T103 18 XV501T 4LV & HV
User Manual: T103
Open the PDF directly: View PDF .
Page Count: 9
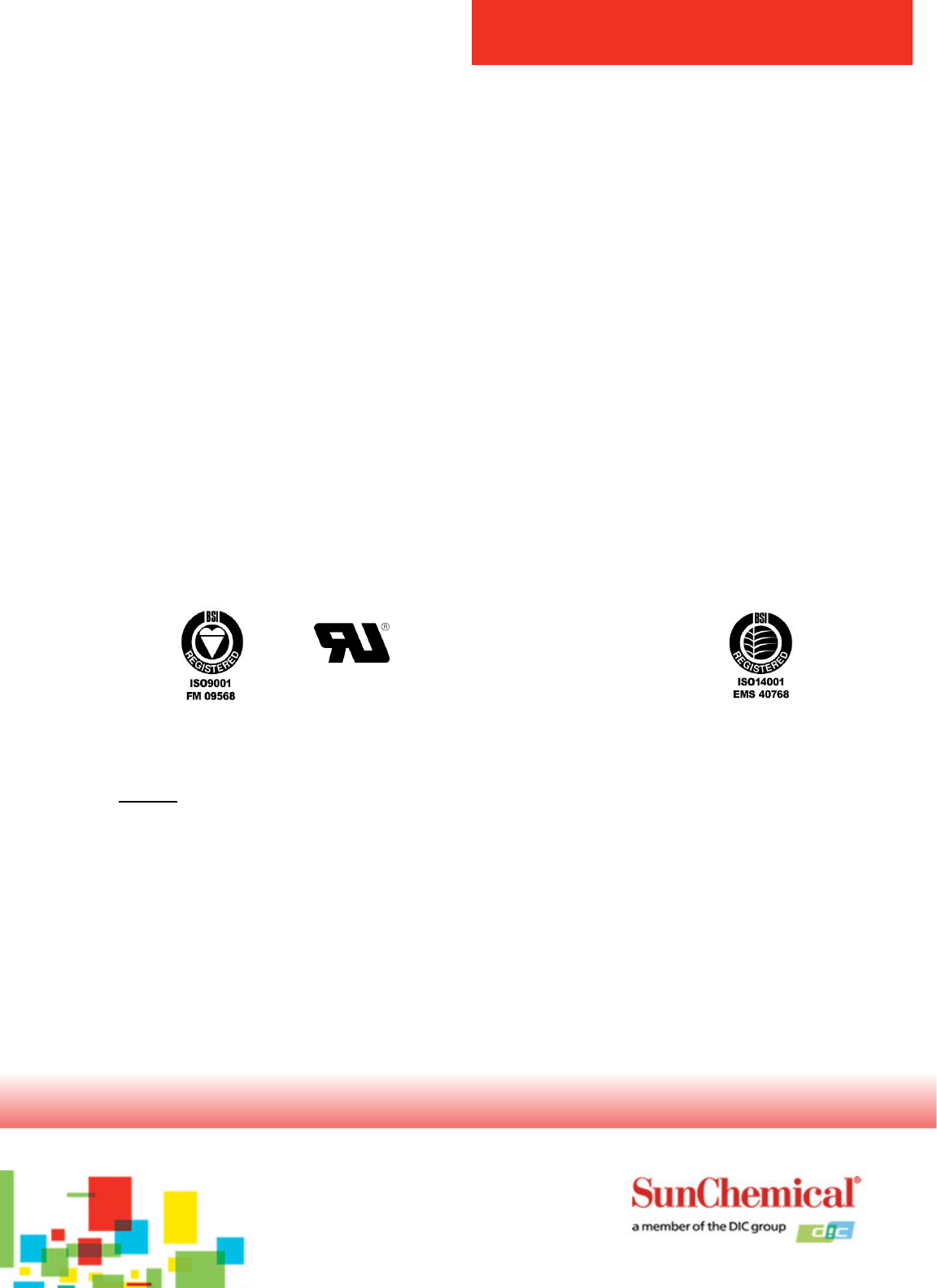
En;alkdjfalkjfadkfjaldkfjalkdj
1
Imagecure® XV501T
-
4 Screen
Technical Data Sheet
T103 Version 18
October 2011
Page 1/9
XV501T-4 Screen From the Imagecure™ family of
Photoimageable Solder masks
1. Description
Imagecure® AQ XV501T-4 Screen is a two component thermal hardening liquid photoimageable solder
resist that dries by solvent evaporation to give a film that can be processed in aqueous potassium or
sodium carbonate solution, or Butyl diglycol (BDG).
This Technical Information Leaflet (TIL) and the relevant Material Safety Data Sheet (MSDS) should be
read carefully prior to using this product.
Imagecure® XV501T-4 screen products are not recommended for use with reflow tin/lead and electrolytic
gold plated conductors. Imagecure® XV501T screen products are recommended for this purpose.
2. Product features
• RoHS & WEEE Directive Compliant
• Excellent adhesion to all clean copper surfaces
• A selection of products is available to suit a wide range of process conditions
• The required colour and finish may be obtained by mixing the resist with the appropriate hardener
U.L. FILE NUMBER E83564
® is a registered trade mark
3. Product Range
SAP No.
90173548 Imagecure® XV501T-4 LV Gloss Red Resist 0.75 kg. CAWN1287
90173541 Imagecure® XV501T-4 LV Gloss Opaque Blue Resist 0.75 kg. CAWN1259
90173549 Imagecure® XV501T-4 LV Gloss Blue Resist 0.75 kg. CAWN1289
90173570 Imagecure® XV501T-4 LV Gloss Yellow Resist 0.75 kg. CAWN1344
90173588 Imagecure® XV501T-4 LV Gloss Black Resist 0.75 kg. CAWN2002
90173584 Imagecure® XV501T-4 HV Matt Black Resist 0.75 kg. CAWN1374
90173607 Imagecure® XV501T-4 HV Extra X Matt Black Resist 0.75 kg. CAWN2147
91134876 Imagecure® XV501T-4 Extra Matt Black Resist 0.75 kg. CAWN2693
90173542 Imagecure® XV501T-4 Clear Hardener 0.25 kg. CAWN1271
90160166 Imagecure® XZ107 Slow Thinner 5.00 L. CDSN4059
90160157 Imagecure® XZ46 Screen Cleaner 5.00 L. CDSN4008
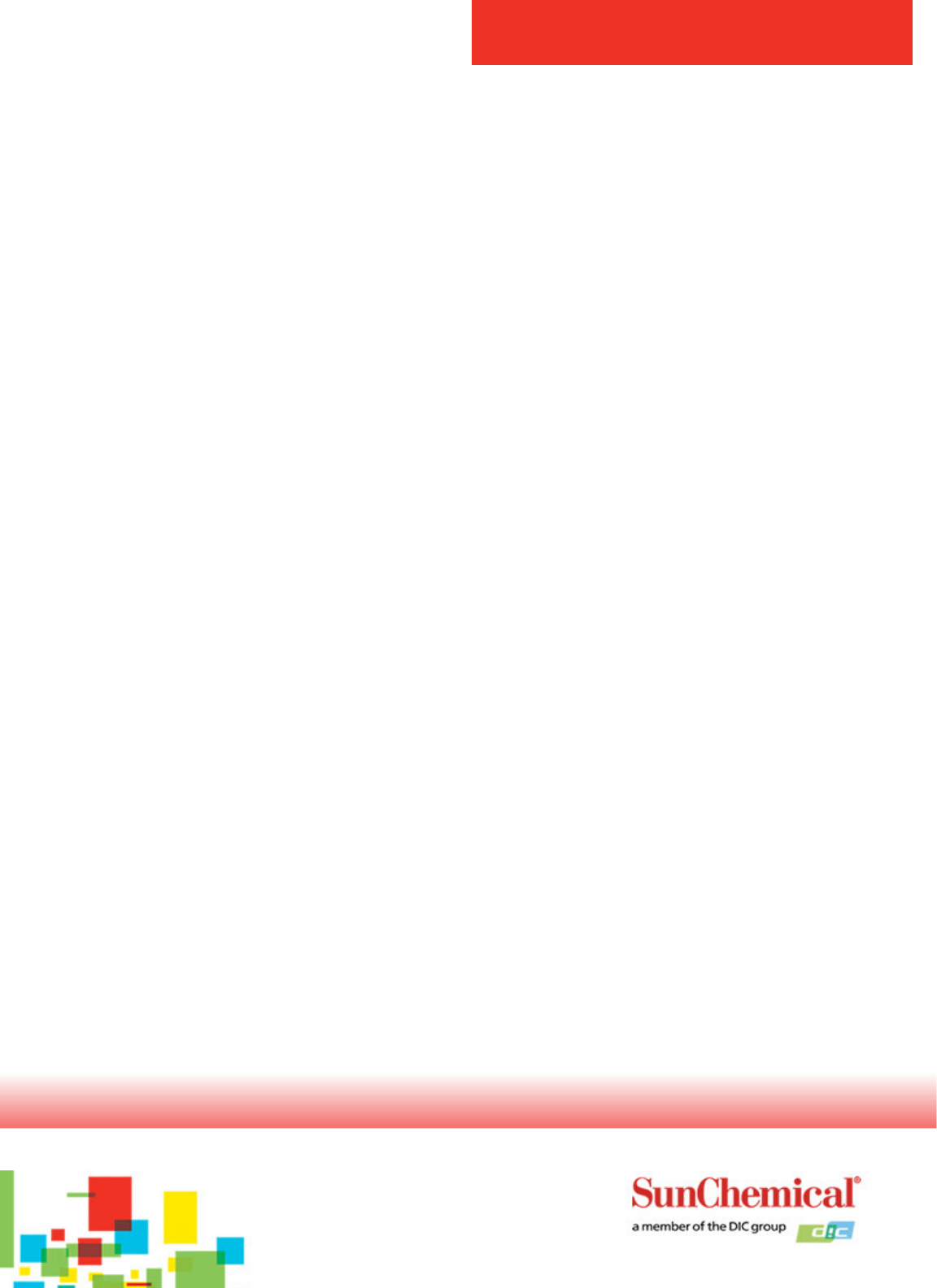
En;alkdjfalkjfadkfjaldkfjalkdj
2
Imagecure® XV501T
-
4 Screen
Technical Data Sheet
T103 Version 18
October 2011
Page 2/9
4. General Handling
4.1 Storage and Shipping
When stored in sealed containers, in a cool place (20ºC / 68ºF), away from sources of direct heat and
sunlight, Imagecure® XV501T-4 resist and hardener components have a shelf life of 18 months.
Imagecure® XV501T-4 can withstand higher temperatures (40 - 60ºC / 104 - 140ºF), whilst in transit for
up to periods of 1 month without any detrimental effect on its performance.
4.2 Waste disposal
Care should be exercised in the disposal of printing ink waste. This should be carried out in accordance
with good industrial practice, observing all the appropriate regulations and guidelines.
For more specific handling advice refer to the detailed Safety Data Sheet (SDS), supplied by your local
Sun Chemical Circuits representative.
5. Application / Processing Conditions
5.1 Mixing
The resist and hardener components must be mixed together in the correct mixing ratio of 3:1 w/w
before use. The hardener component must be added to the resist component.
Note that CAWN2735 Matt Black Resist and CAWN2752 Blue Resist should only be mixed with CAWN2714
Hardener.
For larger pack sizes mechanical mixing is recommended to ensure thorough mixing of the resist and
hardener components. Recommended mixers include those with variable speed motors and paddle
type mixing blades as well as the shaker or rotating type mixers.
Mixing times will depend on the type of mixer or stirrer used but typical mix times of 10 - 15 minutes
with stirrer speeds between 40 - 100 rpm can be expected. Avoid excessively fast speeds as this will
entrap large volumes of air into the mixed resist.
It is recommended that attention be paid to ensuring that any resist at the sides of the container and on
the bottom is completely mixed into the main body of the resist.
After the mixing operation is completed it is recommended to allow the mixed and thinned pack to
debubble for ~ 30 min. before use.
Mixed pot life at 23º± 2ºC (70 - 77ºF) will be approximately 72 hours. Always ensure the lid is replaced
on the container to avoid any contamination and excessive solvent evaporation.
5.2 Thinning
Imagecure® XV501T-4 Screen may be reduced with a maximum of 3% w/w Imagecure® Slow Thinner
XZ107.
N.B. Stir well before use.
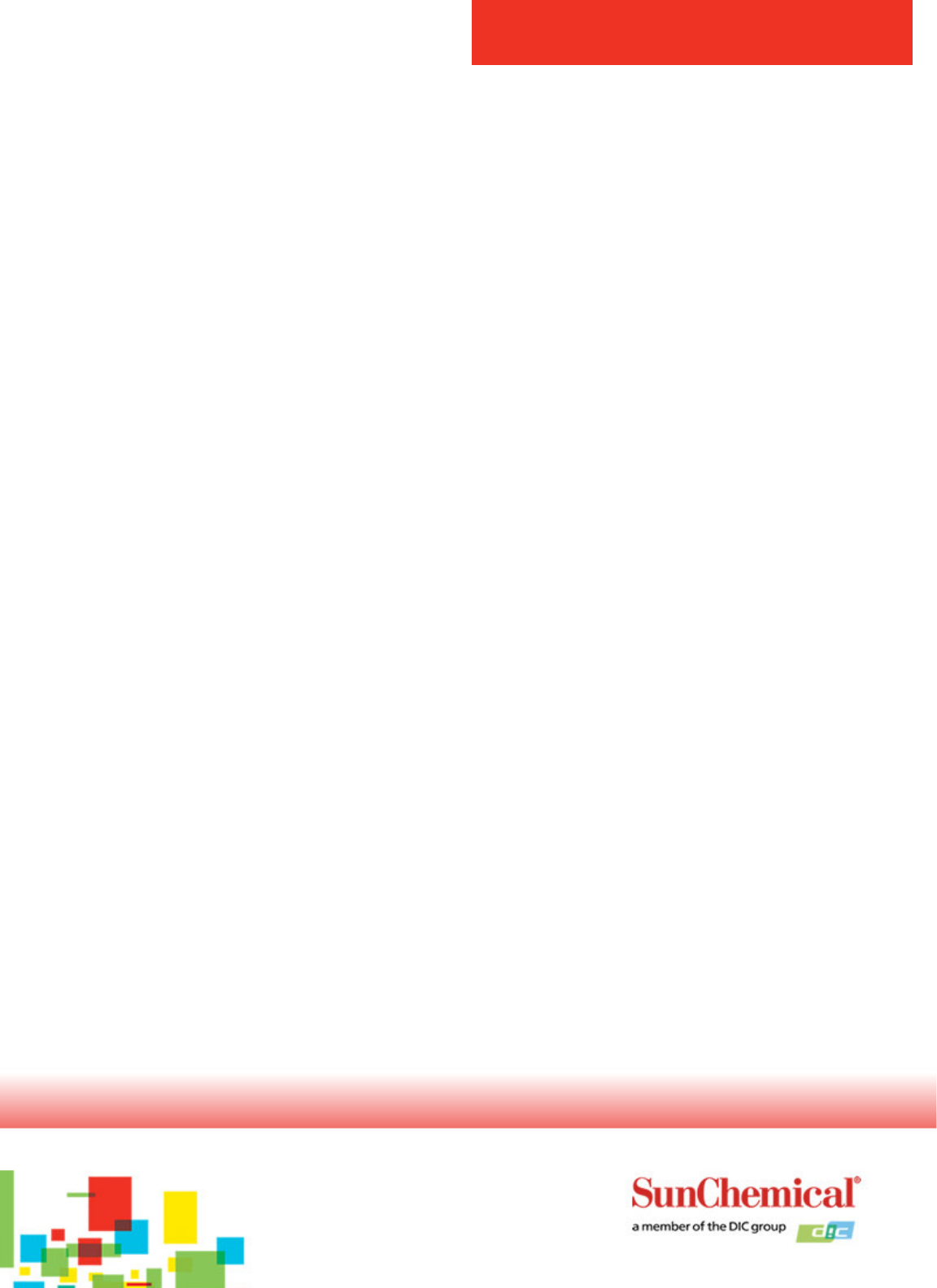
En;alkdjfalkjfadkfjaldkfjalkdj
3
Imagecure® XV501T
-
4 Screen
Technical Data Sheet
T103 Version 18
October 2011
Page 3/9
5.3 Pre-Clean
Ensure that all copper surfaces are completely clean, tarnish free and dry prior to applying Imagecure®.
Mechanical pre-cleaning is recommended as follows: -
Brushing 280 - 400 grit silicon carbide brushes are recommended having a footprint on the copper of
8 - 15mm. (0.3 - 0.6 in). The water rinse and heater sections should be capable of
thoroughly rinsing and drying the panels such that no water is left in the holes or between
closely spaced conductors and that moisture or tarnish is not present on the freshly
brushed panels.
It is important that each brush is regularly checked and dressed as necessary to ensure
optimum efficiency during use.
Please note that Nylon brushes of 600 - 800 grit can also be used.
Pumice Pumice or Aluminium oxide slurry of between 12 - 18% is recommended with an optimum
of 15%. The water rinse and heater sections must be capable of rinsing and drying the
panels such that residual pumice particles are completely removed and that no water is left
in the holes or between closely spaced conductors and that moisture or tarnish is not
present on the freshly cleaned panels.
For panels that are badly oxidised and tarnished then a micro-etch prior to mechanical pre-cleaning is
recommended. The micro-etch should be capable of removing any oxide or tarnish staining and of
thoroughly rinsing and drying the panel before being mechanically cleaned.
Panels which have close track/gap configurations (<100µm./4mil.), may not be suitable for mechanical
precleaning and will need to be micro-etched. The use of either a standard micro-etch or the “deep
etching“ microetch chemistries can be effective in this process. It is recommended that each user
ensures that the Imagecure product is compatible with the particular micro-etch used and all
subsequent metal finishing processes.
Surface roughness figures of:-
Ra 0.2 - 0.4µm.
R delta q 4 - 9º
would be considered to be optimum values for copper surfaces pre-cleaned as above. A minimum Ra
of 0.2µm. with an R delta q value of >4º is recommended (optimum R delta q values 7 - 9º).
Please refer to separate technical document on surface roughness for a fuller explanation of the above
roughness values.
NOTE. It is recommended that all freshly cleaned panels are coated with Imagecure® XV501T-4 within
a maximum time of 2 - 4 hours. The actual maximum time will vary depending upon ambient
temperature and humidity. Panels left longer than 4 hours before coating should be pre-cleaned again.
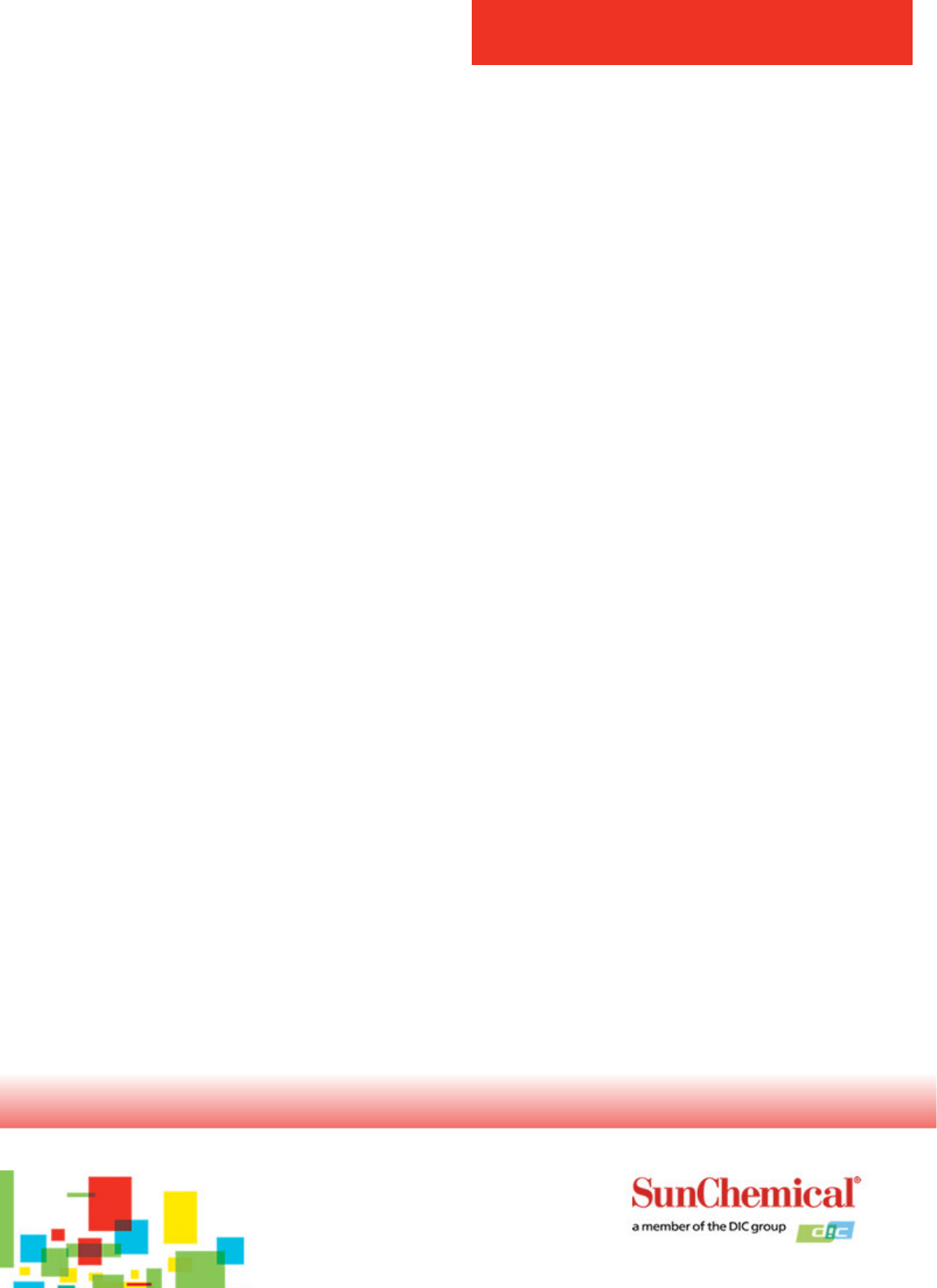
En;alkdjfalkjfadkfjaldkfjalkdj
4
Imagecure® XV501T
-
4 Screen
Technical Data Sheet
T103 Version 18
October 2011
Page 4/9
5.4 Application
The Imagecure® XV501T-4 can be used with all types of vertical screen print units and horizontal
screen print machines.
The low viscosity of the XV501T-4LV series makes them compatible for users who require fast print speeds
with complete encapsulation of all conductors. The higher viscosity specification of the XV501T-4HV series
will give improved track encapsulation of boards with high copper conductors.
Typical polyester meshes will be 36/90 - 43/80cm (90/90 - 125/80inch) with a 65 - 70º shore squeegee
with a square edge profile. The optimum mesh for printing is 43/80cm (110/80inch) and this will be
suitable for most 18µm. and 35µm. base copper board designs.
For boards with 70µm. base copper, or for boards requiring a specific withstand voltage the use of
meshes with lower mesh counts 32/100 - 36/90cm (80/100 - 90/90inch) may be necessary.
Print tests with subsequent micro-sections are recommended to ensure adequate track encapsulation.
5.5 Washing Up
Screen Cleaner XZ46 is recommended for washing up. Alternative cleaners and screenwashes are
available to suit customers’ particular requirements. Your local Sun Chemical Circuits representative
will be pleased to advise on product selection.
5.6 Pre-Dry
Good drying of the printed film is important so ovens with good temperature profiles and extraction are
necessary. Specific drying parameters (time and temperature) will be dependent upon the specific oven
used as well as the thermal mass and quantity of the panels being dried.
It is recommended that printed panels be allowed to debubble for approximately 5 - 10 minutes in still
air at ambient temperature prior to being placed in the oven.
Air flow speeds of 1 - 2m/sec. are recommended to achieve sufficient removal of the volatile solvent.
Drying is less efficient as the air velocity drops below 0.5m./sec.
For vertical screen print systems with a vertical drying oven a set air temperature of 80 - 90ºC (176 -
194ºF) for 30 - 50 min. is recommended. Optimum 85ºC (185ºF) for 45 minutes. Drying will depend on
board thickness and Imagecure thickness as printed, as well as air flow in the oven.
For printing processes that only print one side at a time the following is recommended for box ovens:-
Side 1 10 - 25 min. at 80 - 90ºC (176 - 194ºF)
Side 2 25 - 35 min .at 80 - 90ºC (176 - 194ºF)
The Imagecure® XV501T- 4 series can also be dried in IR ovens. Specific times and temperatures will
depend on the specific Infra red oven used. Please discuss with your Imagecure® partner before use.
Allow an adequate gap between panels. Spacing of 25 - 40 mm (1 - 1.6 in.) is recommended to ensure
sufficient air flow between panels.
After drying it is recommended that all panels be exposed and developed within 24 hours. The
maximum storage time of boards before exposure/development is 72 hours. However it is
recommended that boards be stored in yellow light conditions with controlled temperature and humidity.
If the humidity increases above 60% RH then the storage time of the dried panels will be reduced.
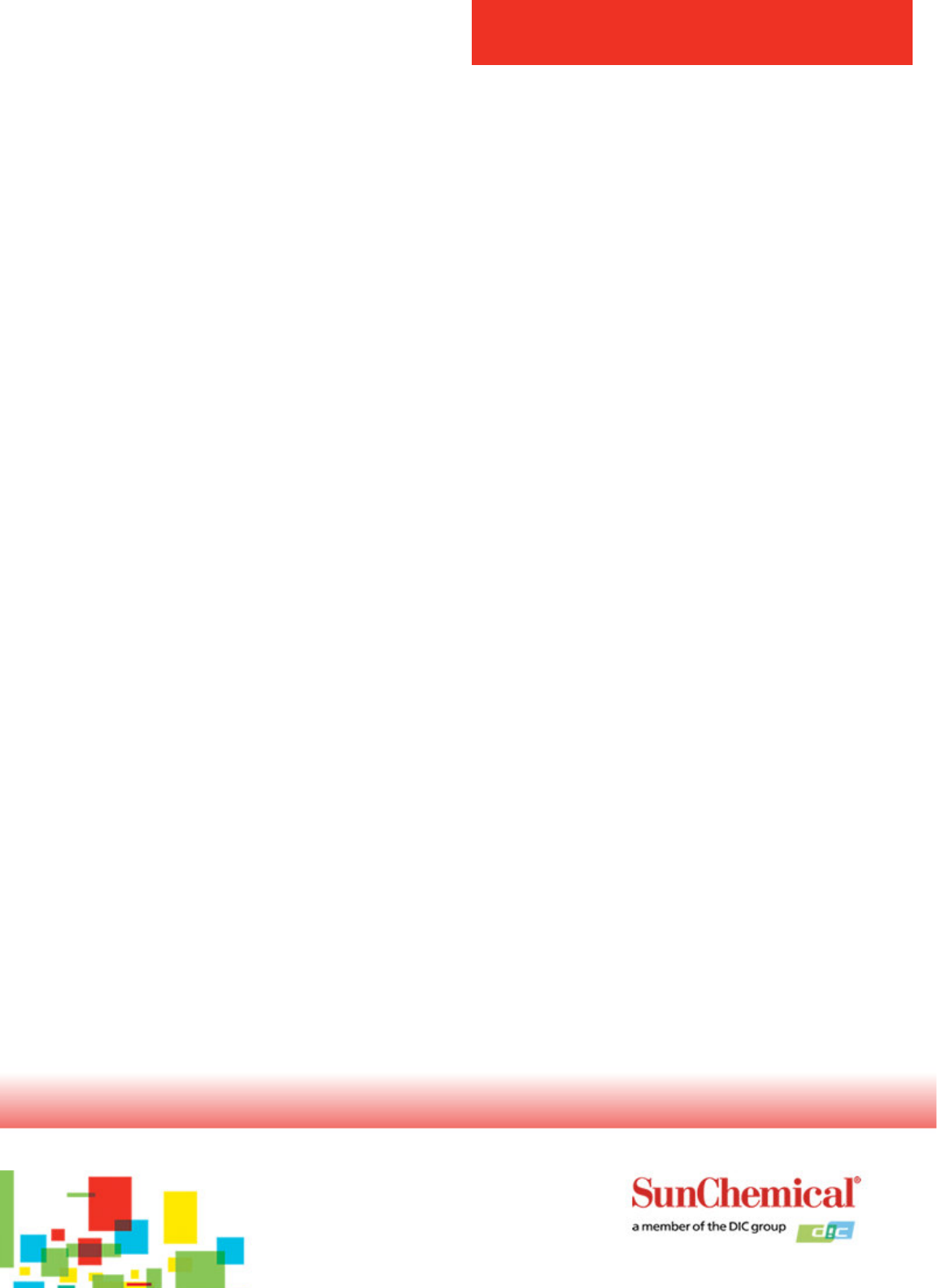
En;alkdjfalkjfadkfjaldkfjalkdj
5
Imagecure® XV501T
-
4 Screen
Technical Data Sheet
T103 Version 18
October 2011
Page 5/9
5.7 Exposure
All Imagecure® XV501T-4 systems are negative working and can be used with all exposure units using
ferric doped mercury vapour lamps with UV wavelengths between 300 - 400nm.
Ferric doped lamps with power ratings of 5 - 10kW are recommended. It is recommended that to
remove the infra red radiation the unit is either cooled or has an infra red filter to keep the temperature
of the artwork < 30ºC (86°F). Optimum working temperature 22 - 25ºC (72 - 77°F).
Exposure readings of 250 - 500 mJ/cm² are typical*.
* Exposure readings taken with an IL390B radiometer from the International Light Co. Inc.
Stouffer values of 8 - 10 (solid resist) using a 21 step wedge are typical. For selective Ni/ Au and or
immersion Sn exposure levels of 11 - 12 (solid resist) are recommended. Increased exposure may be
required for certain colours.
The artwork should have a Dmax > 4.0 and a Dmin < 0.15.
5.8 Development
Imagecure® XV501T-4 will readily develop in either potassium or sodium carbonate solutions. The
recommended carbonate concentration is 10 ± 2g./lit.
The working pH range is 11.3 to 10.8 for aqueous carbonate solutions. To ensure the quality of
development it is recommended that the pH of the developer solution does not drop below 10.8. At a
pH <10.6 the efficiency of the developer solution may drop due to the increased loading of
photopolymer.
Recommended temperature range is 30 - 40ºC (86 - 104°F), optimum 35 - 38ºC (95 - 100°F).
Spray pressures between 2 - 4 bar (30 - 60 PSI), optimum 2.5 bar (37.5 PSI).
Dwell times in the developing chambers of 45 - 80 seconds, optimum 60 seconds. For boards with
small via holes (0.2 - 0.4mm) or with laminate thickness > 3mm, longer dwell times may be necessary
to ensure complete development of the holes.
Water rinse pressures to be 2 -3 bar (30 - 45 PSI), with operating temperatures 15 - 30ºC (59 - 86°F).
It is recommended that hard water (~200 ppm dissolved ions) be used where possible to give good
rinsing, followed by a final rinse in deionised water.
Anti-foams will need to be added to the aqueous developing chambers to avoid foaming. The amount of
anti-foam to be added may vary depending upon the type of anti-foam used, the size and number of
developing chambers and spray bars, spray pressures and the loading of developed resist. In all cases
it is recommended that the minimum amount of anti-foam be added.
Imagecure® XV501T-4 will also develop in BDG (butyl diglycol). The developer temperature should be
30 ±2ºC (82 - 90°F), with a dwell time between 120 and 160 seconds. Spray pressures of 4 - 5 bar (60 -
75 PSI) are normal. Optimum conditions will include a dwell of 150 seconds @ 30°C (86°F) with spray
pressures of 4 - 5 bar.
It should be noted that Imagecure® films needing to be removed can be stripped by dipping in either a
propriety solder mask stripper or 5% sodium hydroxide solution at 50 - 70°C (122 - 158°F).
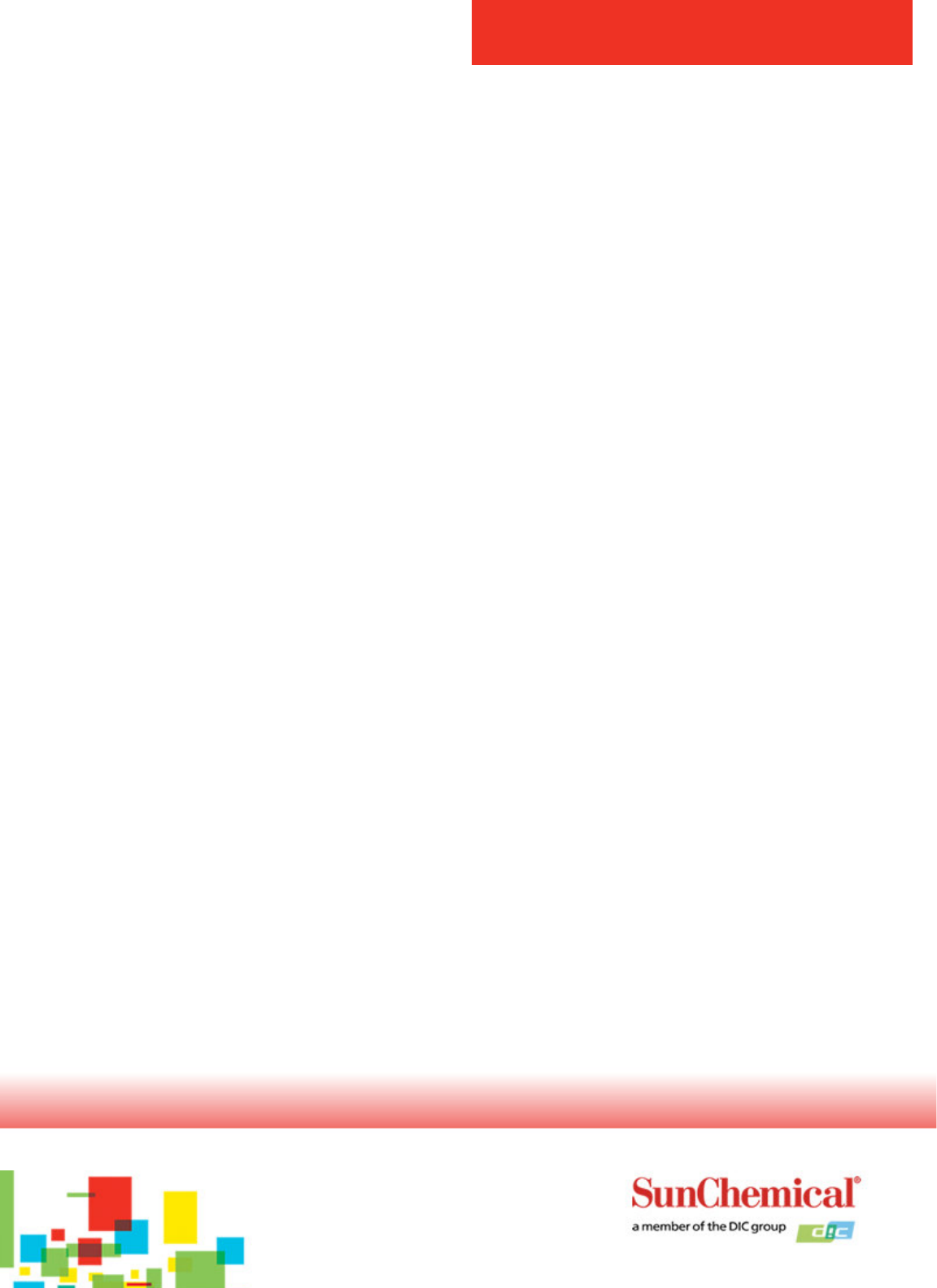
En;alkdjfalkjfadkfjaldkfjalkdj
6
Imagecure® XV501T
-
4 Screen
Technical Data Sheet
T103 Version 18
October 2011
Page 6/9
5.9 UV Bump
Generally Imagecure® XV501T-4 does not require a UV bump. However there may be certain customer
processes or requirements that render the use of a UV bump desirable or necessary.
If a UV bump is required then it is recommended that it be carried prior to post bake, and that a multi
lamp double sided UV cure unit be used. Recommended UV energy is 1200 - 1500 mJ/cm².
A UV bump can also be carried out after post bake, recommended energy of 2500 - 3000mJ/cm².
A UV bump will improve surface hardness, reduce volatile emissions, reduce ionic contamination and
give increased resistance to OEM assembly cleaning processes.
5.10 Post Bake
It is important to ensure that all ovens have an independent thermal profile taken, as the set air
temperature is not always reliable and the air flow in the oven or the door seals may give rise to either
hot or cold spots.
The recommended bake cycle is 140 - 150ºC (284 - 302°F) for 60 - 90 min. Optimum is 150ºC for 60
min. Bake times should be taken when oven temperature reaches the pre-set point.
Sufficient air flow is necessary to ensure a consistent temperature gradient in the oven as well as a
uniform degree of cure for the solder resist.
With respect to batch ovens boards should be racked 25 - 40mm. (1.0 - 1.6 in.) apart.
All exhaust ducting and extraction fans should be adequately insulated to avoid any volatile emissions
condensing around the oven area.
5.11 Notation/ Legend Printing
All Imagecure® XV501T-4 screen products are compatible with a wide range of UV curing, thermal
curing and photoimageable notation inks.
Thermal curing inks can be applied prior to post bake to increase productivity.
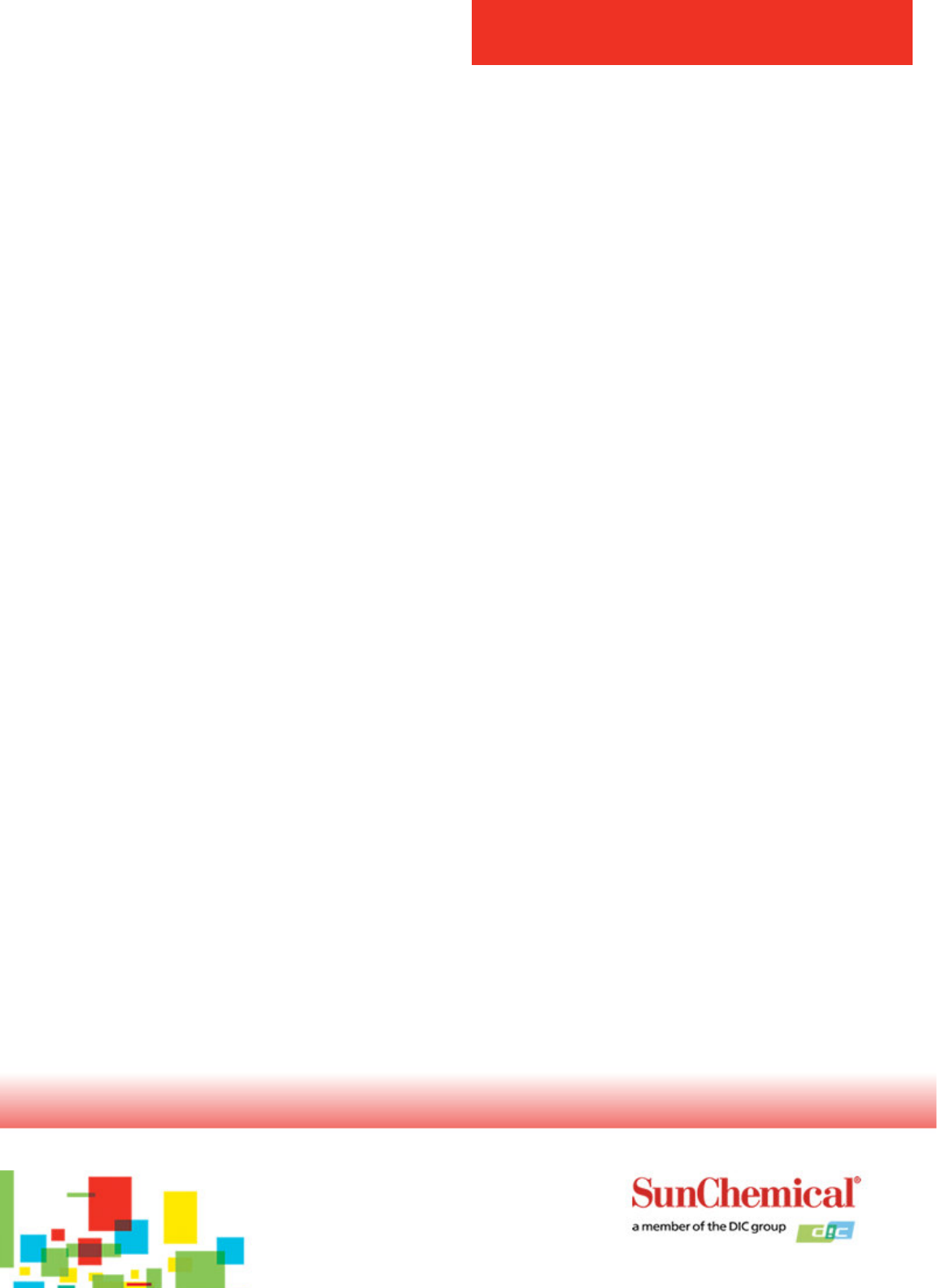
En;alkdjfalkjfadkfjaldkfjalkdj
7
Imagecure® XV501T
-
4 Screen
Technical Data Sheet
T103 Version 18
October 2011
Page 7/9
6. Health and safety
Detailed material safety data sheets will be supplied by your local Sun Chemical Circuits representative.
The products detailed hereon have been tested in accordance with, and meet the requirements of, the
RoHS Directive 2002/96/EC and the European Directive 2003/11/EC, regarding the presence of the metals
- Pb (Lead / Lead compounds), Hexavalent Chromium, Cd (Cadmium), Hg (Mercury), and Poly Brominated
Flame Retardants.
Conforms to Regulation (EC) No. 1907/2006 (REACH), Annex II – Europe.
Registered to the Sony Green Partner Program, Certificate Number 11490
Sony Green Book Number I8880002
As the world’s foremost producer of inks, pigments and colour technology, Sun Chemical is leading our
industry in developing and producing products which minimise our impact – and our customers’ impact – on
the environment and striving to maximise the use of renewable resources. We consider it our responsibility
to be involved in the communities in which we live and work and to offer direction in meeting today’s needs
without compromising the ability of future generations to meet theirs.
7. Film Performance/ Technical Specification
7.1 Physical Properties of IMAGECURE® XV501T-4 Screen
Pack Code Viscosity S.G. Flash point Non volatile content
CAWN1287 8 - 13 Pa.s 1.39 86°C (187°F) 72.8%
CAWN1259 10 - 15 Pa.s 1.39 86°C (187°F) 73.4%
CAWN1289 11 - 16 Pa.s 1.39 86°C (187°F) 72.8%
CAWN1344 11 - 16 Pa.s 1.39 86°C (187°F) 74.2%
CAWN2002 12 - 16 Pa.s 1.39 86°C (187°F) 74.7%
CAWN1374 18 - 21 Pa.s 1.32 86°C (187°F) 72.4%
CAWN2147 / CAWN2693 18 - 22 Pa.s 1.36 86°C (187°F) 60 – 65%
CAWN1271 5.5 - 8.5 Pa.s 1.17 86°C (187°F) 75.6%
*Viscosity measured at 25°C (77°F). Please note viscosity can vary greatly depending on ink
temperature, volume of ink tested, type of viscometer used and the test method.
Volatile Organic Content (VOC) 380 - 420g./L.
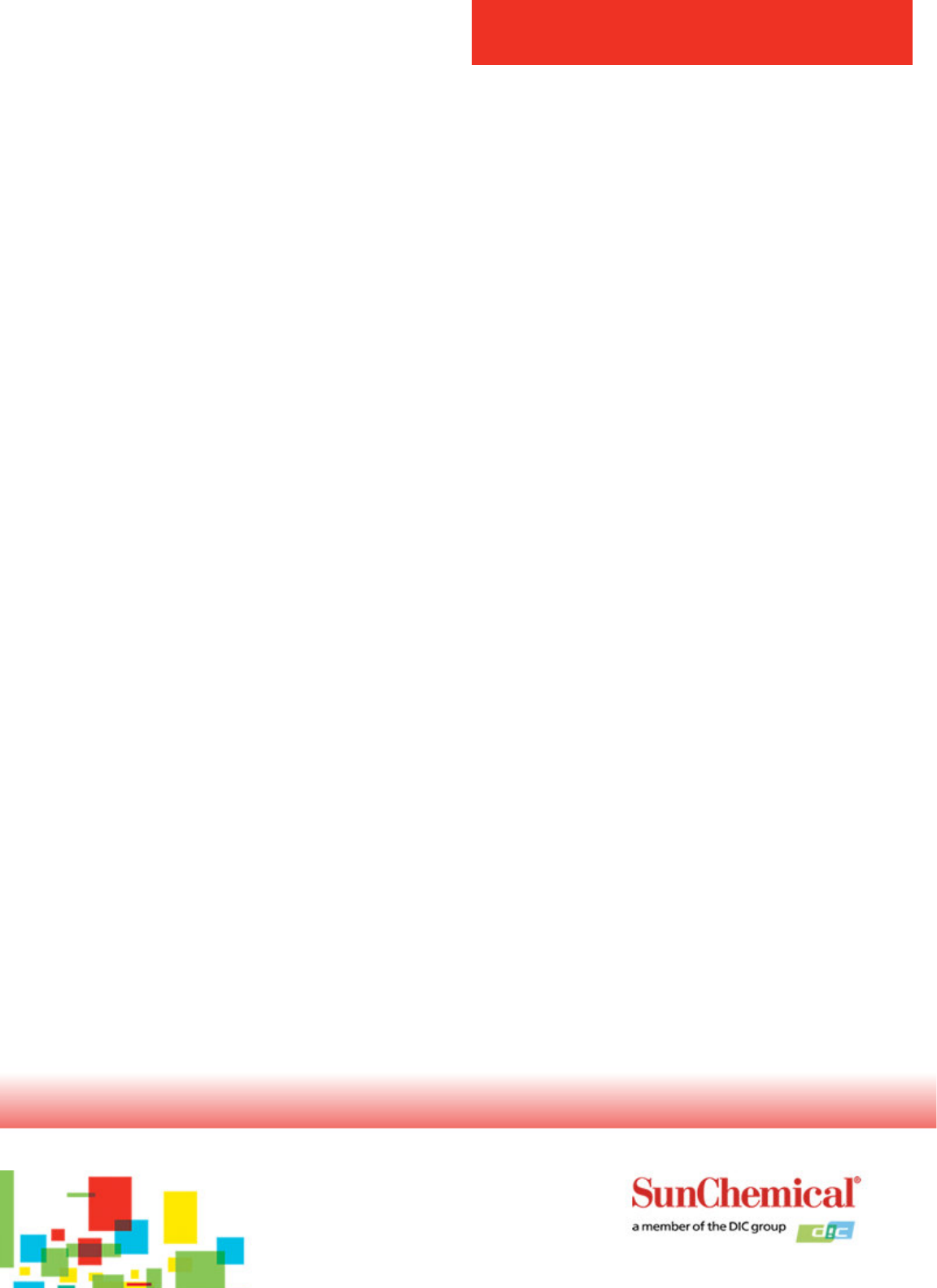
En;alkdjfalkjfadkfjaldkfjalkdj
8
Imagecure® XV501T
-
4 Screen
Technical Data Sheet
T103 Version 18
October 2011
Page 8/9
7.2 Properties of IMAGECURE® XV501T-4 Cured Film
Solder Resistance MIL-PRF-55110F 30 secs @ 288°C (550°F)
IPC SM840E 10 secs @ 260°C (500°F)
Resistance to Fluxes IPC SM840E Pass
Electroless Ni/Au Plating Pass
Hydrolytic Stability IPC SM840E Class H Pass
Solvent, Cleaning Agent, IPC SM840E Class H Pass
& Flux Resistance
Fungal Resistance IPC SM840E Class H Pass
Thermal Shock IPC SM840E Class H Pass
MIL-PRF-55110F Pass
MIL-STD-202G Pass
Chemical Resistance IPA >1 hour
1,1,1 Trichloroethane >1 hour
MEK >1 hour
Methylene Chloride >1 hour
Alkaline Detergent >1 hour
Fluxes >1 hour
Abrasion Pencil Hardness IPC SM840E Class H Pass
Adhesion (Copper) IPC SM840E Class H Pass
Flammability UL 94V0 Rating File No. E83564
Ionic Contamination MIL-PRF-55110F <0.3µg. NaCl/cm²
Using Alpha Ionograph 500M
Bellcore TR-NWT000078 Pass
Insulation Resistance IPC SM840E Classes T and H Pass
Moisture & Insulation Resistance IPC SM840E Classes T and H Pass
Electromigration IPC SM840E Classes T and H Pass
Comparative Tracking Index DIN EN 60112 / IEC 112 >600V
(FR4 Laminate – CTI Rated 500 V)
Siemens E-Corrosion Test SN 57030 Pass
Dielectric Strength IPC SM840E Class H 141kV/mm.
(50 Hz.) DIN53481
Dielectric Constant (range) 1MHz 3.87 – 3.95
10MHz 3.73 – 3.78
100MHz 3.57 – 3.65
1GHz 3.45 – 3.67
Dielectric Loss Factor tangent (10
2
Hz - 10
6
Hz) 0.02
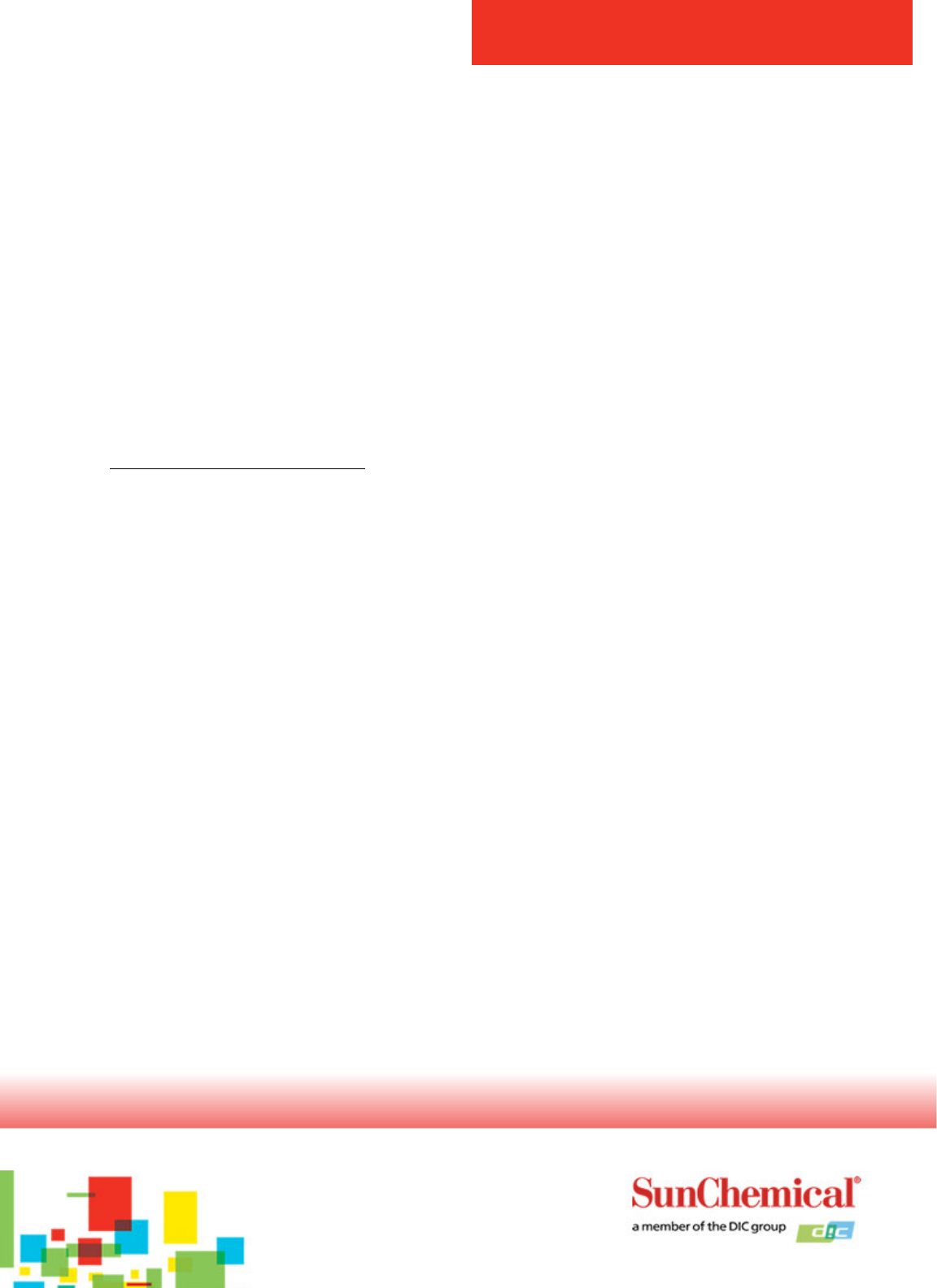
En;alkdjfalkjfadkfjaldkfjalkdj
9
Imagecure® XV501T
-
4 Screen
Technical Data Sheet
T103 Version 18
October 2011
Page 9/9
8. Disclaimers
This information has been carefully compiled from experience gained in field conditions and extensive
laboratory testing. However the products’ performance and its’ suitability for the customers’ purpose depend
on the particular conditions of use and the material being printed. We recommend that customers satisfy
themselves that each product meets their requirements in all respects before commencing a production run.
Since we cannot anticipate or control the conditions under which our products are used, it is impossible to
guarantee their performance. All sales are also subject to our standard terms and conditions.
9. Technical Assistance / Contacts
Sun Chemical Circuits are an international company, and as such can offer technical, engineering and sales
support to our customers worldwide.
For further information regarding this product, or any of our extensive range of materials for PCB
fabrication, please contact your local Sun Chemical team or visit the Technical Help Desk at website:
http://www.sunchemicalhelpdesk.com
Our Products are intended for sale to professional users. The information herein is general information designed to assist customers in
determining the suitability of our products for their applications. All recommendations are made without guarantee, since the
application and conditions of use are beyond our control. We recommend that customers satisfy themselves that each product meets
their requirements in all respects before commencing a print run. There is no implied warranty of merchantability or fitness for purpose
of the product or products described herein. In no event shall Sun Chemical be liable for damages of any nature arising out of the use
or reliance upon this information. Modifications of the product for reasons of improvements might be made without further notice.
Norton Hill, Midsomer Norton Bath, BA3 4RT, England. Telephone: (44) 1761 414471 Fax: (44) 1761 416609