CAM T31 IOM TR 4 CAMERON Fully Welded Ball Valve
User Manual: CAMERON T31 Fully Welded Ball Valve IOM Resource Library
Open the PDF directly: View PDF .
Page Count: 20
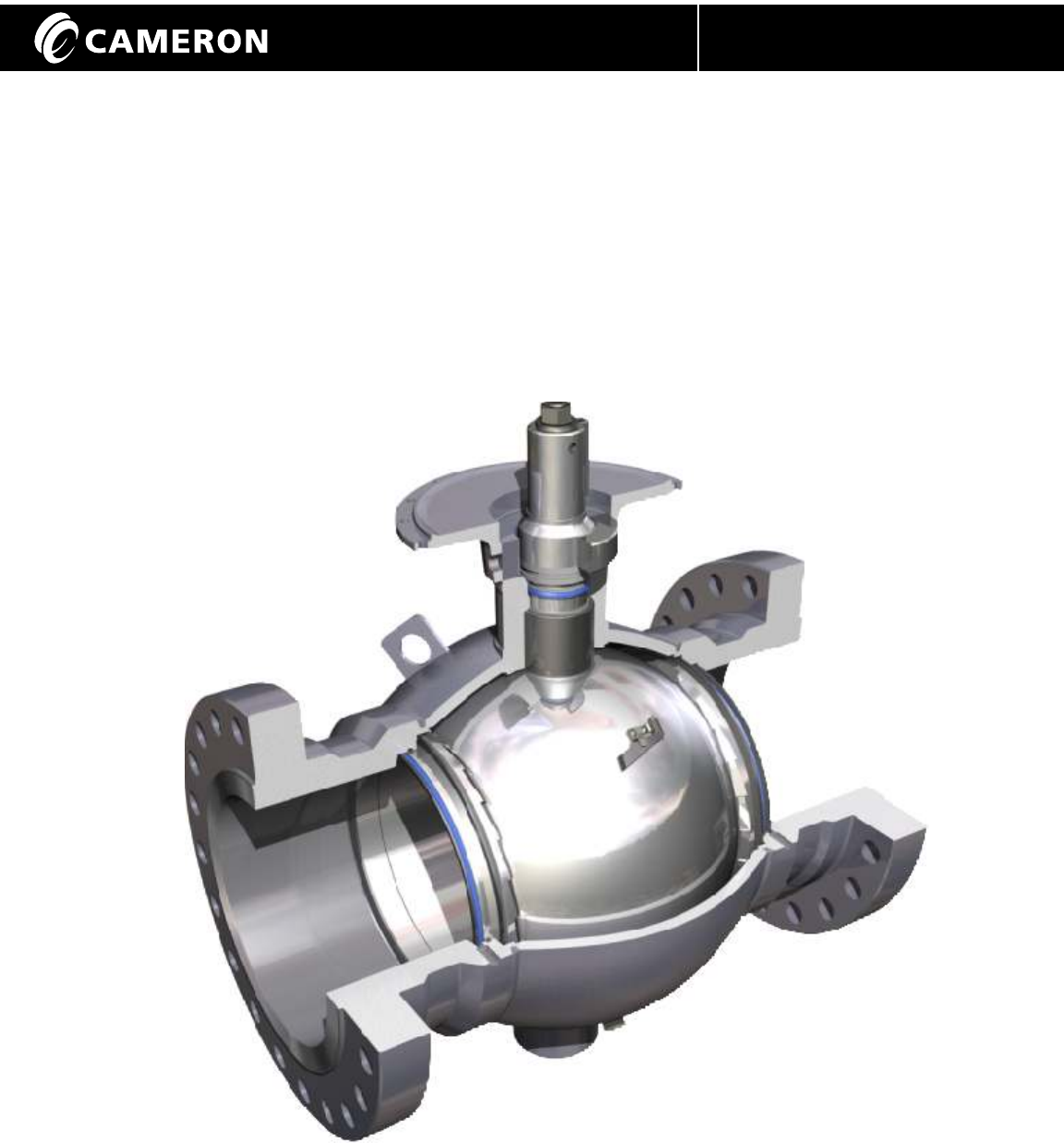
®
CAMERON
®
CAMERON
FULLY WELDED BODY BALL VALVE
TYPE 31
ENGINEERED VALVES
Installation, Operation and Maintenance Manual
Installation, Operation and Maintenance Manual IOM-CAM-BALL-T31

© Cameron’s Valves & Measurement Group IOM-CAM-BALL-T31
Rev. 0 06/09
ENGINEERED VALVES
TABLE OF CONTENTS
CAMERON TYPE 31
FULLY WELDED BODY BALL VALVE
Bill of Materials ................................................ 1
Scope .............................................................. 2
Nameplate Information .................................... 2
Storage ............................................................ 2
Installation ....................................................... 3
Maintenance .................................................... 6
Trouble Shooting ............................................. 8
Injection Procedures ...................................... 10
Valve Cleaning ............................................... 11
Sealant Injection .............................................12
Stem Designs .................................................15
Installation, Operation and Maintenance Manual IOM-CAM-BALL-T31
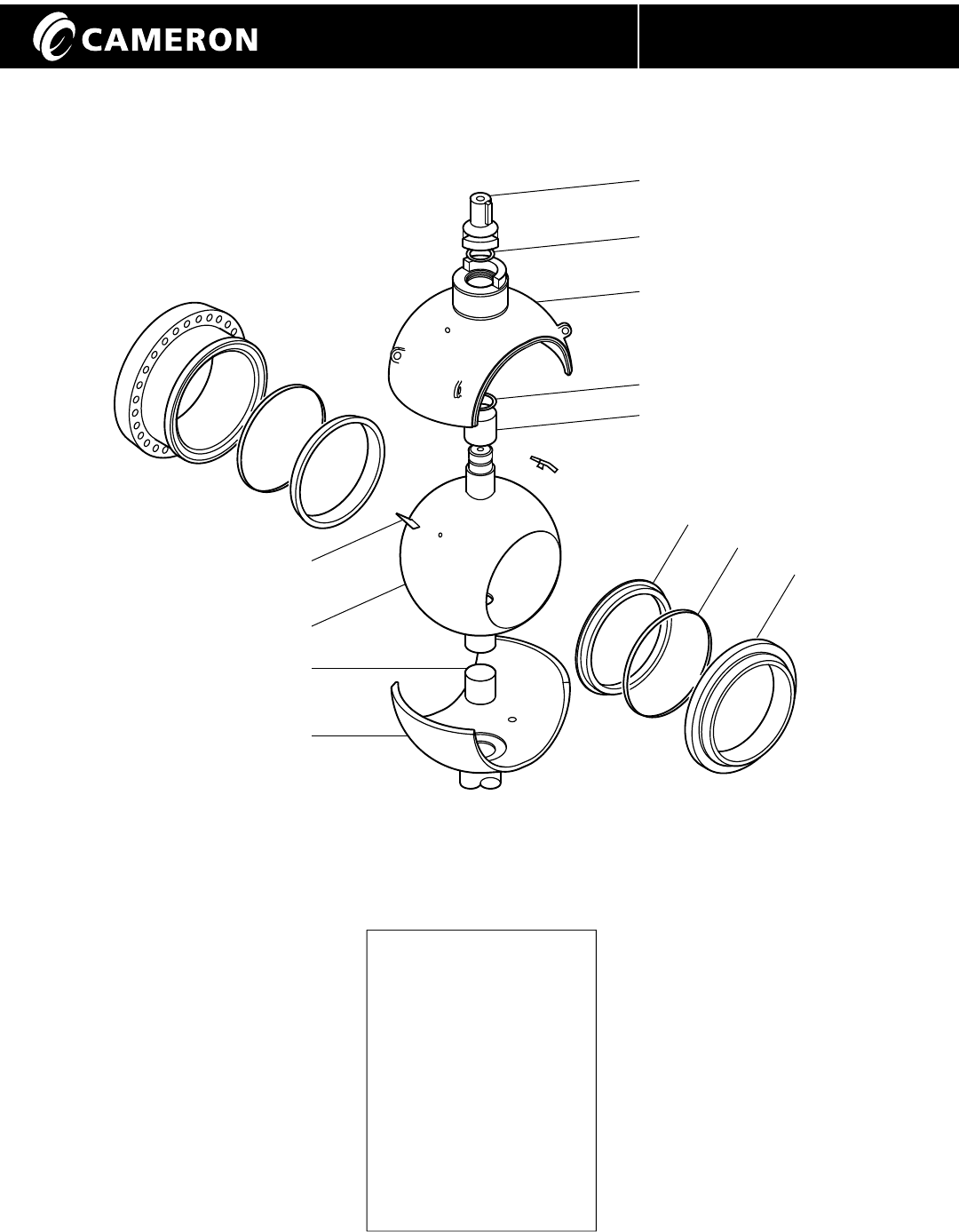
ENGINEERED VALVES
1
Bill of Materials
ITEM DESCRIPTION
1 Keyed Shaft
2 Upper Stem Seal*
3 Upper Body
4 Lower Stem Seal
5 Stem Bearing
6 Dog
7 Ball
8 Seat Ring
9 Lip Seal
10 End Connection
11 Lower Body
Figure 1 - Cameron Fully Welded Body Ball Valve Components.
*Details of stem are on pages 15 and 16.
1
2
3
4
5
6
8
7
11
9
10
5
Installation, Operation and Maintenance Manual IOM-CAM-BALL-T31
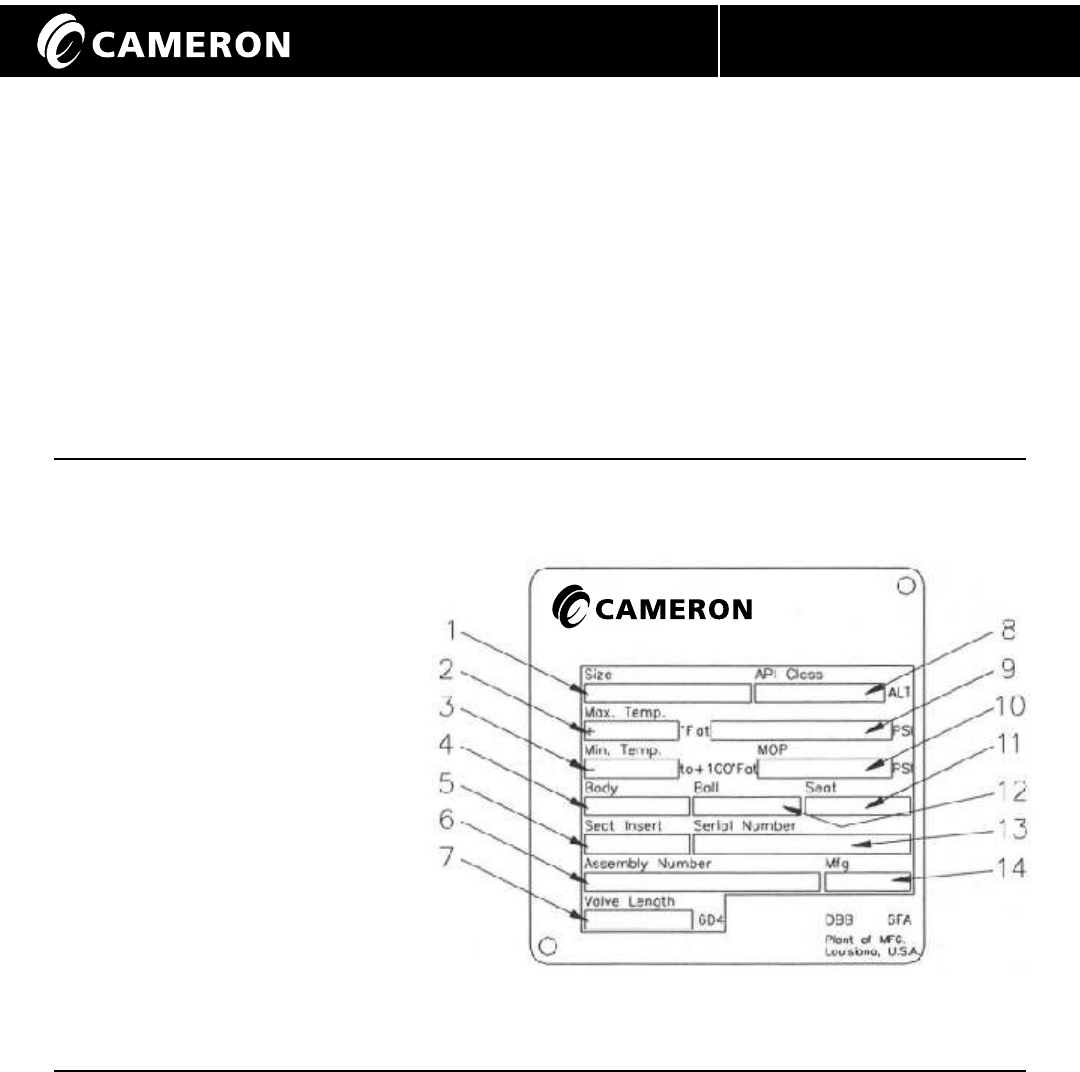
2
Scope
ENGINEERED VALVES
One of the most trusted valves in the petroleum
industry, the CAMERON T31 Fully Welded Body Ball
Valve combines the strength of forged components
with a lightweight and compact spherical design.
CAMERON T31 Fully Welded Body Ball Valves
satisfy ASME 150 through 2500 (PN 20 through
PN 420) and API 2000 through 10000 standards.
Made of forged steel to assure uniform fine grain
structure and toughness, they may be specified
in sizes from 2" to 56" (DN 50 to DN 1400).
Engineered for heavy-duty
maintenance, the CAMERON T31 Fully Welded
Body Ball Valve is commonly selected for a
number of applications. The distinctive design of
the CAMERON T31 Fully Welded Body Ball Valve
gives it maximum strength and minimum weight
as well as maximum resistance both to pipeline
pressure and stresses. The compact, spherical
design also eliminates body flanges, thus reducing
overall size and leak paths.
service and minimal
Nameplate Information
ITEM STAMP
1 Nominal Valve Size x Actual Bore Size.
2 Maximum Temperature
3 Minimum Temperature
4 Body Material Symbol
5 Seat Insert Material Symbol
6 Assembly Part Number
7 Valve Length
8 API Class Designation
9 Maximum Working Pressure
10 Maximum Operating Pressure
11 Seat Material Symbol
12 Ball Material Symbol
13 Valve Assembly Serial Number
14 Month and Year of Manufacture
Storage
The valves are conditioned for a storage period of
approximately six months. The following care should
be taken when storing valves.
1. Make sure the valve end connection covers remain
in place during storage.
2. If the valve does not have an operator already
installed and the valve will be stored outside, the
open stem extension or the stem adapter should
be covered to avoid water buildup.
3. If long-term storage is required, the valve
should be conditioned using a corrosion
inhibitor and end connection covers.
Follow the guidelines found in CAMERON
Engineering Bulletin 476B for long term
storage.
Obtain a copy from your Cameron Valves &
Measurement representative.
Figure 2 - Typical Valve Nameplate.
Installation, Operation and Maintenance Manual IOM-CAM-BALL-T31
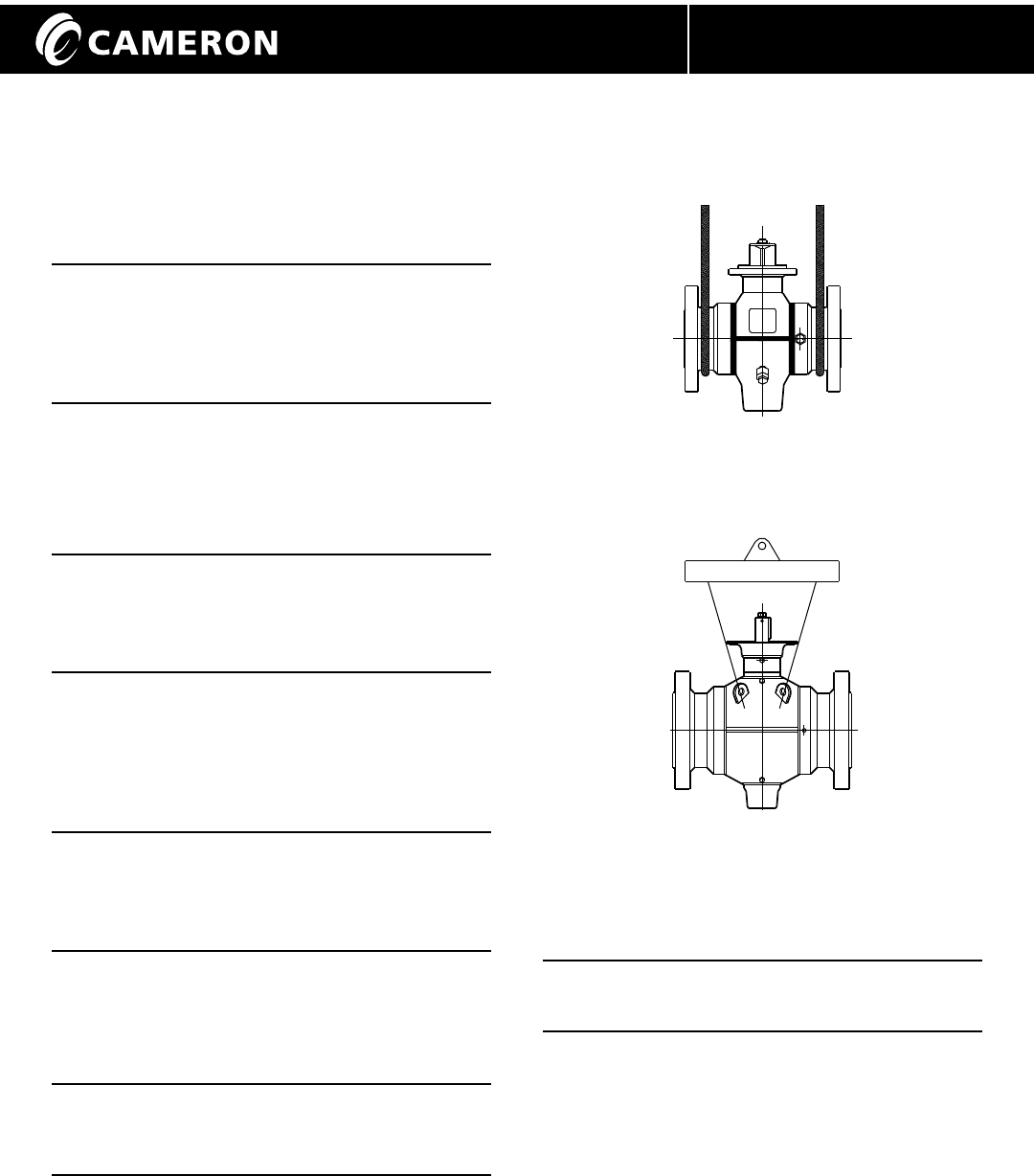
3
Installation
ENGINEERED VALVES
Handling of Valves
1. The valve should be lifted in such a way that
the body supports the load.
CAUTION: The journal and the end connection
necks are suitable places to attach lifting
slings. Never use handwheels or other
protruding parts of the gearbox or actuator
not designated for this purpose.
2. If the valve is equipped with lifting lugs, these
should be used for handling.
3. The end protector covers should be kept in
place on the end connections during all
handling. Remove only during final installation
of the valve.
CAUTION: During handling, protect the end
connection faces and fittings against damage
from the lifting devices. Failure to cover faces
and fittings could cause damage to the valve.
Position of Valve
The ball valve may be installed in any position.
Either end of the valve may be installed as the
upstream end.
Protection of Ball
CAUTION: The ball should be fully open
during the installation of the valve. Failure to
keep the ball fully open during installation
could cause damage to the valve.
If the ball must remain in the closed position
during installation of the valve, coat the
exposed surfaces of the ball with grease.
This will protect the plug from damage due to
weld splatter.
CAUTION: Do not leave the valve in the
partially open position for an extended
period of time.
CAUTION: A weld end valve without pup pipes
should never be installed in the closed position.
Welding Instructions
When preheating, welding or stress relieving, body
temperatures must not exceed 400°F (200°C) at
any point beyond 3" (75 mm) from the weld.
Use tempil sticks to check temperatures. Before
CAMERON T31 Fully Welded Body Ball Valves are
welded into final position in the pipeline, cover the
valve seal areas (ball-to-seat area and seat-to-end
connection area) with 1" wide masking tape from
the 3 o'clock to the 9 o'clock position. This will help
prevent any foreign material from becoming lodged
in these areas. The piping system should also be
pigged before operation or pressure testing to
remove any foreign material from the pipeline.
Figure 3 - Correct valve lifting using End Connection Necks.
Figure 4 - Correct lifting using the valve Lifting Lugs.
EQUALIZING YOKE
Installation, Operation and Maintenance Manual IOM-CAM-BALL-T31
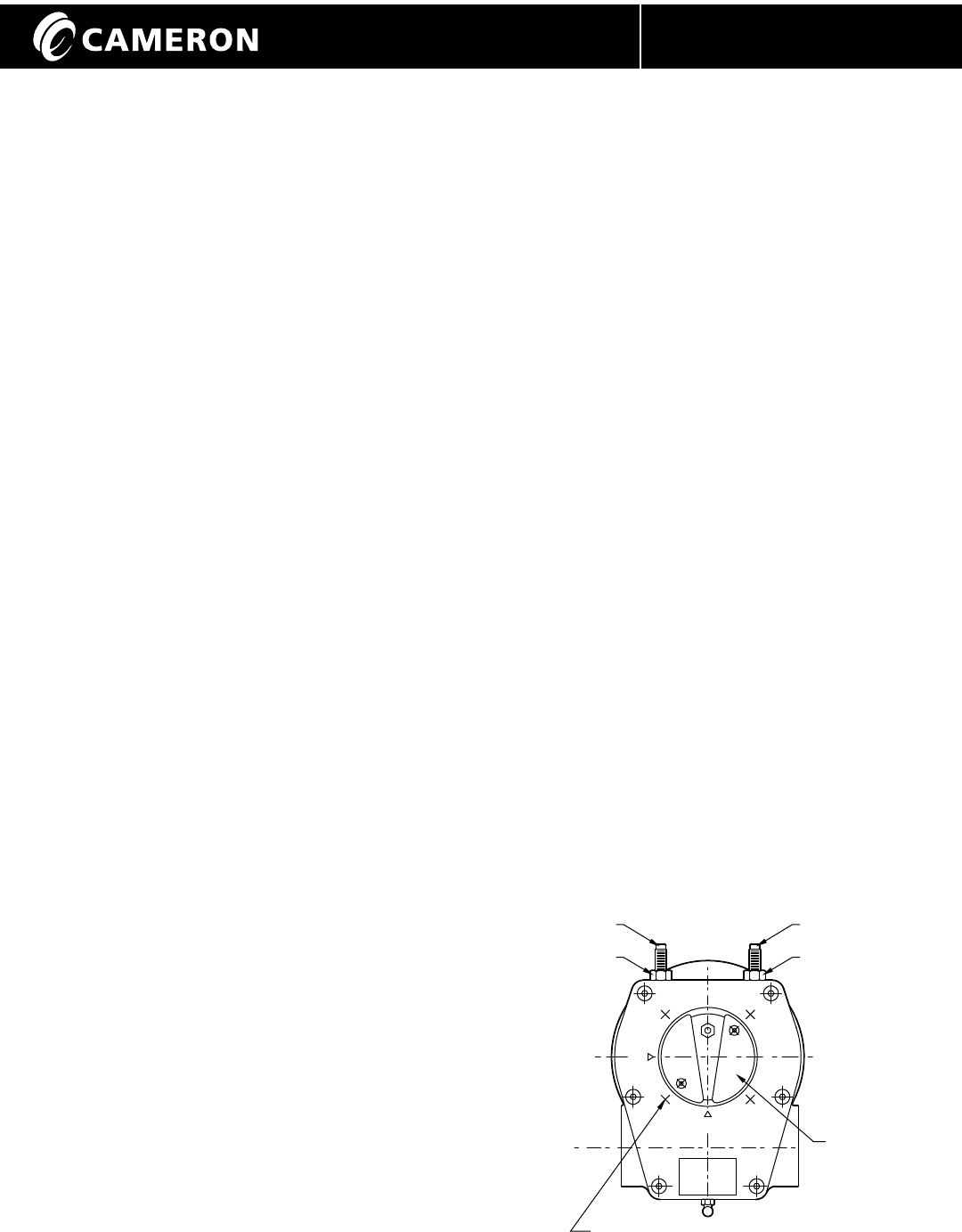
4
ENGINEERED VALVES
Hydrostatic Testing
When CAMERON T31 Fully Welded Body Ball Valves
are installed in a piping system that requires hydrostatic
testing of the adjoining pipe, follow these procedures
to minimize any damage that could occur to the
sealing surfaces and seat seals inside the valve.
1. Valve should be in the fully open position when
the injection of test fluid begins. This will allow
any pipeline debris to be flushed through the
valve bore and out of the piping.
2. Once the piping system has been purged of
debris and the system has been filled completely
with the test fluid, the ball valve should be placed
in the partially open position (approximately 10°
from the fully open position). This allows test
fluid into the body cavity of the valve.
3. The valve is now ready to be pressure tested.
4. Upon completion of hydrostatic testing, the valve
should be returned to the fully open position
before removing the test fluid from the piping
system. The test fluid in the body cavity can be
drained through the body drain port located on
the lower portion of the valve body.
5. Once the valve and piping system have been
pigged and customer product is injected into the
piping system, the valve should be moved to the
partially open position (approximately 10° from
the fully open position). Any remaining test fluid
trapped in the valve body cavity can then be
vented through the body bleed plug, located on
the lower portion of the valve body. If the valve
has been fitted with a stem extension, the vent
fitting will be located below the mounting flange
on top of the extension.
6. Opening the body bleed fitting will force trapped
test fluid out of the body cavity. Keep the bleed
plug open until all fluids have been exhausted
through the body bleed plug.
7. Close the valve body bleed fitting and return the
valve to the fully open position or the required
operating position.
8. The valve seat pockets should be filled with an
approved valve flush product to displace any
test fluid. Refer to Routine Seat Cleaning which
appears on page 7.
Mounting the Gear/Actuator
To mount a gear or power operator on a valve, use
the following guidelines. Note: The guidelines
given are for typical gear and actuator designs.
Specific instructions for each design should be
obtained from the gear / actuator manufacturer.
1. Make sure the valve is in the fully open or closed
position and position the actuator to match.
2. Depending on the valve stem and the actuator/
gear mounting kit, it is possible that the actuator
may be installed in multiple positions. If this is
the case, determine where the customer desires
the handwheel or actuator control panel and
install it accordingly. (A thin layer of antiseeze on
the valve stem is recommended.)
3. Once the operator is mounted, secure it with the
appropriate bolts. If the bolt holes do not line up,
slightly operate to the open or closed to match
the mounting flange. If you are unable to operate
the operator, performing steps 2 and 3 of Setting
Stops may need to be conducted.
4. It is now necessary to set the operator stops as
outlined in the following section.
Setting Stops
Gear Operator with Stops
1. Make sure that operating the valve to the fully
open and fully closed position will not disrupt
current operation of line.
2. Loosen the open and closed stop screw locknuts.
3. Turn stop screws counter-clockwise to increase
gear travel.
4. Operate the valve to the fully open position.
5. Utilize the stem stop viewports to verify valve
position. (Refer to Open and Closed Viewports
on page 6.)
6. Turn the open stop screw clockwise until it stops,
then tighten the locknut. If the stop screws will
not turn, repeat steps 3 and 4.
7. To set the closed stop, conduct steps 3 - 6,
operating the valve to the closed position and
utilize the closed stop.
Figure 5 - Typical Gear Box with Stops.
STOP SCREW (CLOSED) STOP SCREW (OPEN)
LOCKNUT
INDICATOR CAP
(SHOWN OPEN)
APPROXIMATE LOCATION OF BLANKING PLUGS (IF PRESENT)
OPEN
SHUT
LOCKNUT
Installation, Operation and Maintenance Manual IOM-CAM-BALL-T31
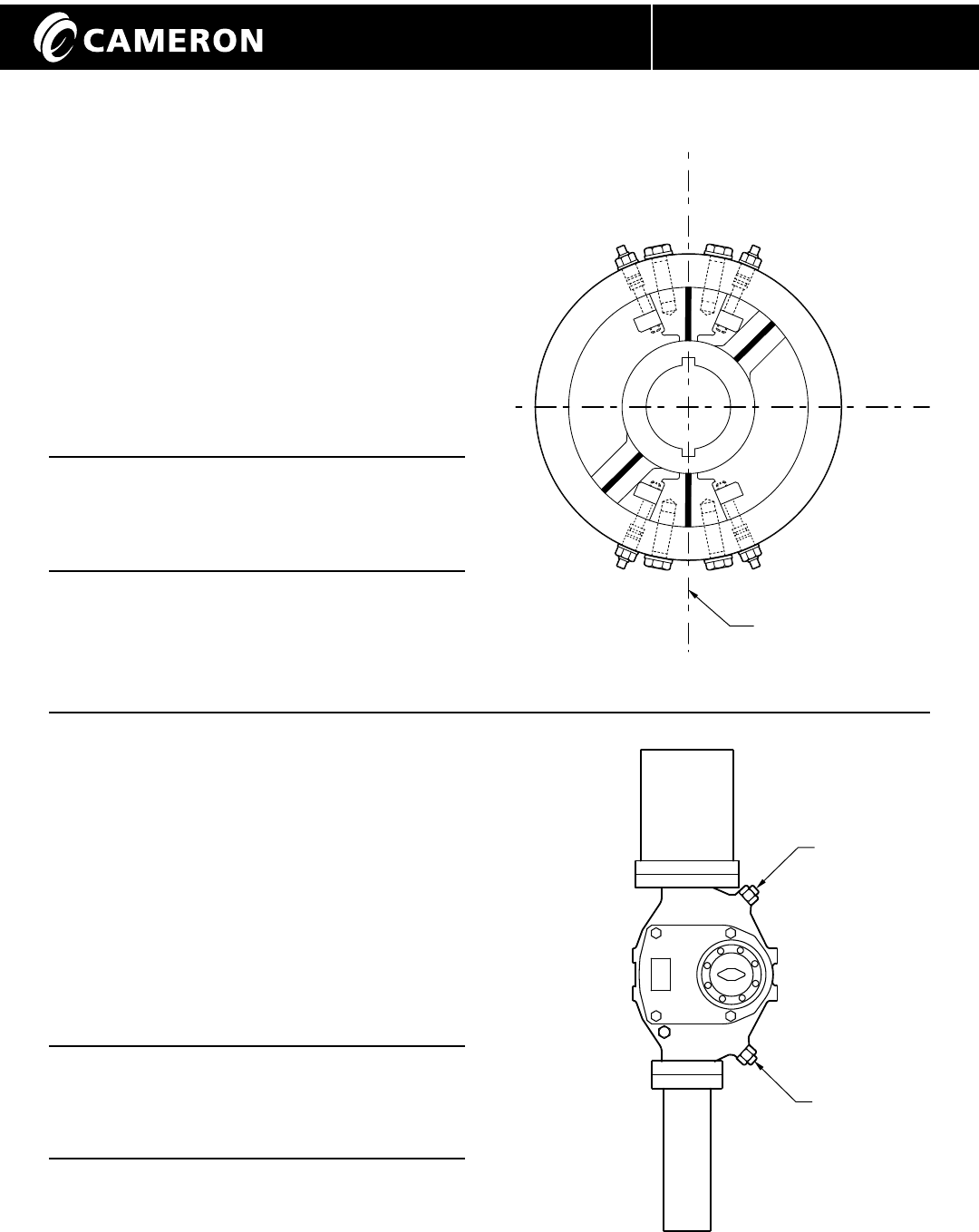
5
ENGINEERED VALVES
Rotary Vane Style Operator (4 Bar Type)
1. Make sure that operating the valve to the fully
open and fully closed position will not disrupt
current operation of line.
2. Loosen the open and closed stop screw locknuts.
3. Turn stop screws clockwise to increase travel.
4. If equipped with a manual override, use it to
operate the valve to the fully open position.
5. Check the stem stop viewports to verify valve
position. (Refer to Open and Closed Viewports
on page 6.)
6. Turn the open stop screw counter-clockwise until
it stops and tighten the locknut.
CAUTION: Once the stop makes contact with
the vane, do not continue to turn the screw.
Continuing to turn the screw could move the
valve off the stops.
7. If the stop screws will not turn repeat steps 3
and 4.
8. To set the closed stop, repeat steps 3 - 6,
operate the valve to the closed position and use
the closed stops.
Scotch Yoke Style Operator
1. Make sure that operating the valve to the fully
open and fully closed position will not disrupt
current operation of line.
2. Loosen the open and closed stop screw locknuts.
3. Turn stop screws counter-clockwise to increase
piston travel.
4. If equipped with a manual override, use it to
operate the valve to the fully open position.
5. Check the stem stop viewports to verify valve
position. (Refer to Open and Closed Viewports
on page 6.)
6. Turn the open stop screw clockwise until it stops
and tighten the locknut.
CAUTION: Once the stop makes contact with
the vane, do not continue to turn the screw.
Continuing to turn the screw could move the
valve off the stops.
7. If the stop screws will not turn repeat steps 3
and 4.
8. To set the closed stop, repeat steps 3 - 6,
operate the valve to the closed position and
use the closed stops.
C/L OF PIPELINE
CLOSE
OPEN
Figure 6 - Rotary Vane-Style Operator.
CLOSED STOP
OPEN STOP
Figure 7 - Scotch Yoke-Style Operator.
Installation, Operation and Maintenance Manual IOM-CAM-BALL-T31
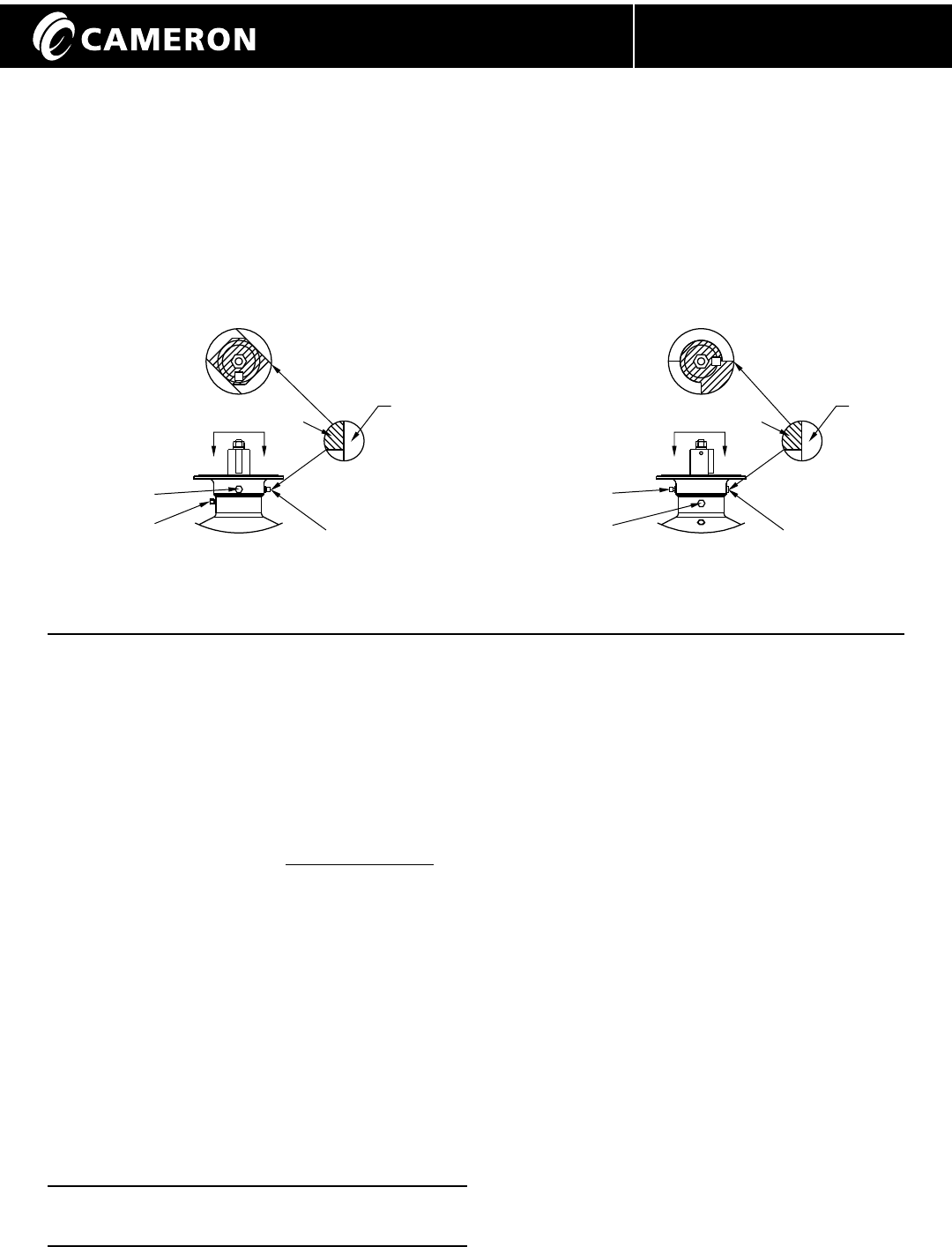
6
ENGINEERED VALVES
Open and Closed Viewports
Once the pipe plug and relief plug are removed from the valve mounting flange, the position of the keyshaft
stop relative to the valve stops can be observed on valves with nominal stem sizes of 3" and larger.
The valve is fully opened when the keyshaft stop butts against the valve stop as viewed through the
"open viewport" and is fully closed when the keyshaft stop butts against the valve stop as viewed through
the "closed viewport".
Figure 8 shows the viewport locations for valves with a 3" stem size and figure 9 shows the viewport locations
for valves with 4" and larger stem sizes.
Operating Times
Quick Operating Time
Opening or closing a valve quickly induces loads in
addition to the normal torsion load. It is therefore
necessary to limit valve operating times in order to
prevent over stressing of the valve.
Valves can be safely operated with an operating
time given by the formula:
*Quick operating time = Valve nominal bore
2
If a faster operating time is required, please call your
Cameron Valves & Measurement Representative.
Longest Operating Time
When the valve is being operated, the seat face is
exposed. Therefore, to minimize the amount of time
in which the seat face is exposed, Cameron Valves
& Measurement group recommends a maximum
operating time as follows:
*Longest Operating Time = 5 x Valve nominal bore
(i.e., one minute
per foot of nominal
bore)
*The time is in seconds and the bore size is in inches.
CAUTION: Failure to follow these operating times
could cause damage to the valve.
Maintenance
The CAMERON T31 Fully Welded Body Ball Valve
requires a minimum of maintenance. In order to
optimize the life of the valve, the maintenance
procedures on pages 6 and 7 should be followed.
Operation
Operating the valve is an important part of routine
maintenance. Operation of the valve will help to
break-up any buildup on the seat face and/or ball
and, if so equipped, will rotate the seat rings 15°,
distributing the wear on the insert.
Figure 9 - Open
and Larger Stem Sizes: Valve shown in open Position.
and Closed Viewport Location for Valves with 4" Figure 8 - Open and Closed Viewport Location for Valves
with 3" Stem Size: Valve shown in Open Position.
VALVE
STOP
KEYSHAFT
STOP
VALVE OPEN
OPEN VIEWPORT
CLOSED VIEWPORT
STEM SEALANT
PORT (REF.)
VALVE
STOP
KEYSHAFT
STOP
VALVE OPEN
OPEN VIEWPORT
STEM SEALANT
PORT (REF.)
CLOSED VIEWPORT
Installation, Operation and Maintenance Manual IOM-CAM-BALL-T31
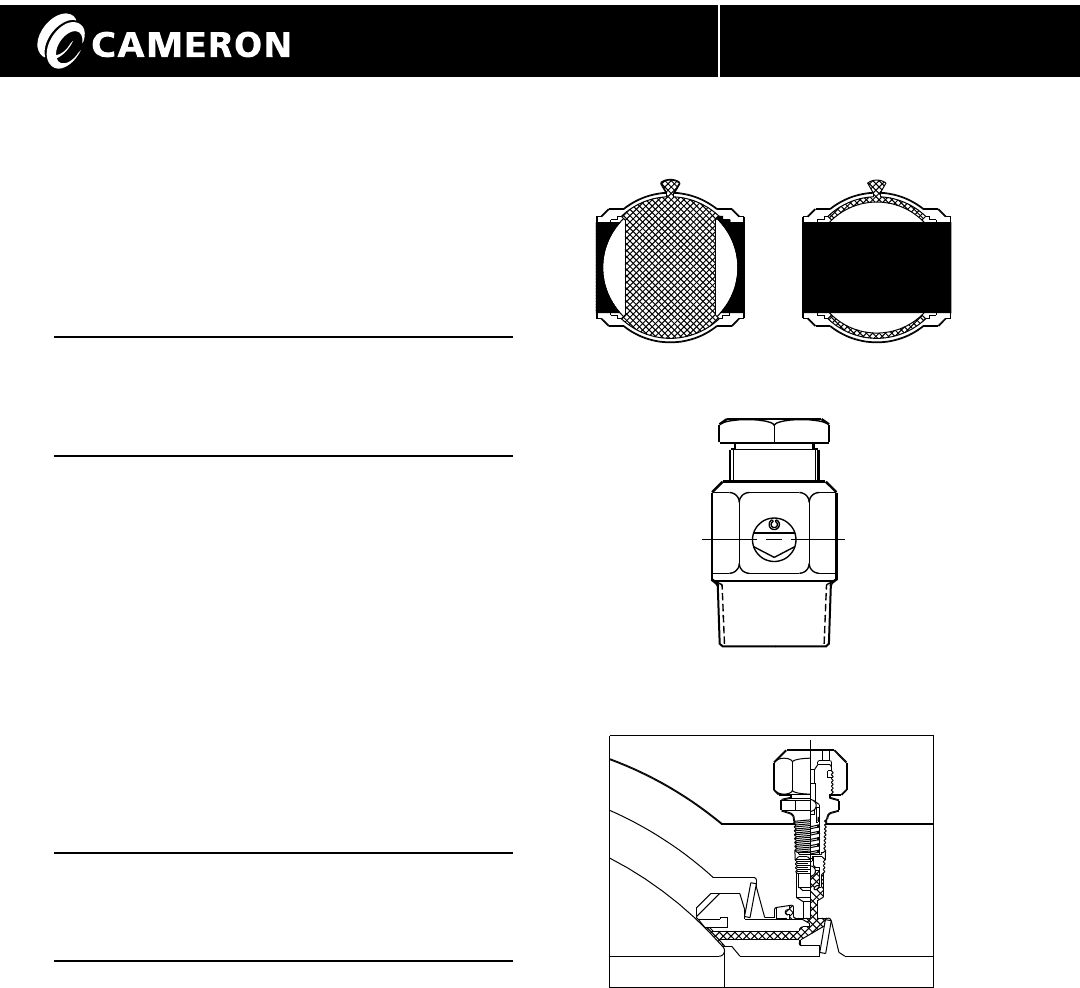
7
ENGINEERED VALVES
Double-Block-and-Bleed
Whether in the open or closed position, pressure
on each side of the ball is blocked from the body
cavity by the seat ring. The body cavity can then
be blown down or drained through the body port.
Take the following steps when block-and-bleeding
a valve:
WARNING: Make sure proper safety garments
are worn, and follow all customer safety
procedures. Failure to do so could injure
you or others.
1. The CAMERON bleed fittings have one or two
exhaust ports. You should be aware of their
orientation. Any debris in the valve or fitting
will be exhausted at a high velocity.
2. If necessary, tighten the fitting to reorient the
exhaust ports.
3. With the valve fully open or fully closed, open
the bleed fitting all the way. When opening the
bleed fitting, a backup wrench may be used to
prevent accidental removal of bleed fitting.
The process of block-and-bleeding the valve is
intended to test the valve integrity.
If the valve does not blow down, this indicates that
the seats are leaking. Consult the Troubleshooting
section.
WARNING: Never try to block-and-bleed the
valve in the partially open position.
Failure to do so could injure you or others.
Seat Cleaning
The seat pocket area is the primary area where
any valve can be affected by contaminants in
the lines. To insure the seat's free movement,
it is recommended that the valve seat pockets
be cleaned routinely with an approved product.
(The frequency of routine cleaning depends
on the severity of service, but once a year is a
good guideline. Contact your Cameron Valves &
Measurement group representative for assistance).
Cleaning procedures can be found on page 10.
Gear Maintenance
The following gear maintenance should be
performed along with the valve maintenance:
1. Inspect housing for damage and wear.
2. Inspect weather seal and replace, if damaged.
This will prevent water from entering the
gearbox and causing corrosion.
3. Lubricate gear, using an approved lubricant.
Figure 12 - Typical Bleed Fitting.
Figure 13 - Cameron T31 Seat Section.
Figure 10 - Valve Closed. Figure 11 - Valve Open.
Installation, Operation and Maintenance Manual IOM-CAM-BALL-T31
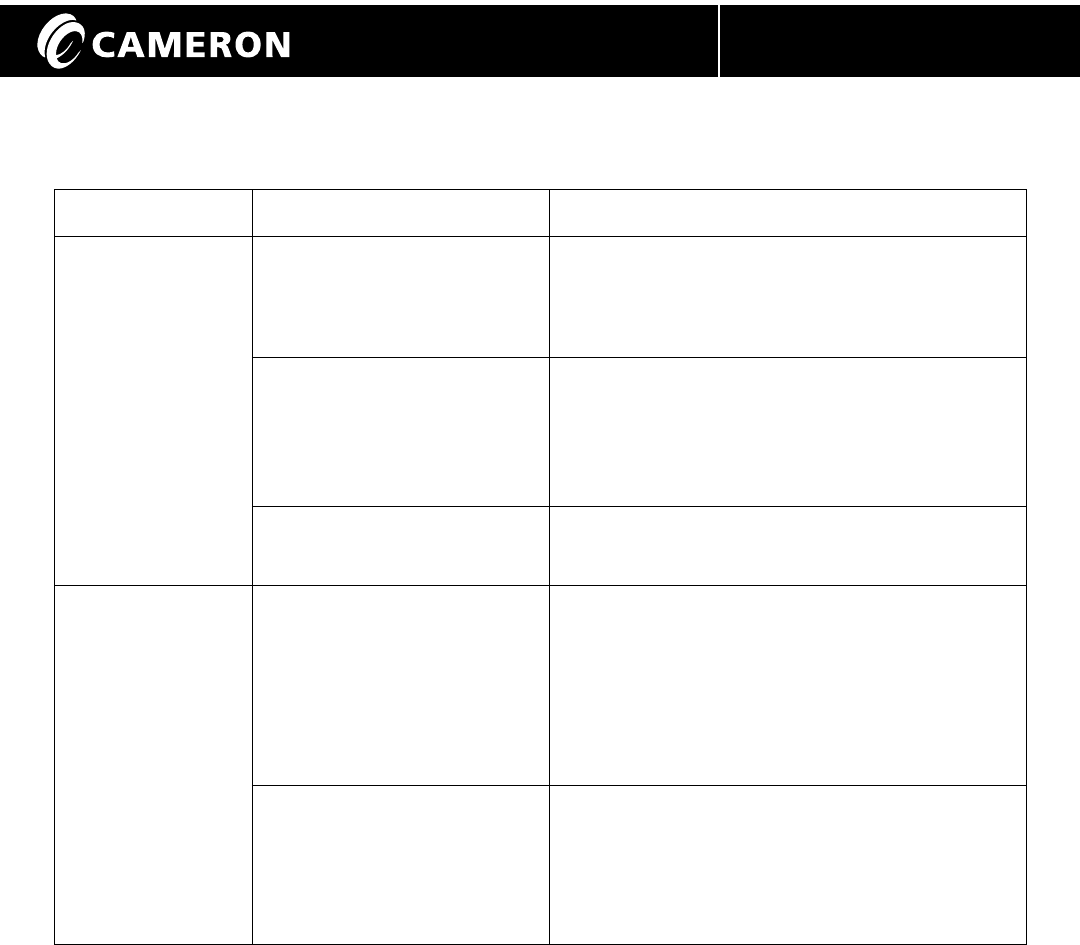
8
ENGINEERED VALVES
Troubleshooting
Trouble Probable Cause Remedy
The seats
are leaking.
The stem
is leaking.
The valve is not closed
completely.
Operate the valve to the fully closed position.
Block-and-Bleed the valve to insure that the
leakage has stopped. Refer to Block-and-
Bleed procedure on page 7.
Properly adjust the operator stops. Refer to
Setting Stops on page 4.
Block-and-Bleed the valve to insure that the
leakage has stopped. Refer to the Block-and-
Bleed procedure on page 7.
Clean and flush the seat rings. Refer to the
Injection Procedure section on pages 10 - 12.
Tighten the stem screw or nut tightly enough
to stop the leak. Do not exceed torque value
for stem screw. Contact your Cameron
Valves & Measurement group representative
to obtain torque values.
Operate the valve to make sure the stem is
causing the leak.
Replace stem seal. Contact your Cameron
Valves & Measurement group representative
for assistance.
Inject a small amount of sealant into the stem
injection fitting.
Operator stops are incorrectly
adjusted.
The seat rings are
malfunctioning.
Stem screw or nut is loose.
The stem seal is damaged.
Installation, Operation and Maintenance Manual IOM-CAM-BALL-T31
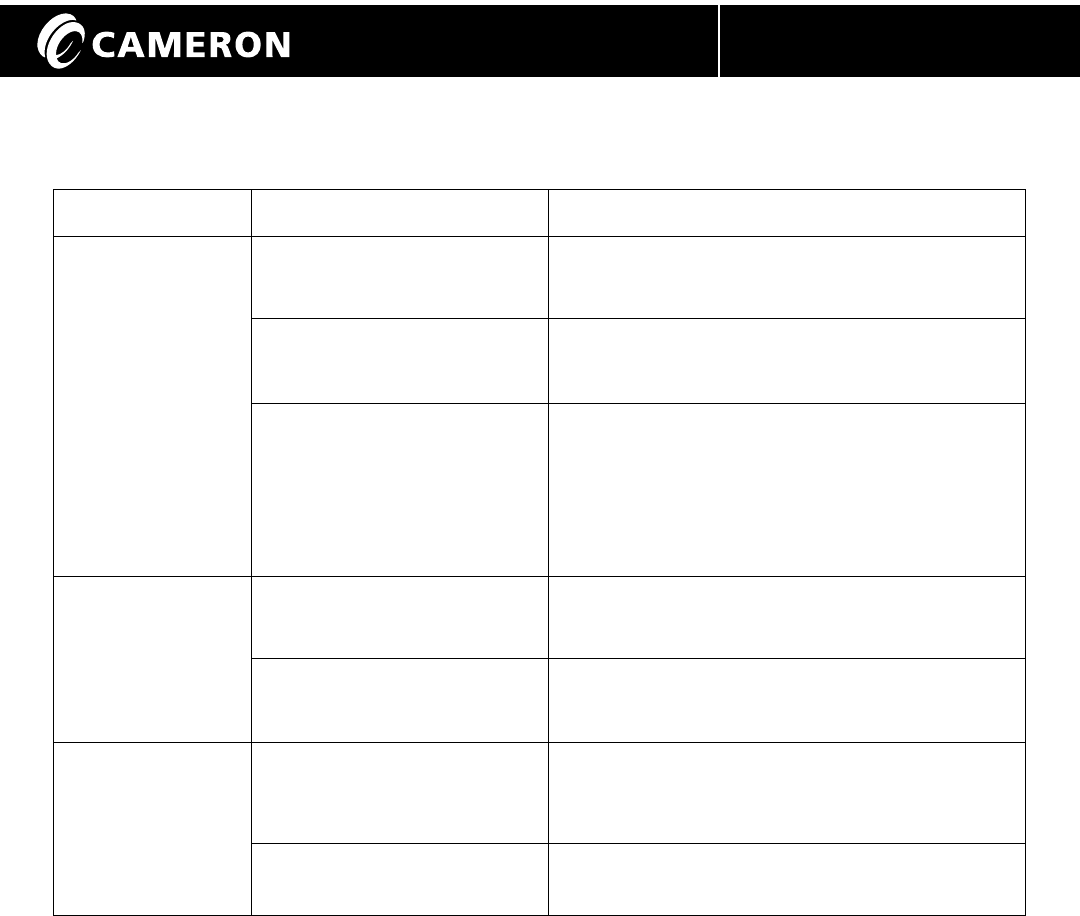
9
ENGINEERED VALVES
Troubleshooting (continued)
Trouble Probable Cause Remedy
The valve is
difficult to operate.
The operator is malfunctioning.
(Worm gear operators only) Perform gear maintenance outlined on page 7.
There is a build up in the seat
area due to line contaminates.
Stem capscrew or nut is too
tight.
Trash in fitting.
Fitting seal is damaged.
Sealant fitting is
leaking.
Fitting leaks
between
coupler and
button head.
Paint or trash is on the surface
of the button head fitting.
Coupler seal is damaged.
Clean the seat area as outlined on page 7.
Loosen the stem screw or nut.
Operate the valve.
Tighten the stem screw or nut to the appropriate
torque value. Contact your Cameron Valves &
Measurement group representative to obtain
torque values.
Inject a small amount of cleaner into fitting to
dislodge trash.
Install an auxiliary fitting.
Replace fitting when line is depressurized.
Clean surface of button head fitting.
Replace seal as per manufacturer's instructions.
Installation, Operation and Maintenance Manual IOM-CAM-BALL-T31
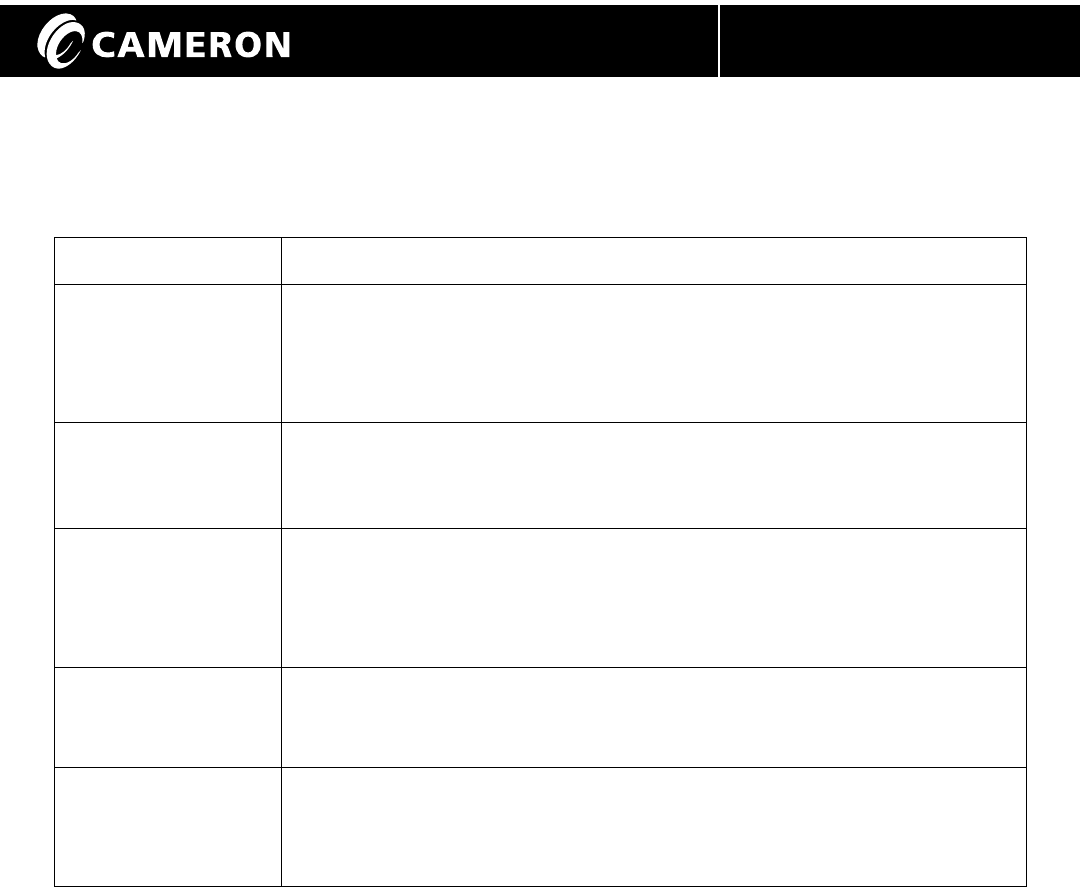
10
ENGINEERED VALVES
Injection Procedures
Routine Cleaning
Steps Procedure
1. Inspect valve.
Inspect:Seat injection fittings.
Stem injection fitting. (Do not inject into this fitting.)
Body / bleed fitting
Make sure the grease gun / pump is in working order and loaded with the
appropriate product.
2. Inspect equipment.
3. Inject standard
valve flush.
Inject full seat capacity into each seat, utilizing the seat injection ports.
(Refer to capacity chart on page 13.) If this is the first time maintenance has
been performed, and the valve has been in service over two years, perform
Valve Cleaning procedures on page 11.
4. Operate valve. Make sure it is safe to operate the valve.
Fully operate valve three times.
5. Inspect valve. Make sure the valve is in the correct position.
Clean the grease fittings.
Replace fitting caps.
Installation, Operation and Maintenance Manual IOM-CAM-BALL-T31
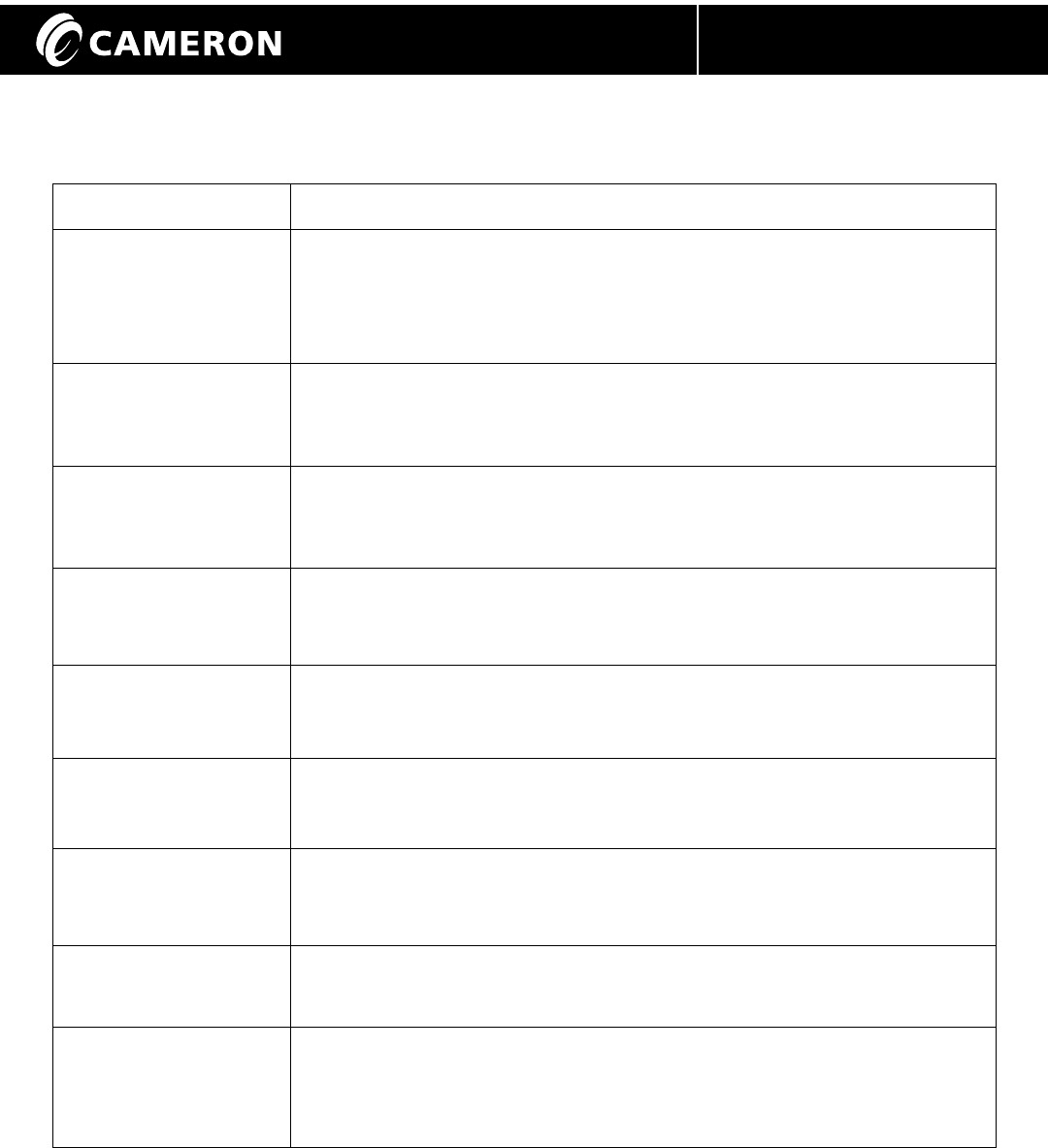
11
ENGINEERED VALVES
Valve Cleaning
Steps Procedure
1. Inspect valve.
Inspect:Seat injection fittings.
Stem injection fitting. (Do not inject into this fitting.)
Body / bleed fitting
Make sure the grease gun / pump is in working order and loaded with the
appropriate product.
2. Inspect equipment.
3. Inject flush. Inject full seat capacity into each seat, utilizing the seat injection ports.
(Refer to capacity chart on page 13.)
4. Operate valve. Make sure it is safe to operate the valve.
Fully operate valve three times.
5. Inject cleaner / flush. Inject full seat capacity into each seat, utilizing seat injection ports.
(Refer to capacity chart on page 13.)
6. Allow valve to soak. Wait one to six hours to allow cleaner to penetrate the buildup and
contaminates.
7. Inject flush. Inject full seat capacity into each seat, utilizing seat injection ports.
(Refer to capacity chart on page 13.)
8. Operate valve. Fully operate the valve three times.
9. Test valve. Block-and-bleed valve. (Refer to Block-and-Bleed procedure on page 7.)
If the valve will not bleed down, follow the sealant injection procedure on
page 12.
Installation, Operation and Maintenance Manual IOM-CAM-BALL-T31

12
ENGINEERED VALVES
Sealant Injection
Steps Procedure
1. Prior steps.
Block-and-Bleed valve. (Refer to Block-and-Bleed procedure on page 7.)
If the valve will not bleed down, continue to the next step.
If the valve leaks in the closed but not in the open position:
- The valve is not going fully closed.
(use the Open and Closed View Ports on page 6 to verify valve position)
- Possible ball damage. Contact your Cameron Valves & Measurement
group representative.
Confirm valve is in the fully closed position. Use the Open and Closed
View Ports (page 6) when available.
3. Inject standard sealant. Inject full seat capacity into each seat, utilizing the seat injection ports.
4. Test valve. Block-and-Bleed valve. (Refer to Block-and-Bleed procedure on page 7.)
If the valve will not bleed down, continue to the next step.
5. Operate valve. Operate valve to the fully open position.
Use the Open and Closed View Ports on page 6 to verify valve position.
6. Inject standard sealant. Inject 1/2 seat capacity into each seat, utilizing seat injection ports.
7. Test valve.
Cycle valve open/close 6 times and return to fully closed position.
Use the Open and Closed View Ports on page 6 to verify valve position.
8. Operate valve.
9. Inject standard sealant.
Block-and-Bleed valve. (Refer to Block-and-Bleed procedure on page 7.)
If the valve will not bleed down, continue to the next step.
Be sure to follow steps found within Troubleshooting section under Seats are
Leaking on page 8 prior to proceeding.
All nine steps found in Valve Cleaning on page 11 should be conducted prior
to proceeding.
2. Verify valve position.
Inject 1/2 seat capacity into each seat, utilizing seat injection ports.
10. Test valve
Inject full seat capacity into each seat, utilizing seat injection ports.
11. Inject severe leak
sealant.
Block-and-Bleed valve. (Refer to Block-and-Bleed procedure on page 7.)
If the valve will not bleed down, continue to the next step.
12. Test valve
Cycle valve open/close 3 times and return to fully closed position.
13. Operate valve
Inject 1/2 seat capacity into each seat, utilizing seat injection ports.
14. Inject severe leak
sealant.
Block-and-Bleed valve. (Refer to Block-and-Bleed procedure on page 7.)
If the valve will not bleed down, continue to the next step.
15. Test valve
16. Contact your
Cameron Valves &
Measurement group
Representative.
When Contacting your Cameron Valves & Measurement group representative
for assistance, please have the following information available:
- Valve Size -Assembly Number - ASME Class -Manufacture Date
- Serial Number (Refer to nameplate on page 2)
The Cameron Valves & Measurement group representative may be able to
provide additional information or schedule an on-site consultation.
Installation, Operation and Maintenance Manual IOM-CAM-BALL-T31
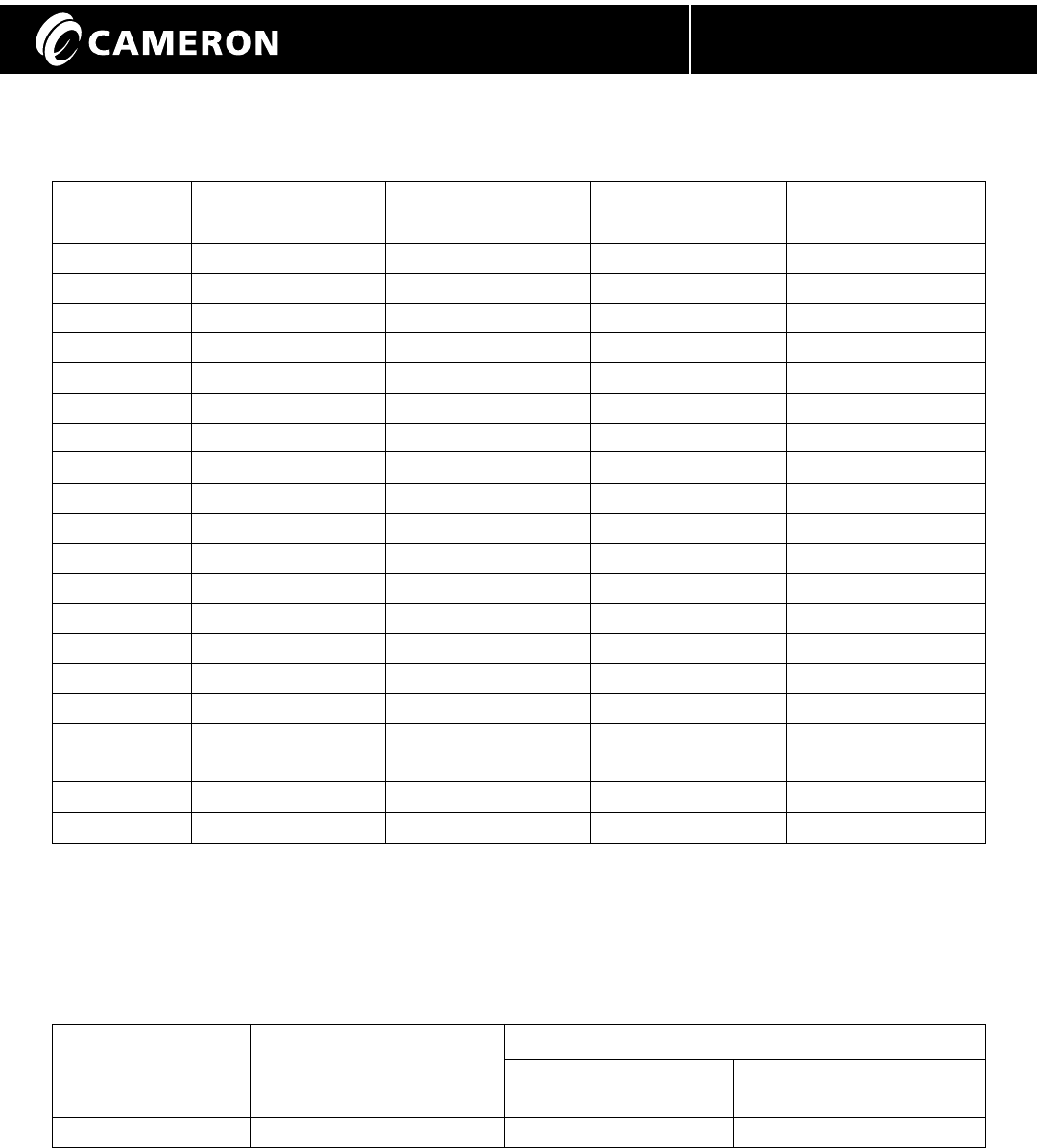
13
ENGINEERED VALVES
Injection Capacity Chart
Valve Volume Volume Volume Volume
3
Size per Seat (oz) per Valve (oz) per Seat (cm )
2" 1 2 25 50
3" 1 2 35 65
4" 2 3 50 100
6" 2 4 65 130
8" 3 6 80 160
10" 3 6 90 180
12" 5 10 135 270
14" 5 10 155 310
16" 6 12 170 335
18" 9 18 265 525
20" 10 20 295 585
22" 11 22 330 655
24" 12 24 350 695
26" 13 26 395 785
28" 13 26 400 800
30" 15 30 445 890
34" 17 34 495 990
36" 21 42 620 1240
40" 32 64 960 1920
42" 34 68 995 1990
3
per Valve (cm )
Extended Sealant Lines Capacity Chart
Nominal Outside Diameter Volume of Sealant Per Length of Pipe
3
Line Size of Pipe oz/ft cm /m
1/4" (6 mm) .540" (13.7 mm) .5 46
1/2" (12 mm) .840" (21.3 mm) 1.6 150
Installation, Operation and Maintenance Manual IOM-CAM-BALL-T31
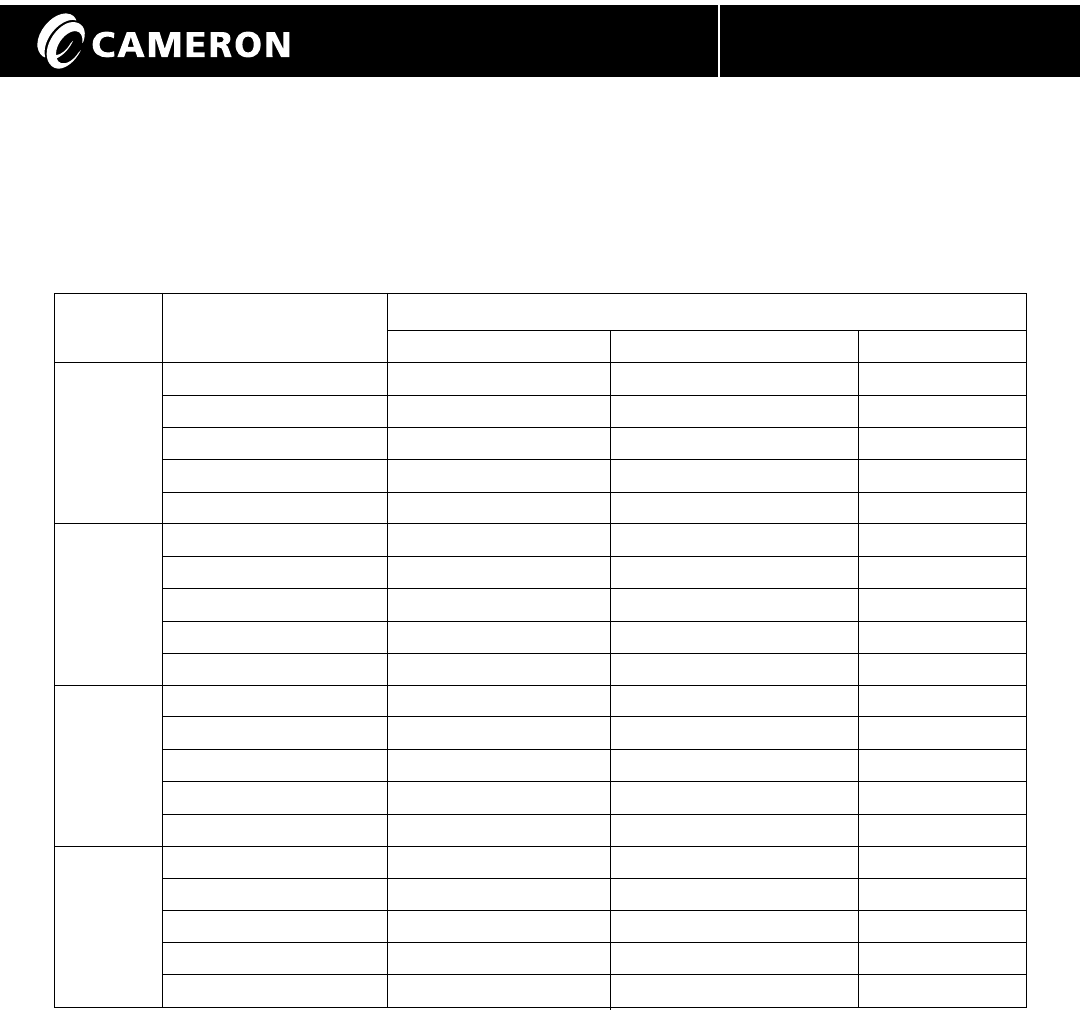
14
ENGINEERED VALVES
Approved Flush / Sealant
The following products are recommended by the cleaner / sealant manufacturers for the indicated service
and condition. Contact your Cameron Valves & Measurement group representative for availability through
Cameron Valves & Measurement.
Cleaner / Sealant Manufacturer
Service
Product Condtions Val-Tex Sealweld Lubchem
Flush Valve Flush Valve Cleaner Plus Valve Saver
Standard Valve Lubricant 2000 Light Lube Equa-Lube 80 Lubchem "50-400"
Natural Gas Standard Sealant 80 bulk / 80-H stick Total Lube 911 * Everlast No. 1
Standard Low Temp 750 bulk / stick Winterlub 7030 * Everlast No. 1 AG
Severe Leak Sealant 80+FTFE bulk / stick * Sealweld #5050 * Formasil RS
Flush Valve Flush Valve Cleaner Plus Valve Saver
Standard Valve Lubricant 2000 Light Lube Equa-Lube 80 Lubchem "50-400"
Sour Gas Standard Sealant 700 bulk / stick Total Lube 911 * Lubchem "50-400"
Standard Low Temp 750 bulk / stick Winterlub 7030 * Lubchem "50-300"
Severe Leak Sealant 700 FTFE bulk / stick * Sealweld #5050 * Formasil RS
Flush Valve Flush Valve Cleaner Plus Valve Saver
Standard Valve Lubricant 2000 Light Lube Sealweld Silicone Lubricant Everlast WR
Dry CO Standard Sealant 700 bulk / stick Sealweld Silicone Lubricant Everlast WR
2
Standard Low Temp 750 bulk / stick Sealweld Silicone Lubricant Everlast WR
Severe Leak Sealant 700 FTFE bulk / stick * Sealweld Silicone Sealant Formasil CO2
Flush Valve Flush Valve Cleaner Plus Valve Saver
Standard Valve Lubricant 2000 Light Lube Equa Lube 80 Lubchem "50-400"
Crude Oil Standard Sealant 700 bulk / stick Total Lube 911 * Lubchem "50-400"
Standard Low Temp 750 bulk / stick Winterlub 7030 * Lubchem "50-300"
Severe Leak Sealant 700 FTFE bulk / stick * Sealweld #5050 * Formasil WR
Val-Tex Sealweld Lubchem Inc.
Valves Incorporated of Texas 6450 Skyview Drive P.O. Box 2626
10600 Fallstone Rd. Houston, TX 77041 Spring, TX 77383
Houston, TX 77099 713/466-7373 281/350-9600
281/530-4848 800/624-4301 800/929-0244
800/627-9771
Valve Cleaner / Sealant Manufacturers
Installation, Operation and Maintenance Manual IOM-CAM-BALL-T31
* Note: Contains PTFE.
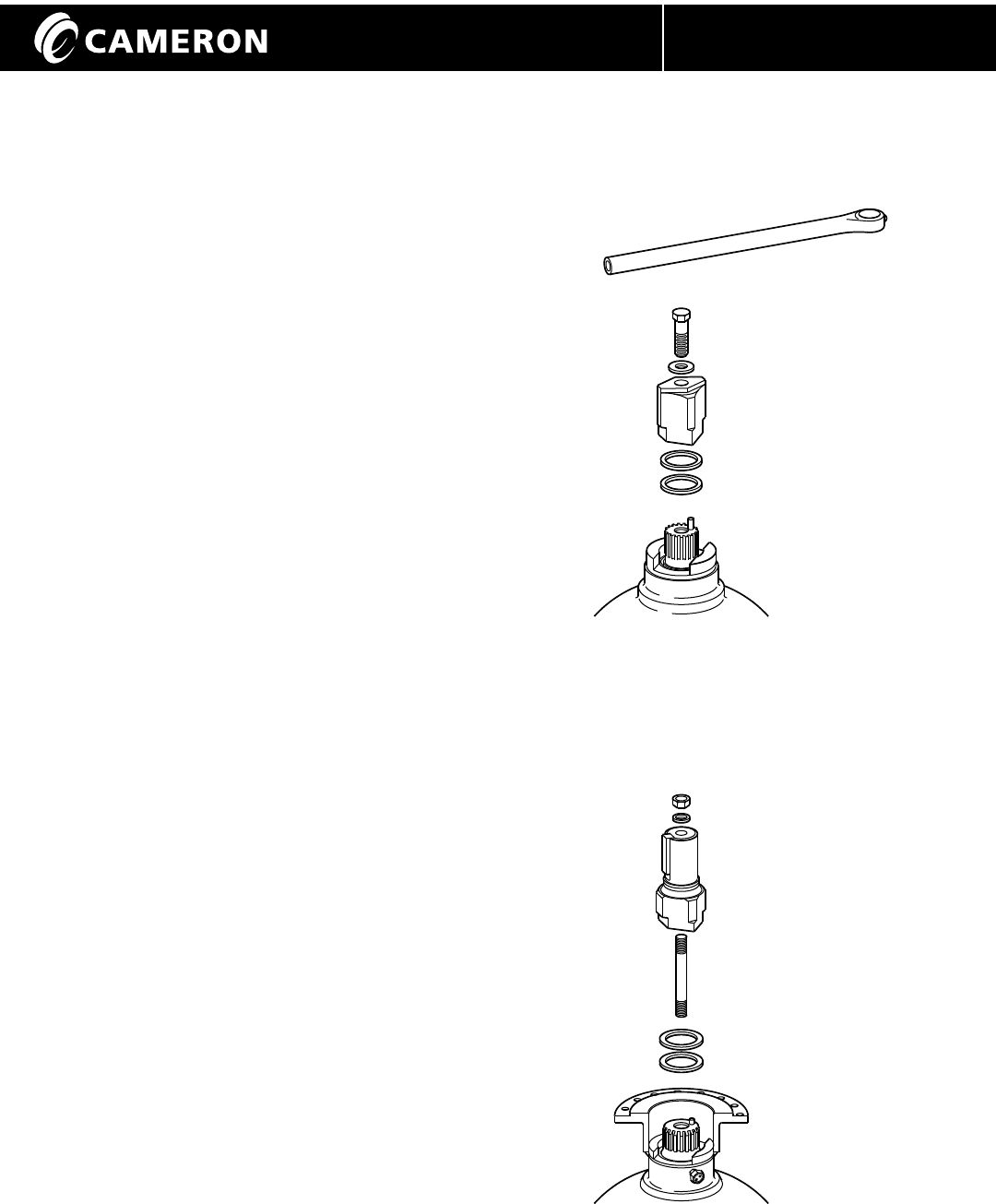
15
ENGINEERED VALVES
Stem Designs
ITEM DESCRIPTION
1 Capscrew
2 Disc Spring
3 Stop Nut
4 Stem Seal Washer
5 Stem Seal
ITEM DESCRIPTION
1 Nut
2 Disc Spring
3 Keyed Shaft
4 Stud
5 Stem Seal Washer
6 Stem Seal
3" Stem Design
1", 1.5" and 2" Stem Design
Figure 14 - 1", 1 1/2" and 2" Stem Design.
Figure 15 - 3" Stem Design.
Installation, Operation and Maintenance Manual IOM-CAM-BALL-T31
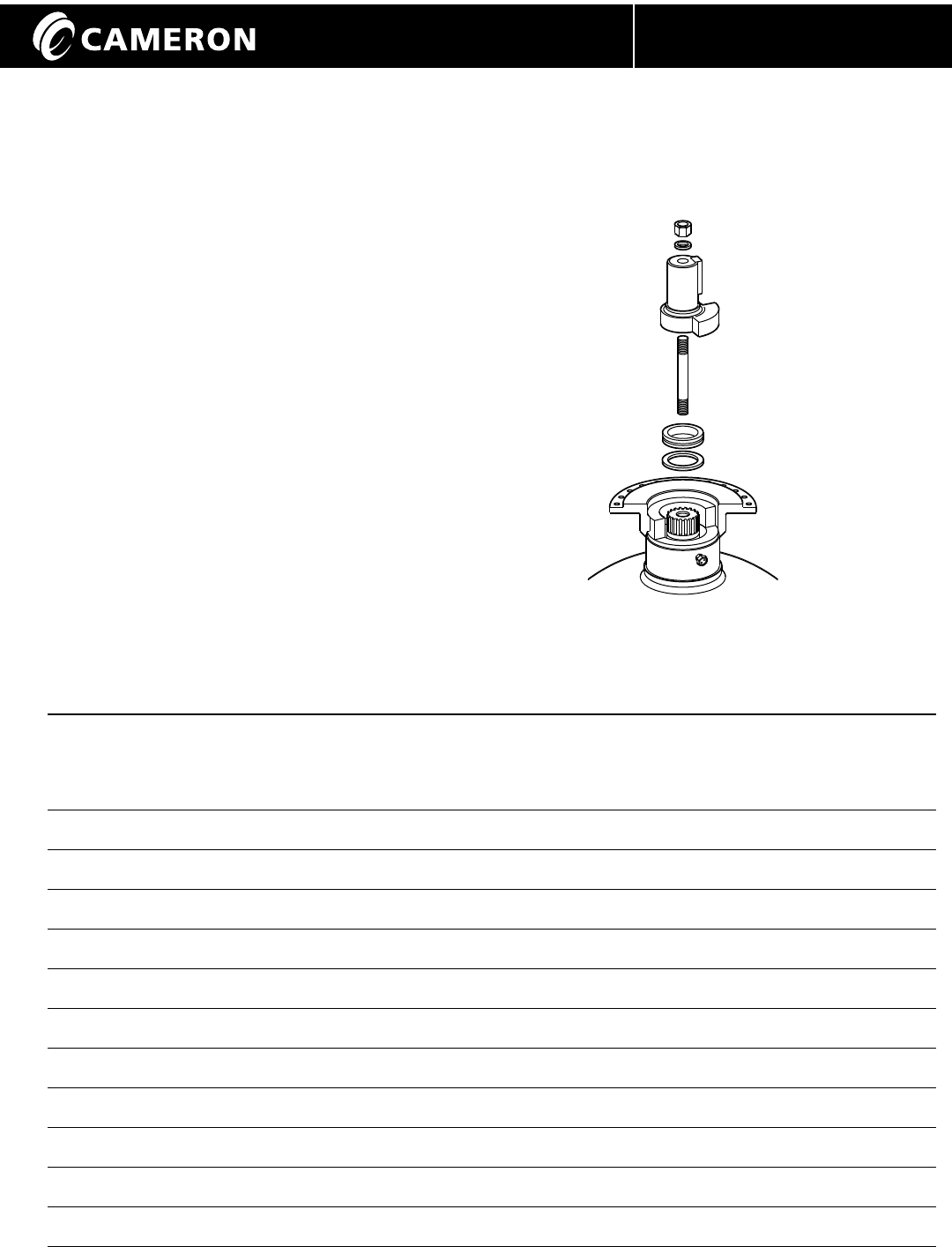
ENGINEERED VALVES
4" and Larger Stem Design
ITEM DESCRIPTION
1 Nut
2 Disc Spring
3 Keyed Shaft
4 Stud
5 Stem Seal Gland
6 Stem seal
NOTES
Stem Designs
Figure 16 - 4"and Larger Stem Design.
Installation, Operation and Maintenance Manual IOM-CAM-BALL-T31
16
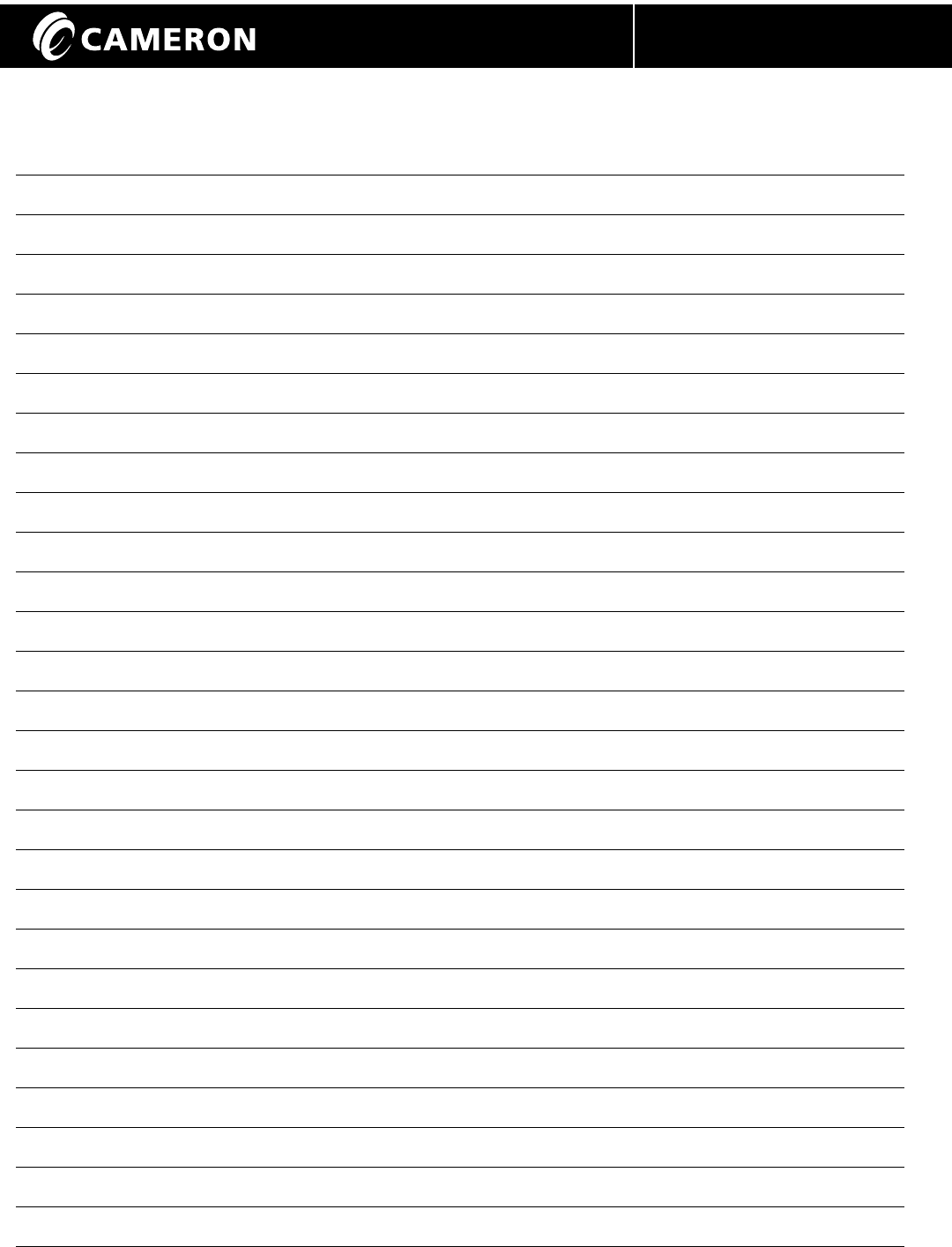
NOTES
ENGINEERED VALVES
Installation, Operation and Maintenance Manual IOM-CAM-BALL-T31
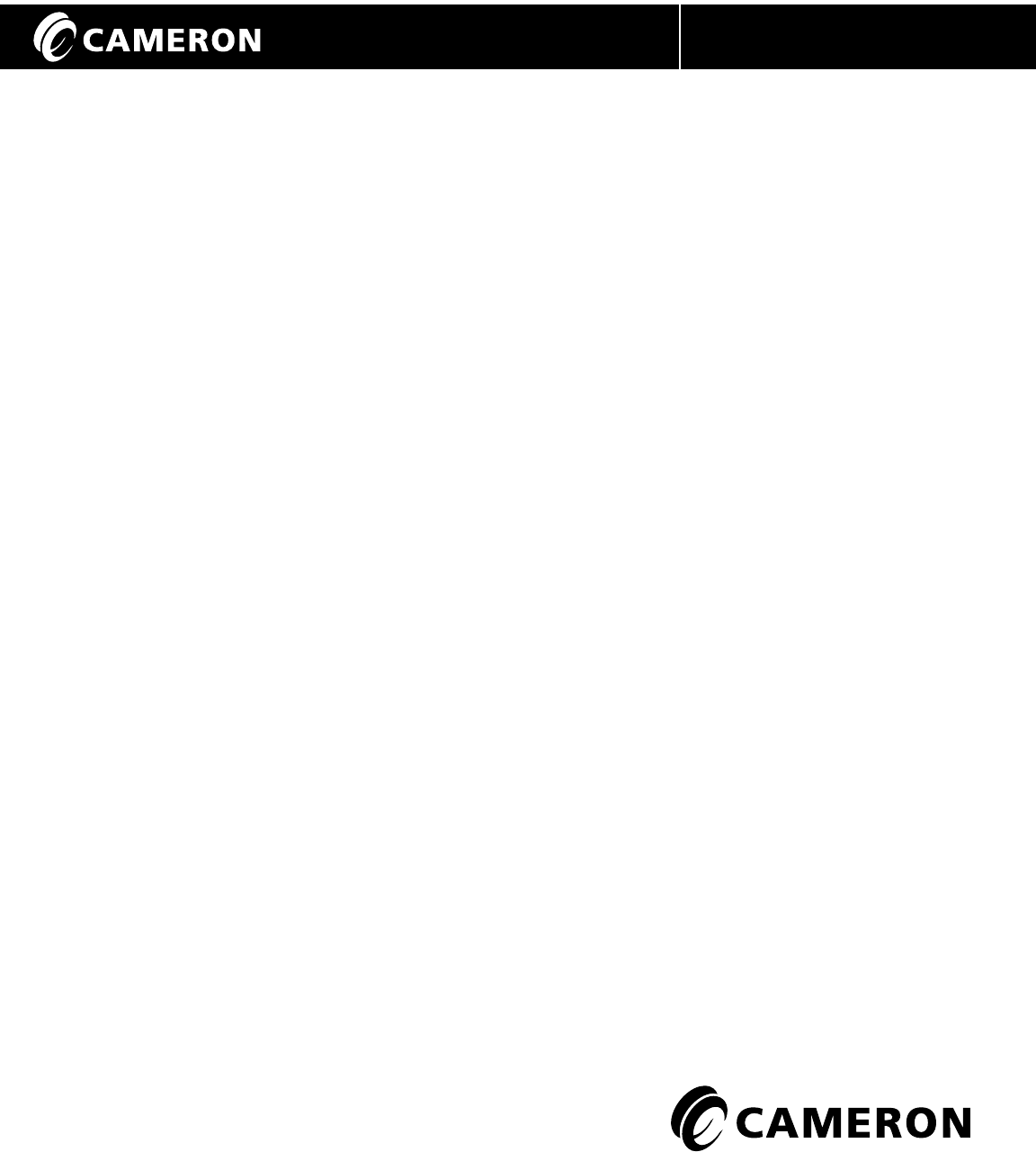
ENGINEERED VALVES
Installation, Operation and Maintenance Manual
®
CAMERON
© Cameron’s Valves & Measurement Group IOM-CAM-BALL-T31
Rev. 0 06/09
3250 Briarpark Drive, Suite 300
Houston, Texas 77042
USA Toll Free 800 323 9160
For the most current contact and location information go to: www.c-a-m.com/valvesandmeasurement
Contact your Cameron’s Valves & Measurement group representative for a Repair Manual
IOM-CAM-BALL-T31