Hitachi L100 Series VFD Manual
L100 Hitachi-L100-Series-VFD-Manual
User Manual: Hitachi-L100-Series-VFD-Manual Igor's of metalworking and electrical manuals
Open the PDF directly: View PDF .
Page Count: 69
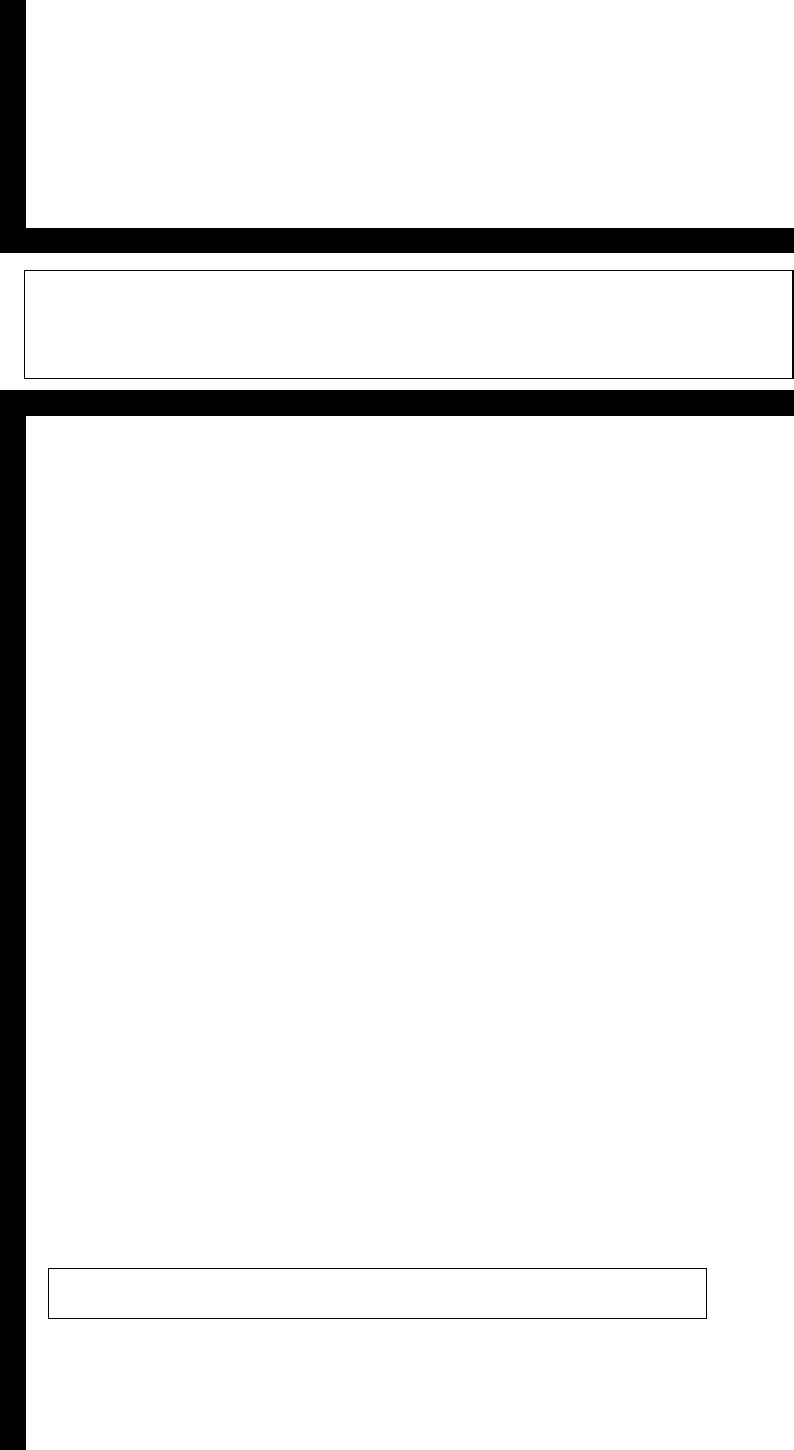
HITACHI INVERTER
SERVICE MANUAL
(ADJUSTMENT AND MAINTENANCE)
Model:
European Version
L100-002NFE to L100-022NFE
L100-004HFE to L100-075HFE
US Version
L100-002NFU to L100-022NFU
L100-004HFU to L100-075HFU
L100-037LFU
L100-002MFU to L100-007MFU
Japanese Version
L100-002LFR to L100-037LFR
L100-004HFR to L100-075HFR
L100-002MFR to L100-007MFR
After reading this manual, keep it at hand for future reference
NBS541X
Hitachi, Ltd.
Tokyo Japan
L100 SERIES

INDEX
1. Pre-operation Check
1-1. Check inverter model and Manufacturing number
1-2. Check inverter parameter and motor specification
2. Measurement of The Internal Voltage Supply
3. Trouble Shoot
3-1. Error messages - Possible Cause and Remedy
3-2. Analysis of Various Operating Problems That Do Not Trigger an Trip Message
3-3. How to Initialize the Data (FACTORY SETTING)
3-4. Error Message Comparison
3-5. Other Displays
4. Ambient Condition of the Frequency Inverter (Temperature, Altitude)
4-1. Required Derating in case of 50deg., 55 deg. of Ambient Temperature
4-2. Required derating toward altitude
5. Level of Each Detection
5-1. DC Bus Voltage Detection Characteristics
5.2. Output Current Detection Characteristics
5.3. Motor Temperature Detection (PTC)
5.4. Over Temperature Detection of the Frequency Inverter
6. Measurement & Replacement of Subassemblies
6-1. Insulation Measurement
6-2. Power Components Measurements
7. Maintenance and Inspection Procedure
7-1. Precautions
7-2. Measurement of Mains Voltage, Current and Power
7-3. Maintenance of Parts
7-4. If you install replacement INV at site
8. Daily Inspection and Periodical Inspection
9. Image block diagram
10. Spare parts list
10-1.
parts list
10-2. I/O board compatibility
10-3. O,OI terminal adjustment procedure
10-4. kW setup procedure
10-5. I/O board schematic(circuit diagram)
1-1
1-1
1-2
2-1
3-1
3-1
3-6
3-7
3-8
3-9
4-1
4-1
4-4
5-1
5-1
5-3
5-4
5-4
6-1
6-1
6-1
7-1
7-1
7-1
7-4
7-4
8-1
9-1
10-1
10-1
10-16
10-17
10-18
10-19
-ⅰ-

Revisions
Revision history table
No. Revision contents Date of issue Manual No.
-ⅰⅰ-

1. Pre-Operation Check
Before starting adjustment and maintenance, be sure to check the following specifications of the inverter
and the motor.
1.1 Check Inverter model and Manufacturing number (MFG No).
NE16452-6
MADE IN JAPAN
Hitachi, Ltd.
HITACHI
Model : L100-015NFE
HP/kW : 2 / 1.5
In
p
ut/Entree: 16.0 A1Ph200-240V50
,
60Hz
9.3 A3Ph200-240V50
,
60Hz
Out
p
ut/Sortie: 1-360Hz 7.1 A3Ph200-240V
MFG No. 78H T1129670060 Date: 9708
You can find these information from the specification label which attached at the side cover of the unit.
(1) Description of the model name.
(2) Description of MFG No.
Inverter model
MFG No.
T112967 0060H87
Unique number
Production code
Revision of the inverter
Production Month
(1 - 9, 0:October, J:November, K:December)
Production year
(The unit digit of the year of grace. 7:1997, 8:1998, 9:1999, 0:2000)
1-1
EF015 HL100
Version number
E: European version
U: US version
R: Japanese versionSeries name Structure type
F: With operator
Input voltage class
005
004
: 7.5kW
: 5.5kW
: 4.0kW
: 3.7kW
: 3.0kW
: 2.2kW
: 1.5kW
: 1.1kW
: 0.75kW
: 0.55kW
: 0.4kW
: 0.2kW002
Applicable motor kW
L: 3 phase 200V class
N: Single/3 phase 200V class
H: 3 phase 400V class
075
055
040
037
030
022
015
011
007
M: Single phase 100V class

1.2 Check Inverter parameter and motor specification.
[1] Inverter specifications.
(1) Inverter specifications (Monitor mode)
Display Function name Category Screen display Initial Remarks
order Code display EU US JPN
1 Output frequency monitor Monitor d01 - - -
2 Output current monitor Monitor d02 - - -
3 Running direction monitor Monitor d03 - - -
4 Feedback data of PID
control monitor Monitor d04 - - -
5 Intelligent input terminal
condition monitor Monitor d05 - - -
6 Intelligent output terminal
condition monitor Monitor d06 - - -
7 Output frequency
converted value monitor Monitor d07 - - -
8 Trip monitor Monitor d08 - - -
9 Trip history monitor Monitor d09 - - -
(2) Inverter specifications (Basic function mode)
Display Function name Category Screen display Initial Remarks
order Code display EU US JPN
1 Output frequency setting set F01 0.0 0.0 0.0
2 Acceleration time 1 set F02 10 10 10
3 Deceleration time 1 set F03 10 10 10
4 Running direction setting set F04 00 00 00
5 Extended function
A group setting set A--
6 Extended function
B group setting set B--
7 Extended function
C group setting set C--
1-2

(3) Inverter specifications (Extended function mode : A group)
Display Function name Category Screen display Initial Remarks
order Code display EU US JPN
1 Frequency destination set A01 01 01 00
2 Running command
destination set A02 01 01 02
3 Base frequency set A03 50 60 60
4 Maximum frequency set A04 50 60 60
5 External frequency setting
start set A11 000
6 External frequency setting
end set A12 000
7 External frequency setting
start rate set A13 000
8 External frequency setting
end rate set A14 100 100 100
9 External frequency start
pattern set A15 01 01 01
10 Time constant of the filter
of analog input set A16 888
11 Multi-speed 1 to 16 set A20 - A35 0 0 Note 1
12 Jogging frequency set A38 1.0 1.0 1.0
13 Stop mode of jogging set A39 00 00 00
14 Torque boost mode set A41 00 00 00
15 Level of
manual torque boost set A42 11 11 11
16 Manual torque boost
frequency set A43 10.0 10.0 10.0
17 V/f characteristics set A44 00 00 00
18 V-gain set A45 100 100 100
19 Selection of DC braking set A51 00 00 00
20 DC braking frequency set A52 0.5 0.5 0.5
21 DC braking waiting time set A53 0.0 0.0 0.0
22 DC braking force set A54 000
23 DC braking time set A55 0.0 0.0 0.0
24 Frequency upper limiter set A61 0.0 0.0 0.0
25 Frequency lower limiter set A62 0.0 0.0 0.0
26 Jump frequency 1-3 set A63, A65, A67 0.0 0.0 0.0
27 Jump frequency width 1-3 set A64, A66, A68 0.5 0.5 0.5
28 Selection of PID control set A71 00 00 00
29 P gain set A72 1.0 1.0 1.0
30 I gain set A73 1.0 1.0 1.0
31 D gain set A74 0.0 0.0 0.0
32 Scale conversion of
PID control set A75 1.0 1.0 1.0
33 Feedback destination set A76 00 00 00
34 Selection of AVR function set A81 02 02 02
35 AVR voltage set A82 230/400 230/460 200/400
36 Second acceleration time set A92 15.0 15.0 15.0
37 Second deceleration time set A93 15.0 15.0 15.0
38 Method to use 2nd
acceleration / deceleration
(Acc2 / Dec2)
set A94 00 00 00
39 Acc1 to Acc2 changing
frequency set A95 0.0 0.0 0.0
40 Dec1 to Dec2 changing
frequency set A96 0.0 0.0 0.0
41 Acceleration characteristic set A97 00 00 00
42 Deceleration characteristic set A98 00 00 00
Note 1 A20;0, A21;5, A22;10, A23;15,A24;20, A25;30, A26;40, A27;50, A28; 60,A29--A35;0
1-3

(4) Inverter specifications (Extended function mode : B group)
Display Function name Category Screen display Initial Remarks
order Code display EU US JPN
1 Selection of restart mode set b01 00 00 00
2 Allowable UV time set b02 1.0 1.0 1.0
3 Retry waiting time set b03 1.0 1.0 1.0
5 Electronic thermal level set b12 note note note Rated current of
each inverter
6 Electronic thermal
characteristics set b13 01 01 00
7 Overload restriction
operation mode set b21 01 01 01
8 Overload restriction level set b22 note note note Rated current
* 1.25 for each
inverter
9 Deceleration rate while
overload restriction set b23 1.0 1.0 1.0
10 Selection of software lock set b31 01 01 01
11 Reactive current setting set B32 note note Note Rated current
*0.58 for each
inverter
13 Analog meter adjustment set b81 80 80 80
14 Start frequency adjustment set b82 0.5 0.5 0.5
15 Carrier frequency set b83 5 5 12
16 Data initialization or
Trip history clear set b84 00 00 00
17 Initialization mode set b85 01 02 00
18 Frequency converting
value set b86 1.0 1.0 1.0
19 STOP key condition set b87 00 00 00
20 Restart mode after FRS
invalid set b88 00 00 00
21 Monitor contents
for OPE-J set b89 01 01 01
1-4

(5) Inverter specifications (Extended function mode : C group)
Display Function name Category Screen display Initial Remarks
order Code display EU US JPN
1 Input terminal 1 assign set C01 00 00 00
2 Input terminal 2 assign set C02 01 01 01
3 Input terminal 3 assign set C03 02 16 02
4 Input terminal 4 assign set C04 03 13 03
5 Input terminal 5 assign set C05 18 18 18
6 Input terminal 1 condition set C11 00 00 00
7 Input terminal 2 condition set C12 00 00 00
8 Input terminal 3 condition set C13 00 00 00
9 Input terminal 4 condition set C14 00 01 00
10 Input terminal 5 condition set C15 00 00 00
11 Output terminal 11 assign set C21 01 01 01
12 Output terminal 12 assign set C22 00 00 00
13 FM terminal condition set C23 00 00 00
14 Output terminal 11
condition set C31 00 00 00
15 Output terminal 12
condition set C32 00 00 00
16 AL output terminal
condition set C33 01 01 01
17 Level of overload signal set C41 note note note Rated current of
each inverter
18 Arrival frequency
while acceleration set C42 0.0 0.0 0.0
19 Arrival frequency
while deceleration set C43 0.0 0.0 0.0
20 Level of deviation signal
under PID control set C44 3.0 3.0 3.0
1-5

[2] Motor specifications.
[3] Load conditions
Output voltage
Output
frequency
V
0Hz Hz
Motor MFG number
kWMotor output
pMotor poles
rpmMotor rated rpm
AmpsRated current
VRated voltage
HzRated frequency
AmpsStarting current
Equipment name
Torque characteristics
NmRequired torque
kgm2
Load inertia (J)
secAcceleration time
secDeceleration time
Hz to
Variable speed range
Hz
1-6/E

2. Measurement of the Internal Voltage Supply
There are PV5L, PV24L and NV12L internal DC voltage supplies. These supplies are isolated from the
main high voltage portion. And it is not possible to measure DC voltages at the non isolated portion.
Please make measurements for above mentioned voltages for the isolated portion.
PV5L supply voltage
Supplies 5V for I/O board.
Nominal voltage : min. 4.90Vdc to max. 5.20Vdc
Check PV5(address 1C) <- L
PV24L supply voltage
Supplies 24V to interface voltage supply, which is supplied to input terminals.
Nominal voltage : min. 21.60Vdc to max. 26.40Vdc
Check PV24(address 1A) <- L
NV12L supply voltage
Supplies -12Vdc to remote operator (DOP/DRW’s yellow backlight).
Nominal voltage : max. -10.80Vdc to min. -17.5Vdc
Check NV12(address 3A) <- L
“H” terminal voltage
Suppiles 10V to “H” terminal
Nominal voltage : min 9.5Vdc to max 11.5Vdc
Check “H”
<-> “L” with VR (1kohm)
“Potentiometer function on the front case
Set “A01” :”00”
Monitor “F01” display 0 <-> 50(60) with clockwise and anti clockwise.
Cooling FAN voltage (PV24N)
Supplies 24V to cooling FAN .
Nominal voltage min 19.9Vdc to max 27.2Vdc.
Check Red wire <- Black wire with the FAN.
Check the FAN working, check the air direction (from down to top)
Check pad of NV12 Check pad of PV24
Check pad of PV5
1 pin of TM2 is “L”common
2-1/E

3. Trouble Shoot
3-1. Error Messages - Possible Cause and Remedy:
(1) Overcurrent 1 (E 01, E 02, E 03, E 04)
Phenomena: Overcurrent for each condition.
E 01 : Overcurrent during constant speed operation.
E 02 : Overcurrent during deceleration.
E 03 : Overcurrent during acceleration.
E 04 : Overcurrent at other condition than above mentioned.
(such as injection brake)
Cause: Load changed rapidly.
Remedy: Eliminate rapid changed in load.
Cause: Sort circuit or earth contact (ground fault) in the motor or the motor cable.
Remedy: Check with Megger. If the motor cable is disconnected from the inverter, the
overcurrent should not be detected anymore.
Cause: A single-phase power failure (fuse, wire, ...) can cause a shutdown in certain
underload situations..
Remedy: Check all these mains phases and the mains fuses, preferably by comparison of
the three (two in case of single phase inverter) mains currents in a steady
operating state.
Cause: The motor is switched with a motor contactor during frequency inverter operation.
Remedy: Switching over the motor is inhibited.
Cause: Defect in the power component.
Remedy: Check the IGBT portion of ISPM.
Cause: Rapid acceleration or deceleration.
Remedy: Set suitable acceleration or deceleration time.
Cause: Starting frequency is too high.
Remedy: Set starting frequency as low as possible.
Way to Reset: A
3-1

(2) Overload (E 05)
Phenomena: Overload of the inverter.
This error can be reset 10 seconds after the E05 came out.
Cause: Motor load is heavy.
Remedy: Reduce the load and/or increase thermal level and/or use bigger capacity of
frequency inverter.
Cause: V-Boost value is high.
Remedy: Reduce V-Boost value or increase thermal level and/or use bigger capacity of
frequency inverter.
Cause: Set wrong value for electronic thermal level [b12] and/or electronic thermal
characteristic [b13].
Remedy: Set suitable value.
Cause: Set wrong value for the reactive current of the motor.
Remedy: Set suitable value. Reactive current value which should be input by function mode
is a value measured at 50Hz (60Hz) without load.
Way to Reset: A
(3) Overvoltage (E 07)
Phenomena: Overvoltage at DC bus line of the frequency inverter.
Cause: Mains voltage too high, mains voltage fluctuation or rapid mains voltage return
(choke energy leads to voltage increase).
Remedy: Make sure that mains voltage is within tolerance limits.
Cause: In case L100 is used in combination with a regenerative braking unit but the
regenerative braking unit does not function.
Remedy: Replace regenerative braking unit.
Cause: In case L100 is used in combination with a raking resistor but the braking resistor
cannot absorb the regenerative energy.
Remedy: Re-calculate and use suitable braking resistor.
Cause: Deceleration time is too short.
Remedy: Make deceleration time longer, use braking unit (resistor), use bigger capacity of
frequency inverter.
Way to Reset: A
(4) Undervoltage (E 09)
Phenomena: Undervoltage at DC bus line of the frequency inverter.
Cause: The mains voltage is not available or not within the tolerance limits.
Remedy: Check all 3 (or 2) mains power supply voltage that it is within its specification.
Cause: Thyristor for smooth charging is defect and DC bus voltage drops while operation
due to current flows through smooth charging resistor.
Remedy: Change ISPM. 3-2

Cause: Period of instantaneous power failure is longer than the set value [b02], or DC bus
voltage go down to its detecting level while instantaneous power failure.
Remedy: Get rid of the instantaneous power failure, evaluate the power supply system, set
bigger value for [b02].
Cause: One of the AC voltage is missing (applied only for 3 phase INV)
Remedy: Check AC line voltage , check the fuses.
Way to Reset: A
(5) EEPROM error (E 08)
Phenomena: Abnormal situation occurs at the memory portion of the frequency inverter due to
incoming noise etc..
Cause: Influenced by Electrical Magnetic Interference.
Remedy: Keep such noise source away from the frequency inverter.
Cause: Ambient temperature is too high.
Remedy: Take countermeasure against high ambient temperature.
Cause: Re-power up the frequency inverter short time after power off. It is necessary to
keep several seconds after power off to memorize the current data at EEPROM. If
this time is too short, this storage performance cannot be done and leads to
EEPROM error.
Remedy: Keep certain time between power off and re-power up.
Cause: You didn’t wait 6 seconds or more at FACTORY SETTING.
Remedy: Please try FACTORY SETTING again.
Cause: RS terminal was keeping “ON” at power off. (If RS is on, INV can not write the
correct data to EPROM at power off, next power on E08 will come out.)
Remedy: Please don’t use “RS” terminal “ON” at power off.
Cause: EEPROM is defect.
Remedy: Change unit.
After you reset the INV, please make sure the parameters especially maximum freq. / Acc /Dec
time / Low limit freq. to prevent any damage.
Way to Reset: A or Power off
(6) CPU error (E 11, E 22)
Phenomena: Abnormal situation or malfunction of micro processor inside frequency inverter.
E 11 : CPU error from MCU inside core.
E 22 : CPU error from MCU on I/O board.
E22 is produced by MCU on I/O board and the causes is communication error between ISPM & MCU
on I/O board.
Cause: Cable (between ISPM and I/O board)was cut. (E22)
Remedy: Replace the cable.
Cause: Dusts on the pins of CN2 on I/O board. (E22)
Remedy: Remove the dusts.
3-3

Cause: Influenced by Electrical Magnetic Interference.
Remedy: Keep such noise source away from the frequency inverter.
Cause: Ambient temperature is too high.
Remedy: Take countermeasure against high ambient temperature.
Cause: Component itself is defect.
Remedy: Replace ISPM (in case of E 11) or I/O board board (in case of E 12).
(7) External Trip (E 12)
Phenomena: Trip due to have inputted an external signal to “EXT” input terminal of the
frequency inverter.
Cause: Faulty external device or equipment gives frequency inverter a trip requirement
when external trip function (EXT) is selected.
Remedy: Evaluate external device or equipment which is connected to frequency inverter.
Way to Reset: A
(8) USP error (E 13)
Phenomena: Unexpected Start Protection. This error can occur when “USP” function is
selected.
Cause: Frequency inverter trips when it is powered up with RUN command is given.
Remedy: Disable RUN command when power up the frequency inverter. Or disable USP
function if possible to the system.
Way to Reset: A or set RUN command off (stop)
(9) Ground fault error (E 14)
Phenomena: Earth contact in the motor or the motor cable or in the IGBT. Frequency inverter
detects this earth contact only at power up.
To resolve the causes , please power off and disconnect the motor wire at INV (UVW)terminal.
Cause: Earth contact in the motor or the motor cable.
Remedy: Check the impedance between output portion(wire and motor) and earth.
Cause: Detection circuit/IGBT of the inverter is defect. If the motor and the motor cable is
disconnected from the frequency inverter, the ground fault should not be detected
anymore.
Remedy: Please disconnect the motor and the motor cable.
If E14 comes out at power on,please replace the unit.
Way to Reset: Don’t reset.
3-4

(10) Over voltage at source (E 15)
Phenomena: High voltage at power source line. Frequency inverter cannot protect source
overvoltage. If it is too high, frequency inverter will be damaged.
Cause: Source voltage is too high.
Remedy: Check the source voltage continously.
Insert AC reactor at source lines.
Way to Reset: A
(11) Over temperature (E 21)
Phenomena: Temperature sensor which located close to IGBT inside ISPM shows a too high
temperature.
Cause: Ventilator blocked. (for models which has ventilator.)
Remedy: Check ventilator
Cause: The frequency inverter does not get enough cooling air.
Remedy: Check cabinet ventilation, air filters, and ventilation openings in the cabinet.
Way to Reset: A
(12) PTC error (E 35)
Phenomena: Resistance of motor thermistor is high. This error can occur when you select
“PTC” function.
Cause: Too much load of the motor.
Remedy: Reduce the load, use bigger motor.
Cause: Motor thermistor is not connected while PTC function is selected.
Remedy: Disable PTC function when it is not used.
Cause: Characteristics of the motor thermistor is not suitable. Frequency inverter gives
PTC error when the resistance value becomes more than 3k ohm +-10%.
Remedy: Use motor which has suitable thermistor for the inverter.
Or change thermistor characteristics of the thermistor by debug mode.
Way to Reset: A
Explanation of the way to reset.
A : Make close the terminals between RS and P24 (CM1 only for Japanese version) on the I/O board, or
press “STOP/RESET” key of the operator.
3-5

3-2. Analysis of Various Operating Problems That Do Not Trigger an Trip
message.
Problem Possible cause Remedy
The motor does not start Mode of frequency command [A01]
and/or Run command [A02] is not
proper
Check each mode again
Incorrect power supply condition Check that the power supply is
within its specification
Inverter is in trip mode Get rid of the trip cause
0 Hz of Multi-stage speed is given
FRS and/or RS is remaining Make FRS and RS invalid
0 Hz command is given
Each phase to phase voltage does
not balance. (out of +-3%) Replace the unit
Load is too heavy Decrease the load or use bigger
capacity of inverter and motor
If you use DOP or DRW, DIP
switch selection of the operator is
incorrect.
Set as follows
Same as J300, J100,SJ100
Inverter Failure Replace the unit
Rotation direction is
opposite Wiring of the motor cable is
incorrect (U, V, W) Check the wiring of the motor
cable
Setting of [F04] is incorrect Check the setting
Motor does not increase
speed Motor load is too heavy
(Overload limitation) Remove or decrease the motor
load
External frequency set (VR) is out
of order replace VR
Frequency limiter [A61] is set Eliminate frequency limiter
Acceleration time is too short Set longer acceleration time
The inverter cannot be
programmed Software lock is selected [b31] Make software lock invalid
RS or FRS command is given Make them invalid
Multi stage speed command is
given Make inverter in stop mode
Loose connection of DOP/DRW Connect DOP/DRW properly
Inverter is in trip mode Reset the inverter
Unstable rotation of the
motor Motor load is changing heavily Reduce the motor load changing
or use bigger capacity of inverter
and motor
Source voltage is changing Reduce the changing
Mechanical resonance Change output frequency
Data is not changed Forgot to press [STR] key Press [STR] key after changing
data
Turn main power off within 6
seconds after pressing [STR] key Make sure to wait at least 6
seconds after [STR] key is pressed
Cannot change data by
Copy Unit Turn power off within 6 seconds
after started copying Make sure to wait at least 6
seconds
OFF
ON
4
3
2
1
3-6
3-6

3-3. How to Initialize the Data (FACTORY SETTING)
1. Select the mode of initialization data to which you want to initialize by [b85].
Japanese version data -----> Set “00” and store
EU version data -----> Set “01” and store
US version data -----> Set “02” and store
2. Set [b84] to “01” to initialize and store.
3. Keep pressing keys at the same time.
(If front case is not closed by the screw, dittcult to press 3keys.)
4. Additionally press key and release key approximately after one second.
5. Keep pressing keys until “d 00” will blink. (Approximately 2 seconds.)
6. Release all the keys after starts blinking.
[c95] ; INV kW code
01;0.2kW , 02;0.4kW , 03;0.75kW (0.5 kW) , 04;1.5kW , 05;2.2kW ,
06;3.7kW(4.0kW) , 07;5.5kW, 08;7.5kW
Initialization end
Release after “d 00”
started blinking
FUNC. 12
FUNC. 12
STOP
RESET STOP
RESET
FUNC.
1
2
ON (press)
ON
ON
ON
1s or more
STOP
RESET
3-7

3-4. Error Message comparison
Digital Panel DOP / DRW Contents
OC. Drive Over current while constant speed
driving
OC. Decel Over current while deceleration
OC. Accel Over current while acceleration
Over. C Over current at other condition than
above(such as 0Hz,injection brake)
Over. L Over load
(Possible to reset after 10 seconds
has passed)
Over. V Over voltage (DC bus)
EEPROM EEPROM error
(Check the parameters again if this
error occurred)
Under. V Under voltage (DC bus)
CPU 1 CPU error
CPU 2
External External error
USP USP error
GND Flt Ground fault at power-on
OV. SRC Over voltage at source (DC bus)
OH FIN Over temperature
PTC PTC error
3-8

3-5. Other Displays
Digital Panel Contents
- Reset terminal is ON
- During initialization (such as at power-on)
- Voltage is within UV level
- Power OFF
- During retry mode
- During initialization as EU settings
- During initialization as US settings
- During initialization as Japanese settings
- Erasing trip histories
- Copying with DRW,DRW-2
- When there is no data
(i.g. feedback data of PID, etc.)
3-9/E

4. Ambient Condition of the Frequency Inverter
4-1. Required Derating in case of 50deg, 55deg of Ambient Temperature
Inverter ratings can be influenced by many factors. You can find in this section, the relation between
ambient temperature and output current (%) and carrier frequency.
Standard ratings in 40 degree C
Top cover removed condition in 50 degree C max.
Top cover removed condition in 55 degree C max.
% rate of output
current L100-002NFE(U)
100%
90%
80%
70%
1614121086420.5
Carrier frequency [kHz]
% rate of output
current L100-004NFE(U)
100%
90%
80%
70%
1614121086420.5
Carrier frequency [kHz]
L100-015NFE(U)
100%
90%
80%
70%
1614121086420.5
Carrier frequency [kHz]
16
L100-007NFE(U)
100%
90%
80%
70%
14121086420.5
Carrier frequency [kHz]
4-1

Carrier frequency [kHz]
100%
80%
90%
60%
70%
40%
50%
L100-037LF(U)
1614121086420.5
Carrier frequency [kHz]
L100-022NFE(U)
100%
90%
80%
70% 1614121086420.5
Carrier frequency [kHz]
L100-007HFE(U)
100%
80%
90%
60%
70%
40%
50%
1614121086420.5
L100-022HFE(U)
100%
80%
90%
60%
70%
40%
50%
1614121086420.5
Carrier frequency [kHz]
Carrier frequency [kHz]
L100-004HFE(U)
100%
80%
90%
60%
70%
40%
50%
1614121086420.5
16
L100-015HFE(U)
100%
80%
60%
40% 14121086420.5
Carrier frequency [kHz]
90%
70%
50%
4-2

4-3
Carrier frequency [kHz]
L100-055LFU
100%
90%
80%
70% 1614121086420.5
Carrier frequency [kHz]
L100-075LFU
100%
90%
80%
70% 1614121086420.5
Carrier frequency [kHz]
L100-055HFE(U)
100%
90%
80%
70% 1614121086420.5
Carrier frequency [kHz]
L100-075HFE(U)
100%
90%
80%
70%
1614121086420.5
Carrier frequency [kHz]
L100-002MFU
L100-004MFU
100%
90%
80%
70% 1614121086420.5
Carrier frequency [kHz]
L100-007MFU
100%
90%
80%
70% 1614121086420.5

4-2. Required derating toward altitude
Example of calculation
L100-007NFE (4 Amps) is installed at 2000m of altitude and 16kHz of carrier frequency.
Required derating of output frequency of this case will be as follows.
4 [Amps] * 90% * 95% = 3.4 [Amps]
<Note 1> When the top cover is removed for the high ambient temperature, inverter should be installed
in an enclosure of IP 4* (see EN60529) to comply with LVD directive.
<Note 2> If class B of EMC directive is required, carrier frequency must be set to 5kHz.
100%
90%
80%
70% 1000 2000 3000 4000
Altitude [m]
Carrier frequency derating
Altitude frequency derating
4-4/E

5. Level of Each Detection
5-1. DC Bus Voltage Detection Characteristics
Frequency inverter has several detection characteristics for DC bus voltage as followings.
[1] 200V class
5-1
Over voltage level
395V +- 20V
400
DC bus
voltage [Vdc]
Actual DC bus
voltage
Trip
on
Display
example of
monitoring output
frequency
Under
voltage
trip or
During
Under
voltage
Over
voltage
trip
Waiting
for Retry
350
300
250
200
150
100
50
0
Trip
Reset
Under voltage
recovering level
220V +- 10V
Under voltage
level
190V +- 10V
on
Trip

[2] 400V class
5-2
Over voltage level
790V +- 40V
800
DC bus
voltage [Vdc]
Actual DC bus
voltage
Trip
Trip
Display
example of
monitoring output
frequency
Under
voltage
trip or
During
Under
voltage
Over
voltage
trip
Waiting
for Retry
Under voltage
recovering level
440V +- 20V
Under voltage
level
380V +- 20V
700
600
500
400
300
200
100
0
Trip
Reset on on

5-2. Output Current Detection Characteristics
Frequency inverter has several detection characteristics for output current to protect IGBT from break
down, or to protect motor from over heat.
[1] Over current
Frequency inverter shuts off the output instantaneously when output current exceeds to 200% of its
rated current.
e.g. Over current protection level of L100-015NFE (7.1 Amps of rated current) is
7.1 [Arms] * 200% = 14.2 [Arms] = 20.1 [A peak]
[2] Over load (Electronic thermal protection)
Frequency inverter shuts off the output when integration value of output current and time exceeds
specific value.
This Electronic thermal level can be changed from 50% to 120%. (Initial setting is 100%.)
200%150%
180s
120s
time
150%, 60s
E-Thermal Level = [100]
No over load trip with
115% load
60s
180%, 10s
% output current of the rated current of the frequency inverter
0100%
200%150%
180s
120s
time
150%, 60s
60s
180%, 10s
% output current of the rated current of the frequency inverter
0100%50%
E-Thermal Level = [50]
5-3

5-3. Motor Temperature Detection (PTC)
Frequency inverter has a motor temperature sensor input (PTC input : PTC resistor).
When the resistance value is more than 3k ohm +-10%, the frequency inverter trips with “E35”.
5-4. Over Temperature Detection of the Frequency Inverter
Frequency inverter has a temperature detection against power devices of the main circuit. Frequency
inverter shuts down the output when temperature around IGBT comes up to 120 degree C.
L100 inverter
V
L5(PTC)
U
Motor
PTC thermistor
W
5-4/E
Except Japanese version

6. Measurement & Replacement of Subassemblies
6-1. Insulation Measurement
For L100 inverter, do not perform insulation measurements , otherwise MOV will be damaged.
(MOV; between R(L1)-G, S(L2)-G, T(L3)-G)
6.2. Power Components Measurements.
When checking the power components, the following procedure is recommended:
z Clear voltage
z Wait for capacitors discharge
z Check capacitors for neutrality
z Disconnect mains and motor wires
z Test the diodes and IGBTs using a universal tester with a diode function.
Visual check is important for the ISPM, check the outlooking such as smoke trace.
Note: In this test, the absolute values are not so important, since they depend strongly on the test
device used. The uniformity of the measured value is more important.
[1] DC BUS Measurement
Check “+” <- “ - ” voltage Zero.
Resistance Measurement
Allowable Value
From
To
+
-
50kohm or more
P1, PD are located on the CB board / snubber board.
Check “+1” and “+” terminal are shorten by (copper) bar.
[2] Softcharge Resistor (RS) , Thyristor (THY) Measurement
Resistance Measurement
Allowable Value
From
To
P1
PD
PD
P1
15 to 25 ohm
(From P1 To PD From PD To P1 ;if RS was opened)
6-1

[3] Rectifier Measurement
This is to measure 3 rectifiers located lower arm of the input side.
Resistance Measurement
Allowable Value
From
To
R(Ll)
S(L2)
50kohm or more
S(L2)
R(Ll)
S(L2)
T(L3)
T(L3)
S(L2)
T(L3)
R(Ll)
R(Ll)
T(L3)
R(Ll)
R(Ll)
S(L2)
S(L2)
T(L3)
T(L3)
Each R(Ll), S(L2) and
T(L3)
-
50kohm or more
-
Each R(Ll), S(L2) and
T(L3)
50 ohm or less
Each R(Ll), S(L2) and
T(L3)
P1
50 ohm or less
P1
Each R(Ll), S(L2) and
T(L3)
50kohm or more
To make sure MOV, visual check of MOV is necessary on the ISPM.
If the result is out of its spec, replace the unit. ( relative check is important )
R(L1)
T(L3)
S(L2)
P1
6-2
+
+1
U
R(Ll)
W
V
T(L3)
S(L2)
Main circuit of L100
+
RS
P1 PD
THY
RSH

[4] IGBT Measurement
Resistance Measurement
Allowable Value
From
To
+
U
50kohm or more
+
V
+
W
U
+
50 ohm or less
V
+
W
+
-
U
50 ohm or less
-
V
-
W
U
-
50kohm or more
V
-
W
-
If the result is out of its spec, replace the unit.
Please note that this cannot cover 100% to find IGBT failure because if the power devices in failure,
sometimes you can find the failure in components while they are activated. (You cannot find the failure
while they are not activated.)
[5] Cooling FAN voltage circuit in the ISPM (PV 24N)
Measurement on the ISPM
Disconnect the cooling FAN
Resistance Measurement
Allowable Value
From
To
Pin (Red)
Pin (Black)
20kohm or more
Pin (Black)
Pin (Red)
50ohm or less
( relative check is important )
[6] Cooling FAN
Disconnect the cooling FAN and measure impeadance of FAN circuit.
Resistance Measurement
Allowable Value
From
To
Red wire
Black wire
50kohm or less
Black wire
Red wire
100kohm or more
( relative check is important )
6-3/E
DC current detecting
resistor (shunt resistor)
(Order of mili ohm)
+
U
W
V

7. Maintenance and Inspection Procedure
7-1. Precautions
(1) Maintenance and Inspection Precautions
Be sure to check the followings before starting maintenance and inspection because there is a
danger of electrical shock.
z Display on the digital operation panel and POWER indication has been turned OFF.
z The voltage between + and - is 15Vdc or lower.
z Discharging resistor (500 ohm 30W for 200V class, 1k ohm 60W for 400V class) has been
connected between + and - terminals for 15 seconds or more after main power had turned off,
(2) General Precautions
z Always keep the unit clean so that no dust nor other foreign materials come inside of the
frequency inverter.
z Pay attention to broken lines and faulty connections. Firmly connect terminals and connectors.
z Keep frequency inverter away from moisture and oil.
z Dusts, steel filings , swarf , and other foreign materials can damage insulation and causing
unexpected accidents/failure. Please pay attention to them.
7-2. Measurement of Mains Voltage, Current and Power
General measuring instruments for mains voltage, current and power are shown in Table 7-1.
The voltage to be measured is the effective value of fundamental wave, and the power to be measured
is the total effective value.
(1) Measurement of output voltage
Moving iron type instrument does not show accurate values for measurement of the output voltage.
Make measurements according to the method shown in Fig. 7-3 (table 7-1) or using the circuit
indicated in Fig. 7-1 and 7-2.
Fig. 7-1. Output voltage measurement circuit (with load)
U
V
W
Frequency
Inverter Load
Motor
2W
220kohm
+
VDC
-
Fundamental wave
effective value : VAC = VDC * 1.1
Moving coil type DC Volt meter
300V (200V class)
600V (400V class)
Diode
600V 0.1A or above (200V class)
1000V 0.1A or above (400V class)
7-1

When there is no motor connected to the inverter, please use additional resistor like Fig. 7-2. There
will be a voltage at output terminal even the frequency command is naught due to the leakage current
of the semiconductor devices.
(2) Measurement of Input voltage and Input / output current
Use moving iron type ampere meter. (Refer to Fig. 7-3 and Table 7-1.)
(3) Measurement of Input and output power
Use electrodynamics type watt meter for single phase use. Make measurements for all 3 phases is
case there is an unbalance in voltages and currents.
Fig. 7-2. Output voltage measurement circuit (without motor)
U
V
W
Frequency
Inverter
2W
220kohm
Additional resistor
5kohm 30W (200V class)
100W (400V class)
+
VDC
-
Fundamental wave
effective value : VAC = VDC * 1.1
Moving coil type DC Volt meter
300V (200V class)
600V (400V class)
Diode
600V 0.1A or above (200V class)
1000V 0.1A or above (400V class)
Fig. 7-3. Measurement Instruments
IR
ER
IS
ES
IT
ET
W11
W12
Frequency Inverter
L1
L2
L3 / N
IU
EU-V
IV
EV-W
IW
EU-W
WO1
WO2
Motor
L1
L2
L3 / N
U/T1
V/T2
W/T3
7-2

Table 7-1 Measuring Instruments
Item
Instruments
Type of Instrument
Remarks
Supply voltage
E1
EL1-L2, EL2-L3 and EL3-L1 Moving iron type voltmeter or
Rectifier type voltmeter
Fundamental wave
effective value
Supply current
I1
IL1, IL2 and IL3 Moving iron type ammeter Total effective value
Supply power
W1
W11 and W12 Electrodynamics wattmeter Total effective value
Supply power
Factor Pf1
Calculate from above measured values E1, I1 and W1
Pf W
EI
13100
1
11
=⋅⋅×(%)
Output voltage
Eo
EU-V, EV-W and EW-U According to Fig.7-1 and Fig.7-2 Total effective value
Output current
Io
IU, IV and IW Moving iron type ammeter Total effective value
Output power
Wo
WO1 and WO2 Electrodynamics wattmeter Total effective value
Output power
factor Pf2 Calculate from above measured values Eo, Io and Wo
Pf W
EI
O
OO
13100
=⋅⋅×(%)
NOTE : Use a meter indicating a fundamental wave effective value for voltage, and meters indicating
total effective values for current and power.
7-3

7-3. Maintenance of Parts
(1) Maintenance of printed circuit board (I/O board)
Printed circuit boards are maintenance free under normal applications except ALARAM relay
(hardware). However, in case which maintenance and inspection are necessary, pay attention to
the prevention of damage caused by static electricity as shown below.
* Prevent damage caused by static electricity
MCU and LSI on the printed circuit board can be destroyed by static electricity. Therefore be
sure to ground work benches, soldering irons and yourself before start working on a printed
circuit board.
(2) Maintenance of DC bus capacitor and cooling fan
We recommend that DC bus capacitors and cooling fans to be regularly replaced every three years
taking their lives into account. Please note that their life span shorten when they are used in high
temperatures and heavy loads.
7-4. If you install replacement INV at site
If you install replacement units at site, please preset the parameter by the panel or copy unit.
If you used the previous I/O board to replacement unit, the parameters are not changed.
Because parameters are memorized in the EEPROM on the control board on J100 /J300 series, and if
we used the previous control board to replacement unit at site to minimize the time. In case of
L100,SJ100 series, EEPROM is on the ISPM, even we replaced I/O board, the parameter is still the
same.
Capacitor Life Curve
0
210
-10
20
10
Ambient
temperature (deg)
40 12 hours a day
operation
Capacitor life time (year)
30
436587109
When the inverter is installed in a cabinet,
ambient temperature is the temperature in
the cabinet.
7-4/E

8. Daily Inspection and Periodical Inspection
Inspection
point
Item
Contents
Cycle
Method
Criteria
Standard
replacement
Instruments
daily periodic
period
Overall Ambient
Environment Check ambient temperature,
humidity, dust, corrosive gas, oil mist,
etc.
9 Ambient temperature
: -10deg to 40deg,
no icing
Thermometer
Devices overall Check for abnormal vibrations and
noise.
9 Visual and aural
inspection Hygrometer
Power supply
voltage Check voltage between input lines. 9 Measure the
voltage
between input
terminals
No abnormalities.
Within its specification Tester
Main
circuit
Overall Check installation for looseness. 9 Tighten
Tightening torque
(except for terminal block)
M3: 0.5 - 0.6 N-m
M4: 0.98 - 1.3 N-m
Check for evidence of over heating in
the various components 9 Visual
inspection
Clean 9
Terminal block No damage 9 Visual
inspection No abnormalities
DC bus
capacitor Check for leaking liquid 9 Visual No abnormalities
Check for swelling
inspection
Relay Check for stuttering noise when
operation 9 Aural
inspection No abnormalities
Resistors Check for cracks or changes in color 9 Visual
inspection No abnormalities Tester
Cooling fan Check for abnormal vibration and
noise
9 -Rotate
manually while
power off
-Increase
tightening
- Smooth rotation
- No abnormalities
2 - 3 years
Check for dust
9 Visual
inspection
8-1

Inspection
point
Item
Contents
Cycle
Method
Criteria
Standard
replacement
Instruments
daily periodic
period
Control circuit Operation check Check the balance of the output
voltage of each phase to phase
without motor.
9 Measure the
output voltage
between U, V
and W
Within 2% of voltage
difference between each
phases.
See next
page
Perform a sequence protection
operation test and make sure that
there are no errors in the protection
and display circuits.
9 Simulate
operation of the
protection
circuit
Operate without any
trouble
Component
check including
PCB
No abnormal odor nor changes in
color. 9 Visual
inspection No abnormalities
No significant corrosion. 9
Capacitors on
I/O board No liquid leakage nor deformation. 9 Visual
inspection No abnormalities
Display Digital operation
panel - No illegible display
- No lack of character
- Segment failure of LEDs
9 Visual
inspection Normal operation.
Display is readable.
NOTE : 1. Life time of capacitor is affected by the ambient temperature. See Capacitor Life Curve in the following.
2. The frequency inverter must be cleaned periodically. If dust accumulates on the fan and heat sink, it can cause overheating.
3. See page 30 for the life time of the capacitor.
8-2/E

9. Image block diagram
(1). IMAGE BLOCK DIAGRAM OF L100-LFU,NFE INVERTER
MCU
REMORT OPERATOR
ISORATION
DC REACTOR
(OPTION)
N(-)
PD(+1)
P
(
+
)
T(L3)
S(L2)
R(L1) INVERTER
CONVERTER
*1
W(T3)
V(T2)
U(T1)
DRIVE CIRCUIT
DETECT V,I
POWER SUPPLY
MCU
EEPROM
COMMUNICATION
PORT
CORE INVERTER
(ISPM)
SERIAL
COMMUNICATION
HITACHI
USER INTERFACE
I/O BLOCK
(I/O board)
TERMINALS
OPERATION PANEL WITH
POTENTIOMETER
SUB CONDENCER BOARD
+
+
RS
EMC DIRECTIVE COMPLIANT WITH DEDICATED NOISE FILTER(OPTION)
9-1

(2). IMAGE BLOCK DIAGRAM OF L100-HFE,HFU INVERTER
MCU
REMORT OPERATOR
ISORATION
DC REACTOR
(OPTION)
N
(
-
)
PD(+1)
P(+)
T(L3)
S(L2)
R(L1) INVERTER
CONVERTER
*1
W(T3)
V(T2)
U(T1)
DRIVE CIRCUIT
DETECT V,I
POWER SUPPLY
MCU
EEPROM
COMMUNICATION
PORT
CORE INVERTER
(ISPM)
SERIAL
COMMUNICATION
HITACHI
USER INTERFACE
I/O BLOCK
(I/O board)
TERMINALS
OPERATION PANEL WITH
POTENTIOMETER
SUB CONDENCER BOARD
+
+
+
+
RS
EMC DIRECTIVE COMPLIANT WITH DEDICATED NOISE FILTER(OPTION)
9-2

(3). IMAGE BLOCK DIAGRAM OF L100-MFU INVERTER
MCU
REMORT OPERATOR
N(-)
P(+)
T(L3)
R(L1)
INVERTER
CONVERTER
*1
W(T3)
V(T2)
U(T1)
DRIVE CIRCUIT
DETECT V,I
MCU
EEPROM
CORE INVERTER
(ISPM)
SERIAL
COMMUNICATION
RUN
FUNC. 12STR
PRG
RUN
A
Hz
STOP
RESET
MAXMIN
POWER
HITACHI
ISORATION
POWER SUPPLY
COMMUNICATION
PORT
USER INTERFACE
I/O BLOCK
(I/O board)
SUB CONDENCER BOARD
TERMINALS
OPERATION PANEL WITH
POTENTIOMETER
+
+
+
EMC DIRECTIVE COMPLIANT WITH DEDICATED NOISE FILTER(OPTION)
9-3/E

10-1. Spare Parts list
No.Class Parts Code DWG.No. Parts Name Remarks Quantity Lot
1 D 254819 2T004353 2 Key PAD (HITACHI) For all models 110
2 D 254821 2T004372 1 Front case (S) L100-002,004NFE;NFU 110
2 D 254818 1T001784 1 Front case (L) L100-005--022NFE;NFU
L100-037--075LFU
L100-004--075HFE;HFU
L100-002--007MFU
110
3 D 254869 3T015677 1 Key cover For all models 110
4 D 254831 4T013420 1 Volume KNOB For all models 110
5 D 254830 4T013419 1 Top cover (S) L100-002,004NFE;NFU 110
5 D 254832 4T013459 1 Top cover (L) L100-005--022NFE
L100-007--022NFU;037LFU
L100-004--040HFE;HFU
Except Japanese version and
L100-MFU
110
5 D 254872 3T016369 1 Top cover (LL) L100-055,075LFU;HFE;HFU 110
6 D 254820 2T004371 1 Case (S) L100-002,004NFE;NFU 110
6 D 254817 1T001783 1 Case (M) L100-005,007NFE
L100-007NFU
L100-004--015HFE;HFU
L100-002
,
004MFU
110
6 D 254816 1T001782 1 Case (L) L100-011--022NFE
L100-015,022NFU;037LFU
L100-022--040HFE;HFU
L100-007MFU
110
6 D 254866 1T001858 1 Case (LL) L100-055,075LFU;HFE;HFU 110
7 D 254829 4T013417 1 Rear cover (S) L100-002,004NFE;NFU 110
7 D 254825 3T015700 1 Rear cover (L) L100-005--022NFE
L100-007--022NFU;037LFU
L100-004--040HFE;HFU
L100-002--007MFU
110
7 D 254871 3T016368 1 Rear cover (LL) L100-055,075LFU;HFE;HFU 110
8 D 254826 3T015710 1 Condensor cover (L) L100-011--022NFE
L100-015,022NFU;037LFU
L100-022--040HFE;HFU
L100-007MFU
110
8 D 254868 2T004495 1 Condensor cover (LL) L100-055,075LFU;HFE;HFU 110
10-1

No.Class Parts Code DWG.No. Parts Name Remarks Quantity Lot
9 C 254270 3T012518 2 Cooling fan L100-015,055,075HFE;HFU
L100-015,055LFU 13
9 C 254270 3T012518 2 Cooling fan L100-075LFU 23
9 D 254822 3T011924 4 Cooling fan L100-022NFE;NFU
L100-037LFU
L100-022--040HFE;HFU
13
10 D 254827 4T013337 1 ISPM-IO Cable (S) L100-002--022NFE;NFU
L100-004--040HFE;HFU
L100-037LFU
110
10 254828 4T013337 4 ISPM-IO Cable (L) L100-055,075LFU;HFE;HFU 110
11 --- 3T015514 3 ISPM (without PCB2) L100-002NFE;NFU 11
11 -- 3T015516 3 ISPM (without PCB2) L100-004NFE;NFU 11
11 -- 3T015523 3 ISPM (without PCB2) L100-005,007NFE
L100-007NFU 11
11 -- 3T015520 3 ISPM (without PCB2) L100-011,015NFE
L100-015NFU 11
11 -- 3T015522 3 ISPM (without PCB2) L100-022NFE;NFU 11
11 -- 3T015524 3 ISPM (without PCB2) L100-037LFU 11
11 -- 3T016566 2 ISPM (without PCB2) L100-055LFU 11
11 -- 3T016567 2 ISPM (without PCB2) L100-075LFU 11
11 -- 3T015526 1 ISPM (without PCB2) L100-004HFE;HFU 11
11 -- 3T015527 1 ISPM (without PCB2) L100-007HFE;HFU 11
11 -- 3T015528 1 ISPM (without PCB2) L100-015HFE;HFU 11
11 -- 3T015529 1 ISPM
(
without PCB2
)
L100-022HFE;HFU 1 1
11 -- 3T015530 1 ISPM (without PCB2) L100-030,040HFE
L100-040HFU 11
11 -- 3T016568 3 ISPM (without PCB2) L100-055HFE;HFU 11
11 -- 3T016569 3 ISPM (without PCB2) L100-075HFE;HFU 11
12 254890 4T013548 1 RS(soft charge resistor) L100-002--022NFE;NFU
L100-037,055LFU
L100-004--055HFE;HFU
L100-002--007MFU
110
12 254890 4T013548 1 RS(soft charge resistor) L100-075HFE;HFU;LFU 210
10-2

No.Class Parts Code DWG.No. Parts Name Remarks Quantity Lot
13 -- 4T013438 1 Copper bar L100-002,004NFE;NFU 110
13 -- 4T013439 1 Copper bar L100-005--022NFE
L100-007--022NFU
L100-037LFU
L100-004--040HFE;HFU
L100-002--007MFU
110
14 -- L100EUL I/O board L100-002--022NFE;NFU
L100-037LFU
L100-004--040HFE;HFU
L100-002--007MFU
11
14 --- L100 075EUL I/O board L100-055,075LFU
L100-055,075HFE;HFU 11
15 -- CB470 Capacitor board L100-011,015NFE
L100-015NFU
L100-037LFU
11
15 -- CB680 Capacitor board L100-022NFE;NFU 11
15 -- CB470H Capacitor board L100-030,040HFE
L100-040HFU 11
15 -- CB680M Capacitor board L100-007MFU 11
15 -- CB68X4L Capacitor board L100-055LFU 11
15 -- CB68X6L Capacitor board L100-075LFU 11
15 -- CB68X4H Capacitor board L100-055HFE;HFU 11
15 -- CB68X6H Capacitor board L100-075HFE;HFU 11
16 --- CB330A PCB2 L100-002NFE;NFU 11
16 --- CB680A PCB2 L100-004NFE;NFU 11
16 --- CB560B2 PCB2 L100-005,007NFE;
L100-007NFU 11
10-3

No.Class Parts Code DWG.No. Parts Name Remark Quantity Lot
16 --- CB470B2T PCB2 L100-011,015NFE
L100-015NFU
L100-037LFU
11
16 --- CB680B2T PCB2 L100-022NFE;NFU 11
16 --- L100SB055L PCB2 L100-055LFU 11
16 --- L100SB075L PCB2 L100-075LFU 11
16 --- CB180B4 PCB2 L100-004HFE;HFU 11
16 --- CB270B4 PCB2 L100-007HFE;HFU 11
16 --- CB470B4 PCB2 L100-015HFE;HFU 11
16 --- CB680B4 PCB2 L100-022HFE;HFU 11
16 --- CB470B4 PCB2 L100-030,040HFE
L100-040HFU 11
16 --- L100SB055H PCB2 L100-055HFE;HFU 11
16 --- L100SB075H PCB2 L100-075HFE;HFU 11
16 --- CB1000B2 PCB2 L100-002MFU 11
16 --- CB1800B2 PCB2 L100-004MFU 11
16 --- CB1800B2T PCB2 L100-007MFU 11
Note No.10 4T013337 3 is usable for 4T01337 4. The difference is the length.
No.13 The copper bar is used between ISPM and heatsink.
C/H version is applied US version except key pad/knob/cover/case etc.
(S) ; 002NFE,004NFE,002NFU,004NFU
(M) ; 005NFE,007NFE,004HFE,007HFE,015HFE,007NFU,004HFU,007HFU,015HFU
(L) ; 011NFE,015NFE,022NFE,015NFU,022NFU,022HFE,030HFE,040HFE,022HFU,040HFU,037LFU
(LL) ; 055HFE,075HFE,055LFU,075LFU,055HFU,075HFU
This spare parts list will be changed without notice. To get latest spare parts list, please contact to sales office.
This service manual may not be revised if the spare parts list was revised.
10-4

10-5
No. Parts name Quantity
1 Keypad 1
2 Front case (L) 1
3Key cover 1
4 Volume knob 1
5 Top cover (S) 1
6 Case (S) 1
7 Rear cover (S) 1
10 ISPM – IO cable (S) 1
11 ISPM 1
12 RS 1
14 I/O board 1
16 PCB2 1
L100-002NFE
002NFU
004NFE
004NFU

10-6
No. Parts name Quantity
1 Keypad 1
2 Front case (L) 1
3Key cover 1
4 Volume knob 1
5 Top cover (L) 1
6 Case (M) 1
7 Rear cover (L) 1
10 ISPM – IO cable (L) 1
11 ISPM 1
12 RS 1
14 I/O board 1
16 PCB2 1
L100-004HFE
004HFU
005NFE
007NFE
007NFU

10-7
No. Parts name Quantity
1 Keypad 1
2 Front case (L) 1
3Key cover 1
4 Volume knob 1
5 Top cover (L) 1
6 Case (M) 1
7 Rear cover (L) 1
10 ISPM – IO cable (L) 1
11 ISPM 1
12 RS 1
14 I/O board 1
16 PCB2 1
L100-007HFE
007HFU

10-8
No. Parts name Quantity
1 Keypad 1
2 Front case (L) 1
3Key cover 1
4 Volume knob 1
5 Top cover (L) 1
6 Case (M) 1
7 Rear cover (L) 1
8 Cooling fan (L) 1
10 ISPM – IO cable (L) 1
11 ISPM 1
12 RS 1
14 I/O board 1
16 PCB2 1
L100-015HFE
015HFU

10-9
No. Parts name Quantity
1 Keypad 1
2 Front case (L) 1
3Key cover 1
4 Volume knob 1
5 Top cover (L) 1
6 Case (L) 1
7 Rear cover (L) 1
8 Condensor cover 1
10 ISPM – IO cable (L) 1
11 ISPM 1
12 RS 1
14 I/O board 1
15 Capacitor board 1
16 PCB2 1
L100-011NFE
015NFE
015NFU

10-10
No. Parts name Quantity
1 Keypad 1
2 Front case (L) 1
3Key cover 1
4 Volume knob 1
5 Top cover (L) 1
6 Case (L) 1
7 Rear cover (L) 1
8 Condensor cover 1
9 Cooling fan (L) 1
10 ISPM – IO cable (L) 1
11 ISPM 1
12 RS 1
14 I/O board 1
15 Capacitor board 1
16 PCB2 1
L100-022NFE
022NFU
030HFE
037LFU
040HFE
040HFU

No. Parts name Quantity
1 Keypad 1
2 Front case (L) 1
3Key cover 1
4 Volume knob 1
5 Top cover (L) 1
6 Case (L) 1
7 Rear cover (L) 1
8 Condensor cover 1
9 Cooling fan (L) 1
10 ISPM – IO cable (L) 1
11 ISPM 1
12 RS 1
14 I/O board 1
16 PCB2 1
L100-022HFE
022HFU
10-11

No. Parts name Quantity
1 Keypad 1
2 Front case (L) 1
3Key cover 1
4 Volume knob 1
5 Top cover (LL) 1
6 Case (LL) 1
7 Rear cover (LL) 1
8 Condensor cover (LL) 1
9 Cooling fan (S) 1
10 ISPM – IO cable (L) 1
11 ISPM 1
12 RS 1
14 I/O board 1
15 Capacitor board 1
16 PCB2 1
L100-055LFU
055HFU
075HFU
055HFE
075HFE
10-12

No. Parts name Quantity
1 Keypad 1
2 Front case (L) 1
3Key cover 1
4 Volume knob 1
5 Top cover (LL) 1
6 Case (LL) 1
7 Rear cover (LL) 1
8 Condensor cover (LL) 1
9 Cooling fan (S) 2
10 ISPM – IO cable (L) 1
11 ISPM 1
12 RS 1
14 I/O board 1
15 Capacitor board 1
16 PCB2 1
L100-075LFU
10-13

10-14
No. Parts name Quantity
1 Keypad 1
2 Front case (L) 1
3Key cover 1
4 Volume knob 1
6 Case (M) 1
7 Rear cover (L) 1
10 ISPM – IO cable (L) 1
11 ISPM 1
12 RS 1
14 I/O board 1
16 PCB2 1
L100-002MFU
004MFU

10-15
No. Parts name Quantity
1 Keypad 1
2 Front case (L) 1
3Key cover 1
4 Volume knob 1
6 Case (L) 1
7 Rear cover (L) 1
8 Condensor cover 1
10 ISPM – IO cable (L) 1
11 ISPM 1
12 RS 1
14 I/O board 1
15 Capacitor board 1
16 PCB2 1
L100-007MFU

10-2. I/O board compatibility
L100 series V: available - : not available
NOTE:B32 function is available from “L” or after .
NOTE: The “A” is not available from the others revision.
NOTE: L100EULH ”F” is available from L100EUL "G","J","K","M","P" .
I/O board Name “Revision”
002NFE-022NFE
002NFU-022NFU
037LFU
004HFE-040HFE
004HFU-040HFU
002LFR-037LFR
004HFR-037HFR
055HFE,075HFE
055LFU,075LFU
055HFU,075HFU
055LFR075LFR
055HFR,075HFR
L100EUL "A" V - - - - -
L100EUL "B","C","G","H","K","M","P" V - - - - -
L100EULH "F" - V - - - -
L100EUL "G","J","K","M","P" - V - - - -
L100L "D","E" ,"G","J","K","M","P" - - V - - -
L100L "G","J","K","M","P" - - - V - -
L100075EUL "L","N","P" - - - - V -
L100075L "L","N","P" - - - - - V
10-16

10-3. O,OI terminal adjustment procedure
If you need fine adjustment with out F31 IN EX%S, IN EX%E function(DOP/DRW), or A group A13,A14
function (on standard panel), please refer to following procedure.
Meaning
set C91 "01" ; Debug on
set C94 "F947" ; O terminal adjustment constant
set C95 "xx" ; adjust this data
power off and wait Power lamp off and power on and check the freq. setting.
(set C91 "01" ; Debug on)
set C94 "F948" ; OI terminal adjustment constant
set C95 "xx" ; adjust this data
power off and wait Power lamp off and power on and check the freq. setting.
set C91 "00" ; Debug off
If the data was added, the freq. setting will be increased. (concept is as same as J100,J300)
10-17

10-4. kW setup procedure
To set up kW, we advise you not to use DOP/DRW !
Meaning
set C91 "01" ; Debug on
set C94 "FAB0" ; kW adress
set C95 "xx" ; kW code
set B84 "01" ; to excecute FACTORY SETTING
Try FACTORY SETTING
Check B12' display (F-23 E-THM LVL)
B12's display table
kW | 200V | 400V
002 | 1.40 | ----
004 | 2.60 | 1.50
005,007 | 4.00 | 2.50
011,015 | 7.10 | 3.80
022 | 10.00 | 5.50
030,040 | 15.90 | 8.60
055 | 24.0 | 13.0
075 | 32.0 | 16.0
kW code table (common L100/SJ100)
xx | kW
01 | 002
02 | 004
03 | 005,007
04 | 011,015
05 | 022
06 | 030,040
07 | 055
08 | 075
In case of L100, SJ100, it automatically detects it's voltage class with hardware in the ISPM, voltage class
setup is not necessary.
10-18







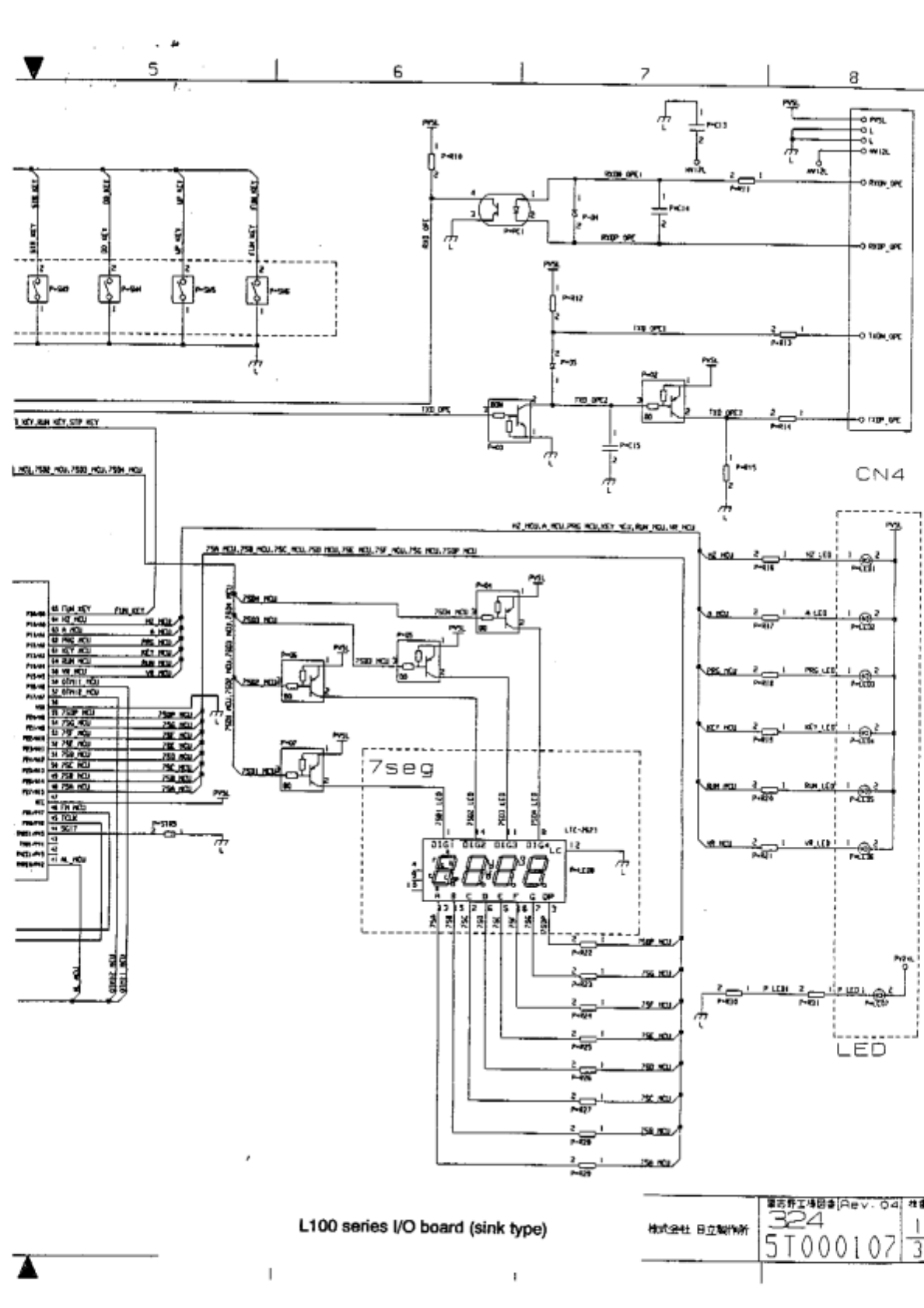


End of page