TIW Reprint For Pdf
User Manual: TIW
Open the PDF directly: View PDF .
Page Count: 4
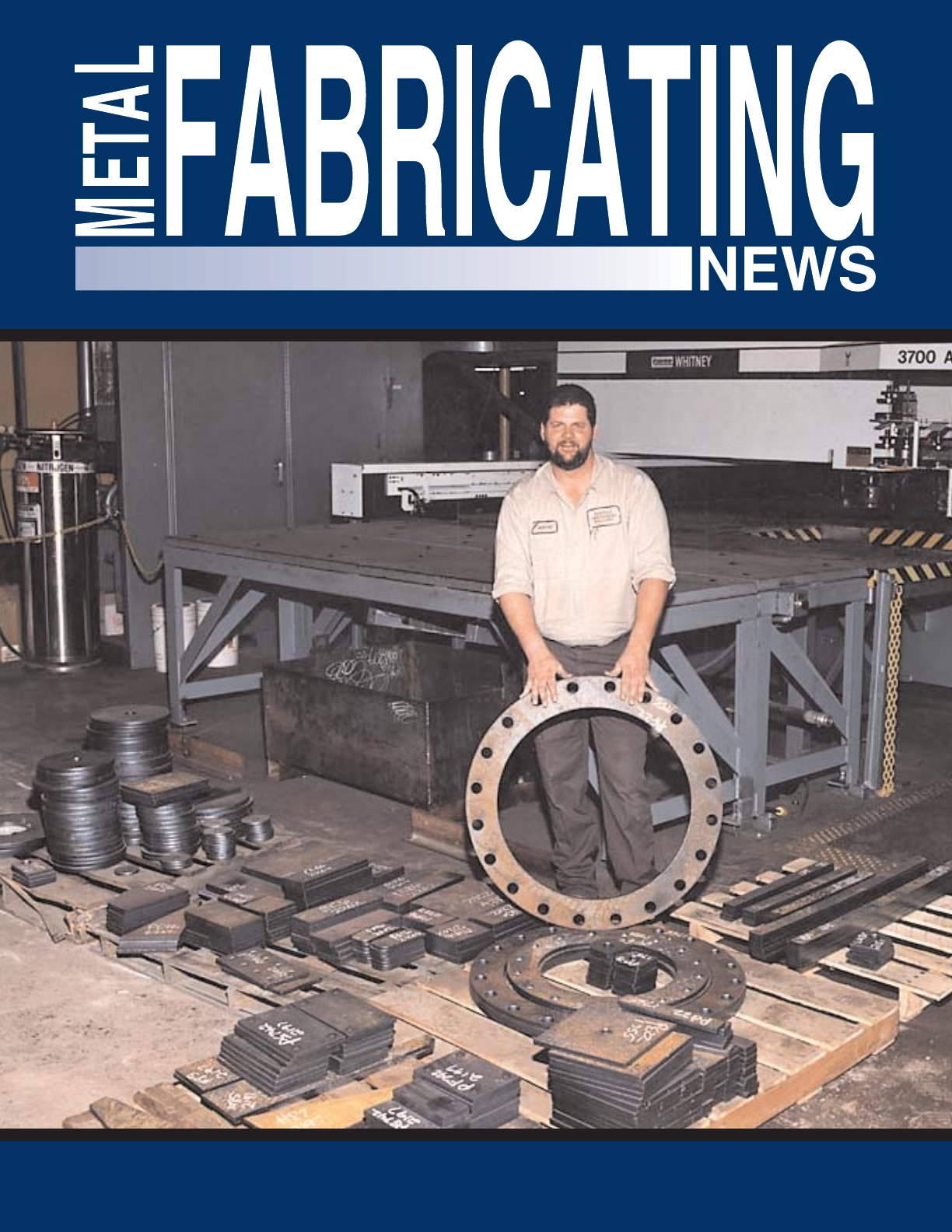
Textile Industrial
Welding, Inc.
Applies 25 Years
Of Experience To
Large Fabrication
Specials
Textile Industrial
Welding, Inc.
Applies 25 Years
Of Experience To
Large Fabrication
Specials
3700 ATC Operator Wayne Tyler supports a typical part fabricated on the Whitney. Wayne enjoys the addition
to T.I.W., “If they start running it twenty-four hours a day—that’ll be me twenty-four hours a day.”
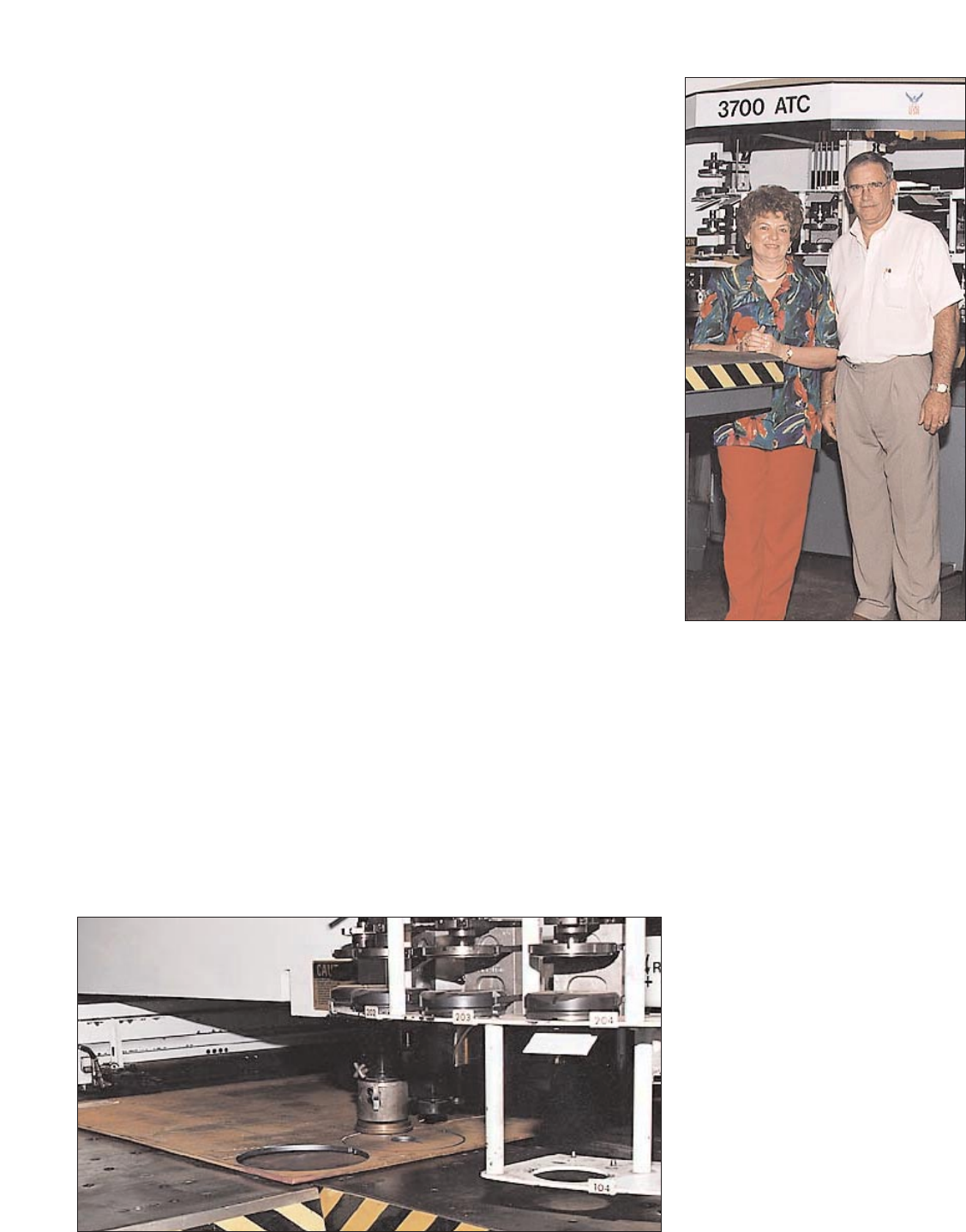
The shipping yard of Textile Indus-
trial Welding in Dalton, Georgia,
never looks the same. The prod-
ucts—always different—have two things in
common. They are constructed of metal
fabrications and they are very LARGE.
What started out 25 years ago as a com-
pany dedicated to producing carpet dyeing
and finishing equipment now builds for a
broad mix of industries. Finished pieces
being prepared for shipment from T.I.W.
might include water and air purification
equipment, non-pressure tanks for the
chemical and glue industries, material han-
dling systems, asphalt recycling equipment,
or food industry machines to extract oil
from soybeans, coat candy, or help brew
one of America’s most popular thirst
quenching beverages.
James (Jimmy) W. McMullen, founded
T.I.W. in 1971, building on experience
gained by constructing dye vats for Master-
piece Finishing Co. which still thrives
today in Dalton, Georgia.
25 Years of Growth
T.I.W.’s first employee was Jimmy’s
brother-in-law Reed Gee, who serves as
one of the top lead men today. The second
was his wife, JoAnn, who functions as the
company’s secretary and treasurer. A strong
employee base of 58, 16 in engineering and
the office and 42 in the shop, now serve
T.I.W.’s diverse customer base.
“We started in 1972 fabricating solely
for the carpet industry, but when construc-
tion declined, so did the carpet industry,”
says JoAnn. “We quickly learned that you
can’t put all your eggs in one basket.”
That kind of thinking has taken T.I.W.
into many industries that need large, cus-
tomized metal products. “All of our work
is custom order. We do not have stock. We
do not have inventory. There has to be a
special application on everything we
build. So it’s really quite challenging,”
says JoAnn.
T.I.W. has a full engineering department
to coordinate designs with their customers
and to handle programming for their exten-
sive collection of CNC machines.
Advanced Service and Equipment
To provide economical, quality service,
T.I.W. continually upgrades and adds to the
machines in their shop. A CNC burn table
cuts fabricated parts in a variety of shapes
and sizes from plate up to two inches thick.
The Aronson Manipulator with a Linde
Submergible Arc welding head is used for
automatic girth and longitudinal seams on
extremely long, large diameter vessels.
New, Better Methods
One of the newest additions in T.I.W.’s
66,000 square foot facility is a W.A. Whit-
ney 3700 ATC hydraulic punch/TRUE-
Cut™ Oxygen Plasma Cutting Combina-
tion Fabricating Center.
The 3700 ATC quickly joined the burn
table as one of the most productive ma-
chines in the shop.
“Before we had either machine, we
would use templates, patterns and track
burners. It took hours laying out the specs,
checking the dimensions, marking it with
chalk, laying out the templates, and form-
ing the track. Plus all the clean-up,” ex-
plains JoAnn who handles financing of
new equipment.
“Now with the 3700 ATC, program-
ming and cutting a part, you are talking
about a few minutes compared to hours of
layout time.”
The addition of the Whitney also helped
Bill Hicks, vice president of sales for the
company, find new markets for T.I.W. Bill
manages to coordinate sales nationally
and—quite often—internationally with
very little road time.
“The Whitney does different kinds of
work for us; we couldn’t do without it,”
says Jimmy McMullen. “I would say in
James W. McMullen, President, and
JoAnn McMullen, Secretary and
Treasurer, Textile Industrial Welding
Dross-free parts cut with the 3700 ATC’s TRUECut Oxygen Plasma Cutting
System reduced part clean-up. Ninety percent of the parts from the Whitney
go directly to welding, a press brake or other process.
Textile Industrial Welding, Inc.
Applies 25 Years of Experience
To Large Fabrication Specials
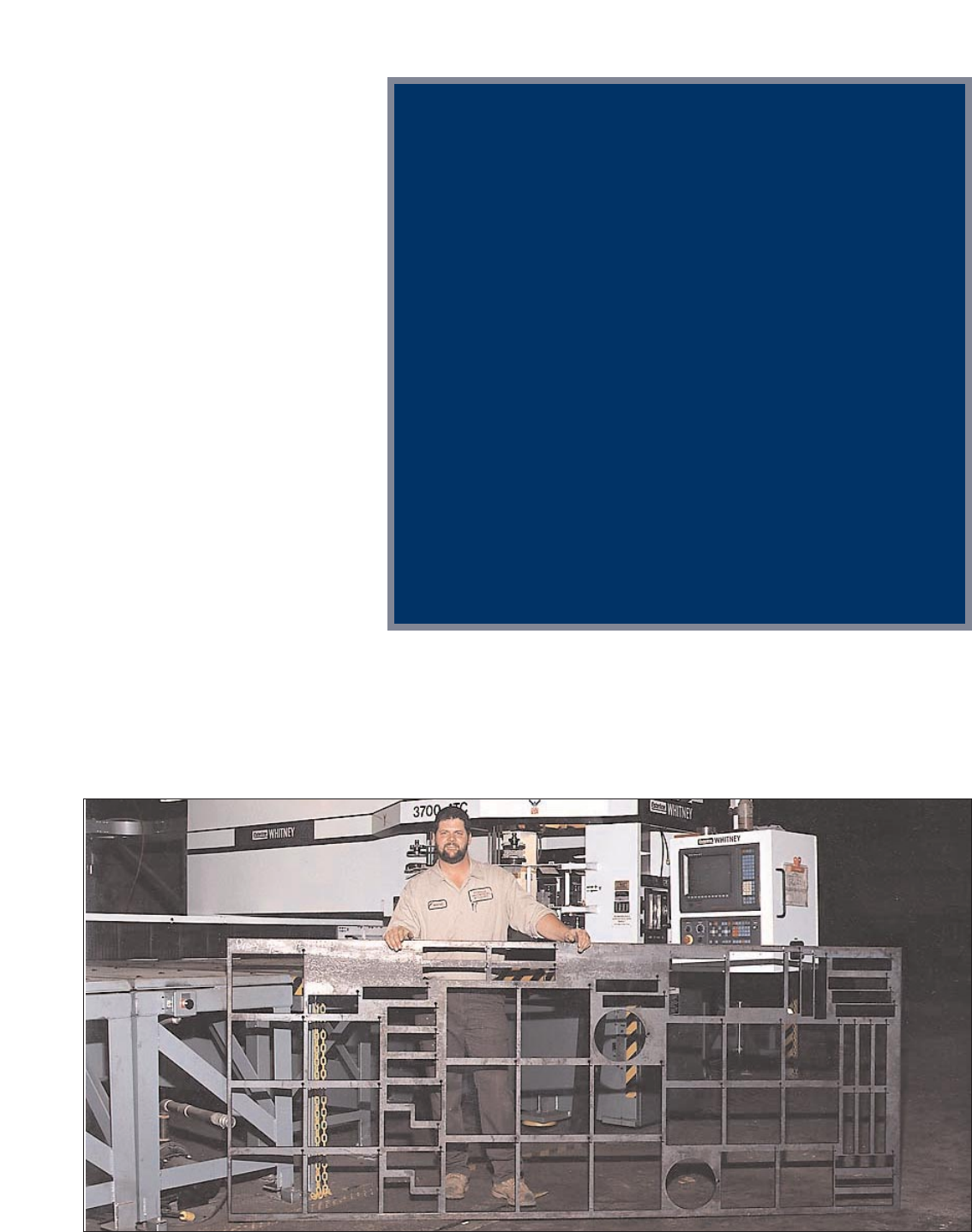
a year’s time it’s probably brought in
more than a million dollars worth of
extra work.”
T.I.W. products are found in countries in
the Middle East, China, Canada, South
America, and several countries in Europe.
The international business means that T.I.W.
is adept at working in both the English and
metric systems. “We don’t seek overseas
business, but some products go international
as an end result of our customers.”
T.I.W.’s Fabrication Process
The T.I.W. fabrication process begins when
raw materials are cut to length, sheared,
burned, rolled, bent, drilled or machined.
T.I.W.’s material tracking system identifies
where each part is at any time, regardless
of the complexity of the project.
Numerous cut parts and formed pieces
are assembled together to be welded,
ground, bolted, and further processed.
The combined punching and cutting of
the 3700 ATC contributes to T.I.W.
economies by eliminating a lot of the mater-
ial handling.
“The other machine may have cut the
part, but then that part had to be trans-
ferred to the machine department for
drilling or to another department for
punching. The material was being handled
twice and the clean-up was not as effi-
cient,” says JoAnn. “And you didn’t get as
clean a cut as on the Whitney.”
The plasma torch, still heavily used,
works well for many applications, but
isn’t fast enough in many cases. And parts
require more clean-up. There were also
some difficulties with removing smaller
parts from the bed.
On the Whitney, parts up to 18-inch by
24-inch are automatically removed through
the drop door.
Typical material thicknesses at
T.I.W. range from 16 gauge to 3⁄4inch,
and they are all punched and cut on the
Whitney. T.I.W. is very pleased with the
accuracy, ±.005 inch, and the dross-free
cut provided by the TRUECut oxygen
plasma system.
Wayne Tyler, T.I.W. 3700 ATC Operator, supports one of the skeletons showing the efficient plate utilization with the
nesting capabilities of Building Block software. Wayne attended training at the Rockford, IL facility to learn how to run
and maintain the machine.
What makes success?
JIMMY AND JOANNE MCMULLEN HAVE DEDICATED THEIR LIVES TO MAKING
Textile Industrial Welding a success. They credit two strong management
philosophies and a vision for the future:
First, a strong, dedicated employee base. Many of their employees have
put in ten or more years with the company, with several reaching eighteen
and twenty-five years.
“The number one thing that makes a company is its employees. If you have
good, skilled, honest, hardworking employees who worry about the quality
of the product, then you are going to produce a good product.”
Second, is their progressive stance on continually upgrading the technolo-
gies within their shop.
“You have to keep up to date. Have good machinery like the Whitney.
We started in 1994 and have really updated a lot of our equipment since
then. We bought the new press brake, plate rolls, the 3700 ATC, and we’re
buying an updated version of the plasma torch. That’s a lot of machinery
being replaced or updated.”
The future of the company is growth and family. The McMullen’s daughters
are both involved in the family business. Connie McMullen Hardin is the Office
Manager. Christa McMullen is a college student and works in the office part-time.
“They are the future of Textile Industrial Welding. And our next genera-
tion…our grandchildren!”
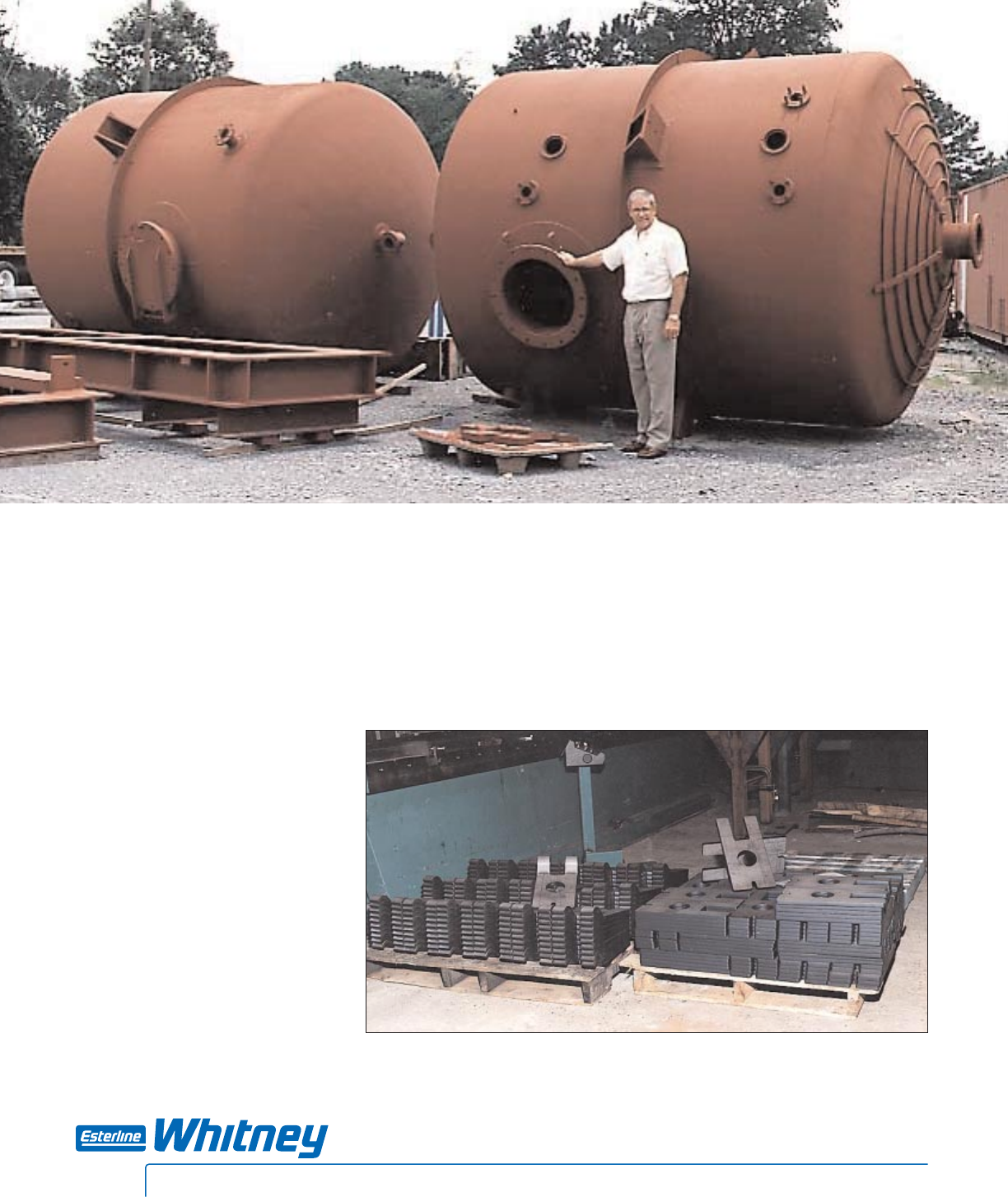
Report #111
Reprinted from Metal Fabricating News,
Jul.-Sep., 1997
“Most parts that come off the Whitney,
maybe 90 percent, go directly to the weld
station or press brake,” says Jimmy. No
clean-up is needed.
Economic Production
T.I.W. has seen a decrease in scrap since
installing the 3700 ATC. The nesting pro-
gram, supplied by Building Blocks, has
made a significant difference in material
utilization. Although T.I.W.’s scrap varies
quite a bit depending on current projects,
the software is flexible enough to provide
the most efficient use of stock on a consis-
tent basis.
“When we found out that there was a
machine like the Whitney, we were very in-
terested. We had looked at quite a few
lasers before we started looking at the
Whitney and we weren’t as impressed,”
Jimmy and JoAnn agree. “A salesman who
sells both lasers and Whitney’s came up to
see the work we were doing. He recom-
mended we look at the 3700 ATC. That’s
how it all got started.”
Most of the time T.I.W. is scheduling
work six to eight months out. A typical
week is one shift of 45 hours but they’ve
been running seventy to seventy-five
hours. “It would be much better if we had
two shifts but if you can’t find the person-
nel you can’t do that. Our guys are real
good in that they want to help out and are
willing to work the long hours. They are
dedicated people.”
The Next 25 Years
Looking to the future, Jimmy McMullen
says, “I look forward to the next twenty-
five years. Textile Industrial Welding plans
to continue to build the best product and to
give the very best in service. That has al-
ways been the company’s goal and will re-
main so in the future.” ◆
T.I.W. President Jimmy McMullen points out one of the several parts on the tank that was punched and cut on the 3700 ATC.
Parts shown are produced on the Whitney and go directly to the press brake
for forming.
W.A. Whitney Co.
AN ESTERLINE COMPANY
650 Race Street
P.O. Box 1206
Rockford, IL 61105, U.S.A.
Tel: 815-964-6771
Fax: 815-964-3175
www.wawhitney.com