VT 9151 Gutters High Front Guide
User Manual: VT 9151
Open the PDF directly: View PDF .
Page Count: 7
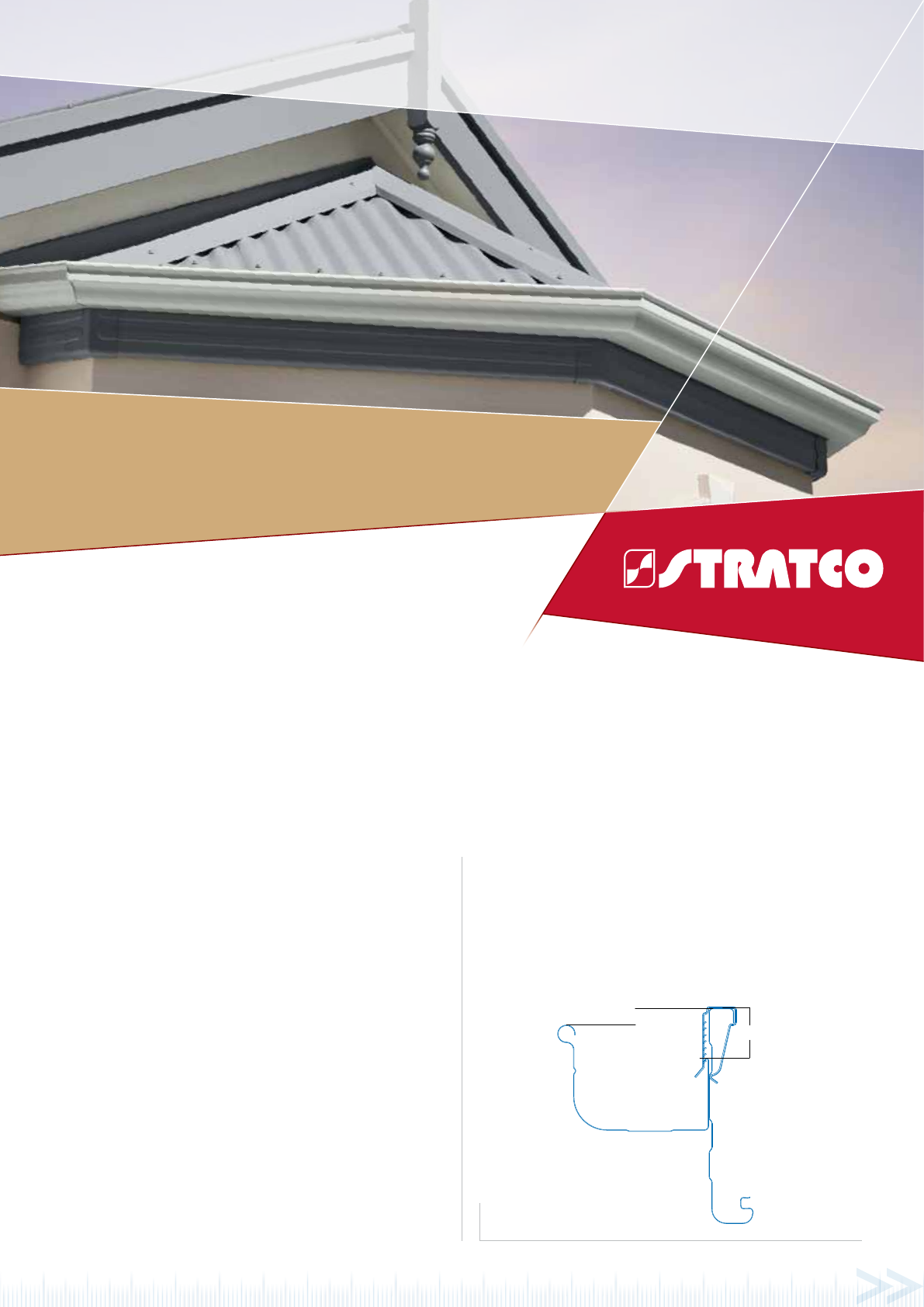
INFORMATION
GUIDE
High Fronted Gutters
High fronted gutters hide the lower edge of tiles or roof cladding which creates an aesthetically pleasing appearance. It is important
that sucient overow measures are included in the design of the guttering system and that high fronted gutters are installed in
such a way that if they overow, it will not result in water owing back into the roof or building.
The design of gutter and downpipe system installations also need to comply with specic rainfall intensities for the area of installation
and adequate overow provisions need to be provided to prevent water from entering the dwelling during heavy rainfall periods.
High Fronted Gutters
Codes
The design and installation of guttering and downpipe systems
needs to comply with the Building Code of Australia and
Australian Standards AS/NZS 3500.3 Plumbing and Drainage,
Stormwater Drainage and AS/NZS 3500.5 National Plumbing
and Drainage, Domestic Installations. It is also important that
relevant State regulations are satised. For example, New South
Wales legislation requires all gutter and downpipe installations
be undertaken by a suitably licensed installer who holds a
current certicate issued by the NSW Oce of Fair Trading.
Natural Eects
There are two natural eects in Stratco guttering that oer
some protection against water owing from eaves gutters
inside a building, when attached to Stratco steel fascia.
• The rst is that when installed on our steel fascia, the “high
front” of the gutter can still be lower than the top face of the
fascia. Water will always ow to the lowest point, and even
if a complete blockage exists, should still overow outside
the eaves line (Figure 1 and 3).
• Secondly, if a complete blockage occurs the additional
weight of the water will cause the gutter to temporarily
deform. The back of the gutter is restrained at 1.2 metre
intervals by xing clips but between these points the gutter
moves outwards from the fascia creating a gap that allows
the additional water to escape (Figure 4).
43.0
14.0
Figure 1
High Front Quad Gutter
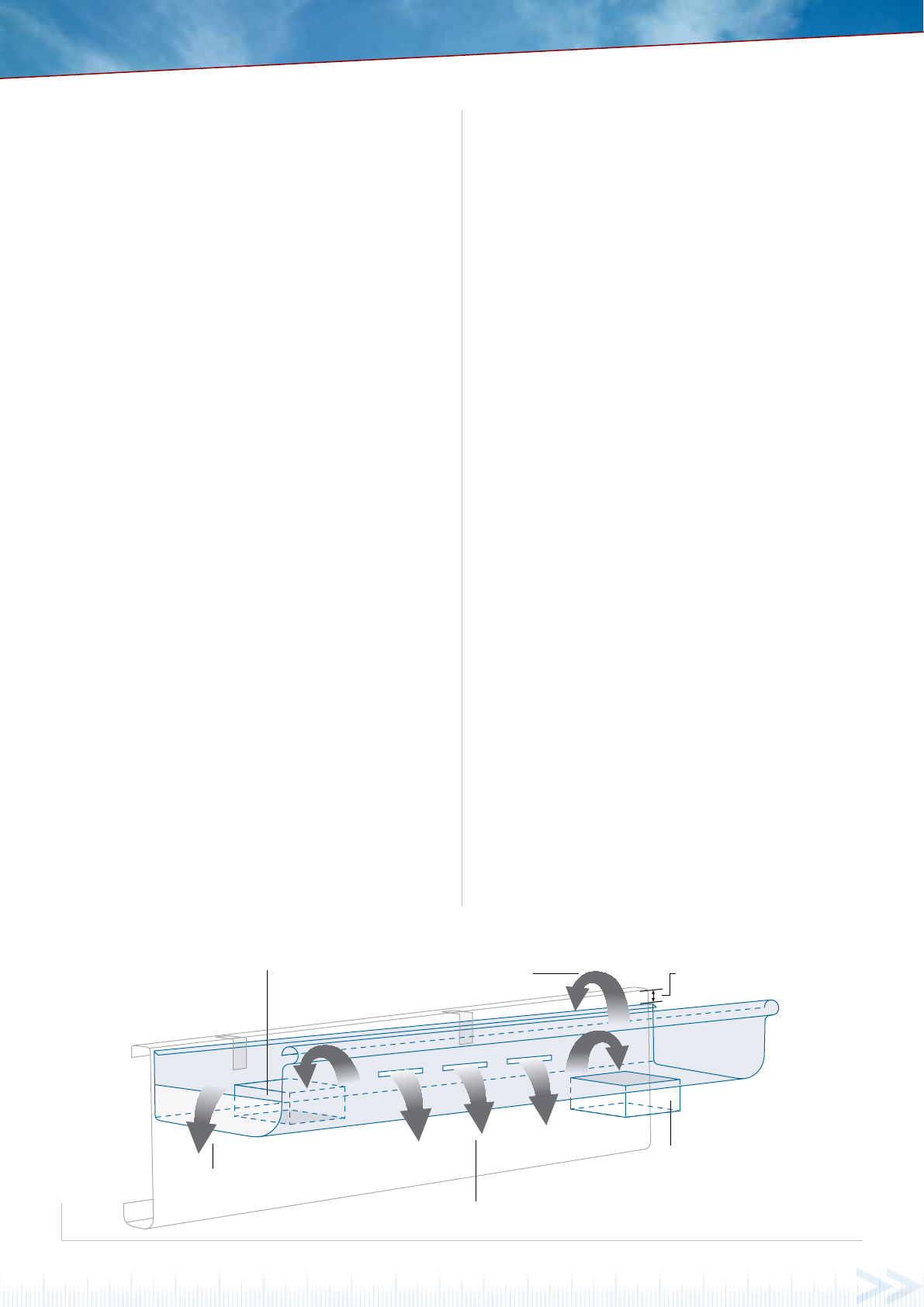
Responsibilities of the Designer
Not withstanding the natural eects mentioned above it is still
the responsibility of the designer of the rainwater goods system
(who may be the architect, builder, hydraulic engineer, home
owner, roong or guttering contractor) to design a rainwater
system which allows adequate drainage to occur. Water should
not be able to ow back into the building.
• For eaves gutters they must determine the rainfall intensity
values (ARI) shown in AS3500 part 3.2 “Stormwater drainage
– Acceptable solutions”.
• For a specic rainfall intensity they should determine the
cross sectional area of gutter best suited to their situation,
when the roof catchment area is taken into account. A table
showing the eective cross sectional area of Stratco gutters
is shown in (Table 2) and a further table (Table 3) allows you
to determine which Stratco gutter suits your needs. While
you can choose whether slotted or non slotted gutter best
suits your needs, Stratco recommend the slotted option
where possible.
• Where the designer is aware of specic local factors that
may impact negatively on the standard design then this
must be taken into account in the design. For example if the
rainwater goods system is required to be used in a leafy area,
then adequate leaf guards may need to be specied. Smaller
mesh leaf guards may be required for ne needle like leaves,
and these may need to be removable to prevent fungal
build-up. All leaf guards need to be removed regularly and
the gutter cleaned. In snow or hail prone areas, then gutter
either may not be suitable, or may need to be situated well
below the level of the fascia with snow breaks installed.
• Increasing the size and frequency of downpipes will assist
in the drainage of the roof. The downpipes used in the
drainage table (Table 3) must be at least the size used in the
cross section area table (Table 2)
• For additional information refer to the Stratco website which
shows a roof drainage calculator.
• Where there is any doubt as to the adequacy of the design,
or where the designer wishes to introduce a further level of
safety, there are a number of additional protective measures
that can be included in the design (Figure 5). They include:
• Using modied stop ends: At the end of gutters normal
height stop ends can be replaced by lower stop ends
which reduce the depth of water able to collect in the
gutter controlling overow to these points.
• Using an internal outlet: An outlet may be able to be
placed in the centre of the gutter which has a top lower
than the back of the gutter which releases water prior
to the gutter overowing.
• Using a cut down front: The front of the gutter can be
notched to a lower level allowing water to escape past
the bead prior to any overow from the gutters rear.
• Using a front spigot: A small tube or outlet can be
attached to the front of the gutter that will allow water
to overow from the gutter front.
• Using a rear exit gap: There are a number of clips and
devices on the market which will create a gap between
the back of the gutter and the front of the fascia.
Whilst this is a satisfactory method, consideration
needs to be given to issues such as spider control, and
the possible ingress of embers in a re prone situation.
• Using slots: Stratco, and most gutter manufacturers
oer their gutter in a slotted format, which will assist
in removing surplus water in a more contr oll ed manner.
• Using other proprietary solutions: There are other
proprietary products available which contain various
measures to prevent gutters blocking (leafguards of
many types) or downpipes blocking (outlets which
contain holes and slots) and these may be selected by
either the builder or consumer.
• Using rainheads or sumps: Rainheads which have
greater inlet areas than ordinary outlets can be placed
at strategic points along the length of the gutter into
which excess water can discharge, providing greater
resilience to sudden downpours and these may be
tted with overows as well.
These measures can either be used singly, or in combination
with each other and will reduce the capacity of the gutter to
move the required volume of water. Figure 2 shows several of
these used together.
Gutter Overow Remedies
Water can overflow from
a cut-down stop end.
Water can overflow from
slots in the face of the gutter.
Downpipe outlet.
Water discharges
from the downpipe
outlet into the
downpipe.
Freeboard at the low end of the gutter,
where the gutter bead will usually be
lower than the top of the fascia.
Water can overflow between the gutter and
the fascia at the low end of the gutter.
Water can overflow from an overflow outlet
placed in the bottom of the gutter.
Figure 2
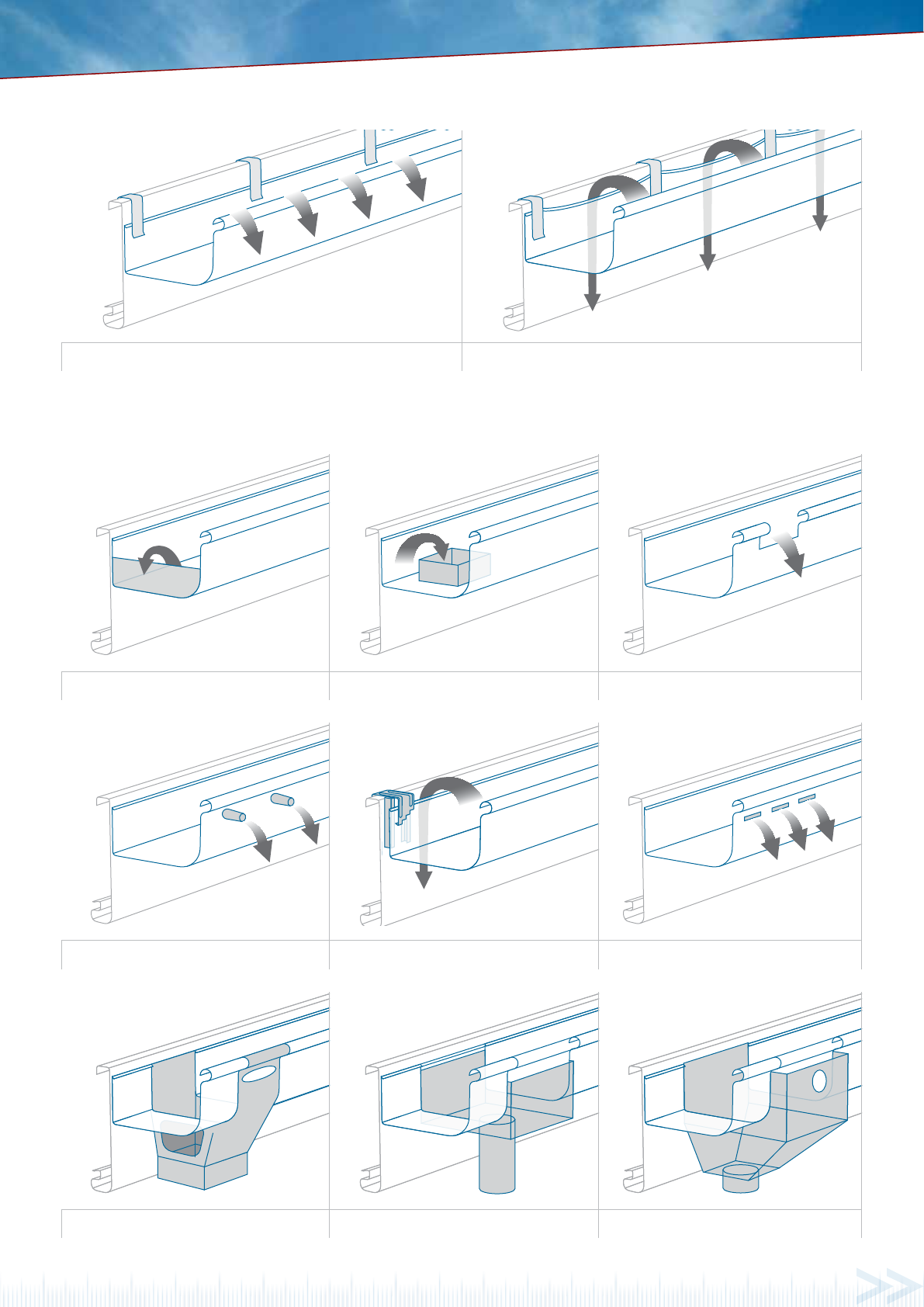
Natural Eects
Additional Measures FIGURE 5
Modied Stop End Internal Outlet Front Cut-Down
Stretch in The Back Face of The GutterFront is Lower Than The Top of The Fascia
Propriety Solution Sump Rainhead
Front Spiggot Rear Exit Gap Front Slots
FIGURE 3 FIGURE 4
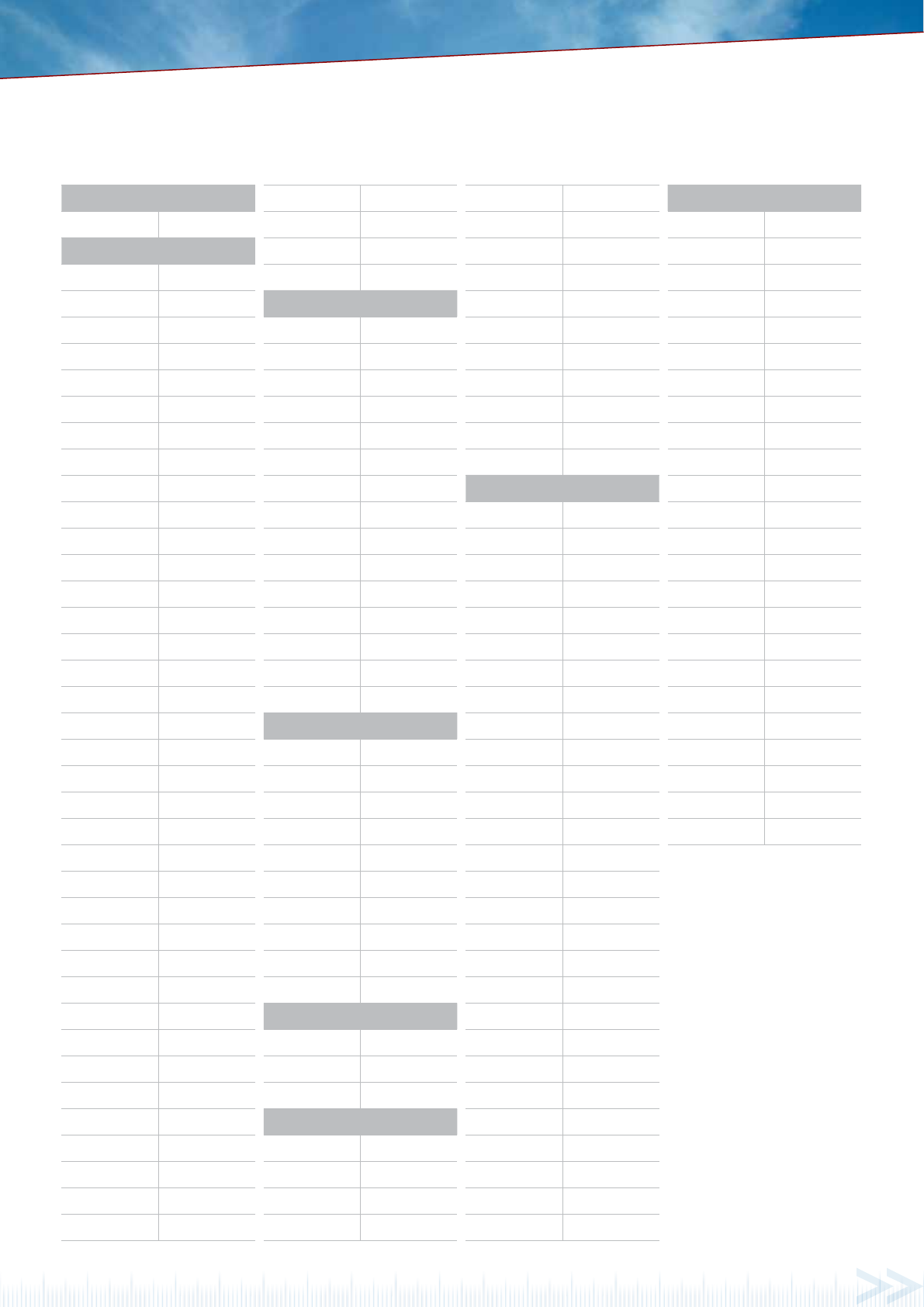
Table 1 | Design Rainfall Intensities (mm/h)
Average Recurrence: Once in 20 Years (Minimum for eaves gutters).
ACT
Canberra 137
NSW
Albury 135
Armidale 154
Batemans Bay 211
Bathurst 143
Bowral 170
Broken Hill 130
Casino 198
Coffs Harbour 232
Cooma 129
Coonabarabran 178
Cowra 144
Dorrigo 214
Dubbo 159
Forbes 151
Glen Innes 159
Gosford 189
Goulburn 145
Inverell 179
Kempseyw 220
Kiama 224
Kiandra 143
Lismore 219
Lithgow 141
Maitland 169
Merimbula 207
Mittagong 172
Mullumbimby 250
Murwillumbah 244
Muswellbrook 141
Newcastle 181
Nowra 219
Orange 152
Penrith 166
Port Macquarie 223
Robertson 228
Singleton 148
Sydney 214
Taree 190
Tweed Heads 245
Wollongong 233
Wyong 186
TAS
Bridgewater 101
Burnie 118
Deloraine 108
Dover 97
Flinders Island 128
Hobart 99
Kingston 98
Launceston 101
Mt Wellington 122
New Norfolk 100
Queenstown 118
Scottsdale 119
Sorell 101
St Helens 131
St Marys 205
SA
Adelaide 123
Arkaroola 134
Ceduna 125
Mt Barker 120
Mt Gambier 108
Murray Bridge 117
Nurioopta 111
Port Augusta 124
Port Pirie 125
Yorketown 118
NT
Alice Springs 139
Darwin 285
Katherine 230
VIC
Bacchus Marsh 126
Ballarat 127
Benalla 133
Geelong 118
Hamilton 120
Healsville 129
Horsham 120
Korumburra 116
Lakes Entrance 124
Melbourne 127
Mildura 125
Morewell 129
Orbost 130
Stawell 127
Wonthaggi 114
QLD
Biloela 220
Brisbane 251
Bundaberg 241
Cairns 282
Cape York 301
Charleville 170
Charters Towers 218
Cloncurry 172
Emerald 220
Goondiwindi 182
Gympie 228
Hughenden 199
Innisfall 254
Kingaroy 208
Longreach 189
Mackay 273
Mareeba 219
Mt Isa 169
Mt Morgan 225
Noosa 253
Proserpine 272
Rockhampton 248
Roma 192
Southport 246
Toowoomba 189
Townsville 260
Warwick 178
Weipa 293
WA
Abydos 199
Albany 142
Broome 252
Bunbury 148
Carnarvon 142
Collie 145
Dampler 231
Derby 254
Geraldton 132
Halls Creek 181
Hammersley 180
Hillside 192
Kalgoorlie 116
Katanning 125
Kununurra 256
Marble Bar 205
Meekatharra 111
Mundaring 139
Newman 143
Perth 146
Port Headland 233
Roy Hill 160
Tom Price 164
Wittenoom 182
Note:
• Data obtained from the Standards Australia
Installation code for metal roofing and wall
cladding SAA HB39-1997.
• Data for other locations may be obtained
from Australian Rainfall and Runoff (1987)
published by the Institution of Engineers,
Australia or may be obtained from local
drainage authorities. Data for any locality
in Australia is available (to a resolution of
1/40th of a degree of latitude or longitude)
from the Bureau of Meteorology.
• Data shown for large cities are the maxima
within the greater city areas. Data for
specific locations within these areas
may be obtained by reference to the
above publication or from the Bureau of
Meteorology.
• More stringent requirements should
be considered for buildings where
the avoidance of gutter overflow is of
paramount importance.
• All gutters and outlets, particularly box
gutters served by internal sumps, need to
be regularly inspected and maintained to
avoid blockages.
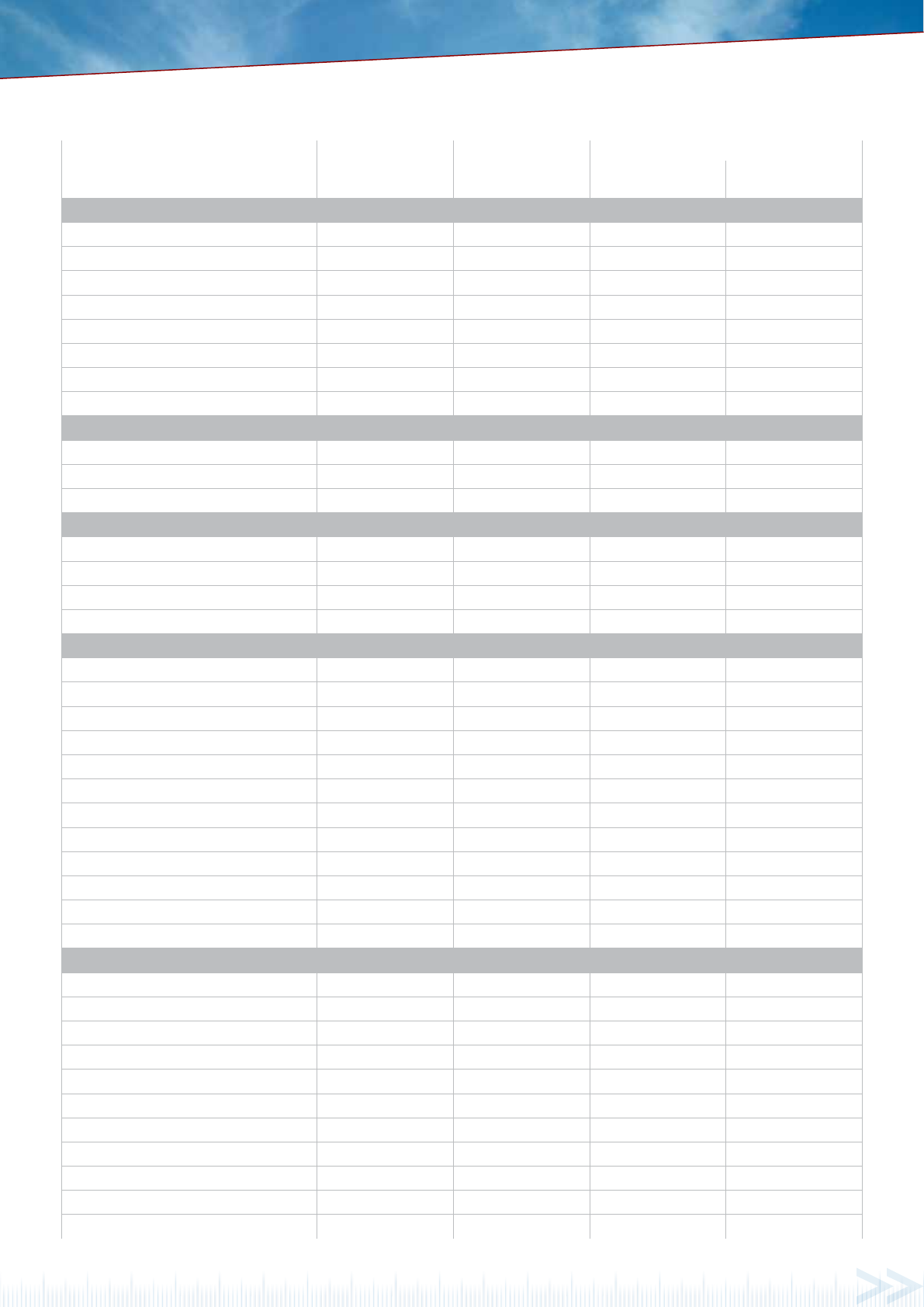
Gutter Prole
Eective Cross
Sectional Area
Capacity (mm2)
Total Cross
Sectional Area
(mm2) Round (dia mm)
Rectangular/
Square (mm)
Quad
115mm Quad 5,621 6,760 90 100 x 50
115mm Quad - Slotted 5,057 6,192 90 100 x 50
115mm Quad - Low Front 4,307 5,429 75 75 x 50
125mm Quad - NSW 6,488 7,833 90 100 x 50
125mm Quad - SA/NT 6,697 7,958 100 75 x 75
125mm Quad - Slotted 5,592 6,842 90 100 x 50
150mm Quad 8,685 10,088 125 100 x 75
175mm Quad 12,213 13,767 125 100 x 100
OG
125mm OG 4,432 5,609 75 75 x 50
125mm OG - Slotted 3,374 4,432 65 75 x 50
150mm OG - Slotted 5,763 7,055 90 100 x 50
Half Round & Smoothline
150mm Smoothline 8,748 10,124 125 100 x 75
150mm Smoothline - Slotted 6,961 8,332 100 100 x 75
150mm Half Round 7,703 9,176 100 100 x 75
150mm Half Round - Slotted 7,126 8,597 100 100 x 75
Square
VC 5,712 6,893 90 100 x 50
VC - Slotted 4,412 5,594 75 75 x 50
LO-Square - Slotted 4,447 5,624 75 75 x 50
VFC 6,775 7,957 100 100 x 75
VFC - Slotted 5,475 6,657 90 100 x 50
VF - SA 7,839 8,970 100 100 x 75
VF - WA 7,333 8,444 100 100 x 75
VF - Slotted 5,475 6,657 90 100 x 50
HI-Square - Slotted 5,974 7,155 90 100 x 50
C-Square - Slotted 5,974 7,155 90 100 x 50
VT - Slotted 6,338 7,583 90 100 x 50
VFM - Slotted 6,711 7,888 100 100 x 75
Miscellaneous
Edge Gutter 14,856 16,833 - -
Edge Gutter WA 9,151 10,936 - -
HK 5,394 6,590 75 100 x 50
HK - Slotted 3,717 4,816 75 75 x 50
S5,315 6,358 75 100 x 50
S - Slotted 4,609 5,622 75 75 x 50
Clickform - Slotted 5,102 6,303 90 100 x 50
450mm Girth OG Big One - Slotted 9,881 11,551 125 100 x 100
600mm Girth OG Big One - Slotted 26,345 28,615 125 100 x 100
Quarter Round 6,292 7,577 90 100 x 50
Quarter Round - Slotted 5,054 6,309 90 100 x 50
Table 2 | Cross Section Area (mm2)
Minimum Downpipe Size
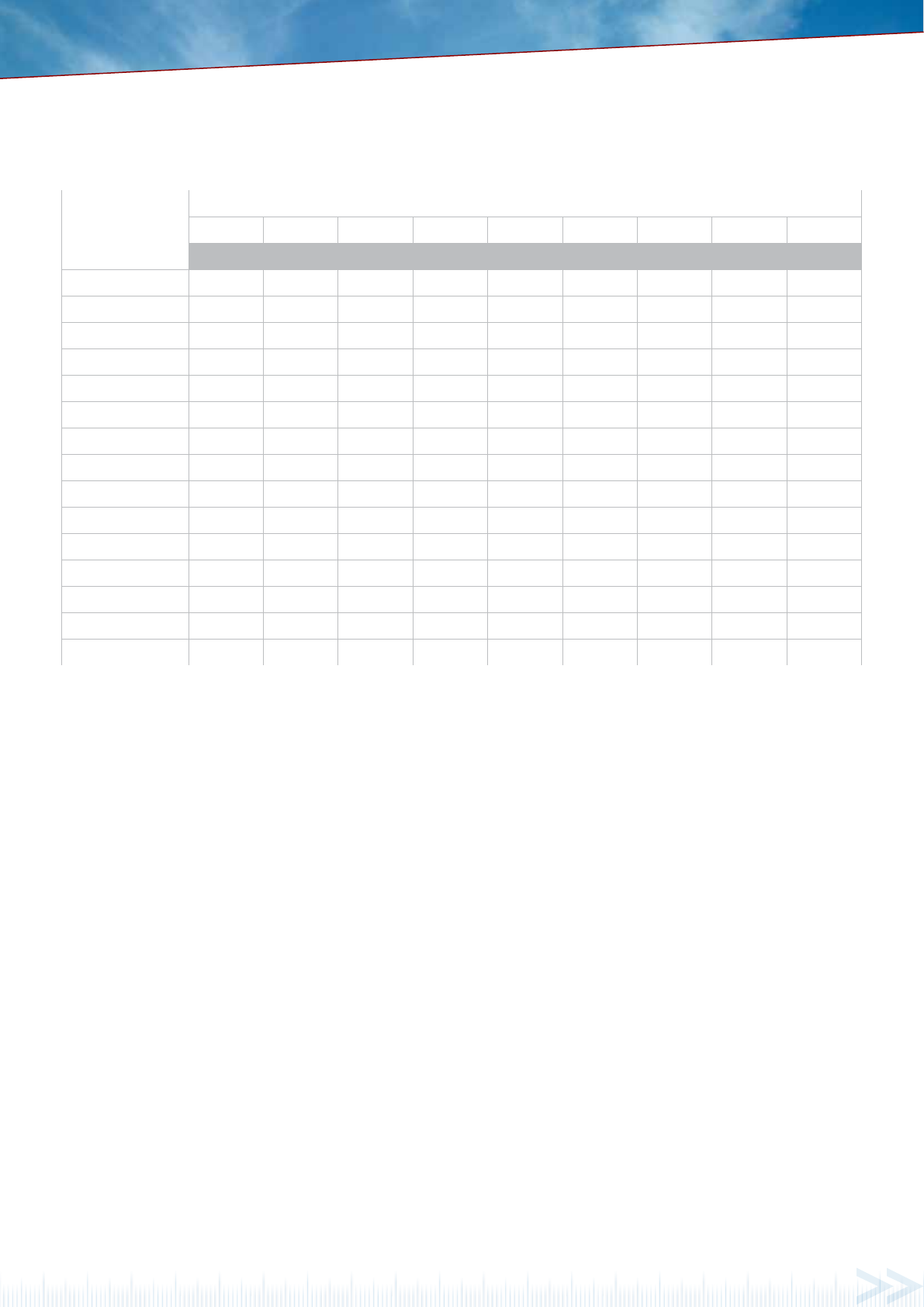
Rainfall Intensity
(mm/hr)
Roof Catchment Area
10m220m230m240m250m275m2100m2150m2200m2
Cross sectional area of gutter (mm2) required to drain above roof catchment area into one downpipe.
90 1620 2440 3060 4090 4890 6790 8500 12380 15240
100 1780 2670 3560 4445 5330 7390 9280 13030 16640
110 1860 2830 3810 4780 5720 7960 9950 14000 18500
120 1930 3000 4080 5150 6170 8540 10220 15060 19250
130 2000 3160 4360 5500 6570 9060 11390 16110 20610
140 2070 3340 4640 5830 6940 9610 12110 17180 22030
150 2170 3540 4900 6230 7390 10170 12790 18080 23120
160 2240 3730 5170 6530 7810 10750 13500 19000 24000
180 2470 4110 5700 7170 8500 11810 14800 20390 25560
200 2610 4440 6210 7780 9310 12880 16110 22360 28000
225 2900 4920 6780 8530 10240 14110 17720 24720 31000
250 3060 5340 7400 9310 11060 15310 19250 27200 34200
275 3270 5760 7970 10040 12000 16560 20610 28930 36130
300 3500 6190 8530 10750 12890 17730 22170 30770 38200
350 4000 7030 9640 12140 14530 20000 25280 34610 42380
Table 3 | Eaves Gutter Sizes For Various Rainfall Intensities
And Roof Catchment Areas Per Downpipe (Based on minimum size downpipe)
Responsibilities of the Installer
It is the responsibility of the installer to ensure that the project is installed as required by the rainwater goods designer. They also
need to ensure that the directions provided in the Codes mentioned above are followed. Adequate fall towards the downpipes must
be given to gutters (a minimum of 1 in 500 for eaves gutters and 1 in 200 for internal gutters). The installer must ensure that the
correct number of downpipes of sucient size are installed, that they are clear of debris and able to discharge correctly.
Responsibilities of the Owner
It is the responsibility of the owner to ensure that their gutters and downpipes are adequately maintained and kept completely free
of leaf debris, branches and twigs, and both organic and inorganic materials. There is no one solution that can be relied upon to do
this, and the best solution may involve a number of strategies. Should the design provided prove inadequate due to local conditions,
many of the additional protective measures described above can be retro tted and may prove benecial.
Overow Measures
Examples of continuous and non-continuous overow measures that may be used in conjunction with each other to meet the
relevant requirements are provided in the Building Code of Australia and examples are shown in Figure 6. Continuous overow
measures allow for overow along the complete length of the gutter, while non-continuous overow measures are located at specic
points along the length of the gutter. Care needs to be taken to ensure the system complies with the Building Code of Australia and
the current Australian Standards.
Gutters may become blocked anywhere along their length which means non-continuous overow measures may not be sucient to
prevent water owing back into a building.
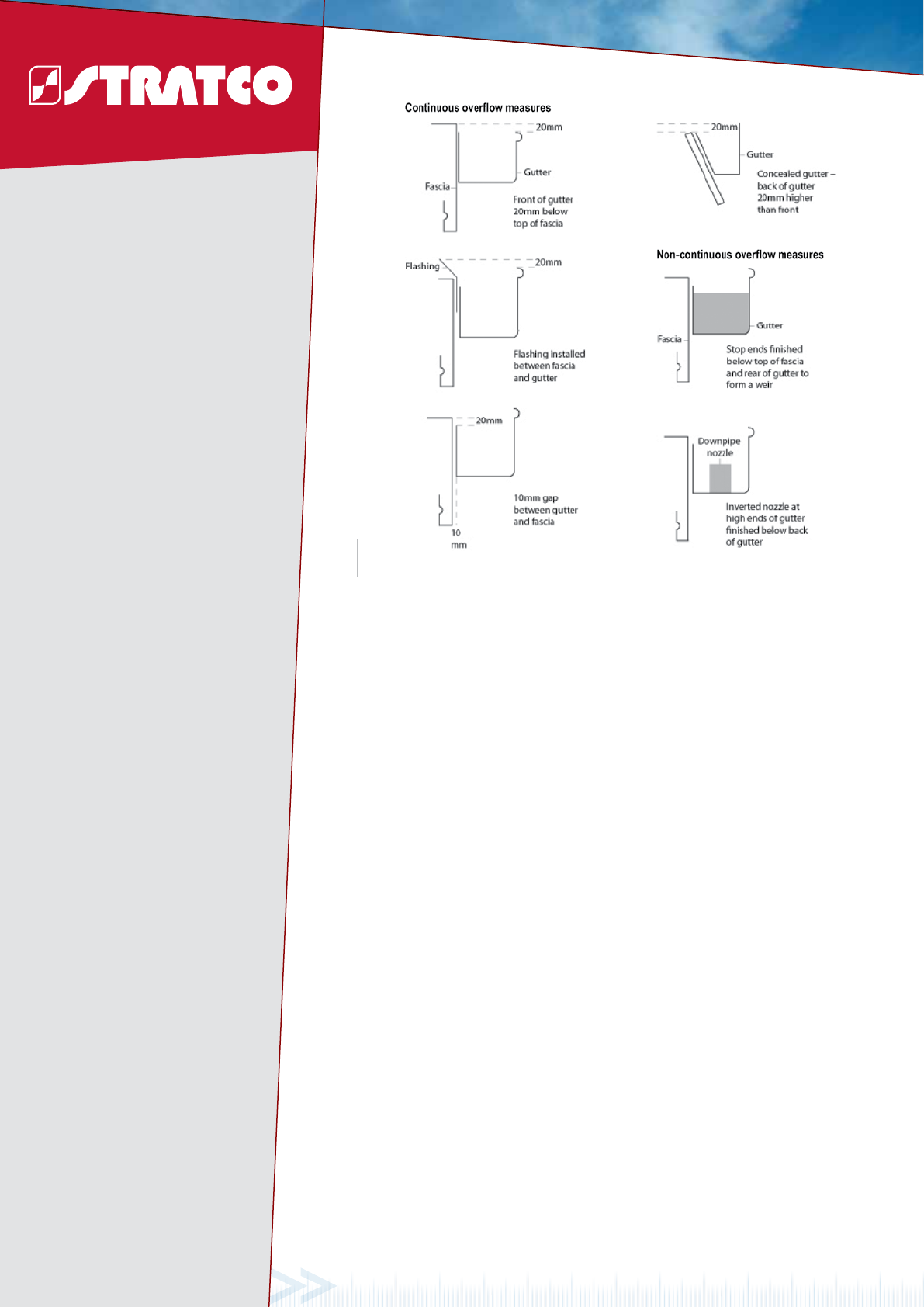
CONTACT
1300 165 165
www.stratco.com.au
All brands and logos/images accompanied by ® or ™ are
trade marks of Stratco (Australia) Pty Limited.
© Copyright November 2010
Additional Information
Up to date information about Stratco products, spans, installation requirements
and technical advice can be found on our website at: www.stratco.com.au. It is
advisable to obtain current information prior to ordering any materials.
Further details about complying with legislation can be found in the Stratco
‘Selection, Use and Maintenance’ brochure.
The NSW Oce of Fair Trading website also provides information on complying
with legislation: http://www.fairtrading.nsw.gov.au/Tenants_and_home_owners/
Home_building_and_renovating/The_building_process/Residential_gutters.html.
If additional information is required contact the Stratco oce in your state.
Maintenance
Regular maintenance is essential to maintain the good looks of all Stratco steel
products and to ensure you receive the maximum life-span possible in your area.
Gutters must be regularly cleaned to prevent the build up of leaf debris, fungus
or any other material that could prevent the free drainage of water from the roof.
Washing with clean water must be frequent enough to prevent the accumulation
of dust, salts, and pollutants or any other material that will reduce the life of
the product. Stratco steel products that are regularly washed by rain require no
additional maintenance. No Stratco steel structure or materials are recommended
for use over, or in close proximity, to swimming pools or spas. No material that
retains water (such as dirt or paving sand) should be placed against the columns.
Care must be taken when determining the location of Stratco steel products so that
they are not placed in close contact with sources of pollution or environmental
factors that could aect the life of the steel. Refer to the ‘Selection, Use and
Maintenance’ brochure for more information.
Figure 6