths) and gages are minimums.
5.3 In jurisdictions adopting the IBC or IRC, gypsum
board must not be used to resist seismic forces in
structures in Seismic Design Category E or F.
5.4 Documentation must be submitted to the code official
verifying that the gypsum board products to be
installed comply with the applicable standard noted in
Section 3.0 of this report.
5.5 Calculations and details must be submitted to the
code official for approval of structural-use
applications.
6.0 EVIDENCE SUBMITTED
6.1 Reports of testing in accordance with ASTM E119
(UL 263).
6.2 Reports of testing in accordance with ASTM E84
(UL 723).
6.3 Reports of transverse load testing in accordance with
UL 1296.
6.4 Reports of sound transmission testing in accordance
with ASTM E90 and ASTM E413.
6.5 Reports of testing in accordance with ASTM C473.
6.6 Reports of racking shear wall testing in accordance
with ASTM E72.
7.0 IDENTIFICATION
Gypsum boards must be identified by the manufacturer’s
name, the thickness, the brand name and the ASTM
specification. Gypsum board products that have been
evaluated by ICC-ES for compliance with the standards
indicated in Section 3.0 of this report must also be
identified by the ICC-ES report number associated with the
specific product.
Bundles of steel studs must be identified as set forth in a
current ICC-ES evaluation report on the product. Screws
must be identified on the packaging by the name, brand or
trademark of the producer or supplier and the ASTM
designation.
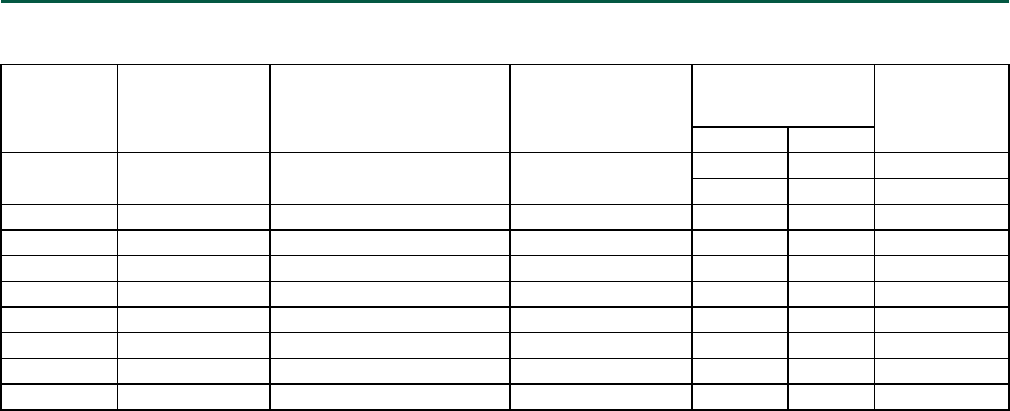
ESR-1338 | Most Widely Accepted and Trusted Page 5 of 5
TABLE 1—ALLOWABLE SHEAR FOR WIND OR SEISMIC FORCES (pounds per foot)
FOR VERTICAL DIAPHRAGMS OF GYPSUM BOARD WOOD-FRAMED WALLS1, 2
BOARD
THICKNESS
(in.)
WALL
CONSTRUCTION
MINIMUM FASTENER SIZE
3
MAXIMUM STUD
SPACING (in.)
MAXIMUM
FASTENER SPACING
(in.)
ALLOWABLE
SHEAR VALUE
(plf)
Edges Field
1/2 Unblocked 5d cooler or wallboard nails 24 7 7 75
4 4 110
5
/8 Unblocked 6d cooler or wallboard nails 24 4 4 145
1
/2 Unblocked No. 6 - 1
1
/4-inch screws 16 8 12 60
1
/2 Blocked
4
No. 6 - 1
1
/4-inch screws 16 4 16 160
1
/2 Blocked
4
No. 6 - 1
1
/4-inch screws 16 4 12 155
1
/2 Blocked
4
No. 6 - 1
1
/4-inch screws 24 8 12 70
1
/2 Blocked
4
No. 6 - 1
1
/4-inch screws 16 6 12 90
5
/8 Unblocked No. 6 - 1
1
/4-inch screws 16 8 12 70
5
/8 Blocked
4
No. 6 - 1
1
/4-inch screws 16 8 12 90
For SI: 1 inch = 25.4 mm, 1 plf = 14.6 N/m.
1Shear walls are not permitted to resist loads imposed by masonry or concrete construction. See Section 2306.3 of the 2018, 2015 and 2012 IBC, Section 2306.7 of
the 2009 IBC, or Section R602.10 of the IRC. Values are for short-term loading from wind or seismic forces. Values must be reduced by 25 percent for normal
loading. Values must not be used in IBC Seismic Design Categories E and F.
2The shear values are permitted to be additive when identical materials applied as specified in the table are applied to both sides of the wall.
3Screws must be Type W or Type S drywall screws.
4All board edges must be blocked.