1 TASC Manual
User Manual:
Open the PDF directly: View PDF .
Page Count: 18
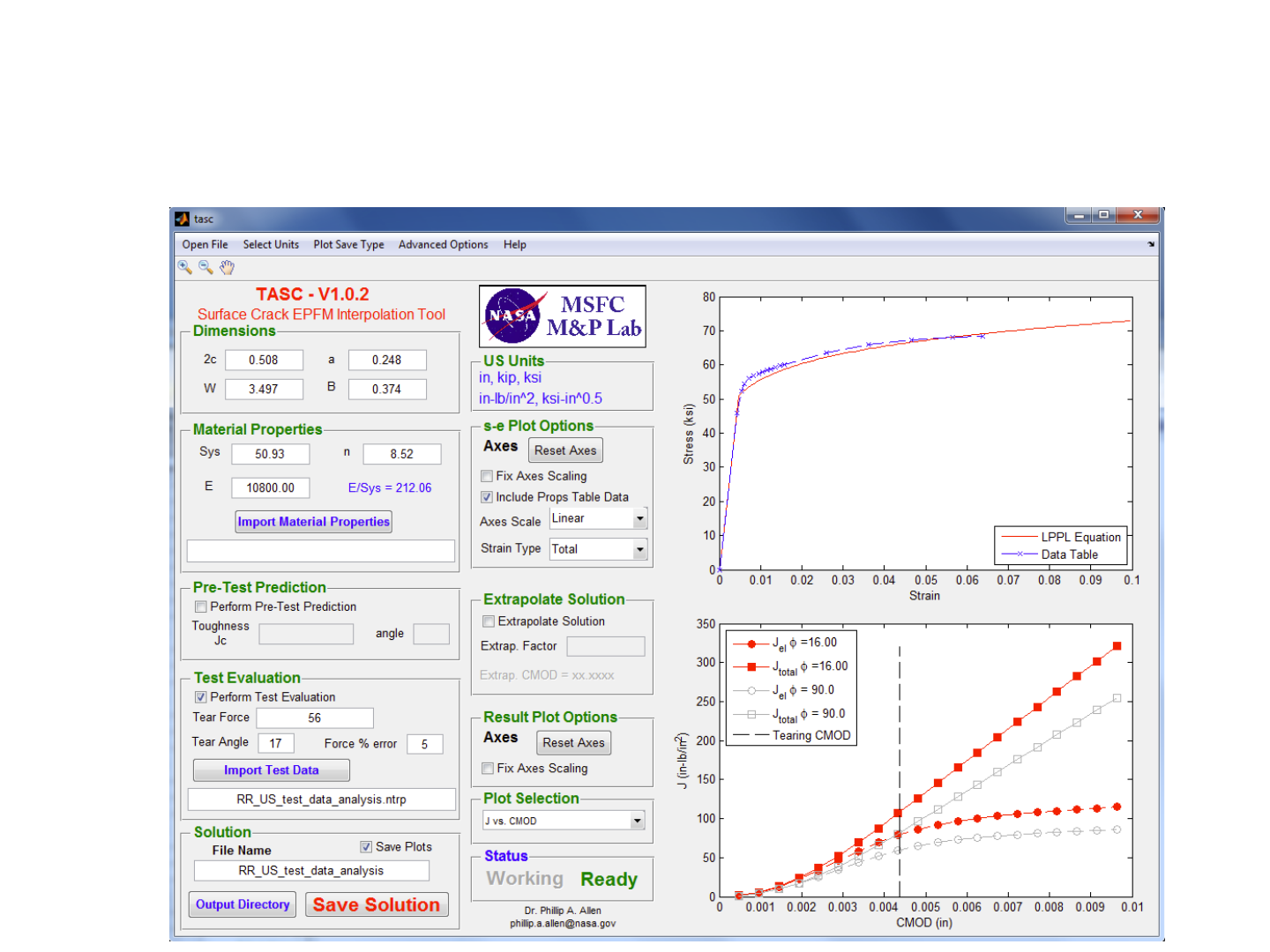
TASC – V1.0.2 (Tool for Analysis of Surface Cracks)
Interpolated Elastic-Plastic J-Integral Solutions
Phillip Allen – NASA MSFC – Phillip.a.allen@nasa.gov
June 2014
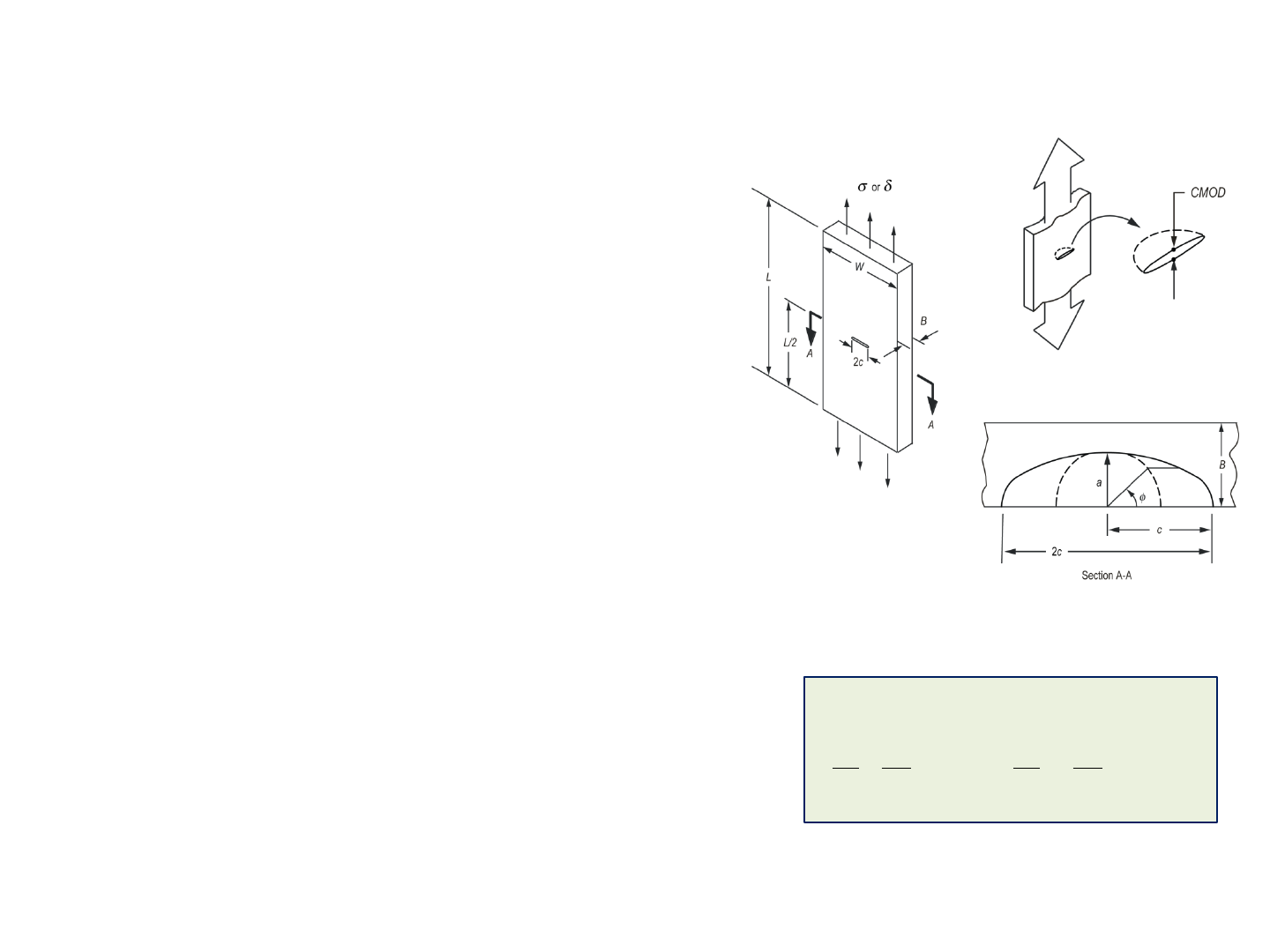
LPPL Equations
Introduction
2
Tool for Analysis of Surface Cracks (TASC) is a computer program created in
MATLAB® to enable easy computation of nonlinear J-integral solutions for
surface cracked plates in tension by accessing and interpolating between the 600
nonlinear surface crack solutions documented in NASA/TP–2011-217480*. The
only required inputs are the surface crack dimensions (2c and a), plate cross-
section dimensions (W and B), and linear plus power law (LPPL) material
properties of elastic modulus, E, yield strength,
s
ys or Sys, and strain hardening
coefficient, n. With the geometry and material parameters entered, TASC
interpolates to the appropriate J(
f
) vs. crack mouth opening displacement
(CMOD) and far-field tension stress,
s,
vs. CMOD solution, providing the full
solution as CMOD ranges from zero out to the CMOD limit of the solution space
for the given input parameters. (Note:
f
is the parametric crack front angle.)
TASC provides interpolated solutions over a wide range of crack shapes and
depths (shape: 0.2 ≤ a/c ≤ 1.0, depth: 0.2 ≤ a/B ≤ 0.8) and material flow
properties (elastic modulus to yield ratio: 100 ≤ E/
s
ys ≤ 1000, and hardening: 3 ≤
n ≤ 20). With surface crack test design and analysis in mind, TASC also has
several other useful features such as:
1. material property import capability with automated material constant
fitting,
2. pre-test prediction capabilities based on a critical J-integral value and
critical
f
location,
3. test record force, P, vs. CMOD evaluation and comparison with analysis,
4. the ability to review multiple result plots such as J(
f
), J vs. CMOD, and
deformation limit comparisons, and,
5. the ability to save the solution, input, and plot files.
;
n
ys ys
ys ys ys ys
s s
s s
* Details of the solution space, interpolation methods, and nomenclature are documented in
NASA/TP-2013-217480, Elastic-Plastic J-Integral Solutions for Surface Cracks in Tension Using
an Interpolation Methodology, which is available for download from the NASA Center for
Aerospace Information (CASI) at <http://www.sti.nasa.gov>.
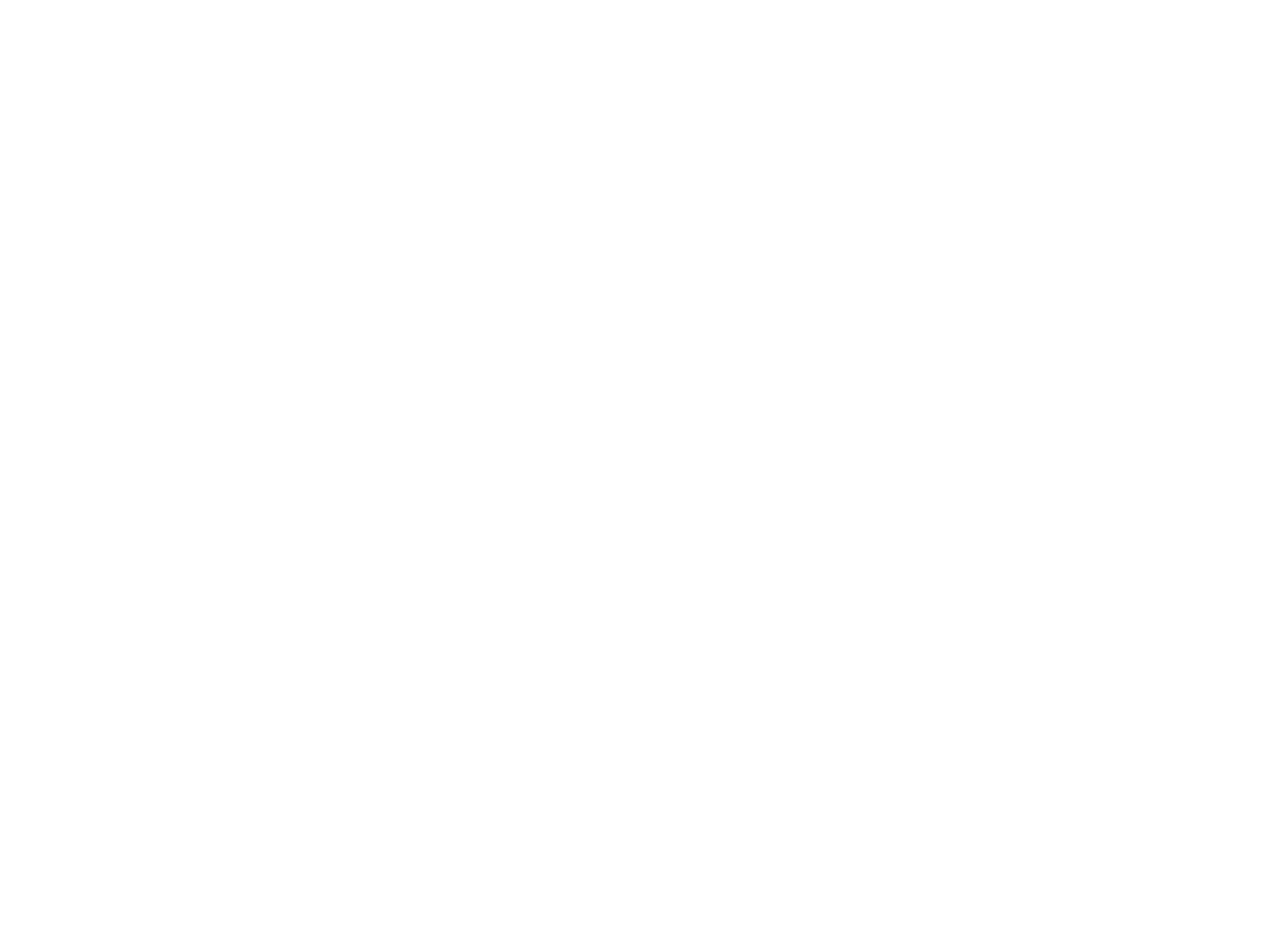
Revision History
3
June 2014 - Version 1.0.2
•interp_solution_SCGui_CMOD_log_int.m – Corrected error in code that sometimes prevented interpolation to first load step
results for very small initial increments of CMOD. In rare cases, this error created “NaN” results for the first load step of the
interpolation solution and prevented the pretest prediction from functioning properly.
•plt_crk_front_condition_int.m – Added this new file that creates a plot of the crack front constraint and deformation
conditions as a function of loading. This plot corresponds to Figure 8 in ASTM E2899.
•Changed three plot routines to plot the
f
(90°) results as light gray to differentiate the 90 results from the tearing prediction
results. Updated code in: plt_crk_front_condition_int.m, plt_deform_epfm_fea_int.m, and plt_J_CMOD_fea_int.m.
February 2014 - Version 1.0.1
•Released standalone executable versions of TASC V1.0.1 for Windows® 64-bit and Mac OS X® 64-bit, and the TASC source
code under the NASA Open Source Agreement. Files are posted the NASA TASC Sourceforge project at
http://sourceforge.net/projects/tascnasa/.
•tasc.m – Added a start-up box that requires users to read and accept the NASA Open Source Agreement before using TASC.
•create_summary_table.m – Added additional output in the results summary file including: E, a, 2c, rfa, and rfb.
•plt_force_CMOD_interp2_int.m – Added J(
f
) value displayed on plot for test analysis prediction.
•plt_stress_CMOD_interp_int.m – Added J(
f
) value displayed on plot for test analysis prediction.
November 2013 - Version 1.0.0
•Released standalone executable versions of TASC V1.0.0 for Windows® 64-bit and Mac OS X® 64-bit under the NASA Public
Release Agreement.
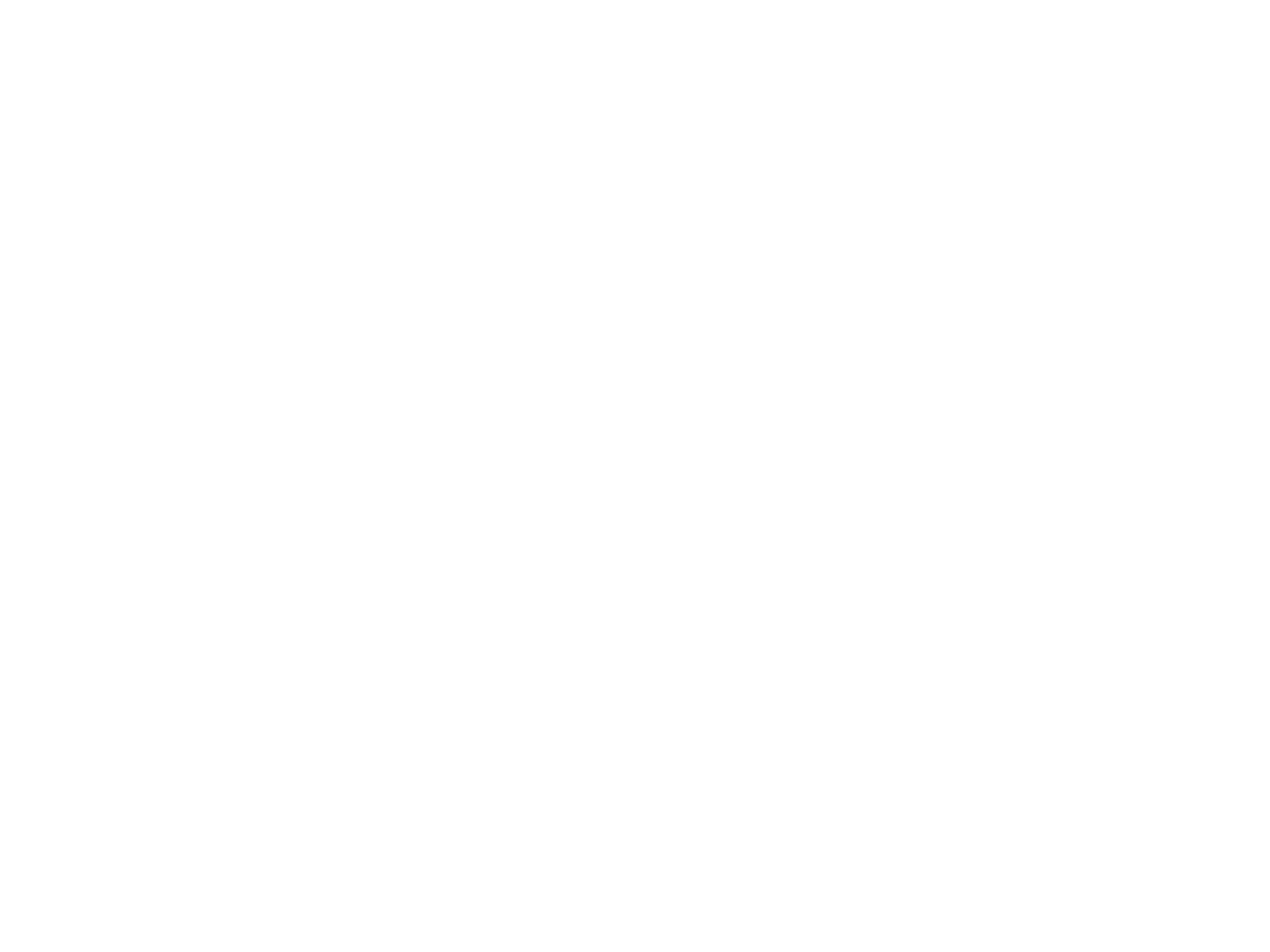
Some Important Standalone Executable Details
4
•TASC is a standalone executable program available for Windows® 64-bit and Mac OS X® 64-bit. Individual users of the
standalone executables do not need a MATLAB license due to the royalty-free MATLAB Complier Runtime (MCR) distribution
provided with the program installation package.
•Installation details are in the readme.txt file included in the distribution package. The correct version of the MCR package
must first be installed on each computer on which you want to run TASC. The correct MCR installation file (MCRInstaller.exe)
is included in the distribution package. The TASC standalone executable file (TASC_V1P0P2.exe for Windows and
TASC_V1P0P2_mac.app for Mac) can be located in any convenient place on your computer. Double click TASC_V1P0P2.exe
for Windows or execute run_TASC_V1P0P2_mac.sh from the terminal for Mac to start TASC.
•TASC takes 10 to 60 seconds to start, depending on your computer because the MCR files are essentially starting a version of
Matlab in the background. Unfortunately using the Matlab graphical user interface (GUI) system, there is no practical way to
have a start up splash screen to show you the program is starting; please be patient. Once the TASC GUI is running, each
elastic-plastic solution is computed in seconds.
•The first time you run TASC, a start up window will appear stating “I have read and accept the terms of the NASA Open
Source Agreement included in the TASC distribution package.” You must select “Yes” to run TASC. Selecting “Yes” creates a
small text file, TASC_lic.txt” in your executable directory. You will not be asked to accept the agreement again unless you
move or copy the executable file to another directory.
•Example TASC input files (*.ntrp ), material property files (*.prop), and test data files (*.txt) for both US and SI units are
included in the Distribution_Example_Files directory. The use and description of these files are explained later in this
manual.
•The GUI was created and formatted on the Windows platform. As a result, on the Mac platform the GUI appearance for
items such as font sizes are not optimized. In addition the Mac version does not have the capability to save an Excel
summary of the results in *.xlsx format. The results are output in text format and drop cleanly into Excel if so desired. Also
the Mac version does not have the ability to save plot images in the *.emf format so instead defaults to the *.tiff format.
•Background information on surface crack tension testing including deformation limits and critical
f
calculation methods is
documented in ASTM E2899, Standard Test Method for Measurement of Initiation Toughness in Surface Cracks Under Tension
and Bending, which is available from ASTM, <http://www.astm.org>.
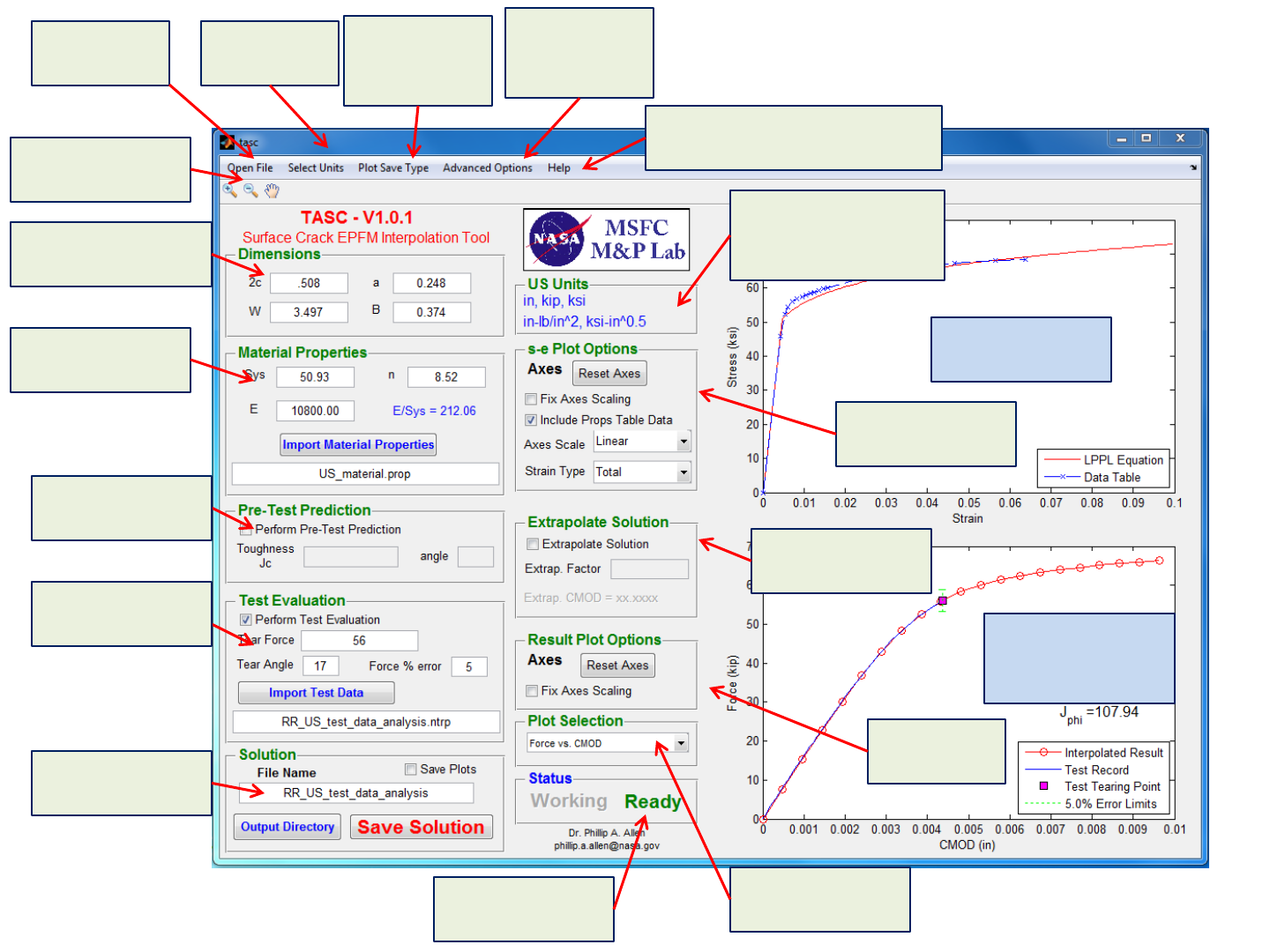
Basic Layout
A. Input plate and
crack dimensions
B. Input Material
Properties
Plot zoom and
pan controls
Open input
(*ntrp) file
Select SI or
US units
Show
interpolation
details
C. Pre-test
prediction inputs
D. Test evaluation
inputs
Save solution
options
Units details:
Length, Force, Stress
J-integral, K
Stress-strain
properties plot
Analysis results
output plots (10
choices)
Stress-strain plot
options
Result plot
options
Extrapolate
Solution options
Analysis Status
Lights
Result plot
selection box
Choose plot
electronic file
type
5
Help: show surface crack
picture or open user manual
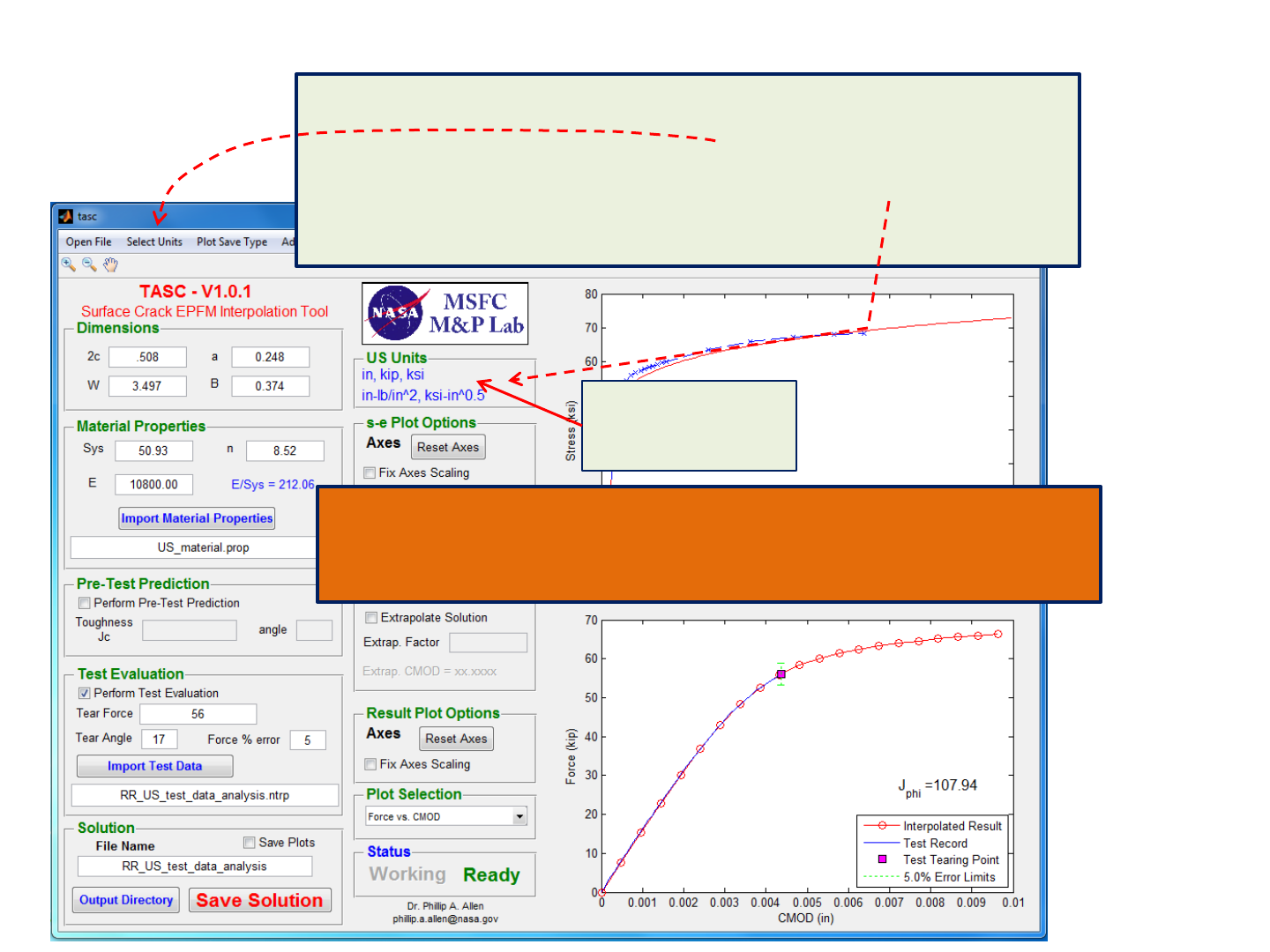
Important Units Considerations
Units Details:
Length, Force, Stress
J-integral, K
6
The underlying solution database is dimensionless. Therefore TASC relies on the user to
input a consistent set of units to get output in the expected and desired units. The user
must first decide on SI or US units by using the Select Units menu or by specifying the
units type in the *.ntrp file. The expected units type for length, force, stress, J-integral
and K (and output units where applicable) are shown in the Units Details Box on the GUI
and at the end of the output file. The units type for SI and US were chosen based on
typical values used in a test lab environment.
CAUTION: Switching units type from SI to US or vice-versa will NOT convert any
previously input numerical data into the new units system. Units must be entered as
specified on the GUI for the given units system. Choosing the units type (SI or US) simply
sets the appropriate internal calculation factors and output labels for that units type.
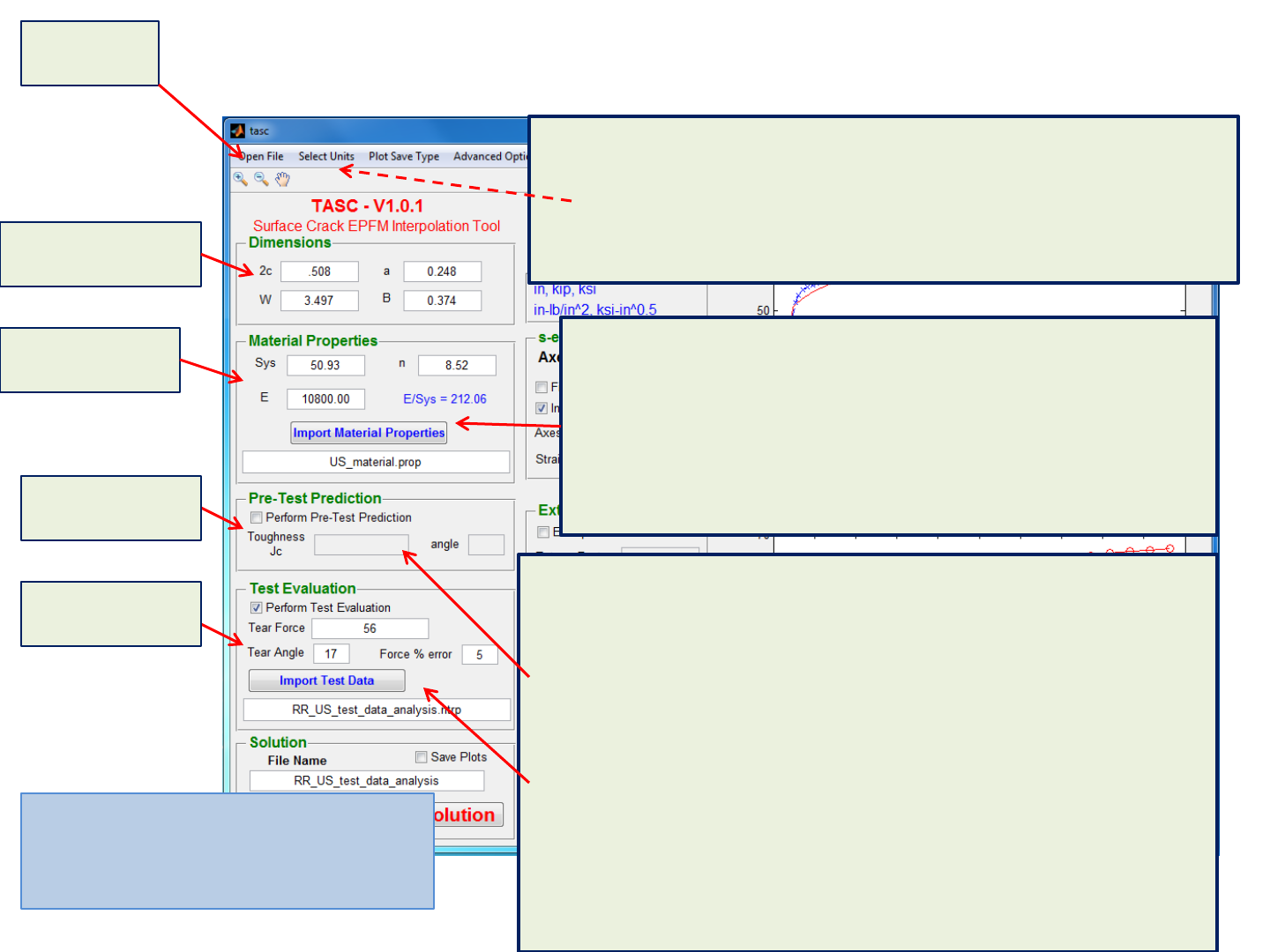
Get started and perform analysis
A. Input plate and
crack dimensions
B. Input Material
Properties
There are three independent analysis options:
1) A elastic-plastic solution with no test data evaluation is performed by
filling in (A )& (B) and not marking (C) and (D) checkboxes. This gives you
esentially all the outputs you would get from running a nonlinear FEM.
2) Choose (C) checkbox and fill in estimations for the critical toughness, Jc,
and the critical crack front angle to get a pre-test prediction of the tearing
force, CMOD, and crack front conditions. This option is intended for pre-
test planning and design.
3) Choose (D) to perform a test analysis. Fill in the tearing force and tearing
crack front angle and import the force-CMOD test record. The code will
attempt to find the test tearing CMOD value corresponding to the tear
force that is input. If the analysis reaction force corresponding to the
tearing CMOD is within 5% of the test tearing force, the code will perform
several calculations and report out tearing analysis results for your test.
The % error allowed can be changed in the Force % error box.
Open input
(*ntrp) file
Two choices to begin analysis:
1) Open a *.ntrp file. Data boxes will be filled in and analysis performed based
on information given in *.ntrp file
2) First select units system, and then manually type in values in boxes (A) and
(B). Once the values are entered and no errors are found, the analysis will
be performed.
Material properties for box (B) can be imported using the “Import
material properties button.” The material properties file can contain:
1. Sys, n and E, or
2. the file can contain E and a stress vs. plastic strain table. If a table is
present, the code will set Sys as the average of the first 3 stress
values in the table and determine a “n” value by fitting the stress-
plastic strain curve. This provides starting approximations for Sys and
n that can then be adjusted as necessary by the user.
C. Pre-test
prediction inputs
D. Test evaluation
inputs
NOTE: Poisson's ratio,
n
, is not a required
material input. All of the solutions have a
fixed value of
n
= 0.30 from the interpolated
solutions data set.
7
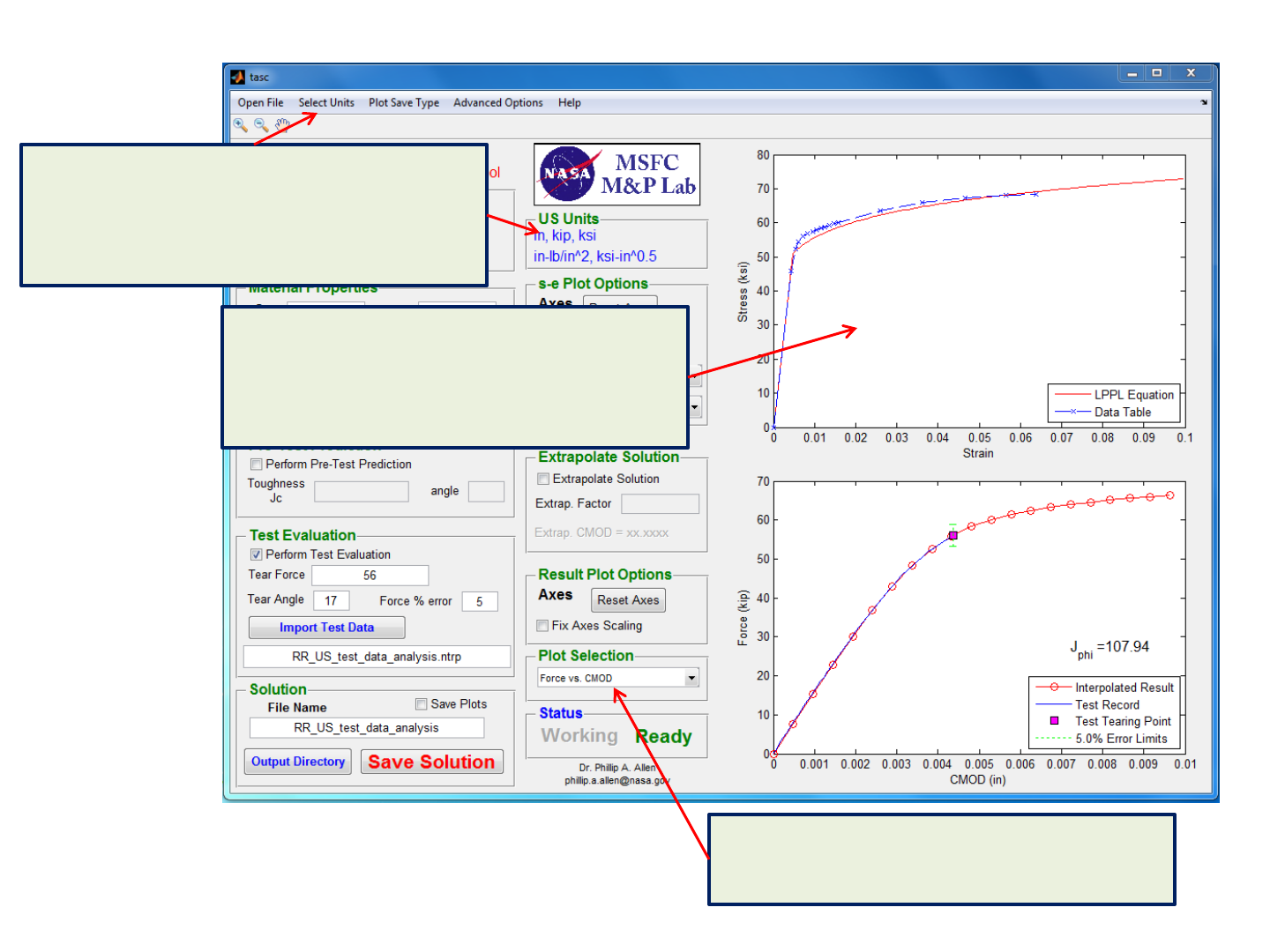
Explore results
The linear plus power law (LPPL) curve for the
analysis is shown in red. If stress-plastic strain data
is available, it is plotted in blue. Any change to
material properties updates the plots and reruns
the analysis.
One of 10 plots can be picked from this list. Any
change to the GUI values reruns the analysis and
updates the plots.
The code supports SI or US units. The units choice
is made through the “Select Units” menu or
specified in the *.ntrp file. The acceptable input
units for length, force, stress and the output units
for K and J are given in the Units graphic.
8
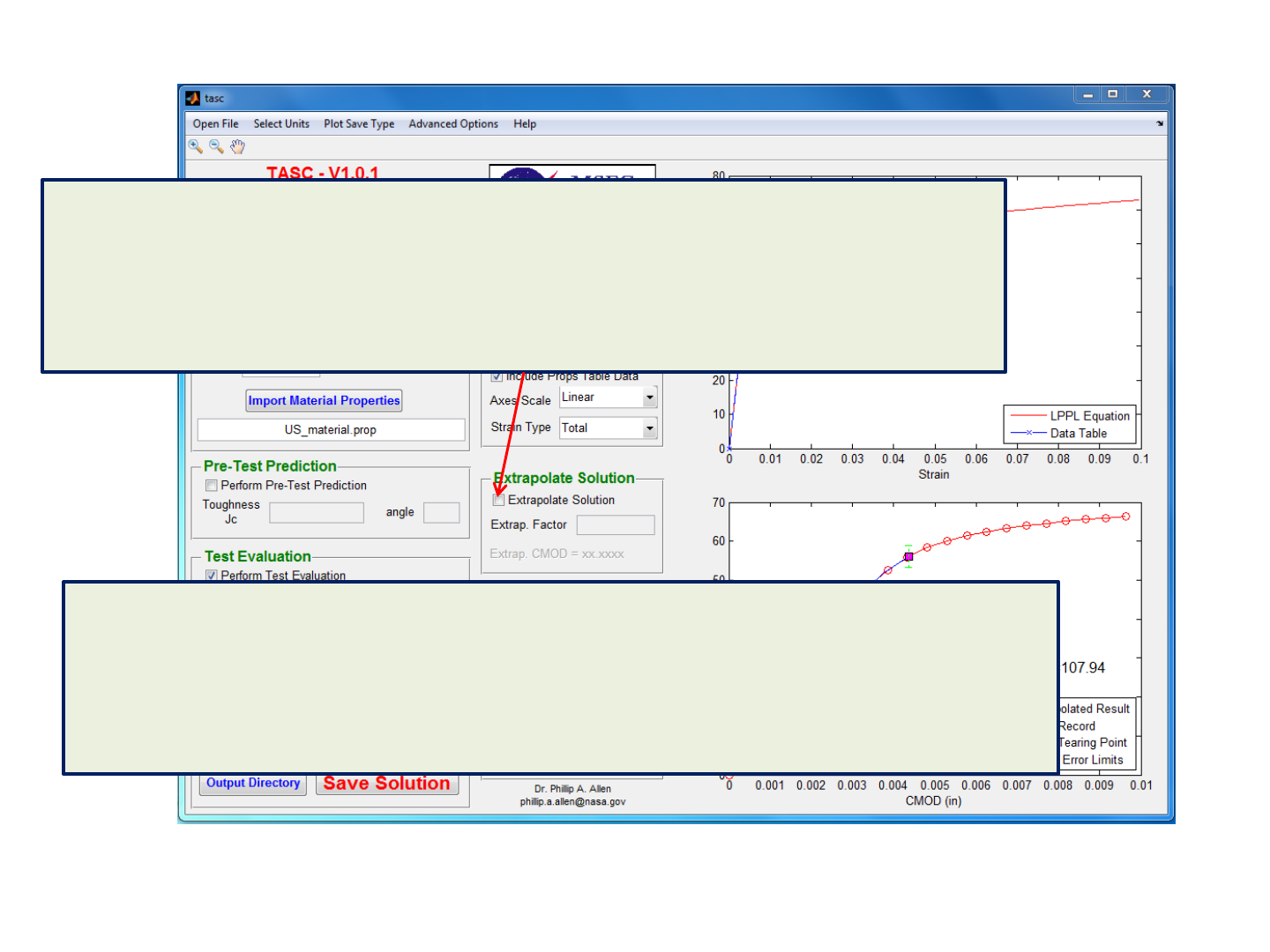
Extrapolate Solution Option
In some instances you may desire a solution at a higher J value or deformation level than what is available
from the last step of the interpolated analysis. The code allows you to extrapolate the solution based upon a
factor on CMOD. The “extrap. factor” is multiplied by the last CMOD value in the interpolated solution and
provides an estimated solution at the new extrapolated CMOD value . This new solution step is listed as
“step 21” in the analysis output. Permissible values for the extrap. factor are between 1 and 2. Please use
extra scrutiny when using the extrapolation option, because these estimated solutions are beyond the final
converged solution sets used in the interpolation routines.
9
When the “extrapolate solution” option is chosen, TASC estimates new J(
f
) values and
s
value corresponding to
the new extrapolated CMOD value. To estimate the J values, the J-CMOD trajectory for each
f
location is linearly
extrapolated to the new extrapolated CMOD value. This should provide a good estimate of the J-values because
the J vs. CMOD response is essentially linear in the elastic-plastic regime. To estimate the
s
(or P) corresponding
to the extrapolated CMOD, TASC fits a power law of the form
s
=
a
(CMOD)
b
+
g
to the last 5
s
vs. CMOD data
points in the solution set and estimates the new
s
using the power law function. Therefore the extrapolated
s
value may not have the same level of accuracy as the extrapolated J values.
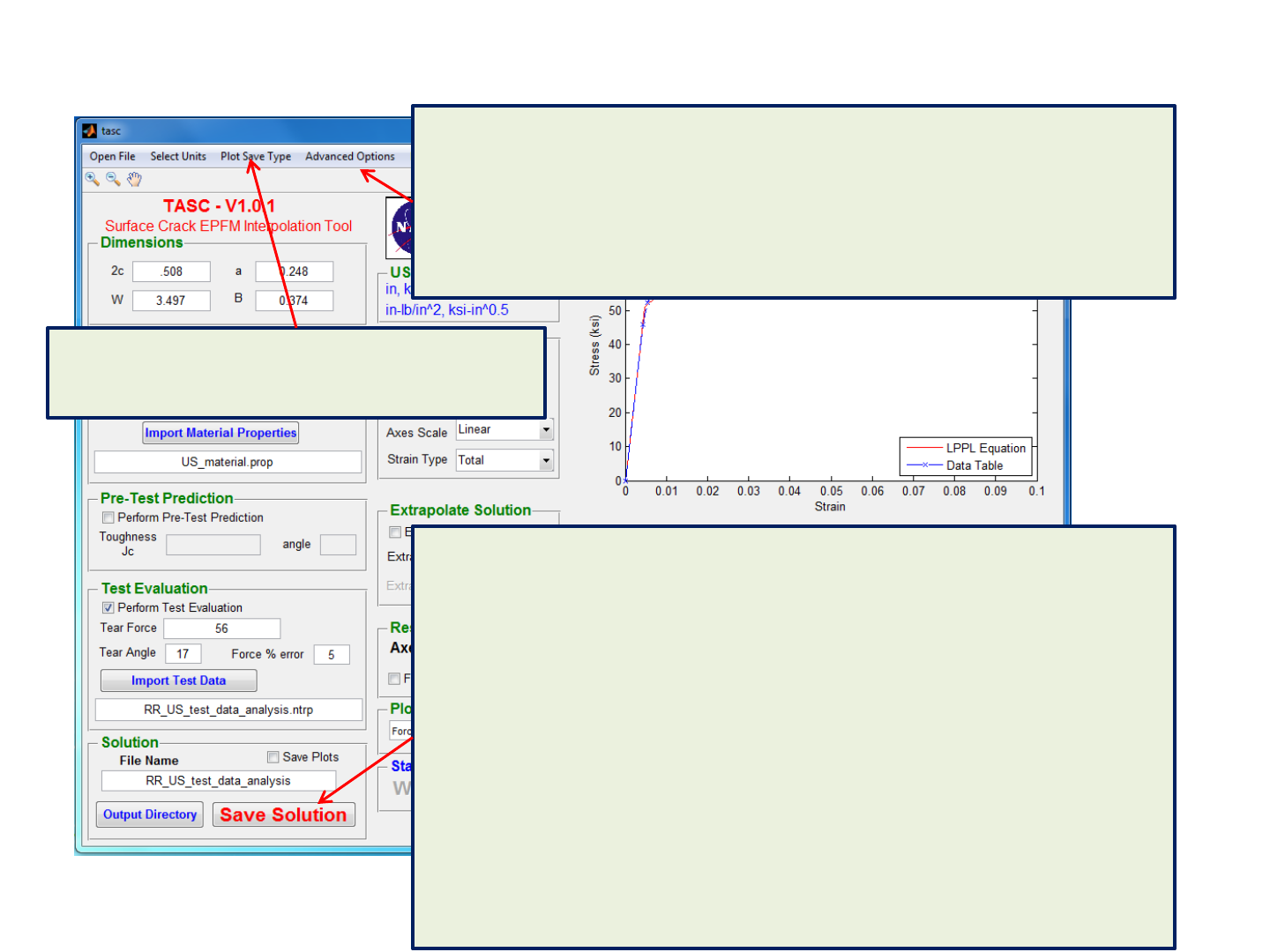
Save results
Once you are satisfied with the analysis, push the “save solution” button to save the
analysis values. The initial default save directory is the directory where the *.exe file
is installed. If you have loaded an *.ntrp file, the default save location is the same
directory as the *.ntrp file. You can change the save location by pushing the “output
directory” button. The file name defaults to a generic name or the name of the
*.ntrp file.
Pressing the “save solution” button creates a “Solution_Files” directory and stores 4
files : (1) an Excel file (Windows only) and (2) a *.txt file with identical summary
information, (3) a Matlab database *.mat file is also created for convenience for
Matlab users, and (4) a filename_inputs.ntrp file that is a new *.ntrp file capturing all
of your current solution inputs.
If “Save Plots” is checked, the code also creates a “Plot_Files” directory and saves
files for all of the plots in the analysis.
The filenames all have the solution filename as a prefix.
If you would like to see some details of the interpolated solution, you can choose
“Advanced Options – Interpolation Details.” The code will then make four sets of
subplots showing the a/c, a/B, n, and E/Sys interpolation process. The plots are
opened in separate windows. The plots are also saved as *.emf or *.tiff files in a
“Interp_Detail_plots” directory. The initial default location for the the
“Interp_Detail_plots” directory where the *.exe file is installed. If you have loaded an
*.ntrp file, the save location is the same directory as the *.ntrp file.
Plot save file type options are *.emf (Win. default),
*jpeg, or *.tiff (Mac default) based on selection in
“Plot Save Type” menu.
10
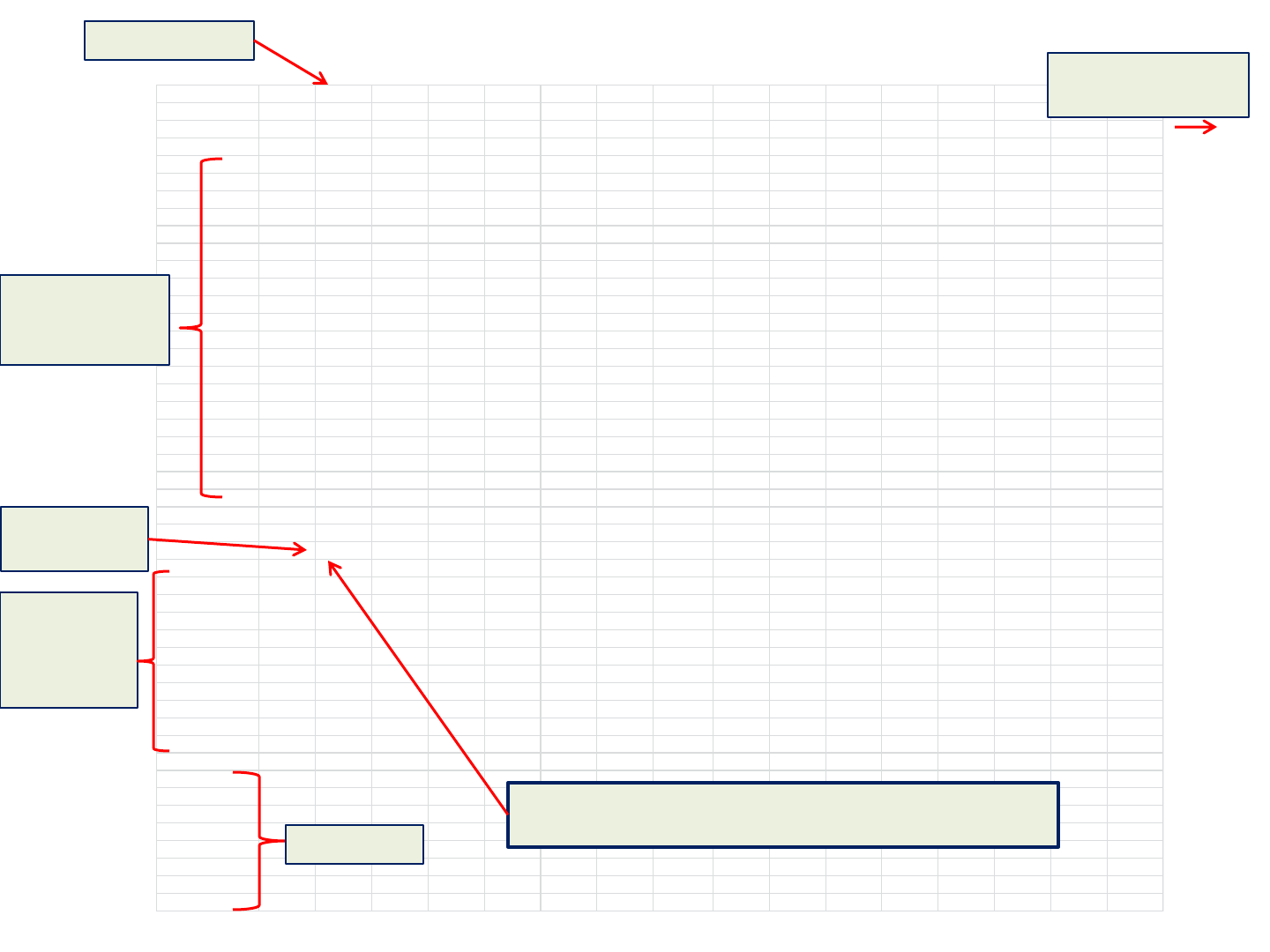
index a/B a/c n E/Sys W B Sys E a 2c
0.66_0.98_9_10800 0.66 0.98 8.52 212.1 3.497 0.374 50.93 10800 0.248 0.508
** ** phi 0246810 12 14 16 18 20 22 24 26
step stress CMOD J0 J2 J4 J6 J8 J10 J12 J14 J16 J18 J20 J22 J24 J26
1 5.85E+00 4.81E-04 1.70E+00 1.72E+00 1.73E+00 1.68E+00 1.64E+00 1.59E+00 1.55E+00 1.52E+00 1.49E+00 1.46E+00 1.43E+00 1.41E+00 1.39E+00 1.37E+00
2 1.17E+01 9.63E-04 6.33E+00 6.59E+00 6.79E+00 6.62E+00 6.44E+00 6.27E+00 6.11E+00 5.98E+00 5.85E+00 5.74E+00 5.63E+00 5.53E+00 5.45E+00 5.37E+00
3 1.74E+01 1.44E-03 1.30E+01 1.41E+01 1.50E+01 1.48E+01 1.45E+01 1.41E+01 1.38E+01 1.35E+01 1.32E+01 1.29E+01 1.27E+01 1.24E+01 1.22E+01 1.21E+01
4 2.29E+01 1.93E-03 2.11E+01 2.35E+01 2.56E+01 2.57E+01 2.56E+01 2.51E+01 2.45E+01 2.40E+01 2.35E+01 2.31E+01 2.26E+01 2.22E+01 2.19E+01 2.15E+01
5 2.82E+01 2.41E-03 3.01E+01 3.42E+01 3.78E+01 3.86E+01 3.91E+01 3.86E+01 3.80E+01 3.73E+01 3.67E+01 3.60E+01 3.54E+01 3.48E+01 3.42E+01 3.37E+01
6 3.29E+01 2.89E-03 3.98E+01 4.57E+01 5.12E+01 5.29E+01 5.42E+01 5.40E+01 5.36E+01 5.29E+01 5.21E+01 5.13E+01 5.06E+01 4.98E+01 4.91E+01 4.84E+01
7 3.69E+01 3.37E-03 5.00E+01 5.79E+01 6.52E+01 6.82E+01 7.04E+01 7.07E+01 7.06E+01 7.00E+01 6.93E+01 6.84E+01 6.76E+01 6.67E+01 6.59E+01 6.51E+01
8 4.02E+01 3.85E-03 6.05E+01 7.05E+01 7.97E+01 8.40E+01 8.73E+01 8.82E+01 8.85E+01 8.81E+01 8.75E+01 8.68E+01 8.59E+01 8.49E+01 8.40E+01 8.31E+01
9 4.28E+01 4.33E-03 7.13E+01 8.34E+01 9.46E+01 1.00E+02 1.05E+02 1.06E+02 1.07E+02 1.07E+02 1.07E+02 1.06E+02 1.05E+02 1.04E+02 1.03E+02 1.02E+02
10 4.46E+01 4.81E-03 8.22E+01 9.64E+01 1.10E+02 1.16E+02 1.22E+02 1.24E+02 1.26E+02 1.26E+02 1.26E+02 1.26E+02 1.25E+02 1.24E+02 1.23E+02 1.22E+02
11 4.60E+01 5.30E-03 9.30E+01 1.09E+02 1.25E+02 1.33E+02 1.40E+02 1.43E+02 1.45E+02 1.45E+02 1.46E+02 1.45E+02 1.45E+02 1.44E+02 1.43E+02 1.42E+02
12 4.70E+01 5.78E-03 1.04E+02 1.22E+02 1.40E+02 1.49E+02 1.57E+02 1.61E+02 1.64E+02 1.65E+02 1.65E+02 1.65E+02 1.65E+02 1.64E+02 1.63E+02 1.62E+02
13 4.78E+01 6.26E-03 1.14E+02 1.35E+02 1.55E+02 1.65E+02 1.74E+02 1.79E+02 1.82E+02 1.84E+02 1.85E+02 1.85E+02 1.85E+02 1.84E+02 1.83E+02 1.82E+02
14 4.84E+01 6.74E-03 1.24E+02 1.48E+02 1.70E+02 1.82E+02 1.92E+02 1.97E+02 2.01E+02 2.03E+02 2.04E+02 2.05E+02 2.05E+02 2.04E+02 2.03E+02 2.02E+02
15 4.90E+01 7.22E-03 1.35E+02 1.61E+02 1.85E+02 1.98E+02 2.09E+02 2.15E+02 2.20E+02 2.22E+02 2.24E+02 2.24E+02 2.24E+02 2.24E+02 2.23E+02 2.22E+02
16 4.94E+01 7.70E-03 1.45E+02 1.73E+02 2.00E+02 2.14E+02 2.27E+02 2.33E+02 2.39E+02 2.41E+02 2.43E+02 2.44E+02 2.44E+02 2.44E+02 2.43E+02 2.42E+02
17 4.98E+01 8.18E-03 1.55E+02 1.86E+02 2.15E+02 2.31E+02 2.44E+02 2.51E+02 2.57E+02 2.61E+02 2.63E+02 2.64E+02 2.64E+02 2.64E+02 2.63E+02 2.63E+02
18 5.01E+01 8.67E-03 1.65E+02 1.98E+02 2.30E+02 2.47E+02 2.62E+02 2.70E+02 2.76E+02 2.80E+02 2.82E+02 2.84E+02 2.84E+02 2.84E+02 2.83E+02 2.83E+02
19 5.05E+01 9.15E-03 1.75E+02 2.11E+02 2.44E+02 2.63E+02 2.79E+02 2.88E+02 2.95E+02 2.99E+02 3.02E+02 3.04E+02 3.04E+02 3.04E+02 3.04E+02 3.03E+02
20 5.07E+01 9.63E-03 1.84E+02 2.23E+02 2.59E+02 2.79E+02 2.97E+02 3.06E+02 3.14E+02 3.18E+02 3.22E+02 3.23E+02 3.24E+02 3.24E+02 3.24E+02 3.23E+02
end
** ** phi 0246810 12 14 16 18 20 22 24 26
T/Sigma -7.32E-01 -7.32E-01 -7.32E-01 -7.32E-01 -6.73E-01 -6.36E-01 -6.14E-01 -6.02E-01 -5.93E-01 -5.84E-01 -5.76E-01 -5.69E-01 -5.64E-01 -5.59E-01
Tearing Point Summary Values ** ** **
J_tear 7.21E+01 8.43E+01 9.56E+01 1.01E+02 1.06E+02 1.07E+02 1.08E+02 1.08E+02 1.08E+02 1.07E+02 1.06E+02 1.05E+02 1.05E+02 1.04E+02
T/Sys -6.16E-01 -6.16E-01 -6.16E-01 -6.16E-01 -5.67E-01 -5.36E-01 -5.17E-01 -5.07E-01 -4.99E-01 -4.92E-01 -4.85E-01 -4.80E-01 -4.75E-01 -4.71E-01
K_Jel 3.29E+01 3.30E+01 3.30E+01 3.26E+01 3.22E+01 3.17E+01 3.13E+01 3.10E+01 3.07E+01 3.04E+01 3.01E+01 2.98E+01 2.96E+01 2.94E+01
K_Jtotal 2.92E+01 3.16E+01 3.37E+01 3.47E+01 3.54E+01 3.57E+01 3.59E+01 3.59E+01 3.58E+01 3.57E+01 3.55E+01 3.54E+01 3.52E+01 3.51E+01
Tearing Point Values At Tearing Phi Location
Stress Force CMOD Phi J T/Sys K_Jel K_Jtotal Sigma/Sys Ma Mb r_phi_a r_phi_b
4.29E+01 5.61E+01 4.37E-03 17 1.08E+02 -4.99E-01 3.07E+01 3.58E+01 0.84 114.46 511.78 0.243 1.085
end_summary
US Units
length (in)
Force (kip)
Stress (ksi)
J (in-lb/in^{2})
K (ksi-in^{0.5})
Phi (deg)
end_units
Output file
Continues every 2
degrees to phi = 90
Values per load
step and phi
location
Summary of
tearing point
values if
available
Output Units
Input Summary
Normalized T-
Stress = T/
s
11
Note: The normalized elastic T-stress values are interpolated
from the T-stress tables in Annex A2 of ASTM E2899
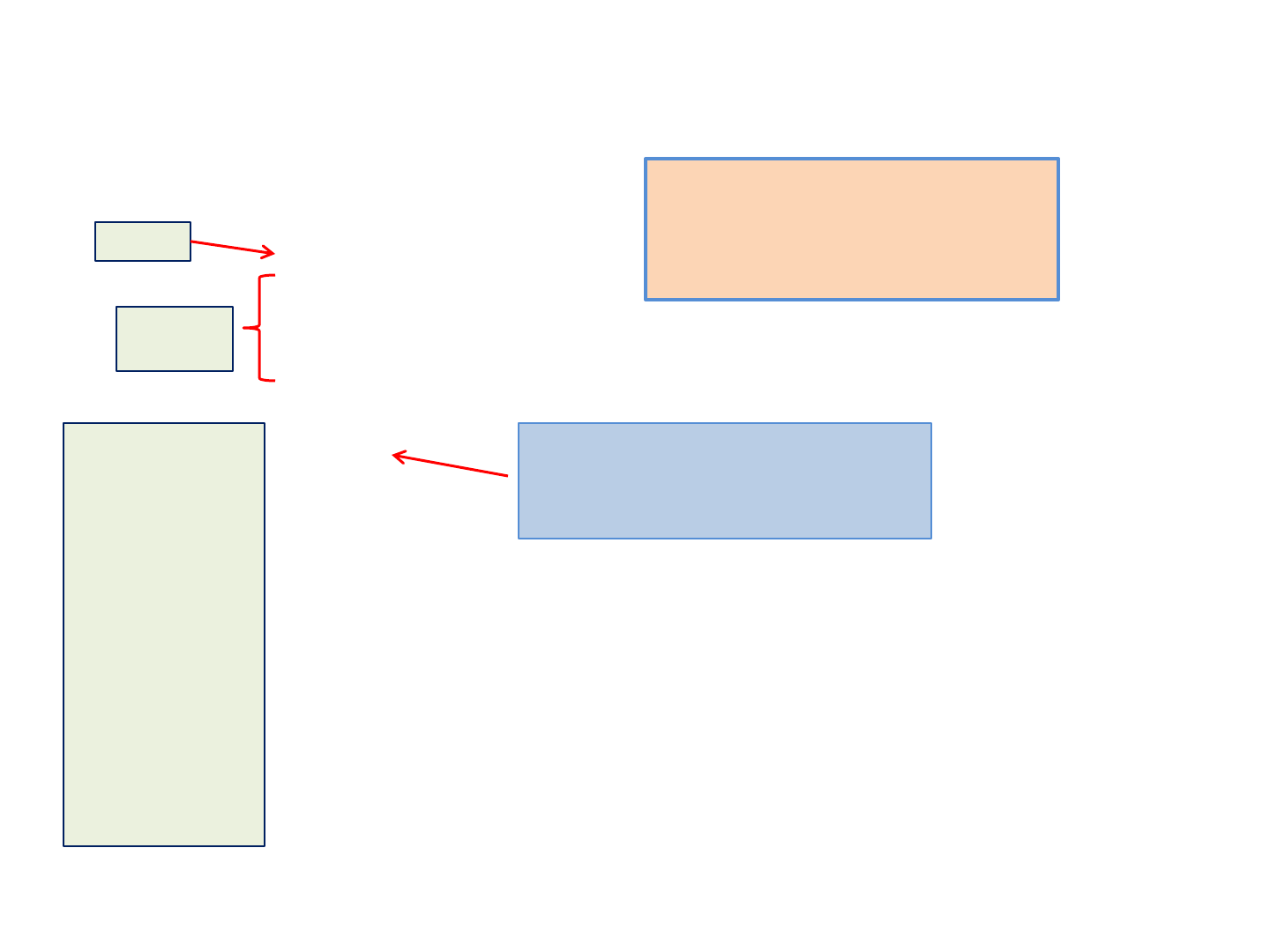
Analysis only *.ntrp (“interp”) file
Geometry
Values
Units
Material properties
E
stress, plastic strain
.
.
.
.
.
.
.
.
.
.
.
end
%-----Interpolation Analysis Input File-----%
%words proceeded with * are keywords for the
%text scanning program
%---Set Units----% (options are SI or US)
*units SI
%---Geometry Values----%
*2c 12.70
*a 6.17
*W 88.82
*B 9.5
%
%---Material Properties----%
*material
*E 74.460e3
*stress pl_strain
317.02,0
361.08,0.00055
375.35,0.00105
385.97,0.00203
391.83,0.00309
396.17,0.00422
399.55,0.0052
402.86,0.00618
405.07,0.00703
408.51,0.00813
411.41,0.00928
414.31,0.01022
437.40,0.02013
454.36,0.03003
464.84,0.04042
469.81,0.05014
472.22,0.05743
*end_material
NOTE: Poisson's ratio,
n
, is not a required
material input. All of the solutions have a
fixed value of
n
= 0.30 from the interpolated
solutions data set.
NOTE: The *keywords are strings that are
searched for in the code and must appear as
shown in this example. The numeric values
next to or below the keywords are changed
to create new analysis input files.
12
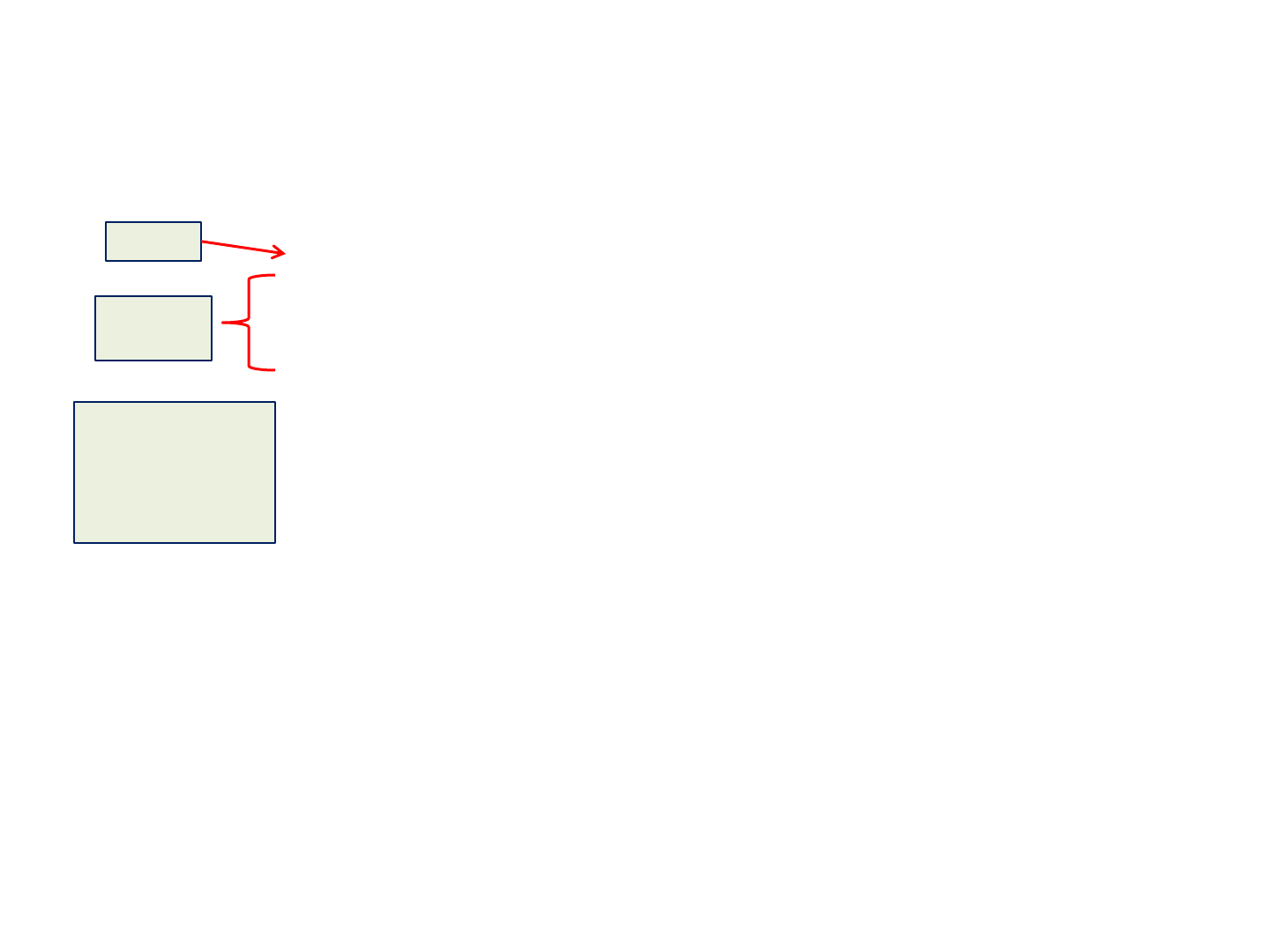
Analysis only *.ntrp file with simple
material definition
Geometry
Values
Units
Material properties
E
Yield Stress
n (hardening)
end
%-----Interpolation Analysis Input File-----%
%words proceeded with * are keywords for the
%text scanning program
%---Set Units----% (options are SI or US)
*units SI
%---Geometry Values----%
*2c 12.70
*a 6.17
*W 88.82
*B 9.5
%
%---Material Properties----%
*material
*E 74.460e3
*Sys 351.6
*n 8.5
*end_material
13
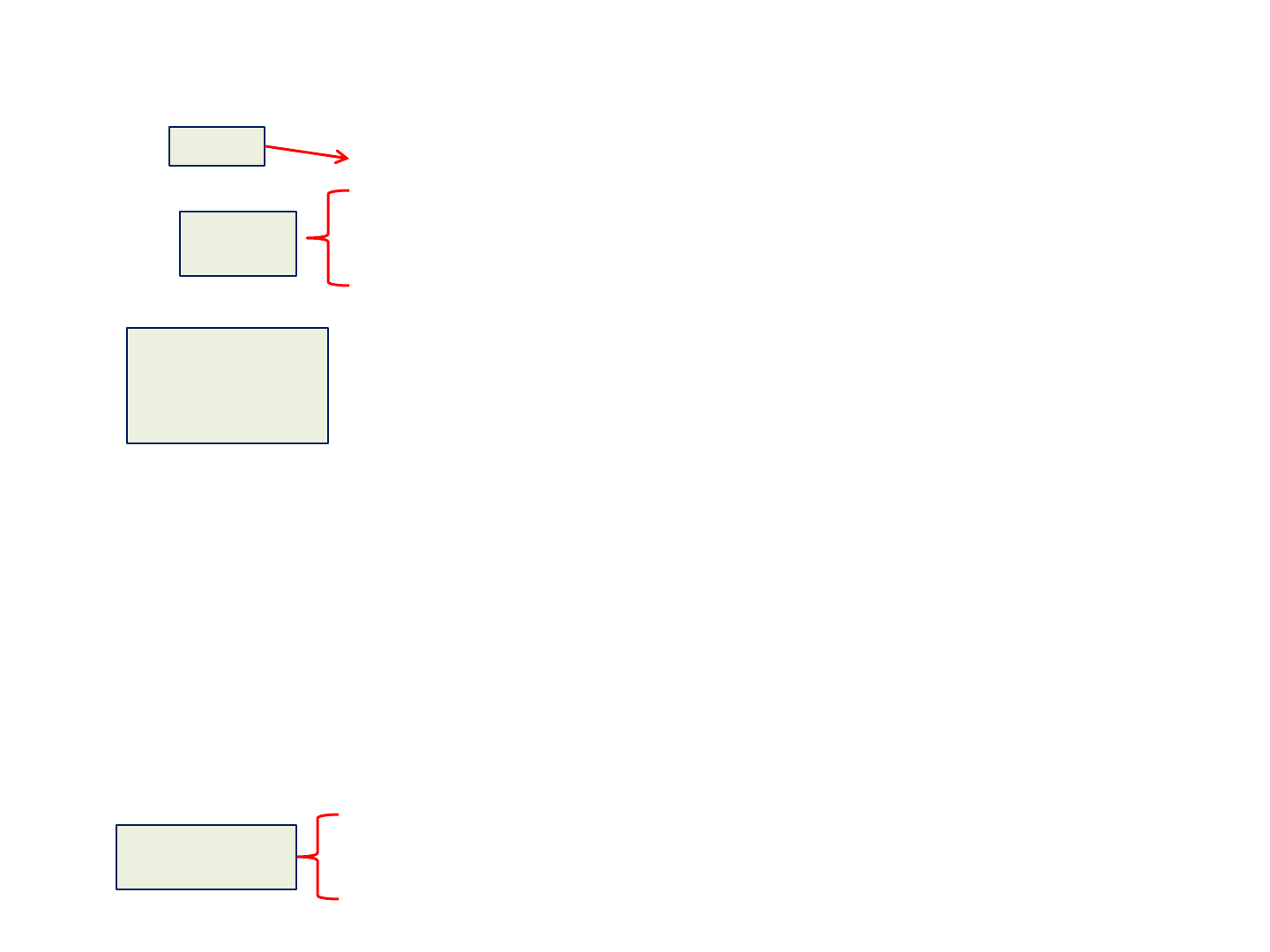
Pre-Test prediction *.ntrp
Geometry
Values
Units
Critical Toughness
Critical angle
Material properties
Can be entered in
table or short
format
%-----Interpolation Analysis Input File-----%
%words proceeded with * are keywords for the
%text scanning program
%---Set Units----% (options are SI or US)
*units SI
%---Geometry Values----%
*2c 12.70
*a 6.17
*W 88.82
*B 9.5
%
%---Material Properties----%
*material
*E 74.460e3
*stress pl_strain
317.02,0
361.08,0.00055
375.35,0.00105
385.97,0.00203
391.83,0.00309
396.17,0.00422
399.55,0.0052
402.86,0.00618
405.07,0.00703
408.51,0.00813
411.41,0.00928
414.31,0.01022
437.40,0.02013
454.36,0.03003
464.84,0.04042
469.81,0.05014
472.22,0.05743
*end_material
%
%
%---Pre-test Prediction Values----%
*pretest
*Jc 21.0
*phi_crit 17
14
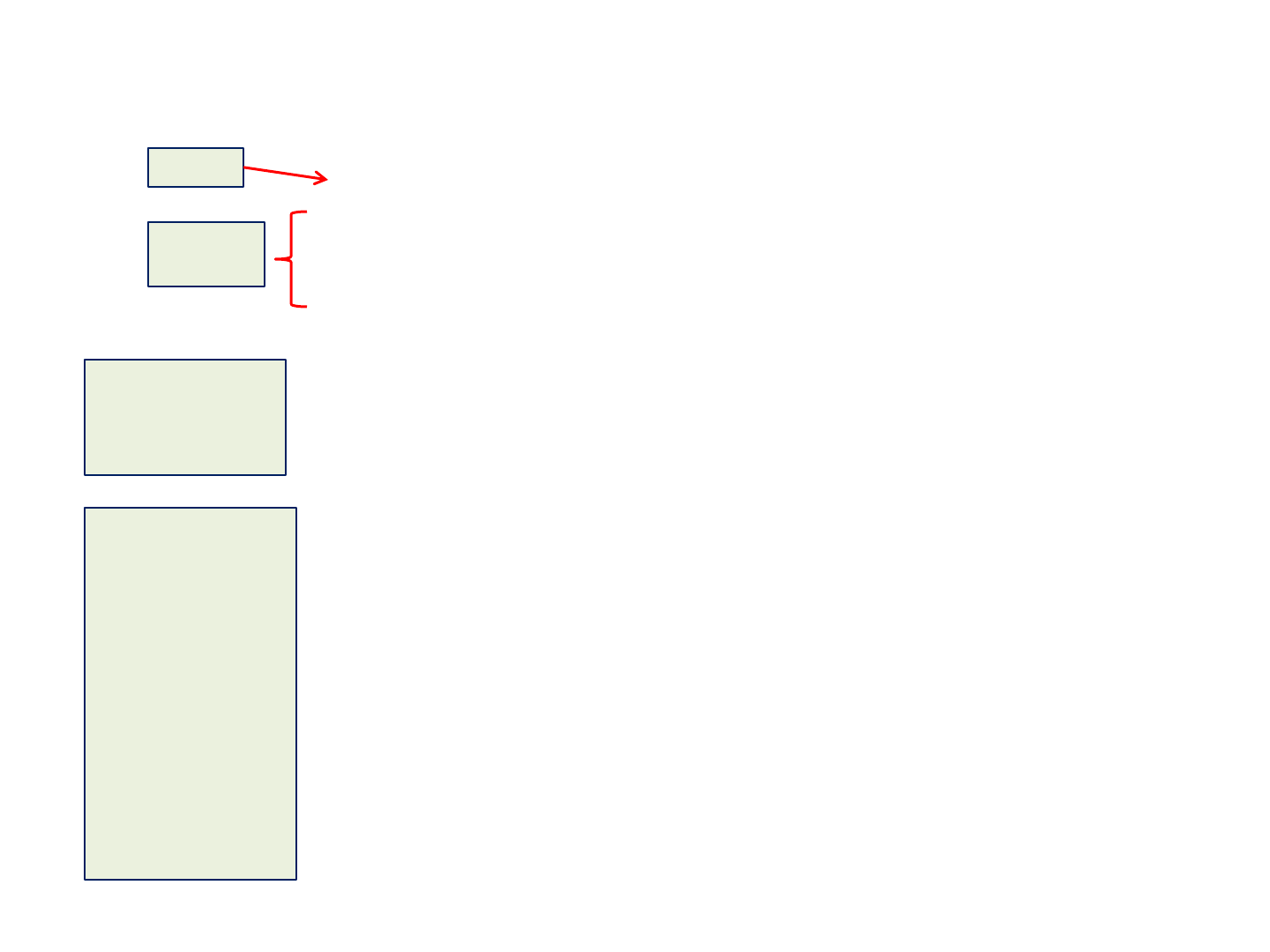
%-----Interpolation Analysis Input File-----%
%words proceeded with * are keywords for the
%text scanning program
%---Set Units----% (options are SI or US)
*units SI
%---Geometry Values----%
*2c 12.70
*a 6.17
*W 88.82
*B 9.5
%
%---Material Properties----%
*material
*E 74.460e3
*Sys 351.6
*n 8.5
*end_material
%
%---Test Evaluation----%
*test_eval
*tear_force 251.8
*tear_phi 17
*CMOD Force
0.0000,0.095
0.0000,0.149
0.0005,1.195
0.0013,3.638
0.0023,6.788
0.0036,10.616
0.0048,14.756
0.0064,19.195
.
.
.
0.1123,250.593
0.1135,251.814
*end_test_data
Test Analysis *.ntrp file
Geometry
Values
Units
Material properties
Can be entered in
table or short
format
Test Tearing force
Tearing angle
CMOD, Force Table
.
.
.
.
.
.
.
.
.
End_test_data
15
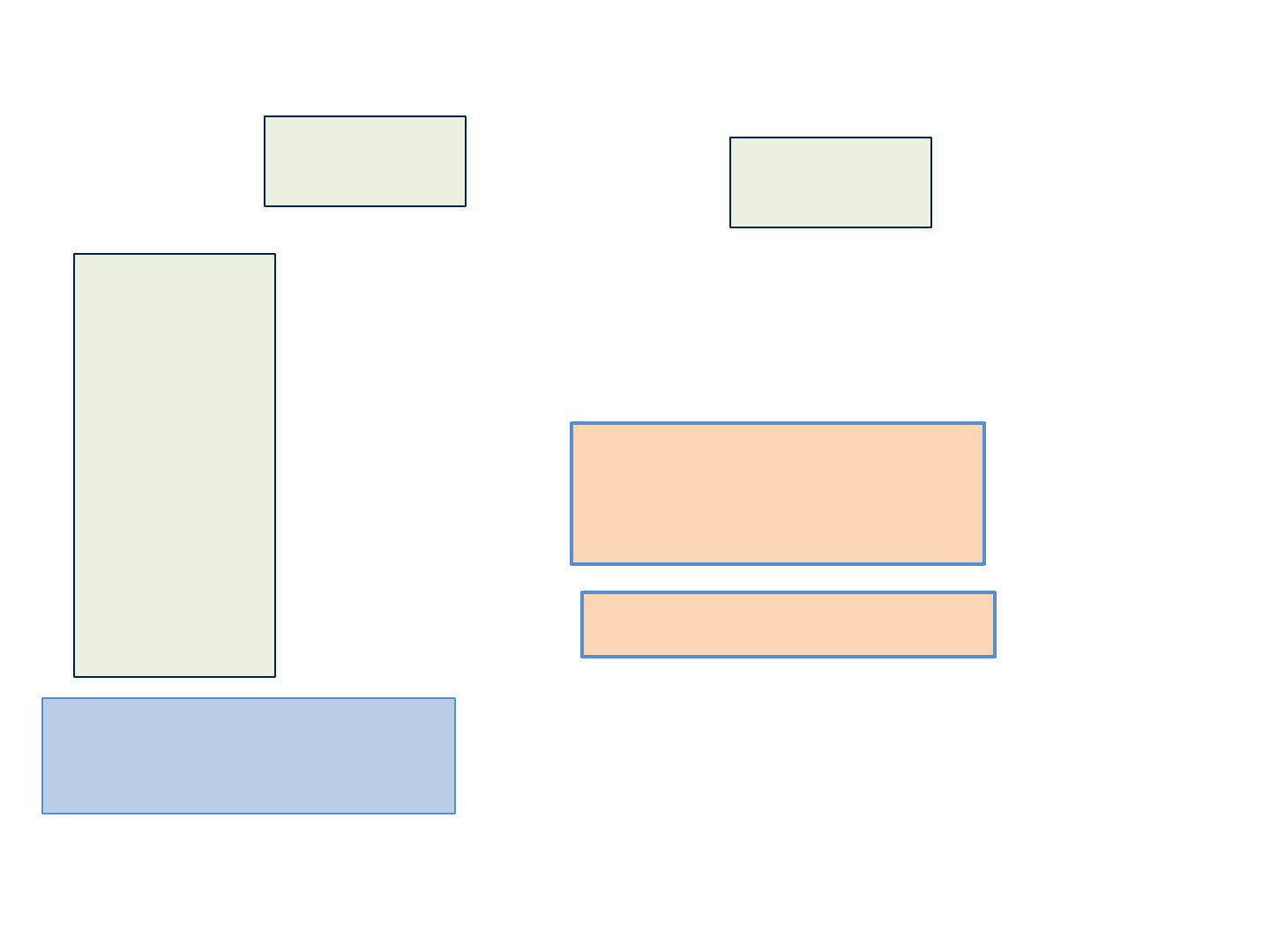
%---Material Properties----%
*material
*E 10.8e3
*stress pl_strain
45.98,0.00000
52.37,0.00055
54.44,0.00105
55.98,0.00203
56.83,0.00309
57.46,0.00422
57.95,0.00520
58.43,0.00618
58.75,0.00703
59.25,0.00813
59.67,0.00928
60.09,0.01022
63.44,0.02013
65.90,0.03003
67.42,0.04042
68.14,0.05014
68.49,0.05743
*end_material
Example material property *.prop files –
Use with the “Import Material Properties Button”
Material properties
E
stress, plastic strain
.
.
.
.
.
.
.
.
.
.
.
end
NOTE: Poisson's ratio,
n
, is not a required
material input. All of the solutions have a
fixed value of
n
= 0.30 from the interpolated
solutions data set.
NOTE: The *keywords are strings that are
searched for in the code and must appear as
shown in this example. The numeric values
next to or below the keywords are changed
to create new analysis input files.
%---Material Properties----%
*material
*E 10.8e3
*Sys 51.0
*n 8.5
*end_material
File containing
stress-plastic_strain
table
Short format file
with no stress-
plastic_strain table
Stress – plastic strain data can be tab, space,
or comma delimited
16
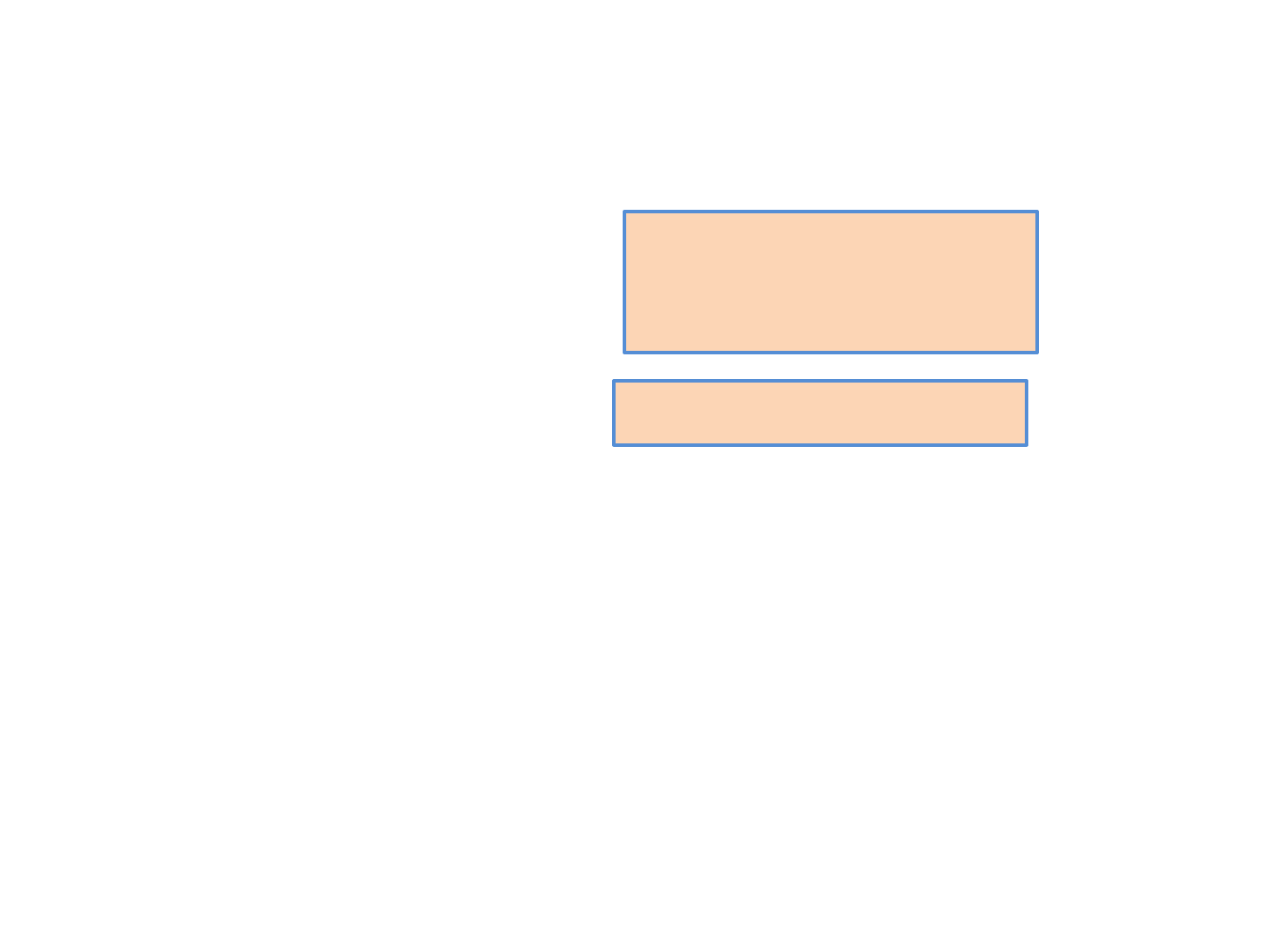
Example test data*.txt files –
Use with the “Import Test Data” button
NOTE: The *keywords are strings that are
searched for in the code and must appear as
shown in this example. The numeric values
next to or below the keywords are changed
to create new analysis input files.
%Unlimited header lines at top
%ensure that "*CMOD" keyword precedes the data
%and "*end_test_data" is at the end of the data
%Example test data in US units
%
*CMOD Force
0 0.0214
0 0.0336
0.00002 0.2686
0.00005 0.8179
0.00009 1.5259
0.00014 2.3865
0.00019 3.3173
0.00025 4.3152
.
.
.
0.00406 54.0283
0.00424 55.2063
0.00442 56.3355
0.00447 56.6101
*end_test_data
CMOD and force data can be tab, space, or
comma delimited
17
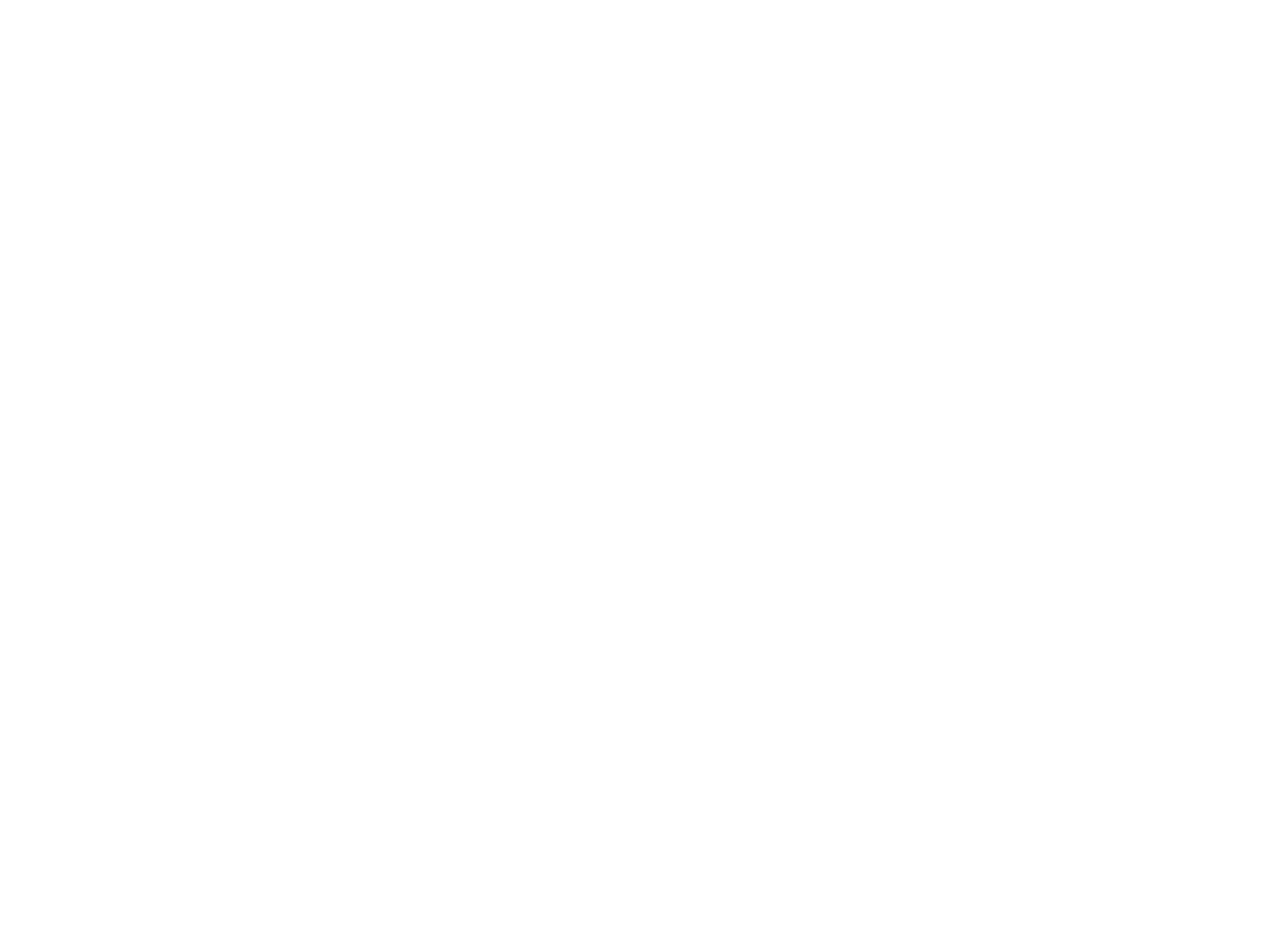
Source File Information
18
•If so desired, TASC can be run from the source files available from the NASA TASC Sourceforge project at
http://sourceforge.net/projects/tascnasa/. Running TASC from the source files requires a current Matlab license along with
a Matlab Curve Fitting Toolbox license and a Matlab Image Processing Toolbox License.
•Type ‘”tasc” from the Matlab command prompt to start TASC.
•The first time you run TASC, a start up window will appear stating “I have read and accept the terms of the NASA Open
Source Agreement included in the TASC distribution package.” You must select “Yes” to run TASC. Selecting “Yes” creates a
small text file, TASC_lic.txt” in your executable directory. You will not be asked to accept the agreement again unless you
move or copy the executable file to another directory.
•The interpolation routines rely on the interpolated solutions database file, interp_solution_database.mat, located in the
source file directory. The *.mat database is a 4-D Matlab structure. The solution database is arranged in a result(I,J,K,L).fea
structure where the result indices are result(a/B, a/c, n ,E/
s
ys). Details of the solution space, interpolation methods, and
nomenclature are documented in NASA/TP-2013-217480, Elastic-Plastic J-Integral Solutions for Surface Cracks in Tension
Using an Interpolation Methodology, which is available for download from the NASA Center for Aerospace Information (CASI)
at <http://www.sti.nasa.gov>.