Drilling Rams Brochure
User Manual: Drilling Rams Brochure Resource Library
Open the PDF directly: View PDF .
Page Count: 8
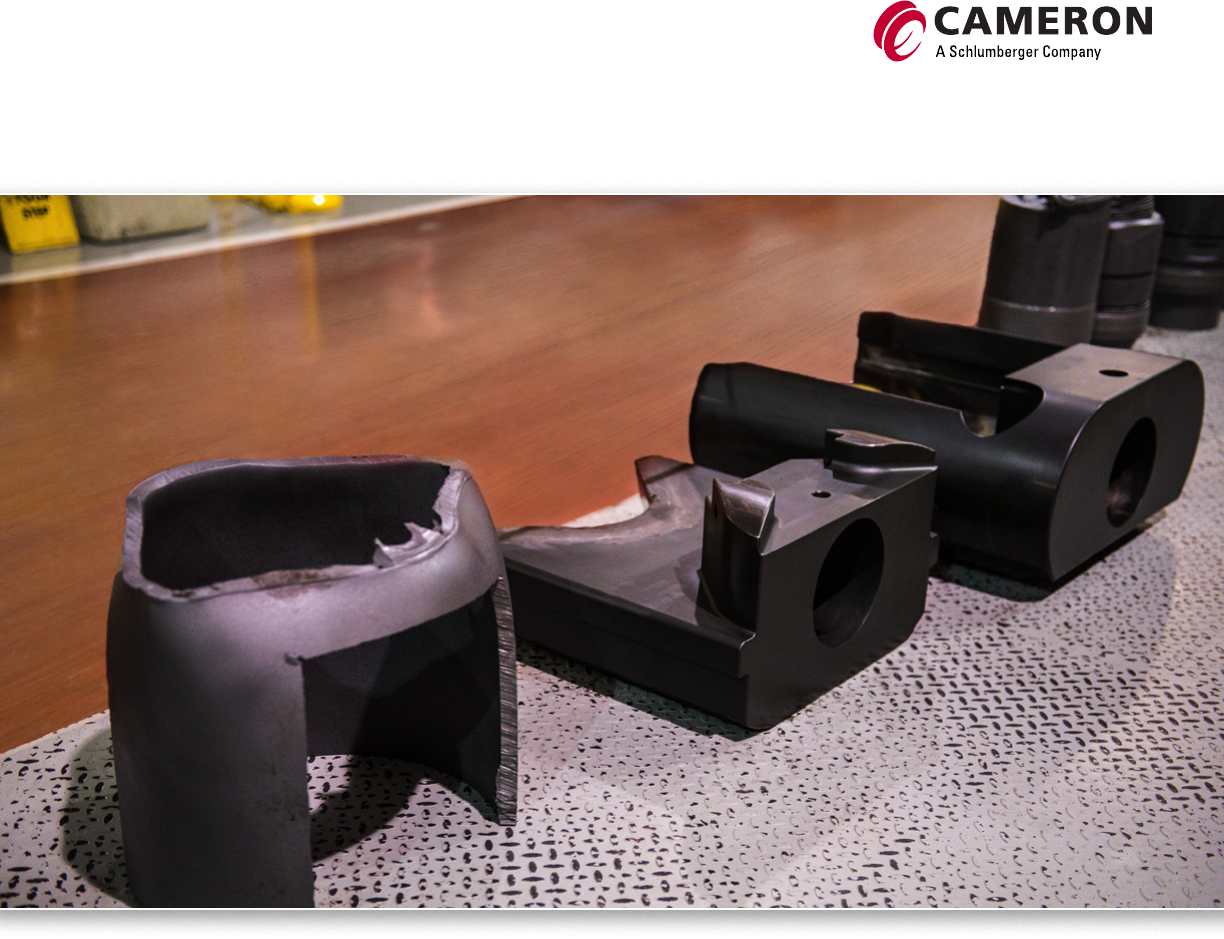
Drilling Rams
Maintain well control and seal annular spaces
with trusted, rugged drilling rams
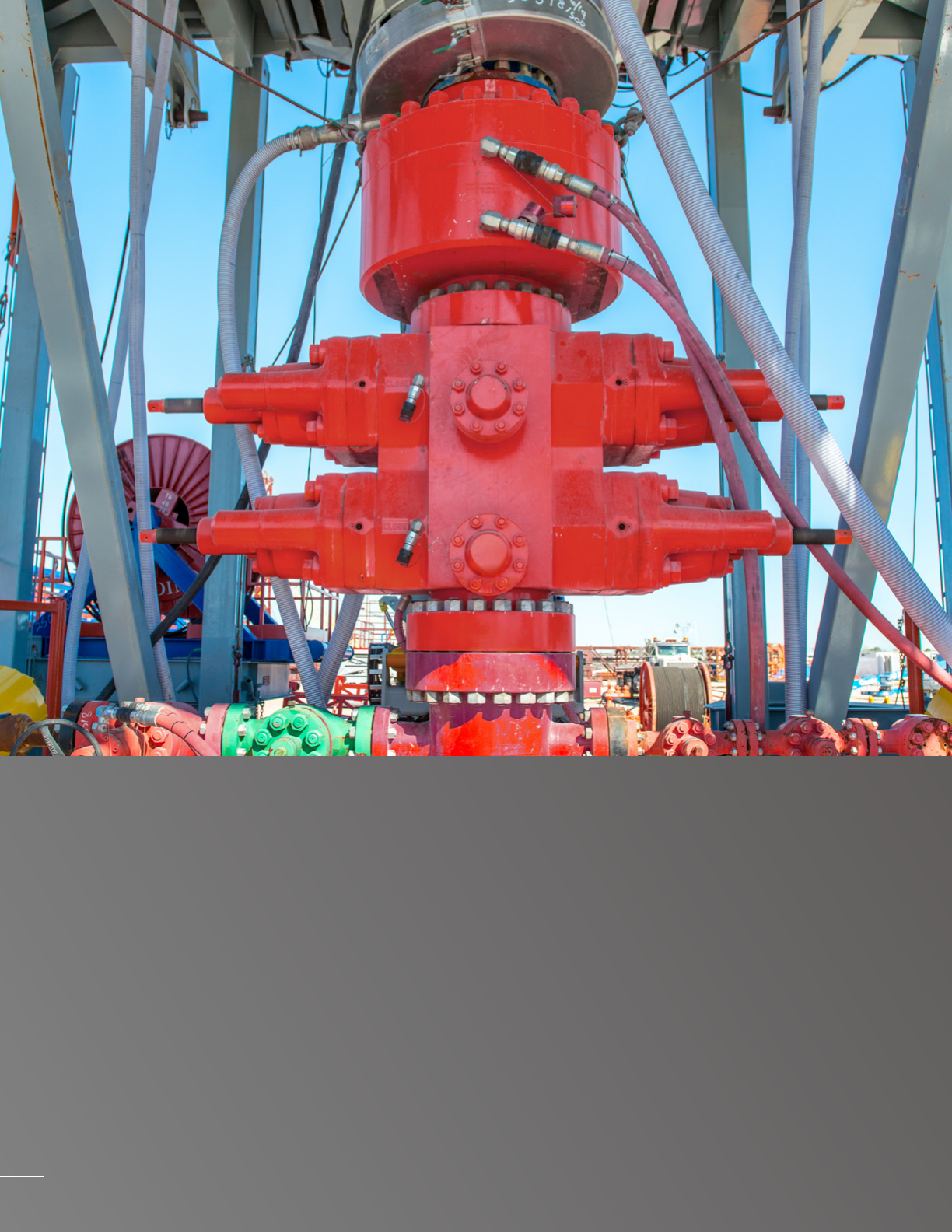
During downhole operations, reliability of equipment components takes
on utmost importance. Successful and safe downhole operations depend
upon rugged drilling rams to maintain well control. These rams, built to the
most exacting performance and safety standards, make it possible to stop
drilling operations and prevent a potential blowout.
Operators must have confidence that the rams inside the BOP will shear
the pipe and contain the well. Cameron rams are designed to perform—
controlling pressure during drilling and closing and sealing around a
range of tubulars—while also meeting existing system concerns, such as
footprint and operational savings.
2
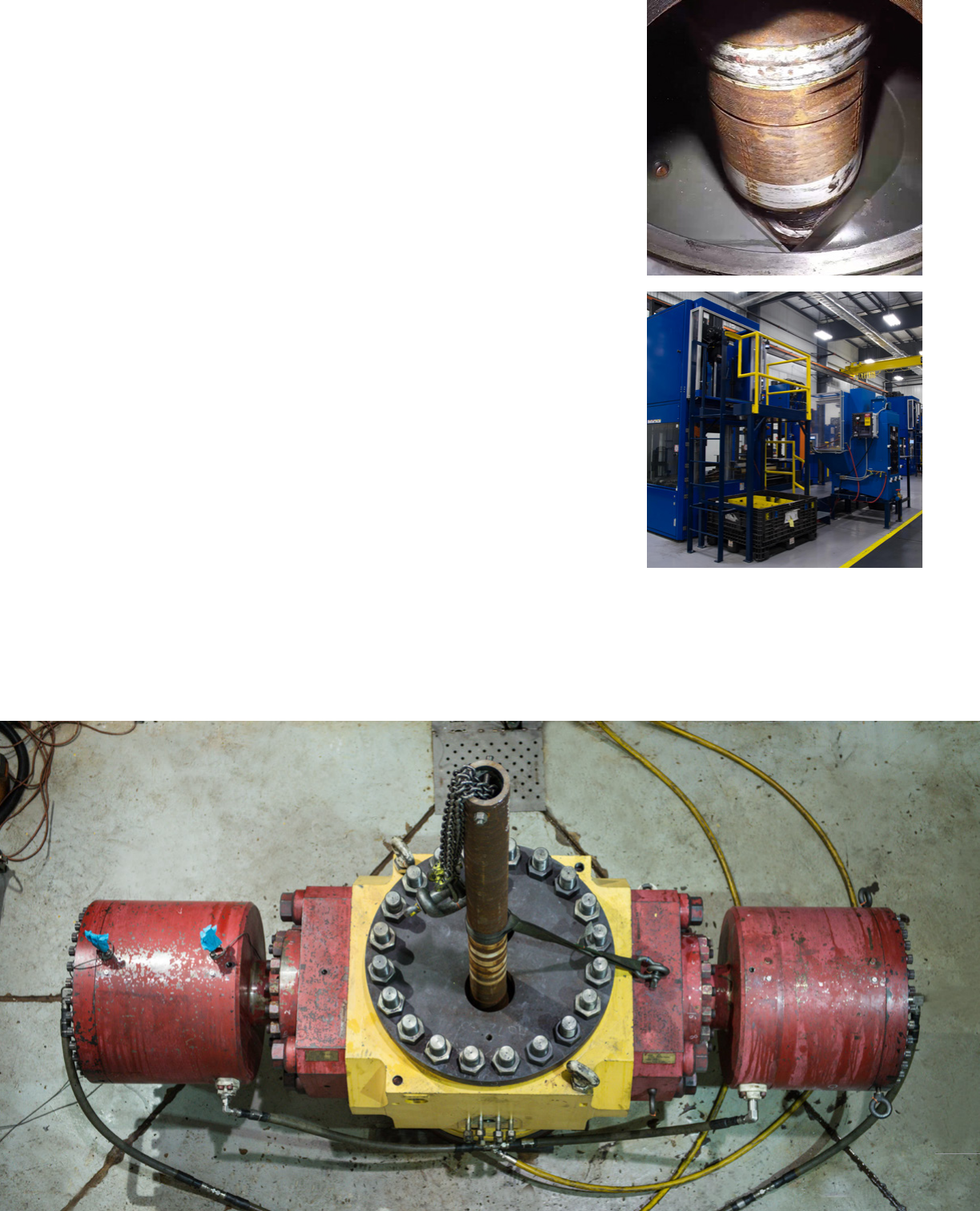
Applications
Drilling and production operations
Land
Subsea
Sour service
Benefits
Enhanced certainty
Optimized HSE profile
Maximized sealing durability
Improved operational efficiency and flexibility
Increased reliability
Features
Compatibility with field-proven Cameron ram-type BOPs
Availability in all common pipe sizes
Sealing on a wide range of pipe diameters
Annular sealing independent of well flow
Shearing rams with blades that are integral to the body
Options for high-temperature and sour service
Options for shearing braided cable, wireline, higher-grade pipe, and thick-wall casing
Drilling Rams
3
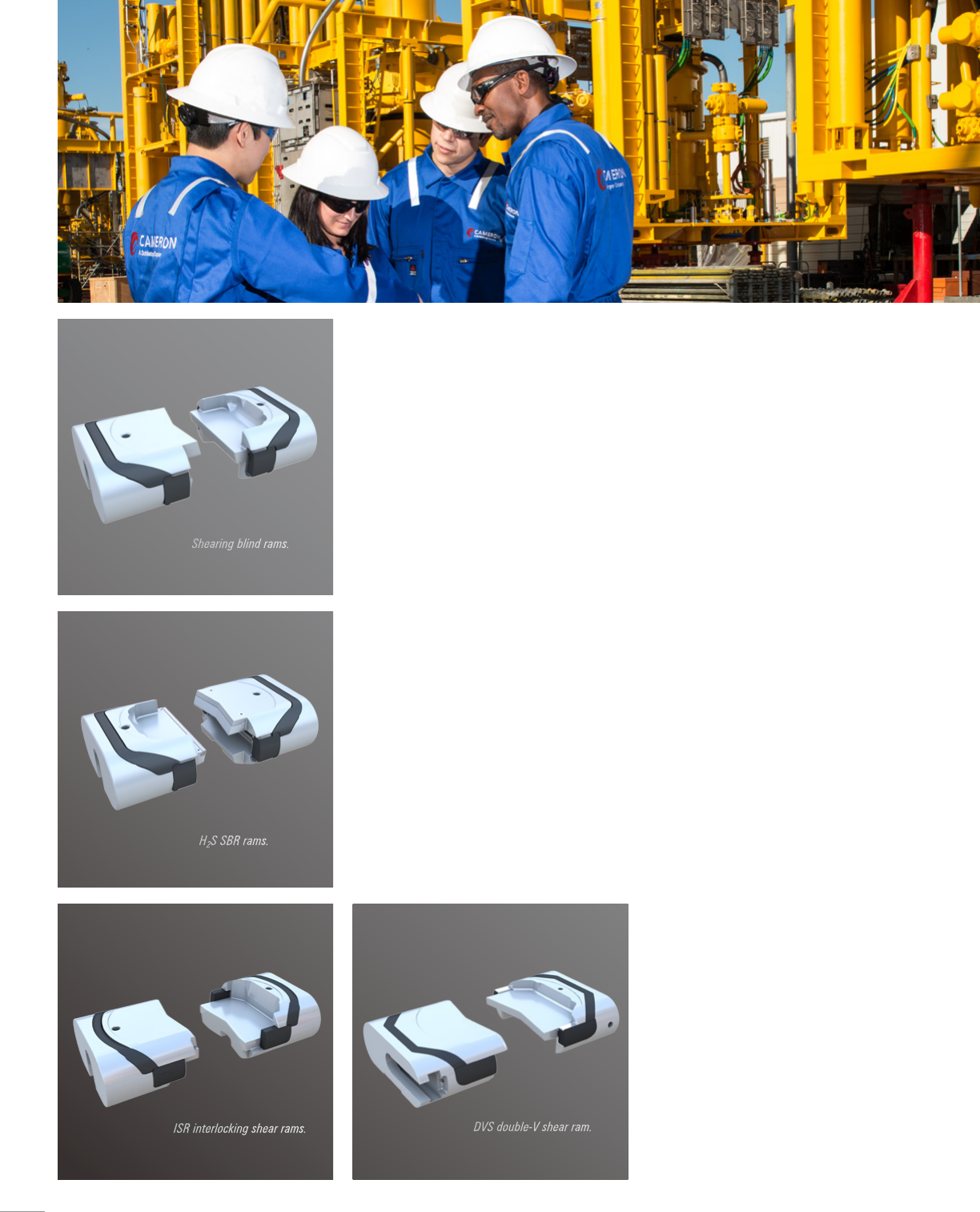
Shearing blind rams (SBRs)—Blind shear rams are designed to cut drillpipe and shut in the
well in an emergency well control situation.
H2S SBR* hydrogen sulfide shearing blind rams—Similar in design to standard SBRs, this
offering features specifically designed blade inserts for H2S service.
ISR* interlocking shear rams—Developed to shear multiple tubing strings, ISRs interlock
in the last inch of travel, keeping the blade seals in the upper ram in contact with the lower
sealing surface.
DVS* double-V shear rams—Upper and lower DVS rams feature a “V” shape butting edge
to reduce the required shear force.
Shearing blind rams.
H2S SBR rams.
ISR interlocking shear rams.
Shearing Rams
The Cameron portfolio of shearing rams feature
solutions for operations involving high H2S content,
high-grade and thick-wall pipe, large-diameter casing,
tool joint hardbanding, off-center tubulars, wireline,
and braided cable.
DVS double-V shear ram.
4
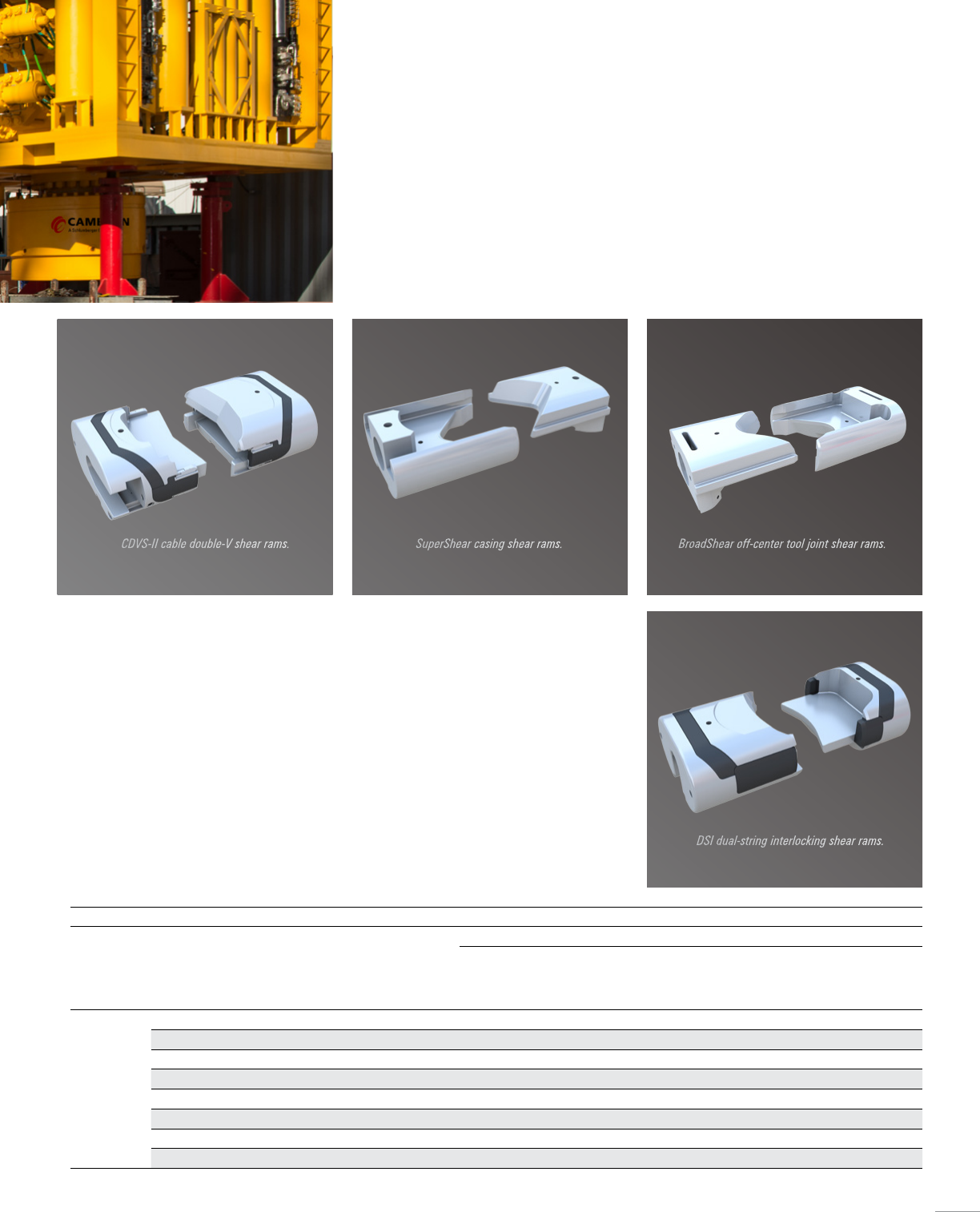
Ram Selection Chart
Ram-Type BOP Models
EVO*
Compact,
Offshore
Ram-Type BOP
TL*
Offshore
Ram-Type BOP
U*
Surface
Ram-Type BOP
UII*
Subsea
Ram-Type BOP
UM*
Convertible-
Bonnet
Ram-Type BOP
Shearing Shearing blind rams (SBRs)
H2S SBR rams
ISR rams – ‡– ‡
DVS rams – ‡ ‡– ‡
CDVS-II rams – ‡–
SuperShear rams† –––
BroadShear rams† –––
DSI rams –– ‡–
† Nonsealing ram; does not contain elastomeric material.
‡ Contact your local Cameron representative to learn more about specific sizes.
CDVS-II* cable double-V shear rams—Featuring increased shear blade width and an
interlocking mechanism, CDVS-II rams provide the ability to shear wireline, cable, and tubulars
with larger wall thicknesses.
SuperShear* casing shear rams—SuperShear rams do not require milling off a preparation
on the sheared pipe, eliminating an additional trip downhole.
BroadShear* off-center tool joint shear rams—The enhanced shearing action of BroadShear
rams extends shearing capabilities to tool joint hardbanding and off-center tubulars, enabling
compliance with BSEE regulations for Gulf of Mexico drilling and production.
DSI* dual-string interlocking shear rams—These rams are used to shear wireline and
braided cable and maintain the seal with zero tension in the line.
CDVS-II cable double-V shear rams.
SuperShear casing shear rams. BroadShear off-center tool joint shear rams.
DSI dual-string interlocking shear rams.
5
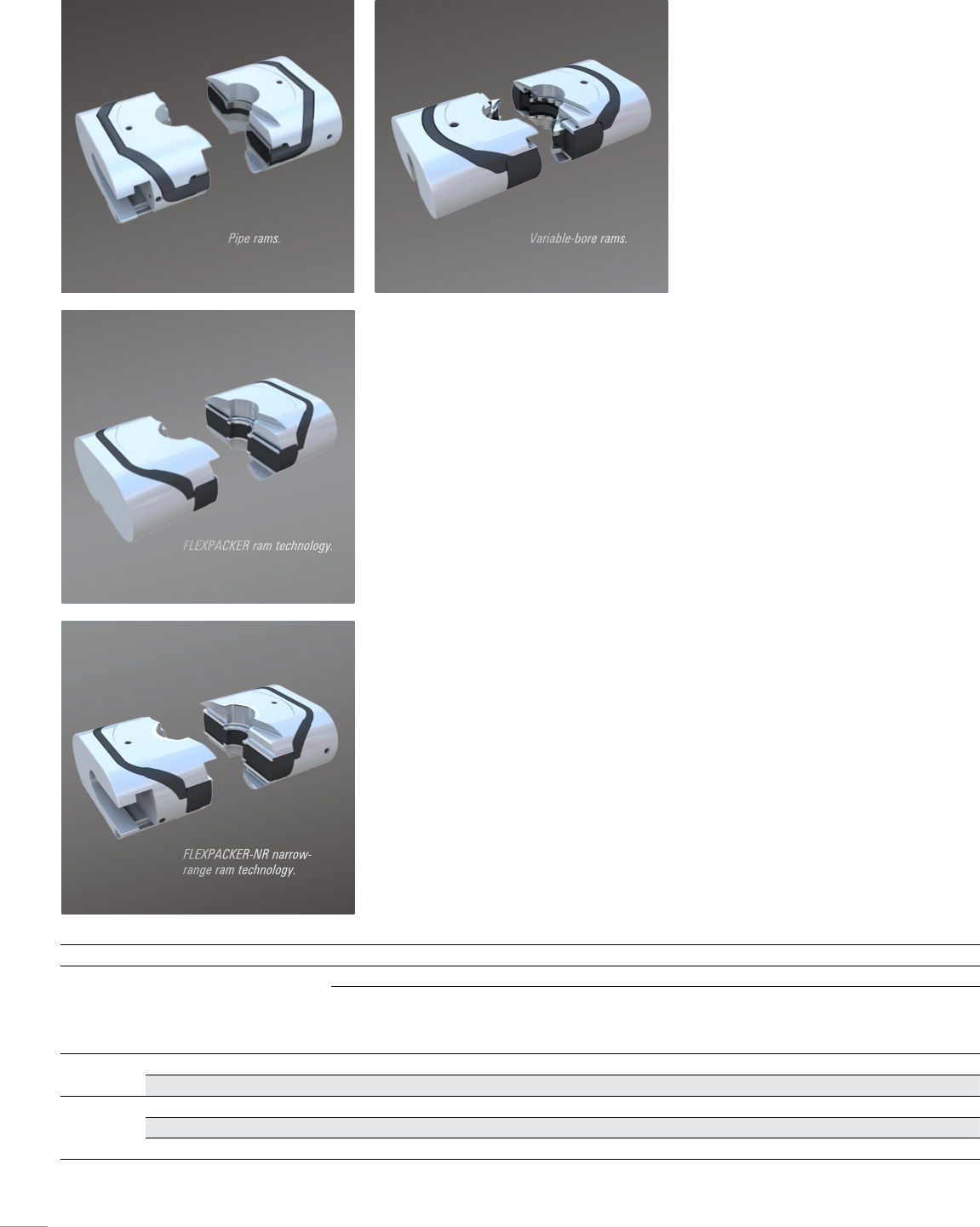
Pipe rams—The rams are designed so that the packer, top seal, and ram body act in unison
to form one half of a ram cavity’s seal.
Variable-bore rams (VBRs)—Cameron VBRs feature a large reservoir of packer rubber to
ensure a long-lasting seal under all conditions.
FLEXPACKER* ram technology—This multibore sealing device uses radially moving, stacked
antiextrusion segments to retain wellbore pressure.
FLEXPACKER-NR* narrow-range ram technology—Designed for use with tapered
drillstrings, this technology provides economical sealing that is not compromised by well flow.
Nonshearing Rams
Sealing the annular space around drillpipe is also
crucial to operations taking place inside the wellbore.
Cameron offers pipe rams that seal around pipe to
close the annular space as well as variable-bore rams
(VBRs) to match drillpipe size.
Ram Selection Chart
Ram-Type BOP Models
EVO*
Compact,
Offshore
Ram-Type BOP
TL*
Offshore
Ram-Type BOP
U*
Surface
Ram-Type BOP
UII*
Subsea
Ram-Type BOP
UM*
Convertible-
Bonnet
Ram-Type BOP
T-81*
Small-Bore
Compact
Ram-Type BOP
T-82*
Compact
Ram-Type BOP
Pipe Standard service
High-temperature service –
Variable bore VBR rams ‡ ‡ ‡ ‡ ‡– –
FLEXPACKER technology ‡ ‡ ‡– ‡–
FLEXPACKER-NR technology ‡ ‡ ‡ ‡– –
† Nonsealing ram; does not contain elastomeric material.
‡ Contact your local Cameron representative to learn more about specific sizes.
Pipe rams. Variable-bore rams.
FLEXPACKER ram technology.
FLEXPACKER-NR narrow-
range ram technology.
6
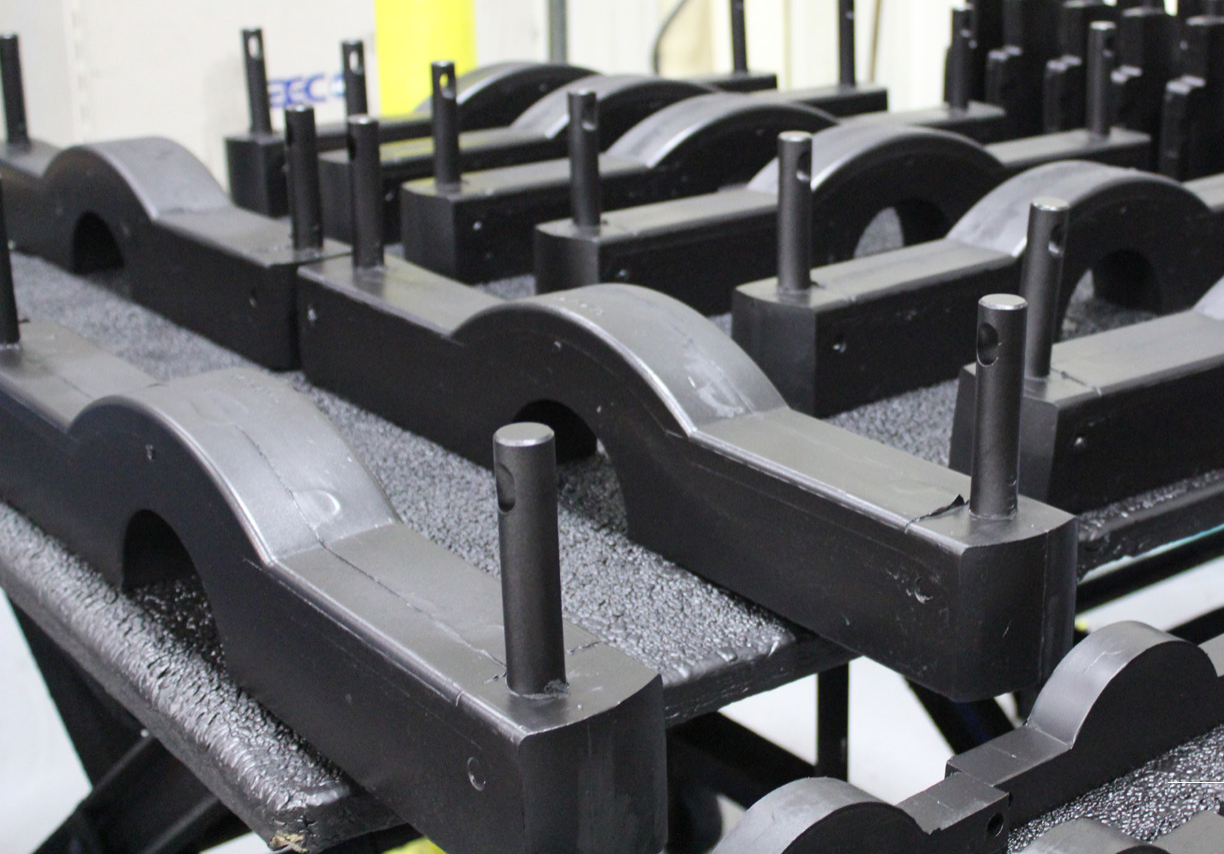
Elastomer Technology
One of the ways to differentiate Cameron drilling products from those of
other manufacturers is the elastomers used in critical sealing areas, such
as ram packers and top seals.
Cameron drilling products exclusively feature proprietary elastomers designed and manufactured by our facility in Katy,
Texas. Cameron provides engineered solutions to elastomeric material problems, and for drilling applications, we have
developed a range of elastomer technology to meet the rigorous demands of the oil field:
CAMRAM* elastomer technology
CAMRAM 350* high-temperature elastomer technology, which is rated to 350 degF [177 degC]
CAMULAR* annular elastomer technology
DUROCAM* subsea elastomer technology.
When used with Cameron BOPs, these technologies help to improve performance, extend service life, reduce downtime, and
lower operating costs. Elastomer components are in-house engineered technology with required API qualification testing as
with all other pressure control equipment.
7