CALDON LEFM 380Ci Gas Ultrasonic Flowmeter Brochure Flow Meter
User Manual: Resource Library
Open the PDF directly: View PDF .
Page Count: 8
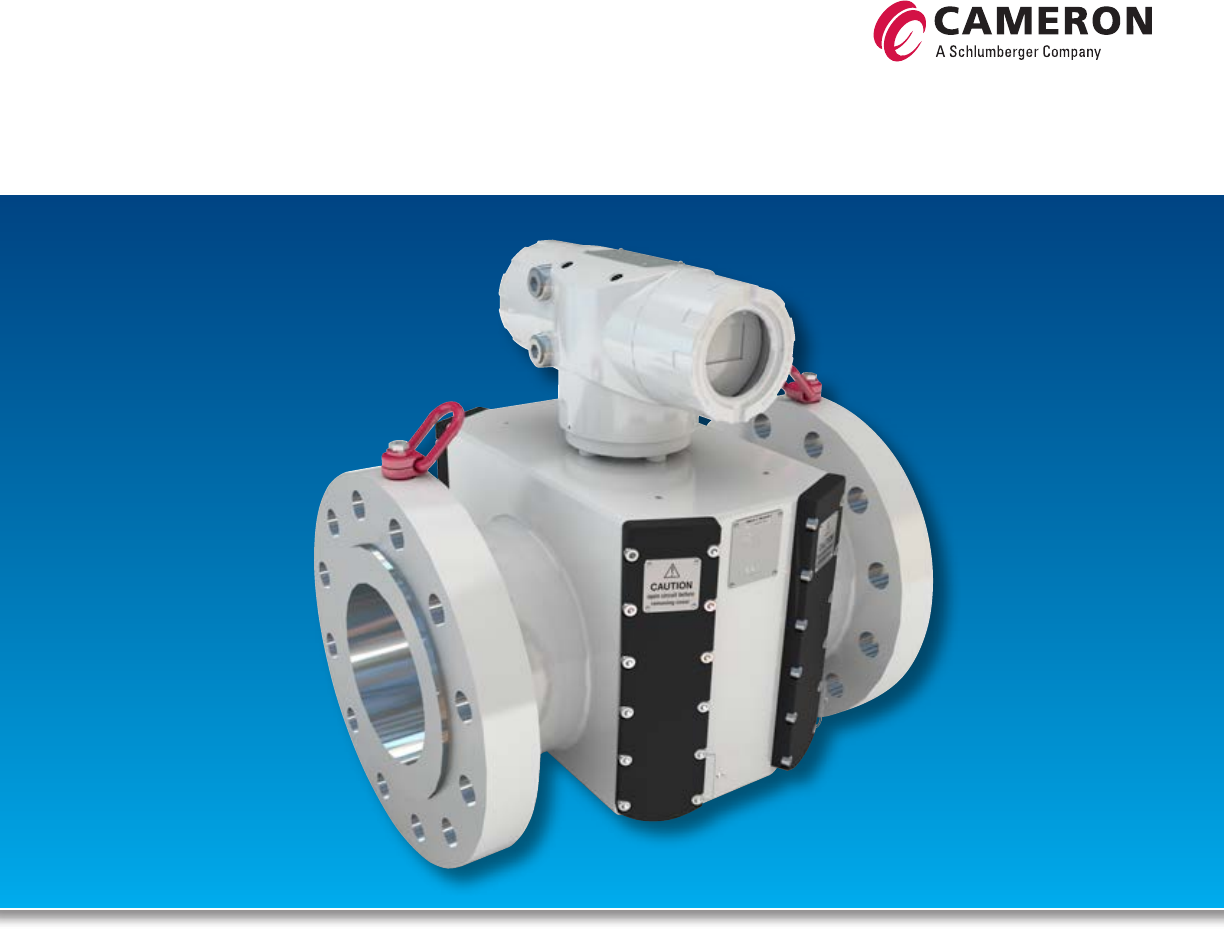
CALDON LEFM 380Ci
Gas Ultrasonic Flowmeter
Integrating experience, proven technology,
and innovation
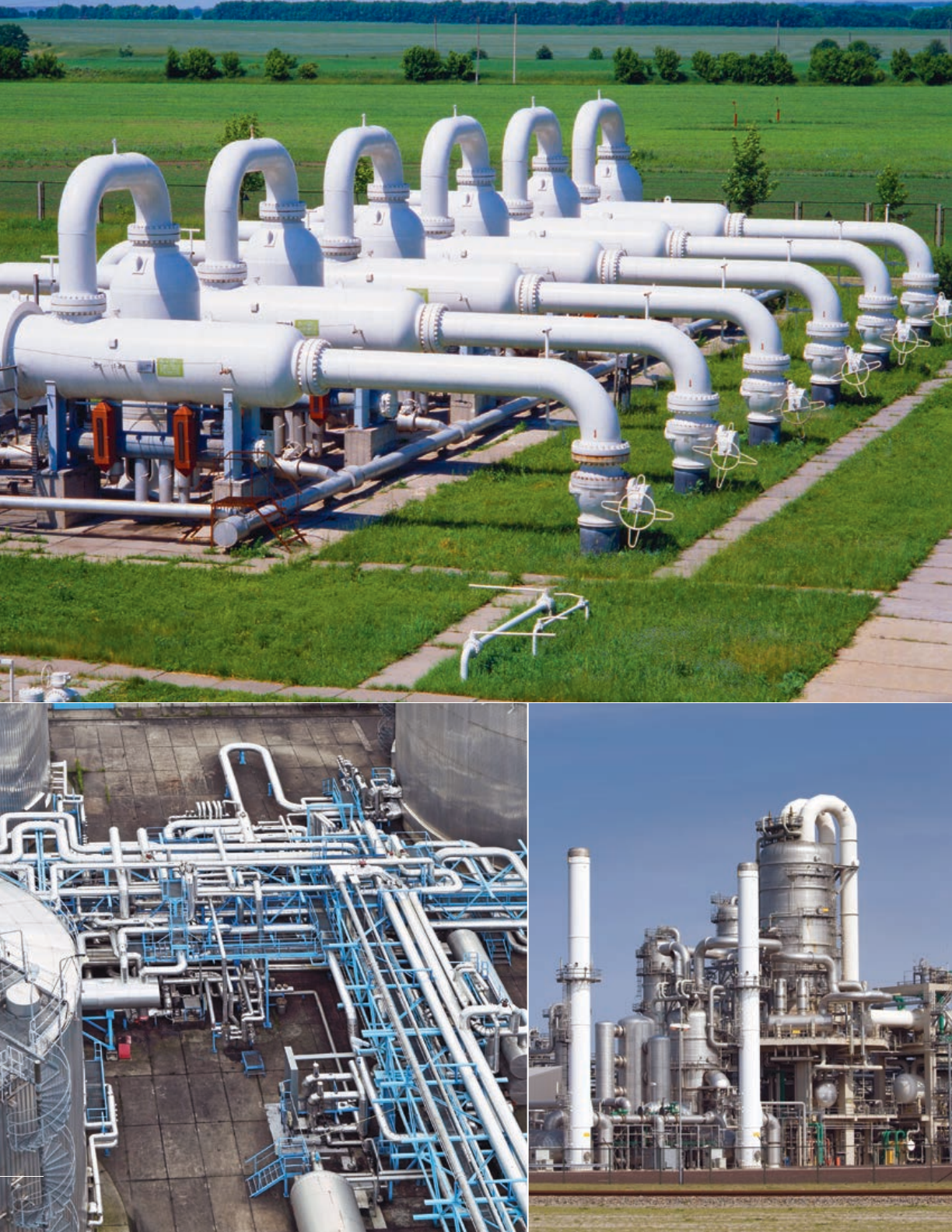
2
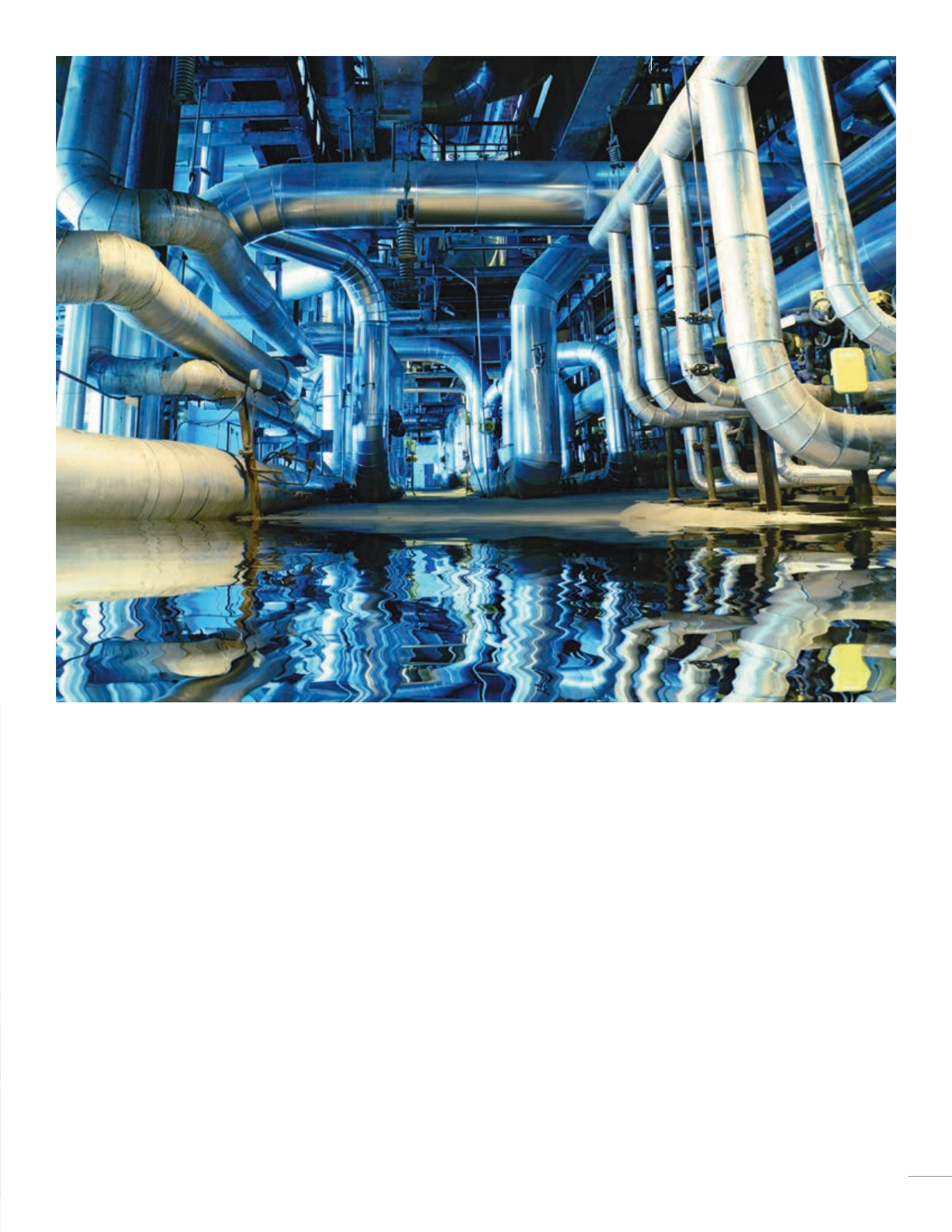
The CALDON* LEFM 380Ci Series eight-path gas
ultrasonic flowmeter combines world-leading flow
measurement technology with one of the lowest costs
of installation and operation of any flowmeter on the
market today for the natural gas industry.
The LEFM 380Ci flowmeter design addresses the needs of the natural gas industry by eliminating
the need for flow conditioning, providing a smaller meter installed footprint, reducing the risk of
corrosion and/or contamination of internal meter surfaces, and improving safety for technicians
servicing the meter.
As a world leader in transit-time ultrasonic technology applications, we have integrated our
eight-path, dual-plane flowmeter design with new technology to introduce the LEFM 380Ci gas
ultrasonic flowmeter for use in natural gas applications, including but not limited to, custody-
transfer metering, fiscal metering, city gate metering, check metering, and transfer of product to
and from underground storage facilities.
Features and benefits
■ The LEFM 380Ci flowmeter has been designed
to reduce the cost of installation, reduce yearly
maintenance and operating costs, and increase
personnel safety.
■ Savings realized in installation, maintenance, and
operating costs can result in a payback of up to
three times the initial cost of the meter over the
life of operation.
■ The unique eight-path, dual-plane, cross-path
design of the LEFM 380Ci flowmeter is insensitive
to velocity profile asymmetry and swirl.
■ Transducer assemblies are inserted into
transducer housings sealed into the meter body.
The transducer housings are pressure boundaries
isolating the transducers from the process. This
eliminates the need to shut down flow and
depressurize the pipeline if a transducer should
ever need to be replaced.
■ Optional proprietary internal coating significantly
reduces the risk of corrosion and/or contamination
of the internal meter surfaces.
3
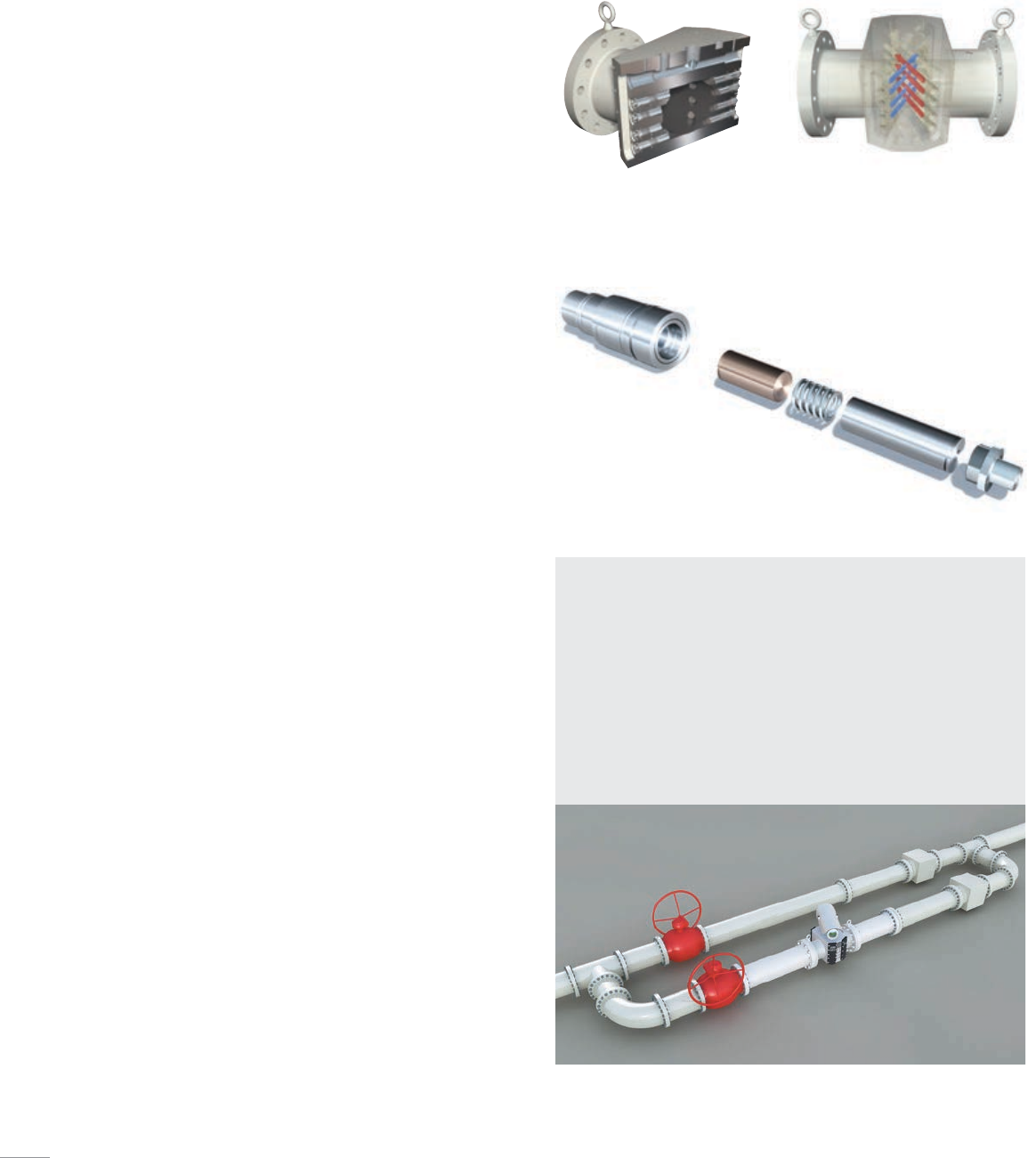
Product Features
Dual-plane, eight-path configuration
The LEFM 380Ci gas ultrasonic flowmeter features our eight-path, dual-
plane, cross-path flowmeter design.
Cameron has conducted extensive
research and testing to develop, validate, and refine the eight-path
configuration for accurate measurement of flow containing both
asymmetry and swirl.
Fluid velocity measurements are averaged over the eight chordal paths
of the two combined planes. Swirl effects in one plane will be equal
but
opposite in magnitude to the effects
in the second plane. Averaging the
velocity measurements has a net result of resolving any effects due to swirl
on the overall measurement.
Sealed transducer housing design
The LEFM 380Ci gas ultrasonic flowmeter has transducers that are installed
into Inconel transducer housings, similar to how a resistance temperature
device (RTD) inserts into a thermowell. The transducer housing is a
pressure boundary between the transducer assembly and the process.
This feature is common in our liquid flowmeters, but is a first for an ultrasonic
natural gas flowmeter.
The operator does not have to block and depressurize the meter if an LEFM
380Ci transducer should ever need to be replaced. A transducer can be
replaced safely with gas flowing in the meter. The design does not require
any special tools or extraction devices for transducer replacement.
Proprietary coating
Corrosion and contamination of the flowmeter and adjacent piping can
be problematic in regards to meter performance. The LEFM 380Ci gas
ultrasonic flowmeter has a proprietary internal coating that significantly
reduces or eliminates the risk of corrosion and/or contamination. This
coating was selected based on our experience with buildups that can occur
in liquid applications. It has good anti-corrosion properties, high thermal
stability, chemical inertness in aggressive environments, and superior
anti-stick properties.
The second image on the following page is a view looking upstream
through the downstream meter spool into an LEFM 380Ci flowmeter that
was in service for six months. The downstream section shows signs of
rust and corrosion, with markings indicative of liquid having run along the
bottom of the pipeline. The coated LEFM 380Ci flowmeter body remained
clean. Cameron can provide upstream and downstream pipe spools with
this coating at the operator’s preference.
A 24-in LEFM 380Ci gas ultrasonic flowmeter was installed in an
application that needed a short footprint. The operator requested that
the entire meter package (upstream piping, meter, and downstream
piping) be no longer than 10 pipe diameters. This meter package
was installed downstream of piping elements that could create
asymmetrical flow profiles and swirl. After the LEFM 380Ci
flowmeter was installed, we remotely monitored the meter using
eCheck and was able to determine that up to 42% swirl was
present. The flowmeter provided measurements well within the
operator’s expectations.
Ultrasonic eight-path configuration.
Isolating transducer housing design.
4
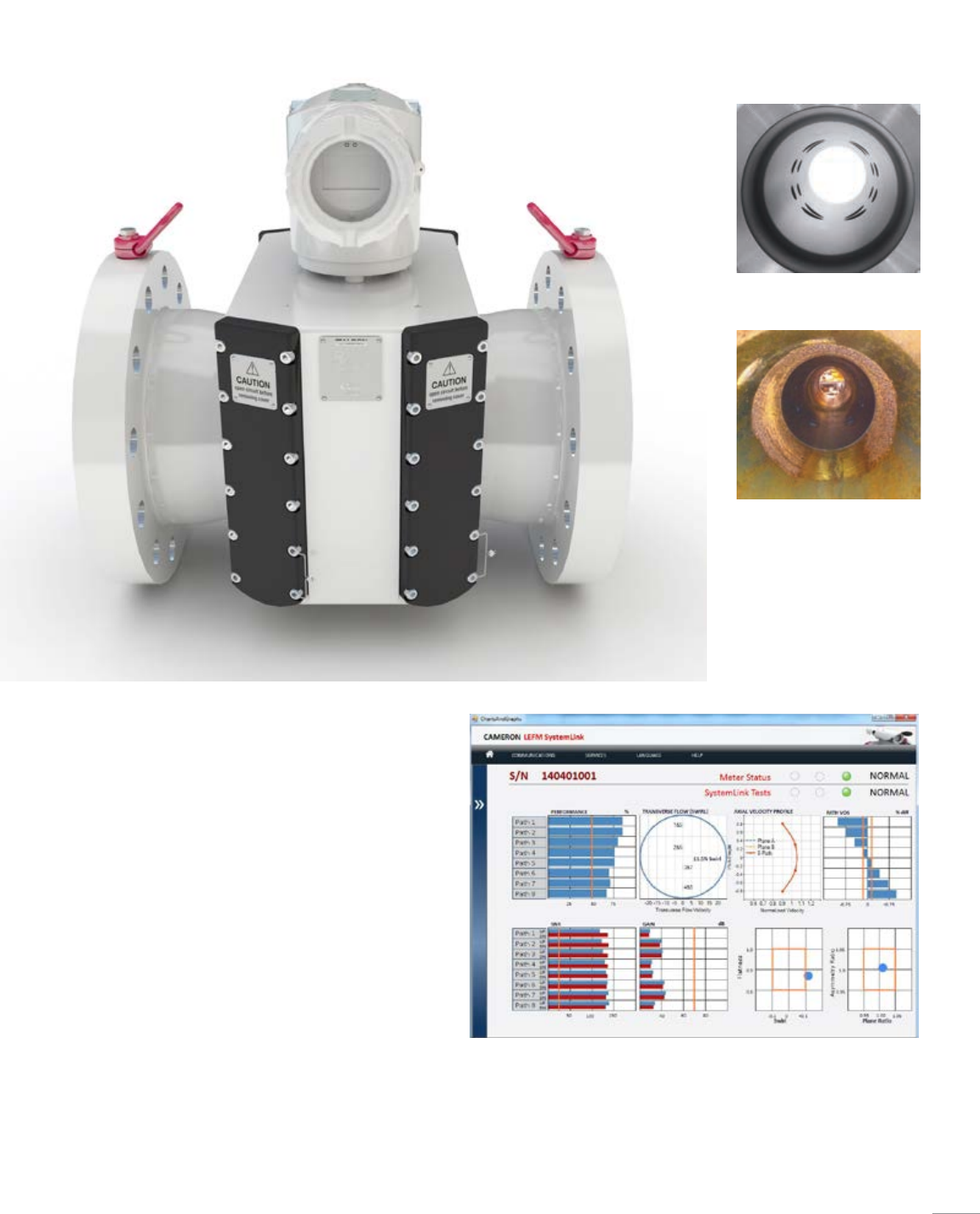
LEFM SystemLink G3
The LEFM SystemLink G3 user interface software technology allows access
to real-time diagnostic data, historical data, and event logs from a G3
ultrasonic flowmeter by using an Ethernet/fiber optic modem connection.
Historical data and event logs are stored within the G3 transmitter, thus
allowing for later retrieval—giving operators ability to monitor and analyze
critical diagnostics, helping prevent unplanned downtime.
LEFM SystemLink G3 features:
■ Health overview report show the current meter status as well as meter
process measurements including flow rate, temperature, and pressure
■ Detailed charts and graphs present the meter diagnostic information in
an easy-to-understand format with alarm limits that help identify issues
■ User defined reference points are built using the meter’s stored
data. These reference points allow the user to graphically compare
current meter performance against user defined reference points. For
example, current performance can be compared against calibration or
commissioning data.
■ Export data as both predefined PDF reports or to customer defined
excel spreadsheets.
flowmeter with proprietary
internal coating
rust and corrosion in downstream
section without proprietary internal
coating after only six months in use
5
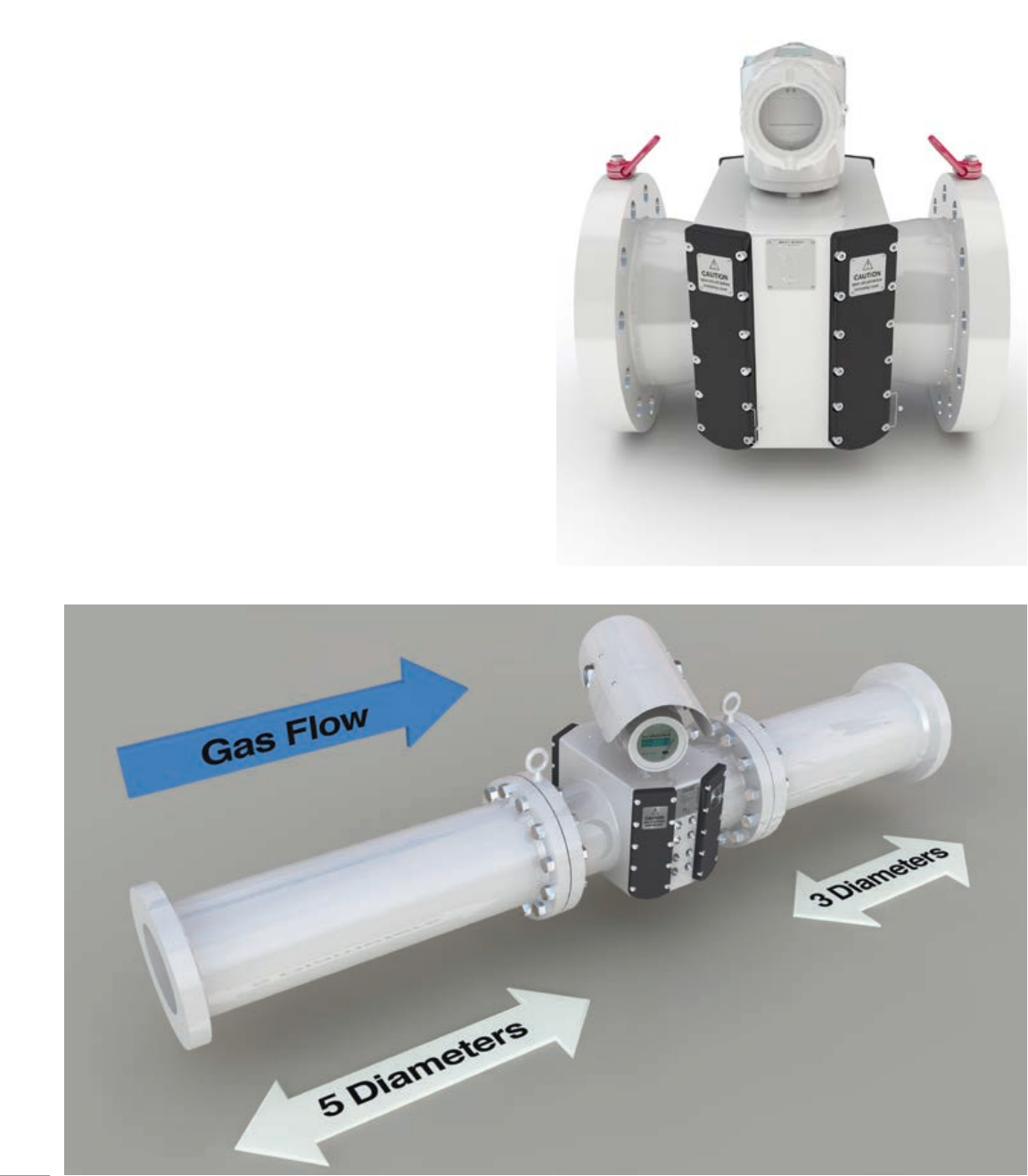
Results You Can Measure
The LEFM 380Ci gas ultrasonic flowmeter is insensitive to velocity
profile asymmetry and swirl. The general installation recommendation is
based on our history with eight-path liquid ultrasonic flowmeters, LEFM
380Ci flowmeter field tests and third-party testing of the LEFM 380Ci, at
independent labs in the USA and Europe. This recommendation meets or
exceeds the the most stringent requirements of AGA Report 9, ISO 17089-1
Class 1 and OIML R137 Accuracy Class 0.5.
Having the smallest installed footprint means a compact installation and
reduction in CAPEX by reducing the length of required upstream pipe and
eliminating a flow conditioner. The ability to isolate the transducers from
the flowing gas in the pipeline means increased safety for the technicians
should a transducer ever need replacing, as well as a simplified, time-
saving replacement procedure. The proprietary coating of the LEFM 380Ci
flowmeter can provide higher accuracy of measurement over the months a
flow metering section is being conditioned by corrosion and contamination
of the process after it is installed, or fewer cleaning cycles for operators
who may need to periodically remove the meter section for cleaning.
The LEFM 380Ci flowmeter has been designed to address technical and
operational challenges associated with natural gas measurement. However,
it also is a flexible design, which allows us to meet the specific local
needs of operators, which is equally important. The LEFM 380Ci flowmeter
is available in various materials of construction and has a design that
is configurable to accept various end connections requirements. The
transmitter can be integrally or remotely mounted from the meter body
and has a wide range of input and output options.
6
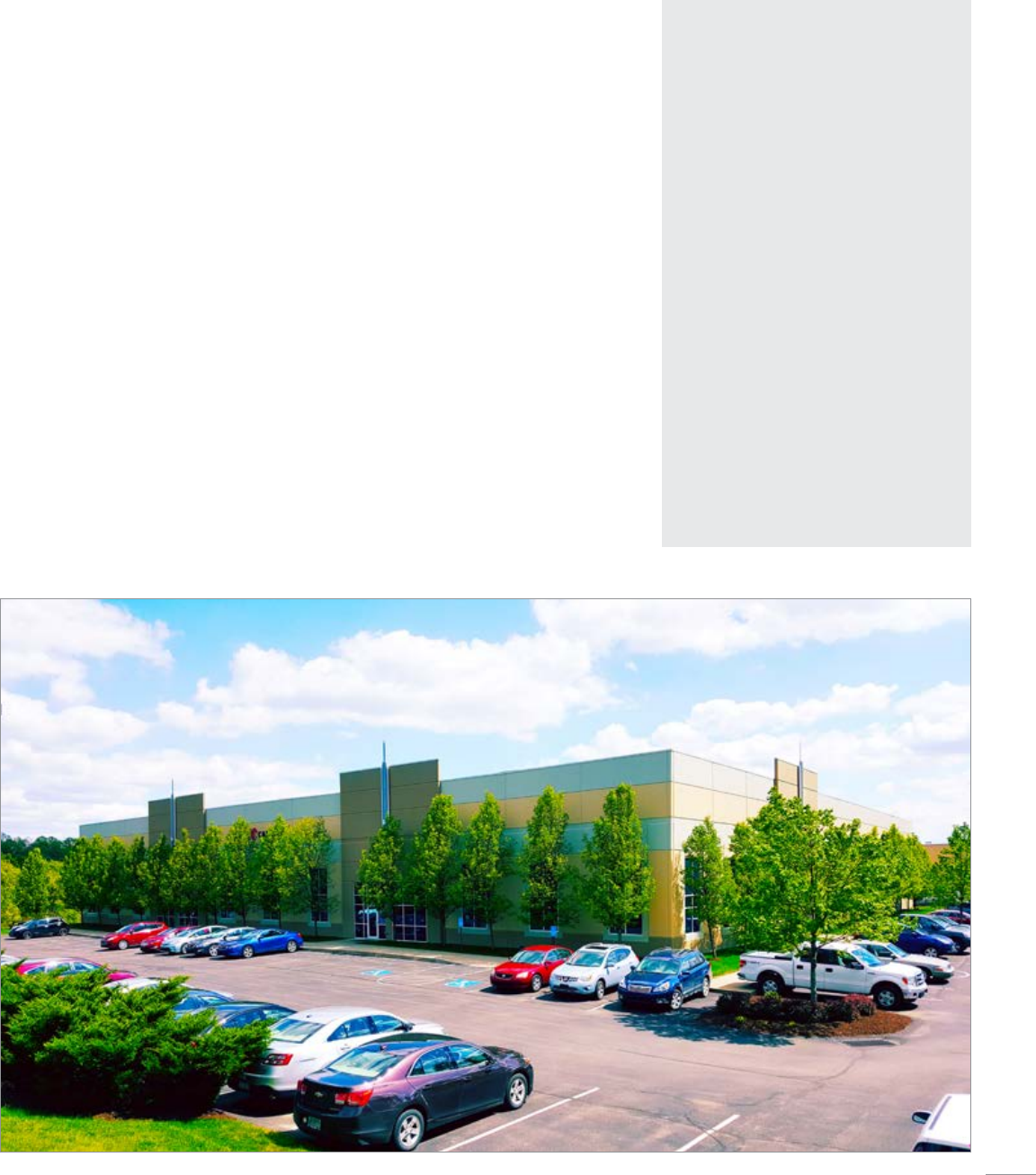
Count On Cameron
Cameron is constantly developing cutting-edge ultrasonic technology to better meet industry demands
for custody transfer. LEFM multipath in-line ultrasonic flowmeters are backed by more than 40 years
of experience and a history of technological firsts for their use.
We designed the LEFM 380Ci flowmeter based on feedback gathered from users of ultrasonic
flowmeters for custody transfer of natural gas:
■ Improve meter reliability over a wide range of application conditions
■ Improve safety for technicians when replacing transducers
■ Simplify installation and reduce the meter footprint and overall metering section weight
■ Reduce maintenance
The LEFM 380Ci gas ultrasonic flowmeter represents the integration of three crucial design elements
to create a truly unique meter to address the above concerns:
■ Eight-path design creates a smaller installed footprint for custody-transfer measurement and
reduces the weight of the metering section by eliminating a flow conditioner and reducing
upstream piping; also delivers high redundancy, and thus, online availability
■ Innovation makes the LEFM 380Ci flowmeter the first custody transfer gas ultrasonic meter with
transducers that are fully isolated from the gas
■ Proprietary coating effectively deals with the potential for corrosion and contamination from
components in the gas stream
Our LEFM 380Ci gas ultrasonic flowmeter can significantly reduce installed cost and yearly operating
cost while increasing personnel safety.
LEFM Technological firsts
1965-70 First LEFM
hydroelectric application
1970-75 First LEFM nuclear reactor
coolant application
1974-75 First LEFM petroleum application
1994-99 First measurement uncertainty
recapture uprate at nuclear facilities
1995 First LEFM MIL-SPEC
2003 First LEFM for custody transfer
of liquid hydrocarbons
2005 First LEFM for custody transfer
of LNG
2008 First LEFM for custody transfer
of heavy, viscous crude oils up
to 3000 cst
2010 First LEFM 380Ci flowmeters
installed on natural gas pipelines
with isolated transducers
Coraopolis, Pennsylvania facility
7