HP Color LaserJet CM2320 MFP Series Service Manual. Www.s Manuals.com. Manual
User Manual: Multi-functional printer HP Color LaserJet CM2320 MFP - Service manuals and Schematics, Disassembly / Assembly. Free.
Open the PDF directly: View PDF .
Page Count: 410 [warning: Documents this large are best viewed by clicking the View PDF Link!]
- Product basics
- Control panel
- Paper and print media
- Manage and maintain the product
- Theory of operation
- Basic operation
- Engine control system
- Laser/scanner system
- Image-formation system
- Pickup-and-feed system
- Scanner and ADF functions and operation
- Memory card system (fax/memory-card models only)
- Fax functions and operation (fax/memory-card models only)
- Removal and replacement
- Removal and replacement strategy
- Print cartridges
- Tray cassettes and optional Tray 3 assembly
- Control-panel bezel
- Control panel
- Paper-feed rollers and pads
- Components and major assemblies
- Link guide
- ADF input tray
- DIMM cover
- Print-cartridge drawer
- Intermediate transfer belt (ITB)
- Motors (drum motor and developer motor)
- Intermediate PCA
- Paper-feed guide assembly
- Rear-door stopper and link caps (simplex product)
- Rear door (simplex product)
- Rear door (duplex product)
- Right cover
- Formatter PCA and fax PCA
- DC controller PCA
- Scanner assembly
- Rear-upper cover (duplex product)
- Rear cover and feed guide (simplex product)
- Rear-lower cover and rear-door links (duplex product)
- Rear-door rib assembly (duplex product)
- Fuser-motor assembly
- Upper-cover assembly
- Left cover
- High-voltage power-supply PCA
- Color-misregistration sensor assembly
- Fan (FM1)
- Right-front cover and power button
- Memory-card cover and PCA (fax/memory-card models)
- Front-door assembly
- Duplex-reverse drive assembly
- Fuser
- Paper-delivery assembly
- Problem solve
- Menu map
- Troubleshooting process
- Troubleshooting tools
- Control-panel messages
- Event-log messages
- Paper-handling problems
- Solve image quality problems
- Solve performance problems
- Solve connectivity problems
- Service mode functions
- Solve fax problems (fax/memory-card models only)
- Memory card problems (fax/memory-card models only)
- Parts and diagrams
- Service and support
- Specifications
- Regulatory information
- Index
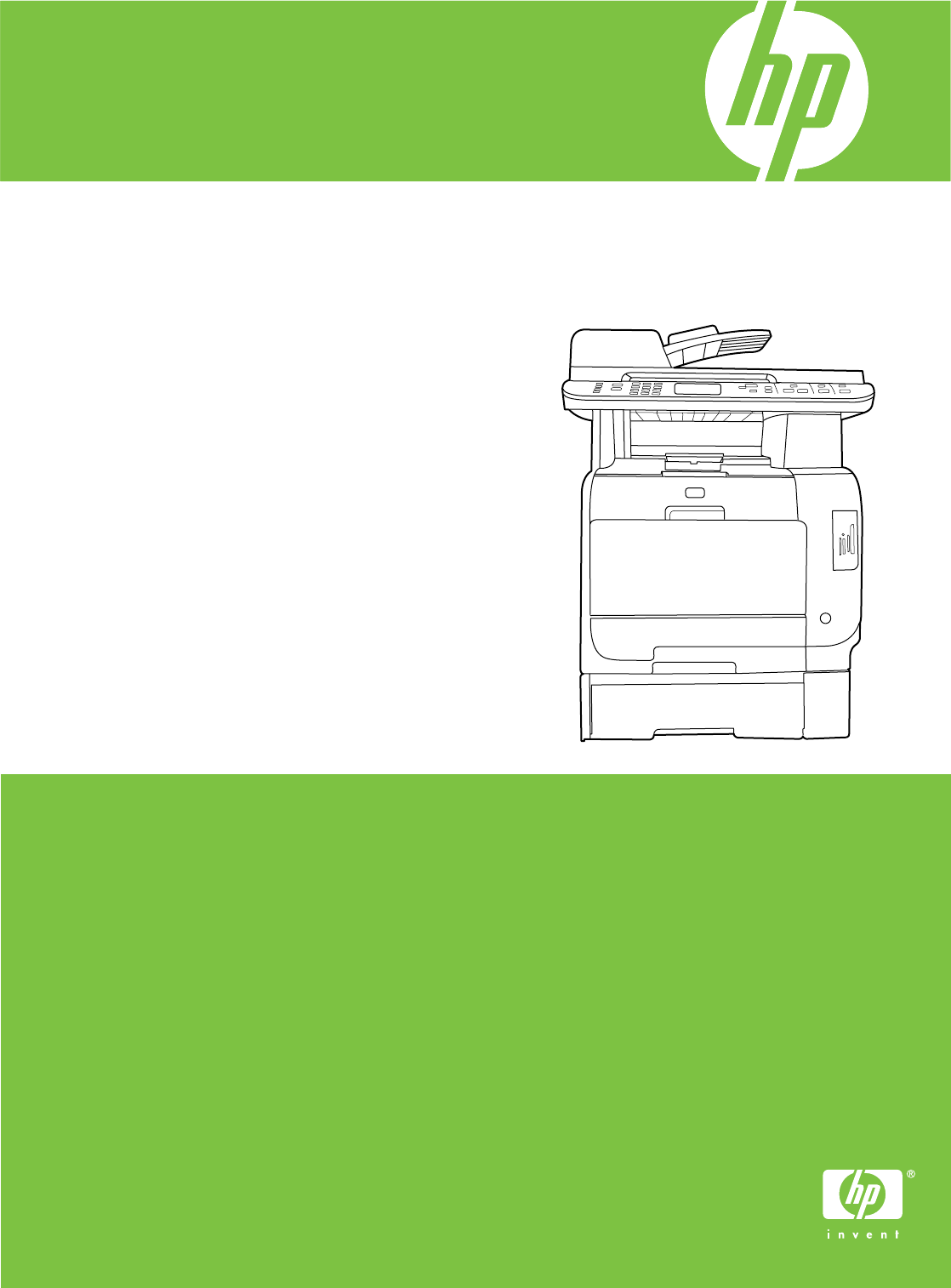
HP Color LaserJet CM2320 MFP Series
Service Manual

HP Color LaserJet CM2320 MFP Series
Service Manual
Copyright and License
© 2008 Copyright Hewlett-Packard
Development Company, L.P.
Reproduction, adaptation, or translation
without prior written permission is prohibited,
except as allowed under the copyright laws.
The information contained herein is subject
to change without notice.
The only warranties for HP products and
services are set forth in the express warranty
statements accompanying such products
and services. Nothing herein should be
construed as constituting an additional
warranty. HP shall not be liable for technical
or editorial errors or omissions contained
herein.
Edition 1, 9/2008
Part number: CC434-90969
Trademark Credits
Adobe®, Acrobat®, and PostScript® are
trademarks of Adobe Systems Incorporated.
Microsoft®, Windows®, and Windows®XP
are U.S. registered trademarks of Microsoft
Corporation.
Windows Vista® is either a registered
trademark or trademark of Microsoft
Corporation in the United States and/or other
countries.
UNIX® is a registered trademark of The Open
Group.
ENERGY STAR and the ENERGY STAR
mark are registered U.S. marks.

Table of contents
1 Product basics
Quick access to product information .................................................................................................... 2
Product comparison ............................................................................................................................. 3
Product features ................................................................................................................................... 4
Product walkaround .............................................................................................................................. 5
Front view ............................................................................................................................ 5
Back view ............................................................................................................................. 6
Interface ports ...................................................................................................................... 7
Supported operating systems ............................................................................................................... 8
Supported operating systems for Windows ......................................................................... 8
Supported operating systems for Macintosh ....................................................................... 8
Supported product software ................................................................................................................. 9
Software included with the product ...................................................................................... 9
Supported printer drivers ................................................................................................... 11
Software for other operating systems ................................................................................ 12
System requirements ......................................................................................................................... 13
Connectivity ........................................................................................................................................ 14
Supported network protocols ............................................................................................. 14
2 Control panel
HP Color LaserJet CM2320 control panel .......................................................................................... 18
HP Color LaserJet CM2320 MFP Fax Model and HP Color LaserJet CM2320 MFP Memory-Card
Model control panel ............................................................................................................................ 19
Control-panel menus .......................................................................................................................... 20
Use the control-panel menus ............................................................................................. 20
Control-panel Setup menu ................................................................................................. 20
Function specific menus .................................................................................................... 30
3 Paper and print media
Understand paper and print media use .............................................................................................. 38
Supported paper and print media sizes .............................................................................................. 39
Supported paper types and tray capacity ........................................................................................... 41
Special paper or print media guidelines ............................................................................................. 42
Load paper and print media ............................................................................................................... 43
ENWW iii
Load Tray 1 ........................................................................................................................ 43
Load Tray 2 or 3 ................................................................................................................ 44
Load originals for copying, scanning, or faxing .................................................................. 45
Configure trays ................................................................................................................................... 48
4 Manage and maintain the product
Information pages ............................................................................................................................... 50
HP ToolboxFX .................................................................................................................................... 52
View the HP ToolboxFX ..................................................................................................... 52
Status ................................................................................................................................. 52
Alerts .................................................................................................................................. 53
Product information ............................................................................................................ 53
Fax ..................................................................................................................................... 54
Help ................................................................................................................................... 56
System Settings ................................................................................................................. 58
Print Settings ..................................................................................................................... 60
Network Settings ................................................................................................................ 61
E-mail ................................................................................................................................. 61
Embedded Web server ....................................................................................................................... 62
Features ............................................................................................................................. 62
Use HP Web Jetadmin software ........................................................................................................ 63
Security features ................................................................................................................................ 63
Turn on password protection using the embedded Web server ........................................ 63
Turn on password protection from the control panel ......................................................... 63
Turn on private receive feature .......................................................................................... 64
Manage supplies ................................................................................................................................ 65
Check and order supplies .................................................................................................. 65
Replace supplies ............................................................................................................... 67
Clean the product .............................................................................................................. 73
Firmware updates .............................................................................................................. 79
5 Theory of operation
Basic operation ................................................................................................................................... 82
Major product systems ....................................................................................................... 82
Product components .......................................................................................................... 83
Sequence of operation ....................................................................................................... 84
Engine control system ........................................................................................................................ 85
DC controller ...................................................................................................................... 86
Power supply ..................................................................................................................... 86
High-voltage power supply ................................................................................................ 92
Laser/scanner system ....................................................................................................................... 93
Laser failure detection ....................................................................................................... 93
Image-formation system ..................................................................................................................... 94
iv ENWW
Image-formation process ................................................................................................... 95
Latent-image formation stage ............................................................................................ 96
Developing stage ............................................................................................................... 96
Transfer stage .................................................................................................................... 98
Fusing stage ...................................................................................................................... 99
ITB cleaning stage ........................................................................................................... 100
Drum cleaning stage ........................................................................................................ 101
Pickup-and-feed system ................................................................................................................... 102
Jam detection .................................................................................................................. 104
Pad transfer ..................................................................................................................... 104
Multiple-feed prevention .................................................................................................. 104
Scanner and ADF functions and operation ...................................................................................... 106
Scanner functions ........................................................................................................... 106
Scanner operation ........................................................................................................... 107
ADF operation .................................................................................................................. 107
ADF paper path and ADF sensors ................................................................................... 108
ADF jam detection ........................................................................................................... 109
Memory card system (fax/memory-card models only) ..................................................................... 110
Fax functions and operation (fax/memory-card models only) .......................................................... 111
Computer and network security features ......................................................................... 111
PSTN operation ............................................................................................................... 111
Receive faxes when you hear fax tones .......................................................................... 111
Distinctive ring function .................................................................................................... 112
Fax by using Voice over IP services ................................................................................ 112
The fax subsystem ........................................................................................................... 113
Fax card in the fax subsystem ......................................................................................... 113
Fax page storage in flash memory .................................................................................. 115
6 Removal and replacement
Removal and replacement strategy ................................................................................................. 118
General cautions during removal and replacement ......................................................... 118
Electrostatic discharge ..................................................................................................... 118
Required tools ................................................................................................................. 119
Types of screws ............................................................................................................... 119
Service approach ............................................................................................................. 120
Print cartridges ................................................................................................................................. 122
Tray cassettes and optional Tray 3 assembly .................................................................................. 123
Control-panel bezel ......................................................................................................................... 124
Control panel .................................................................................................................................... 125
Reinstall the control panel ............................................................................................... 126
Paper-feed rollers and pads ............................................................................................................. 127
Transfer roller .................................................................................................................. 127
Pickup roller (Tray 2 and Tray 3) ..................................................................................... 128
ENWW v
Separation roller (Trays 2 or 3) ........................................................................................ 131
ADF pickup roller assembly ............................................................................................. 133
Paper-pickup roller (Tray 1) ............................................................................................. 134
Separation pad (Tray 1) ................................................................................................... 137
Components and major assemblies ................................................................................................. 138
Link guide ........................................................................................................................ 138
ADF input tray .................................................................................................................. 139
DIMM cover ..................................................................................................................... 140
Print-cartridge drawer ...................................................................................................... 141
Intermediate transfer belt (ITB) ........................................................................................ 142
Motors (drum motor and developer motor) ...................................................................... 147
Intermediate PCA ............................................................................................................ 149
Paper-feed guide assembly ............................................................................................. 150
Rear-door stopper and link caps (simplex product) ......................................................... 151
Rear door (simplex product) ............................................................................................ 152
Rear door (duplex product) .............................................................................................. 154
Right cover ....................................................................................................................... 156
Formatter PCA and fax PCA ............................................................................................ 158
DC controller PCA ........................................................................................................... 161
Scanner assembly ........................................................................................................... 163
Rear-upper cover (duplex product) .................................................................................. 165
Rear cover and feed guide (simplex product) .................................................................. 166
Rear-lower cover and rear-door links (duplex product) ................................................... 170
Rear-door rib assembly (duplex product) ........................................................................ 173
Fuser-motor assembly ..................................................................................................... 175
Upper-cover assembly ..................................................................................................... 181
Left cover ......................................................................................................................... 185
High-voltage power-supply PCA ...................................................................................... 189
Color-misregistration sensor assembly ............................................................................ 192
Fan (FM1) ........................................................................................................................ 196
Right-front cover and power button ................................................................................. 197
Memory-card cover and PCA (fax/memory-card models) ............................................... 200
Front-door assembly ........................................................................................................ 205
Duplex-reverse drive assembly ....................................................................................... 212
Fuser ................................................................................................................................ 215
Paper-delivery assembly ................................................................................................. 221
7 Problem solve
Menu map ........................................................................................................................................ 226
Troubleshooting process .................................................................................................................. 227
Pre-troubleshooting checklist .......................................................................................... 227
Power-on checks ............................................................................................................. 228
Troubleshooting tools ....................................................................................................................... 229
vi ENWW
LED diagnostics ............................................................................................................... 229
Control-panel diagnostics ................................................................................................ 230
Fax reports ....................................................................................................................... 230
Diagrams ......................................................................................................................... 240
Print-quality troubleshooting tools .................................................................................... 252
Internal print quality test pages ........................................................................................ 253
Engine print mode specifications ..................................................................................... 255
HP ToolboxFX software ................................................................................................... 256
Control-panel messages .................................................................................................................. 257
Event-log messages ......................................................................................................................... 277
Print the event log ............................................................................................................ 277
Event log messages ........................................................................................................ 277
Event-log-only messages ................................................................................................ 279
Paper-handling problems ................................................................................................................. 281
Jams ................................................................................................................................ 281
Solve image quality problems .......................................................................................................... 295
General image quality problems ...................................................................................... 295
Solve issues with color documents .................................................................................. 299
Copy problems ................................................................................................................. 300
Scan problems ................................................................................................................. 304
Solve performance problems ........................................................................................................... 308
Solve connectivity problems ............................................................................................................. 309
Solve direct-connection problems .................................................................................... 309
Solve network problems (network models only) .............................................................. 309
Service mode functions .................................................................................................................... 311
Service menu ................................................................................................................... 311
Secondary service menu ................................................................................................. 311
Product resets .................................................................................................................. 313
Solve fax problems (fax/memory-card models only) ........................................................................ 314
Fax logs and reports ........................................................................................................ 314
Change error correction and fax speed ........................................................................... 316
Problems sending faxes .................................................................................................. 317
Problems receiving faxes ................................................................................................. 319
Performance problems .................................................................................................... 322
Memory card problems (fax/memory-card models only) .................................................................. 323
Missing or wrong files ...................................................................................................... 323
Index page not printing .................................................................................................... 323
Proof sheet not printing .................................................................................................... 324
Proof sheet not scanning ................................................................................................. 324
Issues with photo printing ................................................................................................ 325
8 Parts and diagrams
Order parts, accessories, and supplies ............................................................................................ 328
ENWW vii
Part numbers .................................................................................................................................... 328
Supplies ........................................................................................................................... 328
Memory ............................................................................................................................ 328
Cable and interface accessories ...................................................................................... 328
Paper-handling accessories ............................................................................................ 329
User-replaceable parts .................................................................................................... 329
Whole unit replacement part numbers ............................................................................. 329
How to use the parts lists and diagrams .......................................................................................... 330
Scanner assembly ............................................................................................................................ 332
Assembly locations ........................................................................................................................... 336
Covers .............................................................................................................................................. 338
Internal assemblies .......................................................................................................................... 340
PCAs ................................................................................................................................................ 354
Optional 250-sheet paper cassette .................................................................................................. 356
Alphabetical parts list ....................................................................................................................... 358
Numerical parts list ........................................................................................................................... 365
Appendix A Service and support
Hewlett-Packard limited warranty statement .................................................................................... 373
Customer self repair warranty service .............................................................................................. 374
Print cartridge limited warranty statement ........................................................................................ 375
Customer support ............................................................................................................................. 376
Appendix B Specifications
Physical specifications ..................................................................................................................... 378
Electrical specifications .................................................................................................................... 378
Environmental specifications ............................................................................................................ 378
Power consumption and acoustic emissions (HP Color LaserJet CM2320, HP Color LaserJet
CM2320 MFP Fax Model, HP Color LaserJet CM2320 MFP Memory-Card Model) ........................ 379
Paper and print media specifications ............................................................................................... 379
Skew specifications .......................................................................................................................... 379
Appendix C Regulatory information
FCC regulations ............................................................................................................................... 382
Additional statements for telecom (fax) products ............................................................................. 382
EU statement for telecom operation ................................................................................ 382
New Zealand telecom statements ................................................................................... 382
Telephone Consumer Protection Act (United States) ...................................................... 383
IC CS-03 requirements .................................................................................................... 383
Declaration of conformity .................................................................................................................. 384
HP Color LaserJet CM2320 MFP .................................................................................... 384
HP LaserJet CM2320 Fax Model / CM2320 Memory-Card Model .................................. 384
Certificate of volatility ....................................................................................................................... 386
viii ENWW
Country/region specific statements .................................................................................................. 387
Laser safety ..................................................................................................................... 387
Canadian DOC regulations .............................................................................................. 387
VCCI statement (Japan) .................................................................................................. 387
EMI statement (Korea) ..................................................................................................... 387
Laser statement for Finland ............................................................................................. 387
Substances table (China) ................................................................................................ 388
Index ................................................................................................................................................................. 389
ENWW ix
xENWW
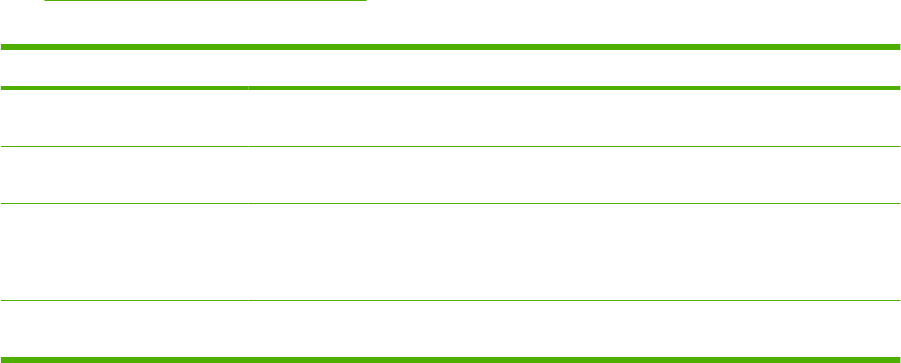
Quick access to product information
Use the following Web site to find information about the product.
●www.hp.com/support/CM2320series
Table 1-1 Product guides
Guide Description
HP Color LaserJet CM2320 MFP
Series Getting Started Guide
Provides step-by-step instructions for installing and setting up the product.
HP Color LaserJet CM2320 MFP
Series User Guide
Provides detailed information for using the product and problem-solving. Available on the
product CD or in the Windows Program Group if the software is installed on a computer.
HP ToolboxFX To check the product status and settings, and to view problem-solving information and online
documentation, use the HP ToolboxFX. You must have performed a complete software
installation in order to use the HP ToolboxFX. See the user guide for more information about
software installation.
Online Help Provides information about options that are available in the printer drivers. To view a Help
file, open the online Help through the printer driver.
2 Chapter 1 Product basics ENWW
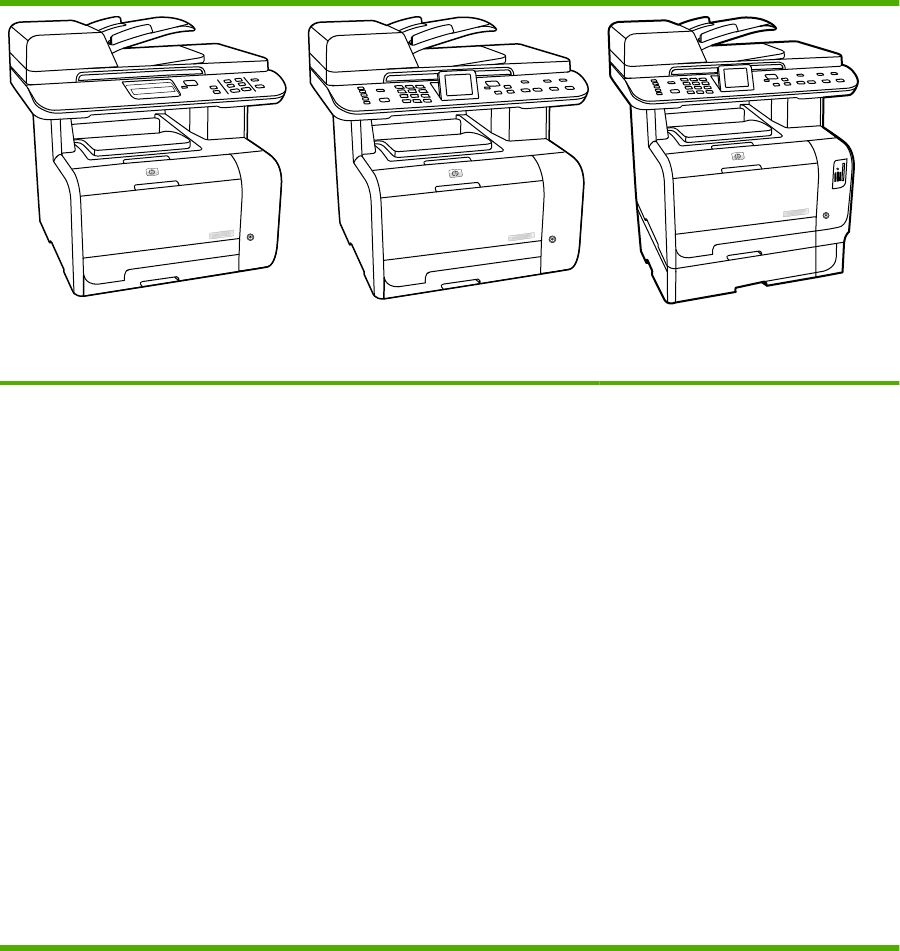
Product comparison
The product is available in the following configurations.
HP Color LaserJet CM2320 MFP HP Color LaserJet CM2320 MFP Fax
Model
HP Color LaserJet CM2320 MFP
Memory-Card Model
●Prints letter-size pages at speeds
up to 21 pages per minute (ppm)
and A4-size pages at speeds up to
19 ppm.
●PCL 6 printer drivers.
●Tray 1 holds up to 50 sheets of print
media or up to 10 envelopes.
●Tray 2 holds up to 250 sheets of
print media.
●Optional 250-sheet input tray
(Tray 3) available.
●Hi-Speed USB 2.0 port and 10/100
Base-T network port.
●160-MB random-access memory
(RAM).
●Flatbed scanner and 50-page
automatic document feeder (ADF).
●One available DIMM slot for
memory expansion (accepts 64 MB
and 128 MB DIMMS).
HP Color LaserJet CM2320 MFP, plus:
●V.34 fax modem and 8-megabyte
(MB) flash fax-storage memory.
●Two RJ-11 fax phone line ports
●Color graphics display
HP Color LaserJet CM2320 MFP Fax
Model, plus:
●Automatic two-sided (duplex)
printing, fax receiving, and copying.
●Four memory card slots
●Additional 250-sheet input tray
(Tray 3) included.
ENWW Product comparison 3
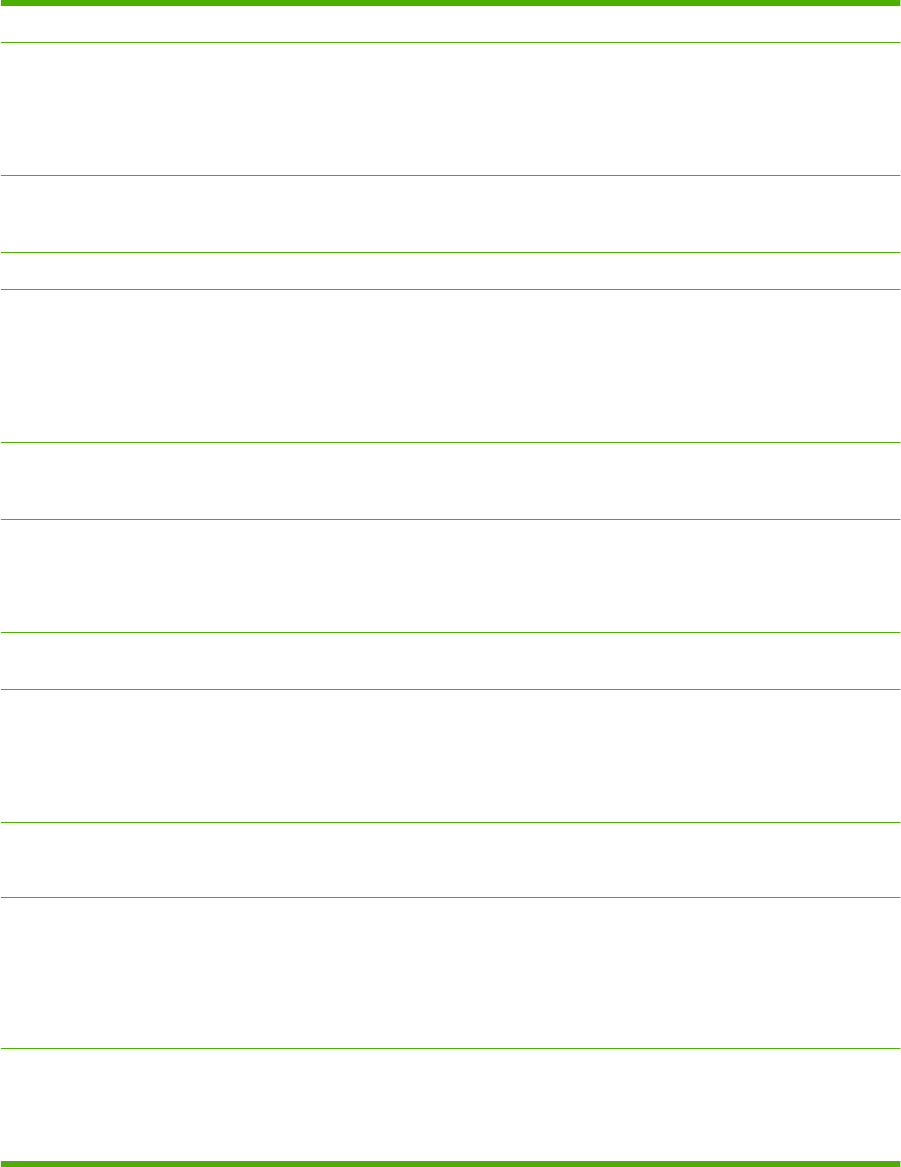
Product features
Performance ●Prints up to 21 ppm (letter) or 19 ppm (A4).
Print quality ●1,200 dots per inch (dpi) with Image REt 2400 text and graphics.
●Adjustable settings to optimize print quality.
●The HP UltraPrecise print cartridge has a finer toner formulation that provides sharper text
and graphics.
Fax (HP LaserJet CM2320
Fax Model / CM2320
Memory-Card Model only)
●Full-functionality fax capabilities with a V.34 fax; includes a phone book, fax/tel, and
delayed-fax features.
Copy ●Includes ADF that allows faster, more efficient copy jobs with multiple-page documents.
Scan ●The product provides 1,200 pixels per inch (ppi), 24-bit full-color scanning from letter/A4-
size scanner glass.
●The product provides 300 ppi, 24-bit full-color scanning from the automatic document
feeder (ADF).
●Includes an ADF that allows faster, more efficient scan jobs with multiple-page documents.
Memory card slots (HP
Color LaserJet CM2320 MFP
Memory-Card Model only)
Supports a variety of memory cards. See the user guide for more information.
Networking ●TCP/IP
◦IPv4
◦IPv6
Printer driver features ●Fast printing performance, built-in Intellifont and TrueType scaling technologies, and
advanced imaging capabilities are benefits of the PCL 6 printer language.
Interface connections ●Hi-Speed USB 2.0 port.
●10/100 Base-T ethernet network port (RJ-45).
●RJ-11 fax/phone cable ports (HP LaserJet CM2320 Fax Model / CM2320 Memory-Card
Model only).
Economical printing ●N-up printing (printing more than one page on a sheet).
●Two-sided printing using the automatic duplexer.
Supplies ●A supplies status page that displays the amount of life remaining in the print cartridge.
●No-shake cartridge design.
●Authentication for HP print cartridges.
●Enabled supplies-ordering capability.
Accessibility ●Online user guide that is compatible with text screen-readers.
●Print cartridges can be installed and removed by using one hand.
●All doors and covers can be opened by using one hand.
4 Chapter 1 Product basics ENWW
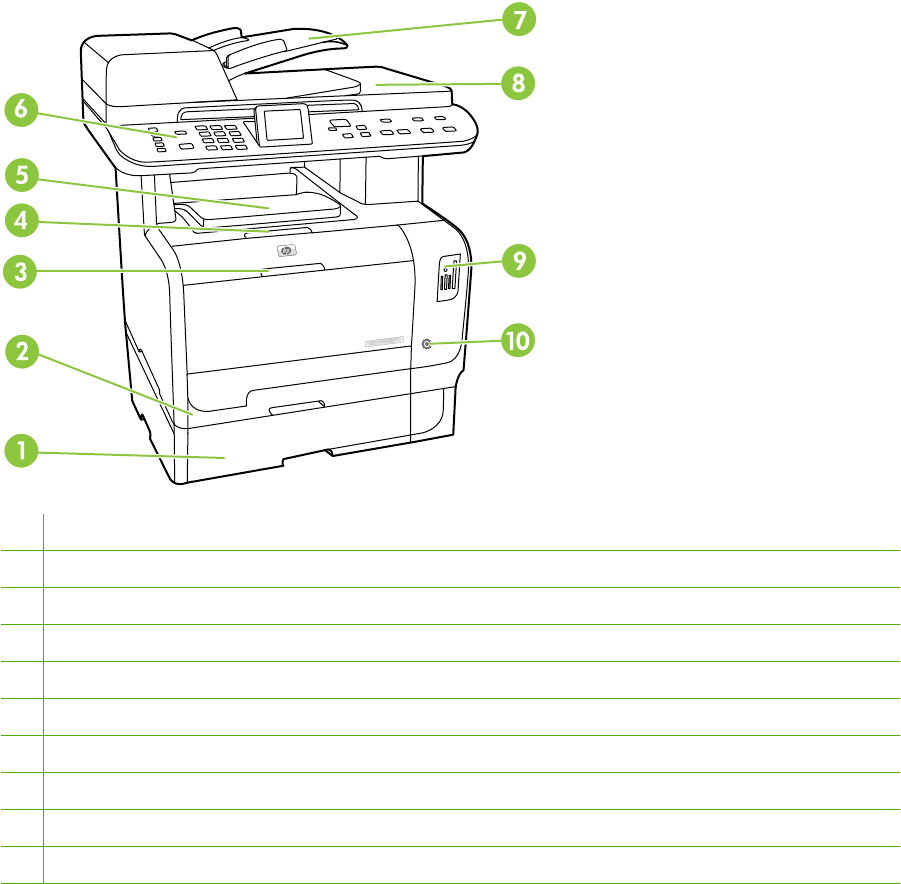
Product walkaround
Front view
1Optional Tray 3 (standard on the HP Color LaserJet CM2320 MFP Memory-Card Model)
2Tray 2
3Tray 1
4Print-cartridge door latch
5Top (face-down) output bin
6Control panel
7Automatic document feeder (ADF) input tray
8Automatic document feeder (ADF) output bin
9Memory card slots (HP Color LaserJet CM2320 MFP Memory-Card Model only)
10 Power switch
ENWW Product walkaround 5
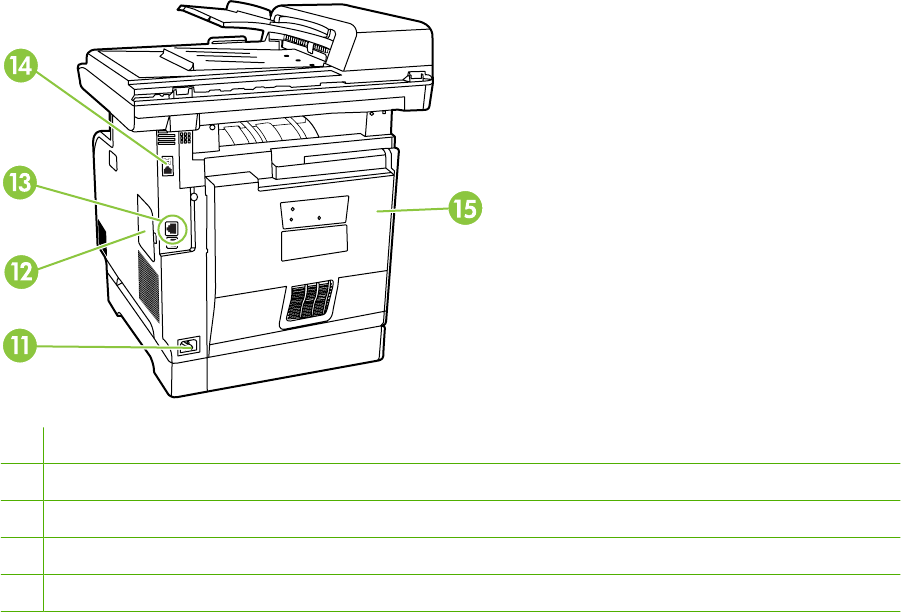
Back view
11 Power connector
12 DIMM door (for adding additional memory)
13 Hi-Speed USB 2.0 port and network port.
14 Fax ports (HP LaserJet CM2320 Fax Model / CM2320 Memory-Card Model only)
15 Rear door for jam access
6 Chapter 1 Product basics ENWW
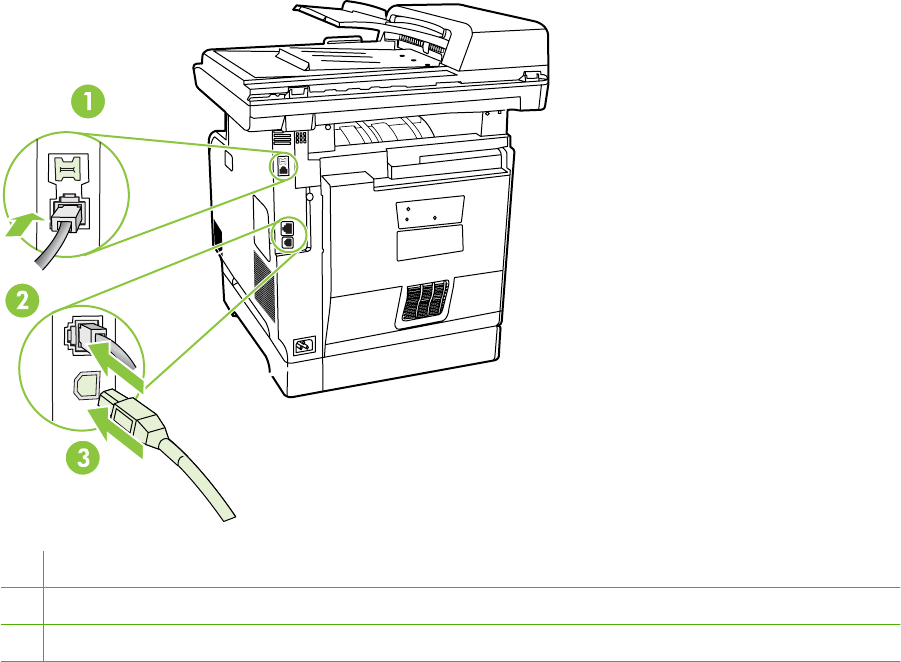
Interface ports
1Fax ports (HP LaserJet CM2320 Fax Model / CM2320 Memory-Card Model only)
2Network port
3Hi-Speed USB 2.0 port
ENWW Product walkaround 7
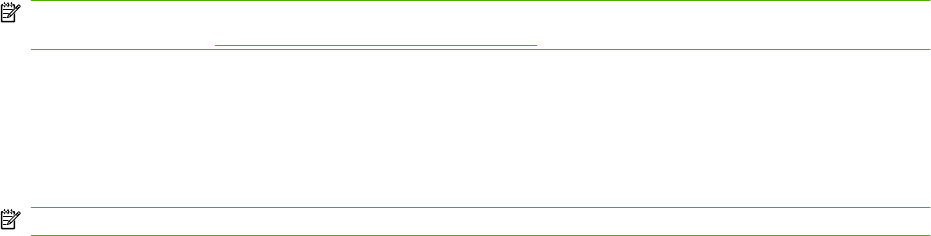
Supported operating systems
Supported operating systems for Windows
The product supports the following Windows operating systems:
Full software installation
●Windows XP (32-bit)
●Windows Vista (32-bit and 64-bit)
Print and scan driver
●Windows XP (64 bit)
●Windows 2000
●Windows 2003 Server (32-bit and 64-bit)
NOTE: The PCL 5 UPD and HP postscript level 3 emulation drivers are available only on the
HP support website: www.hp.com/support/CM2320series.
Supported operating systems for Macintosh
The device supports the following Macintosh operating systems:
●Mac OS X v10.3, v10.4, and later
NOTE: For Mac OS X v10.4 and later, PPC and Intel Core Processor Macs are supported.
8 Chapter 1 Product basics ENWW
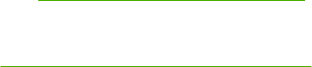
Supported product software
Software included with the product
Software for Windows
Embedded Web server
The device is equipped with an embedded Web server, which provides access to information about
device and network activities. This information appears in a Web browser, such as Microsoft Internet
Explorer, Netscape Navigator, Apple Safari, or Firefox.
The embedded Web server resides on the device. It is not loaded on a network server.
The embedded Web server provides an interface to the device that anyone who has a network-
connected computer and a standard Web browser can use. No special software is installed or
configured, but you must have a supported Web browser on your computer. To gain access to the
embedded Web server, type the IP address for the device in the address line of the browser. (To find
the IP address, print a configuration page. For more information about printing a configuration page,
see Information pages on page 50.)
For a complete explanation of the features and functionality of the embedded Web server, see
Embedded Web server on page 62.
ENWW Supported product software 9
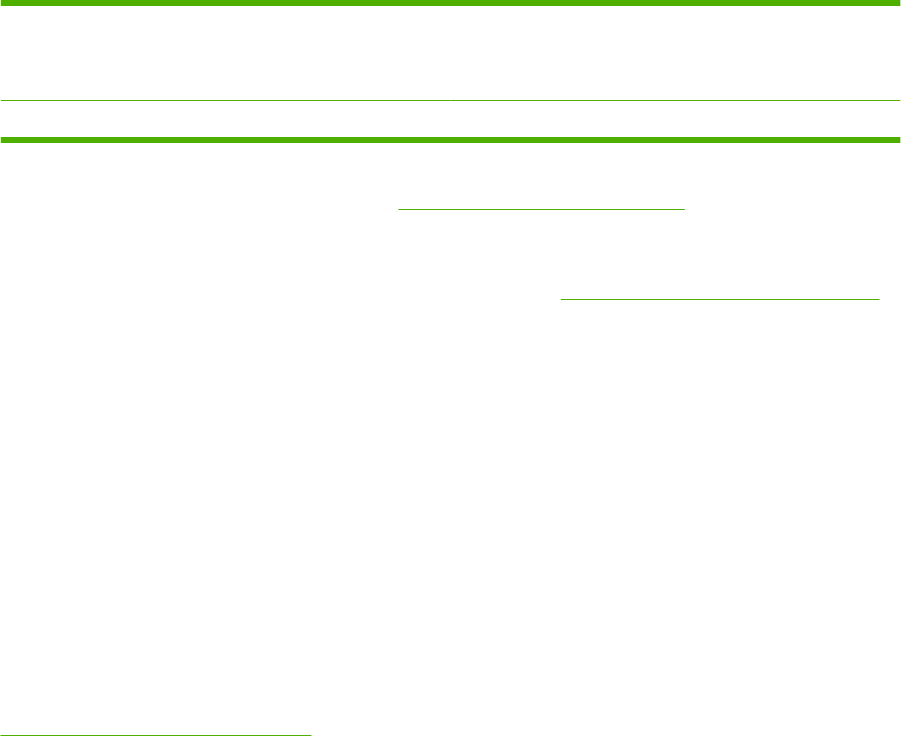
HP ToolboxFX
HP ToolboxFX software is a program that you can use for the following tasks:
●Check the product status
●Check the supplies status and use HP SureSupply to shop online for supplies
●Set up alerts
●View product usage reports
●View product documentation
●Gain access to troubleshooting and maintenance tools
●Use HP Proactive Support to routinely scan your printing system and to prevent potential problems.
HP Proactive Support can update software, firmware, and HP printer drivers.
You can view HP ToolboxFX software when the product is directly connected to your computer or when
it is connected to a network.
Supported operating systems ●Microsoft Windows XP, Service Pack 2 (Home and
Professional editions)
●Microsoft Windows Vista™
Supported browsers ●Microsoft Internet Explorer 6.0 or 7.0
To download HP ToolboxFX software , go to www.hp.com/go/easyprintercare. This Web site also
provides updated information about supported browsers and a list of HP products that support
HP ToolboxFX software.
For more information about using HP ToolboxFX software, see View the HP ToolboxFX on page 52.
Software for Macintosh
Embedded Web server
The product is equipped with an embedded Web server, which provides access to information about
product and network activities. This information appears in a Web browser, such as Netscape Navigator,
Apple Safari, or Firefox.
The embedded Web server resides on the product. It is available on network and direct-connected
devices.
The embedded Web server provides an interface to the product that anyone who has a standard Web
browser can use. No special software is installed or configured, but you must have a supported Web
browser on your computer. To gain access to the embedded Web server, click Maintain Device in
HP Director.
For a complete explanation of the features and functionality of the embedded Web server, see
Embedded Web server on page 62.
10 Chapter 1 Product basics ENWW
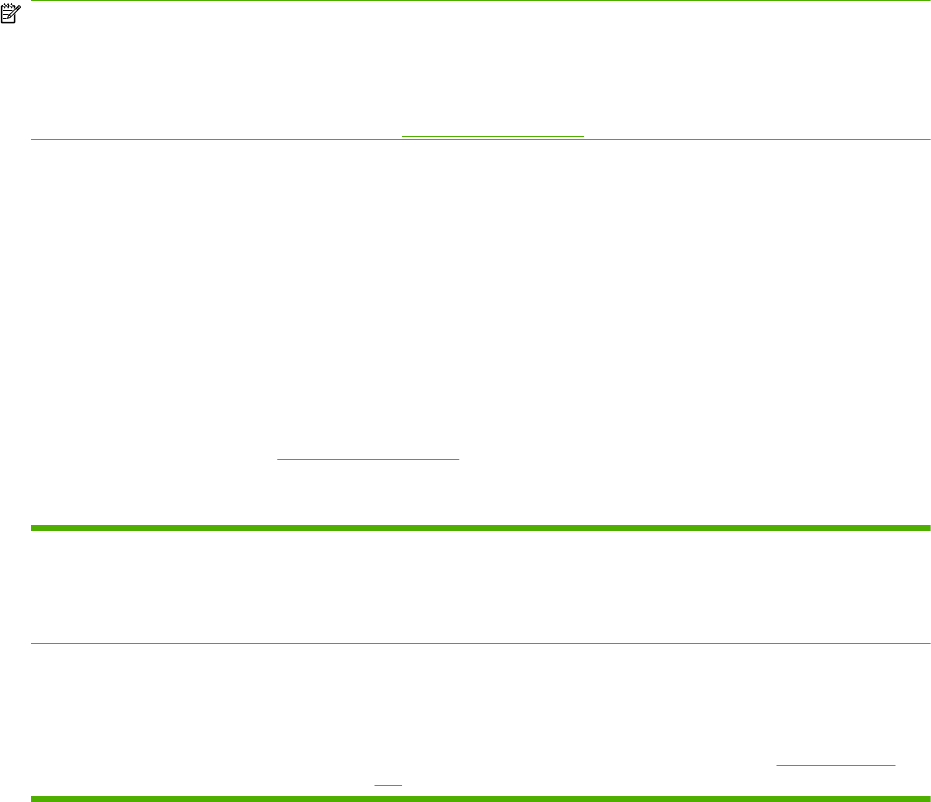
Supported printer drivers
Supported printer drivers for Windows
●PCL 5 UPD
●PCL 6
●HP postscript level 3 UPD
The printer drivers include online Help that has instructions for common printing tasks and also describes
the buttons, checkboxes, and drop-down lists that are in the printer driver.
NOTE: The versions of PCL 5 and HP postscript level 3 emulation that are used in this product are
identical to the PCL 5 and HP postscript level 3 emulation that are used in the HP Universal Print Driver
(UPD) for Windows. It installs and operates in the same manner as previous versions of PCL 5 and
HP postscript level 3 emulation, and it does not require any special configuration.
For more information about the UPD, see www.hp.com/go/upd.
HP Universal Print Driver (UPD)
The HP Universal Print Driver (UPD) for Windows is a single driver that gives you instant access to
virtually any HP LaserJet product, from any location, without downloading separate drivers. It is built on
proven HP print driver technology and has been tested thoroughly and used with many software
programs. It is a powerful solution that performs consistently over time.
The HP UPD communicates directly with each HP product, gathers configuration information, and then
customizes the user interface to show the product’s unique, available features. It automatically enables
features that are available for the product, such as two-sided printing and stapling, so you do not need
to enable them manually.
For more information, go to www.hp.com/go/upd.
UPD installation modes
Traditional mode ●Use this mode if you are installing the driver from a CD for a single computer.
●When installed with this mode, UPD operates like traditional printer drivers.
●If you use this mode, you must install UPD separately for each computer.
Dynamic mode ●Use this mode if you are installing the driver for a mobile computer, so you can
discover and print to HP products in any location.
●Use this mode if you are installing UPD for a workgroup.
●To use this mode, download UPD from the Internet. See www.hp.com/go/
upd.
Supported printer drivers for Macintosh
The HP installer provides PostScript
®
Printer Description (PPD) files, Printer Dialog Extensions (PDEs),
and the HP Printer Utility for use with Macintosh computers.
The PPDs, in combination with the Apple PostScript printer drivers, provide access to device features.
Use the Apple PostScript printer driver that comes with the computer.
ENWW Supported product software 11
System requirements
The product has the following minimum software and hardware requirements.
Windows XP Windows Vista Windows 2000 and Windows
Server 2003
Mac OS X v10.3 and later
●Pentium II processor
(Pentium III or higher
recommended)
●128 MB RAM
●250 MB available hard disk
space
●SVGA 800 x 600 monitor
with 16-bit color
●Internet Explorer 6.0 or
higher (full installation)
●USB port
●CD-ROM drive
●1 GHz processor
●512 MB RAM
●250 MB available hard disk
space
●SVGA 800 x 600 monitor
with 16-bit color
●Internet Explorer 6.0 or
higher (full installation)
●USB port
●CD-ROM drive
●Pentium II processor or
greater
●64 MB RAM
●50 MB available hard disk
space
●SVGA 800 x 600 monitor
with 16-bit color (print driver,
scan driver only)
●USB port
●CD-ROM drive
●PowerPC G3, G4, or G5
processor, or Intel Core
processor
●80 MB RAM
●30 MB available hard disk
space
●USB port
●CD-ROM drive
●Safari or Firefox browser
ENWW System requirements 13
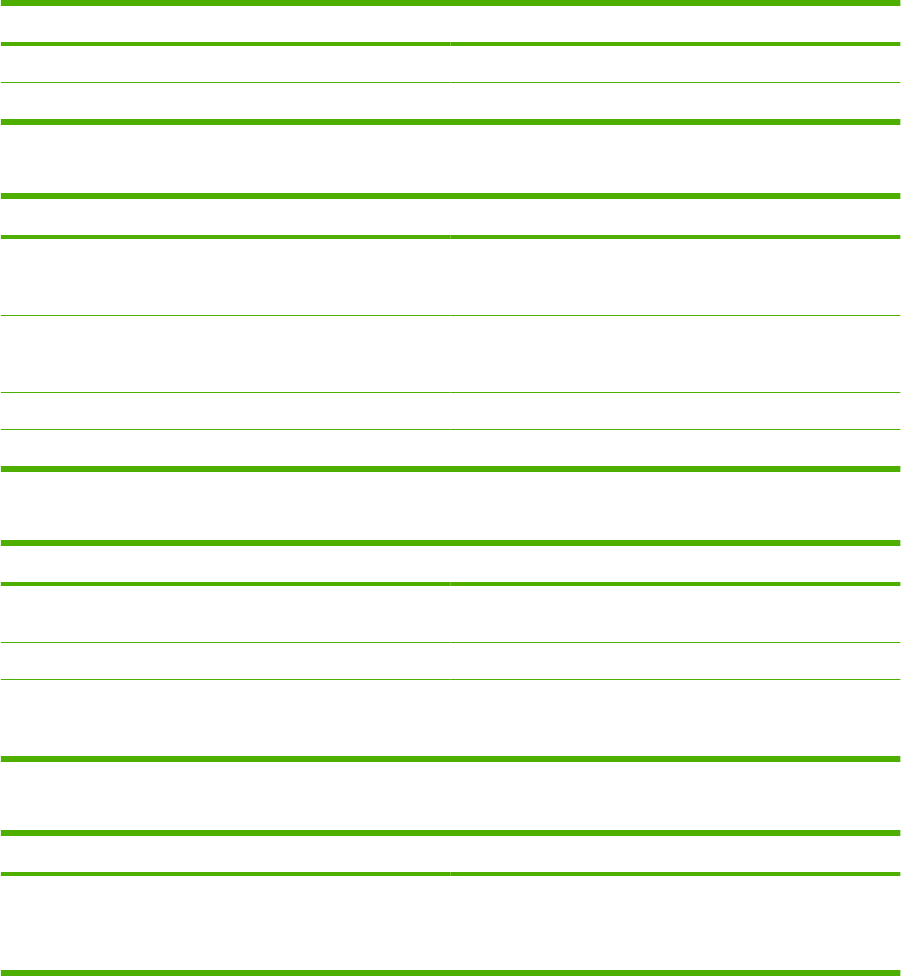
Connectivity
Supported network protocols
The product supports the TCP/IP network protocol. It is the most widely used and accepted networking
protocol. Many networking services utilize this protocol. This product also supports IPv4 and IPv6. The
following tables list the networking services/protocols that are supported on the product.
Table 1-2 Printing
Service name Description
port9100 (Direct Mode) Printing service
Line printer daemon (LPD) Printing service
Table 1-3 Network product discovery
Service name Description
SLP (Service Location Protocol) Device Discovery Protocol, used to help find and configure
network devices. Used primarily by Microsoft-based software
programs.
mDNS (multicast Domain Name Service - also known as
“Rendezvous” or “Bonjour”)
Device Discovery Protocol, used to help find and configure
network devices. Used primarily by Apple Macintosh-based
software programs.
ws-discover Used by Microsoft-based software programs
LLMNR Used when DNS services are not available
Table 1-4 Messaging and management
Service name Description
HTTP (hypertext transfer protocol) Allows Web browsers to communicate with embedded Web
server.
EWS (embedded Web server) Allows a user to manage the product through a Web browser.
SNMP (simple network management protocol) Used by network programs for product management. SNMP
V1 and standard MIB-II (Management Information Base)
objects are supported.
Table 1-5 IP addressing
Service name Description
DHCP (dynamic host configuration protocol), IPv4, and IPv6 For Automatic IP address assignment. DHCP server provides
the product with an IP address. Generally requires no user
intervention for product to obtain IP address from a DHCP
server.
14 Chapter 1 Product basics ENWW
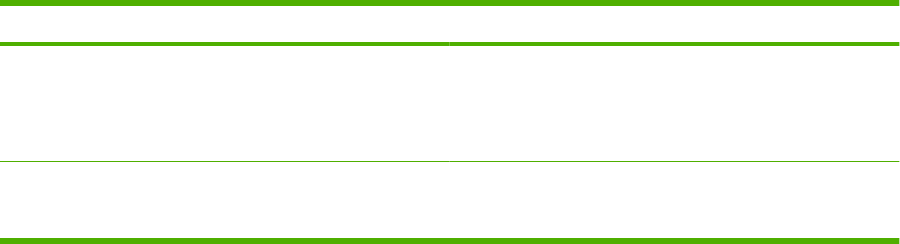
Service name Description
BOOTP (bootstrap protocol) For Automatic IP address assignment. BOOTP server
provides the product with an IP address. Requires
administrator to input the product MAC hardware address on
BOOTP server in order for product to obtain an IP address from
that server.
Auto IP For Automatic IP address assignment. If neither a DHCP
server nor a BOOTP server is present, this service allows the
product to generate a unique IP address.
Table 1-5 IP addressing (continued)
ENWW Connectivity 15
16 Chapter 1 Product basics ENWW
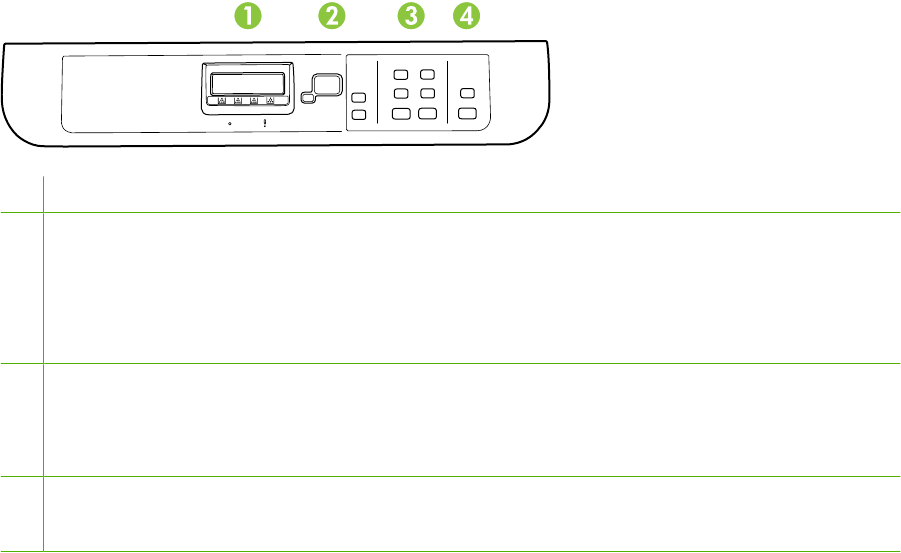
HP Color LaserJet CM2320 control panel
1Liquid Crystal Display
2OK button and navigation arrows. Use these buttons to select and confirm menu choices.
Cancel button. Use this button to cancel the current menu selection.
Setup button. Access the main Setup menu.
Back button. Go back to the previous menu.
3Copy Menu button. Access the Copy menu.
Start Copy Black button. Perform a black and white copy operation.
Start Copy Color button. Perform a color copy operation.
4Scan Menu button. Access the scan menu.
Start Scan button. Perform a scan operation.
18 Chapter 2 Control panel ENWW
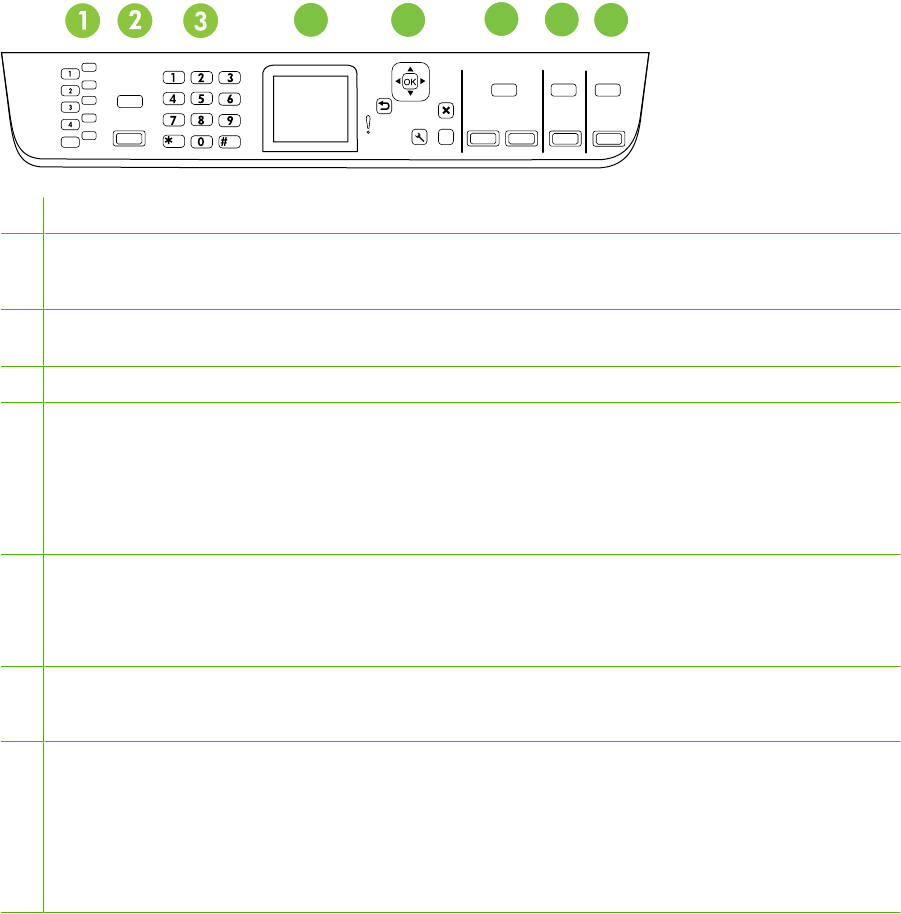
HP Color LaserJet CM2320 MFP Fax Model and HP Color
LaserJet CM2320 MFP Memory-Card Model control panel
?
..
56
48
7
1Speed dials. 4 speed dial buttons and one shift button to support up to 8 speed dials.
2Fax Menu button. Access the fax menu.
Start Fax button. Initiate a fax from the control panel.
3Alphanumeric buttons. Use the alphanumeric buttons to type data into the product control-panel display and dial
telephone numbers for faxing.
4Color graphics display
5OK button and navigation arrows. Use these buttons to select and confirm menu choices.
Cancel button. Use this button to cancel the current menu selection.
Setup button. Access the main Setup menu.
Back button. Go back to the previous menu.
6Copy Menu button. Access the copy menu.
Start Copy Black button. Perform a black and white copy operation.
Start Copy Color button. Perform a color copy operation.
7Scan Menu button. Access the scan menu.
Start Scan button. Perform a scan operation.
8Email Menu button (HP Color LaserJet CM2320 MFP Fax Model only). Access the e-mail menu.
Start Email button (HP Color LaserJet CM2320 MFP Fax Model only). Start a scan to e-mail.
Photo Menu button (HP Color LaserJet CM2320 MFP Memory-Card Model only). Access the photo menu.
Start Photo button (HP Color LaserJet CM2320 MFP Memory-Card Model only). Print the selected photos from the
memory card.
ENWW HP Color LaserJet CM2320 MFP Fax Model and HP Color LaserJet CM2320 MFP Memory-Card
Model control panel
19
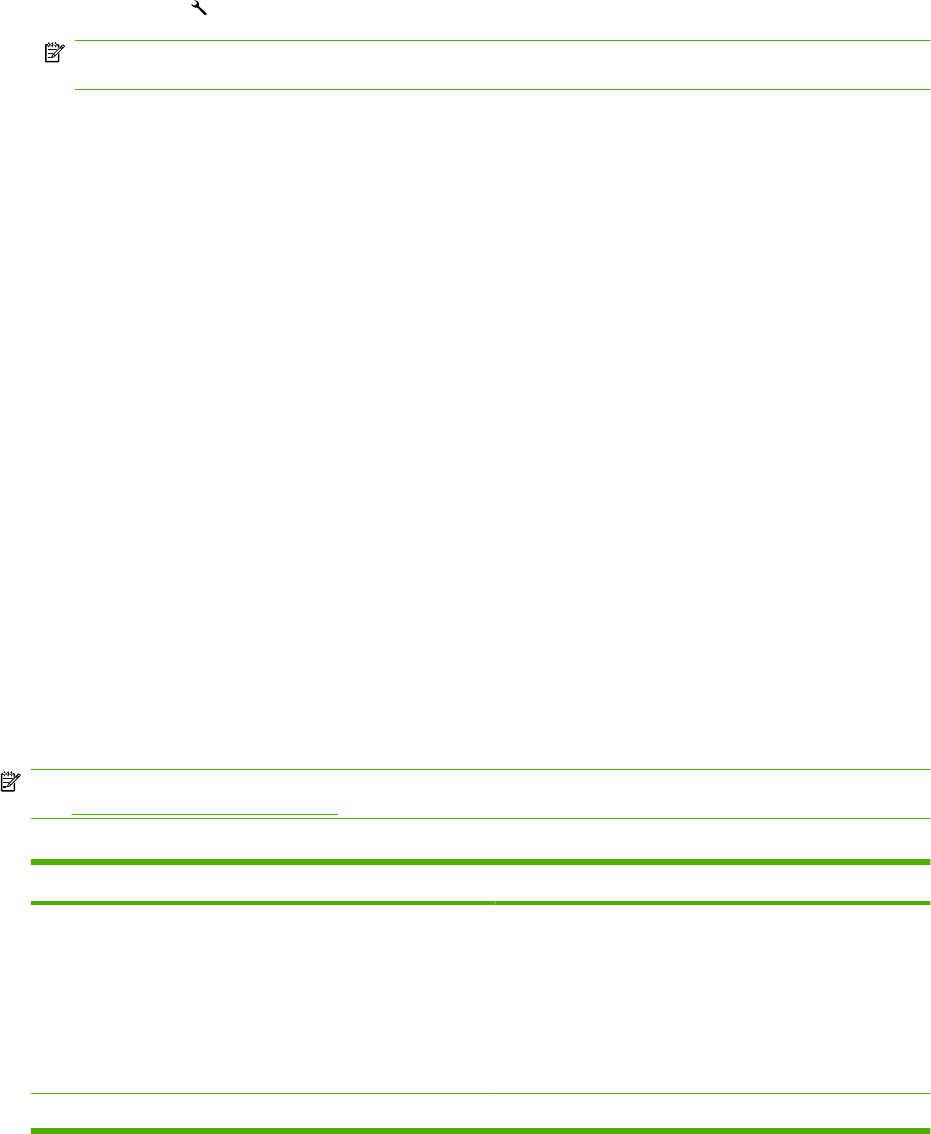
Control-panel menus
Use the control-panel menus
To gain access to the control-panel menus, use the following steps.
1. Press Setup .
NOTE: To access the function-specific menus press Fax Menu, Copy Menu, Scan Menu, or
Photo Menu.
2. Use the arrow buttons to navigate the listings.
●Press OK to select the appropriate option.
●Press Cancel to cancel an action or return to the Ready state.
Control-panel Setup menu
These sub menus are available from the control-panel main Setup menu:
●Use the Copy setup menu to configure basic copy default settings such as contrast, collation, or
the number of copies printed.
●Use the Reports menu to print reports that provide information about the product.
●Use the Fax setup (HP LaserJet CM2320 Fax Model / CM2320 Memory-Card Model only) menu
to configure the fax phone book, the outgoing and incoming fax options, and the basic settings for
all faxes.
●Use the Photo setup (HP Color LaserJet CM2320 MFP Memory-Card Model only) menu to
configure the basic settings for printing photos from a memory card.
●Use the System setup menu to establish basic product settings such as language, print quality,
or volume levels.
●Use the Service menu to restore default settings, clean the product, and activate special modes
that affect print output.
●Use the Network configuration menu to configure network settings such as TCP/IP configuration.
NOTE: To print a detailed list of the entire control-panel menu and its structure, print a menu map.
See Information pages on page 50.
Table 2-1 Copy setup menu
Menu item Sub-menu item Description
Default Optimize Auto Select
Mixed
Printed Picture
Photograph
Text
Sets the default copy quality.
Default lighter/darker Sets the default contrast option.
20 Chapter 2 Control panel ENWW
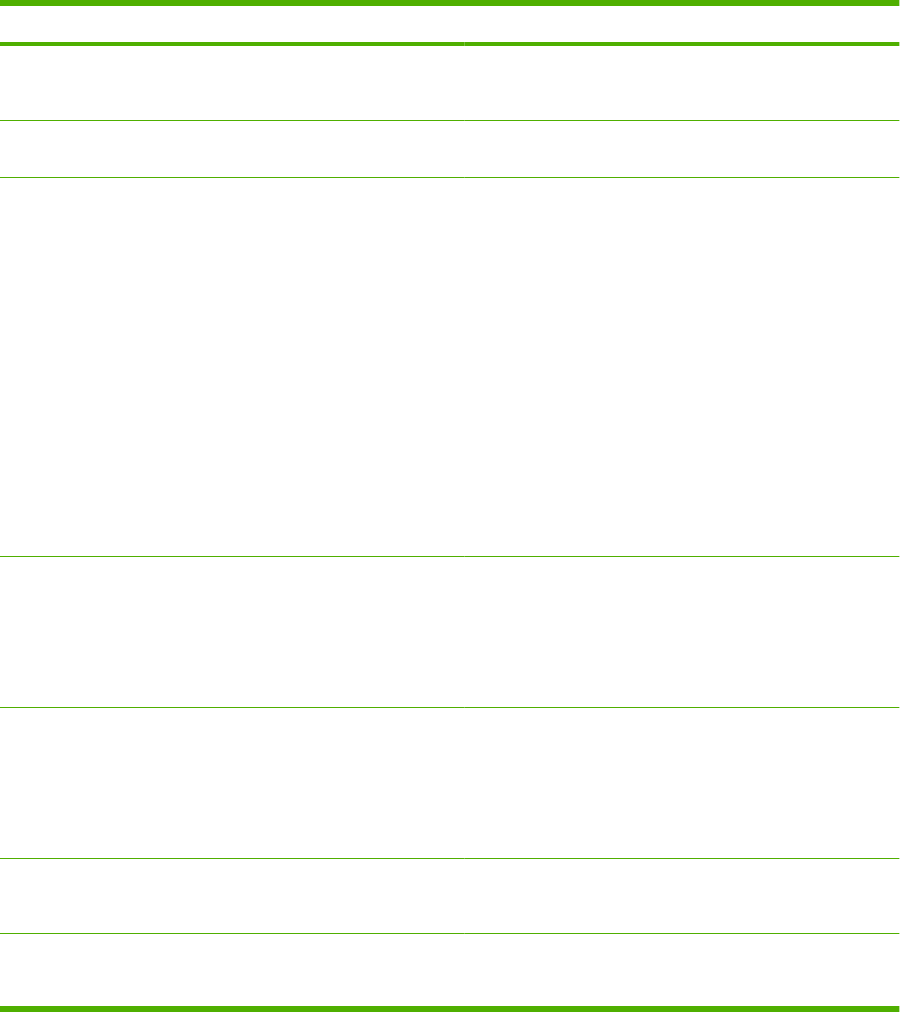
Menu item Sub-menu item Description
Default Collation On
Off
Sets the default collation option.
Default number of
copies
(Range: 1-99) Sets the default number of copies.
Default Reduce/Enlarge Original=100%
Legal to Letter=78%
Legal to A4=83%
A4 to Letter=94%
Letter to A4=97%
Full Page=91%
Fit to page
2 pages per sheet
4 pages per sheet
Custom: 25 to 400%
Sets the default percentage to reduce or enlarge a copied
document.
Default Tray Select Auto Select
Tray 1
Tray 2
Tray 3 (if the tray is installed)
Sets the default input paper tray.
Default 2-Sided
(memory-card models
only)
1 to 1 sided
1 to 2 sided
2 to 2 sided
2 to 1 sided
Sets the default input scan format and the default output
format.
Default Copy Draft On
Off
Sets the default draft mode option.
Default Multi-page On
Off
Sets the default multi-page flatbed copy option.
Table 2-1 Copy setup menu (continued)
ENWW Control-panel menus 21
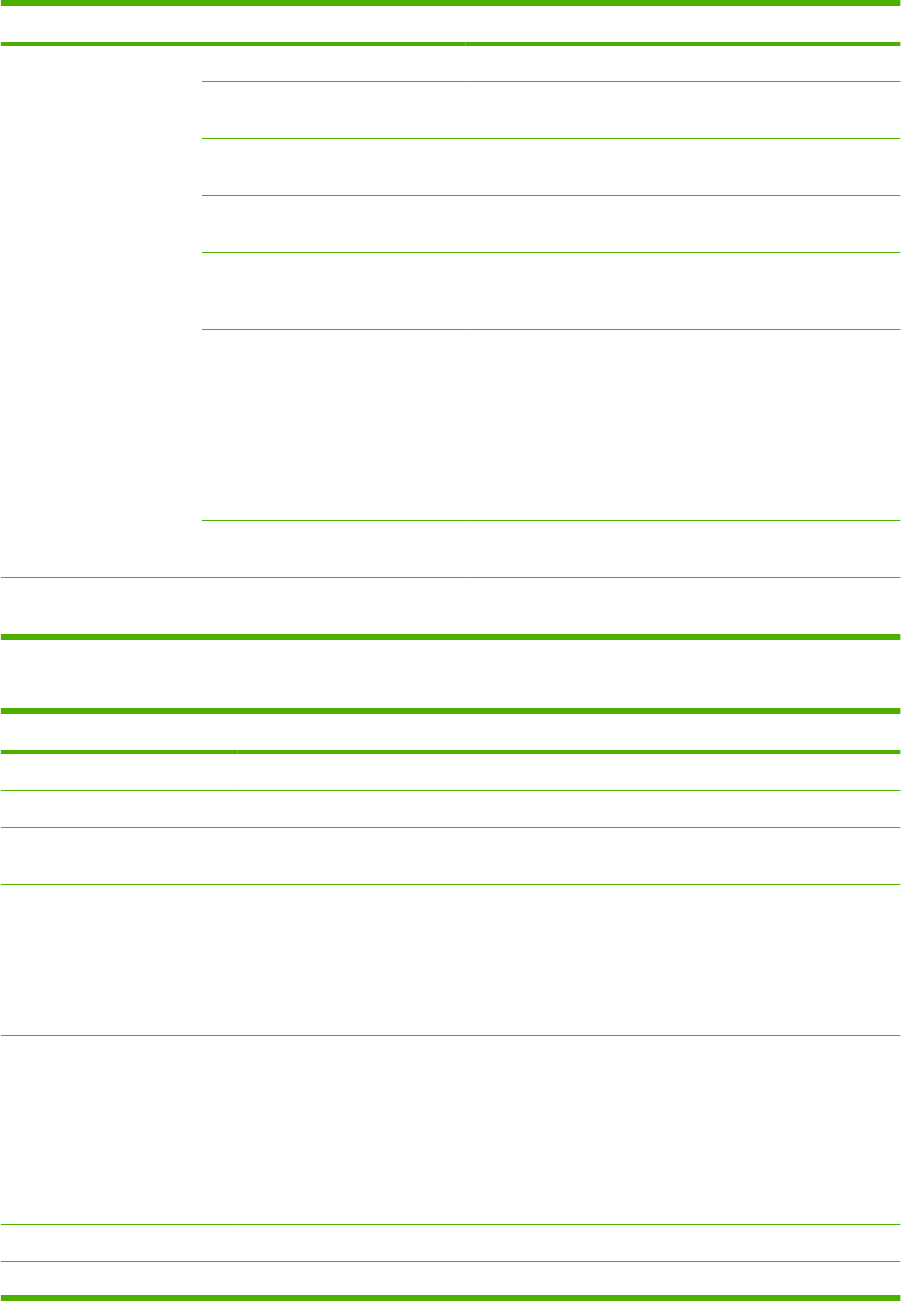
Menu item Sub-menu item Description
Advanced Color Copy Enables or disables the color copy button.
Lightness The default light/dark setting for copies. Possible values
range from 1 to 11 with 6 being the default (no change) value.
Contrast The default contrast setting for copies. Possible values
range from 1 to 11 with 6 being the default (no change) value.
Sharpen The default sharpen setting for copies. Possible values
range from 1 to 11 with 6 being the default (no change) value.
Background Removal The default background removal setting for copies. Possible
values range from 1 to 11 with 6 being the default (no
change) value.
Color Balance The default color balance setting for copies. Possible values
range from 1 to 11 with 6 being the default (no change) value.
Values can be set for each of the following settings:
●Red
●Green
●Blue
Grayness The default grayness setting for copies. Possible values
range from 1 to 11 with 6 being the default (no change) value.
Restore defaults Sets all customized copy settings to the factory default
values.
Table 2-2 Reports menu
Menu Item Description
Demo page Prints a page that demonstrates print quality.
Menu structure Prints a control-panel menu layout map.
Configuration report Prints a list of all the product settings. Includes network information when the product is
connected to the network.
Supplies status page Prints the print-cartridge status. Includes the following information:
●Approximate pages remaining
●Serial number
●Number of pages printed
Network report Displays status for:
●Network hardware configuration
●Enabled features
●TCP/IP and SNMP information
●Network statistics
Usage page Displays the number of pages printed, faxed, copied, and scanned by the product.
PCL font list Prints a list of all installed PCL 5 fonts.
Table 2-1 Copy setup menu (continued)
22 Chapter 2 Control panel ENWW
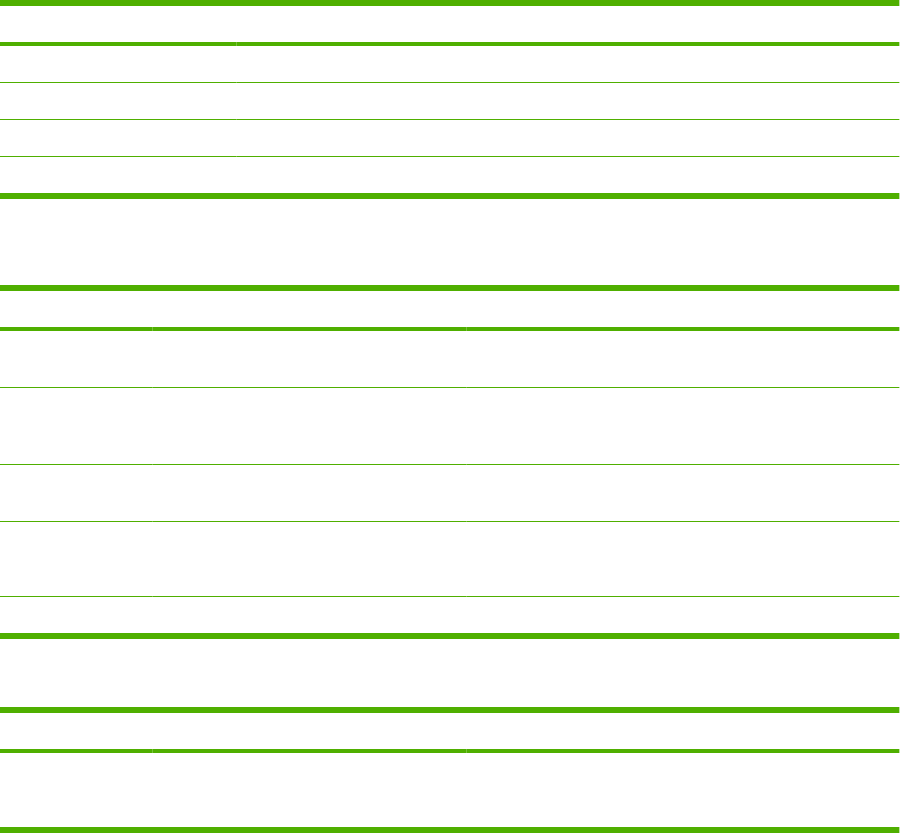
Menu Item Description
PS font list Prints a list of all installed PS fonts.
PCL6 font list Prints a list of all installed PCL 6 fonts.
Color usage log Prints out information about the color toner usage
Service page Prints out diagnostic information about calibration and color quality
Table 2-3 Photo setup menu
Menu Item Sub-menu item Sub-menu item Description
Default image
Size
(List of available
photo image sizes)
The default image size for photos
Default lighter/
darker
The default light/dark setting for photos. Possible values
range from 1 to 11 with 6 being the default (no change)
value.
Default number of
copies
The default number of copies setting for photos. Possible
values range from 1 to 99.
Default output
color
Color
Black & white
Specify the default output for photos.
Restore defaults Restore the factory default settings for photo setup
Table 2-4 Fax setup menu (fax models only)
Menu Item Sub-menu item Sub-menu item Description
Fax Set-up Utility Utility for configuring the fax settings. Follow the on-screen
prompts and select the appropriate response for each
question using the arrow keys.
Table 2-2 Reports menu (continued)
ENWW Control-panel menus 23
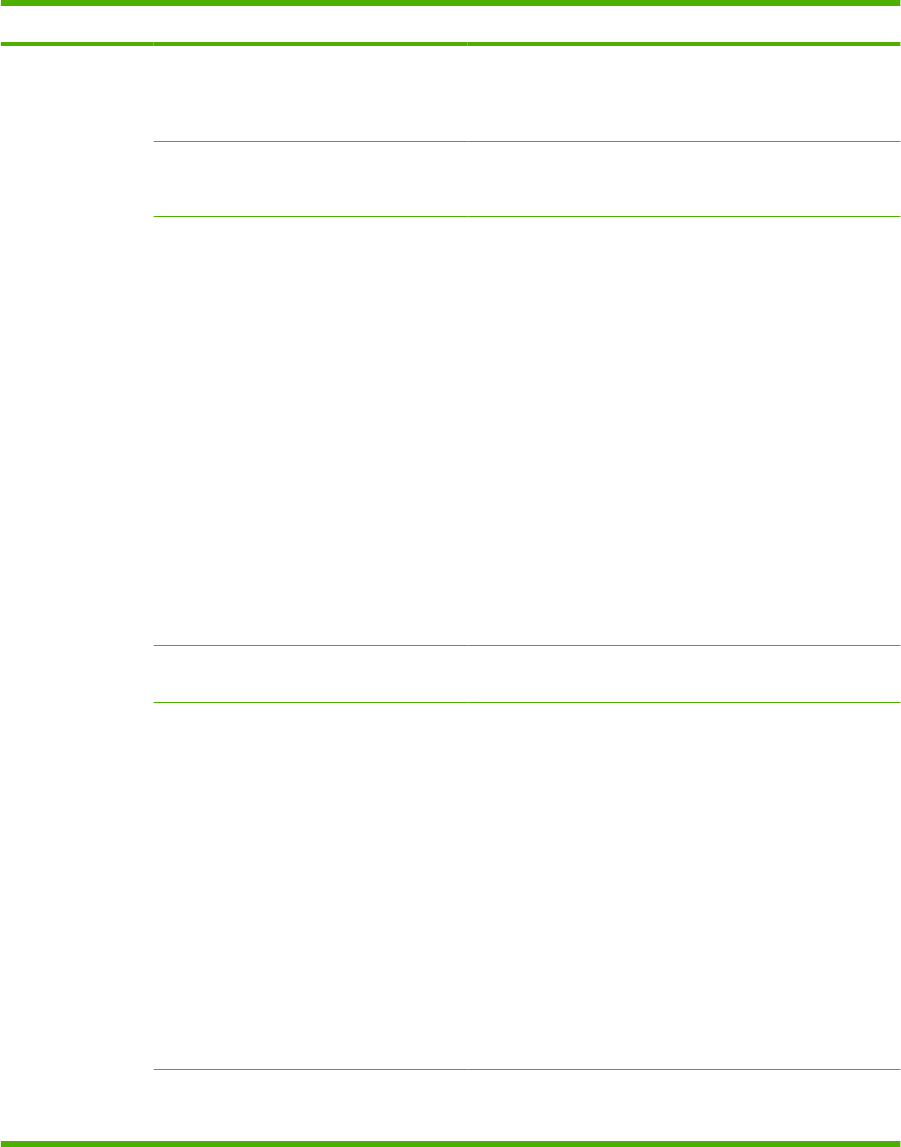
Menu Item Sub-menu item Sub-menu item Description
Basic setup Time/Date (Settings for time
format, current
time, date format,
and current date.)
Sets the time and date setting for the product.
Fax Header Your fax number
Company name
Sets the identifying information that is sent to the receiving
product.
Answer mode Automatic
TAM
Fax/Tel
Manual
Sets the type of answer mode. The following options are
available:
●Automatic: The product automatically answers an
incoming call on the configured number of rings.
●TAM: A telephone answering machine (TAM) is
attached to the Aux phone port of the product. The
product will not pick up any incoming call, but only listen
for fax tones after the answering machine has picked
up the call.
●Fax/Tel: The product must automatically pick up the
call and determine if the call is a voice or fax call. If the
call is a fax call, the product handles the call as usual.
If the call is a voice call, an audible synthesized ring is
generated to alert the user of an incoming voice call.
●Manual : The user must press the Start Fax button or
use an extension phone to make the product answer
the incoming call.
Rings to answer (Range of 1-9) Sets the number of rings that must occur before the fax
modem answers.
Distinctive Ring All Rings
Single
Double
Triple
Double and Triple
Allows a user to have two or three phone numbers on a
single line, each with a different ring pattern (on a phone
system with distinctive-ring service).
●All Rings: The product answers any calls that come
through the telephone line.
●Single: The product answers any calls that produce a
single-ring pattern.
●Double: The product answers any calls that produce a
double-ring pattern.
●Triple: The product answers any calls that produce a
triple-ring pattern.
●Double and Triple: The product answers any calls that
produce a double-ring or triple-ring pattern.
Dial Prefix On
Off
Specifies a prefix number that must be dialed when sending
faxes from the product.
Table 2-4 Fax setup menu (fax models only) (continued)
24 Chapter 2 Control panel ENWW
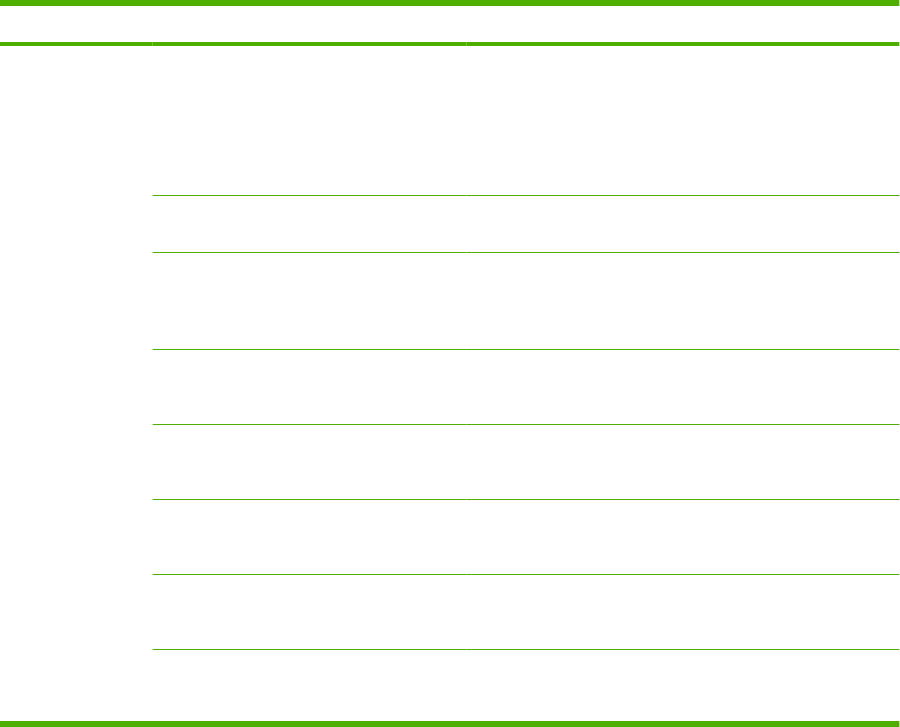
Menu Item Sub-menu item Sub-menu item Description
Advanced setup Default Fax
Resolution
Standard
Fine
Superfine
Photo
Sets the resolution for sent documents. Higher resolution
images have more dots per inch (dpi), so they show more
detail. Lower resolution images have fewer dots per inch and
show less detail, but the file size is smaller.
Default lighter/
darker
Sets the darkness of outgoing faxes.
Fit to page On
Off
Shrinks faxes that are larger than Letter-size or A4-size so
that they can fit onto a Letter-size or A4-size page. If this
feature is set to Off, faxes larger than Letter or A4 will print
on multiple pages.
Default glass size Letter
A4
Sets the default paper size for documents being scanned
from the flatbed scanner.
Dialing Mode Tone
Pulse
Sets whether the product should use tone or pulse dialing.
Redial if busy On
Off
Sets whether or not the product should attempt to redial if
the line is busy.
Redial if no answer On
Off
Sets whether the product should attempt to dial if the
recipient fax number does not answer.
Redial Comm.
Error
On
Off
Sets whether the product should attempt to redial the
recipient fax number if a communication error occurs.
Table 2-4 Fax setup menu (fax models only) (continued)
ENWW Control-panel menus 25
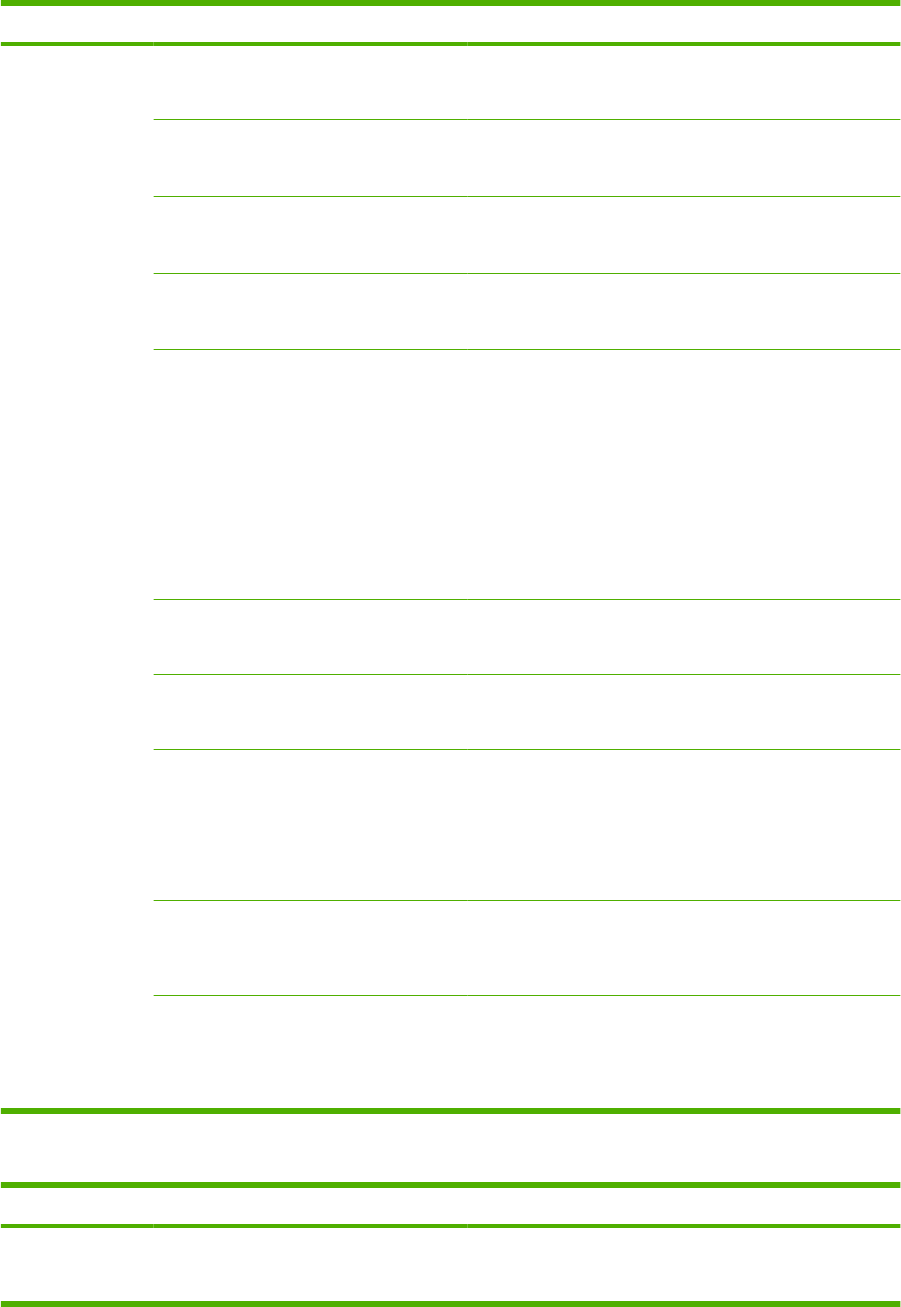
Menu Item Sub-menu item Sub-menu item Description
Advanced setup Detect dial tone On
Off
Sets whether the product should check for a dial tone before
sending a fax.
Billing codes On
Off
Enables the use of billing codes when set to On. A prompt
will appear that asks you to enter the billing code for an
outgoing fax.
Extension Phone On
Off
When this feature is enabled, the user can press the 1-2-3
buttons on the extension phone to cause the product to
answer an incoming fax call.
Stamp faxes On
Off
Sets product to add the date, time, sender's phone number,
and page number to each page of the faxes that this product
receives.
Private receive On
Off
Setting Private receive to On requires the user to have set
a password in product security. After the password is set,
the following options are set:
●Private receive is turned on.
●All old faxes are deleted from memory.
●Fax forwarding set to Off and is not allowed to be
changed.
●All incoming faxes are stored in memory.
Fax Number
Confirmation
On
Off
Verify that a fax number is valid by entering it a second time.
Allow Fax Reprint On
Off
Sets whether all received faxes stored in available memory
can be reprinted.
Fax/Tel Ring Time 20
30
40
70
Sets when the product should stop sounding the Fax/Tel
audible ring to notify the user of an incoming voice call.
Print Duplex
(duplex models
only)
On
Off
Sets whether all received faxes are printed using both sides
of the paper.
Fax Speed Fast(V.34)
Medium(V.17)
Slow(V.29)
Increases or decreases the allowed fax communication
speed.
Table 2-5 System setup menu
Menu Item Sub-menu item Sub-menu item Description
Language (List of available
control-panel
display languages.)
Sets the language in which the control panel displays
messages and product reports.
Table 2-4 Fax setup menu (fax models only) (continued)
26 Chapter 2 Control panel ENWW
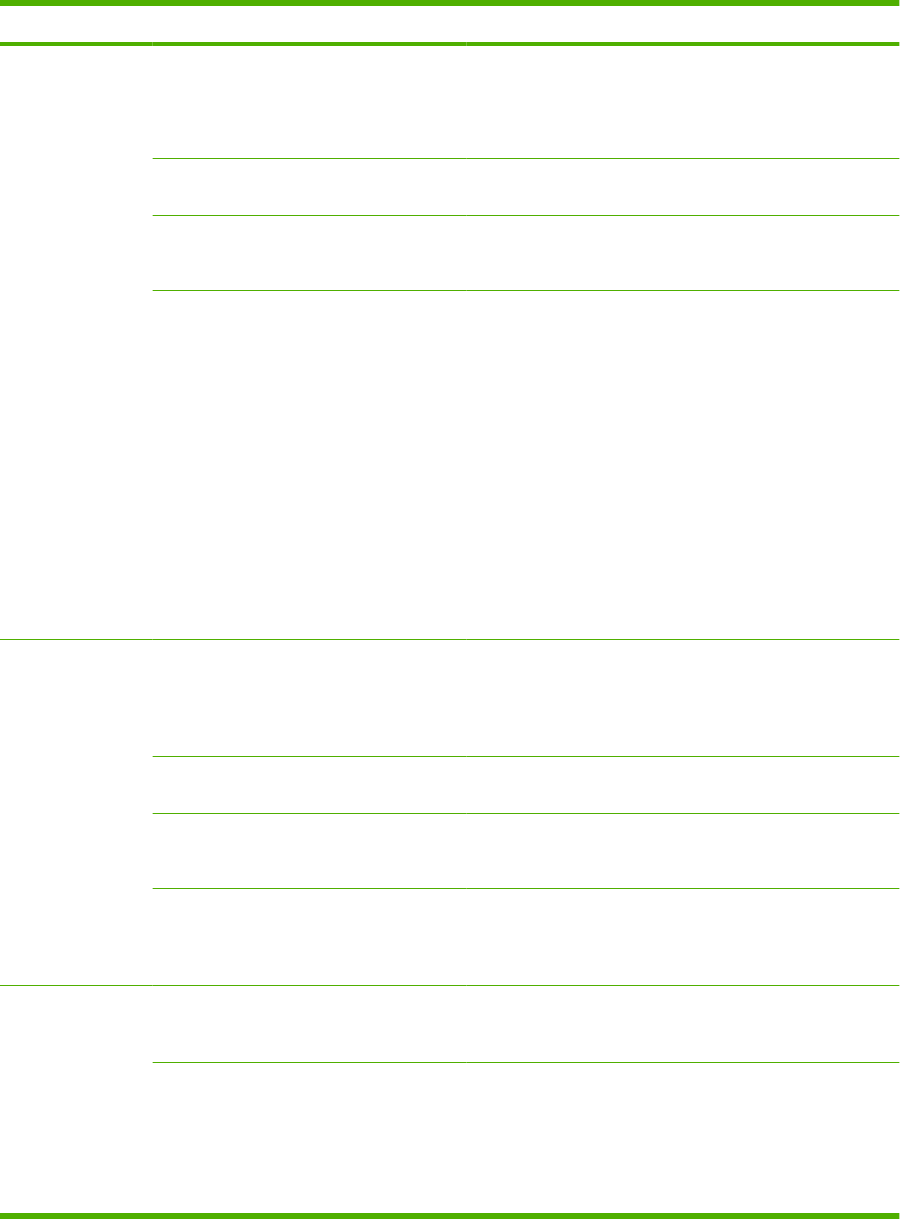
Menu Item Sub-menu item Sub-menu item Description
Paper setup Default paper size Letter
A4
Legal
Sets the size for printing internal reports or any print job that
does not specify a size.
Default paper type Lists available
media types.
Sets the type for printing internal reports or any print job that
does not specify a type.
Tray 1 Paper type
Paper size
Sets the default size and type for Tray 1.
Paper out action Wait forever
Cancel
Override
Determines how the product reacts when a print job requires
a media size or type that is unavailable or when a specified
tray is empty.
●Select Wait forever to make the product wait until the
correct media is loaded.
●Select Override to print on a different size paper after
a specified delay.
●Select Cancel to automatically cancel the print job after
a specified delay.
●If either Override or Cancel is chosen, the control
panel prompts for the number of seconds to delay. Use
the arrow keys to either decrease the time or increase
the time up to 3,600 seconds.
Print quality Calibrate color Calibrate now
After power on
Perform a Color Pane Registration (CPR) and density
calibration. Select Calibrate now to perform an immediate
calibration. Select After power on to specify the minutes/
hours the product should wait after power on to perform an
automatic calibration (the default is 15 minutes).
Cartridge low
threshold
(Range of 1-20) Sets the percentage at which the control panel generates a
low-toner message.
Replace Supplies Stop at out
Override out
Sets how the product reacts when it detects that the print
cartridge is out.
Color Supply Out Stop Printing
Continue Black
Sets how the product should react when it detects that a
color cartridge is empty. Select Stop Printing to stop all
printing until the cartridge is replaced, or select Continue
Black to continue printing in black monochrome mode.
Adjust Alignment
(memory-card
models only)
Print Test Page Print out a tray-specific sheet of instructions and a test page
with a border that can be used to estimate the adjustment
needed to center the printed image on the page.
Adjust Tray 1 After printing the test page, use the options in the Adjust
Tray 1 menu to calibrate the tray. The following settings can
be adjusted for Tray 1:
●X1 Shift
●Y Shift
Table 2-5 System setup menu (continued)
ENWW Control-panel menus 27
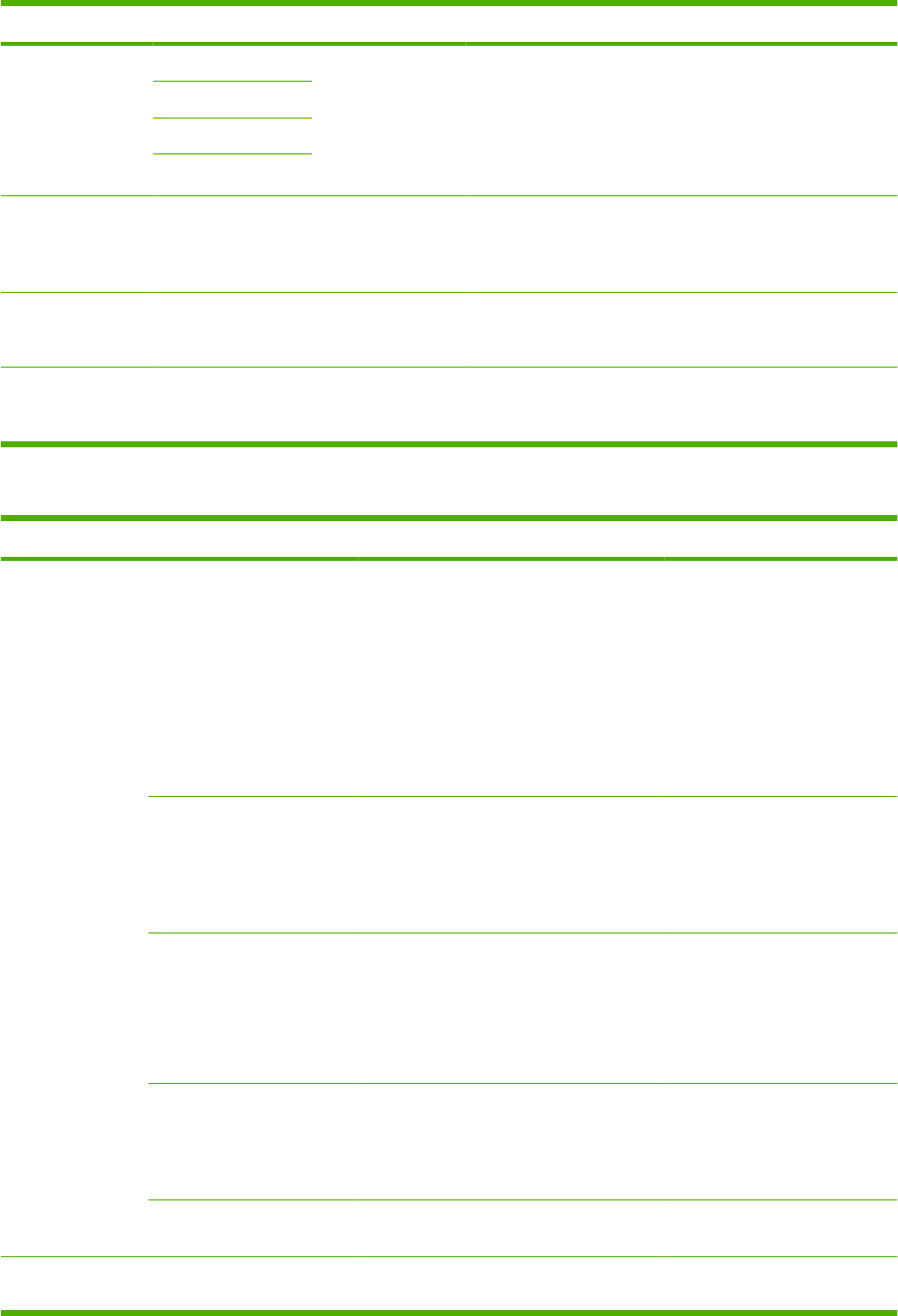
Menu Item Sub-menu item Sub-menu item Description
Volume Settings
(memory-card
models only)
Alarm volume Soft
Medium
Loud
Off
Sets the volume levels for the product.
Ring volume
Key-press volume
Phone line volume
Time/Date (Settings for time
format, current time,
date format, and
current date.)
Sets the time and date setting for the product.
Product security On
Off
Sets the product-security feature. When the setting is set to
On, you must set a personal identification number (PIN).
Courier font Regular
Dark
Sets Courier font values.
Table 2-6 Service menu
Menu item Sub-menu item Sub-menu item Description
Fax Service Clear saved faxes Clear all faxes in memory.
These include any received
faxes (including non-printed,
non-sent PC upload, and non-
forwarded faxes), unsent faxes
(including delayed faxes), and
any printed faxes that are still in
memory. Deleted faxes cannot
be recovered. For each deleted
item, the fax activity log is
updated.
Run Fax Test Perform a fax test to verify that
the phone cord is plugged in
the correct outlet and that there
is a signal on the phone line. A
fax test report is printed
indicating the results.
Print T.30 trace Now
Never
If error
At end of call
Prints or schedules a report
that is used to troubleshoot fax
transmission issues.
Error correction On
Off
The error correction mode
allows the sending device to re-
transmit data if it detects an
error signal. The default setting
is on.
Fax Service Log The fax service log prints out
the last 40 entries in the fax log.
Cleaning mode Cleans the product when
specks or other marks appear
Table 2-5 System setup menu (continued)
28 Chapter 2 Control panel ENWW
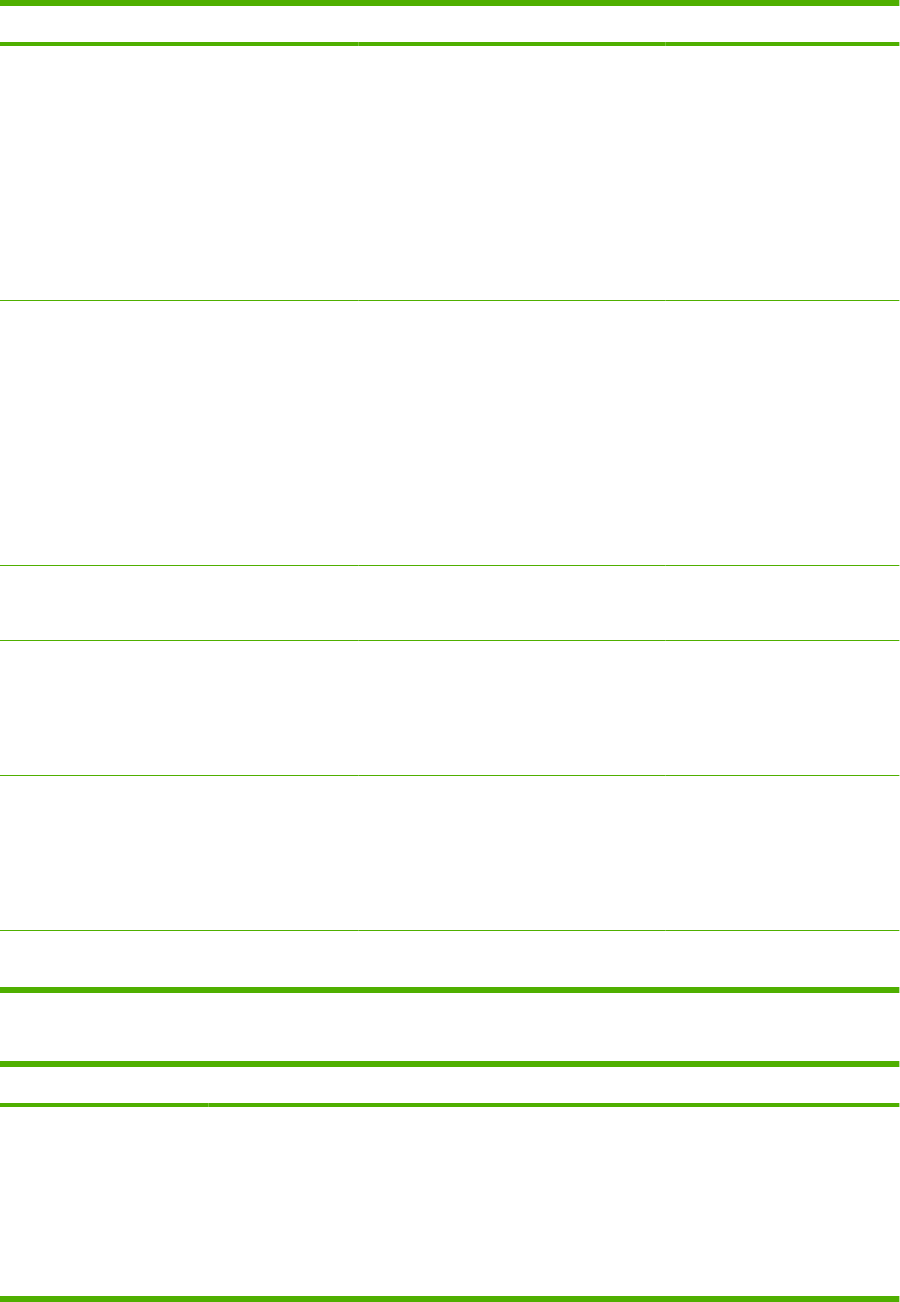
Menu item Sub-menu item Sub-menu item Description
on printed output. The cleaning
process removes dust and
excess toner from the paper
path.
When selected, the product
prompts you to load plain Letter
or A4 paper in Tray 1. Press
OK to begin the cleaning
process. Wait until the process
completes. Discard the page
that prints.
1 minute Off
1 minute
15 minutes
30 minutes
1 hour
2 hours
4 hours
Specify the amount of idle time
before the product enters sleep
mode.
USB speed High
Full
Sets the USB speed.
Less paper curl On
Off
When printed pages are
consistently curled, this option
sets the product to a mode that
reduces curl.
The default setting is Off.
Archive print On
Off
When printing pages that will
be stored for a long time, this
option sets the product to a
mode that reduces toner
smearing and dusting.
The default setting is Off.
Restore defaults Sets all customized settings to
the factory default values.
Table 2-7 Network configuration menu
Menu item Sub-menu item Description
TCP/IP configuration Automatic
Manual
Automatic automatically configures all the TCP/IP settings via
DHCP, BootP or AutoIP.
Manual requires you to manually configure the IP address, subnet
mask, and default gateway.
The control panel prompts you to specify values for each address
section. Use the arrow buttons to increase or decrease the value.
Press OK to accept the value and move the cursor to the next field.
Table 2-6 Service menu (continued)
ENWW Control-panel menus 29
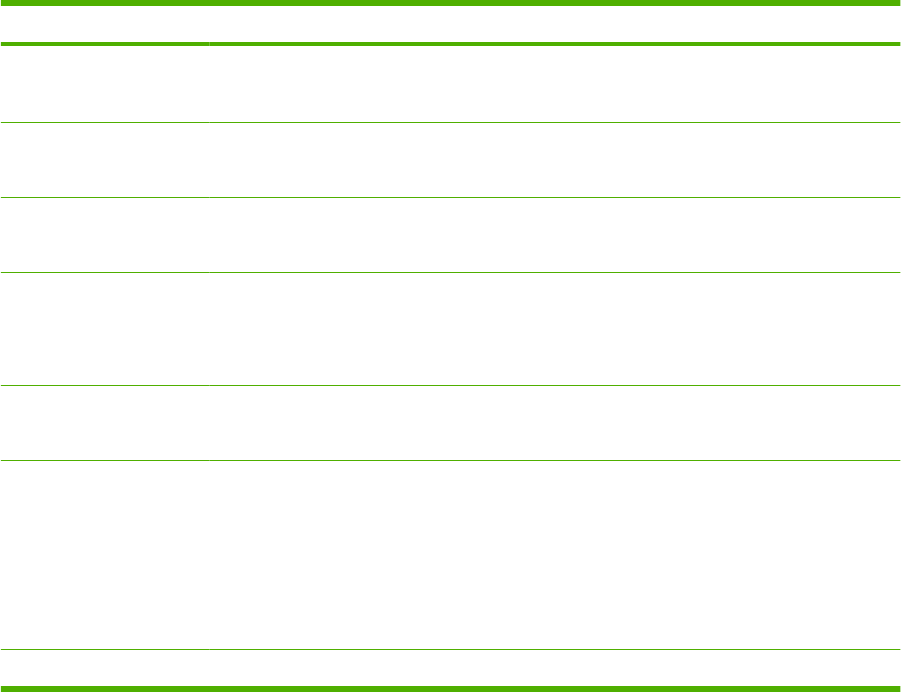
Menu item Sub-menu item Description
As each address is completed, the product prompts for address
confirmation before moving to the next one. After all three
addresses are set, the product automatically restarts.
Memory Card (memory-
card products only)
On
Off
Enables or disables the use of the memory-card slots.
Auto crossover On
Off
Enable or disable the use of a standard 10/100 network cable when
the product is directly connected to a PC.
Network services IPv4
IPv6
DHCPv6
Sets whether the product will use either IPv4, IPv6, or DHCPv6
protocol.
Show IP address Yes
No
Sets whether the product displays the IP address on the control
panel.
Link speed Automatic (Default)
10T Full
10T Half
100TX Full
100TX Half
Sets the link speed manually if needed.
After setting the link speed, the product automatically restarts.
Restore defaults Resets all network configurations to their factory defaults.
Function specific menus
The product features function-specific menus for faxing, copying, scanning, and managing photos on a
memory card. To access these menus, press the Fax Menu, Copy Menu, Scan Menu, or Photo Menu
buttons respectively.
These are the features supported by the function specific menus.
●Use the Fax menu to perform basic fax functions such as sending a fax or editing the phone book,
reprinting faxes that were previously printed, or printing faxes that are stored in memory.
●Use the Copy menu to access basic copy functions and customize the copy output.
●Use the Scan menu to display a list of preconfigured folders and e-mail destinations to select from.
●Use the Email menu (HP Color LaserJet CM2320 MFP Fax Model only) to send e-mail.
●Use the Photo menu (HP Color LaserJet CM2320 MFP Memory-Card Model only) to display a list
of photo options for a valid inserted memory card.
Table 2-7 Network configuration menu (continued)
30 Chapter 2 Control panel ENWW
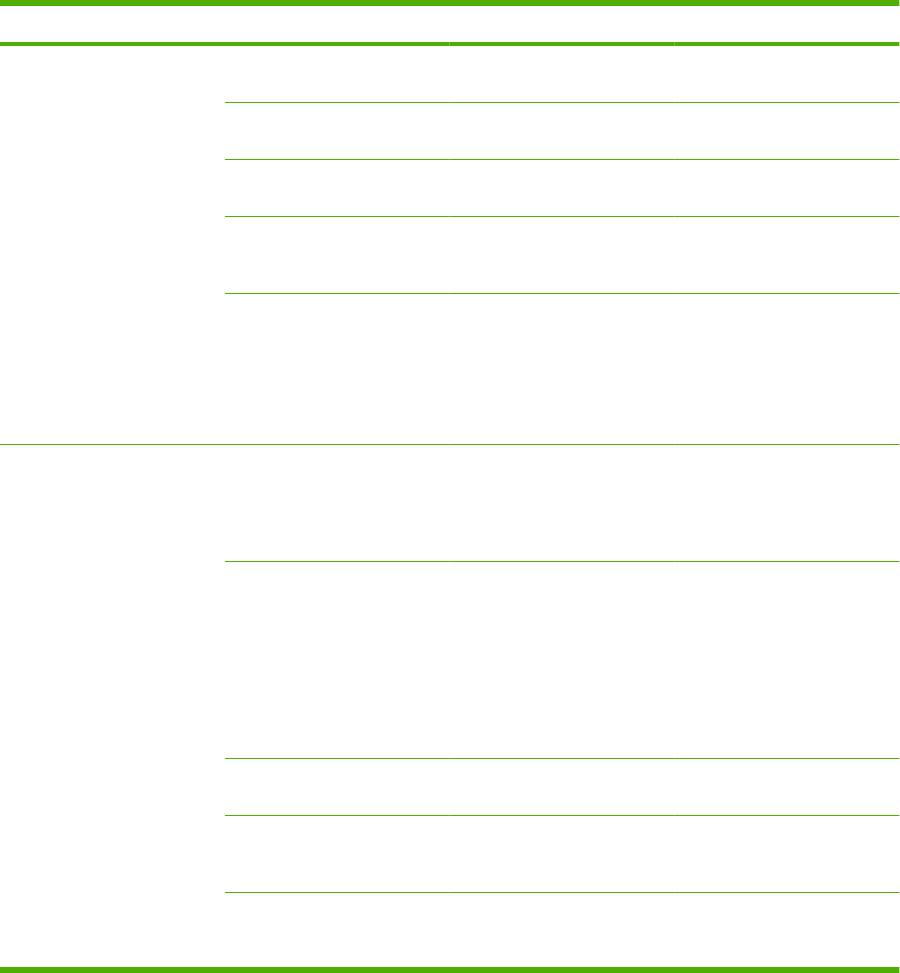
Table 2-8 Fax Menu
Menu item Sub-menu item Sub-menu item Description
Send Send a fax Send a fax. On screen
prompts guide the process.
Redial Redial the last fax number
and resend.
Send fax later Allows a fax to be sent at a
later time and date.
Fax Job status Displays pending fax jobs,
and allows you to cancel
pending fax jobs.
Fax Resolution Standard
Fine
Superfine
Photo
Temporarily change the
resolution of outgoing faxes.
The resolution resets to
default after 2 minutes of idle
fax scan time.
Receive Print faxes Prints stored faxes when the
private-receive feature is on.
This menu item appears only
when the private-receive
feature is turned on.
Block junk faxes Add number
Delete number
Delete All Entries
Junk Fax list
Modifies the junk fax list. The
junk fax list can contain up to
30 numbers. When the
product receives a call from
one of the junk fax numbers, it
deletes the incoming fax. It
also logs the junk fax in the
activity log along with job-
accounting information.
Reprint faxes Prints the received faxes
stored in available memory.
Forward fax On
Off
Sets product to send all
received faxes to another fax
machine.
Polling receive Allows the product to call
another fax machine that has
polling send enabled.
ENWW Control-panel menus 31
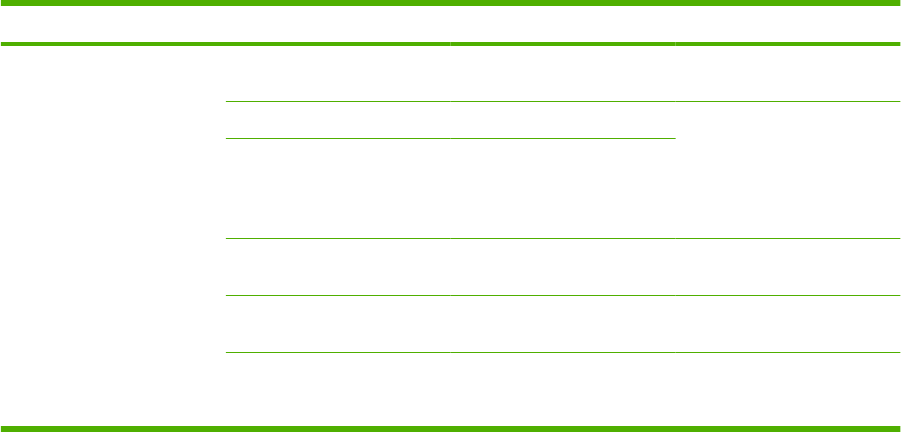
Menu item Sub-menu item Sub-menu item Description
Phone Book Select an entry Select an individual or group
dial entry for faxing.
Individual Setup Edits the fax phone book
speed dials and group-dial
entries. The product supports
up to 120 phone book entries,
which can be either individual
or group entries.
Group setup
Delete entry Delete a specific phone book
entry.
Delete All Entries Delete all entries in the phone
book
Phone Book report Print a list of all the individual
and group dial entries in the
phone book.
Table 2-8 Fax Menu (continued)
32 Chapter 2 Control panel ENWW
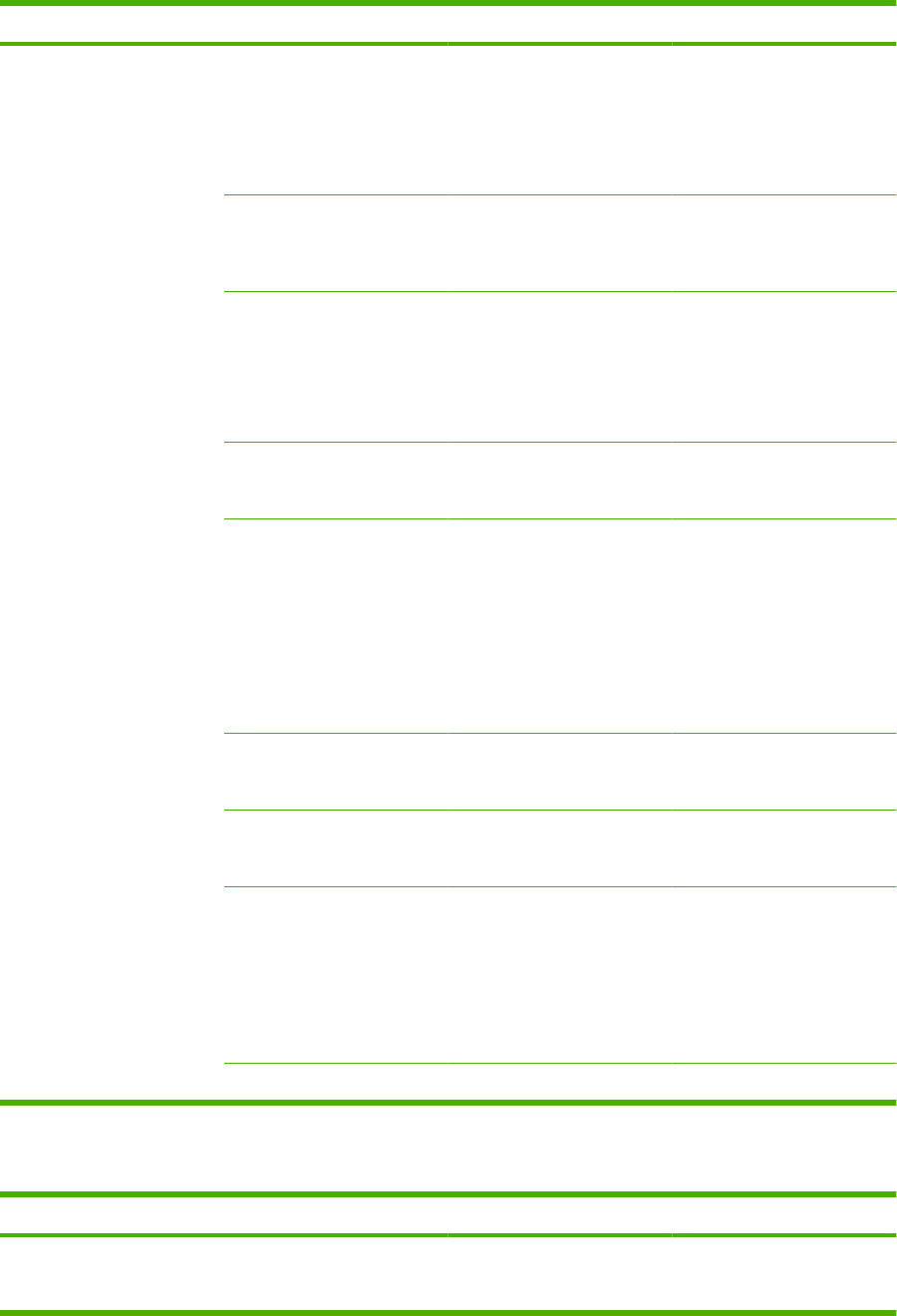
Menu item Sub-menu item Sub-menu item Description
Fax Reports Fax Confirmation Never
Every fax
Send fax only
Receive fax
Sets whether or not the
product prints a confirmation
report after a successful
sending or receiving job.
Include first page On
Off
Sets whether or not the
product includes a thumbnail
image of the first page of the
fax on the report.
Fax Error Report Every error
Send Error
Receive Error
Never
Sets whether or not the
product prints a report after a
failed sending or receiving
job.
Last Call Report Prints a detailed report of the
last fax operation, either sent
or received.
Fax Activity log Print log now
Auto Log Print
Print log now: Prints a list of
the faxes that have been sent
from or received by this
product.
Auto Log Print: Select On to
automatically print a report
after every fax job. Select Off
to turn off the automatic print
feature.
Phone Book report Prints a list of the speed dials
that have been set up for this
product.
Junk Fax list Prints a list of phone numbers
that are blocked from sending
faxes to this product.
Billing report Prints a list of billing codes
that have been used for
outgoing faxes. This report
shows how many sent faxes
were billed to each code. This
menu item appears only when
the billing codes feature is
turned on.
All fax reports Prints all fax-related reports.
Table 2-9 Photo Menu
Menu item Sub-menu item Sub-menu item Description
View View photos on the memory
card. Use the arrow buttons to
navigate through the photos.
Table 2-8 Fax Menu (continued)
ENWW Control-panel menus 33
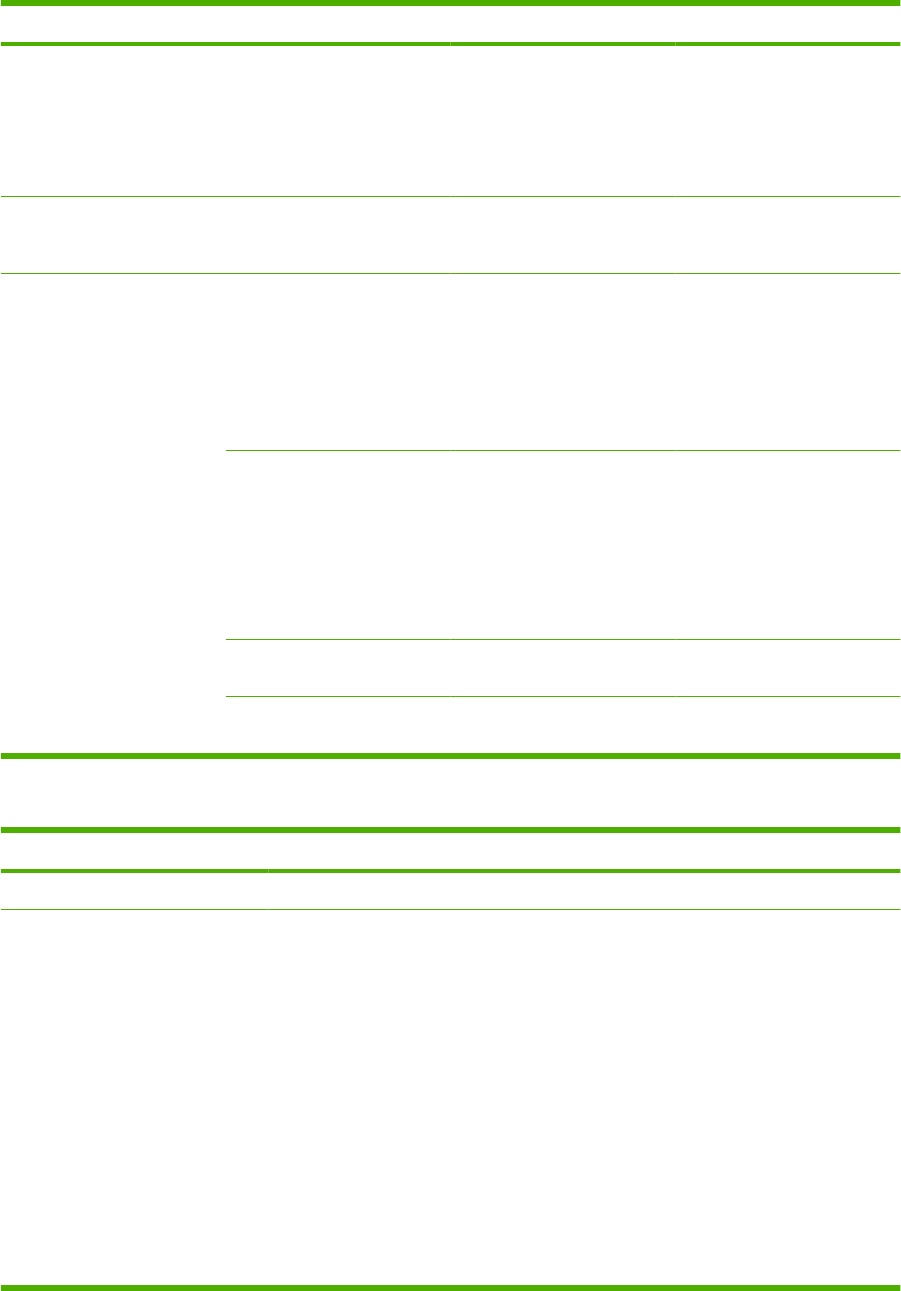
Menu item Sub-menu item Sub-menu item Description
Easy Print Individual photo
All photos (#-#)
A range of photos
Custom
Print photos quickly from the
memory card by selecting the
numbers of the photos you
want to print.
Thumbnail Fast
Best
Print thumbnails of photos
from the memory card (30 per
page).
Options Proof Sheet Print proof sheet
Scan proof sheet
Print a proof sheet or scan a
proof sheet. The proof sheet
is a page of thumbnails (20
per page) generated from a
valid memory card. A marked
proof sheet can then be
scanned and the selected
images are printed at full size.
Current Settings Select image size
Select paper size
Select paper type
Number of copies
Output Color
Adjust the default photo
settings for image size, paper
size, paper type, number of
copies, and output color (color
or black and white).
Rotate Photo Rotate a photo stored on a
memory card.
Slideshow View a slideshow of the
photos on a memory card.
Table 2-10 Copy Menu
Menu item Sub-menu item Description
Copies (1–99) Specify the number of copies
Size Original=100%
Legal to Letter=78%
Legal to A4=83%
A4 to Letter=94%
Letter to A4=97%
Full Page=91%
Fit to page
2 pages per sheet
4 pages per sheet
Custom: 25 to 400%
Specify the size of the copy.
Table 2-9 Photo Menu (continued)
34 Chapter 2 Control panel ENWW
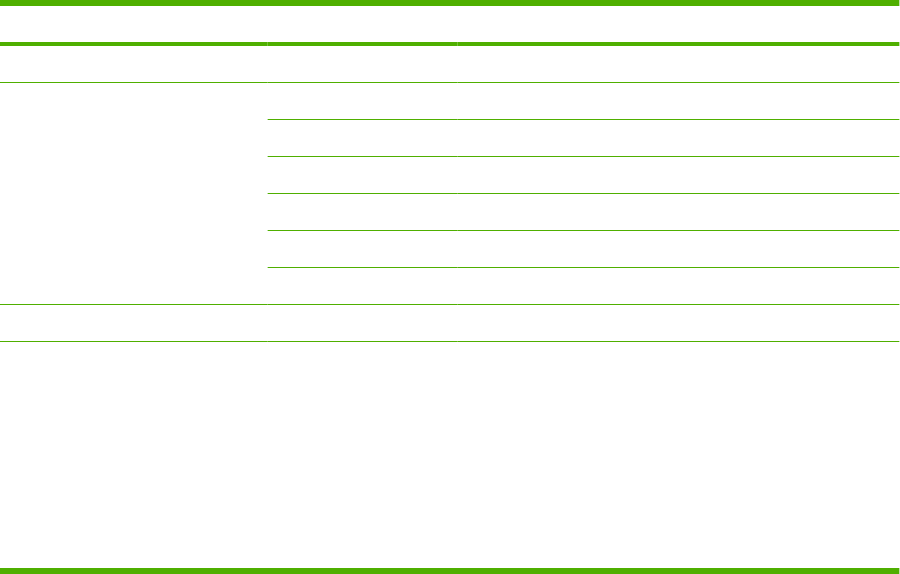
Menu item Sub-menu item Description
Light/Dark Specify the contrast of the copy.
Options Optimize Select settings to optimize the copy print quality.
Copy Paper Specify the paper type for the copies.
Multi-Page Copy Copy multiple pages.
Copy Collation Specify the copy collation
Tray Select Select the tray to copy from.
Copy 2-Sided Copy multiple sides and print duplex.
Copy Draft Specify the print quality for copies.
Image Adjustment Lightness
Contrast
Sharpen
Background
Color Balance
Grayness
Adjust the settings for image quality in a copy.
Table 2-10 Copy Menu (continued)
ENWW Control-panel menus 35
36 Chapter 2 Control panel ENWW

Understand paper and print media use
This product supports a variety of paper and other print media in accordance with the guidelines in this
user guide. Paper or print media that does not meet these guidelines might cause the following problems:
●Poor print quality
●Increased jams
●Premature wear on the product, requiring repair
For best results, use only HP-brand paper and print media designed for laser printers or multiuse. Do
not use paper or print media made for inkjet printers. Hewlett-Packard Company cannot recommend
the use of other brands of media because HP cannot control their quality.
It is possible for paper to meet all of the guidelines in this user guide and still not produce satisfactory
results. This might be the result of improper handling, unacceptable temperature and/or humidity levels,
or other variables over which Hewlett-Packard has no control.
CAUTION: Using paper or print media that does not meet Hewlett-Packard's specifications might
cause problems for the product, requiring repair. This repair is not covered by the Hewlett-Packard
warranty or service agreements.
38 Chapter 3 Paper and print media ENWW
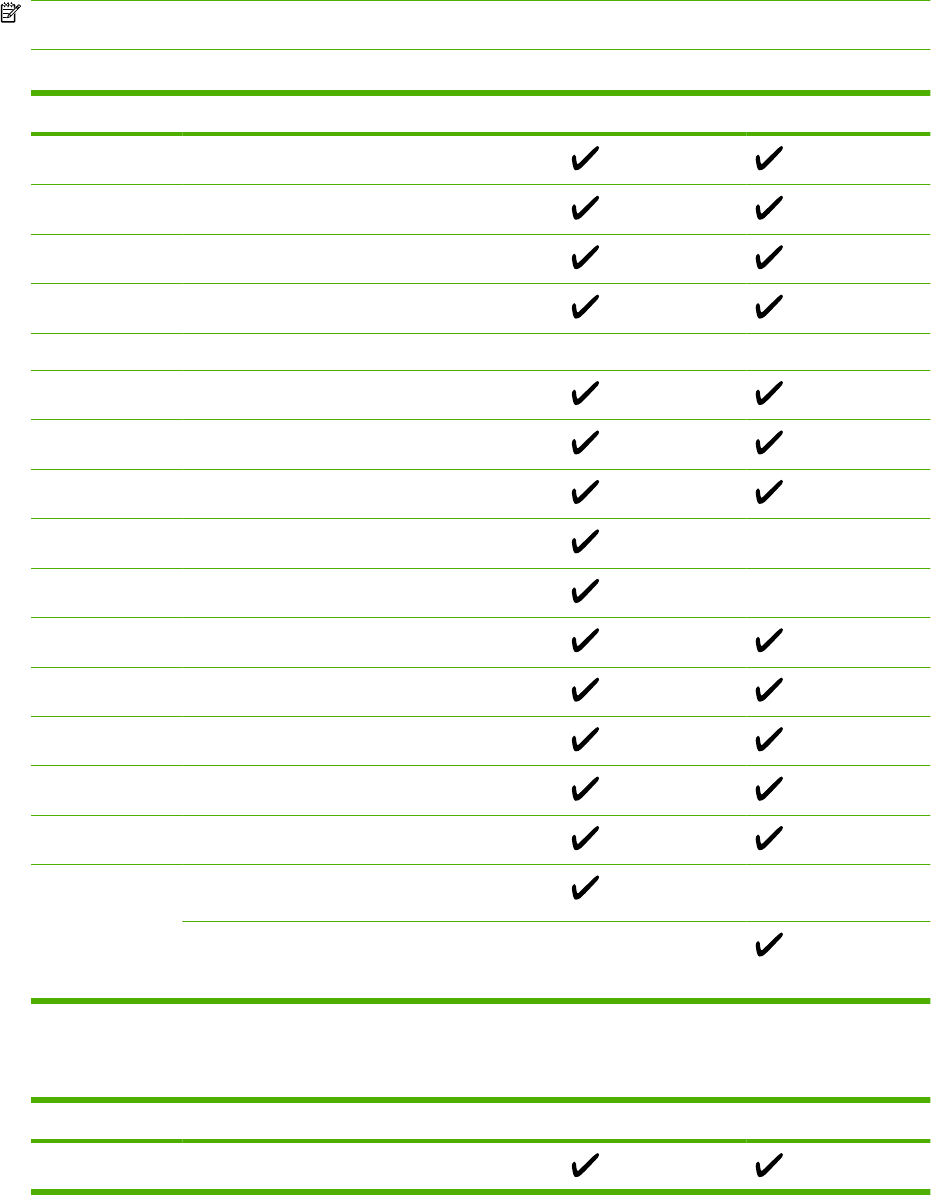
Supported paper and print media sizes
This product supports a number of paper sizes, and it adapts to various media.
NOTE: To obtain best print results, select the appropriate paper size and type in the print driver before
printing.
Table 3-1 Supported paper and print media sizes
Size Dimensions Tray 1 Trays 2 and 3
Letter 216 x 279 mm (8.5 x 11 inches)
Legal 216 x 356 mm (8.5 x 14 inches)
A4 210 x 297 mm (8.27 x 11.69 inches)
Executive 184 x 267 mm (7.24 x 10.51 inches)
A3 297 x 420 mm (11.69 x 16.54 inches)
A5 148 x 210 mm (5.83 x 8.27 inches)
A6 105 x 148 mm (4.13 x 5.83 inches)
B5 (JIS) 182 x 257 mm (7.17 x 10.12 inches)
16k 197 x 273 mm (7.75 x 10.75 inches)
16k 195 x 270 mm (7.7 x 10.6 inches)
16k 184 x 260 mm (7.25 x 10.25 inches)
8.5 x 13 216 x 330 mm (8.5 x 13 inches)
4 x 6
1
107 x 152 mm (4 x 6 inches)
5 x 8
1
127 x 203 mm (5 x 8 inches)
10 x 15 cm
1
100 x 150 mm (3.9 x 5.9 inches)
Custom Tray 1: Minimum—76 x127 mm (3 x 5 inches);
Maximum—216 x 356 mm (8.5 x 14 inches)
Trays 2 and 3: Minimum—100 x 148 mm (3.9 x
5.83 inches); Maximum—216 x 356 mm (8.5 x
14 inches)
1These sizes are supported as custom sizes.
Table 3-2 Supported envelopes and postcards
Size Dimensions Tray 1 Trays 2 and 3
Envelope #10 105 x 241 mm (4.13 x 9.49 inches)
ENWW Supported paper and print media sizes 39
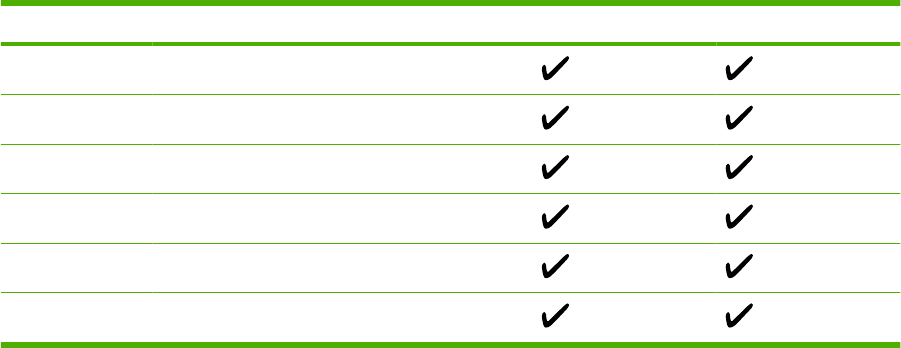
Size Dimensions Tray 1 Trays 2 and 3
Envelope DL 110 x 220 mm (4.33 x 8.66 inches)
Envelope C5 162 x 229 mm (6.93 x 9.84 inches)
Envelope B5 176 x 250 mm (6.7 x 9.8 inches)
Envelope Monarch 98 x 191 mm (3.9 x 7.5 inches)
Postcard 100 x 148 mm (3.94 x 5.83 inches)
Double postcard 148 x 200 mm (5.83 x 7.87 inches)
Table 3-2 Supported envelopes and postcards (continued)
40 Chapter 3 Paper and print media ENWW
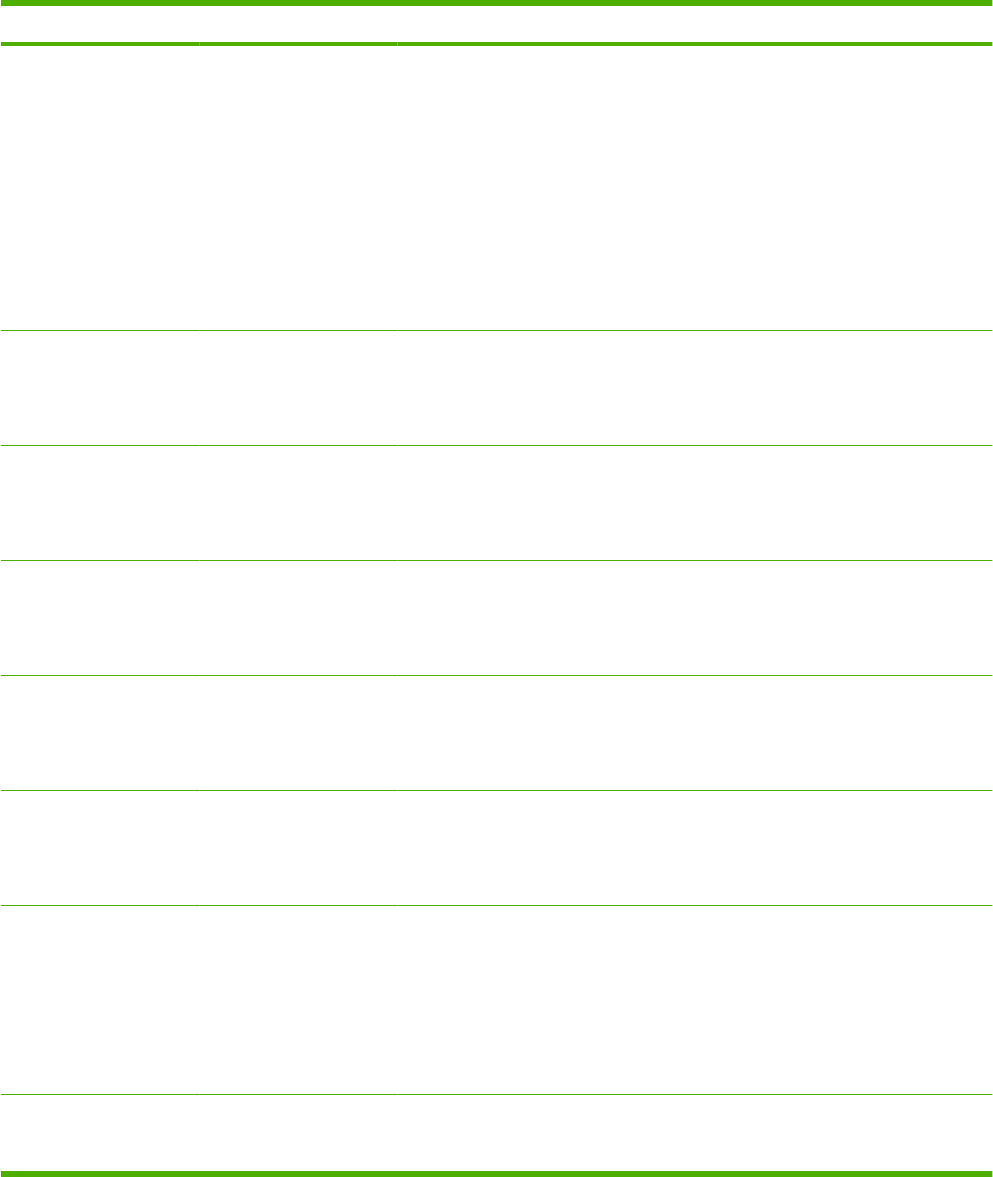
Supported paper types and tray capacity
Media type Dimensions
1
Weight Capacity
2
Paper orientation
Paper, including the
following types:
●Plain
●Letterhead
●Color
●Preprinted
●Prepunched
●Recycled
Minimum: 76 x 127 mm
(3 x 5 inches)
Maximum: 216 x 356 mm
(8.5 x 14 inches)
60 to 90 g/m2 (16 to 24 lb) Tray 1: up to 50 sheets
Trays 2 and 3: up to 250
sheets of
75 g/m2 (20 lb bond)
Side to be printed on face-
up, with the top edge at
the back of the tray
Thick paper Same as for paper Up to 200 g/m2 (53 lb) Tray 1: single sheet only
Trays 2 and 3: up to
25 mm (0.98 inch) stack
height
Side to be printed on face-
up, with the top edge at
the back of the tray
Cover paper Same as for paper Up to 200 g/m2 (53 lb) Tray 1: single sheet only
Trays 2 and 3: up to
25 mm (.98 inch) stack
height
Side to be printed on face-
up, with the top edge at
the back of the tray
Glossy paper
Photo paper
Same as for paper Up to 220 g/m2 (59 lb) Tray 1: single sheet only
Trays 2 and 3: up to
25 mm (.98 inch) stack
height
Side to be printed on face-
up, with the top edge at
the back of the tray
Transparencies A4 or Letter Thickness: 0.12 to
0.13 mm (4.7 to 5.1 mils)
Tray 1: single sheet only
Trays 2 and 3: up to
25 mm (.98 inch) stack
height
Side to be printed on face-
up, with the top edge at
the back of the tray
Labels
3
A4 or Letter Thickness: up to 0.23 mm
(9 mils)
Tray 1: single sheet only
Trays 2 and 3: up to
25 mm (.98 inch) stack
height
Side to be printed on face-
up, with the top edge at
the back of the tray
Envelopes ●COM 10
●Monarch
●DL
●C5
●B5
Up to 90 g/m2 (24 lb) Tray 1: up to 10 envelopes
Trays 2 and 3: up to 30
envelopes
Side to be printed on face-
up, with the stamp-end at
the back of the tray
Postcards or index cards 100 x 148 mm
(3.9 x 5.8 inches)
Tray 1: single sheet only Side to be printed on face-
up, with the top edge at
the back of the tray
ENWW Supported paper types and tray capacity 41
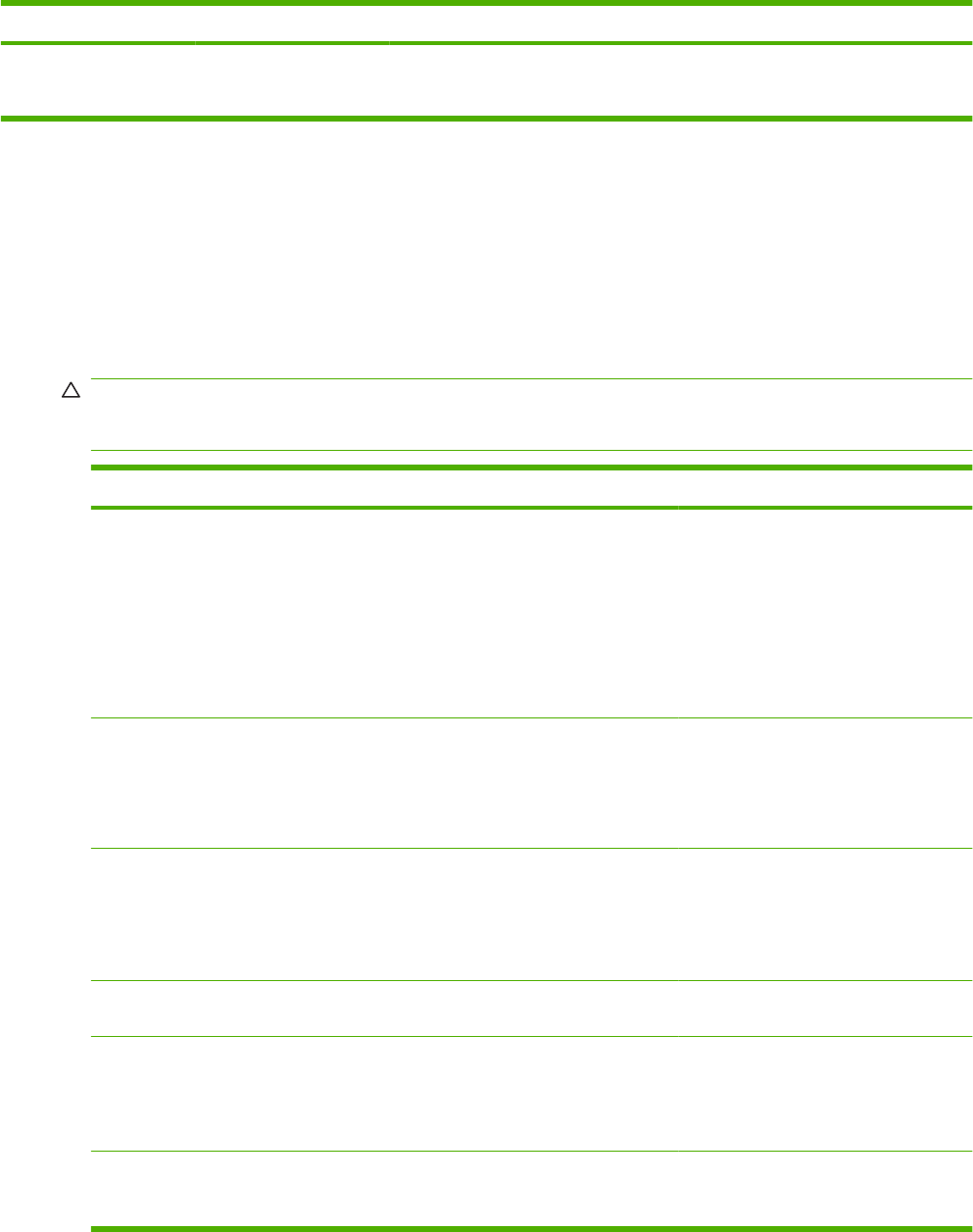
Media type Dimensions
1
Weight Capacity
2
Paper orientation
Trays 2 and 3: up to
25 mm (.98 inch) stack
height
1The product supports a wide range of standard and custom sizes of print media. Check the printer driver for supported sizes.
2Capacity can vary depending on media weight and thickness, and environmental conditions.
3Smoothness: 100 to 250 (Sheffield)
Special paper or print media guidelines
This product supports printing on special media. Use the following guidelines to obtain satisfactory
results. When using special paper or print media, be sure to set the type and size in your print driver to
obtain the best print results.
CAUTION: HP LaserJet printers use fusers to bond dry toner particles to the paper in very precise
dots. HP laser paper is designed to withstand this extreme heat. Using inkjet paper not designed for this
technology could damage your printer.
Media type Do Do not
Envelopes ●Store envelopes flat.
●Use envelopes where the seam
extends all the way to the corner of
the envelope.
●Use peel-off adhesive strips that
are approved for use in laser
printers.
●Do not use envelopes that are
wrinkled, nicked, stuck together, or
otherwise damaged.
●Do not use envelopes that have
clasps, snaps, windows, or coated
linings.
●Do not use self-stick adhesives or
other synthetic materials.
Labels ●Use only labels that have no
exposed backing between them.
●Use Labels that lie flat.
●Use only full sheets of labels.
●Do not use labels that have wrinkles
or bubbles, or are damaged.
●Do not print partial sheets of labels.
Transparencies ●Use only transparencies that are
approved for use in laser printers.
●Place transparencies on a flat
surface after removing them from
the product.
●Do not use transparent print media
not approved for laser printers.
Letterhead or preprinted forms ●Use only letterhead or forms
approved for use in laser printers.
●Do not use raised or metallic
letterhead.
Heavy paper ●Use only heavy paper that is
approved for use in laser printers
and meets the weight specifications
for this product.
●Do not use paper that is heavier
than the recommended media
specification for this product unless
it is HP paper that has been
approved for use in this product.
Glossy or coated paper ●Use only glossy or coated paper
that is approved for use in laser
printers.
●Do not use glossy or coated paper
designed for use in inkjet products.
42 Chapter 3 Paper and print media ENWW
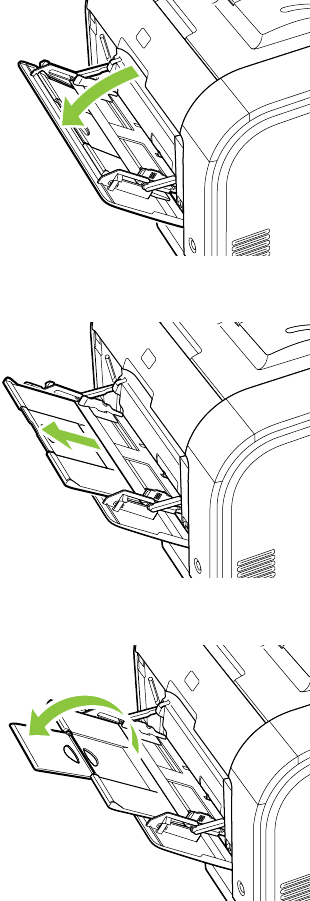
Load paper and print media
Load Tray 1
Tray 1 holds up to 50 sheets of 75 g/m
2
(20 lb) media or five envelopes, ten transparencies, or ten cards.
You can use Tray 1 to print the first page on media different from the remainder of the document.
1. Open Tray 1.
2. If loading long sheets of media, pull out the extension tray.
3. If necessary, flip out the extension.
ENWW Load paper and print media 43
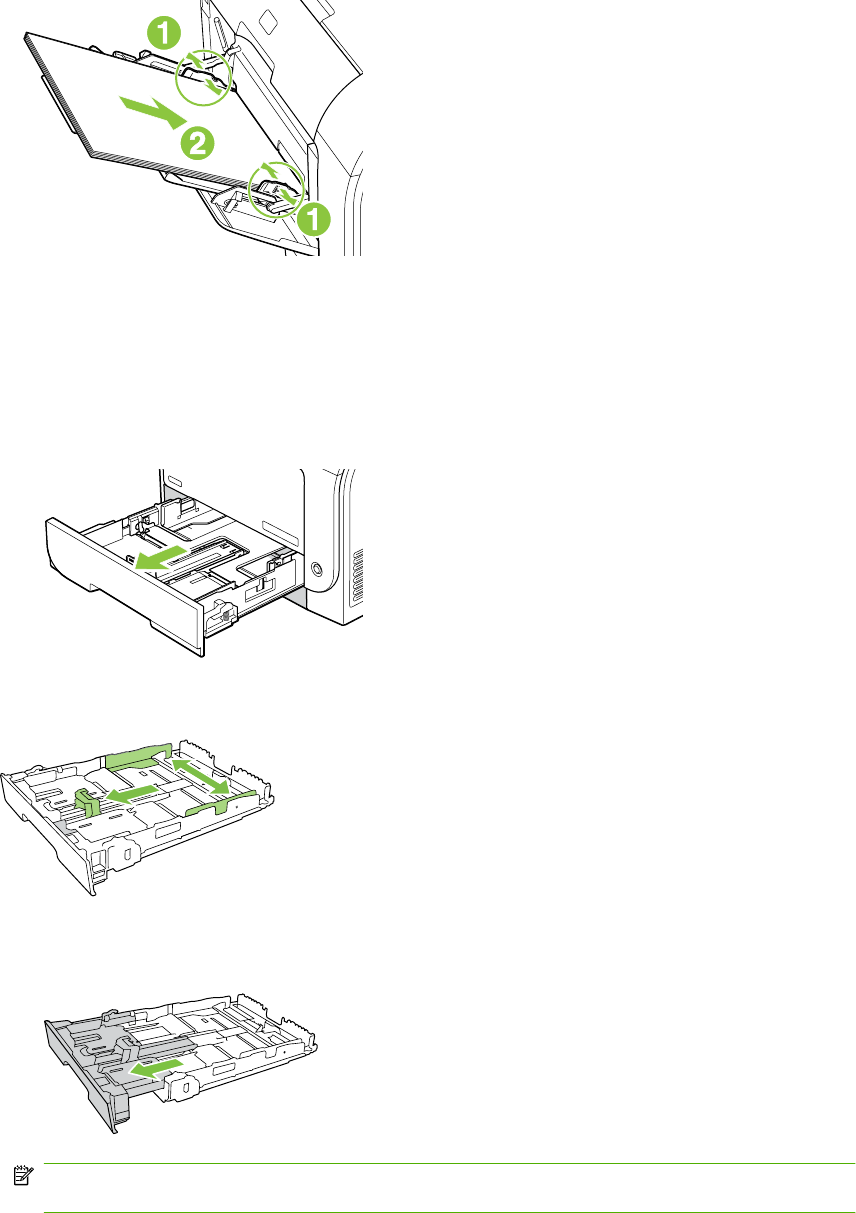
4. Extend the paper guides fully (callout 1) and then load the media stack into Tray 1 (callout 2). Adjust
the paper guides to the size of the paper.
Load Tray 2 or 3
Tray 2 and optional Tray 3 hold up to 250 pages of 75 g/m
2
(20 lb) paper, or fewer pages of heavier
media (25 mm (0.9 in) or less stack height). Load media with the top forward and the side to be printed
on facing up.
1. Pull the tray out of the product.
2. Slide open the paper length and width guides.
●To load Legal-size paper, extend the tray by pressing and holding the extension tab while
pulling the front of the tray toward you.
NOTE: When it is loaded with Legal-size paper, the tray extends from the front of the product
approximately 64 mm (2.5 inches).
44 Chapter 3 Paper and print media ENWW
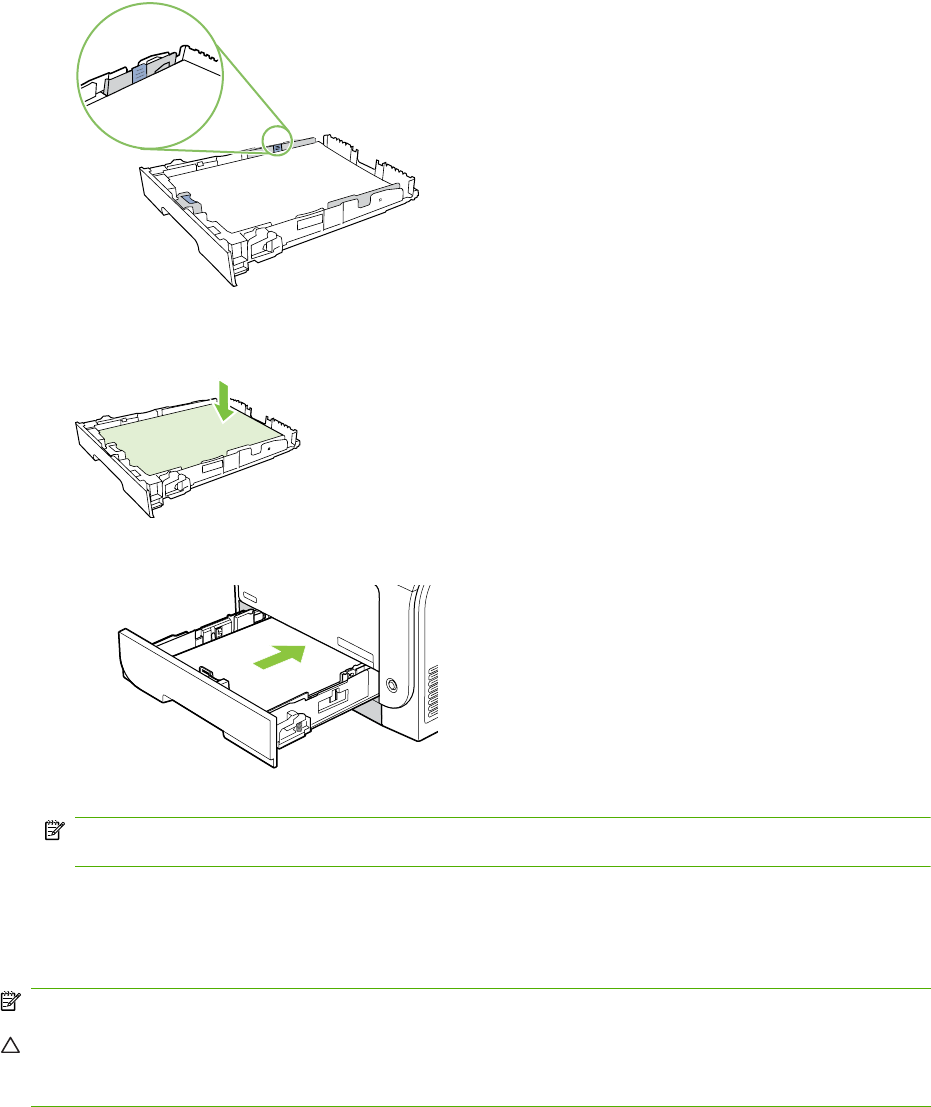
3. Place the paper in the tray and make sure that it is flat at all four corners. Slide the paper length
and width guides so that they are against the stack of paper.
4. Push down on the paper to make sure that the paper stack is below the paper limit tabs on the side
of the tray.
5. Slide the tray into the product.
NOTE: When it is loaded with Legal-size paper, the tray extends from the front of the product
approximately 64 mm (2.5 inches).
Load originals for copying, scanning, or faxing
Automatic document feeder (ADF)
NOTE: The ADF capacity is up to 50 sheets of 80 g/m
2
or 20 lb media.
CAUTION: To prevent damage to the product, do not use an original that contains correction tape,
correction fluid, paper clips, or staples. Also, do not load photographs, small originals, or fragile originals
into the ADF. Use the flatbed glass to scan these items.
1. Insert the top-end of the stack of originals into the ADF input tray, with the media stack face-up
and the first page to be copied or scanned on top of the stack.
If the media is longer than letter- or A4-sized paper, pull out the ADF input tray extension to support
the media.
ENWW Load paper and print media 45
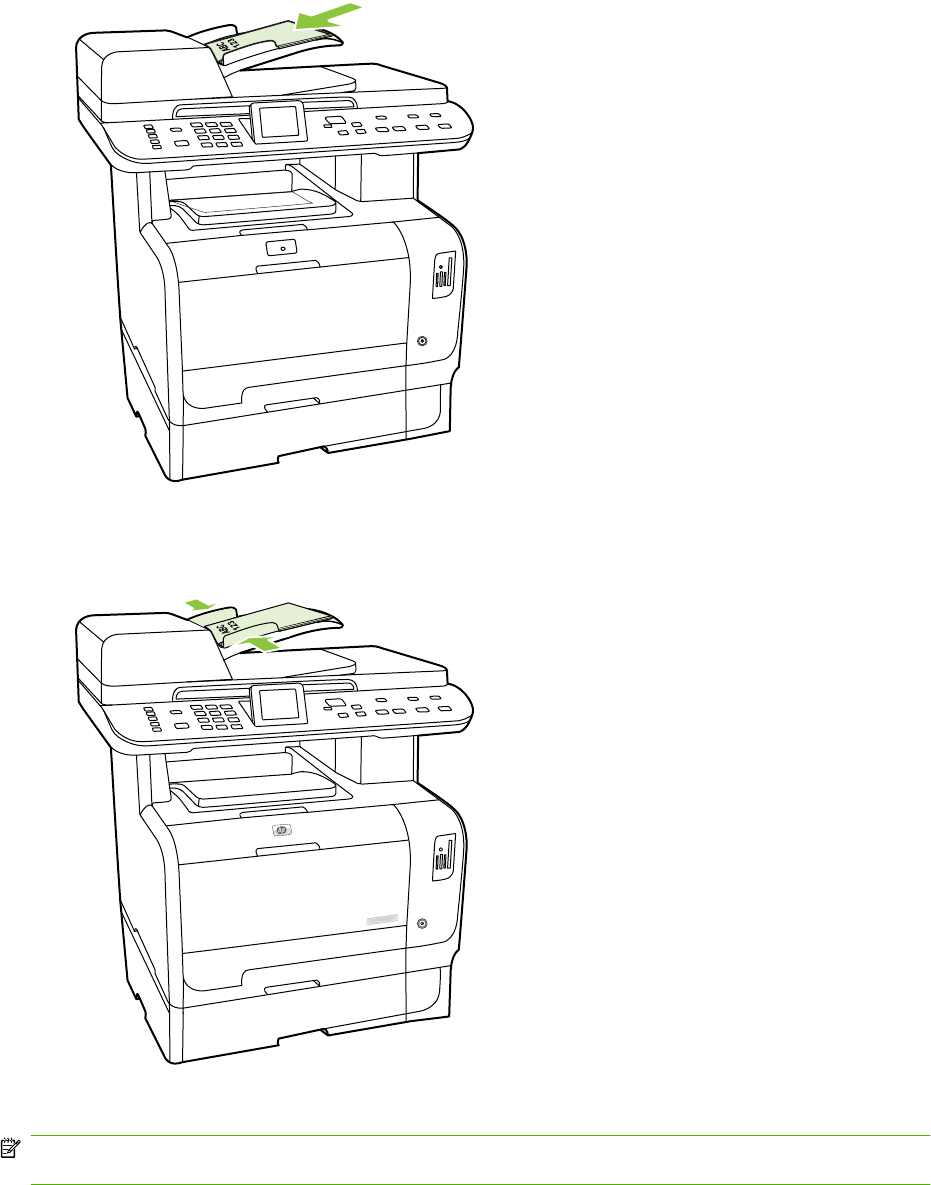
2. Slide the stack into the ADF until it does not move any farther.
Document loaded appears on the control-panel display.
3. Adjust the media guides until they are snug against the media.
Flatbed glass
NOTE: The maximum media size for flatbed copying is letter. Use the ADF for copying or scanning
media larger than letter.
1. Make sure that the automatic document feeder (ADF) contains no media.
2. Lift the flatbed scanner cover.
46 Chapter 3 Paper and print media ENWW
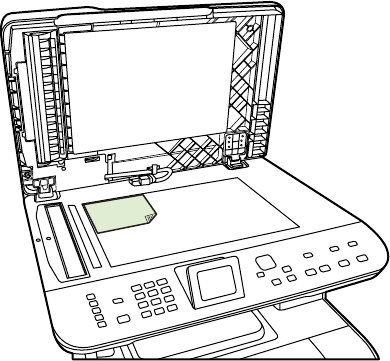
3. Place the original document face-down on the flatbed glass with the upper-left corner of the
document at the corner indicated by the icon on the scanner.
4. Gently close the lid.
ENWW Load paper and print media 47

Configure trays
When using one of the trays for specific size of paper, you can set the default size for the tray in
HP ToolboxFX or from the control panel. In HP ToolboxFX, select Paper handling, and then select the
size for the tray you want to set. When you select that size of paper for a print job in the print dialog, the
product automatically selects that tray for printing.
To set the default paper size or type from the control panel, complete the following steps.
1. On the product control panel, press Setup .
2. Use the arrow buttons to highlight System setup, and then press OK.
3. Use the arrow buttons to highlight Paper setup, and then press OK.
4. Use the arrow buttons to highlight the tray to be configured, and then press OK.
5. Use the arrow buttons to highlight either Paper type or Paper size, and then press OK.
6. Use the arrow buttons to highlight a default type or size for the tray, and then press OK.
48 Chapter 3 Paper and print media ENWW
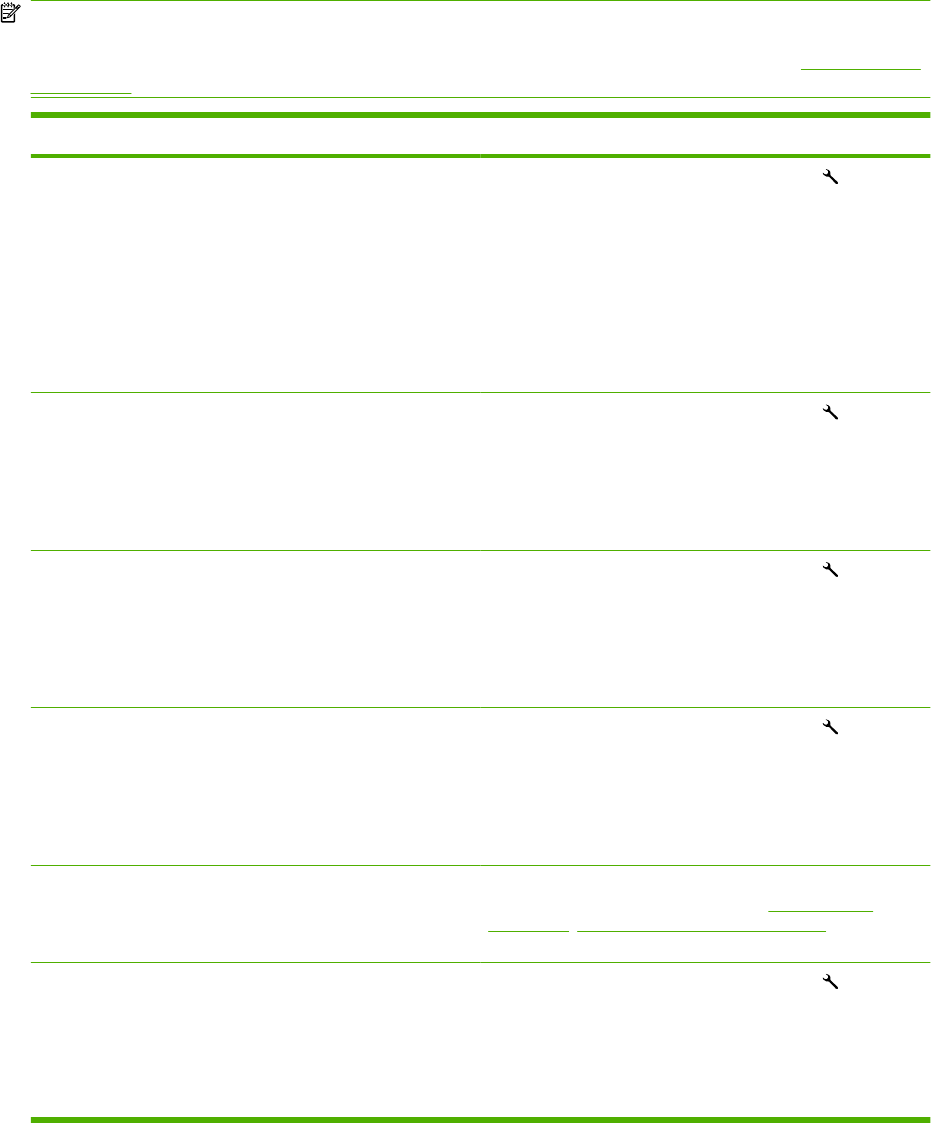
Information pages
Information pages reside within the product memory. These pages help diagnose and solve problems
with the product.
NOTE: If the product language was not correctly set during installation, you can set the language
manually so the information pages print in one of the supported languages. Change the language by
using the System setup menu on the control panel or the embedded Web server. See Control panel
on page 17.
Page description How to print the page
Configuration page
Shows the current settings and product properties.
1. On the product control panel, press Setup .
2. Use the arrow buttons to select Reports, and then press
OK.
3. Use the arrow buttons to select Configuration report,
and then press OK.
A second page also prints (fax models only). On that page, the
Fax Settings section provides details about the product fax
settings.
Supplies status page
Shows the remaining life of the HP print cartridge, the
approximate pages remaining, the number of pages printed,
and other supplies information.
1. On the product control panel, press Setup .
2. Use the arrow buttons to select Reports, and then press
OK.
3. Use the arrow buttons to select Supplies status, and
then press OK.
PCL, PCL 6, or PS font list
Shows which fonts are currently installed in the device.
1. On the product control panel, press Setup .
2. Use the arrow buttons to select Reports, and then press
OK.
3. Use the arrow buttons to select PCL font list, PS font
list, or PCL6 font list, and then press OK.
Demo page
Contains examples of text and graphics.
1. On the product control panel, press Setup .
2. Use the arrow buttons to select Reports, and then press
OK.
3. Use the arrow buttons to select Demo page, and then
press OK.
Event log You can print the event log from HP ToolboxFX, the embedded
Web server, or HP Web Jetadmin. See HP ToolboxFX
on page 52, Embedded Web server on page 62, or the Web
Jetadmin Help.
Usage page
Shows the number of one-sided (simplexed) or two-sided
(duplexed) pages, and the average percentage of coverage.
1. On the product control panel, press Setup .
2. Use the arrow buttons to select Reports, and then press
OK.
3. Use the arrow buttons to select Usage page, and then
press OK.
50 Chapter 4 Manage and maintain the product ENWW
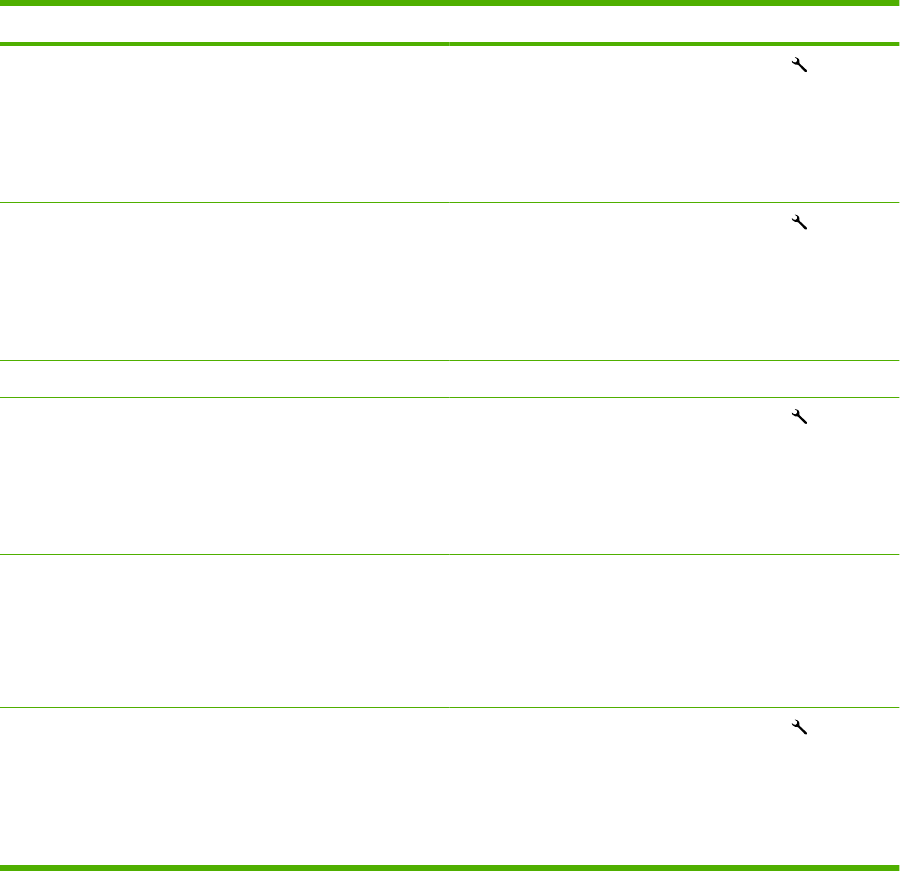
Page description How to print the page
Menu structure
Shows the control-panel menus.
1. On the product control panel, press Setup .
2. Use the arrow buttons to select Reports, and then press
OK.
3. Use the arrow buttons to select Menu structure, and then
press OK.
Network report
Shows the product network settings.
1. On the product control panel, press Setup .
2. Use the arrow buttons to select Reports, and then press
OK.
3. Use the arrow buttons to select Network report, and then
press OK.
Fax reports (fax models only) For information about fax logs and reports, see the user guide.
Color usage job log
Provides a summary of color usage.
1. On the product control panel, press Setup .
2. Use the arrow buttons to select Reports, and then press
OK.
3. Use the arrow buttons to select Color usage job log, and
then press OK.
Service page
Prints a service report.
1. On the product control panel, press Setup.
2. Use the arrow buttons to select Reports, and then press
OK.
3. Use the arrow buttons to select Service page, and then
press OK.
Diagnostics page
Prints a diagnostics page pertaining to color calibration and
color quality.
1. On the product control panel, press Setup .
2. Use the arrow buttons to select Reports, and then press
OK.
3. Use the arrow buttons to select Diagnostics page, and
then press OK.
ENWW Information pages 51
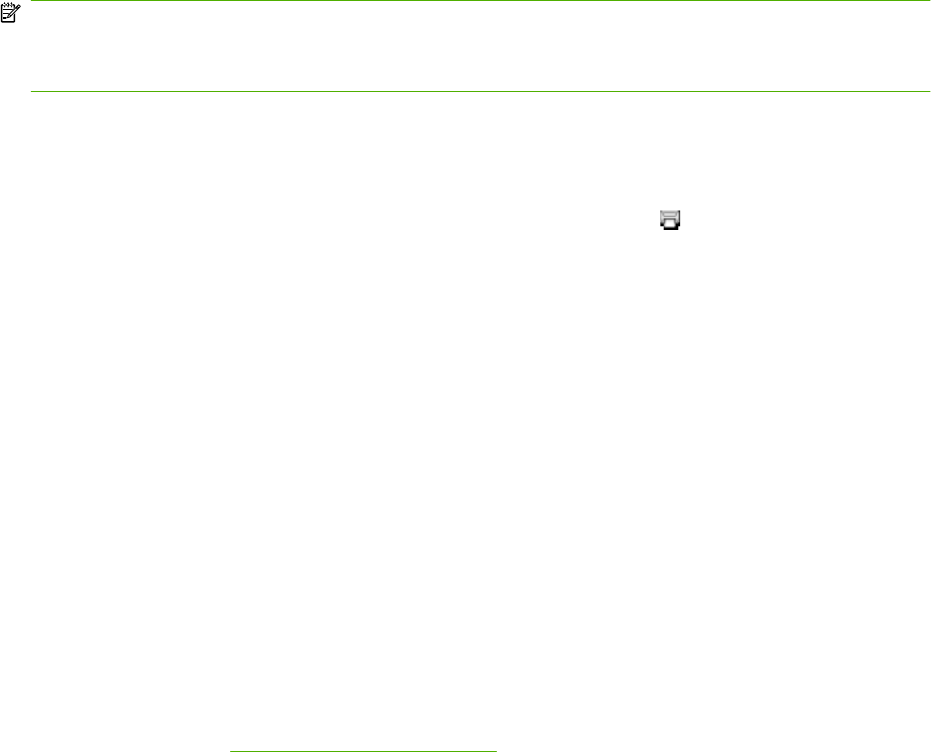
HP ToolboxFX
HP ToolboxFX is a program that you can use to complete the following tasks:
●Check the product status.
●Configure the product settings.
●Configure pop-up-alert messages.
●View troubleshooting information.
●View online documentation.
You can view HP ToolboxFX when the product is directly connected to your computer or is connected
to the network. You must perform a recommended software installation to use HP ToolboxFX.
NOTE: HP ToolboxFX is not supported for Windows Server 2003 or Macintosh operating systems. To
use HP ToolboxFX, you must have TCP/IP protocol installed on your computer.
You do not have to have Internet access to open and use HP ToolboxFX.
View the HP ToolboxFX
Open HP ToolboxFX in one of these ways:
●In the Windows system tray, double-click the HP ToolboxFX icon ( ).
●On the Windows Start menu, click Programs (or All Programs in Windows XP and Vista), click
HP, click HP Color LaserJet CM2320 MFP Series, and then click HP ToolboxFX.
Status
The Status folder contains links to the following main pages:
●Device status. This page indicates product conditions such as a jam or an empty tray. After you
correct a problem, click Refresh status to update the product status.
●Supplies status. View details such as the approximate percent of toner remaining in the print
cartridge and the number of pages that have been printed with the current print cartridge. This page
also has links for ordering supplies and for finding recycling information.
●Device configuration. View a detailed description of the current product configuration, including
the amount of memory installed and whether optional trays are installed.
●Network summary. View a detailed description of the current network configuration, including the
IP address and network status.
●Print info pages. Print the configuration page and other information pages, such as the supplies
status page. See Information pages on page 50.
●Color usage job log. View color usage information for the product.
●Event log. View a history of product errors. The most recent error is listed first.
52 Chapter 4 Manage and maintain the product ENWW
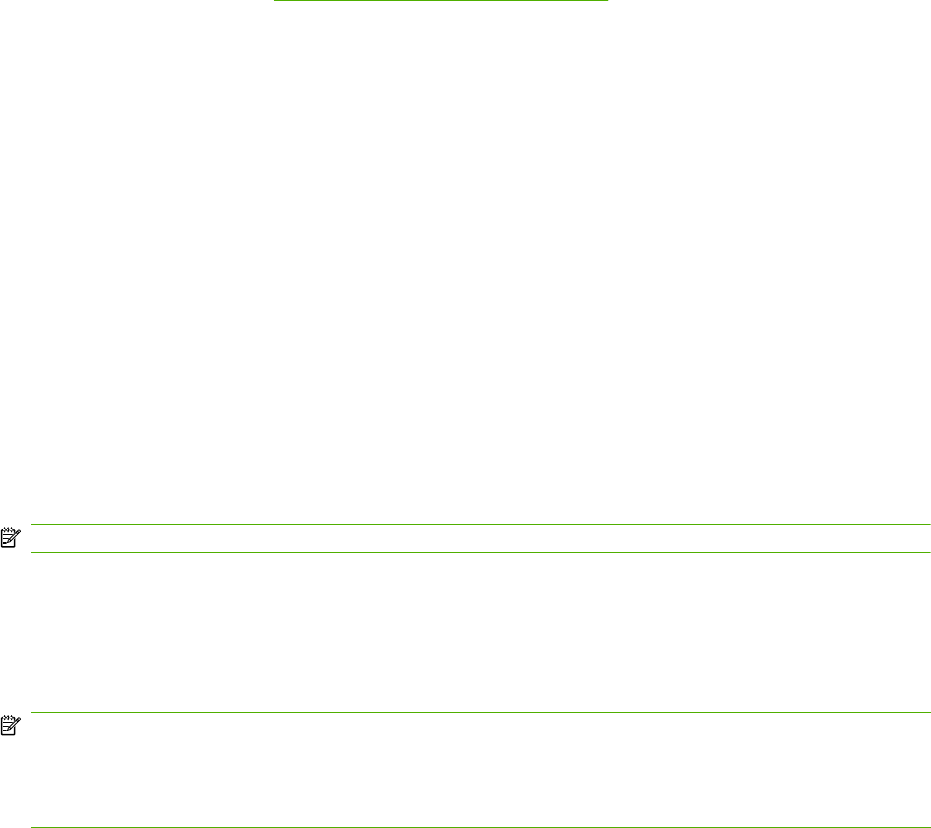
Event log
The event log is a four-column table where the product events are logged for your reference. The log
contains codes that correspond to the error messages that appear on the product control-panel display.
The number in the Page Count column specifies the total number of pages that the product had printed
when the error occurred. The event log also contains a brief description of the error. For more information
about error messages, see Control-panel messages on page 257.
Alerts
The HP ToolboxFX Alerts tab contains links to the following main pages:
●Set up Status Alerts. Set up the product to send you pop-up alerts for certain events, such as low
toner levels.
●Set up E-mail Alerts. Set up the product to send you e-mail alert messages for certain events,
such as low toner levels.
Set up status alerts
Use HP ToolboxFX to set up the product so that it issues pop-up alerts to your computer when certain
events occur. Events that trigger alerts include jams, low levels of toner in HP print cartridges, non-HP
print cartridge in use, empty input trays, and specific error messages.
Select the pop-up format, the tray icon format, or both for the alerts. The pop-up alerts only appear when
the product is printing from the computer on which you set up the alerts.
Change the Cartridge low threshold setting, which sets the toner level that causes a low toner alert,
in System Setup on the System Settings tab.
NOTE: You must click Apply before the changes take effect.
Set up e-mail alerts
Use this to configure up to two e-mail addresses to receive alert messages when certain events occur.
You can specify different events for each e-mail address. Use the information for the e-mail server that
will send out the e-mail alert messages for the product.
NOTE: You can only configure e-mail alerts to be sent from a server that does not require user
authentication. If your e-mail server requires you to log in with a username and password, you cannot
enable e-mail alerts.
NOTE: You must click Apply before your changes take effect.
Product information
The Product information folder contains links to the following page:
●Demonstration Pages. Print pages that show the color print quality potential and overall print
characteristics of the product.
ENWW HP ToolboxFX 53

Fax
Use the HP ToolboxFX Fax tab to perform fax tasks from your computer. The Fax tab contains links to
the following main pages:
●Fax Receive. Set the fax receive mode.
●Fax Phone Book. Add, edit, or delete entries in the product phone book.
●Fax Send Log. View all of the recent faxes that have been sent from the product.
●Fax Receive Log. View all of the recent faxes that have been received by the product.
●Junk Faxes. Add, delete, or view fax numbers that are blocked.
●Fax Data Properties. Manage the space used to store faxes on your computer. These settings
apply only if you have chosen to send or receive faxes remotely from your computer.
Fax Receive
The following options are available when receiving a fax:
●Print the fax. You can also select an option to have a message appear on your computer to notifying
you when the fax was printed.
●Forward the fax to another fax machine.
For more information about fax tasks, see the user guide.
NOTE: You must click Apply before the changes take effect.
Fax phone book
Use the HP ToolboxFX fax phone book to add and remove individuals or groups on your speed-dial list,
import phone books from a variety of sources, and update and maintain the contact list.
●To add an individual contact to the speed-dial list, select the row of the speed dial number that you
want to specify. Type the contact name in the Contact name window. Type the fax number in the
Fax number window. Click Add.
●To add a group of contacts to the speed-dial list, select the row of the speed-dial number that you
want to specify. Click Add Group. Double-click a contact name from the list on the left to move it
to the group list on the right, or select a name on the left and then click the appropriate arrow to
move it to the group list on the right. You can also use those two methods to move names from
right to left. When you have created a group, type a name in the Group name window, and then
click OK.
●To edit an existing individual speed-dial entry, click anywhere on the row containing the contact
name to select it, and then click Update. Type changes in the appropriate windows, and then click
OK.
●To edit an existing group-speed-dial entry, click anywhere on the row containing the group name
to select it, and then click Update Group. Make any required changes, and then click OK.
●To delete an entry from the speed-dial list, select the item, and then click Delete.
●To move speed dial entries, select the entry and then click Move, or select Move and then specify
the entry in the dialog box. Either select Next empty row or specify the number of the row where
you want to move the entry.
54 Chapter 4 Manage and maintain the product ENWW
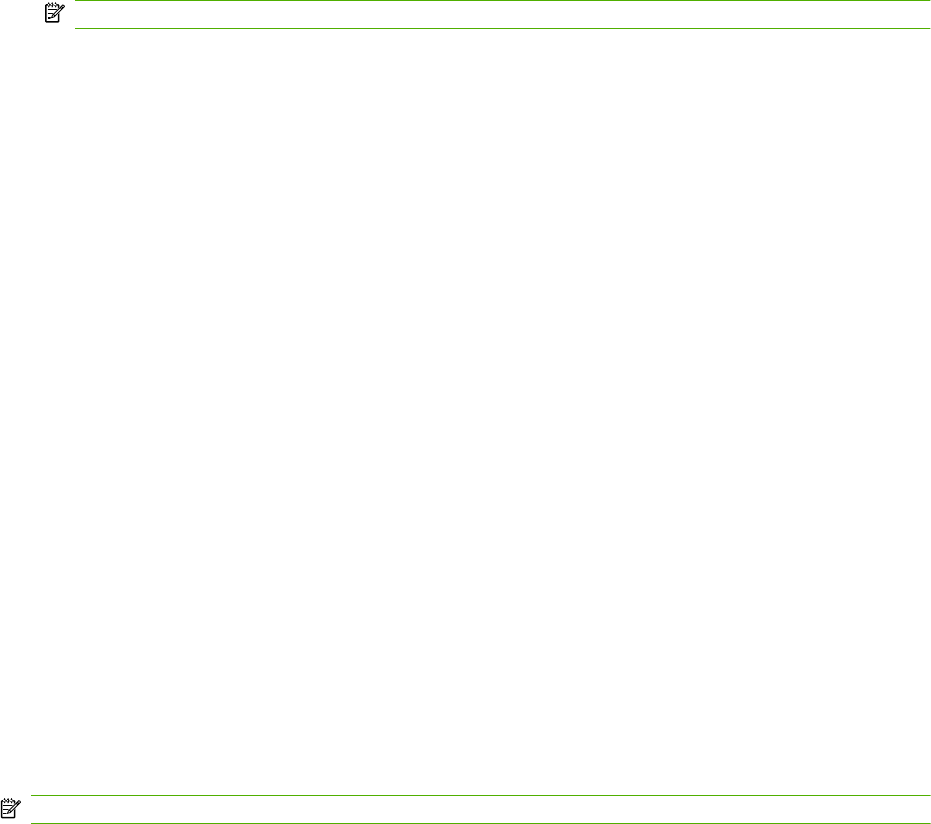
NOTE: If you specify a row that is occupied, the new entry will overwrite the existing entry.
●To import contacts from a phone book that exists in Lotus Notes, Outlook, or Outlook Express, click
Import/Export Phone Book. Select the Import option, and then click Next. Select the appropriate
software program, navigate to the appropriate file, and then click Finish. To export contacts from
a phone book, click Import/Export Phone Book. Select the Export option, and then click Next.
Enter the file name or browse to the file to which you want to export contacts, and then click
Finish. You can also select individual entries from the phone book instead of importing the entire
phone book.
●To delete all entries, click Delete All, and then click Yes.
In addition to numerical digits, the following are valid characters for fax numbers:
●(
●)
●+
●-
●*
●#
●R
●W
●.
●,
●<space>
NOTE: You must click Apply before the changes take effect.
For more information about faxes, see the user guide.
ENWW HP ToolboxFX 55

Fax send log
The HP ToolboxFX fax send log lists all recently sent faxes and information about them, including the
date and time sent, job number, fax number, page count, and the results.
Click any column heading in the fax send log to re-sort the information in that column in ascending or
descending order.
The Results column provides the fax status. If the fax attempt was unsuccessful, this column provides
a description of why the fax was not sent.
For more information about faxes, see the user guide.
Fax receive log
The HP ToolboxFX fax receive log provides a list of all recently received faxes and information about
them including the date and time received, job number, fax number, page count, results, and an
abbreviated fax image.
The fax receive log can be used to block future faxes. Check the Block Fax box next to a received fax
listed on the log.
When a computer that is connected to the product receives a fax, the fax contains a View link. Clicking
this link opens a new page that provides information about the fax.
Click on any column heading in the fax receive log to re-sort the information in that column in ascending
or descending order.
The Results column provides the fax status. If the fax attempt was unsuccessful, this column provides
a description of why the fax was not received.
NOTE: You must click Apply before the changes take effect.
For more information about faxes, see the user guide.
Junk Faxes
Junk Faxes provides a list of all numbers that are blocked. Add, modify, or delete blocked fax numbers
on this tab.
Help
The Help folder contains links to the following main pages:
●Troubleshooting. View troubleshooting help topics, print troubleshooting pages, clean the
product, and open Microsoft Office Basic Colors. For more information about Microsoft Office Basic
Colors, see the user guide.
●Paper and Print Media. Print information about how to obtain optimal results from your product
using various types of paper and print media.
●Color Printing Tools. Open Microsoft Office Basic Colors or the full palette of color with associated
RGB values. For more information about Microsoft Office Basic Colors, see the user guide. Use
the HP Basic Color Match to adjust spot colors in your printed output.
56 Chapter 4 Manage and maintain the product ENWW
●Animated demonstrations. View animated demonstrations for common troubleshooting
procedures.
●User Guide. View information about the product usage, warranty, specifications, and support. The
User Guide is available in both HTML and PDF format.
ENWW HP ToolboxFX 57
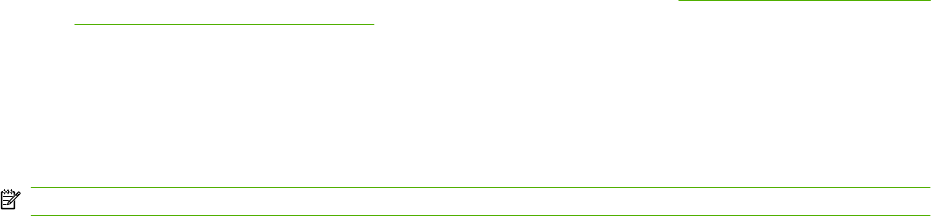
System Settings
The HP ToolboxFX System Settings tab contains links to the following main pages:
●Device Information. View information about the product, such as the product description and a
contact person.
●Paper Handling. Change the product paper-handling settings, such as default paper size and
default paper type.
●Print Quality. Change the product print-quality settings.
●Print Density. Change the print-density settings, such as contrast, highlights, midtones, and
shadows.
●Paper Types. Change the mode settings for each media type, such as letterhead, prepunched, or
glossy paper.
●System Setup. Change the system settings, such as jam recovery and auto-continue. Change the
Cartridge low threshold setting, which sets the toner level that causes a Low toner pop-up alert.
●Service. Gain access to various procedures required to maintain the product.
●Device Polling. Change the product polling settings, which determine how often HP ToolboxFX
collects data from the product.
●Save/Restore Settings. Save the current settings for the product to a file on the computer. Use
this file to load the same settings onto another product or to restore these settings to this product
at a later time.
●Password. Set, change, or clear the product security password (see Turn on password protection
from the control panel on page 63).
Device Information
The Device Information page stores data about your product for future reference. The information that
you type in the fields on this page appears on the Configuration page. You can type any character in
each of these fields.
NOTE: You must click Apply before your changes take effect.
58 Chapter 4 Manage and maintain the product ENWW
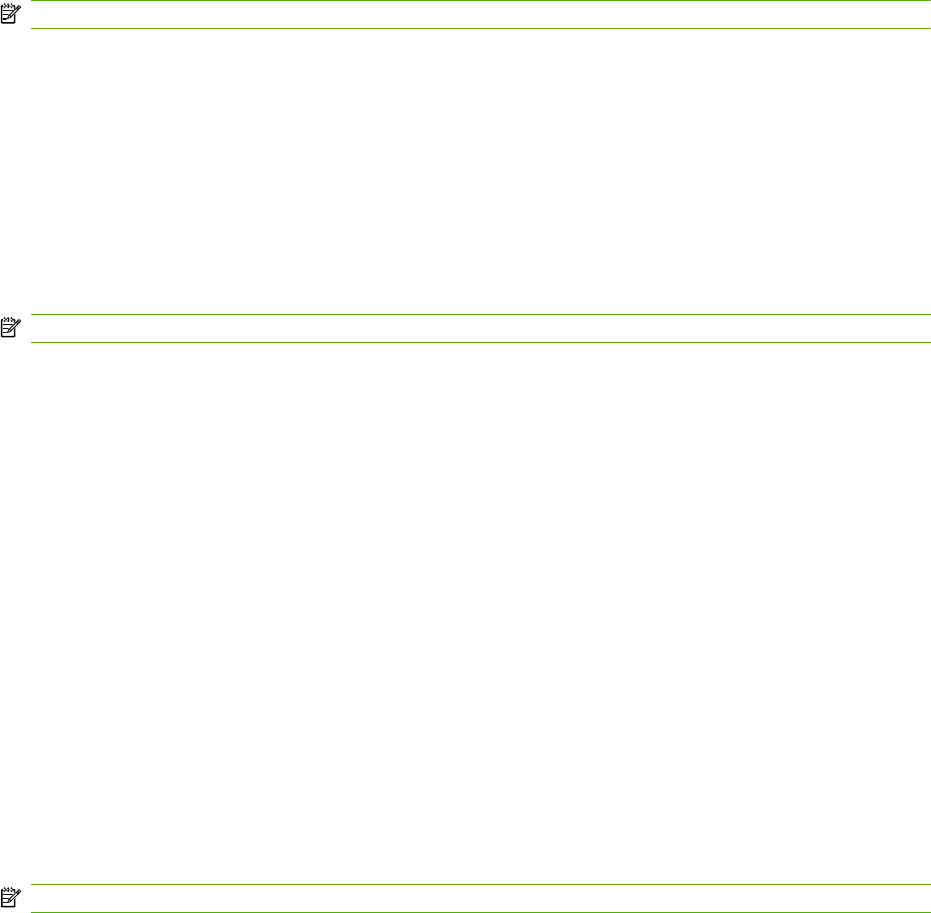
Paper Handling
The following options are available for handling print jobs when the product is out of media:
●Select Wait for paper to be loaded.
●Select Cancel from the Paper out action drop-down list to cancel the print job.
●Select Override from the Paper out action drop-down list to send the print job to another paper
tray.
The Paper out time field specifies how long the product waits before acting on your selections. You
can specify from 0 to 3600 seconds.
NOTE: You must click Apply before your changes take effect.
Print Quality
Use these options to improve the appearance of your print jobs.
Color Calibration
●Power On Calibration. Specify whether the product should calibrate when you turn it on.
●Calibration Timing. Specify how frequently the product should calibrate.
●Calibrate Now. Set the product to calibrate immediately.
NOTE: You must click Apply before your changes take effect.
Print Density
Use these settings to make fine adjustments in the amount of each color of toner that is used for your
printed documents.
●Contrasts. Contrast is the range of difference between light (highlight) and dark (shadow) colors.
To increase the overall range between light and dark colors, increase the Contrasts setting.
●Highlights. Highlights are colors that are nearly white. To darken highlight colors, increase the
Highlights setting. This adjustment does not affect midtone or shadow colors.
●Midtones. Midtones are colors that are halfway between white and solid density. To darken
midtone colors, increase the Midtones setting. This adjustment does not affect highlight or shadow
colors.
●Shadows. Shadows are colors that are nearly solid density. To darken shadow colors, increase
the Shadows setting. This adjustment does not affect highlight or midtone colors.
Paper Types
Use these options to configure print modes that correspond to the various media types. To reset all
modes to factory default settings, select Restore modes.
NOTE: You must click Apply before your changes take effect.
ENWW HP ToolboxFX 59
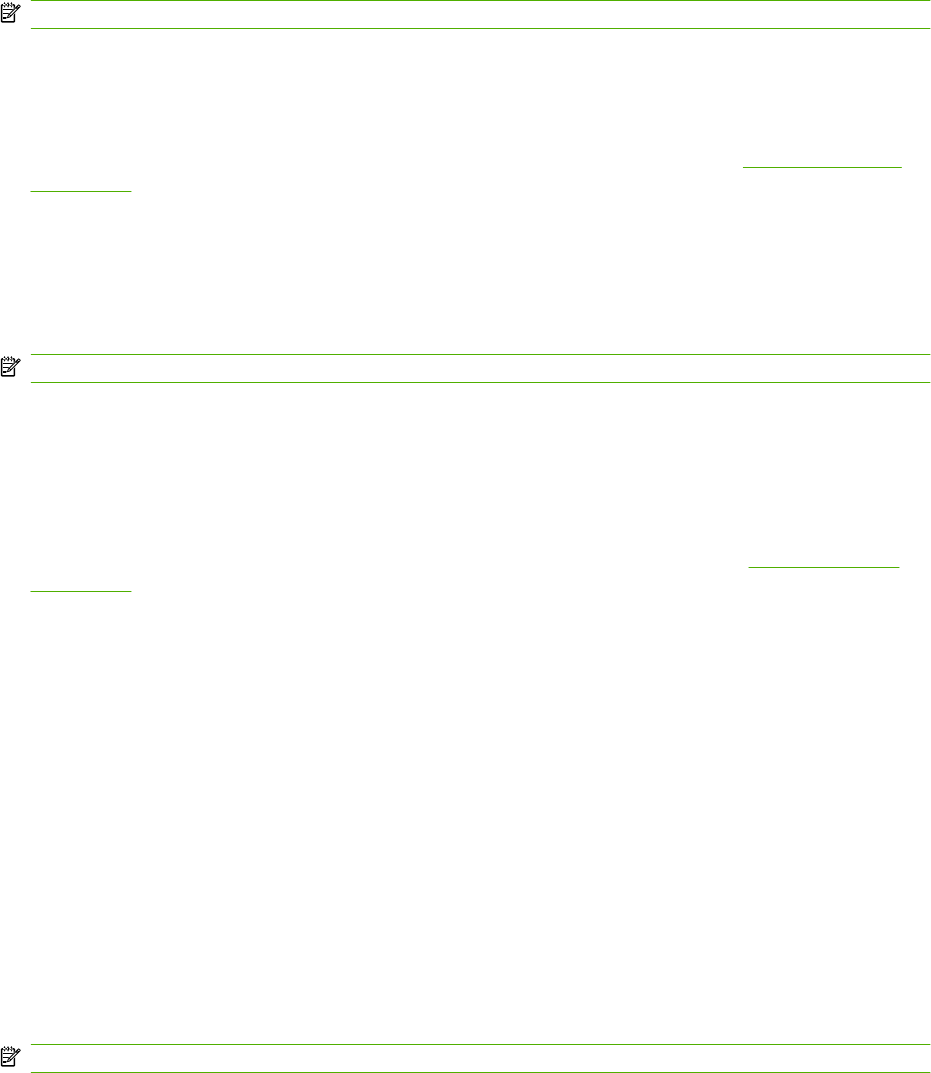
System setup
Use the HP ToolboxFX system settings options to configure global settings for copy, fax, scan, and print,
such as jam recovery and auto-continue.
NOTE: You must click Apply before the changes take effect.
Service
During the printing process, paper, toner and dust particles can accumulate inside the product. Over
time, this buildup can cause print-quality problems such as toner specks or smearing. The HP ToolboxFX
provides an easy method for cleaning the paper path. For more information, see Clean the product
on page 73.
Device polling
You can turn off HP ToolboxFX device polling to reduce network traffic, but doing so also disables some
HP ToolboxFX features: pop-up alerts, fax log updates, the ability to receive faxes to this computer, and
scanning using the Scan To button.
NOTE: You must click Apply before the changes take effect.
Save/Restore
Saves printer settings to a file on your PC for backup.
Password
Set the system password. For more information about the system password, see Security features
on page 63.
Print Settings
The HP ToolboxFX Print Settings tab contains links to the following main pages:
●Printing. Change the default product print settings, such as number of copies and paper
orientation.
●PCL5. View and change the PCL5 settings.
●PostScript. View and change the PS settings.
●Photo. Change the photo settings and enable/disable the photo card slots (photo card models
only).
Printing
Use these options to configure the settings for all print functions. These are the same options that are
available on the control panel.
NOTE: You must click Apply before your changes take effect.
PCL5
Use these options to configure the settings when you are using the PCL print personality.
60 Chapter 4 Manage and maintain the product ENWW
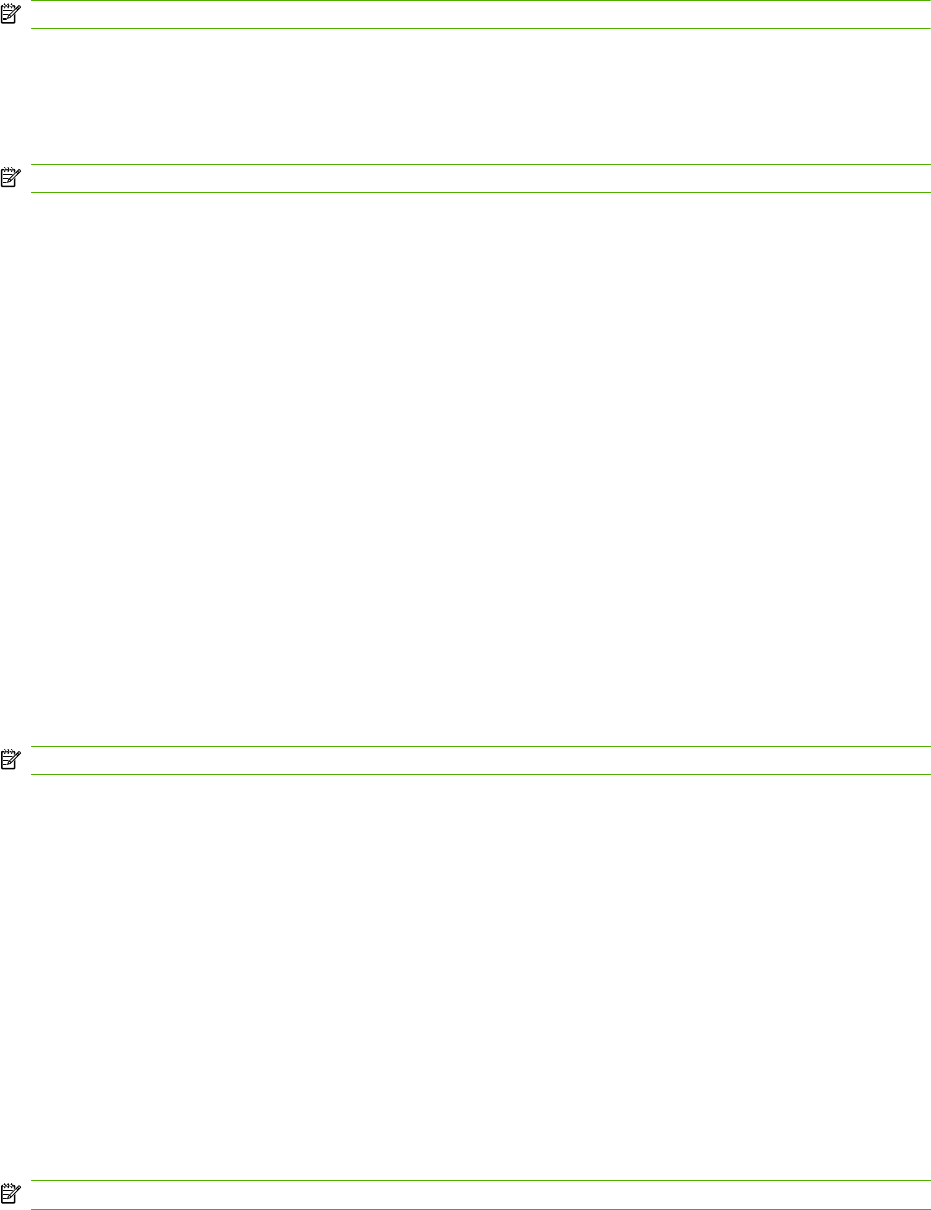
NOTE: You must click Apply before your changes take effect.
PostScript
Use this option when you are using the PostScript print personality. When the Print PostScript error
option is turned on, the PostScript error page automatically prints when PostScript errors occur.
NOTE: You must click Apply before your changes take effect.
Network Settings
The network administrator can use this tab to control the network-related settings for the product when
it is connected to an IP-based network.
E-mail
The HP ToolboxFX E-mail tab contains links to the following main pages:
●E-mail Configuration. Configure scan-to-e-mail settings
●E-mail Contacts. Make changes to the e-mail contacts list associated with the scan-to-e-mail
feature.
E-mail configuration
Use the E-mail Configuration page to enable the scan-to-e-mail features and to specify the SMTP
gateway, SMTP port, and other basic information. The SMTP gateway is a server that is used to send
e-mail; for example, “mail.yourISP.com”. The SMTP port is a number between 0 and 65535. Contact
your system administrator for this information.
Use the Test Settings button to test your scan-to-e-mail settings.
NOTE: You must click Apply before your changes take effect.
E-mail contacts
Use the HP ToolboxFX E-mail Contacts page to add and remove individuals from your e-mail contacts
list. The e-mail contacts list can contain up to 50 entries.
To add a contact to the e-mail contacts list, type the contact’s name in the Contact Name window. Type
the associated e-mail address in the E-mail Address window. Then click Add. You can also add a
contact by double-clicking an empty row in the e-mail contacts list. Then type your contact’s information
in the appropriate windows and click OK. If you select a row that is occupied, the new entry will overwrite
the existing entry.
To edit an existing contact entry, select the row containing the contact name, and then click Update.
Type changes in the appropriate window, and then click OK.
To delete an entry from the e-mail contacts list, select the item, and then click Delete. To delete all
entries, click Delete All, and then click Yes.
NOTE: You must click Apply before your changes take effect.
ENWW HP ToolboxFX 61
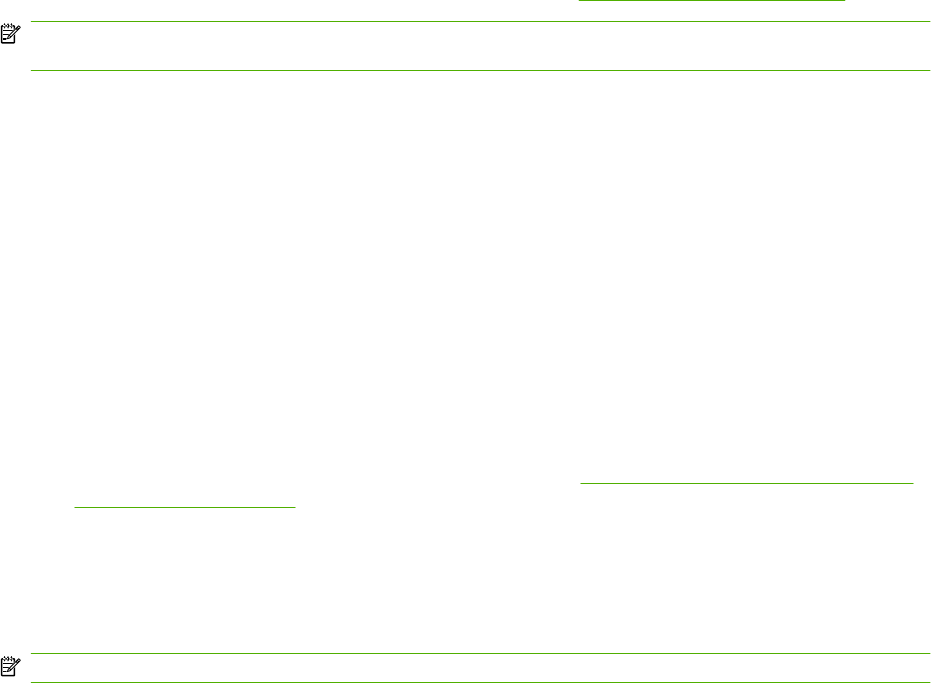
Embedded Web server
This product is equipped with an embedded Web server (EWS), which provides access to information
about product and network activities. A Web server provides an environment in which web programs
may run, much in the same way that an operating system, such as Windows, provides an environment
for programs to run on a computer. The output from these programs can then be displayed by a Web
browser, such as Microsoft Internet Explorer, Safari, or Netscape Navigator.
An “embedded” Web server resides on a hardware device (such as an HP LaserJet product) or in
firmware, rather than as software that is loaded on a network server.
The advantage of an EWS is that it provides an interface to the product that anyone with a network-
connected product and computer can use. There is no special software to install or configure, but you
must have a supported Web browser on the computer. To gain access to the EWS, type the IP address
for the product in the address line of the browser. (To find the IP address, print a configuration page.
For more information about printing a configuration page, see Information pages on page 50.)
NOTE: For Macintosh operating systems, you can use the EWS over a USB connection after installing
the Macintosh software included with the product.
Features
The EWS allows you to view product and network status and manage printing functions from a computer.
With the EWS, you can complete the following tasks:
●View product status information
●Determine the remaining life on all supplies and order new ones
●View and change part of the product configuration
●View and print some internal pages
●Select the language in which to display the EWS pages and control panel messages
●View and change network configuration
●Set, change, or clear the product security password (see Turn on password protection from the
control panel on page 63).
●Enable/disable the photo card slot on the product from the print tab
●Set fax receive and phone book settings.
●Set default copy and print settings.
NOTE: Changing network settings in the EWS might disable some of product software or features.
62 Chapter 4 Manage and maintain the product ENWW
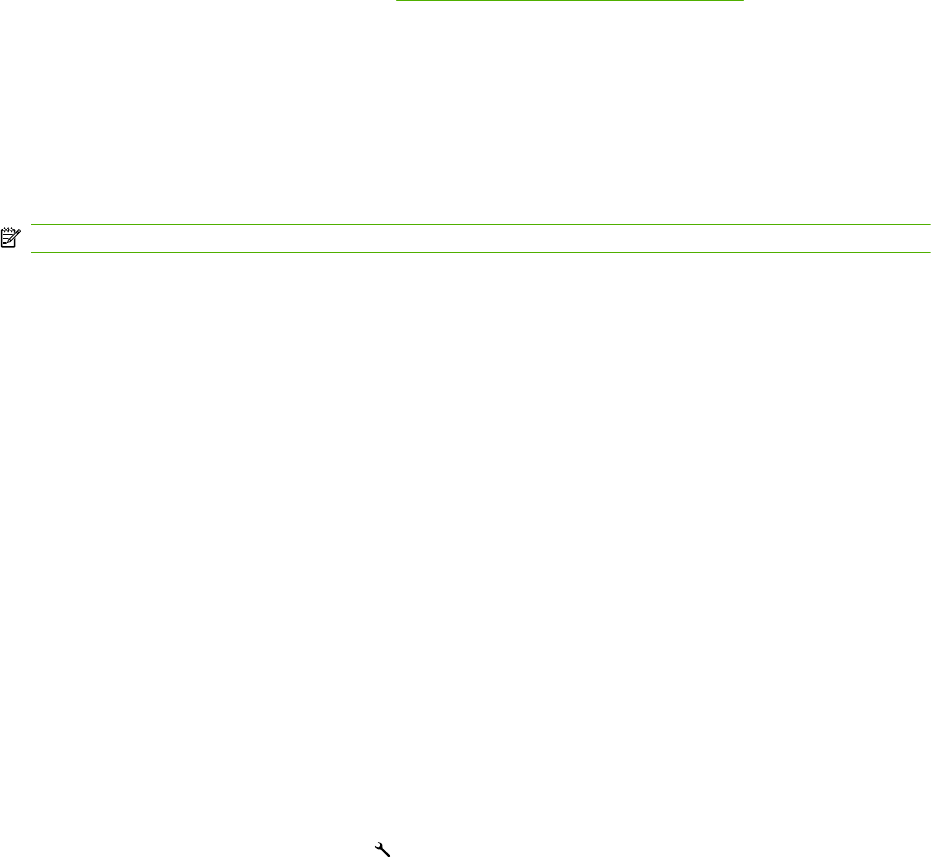
Use HP Web Jetadmin software
HP Web Jetadmin is a Web-based software solution for remotely installing, monitoring, and
troubleshooting network-connected peripherals. The intuitive browser interface simplifies cross-platform
management of a wide range of devices, including HP and non-HP devices. Management is proactive,
allowing network administrators the ability to resolve issues before users are affected. Download this
free, enhanced-management software at www.hp.com/go/webjetadmin_software.
To obtain plug-ins to HP Web Jetadmin, click plug-ins, and then click the download link that is next to
the name of the plug-in that you want. The HP Web Jetadmin software can automatically notify you
when new plug-ins are available. On the Product Update page, follow the directions to automatically
connect to the HP Web site.
If installed on a host server, HP Web Jetadmin is available to any client through a supported Web
browser, such as Microsoft Internet Explorer 6.0 for Windows or Netscape Navigator 7.1 for Linux.
Browse to the HP Web Jetadmin host.
NOTE: Browsers must be Java-enabled. Browsing from an Apple PC is not supported.
Security features
The product includes a password feature that restricts access to setup features while allowing basic
functions to continue. A single system password can be set from the EWS or the control panel.
Private receive can be used to store faxes on the product until you are at the product to print them.
Turn on password protection using the embedded Web server
Use the EWS to set the password.
1. Open the EWS, and then click the System tab.
2. Click Password.
3. In the Password box, type the password you want to set, and then in the Confirm password box,
type the same password again to confirm your choice.
4. Click Apply to save the password.
Turn on password protection from the control panel
To set up the product security password, complete the following steps:
1. On the control panel, press Setup .
2. Use the arrow buttons to select System setup, and then press OK.
3. Use the arrow buttons to select Product security, and then press OK.
4. Use the arrow buttons to select On, and then press OK.
5. Use the alphanumeric buttons to enter the product password, and then press OK.
6. To confirm the product password, use the alphanumeric buttons to re-enter the password, and then
press OK.
ENWW Use HP Web Jetadmin software 63

Turn on private receive feature
The password-protection feature must be turned on before the private-receive feature can be activated.
1. On the control panel, press Setup .
2. Use the arrow buttons to select Fax setup, and then press OK.
3. Use the arrow buttons to select Advanced setup, and then press OK.
4. Use the arrow buttons to select Private receive, and then press OK.
5. Use the arrow buttons to select On, and then press OK.
6. Use the alphanumeric buttons to enter the product security password, and then press OK.
7. To confirm the product security password, use the alphanumeric buttons to re-enter the product
security password, and then press OK.
64 Chapter 4 Manage and maintain the product ENWW
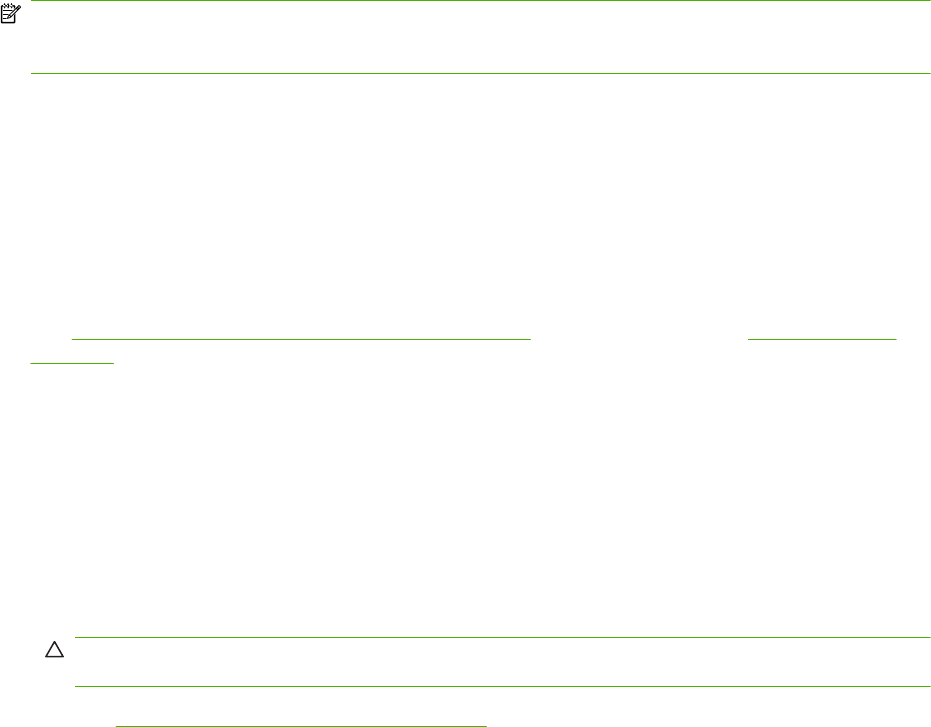
Manage supplies
Check and order supplies
You can check the supplies status by using the product control panel, printing a supplies status page,
or viewing HP ToolboxFX. Hewlett-Packard recommends that you place an order for a replacement print
cartridge when Low message for a print cartridge first appears. Use a new, authentic HP print cartridge
to obtain the following types of supplies information:
●Amount of cartridge life remaining
●Approximate number of pages remaining
●Number of pages printed
●Other supplies information
NOTE: If the product is connected to the network, you can set HP ToolboxFX to notify you by e-mail
when a print cartridge is low. If the product is directly connected to a computer, you can set
HP ToolboxFX to notify you when supplies are low.
Check supplies status by using the control panel
Do one of the following:
●Check the product control panel, which indicates when a print cartridge is low or empty. The control
panel also indicates when a non-HP print cartridge is first installed.
●Print a supplies status page, and then check the supplies levels on the page.
If the supplies levels are low, you can order supplies through a local HP dealer, by telephone, or online.
See Order parts, accessories, and supplies on page 328 for part numbers. Go to www.hp.com/go/
ljsupplies to order online.
Check supplies status by using HP ToolboxFX
You can configure HP ToolboxFX to notify you when the supplies are low. Choose to receive alerts by
e-mail or as a pop-up message or taskbar icon.
Store supplies
Follow these guidelines for storing print cartridges:
●Do not remove the print cartridge from its package until you are ready to use it.
CAUTION: To prevent damage, do not expose the print cartridge to light for more than a few
minutes.
●See Environmental specifications on page 378 for operating and storage temperature ranges.
●Store the supply in a horizontal position.
●Store the supply in a dark, dry location away from heat and magnetic sources.
ENWW Manage supplies 65
HP policy on non-HP supplies
Hewlett-Packard Company cannot recommend the use of non-HP supplies, either new or
remanufactured. Because they are not HP products, HP cannot influence their design or control their
quality. Service or repairs required as a result of using a non-HP supply will not be covered under the
warranty.
HP fraud hotline
Call the HP fraud hotline if the product or HP ToolboxFX indicates that the print cartridge is not an
HP print cartridge and you think that it is genuine. HP will help determine if the product is genuine and
take steps to resolve the problem.
The print cartridge might not be a genuine HP one if you notice the following issues:
●You are experiencing a large number of problems with the print cartridge.
●The print cartridge does not look like it usually does (for example, the pull tab or the box is different).
In the United States, call toll-free: 1-877-219-3183.
Outside the United States, you can call collect. Dial the operator and ask to place a collect call to this
telephone number: 1-770-263-4745. If you do not speak English, a representative at the HP fraud hotline
who speaks your language will assist you. Or, if someone who speaks your language is not available,
a language line interpreter will connect approximately one minute after the beginning of the call. The
language line interpreter is a service that will translate between you and the representative for the HP
fraud hotline.
Recycle supplies
To install a new HP print cartridge, follow the instructions that are included in the box that contains the
new supply, or see the getting started guide.
To recycle supplies, place the used supply in the box in which the new supply arrived. Use the enclosed
return label to send the used supply to HP for recycling. For complete information, see the recycling
guide that is included with each new HP supply item.
66 Chapter 4 Manage and maintain the product ENWW
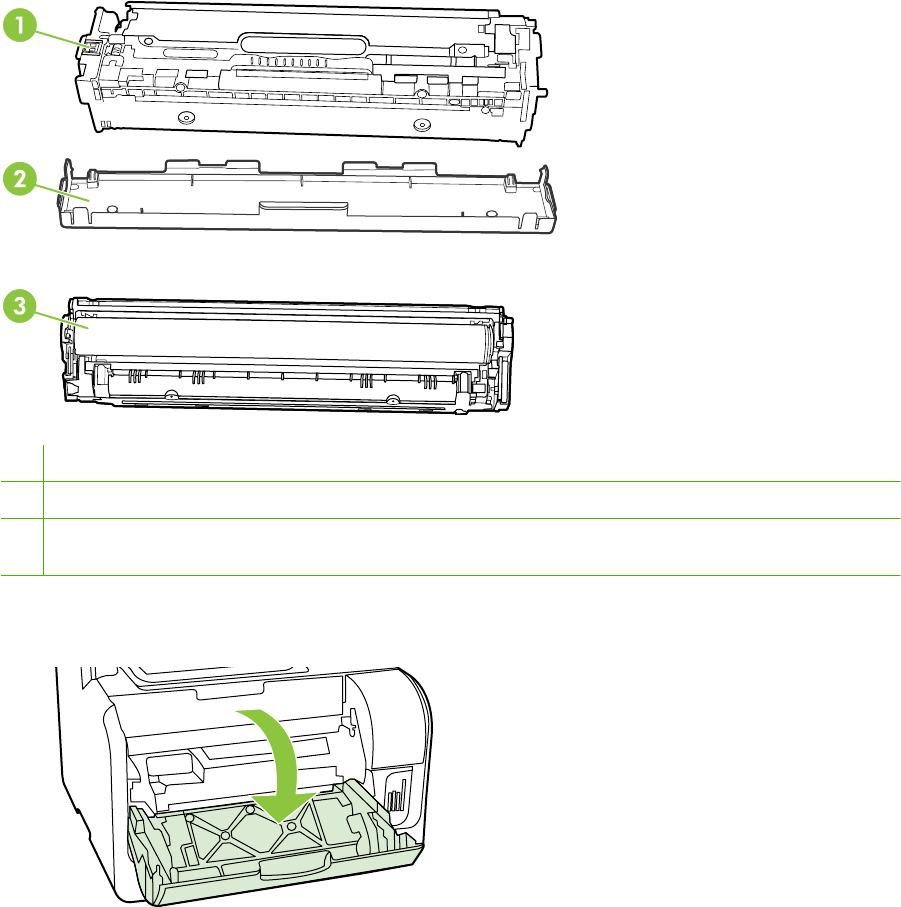
Replace supplies
Print cartridge
1Cartridge E-label
2Plastic shield
3Imaging Drum. Do not touch the imaging drum on the bottom of the print cartridge. Fingerprints on the imaging drum can
cause print-quality problems.
1. Open the front door.
ENWW Manage supplies 67
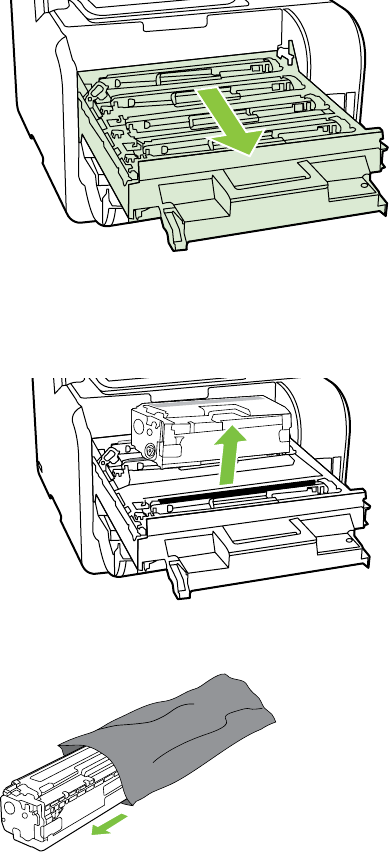
2. Pull out the print-cartridge drawer.
3. Grasp the handle on the old print cartridge and then pull the cartridge straight up to remove it.
4. Remove the new print cartridge from the packaging.
68 Chapter 4 Manage and maintain the product ENWW
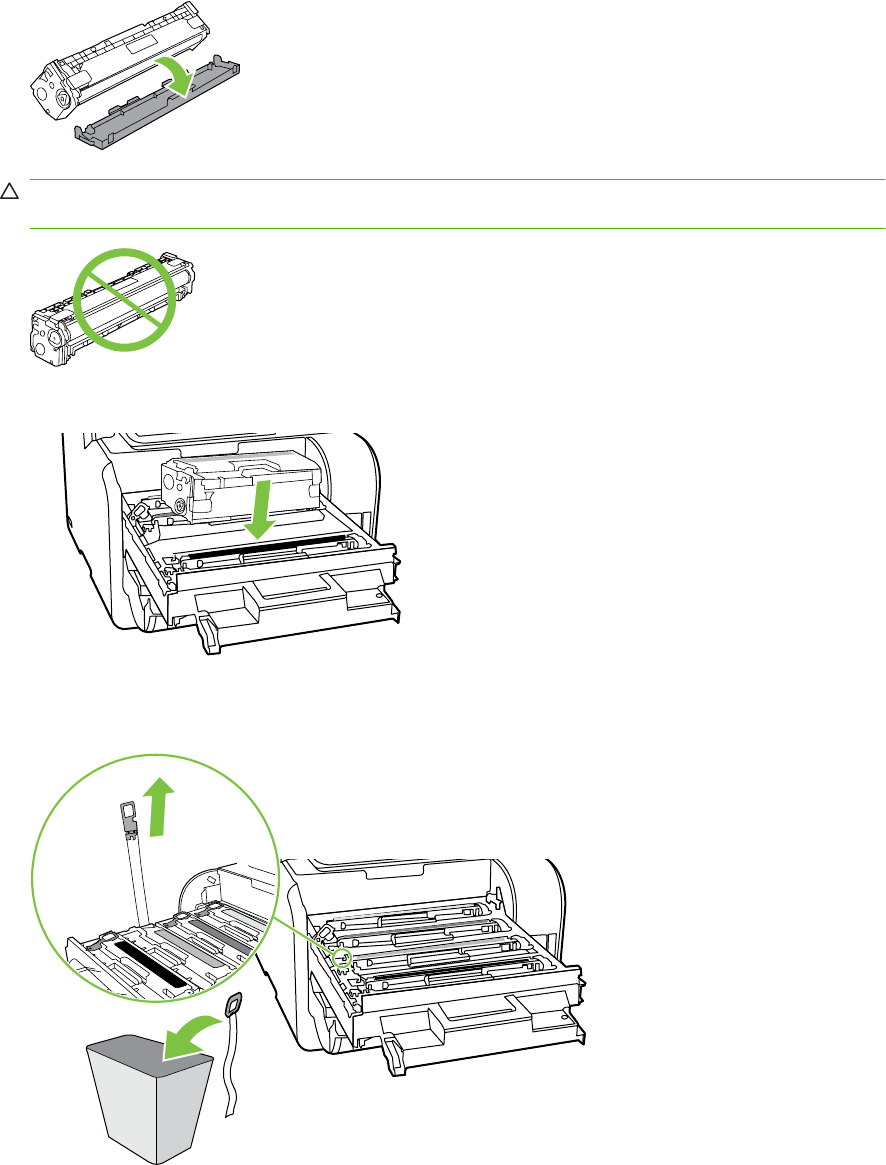
5. Remove the orange, plastic shield from the bottom of the new print cartridge.
CAUTION: Do not touch the imaging drum on the bottom of the print cartridge. Fingerprints on
the imaging drum can cause print-quality problems.
6. Insert the new print cartridge into the product.
7. Pull the tab on the left side of the print cartridge straight up to completely remove the sealing tape.
Discard the sealing tape.
ENWW Manage supplies 69
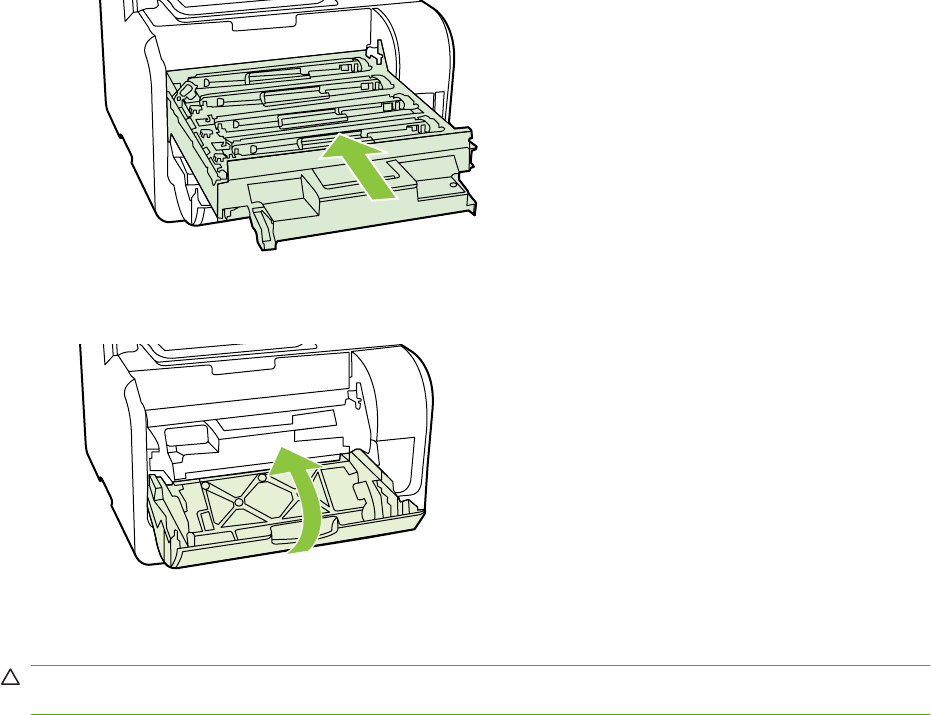
8. Close the print-cartridge drawer.
9. Close the front door.
10. Place the old print cartridge in the box for the new print cartridge. Follow the recycling instructions
that are included in the box.
CAUTION: If toner gets on any clothing, wipe it off with a dry cloth and wash the clothing in cold water.
Hot water sets toner into the fabric.
Memory DIMMs
Information
The product comes with 160 MB of RAM. The product also has one DIMM slot that can be used to add
a 64 MB or 128 MB DIMM. Some available RAM might be used by the product to complete jobs.
70 Chapter 4 Manage and maintain the product ENWW
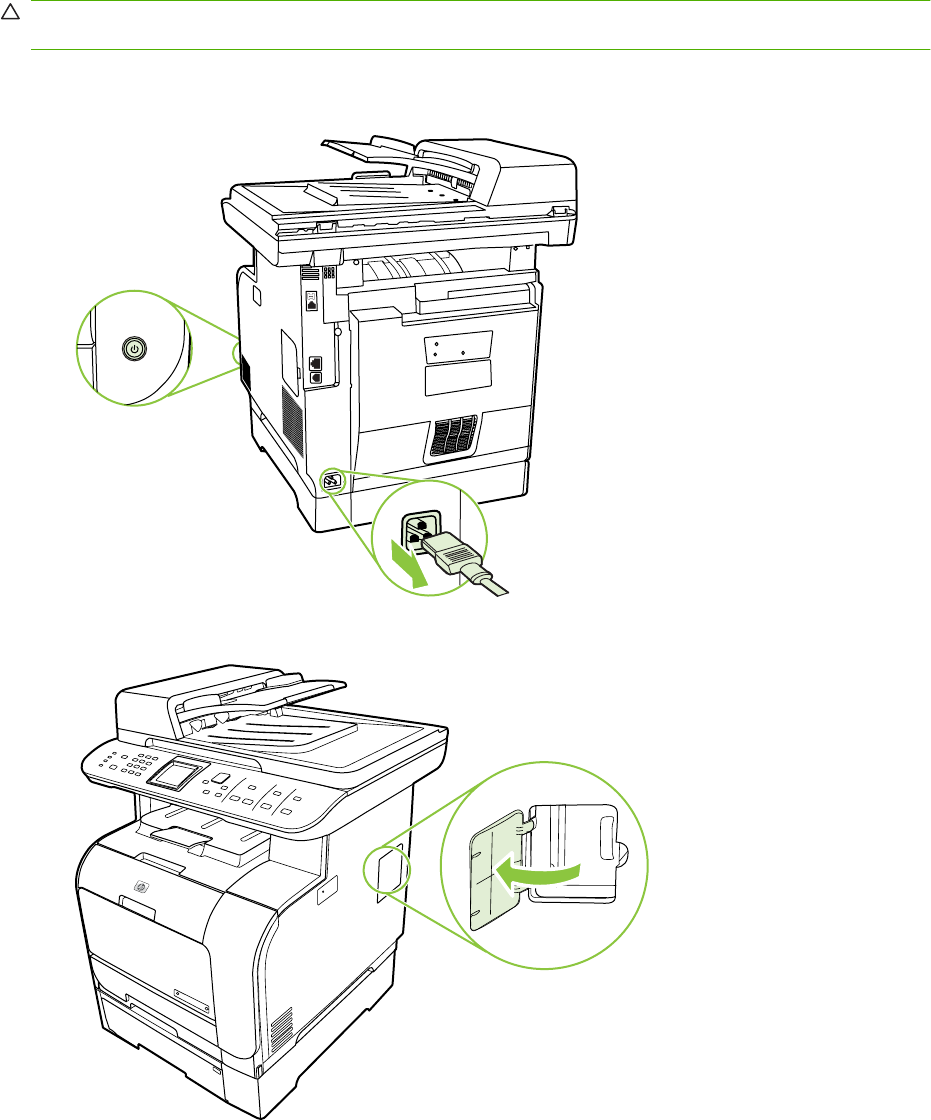
Install a memory DIMM
CAUTION: Handling a DIMM without wearing a grounded, antistatic device might damage the DIMM.
Touch any metal part of the product or other grounded metal before touching the DIMM.
1. Use the power switch to turn off the product, and then unplug all of the cables and cords connected
to the product.
2. Open the DIMM door.
ENWW Manage supplies 71
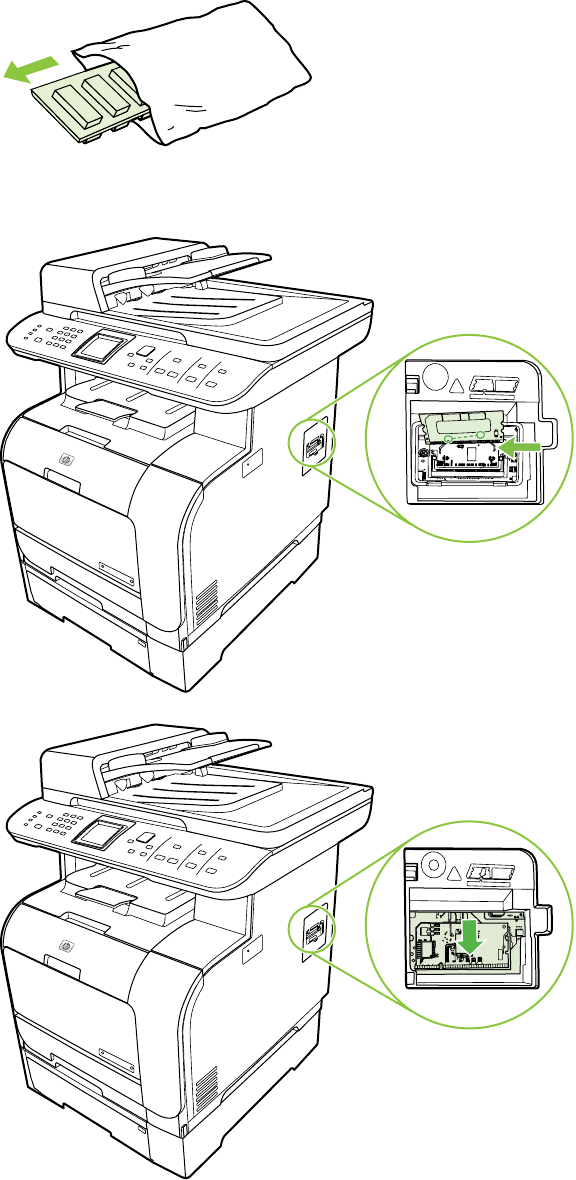
3. Remove the DIMM from the antistatic bag it came in, grasping the DIMM on the top edge.
4. With the gold contacts facing upward, insert the DIMM in the DIMM seat and press the DIMM body
in until the metal retaining pins click.
72 Chapter 4 Manage and maintain the product ENWW
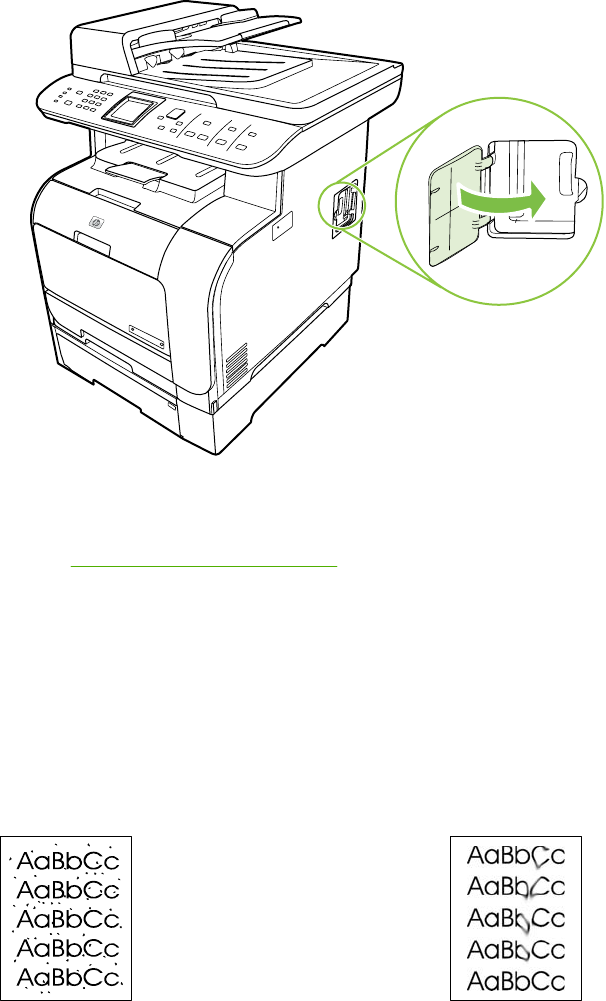
5. Close the DIMM door.
6. Reconnect all cables and cords, and then use the power switch to turn on the product.
7. Print a configuration page, and then verify that the Memory section shows the new memory amount.
See Information pages on page 50.
Clean the product
Clean the paper path
During the printing process, paper, toner, and dust particles can accumulate inside the product. Over
time, this buildup can cause print-quality problems such as toner specks or smearing. This product has
a cleaning mode that can correct and prevent these types of problems.
Specks Smearing
ENWW Manage supplies 73
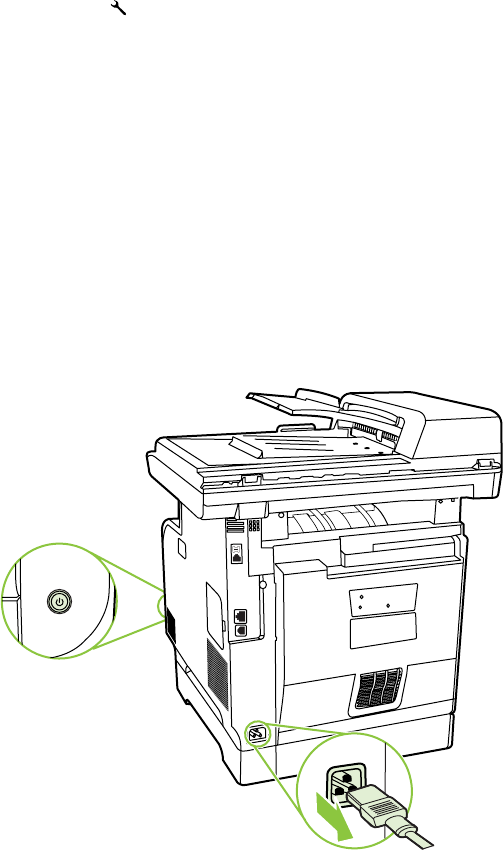
Clean the paper path from HP ToolboxFX
Use HP ToolboxFX to clean the paper path. This is the recommended cleaning method. If you do not
have access to HP ToolboxFX, use the process from the control panel.
1. Make sure that the product is turned on and in the Ready state, and that media is loaded in Tray 1
or Tray 2.
2. Open HP ToolboxFX, click the product, and then click the System Settings tab.
3. Click the Service tab, and then click Start.
A page feeds through the product slowly. Discard the page when the process is completed.
Clean the paper path from the product control panel
If you do not have access to HP ToolboxFX, you can print and use a cleaning page from the product
control panel.
1. Press Setup .
2. Use the arrow buttons to highlight the Service menu, and then press OK.
3. Use the arrow buttons to highlight Cleaning mode, and then press OK.
4. Load plain letter or A4 paper when you are prompted.
5. Press OK again to confirm and begin the cleaning process.
A page feeds through the product slowly. Discard the page when the process is completed.
Clean the automatic document feeder (ADF) pickup roller assembly
If the ADF has trouble feeding documents, clean the ADF pickup roller assembly.
1. Turn off the product and unplug the power cord.
74 Chapter 4 Manage and maintain the product ENWW
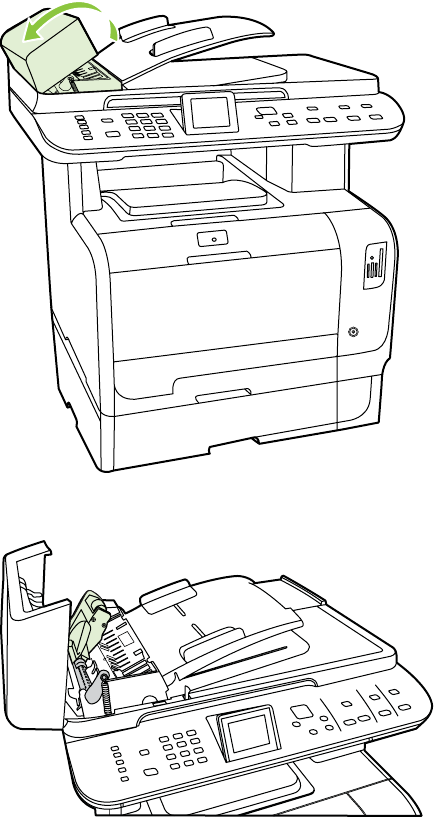
2. Open the ADF cover.
3. Rotate the assembly upward. Wipe it clean and rotate the rollers until the assembly is clean.
ENWW Manage supplies 75
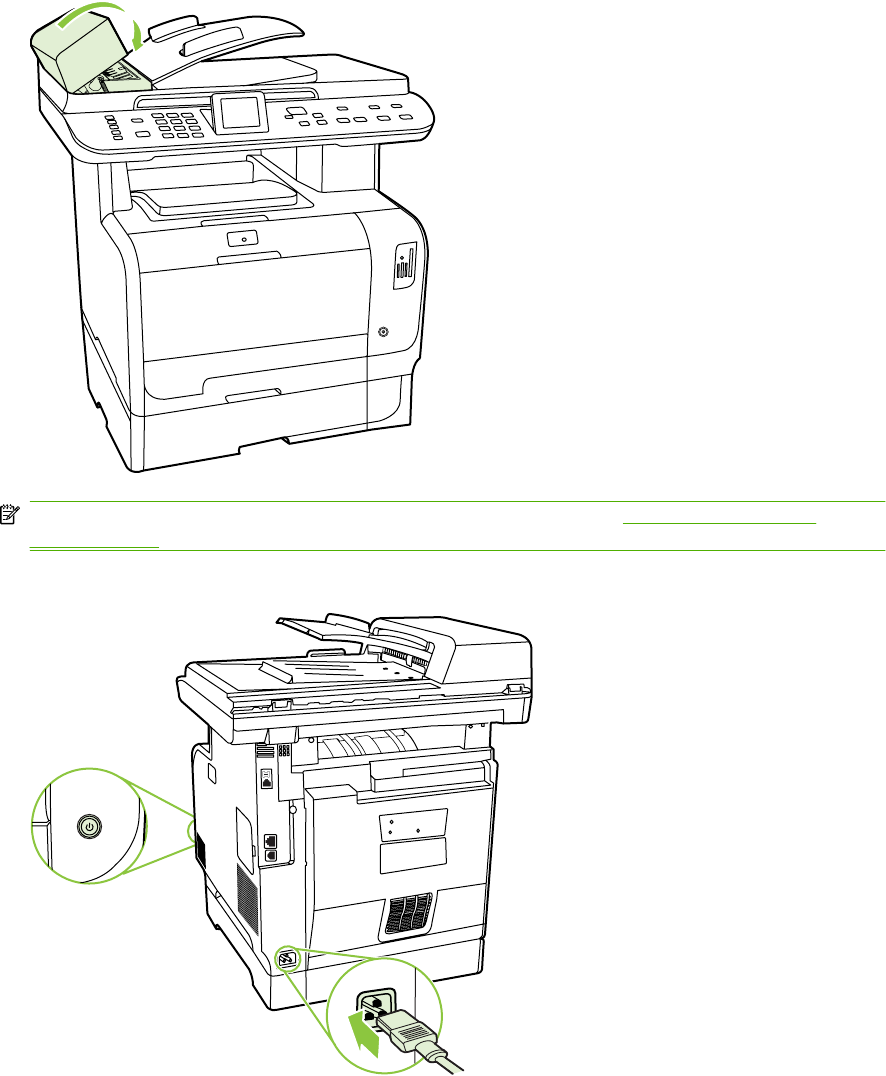
4. Lower the green lever assembly and close the ADF cover.
NOTE: If you are experiencing jams in the ADF, contact HP. See www.hp.com/support/
CM2320series or the support flyer that came in the product box.
5. Plug in the product, and then turn on the product.
Clean the lid backing
Minor debris can accumulate on the white document lid backing that is located underneath the product
lid.
1. Turn off the product, unplug the power cord, and raise the lid.
76 Chapter 4 Manage and maintain the product ENWW
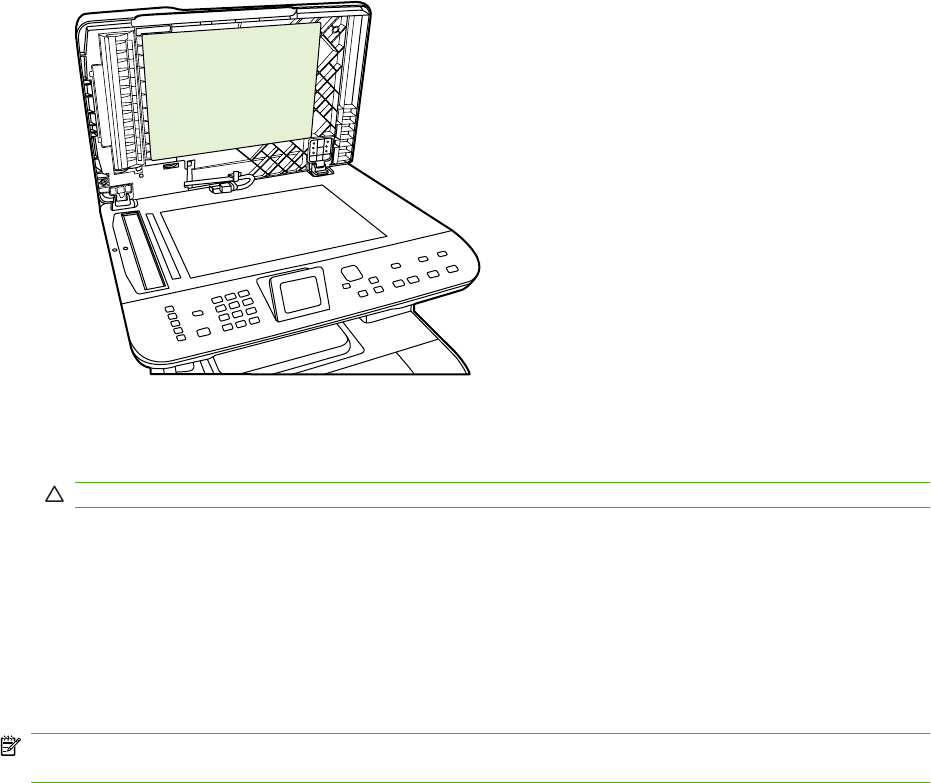
2. Clean the white document lid backing by using a soft cloth or sponge that has been moistened with
a mild soap and warm water. Wash the backing gently to loosen debris; do not scrub the backing.
3. Also, clean the scanner strip next to the ADF scanner glass.
4. Dry the backing by using a chamois or soft cloth.
CAUTION: Do not use paper-based wipes because they might scratch the backing.
5. If this does not clean the backing well enough, repeat the previous steps and use isopropyl alcohol
to dampen the cloth or sponge, and then wipe the backing thoroughly with a damp cloth to remove
any residual alcohol.
Clean the scanner glass
Dirty glass, from fingerprints, smudges, hair, and so on, slows down performance and affects the
accuracy of special features such as fit-to-page and copy.
NOTE: If streaks or other defects appear only on copies produced using the automatic document
feeder (ADF), clean the scanner strip (step 3). It is not necessary to clean the scanner glass.
1. Turn off the product, unplug the power cord from the electrical socket, and raise the lid.
ENWW Manage supplies 77
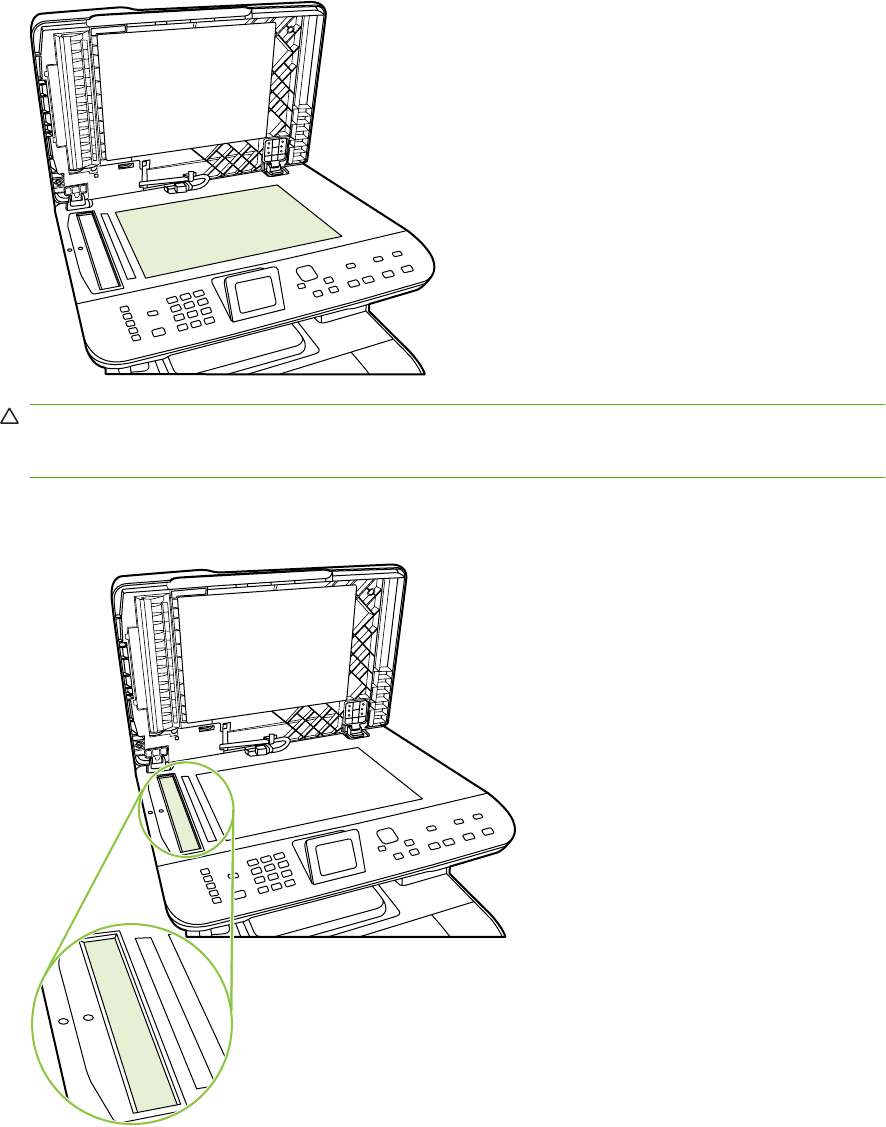
2. Clean the glass by using a soft, lint-free cloth or sponge that has been moistened with nonabrasive
glass cleaner.
CAUTION: Do not use abrasives, acetone, benzene, ammonia, ethyl alcohol, or carbon
tetrachloride on any part of the product; these can damage the product. Do not place liquids directly
on the glass. They might seep under it and damage the product.
3. Clean the scanner strip by using a soft, lint-free cloth or sponge that has been moistened with
nonabrasive glass cleaner..
4. To prevent spotting, dry the glass by using a chamois or cellulose sponge.
78 Chapter 4 Manage and maintain the product ENWW
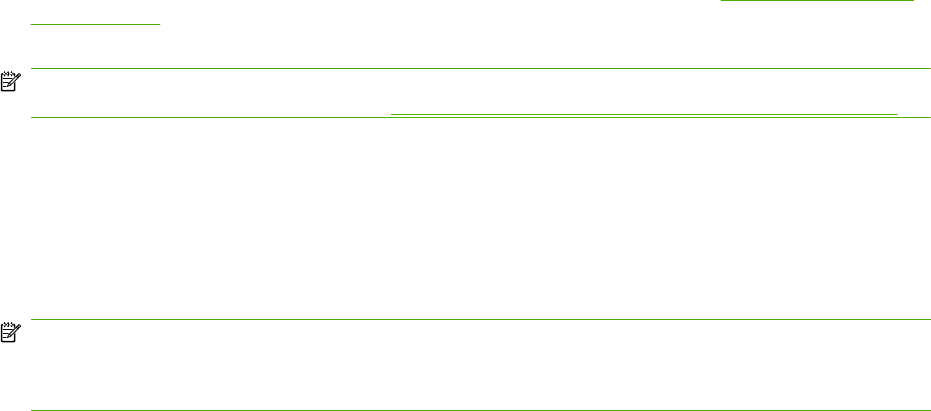
Clean the exterior
Use a soft, damp, lint-free cloth to wipe dust, smudges, and stains off of the exterior of the product.
Firmware updates
Firmware updates and installation instructions for this product are available at www.hp.com/support/
CM2320series. Click Downloads and drivers, click the operating system, and then select the firmware
download for the product.
NOTE: Interrupting the firmware download can cause the product to cease operating. If you
experience a firmware update error, see Recover from a corrupted firmware download on page 79.
Recover from a corrupted firmware download
This process does not require a service call. It can be performed by the customer.
If the product power is interrupted during either the Erasing or Programming phases of the firmware
download, the product will be unusable until the steps below are performed. If power interruption occurs,
the message ready 2 Download appears on the control panel.
NOTE: The product must be attached to the computer via USB, regardless of the current connection
method.
NOTE: The instructions below are for the Microsoft Windows operating system.
If the product power is interrupted during the Erasing or Programming phase, the message ready 2
Download appears, and the Ready and Attention LEDs remain unlit after the product is powered back
on. On the computer, the update tool will not indicate that a failure occurred during the update. The
update tool will show that the download completed and might even have a yellow smiley face at the end
of the progress bar. This is due to the lack of two-way communication between the computer and the
product once the download begins.
1. Close the firmware update tool on the computer if it is still active on the screen, and then turn off
the product.
2. If the product is on a network, connect a USB cable (2 meters or less) from the product to an open
port on the computer. HP recommends that this be a direct connection instead of through a hub.
3. Turn on the product, and then wait for the message ready 2 Download to appear.
4. On the computer, cancel any alerts about a new device being connected.
5. On the computer, open the Printers and Faxes control panel.
6. Right-click the printer driver for the product model that is being updated, and then click
Properties.
7. In the Properties dialog box, click the Ports tab.
8. Note the name of the port that the product is currently connected to for use later when reconnecting
at the end of this process.
9. Click the check box next to USB001. If USB001 is already connected to another USB device, click
USBXXX where “XXX” is the highest-numbered USB device that has a description of “Virtual printer
port for USB”. Using the scroll bars on the right side of the window might be necessary, depending
on the number of devices installed.
ENWW Manage supplies 79

10. Click OK to accept the change and apply the settings.
11. Restart the firmware update tool on the computer, and then select the same product that was just
created.
12. Start the firmware download.
13. Verify that the control panel display shows Erasing and then Programming, indicating that the
update process has begun. Do not interrupt the firmware update process.
14. The product should momentarily show the message Complete. Turn the product off and then back
on. The product will not automatically reboot.
15. When the product reboots, on the computer, cancel any alerts about a new device being connected.
16. Print a configuration page to verify that the update occurred.
17. Return to the Printers and Faxes dialog box, right-click the printer driver for the product model that
is being updated, and then click Properties.
18. In the Properties dialog box, click the Ports tab.
19. Click the check box next to the previous port to which the product was connected before the update
began.
20. Click OK to accept the change and apply the settings.
21. If the product was previously connected via USB, the process is complete. If the product was
network-connected, disconnect the USB cable, and then reconnect the product to the network
cable.
NOTE: In rare instances, the print driver software might need to be uninstalled and reinstalled.
80 Chapter 4 Manage and maintain the product ENWW
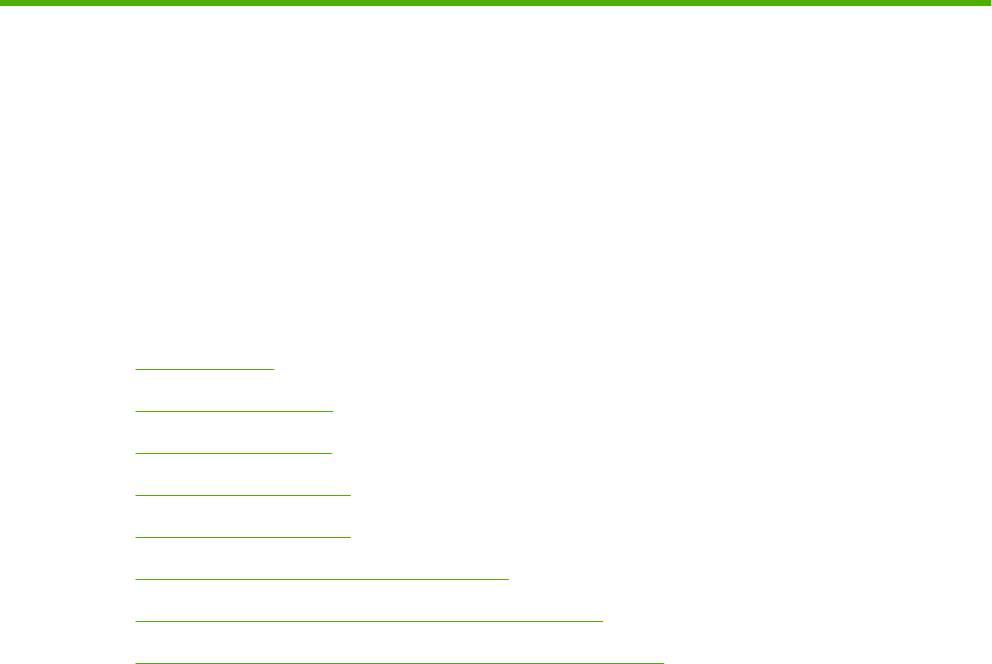
5 Theory of operation
This chapter presents an overview of the major components of the product, and includes a detailed
discussion of the image-formation system.
●Basic operation
●Engine control system
●Laser/scanner system
●Image-formation system
●Pickup-and-feed system
●Scanner and ADF functions and operation
●Memory card system (fax/memory-card models only)
●Fax functions and operation (fax/memory-card models only)
ENWW 81
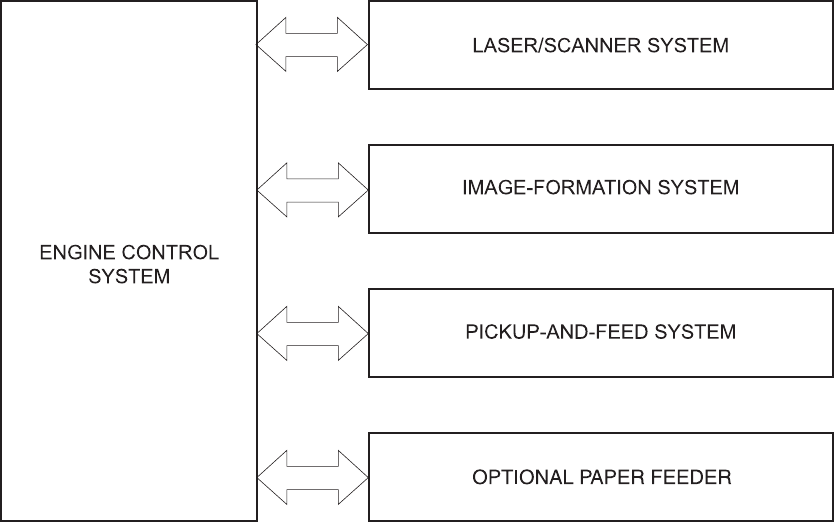
Basic operation
Major product systems
The product includes the following systems:
●Engine control system
●Laser/scanner system
●Image-formation system
●Pickup-and-feed system
Figure 5-1 Product systems
82 Chapter 5 Theory of operation ENWW
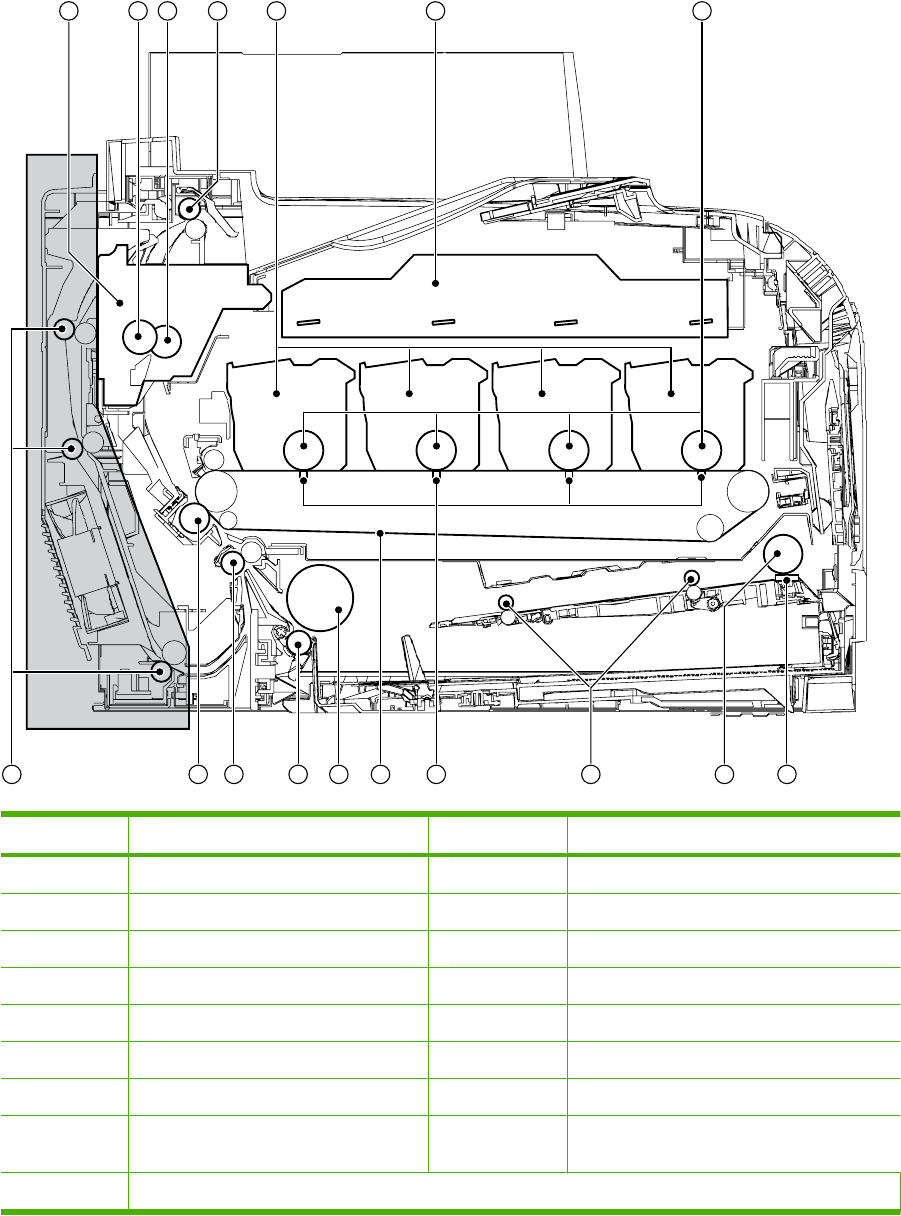
Product components
Figure 5-2 Product components
16 8910111213141517
1 2 3 4 5 6 7
Item Description Item Description
1Fuser unit 10 Multipurpose tray (Tray 1) feed roller
2Pressure roller 11 Primary transfer pad
3Fusing sleeve 12 Intermediate transfer belt (ITB)
4Delivery roller 13 Cassette (Tray 2) pickup roller
5Print cartridge 14 Cassette (Tray 2) separation roller
6Laser/scanner unit 15 Registration roller
7Photosensitive drum 16 Secondary transfer roller
8Multipurpose tray (Tray 1) separation
pad
17 Duplex feed roller (duplex models only)
9Multipurpose tray (Tray 1) pickup roller
ENWW Basic operation 83
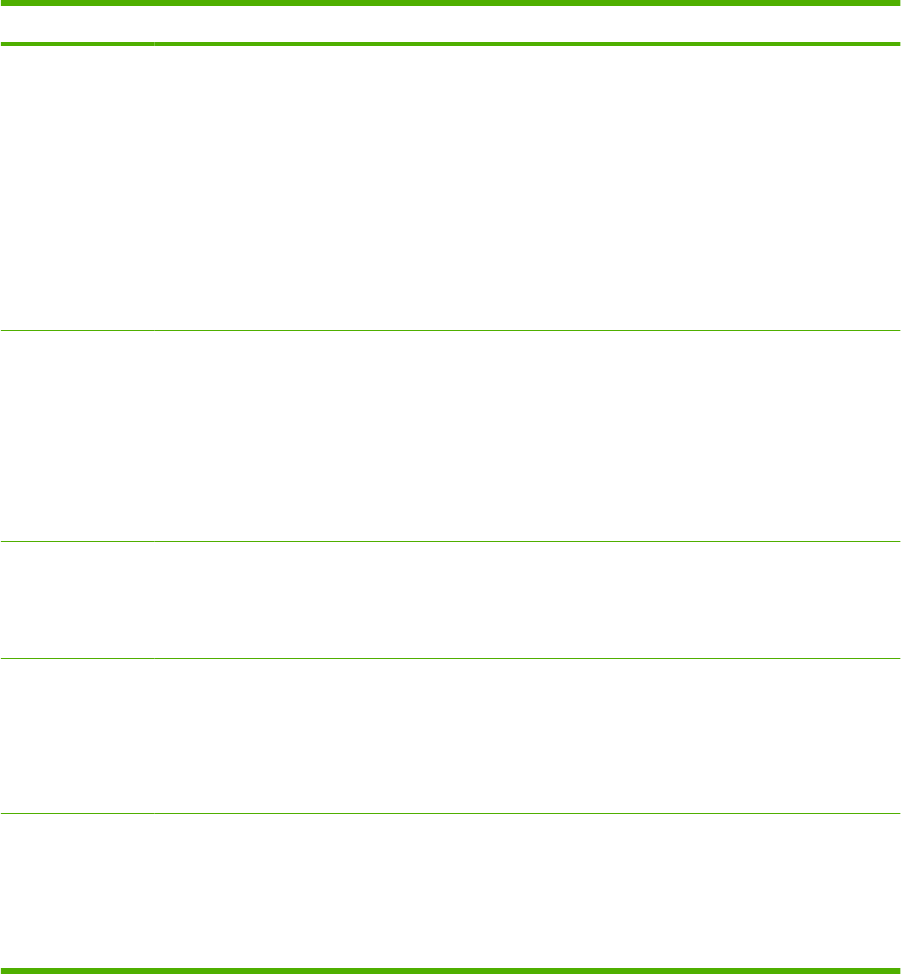
Sequence of operation
Table 5-1 Sequence of operation
Period Duration Operation
WAIT From the time the power is turned on, the
door is closed, or the Sleep mode is
released until the product gets ready for a
print operation.
This period brings the product to printable condition.
During this period the product performs the following actions.
●Detects the pressure roller pressurized status
●Detects the presence of each cartridge and unit
●Determines the home position of the development unit
●Cleans the ITB
●Completes any required calibration, such as color
misregistration and image stabilization control
STBY (Standby
period)
From the end of the WAIT or LSTR period
until either the print command is received
from the formatter or the power is turned
off.
This period maintains the product in printable condition.
During this period the product performs the following actions.
●Enters sleep mode when the formatter sends a sleep
command
●Completes any required calibration, such as color
misregistration and image stabilization control, when
the formatter sends those commands
INTR (Initial
rotation)
From the time the print command is
received from the formatter during the
STBY period until the temperature of the
fuser unit reaches the targeted
temperature.
The product starts each high-voltage bias, laser-scanner unit,
and fuser unit for in preparation for a print operation.
PRINT From the end of INTR period until the last
sheet of media completes the fusing
operation.
The product forms the image on the photosensitive drum
based on the video signals from the formatter, and then
transfers and fuses the toner image to the print media.
The product performs color misregistration control and image
stabilization control at a specified print interval after the
product is turned on.
LSTR (Last
rotation)
From the end of the PRINT period until the
motors stop rotating.
The product moves the last printed sheet out of the product,
and then it stops the laser-scanner unit operation and the
high-voltage biases.
The product enters the INTR period as soon as the LSTR
period is completed, if the formatter sends another print
command.
84 Chapter 5 Theory of operation ENWW
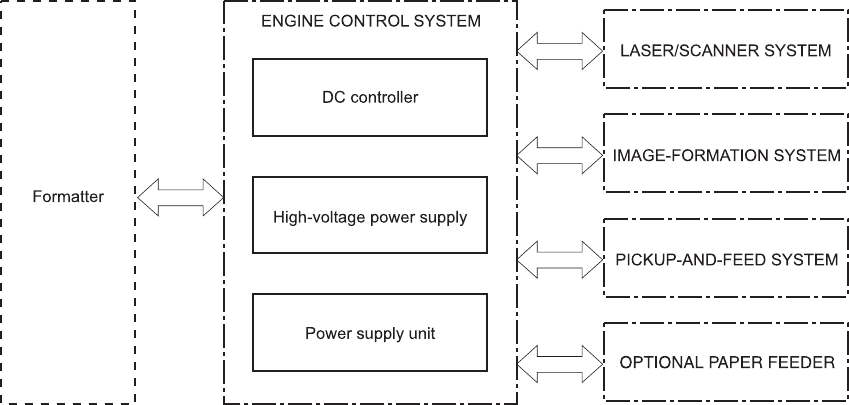
Engine control system
The engine control system coordinates all product functions and drives the other three systems.
The engine control system contains the DC controller, high-voltage power supply PCA, and power
supply unit.
Figure 5-3 Engine control system components
ENWW Engine control system 85
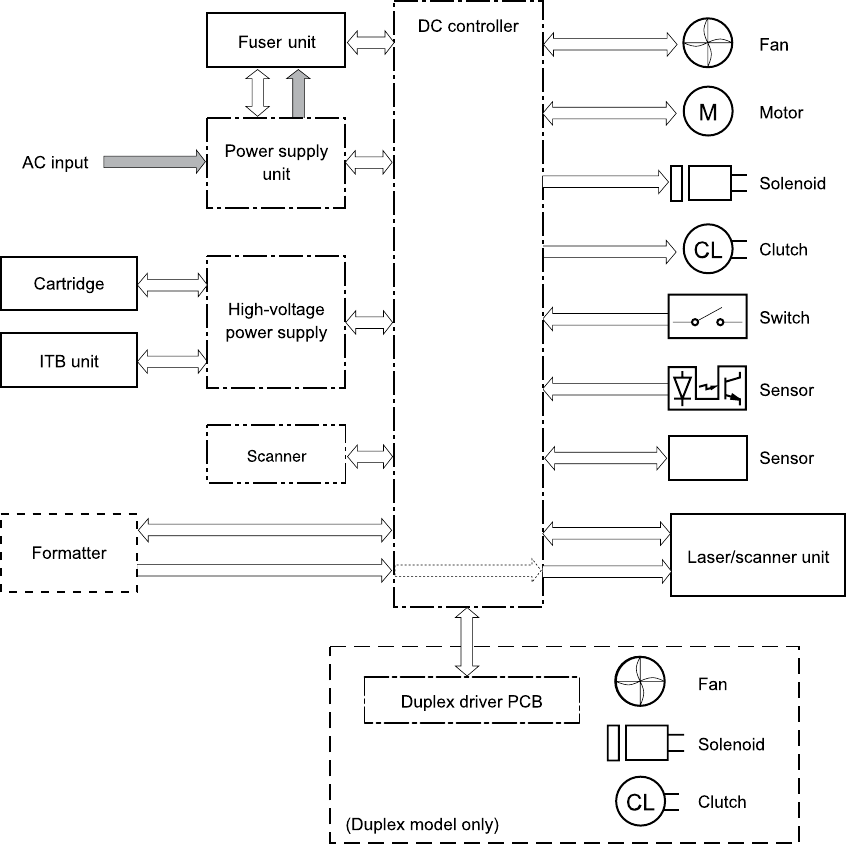
DC controller
The DC controller controls the product operational sequence.
Figure 5-4 DC controller circuit diagram
86 Chapter 5 Theory of operation ENWW
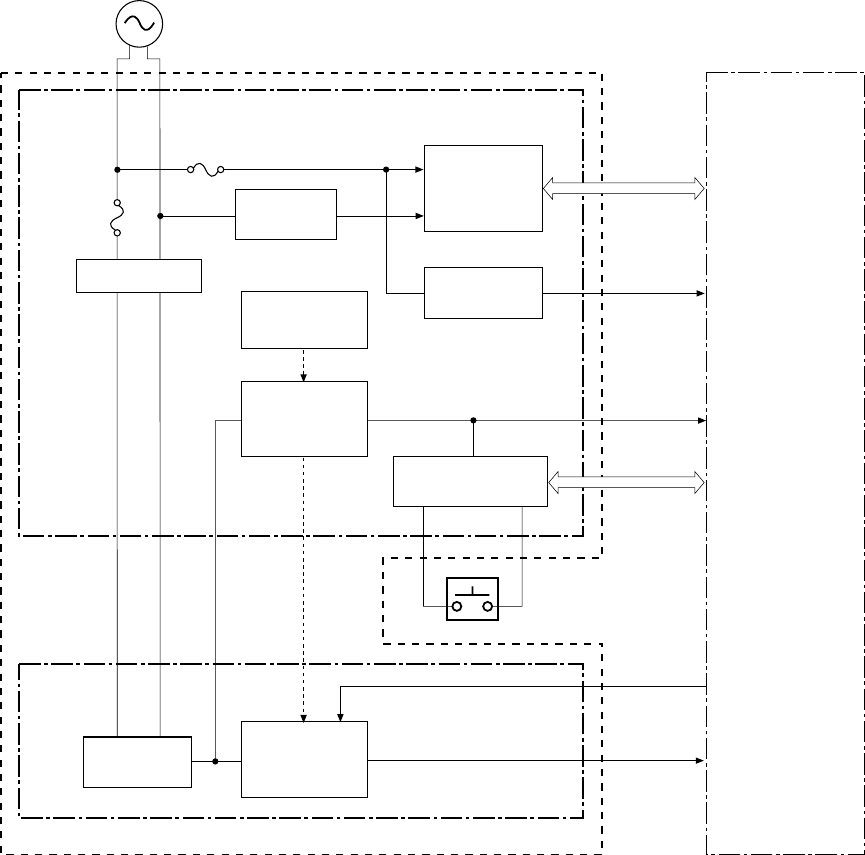
Power supply
The power supply converts AC power from the power receptacle into DC power to cover the DC loads,
and it controls the fuser heater temperature.
Figure 5-5 Power supply
+3.3V
Protection circuit
Rectifying
circuit
Zero crossing
circuit
+24V
ZEROX
PSREM24V
Low-voltage power supply
Power switch
SW3001
AC input
+24V generation
circuit
Noise filter
Fuse
FU2801
DC controller
Fuser power supply
Noise filter
Fuser control
circuit
Fuse
FU2901
Power supply unit
+3.3V generation
circuit
Power switch
control circuit
Protective function
The power supply unit has a protective function against overcurrent and overvoltage to prevent failures
in the power supply circuit. If an overcurrent or overvoltage instance occurs, the system automatically
cuts off the output voltage.
If the DC voltage is not being supplied from the power supply unit, the protective function might be
running. If that is the case, turn off the power switch and unplug the power cord. Do not plug in the power
cord and do not turn the power switch on again until the root cause is found.
In addition, a fuse protects against overcurrent instances. If an overcurrent instance flows into the AC
line, the fuse deactivates and cuts off the power distribution.
ENWW Engine control system 87
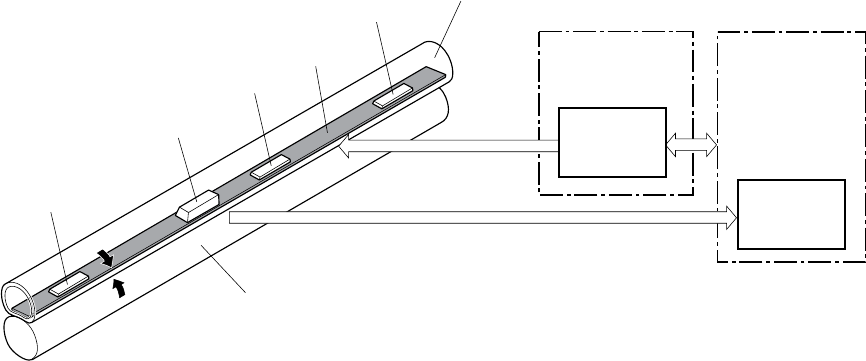
Power-save mode
The power-save mode reduces product power consumption. When the power supply unit receives the
power save (PSREM24V) signal from the DC controller, it stops the power supply from the +24V
generation circuit.
Fuser control
The power supply unit controls the temperature in the fuser unit. The product uses an on-demand fusing
method.
Figure 5-6 Fuser unit
TH801
FU1
H120/H220
TH802
TH803
FUSER HEATER
CONTROL signal
Fuser control
circuit
FUSER TEMPERATURE signal
Pressure roller
Fuser sleeve
DC controllerPower supply unit
Fuser heater
safety circuit
The fuser is composed of the following components.
●Heater (100V model: H120/200V model: H220): Heats the fuser sleeve
●Thermistors
◦Main thermistor (TH801): Detects the center temperature of the fuser heater (contact type)
◦Sub thermistor 1 (TH802): Detects the right side temperature of the fuser heater (contact type)
◦Sub thermistor 2 (TH803): Detects the left side temperature of the fuser heater (contact type)
●Thermal fuse (FU1): Prevents an abnormal temperature rise of the fuser heater
These fuser temperature controls are performed by the fuser control circuit and the fuser heater safety
circuit, which receive commands from the DC controller.
88 Chapter 5 Theory of operation ENWW
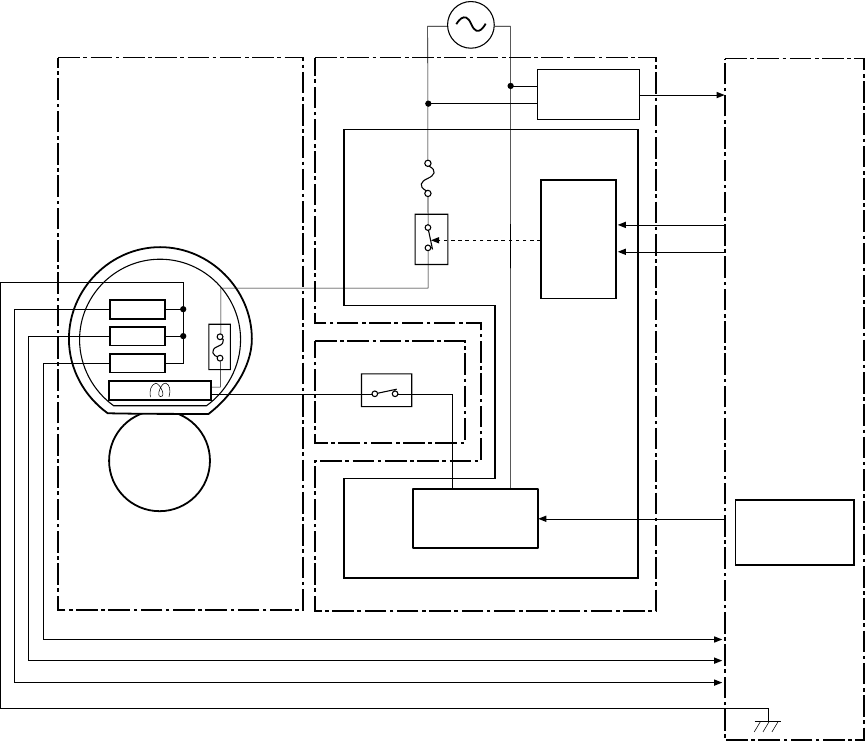
Fuser control circuit
The fuser control circuit maintains the temperature of the fuser heater at its targeted temperature.
Figure 5-7 Fuser control circuit
FU2901
DC controller
Fuser control circuit
FU1: Thermal fuse
TH801: Main thermistor
TH802: Sub thermistor 1
TH803: Sub thermistor 2
Fuser
heater
(H120/H220)
Pressure
roller
Fuser sleeve
Fuser unit
Fuser heater
safety circuit
Fuser heater
control circuit
Relay
drive
circuit
RL2901
TH801
TH802
TH803
Sub power supply
MAINTH
SUBTH
SUB2TH
RLD-
FSRD
/RLD+
RL1
Zero crossing
circuit
ZEROX
Fuser power supply
The DC controller monitors the fuser temperature (MAINTH, SUBTH and SUB2TH) signals and sends
the fuser heater control (FSRD) signal according to the detected temperature. The fuser heater control
circuit controls the fuser heater depending on the signal so that the heater remains at the targeted
temperature.
ENWW Engine control system 89
Fuser protective function
The protective function detects an abnormal temperature rise of the fuser and interrupts power supply
to the fuser heater. The following protective components prevent an abnormal temperature rise of the
fuser heater.
●DC controller: The DC controller monitors the detected temperature of the thermistors. It
deactivates the fuser heater control signal and releases the relay to interrupt the power supply to
the fuser heater under the following conditions.
◦Main thermistor: 253°C (487.4°F) or higher
◦Sub thermistor 1: 273°C (523.4°F) or higher
◦Sub thermistor 2: 273°C (523.4°F) or higher
●Fuser heater safety circuit: The fuser heater safety circuit monitors the detected temperature of
the thermistors. It releases the relay to interrupt the power supply to the fuser heater under the
following conditions.
◦Main thermistor: 320°C (608°F) or higher
◦Sub thermistor 1: 295°C (563°F) or higher
◦Sub thermistor 2: 295°C (563°F) or higher
●Thermal fuse: The thermal fuse blows to interrupt power supply to the fuser heater if the thermal
fuse temperature reaches 228°C (442°F) or higher.
Fuser failure detection
The DC controller determines a fuser unit failure, deactivates the fuser heater control signal, releases
the relay to interrupt power supply to the fuser heater, and then notifies the formatter of a failure state
when it encounters the following conditions.
●Start-up failure conditions
◦The main thermistor temperature does not reach 50°C (122°F) within a specified period of
heater startup during the wait period.
◦The main thermistor temperature does not reach the targeted temperature within a specified
period after the temperature once reaches 50°C (122°F) from the heater startup during the
wait period.
◦The main thermistor temperature does not reach the targeted temperature within a specified
period under the heater temperature control during the initial rotation period.
●Abnormal low temperature conditions
◦The main thermistor temperature remains at 100°C (212°F) or lower for a specified period
under the heater temperature control during the print period.
90 Chapter 5 Theory of operation ENWW
●Abnormal high temperature conditions
◦The main thermistor temperature remains at 253°C (487°F) or higher for a specified period.
◦The temperature of either one of the sub thermistors remains at 273°C (523°F) or higher for
a specified period.
●Fuser heater drive circuit failure
◦The specified count of the zero crossing signal is not detected within a specified period after
the product is turned on.
◦The frequency is out of the specified range (40 to 70 Hz).
ENWW Engine control system 91
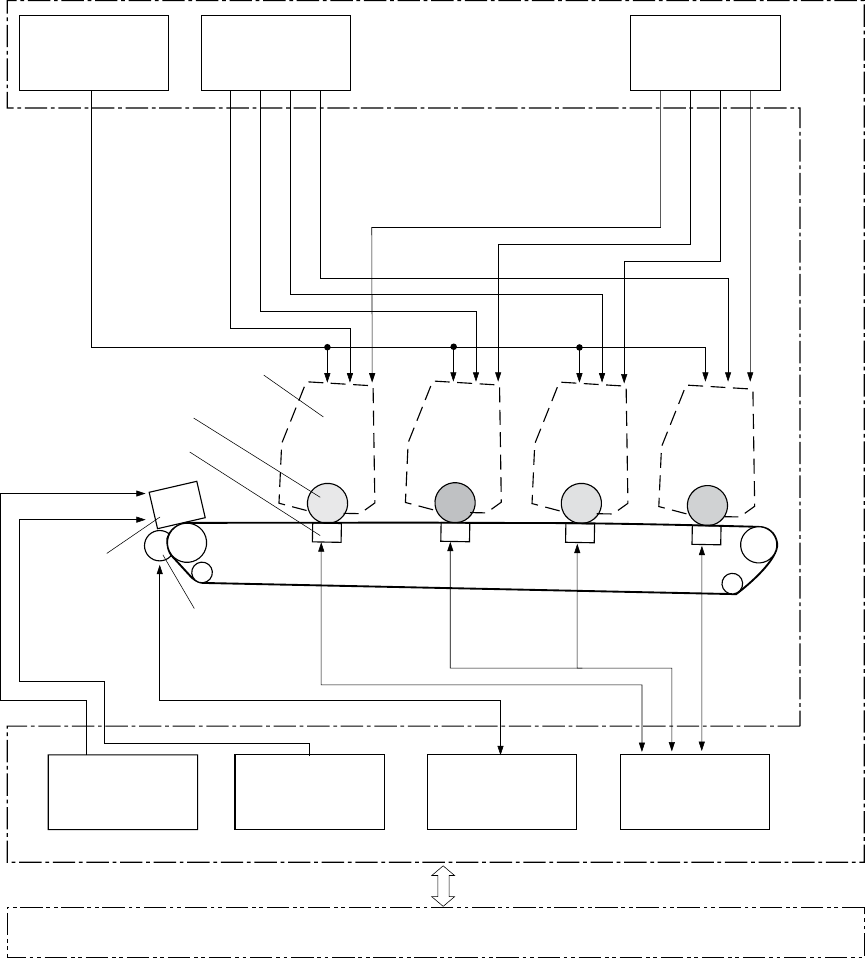
High-voltage power supply
The DC controller controls the high-voltage power supply to generate high-voltage biases. The high-
voltage power supply generates the high-voltage biases that are applied to the primary charging roller,
developing roller, primary transfer pad, secondary transfer roller, and ITB cleaning unit.
Figure 5-8 High-voltage power supply
ITB
TR1_1
TR1_23
TR1_23
TR1_4
TR2
ICLB
BLD1
BLD2
BLD3
BLD4
DEV1
DEV2
DEV3
DEV4
PRI
ICLR
Photosensitive drum
Primary transfer pad
DC controller
High-voltage power supply
Primary charging
bias circuit
Developing bias
circuit
Primary transfer
bias circuit
Cartridge
Secondary transfer
bias circuit
ITB cleaning brush
bias circuit
ITB cleaning roller
bias circuit
Blade bias circuit
Secondary
transfer roller
ITB cleaning unit
YKMC
92 Chapter 5 Theory of operation ENWW
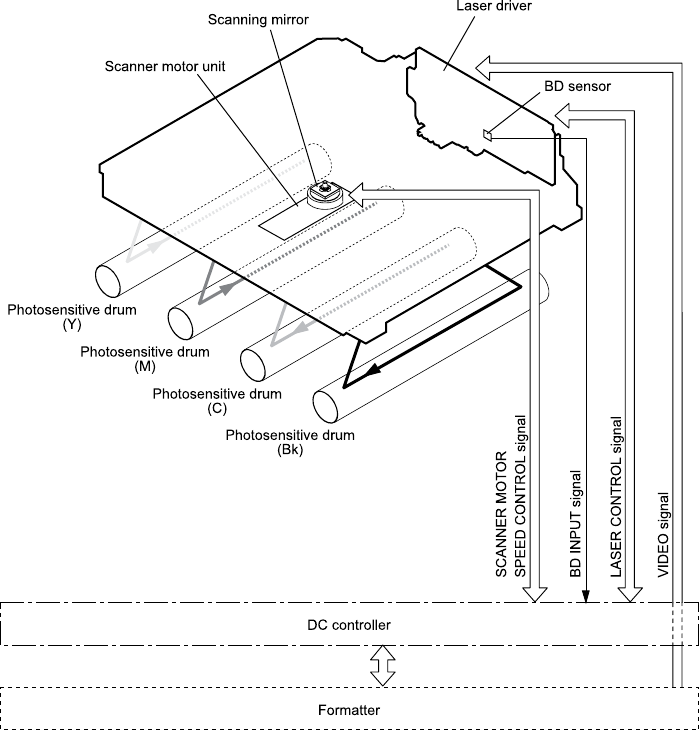
Laser/scanner system
The formatter sends video signals to the DC controller, which controls the laser/scanner. When the laser/
scanner system receives those signals, it converts them to latent images on the photosensitive drum.
Figure 5-9 Laser/scanner system
Laser failure detection
The optical unit failure detection sensor manages the laser/scanner unit failure-detection functions. The
DC controller identifies the laser/scanner unit failure and notifies the formatter if the laser/scanner unit
encounters the following conditions:
●Scanner motor failure
●BD failure
ENWW Laser/scanner system 93
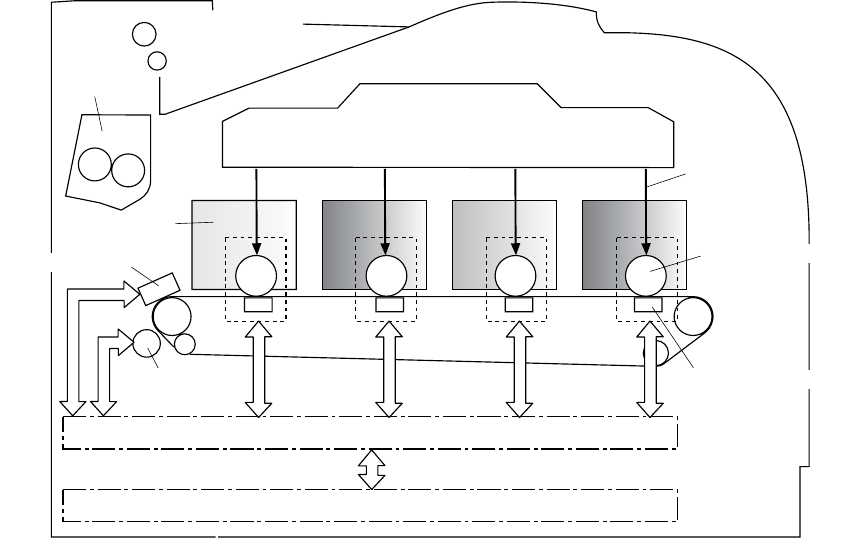
Image-formation system
The image-formation system forms a toner image on media. The product includes four print cartridges
that contain the toner that is used to create the image on the media. Toner is applied in the following
order, using only the colors necessary for a specific image: yellow (Y), magenta (M), cyan (C), and black
(Bk).
The following items are the main components of the image-formation system.
●Print cartridges
●ITB
●Laser scanner
●Fuser
The DC controller controls the laser/scanner unit and the high-voltage power unit to form the toner image
on the ITB according to the video signals, and then to transfer and fuse the image on the media.
Figure 5-10 Image-formation system
DC controller
High-voltage power supply
Laser scanner
Photosensitive drum
Secondary
transfer roller Primary transfer pad
ITB
Cartridge
Laser beam
ITB cleaning unit
Fuser unit
YM C K
94 Chapter 5 Theory of operation ENWW
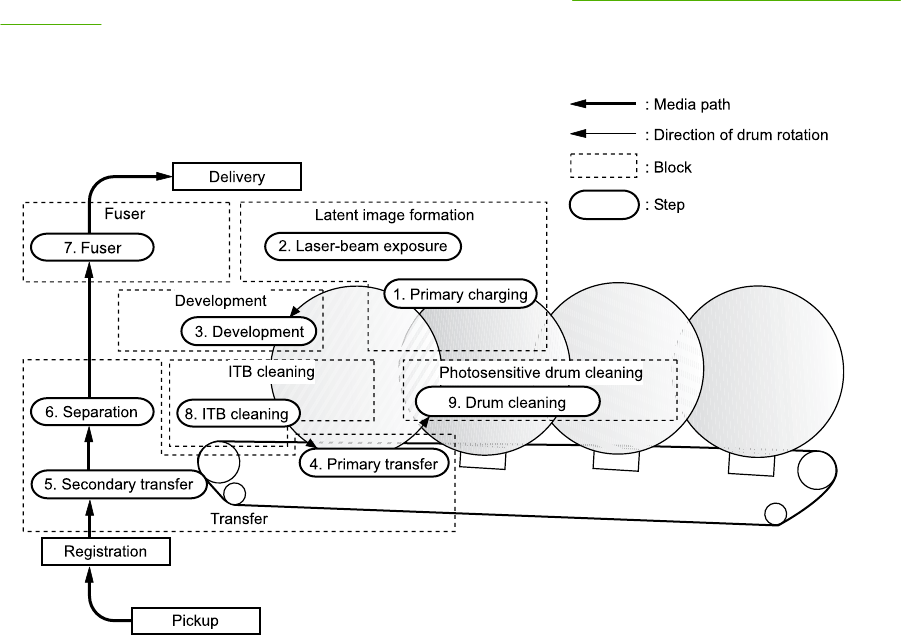
Image-formation process
Laser printing requires the interaction of several different technologies including electronics, optics, and
electrographics to provide a printed page. Each process functions independently and must be
coordinated with the other processes. Image formation consists of the following processes:
●Latent-image formation
◦Primary charging
◦Laser beam exposure
●Development
●Transfer
◦Primary transfer
◦Secondary transfer
◦Separation
●Fuser
●ITB cleaning
●Drum cleaning
These processes are divided into nine steps, which are shown in Figure 5-11 Image-formation process
on page 95 and described in the following sections.
Figure 5-11 Image-formation process
YMC K
ENWW Image-formation system 95
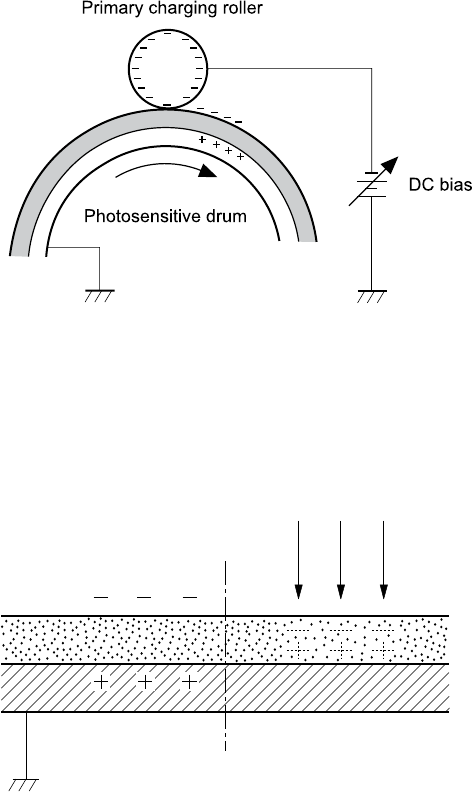
Latent-image formation stage
During the steps that comprise this stage, a latent image is formed by applying a negative charge to the
photosensitive drum. You cannot see this image on the drum.
Step 1: primary charging
A high-voltage DC bias is applied to the primary charging roller, which is made of conductive rubber and
is in contact with the drum surface. As the roller moves across the drum, it applies the negative charge
to that surface.
Figure 5-12 Primary charging
Step 2: laser-beam exposure
The laser beam scans the photosensitive drum to neutralize the negative charge on portions of the drum
surface. An electrostatic latent image is formed where the negative charge was neutralized.
Figure 5-13 Laser-beam exposure
Laser beam
Unexposed area Exposed area
Developing stage
The developing cylinder comes in contact with the photosensitive drum and deposits toner on the
electrostatic latent image.
96 Chapter 5 Theory of operation ENWW
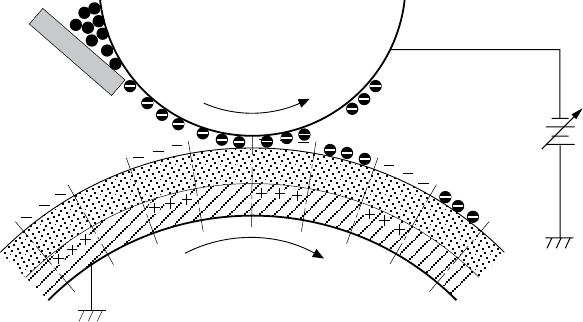
Step 3: development
Toner acquires a negative charge as a result of the friction from the developing cylinder rotating against
the developing blade. When the negatively charged toner comes in contact with the drum, it adheres to
the electrostatic latent image. When the toner is on the drum, the image becomes visible.
Figure 5-14 Development
Developing blade
Developing cylinder
DC negative bias
Photosensitive drum
Unexposed area
Exposed area
Exposed area
Unexposed area
ENWW Image-formation system 97
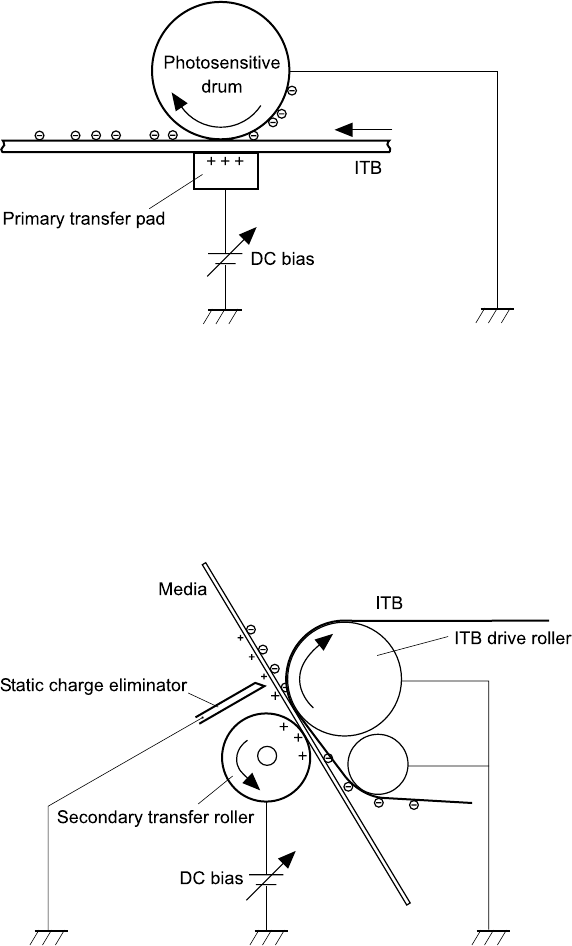
Transfer stage
Step 4: primary transfer
The toner image on the photosensitive drum is transferred to the ITB. The DC positive bias is applied
to the primary transfer pad. The negatively charged toner transfers to the ITB from the drum surface.
Figure 5-15 Primary transfer
Step 5: secondary transfer
The toner image on the ITB is transferred to the print media. The DC positive bias is applied to the
secondary transfer roller. As the media passes between the secondary transfer roller and the ITB, the
toner image is transferred to the media.
Figure 5-16 Secondary transfer
98 Chapter 5 Theory of operation ENWW
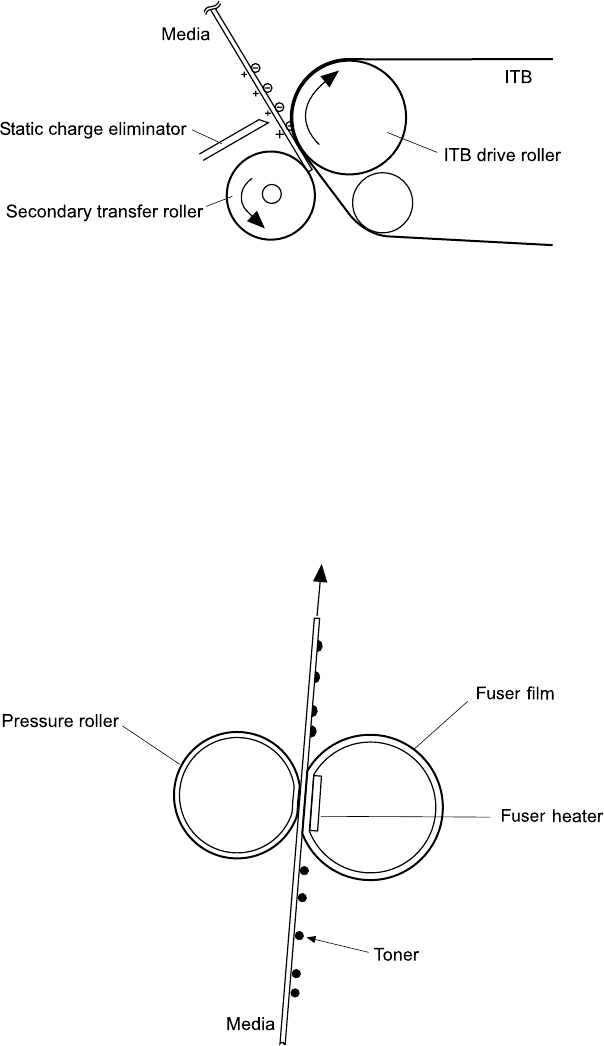
Step 6: separation from the drum
The elasticity of the print media and the curvature of the ITB drive roller cause the media to separate
from the ITB.
Figure 5-17 Separation from the drum
Fusing stage
Until the fusing stage is complete, the image is not permanently affixed to the print media. The toner
can be easily smudged until the heat and pressure of the fusing process fix the image to the sheet.
Step 7: fusing
The product uses an on-demand fusing method to fuse the toner image onto the media. The toner image
is permanently affixed to the print media by the heat and pressure.
Figure 5-18 Fusing
ENWW Image-formation system 99
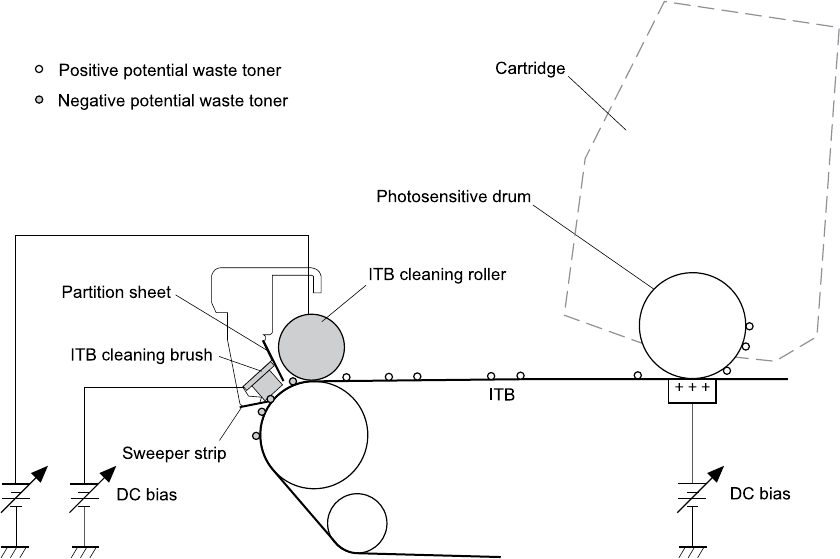
ITB cleaning stage
Step 8: ITB cleaning
The ITB cleaning roller and the cleaning brush are applied with DC positive bias to charge the residual
toner positive. Because the primary transfer pad is also applied with DC positive bias, the positively
charged residual toner is reverse-transferred to the photosensitive drum from the ITB surface.
Figure 5-19 ITB cleaning
100 Chapter 5 Theory of operation ENWW
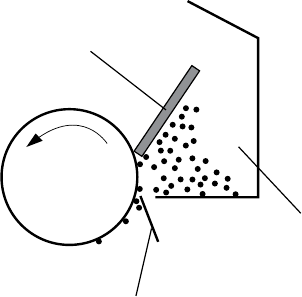
Drum cleaning stage
Not all of the toner is removed from the photosensitive drum during the transfer stage. During the
cleaning stage, the residual, or waste, toner is cleared from the drum surface to prepare the surface for
the next latent-image formation.
Step 9: drum cleaning
The cleaning blade scrapes the residual toner off the surface of the photosensitive drum and deposits
it in the waste-toner container. The drum is now clear, and is ready for the next image-formation process.
Figure 5-20 Drum cleaning
Sweeper strip
Waste toner container
Photosensitive
drum
Cleaning blade
Developing roller engagement/disengagement control
The developing roller engagement/disengagement control engages the required developing roller with
the photosensitive drum according to the print mode—full-color mode or monochrome mode.
The necessary developing roller is engaged with the photosensitive drum only when required, preventing
a deterioration of the drums and making maximum use of the life. The engagement/disengagement of
the developing roller is controlled by the DC controller rotating the main motor and changing the direction
of the developing disengagement cam. The DC controller controls the developing roller state, whether
engaged or disengaged, by detecting the output signal from the developing home position sensor.
All four color developing rollers disengage from the photosensitive drums when the product is turned
on and when a print operation is completed. The color developing rollers engage with the photosensitive
drums when the full-color mode is designated. Only the black developing roller engages with the
photosensitive drum when the monochrome mode is designated.
The DC controller determines an abnormality of the developing roller engagement/disengagement
function and notifies the formatter when it does not sense the signal from the developing home-position
sensor for a specified period during the developing roller engagement/disengagement operation.
ENWW Image-formation system 101
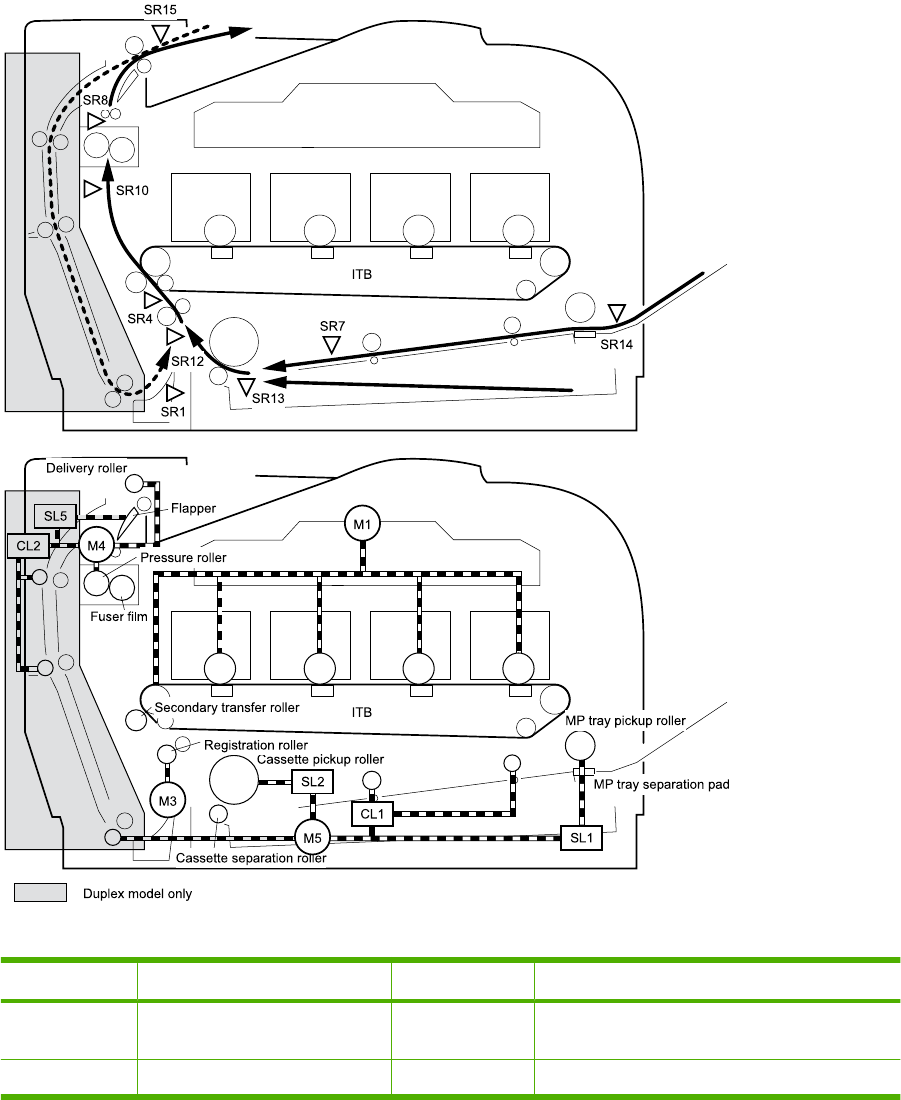
Pickup-and-feed system
The pickup-and-feed system picks up and feeds the print media. It consists of several types of feed
rollers.
Figure 5-21 Pickup-and-feed system
YMCK
YMC K
Number Description Number Description
SR1 Paper feeder pre-registration
sensor
M1 Drum motor
SR4 Registration sensor M3 Registration motor
102 Chapter 5 Theory of operation ENWW
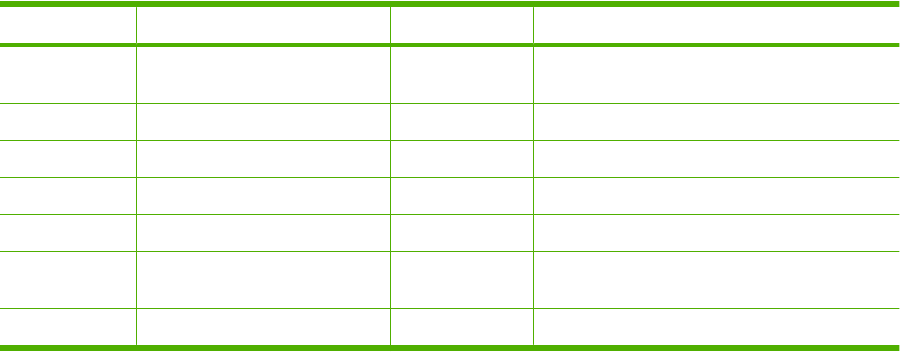
Number Description Number Description
SR7 Multipurpose tray pre-registration
sensor
M4 Fuser motor
SR8 Fuser delivery sensor M5 Pickup motor
SR10 Loop sensor SL1 Multipurpose tray pickup solenoid
SR12 Pre-registration sensor SL2 Cassette pickup solenoid
SR13 Cassette media-presence sensor SL5 Duplex reverse solenoid (duplex models only)
SR14 Multipurpose tray media-
presence sensor
CL1 Multipurpose tray feed clutch
SR15 Output bin media full sensor CL2 Duplex feed clutch (duplex models only)
ENWW Pickup-and-feed system 103
Jam detection
The product uses the following sensors to detect the presence of media and to check whether media is
being fed correctly or has jammed:
●Registration sensor
●Multipurpose tray pre-registration sensor
●Fuser delivery sensor
●Loop sensor
●Pre-registration sensor
●Cassette media-presence sensor
●Multipurpose tray media-presence sensor
●Output bin media full sensor
●Paper feeder pre-registration sensor
The product detects the following jams:
●Pickup delay jam
●Pickup stationary jam
●Delivery delay jam
●Delivery stationary jam
●Fuser wrapping jam
●Residual media jam
●Duplex re-pickup unit jam (duplex models only)
Pad transfer
The product uses a pad transfer method for the primary transfer operation. The pad transfer method
stabilizes an image compared to the conventional separation roller method. The wider nip width between
the transfer pad and the photosensitive drum improves the transfer performance.
Multiple-feed prevention
The product uses a separation roller to prevent multiple sheets of media from entering the product. The
paper separation roller follows the rotational direction of the pickup roller because it does not have its
own driving force.
●Normal-feed: The separation roller is driven by the pickup roller through a sheet of print media.
That is, the separation roller rotates in the media feed direction.
●Multiple-feed: The low friction force between the sheets weakens the rotational force from the
pickup roller. The separation roller is limited in its rotational force and it does not rotate with such
a weak driving force from the pickup roller. Since the separation roller does not rotate, the multiple
sheets do not feed into the product.
104 Chapter 5 Theory of operation ENWW
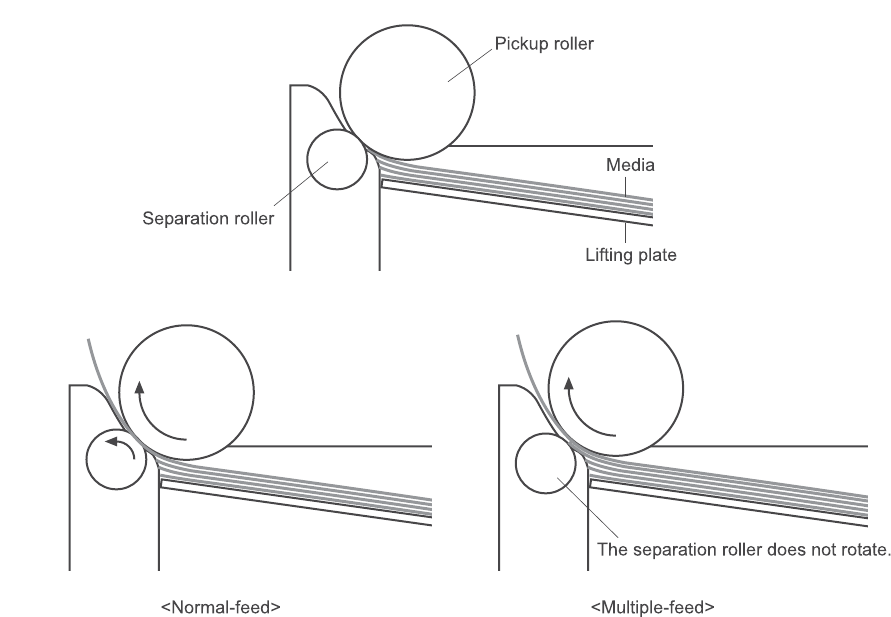
The following figure illustrates the mechanism of the multiple-feed prevention.
Figure 5-22 Multiple-feed prevention
ENWW Pickup-and-feed system 105
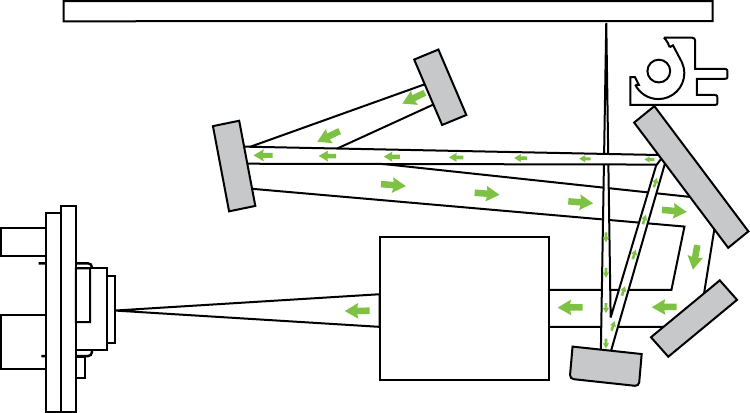
Scanner and ADF functions and operation
The following sections describe how the document scanner and the automatic document feeder (ADF)
function.
Scanner functions
The scanner uses a light source, a color-separation method, and a charge-coupled device (CCD) array
to collect optical information about the document and transform that into an image file. The scanner
consists of these elements:
●A lamp (LED)
●Five mirrors and a lens
●A CCD
Figure 5-23 Optical system
Lens
LED Lam p
Scanner Glass
600 ppi CCD
The scanner lamp illuminates a small strip of the document (called the raster line). The mirrors direct
the light through the lens to the CCD. The CCD senses and records the light, creating an analog
representation of the raster line. If the ADF is being used, the document then advances in the ADF to
the next raster line. If the flatbed is being used, the scanner module advances to the next raster line.
This advancing and collection process continues to the end of the sheet.
The image data is collected in the motor controller board, where it is processed and sent to the formatter.
The formatter then handles the image data, outputting it as a copy, sending it through the fax card as a
fax, or directing it to the computer as scanner output.
The image data collected is 600 pixels per inch (ppi). Each pixel has 8 bits for each of the three colors
(256 gray scale levels for each color), or a total of 24 bits per pixel (24-bit color).
106 Chapter 5 Theory of operation ENWW
Scanner operation
At power-on and periodically at other times, the scanner assembly moves systematically to locate its
home position. It then calibrates to a white strip located under the glass at the left end of the scan tub.
If the product detects a document in the ADF when a copy or scan is initiated (from the software or the
control panel), the scan module moves to the left side of the scan tub and stops. The image is acquired
as the paper is fed through the ADF past the scanner module.
If no document is detected in the ADF, the scan module acquires the image from the flatbed glass while
slowly moving within the scan tub.
ADF operation
Standby (paper-loading) mode: In standby mode, the pickup roller is up and the stack-stop is down,
preventing the user from inserting the original document too far. When a document is inserted correctly,
the paper-present sensor detects its presence.
The standard operation of the ADF consists of the pick, feed, and lift steps.
Pick: When it receives a copy or scan command, the ADF motor engages the gear train to lower the
pickup-roller assembly and raise the stack-stop. The first roller, called the pre-pick roller, moves the top
few sheets forward into the ADF. The next roller is the pickup roller. This roller contacts the ADF
separation pad, which separates multiple pages into single sheets.
Feed: The single sheet continues through the path. Along the way, the form sensor, which is a set
distance from the ADF glass, detects the sheet. This alerts the scanner to start when the page reaches
the glass. The scanner acquires the image, one raster line at a time, until it detects the end of the page.
The page is then ejected. The pick and feed steps are repeated as long as paper is detected in the ADF
input tray.
Lift: When no more paper is detected in the ADF input tray and the form sensor detects the trailing edge
of the last page, the last sheet is ejected and the motor turns in a sequence that lifts the pick-roller
assembly to standby (paper-loading) mode again.
The ADF will not function when the ADF cover is open. The paper path is incomplete if the ADF cover
is lifted from the glass.
When the product duplexes from the ADF, the paper passes through the ADF three times. During the
second instance, the product reverses the page orientation and then scans it. During the third instance,
the product returns the page to the original orientation.
ENWW Scanner and ADF functions and operation 107
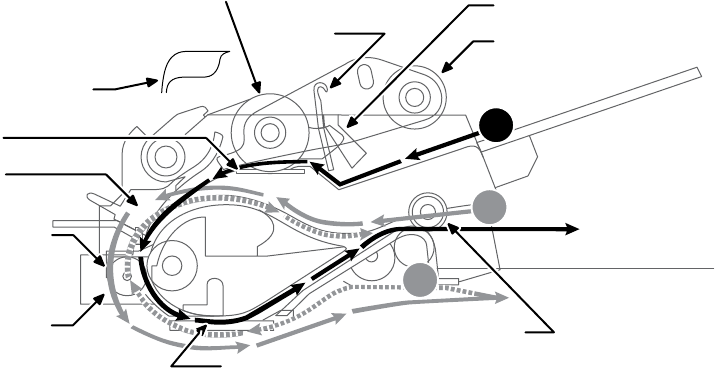
ADF paper path and ADF sensors
The following diagram shows the ADF paper path during a two-sided (duplexed) copy job. The paper
enters the product from the ADF input tray and passes through the paper path for the first time (callout
1). The product then pulls the paper back through the path (callout 2) in order to reorient the page and
scan the second side. The paper then travels back to the end of the paper path, where it is pulled in one
more time to travel through the paper path (callout 3) in order for the product to reorient the page again
before sending it out of the paper path and pulling in the next sheet.
Figure 5-24 ADF paper path routes during duplex job
PAGE EJECTS FULLY
OUTPUT AREA
ADF glass
Prescan rollers
INPUT TRAY
Form sensor
Postscan
rollers
Pre-pick roller
Picks top sheet
Stack stop
Pick roller Paper present sensor
ADF door
open flag
Separation pad
Cleanout
1
2
3
The paper-present sensor determines if paper is in the ADF. The form sensor detects the top and bottom
edges of the document. One other sensor detects an open ADF door.
108 Chapter 5 Theory of operation ENWW
ADF jam detection
The ADF has two sensors that detect paper. The paper-present sensor detects the presence of media
in the ADF input tray. The form sensor detects media moving through the ADF. If a jam is detected, the
ADF immediately stops the paper feeding and a jam message appears on the control-panel display.
A jam can be detected under any of the following conditions:
●Document-feeder jam. When documents are detected in the ADF input tray, and a command to
copy, scan or fax is received, the scan module travels to the left side of the scan assembly and
stops beneath the ADF scanner glass. The ADF then attempts three times, or for about ten
seconds, to advance the paper to the form sensor. If the paper does not advance, the scan module
travels back to the home position on the right side of the scanner assembly. The message
Document feeder mispick. Reload. appears on the control-panel display.
●Long-document jam. If the paper has advanced to trigger the form sensor, but the trailing edge
is not detected within the time allowed for a 381-mm (15-inch) document (the maximum allowable
page length for the ADF), the scanner returns to the home position on the right side of the scanner
assembly. The message Doc feeder jam. Clear, Reload. appears on the control-panel display.
●Stall jam. When a page that is less than 381 mm (15 inches) long has advanced to the form sensor
but has not left it within the expected time, the paper has probably stalled or jammed. The scanner
returns to the home position on the right side of the scanner assembly. The message Doc feeder
jam. Clear, Reload. appears on the control-panel display.
●Other. If the paper stops in the ADF and the scan module remains under the ADF scanner glass,
an internal firmware error has probably occurred. This is usually remedied by cycling the power.
ENWW Scanner and ADF functions and operation 109
Memory card system (fax/memory-card models only)
The memory card reader consists of slots where the following memory cards can be inserted:
●CompactFlash
●Memory Stick
●Memory Stick PRO
●Secure Digital
●MultiMediaCard
●xD
Only one card can be installed at a time.
The green memory card LED will blink when the product is reading the installed memory card. The files
present on the memory card can be accessed from a computer by using the mounted drive for a directly
connected host, or by using the product IP address from a networked computer. For example:
\\192.168.2.12\memory_card
Any .jpg files on the card can be printed directly from the product control panel. Pages also can be
scanned and saved to the memory card directly from the control panel.
110 Chapter 5 Theory of operation ENWW
Fax functions and operation (fax/memory-card models
only)
The following sections describe the product fax capabilities.
Computer and network security features
The product can send and receive fax data over telephone lines that conform to public switch telephone
network (PSTN) standards. The secure fax protocols make it impossible for computer viruses to be
transferred from the telephone line to a computer or network.
The following product features prevent virus transmission:
●No direct connection exists between the fax line and any devices that are connected to the USB
or Ethernet ports.
●The internal firmware cannot be modified through the fax connection.
●All fax communications go through the fax subsystem, which does not use Internet data-exchange
protocols.
PSTN operation
The PSTN operates through a central office (CO) that generates a constant voltage on the TIP and
RING wires (48 V, usually). A device goes on-hook by connecting impedance (such as 600 ohms for
the U.S.) across the TIP and RING so that a line current can flow. The CO can detect this current and
can send impulses like dial tones. The product generates more signaling tones, such as dialing digits,
to tell the CO how to connect the call. The product can also detect tones, such as a busy tone from the
CO, that tell it how to behave.
When the call is finally connected, the CO behaves like a piece of wire connecting the sender and
receiver. This is the period during which all of the fax signaling and data transfer occurs. When a call is
completed, the circuit opens again and the line-current flow ceases, removing the CO connection from
both the sender and the receiver.
On most phone systems, the TIP and RING wires appear on pins 3 and 4 of the RJ-11 modular jack
(the one on the fax card). These two wires do not have to be polarized because all the equipment works
with either TIP or RING on pin 3 and the other wire on pin 4. This means that cables of either polarity
can interconnect and will still work.
These basic functions of PSTN operation are assumed in the design of the fax subsystem. The product
generates and detects the signaling tones, currents, and data signals that are required to transmit and
receive faxes on the PSTN.
Receive faxes when you hear fax tones
In general, incoming faxes to the product are automatically received. However, if other devices are
connected to the same phone line, the product might not be set to answer automatically.
If the product is connected to a phone line that receives both fax and phone calls, and you hear fax
tones when you answer the extension phone, receive the fax in one of two ways:
●If you are near the product, press Start Fax on the control panel.
●Press 1-2-3 in sequence on the extension phone keypad, listen for fax transmission sounds, and
then hang up.
ENWW Fax functions and operation (fax/memory-card models only) 111
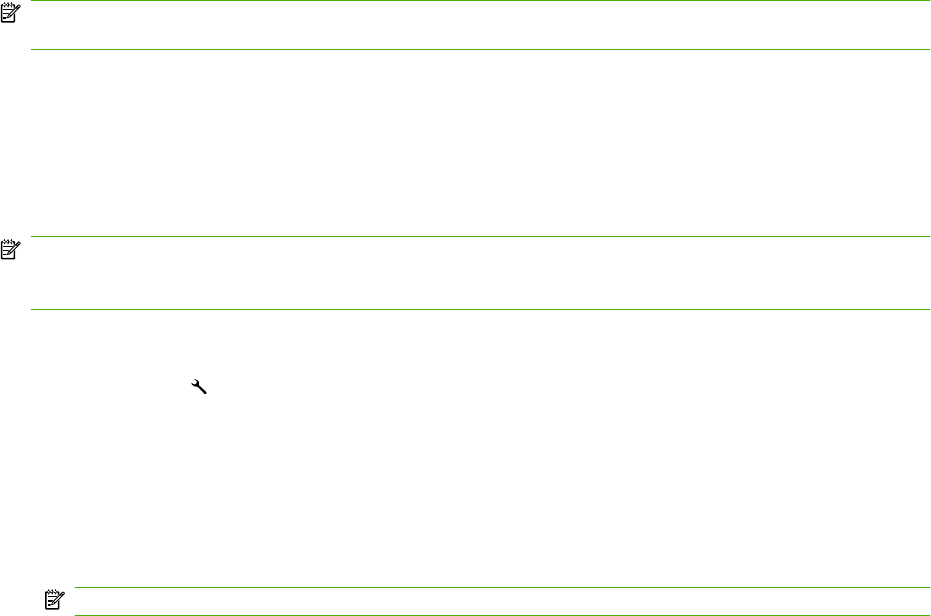
NOTE: In order for the 1-2-3 sequence to work, the extension phone setting must be set to On in the
Fax setup menu.
Distinctive ring function
Distinctive ring is a service that a telephone company provides. The distinctive ring service allows three
phone numbers to be assigned to one phone line. Each phone number has a distinctive ring. The first
phone number has a single ring, the second phone number has a double ring, and the third phone
number has a triple ring.
NOTE: The product has not been tested with all of the distinctive-ring services that telephone
companies provide in all countries/regions. HP does not guarantee that the distinctive-ring function will
operate correctly in all countries/regions. Contact the local phone service provider for assistance.
Set up the distinctive ring function
1. Press Setup .
2. Use the arrow buttons to select Fax setup, and then press OK.
3. Use the arrow buttons to select Basic setup, and then press OK.
4. Use the arrow buttons to select Distinctive Ring, and then press OK.
5. Use the arrow buttons to select one of the following options:
NOTE: The control-panel display might show some of these options as abbreviations.
●All Rings (default setting)
●Single
●Double
●Triple
●Double and Triple
Press OK to save the setting.
Fax by using Voice over IP services
Voice over IP (VoIP) services provide normal telephone service, including long distance service through
a broadband Internet connection. These services use packets to break up the voice signal on a
telephone line and transmit it digitally to the receiver, where the packets are reassembled. The VoIP
services are often not compatible with fax machines. The VoIP provider must state the service supports
fax over IP services.
Because the installation process varies, the VoIP service provider will have to assist in installing the
product fax component.
Although a fax might work on a VoIP network, it can fail when the following events occur:
●Internet traffic becomes heavy and packets are lost.
●Latency (the time it takes for a packet to travel from its point of origin to its point of destination)
becomes excessive.
112 Chapter 5 Theory of operation ENWW
If you experience problems using the fax feature on a VoIP network, ensure that all of the product cables
and settings are correct. Configuring the Fax Speed setting to Medium(V.17) or Slow(V.29) can also
improve your ability to send a fax over a VoIP network.
If you continue to have problems faxing, contact your VoIP provider.
The fax subsystem
The formatter, fax card, firmware, and software all contribute to the fax functionality. The designs of the
formatter and fax card, along with parameters in the firmware, determine the majority of the regulatory
requirements for telephony on the product.
The fax subsystem is designed to support V.34 fax transmission, lower speeds (such as V.17 fax), and
older fax machines.
Fax card in the fax subsystem
Two versions of the fax card are used in the product. One is used in the North American, South American,
and Asian countries/regions. The other is used primarily in European countries/regions.
The fax card contains the modem chipset (DSP and CODEC) that controls the basic fax functions of
tone generation and detection, along with channel control for fax transmissions. The CODEC and its
associated circuitry act as the third-generation silicon data access arrangement (DAA) to comply with
worldwide regulatory requirements.
The only difference between the two versions is that each version is compliant with the 2/4-wire phone
jack system from the respective country/region.
Safety isolation
The most important function of the fax card is the safety isolation between the high-voltage, transient-
prone environment of the telephone network (TNV [telephone network voltage]) and the low-voltage
analog and digital circuitry of the formatter (SELV [secondary extra-low voltage]). This safety isolation
provides both customer safety and product reliability in the telecom environment.
Any signals that cross the isolation barrier do so magnetically. The breakdown voltage rating of barrier-
critical components is greater than 5 kV.
Safety-protection circuitry
In addition to the safety barrier, the fax card protects against over-voltage and over-current events.
Telephone over-voltage events can be either differential mode or common mode. The event can be
transient in nature (a lightning-induced surge or ESD) or continuous (a power line crossed with a phone
line). The fax card protection circuitry provides margin against combinations of over-voltage and over-
current events.
Common mode protection is provided by the selection of high-voltage-barrier critical components
(transformer and relay). The safety barrier of the fax card PCB traces and the clearance between the
fax card and surrounding components also contribute to common mode protection.
A voltage suppressor (a crowbar-type SIDACTOR) provides differential protection. This product
becomes low impedance at approximately 300 V differential, and crowbars to a low voltage. A series
thermal switch works in conjunction with the crowbar for continuous telephone line events, such as
crossed power lines.
ENWW Fax functions and operation (fax/memory-card models only) 113
All communications cross the isolation barrier magnetically. The breakdown voltage rating of barrier-
critical components is greater than 5 kV.
Data path
TIP and RING are the two-wire paths for all signals from the telephone network. All signaling and data
information comes across them, including fax tones and fax data.
The telephone network uses DC current to determine the hook state of the telephone, so line current
must be present during a call. The silicon DAA provides a DC holding circuit to keep the line current
constant during a fax call.
The silicon DAA converts the analog signal to a digital signal for DSP processing, and also converts the
digital signal to an analog signal for transmitting data through a telephone line.
The magnetically coupled signals that cross the isolation barrier go either through a transformer or a
relay.
The DSP in the fax card communicates with the ASIC in the formatter using direct-register access.
Hook state
Another magnetically coupled signal is the control signal that disconnects the downstream telephone
devices (such as a phone or answering machine). A control signal originating on the DSP can change
the relay state, causing the auxiliary jack (downstream jack) to be disconnected from the telephone
circuit.
The product takes control of calls that it recognizes as fax calls. If the product does not directly pick up
the call, it monitors incoming calls for the fax tone or for the user to direct it to receive a fax. This idle
mode is also called eavesdropping. This mode is active when the product is on-hook but current exists
in the downstream phone line because another device is off-hook. During eavesdropping, the receive
circuit is enabled but has a different gain from the current that is generated during normal fax
transmissions.
The product does not take control of the line unless it detects a fax tone or the user causes it to connect
manually. This feature allows the user to make voice calls from a phone that is connected to the product
without being cut off if a fax is not being received.
Downstream device detection
The line voltage monitoring module of the silicon DAA can detect the line state of parallel-connected
devices as well as the downstream device. It tells DSP via DIB that an active device (telephone, modem,
or answering machine) is connected to the auxiliary port on the product (the top port of the RJ-11 jack).
The DSP uses the signal to ensure that the product does not go off-hook (and disconnect a downstream
call) until it has been authorized to do so (by a manual fax start or the detection of the appropriate tones).
Hook switch control
In the silicon DAA the CODEC controls the hook switch directly. The CODEC is activated when it
receives commands from the DSP. When the circuit is drawing DC current from the central office it is
considered off-hook. When no DC current flows the state is considered on-hook.
Ring detect
Ring detect is performed by the line voltage monitoring module of the silicon DAA, and is a combination
of voltage levels and cadence (time on and time off). Both must be present to detect a valid ring. The
114 Chapter 5 Theory of operation ENWW
CODEC works with DSP as well as the firmware to determine if an incoming signal is an answerable
ring.
Line current control
The DC current from the CO needs to have a path to flow from TIP to RING. The DC impedance
emulation line modulator and DC terminations modules in the silicon DAA act as a DC holding circuit,
and works with the firmware to achieve the voltage-current characteristic between TIP and RING. The
impedance (the current-voltage characteristic) changes corresponding to certain special events, such
as pulse dialing or when the product goes on-hook.
Billing- (metering-) tone filters
Switzerland and Germany provide high-frequency AC signals on the phone line in order to bill customers.
A filter in a special fax cable (for certain countries/regions), can filter these signals. Because these billing
signals are not used in the U.S., these filters are not present in the U.S. fax cable.
To obtain a special fax cable, contact your local telephone service provider.
Fax page storage in flash memory
Fax pages are the electronic images of the document page. They can be created in any of three ways:
scanned to be sent to another fax machine, generated to be sent by the computer, or received from a
fax machine to be printed.
The product stores all fax pages in flash memory automatically. After these pages are written into flash
memory, they are stored until the pages are sent to another fax machine, printed on the product,
transmitted to the computer, or erased by the user.
These pages are stored in flash memory, which is the nonvolatile memory that can be repeatedly read
from, written to, and erased. The product has 4 MB of flash memory, of which 3.5 MB is available for
fax storage. The remaining 0.5 MB is used for the file system and reclamation. Adding RAM does not
affect the fax page storage because the product does not use RAM for storing fax pages.
Stored fax pages
The user can reprint stored fax receive pages in case of errors. For a fax send, the product will resend
the fax in case of errors. The product will resend stored fax pages after a busy signal, communication
error, no answer, or power failure. Other fax devices store fax pages in either normal RAM or short-term
RAM. Normal RAM immediately loses its data when power is lost, while short-term RAM loses its data
about 60 minutes after power failure. Flash memory maintains its data for years without any applied
power.
Advantages of flash memory storage
Fax pages that are stored in flash memory are persistent. They are not lost as a result of a power failure,
no matter how long the power is off. Users can reprint faxes in case the print cartridge runs out of toner
or the product experiences other errors while printing faxes.
The product also has scan-ahead functionality that makes use of flash memory. Scan-ahead
automatically scans pages into flash memory before a fax job is sent. This allows the sender to pick up
the original document immediately after it is scanned, eliminating the need to wait until the fax is
transmission is complete.
ENWW Fax functions and operation (fax/memory-card models only) 115
Because fax pages are stored in flash memory rather than RAM, more RAM is available to handle larger
and more complicated copy and print jobs.
116 Chapter 5 Theory of operation ENWW
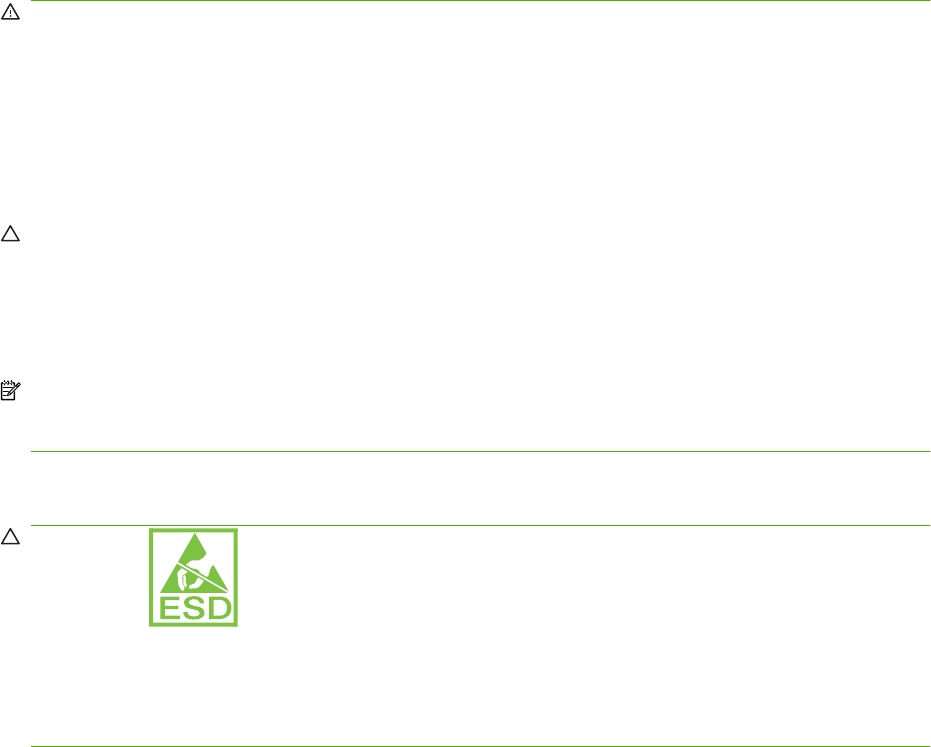
Removal and replacement strategy
This chapter discusses the removal and replacement of field replaceable units (FRUs) only.
Replacing FRUs is generally the reverse of removal. Occasionally, notes and tips are included to provide
directions for difficult or critical replacement procedures.
HP does not support repairing individual subassemblies or problem solving at the component level.
Note the length, diameter, color, type, and location of each screw. Be sure to return each screw to its
original location during reassembly.
Incorrectly routed or loose wire harnesses can interfere with other internal components and can become
damaged or broken. Frayed or pinched harness wires can be difficult to locate. When replacing wire
harnesses, always use the provided wire loops, lance points, or wire-harness guides.
General cautions during removal and replacement
WARNING! Turn the product off, wait 5 seconds, and then remove the power cord before attempting
to service the product. If this warning is not followed, severe injury can result, as well as damage to the
product. The power must be on for certain functional checks during problem solving. However, the power
cord should be disconnected during parts removal.
Never operate or service the product with the protective cover removed from the laser/scanner
assembly. The reflected beam, although invisible, can damage your eyes.
The sheet-metal parts can have sharp edges. Be careful when handling sheet-metal parts.
CAUTION: Do not bend or fold the flat flexible cables (FFCs) during removal or installation. Also, do
not straighten pre-folds in the FFCs. You must make sure that all FFCs are fully seated in their
connectors. Failure to fully seat an FFC into a connector can cause a short circuit in a PCA.
Avoid pulling directly on wires to disconnect wire-harness connectors. Pull on the plastic body of a
connector when ever possible to avoid damaging the connector wires.
NOTE: To install a self-tapping screw, first turn it counterclockwise to align it with the existing thread
pattern, and then carefully turn it clockwise to tighten. Do not overtighten. If a self-tapping screw-hole
becomes stripped, repair the screw-hole or replace the affected assembly.
Electrostatic discharge
CAUTION: Some parts are sensitive to electrostatic discharge (ESD). Look for the ESD
reminder when removing product parts. Always perform service work at an ESD-protected workstation
or mat. If an ESD workstation or mat is not available, ground yourself by touching the sheet-metal chassis
before touching an ESD-sensitive part.
Protect the ESD-sensitive parts by placing them in ESD pouches when they are out of the product.
118 Chapter 6 Removal and replacement ENWW
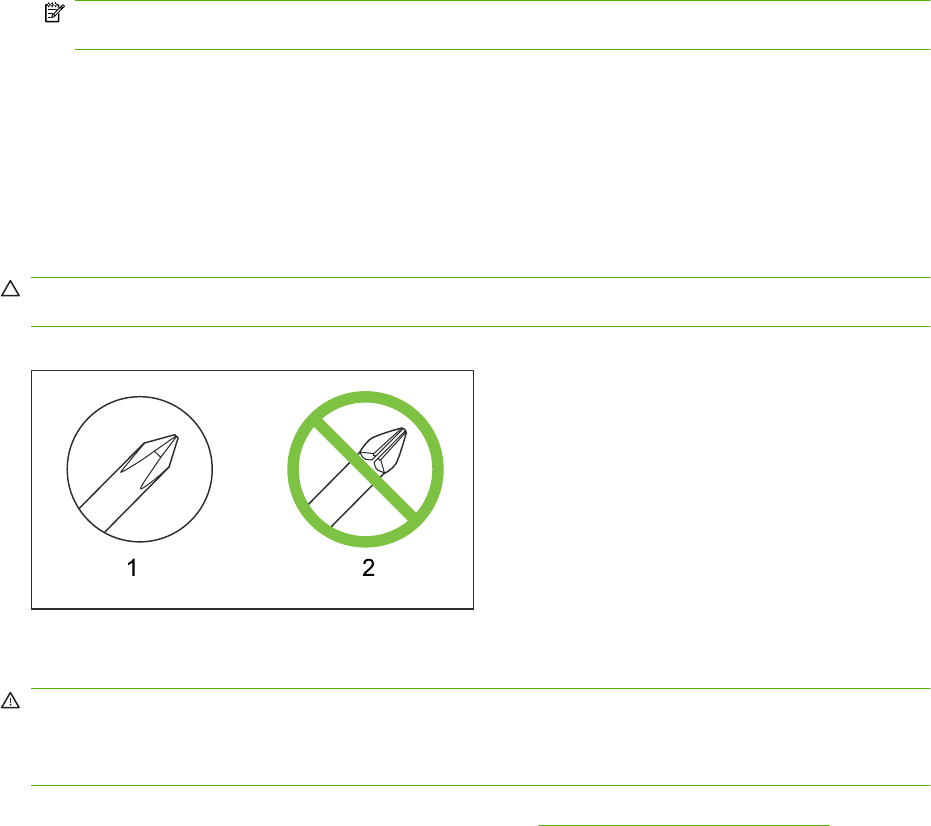
Required tools
●Number 2 Phillips screwdriver with a magnetic tip and a 152-mm (6-inch) shaft length
●Precision slotted screwdriver with a 1 mm (0.04 in) blade width
NOTE: This fine-point tool is required to release the front door pins. The width of the blade must
be 2 mm (0.08 in) or less to be able to drive the door pins out of the mounting holes.
●Small, slotted screwdriver
●Needle-nose pliers
●Snap-ring pliers
●ESD mat (if one is available)
●Penlight (optional)
CAUTION: Always use a Phillips screwdriver (callout 1). Do not use a pozidrive screwdriver (callout 2)
or any motorized screwdriver. These can damage screws or screw threads.
Figure 6-1 Phillips and pozidrive screwdriver comparison
Types of screws
WARNING! Make sure that components are replaced with the correct screw type. Using the incorrect
screw (for example, substituting a long screw for the correct shorter screw) can cause damage to the
product or interfere with product operation. Do not intermix screws that are removed with one component
with the screws that are removed from another component.
For a complete list of screw types and part numbers, see Parts and diagrams on page 327.
ENWW Removal and replacement strategy 119

Service approach
Before performing service
●Remove all media from the product.
●Turn off the power using the power switch.
●Unplug the power cable and interface cable(s).
●Place the product on an ESD mat (if one is available). If an ESD workstation or mat is not available,
ground yourself by touching the sheet-metal chassis before touching an ESD-sensitive part.
●Remove the print cartridges. See Print cartridges on page 122.
●Remove the tray 2 cassette.
After performing service
●Plug in the power cable.
●Reinstall the print cartridges.
●Reinstall the tray 2 cassette.
120 Chapter 6 Removal and replacement ENWW
Post-service tests
After service has been completed, perform the following tests to verify that the repair or replacement
was successful.
Test 1 (print-quality test)
1. Verify that you have completed the necessary reassembly steps.
2. Ensure that the input tray contains clean, unmarked paper.
3. Attach the power cord and interface cable, and then turn on the product.
4. Verify that the expected start-up sounds occur.
5. Print a configuration page, and then verify that the expected printing sounds occur.
6. Print a demo page, and then verify that the print quality is as expected.
7. Send a print job from the host computer, and then verify that the output meets expectations.
8. If necessary, restore any customer-specified settings.
9. Clean the outside of the product with a damp cloth.
Test 2 (copy-quality test)
1. Verify that you have completed the necessary reassembly steps.
2. Ensure that the input tray contains clean, unmarked paper.
3. Attach the power cord, and then turn on the product.
4. Verify that the expected start-up sounds occur.
5. Print a configuration page, and then verify that the expected printing sounds occur.
6. Place the configuration page in the ADF.
7. Print a copy job, and then verify the results.
8. Clean the outside of the product with a damp cloth.
Test 3 (fax-quality test; fax models only)
1. Place the configuration page in the ADF.
2. Type a valid fax number and send the fax job.
3. Verify that the send quality and receive quality meet expectations.
ENWW Removal and replacement strategy 121
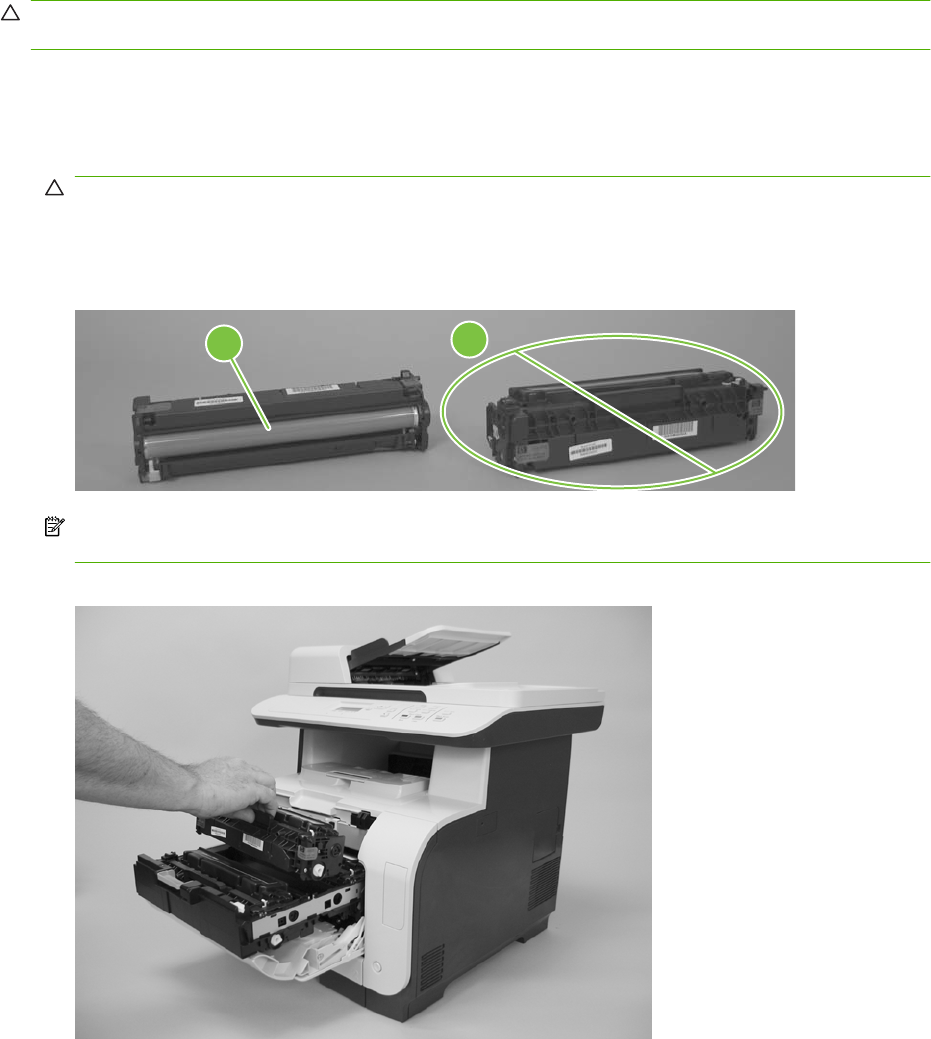
Print cartridges
CAUTION: If toner gets on your clothing, wipe it off with a dry cloth and wash the clothing in cold water.
Hot water sets toner into the fabric.
1. Open the front door and pull out the print-cartridge drawer.
2. Grasp the handle on the print cartridge and then pull the cartridge straight up to remove it. Repeat
this step for the remaining print cartridges.
CAUTION: Do not touch the imaging drum (callout 1) on the bottom of the print cartridge. Skin
oils on the imaging drum can cause print-quality problems.
Do not place the print cartridge on a surface with the image drum down (callout 2). Protect the
image drum at all times. Dust and debris can stick to the drum and cause print-quality problems.
12
NOTE: Do not place the print cartridges where they will be exposed to light for an extended time.
Cover the print cartridges if necessary to protect them.
Figure 6-2 Remove the print cartridge
3. Close the print-cartridge drawer and the front door.
122 Chapter 6 Removal and replacement ENWW
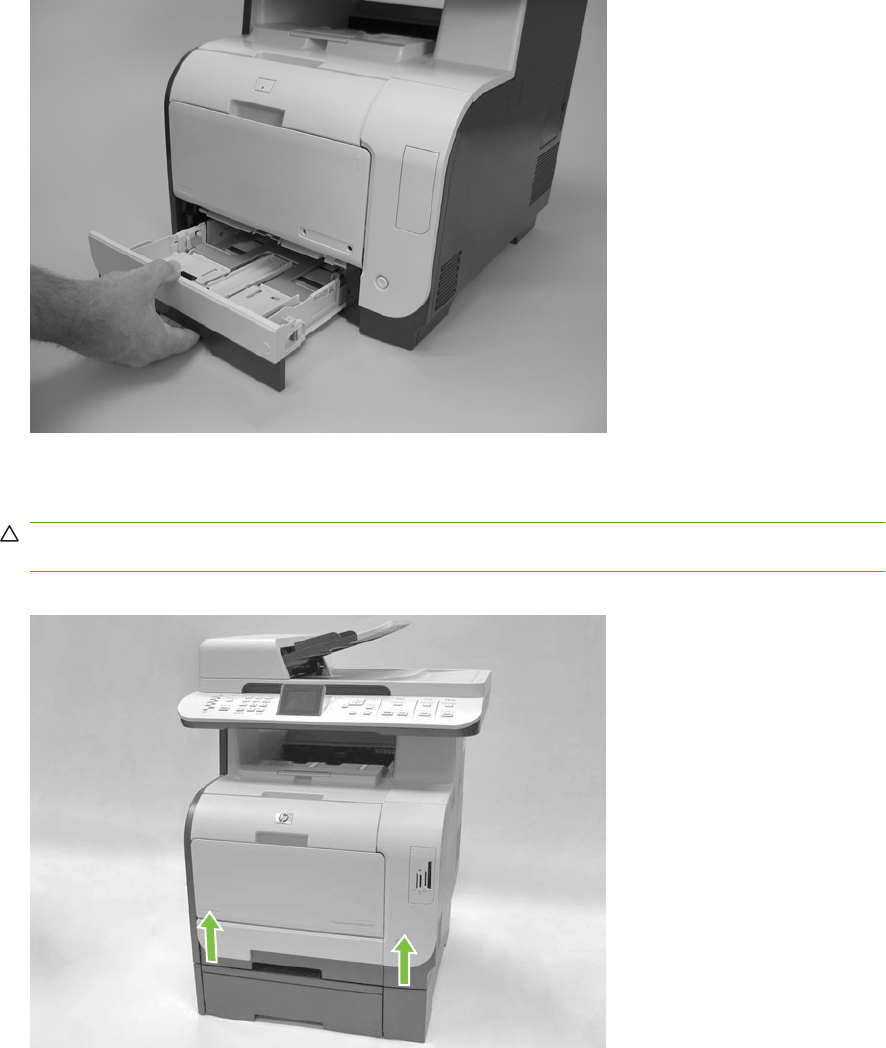
Tray cassettes and optional Tray 3 assembly
1. Tray 2 and Tray 3 cassette: Pull the tray straight out of the product to remove it.
Figure 6-3 Remove the tray cassettes and optional Tray 3 assembly (1 of 2)
2. Optional Tray 3 assembly: Lift the product straight up from the assembly, and then set the product
on a sturdy, level surface.
CAUTION: Lift the product by using the right- and left-side hand-holds. Do not lift the product by
grasping the Tray 2 cassette, or the cavity created if the cassette is removed.
Figure 6-4 Remove the tray cassettes and optional Tray 3 assembly (2 of 2)
ENWW Tray cassettes and optional Tray 3 assembly 123
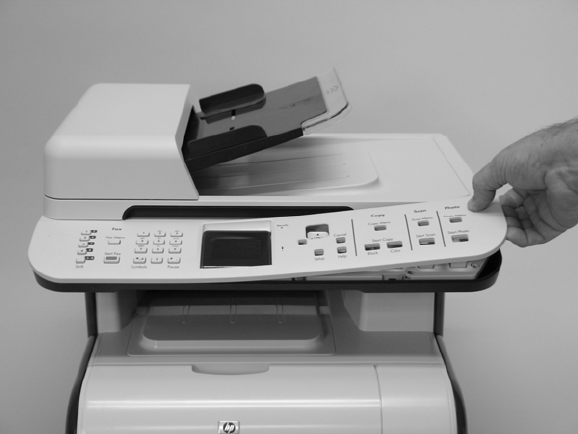
Control-panel bezel
Carefully pry up on one end of the control-panel bezel to release it. Continue to pry up on the bezel to
remove it.
Figure 6-5 Remove the control-panel bezel
124 Chapter 6 Removal and replacement ENWW

Control panel
1. Remove the control-panel bezel. See Control-panel bezel on page 124.
2. Release one tab (callout 1) and then slide the control panel toward the left side of the product to
release it.
Figure 6-6 Remove the control-panel (1 of 2)
1
3. Rotate the control panel up and off of the product, and then disconnect two FFCs (callout 2).
NOTE: The base model only has one FFC.
Figure 6-7 Remove the control-panel (2 of 2)
2
ENWW Control panel 125
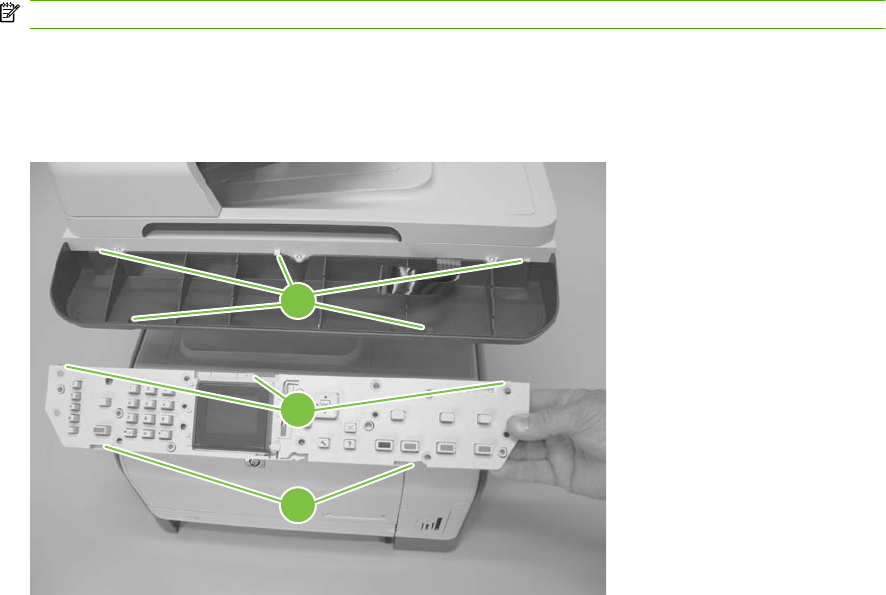
Reinstall the control panel
1. Connect the FFCs and verify that they are fully seated.
NOTE: The base model only has one FFC.
2. When you reinstall the control panel, make sure the two lower tabs on the control panel (callout 3),
and the three upper tabs on the control panel (callout 4) are positioned under the tabs on the
scanner chassis (callout 5).
Figure 6-8 Reinstall the control-panel
4
3
5
126 Chapter 6 Removal and replacement ENWW

Paper-feed rollers and pads
Transfer roller
The transfer roller is a component of the paper-feed assembly and not available as an individual FRU.
To remove and replace the transfer roller, install a replacement paper-feed assembly. See Paper-feed
guide assembly on page 150.
ENWW Paper-feed rollers and pads 127
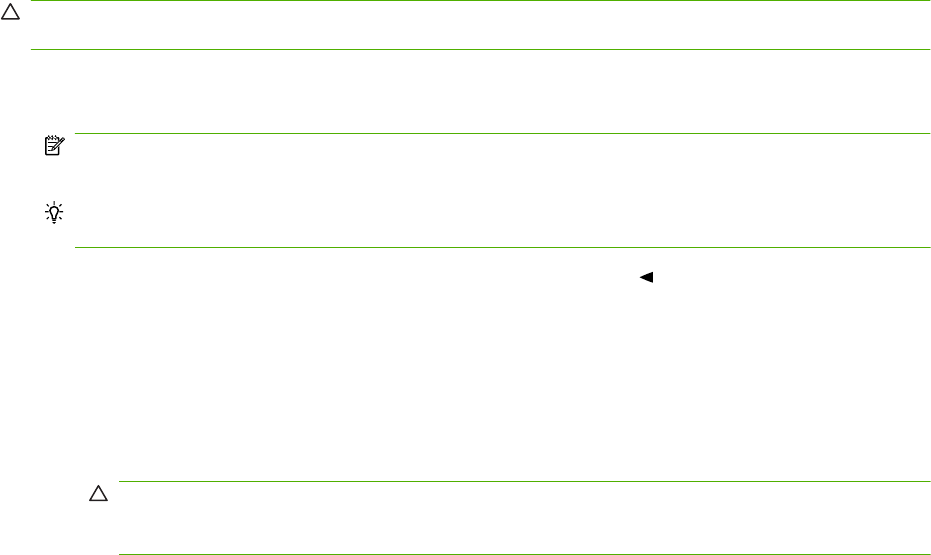
Pickup roller (Tray 2 and Tray 3)
The roller must be rotated into the service position to remove it.
CAUTION: Avoid touching the spongy roller surface unless you are going to replace the roller. Skin
oils on the roller can cause paper pickup problems.
1. Turn the product on, and wait for it to reach the Ready state. Perform the following steps to rotate
the roller to the service position.
NOTE: If you have removed Tray 2 to service the product, reinstall the tray before turning the
power on.
TIP: The following steps rotate the engine paper-pickup roller and the Tray 1 paper-pickup roller
into the service position.
a. Open the 2ndry Service menu by pressing the Left Arrow button and the Cancel button
simultaneously.
b. Use the arrow buttons to select Pick roller, and then press OK.
Press OK again to confirm that you want the roller to rotate.
c. Listen for the roller to rotate. When the roller is done rotating, unplug the power cord and then
place the power switch in the off position.
CAUTION: It is important to place the power switch in the off position after unplugging the
power cord so that the product power does not come on immediately when the power cord is
plugged in again.
d. Remove Tray 2.
e. Perform the remaining steps in this procedure to remove the roller. After replacing the roller,
plug the power cord into the product, and then use the power switch to turn the power on.
128 Chapter 6 Removal and replacement ENWW
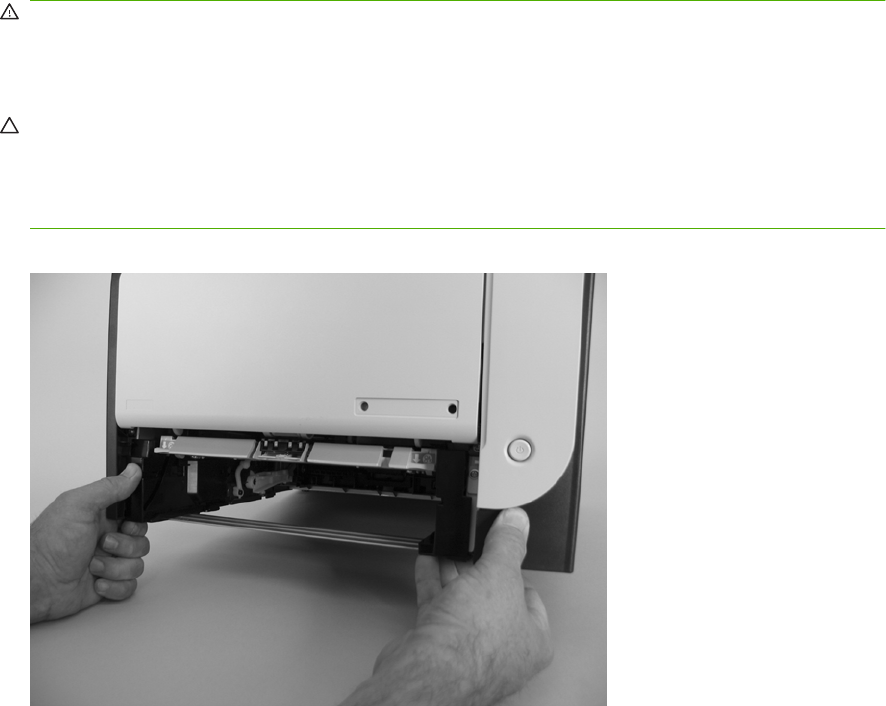
2. Carefully raise the front of the product.
WARNING! Do not place the product face-up resting on the rear cover and rear door. Excess
toner might enter the laser/scanner assembly and contaminate the mirrors, causing print-quality
problems. The laser/scanner is not a FRU. If the laser/scanner mirrors are contaminated, the entire
product must be replaced.
CAUTION: The ADF and scanner cover are not captive and can open suddenly when the product
is placed front-side face up. Always support the ADF and scanner cover before placing the product
front-side face up.
Do not lift the product grasping the front door and Tray 2 cavity.
Figure 6-9 Remove the pickup roller (1 of 2)
ENWW Paper-feed rollers and pads 129
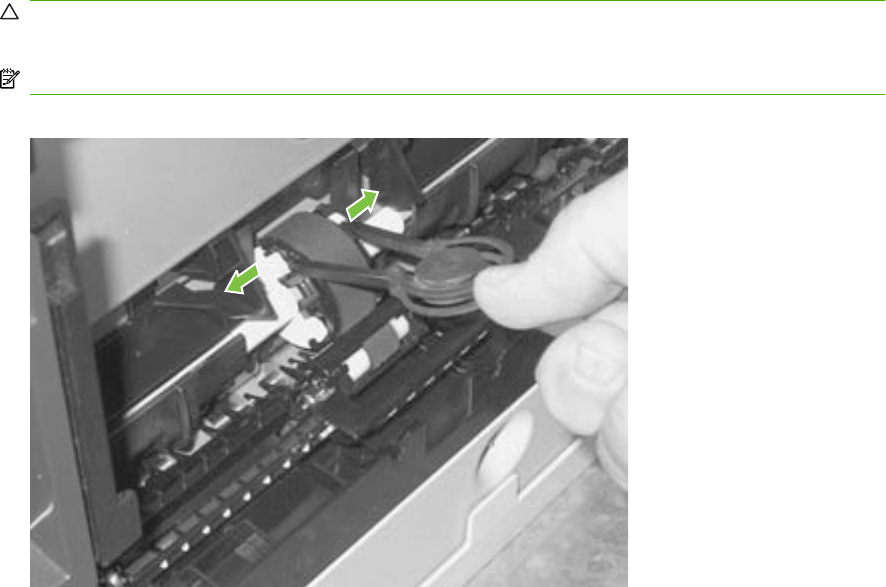
3. Use a pair of snap-ring pliers to release two locking tabs and remove the pickup roller.
CAUTION: Do not touch the spongy roller surface unless you are going to replace the roller. Skin
oils on the roller can cause paper pickup problems.
NOTE: If you do not have a pair of snap-ring pliers, use your fingers to release the tabs.
Figure 6-10 Remove the pickup roller (2 of 2)
130 Chapter 6 Removal and replacement ENWW
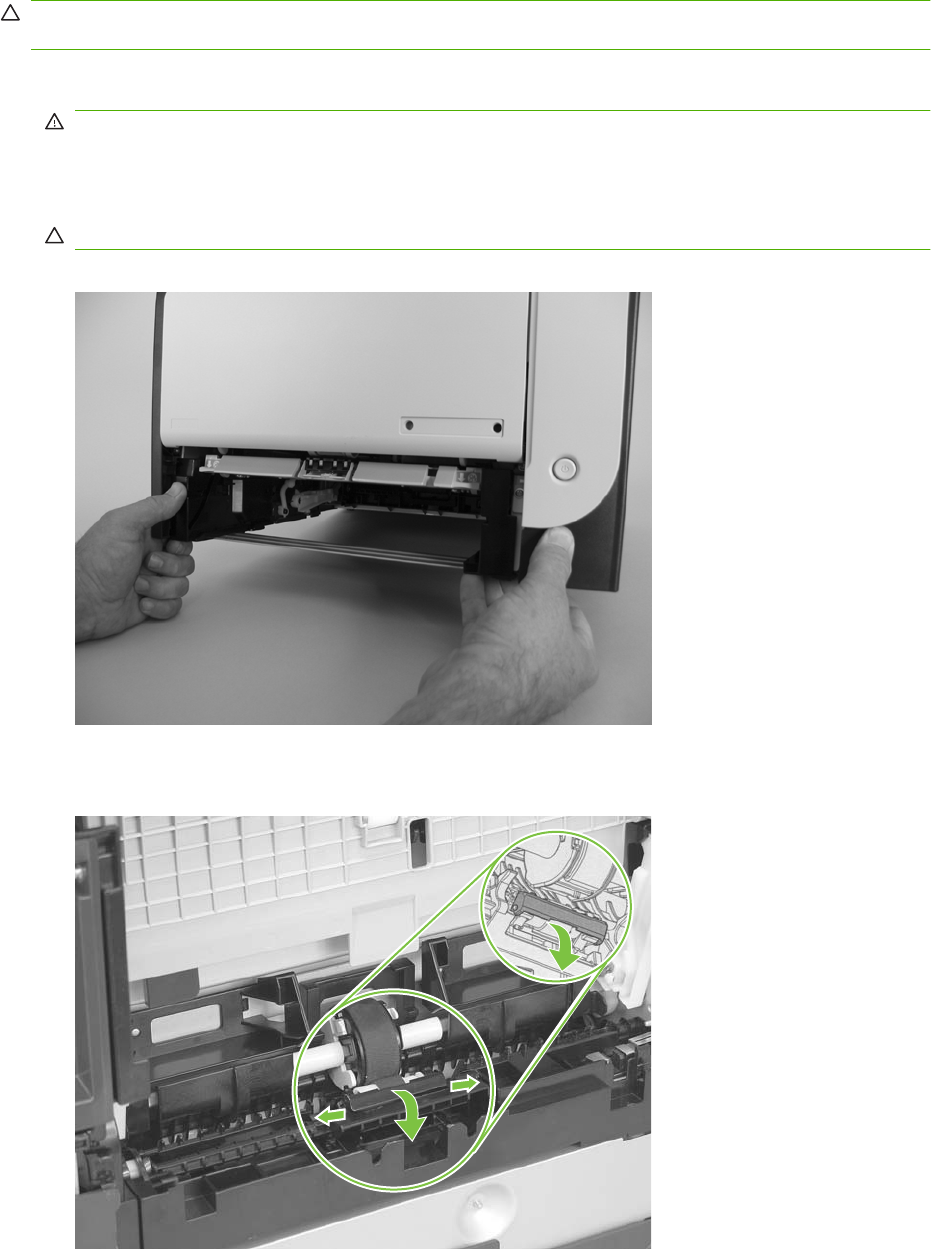
Separation roller (Trays 2 or 3)
CAUTION: Avoid touching the spongy roller surface unless you are going to replace the roller. Skin
oils on the roller can cause paper pickup problems.
1. Remove Tray 2 (if installed), and then carefully raise the front of the product.
WARNING! Do not place the product face-up resting on the rear cover and rear door. Excess
toner might enter the laser/scanner assembly and contaminate the mirrors, causing print-quality
problems. The laser/scanner is not a FRU. If the laser/scanner mirrors are contaminated, the entire
product must be replaced.
CAUTION: Do not lift the product grasping the front door and Tray 2 cavity.
Figure 6-11 Remove the pickup roller (1 of 3)
2. Release the two roller-cover locking pins, and then remove the cover.
Figure 6-12 Remove the separation roller (2 of 3)
ENWW Paper-feed rollers and pads 131
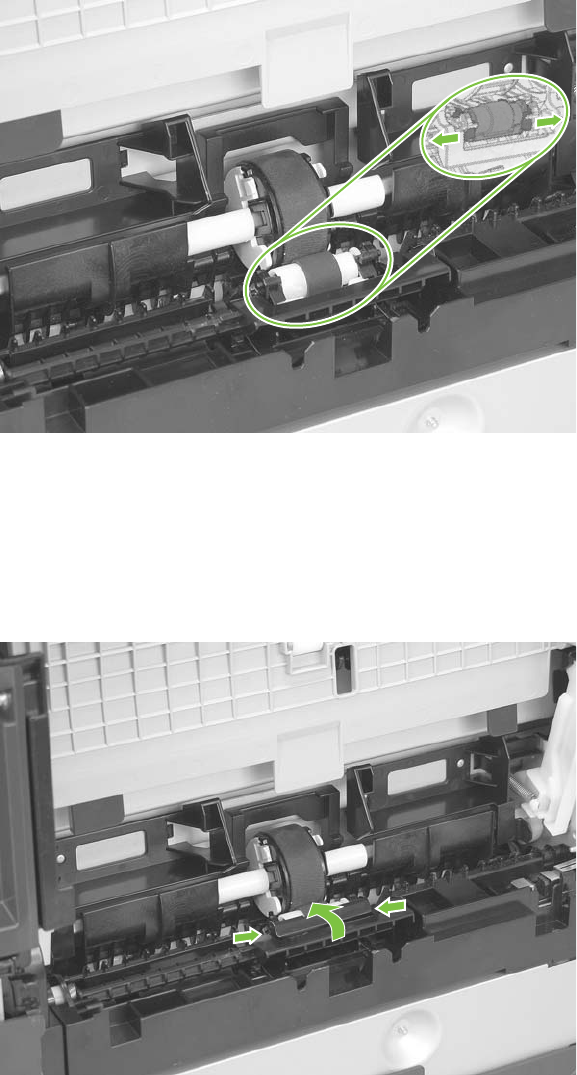
3. Release the roller holder to release the roller-locking pins. Remove the separation roller.
Figure 6-13 Remove the separation roller (3 of 3)
Reinstall the separation roller
1. Install the replacement separation roller.
2. Reinstall the separation roller cover on the locking pins, and then rotate it toward the roller until
you hear it snap into place.
Figure 6-14 Reinstall the separation roller
132 Chapter 6 Removal and replacement ENWW
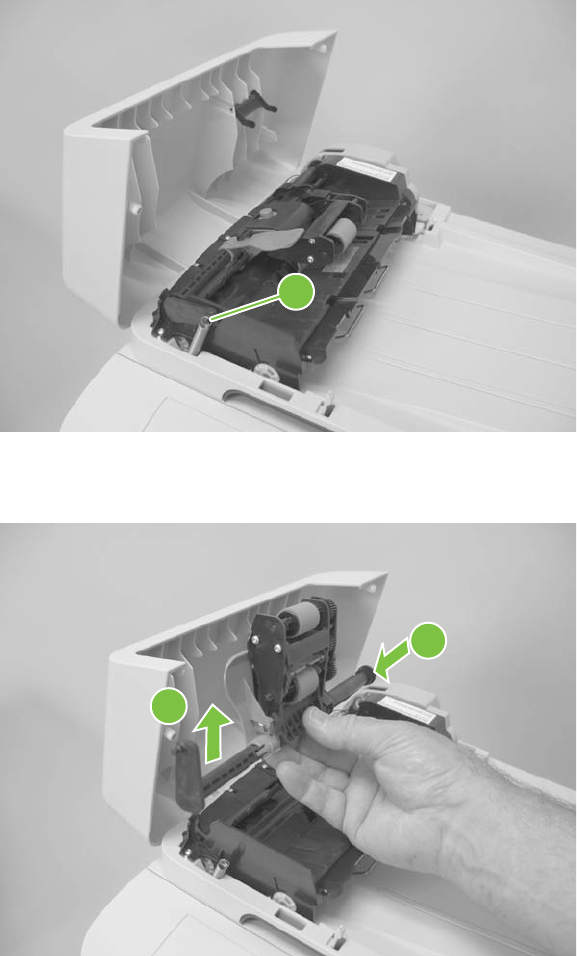
ADF pickup roller assembly
1. Open the ADF cover.
2. Disconnect one spring (callout 1).
Figure 6-15 Remove the ADF pickup roller assembly (1 of 2)
1
3. Lift up on the end of the assembly, and then slide it toward the control panel to remove it.
Figure 6-16 Remove the ADF pickup roller assembly (2 of 2)
2
1
ENWW Paper-feed rollers and pads 133
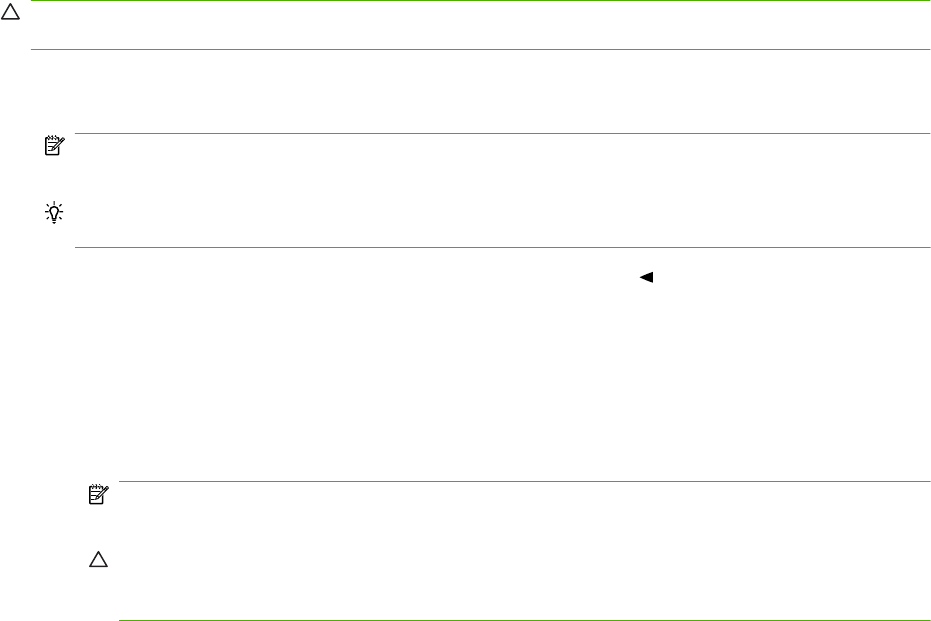
Paper-pickup roller (Tray 1)
The roller must be rotated into the service position to remove it.
CAUTION: Avoid touching the spongy roller surface unless you are going to replace the roller. Skin
oils on the roller can cause paper pickup problems.
1. Turn the product on, and wait for it to reach the Ready state. Perform the following steps to rotate
the roller to the service position.
NOTE: If you have removed Tray 2 to service the product, reinstall the tray before turning the
power on.
TIP: The following steps rotate the engine paper-pickup roller and the Tray 1 paper-pickup roller
into the service position.
a. Open the 2ndry Service menu by pressing the Left Arrow button and the Cancel button
simultaneously.
b. Use the arrow buttons to select Pick roller, and then press OK.
Press OK again to confirm that you want the roller to rotate.
c. Listen for the roller to rotate. When the roller is done rotating, unplug the power cord and then
place the power switch in the off position.
NOTE: Failure to unplug the product at this point will result in the roller being in the incorrect
position for the repair procedure.
CAUTION: It is important to place the power switch in the off position after unplugging the
power cord so that the product power does not come on immediately when the power cord is
plugged in again.
d. Remove Tray 2.
e. Perform the remaining steps in this procedure to remove the roller. After replacing the roller,
plug the power cord into the product, and then use the power switch to turn the power on.
134 Chapter 6 Removal and replacement ENWW
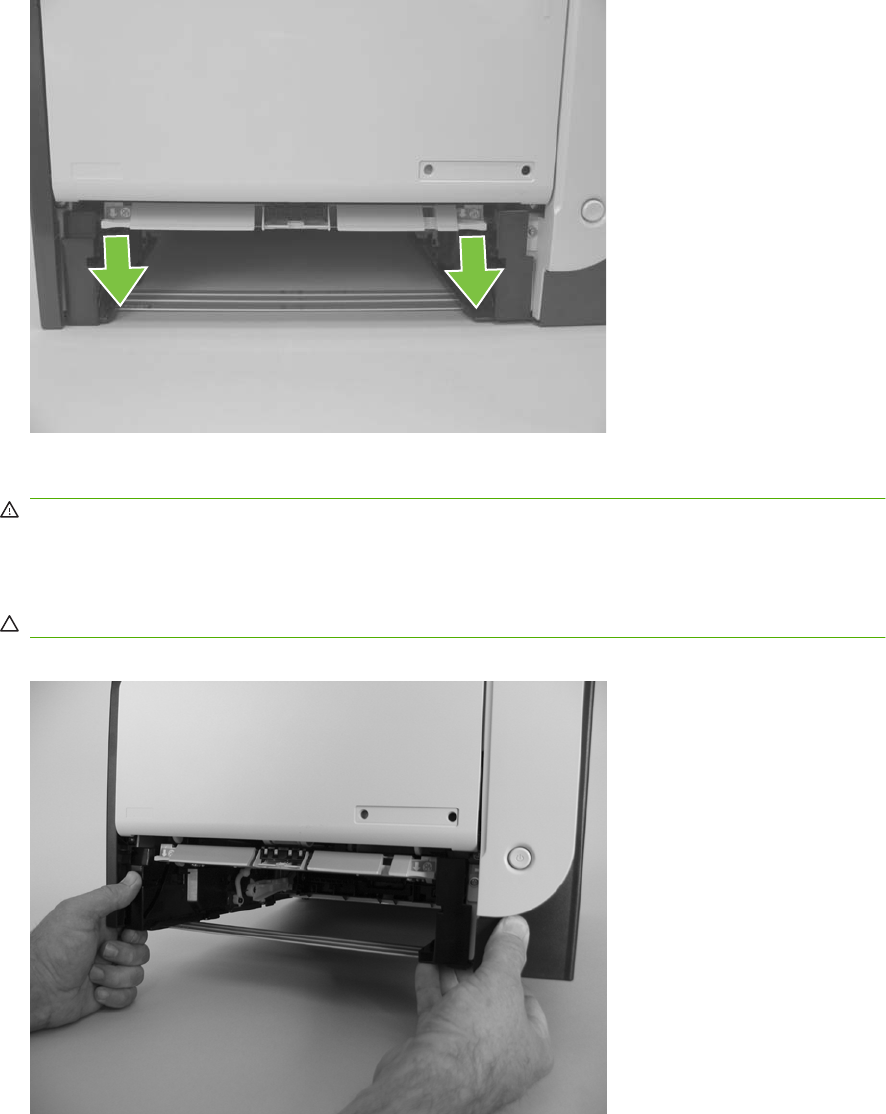
2. Lower the Tray 1 paper pickup assembly by pushing down on the edges of the assembly.
Figure 6-17 Remove the Tray 1 paper-pickup roller (1 of 3)
3. Carefully raise the front of the product.
WARNING! Do not place the product face-up resting on the rear cover and rear door. Excess
toner might enter the laser/scanner assembly and contaminate the mirrors, causing print-quality
problems. The laser/scanner is not a FRU. If the laser/scanner mirrors are contaminated, the entire
product must be replaced.
CAUTION: Do not lift the product grasping the front door and Tray 2 cavity.
Figure 6-18 Remove the Tray 1 paper-pickup roller (2 of 3)
ENWW Paper-feed rollers and pads 135
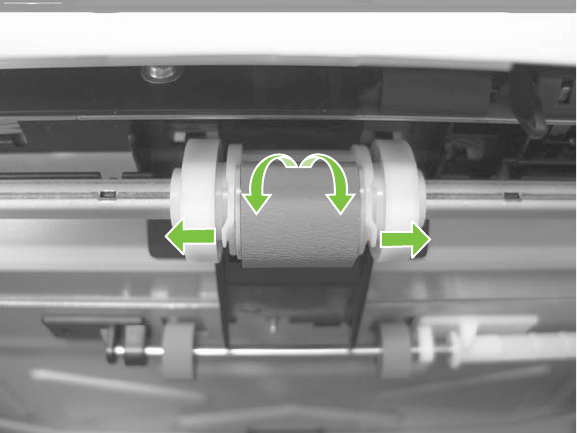
4. Release two tabs, and then rotate the roller away from the product to remove it.
Figure 6-19 Remove the Tray 1 paper-pickup roller (3 of 3)
136 Chapter 6 Removal and replacement ENWW
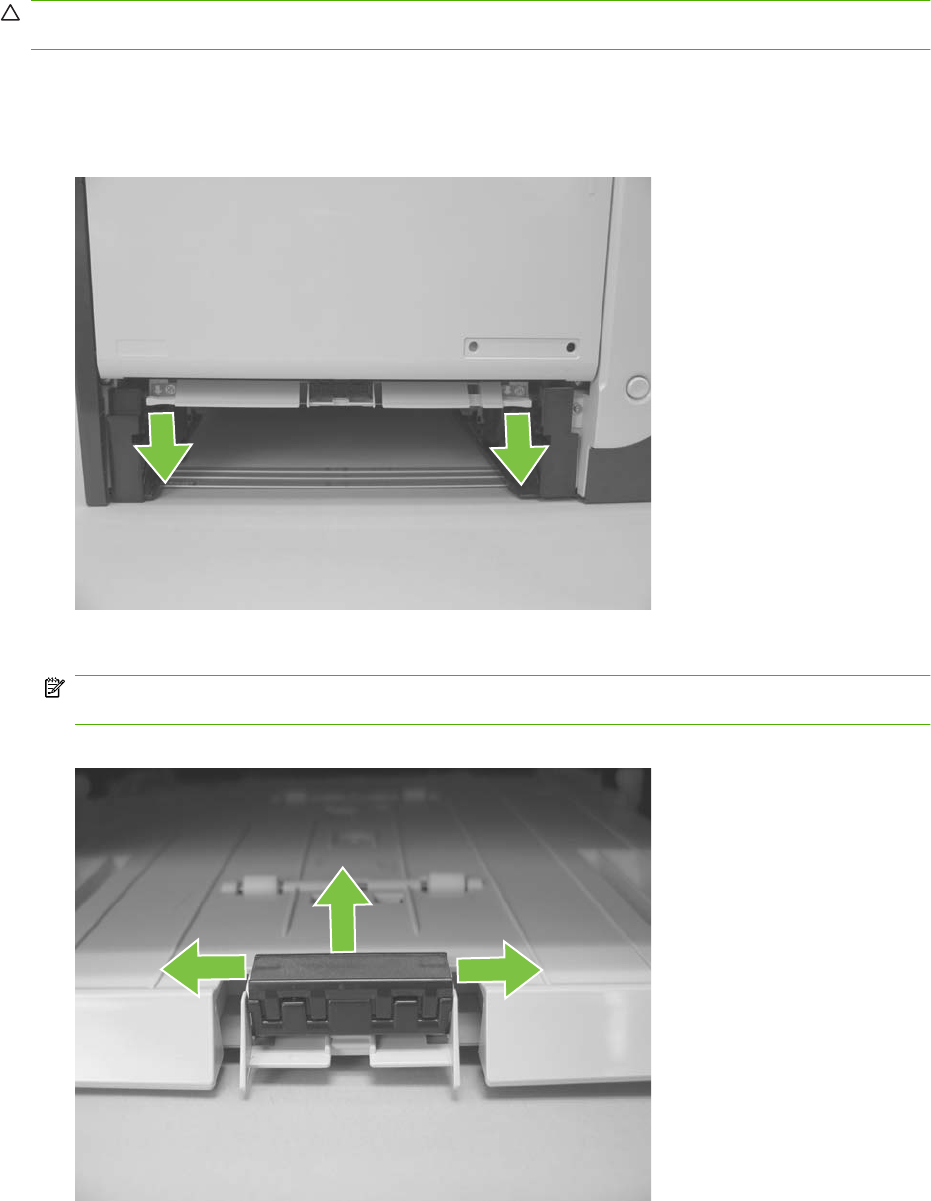
Separation pad (Tray 1)
CAUTION: Avoid touching the pad surface unless you are going to replace the pad. Skin oils on the
pad can cause paper pickup problems.
1. Remove Tray 2 (if installed).
2. Lower the Tray 1 paper pickup assembly by pushing down on the edges of the assembly.
Figure 6-20 Remove the Tray 1 separation pad (1 of 2)
3. Release the retainer tabs, and then remove the separation pad from the base.
NOTE: The separation pad base can easily be dislodged when the pad is removed. If the base
is dislodged, do not loose the spring under the base (it is not captive).
Figure 6-21 Remove the Tray 1 separation pad (2 of 2)
ENWW Paper-feed rollers and pads 137
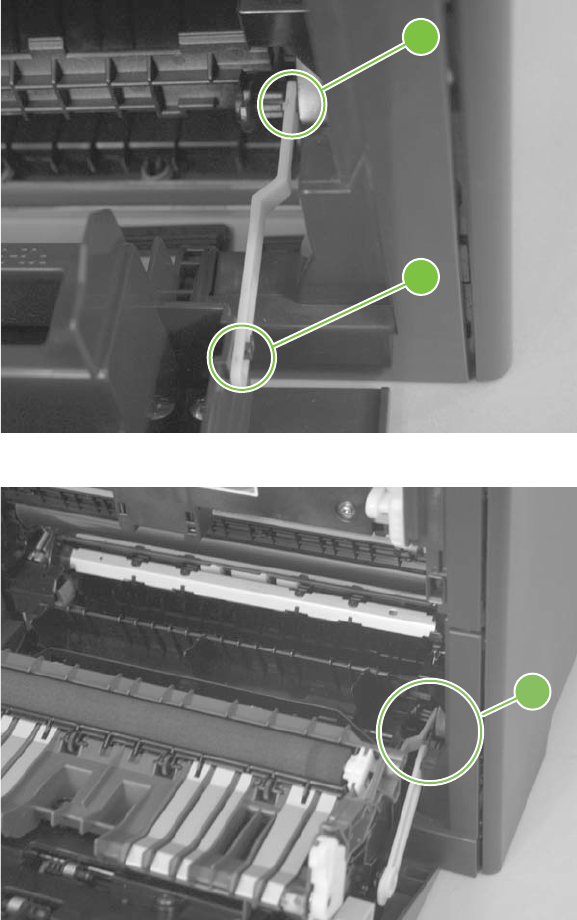
Components and major assemblies
Link guide
The link guide rarely fails and is not a FRU.
The link is attached to the paper guide (callout 1) and the rear door (simplex products; callout 2) or
duplexing-feed guide assembly (duplex products; callout 3).
If the link-guide attachment at the rear door or duplexing-feed guide assembly fails, replace the
appropriate component.
The interior paper guide is not replaceable. If the link-guide to paper guide attachment fails, you must
replace the entire product.
Figure 6-22 Replace the link guide (simplex products)
1
2
Figure 6-23 Replace the link guide (duplex products)
3
138 Chapter 6 Removal and replacement ENWW
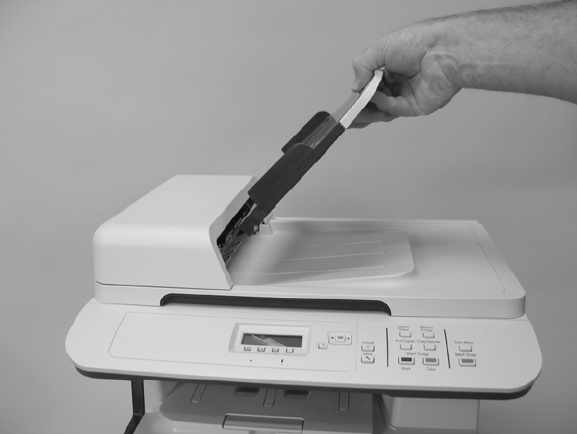
ADF input tray
Rotate the ADF input tray toward the ADF to release it, and then remove the tray.
Figure 6-24 Remove the ADF input tray
ENWW Components and major assemblies 139
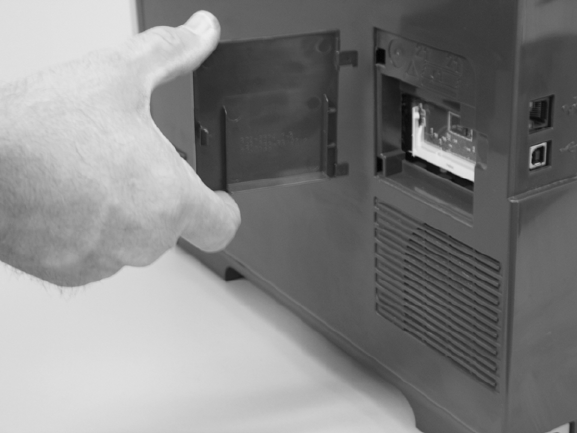
DIMM cover
1. Open the DIMM cover.
2. Lift the cover up to release it, and then remove the cover.
Figure 6-25 Remove the DIMM cover
140 Chapter 6 Removal and replacement ENWW
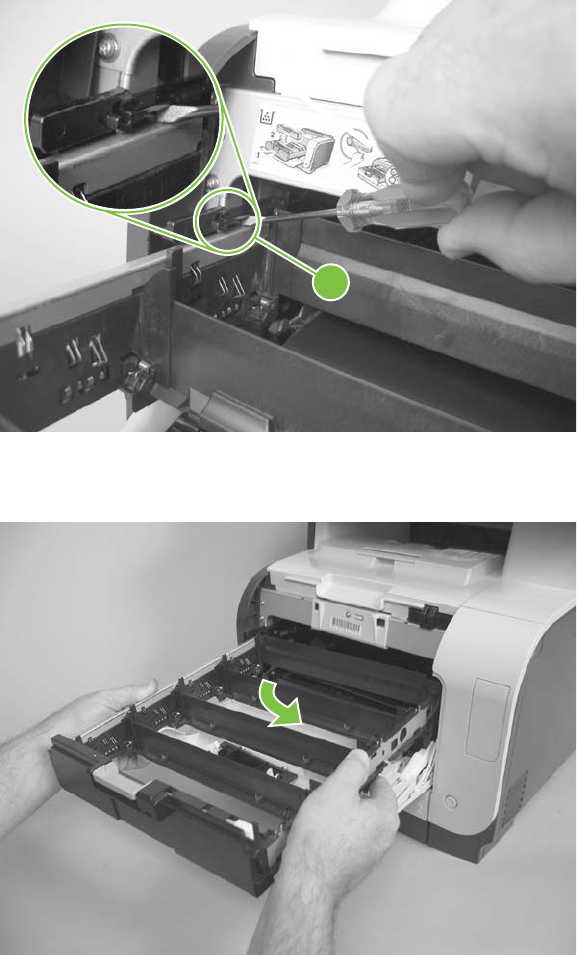
Print-cartridge drawer
1. Open the front door.
2. Partially pull out the print-cartridge drawer, and then use a small flat blade screwdriver to release
one tab (callout 1) on the left side of the product.
Figure 6-26 Remove the print-cartridge drawer (1 of 3)
1
3. Carefully rotate the print-cartridge drawer toward the right side of the product to release it.
Figure 6-27 Remove the print-cartridge drawer (2 of 3)
ENWW Components and major assemblies 141
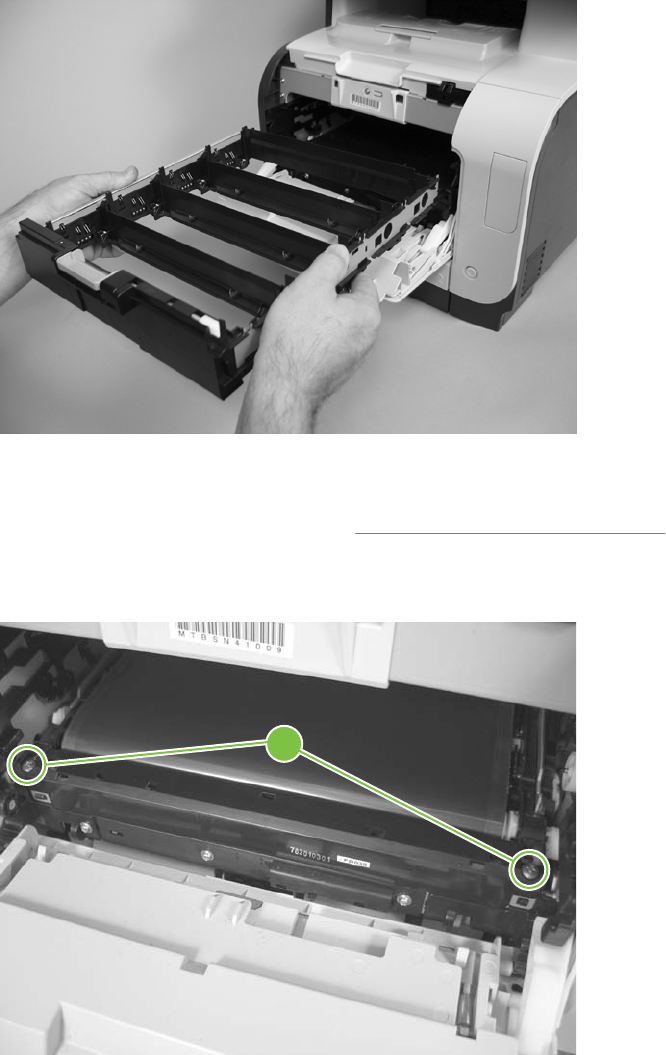
4. Pull the print-cartridge drawer out of the product to remove it.
Figure 6-28 Remove the print-cartridge drawer (3 of 3)
Intermediate transfer belt (ITB)
1. Remove the print-cartridge drawer. See Print-cartridge drawer on page 141.
2. Open the front door, and then remove two screws (callout 1).
Figure 6-29 Remove the ITB (1 of 6)
1
142 Chapter 6 Removal and replacement ENWW
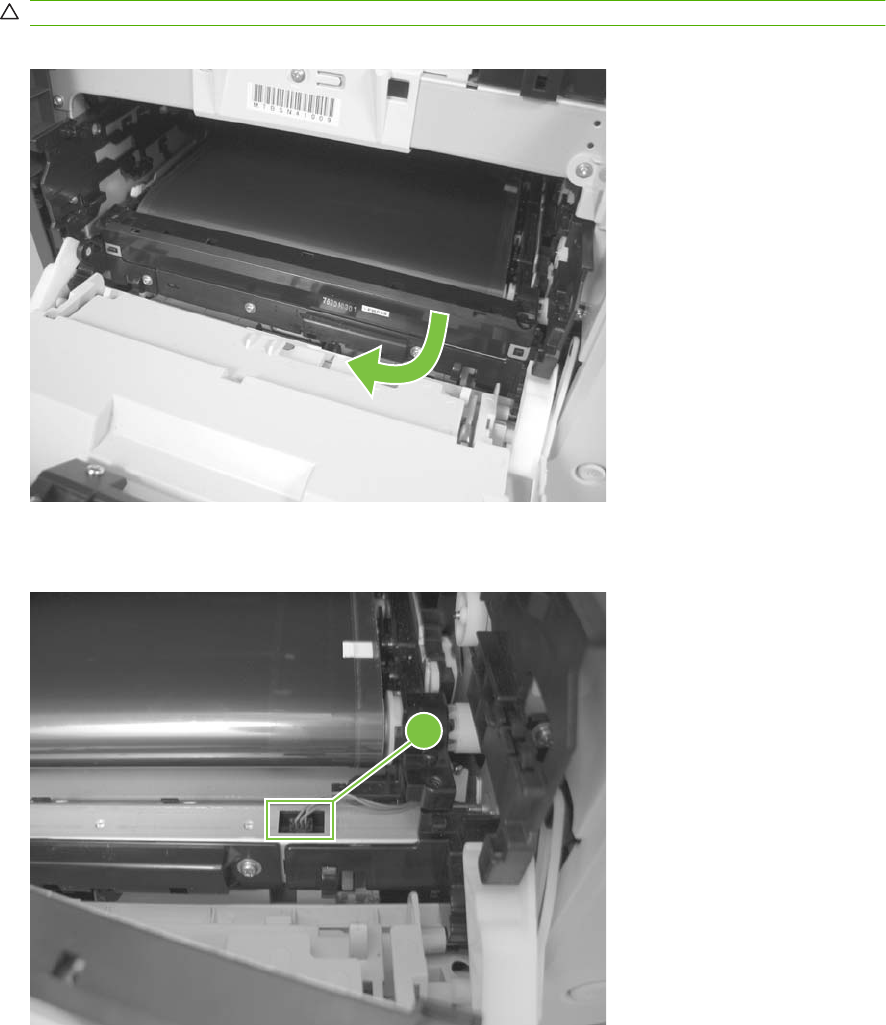
3. Carefully rotate the color-misregistration sensor away from the ITB.
CAUTION: The sensor is still attached to the product and cannot be completely removed.
Figure 6-30 Remove the ITB (2 of 6)
4. Disconnect one connector (callout 2).
Figure 6-31 Remove the ITB (3 of 6)
2
ENWW Components and major assemblies 143
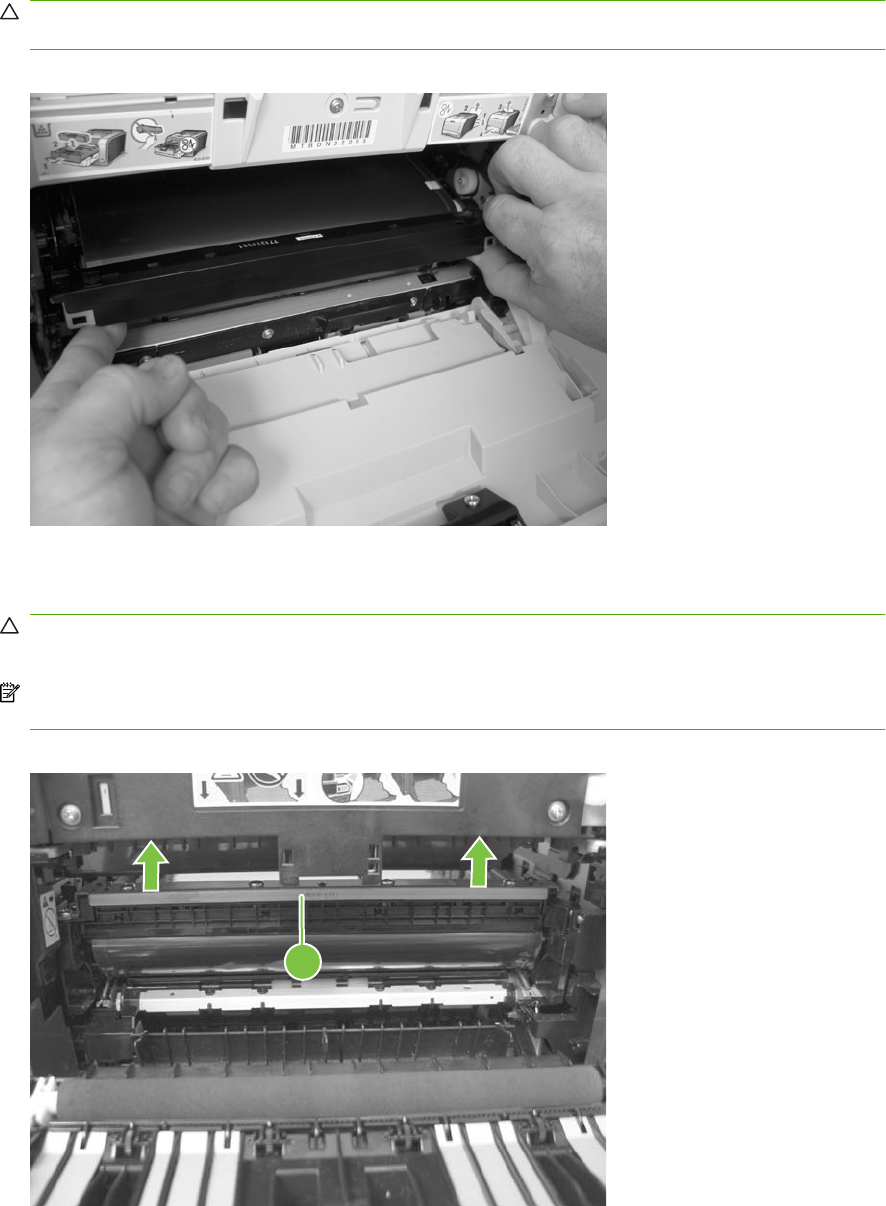
5. Carefully lift up on the front of the ITB to release it.
CAUTION: Avoid touching the black plastic transfer belt. Skin oils on the belt might cause print-
quality problems. Lift the ITB as shown below, by using the hard-plastic edges of the ITB.
Figure 6-32 Remove the ITB (4 of 6)
6. Open the rear door, and carefully lift up on the sheet-metal portion (callout 3) of the ITB to release
it.
CAUTION: Avoid touching the black plastic transfer belt. Skin oils on the belt might cause print-
quality problems.
NOTE: You might need to reach in through the front door and support the front portion of the ITB
to keep it from falling back into place as you perform this step.
Figure 6-33 Remove the ITB (5 of 6)
3
144 Chapter 6 Removal and replacement ENWW
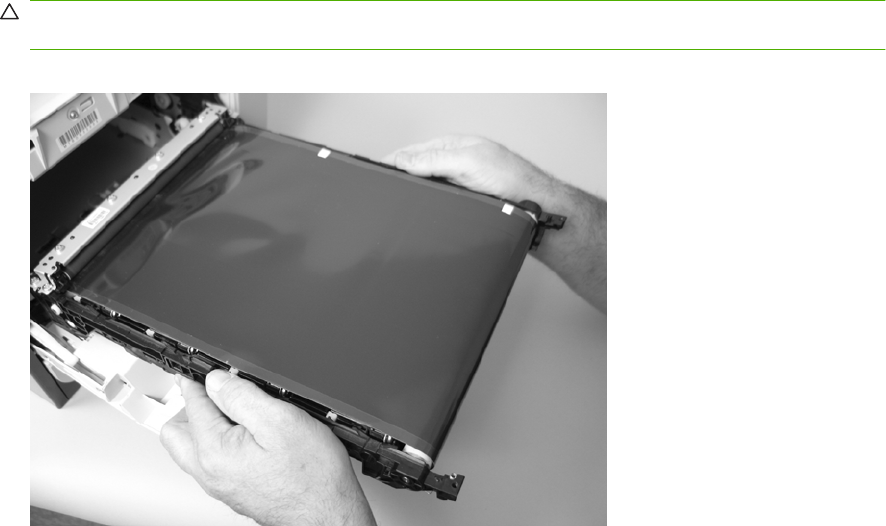
7. Carefully pull the ITB straight out of the product to remove it.
CAUTION: Avoid touching the black plastic transfer belt. Skin oils on the belt might cause print-
quality problems. Handle the ITB as shown below.
Figure 6-34 Remove the ITB (6 of 6)
ENWW Components and major assemblies 145
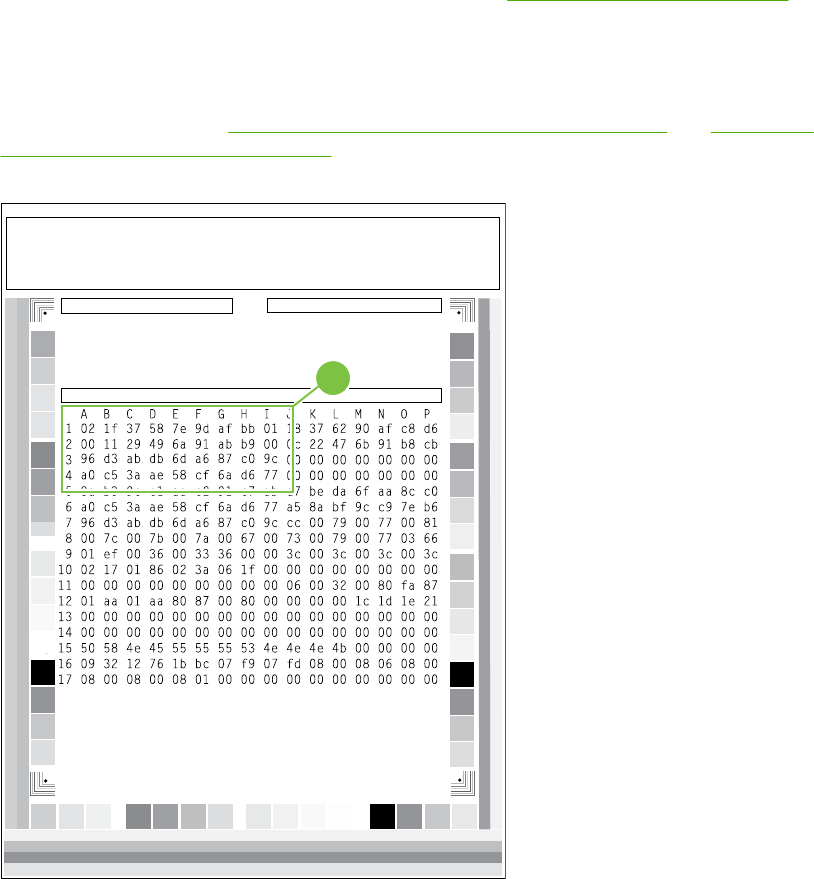
Reinstall the ITB
Use this procedure to verify that the ITB is correctly reinstalled.
1. Use the control panel to print the diagnostics pages. See Diagnostics pages on page 253.
2. Verify that rows one through four, columns A through I (callout 1) contain hexadecimal numbers.
If these rows and columns are all zero, ensure that the calibration sensor was correctly reinstalled.
The sensor must be correctly positioned and fit securely against the chassis before the mounting
screws are installed. See Figure 6-29 Remove the ITB (1 of 6) on page 142 and Figure 6-30
Remove the ITB (2 of 6) on page 143.
Figure 6-35 Reinstall the ITB
HP Color LaserJet CP2320
Diagnostics Page
Calibration Information Color Density
Power-On Calibration : 15 Minutes
Calibration Timing: 48 Hours
C M Y K
Contrast 0 0 0 0
Highlights 0 0 0 0
Midtones 0 0 0 0
Shadows 0 0 0 0
Parameters 04
1
146 Chapter 6 Removal and replacement ENWW
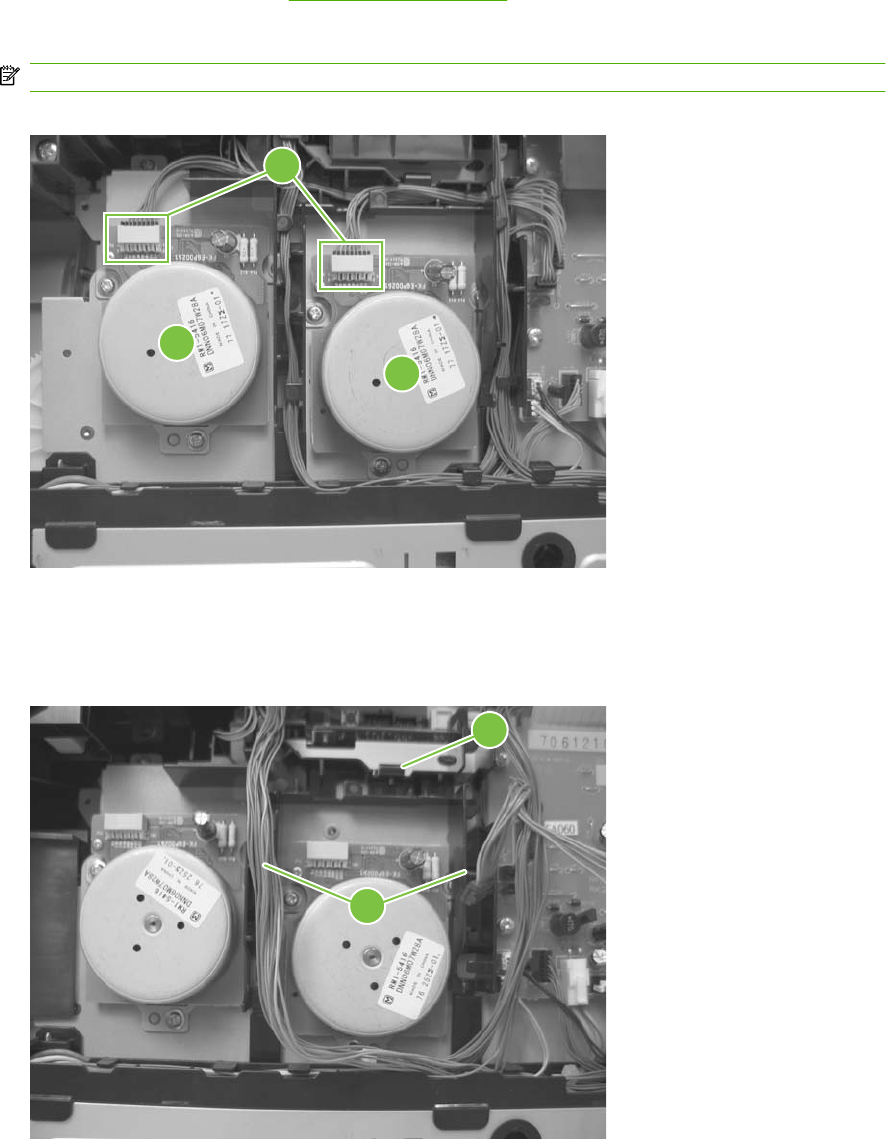
Motors (drum motor and developer motor)
This procedure can be used to remove the drum motor (M1) or the developer motor (M2). HP does not
recommend removing both of the motors at the same time.
1. Remove the right cover. See Right cover on page 156.
2. Disconnect one connector (callout 1) for motor M1 or motor M2.
NOTE: The drum motor (callout 2) is motor M1. The developer motor (callout 3) is motor M2.
Figure 6-36 Remove motor M1 and motor M2 (1 of 3)
1
2
3
3. Release the wire harnesses from the retainer, and then release one tab (callout 4). Move the
retainer (callout 5) to one side (you will not be able to completely remove the retainer from the
product).
Figure 6-37 Remove motor M1 and motor M2 (2 of 3)
4
5
ENWW Components and major assemblies 147

4. Remove three screws (callout 6) to remove motor M1, or remove three screws (callout 7) to remove
motor M2.
Figure 6-38 Remove motor M1 and motor M2 (3 of 3)
7
6
148 Chapter 6 Removal and replacement ENWW
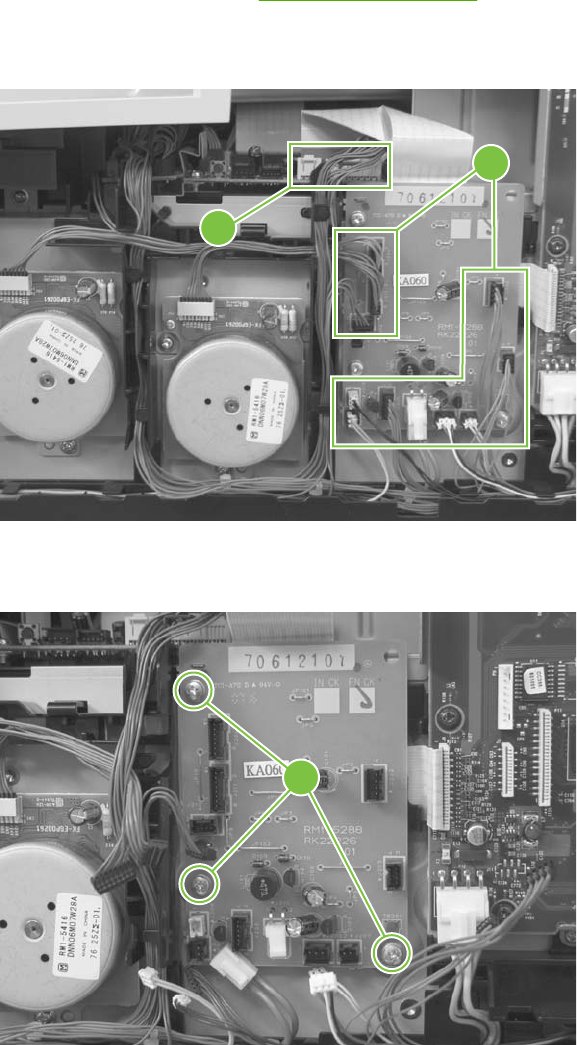
Intermediate PCA
1. Remove the right cover. See Right cover on page 156.
2. Disconnect all of the connectors (callout 1) on the PCA and one FFC (callout 2).
Figure 6-39 Remove the Intermediate PCA (1 of 2)
2
1
3. Remove three screws (callout 3) , and then remove the intermediate PCA.
Figure 6-40 Remove the Intermediate PCA (2 of 2)
3
ENWW Components and major assemblies 149
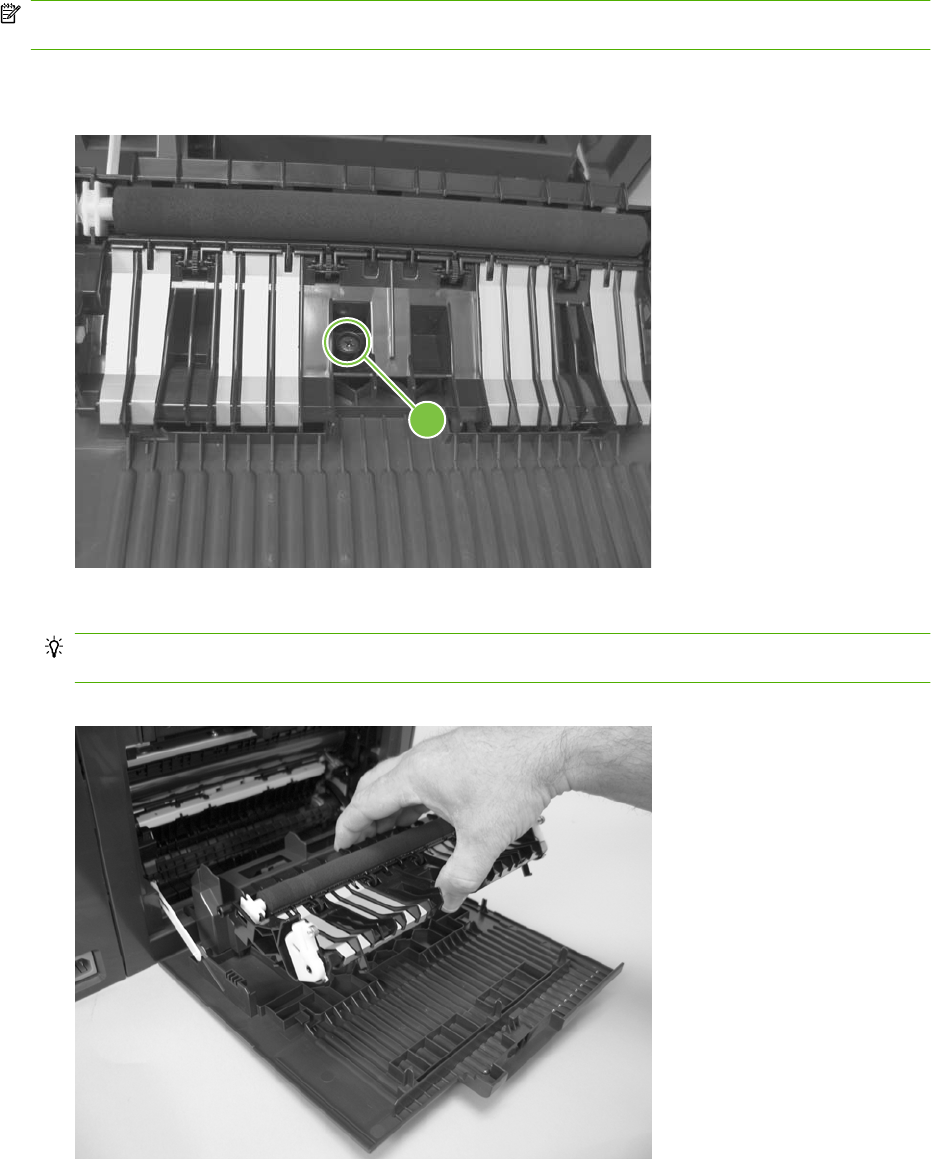
Paper-feed guide assembly
NOTE: A simplex model is shown below. Duplex and simplex models use the same paper-feed guide
assembly, and the removal and replacement processes are identical.
1. Release one screw (callout 1).
Figure 6-41 Remove the feed assembly (1 of 2)
1
2. Remove the feed assembly.
TIP: When the feed assembly is correctly reinstalled, the assembly will be able to move in relation
to the door. It should not be secured firmly to the door.
Figure 6-42 Remove the feed assembly (2 of 2)
150 Chapter 6 Removal and replacement ENWW
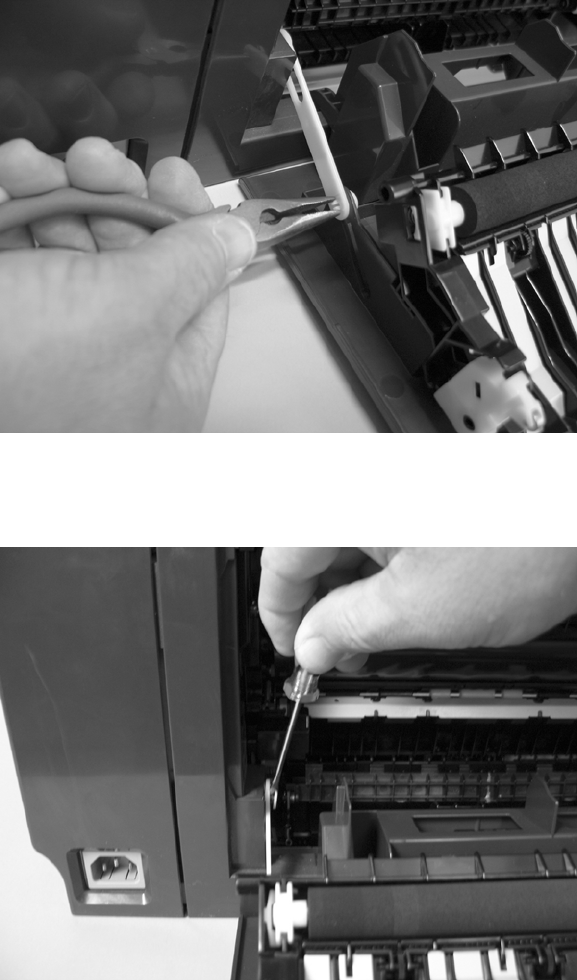
Rear-door stopper and link caps (simplex product)
1. Open the rear door.
2. Use a pair of needle-nose pliers to release two tabs, and then remove the link cap.
Figure 6-43 Remove the Rear-door stopper and link caps (simplex product) (1 of 2)
3. Use a small flat blade screwdriver to carefully remove the remaining link cap, and then remove the
Rear-door stopper.
Figure 6-44 Remove the Rear-door stopper and link cap (simplex product) (2 of 2)
ENWW Components and major assemblies 151
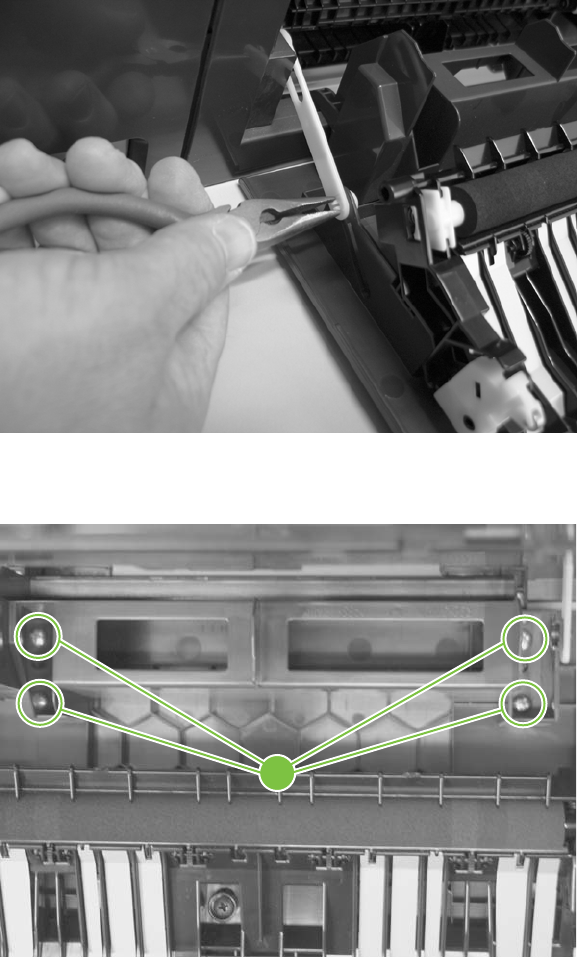
Rear door (simplex product)
1. Open the rear door.
2. Use a pair of needle-nose pliers to release two tabs, and then remove the link cap.
Figure 6-45 Remove the rear door (simplex product) (1 of 4)
3. Remove four screws (callout 1).
Figure 6-46 Remove the rear door (simplex product) (2 of 4)
1
152 Chapter 6 Removal and replacement ENWW
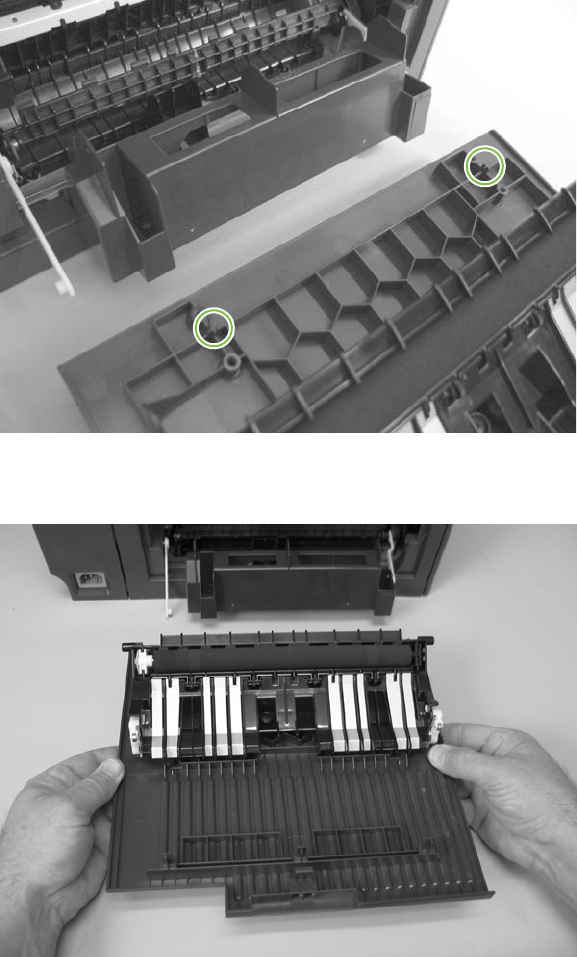
4. Before you remove the rear door, take note of the alignment pins on the door.
Figure 6-47 Remove the rear door (simplex product) (3 of 4)
5. Remove the rear door.
Figure 6-48 Remove the rear door (simplex product) (4 of 4)
ENWW Components and major assemblies 153
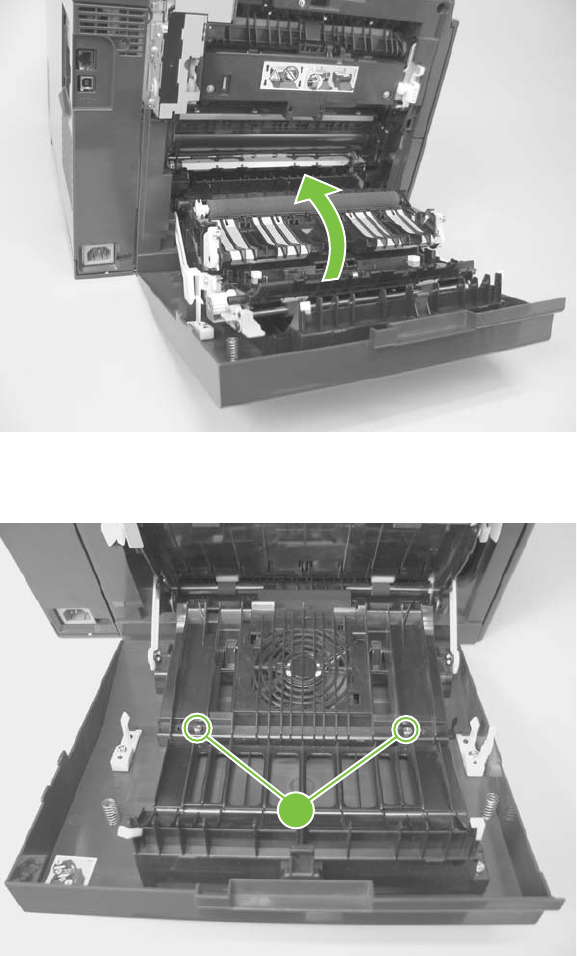
Rear door (duplex product)
1. Open the rear door.
2. Use the green handle to close the duplex-feed assembly.
Figure 6-49 Remove the rear door (duplex product) (1 of 4)
3. Remove two screws (callout 1).
Figure 6-50 Remove the rear door (duplex product) (2 of 4)
1
154 Chapter 6 Removal and replacement ENWW
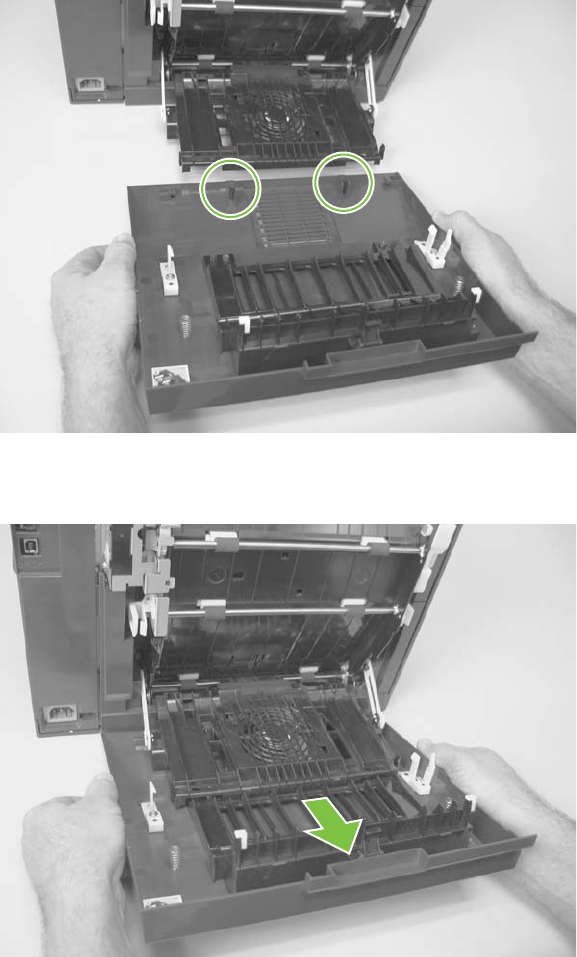
4. Before you remove the rear door, take note of the mounting tabs on the door.
Figure 6-51 Remove the rear door (duplex product) (3 of 4)
5. Slide the door away from the product to release two tabs, and then remove the door.
Figure 6-52 Remove the rear door (duplex product) (4 of 4)
ENWW Components and major assemblies 155
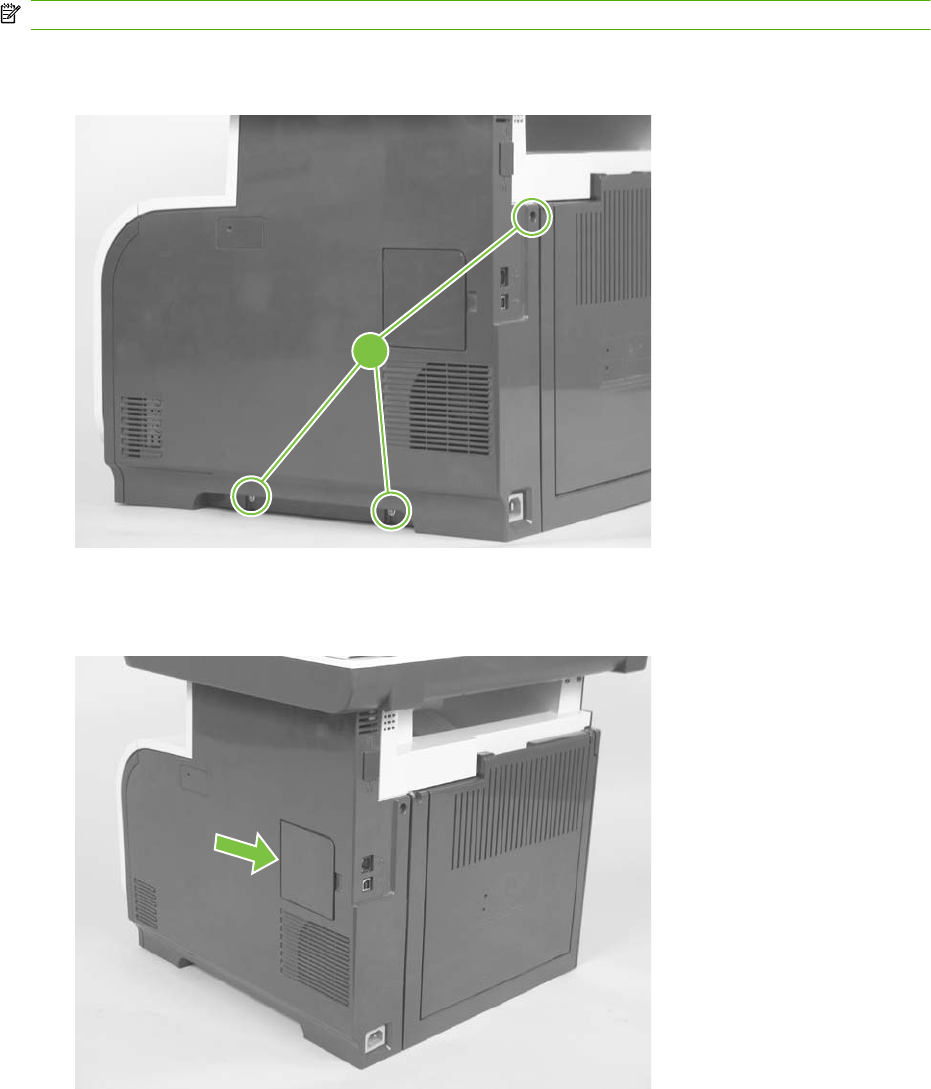
Right cover
NOTE: For duplex products, open the rear door.
1. Remove three screws (callout 1).
Figure 6-53 Remove the right cover (1 of 3)
1
2. Slide the right cover toward the back of the product.
Figure 6-54 Remove the right cover (2 of 3)
156 Chapter 6 Removal and replacement ENWW
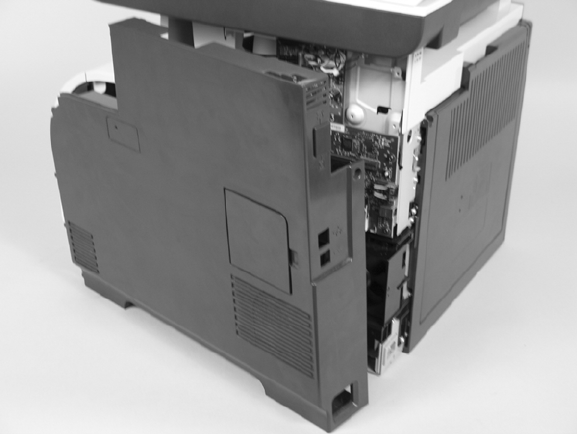
3. Remove the right cover.
Figure 6-55 Remove the right cover (3 of 3)
ENWW Components and major assemblies 157
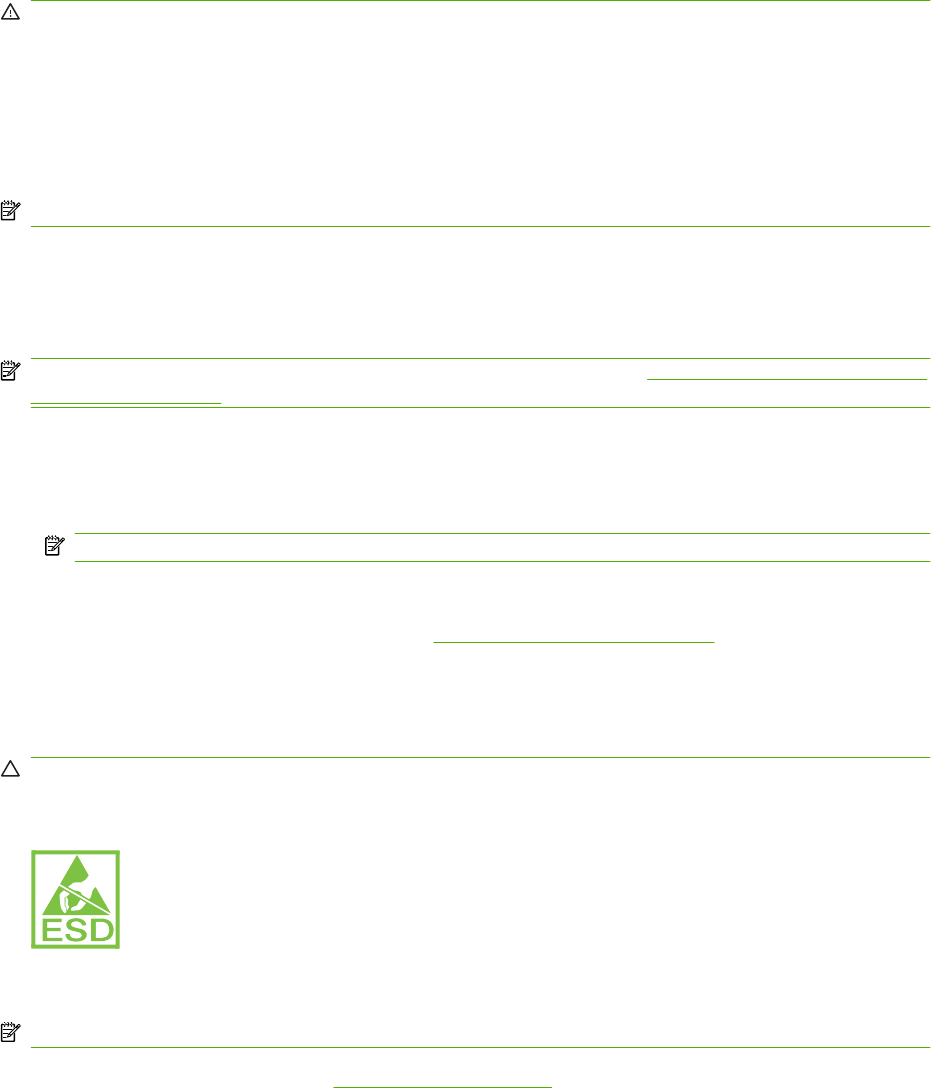
Formatter PCA and fax PCA
Special considerations
WARNING! Do not install a replacement formatter PCA and DC controller PCA at the same time.
The formatter PCA and the DC controller PCA store important product configuration information
(NVRAM data) that is lost if both PCAs are replaced at the same time. When the product power is turned
on, the DC controller restores the NVRAM data on the replacement formatter.
Replacing both the formatter and the DC controller at the same time will result in severe print-quality
problems.
NOTE: The base model does not have a fax card installed.
Replacing the formatter PCA before the DC controller PCA
Use the following procedure if you need to install a replacement formatter PCA and a replacement DC
controller.
NOTE: If you are only installing a replacement formatter PCA, go to Remove the formatter PCA and
fax PCA on page 158.
1. Install a replacement formatter PCA.
2. Turn the product on, and wait for the print-cartridge volume indicators to appear on the control-
panel display.
NOTE: This allows important product information to be written to the replacement formatter PCA.
3. Turn the product off.
4. Install a replacement DC controller. See DC controller PCA on page 161.
5. Turn the product on.
Remove the formatter PCA and fax PCA
CAUTION: Do not bend or fold the flat flexible cables (FFCs) during removal or installation. Also, do
not straighten pre-folds in the FFCs. You must make sure that all FFCs are fully seated in their
connectors. Failure to fully seat an FFC into a connector can cause a short circuit in a PCA.
Some parts are sensitive to electrostatic discharge (ESD). Always perform service work at
an ESD-protected workstation or mat. If an ESD workstation or mat is not available, ground yourself by
touching the sheet-metal chassis before touching an ESD-sensitive part.
NOTE: The base model does not have a fax PCA.
1. Remove the right cover. See Right cover on page 156.
158 Chapter 6 Removal and replacement ENWW
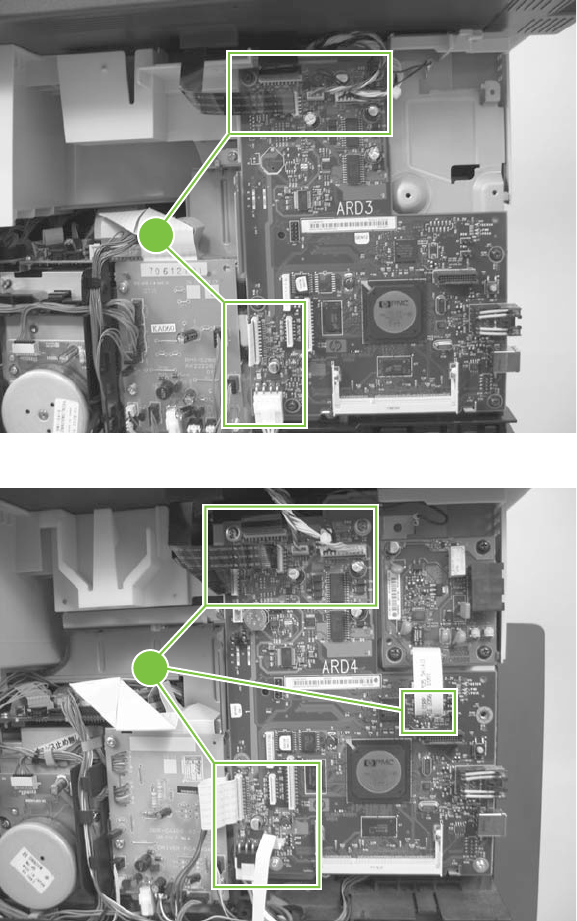
2. Disconnect all of the connectors (callout 1).
Figure 6-56 Remove the formatter (1 of 4; base model)
1
Figure 6-57 Remove the formatter (2 of 4; fax model)
1
ENWW Components and major assemblies 159
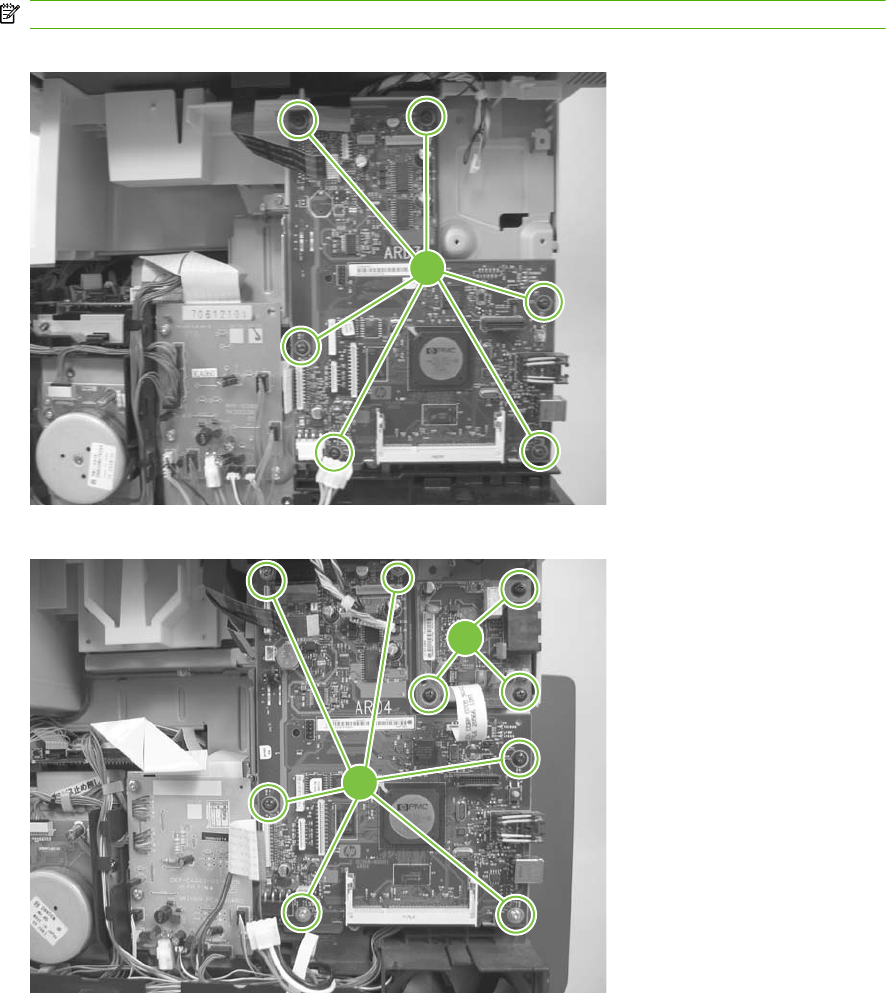
3. Remove six screws (callout 2) for the base model or nine screws (callout 3) for the fax model, and
then remove the formatter PCA and the fax PCA.
NOTE: The base model does not have a fax PCA.
Figure 6-58 Remove the formatter (3 of 4; base model)
2
Figure 6-59 Remove the formatter (4 of 4; fax model)
3
3
160 Chapter 6 Removal and replacement ENWW
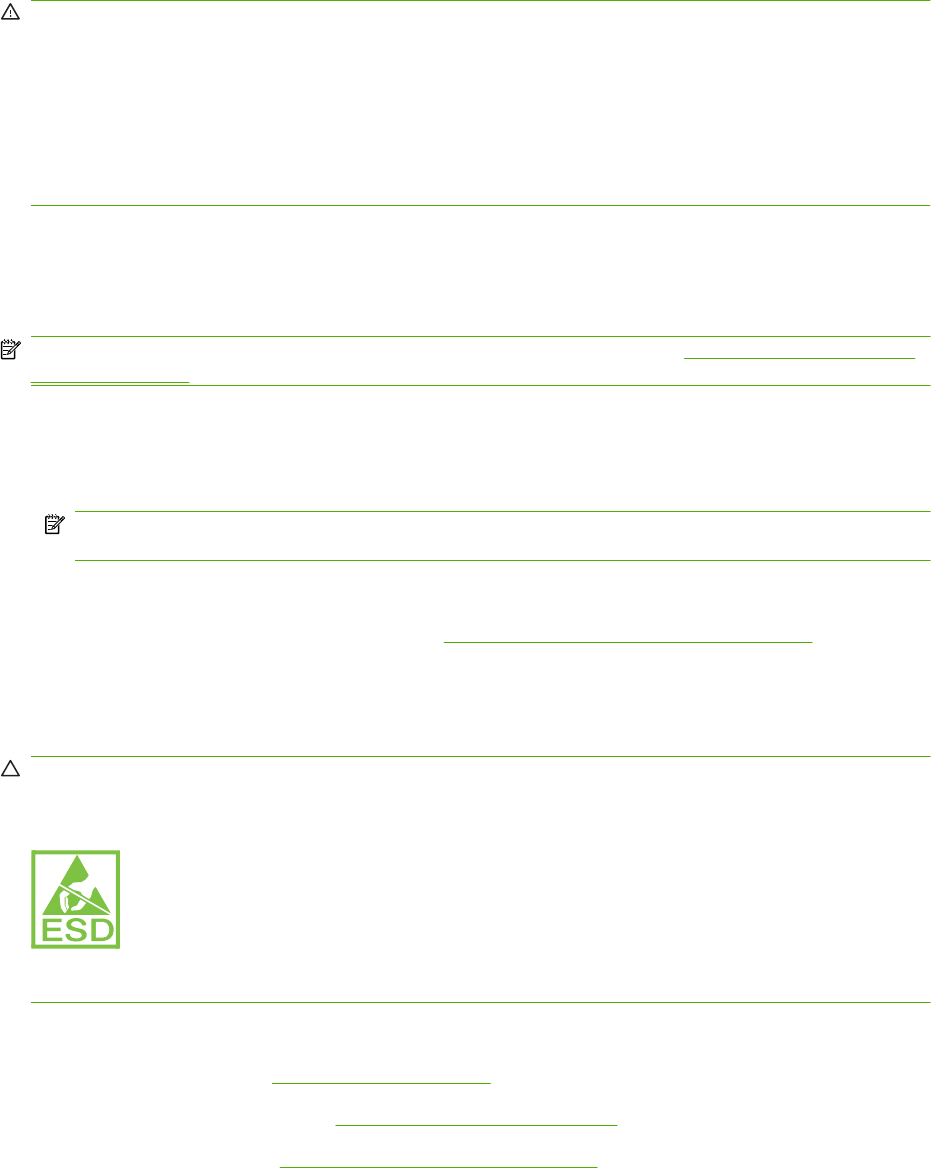
DC controller PCA
Special considerations
WARNING! Do not install a replacement formatter PCA and a replacement DC controller PCA at the
same time.
The formatter PCA and the DC controller PCA store important product configuration information
(NVRAM data) that is lost if both PCAs are replaced at the same time. When the product power is turned
on, the formatter restores the NVRAM data to a replacement DC controller.
Replacing both the DC controller and the formatter at the same time will result in severe print-quality
problems.
Replacing the DC controller PCA before the formatter PCA
Use the following procedure if you need to install a replacement DC controller and a replacement
formatter PCA.
NOTE: If you are only installing a replacement DC controller PCA, go to Remove the DC controller
PCA on page 161.
1. Install a replacement DC controller PCA.
2. Turn the product on, and wait for the print-cartridge volume indicators to appear on the control-
panel display.
NOTE: This allows important product information to be written to the replacement DC controller
PCA.
3. Turn the product off.
4. Install a replacement formatter PCA. See Formatter PCA and fax PCA on page 158.
5. Turn the product on.
Remove the DC controller PCA
CAUTION: Do not bend or fold the flat flexible cables (FFCs) during removal or installation. Also, do
not straighten pre-folds in the FFCs. You must make sure that all FFCs are fully seated in their
connectors. Failure to fully seat an FFC into a connector can cause a short circuit in a PCA.
Some parts are sensitive to electrostatic discharge (ESD). Always perform service work at
an ESD-protected workstation or mat. If an ESD workstation or mat is not available, ground yourself by
touching the sheet-metal chassis before touching an ESD-sensitive part.
1. Remove the following components:
●Right cover. See Right cover on page 156.
●Scanner assembly. See Scanner assembly on page 163.
●Upper cover. See Upper-cover assembly on page 181.
ENWW Components and major assemblies 161
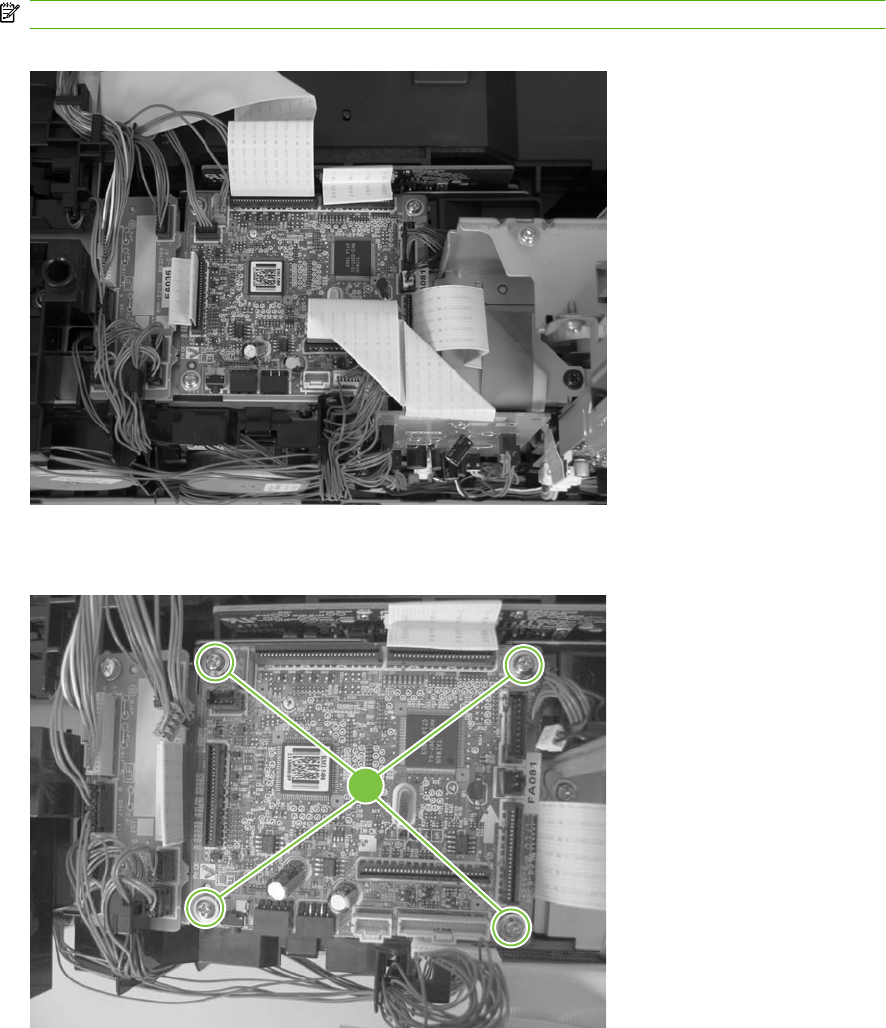
2. Disconnect all of the connectors.
NOTE: The DC controller is located along the top right of the product.
Figure 6-60 Remove the DC controller PCA (1 of 2)
3. Remove four screws (callout 1) and then remove the DC controller PCA.
Figure 6-61 Remove the DC controller PCA (2 of 2)
1
162 Chapter 6 Removal and replacement ENWW
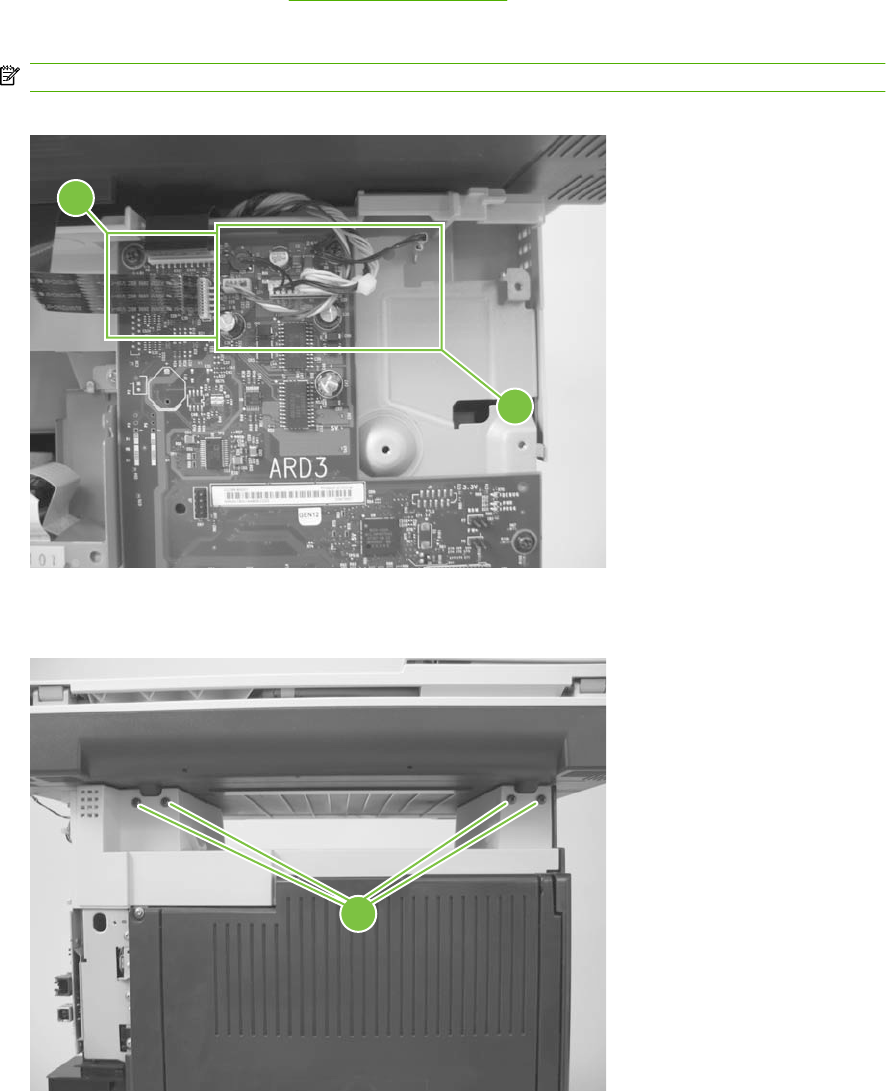
Scanner assembly
1. Remove the right cover. See Right cover on page 156.
2. Disconnect three FFCs (callout 1) and three connectors (callout 2).
NOTE: The base model has two FFCs and three connectors
Figure 6-62 Remove the scanner assembly (1 of 4)
2
1
3. Remove four screws (callout 3).
Figure 6-63 Remove the scanner assembly (2 of 4)
3
ENWW Components and major assemblies 163
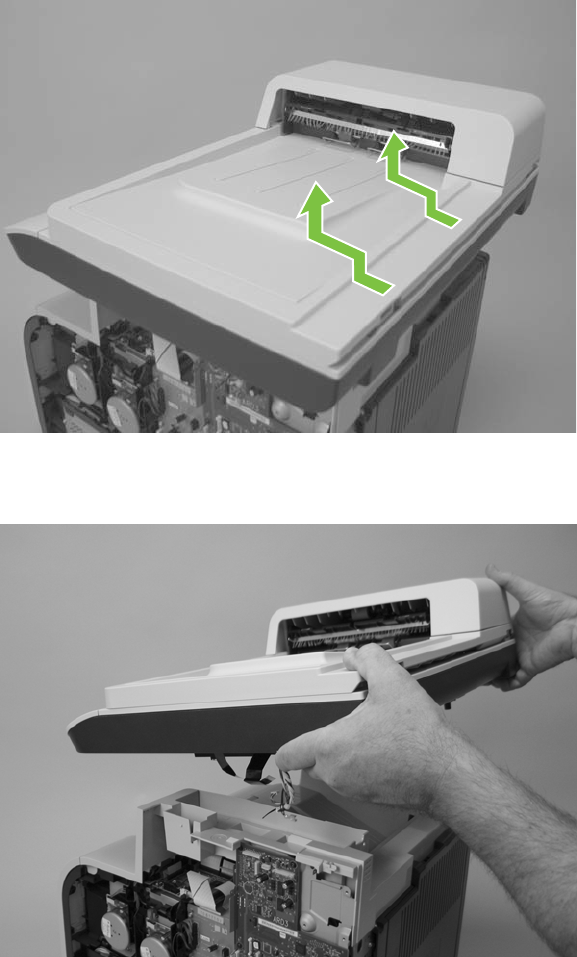
4. Slightly lift up the back of the scanner, and then slide it toward the front of the product.
Figure 6-64 Remove the scanner assembly (3 of 4)
5. Lift the scanner straight up and off of the product.
Figure 6-65 Remove the scanner assembly (4 of 4)
164 Chapter 6 Removal and replacement ENWW
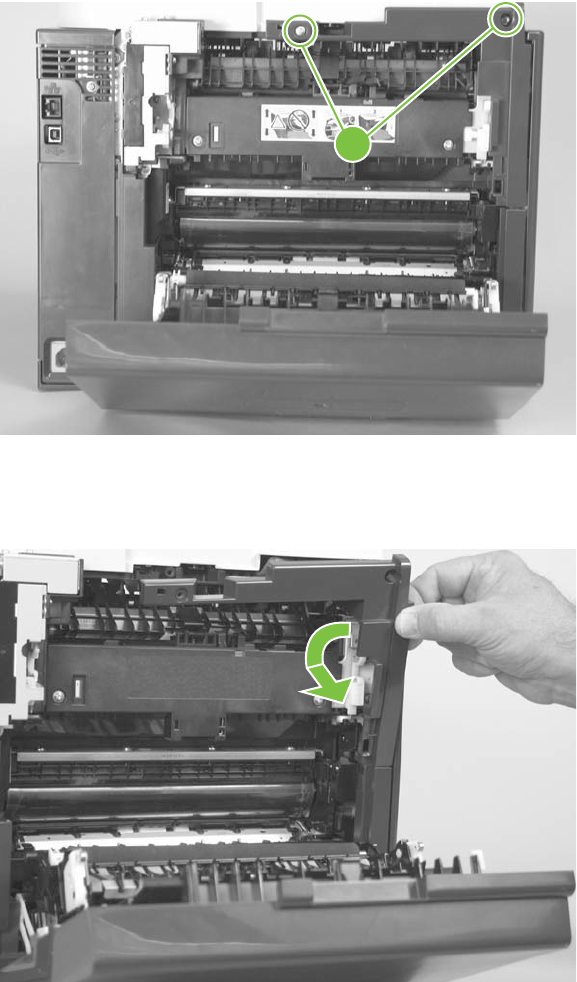
Rear-upper cover (duplex product)
1. Open the rear cover.
2. Remove two screws (callout 1).
Figure 6-66 Remove the rear-upper cover (1 of 2)
1
3. Slightly separate the cover from the product, and then rotate the cover down and then away from
the product to remove it.
Figure 6-67 Remove the rear-upper cover (2 of 2)
ENWW Components and major assemblies 165
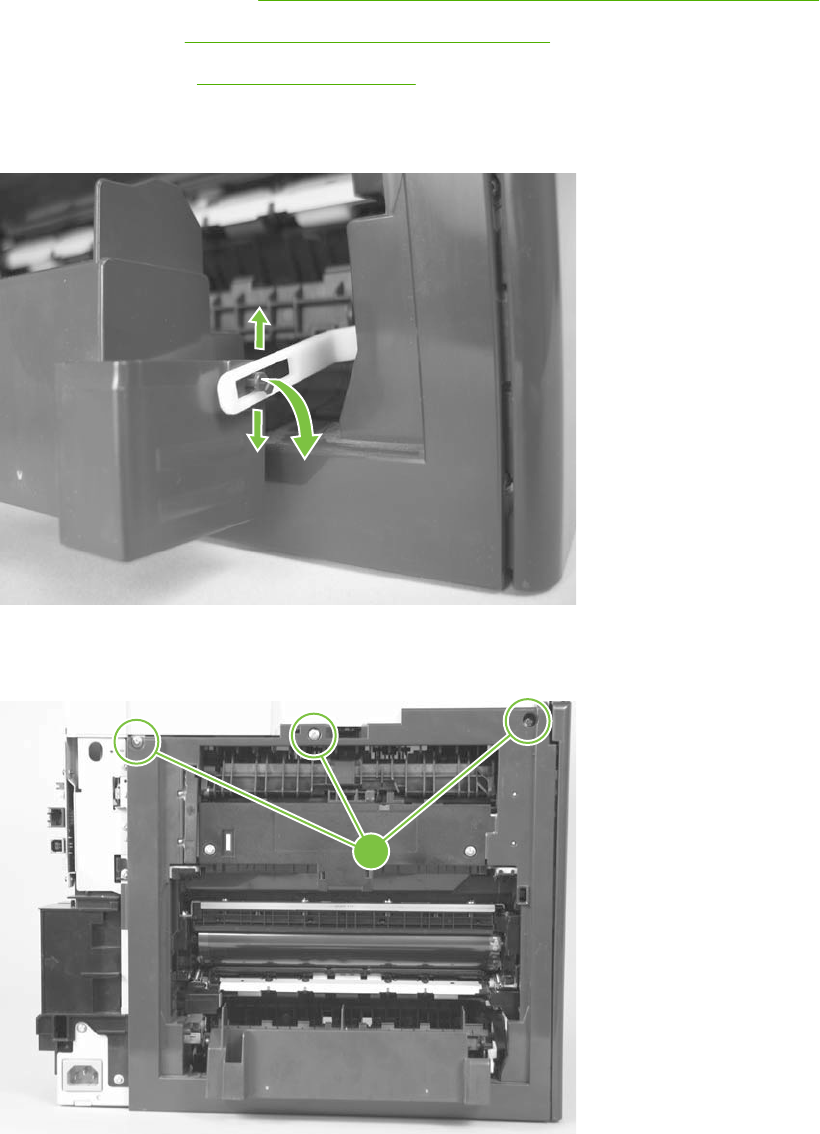
Rear cover and feed guide (simplex product)
1. Remove the following components:
●Rear-door stopper. See Rear-door stopper and link caps (simplex product) on page 151.
●Rear door. See Rear door (simplex product) on page 152.
●Right cover. See Right cover on page 156.
2. Carefully release the link guide from the pivot pin on the feed guide.
Figure 6-68 Remove the rear cover and feed guide (simplex product) (1 of 6)
3. Remove three screws (callout 1).
Figure 6-69 Remove the rear cover and feed guide (simplex product) (2 of 6)
1
166 Chapter 6 Removal and replacement ENWW
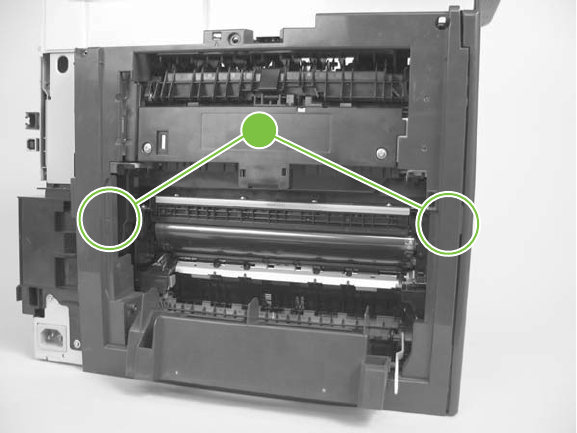
4. Release two tabs (callout 2).
Figure 6-70 Remove the rear cover and feed guide (simplex product) (3 of 6)
2
ENWW Components and major assemblies 167
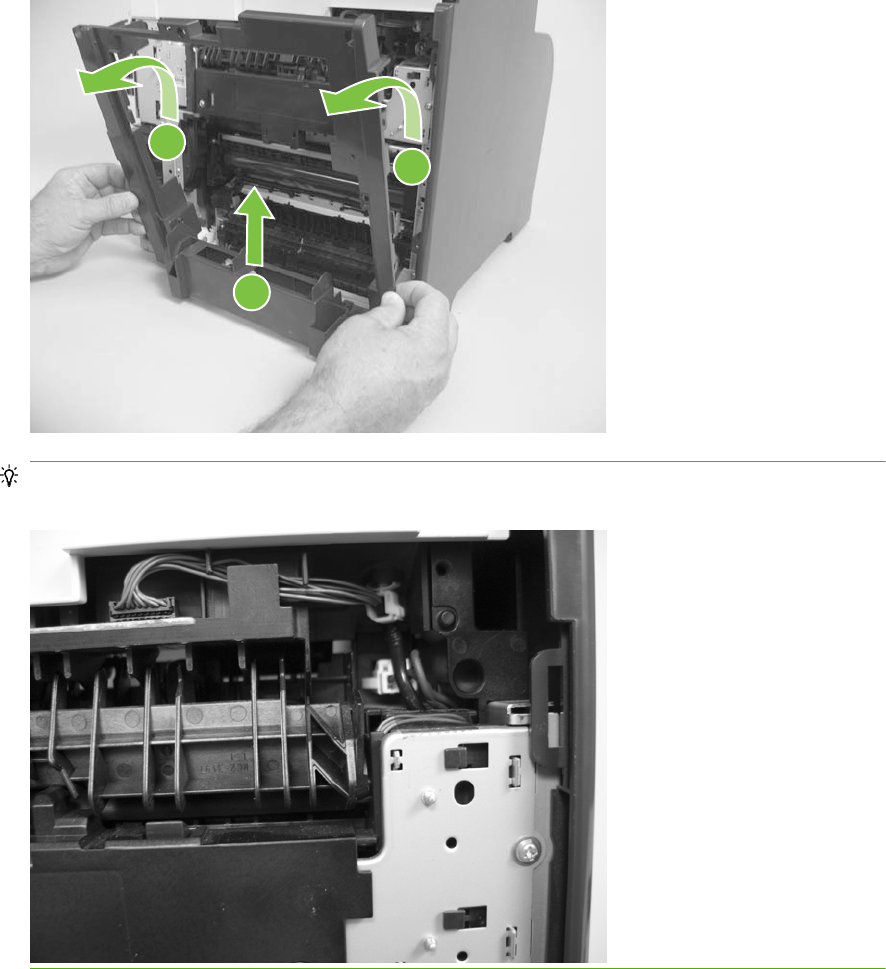
5. Carefully lift the cover up and then rotate it away from the product to remove it.
Figure 6-71 Remove the rear cover and feed guide (simplex product) (4 of 6)
1
2
2
Reinstallation tip Make sure that the wire harnesses at the top of the chassis near the left-side
cover are correctly retained so that they are not pinched when the rear cover is reinstalled.
168 Chapter 6 Removal and replacement ENWW
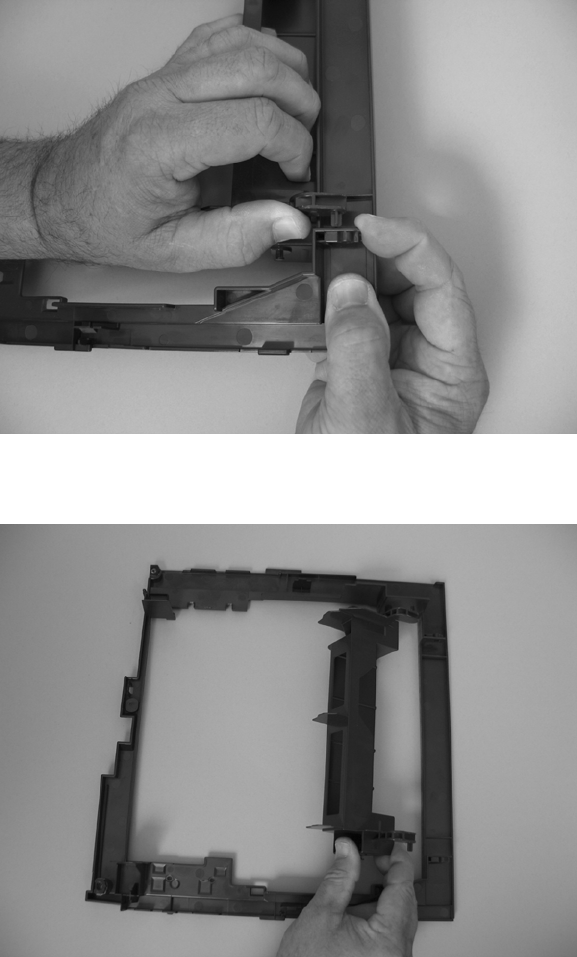
6. Carefully release a feed-guide hinge pin from the rear cover to release the feed guide.
Figure 6-72 Remove the rear cover and feed guide (simplex product) (5 of 6)
7. Remove the feed guide.
Figure 6-73 Remove the rear cover and feed guide (simplex product) (6 of 6)
ENWW Components and major assemblies 169
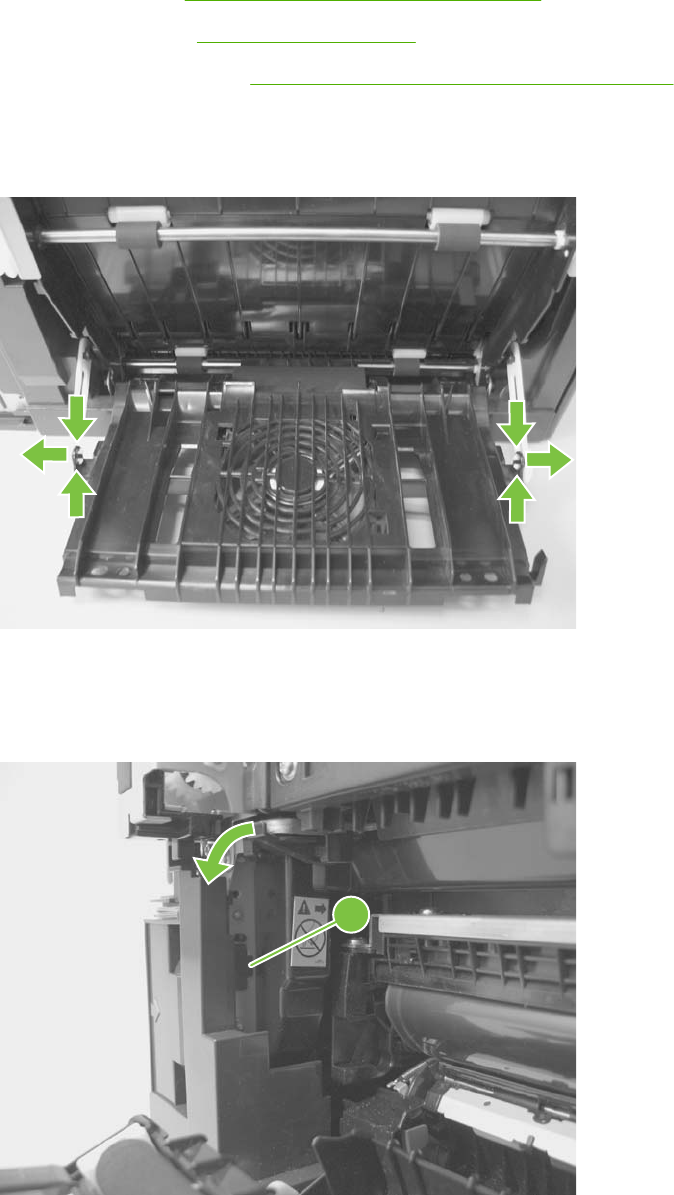
Rear-lower cover and rear-door links (duplex product)
1. Remove the following components:
●Rear door. See Rear door (duplex product) on page 154.
●Right cover. See Right cover on page 156.
●Rear upper cover. See Rear-upper cover (duplex product) on page 165.
2. Use a pair of needle-nose pliers to release two tabs, and then remove the rear-door link cap. Repeat
this step for the remaining rear-door link cap.
Figure 6-74 Remove the rear- lower cover and rear-door links (duplex product) (1 of 6)
3. Open the duplex-feed assembly.
4. Release one tab (callout 1) and slightly separate the cover from the product.
Figure 6-75 Remove the rear-lower cover and rear-door links (duplex product) (2 of 6)
1
170 Chapter 6 Removal and replacement ENWW
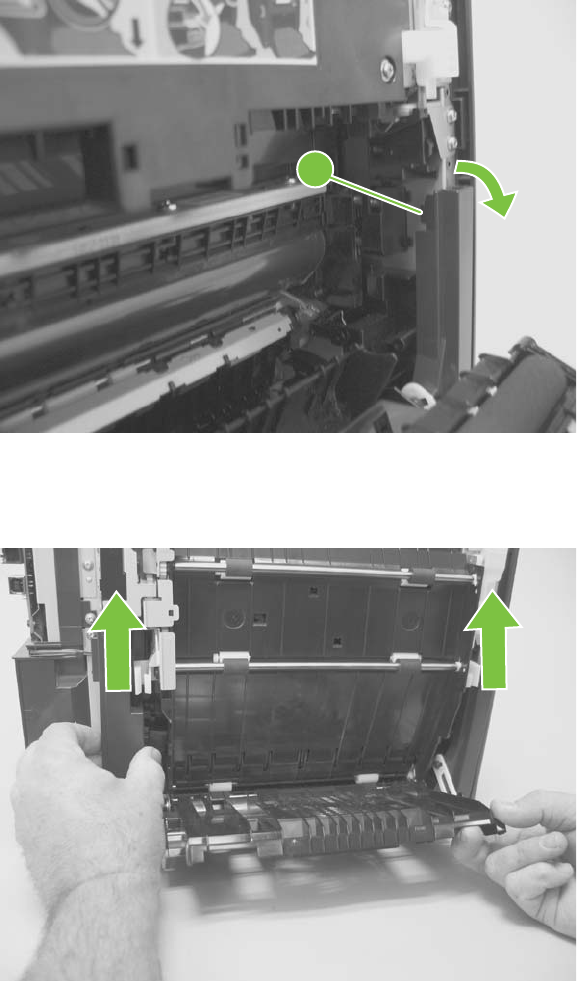
5. Release one tab (callout 2) and slightly separate the cover from the product.
Figure 6-76 Remove the rear-lower cover and rear-door links (duplex product) (3 of 6)
2
6. Close the duplex assembly, and then lift up on one side of the cover, and then the other side of the
cover to release it.
Figure 6-77 Remove the rear-lower cover and link-guides (duplex product) (4 of 6)
ENWW Components and major assemblies 171
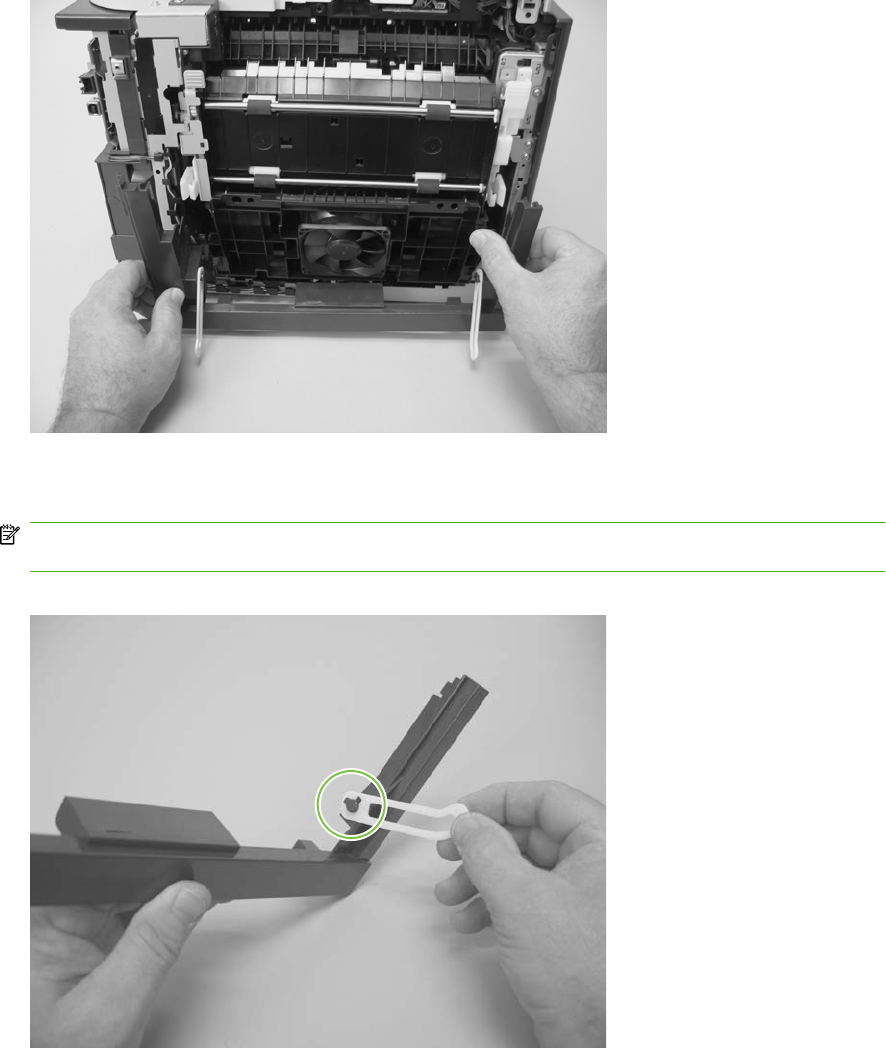
7. Slightly lift up the rear-door rib assembly, and then carefully slide the cover away from the product
to remove it.
Figure 6-78 Remove the rear-lower cover and link-guides (duplex product) (5 of 6)
8. Rotate the rear-door link until the slot in the link aligns with the tap on the link-hinge pin, and then
remove the rear-door link. Repeat this step for the remaining rear-door link.
NOTE: If you are installing a replacement rear-lower cover, remove the rear-door links from the
discarded cover, and then install them on the replacement cover.
Figure 6-79 Remove the rear-lower cover and rear-door links (duplex product) (6 of 6)
172 Chapter 6 Removal and replacement ENWW
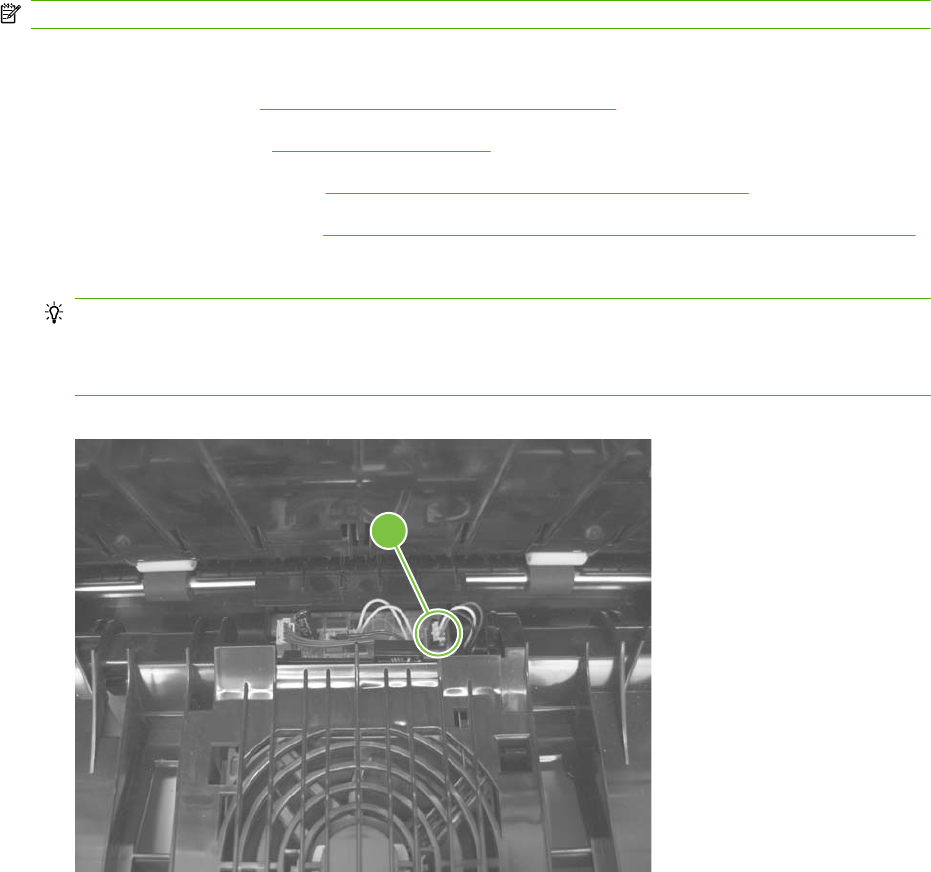
Rear-door rib assembly (duplex product)
NOTE: The duplex fan (FM2) is a component of the rear-door rib assembly.
1. Remove the following components:
●Rear door. See Rear door (duplex product) on page 154.
●Right cover. See Right cover on page 156.
●Rear upper cover. See Rear-upper cover (duplex product) on page 165.
●Rear-lower cover. See Rear-lower cover and rear-door links (duplex product) on page 170.
2. Disconnect one connector (callout 1).
TIP: The PCA can be dislodged when disconnecting the connector. To secure the PCA, carefully
push it towards the inside of the product to clear the mounting tabs near the rib assembly (callout 2
shows the PCA correctly positioned under the tabs). Slide the PCA towards the rib assembly to
position the edge of the PCA under the mounting tabs.
Figure 6-80 Remove the rear-door rib assembly (duplex product) (1 of 3)
1
ENWW Components and major assemblies 173
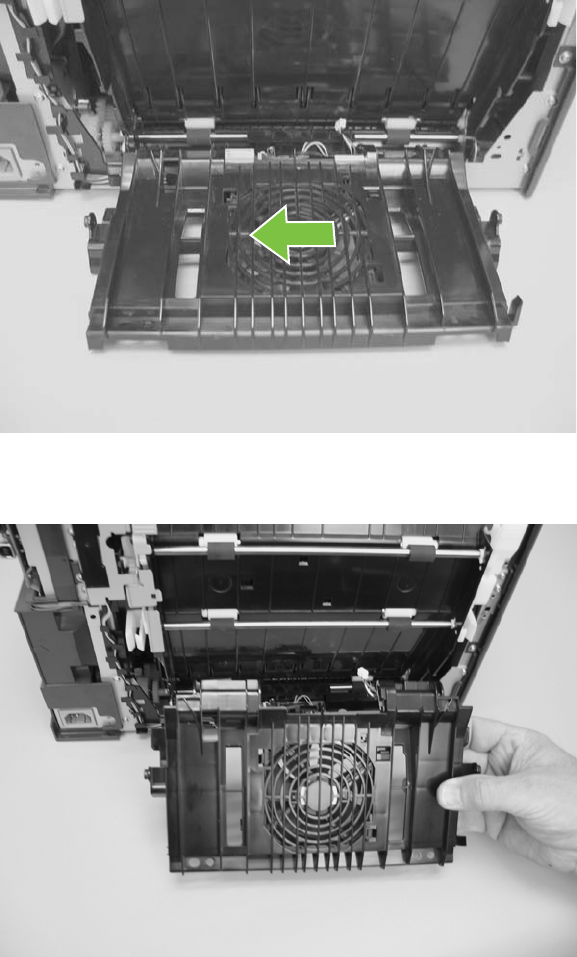
3. Slide the assembly toward the power cord side of the product to release the hinge pin.
Figure 6-81 Remove the rear-door rib assembly (duplex product) (2 of 3)
4. Remove the assembly.
Figure 6-82 Remove the rear-door rib assembly (duplex product) (3 of 3)
174 Chapter 6 Removal and replacement ENWW
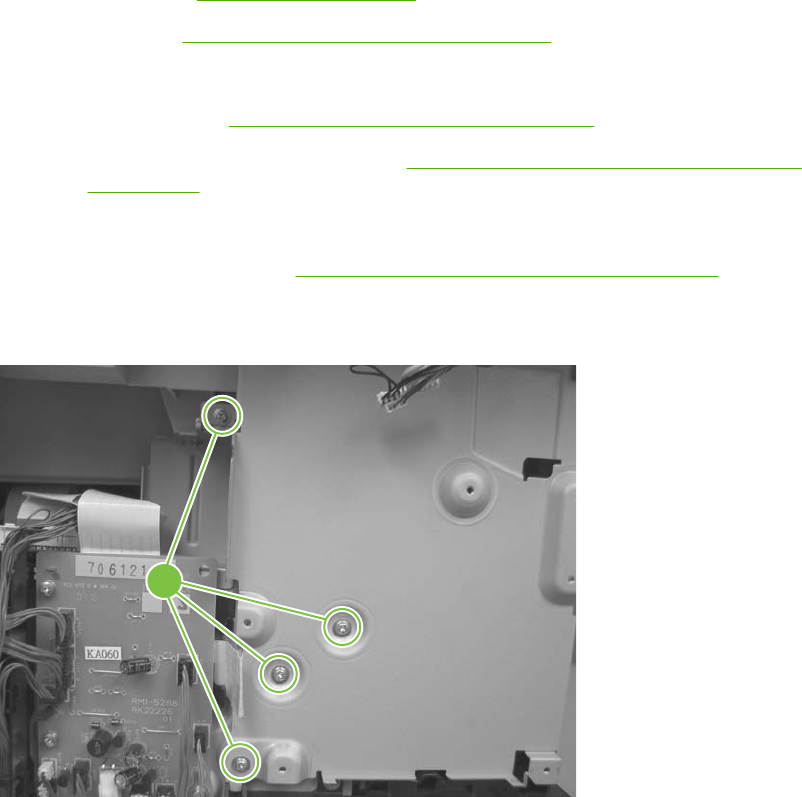
Fuser-motor assembly
1. Remove the following components:
●Right cover. See Right cover on page 156.
●Formatter. See Formatter PCA and fax PCA on page 158.
●Simplex products
◦Rear door. See Rear door (simplex product) on page 152.
◦Rear cover (simplex products). See Rear cover and feed guide (simplex product)
on page 166.
●Duplex products
◦Rear-upper cover. See Rear-upper cover (duplex product) on page 165.
2. Remove four screws (callout 1).
Figure 6-83 Remove the fuser-motor assembly (1 of 10)
1
ENWW Components and major assemblies 175
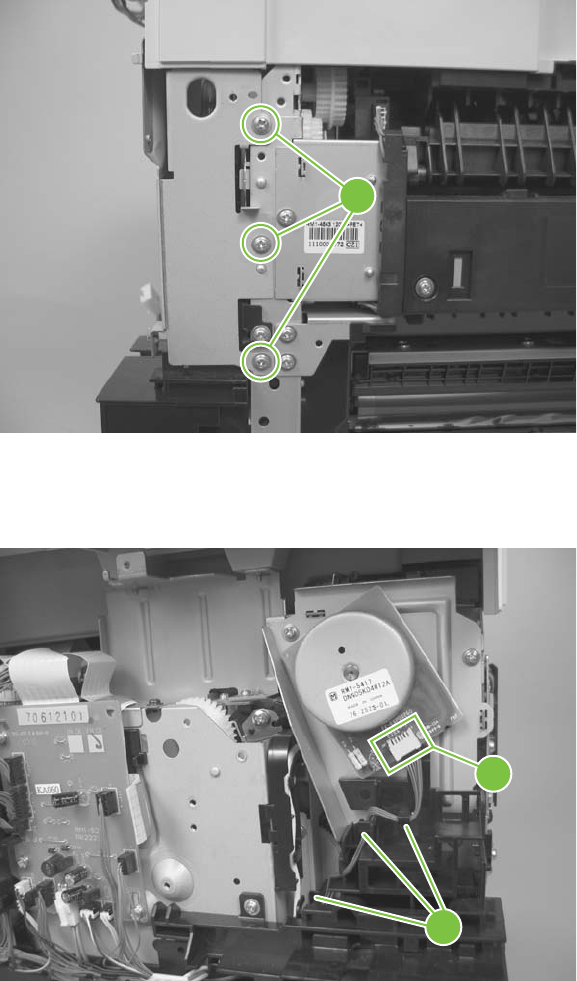
3. Remove three screws (callout 2) and the sheet-metal plate.
Figure 6-84 Remove the fuser-motor assembly (2 of 10)
2
4. Disconnect one connector (callout 3), and then release the wire harnesses from the retainer
(callout 4).
Figure 6-85 Remove the fuser-motor assembly (3 of 10)
4
3
176 Chapter 6 Removal and replacement ENWW
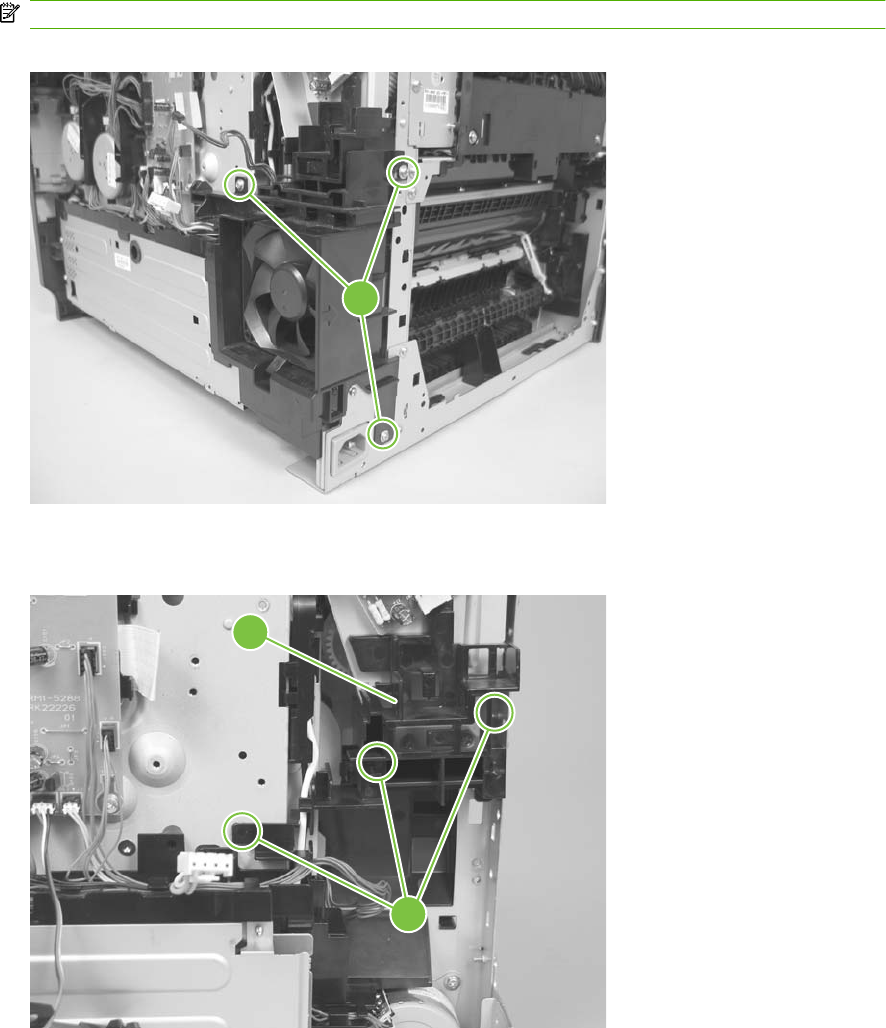
5. Remove three screws (callout 5) and remove the fan assembly.
NOTE: The fan assembly is still attached to the product. Move the fan assembly off to one side.
Figure 6-86 Remove the fuser-motor assembly (4 of 10)
5
6. Release three tabs (callout 6), and then remove the retainer (callout 7).
Figure 6-87 Remove the fuser-motor assembly (5 of 10)
6
7
ENWW Components and major assemblies 177
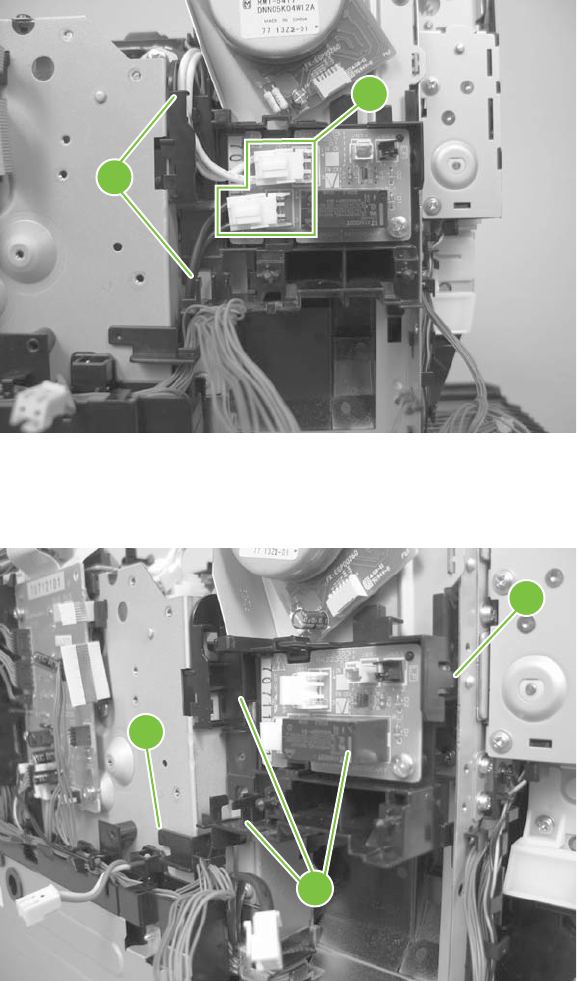
7. Disconnect two connectors (callout 8), and then release the wire harnesses from the retainer
(callout 9).
Figure 6-88 Remove the fuser-motor assembly (6 of 10)
9
8
8. Release one tab (callout 10), and one pin (callout 11) to release the retainer and PCA assembly
(callout 12).
Figure 6-89 Remove the fuser-motor assembly (7 of 10)
12
10
11
178 Chapter 6 Removal and replacement ENWW
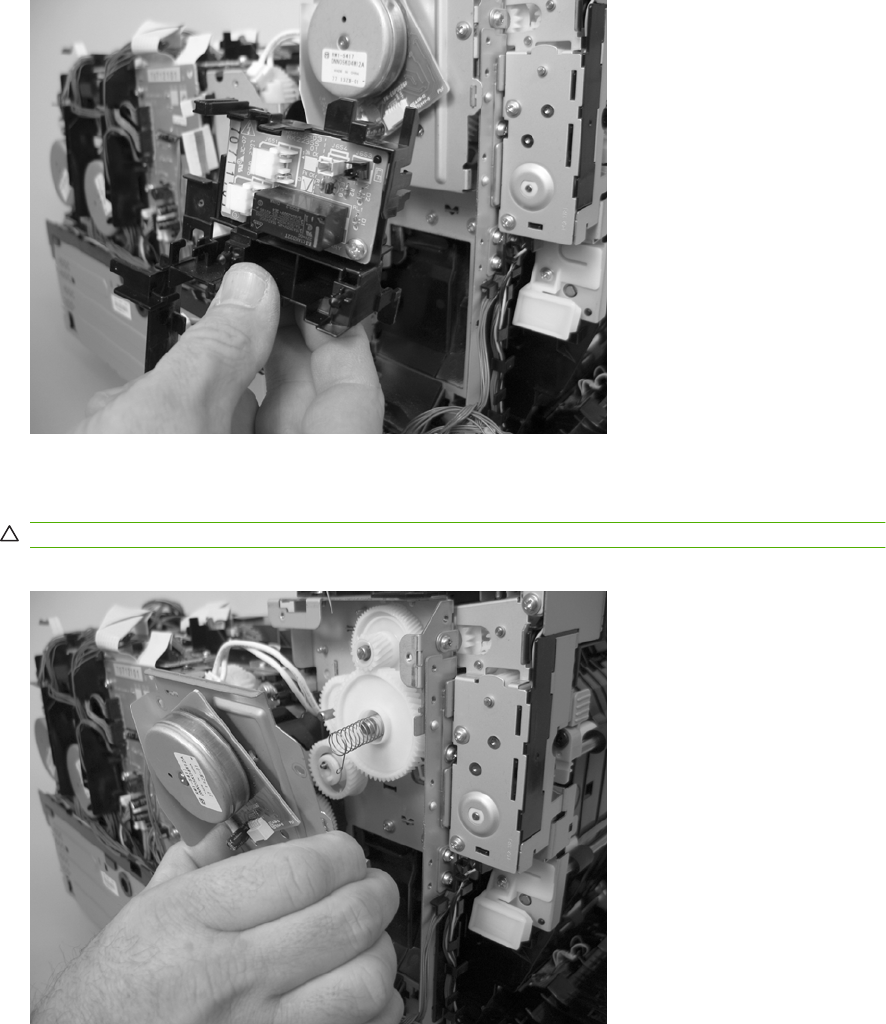
9. Remove the retainer and PCA assembly.
Figure 6-90 Remove the fuser-motor assembly (8 of 10)
10. Before you proceed, take note that the spring and the gears behind the fuser-motor assembly are
not captive.
CAUTION: Do not lose the spring or gears when you remove the fuser-motor assembly.
Figure 6-91 Remove the fuser-motor assembly (9 of 10)
ENWW Components and major assemblies 179
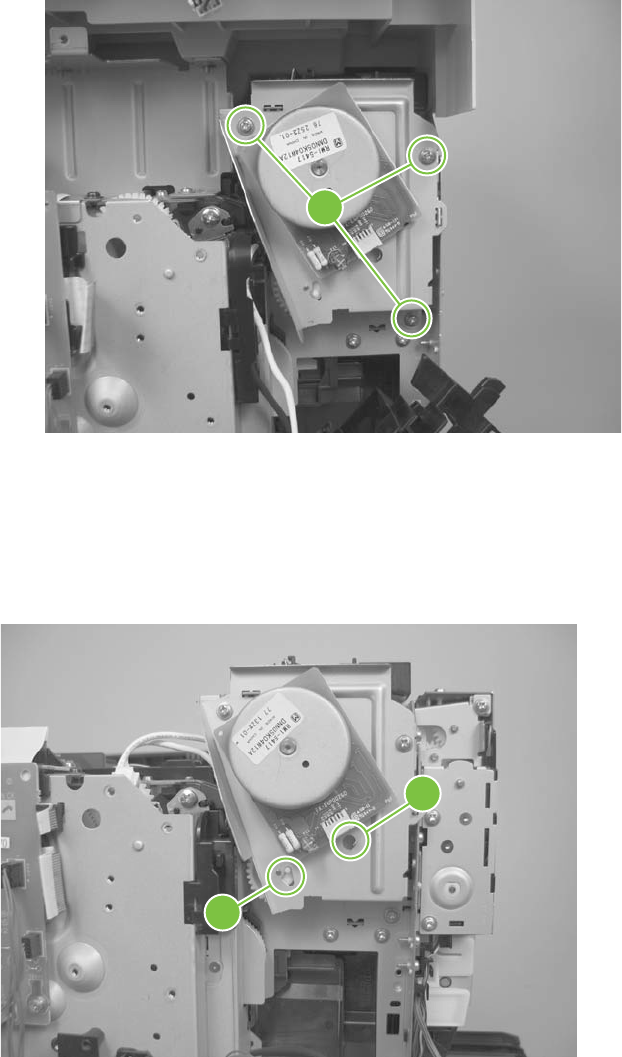
11. Remove three screws (callout 13), and then remove the fuser-motor assembly.
Figure 6-92 Remove the fuser-motor assembly (10 of 10)
13
Reinstall the fuser-motor assembly
Make sure that the fuser-motor assembly spring (callout 1) and gear pin (callout 2) are correctly
positioned in the hole and slot provided in the assembly mounting bracket. The assembly mounting
bracket will fit flat against the product chassis when the fuser-motor assembly is correctly installed.
Figure 6-93 Reinstall the fuser-motor assembly
2
1
180 Chapter 6 Removal and replacement ENWW
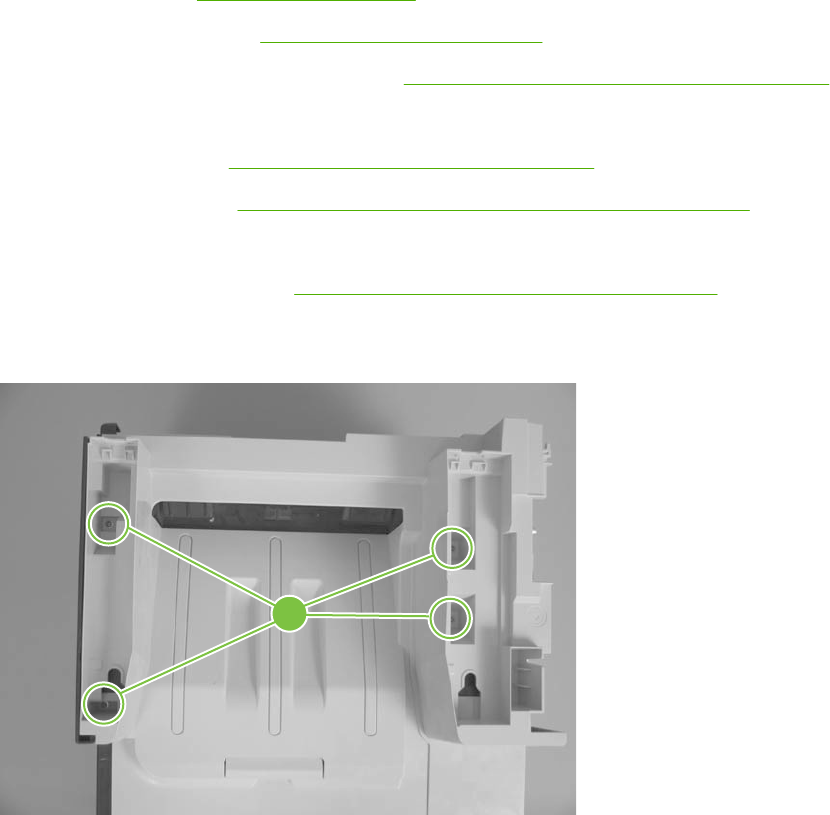
Upper-cover assembly
1. Remove the following components:
●Right cover. See Right cover on page 156.
●Scanner assembly. See Scanner assembly on page 163.
●Right-front cover and power button. See Right-front cover and power button on page 197.
●Simplex products
◦Rear door. See Rear door (simplex product) on page 152.
◦Rear cover. See Rear cover and feed guide (simplex product) on page 166.
●Duplex products
◦Rear upper cover. See Rear-upper cover (duplex product) on page 165.
2. Remove four screws (callout 1).
Figure 6-94 Remove the upper-cover assembly (1 of 3)
1
ENWW Components and major assemblies 181
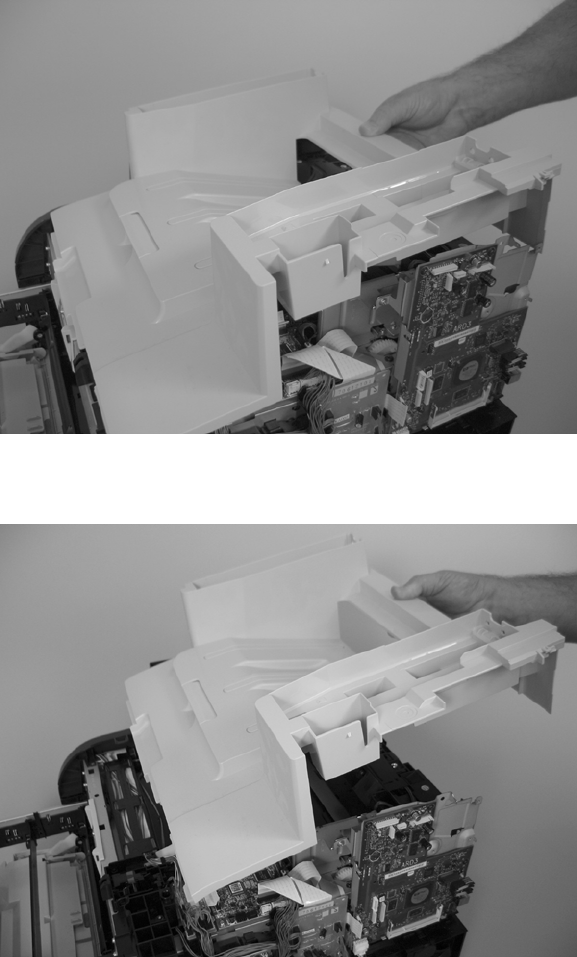
3. Slightly raise the back of the cover up and off of the product.
Figure 6-95 Remove the upper-cover assembly (2 of 3)
4. Slide the cover toward the back of the product to remove it.
Figure 6-96 Remove the upper-cover assembly (3 of 3)
182 Chapter 6 Removal and replacement ENWW
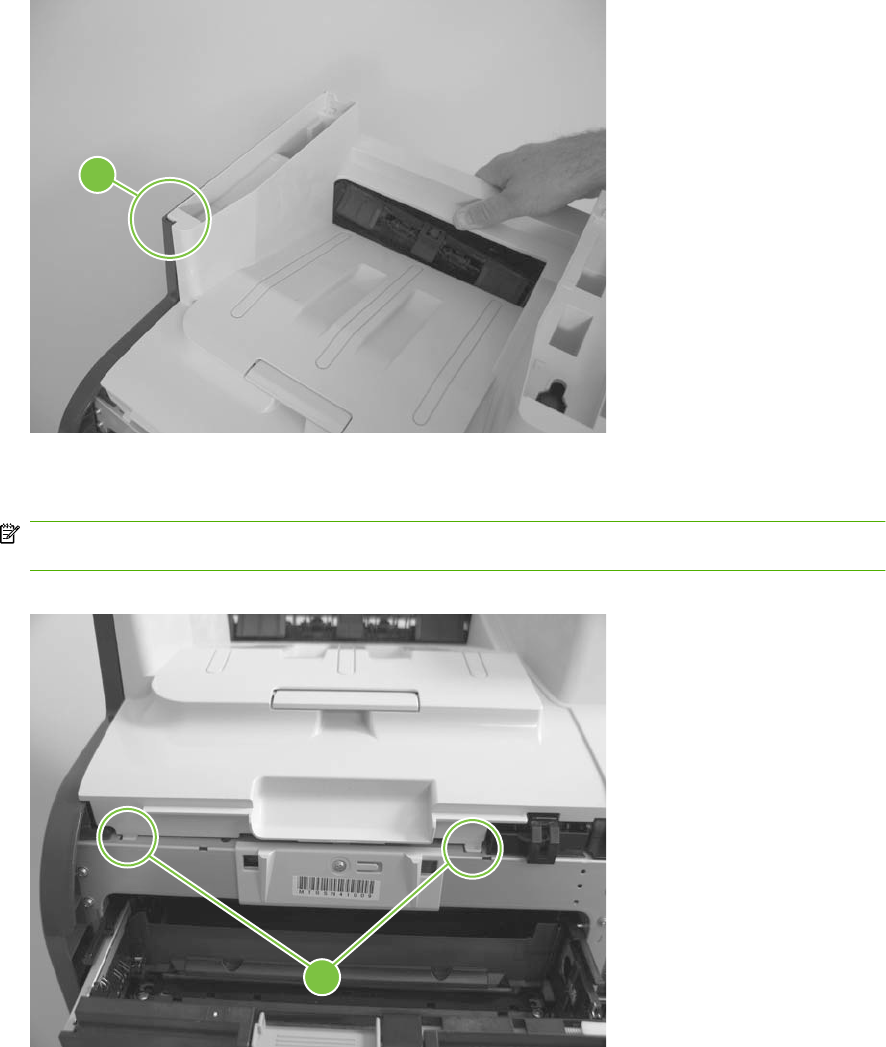
Reinstall the upper-cover assembly
1. Position the upper-cover so that the front-left corner of the upper cover engages the left-side cover
(callout 1).
Figure 6-97 Reinstall the upper-cover assembly (1 of 3)
1
2. Slightly push the cover toward the front of the product to engage the front-locking tabs (callout 2)
with the holes in the chassis.
NOTE: Make sure that the right-front edge of the upper cover (where the product right-front cover
will be installed) is correctly positioned on the chassis.
Figure 6-98 Reinstall the upper-cover assembly (2 of 3)
2
ENWW Components and major assemblies 183
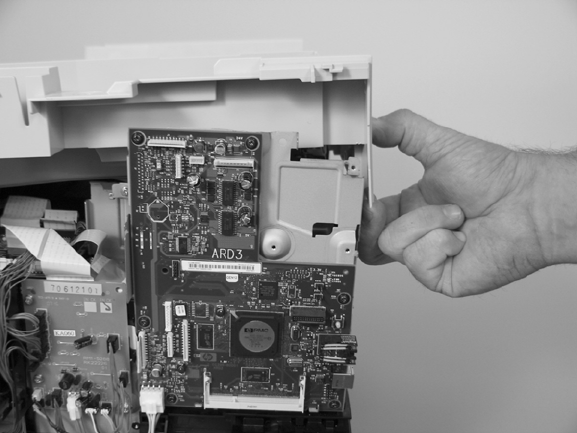
3. Carefully pry the right-rear corner of the upper cover away from the product until the cover fits over
the chassis.
Lower the cover onto the product.
Figure 6-99 Reinstall the upper-cover assembly (3 of 3)
184 Chapter 6 Removal and replacement ENWW
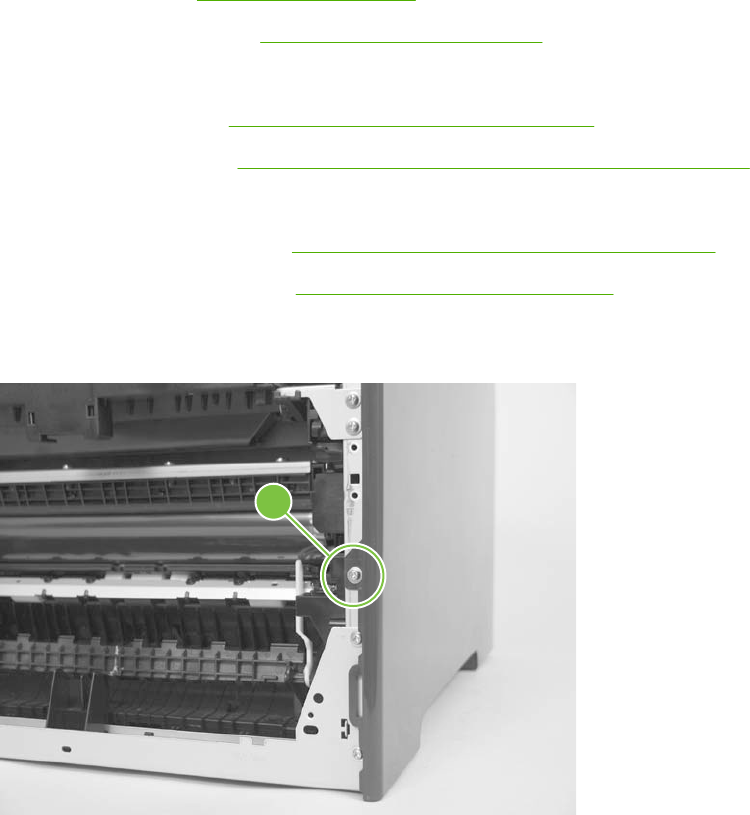
Left cover
1. Remove the following components:
●Right cover. See Right cover on page 156.
●Scanner assembly. See Scanner assembly on page 163.
●Simplex products
◦Rear door. See Rear door (simplex product) on page 152.
◦Rear cover. See Rear cover and feed guide (simplex product) on page 166.
●Duplex products
◦Rear-lower cover. See Rear-upper cover (duplex product) on page 165.
●Upper-cover assembly. See Upper-cover assembly on page 181.
2. Remove one screw (callout 1).
Figure 6-100 Remove the left cover (1 of 4)
1
ENWW Components and major assemblies 185
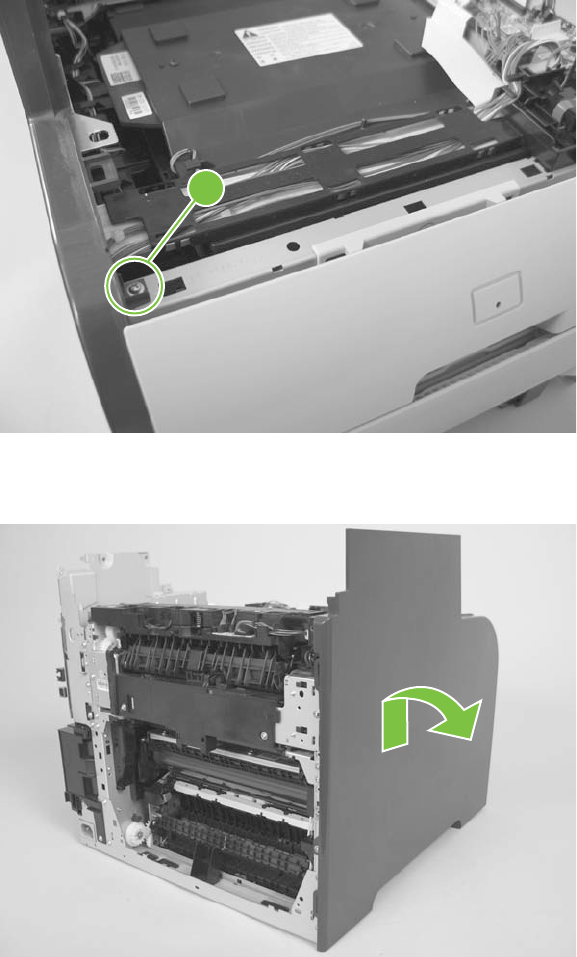
3. Remove one screw (callout 2).
Figure 6-101 Remove the left cover (2 of 4)
2
4. Slightly lift up on the cover, and then rotate the top of the cover away from the product.
Figure 6-102 Remove the left cover (3 of 4)
186 Chapter 6 Removal and replacement ENWW
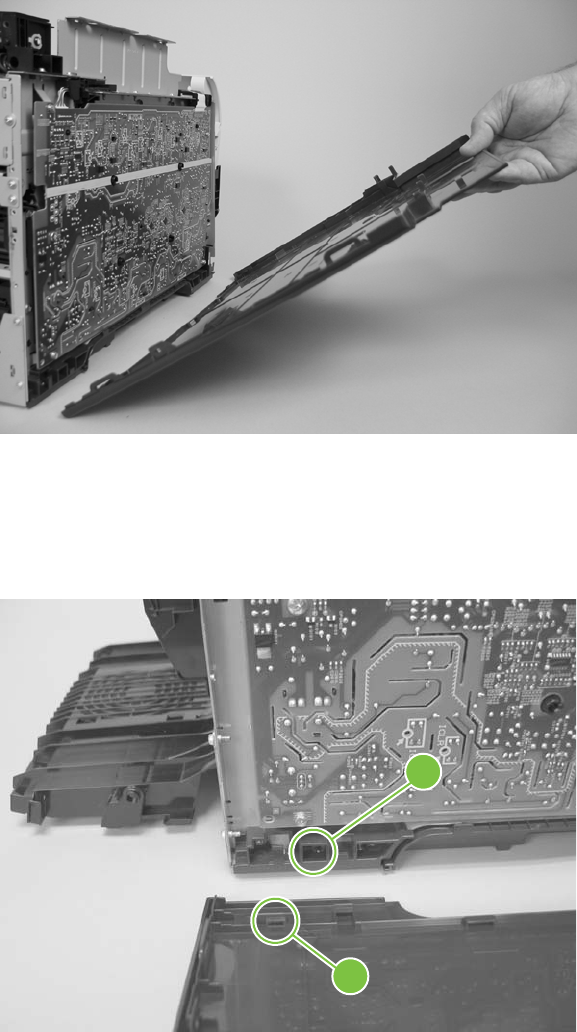
5. Remove the cover.
Figure 6-103 Remove the left cover (4 of 4)
Reinstall the left cover
1. When you reinstall the left cover, make sure that the slot in the cover (callout 1) aligns with the tab
(callout 2) on the product.
Figure 6-104 Reinstall the left cover (1 of 2)
1
2
ENWW Components and major assemblies 187
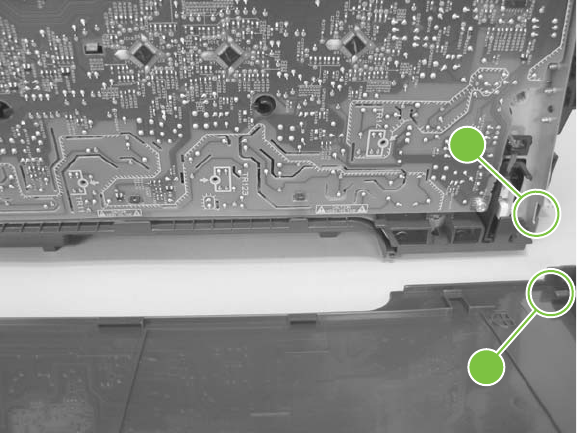
2. When you reinstall the left cover, make sure that the pin on the cover (callout 3) aligns with the slot
(callout 4) in the product.
Figure 6-105 Reinstall the left cover (2 of 2)
3
4
188 Chapter 6 Removal and replacement ENWW
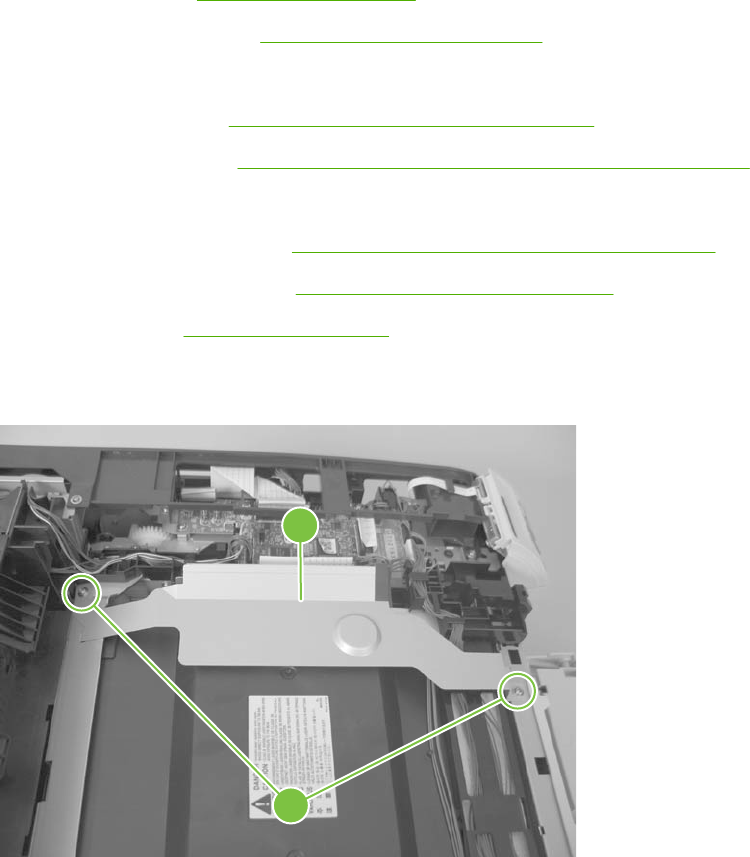
High-voltage power-supply PCA
1. Remove the following components:
●Right cover. See Right cover on page 156.
●Scanner assembly. See Scanner assembly on page 163.
●Simplex products
◦Rear door. See Rear door (simplex product) on page 152.
◦Rear cover. See Rear cover and feed guide (simplex product) on page 166.
●Duplex products
◦Rear-lower cover. See Rear-upper cover (duplex product) on page 165.
●Upper-cover assembly. See Upper-cover assembly on page 181.
●Left cover. See Left cover on page 185.
2. Remove two screws (callout 1), and then remove the sheet-metal plate (callout 2).
Figure 6-106 Remove the high-voltage power-supply PCA (1 of 5)
1
2
ENWW Components and major assemblies 189
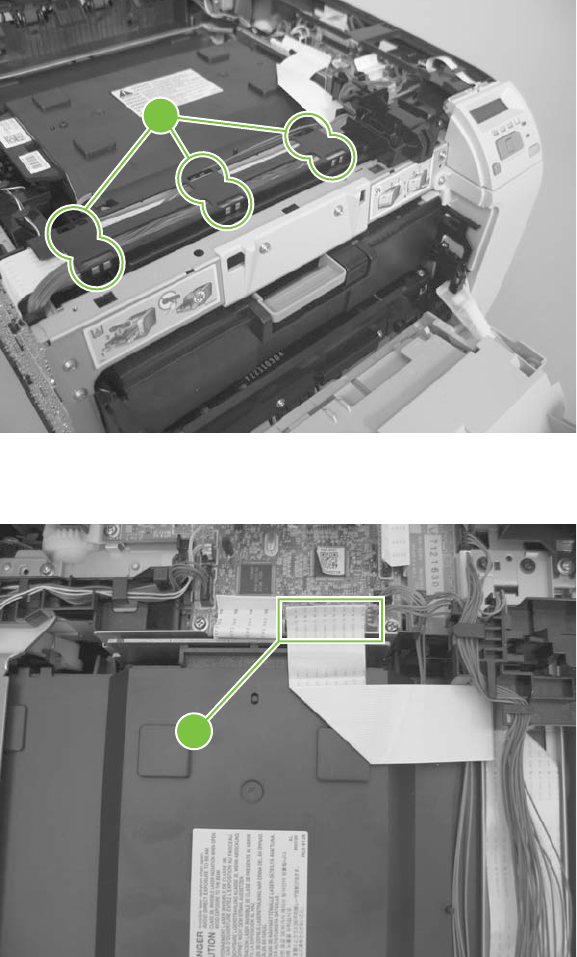
3. Release six tabs (callout 3), and then remove the black-plastic cover.
Figure 6-107 Remove the high-voltage power-supply PCA (2 of 5)
3
4. Disconnect one FFC (callout 4) on the DC controller.
Figure 6-108 Remove the high-voltage power-supply PCA (3 of 5)
4
190 Chapter 6 Removal and replacement ENWW
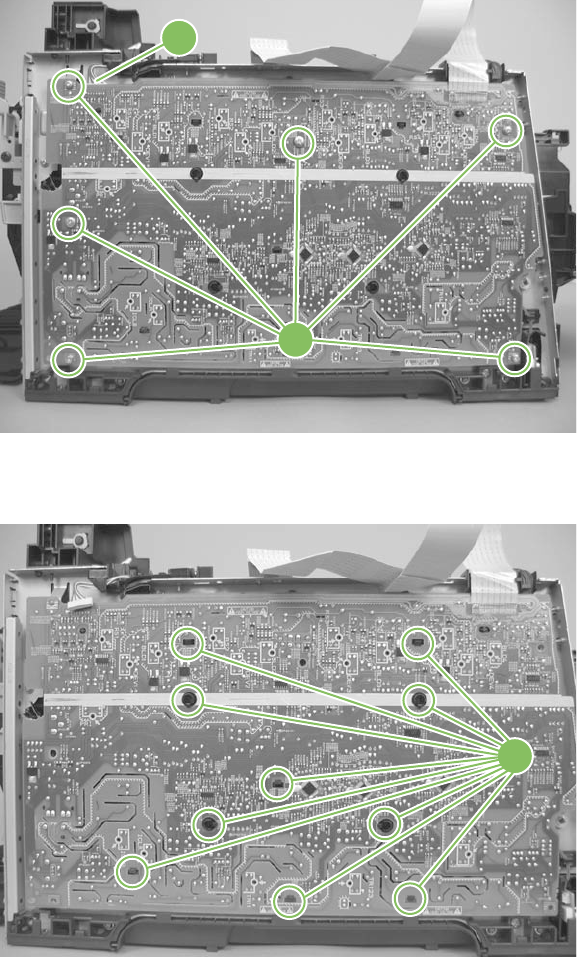
5. Disconnect one connector (callout 5), and then remove six screws (callout 6).
Figure 6-109 Remove the high-voltage power-supply PCA (4 of 5)
5
6
6. Release ten tabs (callout 7), and then remove the high-voltage power-supply PCA.
Figure 6-110 Remove the high-voltage power-supply PCA (5 of 5)
7
ENWW Components and major assemblies 191
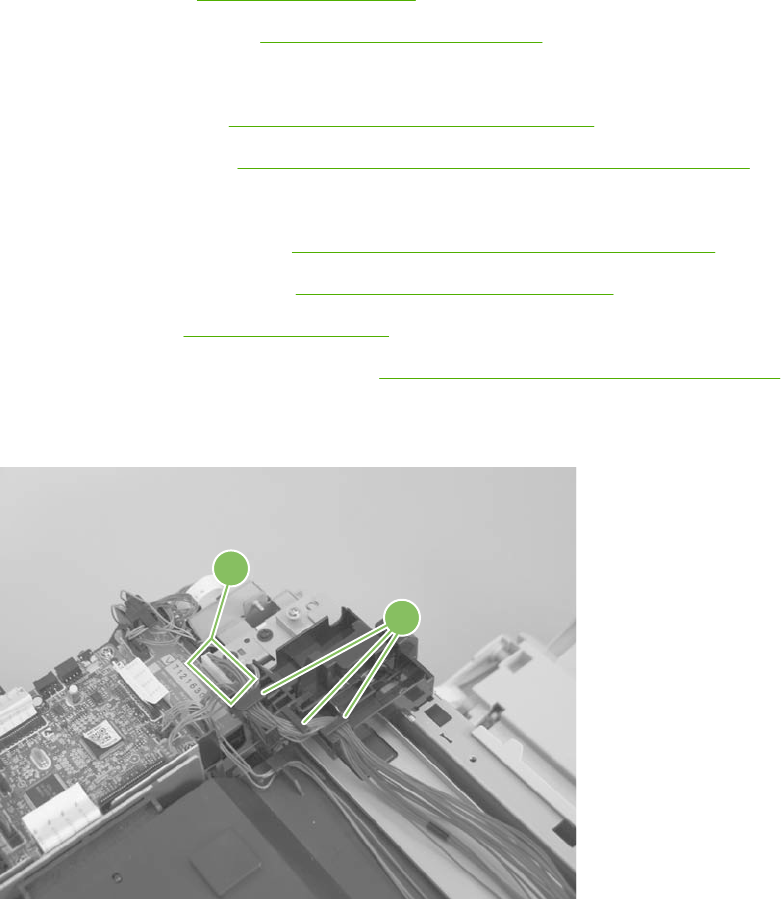
Color-misregistration sensor assembly
1. Remove the following components:
●Right cover. See Right cover on page 156.
●Scanner assembly. See Scanner assembly on page 163.
●Simplex products
◦Rear door. See Rear door (simplex product) on page 152.
◦Rear cover. See Rear cover and feed guide (simplex product) on page 166.
●Duplex products
◦Rear-lower cover. See Rear-upper cover (duplex product) on page 165.
●Upper-cover assembly. See Upper-cover assembly on page 181.
●Left cover. See Left cover on page 185.
●High-voltage power-supply PCA. See High-voltage power-supply PCA on page 189.
2. Disconnect one connector (callout 1), and then release the wire harness from the guide (callout 2).
Figure 6-111 Remove the color-misregistration sensor assembly PCA (1 of 5)
1
2
192 Chapter 6 Removal and replacement ENWW
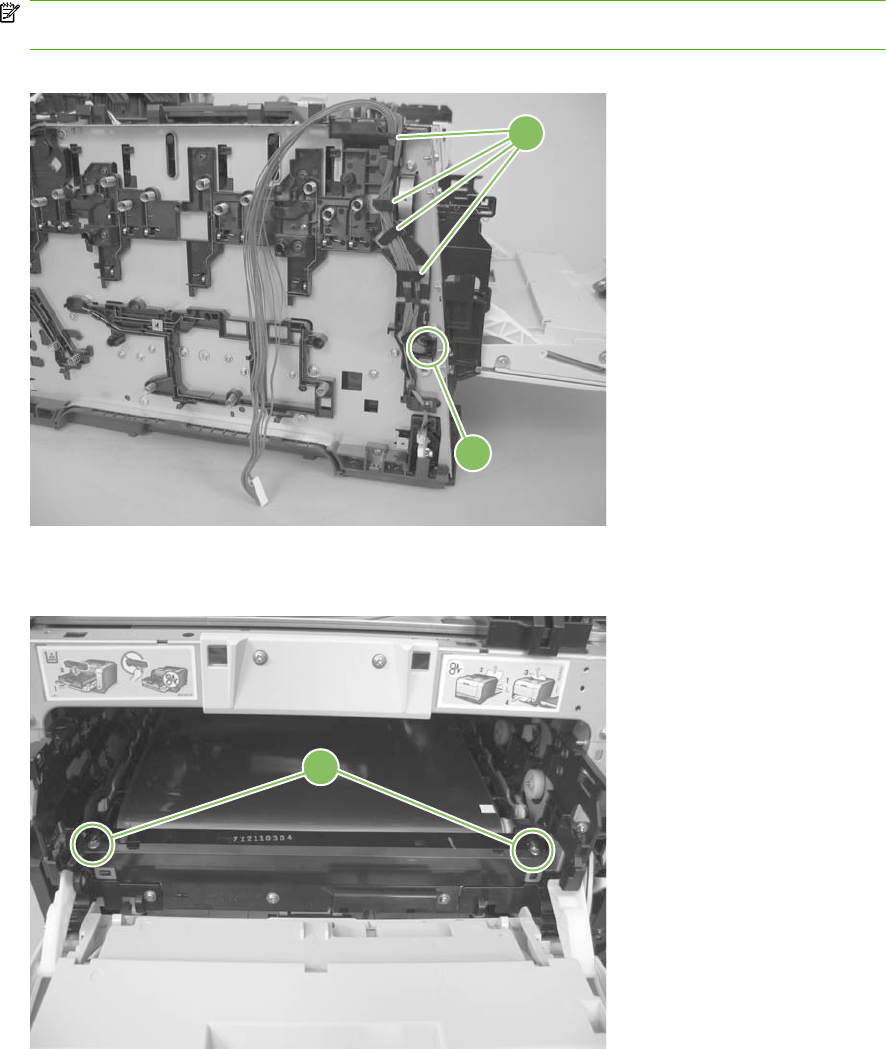
3. Release the wire harness from the guide (callout 3).
NOTE: When you remove the sensor assembly later in this procedure, pass the connector and
wire harness through the hole in the chassis (callout 4).
Figure 6-112 Remove the color-misregistration sensor assembly PCA (2 of 5)
3
4
4. Remove two screws (callout 5).
Figure 6-113 Remove the color-misregistration sensor assembly PCA (3 of 5)
5
ENWW Components and major assemblies 193
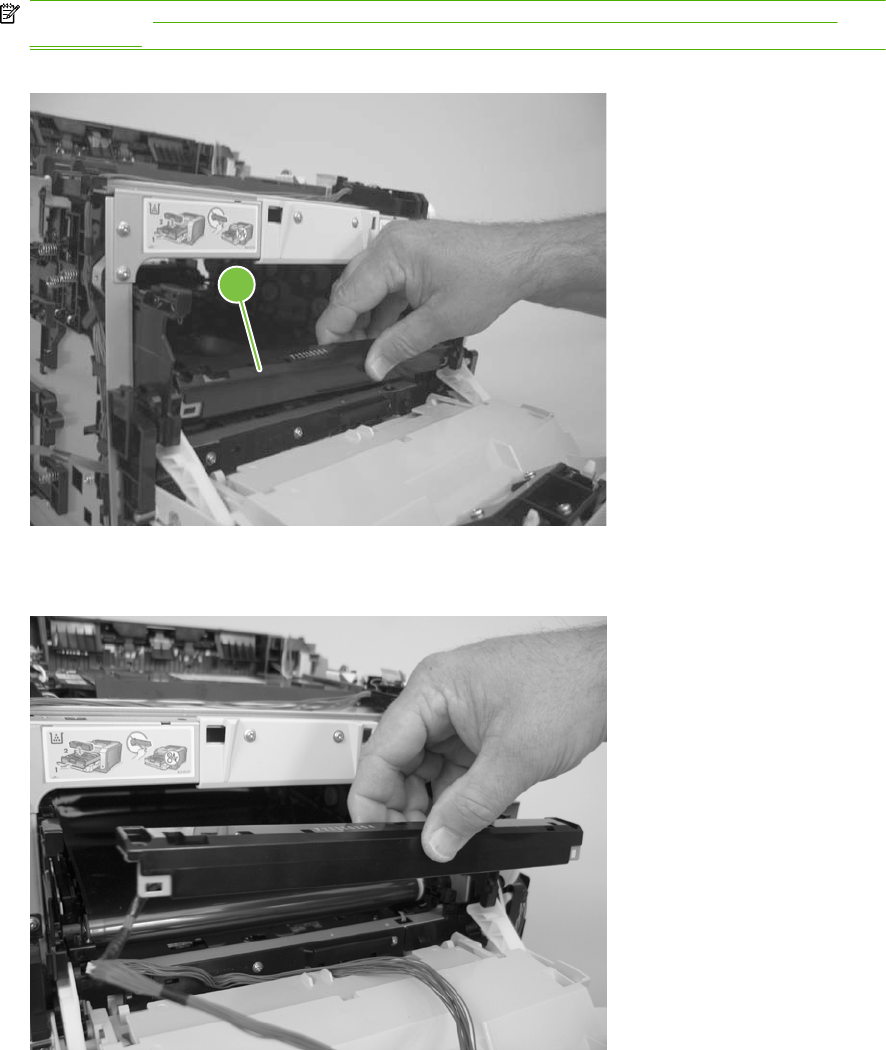
5. Carefully separate the sensor assembly (callout 6) from the product and pass the wire harness
through the hole in the chassis.
NOTE: See Figure 6-112 Remove the color-misregistration sensor assembly PCA (2 of 5)
on page 193.
Figure 6-114 Remove the color-misregistration sensor assembly PCA (4 of 5)
6
6. Remove the sensor assembly from the product.
Figure 6-115 Remove the color-misregistration sensor assembly PCA (5 of 5)
194 Chapter 6 Removal and replacement ENWW
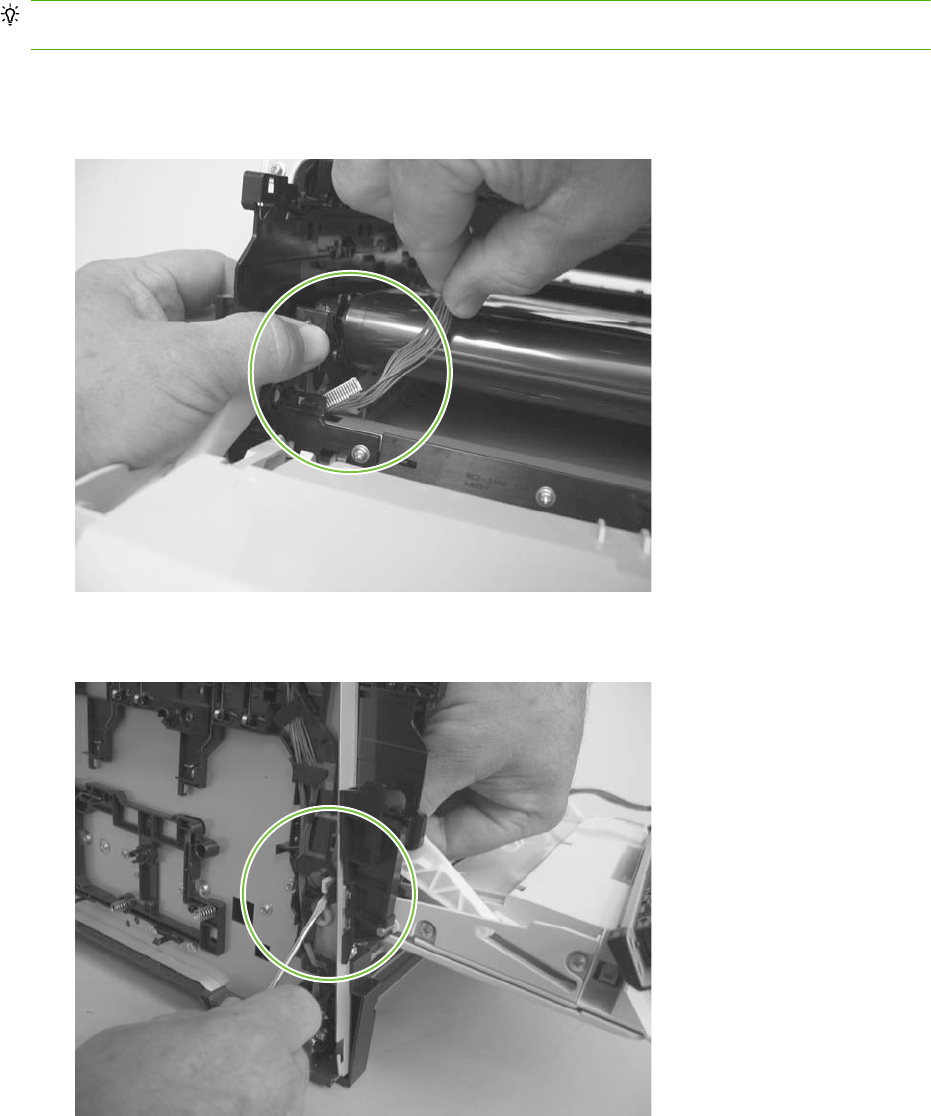
Reinstall the color-misregistration sensor assembly
TIP: You might have to attempt this reinstall procedure several times before you successfully pass the
connector through the hole in the chassis.
1. Push the sensor assembly wire-harness connector into the hole in the chassis from the ITB side
of the product.
Figure 6-116 Reinstall the color-misregistration sensor assembly PCA (1 of 2)
2. Use a small flat blade screwdriver to guide the connector through the hole.
Figure 6-117 Reinstall the color-misregistration sensor assembly PCA (2 of 2)
ENWW Components and major assemblies 195
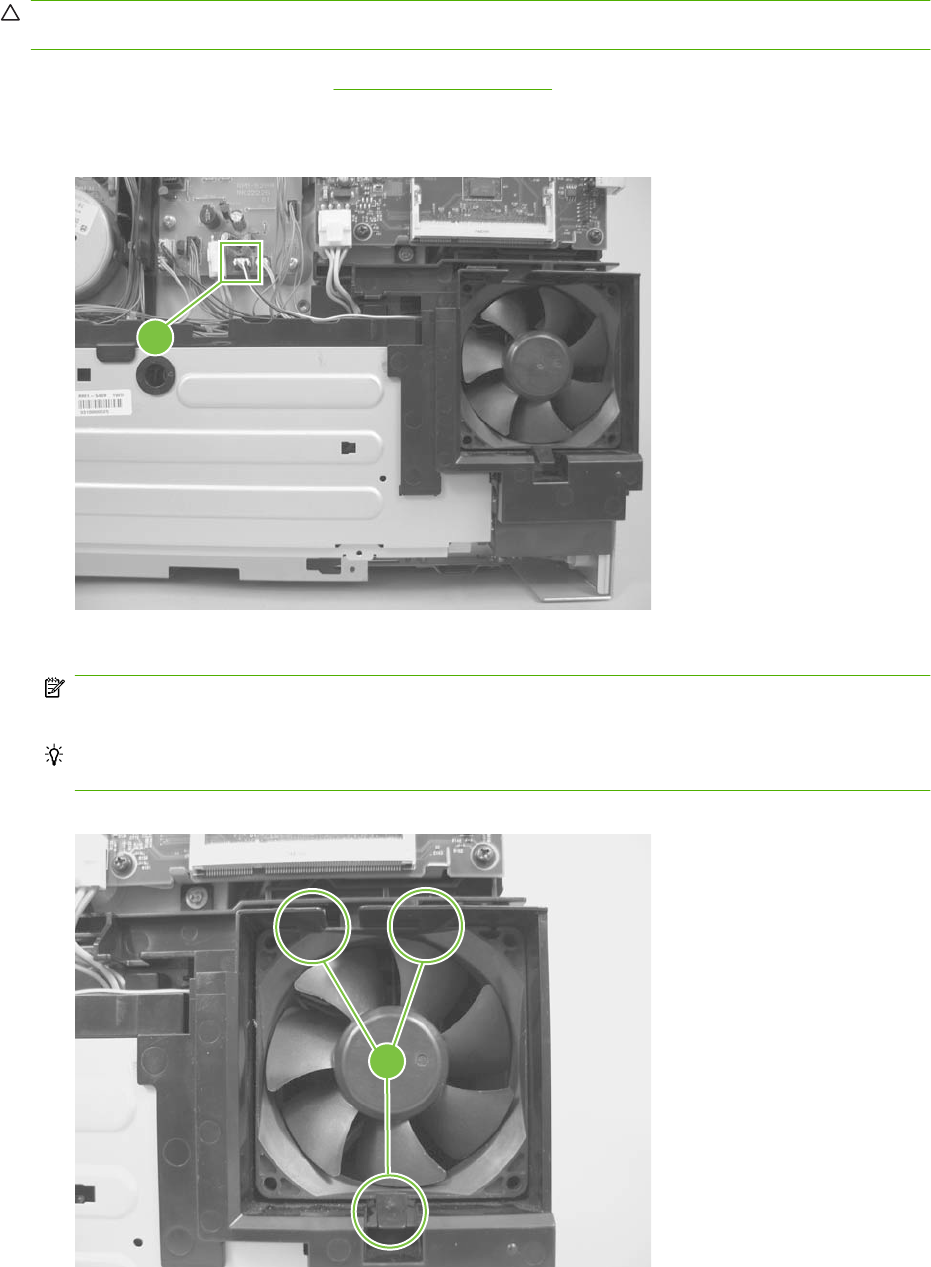
Fan (FM1)
CAUTION: When the fan is reinstalled, it must pull air into the product. The air-flow indicator arrow
embossed on the fan chassis point into the fan duct when the fan is correctly installed.
1. Remove the right cover. See Right cover on page 156.
2. Disconnect one connector (callout 1; J206)
Figure 6-118 Remove the fan (FM1) (1 of 2)
1
3. Release three tabs (callout 2), and then remove the fan.
NOTE: As the fan is removed, you must feed the wire harness through an opening behind the
fan duct.
TIP: Use a small flat blade screwdriver to release the upper to tabs on the fan duct a second time
when the fan is about half way out of the duct.
Figure 6-119 Remove the fan (FM1) (2 of 2)
2
196 Chapter 6 Removal and replacement ENWW
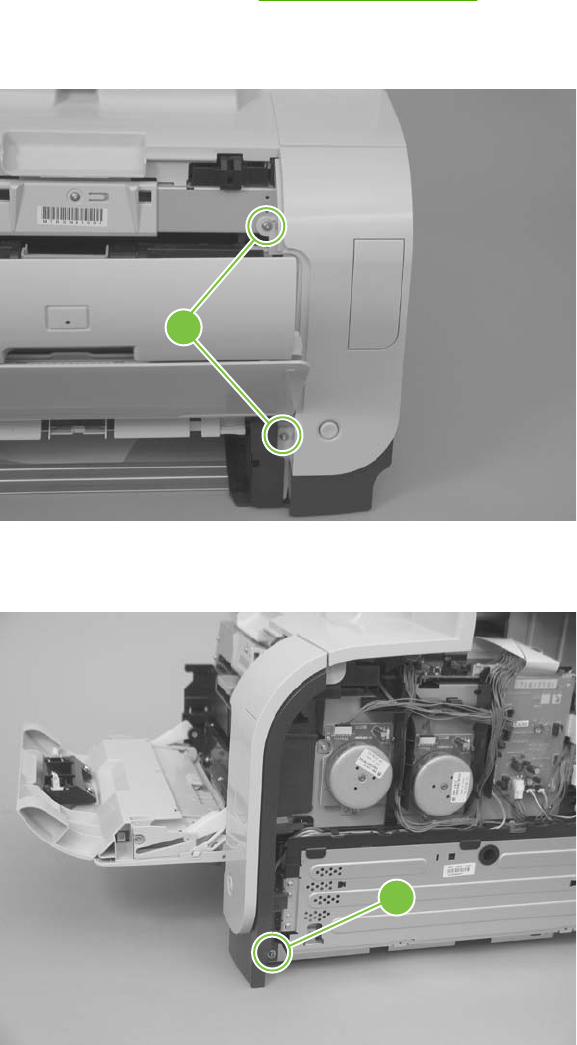
Right-front cover and power button
1. Remove the right cover. See Right cover on page 156.
2. Open the front door and remove two screws (callout 1).
Figure 6-120 Remove the right-front cover and power button (1 of 5)
1
3. Remove one screw (callout 2).
Figure 6-121 Remove the right-front cover and power button (2 of 5)
2
ENWW Components and major assemblies 197
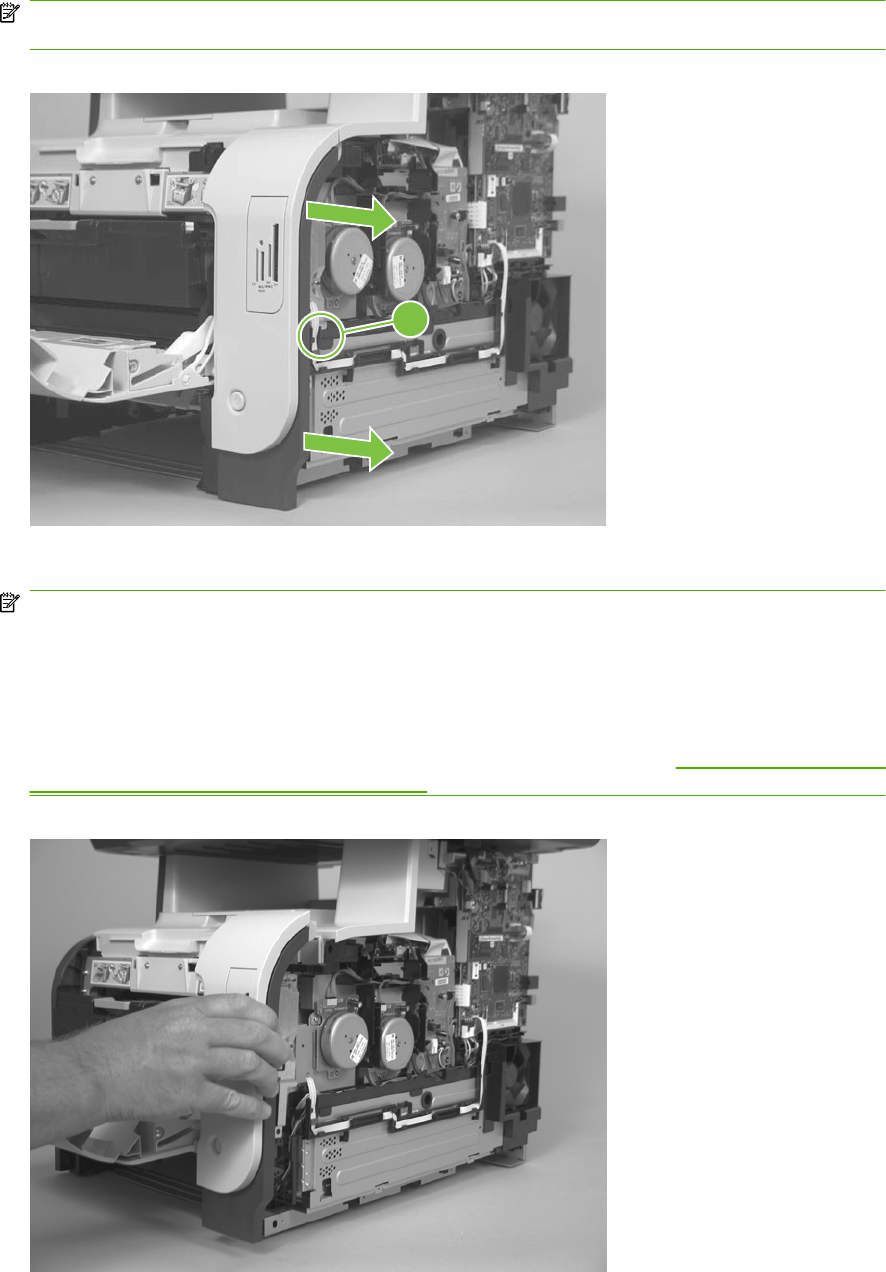
4. Slide the cover slightly toward the right side of the product to release it.
NOTE: For fax/memory-card models only: When the sliding the cover, do not damage the FFC
guide (callout 3).
Figure 6-122 Remove the right-front cover and power button (3 of 5)
3
5. Remove the cover.
NOTE: For all models: If you are replacing the right-front cover, proceed to the following step
and remove the power button. Install the power button on the replacement cover.
For base models only: If you are replacing the right-front cover remove the blanking cover and
install it on the replacement cover.
For fax/memory-card models only: If you are replacing the right-front cover remove the memory-
card cover and PCA, and then install them on the replacement cover. See Memory-card cover and
PCA (fax/memory-card models) on page 200.
Figure 6-123 Remove the right-front cover and power button (4 of 5)
198 Chapter 6 Removal and replacement ENWW
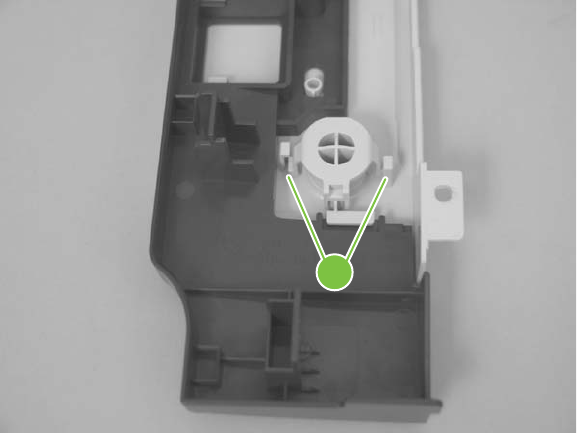
6. Release two tabs (callout 4), and then remove the power button.
Figure 6-124 Remove the right-front cover and power button (5 of 5)
4
ENWW Components and major assemblies 199
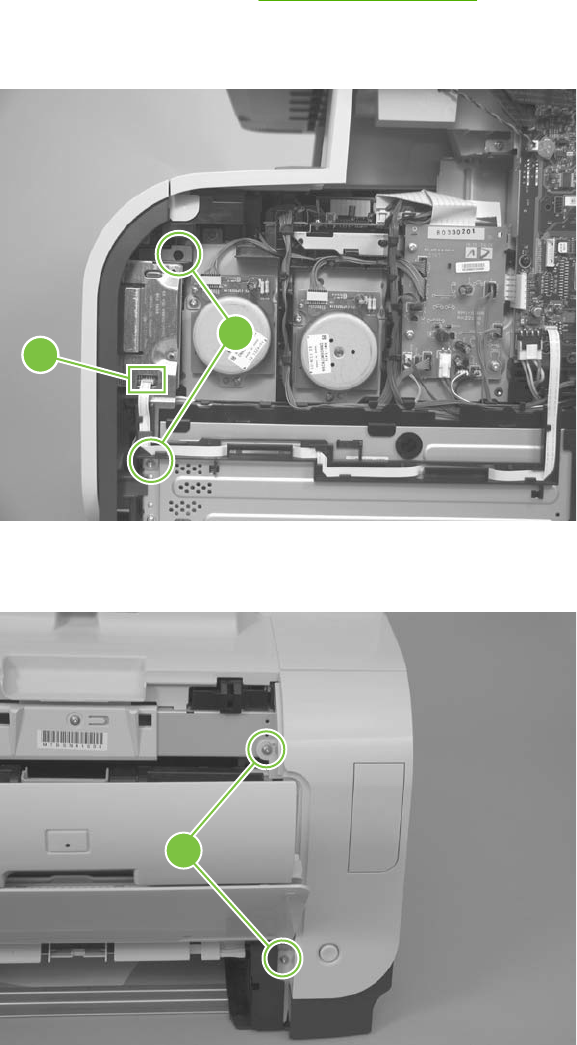
Memory-card cover and PCA (fax/memory-card models)
1. Remove the right cover. See Right cover on page 156.
2. Disconnect one FFC (callout 1) and remove two screws (callout 2).
Figure 6-125 Remove the memory-card cover and PCA (1 of 7)
12
3. Open the front door and remove two screws (callout 3).
Figure 6-126 Remove the memory-card cover and PCA (2 of 7)
3
200 Chapter 6 Removal and replacement ENWW
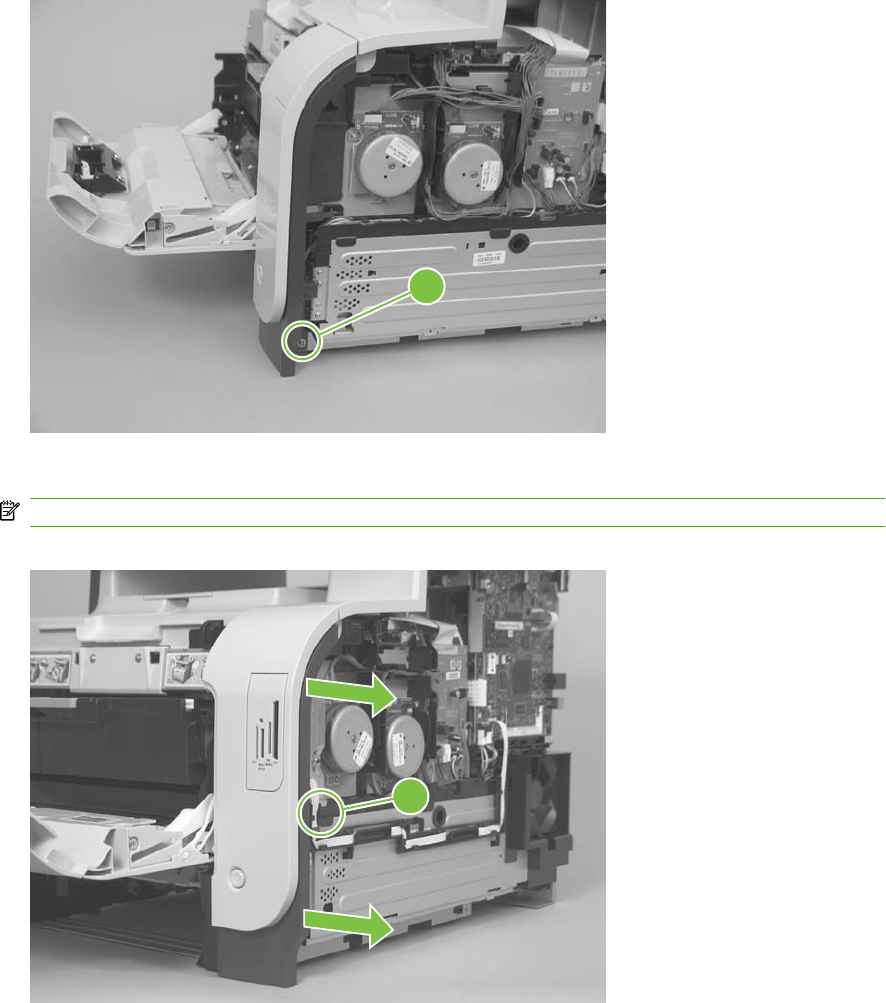
4. Remove one screw (callout 4).
Figure 6-127 Remove the memory-card cover and PCA (3 of 7)
4
5. Slide the cover slightly toward the right side of the product to release it, and then remove the cover.
NOTE: When the sliding the cover, do not damage the FFC guide (callout 5).
Figure 6-128 Remove the memory-card cover and PCA (4 of 7)
5
ENWW Components and major assemblies 201
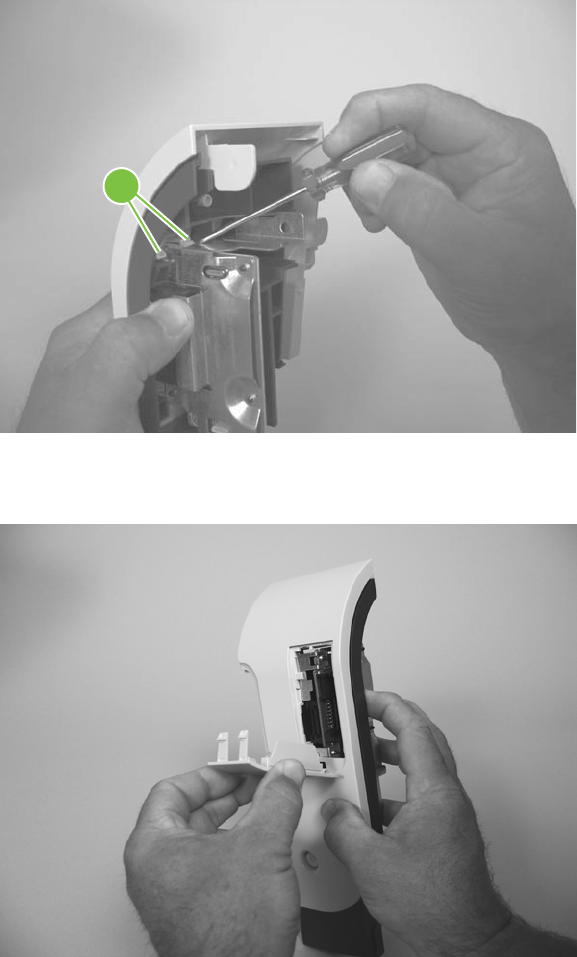
6. Release two tabs (callout 6).
Figure 6-129 Remove the memory-card cover and PCA (5 of 7)
6
7. Support the memory-card PCA, and then remove the memory-card PCA cover.
Figure 6-130 Remove the memory-card cover and PCA (6 of 7)
202 Chapter 6 Removal and replacement ENWW
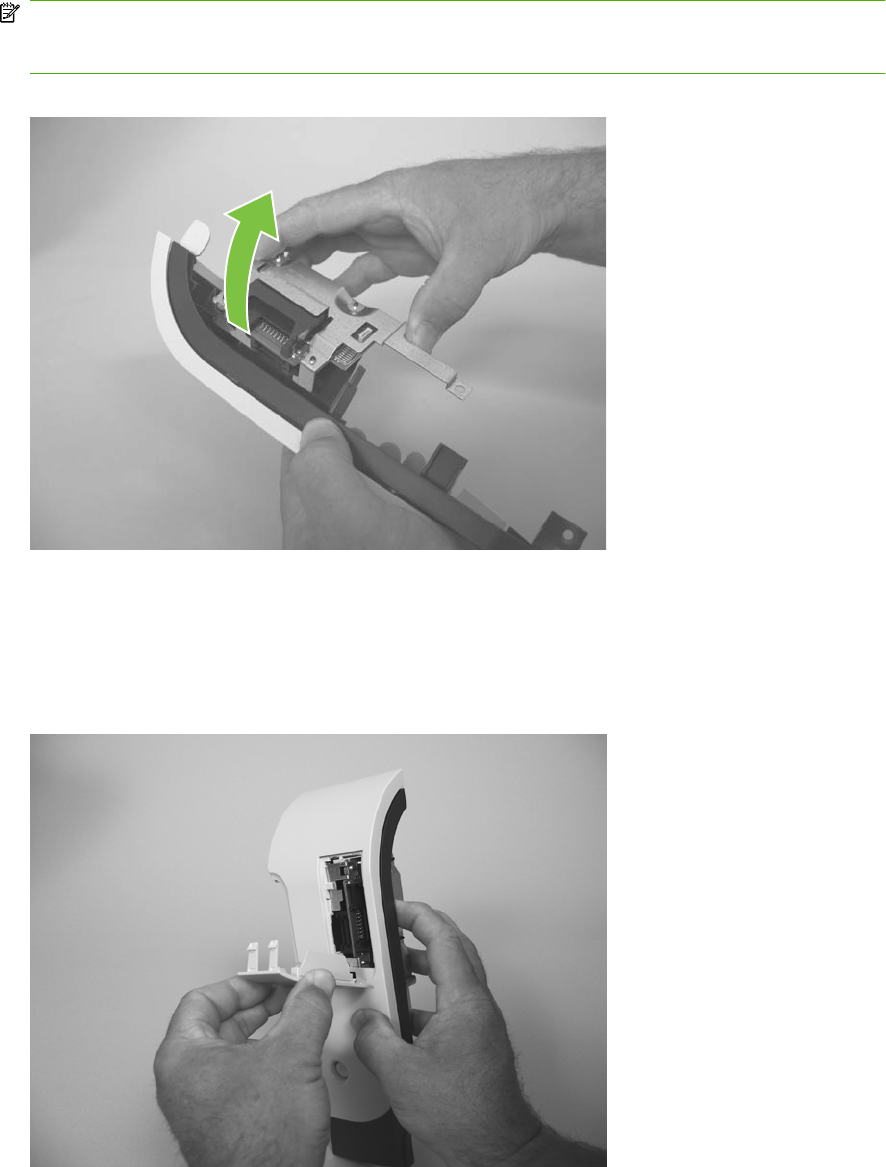
8. Rotate the memory-card PCA away from the cover to release it, and then remove the PCA.
NOTE: Before you remove the PCA, look at how it is installed in the cover. There are two tabs
along the side of the opening in the cover that retain the PCA when the memory-card cover is
installed. The PCA fits over the bottom tab, and behind the upper tab.
Figure 6-131 Remove the memory-card cover and PCA (7 of 7)
Reinstall the memory-card cover and PCA
1. Install the memory-card PCA and hold it in place on the cover.
2. Insert the tabs on the bottom of the PCA cover into the slots on the right-front cover.
Figure 6-132 Reinstall the memory-card cover and PCA (1 of 2)
ENWW Components and major assemblies 203
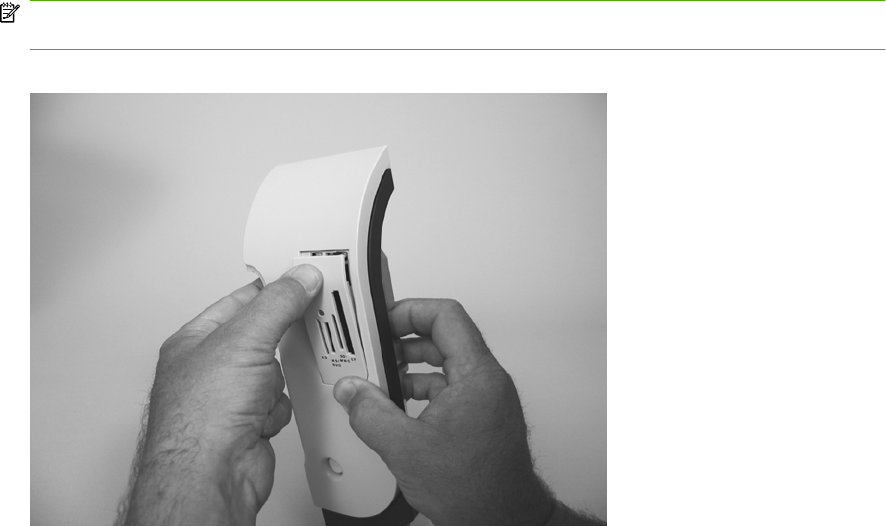
3. Carefully push on the PCA cover until it snaps into place.
NOTE: When the memory-card cover is correctly installed, it securely fastens the PCA to the
right-front cover.
Figure 6-133 Reinstall the memory-card cover and PCA (2 of 2)
204 Chapter 6 Removal and replacement ENWW
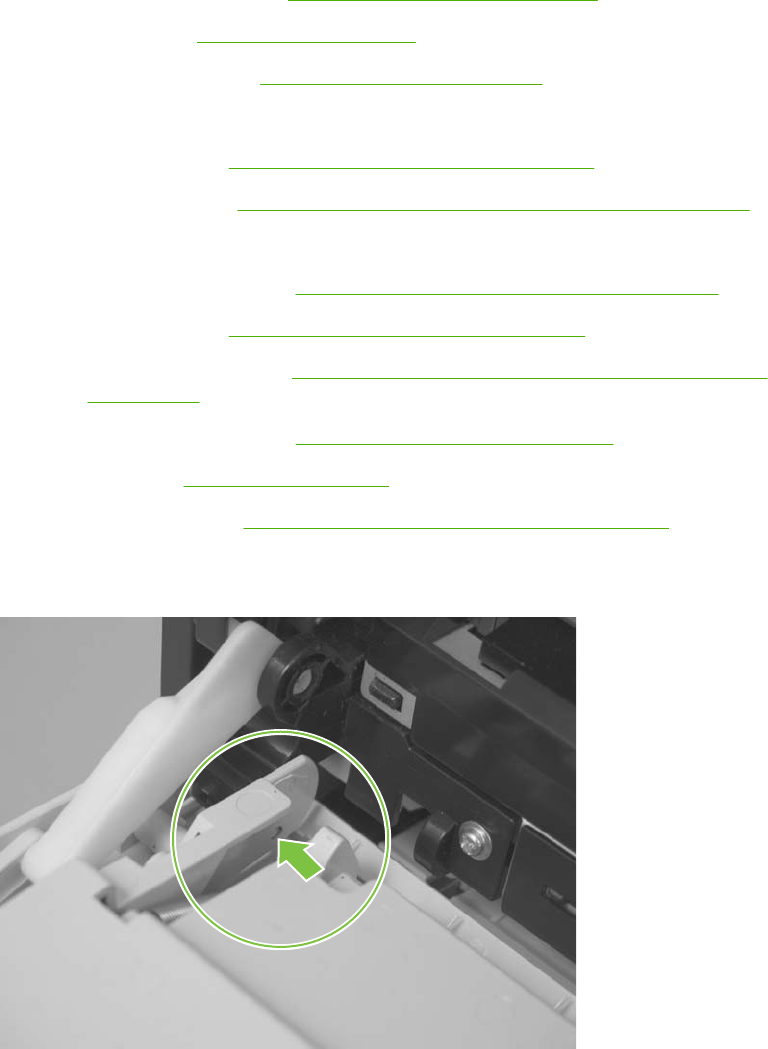
Front-door assembly
1. Remove the following components:
●Print-cartridge drawer. See Print-cartridge drawer on page 141
●Right cover. See Right cover on page 156.
●Scanner assembly. See Scanner assembly on page 163.
●Simplex product
◦Rear door. See Rear door (simplex product) on page 152.
◦Rear cover. See Rear cover and feed guide (simplex product) on page 166.
●Duplex product
◦Rear-upper cover. See Rear-upper cover (duplex product) on page 165.
◦Rear door. See Rear door (duplex product) on page 154.
◦Rear-lower cover. See Rear-lower cover and rear-door links (duplex product)
on page 170.
●Upper-cover assembly. See Upper-cover assembly on page 181.
●Left cover. See Left cover on page 185.
●Right-front cover. See Right-front cover and power button on page 197
2. Locate the front-door pin on the left-side door link.
Figure 6-134 Remove the front-door assembly (1 of 10)
ENWW Components and major assemblies 205
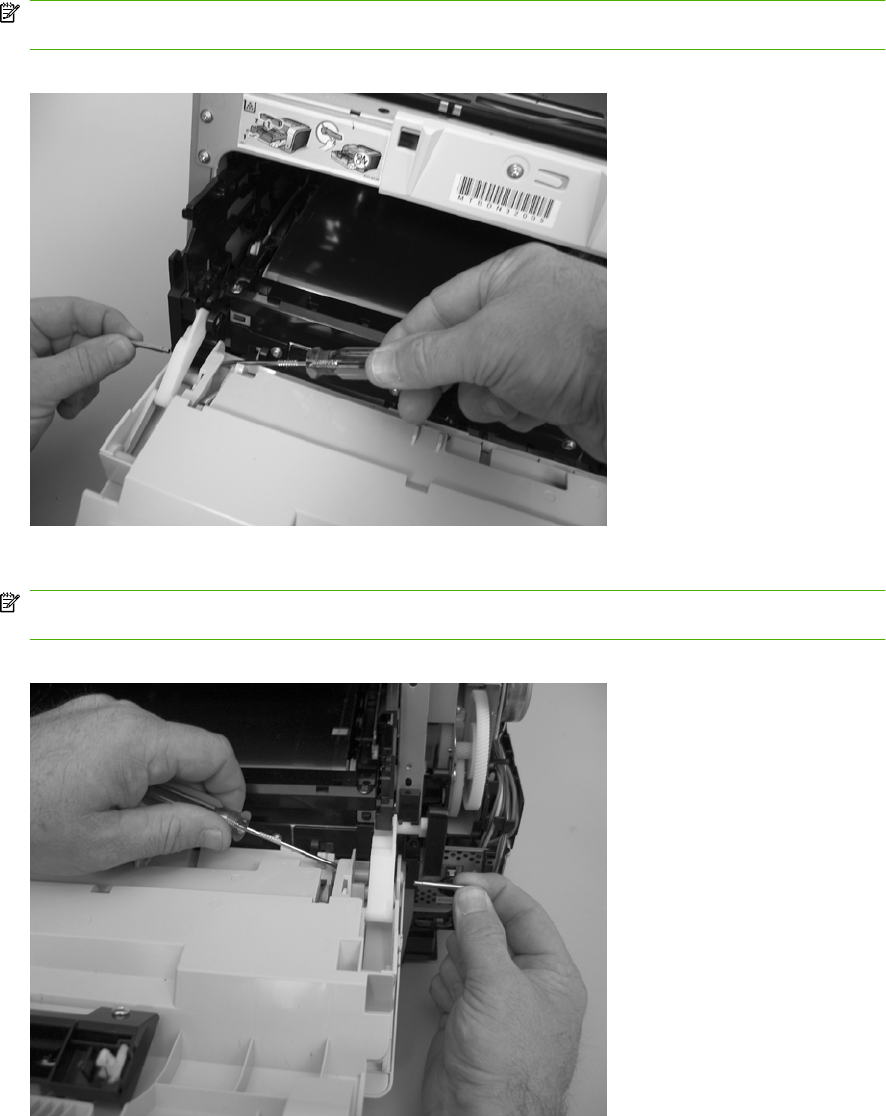
3. Use a precision point screwdriver to push the left-side door pin out of the link.
NOTE: A precision point screwdriver is required to release the front door pins. The width of the
blade must be 2 mm (0.08 in) or less to be able to push the door pins out of the mounting holes.
Figure 6-135 Remove the front-door assembly (2 of 10)
4. Use a precision point screwdriver to push the right-side door pin out of the link.
NOTE: A precision point screwdriver is required to release the front door pins. The width of the
blade must be 2 mm (0.08 in) or less to be able to push the door pins out of the mounting holes.
Figure 6-136 Remove the front-door assembly (3 of 10)
206 Chapter 6 Removal and replacement ENWW
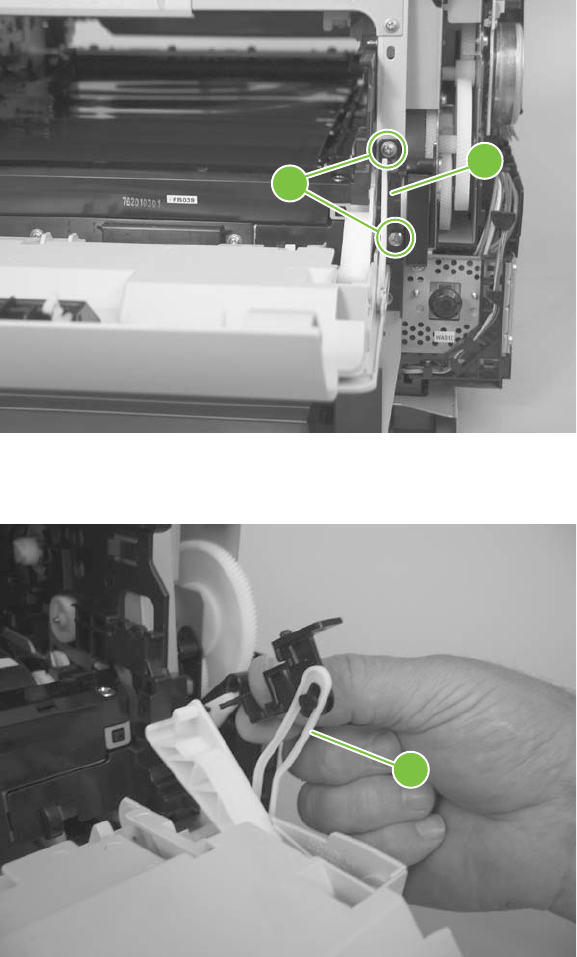
5. Remove two screws (callout 1) and the separate the door bushing (callout 2) from the chassis.
Figure 6-137 Remove the front-door assembly (4 of 10)
1
2
6. Release the bushing from the door-retainer link (callout 3).
Figure 6-138 Remove the front-door assembly (5 of 10)
3
ENWW Components and major assemblies 207
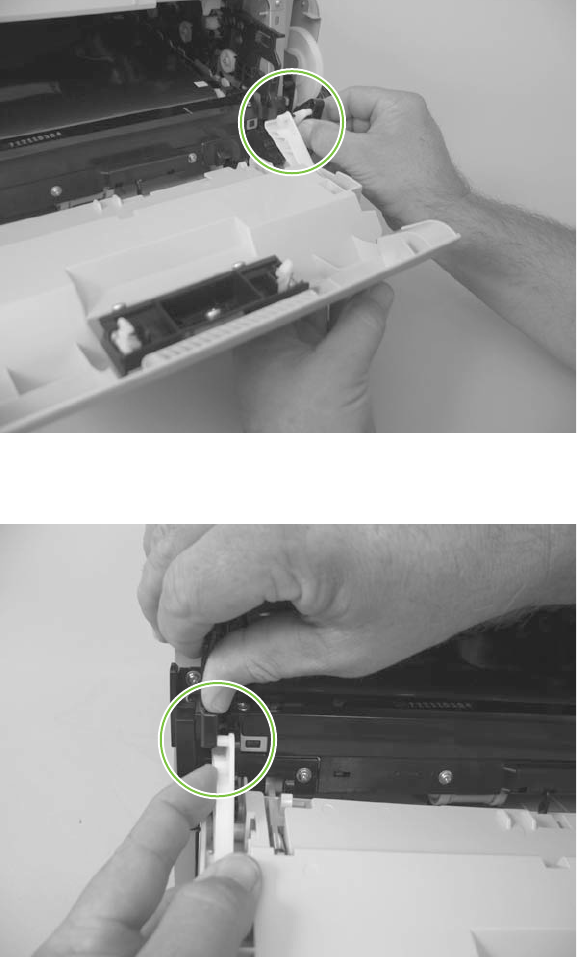
7. Support the door assembly, and carefully release the pin on the right-side link.
Figure 6-139 Remove the front-door assembly (6 of 10)
8. Support the door assembly, and carefully release the upper pin on the left-side link.
Figure 6-140 Remove the front-door assembly (7 of 10)
208 Chapter 6 Removal and replacement ENWW
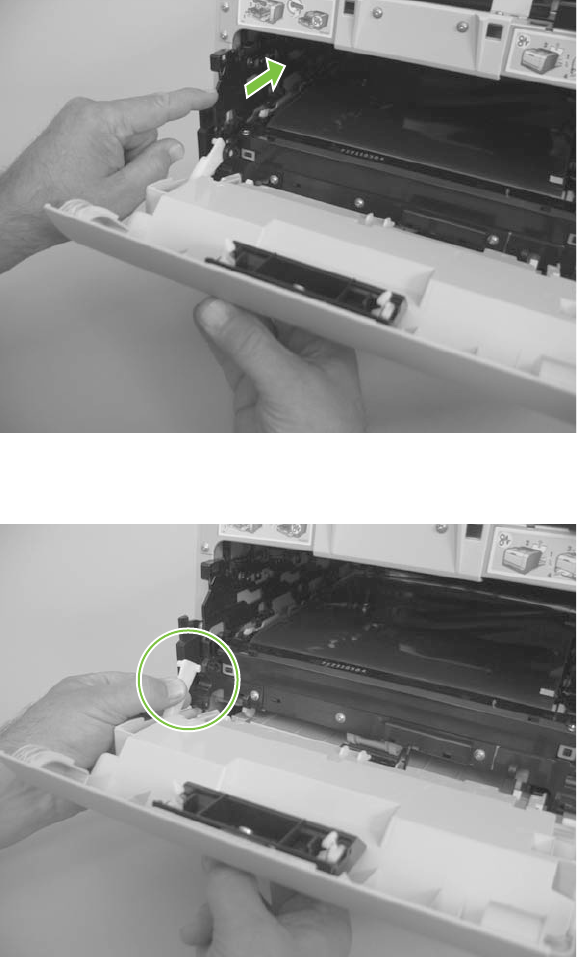
9. Push the black-plastic arm into the product.
Figure 6-141 Remove the front-door assembly (8 of 10)
10. Support the door assembly, and carefully release the lower pin on the left-side link.
Figure 6-142 Remove the front-door assembly (9 of 10)
ENWW Components and major assemblies 209
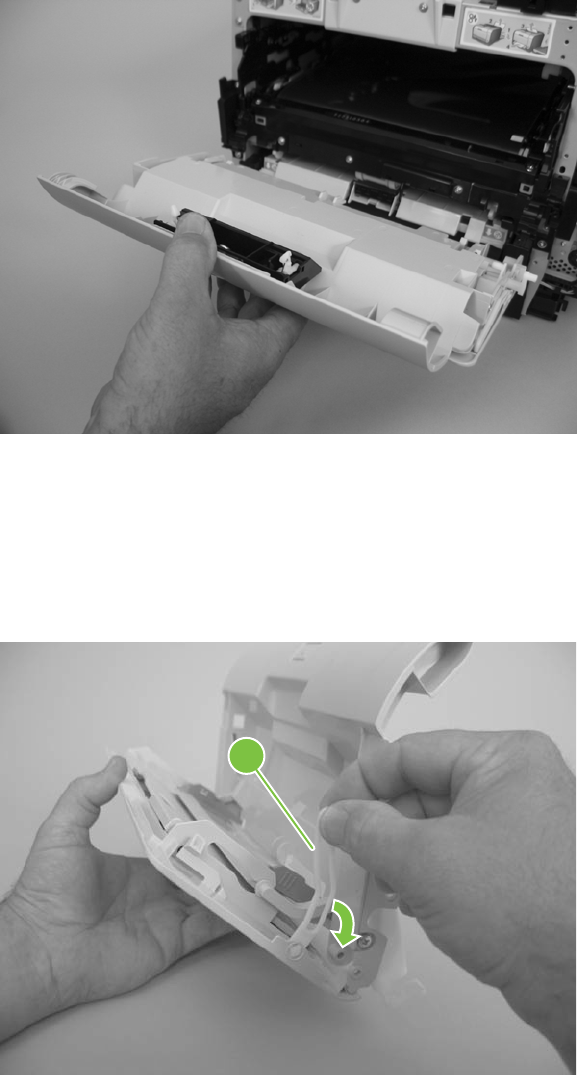
11. Remove the front-door assembly.
Figure 6-143 Remove the front-door assembly (10 of 10)
Reinstall the front-door assembly
Use this procedure if you are installing a replacement front-door assembly.
1. Open Tray 1, and then rotate the retainer arm (callout 1) until the tabs on the arm-hinge pin align
with the slots in the mounting hole on Tray 1.
Figure 6-144 Reinstall the front-door assembly (1 of 2)
1
210 Chapter 6 Removal and replacement ENWW
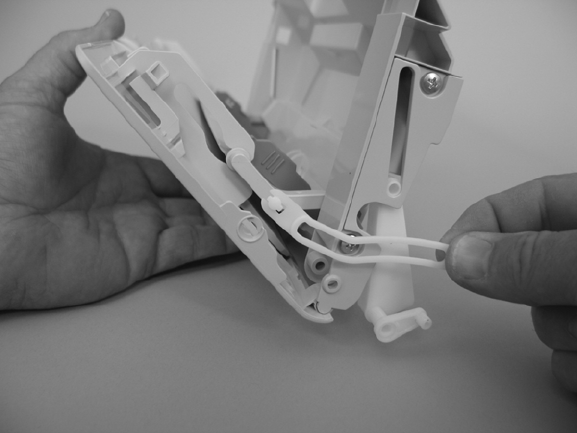
2. Remove the retainer arm from the door assembly, and then install it on the replacement door
assembly.
Figure 6-145 Reinstall the front-door assembly (2 of 2)
ENWW Components and major assemblies 211
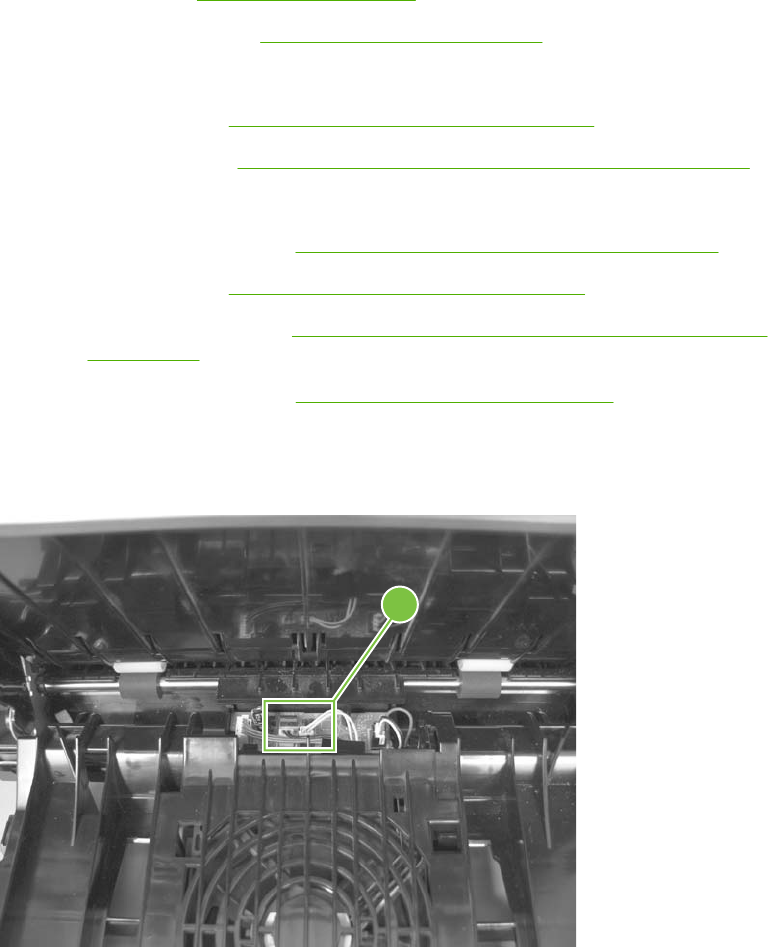
Duplex-reverse drive assembly
1. Remove the following components:
●Right cover. See Right cover on page 156.
●Scanner assembly. See Scanner assembly on page 163.
●Simplex product
◦Rear door. See Rear door (simplex product) on page 152.
◦Rear cover. See Rear cover and feed guide (simplex product) on page 166.
●Duplex product
◦Rear-upper cover. See Rear-upper cover (duplex product) on page 165.
◦Rear door. See Rear door (duplex product) on page 154.
◦Rear-lower cover. See Rear-lower cover and rear-door links (duplex product)
on page 170.
●Upper-cover assembly. See Upper-cover assembly on page 181.
2. Disconnect two connectors (callout 1), and then pass the connectors under the rear-door rib
assembly.
Figure 6-146 Remove the duplex-reverse drive assembly (1 of 4)
1
212 Chapter 6 Removal and replacement ENWW
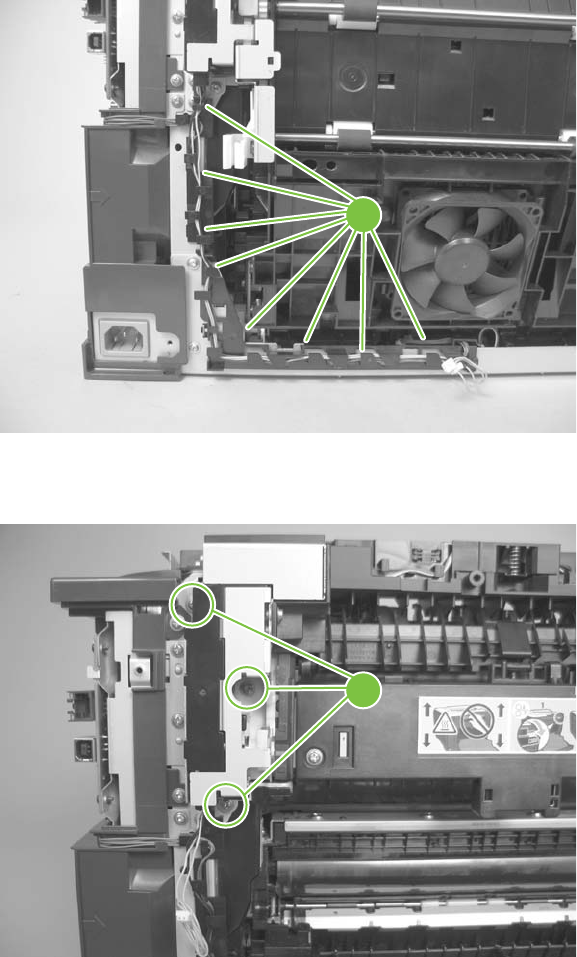
3. Release the wire harnesses from the retainer (callout 2).
Figure 6-147 Remove the duplex-reverse drive assembly (2 of 4)
2
4. Remove three screws (callout 3).
Figure 6-148 Remove the duplex-reverse drive assembly (3 of 4)
3
ENWW Components and major assemblies 213
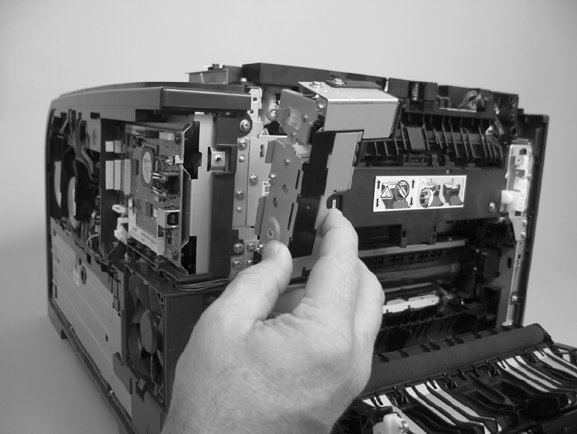
5. Remove the duplex-reverse drive assembly.
Figure 6-149 Remove the duplex-reverse drive assembly (4 of 4)
214 Chapter 6 Removal and replacement ENWW
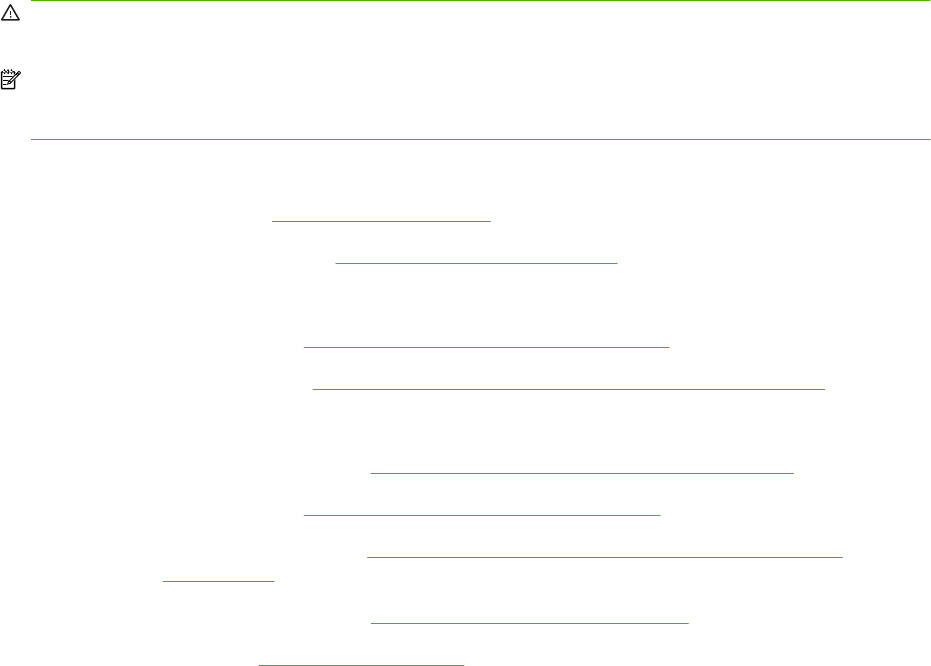
Fuser
WARNING! The fuser might be very hot. After turning off the product power, allow the fuser to cool
for at least 5 minutes before removing it.
NOTE: The fuser can be removed without removing the scanner assembly and the upper-cover
assembly. However, it might be easier to access some of the connectors with these components
removed.
1. Remove the following components:
●Right cover. See Right cover on page 156.
●Scanner assembly. See Scanner assembly on page 163.
●Simplex product
◦Rear door. See Rear door (simplex product) on page 152.
◦Rear cover. See Rear cover and feed guide (simplex product) on page 166.
●Duplex product
◦Rear-upper cover. See Rear-upper cover (duplex product) on page 165.
◦Rear door. See Rear door (duplex product) on page 154.
◦Rear-lower cover. See Rear-lower cover and rear-door links (duplex product)
on page 170.
●Upper-cover assembly. See Upper-cover assembly on page 181.
●Left cover. See Left cover on page 185.
ENWW Components and major assemblies 215
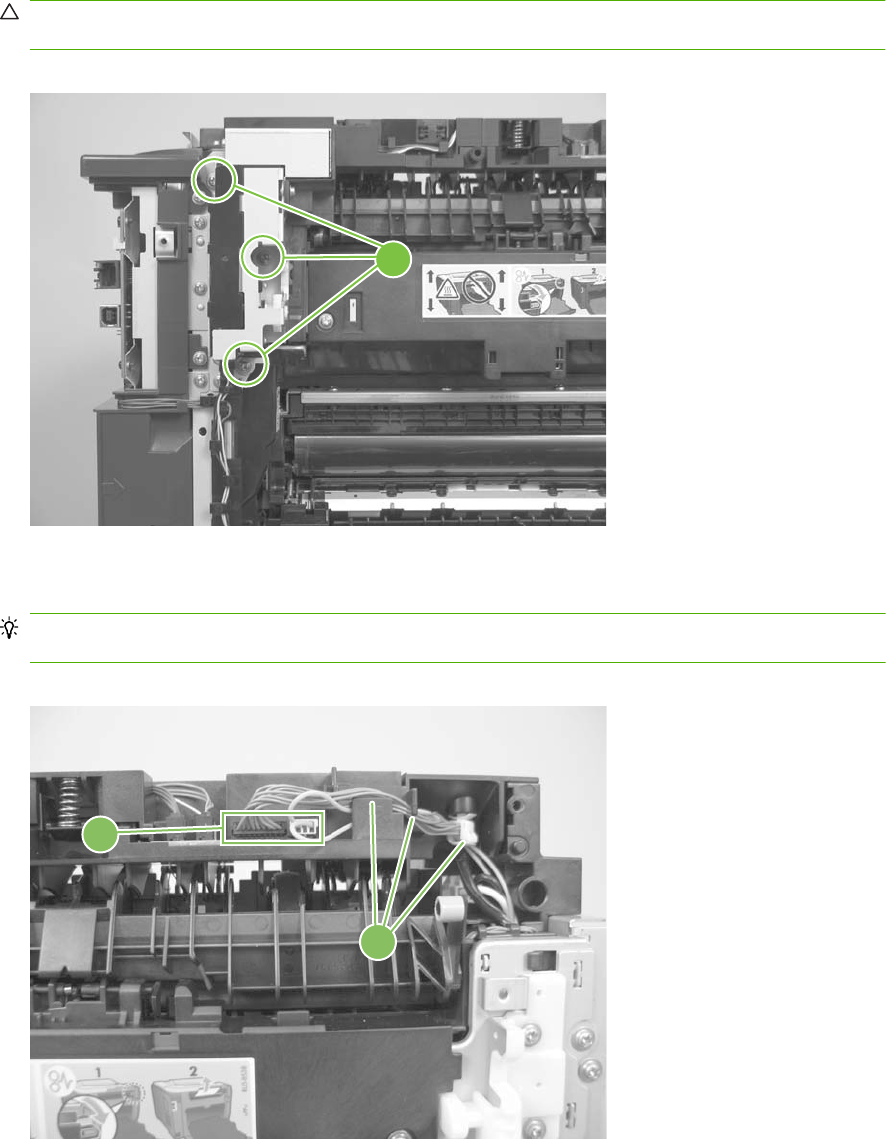
2. Duplex models only: Remove three screws (callout 1) and separate the duplex-reverse drive
assembly from the product.
CAUTION: The duplex-reverse drive assembly is still attached to the product. Carefully set the
assembly out of the way.
Figure 6-150 Remove the fuser (1 of 8)
1
3. Disconnect two connectors (callout 2), and then release the wire harnesses from the guide (callout
3).
Reinstallation tip When the upper cover is reinstalled, make sure that these wire harnesses
(near the connectors) are correctly routed under the cover.
Figure 6-151 Remove the fuser (2 of 8)
2
3
216 Chapter 6 Removal and replacement ENWW
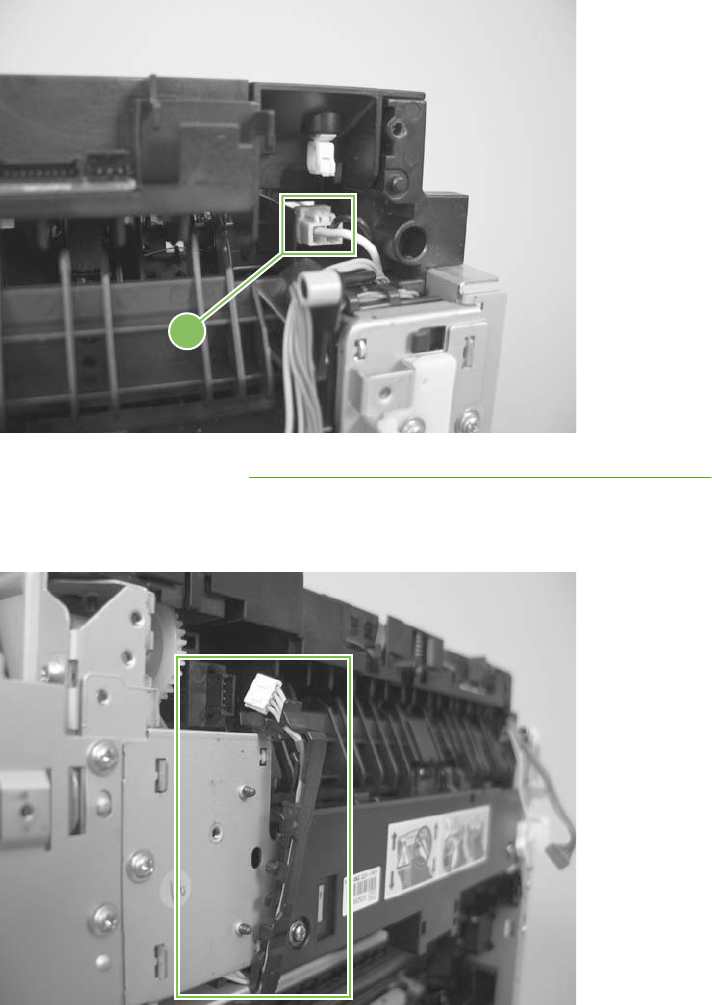
4. Disconnect one connector (callout 4).
Figure 6-152 Remove the fuser (3 of 8)
4
5. Before you proceed, look at Figure 6-153 Remove the fuser (4 of 8) on page 217. In the following
step, the connector and guide will be separated from the fuser. You must not use too much force
and damage the lower portion of the guide. If the guide is damaged, the fuser must be replaced.
Figure 6-153 Remove the fuser (4 of 8)
ENWW Components and major assemblies 217
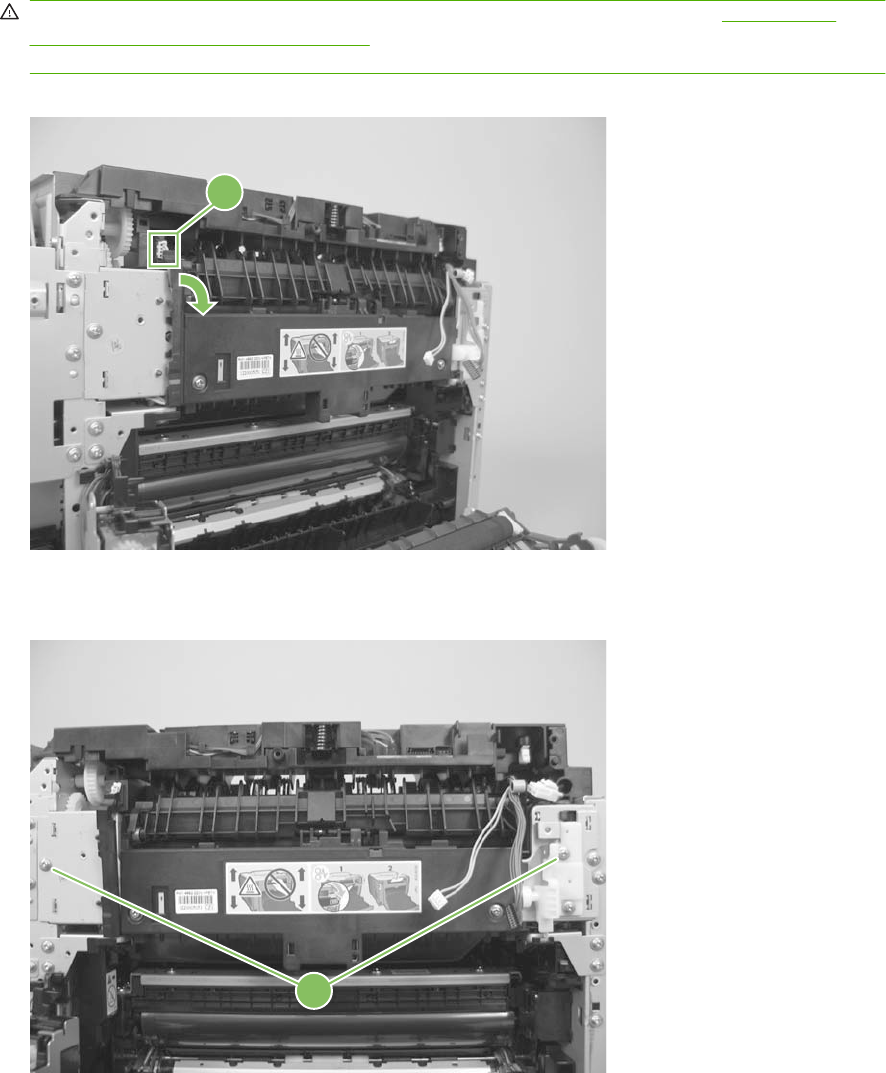
6. Carefully disconnect one connector and rotate the connector and the top portion of the guide away
from the fuser (callout 5).
WARNING! Do not separate the connector and guide more than is shown in Figure 6-153
Remove the fuser (4 of 8) on page 217. If the guide is damaged, you must replace the fuser. Also,
be cautious with the short, fragile connector.
Figure 6-154 Remove the fuser (5 of 8)
5
7. Remove two screws (callout 6).
Figure 6-155 Remove the fuser (6 of 8)
6
218 Chapter 6 Removal and replacement ENWW
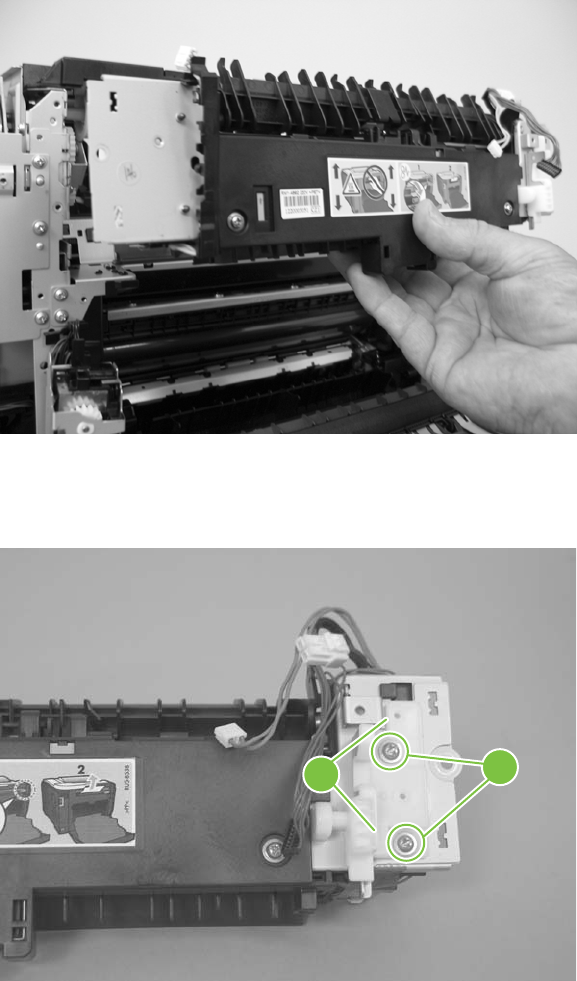
8. Remove the fuser.
Figure 6-156 Remove the fuser (7 of 8)
9. Duplex models only: Remove two screws (callout 7) and remove the duplex-gear assembly
(callout 8). Install the assembly on the replacement fuser.
Figure 6-157 Remove the fuser (8 of 8)
7
8
ENWW Components and major assemblies 219
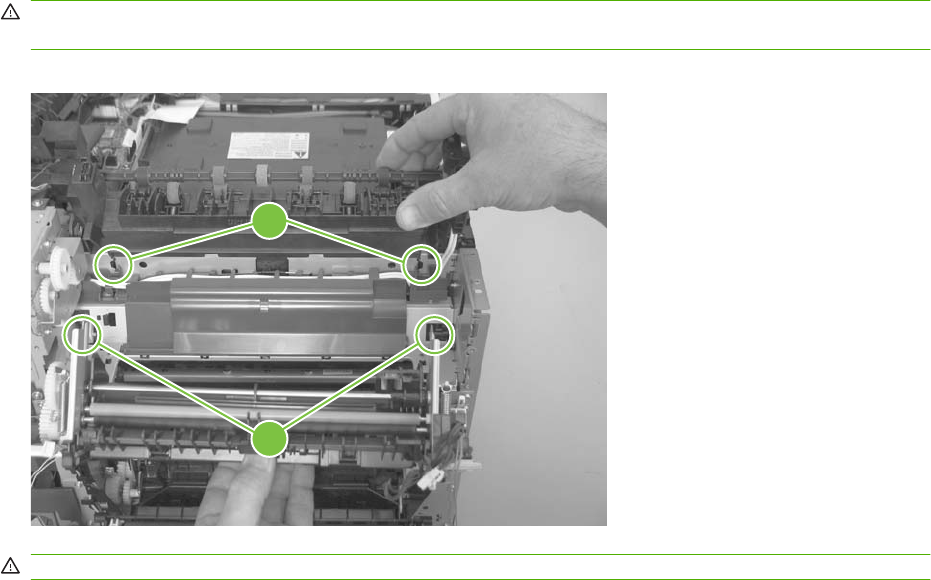
Reinstall the fuser
To reinstalled you must insert the tabs (callout 1) on the fuser frame into the slots on the product chassis
(callout 2).
WARNING! The fuser frame must be flush with the product chassis before you install the two fuser
mounting screws. Do not use the screws to pull the fuser frame against the chassis.
Figure 6-158 Reinstall the fuser
1
2
WARNING! Be cautious with the short, fragile five-pin connector on the upper-left part of the fuser.
220 Chapter 6 Removal and replacement ENWW
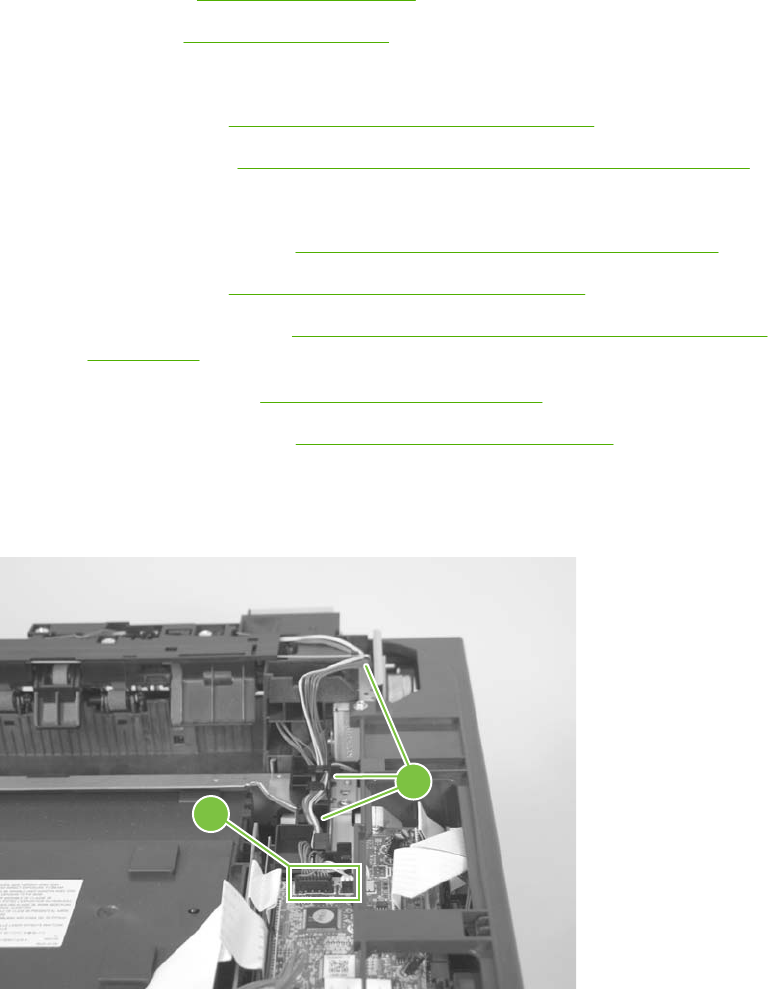
Paper-delivery assembly
1. Remove the following components:
●Right cover. See Right cover on page 156.
●Left cover. See Left cover on page 185.
●Simplex product
◦Rear door. See Rear door (simplex product) on page 152.
◦Rear cover. See Rear cover and feed guide (simplex product) on page 166.
●Duplex product
◦Rear-upper cover. See Rear-upper cover (duplex product) on page 165.
◦Rear door. See Rear door (duplex product) on page 154.
◦Rear-lower cover. See Rear-lower cover and rear-door links (duplex product)
on page 170.
●Scanner assembly. See Scanner assembly on page 163.
●Upper-cover assembly. See Upper-cover assembly on page 181.
2. Disconnect two connectors (callout 1), and then release the wire harnesses from the retainer
(callout 2).
Figure 6-159 Remove the paper-delivery assembly (1 of 4)
1
2
ENWW Components and major assemblies 221
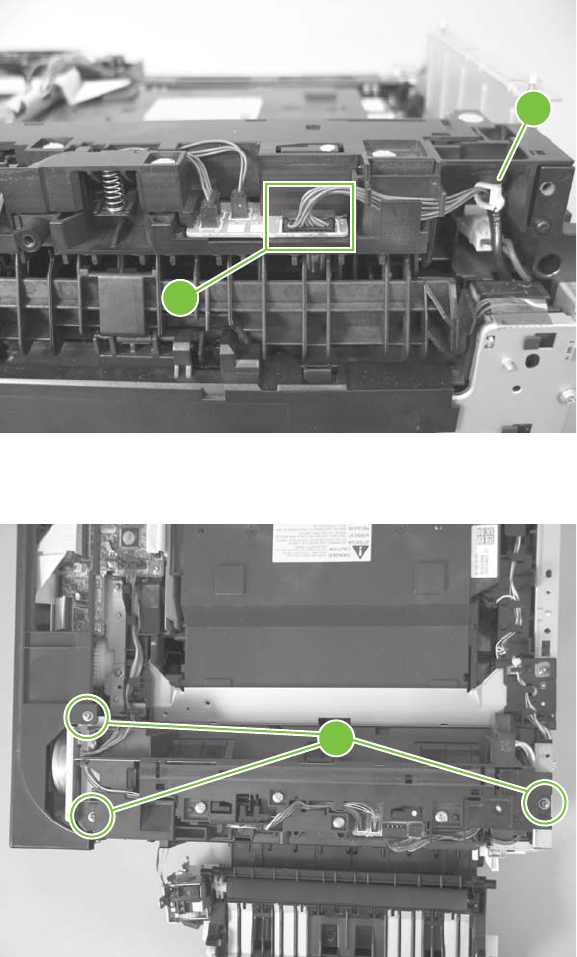
3. Disconnect one connector (callout 3), and then release the wire harness from the wire clip
(callout 4).
Figure 6-160 Remove the paper-delivery assembly (2 of 4)
3
4
4. Remove three screws (callout 5).
Figure 6-161 Remove the paper-delivery assembly (3 of 4)
5
222 Chapter 6 Removal and replacement ENWW
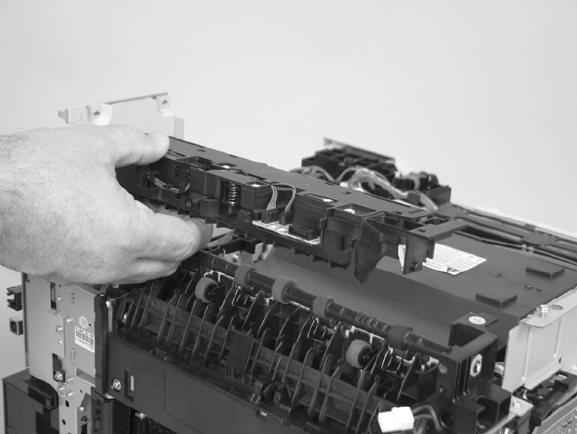
5. Remove the paper-delivery assembly.
Figure 6-162 Remove the paper-delivery assembly (4 of 4)
ENWW Components and major assemblies 223
224 Chapter 6 Removal and replacement ENWW
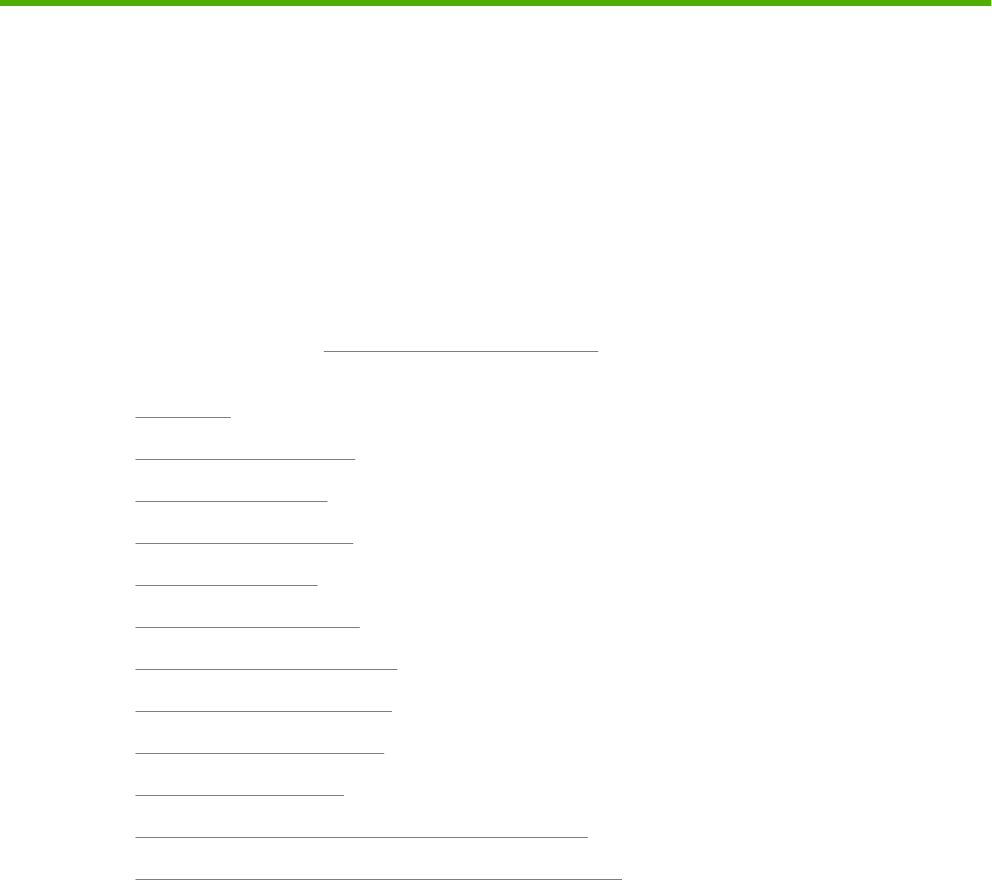
7 Problem solve
To use the information in this chapter, you should have a basic understanding of the HP LaserJet printing
process. Explanations of each mechanical assembly, the printer systems, and the basic theory of
operation are contained in Theory of operation on page 81. Do not perform any of these troubleshooting
processes unless you understand the function of each product component.
●Menu map
●Troubleshooting process
●Troubleshooting tools
●Control-panel messages
●Event-log messages
●Paper-handling problems
●Solve image quality problems
●Solve performance problems
●Solve connectivity problems
●Service mode functions
●Solve fax problems (fax/memory-card models only)
●Memory card problems (fax/memory-card models only)
ENWW 225

Menu map
Print a menu map to find sub-menus and troubleshooting tools in the product menus.
1. Press Setup to open the menus.
2. Use the arrow buttons to select Reports, and then press OK.
3. Use the arrow buttons to select Menu structure, and then press OK to print the report.
4. Press Cancel to exit the menus.
226 Chapter 7 Problem solve ENWW
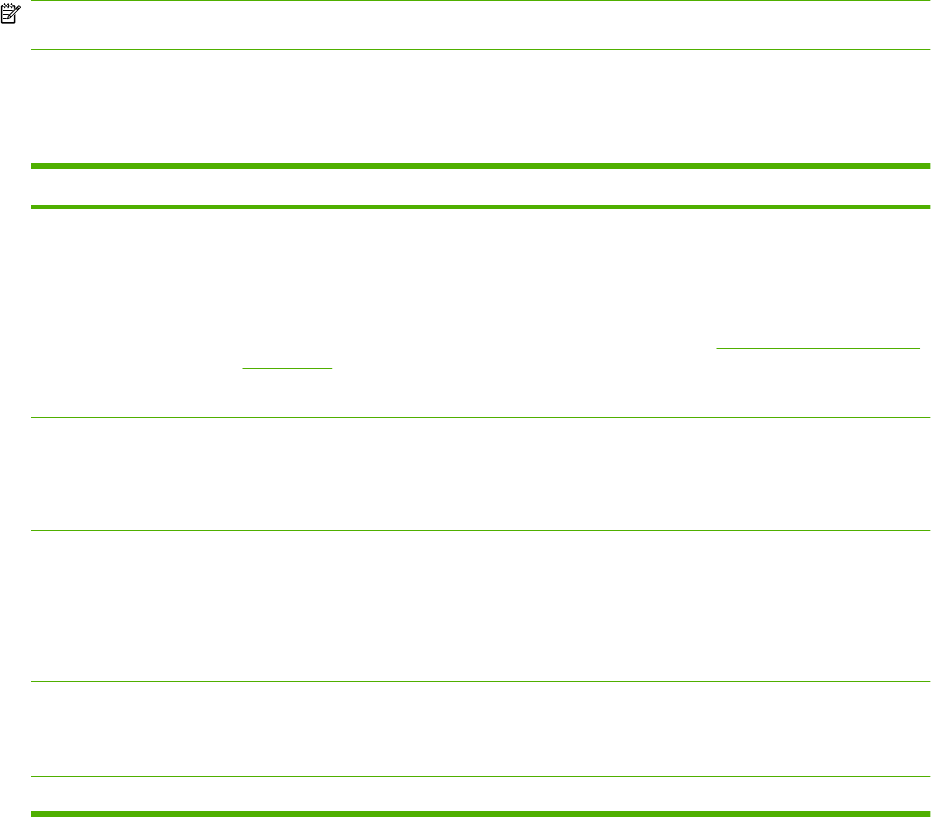
Troubleshooting process
When the product malfunctions or encounters an unexpected situation, the product control panel alerts
you to the situation. This chapter contains information to help diagnose and solve problems.
●Use the pre-troubleshooting checklist to evaluate the source of the problem and to reduce the
number of steps that are required to fix the problem.
●Use the troubleshooting flowchart to pinpoint the root cause of hardware malfunctions. The
flowchart guides you to the section of this chapter that contains steps for correcting the malfunction.
Before beginning any troubleshooting procedure, check the following issues:
●Are supply items within their rated life?
●Does the configuration page reveal any configuration errors?
NOTE: The customer is responsible for checking supplies and for using supplies that are in good
condition.
Pre-troubleshooting checklist
The following table includes basic questions to ask the customer to quickly help define the problem(s).
General topic Questions
Environment ●Is the product installed on a solid, level surface (+/- 1°)?
●Is the power-supply voltage within ± 10 volts of the specified power source?
●Is the power-supply plug inserted in the product and the outlet?
●Is the operating environment within the specified parameters? See Environmental specifications
on page 378.
●Is the product exposed to direct sunlight?
Media ●Does the customer use only supported media?
●Is the media in good condition (no curls, folds, or distortion)?
●Is the media stored correctly and within environmental limits?
Input trays ●Is the amount of media in the tray within specifications?
●Is the media correctly placed in the tray?
●Are the paper guides aligned with the stack?
●Is the input tray correctly installed in the product?
Print cartridges ●Is each HP Genuine print cartridge installed correctly?
●Was a print cartridge opened soon after being moved from a cold to a warm room? If so, allow the
print cartridge to sit at room temperature for 1 to 2 hours.
Covers ●Is the front cover closed?
ENWW Troubleshooting process 227
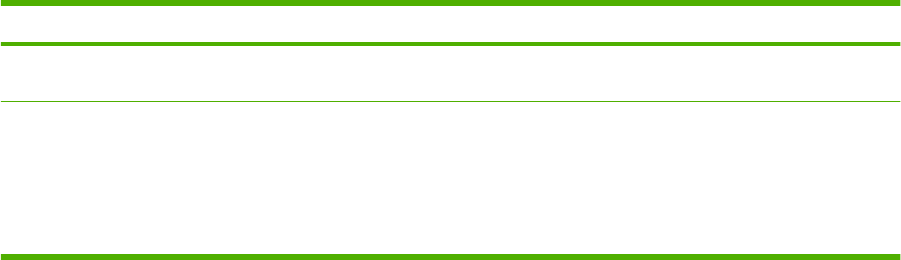
General topic Questions
Condensation ●Does condensation occur following a temperature change (particularly in winter following cold
storage)? If so, wipe affected parts dry or leave the product on for 10 to 20 minutes.
Miscellaneous ●Check for and remove any non-HP components (print cartridges, memory modules, and EIO
cards) from the product.
●Remove the product from the network and ensure that the failure is associated with the product
before beginning troubleshooting.
●For any print-quality issues, calibrate the product.
Power-on checks
When you turn on the product, if it does not make any sound or if the control-panel display is blank,
check the following items:
●Verify that the product is plugged directly into an active electrical outlet that has the correct voltage.
Do not plug the product into a surge protector or power strip.
●Verify that the on/off switch is in the ON position.
228 Chapter 7 Problem solve ENWW
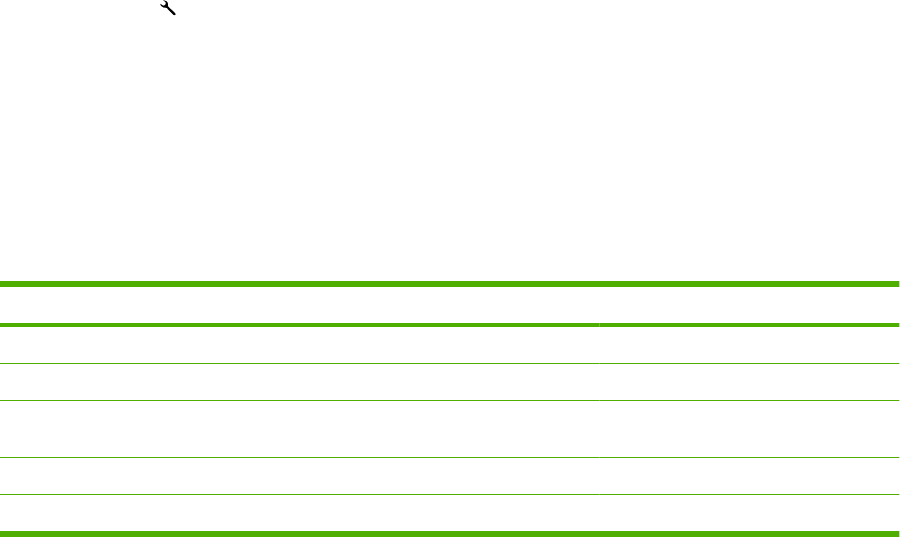
Troubleshooting tools
The section describes the tools that can help you solve problems with the product.
LED diagnostics
Network LEDs (network models only)
The onboard network solution has two network port LEDs. When the product is connected to a properly
working network through a network cable, the yellow LED indicates network activity, and the green LED
indicates the link status. A blinking yellow LED indicates network traffic. If the green LED is off, a link
has failed.
For link failures, check all of the network cable connections. In addition, you can try to manually configure
the link settings on the onboard network solution by using the product control-panel menus.
1. Press Setup .
2. Use the arrow buttons to highlight Network config., and then press OK.
3. Use the arrow buttons to highlight Link speed, and then press OK.
4. Select the appropriate link speed, and then press OK.
Control panel LEDs
The state of the Ready light and Attention light on the product signal the product status. The following
table outlines the possible control-panel light states.
Product state Ready light state Attention light state
Initializing Blinking Blinking
Ready On Off
Receiving data/processing job or
cancelling job
Blinking Off
Error message Off Blinking
Fatal error (49 or 79 error)
1
On On
1The product will power off and then power on after one of these errors occurs.
Memory card LED (memory-card models only)
When a memory card is inserted into the correct memory-card slot, this LED turns on. If the LED is not
lighting, try the following actions:
●Make sure that the memory card is in the correct slot.
●Make sure that the memory card is not defective.
●Verify that the flat flexible cable connection from the formatter to the memory-card reader assembly
is firmly connected.
●If the card is not defective and the card is in the correct slot, the circuit board might have been
inadvertently damaged by an electrostatic discharge from someone inserting a memory card. If this
ENWW Troubleshooting tools 229
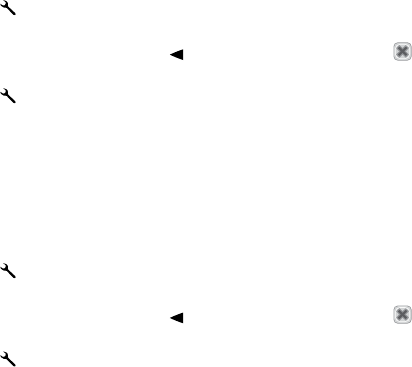
is the case, replace the memory-card reader assembly. If the error still occurs, replace the
formatter.
Control-panel diagnostics
The product includes diagnostic tests for the control panel.
Test the control-panel display
1. Press Setup .
2. Press both the left arrow button and the Cancel button at the same time.
3. Press Setup to return to the main menus.
4. Use the arrow buttons to highlight 2ndry Service, and then press OK.
5. Use the arrow buttons to highlight Display test, and then press OK.
Test the control-panel buttons
1. Press Setup .
2. Press both the left arrow button and the Cancel button at the same time.
3. Press Setup to return to the main menus.
4. Use the arrow buttons to highlight 2ndry Service, and then press OK.
5. Use the arrow buttons to highlight Button Test, and then press OK.
Fax reports
This section describes the fax reports that help you diagnose and solve problems with the product.
Fax activity log
The fax activity log provides a chronological history of the last 40 faxes that were received, sent, or
deleted, and any errors that occurred.
1. On the product control panel, press Fax Menu.
2. Use the arrow buttons to select Fax Reports, and then press OK.
3. Use the arrow buttons to select Fax Activity log, and then press OK.
4. Press OK to select Print log now. The product exits the menu settings and prints the log.
Fax call report
A fax call report is a brief report that indicates the status of the last fax that was sent or received.
1. On the product control panel, press Fax Menu.
2. Use the arrow buttons to select Fax Reports, and then press OK.
3. Use the arrow buttons to select Last Call Report, and then press OK. The product exits the menu
settings and prints the report.
230 Chapter 7 Problem solve ENWW

T.30 protocol trace
Use a T.30 protocol trace report to troubleshoot fax transmission issues.
Send a fax from the product or receive a fax to the product from another fax machine, and then print a
T.30 trace report after the fax prints.
1. On the product control panel, press Setup .
2. Use the arrow buttons to select Service, and then press OK.
3. Use the arrow buttons to select Fax Service, and then press OK.
4. Use the arrow buttons to select Print T.30 trace, and then press OK.
The product exits the menu settings and prints the reports.
Explanations of some of the report’s column headings follow:
●Date and Time identify when the fax begins.
●Type is the type of fax activity: send or receive.
●Identification is the phone number to which a fax is sent.
●Result explains the status of the fax:
◦“OK” means that the fax was successful.
◦“Pending” faxes are in memory or are printing.
◦An error code means that the product might need service. The following tables, Table
7-1 Fax receive error codes on page 231 and Table 7-2 Fax send error codes
on page 235, define the error codes.
NOTE: These codes also appear in the fax call report and the fax activity log.
Table 7-1 Fax receive error codes
Error code Description Solution
200 The fax session has completed without errors. N/A
221 User has pressed theCancel button, causing the
fax session to be prematurely halted.
Have the sender resend the fax.
222 The receiving product has answered a call but has
been unable to detect the presence of a calling fax
product for one of the following reasons:
●Typically this will be due to the receiving fax
product answering a voice call.
●The sender canceled the fax transmission by
pressing the Cancel button immediately
prior to, or just as the receiving product
answered the call.
1. Confirm that the sender is a fax product and
not a voice caller—typically you must rely on
the sender informing the caller that the fax
session is failing.
2. If the sending product ends the call just as the
receiving product starts reception, reduce the
ring count after which the receiving product
answers. Alternatively suggest that the sender
manually dials to the receiving product and
then manually starts the fax session, by
pressing theStart Fax button once fax tones
have been heard from the receiving product.
3. Confirm that the sender is not inadvertently
attempting to poll transmit from the receiving
ENWW Troubleshooting tools 231
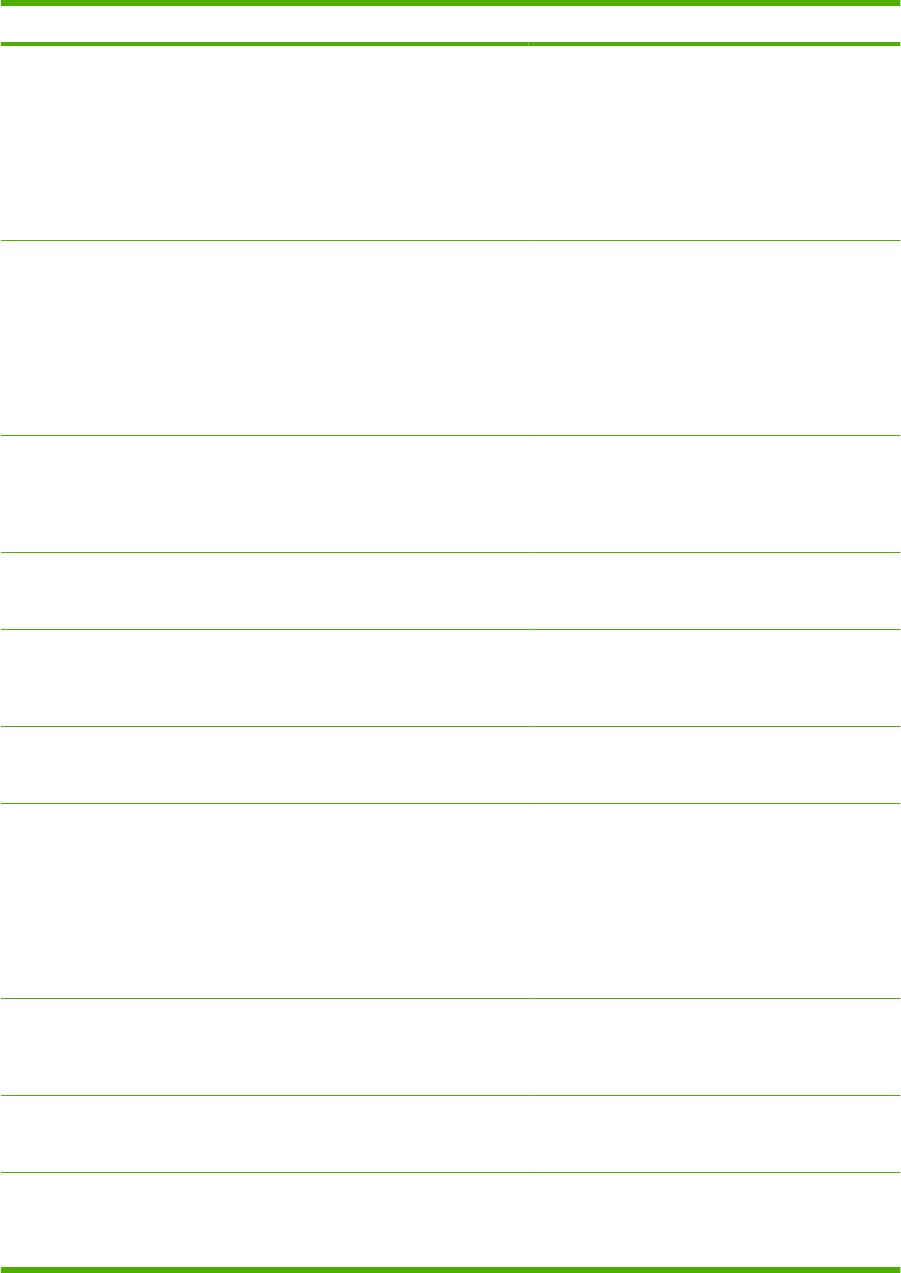
Error code Description Solution
●The sending product automatically ended the
call immediately prior to, or just as the
receiving product answered the call.
●The sending (sending) fax product determined
there was a feature incompatibility between
the two and disconnected immediately before
transmitting any further fax tones or T.30
frames. (This is very rare.)
product, instead of transmitting to the
receiving product.
4. Reconfigure the receiving fax product to use
different configuration settings, toggle the
ECM state, and/or select a slower reception
speed.
223 (ECM error) The receiving product has been unable to receive
an entire page even after multiple attempts to re-
receive the parts of the page that contain errors.
This is usually due to extremely poor line
conditions.
1. Reattempt the fax reception at a different time
when telephone line conditions have
improved.
2. If the error persists, disable ECM. Errors may
still occur, and may result in degraded image
quality on the received page. However, the
ability to receive the entire document will be
improved.
224 The receiving product has received one or more
pages with excessive errors. This is usually due to
extremely poor line conditions. Error correction is
not used during this session so errors are not
corrected.
Reattempt the fax reception at a different time when
telephone line conditions have improved.
225 The sending product has attempted to initiate a
sending diagnostic session with this product even
though sending diagnostic access is disabled.
Enable the sending diagnostics capability on the
receiving product.
226 The sending product has attempted to initiate a
sending diagnostic session with this product but the
sending diagnostic versions supported by the two
products are incompatible.
None. Sending diagnostics cannot occur between
products with incompatible sending versions.
227 The sending product has attempted to initiate a fax
session at a speed and modulation that is not
supported by the receiving product.
Reconfigure the receiving product to receive at a
slower speed.
228 The sending product has attempted to initiate a poll
transmission from the receiving product even
though the receiving product is not configured for
poll transmission.
1. Confirm that polling by the sender is desired.
It is possible that the sender has inadvertently
attempted to poll. If this is the case reattempt
a normal transmission from the sending
product.
2. If polling by the remote user was desired,
confirm that the receiving product was
correctly configured for poll transmission.
229 The sending product has attempted to initiate a
secure poll transmission from the receiving product
but has not provided a valid password.
If the sender is the desired recipient for the polled
document, confirm that the sender has the correct
password, and that the receiving product is
configured with the same password.
230 The sending product has attempted to initiate an
operation that requires error correction but has not
selected error correction for the session.
Enable ECM on both the receiving product and the
sending product.
231 The sending product has attempted to initiate a
transmission to the receiving product even though
the capability to receive is disabled at the receiving
product.
Ensure that the receiving product is capable of
receiving a document. Check that paper is correctly
loaded, paper is not jammed within the product, and
any other system abnormalities have been cleared.
Table 7-1 Fax receive error codes (continued)
232 Chapter 7 Problem solve ENWW
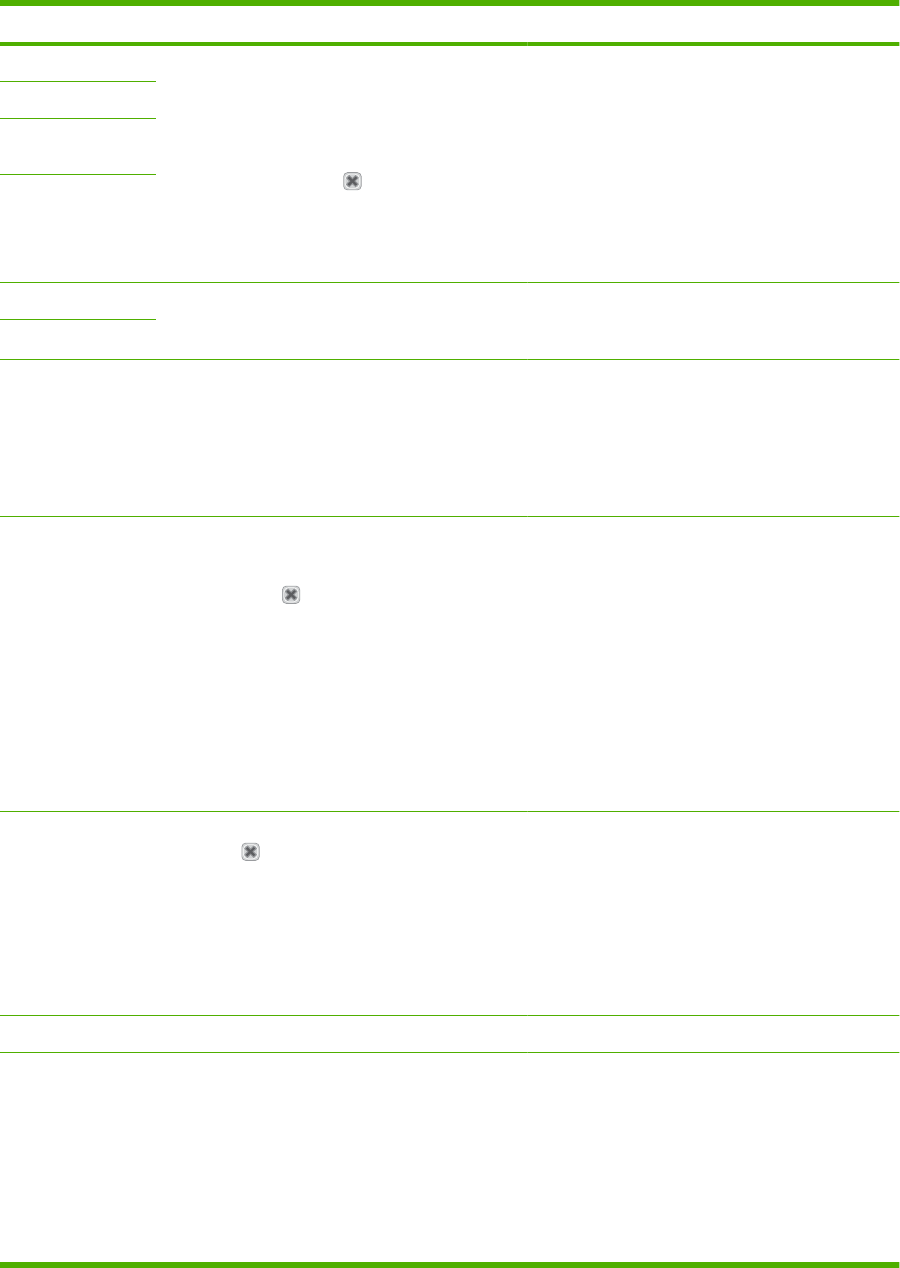
Error code Description Solution
232 One of the following has occurred:
●A communication failure has occurred
between the two products.
●The user at the remote product may have
pressed the Cancel button.
●The power at the remote product has been
interrupted or deliberately turned off, causing
the fax session to be interrupted.
1. Re-attempt the fax reception at a different time
when telephone line conditions have
improved.
2. If the error persists, and error correction is in
use for the fax session, disable ECM.
233 and 234
235 and 236 (ECM
error)
237
238 The sending fax product sent an unexpected
communication. This is a defect in the sending
product.
N/A
239–241
242 The sending fax product is attempting to receive
instead of send. Both products have attempted to
start a reception at the same time. It is possible to
accidentally initiate a fax reception after dialing on
many products, if there is no paper in the product
or if the paper is not correctly loaded and cannot be
sensed by the appropriate document sensor.
Ensure that a document is ready and correctly
loaded in the sending fax product and that the
sending product is attempting to initiate a
transmission and not a reception.
243 and 244 One of the following has occurred:
●The user of the remote product has pressed
the Cancel button, causing the session to
be prematurely terminated.
●The sending fax product determined there
was a feature incompatibility between the two
products and has terminated the session. An
example would be when the receiving product
wanted to initiate polling, but the sending
product did not support this mode of operation.
1. Confirm that the sender is not inadvertently
attempting to poll transmit from the receiving
product, instead of transmitting to the
receiving product. This mode of operation
must be specially configured on the receiving
product. If poll transmission from the receiving
product is the desired mode of operation,
confirm that the receiving product has been
configured for this operation.
2. Reconfigure the receiving fax product to use
different configuration settings, toggle the
ECM state, and/or select a slower reception
speed.
245 and 246 (ECM
error)
The user of the sending product has pressed
theCancel button, causing the session to be
prematurely terminated. The receiving product has
been "holding off" the remote product during
reception of a large and/or complex document due
to lack of available memory. This hold-off time has
exceeded the timeout (typically 60 seconds) used
by the sending product, and it has terminated the
session.
1. If the document was large, ask the sender to
retransmit the document as two or more
smaller documents.
2. Disable ECM and reattempt the fax reception.
247-251 The sending product appears to be "stuck on." N/A
252 Telephone line conditions were too poor to receive
a fax.
1. Reattempt the fax reception at a later time
when line conditions may have improved.
2. Configure the receiving product to start
reception at a lower speed.
3. If the receiving product received successfully
several pages of a larger document, ask the
sender to transmit the document in several
smaller parts.
Table 7-1 Fax receive error codes (continued)
ENWW Troubleshooting tools 233
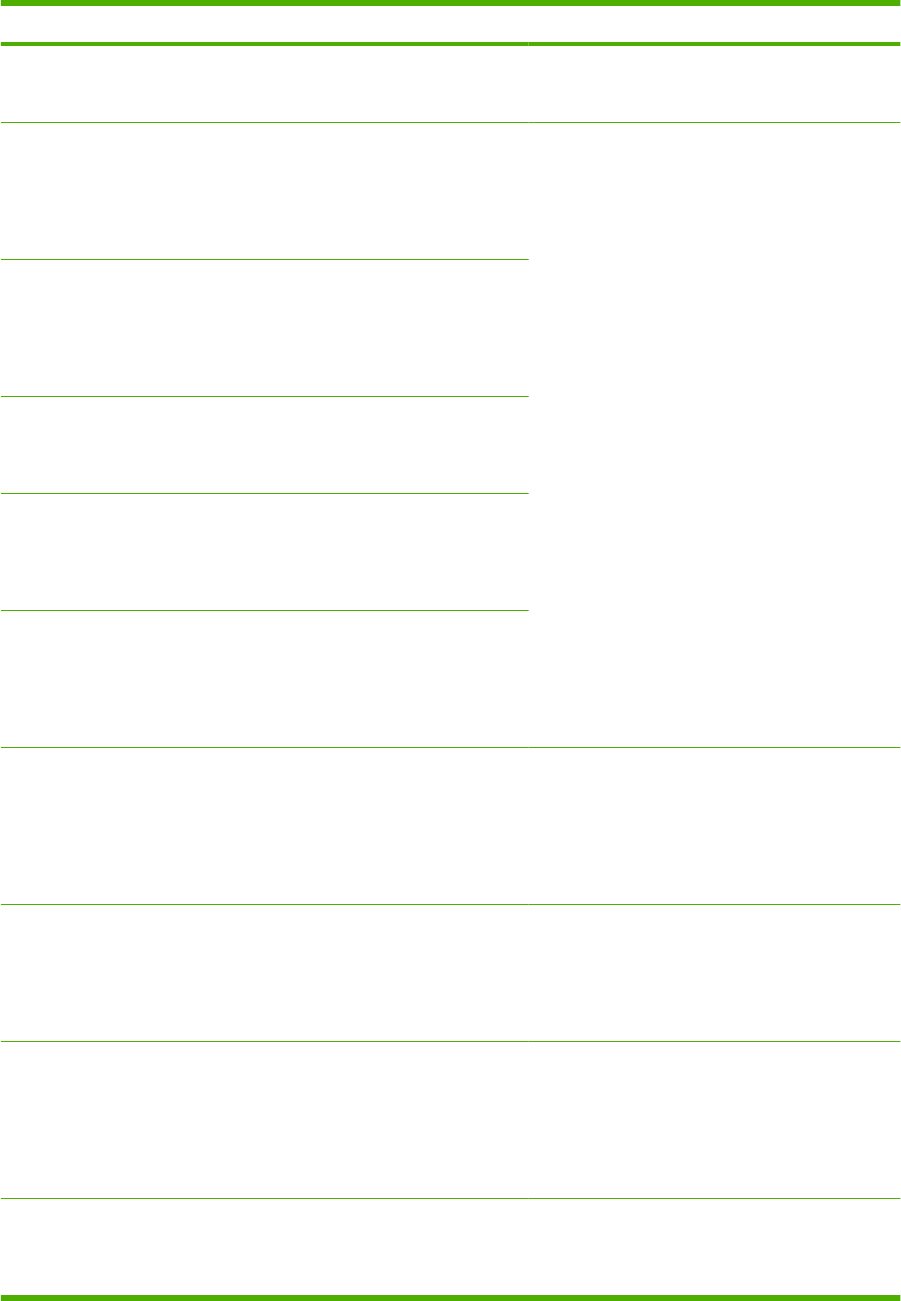
Error code Description Solution
253 The sending product has attempted to initiate a
page transmission using a page width that is not
supported by the receiving product.
Ask the sender to reconfigure the fax product to
transmit using a "normal" (letter/A4) page width.
281 The receiving product has not received any data at
the start of a page during non-ECM reception,
although the modem has not detected a sending
disconnect. The sending product is probably
transmitting fill bytes instead of data and has either
jammed or broken.
Reattempt the fax reception after first requesting
that the sender check the sending product.
282 The receiving product has not received any data at
the start of a page during ECM reception although
the modem has not detected a sending disconnect.
The sending product is probably transmitting sync
frames instead of data and has either jammed or
broken.
283 The receiving product has detected that the modem
carrier has stopped. Either the line has been
disconnected or the sending product has aborted
the transmission.
284 The receiving product has not received any data
during non-ECM page reception and a timeout
failure has occurred. The sending product is
probably transmitting fill bytes instead of data and
has either jammed or broken.
285 The receiving product has stopped receiving any
data during an ECM page reception although the
modem has not detected a sending disconnect.
The sending product is probably transmitting sync
frames instead of data and has either jammed or
broken.
286 The sending product has transmitted invalid data.
The receiving product has received frames with
errors during an ECM reception and requested
retransmission of the errored frames. The data that
is resent does not correspond to the data that was
requested. This is an implementation error from the
sending product.
Disable ECM and reattempt the reception.
290 The sending product has attempted to renegotiate
the session mode from ECM to non-ECM between
pages. This operation is not supported and the
session has been abandoned.
Reattempt the fax reception and split the document
into two portions corresponding to the ECM and
non-ECM portions. Some products will attempt to
use non-ECM for photo mode, so this may be
associated with a between-page encoding change
to support photo mode.
291 This is not a communication error and it is not
expected that this error will occur under non-
development scenarios. Reception has failed
because the receiving product is unable to open a
file to receive data into. May be associated with low
memory, although low memory should be handle
more gracefully than this.
If the error persists, reinitialize the product.
292 The sending product has attempted to renegotiate
the encoding mode from non-JPEG to JPEG. This
operation is not supported and the session has
been abandoned.
Reattempt the fax reception and split the document
into two portions corresponding to the JPEG and
non-JPEG portions. Some products will attempt to
use JPEG for photo mode, so this may be
Table 7-1 Fax receive error codes (continued)
234 Chapter 7 Problem solve ENWW
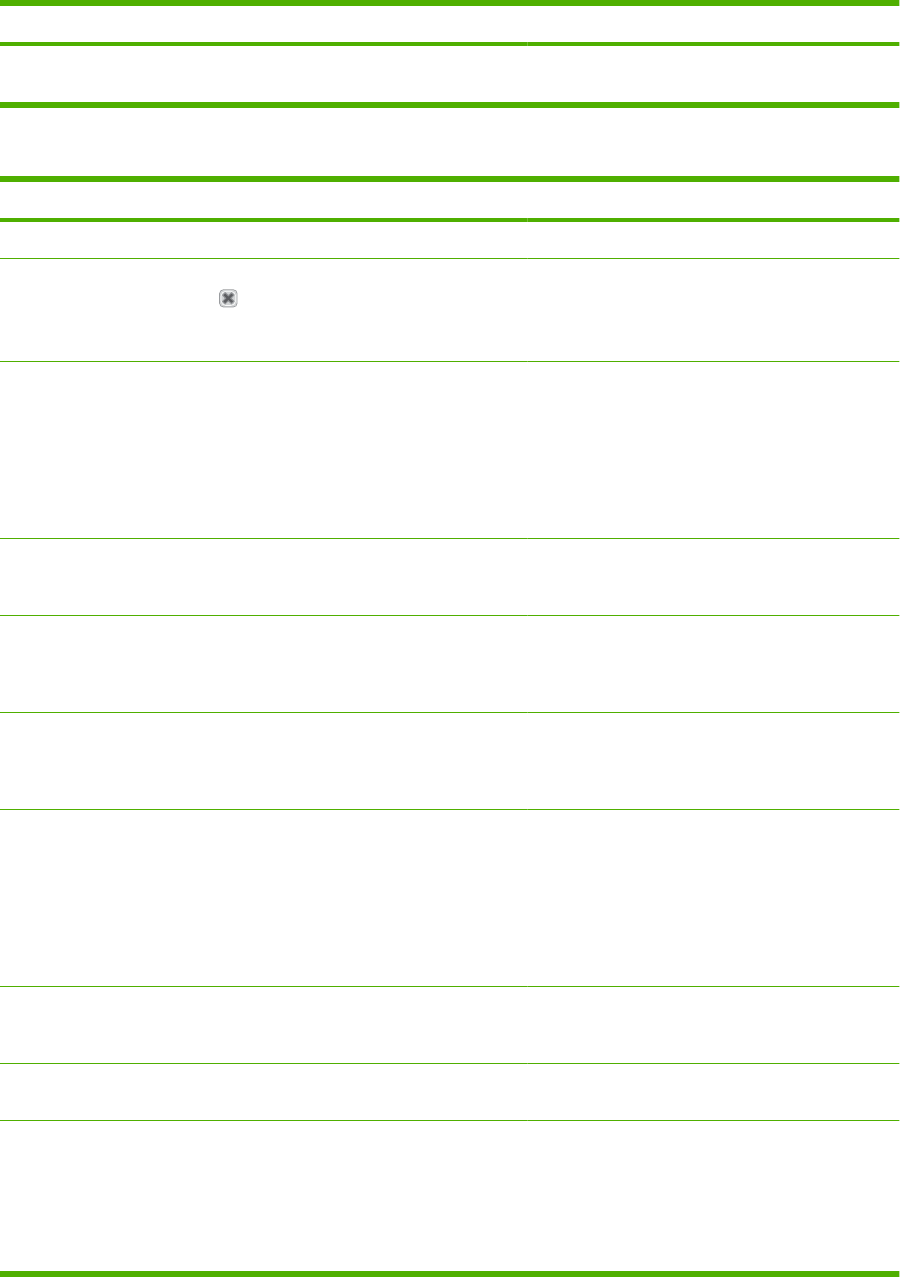
Error code Description Solution
associated with a between-page encoding change
to support photo mode.
Table 7-2 Fax send error codes
Error code Description Solution
300 Fax session has completed without errors N/A
311 The user of the receiving product has pressed the
Cancel button, causing the session to be
prematurely halted before all pages have been
transmitted.
Resend the fax.
312 A sending fax product has failed to answer the call.
Specifically fax tones or the fax handshake from a
sending product has not been detected. Typically
this is due to the user calling the wrong number, the
correct number has been called but the product has
been configured not to answer, or the sending
product has temporarily disabled answering due to
a condition such as lack of paper or a paper jam.
Confirm the sending fax product is ready to receive
a document and reattempt the transmission.
313 A busy signal has been detected each time the
receiving product has attempted to call the sending
product.
Reattempt the fax transmission at a later time when
the line is no longer busy.
314 The receiving product has attempted to initiate a
sending diagnostic session but has detected that
sending diagnostics are disabled at the sending
product.
Enable sending diagnostics on the sending
product.
315 The receiving product has attempted to initiate a
sending diagnostic session but has detected that
the sending diagnostic version supported by the
sending product is incompatible.
No solution. Sending diagnostics cannot occur
between products with incompatible sending
versions.
316 The receiving product is setup to initiate document
transmission, but it has detected that the sending
product is not able to receive a document. This error
should be very rare since normally a sending
product will not answer if it cannot receive a
document. On of the few exceptions to this would
occur if the sending product was configured to poll
transmit a document but was unable to receive.
Configure the sending product for reception.
Typically the sender should ensure paper is loaded
in the product, paper jams are fixed, and any other
system abnormalities are cleared.
317 The sending product cannot support a fax reception
at any speed or modulation that is supported by the
receiving product.
N/A
318 The sending product cannot support a fax reception
at the page width selected by the receiving product.
N/A
319 The receiving product has attempted to initiate a
binary file transfer (BFT) but has detected that the
sending product does not support this mode of
operation.
Do one of the following:
●Enable the BFT capability on the sending
product if it is supported.
●Retransmit the document as a normal fax,
rather than attempting a BFT transfer.
Table 7-1 Fax receive error codes (continued)
ENWW Troubleshooting tools 235
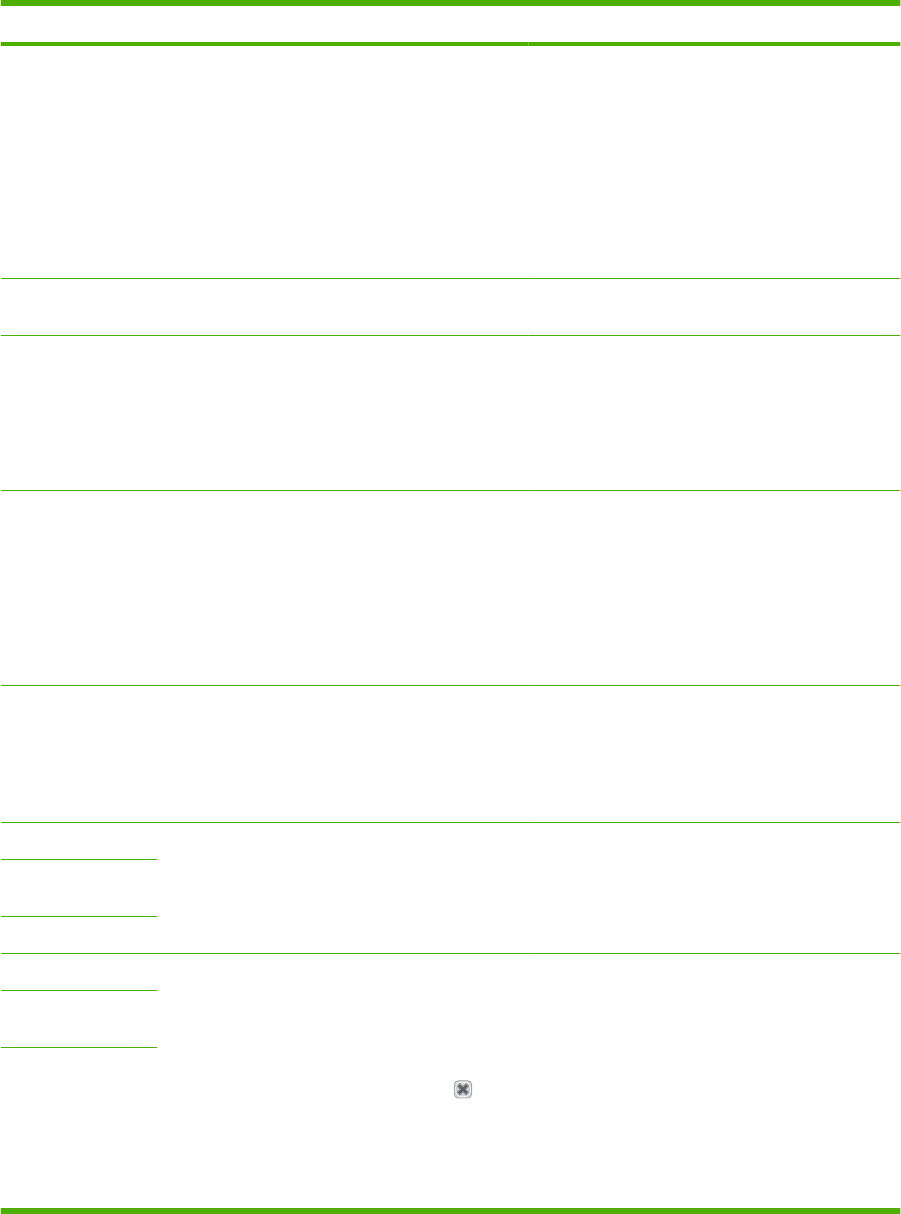
Error code Description Solution
320 The receiving product is set up to initiate poll
reception with a sending product, but it has
detected that the sending product is not configured
to do this. Poll transmission from a sending product
is typically configured on a session-by-session
basis.
Do one of the following:
●Confirm that the receiver really wants to
attempt a poll reception. If not, reconfigure the
receiving product for a normal fax
transmission
●Configure the sending product for poll
transmission. The sender must load a
document to transmit and then configure the
product for polling.
321 There was a communication error with the receiving
fax product due to poor telephone line conditions.
Reattempt the fax transmission at a different time
when telephone line conditions have improved.
322–324 Telephone line conditions were too poor to send a
fax.
1. Reattempt the fax transmission at a different
time when telephone line conditions have
improved.
2. If the session fails after transmitting several
pages of a large document, retransmit the
document as several smaller documents.
325-328 (ECM
error)
Telephone line conditions were very poor. 1. Reattempt the fax transmission at a different
time when telephone line conditions have
improved.
2. If the error persists, disable ECM. Errors may
still occur, and may result in a degraded image
quality on the received page. However, the
ability to transmit the entire document will be
improved.
329–331 The sending product has reported that one or more
pages have been received (non-ECM mode) with
excessive errors. This error does not result in the
session being terminated immediately. Subsequent
page transmission can still occur and later pages
may be received without error.
1. Reattempt the fax transmission at a different
time when telephone line conditions have
improved.
2. If the error persists, select a lower speed for
the initial transmission speed.
332–337 There is a defect in the sending fax product. Send from another product.
338–342 (ECM
error)
343
344–348 One of the following has occurred:
●The sending product has failed to respond to
a fax command from the receiving product due
to the connection being interrupted.
●The sender has pressed the Cancel button
while the reception was in progress.
●In rare conditions, incompatibility between the
two products may cause the sending product
to abandon the call.
1. Reattempt the fax transmission at a different
time when telephone line conditions have
improved.
2. fax session was using error correction, disable
ECM.
349-353 (ECM
error)
354 and 355
Table 7-2 Fax send error codes (continued)
236 Chapter 7 Problem solve ENWW
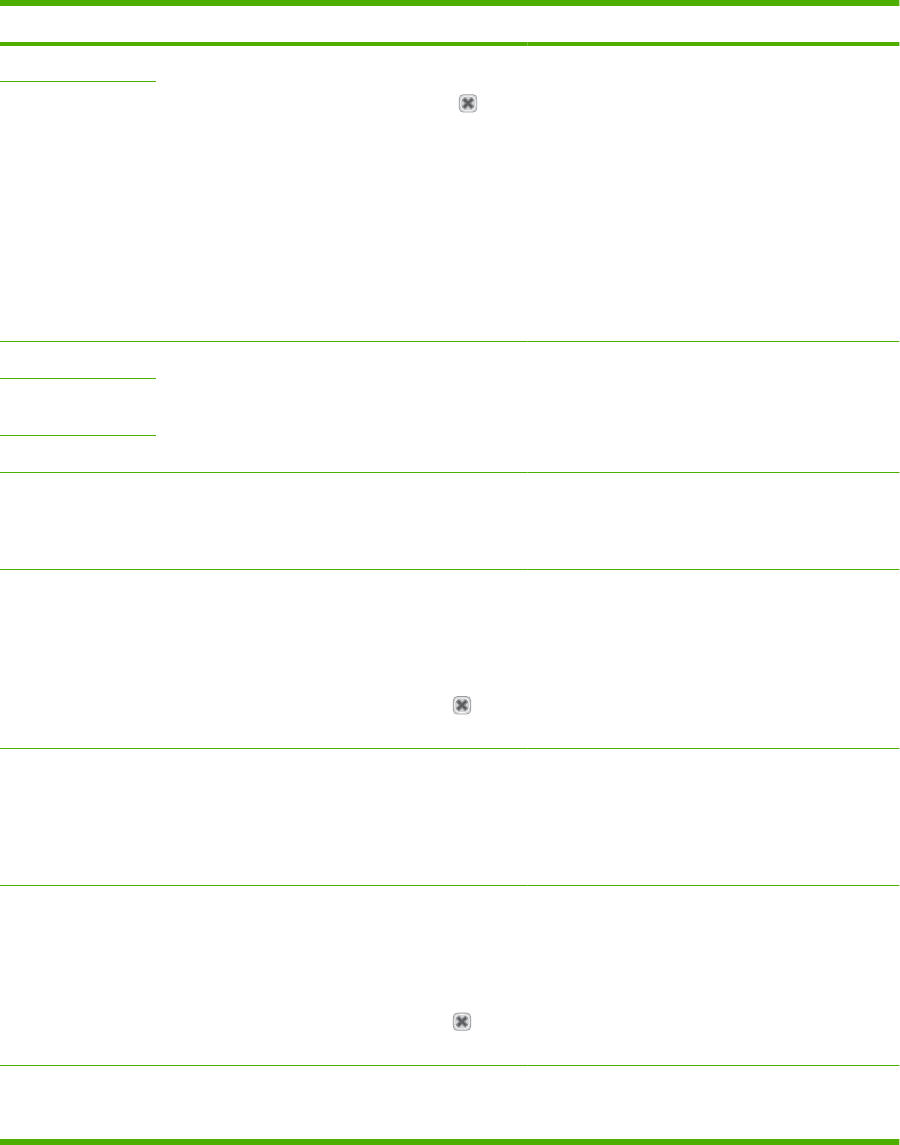
Error code Description Solution
356-361 One of the following has occurred:
●The sender has pressed the Cancel
button, causing the session to be aborted.
●The sending product has encountered a
system problem such as no paper or a paper
jam, which has inhibited it from receiving any
more pages, and which has caused it to
terminate the session prematurely.
●A feature incompatibility has been
encountered by the sending product, causing
it to terminate the session.
1. Configure the sending product for document
reception by clearing any paper jams, loading
sufficient paper, and clearing any other
system errors.
2. Configure the receiving fax product to use
different configurations, toggle the ECM state,
or select a slower reception speed.
362-366 (ECM
error)
367-372 The sending product appears to be "stuck on". N/A
373-377 (ECM
error)
378 and 379
380 The sending product has failed to issue a valid
response to a CTC frame. This occurs during ECM
transmission after multiple retransmissions of erred
data.
Send from another product.
381 One of the following has occurred:
●The sending product has failed to respond to
a fax command from the receiving product due
to the connection being interrupted.
●The sender has pressed the Cancel button
while the reception was in progress.
1. Reattempt the fax transmission at a different
time when telephone line conditions have
improved.
2. If the error persists, disable ECM.
382 The sending fax product has been "holding off" the
receiving fax product from continuing the ongoing
transmission due to a temporary low memory
condition at the sending product. If this "hold-off"
period exceeds a product's specific timeout value,
the session will terminate.
1. Resend the document as two or more
separate fax transmissions. Wait several
minutes between the end of one transmission
and the start of the next transmission.
2. If the error persists, disable ECM.
383 One of the following has occurred:
●The sending product has failed to respond to
a fax command from the receiving product due
to the connection being interrupted
●The sender has pressed the Cancel button
while the reception was in progress.
1. Reattempt the fax transmission at a different
time when telephone line conditions have
improved.
2. If the error persists, disable ECM.
384 The receiving product has attempted a black JPEG
transmission to a product that does not support this
mode.
Reattempt the fax transmission using a different
mode.
Table 7-2 Fax send error codes (continued)
ENWW Troubleshooting tools 237
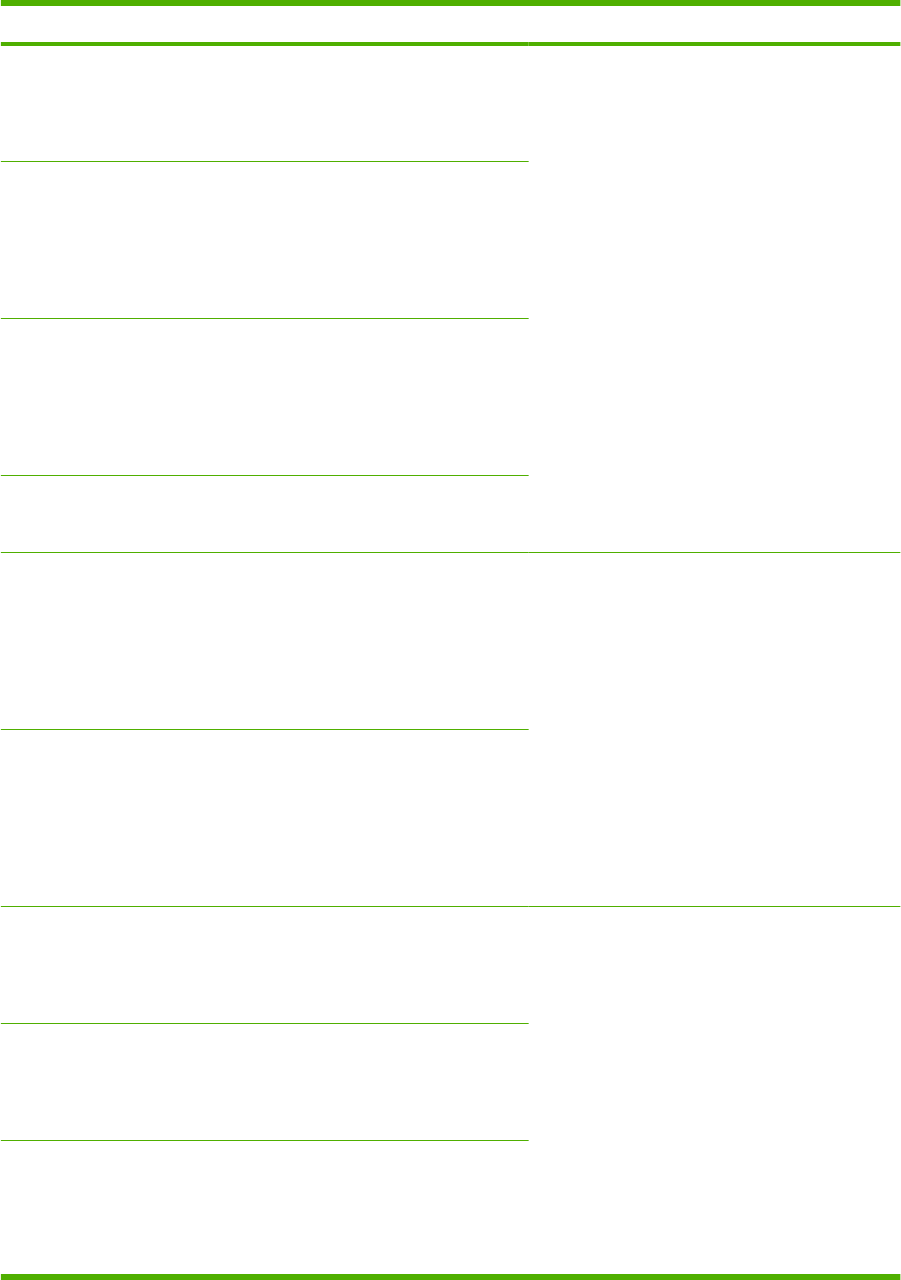
Error code Description Solution
386 The receiving product has failed to complete the
third phase of the initial V.34 handshake after
originating a fax session. This is usually due to poor
line conditions although it may be a compatibility
issue with certain products and/or line conditions.
1. Reattempt the fax transmission at a different
time when telephone line conditions have
improved.
2. Disable V.34 on the receiving product and
attempt the transmission using the V.17
mode.
387 The receiving product has failed to successfully
negotiate the initial V.8 handshake with the sending
product after originating a fax session. Typically this
will occur when the sending product is not fax
capable or has disabled reception. It may also be a
compatibility issue with certain products and/or line
conditions.
388 The receiving product has originated a fax session
and detected a sending fax product but has been
unable to detect any T30 frames. If the product is
in V.17 mode it is likely that the connection has
been interrupted. In V.34 mode is also possible for
this error to occur due to compatibility problems
with certain products and/or line conditions.
389 The receiving product has originated a fax session
and has reattempted V.8 negotiations multiple
times without success.
390 The receiving product has originated a fax session
using error correction (either V.34 or V.17).
Transmission of an image has been abandoned
after a timeout when no data has become ready for
transmission. This is most likely due to a low
memory condition although it could be due to other
internal problems that cause generation of data for
transmission to stall.
Reattempt the transmission after making sure
documents stored in memory are printed and the
product has paper ready for printing. If the problem
persists reinitialize permanent storage.
391 The receiving product has originated a fax session
without error correction (not V.34 ). Transmission of
an image has been abandoned after a timeout
when no data has become ready for transmission.
This is most likely due to a low memory condition
although it could be due to other internal problems
that cause generation of data for transmission to
stall.
392 The receiving product has answered a fax session
and completed the initial V.34 handshake but has
been to detect any T30 frames. This failure is either
a compatibility problems with certain products or is
due to line conditions.
1. Reattempt the fax reception at a different time
when telephone line conditions have
improved.
2. Disable V.34 on the receiving product and
attempt the transmission using the V.17
mode.
393 The receiving product has failed to complete the
third phase of the initial V.34 handshake after
answering a fax session. This is usually due to poor
line conditions although it may be a compatibility
issue with certain products and/or line conditions.
394 The receiving product has failed to successfully
negotiate the initial V.8 handshake with the sending
product after answering a fax session. Typically this
will occur when the calling product is not fax
capable. It may also be a compatibility issue with
certain products and/or line conditions.
Table 7-2 Fax send error codes (continued)
238 Chapter 7 Problem solve ENWW
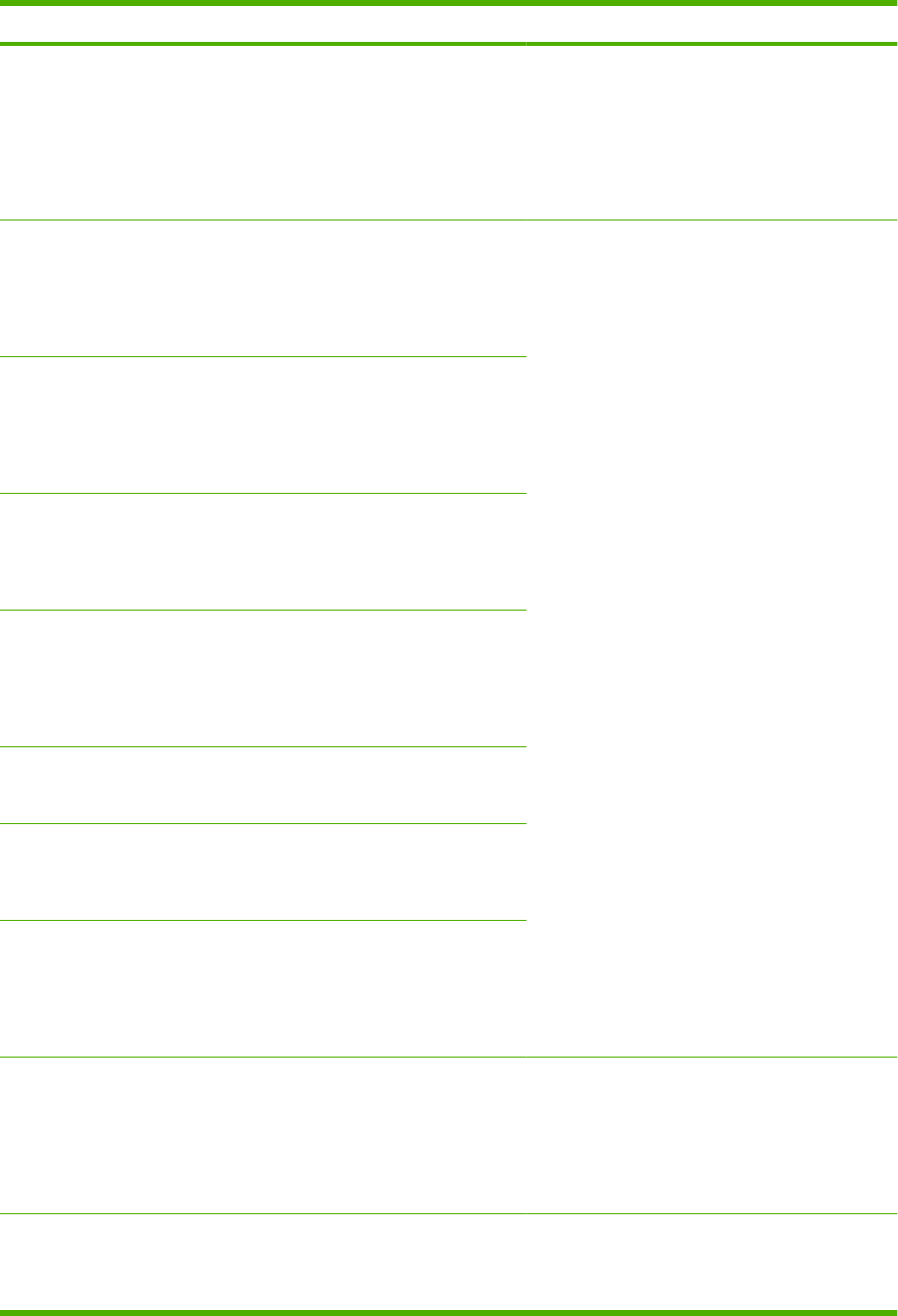
Error code Description Solution
395 An unexpected T.30 frame has been received
between pages during a multipage V.34 reception.
This is almost certainly a compatibility problem with
the sending product and may be due to an error with
the implementation of the sending product.
1. Reattempt the fax reception. If transmission
errors are not encountered because line
conditions have improved, then this error will
probably be avoided.
2. Disable V.34 on the receiving product and
attempt the transmission using the V.17
mode.
396–409 An error occurred during a V.34 transmission when
the receiving product was unable to correctly
handshake with the sending product and was
consequently unable to transmit a T30 frame. This
occurs when the line was disconnected or if line
conditions degrade during the session.
Reattempt the fax transmission at a different time
when telephone line conditions have improved.
410–419 An error occurred during a V.34 reception when the
receiving product was unable to correctly
handshake with the sending product and was
consequently unable to transmit a T30 frame. This
occurs when the line is disconnected or if line
conditions degrade during the session.
420 V.34 negotiations have failed from the originating
product during phase four, which occurs after V.8
and before the first T.30 frames are exchanged.
Compatibility problems have been observed in this
area when sending to non-HP units.
421 V.34 negotiations have failed from the originating
product during phase three, which occurs after V.8,
before phase four, and before the first T.30 frames
are exchanged. Compatibility problems have been
observed in this area when sending to non-HP
units.
422 V.34 negotiations have failed from the answering
product during phase four, which occurs after V.8
and before the first T.30 frames are exchanged.
423 V.34 negotiations have failed from the answering
product during phase three, which occurs after V.8,
before phase4, and before the first T.30 frames are
exchanged.
430 The transmitting product is unable to send
continuous ones at the end of the control channel
prior to starting the primary channel. This is a V.34
error. This error may be associated with line
conditions although it is more likely to be due to
internal problems with the modem.
431 The transmitting product has not received a
response after aborting a transmission. Depending
upon when the session is aborted, some sending
products may not respond. It should be noted that
the receiving unit always attempts to abort the
session in a way that allows the sending product to
respond to the final PPS_EOP.
N/A
440–444 An error occurred during a V.34 transmission after
one or more partial pages (image data) were
transmitted using the primary channel. The
transmitting product was unable to restart the
Reattempt the fax reception at a different time when
telephone line conditions have improved.
Table 7-2 Fax send error codes (continued)
ENWW Troubleshooting tools 239
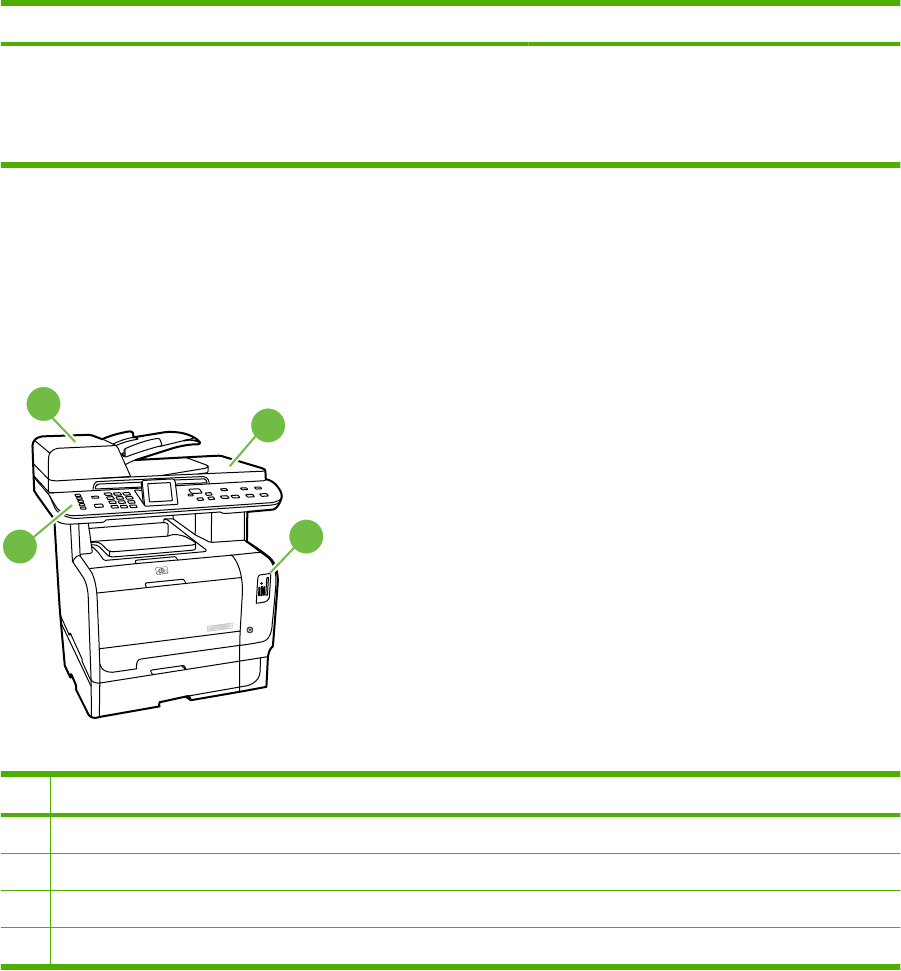
Error code Description Solution
control channel in order to resume the T30
handshake. This typically occurs when the
receiving product prematurely disconnects during
partial page reception, although it is possible it may
also be due to compatibility issues.
Diagrams
Block diagrams
Scanner and automatic document feeder (ADF) assemblies
Figure 7-1 Scanner and ADF assemblies
1
23
4
Table 7-3 Scanner and ADF assemblies
Item Description
1Control panel
2ADF
3Scanner
4Memory-card reader (memory-card models only)
Table 7-2 Fax send error codes (continued)
240 Chapter 7 Problem solve ENWW
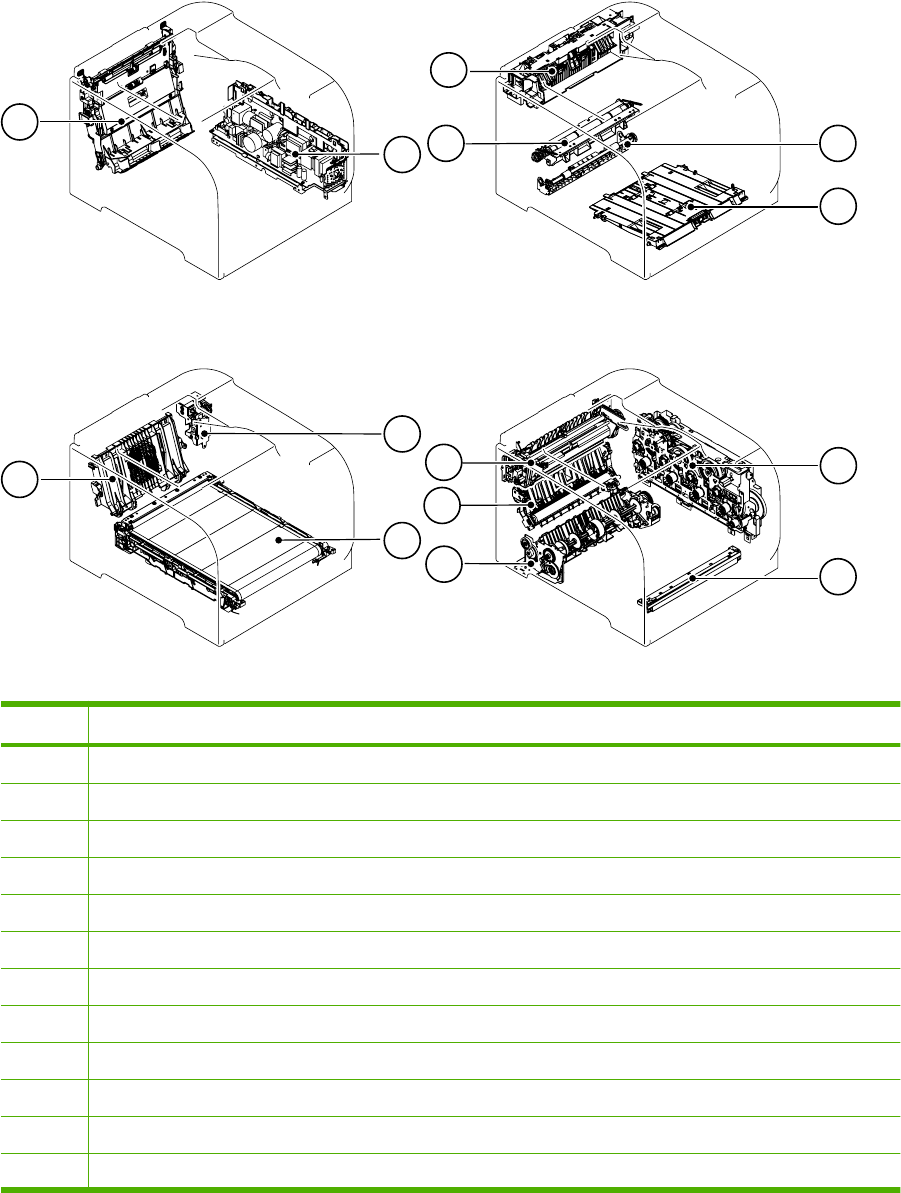
Major components
Figure 7-2 Major components
1
2
3
4
13
14
5
6
7
8
9
10
11
12
Table 7-4 Major components
Item Description
1Duplex feed assembly (duplex models only)
2Rear door rib assembly (duplex models only)
3Power supply assembly
4Duplex reverse drive assembly (duplex models only)
5ITB assembly
6Delivery assembly
7Registration assembly
8Fuser assembly
9Secondary transfer feed assembly
10 Cassette pickup assembly
11 Duplex re-pickup guide assembly (duplex models only)
12 Multipurpose tray pickup assembly
ENWW Troubleshooting tools 241

Item Description
13 Drive assembly
14 Color misregistration and density sensor
Table 7-4 Major components (continued)
242 Chapter 7 Problem solve ENWW
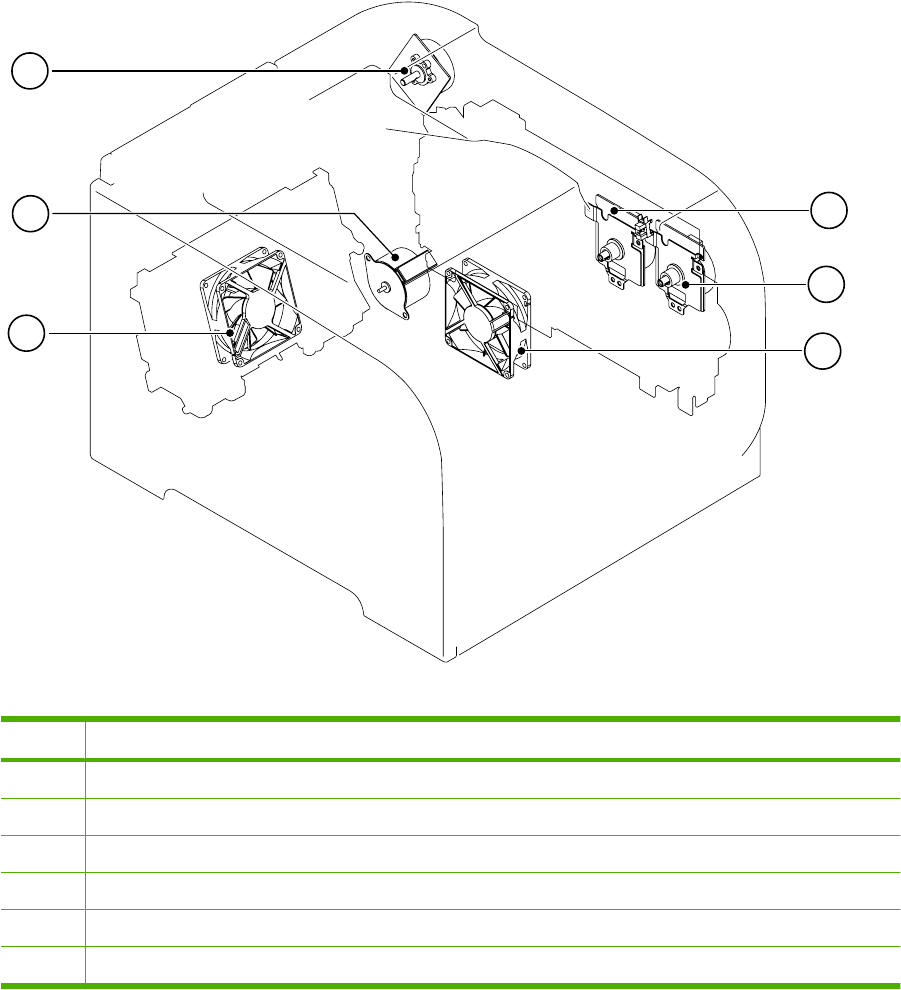
Motors and fans
Figure 7-3 Motors and fans
4
6
1
2
3
5
Table 7-5 Solenoid, sensors, and motors
Item Description
1Fuser motor
2Drum motor (M1)
3Developing motor (M2)
4Fan 1
5Fan 2 (duplex models only)
6Pickup motor
ENWW Troubleshooting tools 243
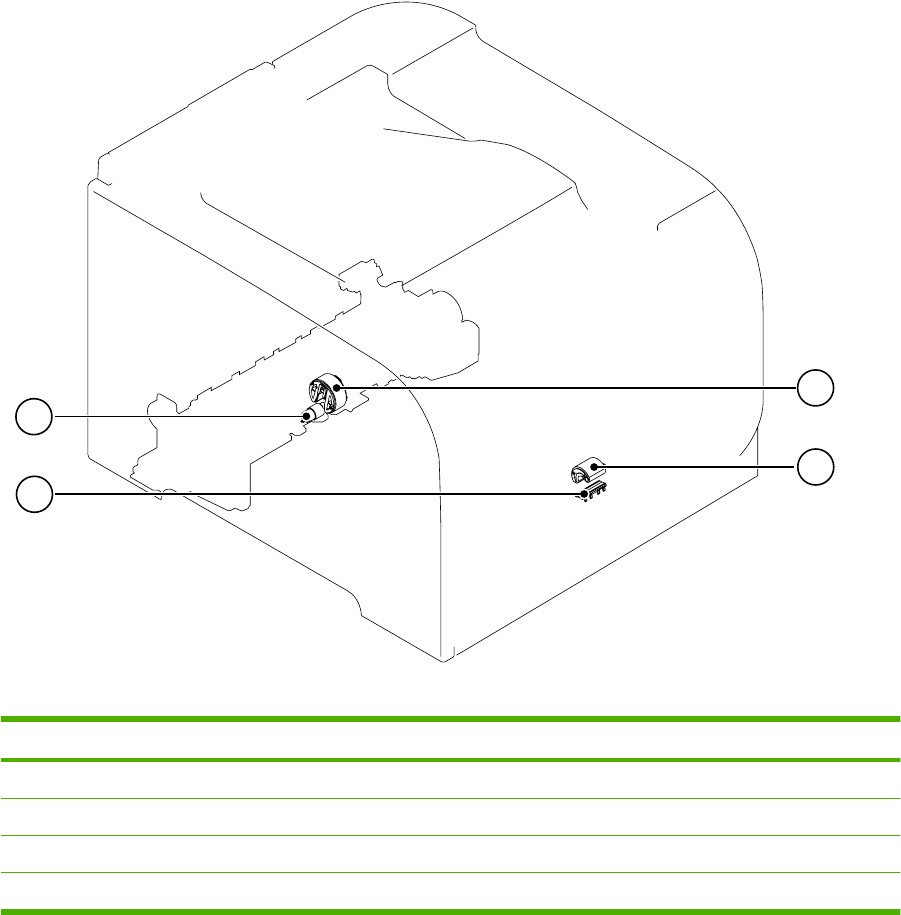
Rollers
Figure 7-4 Rollers
1
2
3
4
Table 7-6 Rollers
Item Description
1Cassette pickup roller
2Multipurpose tray pickup roller
3Multipurpose tray separation pad
4 Cassette separation roller
244 Chapter 7 Problem solve ENWW
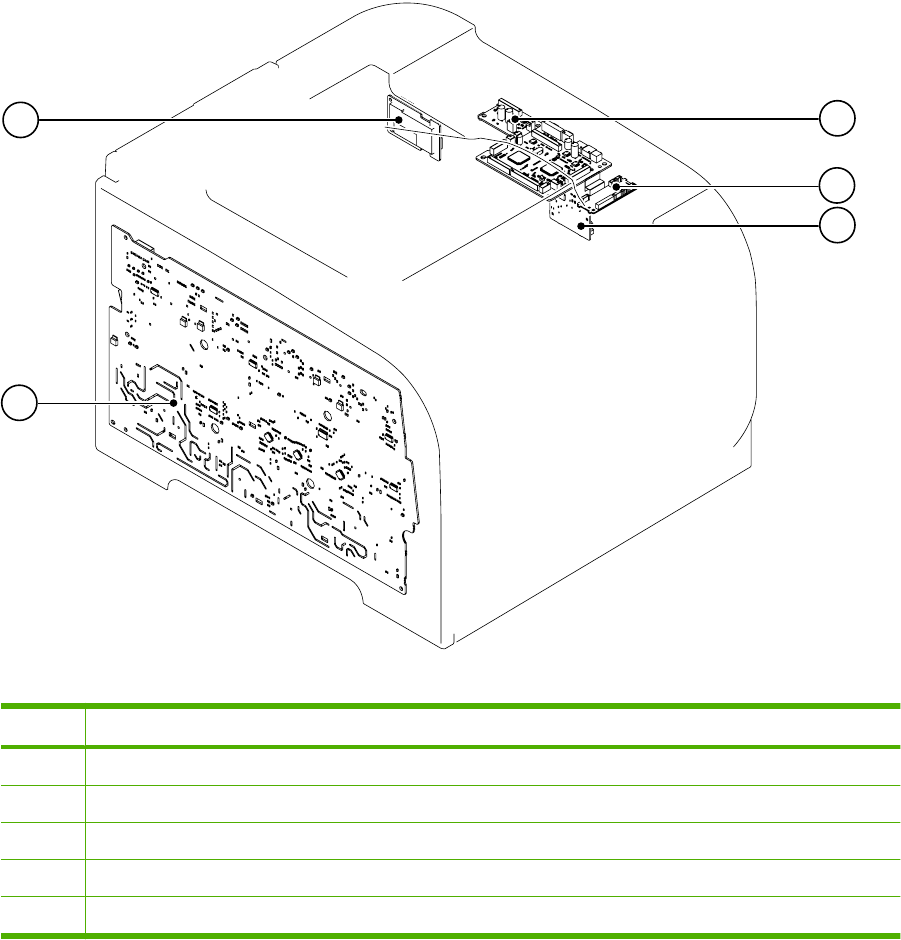
PCAs
Figure 7-5 PCAs
51
4
3
2
Table 7-7 PCAs
Item Description
1DC controller PCA
2Connector PCA
3Driver PCA
4High-voltage power supply PCA
5Sub power supply PCA
ENWW Troubleshooting tools 245
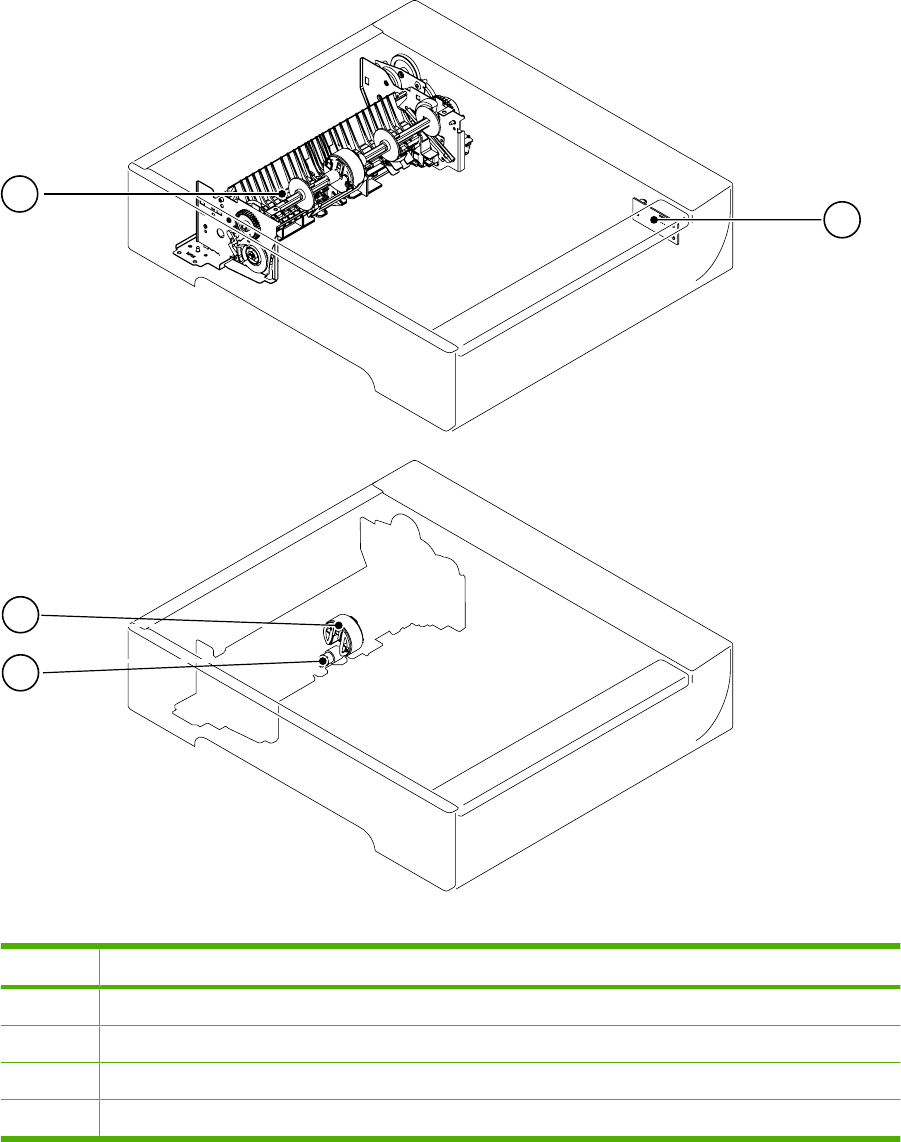
Optional 250-sheet cassette
Figure 7-6 Optional 250-sheet cassette
12
3
4
Table 7-8 Optional 250-sheet cassette
Item Description
1Paper feeder pickup assembly
2Paper feeder connector PCA
3Paper feeder separation roller
4Paper feeder pickup roller
246 Chapter 7 Problem solve ENWW
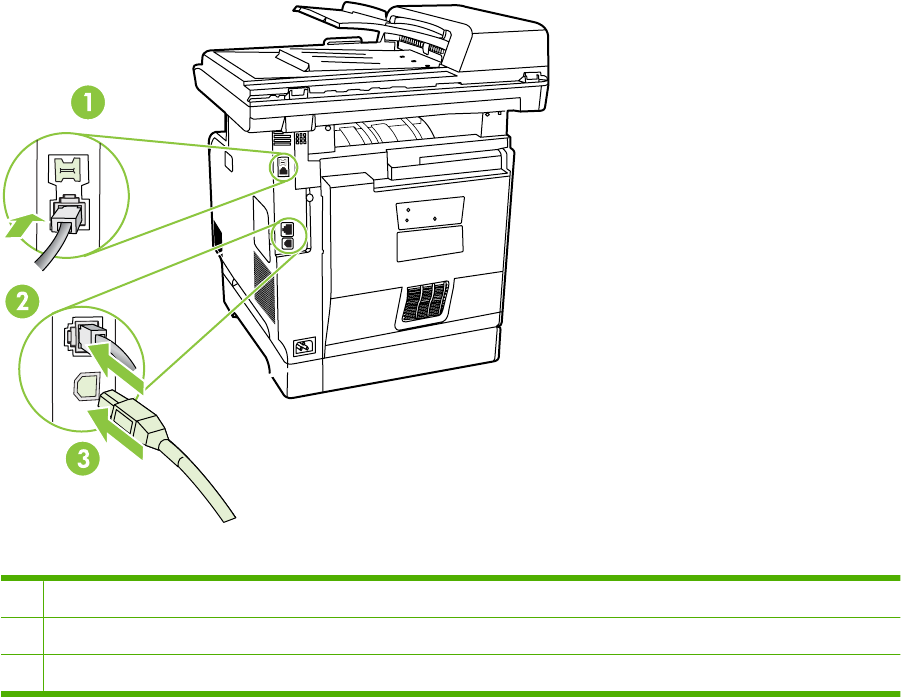
Interface ports
Figure 7-7 Interface ports
Table 7-9 Interface ports
1Fax ports (fax/memory-card models only)
2Network port
3Hi-Speed USB 2.0 port
ENWW Troubleshooting tools 247
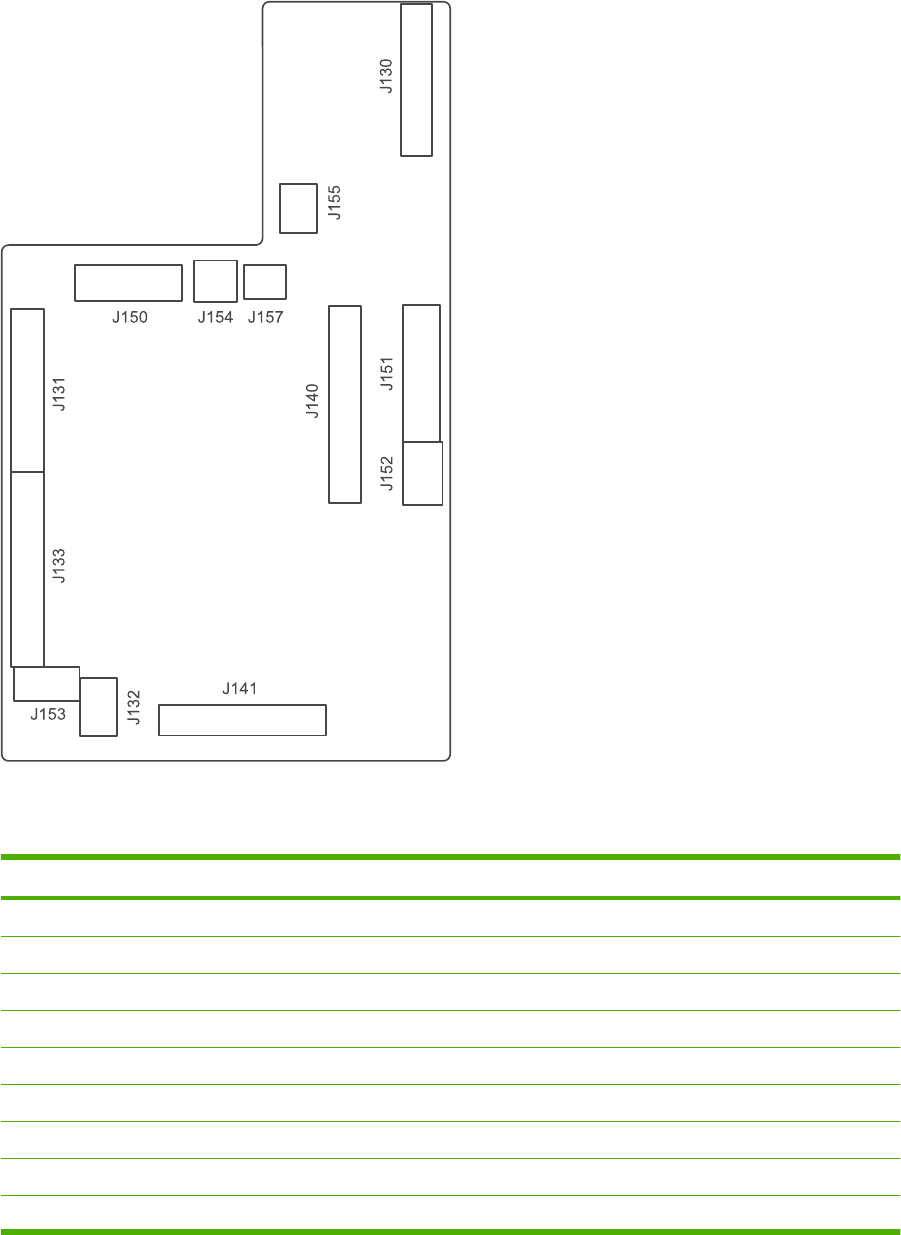
DC controller PCA
Figure 7-8 DC controller connectors
Loose DC controller connections can cause issues. Check the following connections when
troubleshooting product problems.
Connector Board Product response
J130 DC controller Engine Comm. Error message
J131 DC controller 51.23 Error message
J132 DC controller 51.23 Error message
J133 DC controller The graphical display is purple, and then a Rear door open message displays
J140 DC controller 59.F0 Error message
J141 DC controller No startup sounds, and then a Door open message displays
J150 DC controller No startup sounds, and then a 50.7 Fuser Error message displays
J151 DC controller LCD is very faint, and the product produces no startup sounds
J152 DC controller No error displays, but duplexing model will not allow duplex copy jobs
248 Chapter 7 Problem solve ENWW
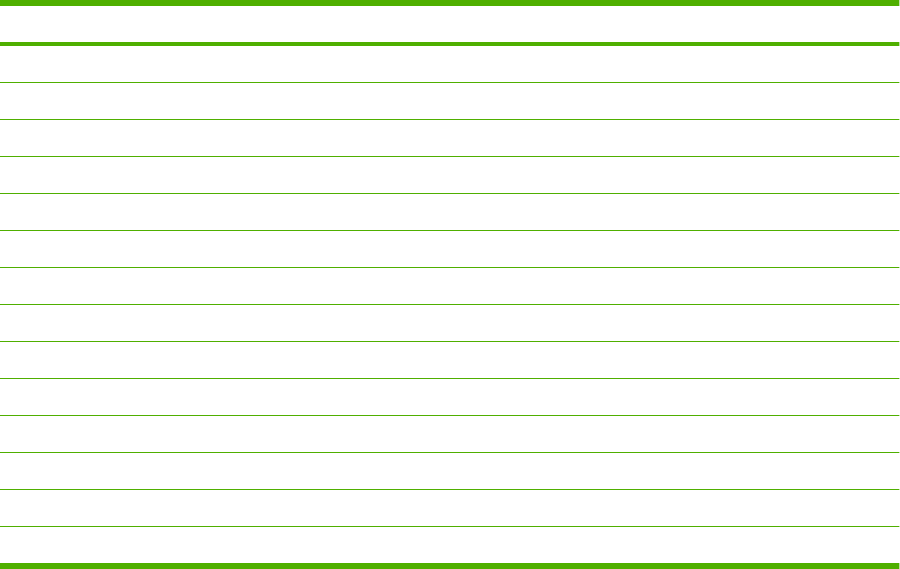
Connector Board Product response
J153 DC controller No error displays
J154 DC controller 59.C0 Error message
J156 DC controller Ready status followed by a 50.2 Fuser Error message
J157 DC controller Long initialization followed by a 50.8 Fuser Error message
J1 Formatter Long initialization, then scanner click cannot find home position while LEDs blink
J2 Formatter LCD backlit only, but control-panel keys still function
J3 Formatter LCD blank
J4 Formatter Long initialization followed by a Scanner Error 5 message
J6 Formatter LCD backlighting is purple and LEDs blink
J9 Formatter Engine Comm. Error message
J11 Formatter No error displays. Memory-card settings do not appear on configuration page.
P1 Formatter ADF door is open message
P2 Formatter No audio (fax/memory-card models only
P12 Formatter LCD blank
ENWW Troubleshooting tools 249
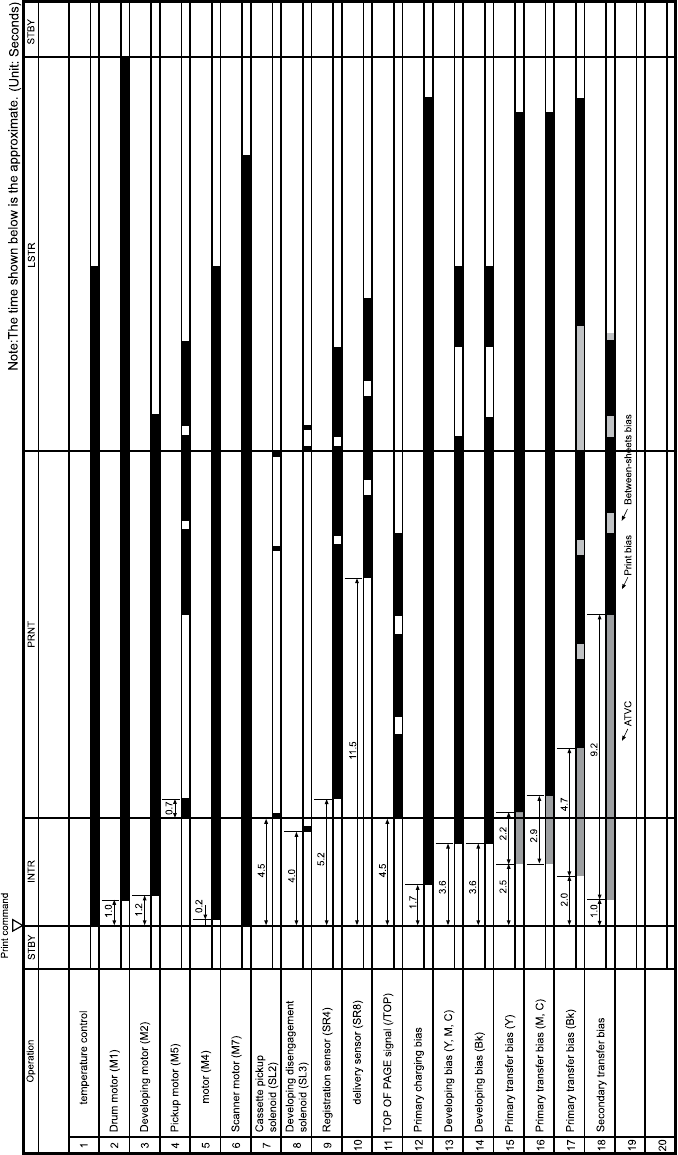
Timing diagram
Approximate timing in seconds.
Figure 7-9 Timing diagram
Fuser
Fuser
Fuser
250 Chapter 7 Problem solve ENWW
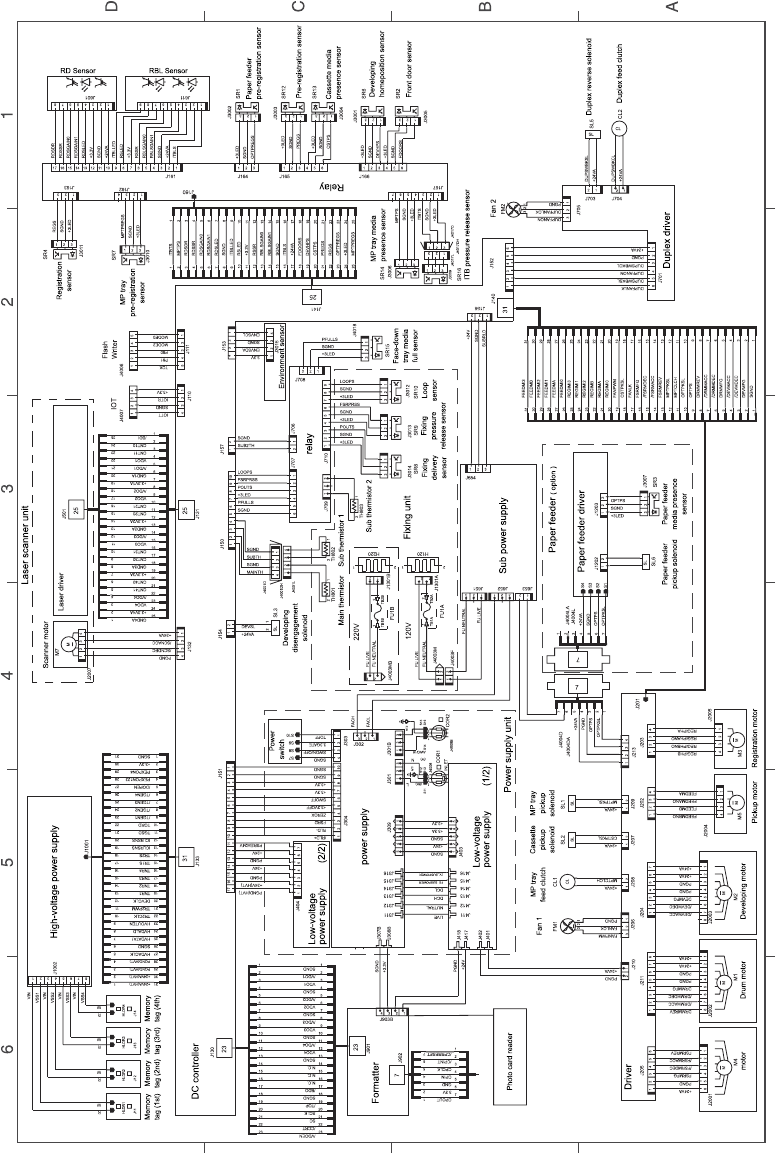
Circuit diagram
Figure 7-10 Circuit diagram
PCA
PCA
PCA
PCA
PCA
Fuser
PCA
PCA
Fuser
PCA
PCA
PCA
PCA
PCA
Fuser
PCA
ENWW Troubleshooting tools 251
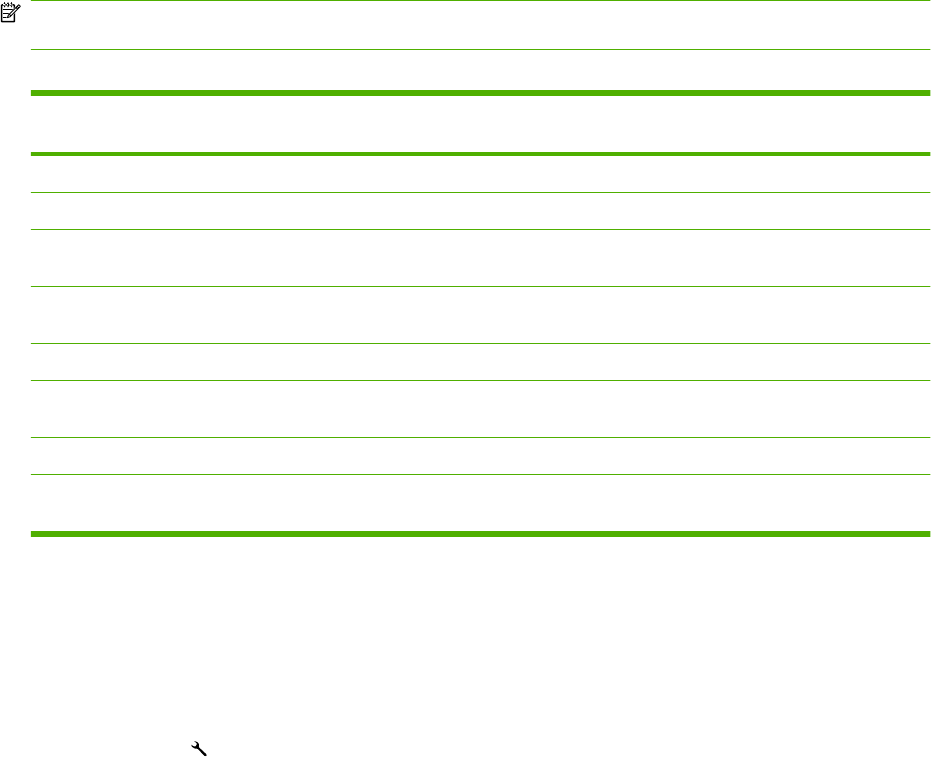
Print-quality troubleshooting tools
Repetitive image defects
If the product output has a consistent, repetitive defect, then use the table in this section to determine
which part needs to be replaced based on the measured distance between the repetitions of the defect.
NOTE: The following table replaces the graphical repetitive defect ruler. You can make your own ruler
by using these measurements. For the most accurate results, use a metric ruler.
Table 7-10 Repetitive image defects
Distance between identical
defects
Component Notes
22 mm (0.87 in) Developer roller Replace the print cartridge.
38 mm (1.5 in) Primary charging roller Replace the print cartridge.
44.0 mm (1.73 in) Registration roller Clean the roller. If dirt still appears on the page, replace the
registration unit.
58 mm (2.3 in) Fuser sleeve Process a cleaning page. If dirt still appears on the page,
replace the fuser.
58 mm (2.3 in) Transfer roller Replace the secondary transfer feed unit.
63 mm (2.5 in) Pressure roller (one rotation) Process a cleaning page. If dirt still appears on the page,
replace the fuser.
75 mm (2.9 in) OPC drum Replace the print cartridge.
78 mm (3 in) ITB Calibrate the product. If dirt still appears on the page,
replace the ITB unit.
Calibrate the product
Calibration is a product function that optimizes print quality. If you experience any print-quality problems,
calibrate the product.
Calibrate the product from the control panel
1. Press Setup .
2. Use the arrow buttons to highlight System setup, and then press OK.
3. Use the arrow buttons to highlight Print quality, and then press OK.
4. Use the arrow buttons to highlight Calibrate color, and then press OK.
5. Use the arrow buttons to highlight Calibrate now, and then press OK.
Calibrate the product from HP ToolboxFX
1. Open HP ToolboxFX.
2. Click the Device Settings folder, and then click the Print Quality page.
3. In the area for Color Calibration, select the Calibrate Now check box.
4. Click Apply to calibrate the product immediately.
252 Chapter 7 Problem solve ENWW
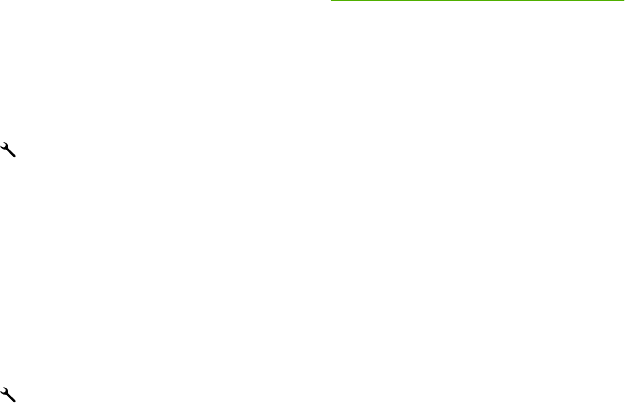
Internal print quality test pages
This section describes the pages and reports that help you diagnose and solve product problems.
Cleaning page
To clean the paper path, process a cleaning page. See Clean the paper path on page 73
Service page
The service page lists information about paper type settings, copy quality settings, and other status
settings.
1. Press Setup .
2. Use the arrow buttons to highlight Reports, and then press OK.
3. Use the arrow buttons to highlight Service page, and then press OK.
Diagnostics pages
The diagnostics page shows the current color settings and properties of the product. You can use this
page to check for color plane registration and color density information.
1. Press Setup .
2. Use the arrow buttons to highlight Reports, and then press OK.
3. Use the arrow buttons to highlight Diagnostics page, and then press OK.
ENWW Troubleshooting tools 253
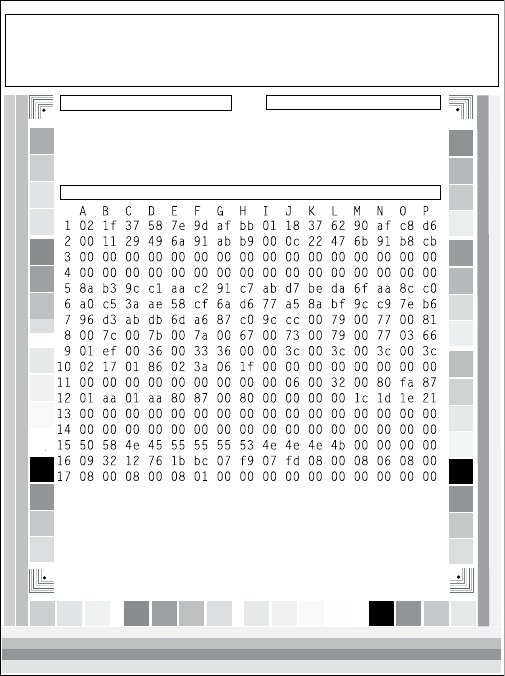
On the first page, verify that all four print cartridge colors appear on the page. Also, verify that the 90-
degree angles in the corners are single toner colors and that the color plane registration is correct.
Figure 7-11 Diagnostic page 1
HP Color LaserJet CM#### Series
Diagnostics Page
Calibration Information Color Density
Power-On Calibration : 15 Minutes
Calibration Timing: 48 Hours
C M Y K
Contrast 0 0 0 0
Highlights 0 0 0 0
Midtones 0 0 0 0
Shadows 0 0 0 0
Parameters
On the second page, verify that there are four print-cartridge color sweep bars near the top of the page.
From right to left, there should be even steps of toner gradation from light to 100%. The other squares
on the page are for use only during manufacturing.
254 Chapter 7 Problem solve ENWW
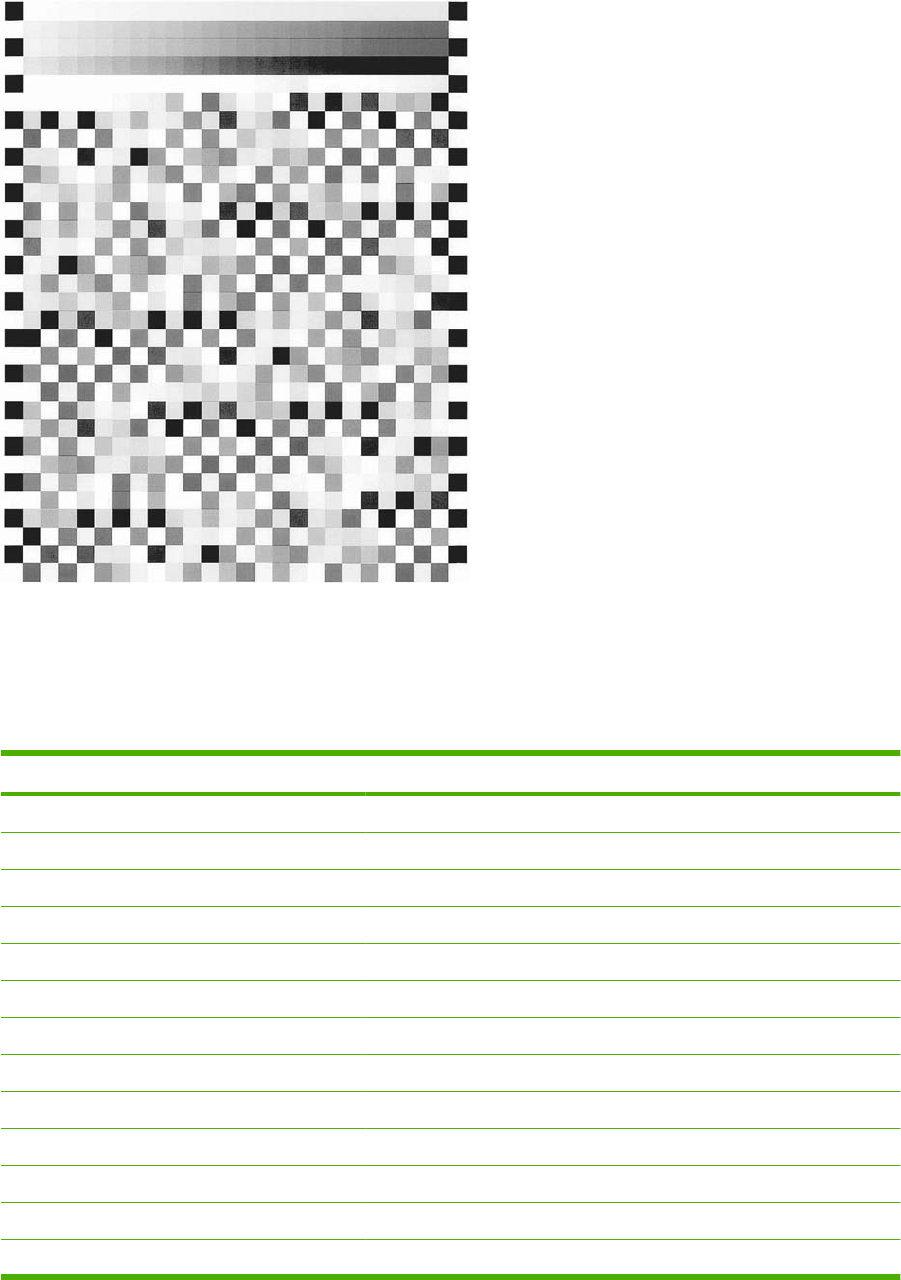
Figure 7-12 Diagnostic page 2
Engine print mode specifications
The media type being used in the product can affect the print speed. The following table provides print-
speed specifications for the different media types.
Table 7-11 Engine print mode specifications
Print mode Print speed
1
Normal Full speed
Light media Full speed
Heavy media 1 Full speed (1/2-speed
2
)
Heavy media 2 Full speed (1/2-speed
2
)
Heavy media 3 1/2-speed (1/3-speed
2
)
Glossy media 1 1/3-speed
Glossy media 2 1/3-speed
Glossy media 3 1/3-speed
Glossy film 1/3-speed
Overhead transparency 1/3-speed
Envelope 1 1/2-speed
Envelope 2 1/3-speed
Label 1/2-speed
ENWW Troubleshooting tools 255
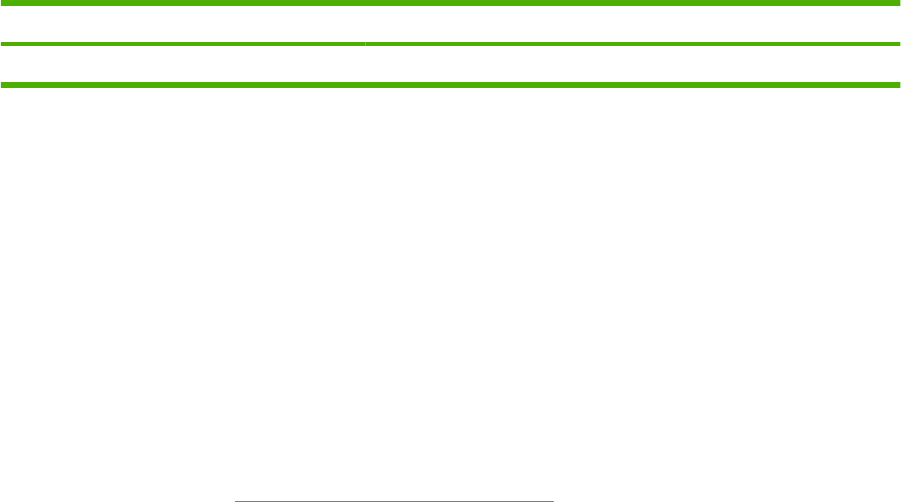
Print mode Print speed
1
Photo media 1/3-speed
1Speeds shown are for monochrome printing.
2Speeds in parentheses denote print speed when the environmental temperature is 20° C (68° F) or lower.
HP ToolboxFX software
The HP ToolboxFX is a program that you can use for the following tasks:
●Checking the product status
●Checking the supplies status
●Setting up alerts
●Viewing product documentation
●Gaining access to troubleshooting and maintenance tools
For more information, see View the HP ToolboxFX on page 52.
Table 7-11 Engine print mode specifications (continued)
256 Chapter 7 Problem solve ENWW
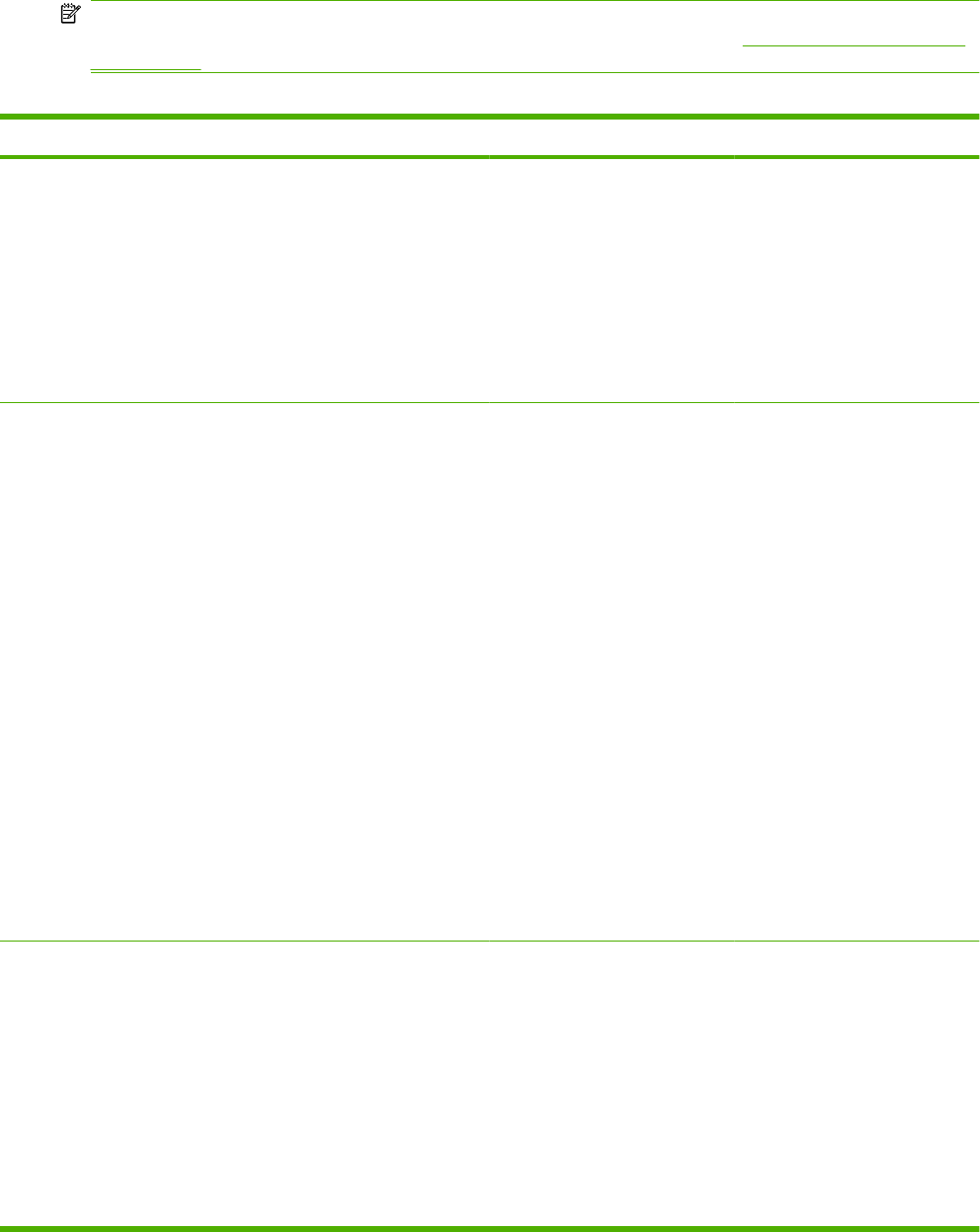
Control-panel messages
NOTE: Not every product error produces a control-panel message. Some errors display only in the
error log. To view the error-log-only messages and possible solutions, see Event-log-only messages
on page 279.
Table 7-12 Control-panel messages
Control panel message Event log error message Description Recommended action
10.000X Supply Memory Error A specific print cartridge has an
e-label error.
"X" indicates the cartridge.
●0=black
●1=cyan
●2=magenta
●3=yellow
Remove and reinstall the print
cartridge.
Turn off and then turn on the
product.
If the problem is not solved,
replace the cartridge.
10.100X Supply Memory Error A specific print cartridge has a
faulty or missing e-label.
"X" indicates the cartridge.
●0=black
●1=cyan
●2=magenta
●3=yellow
Check the e-label. If it is broken
or damaged, replace the
cartridge.
Verify that the cartridge is
installed in the correct location.
Reinstall the print cartridge.
Turn off and then turn on the
product.
If the error is with a color
cartridge, try swapping it with a
different color cartridge in the
tray. If the same message
appears, then there is an engine
problem. If a different 10.100X
message appears, replace the
cartridge.
If the problem is not solved,
replace the print-cartridge
drawer.
If the error persists, replace the
DC controller.
49 Error
Turn off then on
The product has experienced an
embedded firmware error. Under
most conditions, the product will
power cycle automatically.
Turn off the power by using the
power switch, wait at least
30 seconds, and then turn on the
power and wait for the product to
initialize.
If the error persists, perform an
NVRAM initialization.
If the error persists, update the
firmware.
If the error persists, replace the
formatter.
ENWW Control-panel messages 257
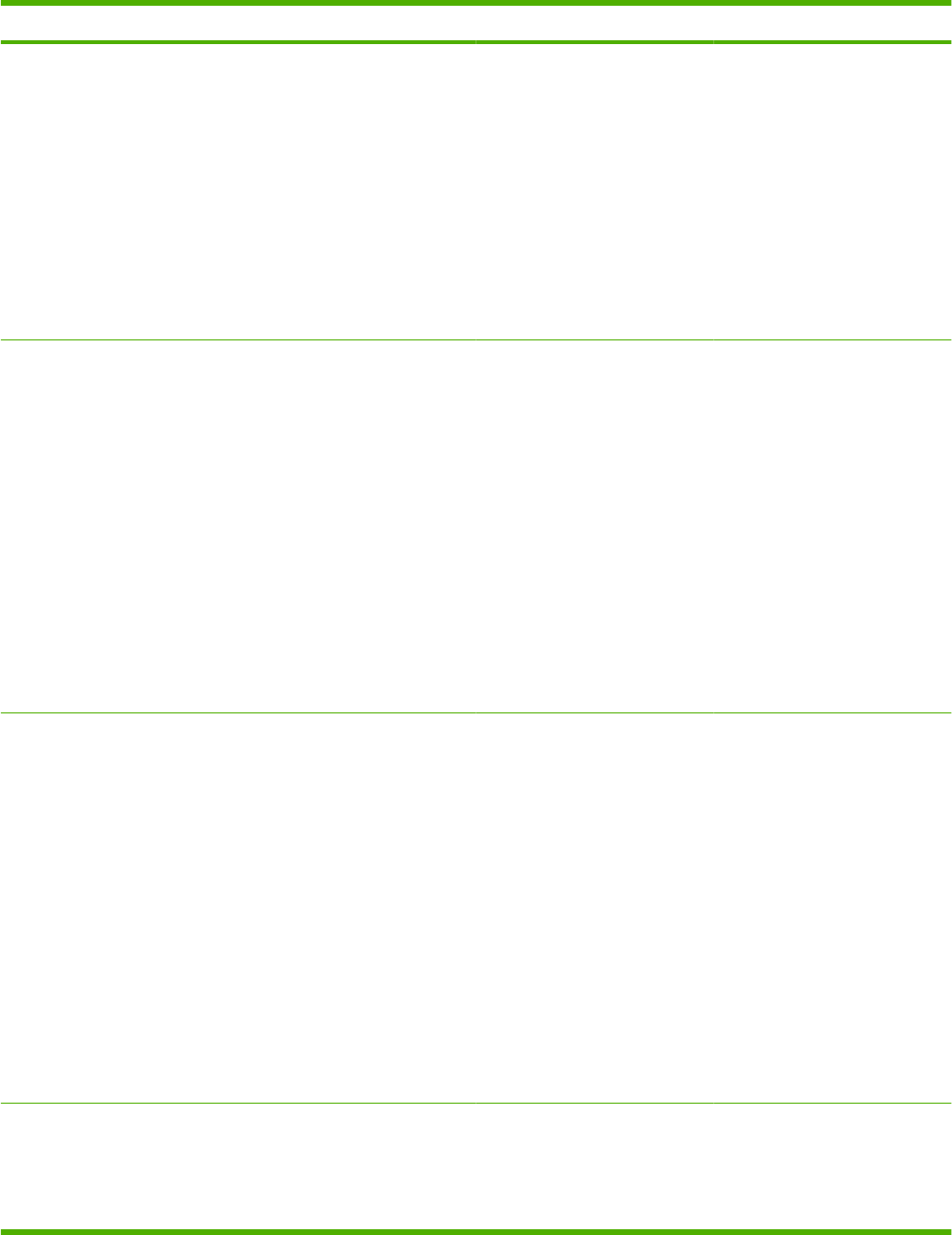
Control panel message Event log error message Description Recommended action
49 Service Error
Turn off then on
The product has experienced a
firmware error.
1. Turn off the power by using
the power switch, and then
wait at least 30 seconds.
2. Turn on the power and wait
for the product to initialize.
If the error persists, perform an
NVRAM initialization.
If the error persists, update the
firmware.
If the error persists, replace the
formatter.
50.1 Fuser Error
Turn off then on
50.1000 The product has experienced a
low fuser temperature error.
1. Turn off the power by using
the power switch, and then
wait at least 30 seconds.
2. Turn on the power and wait
for the product to initialize.
If the error persists, verify that the
thermistor connection in the
upper left of the fuser area is
firmly connected.
If the error persists, verify that the
J150, J156, and J157
connections on the DC controller
are firmly connected.
If the error persists, replace the
fuser.
50.2 Fuser Error
Turn off then on
50.2000 The product has experienced a
slow fuser error.
1. Turn off the power by using
the power switch, and then
wait at least 30 seconds.
2. Turn on the power and wait
for the product to initialize.
If the error persists, verify that the
fuser heat roller and pressure
roller surfaces are not damaged.
If the error persists, verify that the
fuser motor rotates freely and
that the gears are not damaged.
If the error persists, replace the
fuser.
If the error persists, replace the
DC controller.
50.3 Fuser Error
Turn off then on
50.3000 The product has experienced a
general fuser error.
1. Turn off the power by using
the power switch, and then
wait at least 30 seconds.
2. Turn on the power and wait
for the product to initialize.
Table 7-12 Control-panel messages (continued)
258 Chapter 7 Problem solve ENWW
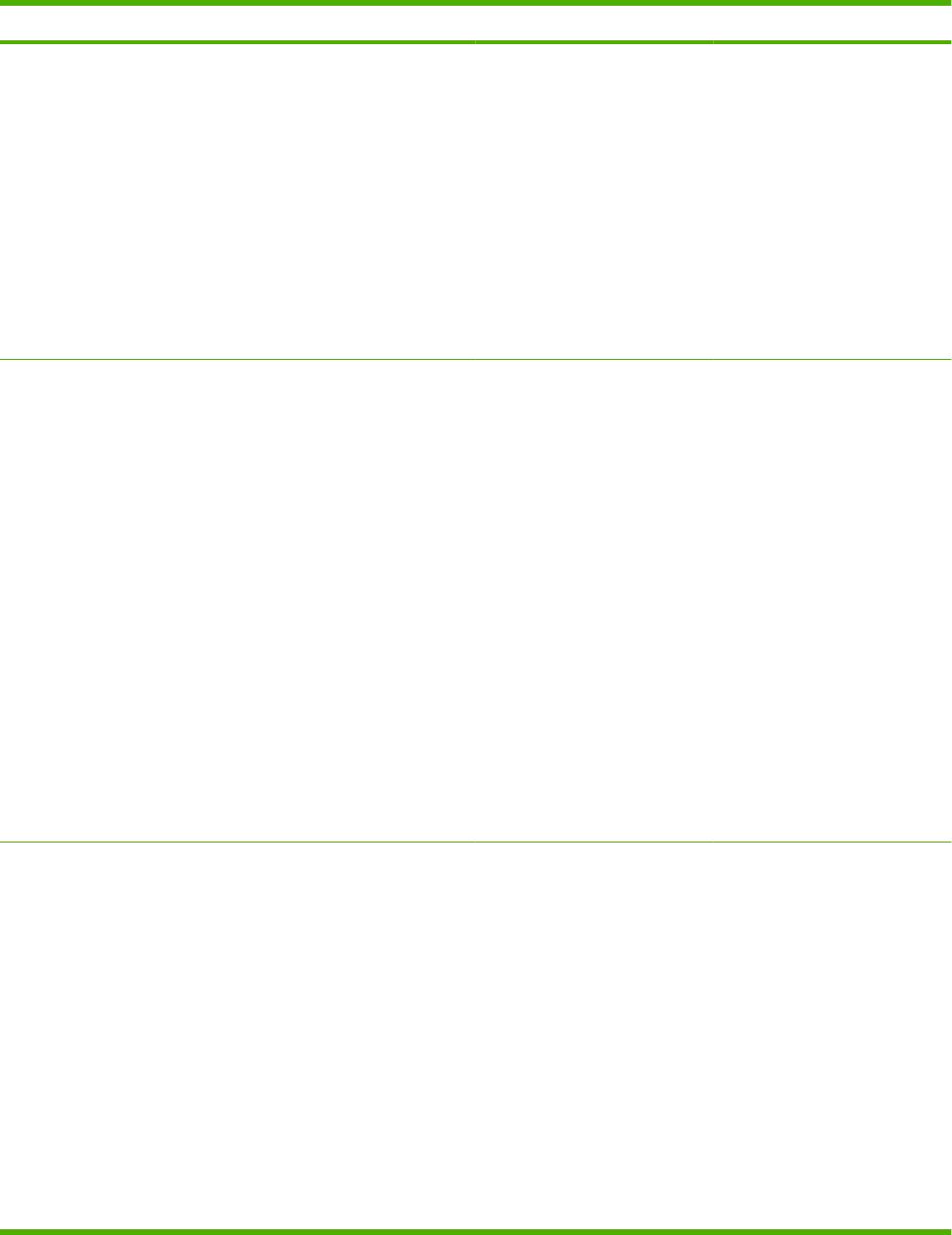
Control panel message Event log error message Description Recommended action
If the error persists, verify that
thermistor connection J706 in the
upper left of the fuser area is
firmly connected.
If the error persists, replace the
fuser.
If the error persists, replace the
power supply.
If the error persists, replace the
DC controller.
If the error persists, replace the
low-voltage power supply.
50.4 Fuser Error
Turn off then on
50.4000 The product has experienced a
fuser drive circuit error.
1. Turn off the power by using
the power switch, and then
wait at least 30 seconds.
2. Turn on the power and wait
for the product to initialize.
If the error persists, verify that the
fuser heat roller and pressure
roller surfaces are not damaged.
If the fuser is damaged, replace
the fuser.
If the error persists, replace the
fuser motor.
If the error persists, replace the
power supply.
If the error persists, replace the
DC controller.
If the error persists, replace the
low-voltage power supply.
50.7 Fuser Error
Turn off then on
50.7000 The product has experienced a
fuser open error.
1. Turn off the power by using
the power switch, and then
wait at least 30 seconds.
2. Turn on the power and wait
for the product to initialize.
If the error persists, verify that the
J150, J156, and J157
connections on the DC controller
are firmly connected.
If the error persists, replace the
fuser.
If the error persists, replace the
power supply.
If the error persists, replace the
DC controller.
Table 7-12 Control-panel messages (continued)
ENWW Control-panel messages 259
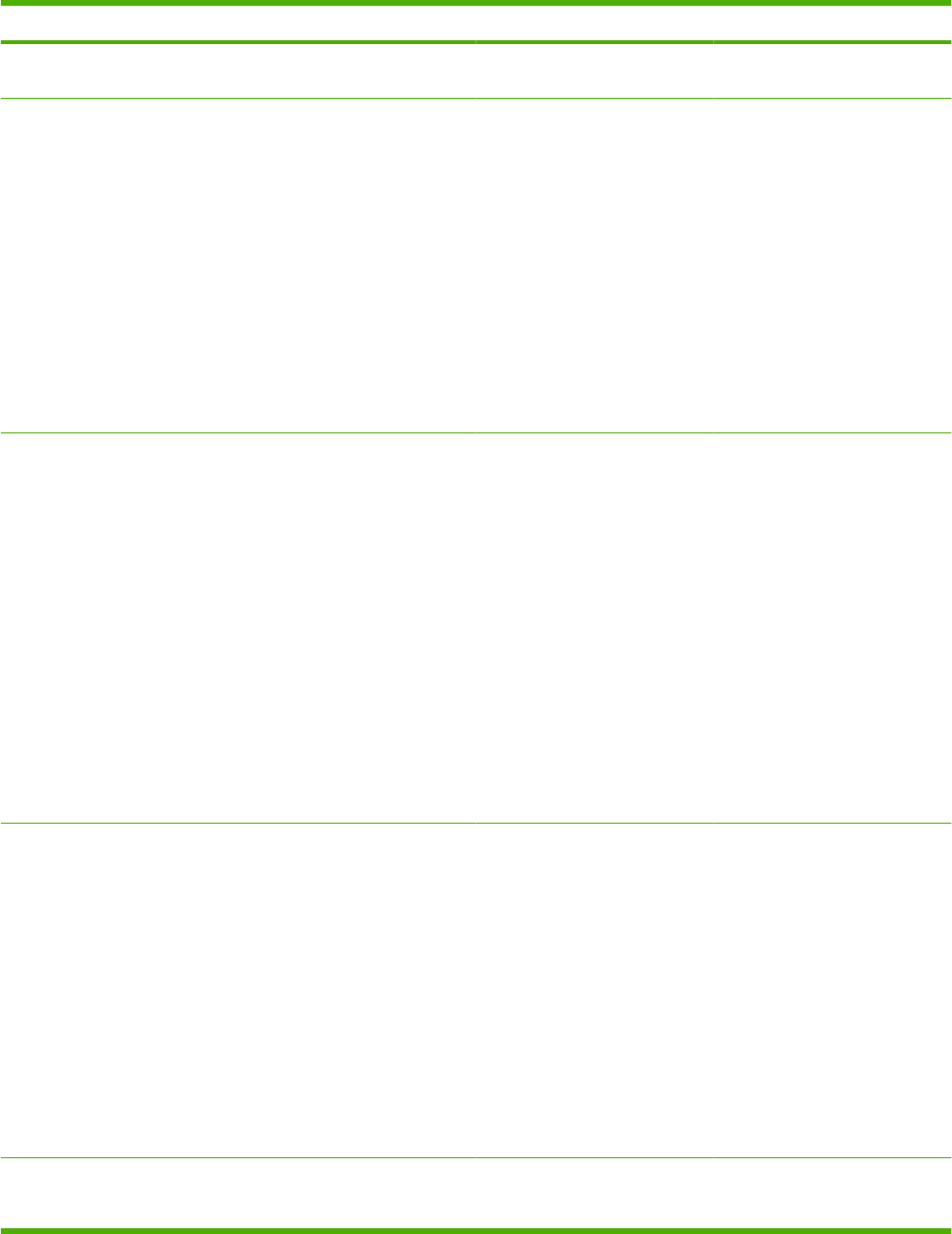
Control panel message Event log error message Description Recommended action
If the error persists, replace the
product.
50.8 Fuser Error
Turn off then on
50.8000 The product has experienced a
low subthermistor fuser error.
1. Turn off the power by using
the power switch, and then
wait at least 30 seconds.
2. Turn on the power and wait
for the product to initialize.
If the error persists, verify that the
thermistor connection in the
upper left of the fuser area is
firmly connected.
If the error persists, replace the
fuser.
If the error persists, replace the
DC controller.
50.9 Fuser Error
Turn off then on
50.9000 The product has experienced a
high subthermistor fuser error.
1. Turn off the power by using
the power switch, and then
wait at least 30 seconds.
2. Turn on the power and wait
for the product to initialize.
If the error persists, verify that the
thermistor connection in the
upper left of the fuser area is
firmly connected.
If the error persists, replace the
fuser.
If the error persists, replace the
power supply.
If the error persists, replace the
DC controller.
51.XX Error
Turn off then on
51.2000
51.2100
51.2200
51.2300
The product has experienced a
laser scanner error. The value for
XX indicates the following issues.
●XX=20: Black laser scanner
error
●XX=21: Cyan laser scanner
error
●XX=22: Magenta laser
scanner error
●XX=23: Yellow laser
scanner error
1. Turn off the power by using
the power switch, and then
wait at least 30 seconds.
2. Turn on the power and wait
for the product to initialize.
If the error persists, verify that the
J131 and J132 connections on
the DC controller are firmly
connected.
If the error persists, replace the
DC controller.
If the error persists, replace the
product.
52 Scanner Error The product has experienced an
internal hardware error.
Turn off the power by using the
power switch, wait at least
30 seconds, and then turn on the
Table 7-12 Control-panel messages (continued)
260 Chapter 7 Problem solve ENWW
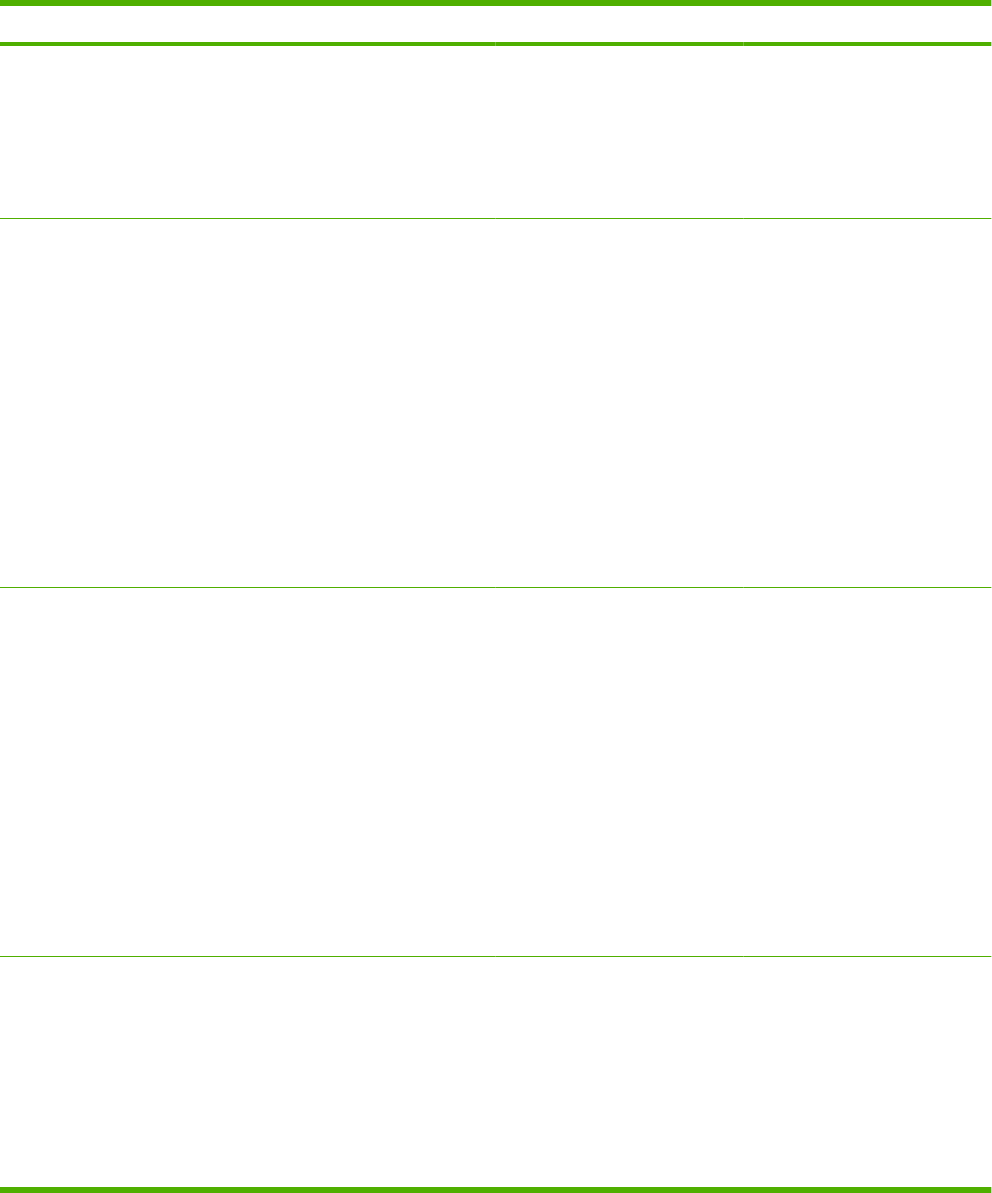
Control panel message Event log error message Description Recommended action
power and wait for the product to
initialize.
If the error persists, replace the
DC controller.
If the error persists, replace the
product.
54.15 Error
Turn off then on
54.1500 The product has experienced a
yellow toner level sensor error.
1. Turn off the power by using
the power switch, and then
wait at least 30 seconds.
2. Turn on the power and wait
for the product to initialize.
If the error persists, verify that the
cables between the DC
controller, print-cartridge tray,
and color misregistration sensor
are firmly connected.
If the error persists, replace the
color misregistration sensor.
If the error persists, replace the
DC controller.
54.16 Error
Turn off then on
54.1600 The product has experienced a
magenta toner level sensor error.
1. Turn off the power by using
the power switch, and then
wait at least 30 seconds.
2. Turn on the power and wait
for the product to initialize.
If the error persists, verify that the
cables between the DC
controller, print-cartridge tray,
and color misregistration sensor
are firmly connected.
If the error persists, replace the
color misregistration sensor.
If the error persists, replace the
DC controller.
54.17 Error
Turn off then on
54.1700 The product has experienced a
cyan toner level sensor error.
If the error persists, verify that the
cables between the DC
controller, print-cartridge tray,
and color misregistration sensor
are firmly connected.
If the error persists, replace the
color misregistration sensor.
If the error persists, replace the
DC controller.
Table 7-12 Control-panel messages (continued)
ENWW Control-panel messages 261
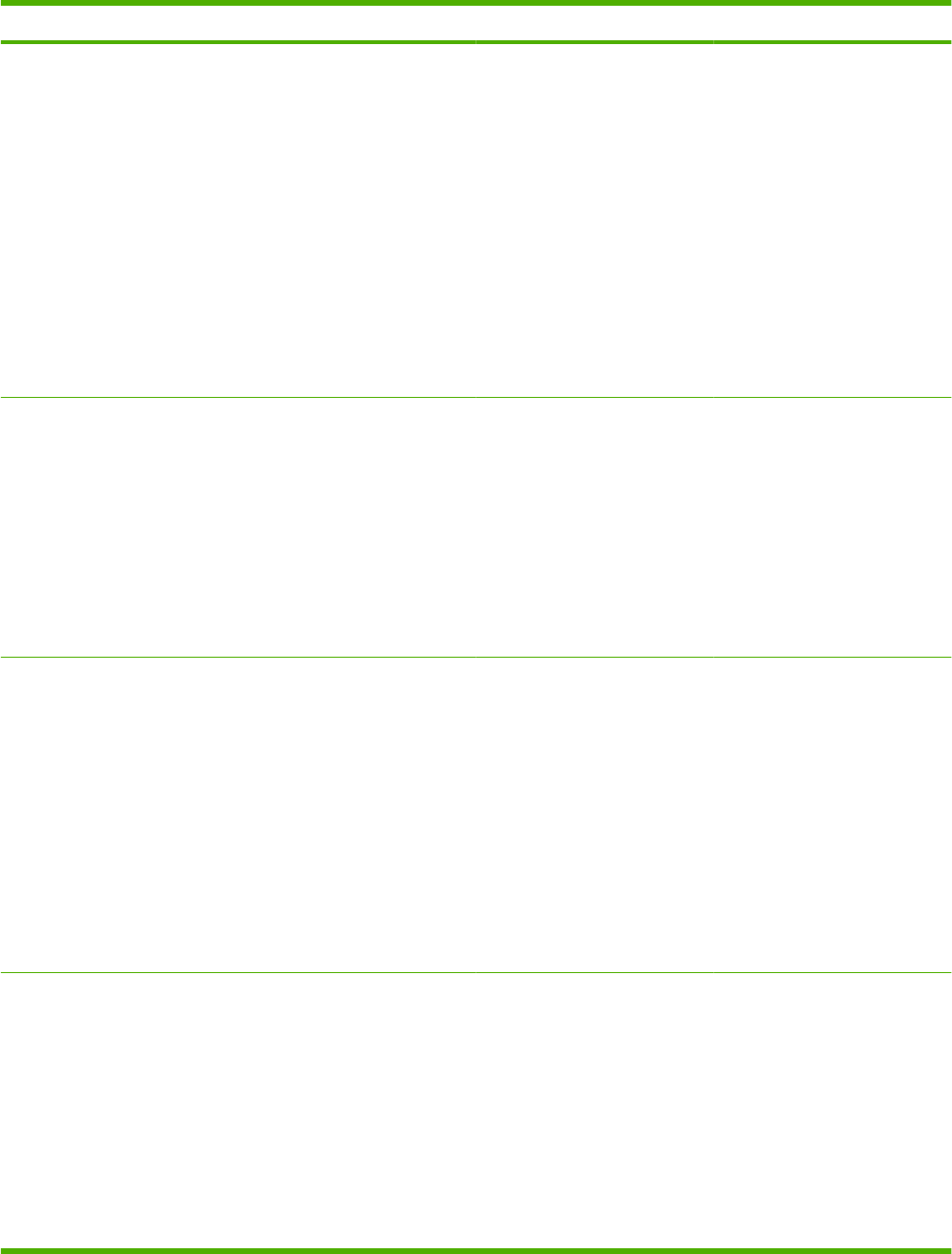
Control panel message Event log error message Description Recommended action
54.18 Error
Turn off then on
54.1800 The product has experienced a
black toner level sensor error.
1. Turn off the power by using
the power switch, and then
wait at least 30 seconds.
2. Turn on the power and wait
for the product to initialize.
If the error persists, verify that the
cables between the DC
controller, print-cartridge tray,
and color misregistration sensor
are firmly connected.
If the error persists, replace the
color misregistration sensor.
If the error persists, replace the
DC controller.
54.19 Error
Turn off then on
54.1900 The product has experienced a
top-of-page sensor error.
1. Turn off the power by using
the power switch, and then
wait at least 30 seconds.
2. Turn on the power and wait
for the product to initialize.
If the error persists, verify that the
DC controller connectors are
firmly connected.
If the error persists, replace the
DC controller.
55.X Error
Turn off then on
55.0000
55.0601
55.0602
55.1000
The product has experienced a
communication timeout error.
The value for X indicates the
following issues.
●X=0: DC controller
communication error
●X=0601: DC controller
NVRAM data error
●X=0602: DC controller
NVRAM access error
●X=1: DC controller memory
error
1. Turn off the power by using
the power switch, and then
wait at least 30 seconds.
2. Turn on the power and wait
for the product to initialize.
If the error persists, verify that the
DC controller connectors are
firmly connected.
If the error persists, upgrade the
firmware.
If the error persists, replace the
DC controller.
56.01 Error
Turn off then on
56.0100 The product has experienced an
input tray error.
1. Turn off the power by using
the power switch, and then
wait at least 30 seconds.
2. Reinstall Tray 2 and, if
installed, Tray 3.
3. Turn on the power and wait
for the product to initialize.
If the error persists, verify that the
connections between the product
and the tray sensor are firmly
connected.
Table 7-12 Control-panel messages (continued)
262 Chapter 7 Problem solve ENWW
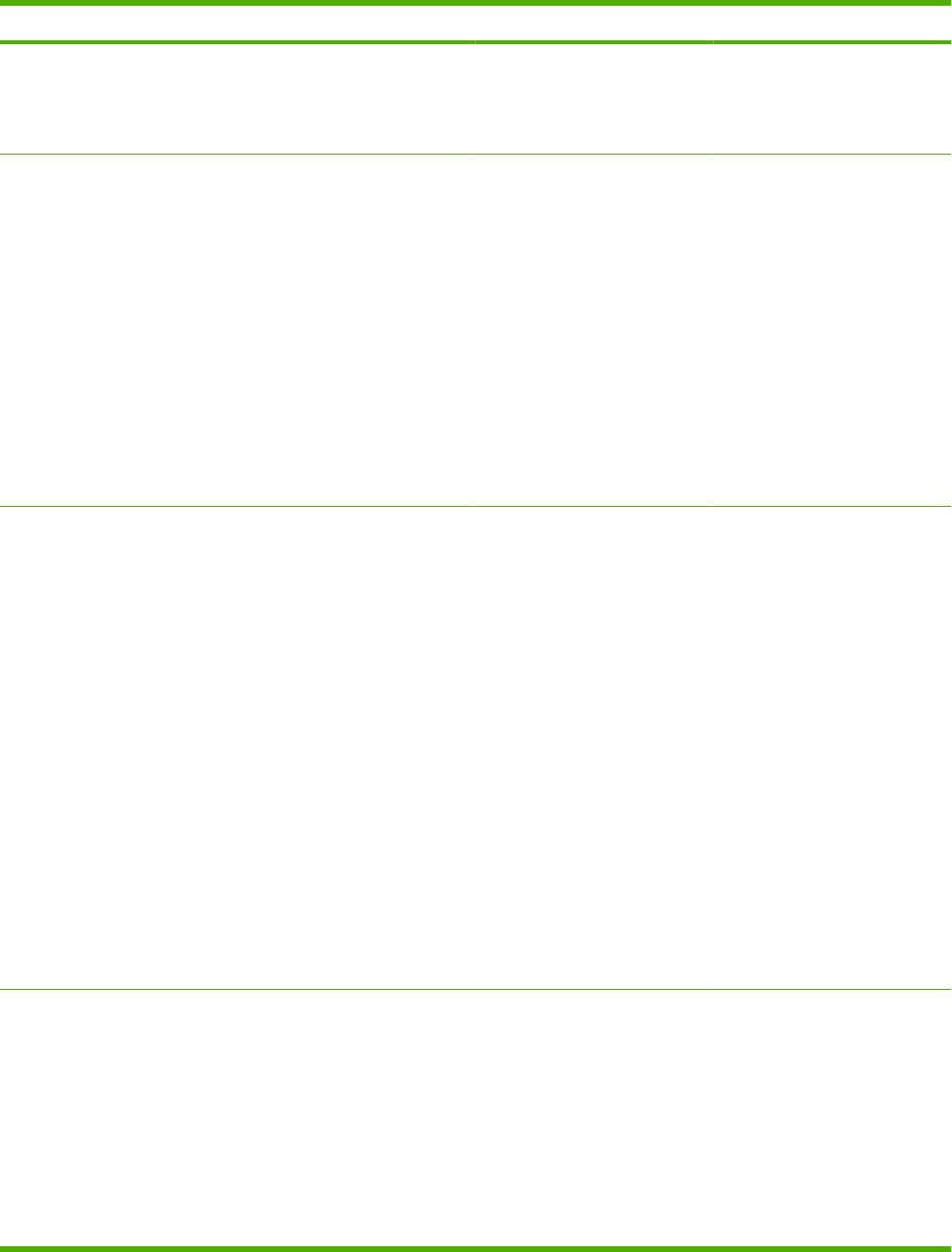
Control panel message Event log error message Description Recommended action
If the error persists, verify that the
tray flag moves correctly.
If the error persists, replace the
DC controller.
57.XX Error, Turn off then on 57.0100
57.0200
The product has experienced a
problem with an internal fan. The
value for XX indicates the
following issues.
●XX=01: Fan 1 (engine fan)
error
●XX=02: Fan 2 (duplex fan)
error
1. Turn off the power by using
the power switch, and then
wait at least 30 seconds.
2. Turn on the power and wait
for the product to initialize.
If the error persists, verify that the
fan rotates freely.
If the error persists, replace the
fan.
If the error persists, replace the
DC controller.
If the error persists, replace the
low-voltage power supply.
59.3 Error
Turn off then on
59.3000 The product has experienced a
fuser motor startup error.
1. Turn off the power by using
the power switch, and then
wait at least 30 seconds.
2. Turn on the power and wait
for the product to initialize.
If the error persists, verify that the
DC controller connectors are
firmly connected.
If the error persists, replace the
fuser motor.
If the error persists, replace the
fuser.
If the error persists, replace the
sub-controller board.
If the error persists, replace the
DC controller.
If the error persists, replace the
low-voltage power assembly.
59.4 Error
Turn off then on
59.4000 The product has experienced a
fuser motor error.
1. Turn off the power by using
the power switch, and then
wait at least 30 seconds.
2. Turn on the power and wait
for the product to initialize.
If the error persists, verify that the
DC controller connectors are
firmly connected.
If the error persists, replace the
fuser motor.
Table 7-12 Control-panel messages (continued)
ENWW Control-panel messages 263
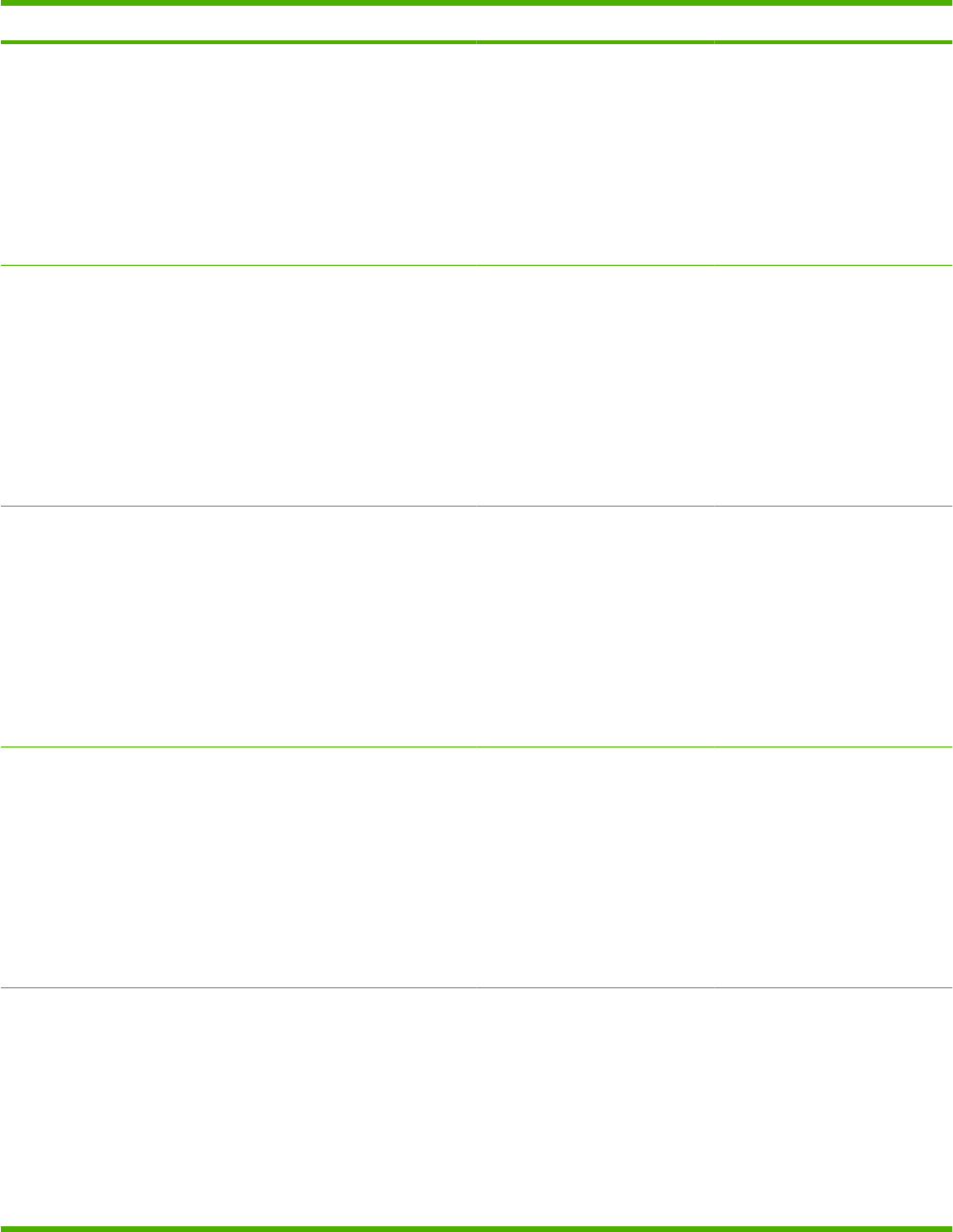
Control panel message Event log error message Description Recommended action
If the error persists, replace the
fuser.
If the error persists, replace the
sub-controller board.
If the error persists, replace the
DC controller.
If the error persists, replace the
product.
59.50 Error
Turn off then on
59.5000 The product has experienced a
black image drum motor startup
error.
1. Turn off the power by using
the power switch, and then
wait at least 30 seconds.
2. Turn on the power and wait
for the product to initialize.
If the error persists, replace the
image drum motor.
If the error persists, replace the
DC controller.
59.53 Error
Turn off then on
59.5300 The product has experienced a
yellow-magenta-cyan image
drum motor startup error.
1. Turn off the power by using
the power switch, and then
wait at least 30 seconds.
2. Turn on the power and wait
for the product to initialize.
If the error persists, replace the
image drum motor.
If the error persists, replace the
DC controller.
59.60 Error
Turn off then on
59.6000 The product has experienced a
black image drum motor rotation
error.
1. Turn off the power by using
the power switch, and then
wait at least 30 seconds.
2. Turn on the power and wait
for the product to initialize.
If the error persists, replace the
image drum motor.
If the error persists, replace the
DC controller.
59.63 Error
Turn off then on
59.6300 The product has experienced a
yellow-magenta-cyan image
drum motor rotation error.
1. Turn off the power by using
the power switch, and then
wait at least 30 seconds.
2. Turn on the power and wait
for the product to initialize.
If the error persists, replace the
image drum motor.
If the error persists, replace the
DC controller.
Table 7-12 Control-panel messages (continued)
264 Chapter 7 Problem solve ENWW
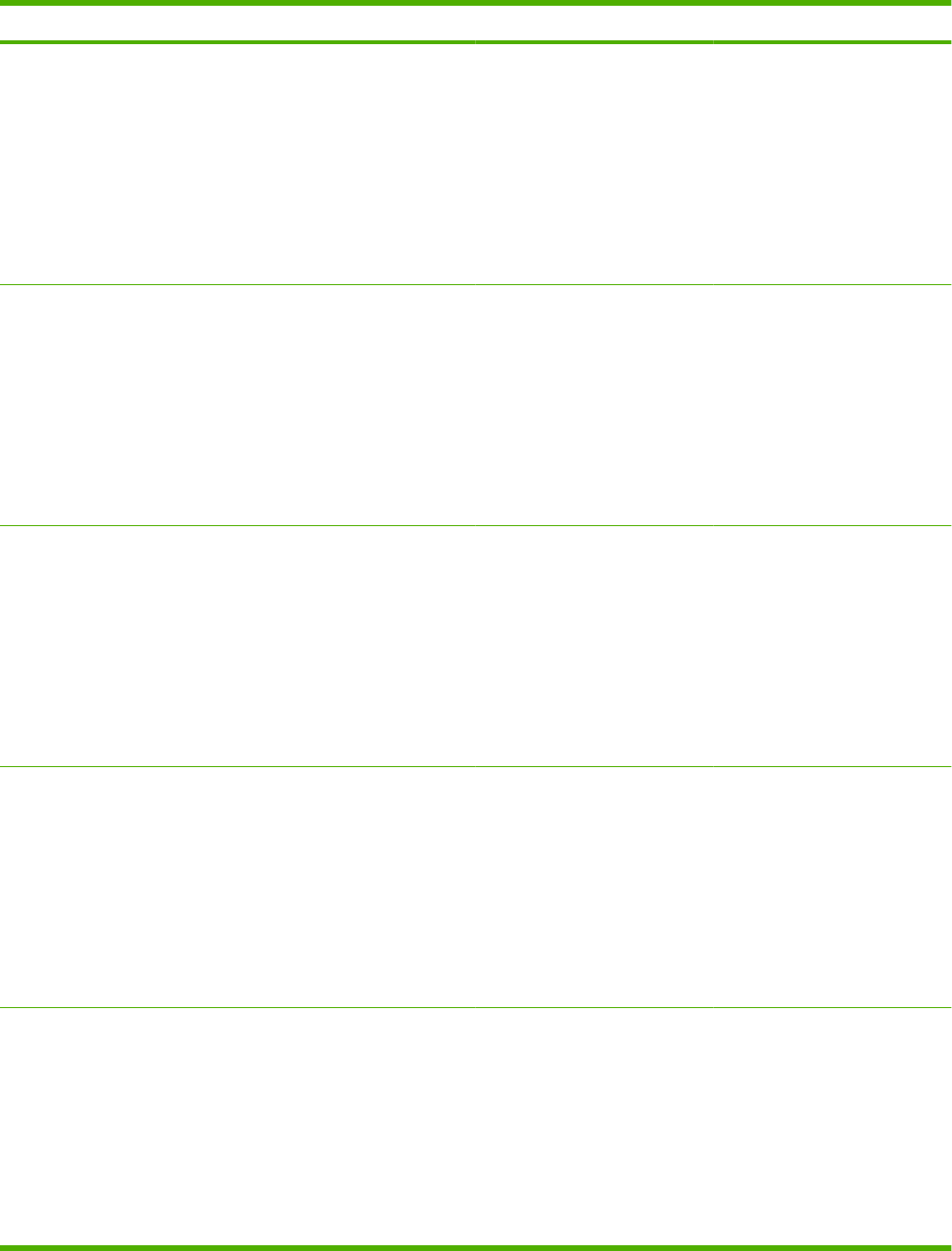
Control panel message Event log error message Description Recommended action
59.70 Error
Turn off then on
59.7000 The product has experienced a
black developer motor startup
error.
1. Turn off the power by using
the power switch, and then
wait at least 30 seconds.
2. Turn on the power and wait
for the product to initialize.
If the error persists, replace the
developer motor.
If the error persists, replace the
DC controller.
59.73 Error
Turn off then on
59.7300 The product has experienced a
yellow-magenta-cyan developer
motor startup error.
1. Turn off the power by using
the power switch, and then
wait at least 30 seconds.
2. Turn on the power and wait
for the product to initialize.
If the error persists, replace the
developer motor.
If the error persists, replace the
DC controller.
59.80 Error
Turn off then on
59.8000 The product has experienced a
black developer motor rotation
error.
1. Turn off the power by using
the power switch, and then
wait at least 30 seconds.
2. Turn on the power and wait
for the product to initialize.
If the error persists, replace the
developer motor.
If the error persists, replace the
DC controller.
59.83 Error
Turn off then on
59.8300 The product has experienced a
yellow-magenta-cyan developer
motor rotation error.
1. Turn off the power by using
the power switch, and then
wait at least 30 seconds.
2. Turn on the power and wait
for the product to initialize.
If the error persists, replace the
developer motor.
If the error persists, replace the
DC controller.
59.9 Error
Turn off then on
59.9000 The product has experienced an
ITB motor startup error.
1. Turn off the power by using
the power switch, and then
wait at least 30 seconds.
2. Turn on the power and wait
for the product to initialize.
If the error persists, replace the
ITB.
If the error persists, replace the
drum motor.
Table 7-12 Control-panel messages (continued)
ENWW Control-panel messages 265
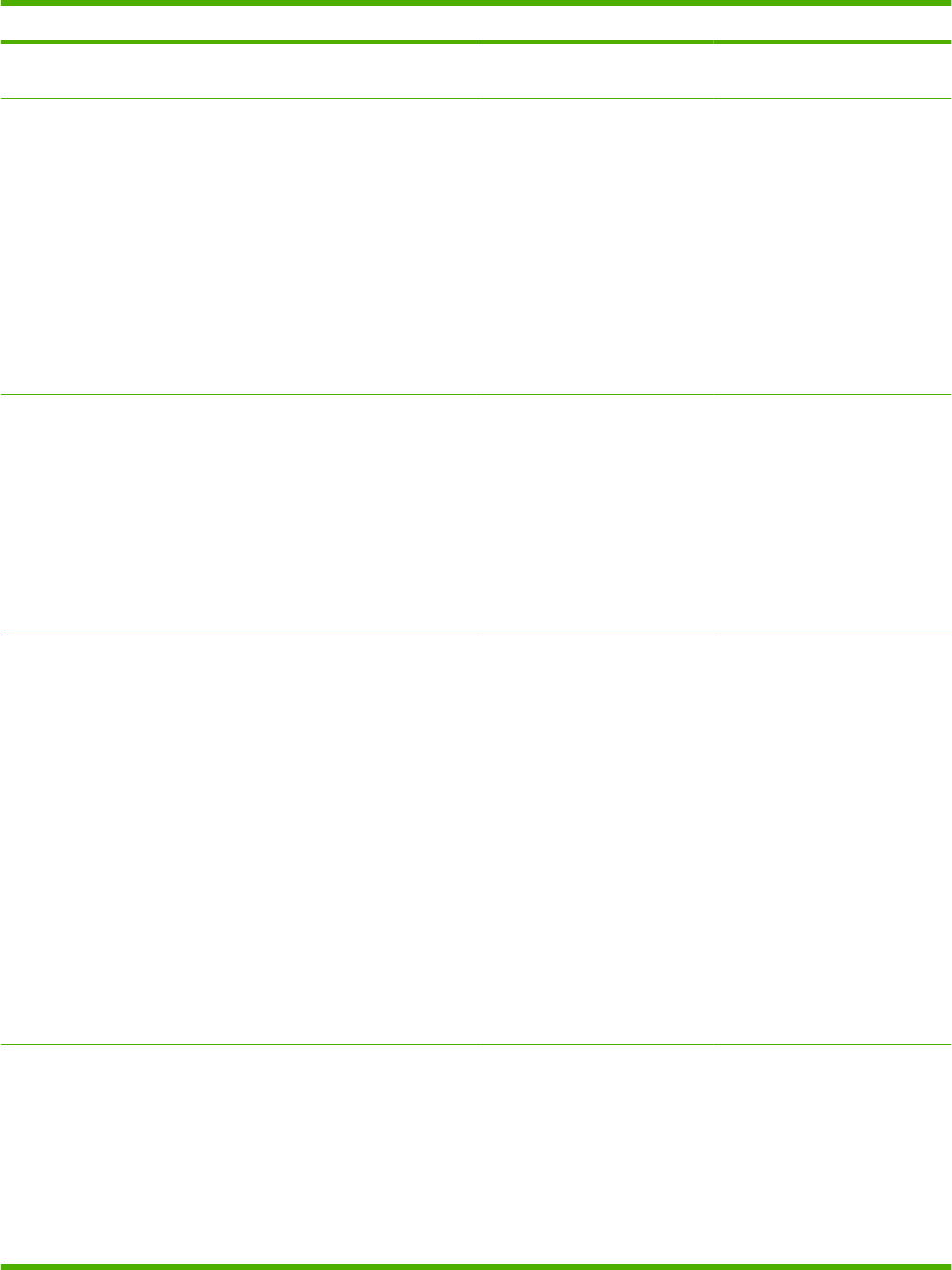
Control panel message Event log error message Description Recommended action
If the error persists, replace the
DC controller.
59.A0 Error
Turn off then on
59.0160 The product has experienced an
ITB motor or main motor rotation
error.
1. Turn off the power by using
the power switch, and then
wait at least 30 seconds.
2. Turn on the power and wait
for the product to initialize.
If the error persists, replace the
ITB.
If the error persists, replace the
drum motor.
If the error persists, replace the
DC controller.
59.C0 Error
Turn off then on
59.0192 The product has experienced a
developer motor error.
1. Turn off the power by using
the power switch, and then
wait at least 30 seconds.
2. Turn on the power and wait
for the product to initialize.
If the error persists, replace the
developer motor.
If the error persists, replace the
DC controller.
59.F0 Error
Turn off then on
59.0240 The product has experienced a
transfer alienation error.
1. Turn off the power by using
the power switch, and then
wait at least 30 seconds.
2. Turn on the power and wait
for the product to initialize.
If the error persists, verify that the
DC controller connectors are
firmly connected.
If the error persists after a print-
cartridge replacement, examine
the cartridge, and then replace it
if necessary.
If the error persists, replace the
DC controller.
If the error persists, replace the
cartridge tray.
79 Error
Turn off then on
The product has experienced an
internal firmware error. Under
most conditions, the product will
power cycle automatically.
Turn off the power by using the
power switch, wait at least
30 seconds, and then turn on the
power and wait for the product to
initialize.
If the error persists, perform an
NVRAM initialization.
If the error persists, update the
firmware.
Table 7-12 Control-panel messages (continued)
266 Chapter 7 Problem solve ENWW
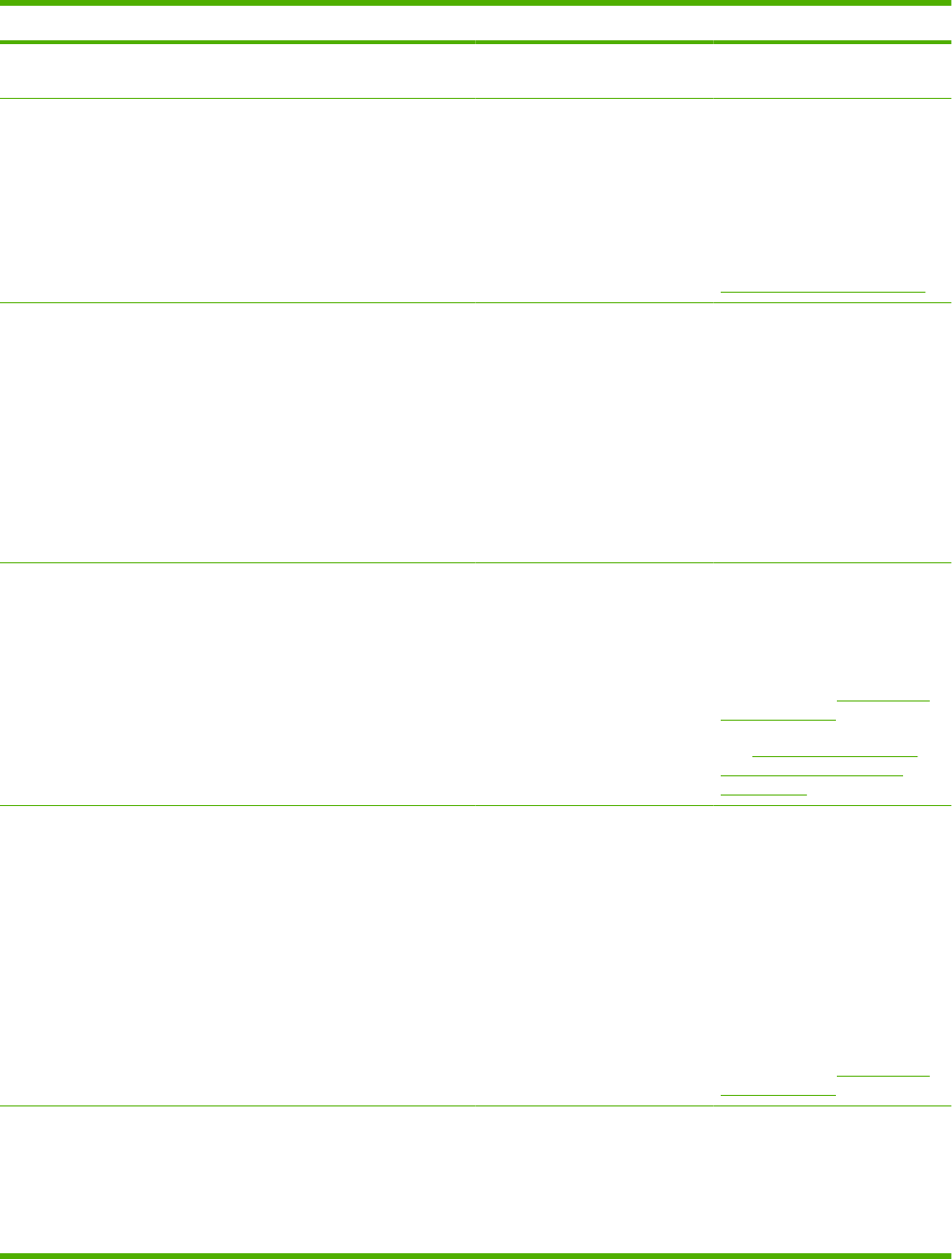
Control panel message Event log error message Description Recommended action
If the error persists, replace the
formatter.
79 Service Error
Turn off then on
The product has experienced a
firmware error.
1. Turn off the power by using
the power switch, and then
wait at least 30 seconds.
2. Turn on the power and wait
for the product to initialize.
If the error persists, update or
reload the firmware. See
Firmware updates on page 79.
ADF door is open (fax/memory-
card models only)
The ADF lid is open or a sensor
is malfunctioning.
Make sure that the ADF lid is
closed.
Remove the ADF and reinstall it.
If the message persists, turn off
the power by using the power
switch, wait at least 30 seconds,
and then turn on the power and
wait for the product to initialize.
If the error persists, replace the
ADF assembly.
Comm. error (fax/memory-card
models only)
A fax communication error
occurred between the product
and the sender or receiver.
Allow the product to retry sending
the fax.
If the error persists, perform a fax
test to verify that the phone line
works and is plugged into the
correct port (see Perform a fax
test on page 316).
See Solve fax problems (fax/
memory-card models only)
on page 314.
Comm. error [Receiver CSID]
(fax/memory-card models only)
A fax communication error
occurred between the product
and the receiver.
Allow the product to retry sending
the fax. Unplug the product
telephone cord from the wall,
plug in a telephone, and try
making a call. Plug the product
phone cord into a jack for another
phone line.
Try a different phone cord.
If the error persists, perform a fax
test to verify that the phone line
works and is plugged into the
correct port (see Perform a fax
test on page 316).
Comm. error [Sender CSID]
(fax/memory-card models only)
A fax communication error
occurred between the product
and the sender.
Allow the product to retry sending
the fax. Unplug the product
telephone cord from the wall,
plug in a telephone, and try
making a call. Plug the product
phone cord into a jack for another
phone line.
Table 7-12 Control-panel messages (continued)
ENWW Control-panel messages 267
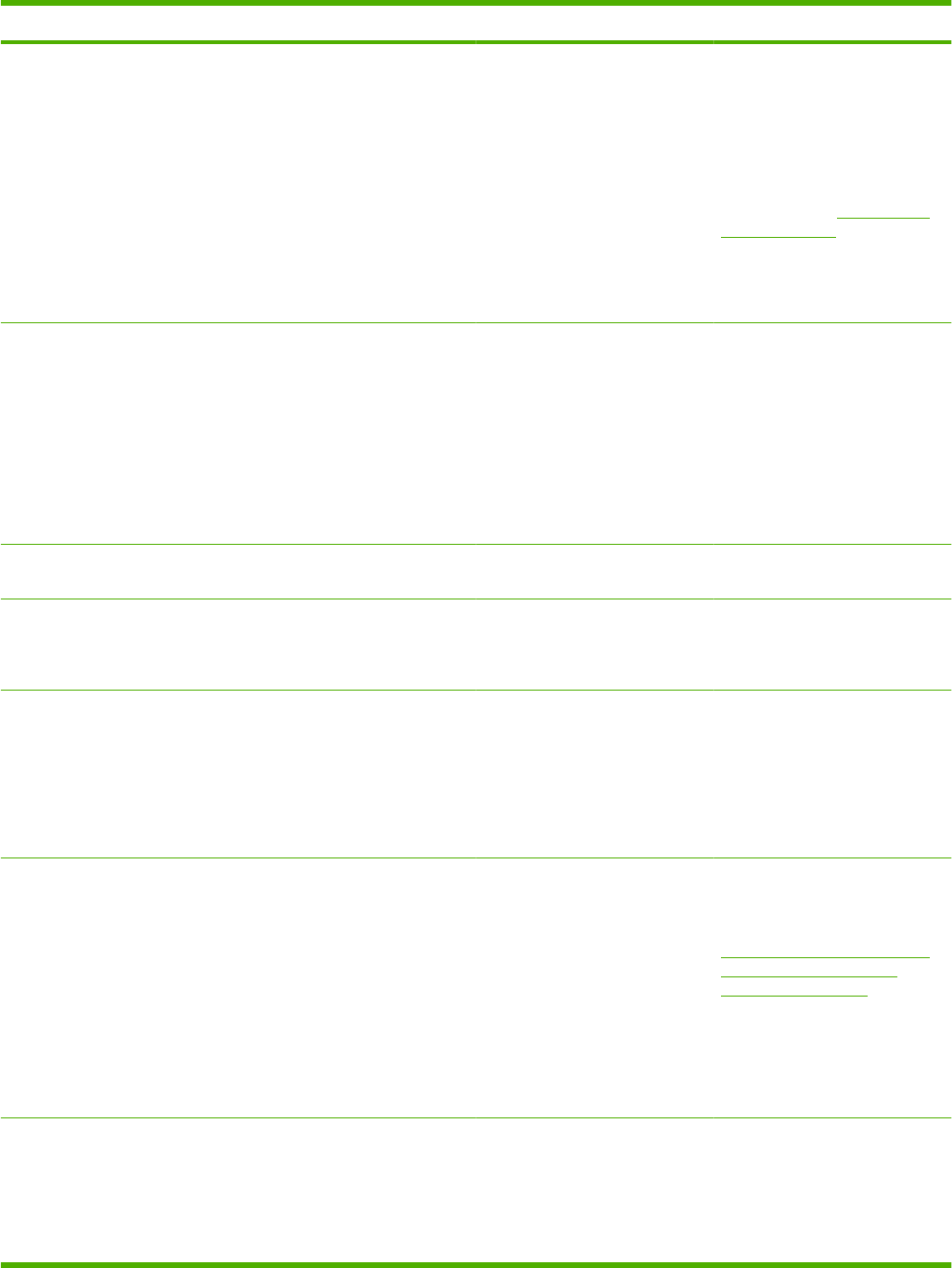
Control panel message Event log error message Description Recommended action
Try a different phone cord.
Try sending to a different
receiver.
If the error persists, perform a fax
test to verify that the phone line
works and is plugged into the
correct port (see Perform a fax
test on page 316).
If the error persists, replace the
fax card (data access
arrangement (DAA)).
Device error, press OK The product has experienced a
generic engine error.
This is a warning message only.
Job output might be affected.
If the error persists, perform an
NVRAM initialization.
If the error persists, update the
firmware.
If the error persists, replace the
product.
Device is busy. Try again later The product is currently in use. Wait for the product to finish the
current job.
Doc feeder jam The ADF has not been cleared
since previous jam.
Clear the jam.
If jams continue, replace the
ADF.
Doc feeder jam Clear, Reload A piece of media is jammed in the
ADF tray.
Open the document release
door, clear the jam, close the
document release door, and
reload the paper into the ADF
tray.
If the error persists, replace the
ADF pickup roller assembly.
Document feeder mispick.
Reload
Media in the ADF tray was not
picked up.
Remove the media from the ADF
tray, and then reload it.
Clean the ADF pickup roller. See
Clean the automatic document
feeder (ADF) pickup roller
assembly on page 74.
If the error persists, replace the
ADF pickup roller assembly.
If the error persists, replace the
ADF.
Door open The print-cartridge door is open. Close the print-cartridge door.
If the error persists, replace the
print-cartridge drawer.
If the error persists, replace the
DC controller.
Table 7-12 Control-panel messages (continued)
268 Chapter 7 Problem solve ENWW
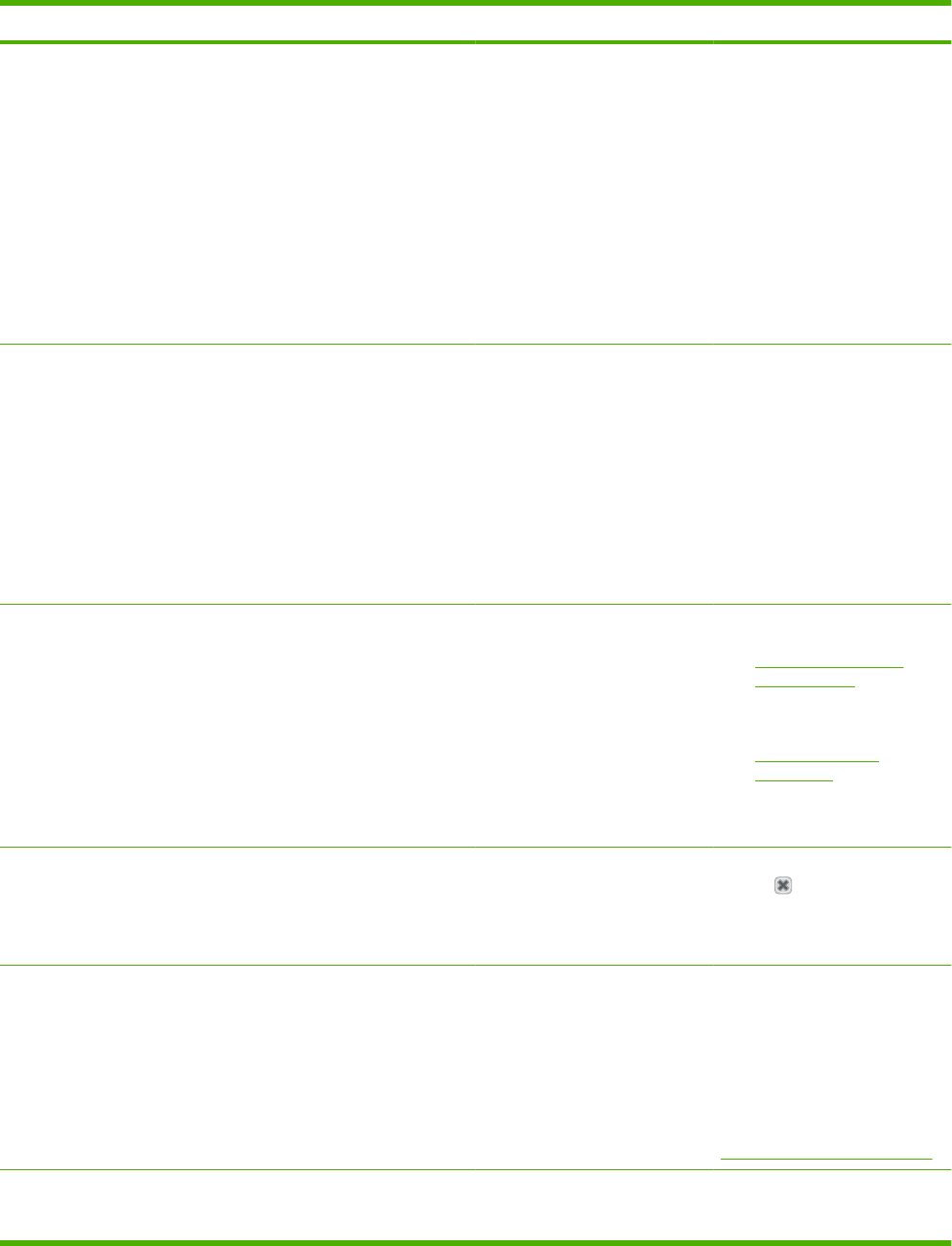
Control panel message Event log error message Description Recommended action
Engine Comm. Error The product has experienced an
engine communication timeout
error.
Turn off the power by using the
power switch, wait at least
30 seconds, and then turn on the
power and wait for the product to
initialize.
If a surge protector is being used,
remove it. Plug the product
directly into the wall socket. Use
the power switch to turn the
product on.
If the error persists, verify that the
connector in DC controller
connector J130 is firmly seated.
Engine error, press OK 41.2000 The product experienced a print
engine error.
This is a warning message only.
Job output might be affected.
If the error persists, verify that
connections J131 and J132 on
the DC controller are firmly
connected.
If the error persists, replace the
DC controller.
If the error still persists, replace
the product.
FATAL ERROR X! CALL HP
SUPPORT
An attempted firmware upgrade
has failed.
1. Re-download the firmware
update package from
www.hp.com/support/
CM2320series.
2. Install the new firmware
update package. See
Firmware updates
on page 79.
If the error persists, replace the
formatter.
Fax delayed – Send memory
full (fax/memory-card models
only)
Fax memory is full. Cancel the fax by pressing OK or
Cancel . Resend the fax. You
might need to send the fax in
multiple sections if the error
occurs again.
Fax is busy Canceled send
(fax/memory-card models only)
The fax line to which you were
sending a fax was busy. The
product has canceled sending
the fax.
Check that you are dialing the
correct fax number.
Check that the Redial if busy
option is enabled.
Perform a fax test to verify that
the phone line works and is
plugged into the correct port (see
Perform a fax test on page 316).
Fax is busy Redial pending
(fax/memory-card models only)
The fax line to which you were
sending a fax was busy. The
product automatically redials the
Check that you are dialing the
correct fax number.
Table 7-12 Control-panel messages (continued)
ENWW Control-panel messages 269
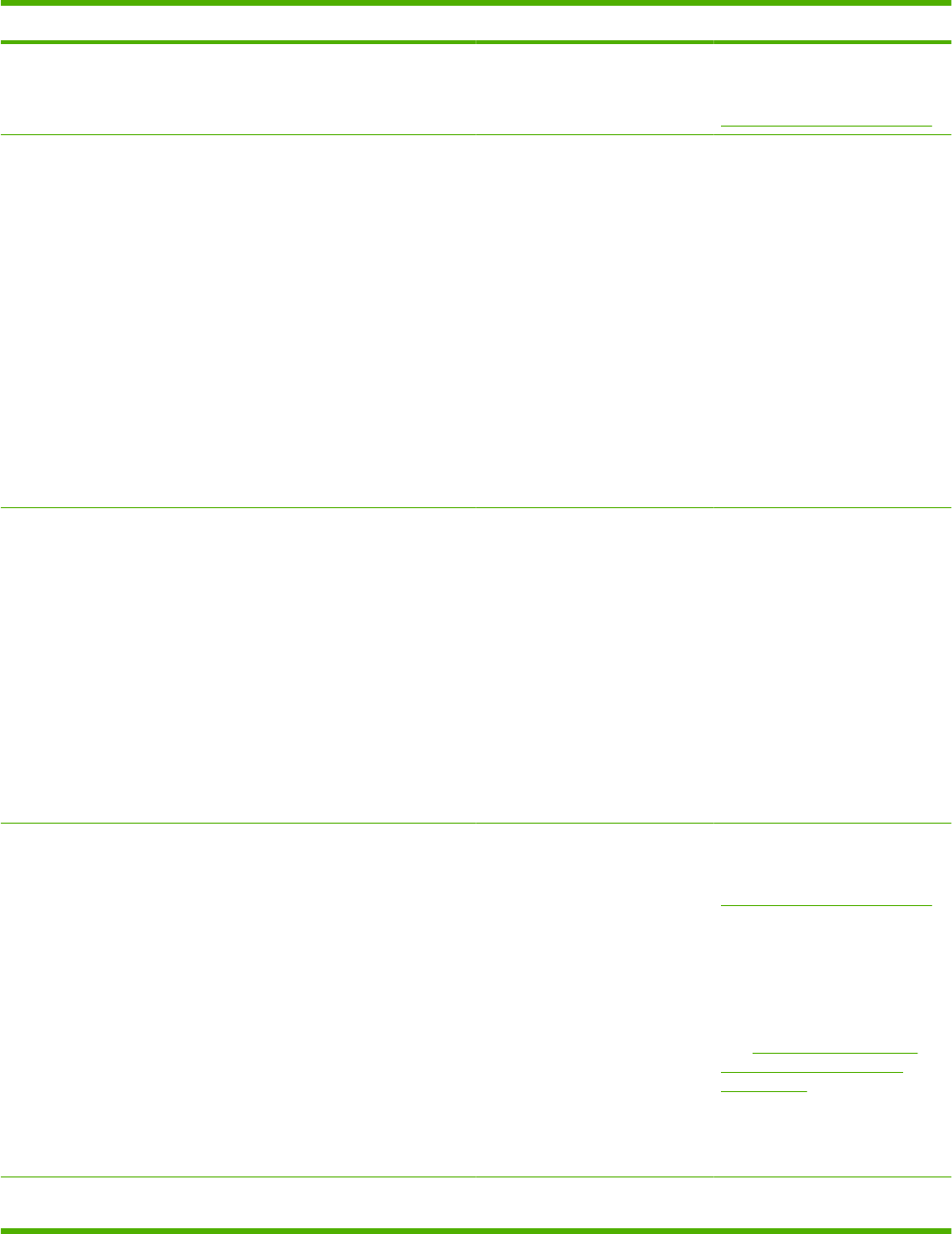
Control panel message Event log error message Description Recommended action
busy number. See the user
guide.
Perform a fax test to verify that
the phone line works and is
plugged into the correct port (see
Perform a fax test on page 316).
Fax memory full Canceling
recv. (fax/memory-card models
only)
During the fax transmission, the
product ran out of memory. Only
the pages that fit into memory will
be printed.
Print all of the faxes, and then
have the sender resend the fax.
Have the sender divide the fax
job into multiple jobs before
resending.
Cancel all fax jobs or, in the
Service menu Fax Service
submenu, clear the faxes from
memory.
If the error persists, perform an
NVRAM initialization.
If the error persists, update the
firmware.
If the error persists, replace the
formatter.
Fax memory full Canceling
send (fax/memory-card models
only)
During the fax job, the memory
filled. All pages of the fax have to
be in memory for a fax job to work
correctly. Only the pages that fit
into memory were sent.
Print all received faxes or wait
until all pending faxes are sent.
Cancel all fax jobs or, in the
Service menu Fax Service
submenu, clear the faxes from
memory.
If the error persists, perform an
NVRAM initialization.
If the error persists, update the
firmware.
If the error persists, replace the
formatter.
Fax recv. error An error occurred while trying to
receive a fax.
Perform a fax test to verify that
the phone line works and is
plugged into the correct port (see
Perform a fax test on page 316).
Send the fax to a device known to
be working correctly.
Receive a fax from a device
known to be working correctly.
See Solve fax problems (fax/
memory-card models only)
on page 314.
If the error persists, replace the
fax card (data access
arrangement (DAA)).
Fax Send error (fax/memory-
card models only)
An error occurred while trying to
send a fax.
Perform a fax test to verify that
the phone line works and is
Table 7-12 Control-panel messages (continued)
270 Chapter 7 Problem solve ENWW
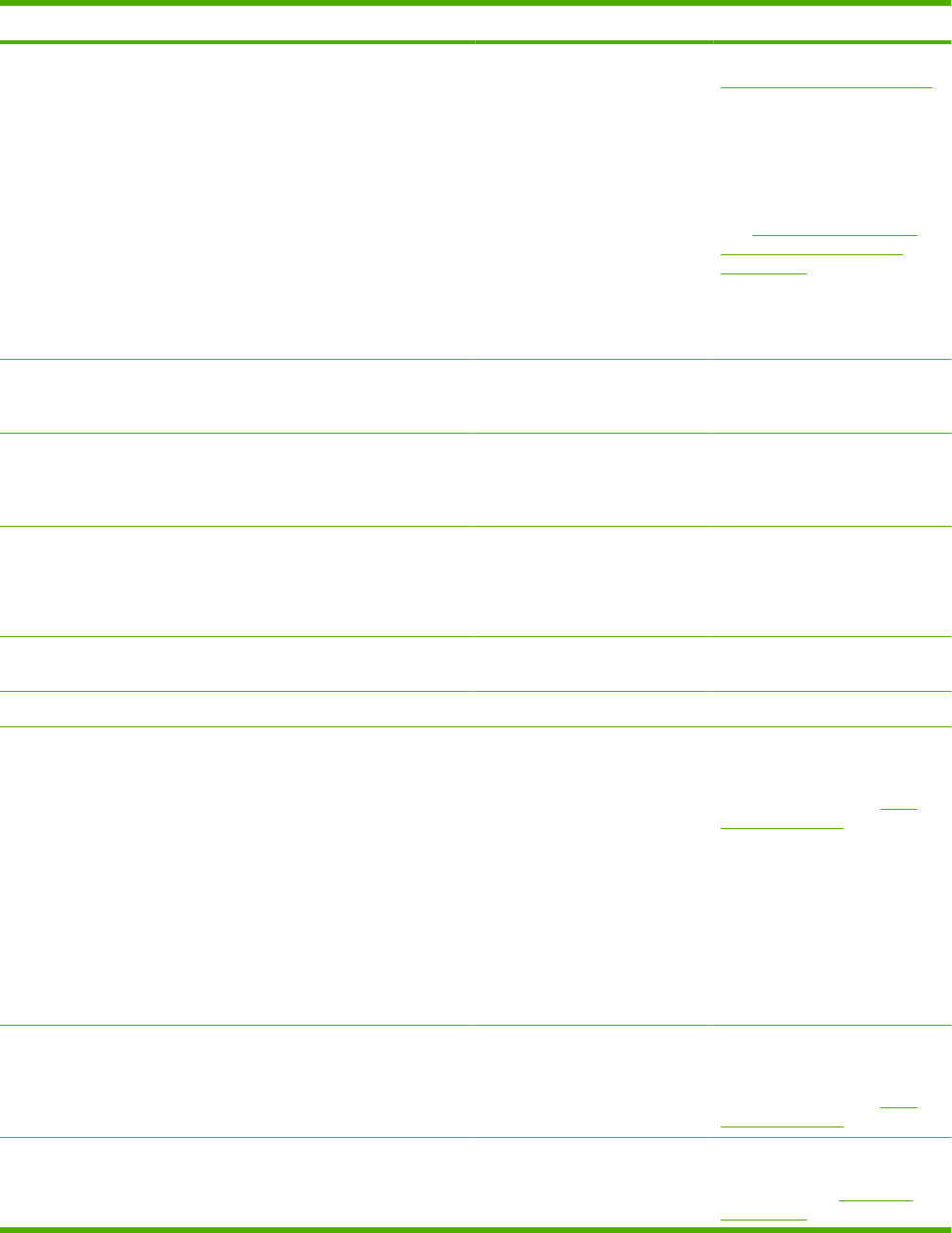
Control panel message Event log error message Description Recommended action
plugged into the correct port (see
Perform a fax test on page 316).
Send the fax to a device known to
be working correctly.
Receive a fax from a device
known to be working correctly.
See Solve fax problems (fax/
memory-card models only)
on page 314.
If the error persists, replace the
fax card (data access
arrangement (DAA)).
Fax storage is full. Unable to
answer call (fax/memory-card
models only)
Memory is full Print out the private receive faxes
or delayed faxes. Clear the
product memory.
Fit to Page on flatbed only The copy reduce/enlarge feature
(called "Fit to Page") applies only
to copies made from the flatbed
scanner.
Use the flatbed or select another
reduction/enlargement setting.
Install <Color> Cartridge One of the color cartridges is not
installed with the door closed.
Install or reinstall the indicated
color cartridge.
If the error persists, replace the
print-cartridge drawer.
Invalid driver Press OK You are using the incorrect
printer driver.
Select the printer driver that is
appropriate for the product.
Invalid entry Invalid data or response. Correct the entry.
Jam in (area), Open door and
clear jam
13.0000 There is a paper jam in the print
paper path or output bin.
Clear the jam from the area
indicated on the product control
panel, and then follow the control
panel instructions. See Clear
jams on page 283.
Remove any debris from the
paper path.
Clean the paper sensors.
Verify the pickup roller,
separation roller, and fuser are
working correctly. If necessary,
replace the rollers.
Jam in Tray #, Clear jam and
then press OK
13.0000 The product has detected a jam
in one of the following areas:
Tray 1, Tray 2, or Tray 3.
Clear the jam from the area
indicated on the product control
panel, and then follow the control
panel instructions. See Clear
jams on page 283.
Jam in Tray 1, Clear jam and
then press OK
13.0000 The product has detected a jam
in Tray 1.
Clear the jam from Tray 1, and
then follow the control panel
instructions. See Clear jams
on page 283.
Table 7-12 Control-panel messages (continued)
ENWW Control-panel messages 271
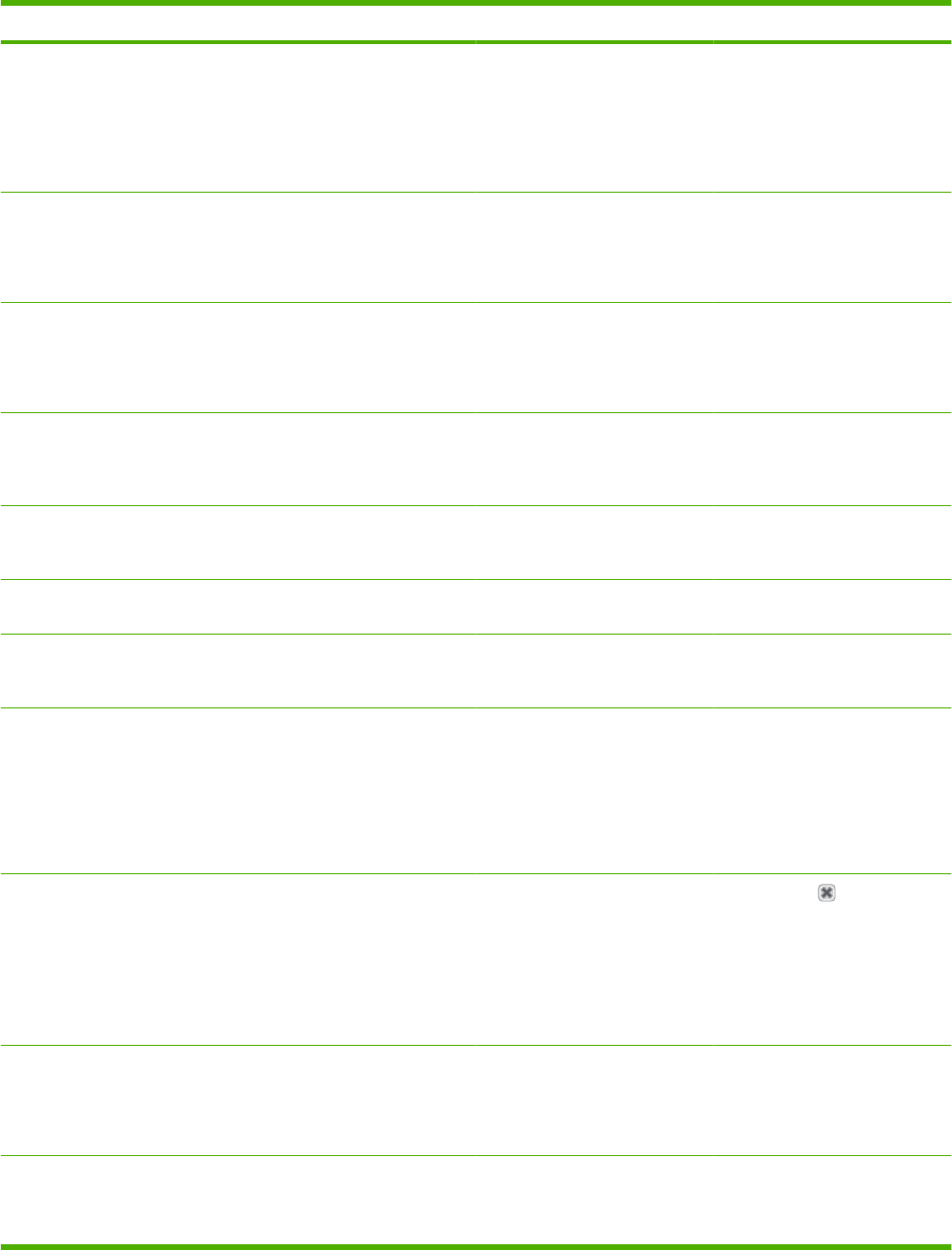
Control panel message Event log error message Description Recommended action
Verify the pickup roller and
separation roller are working
correctly. If necessary, replace
the rollers.
If the error persists, replace the
product.
Load Paper <Type> Out of paper in all available trays. If paper is already loaded in the
tray, test the paper sensors.
Verify that all DC controller
connectors are firmly connected.
Load Tray 1 <TYPE> <SIZE>,
Press OK to use available
media
The product is processing a job,
but no trays match.
Load paper in the correct
orientation.
Press OK to use existing tray
settings.
Load Tray 1, <PLAIN> <SIZE> /
Cleaning mode, OK to start
This is the product cleaning mode
paper prompt.
Load a clean sheet of paper in the
correct orientation, then press
OK to begin the cleaning
procedures.
Load Tray X <TYPE> <SIZE>,
Press OK to use available
media
The product is processing a job,
but a matching tray is empty.
Press OK to use existing
available media.
Manual Duplex Load Tray 1,
Press OK
The product is set to the manual
duplex mode.
Load paper in the correct
orientation.
Manual feed <SIZE> <TYPE>,
Press OK to use available
media
The product is in manual feed
mode.
Load paper into the indicated
tray.
Memory is low Try again later The product does not have
enough memory to start a new
job.
Turn the product off and then on
to clear the memory.
If the error persists, perform an
NVRAM initialization.
If the error persists, update the
firmware.
Memory is low. Press OK The product memory has been
almost completely filled. Press Cancel to clear the
error.
Break the job into smaller jobs
that contain fewer pages.
Turn the product off and then on
to clear the memory.
Memory low Only 1 copy made.
Press OK to continue.
The product does not have
enough memory to complete the
collated copy job.
Break the job into smaller jobs
that contain fewer pages.
Turn the product off and then on
to clear the memory.
Misprint, Press OK Feed delay misprint. Verify that paper is loaded in the
input tray.
Reload the paper.
Table 7-12 Control-panel messages (continued)
272 Chapter 7 Problem solve ENWW
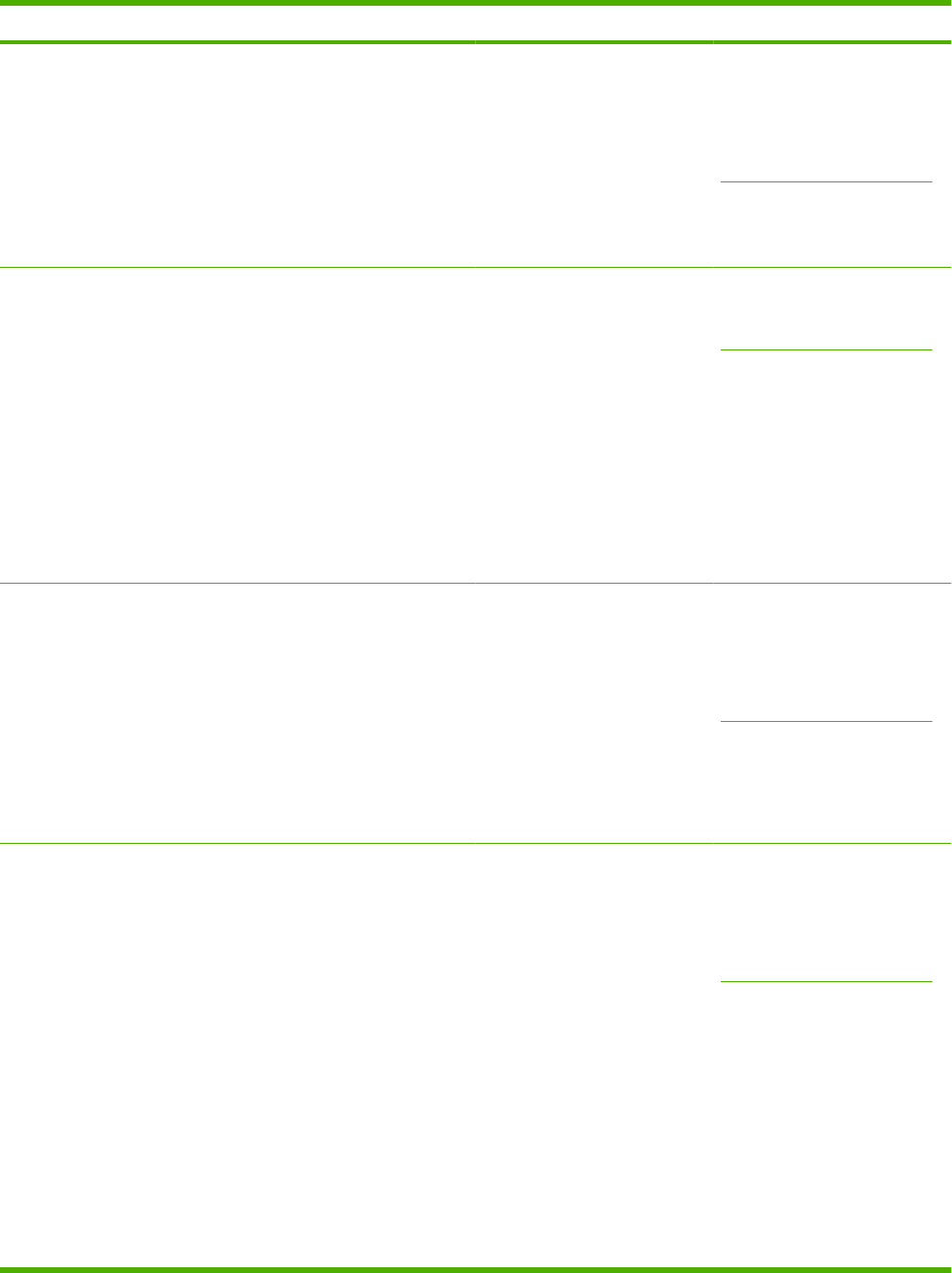
Control panel message Event log error message Description Recommended action
No Dial Tone (fax/memory-card
models only)
The product could not detect a
dial tone.
Check for a dial tone on the
phone line by pressing Start Fax.
Perform a fax test to verify that
the phone line works and is
plugged into the correct port (see
Perform a fax test on page 316).
If the error persists, replace the
fax card (data access
arrangement (DAA)).
No document sent (fax/
memory-card models only)
The product did not scan any
pages, or it did not receive any
pages from the computer to
transmit a fax.
Perform a fax test to verify that
the phone line works and is
plugged into the correct port (see
Perform a fax test on page 316).
Check the fax log for errors.
Print a T.30 trace report, and then
check it for errors.
If the error persists, perform an
NVRAM initialization.
If the error persists, replace the
fax card (data access
arrangement (DAA)).
No fax answer Redial pending
(fax/memory-card models only)
The receiving fax line did not
answer. The product attempts to
redial after a few minutes.
Allow the product to retry sending
the fax.
Perform a fax test to verify that
the phone line works and is
plugged into the correct port (see
Perform a fax test on page 316).
If the error persists, perform an
NVRAM initialization.
If the error persists, update the
firmware.
No fax answer. Canceled send
(fax/memory-card models only)
Attempts to redial a fax number
failed, or the “Redial-no answer”
option was turned off.
Check that the redial option is
enabled.
Perform a fax test to verify that
the phone line works and is
plugged into the correct port (see
Perform a fax test on page 316).
Check the fax log for errors.
Print a T.30 trace report, and then
check it for errors.
If the error persists, update the
firmware.
If the error persists, perform an
NVRAM initialization.
If the error persists, use the
Service menu Restore defaults
function to reset the product.
Table 7-12 Control-panel messages (continued)
ENWW Control-panel messages 273
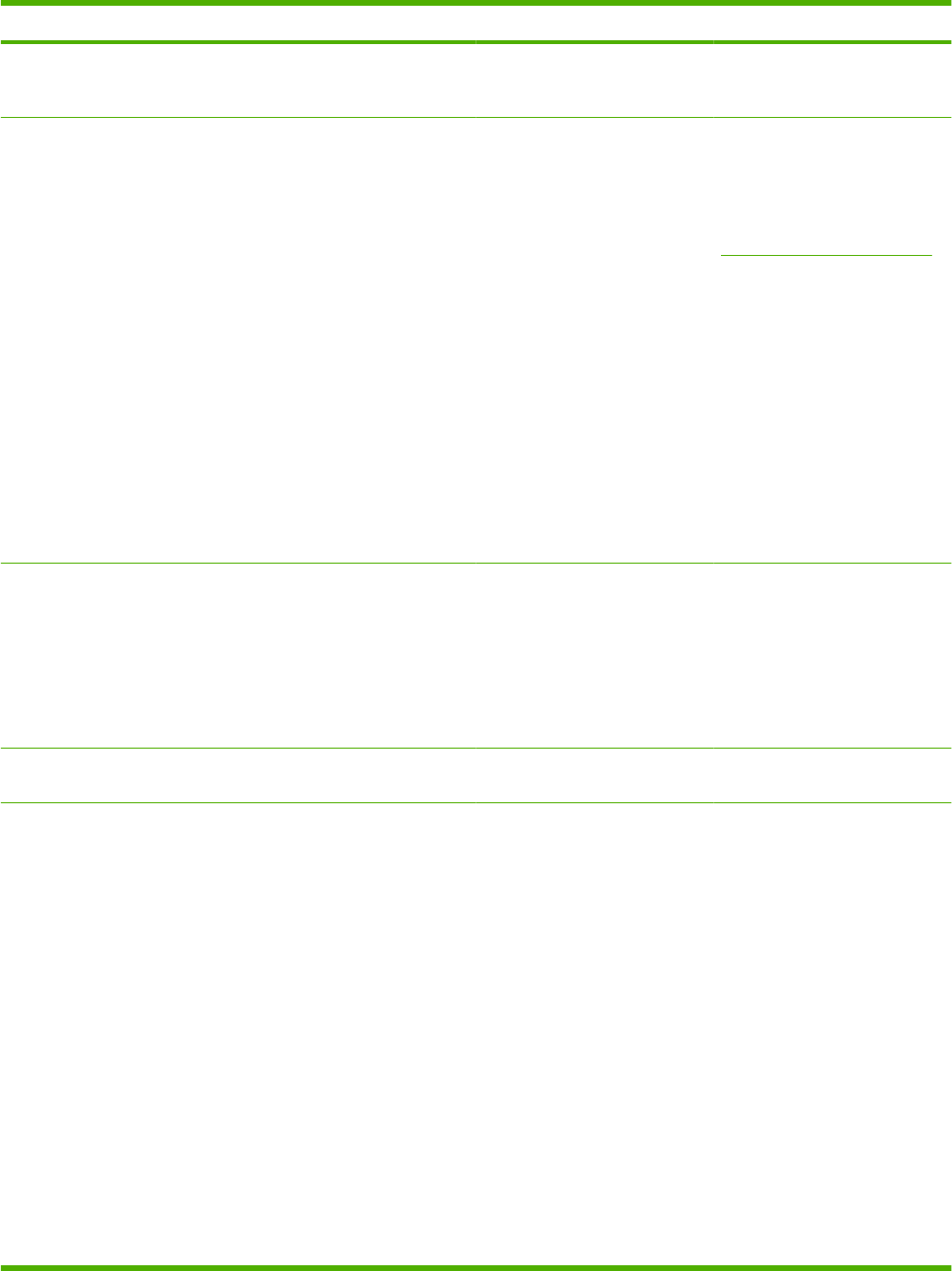
Control panel message Event log error message Description Recommended action
If the error persists, replace the
fax card (data access
arrangement (DAA)).
No fax detected (fax/memory-
card models only)
The product answered the
incoming call but did not detect
that a fax machine was calling.
Allow the product to retry
receiving the fax.
Perform a fax test to verify that
the phone line works and is
plugged into the correct port (see
Perform a fax test on page 316).
Check the fax log for errors.
Print a T.30 trace report, and then
check it for errors.
If the error persists, update the
firmware.
If the error persists, use the
Service menu Restore defaults
function to reset the product.
If the error persists, replace the
fax card (data access
arrangement (DAA)).
Non-HP supply Installed A new supply has been installed
that is not made by HP. This
message is appears for several
seconds, and then the product
returns to the Ready state.
Install a genuine HP print
cartridge.
If the error persists, verify that all
DC controller connectors are
firmly connected.
If the error persists, replace the
print-cartridge drawer.
Order <Color> Cartridge A color print cartridge is low. Order the indicated color print
cartridge.
Print failure, press OK. If error
repeats, turn off then on.
21.0000 The product could not print the
current page because of its
complexity.
1. Press OK to clear the
message.
2. Turn off the power by using
the power switch, and then
wait at least 30 seconds.
3. Turn on the power and wait
for the product to initialize.
If the error persists, break the job
into smaller units, and then
resend them.
If the error persists, verify that the
correct print driver is being used.
If the error persists, update the
firmware.
NOTE: For memory-card
models, adding memory to the
DIMM slot might help solve this
problem.
Table 7-12 Control-panel messages (continued)
274 Chapter 7 Problem solve ENWW
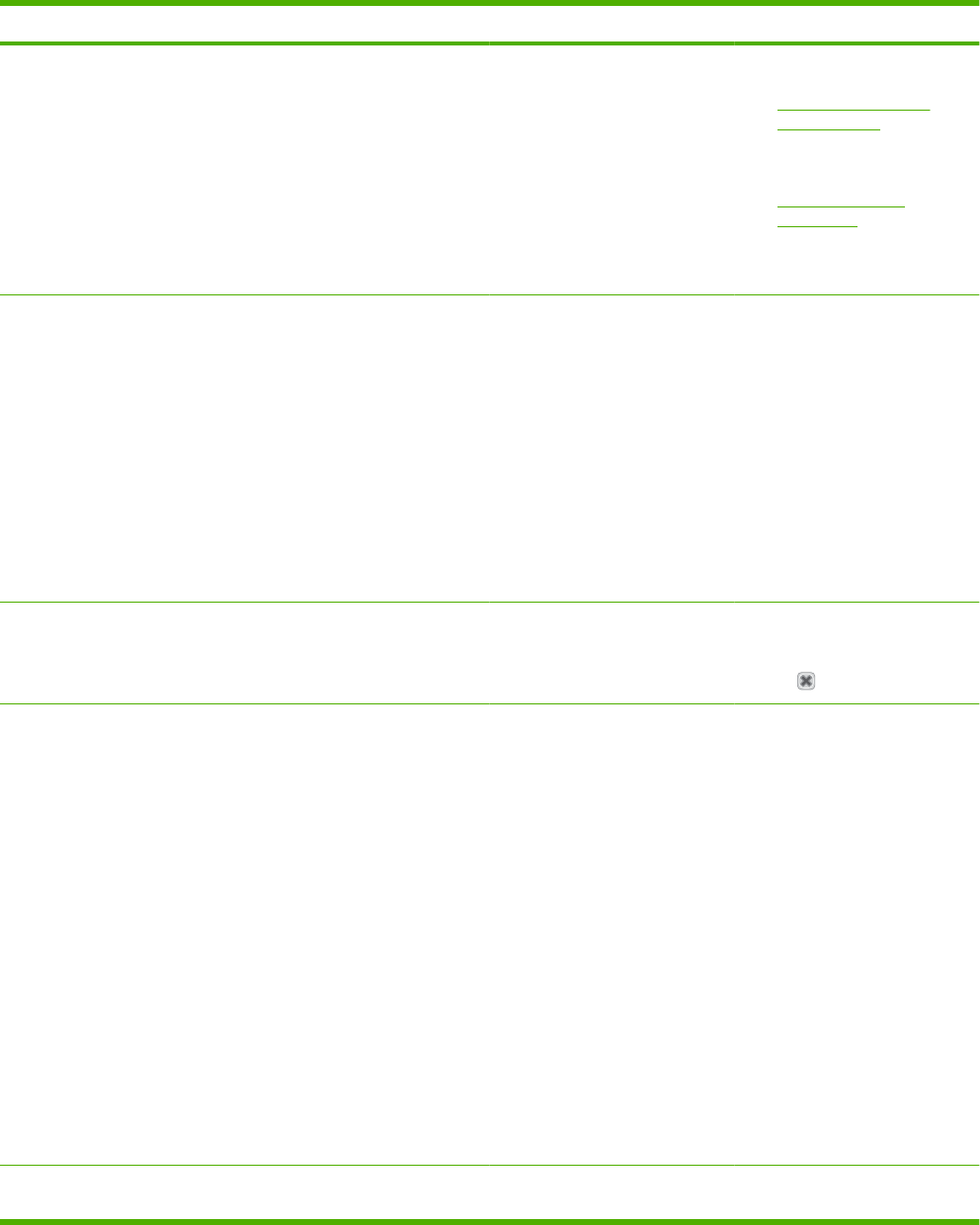
Control panel message Event log error message Description Recommended action
Resend upgrade An attempted firmware upgrade
has failed.
1. Re-download the firmware
update package from
www.hp.com/support/
CM2320series.
2. Install the new firmware
update package. See
Firmware updates
on page 79.
If the error persists, replace the
DC controller.
Scanner error #, Turn off then
on
The product has experienced an
error in the scanner sub-
assembly area.
Turn off the power by using the
power switch, wait at least
30 seconds, and then turn on the
power and wait for the product to
initialize.
If the error persists, verify that all
formatter connectors are firmly
connected.
If the error persists, replace the
scanner assembly.
If the error persists, replace the
formatter.
Scanner reserved for PC scan A computer is using the product
to create a scan.
Wait until the computer scan has
finished, or cancel the scan from
the computer software, or press
Cancel .
Scanning error Cannot
connect
The product cannot transmit scan
information to a computer.
If this is a persistent error, turn the
product off, and then turn it on.
Also, turn the computer off, and
then turn it on.
Verify that the connection cable is
not loose or damaged. Replace
the cable if necessary, and try the
scan again.
Verify that the computer prints in
order to confirm a working USB or
network connection.
Verify that the scan-to destination
folder or software program path is
correct.
Remove and then reinstall the
software program.
If the error persists, replace the
formatter.
Settings cleared The product has cleared job
settings.
Re-enter any appropriate job
settings.
Table 7-12 Control-panel messages (continued)
ENWW Control-panel messages 275
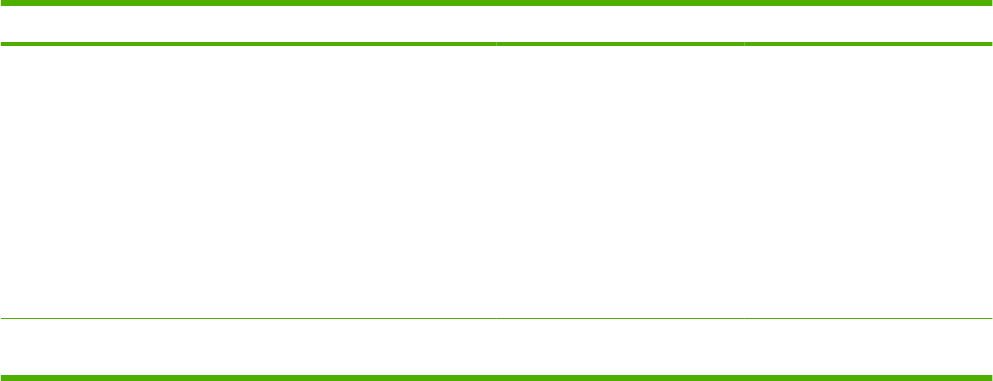
Control panel message Event log error message Description Recommended action
Unexpected size in tray X
Load <size> press OK
41.3000 The product has experienced a
media-size mismatch in the tray
indicated.
●Verify that the default
product settings for the tray
are correct.
●Print a configuration page,
and then verify that the tray
settings are correct.
●Restore the tray Paper
Type setting to Any type
and the Paper Size setting
to Any size, and then
resend the print job.
Used [color] installed, to
accept press OK
A used color printer cartridge has
been installed or moved.
Press OK to return to the Ready
state.
Table 7-12 Control-panel messages (continued)
276 Chapter 7 Problem solve ENWW
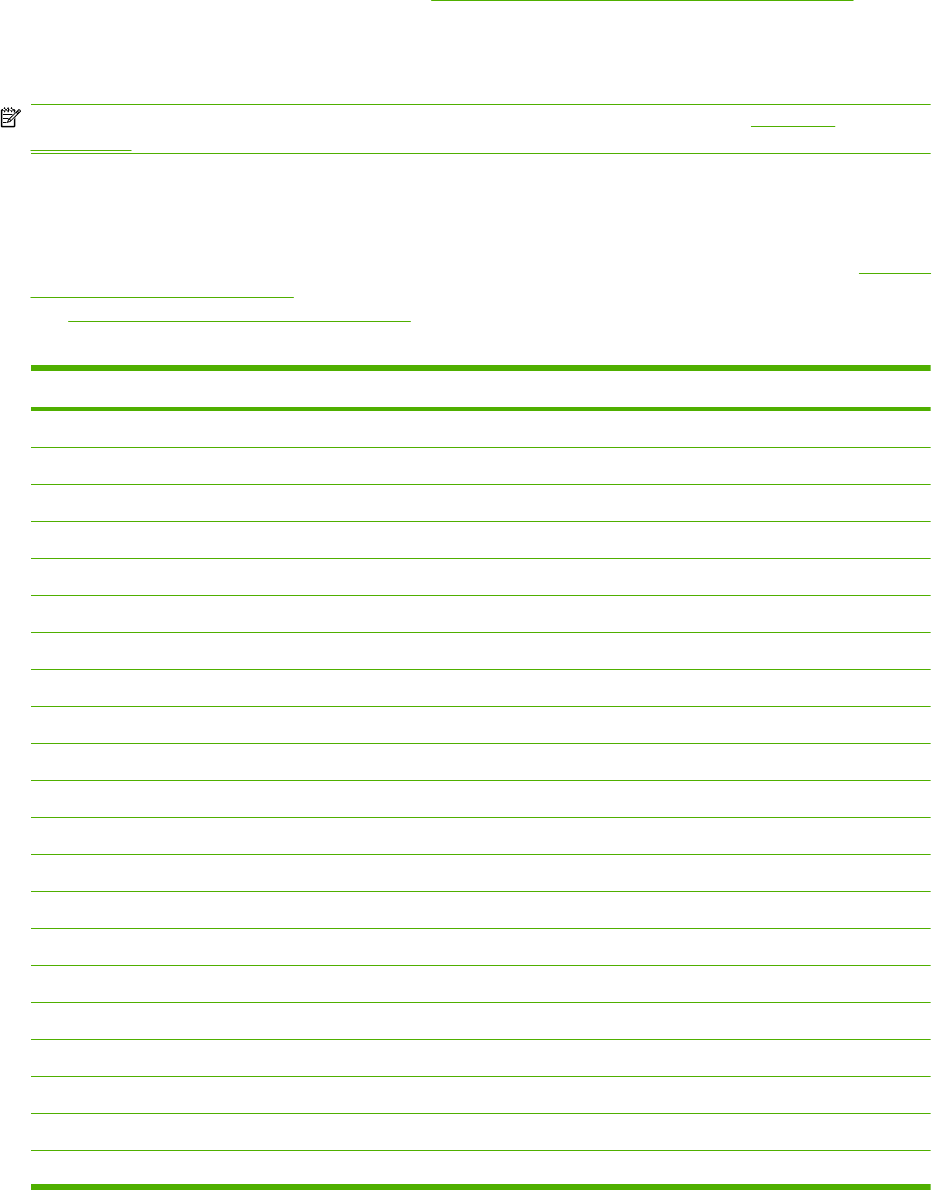
Event-log messages
Print the event log
1. Open the secondary service menu. See Open the secondary service menu on page 311.
2. Use the arrow buttons to select Service Reports, and then press OK.
3. Use the arrow buttons to select Error Report, and then press OK.
NOTE: You can use HP ToolboxFX to view the event log from a computer. See Event log
on page 53.
Event log messages
The following table contains all event log codes for this product. Many event log codes correspond to a
control-panel error message. For information about solving control-panel error messages, see Control-
panel messages on page 257. For information about solving errors that display only in the event log,
see Event-log-only messages on page 279.
Table 7-13 Event-log messages
Event code Description
13.0000 Paper jam
20.0000 Memory out
21.0000 Page misfeed or mispick
41.2000 Beam detect malfunction
41.3000 Unexpected size
50.1000 Low fuser temperature error
50.2000 Slow fuser error
50.3000 High fuser temperature error
50.4000 Fuser drive circuit error
50.7000 Fuser open error
50.8000 Low sub-thermistor fuser error
50.9000 High sub-thermistor fuser error
51.2000 Black scanner laser error (inline devices only)
51.2100 Cyan scanner laser error (inline devices only)
51.2200 Magenta scanner laser error (inline devices only)
51.2300 Yellow scanner laser error (inline devices only)
54.0100 Environmental sensor error
54.0600 Density sensor error
54.1100 Black density out of range
54.1101 Cyan density out of range
54.1102 Magenta density out of range
ENWW Event-log messages 277
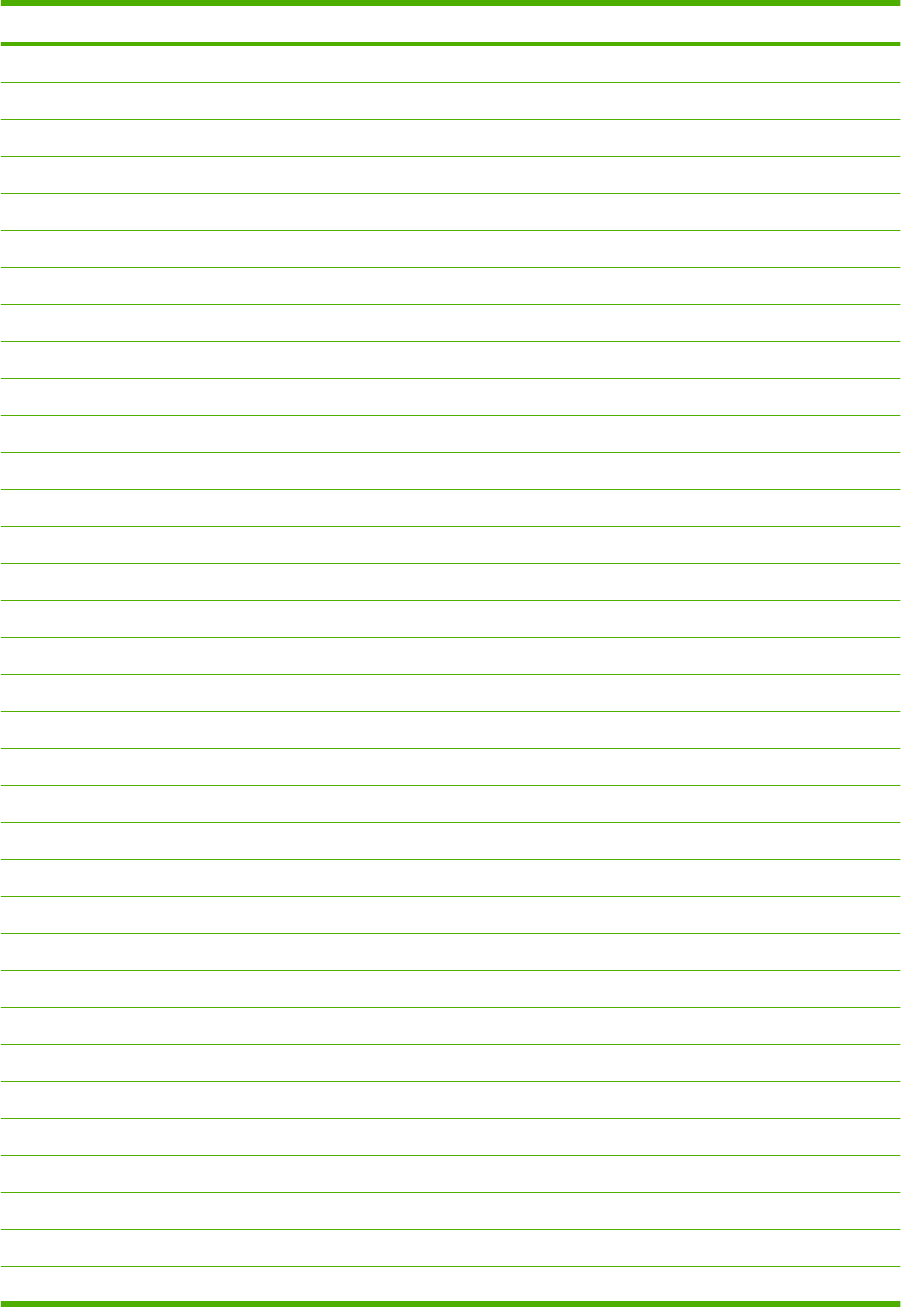
Event code Description
54.1103 Yellow density out of range
54.1200 Black density measurement abnormality
54.1201 Cyan density measurement abnormality
54.1202 Magenta density measurement abnormality
54.1203 Yellow density measurement abnormality
54.1400 Color plane registration sensor error (inline devices only)
54.1599 Black CPR pattern cannot be read
54.1501 Cyan CPR pattern cannot be read
54.1502 Magenta CPR pattern cannot be read
54.1503 Yellow CPR pattern cannot be read
54.1500 Yellow toner level sensor error
54.1600 Magenta toner level sensor error
54.1700 Cyan toner level sensor error
54.1800 Black toner level sensor error
54.1900 Bad top-of-page (TOP) sensor
54.2100 Beam detect (BD) error
54.2500 Top-of-page sensor error
55.0000 Engine internal communication error
55.0601 DC controller NVRAM data error
55.0602 DC controller NVRAM access error
55.1000 DC controller memory error
57.0100 Fan motor error
57.0200 Fan error
59.0160 ITB or main motor rotation error (59.A0)
59.0192 Developer motor rotation error (59.C0)
59.0240 Transfer alienation failure (59.F0)
59.3000 Fuser motor startup error
59.4000 Fuser motor error
59.5000 Image drum motor startup error—black
59.5300 Image drum motor startup error—yellow
59.6000 Image drum motor rotation error—black
59.6300 Image drum motor rotation error—yellow
59.7000 Black developer motor startup error
59.7300 Yellow developer motor startup error
Table 7-13 Event-log messages (continued)
278 Chapter 7 Problem solve ENWW
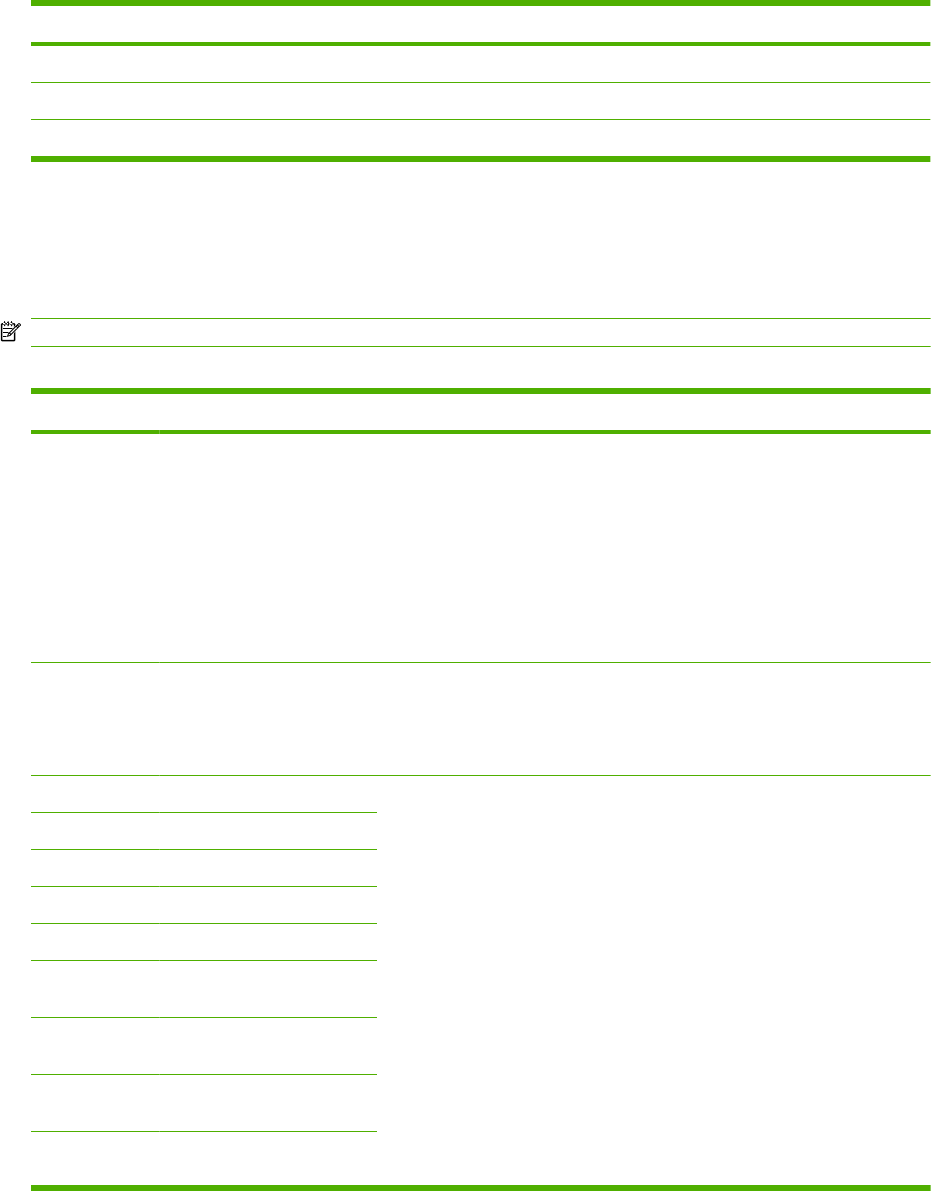
Event code Description
59.8000 Black developer motor rotation error
59.8300 Yellow developer motor rotation error
59.9000 ITB motor start error
Event-log-only messages
The following product events do not produce a message that appears on the control panel. Instead, they
are recorded in the event log.
NOTE: The following solutions are suggested for very persistent error-log entries.
Table 7-14 Event-log-only messages
Event code Description Solution
20.0000 Memory out 1. Turn off the power by using the power switch, and then wait at least 30
seconds.
2. Turn on the power and wait for the product to initialize.
If the error persists, break the job into smaller jobs that contain fewer pages.
If the error persists, update the firmware.
NOTE: For memory-card models, adding memory to the DIMM slot might
help solve this problem.
54.0100 Environmental sensor error Verify that the DC controller connectors are firmly connected.
If the error persists, replace the temperature/humidity sensor.
If the error persists, replace the DC controller.
54.0600 Density sensor error Verify that the cables between the DC controller and the ITB are firmly
connected.
If the error persists, replace the color misregistration sensor.
If the error persists, replace the ITB.
If the error persists, replace the DC controller.
54.1100 Black density out of range
54.1101 Cyan density out of range
54.1102 Magenta density out of range
54.1103 Yellow density out of range
54.1200 Black density measurement
abnormality
54.1201 Cyan density measurement
abnormality
54.1202 Magenta density
measurement abnormality
54.1203 Yellow density
measurement abnormality
Table 7-13 Event-log messages (continued)
ENWW Event-log messages 279
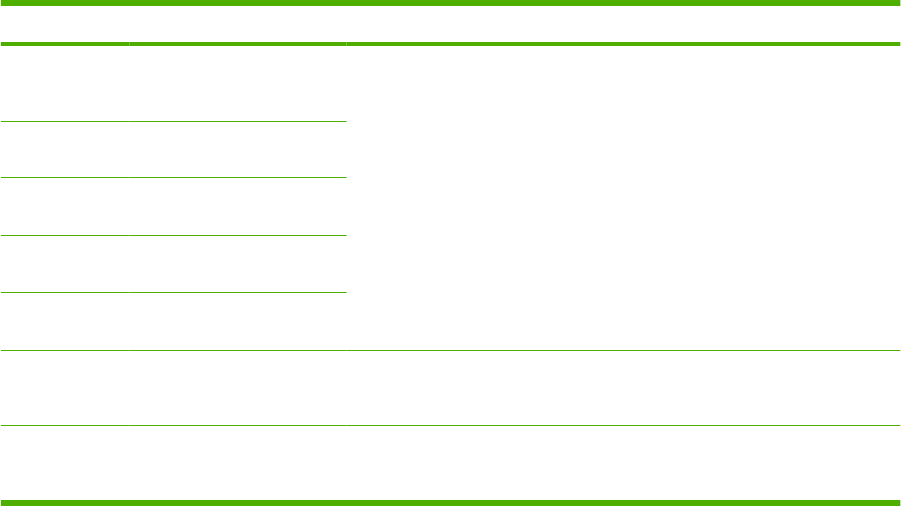
Event code Description Solution
54.1400 Color plane registration
sensor error (inline devices
only)
1. Turn off the power by using the power switch, and then wait at least
30 seconds.
2. Turn on the power and wait for the product to initialize.
If the error persists, verify that the cables between the color misregistration
sensor and the DC controller are firmly connected.
If the error persists, replace the color misregistration sensor.
If the error persists, replace the ITB.
If the error persists, replace the print cartridge tray.
If the error persists, replace the DC controller.
54.1501 Cyan CPR pattern cannot be
read
54.1502 Magenta CPR pattern
cannot be read
54.1503 Yellow CPR pattern cannot
be read
54.1599 Black CPR pattern cannot be
read
54.2100 Beam detect (BD) error If the error persists, replace the DC controller.
If the error persists, replace the product.
54.2500 Top-of-page sensor error Verify that the DC controller connectors are firmly connected.
If the error persists, replace the DC controller.
Table 7-14 Event-log-only messages (continued)
280 Chapter 7 Problem solve ENWW
Paper-handling problems
Jams
Recover jams
When the jam recovery feature is turned on, the product reprints any pages that are damaged during a
jam. To turn on jam recovery, you must use the embedded Web server (EWS) or HP ToolboxFX.
Use the EWS to set jam recovery (network models only)
1. At a networked computer, open the EWS.
2. Click the System tab.
3. Click System Setup.
4. In the Jam Recovery drop-down list, select On.
5. Click Apply.
Use HP ToolboxFX to set jam recovery
1. Open HP ToolboxFX.
2. Click the Device Settings folder, and then click System Setup.
3. Next to Jam Recovery, select On from the drop-down list.
ENWW Paper-handling problems 281
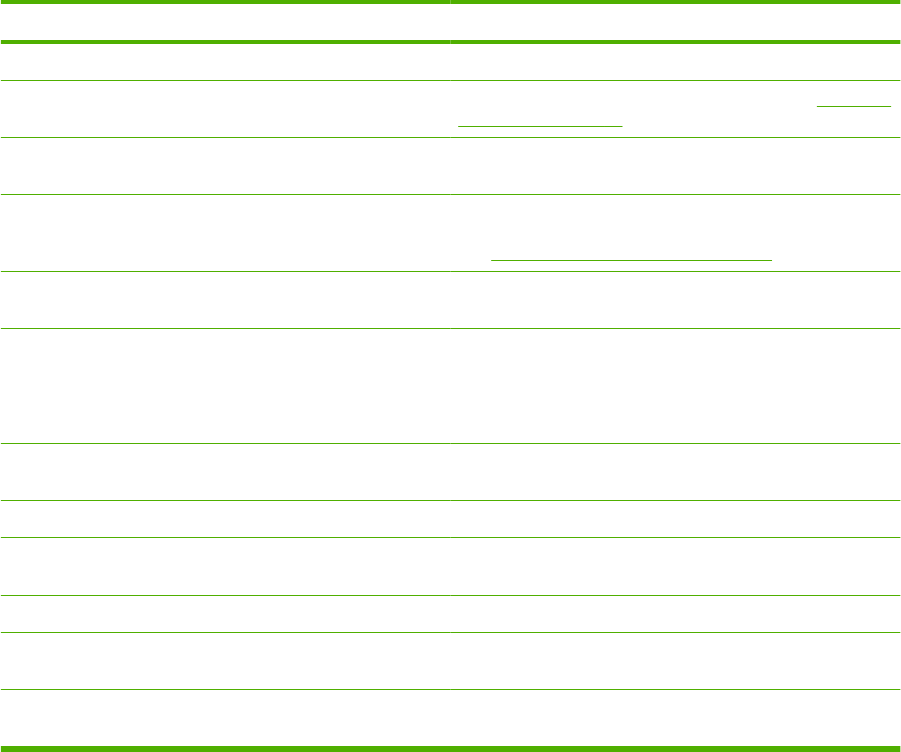
Common causes of jams
Common causes of jams
1
Cause Solution
The paper length and width guides are not adjusted correctly. Adjust the guides so they are against the paper stack.
The media does not meet specifications. Use only media that meets HP specifications. See Paper and
print media on page 37.
You are using media that has already passed through a printer
or copier.
Do not use media that has been previously printed on or
copied.
An input tray is loaded incorrectly. Remove any excess media from the input tray. Make sure that
the stack is below the maximum stack height mark in the tray.
See Load paper and print media on page 43.
The media is skewed. The input-tray guides are not adjusted correctly. Adjust them
so they hold the stack firmly in place without bending it.
The media is binding or sticking together. Remove the media, flex it, rotate it 180 degrees, or flip it over.
Reload the media into the input tray.
NOTE: Do not fan paper. Fanning can create static
electricity, which can cause paper to stick together.
The media is removed before it settles into the output bin. Wait until the page completely settles in the output bin before
removing it.
The media is in poor condition. Replace the media.
The internal rollers from the tray are not picking up the media. Remove the top sheet of media. If the media is heavier than
163 g/m2 (43 lb), it might not be picked from the tray.
The media has rough or jagged edges. Replace the media.
The media is perforated or embossed. Perforated or embossed media does not separate easily. Load
sheets one at a time.
Paper was not stored correctly. Replace the paper in the trays. Paper should be stored in the
original packaging in a controlled environment.
1If the product continues to jam, contact HP Customer Support or your authorized HP service provider.
282 Chapter 7 Problem solve ENWW

Clear jams
Causes of jams
Occasionally, paper or other print media can become jammed during a print job. Some causes include
the following events:
●The input trays are loaded improperly or overfilled, or the media guides are not set properly.
●Media is added to or removed from an input tray during a print job or an input tray is removed from
the product during a print job.
●The cartridge door is opened during a print job.
●Too many sheets have accumulated in an output area, or sheets are blocking an output area.
●The print media that is being used does not meet HP specifications. See Paper and print media
on page 37.
●The media is damaged or has foreign objects attached to it, such as staples or paper clips.
●The environment in which the print media was stored is too humid or too dry. See Paper and print
media on page 37.
ENWW Paper-handling problems 283
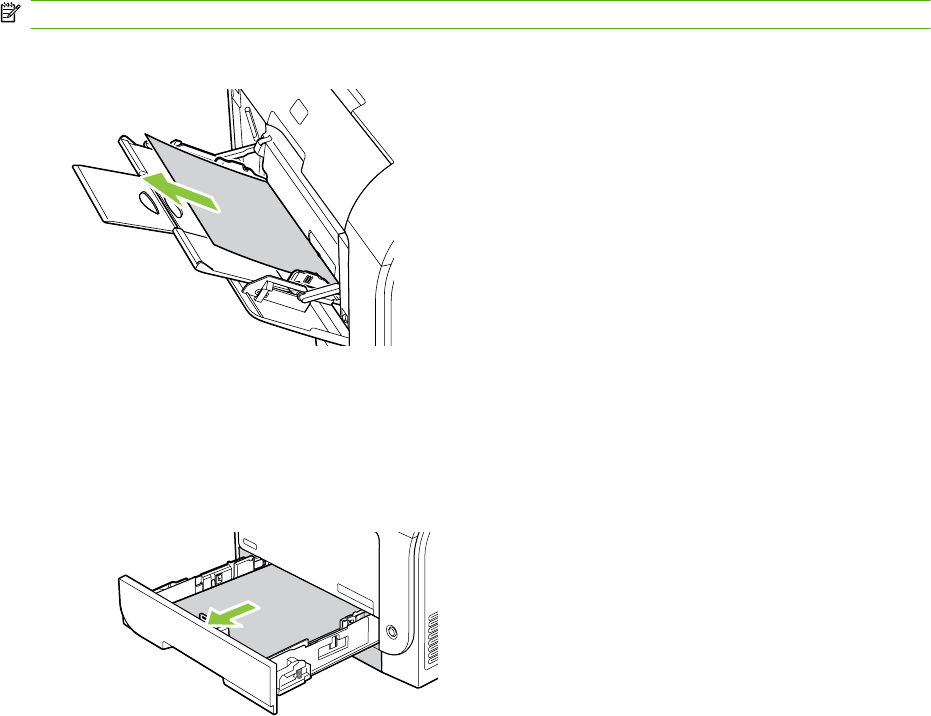
Where to look for jams
Jams can occur in these locations:
●In the automatic document feeder (ADF)
●In input areas
●In the automatic duplexer (where applicable)
●In output areas
●Inside the product (paper path)
Find and remove the jam by using the instructions on the following pages. If the location of the jam is
not obvious, first look inside the product.
Loose toner might remain in the product after a jam. This problem typically resolves itself after a few
sheets have been printed.
Clear jams in Tray 1
NOTE: If the sheet tears, make sure that all of the fragments are removed before you resume printing.
Pull the jammed sheet from Tray 1.
If paper has entered far enough into Tray 1, remove Tray 2, drop the Tray 1 plate down, and then remove
the paper from the opening.
Clear jams in Tray 2
1. Pull out Tray 2 and place it on a flat surface.
284 Chapter 7 Problem solve ENWW
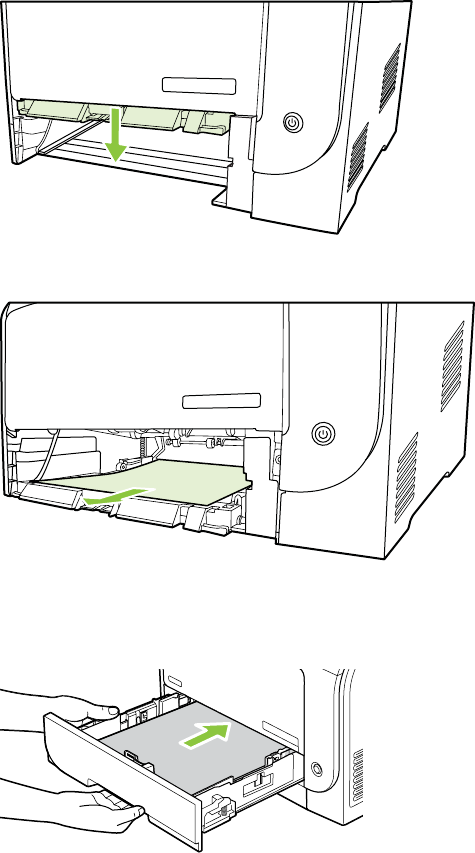
2. Lower the jam-access tray.
3. Remove the jammed sheet by pulling it straight out.
4. Close the jam-access tray.
5. Replace Tray 2.
6. Press OK to continue printing.
ENWW Paper-handling problems 285
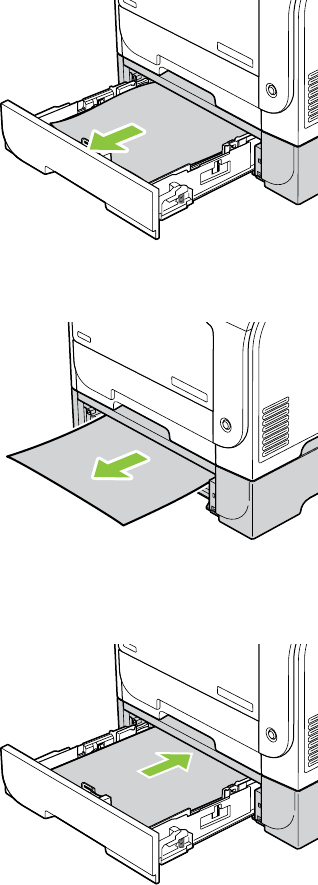
Clear jams in Tray 3
1. Pull out Tray 3 and place it on a flat surface.
2. Remove the jammed sheet by pulling it straight out.
3. Replace Tray 3.
4. Press OK to continue printing.
286 Chapter 7 Problem solve ENWW
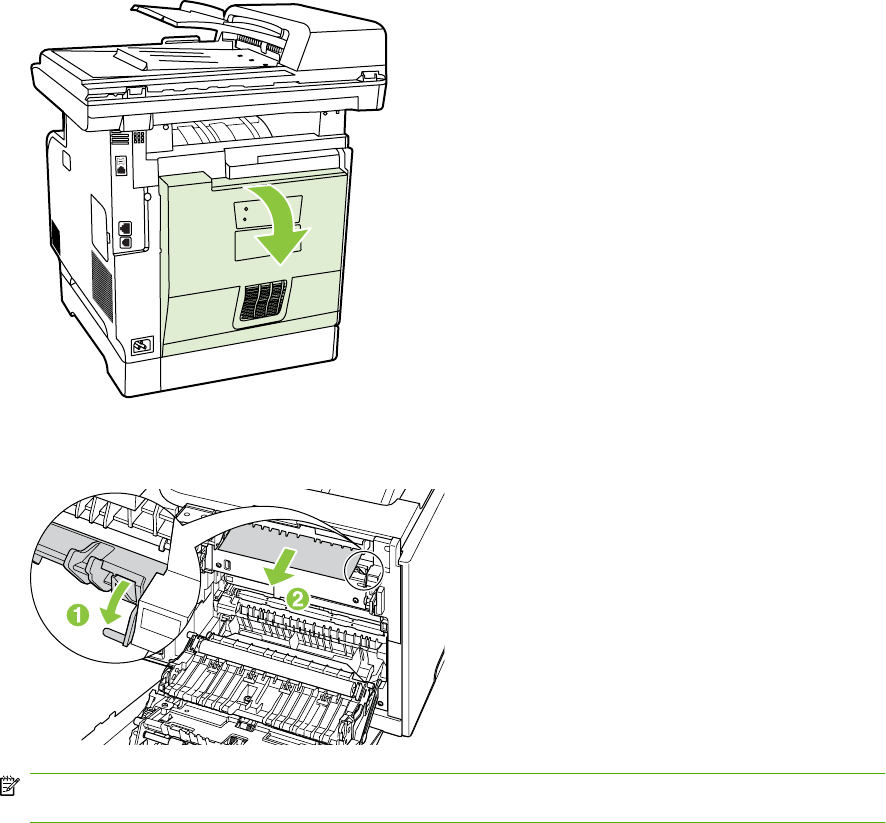
Clear jams in fuser area
1. Open the rear door.
2. If necessary, push the guide (callout 1) and remove any visible paper (callout 2) from the bottom
of the delivery area.
NOTE: If the sheet tears, make sure that all fragments are removed before you resume printing.
Do not use sharp objects to remove fragments.
3. Close the rear door.
ENWW Paper-handling problems 287
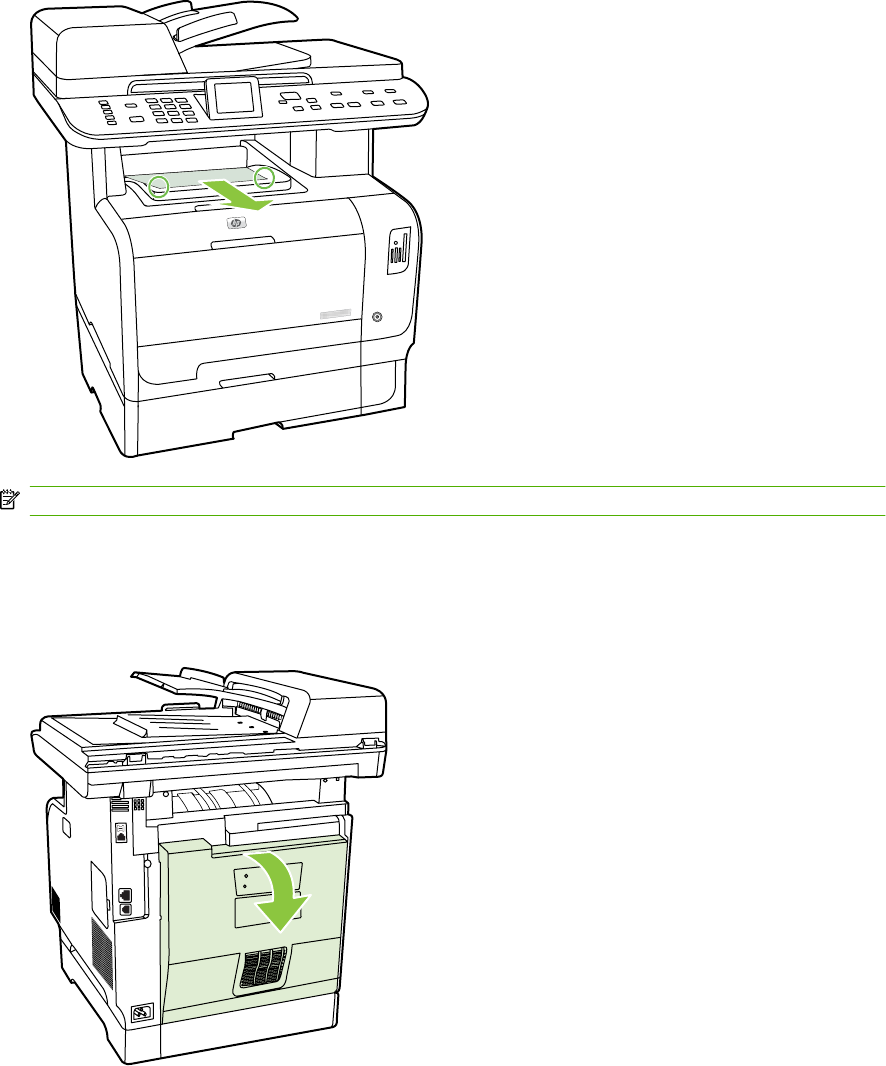
Clear jams in output bin
1. Look for jammed paper in the output bin area.
2. Remove any visible media. With both hands, grasp the side of the media that is most visible (this
includes the middle), and carefully pull it free from the product.
NOTE: If the sheet tears, make sure that all fragments are removed before resuming printing.
3. Open and then close the rear door to clear the message.
Clear jams in duplexer (duplexing models only)
1. Open the rear door.
288 Chapter 7 Problem solve ENWW

2. If necessary, pull the guide (callout 1) and remove any visible paper (callout 2) from the bottom of
the delivery area.
3. If necessary, remove any visible paper from bottom side of the duplexing unit.
4. If you can not see any jammed paper, lift the duplexing unit using the tab on the side of the duplexing
unit.
5. If you can see the trailing edge of the paper, remove the paper from the product.
ENWW Paper-handling problems 289
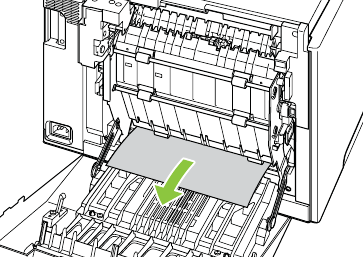
6. If you can see the leading edge of the paper, remove it from the product.
7. Close the rear door.
290 Chapter 7 Problem solve ENWW
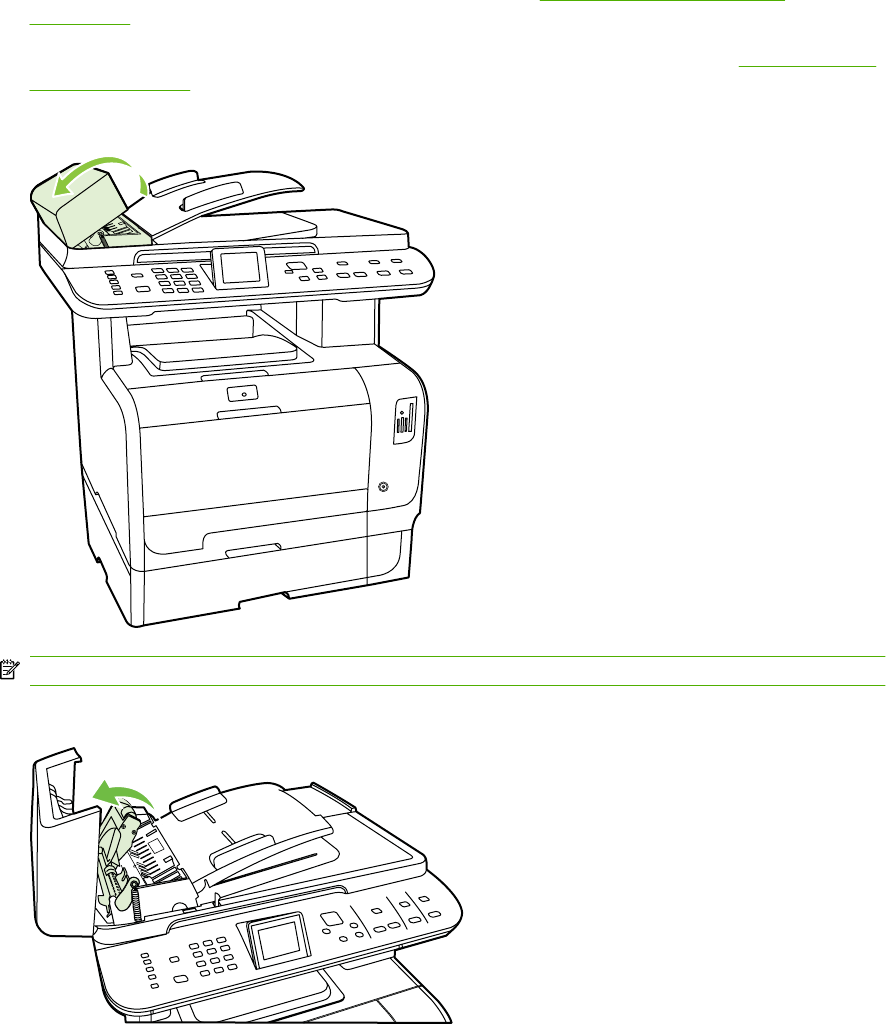
Clear jams from the ADF
Occasionally, media becomes jammed during a fax, copy, or scan job.
You are notified of a media jam by the Doc feeder jam Clear, Reload message that appears on the
product control-panel display.
●The ADF input tray is loaded incorrectly or is too full. See Load paper and print media
on page 43 for more information.
●The media does not meet HP specifications, such as those for size or type. See Paper and print
media on page 37 for more information.
1. Open the ADF cover.
NOTE: Verify that any shipping tape inside the ADF has been removed.
2. Lifting the green lever, rotate the pick mechanism until it stays open.
ENWW Paper-handling problems 291
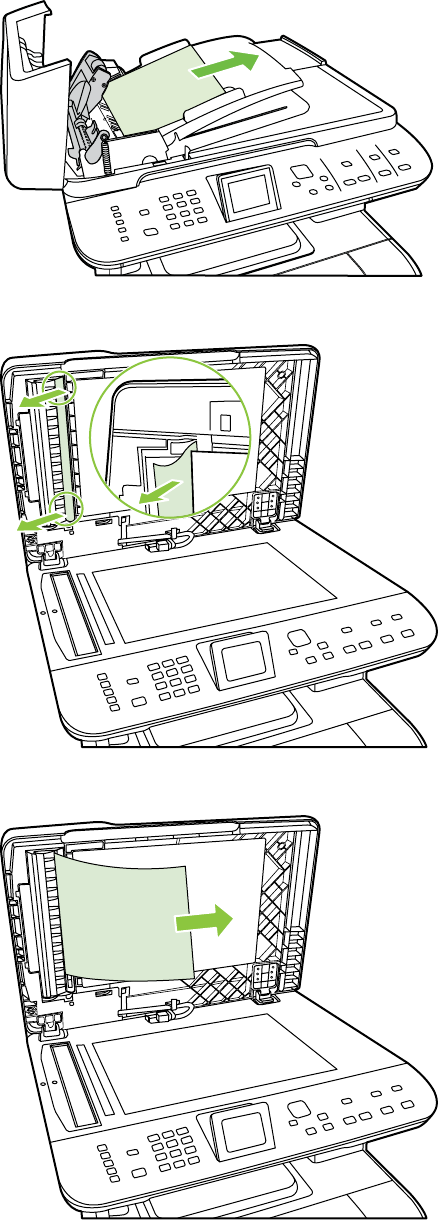
3. Gently try to remove the page without tearing it. If you feel resistance, go to the next step.
4. Open the ADF lid and gently loosen the media by using both hands.
5. When the media is free, gently pull it out in the direction shown.
292 Chapter 7 Problem solve ENWW
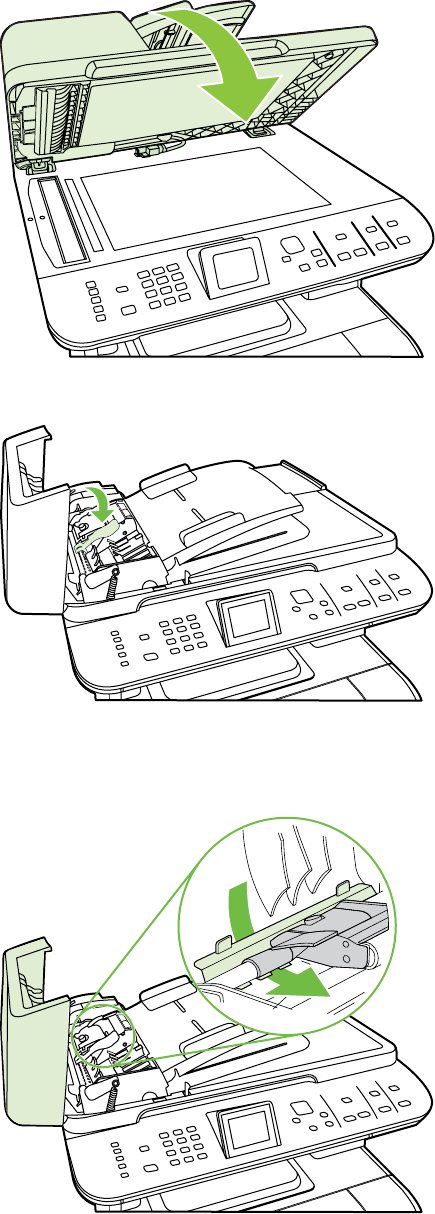
6. Close the lid to the flatbed scanner.
7. Lower the green lever.
8. Reinstall the cleanout part by inserting it as shown. Push down on the two tabs until the part snaps
into place. Install the cleanout part correctly, because future jamming might occur if the cleanout
part is not replaced correctly.
ENWW Paper-handling problems 293
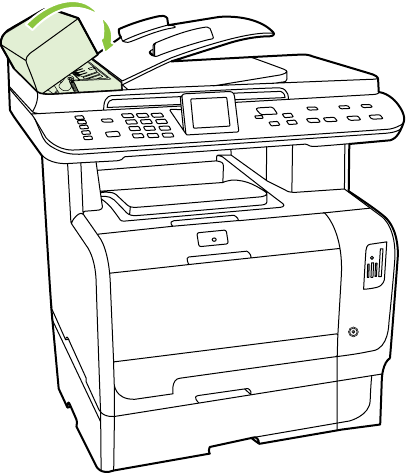
9. Close the ADF lid.
294 Chapter 7 Problem solve ENWW
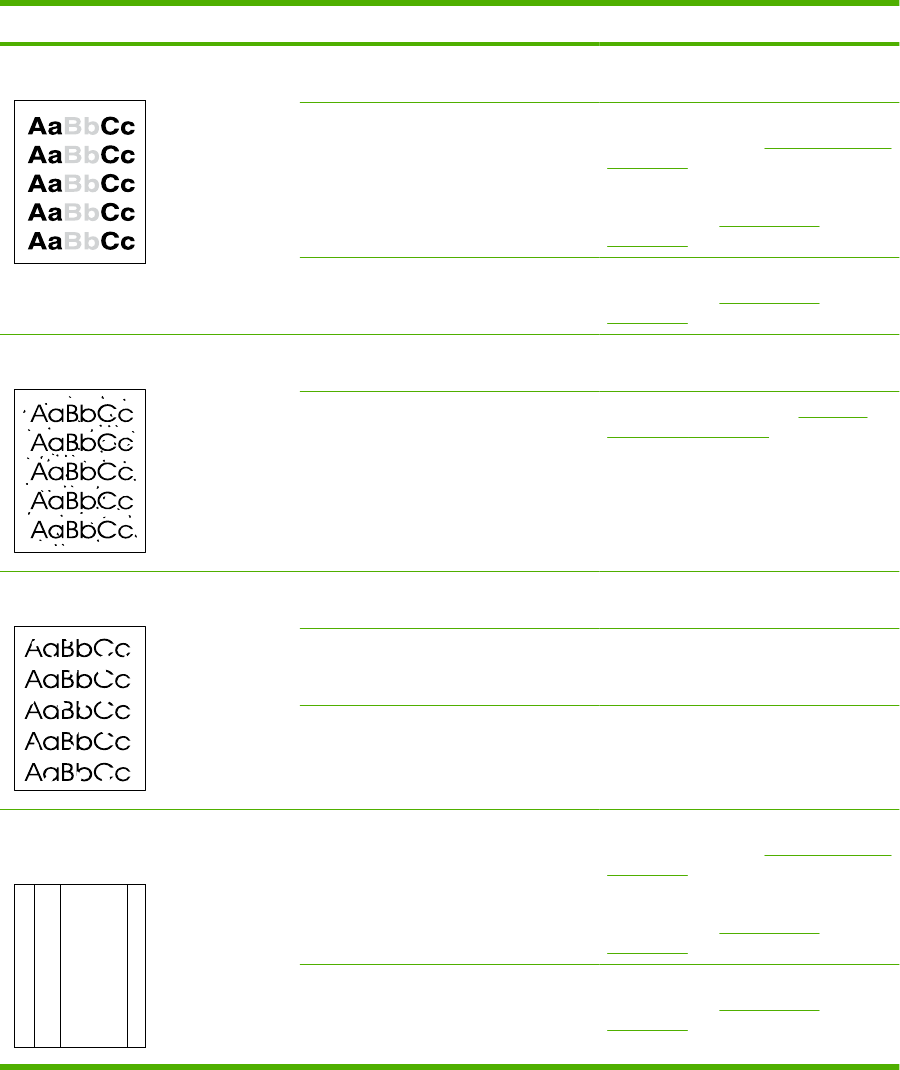
Solve image quality problems
General image quality problems
The following examples depict letter-size paper that has passed through the product short-edge first.
These examples illustrate problems that would affect all of the pages that you print, whether you print
in color or in black only. The topics that follow list the typical cause and solution for each of these
examples.
Problem Cause Solution
Print is light or faded. The media might not meet
HP specifications.
Use media that meets HP specifications.
One or more print cartridges might be
defective.
Print the supplies status page to check
the remaining life. See Information pages
on page 50.
Replace any empty or used (refilled) print
cartridges. See Print cartridge
on page 67.
The product is set to override the
Replace <Color> Cartridge message
and to continue printing.
Replace any empty or used (refilled) print
cartridges. See Print cartridge
on page 67.
Toner specks appear. The media might not meet
HP specifications.
Use media that meets HP specifications.
The paper path might need cleaning. Clean the paper path. See Clean the
paper path on page 73.
Dropouts appear. A single sheet of print media might be
defective.
Try reprinting the job.
The moisture content of the paper is
uneven or the paper has moist spots on
its surface.
Try different paper, such as high-quality
paper that is intended for color laser
printers.
The paper lot is flawed. The
manufacturing processes can cause
some areas to reject toner.
Try different paper, such as high-quality
paper that is intended for color laser
printers.
Vertical streaks or bands appear on the
page.
A
A
A
A
A
B
B
B
B
B
C
C
C
C
C
a
a
a
a
a
c
c
c
c
c
b
b
b
b
b
One or more print cartridges might be
defective.
Print the supplies status page to check
the remaining life. See Information pages
on page 50.
Replace any empty or used (refilled) print
cartridges. See Print cartridge
on page 67.
The product is set to override the
Replace <Color> Cartridge message
and to continue printing.
Replace any empty or used (refilled) print
cartridges. See Print cartridge
on page 67.
ENWW Solve image quality problems 295
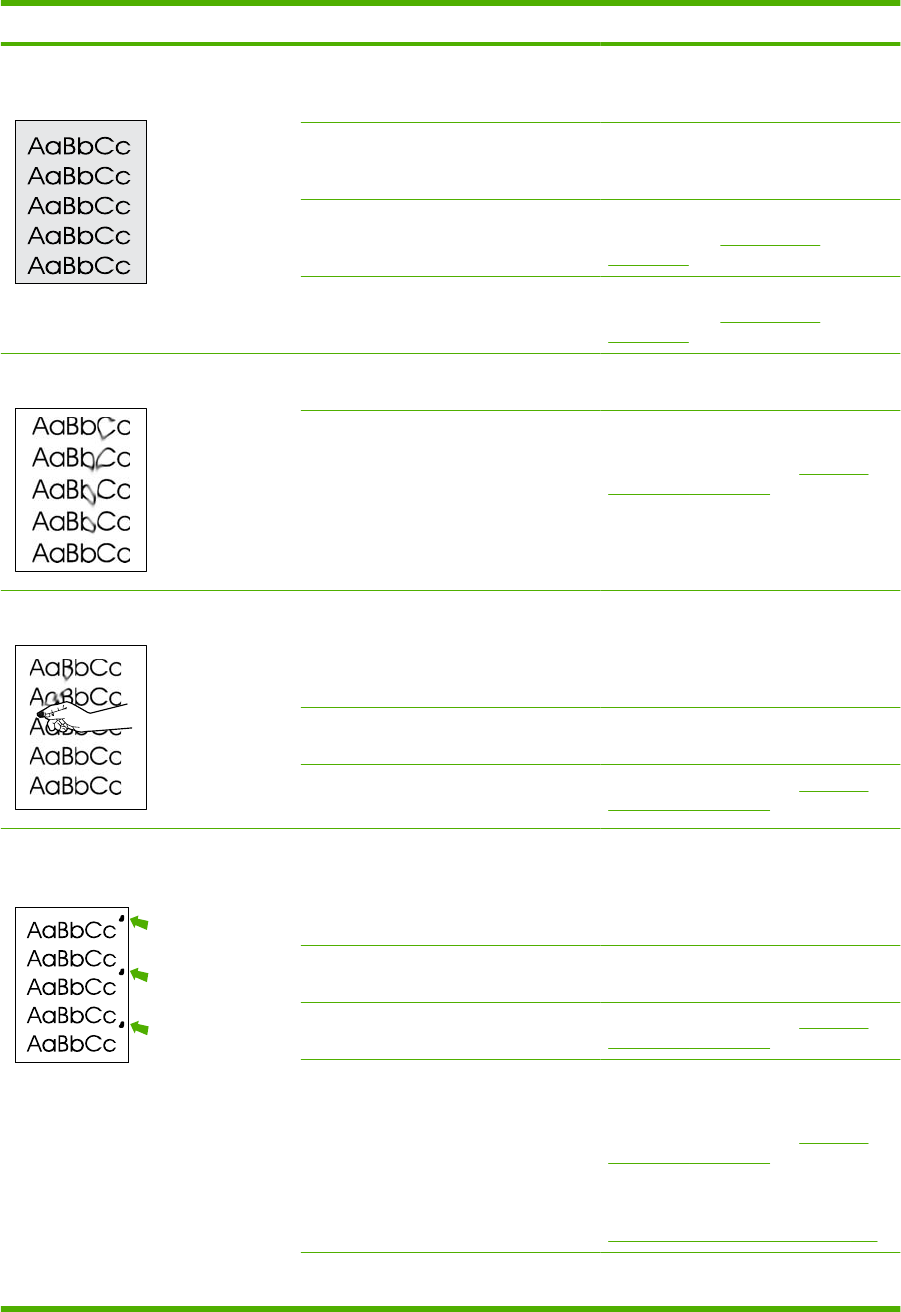
Problem Cause Solution
The amount of background toner
shading becomes unacceptable.
Very dry (low humidity) conditions can
increase the amount of background
shading.
Check the product environment.
The extended print mode setting is
incorrect.
Try the print job again using the
Transfer extended print mode, Dry
paper setting. See the user guide.
One or more print cartridges might be
defective.
Replace any empty or used (refilled) print
cartridges. See Print cartridge
on page 67.
The product is set to override the
Replace <Color> Cartridge message
and to continue printing.
Replace any empty or used (refilled) print
cartridges. See Print cartridge
on page 67.
Toner smears appear on the media. The media might not meet
HP specifications.
Use media that meets HP specifications.
If toner smears appear on the leading
edge of the paper, the media guides are
dirty, or debris has accumulated in the
print path.
Clean the media guides.
Clean the paper path. See Clean the
paper path on page 73.
The toner smears easily when touched. The product is not set to print on the type
of media on which you want to print.
In the printer driver, select the Paper tab
and set Type is to match the type of
media on which you are printing. Print
speed might be slower if you are using
heavy paper.
The media might not meet
HP specifications.
Use media that meets HP specifications.
The paper path might need cleaning. Clean the paper path. See Clean the
paper path on page 73.
Marks repeatedly appear at even
intervals on the printed side of the page.
The product is not set to print on the type
of media on which you want to print.
In the printer driver, select the Paper tab
and set Type is to match the type of
paper on which you are printing. Print
speed might be slower if you are using
heavy paper.
Internal parts might have toner on them. The problem typically corrects itself after
a few more pages.
The paper path might need cleaning. Clean the paper path. See Clean the
paper path on page 73.
The fuser might be damaged or dirty. To determine if the fuser has a problem,
print the diagnostics page.
Clean the paper path. See Clean the
paper path on page 73.
Use the image defect ruler to determine
where the defect is occurring. See
Repetitive image defects on page 252.
A print cartridge may have a problem. To determine which cartridge has a
problem, print the diagnostics page.
296 Chapter 7 Problem solve ENWW
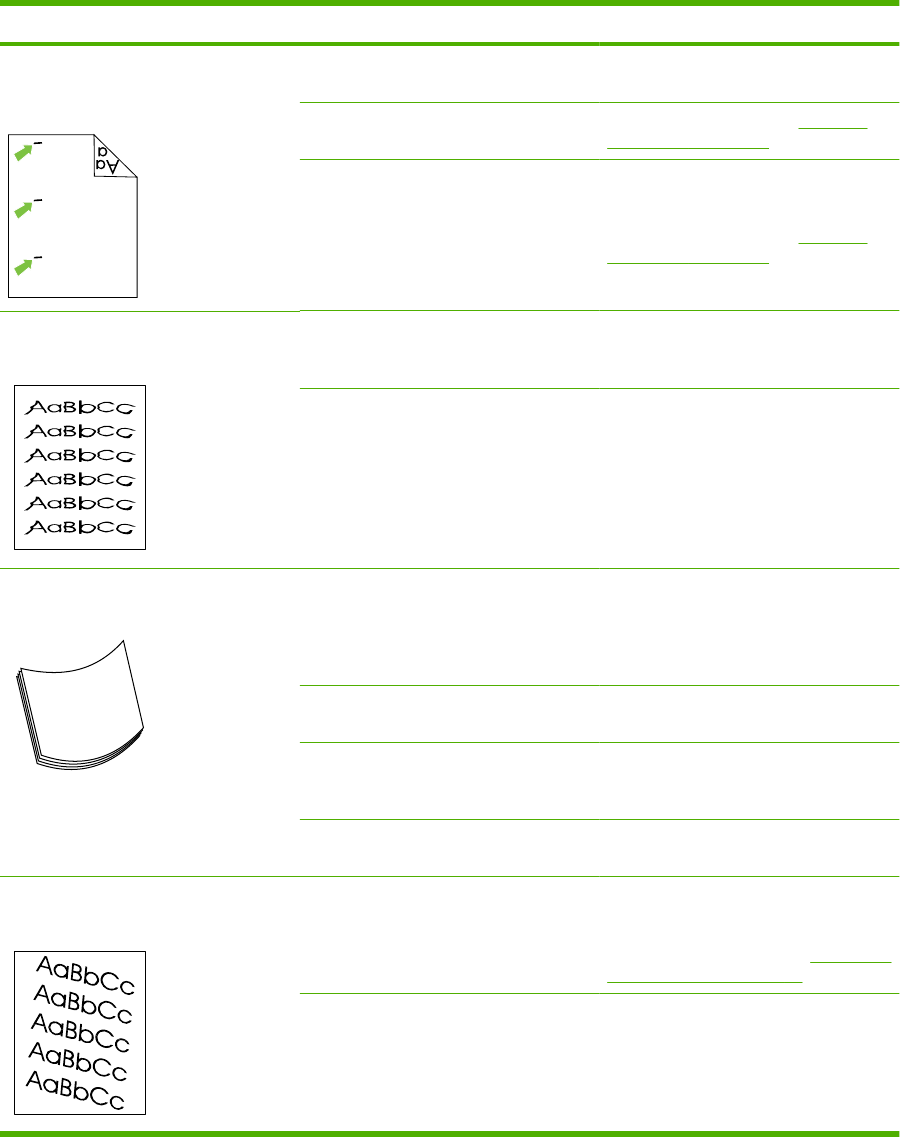
Problem Cause Solution
Marks repeatedly appear at even
intervals on the unprinted side of the
page.
Internal parts might have toner on them. The problem typically corrects itself after
a few more pages.
The paper path might need cleaning. Clean the paper path. See Clean the
paper path on page 73.
The fuser might be damaged or dirty. To determine if the fuser has a problem,
print the diagnostics page.
Clean the paper path. See Clean the
paper path on page 73.
The printed page contains misformed
characters.
The media might not meet
HP specifications.
Use a different paper, such as high-
quality paper that is intended for color
laser printers.
If characters are incorrectly formed so
that they produce a wavy effect, the laser
scanner might need service.
Verify that the problem also occurs on
the configuration page. If so, replace the
product.
The printed page is curled or wavy. The product is not set to print on the type
of media on which you want to print.
In the printer driver, select the Paper tab
and set Type is to match the type of
paper on which you are printing. Print
speed might be slower if you are using
heavy paper.
The Service menu item Less paper
curl is set to Off.
Change the setting to On.
The media might not meet
HP specifications.
Use a different paper, such as high-
quality paper that is intended for color
laser printers.
Both high temperature and humidity can
cause paper curl.
Check the product environment.
Text or graphics are skewed on the
printed page.
The media might be loaded incorrectly. Make sure that the paper or other print
media is loaded correctly and that the
media guides are not too tight or too
loose against the stack. See Load paper
and print media on page 43.
The media might not meet
HP specifications.
Use a different paper, such as high-
quality paper that is intended for color
laser printers.
ENWW Solve image quality problems 297
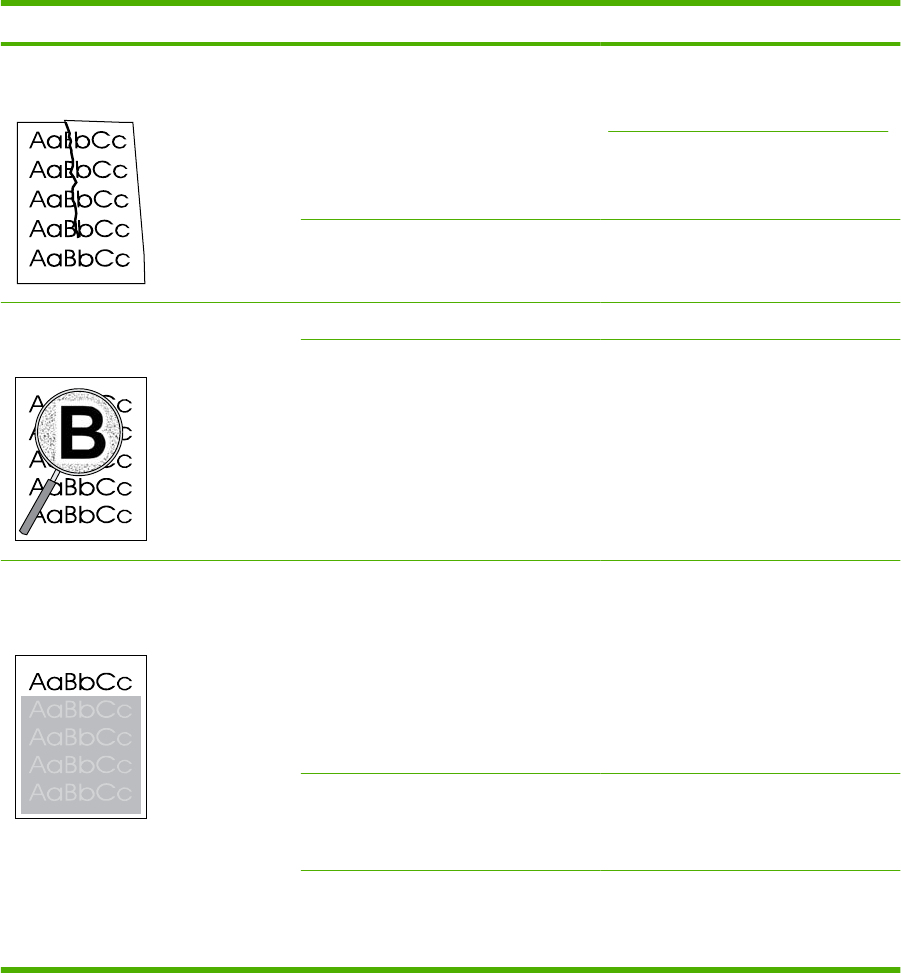
Problem Cause Solution
The printed page contains wrinkles or
creases.
The media might be loaded incorrectly. Verify that the media is loaded correctly
and that the media guides are not too
tight or too loose against the stack. See
Load paper and print media on page 43.
Turn over the stack of paper in the input
tray, or try rotating the paper 180° in the
input tray.
The media might not meet
HP specifications.
Use a different paper, such as high-
quality paper that is intended for color
laser printers.
Toner appears around the printed
characters.
The media might be loaded incorrectly. Turn over the stack of paper in the tray.
If large amounts of toner have scattered
around the characters, the paper might
have high resistivity.
Use a different paper, such as high-
quality paper that is intended for color
laser printers.
An image that appears at the top of the
page (in solid black) repeats farther
down the page (in a gray field).
Software settings might affect image
printing.
In your software program, change the
tone (darkness) of the field in which the
repeated image appears.
In your software program, rotate the
whole page 180° to print the lighter
image first.
In the printer driver, verify that the correct
media type is selected.
The order of images printed might affect
printing.
Change the order in which the images
are printed. For example, have the lighter
image at the top of the page, and the
darker image farther down the page.
A power surge might have affected the
product.
If the defect occurs later in a print job,
turn the product off for 10 minutes, and
then turn on the product to restart the
print job.
298 Chapter 7 Problem solve ENWW
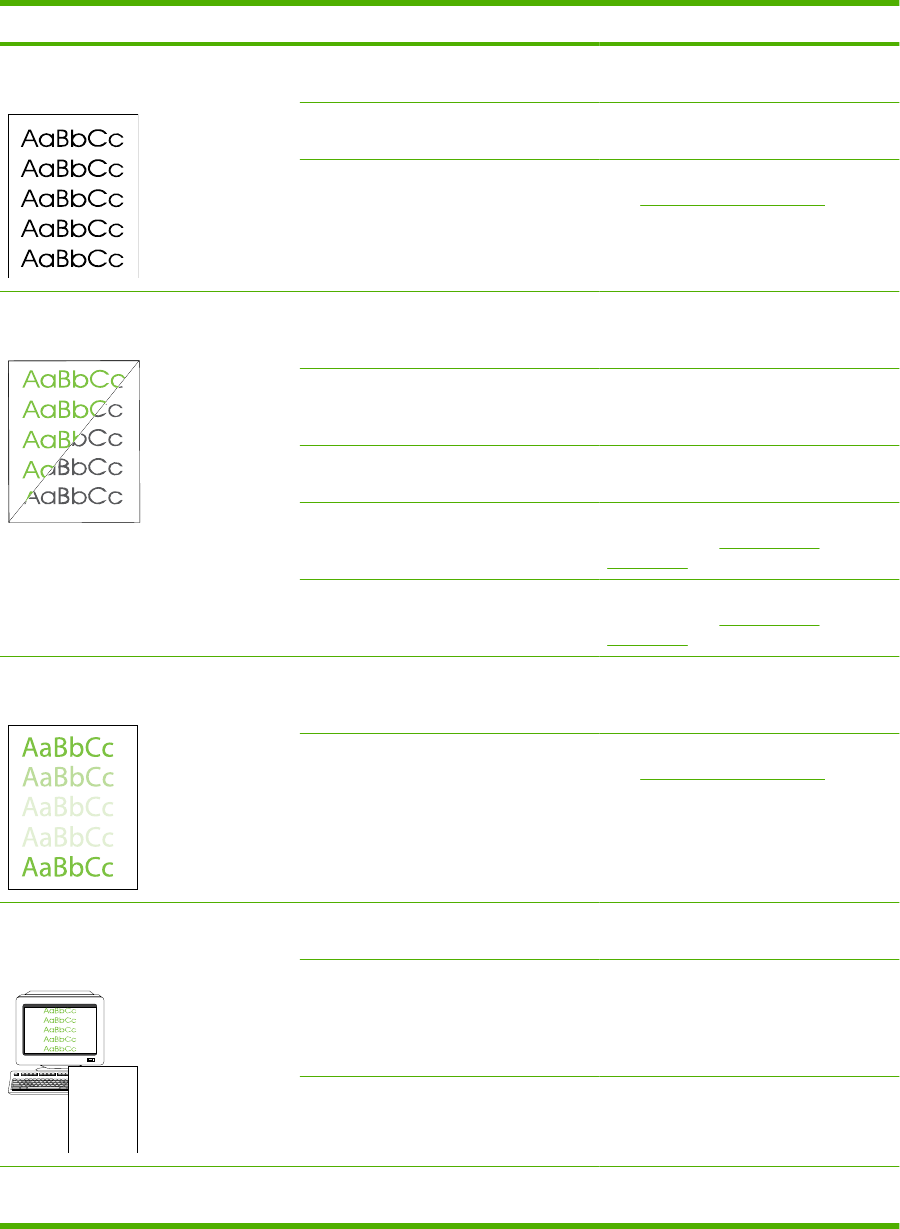
Solve issues with color documents
This section describes issues that can occur with color print jobs.
Problem Cause Solution
Only black is printing when the document
should be printing in color.
Color mode is not selected in your
program or printer driver.
Select color mode instead of grayscale
mode.
The correct printer driver might not be
selected in the program.
Select the correct printer driver.
One of the color print cartridges might be
empty. If the product is configured to
continue printing after a color cartridge
has reached the end of its capacity, it will
print in black and white.
Replace any empty color print cartridges.
See Print cartridge on page 67.
One or more colors are not printing, or
are inaccurate.
Sealing tape might be on the print
cartridges.
Verify that the sealing tape has been
completely removed from the print
cartridges.
The media might not meet HP
specifications.
Use a different paper, such as high-
quality paper that is intended for color
laser printers.
The product might be operating in
excessively humid conditions.
Verify that the product environment is
within humidity specifications.
One or more print cartridges might be
defective.
Replace any empty or used (refilled) print
cartridges. See Print cartridge
on page 67.
The product is set to override the
Replace <Color> Cartridge message
and to continue printing.
Replace any empty or used (refilled) print
cartridges. See Print cartridge
on page 67.
A color is printing inconsistently after you
load a new print cartridge.
Another print cartridge might be
defective.
Remove the print cartridge for the color
that is printing inconsistently and reinstall
it.
The product is set to override the
Replace <Color> Cartridge message
and to continue printing.
Replace any empty color print cartridges.
See Print cartridge on page 67.
The colors on the printed page do not
match the colors as they appear on the
screen.
AaBbCc
AaBbCc
AaBbCc
AaBbCc
AaBbCc
The colors on a computer monitor might
differ from the product output.
See the user guide.
If extremely light colors or extremely dark
colors on screen are not printing, the
software program might interpret
extremely light colors as white or
extremely dark colors as black.
If possible, avoid using extremely light or
extremely dark colors.
The media might not meet HP
specifications.
Use a different paper, such as high-
quality paper that is intended for color
laser printers.
The finish on the printed color page is
inconsistent.
The media might be too rough. Use a smooth paper or print media, such
as a high-quality paper that is made for
ENWW Solve image quality problems 299
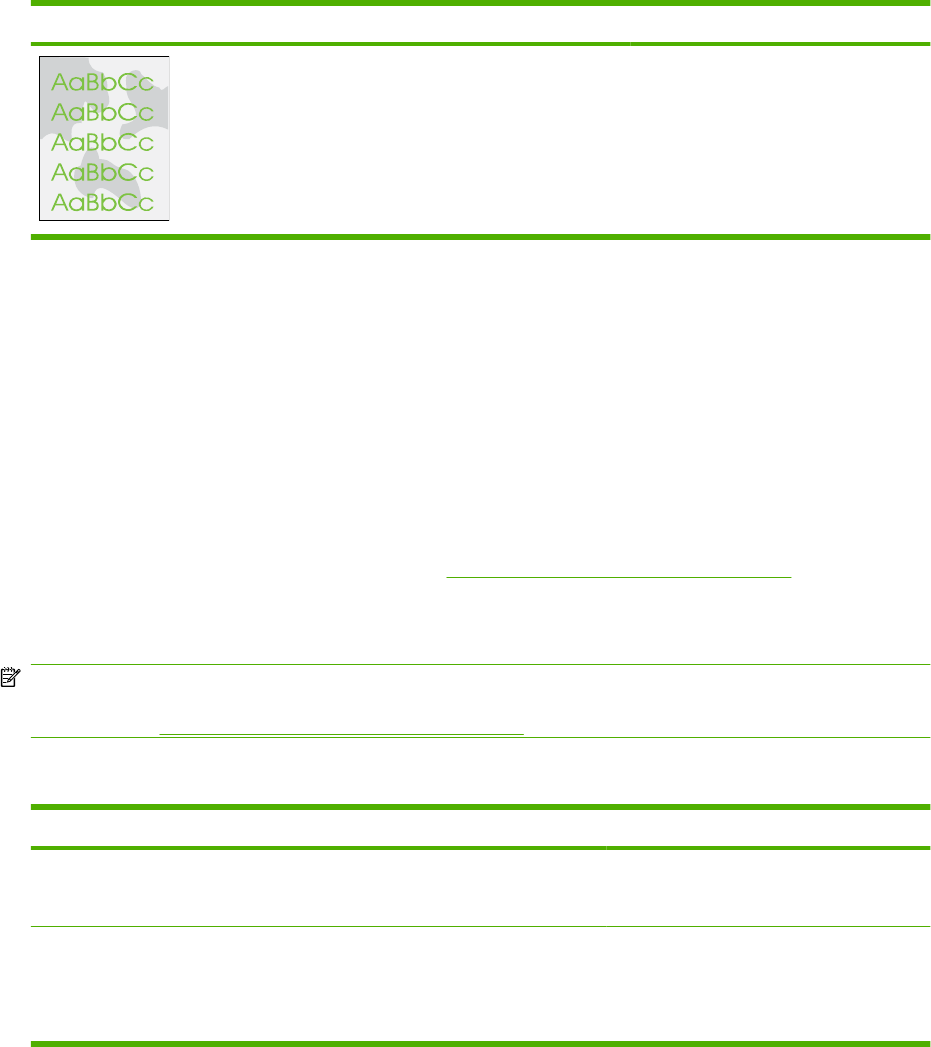
Problem Cause Solution
color laser printers. Generally, smoother
media produces better the results.
Copy problems
Prevent copy problems
The following are a few simple steps you can take to improve copy quality:
●Copy from the flatbed scanner. This will produce a higher quality copy than copying from the
automatic document feeder (ADF).
●Use quality originals.
●Load the media correctly. If the media is loaded incorrectly, it might skew, causing unclear images
and problems with the OCR program. See Load paper and print media on page 43 for instructions.
●Adjust the control panel settings for the type of original if the automatic settings do not produce the
desired result.
NOTE: Verify that the media meets HP specifications. If the media meets HP specifications, recurring
feed problems indicate a pickup roller, a separation roller, or a separtion pad is worn and needs to be
replaced. See Paper-feed rollers and pads on page 127.
Image problems
Problem Cause Solution
Copy edges are cropped when
copying from the glass.
The original is edge-to-edge or has smaller
margins than those supported by this
product.
Position the original 6.35 mm (1/4 inch)
away from the registration corner on the
glass.
Copy edges are cropped when
copying from the ADF.
The original is too long, edge-to-edge, or has
smaller margins than those supported by
this product.
On the control panel, press Copy setup. Use
the arrow buttons to select Reduce/
Enlarge and press OK. Use the arrow
buttons to select Full Page=91% and press
OK. Try copying again.
300 Chapter 7 Problem solve ENWW
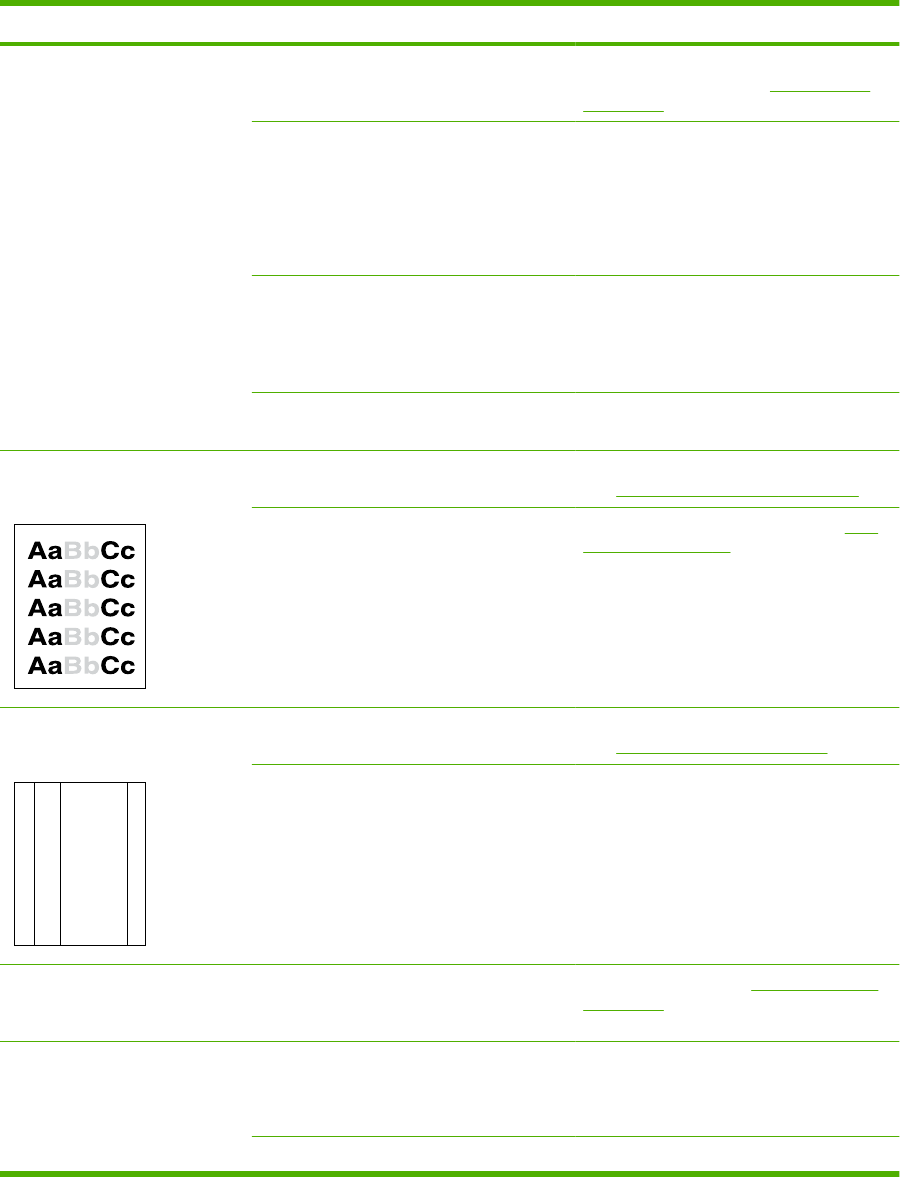
Problem Cause Solution
Images are missing or faded. The print-cartridge might be low. Replace any low print cartridge and then
calibrate the product. See Print cartridge
on page 67.
The original might be of poor quality. If your original is too light or damaged, the
copy might not be able to compensate, even
if you adjust the contrast. If possible, find an
original document in better condition.
Use the control-panel to change the contrast
setting.
The original might have a colored
background.
Colored backgrounds might cause images in
the foreground to blend into the background,
or the background might appear in a
different shade. If possible, use an original
document without a colored background.
The original is larger than the scannable
area
Use supported media sizes.
Vertical white or faded stripes
appear on the copy.
The media might not meet
HP specifications.
Use media that meets HP specifications.
See Paper and print media on page 37.
One or more of the print cartridges may be
low.
Replace any low print cartridge. See Print
cartridge on page 67.
If the error persists, contact HP support.
Unwanted lines appear on copy
jobs only.
A
A
A
A
A
B
B
B
B
B
C
C
C
C
C
a
a
a
a
a
c
c
c
c
c
b
b
b
b
b
The flatbed scanner or the ADF glass might
be dirty.
Clean the flatbed scanner or the ADF glass.
See Clean the product on page 73.
An image exists on the back of the original,
or defects exist on the scanner cover.
On the flatbed scanner, place three sheets
of clean paper on top of the original, close
the flatbed scanner cover, then re-scan the
original.
Black dots or streaks appear on
copy jobs only.
Ink, glue, correction fluid, or an unwanted
substance might be on the automatic
document feeder (ADF) or flatbed scanner.
Clean the product. See Clean the product
on page 73.
Copies are too light or dark. The printer driver or product software
settings may be incorrect.
Verify that the quality settings are correct.
See the product software Help for more
information about changing the settings.
The product may not be calibrated. Calibrate the product.
ENWW Solve image quality problems 301
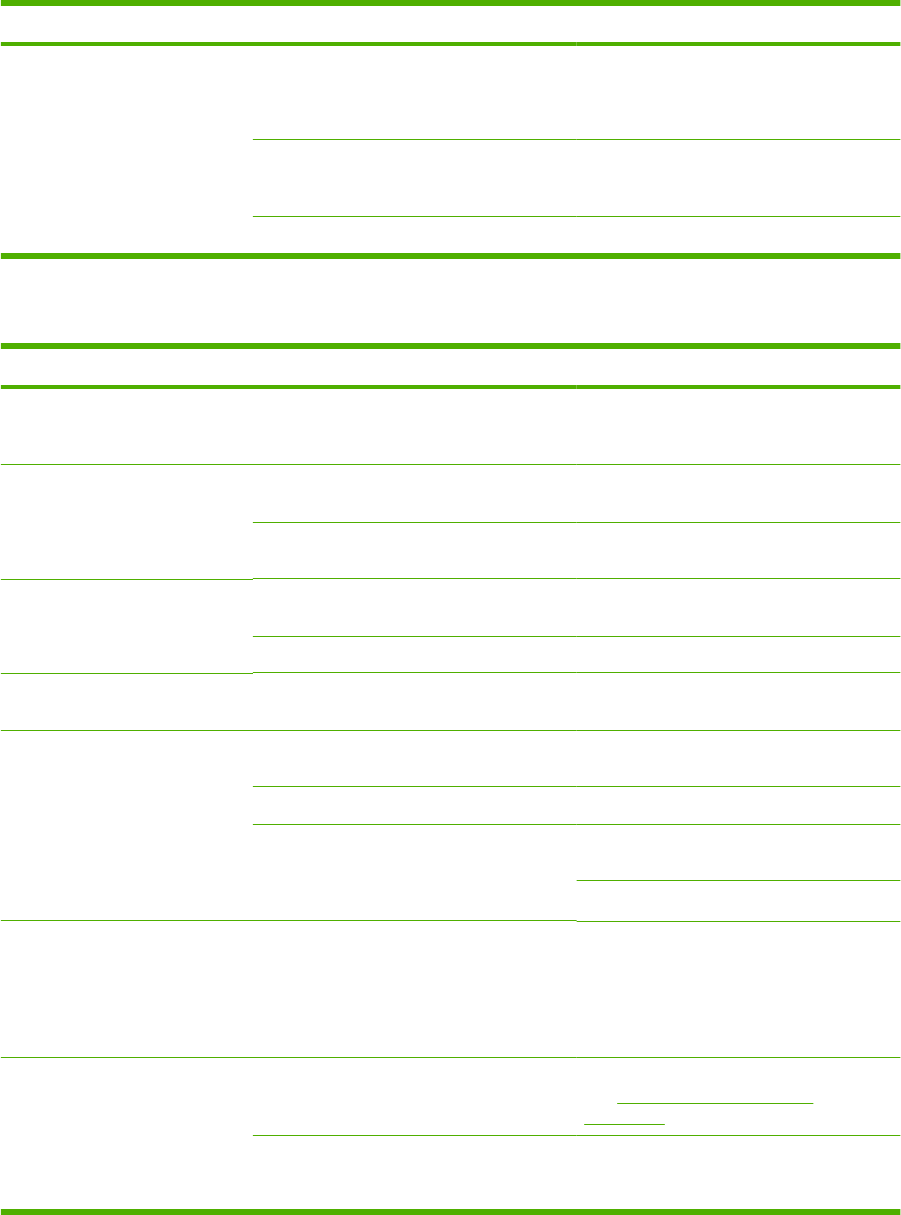
Problem Cause Solution
Text is unclear. The printer driver or product software
settings may be incorrect.
Verify that the quality settings are correct.
See the product software Help for more
information about changing the settings.
The original is of poor quality. Try copying another document. If the copy is
free of defects, obtain a better-quality
original.
The product may not be calibrated. Calibrate the product.
Media-handling problems
Problem Cause Solution
Poor print quality or toner
adhesion
The paper is too moist, too rough, too heavy
or too smooth, or it is embossed or from a
faulty paper lot.
Try another kind of paper, between 100 and
250 Sheffield, 4 to 6% moisture content.
Dropouts, jamming, or curl The paper has been stored incorrectly. Store paper flat in its moisture-proof
wrapping.
The paper has variability from one side to the
other.
Turn the paper over.
Excessive curl The paper is too moist, has the wrong grain
direction, or is of short-grain construction
Use long-grain paper.
The paper varies from side-to-side. Turn the paper over.
Jamming, damage to paper The paper has cutouts or perforations. Use paper that is free of cutouts or
perforations.
Problems with feeding The paper has ragged edges. Use high-quality paper that is made for laser
printers.
The paper varies from side-to-side. Turn the paper over.
The paper is too moist, too rough, too heavy
or too smooth, has the wrong grain direction,
or is of short-grain construction or it is
embossed or from a faulty paper lot.
Try another kind of paper, between 100 and
250 Sheffield, 4 to 6% moisture content.
Use long-grain paper.
Print is skewed (crooked). The media guides might be incorrectly
adjusted.
Remove all media from the input tray,
straighten the stack, and then load the
media in the input tray again. Adjust the
media guides to the width and length of the
media that you are using and try printing
again.
More than one sheet feeds at one
time.
The media tray might be overloaded. Remove some of the media from the tray.
See Load paper and print media
on page 43.
The media might be wrinkled, folded, or
damaged.
Verify that the media is not wrinkled, folded,
or damaged. Try printing on media from a
new or different package.
302 Chapter 7 Problem solve ENWW
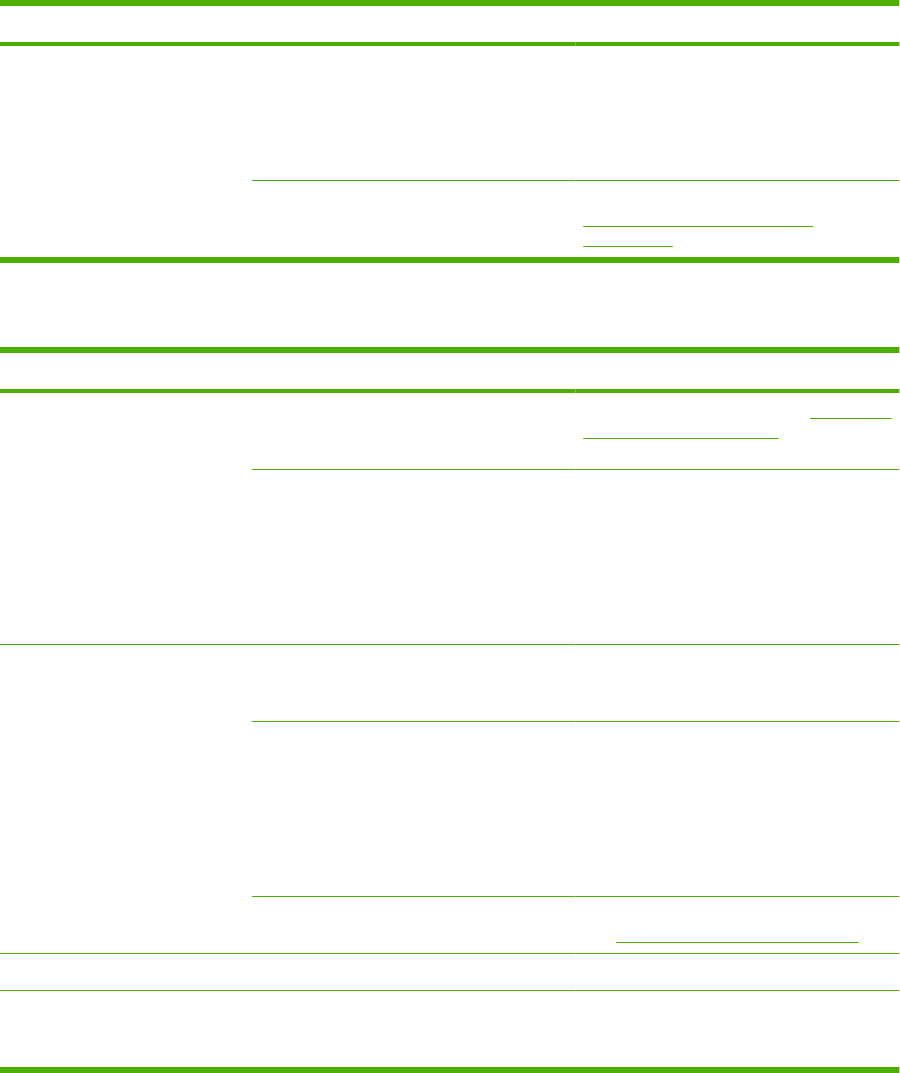
Problem Cause Solution
The product does not pull media
from the media input tray.
The product might be in manual feed mode. ●If Manual appears on the product
control-panel display, pressOK to print
the job.
●Verify that the product is not in manual
feed mode and print your job again.
The pickup roller might be dirty or damaged. Replace the pickup roller assembly. See
Pickup roller (Tray 2 and Tray 3)
on page 128.
Performance problems
Problem Cause Solution
No copy came out. The input tray might be empty. Load media in the product. See Load paper
and print media on page 43 for more
information.
The original might have been loaded
incorrectly.
In the automatic document feeder (ADF),
load the original with the narrow side forward
and the side to be scanned facing up.
Place the original document face-down on
the flatbed scanner with the upper-left
corner of the document at the corner
indicated by the icon on the scanner.
Copies are blank. The sealing tape might not have been
removed from the print cartridge.
Remove the print cartridge from the product,
pull out the sealing tape, and reinstall the
print cartridge.
The original might have been loaded
incorrectly.
In the ADF, load the original with the narrow
side leading into the ADF and the side to be
scanned facing up.
On the flatbed scanner, make sure that the
original document is placed face-down with
the upper-left corner of the document at the
lower-right corner of the glass.
The media might not meet
HP specifications.
Use media that meets HP specifications.
See Paper and print media on page 37.
The wrong original was copied. The ADF might be loaded. Make sure that the ADF is empty.
Copies are reduced in size. The product settings might be set to reduce
the scanned image.
On the control panel, select Reduce/
Enlarge from the Copy Menu and verify that
it is set to Original=100%.
ENWW Solve image quality problems 303
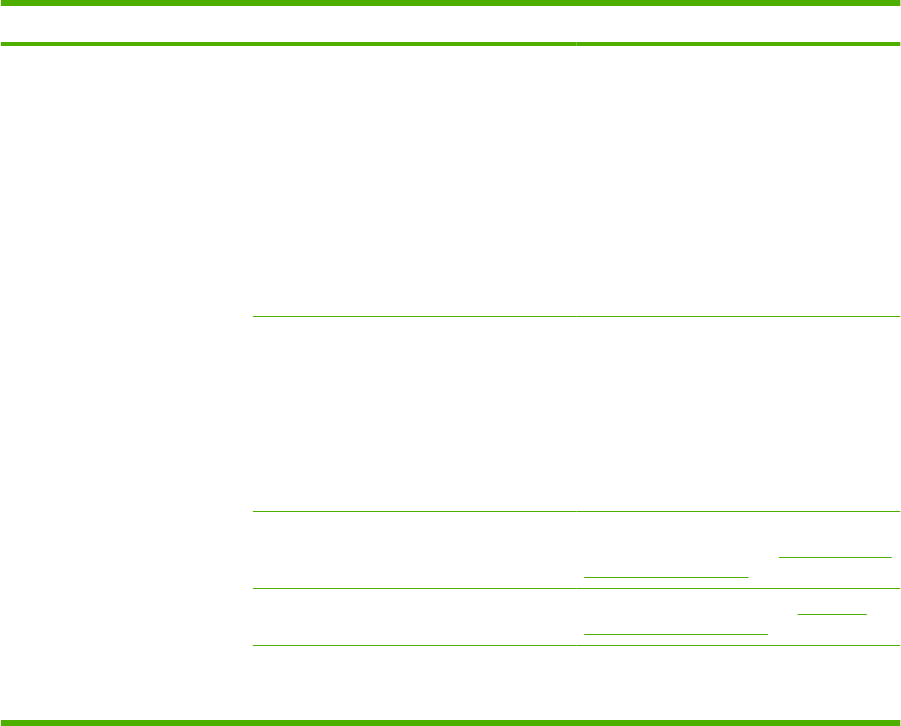
Scan problems
Solve scanned-image problems
Problem Cause Solution
The scanned image is of poor
quality.
The original might be a second-generation
photo or picture.
●To eliminate the patterns, try reducing
the size of the image after scanning.
●Print the scanned image to see if the
quality is better.
●Verify that the resolution settings are
correct for the type of scan job that you
are performing. See the user guide.
●For best results, use the flatbed
scanner for scanning rather than the
automatic document feeder (ADF).
The image that appears on the screen might
not be an accurate representation of the
quality of the scan.
●Try adjusting your computer monitor
settings to use more colors (or levels of
gray). Typically, you make this
adjustment by opening Display in
Windows Control Panel.
●Try adjusting the resolution settings in
the scanner software. See the user
guide.
The original might have been loaded
incorrectly.
Use the media guides when you load the
originals into the ADF. See Load paper and
print media on page 43.
The scanner glass might be dirty. Clean the scanner glass. See Clean the
scanner glass on page 77.
The graphics settings might not be suitable
for the type of scan job that you are
performing.
Try changing the graphics settings. See the
user guide.
304 Chapter 7 Problem solve ENWW
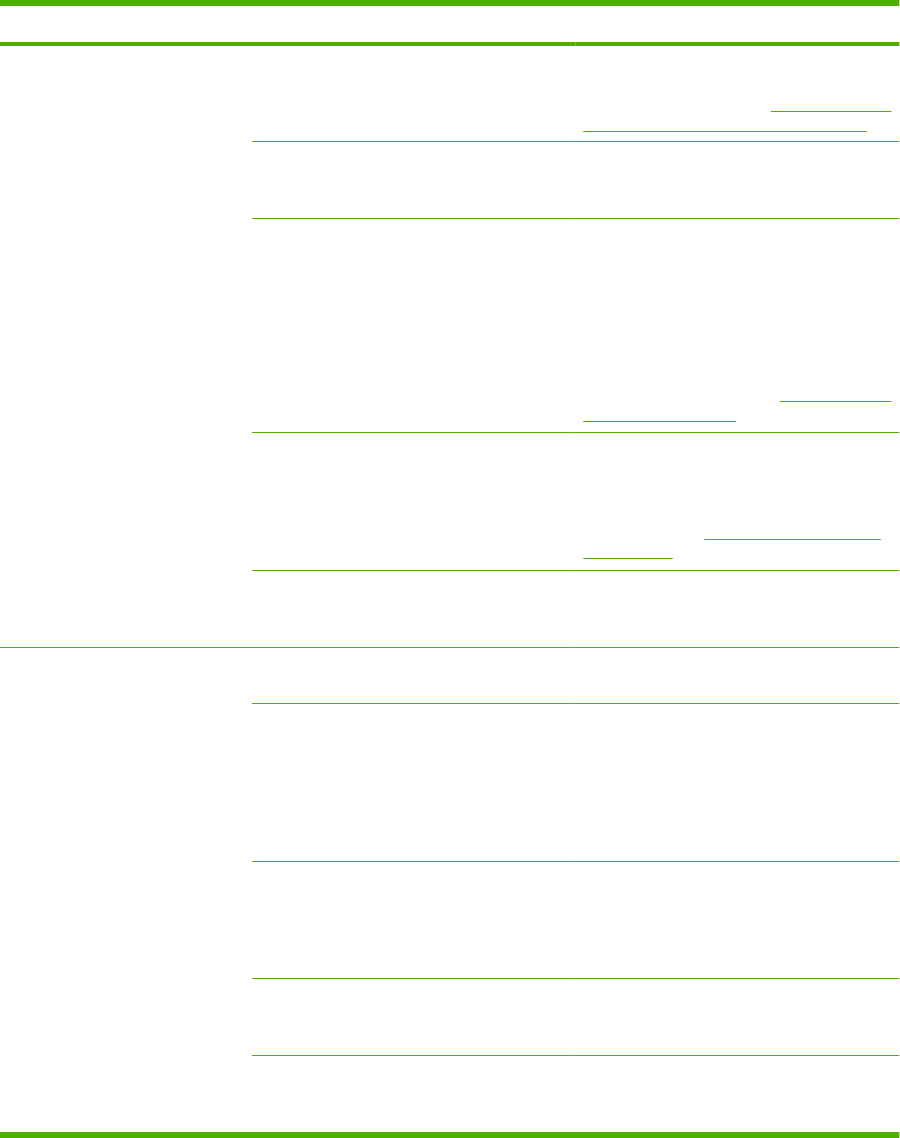
Problem Cause Solution
Part of the image did not scan. The original might have been loaded
incorrectly.
Load the original on the flatbed glass or use
the media guides when you load the
originals into the ADF. See Load originals for
copying, scanning, or faxing on page 45.
A colored background might be causing
images in the foreground to blend into the
background.
Try adjusting the settings before you scan
the original or enhancing the image after you
scan the original.
The original is longer than 381 mm (15
inches).
The maximum scannable length is 381 mm
(15 inches) when you use the automatic
document feeder (ADF) input tray. If the
page exceeds the maximum length, the
scanner stops. (Copies can be longer.)
CAUTION: Do not try to pull the original
from the ADF; you might damage the
scanner or the original. See Clear jams from
the ADF on page 291.
The original is too small. The minimum size that the flatbed scanner
supports is 25 x 25 mm (1 x 1 inch). The
minimum size that the ADF supports is 127
x 127 mm (5 x 5 inches). The original might
be jammed. See Clear jams from the ADF
on page 291.
The media size is incorrect. In Scan settings, make sure that the input
media size is large enough for the document
that you are scanning. .
The scan takes too long The resolution is set too high. Change the resolution settings to the correct
settings for your job. See the user guide.
The software is set to scan in color. The system default is color, which takes
longer to scan even when scanning a
monochrome original. If you acquire an
image through TWAIN or WIA, you can
change the settings so that the original
scans in grayscale or black-and-white. See
the product software Help for information.
A print job or copy job was sent before you
tried to scan.
If someone sent a print job or copy job before
you tried to scan, the scan will start if the
scanner is not busy. However, because the
product and scanner share memory, the
scan might be slower.
The scanning computer may not have
enough available resources.
Close unused applications on the computer.
If the scan is still too slow, try rebooting the
scanning computer.
Antivirus, antispyware, or firewall software
on the scanning computer may slow
scanning.
Consult your antivirus, antispyware, or
firewall software documentation.
ENWW Solve image quality problems 305

Scan-quality problems
Prevent scan-quality problems
The following are a few simple steps you can take to improve copy and scan quality.
●Use the flatbed scanner, rather than the automatic document feeder (ADF) input tray, to scan.
●Use high-quality originals.
●Load the media correctly. If the media is loaded incorrectly, it might skew, which causes unclear
images. See Load paper and print media on page 43 for instructions.
●Adjust the software program settings according to how you plan to use the scanned page. See the
software program help for more information.
●If the product frequently feeds more than one page at a time, the separation roller might need to
be replaced. See Paper-feed rollers and pads on page 127.
Solve scan-quality problems
Problem Cause Solution
Blank pages The original might have been loaded upside
down.
In the automatic document feeder (ADF), put
the top end of the stack of originals into the
ADF input tray, with the media stack face-up
and the first page to be scanned on top of
the stack.
Place the original document face-down on
the flatbed scanner with the upper-left
corner of the document at the corner
indicated by the icon on the scanner.
Too light or dark The resolution and color levels may be set
incorrectly.
Verify that you have the correct resolution
and color settings. See the user guide.
Unwanted lines The ADF scanner window might be dirty. Clean the ADF scanner window. See Clean
the scanner glass on page 77 (step 3).
Black dots or streaks Ink, glue, correction fluid, or an unwanted
substance might be on the glass.
Clean the flatbed scanner surface. See
Clean the scanner glass on page 77.
The power to the product might have
fluctuated.
Rescan the job.
Unclear text The resolution levels might be set
incorrectly.
Verify that the correct resolution settings are
correct. See the user guide.
The media is not laying flat on the glass. Close the scanner lid tightly.
NOTE: On base models, the depth of scan
might not allow a good scan of originals that
will not sit flat, such as a hardcover book.
306 Chapter 7 Problem solve ENWW
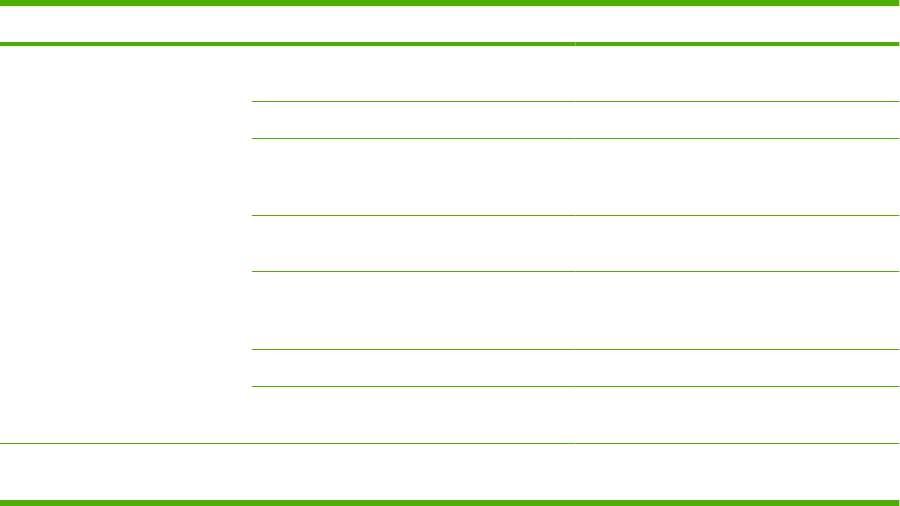
Problem Cause Solution
Communication errors on the
computer
One or more of the product cables is loose. Check the product cables and make sure
they are plugged in securely.
The product is not on. Turn the product on.
If the product is connected through a
network, the IP address might have
changed.
Verify that the product IP address is correct.
Antivirus, antispyware, or firewall software
may be interfering with communication.
Consult the antivirus, antispyware, or
firewall software documentation.
The product is in an error state. Check the product control panel and clear
any errors by following the onscreen
instructions.
The product is busy with another task. Wait for the product to finish.
The wrong scanner driver is selected for the
product.
Verify that the scanner driver is correct.
The scan job does not complete. The resolution may be too high for the
available memory on the computer.
Try scanning at a lower resolution.
ENWW Solve image quality problems 307
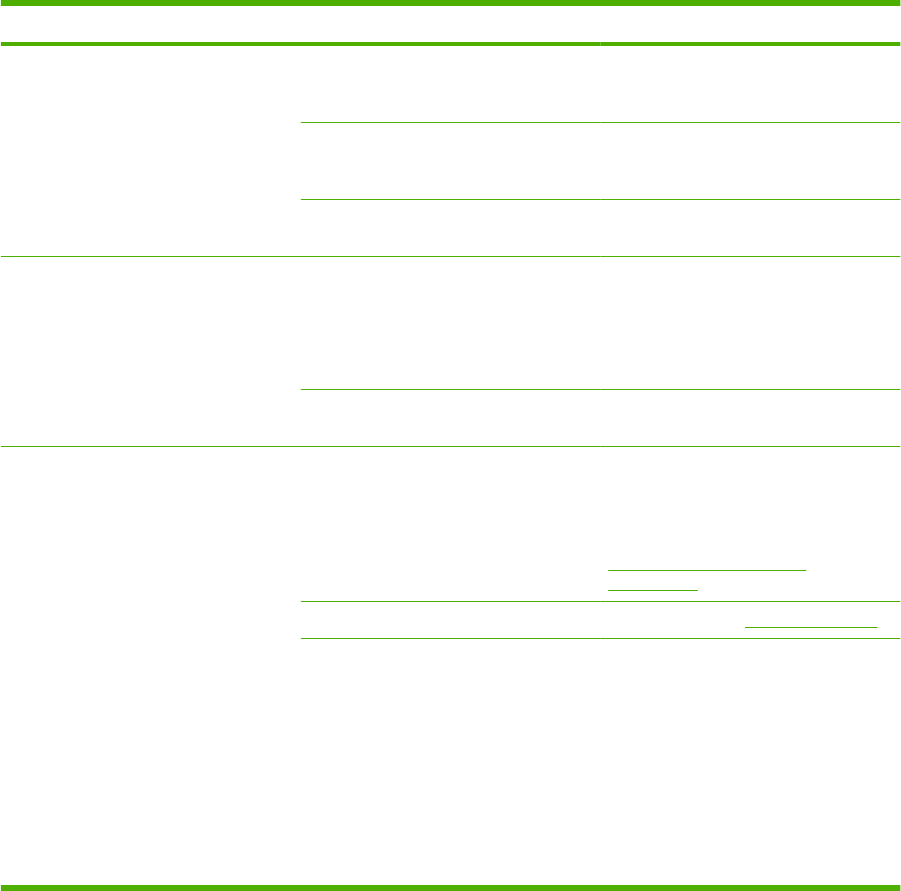
Solve performance problems
Problem Cause Solution
Pages print but are totally blank. The sealing tape might still be in the print
cartridges.
Verify that the sealing tape has been
completely removed from the print
cartridges.
The document might contain blank
pages.
Check the document that you are printing
to see if content appears on all of the
pages.
The product might be malfunctioning. To check the product, print a
configuration page.
Pages print very slowly. Heavier media types can slow the print
job.
Print on a different type of media.
If the error persists, update the firmware.
If the error persists, perform an NVRAM
initialization.
Complex pages can print slowly. Proper fusing may require a slower print
speed to ensure the best print quality.
Pages did not print. The product might not be pulling media
correctly.
Make sure paper is loaded in the tray
correctly.
If the problem persists, replace the
pickup and separation rollers. See
Paper-feed rollers and pads
on page 127.
The media is jamming in the device. Clear the jam. See Jams on page 281.
If the error persists, try the following solutions:
●Verify that the product will print through the USB or network connection.
●Print a configuration page in order to verify that the product will print internal
pages.
●Perform an NVRAM initialization.
●Update the firmware.
●Replace the formatter.
308 Chapter 7 Problem solve ENWW
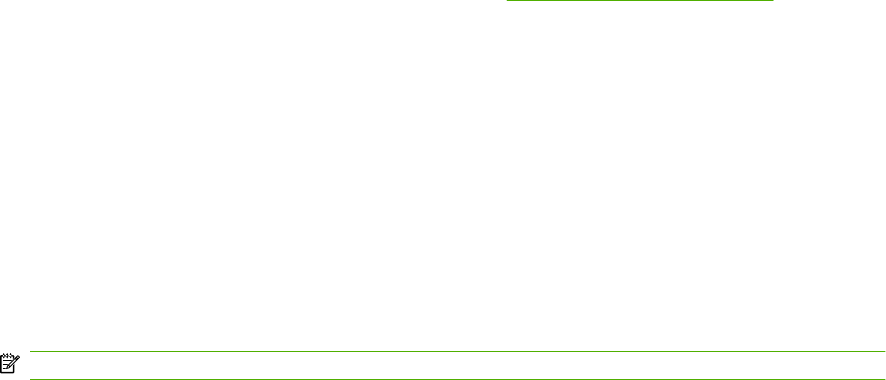
Solve connectivity problems
Solve direct-connection problems
If the product is experiencing connection issues while directly connected to a computer, complete the
following steps:
1. Make sure that USB cable is no longer than 2 meters (6 feet).
2. Make sure that both ends of the USB cable are connected.
3. Make sure that the cable is a USB 2.0 Hi-Speed-certified cable.
4. If the error persists, replace the USB cable with a known good USB 2.0 Hi-Speed-certified cable.
5. At the product control panel, in the Service menu, verify that the USB speed setting is set to
Full.
6. If the error persists, update the USB drivers on the computer.
Solve network problems (network models only)
Check the following items to verify that the product is communicating with the network. Before you begin
this troubleshooting procedure, print a network report. See Information pages on page 50.
1. Are any physical connection problems evident between the workstation or file server and the
product?
Verify that the network cabling, connections, and router configurations are correct. Verify that the
network cable lengths meet network specifications.
2. Are the network cables connected correctly?
Make sure that the product is attached to the network through the appropriate port and cable. Check
each cable connection to make sure that it is secure and in the right place. If the problem continues,
try a different cable or connect to different ports on the hub or transceiver. The amber activity light
and the green link status light next to the port connection on the back of the product should be lit.
3. Can you "ping" the product? (Windows)
NOTE: Mac, Unix, and Linux users can use a terminal window to “ping” the product.
a. Click Start, click Run, type cmd, and click OK to open an MS-DOS command prompt.
b. Type ping followed by the product IP address. For example, type: ping 192.168.45.39
If the ping command is successful, a list of replies from the product appears in the window.
c. If you can ping the product, print a configuration page to verify that the IP address configuration
for the product is correct on the computer. If it is correct, uninstall the product software, and
then reinstall it.
-or-
If the ping command failed, verify that the network hubs are on, and then verify that the network
settings, the product, and the computer are all configured for the same network. Also, verify
that no firewall or spyware filters are on.
ENWW Solve connectivity problems 309
4. Have any software programs been added to the network?
Make sure new programs are compatible and that they are installed correctly and use the correct
printer drivers.
5. Can other users print?
The problem might be workstation-specific. Check the workstation network drivers, printer drivers,
and redirection.
6. If other users can print, are they using the same network operating system?
Check your system for the correct network operating system setup.
7. Is the protocol enabled on the product?
Check the network protocol status on the network report. You can also use the embedded Web
server, HP ToolboxFX, or Macintosh Configure Device to check the status of other protocols.
310 Chapter 7 Problem solve ENWW
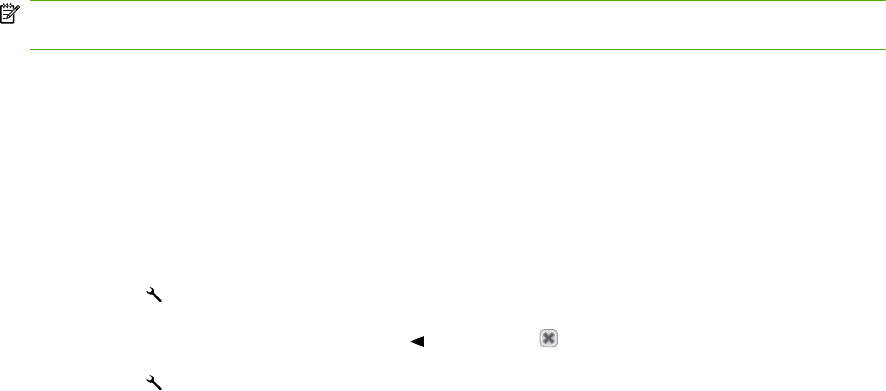
Service mode functions
Service menu
Use the control-panel Service menu to troubleshoot product problems.
Service menu settings
The Service menu is used to calibrate, restore factory default settings, and clean the print paper path.
The following Service menu items are available:
●Fax Service—used to test, diagnose, and maintain the fax functionality.
●Cleaning mode—used to remove dust and toner from the print paper path
●PowerSave Time—used to configure the amount of idle time before the engine enters sleep mode
●USB Speed—used to set the USB speed
●Less Paper Curl—used to decrease the fuser temperature, which can reduce paper curl
●Archive Print—used to decrease the likelihood of toner smearing on a print job
●Restore defaults—used to reset all customer-accessible menu settings back to the factory default
settings (except language) via the control panel or software
NOTE: This menu item does not reset factory-settable settings, including formatter number, page
counts, factory paper settings, language, and so on.
Secondary service menu
Use the secondary service menu to print service-related reports and to run special tests. Customers do
not have access to this menu.
Open the secondary service menu
1. Make sure the product is in the Ready state.
2. Press Setup to enter the main menus.
3. Simultaneously press the left arrow button and Cancel .
4. Press Setup to return to the main menus.
5. Use the arrow buttons to highlight 2ndry Service, and then press OK.
6. Use the arrow keys to navigate through the menu.
ENWW Service mode functions 311
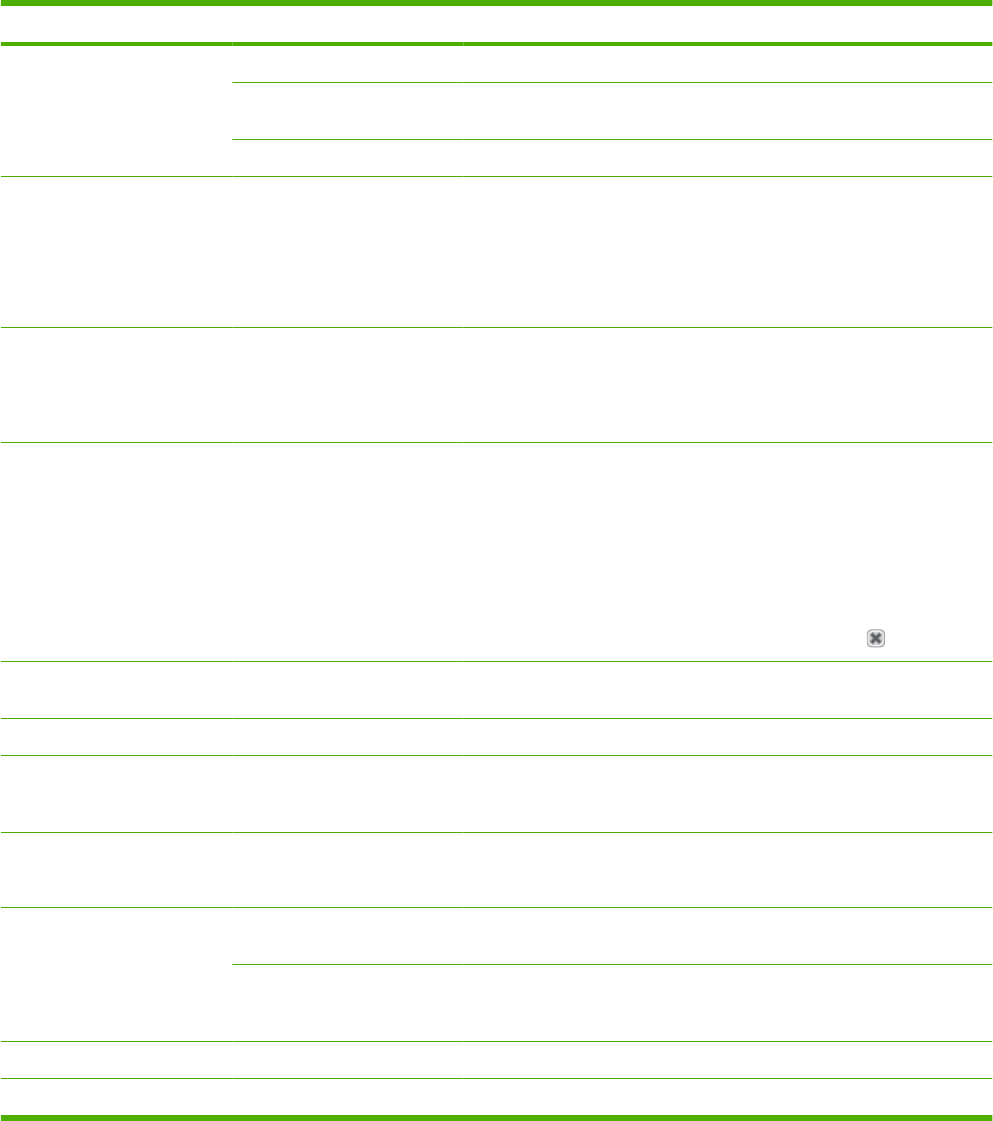
Secondary service menu structure
Table 7-15 Secondary service menu
Menu item Sub-menu item Description
Service Reports Cont. Self-Test This item prints a continuous configuration page.
Extended Keymap (fax/
memory-card models only)
This item prints an extended key map for the alphanumeric keypad on the
control panel.
Error report This item prints an error report.
Scan Calibration Calibrate
Corrected
Tables
Test
This item calibrates the product.
Location A list of available locations
appears
This item sets certain product parameters that are dependent on the
location, such as the default paper size and the symbol set.
Scroll to the appropriate location and select Yes to set the location. The
product automatically restarts after you change the location.
Display test This test verifies that the LEDs and characters on the control-panel display
function correctly.
At the beginning of the test, each of the LEDs is turned on one-at-time.
Press OK to continue to the next LED.
After the LED test is complete, the character test begins by testing the
pixels on each line. Then, each of the 255 characters is displayed in
groups of 16. Press OK to continue to the next group of 16 characters.
You can cancel the test at any time by pressing Cancel .
Button test This test verifies that the control-panel buttons function correctly. The
display prompts you to press each button.
Show FW Version This item shows the current date code of the firmware.
Ethernet reset (network
models only)
This item resets the ethernet driver. This should be used when the network
is not accessible. This is a low-level, internal reset and does not affect
network settings.
Memory Cards (fax/memory-
card models only)
Enable
Disable
This item enables or disables the product memory-card functions.
Color Cal. Adjust color This item adjusts density settings for contrast, highlights, midtones, and
shadows. Adjust each color individually.
Timing This item specifies how frequently the product should automatically
perform a color calibration. The default setting is 48 hours. You can turn
automatic calibration off.
Clean Belt This item runs additional belt-cleaning cycles.
Pick roller This item puts the pickup roller in position for replacement.
312 Chapter 7 Problem solve ENWW
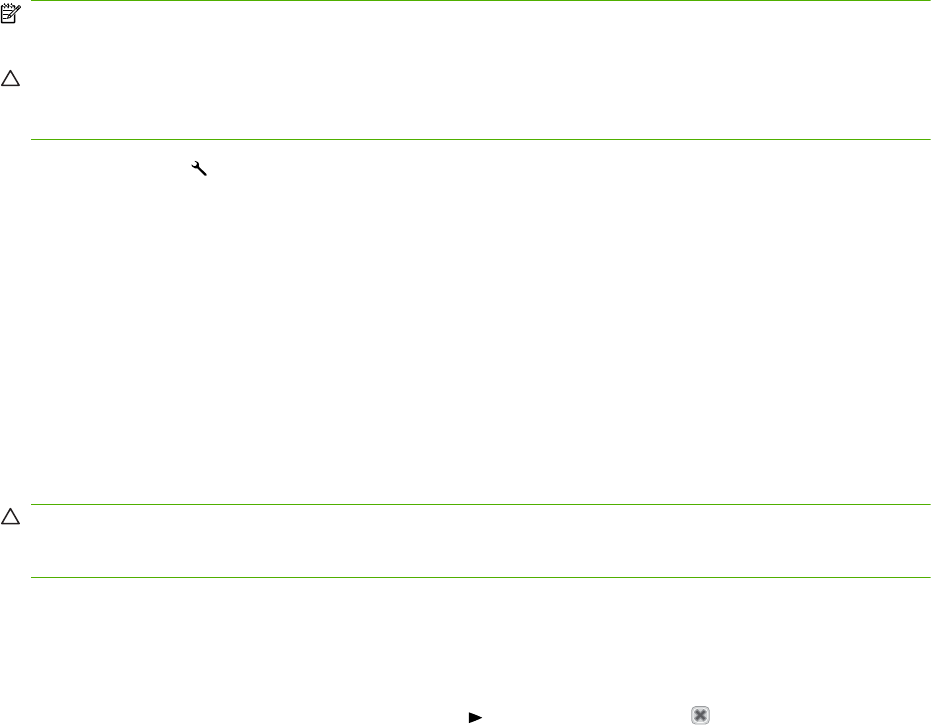
Product resets
The product resets—Restore defaults and the NVRAM initialization—perform the same function. If
possible, use the Restore defaults function in the Service menu. If that menu is not accessible, use
the NVRAM sequence.
Restore the factory-set defaults
NOTE: Before restoring defaults, print a menu structure report and a configuration page. Use the
information on these pages to reset customer-specific settings.
CAUTION: All onboard network settings are also reset. Be sure to print a configuration page before
restoring defaults. Make note of the IP address that is listed on the Jetdirect configuration page. You
might need to restore the IP address after restoring the defaults.
1. Press Setup to open the menus.
2. Use the arrow buttons to select Service, and then press OK.
3. Use the arrow buttons to select Restore defaults, and then press OK.
The product automatically restarts.
NVRAM initialization
Performing an NVRAM initialization resets the following settings and information:
●All menu settings are reset to factory default values.
●All localization settings, including language and country/region, are reset.
CAUTION: All onboard network settings are also reset. Be sure to print a configuration page before
restoring defaults. Make note of the IP address that is listed on the Jetdirect configuration page. You
might need to restore the IP address after an NVRAM initialization.
After performing an NVRAM initialization, reconfigure any computers that print to this product. Uninstall
and then reinstall the product software on the computers.
1. Turn the product off.
2. Simultaneously press the right arrow button and the Cancel button . Hold these buttons as
you turn the product on.
3. When Permanent storage init. appears on the display, release both buttons.
When the product has finished the NVRAM initialization, it returns to the Ready state.
ENWW Service mode functions 313
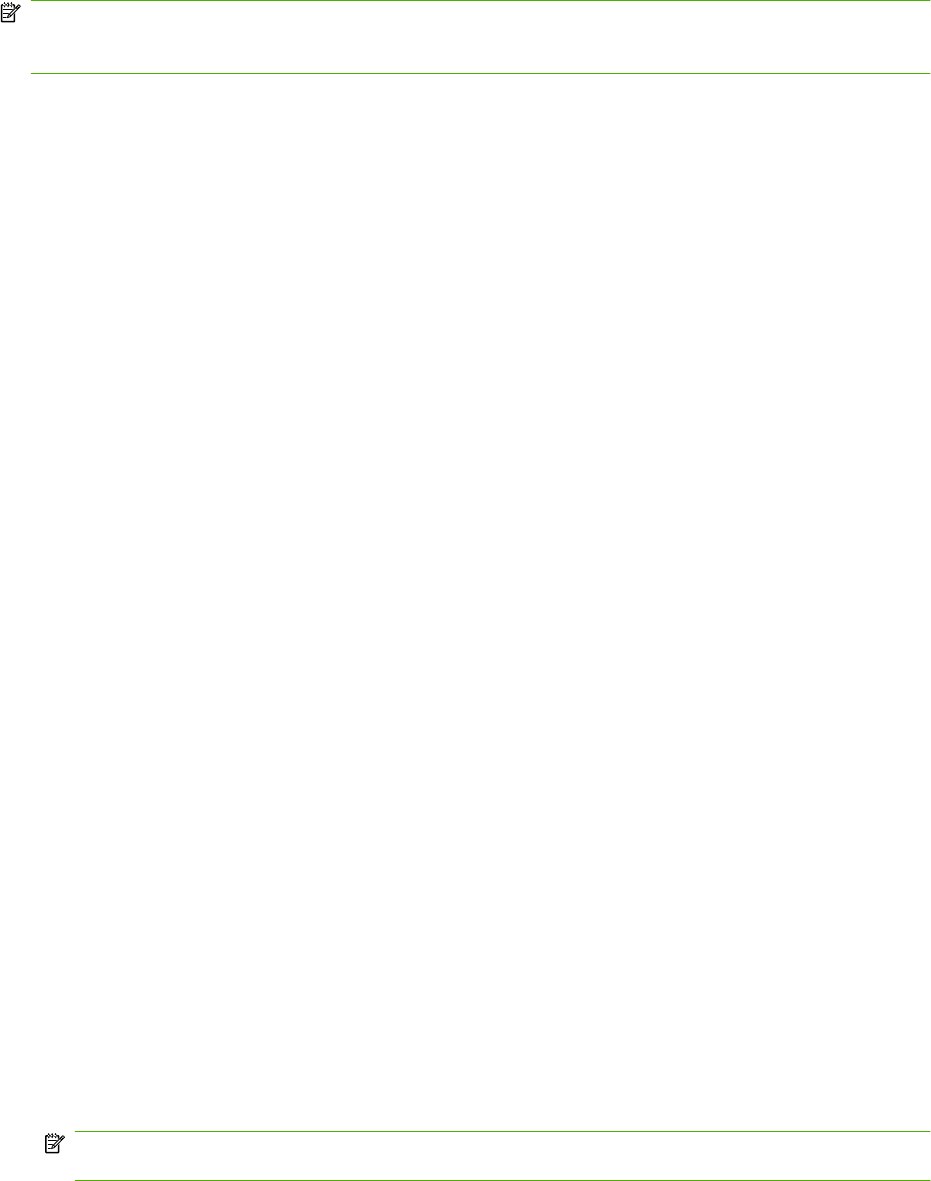
Solve fax problems (fax/memory-card models only)
Fax logs and reports
NOTE: Not all fax products are compatible with DSL or ISDN services. HP does not guarantee that
the product will be compatible with all DSL/ISDN service lines or providers. If you are having problems
using the product with these services, contact the service provider for more information or for assistance.
Print all fax reports
Use this procedure to print all of the following reports at one time:
●Fax activity log
●Phone book report
●Configuration report
●Usage page
●Junk-fax list
●Billing report (if the option is turned on)
1. On the control panel, press Fax Menu.
2. Use the arrow buttons to select Reports, and then press OK.
3. Use the arrow buttons to select All fax reports, and then press OK. The product exits the menu
settings and prints the reports.
Print individual fax reports
Use the control panel to print the following fax logs and reports:
●Fax activity log: Provides a chronological history of the last 40 faxes that were received, sent, or
deleted, and any errors that occurred.
●Phone book report: Lists the fax numbers that are assigned to the phone book entries, including
speed dials and group-dial entries.
●Block-fax list: Lists the fax numbers that are blocked from sending faxes to the product.
●Last call report: Provides information about the last fax sent from or received at the product.
1. On the control panel, press Fax Menu.
2. Use the arrow buttons to select Reports, and then press OK.
3. Use the arrow buttons to select the report to be printed, and then press OK. The product exits the
menu settings and prints the report.
NOTE: If you selected Fax Activity log and pressed OK, press OK again to select Print log
now. The product exits the menu settings and prints the log.
314 Chapter 7 Problem solve ENWW

Set the fax activity log to print automatically
You can decide whether or not you want the fax log to print automatically after every 40 entries. The
factory-set default is On. Use the following steps to set the fax activity log to print automatically:
1. On the control panel, press Fax Menu.
2. Use the arrow buttons to select Reports, and then press OK.
3. Use the arrow buttons to select Fax Activity log, and then press OK.
4. Use the arrow buttons to select Auto Log Print, and then press OK.
5. Use the arrow buttons to select On, and then press OK to confirm the selection.
Set the fax error report
A fax error report is a brief report that indicates the product experienced a fax job error. It can be set to
print after the following events:
●on Every error (the factory-set default)
●on Send error
●on Receive error
●Never
NOTE: If you select Never, you will have no indication that a fax failed to be transmitted unless you
print a fax activity log.
1. On the control panel, press Fax Menu.
2. Use the arrow buttons to select Reports, and then press OK.
3. Use the arrow buttons to select Fax Error Report, and then press OK.
4. Use the arrow buttons to select the option for when you want the fax error reports to be printed.
5. Press OK to save the selection.
Set the fax confirmation report
A confirmation report is a brief report that indicates the product successfully sent or received a fax job.
It can be set to print after the following events:
●on Every fax
●on Send fax only
●on Receive fax only
●Never (the factory-set default)
1. On the control panel, press Fax Menu.
2. Use the arrow buttons to select Reports, and then press OK.
3. Use the arrow buttons to select Fax Confirmation, and then press OK.
ENWW Solve fax problems (fax/memory-card models only) 315

4. Use the arrow buttons to select the option for when you want the fax error reports to be printed.
5. Press OK to save the selection.
Include the first page of each fax on the fax confirmation, fax error, and last call
reports
If this option is turned on and the page image still exists in the product memory, the fax configuration,
fax error, and last call reports include a thumbnail (50% reduction) of the first page of the most recent
fax that was sent or received. The factory-set default for this option is On.
1. On the control panel, press Fax Menu.
2. Use the arrow buttons to select Reports, and then press OK.
3. Use the arrow buttons to select Include first page, and then press OK.
4. Use the arrow buttons to select On, and then press OK to confirm the selection.
Perform a fax test
The fax test checks for an working phone line and verifies that the phone cord is plugged into the correct
port.
To perform a fax test:
1. On the control panel, press Setup .
2. Use the arrow buttons to select Service, and then press OK.
3. Use the arrow buttons to select Fax Service, and then press OK.
4. Use the arrow buttons to select Run Fax Test, and then press OK.
When the fax test completes, a report is printed from the product. The report contains one of three
possible results:
●Pass: the report contains all of the current fax settings for review.
●Fail - the cord is in the wrong port: the report contains suggestions for how to resolve the issue.
●Fail - the phone line is not active: the report contains suggestions for how to resolve the issue.
Change error correction and fax speed
Set the fax-error-correction mode
Usually, the product monitors the signals on the telephone line while it is sending or receiving a fax. If
the product detects an error during the transmission and the error-correction setting is On, the product
can request that the portion of the fax be resent. The factory-set default for error correction is On.
You should turn off error correction only if you are having trouble sending or receiving a fax, and you
are willing to accept the errors in the transmission. Turning off the setting might be useful when you are
trying to send a fax internationally or receive one, or if you are using a satellite telephone connection.
1. On the control panel, press Setup .
2. Use the arrow buttons to select Service, and then press OK.
316 Chapter 7 Problem solve ENWW
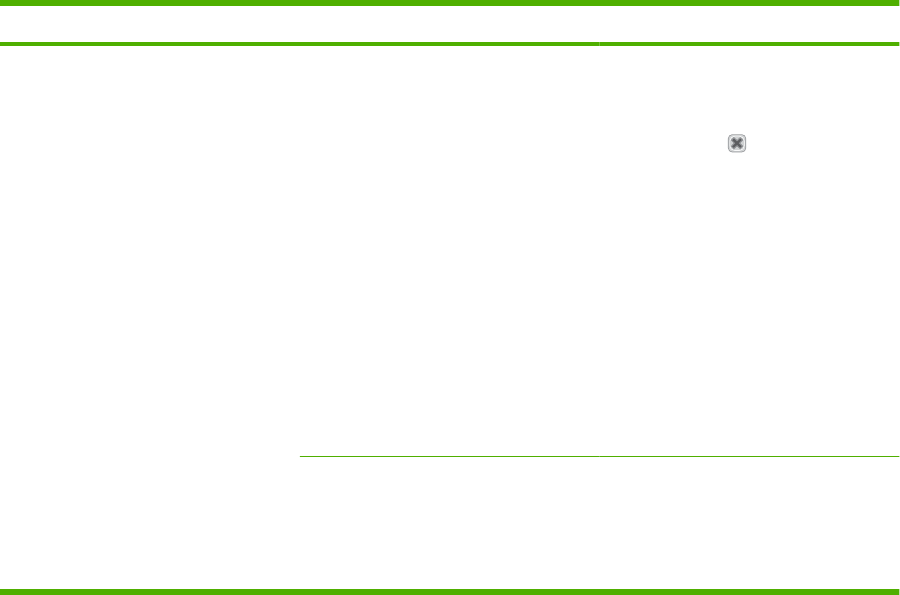
3. Use the arrow buttons to select Fax Service, and then press OK.
4. Use the arrow buttons to select Error correction, and then press OK.
5. Use the arrow buttons to select On or Off, and then press OK to save the selection.
Change the fax speed
The fax-speed setting is the modem protocol that the product uses to send faxes. It is the worldwide
standard for full-duplex modems that send and receive data across telephone lines at up to 33,600 bits
per second (bps). The factory-set default for the fax-speed setting is High (V.34).
You should change the setting only if you are having trouble sending a fax to or receiving a fax from a
particular device. Decreasing the fax speed might be useful when you are trying to send a fax overseas,
or receive one from overseas, or if you are using a satellite telephone connection.
1. On the control panel, press Fax Menu.
2. Use the arrow buttons to select Advanced setup, and then press OK.
3. Use the arrow buttons to select Fax Speed, and then press OK.
4. Use the arrow buttons to select a speed setting, and then press OK.
Problems sending faxes
Problem Cause Solution
The document stops feeding in the
middle of faxing.
The maximum length of a page that you
can load is 381 mm (15 inches). Faxing
of a longer page stops at 381 mm (15
inches).
Print the document on shorter media.
If no jam exists and less than one minute
has elapsed, wait a moment before
pressing Cancel . If a jam exists,
remove the jam. Then, resend the job.
Verify that the document feeder (ADF) is
working correctly. If it is not, replace the
ADF.
Clear the fax memory.
If the error persists, perform an NVRAM
initialization.
If the error persists, update the firmware.
If the error persists, replace the
formatter.
If the item is too small, it can jam inside
the automatic document feeder (ADF).
Use the flatbed scanner. The minimum
page size for the ADF is 127 x 127 mm
(5 x 5 inches).
If a jam exists, remove the jam. Then,
resend the job.
ENWW Solve fax problems (fax/memory-card models only) 317
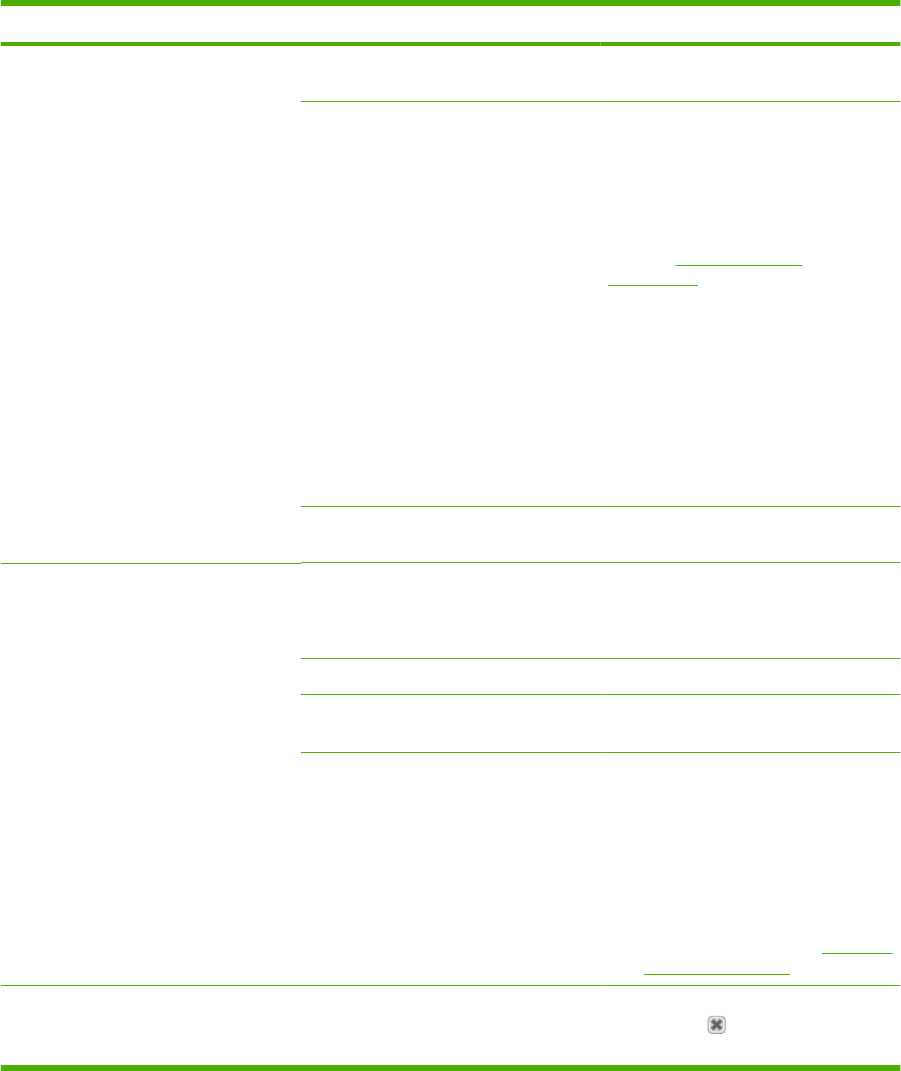
Problem Cause Solution
Faxes stop during sending. The receiving fax machine might be
malfunctioning.
Try sending to another fax machine.
The telephone line might not be working. Turn up the volume on the product, and
then press Start Fax on the control panel.
If you hear a dial tone, the telephone line
is working.
Perform a fax test to verify that the phone
line works and is plugged into the correct
port (see Perform a fax test
on page 316).
Check the fax log for errors.
Check the T.30 trace report for errors.
Clear the fax memory.
If the error persists, perform an NVRAM
initialization.
If the error persists, update the firmware.
A communication error might be
interrupting the fax job.
Change the redial-on-communication-
error setting to On.
The product is receiving faxes but is not
sending them.
If the product is on a digital system, the
system might be generating a dial tone
that the product cannot detect.
Disable the detect-dial-tone setting.
If the error persists, contact the system
service provider.
A poor telephone connection might exist. Try again later.
The receiving fax machine might be
malfunctioning.
Try sending to another fax machine.
The telephone line might not be working. Do one of the following:
●Turn up the volume on the product
and press Start Fax on the control
panel. If a dial tone exists, the
telephone line is working.
●Perform a fax test to verify that the
phone line works and is plugged
into the correct port (see Perform a
fax test on page 316).
Outgoing fax calls continue to be dialed. The product automatically redials a fax
number if the redial options are set to
On.
To stop the product from redialing a fax,
press Cancel . Or change the redial
setting.
318 Chapter 7 Problem solve ENWW
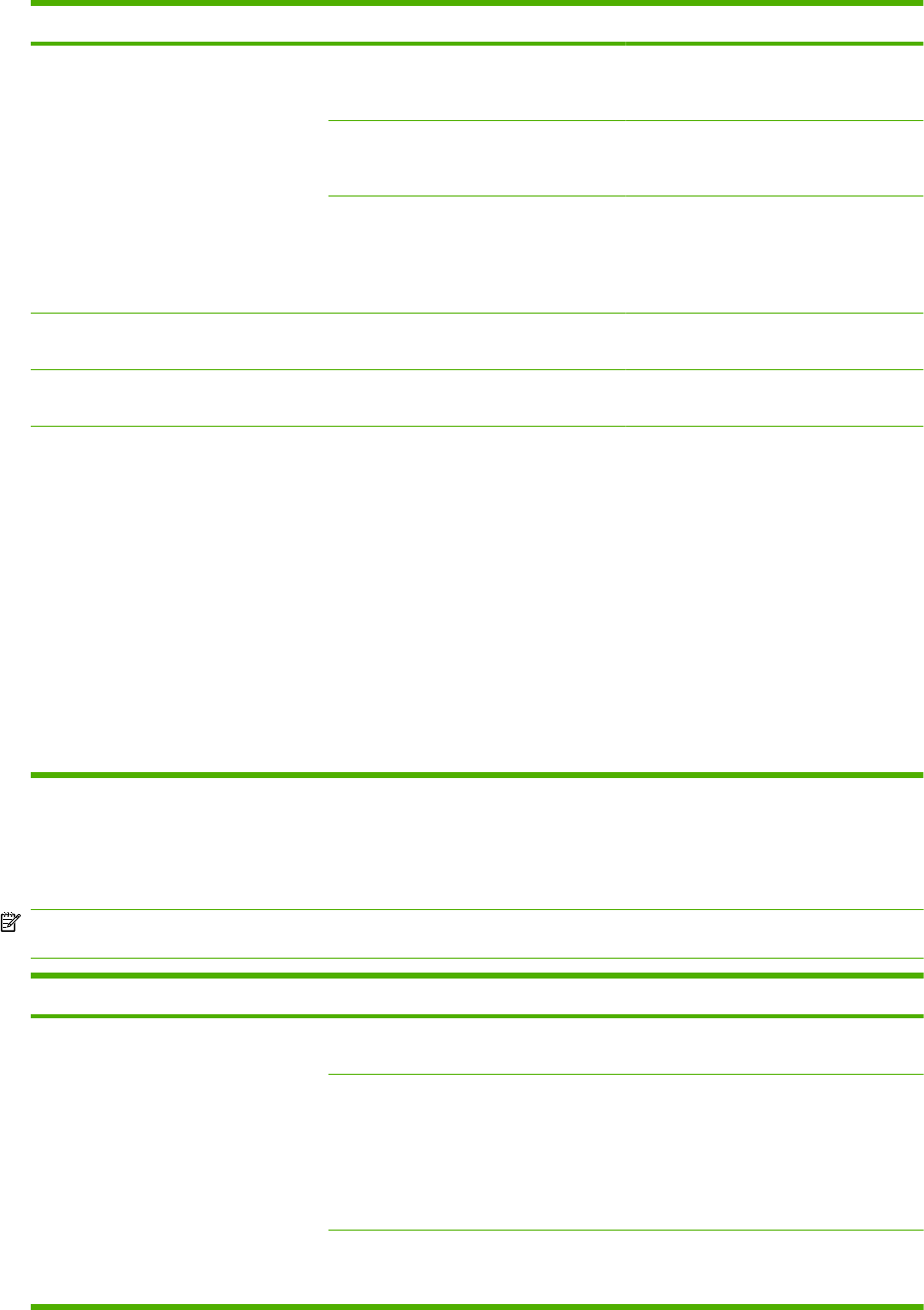
Problem Cause Solution
Sent faxes are not arriving at the
receiving fax machine.
The receiving fax machine might be off
or might have an error condition, such as
being out of paper.
Call the recipient to verify that the fax
machine is on and ready to receive
faxes.
The originals might be incorrectly loaded. Verify that the original documents are
correctly loaded into the ADF input tray
or flatbed scanner.
A fax might be in memory because it is
waiting to redial a busy number, other
jobs that are ahead of it are waiting to be
sent, or the fax is set up for a delayed
send.
If a fax job is in memory for any of these
reasons, an entry for the job appears in
the fax log. Print the fax activity log and
check the Status column for jobs that
show a Pending designation.
Sent faxes include a block of gray
shading at the end of each page.
The glass-fax size might be set
incorrectly.
Verify that the setting is correct.
Sent faxes have data missing from the
end of each page.
The glass-fax size might be set
incorrectly.
Verify that the setting is correct.
The control panel shows a low-memory
error.
The fax might be too large, or the
resolution might be too high.
Try one of the following:
●Divide a large fax into smaller
sections, and then fax them
individually.
●Clear stored faxes to make more
memory available for outgoing
faxes.
●Configure the outgoing fax as a
delayed fax, and then verify that it
will send completely.
●Make sure that the product is using
the lowest resolution setting
(Standard).
Problems receiving faxes
Use the table in this section to solve problems that might occur when receiving faxes.
NOTE: Use the fax cord that came with the product in order to ensure that the product functions
correctly.
Problem Cause Solution
The product cannot receive faxes from
an extension telephone.
The extension-telephone setting might
be disabled.
Change the extension-telephone setting.
The fax cord might not be securely
connected.
Verify that the fax cord is securely
connected between the telephone jack
and the product (or another device that is
connected to the product). Wait until you
hear fax tones, then press 1-2-3 in
sequence, wait for three seconds and
hang up.
The product dialing mode might be
incorrectly set, or the extension phone
might be incorrectly set.
Verify that the product dialing mode is set
to Tone. Verify that the extension phone
is set up for tone dialing as well.
ENWW Solve fax problems (fax/memory-card models only) 319
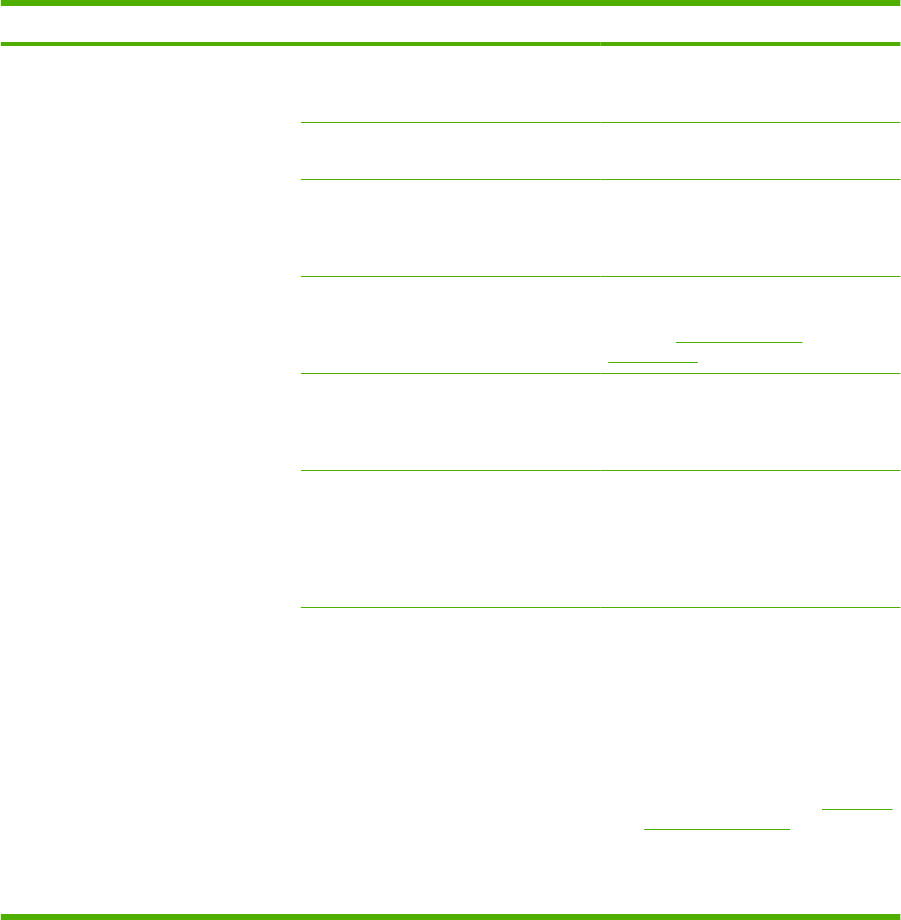
Problem Cause Solution
The product is not answering incoming
fax calls.
The answer mode might be set to
Manual.
If the answer mode is set to Manual, the
product does not answer calls. Start the
fax-receiving process manually.
The rings-to-answer setting might not be
set correctly.
Check the rings-to-answer setting to
verify that it is set properly.
The answer-ring pattern feature might be
turned on, but you do not have the
service, or you do have the service and
the feature is not set correctly.
Check the answer-ring pattern feature to
verify that it is set properly.
The fax cord might not be correctly
connected, or the fax cord is not working.
Perform a fax test to verify that the phone
line works and is plugged into the correct
port (see Perform a fax test
on page 316).
The product might not be able to detect
incoming fax tones because the
answering machine is playing a voice
message.
Re-record the answering machine
message, leaving at least two seconds of
silence at the beginning of the message.
Too many devices might be connected to
the telephone line.
Do not attach more than three devices to
the line. Remove the last device that was
connected and determine whether the
product works. If not, continue removing
devices one at a time and retry after
removing each one.
The telephone line might not be working. Do one of the following:
●Increase the volume on the product,
and then press Start Fax on the
control panel. If a dial tone exists,
the telephone line is working.
●Perform a fax test to verify that the
phone line works and is plugged
into the correct port (see Perform a
fax test on page 316).
●Replace the phone cord.
●Perform an NVRAM initialization.
320 Chapter 7 Problem solve ENWW
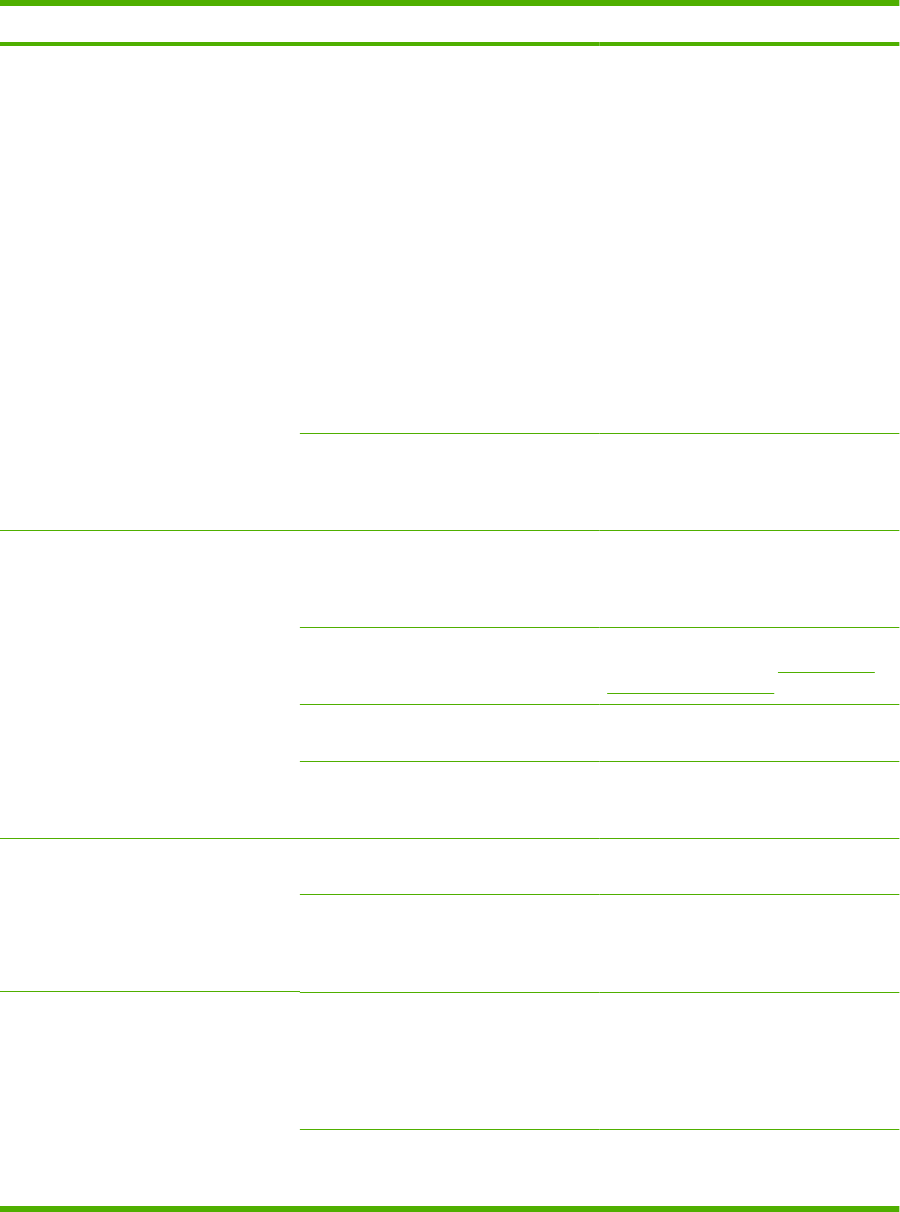
Problem Cause Solution
The product is not answering incoming
fax calls.
A voice-messaging service might be
interfering with the product as it attempts
to answer calls.
Do one of the following:
●Disable the messaging service.
●Get a telephone line that is
dedicated to fax calls.
●Set the product answer mode to
Manual. In manual mode, you must
start the fax-receive process
yourself.
●Leave the product set to automatic
mode and lower the rings-to-
answer setting for the product to a
number less than the rings-to-
answer setting for the voice mail.
The product will answer all
incoming calls.
The product might be out of paper and
the memory is full.
Refill the media input tray. Press OK. The
product prints all of the faxes it has saved
in memory and then resumes answering
fax calls.
Faxes are not printing. The media input tray is empty. Load media. Any faxes that are received
while the input tray is empty are stored in
memory and will print after the tray has
been refilled.
The product has encountered an error. Check the control panel for an error
message, and then see Control-panel
messages on page 257.
The sending fax number is on the junk
faxes list.
Check the junk faxes list and remove the
number.
The Private Receive feature is turned on. Turn off the Private Receive feature or
access the saved faxes using the preset
PIN.
Faxes are printing on two pages instead
of one.
The autoreduction setting might not be
set correctly.
Turn on the autoreduction setting.
The incoming faxes might have been
sent on larger media.
Adjust the fit-to-page setting to allow
larger pages to be printed on one page.
For more information, see the user
guide.
Received faxes are too light, are blank,
or have poor print quality.
The product ran out of toner while
printing a fax.
The product stores the most recently
printed faxes. (The amount of memory
that is available determines the actual
number of faxes stored for reprinting.) As
soon as possible, replace the print
cartridge, and then reprint the fax.
The fax that was sent was too light. Contact the sender and have the sender
resend the fax after altering the contrast
settings.
ENWW Solve fax problems (fax/memory-card models only) 321
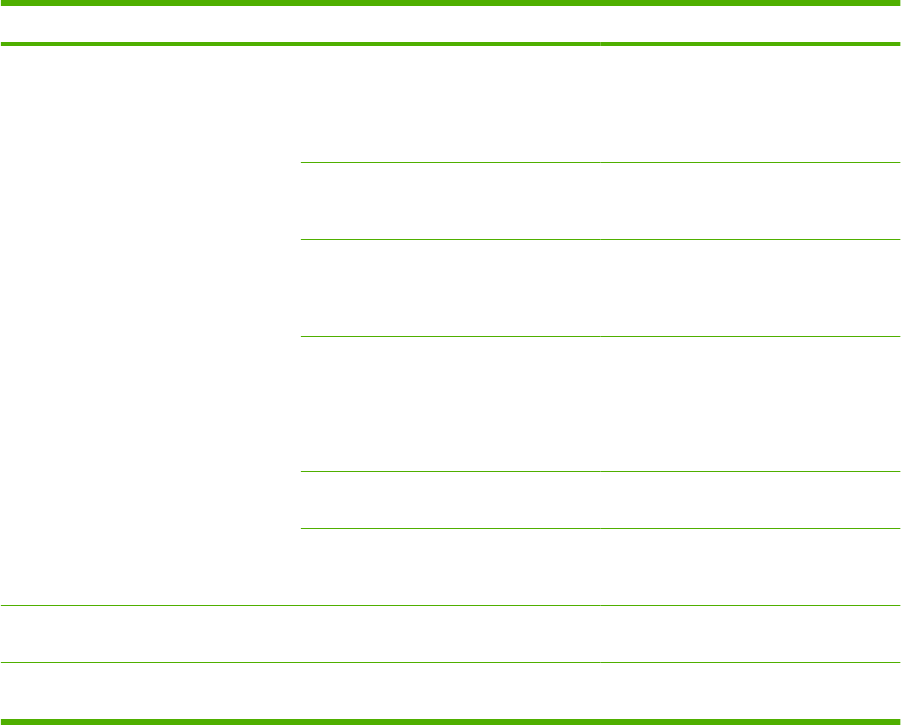
Performance problems
Problem Cause Solution
Faxes are transmitting or being received
very slowly.
The fax might be very complex, such as
one with many graphics.
Complex faxes take longer to be sent or
received. Breaking longer faxes into
multiple jobs and decreasing the
resolution can increase the transmission
speed.
The receiving fax machine might have a
slow modem speed.
The product sends the fax only at the
fastest modem speed that the receiving
fax machine can accept.
The resolution at which the fax was sent
or is being received might be very high.
To receive the fax, call and ask the
sender to lower the resolution and
resend the fax. To send the fax, lower the
resolution and resend the fax.
The telephone line might be
experiencing line noise.
Hang up and resend the fax. Have the
telephone company check the telephone
line.
If the fax is being sent via a digital phone
line, contact the service provider.
The fax is being sent via an international
call.
Allow more time to transmit fax jobs
internationally.
The original document has a colored
background.
Reprint the original document with a
white background, and then resend the
fax.
The fax activity logs or fax call reports are
printing at inappropriate times.
The fax activity log or fax call reports
settings are not correct.
Print a configuration page and check
when the reports print.
The product sounds are too loud or too
soft.
The volume setting might not be adjusted
correctly.
Adjust the product volume setting.
322 Chapter 7 Problem solve ENWW
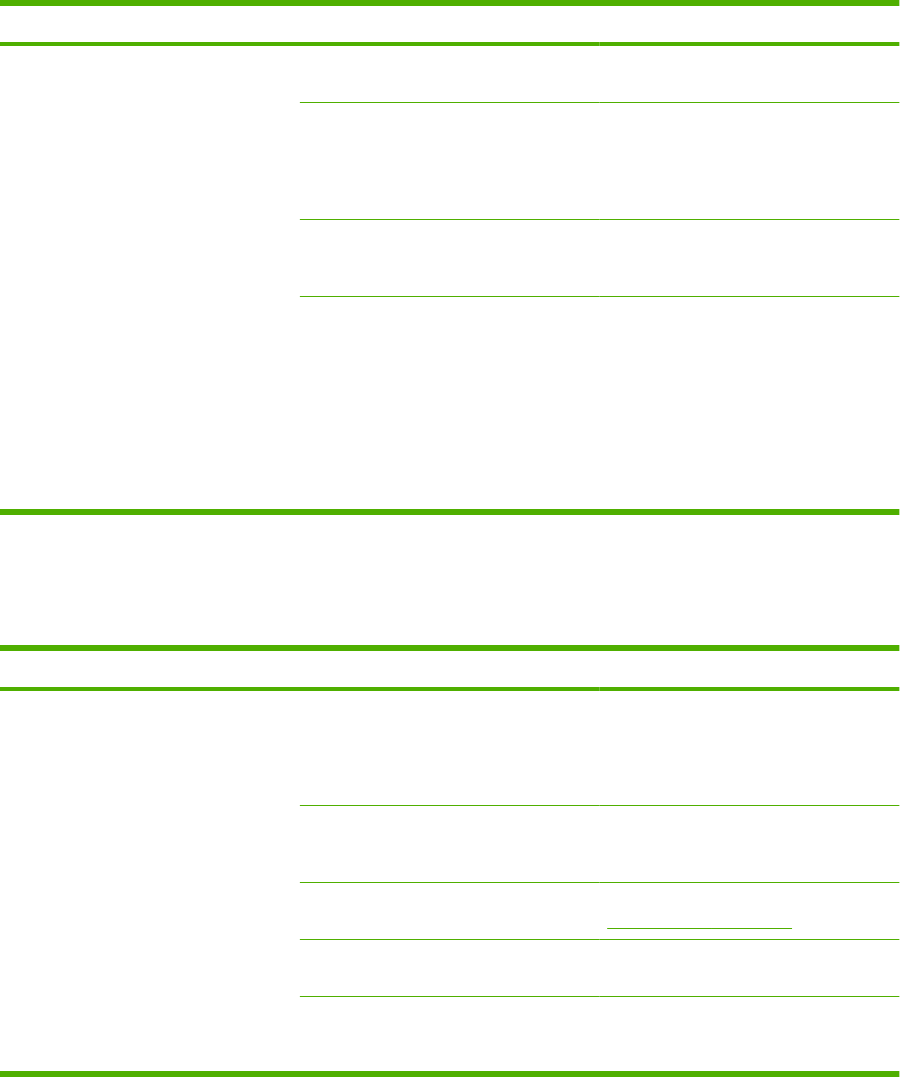
Memory card problems (fax/memory-card models only)
This section helps you identify and resolve memory card-related problems.
Missing or wrong files
Use the table in this section to solve problems with memory-card files.
Problem Cause Solution
The product cannot detect files on the
memory card.
The memory card might be missing or
inserted incorrectly.
Verify that the memory card is inserted
correctly.
The files might not be in the correct
format.
To print from the product control panel,
the files must be in the sRGB JPEG
format. To print other formats, you must
use a software program on your
computer.
You might have inserted more than one
memory card.
Only one card slot can be occupied for
the product to detect JPEG files. Verify
that only one card is inserted.
There might be a hardware problem. If a memory card is inserted in the correct
slot and the memory card LED is not lit,
verify that all formatter connectors are
firmly connected.
If the error persists, replace the memory-
card reader assembly.
If the error persists, replace the
formatter.
Index page not printing
Use the table in this section to solve problems with index-page printing.
Problem Cause Solution
The index page will not print. The memory card might have been
removed before the product could print
the page.
Reinsert the card and reprint the index
page.
If the error persists, try printing from
another memory card.
You might have inserted more than one
memory card.
Only one card slot can be occupied for
the product to detect JPEG files. Verify
that only one card is inserted.
One or more print cartridges might be
low.
Replace any low print cartridges. See
Print cartridge on page 67.
The files on the memory card might not
be in the sRGB JPEG format.
Verify that the files on the memory card
are in the sRGB JPEG format.
If the error persists, perform an NVRAM initialization.
If the error persists, update the firmware.
ENWW Memory card problems (fax/memory-card models only) 323
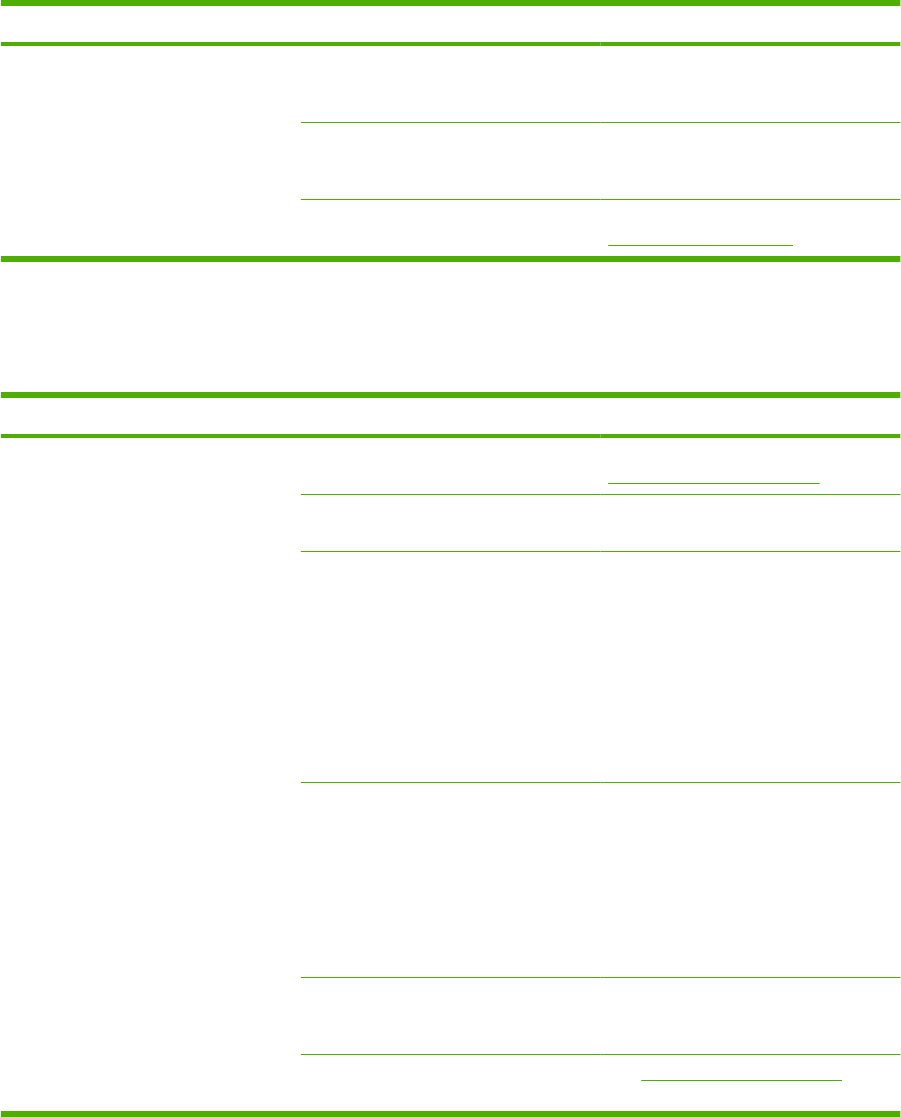
Proof sheet not printing
Use the table in this section to solve problems with proof-sheet printing.
Problem Cause Solution
The proof sheet will not print. The memory card might have been
removed before the product could print
the page.
Reinsert the card and reprint the proof
sheet.
You might have inserted more than one
memory card.
Only one card slot can be occupied for
the product to detect JPEG files. Verify
that only one card is inserted.
One or more print cartridges might be
low.
Replace any low print cartridges. See
Print cartridge on page 67.
Proof sheet not scanning
Use the table in this section to solve problems with proof-sheet scanning.
Problem Cause Solution
The proof sheet will not scan correctly. The flatbed scanner glass might be dirty. Clean the flatbed scanner glass. See
Clean the product on page 73.
The automatic document feeder (ADF)
might be loaded.
Remove any media from the ADF.
The scanner might not be able to read
the photo selections. This feature has
been optimized and tested for use with
Genuine HP Toner Supplies (variations
in color shading can impact the
performance of this feature).
Use a software program to print the
photo from your computer.
Print photos directly from the memory
card by using the control panel.
Verify that you have colored the bubbles
darkly enough for the scanner to read.
Install HP supplies in the product and
reprint the proof sheet.
The proof sheet might be loaded
incorrectly.
On the flatbed scanner, place the original
document face-down with the upper-left
corner of the document at the corner
indicated by the icon on the scanner.
Make sure that the proof sheet is not
crooked.
The product will not scan a proof sheet
from the ADF.
The proof sheet might have been
skewed when it was printed.
Reprint the proof sheet with correctly
loaded paper. Verify that the proof sheet
is not skewed when it exits the product.
The scanner might be experiencing
problems.
See Scan problems on page 304.
324 Chapter 7 Problem solve ENWW
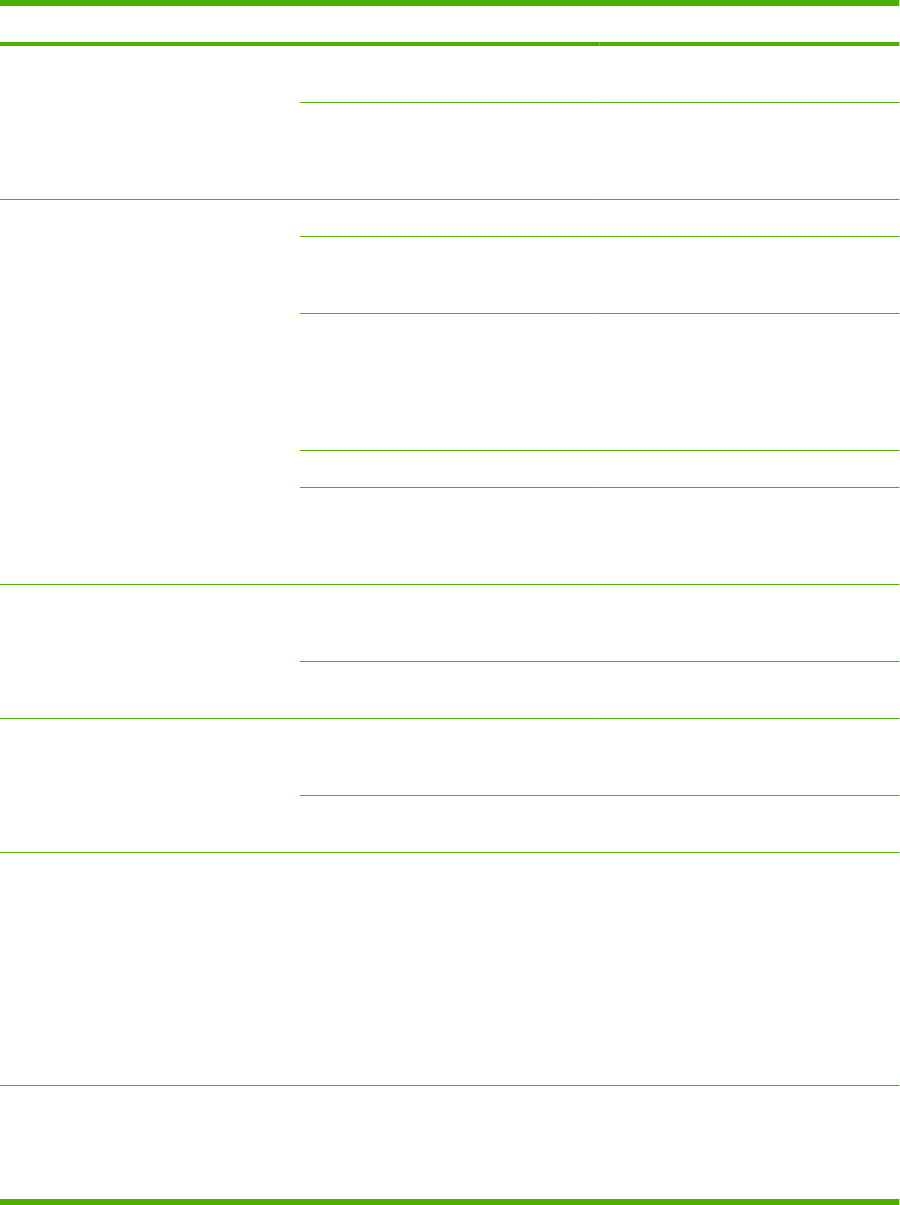
Issues with photo printing
Use the table in this section to solve problems with photo printing.
Problem Cause Solution
The wrong photo printed. An incorrect memory card might be
inserted.
Verify that the correct memory card is
inserted.
You might have selected the wrong
number from the memory card.
If you cannot remember the number of
the photo that you wish to print, print an
index page to verify the file number. See
the user guide.
The photo did not print. The media input tray might be empty. Load media into the input tray.
The memory card might have been
removed before the product could print
the photo.
Reinsert the card and reprint the photo.
The proof sheet is skewed. Verify that the paper guides are
positioned correctly against the paper in
the input tray. Reprint the proof sheet.
Verify that the images on the proof sheet
are aligned properly, and then reselect
the images you want to print.
The memory card might be defective. Try printing from another memory card.
The proof sheet is not aligned properly
on the scanner.
Realign the proof sheet face-down on the
flatbed scanner, with the upper-left
corner of the document located in the
lower-right corner of the glass.
The photo quality is unacceptable. The original photo quality might be poor,
or it might have a low resolution.
Use a software program to enhance
photo quality, and then print the photo
from your computer.
The default settings on the printer might
not produce the desired quality.
Use a software program to print the
photo at the desired settings.
The photo is the wrong size. The appropriate job size might not be
available from the product control panel.
Use a software program to resize the
photo at the desired settings, and then
print the photo from your computer.
You might have selected an incorrect job
size.
Verify that the correct setting is selected
at the product control panel.
Cannot edit, save, or delete images on
the memory card.
The product cannot read the memory
card.
Verify that the memory card is properly
inserted and that the card is one that is
supported.
Verify that the memory card is not write-
protected.
NOTE: You cannot edit memory-card
files from the product control panel. Use
a software program to edit, delete, or
save images.
Scanner did not read proof sheet. The product is using non-HP supplies.
This feature has been optimized and
tested for use with Genuine HP Toner
Supplies (variations in color shading can
impact the performance of this feature).
Use a software program to print the
photo from your computer.
Print photos directly from the memory
card by using the control panel.
ENWW Memory card problems (fax/memory-card models only) 325
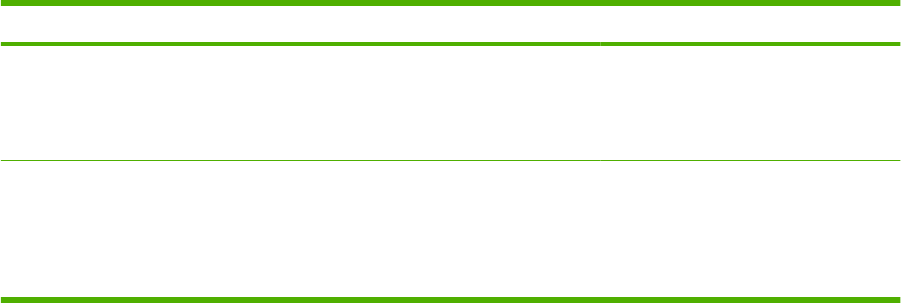
Problem Cause Solution
Verify that you have colored the bubbles
darkly enough for the scanner to read.
Install HP supplies in the product and
reprint the proof sheet.
The proof sheet is skewed. Verify that the paper guides are
positioned correctly against the paper in
the input tray. Reprint the proof sheet.
Verify that the images on the proof sheet
are aligned properly, and then reselect
the images you want to print.
326 Chapter 7 Problem solve ENWW
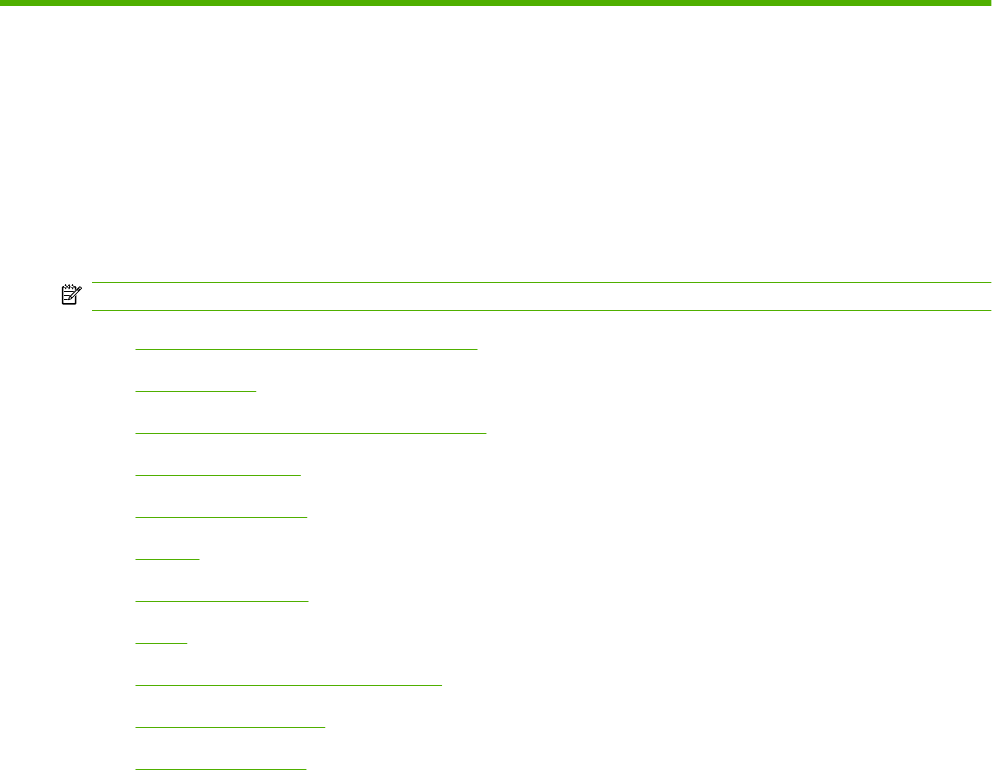
8 Parts and diagrams
NOTE: In this chapter, part numbers are listed only for available replaceable parts.
●Order parts, accessories, and supplies
●Part numbers
●How to use the parts lists and diagrams
●Scanner assembly
●Assembly locations
●Covers
●Internal assemblies
●PCAs
●Optional 250-sheet paper cassette
●Alphabetical parts list
●Numerical parts list
ENWW 327
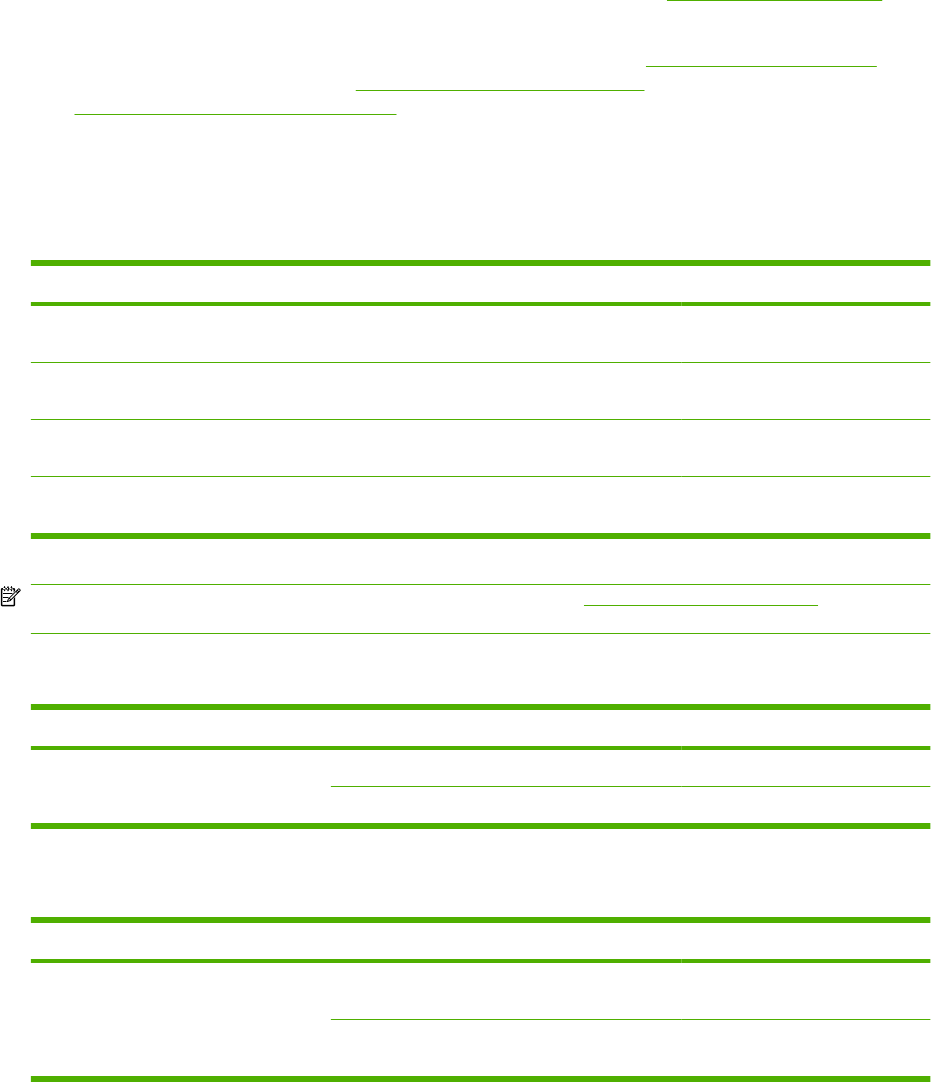
Order parts, accessories, and supplies
You can obtain the following items directly from HP:
●Replacement parts: To order replacement parts in the U.S., go to www.hp.com/go/hpparts.
Outside the United States, order parts by contacting your local authorized HP service center.
●Supplies and accessories: To order supplies in the U.S., go to www.hp.com/go/ljsupplies. To
order supplies worldwide, go to www.hp.com/ghp/buyonline.html. To order accessories, go to
www.hp.com/support/CM2320series.
Part numbers
Supplies
Product name Part number Service part number
Black print cartridge with HP
ColorSphere toner
CC530A CC530-67901
Cyan print cartridge with HP
ColorSphere toner
CC531A CC531-67901
Yellow print cartridge with HP
ColorSphere toner
CC532A CC532-67901
Magenta print cartridge with HP
ColorSphere toner
CC533A CC533-67901
NOTE: For information about the yield for the cartridges, see www.hp.com/go/pageyield. Actual yield
depends on specific use.
Memory
Product name Description Part number
Memory upgrades (DIMMs) 64 MB C1887A
128 MB C9121A
Cable and interface accessories
Product name Description Part number
USB cable 2-meter standard USB-compatible device
connector
Q6264A
3-meter standard USB-compatible device
connector
C6520A
328 Chapter 8 Parts and diagrams ENWW
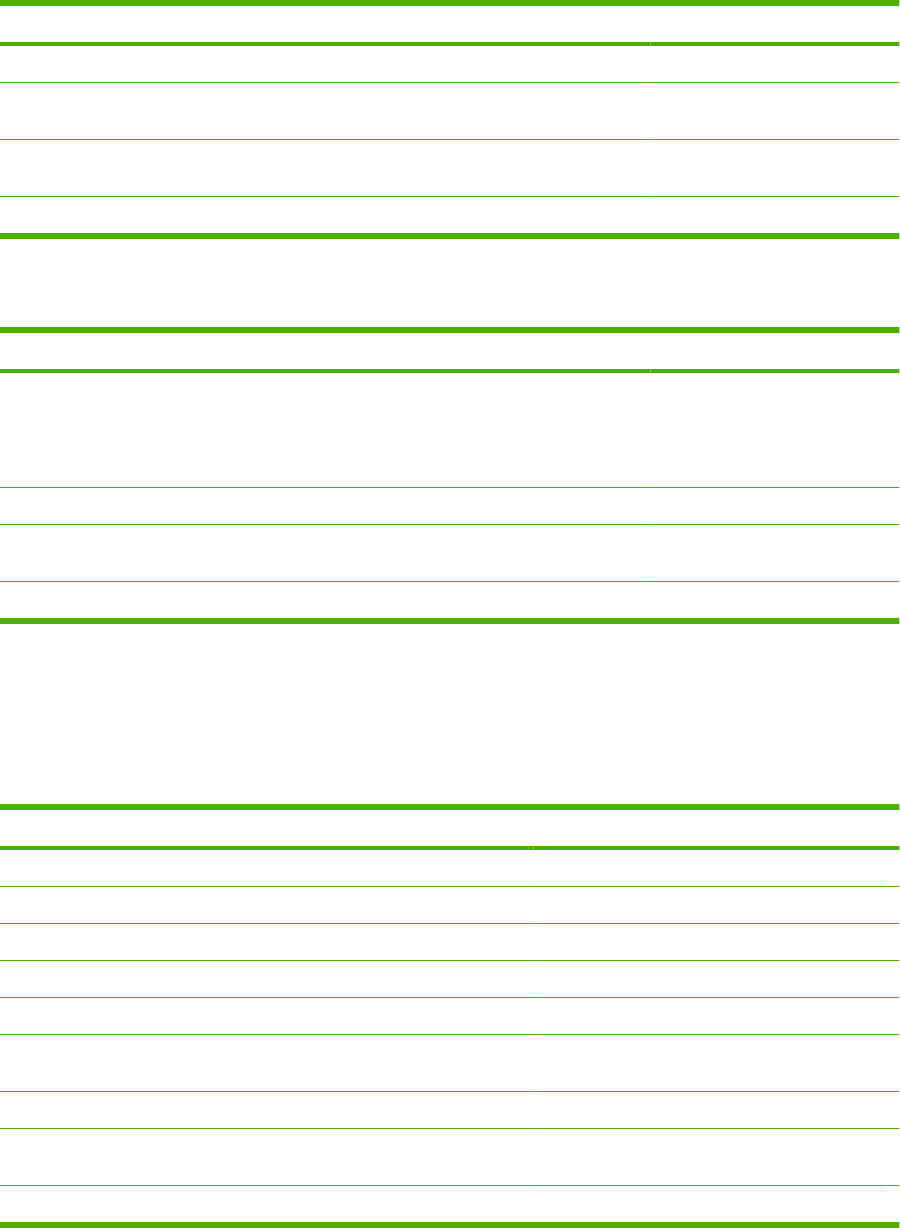
Repair kits
Product name Description Part number
Multipurpose tray paper pickup kit Tray 1 paper pickup roller and separation pad CC436-67904
Paper pickup roller kit Pickup roller assembly, separation roller
assembly, and holder cover
CC430-67901
Scanner assembly (fax/memory-card
models)
Scanner assembly for fax/memory-card models CC436-67902
Scanner assembly (base models) Scanner assembly for base models CC436-67903
User-replaceable parts
Product name Description Part number
Automatic document feeder (ADF) Replace when the ADF is damaged or not working
correctly.
CC434-67902 (base models and
fax models)
CC436-67901 (memory-card
models only)
ADF pickup roller assembly Replace when the ADF pages skew or jam. 5851-3580
Legal media cover kit Optional cover (used when the tray is loaded with
legal-size media)
CB493-60101
Tray 3 250-sheet input tray for standard sizes CB500-67902
Whole unit replacement part numbers
If a lower-level replacement part is not available, use the tables in this section to find the engine
replacement part number for a specific product bundle and localized configuration.
Table 8-1 Whole unit replacement, product bundle CC434 (base models)
Country/region Replacement part number
Brazil CC434-69001
Mexico CC434-69002
Taiwan CC434-69003
Singapore, Malaysia, Brunei, Vietnam, Australia, New Zealand CC434-69004
Argentina, Chile, Peru CC434-69005
Germany, France, Netherlands, Italy, Spain, Great Britain, Switzerland,
Belgium, Portugal, South Africa, Middle East
CC434-69006
Norway, Sweden, Finland, Denmark CC434-69007
Czech Republic, Slovakia, Poland, Hungary, Russia, Turkey, Croatia,
Romania, Slovenia, Greece, Israel
CC434-69008
Korea, China, Thailand, Hong Kong SAR CC434-69009
ENWW Part numbers 329
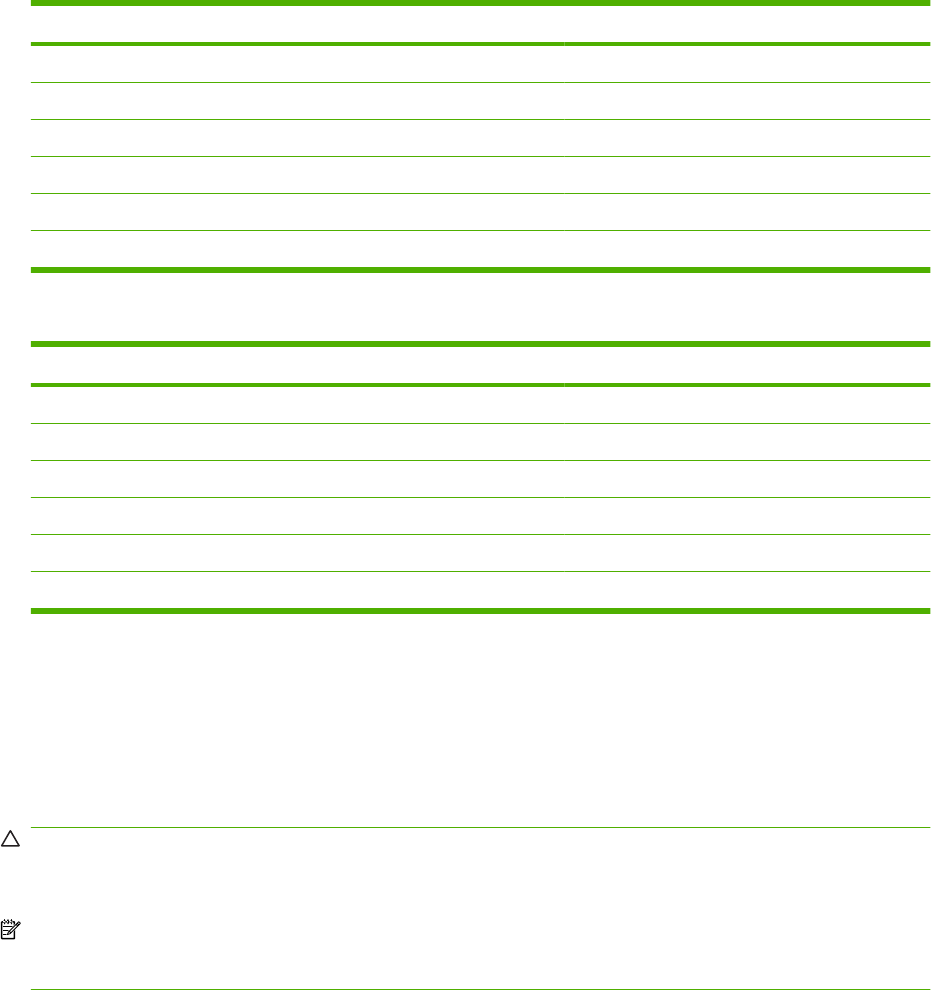
Table 8-2 Whole unit replacement, product bundle CC436 (fax models)
Country/region Replacement part number
Brazil CC436-69001
Taiwan, Canada, United States, Mexico CC436-69002
Argentina, Chile, Peru CC436-69003
Singapore, Malaysia CC436-69004
All other unlisted 220V Asian-Pacific countries/regions CC436-69005
All European Union countries/regions CC436-69006
Table 8-3 Whole unit replacement, product bundle CC435 (memory-card models)
Country/region Replacement part number
Brazil CC435-69001
Taiwan, Canada, United States, Mexico CC435-69002
Argentina, Chile, Peru CC435-69003
Singapore, Malaysia CC435-69004
All other unlisted 220V Asian-Pacific countries/regions CC435-69005
All European Union countries/regions CC435-69006
How to use the parts lists and diagrams
The figures in this chapter show the major subassemblies in the product and their component parts. A
parts list table follows each exploded view assembly diagram. Each table lists the item number, the
associated part number, and the description of each part. If a part is not listed in the table, then it is not
a field replacement unit (FRU).
CAUTION: Be sure to order the correct part. When looking for part numbers for electrical components,
pay careful attention to the voltage that is listed in the description column. Doing so will ensure that the
part number selected is for the correct all-in-one model.
NOTE: In this manual, the abbreviation “PCA” stands for “printed circuit-board assembly.”
Components described as a PCA might consist of a single circuit board or a circuit board plus other
parts, such as cables and sensors.
330 Chapter 8 Parts and diagrams ENWW
ENWW How to use the parts lists and diagrams 331
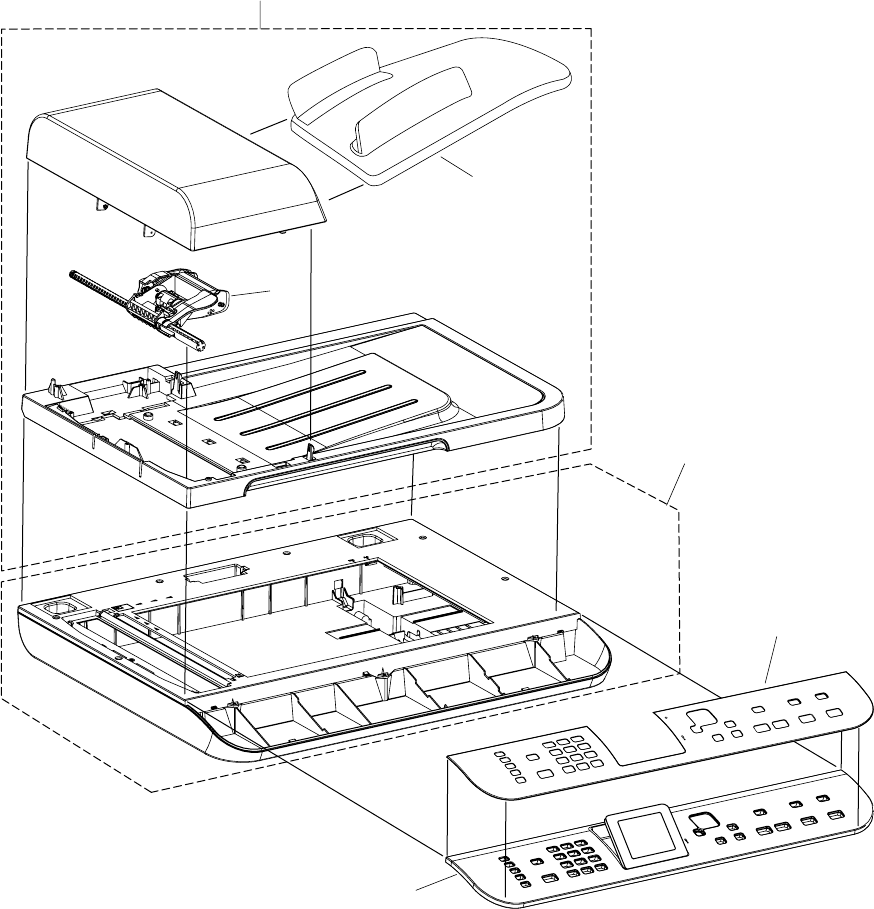
Scanner assembly
Figure 8-1 Scanner assembly
3
1
4
2
6
5
332 Chapter 8 Parts and diagrams ENWW
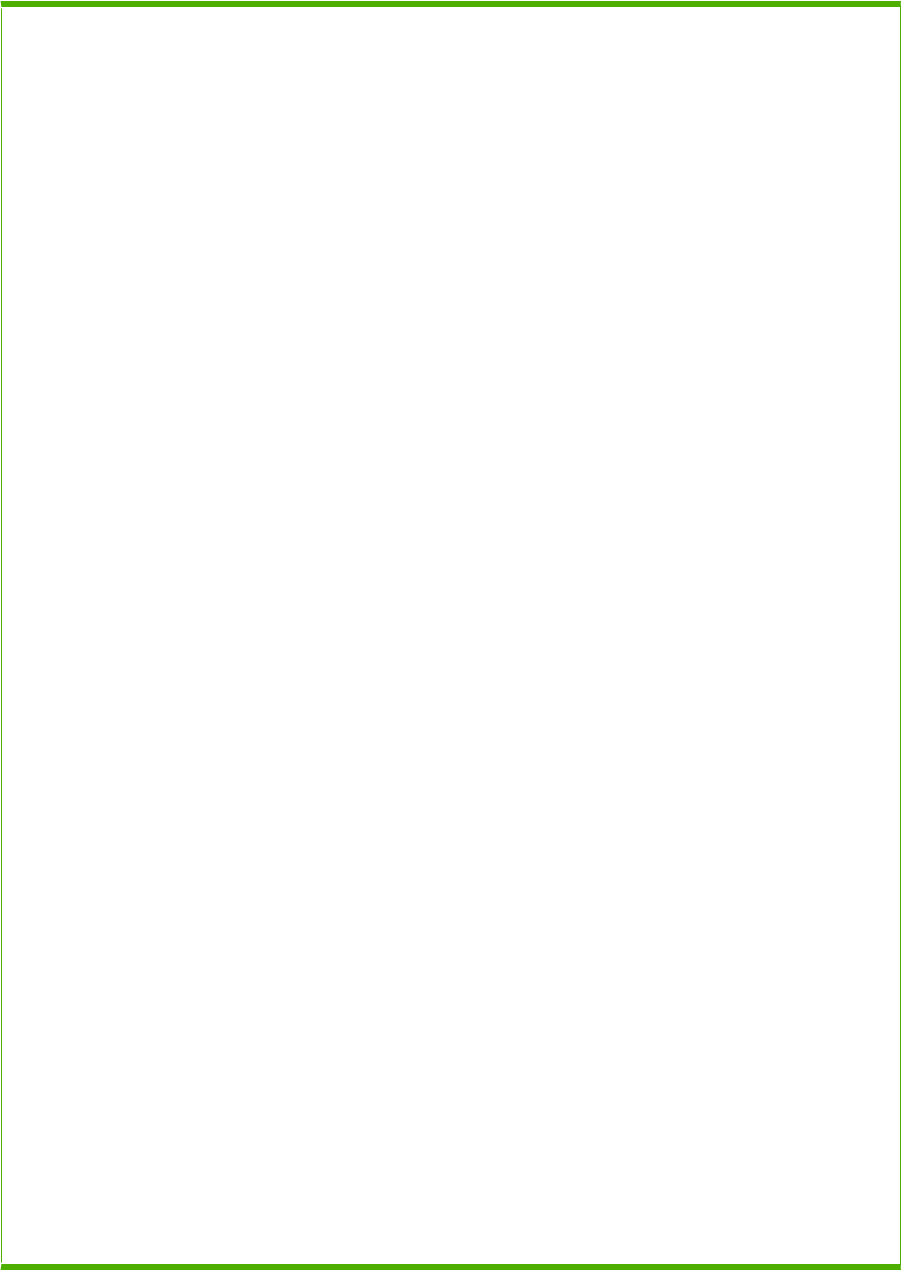
Table 8-4 Scanner assembly
Ref Description Part number Qty
1 Automatic document feeder (ADF) assembly—simplex models CC434-67902 1
1 Automatic document feeder (ADF) assembly—duplex models CC436-67901 1
2 ADF input tray CC431-60119 1
3 ADF pickup roller assembly 5851-3580 1
4 Scanner assembly, base CC436-67903 1
Scanner assembly, business/imaging CC436-67902 1
5 Control-panel overlay, base model, English CC434-60105 1
5 Control-panel overlay, base model, Spanish CC434-00006 1
5 Control-panel overlay, base model, Portuguese CC434-00007 1
5 Control-panel overlay, base model, German CC434-00008 1
5 Control-panel overlay, base model, French CC434-00009 1
5 Control-panel overlay, base model, Dutch CC434-00010 1
5 Control-panel overlay, base model, Italian CC434-00011 1
5 Control-panel overlay, base model, Swedish CC434-00012 1
5 Control-panel overlay, base model, Norwegian CC434-00013 1
5 Control-panel overlay, base model, Finnish CC434-00014 1
5 Control-panel overlay, base model, Danish CC434-00015 1
5 Control-panel overlay, base model, Russian CC434-00016 1
5 Control-panel overlay, base model, Czech CC434-00017 1
5 Control-panel overlay, base model, Hungarian CC434-00018 1
5 Control-panel overlay, base model, Polish CC434-00019 1
5 Control-panel overlay, base model, Slovak CC434-00020 1
5 Control-panel overlay, base model, Turkish CC434-00021 1
5 Control-panel overlay, base model, Greek CC434-00022 1
5 Control-panel overlay, base model, Hebrew CC434-00023 1
5 Control-panel overlay, base model, Arabic CC434-00024 1
5 Control-panel overlay, base model, Chinese, traditional CC434-00025 1
5 Control-panel overlay, base model, Korean CC434-00026 1
5 Control-panel overlay, base model, Chinese, simplified CC434-00027 1
5 Control-panel overlay, base model, Thai CC434-00028 1
5 Control-panel overlay, base model, Vietnamese CC434-00029 1
5 Control-panel bezel, fax model, English CC436-40003 1
5 Control-panel bezel, fax model, Spanish CC436-40004 1
5 Control-panel bezel, fax model, Portuguese CC436-40005 1
ENWW Scanner assembly 333
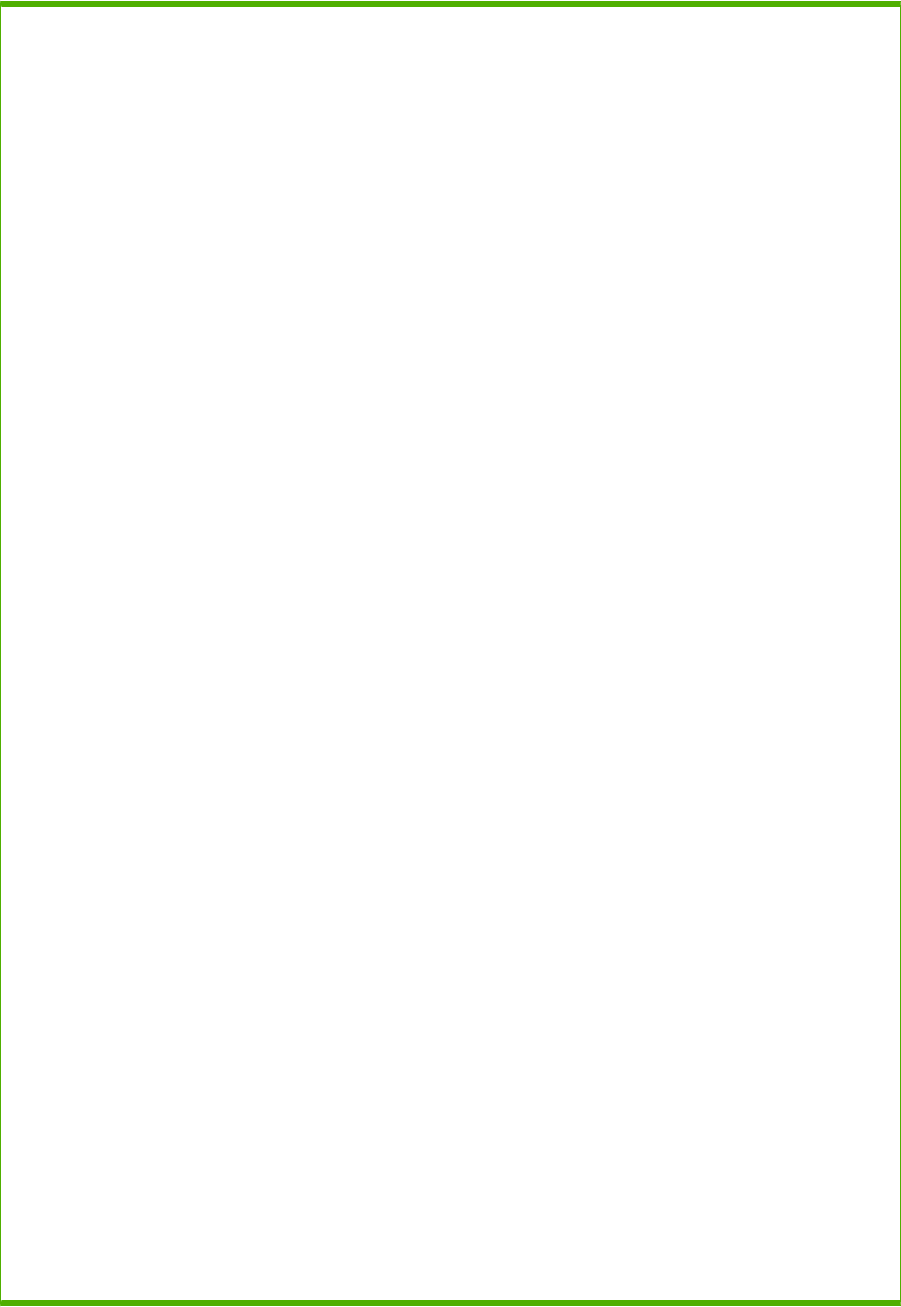
Ref Description Part number Qty
5 Control-panel bezel, fax model, German CC436-40006 1
5 Control-panel bezel, fax model, French CC436-40007 1
5 Control-panel bezel, fax model, Dutch CC436-40008 1
5 Control-panel bezel, fax model, Italian CC436-40009 1
5 Control-panel bezel, fax model, Swedish CC436-40010 1
5 Control-panel bezel, fax model, Norwegian CC436-40011 1
5 Control-panel bezel, fax model, Finnish CC436-40012 1
5 Control-panel bezel, fax model, Danish CC436-40013 1
5 Control-panel bezel, fax model, Russian CC436-40014 1
5 Control-panel bezel, fax model, Czech CC436-40015 1
5 Control-panel bezel, fax model, Hungarian CC436-40016 1
5 Control-panel bezel, fax model, Polish CC436-40017 1
5 Control-panel bezel, fax model, Slovak CC436-40018 1
5 Control-panel bezel, fax model, Turkish CC436-40019 1
5 Control-panel bezel, fax model, Greek CC436-40020 1
5 Control-panel bezel, fax model, Hebrew CC436-40021 1
5 Control-panel bezel, fax model, Arabic CC436-40022 1
5 Control-panel bezel, fax model, Chinese, traditional CC436-40023 1
5 Control-panel bezel, fax model, Korean CC436-40024 1
5 Control-panel bezel, fax model, Chinese, simplified CC436-40025 1
5 Control-panel bezel, fax model, Thai CC436-40026 1
5 Control-panel bezel, fax model, Vietnamese CC436-40027 1
5 Control-panel bezel, memory-card model, English CC431-40002 1
5 Control-panel bezel, memory-card model, Spanish CC431-40003 1
5 Control-panel bezel, memory-card model, Portuguese CC431-40004 1
5 Control-panel bezel, memory-card model, German CC431-40005 1
5 Control-panel bezel, memory-card model, French CC431-40006 1
5 Control-panel bezel, memory-card model, Dutch CC431-40007 1
5 Control-panel bezel, memory-card model, Italian CC431-40008 1
5 Control-panel bezel, memory-card model, Swedish CC431-40009 1
5 Control-panel bezel, memory-card model, Norwegian CC431-40010 1
5 Control-panel bezel, memory-card model, Finnish CC431-40011 1
5 Control-panel bezel, memory-card model, Danish CC431-40012 1
5 Control-panel bezel, memory-card model, Russian CC431-40013 1
5 Control-panel bezel, memory-card model, Czech CC431-40014 1
Table 8-4 Scanner assembly (continued)
334 Chapter 8 Parts and diagrams ENWW
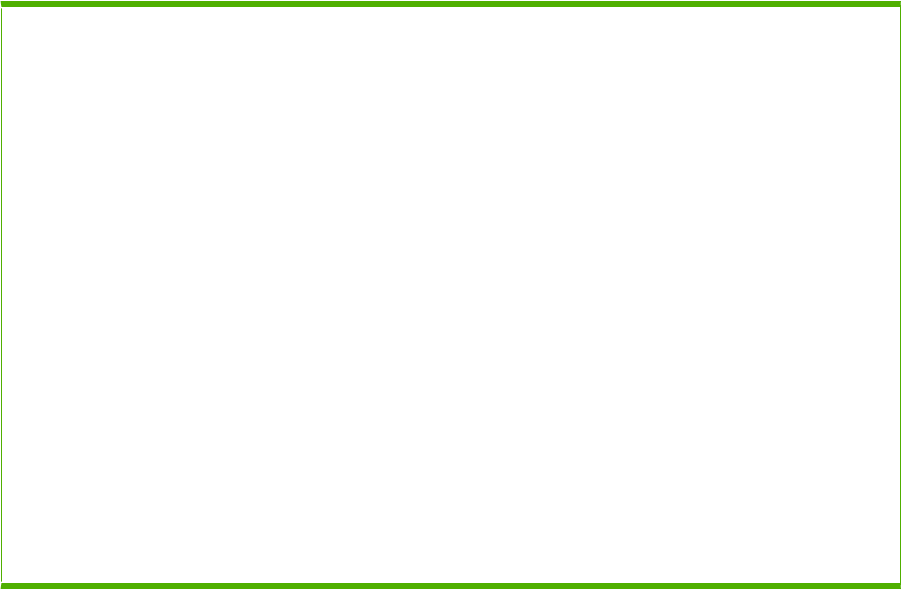
Ref Description Part number Qty
5 Control-panel bezel, memory-card model, Hungarian CC431-40015 1
5 Control-panel bezel, memory-card model, Polish CC431-40016 1
5 Control-panel bezel, memory-card model, Slovak CC431-40017 1
5 Control-panel bezel, memory-card model, Turkish CC431-40018 1
5 Control-panel bezel, memory-card model, Greek CC431-40019 1
5 Control-panel bezel, memory-card model, Hebrew CC431-40020 1
5 Control-panel bezel, memory-card model, Arabic CC431-40021 1
5 Control-panel bezel, memory-card model, Chinese, traditional CC431-40022 1
5 Control-panel bezel, memory-card model, Korean CC431-40023 1
5 Control-panel bezel, memory-card model, Chinese, simplified CC431-40024 1
5 Control-panel bezel, memory-card model, Thai CC431-40025 1
5 Control-panel bezel, memory-card model, Vietnamese CC431-40026 1
6 Control-panel assembly, Western, base model CC434-60101 1
6 Control-panel assembly, Western, fax/memory-card models CC431-60101 1
6 Control-panel assembly, Asian CC434-60102 1
Table 8-4 Scanner assembly (continued)
ENWW Scanner assembly 335

Assembly locations
Figure 8-2 Assembly locations
3
4
5
6
1
2
336 Chapter 8 Parts and diagrams ENWW
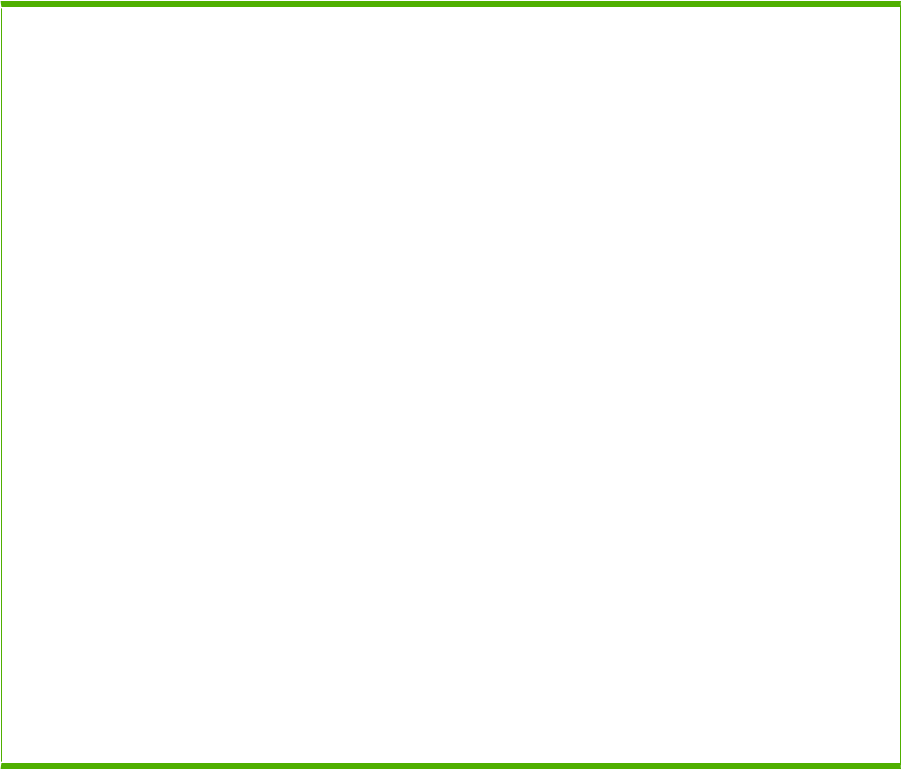
Table 8-5 Assembly locations
Ref Description Part number Qty
1 Fuser assembly (110-127 V) RM1-6740-000CN 1
1 Fuser assembly (220-240 V) RM1-6741-000CN 1
2 Paper input cassette RM1-4860-000CN 1
3 Formatter, fax models CC400-67901 1
3 Formatter, business CE684-67901 1
4 DAA (fax card), Americas/Asia (fax models only) CC367-60001 1
4 DAA (fax card), Europe (fax models only) CC514-60002 1
5 Formatter, base model CC399-67901 1
6 Memory-card assembly (memory-card models only) CC401-67901 1
Formatter bracket, fax/memory-card models (not shown) CC431-00002 1
Formatter bracket, base models (not shown) CC430-00027 1
DAA flat flexible cable (not shown) 5851-3054 1
Memory card cable guide (not shown) CC435-40001 1
Memory card bracket (not shown) CC435-00001 1
Fax insulator (not shown) 5851-3375 1
Speaker (not shown) Q3948-60113 1
Core ferrite (not shown) 9170-2452 1
Memory card cable (not shown) 5851-3055 1
Blank bezel (not shown) CC434-67901 1
Memory card bezel (not shown) CC435-67901 1
ENWW Assembly locations 337
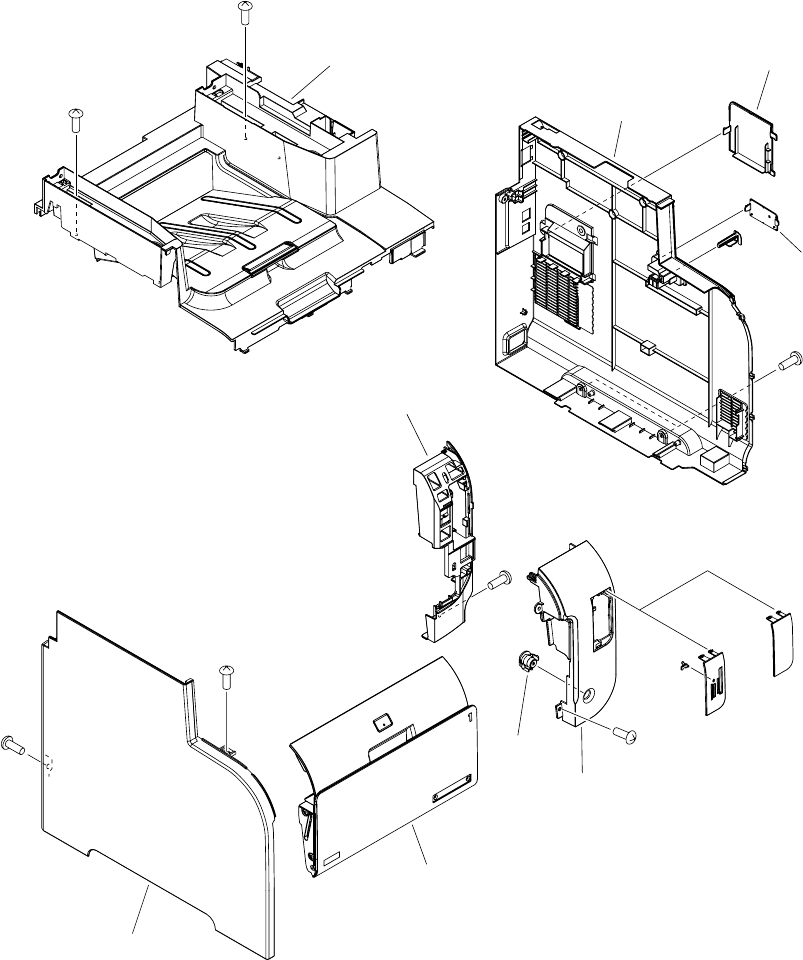
Covers
Figure 8-3 External panels and covers
1
10
7
9
8
4
5
3
2
338 Chapter 8 Parts and diagrams ENWW
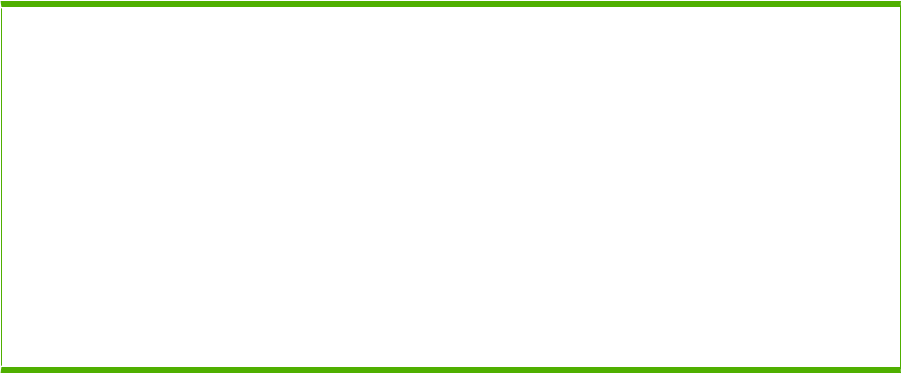
Table 8-6 External panels and covers
Ref Description Part number Qty
1 Cover, left RC2-3913-000CN 1
2 Upper cover assembly RM1-4911-000CN 1
3 Cover, DIMM RC2-3614-000CN 1
4 Cover, right RC2-3912-000CN 1
5 Cover, IOT RC2-3918-000CN 1
7 Cover, right front, lower RC2-3915-000CN 1
8 Cover, right front RC2-3914-000CN 1
9 Button, power RC2-3612-000CN 1
10 Front door assembly RM1-4848-000CN 1
ENWW Covers 339
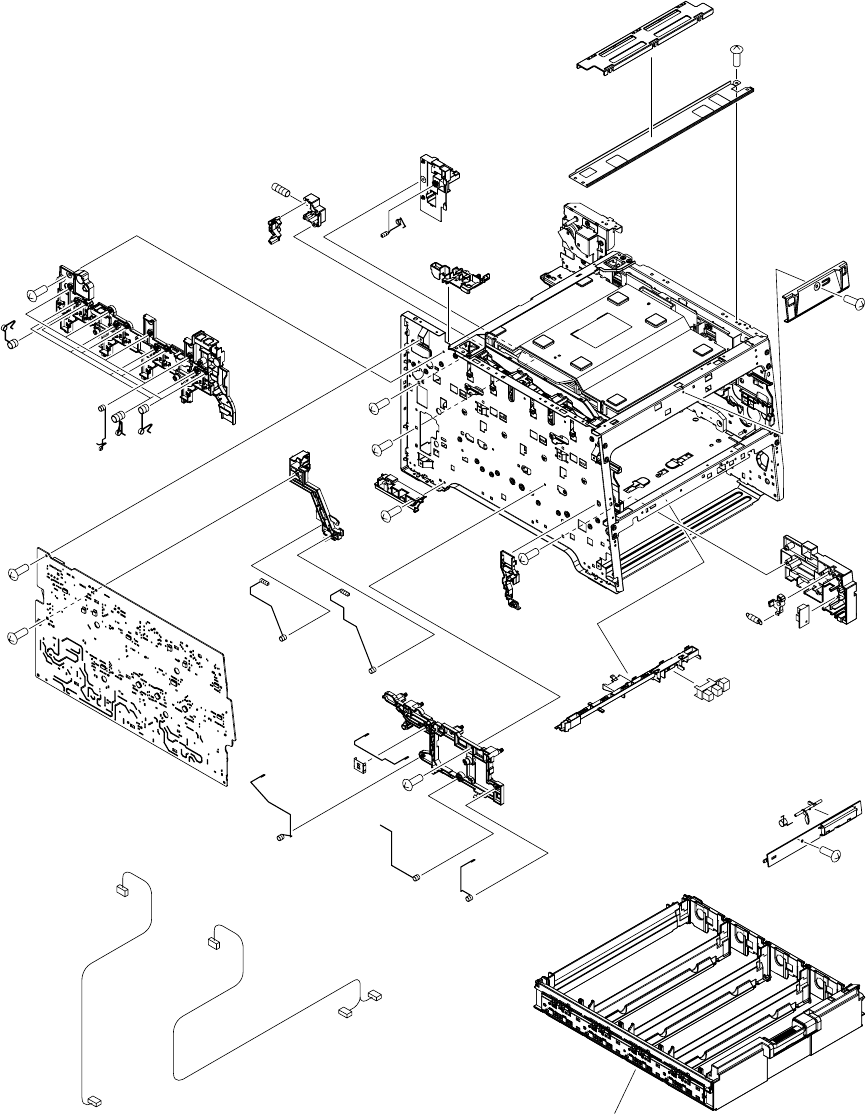
Internal assemblies
Figure 8-4 Internal components (1 of 7)
(J153)
(J3015)
(J167)
(J3006)
(J4017)
(J3006)
(SR14)
5
340 Chapter 8 Parts and diagrams ENWW

Table 8-7 Internal components (1 of 7)
Ref Description Part number Qty
5 Cartridge tray assembly RM1-4836-000CN 1
ENWW Internal assemblies 341
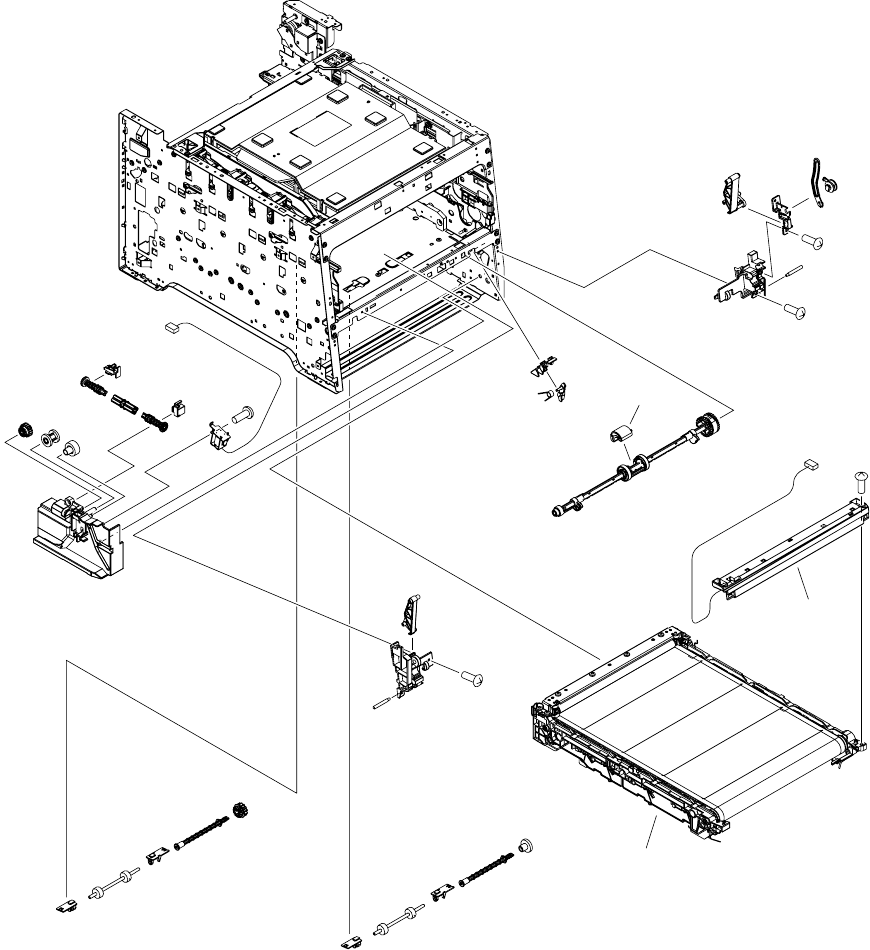
Figure 8-5 Internal components (2 of 7)
(SL1)
(J209)
(J161)
3
4
2
342 Chapter 8 Parts and diagrams ENWW

Table 8-8 Internal components (2 of 7)
Ref Description Part number Qty
2 Color misregistration sensor assembly RM1-4850-000CN 1
3 Intermediate transfer belt assembly RM1-4852-000CN 1
4 Roller, paper pickup RL1-1802-000CN 1
ENWW Internal assemblies 343
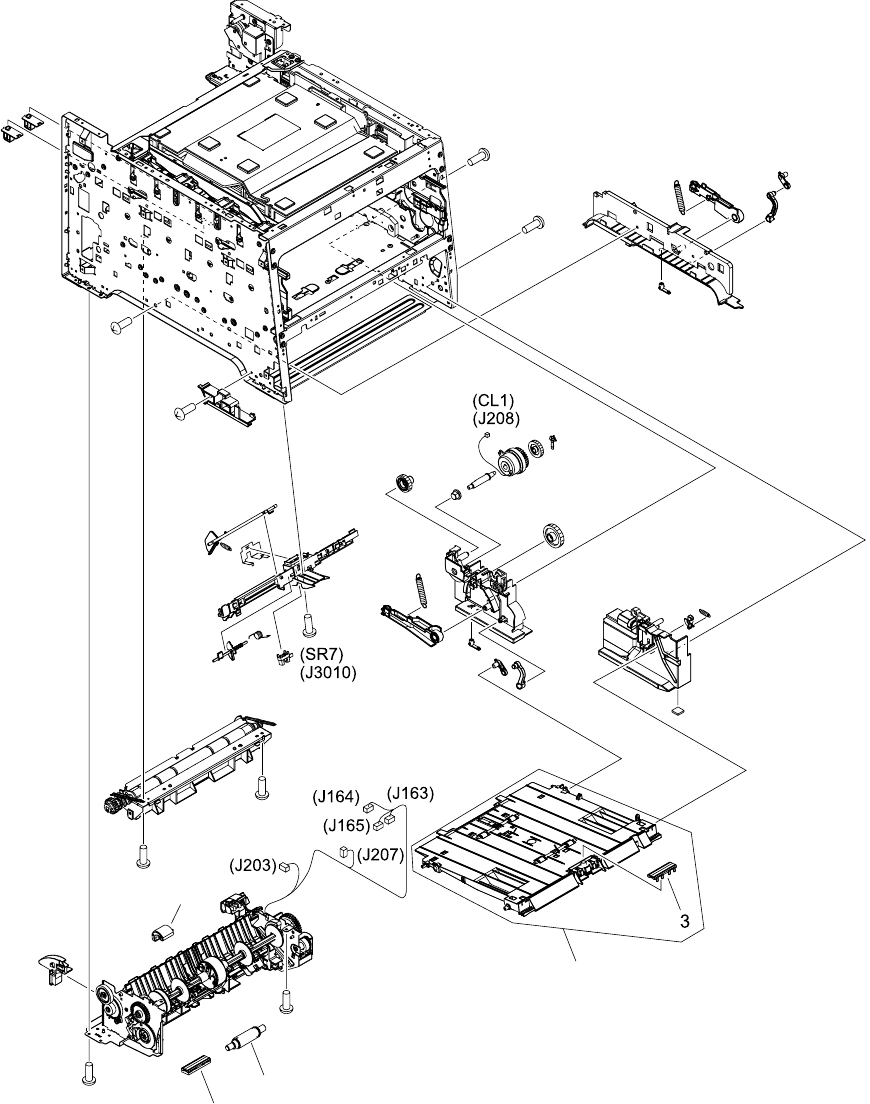
Figure 8-6 Internal components (3 of 7)
9
6
7
8
344 Chapter 8 Parts and diagrams ENWW
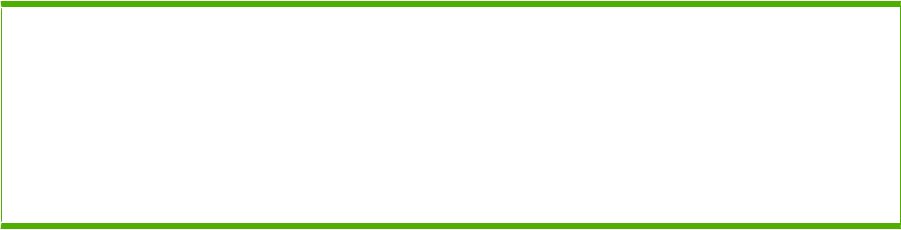
Table 8-9 Internal components (3 of 7)
Ref Description Part number Qty
3 Pad, separation RL1-1785-000CN 1
6 Pickup roller assembly RM1-4426-000CN 1
7 Separation roller assembly RM1-4840-000CN 1
8 Cover, holder RC2-2014-000CN 1
9 MP paper pickup assembly (Tray 1) RM1-4839-000CN 1
ENWW Internal assemblies 345
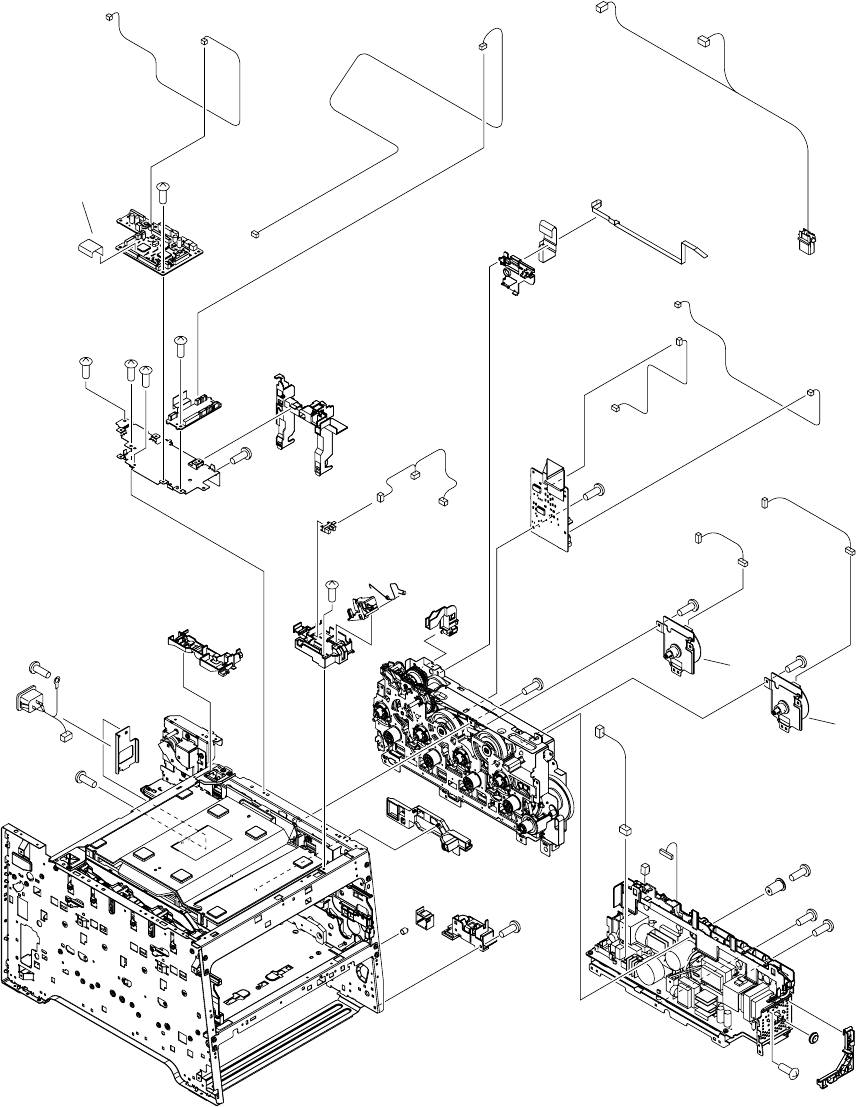
Figure 8-7 Internal components (4 of 7)
(J3001)
(J166)
(J3005)
(J3005)
(SR2)
(M1)
(M2)
(J301)
(J156) (J654)
(J131)
(J501)
(J162)
(J3010)
(J202)
(J2004)
(J205)
(J2001)
(J211)
(J2002)
(J204)
(J2002)
(J2003)
(J2003)
(J302)
(J652)
(J653) (J213)
(J991)
(J902)
(J901)
(J130) (J4004)
10
16
16
346 Chapter 8 Parts and diagrams ENWW

Table 8-10 Internal components (4 of 7)
Ref Description Part number Qty
10 Cable, flat RK2-2302-000CN 1
16 Motor, DC RL1-1800-000CN 2
ENWW Internal assemblies 347
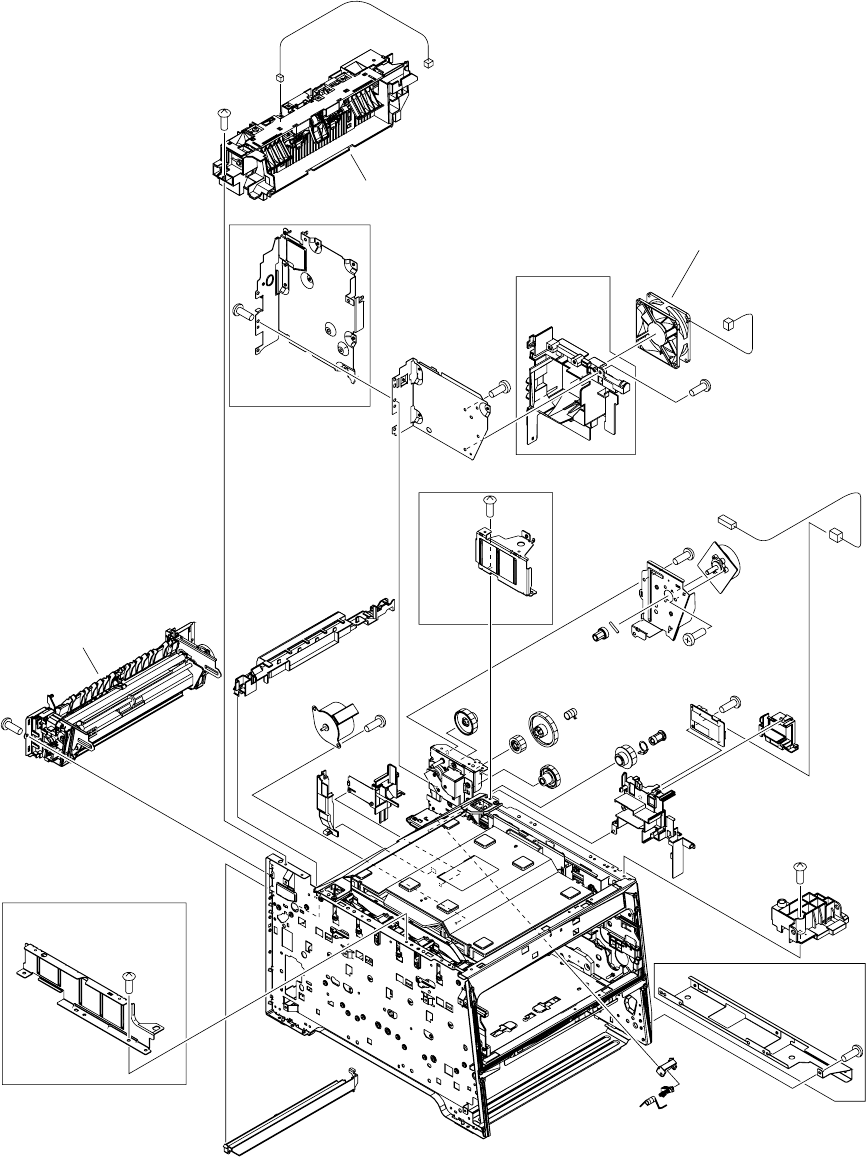
Figure 8-8 Internal components (5 of 7)
(J706) (J157)
(J206)
(J4003)
(J651)
(FM1)
(M5)
(M4)
6
4
7
348 Chapter 8 Parts and diagrams ENWW
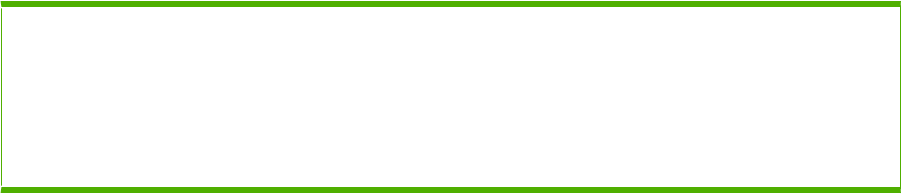
Table 8-11 Internal components (5 of 7)
Ref Description Part number Qty
4 Fan RK2-2276-000CN 1
6 Paper delivery assembly RM1-4873-000CN 1
7 Fuser assembly (110-127 V) RM1-6740-000CN 1
7 Fuser assembly (220-240 V) RM1-6741-000CN 1
ENWW Internal assemblies 349
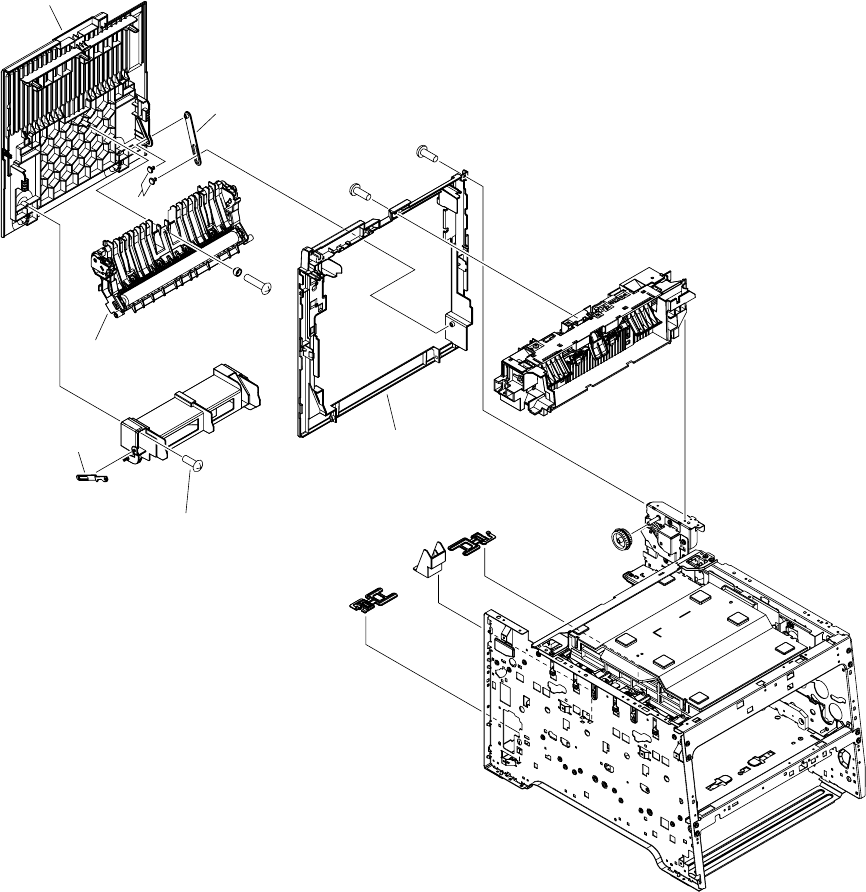
Figure 8-9 Internal components (6 of 7)—simplex models
5
4
2
8
1
6
3
350 Chapter 8 Parts and diagrams ENWW
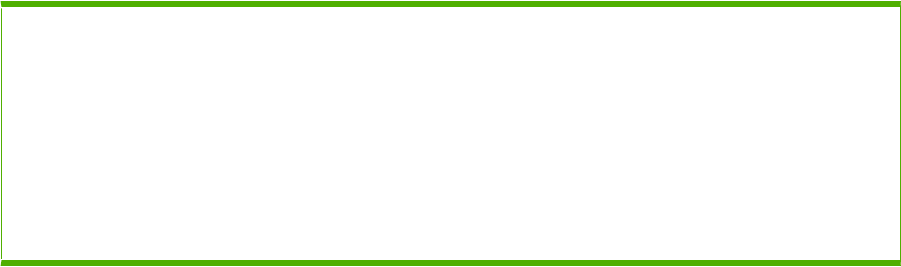
Table 8-12 Internal components (6 of 7)
Ref Description Part number Qty
1Link, guide1Not orderable 1
2 Door, rear RC2-3604-000CN 1
3 Cover, rear RL1-1822-000CN 1
4 Stopper, door, rear RC2-3598-000CN 1
5 Cap, link RC2-3599-000CN 2
6Paper feed guide assembly (simplex and duplex products)2RM1-4838-000CN 1
1Depending on which end of the link-guide attachment point has failed, replace either the rear door, or the entire product (the
interior paper guide is not replaceable).
2The paper-feed guide includes the transfer roller.
ENWW Internal assemblies 351
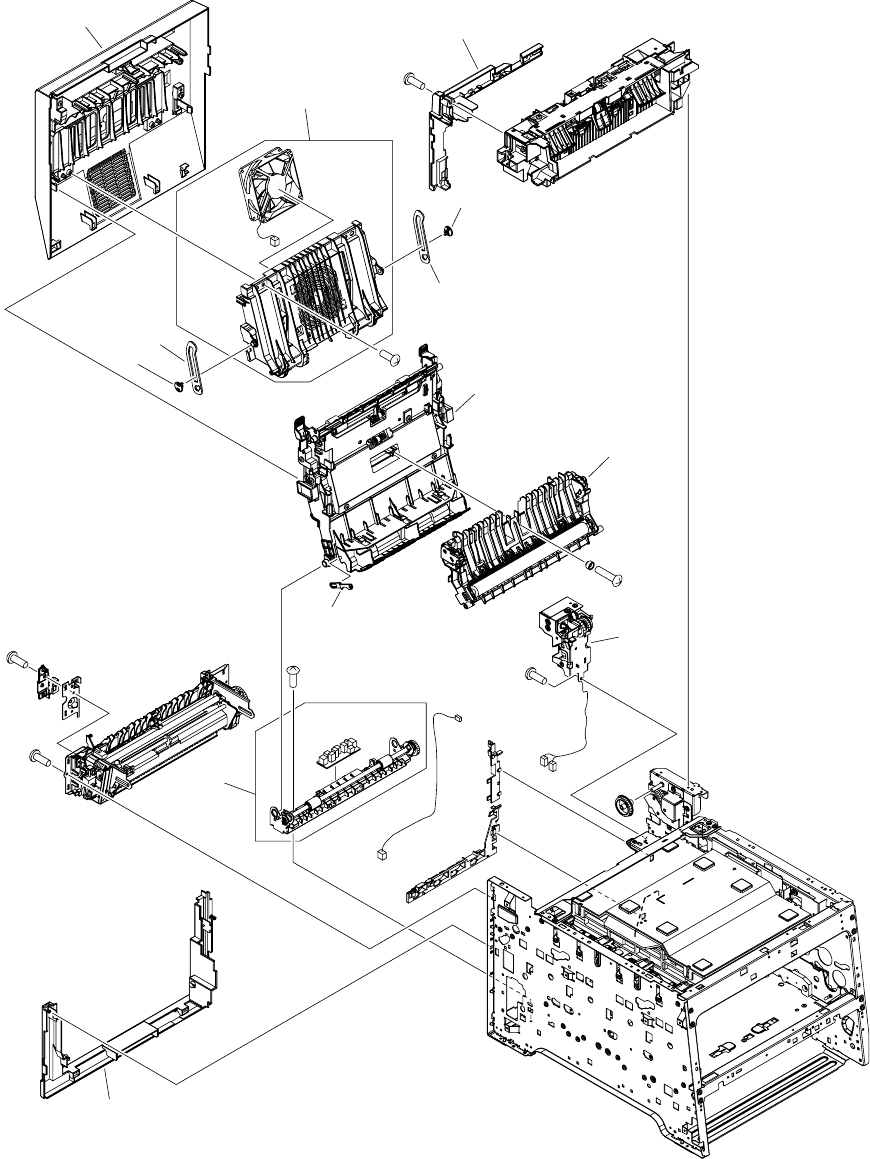
Figure 8-10 Internal components (7 of 7)—duplex models
(FM2)
(J705)
(J703)
(J704)
(J701)
(J152)
4
6
9
12
1
10
11
7
3
5
3
5
2
352 Chapter 8 Parts and diagrams ENWW
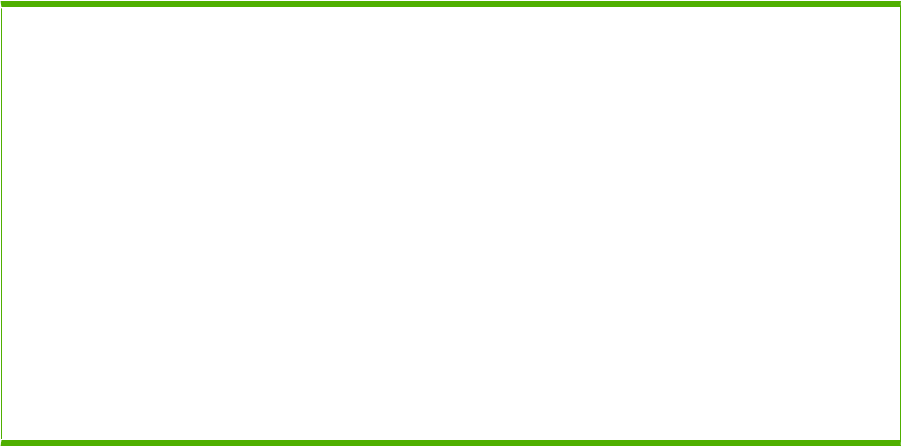
Table 8-13 Internal components (7 of 7)
Ref Description Part number Qty
1 Cover, upper rear RL1-1823-000CN 1
2 Cover, lower rear RC2-3748-000CN 1
3 Cap, link RC2-3774-000CN 2
4Link, guide1Not orderable 1
5 Link, door RC2-3750-000CN 2
6Paper feed guide assembly (simplex and duplex products)2RM1-4838-000CN 1
7 Rear door rib assembly RM1-4876-000CN 1
9 Paper re-pickup guide assembly RM1-4877-000CN 1
10 Rear door assembly RM1-4878-000CN 1
11 Duplexing-feed guide assembly RM1-4879-000CN 1
12 Reverse drive assembly RM1-4880-000CN 1
1Depending on which end of the link-guide attachment point has failed, replace either the duplexing-feed guide assembly, or
the entire product (the interior paper guide is not replaceable).
2The paper-feed guide includes the transfer roller.
ENWW Internal assemblies 353
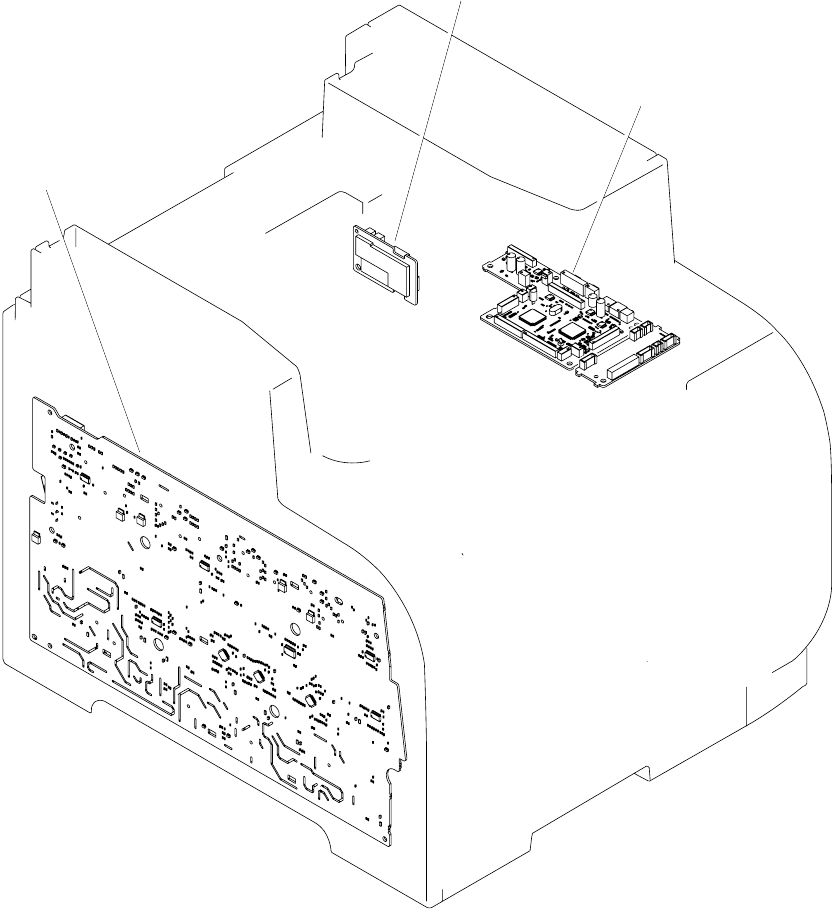
PCAs
Figure 8-11 PCA locations
3
1
2
354 Chapter 8 Parts and diagrams ENWW

Table 8-14 PCA locations
Ref Description Part number Qty
1 High-voltage power supply PCA RM1-5294-000CN 1
2 Power supply sub PCA RM1-5303-000CN 1
3 DC controller PCA RM1-5431-000CN 1
ENWW PCAs 355
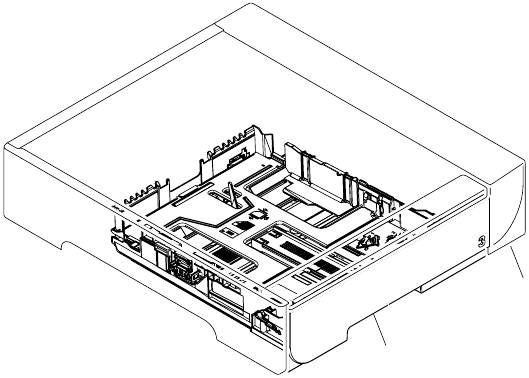
Optional 250-sheet paper cassette
Figure 8-12 Optional 250-sheet paper cassette
1
2
356 Chapter 8 Parts and diagrams ENWW

Table 8-15 250-sheet paper cassette
Ref Description Part number Qty
1 Optional 250-sheet paper feeder (includes cassette) CB500-67902 1
2 Optional 250-sheet paper cassette RM1-4901-000CN 1
ENWW Optional 250-sheet paper cassette 357
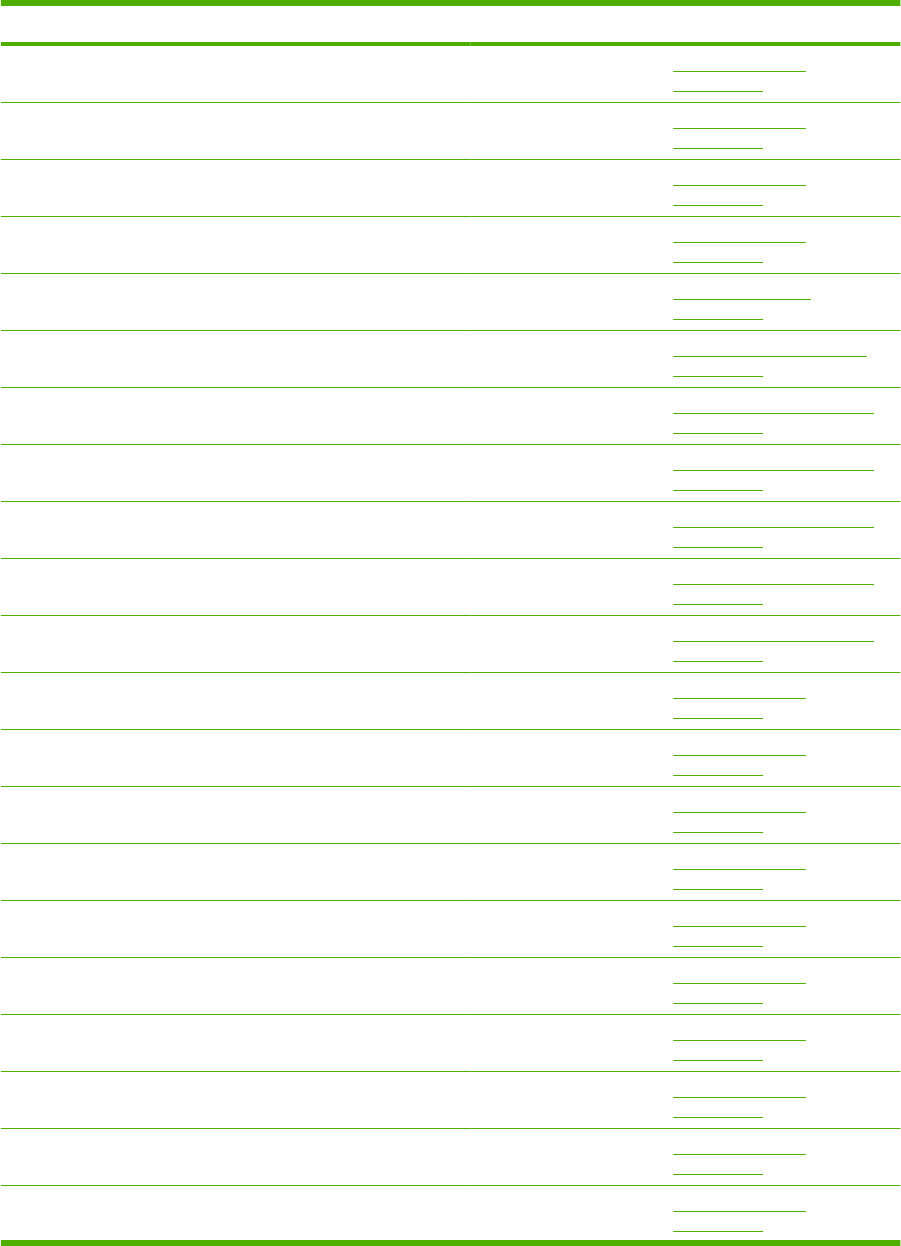
Alphabetical parts list
Table 8-16 Alphabetical parts list
Description Part number Table and page
ADF input tray CC431-60119 Scanner assembly
on page 333
ADF pickup roller assembly 5851-3580 Scanner assembly
on page 333
Automatic document feeder (ADF) assembly—duplex models CC436-67901 Scanner assembly
on page 333
Automatic document feeder (ADF) assembly—simplex models CC434-67902 Scanner assembly
on page 333
Blank bezel (not shown) CC434-67901 Assembly locations
on page 337
Button, power RC2-3612-000CN External panels and covers
on page 339
Cable, flat RK2-2302-000CN Internal components (4 of 7)
on page 347
Cap, link RC2-3599-000CN Internal components (6 of 7)
on page 351
Cap, link RC2-3774-000CN Internal components (7 of 7)
on page 353
Cartridge tray assembly RM1-4836-000CN Internal components (1 of 7)
on page 341
Color misregistration sensor assembly RM1-4850-000CN Internal components (2 of 7)
on page 343
Control-panel assembly, Asian CC434-60102 Scanner assembly
on page 333
Control-panel assembly, Western, base model CC434-60101 Scanner assembly
on page 333
Control-panel assembly, Western, fax/memory-card models CC431-60101 Scanner assembly
on page 333
Control-panel bezel, fax model, Arabic CC436-40022 Scanner assembly
on page 333
Control-panel bezel, fax model, Chinese, simplified CC436-40025 Scanner assembly
on page 333
Control-panel bezel, fax model, Chinese, traditional CC436-40023 Scanner assembly
on page 333
Control-panel bezel, fax model, Czech CC436-40015 Scanner assembly
on page 333
Control-panel bezel, fax model, Danish CC436-40013 Scanner assembly
on page 333
Control-panel bezel, fax model, Dutch CC436-40008 Scanner assembly
on page 333
Control-panel bezel, fax model, English CC436-40003 Scanner assembly
on page 333
358 Chapter 8 Parts and diagrams ENWW
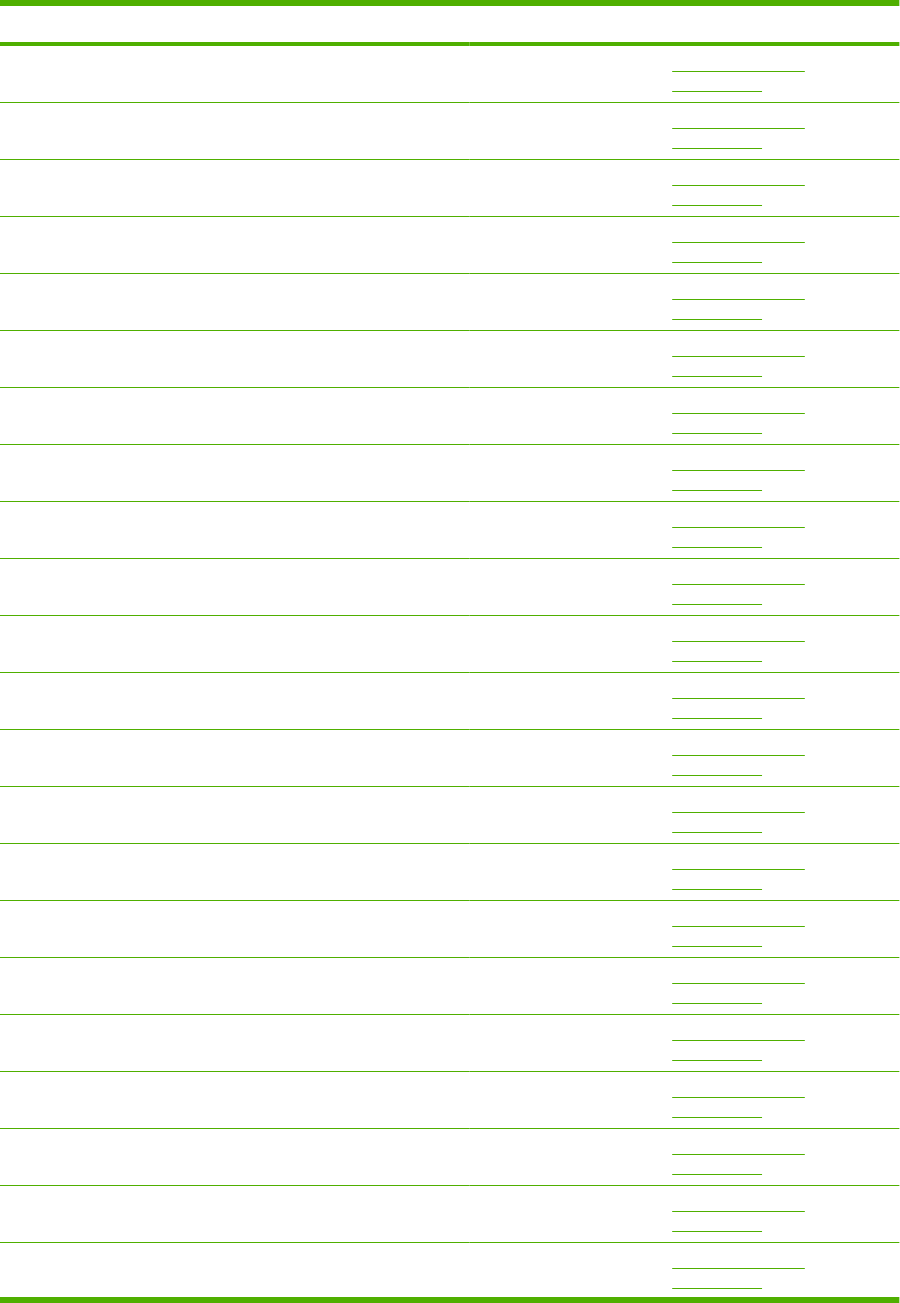
Description Part number Table and page
Control-panel bezel, fax model, Finnish CC436-40012 Scanner assembly
on page 333
Control-panel bezel, fax model, French CC436-40007 Scanner assembly
on page 333
Control-panel bezel, fax model, German CC436-40006 Scanner assembly
on page 333
Control-panel bezel, fax model, Greek CC436-40020 Scanner assembly
on page 333
Control-panel bezel, fax model, Hebrew CC436-40021 Scanner assembly
on page 333
Control-panel bezel, fax model, Hungarian CC436-40016 Scanner assembly
on page 333
Control-panel bezel, fax model, Italian CC436-40009 Scanner assembly
on page 333
Control-panel bezel, fax model, Korean CC436-40024 Scanner assembly
on page 333
Control-panel bezel, fax model, Norwegian CC436-40011 Scanner assembly
on page 333
Control-panel bezel, fax model, Polish CC436-40017 Scanner assembly
on page 333
Control-panel bezel, fax model, Portuguese CC436-40005 Scanner assembly
on page 333
Control-panel bezel, fax model, Russian CC436-40014 Scanner assembly
on page 333
Control-panel bezel, fax model, Slovak CC436-40018 Scanner assembly
on page 333
Control-panel bezel, fax model, Spanish CC436-40004 Scanner assembly
on page 333
Control-panel bezel, fax model, Swedish CC436-40010 Scanner assembly
on page 333
Control-panel bezel, fax model, Thai CC436-40026 Scanner assembly
on page 333
Control-panel bezel, fax model, Turkish CC436-40019 Scanner assembly
on page 333
Control-panel bezel, fax model, Vietnamese CC436-40027 Scanner assembly
on page 333
Control-panel bezel, memory-card model, Arabic CC431-40021 Scanner assembly
on page 333
Control-panel bezel, memory-card model, Chinese, simplified CC431-40024 Scanner assembly
on page 333
Control-panel bezel, memory-card model, Chinese, traditional CC431-40022 Scanner assembly
on page 333
Control-panel bezel, memory-card model, Czech CC431-40014 Scanner assembly
on page 333
Table 8-16 Alphabetical parts list (continued)
ENWW Alphabetical parts list 359
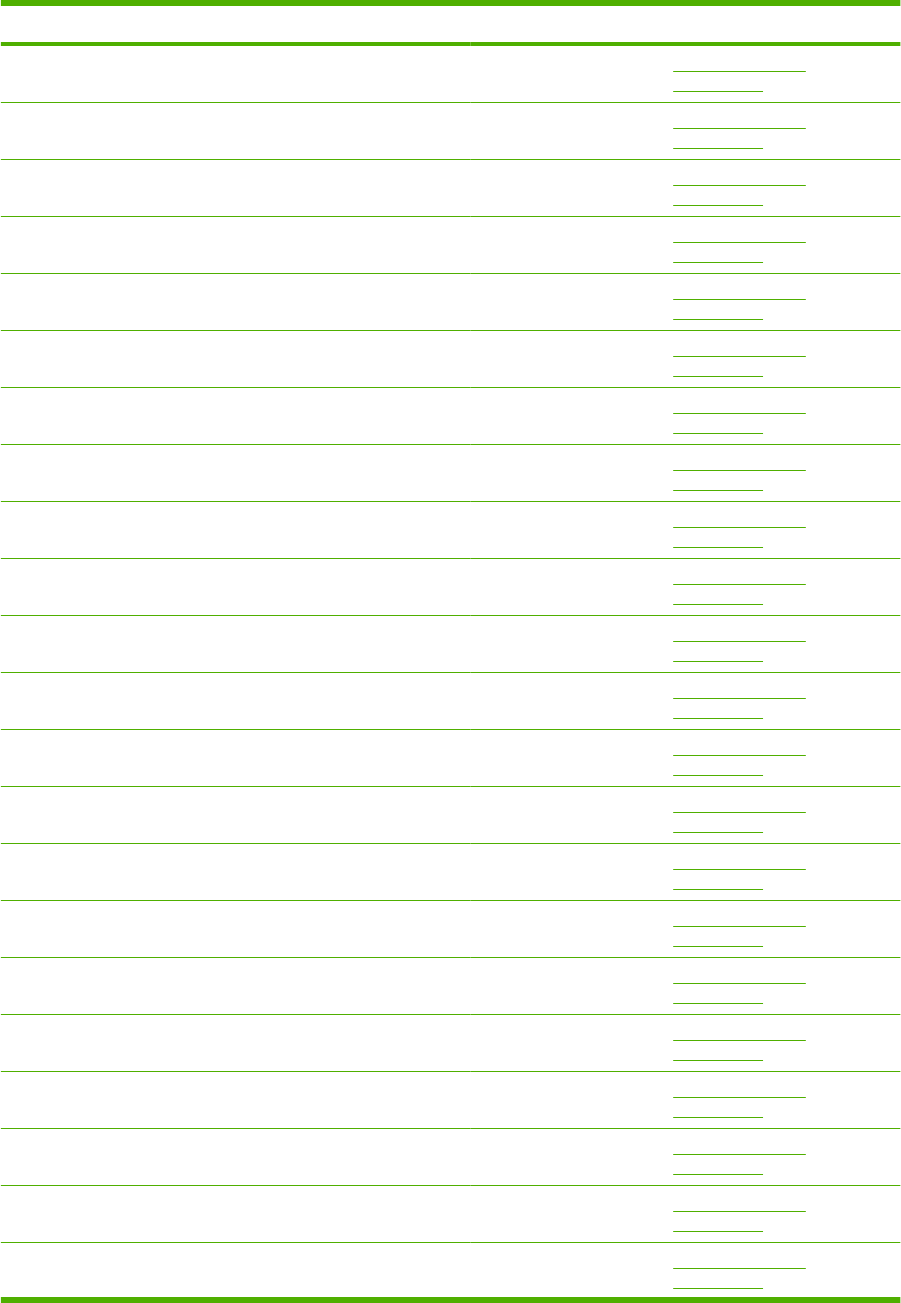
Description Part number Table and page
Control-panel bezel, memory-card model, Danish CC431-40012 Scanner assembly
on page 333
Control-panel bezel, memory-card model, Dutch CC431-40007 Scanner assembly
on page 333
Control-panel bezel, memory-card model, English CC431-40002 Scanner assembly
on page 333
Control-panel bezel, memory-card model, Finnish CC431-40011 Scanner assembly
on page 333
Control-panel bezel, memory-card model, French CC431-40006 Scanner assembly
on page 333
Control-panel bezel, memory-card model, German CC431-40005 Scanner assembly
on page 333
Control-panel bezel, memory-card model, Greek CC431-40019 Scanner assembly
on page 333
Control-panel bezel, memory-card model, Hebrew CC431-40020 Scanner assembly
on page 333
Control-panel bezel, memory-card model, Hungarian CC431-40015 Scanner assembly
on page 333
Control-panel bezel, memory-card model, Italian CC431-40008 Scanner assembly
on page 333
Control-panel bezel, memory-card model, Korean CC431-40023 Scanner assembly
on page 333
Control-panel bezel, memory-card model, Norwegian CC431-40010 Scanner assembly
on page 333
Control-panel bezel, memory-card model, Polish CC431-40016 Scanner assembly
on page 333
Control-panel bezel, memory-card model, Portuguese CC431-40004 Scanner assembly
on page 333
Control-panel bezel, memory-card model, Russian CC431-40013 Scanner assembly
on page 333
Control-panel bezel, memory-card model, Slovak CC431-40017 Scanner assembly
on page 333
Control-panel bezel, memory-card model, Spanish CC431-40003 Scanner assembly
on page 333
Control-panel bezel, memory-card model, Swedish CC431-40009 Scanner assembly
on page 333
Control-panel bezel, memory-card model, Thai CC431-40025 Scanner assembly
on page 333
Control-panel bezel, memory-card model, Turkish CC431-40018 Scanner assembly
on page 333
Control-panel bezel, memory-card model, Vietnamese CC431-40026 Scanner assembly
on page 333
Control-panel overlay, base model, Arabic CC434-00024 Scanner assembly
on page 333
Table 8-16 Alphabetical parts list (continued)
360 Chapter 8 Parts and diagrams ENWW
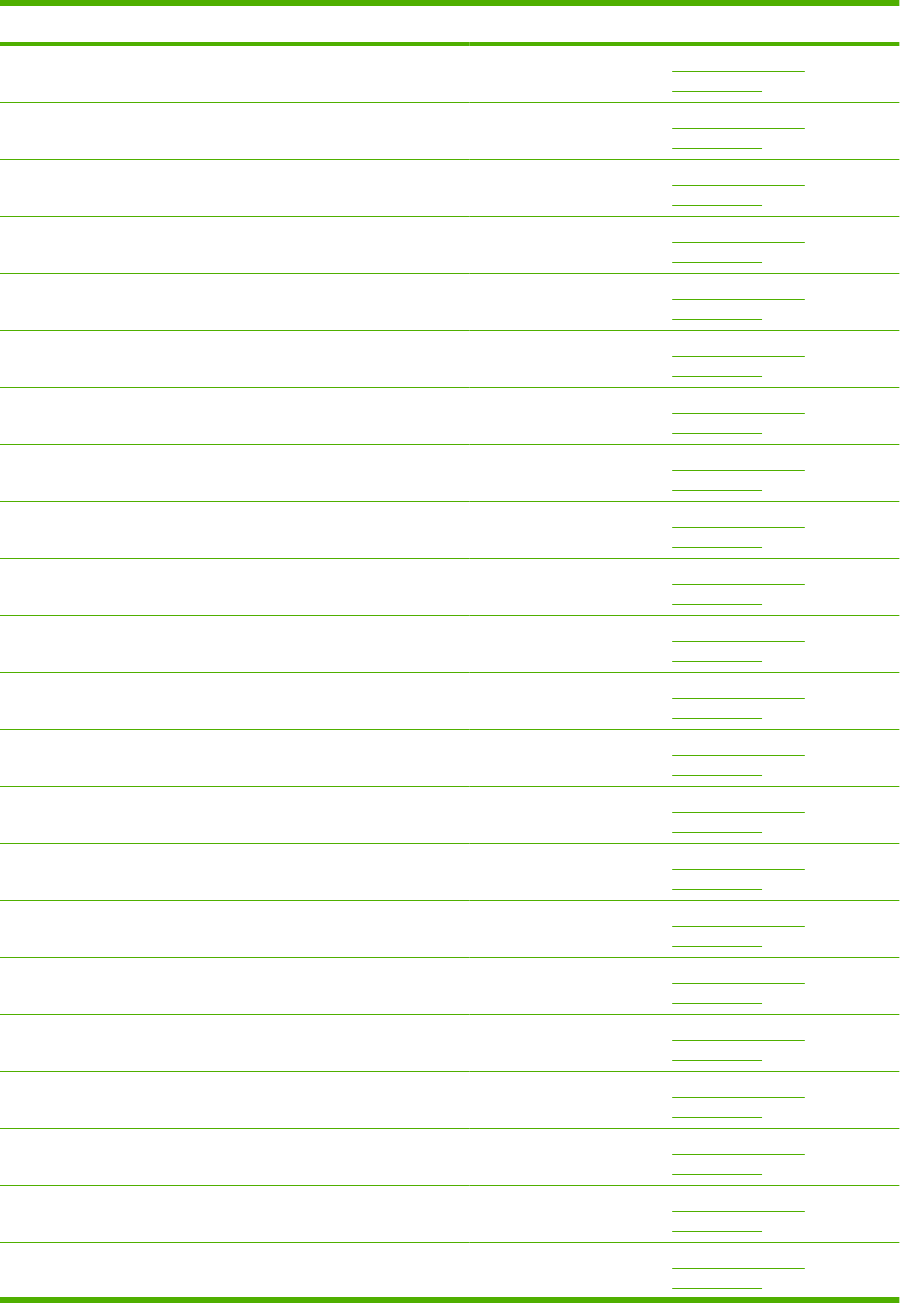
Description Part number Table and page
Control-panel overlay, base model, Chinese, simplified CC434-00027 Scanner assembly
on page 333
Control-panel overlay, base model, Chinese, traditional CC434-00025 Scanner assembly
on page 333
Control-panel overlay, base model, Czech CC434-00017 Scanner assembly
on page 333
Control-panel overlay, base model, Danish CC434-00015 Scanner assembly
on page 333
Control-panel overlay, base model, Dutch CC434-00010 Scanner assembly
on page 333
Control-panel overlay, base model, English CC434-60105 Scanner assembly
on page 333
Control-panel overlay, base model, Finnish CC434-00014 Scanner assembly
on page 333
Control-panel overlay, base model, French CC434-00009 Scanner assembly
on page 333
Control-panel overlay, base model, German CC434-00008 Scanner assembly
on page 333
Control-panel overlay, base model, Greek CC434-00022 Scanner assembly
on page 333
Control-panel overlay, base model, Hebrew CC434-00023 Scanner assembly
on page 333
Control-panel overlay, base model, Hungarian CC434-00018 Scanner assembly
on page 333
Control-panel overlay, base model, Italian CC434-00011 Scanner assembly
on page 333
Control-panel overlay, base model, Korean CC434-00026 Scanner assembly
on page 333
Control-panel overlay, base model, Norwegian CC434-00013 Scanner assembly
on page 333
Control-panel overlay, base model, Polish CC434-00019 Scanner assembly
on page 333
Control-panel overlay, base model, Portuguese CC434-00007 Scanner assembly
on page 333
Control-panel overlay, base model, Russian CC434-00016 Scanner assembly
on page 333
Control-panel overlay, base model, Slovak CC434-00020 Scanner assembly
on page 333
Control-panel overlay, base model, Spanish CC434-00006 Scanner assembly
on page 333
Control-panel overlay, base model, Swedish CC434-00012 Scanner assembly
on page 333
Control-panel overlay, base model, Thai CC434-00028 Scanner assembly
on page 333
Table 8-16 Alphabetical parts list (continued)
ENWW Alphabetical parts list 361
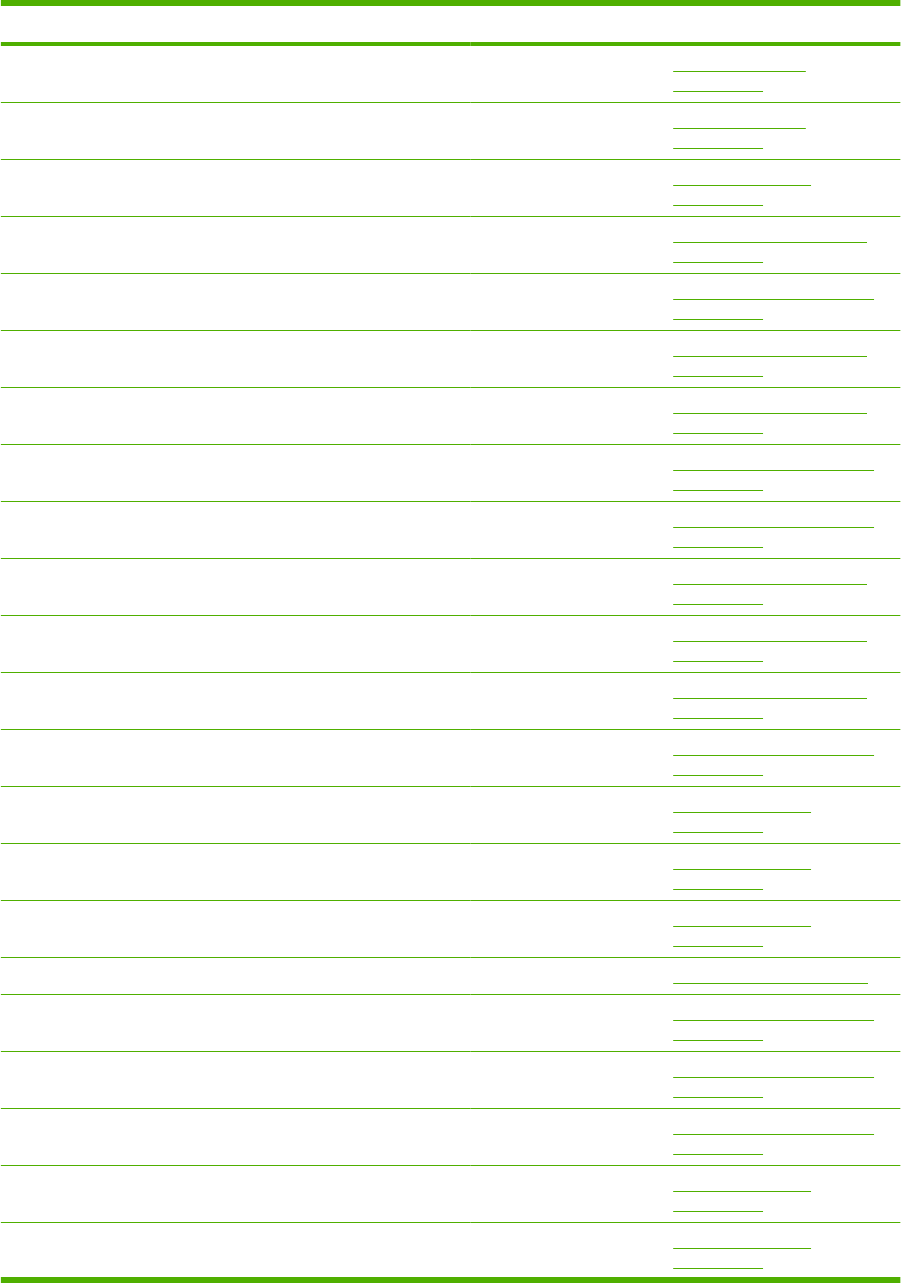
Description Part number Table and page
Control-panel overlay, base model, Turkish CC434-00021 Scanner assembly
on page 333
Control-panel overlay, base model, Vietnamese CC434-00029 Scanner assembly
on page 333
Core ferrite (not shown) 9170-2452 Assembly locations
on page 337
Cover, DIMM RC2-3614-000CN External panels and covers
on page 339
Cover, holder RC2-2014-000CN Internal components (3 of 7)
on page 345
Cover, IOT RC2-3918-000CN External panels and covers
on page 339
Cover, left RC2-3913-000CN External panels and covers
on page 339
Cover, lower rear RC2-3748-000CN Internal components (7 of 7)
on page 353
Cover, rear RL1-1822-000CN Internal components (6 of 7)
on page 351
Cover, right RC2-3912-000CN External panels and covers
on page 339
Cover, right front RC2-3914-000CN External panels and covers
on page 339
Cover, right front, lower RC2-3915-000CN External panels and covers
on page 339
Cover, upper rear RL1-1823-000CN Internal components (7 of 7)
on page 353
DAA (fax card), Americas/Asia (fax models only) CC367-60001 Assembly locations
on page 337
DAA (fax card), Europe (fax models only) CC514-60002 Assembly locations
on page 337
DAA flat flexible cable (not shown) 5851-3054 Assembly locations
on page 337
DC controller PCA RM1-5431-000CN PCA locations on page 355
Door, rear RC2-3604-000CN Internal components (6 of 7)
on page 351
Duplexing-feed guide assembly RM1-4879-000CN Internal components (7 of 7)
on page 353
Fan RK2-2276-000CN Internal components (5 of 7)
on page 349
Fax insulator (not shown) 5851-3375 Assembly locations
on page 337
Formatter bracket, base models (not shown) CC430-00027 Assembly locations
on page 337
Table 8-16 Alphabetical parts list (continued)
362 Chapter 8 Parts and diagrams ENWW
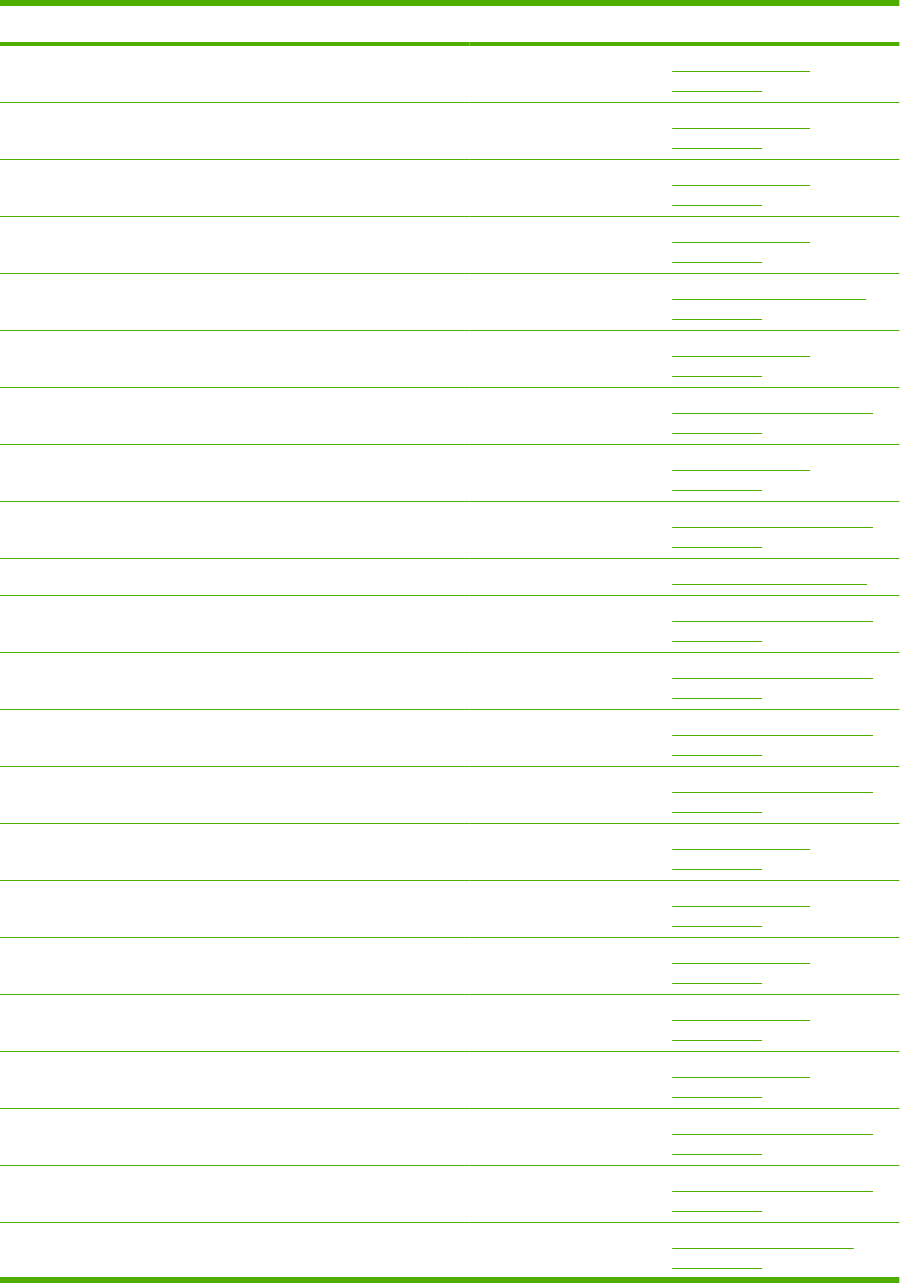
Description Part number Table and page
Formatter bracket, fax/memory-card models (not shown) CC431-00002 Assembly locations
on page 337
Formatter, base model CC399-67901 Assembly locations
on page 337
Formatter, business CE684-67901 Assembly locations
on page 337
Formatter, fax models CC400-67901 Assembly locations
on page 337
Front door assembly RM1-4848-000CN External panels and covers
on page 339
Fuser assembly (110-127 V) RM1-6740-000CN Assembly locations
on page 337
Fuser assembly (110-127 V) RM1-6740-000CN Internal components (5 of 7)
on page 349
Fuser assembly (220-240 V) RM1-6741-000CN Assembly locations
on page 337
Fuser assembly (220-240 V) RM1-6741-000CN Internal components (5 of 7)
on page 349
High-voltage power supply PCA RM1-5294-000CN PCA locations on page 355
Intermediate transfer belt assembly RM1-4852-000CN Internal components (2 of 7)
on page 343
Link, door RC2-3750-000CN Internal components (7 of 7)
on page 353
Link, guide1Not orderable Internal components (6 of 7)
on page 351
Link, guide1Not orderable Internal components (7 of 7)
on page 353
Memory card bezel (not shown) CC435-67901 Assembly locations
on page 337
Memory card bracket (not shown) CC435-00001 Assembly locations
on page 337
Memory card cable (not shown) 5851-3055 Assembly locations
on page 337
Memory card cable guide (not shown) CC435-40001 Assembly locations
on page 337
Memory-card assembly (memory-card models only) CC401-67901 Assembly locations
on page 337
Motor, DC RL1-1800-000CN Internal components (4 of 7)
on page 347
MP paper pickup assembly (Tray 1) RM1-4839-000CN Internal components (3 of 7)
on page 345
Optional 250-sheet paper cassette RM1-4901-000CN 250-sheet paper cassette
on page 357
Table 8-16 Alphabetical parts list (continued)
ENWW Alphabetical parts list 363
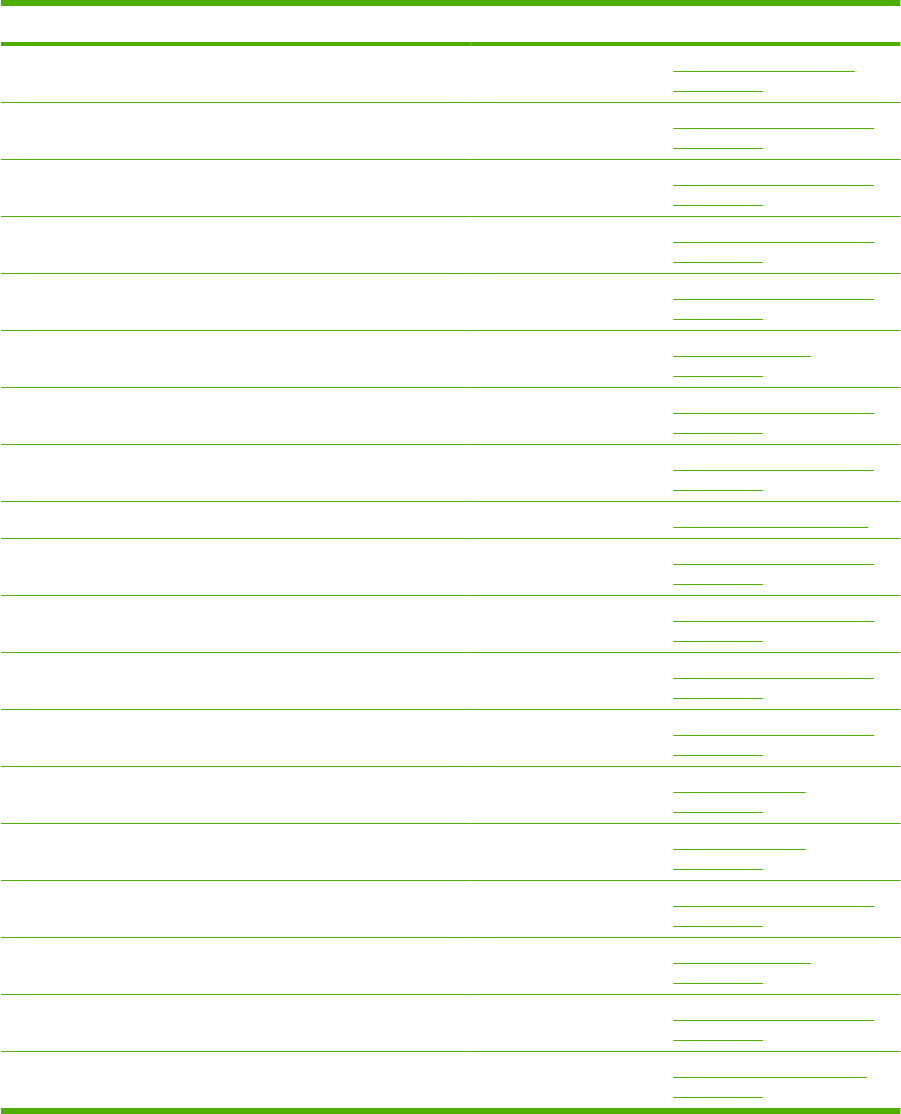
Description Part number Table and page
Optional 250-sheet paper feeder (includes cassette) CB500-67902 250-sheet paper cassette
on page 357
Pad, separation RL1-1785-000CN Internal components (3 of 7)
on page 345
Paper delivery assembly RM1-4873-000CN Internal components (5 of 7)
on page 349
Paper feed guide assembly (simplex and duplex products)2RM1-4838-000CN Internal components (6 of 7)
on page 351
Paper feed guide assembly (simplex and duplex products)2RM1-4838-000CN Internal components (7 of 7)
on page 353
Paper input cassette RM1-4860-000CN Assembly locations
on page 337
Paper re-pickup guide assembly RM1-4877-000CN Internal components (7 of 7)
on page 353
Pickup roller assembly RM1-4426-000CN Internal components (3 of 7)
on page 345
Power supply sub PCA RM1-5303-000CN PCA locations on page 355
Rear door assembly RM1-4878-000CN Internal components (7 of 7)
on page 353
Rear door rib assembly RM1-4876-000CN Internal components (7 of 7)
on page 353
Reverse drive assembly RM1-4880-000CN Internal components (7 of 7)
on page 353
Roller, paper pickup RL1-1802-000CN Internal components (2 of 7)
on page 343
Scanner assembly, base CC436-67903 Scanner assembly
on page 333
Scanner assembly, business/imaging CC436-67902 Scanner assembly
on page 333
Separation roller assembly RM1-4840-000CN Internal components (3 of 7)
on page 345
Speaker (not shown) Q3948-60113 Assembly locations
on page 337
Stopper, door, rear RC2-3598-000CN Internal components (6 of 7)
on page 351
Upper cover assembly RM1-4911-000CN External panels and covers
on page 339
Table 8-16 Alphabetical parts list (continued)
364 Chapter 8 Parts and diagrams ENWW
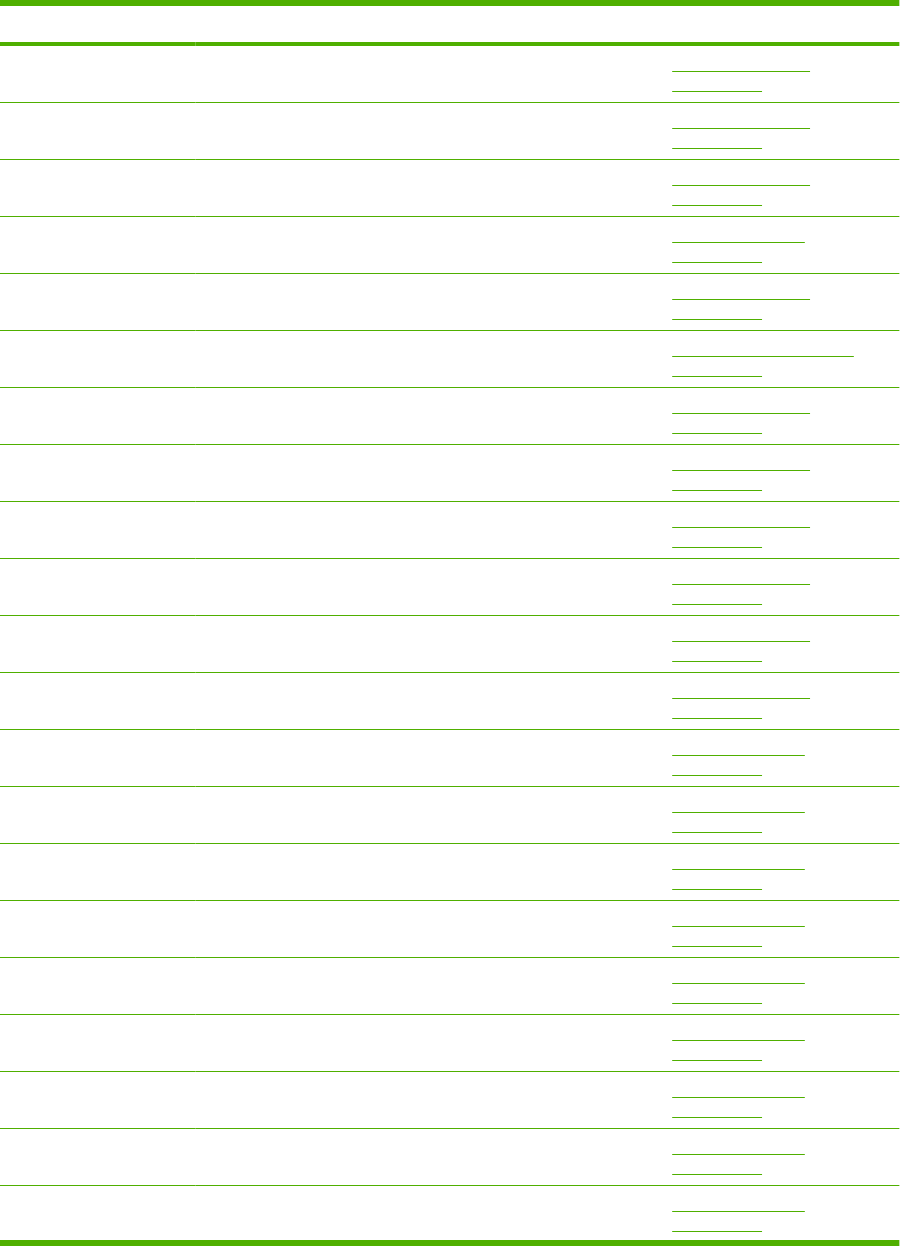
Numerical parts list
Table 8-17 Numerical parts list
Part number Description Table and page
5851-3054 DAA flat flexible cable (not shown) Assembly locations
on page 337
5851-3055 Memory card cable (not shown) Assembly locations
on page 337
5851-3375 Fax insulator (not shown) Assembly locations
on page 337
5851-3580 ADF pickup roller assembly Scanner assembly
on page 333
9170-2452 Core ferrite (not shown) Assembly locations
on page 337
CB500-67902 Optional 250-sheet paper feeder (includes cassette) 250-sheet paper cassette
on page 357
CC367-60001 DAA (fax card), Americas/Asia (fax models only) Assembly locations
on page 337
CC399-67901 Formatter, base model Assembly locations
on page 337
CC400-67901 Formatter, fax models Assembly locations
on page 337
CC401-67901 Memory-card assembly (memory-card models only) Assembly locations
on page 337
CC430-00027 Formatter bracket, base models (not shown) Assembly locations
on page 337
CC431-00002 Formatter bracket, fax/memory-card models (not shown) Assembly locations
on page 337
CC431-40002 Control-panel bezel, memory-card model, English Scanner assembly
on page 333
CC431-40003 Control-panel bezel, memory-card model, Spanish Scanner assembly
on page 333
CC431-40004 Control-panel bezel, memory-card model, Portuguese Scanner assembly
on page 333
CC431-40005 Control-panel bezel, memory-card model, German Scanner assembly
on page 333
CC431-40006 Control-panel bezel, memory-card model, French Scanner assembly
on page 333
CC431-40007 Control-panel bezel, memory-card model, Dutch Scanner assembly
on page 333
CC431-40008 Control-panel bezel, memory-card model, Italian Scanner assembly
on page 333
CC431-40009 Control-panel bezel, memory-card model, Swedish Scanner assembly
on page 333
CC431-40010 Control-panel bezel, memory-card model, Norwegian Scanner assembly
on page 333
ENWW Numerical parts list 365
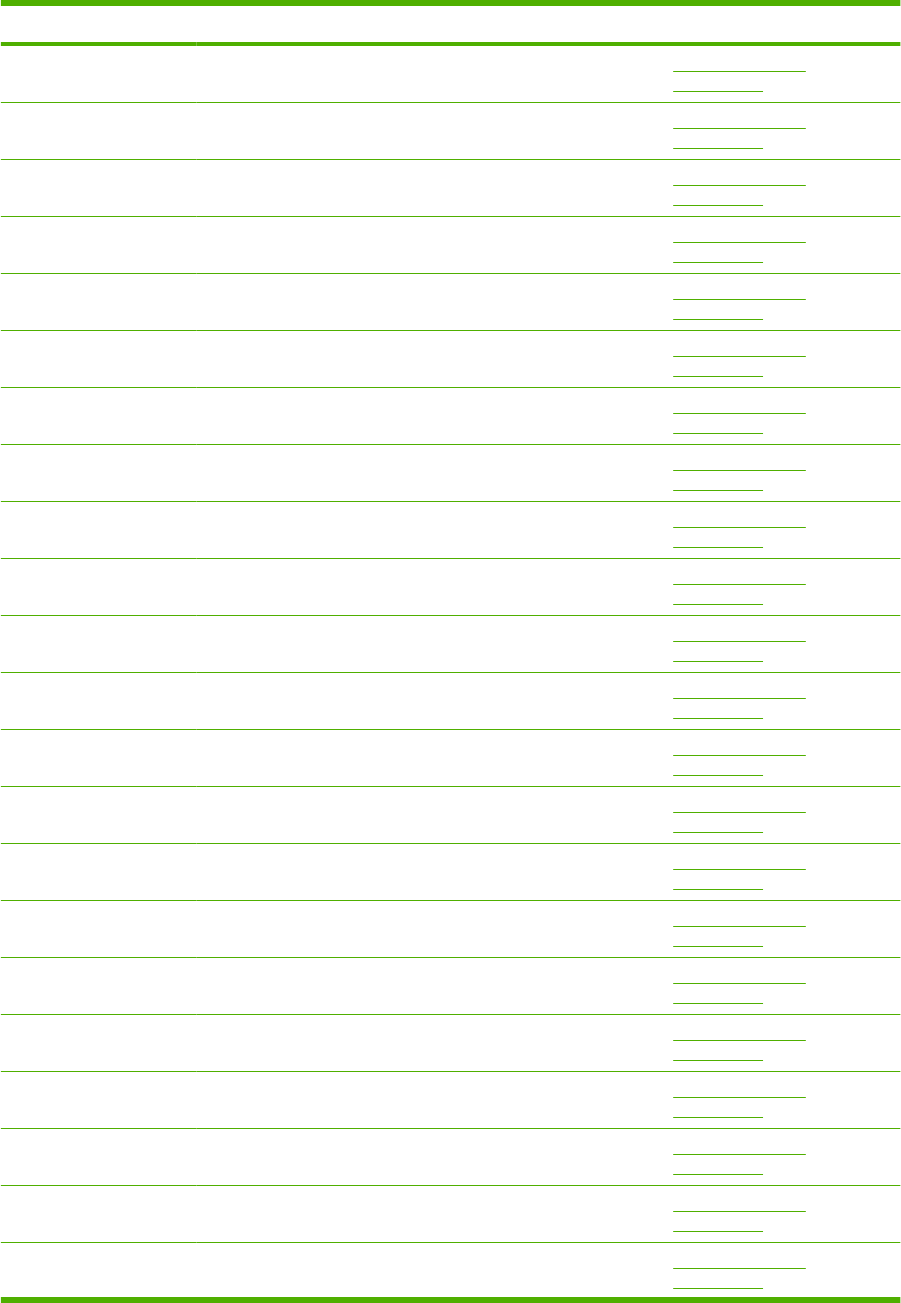
Part number Description Table and page
CC431-40011 Control-panel bezel, memory-card model, Finnish Scanner assembly
on page 333
CC431-40012 Control-panel bezel, memory-card model, Danish Scanner assembly
on page 333
CC431-40013 Control-panel bezel, memory-card model, Russian Scanner assembly
on page 333
CC431-40014 Control-panel bezel, memory-card model, Czech Scanner assembly
on page 333
CC431-40015 Control-panel bezel, memory-card model, Hungarian Scanner assembly
on page 333
CC431-40016 Control-panel bezel, memory-card model, Polish Scanner assembly
on page 333
CC431-40017 Control-panel bezel, memory-card model, Slovak Scanner assembly
on page 333
CC431-40018 Control-panel bezel, memory-card model, Turkish Scanner assembly
on page 333
CC431-40019 Control-panel bezel, memory-card model, Greek Scanner assembly
on page 333
CC431-40020 Control-panel bezel, memory-card model, Hebrew Scanner assembly
on page 333
CC431-40021 Control-panel bezel, memory-card model, Arabic Scanner assembly
on page 333
CC431-40022 Control-panel bezel, memory-card model, Chinese, traditional Scanner assembly
on page 333
CC431-40023 Control-panel bezel, memory-card model, Korean Scanner assembly
on page 333
CC431-40024 Control-panel bezel, memory-card model, Chinese, simplified Scanner assembly
on page 333
CC431-40025 Control-panel bezel, memory-card model, Thai Scanner assembly
on page 333
CC431-40026 Control-panel bezel, memory-card model, Vietnamese Scanner assembly
on page 333
CC431-60101 Control-panel assembly, Western, fax/memory-card models Scanner assembly
on page 333
CC431-60119 ADF input tray Scanner assembly
on page 333
CC434-00006 Control-panel overlay, base model, Spanish Scanner assembly
on page 333
CC434-00007 Control-panel overlay, base model, Portuguese Scanner assembly
on page 333
CC434-00008 Control-panel overlay, base model, German Scanner assembly
on page 333
CC434-00009 Control-panel overlay, base model, French Scanner assembly
on page 333
Table 8-17 Numerical parts list (continued)
366 Chapter 8 Parts and diagrams ENWW
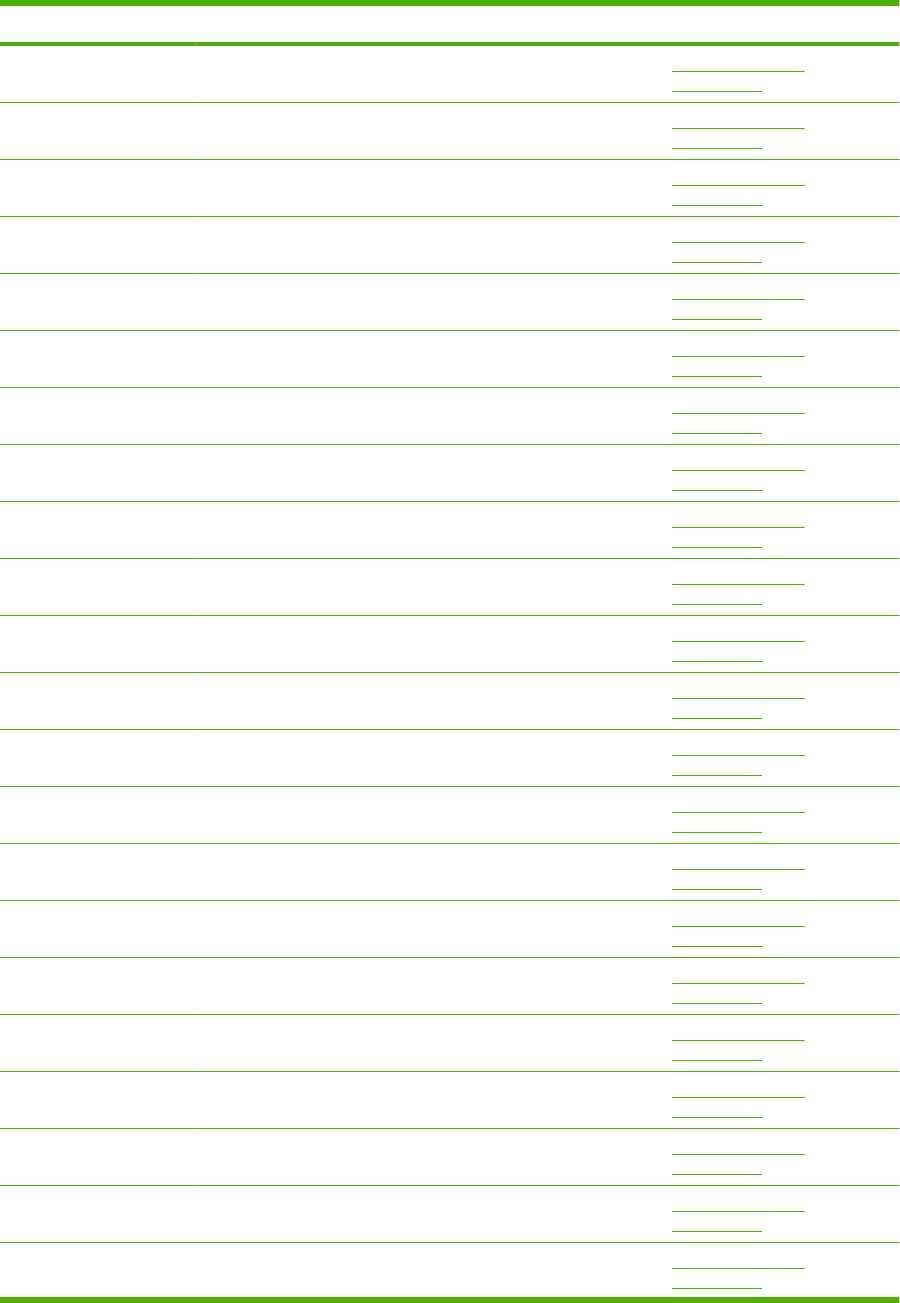
Part number Description Table and page
CC434-00010 Control-panel overlay, base model, Dutch Scanner assembly
on page 333
CC434-00011 Control-panel overlay, base model, Italian Scanner assembly
on page 333
CC434-00012 Control-panel overlay, base model, Swedish Scanner assembly
on page 333
CC434-00013 Control-panel overlay, base model, Norwegian Scanner assembly
on page 333
CC434-00014 Control-panel overlay, base model, Finnish Scanner assembly
on page 333
CC434-00015 Control-panel overlay, base model, Danish Scanner assembly
on page 333
CC434-00016 Control-panel overlay, base model, Russian Scanner assembly
on page 333
CC434-00017 Control-panel overlay, base model, Czech Scanner assembly
on page 333
CC434-00018 Control-panel overlay, base model, Hungarian Scanner assembly
on page 333
CC434-00019 Control-panel overlay, base model, Polish Scanner assembly
on page 333
CC434-00020 Control-panel overlay, base model, Slovak Scanner assembly
on page 333
CC434-00021 Control-panel overlay, base model, Turkish Scanner assembly
on page 333
CC434-00022 Control-panel overlay, base model, Greek Scanner assembly
on page 333
CC434-00023 Control-panel overlay, base model, Hebrew Scanner assembly
on page 333
CC434-00024 Control-panel overlay, base model, Arabic Scanner assembly
on page 333
CC434-00025 Control-panel overlay, base model, Chinese, traditional Scanner assembly
on page 333
CC434-00026 Control-panel overlay, base model, Korean Scanner assembly
on page 333
CC434-00027 Control-panel overlay, base model, Chinese, simplified Scanner assembly
on page 333
CC434-00028 Control-panel overlay, base model, Thai Scanner assembly
on page 333
CC434-00029 Control-panel overlay, base model, Vietnamese Scanner assembly
on page 333
CC434-60101 Control-panel assembly, Western, base model Scanner assembly
on page 333
CC434-60102 Control-panel assembly, Asian Scanner assembly
on page 333
Table 8-17 Numerical parts list (continued)
ENWW Numerical parts list 367
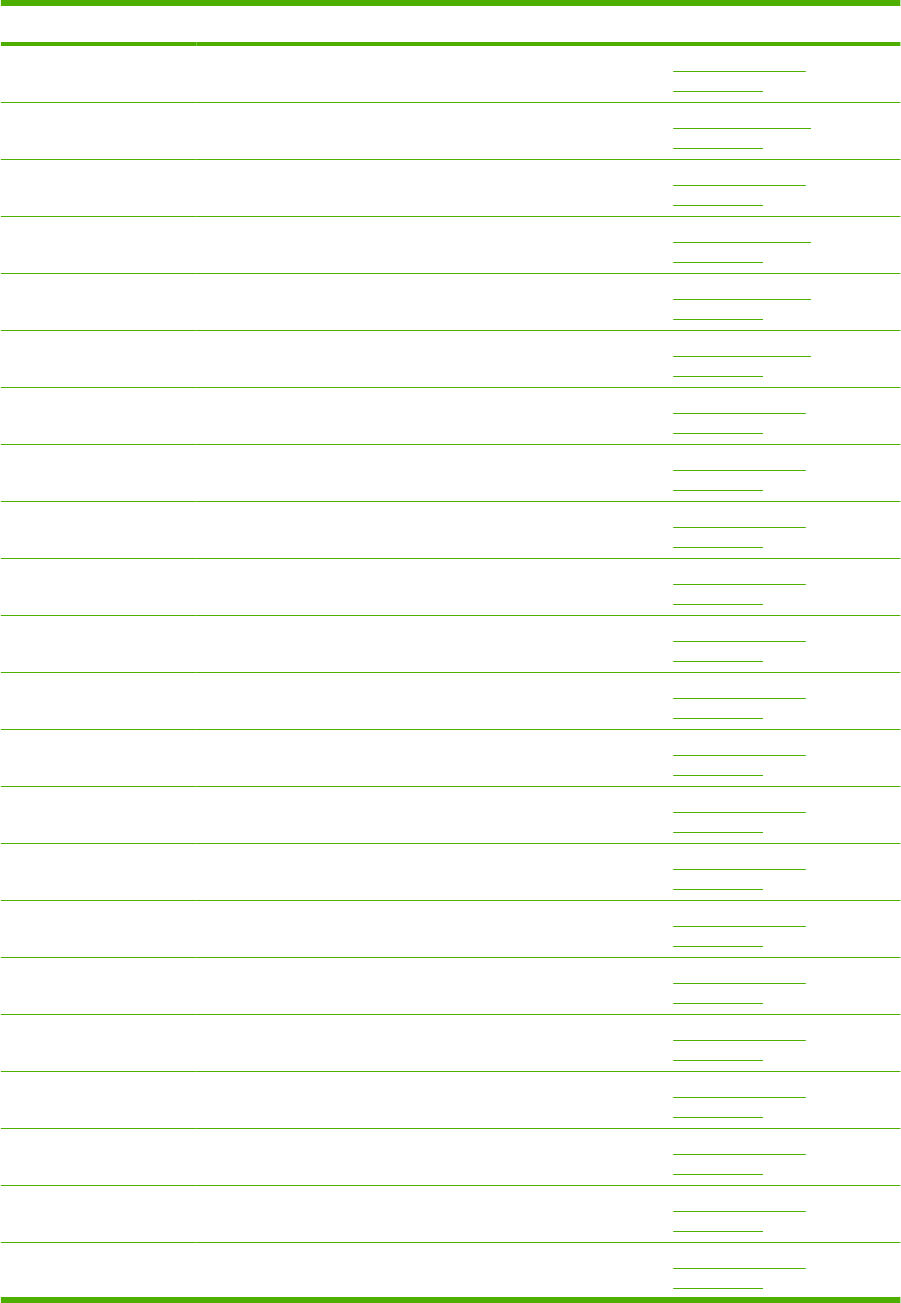
Part number Description Table and page
CC434-60105 Control-panel overlay, base model, English Scanner assembly
on page 333
CC434-67901 Blank bezel (not shown) Assembly locations
on page 337
CC434-67902 Automatic document feeder (ADF) assembly—simplex models Scanner assembly
on page 333
CC435-00001 Memory card bracket (not shown) Assembly locations
on page 337
CC435-40001 Memory card cable guide (not shown) Assembly locations
on page 337
CC435-67901 Memory card bezel (not shown) Assembly locations
on page 337
CC436-40003 Control-panel bezel, fax model, English Scanner assembly
on page 333
CC436-40004 Control-panel bezel, fax model, Spanish Scanner assembly
on page 333
CC436-40005 Control-panel bezel, fax model, Portuguese Scanner assembly
on page 333
CC436-40006 Control-panel bezel, fax model, German Scanner assembly
on page 333
CC436-40007 Control-panel bezel, fax model, French Scanner assembly
on page 333
CC436-40008 Control-panel bezel, fax model, Dutch Scanner assembly
on page 333
CC436-40009 Control-panel bezel, fax model, Italian Scanner assembly
on page 333
CC436-40010 Control-panel bezel, fax model, Swedish Scanner assembly
on page 333
CC436-40011 Control-panel bezel, fax model, Norwegian Scanner assembly
on page 333
CC436-40012 Control-panel bezel, fax model, Finnish Scanner assembly
on page 333
CC436-40013 Control-panel bezel, fax model, Danish Scanner assembly
on page 333
CC436-40014 Control-panel bezel, fax model, Russian Scanner assembly
on page 333
CC436-40015 Control-panel bezel, fax model, Czech Scanner assembly
on page 333
CC436-40016 Control-panel bezel, fax model, Hungarian Scanner assembly
on page 333
CC436-40017 Control-panel bezel, fax model, Polish Scanner assembly
on page 333
CC436-40018 Control-panel bezel, fax model, Slovak Scanner assembly
on page 333
Table 8-17 Numerical parts list (continued)
368 Chapter 8 Parts and diagrams ENWW
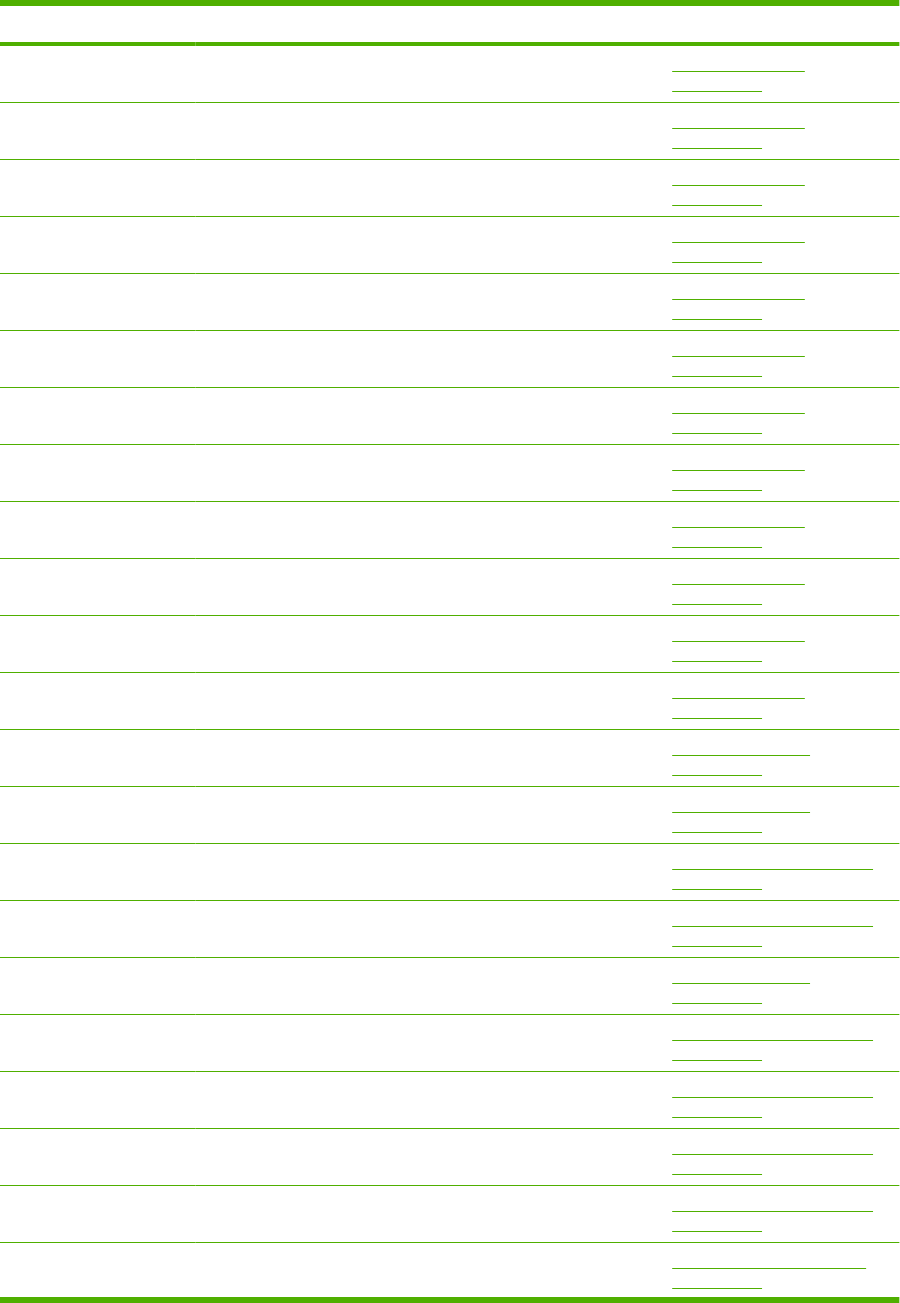
Part number Description Table and page
CC436-40019 Control-panel bezel, fax model, Turkish Scanner assembly
on page 333
CC436-40020 Control-panel bezel, fax model, Greek Scanner assembly
on page 333
CC436-40021 Control-panel bezel, fax model, Hebrew Scanner assembly
on page 333
CC436-40022 Control-panel bezel, fax model, Arabic Scanner assembly
on page 333
CC436-40023 Control-panel bezel, fax model, Chinese, traditional Scanner assembly
on page 333
CC436-40024 Control-panel bezel, fax model, Korean Scanner assembly
on page 333
CC436-40025 Control-panel bezel, fax model, Chinese, simplified Scanner assembly
on page 333
CC436-40026 Control-panel bezel, fax model, Thai Scanner assembly
on page 333
CC436-40027 Control-panel bezel, fax model, Vietnamese Scanner assembly
on page 333
CC436-67901 Automatic document feeder (ADF) assembly—duplex models Scanner assembly
on page 333
CC436-67902 Scanner assembly, business/imaging Scanner assembly
on page 333
CC436-67903 Scanner assembly, base Scanner assembly
on page 333
CC514-60002 DAA (fax card), Europe (fax models only) Assembly locations
on page 337
CE684-67901 Formatter, business Assembly locations
on page 337
Not orderable Link, guide1Internal components (6 of 7)
on page 351
Not orderable Link, guide1Internal components (7 of 7)
on page 353
Q3948-60113 Speaker (not shown) Assembly locations
on page 337
RC2-2014-000CN Cover, holder Internal components (3 of 7)
on page 345
RC2-3598-000CN Stopper, door, rear Internal components (6 of 7)
on page 351
RC2-3599-000CN Cap, link Internal components (6 of 7)
on page 351
RC2-3604-000CN Door, rear Internal components (6 of 7)
on page 351
RC2-3612-000CN Button, power External panels and covers
on page 339
Table 8-17 Numerical parts list (continued)
ENWW Numerical parts list 369
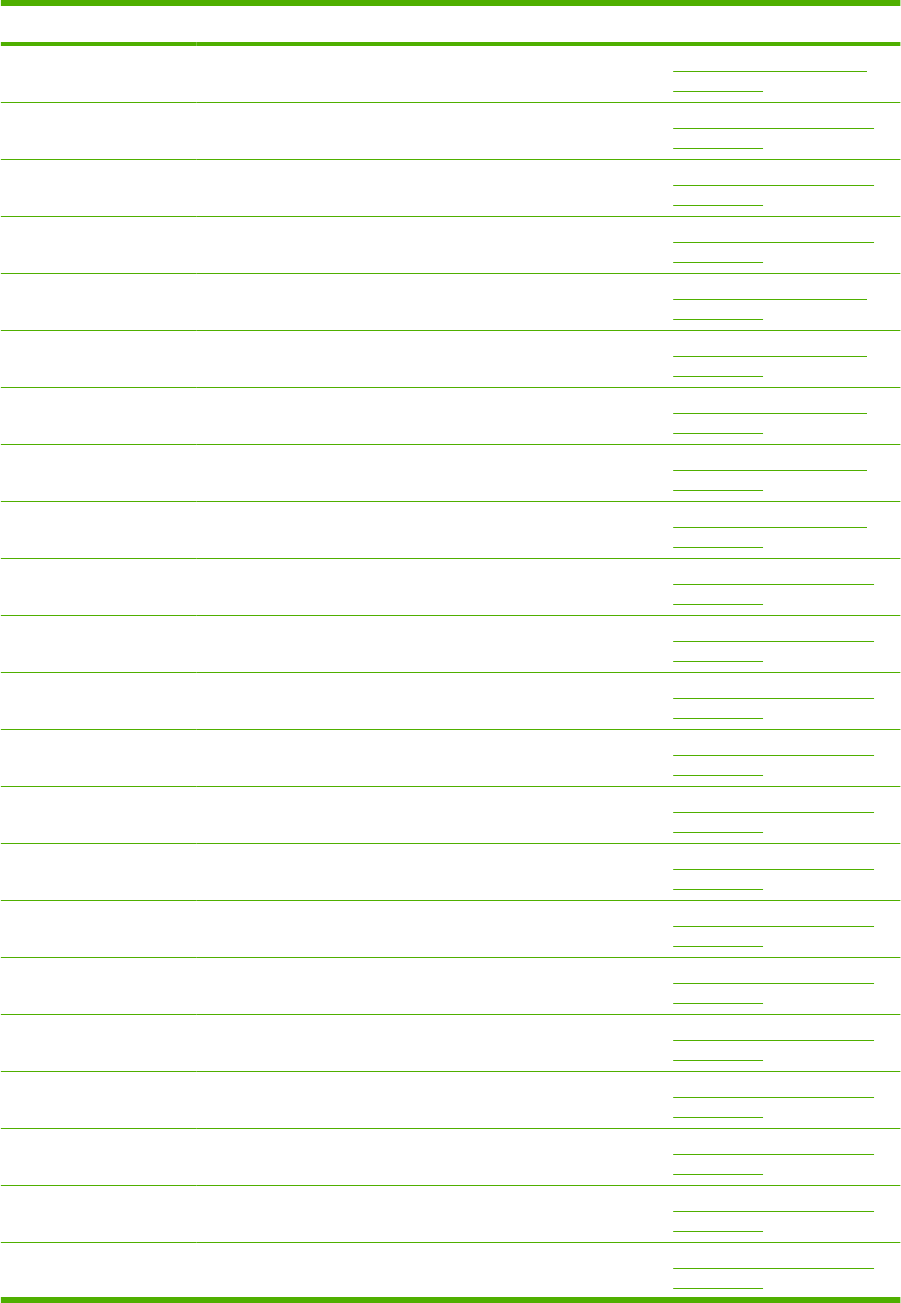
Part number Description Table and page
RC2-3614-000CN Cover, DIMM External panels and covers
on page 339
RC2-3748-000CN Cover, lower rear Internal components (7 of 7)
on page 353
RC2-3750-000CN Link, door Internal components (7 of 7)
on page 353
RC2-3774-000CN Cap, link Internal components (7 of 7)
on page 353
RC2-3912-000CN Cover, right External panels and covers
on page 339
RC2-3913-000CN Cover, left External panels and covers
on page 339
RC2-3914-000CN Cover, right front External panels and covers
on page 339
RC2-3915-000CN Cover, right front, lower External panels and covers
on page 339
RC2-3918-000CN Cover, IOT External panels and covers
on page 339
RK2-2276-000CN Fan Internal components (5 of 7)
on page 349
RK2-2302-000CN Cable, flat Internal components (4 of 7)
on page 347
RL1-1785-000CN Pad, separation Internal components (3 of 7)
on page 345
RL1-1800-000CN Motor, DC Internal components (4 of 7)
on page 347
RL1-1802-000CN Roller, paper pickup Internal components (2 of 7)
on page 343
RL1-1822-000CN Cover, rear Internal components (6 of 7)
on page 351
RL1-1823-000CN Cover, upper rear Internal components (7 of 7)
on page 353
RM1-4426-000CN Pickup roller assembly Internal components (3 of 7)
on page 345
RM1-4836-000CN Cartridge tray assembly Internal components (1 of 7)
on page 341
RM1-4838-000CN Paper feed guide assembly (simplex and duplex products)2Internal components (6 of 7)
on page 351
RM1-4838-000CN Paper feed guide assembly (simplex and duplex products)2Internal components (7 of 7)
on page 353
RM1-4839-000CN MP paper pickup assembly (Tray 1) Internal components (3 of 7)
on page 345
RM1-4840-000CN Separation roller assembly Internal components (3 of 7)
on page 345
Table 8-17 Numerical parts list (continued)
370 Chapter 8 Parts and diagrams ENWW
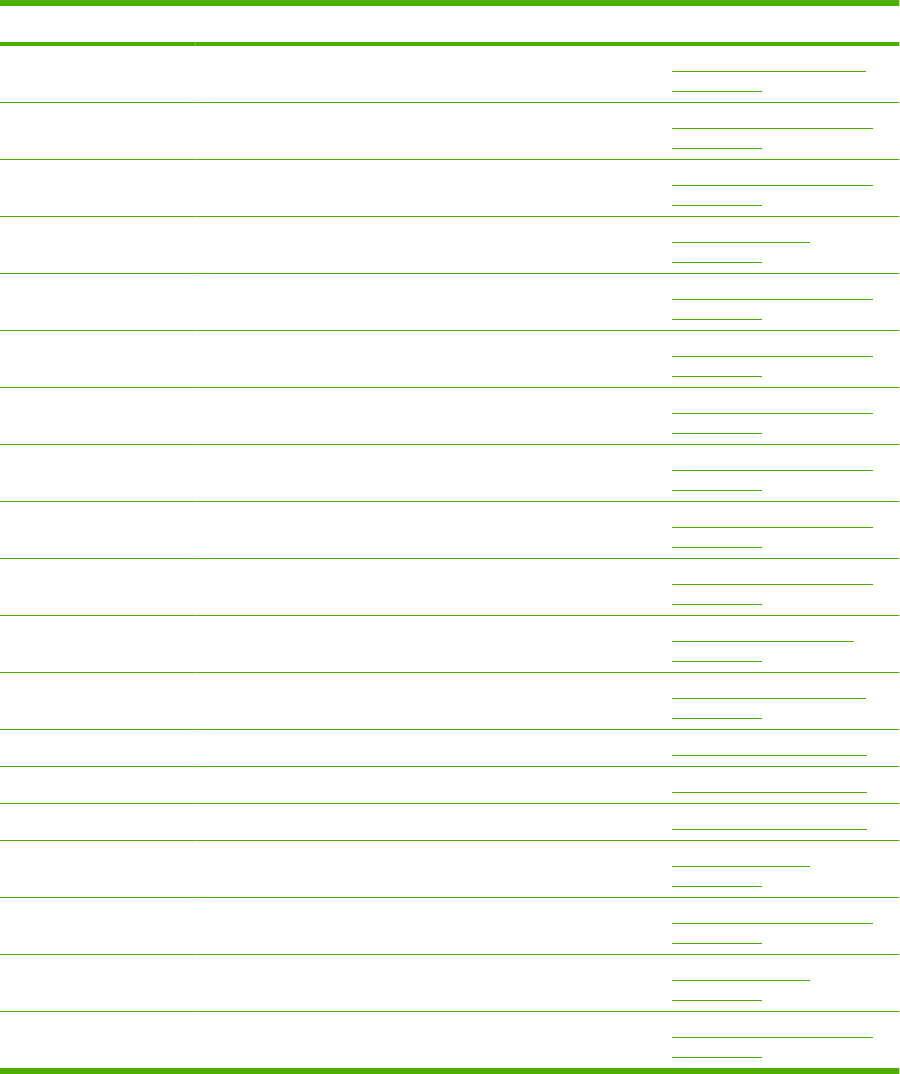
Part number Description Table and page
RM1-4848-000CN Front door assembly External panels and covers
on page 339
RM1-4850-000CN Color misregistration sensor assembly Internal components (2 of 7)
on page 343
RM1-4852-000CN Intermediate transfer belt assembly Internal components (2 of 7)
on page 343
RM1-4860-000CN Paper input cassette Assembly locations
on page 337
RM1-4873-000CN Paper delivery assembly Internal components (5 of 7)
on page 349
RM1-4876-000CN Rear door rib assembly Internal components (7 of 7)
on page 353
RM1-4877-000CN Paper re-pickup guide assembly Internal components (7 of 7)
on page 353
RM1-4878-000CN Rear door assembly Internal components (7 of 7)
on page 353
RM1-4879-000CN Duplexing-feed guide assembly Internal components (7 of 7)
on page 353
RM1-4880-000CN Reverse drive assembly Internal components (7 of 7)
on page 353
RM1-4901-000CN Optional 250-sheet paper cassette 250-sheet paper cassette
on page 357
RM1-4911-000CN Upper cover assembly External panels and covers
on page 339
RM1-5294-000CN High-voltage power supply PCA PCA locations on page 355
RM1-5303-000CN Power supply sub PCA PCA locations on page 355
RM1-5431-000CN DC controller PCA PCA locations on page 355
RM1-6740-000CN Fuser assembly (110-127 V) Assembly locations
on page 337
RM1-6740-000CN Fuser assembly (110-127 V) Internal components (5 of 7)
on page 349
RM1-6741-000CN Fuser assembly (220-240 V) Assembly locations
on page 337
RM1-6741-000CN Fuser assembly (220-240 V) Internal components (5 of 7)
on page 349
Table 8-17 Numerical parts list (continued)
ENWW Numerical parts list 371
372 Chapter 8 Parts and diagrams ENWW

A Service and support
Hewlett-Packard limited warranty statement
HP PRODUCT DURATION OF LIMITED WARRANTY
HP Color LaserJet CM2320, CM2320nf, and CM2320fxi One-year limited warranty
HP warrants to you, the end-user customer, that HP hardware and accessories will be free from defects in materials
and workmanship after the date of purchase, for the period specified above. If HP receives notice of such defects
during the warranty period, HP will, at its option, either repair or replace products which prove to be defective.
Replacement products may be either new or equivalent in performance to new.
HP warrants to you that HP software will not fail to execute its programming instructions after the date of purchase,
for the period specified above, due to defects in material and workmanship when properly installed and used. If
HP receives notice of such defects during the warranty period, HP will replace software which does not execute
its programming instructions due to such defects.
HP does not warrant that the operation of HP products will be uninterrupted or error free. If HP is unable, within a
reasonable time, to repair or replace any product to a condition as warranted, you will be entitled to a refund of
the purchase price upon prompt return of the product.
HP products may contain remanufactured parts equivalent to new in performance or may have been subject to
incidental use.
Warranty does not apply to defects resulting from (a) improper or inadequate maintenance or calibration, (b)
software, interfacing, parts or supplies not supplied by HP, (c) unauthorized modification or misuse, (d) operation
outside of the published environmental specifications for the product, or (e) improper site preparation or
maintenance.
TO THE EXTENT ALLOWED BY LOCAL LAW, THE ABOVE WARRANTIES ARE EXCLUSIVE AND NO OTHER
WARRANTY OR CONDITION, WHETHER WRITTEN OR ORAL, IS EXPRESSED OR IMPLIED AND HP
SPECIFICALLY DISCLAIMS ANY IMPLIED WARRANTIES OR CONDITIONS OF MERCHANTABILITY,
SATISFACTORY QUALITY, AND FITNESS FOR A PARTICULAR PURPOSE. Some countries/regions, states or
provinces do not allow limitations on the duration of an implied warranty, so the above limitation or exclusion might
not apply to you. This warranty gives you specific legal rights and you might also have other rights that vary from
country/region to country/region, state to state, or province to province. HP's limited warranty is valid in any country/
region or locality where HP has a support presence for this product and where HP has marketed this product. The
level of warranty service you receive may vary according to local standards. HP will not alter form, fit or function
of the product to make it operate in a country/region for which it was never intended to function for legal or regulatory
reasons.
TO THE EXTENT ALLOWED BY LOCAL LAW, THE REMEDIES IN THIS WARRANTY STATEMENT ARE YOUR
SOLE AND EXCLUSIVE REMEDIES. EXCEPT AS INDICATED ABOVE, IN NO EVENT WILL HP OR ITS
SUPPLIERS BE LIABLE FOR LOSS OF DATA OR FOR DIRECT, SPECIAL, INCIDENTAL, CONSEQUENTIAL
ENWW Hewlett-Packard limited warranty statement 373
(INCLUDING LOST PROFIT OR DATA), OR OTHER DAMAGE, WHETHER BASED IN CONTRACT, TORT, OR
OTHERWISE. Some countries/regions, states or provinces do not allow the exclusion or limitation of incidental or
consequential damages, so the above limitation or exclusion may not apply to you.
THE WARRANTY TERMS CONTAINED IN THIS STATEMENT, EXCEPT TO THE EXTENT LAWFULLY
PERMITTED, DO NOT EXCLUDE, RESTRICT OR MODIFY AND ARE IN ADDITION TO THE MANDATORY
STATUTORY RIGHTS APPLICABLE TO THE SALE OF THIS PRODUCT TO YOU.
Customer self repair warranty service
HP products are designed with many Customer Self Repair (CSR) parts to minimize repair time and
allow for greater flexibility in performing defective parts replacement. If during the diagnosis period, HP
identifies that the repair can be accomplished by the use of a CSR part, HP will ship that part directly to
you for replacement. There are two categories of CSR parts: 1) Parts for which customer self repair is
mandatory. If you request HP to replace these parts, you will be charged for the travel and labor costs
of this service. 2) Parts for which customer self repair is optional. These parts are also designed for
Customer Self Repair. If, however, you require that HP replace them for you, this may be done at no
additional charge under the type of warranty service designated for your product.
Based on availability and where geography permits, CSR parts will be shipped for next business day
delivery. Same-day or four-hour delivery may be offered at an additional charge where geography
permits. If assistance is required, you can call the HP Technical Support Center and a technician will
help you over the phone. HP specifies in the materials shipped with a replacement CSR part whether
a defective part must be returned to HP. In cases where it is required to return the defective part to HP,
you must ship the defective part back to HP within a defined period of time, normally five (5) business
days. The defective part must be returned with the associated documentation in the provided shipping
material. Failure to return the defective part may result in HP billing you for the replacement. With a
customer self repair, HP will pay all shipping and part return costs and determine the courier/carrier to
be used.
374 Appendix A Service and support ENWW
Print cartridge limited warranty statement
This HP product is warranted to be free from defects in materials and workmanship.
This warranty does not apply to products that (a) have been refilled, refurbished, remanufactured or
tampered with in any way, (b) experience problems resulting from misuse, improper storage, or
operation outside of the published environmental specifications for the printer product or (c) exhibit wear
from ordinary use.
To obtain warranty service, please return the product to place of purchase (with a written description of
the problem and print samples) or contact HP customer support. At HP's option, HP will either replace
products that prove to be defective or refund your purchase price.
TO THE EXTENT ALLOWED BY LOCAL LAW, THE ABOVE WARRANTY IS EXCLUSIVE AND NO
OTHER WARRANTY OR CONDITION, WHETHER WRITTEN OR ORAL, IS EXPRESSED OR
IMPLIED AND HP SPECIFICALLY DISCLAIMS ANY IMPLIED WARRANTIES OR CONDITIONS OF
MERCHANTABILITY, SATISFACTORY QUALITY, AND FITNESS FOR A PARTICULAR PURPOSE.
TO THE EXTENT ALLOWED BY LOCAL LAW, IN NO EVENT WILL HP OR ITS SUPPLIERS BE
LIABLE FOR DIRECT, SPECIAL, INCIDENTAL, CONSEQUENTIAL (INCLUDING LOST PROFIT OR
DATA), OR OTHER DAMAGE, WHETHER BASED IN CONTRACT, TORT, OR OTHERWISE.
THE WARRANTY TERMS CONTAINED IN THIS STATEMENT, EXCEPT TO THE EXTENT
LAWFULLY PERMITTED, DO NOT EXCLUDE, RESTRICT OR MODIFY AND ARE IN ADDITION TO
THE MANDATORY STATUTORY RIGHTS APPLICABLE TO THE SALE OF THIS PRODUCT TO YOU.
ENWW Print cartridge limited warranty statement 375
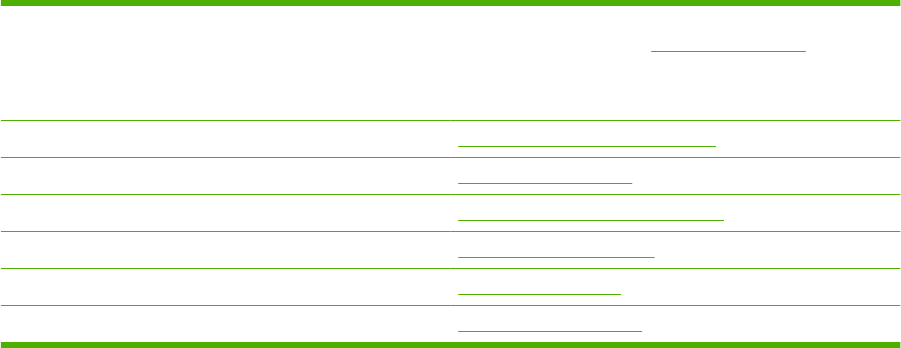
Customer support
Get telephone support, free during your warranty period, for
your country/region
Have the product name, serial number, date of purchase, and
problem description ready.
Country/region phone numbers are on the flyer that was in the
box with your product or at www.hp.com/support/.
Get 24-hour Internet support www.hp.com/support/CM2320series
Get support for products used with a Macintosh computer www.hp.com/go/macosx
Download software utilities, drivers, and electronic information www.hp.com/go/LJCM2320_software
Order supplies and paper www.hp.com/go/suresupply
Order genuine HP parts or accessories www.hp.com/buy/parts
Order additional HP service or maintenance agreements www.hp.com/go/carepack
376 Appendix A Service and support ENWW
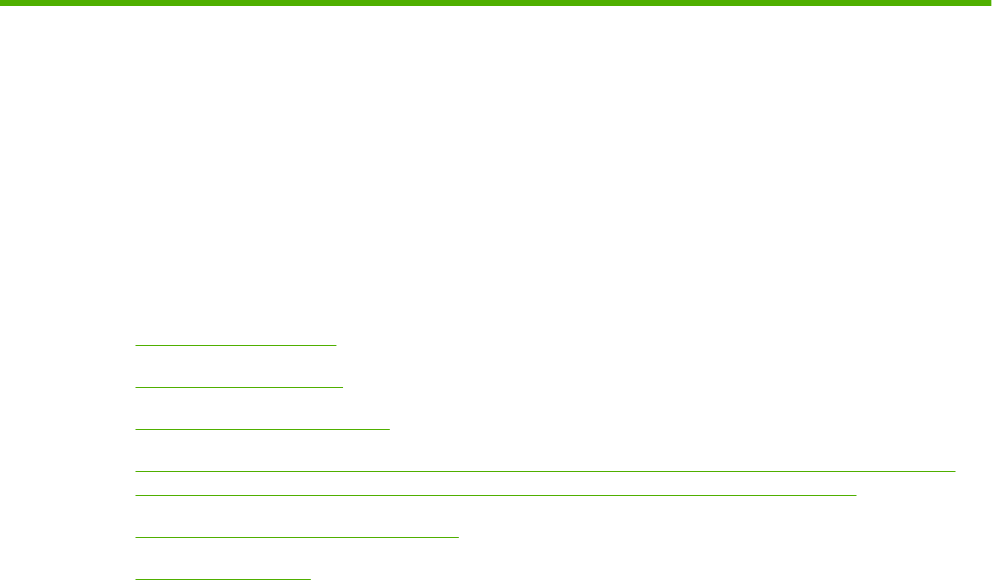
B Specifications
This section contains the following information about the product:
●Physical specifications
●Electrical specifications
●Environmental specifications
●Power consumption and acoustic emissions (HP Color LaserJet CM2320, HP Color LaserJet
CM2320 MFP Fax Model, HP Color LaserJet CM2320 MFP Memory-Card Model)
●Paper and print media specifications
●Skew specifications
ENWW 377
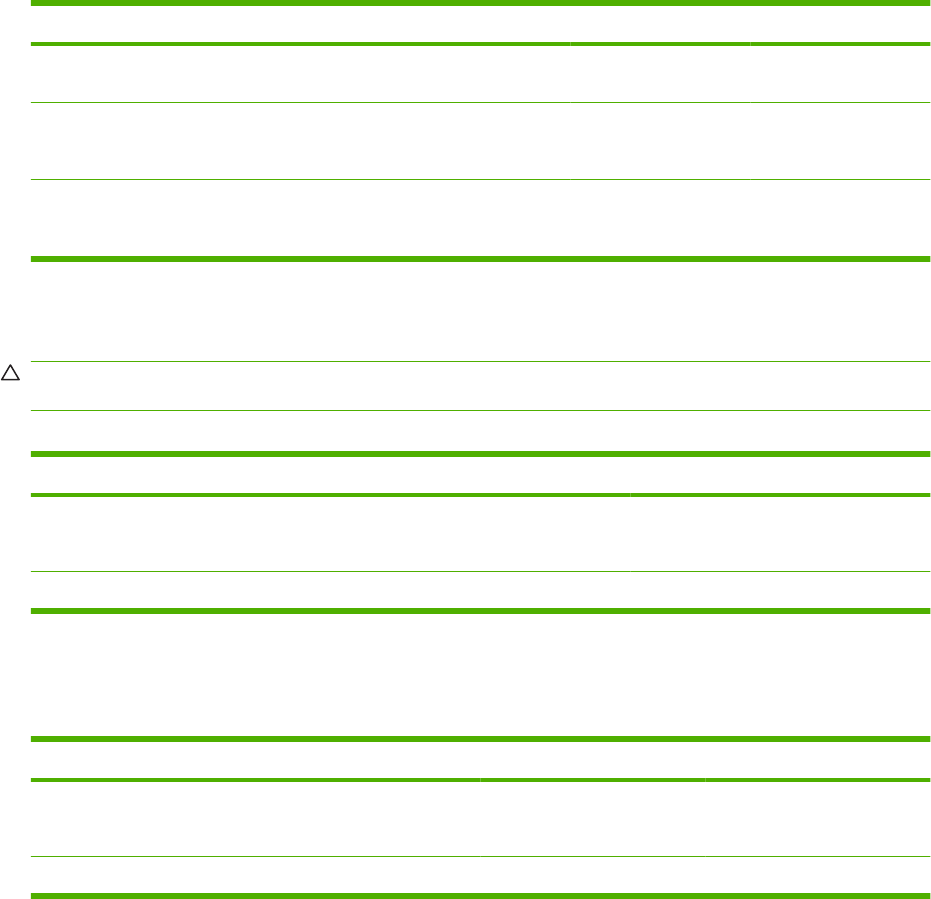
Physical specifications
Table B-1 Physical specifications
Product Height Depth Width Weight
HP Color LaserJet
CM2320
532 mm (21.0 inches) 492 mm (19.4 inches) 497 mm (19.6 inches) 29.4 kg (64.8 lb)
HP Color LaserJet
CM2320 MFP Fax
Model
532 mm (21.0 inches) 492 mm (19.4 inches) 497 mm (19.6 inches) 31.1 kg (68.5 lb)
HP Color LaserJet
CM2320 MFP Memory-
Card Model
532 mm (21.0 inches) 492 mm (19.4 inches) 497 mm (19.6 inches) 31.1 kg (68.5 lb)
Electrical specifications
CAUTION: Power requirements are based on the country/region where the product is sold. Do not
convert operating voltages. This will damage the product and void the product warranty.
Table B-2 Electrical specifications
Item 110-volt models 230-volt models
Power requirements 100 to 127 VAC (+/- 10%)
60 Hz (+/- 3 Hz)
220 to 240 VAC (+/- 10%)
50 Hz (+/- 3 Hz)
Rated current 6.0 A 3.0 A
Environmental specifications
Table B-3 Environmental specifications
1
Recommended Operating Storage
Temperature 15° to 32.5° C
(59° to 90.5° F)
15° to 32.5° C
(59° to 90.5° F)
–20° to 40° C
(–4° to 104° F)
Relative humidity 20 to 70% 15 to 80% 85% or less
1Values are subject to change.
378 Appendix B Specifications ENWW
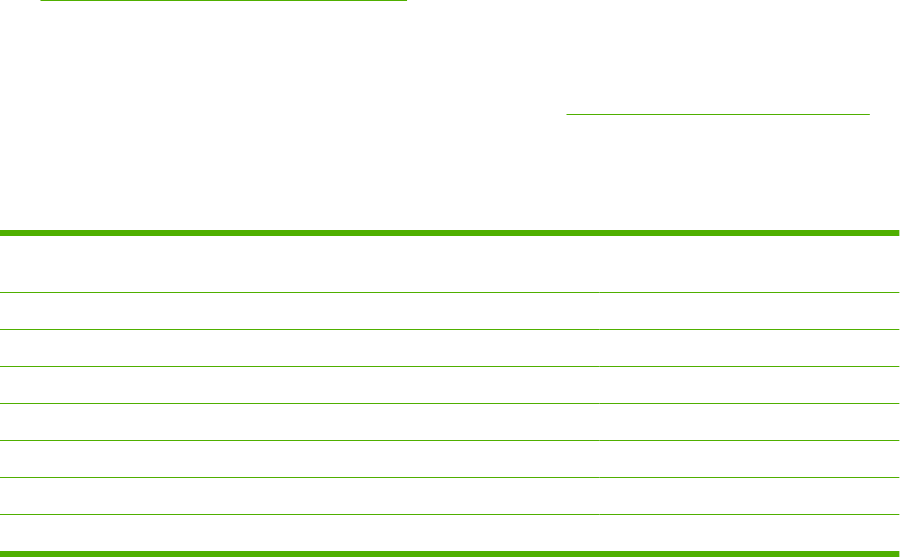
Power consumption and acoustic emissions (HP Color
LaserJet CM2320, HP Color LaserJet CM2320 MFP Fax
Model, HP Color LaserJet CM2320 MFP Memory-Card
Model)
See www.hp.com/go/cljcm2320mfp/regulatory for current information.
Paper and print media specifications
For information about the supported paper and print media, see Paper and print media on page 37.
Skew specifications
Table B-4 Media registration and image placement accuracy
Cut sheet simplex and automatic
duplex
1
Envelopes and postcards
Skew - vertical ≤ 1.5 mm / 260 mm ≤ 3.0 mm / 220 mm
First line / leading edge position 5.0 mm ± 2.0 mm 10.0 mm ± 3.5 mm
Left margin accuracy 5.0 mm ± 2.0 mm 10 mm ± 2.5 mm
Parallelism ≤ 1.5 mm N/A
Image or text stretching - vertical ≤ 1.0 % N/A
Image or text stretching - horizontal ≤ 1.0 % N/A
Duplex registration - vertical, horizontal ≤ 2.0 mm N/A
1Xerox 4024 (#20) should be used for measurement.
ENWW Power consumption and acoustic emissions (HP Color LaserJet CM2320, HP Color LaserJet
CM2320 MFP Fax Model, HP Color LaserJet CM2320 MFP Memory-Card Model)
379
380 Appendix B Specifications ENWW

FCC regulations
This equipment has been tested and found to comply with the limits for a Class B digital device, pursuant
to Part 15 of the FCC rules. These limits are designed to provide reasonable protection against harmful
interference in a residential installation. This equipment generates, uses, and can radiate radio
frequency energy. If this equipment is not installed and used in accordance with the instructions, it may
cause harmful interference to radio communications. However, there is no guarantee that interference
will not occur in a particular installation. If this equipment does cause harmful interference to radio or
television reception, which can be determined by turning the equipment off and on, the user is
encouraged to try to correct the interference by one or more of the following measures:
●Reorient or relocate the receiving antenna.
●Increase separation between equipment and receiver.
●Connect equipment to an outlet on a circuit different from that to which the receiver is located.
●Consult your dealer or an experienced radio/TV technician.
NOTE: Any changes or modifications to the printer that are not expressly approved by HP could void
the user’s authority to operate this equipment.
Use of a shielded interface cable is required to comply with the Class B limits of Part 15 of FCC rules.
Additional statements for telecom (fax) products
EU statement for telecom operation
This product is intended to be connected to the analog Public Switched Telecommunication Networks
(PSTN) of European Economic Area (EEA) countries/regions. It meets requirements of EU R&TTE
Directive 1999/5/EC (Annex II) and carries appropriate CE conformity marking. For more details, see
Declaration of Conformity issued by the manufacturer in another section of this manual. However, due
to differences between individual national PSTNs, the product may not guarantee unconditional
assurance of successful operation on every PSTN termination point. Network compatibility depends on
the correct setting being selected by the customer in preparation of its connection to the PSTN. Please
follow the instructions provided in the user manual. If you experience network compatibility issues,
please contact your equipment supplier or Hewlett-Packard help desk in the country/region of operation.
Connecting to a PSTN termination point may be the subject of additional requirements set out by the
local PSTN operator.
New Zealand telecom statements
The grant of a Telepermit for any item of terminal equipment indicates only that Telecom has accepted
that the item complies with minimum conditions for connection to its network. It indicates no endorsement
of the product by Telecom, nor does it provide any sort of warranty. Above all, it provides no assurance
that any item will work correctly in all respects with another item of Telepermitted equipment of a different
make or model, nor does it imply that any product is compatible with all of Telecom’s network services.
This equipment may not provide for the effective hand-over of a call to another device connected to the
same line.
This equipment shall not be set up to make automatic calls to the Telecom “111” Emergency Service.
This product has not been tested to ensure compatibility with the FaxAbility distinctive ring service for
New Zealand.
382 Appendix C Regulatory information ENWW

Telephone Consumer Protection Act (United States)
The Telephone Consumer Protection Act of 1991 makes it unlawful for any person to use a computer
or other electronic device, including fax machines, to send any message unless such message clearly
contains, in a margin at the top or bottom of each transmitted page or on the first page of the
transmission, the date and time it is sent and an identification of the business, other entity, or individual
sending the message and the telephone number of the sending machine or such business, other entity,
or individual. (The telephone number provided cannot be a 900 number or any other number for which
charges exceed local or long-distance transmission charges.)
IC CS-03 requirements
Notice: The Industry Canada label identifies certified equipment. This certification means the equipment
meets certain telecommunications network protective, operational, and safety requirements as
prescribed in the appropriate Terminal Equipment Technical Requirement document(s). The
Department does not guarantee the equipment will operate to the user’s satisfaction. Before installing
this equipment, users should ensure that it is permissible for the equipment to be connected to the
facilities of the local telecommunications company. The equipment must also be installed using an
acceptable method of connection. The customer should be aware that compliance with the above
conditions may not prevent degradation of service in some situations. Repairs to certified equipment
should be coordinated by a representative designated by the supplier. Any repairs or alterations made
by the user to this equipment, or equipment malfunctions, may give the telecommunications company
cause to request the user to disconnect the equipment. Users should ensure for their own protection
that the electrical ground connections of the power utility, telephone lines, and internal metallic water
pipe system, if present, are connected together. This precaution can be particularly important in rural
areas.
CAUTION: Users should not attempt to make such connections themselves, but should contact the
appropriate electric inspection authority, or electrician, as appropriate. The Ringer Equivalence Number
(REN) of this device is 0.0.
Notice: The Ringer Equivalence Number (REN) assigned to each terminal device provides an indication
of the maximum number of terminals allowed to be connected to a telephone interface. The termination
on an interface may consist of any combination of devices subject only to the requirement that the sum
of the Ringer Equivalence Number of all the devices does not exceed five (5.0). The standard connecting
arrangement code (telephone jack type) for equipment with direct connections to the telephone network
is CA11A.
ENWW Additional statements for telecom (fax) products 383
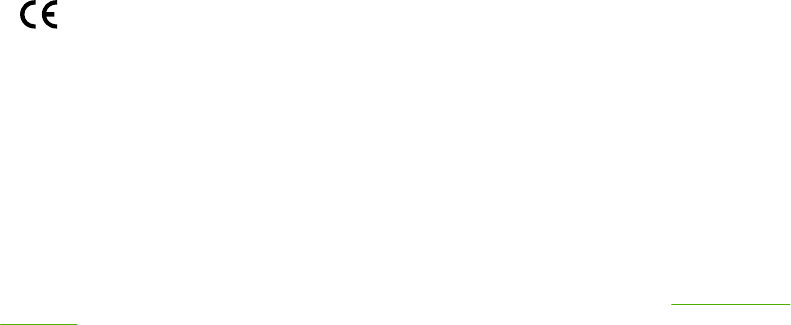
Declaration of conformity
HP Color LaserJet CM2320 MFP
Declaration of Conformity
according to ISO/IEC 17050-1 and EN 17050-1
Manufacturer's Name: Hewlett-Packard Company DoC#: BOISB-0701-01-rel.1.0
Manufacturer's Address: 11311 Chinden Boulevard,
Boise, Idaho 83714-1021, USA
declares, that the product
Product Name: HP Color LaserJet CM2320 MFP
Regulatory Model Number2) BOISB-0701-01
Product Options: ALL
Print Cartridges: CC530A, CC531A, CC532A, CC533A
conforms to the following Product Specifications:
SAFETY: IEC 60950-1:2001 / EN60950-1: 2001 +A11
IEC 60825-1:1993 +A1 +A2 / EN 60825-1:1994 +A1 +A2 (Class 1 Laser/LED Product)
GB4943-2001
EMC: CISPR22:2005 / EN55022:2006 – Class B1)
EN 61000-3-2:2000 +A2
EN 61000-3-3:1995 +A1
EN 55024:1998 +A1 +A2
FCC Title 47 CFR, Part 15 Class B / ICES-003, Issue 4
GB9254-1998, GB17625.1-2003
Supplementary Information:
The product herewith complies with the requirements of the EMC Directive 2004/108/EC and the Low Voltage Directive 2006/95/EC and
carries the CE-Marking accordingly.
This Device complies with Part 15 of the FCC Rules. Operation is subject to the following two Conditions: (1) this device may not cause
harmful interference, and (2) this device must accept any interference received, including interference that may cause undesired operation.
1) The product was tested in a typical configuration with Hewlett-Packard Personal Computer Systems.
2) For regulatory purposes, this product is assigned a Regulatory model number. This number should not be confused with the product name
or the product number(s).
Boise, Idaho , USA
January 2008
For regulatory topics only:
European Contact: Your Local Hewlett-Packard Sales and Service Office or Hewlett-Packard GmbH, Department HQ-TRE / Standards
Europe,, Herrenberger Strasse 140, D-71034 Böblingen, Germany, (FAX: +49-7031-14-3143), www.hp.com/go/
certificates
USA Contact: Product Regulations Manager, Hewlett-Packard Company,, PO Box 15, Mail Stop 160, Boise, Idaho 83707-0015, ,
(Phone: 208-396-6000)
HP LaserJet CM2320 Fax Model / CM2320 Memory-Card Model
Declaration of Conformity
according to ISO/IEC 17050-1 and EN 17050-1
Manufacturer's Name: Hewlett-Packard Company DoC#: BOISB-0701-02-rel.1.0
Manufacturer's Address: 11311 Chinden Boulevard,
Boise, Idaho 83714-1021, USA
declares, that the product
Product Name: HP Color LaserJet CM2320nf MFP
HP Color LaserJet CM2320fxi MFP
Accessories4) BOISB-0704-00 (US-Fax Module LIU)
BOISB-0704-01 (EURO-Fax Module LIU)
384 Appendix C Regulatory information ENWW
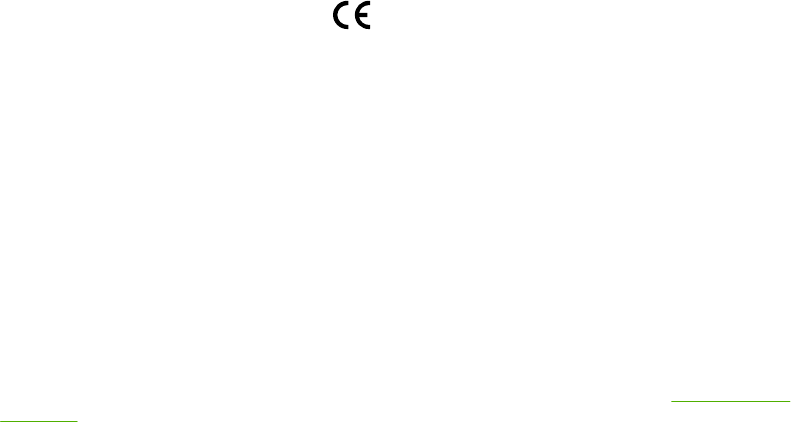
Declaration of Conformity
according to ISO/IEC 17050-1 and EN 17050-1
Regulatory Model Number2) BOISB-0701-02
Product Options: ALL
Print Cartridges: CC530A, CC531A, CC532A, CC533A
conforms to the following Product Specifications:
SAFETY: IEC 60950-1:2001 / EN60950-1: 2001 +A11
IEC 60825-1:1993 +A1 +A2 / EN 60825-1:1994 +A1 +A2 (Class 1 Laser/LED Product)
GB4943-2001
EMC: CISPR22:2005 / EN55022:2006 – Class B1)
EN 61000-3-2:2000 +A2
EN 61000-3-3:1995 +A1
EN 55024:1998 +A1 +A2
FCC Title 47 CFR, Part 15 Class B / ICES-003, Issue 4
GB9254-1998, GB17625.1-2003
TELECOM: ES 203 021; FCC Title 47 CFR, Part 683)
Supplementary Information:
The product herewith complies with the requirements of the EMC Directive 2004/108/EC and the Low Voltage Directive 2006/95/EC, the
R&TTE Directive 1999/5/EC (Annex II), and carries the CE-Marking accordingly.
This Device complies with Part 15 of the FCC Rules. Operation is subject to the following two Conditions: (1) this device may not cause
harmful interference, and (2) this device must accept any interference received, including interference that may cause undesired operation.
1) The product was tested in a typical configuration with Hewlett-Packard Personal Computer Systems.
2) For regulatory purposes, this product is assigned a Regulatory model number. This number should not be confused with the product name
or the product number(s).
3) Telecom approvals and standards appropriate for the target countries/regions have been applied to this product, in addition to those listed
above.
4.) This product uses an analog fax accessory module which Regulatory Model numbers are: BOISB-0704-00 (US-LIU) or BOISB-0704-01
(EURO LIU), as needed to meet technical regulatory requirements for the countries/regions this product will be sold.
Boise, Idaho , USA
January 2008
For regulatory topics only:
European Contact: Your Local Hewlett-Packard Sales and Service Office or Hewlett-Packard GmbH, Department HQ-TRE / Standards
Europe,, Herrenberger Strasse 140, D-71034 Böblingen, Germany, (FAX: +49-7031-14-3143), www.hp.com/go/
certificates
USA Contact: Product Regulations Manager, Hewlett-Packard Company,, PO Box 15, Mail Stop 160, Boise, ID 83707-0015, , (Phone:
208-396-6000)
ENWW Declaration of conformity 385

Certificate of volatility
This is a statement of volatility regarding customer stored data in the memory devices of the HP Color
LaserJet CM2320 MFP Series Series printer.
The product uses volatile memory to store customer data during the printing process. When the product
power is off, the data is erased. The product also uses non-volatile memory to store customer set product
configuration information. This non-volatile memory can be erased and restored to factory default values
by using the Restore defaults option of the Service menu. See Restore the factory-set defaults
on page 313.
386 Appendix C Regulatory information ENWW
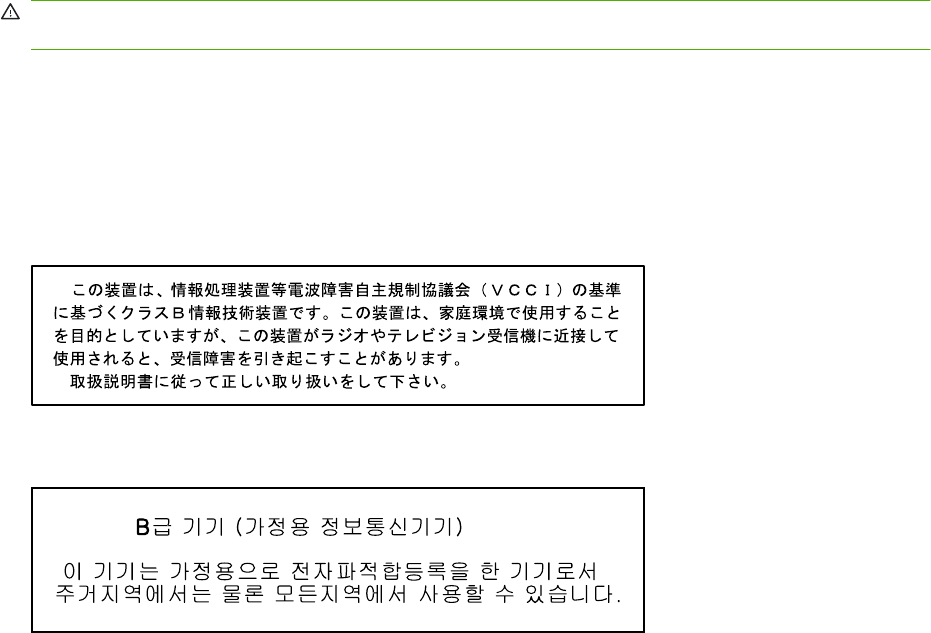
Country/region specific statements
Laser safety
The Center for Devices and Radiological Health (CDRH) of the U.S. Food and Drug Administration has
implemented regulations for laser products manufactured since August 1, 1976. Compliance is
mandatory for products marketed in the United States. The device is certified as a “Class 1” laser product
under the U.S. Department of Health and Human Services (DHHS) Radiation Performance Standard
according to the Radiation Control for Health and Safety Act of 1968. Since radiation emitted inside the
device is completely confined within protective housings and external covers, the laser beam cannot
escape during any phase of normal user operation.
WARNING! Using controls, making adjustments, or performing procedures other than those specified
in this user guide may result in exposure to hazardous radiation.
Canadian DOC regulations
Complies with Canadian EMC Class B requirements.
« Conforme à la classe B des normes canadiennes de compatibilité électromagnétiques. « CEM ». »
VCCI statement (Japan)
EMI statement (Korea)
Laser statement for Finland
Luokan 1 laserlaite
Klass 1 Laser Apparat
HP Color LaserJet CM2320, CM2320nf, CM2320fxi, laserkirjoitin on käyttäjän kannalta turvallinen
luokan 1 laserlaite. Normaalissa käytössä kirjoittimen suojakotelointi estää lasersäteen pääsyn laitteen
ulkopuolelle. Laitteen turvallisuusluokka on määritetty standardin EN 60825-1 (1994) mukaisesti.
VAROITUS !
Laitteen käyttäminen muulla kuin käyttöohjeessa mainitulla tavalla saattaa altistaa käyttäjän
turvallisuusluokan 1 ylittävälle näkymättömälle lasersäteilylle.
VARNING !
ENWW Country/region specific statements 387
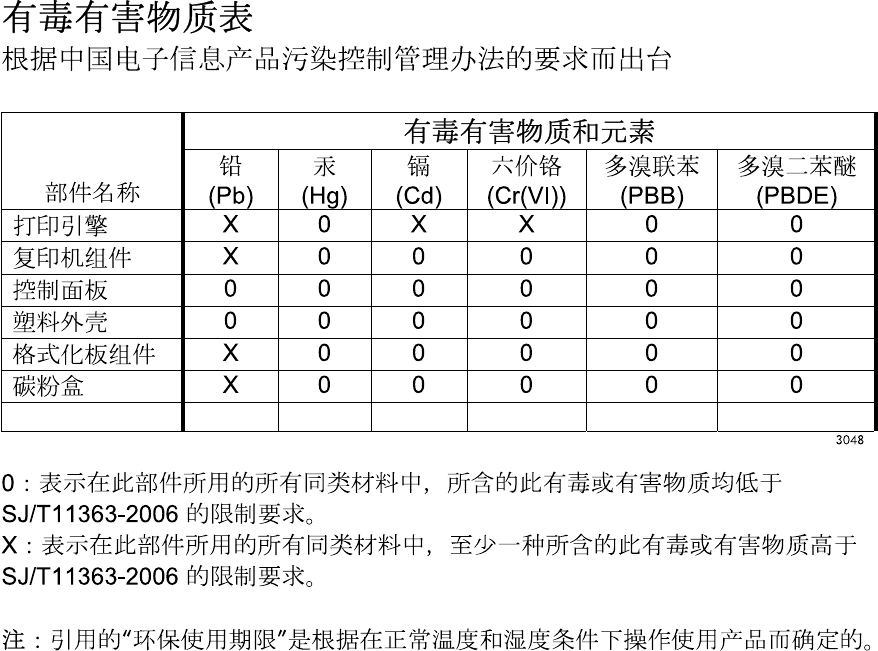
Om apparaten används på annat sätt än i bruksanvisning specificerats, kan användaren utsättas för
osynlig laserstrålning, som överskrider gränsen för laserklass 1.
HUOLTO
HP Color LaserJet CM2320, CM2320nf, CM2320fxi - kirjoittimen sisällä ei ole käyttäjän huollettavissa
olevia kohteita. Laitteen saa avata ja huoltaa ainoastaan sen huoltamiseen koulutettu henkilö.
Tällaiseksi huoltotoimenpiteeksi ei katsota väriainekasetin vaihtamista, paperiradan puhdistusta tai
muita käyttäjän käsikirjassa lueteltuja, käyttäjän tehtäväksi tarkoitettuja ylläpitotoimia, jotka voidaan
suorittaa ilman erikoistyökaluja.
VARO !
Mikäli kirjoittimen suojakotelo avataan, olet alttiina näkymättömällelasersäteilylle laitteen ollessa
toiminnassa. Älä katso säteeseen.
VARNING !
Om laserprinterns skyddshölje öppnas då apparaten är i funktion, utsättas användaren för osynlig
laserstrålning. Betrakta ej strålen. Tiedot laitteessa käytettävän laserdiodin säteilyominaisuuksista:
Aallonpituus 775-795 nm Teho 5 m W Luokan 3B laser.
Substances table (China)
388 Appendix C Regulatory information ENWW

Index
Symbols/Numerics
2ndary service menu 311
A
accessibility features 4
accessories
ordering 328
part numbers 328
activity log, fax
troubleshooting 322
ADF
assembly diagram 240
functions 107
jams 291
locating 5
operations 107
page sizes supported 317
paper path 108
part number 329
sensors 108
ADF jam detection
detection operations 109
document-feeder jam 109
long-document jam 109
stall jam 109
trailing edge detection 109
ADF pickup roller
removing 133
advanced setup
fax 25
after service checklist 120
alerts, setting up 52
assembly
locations 336
parts list 336
automatic document feeder (ADF)
capacity 45
jams 291
load for copying, scanning, or
faxing 45
locating 5
part number 329
B
background, gray 296
bands, troubleshooting 295
billing filters
fax 115
tone 115
bin, output
jams, clearing 288
bins, output
locating 5
black and white printing
troubleshooting 299
blanks, troubleshooting
copies 303
pages 308
scans 306
C
cables
part numbers 328
calibrating color 59, 252, 312
call report, fax
troubleshooting 322
Canadian DOC regulations 387
cartridge-door release, locating 5
cartridges
HP fraud hotline 66
image-formation system 94
part numbers 328
recycling 66
removing 122
replacing 67
status, checking 65
status, viewing with HP Toolbox
FX 52
storing 65
warranty 375
certificate of volatility 386
characters, troubleshooting 297
checklists
after service 120
pre-troubleshooting 227
preservice 120
circuit diagram 251
cleaning
automatic document
feeder 74
exterior 79
glass 79
lid backing 76
mode 311
page 253
paper path 73
scanner glass 77
scanner strip 77, 78
cleaning stage
drum 101
ITB 100
CO operations 111
color
calibrating 59, 252, 312
troubleshooting 299
comparison, product models 1
components
diagram 241
configuration page
printing 50
connectors
DC controller 248
contrast
print density 59
control panel
blank, troubleshooting 228
button test 312
cleaning page, printing 73
display test 312
ENWW Index 389
HP ToolboxFX system
settings 60
menus 20
messages 257
reinstalling 126
removing the bezel 124
removing the control
panel 125
supplies status, checking
from 65
controls
hook switch control 114
copy menu 34
copy-quality test 121
copying
loading ADF 45
loading flatbed scanner 46
media, troubleshooting 302
performance,
troubleshooting 303
quality, troubleshooting 300
setup menu 20
size, troubleshooting 303
troubleshooting 303
covers
left, removing 185
locations 338
parts list 338
right, removing 156
upper, removing 181
creases, troubleshooting 298
crooked pages 297
curled media 297
current control, fax line 115
customer support
online 376
D
dark copying 301
data path
fax 114
DC controller
connectors 248
engine control system 85
laser/scanner system
operations 93
pickup-and-feed system
operations 102
DC controller PCA, removing 161
defaults
NVRAM initialization 313
restoring 311, 313
defects, repetitive 252
demo page
troubleshooting 229
demo page, printing 50
density settings 59
developing stage 96
device
downstream detection,
fax 114
device polling 60
diagrams
ADF 240
assemblies 336
covers 338
internal assemblies 340
scanner 240
scanner assembly 332
troubleshooting 240
dialing
pulse 114
troubleshooting 318
dimensions
media 39
DIMMs
adding 71
part numbers 328
distinctive ring 112
documentation 2
doors
front, removing 205
dots per inch (dpi)
specifications 4
dots, troubleshooting 295
downstream device detection
fax 114
dpi (dots per inch)
faxing 25
specifications 4
drive components
diagrams 241
drivers
specifications 4
supported 11
universal 11
drum, image formation
operations 96
E
e-mail
setting alerts in
HP ToolboxFX 53
e-mail alerts, setting up 52
electrical specifications 378
electrostatic discharge
(ESD) 118
embedded Web server 9, 10
embedded Web server (EWS)
features 62
engine control
DC controller 86
high-voltage power supply 92
environmental specifications 378
error messages
ADF paper jams 109
control panel 257
error report 277
event log 277
event-log-only 279
error report, fax
printing 315
error-correction setting, fax 316
EU statement for telecom
operation 382
event log 53, 229
F
factory defaults, restoring
NVRAM initialization 313
faded print 295
fans
location 243
fax
answer mode 24
billing (metering) tone
filters 115
card 113
data path 114
distinctive ring 112
downstream current
detection 114
error codes 231
flash memory storage 115
functions 111
hook state 114
hook switch control 114
jams, troubleshooting 283
line current control 115
390 Index ENWW
operations 111
page storage 115
PSTN operations 111
pulse dialing 114
receive log 56
receiving 111
receiving, troubleshooting 231
reports 33
reports, printing 230
ring detect 114
ring type 24
safety isolation 113
safety protection circuitry 113
security, password
protection 63
security, private receive 64
send log 56
sending, troubleshooting 235
subsystem 113
V.34 setting 317
voice over IP (VoIP)
services 112
fax card
CODEC 113
DSP 113
fax subsystem 113
hook switch control 114
pulse dialing 114
regional versions 113
ring detect 114
fax menu 31
fax PCA, removing 158
fax ports, locating 7
fax reports, printing 33
fax security
security features,
computer 111
security features, network 111
fax subsystem
fax card 113
operations 113
Fax tab, HP ToolboxFX 54
fax troubleshooting
automatic activity log 315
confirmation report 315
confirmation with first
page 316
error messages 269
error report with first page 316
error report, printing 315
error-correction 316
fax-quality test 121
individual reports 314
last call with first page 316
perform test 316
receiving 319
reports 322
reports, printing all 314
sending 317
fax-quality test 121
faxing
loading ADF 45
features
product 4
feed system, ADF 107
Finnish laser safety
statement 387
firmware
version 312
firmware updates
recovering 79
flash memory, fax 115
fonts
printing font lists 50
formatter PCA, removing 158
fraud hotline 66
front door, removing 205
fuser
assembly diagrams 241
jams, clearing 287
fusing stage 99
G
Getting Started Guide 2
glass, cleaning 79
gray background,
troubleshooting 296
grayscale
troubleshooting 299
guides. See documentation
H
Help tab, HP ToolboxFX 56
hook state
fax 114
hook switch control 114
HP Customer Care 376
HP fraud hotline 66
HP Jetdirect print server
NVRAM initialization 313
HP Toolbox FX
Status tab 52
HP ToolboxFX
density settings 59
description 10
downloading 10
Fax tab 54
Help tab 56
Network Settings tab 61
opening 52
Password tab 60
Print Settings tab 60
Product information tab 53
Save/Restore tab 60
supplies status, checking
from 65
supported browsers 10
supported operating
systems 10
System Settings tab 58
HP Universal Print Driver 11
HP Web Jetadmin 63
HP-UX software 12
humidity specifications
environment 378
I
IC CS-03 requirements 383
image defects,
troubleshooting 295
image formation
cleaning stage 101
developing stage 96
fusing stage 99
latent-image stage 96
process 95
systems 94
transfer stage 98
image placement accuracy 379
image quality
copy, troubleshooting 300
HP ToolboxFX settings 59
repetitive image defects 252
scans, troubleshooting 304,
306
image transfer stage 98
index page, troubleshooting 323
initialization
NVRAM 313
ENWW Index 391
input tray
loading media 44
interface ports
cables, ordering 328
locating 7, 247
types included 4
internal assembly
locations 340
parts list 340
IP address
protocols supported 14
ITB
assembly diagrams 241
J
jam detection
ADF 109
detection operations 104
trailing edge detection,
ADF 109
jam recovery 281
jams
ADF, clearing 291
causes of 283
common causes of 282
fax, clearing 291
locating 284
locations 281
output bin, clearing 288
paper path, clearing 287
Japanese VCCI statement 387
Jetadmin, HP Web 63
Jetdirect print server
NVRAM initialization 313
K
Korean EMI statement 387
L
laser
-beam exposure stage 96
scanner system operations 93
laser safety statements 387
latent-image formation stage 96
LEDs, troubleshooting 229
left cover, removing 185
lid, cleaning 76
light copying 301
light print, troubleshooting 295
line current control, fax 115
lines, troubleshooting
copies 301
printed pages 295
scans 306
Linux 12
Linux software 12
loading media
optional tray 3 44
tray 1 43
tray 2 44
location
setting 312
logs, fax
error 315
printing all 314
troubleshooting 322
loose toner, troubleshooting 296
M
Macintosh
support 376
supported operating
systems 8
manuals. See documentation
media
ADF feeding operations 107
ADF, sizes supported 317
curled, troubleshooting 297
default settings 59
default size for tray 48
feed stage 98
jam detection operations 104
jams 283
originals, loading 45
supported sizes 39
wrinkled 298
media registration accuracy 379
memory
error messages 272
flash, fax 115
installing 71
NVRAM initialization 313
part numbers 328
memory cards
missing files 323
printing pictures,
troubleshooting 325
troubleshooting 323
wrong files 323
menu
control panel, access 20
copy 34
Copy setup 20
fax 31
Fax setup 23
Network config 29
photo 33
Photo setup 23
Reports 22
Service 28
System setup 26
menu map
printing 51
model
comparison 1
motors
location 243
N
network
configuring 14, 29
device polling 60
product discovery 14
protocols supported 14
Network config menu 29
network port
locating 7
network report, printing 51
Network Settings tab, HP
ToolboxFX 61
networks
HP Web Jetadmin 63
locating ports 247
security features 111
troubleshooting 309
New Zealand telecom
statements 382
NVRAM initialization 313
O
off-hook 114
on-hook 114
on/off switch, locating 5
online support 376
operating environment,
specifications 378
operating systems supported 8
operations
ADF 107
392 Index ENWW
fax 111
fax card in subsystem 113
fax subsystem 113
fax, PSTN 111
image-formation system 94
jam detection 104
laser/scanner system 93
memory card system 110
optical system 106
pickup-and-feed system 102
product systems 85
PSTN 111
sequence of 84
optical system operations 106
ordering
supplies and accessories 328
ordering supplies and
accessories 328
output bin
jams, clearing 288
output bins
locating 5
output quality
copy, troubleshooting 300
HP ToolboxFX settings 59
repetitive image defects 252
scans, troubleshooting 304,
306
P
pages
blank 308
not printing 308
printing slowly 308
skewed 297
paper
ADF feeding operations 107
ADF, sizes supported 317
curled, troubleshooting 297
default settings 59
HP ToolboxFX settings 59
jam detection operations 104
jams 283
supported sizes 39
wrinkled 298
paper jams
ADF detection operations 109
error messages, ADF 109
trailing edge detection,
ADF 109
paper path
ADF 108
ADF feeding operations 108
jams, clearing 287
paper-feed rollers and pads
removing 127
part numbers
cables 328
memory 328
repair kits 329
supplies 328
user-replaceable parts 329
parts
assembly locations 336
cover locations 338
internal assembly
locations 340
scanner assembly 332
screws 119
using lists and diagrams 330
parts, user-replaceable 329
password protection 63
Password tab, HP ToolboxFX 60
PCAs, diagrams 245
PCL drivers
universal 11
PCL settings, HP ToolboxFX 60
phone book, fax
HP ToolboxFX tab 54
phone numbers
HP fraud hotline 66
photo menu 33
Photo setup menu 23
photos
index page,
troubleshooting 323
printing, troubleshooting 325
scanning, troubleshooting 304
troubleshooting 323
photosensitive drum
image formation
operations 96
physical specifications 378
pickup and feed system
ADF 107
pickup roller
locating 244
removing 128
pickup-and-feed system
operations 102
pictures. See photos
pliers, required 119
polling, device 60
ports
cables, ordering 328
locating 7, 247
types included 4
post-service tests 121
PostScript settings, HP
ToolboxFX 61
power
fax line current control 115
high-voltage supply 92
low-voltage supply 87
requirements 378
supplies diagrams 241
power switch, locating 5
power-on
troubleshooting 228
powersave 311
pre-troubleshooting checklist 227
preservice checklist 120
primary charging stage 96
print cartridges
door release, locating 5
HP fraud hotline 66
image-formation system 94
part numbers 328
recycling 66
removing 122
replacing 67
status, checking 65
status, viewing with HP Toolbox
FX 52
storing 65
warranty 375
print density settings 59
print media
supported 39
print quality
HP ToolboxFX settings 59
repetitive image defects 252
troubleshooting image
defects 295
Print Settings tab,
HP ToolboxFX 60
print-quality test 121
printer drivers
specifications 4
ENWW Index 393
printing
configuration page 50
demo page 50
font lists 50
menu map 51
network report 51
supplies status page 50
troubleshooting 308
usage page 50
private receive 64
product
ADF functions 106
components 83
fax, functions 111
major systems 82
model comparison 1
operation sequence 84, 86
scanner functions 106
product discovery over
network“ 14
Product information tab, HP
ToolboxFX 53
proof sheet, troubleshooting 324
protocol settings, fax 317
protocols, networks 14
PS Emulation drivers 11
PSTN operations 111
pulse dialing 114
Q
quality
copy, troubleshooting 300,
303
HP ToolboxFX settings 59
repetitive image defects 252
scans, troubleshooting 304,
306
R
receiving faxes
distinctive ring 112
error report, printing 315
log, HP ToolboxFX 56
troubleshooting 319
receiving faxes,
troubleshooting 231
recycling supplies 66
regional versions
fax card 113
reinstalling parts
control panel 126
DC controller PCA 161
removing parts
ADF pickup roller 133
bezel 124
cautions for 118
checklists 120
control panel 125
DC controller PCA 161
fax PCA 158
formatter PCA 158
front door 205
left cover 185
pickup roller 128
print cartridges 122
right cover 156
rollers 127
separation pad, tray 1 137
separation roller 131
tools, required 119
upper cover 181
repetitive defects,
troubleshooting 252, 298
replacement parts, and
supplies 328
replacing
parts 118
replacing print cartridges 67
reports
configuration page 22, 50
demo page 22, 50
error 277, 312
error, event-log-only 279
fax 33
menu map 22, 51, 226
network report 22, 51
PCL 6 font list 23
PCL font list 22
PS font list 23
service 312
service page 23
supplies status page 22, 50
usage page 22, 50
reports, fax
error 315
printing all 314
troubleshooting 322
resets
NVRAM initialization 313
resolution
specifications 4
restoring
default settings 313
defaults 311
factory defaults 313
NVRAM initialization 313
right cover, removing 156
ring detect
fax card 114
RING operations 111
rollers
image formation
operations 96
locating 244
pickup and separation,
removing 127
repetitive image defects 252
S
safety
-protection circuitry, fax 113
isolation, fax 113
safety statements 387
Save/Restore tab,
HP ToolboxFX 60
scanner
assembly, removing 163
functions 106, 107
glass, cleaning 77
load for copying 46
optical system operations 106
strip, cleaning 78
scanning
blank pages,
troubleshooting 306
loading ADF 45
proof sheet,
troubleshooting 324
quality, troubleshooting 304,
306
speed, troubleshooting 305
scatter, troubleshooting 298
screwdrivers, required 119
screws
replacing 118
secondary service menu 311
security features
computer 111
network 111
394 Index ENWW
sending faxes
error report, printing 315
log, HP ToolboxFX 56
troubleshooting 317
sending faxes,
troubleshooting 235
sensors
ADF 108, 109
form sensor, ADF 109
jam detection 104
paper-present sensor,
ADF 109
trailing edge detection,
ADF 109
separation pad (tray 1),
removing 137
separation roller, removing 131
separation rollers
locating 244
separation stage, image
formation 99
sequence of operations 84
service
part numbers 328
tools, required 119
Service menu
cleaning mode 311
powersave 311
restoring defaults 311
secondary 311
settings 311
Service tab
HP ToolboxFX settings 60
settings
HP ToolboxFX 58
size
copy 303
troubleshooting 303
skewed pages 297
slow speed, troubleshooting
faxing 322
scanning 305
smeared toner,
troubleshooting 296
software
embedded Web server 9, 10
HP ToolboxFX 10, 52, 256
Linux 12
Solaris 12
supported operating
systems 8
UNIX 12
Solaris software 12
spare parts 328
special media
guidelines 42
special paper
guidelines 42
specifications
electrical 378
environmental 378
physical 378
product features 4
specks, troubleshooting 295
speed
fax, troubleshooting 322
scanning, troubleshooting 305
spots, troubleshooting 295
stapler
locating 5
static precautions 118
status
alerts, HP Toolbox FX 52
page 229
supplies, checking 65
viewing with HP Toolbox
FX 52
Status tab, HP Toolbox FX 52
storing
environmental
specifications 378
fax pages in flash
memory 115
print cartridges 65
streaks, troubleshooting 295
supplies
HP fraud hotline 66
ordering 328
recycling 66
replacing print cartridges 67
status page, printing 50
status, checking 65
status, viewing with HP Toolbox
FX 52
storing 65
support
online 376
supported media 39
System Settings tab, 58
System setup menu 26
systems 85
T
T.30 protocol trace 231
TCP/IP
protocols supported 14
technical support
online 376
Telephone Consumer Protection
Act 383
telephone numbers
HP fraud hotline 66
temperature specifications
environment 378
tests
copy-quality 121
diagnostics pages 253
fax 316
fax-quality 121
internal print quality 253
post-service 121
print-quality 121
service page 253
timing diagram 250
TIP operations 111
toner cartridges. See print
cartridges
toner troubleshooting
loose 296
scatter 298
smeared 296
specks 295
Toolbox. See HP ToolboxFX
tools, required 119
trailing edge detection
ADF 109
transfer stage 98
tray
capacities 41
media types supported 41
media weights 41
Tray 1
jams, clearing 284
tray 1
loading 43
locating 5
tray 1 separation pad,
removing 137
ENWW Index 395
Tray 2
jams, clearing 284
tray 2
loading 44
locating 5
Tray 3
jams, clearing 286
part number 329
tray 3
loading 44
locating 5
trays
default media size 48
jams, clearing 284, 286
locating 5
part numbers 329
settings 59
troubleshooting
about 227
blank pages 308
blank scans 306
calibration 252
checklist 227
color 299
configuration page 229
control-panel diagnostics 230
control-panel messages 257
copy quality 300
copy size 303
copying 303
curled media 297
demo page 229
diagrams 240
dialing 318
event log 229
faded print 295
fax 314
fax error-correction
setting 316
fax reports 314, 322
image defects 295
index page 323
jams 281, 283
LED diagnostics 229
lines, copies 301
lines, printed pages 295
lines, scans 306
loose toner 296
memory cards 323
misformed characters 297
networks 309
NVRAM initialization 313
pages not printing 308
pages printing slowly 308
pages too dark 301
pages too light 301
performance 308, 322
power-on 228
printing photos 325
proof sheet 324
receiving faxes 231, 319
repetitive defects 298
reports and tools 229
scan quality 304, 306
sending faxes 235, 317
skewed pages 297
speed, faxing 322
status page 229
text 297
toner scatter 298
toner smear 296
toner specks 295
using service mode 311
wrinkles 298
types, media
HP ToolboxFX settings 59
U
universal print driver 11
UNIX 12
UNIX software 12
upper cover, removing 181
usage page, printing 50
USB port
locating 7, 247
type included 4
User Guide 2
user-replaceable parts 329
V
V.34 setting 317
vertical lines,
troubleshooting 295
vertical white or faded
stripes 301
voice over IP (VoIP) services 112
voltage requirements 378
volume
settings 28
W
warranty
Customer self repair 374
print cartridges 375
product 373
wavy paper, troubleshooting 297
Web sites
customer support 376
HP Web Jetadmin,
downloading 63
Macintosh customer
support 376
ordering supplies 328
universal print driver 11
weight 378
white or faded stripes,
troubleshooting 301
Windows
drivers supported 11
supported operating
systems 8
universal print driver 11
wrinkles, troubleshooting 298
396 Index ENWW
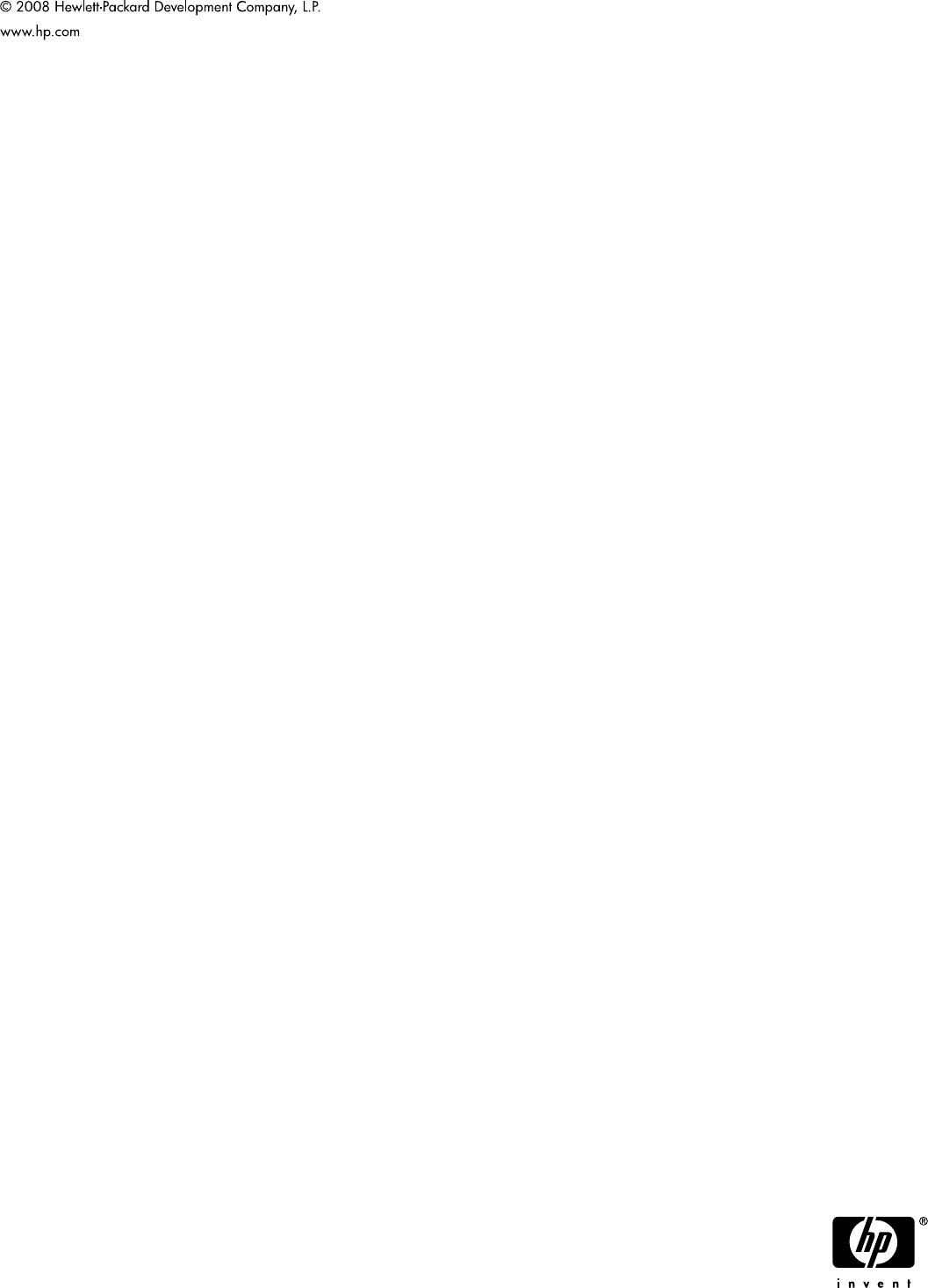
*CC434-90969*
*CC434-90969*
CC434-90969