USR_ProductName MMS 223 Philips Intelli Vue MP20,MP30 Patient Monitor Service Manual
User Manual: MMS 223
Open the PDF directly: View PDF .
Page Count: 310 [warning: Documents this large are best viewed by clicking the View PDF Link!]
- Introduction
- Theory of Operation
- Testing and Maintenance
- Introduction
- Terminology and Definitions
- Recommended Frequency
- When to Perform Tests
- Testing Sequence
- Visual Inspection
- Safety Tests
- Warnings, Cautions, and Safety Precautions
- Safety Test Procedures
- Hints for Correct Performance of Safety Tests
- Guideline for Performance of Safety Tests
- Safety Test Adapter Cable - Schematics
- S(1): Protective Earth Resistance Test
- S(2): Equipment Leakage Current Test - Normal Condition
- S(3): Equipment Leakage Current Test - Single Fault Condition
- S(4): Applied Part Leakage Current - Mains on Applied Part
- System Test
- Preventive Maintenance Procedures
- Performance Assurance Tests
- Basic Performance Assurance Test
- Full Performance Assurance Test
- ECG/Resp Performance Test
- ECG Sync Performance Test
- SpO2 Performance Test
- NBP PerformanceTest
- Invasive Pressure Performance Test
- Temperature Performance Test
- M3014A Capnography Extension Performance Tests
- Microstream CO2 Performance Test
- BIS Performance Test
- Nurse Call Relay Performance Test
- Power Loss Alarm Buzzer Performance Test (only if Multi-Port Nurse Call Connector Board is installed)
- Docking Station Performance Test
- IIT Communication Test
- IntelliVue 802.11 Bedside Adapter Communication Test
- Reporting of Test Results
- Other Regular Tests
- Touchscreen Calibration
- Disabling/Enabling Touch Operation
- Printer Test Report
- Battery Handling, Maintenance and Good Practices
- After Installation, Testing or Repair
- Troubleshooting
- Introduction
- How To Use This Section
- Who Should Perform Repairs
- Replacement Level Supported
- Software Revision Check
- Obtaining Replacement Parts
- Troubleshooting Guide
- Checks for Obvious Problems
- Checks Before Opening the Instrument
- Troubleshooting Tables
- How to use the Troubleshooting tables
- Boot Phase Failures
- Integrated Display is blank
- Integrated Touch Display not functioning
- External Display is blank (Slave Display)
- External Touch Display not functioning
- General Monitor INOP Messages
- Remote Alarm Device
- Remote Extension Device
- Navigation Point
- Keyboard/Mouse not functioning
- Battery related problems
- Bedside Network Status Icons
- Network related problems
- Wireless Ethernet Adapter (Proxim)
- IIT-related Problems
- IntelliVue 802.11 Bedside Adapter Problems
- Multi-Measurement Module
- MSL-related problems
- Alarm Issues
- Alarm Lamps
- Alarm Tones
- Alarm Behavior
- Individual Parameter INOPS
- Printer
- Recorder
- MIB / RS232
- USB
- Flexible Nurse Call Relay
- Basic Nurse Call Relay
- Troubleshooting the ECG OUT
- Docking Station Problems
- Image Sticking
- Data Flow Marker In and ECG Wave
- Status Log
- List of Error Codes
- Troubleshooting with the Support Tool
- Troubleshooting the Individual Measurements or Applications
- Repair and Disassembly
- Tools required
- How to find the Correct Procedure
- Removing Directly Accessible Parts
- 2.0 Opening the Front of the Monitor
- 2.1 Removing the Backlight Tubes
- 2.2 Removing the Backlight Inverter Board
- 2.3 Removing Power On LED board and Silicon Pad
- 2.4 Removing the HIF Board, Silicon Pad and Spacer
- 2.5 Removing the Flex Adapter Cable
- 2.6 Removing the Battery Board
- 2.7 Removing Recorder Board Assembly
- 2.8 Removing the Loudspeaker
- 2.9 Removing the Branding Cover
- 3.0 Separating the Front and Back Half of the Monitor
- 3.1 Removing the LCD Flat Panel Display, Touch Panel and Front Housing
- 3.2 Removing the Main Board
- 3.3 Removing the MSL Assembly
- 3.4 Removing the Power Supply
- 3.5 Removing the Frame Housing and Serial Number Plate
- Multi-Measurement Module (MMS) Disassembly
- Tools required
- Removing the Front Cover
- Removing the Mounting Pin
- Removing the Top Cover
- Removing the DC/DC Board
- Removing the MSL Flex Assembly
- Reassembling the MSL Flex Assembly
- Removing the NBP pump
- Refitting the new NBP Pump
- Refitting the DC/DC board
- Refitting the Cover
- Refitting the Front Cover
- Final Inspection
- MMS Extensions - Exchanging the Top Cover, MSL Flex Cable and the Dual Link Bar
- Disassembly Procedures for the M3015A MMS Extension (HW Rev. A)
- Smart Battery Charger LG1480 (M8043A)
- IntelliVue Instrument Telemetry (IIT)
- Docking Station
- Parts
- MP20/MP30 Parts
- Multi-Measurement Module (MMS) Parts
- MMS Extension Parts (M3012A, M3014A, M3015A and M3016A)
- IntelliVue X2 Part Numbers
- Smart Battery Charger Part Numbers
- IntelliVue Instrument Telemetry Part Numbers
- IntelliVue 802.11 Bedside Adapter Part Numbers
- Docking Station Part Numbers
- External Display Part Numbers
- Remote Alarm Device Part Numbers
- Remote Extension Device Part Numbers
- Installation Instructions
- Installation Checklist
- Unpacking the Equipment
- Initial Inspection
- Connecting the Monitor to AC Mains
- Installing the Docking Station
- Installing Remote Devices
- Philips Clinical Network (Wired)
- Philips Clinical Network (Wireless)
- Nurse Call Relay
- ECG Out Functionality
- Configuration Tasks
- Checking Country-Specific Default Settings
- Setting Altitude, Line Frequency, ECG Cable Colors and Height & Weight Units
- Setting Altitude and Line Frequency
- Configuring the Equipment Label
- Configuring the printer
- Configuring IP Address, Subnet Mask and Default Gateway
- Configuration Settings for CSCN Routed Bedside Monitors (RBM)
- Configuring Routed Bedside Monitors Support
- Handing Over the Monitor
- Site Preparation
- Introduction
- Monitor M8001A and M8002A Site Requirements
- Remote Device Site Requirements
- Philips Medical LAN
- RS232/MIB/LAN Interface
- Nurse Call Relay Interface
- ECG Out Interface
- Gas Analyzers
- Index
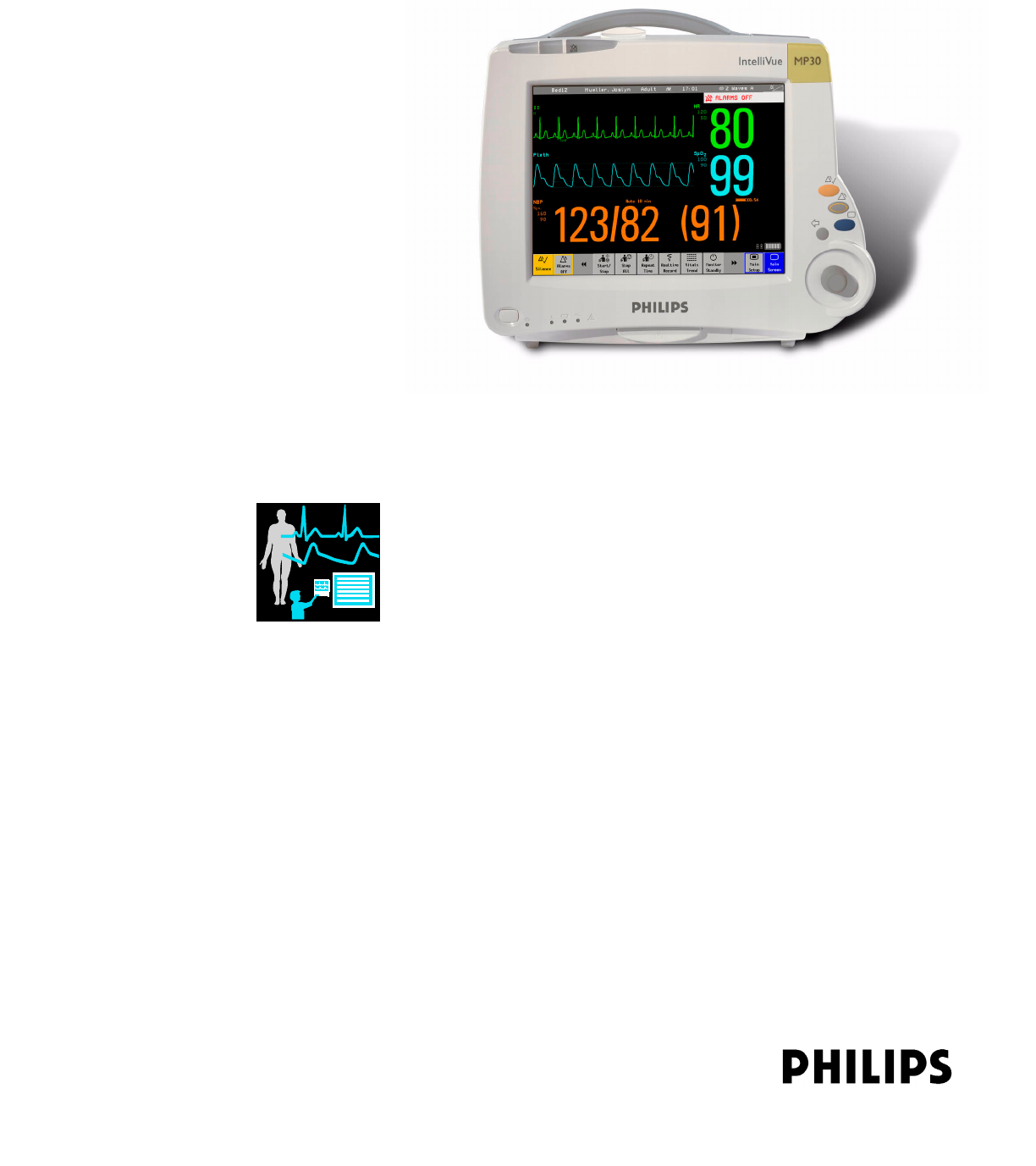
Patient Monitoring
Service Guide
IntelliVue MP20/30
IntelliVue Patient Monitor
MP20/MP20Junior/MP30

Part Number M8001-9301F
453564112561
*M8001-9301F*

3
Contents
1 Introduction 9
Who Should Use This Guide 9
How to Use This Guide 9
Abbreviations 9
Responsibility of the Manufacturer 10
Passwords 11
Warnings and Cautions 11
2 Theory of Operation 13
Monitor Theory of Operation 13
System Boundaries 14
Hardware Building Blocks 15
Data Flow 21
How does the Support Tool Work with the Monitor 24
Monitor Software Block Diagram 25
Block Diagram Legend 26
3 Testing and Maintenance 31
Introduction 31
Terminology and Definitions 32
Recommended Frequency 33
When to Perform Tests 34
Testing Sequence 37
Visual Inspection 38
Before Each Use 38
After Each Service, Maintenance or Repair Event 38
Power On Test 38
Safety Tests 39
Warnings, Cautions, and Safety Precautions 40
Safety Test Procedures 41
System Test 66
What is a Medical Electrical System? 66
General Requirements for a System 67
System Example 67
System Installation Requirements 69
Required Protective Measures at System Installation 70
System Test Procedure 80
Preventive Maintenance Procedures 81
Noninvasive Blood Pressure Measurement Calibration 81
Microstream CO2 Calibration 81

4
Performance Assurance Tests 81
Basic Performance Assurance Test 82
Full Performance Assurance Test 82
ECG/Resp Performance Test 82
ECG Sync Performance Test 83
SpO2 Performance Test 83
NBP PerformanceTest 84
Invasive Pressure Performance Test 86
Temperature Performance Test 87
M3014A Capnography Extension Performance Tests 87
Microstream CO2 Performance Test 90
BIS Performance Test 95
Nurse Call Relay Performance Test 96
Power Loss Alarm Buzzer Performance Test (only if Multi-Port Nurse Call Connector Board is installed) 98
Docking Station Performance Test 98
IIT Communication Test 98
IntelliVue 802.11 Bedside Adapter Communication Test 99
Reporting of Test Results 101
Carrying Out and Reporting Tests 101
Evaluation of Test Results 104
Other Regular Tests 105
Touchscreen Calibration 105
Disabling/Enabling Touch Operation 106
Printer Test Report 107
Battery Handling, Maintenance and Good Practices 107
About the Battery 108
Checking the Battery Status 109
Battery Status on the Main Screen 110
Battery Status Window 112
Conditioning a Battery 114
Conditioning Batteries 115
After Installation, Testing or Repair 116
4 Troubleshooting 119
Introduction 119
How To Use This Section 119
Who Should Perform Repairs 119
Replacement Level Supported 120
Software Revision Check 120
Obtaining Replacement Parts 120
Troubleshooting Guide 120
Checks for Obvious Problems 121
Checks Before Opening the Instrument 121
Troubleshooting Tables 123

5
Status Log 153
List of Error Codes 154
Troubleshooting with the Support Tool 155
Troubleshooting the Individual Measurements or Applications 155
5 Repair and Disassembly 157
Tools required 157
How to find the Correct Procedure 158
Removing Directly Accessible Parts 159
1.1 Removing the Handle 160
1.2 Removing the Measurement Server Holder 160
1.3 Removing the I/O Boards and Interface Board 162
1.4 Removing the Recorder 163
1.5 Removing the Navigation Point Knob 164
1.6 Removing the Quick Release Mount and Knob 164
1.7 Removing the Fix Mount 164
2.0 Opening the Front of the Monitor 166
2.1 Removing the Backlight Tubes 167
2.2 Removing the Backlight Inverter Board 168
2.3 Removing Power On LED board and Silicon Pad 169
2.4 Removing the HIF Board, Silicon Pad and Spacer 170
2.5 Removing the Flex Adapter Cable 171
2.6 Removing the Battery Board 172
2.7 Removing Recorder Board Assembly 173
2.8 Removing the Loudspeaker 174
2.9 Removing the Branding Cover 175
3.0 Separating the Front and Back Half of the Monitor 175
3.1 Removing the LCD Flat Panel Display, Touch Panel and Front Housing 176
3.2 Removing the Main Board 177
3.3 Removing the MSL Assembly 179
3.4 Removing the Power Supply 180
3.5 Removing the Frame Housing and Serial Number Plate 180
Multi-Measurement Module (MMS) Disassembly 181
Tools required 181
Removing the Front Cover 181
Removing the Mounting Pin 181
Removing the Top Cover 182
Removing the DC/DC Board 183
Removing the MSL Flex Assembly 183
Reassembling the MSL Flex Assembly 184
Removing the NBP pump 186
Refitting the new NBP Pump 186
Refitting the DC/DC board 188
Refitting the Cover 188
Refitting the Front Cover 189

6
Final Inspection 190
MMS Extensions - Exchanging the Top Cover, MSL Flex Cable and the Dual Link Bar 190
Exchange Procedures 191
Disassembly Procedures for the M3015A MMS Extension (HW Rev. A) 202
Removing the Front Cover 202
Refit Procedures for the MMS Extension 206
Smart Battery Charger LG1480 (M8043A) 207
Cleaning the Air Filter Mats 208
Replacing the Fan 208
IntelliVue Instrument Telemetry (IIT) 210
Docking Station 211
Exchanging the Main Board 211
Exchanging the Flex Cable 214
6 Parts 217
MP20/MP30 Parts 218
Multi-Measurement Module (MMS) Parts 223
MMS Part Number Overview and Identification 223
MMS Firmware Overview 225
MMS Part Numbers - Front Bezel for M3001 #A01 & #A03 226
MMS Part Numbers - Front Bezel for M3001 #A02 226
MMS Part Numbers - Top Cover and MSL Assembly 227
MMS Exchange Part Numbers 228
MMS Part Numbers - Label Kits 230
MMS Part Numbers - NBP Assembly 230
MMS Extension Parts (M3012A, M3014A, M3015A and M3016A) 230
MMS Extension Part Numbers - Release Mechanisms 231
MMS Extension Part Numbers - Top Cover, Flex Cable and Link Bar 231
MMS Extension Part Numbers - Front Bezels 231
Exchange Parts List 233
IntelliVue X2 Part Numbers 234
BISx Solution Replacable Parts 234
Smart Battery Charger Part Numbers 235
IntelliVue Instrument Telemetry Part Numbers 236
IntelliVue 802.11 Bedside Adapter Part Numbers 236
Docking Station Part Numbers 237
External Display Part Numbers 237
Remote Alarm Device Part Numbers 239
Remote Extension Device Part Numbers 240
7 Installation Instructions 241
Installation Checklist 241
Unpacking the Equipment 242
Initial Inspection 242

7
Mechanical Inspection 242
Electrical Inspection 242
Claims For Damage and Repackaging 243
Mounting Instructions 243
Connecting the Monitor to AC Mains 245
Connections 246
Installing Interface Boards 247
Connection of Devices via the MIB/RS232 Interface 250
Connection of USB Devices 250
Installing the Docking Station 254
Installing Remote Devices 254
Mounting the 15” Remote Display (M8031A) 254
Mounting the 15” Remote Display (M8031B) 255
Mounting the 17” Remote Display (M8033A/B/C) 255
Multi-Measurement Module 257
PS/2 Keyboard/Mouse 266
Philips Clinical Network (Wired) 266
Philips Clinical Network (Wireless) 266
Nurse Call Relay 267
Connections 267
ECG Out Functionality 267
Connections 267
Configuration Tasks 268
Checking Country-Specific Default Settings 268
Setting Altitude, Line Frequency, ECG Cable Colors and Height & Weight Units 269
Setting Altitude and Line Frequency 269
Configuring the Equipment Label 269
Configuring the printer 270
Configuring IP Address, Subnet Mask and Default Gateway 270
Configuration Settings for CSCN Routed Bedside Monitors (RBM) 271
Configuring Routed Bedside Monitors Support 271
Handing Over the Monitor 272
8 Site Preparation 275
Introduction 275
Site Planning 275
Roles & Responsibilities 276
Monitor M8001A and M8002A Site Requirements 278
Space Requirements 278
Environmental Requirements 278
Electrical and Safety Requirements (Customer or Philips) 279
Remote Device Site Requirements 280
Connecting Non-Medical Devices 281
Multi-Measurement Module (MMS) M3001A and IntelliVue X2 M3002A 281

8
Remote Displays (M8031A) 284
Remote Displays (M8031B) 285
Remote Displays - M8033A 286
Remote Displays - M8033B 287
Remote Displays - M8033C 288
Remote Alarm Devices 290
Remote Extension Device 291
Local Printer 292
Philips Medical LAN 293
RS232/MIB/LAN Interface 293
Nurse Call Relay Interface 294
ECG Out Interface 294
9 Gas Analyzers 297
10 Index 299

9
1
1Introduction
This Service Guide contains technical details for the IntelliVue MP20, MP20 Junior and MP30
Patient Monitor, the Multi-Measurement Module (MMS), the IntelliVue X2, and the
Measurement Server Extensions.
This guide provides a technical foundation to support effective troubleshooting and repair. It is
not a comprehensive, in-depth explanation of the product architecture or technical
implementation. It offers enough information on the functions and operations of the monitoring
systems so that engineers who repair them are better able to understand how they work.
It covers the physiological measurements that the products provide, the Measurement Server that
acquires those measurements, and the monitoring system that displays them.
Who Should Use This Guide
This guide is for biomedical engineers or technicians responsible for troubleshooting, repairing,
and maintaining Philips’ patient monitoring systems.
How to Use This Guide
This guide is divided into eight sections. Navigate through the table of contents at the left of the
screen to select the desired topic. Links to other relevant sections are also provided within the
individual topics. In addition, scrolling through the topics with the page up and page down keys
is also possible.
Abbreviations
Abbreviations used throughout this guide are:
Name Abbreviation
IntelliVue MP20/MP30 Patient Monitor the monitor
Multi-Measurement Module MMS

1 Introduction Responsibility of the Manufacturer
10
Name Abbreviation
Measurement Link MSL
Medical Information Bus MIB
Anesthetic Gas Module AGM
Responsibility of the Manufacturer
Philips only considers itself responsible for any effects on safety, EMC, reliability and
performance of the equipment if:
- assembly operations, extensions, re-adjustments, modifications or repairs are carried out by
persons authorized by Philips, and
- the electrical installation of the relevant room complies with national standards, and
- the instrument is used in accordance with the instructions for use.
To ensure safety and EMC, use only those Philips parts and accessories specified for use with
the monitor. If non-Philips parts are used, Philips is not liable for any damage that these parts
may cause to the equipment.
This document contains proprietary information which is protected by copyright. All Rights
Reserved. Reproduction, adaptation, or translation without prior written permission is prohibited,
except as allowed under the copyright laws.
Philips Medizin Systeme Böblingen GmbH
Hewlett-Packard Str. 2
71034 Böblingen, Germany
The information contained in this document is subject to change without notice.
Philips makes no warranty of any kind with regard to this material, including, but not limited to,
the implied warranties or merchantability and fitness for a particular purpose.
Philips shall not be liable for errors contained herein or for incidental or consequential damages
in connection with the furnishing, performance, or use of this material.

Passwords 1 Introduction
11
Passwords
In order to access different modes within the monitor a password may be required. The
passwords are listed below.
Monitoring Mode: No password required
Configuration Mode: 71034
Demo Mode: 14432
Service Mode: 1345
Consult the configuration guide before making any changes to the monitor configuration.
Warnings and Cautions
In this guide:
- A warning alerts you to a potential serious outcome, adverse event or safety hazard. Failure
to observe a warning may result in death or serious injury to the user or patient.
- A caution alerts you where special care is necessary for the safe and effective use of the
product. Failure to observe a caution may result in minor or moderate personal injury or
damage to the product or other property, and possibly in a remote risk of more serious
injury.

1 Introduction Warnings and Cautions
12

13
2
2Theory of Operation
Monitor Theory of Operation
The IntelliVue MP20/MP20Junior/MP30 Patient Monitor:
- displays real-time data
- controls the attached measurement server
- alarms in the case of patient or equipment problems
- offers limited data storage and retrieval (trending)
- interfaces to the Philips Clinical Network and other equipment
A monitor with just a single integrated measurement server can be connected to additional
building blocks to form a monitoring system with a large number of measurements, additional
interface capabilities and slave display. These elements cooperate as one single integrated
real-time measurement system.
NOTE
The following descriptions may vary depending on the monitor option purchased.
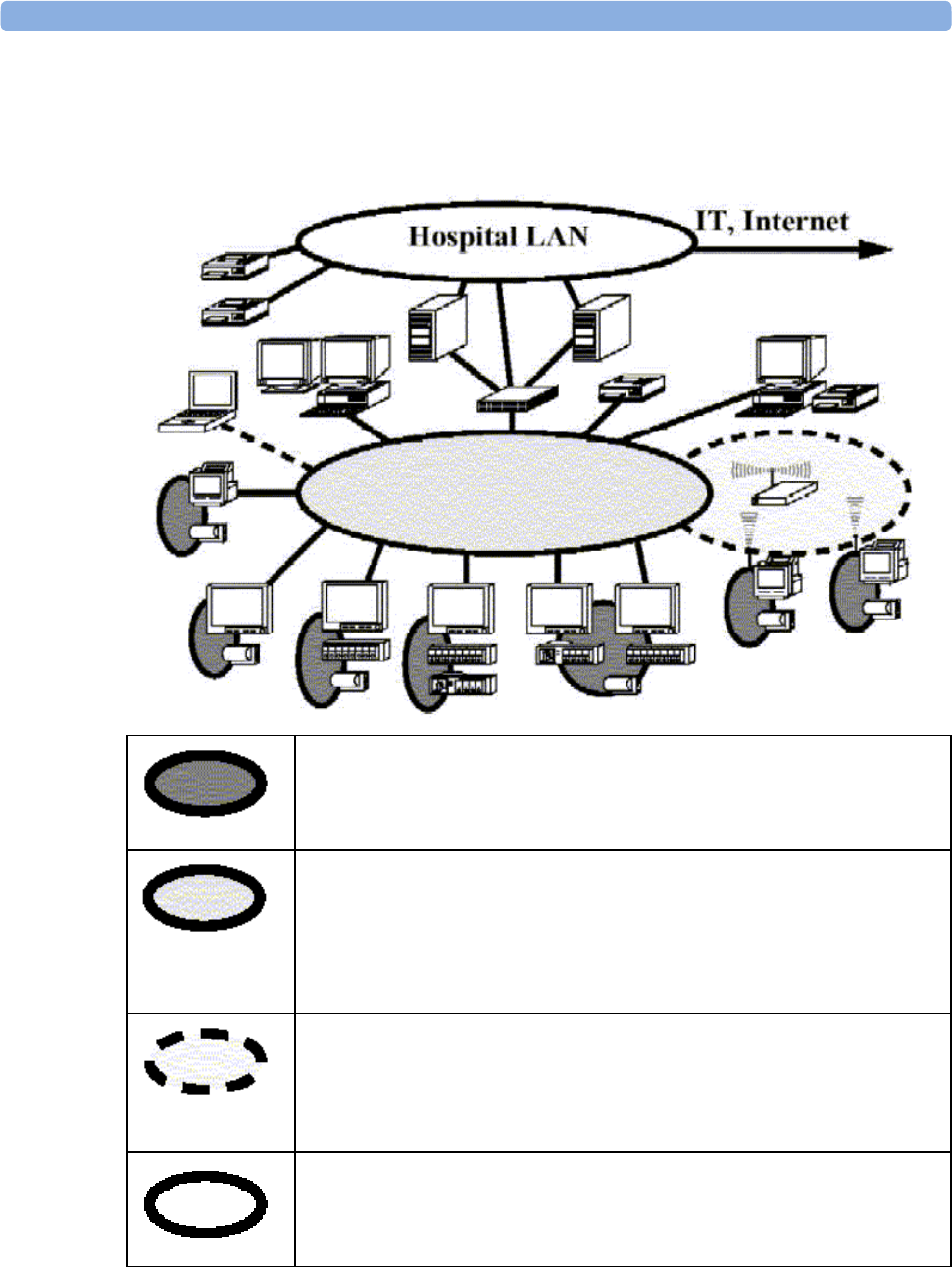
2 Theory of Operation Monitor Theory of Operation
14
System Boundaries
The following diagram discusses specific boundaries within the overall system with respect to
their openness and real-time requirements:
Measurement LAN
combines components of one patient monitor; real time requirements across
all interconnected elements
Philips Clinical Network (wired LAN)
connects multiple patient monitors, information centers, application servers;
closed system, only Philips qualified products (tested and with regulatory
approval) are connected, Philips is responsible for guaranteed real-time
functionality and performance
Philips Clinical Network (wireless)
like Philips Clinical Network (wired) LAN, however due to current wireless
technologies available it has reduced bandwidth, longer latencies, reduced
functionality
Hospital LAN, Internet
Standard Network, not under Philips control, no guaranteed service, no
real-time requirements

Monitor Theory of Operation 2 Theory of Operation
15
Hardware Building Blocks
The following hardware building blocks make up the monitoring system:
IntelliVue MP20
The MP20 monitor:
- integrates the display and processing unit into a single package
- uses a 10.4” TFT SVGA color display
- uses the Philips Navigation Point as primary input device; computer devices such as mice,
trackball, and keyboard can be added optionally
- supports the MMS and MMS extensions.
Building Blocks:

2 Theory of Operation Monitor Theory of Operation
16
IntelliVue MP30
The MP30 monitor:
- integrates the display and processing unit into a single package
- uses a 10.4” TFT XGA color display
- uses the Touchscreen and Philips Navigation Point as primary input devices. Computer
devices such as mice, trackball, and keyboard can be added optionally.
- supports the MMS and MMS extensions
Building Blocks:
Optional Hardware
One slot is provided for one of three available system interface boards. If the monitor is ordered
with the wireless LAN option a wireless transmitter is required. For further details regarding the
wireless network please refer to the M3185A Philips Clinical Network documentation.

Monitor Theory of Operation 2 Theory of Operation
17
Compatible Devices
M8045A Docking Station
M3001A Multi-Measurement Module (MMS)
M3002A IntelliVue X2
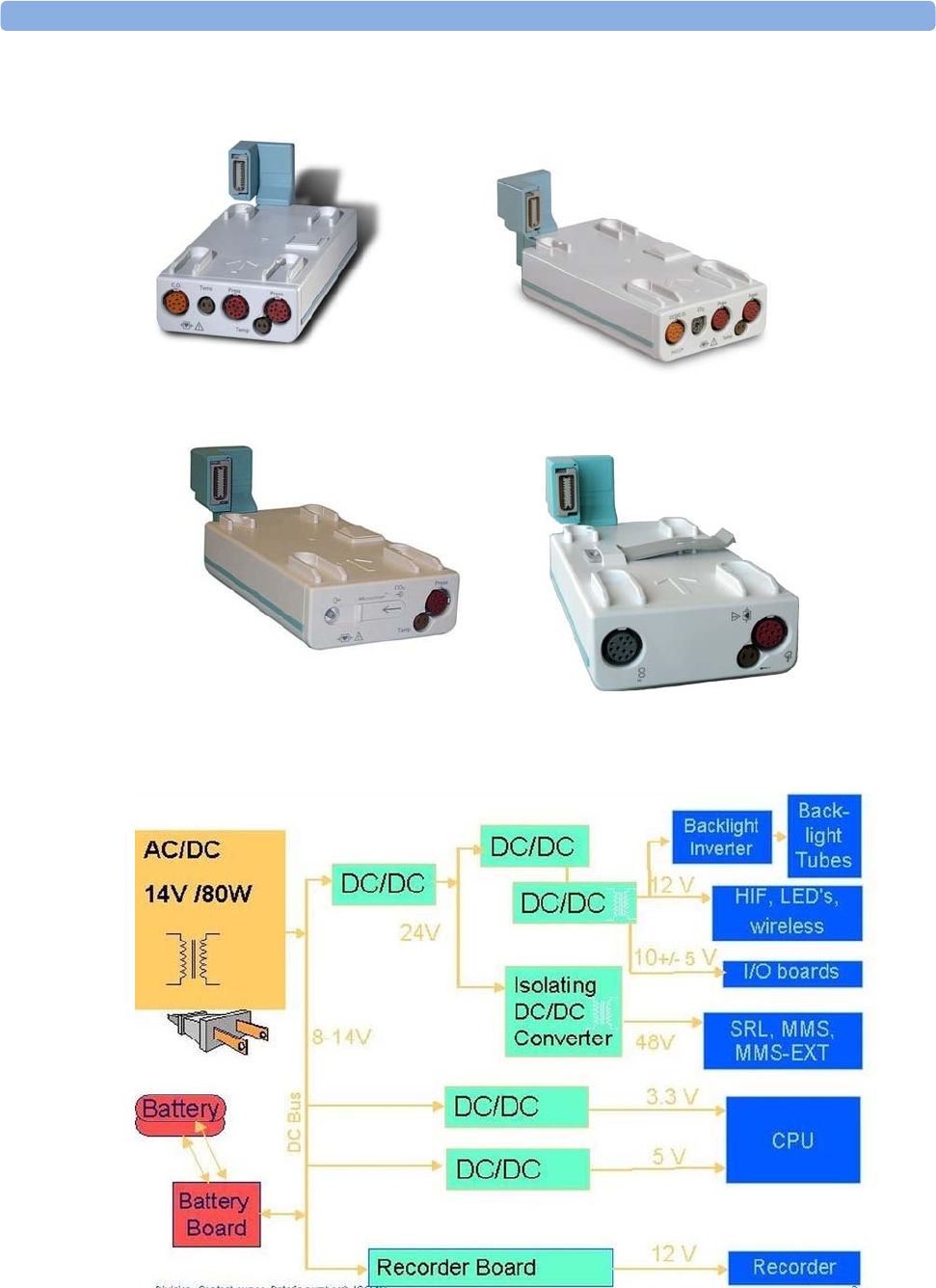
2 Theory of Operation Monitor Theory of Operation
18
M3012A, M3014A, M3015A, M3016A MMS Extensions
Power Supply
Power Supply Architecture

Monitor Theory of Operation 2 Theory of Operation
19
The AC/DC converter transforms the AC power coming from the power plug into 14 V/80W DC
source and isolates the monitoring system from the AC power mains.The 14V is distributed via
power bus and supplies power to all the components of the system: The 48V DC power needed
for the MMS and MMS Extension is created by an isolating DC/DC converter. The power
needed for the backlights is converted to 12V DC by the backlight DC/DC converter. The CPU
and the non-isolated I/O boards are supplied with 3.3 V and 5 V DC power. Isolated interface
boards require a power of 10V AC. The remote HIF board and the LEDs are supplied with 12V
DC power.
CPU Boards
The CPU boards have an MPC852/50 MHz processor in the patient monitor and an
MPC860/50MHz in the MMS that provides a number of on-chip, configurable interfaces. An
array of fast UARTS with configurable protocol options are implemented in an ASIC (along
with other system functions such as independent watchdogs etc.), providing interfacing
capabilities to measurement modules and System Interface and I/O boards. The serial interfaces
can easily be electrically isolated. The main board contains additional video hardware.
The CPUs provide two LAN interfaces to interconnect CPUs (via the MSL) and to connect to the
Philips Clinical Network.
The CPU capabilities are identical. Different loading options are coded on serial EEPROMs to
support the automatic configuration of the operating system at boot time.

2 Theory of Operation Monitor Theory of Operation
20
System Interface and I/O Boards
Interfaces to the monitor are implemented via I/O boards. The location of these boards is
restricted by general rules. The I/O slot designations diagram and the I/O matrix which outline
the I/O board placement rules can be found in the Installation Instructions section.
The following is a list of Interface (I/O) boards which may be present in your monitor,
depending on your purchased configuration:
System Interface boards:
- Video for slave display
- Philips Clinical Network (LAN wired or wireless)
- Basic Alarm Relay (Nurse Call)
- Docking Interface
I/O boards:
- PS/2
- MIB/RS232
- Flexible Nurse Call
- Parallel printer
- USB
- Remote devices (Remote Alarm Device, Remote Extension Device)
- BISx Interface
- IntelliVue 802.11 Bedside Adapter
The specifications for the above listed interfaces can be found in the technical data sheet for the
monitor and in the Installation and Specifications chapter of the Instructions for Use.
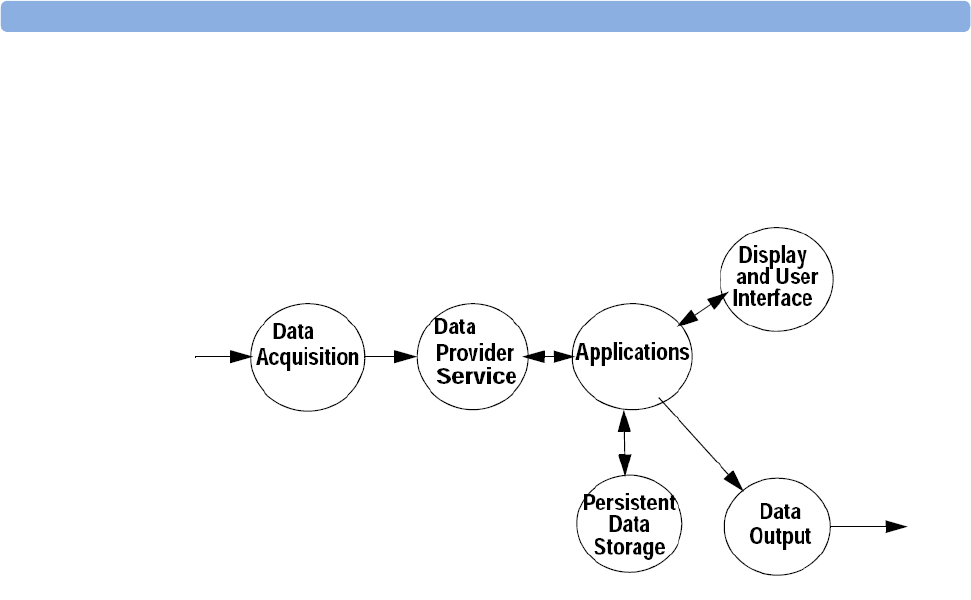
Monitor Theory of Operation 2 Theory of Operation
21
Data Flow
The following diagram shows how data is passed through the monitoring system. The individual
stages of data flow are explained below.
Data Acquisition
Monitoring data (for example patient measurement data in the form of waves, numerics and
alerts) is acquired from a variety of sources:
- Measurement Server
The Measurement Server connected to the internal LAN convert patient signals to digital
data and applies measurement algorithms to analyze the signals.
- External measurement devices
Data can be also acquired from devices connected to interface boards of the monitor.
Software modules dedicated to such specific devices convert the data received from an
external device to the format used internally. This applies to the Anesthetic Gas Module.
- Server systems on the Philips Clinical Network
To enable networked applications such as the other bed overview, data can be acquired from
server systems attached to the Philips Clinical Network, for example a Philips Information
Center

2 Theory of Operation Monitor Theory of Operation
22
Data Provider System Service
All data that is acquired from measurement servers or external measurement devices is
temporarily stored by a dedicated data provider system service. All monitor applications use this
central service to access the data in a consistent and synchronized way rather than talking to the
interfaces directly.
This service makes the applications independent of the actual type of data acquisition device.
The amount of data stored in the data provider system service varies for the different data types.
For example several seconds of wave forms and the full set of current numerical values are
temorarily stored in RAM.
Persistent Data Storage System Service
Some applications require storage of data over longer periods of time. They can use the
persistent data storage system service. Dependent on the application requirements, this service
can store data either in battery backed-up (buffered) memory or in flash memory. The buffered
memory will lose its contents if the monitor is without power (not connected to mains) for an
extended period of time. The flash memory does not lose its contents.
The trend application for example stores vital signs data in a combination of flash memory and
buffered memory, while the system configuration information (profiles) is kept purely in flash
memory.
Display and User Interface Service
Applications can use high level commands to display monitoring data or status and command
windows on the internal LCD panel. These commands are interpreted by the display manager
application. This application controls the dedicated video hardware which includes video
memory and a special ASIC.
User input is acquired from a variety of input devices, for example the Navigation Point, the
touchscreen or other standard input devices (keyboard, mouse) which may be attached to I/O
boards. The system software makes sure that the user input is directed to the application which
has the operating focus.
Data Output
The monitoring system is very flexible and customizable regarding its data output devices.
Built-in devices (for example LAN, alarm lamps, speaker, video) provide the basic output
capabilities.
These capabilities can be enhanced by adding additional I/O boards, as required in the specific
end-user setup. The additional I/O boards typically provide data to externally attached devices,
for example to printers, RS232 based data collection devices, nurse call systems etc.
The monitor can identify I/O boards by means of a serial EEPROM device that stores type and
version information. The operating system detects the I/O boards and automatically connects
them with the associated (interface driver) application. For some multi-purpose cards it is
necessary to configure the card for a particular purpose first (for example the dual MIB/RS232
card can support external touch display, data import, data export).
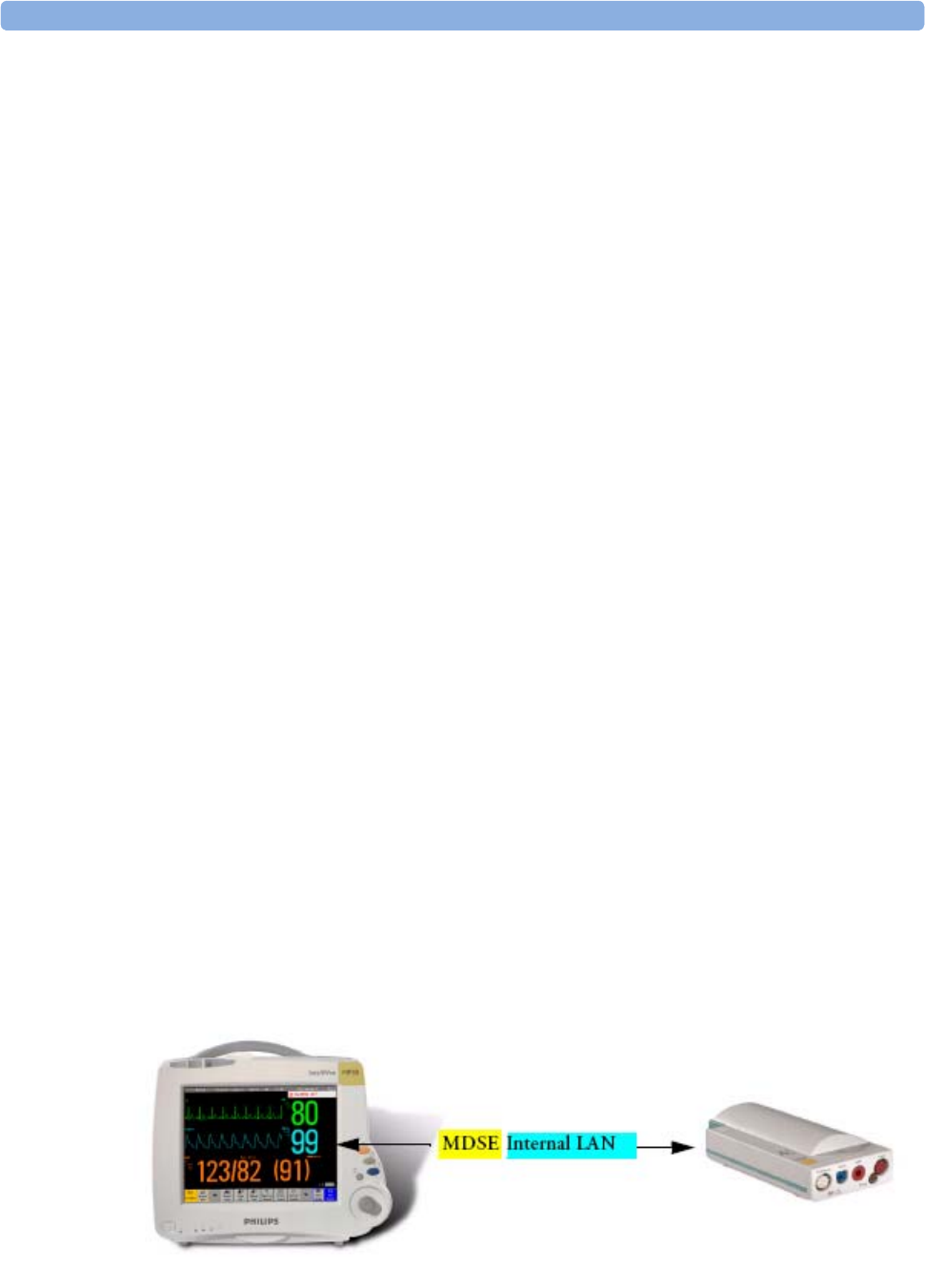
Monitor Theory of Operation 2 Theory of Operation
23
Monitor Applications
The monitor applications provide additional system functionality over the basic measurement
and monitoring capabilities. This includes for example trending, report generating, event storage
or derived measurements.
In general, the monitor applications use the data provider system service to access the
measurement data. Application interfaces to the other system services allow the application to
visualize data, to store data over extended periods of time or to output data to other devices.
Internal LAN (Measurement Link)
All components of the monitoring system (including measurement servers and CPUs in the
monitor) communicate using an IEEE802.3/ Ethernet LAN in the Measurement Link (MSL).
This network is used to distribute data between the components, for example:
- Digitized patient signals including wave data, numerical data and status information
(typically from the measurement server to a display unit)
- Control data representing user interactions (typically from the display unit to a measurement
server)
- Shared data structures, for example representing patient demographical data and global
configuration items
The internal LAN allows plug and play configuration of the monitoring system. The system
automatically detects plugging or unplugging of measurement servers and configures the system
accordingly.
The components on the internal LAN are time-synchronized to keep signal data consistent in the
system. Dedicated hardware support for synchronization eliminates any latency of the network
driver software.
The integrated LAN provides deterministic bandwidth allocation/reservation mechanisms so that
the real-time characteristic of signal data and control data exchange is guaranteed. This applies
to the data flow from the measurement server to the monitor (for example measurement signal
data) and the data flow from the monitor to a measurement server (for example to feed data to a
recorder module).
Integrated communication hubs in the monitor allow flexible cabling options (star topology,
daisy chaining of servers).

2 Theory of Operation Monitor Theory of Operation
24
Philips Clinical Network
The monitoring system may be connected to the Philips Clinical Network, for example to
provide central monitoring capabilities or other network services. This connection may be
through a normal wired connection or through a wireless connection.
The monitor supports the connection of an external wireless adapter or an internal wireless
adapter (#J35). Switching between wired and wireless networks is automatically triggered by the
plugging or unplugging of the network cable.
The Philips Clinical Network protocols function very similarly to the protocols used on the
internal LAN.
After configuration, the monitoring system sends the digitized patient signals including wave
data, numerical data and status information onto the network. Control data representing user
interactions can be exchanged between the monitoring system and a central station
bi-directionally.
Additional protocols are supported for networked applications, for example for the other bed
overview function, which allows viewing of monitoring data from other patients on the network.
For plug and play operation, the monitoring system uses the standard BootP protocol to
automatically acquire a network address.
How does the Support Tool Work with the Monitor
The support tool is a Windows application typically installed on the laptop of a customer
engineer or a biomedical engineer working in the customer’s own service department.
The purpose of the support tool is to upgrade, configure and diagnose all monitoring components
(modules, measurement servers, and monitors) in the system over the network.
The service protocol developed for this purpose uses a raw access to the devices without the
need for IP addresses etc. over a standard customer network installation, so that even defective
devices can be upgraded as long as the few kBytes of initial boot code are working. The boot
code itself can also be upgraded using the same protocol.
The tool allows access to internal service information and to serial numbers. It can be remote-
controlled, for example via a dial-up connection from a response center, provided the proper
infrastructure is in place.
For details see the Instructions for Use for the Support Tool.

Monitor Theory of Operation 2 Theory of Operation
25
Monitor Software Block Diagram
shows the functional block diagram for the monitoring system. A legend explaining terms and
diagram elements follows. The information below varies depending on the purchased monitor
options.
IntelliVue Patient Monitoring System Functional Block Diagram

2 Theory of Operation Monitor Theory of Operation
26
Block Diagram Legend
Functional Block Description
Services
Operating System The Operating System (OS) provides a layer of isolation between the specific
hardware implementation and the application software. The OS performs system
checks and allocates resources to ensure safe operation when the system is first
started. This includes internal self-tests on several hardware modules and
configuration checks for validity of configuration with the operating software.
During normal operation, the OS continues to run checks on system integrity. If
error conditions are detected the OS will halt monitoring operations and inform
the operator about the error condition.
System Services The System Services provide generic common system services.
In particular:
They use a real-time clock component to track time. They synchronize to network
time sources and verify the accuracy of the system time information. They are also
responsible for managing persistent user configuration data for all Measurement
Servers and IntelliVue Patient Monitoring System software modules. User
configuration data is stored in a non-volatile read/write storage device
Applications
Reports The Reports Service retrieves current and stored physiological data and status data
to format reports for printing paper documentation. The following reports are
supported:
- Vital Signs Report
- Graphical Trend Report
- Event Review Report
- Event Episode Report
- ECG Report (12 Lead/Multi-Lead)
- Cardiac Output Report
- Calculations Report (Hemodynamic/Oxygenation/Ventilation)
- Calculations Review Report
- Wedge Report
- Test Report
The Reports service generates report data which can be printed on a local or a
central printer.

Monitor Theory of Operation 2 Theory of Operation
27
Functional Block Description
Record The Record Service retrieves current and stored physiological data and status data
to format a continuous strip recording. A recording can be triggered manually by
the operator or automatically by an alarm condition. The Record Service uses the
services of the Recorder Interface to control an M1116B Recorder. The Record
Service can also send data to a central recorder.
Alarm The Alarm Service contains logic that prioritizes alarm conditions that are
generated either by the Measurement Servers or by IntelliVue Patient Monitoring
System software modules. Visual alarm signals (messages) are displayed at the top
of the IntelliVue Patient Monitoring System display and alarm sounds are
generated by a loudspeaker. Alarm conditions may be generated when a
physiological parameter exceeds preselected alarm limits or when a physiological
parameter or any other software module reports an inoperative status (technical
alarm, for example, the ECG leads may have fallen off the patient). The Alarm
service manages the alarm inactivation states, for example suspension of alarms,
silencing of alarms, and alarm reminder. Alarm signals may also be configured as
latching (alarm signals are issued until they are acknowledged by the operator,
even when the alarm condition is no longer true). The Alarm service controls the
visual alarm signals (alarm lamps).
Trend The Trend service stores the sample values of physiological data and status data
with a resolution of 12 seconds, 1 minute or 5 minutes for a period of up to 48
hours. The data is kept in battery buffered read/write storage and flash memory
devices to be preserved across power failures. The stored data is protected via
consistency checks and checksums. When a new patient is admitted, the trend
database erases all data of the previous patient.
HiRes The OxyCRG (Oxygen CardioRespiroGram) service derives a high-resolution
trend graph from the Beat-to-Beat Heart Rate, SpO2 or tcpO2, and Respiration
physiological data. The OxyCRG is specialized for neonatal applications, allowing
the operator to identify sudden drops in Heart Rate (Bradycardia) and SpO2
(Desaturation), and supporting the operator in visualizing Apnea situations.
ADT The ADT (Admit/Discharge/Transmit) service maintains the patient demographics
information. The operator may admit a new patient, discharge the old patient and
enter or modify the patient demographics. The ADT service also supports the
transport of a patient (trend database) with the M3001A Multi-Measurement
Module. The ADT service controls the deletion of old patient data, the upload of
trend data from the M3001A and the switching back of all settings to user
defaults. It also synchronizes patient information with a central station on the
network.
Calc Param The Calc Param (Calculated Parameters) service accesses current, stored and
manually entered physiological data as input to calculation formulas. With these
formulas, derived hemodynamic, oxygenation and ventilation variables are
computed. The calculation results, including the input parameters, are stored for
later review using the Trend service.

2 Theory of Operation Monitor Theory of Operation
28
Functional Block Description
Interface Managers
MDSE The MDSE (Medical Data Service Element) Interface Manager is responsible for
the exchange of real-time data between the IntelliVue Patient Monitoring System
display unit and the Measurement Servers and Flexible Module Rack as well as
between the IntelliVue Patient Monitoring System display unit and other devices
attached to the network. MDSE establishes and maintains a data communication
link between the devices. It provides configuration information about the remote
device to applications in the local device and it allows the exchange of
measurement data and status information between the devices.
Printer The Printer Interface Manager provides a high level interface to a printer. It
provides means to:
- establish a connection to the printer
- transfer data to the printer
- get status of the printer
- close connection to the printer
The Printer Interface Manager also supervises the connection to the printer and
whether the printer accepts data (for example paper out). The Printer Interface
Manager notifies the operator in such cases.
Display & Operator
Interface The Display and Operator Interface Manager performs the following tasks:
- Screen presentation of real-time and stored physiological measurement data,
alarm condition data and status information received from the MDSE
interface manager, the Alarm service or other IntelliVue Patient Monitoring
System modules
- Screen presentation of operating controls (control windows)
- Processing of operating control commands received from HIF Control
interface. The module verifies and interprets the received commands and
forwards them to other software modules of the IntelliVue Patient Monitoring
System display unit, Measurement Servers or Flexible Module Rack
- Sound generation (issues audible alarm signals and generates audible
information signals, for example QRS and SpO2 tones, operator audible
feedback)
Interfaces
LAN The LAN interface implements the physical layer of IEEE 802.3. The LAN
interface performs Manchester encoding/decoding, receive clock recovery,
transmit pulse shaping, jabber, link integrity testing, reverse polarity
detection/correction, electrical isolation, and ESD protection. Electronically
separated interfaces are used for communication to the Measurement Servers or
Flexible Module Rack and to the network.
Centronics The Centronics interface implements the standard signaling method for
bi-directional parallel peripheral devices according to IEEE 1284-I. The interface
is used as a parallel interface to a standard printer with electrical isolation and
ESD protection.

Monitor Theory of Operation 2 Theory of Operation
29
Functional Block Description
Display Controller The Display Controller Interface consists of a video controller chip, video RAM
and the controlling software. The Display Controller interface processes the high
level display commands (character and graphic generation, wave drawing) and
translates them into pixels, which are written into the video RAM where the video
controller chip generates the video synchronization signals and the pixel stream
for the Color LCD Display.
HIF Control The HIF (Human Interface Control) interface scans the Human Interface devices
for operator controls (Touch Screen, Speed Point, USB and PS/2 devices), formats
the collected data and sends it to the display and Operating Interface.
ECG-Out Marker-In The ECG Out/Marker In interface receives the ECG waveform directly from the
ECG/Resp Arrhythmia ST-Segment physiological algorithm via an RS-422 serial
interface and converts the digital ECG signal to an analog ECG signal. In addition,
the ECG Out controller receives from a connected device the marker information
and forwards this data to the ECG/Resp Arrhythmia ST-Segment physiological
algorithm. The converted analog signal is used to synchronize a connected device
to the patient’s ECG
RS-422 The serial link RS-422 interface communicates the ECG signal to the ECG
Output/Marker In of the IntelliVue Patient Monitoring System display unit. The
interface is a serial, differential, full-duplex link. The interface is ESD protected.
PS/2 The PS/2 interface supports the serial protocol of standard PS/2 devices (mouse).
The PS/2 serial protocol is interpreted by the HIF Control interface.
Nurse Call The Nurse Call board contains 2 connectors. A phone jack type connector and a
multi-port connector. The phone jack type connector has a single close-on-alarm
relay. The multi-port connector has three alarm relays which are configurable to
be open or closed on alarm. In addition, this interface has an audible alert
capability for loss of AC power.
MIB The MIB interface allows full-duplex, short-haul asynchronous binary
communication between the monitor and an arbitrary (medical/non-medical)
device using an eight-pin RJ45 modular connector. Switching between MIB and
RS232 protocol is possible.
Docking Interface The docking interface provides necessary connections for docking an MP20/30 or
MP40/50 monitor onto the docking station.
BISx Interface The BISx interface allows the usage of Aspect’s BISx solution with an MP20/30
monitor.
IIT Interface The IIT interface allows operation of the MP2/X2/MP5/MP20/MP30/MP40/MP50
monitors with IntelliVue Instrument Telemetry.

31
3
3Testing and Maintenance
Introduction
This chapter provides a checklist of the testing and maintenance procedures to ensure the
performance and safety of the monitor, the Multi-Measurement Module (MMS) and the MMS
Extensions.
These tests must be performed only by qualified personnel certified by the responsible
organization. Qualifications required are: training on the subject, knowledge, experience and
acquaintance with the relevant technologies, standards and local regulations. The personnel
assessing safety must be able to recognize possible consequences and risks arising from
non-conforming equipment.
All recurring safety and performance assurance tests must be performed under equal
environmental conditions to be comparable.
Preventive Maintenance refers specifically to the series of tests required to make sure the
measurement results are accurate. The accuracy and performance procedures are designed to be
completed as specified in the following sections or when readings are in question.
For detailed instructions on the maintenance and cleaning of the monitor and its accessories, see
Care and Cleaning, Using Batteries and Maintenance and Troubleshooting in the monitor's
Instructions for Use.

3 Testing and Maintenance Terminology and Definitions
32
Terminology and Definitions
The following terms and definitions are used throughout this chapter and taken from the
international standards IEC 60601-1, IEC 60601-1-1 and IEC 62353.
- Medical System: a medical electrical system is a combination of at least one medical
electrical device and other electrical equipment, interconnected by functional connection or
use of a multiple portable socket-outlet.
- Patient Vicinity: any area in which intentional or unintentional contact can occur between
the patient and parts of the medical system or between the patient and other persons who
have had contact with parts of the medical system. The patient vicinity is defined anywhere
within 1.5m (5 feet) of the perimeter of the patient's bed and 2.5m (8.2 feet) from the floor.
- Separation Device/Transformer: a component or arrangement of components with input
parts and output parts that, for safety reasons, prevent a transfer of unwanted voltage or
current between parts of a medical system.
- Multiple Portable Socket-Outlet: a combination of two or more socket-outlets intended to
be connected to or integrated with flexible cables or cords, which can easily be moved from
one place to another while connected to the power mains.
- Functional Connection: an electrical connection for transfer of signals and/or power.
- Tests: Safety or Performance Assurance test procedures which may consist of several steps.

Recommended Frequency 3 Testing and Maintenance
33
Recommended Frequency
Perform the procedures as indicated in the suggested testing timetable. These timetable
recommendations do not supersede local requirements.
Table 1: Suggested Testing Timetable
Tests Frequency
NBP Performance Once every two years, or more often if
specified by local laws.
Preventive Maintenance*
Microstream CO2 Calibration
(M3015A) Once a year or after 4000 hours of
continuous use and following any
instrument repairs or the replacement of
any instrument parts.
Visual Inspection
Other Regular Tests
Power On Test
Before each use.
ECG/Resp Performance
ECG Sync Pulse Performance
SpO2 Performance
NBP Performance
Invasive Pressure Performance
Temperature Accuracy
M3014A Capnography Extension
Performance Tests
Microstream CO2 Performance Test
BIS Performance
Performance Assurance
Tests
Nurse Call Relay Performance
Once every two years, or if you suspect
the measurement is incorrect, except
Mainstream CO2 Accuracy Check,
Sidestream CO2 Accuracy Check and
Flow Check - required once a year.
Visual Visual Inspection After each service event.
Protective Earth
Equipment Leakage Current
Patient Leakage Current
Once every two years and after repairs
where the power supply has been
removed or replaced or the monitor has
been damaged by impact.
Safety
Tests
Electrical
System Test Once every two years
*M3015A with the old hardware Rev. A (i.e. Serial No. DE020xxxxx) also require the CO2
pump/CO2 scrubber replacement procedure. This is required every three years or after 15000
operating hours.

3 Testing and Maintenance When to Perform Tests
34
When to Perform Tests
This table tells you when to perform specific tests.The corresponding test procedures are
described in the following sections All tests listed below must be performed on the monitor
itself, any attached MMS/X2 and FMS incl. parameter modules.
When to perform tests
Service Event
(When performing...
Tests Required
...Complete these tests)
Installation
Installation of a monitor in combination with
a medical or non-medical device connected to
the same multiple socket outlet.
Perform Visual Inspection, Power On and
System Tests
Installation of a standalone monitor with no
display connected to the video output Perform Visual Inspection and Power On Test
Installation of a monitor with a medical
display specified by Philips Perform Visual Inspection and Power On Test
Installation of a monitor with an off-the-shelf
display (non-compliant with IEC60601-1) Perform Visual Inspection, Power On and
System Test
Installation of monitor with IntelliVue
Instrument Telemetry (IIT) Perform Visual Inspection, Power On and IIT
communication test
Installation of a monitor with AGM or
IntelliVue G1/G5, connected to separate
mains sockets.
Perform Visual Inspection and Power On Tests
Installation of a monitor with IT equipment
e.g. printer, PC connected via a functional
connection e.g. Centronics or USB.
Perform Visual Inspection, Power On and
System Tests
Installation of monitor with IntelliVue
802.11 Bedside Adapter Perform Visual Inspection, Power On and
IntelliVue 802.11 Bedside Adapter
Communication Test
Installation of networked monitor (LAN) Perform Visual Inspection and Power On Test
Preventive Maintenance
Preventive Maintenance* Perform preventive maintenance tests and
procedures:
- NBP calibration
- Microstream CO2 calibration (M3015A)

When to Perform Tests 3 Testing and Maintenance
35
Service Event
(When performing...
Tests Required
...Complete these tests)
Other Regular Tests and Tasks
Visual Inspection Perform Visual Inspection test block
Power On Test Perform Power On test block
Repairs
Repairs where the monitor, MMS or X2 have
been damaged by impact, liquid ingression,
fire, short circuit or electrical surge.
Perform Visual Inspection, Power On, all
Safety Tests and Full Performance Assurance
Tests
Repairs where the power supply, the mains
socket or an interface board is removed or
replaced or the protective earth ground
connection is disrupted.
Perform Visual Inspection, Power On, all
Safety Tests and Basic Performance Assurance
Test
Repairs where the unit has been opened
(front and back separated). Perform Visual Inspection, Power On, all
Safety Tests and Basic Performance Assurance
Test
Repairs of IntelliVue Instrument Telemetry
(IIT) Module Perform Visual Inspection, Power On Test
Block and IIT communication test
Repairs of IntelliVue 802.11 Bedside
Adapter Perform Visual Inspection, Power On and
IntelliVue 802.11 Bedside Adapter
Communication Test
Repairs of the MMS or X2 (all service events
where the MMS or X2 have been opened) Perform Visual Inspection, Power On, all
Safety Tests and Basic Performance Assurance
Test.
If a certain parameter seems suspicious,
perform Full Performance Assurance Test for
this parameter.
Repairs where the NBP pump of the MMS or
X2 has been replaced Perform Visual Inspection, Power On, all
Safety Tests, Basic Performance Assurance
Test and NBP Performance Test and
Calibration
Repairs of the AGM or IntelliVue G1/G5 Perform Basic Performance Assurance Test.
For further testing requirements, see AGM or
IntelliVue G1/G5 Service Guide
Repairs where the MMS or X2 has been
replaced. Perform Visual Inspection, Power On and
Basic Performance Assurance
Repairs where the printer connected via
Centronics or USB I/O board has been
replaced.
Perform Visual Inspection, Power On, System
Test and Printer Test.

3 Testing and Maintenance When to Perform Tests
36
Service Event
(When performing...
Tests Required
...Complete these tests)
All other IntelliVue Monitoring System
repairs (except when power supply is
removed)
Perform Visual Inspection, Power On Test and
Basic Performance Assurance Test
Performance Assurance
Basic Performance Assurance Perform basic performance assurance tests for
the respective monitoring system component.
Full Performance Assurance Perform all accuracy and performance test
procedures listed in the following sections. If a
particular measurement is in question, perform
the measurement performance test only.
Upgrades
Software Upgrades Perform Visual Inspection, Power On Test and
Basic Performance Assurance Test unless
otherwise specified in the Upgrade Installation
Notes shipped with the upgrade.
Hardware Upgrades Perform Visual Inspection, Power On Test and
Basic Performance Assurance Test unless
otherwise specified in the Upgrade Installation
Notes shipped with the upgrade.
Hardware Upgrades where IntelliVue
Instrument Telemetry (IIT) is installed Perform Visual Inspection, Power On Test,
Basic Performance Assurance Test and IIT
communication Test
Hardware Upgrades where IntelliVue 802.11
Bedside Adapter is installed Perform Visual Inspection, Power On Test,
Basic Performance Assurance Test and
IntelliVue 802.11 Bedside Adapter
Communication Test
Installation of Interfaces or Hardware
Upgrades where the power supply or
parameter boards need to be removed.
Perform Visual Inspection, Power On Test,
Basic Performance Tests and all Safety Tests
Combining or Exchanging System
Components
Perform the System Test for the respective
system components
*M3015A with the old hardware Rev. A (i.e. Serial No. DE020xxxxx) also require the pump and
scrubber replacement procedures.
NOTE
It is the responsibility of the facility operator or their designee to obtain reference values for
recurring safety and system tests. These reference values are the results of the first test cycles
after an installation. You may also purchase this service from Philips.

Testing Sequence 3 Testing and Maintenance
37
Testing Sequence
Summary of the recommended sequence of testing:
See When to Perform Tests
See Visual Test (see "Before Each Use" on
page 38).
See Safety Test Procedures (on page 41).
See Performance Assurance Tests (on page
81).
See Reporting of Test Results (on page 101)
See Evaluation of Test Results (on page 104)
Start
Select the test
Visual Inspection
Safety Tests
Performance Tests
Reporting of Results
Evaluation of Results
Check and prepare for normal use
NOTE
If any single test fails, testing must be discontinued immediately and the device under test must
be repaired or labeled as defective.

3 Testing and Maintenance Visual Inspection
38
Visual Inspection
Before Each Use
Check all exterior housings for cracks and damage. Check the condition of all external cables,
especially for splits or cracks and signs of twisting. If serious damage is evident, the cable should
be replaced immediately. Check that all mountings are correctly installed and secure. Refer to
the instructions that accompany the relevant mounting solution.
After Each Service, Maintenance or Repair Event
Ensure all fuses accessible from the outside comply with the manufacturer’s specification.
Check:
- the integrity of mechanical parts, internally and externally.
- any damage or contamination, internally and externally
- that no loose parts or foreign bodies remain in the device after servicing or repair.
- the integrity of all relevant accessories.
Power On Test
1. Connect the monitoring system to mains and switch it on. This includes connected displays,
MMS, X2, MMS Extensions and gas analyzers.
2. Make sure that all steps listed in the table Initial Instrument Boot Phase in the
Troubleshooting section are completed successfully and that an ECG wave appears on the
screen.
The expected test result is pass: the monitor boots up and displays an ECG wave. The wave
might be a flat line if no simulator is attached.

Safety Tests 3 Testing and Maintenance
39
Safety Tests
Safety tests are comprised of the following tests performed on the monitoring system:
- protective earth resistance
- equipment leakage current
- applied part leakage current
- system test (if required)
Safety test requirements are set according to international standards, their national deviations and
specific local requirements. The safety tests detailed in this Service Guide are derived from
international standards but may not be sufficient to meet local requirements. We recommend that
you file the results of safety tests. This may help to identify a problem early particularly if the
test results deteriorate over a period of time.
Each individual piece of equipment of the monitoring system which has its own connection to
mains or which can be connected or disconnected from mains without the use of a tool must be
tested individually. The monitoring system as a whole must be tested according to the System
Test (on page 66) procedure.
Accessories of the monitoring system which can affect the safety of the equipment under test or
the results of the safety test must be included in the tests and documented.

3 Testing and Maintenance Safety Tests
40
Warnings, Cautions, and Safety Precautions
- These tests are well established procedures of detecting abnormalities that, if undetected,
could result in danger to either the patient or the operator.
- Disconnect the device under test from the patient before performing safety tests.
- Disconnect the device under test from mains before performing safety tests. If this is not
possible, ensure that the performance of these tests does not result in danger to the safety
analyzer operator, patients or other individuals.
- Test equipment (for example, a Safety Analyzer) is required to perform the safety tests.
Please refer to Annex C of IEC/EN 62353 for exact requirements for the measurement
equipment and for measurement circuits for protective earth resistance and leakage currents.
Refer to the documentation that accompanies the test equipment. Only certified technicians
should perform safety testing.
- The consistent use of a Safety Analyzer as a routine step in closing a repair or upgrade is
emphasized as a mandatory step to maintain user and patient safety. You can also use the
Safety Analyzer as a troubleshooting tool to detect abnormalities of line voltage and
grounding plus total current loads.
- During safety testing, mains voltage and electrical currents are applied to the device under
test. Ensure that there are no open electrical conductive parts during the performance of
these tests. Avoid that users, patients or other individuals come into contact with touch
voltage.
- For Europe and Asia/Pacific, the monitor complies with:
IEC60601-1:1988 + A1:1991 + A2:1995 = EN60601-1:1990 +A1:1993 + A2:1995
IEC60601-1-1:2000
For USA, the monitor complies with:
UL60601-1
For Canada, CAN/CSA C22.2#601.1-M90
- Local regulations supersede the testing requirements listed in this chapter.
- If a non-medical electrical device is connected to a medical electrical device, the resulting
medical electrical system must comply with IEC/EN 60601-1-1.
- Perform safety tests as described on the following pages.

Safety Tests 3 Testing and Maintenance
41
Safety Test Procedures
Use the test procedures outlined here only for verifying safe installation or service of the
product. The setups used for these tests and the acceptable ranges of values are derived from
local and international standards but may not be equivalent. These tests are not a substitute for
local safety testing where it is required for an installation or a service event. If using an approved
safety tester, perform the tests in accordance with the information provided by the manufacturer
of the tester and in accordance with your local regulations, for example IEC/EN 60601-1,
UL60601-1 (US), IEC/EN 62353, and IEC/EN 60601-1-1. The safety tester should print results
as detailed in this chapter, together with other data.
Please refer to Annex C of IEC/EN 62353 for requirements for the measurement equipment and
for measurement circuits for protective earth resistance and leakage currents.
The following symbols are used in the diagrams illustrating the safety tests:
Supply mains
Protective earth
L, N Supply mains terminals PE Protective earth terminal
Mains part
Applied part
F-type applied part
Measuring device
Resistance measuring
device
Connection to accessible
conductive parts
......... Optional connection
CAUTION
After each service, maintenance or repair event:
Ensure all fuses accessible from the outside comply with the manufacturer’s specification.
Check:
- the integrity of mechanical parts, internally and externally.
- any damage or contamination, internally and externally.
- that no loose parts or foreign bodies remain in the device after servicing or repair.
- the integrity of all relevant accessories.

3 Testing and Maintenance Safety Tests
42
Hints for Correct Performance of Safety Tests
- Perform a visual inspection on all detachable power cords used with the monitoring system
and include these in all safety test procedures.
- Connection lines such as data lines or functional earth conductors may appear to act like
protective earth connections. These may lead to incorrect measurements and need to be
considered during testing. If necessary, unplug these connections.
- Position all cables and cords in such a manner that they do not influence the safety tests.
- Measurement of insulation resistance is not required.
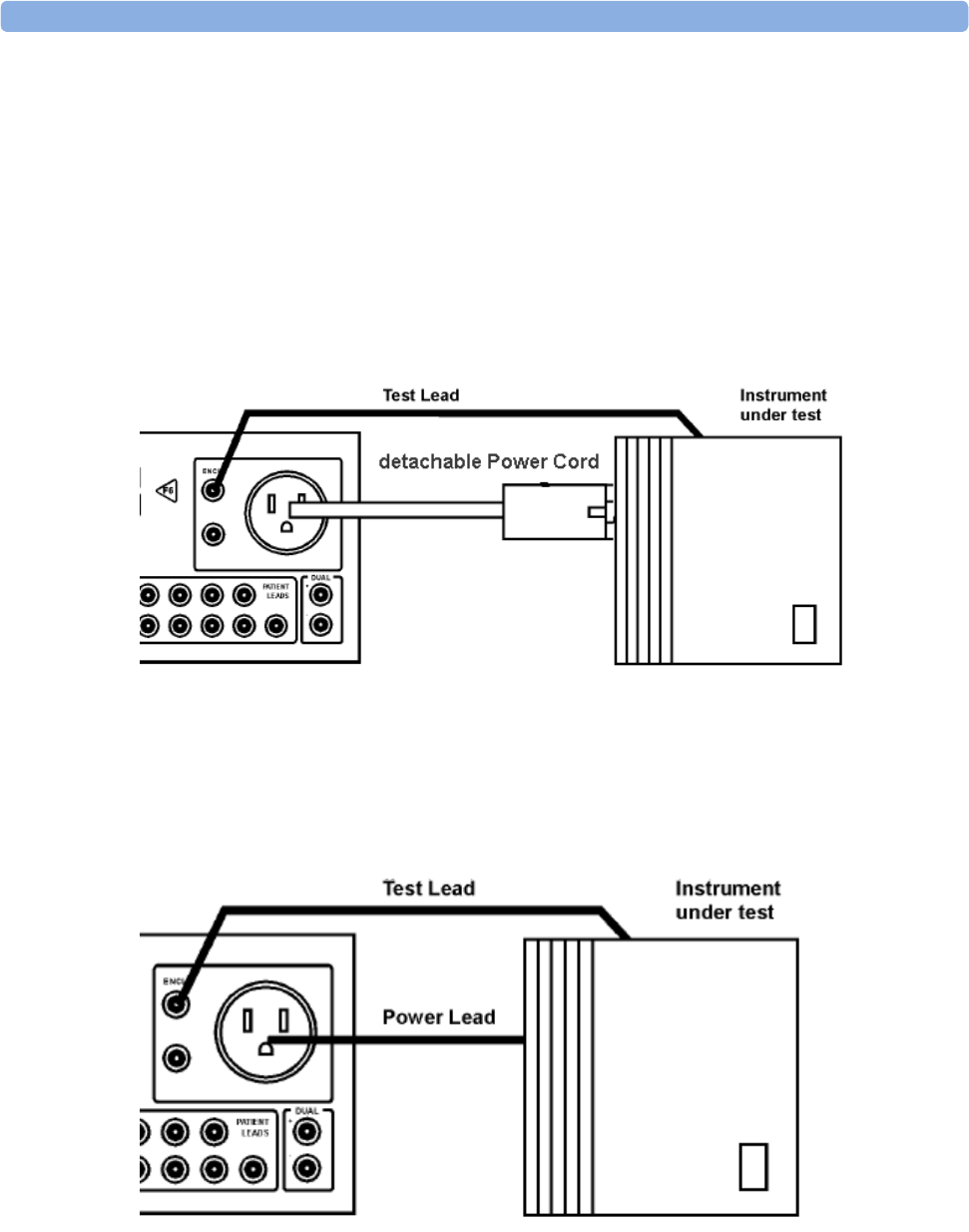
Safety Tests 3 Testing and Maintenance
43
Guideline for Performance of Safety Tests
Connect the detachable power cord of the device under test to the safety analyzer's test mains
port. Connect the enclosure test lead of the safety analyzer to the enclosure of the device under
test, e.g. to the equipotential connector. For testing the applied part leakage current, connect all
applied parts to the safety analyzer using the appropriate patient lead or adapter cable. For the
ECG parameter all ten ECG-leads need to be connected to the safety analyzer. If necessary, use
an adapter cable to connect all ten ECG-leads. If necessary, repeat the safety test procedure until
all available applied parts have been tested. Refer to the documentation that accompanies the
safety analyzer for further details on how to set up and perform the test.
Protective Earth Resistance Test - Setup Example
Equipment Leakage Current Test - Setup Example

3 Testing and Maintenance Safety Tests
44
Applied Part Current Test - Setup Example
NOTE
The above graphics resemble the Metron QA-90 setup and are protected by copyright. Copyright
owned by Fluke (Metron).

Safety Tests 3 Testing and Maintenance
45
Safety Test Adapter Cable - Schematics
The following graphics provide schematics of safety test (patient lead) adapter cables which can
be used for electrical safety testing. These schematics can also be used as a guideline for making
your own safety test adapter cables. Alternatively, other methods to make safety test adapter
cables can be used, e.g. using a modified accessory cable.
NOTE
You may not need all of the cables displayed below for electrical safety testing of your
respective monitor.
ECG:

3 Testing and Maintenance Safety Tests
46
SpO2 (MP2/X2, MP5, M3001A & M1020B #A01, #A02, #A03):

Safety Tests 3 Testing and Maintenance
47
SpO2 (M1020A):

3 Testing and Maintenance Safety Tests
48
Invasive Pressure:
M1006B #C01:

Safety Tests 3 Testing and Maintenance
49
Temperature:

3 Testing and Maintenance Safety Tests
50
CO2 (MP5, M3014A):

Safety Tests 3 Testing and Maintenance
51
CO2 (M1016A, M3016A):
4 = all resistors 120 KOhm

3 Testing and Maintenance Safety Tests
52
Cardiac Output:

Safety Tests 3 Testing and Maintenance
53
BIS:
Use Clamp Adapter Cable and M1034-61650 BIS sensor simulator.

3 Testing and Maintenance Safety Tests
54
VueLink:
4 = 220 Ohm

Safety Tests 3 Testing and Maintenance
55
IntelliBridge:
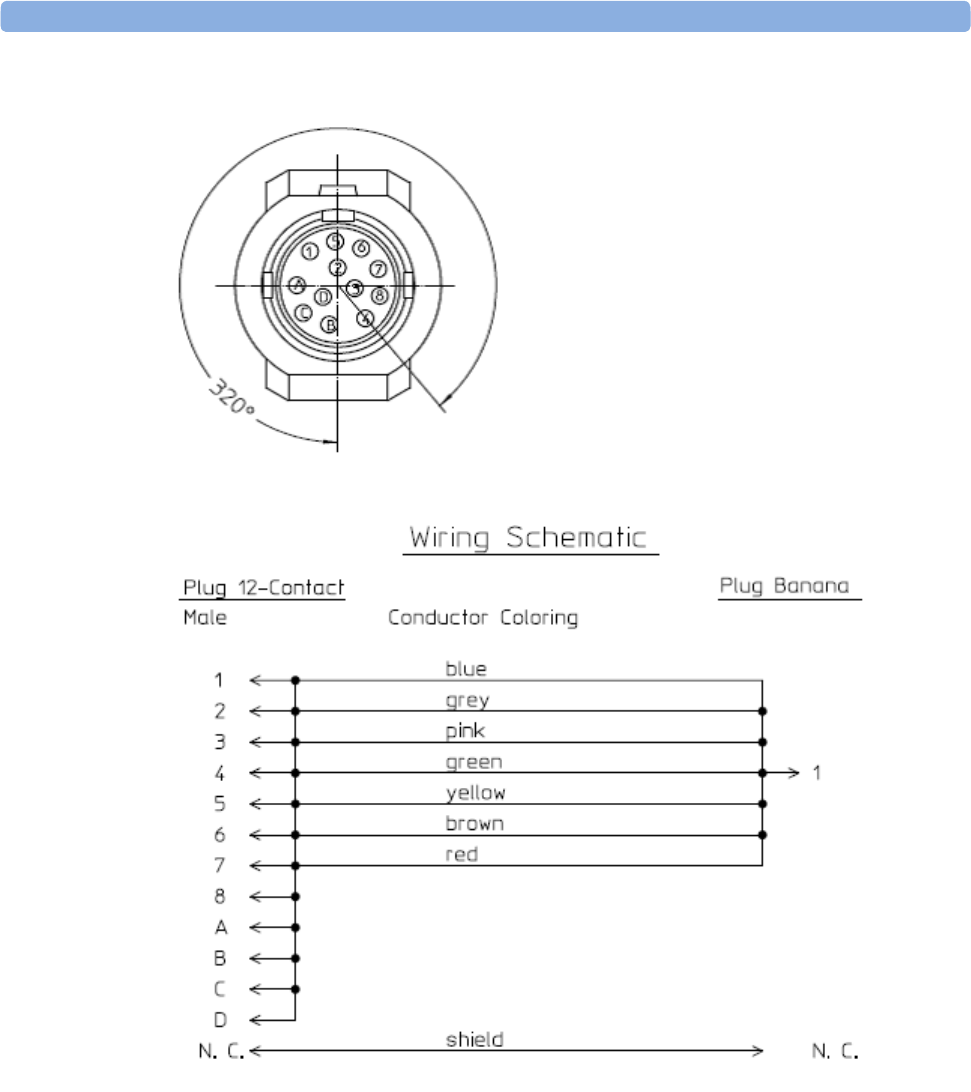
3 Testing and Maintenance Safety Tests
56
EEG:

Safety Tests 3 Testing and Maintenance
57
SvO2 (M1021A):

3 Testing and Maintenance Safety Tests
58
ScvO2 (M1011A):
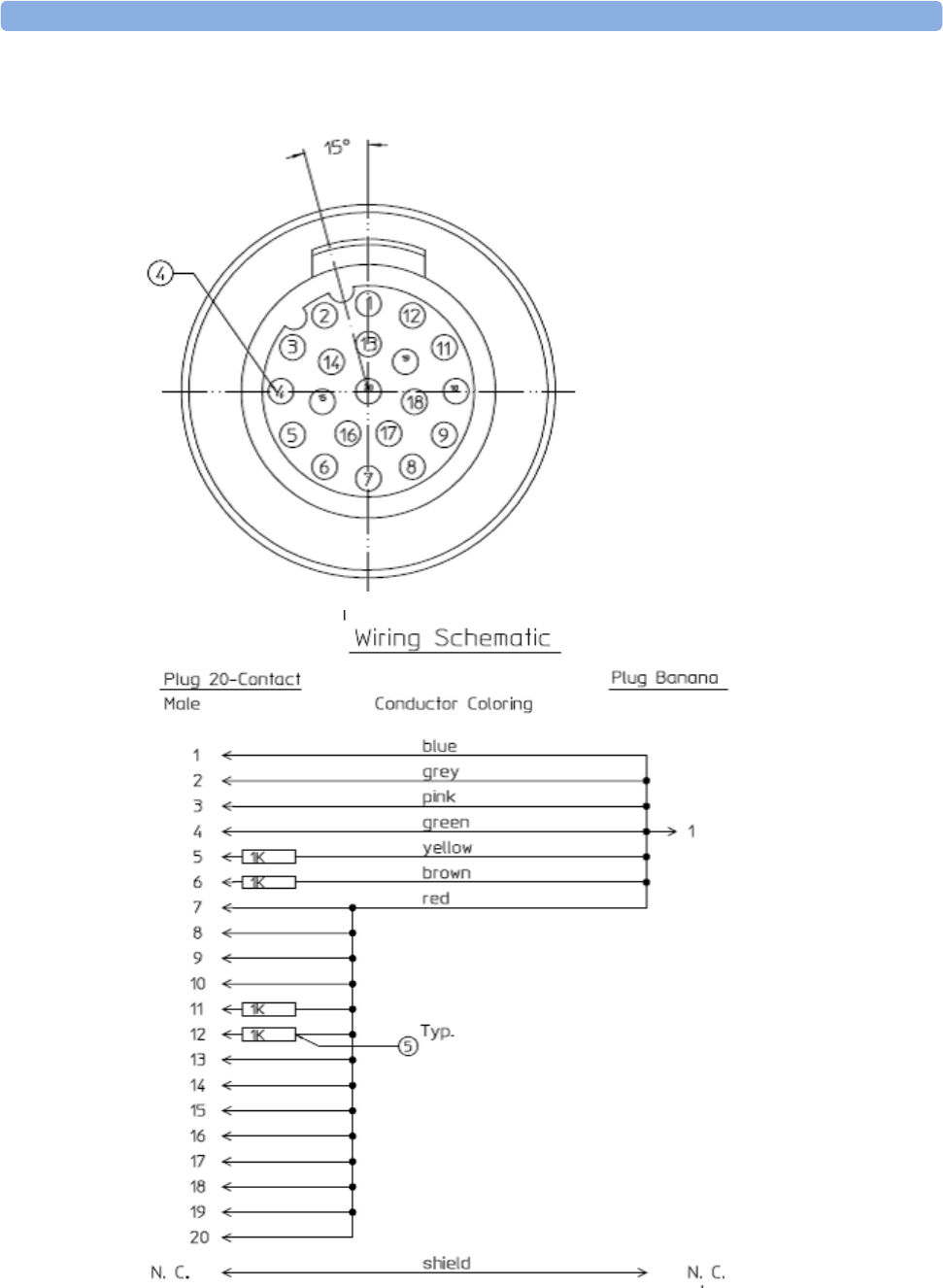
Safety Tests 3 Testing and Maintenance
59
tcpO2/tcpCO2:

3 Testing and Maintenance Safety Tests
60
MP5 predicitive Temperature:
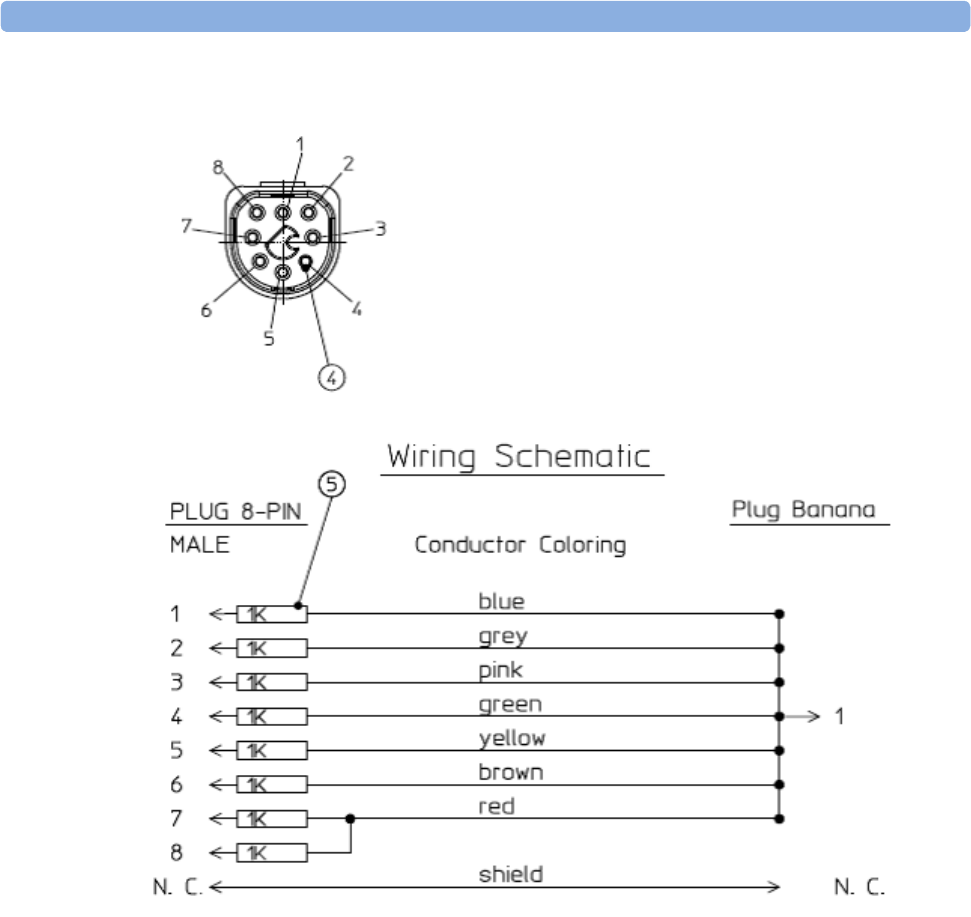
Safety Tests 3 Testing and Maintenance
61
MP5 TAAP:

3 Testing and Maintenance Safety Tests
62
S(1): Protective Earth Resistance Test
Test to perform:
Measuring circuit for the measurement of Protective Earth Resistance in medical electrical
equipment that is disconnected from the supply mains.
This measures the impedance of the Protective Earth (PE) terminal to all exposed metal parts of
the Instrument under Test (IUT), which are for safety reasons connected to the Protective Earth
(PE).
Measurements shall be performed using a measuring device capable to deliver a current of at
least 200 mA into 500 mOhms with maximum 24V
This safety test is based on IEC/EN 60601-1, IEC/EN 62353, UL2601-1 Ed. 2/UL60601-1:2003
and CSA 601.1-M90.
For measurement limits, refer to Safety (1) test, Test and Inspection Matrix.
Report the highest value (X1).
Test Expected test results
Protective Earth Resistance Test (with
mains cable) X1 <= 300mOhms
NOTE
- If the protective earth resistance test fails, testing must be discontinued immediately and the
device under test must be repaired or labeled as defective.
- All values for current and voltage are the root mean square (r.m.s.) values, unless otherwise
stated.
- Flex the power cord during the protective earth resistance test to evaluate its integrity. If it
does not pass the test, exchange the power cord.

Safety Tests 3 Testing and Maintenance
63
S(2): Equipment Leakage Current Test - Normal Condition
Test to perform:
Measuring circuit for the measurement of Equipment Leakage Current - Direct method
according to IEC/EN 62353.
This test measures leakage current of exposed metal parts of the monitor and the functional earth
leakage current. It tests normal and reversed polarity. Perform the test with S1 closed (Normal
Condition).
There are no parts of the equipment that are not protectively earthed.
This safety test is based on IEC/EN 60601-1, IEC/EN 62353, UL2601-1 Ed. 2/UL60601-1:2003
and CSA 601.1-M90.
For measurement limits, refer to Safety (2) test, Test and Inspection Matrix.
Report the highest value (X1).
Test Expected test results
Equipment Leakage Current Test
(Normal Condition - with mains
cable)
X1 <= 100μA
NOTE
All values for current and voltage are the root mean square (r.m.s.) values, unless otherwise
stated.

3 Testing and Maintenance Safety Tests
64
S(3): Equipment Leakage Current Test - Single Fault Condition
Test to perform:
Measuring circuit for the measurement of Equipment Leakage Current - Direct method
according to IEC/EN 62353.
This test measures leakage current of exposed metal parts of the monitor and the functional earth
leakage current. It tests normal and reversed polarity. Perform the test with S1 open (Single Fault
Condition).
There are no parts of the equipment that are not protectively earthed.
This safety test is based on IEC/EN 60601-1, IEC/EN 62353, UL2601-1 Ed. 2/UL60601-1:2003
and CSA 601.1-M90.
For measurement limits, refer to Safety (3) test, Test and Inspection Matrix.
Report the highest value (X2).
Test Expected test results
Equipment Leakage Current Test
(Single Fault Condition - with mains
cable)
X2 <= 300μA
NOTE
All values for current and voltage are the root mean square (r.m.s.) values, unless otherwise
stated.

Safety Tests 3 Testing and Maintenance
65
S(4): Applied Part Leakage Current - Mains on Applied Part
NOTE
During measurement of the Applied Part Leakage Current it is possible that the measured current
can exceed the allowed limit (per IEC/EN 60601-1 or IEC/EN 62353).
This can occur when the safety tester is connected to the invasive blood pressure and
temperature connectors at the same time during the applied leakage current measurement.
The connectors for the invasive blood pressure and temperature are independently functioning
connectors.
Although there are individual connectors on the front end, internally those parameters use the
same electrical insulation interface and are hardwired to each other. This results in an electrical
short of those connectors during measurement if a test current is applied simultaneously.
Therefore this should be avoided.
Due to the combined insulation interface, it is sufficient to connect to only one parameter
interface (that is, Invasive Blood Pressure or Temperature) of the invasive blood
pressure/temperature measurement block. This avoids a short and the potential of exceeding the
limit for the current.
Test to perform:

3 Testing and Maintenance System Test
66
Measuring circuit for the measurement of Applied Part Leakage Current - Direct method
according to IEC/EN 62353.
This test measures applied part leakage current from applied part to earth caused by external
main voltage on the applied part. Each polarity combination possible shall be tested. This test is
applicable for ECG measurement inputs.
There are no parts of the equipment that are not protectively earthed.
This safety test is based on IEC/EN 60601-1, IEC/EN 62353, UL2601-1 Ed. 2/UL60601-1:2003
and CSA 601.1-M90.
For measurement limits and test voltage, refer to Safety (4) test, Test and Inspection Matrix.
Report the highest value. (X1).
Test Expected test results
Applied Part Leakage Current Test
(Single Fault Condition - mains on
applied part)
S4 <= 50μA
NOTE
All values for current and voltage are the root mean square (r.m.s.) values, unless otherwise
stated.
System Test
After mounting and setting up a system, perform system safety tests according to IEC/EN
60601-1-1.
What is a Medical Electrical System?
A medical electrical system is a combination of at least one medical electrical piece of
equipment and other electrical equipment, interconnected by functional connection or use of a
multiple portable socket-outlet.
- Devices forming a medical electrical system must comply with IEC/EN 60601-1-1.
- Any electrical device such as IT equipment that is connected to the medical electrical
equipment must comply with IEC/EN 60601-1-1 and be tested accordingly.

System Test 3 Testing and Maintenance
67
General Requirements for a System
After installation or subsequent modification, a system must comply with the requirements of the
system standard IEC/EN 60601-1-1. Compliance is checked by inspection, testing or analysis, as
specified in the IEC/EN 60601-1-1 or in this book.
Medical electrical equipment must comply with the requirements of the general standard IEC/EN
60601-1, its relevant particular standards and specific national deviations. Non-medical electrical
equipment shall comply with IEC safety standards that are relevant to that equipment.
Relevant standards for some non-medical electrical equipment may have limits for equipment
leakage currents higher than required by the standard IEC/EN 60601-1-1. These higher limits are
acceptable only outside the patient environment. It is essential to reduce equipment leakage
currents to values specified in IEC 60601-1 when non-medical electrical equipment is to be used
within the patient environment.
System Example
This illustration shows a system where both the medical electrical equipment and the
non-medical electrical equipment are situated at the patient’s bedside.

3 Testing and Maintenance System Test
68
WARNING
- Do not use additional AC mains extension cords or multiple portable socket-outlets. If a
multiple portable socket-outlet is used, the resulting system must be compliant with IEC/EN
60601-1-1. Do not place multiple socket-outlets on the floor. Do not exceed the maximum
permitted load for multiple socket-outlets used with the system. Do not plug additional
multiple socket outlets or extension cords into multiple socket outlets or extension cords
used within the medical electrical system.
- Do not connect any devices that are not supported as part of a system.
- Do not use a device in the patient vicinity if it does not comply with IEC/EN 60601-1. The
whole installation, including devices outside of the patient vicinity, must comply with
IEC/EN 60601-1-1. Any non-medical device placed and operated in the patient’s vicinity
must be powered via a separating transformer (compliant with IEC/EN 60601-1-1) that
ensures mechanical fixing of the power cords and covering of any unused power outlets.

System Test 3 Testing and Maintenance
69
System Installation Requirements
- Ensure that the the medical electrical system is installed in a way that the user achieves
optimal use.
- Make sure the user is informed about the required cleaning, adjustment, sterilization and
disinfection procedures listed in the Instructions for Use.
- The medical electrical system must be installed in such a way that the user is able to carry
out the necessary cleaning, adjustment, sterilization and disinfection procedures listed in the
Instructions for Use.
- Ensure that the medical electrical system is installed in a way that an interruption and
restoration of power to any part of the medical electrical system does not result in a safety
hazard.
- We recommend using fixed mains socket outlets to power the medical system or parts
thereof. Avoid using multiple portable socket-outlets.
- Any multiple portable socket outlets used must be compliant with IEC 60884-1 and IEC
60601-1-1.
- Ensure that any part of the system connected to multiple portable socket-outlets is only
removable with a tool, i.e. the multiple portable socket-outlet provides a locking mechanism
to prevent power cords from being plugged or unplugged unintentionally. Otherwise, the
multiple portable socket-outlet must be connected to a separation device. Multiple Socket
Outlets used within the medical electrical system must only be used for powering medical
electrical equipment which is part of the system.
- Ensure that any functional connections between parts of the medical electrical system are
isolated by a separation device according to IEC 60601-1-1 to limit increased equipment
leakage currents caused by current flow through the signal connections. This only works if
the equipment leakage current of the respective medical electrical system parts is not
exceeded under normal conditions.
- Avoid increase of equipment leakage currents when non-medical electrical equipment within
the medical electrical system is used. This only works if the equipment leakage current of
the respective medical electrical system parts is not exceeded under normal conditions. Use
additional protective earth connection, separation device or additional non-conductive
enclosures.
- Within the patient environment it is important to limit electrical potential differences
between different parts of a system. If necessary, use potential equalization equipment
(equipotential cable) or additional protective earth connections.
- Medical electrical equipment used in medical rooms must be connected to potential
equalization equipment (equipotential cable) to avoid electrical potential differences. Check
your local requirements for details.

3 Testing and Maintenance System Test
70
Required Protective Measures at System Installation
For any IT equipment (IEC60950) operated in patient vicinity ensure that the equipment leakage
current does not exceed the limits described in IEC 60601-1. Use a separation device to ensure
compliance. After installation of IT equipment in patient vicinity, an enclosure leakage current
test is required.
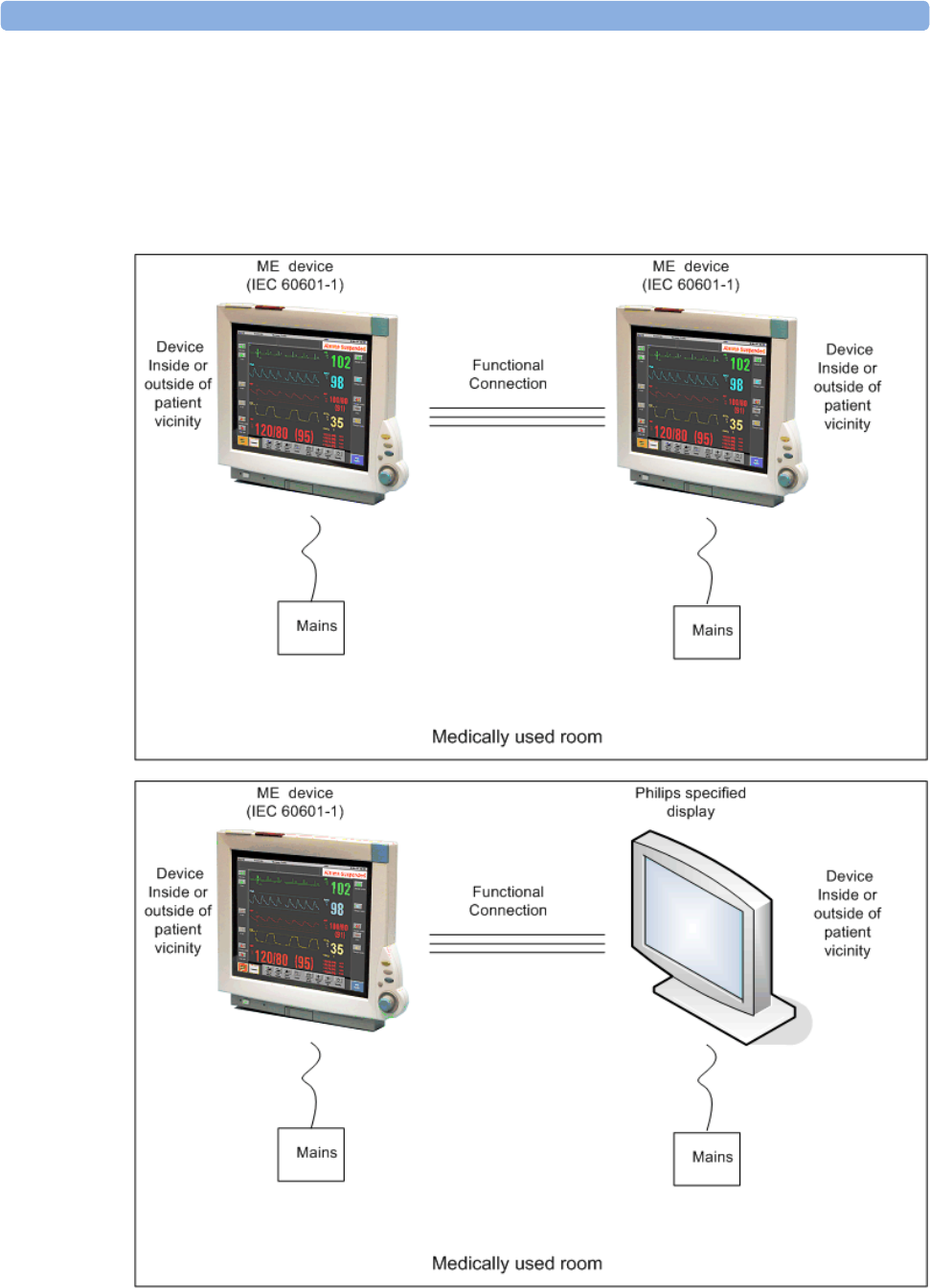
System Test 3 Testing and Maintenance
71
Case 1: Medical Device Combined with Medical Device
If you combine a medical device with another medical device (incl. Philips specified displays) to
form a medical electrical system according to IEC60601-1-1, no additional protective measures
are required. The medical electrical devices may be located in or outside the patient vicinity in a
medically used room. This is valid as long as the medical devices are connected to separate
mains outlets. No system test is required.
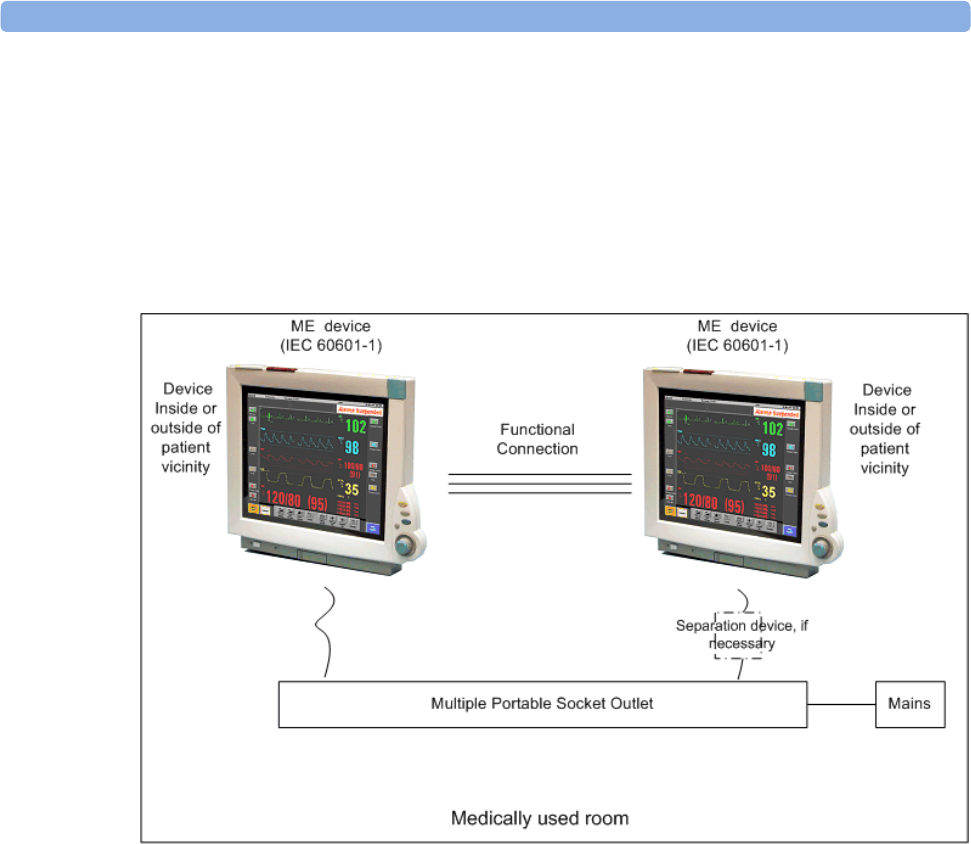
3 Testing and Maintenance System Test
72
If the combined medical devices are connected to the same multiple portable socket outlet an
enclosure leakage current test of the entire device combination on the multiple portable socket
outlet is required to ensure that the resulting protective earth leakage current and equipment
leakage current does not exceed the limits of IEC 60601-1-1. Avoid using multiple portable
socket outlets. The medical electrical devices may be located in or outside the patient vicinity in
a medically used room. If the limits are exceeded, additional protective measures are required,
e.g. a separation device or the connection of each device to separate mains.

System Test 3 Testing and Maintenance
73
Case 2: Medical Device Combined with a Non-Medical Device
If you combine a medical device with a non-medical device to form a medical electrical system
according to IEC60601-1-1, additional protective measures are required, e.g. usage of a
separation device. The medical electrical devices or the IT equipment may be located in or
outside the patient vicinity in a medically used room. After system installation incl. protective
measures, a system test is required to ensure that the resulting equipment leakage current and
applied part leakage current does not exceed the limits of IEC 60601-1-1.

3 Testing and Maintenance System Test
74
For any IT equipment (IEC60950) operated in patient vicinity ensure that the equipment leakage
current does not exceed the limits described in IEC 60601-1. Use a separation device to ensure
compliance. After installation of IT equipment in patient vicinity, an enclosure leakage current
test is required.

System Test 3 Testing and Maintenance
75
If the combined devices forming the medical electrical system are connected to the same
multiple portable socket outlet, ensure that the resulting protective earth leakage current and
equipment leakage current do not exceed the limits of IEC 60601-1-1. The medical electrical
devices or IT equipment may be located in or outside the patient vicinity in a medically used
room. Avoid using multiple portable socket outlets. If the limits of IEC 60601-1-1 are exceeded,
additional protective measures are required, e.g. a separation device or the connection of each
device to separate mains.

3 Testing and Maintenance System Test
76
For any IT equipment (IEC60950) operated in patient vicinity ensure that the equipment leakage
current does not exceed the limits described in IEC 60601-1. Use a separation device to ensure
compliance. After installation of IT equipment in patient vicinity, an enclosure leakage current
test is required.

System Test 3 Testing and Maintenance
77
Case 3: Medical Device Combined with a Medical or Non-Medical Device with one Device in a
Non-Medically-Used Room
If you combine a medical device with a medical or non-medical device to form a medical
electrical system according to IEC60601-1-1 using a common protective earth connection and
one of the devices is located in a non-medically used room, additional protective measures are
required, e.g. usage of a separation device or additional protective earth connection. The medical
electrical devices or IT equipment may be located in or outside the patient vicinity. After system
installation incl. protective measures, a system test is required to ensure that the resulting
equipment leakage current does not exceed the limits of IEC 60601-1-1.

3 Testing and Maintenance System Test
78

System Test 3 Testing and Maintenance
79
If you combine a medical device with a medical or non-medical device to form a medical
electrical system according to IEC60601-1-1 using two separate protective earth connections and
one of the devices is located in a non-medically used room creating a potential voltage
difference, additional protective measures are required, e.g. usage of a separation device or
additional protective earth connection. The medical electrical devices or IT equipment may be
located in or outside the patient vicinity. After system installation incl. protective measures, a
system test is required to ensure that the resulting equipment leakage current does not exceed the
limits of IEC 60601-1-1.

3 Testing and Maintenance System Test
80
System Test Procedure
If the medical electrical device has already been tested as a standalone device e.g. during factory
safety testing, an equipment leakage current test must only be performed once the device is
connected to the LAN network. If the medical electrical system has not been tested as a
standalone device, the device has to be tested as a standalone device (without connection to the
system) and as part of the system (with connection to the system).
Connect the detachable power cord of the device under test to the safety analyzer's test mains
port. Connect the enclosure test lead of the safety analyzer to the enclosure of the device under
test, e.g. to the equipotential connector. Refer to the documentation that accompanies the safety
analyzer for further details on how to set up the test.
Test Expected test results
Equipment Leakage Current Test
(Normal Condition) Sys1 <= 100μA
Equipment Leakage Current Test
(Single Fault Condition) Sys2 <= 300μA

Preventive Maintenance Procedures 3 Testing and Maintenance
81
After the testing of the device as a standalone device and as part of the system, check that the
resulting values (without connection and with connection to the system) do not differ by more
than +/- 10% from each other.
If the devices in the medical electrical system are connected to a multiple portable socket outlet
the resulting protective earth leakage current needs to be determined. All system components
must be connected to the multiple portable socket outlet and be switched on during this
measurement.
Test Expected test results
Protective Earth Leakage Current of
Multiple Socket Outlets Sys3 <= 300μA
Refer to the documentation that accompanies the safety analyzer for further details on how to set
up the test.
Preventive Maintenance Procedures
Noninvasive Blood Pressure Measurement Calibration
Carry out the noninvasive blood pressure measurement performance tests at least every two
years , or as specified by local laws (whichever comes first).
Microstream CO2 Calibration
Perform the Microstream CO2 calibration once a year or after 4000 hours of continuous use
(whichever comes first) and following any repairs or the replacement of any instrument parts.
See Microstream CO2 Performance Test (on page 90) for details.
Performance Assurance Tests
Some of the following test procedures must be performed in service mode. To enter service
mode select Operating Modes in the main menu. Then select Service Mode and enter the
password.
If required, open the screen menu in the monitor info line at the top of the screen and select
Service to access the service screen. This is required particularly for Anesthetic Gas Module
testing procedures.

3 Testing and Maintenance Performance Assurance Tests
82
Basic Performance Assurance Test
This section describes the basic performance test procedure. Please refer to the section When to
Perform Tests for detailed information on when which test procedure is required.
Procedure:
Power on the monitoring system and go into demo mode. Check that each connected parameter
(integrated, module, MMS, Gas Analyzer, Vuelink connected device) displays values.
Full Performance Assurance Test
The following sections describe the full performance testing procedures i.e. detailed testing of
each parameter with a patient simulator or specified tools. Please refer to the section When to
perform Tests for information on when which testing procedure is required.
ECG/Resp Performance Test
This test checks the performance of the ECG and respiration measurements.
Tools required: Patient simulator.
ECG Performance
1. Connect the patient simulator to the ECG/Resp connector.
2. Configure the patient simulator as follows:
- ECG sinus rhythm.
- HR = 100 bpm or 120 bpm (depending on your patient simulator).
3. Check the displayed ECG wave and HR value against the simulator configuration.
4. The value should be 100bpm or 120 bpm+/- 2 bpm.
Respiration Performance
1. Change the Patient Simulator configuration to:
- Base impedance line 1500 Ohm.
- Delta impedance 0.5 Ohm.
- Respiration rate 40 rpm or 45 rpm.
2. The value should be 40 rpm +/- 2 rpm or 45 rpm +/- 2 rpm.
Test Expected test results
ECG Performance Test 100bpm +/- 2bpm or
120bpm +/- 2bpm
Respiration Performance Test 40 rpm +/- 2 rpm or
45 rpm +/- 2 rpm

Performance Assurance Tests 3 Testing and Maintenance
83
ECG Sync Performance Test
This test checks the performance of ECG synchronization between the monitor and a
defibrillator. It only needs to be performed when this feature is in use as a protocol at the
customer site.
Tools required:
- Defibrillator with ECG Sync and Marker Output.
- Patient simulator.
1. Connect the patient simulator to the ECG connector and the defibrillator to the ECG Sync
Output on the monitor.
2. Set the patient simulator to the following configuration:
- HR = 100 bpm or 120 bpm (depending on your patient simulator).
- ECG sinus rhythm.
3. Switch the defibrillator to simulation mode.
4. Check that the marker pulse is displayed before the T-wave begins.
Test Expected test results
ECG Sync Performance Test Marker pulse is displayed before
the T-wave begins
SpO2 Performance Test
This test checks the performance of the SpO2 measurement.
Tools required: none
1. Connect an adult SpO2 transducer to the SpO2 connector.
2. Measure the SpO2 value on your finger (this assumes that you are healthy).
3. The value should be between 95% and 100%.
Test Expected test results
SpO2 Performance Test 95% and 100%

3 Testing and Maintenance Performance Assurance Tests
84
Measurement Validation
The SpO2 accuracy has been validated in human studies against arterial blood sample reference
measured with a CO-oximeter. In a controlled desaturation study, healthy adult volunteers with
saturation levels between 70% and 100% SaO2 were studied. The population characteristics for
those studies were:
- about 50% female and 50% male subjects
- age range: 18 to 45
- skin tone: from light to black
NOTE
A functional tester cannot be used to assess the accuracy of a pulse oximeter monitor. However,
it can be used to demonstrate that a particular pulse oximeter monitor reproduces a calibration
curve that has been independently demonstrated to fulfill a particular accuracy specification.
NBP PerformanceTest
This section describes NBP test procedures.The monitor must be in service mode and the screen
“Service A” must be selected to perform these tests. The NBP Performance Test consists of:
- NBP Accuracy Test
- NBP Leakage Test
- NBP Linearity Test
- Valve Test
NBP Accuracy Test
This test checks the performance of the non-invasive blood pressure measurement. Connect the
equipment as shown:

Performance Assurance Tests 3 Testing and Maintenance
85
Tools required:
- Reference manometer (includes hand pump and valve), accuracy 0.2% of reading.
- Expansion chamber (volume 250 ml +/- 10%)
- Appropriate tubing.
In service mode, the systolic and diastolic readings indicate the noise of NBP channels 1 and 2
respectively. When static pressure is applied, the reading in NBP channel 1 should be below 50.
The value in parentheses indicates the actual pressure applied to the system.
1. Connect the manometer and the pump with tubing to the NBP connector on the MMS and to
the expansion chamber.
2. In service mode, select the Setup NBP menu.
3. Select Close Valves: On
4. Raise the pressure to 280 mmHg with the manometer pump.
5. Wait 10 seconds for the measurement to stabilize.
6. Compare the manometer values with the displayed values.
7. Document the value displayed by the monitor (x1).
8. If the difference between the manometer and displayed values is greater than 3 mmHg,
calibrate the MMS. If not, proceed to the leakage test.
9. To calibrate the MMS, select Close Valves off then Calibrate NBP and wait for the
instrument to pump up the expansion chamber.Wait a few seconds after pumping stops until
EnterPrVal is highlighted and then move the cursor to the value shown on the
manometer. If one of the following prompt messages appears during this step, check
whether there is leakage in the setup:
- NBP unable to calibrate–cannot adjust pressure
- NBP unable to calibrate–unstable signal
10. Press Confirm.
If the INOP NBP Equipment Malfunction message occurs in monitoring mode, go back to
service mode and repeat the calibration procedure.
NBP Leakage Test
The NBP leakage test checks the integrity of the system and of the valve. It is required once
every two years and when you repair the monitor or replace parts.
1. If you have calibrated, repeat steps 2 to 6 from the accuracy test procedure so that you have
280 mmHg pressure on the expansion chamber.
2. Watch the pressure value for 60 seconds.
3. Calculate and document the leakage test value (x2).
x2 = P1 - P2
where P1 is the pressure at the beginning of the leakage test and P2 is the pressure displayed
after 60 seconds.
The leakage test value should be less than 6 mmHg.

3 Testing and Maintenance Performance Assurance Tests
86
NBP Linearity Test
1. Reduce the manometer pressure to 150 mmHg.
2. Wait 10 seconds for the measurement to stabilize.
3. After these 10 seconds, compare the manometer value with the displayed value.
4. Document the value displayed by the monitor (x3)
5. If the difference is greater than 3 mmHg, calibrate the MMS (see steps 9 to 10 in the
accuracy test procedure).
Valve Test
1. Raise the pressure again to 280 mmHg.
2. Select Close valves: Off.
3. Wait five seconds and then document the value displayed. The value should be less than 10
mmHg.
4. Document the value displayed by the monitor (x4).
Expected Test Results for NBP Accuracy Test, Leakage Test, Linearity Test & Valve Test
Test Expected test results
Accuracy test x1 = value displayed by monitor
Difference ≤ 3mmHg
Leakage test x2 = leakage test value
x2 < 6 mmHg
Linearity test x3 = value displayed by monitor
Difference ≤ 3mmHg
Valve Test x4 = value < 10 mmHg
Invasive Pressure Performance Test
This test checks the performance of the invasive pressure measurement.
Tools required: Patient simulator.
1. Connect the patient simulator to the pressure connector.
2. Set the patient simulator to 0 pressure.
3. Make a zero calibration.
4. Configure the patient simulator as P(static) = 200 mmHg.
5. Wait for the display.

Performance Assurance Tests 3 Testing and Maintenance
87
6. The value should be 200 mmHg ± 5 mmHg. If the value is outside these tolerances, calibrate
the Invasive Pressure measurement. If the measurement was calibrated with a dedicated
reusable catheter, check the calibration together with this catheter.
Table 4:
Test Expected test results
Invasive Pressure Performance Test 200 mmHg ± 5 mmHg
Temperature Performance Test
This test checks the performance of the temperature measurement.
Tools required: Patient simulator (with 0.1°C or 0.2°F).
1. Connect the patient simulator to the temperature connector.
2. Configure the patient simulator to 40°C or 100°F.
3. The value should be 40°C ± 0.2°C or 100°F ± 0.4°F.
Table 2:
Test Expected test results
Temperature Performance Test 40°C ± 0.2°C or 100°F ± 0.4°F
M3014A Capnography Extension Performance Tests
The procedures below describe the mainstream and sidestream CO2 performance tests for the
M3014A Capnography Extension.
Mainstream CO2 Accuracy Check
Tools Required:
- three airway adapters
- Verification Gas M2506A
- Gas cylinder regulator M2505A
You also need a local barometric pressure rating received from a reliable local source (airport,
regional weather station or hospital weather station) which is located at the same altitude as the
hospital.
Procedure:
1. Attach the M2501A CO2 sensor to the patient monitor. Attach an airway adapter to the
sensor. Make sure that the sensor is disconnected from the patient circuit.
2. Switch on the patient monitor.
3. Enter the monitor’s Service Mode.

3 Testing and Maintenance Performance Assurance Tests
88
4. Using the sensor status provided in the M2501A Serial protocol, wait for the M2501A
sensor to warm up to its operating temperature.
5. The default setting for gas temperature is 22°C. If the gas temperature is significantly above
or below this value, correct the gas temperature setting.
6. Zero the sensor on the airway adapter being used in this test. Ensure Zero Gas is set to Room
Air
7. Attach a regulated flowing gas mixture of 5% CO2, balance N2 to the airway adapter.
8. Set the gas correction to off.
9. Allow a few seconds for the gas mixture to stabilize and observe the CO2 value. The
expected value is 5% of the ambient pressure ±2mmHg
NOTE
Make sure that you follow the above steps correctly. If the sensor fails this check it must be
exchanged. The sensor cannot be calibrated.
Example for an expected test result:
The expected test result for an altitude of 0 m (sea level) at approximately 760 mmHg ambient
pressure is:
Table 6:
Test Expected test results (x1) Acceptance Range
Mainstream CO2 Accuracy
Test 5% of 760 mmHg pressure ±2mmHg 36 mmHg -
40 mmHg
NOTE
The expected test results will differ depending on the conditions (i.e. altitude or ambient
pressure).
Sidestream CO2 Accuracy Check
Tools Required:
- Cal gas flow regulator M2267A
- Cal tube 13907A
- Verification Gas M2506A
- Straight Sample Line M2776A
You also need a local barometric pressure rating received from a reliable local source (airport,
regional weather station or hospital weather station) which is located at the same altitude as the
hospital.
Procedure:
1. Attach the M2741A CO2 sensor to the patient monitor. Attach the sample line and the cal
tube to the sensor. Make sure that the sensor is disconnected from the patient circuit.
2. Switch on the patient monitor.
3. Enter the monitor’s Service Mode.

Performance Assurance Tests 3 Testing and Maintenance
89
4. Using the sensor status provided in the M2741A Serial protocol, wait for the M2741A
sensor to warm up to its operating temperature.
5. Zero the sensor. Ensure Zero Gas is set to Room Air
6. Attach a regulated flowing gas mixture of 5% CO2, balance N2 to the cal tube.
7. Set the gas correction to off.
8. Allow a few seconds for the gas mixture to stabilize and observe the CO2 value. The
expected value is 5% of the ambient pressure ±2mmHg
NOTE
Make sure that you follow the above steps correctly. If the sensor fails this check it must be
exchanged. The sensor cannot be calibrated
Example for an expected test result:
The expected test result for an altitude of 0 m (sea level) at approximately 760 mmHg ambient
pressure is:
Test Expected test results (x2) Acceptance Range
Sidestream CO2 Accuracy
Test 5% of 760 mmHg pressure ±2mmHg 36 mmHg -
40 mmHg
NOTE
The expected test results will differ depending on the conditions (i.e. altitude or ambient
pressure).
Sidestream CO2 Flow Check
Check the flow rate in the Sidestream CO2 extension as follows:
1. Connect the flowmeter to the sample line
2. Check on the flowmeter the flow that the Sidestream CO2 extension pump draws. It should
be 50 ml/min ± 10 ml/min. If the value is not within tolerance check your setup again and
perform another flow check. If it fails again, the sensor must be replaced. The sensor cannot
be calibrated.

3 Testing and Maintenance Performance Assurance Tests
90
Microstream CO2 Performance Test
Allow five seconds between individual service procedures to ensure stable equipment conditions.
When certain monitor procedures are running, service procedures are not possible and trying to
start them will result in a message Service Operation Failed in the monitor’s status line.
Wait until the monitor completes the current operation, then restart the service procedure.
This test checks the performance of the Microstream CO2 measurement. The Microstream CO2
measurement can either be integrated into the IntelliVue MP5 monitor or, for other IntelliVue
monitors, into the M3015A MMS Extension. The Microstream CO2 performance test is required
once per year and when the instrument is repaired or when parts are replaced.
This test uses calibration equipment that you can order (see the Parts section for the part
number). The procedure is summarized in the following steps. Refer to the documentation
accompanying the equipment for detailed instructions.
Tools Required:
- Standard tools, such as screwdriver, tweezers
- Electronic flowmeter, M1026-60144
- Gas calibration equipment:
- Cal 1 gas 15210-64010 (5% CO2)
- Cal 2 gas 15210-64020 (10% CO2)
- Cal gas flow regulator M2267A
- Cal tube 13907A
- Calibration Line M3015-47301
You also need a local barometric pressure rating received from a reliable local source (airport,
regional weather station or hospital weather station) which is located at the same altitude as the
hospital.
The CO2 calibration for the Microstream extension consists of the following steps:
- Leakage check
- Barometric pressure check and calibration, if required.
- Pump check
- Flow check and calibration, if required
- Noise check
- CO2 Cal check and calibration, if required
- CO2 Cal verification using 2nd cal gas
Perform all checks in the same session.

Performance Assurance Tests 3 Testing and Maintenance
91
Leakage Check
The leakage check consists of checking the tubing between:
- the pump outlet and the mCO2 outlet and
- the pump inlet and FilterLine inlet.
Check the user’s guide of the flowmeter for details on how to make a correct flow reading.
Part 1
1. Go into service mode and select Setup CO2 menu.
2. Connect a FilterLine to the Microstream CO2 input to start the pump running.
3. Check the ambient pressure and the cell pressure shown in the monitor’s status line. The cell
pressure should be approximately 20 mmHg lower than ambient pressure.
4. Connect the flowmeter outlet to the FilterLine inlet using a flexible connecting tube.
5. Block the mCO2 outlet using your fingertip and observe the flowmeter display. The value on
the flowmeter (x1) should decrease to between 0 and 4 ml/min, accompanied by an audible
increase in pump noise. If the value is within the tolerance limits, continue with part 2 of the
leakage check.
6. If the value is outside the tolerance limits, there is a leakage between the pump outlet and the
mCO2 outlet.
7. Open the MMS Extension or MP5 and check the tubing connections at the pump outlet and
the extension gas outlet. If the connections are good, then there is a leakage in the tubing and
you must exchange the MMS Extension or the mCO2 Assembly of the MP5 respectively.
Part 2
1. Disconnect the flowmeter from the Part 1 setup and connect the flowmeter inlet to the
M3015A gas outlet or the MP5 mCO2 gas outlet.
2. Leave the Filterline connected to the M3015A inlet or the MP5 mCO2 inlet..
3. Block the inlet of the FilterLine using your fingertip and observe the flowmeter display. The
value on the flowmeter (x2) should decrease to between 0 and 4 ml/min, accompanied by an
audible increase in pump noise. The cell pressure shown in the status line on the display
should decrease to between 300 and 500 mmHg. Do not block the inlet for longer than 25
seconds as this will lead to an “Occlusion” INOP. If the value is within the tolerance limits,
there are no leakages and the leakage check is completed; proceed to the pump check.
4. If the value is not within the tolerance limits, there is a leakage between the FilterLine inlet
and the pump inlet.
5. Check the FilterLine connections and open the M3015A or MP5 to check the tubing
connections at the pump inlet and the M3015A or MP5 mCO2 gas inlet. If the connections
are good, try replacing the FilterLine and repeating the leakage check. If the situation
remains, there is a leakage in the tubing and the M3015A or the mCO2 assembly of the MP5
must be exchanged.

3 Testing and Maintenance Performance Assurance Tests
92
Barometric Pressure Check and Calibration
Check the barometric pressure value in the M3015A MMS Extension or the MP5 as follows:
1. Go into service mode and select Setup CO2 menu.
2. Connect a FilterLine to the Microstream CO2 input. This activates the pump in the M3015A
MMS Extension or the MP5.
3. The status line at the bottom of the screen displays “CO2 pressure reading (ambient/cell)
xxx/yyy” where xxx is the ambient pressure and yyy is the measured cell pressure. Check
whether the ambient pressure value (x3) matches (within the acceptable tolerance of ±12mm
Hg) the reference value you have received. If so, proceed to the leakage check. If the value
is not correct, calibrate as follows.
a. Select CO2 then select Barom.Press to activate a table of values.
b. Select the value in the table which matches the reference value received from a reliable local
source (airport, regional weather station or hospital weather station). (The values are
displayed with a resolution of 2 mmHg up to 500 mmHg and a resolution of 1 mmHg from
500 mmHg to 825 mmHg.) Note: the selected value must be within ±10% of the current
measured ambient pressure, otherwise an error message will occur at restarting the monitor.
c. Confirm the barometric pressure setting.
d. Check that the ambient pressure displayed in the status line at the bottom of the screen is the
same as the value which you selected from the list in step b.
Pump Check
1. Connect the flowmeter inlet to the mCO2 gas outlet.
2. Connect the FilterLine to the mCO2 inlet.
3. Block the inlet of the FilterLine using your fingertip and observe the cell pressure on the
monitor display. The cell pressure (x4) should be more than 120 mmHg below the ambient
pressure shown. If the pressure difference is less than 120 mmHg, the pump is not strong
enough and you should replace it, irrespective of the Pump OpTime.
Flow Rate Check and Calibration
Check the flow rate in the M3015A MMS Extension or the MP5 as follows:
1. Connect the flowmeter to the CO2 FilterLine.
2. Check on the flowmeter the flow that the M3015A MMS Extension or MP5 mCO2 pump
draws (x5). It should be 50 ml/min ± 7.5 ml/min. If the value is within tolerance, proceed to
the CO2 Gas calibration check. If the value is not within tolerance, calibrate as follows.
3. Adjust the flow in the instrument by selecting Increase Flow or Decrease Flow until
it is as close as possible to 50 ml per minute as indicated on the flowmeter gauge.
4. When you are satisfied that the flow is set as close as possible to 50 ml per minute, select
Store Flow and confirm the setting. If you do not store the adjusted flow within 60
seconds of the adjustment, the old flow setting is restored.

Performance Assurance Tests 3 Testing and Maintenance
93
5. If you cannot adjust the flow to within tolerance, replace the pump . If you still cannot make
the flow adjustment, this indicates a fault in the measurement extension, which must be
replaced.
Note that the pump can only be replaced on M3015A with the old hardware Rev. A (i.e.
Serial No. DE020xxxxx
Noise Check
1. With the monitor in service mode, select Setup CO2 menu.
2. Disconnect the flowmeter and connect the 5% calibration gas and flow regulator in its place.
3. Open the valve to apply the 5% calibration gas and wait until the value is stable.
4. Check the noise index (x6) displayed next to the CO2 value on the display (this indicates the
level of noise on the CO2 wave). If the value exceeds 3 mmHg, replace the measurement
extension.
CO2 Gas Measurement Calibration Check
After switching the measurement extension on, wait at least 20 minutes before checking the
calibration. Check the calibration of the CO2 gas measurement as follows:
1. Check that the 5% calibration gas and flow regulator are connected.
2. Calculate the expected measurement value in mmHg as follows:
0.05 x (ambient pressure) = value mmHg
for example 0.05 x 736 = 36.8 mmHg (with an ambient pressure of 736 mmHg)
3. Open the valve on the flow regulator to allow 5% CO2 gas to flow into the extension. Allow
the value to stabilize.
4. Check that the value on the instrument (measurement value on the main screen, x7) matches
the calculated mmHg value ± 2.6 mmHg. If the value is outside the tolerance, calibrate as
described in step in this procedure onwards.
5. Disconnect the 5% calibration gas and connect the 10% calibration gas.
6. Calculate the expected measurement value and tolerance in mmHg as follows:
0.1 x (ambient pressure) = value mmHg
±0.07 x (value mmHg) = tolerance
for example 0.1 x 737 mmHg = 73.7 mmHg (with an ambient pressure of 737 mmHg)
±0.07 x 73.7 mmHg = ±5.16 mmHg tolerance
7. Open the valve on the flow regulator to allow 10% CO2 gas to flow into the extension.
Allow the value to stabilize.
8. Check that the value on the instrument (x8) matches the calculated mmHg value within the
calculated tolerance. If so, the measurement extension is correctly calibrated. If the value is
outside the tolerance, calibrate as follows.
9. If not already connected, connect the 5% calibration gas.
10. Select Cal. CO2.
11. Select the value for the calibration gas. (The default value is 5.0%.)

3 Testing and Maintenance Performance Assurance Tests
94
12. Open the valve on the calibration gas to allow CO2 gas to flow into the extension. Allow the
value to stabilize before the start of the calibration. Leave the valve open until the instrument
gives a prompt that gas can be removed.
13. The extension calibrates and prompts when calibration is successful.
Calibration Verification
1. Reopen the 5% gas valve and allow the value to stabilize.
2. Check that the value displayed on the monitor is correct within the tolerance (see step
above).
3. Disconnect the 5% calibration gas and connect the 10% calibration gas.
4. Open the valve on the flow regulator to allow 10% CO2 gas to flow into the extension.
Allow the value to stabilize.
5. Check that the value displayed on the monitor is correct within the tolerance (see step
above).
If one or both values are not within tolerances, you must exchange the M3015A MMS Extension
or the MP5 mCO2 Assembly.
Test Expected Test Results
Leakage Check
parts 1 and 2 x1 = value of part 1 leakage check on flowmeter
(x1< 4.0 ml/min)
x2 = value of part 2 leakage check on flowmeter
(x2< 4.0 ml/min)
Barometric
Pressure Check x3 = difference between the reference pressure and the
measured ambient pressure displayed on the monitor
(x3<12 mmHg)
Pump Check x4 = difference in pressure between cell pressure and
ambient pressure displayed on the monitor during
occlusion (x4 >120 mmHg)
Flow Check x5 = difference between measured value and 50.0
ml/min (x5<7.5 ml/min)
Noise Check x6 = noise index displayed on monitor (x6<3.0)
CO2 Gas
Calibration Check x7 = difference between measured CO2 value and
calculated value, based on 5% CO2 cal. gas. (x7 < 2.6
mmHg)
CO2 Cal
Verification x8 = difference between measured CO2 value and
calculated value, based on 10% CO2 cal. gas.
(x8 < ± {0.07 x value calculated})

Performance Assurance Tests 3 Testing and Maintenance
95
Reset Time Counters
NOTE
This procedure only applies to M3015A with the old hardware Rev. A (i.e. Serial No.
DE020xxxxx
You must check the time counters on the Microstream CO2 extension before calibrating the
instrument. As well, when parts are replaced, the appropriate counters must be reset to zero.
The counters for CO2 pump, IR Src and Last Cal are displayed in the status line. The values are
updated when entering the Setup CO2 menu.
Observe the following guidelines:
- When calibrating the CO2 extension, if no parts have been replaced, check the displayed
values of Reset PumpOpTime and Reset IRSourceTime selections to make sure that
they are within suggested guidelines for use (15, 000 hours of continuous use). If the counter
time is greater than 15, 000 hours, replace the appropriate part. See Repair and Disassembly
for details.
- When calibrating the CO2 extension, if parts have been replaced, reset the appropriate values
using the Reset PumpOpTime and Reset IRSourceTime selections. See Repair and
Disassembly for details.
Resetting the PumpOpTime generates the INOP: “CO2 OCCLUSION”. To clear this INOP you
must perform a flow check and store the flow in service mode (select Store Flow).
CO2 Pump / CO2 Scrubber Replacement
NOTE
This procedure only applies to M3015A with the old hardware Rev. A (i.e. Serial No.
DE020xxxxx
Refer to the Repair and Disassembly section for the replacement procedures.
BIS Performance Test
These tests check the performance of the BIS measurement.
PowerLink Test
1. In monitoring mode connect the BIS sensor simulator (P/N: M1034-61650, 453563233731)
(for maximum usage please refer to the documentation delivered with the sensor simulator)
to the patient interface cable.
2. Enter the BIS menu and select Show Sensor.
3. Start impedance check by pressing StartCyclicCheck. Check the displayed results.
Expected results are:

3 Testing and Maintenance Performance Assurance Tests
96
Test Expected test results
BIS Performance Test Electrode 1 (+): 4-6 kΩ
Electrode 2 (Ref): 8-17 kΩ
Electrode 3 (1-): 2-4 kΩ
Electrode 4 (2-): 3-5 kΩ
Nurse Call Relay Performance Test
The nurse call relay performance test can be performed either at the phone jack type connector
(this only tests one relay) or at the multi-port nurse call connector (to test all three relays).
Phone Jack Type Connector Test (Traditional Nurse Call)
This test checks the operation of the traditional Nurse Call Relay. The Nurse Call Relay test is
recommended for customer sites where the nurse call is in use. The Nurse Call relay functions as
follows:
- Standard Operation—Relay open.
- Alarm Condition—Relay closed.
Tools required: Ohmmeter.
1. Plug a phono connector into the Nurse Call Relay connector.
2. Connect the ohmmeter.
3. If no alarm occurs, the relay contacts are open. When an alarm occurs, the relay contacts
close.
Tip
Ring
Sleeve
black
red
(relay loop)
(relay loop)
(ground)
4. The expected test result is: Alarm condition - Relay closed.
Test Expected test results
Nurse Call Relay Performance Test Alarm Condition—Relay closed

Performance Assurance Tests 3 Testing and Maintenance
97
Multi-Port Nurse Call Connector Test (Flexible Nurse Call)
This test checks the operation of the Flexible Nurse Call Relay. The Nurse Call Relay test is
recommended for customer sites where the nurse call is in use. The following diagram and table
show the pins and relay identifiers of the connector:
Pin Cable Color
Coding
Relay
1 black R2-closure
2 brown R2-middle
3 red R2-opener
4 orange R3-closure
5 yellow R3-middle
6 green R3-opener
7 blue n/a
8 purple n/a
9 gray n/a
10 white n/a
11 pink R1-closure
12 light green R1-middle
13 black/white R1-opener
14 brown/white n/a
15 red/white n/a
16 orange/white n/a
17 blue/white R_failure_closure
18 purple/white R_failure_middle
19 green/white R_failure_opener
20 red/black n/a

3 Testing and Maintenance Performance Assurance Tests
98
The Nurse Call relay functions as follows:
- During standard operation R1,R2,R3 _opener are closed; R1,R2,R3_closure are open.
- During alarm condition—R1,R2,R3_opener are open; R1,R2,R3_closure are closed.
Tools required: Ohmmeter.
1. Plug an M8087-61001 cable into the Nurse Call Relay connector.
2. Connect the ohmmeter and measure the pins as indicated in the diagram and table.
3. The relay contacts should behave as described above. The behavior may vary depending on
configuration choices. See the Configuration Guide for details on Alarm Relay settings.
4. The expected test results depend on the relay contact used. Please check that the correct
relay activity is initiated during alarm condition.
Power Loss Alarm Buzzer Performance Test (only if Multi-Port Nurse Call Connector Board
is installed)
1. Switch on the monitor.
2. Remove the battery and disconnect the monitor from AC power.
3. The Power Loss Alarm Buzzer should beep for about one minute.
4. To switch off the alarm sound, either press the power button, connect the monitor to AC
power or insert a battery
Test Expected test results
Power Loss Alarm Buzzer
Performance Test Beep for one minute
Docking Station Performance Test
1. Place the monitor on the docking station and close the lever.
2. Check that the green power LED lights up when the docking station is connected to AC
Power.
3. Check that the monitor’s AC Power LED lights up to indicate it is receiving power through
the docking station. (PO:P)
IIT Communication Test
1. Make sure the LAN cable is disconnected from the rear of the monitor, then switch on the
monitor.
2. Go into Configuration mode and, in the Network menu, set the RF Access Code in each
profile to match your installation.
3. Go into Service Mode. Select Main Setup -> Instr. Telemetry to access the
Instrument Telemetry Service window.

Performance Assurance Tests 3 Testing and Maintenance
99
4. Proper installation of the IIT module is assured by connecting to an access point over the
wireless link. Place the monitor with the IIT module installed in close proximity to the
access point (e.g. if the access point is mounted on the ceiling, place the monitor directly
below). Wait until the Conn.Status field in the Instrument Telemetry Service window
shows Active. Take the monitor approximately 5 m away from the access point. There should
be no walls or other obstacles between the monitor and the access point. The following
should apply:
- Observe the RSSI (Received Signal Strength Indicator) value for at least 5 - 10 seconds.
The RSSI value should be around -50 ±10 in a 5 m distance from the access point used
and the IIT link should be active, i.e. the Conn.Status field should be Active and the
other fields should contain values. If the RSSI value is significantly lower, check the
distance to the access point and the antenna orientation at both the monitor and the
access point (both should be vertical).
- Remove the antenna. The RSSI value should be around -90 ±10. The IIT link may be
active but the connection could be unreliable. The Conn. Status field may toggle
between Inactive and Seeking. If the difference between the RSSI values measured with
and without antenna is significantly lower, check the antenna and the antenna connector
for damage and verify that the cable fom the IIT adapter to the antenna connector plate
is connected properly.
5. If this test fails, retry in a different physical area with a different access point.
Error Conditions:
- The field MAC Instr. Tele should show a value unequal to 0000 0000 0000. If it
does not, there is a communication problem between the monitor and the IIT adapter.
- With an incorrect RF Access Code or an incorrect or defective antenna installation, the
fields IP Address,Server IP, Subnet Mask, and RSSI in the Instrument
Telemetry Service window will stay blank. The field Conn. Status will slowly toggle
between Inactive and Seeking.
6. Perform the Access Point Controller (APC) test blocks as described in the Philips
-USR_ProductName- Wireless Network Installation and Configuration Guide.
IntelliVue 802.11 Bedside Adapter Communication Test
1. Make sure the LAN cable is disconnected from the rear of the monitor, then switch on the
monitor.
2. Go into Service Mode and select Main Setup -> Network -> Setup WLAN. In the
Setup WLAN menu:
- set Mode to either 802.11Ah, 802.11G, 802.11Bg (not recommended), Auto (not
recommended) or None (this setting disables the wireless LAN functionality
permanently), to match your wireless infrastructure installation.
- set SSID to match your installation.
- set the Country code to “1000”. Setting the country code to this value will
automatically adjust the regulatory domain to match the configuration of the
infrastructure. Do not set the country code to values other than “1000” unless otherwise
instructed.

3 Testing and Maintenance Performance Assurance Tests
100
- set the Security Mode to WPA(PSK) and enter the WPA password (string between
8 and 63 characters).
3. Select Main Setup -> WLAN Diagnostic to access the service window.
4. Proper installation of the IntelliVue 802.11 Bedside Adapter is assured by connecting to an
access point over the wireless link. Place the monitor with the IntelliVue 802.11 Bedside
Adapter installed in close proximity to the access point (e.g. if the access point is mounted
on the ceiling, place the monitor directly below). Wait until the Conn.Status field in the
service window shows Authenticatd (for Rel. C.0 monitors)or Connected (for Rel D.0 or
higher). Take the monitor approximately 5 m away from the access point. There should be
no walls or other obstacles between the monitor and the access point. The following should
apply:
- Observe the RSSI (Received Signal Strength Indicator) value for at least 5 - 10 seconds.
The RSSI value wil fluctuate but should stay above 30 in a 5 m distance from the access
point used. The wireless link should be active, i.e. the Conn.Status field should be
Authenticatd (for Rel. C.0 monitors)or Connected (for Rel D.0 or higher), and the other
fields should contain values. If the RSSI value is significantly lower, check the distance
to the access point and the antenna orientation at the monitor. The antenna orientation
should be vertical, but the physical placement of the monitor or other equipment within
its vicinity as well as walls or other obstacles may influence the antenna orientation
required to receive the best RSSI value.
5. If this test fails, retry in a different physical area with a different access point.
6. Perform the Wireless Switch test blocks as described in the Philips IntelliVue 802.11 a/g
Infrastructure Installation and Configuration Guide.
Test Expected test results
IntelliVue 802.11 Bedside Adapter
Performance Test RSSI value above 30
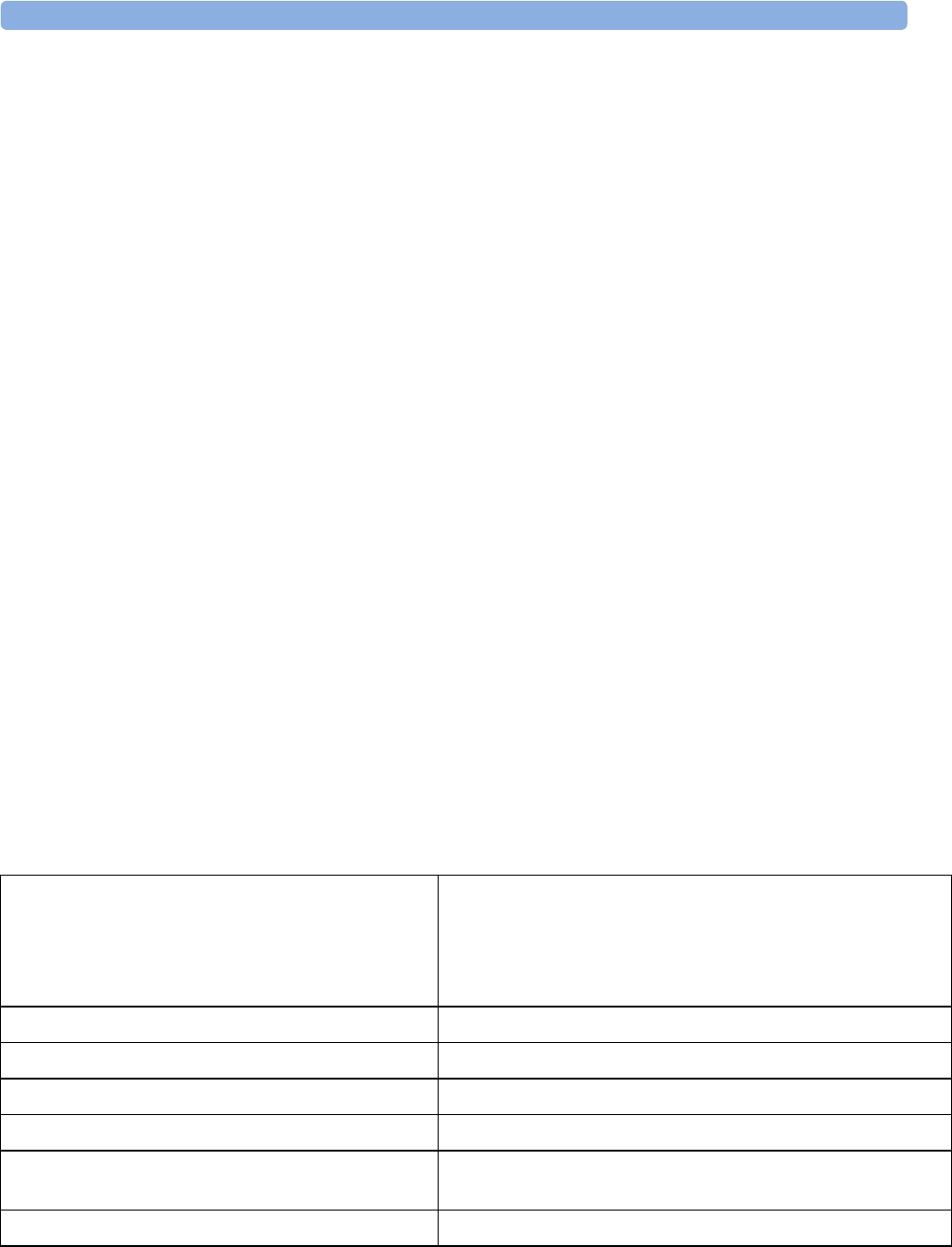
Reporting of Test Results 3 Testing and Maintenance
101
Reporting of Test Results
Philips recommends all test results are documented in accordance with local laws. Authorized
Philips personnel report test result back to Philips to add to the product development database.
While hospital personnel (biomedical engineers or technicians) do not need to report results to
Philips, Philips recommends that they record and store the test results in accordance with local
laws.
The following table lists what to record after completing the tests in this chapter. Record the
results in the empty column in Table 16.
The following is a guide as to what your documentation should include:
- Identification of the testing body (for example, which company or department carried out the
tests).
- Name of the person(s) who performed the tests and the concluding evaluation.
- Identification of the device(s) and accessories being tested (serial number, etc.).
- The actual tests (incl. visual inspections, performance tests, safety and system tests) and
measurements required
- Date of testing and of the concluding evaluation.
- A record of the actual values of the test results, and whether these values passed or failed the
tests.
- Date and confirmation of the person who performed the tests and evaluation.
The device under test should be marked according to the test result: passed or failed.
Carrying Out and Reporting Tests
Test Report
Testing Organization:
Name of testing person:
Test before putting into service (reference value)
Recurrent Test
Test after Repair
Responsible Organization:
Device Under Test: ID-Number
Product Number: Serial No.:
Accessories:
Measurement Equipment (Manufacturer, Type,
Serial No.):
Functional Test (parameters tested):

3 Testing and Maintenance Reporting of Test Results
102
Test and Inspection Matrix
Test
Test or
Inspection to be
Performed
Expected Test Results
Record the Results (mandatory for
Philips Personnel only)
What to record Actual
Results
Visual
Inspection Perform Visual
Inspection Pass or Fail V:P or V:F
Power On Power on the
unit. Does the
self-test complete
successfully
If Yes, Power On test is
passed PO:P or PO:F
Perform the
Accuracy Test X1 = value displayed by
monitor
Difference <= 3mmHg
PN:P/X1 or
PN:F/X1
Performance
Leakage Test X2 = leakage test value
X2 < 6 mmHg
PN:P/X2 or
PN:F/X2
Performance
Linearity Test X3 = value displayed by
monitor
Difference <= 3mmHg
PN:P/X3 or
PN:F/X3
Noninvasive
Blood
Pressure
Performance
Tests
Performance
Valve Test X4 = value < 10 mmHg PN:P/X4 or
PN:F/X4
Temperature
Performance
Test
Perform the
Temperature
Performance Test
X1= 40°C ± 0.2°C or 100°F ±
0.4°F PT: P/X1 or
PT: F/X1
All other
performance
tests
Perform the
remaining
parameter
performance
tests, if applicable
See expected results in test
procedures P: P or
P: F
Safety (1) Perform Safety
Test (1):
Protective Earth
Resistance
With mains cable:
Maximum impedance (X1):
<=300 mOhms
S(1):P/X1 or
S(1):F/X1
Safety (2) Perform Safety
Test (2):
Equipment
Leakage Current
- Normal
Condition.
With mains cable:
Maximum leakage current
(X1):<= 100 μA
S(2): P/X1 or
S(2): F/X1

Reporting of Test Results 3 Testing and Maintenance
103
Test
Test or
Inspection to be
Performed
Expected Test Results
Record the Results (mandatory for
Philips Personnel only)
What to record Actual
Results
Safety (3) Perform Safety
Test (3):
Equipment
Leakage Current
- Single Fault
Condition (Open
Earth)
With mains cable:
Maximum leakage current
(X2):<= 300 μA
S(3): P/X2 or
S(3): F/X2
Safety (4) Perform Safety
Test (4): Patient
Leakage Current
- Single Fault
Condition, mains
on applied part.
Maximum leakage current
(X1): <=50 μA
S(4): P/X1 or
S(4): F/X1
System
(Sys 1-2) Perform the
system test
according to
subclause 19.201
of IEC/EN
60601-1-1, if
applicable, after
forming a system
Equipment Leakage Current:
Sys1 <= 100 μA (Normal
Condition)
Sys2 <= 300μA (Single Fault
Condition
Sys: PSys1/PSys2
or
Sys: FSys1/Fsys2
System
(Sys 3) Perform the
system test
according to
subclause 19.201
of IEC/EN
60601-1-1, if
applicable, after
forming a system
Protective Earth Leakage
Current if medical electrical
system components are
connected to the same
Multiple Portable Socket
Outlet:
Sys3 <= 300 μA
Sys: PSys3
or
Sys: FSys3
Key: P = Pass, F = Fail, X or Sys = test value to be recorded
NOTE
All values for current and voltage are the root mean square (r.m.s.) values, unless otherwise
stated.

3 Testing and Maintenance Reporting of Test Results
104
Evaluation
Yes No
Safety and Functional Test passed
Repair required at a later date, safety and functional test passed
Device must be taken out of operation until repair and passed tests
Device failed and must be taken out of operation.
Notes:
Next Recurrent Test:
Name:____________________________________________________
Date/Signature:_____________________________________________
Evaluation of Test Results
The evaluation of the test results must be performed by appropriately trained personnel with
sufficient product, safety testing and application knowledge.
If any test results are between 90% and 100% of the respective expected result, the previously
measured reference values must be taken into consideration for the assessment of the electrical
safety of the device under test. If no reference values are available, you should consider shorter
intervals between upcoming recurrent tests.
NOTE
If any single test fails, testing must be discontinued immediately and the device under test must
be repaired or labeled as defective. Be sure to inform the user about the test failure in writing.

Other Regular Tests 3 Testing and Maintenance
105
Other Regular Tests
The care and cleaning requirements that apply to the monitor and its accessories are described in
the Instructions for Use. This section details periodic maintenance procedures recommended for
the monitor and its accessories.
Touchscreen Calibration
To access the touchscreen calibration screen:
1. Enter service mode
2. Select Main Setup
3. Select Hardware
4. Select Touch Calibration
Please touch slowly each target as it appears on screen.
Do not power off the monitor until this calibration has
completed.
Touchscreen Calibration Screen

3 Testing and Maintenance Disabling/Enabling Touch Operation
106
Make sure you complete the calibration procedure without powering off the monitor mid-way. If
the monitor is powered off after the first point is touched, the touch panel will be deactivated
until the touch calibration is performed again.
If the touchscreen is accidentally mis-calibrated by selecting the wrong spot, you must use
another input device to re-enter calibration mode. If you have the support tool, you can select
Reset Touch Calibration to Default and it will create a rough calibration which will
allow you to access the calibration menu again via the touchscreen.
Please refer to the documentation shipped with your selected display for further details on
touchscreen calibration procedures.
Disabling/Enabling Touch Operation
There are two ways to disable/enable touchscreen operation:
1. To temporarily disable touchscreen operation of the monitor, press and hold the Main
Screen key. A padlock symbol will appear on the key. Press and hold the Main Screen
key again to re-enable touchscreen operation.
2. To permanently disable touchscreen operation:
a. Enter Service Mode.
b. Select Main Setup
c. Select User Interface
d. Change the Touch Enable selection to no.
To re-enable touchscreen functionality change the Touch Enable selection to yes.

Printer Test Report 3 Testing and Maintenance
107
Printer Test Report
To verify your printer configuration you may want to print a test report.
To print a test report select Main Setup -> Reports -> Setup Printers -> Print
Test Rep.
Your test report should look like this:
Battery Handling, Maintenance and Good Practices
This section provides some information on how to handle and maintain the batteries in order to
get the best usage from them. Additionally, some good working practices are also given
regarding the correct disposal of the batteries. This section only applies if a battery board is
installed in the monitor.
NOTE
If your monitor is connected to an -USR_ProductName- Information Center, you should make
sure that the IIC uses the text catalog revision B.1 or later, otherwise battery INOPs may not
display correctly on the IIC. Consult your IIC documentation for instructions on upgrading the
text catalog.

3 Testing and Maintenance Battery Handling, Maintenance and Good Practices
108
About the Battery
The rechargeable Lithium-Ion batteries used in the monitor are regarded as Smart batteries
because they have built-in circuitry. (This circuitry communicates battery-status information to
the Monitor.)
To get the most out of the batteries, observe the following guidelines:
- Condition the batteries only upon maintenance request prompt on display.
- If a battery shows damage or signs of leakage, replace it immediately. Do not use a
faulty battery in the Monitor.
- Capabilities of integrated battery charger: 12.6V, 5 Amps mx.
Actual current / voltage: depends on smart battery request and monitor configuration
The approximate charging time is 4 hours with the monitor switched off and up to 12 hours
during monitor operation, depending on the monitor configuration.
- Battery Disposal—Batteries should be disposed of in an environmentally-responsible
manner. Consult the hospital administrator or your local Philips representative for local
arrangements.
Do not dispose of the battery in normal waste containers.
- Battery Storage — Batteries should not remain inside the monitor if they are not used for a
longer period of time. Batteries should be max. 50% charged for storage.
NOTE
Batteries will discharge within about 20 days if they are stored inside the monitor without AC
power connection.

Battery Handling, Maintenance and Good Practices 3 Testing and Maintenance
109
Checking the Battery Status
When the Monitor is connected to the AC power supply, the battery charges automatically. The
battery can be charged remotely from the Monitor by using the battery charger. Use only
Lithium Ion battery chargers approved by Philips.
Battery status (level of charge) is indicated several ways:
- LED on the front panel of the Monitor.
- Battery gauge.
- Display of battery time below gauge.
- Battery status window.
- INOP messages.
The AC Power LED is only on when the power cord is connected and AC power is available to
the Monitor. In this case, the battery can be either charging or fully charged.
The battery LED can be green, yellow, or red depending on the following conditions:
Battery LED Colors If the monitor is connected
to AC power, this means
If the monitor is running on
battery power, this means
Green batteries full (>90%)
Yellow batteries charging
(battery power < 90%)
or
battery down2
Red, flashing less than 10 minutes power
remaining
Red, flashes
intermittently
battery malfunction1 battery malfunction1
Red, flashes once when
on/standby switch is
pressed
not enough battery power left
to power monitor
1 indicated by malfunction symbol and INOP
2 indicated by “battery has no power left” symbol
NOTE
If the batteries were charged to 100%, they will not charge again until the charging status goes
below 90%.
If the remaining battery-operating time is less than 10 minutes, the LED flashes red at a
repetition rate of approximately 1.5 flashes per second.

3 Testing and Maintenance Battery Handling, Maintenance and Good Practices
110
When the batteries are empty, the Monitor switches off automatically (including the green
On-Off/Standby LED on the front panel). Attempts to restart the Monitor (by pressing the
On-Off/Standby) causes the red LED to emit a single flash. (The flash may have a delay of up to
2.5 sec after pressing the On-Off/Standby key). In this case either recharge the batteries
(externally or internally) or exchange the batteries.
NOTE
If the batteries become too warm or too cold, they will not begin the recharging cycle until the
battery temperature is within range.
Battery Status on the Main Screen
Battery status information can be configured to display permanently on all Screens. It shows the
status of each of the batteries and the combined battery power and battery time remaining. These
symbols are displayed if a battery board is installed, no matter whether batteries are inserted or
not.
Battery status symbols:
These symbols tell you the status of the batteries detected and which battery compartment they
are in, either 1 or 2.
Battery power gauge:
This shows the remaining battery power in the combined batteries. It is divided into sections,
each representing 20% of the total power. If three and a half sections are shaded, as in this
example, this indicates that 70% battery power remains. If no batteries are detected, the battery
gauge is greyed out.
Battery malfunction symbols:
If a problem is detected with one of the batteries, these symbols alternate with the battery
number to indicate which battery is affected. They may be accompanied by an INOP message or
by a battery status message in the monitor information line (if battery window is open) providing
more details.

Battery Handling, Maintenance and Good Practices 3 Testing and Maintenance
111
Battery status symbols Battery malfunction symbols
Battery 1
is present Battery
compartment
s are empty
Battery
requires
maintenance
Incompatible
battery
(Battery 1)
Battery
malfunctio
n (Battery
1)
Battery 2 is
missing, insert
battery
battery is
empty battery not
charging as
the
temperature
is above or
below the
specified
range
(red)
battery
temperatur
e too high
Battery 2 has
no power left
Explanations of Battery Status and Malfunction Symbols:
Battery requires maintenance: The batteries require conditioning. Refer to “Conditioning
Batteries” for details.
Incompatible Battery: The inserted batteries are checked for certain battery internal parameters.
If these are not correct, the incompatible battery symbol is displayed. Please use only the
M4605A batteries with the -USR_ProductName- monitor. Note that the incompatible battery
symbol may also appear if there is a communication problem between the battery and the battery
board.
Temperature outside specified range: The charging of the battery is stopped if the temperature is
below 15°C or above 50°C in order to protect the battery. Charging is resumed as soon as the
temperature is within this range.
Battery Temperature too high: This symbol is displayed if the battery temperature goes above
65°C. In addition the INOP message CHECK BATT TEMP is displayed. If the battery
temperature increases further above 70°C the batteries will switch off for safety reasons. Allow
the batteries to cool down to avoid the monitor switching off.

3 Testing and Maintenance Battery Handling, Maintenance and Good Practices
112
Battery is empty: The capacity of the battery is ≤200 mAh. Recharge the battery as soon as
possible.
Battery has no power left: Either the battery has switched off power delivery but is still
communicating with the battery board - in this case recharge the battery immediately - or the
battery is in deep discharge, i.e. it has switched off power delivery, has stopped communicating
with the battery board and requires pre-charging to restore communication. The INOP CHARGE
BATT 1/ BATT 2 is issued to indicate that pre-charging is required. To avoid this condition
charge batteries to 50% for storage. Note that the battery malfunction INOP will eventually be
issued if the pre-charging does not restore battery communication within about 10 minutes.
NOTE
Battery Malfunction:Communication between the battery and the battery board could not be
established within about 10 minutes or battery internal data indicates malfunction. Please see the
“Troubleshooting” section for remedies.
NOTE
If both batteries are malfunctioning or incompatible or require pre-charging and the monitor is
not connected to AC power, it will switch off automatically for safety reasons.
Battery Status Window
To access the Battery Status window and its associated pop-up keys, select the
battery status information on the Screen, or select Main Setup -> Battery.

Battery Handling, Maintenance and Good Practices 3 Testing and Maintenance
113
Capacity, Remaining tells you how much power is left in each battery.
Capacity, Full Charge tells you how much power each battery can hold when fully
charged.
Time To Empty tells you approximately how long you can continue to use the monitor with
these batteries. Note that this time fluctuates depending on the system load (how many
measurements and recordings you carry out), the age of the battery, and the remaining capacity
of the battery. The time indication is blanked after unplugging AC or after changing batteries for
about 30 seconds (during calculation of the Time to Empty)
Time To Full is shown in place of Time To Empty if the monitor is connected to AC power,
and tells you how much time is left until the batteries are charged to 90%. Please allow
indication to stabilize for 3 to 5 minutes after beginning the charging cycle. If batteries are
charged over 90% Batteries Full (>90%) is displayed until they are charged to 100%.
Then Batt1/Batt2 Fully Charged is displayed.
Viewing Individual Battery Status
To view information for individual batteries, select the pop-up key Battery 1 or
Battery 2.
Documenting Battery Status
To print all battery information in the Battery Status window,
1. Select the battery status information on the Screen or select Main Setup -> Battery to
open the Battery Status window
2. Select the Record Status pop-up key to print the information on a connected recorder
or
Select the Print Status pop-up key to print the information on a connected printer.

3 Testing and Maintenance Battery Handling, Maintenance and Good Practices
114
Conditioning a Battery
What is Battery Conditioning?
Battery conditioning recalibrates the battery to ensure that it has accurate information on the
actual battery capacity.
Why is Battery Conditioning Necessary?
The capacity of a battery decreases gradually over the lifetime of a battery. Each time a battery is
charged its capacity decreases slightly. Therefore, the operating time of a monitor running on
batteries also decreases with each charge cycle.
Battery conditioning ensures that the value stored in the battery for its full capacity takes account
of this decrease, so that the remaining battery charge can be calculated accurately, and the low
battery warning given at the right time.
When Should Battery Conditioning be Performed?
Battery conditioning should be performed when indicated by the Battery Status.
NOTE
When the battery status signals a conditioning request, the displayed Time to Full or Time to
Empty may not be reliable.
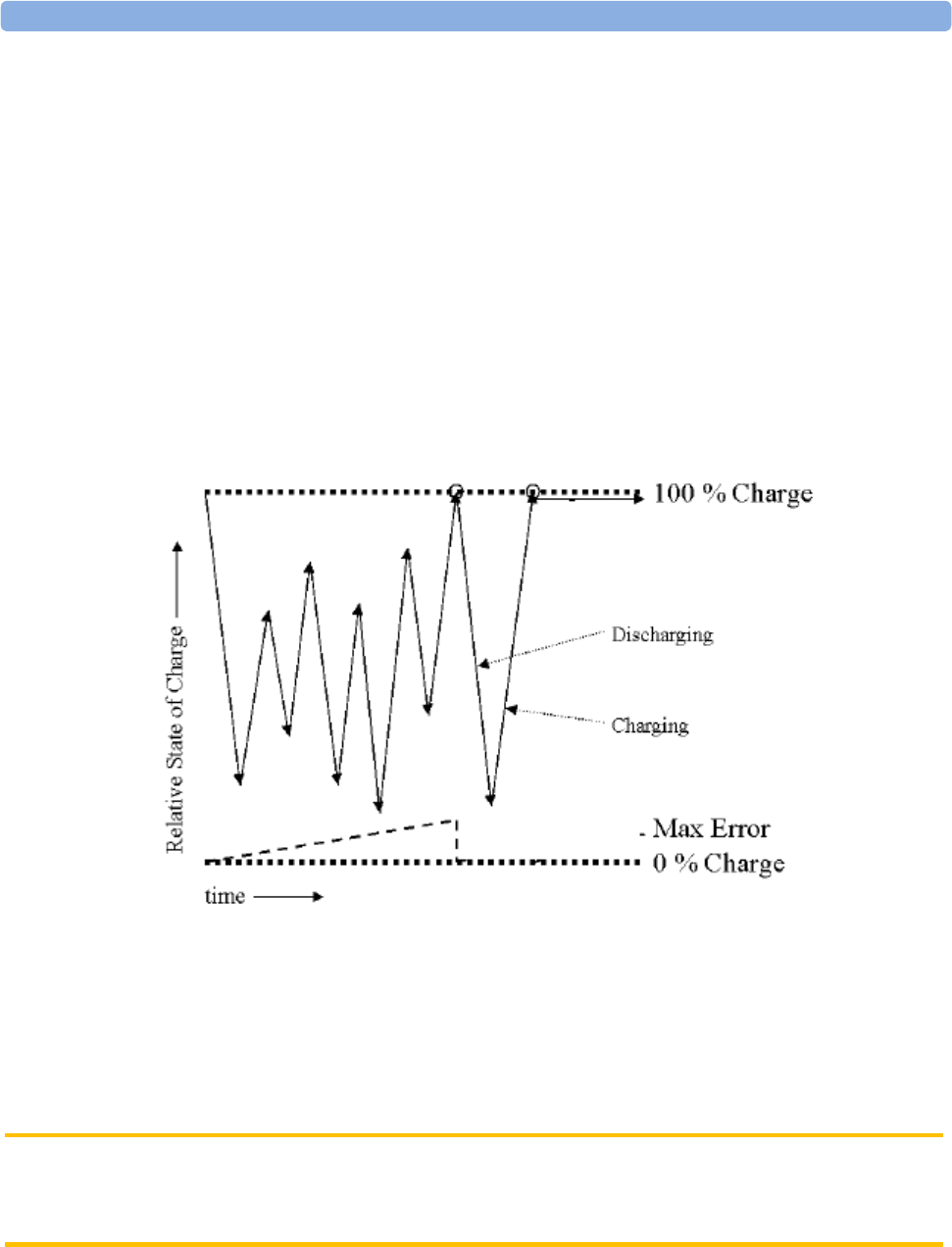
Battery Handling, Maintenance and Good Practices 3 Testing and Maintenance
115
What Causes the Conditioning Message on the Monitor?
In addition to the value for the full capacity, the battery also stores a value for the Max Error.
The Max Error tracks the maximum possible deviation of the estimated charge of a battery from
the actual charge.
If a battery is charged or discharged partially, or if it is charged while the monitor is being used,
the accuracy of the “reference points” for the fully discharged and fully charged states decreases,
causing an increase in the value for the Max Error (see diagram, below).
When the Max Error rises over a certain limit, a message is displayed prompting the user to
condition the battery, as described in Conditioning Batteries.
You can reset the value for the Max Error before the battery needs conditioning, by performing
the steps described in”Conditioning Batteries”. The minimum value of the Max Error after
conditioning is 2%.
Conditioning Batteries
Battery conditioning can either be performed in the monitor or with an external battery charger.
Battery Conditioning in the Monitor
CAUTION
Do not use a monitor being used to monitor patients to condition batteries. The monitor switches
off automatically when the batteries are empty.

3 Testing and Maintenance After Installation, Testing or Repair
116
You should condition a battery when its “battery requires maintenance” symbol shows on the
Screen. If conditioning is not performed immediately the monitor will still function according to
specifications. However, the displayed time to empty and time to full will show increasing
inaccuracy. Do not interrupt the charge or discharge cycle during conditioning. To condition a
battery,
1. Insert the battery into a monitor connected to mains power.
2. Charge the battery until it is completely full. Switch the monitor off to decrease the charging
time When the battery LED turns green i.e. the batteries are >90% charged, switch on the
monitor and open the Battery Status window. Check that the Batteries fully
charged or Battery 1 / Battery 2 fully charged message is displayed.
3. Disconnect the monitor from mains power, and let the monitor run until the battery is empty
and the monitor switches itself off.
4. Reconnect the monitor to mains power and charge the battery until it is full for use or charge
to 50% for storage.
Battery Conditioning with an External Charger
You can use the M8043A Smart Battery Charger for external battery conditioning. For details
please see the IfU for the Smart Battery Charger.
After Installation, Testing or Repair
Before handing the patient monitor over to the end-user, make sure it is configured appropriately
and that it is in monitoring mode. Ensure that the user receives the current revision of the
monitor documentation.

After Installation, Testing or Repair 3 Testing and Maintenance
117

119
4
4Troubleshooting
Introduction
This section explains how to troubleshoot the monitor if problems arise. Links to tables that list
possible monitor difficulties are supplied, along with probable causes, and recommended actions
to correct the difficulty.
How To Use This Section
Use this section in conjunction with the sections Testing and Maintenance and Parts. To remove
and replace a part you suspect is defective, follow the instructions in the section Repair and
Disassembly. The Theory of Operation section offers information on how the monitor functions.
Who Should Perform Repairs
Only qualified service personnel should open the monitor housing, remove and replace
components, or make adjustments. If your medical facility does not have qualified service
personnel, contact Philips’ Response Center or your local Philips representative.
WARNING
High Voltage - Voltages dangerous to life are present in the instrument when it is connected to
the mains power supply. Do not perform any disassembly procedures (other than server
removal) with power applied to the instrument. Failure to adhere to this warning could cause
serious injury or death.

4 Troubleshooting Replacement Level Supported
120
Replacement Level Supported
The replacement level supported for this product is to the printed circuit board (PCB) and major
subassembly level. Once you isolate a suspected PCB, follow the procedures in the Repair and
Disassembly section, to replace the PCB with a known good PCB. Check to see if the symptom
disappears and that the monitor passes all performance tests. If the symptom persists, swap back
the replacement PCB with the suspected malfunctioning PCB (the original PCB that was
installed when you started troubleshooting) and continue troubleshooting as directed in this
section.
Software Revision Check
Some troubleshooting tasks may require that you identify the Software Revision of your monitor.
You can find the software revision along with other information, such as the system serial
number, in the monitor revision screen.To access the monitor revision screen:
1. Enter the Main Setup menu and select Revision
2. Select Product
3. Select Software Revision
4. Select the pop-up key for the device you want to check (e.g. M8002A or M3001A)
NOTE
The part numbers listed in the monitor revision screen do not necessarily reflect the part numbers
required for ordering parts. Please refer to the Parts section for the ordering numbers.
NOTE
The system serial number can also be found on the lower right corner on the front of the monitor.
** For further information on M3001A HW/SW compatibility, please refer to the Parts section.
Obtaining Replacement Parts
See Parts section for details on part replacements.
Troubleshooting Guide
Problems with the monitor are separated into the categories indicated in the following sections
and tables. Check for obvious problems first. If further troubleshooting instructions are required
refer to the Troubleshooting Tables (on page 123).
Taking the recommended actions discussed in this section will correct the majority of problems
you may encounter. However, problems not covered here can be resolved by calling Philips
Response Center or your local representative.

Troubleshooting Guide 4 Troubleshooting
121
Checks for Obvious Problems
When first troubleshooting the instrument, check for obvious problems by answering basic
questions such as the following:
1. Is the power switch turned on?
2. Is the battery adequately charged?
3. Is the AC power cord connected to the instrument and plugged into an AC outlet?
4. Are the MMS and, if present, the MMS Extension inserted correctly?
Checks Before Opening the Instrument
You can isolate many problems by observing indicators on the instrument before it is necessary
to open the instrument.
NOTE
It takes several seconds for the AC Power LED to switch on / off after the mains power cord has
been connected / disconnected.
Checks with the Instrument switched Off
- AC connected, without battery:
- AC Power LED is on (green).
- AC connected, with battery:
- AC Power LED is on (green).
- Battery LED is green if fully loaded, yellow if being charged and off if only one battery
is inserted and fully charged.
- Battery LED red and blinking signals battery malfunction.
- No AC connected, with battery:
- All LEDs are off.
Checks with the Instrument Switched On, AC connected, without battery
When the monitor is first switched on, the Power On LED and the AC Power LED switch on and
stay on. The Error LED and the Battery LED light up momentarily.
Checks with the Instrument switched On, AC connected, with battery
When the monitor is first switched on, the Power On LED and the AC Power LED switch on and
stay on. The Error LED and the Battery LED light up momentarily. Before and after the Battery
LED flashes it shows the current battery status as described in the Testing and Maintenance
section.

4 Troubleshooting Troubleshooting Guide
122
Checks with the Instrument switched On, AC not connected, with battery
When the monitor is first switched on, the Power On LED switches on and stays on. The AC
Power LED, the Error LED and the Battery LED light up momentarily.
No. Description
1 Power On LED (Green)
2 Error LED (Red)
3 Battery LED (Green/Red/Yellow)
4 AC Power LED (Green)
Initial Instrument Boot Phase
The following tables describe the regular initial boot phase of the monitor and its components. If
the boot phase does not proceed as described below go to Boot Phase Failures for
Troubleshooting information.
Monitor Boot Phase:
For these steps it is assumed that the Monitor is powered correctly and the +3,3 V System Board
supply voltage is okay. This is indicated by the green Power On LED.
Time
(sec.)
after
Power
On
Event
0 When the Power On/Off button is pressed, the green Power On LED and the red
error LED switch on immediately.
3 The alarm LEDs are switched on with low intensity. Colors: Left LED:cyan;
Middle LED:red; Alarm Suspend LED (right): red. Red Error LED is switched off.
5 Boot Screen with the Philips Logo appears on the display. Test Sound is issued.
9 All Alarm LEDs are switched off.

Troubleshooting Guide 4 Troubleshooting
123
Time
(sec.)
after
Power
On
Event
10 Alarm LEDs are tested in the following sequence:
Cyan on-off (left LED only)
Yellow on-off (left & middle LED)
Red on-off (all LEDs)
Boot Screen with the Philips Logo disappears
Fixed screen elements (for example smart keys, alarm fields) appear on the screen.
15-30 First measurement information appears on the screen,user input devices (for
example Mouse, Touch, NavigationPoint) are functional
Troubleshooting Tables
The following tables list troubleshooting activities sorted according to symptoms. Click on the
links below to view a particular table.

4 Troubleshooting Troubleshooting Guide
124
How to use the Troubleshooting tables
The possible causes of failure and the remedies listed in the troubleshooting tables should be
checked and performed in the order they appear in the tables. Always move on to the next
symptom until the problem is solved.
Boot Phase Failures
Integrated Display is blank (on page 127)
Integrated Touch Display not functioning (on page 128)
External Display is blank (Slave Display) (on page 128)
External Touch Display not functioning
Remote Alarm Device
Remote Extension Device (on page 291)
Navigation Point (on page 132)
Keyboard/Mouse not functioning (on page 132)
Battery related problems
Network related problems
Wireless Ethernet Adapter (Proxim)
Multi-Measurement Module
MSL-related problems
Alarm Lamps
Alarm Tones
Individual Parameter INOPS
Printer
MIB / RS232
Flexible Nurse Call Relay

Troubleshooting Guide 4 Troubleshooting
125
Boot Phase Failures
Symptoms Possible Causes of Failure Failure Isolation and Remedy
AC LED
does not light
up
AC Connection not ok Check that the AC-Mains are powered
and the power cord is ok and
connected
Carrier Power on LED PCA not
connected to the main board Check if Carrier Power on LED PCA
is connected correctly to the Main
Board
Carrier Power on LED PCA defective Exchange Carrier Power on LED PCA
Main Board defective Exchange Main Board
Power supply defective Exchange Power Supply
Green Power
On LED and
Red Error
LED remain
off after
pressing
power on
button:
Remote Devices Disconnect all connections to the
remote devices and try to switch on the
monitor again
Power Switch Micro Controller hung Unplug AC Mains and replug after 10
seconds. Try to switch on the monitor
again.
Carrier Power on LED PCA not
connected to the main board Check if Carrier Power on LED PCA
is connected correctly to the Main
Board
I/O Board defective Remove all I/O boards and try to
switch the monitor on again
Touch controller defective
Flex adapter cable defective
MSL board defective
Recorder PCA defective
Battery PCA defective
IIT module defective
Disconnect cables and boards: (except
Power DC/DC cable):
- Flex adapter cable
- MSL
- Recorder PCA
- Battery PCA
- IIT module
then try to switch on the monitor
again.
Carrier Power on LED PCA defective Exchange Carrier Power on LED PCA
and try to switch the monitor on again.
Main Board defective Exchange main board. Add boards in
reverse order and try again with each
board.
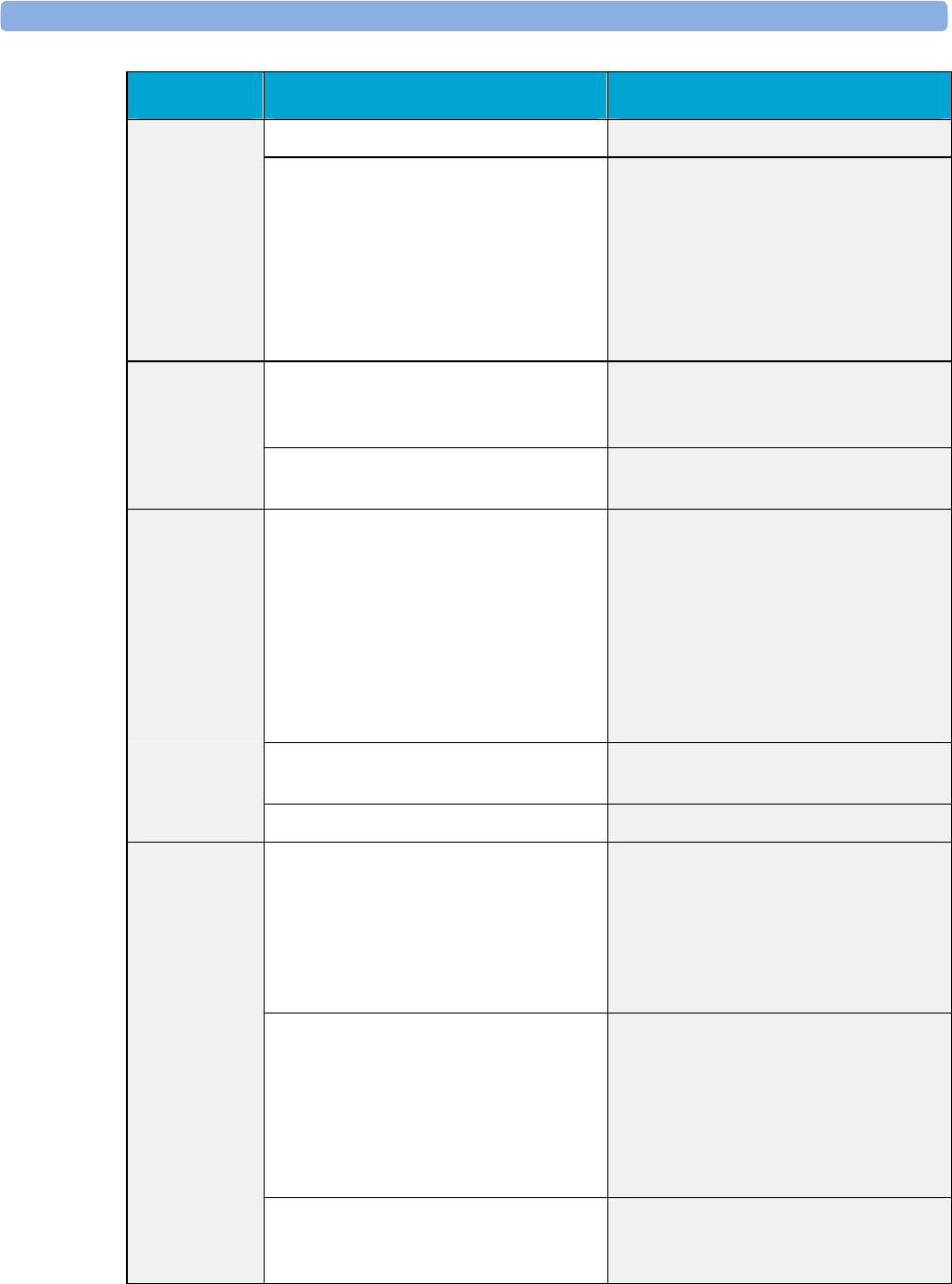
4 Troubleshooting Troubleshooting Guide
126
Symptoms Possible Causes of Failure Failure Isolation and Remedy
Carrier Power on LED PCA defective Exchange Carrier Power on LED PCA Green
On/Standby
LED or Red
Error LED
remain off
after pressing
Power on
button:
Main board defective exchange main board
Red Error
LED stays on
continuously
External connected device defective disconnect all external cables (except
AC) and switch the monitor on again
I/O Board defective Remove all I/O boards and switch the
monitor on again.
Touch controller defective
Flex adapter cable defective
MSL board defective
Recorder PCA defective
Battery PCA defective
IIT module defective
Disconnect cables and boards: (except
Power DC/DC cable):
- Flex adapter cable
- MSL
- Recorder PCA
- Battery PCA
- IIT module
then try to switch on the monitor
again.
Measurement Server Mount defective Disconnect Measurement Server
Mount and switch on again
Main board defective Exchange Main board
Hardware Failure
connect Support Tool directly to
monitor with crossover cable and start
“search for defective devices”
If no device is detected, proceed as
described above in section “Red error
LED stays on continuously”
Software Fault If the Support Tool can detect the
device and it indicates the Operating
Mode is ‘Boot’, download and store
the status log. Reload software and
re-clone the monitor. If this fixes the
problem e-mail the status log to your
local response center
Red Error
LED blinks
(indicating
cyclic
reboots)
Hardware Failure If this does not rectify the problem
follow instructions under “Red Error
LED stays on continuously”.

Troubleshooting Guide 4 Troubleshooting
127
Symptoms Possible Causes of Failure Failure Isolation and Remedy
Alarm LEDs
remain off: Main board defective Exchange Main board
Speaker defective
check for INOPs and follow
instructions
exchange speaker
No Test
Sound issued
Main board defective exchange main board
Integrated Display is blank
Symptoms Possible Causes of
Failure
Failure Isolation and Remedy
Integrated display is
blank or brightness is
reduced
(The information
listed in this table is
only valid if the boot
phase has completed
without error. See
Boot Phase Failures
table for a description
of the Boot phase.)
Display brightness is
reduced when room
temperature, or instruments
placed near patient monitor,
causes the monitor display
to overheat.
Instrument should be placed in an
environment that does not exceed
40 degrees C or below 5 degrees C.
If you have an external display,
connect it to the video port. If the
external display works, you can
eliminate the main board as the
cause of failure.
Flat Panel Adapter flex not
connected Check flex connection of Flat Panel
Adapter Board to main board and
display
Backlight Inverter Cable
not connected Check cable connection of Flat
Panel AdapterBoard to Backlight
Inverter Board
Backlight tubes defective Replace backlight tubes
Backlight Inverter board
defective If backlight tubes have already
been replaced, replace backlight
inverter board.
Flat Panel Adapter flex
defective Replace Flat Panel Adapter flex
LCD Flat panel defective Replace LCD Flat panel

4 Troubleshooting Troubleshooting Guide
128
Symptoms Possible Causes of
Failure
Failure Isolation and Remedy
Main board defective Replace main board
Integrated Touch Display not functioning
Symptoms Possible Causes of Failure Failure Isolation and
Remedy
Touch Screen not
functioning Touchscreen functionality has
been temporarily disabled Check if touchscreen
functionality has been
temporarily disabled
(padlock symbol on Main
Screen key). If yes, press and
hold the Main Screen key to
re-enable touchscreen
operation.
Touchscreen functionality has
been permanently disabled In service mode, select Main
Setup -> User Interface and
change the “Touch Enable”
selection to “yes”.
HIF PCA not connected Check connection from HIF
PCA to main board
Touch panel cable not
connected Check connection from HIF
PCA to touch panel
HIF PCA or touch sensor
defective Replace HIF PCA and touch
sensor
Main board defective Replace main board
Touch Position invalid Touch not calibrated Perform touch calibration:
1. Enter the Main Setup
Menu
2. Select Hardware
3. Select Touch Calibration

Troubleshooting Guide 4 Troubleshooting
129
External Display is blank (Slave Display)
Symptoms Possible Causes of
Failure
Failure Isolation and Remedy
If integrated display is also blank
proceed as described under
“Integrated Display is blank”
Video cable to external
display not connected or
defective
Check video cable connection to
external display
External display has no
power Check electricity supply of external
display
External display is defective Check external display and video
cable on another monitor or PC
System Interface board
defective Replace System Interface board
External Display is
blank
Main board defective Replace main board
External Touch Display not functioning
Symptoms Possible Causes of Failure Failure Isolation and
Remedy
Touchscreen functionality has
been temporarily disabled Check if touchscreen
functionality has been
temporarily disabled
(padlock symbol on Main
Screen key). If yes, press and
hold the Main Screen key to
re-enable touchscreen
operation.
Touchscreen functionality has
been permanently disabled In service mode, select Main
Setup -> User Interface and
change the “Touch Enable”
selection to “yes”.
External Touch Screen
not functioning
External Touch cable not
connected Check cable connection from
external touch to MIB board
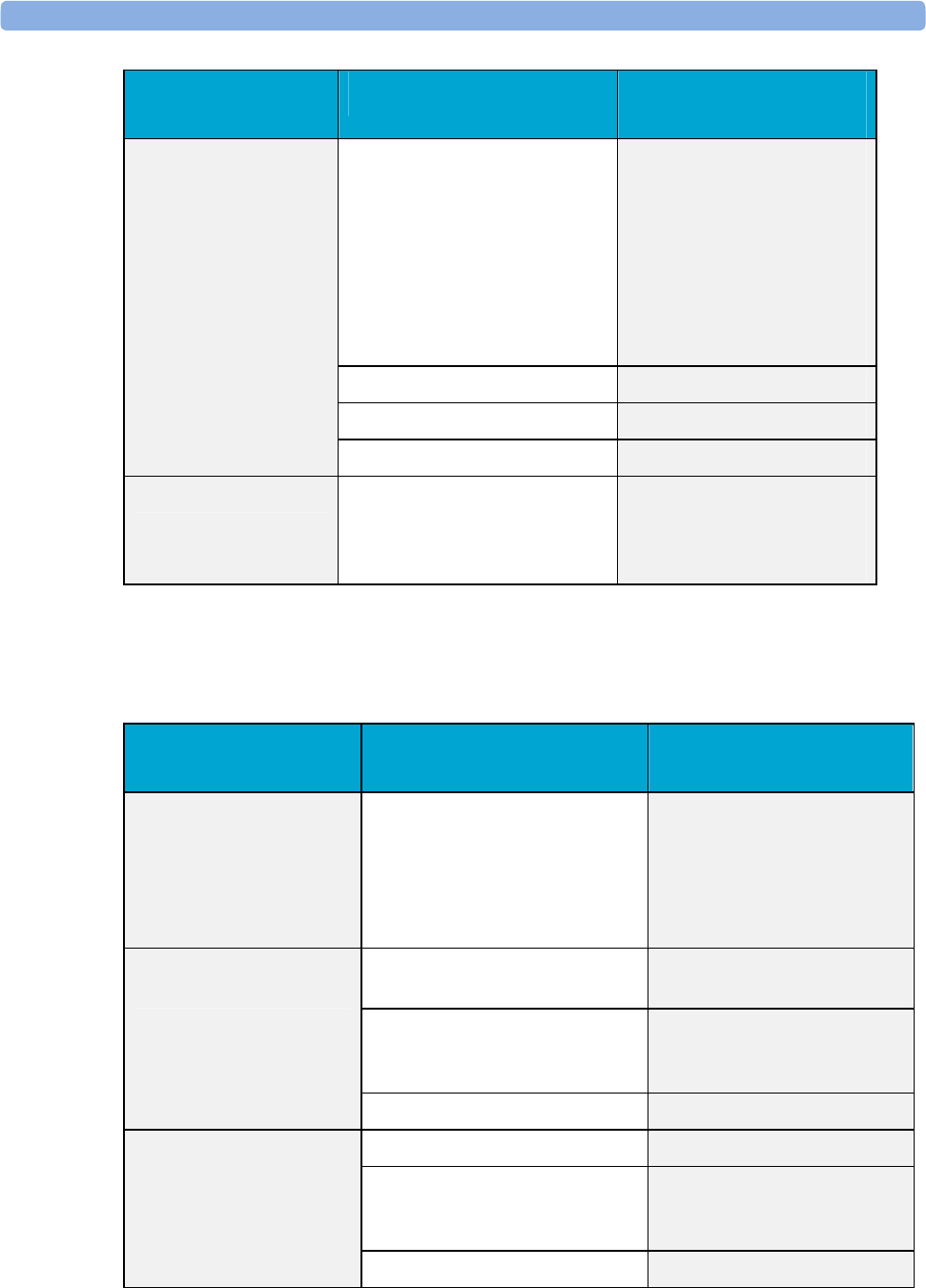
4 Troubleshooting Troubleshooting Guide
130
Symptoms Possible Causes of Failure Failure Isolation and
Remedy
External Touch driver
configuration Check RS232/MIB
configuration:
1. Enter Main Setup menu
2. Select Monitor
3. Select Hardware
4. Reconfigure RS232/MIB
drivers
5. if problem persists,
proceed to the next step
MIB Board defective Replace MIB board
External touch defective Replace external touch
Main board defective Replace Main board
Touch position invalid Touch not calibrated Perform touch calibration:
1. Enter Main Setup menu
2. Select Hardware
3. Select Touch Calibration
General Monitor INOP Messages
INOP Message Possible Causes of Failure Failure Isolation and
Remedy
CHECKINTERNVOLTA
GE
CHECK MONITOR
FUNC
Problem with too low voltages
(5V, 12V) in the monitor. Alarm
lamps, display or interfaces may
not function correctly.
Remove all I/O boards and
put them back in one at a time
to isolate any defective board.
If this does not resolve the
problem, replace the main
board
The temperature inside the
monitor is too high Check the environment for
possible causes
Monitor ventilation obstructed Clean the monitor ventilation
internally and then cool
monitor down for 8 hours
CHECK MONITOR
TEMP
Main Board defective replace Main Board
Problem during cloning process. Reclone configuration file
Memory space in which the
settings are stored has been
corrupted
Reclone configuration file.
This will reload the memory
space.
SETTINGS
MALFUNCTION
Main board defective Replace Main board

Troubleshooting Guide 4 Troubleshooting
131
Remote Alarm Device
Symptoms Possible Causes of Failure Failure Isolation and
Remedy
Alarm LEDs
illuminate, but no alarm
sound is issued
speaker defective replace Remote Alarm
Device
remote device I/F defective replace I/O board
cabling not connected check cabling
cabling defective replace cable
I/O board defective replace I/O board
Alarm occurs on
screen, but no LED or
alarm sound on the
alarm device
Remote Alarm Device defective replace Remote Alarm
Device
Alarm sound is isued,
but no LEDs light up LED failure Replace Remote Alarm
Device
Remote Extension Device
Symptoms Possible Causes of Failure Failure Isolation and
Remedy
Remote Extension Device is not
connected to the monitor. Check cabling and
connections
Input Device not connected
properly Check cabling to Input
Device in the Remote
Extension Device
Input Device defective Replace Input Device
Remote Extension Device
defective Replace Remote Extension
Device
Remote input device
(for example
mouse/keyboard)
attached to the Remote
Extension Device does
not function
Remote Device I/O board
defective Replace I/O board
Buttons on the Remote
Extension Device do
not function but input
device attached is
functioning
Remote Extension Device
defective replace Remote Extension
Device

4 Troubleshooting Troubleshooting Guide
132
Navigation Point
Symptoms Possible Causes of Failure Failure Isolation and
Remedy
Navigation Point
attached directly to the
monitor not functioning
Navigation Point not connected
properly Check cabling
Navigation Point defective Replace Navigation Point
Remote Extension Device is not
connected to the monitor. Check cabling and
connections
SpeedPoint not connected
properly Check cabling to SpeedPoint
in the Remote Extension
Device
SpeedPoint defective Replace SpeedPoint
Remote Extension Device
defective Replace Remote Extension
Device
Speed Point attached to
Remote Extension Box
not functioning
Remote Device I/O board
defective Replace I/O board
Navigation Point Knob
Rotation or Selection
control not functioning
Navigation Point defective Replace Navigation Point
INOP Message
CHECK INPUT
DEVICES is issued
Navigation Point or other input
device defective Perform a visual and
functional check of all the
monitor input devices.
Replace input devices if
necessary.
Keyboard/Mouse not functioning
Symptoms Possible Causes of Failure Failure Isolation and
Remedy
Keyboard/Mouse not connected
properly Check cabling
Keyboard/Mouse defective Replace Keyboard/Mouse
Keyboard/Mouse
attached directly to the
monitor not functioning
PS/2 or USB I/O Board
defective replace I/O board
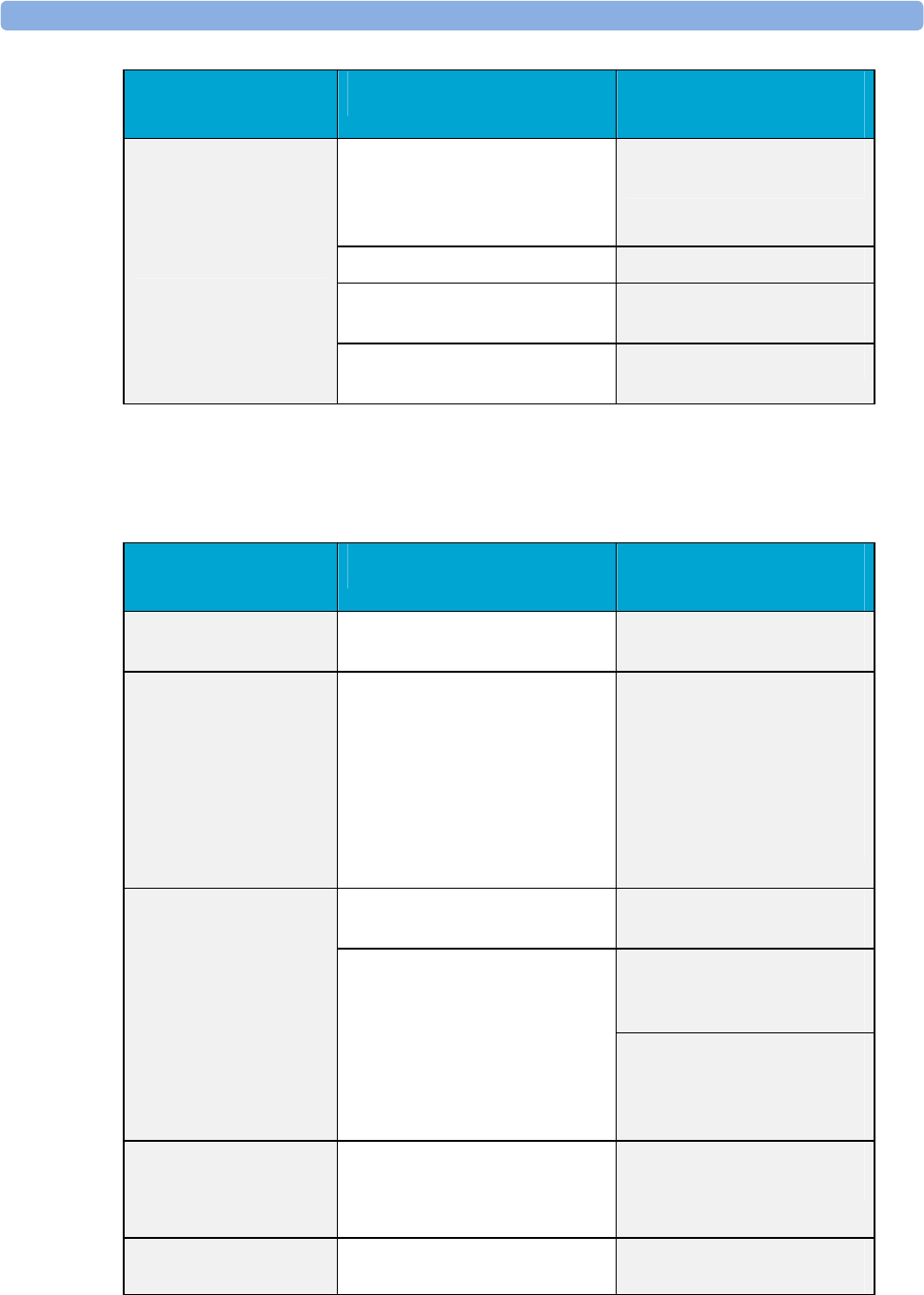
Troubleshooting Guide 4 Troubleshooting
133
Symptoms Possible Causes of Failure Failure Isolation and
Remedy
Remote Extension Box is not
connected to the monitor or
Input Device is not connected
to Remote Extension Box
Check cabling and
connections
Keyboard/Mouse defective Replace Keyboard/Mouse
Remote Extension Device
defective Replace Remote Extension
Device
Keyboard/Mouse
attached to Remote
Extension Box not
functioning
Remote Device I/O board
defective Replace I/O board
Battery related problems
Symptoms Causes of Failure Failure Isolation and
Remedy
Battery symbol is not
displayed The monitor is not configured
for battery operation. Make sure a battery board is
installed.
BATTERIES EMPTY or
BATT 1/BATT 2
EMPTY
INOP tone, battery
LED flashes
During this INOP,
alarms cannot be
paused or switched off.
The estimated remaining
battery-powered operating time
of the indicated battery or
batteries is less than 10
minutes.
Insert full batteries or
recharge the batteries
immediately.
If the condition persists, this
INOP is re-issued two
minutes after you
acknowledge it.
The indicated batteries cannot
be used with this monitor. Replace with the correct
batteries (M4605A).
Check batteries in a different
monitor. If INOP persists
replace batteries.
BATTERIES
INCOMPAT or BATT
1/BATT 2 INCOMPAT
INOP tone Communication problem
between battery and battery
board.
Check battery board using
known good batteries. If
INOP persist, replace battery
board.
BATTERIES LOW or
BATT 1/BATT 2 LOW
INOP tone
The estimated battery-powered
operating time remaining is less
than 20 minutes.
Insert full batteries or
recharge the batteries.
BATTERIES MALF or
BATT 1/BATT 2
The monitor cannot determine
the battery status or there is a Replace the faulty battery or
batteries. If the condition

4 Troubleshooting Troubleshooting Guide
134
Symptoms Causes of Failure Failure Isolation and
Remedy
MALFUNCTION
INOP tone, battery
LED flashes
During this INOP,
alarms cannot be
paused or switched off
if the monitor is not
connected to mains
power.
communication problem
between the battery and the
battery board.
persists and the monitor is
not connected to AC power,
this INOP is re-issued two
minutes after you
acknowledge it.
Check the batteries in a
different monitor or in a
battery charger. If the INOP
persists the battery is faulty.
Check the battery board with
known good batteries. If the
INOP persists, replace
battery board..
CHARGER MALFUNCT
INOP tone, battery
LED may flash
There is a problem with the
battery charger in the monitor. Switch the monitor off and
back on again. If the problem
persists replace batteries with
known good batteries. If the
INOP is shown again replace
the battery board. If the
problem persists replace the
main board.
CHECK BATT TEMP
INOP tone
The temperature of one or both
batteries is too high. Check that ventilation
openings are not blocked and
monitor is not exposed to
heat.
CHARGE
BATT1/BATT2
INOP tone
Battery is deeply discharged
and/or does not communicate
and requires pre-charging.
Connect the monitor to AC
power.

Troubleshooting Guide 4 Troubleshooting
135
Bedside Network Status Icons
The following table shows the icons displayed on the monitor when network related issues
occur.
Wireless Icon Wired Icon Inverse
Video Blinks Icon
Comments Inop Message What does it mean?
MONITOR does not have a LAN connection
(Wireless MONITOR cannot find an access point
to talk to, wired MONITOR cannot hear anything
on its LAN connection)
MONITOR ha a LAN connection but does not
have an IP address assignment
(Wireless MONITOR has found an access point to
talk to, wired MONITOR hears traffic on the LAN)
MONITOR is connected to the LAN and has an IP
address assignment, but the bed is not being
monitored at the central
1. MONITOR is not assigned to a sector
2. There is another monitor on the network with
the same “Equipment Label”
Normal Operation - MONITOR assigned to a
sector and is being monitored by a central
Wireless MONITOR that currently is being
monitored by a central is losing contact with the
access point and cannot find another to talk to
Monitor lost connection to the Information Center:
1. LAN cable was disconnected
2. Information Center was disconnected
3. Network infrastructure failure (switch, etc.)
4. Out of range (wireless MONITOR)
”UNSUPPORTED LAN”
(after 1 minute)
1. “NO CENTRAL
MONITORING”
2. “MONITOR LABEL
DUPLICATE”
”WIRELESS OUT OF
RANGE”
”NO CENTRAL
MONITORING”
No Icon -
Yes
No
Central -
outline only
No Icon ---
Yes
Yes
Yes Yes
No
No No
No No
No
Central -
outline only
Central -
solid box
Central -
solid box,
network line
extended
Central -
solid box
Central - outline
only, line for
broken
connection to
central
-
-
Normal Operation - MONITOR assigned to a
sector and is being monitored by a central
This monitor also has OVERVIEW functionality
on other beds
-
-
Network related problems
Symptoms Possible Causes of Failure Failure Isolation and
Remedy
The monitor label is not set in
the monitor (if the beds are
“monitor labeled” in the Philips
Information Center)
Set Monitor Label in Config
Mode
Prompt Message “no
central assigned to this
bed” is issued
Problem with the Philips
Information Center to Switch
communication (if the beds are
“port mapped” in the Philips
Information center
Check PIC to Switch
communication, Switch
configuration and Firmware
status
INOP “Unsupported
LAN” is issued. One of
the following icons is
displayed.
Network failure Check if network switches,
Philips Information Center
and Database Server are all
running and connected to the
network

4 Troubleshooting Troubleshooting Guide
136
Symptoms Possible Causes of Failure Failure Isolation and
Remedy
Monitor connected to wrong
network Check if monitor has been
connected for example to a
different hospital network
instead of the Philips Clinical
Network
IP address conflict after
infrastructure re-installation Reboot Database Server and
Philips Information Center
Check LAN cable connection
Check System Interface
Board in Monitor
Hardware Defect
Check network switch
No connectivity to PIC,
no prompt or error
message on monitor
Configuration problem Check switch configuration
and firmware revision
Check configuration in PIC
regarding other bed overview
(care group assignment)
Configuration Problem
Verify configuration of
switch (setting of multicast
filters)
Other Bed Overview
not available
This function is not available
for wireless beds Switch to a wired
configuration
“Other Bed” Alarms
are not appearing Configuration problem Verify configuration in PIC,
in Monitor (Config Mode)
and check that the feature is
not temporarily disabled by
the user (Bed Info Window)

Troubleshooting Guide 4 Troubleshooting
137
Wireless Ethernet Adapter (Proxim)
Symptoms Possible Causes of Failure Failure Isolation and
Remedy
Move monitor back into
coverage area
Monitor is out of range of the
access point (in this case the
yellow sync LED on the
wireless adapter on the bottom
of the device next to the power
connector is not on steady)
Verify size of coverage with
the site survey tool
Check splitter cable and
replace if necessary
Check System Interface
Board in monitor and replace
if necessary
Wireless Adapter has no power
(LEDs on adapter are all off)
Check adapter itself. Replace
if necessary
(Only after first install)
Firmware revision in adapter is
wrong
Update adapter frimware
with wireless support tool
Wireless adapter defective (the
red status LED on the adapter’s
top panel is on)
Replace wireless adapter
No central monitoring
possible (see also
Network related
problems)
Wrong configuration in
wireless adapter or in access
point
Check configuration with
wireless support tool
No connectivity
(coverage area consists
of multiple access
points and in some
parts of the area there is
no connectivity)
Configuration problem Verify the channel, domain
and security ID settings of
the access points in the
coverage area
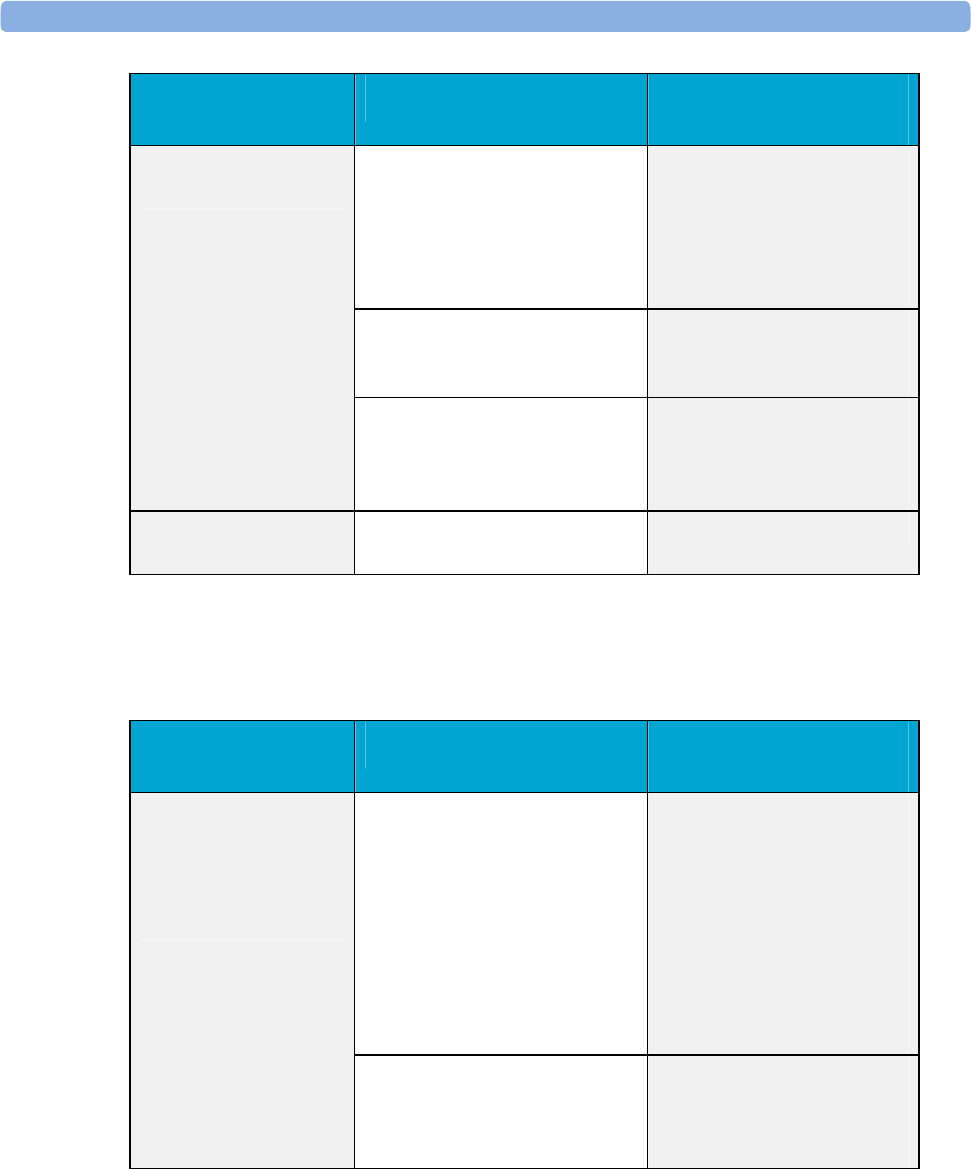
4 Troubleshooting Troubleshooting Guide
138
Symptoms Possible Causes of Failure Failure Isolation and
Remedy
Excessive interference by other
radio equipment or by
microwave ovens
Check statistics that can be
read from the wireless
adapter via RS232 or via
logging application in the
PIC. Remove interfering
equipment.
System capacity exceeded in
coverage area Check configuration
guidelines for number of
monitors per access point.
Frequent dropouts and
network disconnects
Configuration problem Check access point
configuration with wireless
support tool, in particular the
multicast filters
Overview, Printing
does not work Some functions are not
available on a wireless network Connect to cabled network
IIT-related Problems
Symptoms Cause of Failure Failure Isolation and
Remedy
Communication problem
between the monitor and the IIT
adapter. MAC Instr. Tele. field
in Instrument Telemetry
Service Window is 0000 0000
0000
Check that RF Access Code
is set correctly and the
network is correctly set up.
Check the flat cable
connection between the main
board and the IIT module.
Check the antenna cable
connection between the IIT
module and the antenna..
No Network icon or
Network icon flashes.
No association to
central station.
Incorrect RF Access Code. No
IP Address. Check that RF Access Code
is set correctly. Make sure
that network is set up
correctly.

Troubleshooting Guide 4 Troubleshooting
139
IntelliVue 802.11 Bedside Adapter Problems
Symptoms Cause of Failure Failure Isolation and
Remedy
Communication problem
between the monitor and the
IntelliVue 802.11 Bedside
Adapter or RSSI value below
30.
Ensure that the network
infrastructure is functioning
properly. See
Troubleshooting tables in the
IntelliVue 802.11
a/g Infrastructure Installation
and Configuration Guide for
details.
Check the antenna cable
connection on the I/O board.
Check the cable connection
between the IntelliVue
802.11 Bedside Adapter and
the system interface board.
Replace cable, antenna or
IntelliVue 802.11 Bedside
Adapter if necessary.
No Network icon or
Network icon flashes.
No association to
central station.
Configuration problem. Make sure that the Mode,
SSID, Country and Security
settings in the Setup WLAN
menu match your installation

4 Troubleshooting Troubleshooting Guide
140
Symptoms Cause of Failure Failure Isolation and
Remedy
LEDs on IntelliVue
802.11 Bedside
Adapter are off and
remain off
Communication problem Check that the cable
connection between the
IntelliVue 802.11 Bedside
Adapter and the system
interface board is correct.
Disconnect and reconnect the
cable and try again. If
problem persists, switch
monitor off and on again. If
problem persists, exchange
cable and or
IntelliVue 802.11 Bedside
Adapter. If the new adapter
does not function either,
exchange system interface
board.
When functioning correctly,
The LEDs on the bedside
adapter should both light up
for about 3 seconds after the
monitor is switched on or the
bedside adapter is first
connected to the monitor. If
the wireless LAN
functionality has been
disabled permanently both
LEDs will remain off during
monitor operation. In this
case, to check the electrical
connection, power-cycle the
monitor and observe the
LEDs on the adapter.
Multi-Measurement Module
Symptoms Possible Causes of Failure Failure Isolation and
Remedy
An unsupported MMS
Extension has been connected Disconnect the MMS
Extension
MMS Extension is defective Replace MMS Extension
Prompt message
“Measurement Server
Configuration not
supported” is issued
Measurement Server defective Replace Measurement Server

Troubleshooting Guide 4 Troubleshooting
141
Symptoms Possible Causes of Failure Failure Isolation and
Remedy
Wrong Software Revison Upgrade monitor and/or
measurement server to a
matching software version.
Too many measurement servers
connected Disconnect unsupported
measurement servers for
proper operation.
INOP Message
“MsmtSrv not Supp” is
issued
Unsupported type of
measurement server (for
example M3000A on a
M800xA monitor) connected.
Disconnect the unsupported
measurement server.
Prompt message
“Measurement Server
not supported, unplug
device, switch monitor
off/on” and INOP “Bad
Measurement Server
are issued
M3000A Measurement Server
Revision A is plugged. This
Measurement Server is not
compatible with the IntelliVue
patient monitors
Disconnect the measurement
server and cycle power.
MSL-related problems
Symptoms Possible Causes of Failure Failure Isolation and
Remedy
Check MSL cable and
replace if necessary
Measurement Server
does not start up (no
LEDs active), no INOP
or prompt displayed
No Power
Check MSL connector board
incl. internal cable to main
board and replace if
necessary
Communication lines in MSL
cable or MSL connector broken Check MSL cable and MSL
connectors
Measurement Server
does not start but LEDs
are normal MSL connector board defective Check MSL connector board
incl. internal cable to main
board and replace if
necessary

4 Troubleshooting Troubleshooting Guide
142
Symptoms Possible Causes of Failure Failure Isolation and
Remedy
MSL Power High
INOP is issued
Note: if this condition
persists for longer than
15 minutes, the INOP
MSL Power Off will
appear (see below)
Attached devices drawing too
much power from the monitor.
MSL Power Off INOP
is issued
Attached devices drawing too
much power from the monitor. Disconnect all MMS from
the monitor
Cycle power to restore power
to the MSL devices.
If the message disappears,
reconnect MMS , waiting
15 minutes to see if
message reoccurs. If yes, the
respective MMS is faulty.
See Multi-Measurement
Module or Printer for
troubleshooting tasks.
Note: If an individual
defective device is connected
the MSL Power High or
MSL Power Overload INOPs
will appear initially. The
MSL Power Off INOP will
not occur for at least 15
minutes.

Troubleshooting Guide 4 Troubleshooting
143
Symptoms Possible Causes of Failure Failure Isolation and
Remedy
MSL Power Overload
INOP is issued Short Circuit within MSL
system Disconnect MSL connection
. If message persists,
replace main board.
Unexpected data detected on
MSL Check cable and power cycle
the monitor
An MMS with an
incompatible software revision
is connected to the monitor.
Connect MMS with
compatible software revsion
INOP BAD SERVER
LINK is issued
Communication between the
components not functioning Check software versions and
model number of devices for
compatibility
INOP Message
SERVERLINK MALF
is displayed, audible
indicator: a beep every
two seconds
The hardware for
communicating with the
Multi-Measurement Server is
faulty.
Check MSL cable, replace if
necessary.
Check MMS connector
board. Replace if necessary.
A measurement
supported by a server
does not come up on
the monitor
Label conflict A parameter label from this
measurement is already in
use in the monitor. Check the
conflict window to select the
measurement.
Hardware problem Check MSL cable
Check the MSL connector in
the measurement server
MSL connector board defective Check MSL connector board
incl. internal cable to main
board and replace if
necessary
The ECG Out/ Marker
In function does not
function
ECG Out / Marker IN on main
board defective Replace main board
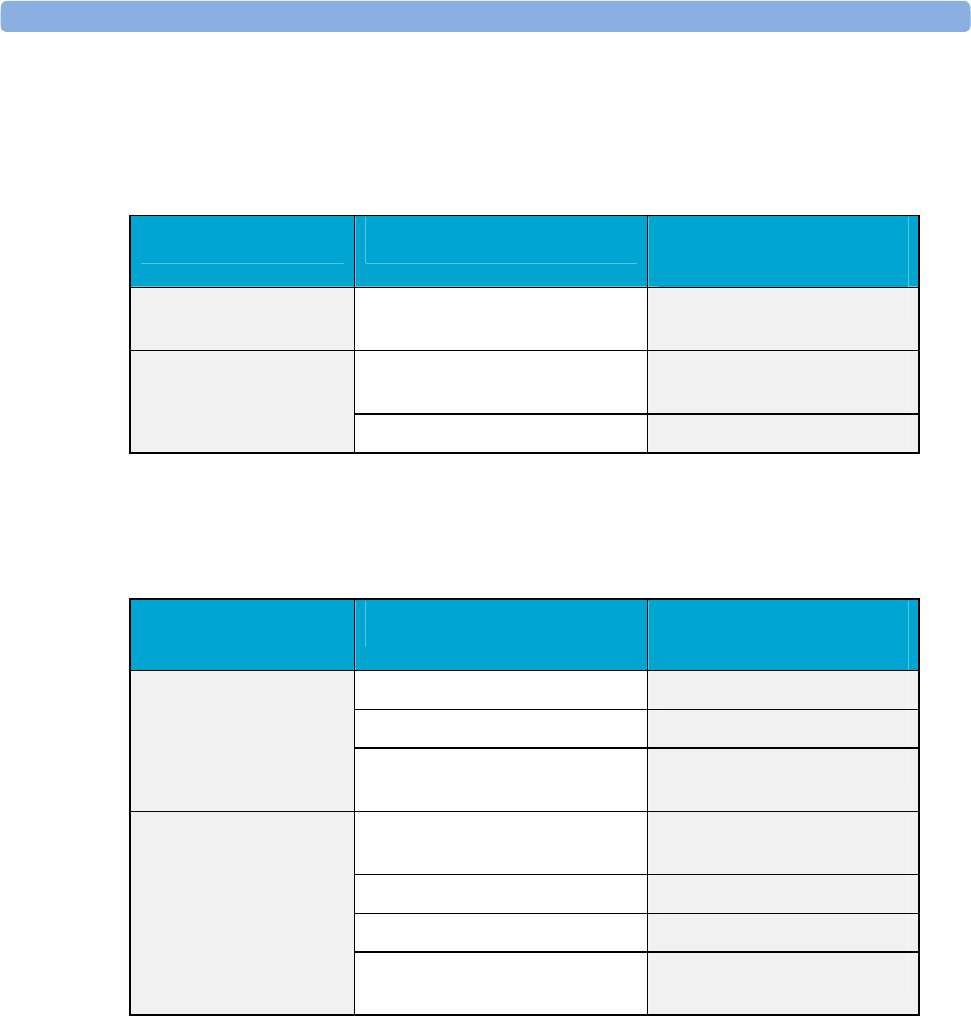
4 Troubleshooting Troubleshooting Guide
144
Alarm Issues
Alarm Lamps
Symptoms Possible Causes of Failure Failure Isolation and
Remedy
INOP Message Check
Alarm Lamps is issued Main board defective replace Main board
Alarm occurs, but no
LED lights up Environmental lighting too
bright Place monitor in a darker
environment
Main Board defective Main board
Alarm Tones
Symptoms Possible Causes of Failure Failure Isolation and
Remedy
Speaker cable disconnected Reconnect speaker cable
Speaker defective Replace speaker
INOP Message
SPEAKER
MALFUNCTION is
displayed Sound amplifier on main board
defective Replace main board
Audible alarm indicators have
been switched off Switch audible alarm
indicators back on
Volume set to 0 Increase volume
Speaker defective Replace speaker
Alarm occurs but no
alarm sound is issued
Sound amplifier on main board
defective Replace main board
Alarm Behavior
If your monitor did not alarm in the way in which the end user expected, please consult the
Instructions for Use for possible setup issues or configuration settings which could affect alarm
behavior.

Troubleshooting Guide 4 Troubleshooting
145
Individual Parameter INOPS
If any of the following parameter INOP messages are issued try the respective parameter in
another device. If the INOP message persists replace the parameter module, the MMS or other
indicated device.
- CO2 EQUIP MALF
- ECG EQUIP MALF
- NBP EQUIP MALF
- <Pressure Label> EQUIP MALF
- RESP EQUIP MALF
- SpO2 EQUIP MALF
- SpO2 TRANSDUC MALF
- <Temp Label> EQUIP MALF
Printer
Symptoms Cause of Failure Failure Isolation and
Remedy
Prompt message “Print
job could not be
queued” is issued. No
print device is found.
Printer is disabled in the Setup
Printers menu
Paper size of printer does not
match paper size of report
Enable the correct printer in
the Setup Printers menu
Change paper size of the
printer in the Setup Printers
menu or change paper size of
the report in the Setup
Reports menu.
Status message “Print
device Local 1 (Local
2) unavailable” is
issued. Printer job is
stalled.
Printer not switched on
Printer paper tray empty
Cabling not connected correctly
PS/2 or USB I/O board
defective
Switch on printer power
fill printer paper tray
Check cabling
replace I/O board
Status message “Print
device Remote 1
(Remote 2, Remote 3)
unavailable” is issued.
Printer job is stalled
Print error on Philips
Information Center
Network Connection to Philips
Information Center not
functioning
Print a test report on the
Philips Information center. If
this fails, refer to Philips
Information Center
documentation
Check that the network
connection between the
monitor and the Philips
Information Center is
working

4 Troubleshooting Troubleshooting Guide
146
Symptoms Cause of Failure Failure Isolation and
Remedy
Status message
“Printing on device
Remote 1... (Remote 2,
Remote 3)” is issued
but no report is printed
Print queue on Philips
Information Center is full.
Reasons for this may be:
- Printer is not switched on
- Printer paper tray is empty
Switch on printer power
Fill printer paper tray
Printouts are not as
expected Printer paper size is not
correctly configured
Printer resolution is not
correctly configured
Printer color support is
configured to “On” although
the printer does not support
color
Printer not compatible
Configure the paper size
according to the inserted
print media
Configure the printer
resolution according to the
printer capabilities
Configure the printer color
support to “Off”
Check specifications
Recorder
Symptom Possible Cause Corrective Action
Monitor thinks that
door is open when it
is not.
Defective door switch. Replace door switch. Exchange
recorder.
Monitor thinks that
the recorder is out of
paper when it is not.
Paper-out sensor dirty. Clean paper-out sensor.
Recorder not
communicating with
System.
Monitor not configured
properly. Check the configuration of the
connected monitor.
Printhead dirty. Clean the Printhead.
Printhead failure. Exchange the recorder.
Poor print quality.
Paper not inserted
correctly Check that paper is inserted correctly
Paper roll off center. Center paper roll on roller guides. Paper not feeding
properly. Dirty roller. Clean roller.

Troubleshooting Guide 4 Troubleshooting
147
MIB / RS232
Symptoms Cause of Failure Failure Isolation and
Remedy
The MIB/RS232 port is not
configured for AGM Check configuration of the
MIB/RS232 ports in
configuration mode
The cable between AGM and
monitor is not connected
correctly or defective
Check cable connection,
replace cable if necessary
The MIB/RS232 board is in a
wrong slot (slot has been
changed after software
configuration or an additional
board has been plugged in)
Verify correct placement of
the I/O boards
AGM connected to an
RS232 port not
functioning
The MIB/RS232 board is
defective Check board and replace if
necessary

4 Troubleshooting Troubleshooting Guide
148
Symptoms Cause of Failure Failure Isolation and
Remedy
The MIB/RS232 port is not
configured for data export Check configuration of the
MIB/RS232 ports in
configuration mode
The wrong data export protocol
driver is configured in the
monitor
Check the export protocol
required by the attached
device and configure the
monitor accordingly
The cable between the external
device and the monitor is not
connected correctly or defective
Check cable and replace if
necessary
The external device does not
support the version of the data
export protocol used in the
monitor
Check if the device supports
the version of the data export
protocol. Upgrade device or
monitor if necessary (if
matching versions exist).
A terminal concentrator is used
in between the device and the
monitor and a protocol with
dynamic speed negotiation is
used
Some terminal concentrators
do not support changing the
transmission speed (baud
rate) dynamically. Check if
the connection works without
the concentrator
The MIB/RS232 board is in a
wrong slot (slot has been
changed after software
configuration or an additional
board has been plugged in)
Verify correct placement of
the I/O boards
External device not
receiving data
The MIB/RS232 board is
defective Check board and replace if
necessary
Detailed Protocol
Problem Consult the Data Export
Protocol document.

Troubleshooting Guide 4 Troubleshooting
149
USB
Symptoms Cause of Failure Failure Isolation and
Remedy
The device connected to the
port with the switched off LED
is not supported.
Unplug the unsupported
device.
A printer connected to the port
is not switched on Switch on the printer.
One LED next to a port
with a connected USB
device is off
Short-Circuit Unplug the device in the
respective port and try again.
The connected devices are
drawing too much electricity. Unplug the connected
devices one by one until the
LEDs come back on.
All LEDs on the USB
board are off, even
though devices are
connected Unsupported combination of
devices. Unplug the connected
devices one by one until the
LEDs come back on. See
Connection of USB Devices
(on page 250) for details on
supported combinations.
None of the connected
devices are functioning. Connected devices or USB
board defective. Unplug all devices and
reboot the monitor. The
LEDs on the USB board
should switch on briefly and
then turn off. If they remain
on, the USB board is
defective and needs to be
exchanged.
Flexible Nurse Call Relay
Symptoms Cause of Failure Failure Isolation and
Remedy
INOP message CHECK
NURSE CALL
RELAY is issued
Nurse Call Relay board
defective Replace Nurse Call Relay
I/O board.

4 Troubleshooting Troubleshooting Guide
150
Symptoms Cause of Failure Failure Isolation and
Remedy
Incorrect configuration (Relay
latency, Relay trigger) Check monitor configuration
(see configuration guide)
Connection of cable to monitor
or nurse call system not correct Check cable connections
Nurse Call Relay board is in the
wrong slot. Verify correct placement of
the
I/O boards
Monitor alarmed, Nurse
Call did not activate
The Nurse Call Relay board is
defective Replace Nurse Call Relay
board
Basic Nurse Call Relay
Symptoms Cause of Failure Failure Isolation and
Remedy
Incorrect configuration (Relay
latency, Relay trigger) Check monitor configuration
(see configuration guide)
Connection of cable to monitor
or nurse call system not correct Check cable connections
Monitor alarmed, Nurse
Call did not activate
The system interface board is
defective Replace system interface
board
Troubleshooting the ECG OUT
Symptoms Cause of Failure Failure Isolation and Remedy
Disconnect the MMS and Defib
cable.
Connect Known good Defib, Defib
cable MMS and MMS cable. Check
Marker pulse and ECG OUT signal
at defib again. If there is still no
signal:
No ECG-OUT
signal to the Defib
Main Board defective Replace main board
No marker pulse is
displayed on the
monitor
Defib does not send marker Check whether defib is able to send
marker or check for internal
electronic defects.

Troubleshooting Guide 4 Troubleshooting
151
Docking Station Problems
NOTE
Before checking for further problems, make sure that the monitor is properly and firmly inserted
into the docking station (indicated by a click).
Symptoms Cause of Failure Failure Isolation and
Remedy
AC connection not ok Check that the AC-Mains are
powered and the power cord
is properly connected.
AC LED on Docking
Station does not light
up
Docking Station or Docking
System Interface board
defective
Exchange the docking
system interface board or the
docking station.
Monitor not docked correctly Check whether the lever is in
the right-hand position.
Check if the monitor AC
LED lights up when the
monitor is connected directly
to AC mains. If yes;
AC LED on Docking
Station lights up but
AC LED on monitor
does not.
Docking Station defective Exchange Docking Station
Monitor cannot be
properly docked to the
docking station
Docking interface board not
correctly installed in the
monitor
Make sure that docking
interface board is installed in
the monitor

4 Troubleshooting Troubleshooting Guide
152
Symptoms Cause of Failure Failure Isolation and
Remedy
Docking interface board not
installed in monitor Make sure that docking
interface board is installed in
the monitor
LAN cable not connected or
defective Check the LAN cable
connection. Try the LAN
cable directly in the monitor.
If it functions in the monitor
but not in the docking
station, see other possible
causes below. If it doesn’t
function in the monitor,
exchange the LAN cable
Flex cable in docking station
not connected properly or
defective
Check the flex cable
connection in the docking
station. Exchange flex cable
if necessary.
Docking Station main board
defective Exchange docking station
main board
Monitor in docking
station has AC Power
but network connection
could not be established
Other network related
problems. See Network related
problems
Flex cable in docking station
not connected properly or
defective
Check the flex cable
connection in the docking
station. Exchange flex cable
if necessary.
Docking Connector soiled or
blocked. Make sure there is no dirt or
other foreign bodies in the
docking connectors
Monitor does not boot
or constantly reboots
but functions properly
outside docking station
Docking Station main board
defective Exchange docking station
main board
Image Sticking
If a static image is displayed for a long time on an LCD display, image sticking, i.e. a
temporarily retained image, may occur. To eliminate image sticking, switch off the display and
switch it back on again. It is also recommended to use the moving image in standby mode.

Troubleshooting Guide 4 Troubleshooting
153
Data Flow Marker In and ECG Wave
The following illustration of the data flow for Marker In and ECG Wave may assist in
troubleshooting.
Status Log
Many events that occur during start-up or regular monitoring are logged in the Status Log. The
Status Log can be printed and cleared. Not all entries in the Status Log are errors.
Monitor
H 1720 20050 1 4 Apr 02 16:37
C 1721 21050 1 4 Apr 02 15:37

4 Troubleshooting Troubleshooting Guide
154
The window title is either Monitor or MeasServ, dependent on which system component’s
status log is currently displayed.
The Status Log window shows logged events which caused a reboot of the system component
(monitor or measurement server).
To enter the Status Log Window, select Main Setup -> Revision. The following list opens up:
- Status Log
- Product
- Appl. SW
- Config
- Boot
- Language
Select Status Log.
The first column in the log identifies the event class (“C”: caused a cold start, “H”: caused a hot
start, “N”: no retstart, for information only). Column 3 and 4 identify the event source and event
code. Column 4 counts the number of occurrences of the event. The last column shows the time
and date of the last occurrence of the event.
The following pop-up keys overlay the SmartKeys:
Clear
StatLog M8001 M3001
Clear StatLog
This key clears the currently displayed Status Log
M8001 or M8002
This key switches to the Monitor Revision Window
M3001
NOTE
This key switches to the Multi Measurement Server (MMS) Revision Window
If an event occurs repeatedly, contact your Philips Service Representative.
NOTE
It is possible, using the support tool, to download the status log and send it to your Philips
Service Representative as a file (for example via e-mail).
List of Error Codes
There are no error codes at this point.

Troubleshooting Guide 4 Troubleshooting
155
Troubleshooting with the Support Tool
Using the support tool you can:
- access the full status log which can be saved as a file
- reload software
- identify defective devices
- reset touch screen calibration
For details on how to perform these tasks see the Support Tool User Manual.
Troubleshooting the Individual Measurements or Applications
For problems isolated to an individual parameter or application, please consult the Instructions
for Use and configuration information.
If the instructions for use did not resolve an individual parameter problem, then another
measurement server should be tried.
If you are getting questionable readings for individual measurements you may want to do the
Performance Verification tests in the Testing and Maintenance section.
The performance of the individual applications (arrhythmia, trending) are affected by the
configuration of the monitor. When contacting Philips support you may be asked about the
configuration of the monitor to aid in troubleshooting.
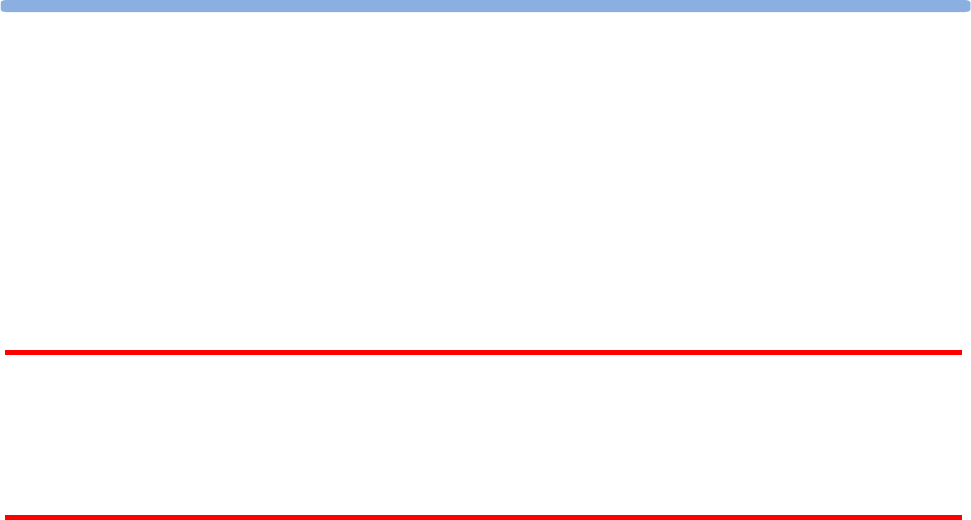
157
5
5Repair and Disassembly
The following section describes the disassembly and reassembly procedures for the monitor and
its components to the extent required to remove and replace faulty assemblies. Do not further
disassemble the product past the point described in these procedures.
WARNING
High Voltage - Voltages dangerous to life are present in the instrument. Do not perform any
disassembly or reassembly procedures (other than MMS, MMS extension or parameter module
removal) with power applied to the instrument. Failure to adhere to this warning could cause
serious injury or death.
Before doing any disassembly, turn power off, disconnect the Local Distribution Cable, AC
power cable, MSL cable, Defib sync’ cable and RS232 cable (where appropriate), disconnect
the MMS and remove batteries.
Tools required
- Torx screwdrivers (sizes 8, 10, 20)
- 4 mm Allen Wrench
- Small flat head screwdriver
- Socket Wrench
- 5.0 Hexagon Socket
- M6 Screw Wrench
- SPH size 1 cross-tipped Screwdriver
- Needle Nose Pliars
- ESD mat and wrist strap
- Cleaning Agent
Recommended cleaning agents are:

5 Repair and Disassembly How to find the Correct Procedure
158
Tensides (dishwasher detergents) Edisonite Schnellreinigerâ, Alconoxâ
Ammonias Dilution of Ammonia <3%,
Window cleaner
Alcohol Ethanol 70%, Isopropanol 70%,
Window cleaner
How to find the Correct Procedure
The following disassembly procedures are described:
1.1 Removing the Handle
1.2 Removing Measurement Server Holder
1.3 Removing the I/O Boards and Interface Board
1.4 Removing the Recorder
1.5 Removing the Navigation Point Knob
1.6 Removing the Quick Release Mount and Knob
2.0 Opening the Front of the Monitor
2.1 Removing the Backlight Tubes
2.2 Removing the Backlight Inverter Board
2.3 Removing Power On LED board and Silicon Pad
2.4 Removing the HIF Board, Silicon Pad and Spacer
2.5 Removing the Flex Adapter Cable
2.6 Removing the Battery Board
2.7 Removing Recorder Board Assembly
2.8 Removing the Loudspeaker
2.9 Removing the Branding Cover
3.0 Separating the Front and Back Half of the Monitor
3.1 Removing the LCD Flat Panel Display, Touch Panel and Front Housing
3.2 Removing the Main Board
3.3 Removing the MSL Assembly
3.4 Removing the Power Supply
3.5 Removing the Bezel and Serial Number Plate
At the beginning of each procedure there is a list of any other steps which must be completed
before starting this procedure.

Removing Directly Accessible Parts 5 Repair and Disassembly
159
Removing Directly Accessible Parts
Several replaceable parts are accessible before the monitor is disassembled. These are:
- Handle
- Measurement Server holder (picco snap assembly)
- I/O boards and interface board
- Recorder
- NavigationPoint knob
- Quick release mount
- Quick release mount - release knob
No. Description
1 Handle
2 MMS Holder
3 Battery Door
4 System Interface Board and I/O Boards

5 Repair and Disassembly Removing Directly Accessible Parts
160
No. Description
1 Recorder
2 Navigation Point Knob
3 Quick Release Mount Knob
1.1 Removing the Handle
1. Remove the two screws securing the handle.
2. The handle can be removed
1.2 Removing the Measurement Server Holder
Removing the old MMS Holder
1. First remove the handle as described above.
2. Pull the holder away from the monitor and upwards to remove.
3. Insert the new measurement server holder

Removing Directly Accessible Parts 5 Repair and Disassembly
161
Removing the new MMS Holder
NOTE
The handle does not need to be removed for this procedure
1. Pull the MMS holder forward and then up.

5 Repair and Disassembly Removing Directly Accessible Parts
162
1.3 Removing the I/O Boards and Interface Board
1. Remove the two screws securing each I/O board and the interface board and then remove the
boards using the board removal tool located in the battery compartment.
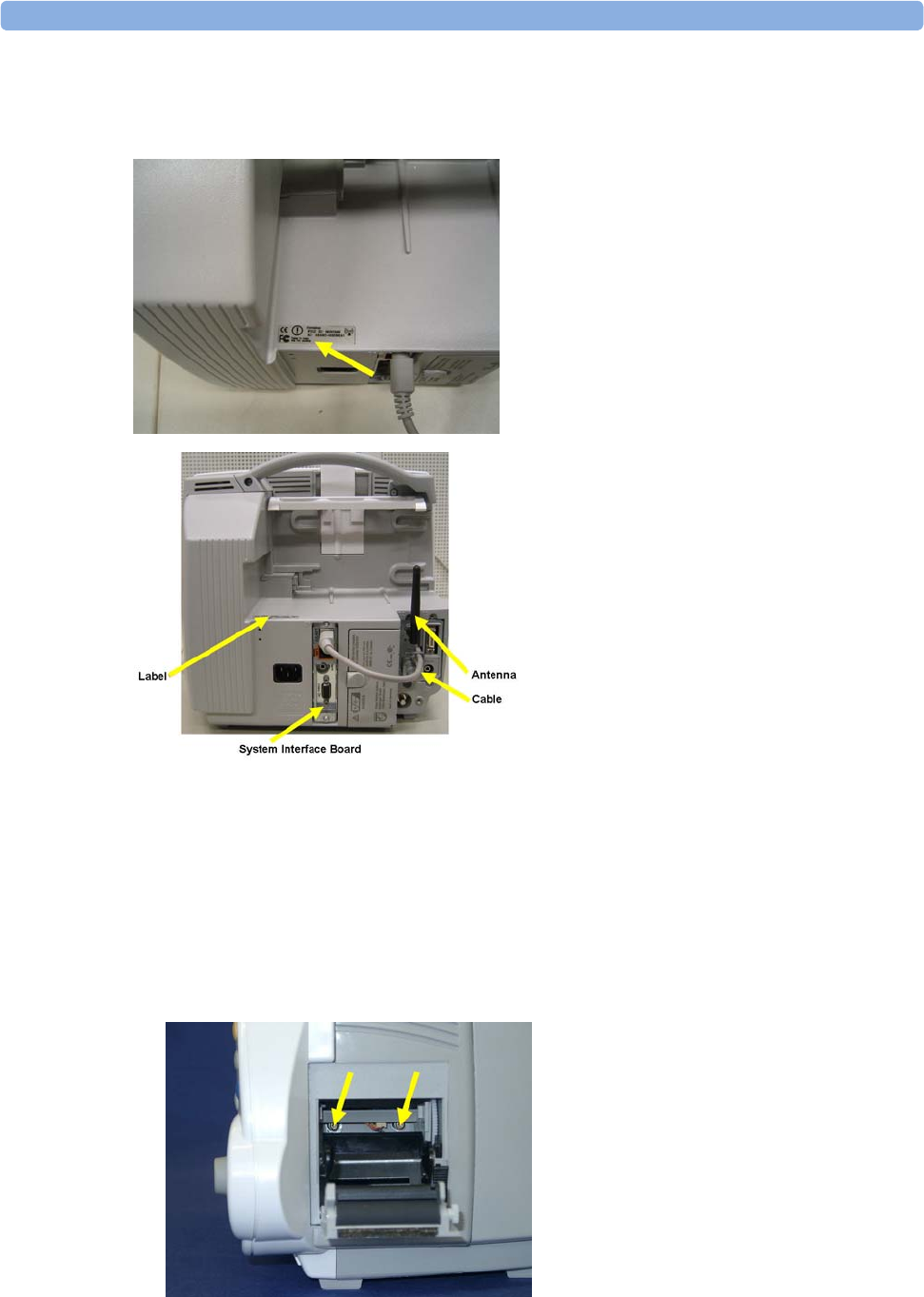
Removing Directly Accessible Parts 5 Repair and Disassembly
163
Reassembly Note: If you have installed #J35 (-USR_ProductName- 802.11 Bedside Adapter)
please attach the approval label or the WLAN Label for Japan (country specific) and the antenna
and plug in the cable as shown below.
NOTE
The installation of #J35 requires a system interface board with wireless functionality.
1.4 Removing the Recorder
1. Press on the door release lever to open the recorder door.
2. Remove the paper roll.
3. Remove the two screws securing the recorder and pull the recorder out.
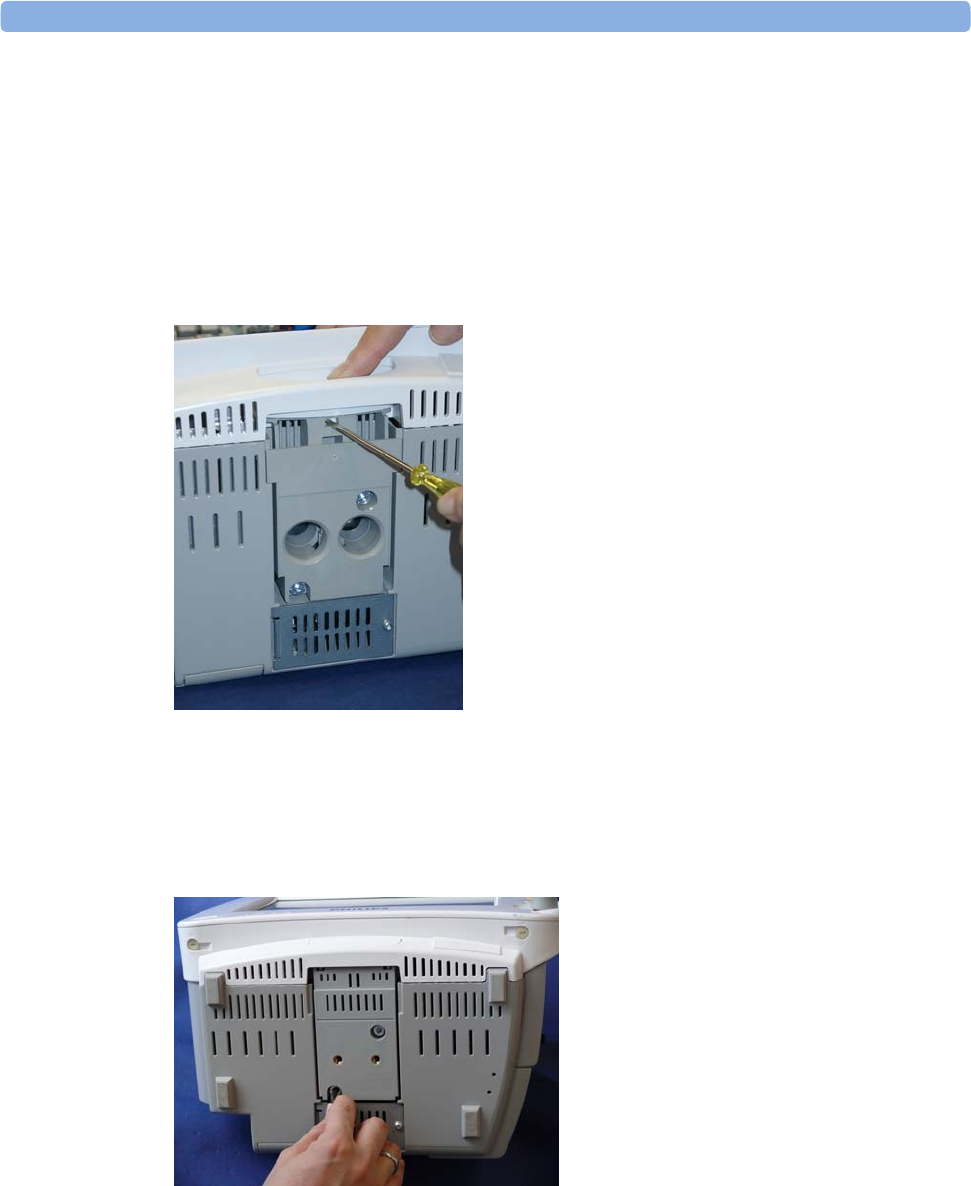
5 Repair and Disassembly Removing Directly Accessible Parts
164
1.5 Removing the Navigation Point Knob
The NavigationPoint knob can be removed by hand. Pull the knob forwards, away from the
monitor.
1.6 Removing the Quick Release Mount and Knob
1. Press the knob down and release the lock with a small screwdriver. You can now pull out the
knob.
2. Remove the two Allen screws securing the quick mount and pull the mount out of the recess
in the monitor.
1.7 Removing the Fix Mount
1. Remove the two screws securing the fix mount.

Removing Directly Accessible Parts 5 Repair and Disassembly
165
2. Pull out the fix mount

5 Repair and Disassembly 2.0 Opening the Front of the Monitor
166
2.0 Opening the Front of the Monitor
When the front of the monitor is opened the following replaceable parts are accessible:
- Backlight inverter PCA
- Backlight tubes
- Battery board
- Recorder board assembly
- Power on LED board
- HIF board
- Loudspeaker
- LCD flat panel display
- Main board
- MSL assembly
- Power supply
- Branding cover
- Serial number plate
1. Turn the two plastic screw pins 180 degrees counterclockwise and pull them out. Use a
small screwdriver to pull the screw head out of the recess in the housing.

2.0 Opening the Front of the Monitor 5 Repair and Disassembly
167
2. The hinges allow the monitor to be opened like a book. Support the display before
proceeding further.
2.1 Removing the Backlight Tubes
Previous steps: 2.0 Opening the front of the monitor
1. Unplug the two upper cables from the backlight inverter board.
2. Slide out the backlight tubes.

5 Repair and Disassembly 2.0 Opening the Front of the Monitor
168
NOTE
At reassembly make sure that the cables are laid through the slit and under the cable retention
tab.
2.2 Removing the Backlight Inverter Board
Previous steps: 2.0 Opening the front of the monitor, 2.1 Removing the backlight tubes - Step 1
1. Unplug the backlight inverter board cable. This cable can be removed for exchange by also
unplugging it from the socket at the flex adapter cable.
2. Remove the two screws securing the board, and remove the board.

2.0 Opening the Front of the Monitor 5 Repair and Disassembly
169
2.3 Removing Power On LED board and Silicon Pad
Previous steps: 2.0 Opening the front of the monitor
1. Unplug the power on LED board cable from the main board.
2. Remove the three screws securing the power on LED board.
NOTE
Photos 2 and 3 show the front and back halves of the monitor separated, this is however not
necessary at this stage of disassembly.
3. Remove the board and the silicon pad.
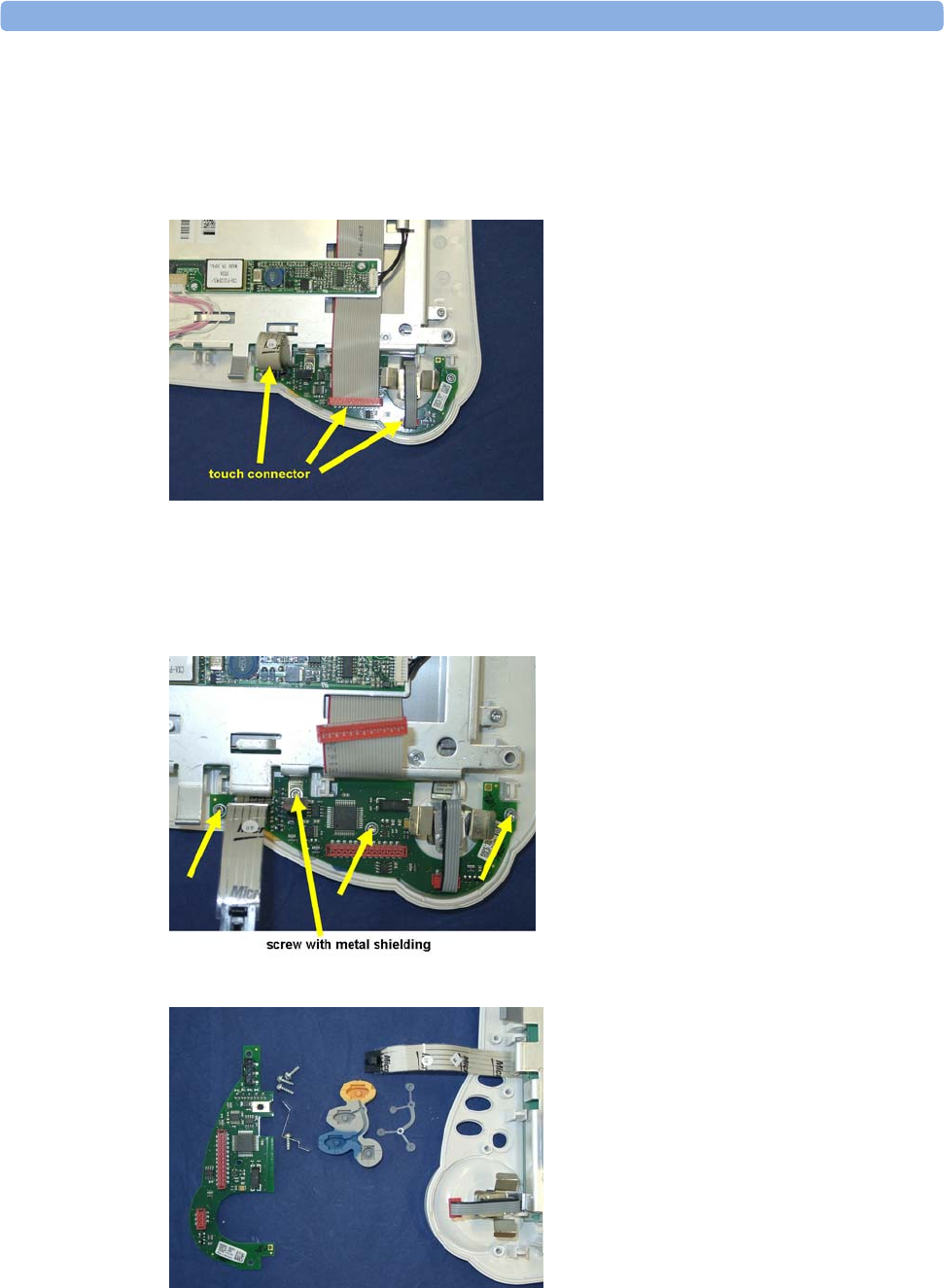
5 Repair and Disassembly 2.0 Opening the Front of the Monitor
170
2.4 Removing the HIF Board, Silicon Pad and Spacer
Previous steps: 2.0 Opening the front of the monitor
1. Unplug the two connectors (three on the touch version). For HIF cable replacement unplug
the cable also on the main board.
NOTE
At reassembly feed the lower section of the touch cable through the retainer tab on the metal
chassis. Make sure that the cable is not kinked.
2. Remove the four screws securing the board. Note the positon of the metal shielding
associated with one of the screws in order to replace it correctly during reassembly.
3. You can now remove the board, the silicon pad, and the plastic spacer.

2.0 Opening the Front of the Monitor 5 Repair and Disassembly
171
4. To remove the encoder (the part exposed when the navigation point knob has been removed)
use needle-nosed pliers to unscrew the split nut so that the encoder can be removed from the
inside.
NOTE
Note the position of the metal shielding on the rear side of the encoder in order to position it
correctly at reassembly.
2.5 Removing the Flex Adapter Cable
Previous steps: 2.0 Opening the front of the monitor
1. Unplug the backlight inverter board cable.
2. Remove the two screws securing the flex adapter cable and unplug it from the mother board
and the display chassis.

5 Repair and Disassembly 2.0 Opening the Front of the Monitor
172
NOTE
At reassembly make sure that the EMC pads are still in position before replacing the screws.
2.6 Removing the Battery Board
Previous steps: 2.0 Opening the front of the monitor
1. Remove the three screws securing the board.
2. Remove the board by pulling forwards to unplug the connector on the rear.
Reassembly Note: When reinserting the battery board, make sure the connector is plugged
tightly into the board in order to avoid any short circuit of the board with the metal chassis
when the display is reassembled.

2.0 Opening the Front of the Monitor 5 Repair and Disassembly
173
2.7 Removing Recorder Board Assembly
Previous steps: 2.0 Opening the front of the monitor
1. Unplug the recorder cable from the main board.
2. Remove the recorder as described on on page 1.
3. Remove the 2 screws securing the metal recorder housing and pull out the housing with
board and cable.

5 Repair and Disassembly 2.0 Opening the Front of the Monitor
174
2.8 Removing the Loudspeaker
Previous steps: 2.0 Opening the front of the monitor
1. Unplug the loudspeaker cable from the main board.
2. Remove the three plastic pins securing the side cover and remove the cover.
3. Remove the three screws securing the loudspeaker and remove the loudspeaker.

2.0 Opening the Front of the Monitor 5 Repair and Disassembly
175
NOTE
At reassembly, position the loudspeaker on the mounting plate so that the hook on the
loudspeaker fits in the groove on the mounting plate.
2.9 Removing the Branding Cover
Previous steps: 2.0 Opening the front of the monitor
1. On the inside of the front housing, push together the clip holding the branding cover (with
the help of a screwdriver, if necessary) to release the cover.
3.0 Separating the Front and Back Half of the Monitor
Before all further disassembly steps it is necessary to separate the front part of the monitor from
the main housing.
1. Disconnect the three cables connecting the front and back halves of the monitor.
2. Unscrew the four screws securing the hinges to the back half of the monitor.

5 Repair and Disassembly 2.0 Opening the Front of the Monitor
176
3.1 Removing the LCD Flat Panel Display, Touch Panel and Front Housing
Previous steps: 2.0 Opening the front of the monitor, 3.0 Separating the front and back half of
the monitor
1. Unplug the HIF cable and the touch cable from the HIF board. Remove the power on LED
cable from its retainer to gain access to the mounting screw.
2. Remove the eight screws securing the display assembly on the front panel.
3. Unplug the backlight inverter board cable, the backlight tubes cables and the LCD cable.
4. Remove the four screws securing the display to the metal chassis. The two lower screws are
special adjustment screws and must be replaced in the correct positions.

2.0 Opening the Front of the Monitor 5 Repair and Disassembly
177
NOTE
At reassembly, replace the two adjustment screws first, followed by the two upper screws.
5. Remove the HIF board and Power on LED board (procedures 2.4 and 2.5) to obtain the front
housing for replacement.
3.2 Removing the Main Board
CAUTION
All I/O boards and interface boards must be removed before removing the main board .

5 Repair and Disassembly 2.0 Opening the Front of the Monitor
178
Previous steps: 1.3 Removing the I/O boards and Interface board, 2.0 Opening the front of the
monitor, 3.0 Separating the front and back half of the monitor
1. Unplug the power supply cable, the loudspeaker cable, the MSL cable and the recorder cable
from the main board.
2. Remove the screw securing the lightpipe assembly and remove the assembly.
3. Remove the eight screws securing the main board.
4. Lift the right side of the main board up and pull out to the right.

2.0 Opening the Front of the Monitor 5 Repair and Disassembly
179
NOTE
When replacing the main board, make sure that the white seal on the left (ECG-out connector) is
positioned to seal well. Ensure also that the screw with the metal shielding is replaced in the
correct position, and with the metal “wings” oriented horizontally.
3.3 Removing the MSL Assembly
Previous steps: 2.0 Opening the front of the monitor, 3.0 Separating the front and back half of
the monitor, 3.2 Removing the main board
1. Remove the screw securing the assembly.

5 Repair and Disassembly 2.0 Opening the Front of the Monitor
180
3.4 Removing the Power Supply
Previous steps: 2.0 Opening the front of the monitor, 3.0 Separating the front and back half of
the monitor, 3.2 Removing the main board
1. Remove the five screws securing the power supply - one must be unscrewed through the
hole in the white protective cover.
2. Pull the power supply out of the monitor.
3.5 Removing the Frame Housing and Serial Number Plate
Previous steps: 2.0 Opening the front of the monitor, 3.0 Separating the front and back half of
the monitor,
1. Remove the four screws and two pins which secure the frame housing to the rear housing.
2. Remove the serial number plate by pushing together the two retention clips on the inside of
the frame housing.

Multi-Measurement Module (MMS) Disassembly 5 Repair and Disassembly
181
Multi-Measurement Module (MMS) Disassembly
Please follow the disassembly and reassembly steps below closely. Do not disassemble the MMS
past the point described in the procedures below.
Tools required
- thin-bladed screwdriver
- ESD mat and wrist strap
WARNING
- Do not open the MMS while it is connected to a monitor.
- Parts inside the instrument may be contaminated with bacteria. Protect yourself from
possible infection by wearing examination gloves during this procedure.
Removing the Front Cover
1. Position the thin-bladed screwdriver in the small slot provided for this purpose. Remove the
front cover by pulling it away from the MMS until it snaps off. There may be a slight
resistance when removing the front cover.
Removing the Mounting Pin
1. Position the MMS with the connectors facing towards you. There are four long mounting
pins threaded into the MMS in each of the four corners under the cover. Locate the heads of
the two long mounting pins on the top cover and only remove these.

5 Repair and Disassembly Multi-Measurement Module (MMS) Disassembly
182
2. Use the thin-bladed screwdriver to lift the pins gently out, far enough that they can be
removed manually.
3. Remove the two pins and set them aside for refitting.
NOTE
Without these long mounting pins, the MMS will not function properly
Removing the Top Cover
Begin by gently pulling the top cover away from the MMS. The top cover is press-latched at the
MMS connector. There might be a resistance due to the rubber sealing. Remove the cover
slowly, without hitting or touching the inside of the MMS.

Multi-Measurement Module (MMS) Disassembly 5 Repair and Disassembly
183
Removing the DC/DC Board
NOTE
The HW Rev C MMS (S/N prefix DE610xxxxx) does not have a separate DC/DC board
anymore.
The DC/DC board is connected to the main board. Loosen the pin connection to the main board
and remove the DC/DC board by gently lifting it up. Avoid touching the surface of the board.
Set it aside where it is ESD protected.
Removing the MSL Flex Assembly
1. After the DC/DC board is removed, lift up the MSL frame connector to which the MSL Flex
is attached.
At the beginning there might be resistance due to the special fixing mechanism shown in the
picture below.

5 Repair and Disassembly Multi-Measurement Module (MMS) Disassembly
184
2. Lift up the flex connector carefully. Do not bend the connector pins on the main board.
Reassembling the MSL Flex Assembly
1. Insert the MSL Flex layer into the frame connector as shown below by moving it into the
appropriate dove tail.
2. To insert the MSL Flex into the MMS, it has to be bent carefully. Bend the MSL Flex in a
180 degree angle as shown below. Do not crease the flex.

Multi-Measurement Module (MMS) Disassembly 5 Repair and Disassembly
185
3. The second bend has to be done as shown below. To be able to connect the MSL flex to the
main board afterwards, the flex has to be bent in a 90 degree angle as shown in the picture.
Do not crease the flex.
4. Insert the frame connector with the attached and bent MSL Flex. Be careful not to damage
the MSL flex when pushing the frame connector downwards.
5. Position the connector correctly and push it into place.

5 Repair and Disassembly Multi-Measurement Module (MMS) Disassembly
186
Removing the NBP pump
1. Remove the pump by lifting it up. Set the pump aside. Also remove the old silicon tubes.
2. Remove the connector of the NBP pump assembly. The connector may sit tightly. Gently
loosen the connector.
Refitting the new NBP Pump
1. Insert new silicon tubes. Make sure they are seated correctly by pressing them into their
position.

Multi-Measurement Module (MMS) Disassembly 5 Repair and Disassembly
187
2. Insert the new pump assembly. Lift up the back and press the airways onto the silicon tubes.
3. Make sure the airways have a tight connection to the silicon tubes.
4. Insert the connector of the NBP assembly into the connector on the main board. Do not
crease the flex cable. M3001A HW A/B and M3000A have a post connector with long pins.
Press down the connector until there is no gap between the connectors.

5 Repair and Disassembly Multi-Measurement Module (MMS) Disassembly
188
Refitting the DC/DC board
NOTE
This step only has to be done on HW A/B
Position the DC/DC board and press it down gently. Make sure it is connected properly to both
connectors indicated in the picture.
Refitting the Cover
NOTE
To change the top cover of a HW Rev C MMS (S/N prefix DE610xxxxx) you have to attach the
two cushions which are part of the Top Cover Assembly. These two cushions secure the
connection of the MSL Flex and the NBP Flex.
NOTE
Perform the following two steps only on an MMS HW Rev C
1. Stick the two cushions onto the marked positions inside the top cover.
2. Position the top cover, then press it back into place until you hear a click or there is no
longer a gap between the two covers.

Multi-Measurement Module (MMS) Disassembly 5 Repair and Disassembly
189
3. The cover has a rubber seal, press the cover firmly together.
4. Holding the bottom cover firmly in place, slide the two long mounting pins completely back
into the MMS. Make sure there is no gap between the top and bottom cover.
Refitting the Front Cover
To refit the front cover, press it back into place over the measurement connector hardware until
you hear a click.

5 Repair and Disassembly MMS Extensions - Exchanging the Top Cover, MSL Flex Cable and the Dual
Link Bar
190
Final Inspection
Perform a final inspection to ensure that:
- The MSL connector is positioned correctly
- There are no gaps between the MSL connector and the cover
- there is no gap between the top and bottom cover
Testing
To ensure that the MMS is functioning correctly, you must perform safety tests and a
performance check on it. Please refer to the sections "Maintaining the Instrument" and "Testing
the Instrument".
MMS Extensions - Exchanging the Top Cover, MSL
Flex Cable and the Dual Link Bar
This section describes the exchange procedures for:
- The Top Cover with new release mechanism
- The Dual Link Bar incl. the MSL Flex Cable.
for all MMS Extension (MSE) types (M3012A, M3014A, M3015A, M3016A).

MMS Extensions - Exchanging the Top Cover, MSL Flex Cable and the Dual Link Bar 5 Repair and
Disassembly
191
Exchange Procedures
NOTE
Please follow the disassembly and reassembly steps closely.
Tools Required:
A thin-bladed screwdriver and a thick-bladed screwdriver, ESD mat and wrist strap
WARNING
- Do not open the MSE while it is connected to a monitor.
- Parts inside the instrument may be contaminated with bacteria. Protect yourself from
possible infection by wearing examination gloves during this procedure.
NOTE
Once you have reassembled the MSE, you must perform a performance check on it. Please refer
to the sections "Maintaining the Instrument" and "Testing the Instrument" .
Removing the Front Cover
1. Position the thin-bladed screwdriver in the small slot provided for this purpose. The front
cover (Bezel) then clicks away from the Extension. Remove the front cover
NOTE
There might be a slight resistance when you remove the front cover.

5 Repair and Disassembly MMS Extensions - Exchanging the Top Cover, MSL Flex Cable and the Dual
Link Bar
192
Removing the Mounting Pin
1. Position the MSE on the dual link bar with the measurement connector hardware facing
upwards and the arm of the dual link bar away from you. There are four long mounting pins
threaded into the MSE in each of the four corners under the cover. Locate the heads of the
two long mounting pins on the top housing and only remove these.
2. Use the thin-bladed screwdriver to lift the pins gently out far enough so they can be removed
manually.
3. Remove the two pins and set them aside for refitting.
NOTE
Without these long mounting pins the MSE will not function properly.

MMS Extensions - Exchanging the Top Cover, MSL Flex Cable and the Dual Link Bar 5 Repair and
Disassembly
193
Removing the Dual Link Bar
The Dual Link Bar consists of three parts as shown below. Follow the specific steps carefully to
remove the Link Bar.
CAUTION
Do not try to remove the link bar with force as this can damage the MSL Flex Cable
1. Position the MSE with the measurement connector hardware facing towards you.
2. Hold the link bar as shown below. While pressing gently on part B, insert a thick-bladed
screwdriver between the MSL connector and part A. Twist the screwdriver to the left and
at the same time slide part B to the right, so it is released at the top.

5 Repair and Disassembly MMS Extensions - Exchanging the Top Cover, MSL Flex Cable and the Dual
Link Bar
194
3. Repeat Step 2 at the bottom.
4. Slide part B to the right. If part B fails to move to the side, please repeat steps 2 and 3.
5. Now the MSL Flex connector can be moved to the right.
NOTE
Make sure that the movement of the screwdriver does not pinch the MSL flex cable.
6. Insert the thin-blade screwdriver behind the release mechanism of part C. Carefully twist the
screwdriver, then press gently so that part C drops down.

MMS Extensions - Exchanging the Top Cover, MSL Flex Cable and the Dual Link Bar 5 Repair and
Disassembly
195
7. Lift part A upwards. It is fixed in a dovetail. Be careful with the MSL flex.

5 Repair and Disassembly MMS Extensions - Exchanging the Top Cover, MSL Flex Cable and the Dual
Link Bar
196
Removing the Top Cover
Begin by gently pulling away the top cover from the MSE. The top cover is press-latched at the
link bar end. Remove it slowly, without hitting or touching the inside of the MSE.
Replacing the Flex Cable Assembly
1. Hold the Extension firmly and push upwards against the connector. Then slide connector
(together with the connector holder) out of the dovetail connection.
NOTE
You will probably need to apply some more force at first until the holder slides out of its
mechanical lock.
2. Slide the connector out of its holder.

MMS Extensions - Exchanging the Top Cover, MSL Flex Cable and the Dual Link Bar 5 Repair and
Disassembly
197
3. Remove the flex cable connector on the MSE board. Be careful not to bend any pins on the
female part of the MSE connector.
NOTE
Some units may have a foam pad on the connector of the inner flex cable of the MSEs (as
shown below) and some units may not. This has no impact on the functionality of these
units.
4. Stick the correct foam pad on the rear side of the inner connector. Use the thick pad for :
M3012A, M3014A, M3016A. Use the thin pad for: M3015A. You can also check the old
flex cable for the correct pad.
5. Insert the flex cable connector into the female receptacle on the MSE board. Check from
the side and the front that the connector is inserted correctly (there is no mechanical
guidance) and that no pins are bent, otherwise you may damage the MSE when
powering it on.

5 Repair and Disassembly MMS Extensions - Exchanging the Top Cover, MSL Flex Cable and the Dual
Link Bar
198
WARNING
A misplaced connector might damage the MSE or the monitor.
6. Slide the connector into the holder as shown below. Arrange the flex cable in the space
beside and underneath the board (be careful not to bend the cable) while positioning the
holder for insertion.
7. Insert the holder with the connector into the dovetail connection and slide it down until you
hear a click.

MMS Extensions - Exchanging the Top Cover, MSL Flex Cable and the Dual Link Bar 5 Repair and
Disassembly
199
Refitting the Top Cover
NOTE
Be careful with the MSL Flex cable. Make sure it does not get stuck between the covers.
1. Position top cover, then press the bottom cover back into place until a click is heard.
2. The cover has a rubber seal. Press the covers firmly together and make sure there is no gap
between the top and bottom cover.
3. Holding the bottom cover firmly in place, slide the two long mounting pins completely back
into the MSE.
Assembling the dual Link Bar
CAUTION
Do not try to assemble any part of the link bar with force as this can damage the MSL Flex
Cable.

5 Repair and Disassembly MMS Extensions - Exchanging the Top Cover, MSL Flex Cable and the Dual
Link Bar
200
1. Position part A into the dovetail and slide it down.
2. Make sure the MSL Flex connector is positioned in the correct slot (See indicated slots
below). Then push it gently into part A.
3. Making sure the MSL flex cable lies flat in part A of the assembly, place part B into the
dovetail and close the open link bar.

MMS Extensions - Exchanging the Top Cover, MSL Flex Cable and the Dual Link Bar 5 Repair and
Disassembly
201
4. Turn the MSE around and insert part C into the bottom part of the link bar. When you hear a
click, part C is correctly inserted.
Refitting the Front Cover
To refit the front cover, press it back into place over the measurement connector hardware until
you hear a click.
Final Inspection
Perform a final inspection to ensure that:
- The link bar is positioned correctly
- There are no gaps between the link bar parts
- There is no gap between the top and bottom cover

5 Repair and Disassembly Disassembly Procedures for the M3015A MMS Extension (HW Rev. A)
202
Testing
To ensure that the MSE is functioning correctly, you must perform a performance check on it.
Please refer to the sections "Maintaining the Instrument" and "Testing the Instrument".
Disassembly Procedures for the M3015A MMS
Extension (HW Rev. A)
NOTE
These procedures apply only to M3015A MMS with Serial Numbers DE020xxxxx.
It is recommended that you replace all the replaceable parts in the Extension (CO2 Scrubber and
Pump) after 15 000 hours (approximately 3 years) of continuous use.
Tools Required:
- A thin-bladed screwdriver.
- A pair of large tweezers.
- In addition, for removing the pump, you will need a large-bladed screwdriver.
WARNING
There is high voltage inside the Instrument (800V). Do not connect the MMS Extension to a
Monitor while the Extension housing is open.
As well, parts inside the Instrument may be contaminated with bacteria. Protect yourself from
possible infection by wearing examination gloves during these procedures.
Removing the Front Cover
To remove the front cover, do the following:
1. Remove the server and the monitor from the extension.
2. Use a thin-bladed screwdriver to prise the grey front cover (the console covering the
measurement connector hardware) gently from the bottom of the extension. Position the
screwdriver in the small slits provided for this purpose. The front cover then clicks away
from the extension.

Disassembly Procedures for the M3015A MMS Extension (HW Rev. A) 5 Repair and Disassembly
203
3. Remove the front cover.
Removing the Extension Bottom Cover
To remove the Extension bottom cover, do the following:
1. Position the extension on the dual link bar with the measurement connector hardware facing
upwards and the arm of the dual link bar towards you. There are four long mounting pins
threaded into the extension in each of the four corners under the cover. Locate the heads of
the two long mounting pins on the side away from you
2. Use tweezers to prise the pins gently out enough to be removed by hand.
3. Remove the two pins and set them aside for refitting.
NOTE
Do not lose these long mounting pins since the Extension will not function unless they are in
place.
4. Using your hands, gently pry the bottom cover away from the Extension at the link bar end
first. The bottom cover is press-latched at the link bar end. Remove it gently making sure not
to bang or touch the inside of the Extension.

5 Repair and Disassembly Disassembly Procedures for the M3015A MMS Extension (HW Rev. A)
204
NOTE
If you accidentally try to remove the wrong side of the bottom cover, you will notice that it is
attached to the inside of the Extension with a ribbon connector and that the dual link bar prevents
you from removing it completely. Do not try to forcibly remove the wrong side of the
M3015A cover; you cannot access replaceable parts from this side.
The following illustration shows the location of the replaceable parts in the M3015A
Measurement Server Extension.
Removing the CO2 Scrubber
To remove the CO2 Scrubber, do the following:
1. Locate the CO2 Scrubber in the Extension.
2. Being careful not to touch anything else in the Extension, use tweezers to pull the body of
the CO2 Scrubber out of the bracket.
3. Holding the body of the CO2 Scrubber with your fingers, carefully disconnect the Extension
intake tube from the scrubber end and remove the CO2 Scrubber from the Extension.

Disassembly Procedures for the M3015A MMS Extension (HW Rev. A) 5 Repair and Disassembly
205
4. Dispose of the CO2 Scrubber according to local legal requirements for low volume chemical
waste.
NOTE
Now that it is exposed, do NOT allow anything to fall into the Infrared Lamp assembly.
Removing the Pump
To remove the Pump, do the following:
1. Locate the Pump in the Extension.
2. Being careful not to touch anything else in the Extension, unscrew the screw holding the
pump bracket in position. Lift the top part of the bracket away and lift out the pump.
3. Gently disconnect the flow tubing attached to the Extension from the Pump.
NOTE
Be sure to note which tube attaches to the inlet and which tube attaches to the outlet.
4. Gently disconnect the power lead which attaches the Pump to the Extension.
5. Remove the Pump.
NOTE
After replacing the Pump, reset the displayed value displayed using the Reset PumpOpTime
selection (Service Mode>CO2 Setup). When the PumpOpTime has been reset an INOP will
be generated: “CO2 OCCLUSION”. To clear this INOP you must perform a flow check and
store the flow in Service Mode (select “Store Flow”)

5 Repair and Disassembly Disassembly Procedures for the M3015A MMS Extension (HW Rev. A)
206
Refit Procedures for the MMS Extension
Tools Required:
- A thin-bladed screwdriver.
- A pair of large tweezers.
- In addition, for refitting the Pump, you will need a large-bladed screwdriver.
WARNING
There is high voltage inside the Instrument (800V). Do not connect the MMS Extension to a
Monitor while the Extension housing is open.
As well, parts inside the instrument may be contaminated with bacteria. protect yourself from
possible infection by wearing examination gloves during these procedures.
Refitting the CO2 Scrubber
WARNING
The CO2 Scrubber contains lithium hydroxide monohydrate. This is a strong base. Do not open
or damage the CO2 Scrubber. If you come into contact with the CO2 Scrubber material, flush the
area immediately with water and consult a doctor.
To refit the CO2 Scrubber, do the following:
1. O2 Scrubber through the bracket to meet the Extension intake tube.
2. Push the intake tube firmly into the scrubber end to connect it.
3. Holding the body of the CO2 Scrubber with tweezers, feed the CO2 Scrubber fresh air
intake under the second bracket and position it.
Refitting the Pump
To refit the Pump, do the following:
1. Gently connect the power lead to the Extension.
NOTE
The power lead can only be connected one way.Do not try to force the power lead into
position. Instead, align it correctly and connect it gently.
2. Connect the flow tubing to the Pump.
NOTE
Be sure to reconnect the inlet tube to the inlet valve and the outlet tube to the outlet valve.
3. Being careful not to touch anything else in the Extension, insert the pump into the bracket on
the PC board. Make sure that the pump is horizontal and does not touch the PC board.
(Vibration from the pump in operation will damage the Extension if the pump touches the
PC board.)
4. Replace the top part of the bracket and screw firmly into position.

Smart Battery Charger LG1480 (M8043A) 5 Repair and Disassembly
207
NOTE
After replacing the Pump, reset the displayed value using the Reset PumpOpTime selection
(Service Mode>CO2 Setup). When the PumpOpTime has been reset an INOP will be generated:
“CO2 OCCLUSION”. To clear this INOP you must perform a flow check and store the flow in
Service Mode (select “Store Flow”).
Refitting the Extension Bottom Cover
To refit the Extension bottom cover, do the following:
1. Latch the link bar end into place then press-click the bottom cover back into place covering
the interior of the Extension.
2. Holding the bottom cover firmly in place, thread the two long mounting pins back into the
Extension making sure to thread them all the way to the end.
Refitting the Front Cover
To refit the front cover, press-click it back into place over the measurement connector hardware.
General Reassembly/Refitting Comments
- Ribbon Connections—Make sure male-female ribbon connections are correctly lined-up.
- Open Component—Do not allow anything to fall into the open component.
Following Reassembly
Once you have reassembled the Instrument, you must perform a safety and performance check
on the Instrument. Refer to Testing and Maintenance.
Smart Battery Charger LG1480 (M8043A)
You should clean both air filter mats on a regular basis. Depending on the frequency of use and
the environmental conditions (dust etc.), the interval can range from 6 to 24 months.

5 Repair and Disassembly Smart Battery Charger LG1480 (M8043A)
208
Cleaning the Air Filter Mats
The air filters are located on the right and left side of the battery conditioner. Perform the
procedure below for each side.
1. Remove the 2 screws securing the filter cover and take off the cover.
2. Remove the filter mat and clean the dust out by shaking.
3. Re-insert the mat and refit the cover and screws.
Replacing the Fan
1. Turn the battery conditioner upside down and remove the 5 screws at the bottom with a T20
screwdriver.
2. Lift the bottom cover up at the front and pull it off.

Smart Battery Charger LG1480 (M8043A) 5 Repair and Disassembly
209
3. Unplug the fan connector from the main board.
4. Lift the fan out of the battery conditioner housing.

5 Repair and Disassembly IntelliVue Instrument Telemetry (IIT)
210
5. When replacing the fan make sure the connector is plugged in correctly as shown in the
photograph below.
IntelliVue Instrument Telemetry (IIT)
The following section describes how to exchange the IIT module.
1. Perform the steps described in 2.0 Opening the Front of the Monitor (on page 166) and 3.0
Separating the Front and Back Half of the Monitor (on page 175)
2. Remove the three plastic pins securing the side cover.
3. Disconnect the IIT module from the main board.

Docking Station 5 Repair and Disassembly
211
4. Disconnect the IIT module from the antenna connector plate.
5. Remove the two M3x6 screws securing the IIT module and pull out the module from behind
the metal tab.
Docking Station
The following sections describe the exchange of the main board and the flex cable of the
Docking Station.
Exchanging the Main Board
1. Remove the metal covers covering the alarm and video connectors and I/O slots.

5 Repair and Disassembly Docking Station
212
2. Remove the six screws at the bottom of the docking station and lift the bottom cover off.
3. Remove the four screws securing the metal plate and lift it off.
4. Remove the two screws next to the video connector.

Docking Station 5 Repair and Disassembly
213
5. Remove the two screws on the main board.
6. Push the plastic tips through the board, lift the board up and remove the flex cable holder
under the board.
7. Unplug the flex cable from the main board and remove the board.
8. Perform the above steps in reverse order to reassemble the docking station.

5 Repair and Disassembly Docking Station
214
Reassembly Note: Make sure that the main board is placed on top of the metal flaps at the front
of the docking station and not below..
Exchanging the Flex Cable
1. Perform the steps listed under “Exchanging the Main Board”.
2. Remove the eight screws and lift off the metal sheet to the side.
3. Remove the guide pins next to the flex connector on the front side of the power block.

Docking Station 5 Repair and Disassembly
215
4. Remove the two screws from the bottom cover of the power block.
Reassembly Note: When reassembling the bottom cover of the power block, make sure that
the grounding cable , the optic fiber and the flex cable run through the holes provided in the
cover.
5. Remove the black Split Core and pull out the flex cable from the bottom.
6. Perform the above steps in reverse order to reassemble the docking station.

5 Repair and Disassembly Docking Station
216
Reassembly Note: When re-inserting the flex cable it is recommended to secure it with the
guide pins immediately.

217
6
6Parts
This section lists the replacement and exchange parts for the following Philips IntelliVue Patient
Monitoring System components:
- MP20/MP30 Parts
- Multi-Measurement Module (MMS) Parts (on page 223)
- MMS Extension Parts (M3012A, M3014A, M3015A and M3016A) (on page 230)
- Smart Battery Charger Part Numbers (on page 235)
- External Display Part Numbers (on page 237)
- Remote Alarm Device Part Numbers (on page 239)
- Remote Extension Device Part Numbers (on page 240)

6 Parts MP20/MP30 Parts
218
MP20/MP30 Parts

MP20/MP30 Parts 6 Parts
219
Note: Part numbers printed on the boards may be different from those listed here.
Ordering Part
Number
Ordering Part
Number 12NC
Description New or
Exchange
No. in
Diagra
m
M8001-605011 451261003241 Rear Housing New 1
M8001-42307 451261016801 MMS Lock New 2
M8063-69501
or
M8063-695612
453563499191
or
4512610119012
MSL Assembly (w/o cable) New 11
M8001-605063 4512610111113 Frame Housing Assembly New 7
M8001-60502 451261002051 Power Supply Assembly New 8
M8001-68002 451261001741 Power Supply Assembly Exchange
M8058-684047 4512610266217 Main Board PCA (see note 7
below for monitors with serial
number <DE540xxxx)
Exchange
M8067-66561 451261003381 Battery PCA New 14
M8067-68461 451261003451 Battery PCA Exchange
M8003-69503 453563499111 Loudspeaker Assembly New
M8001-64603 451261003331 Backlight Tubes New
M8001-640224 ,5 451261015341 Touch Screen & Front Housing
Assy (Text, English) New 19 & 16
M8001-640234,5 451261015351 Touch Screen & Front Housing
Assy (Symbols) New 19 & 16
M8001-640124,5 451261015361 Non-Touch Screen & Front
Housing Assy (Text, English) New 19 & 16
M8001-640134,5 451261015371 Non-Touch Screen & Front
Housing Assy (Symbols) New 19 & 16
M8086-665624,6 451261015381 HIF Board (Touch) New 18
M8086-665824 451261015391 HIF Board (Non-Touch) New 18
M8001-00111 451261015401 Chassis New
M8001-64001 451261003271 LCD Display 10.4 inch New
M8001-66051 451261003341 Backlight Inverter PCA New 22
M8077-66501 451261003391 Flex Adapter Cable New 24
M8001-60003 451261003221 Side Cover Blank New 4
M8001-44102 451261003201 Side Cover Recorder New 5
M8001-44106 451261007921 Side Cover Recorder Antenna
(IIT) New n/a

6 Parts MP20/MP30 Parts
220
Ordering Part
Number
Ordering Part
Number 12NC
Description New or
Exchange
No. in
Diagra
m
M8001-60004 451261007931 Side Cover w/o Recorder Antenna
(IIT) New n/a
M8001-60901 451261003261 Handle New 3
M8003-69021 453563499091 Quick Release Mount New 10
M8001-64010 451261003291 Cable Kit (MSL, Backlight) New
M8001-64011 451261003301 Cable Kit (Rec, HIF, Power on) New
M8062-61002 451261030071 MP30 Cable Rec./SRL cable New
M8065-66581 451261003371 Carrier Power on LED PCA New 23
M8001-60100 451261003231 Recorder New 9
M8062-66561 451261003361 PCA recorder New 12
M8092-67521 451261003421 Option Board Standard Assembly New
n/a 453564112081 Docking System Interface Board
MP20/30
(includes 453564099331
IntelliVue Plastic Protective
Bracket)
New
n/a 453564099331 IntelliVue Plastic Protective
Bracket Docking New
M8092-67501 451261003411 LAN-Wireless SVGA - nurse call New
M8081-67501 453563469621 IF MIB/RS232 New
M8082-67501 453563469631 IF Centronics Printer New
M8086-67501 453563469651 IF HIF, Integral, PS 2 New
M8089-67501 451261028241 IF USB New
M8087-67501 453563469681 IF Flexible Nurse Call Relay New
M8086-67521 453563469661 Remote IF New
M8003-47402 451261019561 Knob Navigation Point New
M8001-47402 45126101471 Key Silicone Pad New
M8001-44701 451261019571 Spacer HIF board New
M8003-60005 451261015961 Battery Door Assembly New

MP20/MP30 Parts 6 Parts
221
Ordering Part
Number
Ordering Part
Number 12NC
Description New or
Exchange
No. in
Diagra
m
M8001-64015 451261003311
M8001-60501 Small Parts Kit including:
Quick mount release cover
Branding cover MP20
Branding cover MP30
Silicon pad - Power on/off LED
Silicon pad - navigation point
Spacer - navigation point
ECG-out seal
Lightpipe assembly
Knob - navigation point
Slit washer - navigation point
knob
Shielding - navigation point knob
Encoder - navigation point knob
Pin - front housing
Pin - side cover
Screw K30x8
Screw M3x6
Screw M4x10
New 6, 25
and
photo
below
1If this part is required for an MP20/MP20Junior with a serial number below DE50403738 or an MP30 with a serial number below DE50406811,
you must also order a new quick release mount (M8003-69021).
2For monitors with a serial number of DE540XXXXX or higher. For monitors below this serial number order the older version.
3For monitors with a serial number of DE526XXXXX or higher. For monitors below this serial number, both the Frame Housing Assembly and
the Front Housing Assembly must be replaced with a new version together.
4For monitors with a serial number of DE622XXXXX or higher. For monitors below this serial number order the older version.
5The new screens (touch and non-touch) M8001-64022/23/12/13 come together with the bezel, because the screen and bezel need to be factory
adjusted (glued together)
6The new HIF board (touch) can now be replaced individually, since it no longer contains calibration constants of the touch screen.
7For monitors with a serial number smaller than DE540xxxxx, the new main board is not fully backwards compatible. If the main board for these
monitors needs to be exchanged, the following parts need to be ordered in addition: M8063-69561(451261011901) MSL Assy and M8062-61002
(451261030071) SRL cable. See table above for details.
Tools
Part Number
12NC Part No.
Description
M2267A
989803106081 Calibration Regulator
M1026-60144
453563230731 AGM Electronic Mass FlowMeter
15210-64010
989803100841 Gas Cal 1 cylinders for tcpCO2

6 Parts MP20/MP30 Parts
222
Part Number
12NC Part No.
Description
15210-64020
989803100851 Gas Cal 2 cylinders for tcpCO2
13907A
989803100361 Calibration Tube Assembly
M2505A
989803142701 Gas Cylinder Regulator
M2506A
989803142711 Verification Gas
M2776A
989803144561 Straight Sample Line
M3199-60101
453563337371 3ft UTP crossover cable orange,
0.9m
M3199-60102
453563337381 12ft UTP crossover cable orange,
3.6m
Small Parts Kit

Multi-Measurement Module (MMS) Parts 6 Parts
223
Multi-Measurement Module (MMS) Parts
The primary support strategy for the Multi-Measurement Module is a unit exchange. However,
some exchange parts are available: the MMS Top Cover, the MSL Connector Assembly and the
front bezel. In order to determine which exchange parts need to be ordered check the serial
number and the option string of the MMS as described below.
M3001A Multi-Measurement Module
MMS Part Number Overview and Identification
Identify the correct MMS part number by checking the serial number prefix and the option string
on the label on the rear of the MMS housing. The following picture shows the label of an
M3001A. Use the table below to determine the hardware revision and the required exchange
part.
Option M3001A Option Description
#A01 Philips FAST SpO2
#A02 Nellcor OxiMax compatible
#A03 Masimo SET Technology
(#C00) Standard
#C06 Add Pressure/Temp
#C12 Add 12 Lead ECG (only older revisions - see table below
(#C18) (Add Pressure/Temp and 12 Lead ECG) old

6 Parts Multi-Measurement Module (MMS) Parts
224
With Rel. G.0 option #C18 is split into #C06#C12
HW
Revision
Possible
MMS
Software
Revision
Serial
Number
Prefix
SW of
monitor the
MMS is
connected to
Option String Exchange
MMS
(for 12NC
information
please refer to
tables in the
following
sections)
DE227 A.0, A.1 --, C06, C12,
C18, C06C12
DE441 A.0, A.1 A01, A01C06,
A01C12,
A01C18,
A01C06C12
M3001-68x10
DE227 >=A.2 --, C06, C12,
C18,
A01C06C12
HW A A.0 to G.0
DE441 >=A.2 A01, A01C06,
A01C12,
A01C18,
A01C06C12
M3001-68x02
DE441 >=A.2 A02, A02C06,
A02C18,
A01C06C12
>=A.2 A02, A02C06,
A02C18,
A01C06C12
M3001-68113
M3001-68x03
HW B B.1 to G.0
DE512
>=A.2 A01,A01C06,
A01C12,
A01C18,
A01C06C12
M3001-68114
M3001-68x04
>=A.2 A01, A01C06,
A01C18,
A01C06C12
M3001-68x05 DE610
DE632
DE717
>=A.2 A02, A02C06,
A02C18,
A01C06C12
M3001-68x08
HW C D.0 to G.0
DE632
DE717 >=A.2 A03, A03C06,
A03C18,
A01C06C12
M3001-68x07

Multi-Measurement Module (MMS) Parts 6 Parts
225
For further compatibilty information please refer to the Software Compatibilty Matrix in the
Troubleshooting section.
Exchange Multi-Measurement Modules are shipped with English front bezels only. If you
require a bezel in another language (compare the part numbers of your language to the English
ones to check this) the front bezel has to be ordered additionally. Attach the appropriate bezel
before putting the MMS into operation.
MMS Firmware Overview
NOTE
Multi-Measurement Modules (MMS) with HW Rev. A have a fixed firmware that cannot be
upgraded. HW B and HW C MMSs allow upgrading of the SpO2 and ECG firmware.
To perform a FW upgrade, the MMS must have SW Revision C.0 or higher and be connected to
an -USR_ProductName- patient monitor.
SpO2
Option Serial Number
Prefix
SpO2 FW Rev Comment
#A01 DE227xxxxx
DE441xxxxx A.01.04 The HW and its interface do not
allow a FW upgrade
(A.01.41) ->
A.01.46
#A01
#A02 DE441xxxxx
DE512xxxxx
DE610xxxxx
DE632xxxxx (A.01.42) ->
A.01.46
Must be upgraded to A.01.46 -
see internal Field Notification
#A01
#A02 DE632xxxxx
DE717xxxxx A.01.46 Currently shipped FW
#A03 DE632xxxxx
DE717xxxxx Masimo SET FW Not upgradeable by Philips
ECG
Option Serial Number
Prefix
ECG FW Rev Comment
#A01 DE227xxxxx C.00.13
#A01 DE441xxxxx C.01.19
The HW and its interface do not
allow a FW upgrade

6 Parts Multi-Measurement Module (MMS) Parts
226
Option Serial Number
Prefix
ECG FW Rev Comment
D.01.70
D.01.76
D.01.77
D.01.78
D.01.89
Upgradeable - see internal Field
Notifications
#A01
#A02
#A03
DE441xxxxx
DE512xxxxx
DE610xxxxx
DE632xxxxx
DE717xxxxx
D.02.02 Currently shipped FW (requires
MMS SW Revision F.0)
MMS Part Numbers - Front Bezel for M3001 #A01 & #A03
Part Number Description Options
451261024391 MS_X1 Bezel w/o P/T Eng. Text #C00, #C12
451261024401 MS_X1 Bezel w P/T Eng. Text #C06 (#C18) #C06C12
451261024411 MS_X1 Bezel w/o P/T Symbols #C00, #C12
451261024421 MS_X1 Bezel w P/T Symbols #C06 (#C18) #C06C12
MMS Part Numbers - Front Bezel for M3001 #A02
Part Number Description Options
451261024431 MS_X1 Bezel Nellcor w/o P/T Eng. Text #C00, #C12
451261024441 MS_X1 Bezel Nellcor w P/T Eng. Text #C06 (#C18) #C06C12
451261024451 MS_X1 Bezel Nellcor w/o P/T Symbols #C00, #C12
451261024461 MS_X1 Bezel Nellcor w P/T Symbols #C06 (#C18) #C06C12

Multi-Measurement Module (MMS) Parts 6 Parts
227
MMS Part Numbers - Top Cover and MSL Assembly
Option
String
Description 12NC Orderable Part #
--, A01 MMS Top Cover 5ld w/o P/T Text,
FAST 451261016401 M3001-68010
C06,
A01C06 MMS Top Cover 5ld w/ P/T Text,
FAST 451261016411 M3001-68011
C12,
A01C12 MMS Top Cover 12ld w/o P/T Text
FAST 451261016421 M3001-68012
C18,
A01C18 MMS Top Cover 12ld w/ P/T Text,
FAST 451261016431 M3001-68013
--, A01 MMS Top Cover 5ld w/o P/T
Symbol, FAST 451261016441 M3001-68014
C06,
A01C06 MMS Top Cover 5ld w/ P/T
Symbol, FAST 451261016451 M3001-68015
C12,
A01C12 MMS Top Cover 12ld w/o P/T
Symbol FAST 451261016461 M3001-68016
C18,
A01C18 MMS Top Cover 12ld w/ P/T
Symbol FAST 451261016471 M3001-68017
A02 MMS Top Cover 5ld w/o P/T Text
NELLCOR 451261016481 M3001-68018
A02C06 MMS Top Cover 5ld w/ P/T Text
NELLCOR 451261016491 M3001-68019
A02C18 MMS Top Cover 12ld w/ P/T Text
NELLCOR 451261016501 M3001-68020
A02 MMS Top Cover 5ld w/o P/T
Symbol NELLCOR 451261016511 M3001-68021
A02C06 MMS Top Cover 5ld w/ P/T Symbol
NELLCOR 451261016521 M3001-68022
A02C18 MMS Top Cover 12ld w/ P/T
Symbol NELLCOR 451261016531 M3001-68023
A03 MMS Top Cover 5ld w/o P/T Text
MASIMO 451261016541 M3001-68024
A03C06 MMS Top Cover 5ld w/ P/T Text
MASIMO 451261016551 M3001-68025
A03C18 MMS Top Cover 12ld w/o P/T Text
MASIMO 451261016561 M3001-68026

6 Parts Multi-Measurement Module (MMS) Parts
228
Option
String
Description 12NC Orderable Part #
A03 MMS Top Cover 5ld w/o P/T
Symbol MASIMO 451261016571 M3001-68027
A03C06 MMS Top Cover 5ld w/P/T Symbol
MASIMO 451261016581 M3001-68028
A03C18 MMS Top Cover 12ld w/ P/T
Symbol MASIMO 451261016591 M3001-68029
n/a MMS MSL Connector Assembly 451261016391 M3001-64050
n/a M3015A Mounting Pin 453563100081 5041-8114
MMS Exchange Part Numbers
NOTE
The MMS always ships with the latest Software Revision. In order to make it compatible with
the respective monitor the MMS may need to be upgraded or downgraded. From Support Tool
version E.03.01 onwards the MMS can be up- or downgraded with every support tool license
key (except general).
M3001A #A01 Philips FAST SpO2 MMS Exchange Numbers
Language Basic Pressure/Temp
Extension
Option #C06
Conventional
12 Lead
Option #C12
Conventional
12 Lead &
Pressure/Temp
Extension
Option #C18
English
Text Exchange
Part No.
12NC
M3001-68102
453563462911
or
M3001-68110
451261017491
or
M3001-68114
451261006041
or
M3001-68105
451261013041
M3001-68202
453563486921
or
M3001-68210
451261017501
or
M3001-68204
451261006061
or
M3001-68205
451261013061
M3001-68302
453563486931
or
M3001-68310
451261017511
or
M3001-68304
451261006081
M3001-68402
453563486941
or
M3001-68410
451261017521
or
M3001-68404
451261006101
or
M3001-68405
451261013081

Multi-Measurement Module (MMS) Parts 6 Parts
229
Language Basic Pressure/Temp
Extension
Option #C06
Conventional
12 Lead
Option #C12
Conventional
12 Lead &
Pressure/Temp
Extension
Option #C18
Symbol
(Internati
onal)
Exchange
Part No.
12NC
M3001-68502
453563486951
or
M3001-68510
451261017531
or
M3001-68504
451261006121
or
M3001-68505
451261013101
M3001-68602
453563486961
or
M3001-68610
451261017541
or
M3001-68604
451261006141
or
M3001-68605
451261013121
M3001-68702
453563486971
or
M3001-68710
451261017551
or
M3001-68704
451261006161
M3001-68802
453563486981
or
M3001-68810
451261017561
or
M3001-68804
451261006181
or
M3001-68805
451261013141
M3001A #A02 Nellcor OxiMAX-compatible MMS Exchange Numbers
Language Basic Pressure/Temp
Extension
Option #C06
Conventional 12
Lead &
Pressure/Temp
Extension
Option #C18
English
Text Exchange
Part No.
12NC
M3001-68113
451261005361
or
M3001-68108
451261015171
M3001-68203
451261005381
or
M3001-68208
451261015191
M3001-68403
451261005401
or
M3001-68408
451261015211
Symbol
(Inter-nati
onal)
Exchange
Part No.
12NC
M3001-68503
451261005421
or
M3001-68508
451261015231
M3001-68603
451261005441
or
M3001-68608
451261015251
M3001-68803
451261005461
or
M3001-68808
451261015271

6 Parts MMS Extension Parts (M3012A, M3014A, M3015A and M3016A)
230
M3001A #A03 MMS with Masimo SET SpO2 - Exchange Numbers
Language Basic Pressure/Temp
Extension
Option #C06
Conventional 12
Lead &
Pressure/Temp
Extension
Option #C18
English
Text Exchange
Part No.
12NC
M3001-68107
451261013281 M3001-68207
451261013311 M3001-68407
451261013321
Symbol
(Inter-nati
onal)
Exchange
Part No.
12NC
M3001-68507
451261013341 M3001-68607
451261013371 M3001-68807
451261013381
MMS Part Numbers - Label Kits
Part Number 12NC Part Number Description
M3001-64003 451261001191 Label Kit Alarm Symbols for MMS
MMS Part Numbers - NBP Assembly
Part Number 12NC Part Number Description
M3001-64500 451261020561 NBP Assembly for MMS
MMS Extension Parts (M3012A, M3014A, M3015A
and M3016A)
Exchange MMS Extensions are shipped with English front bezels only. If you require a bezel in
another language (compare the part numbers of your language to the English ones to check this)
the front bezel has to be ordered additionally. Attach the appropriate bezel before putting the
MMS extension into operation.
The part numbers in the following parts table below, are used to order parts from your Philips
representative. The item numbers correspond to the illustration which follows.

MMS Extension Parts (M3012A, M3014A, M3015A and M3016A) 6 Parts
231
MMS Extension Part Numbers - Release Mechanisms
Part Number 12NC Part Number Description
M3014-64200 451261012731 MMS Extension clips and springs (10
each) for MMS extension release
mechanism
(old version)
M3001-64600 451261012721 MMS Extension lever locks.(packet
of 5) for MMS extesnion release
mechanism (new version)
MMS Extension Part Numbers - Top Cover, Flex Cable and Link Bar
Part Number 12NC Part Number Description
M3012-64620 451261016601 MSE Top Cover Assembly
M3012-64621 451261016611 MSE Link Bar Assembly
n/a 453564088851 MSE Flex Cable Connector Assembly
MMS Extension Part Numbers - Front Bezels
12NC Part No. Description
M3012A #C00 - Pressure, Temp & Press/Temp
451261024471 M3012A Front Bezel P, T, P/T Eng. Text
451261024481 M3012A Front Bezel P, T, P/T Symbols

6 Parts MMS Extension Parts (M3012A, M3014A, M3015A and M3016A)
232
12NC Part No. Description
M3012A #C05 - Cardiac Output, Pressure, Temp & Press/Temp
451261024491 M3012A Front Bezel C.O.,P, T, P/T Eng. Text
451261024501 M3012A Front Bezel C.O.,P, T, P/T Symbols
M3012A #C10 - Cardiac Output, Continuous Cardiac Output, Pressure, Temp &
Press/Temp
451261024511 M3012A Front Bezel CCO, C.O.,P, T, P/T Eng. Text
451261024521 M3012A Front Bezel CCO, C.O.,P, T, P/T Symbols
M3014A #A01 - Capnography Extension
451261024531 M3014A Front Bezel CO2 only Eng. Text/Symbols
M3014A #C05 - Cardiac Output, Mainstream CO2, Pressure & Press/Temp
451261024541 M3014A Front Bezel C.O., CO2, P, P/T Eng. Text
451261024551 M3014A Front Bezel C.O., CO2, P, P/T Symbols
M3014A #C07 - Mainstream CO2, Pressure & Press/Temp
451261024561 M3014A Front Bezel CO2, P, P/T Eng. Text
451261024571 M3014A Front Bezel CO2, P, P/T Symbols
M3014A #C10 - Cardiac Output, Continuous Cardiac Output, Mainstream CO2,
Pressure & Press/Temp
451261024581 M3014A Front Bezel C.O., CCO, CO2, P, P/T Text
451261024591 M3014A Front Bezel C.O.,CCO, CO2, P, P/T Symb.
M3015A #C06 Sidestream CO2 with Press/Temp
451261024601 M3015A Front Bezel CO2 w P/T Eng. Text
451261024611 M3015A Front Bezel CO2 w P/T Symbols
M3015A Sidestream CO2 without Press/Temp
451261024621 M3015A Front Bezel CO2 w/o P/T Eng. Text
451261024631 M3015A Front Bezel CO2 w/o P/T Symbols

MMS Extension Parts (M3012A, M3014A, M3015A and M3016A) 6 Parts
233
12NC Part No. Description
M3015A Pump Kit And Mounting Pin (only for HW Rev. A)
453563332261
(M3015-29303) M3015A Pump Kit (including CO2 scrubber)
453563100081
(5041-8114) Mounting Pin for M3015A
M3016A (Press/Temp with Mainstream CO2)
451261024641 M3016A Front Bezel CO2, P/T Eng. Text
451261024651 M3016A Front Bezel CO2, P/T Symbols
Exchange Parts List
Exchange parts are parts that have been returned to Philips and reconditioned for further use.
Parts offered as exchange parts are in excellent service order according to rigorous Philips
standards but offer you a considerable price advantage.
A front bezel with symbols instead of English text is provided with each exchange MMS
Extension.
Part Number 12NC Part No. Description
M3012-6801A 451261000201 exchange M3012A MMS Extension
with Pressure, Temperature,
Press/Temp
M3012-6831A 451261000341 exchange M3012A MMS Extension
with Cardiac Output, Pressure,
Temperature, Press/Temp
M3012-6861A 451261000491 exchange M3012A MMS Extension
with Continuous Cardiac Output,
Pressure, Temperature, Press/Temp
M3014-6801A 451261009281 exchange M3014A MMS Extension
with CO2
M3014-6831A 451261009311 exchange M3014A MMS Extension
with CO2, Cardiac Output, Pressure,
Press/Temp
M3014-6891A 451261009461 exchange M3014A MMS Extension
with CO2,Pressure, Press/Temp
M3014-6861A 451261009601 exchange M3014A MMS Extension
with CO2, Cardiac Output/Continuous
Cardiac Output, Pressure, Press/Temp

6 Parts IntelliVue X2 Part Numbers
234
Part Number 12NC Part No. Description
M3015-6801A 453563332431 exchange M3015A MMS Extension
with Pressure/Temperature, English.
(old hardware, S/N prefix:
DE020xxxxx)*
M3015-6802A 451261005311 exchange M3015A MMS Extension
with Pressure/Temperature, English.
(new hardware, S/N prefix:
DE435xxxxx)*
M3015-6831A 453563477871 exchange M3015A MMS Extension
without Pressure/Temperature, English.
(old hardware, S/N prefix:
DE020xxxxx)*
M3015-6832A 451261005331 exchange M3015A MMS Extension
without Pressure/Temperature, English.
(new hardware, S/N prefix:
DE435xxxxx)*
M3016-6801A 453563332581 exchange M3016A MMS Extension
with CO2, English. #A01
M3016-6831A 453563483901 exchange M3016A MMS Extension
without CO2, English. #A02
*The new M3015 hardware offers an improved warm up time compared to the old hardware and
the gas sample flow rate specification has been changed to 50 ml/min -7,5ml/min/+15 ml/min.
Also, the Suppress Auto Zero feature and the capability to turn off the M3015A pump have been
added. The new hardware is backwards compatible with all MP20-90 host monitors, but the new
features will only be available in combination with a monitor with SW Rev. B.1 or higher.
IntelliVue X2 Part Numbers
Please refer to the IntelliVue X2 Service Guide for IntelliVue X2 part numbers.
BISx Solution Replacable Parts
Exchange Part
Number
New Part
Number
Description
n/a M1034-61630
453563233721
BIS PIC (Patient Inetrface Cable)
n/a M1034-61650
453563233731
BIS Sensor Simulator

Smart Battery Charger Part Numbers 6 Parts
235
Exchange Part
Number
New Part
Number
Description
M1034-68521
451261003621
n/a BISx Power Link
n/a M1034-61660 BISx Host Cable
n/a M1034-47600 BISx bulkhead connector
n/a M8080-67501
451261009241
BISx Interface Board
M1034-68500
453563233751
n/a BIS Interface Module
BISx Solution Components
BISx Solution
Smart Battery Charger Part Numbers
Exchange Assemblies
Exchange Part
No.
12NC (Exch.) Description
M8043-68000 453563498911 Exchange Smart
Battery Charger
Non-Exchange Assemblies
Exchange Part
No.
12NC (Exch.) Description
M8043-60010 451261001281 Replacement Kit: Air Fan & 2 Filter Mats
M8043-60011 451261001291 Replacement Kit: 2 Filter Mats

6 Parts IntelliVue Instrument Telemetry Part Numbers
236
IntelliVue Instrument Telemetry Part Numbers
Ordering Part
Number
Ordering Part
Number 12NC
Description New or
Exchange
M4840-65508 451261009031 IIT Module (incl. antenna cable)
US Version New
n/a 453564053561 IIT Module (incl. antenna cable)
Non-US Version New
M4840-68708 451261009041 IIT Module (incl. antenna cable)
US Version Exchange
M8058-61001 451261007891 IIT Flat Ribbon Cable New
M4842-61300 453564007571 1.4 GHz AP Antenna
US Version New
n/a 453564052521 2.4 GHz AP Antenna
Non-US Version New
IntelliVue 802.11 Bedside Adapter Part Numbers
Ordering Part
Number
Ordering Part
Number
12NC
Description New or
Exchange
M8096-68011 451261013031 IntelliVue 802.11 Bedside
Adapter incl. cable and cable
holder
Exchange
M2639-61001 451261013011 Cable Assembly New
0955-1495 451261013001 Antenna WLAN Tri-band New

Docking Station Part Numbers 6 Parts
237
Docking Station Part Numbers
Ordering Part
Number
Ordering Part
Number
12NC
Description New or
Exchange
M8045-68001 451261009751 Docking Station Exchange Exchange
M8098-67501 451261009761 Main Board Docking New
M8098-66421 451261009771 Flex Cable Docking Station New
External Display Part Numbers
M8031A and M8031B External XGA Displays
External XGA Display Parts
Product
Number
Part Number 12NC Part No. Description
M8031A M1097-68004 453563241761 Exchange 15” Dual Mode XGA Color Touch
Screen Display.
M1097-64001 453563241731 Power Supply Mounting Clamp for M1097A.
M1097-01201 453563241611 Mounting Bracket for M1097A.
M1097-60006 453563282651 Power Supply.
M1097-61604 453563241721 Adapter Cable.
M1097-04702 453563241631 Desk Stand for M1097A Display.
M1097-64100 451261012741 Replacement Kit for M1097A & M8031A
M8031B M8031-68001 451261001941 Exchange 15” Medical Grade Display with
Touch

6 Parts External Display Part Numbers
238
Product
Number
Part Number 12NC Part No. Description
M8031-60005 451261001921 Power Supply 12V for M8031B Display
M8031-64001 451261001931 Power Supply Mounting for M8031B Display
M8031-04701 451261001901 Monitor Desk Stand for M8031B/M8033C
2090-0860 453563463201 Backlights for M8031B (old)
for displays w/ serial no. < ANxx0645xxxxxx
2090-0985 451261014381 Backlights for M8031B (new)
for displays w/ serial no. >ANxx0649xxxxxx
M8033A and M8033B External SXGA Displays
M8033C External SXGA Display
External SXGA Display Parts
Product
Number
Part Number 12NC Part No. Description
M8033A M8033-68001 453563480951 Exchange 17” SXGA Color Touch Screen
Display.
M8033-64100 451261014891 M8033A and M8033B Replacement Kit
M8033-64001 453563480971 Power Supply Bracket Mount
M8033-60005 453563480961 Power Supply.
M8033-04701 453563480981 Desk Stand for M8033A and M8033B
Display.

Remote Alarm Device Part Numbers 6 Parts
239
Product
Number
Part Number 12NC Part No. Description
M8033B M8033-60002 451261006271 M8033B New 17” Medical Grade Display
with Touch
M8033-64100 451261014891 M8033A and M8033B Replacement Kit
M8033-60006 451261006291 Power Supply 12V for M8033B Display
M8033-64002 451261006301 Power Supply Mounting for M8033B
Display
M8033-04701 453563480981 Monitor Desk Stand for M8033A and
M8033B Display
M8033C M8033-68071 451261009161 M8033C Exchange 17” Medical Grade
Monitor with Touch
M8031-04701 451261001901 Monitor Desk Stand for M8031B/M8033C
M8033-64603 451920880311 Backlights for M8033C
Remote Alarm Device Part Numbers
The Remote Alarm Device contains no servicable parts and can only be replaced in its entirety (
part number M8025-60501 (12NC: 453563469801)). For cable part numbers please see the Site
Preparation section.
Remote Alarm Device Front and Rear View

6 Parts Remote Extension Device Part Numbers
240
Remote Extension Device Part Numbers
The Remote Extension Device contains no servicable parts and can only be replaced in its
entirety (part number: M8026-60504 (12NC: 453563469821)). For cable part numbers, please
see the Site Preparation section.
Remote Extension Device Front and Rear View

241
7
7Installation Instructions
The information contained in this chapter should enable the -USR_ProductName- to be installed
ready for use (the preparation and planning should be adhered to as specified in the Site
Preparation section). Configuration of the system is explained in the Configuration Guide.
Installation Checklist
Use this checklist to document your installation. Please file this installation record
Step Task Check Box
when Task
Done
1 Perform initial inspection of delivery, unpack and check the
shipment o
2 Mount the monitor as appropriate for your installation o
3 Connect the monitor to AC mains using the supplied power cord o
4 Perform Visual, Power On and Functional test blocks o
5 Perform Safety Tests, if required by local laws and regulations o
6 Load paper into the recorder, if present o
7 Check/set the time and date o
8 Check that the country-specific default settings are appropriate o
9 Perform System Test as necessary o

7 Installation Instructions Unpacking the Equipment
242
Unpacking the Equipment
Your equipment will arrive in a carton similar to the ones pictured below. All components of the
monitoring system are consolidated into a single packing crate. The contents of this crate depend
on the options you have purchased. In addition to the monitor it can contain the following:
- MMS and user manuals
- MMS Extensions and accessories
Accessory and Monitor Packaging
In the unlikely event of a defect on arrival, please keep the packing materials until you have
completed the initial inspection.
Initial Inspection
Mechanical Inspection
Open the shipping container(s) and examine each part of the instrument for visible damage, such
as broken connectors or controls, or scratches on the equipment surfaces. If the shipping
carton/container is undamaged, check the cushioning material and note any signs of severe stress
as an indication of rough handling in transit. This may be necessary to support claims for hidden
damage that may only become apparent during subsequent testing.
Electrical Inspection
The instrument has undergone extensive testing prior to shipment. Safety testing at installation is
not required (except in situations where devices are interconnected forming a system, see
Connecting Non-Medical Devices). An extensive self check may be performed. This
recommendation does not supersede local requirements.
All tests are described in the Testing and Maintenance section of this manual.

Initial Inspection 7 Installation Instructions
243
Claims For Damage and Repackaging
Claims for Damage
When the equipment is received, if physical damage is evident or if the monitor does not meet
the specified operational requirements of the patient safety checks or the extended self check,
notify the carrier and the nearest Philips Sales/Support Office at once. Philips will arrange for
immediate repair or replacement of the instrument without waiting for the claim settlement by
the carrier.
Repackaging for Shipment or Storage
If the instrument is to be shipped to a Philips Sales/Support Office, securely attach a label
showing the name and address of the owner, the instrument model and serial numbers, and the
repair required (or symptoms of the fault). If available and reusable, the original Philips
packaging should be used to provide adequate protection during transit. If the original Philips
packaging is not available or reusable please contact the Philips Sales/Support Office who will
provide information about adequate packaging materials and methods.
Mounting Instructions
Every type of compatible mounting solution is delivered with a complete set of mounting
hardware and instructions. Refer to the documentation delivered with the mounting hardware for
instructions on assembling mounts.
WARNING
It is the customer's responsibility to have the attachment of the mounting hardware to the ceiling,
wall, or mounting rail and the construction of the ceiling, wall, or mounting rail evaluated for
structural integrity and compliance with all local, state and any other required codes by a
registered, professional, structural and/or mechanical engineer.
Ensure that this commitment has been met before assembling mounts.

7 Installation Instructions Initial Inspection
244
....
Table Mount (M4046-64100, 12NC: 451261001381) - MP5 shown as an example
A (B)
MP5 24 51.5
MP20/30 85.5 113
MP40/50 79.5 107
MP60/70 62 89.5

Connecting the Monitor to AC Mains 7 Installation Instructions
245
Connecting the Monitor to AC Mains
The monitor has a wide-range power supply that allows you to operate the monitor from an AC
(alternatin g current) power source of 100 V to 240 V (± 10%) and 50/60 Hz (± 5%).
WARNING
- Always use the supplied power cord with the earthed mains plug to connect the monitor to
an earthed AC mains socket. Never adapt the mains plug from the power supply to fit an
unearthed AC mains socket.
- Do not use AC mains extension cords or multiple portable socket-outlets. If a multiple
portable socket-outlet without an approved isolation transformer is used, the interruption of
its protective earthing may result in enclosure leakage currents equal to the sum of the
individual earth leakage currents, so exceeding allowable limits.
- Do not connect any devices that are not supported as part of a system.
- Any non-medical device placed and operated in the patient’s vicinity must be powered via
an approved isolation transformer that ensures mechanical fixing of the power cords and
covering of any unused power outlets.

7 Installation Instructions Connecting the Monitor to AC Mains
246
Connections
The following figure shows the cable and interface board connections.
MP20/MP30 Cable and Interface Board Connections

Connecting the Monitor to AC Mains 7 Installation Instructions
247
Installing Interface Boards
If you add interface boards to your monitor, you must insert them into the device according to
the following rules:
- The following boards can be inserted into slot 1:
- System Interface Board Standard
- System Interface Board Advanced
- Docking System Interface Board
- The following boards can be inserted into either slot 2 or slot 3:
- PS/2 (Input Device) Interface
- Remote Interface
- Parallel printer
- Nurse Call Relay
- MIB/RS232
- BISx Interface
- IntelliVue 802.11 Bedside Adapter
- USB

7 Installation Instructions Connecting the Monitor to AC Mains
248
NOTE
Only one of each of the boards listed above can be installed at a time except the MIB/RS232
board, of which a second board is allowed.
NOTE
Connections to the Remote Interface Board must be made as follows: the remote alarm device
must be connected to the upper port and the remote input device to the lower port of the board.
The following table shows possible configurations for the MP20/30 patient monitors:
I/O Board Possible Configurations
Name Possible
I/O Slots
1 2 3 4 5 6 7 8 9 10 11 12 13 14 15
IntelliVue
802.11
Bedside
Adapter
02,03 02 - - - - - - - - - - - - - -
BIS Interface 03,02 03 03 03 03 03 03 03 03 - - - - - - -
USB
Interface
02,03 x x 02 - x 02 - - x 02 x x 02 x 02
Input Device
IF
02,03 x 02 x - - - - - 02 x 02 02 x 02 x
Remote
Device IF
02,03 x x x 02 - - - - 03 03 - - - - -
Parallel Port
IF
02,03 x x x x 02 x - - x x 03 - x - -
Nurse Call
Relays
02,03 x x x x x x 02 - x x x 03 03 - -
MIB/RS232
(2x)
03,02 x x x x x x x 02 x x x x x 03 03
2nd
MIB/RS232
(2x)
03.02 x x x x x x x x x x x x x x x
I/O Board Possible Configurations
Name Possible
I/O Slots
16 17 18 19 20 21 22 23 24 25 26 27 28 29 30
IntelliVue
802.11
Bedside
Adapter
02,03 - - - - - - - - 02 02 02 02 02 02 02
BIS Interface 03,02 - - - - - - - - - - - - - - -

Connecting the Monitor to AC Mains 7 Installation Instructions
249
I/O Board Possible Configurations
Name Possible
I/O Slots
16 17 18 19 20 21 22 23 24 25 26 27 28 29 30
USB
Interface
02,03 x 03 - - x 02 - - x 03 - x 03 - -
Input Device
IF
02,03 - x - - - x - - 03 x - - x - -
Remote
Device IF
02,03 02 02 02 02 - - - - x x 03 - x - -
Parallel Port
IF
02,03 03 x - - 02 x - - x x x 03 x - -
Nurse Call
Relays
02,03 x x 03 - 03 03 02 - x x x x x 03 -
MIB/RS232
(2x)
03,02 x x x 03 x x 03 03 x x x x x x 03
2nd
MIB/RS232
(2x)
03,02 x x x x x x - 02 x x x x x x x
“-” This board is assumed to not be required for this configuration
“x” This board cannot be assigned in this configuration
NOTE
Ensure that the board removal tool is snapped properly into place inside the battery compartment
door after each use.
If two MIB/RS232 boards are installed, only one can be configured to Data Out. The other one
can then only be configured to GM, Touch1 or Touch2.
If you have installed #J35 (IntelliVue 802.11 Bedside Adapter) please attach the approval label
or the WLAN Label for Japan (country specific) and the antenna and plug in the cable as shown
below.

7 Installation Instructions Connecting the Monitor to AC Mains
250
NOTE
The installation of #J35 requires a system interface board with wireless functionality.
Connection of Devices via the MIB/RS232 Interface
The configuration of a specific MIB/RS232 port can be viewed in config mode and altered in
service mode. This is required, for example, when a slave display with touchscreen is installed.
To alter the configuration of an MIB port select Main Setup then Hardware then
Interfaces.
NOTE
Be aware that if you change a port assignment this assignment is not reset upon boot up. If the
MIB/RS232 board is removed and replaced with a different type of board the settings are
deleted. If the MIB/RS232 board is then refitted, you must reconfigure the MIB/RS232 port. The
configuration of MIB/RS232 is not cloned between services.
Connection of USB Devices
The USB IF board supports the following USB devices:
- printer
- keyboard
- barcode scanner
- computer mouse or trackball
NOTE
Connect only the above mentioned devices to the USB Interface. Other devices are not
supported.

Connecting the Monitor to AC Mains 7 Installation Instructions
251
As the patient monitor software only supports two input devices, only two input devices can be
connected to the USB board. For this purpose, the USB ports are divided into two groups, a and
b. Only one input device per group is allowed. In the graphic below, a mouse is connected to a
port in each group. Therefore the keyboard is not recognized.
It is, however, possible to connect a mouse, a keyboard and a barcode scanner. In this case, the
keyboard and barcode scanner are treated as one input device and must be connected to two ports
of the same group.
NOTE
Other USB devices, e.g. USB sticks, iPods etc. are not supported by the USB IF board.Do not
use USB adapters to connect PS/2 or other devices to the USB board.

7 Installation Instructions Connecting the Monitor to AC Mains
252
Possible USB Device Combinations
The following three groups of USB device combinations are supported:
- mouse/mouse combination
- keyboard/mouse combination
- keyboard/keyboard combination.
The figures below show the possible device combinations for each of the three groups.
Possible Mouse/Mouse combinations
Possible Mouse/Keyboard combinations

Connecting the Monitor to AC Mains 7 Installation Instructions
253
Possible Keyboard/Keyboard combinations
NOTE
Every time a new device is connected to the USB board, all connected USB devices are stopped
and the ports are scanned. Depending on whether the combination is allowed or not, the devices
will function again after the scan.
Combined input devices such as a keyboard with an integrated trackball are also supported.
However, no additional mouse can be connected in this case. Multiple combined devices are also
not allowed.
CAUTION
The USB interface does not provide an electrical separation. When connecting a USB device
which uses an additional power supply e.g. printer, a separation device according to EN/IEC
60601-1-1 is required. After installation a system test is required to ensure that the resulting
equipment leakage current does not exceed the limits of EN/IEC 60601-1-1. For detailed
information see the Testing and Maintenance chapter.
NOTE
The USB board is not compatible with SW Revisions A.0x.xx. All other available SW Revisions
are compatible.
USB Error Indication
The USB ports have a green LED each. If an error occurs, the LED is off. If the LED is on, the
connected device is ready for operation.

7 Installation Instructions Installing the Docking Station
254
Installing the Docking Station
Make the power connection and the LAN connection to the docking station as shown in the
photograph below.
Installing Remote Devices
This section provides instructions for Philips products. Installation instructions for devices not
sold by Philips must be provided by the device manufacturer.
Mounting the 15” Remote Display (M8031A)
The Philips M8031A Color Flatscreen Display with the monitor as a slave display. A
bracket is supplied with the display to connect it to a variety of Philips mounting devices.
A - Removing the desktop stand (if installed):
1. Remove the covers from the screws on the back of the flatscreen display
2. Remove the four screws from the back cover of the display and detach the cover.
3. Remove the four screws from the desktop stand and detach the desktop stand.
B - Attaching the bracket:
1. Place the bracket on the back of the display with the slits facing upwards.
2. Attach the bracket to the display with four M4x8 screws.
NOTE
Attach the desired mounting device to bracket.
NOTE
Do not mount the display in a position where liquid could spill onto it.

Installing Remote Devices 7 Installation Instructions
255
Connections
Connect the cables to the display as shown in the photograph.
Mounting the 15” Remote Display (M8031B)
Mounting solutions for the M8031B must be purchased separately. Please refer to the installation
instructions which ship with the mounting solution purchased.
Connections
Connect the cables to the display as shown in the photographs below.
Mounting the 17” Remote Display (M8033A/B/C)
Mounting solutions for the M8033A/B/C must be purchased separately. Please refer to the
installation instructions which ship with the mounting solution purchased.

7 Installation Instructions Installing Remote Devices
256
Connections
Connect the cables to the display as shown in the photographs below.
Connections M8033A
Connections M8033B (old and new version)
Connections M8033C

Installing Remote Devices 7 Installation Instructions
257
Video Cable Wiring Schematics
Analog Video Cable Wiring Schematic
Multi-Measurement Module
Attaching the MMS to a Mount
1. Make sure the Measurement Server is oriented correctly relative to the mount (see the
picture below).
2. Place the Measurement Server on the back mount. If it is not tight against the mount, slip it
in the direction of the measurement connectors until it is.
3. Slip the Measurement Server forward until it clicks into place.
Detaching the Measurement Server from a Mount
1. Press and hold the latch (in the middle at the top of the mount) away from the Measurement
Server.
2. Slide the Measurement Server off the mount in the direction of the measurement connectors.

7 Installation Instructions Installing Remote Devices
258
Positioning the Measurement Server on a Clamp Mount
If you have your Measurement Server on the clamp mount, you can have it in one of four
positions. You can reposition it as follows:
1. Press and hold the mount latch toward the clamp screw.
Rotate the Measurement Server and mount until you get it to the position you want.
2. Release the mount latch, and make sure it is clicked into one of the four slots on the back of
the mount.
Mounting the Wireless Ethernet Adapter to the Monitor
NOTE
The following procedure applies to the external (Proxim) wireless adapter only. To install the
IntelliVue 802.11 Bedside Adapter, please refer to the section on installing interface boards.
1. Plug in the cable connection to the Wireless Ethernet Adapter.
2. Attach the Wireless Ethernet Adapter to the mounting device with the four cross-head
screws provided.

Installing Remote Devices 7 Installation Instructions
259
3. Attach the mount to the monitor using the four M3x6 Torx screws provided. Plug in the
cable to the monitor as shown below.
Installing the IntelliVue Instrument Telemetry Adapter
1. Turn the two plastic screw pins 180 degrees counterclockwise and pull them out. Use a
small screwdriver to pull the screw head out of the recess in the housing.

7 Installation Instructions Installing Remote Devices
260
2. The hinges allow the monitor to be opened like a book. Support the display before
proceeding further.
3. Remove the three plastic pins securing the side cover and remove the cover.
4. Remove the label from the top right of the monitor.

Installing Remote Devices 7 Installation Instructions
261
5. Insert the IIT adapter and secure it behind the metal tab with two M3x6 screws.
6. Connect the IIT adapter to the antenna connector plate. Be careful not to pull on the cable.
7. Insert the connector plate for the antenna from the bottom and tighten the two M2.5 x 8
screws on top.
8. Connect the IIT adapter to the main board.

7 Installation Instructions Installing Remote Devices
262
9. Take one of the side covers from the upgrade kit (either with or without recorder slot) with
the hole for the antenna and put it on the monitor, securing it with the three plastic pins.
10. Reassemble the monitor by performing steps 1 & 2 in reverse order.
11. Screw on the antenna.
12. Perform the Power On Test block and the Safety Test block as described in your service
guide.

Installing Remote Devices 7 Installation Instructions
263
Frequency Coordination (USA only):
Frequency coordination is a registration and coordination process for wireless medical telemetry
devices used in the U.S.A. which operate in the FCC-allocated Wireless Medical Telemetry
Service (WMTS) bands (608-614 MHz, 1395-1400 MHz, 1427-1432 MHz). The M8001/2A
#J45 and the M8004/5A with the IntelliVue Instrument Telemetry adapter M2638A operate in
both of the 1395-1400 and 1427-1432 MHz bands.
Under U.S. Federal Communications Commission (FCC) rules, authorized healthcare providers
must register their WMTS devices with an authorized Frequency Coordinator designated by the
FCC. The American Society for Healthcare Engineering (ASHE) is the current designated
Frequency Coordinator.
Registration/Coordination is a two-step process.
Step 1: Registration: Register the healthcare facility on-line, from the ASHE website
(www.ashe.org (http://www.ashe.org\n)). Click on the link for Wireless Medical Telemetry
Service and come to the registration page. Fill out the details, and pay the associated fee
as per the instructions provided. You will receive confirmation of this registration.
Confirmation must be received before proceeding to the next step.
Step 2: Frequency Coordination: Along with confirmation of registration, you will receive
access information necessary to perform this second step, frequency coordination. This step
involves logging the equipment and frequencies used into the FCC’s database, so as to identify
any existing potential interference and to help prevent potential future interference.
Coordination is accomplished via the ASHE website. Click on the links for Wireless Medical
Telemetry Service and then Frequency Coordination. The way the coordination process is
executed as of today, it will need to be repeated twice for the M4840A system; once for the
1395-1400 MHz band, and then again for the 1427-1432 MHz band, both of which are used
concurrently by the Philips product. There is a separate fee for each coordination request,
which varies between $250 and $2000, depending upon the number of transmitting devices used
and the band/s of operation. Coordination is executed by a company named Comsearch, on
behalf of ASHE.
- To fill in the frequency coordination forms, you’ll need to know the following:
- The county.
- Latitude and longitude that represents the center of the area where the transmitting devices
will be deployed. Comsearch can help provide this information; www.comsearch.com
provides contact information.
- The name/s of the Clinical Unit/s using the devices (e.g. ICU4, CCU-West, ER1, Step-Down
North, etc)
- The radius of deployment, expressed in meters. Imagine drawing a circle around the center
of the clinical unit, that encloses/encompasses the unit. What is its radius?
- The number of the highest floor on which a transmitting device will operate.
- How many transmitting devices will be used, i.e. the total number of M8001/2A #J45 and
M2638A IntelliVue Instrument Telemetry adapter devices combined.
- The Effective Radiating Power: 6.3 mW.
- The Equipment Manufacturer: Philips Medical Systems.

7 Installation Instructions Installing Remote Devices
264
- The Model numbers: M8001/2A #J45 (MP20/30) and M2638A IntelliVue Instrument
Telemetry adapter used with M8004/5A (MP40/50)
- The Frequency Range to be used: Two separate coordinations are required: For the first
one, click on the range of 1395.0 through 1400.0 MHz. For the second one, click on all the
frequency ranges listed in the range of 1427.0 through 1432.0 MHz.
When both Registration and Frequency Coordination have been successfully completed, the
IntelliVue Instrument Telemetry System can be activated. Note that this process is the
responsibility of the customer, as the final “operator” of the transmitting equipment.
Connections
The cable specifications and part numbers for through wall solutions of the M3001A are
described in the Site Preparation section of this manual.
MSL Cable Termination
The following installation procedure describes how to install the wall installation cable kit when
the patient monitor and the measurement server are not located at the same site. The kit consists
of two connector boxes and a cable (15m or 25m).
For this procedure you need the insertion tool (M3086-43801) and a small screwdriver.
1. Draw the MSL cable through the wall from the site of the monitor to the site of the
measurement server.
Each MSL face plate kit contains two connector boxes; one in-going and one out-going.
(The US version contains an additional rectangular wall-mounting plate).
NOTE
The installation procedure is the same for both connector boxes. This means you must
perform steps 3 to 8 of this procedure twice.
The connectors on each box are different, so you must ensure that the correct box is placed at
the correct location. The dots on the plastic angled cover indicates at which site you should
install the box:

Installing Remote Devices 7 Installation Instructions
265
If there are no dots on the cover, symbols are used:
Symbol: is connector box (in) and must be placed at the monitor site.
Symbol: is connector box (out) and must be placed at the measurement server site.
The correct connector cable (M3081-61601, M3081-61602 or M3081-61603) has the
opposite symbol:
2. Detach the PCB assembly (in/out) from the metallic mounting flange.
3. Use the Insertion Tool (M3086-43801) to position each wire on the PCB according the
wiring schematic below, where each color corresponds to a number.
NOTE
The Insertion Tool should be set to cutting mode &= on.
Wiring Schematic
4. Use a small screwdriver to connect the two drain wires to the PCB, see the wiring schematic
in .
5. Slide the PCB back on to the metallic mounting flange.
6. Use screws to fasten the mounting flange to the wall.
NOTE
US version only: Fasten the rectangular wall-mounting plate to the wall. Attach the
mounting flange to the wall-mounting plate.
7. Mount the plastic cover. The plastic cover consists of two pieces:
- Frame
- Angled cover
Put the frame over the mounting insert and the PCB. Place the angled cover on top and
fasten with two screws.
8. Connect the monitor and the measurement server to the wall installation.
9. Perform the following tests as described in the Test and Maintenance section of this manual:

7 Installation Instructions Philips Clinical Network (Wired)
266
- Power-on test blocks
- Safety test blocks
- ECG Sync Performance Test
PS/2 Keyboard/Mouse
Switch off the monitor before connecting any PS/2 compatible device.
Connect the PS/2 connector either to the remote extension device or the PS/2 Interface board in
the monitor at the slot indicated by the appropriate symbol.
The default keyboard language setting for all initial configurations is “US”. However, the
monitor will not automatically select the best matching language for the keyboard depending on
the language of its software. This means that there is no such choice as “Automatic” for the
keyboard language.
To configure the keyboard language manually, go to Service Mode, select Main Setup ->
Hardware -> Keyboard and then select the proper language. Please note that this setting does
not clone.
Philips Clinical Network (Wired)
Installation of the Philips Clinical Network should be performed by Philips service personnel.
Use unshielded twisted pair (UTP) cables for installation of the clinical network. Refer to the
installation instructions in the M3185A Installation Manual for further details.
Philips Clinical Network (Wireless)
Refer to the installation instructions in the M3185A Philips Clinical Network Installation Manual
for network installation instructions when using the wireless ethernet adapter. For instructions on
connecting the wireless ethernet adapter, please refer to the instruction sheet shipped with the
mounting device for the adapter.
NOTE
The wireless ethernet adapter is not waterproof and therefore should not be installed anywhere
where liquid could spill onto it.
Refer to the IntelliVue 802.11 a/g Infrastructure Installation and Configuration Guide for
network installation instructions when using the IntelliVue 802.11 Bedside Adapter. For
instructions on connecting the IntelliVue 802.11 Bedside Adapter, please refer to the Hardware
Upgrade Guide for your bedside monitor.

Nurse Call Relay 7 Installation Instructions
267
Nurse Call Relay
Connections
Flexible Nurse Call Relay Connections at Monitor
Nurse Call Relay Connectors Contact Isolation
Basic Nurse Call
Relay 3.5 mm phone jack
active closed contact only
≤
100 mA,
≤
24 VDC
1.5 kV
Flexible Nurse Call
Relay 20 pin MDR (Mini D-Ribbon),
active open and closed contacts,
3.5 mm phone jack, active closed contact
only
≤
100 mA,
≤
24 VDC
1.5 kV
See Multi-Port Nurse Call Connector Test (Flexible Nurse Call) for details on the Nurse Call
Relay Connector pin assignment.
ECG Out Functionality
Connections
The cable M1181A #A62 has both ends terminated. The photograph above shows the monitor
side connection.
If using a non-terminated cable:
1. Strip 5 mm (3/16") insulation from leads and twist conductor strands tightly.
2. Solder leads to the connector as shown in the following diagram.

7 Installation Instructions Configuration Tasks
268
WARNING
According to AAMI specifications the peak of the synchronized defibrillator discharge should be
delivered within 60 ms of the peak of the R wave. The signal at the ECG output on the IntelliVue
patient monitors is delayed by a maximum of 30 ms. Your biomedical engineer should verify
that your ECG/Defibrillator combination does not exceed the recommended maximum delay of
60 ms.
Configuration Tasks
You must configure these settings during installation in configuration mode.
- Line Frequency
- Printer
- Altitude
- Equipment Label (for wireless networked monitors, or when the Information center is in
flexible monitoring mode).
- IP Address, Subnet Mask and Default Gateway (for manual IP Address Configuration - only
in service mode)
- ECG cable colors
- Height and Weight units
- IGMP, CI Mode, CI Address, CI TTL (for Customer Supplied Clinical Network (CSCN)
Routed Bedside Configurations - only in service mode)
Checking Country-Specific Default Settings
Some settings are made in the factory to match the typical requirements in a specific country.
Line frequency, units for weight and height, and ECG cable colors (AAMI or IEC) have been set
to appropriate values. If you suspect that these settings may not match your institution’s
requirements, check the settings and change them if necessary as described in the Configuration
Guide.
WARNING
Before starting monitoring, check that the configuration meets your requirements, especially
patient category, alarm limits and paced setting.
If you need to enter configuration mode:
1. In the Main Setup menu, select Operating Modes.
2. Select Config and enter the passcode.
The passcode for configuration mode is given in the monitor’s service documentation.

Configuration Tasks 7 Installation Instructions
269
The monitor displays Config at the right hand side of the status line and in the center of the
Screen while you are in configuration mode.
Before you leave configuration mode, always be sure to store any changes you made. You must
store changes made to each Settings Block and to each Profile, individually. As it may be
difficult to remember whether the settings you changed belong to a Monitor Settings block or a
Measurement Settings block, we recommend that you store each block before you leave
configuration mode.
To leave configuration mode:
In the Main Setup menu, select Operating Modes and then select Monitoring.
Setting Altitude, Line Frequency, ECG Cable Colors and Height & Weight Units
You require a local barometric pressure rating from a reliable source (such as airport, regional
weather station, or hospital weather station) that is located at the same altitude as the institution.
1. From the Main Setup menu, select Global Setting. Select Altitude and enter the
altitude.
2. From the Main Setup menu, select Global Setting. Select Line Frequency and
choose the Line Frequency.
3. From the Main Setup menu, select Global Setting. Select ECG Cable Color and
choose the Cable Color.
4. From the Main Setup menu, select Global Setting. Select Height Unit and choose
the Height unit.
5. From the Main Setup menu, select Global Setting. Select Weight Unit and choose
the Weight unit.
Setting Altitude and Line Frequency
You require a local barometric pressure rating from a reliable source (such as airport, regional
weather station, or hospital weather station) that is located at the same altitude as the institution.
1. From the Main Setup menu, select Global Setting. Select Altitude and enter the
altitude.
2. From the Main Setup menu, select Global Setting. Select Line Frequency and
choose the Line Frequency.
Configuring the Equipment Label
If the Information Center is in fixed monitoring mode, it controls the equipment label. You do
not need to follow this procedure.
However, if you are on a wireless network, or your Information Center is configured for flexible
monitoring mode, you must set the equipment label. This associates the monitor with a central
monitoring sector. An identical monitor label must also be configured in the Information Center.
1. Select the Bed Label screen element to call up the Bed Info menu.

7 Installation Instructions Configuration Tasks
270
2. Select Equipment Label to call up the onscreen keyboard.
3. Enter the system identifier. This needs to be set up in either the monitor or the information
Center. If the Information Center is in flexible monitoring mode, the monitor must be setup
to match the Information Center’s monitor label.
Configuring the printer
1. From the Main Setup menu select Reports.
2. Select Printer Settings and configure Local to enabled if the printer is connected
directly to the monitor. See configuration guide for further details.
Configuring IP Address, Subnet Mask and Default Gateway
Typically the automatic configuration via the BOOTP Server of the central station is used. In this
case all fields are set to 0.0.0.0. For special requirements, it is possible to switch to a manual/fix
IP address configuration.
NOTE
- Only limited checks of the manual values are possible. Therefore, it is mandatory that a
manual configuration is only performed by an experienced service person to avoid problems
such as duplicate IP addresses, non matching subnet mask, etc.
- The second CPU of an MP90 does not support a manual configuration and therefore will
always request the IP configuration via BOOTP.
1. Select the Bed Label screen element to call up the Bed Info menu.
2. Select IP Address. If the IP Address is set to 0.0.0.0, all values are dynamically requested
from a BOOTP Server. Otherwise the manually entered address is used.
3. Select Subnet Mask. The Subnet Mask must be provided for manual IP addresses. The
Subnet Mask must consist of a single consecutive series of "1" bits; e.g. 255.255.248.0. The
configured value is ignored when the IP Address is provided by a BOOTP Server.
4. Select Default Gateway. The IP Address of the Default Gateway can be optionally
configured. The configured value is ignored if IP Address and gateway are provided by a
BOOTP Server. The configured value must be within the range of the Subnet Mask.

Configuration Tasks 7 Installation Instructions
271
Configuration Settings for CSCN Routed Bedside Monitors (RBM)
The following settings are used for Customer Supplied Clinical Network (CSCN) Routed
Bedside monitors. To access these settings, select the Bed Label screen element to call up the
Bed Info menu.
IGMP:Shows status of IGMP Support (On or Off). IGMP (Internet Group Multicast Protocol) is
used by many switch manufacturers to limit the number of destinations targeted by a multicast
packet.
CI Mode: The mode in which CI messages (Connect Indication messages) are send (Broadcast,
Multicast, Manual).
CI Address: IP Address for Connect Indication messages only being used if CI Mode is set to
Manual. If CI Mode is Broadcast the CI Address is implicitly the subnet broadcast address. If CI
Mode is Multicast the CI Address is implicitly 224.0.23.63.
CI TTL: Sets the TTL (Time To Live) of the CI message. Defaults to 1.
Configuring Routed Bedside Monitors Support
An IntelliVue MP2/X2, MP5/MP5T or MP20-90 monitor must be running software revision
level G.0 or higher to be used as a routed bedside monitor (RBM).
CAUTION
A Philips Routed Bedside Monitor may temporarily stop displaying its Care Group overview bar
for up to 60 seconds if a network link carrying multicast traffic between the Philips IntelliVue
Information Center and the network routers is lost. While the multicast traffic is being re-routed,
the monitor will not display the Care Group overview bar but will maintain connectivity to its
associated Philips IntelliVue Information Center. Primary monitoring/alarms will remain
available at the Routed Bedside Monitor and its associated Philips IntelliVue Information Center
while the multicast traffic is being re-routed.
To configure an IntelliVue Patient Monitor to function as an RBM:
1. Put the monitor into Service Mode
2. Select Main Setup => Bed Information => IGMP and set IGMP to On.
3. Select Main Setup => Bed Information => CI Mode and set CI Mode to Multicast.
4. Select Main Setup => Bed Information => CI TTL, and set CI TTL to a value of 8.
5. Store the settings.
6. The CI Address will change to 224.0.23.63.
7. Return the monitor to its normal operational mode.
For further information regarding CSCN Routed Bedside Monitors refer to the CSCN
Specifications (P/N: 4535 640 24951)

7 Installation Instructions Handing Over the Monitor
272
Handing Over the Monitor
If you are handing over the monitor to the end-users directly after configuration, make sure that
it is in Monitoring mode.
Ensure that the users have access to the following documentation delivered with the monitor:
- Training Program - M8000-9461x - for self-training on the monitor before use
- Instructions for Use - M8000-9001x - for more detailed questions during use
WARNING
All users must complete the training program (M8105-9441x) and read the Instructions for Use
before working with the monitor.
These training materials (in combination with this service guide) can also be used to train service
personnel on how to use and service monitor.

Handing Over the Monitor 7 Installation Instructions
273

275
8
8Site Preparation
Introduction
This section describes the procedures you should follow to plan and prepare a site for an
IntelliVue monitor installation. It describes:
- Site planning.
- Roles and responsibilities for local and Philips personnel.
- Remote installation planning.
Site Planning
The careful planning of the site for the IntelliVue monitor is essential for its safe and efficient
operation. A consulting schedule should be established between the Customer and Philips Sales
and Support Representatives, to ensure that all preparations are completed when the system is
delivered.
The site planning phases prior to equipment installation are:
Location: Planning the location of the various system components.
Environment: Confirming and correcting, as necessary, the environment of the proposed
installation site(s).
System Capabilities: Explaining the possibilities for system expansion.
Mounting: Referencing the mounting hardware information website for the listing of suitable
mounting hardware recommended for use with the various system components, and all details on
the available mounts and accessories.
Cabling: Identifying the requirements for the cabling, conduiting and faceplates for connecting
the various system components.

8 Site Preparation Introduction
276
Roles & Responsibilities
This section describes the procedures necessary to prepare a site for a system installation. The
procedures are grouped into two parts: procedures that local staff or contractors are responsible
for, and procedures that Philips personnel are responsible for.
Site Preparation Responsibilities
Local Staff
- Ensure that all safety, environmental and power requirements are met.
- Provide power outlets.
- Prepare mounts.
- Pull cables, install conduit, install wallboxes.
- Terminate network cables if a Philips Clinical Network is in use.
- It may be necessary to certify the network cable plant, see Philips Clinical Network
Installation Manual for details.
Philips Personnel
- Provide the customer with the safety, environmental and power requirements.
- Assemble mounts.
- Prepare monitor remote cabling.
Procedures for Local Staff
The following tasks must be completed before the procedures for Philips personnel may be
started.
- Providing Power Outlets
One power outlet for each display and for any peripheral device (for example, a printer or
slave display) is required by the system. Provide a power outlet in the vicinity (1 m or 3 ft)
of each component that requires power.
WARNING
Only the power cables provided with the system may be used. For reasons of safety, power
(mains) extension cables or adapters shall not be used.
- Preparing Mounts
Where ceiling, wall, or shelf mounts are required for mounting the equipment, the customer
is responsible for the following:
- Providing and installing all hardware which is required to install the mounting hardware
supplied by Philips as detailed in the installation notes.
- Making sure that all ceilings, walls, and mounting rails that supports mounting hardware
are suitable for their proposed load.

Introduction 8 Site Preparation
277
WARNING
It is the customer's responsibility to have the attachment of the mounting hardware to the ceiling,
wall, or mounting rail and the construction of the ceiling, wall, or mounting rail evaluated for
structural integrity and compliance with all local, state and any other required codes by a
registered, professional, structural and/or mechanical engineer.
Although considerable effort has been made to ensure the safety of the ceiling mount installation
and or mounting guidelines, it is to be understood that the installation itself is beyond the control
of Philips Medical Systems. Accordingly, Philips Medical Systems will not be responsible for
the failure of any such installation.
- Providing Conduit
Where a remote installation is required, for example the installation of a remote display, the
customer is responsible for the following hardware installations:
- Providing conduit and/or trunking of a sufficient cross-sectional area for the planned
cables and possible future expansion (for additional components or systems). See
Cabling Options and Conduit Size Requirements for cable specifications for remote
installations.
- Providing and/or installing suitable wall boxes to accommodate the faceplates.
- Pulling Cables
WARNING
NEVER run power cables through the same conduit or trunking used for system cables.
- Installing Wall Boxes
It is the customer's responsibility to provide and install wallboxes to house faceplates. The
customer must notify the Philips installation coordinator of which size is to be used.
Procedures for Philips Personnel
Before you begin the procedures in the installation sections, ensure that the customer has
completed all necessary preparations outlined in the previous section, "Procedures for Local
Staff."

8 Site Preparation Monitor M8001A and M8002A Site Requirements
278
Monitor M8001A and M8002A Site Requirements
Space Requirements
The situating of the monitor should be planned such that the nursing staff are able to monitor the
patient with relative ease, with all patient connectors and controls readily available and the
displays clearly visible. The location should also allow access to service personnel without
excessive disruption and should have sufficient clearance all round to allow air circulation.
Dimensions and weight:
Size (W x H x D)
345 x 275 x 230 mm (13.6 x 10.8 x 9 in)
Weight (with M3001A and battery, without options)
6.0 kg (13.2 lb)
Environmental Requirements
The environment where the MP20/MP30 monitor will be used should be reasonably free from
vibration, dust and corrosive or explosive gases. The ambient operating and storage conditions
for the MP20/MP30 monitor must be observed. If these conditions are not met, the accuracy of
the system will be affected and damage can occur.
Temperature
Operating: 0 to 40ºC (32 to 100ºF)
Storage: -20 to 60ºC (-4 to 140ºF)
NOTE
Operation with IntelliVue Instrument Telemetry and battery charging is only allowed at
temperatures below 35°C (95°F)
Humidity
Operating: 20% to 85% Relative Humidity (RH) (non-condensing)
Storage: 5% to 85% Relative Humidity (RH)
Altitude
Operating: -500m to 3000m (10000 ft.)
Storage: -500m to 12000m (40000 ft.)

Monitor M8001A and M8002A Site Requirements 8 Site Preparation
279
Battery Storage
-20 to 50ºC (-4 to 122ºF)
Electrical and Safety Requirements (Customer or Philips)
Safety Requirements
If the M20/MP30 monitor is to be used in internal examinations on the heart or brain ensure that
the monitor is connected to an equipotential grounding system.
Grounding
The MP20/MP30 monitor MUST be grounded during operation (Class I equipment according to
IEC 60601-1). If a three-wire receptacle is not available then the hospital electrician must be
consulted to ensure that proper grounding is available on installation. NEVER attempt to use a
three-wire to two-wire adapter with the MP20/MP30 monitor.
WARNING
Each component must be individually grounded for safety and interference suppression
purposes.
Electrical Requirements
Line Voltage Connection
The MP20/MP30 monitor uses < 100 W (1.8 to 1.0 A).
Line Voltage
The MP20/MP30 monitor may be operated on ac line voltage ranges of
100 to 240V (50/60 Hz).

8 Site Preparation Remote Device Site Requirements
280
Remote Device Site Requirements
The system can be installed with one or more combinations of the following remote devices.
Multi-Measurement Module
Remote Display
Remote Alarm Device
Remote Extension Device (with or without SpeedPoint)
Where more than one site is used for locating equipment (a remote installation), the following
sections should be considered for EACH device:
- Space Requirements
- Environmental Requirements
- Mounting
- Electrical and Safety Requirements
- Cabling Options and Conduit Size Requirements

Remote Device Site Requirements 8 Site Preparation
281
Connecting Non-Medical Devices
The standard IEC-60601-1-1 applies to any combination of medical and non-medical electrical
devices, where at least one is a medical electrical device. Therefore IEC-60601-1-1 must still be
met after all devices are connected.
WARNING
Do not use a device in the patient vicinity if it does not comply with IEC-60601-1. The whole
installation, including devices outside of the patient vicinity, must comply with IEC-60601-1-1;
one reasonable solution may be the use of an isolation transformer. If the monitor is used with
battery operation, always use an isolation transformer when connnecting an additional display.
Equipment Location in the Patient Vicinity
NOTE
The site planning requirements, with the exception of the cabling, must be provided by the
device manufacturer, if the remote device is not purchased from Philips.
Multi-Measurement Module (MMS) M3001A and IntelliVue X2 M3002A
Space Requirements Multi-Measurement Module M3001A
Size (W x D x H)
188.0mm x 96.5 mm x 51.5 mm
(7.40” x 3.80” x 2.03”)
Weight
650g (1.4 lb)

8 Site Preparation Remote Device Site Requirements
282
Space Requirements IntelliVue X2 M3002A
Size (W x D x H)
188.0mm x 99 mm x 86 mm
(7.4” x 3.9” x 3.4”)
Weight
1.5 kg (3.3 lb)
Environmental Requirements Multi-Measurement Module M3001A and IntelliVue X2 M3002A
Temperature
Operating: 0 to 45ºC (32 to 113ºF)
Storage: -40 to 70ºC (-40 to 158ºF)
Humidity
Operating: 95% relative humidity (RH) max. @ 40ºC (104ºF)
Storage: 90% relative humidity (RH) max. @ 65ºC (150ºF)
Altitude
Operating: -500m to 4600m (-1600 to 15000 ft.)
Storage: -500m to 15300m (-1600 to 50000 ft.)
Cabling Options and Conduit Size Requirements
The following table describes the cabling options for the MMS.
M8048A and M3001A Cables
Product Option
Number
Part Number
12NC Part No.
Description Conduit
Sizes
Bend
Radius
Connector
Size
(L x W)
Both ends are terminated with straight MSL connectors.
M8022A #SC1 M3081-61626
453563474781
0.75m Measurement Server to
Monitor 72 mm2 40 mm 40 mm
x 17 mm
n/a M3081-61601
453563402721
1 m Measurement Server to Monitor 72 mm2 40 mm 40 mm
x 17 mm
M8022A #SC2 M3081-61602
453563377851
2m Measurement Server to Monitor 72 mm2 40 mm 40 mm
x 17 mm

Remote Device Site Requirements 8 Site Preparation
283
Product Option
Number
Part Number
12NC Part No.
Description Conduit
Sizes
Bend
Radius
Connector
Size
(L x W)
M8022A #SC4 M3081-61603
453563402731
4m Measurement Server to Monitor 72 mm2 40 mm 40 mm
x 17 mm
M8022A #SC6 M3081-61627
453563484501
10m Measurement Server to
Monitora 72 mm2 40 mm 40 mm
x 17 mm
M8022A #SC7 M3081-61628
453563484511
15m Measurement Server to
Monitora 72 mm2 40 mm 40 mm
x 17 mm
M8022A #SC9 M3081-61629
453563484521
25m Measurement Server to
Monitora 72 mm2 40 mm 40 mm
x 17 mm
Unterminated Cables
M3081A #A15 M3081-61615
453563484481
MSL Installation Cable 15m 72 mm2 40 mm 40 mm
x 17 mm
M3081A #A25 M3081-61625
453563484491
MSL Installation Cable 25m 72 mm2 40 mm 40 mm
x 17 mm
Faceplates
M3081A #C06 M3081-68708
453563484541
MSL Face Plate US version (pair of
connector boxes) n/a n/a n/a
M3081A #C07 M3081-68707
453563484531
MSL Face Plate non-US version
(pair of connector boxes) n/a n/a n/a
Insertion Tool
n/a M3086-43801
453563484771
MSL Insertion Too;l n/a n/a n/a
aBuilt on demand..
Mounting
M3001A Multi-Measurement Module (MMS) and M3002A IntelliVue X2 Mounts
Product Option
Number
Part Number
12NC Part No.
Description
M3080A #A01 n/a Wall Mounting Plate
M8007A #E20 M4046-62501
453563469731
Mount for back of MP60/70

8 Site Preparation Remote Device Site Requirements
284
Remote Displays (M8031A)
Space Requirements
Size (W x D x H)
With mounting bracket: 333mm x 408mm x 85mm (13.1” x 16” x 3.4”)
With desk stand: 387mm x 408mm x 175mm (15.2” x 16” x 6.9”)
Weight
With mounting bracket: 4900g (10.8lb)
With desk stand: 6900g (15.2lb)
Environmental Requirements
Temperature
Operating: 5 to 45ºC (41 to 113ºF
Storage: -20 to 60ºC (-4 to 140ºF)
Humidity
Operating: 95% RH max @ 40ºC (104ºF)
Storage: 85% RH max @ 50ºC (122ºF)
Altitude
Operating: Up to 4600m (15000 ft.)
Storage: Up to 4600m (15000 ft.)
Electrical and Safety Requirements
Voltage ranges:
90V to 264V
Voltage selection:
Wide range input, no voltage selection required
Max. Power consumption: 40W

Remote Device Site Requirements 8 Site Preparation
285
Remote Displays (M8031B)
Space Requirements
Size (W x D x H)
372mm x 308mm x 74.1mm (14.65” x 12.13” x 2.92”)
Weight
Without deskstand: 5200g (11.5lb)
With desk stand: 9000g (19.8lb)
Environmental Requirements
Temperature
Operating: 0 to 40ºC (32 to 104ºF)
Storage: -20 to 60ºC (-4 to 140ºF)
Humidity
Operating: 20 to 85% RH (Non-condensing)
Storage: 5 to 85% RH (Non-condensing)
Altitude
Operating: Up to 4000m (13123.36 ft.)
Storage: Up to 12000m (39370,08 ft.)
Electrical and Safety Requirements
Voltage ranges:
90V to 264V
Voltage selection:
Wide range input, no voltage selection required
Power consumption: ~30W

8 Site Preparation Remote Device Site Requirements
286
Remote Displays - M8033A
Space Requirements
Size (W x Hx D)
Landscape mode: 457mm x 457mm x 216mm (18” x 18” x 8.5”)
Portrait mode: 457mm x 495mm x 216mm (18” x 19.5” x 8.5”)
Weight: 8.9 kg (20 lbs)
Environmental Requirements
Temperature
Operating: 0 to 40ºC (32 to 104ºF)
Storage: -20 to 60ºC (-4 to 140ºF)
Humidity
Operating: 10 to 90% RH (Non-condensing)
Storage: 10 to 90% RH (Non-condensing)
Altitude
Operating: Up to 2400m (8000 ft.)
Storage: Up to 12200m (40000 ft.)
Electrical and Safety Requirements
Voltage ranges:
90V to 264V (13.5A fuse)
Voltage selection:
Wide range input, no voltage selection required
Power consumption: 60 watts maximum

Remote Device Site Requirements 8 Site Preparation
287
Remote Displays - M8033B
Space Requirements
Size (W x Hx D)
404mm x 401mm x 234mm (15.9” x 15.8” x 9.2”)
Weight
Without deskstand: 4.8 kg (10.6 lbs)
With deskstand: 8.8 kg (20 lbs)
Environmental Requirements
Temperature
Operating: 0 to 40ºC (32 to 104ºF)
Storage: -20 to 65ºC (-4 to 140ºF)
Humidity
Operating: 10 to 90% RH (Non-condensing)
Storage: 10 to 90% RH (Non-condensing)
Altitude
Operating: Up to 2438m (8000 ft.)
Storage: Up to 12192m (40000 ft.)
Electrical and Safety Requirements
Voltage ranges:
100V to 240V
Voltage selection:
Wide range input, no voltage selection required
Power consumption: 50 watts maximum

8 Site Preparation Remote Device Site Requirements
288
Remote Displays - M8033C
Space Requirements
Size (W x Hx D)
410mm x 362mm x 103mm (16.1” x 14.25” x 4.1”)
Weight
Without deskstand: 7 kg (15.4 lbs)
With deskstand: 10.8 kg (20 lbs)
Environmental Requirements
Temperature
Operating: 0 to 40ºC (32 to 104ºF)
Storage: -20 to 60ºC (-4 to 140ºF)
Humidity
Operating: 20 to 85% RH (Non-condensing)
Storage: 5 to 85% RH (Non-condensing)
Altitude
Operating: Up to 4000m (8000 ft.)
Storage: Up to 12000m (40000 ft.)
Electrical and Safety Requirements
Voltage ranges:
90V to 264V
Voltage selection:
Wide range input, no voltage selection required
Power consumption: 60 watts maximum
Cabling Options and Conduit Size Requirements
The following table describes the cabling options for the M8031A/B 15” and the M8033A/B/C
17” TFT Medical Grade Touch Displays.

Remote Device Site Requirements 8 Site Preparation
289
Analogue Video Cables
Product Option
Number
Part Number
12NC Part No.
Description Conduit
Sizes
Bend
Radius
Connector
Size (L x W)
M8022A #VA2 M3080-61606
453563484451
1.5m Analogue Video
Cable Kit 64 mm2 40 mm 35 x 16 mm
M8022A #VA3 M3080-61602
453563334661
3m Analogue Video Cable
Kit 64 mm2 40 mm 35 x 16 mm
M8022A #VA6 M3080-61603
453563334671
10m Analogue Video Cable
Kita 64 mm2 40 mm 35 x 16 mm
M8022A #VA7 M3080-61607
453563484461
15m Analogue Video Cable
Kita 64 mm2 40 mm 35 x 16 mm
M8022A #VA9 M3080-61608
453563484471
25m Analogue Video Cable
Kita 64 mm2 40 mm 35 x 16 mm
M1181A #A78 M1181-61695
453563255281
3m XGA Video Cable with
right-angled connector.
Patient Monitor to display.
M1181A #A79 M1181-61698
453563255291
10m XGA Video Cable
with right-angled
connector.
Patient Monitor to display.
Both ends are terminated with HDSUB15 (“VGA”) straight connectors
aBuilt on demand
Touch Cable
Product Option
Number
Part Number Description Conduit
Sizes
Bend
Radius
Connector
Size (L x W)
M8022A #TC2 M8081-61010
451261006551 Touch Cable, 1.5m 30mm2 25mm 35 x 16 mm
M8022A #TC3 M8081-61011
451261006561 Touch Cable, 3m 30mm2 25mm 35 x 16 mm
M8022A #TC6 M8081-61012
451261006571 Touch Cable, 10m 30mm2 25mm 35 x 16 mm
M8022A #TC7 M8081-61013
451261006581 Touch Cable, 15m 30mm2 25mm 35 x 16 mm
M8022A # TC9 M8081-61014
451261006591 Touch Cable, 25m 30mm2 25mm 35 x 16 mm

8 Site Preparation Remote Device Site Requirements
290
Remote Alarm Devices
Space Requirements
Size (W x D x H)
62mm x 125mm x 63 mm (2.4” x 5” x 2.5”)
Weight
< 300 g (< 0.7 lb)
Mounting
Remote Alarm Device Mounting
Note that the Universal Mounting Clamp (5061-8363) must be ordered separately
Product Option Number Part Number Description
n/a M8026-64001
451261006641 Wall Mount
Cabling Options and Conduit Size Requirements
The following table describes the cabling options for the Remote Alarm Device M8025A.
M8025A Remote Alarm Device Cables
Product Option
Number
Part Number Description Conduit
Sizes
Bend
Radius
Connector
Size (L x W)
M8022A #HF2 M8086-61003
453563484641 1.5m Monitor to Remote
Device 30 mm2 30 mm 27 x 13 mm
M8022A #HF3 M8086-61004
453563484651 3m Monitor to Remote
Device 30 mm2 30 mm 27 x 13 mm
M8022A #HF6 M8086-61005
453563484661 10m Monitor to Remote
Devicea 30 mm2 30 mm 27 x 13 mm
M8022A #HF7 M8086-61006
453563484671 15m Monitor to Remote
Devicea 30 mm2 30 mm 27 x 13 mm
M8022A #HF9 M8086-61007
453563484681 25m Monitor to Remote
Devicea 30 mm2 30 mm 27 x 13 mm
Both ends are terminated with straight MDR connectors.
aBuilt on demand.

Remote Device Site Requirements 8 Site Preparation
291
Remote Extension Device
Space Requirements
Size (W x D x H):
103mm x 139mm x 63 mm (4” x 5.5” x 2.5”)
Weight:
< 400 g (< 0.9 lb)
Mounting
Remote Extension Device Mounting
Product Option
Number
Part Number Description
n/a M8026-64001
451261006641 Wall Mount
n/a M8026-64002
451261015161 Mount to FMS
Cabling Options and Conduit Size Requirements
The following table describes the cabling options for the M8026A Remote Extension Device.
M8026A Remote Input Extension Device Cables
Product
Option
Number
Part Number Description Conduit
Sizes
Bend
Radius
Connector
Size (L x W)
M8022A #HF2 M8086-61003 1.5m Monitor to Remote Device 30 mm2 30 mm 27 x 13 mm
M8022A #HF3 M8086-61004 3m Monitor to Remote Device 30 mm2 30 mm 27 x 13 mm
M8022A #HF6 M8086-61005 10m Monitor to Remote Devicea 30 mm2 30 mm 27 x 13 mm
M8022A #HF7 M8086-61006 15m Monitor to Remote Devicea 30 mm2 30 mm 27 x 13 mm
M8022A #HF9 M8086-61007 25m Monitor to Remote Devicea 30 mm2 30 mm 27 x 13 mm
Both ends are terminated with straight MDR connectors.
aBuilt on demand.

8 Site Preparation Remote Device Site Requirements
292
Input Devices
The following tables describes the input devices which can be connected to the Remote
Extension Device M8024A, or directly to the monitor.
M8024A Input Devices
Product Option
Number
Part Number 12NC Part Number Description
- - Slimline Keyboard/Trackball USB
- 453564115901 Keyboard French Trackball USB
- 453564115911 Keyboard Italian Trackball USB
- 453564115921 Keyboard German Trackball USB
- 453564115931 Keyboard Danish Trackball USB
- 453564115941 Keyboard Swedish Trackball USB
- 453564115951 Keyboard English Trackball USB
M8024A #A02
- 453564119161 Keyboard Spanish Trackball USB
- - Compact Keyboard USB
- 453564115961 Keyboard French standard USB
- 453564115971 Keyboard Italian standard USB
- 453564115981 Keyboard German standard USB
- 453564115991 Keyboard Danish standard USB
- 453564116001 Keyboard Swedish standard USB
- 453564116011 Keyboard English standard USB
M8024A #A03
- 453564119171 Keyboard Spanish standard USB
M8024A #B01 M4046-60104 451261000661 Optical Mouse USB PS/2
M8024A #C02 M4046-60105 451261000671 Wireless Track Ball USB PS/2
M8024A #C03 M4046-60106 451261000681 Wired Track Ball USB PS/2
M8024A #C04 - 453564119281 Wireless Off Table Mouse
Local Printer
See printer documentation

Philips Medical LAN 8 Site Preparation
293
Philips Medical LAN
For information refer to the IntelliVue Information Center documentation.
Wireless LAN Adapter Cable
Product Option
Number
Part Number
12NC Part No.
Description Conduit
Sizes
Bend
Radius
M8022A #WL0 M8080-61001
453563484581
~30cm
Y-piece; DC supply plus LAN for Wireless
Ethernet Adapter and IIT Adapter
30 mm2 30 mm
n/a M2639-61001
451261013011 Cable Assembly Mini Din 8 Pin 1:1r for
IntelliVue 802.11 Bedside Adapter
RS232/MIB/LAN Interface
MIB Cable and Serial Cable
Product Option
Number
Part Number
12NC Part No.
Description Conduit Sizes Max. Bend Angle Connector
Size (L x W)
M8022A #SR2 M8081-61001
453563484591
1.5m cable 30 mm2 25 mm 15 x 15 mm
M8022A #SR3 M8081-61002
453563484601
3m cable 30 mm2 25 mm 15 x 15 mm
M8022A #SR6 M8081-61003
453563484611
10m cable 30 mm2 25 mm 15 x 15 mm
M8022A #SR7 M8081-61004
453563484621
15m cable 30 mm2 25 mm 15 x 15 mm
M8022A #SR9 M8081-61005
453563484631
25m cable 30 mm2 25 mm 15 x 15 mm
Both ends are terminated with 8 pin RJ45 connectors. CAT5 cable; straight through wiring.

8 Site Preparation Nurse Call Relay Interface
294
Cable and Adapter Set
Nurse Call Relay Interface
Nurse Paging Cable
Product Option
Number
Part Number
12NC Part No.
Description Conduit
Sizes
Bend
Radius
Connector
Size
M8022A #NC3 M1181-61648
453563375601
3m traditional nurse
paging relay cable.
One end terminated
with phone plug, one
end without connector.
13 mm2 20 mm Diameter
12 mm
M8022A #NC6 M8087-61001
453563484741
10m flexible nurse
paging cable.
One end terminated
with straight MDR
connector, one end
without connector.
40 mm2 30 mm 35 x 16 mm
ECG Out Interface
ECG Out Cable
Product Option
Number
Part Number
12NC Part No.
Description Conduit
Sizes
Bend Radius Connector
Size
(Diameter)
M8022A #A62 8120-1022
453563198151
3m cable (Both ends are
terminated with .25”
phone plugs)
40 mm2 30 mm 13 mm
n/a M1181-61625
453563255091
cable kit consisting of:
25 m raw cable, 2 x 1/4”
socket, 1 x 1/4” plug

ECG Out Interface 8 Site Preparation
295

297
9
9Gas Analyzers
For details on the M1026A/B Anesthetic Gas Module, the M1013A IntelliVue G1 and the
M1019A IntelliVue G5, please refer to the respective Service Guides on your documentation
CD.
For details on configuring the RS232/MIB port for the gas analyzers, see Connection of Devices
via the MIB/RS232 Interface in the Installation Instructions chapter

9 Gas Analyzers ECG Out Interface
298

299
10Index
1
1.1 Removing the Handle • 158
1.2 Removing the Measurement Server Holder • 158
1.3 Removing the I/O Boards and Interface Board • 160
1.4 Removing the Recorder • 161
1.5 Removing the Navigation Point Knob • 162
1.6 Removing the Quick Release Mount and Knob • 162
1.7 Removing the Fix Mount • 162
2
2.0 Opening the Front of the Monitor • 164, 208
2.1 Removing the Backlight Tubes • 165
2.2 Removing the Backlight Inverter Board • 166
2.3 Removing Power On LED board and Silicon Pad • 167
2.4 Removing the HIF Board, Silicon Pad and Spacer • 168
2.5 Removing the Flex Adapter Cable • 169
2.6 Removing the Battery Board • 170
2.7 Removing Recorder Board Assembly • 171
2.8 Removing the Loudspeaker • 172
2.9 Removing the Branding Cover • 173
3
3.0 Separating the Front and Back Half of the Monitor • 173, 208
3.1 Removing the LCD Flat Panel Display, Touch Panel and Front Housing • 174
3.2 Removing the Main Board • 175
3.3 Removing the MSL Assembly • 177
3.4 Removing the Power Supply • 178
3.5 Removing the Frame Housing and Serial Number Plate • 178
A
Abbreviations • 9
About the Battery • 110
adjustments • 10
After Each Service, Maintenance or Repair Event • 38

300
After Installation, Testing or Repair • 117
Alarm Behavior • 143
Alarm Issues • 143
Alarm Lamps • 143
Alarm Tones • 143
Altitude • 276
analyzer,safety • 40
Assembling the dual Link Bar • 197
assembly • 10
Attaching the MMS to a Mount • 256
B
Barometric Pressure Check and Calibration • 94
Basic Nurse Call Relay • 149
Basic Performance Assurance Test • 84
battery
malfunction symbols • 112
power gauge • 112
Battery Conditioning in the Monitor • 117
Battery Conditioning with an External Charger • 117
Battery Handling, Maintenance and Good Practices • 109
Battery related problems • 133
Battery Status
checking • 111
Battery Status on the Main Screen • 112
battery status recording • 115
battery status window • 114
Battery Status Window • 114
Battery Storage • 277
Bedside Network Status Icons • 135
Before Each Use • 37, 38
BIS Performance Test • 97
BISx Solution Components • 233
BISx Solution Replacable Parts • 232
Block Diagram Legend • 25
Boot Phase Failures • 124
C
Cabling Options and Conduit Size Requirements • 280, 286, 288, 289
Calibration Verification • 96
Carrying Out and Reporting Tests • 103
Case 1
Medical Device Combined with Medical Device • 73
Case 2

301
Medical Device Combined with a Non-Medical Device • 75
Case 3
Medical Device Combined with a Medical or Non-Medical Device with one Device in a Non-Medically-Used
Room • 79
Check for Obvious Problems • 121
Checking Country-Specific Default Settings • 267
Checking the Battery Status • 111
checklist
installation • 239
Checks before opening the instrument • 121
Checks Before Opening the Instrument • 121
Checks for Obvious Problems • 121
Checks with the Instrument switched Off • 121
Checks with the Instrument switched On, AC connected, with battery • 121
Checks with the Instrument Switched On, AC connected, without battery • 121
Checks with the Instrument switched On, AC not connected, with battery • 122
Claims for Damage • 241
Claims For Damage and Repackaging • 241
cleaning
recommended substances • 155
Cleaning the Air Filter Mats • 206
CO2
Calibration Verification • 96
Flow Rate Check and Calibration • 94
Noise Check • 95
Pump check • 94
CO2 Gas Measurement Calibration Check • 95
CO2 Pump / CO2 Scrubber Replacement • 97
Compatible Devices • 17
Conditioning a Battery • 115
Conditioning Batteries • 116
configuration mode
entering • 267
Configuration Settings for CSCN Routed Bedside Monitors (RBM) • 270
Configuration Tasks • 267
Configuring IP Address, Subnet Mask and Default Gateway • 269
Configuring Routed Bedside Monitors Support • 270
Configuring the Equipment Label • 268
Configuring the printer • 269
Connecting Non-Medical Devices • 279
connecting power • 243
Connecting the Monitor to AC Mains • 243
Connection of Devices via the MIB/RS232 Interface • 249

302
Connection of USB Devices • 148, 249
Connections • 244, 254, 255, 263, 266
CPU Boards • 19
D
Data Acquisition • 21
Data Flow • 21
Data Flow Marker In and ECG Wave • 152
Data Output • 22
Data Provider System Service • 22
Detaching the Measurement Server from a Mount • 256
Disabling/Enabling Touch Operation • 108
Disassembly Procedures for the M3015A MMS Extension (HW Rev. A) • 200
Display and User Interface Service • 22
Docking Station • 209
Docking Station Part Numbers • 235
Docking Station Performance Test • 100
Docking Station Problems • 150
Documenting Battery Status • 115
E
ECG • 223
ECG Out Functionality • 266
ECG Out Interface • 292
ECG Performance • 84
ECG Sync
Performance Test • 85
ECG Sync Performance Test • 85
ECG synch • 85
ECG/Resp
Performance check • 84
ECG/Resp Performance Test • 84
Electrical and Safety Requirements • 282, 283, 284, 285, 286
Electrical and Safety Requirements (Customer or Philips) • 277
Electrical Inspection • 240
Electrical Requirements • 277
enclosure leakage current test • 64, 65
Environmental Requirements • 276, 282, 283, 284, 285, 286
Environmental Requirements Multi-Measurement Module M3001A and IntelliVue X2 M3002A • 280
Evaluation • 106
Evaluation of Test Results • 37, 106
Exchange Parts
listing • 231
Exchange Parts List • 231

303
Exchange Procedures • 189
Exchanging the Flex Cable • 212
Exchanging the Main Board • 209
extensions • 10
External Display is blank (Slave Display) • 124, 128
External Display Part Numbers • 215, 235
External Touch Display not functioning • 129
F
Final Inspection • 188, 199
Flexible Nurse Call Relay • 148
Flow Rate Check and Calibration • 94
Following Reassembly • 205
Full Performance Assurance Test • 84
G
Gas Analyzers • 295
General Monitor INOP Messages • 130
General Reassembly/Refitting Comments • 205
General Requirements for a System • 69
Guideline for Performance of Safety Tests • 43
H
Handing Over the Monitor • 271
Hardware Building Blocks • 15
Hints for Correct Performance of Safety Tests • 42
How does the Support Tool Work with the Monitor • 24
How to find the Correct Procedure • 156
How to use the Troubleshooting tables • 124
How to Use This Guide • 9
How To Use This Section • 119
Humidity • 276
I
IIT Communication Test • 100
IIT-related Problems • 138
Image Sticking • 151
Individual Parameter INOPS • 144
Initial Inspection • 240
Initial Instrument Boot Phase • 122
Input Devices • 290
installation • 10
checklist • 239
Installation Checklist • 239

304
Installation Instructions • 239
Installing Interface Boards • 245
Installing Remote Devices • 253
Installing the Docking Station • 253
Installing the IntelliVue Instrument Telemetry Adapter • 258
Integrated Display is blank • 124, 127
Integrated Touch Display not functioning • 124, 128
IntelliVue 802.11 Bedside Adapter Communication Test • 101
IntelliVue 802.11 Bedside Adapter Part Numbers • 234
IntelliVue 802.11 Bedside Adapter Problems • 139
IntelliVue Instrument Telemetry (IIT) • 208
IntelliVue Instrument Telemetry Part Numbers • 233
IntelliVue MP20 • 15
IntelliVue MP30 • 16
IntelliVue X2 Part Numbers • 232
Internal LAN (Measurement Link) • 23
Introduction • 9, 31, 119, 273
Invasive Pressure Performance Test • 88
Isolating problems to the correct subassembly • 119
K
Keyboard/Mouse not functioning • 124, 133
L
Leakage Check • 93
List of Error Codes • 153
Local Printer • 290
M
M3001A #A01 Philips FAST SpO2 MMS Exchange Numbers • 226
M3001A #A02 Nellcor OxiMAX-compatible MMS Exchange Numbers • 227
M3001A #A03 MMS with Masimo SET SpO2 - Exchange Numbers • 227
M3014A Capnography Extension Performance Tests • 89
mains power
connecting to • 243
Mainstream CO2 Accuracy Check • 89
malfunction symbols
battery • 112
Measurement Validation • 86
Mechanical Inspection • 240
MIB / RS232 • 146
Microstream CO2 Calibration • 83
Microstream CO2 Performance Test • 83, 92
MMS Exchange Part Numbers • 226

305
MMS Extension Part Numbers - Front Bezels • 229
MMS Extension Part Numbers - Release Mechanisms • 228
MMS Extension Part Numbers - Top Cover, Flex Cable and Link Bar • 229
MMS Extension Parts (M3012A, M3014A, M3015A and M3016A) • 215, 228
MMS Extensions - Exchanging the Top Cover, MSL Flex Cable and the Dual Link Bar • 188
MMS Firmware Overview • 223
MMS Part Number Overview and Identification • 221
MMS Part Numbers - Front Bezel for M3001 #A01 & #A03 • 224
MMS Part Numbers - Front Bezel for M3001 #A02 • 224
MMS Part Numbers - Label Kits • 228
MMS Part Numbers - NBP Assembly • 228
MMS Part Numbers - Top Cover and MSL Assembly • 224
modifications • 10
Monitor Applications • 23
Monitor M8001A and M8002A Site Requirements • 276
Monitor Software Block Diagram • 25
Monitor Theory of Operation • 13
Mounting • 281, 288, 289
Mounting Instructions • 241
Mounting the 15 • 253, 254
Mounting the 17 • 254
Mounting the Wireless Ethernet Adapter to the Monitor • 257
MP20/MP30 Parts • 216
MSL Cable Termination • 263
MSL-related problems • 141
Multi-Measurement Module • 140, 256
Multi-Measurement Module (MMS) Disassembly • 179
Multi-Measurement Module (MMS) M3001A and IntelliVue X2 M3002A • 279
Multi-Measurement Module (MMS) Parts • 215, 221
Multi-Port Nurse Call Connector Test (Flexible Nurse Call) • 99
N
Navigation Point • 124, 132
NBP
Accuracy Test • 86
Leakage Test • 87
Linearity Test • 88
valve test • 88
NBP Accuracy Test • 86
NBP Leakage Test • 87
NBP Linearity Test • 88
NBP PerformanceTest • 86
Network related problems • 135

306
Noise Check • 95
Noninvasive Blood Pressure Measurement Calibration • 83
non-medical devices
in patient vicinity • 69
Nurse Call Relay • 266
Nurse Call Relay Interface • 292
Nurse Call Relay Performance Test • 98
O
OB TraceVue, connecting to • 69
Obtaining Replacement Parts • 120
Optional Hardware • 16
Other Regular Tests • 107
P
Parts • 215
parts and accessories • 10
Passwords • 11
patient leakage current test • 67
patient safety checks • 68
PCB
replacement level support • 120
performance • 10
Performance Assurance Tests • 37, 83
Persistent Data Storage System Service • 22
Philips Clinical Network • 24
Philips Clinical Network (Wired) • 265
Philips Clinical Network (Wireless) • 265
Philips Medical LAN • 291
Phone Jack Type Connector Test (Traditional Nurse Call) • 98
Positioning the Measurement Server on a Clamp Mount • 257
Possible USB Device Combinations • 251
power
connecting • 243
connection • 243
Power Loss Alarm Buzzer Performance Test (only if Multi-Port Nurse Call Connector Board is installed) • 100
Power On Test • 38
Power Supply • 18
PowerLink Test • 97
Preventive Maintenance Procedures • 83
Printer • 144
Printer Test Report • 109
Procedures for Local Staff • 274
Procedures for Philips Personnel • 275

307
PS/2 Keyboard/Mouse • 265
Pump Check • 94
R
Reassembling the MSL Flex Assembly • 182
Recommended Frequency • 32
Recorder • 145
recording
battery status • 115
Refit Procedures for the MMS Extension • 204
Refitting the CO2 Scrubber • 204
Refitting the Cover • 186
Refitting the DC/DC board • 186
Refitting the Extension Bottom Cover • 205
Refitting the Front Cover • 187, 199, 205
Refitting the new NBP Pump • 184
Refitting the Pump • 204
Refitting the Top Cover • 197
reliability • 10
Remote Alarm Device • 131
Remote Alarm Device Part Numbers • 215, 238
Remote Alarm Devices • 288
Remote Device Site Requirements • 278
Remote Displays - M8033A • 284
Remote Displays - M8033B • 285
Remote Displays - M8033C • 286
Remote Displays (M8031A) • 282
Remote Displays (M8031B) • 283
Remote Extension Device • 124, 132, 289
Remote Extension Device Part Numbers • 215, 238
Remove/Replace
Plug-in Module
tcpO2/tcpCO2 Calibration Chamber • 179
Removing Directly Accessible Parts • 157
Removing the CO2 Scrubber • 202
Removing the DC/DC Board • 181
Removing the Dual Link Bar • 191
Removing the Extension Bottom Cover • 201
Removing the Front Cover • 179, 189, 200
Removing the Mounting Pin • 179, 190
Removing the MSL Flex Assembly • 181
Removing the NBP pump • 184
Removing the new MMS Holder • 159

308
Removing the old MMS Holder • 158
Removing the Pump • 203
Removing the Top Cover • 180, 194
Repackaging for Shipment or Storage • 241
Repair and Disassembly • 155
repairs • 10
qualified personnel • 119
Replacement level
major subassembly • 120
PCB • 120
Replacement Level Supported • 120
Replacement parts. See Spare parts • 120
Replacing the Fan • 206
Replacing the Flex Cable Assembly • 194
Reporting of Test Results • 37, 103
Required Protective Measures at System Installation • 72
Reset Time Counters • 97
Respiration Performance • 84
Responsibility of the Manufacturer • 10
Roles & Responsibilities • 274
RS232/MIB/LAN Interface • 291
S
S(1)
Protective Earth Resistance Test • 63
S(2)
Equipment Leakage Current Test - Normal Condition • 64
S(3)
Equipment Leakage Current Test - Single Fault Condition • 65
S(4)
Applied Part Leakage Current - Mains on Applied Part • 67
safety • 10
tests • 39
procedures • 41
system • 68
Safety Requirements • 277
Safety Test Adapter Cable - Schematics • 45
Safety Test Procedures • 37, 41
safety tests • 39
Safety Tests • 39
Setting Altitude and Line Frequency • 268
Setting Altitude, Line Frequency, ECG Cable Colors and Height & Weight Units • 268
Sidestream CO2 Accuracy Check • 90

309
Sidestream CO2 Flow Check • 91
Sidestream CO2 Performance Test • 92
Site Planning • 273
Site Preparation • 273
Site Preparation Responsibilities • 274
Smart Battery Charger LG1480 (M8043A) • 205
Smart Battery Charger Part Numbers • 215, 233
Software Revision Check • 120
Space Requirements • 276, 282, 283, 284, 285, 286, 288, 289
Space Requirements IntelliVue X2 M3002A • 280
Space Requirements Multi-Measurement Module M3001A • 279
Spare parts
obtaining • 120
SpO2 • 223
Performance Test • 85
SpO2 Performance Test • 85
Status Log • 152
symbols
battery • 112
system
example • 69
medical electrical • 68
test • 68
System Boundaries • 14
System Example • 69
System Installation Requirements • 71
System Interface and I/O Boards • 20
system test • 68
System Test • 39, 68
System Test Procedure • 82
T
Temperature • 276
Accuracy check • 89
Temperature Performance Test • 89
Terminology and Definitions • 32
Test and Inspection Matrix • 104
Test Report • 103
Testing • 188, 200
Testing and Maintenance • 31
Testing Sequence • 37
tests
enclosure leakage current • 64, 65

310
patient leakage current • 67
safety • 39
Theory of Operation • 13
Time counters
resetting • 89, 97
Tools required • 155, 179
Touch Cable • 287
Touchscreen Calibration • 107
Troubleshooting • 119
Troubleshooting Guide • 120
Troubleshooting Tables • 120, 123
Troubleshooting the ECG OUT • 149
Troubleshooting the Individual Measurements or Applications • 154
Troubleshooting with the Support Tool • 154
U
Unpacking the Equipment • 240
USB • 147
USB Error Indication • 252
V
Valve Test • 88
Video Cable Wiring Schematics • 256
Viewing Individual Battery Status • 115
Visual Inspection • 38
voltage setting • 243
W
Warnings and Cautions • 11
Warnings, Cautions, and Safety Precautions • 40
What Causes the Conditioning Message on the Monitor? • 116
What is a Medical Electrical System? • 68
What is Battery Conditioning? • 115
When Should Battery Conditioning be Performed? • 116
When to Perform Tests • 33
Who Should Perform Repairs • 119
Who Should Use This Guide • 9
Why is Battery Conditioning Necessary? • 115
window
battery status • 114
Wireless Ethernet Adapter (Proxim) • 137