Bananas Organic Cultivation Guide By Natand
bananas_organic_cultivation-guide_by_natand
User Manual:
Open the PDF directly: View PDF .
Page Count: 37
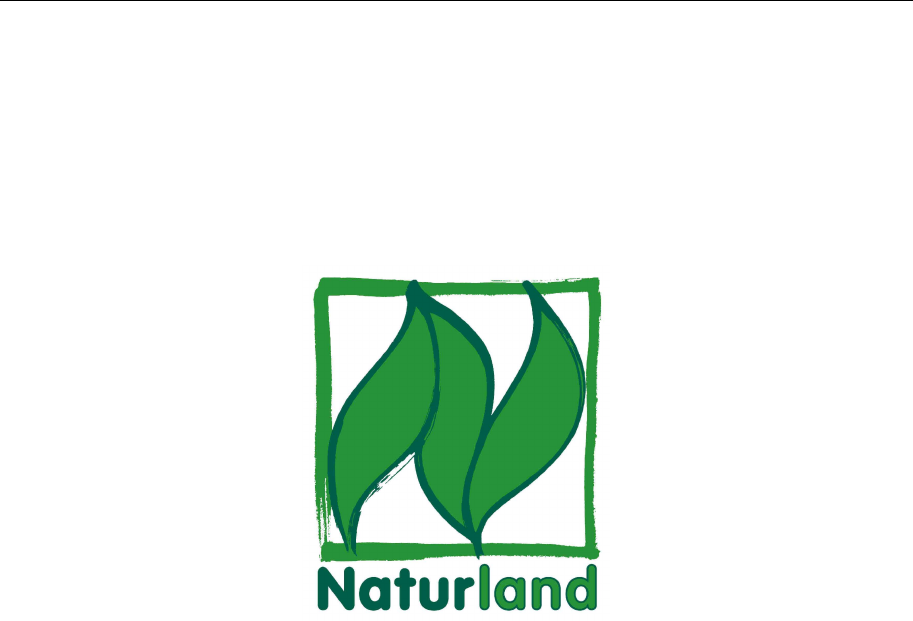
Organic Farming in the
Tropics and Subtropics
Exemplary Description of 20 Crops
Bananas
© Naturland e.V. - 2nd edition 2001
These cultivation guidelines have been published by Naturland e.V. with the kind support of
the Deutsche Gesellschaft für Technische Zusammenarbeit mbH (GTZ, German Agency for
Technical Cooperation) financed by the Bundesministerium für Wirtschaftliche Zusammenar-
beit (BMZ, Federal Ministry for Development Cooperation). The cultivation recommendations
at hand for 20 crops of the tropics and subtropics being of significant importance for the
world economy were written by various authors.
Naturland would like mention the following authors and thank them for their contributions:
Franz Augstburger, Jörn Berger, Udo Censkowsky,
Petra Heid, Joachim Milz, Christine Streit.
The cultivation guidelines are available in English, Spanish and German for the following
crops:
banana, brazil nut, cashew nut, cocoa, coconut, coffee,
cotton, hibiscus, macadamia, mango, papaya, peanut,
pepper, pineapple, sugar cane, sesame, tea, vanilla.
The cultivation guidelines for bananas, mango, pineapple and pepper were revised in 2001
for the United Nations Conference on Trade and Development (UNCTAD) by Udo
Censkowsky and Friederike Höngen.
In 2002 two more guidelines, for rice and date palms, were published in English.
All the authors emphasize, that the cultivation recommendations at hand can just provide
general information. They do not substitute technical assistance to the farmers with regard to
the location.
All indications, data and results of this cultivation guidelines have been compiled and cross-
checked most carefully by the authors. Yet mistakes with regard to the contents cannot be
precluded. The indicated legal regulations are based on the state of the year 1999 and are
subject to alterations in future. Consequently all information has to be given in exclusion of
any obligation or guarantee by Naturland e.V. or the authors. Both Naturland e.V. and au-
thors therefore do not accept any responsibility or liability.
Furthermore the authors kindly call upon for critical remarks, additions and other important
information to be forwarded to the address below. The cultivation guidelines will be updated
regularly by Naturland e.V.
Naturland e.V.
Kleinhaderner Weg 1
82166 Gräfelfing
Germany
phone: +49 - (0)89 - 898082-0
fax: +49 - (0)89 - 898082-90
e-mail: naturland@naturland.de
website: www.naturland.de
We pass our gratitude to Peter Brul of Agro Eco for his helpful comments on the manuscript.
Our best thanks are also devoted to all supporters of this publication, in particular Mrs Sybille
Groschupf who cleaned up the text from errors in strenuous detail work and did the attractive
layout.
II Special section: Organic Cultivation of Bananas
Naturland e.V. – 2
nd
edition 2001
Index
1. Introduction ................................................................................................ 1
1.1. Botany .......................................................................................................... 1
1.2. Varieties and countries of origin................................................................... 1
1.3. Uses and contents ....................................................................................... 3
2. Aspects of plant cultivation ...................................................................... 4
2.1. Site requirements ......................................................................................... 4
2.2. Seeds and seedlings.................................................................................... 4
2.3. Methods of planting...................................................................................... 4
2.4. Diversification Strategies.............................................................................. 5
2.5. Nutrients and organic fertilisation management........................................... 6
2.5.1. Nutrient requirements................................................................................... 6
2.5.2. Organic fertilisation strategies...................................................................... 7
2.6. Biological methods of plant protection ......................................................... 7
2.6.1. Diseases ...................................................................................................... 7
2.6.2. Pests ............................................................................................................ 8
2.7. Monitoring and Maintenance........................................................................ 8
2.7.1. Crop Establishment...................................................................................... 8
2.7.2. Crop production............................................................................................ 9
2.8. Harvesting and post- harvest treatment ....................................................... 9
2.8.1. Harvesting .................................................................................................... 9
2.8.2. Preparation, transport and storage ............................................................ 10
2.8.3. Controlled ripening ..................................................................................... 11
3. Product specifications and quality standards....................................... 11
3.1. Processing ................................................................................................. 11
3.1.1. Handling ..................................................................................................... 11
3.1.2. Packaging and storage .............................................................................. 11
3.2. Dried bananas............................................................................................ 12
3.2.1. Processing ................................................................................................. 12
3.2.2. Quality requirements .................................................................................. 13
3.2.3. Packaging and storage .............................................................................. 14
II Special section: Organic Cultivation of Bananas
Naturland e.V. – 2
nd
edition 2001
3.3. Banana marmalades .................................................................................. 16
3.3.1. Processing ................................................................................................. 16
3.3.2. Quality requirements .................................................................................. 18
3.3.3. Packaging and storage .............................................................................. 19
3.4. Canned bananas........................................................................................ 21
3.4.1. Processing ................................................................................................. 21
3.4.2. Quality requirements .................................................................................. 23
3.4.3. Packaging and storage .............................................................................. 23
3.5. Banana pulp ............................................................................................... 25
3.5.1. Processing ................................................................................................. 25
3.5.2. Quality requirements .................................................................................. 26
3.5.3. Packaging and storage .............................................................................. 28
Annex: Quality Requirements............................................................................... 30
II Special section: Organic Cultivation of Bananas
Naturland e.V. – 2
nd
edition 2001 page 1
Organic Cultivation of Bananas
1. Introduction
Economically, the most important type of tropical fruit is the banana (Musa x paradi-
siaca L.). Marketing of bananas was begun largely by multinational companies, and
has altered in this respect little to this day. These companies often maintain a pro-
duction chain stretching from their own plantations to ripening stations at the final
ports of destination. Certain types of banana, but especially the plantain, form part
of the staple diet in many tropical countries.
Bananas grown organically have only appeared in recent years, and are invariably
intended for shipment to the European markets.
1.1. Botany
The banana belongs to the Musaceae family and includes the genera Musa and
Ensete. The economically important banana sorts belong to the Eumusa section.
The name Musa x paradisiaca is generally retained for the entire group of fruit and
cooking bananas, because many of the varieties are of a hybrid nature.
Edible bananas contain no seeds. Reproduction is carried out via its subterranean
rhizome, the shoots of which regularly forms fruitful buds. The banana plant pos-
sesses a so-called pseudo-stem, which is created by the leaf sheathes. Inflores-
cence usually begins around 7-9 months after planting, depending on climatic condi-
tions and type of soil. Parthenokarpy (unfertilised) fruits, standing together in groups
(clusters), develop from the female blossoms. Seed formation is still visible in the
fruit as blackened bands. The development period of the fruit can last up to ca. 3-4
months, depending on weather conditions. After the bunch has been fully formed,
the parent plant dies off.
1.2. Varieties and countries of origin
As a tropical culture, the banana places heavy demands on temperature (opt. 25°C)
and rainfall (opt. 1500-4000 mm). Nevertheless, bananas are also grown in sub-
tropical areas such as South Africa, Lebanon, Israel and on the Canary Islands, al-
though additional irrigation is generally necessary in these regions. In practical
terms, only cold-resistant dwarf bananas (”Dwarf Cavendish”) are suitable for these
regions.
Varieties of the Cavendish group currently dominate in commercial plantations, after
the taller ”Gros Michel” bananas were decimated by the Panama disease. In addi-
tion to the extensively grown commercial varieties, a large number of local varieties
are found in the tropical regions world-wide. These can be utilised in various ways to
accommodate different sites and production systems, and also combined with one
another.

II Special section: Organic Cultivation of Bananas
Naturland e.V. – 2
nd
edition 2001 page 2
Overview of the most important varieties and their characteristics 1
Varieties Characteristics and Genome
“Sucrier” Around 60 varieties, mostly in SEA, resistant against Panama
disease, low yield. Genome: AA
”Ney Poovan” From South India, varieties barely described, highly resistant
against Panama and Sigatoka diseases. Genome: AB
”Gros Michel” Strong growth, fruitful, susceptible to Panama disease.
Genome: AB
”Robusta” and ”Lacatan” Not as susceptible to Panama disease and wind break as ”Gros
Michel”. Genome: AB
”Dwarf Cavendish”
Especially suited to unfavourable climatic conditions, resistant
against Panama disease, but very susceptible to the Sigatoka
disease, widely distributed, especially in Australia, South Africa,
Israel and the Canary Islands, distributed world-wide
“Mysore” Resistant against Panama disease and banana root
borer,grown in India, strong growth. Genome: AAB
”Silk”, Grows fairly strong, widely distributed, resistant against Siga-
toka disease, but not against Panama disease. Genome: AAB
”Pome”
Strong growth, medium harvest, resistant against Panama and
Sigatoka diseases, distributed throughout southern India, Ha-
waii and E. Australia. Genome: AAB
“Bluggoe”
Strong growth, resistant against Panama and Sigatoka dis-
eases, only a few clusters with large, green fruits, high starch
plantain. Genome: ABB
“Pisank awak”
Very strong growth, resistant against Sigatoka disease, different
mutations, red flesh, contains seeds after fertilisation, grown in
Thailand. Genome: ABB
”Bodles Altafor"
Fruitful, resistant to diseases, but not tested sufficiently yet,
cross between ”Gros Michel” and ”Pisang lilin” (AA\ clone).
Genome: AAAA
”I.C.2”
Found in West India, Honduras and the Pacific region, cross
between ”Gros Michel” and M. acuminata, resistant against
Sigatka disease, less resistant against Panama disease.
Genome: AAAA
”Klue teparod”
Only natural tetraploide variety, fruit is matt grey, mushy,
stringy, sweet plantain in Thailand and Burma, a robust and
disease-resistant variety. Genome: ABBB
1
L
ÜDDERS
,
P. (1989) in: Manual about Agriculture and Nutrition in Developing Countries, Volume 4,
Ulmer.

II Special section: Organic Cultivation of Bananas
Naturland e.V. – 2
nd
edition 2001 page 3
There are many other local varieties, as well as common commercial varieties
grown under different local names.
Organically produced bananas have become more widespread in the past few
years. Most of the bananas intended for the European market are grown in the Ca-
nary Islands, as well as from Ecuador, the Dominican Republic, Costa Rica, Uganda
and Israel. Smaller organic projects also exist serving regional markets (e.g. Bo-
livia).
1.3. Uses and contents
The main form of the common eating banana is as fresh fruit, only a small proportion
enter the market in dried form. In Europe and North America, the common eating
banana, produced and marketed by a handful of major companies, is most wide-
spread. In contrast to this, smallholders produce mainly for themselves and for re-
gional markets, where the banana represents an important part of the daily diet.
Plantains play a large role here, and a wide variety are thereby cultivated.
The following represents nutritional values of the common eating banana2
Nutritional value of bananas per 100g fresh weight of the edible parts:
Contents Amount
water 75 g
Edible carbohydrates 20 g
Raw fat 0,3 g
Raw fibres 0,3 g
Vitamin A 400 I.E.
Vitamin C 10 mg
Energy 460 kJ
Reduction before eating 33%
Flour is produced from both plantains and eating bananas in many regions, which
can then be used in soups, baking or as a drink. The banana can also be used to
make vinegar and to brew alcoholic beverages. The stamina flowers can be used as
a vegetable, after briefly heating them in salty water (to remove the bitterness). Ba-
nanas can also be used as a starch-rich animal feed (pig farming). The fresh leaves
are high in protein content, and are preferred for their taste by cattle and chickens.
The leaves are also commonly used as packing material and for roofing. Along with
the pseudo-stem they offer excellent mulching material.
2
R
EHM
,
S.
und
E
SPIG
,
G. (1976): Crops in tropical and subtropical regions, Ulmer Taschenbuch.
II Special section: Organic Cultivation of Bananas
Naturland e.V. – 2
nd
edition 2001 page 4
2. Aspects of plant cultivation
2.1. Site requirements
The ancestors of our commercial bananas originated from the Malaysian peninsula,
New Guinea and South-East Asia. They grow in alluvial and volcanic soils, as well
as in river deltas and forest perimeters, where the soil is rich in organic material.
They are part of both young and old secondary forest formations, where they are
located either at the top or the middle of the forest, according to variety and devel-
opment stage. This means that they are more or less adaptable to shade, according
to variety. In comparison with eating bananas, plantains require more soil fertility.
They grow in the upper layers of natural vegetation, therefore requiring more light,
and cannot tolerate extended periods of shadow. Commercially used varieties can-
not endure stagnant water conditions, and are susceptible to wind break (especially
when not grown in agroforestry system).
2.2. Seeds and seedlings
Bananas are reproduced vegetative. In accordance with availability, required
amounts and transport possibilities, the following are suitable:
Whole rhizomes
Rhizome pieces
Shoots with inflorescence in the pseudo-stem
Shoots lacking inflorescence in the pseudo-stem.
Using whole rhizomes is laborious. It requires a large amount of starting material
and generates high transport costs. Rhizome pieces and shoots lacking inflores-
cence in the pseudo-stem are less expensive.
It is very important that the shoots are undamaged, and originate from nematode-
free plantations. Prior to planting, the roots and any damaged spots should be re-
moved with a sharp knife.
2.3. Methods of planting
The distances between plants is determined by the variety, soil conditions and the
type of planting system. Slow growing plants, such as the Dwarf Cavendish, can be
planted in a density of 2500 plants/ha. The more robust Giant Cavendish, Robusta
or other strongly developing varieties are set at 600-1200 plants/ha. Experiences
culled in the different regions have led to a variety of recommendations regarding
size and depth of hole required, which should be heeded. It is recommended to
cover the planted rhizome with mulching.
The most suitable planting period is towards the end of the dry season, or at the
beginning of the rainy season, and is also dependent upon any accompanying

II Special section: Organic Cultivation of Bananas
Naturland e.V. – 2
nd
edition 2001 page 5
crops. Several seeds from different local shrubs and trees should be dropped into
each plant hole. Cuttings from varieties which reproduce vegetative can also be
used (Morbus albus, Malvaviscus arboreus, Gliricidia sepium, etc.).
In regions of intensive banana production, it is important to ensure that no undesir-
able pesticide-drift from conventional neighbouring plantations occurs. This is espe-
cially the case when aero spraying takes place. Under these circumstances, it is
necessary to plant high, growing hedges of sufficient depth.
2.4. Diversification Strategies
On conventional plantations, bananas are grown over large areas as part of a mono-
culture. A wide variety of combination possibilities is available for organic cultivation,
especially in connection with permanent crops and agroforestry systems.
The following recommendations pertain to the common eating banana. Due to their
high demands on soil (comp. 2.1.), an intensive accompanying vegetation is re-
quired. With sufficient foresight and planning, this can later be used to replace the
bananas. Due to the fact that specific plantation systems with the suitable variety of
plant need to be established for each region, site, and even for individual plots, it is
only possible to provide an overview of the basic guidelines here.
In principle, bananas can be combined with practically any type of cultivated or wild
plant which has similar eco-physiological requirements. Young banana plants are
excellent ”wet nurses” for other crops and forest plants, which can be planted very
close to the bananas.
Three examples:
1.
1. year 2. year 3. year 5. - 10. year from 11. year
Maize
Papaya Papaya
Banana Banana Banana Banana
Cocoa Cocoa Cocoa Cocoa Cocoa
Forest trees Forest trees Forest trees Forest trees Forest trees
2.
1. year 2. year 3. year 5. - 10. year from 11. year
Hibiscus
Banana Banana Banana Banana
Coffee Coffee Coffee Coffee Coffee
Forest trees Forest trees Forest trees Forest trees Forest trees

II Special section: Organic Cultivation of Bananas
Naturland e.V. – 2
nd
edition 2001 page 6
3.
1. year 2. year 3. year 5. year 6. - 10. year from 11. year
Maize/Manioc
Pineapple Pineapple Pineapple Pineapple
Banana Banana Banana Bananas Bananas
Forest trees Forest trees Forest trees Forest trees Forest trees Forest trees
If no other crops are to be integrated into the system, then it is sufficient to combine
the bananas with forest trees and native fruit trees.
If other crops are to be introduced onto an existing monoculture plantation, then
especially the fruit carrying pseudo-stems will need to be thinned out.
Depending upon which plantation system is used, the planting times for the different
crops need to be co-ordinated, to ensure each receives its optimum location. Each
crop can thereby be planted as if in a one-crop system. The types of maintenance
employed are most important in this approach. Native species with varying heights,
as well as trees that can withstand frequent cutting – such as Inga ssp., Erytrina
ssp. Etc, depending on the site – which have been tested in standard agroforestry
systems, should be used as forest trees. A wide variety of species and high density
of plants should be striven for. The high plant density can be useful for example in
suppressing the growth of other vegetation (like grasses etc.). It also provides suffi-
cient mulching material, which needs to be continually cut and added to the soil.
Satisfactory banana production can only be achieved with a large amount of organic
material produced on the plantation itself (compare 2.5.).
2.5. Nutrients and organic fertilisation management
2.5.1. Nutrient requirements
On conventional plantations in prime locations, bananas are planted over many
years as monocultures. This results in a continual loss of organic material, and to a
general degeneration of the soil, which then needs to be compensated for with a
high input of mineral fertilisers.
The following ”nutrient depletion” results for each 1000 kg bananas3 (in kg):
N [kg] P [kg] K [kg] Ca [kg] Mg [kg]
2 0,3 5 0,4 0,5
3
J
AKOB
,
A., u. U
EXKÜLL
,
H.
V
.
(1963): Fertilizer Use. Nutrition and Manuring of Tropical Crops. 3. Aufl.
Verlagsgesellschaft für Ackerbau, Hannover.

II Special section: Organic Cultivation of Bananas
Naturland e.V. – 2
nd
edition 2001 page 7
Understandably, the amounts of nutrients recommended vary quite strongly, de-
pending on which literature one consults. The following refer to individual plant
parts:
Required amounts of nutrients (in kg/ha) for a harvest of 1000 kg/ha of bananas
(adjusted acc. to4):
Plant part N [kg] P [kg] K [kg] Ca [kg]
Pseudo-stem 0,96 0,16 2,5 0,56
Leaves 6,38 0,6 10,5 3,43
bunch 2,13 0,26 4,53 0,1
Total 9,46 1,03 17,6 4,2
2.5.2. Organic fertilisation strategies
These values for nutrient depletion and fertilisation are given from a viewpoint of
conventional plantation systems. They are not capable of solving the problems of
decreasing yield and soil fertility. The majority of banana varieties cultivated for ex-
port purposes require a high soil quality. In natural forest ecosystems, they appear
towards the beginning of the new growth, and must be replaced by other species
about every 10-15 years. If this is not carried out on the plantation, then sooner or
later a crisis will occur, which can only be solved in the short term by applying fertil-
isers and pesticides.
Regular application of organic material gained from cutting work helps to maintain a
layer of humus and activity in the soil. This includes adding dead leaves and
pseudo-stems grown on the plantation as mulching material. It is important that the
material is spread evenly throughout the entire plantation. Organic manure should
only be seen as an additional fertiliser, and not as the main source of nutrients for
the bananas. These measures will suffice to maintain the fertility of the soil on sites
suited to growing bananas, despite continual harvests.
2.6. Biological methods of plant protection
2.6.1. Diseases
The most important diseases in conventional banana plantations are:
Panama disease (Fusarium oxisporum f. sp. Cubense)
Black and yellow Sigatoka disease (Mycosphaerella musicola, (Mycospheerella fijiensis)
Root rot (Poria sp., Pytium sp., Armillaria mellea, Rhizoctonia solani)
Bacterial rot (Pseudomonas solanacearum)
Rhizome rot (Erwinia carotovora)
4
B
OUFFIL
, in Franke, G. (1984): Nutzpflanzen der Tropen und Subtropen, Hirzel Verlag Leipzig.
II Special section: Organic Cultivation of Bananas
Naturland e.V. – 2
nd
edition 2001 page 8
Virus diseases (Mosaic virus, banana bunchy top virus, infectious chlorosis etc.)
The above mentioned diseases occur mainly in conventional plantation systems,
and are combated by using resistant varieties (Cavendish instead of Gros Michel),
or in conventional farms by spraying with mineral oil and fungicide by aeroplane. In
organic plantation systems these phytosanitary problems must be prevented by cul-
tivation methods and also the use of resistant plants (compare 2.7.).
2.6.2. Pests
The most important pests also occur mainly on monoculture plantations, these are:
Root nematodes
Banana root borer (Cosmopolites sordidus)
The exclusive use of healthy seeds, and application of appropriate measures, offer
the most effective preventative and thus alternative methods of controlling insects
and nematodes (comp. 2.7.). The application of waste from extensive shrimp farms
in Ecuador (shrimp shells) has shown good results against nematodes beside being
a good organic fertilizer.
In conventional plantations, the bunches are often protected by covering them with
polyethylene sacks. When protective bags are used in organic systems, the follow-
ing must be heeded: That the insides are pesticide-free (quite normal on conven-
tional plantations), and that the plastic coverings are bio-degradable.
2.7. Monitoring and Maintenance
2.7.1. Crop Establishment
Around 4-6 months after the bananas and additional crops have been planted, a
primary selective weed regulation should be performed. The actual time depends
largely on the type of additional crops (annual crops, annual or biannual under
seeds), and also from the preliminary condition of the plot. Strong growths of
Graminea and Cyperacea will occur in soils already degraded. These should be
pulled up, and exchanged for seeds of the Canavalis ensiformis, Crotalaria ssp. or
other similar under seeds from non-creeping plants. Foliage regulation consists in
the main of cutting back the blossoms and removing grasses, as mentioned above,
which are both then left on the surface as mulching material.
Surplus shoots need to be regularly cut away from the planted bananas. Three
shoots should be left, which can then grow until they are ripe. Thereafter, only one
shoot is left remaining, so that after one year three times the density has been
achieved, which is then maintained.
The accompanying vegetation (bushes and trees which can be cut) is cut back, and
the resulting material chopped up and spread around the surface as mulching mate-
rial. This should be carried out once or twice a year, according to growth. This cut-
ting regulation results in a continual supply of organic material in varying consis-
tency, and also increases the amount of available light, thus stimulating new growth.
II Special section: Organic Cultivation of Bananas
Naturland e.V. – 2
nd
edition 2001 page 9
Trees which cast no foliage (e.g.. Inga ssp, Glyricidia sepium, Leucaena leuco-
cephala), should be cut back at the banana plant’s height once a year, so that
around 15% of their leaves remain. Depending on which variety of bananas have
been planted, more or less shade can then be controlled. The tall varieties such as
Red, Green Red (manzano, manzano rojo) and Giant Cavendish belong to those
that can cope with a lot of shade, whereas Dwarf Cavendish requires less.
2.7.2. Crop production
After around one to two years, usually no weeding activities are necessary, and
pruning remains as the main work. In addition to regularly removing the shoots, the
inactive leaves should also be cut away (these usually hang bent downwards). In
the course of time, the plantation will tend to ”wander”, in that the original gaps be-
tween the plants change. This means that it may be necessary to remove plants that
now stand too close to one another. Depending on the initial situation at the site and
the type of plantation, the production of bananas is lessened by the gradual cover-
age of accompanying vegetation. If the plantation has been established with addi-
tional economically interesting crops, then these can continue to be harvested. If
there is no relevant alternative to the banana production, then the plantation can be
cleared, and newly planted. In the latter case, the farmer now has soil with an im-
proved fertility.
2.8. Harvesting and post- harvest treatment
2.8.1. Harvesting
Harvesting the banana bunches is usually spread evenly throughout the whole year.
A slowing down in production, or even cessation, only generally occurs at sites
which experience either a noticeable drop in temperature during the winter months,
or distinctive dry periods.
Whilst still green, the fruits have a distinctly edged appearance, which gradually be-
comes almost round as they ripen. The fruits of a bunch do not ripen at the same
pace. If some fruits have begun to turn yellow on the plant, then it is already too late
to transport them any great distance, as they quickly become too soft and burst. The
bananas must therefore be harvested while still green. The optimal cutting stage is
established by the diameter of individual fruits. To simplify the harvest, the bushes
are marked with different coloured bands as the fruits appear. The workers will then
only cut bananas of a particular colour, which are now ripe enough. Terms which
characterise the thickness of the fruit, such as ”three-quarters”, ”light full three-
quarters”, ”full three quarters” and ”full”, are also used. The duration of a proposed
transport determines in which stage a fruit destined for export is judged to be ripe.
II Special section: Organic Cultivation of Bananas
Naturland e.V. – 2
nd
edition 2001 page 10
In order to achieve a uniform ripeness during shipping, the maturity stage of an en-
tire bunch should be as consistent as possible. Harvests are therefore usually car-
ried out at one to two week intervals.
The bunches are harvested by cutting them away from the plant just above where
the fruit begins. The tall varieties must also be freed of their pseudo-stems, which
are bent back and cut off, in order that the bunches become visible. Thereby, it is
very important that the bunches do not fall, or are otherwise bumped during ship-
ping, as this causes them to blacken and rot.
It is advisable to leave behind a ca. 2 m high stub (depending on the variety) of the
pseudo-stem, because nutrients and water are still transported to the remaining
shoots for several weeks, and thereby encouraged in their development. The cut
away part of the pseudo-stem is lain with the cut side facing downwards directly next
to the neighbouring trees. This type of mulching prevents a damaging anaerobe
oxidation by butyric acid bacteria inside the stalk, and encourages an intensive
stimulation of the soil flora. The remains of the stalk are then cut off at the base dur-
ing the next bout of maintenance work, and also lain on the ground. The large sur-
face of the banana leaves should be trimmed away along the petiole and chopped
up, in order that the secondary vegetation be allowed to develop.
2.8.2. Preparation, transport and storage
On large plantations, the harvested clusters are transported to distant packaging
sites by fastening them down with ropes, or hanging them from the lorries to avoid
bruising. Once there, the clusters are prepared by cutting away any badly formed
fruits at their tops and base. Any leaking milk which drops onto the fruit will cause it
to blacken during ripening and sale will be impossible. This can be avoided when
the individual, separated bunches are washed in cold water, where they can be
drained.
Conventionally, the fruit is washed with disinfectant (Na-Bisulfite, Na-Hypochlorite)
and/or treated in a fungicide bath.
The use of fungicides is out of the question on organic plantations. Either alum salt
(potassium alum) or extracts from lemons or orange pips (kernels) can be used to
disinfect. So called crown rot (Colletotrichum musae) can be prevented by wetting
the cut with vinegar.
The cleansing water that collects at preparation sites contains many organic com-
pounds, and must therefore be biologically treated before allowing it to flow into a
drainage ditch. Organic material that collects during preparation (e.g. unusable,
damaged fruits) should be composted and returned to the soil.
The ratio of harvested to exportable fruits is between 1 : 1 and 1 : 1.7 , whereby the
latter is more usual.
The individual bunches are packaged in cartons of 12 kg or 20 kg (Costa Rica),
which are lined with polyethylene foil. Cooling equipment must then be used to delay
the ripening process during shipping. Optimum temperatures are dependant on the

II Special section: Organic Cultivation of Bananas
Naturland e.V. – 2
nd
edition 2001 page 11
variety, and vary between 12-15°C. At too low temperatures, frost damage can oc-
cur, such as lack of ripening, production of tannins, discolouring of the skins, inhibi-
tion of starch transformation as well as an increased production of ascorbic acid. An
additional delay in the ripening process can be achieved by increasing the CO2 con-
tent and reducing the O2 content of the storage room atmosphere during shipping.
2.8.3. Controlled ripening
Special warehouses must be available at the destination port (ripening plant), in
order to subject the fruits to a controlled ripening process. This takes place at about
20°C and at an atmospheric concentration of 0,1% ethylene. The use of ethylene to
accelerate the ripening process, as well as the use of kalinite to delay the ripening of
bananas is allowed in the EEC-regulation for organic agriculture (EEC) 2092/91.
3. Product specifications and quality standards
3.1. Processing
3.1.1. Handling
The banana is the most commonly cultivated tropical fruit. It is used in many areas,
in the form of plantains, horse bananas, common eating bananas and fibrous ba-
nanas. They can be turned into dried products, such as flour, starch, powder, flakes,
chips, and dried fruit, as well as pulp, concentrate, juice and dried fruit or wine, spir-
its and liquor. A whole range of eating banana varieties in particular are exported
fresh.
It is recommended to harvest bananas for the export market whilst they are still
green. After harvesting, the 30-45 kg heavy clusters are washed, whereby thyme
extract can be added to the water to aid disinfecting. After drying, the bundles
(”bunches”) are separated, sorted, classified, packed in standard cartons of 12 kg or
18 kg and placed into cold storage.
♦ The EU quality standards for Bananas are shown in the Annex.
3.1.2. Packaging and storage
Packaging
The regulations concerning carton labelling were dealt with in section VI of the ‘EU
quality standards for bananas’.
Storage
Unripe, originally bananas can be shipped within 10-14 days by boat at 14-15°C and
90-95% relative humidity. The final ripening process takes place in special banana
ripening plants, at temperatures from 14.5-18 °C and lasts 4-8 days.
Bananas cannot be stored for long. They can be stored for up to 10 days at 13-15°C
and 90% relative humidity, just prior to being ripe enough to eat.

II Special section: Organic Cultivation of Bananas
Naturland e.V. – 2
nd
edition 2001 page 12
3.2. Dried bananas
3.2.1. Processing
Drying is the oldest method of making food storable for longer periods. It is based
on the fact that micro-organisms tend to cease growing below a certain level of wa-
ter content. During drying, it is important to extract the water from the fruit as care-
fully as possible. The most important features are a good circulation of air and not
too high temperatures
The preparation stages from fresh to dried fruit are outlined and then described
more fully below:
Fruit
sorting
washing
peeling
pulping
drying
Sorting and packaging
Labelling and storing
Sorting
After harvesting, the fruits are sorted as only fresh, unripe and not fermented fruits
can be used for drying.
Washing and peeling
Bananas must be washed very carefully, in order not to damage them. Afterwards,
inedible parts such as leaves, seeds, pips, heartwood and skins are removed.
Pulping and drying the fruits
The fruits are now cut into same-sized pieces, and laid out to dry in the air and sun
in thin layers on racks, in solar dryers (drying tunnels) or drying ovens (artificial dry-
ing at 70°C).
Sorting and packaging
Before they are packed, the fruits are inspected and sorted again, to rid them of dis-
coloured, skin remnants and seeds etc..

II Special section: Organic Cultivation of Bananas
Naturland e.V. – 2
nd
edition 2001 page 13
Labelling and storage
The packaged fruits can now be labelled and stored prior to being shipped.
During and after drying, the dried fruits are not permitted to be treated with methyl
bromide, ethylene oxide, sulphur oxides or with ionising radiation.
3.2.2. Quality requirements
The following is a list of quality characteristics with minimum and maximum values
for dried fruits, that are usually required officially or by importers. Different minimum
and maximum values can be agreed between importers and exporters, providing
these do not clash with official regulations.
Quality characteristics Minimum and maximum values
Taste and smell Variety-specific, aromatic, fresh, not mouldy
Cleanliness Free from foreign particles, such as insects, sand, small
stones etc.
Water content max. 18 %
aw-value 0.55 to 0.65 (at 20 °C)
Residues
Pesticides Not measurable
Sulphur oxide Not measurable
Bromide and ethylene oxide Not measurable
Micro-organisms
Total number of parts max. 10,000/g
Yeasts max. 10/g
Mould fungus max. 10/g
Staphylococcus aureus max. 10/g
Coliforms max. 1/g
Escherichia coli Not measurable in 0.01 g
Enterococci Not measurable in 1 g
Salmonella Not measurable in 20 g
Mycotoxins
Staphylococcus enterotoxin Not measurable
Aflatoxin B1 max. 2 µg/kg
Total aflatoxins B1, B2, G1, G2 max. 4 µg/kg
Patulin max. 50 µg/kg
Heavy metals
Lead (Pb) max. 1.25 mg/kg
Cadmium (Cd) max. 0.125 mg/kg
Mercury (Hg) max. 0.10 mg/kg

II Special section: Organic Cultivation of Bananas
Naturland e.V. – 2
nd
edition 2001 page 14
In order that the quality requirements are upheld, and no contamination of the fruits
occurs, preparation should take place under clean, hygienic and ideal conditions.
The following aspects should be adhered to:
Equipment (tubs, knives etc.), as well as working and drying surfaces (racks, mats
etc.) and preparing and storage rooms, should be cleaned regularly.
Personnel should be healthy, and have the possibility to wash themselves, or at
least their hands (washrooms, toilets) and wear clean, washable garments.
Water used for cleansing purposes must be free from faeces and other contami-
nants.
Animals or animal faeces must not come into contact with the fruits. If the fruits are
to be dried in the open, then fences must be erected to guard the racks against
birds and nearby animals.
3.2.3. Packaging and storage
Details given on packaging
The label on the jar must display the following:
♦ Packaging types and material
In order to be exported to Europe, the dried fruits can be packed in consumer packs,
or wholesaler packs (bulk) in bags made of foils, impermeable to steam (e.g. poly-
ethylene or polypropylene). Before sealing, a gas (e.g. nitrogen) may be added (ni-
trogen flushing).
♦ Details given on packaging
If the dried fruits are packed directly for consumers, then the following details must
be included on the outside of the packets:
♦ Product name (‘trade name’)
The name of the product, e.g. organically grown dried banana slices 5
Manufacturer
♦ Name and address of the manufacturer, importer, exporter or trader within the
country of origin, and which country.
♦ List of contents
A list of ingredients and additions, beginning with the heaviest proportion of total
weight at the time of packaging.
♦ Weight
Details of the total packed weight in gram
5
Organic products must be protected from contamination by non-compliant substances at each stage
in the process, i.e. processing, packaging, shipping. Therefore, products originating from a certified
organic plantation must be recognisably declared as such.

II Special section: Organic Cultivation of Bananas
Naturland e.V. – 2
nd
edition 2001 page 15
The numbers describing the weight of the contents must be of the following sizes
Weight of contents Letter size
Less than 50 g 2 mm
More than 50 g to 200 g 3 mm
More than 200 g to 1000 g 4 mm
More than 1000 g 6 mm
♦ Best before date
The ‘Best before ...’ details must include day, month and year; e.g.. best before
30.11.2001
♦ Batch number
Function of the product packaging
The product packaging should fulfil the following functions:
Protect it from loss of aroma and against undesirable smells and tastes from its sur-
roundings (aroma protection).
Offer sufficient conservation properties, especially against loss or gain of moisture.
Protect the contents against damaging.
Provide a surface area for advertising and product information.
Transport packaging
Some form of transport packaging is required in order to ship the bulk or singly
packed fruits. In choosing a type of packaging, the following should be heeded:
Transport packaging made, for example, out of cardboard, should be strong enough
to protect the contents against being damaged by outside pressure.
The packaging should be dimensioned to allow the contents to be held firmly, but
not too tightly in place.
The dimensions should be compatible with standard pallet and container dimen-
sions.
Information printed on transport packaging
The transport packaging should display details of the following:
♦ Name and address of the manufacturer/packer and country of origin
♦ Description of the product and its quality class
♦ Year harvested
♦ Net weight, number
♦ Batch number
♦ Destination, with the trader’s/importer’s address
♦ Visible notice of the organic nature of the product6
6
When products from organic plantations are being labelled as such, it is necessary to adhere to the
requisite government regulations of the importing country. Information concerning this is available from

II Special section: Organic Cultivation of Bananas
Naturland e.V. – 2
nd
edition 2001 page 16
Storage
The dried fruits should be stored in dark areas at low temperatures and relative hu-
midity.
Under optimum conditions, dried fruits can be stored for up to 1 year.
If the organic product is being stored in a single warehouse together with conven-
tional bananas mixing of the different qualities must be avoided. This is best
achieved using the following methods:
Training and informing of warehouse personnel
Explicit signs in the warehouse (silos, pallets, tanks etc.)
Colour differentiation (e.g. green for the organic product)
Incoming/dispatched goods separately documented (warehouse logbook)
It is prohibited to carry out chemical storage measures (e.g. gassing with methyl
bromide) in mixed storage spaces. Wherever possible, storing both organic and
conventional products together in the same warehouse should be avoided.
3.3. Banana marmalades
3.3.1. Processing
Jams are basically preparations made of fruit (jams) and various sugars that are
made conservable mainly by heat treatment (boil down). The half-set yet spread
able consistency of these products is achieved by releasing the pectin found in the
fruit pulp during the boiling process, and using this together with further pectin
added to form a jelly-like mass.
The preparation stages from fresh fruit to jam are outlined and then described more
fully below:
Fruit
sorting
washing
Peeling and sorting
pulping
addition of sugar
heating and boiling down
the appropriate certification body. The regulation for organic agriculture (EEC) 2092/91 is applicable to
organic products being imported into Europe.

II Special section: Organic Cultivation of Bananas
Naturland e.V. – 2
nd
edition 2001 page 17
possible addition of pectin, citric acid and
spices, then renewe
d heating
filling into jars
vacuum sealing
Pasteurising
cooling
labelling and storing
Sorting
After harvesting, the fruits are sorted, because only those that are fresh, ripe and
not rotten can be used to make jams. Jams can also be made from previously pre-
pared, frozen fruits and pulp.
Washing
The fruit should be washed very carefully as it can easily be damaged.
Peeling and sorting
This follows the procedure of removing leaves, wooden pieces, pips or seeds and
peel. Peeling is often done manually, or with knives, yet sometimes the skin is loos-
ened with steam and then subsequently rubbed away mechanically. Finally, the
fruits are sorted again to remove any blackened pieces, bits of peeling seeds etc.
Pulping and adding sugar
The peeled fruits are then pulped, and sugar added. They might also be mixed with
water or fruit juice. To make jam, at least 350 g fruit per 1000 g finished product
must be used; to make jam extra, at least 450 g fruit per 1000 g finished product
must be used. The sugar must be ecologically grown.
Description Fruit content during manufacture
Jam, extra 450 g fruit per 1000 g product
Jam 350 g fruit per 1000 g product
Heating and boiling
The mixture is now heated to 70-80°C and boiled down, while constantly being
stirred, at 65°C until shortly before it reaches the desired consistency.

II Special section: Organic Cultivation of Bananas
Naturland e.V. – 2
nd
edition 2001 page 18
Adding citric acid, pectin and spices (optional)
If necessary or desired, citric acid, pectin and spices (from certified organic produc-
tion) can be added, and the mixture again briefly heated to 80°C.
Filling into jars, vacuum-sealing and Pasteurising
The liquid mass is now poured into jars, vacuum-sealed and pasteurised.
Cooling, labelling and storage
After the heating process, the jams are first cooled to 40°C, and then subsequently
down to storage temperature, labelled, and finally stored.
3.3.2. Quality requirements
In addition to the previously mentioned quality requirements, such as clearly defined
fruit content, the jams also have to conform to the following specifications. These
quality requirements, with their minimum and maximum values, are generally issued
by the authorities or importers. Yet agreements may be reached between individual
manufacturers and importers upon different values, providing they still conform to
official requirements.
Quality requirements Minimum and maximum values
Smell and taste Variety-specific, aromatic
Cleanliness Free of foreign substances such as peel, stalks etc.
Contents of jam extra Min. 450 g per 1000 g product
Contents of jam min. 350 g per 1000 g product
Soluble dry mass in percent (meas-
ured refractometrically)
min. 60 %
Mycotoxins
Aflatoxin B1 max. 2 µg/kg
Total aflatoxins B1, B2, G1, G2 max. 4 µg/kg
Patulin max. 50 µg/kg
Residues
Pesticides Not measurable
Sulphur oxide Not measurable
Bromide Not measurable
Ethylene oxide Not measurable
In order to conform to the quality requirements, and to prevent the fruit becoming
contaminated, all preparations must be carried out under clean, hygienic and ac-
ceptable conditions. The following aspects must be heeded:

II Special section: Organic Cultivation of Bananas
Naturland e.V. – 2
nd
edition 2001 page 19
• Equipment (tubs, knives etc.), as well as working surfaces (tables etc.) and pre-
paring and storage rooms, should be cleaned regularly.
• Personnel should be healthy, and have the possibility to wash themselves, or at
least their hands (washrooms, toilets) and wear clean, washable over garments.
• Water used for cleansing purposes must be free from faeces and other con-
taminants.
• Animals or animal faeces must not come into contact with the processed fruits.
3.3.3. Packaging and storage
Packaging types and material
In order to be exported to Europe, the jams are usually filled into consumer-size jars
with twist-off lids.
Details given on packaging
The label on the jar must display the following:
♦ Product name (‘Trade name’)
The name of the product, consisting of: Name of the fruit with or without the descrip-
tion extra – according to fruit content; e.g.: Banana jam extra, organically grown7
♦ Manufacturer
Name and address of the manufacturer, importer, exporter or product trader, plus
country of origin.
♦ List of contents
A list of ingredients and additives in the jam, beginning with the heaviest proportion
of total weight at the time of packaging
♦ Details of the total sugar content
Total sugar content per 100 g product (measured refract metrically at 20 °C) must
be represented with the words ”Total sugar content ....g per 100 g”.
e.g.: Total sugar content 55 g per 100 g.
♦ Details of fruit content
The fruit content per 100 g product must be given with the words ”manufactured
from....g fruit per 100 g”. E.g.: manufactured from 45 g fruit per 100 g.
♦ Notice about cooling
The notice about storing the product in a cool place must be given with the words:
”After opening, store in a cool place”.
♦ Weight
Details of the total weight in grams
♦ Best before date
The ‘Best before ...’ details must include day, month and year; e.g.. best before
30.11.2001
7
Compare footnote No. 5

II Special section: Organic Cultivation of Bananas
Naturland e.V. – 2
nd
edition 2001 page 20
♦ Batch number
Transport packaging
A form of transport packaging is required to ship the sales packages. In choosing
them, the following aspects should be heeded:
Transport packaging made, for example, out of cardboard, should be strong enough
to protect the contents against being damaged by outside pressure.
The packaging should be dimensioned to allow the contents to be held firmly, but
not too tightly in place.
The dimensions should be compatible with standard pallet and container dimen-
sions.
Information printed on transport packaging.
The transport packaging should display details of the following:
♦ name and address of the manufacturer/packer and country of origin
♦ Description of the product and its quality class
♦ Year harvested
♦ Net weight, number
♦ Batch number
♦ Destination, with the trader’s/importer’s address
♦ Visible notice of the organic nature of the product8
Storage
The jams should be stored in a dark, cool room at temperatures of max. 15°C. Un-
der optimum conditions, jam may be stored for 1-2 years.
If the organic product is being stored in a single warehouse together with conven-
tional banana jam mixing of the different qualities must be avoided. This is best
achieved using the following methods:
Training and informing of warehouse personnel
♦ Explicit signs in the warehouse (silos, pallets, tanks etc.)
♦ Colour differentiation (e.g. green for the organic product)
♦ Incoming/dispatched goods separately documented (warehouse logbook)
It is prohibited to carry out chemical storage measures (e.g. gassing with methyl
bromide) in mixed storage spaces. Wherever possible, storing both organic and
conventional products together in the same warehouse should be avoided.
8
compare footnote No. 6

II Special section: Organic Cultivation of Bananas
Naturland e.V. – 2
nd
edition 2001 page 21
3.4. Canned bananas
3.4.1. Processing
Canned foods are products that can be stored over a long period in airtight contain-
ers (metal or glass jars). They are preserved mainly by heat treatment, during which
the micro-organisms present in the fruit are significantly reduced in number, or their
development so restricted, that they are prevented from spoiling the product.
The process involved in turning fresh fruit into canned products is described sche-
matically, and then in more detail below:
Fruit
Sorting
Washing
Peeling and sorting
Pulping
Filling into jars or cans
with syrup
Vacuum sealing
Pasteurising or sterilising
Cooling
Labelling and storage
Sorting
After harvesting, the fruits are sorted, because only those that are fresh, ripe and
not rotten can be used to make jams. Jams can also be made from previously pre-
pared, frozen fruits and pulp.
Washing
The fruit should be washed very carefully as it can easily be damaged.
Peeling and sorting
This follows the procedure of removing leaves, wooden pieces, pips or seeds and
peel. Peeling is often done manually, or with knives, yet sometimes the skin is loos-
ened with steam and then subsequently rubbed away mechanically. Finally, the
fruits are sorted again to remove any blackened pieces, bits of peeling seeds etc.

II Special section: Organic Cultivation of Bananas
Naturland e.V. – 2
nd
edition 2001 page 22
Pulping
The peeled fruit can be cut into a variety of shapes, according to type (indicated by
the crosses in the table). The shape of the cut fruit must be given on the can (slices,
diced, pieces etc.).
Description
Cut shape Pine-
apple
Mango Papaia Ba-
nana
Whole fruit Peeled X
Slices Slices of fruit cut into approximately the
same size X X X X
Half slices Uniformly cut, semi-circle shaped slices. X
Diced Fruit cut into dice shapes of roughly the
same size. X X X
Balls Fruit pulp pieces cut into roughly ball
shapes X
Pieces Pieces of fruit cut into irregular shapes X
Grated Irregular thin strips and pieces of fruit X
Chunks Large regularly cut pieces of pineapple X
Titbits Trapeze-shaped segments of pineapple X
Filling in jars or cans
The cut pieces are now filled into jars or cans and covered with syrup. Additional
information must be given on the can according to the sugar content of the syrup.
Sugar concentration* of the syrup Description on the can
9-14 % Very lightly sugared
14-17 % Lightly sugared
17-20 % Sugared
over 20 % Strongly sugared
* The sugar must be organically grown.
If the appropriate fruit juice has been used as syrup then ”...in natural juice” must be
included on the label, e.g.: Organically grown bananas in natural juice.
Vacuum sealing, pasteurising or sterilising
After the jars or cans have been vacuum sealed, they are either pasteurised (tem-
peratures above 80°C) or sterilised (temperatures above 100°C).
Cooling
After the heating process, the canned fruits are first cooled to 40°C, and then sub-
sequently down to storage temperature.
Labelling and storage
After they have been cooled, the canned fruits are labelled and stored.

II Special section: Organic Cultivation of Bananas
Naturland e.V. – 2
nd
edition 2001 page 23
3.4.2. Quality requirements
In addition to the previously listed quality requirements, such as clearly defined
sugar concentrations of the syrup and shapes specific to certain fruits, the contents
should also conform to the following characteristics. These quality requirements,
with their minimum and maximum values, are generally issued by the authorities or
importers. Yet agreements may be reached between individual manufacturers and
importers upon different values, providing they still conform to official requirements.
Quality requirements Minimum and maximum values
Taste and smell Variety-specific, aromatic, not mouldy
Cleanliness Free of foreign substances such as peel, stalks etc.
Mycotoxins
Aflatoxins B1 max. 2 µg/kg
Total aflatoxines B1, B2, G1, G2 max. 4 µg/kg
Patulin max. 50 µg/kg
Residue
Pesticide Not measurable
Sulphur oxide Not measurable
Bromide Not measurable
Ethylene oxide Not measurable
In order to conform to the quality requirements, and to prevent the fruit becoming
contaminated, all preparations must be carried out under clean, hygienic and ac-
ceptable conditions. The following aspects must be heeded:
Equipment (tubs, knives etc.), as well as working surfaces (tables etc.) and prepar-
ing and storage rooms, should be cleaned regularly.
Personnel should be healthy, and have the possibility to wash themselves, or at
least their hands (washrooms, toilets) and wear clean, washable garments.
Water used for cleansing purposes must be free from faeces and other contami-
nants.
Animals or animal faeces must not come into contact with the processed fruits.
3.4.3. Packaging and storage
Packaging type and material
In order to be exported to Europe, the fruits can be packed into single or wholesale
packages (bulk) made of glass, aluminium or tin cans.

II Special section: Organic Cultivation of Bananas
Naturland e.V. – 2
nd
edition 2001 page 24
Details given on packaging
The label on the jar must display the following:
♦ Product name (‘Trade name’)
The name of the product, consisting of: Name of the fruit with or without the descrip-
tion extra – according to fruit content; e.g.: Bananas in slices, lightly sugared, or-
ganically grown9
♦ Manufacturer
Name and address of the manufacturer, importer, exporter or product trader, plus
country of origin.
♦ List of contents
A list of ingredients and additives in the jam, beginning with the heaviest proportion
of total weight at the time of packaging
♦ Weight
Total and dry weight of the fruit
The numbers describing the weight of the contents must be of the following sizes
Weight of contents Letter size
Less than 50 g 2 mm
More than 50 g to 200 g 3 mm
More than 200 g to 1000 g 4 mm
More than 1000 g 6 mm
♦ Best before date
The ‘Best before ...’ details must include day, month and year
♦ Batch number
Transport packaging
A form of transport packaging is required to ship the packages. In choosing them,
the following aspects should be heeded:
♦ Transport packaging made, for example, out of cardboard, should be strong
enough to protect the contents against being damaged by outside pressure.
♦ The packaging should be dimensioned to allow the contents to be held firmly,
but not too tightly in place.
♦ The dimensions should be compatible with standard pallet and container dimen-
sions.
♦ Information printed on transport packaging
The transport packaging should display details of the following:
♦ Name and address of the manufacturer/packer and country of origin
♦ Description of the product and its quality class
♦ Year harvested
♦ Net weight, number
9
compare footnote No. 5

II Special section: Organic Cultivation of Bananas
Naturland e.V. – 2
nd
edition 2001 page 25
♦ Batch number
♦ Destination, with the trader’s/importer’s address
♦ Visible notice of the organic nature of the product10
Storage
The conserved fruit (especially in jars) should be stored in dark rooms at low tem-
peratures (max. 15°C). Under optimum conditions, conserved fruit can be stored for
1 year (when pasteurised) or 2 years (when sterilised).
If the organic product is being stored in a single warehouse together with conven-
tional bananas mixing of the different qualities must be avoided. This is best
achieved using the following methods:
Training and informing of warehouse personnel
♦ Explicit signs in the warehouse (silos, pallets, tanks etc.)
♦ Colour differentiation (e.g. green for the organic product)
♦ Incoming/dispatched goods separately documented (warehouse logbook)
It is prohibited to carry out chemical storage measures (e.g. gassing with methyl
bromide) in mixed storage spaces. Wherever possible, storing both organic and
conventional products together in the same warehouse should be avoided.
3.5. Banana pulp
3.5.1. Processing
Canned foods are products that can be stored over a long period in airtight contain-
ers (metal or glass jars). They are preserved mainly by heat treatment, during which
the micro-organisms present in the fruit are significantly reduced in number, or their
development so restricted, that they are prevented from spoiling the product.
The process involved in turning fresh fruit into canned products is described sche-
matically, and then in more detail below:
10
compare footnote No. 6

II Special section: Organic Cultivation of Bananas
Naturland e.V. – 2
nd
edition 2001 page 26
Banana pulp processing:
Fruit
Sorting
Washing
Peeling and sorting
Pulping and straining
De-aeration (partially)
Pasteurising or sterilising
Filling
Cooling, labelling and storage
Manufacturing banana pulp
In producing pulp, only fresh, ripe fruit should be used, that has not yet turned
mouldy. The skin of fully ripened bananas is entirely yellow, and easy to peel from
the fruit. After harvesting, the fruit are first sorted and washed, before being peeled
by hand and placed directly in a solution of 4% citric acid and 1% ascorbic acid, to
prevent discolouring.
Afterwards, the fruits are placed in a heat exchanger, where they are heated to a
temperature of 93° C in order to deactivate any enzymes, and to break down the
fruit
pulp. The pulp then passes through a two-stage sieve equipped with a 0.8 mm and
a 0.5 mm screen. After de-aeration, the pulp is homogenised at a pressure of 100-
300 bar and sterilised for 40-45 seconds at 100° C.
The banana pulp can now be filled into tin cans whilst still hot, whereby the cans are
sealed while being steamed, the temperature maintained for 5 min., and then rapidly
cooled down. At temperatures of around 15° C, the pulp can be stored for up to
1 year. After pasteurising, the pulp can also be cooled down and filled into polyeth-
ylene bags placed in 50-200 kg barrels. It is then rapidly frozen, and can be stored
at -18° C for 18 months. Pulp which has been filled under antiseptic conditions (bag-
in-box) can be stored for up to 1 year at room temperature.
3.5.2. Quality requirements
These quality requirements, with their minimum and maximum values, are generally
issued by the authorities or importers. Yet agreements may be reached between

II Special section: Organic Cultivation of Bananas
Naturland e.V. – 2
nd
edition 2001 page 27
individual manufacturers and importers upon different values, providing they still
conform to official requirements.
Quality requirements MINIMUM AND MAXIMUM VALUES
Smell and taste Variety-specific, aromatic
Cleanliness Free of foreign substances such as peel,
stalks etc.
Relative density (20/20) for pineapple juice min 1.045
Brix value11 for pineapple juice min 11.2 %
Relative density (20/20) for Banana pulp min 1.083
Brix value for Banana pulp min 20.0 %
Relative density (20/20) for Mango pulp min 1.057
Brix value for Mango pulp min 14.0 %
Ethanol max 3.0 g/kg
Volatile acids, evaluated as acetic acid max 0.4 g/kg
Lactic acid max 0.5 g/kg
D-Malic acid Not measurable
Sulphuric acid Not measurable
Hydroxymethylfurfural (HMF) max 20 mg/kg
Heavy metals
Arsenic (As) max 0.1 mg/kg
Lead (Pb) max 0.2 mg/kg
Copper (Cu) max 5.0 mg/kg
Zinc (Zn) max 5.0 mg/kg
Iron (Fe) max 5.0 mg/kg
Tin (Sn) max 1.0 mg/kg
Mercury (Hg) max 0.01 mg/kg
Cadmium (Cd) max 0.02 mg/kg
Residues
Pesticide Not measurable
Sulphur oxide Not measurable
Bromide Not measurable
Ethylene oxide Not measurable
Mycotoxins
Aflatoxin B1 max 2 µg/kg
Total aflatoxins B1, B2, G1, G2 max 4 µg/kg
Patulin max 50 µg/kg
11
A Brix value is the measure of the concentration of sugars, acids, and other identifying compounds in
a juice. Every fruit juice has a slightly different Brix value.

II Special section: Organic Cultivation of Bananas
Naturland e.V. – 2
nd
edition 2001 page 28
In order to conform to the quality requirements, and to prevent the fruit becoming
contaminated, all preparations must be carried out under clean, hygienic and ac-
ceptable conditions. The following aspects must be heeded:
• Equipment (tubs, knives etc.), as well as working surfaces (tables etc.) and pre-
paring and storage rooms, should be cleaned regularly.
• Personnel should be healthy, and have the possibility to wash themselves, or at
least their hands (washrooms, toilets) and wear clean, washable over garments.
• Water used for cleansing purposes must be free from faeces and other con-
taminants.
• Animals or animal faeces must not come into contact with the processed fruits.
3.5.3. Packaging and storage
♦ Packaging type and material
In order to be exported to Europe, the pulp/juices can be packed into single or
wholesale packages (bulk) consisting of glass jars, tin cans or polyethylene or poly-
propylene bags, and also filled antiseptically into ‘bag-in-boxes’.
♦ Details given on packaging
The label on the jar must display the following:
♦ Product name (‘Trade name’)
The name of the product, e.g.: Organic banana pulp12
♦ Manufacturer
Name and address of the manufacturer, importer, exporter or product trader, plus
country of origin.
♦ List of contents
A list of ingredients and additives, beginning with the heaviest proportion of total
weight at the time of packaging, e.g.: bananas, citric acid…
♦ Weight
Total weight
The numbers describing the weight of the contents must be of the following sizes
Weight of contents Letter size
Less than 50 g 2 mm
More than 50 g to 200 g 3 mm
More than 200 g to 1000 g 4 mm
More than 1000 g 6 mm
♦ Best before date
The ‘Best before ...’ details must include day, month and year; e.g.. best before
30.11.2001
♦ Batch number
12
compare footnote No. 5

II Special section: Organic Cultivation of Bananas
Naturland e.V. – 2
nd
edition 2001 page 29
Transport packaging
A form of transport packaging is required to ship the sales packages. In choosing
them, the following aspects should be heeded:
Transport packaging made, for example, out of cardboard, should be strong enough
to protect the contents against being damaged by outside pressure.
The packaging should be dimensioned to allow the contents to be held firmly, but
not too tightly in place.
The dimensions should be compatible with standard pallet and container dimen-
sions.
Information printed on transport packaging The transport packaging should display
details of the following:
♦ Name and address of the manufacturer/packer and country of origin
♦ Description of the product and its quality class
♦ Year harvested
♦ Net weight, number
♦ Batch number
♦ Destination, with the trader’s/importer’s address
Visible notice of the organic nature of the product13
Storage
Pasteurised pineapple juice, as well as pasteurised banana, mango and papaya
pulp can be stored as follows:
Packaging material/
storage temperature
Pineapple-
juice
Banana-
pulp
Mango-
pulp
Papaya-
pulp
Tin cans/glass jars
storage temperature below 15°C
1 year 1 year 1 year 9-12 months
Polyethylene bags/
Deep frozen at -18°C
- 18 months 18 months 12 months
Filled antiseptically, bag-in-box/
Room temperature
1 year 1 year 1 year 6-9 months
If the organic product is being stored in a single warehouse together with conven-
tional banana pulp mixing of the different qualities must be avoided. This is best
achieved using the following methods:
Training and informing of warehouse personnel
♦ Explicit signs in the warehouse (silos, pallets, tanks etc.)
♦ Colour differentiation (e.g. green for the organic product)
♦ Incoming/dispatched goods separately documented (warehouse logbook)
13
compare footnote No. 6

II Special section: Organic Cultivation of Bananas
Naturland e.V. – 2
nd
edition 2001 page 30
It is prohibited to carry out chemical storage measures (e.g. gassing with methyl
bromide) in mixed storage spaces. Wherever possible, storing both organic and
conventional products together in the same warehouse should be avoided.
Annex: Quality Requirements
The ‘EU quality standard for bananas’ clearly defines the quality requirements
placed upon trade with fresh bananas. The regulations must be strictly adhered to
until the fruit reaches the ripening plants.
The following is an excerpt from the ‘EU quality standard for bananas’:
I. Definition
The standards apply to bananas of the following listed varieties of the genus Musa
(AAA) ssp., subgroups Cavendish and Gros Michel, to be transported in a fresh
state to consumers. Flour bananas and Fig bananas, as well as bananas intended
for industrial processing are not included.
Group Subgroup Main variety
AAA Cavendish Petite naine (Dwarf Cavendish)
Grande naine (Giant Cavendish)
Lacatan
Poyo (Robusta)
Williams
Americani
Valéry
Arvis
Gros Michel Gros Michel
Highgate
II. Quality characteristics regulations
The standard regulates the quality characteristics that green, unripe bananas must
exhibit after packing and processing.
a. Minimum characteristics
Subject to the pertinent regulations and tolerances for each class, the bananas in all
quality classes must be configured as follows:
♦ green, unripe
♦ whole, firm
♦ clean, practically free of visible foreign matter
♦ practically free of pests and the damage caused by them
with a unbroken, intact stalk which is not dried out and is free of fungus
♦ the fruit must not be misshapen, and not abnormally bent
♦ free of bruising and frost damage
♦ free of strange smells and/or taste
Furthermore, the bunches or clusters must also have:
♦ a sufficient, healthy length of normally-coloured coronet, free of fungus

II Special section: Organic Cultivation of Bananas
Naturland e.V. – 2
nd
edition 2001 page 31
♦ a clean cut of the coronet, without evidence of nicks or tearing
The development and ripeness of the fruit must be so that they:
♦ can withstand handling and transporting
♦ are in a satisfactory condition when they arrive at the port, and will achieve a
reasonable state of ripeness after ripening has taken place.
b. Classifications
♦ Class extra
Bananas in this class must be of the highest quality. They must possess the charac-
teristics typical of their variety and/or trading type.
The fruits must be unblemished, with the exception of very light surface flaws that
cover less than 1 cm² of the fruit’s surface, and providing this does not detract from
the fruit’s general appearance, quality, the time it will keep and the presentation of
the bunch or cluster in their packaging.
♦ Class I
Bananas in this class must be of good quality. They must possess the characteris-
tics typical of their variety and/or trading type. The following blemishes are permissi-
ble, providing they do not detract from the fruit’s general appearance, quality, the
time it will keep and the presentation of the bunch or cluster in their packaging:
- Slightly misshapen
- Light flaws in the skin caused by friction or by other means, providing the area
does not exceed 2 cm² of the total surface area of the fruit.
♦ Class II
This class is composed of those bananas that cannot be placed in the upper
classes, yet which fulfil the definitions of minimum requirements. The following faults
are allowed, providing the bananas retain their essential characteristics in terms of
quality, preserve ability and presentation:
- Shape defects,
- Skin flaws, caused by scratches, friction or other means, providing the less than
4 cm² of the total surface is affected.
The flaws are not permitted to affect the fruit’s pulp.
III. Size classification regulations
Size classification is performed according to:
♦ The length of the fruit in cm measured along the outer curve from the stem to the
blossom end.
♦ The thickness in mm, measured as the diameter of the middle, cutting across its
longitudinal axis.
Size classification of a reference fruit is carried out by measuring the length and
thickness
- Of the outer, middle fruit of a bunch
- Of the first fruit of a outer row of a cluster, next to the cut that separated the bunch.
The length must be at least 14 cm and the thickness at least 27 mm.

II Special section: Organic Cultivation of Bananas
Naturland e.V. – 2
nd
edition 2001 page 32
Deviations to the previous paragraph are allowed in the following regions: Madeira,
Azores, Algarve, Crete and Laconia, where bananas measuring less than 14 cm
may still be marketed within the union, providing they are classified as class II fruits.
IV. Tolerance regulations
Not dealt with here.
V. Presentation regulations
a. Uniformity
The contents of a carton must be uniform, and may only contain bananas of identi-
cal origin, variety and/or trade type, and quality.
The visible part of the carton must be representative of the entire contents.
b. Packaging
The bananas must be packed in a way that ensures they are sufficiently protected
Packing material used inside the carton must be new, clean, and so shaped that it
cannot cause any damage to either the inside or outside of the fruit. The usage of
materials such as papers and stickers with company details on them is permitted
providing the no toxic inks, dyes or glues have been used.
The packaging must be free of all other materials.
c. Presentation
Presentation is in bunches comprising at least 4 fruits.
Clusters with a maximum of two fruits missing are permitted when the stalks have
been cleanly cut off, and not torn, leaving the other fruits unharmed.
A maximum of one cluster with three fingers is permitted in each row, providing it
conforms to the characteristics of the other fruits in the carton.
VI. Regulations of carton labelling
Each carton must display the following details in unbroken, legible, permanent let-
ters visible from the outside:
a. Identification
Name and address of the packer
b. Type of product
‘Bananas’, when the contents are not visible
Name of the variety
c. Origin of product
Country of origin, and optionally, national, regional or local description
d. Commercial characteristics
♦ Class
♦ Net weight
♦ Size, depicted as the minimum and (optionally) maximum length
e. Official stamp

II Special section: Organic Cultivation of Bananas
Naturland e.V. – 2
nd
edition 2001 page 33
(optional)
The following characteristics are not laid down in the ‘EU quality standards for ba-
nanas’, but should nevertheless be adhered to:
Quality characteristics Minimum and maximum values
Heavy metals
lead (Pb) max. 0.50 mg/kg
Cadmium (Cd) max. 0.05 mg/kg
Mercury (Hg) max. 0.03 mg/kg
Residues
Pesticides not measurable
Sulphur oxide not measurable
Bromide not measurable
Ethylene oxide not measurable