S4 ISP/JTAG Module Phil40 06 V04
User Manual: pasat -
Open the PDF directly: View PDF .
Page Count: 4
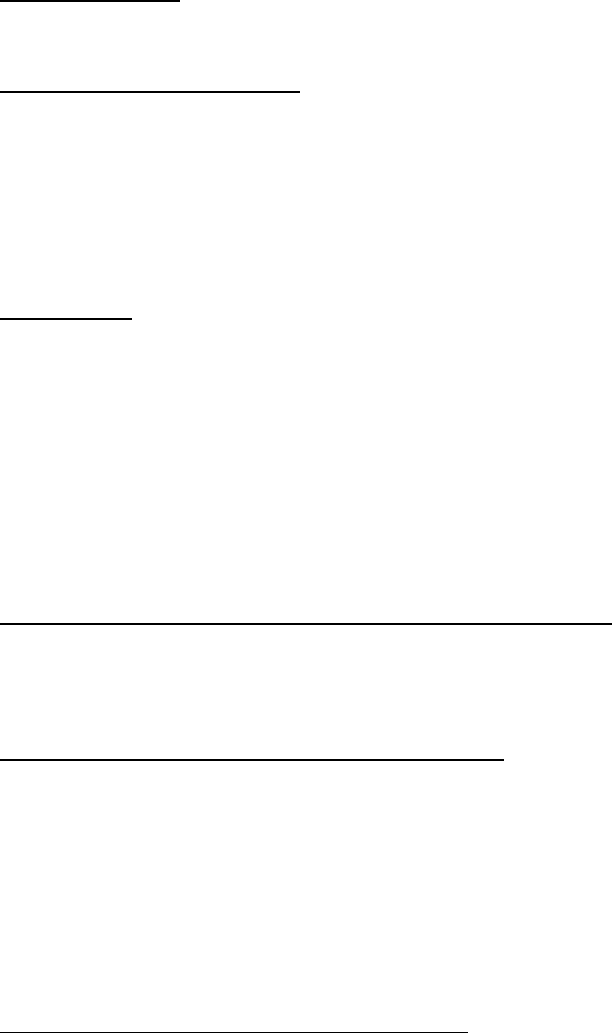
TinyARM PHIL40-06 LPC2106 Module v0.4
Philips TinyARM PHIL40-06 Module
1. Introduction
The purpose of this document is to specify mechanical dimensions and
electrical behavior of TinyARM LPC2106 PHIL40-06 module.
2. Reason for development
Philips introduced LPC2106 processor housed in LQFP 48 pin package.
It features 32kbyte Flash memory and 8kbyte SRAM. This chip can be used
as a replacement for 8/16 microcontrollers.
There are following problems when using this chip:
A. Price of development tools, both software and hardware.
B. Unusual package which is not convenient for development.
C. The chip requires 2 different voltages.
D. Battery voltage (for RTC and RAM backup) range is not sufficient.
3. Solution
PHIL40-06 module intends to solve all problems:
A. The module is housed in DIP40 package which has pin out similar
to 8751 microcontroller.
B. The module requires just one convenient 5V supply. All the voltages
for Philips LPC2106 processor are generated on-board. The module can
supply 1.8V and 3.3V supply to external (low power) circuitry.
C. The module features built-in 10 MHz oscillator.
D. The module includes Reset generator.
E. The module is re-usable. It can be used in several designs, the only
additional investment is DIL40 socket for each design.
F. Software tools are either IAR or free GNU .
4. List of required signals for development version
All the signals required for standard ARM Test/Debug JTAG interface are
generated on PHIL40-06 board. This includes standard JTAG TRSTN,TCLK,
TMS,TDI and TDO signals and handling of RTCK and DBGSEL signals.
Reset signal for all circuitry is generated on board.
5. Voltage levels and electrical behaviour
PHIL40-06 module runs from 5V supply applied to DIL40 pin 40.
The supply voltage for this version can be from 4.5V to 5.5V.
The estimated current consumption is 100mA from 5V supply.
PHIL40-06 module can supply 1.8 and 3.3V voltage from pins located in the
middle of the board. Do not draw more than 20mA from any supply !
Voltage levels for ARM I/O pins are 3.3V compliant. The specs says that
I/O pins are 5V tolerant.
6. Method of programming internal Flash
There are 2 methods to program Flash – either JTAG or ISP (using UART0 of
Philips LPC2106 chip). Please, refer to the relevant Philips LPC2106
manual.
Note: P0.14 must be logic low for LPC2106 processor to enter boot
loader mode. For normal operation, use pull up resistor to 3.3V
so that PHIL40-06 does not enter boot loader mode.
1
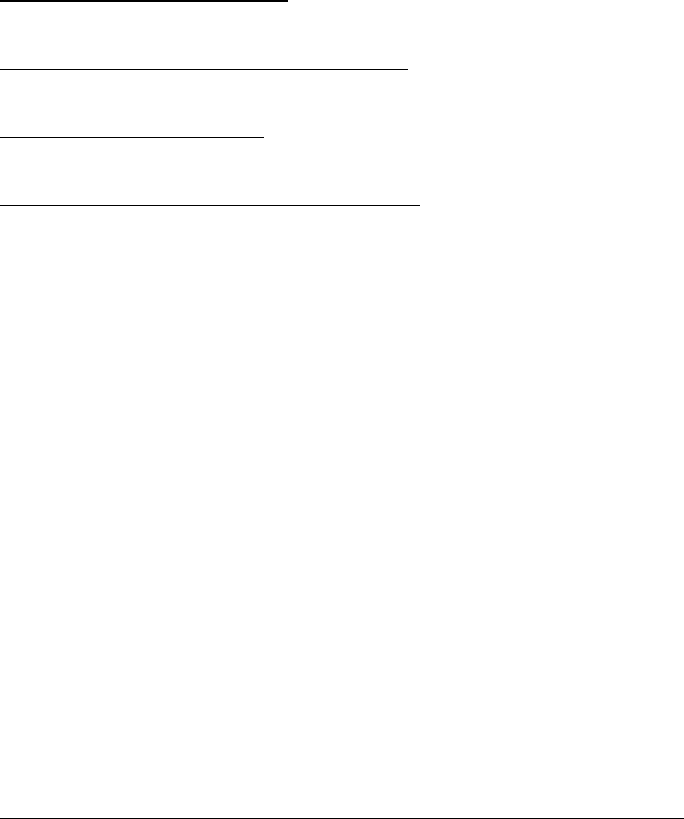
TinyARM PHIL40-06 LPC2106 Module v0.4
7. Mechanical dimensions
The module should fit into the standard 600 mils DIL40 socket.
8. Tips and tricks for development
None
9. Preliminary drawing
None
10. PHIL40-06 board control signals
RSTN – input for external reset signal, active low. Leave unconnected if
not used. PHIL40-06 board generates proper internal Reset signal upon
power-up. An external push button can be connected to RSTN to generate
reset signal. No debounce is needed for the push button.
Note: If driving RSTN pin by external circuitry, then it must be open
collector (open drain) with pull-up resistor. Do NOT use push-pull
to drive RSTN !
RST_OUTN – output of PHIL40-06 internal reset generator, active low, open
drain output.
PWRENN – input controlling PHIL40-06 voltage regulators. Default is low
when the voltage regulators are enabled and generate 3.3V and 1.8V
respectively. This signal is pulled down on PHIL40-06 board. Normally
leave this pin unconnected (N.C.). Driving this pin high will disable
voltage regulators.
DBGSEL – this is Debug Select input. Default is low when the part
operates normally, executing code in internal Flash or SRAM.
Leave this pin unconnected for normal operation as it is pulled down
by 10k resistor on the module. Drive this pin high if there is a need to
enter Debug Mode.
RTCK – leave this pin unconnected for normal operation.
11. Interfacing PHIL40-06 board to various voltage levels
PHIL40-06 board runs from 5V supply and generates 3.3V voltage for I/O
pins logic levels reference. All PHIL40-06 I/Os are 3.3V compliant,
meaning they can directly interface with 3.3V logic. They can also
interface directly 5V LV TTL and HCT MOS logic.
PHIL40-06 I/Os are 5V resistant so they can receive 5V TTL/HC/HCT logic
levels. However, I/O cannot drive 5V HC MOS inputs directly, some level
conversion is necessary. The simplest method for slow signals is using
pull up resistor to 5V supply.
2
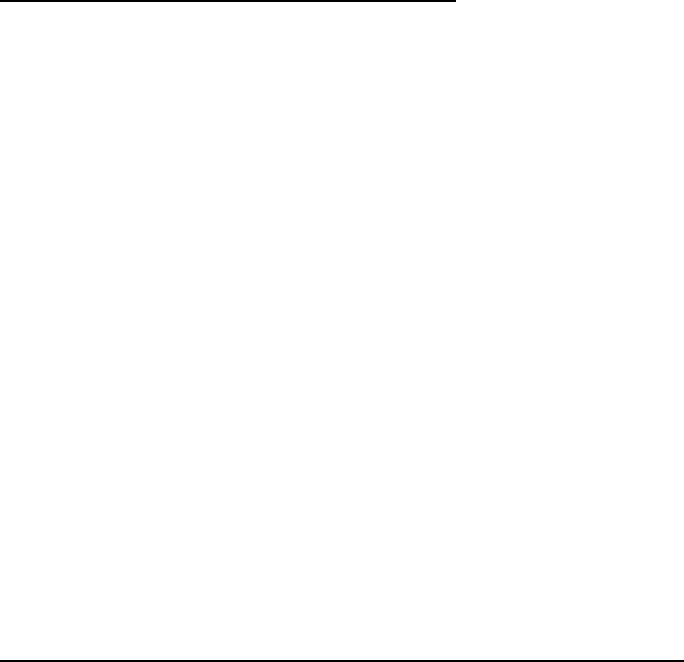
TinyARM PHIL40-06 LPC2106 Module v0.4
12. Simple test / First use of TinyARM
It is easy to start with PHIL40-06 module. All what you need is and
experimental board, DIL40 socket, RS232 interface circuit like MAX232 and
5V power supply. Philips supplies LPC210x ISP utility for Windows which
can talk to PHIL40-06 UART0 serial interface.
Make the connections like the following:
-connect ground to DIL40 pin 20
-connect +5V to DIL40 pin 40
-connect logic low (pull down 3k9 to ground) to DIL40 pin 16 which
corresponds to PHIL40-06 Port0.14. This pin is samples during reset or
power-up to indicate whether to start ISP utility.
-connect DIL40 pin 1 which corresponds to PHIL40-06 Port00/TxD0 to the
input of MAX232 driver, e.g. to T1in (MAX232 pin 11). The output of
MAX232 driver, e.g. T1out (MAX232 pin 14) is connected to DB9 or DB25
connector as TxD signal.
-connect DIL40 pin 2 which corresponds to PHIL40-06 Port01/RxD0 to the
output of MAX232 receiver, e.g. to R1out (MAX232 pin 12). The input of
MAX232 driver, e.g. R1in (MAX232 pin 13) is connected to DB9 or DB25
connector as RxD signal.
-Connect a push-button between DIL40 pin 9 RSTN and ground.
-Insert PHIL40-06 board into DIL40 socket.
-Connect RS232 cable to the PC on one side and to your board on the
other side.
-Apply power from 5V supply.
-Start Philips LPC210x utility
-Press push button to connect PHIL40-06 to the PC, if necessary.
-ENJOY !
13. Connecting Macraigor Systems WIGGLER to TinyARM board
The easiest way is to use extra DIL40 socket and connect DIL40 pins
to the male dual-row 20 pin header as follows:
DIL40 pin Header pin Signal name
20 4,6,8,10,12,14 GND
16,18,20
22 3 TRSTN
23 7 TMS
24 9 TCK
25 5 TDI
26 13 TDO
9 15 RESETN
30 11 RTCK
42 1,2 VCC (3.3V)
Some additional resistors are strongly recommended to apply correct
default voltage levels on JTAG pins.
Notes:
a. DBGSEL pin should be driven high, i.e. pull up resistor 1k to Vcc
for the part to enter debug mode when debugging is possible.
b. PHIL40-06 module can supply 1.8V and 3.3V voltage to other (low power)
peripherals.
3
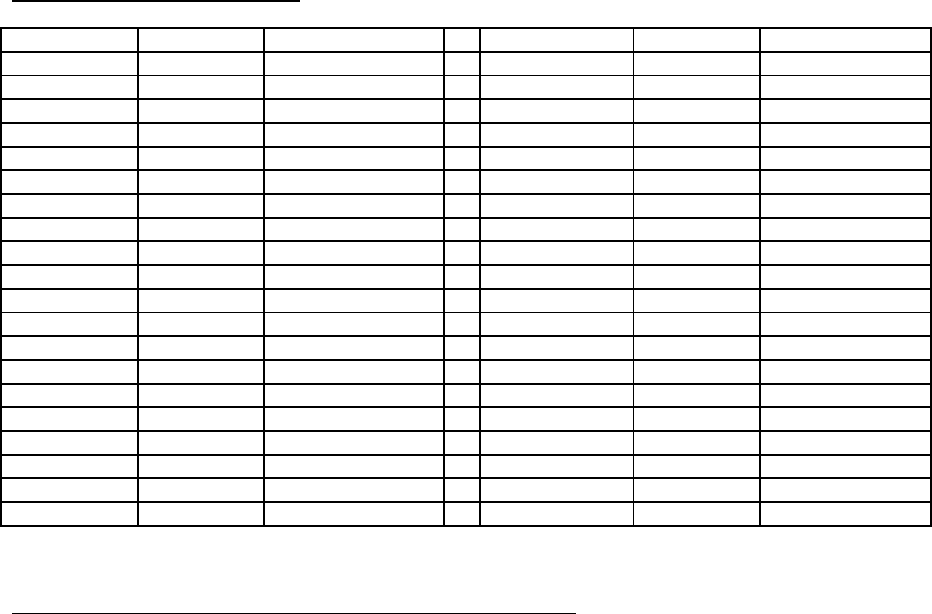
TinyARM PHIL40-06 LPC2106 Module v0.4
14. TinyARM board pinout
Pin Nr. Pin Name Altern. Pin Nr. Pin Name Altern.
1 P0.0 TxD0/PWM1 40 VCC 5V
2 P0.1 RxD0/PWM3 39 P0.31 EXTIN0/*
3 P0.2 SCL/CAP0.0 38 P0.30 TRACEPKT3/*
4 P0.3 SDA/MAT0.0 37 P0.29 TRACEPKT2/*
5 P0.4 SCK/CAP0.1 36 P0.28 TRACEPKT1/*
6 P0.5 MISO/MAT0.1 35 P0.27 TRACEPKT0/*
7 P0.6 MOSI/CAP0.2 34 P0.26 TRACESYNC
8 P0.7 SSEL/PWM 33 P0.25 PIPESTAT2
9 RSTN 32 P0.24 PIPESTAT1
10 P0.8 TxD1/PWM4 31 RSTN_OUT
11 P0.9 RxD1/PWM6 30 RTCK
12 P0.10 RTS1/CAP1.0 29 DBGSEL
13 P0.11 CTS1/CAP1.1 28 P0.23 PIPESTAT0
14 P0.12 DSR1/MAT1.1 27 P0.22 TRACECLK
15 P0.13 DTR1/MAT1.1 26 P0.21 PWM5/TDO
16 *Note P0.14 DCD1/EINT1 25 P0.20 MAT1.3/TDI
17 P0.15 RI1/EINT2 24 P0.19 MAT1.2/TCK
18 PWRENN 23 P0.18 CAP1.3/TMS
19 N.C. 22 P0.17 CAP1.2/TRST
20 GND 21 P0.16 EINT0/MAT0.2
Note: P0.14 must be logic low for PHIL40-06 to enter boot loader mode.
15. Known problems of Philips LPC2106 processor
a. External interrupts 0 to 2 (EINT0 to EINT2) are level sensitive.
It is not possible to set them to edge sensitive mode.
b. SPI interface requires to use pull up resistor on SSEL pin even
if it is set to Master mode. That results in pin wasting, pin SSEL
cannot be used as GPIO P0.7 when SPI is used.
4