DL8000 Preset Hoja De Datos
User Manual: Hoja-de-Datos DL8000-Preset
Open the PDF directly: View PDF .
Page Count: 9
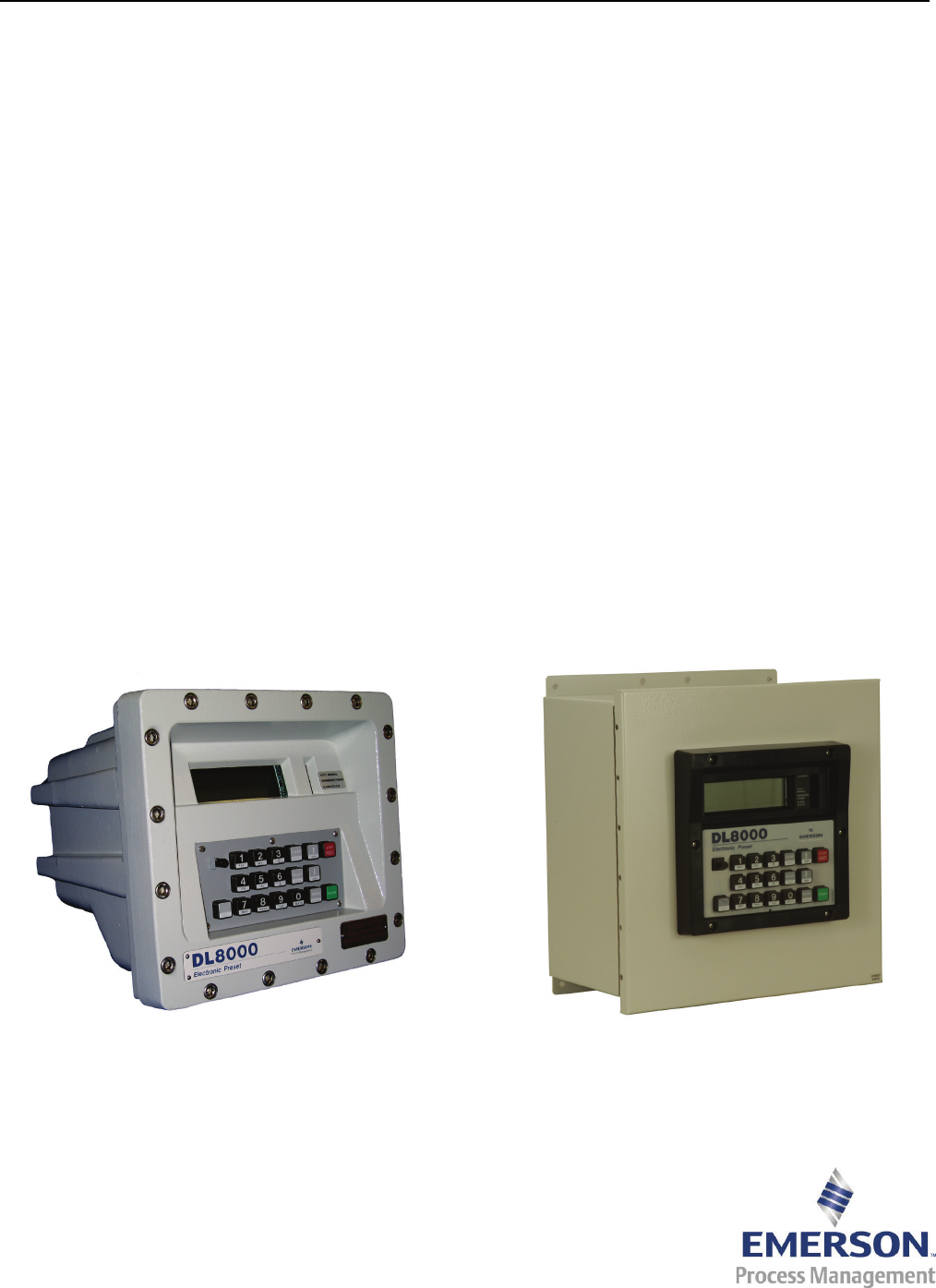
DL8000 Product Data Sheet
D301255X012 August 2012
Remote Automation Solutions
DL8000 Preset
The DL8000 Preset is a rugged electronic preset that
provides precise custody transfer batches for petroleum,
industrial chemicals, and other products. It accepts
volumetric and mass inputs from turbine, Coriolis,
ultrasonic, or other flow measurement devices using single
or linearized meter factors. (Pulse-generating meters are
recommended for improved valve closure accuracy.)
The DL8000 also performs density, temperature, and
pressure corrections using the latest standards and
accurately calculates delivered volumes at standard
conditions (60°F, 15°C, 20°C, or user-selectable) using
double precision math. The DL8000 can control and blend
up to four products sequentially or simultaneously (ratio
blending). It can control up to six additives through metered
injection, and can store up to 30 recipes for blending.
Density Correction
The DL8000 accepts density signals as a frequency, 4–20
mA, or through a communications device. It accepts inputs
from a flowing density meter (such as a Micro Motion
frequency densitometer or a Micro Motion Coriolis meter).
The DL8000 corrects observed density to standard
conditions and calculates the temperature and pressure
volume correction factors.
Temperature Compensation
The DL8000 can accept an input from an RTD, 4–20 mA, or
thermocouple device. It then calculates a temperature
volume correction factor in accordance with the following
standards:
API MPMS Chapter 11.1 (1980) / API2540 (1980) /
ASTM D1250 / ANSI D1250 / IP200
Tables: 5A, 5B, 5D, 6A, 6B, 6C, 6D, 23A, 23B, 23D, 24A,
24B, 24C, 24D, 53A, 53B, 53D, 54A, 54B, 54C, 54D.
API MPMS 11.1 (2004) / ASTM D1250-04 / IP200/04
ISO 91.1 (1992)
ISO 91.2 (1991) / IP3 (1988)
Tables: 59A, 59B, 59D, 60A, 60B, 60D.
GPA TP27 (2007) (supersedes TP-25) / API MPMS
Chapter 11.2.4
Tables: 23E, 24E, 53E, 54E, 59E, 60E.
DL8000 Preset
(Class I, Zone 1 Version)
DL8000 Preset
(Class I, Div. 2 Version)

August 2012 DL8000
2 www.EmersonProcess.com/Remote
Pressure Compensation
The DL8000 can accept a 4–20 mA signal from a pressure
transducer and compensate flow calculations for
volumetrics due to pressure in accordance with the
following standards:
API MPMS 11.1 (2004) / ASTM D1250-04 / IP200/04
API MPMS 11.2.1
API MPMS 11.2.2
API MPMS 11.2.1(M)
API MPMS 11.2.2(M)
Pulse Fidelity
The DL8000 monitors dual pulse inputs for integrity in
accordance with the following standards:
ISO 6551-1982 and BS 6439-1983
API Petroleum Measurement Standard, Chapter 5.5,
level B and Institute of Petroleum Standard, IP 252.76,
Part XIII, Section 1, Level B.
Meter Factor Linearization
The DL8000 can perform linearization of meter factors and K
factors using up to 12 points to ensure accuracy over the
entire range of flow.
Reporting
The DL8000 generates reports in compliance with NIST
Handbook 44 – 2006 Edition and 2003 Update and NCWM
Publication 14.
Other Features
Archival storage of 200 transactions with up to four
batches each and 450 alarms.
Storage of the last 1000 weights & measures events (in
accordance with NIST Handbook 44).
Integral Weights & Measures switch.
Independent permissive sensing AC power.
Digital valve control with automatic high flow rate
recovery.
Independent temperature compensation methods for
individual products.
Automatically sensing or user-entered values for
thermal expansion and linear equation.
User-entered vapor pressure of light hydrocarbons.
Operations
The DL8000’s user-friendly multi-language display prompts
the operator through the entire loading sequence, assuring
a safe and reliable loading operation. The loading sequence
starts after the operator connects the safety circuits, selects
a recipe, enters a preset quantity, and presses the Start
button. The DL8000 automatically turns on the required
product pumps and additive injection equipment and opens
the digital flow control valves.
A low-flow start sequence can be initiated to reduce static
build-up when delivering petroleum products. To keep
loading time to a minimum, the DL8000 automatically
maintains the highest possible flow rate the system can
deliver. When additives are present, the maximum flow rate
is 2700 units/minute. Three different flow profiles for each
recipe provide maximum system flexibility regardless of the
meter size. When certain recipes require small percentages
of one or more components, you can configure the
programmable flow profiles to automatically deliver small-
percentage component(s) only during the high flow stage of
the delivery.
As the end of the batch sequence approaches, the
component streams slow to a pre-defined low-flow/stop
flow rate. The high-speed digital valve control algorithm,
working in conjunction with the linear digital control valve,
ensures a smooth, repeatable, low-flow/final stop without
line shock.
To assure product quality, you can program an automatic
single product line-flush sequence at the end of the delivery
to flush the loading arm with a single base product.
Blend Recipes
Memory allows up to 30 blend recipes. Each recipe has
individual totalizers and is highly configurable, providing
maximum flexibility.
Linearization
Multi-point linearization is programmable with up to 12
points. The DL8000 automatically interpolates between the
12-meter factor setpoints to assure system accuracy over
the required flow ranges.
Vapor Recovery
Measures the amount of returned or recovered vapor during
the loading of light hydrocarbons, and computes the Net
delivered for billing purposes. This feature is available for
mass delivery only and the delivered quantity will be equal
to the preset amount.
Metered Additive Injection
Measures and controls the additive amount injected into the
product stream for up to ten additives. The injection site can
be selected as either upstream or downstream, and the
additive amount can be included in total or in addition to
the delivered quantity.
DanLoad 6000 Protocol Support
The DL8000 supports all terminal automation commands
necessary for terminal operation and some for terminal
automation configuration. In most cases, this allows you to

DL8000 August 2012
www.EmersonProcess.com/Remote 3
multi-drop your existing DanLoad 6000s with the DL8000
without changes to the host.
Swing Arm Position Detection
The DL8000 allows swing arm safety circuit operation, and
you have the option to select which side (one, two, or both)
is applicable per circuit.
Alarms
The DL8000 offers comprehensive alarms for blending
systems. You can define each alarm action for no action,
display only, close relay contact, stop loading process, or
lock the unit. Built-in programmable alarm conditions are
also user-selectable. You can also configure the reference
base temperature for compensation corrections.
Data Security
Data is secured with a 4-digit user-defined access code. All
calibration data is secured with the access code and a wire-
sealable mechanical security switch that is integrally
mounted in the DL8000 keypad.
Data Communications
The DL8000 has three built-in communication ports. The
unit can support up to three additional ports (via optional
communications cards) for a total of six ports. The built-in
communication ports are:
Local Operator Interface (RS-232D) – LOI.
Ethernet – Comm1.
EIA-232 (RS-232) – Comm2.
The Local Operator Interface (LOI) port’s standard RJ-45
connector provides an EIA-232 (RS-232D) link between the
CPU and a PC. Use ROCLINK™ 800 Configuration software to
configure the CPU, extract data, and monitor its operation.
All DL8000 ports support Modbus slave protocol; master
protocol is supported on all but the LOI and Ethernet ports.
Communications Modules
You can install up to three additional communication
modules in the DL8000 to provide ports for communicating
with a host computer or other devices. The DL8000
accommodates the following module types, in any
combination:
EIA-232 (RS-232).
EIA-422/EIA-485 (RS-422/RS-485).
Dial-up modem.
I/O Modules
The DL8000 supports a variety of I/O modules. You can add
up to nine optically isolated I/O modules as needed to satisfy
a wide variety of field I/O requirements. Available modules
include:
Alternating Current Input/Output (AC I/O).
Advance Pulse Module (APM) with densitometer
processing.
Analog Inputs (AI).
Analog Outputs (AO).
Discrete Inputs (DI).
Discrete Outputs (DO).
Discrete Output Relay (DOR).
HART Input/Output.
Pulse Inputs (PI) – High or Low speed.
RTD Inputs (RTD).
Note: CE approved I/O configurations are shown in the
Approvals section of the specifications table.
Product Options
The DL8000 product options consist of a Class I, Zone 1
flameproof version and a Class I, Division 2 Type 4 version.
Both versions contain the same keypad and display.
The Class I, Zone 1 version includes a cast aluminum casing
with sixteen stainless steel front cover bolts (M10 – 1.5
metric) that secure the lid to the housing. With the front
cover bolts removed, the lid hinges down to reveal the
electronic compartment. It is flame-proof (in accordance
with Class I, Zone 1, Groups IIB) and weatherproof (rated
IP66). The viewing window in the enclosure lid is made from
non-glare glass.
The Class I, Division 2 version includes a 14 gauge stainless
steel box with 12 gauge stainless steel mounting flanges.
The door is made of .090 inch thick aluminum and is secured
to the box via a stainless steel piano hinge and two stainless
steel spring latches. The latches include features for
padlocking or installing wire seals. The assembly includes a
door stop that locks the door in position at approximately
120 degrees from the closed position. The viewing window
in the enclosure door is made from scratch / UV resistant
polycarbonate/acrylic blend (PC/PMMA). The keypad bezel
is mounted to the front of the door and is made from UV
resistant polycarbonate. The assembly is rated by CSA as a
Type 4 enclosure.
The operator keypad is the same for both versions and
provides 18 rugged, Hall-effect push keys which are
impervious to chemicals commonly associated with
petroleum applications. A sealable Weights & Measures
switch provides security to flow measurement parameters.
The liquid crystal display (LCD) is the same for both versions
and provides an 8-line by 40-column message area for
operator interface. The display uses a photo sensor and
temperature sensor which can be set to automatically adjust
contrast and backlighting for optimal viewing.
Light-emitting diodes (LEDs) display the status of alarms,
operating mode, and permissive powers. LEDs are located to
the right of the display on both versions.
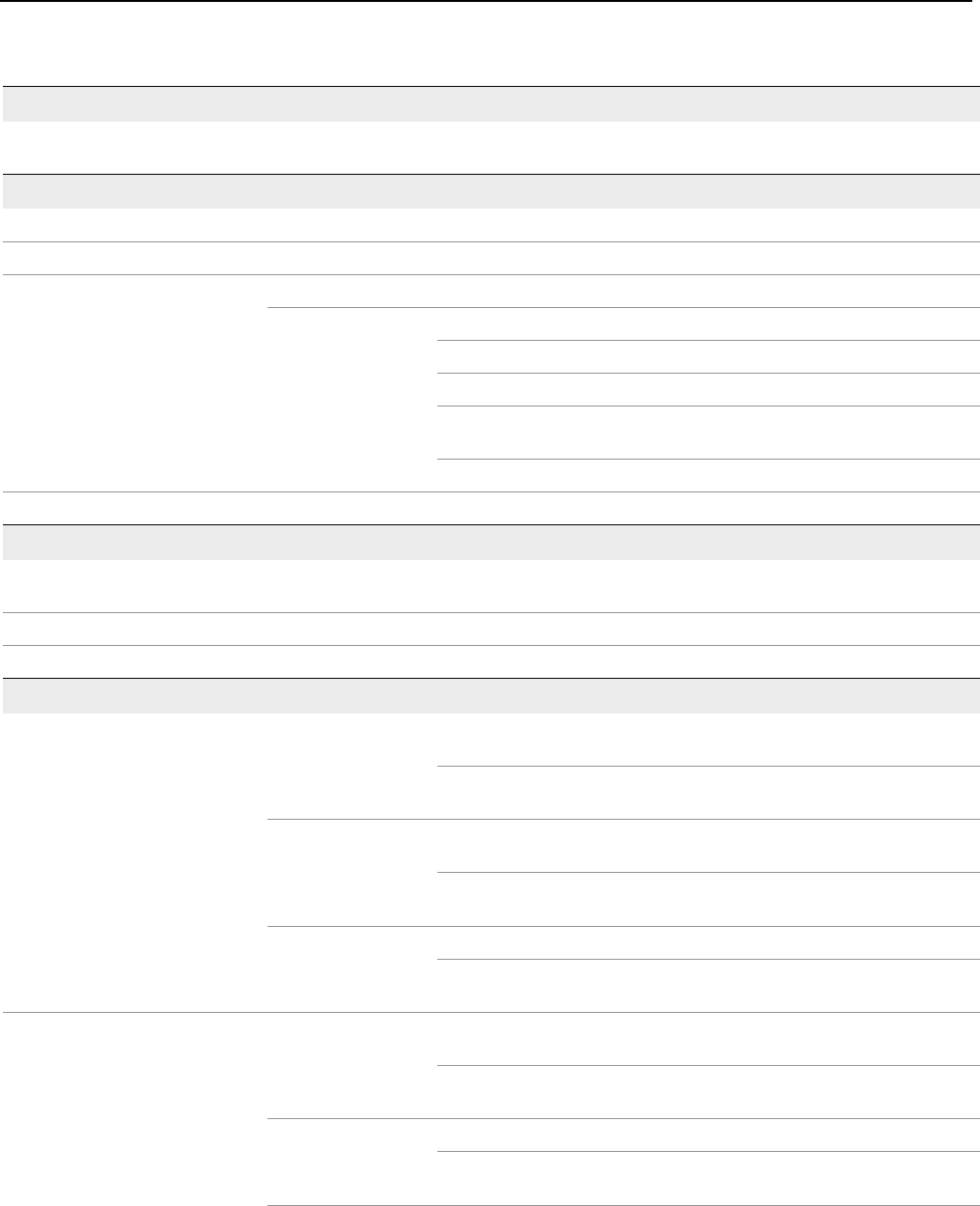
August 2012 DL8000
4 www.EmersonProcess.com/Remote
DL8000 Common Specifications
Processor
Type 32-bit microprocessor based on the Motorola MPC862 Quad Integrated Communications
Controller (PowerQUICC™) PowerPC processor running at 65 MHz
Memory
Boot Flash 256 KB for system initialization and diagnostics
Flash 16 MB for firmware image
SRAM 2 MB for historical data logs and configuration
Battery Backup User-replaceable
Type Sanyo 3 V CR2430 lithium
Normal use life 10 years while power is applied to unit
Backup life 1 year minimum while maintaining SRAM and RTC
data and no power is applied to unit
Shelf life 10 years (jumper disengaged)
Synchronous DRAM 32 MB for firmware execution and execution memory
Time Functions
Clock Type 32 KHz crystal oscillator with regulated supply, battery-backed, Year/Month/Day and
Hour/Minute/Second
Clock Accuracy 0.01%
Watchdog Timer Hardware monitor expires after 3 seconds and resets the processor
Communications
On Board EIA-232 (RS-232)
Port
Type Single
Maximum Data
Rate
57.6K bps
Ethernet Port 10BASE-T twisted pair. IEEE multi-segment 10 MB/second baseband
Ethernet.
Maximum
Segment
100 m (330 ft).
LOI Port Type EIA-232D (RS-232D) Standard
Maximum Data
Rate
57.6K bps
Modules (optional) EIA-232 (RS-232)
Module
Type Single
Maximum Data
Rate
57.6K bps
EIA-422/485
(RS-422/485)
Module
Type Single
Maximum Data
Rate
57.6K bps
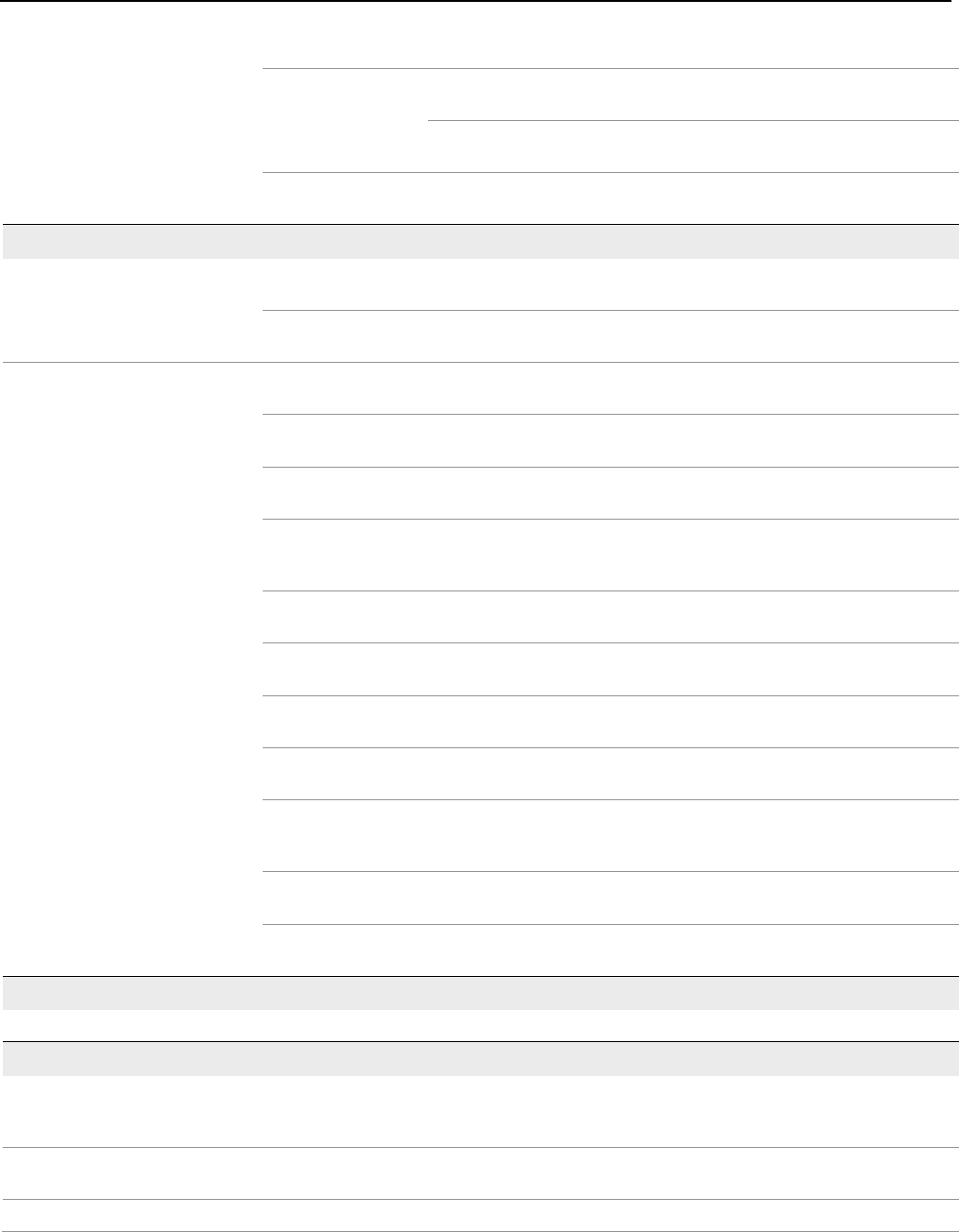
DL8000 August 2012
www.EmersonProcess.com/Remote 5
Modules (continued) Dial-Up Modem
Module
Type Single
Maximum Data
Rate
57.6K bps
Note: For more information about optional communications modules, refer to Technical
Specifications ROC800:COM.
Inputs/Outputs
On Board Board Temperature
Accuracy
1% typical, 2% maximum
Voltage Monitor
Accuracy
0.75% typical, 1% maximum
Modules (optional) Analog Input-12 4 channels, 12 bits of resolution. For more information, refer to
Technical Specifications ROC800:AI.
Analog Input-16 4 channels, 16 bits of resolution. For more information, refer to
Technical Specifications ROC800:AI.
Alternating Current
I/O
6 channels. For more information, refer to Technical Specifications
ROC800:ACIO.
Advance Pulse
Module
4 channels, 4 single or 2 dual (one configurable as a densitometer
input and one as a pulse output). For more information, refer to
Technical Specifications ROC800:APM.
Analog Output 4 channels. For more information, refer to Technical Specifications
ROC800:AO.
Discrete Input 8 channels. For more information, refer to Technical Specifications
ROC800:DI.
Discrete Output 5 channels. For more information, refer to Technical Specifications
ROC800:DO.
Discrete Output
Relay
5 channels. For more information, refer to Technical Specifications
ROC800:DOR.
HART Input/Output 4 channels, each capable of communications with up to 5 HART
devices (when in input multi-drop mode). For more information, refer
to Product Data Sheet ROC800:HART2.
Pulse Input 2 channels, user-selectable high speed or low speed per channel. For
more information, refer to Technical Specifications ROC800:PI.
RTD Input 2 channels. For more information, refer to Technical Specifications
ROC800:RTD.
Power
Requirements 115 to 240 V ac (+ 10%/– 15%), 50 to 60 Hz, 1-phase 30-watt nominal
Physical
Keypad 18 rugged, Hall-effect push keys which are impervious to chemicals commonly associated
with petroleum applications. A sealable Weights & Measures switch is incorporated into the
front panel to provide security to flow measurement parameters.
Display A single, 8-line by 40-column super-twist LCD display. Status LEDs identifying alarm,
permission power, and operational mode (Auto or Manual).
Wiring Size 12 to 22 AWG for terminal blocks
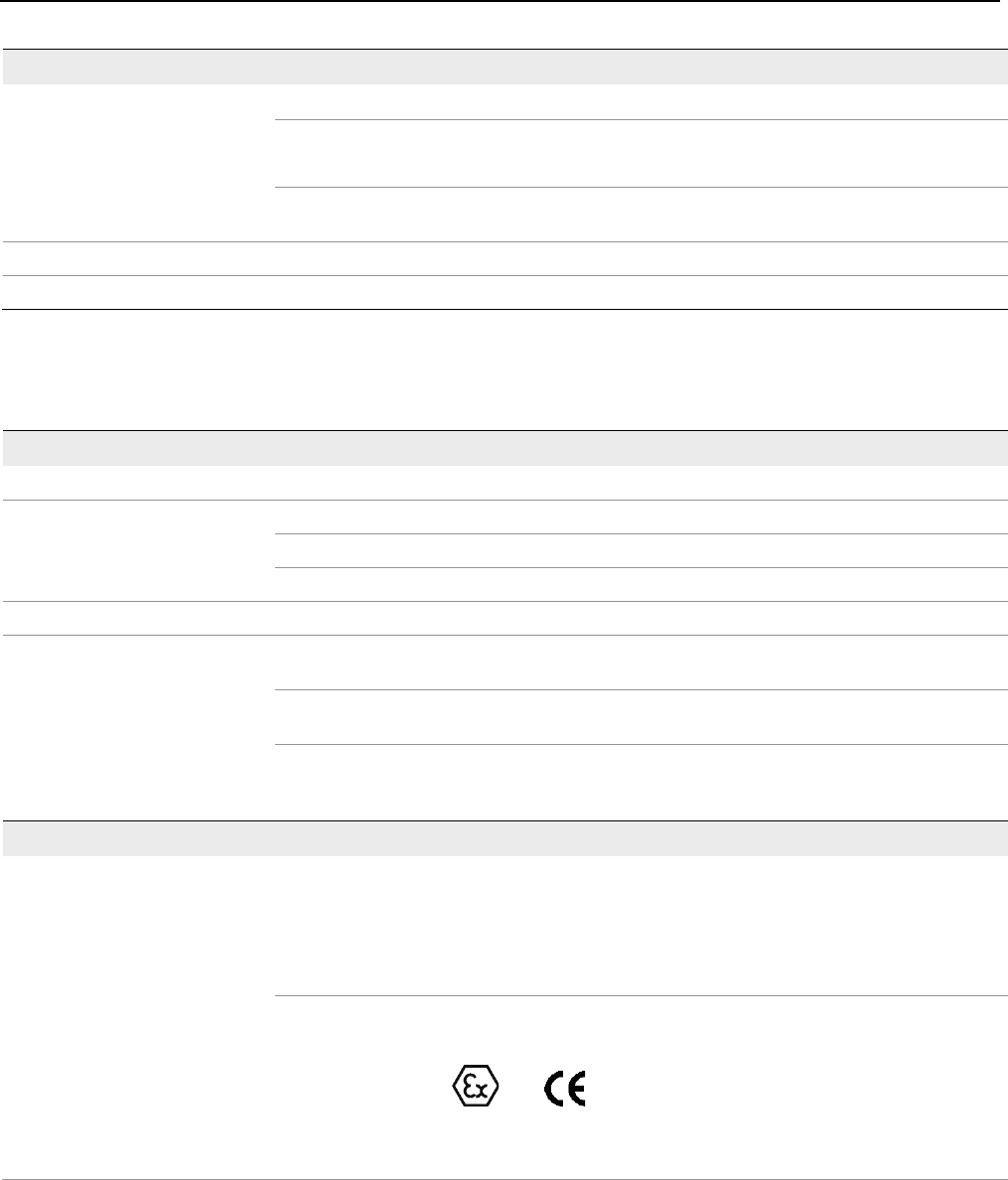
August 2012 DL8000
6 www.EmersonProcess.com/Remote
Environmental
Temperature Operating –20°C to +65°C (–4°F to +149°F)
Certified by NMI –25°C to +55°C (–4°F to +131°F)
Note: Class I, Zone 1 version only
Storage
(non-operating)
–30°C to +80°C (–22°F to +176°F)
Relative Humidity 5 to 95 percent (non-condensing)
Radiated/Conducted Immunity Meets requirements of IEC 61326 Electrical Equipment for use in industrial locations
Class I, Zone 1 Version Specifications
Physical
Construction Cast aluminum enclosure with sixteen stainless steel front cover bolts
Dimensions Height 330 mm (13 inches)
Width 355 mm (14 inches)
Depth 366 mm (14.4 inches)
Weight 34 kg (75 pounds)
Wiring Access Center 50 mm (2 in.) female NPSM; normally used for all DC signal (meter
pulse, RTD, analog, communication, or status/control) cabling
Left 25 mm (1 in.) female NPSM; normally used for AC power input and AC
status/control signals
Right 25 mm (1 in.) female NPSM; normally used for meter pulse, RTD,
communication, or analog signals when separate signal routing is
required
Approvals
Product Markings for Hazardous
Locations
CSA CUS IP66
Class I, Zone 1, Groups IIB flame-proof
Ex d IIB T6, AEx d IIB T6, (Ta=+65°C )
Certified by CSA as Model W40161
Certified by NTEP as Model W40161 per NTEP certification
number 08-056
CE Marked Certified by Sira as Model W40176
Certified by NMi as DL8000 (NMi version)
Ex d IIB T6 (Ta = +65°C), IP66
II 2 G 0081
ATEX Cert. Sira 08ATEX1063
IEC Cert. IECEx SIR 08.0019
NMi Evaluation Cert. TC7661 (NMi version)
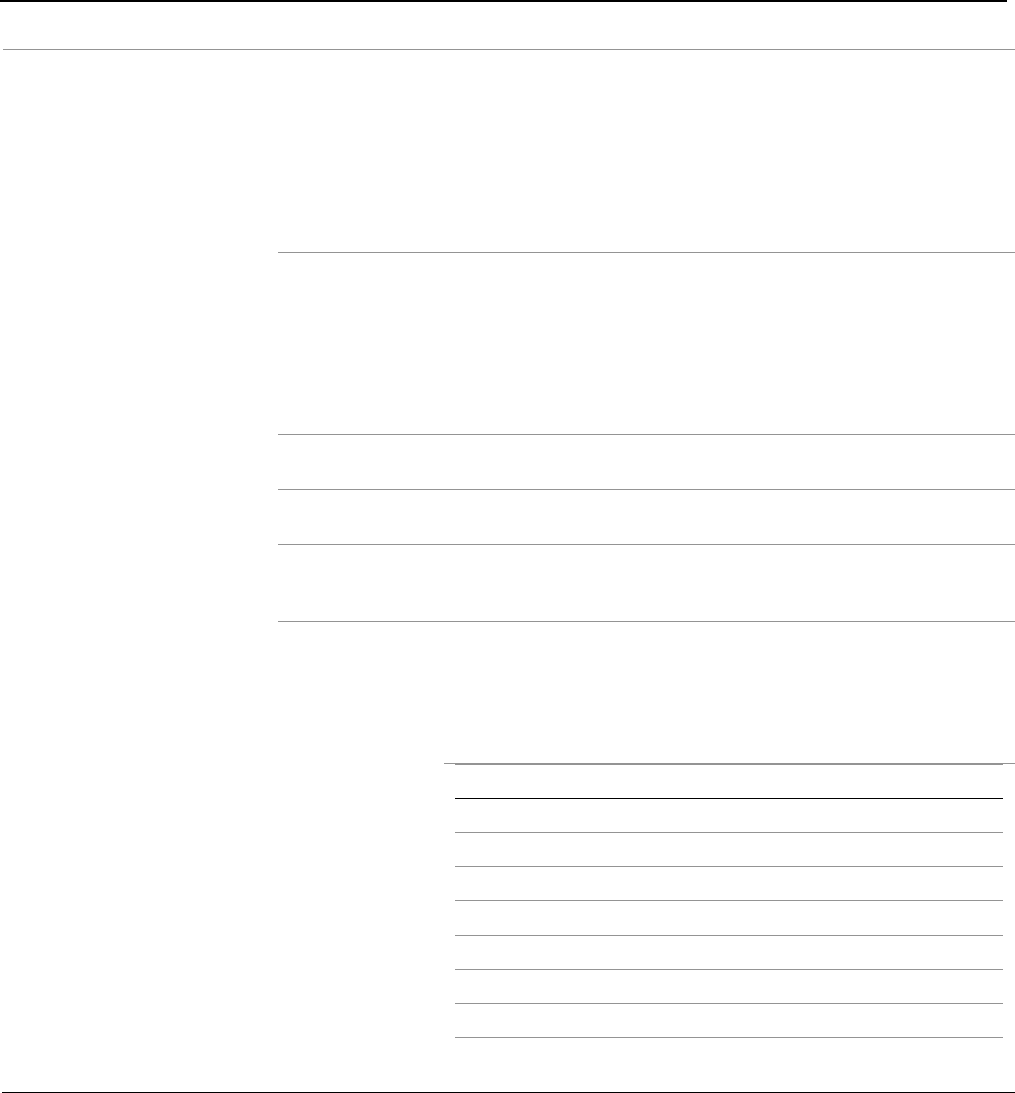
DL8000 August 2012
www.EmersonProcess.com/Remote 7
Certification Standards CSA/UL Standards CSA C22.2 No. 0-M91
CSA C22.2 No. 142-M1987
CSA C22.2 No. 60079-0-07
CSA C22.2 No. 60079-1-07
CSA 60529:05
UL913, 3rd Edition
UL 60079-0-2005
UL 60079-1-2005
IEC 60529:2004
EMC Standards EN 55011 (Emissions)
EN 61000-4-2 (Electrostatic Discharge Immunity)
EN 61000-4-3 (Electromagnetic Field Immunity)
EN 61000-4-4 (Electrical Fast Transients Immunity)
EN 61000-4-5 (Surge Immunity)
EN 61000-4-6 (Conducted Immunity)
EN 61000-4-8 (Magnetic Field Immunity)
EN 61000-4-11 (AC Voltage Dips + Interruptions).
ATEX Standards EN 60079-0:2006 Incl Corrigendum1
EN 60079-1:2007
IECEx Standards IEC 60079-0:2004 Edition 4.0
IEC 60079-1:2007-04 Edition 6
MID Standards
NMi version
OIML R117-1 Edition 2007 (E)
WELMEC 8.8
WELMEC 7.2, Issue 3
Valid I/O
Configurations for
ATEX/IECEx (CE)
Approval
Notes:
To maintain CE approval, you can
only
use the following I/O
modules connected to the valid I/O types as shown in the table
below.
Review the corresponding certificates to ensure full compliance.
I/O Modules I/O Type 1 I/O Type 2
AI-12 Pressure Density
DI Feedback Signals
RS 485 Communication
RTD Temperature
DO Control Signals
APM Pulse In (level B)
HART Temperature
AC I/O Control Signals
(output)
Feedback Signals
(input)
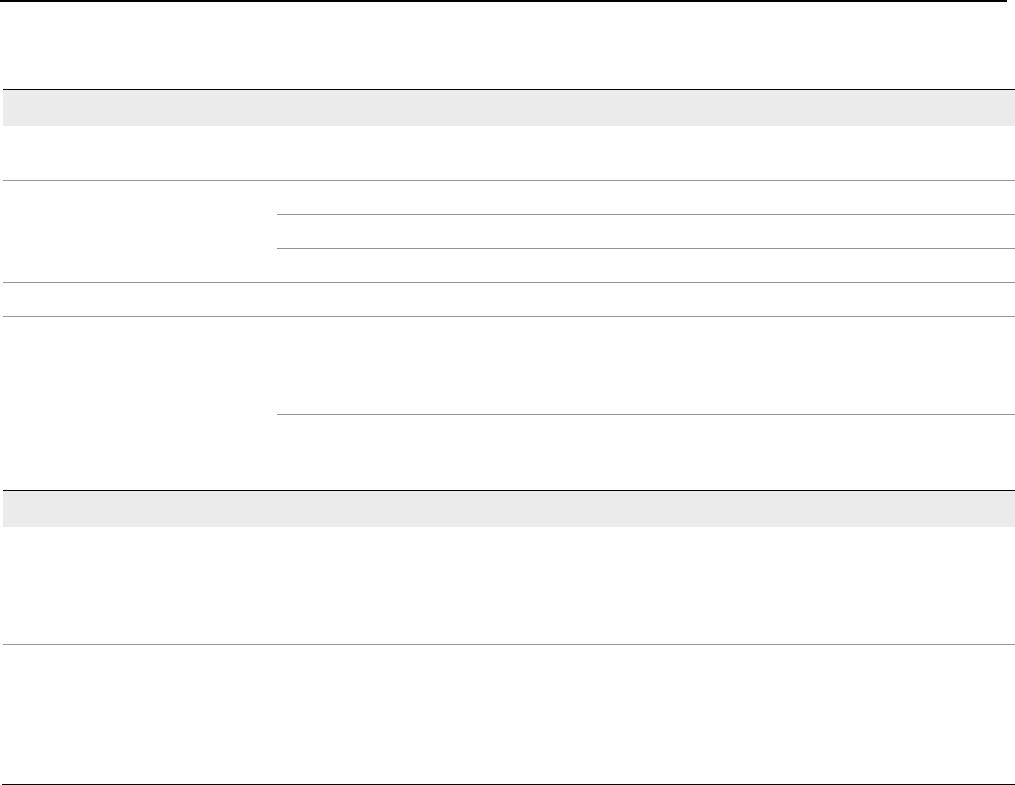
August 2012 DL8000
8 www.EmersonProcess.com/Remote
Class I, Division 2 Version Specifications
Physical
Construction 14 gauge, painted, stainless steel enclosure with 3 mm (0.12 inches) thick aluminum door
and stainless steel spring catches
Dimensions Height 432 mm (17 inches)
Width 410 mm (16.14 inches)
Depth 276 mm (10.86 inches)
Weight 16 kg (36 pounds)
Wiring Access Center Two 35 mm (1.375 inches) diameter holes for customer supplied 1-
inch Type 4 rated conduit hub; normally used for I/O. Four additional
center punch locations included to aid customer placement of
additional entries.
Right 35 mm (1.375 inches) diameter hole for customer supplied 1-inch Type
4 rated conduit hub; normally used for AC power input and AC
status/control signals.
Approvals
Product Markings for Hazardous
Locations
CSA CUS Class I, Division 2, Groups A, B, C, & D T4
CSA Type 4 Enclosure
Certified by CSA as Model W40201
Certified by NTEP as Model W40201 per NTEP certification number 08-
056
Certification Standards CSA/UL Standards CSA C22.2 No. 0-M91
CSA C22.2 No. 94
CSA C22.2 No. 142
CSA C22.2 No. 213
UL 50, 11th Edition
UL 1604, 3rd Edition
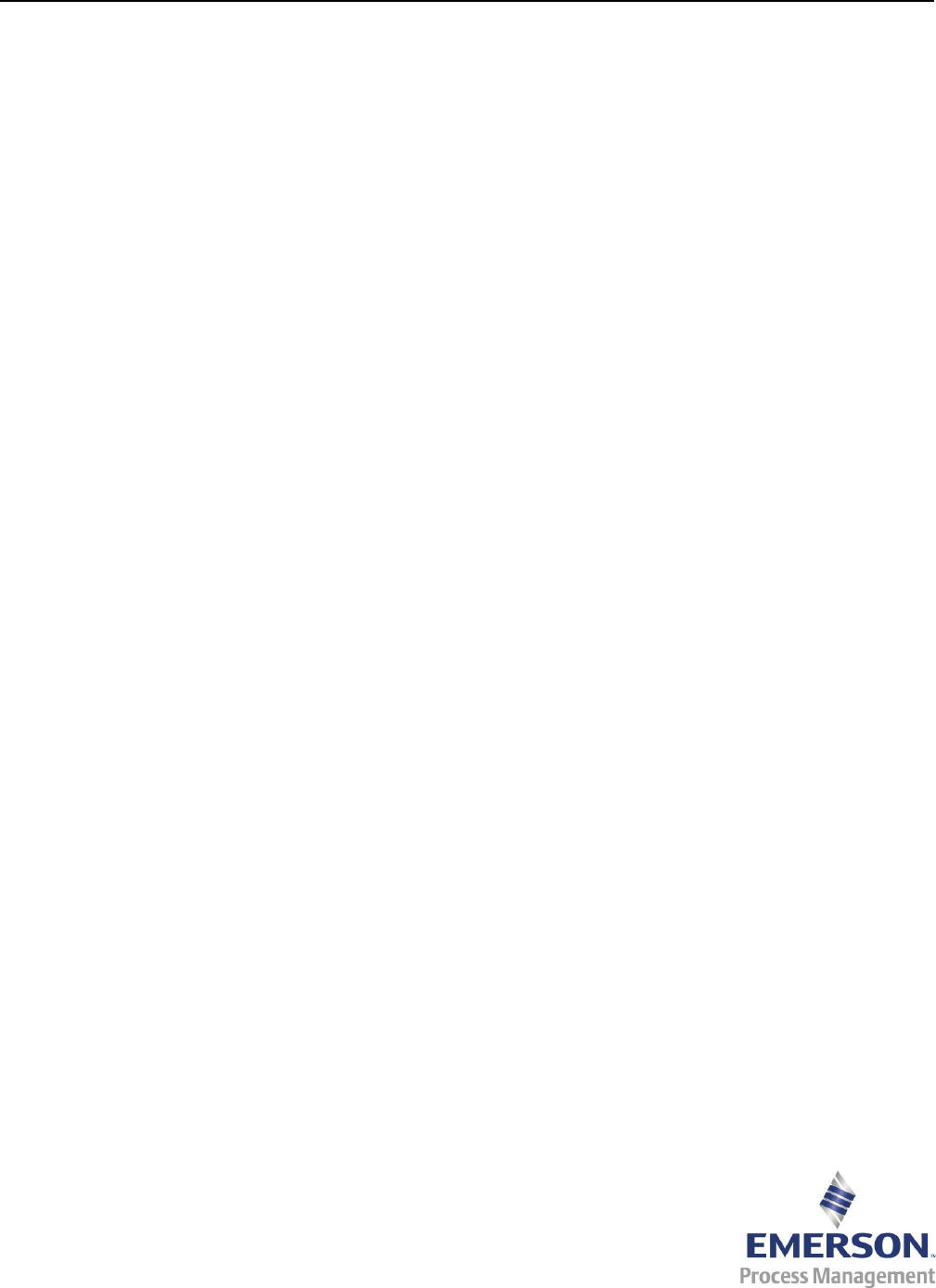
DL8000 August 2012
Headquarters:
Emerson Process Management
Remote Automation Solutions
6005 Rogerdale Road
Houston, TX 77072 U.S.A.
T +1 281 879 2699 | F +1 281 988 4445
www.EmersonProcess.com/Remote
© 2007-2012 Remote Automation Solutions, a business unit of Emerson Process
Management. All rights reserved.
Bristol, Inc., Bristol Canada, BBI SA de CV and Emerson Process Management Ltd, Remote
Automation Solutions division (UK), are wholly owned subsidiaries of Emerson Electric Co.
doing business as Remote Automation Solutions, a business unit of Emerson Process
Management. FloBoss, ROCLINK, Bristol, Bristol Babcock, ControlWave, TeleFlow, Helicoid,
OpenEnterprise, and METCO are trademarks of Remote Automation Solutions. AMS,
PlantWeb and the PlantWeb logo are marks of Emerson Electric Co. The Emerson logo is a
trademark and service mark of the Emerson Electric Co. All other marks are property of their
respective owners.
The contents of this publication are presented for informational purposes only. While every
effort has been made to ensure informational accuracy, they are not to be construed as
warranties or guarantees, express or implied, regarding the products or services described
herein or their use or applicability. Remote Automation Solutions reserves the right to modify
or improve the designs or specifications of such products at any time without notice. All sales
are governed by Remote Automation Solutions’ terms and conditions which are available
upon request. Remote Automation Solutions does not assume responsibility for the
selection, use or maintenance of any product. Responsibility for proper selection, use and
maintenance of any Remote Automation Solutions product remains solely with the purchaser
and end-user.
Europe:
Emerson Process Management
Remote Automation Solutions
Emerson House
Kirkhill Drive Kirkhill Industrial Estate
Aberdeen UK AB21 OEU
T +44 1224 215700 | F +44 1224 215799
www.EmersonProcess.com/Remote
North American/Latin America:
Emerson Process Management
Remote Automation Solutions
6005 Rogerdale Road
Houston TX USA 77072
T +1 281 879 2699 | F +1 281 988 4445
www.EmersonProcess.com/Remote
Middle East/Africa:
Emerson Process Management
Remote Automation Solutions
Emerson FZE
P.O. Box 17033
Jebel Ali Free Zone – South 2
Dubai U.A.E.
T +971 4 8118100 | F +971 4 8865465
www.EmersonProcess.com/Remote
Asia-Pacific:
Emerson Process Management
Remote Automation Solutions
1 Pandan Crescent
Singapore 128461
T +65 6777 8211| F +65 6777 0947
www.EmersonProcess.com/Remote
Remote Automation Solutions