Emerson Process Management 3000 Users Manual World Class Oxygen Analyzer With IFT
3000 749c9564-f81a-4cf4-bd14-c162948738c1 Emerson Process Management Oxygen Equipment 3000 User Guide |
2015-02-06
: Emerson-Process-Management Emerson-Process-Management-3000-Users-Manual-540116 emerson-process-management-3000-users-manual-540116 emerson-process-management pdf
Open the PDF directly: View PDF .
Page Count: 182 [warning: Documents this large are best viewed by clicking the View PDF Link!]
- COVER
- ESSENTIAL INSTRUCTIONS
- HIGHLIGHTS OF CHANGES
- TABLE OF CONTENTS
- PREFACE P-1
- LIST OF TABLES
- NOTE TO USERS
- SAFETY INSTRUCTIONS
- GLOSSARY OF TERMS
- QUICK START GUIDE FOR IFT 3000 SYSTEMS
- QUICK REFERENCE GUIDEIFT 3000 INTELLIGENT FIELD TRANSMITTER
- HART COMMUNICATOR FAST KEY SEQUENCES
- DESCRIPTION AND SPECIFICATIONS
- INSTALLATION
- SETUP
- CALIBRATION
- GENERAL USER INTERFACE (GUI) OPERATION
- TROUBLESHOOTING
- RETURN OF MATERIAL
- APPENDICES
- APPENDIX A, REV.3.8 WORLD CLASS 3000 PROBE
- APPENDIX A, REV. 3.8WORLD CLASS 3000 OXYGEN ANALYZER (PROBE)
- DESCRIPTION
- PROBE TROUBLESHOOTING
- SERVICE AND NORMAL MAINTENANCE
- OVERVIEW
- PROBE RECALIBRATION
- CELL REPLACEMENT
- OPTIONAL CERAMIC DIFFUSION ELEMENT REPLACEMENT
- REPLACEMENT OF CONTACT ANDTHERMOCOUPLE ASSEMBLY
- REPLACEMENT OF HEATER, V˚STRUT AND BACKPLATE ASSEMBLY (INNER PROBE ASSEMBLY; INCLUDES CONTACT AND THERMOCOUPLE ASSEMBLY)
- CALIBRATION GAS AND REFERENCE AIR LINES FOR HIGH TEMPERATURE ˚ CORROSIVE ENVIRONMENT OPERATION
- REPLACEMENT PARTS
- APPENDIX B, REV. 2.2 HPS 3000 HEATER POWER SUPPLY
- APPENDIX D, REV 2.4 MPS 3000 MULTIPROBE CALIBRATION GAS SEQUENCER
- APPENDIX E
- APPENDIX J
- APPENDIX A, REV.3.8 WORLD CLASS 3000 PROBE
- INDEX
- ROSEMOUNT WARRANTY

Instruction Manual
IB-106-300NH Rev. 4.2
July 2002
http://www.processanalytic.com
World Class 3000
Oxygen Analyzer
with IFT 3000 Intelligent
Field Transmitter

Emerson Process Management
Rosemount Analytical Inc.
Process Analytic Division
1201 N. Main St.
Orrville, OH 44667-0901
T (330) 682-9010
F (330) 684-4434
e-mail: gas.csc@EmersonProcess.com
http://www.processanalytic.com
ESSENTIAL INSTRUCTIONS
READ THIS PAGE BEFORE PROCEEDING!
Rosemount Analytical designs, manufactures and tests its products to meet many national and
international standards. Because these instruments are sophisticated technical products, you
MUST properly install, use, and maintain them to ensure they continue to operate within their
normal specifications. The following instructions MUST be adhered to and integrated into your
safety program when installing, using, and maintaining Rosemount Analytical products. Failure to
follow the proper instructions may cause any one of the following situations to occur: Loss of life;
personal injury; property damage; damage to this instrument; and warranty invalidation.
• Read all instructions prior to installing, operating, and servicing the product.
• If you do not understand any of the instructions, contact your Rosemount Analytical repre-
sentative for clarification.
• Follow all warnings, cautions, and instructions marked on and supplied with the product.
• Inform and educate your personnel in the proper installation, operation, and mainte-
nance of the product.
• Install your equipment as specified in the Installation Instructions of the appropriate In-
struction Manual and per applicable local and national codes. Connect all products to the
proper electrical and pressure sources.
• To ensure proper performance, use qualified personnel to install, operate, update, program,
and maintain the product.
• When replacement parts are required, ensure that qualified people use replacement parts
specified by Rosemount. Unauthorized parts and procedures can affect the product’s per-
formance, place the safe operation of your process at risk, and VOID YOUR WARRANTY.
Look-alike substitutions may result in fire, electrical hazards, or improper operation.
• Ensure that all equipment doors are closed and protective covers are in place, except
when maintenance is being performed by qualified persons, to prevent electrical shock
and personal injury.
If a Model 275 Universal HART® Communicator is used with this unit, the software within the
Model 275 may require modification. If a software modification is required, please contact
your local Fisher-Rosemount Service Group or National Response Center at 1-800-654-7768.
The information contained in this document is subject to change without notice.
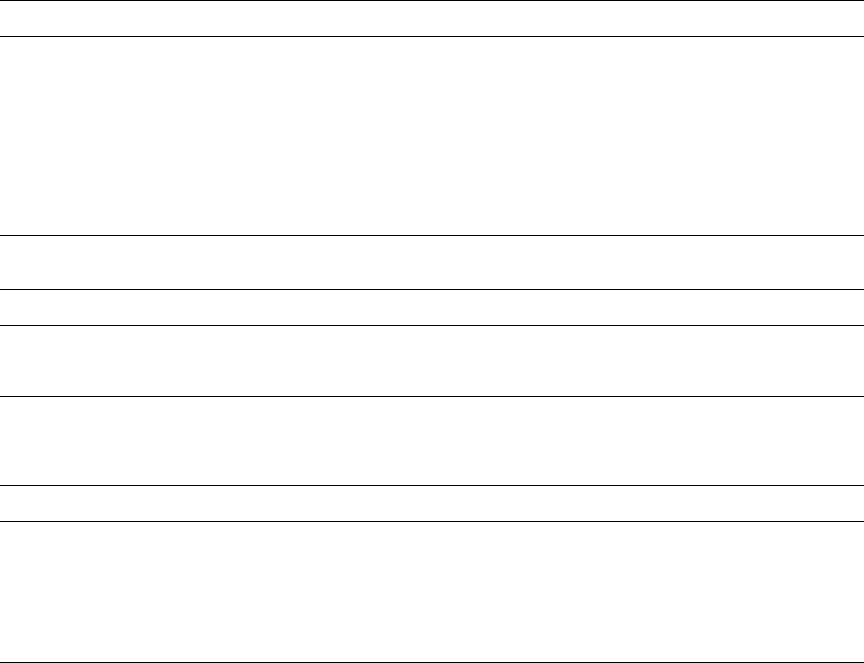
HIGHLIGHTS OF CHANGES
Effective May, 1999 Rev. 4.0
Page Summary
Page P-6 Added new Quick Start Guide.
Page 3-1 Added Section 3, Setup.
Page 4-1 Removed calibration information from Operation section, and created
Section 4, Calibration.
Page 6-2 Expanded explanations of IFT status codes.
Section 6 Added new troubleshooting procedures.
Effective November, 2001 Rev. 4.1
Page Summary
Highlights Updated Highlights of Changes Appendix A page.
Appendix A Replaced Appendix A, Rev. 3.6 with Rev. 3.7.
Effective July, 2002 Rev. 4.2
Page Summary
Highlights Updated Highlights of Changes Appendix A page.
Page 4-1 Added reference to new Calibration Record sheet.
Page 4-9 Added new Calibration Record sheet.
Appendix A Replaced Appendix A, Rev. 3.7 with Rev. 3.8.

HIGHLIGHTS OF CHANGES
APPENDIX A
Effective May, 1996 Rev. 3
Page Summary
-- General. Updated appendix to reflect probe design changes.
Page A-13 Added “Extended temperature by-pass arrangements” to Figure A-13
(Sheet 3 of 3)
Effective June, 1996 Rev. 3.1
Page Summary
Page A-13 Updated part ordering information.
Effective August, 1996 Rev. 3.2
Page Summary
Page A-25 Updated cell replacement kit part numbers for the probe.
Effective October, 1996 Rev. 3.3
Page Summary
Page A-6 Added NOTE to Figure A-7.
Effective January, 1997 Rev. 3.4
Page Summary
Page A-1 Added warning to read new safety instructions.
Page A-12 Added protective covers and grounds warning.
Page A-16 Added protective covers and grounds warning.
Effective February, 1998 Rev. 3.5
Page Summary
Page A-18 Changed screw torque in paragraph A-11h.
Effective July, 1998 Rev. 3.6
Page Summary
-- Changed test gas to calibration gas and reference gas to reference
air throughout the appendix.

HIGHLIGHTS OF CHANGES (CONTINUED)
Effective November, 2001 Rev. 3.7
Page Summary
A-8 Added new cup type diffusion assembly description, paragraph A-6.e.
and diffusion assembly illustrations, Figure A-13 and A-14.
A-26 Added new cup type diffusion assembly part numbers 4851B89G04
and 4851B90G04 to replacement parts list. Deleted stainless steel
diffuser assembly from replacement parts list.
Effective July, 2002 Rev. 3.8
Page Summary
A-13 Added troubleshooting symptoms 5 and 6 to Table A-2.

HIGHLIGHTS OF CHANGES
APPENDIX B
Effective February, 1992 Rev. 2
Page Summary
Page B-1 Figure B-1. New HPS 3000 Optional Class 1, Division 1, Group B
(IP56) Explosion-Proof Enclosure added.
Page B-11 Figure and Index No. column added to Table B-2. Replacement Parts
for Heater Power Supply.
Effective January, 1995 Rev. 2.1
Page Summary
Page B-3 Updated Figure B-3, Heater Power Supply Block Diagram for IB
consistency.
Effective January, 1997 Rev. 2.2
Page Summary
Page B-1 Added warning to read new safety instructions.
Page B-3 Corrected Table B-1 specifications list.
Page B-4 Added protective covers and grounds warning.
Page B-8 Added protective covers and grounds warning.
Page B-11 Added expanded fuse description.

HIGHLIGHTS OF CHANGES
APPENDIX D
Effective June, 1994 Rev. 2
Page Summary
Page D-1
Page D-2
Page D-3
Page D-4
Page D-7
Page D-8
Page D-10
Page D-11
MPS outline drawing changed to show new MPS.
MPS interior view replaced with new MPS in Figure D-2.
"Optional" for check valve deleted in Figure D-3.
Drawing showing location of optional Z-Purge added as Figure D-4.
Power supply replacement procedures in paragraph D-7 changed to
reflect new design in the MPS. Solenoid valve replacement proce-
dures in paragraph D-8 changed to reflect new design in the MPS.
Old exploded view of MPS replaced with new MPS.
Paragraph D-11, Adding Probes to the new MPS, added.
Change part numbers for the power supply, solenoid valve, and test
gas flowmeter assembly. Add part numbers for reference gas flow-
meter assembly and all the parts in the probe adder kit.
Effective January, 1995 Rev. 2.1
Page Summary
Page D-1 Updated Figure D-1, MPS 3000 to include hinge.
Effective May, 1996 Rev. 2.2
Page Summary
Page D-11 Updated replacement parts list to reflect new part numbers.
Effective January, 1997 Rev. 2.3
Page Summary
Page D-1
Page D-2
Page D-5
Page D-7
Page D-11
Added warning to read new safety instructions.
Corrected Table D-1 Specifications listing, 1st entry.
Added protective covers and grounds warning.
Added protective covers and grounds warning, corrected item num-
ber errors in paragraph D-6.
Added expanded fuse descriptions.
Effective July, 1998 Rev. 2.4
Page Summary
--- Changed test gas to calibration gas and reference gas to reference
air throughout the appendix.

HIGHLIGHTS OF CHANGES
APPENDIX E
Effective May, 1996 Rev. 4
Page Summary
--- General. Updated text and illustrations to reflect new version of IFT.
Page E-4 Updated IFT display status codes and placed in priority sequence.
Effective June, 1996 Rev. 4.1
Page Summary
Page E-2 Updated specification table.
Effective October, 1996 Rev. 4.2
Page Summary
Page E-4 Added new status displays for password protection features.
Effective January, 1997 Rev. 4.3
Page Summary
Front matter Added "Safety instructions for the wiring and installation of this
apparatus.”
Page E-1 Added warning to read new safety instructions.
Page E-2 Deleted NOTE.
Page E-4 Added protective covers and grounds warning.
Page E-8 Added protective covers and grounds warning.
Page E-15 Added expanded fuse description.
Effective July, 1998 Rev. 4.4
Page Summary
--- Changed test gas to calibration gas throughout the appendix.
Effective June, 1999 Rev. 4.5
Page Summary
Page E-1 Changed “real time clock” to “timer”.

HIGHLIGHTS OF CHANGES
APPENDIX J
Effective April, 1995 Rev. 1
Page Summary
Page J-13 Added statement of reference to the return authorization number.
Effective June, 1995 Rev. 1.1
Page Summary
— Figure J-4. Updated figure to include “Status group” and “K3 eff” in
calculations.

Instruction Manual
IB-106-300NH Rev. 4.2
July 2002
Rosemount Analytical Inc. A Division of Emerson Process Management i
World Class 3000
TABLE OF CONTENTS
PREFACE........................................................................................................................ P-1
Definitions ........................................................................................................................ P-1
Safety Instructions .......................................................................................................... P-2
Glossary of Terms ......................................................................................................... P-3
Quick Start Guide .......................................................................................................... P-6
1-0 DESCRIPTION AND SPECIFICATIONS...................................................................... 1-1
1-1 Component Checklist of Typical System (Package Contents).................................. 1-1
1-2 System Overview............................................................................................................ 1-2
2-0 INSTALLATION .............................................................................................................. 2-1
2-1 Oxygen Analyzer (Probe) Installation........................................................................... 2-1
2-2 Intelligent Field Transmitter (IFT) Installation .............................................................. 2-9
2-3 Heater Power Supply Installation ............................................................................... 2-14
2-4 Multiprobe Calibration Gas Sequencer Installation .................................................. 2-22
3-0 SETUP............................................................................................................................. 3-1
3-1 Overview.......................................................................................................................... 3-1
3-2 Configuring the Analog Output ..................................................................................... 3-1
3-3 Setting Calibration Parameters....................................................................................... 3-1
3-4 Setting the O2 Alarm Setpoints.................................................................................... 3-2
3-5 Configuring Efficiency Calculations ............................................................................... 3-2
3-6 Configuring the Relay Outputs ..................................................................................... 3-2
4-0 CALIBRATION ................................................................................................................ 4-1
4-1 Analog Output Calibration ............................................................................................. 4-1
4-2 System Calibration ......................................................................................................... 4-1
5-0 GENERAL USER INTERFACE (GUI) OPERATION .................................................. 5-1
5-1 Overview.......................................................................................................................... 5-1
5-2 Deluxe Version IFT Displays and Controls................................................................. 5-2
5-3 Help Key ......................................................................................................................... 5-3
5-4 Status Line...................................................................................................................... 5-3
5-5 Quick Reference Chart .................................................................................................. 5-3
5-6 Main Menu ...................................................................................................................... 5-3
5-7 Probe Data Sub-Menu................................................................................................... 5-3
5-8 Calibrate O2 Sub-Menu.................................................................................................. 5-4
5-9 Setup Sub-Menu............................................................................................................. 5-4
6-0 TROUBLESHOOTING .................................................................................................... 6-1
6-1 Overview.......................................................................................................................... 6-1
6-2 Special Troubleshooting Notes...................................................................................... 6-1
6-3 System Troubleshooting................................................................................................. 6-1
6-4 Heater Problem ..............................................................................................................6-3
6-5 Cell Problem ................................................................................................................... 6-5
6-6 IFT Problem .................................................................................................................... 6-7
6-7 MPS Problem .................................................................................................................6-8
6-8 Performance Problem (Process Response is Suspect) ............................................. 6-9

Instruction Manual
IB-106-300NH Rev. 4.2
July 2002
ii Rosemount Analytical Inc. A Division of Emerson Process Management
World Class 3000
7-0 RETURN OF MATERIAL .............................................................................................. 7-1
8-0 APPENDICES ................................................................................................................. 8-1
Appendix A .....................................................................................................................A-1
Appendix B .....................................................................................................................B-1
Appendix D .....................................................................................................................D-1
Appendix E .....................................................................................................................E-1
Appendix J .......................................................................................................................J-1
9-0 INDEX.............................................................................................................................. 9-1
LIST OF ILLUSTRATIONS
Figure 1. Complete World Class 3000 System ..................................................................... P-5
Figure 2. Wiring Layout for World Class 3000 System without HPS or MPS ....................... P-8
Figure 1-1. Typical System Package ....................................................................................... 1-1
Figure 1-2. Typical System Installation .................................................................................... 1-5
Figure 1-3. World Class 3000 Typical Application with Intelligent Field Transmitters ............. 1-6
Figure 2-1. Probe Installation ................................................................................................... 2-2
Figure 2-2. Orienting the Optional Vee Deflector ..................................................................... 2-7
Figure 2-3. Air Set, Plant Air Connection ................................................................................. 2-8
Figure 2-4. Outline of Intelligent Field Transmitter................................................................... 2-9
Figure 2-5. Power Supply Board Jumper Configuration ........................................................ 2-10
Figure 2-6. Signal Wire Routing ............................................................................................. 2-11
Figure 2-7. IFT Power Supply Board Jumpers....................................................................... 2-12
Figure 2-8. Wiring Layout for IFT Systems without HPS ....................................................... 2-13
Figure 2-9. Microprocessor Board Jumper Configuration ..................................................... 2-14
Figure 2-10. IFT Microprocessor Board ................................................................................... 2-15
Figure 2-11. Interconnect Board Jumper Configuration........................................................... 2-16
Figure 2-12. IFT Interconnect Board Output Connections ....................................................... 2-16
Figure 2-13. Outline of Heater Power Supply .......................................................................... 2-17
Figure 2-14. Wiring Layout for Complete IFT 3000 System with HPS (Sheet 1of 2)............... 2-18
Figure 2-15. Heater Power Supply Wiring Connections .......................................................... 2-20
Figure 2-16. Jumper Selection Label ....................................................................................... 2-21
Figure 2-17. Jumpers on HPS Mother Board........................................................................... 2-21
Figure 2-18. MPS Module ........................................................................................................2-22
Figure 2-19. MPS Gas Connections ........................................................................................ 2-23
Figure 2-20. MPS Probe Wiring ............................................................................................... 2-24
Figure 4-1. Typical Calibration Setup....................................................................................... 4-4
Figure 4-2. Portable Rosemount Oxygen Calibration Gas Kit ................................................. 4-5
Figure 4-3. Typical Portable Calibration Setup ........................................................................ 4-6
Figure 4-4. Typical Automatic Calibration System ................................................................... 4-7
Figure 5-1. Deluxe Version IFT Displays and Controls............................................................ 5-2
Figure 5-2. Quick Reference Chart .......................................................................................... 5-5

Instruction Manual
IB-106-300NH Rev. 4.2
July 2002
Rosemount Analytical Inc. A Division of Emerson Process Management iii
World Class 3000
LIST OF TABLES
Table 4-1. Automatic Calibration Parameters......................................................................... 4-8
Table 5-1. Sample HELP Messages....................................................................................... 5-3
Table 5-2. MAIN menu ............................................................................................................ 5-3
Table 5-3. PROBE DATA Sub-Menu ...................................................................................... 5-4
Table 5-4. CALIBRATE O2 Sub-Menu .................................................................................. 5-10
Table 5-5. SETUP Sub-Menu ............................................................................................... 5-12
Table 5-6. Efficiency Constants ............................................................................................ 5-14
Table 6-1. IFT Status Codes ................................................................................................... 6-2
Table 6-2. Heater Troubleshooting ......................................................................................... 6-3
Table 6-3. Cell Troubleshooting.............................................................................................. 6-5
Table 6-4. IFT Troubleshooting............................................................................................... 6-7
Table 6-5. MPS Troubleshooting ............................................................................................ 6-8
Table 6-6. Performance Problem Troubleshooting................................................................. 6-9

Instruction Manual
IB-106-300NH Rev. 4.2
July 2002
iv Rosemount Analytical Inc. A Division of Emerson Process Management
World Class 3000

Instruction Manual
IB-106-300NH Rev. 4.2
July 2002
Rosemount Analytical Inc. A Division of Emerson Process Management P-1
World Class 3000
NOTE
!
Only one probe can be calibrated at a time.
Probe calibrations must be scheduled
appropriately in multiple probe applications.
PREFACE
The purpose of this manual is to provide a comprehensive understanding of the World
Class 3000 Oxygen Analyzer components, functions, installation, and maintenance.
This manual is designed to provide information about the World Class 3000 Oxygen Ana-
lyzer. We recommend that you familiarize yourself with the Overview and Installation sec-
tions before installing your emissions monitor.
The overview presents the basic principles of the oxygen analyzer along with its perform-
ance characteristics and components. The remaining sections contain detailed proce-
dures and information necessary to install and service the oxygen analyzer.
DEFINITIONS
The following definitions apply to WARNINGS, CAUTIONS, and NOTES found throughout this
publication.
Highlights an operation or maintenance
procedure, practice, condition, state-
ment, etc. If not strictly observed, could
result in injury, death, or long-term
health hazards of personnel.
Highlights an operation or maintenance
procedure, practice, condition, state-
ment, etc. If not strictly observed, could
result in damage to or destruction of
equipment, or loss of effectiveness.
NOTE
Highlights an essential operating procedure,
condition, or statement.
: EARTH (GROUND) TERMINAL
: PROTECTIVE CONDUCTOR TERMINAL
: RISK OF ELECTRICAL SHOCK
: WARNING: REFER TO INSTRUCTION BULLETIN
NOTE TO USERS
The number in the lower right corner of each illustration in this publication is a manual illus-
tration number. It is not a part number, and is not related to the illustration in any technical
manner.

Instruction Manual
IB-106-300NH Rev. 4.2
July 2002
P-2 Rosemount Analytical Inc. A Division of Emerson Process Management
World Class 3000
IMPORTANT
SAFETY INSTRUCTIONS
FOR THE WIRING AND INSTALLATION
OF THIS APPARATUS
The following safety instructions apply specifically to all EU member states. They should
be strictly adhered to in order to assure compliance with the Low Voltage Directive. Non-
EU states should also comply with the following unless superseded by local or National
Standards.
1. Adequate earth connections should be made to all earthing points, internal and external,
where provided.
2. After installation or troubleshooting, all safety covers and safety grounds must be replaced.
The integrity of all earth terminals must be maintained at all times.
3. Mains supply cords should comply with the requirements of IEC227 or IEC245.
4. All wiring shall be suitable for use in an ambient temperature of greater than 75°C.
5. All cable glands used should be of such internal dimensions as to provide adequate cable
anchorage.
6. To ensure safe operation of this equipment, connection to the mains supply should only be
made through a circuit breaker which will disconnect all circuits carrying conductors during a
fault situation. The circuit breaker may also include a mechanically operated isolating switch.
If not, then another means of disconnecting the equipment from the supply must be provided
and clearly marked as such. Circuit breakers or switches must comply with a recognized
standard such as IEC947. All wiring must conform with any local standards.
7. Where equipment or covers are marked with the symbol to the right, hazard-
ous voltages are likely to be present beneath. These covers should only be
removed when power is removed from the equipment — and then only by
trained service personnel.
8. Where equipment or covers are marked with the symbol to the right, there is a
danger from hot surfaces beneath. These covers should only be removed by
trained service personnel when power is removed from the equipment. Cer-
tain surfaces may remain hot to the touch.
9. Where equipment or covers are marked with the symbol to the right, refer to
the Operator Manual for instructions.
10. All graphical symbols used in this product are from one or more of the follow-
ing standards: EN61010-1, IEC417, and ISO3864.

Instruction Manual
IB-106-300NH Rev. 4.2
July 2002
Rosemount Analytical Inc. A Division of Emerson Process Management P-3
World Class 3000
GLOSSARY OF TERMS
Abrasive Shield
An optional component that shields the probe from high velocity particulate entrained in the flue
gas stream.
Automatic Calibration
An automatic calibration can only be performed if the system is equipped with an MPS 3000 Mul-
tiprobe Calibration Gas Sequencer. Once a calibration is initiated by the operator or by the IFT on
a scheduled interval, all calibration actions are performed by the IFT. The MPS switched calibra-
tion gases under direction from the IFT.
Calibration
The process of measuring gases of a known concentration, and comparing that known concen-
tration to the actual values sensed by the instrument. After reading the calibration gases, the IFT
automatically adjusts the slope and constant values to ensure that the system is correctly reading
the process gas O2 values.
Cold Junction Compensation
A method for compensating for the small voltage developed at the junction of the thermocouple
leads in the probe junction box.
Dead Band
The range through which a signal can be varied without initiating a response. In the IFT 3000,
dead band is used to prevent an oxygen signal near an alarm setpoint from cycling the alarm on
and off.
GUI
General User Interface. The GUI is the operator interface for the IFT 3000.
HART
A communications protocol using frequency shift keying (FSK) to transmit data on an analog out-
put line without affecting the analog output signal.
HPS
Heater Power Supply. An HPS should be used to provide power for the probe heater if the probe
is more than 150 ft (45 m) from the IFT.
IFT
Intelligent Field Transmitter.
In Situ
A method of analyzing process gases without removing them from the process stream.
MPS
Multiprobe Calibration Gas Sequencer. The MPS can provide automatic calibration gas se-
quencing for up to four probes.

Instruction Manual
IB-106-300NH Rev. 4.2
July 2002
P-4 Rosemount Analytical Inc. A Division of Emerson Process Management
World Class 3000
Reference Air
Provides a known oxygen concentration to the reference side of the oxygen sensing cell.
Semiautomatic Calibration
Semiautomatic calibration is performed when the system does not include an MPS 3000 Multi-
probe Calibration Gas Sequencer. The IFT 3000 provides prompts to direct the user to switch
calibration gases when performing the calibration.
Thermocouple
An electrical device made of two dissimilar metals. A thermocouple develops a millivolt signal
proportional to its temperature.
Vee Deflector
Protects the optional ceramic diffusor from the process gases. The vee deflector must be posi-
tioned so it points toward the direction of the process gas flow. See Figure 2-2 for an illustration of
the vee deflector.

Instruction Manual
IB-106-300NH Rev. 4.2
July 2002
Rosemount Analytical Inc. A Division of Emerson Process Management P-5
World Class 3000
WHAT YOU NEED TO KNOW
BEFORE INSTALLING AND WIRING A ROSEMOUNT IFT 3000
INTELLIGENT FIELD TRANSMITTER
WITH WORLD CLASS 3000 PROBE
1. What is the line voltage being supplied to the IFT 3000?
Write the line voltage here __________
2. Use the following drawing, Figure 1, to identify which parts of the World Class 3000 system
are included in your system. Components in the shaded area are optional components.
WC PROBE 3000
STACK
THERMOCOUPLE
(OPTIONAL) HPS 3000
(OPTIONAL)
LINE
VOLTAGE
LINE
VOLTAGE
IFT 3000
LINE
VOLTAGE
MPS 3000
(OPTIONAL)
CALIBRATION
GAS
BOTTLES
29850003
Figure 1. Complete World Class 3000 System

Instruction Manual
IB-106-300NH Rev. 4.2
July 2002
P-6 Rosemount Analytical Inc. A Division of Emerson Process Management
World Class 3000
QUICK START GUIDE
Use this Quick Start Guide if ...
1. You are using a World Class 3000 probe.
2. You are NOT using any optional components. Optional components are shown in the
shaded area in Figure 1.
3. You are familiar with the installation requirements for the IFT 3000 Intelligent Field Trans-
mitter and World Class 3000 probe.
4. You are familiar with the procedures for changing the jumpers located in the IFT 3000, as
described in Section 2, Installation.
If you cannot use the Quick Start Guide, turn to Section 2, Installation, in this Instruction
Bulletin.

Instruction Manual
IB-106-300NH Rev. 4.2
July 2002
Rosemount Analytical Inc. A Division of Emerson Process Management P-7
World Class 3000
QUICK START GUIDE FOR IFT 3000 SYSTEMS
Before using the Quick Start Guide, please read “WHAT YOU NEED TO KNOW BEFORE
INSTALLING AND WIRING A ROSEMOUNT IFT 3000 INTELLIGENT FIELD TRANSMIT-
TER WITH WORLD CLASS 3000 PROBE” on the preceding page.
1. Install the probe in an appropriate location on the stack or duct. Refer to Section 2, para-
graph 2-1a for information on selecting a location for the probe.
2. Connect calibration gas and reference air to the probe.
3. Verify the jumper selection on the IFT 3000 power supply board, microprocessor board, and
interconnect board, as shown in Figure 2.
4. Install the IFT 3000 in the desired location. Refer to Section 2, paragraph 2-2a for informa-
tion on selecting a location for the IFT 3000.
5. Wire the probe to the IFT as shown in Figure 2.
6. Connect line voltage to the IFT as shown in Figure 2.
7. Apply power to the IFT 3000. Allow sufficient time for the probe to reach normal operating
temperature. The time required will vary based on process temperature and other variables.
8. Perform a manual (semiautomatic) calibration. Press the CAL key on the GUI. Select the
PERFORM CALIBRATION sub-menu. “Press ENTER to start Manual Calibration” will
appear on the LCD display. Press ENTER to start the calibration process. Follow the in-
structions on the LCD display. Refer to Section 4, Calibration, for more information on per-
forming a calibration.

Instruction Manual
IB-106-300NH Rev. 4.2
July 2002
P-8 Rosemount Analytical Inc. A Division of Emerson Process Management
World Class 3000
BK
GN
WH
PU
SHIELD
SHIELD
SHIELD
STACK TC -
STACK TC +
PROBE MV+
PROBE MV -
PROBE TC +
PROBE TC -
RD
YE
BL
OR
BL
OR
YE
RD
WORLD CLASS
PROBE
12345678
BL
PROBE MV -
PROBE MV +
PROBE TC +
PROBE TC -
OR
YE
RD
GN
E
R
H
WH
BK
GN CELL -VE
OR CELL +VE
YE CHROMEL
RD ALUMEL
GN
BK
BK
}
HEATER
PROBE JUNCTION
BOX WIRING
LINE VOLTAGE
JUMPERS ON IFT
POWER SUPPLY
BOARD
INSTALL JUMPER ACROSS TERMINALS 13 AND 14.
INSTALL JUMPER ACROSS TERMINALS 7 AND 8.
NOTES:
LINE
VOLTAGE
SECTION
LINE
VOLTAGE
SECTION
JUMPER
(INSTALL)
JUMPER
(INSTALL)
120 V.A.C.
120 V.A.C.
100 V.A.C.
100 V.A.C.
220 V.A.C.
220 V.A.C.
240 V.A.C.
240 V.A.C.
J1
J5 J6
J1
JM1
J2 J3 J4 J5 J6 J7 J8 J9
3D39122G REV
POWER SUPPLY BOARD
3D39120G REV
INTERCONNECT BOARD
JM8, JM7, JM1
JM8, JM7, JM1
JM3, JM7, JM2
JM3, JM7, JM2
JM6, JM5, JM2
JM6, JM5, JM2
JM6, JM5, JM1
JM6, JM5, JM1
EN
L
LINE
VOLTAGE
ER
H
29850002
Figure 2. Wiring Layout for World Class 3000 System without HPS or MPS

Instruction Manual
IB-106-300NH Rev. 4.2
July 2002
Rosemount Analytical Inc. A Division of Emerson Process Management P-9
World Class 3000
QUICK REFERENCE GUIDE
IFT 3000 INTELLIGENT FIELD TRANSMITTER
Performing a Manual (Semiautomatic) Calibration
1. Connect the high calibration gas to the probe fitting.
2. Press the CAL key.
3. Select the PERFORM CALIBRATION sub-menu.
4. Press the ENTER key.
5. Turn on the high calibration gas.
6. When the O2 reading is stable, press ENTER.
7. Turn off the high calibration gas and turn on the low calibration gas.
8. Press Enter.
9. When the O2 reading is stable, press ENTER.
10. The LCD display will show “Resistance Check”. When the display changes to “Turn off low
calibration gas”, turn off the low calibration gas and press ENTER.
11. When the oxygen reading has stabilized at the process value, press ENTER.
Setting up the Analog Output
1. Press the SETUP key.
2. Select the Analog Output sub-menu.
3. Set the SOURCE to O2. For information on configuring the analog output for Efficiency or
Dual Range O2, refer to Section V, Operation.
4. Set the AOUT TYPE to the desired setting. Note that the setting must agree with the position
of the analog output selector switch. If you will communicate with the IFT using HART com-
munications, the AOUT TYPE must be set to HART 4-20mA.
5. Select Range Setup and press ENTER.
6. Set the Xfer Fnct to Lin or Log, as desired.
7. Select Range Values and press ENTER.
8. Set the High End to the oxygen concentration to be represented by the high analog output
value, i.e., 20mA or 10V.
9. Set the Low End to the oxygen concentration to be represented by the low analog output
value, i.e., 0 or 4mA or 0V.
10. Press the ESC key until you are back at the Main menu.

Instruction Manual
IB-106-300NH Rev. 4.2
July 2002
P-10 Rosemount Analytical Inc. A Division of Emerson Process Management
World Class 3000
HART COMMUNICATOR FAST KEY SEQUENCES
Perform Calibration Analog Output Upper Range Value
2313 324
Trim Analog Output Analog Output Lower Range Value
24 325
Toggle Analog Output Tracking View O2 Value
2312 111
View Analog Output
121
Technical Support Hotline:
For assistance with technical problems, please call the Customer Support Center (CSC). The
CSC is staffed 24 hours a day, 7 days a week.
Phone: 1-800-433-6076
In addition to the CSC, you may also contact Field Watch. Field Watch coordinates Rosemount’s
field service throughout the US and abroad.
Phone: 1-800-654-RSMT (1-800-654-7768)
Rosemount may also be reached via the Internet through e-mail and the World Wide Web:
E-mail: GAS.CSC@emersonprocess.com
World Wide Web: www.processanalytic.com

Instruction Manual
IB-106-300NH Rev. 4.2
July 2002
Rosemount Analytical Inc. A Division of Emerson Process Management Description and Specifications 1-1
World Class 3000
o
HART
Communicator
FISHER-ROSEMOUNT
TM
MAN 4275A00
English
October 1994
1
3
4
5
6
7
8
9
2
21190001
SECTION 1
DESCRIPTION AND SPECIFICATIONS
1-1 COMPONENT CHECKLIST OF TYPICAL
SYSTEM (PACKAGE CONTENTS)
A typical Rosemount World Class 3000 Oxygen
Analyzer with IFT 3000 Intelligent Field Trans-
mitter should contain the items shown in Figure
1-1. Record the part number, serial number, and
order number for each component of your sys-
tem in the table located on the first page of this
manual.
1. Intelligent Field Transmitter
2. Instruction Bulletin
3. Multiprobe Calibration Gas Sequencer (Optional)
4. Heater Power Supply (Optional)
5. Oxygen Analyzer (Probe)
6. System Cable
7. M Adapter Plate with mounting
hardware and gasket
8. Reference Air Set (If MPS not supplied)
9. HART® Communicator Package (Optional)
Figure 1-1. Typical System Package
1

Instruction Manual
IB-106-300NH Rev. 4.2
July 2002
1-2 Description and Specifications Rosemount Analytical Inc. A Division of Emerson Process Management
World Class 3000
1-2 SYSTEM OVERVIEW
a. Scope
This Instruction Bulletin has been designed
to supply details needed to install, startup,
operate, and maintain the Rosemount
World Class 3000 Oxygen Analyzer with IFT
3000 Intelligent Field Transmitter. The Intel-
ligent Field Transmitter (IFT) can be inter-
faced with one World Class 3000 probe.
The IFT provides all necessary intelligence
for controlling the probe and optional MPS
3000 Multiprobe Calibration Gas Se-
quencer. Appendices at the back of this
manual detail each component and option
from the standpoint of troubleshooting, re-
pair, and spare parts.
Operator/Technician interface to the IFT
can be provided from the displays and key-
pads on the front panel, and remotely
through HART® communications protocol,
utilizing the 4-20 mA out-put signal from the
IFT interconnect board. HART Communi-
cator IFT applications are detailed in
Appendix J.
b. System Description
The Rosemount Oxygen Analyzer (Probe) is
designed to measure the net concentration
of oxygen in an industrial process; i.e., the
oxygen remaining after all fuels have been
oxidized. The probe is permanently posi-
tioned within an exhaust duct or stack and
performs its task without the use of a sam-
pling system.
The equipment measures oxygen percent-
age by reading the voltage developed
across a heated electrochemical cell, which
consists of a small yttria-stabilized, zirconia
disc. Both sides of the disc are coated with
porous metal electrodes. When operated at
the proper temperature, the millivolt output
voltage of the cell is given by the following
Nernst equation:
EMF = KT log10(P1/P2) + C
Where:
1. P2 is the partial pressure of the oxygen
in the measured gas on one side of the
cell,
2. P1 is the partial pressure of the oxygen
in the reference air on the other side,
3. T is the absolute temperature,
4. C is the cell constant,
5. K is an arithmetic constant.
NOTE
For best results, use clean, dry, in-
strument air (20.95% oxygen) as a ref-
erence air.
When the cell is at operating temperature
and there are unequal oxygen concentra-
tions across the cell, oxygen ions will travel
from the high partial pressure of oxygen
side to the low partial pressure side of the
cell. The resulting logarithmic output voltage
is approximately 50 mV per decade. Be-
cause the magnitude of the output is pro-
portional to the logarithm of the inverse of
the sample of the oxygen partial pressure,
the output signal increases as the oxygen
concentration of the sample gas decreases.
This characteristic enables the oxygen
analyzer to provide exceptional sensitivity at
low oxygen concentrations.
Oxygen analyzer equipment measures net
oxygen concentration in the presence of all
the products of combustion, including water
vapor. Therefore, it may be considered an
analysis on a "wet" basis. In comparison
with older methods, such as the Orsat ap-
paratus, which provides an analysis on a
"dry" gas basis, the "wet" analysis will, in
general, indicate a lower percentage of
oxygen. The difference will be proportional
to the water content of the sampled gas
stream.

Instruction Manual
IB-106-300NH Rev. 4.2
July 2002
Rosemount Analytical Inc. A Division of Emerson Process Management Description and Specifications 1-3
World Class 3000
c. System Configuration
The equipment covered in this manual con-
sists of three major components: the oxy-
gen analyzer (probe), the intelligent field
transmitter (IFT), and an optional heater
power supply (HPS). The HPS is required
where the cable run between the probe and
the electronics is greater than 150 ft (45 m).
There is also an optional multiprobe calibra-
tion gas sequencer (MPS) to facilitate
automatic calibration of the probe.
Probes are available in five length options,
giving the user the flexibility to use an in situ
penetration appropriate to the size of the
stack or duct. The options on length are 18
in. (457 mm), 3 ft (0.91 m), 6 ft (1.83 m), 9 ft
(2.7 m), or 12 ft (3.66 m).
The IFT contains electronics that control
probe temperature (in conjunction with the
optional HPS), supply power, and provide
isolated outputs that are proportional to the
measured oxygen concentration. The oxy-
gen sensing cell is maintained at a constant
temperature by modulating the duty cycle of
the probe heater. The IFT accepts millivolt
signals generated by the sensing cell and
produces outputs to be used by remotely
connected devices. The IFT output is iso-
lated and selectable to provide linearized
voltage or current.
The heater power supply (HPS) can provide
an interface between the IFT and the probe.
The HPS contains a transformer for sup-
plying proper voltage to the probe heater.
The enclosure has been designed to meet
NEMA 4X (IP56) specifications for water
tightness; an optional enclosure to meet
Class 1, Division 1, Group B (IP56) explo-
sion proof is also available.
Systems with multiprobe and multiple IFT
applications may employ an optional MPS
3000 Multiprobe Calibration Gas Se-
quencer. The MPS 3000 provides automatic
calibration gas sequencing for up to four
probes and IFTs to accommodate automatic
calibration.
d. System Features
1. Unique and patented electronic cell
protection action that automatically
protects sensor cell when the analyzer
detects reducing atmospheres.
2. Output voltage and sensitivity increase
as the oxygen concentration
decreases.
3. User friendly, menu driven operator
interface with context-sensitive on-line
help.
4. Field replaceable cell.
5. Analyzer constructed of rugged 316
LSS for all wetted parts.
6. The intelligent field transmitter (IFT)
can be located up to 150 ft (45 m) from
the probe when used without optional
heater power supply (HPS). When the
system includes the optional HPS, the
HPS can be located up to 150 ft (45 m)
from the probe and the IFT may be lo-
cated up to 1200 ft (364 m) from the
HPS.
7. All electronic modules are adaptable to
100, 120, 220, and 240 line voltages.
8. Five languages may be selected for
use with the Intelligent Field
Transmitter:
English Italian
French Spanish
German
1

Instruction Manual
IB-106-300NH Rev. 4.2
July 2002
1-4 Description and Specifications Rosemount Analytical Inc. A Division of Emerson Process Management
World Class 3000
9. An operator can set up, calibrate, or
troubleshoot the IFT in one of two
ways:
(a) Optional General User Interface
(GUI). The GUI is housed within
the IFT electronics enclosure and
makes use of an LCD and keypad.
(b) Optional HART Interface. The IFT's
4-20 mA output line transmits an
analog signal proportional to oxy-
gen level. The line also carries all
information normally accessed by
use of the General User Interface
LCD and keypad. This information
can be accessed through the
following:
1 Rosemount Model 275 Hand-
held Communicator - The
handheld communicator re-
quires Device Descriptor (DD)
software specific to the World
Class 3000 product. The DD
software will be supplied with
many model 275 units, but
can also be programmed into
existing units at most Fisher-
Rosemount service offices.
2 Personal Computer (PC) -
The use of a personal com-
puter requires Cornerstone
software with Module Library
(ModLib) specific to the World
Class 3000 product.
3 Selected Distributed Control
Systems - The use of distrib-
uted control systems requires
input/output (I/O) hardware
and software which permit
HART communications.
e. Handling the Oxygen Analyzer.
It is important that printed circuit
boards and integrated circuits are
handled only when adequate antistatic
precautions have been taken to pre-
vent possible equipment damage.
The oxygen analyzer is designed for
industrial application. Treat each
component of the system with care to
avoid physical damage. The probe
contains components made from ce-
ramics, which are susceptible to
shock when mishandled.
NOTE
Retain packaging in which the oxygen
analyzer arrived from the factory in
case any components are to be
shipped to another site. This packag-
ing has been designed to protect the
product.
f. System Considerations
Prior to installation of your Rosemount
World Class 3000 Oxygen Analyzer with
Intelligent Field Transmitter make sure that
you have all of the components necessary
to make the system installation. Ensure that
all the components are properly integrated
to make the system functional.
Once you have verified that you have all the
components, select mounting locations and
determine how each component will be
placed in terms of available power supply,
ambient temperatures, environmental con-
siderations, convenience, and serviceability.
A typical system installation is illustrated in
Figure 1-2. Figure 1-3 shows a typical sys-
tem wiring. For details on installing the indi-
vidual components of the system, refer to
Section 2, Installation.

Instruction Manual
IB-106-300NH Rev. 4.2
July 2002
Rosemount Analytical Inc. A Division of Emerson Process Management Description and Specifications 1-5
World Class 3000
STANDARD
OPTIONS
DUCT
STACK
GASES
CALIBRATION
GAS
INSTRUMENT
AIR SUPPLY
(REF. AIR)
PRESSURE
REGULATOR
FLOWMETER
INTELLIGENT
FIELD TRANSMITTER
MULTIPROBE
CALIBRATION GAS
SEQUENCER
REFERENCE AIR
CALIBRATION
GAS
HEATER
POWER
SUPPLY
OXYGEN
ANALYZER
(PROBE)
INTELLIGENT FIELD
TRANSMITTER
OXYGEN
ANALYZER
(PROBE)
ADAPTER
PLATE
ADAPTER
PLATE
STACK
DUCT
GASES
CAL GAS 1
CAL GAS 2
INST. AIR
SUPPLY
}
}
LINE
VOLTAGE
LINE
VOLTAGE
27270001
Figure 1-2. Typical System Installation
1

Instruction Manual
IB-106-300NH Rev. 4.2
July 2002
1-6 Description and Specifications Rosemount Analytical Inc. A Division of Emerson Process Management
World Class 3000
MPS 3000
CALIBRATION GAS
SEQUENCER
HPS 3000
HPS 3000
(OPTIONAL)
(OPTIONAL)
Explosion Proof
Required only for
Hazardous Area
Applications, otherwise
use NEMA 4X.
Lengths Exceeding
150 ft (45 m).
2-Conductor T/C
Wire [150 Ft (45 m) Max]
(optional)
Line Voltage
Line Voltage
Line Voltage
Line Voltage
HART Model 275
Hand Held
Interface
Customer's Laptop with
Cornerstone Software
Customer's Distributed
Control System
with HART
Interface Capability
Line Voltage
Line Voltage
2-Conductor T/C
Wire [150 Feet (45 m) Max]
(optional)
7-Conductor Cable
[150 Feet (45 m) Max]
2-Calibration Gas Lines
by Customer
[300 Ft (90 m) Max]
4 Twisted Pair, plus 2 Twisted Pair
for Options [1200 Ft (364 m) Max]
4 Twisted Pair Plus 2 Twisted Pair
for Options [1200 Ft (364 m) Max]
5 Conductor
[1000 Ft (309 m) Max]
Modular Design
Up to 4 Probes
IFT 3000
IFT 3000
IFT 3000
Intelligent Field Transmitter
NEMA 4X Enclosure
Line Voltage
100 to 120 Volt
220 to 240 Volt
Intelligent Field Transmitter
NEMA 4X Enclosure
Line Voltage
100 to 120 Volt
220 to 240 Volt
Intelligent Field Transmitter
NEMA 4X Enclosure
Line Voltage
100 to 120 Volt
220 to 240 Volt
Stack Thermocouple
(optional)
Stack Thermocouple
(optional)
World Class 3000
Probe
World Class 3000
Probe
World Class 3000
Probe
Termination in
Control Room
7-Conductor Cable
[150 Ft (45 m) Max]
7-Conductor Cable
[150 Ft (45 m) Max]
Heater Power Supply
[Optional,
Required for > 150 Ft (45 m)]
2-Calibration Gas Lines
by Customer
[300 Ft (90 m) Max]
Calibration Gas
by
Customer
(HPS not required for lengths of less than 150 feet)
HPS 3000
4-20 mA Output
(Twisted Pair)
27270002
Figure 1-3. World Class 3000 Typical Application with Intelligent Field Transmitters

Instruction Manual
IB-106-300NH Rev. 4.2
July 2002
Rosemount Analytical Inc. A Division of Emerson Process Management Description and Specifications 1-7
World Class 3000
After selecting the probe mounting location,
provision should be made for a platform
where the probe can be easily serviced.
The intelligent field transmitter (IFT) can be
located up to 150 ft (45 m) cabling distance
from the probe when used without optional
heater power supply (HPS). When the sys-
tem includes the optional HPS, the HPS can
be located up to 150 ft (45 m) cabling dis-
tance from the probe and the IFT may be
located up to 1200 ft (364 m) cabling dis-
tance from the HPS.
A source of instrument air is required at the
probe for reference air use. Since the probe
is equipped with an in-place calibration
feature, provision should be made for con-
necting calibration gas tanks to the oxygen
analyzer when the probe is to be calibrated.
If the calibration gas bottles will be perma-
nently hooked up, a check valve is required
next to the calibration fittings on the probe
junction box. This is to prevent breathing of
calibration gas line and subsequent flue gas
condensation and corrosion. The check
valve is in addition to the stop valve in the
calibration gas kit or the solenoid valve in
the multiprobe calibration gas sequencer
units.
An optional Z-purge arrangement is avail-
able for applications where hazardous area
classification may be required (See Appli-
cation Data Bulletin AD 106-300B).
1

Instruction Manual
IB-106-300NH Rev. 4.2
July 2002
1-8 Description and Specifications Rosemount Analytical Inc. A Division of Emerson Process Management
World Class 3000

Instruction Manual
IB-106-300NH Rev. 4.2
July 2002
Rosemount Analytical Inc. A Division of Emerson Process Management Installation 2-1
World Class 3000
SECTION 2
INSTALLATION
2-1 OXYGEN ANALYZER (PROBE)
INSTALLATION
Before starting to install this equip-
ment, read the "Safety instructions for
wiring and installation of this appara-
tus" at the front of this Instruction
Bulletin. Failure to follow the safety
instructions could result in serious
injury or death.
a. Selecting Location
1. The location of the probe in the stack
or flue is most important for maximum
accuracy in the oxygen analyzing pro-
cess. The probe must be positioned so
that the gas it measures is representa-
tive of the process. Best results are
normally obtained if the probe is posi-
tioned near the center of the duct (40
to 60% insertion). A point too near the
edge or wall of the duct may not pro-
vide a representative sample because
of the possibility of gas stratification. In
addition, the sensing point should be
selected so that the process gas tem-
perature falls within a range of 50° to
1300°F (10° to 704°C). Figure 2-1 pro-
vides mechanical installation
references.
2. Check the flue or stack for holes and
air leakage. The presence of this con-
dition will substantially affect the accu-
racy of the oxygen reading. Therefore,
either make necessary repairs or install
the probe upstream of any leakage.
3. Ensure that the area is clear of ob-
structions internal and external that will
interfere with installation. Allow ade-
quate clearance for removal of probe
(Figure 2-1).
4. If the probe is to be mounted outside,
subject to rain and snow conditions,
make sure the back of the probe (out-
side of the duct) is insulated to prevent
the formation of flue gas condensate in
the calibration gas lines.
Do not allow the temperature of the
probe junction box to exceed 300°F
(149°C) or damage to the unit may re-
sult. If the probe junction box tempera-
ture exceeds 300°F (149°C), the user
must fabricate a heat shield or provide
adequate cooling air to the probe junc-
tion box.
b. Mechanical Installation
1. Ensure that all components are avail-
able for installation of the probe. En-
sure that the system cable is the
required length. If equipped with the
optional ceramic diffusor element, en-
sure that it is not damaged.
2. The probe may be installed intact as it
is received. It is recommended that you
disassemble the adapter plate for each
installation.
NOTE
An abrasive shield is recommended
for high velocity particulate in the flue
stream (such as those in coal fired
boilers, kilns, and recovery boilers).
Vertical and horizontal brace clamps
are provided for 9 ft and 12 ft (2.75 m
and 3.66 m) probes to provide me-
chanical support of the probe. Refer to
Figure 2-1, sheet 5.
3. Weld or bolt adapter plate (Figure 2-1)
onto the duct.
2

Instruction Manual
IB-106-300NH Rev. 4.2
July 2002
2-2 Installation Rosemount Analytical Inc. A Division of Emerson Process Management
World Class 3000
ROSEMOUNT
CAL
GAS
REF
AIR
FLANGE
DIA.
HOLE
DIA.
(4) HOLES
EQ SP ON BC
ANSI
4512C17H01
6.00
(153)
7.28
(185)
6.10
(155)
0.59
(15)
5.12
(130)
0.75
(20)
0.71
(18)
5.71
(145)
4.75
(121)
DIN
4512C19H01
JIS
4512C18H01
TABLE I MOUNTING FLANGE
PROCESS FLOW MUST
BE IN THIS DIRECTION
WITH RESPECT TO
DEFLECTOR 3534848G01
BOTTOM VIEW
INSTALL WITH CONNECTIONS
AT THE BOTTOM
7.58 (192)
5.85 (148.6)
DIM "A"
WITH STANDARD
SNUBBER
DIFFUSER
2.27 (58)
DIA MAX
DIM "B" REMOVAL ENVELOPE
CAL GAS
ANSI
DIN
JIS
1/4 IN. TUBE
6 MM TUBE
6 MM TUBE
REF AIR
0.062 THK GASKET FURNISHED IN - XIT
ADAPTER & ACCESSORY
ANSI
JIS
DIN
3535B18H02
3635B48H01
3535B45H01
4512C34
4512C35
4512C36
INSULATE IF EXPOSED
TO AMBIENT
WEATHER CONDITIONS
ELEC
CONN
1/2"
CONDUIT
16 (406)
34 (864)
106 (2692)
142 (3607)
DIM "A"
27.3 (694)
45.3 (1151)
117.3 (2980)
153.3 (3894)
DIM "B"
TABLE II INSTALLATION/REMOVAL
18 IN.
3FT
70 (1778) 81.3 (2065)
6FT
9FT
12 FT
PROBE
NOTES: 1. DIMENSIONS ARE IN INCHES WITH MILLIMETERS IN
PARENTHESES.
2. THESE FLAT FACED FLANGES ARE MANUFACTURED
TO ANSI, DIN, AND JIS BOLT PATTERNS AND ARE NOT
PRESSURE RATED.
27270009
3.80 (96.5)
ADD TO DIM "A"
FOR PROBE
WITH CERAMIC
DIFFUSER
4.90 (124.5)
ADD TO DIM "A" FOR
PROBE WITH CERAMIC
DIFFUSER AND FLAME
ARRESTOR
1.88 (48)
Figure 2-1. Probe Installation (Sheet 1 of 5)

Instruction Manual
IB-106-300NH Rev. 4.2
July 2002
Rosemount Analytical Inc. A Division of Emerson Process Management Installation 2-3
World Class 3000
SNUBBER DIFFUSION/
DUST SEAL ASSEMBLY
(P/N 4843B38G02)
7.00
(178)
SEE TABLE IV
FOR FLANGE
SIZES
3.6
NOMINAL
INSULATE IF
EXPOSED TO
AMBIENT WEATHER
CONDITIONS
ELECTRICAL
CONNECTOR REF AIR AND
CAL GAS
CONNECTOR
CHECK VALVE FOR
CAL GAS LINES
5.7
(145)
14.5
(369)
DIM "C"
DIM "D" REMOVAL ENVELOPE
DIM "E" (WITH FLAME ARRESTOR)
DIM "C" DIM "D" DIM "E"
3FT
6FT
9FT
12 FT
27
(686)
63
(1600)
81.3
(2065)
67.1
(1704)
103.1
(2619)
139.1
(3533)
99
(2515)
117.3
(2980)
153.3
(3894)
135
(3429)
45.3
(1151)
31.1
(790)
TABLE III. REMOVAL / INSTALLATION
NOMINAL MEASUREMENTS
NOTE: DIMENSIONS ARE IN INCHES WITH
MILLIMETERS IN PARENTHESES.
0.06 THK GASKET FURNISHED
IN HARDWARE PACKAGE
(P/N 3535B58G02 - ANSI)
(P/N 3535B58G04 - JIS)
(P/N 3535B58G06 - DIN)
27270010
FLANGE
DIAMETER
(8) HOLES
DIAMETER
BOLT
CIRCLE
ANSI
JIS
DIN
*
*
*
* FLANGES ARE MANUFACTURED TO ANSI,
DIN, AND JIS BOLT PATTERNS AND ARE
FLAT FACED. THESE FLANGES ARE NOT
PRESSURE RATED.
9.00 (153)
9.25 (235)
9.25 (235)
0.75
0.75
0.945
7.50
7.48
7.48
TABLE IV. FLANGE SIZE
Figure 2-1. Probe Installation (Sheet 2 of 5)
2

Instruction Manual
IB-106-300NH Rev. 4.2
July 2002
2-4 Installation Rosemount Analytical Inc. A Division of Emerson Process Management
World Class 3000
22.5
o
BC
8 THREADED HOLES
EQUALLY SPACED ON
D DIA B.C.
ABRASIVE SHIELD
FLANGE O.D.
A
A
TABLE V. ADAPTOR PLATE DIMENSIONS FOR PROBE TABLE VI. ADAPTOR PLATE DIMENSIONS FOR ABRASIVE SHIELD
DIMENSIONS
IN.
(mm)
DIMENSIONS
IN.
(mm)
ANSI
(P/N 4512C34G01)
ANSI
(P/N 3535B58G02)
DIN
(P/N 4512C36G01)
DIN
(P/N 3535B58G06)
JIS
(P/N 4512C35G01)
JIS
(P/N 3535B58G04)
"A" "A"
"B"
THREAD
"B"
DIA
"D"
DIA
"C"
DIA
"C"
THREAD
6.00
(153)
9.00
(229)
0.625-11 4.75
(121)
7.50
(191)
4.75
(121)
0.625-11
7.5
(191)
9.25
(235)
(M-16 x 2) 3.94
(100)
7.48
(190)
5.708
(145)
(M-16 x 2)
6.50
(165)
9.25
(235)
(M-12 x 1.75) 4.92
(125)
7.894
(200)
5.118
(130)
(M-20 x 2.5)
NOTE: PART NUMBERS FOR ADAPTOR PLATES INCLUDE
ATTACHING HARDWARE.
NOTE: PART NUMBERS FOR ADAPTOR PLATES INCLUDE
ATTACHING HARDWARE.
ADAPTOR PLATE FOR 3, 6, 9,
AND 12 FT ABRASIVE SHIELD
INSTALLATIONS. SEE SHEET 2.
CROSSHATCHED AREA IN 4
CORNERS MAY BE USED TO
PROVIDE ADDITIONAL HOLES FOR
FIELD BOLTING OF PLATE TO
OUTSIDE WALL SURFACE.
ADAPTOR PLATE FOR
STD WORLD CLASS 3000
PROBE INSTALLATION.
SEE SHEET 1.
4 STUDS,
LOCKWASHERS AND
NUTS EQUALLY
SPACED ON
C DIA B.C.
A
A
2.500 DIA
45
o
C
B
16860021
Figure 2-1. Probe Installation (Sheet 3 of 5)

Instruction Manual
IB-106-300NH Rev. 4.2
July 2002
Rosemount Analytical Inc. A Division of Emerson Process Management Installation 2-5
World Class 3000
NOTE: ALL MASONRY STACK WORK AND JOINTS EXCEPT
ADAPTOR PLATE NOT FURNISHED BY ROSEMOUNT.
INSTALLATION FOR MASONRY
WALL STACK CONSTRUCTION
INSTALLATION FOR METAL
WALL STACK OR DUCT
CONSTRUCTION
0.50 [13]
3.75 [95]
MIN DIA HOLE
IN WALL
STACK OR DUCT
METAL WALL
MTG HOLES
SHOWN ROTATED
45 OUT OF
TRUE POSITION
o
WELD OR BOLT ADAPTOR
PLATE TO METAL WALL
OF STACK OR DUCT.
JOINT MUST BE AIR TIGHT.
0.50 [13]
4.50 [114]
O.D. REF
PIPE 4.00 SCHED 40
PIPE SLEEVE (NOT
BY ROSEMOUNT)
LENGTH BY CUSTOMER
MASONRY
STACK WALL
OUTSIDE WALL
SURFACE
JOINT MUST
BE AIRTIGHT
MTG HOLES
SHOWN ROTATED
45 OUT OF
TRUE POSITION
o
FIELD WELD
PIPE TO
ADAPTOR PLATE
BOLT ADAPTOR
PLATE TO OUTSIDE
WALL SURFACE
NOTE: DIMENSIONS IN INCHES WITH
MILLIMETERS IN PARENTHESES.
2.50 [63.5]
MIN DIA HOLE
IN WALL
STACK OR DUCT
METAL WALL
WELD OR BOLT ADAPTOR
PLATE TO METAL WALL
OF STACK OR DUCT.
JOINT MUST BE AIR TIGHT.
FIELD WELD
PIPE TO
ADAPTOR PLATE
3.50 [89]
O.D. REF
PIPE 3.00 SCHED 40
PIPE SLEEVE (NOT
BY ROSEMOUNT)
LENGTH BY CUSTOMER
MASONRY
STACK WALL
OUTSIDE WALL
SURFACE
JOINT MUST
BE AIRTIGHT
BOLT ADAPTOR
PLATE TO OUTSIDE
WALL SURFACE
624038
Figure 2-1. Probe Installation (Sheet 4 of 5)
2

Instruction Manual
IB-106-300NH Rev. 4.2
July 2002
2-6 Installation Rosemount Analytical Inc. A Division of Emerson Process Management
World Class 3000
BRACE BARS
(NOT BY ROSEMOUNT)
2.00
(51)
NOTE: DIMENSIONS IN INCHES WITH
MILLIMETERS IN PARETHESES.
VERTICAL BRACE CLAMP ASSY.
HORIZONTAL BRACE CLAMP ASSY.
(BOTH BRACE CLAMP ASSEMBLIES ARE THE SAME.
INSTALLATION AND LOCATION OF CLAMP ASSEMBLIES
AND BRACE BARS TO BE DONE IN FIELD.)
BY ROSEMOUNT
}
2 HOLES - 0.625
(16) DIA. FOR
0.50 (12) DIA.
BOLT
ABRASIVE SHIELD
NOTE: BRACING IS FOR VERTICAL AND HORIZONTAL PROBE INSTALLATION.
1.00
(25) MAX.
0.375
(10)
1.00
(25)
4.12
(105)
4.12
(105)
60 MAX.
o
30 MIN.
o
5.62
(143)
5.62
(143)
36.00 (914)
EXTERNAL BRACING REQUIRED FOR 9 FT AND 12 FT
(2.75 M AND 3.66 M) PROBES AS SHOWN ABOVE. 27270008
Figure 2-1. Probe Installation (Sheet 5 of 5)

Instruction Manual
IB-106-300NH Rev. 4.2
July 2002
Rosemount Analytical Inc. A Division of Emerson Process Management Installation 2-7
World Class 3000
4. If using the optional ceramic diffusor
element, the vee deflector must be cor-
rectly oriented. Before inserting the
probe, check the direction of flow of the
gas in the duct. Orient the vee deflector
on the probe so that the apex points
upstream toward the flow (Figure 2-2).
This may be done by loosening the
setscrews, and rotating the vee de-
flector to the desired position.
Retighten the setscrews.
5. In horizontal installations, the probe
junction box should be oriented so that
the system cable drops vertically from
the probe junction box. In a vertical in-
stallation, the system cable can be ori-
ented in any direction.
6. If the system has an abrasive shield,
check the dust seal packings. The
joints in the two packings must be
staggered 180°. Also, make sure that
the packings are in the hub grooves as
the probe slides into the 15° forcing
cone in the abrasive shield.
NOTE
If process temperatures will exceed
392°F (200°C), use anti-seize com-
pound on stud threads to ease future
removal of probe.
7. Insert probe through the opening in the
mounting flange and bolt the unit to the
flange. When probe lengths selected
are 9 or 12 ft (2.75 or 3.66 m), special
brackets are supplied to provide addi-
tional support for the probe inside the
flue or stack. See Figure 2-1, sheet 5.
NOTE
Probe Installation
To maintain CE compliance, ensure
there is a good connection between
the chassis of the probe and earth.
VEE
DEFLECTOR
VEE
DEFLECTOR
DIFFUSION
ELEMENT
SETSCREW
FILTER
GAS FLOW
DIRECTION
APEX
624017
Figure 2-2. Orienting the Optional Vee Deflector
2

Instruction Manual
IB-106-300NH Rev. 4.2
July 2002
2-8 Installation Rosemount Analytical Inc. A Division of Emerson Process Management
World Class 3000
c. Reference Air Package
After the oxygen analyzing (probe) unit is
installed, connect the reference air set to
the probe junction box. The reference air
set should be installed in accordance with
Figure 2-3.
d. Service Required
1. Power input: 100, 115 or 220 Vac sin-
gle phase, 50 to 60 Hz, 3 amp mini-
mum. (See label.)
2. Compressed air: 10 psig (68.95 kPa)
minimum, 225 psig (1551.38 kPa)
maximum at 2 scfh (56.6 L/hr) maxi-
mum; supplied by one of the following
(less than 40 parts-per-million total hy-
drocarbons). Regulator outlet pressure
should be set at 5 psi (35 kPa).
(a) Instrument air - clean, dry.
(b) Bottled standard air with step-down
regulator.
(c) Bottled compressed gas mixture
(20.95% oxygen in nitrogen).
(d) Other equivalent clean, dry, oil-free
air supply.
TO PROBE HEAD
REF AIR SET
263C152G01
1 FLOWMETER 0.2-2.0 SCFH 771B635H02
2 2" PRESSURE GAGE 0-15 PSIG 275431-006
3 COMBINATION FILTER-REG. 0-30 PSIG 4505C21G01
NOTE: DIMENSIONS ARE IN INCHES WITH
MILLIMETERS IN PARENTHESES.
123
4.81 (122.17)
FLOW SET
POINT KNOB
0.125-27 NPT FEMALE
OUTLET CONNECTION
1.19
(30.22)
10.0 REF
(254)
DRAIN VALVE
3.12 (79.25) MAX
8.50 MAX
(215.90)
2.0
(50.80) 2 MOUNTING HOLES
3.19 (81.03) LG
THROUGH BODY FOR
0.312 (7.92) DIA BOLTS
1.50
(38.10)
2.250 (57.15)
SCHEMATIC HOOKUP FOR REFERENCE AIR SUPPLY ON OXYGEN ANALYZER PROBE HEAD.
OUTLET
0.25-18 NPT FEMALE
INLET CONNECTION
COMPRESSED AIR SUPPLY
10-225 PSIG MAX PRESSURE
27270003
0.250 OR 6 MM OD TUBING
(SUPPLIED BY CUSTOMER)
0.250 OR 6 MM OD
TUBE COMPRESSION
FITTING (SUPPLIED BY WECO)
Figure 2-3. Air Set, Plant Air Connection

Instruction Manual
IB-106-300NH Rev. 4.2
July 2002
Rosemount Analytical Inc. A Division of Emerson Process Management Installation 2-9
World Class 3000
2-2 INTELLIGENT FIELD TRANSMITTER (IFT)
INSTALLATION
a. Mechanical Installation
The outline drawing of the IFT module in
Figure 2-4 shows mounting centers and
clearances. The NEMA 4X enclosure is de-
signed to be mounted on a wall or bulk-
head. The IFT should be installed no more
than 1200 feet (364 m) from the optional
HPS or 150 feet (45 m) from the probe if
HPS is not installed in the system.
b. Electrical Connections
To meet the Safety Requirements of
IEC 1010 (EC requirement), and ensure
safe operation of this equipment, con-
nection to the main electrical power
supply must be made through a circuit
breaker (min 10A) which will discon-
nect all current carrying conductors
during a fault situation. This circuit
breaker should also include a me-
chanically operated isolating switch. If
not, then another external means of
disconnecting the supply from the
equipment should be located close by.
Circuit breakers or switches must
comply with a recognized standard
such as IEC 947.
NOTE
Refer to Figure 2-7 for fuse locations
and specifications.
1. The IFT can be configured for 100,
120, 220, or 240 line voltages. For 120
Vac usage, install JM8, JM7, and JM1
on the power supply board. For 220
Vac usage, install jumpers JM6, JM5,
JM2 (refer to Figure 2-5 and Figure
2-7).
2. For installations where the cable run is
less than 150 feet (45 m), the IFT can
5.76 (146.3)
9.00 (228.6)
1.25
(31.75)
21190002
6.0
(152.4)
DESIGN DIMENSIONS ARE IN INCHES
WITH MILLIMETERS IN PARENTHESES.
NOTE:
8.00 (203.2)
11.24 (285.5)
0.31
(7.9)
13.24
(336.3)
15.00
(381.0)
16.00
(406.4)
2.00
(50.8)
1.62
(41.1)
2.25
(57.15) 0.867
(22.00)
11.5 (292.1) MINIMUM DOOR
SWING CLEARANCE
3.36
(85.3)
Figure 2-4. Outline of Intelligent Field Transmitter
be configured to connect directly to a
probe. An optional HPS is available for
cable runs over 150 feet (45 m). The
electrical connections for a non-HPS
equipped system should be made as de-
scribed in the electrical installation dia-
gram, Figure 2-8. Refer to Figure 2-14
for connections for an HPS equipped
system.
2

Instruction Manual
IB-106-300NH Rev. 4.2
July 2002
2-10 Installation Rosemount Analytical Inc. A Division of Emerson Process Management
World Class 3000
Do not install jumper JM6 on the mi-
croprocessor board, or JM1 on the in-
terconnect board, if an HPS is
installed in the system. This will result
in system failure.
3. The IFT must have JM6 on the micro-
processor board (Figure 2-9 and Figure
2-10) and JM1 on the interconnect
board (Figure 2-11 and Figure 2-12)
installed if an HPS is not installed in
the system.
4. If an MPS is not used in the system,
wire jumper between CAL RET and
NO GAS must be installed on the in-
terconnect board. Remove wire jumper
if MPS is installed in the system. Refer
to Figure 2-8, note 6.
5. The power cable should comply with
the safety regulations in the user's
country and should not be smaller than
16 gauge, 3 amp.
6. Before supplying power to the IFT, ver-
ify that the jumpers have been properly
set in the IFT (Figure 2-5, Figure 2-9,
and Figure 2-11).
7. Terminal strip J5 on the power supply
board is used for supplying the IFT with
power. Terminal strip J6 on the power
supply board is used to supply the
probe heater with power if an HPS is
not used (Figure 2-7).
ALWAYS DISCONNECT LINE VOLTAGE
FROM INTELLIGENT FIELD TRANSMITTER
BEFORE CHANGING JUMPERS.
JUMPER
CONFIGURATION
LINE VOLTAGE
SELECTION
JUMPER
(INSTALL)
PROBE HEATER
VOLTAGE SELECTION
JUMPER
(INSTALL)
100 V.A.C.
120 V.A.C.
220 V.A.C.
240 V.A.C.
JM3, JM7, JM2
JM8, JM7, JM1
JM6, JM5, JM2
JM6, JM5, JM1
WORLD CLASS PROBE (44V)
WORLD CLASS "DIRECT
REPLACEMENT" PROBE (115V)
218 PROBE (115V)
JM10
JM9
JM9
21190012
If incorrect heater voltage is selected, damage to the probe may occur. For HPS voltage se-
lection jumper, refer to Figure 2-15. Always update the relevant labeling to reflect the set
voltage.
Figure 2-5. Power Supply Board Jumper Configuration

Instruction Manual
IB-106-300NH Rev. 4.2
July 2002
Rosemount Analytical Inc. A Division of Emerson Process Management Installation 2-11
World Class 3000
NOTE
General Wiring Recommendations
To maintain CE compliance and ensure proper EMC performance, all signal wires to the Inter-
connect Board, with the exception of the probe cable, should be looped through the ferrite
beads provided as shown in Figure 2-6 (P/N 1L04253H01). Signal wires may be grouped to-
gether and looped through before exiting the enclosure. Ferrite beads should be placed as
close as possible to the exit point. Ferrite beads are provided for European Common Market
applications only.
Figure 2-6. Signal Wire Routing
2

Instruction Manual
IB-106-300NH Rev. 4.2
July 2002
2-12 Installation Rosemount Analytical Inc. A Division of Emerson Process Management
World Class 3000
FUSES
FUSES
NOTE: ALL FUSES (F1 THROUGH F5)
ARE 5A @ 250 VAC, ANTI-
SURGE, CASE SIZE5X20MM,
TYPE T TO IEC127, SCHURTER.
Figure 2-7. IFT Power Supply Board Jumpers

Instruction Manual
IB-106-300NH Rev. 4.2
July 2002
Rosemount Analytical Inc. A Division of Emerson Process Management Installation 2-13
World Class 3000
BK
GN
WH
PU
SHIELD
SHIELD
CAL RET
NO GAS
LO GAS
HI GAS
IN GAS
SHIELD
SHIELD
STACK TC -
STACK TC +
PROBE MV+
PROBE MV -
PROBE TC +
PROBE TC -
RD
YE
BL
OR
BL
OR
YE
RD
INTELLIGENT FIELD
TRANSMITTER IFT 3000
WORLD CLASS
PROBE
12345678
BL
PROBE MV -
PROBE MV +
PROBE TC +
PROBE TC -
OR
YE
RD
GN
E
R
H
WH
BK
GN CELL -VE
OR CELL +VE
YE CHROMEL
RD ALUMEL
GN
BK
BK
}
HEATER
PROBE JUNCTION
BOX WIRING
STACK TC WIRING AS REQUIRED.
SPECIAL PROBE CABLE BETWEEN PROBE
AND IFT BY ROSEMOUNT.
INSTALL JM1 ON INTERCONNECT BOARD.
INSTALL JM6 ON MICROPROCESSOR
BOARD.
IF STACK TEMPERATURE NOT USED.
IF MPS 3000 NOT USED.
1 RELAY PER PROBE AVAILABLE FOR
CALIBRATION STATUS INDICATION. (48 V
max, 100 mA max)
CURRENT/VOLTAGE SELECTOR SWITCH
MUST BE SELECTED TO CURRENT (I) FOR
HART COMMUNICATIONS APPLICATIONS.
JUMPER JM7 INFORMATION APPEARS IN
FIGURE 2-9.
NOTES:
ALWAYS DISCONNECT LINE VOLTAGE
FROM INTELLIGENT FIELD TRANSMITTER
BEFORE CHANGING JUMPERS.
LINE
VOLTAGE
SECTION JUMPER
(INSTALL)
PROBE HEATER
VOLTAGE SECTION
JUMPER
(INSTALL)
120 V.A.C.
100 V.A.C.
220 V.A.C.
240 V.A.C.
J1
J5 J6
J1
JM1
JM7
JM6
J2 J3 J4 J5 J6 J7 J8 J9
3D39122G REV
POWER SUPPLY BOARD
3D39513G
MICROPROCESSOR
BOARD
3D39120G REV
INTERCONNECT BOARD
JM8, JM7, JM1
JM3, JM7, JM2
JM6, JM5, JM2
JM6, JM5, JM1
WORLD CLASS PROBE
WORLD CLASS "DIRECT
REPLACEMENT" PROBE
218 PROBE
JM10
JM9
JM9
JUMPER CONFIGURATION
5 CONDUCTOR SHIELDED CABLE
PER PROBE #16 AWG BY CUSTOMER
EN
L
LINE
VOLTAGE
MPS TERMINATION BOARD
MPS 3000 MULTIPROBE CALIBRATION GAS SEQUENCER (OPTIONAL)
ER
H
L
E
N
LINE
VOLTAGE
J13 J14 J15 J16 J17 J18
J12
CAL RET
HI GAS
IN CAL
NO GAS
CAL RET
HI GAS
IN CAL
NO GAS
CAL RET
HI GAS
IN CAL
NO GAS
CAL RET
HI GAS
IN CAL
NO GAS
LOW GAS
LOW GAS
LOW GAS
LOW GAS
NC C NO NC C NO NC C NO NC C NO
L
N
L
N
LINE OUT LINE IN
J10
J11
PROBE 1 PROBE 2 PROBE 3 PROBE 4
PROBE 1 PROBE 2 PROBE 3 PROBE 4
PROBE 1
SOLENOID
PROBE 2
SOLENOID
PROBE 3
SOLENOID
PROBE 4
SOLENOID
HIGH GAS
SOLENOID
LOW GAS
SOLENOID
PRESSURE
SWITCH
I
V
CURRENT/VOLTAGE
SELECTOR SWITCH
27270011
Figure 2-8. Wiring Layout for IFT Systems without HPS
2

Instruction Manual
IB-106-300NH Rev. 4.2
July 2002
2-14 Installation Rosemount Analytical Inc. A Division of Emerson Process Management
World Class 3000
OUTPUT JUMPER
HPS Remove JM6
Probe (No HPS) Install JM6
ANALOG OUTPUT
(Condition during
microcontroller failure) Jumper
Output = zero Install JM7
Output = maximum Remove JM7
(See Figure 2-10 for jumper locations.)
Figure 2-9. Microprocessor Board
Jumper Configuration
c. Analog Output and Relay Output
Connections
1. The microprocessor board has a se-
lector for voltage or current operations.
Figure 2-10 shows switch orientation.
In voltage mode, output is 0-10 V. In
the current mode, the output can be
configured from the SETUP menu to
be 0-20 mA or 4-20 mA.
2. The analog output and relay outputs
are programmed by the user as
needed. The analog output is typically
sent to recording equipment such as
chart recorders. Relay outputs are typi-
cally sent to annunciators.
3. Relays K1 and K2 are user configur-
able from the probe SETUP sub-menu
(Table 5-5). Typically these are used to
indicate O2 values above or below
specified tolerances. OK relay is ener-
gized when unit is functioning properly.
4. All wiring must conform to local and
national codes.
5. Connect the analog output and relay
outputs as shown in Figure 2-12.
2-3 HEATER POWER SUPPLY INSTALLATION
a. Mechanical Installation
The outline drawing of the heater power
supply enclosure in Figure 2-13 shows
mounting centers and clearances. The
NEMA 4X enclosure is designed to be
mounted on a wall or bulkhead. The heater
power supply should be installed no further
than 150 feet (45 m) from the probe. The
heater power supply must be located in a
location free from significant ambient tem-
perature changes and electrical noise. Am-
bient temperature must be between -20°
and 140°F (-30° and 60°C).

Instruction Manual
IB-106-300NH Rev. 4.2
July 2002
Rosemount Analytical Inc. A Division of Emerson Process Management Installation 2-15
World Class 3000
JM7
JM6
J4
SW1
TO I/O
BOARD
3D39513G REV
TO LDP CARD
TO POWER
SUPPLY CARD
TP4
+30VISO-C GNDC +5VISO-C
TP5 TP6
TO GUI CARD
J3
J2 J1
TP1
-5V TP2
+15V
TP8
+5V
TP3
-15V
TP7
JM7
CURRENT/VOLTAGE
SELECTOR SWITCH
JM6
29850004
Figure 2-10. IFT Microprocessor Board
2

Instruction Manual
IB-106-300NH Rev. 4.2
July 2002
2-16 Installation Rosemount Analytical Inc. A Division of Emerson Process Management
World Class 3000
OUTPUT JUMPER
HPS Remove JM1
Probe (No HPS) Install JM1
Figure 2-11. Interconnect Board Jumper Configuration
22
11
33
44
55
66
77
88
99
10 10
11 11
12 12
13 13
14 14
15 15
16 16
17 17
18 18
19 19
20 20
21 21
22 22
23 23
24 24 OK-COM
OK-NO
K1-COM
K1-NO
K2-COM
K2-NO
ANOUT-
ANOUT+
STACK T/C
STACK T/C
PROBE T/C
PROBE T/C
PROBE MV-
PROBE MV+
OK-NC
K1-NC
K2-NC
CAL INIT-2
CAL INIT-1
CALRET
NOGAS
LOGAS
HIGAS
INCAL
RELAY-
RELAY+
AD590-
AD590+
TRIAC-
TRIAC+ JM1
(UNDER
SHIELD)
NOTES:
DENOTES SHIELD CONNECTION.
OK RELAY IS ENERGIZED WHEN
UNIT IS FUNCTIONING PROPERLY.
16860010
Figure 2-12. IFT Interconnect Board Output Connections

Instruction Manual
IB-106-300NH Rev. 4.2
July 2002
Rosemount Analytical Inc. A Division of Emerson Process Management Installation 2-17
World Class 3000
CLASS 1, DIVISION 1, GROUP B ENCLOSURE
#10-32 UNF 2A
THREADED INSERT
(0.31 x 0.31 FROM CORNER OF PLATE)
0.13" (3.3) THK U. L. APPROVED
GASKET
7.00
(177.8)
3.25
(82.6) 3.63
(92.2)
0.31
(7.9)
NEMA 4X
(NON-HAZARDOUS)
NOTE: DIMENSIONS IN INCHES
WITH MILLIMETERS IN PARENTHESES.
10.39
(264)
9.17
(233)
9.96
(253)
8.50
(215.9)
6.18
(156.9)
4.72
(120)
8.50
(215.9) 8.00
(203.2)
11.00
(279.4)
6.75
(171.5)
0.56 (14)
DIA (2)
MOUNTING
HOLES
1.00 (25.4) MINIMUM CLEARANCE
FOR REMOVING COVER
4.38
(111.3)
4.88
(124)
0.38
(9.7)
1.81
(46)
6.00
(152.4)
4.00
(101.6)
#0.31
686029
Figure 2-13. Outline of Heater Power Supply
b. Electrical Connections
1. Electrical connections should be made
as described in the electrical installa-
tion diagram, Figure 2-14. The wiring
terminals are divided into two layers;
the bottom (FROM PROBE) terminals
should be connected first, the top
(FROM ELECTRONICS) terminals
should be connected last (Figure 2-15).
Each terminal strip has a protective
cover which must be removed when
making connections. To remove the
terminal covers, remove two slotted
screws holding cover in place. Always
reinstall terminal covers after making
connections. All wiring must conform to
local and national codes.
NOTE
Refer to Figure 2-17 for fuse locations
and specifications.
2. Power Input: 120, 220 or 240 Vac. For
120 Vac usage, install jumpers JM4
and JM1. For 220 or 240 Vac usage,
install jumper JM5 (see label, Figure
2-16).
NOTE
For 100 Vac usage, the heater power
supply is factory-supplied with a dif-
ferent transformer. When using the
HPS with 100 Vac transformer, install
jumpers JM1 and JM4.
3. The power cable should comply with
safety regulations in the user's country
and should not be smaller than 16
gauge, 3 amp.
2

Instruction Manual
IB-106-300NH Rev. 4.2
July 2002
2-18 Installation Rosemount Analytical Inc. A Division of Emerson Process Management
World Class 3000
+
+
+
+
+
+
+
+
+
-
-
-
-
-
-
-
-
-
BK WH
J9
J8
J3
J2 J1
TRIAC RELAY
STACK
TC
ANALOG
HEATER
PROBE
MV
PROBE
MV
PROBE
TC
PROBE
TC
AD590
(INTERNAL
WIRING)
WHBK
OR CELL+
YE HTR TC +
BL CELL -
RD HTR TC
-
BK
WH
GN
STACK
TC
PROBE
HEATER
RH NL
LINE
VOLTAGE
GN/YE
TOP
BOTTOM
4 TWISTED PAIR SHIELDED
#22 AWG BY CUSTOMER
2 TWISTED PAIR SHIELDED
#22 AWG BY CUSTOMER
(OPTIONAL)
HPS 3000 INTERFACE MODULE
LINE
1
2
2
7
11
1
4
1
2
3
4
5
6
7
8
9
10
WORLD CLASS PROBE
ALWAYS DISCONNECT LINE VOLTAGE
FROM HEATER POWER SUPPLY
BEFORE CHANGING JUMPERS.
JUMPER
CONFIGURATION
LINE VOLTAGE
SELECTION
JUMPER
(INSTALL)
JUMPER
(INSTALL)
HEATER
POWER ON
120 V.A.C./100 V.A.C.
220/240 V.A.C.
JM4, JM1
JM5
REMOTE
ON
REMOVE JM2
INSTALL JM2
ELECTRONICS
SELECTION JUMPER
PROBE HEATER
VOLTAGE SECTION
REMOVE JM3, JM6DIGITAL
(NEXT GENERATION)
WORLD CLASS PROBE JM7
RELAY WIRE IS OPTIONAL, RELAY CAN BE BYPASSED
WITH JUMPER JM-2 IF NOT WIRED TO THE IFT.
STACK TC WIRING AS REQUIRED.
ALL WIRES #16-#22 AWG TWISTED PAIR WITH SHIELD
BY CUSTOMER EXCEPT AS NOTED.
STANDARD PROBE CABLE BETWEEN PROBE AND
HPS BY ROSEMOUNT.
REMOVE JM1 ON INTERCONNECT BOARD.
REMOVE JM6 ON MICROPROCESSOR BOARD.
IF RELAY WIRE OF NOTE 1 INSTALLED THEN
REMOVE JM2 ON HPS 3000.
IF STACK TEMPERATURE NOT USED.
IF MPS 3000 NOT USED.
1 RELAY PER PROBE AVAILABLE FOR CALIBRATION
STATUS INDICATION (48 V max, 100 mA max).
100 V.A.C. REQUIRES TRANSFORMER PART
NUMBER 1M02961G02.
JUMPER JM7 INFORMATION APPEARS IN FIGURE 2-9.
NOTES
12345678
BL
PROBE MV -
PROBE MV +
PROBE TC +
PROBE TC -
OR
YE
RD
GN
E
R
H
WH
BK
GN CELL -VE
OR CELL +VE
YE CHROMEL
RD ALUMEL
GN
BK
BK
}
HEATER
PROBE JUNCTION
BOX WIRING
A
B
11
22540001
Figure 2-14. Wiring Layout for Complete IFT 3000 System with HPS (Sheet 1of 2)

Instruction Manual
IB-106-300NH Rev. 4.2
July 2002
Rosemount Analytical Inc. A Division of Emerson Process Management Installation 2-19
World Class 3000
JM7
I
V
MPS TERMINATION BOARD
MPS 3000 MULTIPROBE CALIBRATION GAS SEQUENCER (OPTIONAL)
L
E
N
LINE
VOLTAGE
J13 J14 J15 J16 J17 J18
J12
CAL RET
HI GAS
IN CAL
NO GAS
CAL RET
HI GAS
IN CAL
NO GAS
CAL RET
HI GAS
IN CAL
NO GAS
CAL RET
HI GAS
IN CAL
NO GAS
LOW GAS
LOW GAS
LOW GAS
LOW GAS
NC C NO NC C NO NC C NO NC C NO
L
N
L
N
LINE OUT LINE IN
J10
J11
PROBE 1 PROBE 2 PROBE 3 PROBE 4
PROBE 1
PROBE 2 PROBE 3 PROBE 4
PROBE 1
SOLENOID
PROBE 2
SOLENOID
PROBE 3
SOLENOID
PROBE 4
SOLENOID
HIGH GAS
SOLENOID
LOW GAS
SOLENOID
PRESSURE
SWITCH
SHIELD
SHIELD
RELAY –
RELAY +
TRIAC +
CAL RET
SHIELD
NO GAS
AD590 –
LO GAS
AD590 +
HI GAS
SHIELD
IN CAL
TRIAC –
SHIELD
SHIELD
STACK TC –
STACK TC +
PROBE MV –
PROBE MV +
PROBE TC +
PROBE TC –
INTELLIGENT FIELD
TRANSMITTER IFT 3000
ALWAYS DISCONNECT LINE VOLTAGE
FROM INTELLIGENT FIELD TRANSMITTER
BEFORE CHANGING JUMPERS.
LINE
VOLTAGE
SECTION JUMPER
(INSTALL)
PROBE HEATER
VOLTAGE SECTION
JUMPER
(INSTALL)
100 V.A.C.
120 V.A.C.
220 V.A.C.
200 V.A.C.
240 V.A.C.
J1
J5 J6
J1
JM1
JM6
J2 J3
J4
J5 J6 J7 J8 J9
3D39122G REV
POWER SUPPLY BOARD
3D39513G
MICROPROCESSOR
BOARD
3D39120G REV
INTERCONNECT BOARD
JM3, JM7, JM2
JM8, JM7, JM1
JM6, JM5, JM2
JM4, JM5, JM2
JM6, JM5, JM1
NOT USED REMOVE
JM9, JM10
JUMPER CONFIGURATION
EN
L
LINE
VOLTAGE
NOT USED
5 CONDUCTOR SHIELDED CABLE
PER PROBE #16 AWG BY CUSTOMER
CURRENT/VOLTAGE
SELECTOR SWITCH
27270012
A
B
Figure 2-14. Wiring Layout for Complete IFT 3000 System with HPS (Sheet 2 of 2)
2

Instruction Manual
IB-106-300NH Rev. 4.2
July 2002
2-20 Installation Rosemount Analytical Inc. A Division of Emerson Process Management
World Class 3000
TRANSFORMER
TRANSFORMER
SCREW
(2 PER COVER)
TERMINAL
COVERS
FRONT
SIDE
TERMINAL STRIP
(FROM ELECTRONICS)
TERMINAL STRIP
(FROM ELECTRONICS)
29850005
Figure 2-15. Heater Power Supply Wiring Connections

Instruction Manual
IB-106-300NH Rev. 4.2
July 2002
Rosemount Analytical Inc. A Division of Emerson Process Management Installation 2-21
World Class 3000
1
2
NOTES:
100 V.A.C. OPERATION REQUIRES TRANSFORMER PART
NUMBER 1M02961G02.
REFER TO TABLE 3-5 FOR PROPER SET POINT SELECTION.
1
2
0310122
Figure 2-16. Jumper Selection Label
NOTE
Before supplying power to the heater
power supply, verify that jumpers JM3,
JM6 are removed and JM7 is installed.
If relay wire (Figure 2-14, note 1) is in-
stalled, JM2 must be removed from
HPS Mother Board (Figure 2-17).
4. Before supplying power to the heater
power supply, verify that the jumpers
on the mother board, Figure 2-17, are
properly configured. Jumpers JM3 and
JM6 should be removed and JM7
should be installed.
Additionally, make sure that the proper
jumper for your line voltage is installed,
Figure 2-16. If relay wire (Figure 2-14,
note 1) is not installed, JM 2 should be
installed on the HPS Mother Board
(Figure 2-17).
NOTE
Refer to Figure 2-9 and Figure 2-11 for
proper IFT jumper configuration. IFT
microprocessor and interconnect
board jumper configurations must be
set correctly in order for HPS to work
properly.
29850001
NOTE: ALL FUSES ARE 5A @ 250 VAC,
ANTI-SURGE, CASE SIZE
5 X 20 MM, TYPE T TO IEC127,
SCHURTER.
3D3 080G REV
JM1
JM2
JM4
JM5
JM7
FUSE
FUSES
Figure 2-17. Jumpers on HPS Mother Board
2

Instruction Manual
IB-106-300NH Rev. 4.2
July 2002
2-22 Installation Rosemount Analytical Inc. A Division of Emerson Process Management
World Class 3000
2-4 MULTIPROBE CALIBRATION GAS
SEQUENCER INSTALLATION
a. Mechanical Installation
The outline drawing of the MPS module in
Figure 2-18 shows mounting centers and
clearances. The box is designed to be
mounted on a wall or bulkhead. The MPS
module should be installed no further than
300 feet (91 mz) piping distance from the
probe, and no more than 1000 feet (303 m)
cabling distance from the IFT. Install the
MPS module in a location where the ambi-
ent temperature is between -20° and 160°F
(-30° and 71°C).
b. Gas Connections
Figure 2-19 shows the bottom of the MPS
where the gas connections are made. 1/4
inch threaded fittings are used.
1. Connect the reference air supply to
INSTR. AIR IN. The air pressure regu-
lator valve is set at the factory to 20 psi
(138 kPa). If the reference air pressure
should need readjustment, turn the
knob on the top of the valve until the
desired pressure is obtained.
2. Connect the high O2 calibration gas to
HIGH GAS. The calibration gas pres-
sure should be set at 20 psi (138 kPa).
HIGH CAL
GAS IN
LOW CAL
GAS IN
CAL GAS
OUT
REF AIR
OUT
INSTR
AIR
REF AIR
OUT
REF AIR
OUT
REF AIR
OUT
CAL GAS
OUT
CAL GAS
OUT
CAL GAS
OUT
PROBE 1 PROBE 2 PROBE 3 PROBE4
0.84 (21.34)
27270013
1.96 (49.78)
4.21 (106.93)
3.09 (78.49)
5.25 (133.35)
5.54 (140.72)
14.00 (355.60) REF
12.00
(304.80)
12.00
(304.80)
10.00
(254.00)
NOTE: DIMENSIONS ARE IN INCHES
WITH MILLIMETERS IN
PARENTHESES.
Figure 2-18. MPS Module

Instruction Manual
IB-106-300NH Rev. 4.2
July 2002
Rosemount Analytical Inc. A Division of Emerson Process Management Installation 2-23
World Class 3000
3. Connect the low O2 calibration gas to
LOW GAS. The calibration gas pres-
sure should be set at 20 psi (138 kPa).
4. Connect the REF AIR OUT to the ref-
erence air fitting on the probe junction
box.
5. Connect the CAL GAS OUT to the
calibration gas fitting on the probe
junction box.
6. If the MPS is configured for multiple
probes (up to four), repeat steps 4 and
5 for each additional probe.
A check valve is required for each
probe connected to an MPS to prevent
condensation of flue gas in the cali-
bration gas lines. The check valve
must be located between the calibra-
tion fitting and the gas line.
c. Electrical Connections
Electrical connections should be made as
described in the electrical installation dia-
gram, Figure 2-20. All wiring must conform
to local and national codes. The electrical
connections will exist only between the
electronics package and the MPS to enable
automatic and semiautomatic calibration. If
more than one probe system is being used,
the additional probes and electric packages
would be wired similar to the first probe.
NOTE
Refer to Figure 2-20 for fuse locations
and specifications.
1. Run the line voltage through the bulk-
head fitting on the bottom of the MPS
where marked LINE IN, Figure 2-19.
Connect the line voltage as shown in
Figure 2-20 to the LINE IN terminal on
the MPS termination board located in-
side the unit. Tighten the cord grips to
provide strain relief.
2. The MPS can accommodate up to four
probes. The terminal strips on the MPS
termination board are marked PROBE
1, PROBE 2, PROBE 3, and PROBE 4.
Select PROBE 1 if this is the first probe
and electronic package installed on the
MPS.
3. Make the connections from the MPS to
the IFT as shown in Figure 2-20. Run
wires from the MPS Termination Board
inside the unit through the bulkhead fit-
ting on the bottom of the unit where
marked SIGNAL IN, Figure 2-19. After
the connections are made, tighten the
cord grips to provide strain relief.
HIGH CAL
GAS IN
LOW CAL
GAS IN
CAL GAS
OUT
REF AIR
OUT
INSTR
AIR
REF AIR
OUT
REF AIR
OUT
REF AIR
OUT
CAL GAS
OUT
CAL GAS
OUT
CAL GAS
OUT
PROBE 1 PROBE 2 PROBE 3 PROBE4
LINE IN
SIGNAL IN
27270014
DRAIN
Figure 2-19. MPS Gas Connections
2

Instruction Manual
IB-106-300NH Rev. 4.2
July 2002
2-24 Installation Rosemount Analytical Inc. A Division of Emerson Process Management
World Class 3000
MPS TERMINATION BOARD
L
E
N
LINE
VOLTAGE
J13 J14 J15 J16 J17 J18
J12
CAL RET
HI GAS
IN CAL
NO GAS
CAL RET
HI GAS
IN CAL
NO GAS
CAL RET
HI GAS
IN CAL
NO GAS
CAL RET
HI GAS
IN CAL
NO GAS
LOW GAS
LOW GAS
LOW GAS
LOW GAS
NC C NO NC C NO NC C NO NC C NO
L
N
L
N
LINE OUT LINE IN
J10
J11
PROBE 1 PROBE 2 PROBE 3 PROBE 4
PROBE 1
PROBE 2 PROBE 3 PROBE 4
PROBE 1
SOLENOID
PROBE 2
SOLENOID
PROBE 3
SOLENOID
PROBE 4
SOLENOID
HIGH GAS
SOLENOID
LOW GAS
SOLENOID
PRESSURE
SWITCH
J2 J3 J4 J5 J6 J7 J8 J9
J1
MH1
MH2
MH4
MH3
3D39120G REV
CAL RET
NO GAS
LO GAS
HI GAS
IN CAL
IFT
INTERCONNECT
BOARD
NOTE: FUSES FOR 115 VOLT MPS UNIT ARE
FAST ACTING, 1A @ 250 VAC,
SIZE: 1/4 IN. DIA X 1-1/4 IN. LG.,
GLASS BODY, NON-TIME DELAY,
BUSSMAN PART NO. BK/AGC-1
(ROSEMOUNT APRT NO. 138799-004).
FUSES FOR 220 VOLT MPS UNIT ARE
FAST ACTING, 0.5 A @ 250 VAC,
SIZE 1/4 IN. DIA. X 1-1/4 IN. LG.,
GLASS BODY, NON-TIME DELAY,
BUSSMAN PART NO. BK/AGC-1/2
(ROSEMOUNT PART NO. 138799-014).
29850006
FUSES LOCATED BEHIND
TERMINATION BOARD
Figure 2-20. MPS Probe Wiring

Instruction Manual
IB-106-300NH Rev. 4.2
July 2002
Rosemount Analytical Inc. A Division of Emerson Process Management Installation 2-25
World Class 3000
NOTE
Upon completing installation, make sure that the probe is turned on and operating prior to
firing up the combustion process. Damage can result from having a cold probe exposed to
the process gases.
Power down all probes during outages. Sensor chamber is heated to 736°C. Further, if ducts
will be washed down during the outage, remove the probes to prevent water damage.
2

Instruction Manual
IB-106-300NH Rev. 4.2
July 2002
2-26 Installation Rosemount Analytical Inc. A Division of Emerson Process Management
World Class 3000

Instruction Manual
IB-106-300NH Rev. 4.2
July 2002
Rosemount Analytical Inc. A Division of Emerson Process Management Setup 3-1
World Class 3000
SECTION 3
SETUP
3-1 OVERVIEW
This section provides information on configuring
the IFT 3000 Intelligent Field Transmitter. This
section assumes that you are familiar with the
operation of the IFT and the General User In-
terface (GUI). If you need additional information
on operating the IFT or using the GUI, refer to
Section 5, General User Interface (GUI)
Operation.
3-2 CONFIGURING THE ANALOG OUTPUT
Use the following procedure to configure the
analog output.
a. Press the SETUP key on the GUI keypad.
b. Set the Source to the desired measurement
value to be represented by the analog out-
put. The choices are O2, Efficiency, or Dual
Rng O2.
c. Set the Type to the desired output signal
style. The choices are HART 4-20mA, 0-
20mA, and 0-10V. The choice selected
must agree with the position of the
current/voltage selector switch on the IFT
microprocessor board. An invalid choice will
be discarded. Note that if you are using
HART to communicate with the IFT, you
must set the analog output type to HART 4-
20mA.
d. The next choice, Range Setup, will vary
based on the source selected.
1. Source set to Efficiency. No range
setup is allowed when the source is set
to efficiency. Analog output range is
fixed at 0-100% efficiency.
2. Source set to O2. Range setup allows
you to set the transfer function (Xfer
Fnct) to either linear or log output. You
can also specify the O2 values repre-
sented by the high and low analog out-
put values.
3. Source Set to Dual Rng O2. Range
setup allows you to set the transfer
function (Xfer Fnct) to either linear or
log output. You can also specify the O2
values represented by the high and low
analog output values for both the nor-
mal and high range.
The Mode Setup sub-menu contains
entries for setting the range mode,
whether the high range is used during
calibration, and the point at which the
output switches from normal to high
range.
For a complete description of all pa-
rameters associated with configuring
the analog output, refer to Table 5-5.
3-3 SETTING CALIBRATION PARAMETERS
To successfully calibrate a World Class 3000
system, several calibration parameters must be
set. These parameters are generally set once
and left at those values. These values should
only be changed if the system is not calibrating
properly, or when changing test gas bottles.
a. Press the SETUP key on the GUI keypad.
b. Select the Calibration sub-menu.
c. Set the High Gas parameter to the oxygen
concentration of the high calibration gas.
For high calibration gas, 8% oxygen with a
balance of nitrogen is recommended.
d. Set the Low Gas parameter to the oxygen
concentration of the low calibration gas. For
low calibration gas, 0.4% oxygen with a
balance of nitrogen is recommended.
e. The Auto Cal parameter determines
whether the IFT performs automatic or
semiautomatic calibrations. In order to per-
form automatic calibration, the system must
be equipped with an MPS 3000 Multiprobe
Calibration Gas Sequencer. To perform
3

Instruction Manual
IB-106-300NH Rev. 4.2
July 2002
3-2 Setup Rosemount Analytical Inc. A Division of Emerson Process Management
World Class 3000
automatic calibrations, set the Auto Cal pa-
rameter to Yes.
f. The Output Tracks setting determines
whether the analog output tracks the oxy-
gen reading during a calibration. Setting
Output Tracks to No locks the analog output
value to the last measured oxygen reading
until the calibration is complete.
g. The Cal Interval parameter sets the time in
hours and days between automatic calibra-
tions. When Auto Cal is set to NO, this pa-
rameter is set to OFF.
h. The Next Cal parameter displays the time
until the next scheduled automatic calibra-
tion. If automatic calibration is not enabled,
this parameter displays Disabled.
i. The Gas Time parameter sets the amount
of time that calibration gas flows during an
automatic calibration before a reading is
taken. This value is not used for semiauto-
matic calibrations.
j. The Purge Time parameter sets the amount
of time after an automatic calibration before
the system is returned to normal operation.
This allows time for the calibration gases to
clear the lines and the system to return to
the process gas concentration. This value is
not used for semiautomatic calibrations.
k. The Res Alarm parameter displays the set-
point for the Res Hi alarm. Do not change
this parameter unless directed by a qualified
Rosemount Service Engineer.
l. Press the ESC key twice to return to the
Main menu.
3-4 SETTING THE O2 ALARM SETPOINTS
The IFT has a high and low O2 alarm. To
change the alarm setpoints, press the SETUP
key on the GUI keypad and select the O2
Alarms sub-menu.
The Hi Alarm and Lo Alarm values are the set-
tings for the high and low oxygen concentration
alarms, respectively. The Alarm DB parameter
allows the setting of an alarm dead band. When
a dead band is set, the O2 value must change
by the dead band value before the alarm will re-
set. For example, if the Hi Alarm is set to 8.00%
and the dead band is set to 0.25%, the O2 con-
centration must drop to below 7.75% before the
O2 alarm will clear. This prevents the alarms
from continually activating and clearing when
the oxygen value is near the alarm setpoint.
3-5 CONFIGURING EFFICIENCY
CALCULATIONS
To enable efficiency calculations and set the ef-
ficiency constants, press the SETUP key on
GUI keypad, and select the Efficiency Calc sub-
menu. The Enable Calc selection turns effi-
ciency calculation on and off. Enter the K1, K2,
and L3 constant values in the appropriate fields.
Efficiency constant values are listed in Table 5-6
for oil and gas for the US and Europe.
3-6 CONFIGURING THE RELAY OUTPUTS
The IFT has two relays that can be individually
configured. Each relay can be triggered by three
separate events selected from a list of eight
events. Use the following procedure to configure
the relay outputs.
a. Press the SETUP key on the GUI keypad.
Select the Relay Outputs sub-menu.
b. Select K1 Setup or K2 Setup to configure
relay one or relay two, respectively.
c. Set Event 1, Event 2, and Event 3 to the
desired triggering event. The relay will be
energized when any of the three events oc-
curs. If you do not want a relay to trigger on
three events, set the desired trigger or trig-
gers and set the remaining events to Off.
Note that the TG Low event will only func-
tion if the system includes an MPS 3000
Multiprobe Test Gas Sequencer.
d. Press the ESC key and select the other re-
lay. Configure the relay as described above.
e. Press the ESC key three times to return to
the Main menu.

Instruction Manual
IB-106-300NH Rev. 4.2
July 2002
Rosemount Analytical Inc. A Division of Emerson Process Management Calibration 4-1
World Class 3000
SECTION 4
CALIBRATION
4-1 ANALOG OUTPUT CALIBRATION
For the analog output to perform within the pub-
lished specifications, it must be manually cali-
brated. The only equipment needed to perform
the calibration is a voltage or current meter, de-
pending on which mode of operation is to be
calibrated. Prior to manual calibration, remove
the IFT from any control loops it may be in.
Prior to manual calibration, the IFT
should be removed from any auto-
matic control loops. Failure to remove
the IFT from control loops prior to
calibration may result in faulty equip-
ment performance.
Once initiated from the Setup - Analog Outputs
menu, the calibration procedure is self guiding.
4-2 SYSTEM CALIBRATION
a. Overview
The primary purpose of an oxygen analyzer
is to give an accurate representation of the
percentage of O2 in the gas stream. The
system should be calibrated periodically to
maintain an accuracy which may otherwise
be reduced over time due to cell aging. A
calibration record sheet is provided at the
end of this section to track cell performance.
A requirement for calibration is a set of two
accurate calibration gases spanning the
oxygen range of most interest. For example,
0.4% and 8% for a 0-10% oxygen range.
Under normal conditions the probe should
not need frequent calibration. Because cali-
bration is necessary, the system can be
equipped with the optional MPS 3000 Multi-
probe Calibration Gas Sequencer for fully
automatic calibration at regular intervals.
Without an MPS, the probes must be cali-
brated manually (semiautomatically).
b. Probe Calibration
1. Previous Calibration Constants
Functionality
There are three sets of registers used
to store calibration constants. These
are: Latest Calibration, Previous Cali-
bration, and Calculation. Only the val-
ues in the Calculation register are used
to calculate the oxygen value for dis-
play and representation on the analog
output signal. These values may be
changed in two ways.
(a) The operator may change the val-
ues through the SETUP menu. The
operator may adjust the slope and
constant individually, or reset both
to the values calculated during the
last good calibration. To reset the
values, move the cursor to RESET
SLOPE & CONST and push
ENTER.
(b) The IFT will automatically change
the values after each calibration as
follows:
The values in the Latest Calibra-
tion registers are updated after
every complete calibration, even if
the calibration is not successful. If
the calibration is successful, the
values in the Latest Calibration
registers are copied into the Previ-
ous Calibration registers. This is
accomplished prior to the update of
the Latest Calibration registers.
The new slope and constant are
copied into the Calculation register.
If the calibration fails, the Previous
Calibration registers retain their
existing values, while the Latest
Calibration registers record the
values of the failed calibration. The
Calculation register is not updated
when the calibration fails.
4

Instruction Manual
IB-106-300NH Rev. 4.2
July 2002
4-2 Calibration Rosemount Analytical Inc. A Division of Emerson Process Management
World Class 3000
2. Calibration Methods
There are three calibration methods:
manual (semiautomatic), manually ini-
tiated automatic, and fully automatic.
Manual (semiautomatic) calibration is
done without an MPS unit. Calibration
gases are switched on and off by the
operator and the IFT is sequenced
through the calibration procedure by
the operator with the front panel key-
board. The IFT prompts the operator
for the correct action. Manually initiated
automatic calibration is done with an
MPS. The operator manually initiates
the calibration at the IFT or through a
remote switch, and the IFT controls the
operation of the MPS unit and the cali-
bration sequencing. Fully automatic
calibration requires no action from the
operator. The setup is the same as
semiautomatic except the IFT auto-
matically initiates the calibration at a
fixed calibration interval. In this mode
the operator can also manually initiate
calibrations between the intervals in
the same manner as semiautomatic
calibrations.
c. Manual (Semiautomatic) Calibration
1. Calibration Gases For Manual
(Semiautomatic) Calibration
There are two options for supplying
calibration gases to the probe during
semiautomatic calibration. The first "A"
uses refillable bottles and adjustable 2-
stage pressure regulators; the second
"B" uses disposable bottles and a fixed
single stage regulator to provide a
mixed flow. Normally, the first (method
"A") will have a higher cost and not be
portable. The second ("B") is less
costly, portable, and weighs about 10
lbs (4.5 kg).
Test Method "A" Fixed Tanks and
Manifolds
(a) Required Equipment
Do not use 100% nitrogen as a zero
gas. It is suggested that gas for the
zero be between 0.4% and 2.0% O2. Do
not use gases with hydrocarbon con-
centrations of more than 40 parts per
million. Failure to use proper gases
will result in erroneous readings.
NOTE
Ambient air is not recommended for
use as high calibration gas. An 8% O2
balance in nitrogen is recommended
for high calibration gas.
1 Two tanks of precision cali-
bration gas mixtures. Rec-
ommended calibration gases
are nominally 0.4% and 8.0%
oxygen in nitrogen.
Two sources of calibrated gas
mixtures are:
LIQUID CARBONIC GAS
CORP.
SPECIALTY GAS
LABORATORIES
700 South Alameda Street
Los Angeles, California
90058
213/585-2154
767 Industrial Road
San Carlos, California 94070
415/592-7303
9950 Chemical Road
Pasadena, Texas 77507
713/474-4141
12054 S.W. Doty Avenue
Chicago, Illinois 60628
312/568-8840
603 Bergen Street
Harrison, New Jersey 07029
201/485-1995

Instruction Manual
IB-106-300NH Rev. 4.2
July 2002
Rosemount Analytical Inc. A Division of Emerson Process Management Calibration 4-3
World Class 3000
255 Brimley Road
Scarborough, Ontario,
Canada
416/266-3161
SCOTT ENVIRONMENTAL
TECHNOLOGY, INC.
SCOTT SPECIALTY
GASES
2600 Cajon Blvd.
San Bernardino, CA 92411
714/887-2571
TWX: 910-390-1159
1290 Combermere Street
Troy, MI 48084
314/589-2950
Route 611
Plumsteadville, PA 18949
215/766-8861
TWX: 510-665-9344
2616 South Loop, West
Suite 100
Houston, TX 77054
713/669-0469
2 If gas bottles will be perma-
nently hooked up to the
probe, a manual block valve is
required at the probe (be-
tween the calibration fitting
and the gas line) to prevent
the migration of process
gases down the calibration
gas line.
If an MPS 3000 Multiprobe
Gas Sequencer is used, a
check valve is required at the
probe.
3 Two, 2-stage pressure regu-
lators with stainless steel dia-
phragms for tanks. Maximum
output required: 20 psi (138
kPa).
4 One instrument air pressure
regulator: 20 psi (138 kPa)
maximum and a supply of
clean, dry instrument air.
5 Two zero-leakage shutoff
valves.
6 Miscellaneous oil-free tubing
and fittings.
(b) Calibration
1 A typical calibration setup is
shown in Figure 4-1. Care
must be taken that all fittings
are tight and free from oil or
other organic contaminants.
Small openings can cause
back diffusion of oxygen from
the atmosphere even though
positive pressures are main-
tained in the lines.
NOTE
The probe calibration gas fitting has a
seal cap which must be in place at all
times except during calibration.
In addition to the precision
calibration gas mixtures,
clean, dry, oil-free instrument
air should be used for
calibration.
For optimum accuracy, this calibration
should be run with the process at
normal temperature and operating
conditions.
When the calibration gas line
exceeds 6 ft (1.8 m) in length
from the leak tight valves,
check valve, Rosemount P/N
6292A97H02, should be in-
stalled next to the calibration
gas connection on the probe
to prevent breathing of the
line with the process gas and
subsequent gas condensation
and corrosion.
4

Instruction Manual
IB-106-300NH Rev. 4.2
July 2002
4-4 Calibration Rosemount Analytical Inc. A Division of Emerson Process Management
World Class 3000
REFERENCE AIR
CONNECTION
REFERENCE
AIR
SET
FLOW METER
INSTR.
AIR
IN
LEAK TIGHT
VALVES
2 SCFH
5 SCFH
PROBE
(END VIEW)
CALIBRATE
IN-PLACE
FITTING CHECK
VALVE
REG
0.4%
O2
8.0%
O2
PROBE CALIBRATION GAS FITTING
HAS A SEAL CAP WHICH MUST
BE IN PLACE AT ALL TIMES
EXCEPT DURING CALIBRATION.
NOTE:
Figure 4-1. Typical Calibration Setup
NOTE
Only set the calibration gas flowmeter
upon initial installation and after
changing the diffusion element. A
slightly lower calibration gas flow rate
may indicate a plugged diffusion
element.
2 Set the calibration gas pres-
sure regulators and the flow
meter for a flow of 5 SCFH at
20 psi (138 kPa) for both
gases. The reference air
should be flowing as in normal
operation.
3 Refer to paragraph 4-2d of
this section for Manual (Semi-
automatic) Calibration setup
and procedure using the IFT.
4 Calibration gases will be
switched on and off using the
shutoff valves.
Test Method "B" Rosemount Oxygen
Calibration Gas and Service Kit.
(a) Required Equipment
Do not use 100% nitrogen as a zero
gas. It is suggested that gas for the
zero be between 0.4% and 2.0% O2. Do
not use gases with hydrocarbon con-
centrations of more than 40 parts per
million. Failure to use proper gases
will result in erroneous readings.
NOTE
Ambient air is not recommended for
use as high calibration gas. An 8% O2
balance in nitrogen is recommended
for high calibration gas.
1 Portable Rosemount Oxygen
Calibration Gas Kits (Figure
4-2), Rosemount P/N
6296A27G01, containing 8%
and 0.4% gases in a portable
carrying case with regulator,
built-in valve, hose and con-
necting adapter to the calibra-
tion gas connection.

Instruction Manual
IB-106-300NH Rev. 4.2
July 2002
Rosemount Analytical Inc. A Division of Emerson Process Management Calibration 4-5
World Class 3000
27270007
CALIBRATION
GAS KIT #1
(P/N 6296A27G01)
Figure 4-2. Portable Rosemount Oxygen
Calibration Gas Kit
2 Extra gas bottles are available
at:
Rosemount Analytical Inc.
Box 901
Orrville, Ohio 44667
U.S.A.
Rosemount Limited
Burymead Road
Hitchin, Herts. U.K.
Rosemount Italy
VIA Guido Cavalcanti 8
20127 Milan, Italy
Rosemount Spain
Saturnino Calleja 6
28002 Madrid
Spain
Rosemount France
165 Boulevard de Vallmy
92706, Colombes, France
Rosemount P/N 3530B07G01
for probe 0.4% oxygen in ni-
trogen in disposable bottle.
Rosemount P/N 3530B07G02
for probe 8% oxygen in nitro-
gen in disposable bottle.
3 A check valve is required at
the probe (between the cali-
bration fitting and the gas line)
to prevent the migration of
process gases down the cali-
bration gas line.
(b) Calibration with a Portable Rose-
mount Oxygen Calibration Gases
Kit.
1 A typical portable calibration
setup is shown in Figure 4-3.
For manual (semiautomatic)
calibration, remove cap plug
from the calibrate in place fit-
ting. The cap plug must be
retained to seal this fitting af-
ter calibration is complete;
failure to do so may render
the probe useless if the sys-
tem pressure is slightly nega-
tive. The reference air should
be flowing as in normal
operation.
2 Refer to paragraph 4-2.d of
this section for Manual (Semi-
automatic) Calibration setup
and procedure using the IFT.
3 Screw the pushbutton regu-
lator with contents gage on to
the calibration gas of choice
and inject the calibration gas
by opening the valve. Gas is
on continuously when the
valve is opened.
4

Instruction Manual
IB-106-300NH Rev. 4.2
July 2002
4-6 Calibration Rosemount Analytical Inc. A Division of Emerson Process Management
World Class 3000
0.4
%
O
2
8.0
%
O
2
27270005
CALIBRATE
IN PLACE
CONNECTION CHECK
VALVE
PUSHBUTTON
REGULATOR
WITH CONTENTS
GAGE - SET 5 SCFH
REFERENCE AIR
CONNECTION
CALIBRATION
GAS HOSE
CONNECTS
TO CHECK
VALVE
NOTE: PROBE CALIBRATION GAS
FITTING HAS A SEAL CAP
WHICH MUST BE IN PLACE
EXCEPT DURING CALIBRATION.
Figure 4-3. Typical Portable Calibration Setup
d. Manual (Semiautomatic) Calibration
Procedure
The following procedure relates to an op-
erator initiated calibration selected at the
IFT by pressing the CAL key. The calibra-
tion is manually performed by the operator
upon data queues from the IFT. Any system
without an MPS 3000 Multiprobe Calibration
Gas Sequencer must follow these steps.
1. Press SETUP to display the SETUP
menu. Select PROBE CALIBRATION
sub-menu. Ensure that Auto Cal is dis-
abled. Set the cursor on Auto Cal.
Press ENTER. Set Auto Cal to NO if
not already done.
2. Press the CAL key. Select PERFORM
CALIBRATION sub-menu. "Press EN-
TER to start Manual Calibration" will
appear on the LCD display. Press
ENTER to start. Follow the data
queues. Refer to Table 5-4, CALI-
BRATE O2 Sub-menu.
e. Fully Automatic Calibration
1. Calibration Gases For Fully Automatic
Calibration. For fully automatic calibra-
tion, an MPS 3000 Multiprobe Calibra-
tion Gas Sequencer is required as well
as the two types of calibration gas.
Do not use 100% nitrogen as a zero
gas. It is suggested that gas for the
zero be between 0.4% and 2.0% O2. Do
not use gases with hydrocarbon con-
centrations of more than 40 parts per
million. Failure to use proper gases
will result in erroneous readings.
NOTE
Ambient air is not recommended for
use as high calibration gas. An 8% O2
balance in nitrogen is recommended
for high calibration gas.
Two tanks of precision calibration gas
mixtures. Recommended calibration
gases are nominally 0.4% and 8.0%
oxygen in nitrogen set calibration gas
pressure at 20 psi (138 kPa).
A typical automatic calibration system
is shown in Figure 4-4.

Instruction Manual
IB-106-300NH Rev. 4.2
July 2002
Rosemount Analytical Inc. A Division of Emerson Process Management Calibration 4-7
World Class 3000
PROBE
(END VIEW)
IFT
CALIBRATION GAS HPS
OPTIONAL
CHECK
VALVE
PROBE
SIGNAL CONNECTIONS
MPS-IFT
SIGNAL
CONNECTIONS
MPS
INSTRUMENT
AIR IN
CALIBRATION
GAS 1
(HIGH )O
2
CALIBRATION
GAS 2
(LOW O )
2
27270006
NOTE: THE MPS CAN BE USED WITH UP
TO FOUR PROBES. ONLY ONE PROBE
CAN BE CALIBRATED AT A TIME.
PROBE CALIBRATIONS MUST BE
SCHEDULED IN MULTIPLE PROBE
APPLICATIONS.
NOTE: SHOWN WITH HPS OPTION.
REFERENCE
AIR
Figure 4-4. Typical Automatic Calibration System
4

Instruction Manual
IB-106-300NH Rev. 4.2
July 2002
4-8 Calibration Rosemount Analytical Inc. A Division of Emerson Process Management
World Class 3000
Table 4-1. Automatic Calibration Parameters
Auto Cal YES/NO Set to YES
Output Tracks YES/NO Set as desired to con-
figure analog output
tracking.
Cal Intvl XD XH Set the desired time
between calibrations in
number of days and
hours (1 year max).
Next Cal. XD XH Displays the time left to
the start of the next
calibration. Set the de-
sired time until the start
of the next calibration (1
year max). If nothing is
entered here, the unit
will automatically enter
the Cal Intvl and count
down from that.
Gas Time 0:00 Set the amount of time
for calibration gases to
be turned on in minutes
and seconds; allow
enough time for signal
value to stabilize.
Gas Time 0:00 Set the amount of time
for calibration gases to
be turned on in minutes
and seconds; allow
enough time for signal
value to stabilize.
Purge Time 0:00 Set the amount of time
for the gas lines to clear
in number of minutes
and seconds.
Abort Time 0:00 Set the amount of time
allowed between key
functions before the
calibration procedure is
aborted in number of
minutes and seconds.
Res Alarm ____ Set the desired resis-
tance alarm between 50
to 10,000 ohms.
2. Fully Automatic Calibration Setup. In
order for the IFT system to calibrate
automatically, the parameters from the
CALIBRATE sub-menu (shown in
Table 4-1) in the IFT have to be
entered.
Once these parameters have been set,
the system will initiate calibration with-
out operator intervention as set by the
CAL INTVL
parameter.
3. Manually Initiated Fully Automatic Cali-
bration Procedure. The following pro-
cedure relates to an operator initiated
calibration, either by a remote switch
(CAL INIT on interconnect board) or
selected at the IFT by pressing the
CAL key using an MPS 3000 Multi-
probe Gas Sequencer.
(a) Press SETUP to display the
SETUP sub-menu. Select Calibra-
tion. Ensure that Auto Cal is en-
abled. Set the cursor on Auto Cal.
Press ENTER. Set Auto Cal to
YES if not already done.
(b) Press the CAL key. Select Perform
Calibration. "Press ENTER to start
Automatic Calibration" will appear
on the LCD display. Press ENTER
to start. Refer to Table 5-5, CALI-
BRATE O2 Sub-Menu.

Instruction Manual
IB-106-300NH Rev. 4.2
July 2002
Rosemount Analytical Inc. A Division of Emerson Process Management Calibration 4-9
World Class 3000
Calibration Record
For
Rosemount Analytical In Situ O
2 Probe
Probe Serial Number:
Probe Tag Number:
Probe Location:
Date Placed Into Service:
Date Slope Constant Impedance Responseinitial Responsefinal
Notes: Responseinitial When the second calibration gas is turned off, note the number of seconds required for
the O2 value to begin migrating back to the process value.
Responsefinal When the second calibration gas is turned off, note the number of seconds required for
the O2 value to settle out at the process value.
4

Instruction Manual
IB-106-300NH Rev. 4.2
July 2002
4-10 Calibration Rosemount Analytical Inc. A Division of Emerson Process Management
World Class 3000

Instruction Manual
IB-106-300NH Rev. 4.2
July 2002
Rosemount Analytical Inc. A Division of Emerson Process Management General User Interface (GUI) Operation 5-1
World Class 3000
SECTION 5
GENERAL USER INTERFACE (GUI) OPERATION
5-1 OVERVIEW
Ensure that the oxygen analyzer, heater power
supply, and intelligent field transmitter have
been properly connected. It is important to
check that grounding and screening of termina-
tions are correctly made to prevent the introduc-
tion of ground loops. The IFT is equipped with
noise suppression circuitry on the power supply
and signal input lines. Proper grounding at in-
stallation will ensure accuracy of function.
The following five languages are can be se-
lected within the IFT:
English Italian
French Spanish
German
NOTE
Support the keypad with the free hand
to prevent bounce back of the IFT
door.
a. Intelligent Field Transmitter (IFT)
The Intelligent Field Transmitter may be
supplied with either of two configurations.
These are the blind version and the deluxe
version. The two versions differ as follows:
1. Blind Version. The blind version has
no display and no keypad. With this
version an external HART communica-
tions device is required.
2. Deluxe Version (GUI). The deluxe
version is also known as the General
User Interface (GUI) version. This IFT
contains an LED display, liquid crystal
display panel, and an eight-key pad
from which the probe and electronics
can be configured, calibrated and
troubleshooted.
b. HART Communicator Interface Devices
The HART communications protocol can
interface with any of the above IFT ver-
sions. To interface a HART communicator
with an IFT, one of three interface devices
is required. The interface devices are as
follows:
1. Rosemount Model 275 Handheld
Communicator. The handheld com-
municator requires Device Descriptor
(DD) software specific to the World
Class 3000 product. The DD software
will be supplied with many model 275
units, but can also be programmed into
existing units at most Fisher-
Rosemount service offices.
2. Personal Computer (PC). The use of a
personal computer requires Corner-
stone software with Module Library
(ModLib) specific to the World Class
3000 product.
3. Selected Distributed Control Systems.
The use of distributed control systems
requires input/output (I/O) hardware
and software which permit HART
communications.
This section of the manual deals with op-
erator controls and displays available with
the GUI equipped IFT. Operating parame-
ters are listed and instructions are included
for viewing and changing them.
Any procedures not associated with normal
operation are included in Section 2, Instal-
lation, or Section 5, Troubleshooting.
5
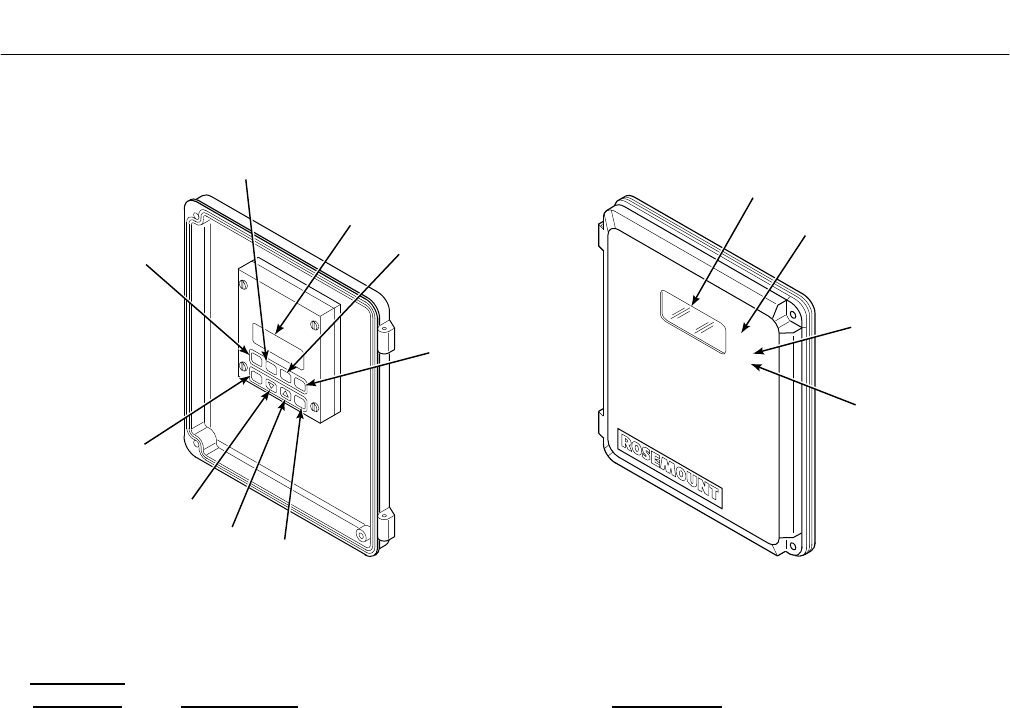
Instruction Manual
IB-106-300NH Rev. 4.2
July 2002
5-2 General User Interface (GUI) Operation Rosemount Analytical Inc. A Division of Emerson Process Management
World Class 3000
5-2 DELUXE VERSION IFT DISPLAYS AND CONTROLS
ENTER
ESC
DATA CALSETUP
HELP
1
2
3
4
5
6
7
8
9
INTERNAL VIEW
CAL
TGH
TGL
10
11
12
13
21190003EXTERNAL VIEW
IFT COVER DOOR
SHOWN FOR
REFERENCE.
NOTE:
Figure 5-1. Deluxe Version IFT Displays and Controls
Figure 5-1
Index No. Control/LED Description
1 LCD Display Top line displays system status, menu, and probe number.
2 HELP Context sensitive HELP is displayed when this key is pressed.
3 DATA DATA key is used to access DATA menu.
4 CAL CAL key used to access CALIBRATE menu.
5 SETUP SETUP key used to access SETUP menu.
6 ESC The escape key is used to exit to a high level menu or to abort a
parameter change.
7∨The decrease key is used to move the cursor (asterisk) when scrolling
through lists or to decrease a parameter value.
8∧The increase key is used to move the cursor (asterisk) when scrolling
through lists or to increase a parameter value.
9 ENTER The ENTER key is used to select a lower level menu, initiate calibra-
tion, or select a parameter to change.
10 LED Display Indicates current O2 or calibration gas value.
11 CAL Calibration in progress indicator light.
12 TGH High calibration gas indicator light. High calibration gas is being used in
calibration process.
13 TGL Low calibration gas indicator light. Low calibration gas is being used in
calibration process.

Instruction Manual
IB-106-300NH Rev. 4.2
July 2002
Rosemount Analytical Inc. A Division of Emerson Process Management General User Interface (GUI) Operation 5-3
World Class 3000
Table 5-1. Sample HELP Messages
MENU, SUB-MENU, HELP
OR PARAMETER NAME MESSAGE
PROBE DATA Press ENTER key to access DATA menu.
CALIBRATE O2The CAL menu is used to start calibration and view calibration.
SETUP The SETUP menu is used to configure the IFT 3000.
5-3 HELP KEY
The HELP key will display explanatory informa-
tion about a menu, sub-menu, or parameter that
the asterisk is next to when pressed. The HELP
key is not available during calibration routines.
Refer to Table 4-1 for sample HELP messages.
5-4 STATUS LINE
The top line of the LCD display (1, Figure 5-1) is
a status line that always displays system status,
menu name, and O2 level. System status dis-
plays will be displayed one at a time in priority
sequence, as follows:
a. Off - The probe has been turned off be-
cause the IFT cannot control the heater
temperature.
b. PrbEr - The probe is disconnected, cold, or
leads are reversed.
c. HtrEr - Heater error.
d. InCAL - Calibration in progress.
e. Low O2 - O2 value is below the low alarm
limit.
f. HiO2 - O2 value is above the high alarm
limit.
g. NoGas - Calibration gas pressure is low.
h. CalEr - Calibration error.
i. ResHi - Resistance is above the high limit.
j. OK - System is functioning correctly.
5-5 QUICK REFERENCE CHART
The quick reference chart (Figure 5-2) is de-
signed to help you get where you want to be in
the menu system. The chart shows all the avail-
able menu and sub-menu options for the IFT.
Follow the lines to determine which menu
choices to make. Moving down a level on the
chart is accomplished by the use of the ENTER
key. To move up a level on the chart, press the
ESCAPE key.
5-6 MAIN MENU
When power is first applied to the IFT, the MAIN
menu (Table 5-2) is initially displayed. It is from
the MAIN menu that the PROBE DATA (Table
5-3), CALIBRATE O2 (Table 5-4), and SETUP
(Table 5-5) menus can be accessed.
Table 5-2. MAIN menu
MENU SELECTION DESCRIPTION
PROBE DATA Refer to Table 5-3.
CALIBRATE O2Refer to Table 5-4.
SETUP Refer to Table 5-5.
5-7 PROBE DATA SUB-MENU
The PROBE DATA sub-menu is a list of all the
parameters of the system as it is currently
configured. To access the PROBE DATA
sub-menu, press the DATA key at any time. The
increase and decrease keys are used to scroll
through the list. The PROBE DATA sub-menu
can be viewed but not changed. The operator
must use the SETUP menu to change any of
the parameters.
There are two selections available on the
PROBE DATA sub-menu; Process Data and
Diagnostic Data. Refer to Table 5-3 for contents
of the sub-menu.
5

Instruction Manual
IB-106-300NH Rev. 4.2
July 2002
5-4 General User Interface (GUI) Operation Rosemount Analytical Inc. A Division of Emerson Process Management
World Class 3000
5-8 CALIBRATE O2 SUB-MENU
The CALIBRATE O2 sub-menu (Table 5-4) is
used to enter the calibration mode. To access
the CALIBRATE O2 sub-menu, press the CAL
key at any time. The increase and decrease
keys are used to scroll through the list.
The CALIBRATE O2 sub-menu has three se-
lections available: Perform Calibration, View
Constants, and Calibration Status. Refer to
Table 5-4 for contents of the sub-menus.
Perform Calibration has two options depending
on how Auto Cal is selected in Probe Setup.
Refer to SETUP Setting in Table 5-4.
For information on performing a calibration, re-
fer to Section 4, Calibration.
5-9 SETUP SUB-MENU
The SETUP sub-menu is used to enter all op-
erator set variables into the system. To access
the SETUP sub-menu press the SETUP key at
any time. To select the parameter to be
changed, move the cursor to the desired pa-
rameter using the arrow keys. Press ENTER to
select that parameter. To change the value for
that parameter, use the arrow keys to increase
or decrease the value. Press ENTER to save
changes.
There are six selections available on the
SETUP sub-menu: Calibration, O2 Calculation,
O2 Alarms, Efficiency Calc., Relay Outputs, and
Analog Outputs. Refer to Table 5-5 for the con-
tents of the SETUP sub-menu, or ESCAPE to
abort changes.
Table 5-3. PROBE DATA Sub-Menu
SUB-MENU
SELECTION PARAMETER DESCRIPTION
Process Data O2__% O2O2 value for the probe.
Efficiency __% Efficiency display.
Stack Temp __DegC Stack temperature.
Diagnostic Data
Temperature Cell __DegC Cell temperature of the probe.
Stack __DegC Stack temperature.
Cold Junct __DegC Cold Junction temperature.
Voltages Cell __mV Cell voltage of the probe.
Cell T/C __mV Cell thermocouple voltage of the probe.
Stk T/C __mV Stack thermocouple voltage.
Cold Jnt __mV Cold junction voltage.
Output Values Analog __% FS Analog output voltage.
K1 State OFF/ON Status of relay 1.
K2 State OFF/ON Status of relay 2.

Instruction Manual
IB-106-300NH Rev. 4.2
July 2002
Rosemount Analytical Inc. A Division of Emerson Process Management General User Interface (GUI) Operation 5-5
World Class 3000
(CONTINUED ON
SHEET 2) 686022
PROBE DATA DIAGNOSTIC
DATA
VOLTAGES
PROCESS DATA
TEMPERATURE
Cell
Stack
Cold Junct
Cell
Cell T/C
Stk T/C
Cold Jnt
OUTPUT
VALUES
Analog
K1 State
K2 State
LATEST
CALIBRATION
Slope
Constant
Resist
PREVIOUS CAL
Slope
Constant
Resist
Next Cal
Slope
Constant
Resist
CALIBRATION
STATUS
CALIBRATE O2 VIEW
CONSTANTS
PERFORM
CALIBRATION
O2
Efficiency
Stack Temp
Figure 5-2. Quick Reference Chart (Sheet 1 of 5)
5

Instruction Manual
IB-106-300NH Rev. 4.2
July 2002
5-6 General User Interface (GUI) Operation Rosemount Analytical Inc. A Division of Emerson Process Management
World Class 3000
(CONTINUED ON
SHEET 3)
(CONTINUED ON
SHEET 3)
(CONTINUED FROM
SHEET 1)
See sheet 4
SLOPE
CONSTANT
SET POINT
RESET SLOPE
AND CONST
34.5 mV/D-
57.5 mV/D
-20.0 mV-
20.0 mV
736 C
843 C
o
o
0.1000% O2-
25.00% O2
0.00% O2-
25.00% O2
ENABLE CALC
K1 VALUE
K2 VALUE
K3 VALUE
Yes
No
0.0000-
1.000
0.0000-
20.00
K1 SETUP
K2 SETUP
EVENT 1
EVENT 2
EVENT 3
EVENT 1
EVENT 2
EVENT 3
Off
In Cal
Hi O2
Lo O2
Htr Fail
Cal Fail
TG Low
Cell Res
High Range
HI ALARM
LO ALARM
ALARM DB
SETUP
CALIBRATION
O2 CALIBRATION
O2 ALARMS
EFFICIENCY
CALC
RELAY OUTPUT
19860023
Figure 5-2. Quick Reference Chart (Sheet 2 of 5)

Instruction Manual
IB-106-300NH Rev. 4.2
July 2002
Rosemount Analytical Inc. A Division of Emerson Process Management General User Interface (GUI) Operation 5-7
World Class 3000
(CONTINUED FROM
SHEET 2)
SETUP
(CONTINUED FROM
SHEET 2)
ANALOG
OUTPUTS
SOURCE
AOUT TYPE
RANGE SETUP
O2
Efficiency
Dual Rng O2
HART 4-20 mA
0-20 mA
0-10 V
See sheet 5
USA
GBR
FRA
ESP
GER
COUNTRY
27270004
Figure 5-2. Quick Reference Chart (Sheet 3 of 5)
5

Instruction Manual
IB-106-300NH Rev. 4.2
July 2002
5-8 General User Interface (GUI) Operation Rosemount Analytical Inc. A Division of Emerson Process Management
World Class 3000
(CONTINUED FROM
SHEET 2)
CALIBRATION
HIGH GAS
LOW GAS
AUTO CAL
OUTPUT TRACKS
CAL INTRVL
NEXT CAL
GAS TIME
PURGE TIME
RES ALARM
0.1000% O2
25.00% O2
0.1000% O2
25.00% O2
Yes
No
Yes
No
Off,
1H -
365 D OH
(1 hour to 365 days
and no hours)
(1 hour to 365 days
and no hours)
Disabled,
1H -
365 D OH
00:30 -
20:00
00:30 -
20:00
50 -
10000
Ω
Ω
16860025
Figure 5-2. Quick Reference Chart (Sheet 4 of 5)

Instruction Manual
IB-106-300NH Rev. 4.2
July 2002
Rosemount Analytical Inc. A Division of Emerson Process Management General User Interface (GUI) Operation 5-9
World Class 3000
(CONTINUED FROM
SHEET 3)
RANGE SETUP
Log
LIN
Log
LIN
HIGH END
LOW END
0.000% O2
25.00% O2
0.000% O2
25.00% O2
0.000% O2
25.00% O2
0.000% O2
25.00% O2
0.000% O2
25.00% O2
0.000% O2
25.00% O2
0.000% O2
25.00% O2
Range Setup
(Source not set to:
Dual Rng O2)
Range Setup
(Source not set to:
Dual Rng O2) NORMAL RANGE
VALUES
HIGH END
HIGH END
LOW END
LOW END
XFER FNCT
XFER FNCT
RANGE VALUES
DUAL RANGE
SETUP
MODE SETUP
HIGH RANGE
VALUES
RANGE MODE
HIGH IN CAL
SWITCHES AT
Normal
Auto
High
Yes
No
16860026
Figure 5-2. Quick Reference Chart (Sheet 5 of 5)
5

Instruction Manual
IB-106-300NH Rev. 4.2
July 2002
5-10 General User Interface (GUI) Operation Rosemount Analytical Inc. A Division of Emerson Process Management
World Class 3000
Table 5-4. CALIBRATE O2 Sub-Menu
SUB-MENU
SELECTION
SETUP SETTING
(SEE TABLE 3-5) DISPLAY DESCRIPTION
Perform
Calibration
Auto Cal in Probe
Setup is YES
Press ENTER to start Auto
Calibration.
MPS will start calibrating probe.
Starting Automatic Calibration
High Gas _____% O2
Time Left 0:00
Value for high O2 calibration gas.
Amount of time necessary to com-
plete the current testing phase in
min:sec.
Cell mV ______mV Cell voltage of the probe.
Low Gas _____% O2
Time Left 0:00
Value for low O2 calibration gas.
Amount of time necessary to com-
plete the current testing phase in
min:sec.
Cell mV ______mV Cell voltage of the probe.
Resistance Check
Time Left 0:00
Resistance check in progress.
Cell _____mV _____C
Calibration Complete
Purging 0:00
Cell voltage and probe temperature.
Gas lines are being purged of cali-
bration gas.
Cell _____mV _____C
Calibration Complete
Cell voltage and probe temperature.
Auto Cal in Probe
Setup is NO.
Press ENTER to start Manual
Calibration.
Manual calibration sequence will
begin when ENTER is pressed.
Switch ON high calibration gas.
Press ENTER when ready.
High gas ______% O2High O2 calibration gas value.
Press ENTER when O2 reading
is stable.
Turn OFF high calibration gas
and ON low calibration gas.
Press ENTER when ready.
Low gas ______% O2Low O2 calibration gas value.
Press ENTER when O2 reading
is stable.
Resistance Check. Resistance check in progress.
Turn off low calibration gas.
Press ENTER when ready.
Press ENTER when probe has
returned to process.

Instruction Manual
IB-106-300NH Rev. 4.2
July 2002
Rosemount Analytical Inc. A Division of Emerson Process Management General User Interface (GUI) Operation 5-11
World Class 3000
Table 5-4. CALIBRATE O2 Sub-Menu (continued)
SUB-MENU
SELECTION
SETUP SETTING
(SEE TABLE 3-5) DISPLAY DESCRIPTION
View
Constants
Latest
Calibration
Slope _____mV/D
Constant _____mV
Resist _____ohms
Slope for probe from latest calibration.
Latest calibration offset for probe.
Latest calibration resistance of probe.
Previous
Calibration
Slope _____mV/D
Constant _____mV
Resist _____ohms
Slope for probe from previous calibration.
Previous calibration offset for probe.
Previous calibration resistance of probe.
Calibration
Status
N/A Next Cal XD XH Time until next calibration in number of
days and number of hours.
Slope _____
Constant _____
Resist _____
Status of the slope.
Status of the offset.
Status of the resistance.
5

Instruction Manual
IB-106-300NH Rev. 4.2
July 2002
5-12 General User Interface (GUI) Operation Rosemount Analytical Inc. A Division of Emerson Process Management
World Class 3000
Table 5-5. SETUP Sub-Menu
SUB-MENU
SELECTION PARAMETERS DESCRIPTION
Calibration High Gas ____% O2Value of high O2 calibration gas (0.1000% - 25.00%
O2).
Low Gas ____% O2Value of low O2 calibration gas (0.1000% - 25.00%
O2).
Auto Cal YES/NO MPS required for Auto Cal.
Output Tracks YES/NO NO, locks output during calibration.
Cal Intrvl XD XH Select time between calibrations in number of days
and hours (1 year max).
Next Cal XH Time until next calibration in number of hours
(1 year max).
Gas Time 0:30 - 20:00 Amount of time calibration gases will be turned on in
number of minutes and seconds; allow enough time
for signal values to stabilize.
Purge Time 0:30 - 20:00 Amount of time for gas lines to clear of calibration
gas.
Res Alarm 50 W – 10 kW Resistance alarm set from 50 to 10,000 ohms.
O2 Calculation Slope ____ mV/D
Constant ____ mV
Set Point ____°C
Set value between 34.5 and 57.5.
Set value between -20.0 and +20.0 mV.
Set either 736 for World Class 3000 probes or 843
for 218 probes.
Ensure the correct voltage is selected when using HPS 3000 with either World
Class 3000 probes or 218 probes. Refer to Figure 2-15, Jumper Selection Label
for proper voltage selections. If incorrect SET POINT is selected, damage to
the probe may occur.
Reset slope and constants. Press ENTER to reset slope and constants to values
from the latest successful calibration.
O2 Alarms Hi Alarm ____% O2
Lo Alarm ____% O2
Alarm DB ____% O2
Set value for high alarm limit (0.1000% - 25.00%).
Set value for low alarm limit (0.1000% - 25.00%).
Set value for alarm dead band (0.0000% - 25.00%).
Efficiency Calc. Enable Calc. YES/NO
K1 Value _______
K2 Value _______
K3 Value _______
Select YES to enable, NO to disable.
Set between 0.0000 and 1.000. Refer to Table 5-6.
Set between 0.0000 and 1.000. Refer to Table 5-6.
Set between 1.000 and 20.00. Refer to Table 5-6.

Instruction Manual
IB-106-300NH Rev. 4.2
July 2002
Rosemount Analytical Inc. A Division of Emerson Process Management General User Interface (GUI) Operation 5-13
World Class 3000
Table 5-5. SETUP Sub-Menu (continued)
SUB-MENU
SELECTION PARAMETERS DESCRIPTION
Relay
Outputs
NOTE
K1 and K2 relay outputs can be configured for "OFF" or any one of the eight
events listed below. Up to three events can control each relay output. Events are
selected in the SETUP sub-menu.
K1 Setup
K2 Setup
-Off
Event 1 1. In Cal
Event 2 2. Hi O2
Event 3 3. Lo O2
Event 1 4. Htr Fail
Event 2 5. Cal Fail
Event 3 6. TG Low
7. Cell Res
8. High Range
No effect.
Probe goes into calibration status.
Output exceeds high end alarm limit.
Output goes below low alarm limit.
Probe heater fault occurs.
Probe failed last calibration.
Calibration gas pressure gets too low.
Probe resistance exceeds high limit.
High analog output range is selected.
Analog
Output
SOURCE O2
Efficiency
Dual Rng O2
Select the measurement value to be represented on
the analog output.
AOUT TYPE
HART 4-20mA
0-20mA
0-10V
Select one of the listed options to define upper and
lower limits of probe analog output. Only a selection
that matches the position of the analog output selector
switch on the microprocessor board (Figure 2-9) will
be accepted. The defined limits correspond to the
upper-lower %O2 values defined in the Range Setup
menu.
RANGE SETUP
(Source not set to Dual Rng O2)
Xfer Fnct Log
Lin
Select the transfer function used on the analog output.
Selecting Log will not effect the output when Efficiency
is selected as the Source.
Range Values
High End
0.000% O2 - 25.00% O2
Low End
0.000% O2 - 25.00% O2
Enter the upper and lower analog output range values.
The High End value defines the measured O2 value
corresponding to the high analog output value, i.e.,
20mA or 10V, and the Low End value corresponds to
the low analog output value, i.e., 0mA, 4mA, or 0V.
5

Instruction Manual
IB-106-300NH Rev. 4.2
July 2002
5-14 General User Interface (GUI) Operation Rosemount Analytical Inc. A Division of Emerson Process Management
World Class 3000
Table 5-5. SETUP Sub-Menu (continued)
SUB-MENU
SELECTION PARAMETERS DESCRIPTION
Analog Output RANGE SETUP
(continued) (Source set to Dual Rng O2)
Xfer Fnct Log
Lin
Select the transfer function used on the analog output.
Selecting Log will not effect the output when Efficiency
is selected as the Source.
Normal Range Values
High End
0.000% O2 - 25.00% O2
Low End
0.000% O2 - 25.00% O2
Enter the upper and lower analog output range values
for Normal Operating Range. The High End value de-
fines the measured O2 value corresponding to the high
analog output value, i.e, 20mA or 10V, and the Low
End value corresponds to the low analog output value,
i.e., 0mA, 4mA, or 0V.
Dual Range Setup
Mode Setup
Range Mode Normal Forces the output to the Normal Range.
Auto Allows the IFT to select either the High Range or the
Normal Range based on the present O2 value and the
Mode Setup Values.
High Forces the output to the High Range.
High in Cal Yes/No Selecting Yes will cause the High Range to be used
whenever the probe is being calibrated.
Switches at
0.000% O2 - 25.00% O2
Enters the switching point between the High and Nor-
mal Ranges. O2 values above this point will use the
High Range and values below this point will use the
Normal Range. The O2 value must be below the switch
point by 10% (of the "Switches at" value) to cause a
switch from High to Normal Range.
High Range Values
High End
0.000% O2 - 25.00% O2
Low End
0.000% O2 - 25.00% O2
Enter the upper and lower analog output range values
for High Operating Range. The High End value defines
the measured O2 value corresponding to the high
analog output value, i.e., 20mA or 10V, and the Low
End value corresponds to the low analog output value,
i.e., 0mA, 4mA, or 0V.
NOTE: Relay output can be initiated upon range change. (See page 5-12 of Table 5-5.)
Table 5-6. Efficiency Constants
UNITED STATES EUROPE
CONSTANT GAS OIL GAS OIL
K1 0.407 0.432 0.66 0.69
K2 0.0 0.0 0.0082 0.0051
K3 5.12 5.12 12.28 8.74

Instruction Manual
IB-106-300NH Rev. 4.2
July 2002
Rosemount Analytical Inc. A Division of Emerson Process Management Troubleshooting 6-1
World Class 3000
SECTION 6
TROUBLESHOOTING
6-1 OVERVIEW
The system troubleshooting describes how to
identify and isolate faults which may develop in
the Oxygen Analyzer System. Refer to Probe,
IFT, HPS, MPS, and HART Communicator
appendices.
Install all protective equipment covers
and safety ground leads after trouble-
shooting. Failure to replace covers
and ground leads could result in seri-
ous injury or death.
6-2 SPECIAL TROUBLESHOOTING NOTES
a. Grounding
It is essential that adequate grounding pre-
cautions are taken when the system is be-
ing installed. A very thorough check must
be made at both the probe and electronics
to ensure that the grounding quality has not
degraded during fault finding. The system
provides facilities for 100% effective
grounding and the total elimination of
ground loops.
b. Electrical Noise
The IFT has been designed to operate in
the type of environment normally found in a
boiler room or control room. Noise suppres-
sion circuits are employed on all field termi-
nations and main inputs. When fault finding,
the electrical noise being generated in the
immediate circuitry of a faulty system should
be evaluated. All cable shields must be
connected to earth.
c. Loose Integrated Circuits
The IFT uses a microprocessor and sup-
porting integrated circuits. Should the elec-
tronics unit receive rough handling during
installation in a location where it is sub-
jected to severe vibration, an Integrated
Circuit (IC) could work loose. The fault find-
ing guides in paragraph 6-3 and Table E-2
in Appendix E, show the resulting variety of
failure modes. It is recommended that all
IC's be confirmed to be fully seated before
troubleshooting on the system begins.
d. Electrostatic Discharge
Electrostatic discharge can damage the IC's
used in the electronics unit. It is essential
that the user ensure he/she is at ground
potential before removing or handling the
processor board or the IC's used on it.
6-3 SYSTEM TROUBLESHOOTING
The status line of the GUI equipped IFT will dis-
play one of ten conditions. The system status
displays will be displayed one at a time in prior-
ity sequence, as indicated in Table 6-1.
6

Instruction Manual
IB-106-300NH Rev. 4.2
July 2002
6-2 Troubleshooting Rosemount Analytical Inc. A Division of Emerson Process Management
World Class 3000
Table 6-1. IFT Status Codes
Off Heater power has been turned OFF by the electronics. The display shows 0% O2. Several con-
ditions may cause the OFF status:
1. The cell heater temperature is below -50°C. The thermocouple wires may be reversed.
2. The cell temperature is more than 70°C above the set point. The heater is out of control.
The triac module may have failed.
3. The cell heater thermocouple voltage has remained within +1.5 mV for more that 4 minutes.
The thermocouple may be shorted.
4. The AD590 voltage is below 50.0 mV (50K or -223°C). The AD590 is not connected.
5. The AD590 voltage is above 363 mV (363K or 90°C). If HPS is used with IFT, then IFT in-
terconnect board has JM1 in position connecting two AD590s in parallel.
PrbEr The probe is disconnected or cold, or leads are reversed.
HtrEr There is a fault within the heater system. The heater temperature is more than +25°C from the
set point. When the unit is first turned ON, HtrEr is normal. The heater may take 0.5 to 1.0
hours to warm up.
InCal The system is currently undergoing calibration. If Output Tracks is set to YES, the output will
show changing O2 values. If Output Tracks is set to NO, the output will hold the pre-calibration
value.
LowO2The measured O2 value is below the low O2 alarm limit. The problem may be in the probe or the
process.
HiO2The measured O2 value is above the high O2 alarm limit. The problem may be in the probe or
the process.
NoGas Test gas pressure is too low. Pressure switches are set to trigger this alarm at 12 to 16 psig (83
to 110 kPa gage). Test gas regulators are usually set at 20 to 25 psig (138 to 172 kPa gage).
Possible causes are:
1. At least one test gas pressure switch is open.
2. A test gas cylinder is empty.
3. There is an MPS or piping failure.
4. If MPS is not connected, CALRET and NOGAS signals should be jumpered on the intercon-
nect board.
CalEr An error occurred during the last calibration. The error may be one of the following:
1. The new calculated slope value is outside the range 34.5 to 57.6 mV/decade.
2. The new calculated constant value is outside the range +20.0 to -20.0 mV.
3. The test gas pressure switch opened during calibration.
Ensure that the proper test gases are being used, and that the gas flows are set properly. Refer
to Appendix D for additional MPS troubleshooting information.
ResHi The resistance calculated during the last good calibration was greater than the High Resistance
Alarm limit set in the calibration setup. The resistance limit may be set wrong, or there is a
problem with the probe.
Ok Operation appears to be normal.
(blank
screen)
A possible failure within the IFT. Check the LED on the microprocessor board to help isolate
problems. See IFT Problem in the troubleshooting tables.

Instruction Manual
IB-106-300NH Rev. 4.2
July 2002
Rosemount Analytical Inc. A Division of Emerson Process Management Troubleshooting 6-3
World Class 3000
6-4 HEATER PROBLEM
For all heater troubleshooting, allow at least 30
minutes for the operating temperature to stabi-
lize. After the warmup period, observe the sys-
tem status and the voltages of the cell TC and
the cold junction AD590. For heater related
problems:
a. The status line may read: HtrEr or OFF.
b. The displayed O2 value will read 0%.
c. Cell TC voltages will vary from normal.
These voltages are found by accessing the
proper menu. In the IFT, use the DIAG-
NOSTIC DATA sub-menu of the PROBE
DATA menu.
Refer to Table 6-2 to troubleshoot heater related
problems.
Table 6-2. Heater Troubleshooting
Problem
Cause
Corrective Action
Status is HtrEr or OFF.
Cell TC < 28.4 mV.
Cold Junction 273 to 330 mV (normal).
O2 Display = 0%
1. Blown fuse or faulty wiring.
Check all fuses and wiring for continuity and repair as needed. Verify that input power
jumpers are installed correctly. Check jumpers for proper configuration in IFT and HPS if used.
2. Heater failure.
In HPS with power OFF, check heater resistance at J2, terminals R/H. For 44 V heater, resis-
tance should be 11 to 14 ohms. For 115 V heater, resistance should be 67 to 77 ohms. Check
wiring, and replace heater if needed. Heater resistance can also be checked at the probe junc-
tion box:
• 44 V heater: terminals 7 and 8 should measure 11 to 14 ohms.
• 115 V heater: terminals 5 and 6 should measure 67 to 77 ohms. (Terminals 6 to 7 and 6 to
8 should be open circuits.)
3. Triac open.
Check the triac. Repair as needed.
4. Electronics failure.
First check and repair all related wiring. Check and repair electronics as needed.
5. Missing insulation around heater.
Check that insulation is in place and undamaged. Repair or replace insulation as needed.
6

Instruction Manual
IB-106-300NH Rev. 4.2
July 2002
6-4 Troubleshooting Rosemount Analytical Inc. A Division of Emerson Process Management
World Class 3000
Table 6-2. Heater Troubleshooting (continued)
Problem
Cause
Corrective Action
Status is HtrEr or OFF.
Cell TC > 28.4 mV.
Cold Junction 273 to 330 mV (normal).
O2 Display = 0%
1. Triac failure.
Check the triac. Repair as needed.
2. Wrong TC set point.
Check electronics manual and verify the set point; typically 1356°F (736°C).
3. Wrong heater voltage selected. HPS voltage jumpers setup wrong.
For 44 V heater, make sure JM7 is installed and JM8 is removed. For 115 V heater, JM7 is
removed and JM8 is installed. The 115 V heater has an identifying stainless steel tag attached
in the junction box.
Status is HtrEr or OFF.
Cell TC < 28.4 mV.
Cold Junction < 273 mV.
O2 Display = 0%
1. Wiring error, thermocouple wires reversed.
Verify TC wiring at junction box terminal and electronics. The yellow chromel line connects to
terminal 3. The red alumel line connects to terminal 4. Trace line through the HPS (if used)
and the electronics. Reverse wires if needed.
2. Faulty thermocouple. At a cold junction reference of 77°F (25°C), the probe TC should read about
29.3 mV.
Replace faulty thermocouple.
3. Faulty AD590. At normal ambient temperatures, cold junction sensor should be 273 to 330 mV.
Replace faulty sensor.
Status is HtrEr or OFF.
Cell TC = -40 mV.
Cold Junction 273 to 330 mV (normal).
O2 Display = 0%
1. Faulty thermocouple connection or open.
Verify TC wiring at junction box terminal and electronics. The yellow chromel line connects to
terminal 3. The red alumel line connects to terminal 4. Trace line through the HPS (if used)
and the electronics. Repair connection or wiring as needed.
2. Thermocouple fault. At a cold junction reference of 77°F (25°C), the probe TC should read about
29.3 mV.
Replace faulty thermocouple.

Instruction Manual
IB-106-300NH Rev. 4.2
July 2002
Rosemount Analytical Inc. A Division of Emerson Process Management Troubleshooting 6-5
World Class 3000
6-5 CELL PROBLEM
For cell troubleshooting, as in heater problems,
you should allow at least 30 minutes for operat-
ing temperature to stabilize. After this warmup
period, observe the system status and cell volt-
age. If the heater is working, troubleshoot the
cell. If the heater is not working, refer to Heater
Problem, paragraph 6-4.
• The status line may read: Low O2, Hi O2,
CalEr, ResHi.
• Access voltage values in the proper menu.
Use the DIAGNOSTIC DATA sub-menu of
the PROBE DATA menu.
• The displayed O2 value will read 0% to
99%.
• It may be helpful to observe the calibration
status and parameters from the last calibra-
tion: Slope, Constant, and Cell Resistance.
In the CALIBRATE menu, VIEW CON-
STANTS shows previous calibration values,
and CALIBRATION STATUS shows the
latest values. If these values appear out of
range, perform a calibration before trouble-
shooting the cell.
Refer to Table 6-3 to troubleshoot cell related
problems.
Table 6-3. Cell Troubleshooting
Problem
Cause
Corrective Action
Status is LowO2.
Cell mV = -127 mV.
1. Faulty cell connection or open. If the cell circuit is open, the cell output will show about -127 mV.
Check cable connection between the probe and the electronics. Check that the probe spring
presses the contact pad firmly onto the cell. Repair or replace faulty wires, spring, or connectors.
2. Electronics fault. Cell output is good, and the input to the electronics is good.
Check the electronics package. In an IFT, replace the microprocessor or interface board as
needed. In a CRE, replace the DPI board if needed.
Status is ResHi or CalEr.
Cell mV = -20 to 120 mV (normal).
1. Test gas flow not 5 scfh (2.4 L/min).
Check test gas flow and related piping. Rotameter should show 5 scfh. Adjust needle valve for
correct flow rate.
2. Incorrect test gas.
Confirm labels on test gas bottles are correct. Confirm High Gas and Low Gas values agree with
labels on test gas bottles. (Refer to menu map — SETUP-CALIBRATION, High Gas, Low Gas.)
Check all ports, cylinders, and gas lines for proper hookup. Change piping if necessary. Label
pipes for reference.
6

Instruction Manual
IB-106-300NH Rev. 4.2
July 2002
6-6 Troubleshooting Rosemount Analytical Inc. A Division of Emerson Process Management
World Class 3000
Table 6-3. Cell Troubleshooting (continued)
Problem
Cause
Corrective Action
Status is ResHi or CalEr.
Cell mV = -20 to 120 mV (normal) (continued).
1. Reference air contamination (oil/water).
Clean or replace lines and valves as needed.
2. Cell leads reversed.
Check cell signal wiring from probe junction box to electronics, and correct wiring if needed.
3. Reference/test gas lines reversed.
Switch piping as needed.
4. Diffusion element fault. Diffusion element cracked, broken, missing, or plugged.
Replace diffusor or snubber as needed. Diffusors are disposable because it is difficult to clean a
diffusor and know the tiny pores are open. A flow and pressure test with a manometer is possi-
ble but usually not practical. To clean a snubber, blow off surface dirt with pressurized air and
clean the unit in an ultrasonic bath.
5. Faulty cell. Low sensor cell output when test gas is applied.
If test gas flow is good and there is low cell signal, replace the cell, or call the SCAN line for
assistance.
Typical cell output:
Test Gas mV
8.0% 18 to 25
0.4% 76 to 86
6. Cell performance degraded from aging.
Replace the sensor cell if its resistance has increased beyond 1 kOhm and the slope calculated
during calibration has decreased lower than 40 mV/decade.
7. Electronics fault. Cell output is good, and the input to the electronics is good.
Check the electronics package. In an IFT, replace the microprocessor or interface board as
needed. In a CRE, replace the DPI board if needed.
Status is Res Hi.
Cell mV = -120 to 20 mV.
1. Cell leads reversed.
Check cell signal wiring from probe junction box to electronics, and correct wiring if needed.
2. Reference/test gas lines reversed.
Switch piping as needed.
3. Reference air (nitrogen).
Confirm labels on test gas bottles are correct. 100% nitrogen must NOT be used as a zero gas
because cell protection will engage and affect the O2 reading. Reference air should be clean, dry
instrument air prepared from ambient air with 20.95% O2.

Instruction Manual
IB-106-300NH Rev. 4.2
July 2002
Rosemount Analytical Inc. A Division of Emerson Process Management Troubleshooting 6-7
World Class 3000
6-6 IFT PROBLEM
When an IFT problem is suspected, look at the
LED on the microprocessor board. The LED
may be OFF, ON, or flashing.
Refer to Table 6-4 to troubleshoot IFT related
problems.
Table 6-4. IFT Troubleshooting
Problem
Cause
Corrective Action
IFT LED is OFF. IFT failure.
Fuse fault.
Check fuses on power supply board. Replace fuses as needed.
1. Power fault.
Check line voltage. Correct or turn main power ON.
2. Power supply fault.
Check voltage test points on the microprocessor board. Replace power supply board if needed.
3. Microprocessor board fault.
Replace microprocessor board.
IFT LED is steady ON. Heater or cell wiring problem.
1. Faulty wiring.
Check thermocouple and heater wires and connections for continuity. Repair as needed.
2. Jumpers set up wrong. JM1 on interconnect board, JM6 on microprocessor board, or JM9 and JM10
on power supply board are configured incorrectly.
Check that jumpers are set up as follows:
• Without an HPS, JM1 and JM6 should be installed.
• With a 115 V probe heater, JM9 is installed.
• With a 44 V probe heater, JM10 is installed.
3. Status line is “OFF”.
Turn OFF IFT power and restart. If light stays ON and both wiring and jumpers are OK, then re-
place the microprocessor board.
Faulty GUI or LDP (IFT LED is Flashing).
1. Microprocessor is normal, but front panel indicators are not working properly.
Check connections to GUI or LDP, and repair or replace as needed.
6

Instruction Manual
IB-106-300NH Rev. 4.2
July 2002
6-8 Troubleshooting Rosemount Analytical Inc. A Division of Emerson Process Management
World Class 3000
6-7 MPS PROBLEM
MPS problems can occur with a status of C Err,
R Hi, TGLow. The O2 reading can be 0% to
99%, and probe data will be in the normal
ranges. Consider two conditions, A and B.
Refer to Table 6-5 to troubleshoot problems with
the MPS.
Table 6-5. MPS Troubleshooting
Problem
Cause
Corrective Action
Status is NoGas.
Cell mV is between -20 to 120 mV.
1. Regulator or plumbing fault. The test gas pressure is low for the indicated probe [20 to 25 psig (138 to
172 kPa gage)].
Check test gas pressure [should be 20 psig (138 kPa gage)], regulator, and lines. Reset, repair,
or replace the regulator as needed. If only one probe has low flow [less than 5 scfh (2.4 L/min)],
check lines, needle valve, connectors, and MPS solenoid for that probe.
2. Test gas low.
Replace empty test gas cylinder with full cylinder. Verify O2 concentration.
3. Wiring fault.
Confirm proper wiring and continuity between MPS and electronics. Repair as needed.
4. Pressure switch fault.
Pressure switch is factory set at 16 psig (68.9 kPa gage). Set test gas regulator pressure to 20
psig (138 kPa gage) to avoid nuisance alarms. Replace faulty switch with a new one if test gas
supply is good.
Status is ResHi or CalEr.
Cell mV is between -20 to 120 mV.
The CalEr occurs when the slope calculated from the last calibration was out of range. CalEr can be
caused by leaks, a faulty diffusor or sensor cell, erroneous test gas values, or not enough test gas time.
Each test gas should be supplied for at least three minutes.
1. Flowmeter set incorrectly.
The flowmeter for each probe must be set individually. Flow should be 5 scfh (2.4 L/min).
2. Wiring fault.
Confirm proper wiring and continuity between MPS and electronics.
3. Piping fault. Faulty gas line or regulator.
Check gas line, valves, and regulators for blockage or corrosion. Repair or replace as needed.
4. Solenoid fault.
Verify nominal 24 VDC at HI GAS, LOW GAS, IN CAL, and CAL RET connections. Voltages
should drop to about 4 VDC. If voltage is present but solenoid does not work, replace the
solenoid.
5. Termination board fault.
Verify 24 VDC at J11 on termination board. Repair or replace termination board or connectors as
needed.
6. Power supply fault.
Verify power supply fuses and output are good and that line voltage is present at J1. Repair or
replace the power supply as needed.
7. Power fault.
Check fuses, mains, and circuit breakers. Repair or replace as needed.

Instruction Manual
IB-106-300NH Rev. 4.2
July 2002
Rosemount Analytical Inc. A Division of Emerson Process Management Troubleshooting 6-9
World Class 3000
6-8 PERFORMANCE PROBLEM (PROCESS
RESPONSE IS SUSPECT)
O2 readings may not always agree with known
process conditions. Such a discrepancy can be
the first sign of a problem either in the process
or the World Class 3000. The O2 display will
read between 0 to 99%, but the reading may be
unstable. The status line may read OK, and
PROBE DATA voltages may read normal.
Refer to Table 6-6 to troubleshoot performance
problems.
Table 6-6. Performance Problem Troubleshooting
Problem
Cause
Corrective Action
Status is OK.
Cell mV is -20 to 120 mV (normal).
O2 display is stable but not expected value.
Such a condition occurs during various kinds of leaks and data output faults.
1. Mounting flange leak.
Reseal the flange, and tighten bolts properly.
2. Test gas line leak.
Since the test gas line is under positive pressure, the line can be tested with a bubbling liquid
such as SNOOPTM. Repair or replace as needed.
3. Silicon hose break. Leaks may occur in the silicon rubber hose in the probe junction box.
Replace hose.
4. Air ingress from leaky duct.
Check condition of duct, gas lines, and fittings. If duct has air ingress upstream of probe, re-site
the probe or fix the leak.
5. Analog output or recorder fault.
Measure analog output in voltage or milliamps as set up on the analog output board and soft-
ware. If analog output is not in range, replace the analog output board in a CRE or the micro-
processor board in an IFT. Check recorder function, and repair as needed.
6. Random spiking of the analog output to 0 mA dc.
Check the power supply voltage. If suspect, replace the power supply in the CRE or the power
supply board in the IFT.
Status is OK.
Cell mV is -20 to 120 mV (normal).
O2 display is unstable.
1. Process variations.
Analyze the process for even flows of gases or materials. Check the operation of dampers and
control valves. Repair process devices, procedures, and flows as needed. Depending on the
process, some variation may be normal.
2. Pad to cell connection fault.
Check pad and contact for cleanliness, and clean as needed. Check spring tension, and replace
as needed.
3. Grounding fault.
Check all wiring for continuity and connections for cleanliness and lack of corrosion. Repair as
needed.
4. Improper line voltage.
Check line voltage circuit for proper polarity and/or "hot" and "neutral" circuitry.
6

Instruction Manual
IB-106-300NH Rev. 4.2
July 2002
6-10 Troubleshooting Rosemount Analytical Inc. A Division of Emerson Process Management
World Class 3000

Instruction Manual
IB-106-300NH Rev. 4.2
July 2002
Rosemount Analytical Inc. A Division of Emerson Process Management Return of Material 7-1
World Class 3000
SECTION 7
RETURN OF MATERIAL
7-1 If factory repair of defective equipment is re-
quired, proceed as follows:
a. Secure a return authorization number from
a Rosemount Analytical Sales Office or rep-
resentative before returning the equipment.
Equipment must be returned with complete
identification in accordance with Rosemount
instructions or it will not be accepted.
In no event will Rosemount be responsible
for equipment returned without proper
authorization and identification.
b. Carefully pack defective unit in a sturdy box
with sufficient shock absorbing material to
insure that no additional damage will occur
during shipping.
c. In a cover letter, describe completely:
1. The symptoms from which it was de-
termined that the equipment is faulty.
2. The environment in which the equip-
ment has been operating (housing,
weather, vibration, dust, etc.).
3. Site from which equipment was
removed.
4. Whether warranty or nonwarranty
service is requested.
5. Complete shipping instructions for re-
turn of equipment.
6. Reference the return authorization
number.
d. Enclose a cover letter and purchase order
and ship the defective equipment according
to instructions provided in Rosemount Re-
turn Authorization, prepaid, to:
Rosemount Analytical Inc.
RMR Department
1201 N. Main Street
Orrville, Ohio 44667
If warranty service is requested, the defec-
tive unit will be carefully inspected and
tested at the factory. If failure was due to
conditions listed in the standard Rosemount
warranty, the defective unit will be repaired
or replaced at Rosemount's option, and an
operating unit will be returned to the cus-
tomer in accordance with shipping instruc-
tions furnished in the cover letter.
For equipment no longer under warranty,
the equipment will be repaired at the factory
and returned as directed by the purchase
order and shipping instructions.
7

Instruction Manual
IB-106-300NH Rev. 4.2
July 2002
7-2 Return of Material Rosemount Analytical Inc. A Division of Emerson Process Management
World Class 3000

Instruction Manual
IB-106-300NH Rev. 4.2
July 2002
Rosemount Analytical Inc. A Division of Emerson Process Management Appendices 8-1
World Class 3000
SECTION 8
APPENDICES
APPENDIX A. WORLD CLASS 3000 OXYGEN ANALYZER (PROBE)
APPENDIX B. HPS 3000 HEATER POWER SUPPLY
APPENDIX D. MPS 3000 MULTIPROBE CALIBRATION GAS SEQUENCER
APPENDIX E. IFT 3000 INTELLIGENT FIELD TRANSMITTER
APPENDIX J. HART COMMUNICATOR MODEL 275D9E IFT 3000 APPLICATIONS
8

Instruction Manual
Appendix A Rev. 3.8
July 2002
A-0 Appendices Rosemount Analytical Inc. A Division of Emerson Process Management
World Class 3000
2
3
NOTE: NOT ALL PARTS SHOWN ARE AVAILABLE FOR
PURCHASE SEPARATELY. FOR LIST OF
AVAILABLE PARTS, SEE TABLE A-3.
29
1
27
28
25
24
26
20
19 17
7
8
15 13
16
18
23
22
10
11
21
20
11
14
12
10
9
4
5
6
NOTE: ITEM , CALIBRATION GAS TUBE,
FITS INTO HOLES WHEN PROBE IS
ASSEMBLED.
21240005
APPENDIX A
1. Heater, Strut, and Backplate Assembly
2. Diffusion Assembly
3. Retainer Screw
4. Cell and Flange
5. Corrugated Seal
6. Probe Tube Assembly
7. Screw
8. Washer
9. Cover Chain Screw
10. Cover Chain
11. Probe Junction Box Cover
12. Cover Gasket
13. Wiring Diagram
14. O-Ring
15. Terminal Block Screws
16. Terminal Block
17. Terminal Block Marker
18. Terminal Block Mounting Plate
19. Probe Junction Box Screws
20. Hose Clamp
21. Hose
22. Gas Connection
23. Seal Cap
24. Label
25. Probe Junction Box
26. Ground Wires
27. Insulating Gasket
28. Washer
29. Screw
Figure A-1. Oxygen Analyzer (Probe) Exploded View

Instruction Manual
Appendix A Rev. 3.8
July 2002
Rosemount Analytical Inc. A Division of Emerson Process Management Appendices A-1
World Class 3000
APPENDIX A, REV. 3.8
WORLD CLASS 3000 OXYGEN ANALYZER (PROBE)
DESCRIPTION
Read the “Safety instructions for the
wiring and installation of this appara-
tus” at the front of this Instruction
Bulletin. Failure to follow the safety
instructions could result in serious
injury or death.
A-1 OXYGEN ANALYZER (PROBE) - GENERAL
The Oxygen Analyzer (Probe), Figure A-1, con-
sists of three component groups: probe exterior,
inner probe, and probe junction box, Figure A-2.
PROBE
EXTERIOR
(SENSING CELL INSTALLED)
PROBE
INTERIOR
PROBE
JUNCTION
BOX
21240006
Figure A-2. Main Probe Components
A

Instruction Manual
Appendix A Rev. 3.8
July 2002
A-2 Appendices Rosemount Analytical Inc. A Division of Emerson Process Management
World Class 3000
Table A-1. Specifications for Oxygen Analyzing Equipment.1, 2
Probe lengths, nominal ..................................................................18 inches (457 mm), 3 feet (0.91 m), 6 feet
(1.83 m), 9 feet (2.74 m), or 12 feet (3.66 m),
depending on duct dimensions
Temperature limits in process
measurement area ............................................................50° to 1300°F (10° to 704°C)
Standard/current output..................................................................4-20 mA dc signal (factory set)
O2 indication (Digital display
and analog output).............................................................0.1% O2 or ±3% of reading, whichever is
greater using Rosemount calibration gases
System speed of response .............................................................less than 3 seconds (amplifier output)
Resolution sensitivity ......................................................................0.01% O2 transmitted signal
HPS 3000 housing..........................................................................NEMA 4X (IP56)
Probe reference air flow .................................................................2 scfh (56.6 L/hr) clean, dry, instrument quality
air (20.95% O2), regulated to 5 psi (34 kPa)
Calibration gas mixtures .................................................................Rosemount Hagan Calibration Gas Kit Part No.
6296A27G01 contains 0.4% O2N2 Nominal and
8% O2N2 Nominal
Calibration gas flow ........................................................................5 scfh (141.6 L/hr)
HPS 3000 Power supply...............................................................100/110/220 ±10% Vac at 50/60 Hz
HPS 3000 Power requirement......................................................200 VA
HPS 3000 Ambient Operating Temperature ................................32° to 120°F (0° to 50°C)
Ambient operating temperature (Probe Junction Box) ...................300°F (150°C) max
Approximate shipping weights:
18 inch (457 mm) package................................................55 pounds (24.97 kg)
3 foot (0.91 m) package.....................................................60 pounds (27.24 kg)
6 foot (1.83 m) package.....................................................65 pounds (29.51 kg)
9 foot (2.74 m) package.....................................................72 pounds (32.66 kg)
12 foot (3.66 m) package...................................................78 pounds (35.38 kg)
1All static performance characteristics are with operating variables constant.
2Equipment ordered utilizing this document as reference will be supplied to the USA standard design. Custom-
ers requiring the EEC standard design should request the EEC documentation and utilize its ordering data.
Temperatures over 1000°F (537°C) may affect the ease of field cell replaceability.

Instruction Manual
Appendix A Rev. 3.8
July 2002
Rosemount Analytical Inc. A Division of Emerson Process Management Appendices A-3
World Class 3000
A-2 PROBE ASSEMBLY EXTERIOR
Primary probe exterior components include a
flange-mounted zirconium oxide cell, mounted
on a tube assembly and protected by a snubber
diffusion assembly.
a. Cell and Flange Assembly
The primary component in the cell and
flange assembly, Figure A-3, is a
yttria-stabilized zirconium oxide cell. It cre-
ates an electrical signal when the oxygen
level on one side is out of balance with the
oxygen level on the other side. This signal
is proportional to the difference in oxygen
levels.
b. Probe Tube Assembly
Four screws secure the cell and flange as-
sembly, Figure A-3, to the probe tube as-
sembly. When in place, the cell is inside the
tube.
The tube assembly includes a flange which
mates with a stack-mounted flange (shown
attached to the probe flange in Figure A-2).
Studs on the stack flange make installation
easy. There is also a tube to carry
calibration gas from the probe junction box
to the process side of the cell during
calibration.
PROBE TUBE
CORRUGATED
SEAL
CELL AND
FLANGE
ASSEMBLY
21240007
Figure A-3. Cell and Tube Assemblies
c. Snubber Diffusion Assembly
The snubber diffusion assembly protects
the cell from heavy particles and isolates
the cell from changes in temperature. The
snubber diffusion assembly threads onto
the cell and flange assembly. Pin spanner
wrenches (probe disassembly kit
3535B42G01) are applied to holes in the
snubber diffusion element hub to remove or
install the snubber diffusion assembly.
An optional ceramic diffusor element and
vee deflector, shown in Figure A-4, is
available. The ceramic diffusor assembly is
also available in a flame arresting version to
keep heat from the cell from igniting flue
gases.
Systems that use an abrasive shield require
a special snubber diffusion assembly with a
hub that is grooved to accept two dust seal
gaskets. This special diffusor is available in
both snubber and ceramic versions. See
Probe Options, section A-6.
DIFFUSION
ELEMENT
VEE
DEFLECTOR
PIN
WRENCH
HUB
21240024
Figure A-4. Optional Ceramic Diffusor and Vee
Deflector Assembly
A

Instruction Manual
Appendix A Rev. 3.8
July 2002
A-4 Appendices Rosemount Analytical Inc. A Division of Emerson Process Management
World Class 3000
d. Cell - General
The components which make up the cell are
machined to close tolerances and
assembled with care to provide accurate
oxygen measurements. Any replacement
requires attention to detail and care in
assembly to provide good results.
Failure to follow the instructions in
this manual could cause danger to
personnel and equipment. Read and
follow instructions in this manual
carefully.
The oxygen probe includes an inner
electrode for the cell assembly. It consists of
a platinum pad and a platinum/inconel
composite wire which produces the cell
constant offset voltage described in the
Nernst equation.
With this pad and wire, the constant will be
between -10 and +15 mV. The cell constant
is noted in the calibration data sheet
supplied with each probe.
Every probe should be calibrated and
checked after repair or replacement of cell,
pad and wire, heater, and thermocouple, or
after disassembly of the probe.
A-3 INNER PROBE ASSEMBLY
The inner probe assembly, Figure A-5, consists
of six main parts:
a. Ceramic support rod with four holes running
through the length. The holes serve as
insulated paths for the cell signal wire and
thermocouple wires.
b. A heater that is helically wrapped on a
quartz support cylinder and insulated.
c. A chromel-alumel thermocouple which acts
as the sensing element for the temperature
controller. (Not visible in Figure A-5; located
within ceramic support rod.)
d. A platinum screen pad which forms
electrical contact with the inner electrode of
the electrochemical cell. (Not visible in
Figure A-5; located at end of ceramic
support rod.) The pad is attached to an
inconel wire which carries the signal to the
terminal strip.
e. A V-strut assembly to give support to the
inner probe assembly.
f. A tube to carry reference air to the cell.
Turn to Service and Normal Maintenance, for
repair procedures for probe components.
HEATER
V-STRUT
CERAMIC
SUPPORT
ROD
INSULATING
GASKET
27270015
REFERENCE
AIR TUBE
Figure A-5. Inner Probe Assembly

Instruction Manual
Appendix A Rev. 3.8
July 2002
Rosemount Analytical Inc. A Division of Emerson Process Management Appendices A-5
World Class 3000
CALIBRATION
GAS FITTING
PROBE
JUNCTION BOX
COVER
TERMINAL
STRIP
REFERENCE
AIR FITTING
27270016
Figure A-6. Probe Junction Box
A-4 PROBE JUNCTION BOX
The probe junction box, Figure A-6, is
positioned at the external end of the probe and
contains a terminal strip for electrical
connections and fittings for reference air and
calibration gases. Fittings are for 0.250 inch
stainless steel tubing on American units and
6 mm on European units. The calibration fitting
has a seal cap which must remain in place
except during calibration. A tubing fitting is also
supplied to be used with the calibration gas
supply during calibration.
If the calibration gas bottles will be permanently
hooked up to the probe, a manual block valve is
required at the probe (between the calibration
fitting and the gas line) to prevent condensation
of flue gas down the calibration gas line.
During operation and calibration, reference air is
supplied through the reference air fitting to the
reference side of the cell. This gives the system
a known quantity of oxygen with which to
compare the oxygen level in the process gas.
Though ambient air can be used for this
purpose, accuracy can only be assured if a
reference air set is used.
During calibration, two gases of different known
oxygen concentrations are injected one at a
time through the calibration gas fitting. Stainless
steel tubing delivers this gas to the process side
of the cell. In a healthy cell, the difference in
oxygen pressure from the process side to the
reference side of the cell will cause a millivolt
output proportional to the difference in oxygen
levels. The electronics unit can use the two
millivolt outputs caused by the two calibration
gases for either automatic or semi-automatic
calibration.
Do not attempt to remove a process
gas sample through either gas fitting.
Hot gases from the process would
damage gas hoses in the probe
junction box.
A-5 CABLE ASSEMBLY
The system uses a 7-conductor cable to
connect the probe to the electronics package.
Standard length for this cable is 20 feet (6 m),
but lengths up to 150 feet (45 m) are available.
The seven conductors include one shielded pair
of wires for the cell millivolt signal, one shielded
pair of type K wires for the thermocouple, and
three individual 16-gauge wires for the heater
and for ground. The assembled conductors are
wrapped by a type K TeflonTM jacket and
braided stainless steel shield. The TeflonTM and
stainless steel jacketing is suitable for high
temperature use. All metal shields are isolated
at the probe end and connect by drain wires to
ground at the electronics.
A-6 PROBE OPTIONS
a. Abrasive Shield Assembly
The abrasive shield assembly, Figure A-7,
is a stainless-steel tube that surrounds the
probe assembly. The shield protects the
probe against particle abrasion and
corrosive condensations, provides a guide
for ease of insertion, and acts as a probe
position support, especially for longer length
probes. The abrasive shield assembly uses
a modified diffusor and vee deflector
assembly, fitted with dual dust seal packing.
A

Instruction Manual
Appendix A Rev. 3.8
July 2002
A-6 Appendices Rosemount Analytical Inc. A Division of Emerson Process Management
World Class 3000
VIEW A VIEW B
A
B
A
B
15
o
2.187 1
ON INSIDE BREAK
FOR SMOOTH
ROUNDED EDGE ON
BOTH ENDS
OF CHAMFER
.187
6.00
125
.45 MIN
90
o
3.584
3.554
SKIN CUT FACE FOR 90
o
22.5
o
DIA ON A 7.50 DIA B.C. (REF)
.745
.755
0.75 THRU 4 PLS,
EQ SP ON 4.75 B.C.
NOTES: 1 WELD ON BOTH SIDES WITH EXPANDING
CHILL BLOCK.
2 BEFORE WELDING, BUTT ITEM 2 OR 4 WITH
ITEM 1 AS SHOWN.
.187
16860033
Figure A-7. Abrasive Shield Assembly
NOTE
In highly abrasive applications, rotate the shield 90 degrees at normal
service intervals to present a new wear surface to the abrasive flow stream.

Instruction Manual
Appendix A Rev. 3.8
July 2002
Rosemount Analytical Inc. A Division of Emerson Process Management Appendices A-7
World Class 3000
P0010
Figure A-8. Ceramic Diffusion/Dust Seal Assembly
These modified diffusion and vee deflector
assemblies are available in standard, Figure
A-8, and flame arrestor version, Figure A-9.
b. Ceramic Diffusion Assembly
The ceramic diffusion assembly, Figure
A-10, is the traditional design for the probe.
Used for over 25 years, the ceramic diffu-
sion assembly provides a greater filter sur-
face area for the probe.
P0011
Figure A-9. Flame Arrestor Diffusion/Dust
Seal Assembly
19280010
Figure A-10. Ceramic Diffusion Assembly
c. Flame Arrestor Diffusion Assembly
Where a high concentration of unburned
fuel is present in the exhaust gases, a flame
arrestor diffusion assembly, Figure A-9 and
Figure A-11 is recommended.
The flame arrestor diffusion assembly in-
cludes a set of baffles between the cell and
the stack gases. This keeps 1500°F (816°C)
cell temperatures from igniting unburned
fuel in the stack.
P0012
Figure A-11. Flame Arrestor Diffusion Assembly
A

Instruction Manual
Appendix A Rev. 3.8
July 2002
A-8 Appendices Rosemount Analytical Inc. A Division of Emerson Process Management
World Class 3000
d. Snubber Diffusion/Dust Seal Assembly
The snubber diffusion/dust seal assembly,
Figure A-12, is used in applications where
an abrasive shield is to be used with a
snubber type diffusion element. The dust
seal consists of two rings of packing to pre-
vent abrasive dust from collecting inside the
abrasive shield.
Figure A-12. Snubber Diffusion/Dust
Seal Assembly
e. Cup-Type Diffusion Assembly
The cup-type diffusion assembly, Figure
A-13, is used in high-temperature applica-
tions where frequent diffusion element
plugging is a problem. This element may be
used with or without an abrasive shield.
Figure A-13. Cup-Type Diffusion/Dust
Seal Assembly
Figure A-14. Cup-Type Diffusion Assembly
f. Bypass Probe Options
For processes where the flue gas exceeds
the maximum allowable temperature of
1300°F (704°C) a bypass sensor package
can be employed. The bypass system uses
an 18 inch (457 mm) or 3 foot (0.92 m)
probe mounted externally on the stack or
duct. The process or exhaust gases are di-
rected out to the probe through a passive
sampling system using inconel tubes. Flue
gas flow induces the movement of gases
into, through, and out of the bypass unit.
The bypass arrangement does not require
the use of aspiration air and the gas which
flows past the probe is returned to the stack
or duct.
The bypass probe package is normally used
for process temperatures of 1300°F (704°C)
to 2000°F (1094°C). A higher temperature
version of the bypass provides for operation
at temperatures up to 2500°F (1372°C). In
this version the pick up tubes are made of a
special high-temperature alloy.
Overall dimensions and mounting details of
the American and European bypass sys-
tems are shown in Figure A-15.
g. Probe Mounting Jacket Options
A probe mounting jacket option is available to
allow the probe to operate at temperatures of
up to 2000°F (1095°C). A separate instruction
bulletin is available for this option.

Instruction Manual
Appendix A Rev. 3.8
July 2002
Rosemount Analytical Inc. A Division of Emerson Process Management Appendices A-9
World Class 3000
06 GASKET AND
HARDWARE
6.50
(165.1) REF
DRAIN
AA
STD 20 FT
(6.1 M) CABLE
27.31 (693.67)
CLEARANCE REQ
FOR PROBE
INSERTION
AND REMOVAL FLANGE
06
01
02 03 04
05
GASKET AND HARDWARE
4
3
6
19.80 (502.92)
FOR
3D3947G01
6.0
(152.4) REF
62.50 (1587.5) REF (4507C26G03)
26.50 (673.1) REF (4507C26G01 AND G02)
30.62 (777.75) REF (4507C26G01)
73.00 (1854.2) REF (4507C26G02)
109.00 (2768.6) REF (4507C26G03)
37.00 (939.8) REF (4507C26G01)
DIRECTION
OF FLOW
OPTIONAL MOUNTING
ARRANGEMENT,4IN.
150# FLANGE SUPPLIED
BY CUSTOMER
NOTES: REFERENCE AIR SUPPLY CONNECTION BITE TYPE FITTING (PARKER CPI) FOR
0.250 O.D. TUBING. 2 SCFH AT 3 PSIG MAX. CLEAN DRY AIR REQUIRED. FITTING
IS LOCATED ON FAR SIDE.
LAG TO ENSURE GAS TEMPERATURE DOES NOT GO BELOW DEW POINT OR
EXCEED 500 C.
o
INSTALL WITH ANALYZER IN A VERTICALLY DOWNWARDS DIRECTION ONLY.
FLUE GAS OPERATING TEMPERATURE RANGE 1200 TO 1800 F (650 TO 980 C).
oooo
RECOMMENDED TWO INCH THK INSULATION. THERMAL CONDUCTIVITY K
EQUALS 0.5 FOR INSULATION.
DIMENSIONS ARE IN INCHES WITH MILLIMETERS IN PARENTHESES.
1.
2.
3.
4.
5.
6.
7.
4.026
(102.26)
I.D.
2
1REF
AIR
CAL
GAS
ELECT CABLE
VIEW A-A
GROUP NOTE
A 3 FT (914.4) GAS TUBE PICK-UP
B6FT(1828.8) GAS TUBE PICK-UP
C9FT(2743.2) GAS TUBE PICK-UP
CALIBRATION AND PURGE GAS CONNECTION. BITE TYPE FITTING (PARKER CPI)
10 SCFH AT 32 PSIG MAX. CALIBRATION GAS REQUIRED.
IF EQUIPPED WITH THE OPTIONAL
CERAMIC DIFFUSOR ASSEMBLY, PROBE
ASSEMBLY MUST BE ORIENTED SO THAT
VEE SHIELD IS SQUARE TO GAS FLOW.
27270017
Figure A-15. Bypass Probe Option (Sheet 1 of 3)
A

Instruction Manual
Appendix A Rev. 3.8
July 2002
A-10 Appendices Rosemount Analytical Inc. A Division of Emerson Process Management
World Class 3000
NOTES: REFERENCE AIR SUPPLY CONNECTION BITE TYPE FITTING (PARKER CPI) FOR
0.250 O.D. TUBING. 2 SCFH AT 3 PSIG (20.69 kPa GAUGE) MAX. CLEAN DRY AIR
REQUIRED. FITTING IS LOCATED ON FAR SIDE.
CALIBRATION AND PURGE GAS CONNECTION. BITE TYPE FITTING (PARKER CPI)
10 SCFH AT 32 PSIG (220.64 kPa GAUGE) MAX. CALIBRATION GAS REQUIRED.
LAG TO ENSURE GAS TEMPERATURE DOES NOT GO BELOW DEW POINT OR
EXCEED 932 F (500 C).
INSTALL WITH ANALYZER IN A VERTICALLY DOWNWARDS DIRECTION ONLY.
FLUE GAS OPERATING TEMPERATURE RANGE 1200 TO 1800 F (650 TO 980 C).
RECOMMENDED 2.0 INCH (50.8) THK INSULATION. THERMAL CONDUCTIVITY K EQUAL
0.5 FOR INSULATION.
DIMENSIONS ARE IN INCHES WITH MILLIMETERS IN PARENTHESES.
20 FT (6.1 M)
STD CABLE
A
A
01
06 07 08
GASKET
AND
HARDWARE
05 09 10
4
3
6
DRAIN
PLATE
WELDED
TO STACK
2
1REF
AIR
CAL
GAS
ELECT
CABLE
VIEW
A-A
GROUP NOTE
A 3 FT (914.4) GAS TUBE PICK-UP
B6FT(1828.8) GAS TUBE PICK-UP
C9FT(2743.2) GAS TUBE PICK-UP
4.026
(102.26)
I.D.
DIRECTION
OF FLOW
14 15 16
11 12 13
02 03 04
FLANGE
o
oo
o
o
1.
2.
3.
4.
5.
6.
7.
o
62.5 (1587.5) ON 9 FT (2743.2) PICKUP (3D390004G09)
26.5 (673.1) ON 3 FT (914.4) OR 6 FT (1828.8)
PICKUP (3D390004G07 OR G08)
73.0 (1854.2) ON 6 FT (1828.8) PICKUP (3D390004G08)
37.0 (939.8) ON 3 FT (914.4) PICKUP (3D390004G07)
109.0 (2768.6) ON 9 FT (2743.2) PICKUP (3D390004G09)
6.50 (165.1) REF
27.31 (693.67)
CLEARANCE REQ
FOR PROBE
INSERTION
AND REMOVAL
19.80
(502.92)
FOR
3D3947G01
WELD BY CUSTOMER
IF EQUIPPED WITH THE OPTIONAL
CERAMIC DIFFUSOR ASSEMBLY, PROBE
ASSEMBLY MUST BE ORIENTED SO THAT
VEE SHIELD IS SQUARE TO GAS FLOW.
27270018
Figure A-15. Bypass Probe Option (Sheet 2 of 3)

Instruction Manual
Appendix A Rev. 3.8
July 2002
Rosemount Analytical Inc. A Division of Emerson Process Management Appendices A-11
World Class 3000
Extended Temperature By-Pass Arrangements (2400°
°°
°F; 1300°
°°
°C)
PART NO.
GROUP
CODE DESCRIPTION
1U0571 G01 3’ By-pass Package with ANSI bolt pattern.
1U0571 G02 6’ By-pass Package with ANSI bolt pattern.
1U0571 G03 9’ By-pass Package with ANSI bolt pattern.
1U0571 G04 3’ By-pass Package with JIS bolt pattern.
1U0571 G05 6’ By-pass Package with JIS bolt pattern.
1U0571 G06 9’ By-pass Package with JIS bolt pattern.
1U0571 G07 3’ By-pass Package with DIN bolt pattern.
1U0571 G08 6’ By-pass Package with DIN bolt pattern.
1U0571 G09 9’ By-pass Package with DIN bolt pattern.
Figure A-15. Bypass Probe Option (Sheet 3 of 3)
A

Instruction Manual
Appendix A Rev. 3.8
July 2002
A-12 Appendices Rosemount Analytical Inc. A Division of Emerson Process Management
World Class 3000
PROBE TROUBLESHOOTING
A-7 OVERVIEW
The probe troubleshooting section describes
how to identify and isolate faults which may de-
velop in the probe assembly.
Install all protective equipment and
safety ground leads after trouble-
shooting. Failure to replace covers
and ground leads could result in seri-
ous injury or death.
A-8 PROBE TROUBLESHOOTING
a. Probe Faults
Listed below are the four symptoms of
probe failure.
1. The system does not respond to
changes in the oxygen concentration.
2. The system responds to oxygen
changes but does not give the correct
indication.
3. The system does not give an accept-
able indication of the value of the oxy-
gen calibration gas being applied
during calibration.
4. The system takes a long time to return
to the flue gas value after the calibra-
tion gas is turned off.
b. Table A-2 provides a guide to fault finding
for the above symptoms.
c. Figure A-16 and Figure A-17 provide an al-
ternate approach to finding probe related
problems.
Table A-2. Fault Finding
Symptom Check Fault Remedy
1. No response to oxy-
gen concentration
change when:
Thermocouple continuity Thermocouple failure Replace thermocouple
or return probe to
Rosemount.
Heater cold resistance to
be 11 ohm to 14 ohm
Heater failure Replace heater or return
probe to Rosemount.
Heater is cold and TC
mV output is less than
set point
Triac O/P to heater Failure of electronics Check HPS and electron-
ics package.
Heater is hot and T/C
mV output is at set
point ±0.2 mV
Recorder chart Recorder failure See Recorder Instruction
Manual.
Cell mV input to electron-
ics and cell mV at probe
junction box
No cell mV at probe when
calibration gas applied
Replace cell or return
probe to Rosemount.
Probe cell mV OK but no
input to electronics
Check out cable
connection.
Cell mV satisfactory both
at probe junction box and
input to electronics - fail-
ure of electronics
Check electronics
package.

Instruction Manual
Appendix A Rev. 3.8
July 2002
Rosemount Analytical Inc. A Division of Emerson Process Management Appendices A-13
World Class 3000
Table A-2. Fault Finding (Continued)
Symptom Check Fault Remedy
2. System responds to
oxygen concentration
changes but does not
give correct indication
Recorder or remote
indicator
Calibration error Recalibrate recorder or
indicator. Reference Re-
corder Instruction Manual.
System calibration Calibration error Recalibrate system.
Probe mounting and con-
dition of duct
Air ingress into duct Stop air leaks or resite
probe.
Good response, with
incorrect indication
Cell mV input to
electronics
Failure of electronics Check electronics
package.
Calibration gas input port Blocked port Clean port. If the flue gas
is condensing in the cali-
bration gas line, insulate
the back of the probe.
Make sure that the cali-
bration gas line is capped
between calibrations, or a
check valve is installed.
3. System does not give
accurate indication of
applied calibration gas
Ceramic diffusion element Diffusion element cracked,
broken, or missing
Replace diffusion element.
4. System takes a long
time to return to flue
gas value after calibra-
tion gas is turned off
Diffusion element Plugged diffusion element Change diffusion element
or snubber diffusion
element.
Check calibration gas fit-
ting.
Leak in gasket, or calibra-
tion gas fittings or tubing.
Repair leak.
Check calibration gas
hoses or tubing.
Leak in calibration gas
hose or tubing.
Repair hose or tubing.
Cell flange corrugated
seal.
Leaking seal. Replace seal.
5. Probe passes calibra-
tion, but appears to
read high.
If equipped with an abra-
sive shield, check flange
mounting gasket.
Leaking gasket. Replace gasket.
6. Probe passes calibra-
tion, but appears to
read low.
Flow calibration gas to the
probe until reading stabi-
lizes. Shut off calibration
gas and note the time re-
quired to return to process
gas values. Time should
be <20 sec. (<40 sec. for
hazardous area probes).
Plugged diffuser element
from high process par-
ticulate may cause a cali-
bration shift.
Replace diffuser.
A

Instruction Manual
Appendix A Rev. 3.8
July 2002
A-14 Appendices Rosemount Analytical Inc. A Division of Emerson Process Management
World Class 3000
Figure A-16. Flowchart of Probe Related Problems, #1

Instruction Manual
Appendix A Rev. 3.8
July 2002
Rosemount Analytical Inc. A Division of Emerson Process Management Appendices A-15
World Class 3000
Figure A-17. Flowchart of Probe Related Problems, #2
A

Instruction Manual
Appendix A Rev. 3.8
July 2002
A-16 Appendices Rosemount Analytical Inc. A Division of Emerson Process Management
World Class 3000
NOTE
!
SERVICE AND NORMAL MAINTENANCE
UPON COMPLETING INSTALLATION, MAKE SURE THAT THE PROBE IS TURNED ON AND OPERATING
PRIOR TO FIRING UP THE COMBUSTION PROCESS. DAMAGE CAN RESULT FROM HAVING A COLD
PROBE EXPOSED TO THE PROCESS GASES.
During outages, and if possible, leave all probes running to prevent condensation and prema-
ture aging from thermal cycling.
If the ducts will be washed down during outage, MAKE SURE to power down the probes and
remove them from the wash area.
A-9 OVERVIEW
This section describes routine maintenance of
the oxygen analyzer probe. Spare parts referred
to are available from Rosemount. Probe disas-
sembly kit 3535B42G01 contains the required
spanner and hex wrenches. Refer to the follow-
ing section of this appendix for part numbers
and ordering information.
Install all protective equipment covers
and safety ground leads after equip-
ment repair or service. Failure to in-
stall covers and ground leads could
result in serious injury or death.
A-10 PROBE RECALIBRATION
The oxygen analyzer system should be cali-
brated when commissioned. Under normal cir-
cumstances the probe will not require frequent
calibration. When calibration is required, follow
the procedure described in the Instruction Bulle-
tin applicable to your electronics package.
A-11 CELL REPLACEMENT
This paragraph covers oxygen sensing cell re-
placement. Do not attempt to replace the cell
until all other possibilities for poor performance
have been considered. If cell replacement is
needed, order cell replacement kit, Table A-3.
The cell replacement kit contains a cell and
flange assembly, corrugated seal, setscrews,
socket head cap screws, and anti-seize com-
pound. Items are carefully packaged to preserve
precise surface finishes. Do not remove items
from packaging until they are ready to be used.
Spanner wrenches and hex wrenches needed for
this procedure are part of an available special
tools kit, Table A-3.
Wear heat resistant gloves and cloth-
ing to remove probe from stack. Nor-
mal operating temperatures of diffusor
and vee deflector are approximately
600° to 800°F (316° to 427°C). They
could cause severe burns.
Disconnect and lock out power before
working on any electrical components.
There is voltage up to 115 Vac.
Do not remove cell unless it is certain
that replacement is needed. Removal
may damage cell and platinum pad. Go
through complete troubleshooting
procedure to make sure cell needs re-
placement before removing it.
a. Disconnect and lock out power to electron-
ics. Shut off and disconnect reference air
and calibration gas supplies from probe
junction box, Figure A-18. Wearing heat re-
sistant gloves and clothing, remove probe
assembly from stack carefully and allow to
cool to room temperature. Do not attempt to
work on unit until it has cooled to a comfort-
able working temperature.

Instruction Manual
Appendix A Rev. 3.8
July 2002
Rosemount Analytical Inc. A Division of Emerson Process Management Appendices A-17
World Class 3000
CELL EXTENSION
WIRE (ORANGE)
BOMB TAIL
CONNECTOR
INCONEL
CELL WIRE
(CLEAR
SLEEVING)
HEATER
WIRES
(BLACK
SLEEVING)
THERMOCOUPLE -
(RED ALUMEL)
THERMOCOUPLE +
(YELLOW CHROMEL)
CALIBRATION
GAS FITTING
REFERENCE
AIR FITTING
PROBE JUNCTION
BOX COVER
CABLE
27270019
Figure A-18. Cell Wiring Connection
b. If the probe uses the standard diffusion
element, use a spanner wrench to remove
the diffusion element.
c. If equipped with the optional ceramic diffusor
assembly, remove and discard setscrews,
Figure A-19, and remove vee deflector. Use
spanner wrenches from probe disassembly
kit, Table A-3, to turn hub free from retainer.
Inspect diffusion element. If damaged, re-
place element.
d. Loosen four socket head cap screws from
the cell and flange assembly and remove
the assembly and the corrugated seal. The
cell flange has a notch which may be used
to gently pry the flange away from the
probe. Note that the contact pad inside the
probe will sometimes fuse to the oxygen
sensing cell. If the cell is fused to the con-
tact pad, push the cell assembly back into
the probe (against spring pressure), and
quickly twist the cell assembly. The cell and
contact pad should separate. If the contact
pad stays fused to the cell, a new con-
tact/thermocouple assembly must be in-
stalled. Disconnect the cell and the
thermocouple wires at the probe junction
box, and withdraw the cell with the wires still
attached (see paragraph A-13).
A

Instruction Manual
Appendix A Rev. 3.8
July 2002
A-18 Appendices Rosemount Analytical Inc. A Division of Emerson Process Management
World Class 3000
OPTIONAL CERAMIC
DIFFUSION ELEMENT
VEE
DEFLECTOR
HUB
PIN
WRENCH
SETSCREW
RETAINER
CEMENT
PORT CEMENT
FILLET
21240026
Figure A-19. Removal of Optional Diffusor
and Vee Deflector
PROBE TUBE
(NOT INCLUDED
IN KIT)
SOCKET HEAD
CAP SCREWS
CORRUGATED
SEAL
CELL AND
FLANGE
ASSEMBLY
CALIBRATION GAS
PASSAGE
21240009
Figure A-20. Cell Replacement Kit
e. If contact assembly is damaged, replace
contact and thermocouple according to
paragraph A-13, Replacement of Contact
and Thermocouple Assembly.
f. Remove and discard corrugated seal. Clean
mating faces of probe tube and retainer.
Remove burrs and raised surfaces with
block of wood and crocus cloth. Clean
threads on retainer and hub.
g. Rub a small amount of anti-seize on both
sides of new corrugated seal.
h. Assemble cell and flange assembly, corru-
gated seal, and probe tube. Make sure the
calibration tube lines up with the calibration
gas passage in each component. Apply a
small amount of anti-seize compound to
screw threads and use screws to secure
assembly. Torque to 55 in-lbs (4 N•m).
i. Apply anti-seize compound to threads of
cell assembly, hub, and setscrews. Reinstall
hub on cell assembly. Using pin spanner
wrenches, torque to 10 ft-lbs (14 N•m). If
applicable, reinstall vee deflector, orienting
apex toward gas flow. Secure with
setscrews and anti-seize compound.
Torque to 25 in-lbs (2.8 N•m).
j. On systems equipped with an abrasive
shield, install dust seal gaskets, with joints
180o apart.
k. Reinstall probe and gasket on stack flange.
If there is an abrasive shield in the stack,
make sure dust seal gaskets are in place as
they enter 15o reducing cone.
l. Turn power on to electronics and monitor
thermocouple output. It should stabilize at
29.3 ±0.2 mV. Set reference air flow at 2 scfh
(56.6 L/hr). After probe stabilizes, calibrate
probe per Instruction Bulletin applicable to
your electronics package. If new components
have been installed, repeat calibration after
24 hours of operation.
A-12 OPTIONAL CERAMIC DIFFUSION
ELEMENT REPLACEMENT
a. General
The diffusion element protects the cell from
particles in process gases. It does not nor-
mally need to be replaced because the vee
deflector protects it from particulate erosion.
In severe environments the filter may be
broken or subject to excessive erosion. Ex-
amine the diffusion element whenever re-
moving the probe for any purpose. Replace
if damaged.

Instruction Manual
Appendix A Rev. 3.8
July 2002
Rosemount Analytical Inc. A Division of Emerson Process Management Appendices A-19
World Class 3000
Damage to the diffusion element may be-
come apparent during calibration. Compare
probe response with previous response. A
broken diffusion element will cause a slower
response to calibration gas.
Hex wrenches needed to remove setscrews
and socket head screws in the following pro-
cedure are available as part of a special tool
kit, Table A-3.
Wear heat resistant gloves and cloth-
ing to remove probe from stack. Nor-
mal operating temperatures of diffusor
and vee deflector are approximately
600° to 800°F (300° to 425°C). They can
cause severe burns.
Disconnect and lock out power before
working on any electrical component.
There is voltage up to 115 Vac.
It is not necessary to remove the cell
unless it is certain that replacement is
necessary. Cell cannot be removed for
inspection without damaging it. Refer
to paragraph A-11, Cell Replacement.
b. Replacement Procedure
1. Shut off power to electronics. Discon-
nect cable conductors and remove ca-
ble, Figure A-18. Shut off and
disconnect reference air and calibration
gas supplies from probe junction box.
Wearing heat resistant gloves and
clothing, carefully remove probe as-
sembly from stack and allow to cool to
room temperature. Do not attempt to
work on unit until it has cooled to a
comfortable working temperature.
2. Loosen setscrews, Figure A-19, using
hex wrench from special tools kit,
Table A-3, and remove vee deflector.
Inspect setscrews. If damaged, replace
with M-6 x 6 stainless setscrews
coated with anti-seize compound.
3. On systems equipped with abrasive
shield, remove dual dust seal gaskets.
4. Use spanner wrenches from special
tools kit, Table A-3, to turn hub free
from retainer.
5. Put hub in vise. Break out old diffusion
element with chisel along cement line
and 3/8 inch (9.5 mm) pin punch
through cement port.
6. Break out remaining diffusion element
by tapping lightly around hub with
hammer. Clean grooves with pointed
tool if necessary.
7. Replace diffusion element, using re-
placement kit listed in Table A-3. This
consists of a diffusion element, ce-
ment, setscrews, anti-seize compound
and instructions.
8. Test fit replacement element to be sure
seat is clean.
Do not get cement on diffusion ele-
ment except where it touches the hub.
Any cement on ceramic element
blocks airflow through element. Wip-
ing wet cement off of ceramic only
forces cement into pores.
9. Thoroughly mix cement and insert tip
of squeeze bottle into cement port. Tilt
bottle and squeeze while simultane-
ously turning diffusion element into
seat. Do not get any cement on upper
part of diffusion element. Ensure com-
plete penetration of cement around
three grooves in hub. Cement should
extrude from opposite hole. Wipe ex-
cess material back into holes and wipe
top fillet of cement to form a uniform
fillet. (A Q-Tip is useful for this.) Clean
any excess cement from hub with
water.
10. Allow filter to dry at room temperature
overnight or 1 to 2 hours at 200°F
(93°C).
A

Instruction Manual
Appendix A Rev. 3.8
July 2002
A-20 Appendices Rosemount Analytical Inc. A Division of Emerson Process Management
World Class 3000
11. Wipe a heavy layer of anti-seize com-
pound onto the threads and mating
surfaces of the diffusion hub and
retainer.
12. Assemble retainer and diffusion hub
with two pin spanner wrenches. Torque
to 10 ft-lbs (14 N·m).
13. On systems equipped with abrasive
shield, install dust seal gaskets with
joints 180° apart.
14. Reinstall vee deflector, orienting apex
toward gas flow. Apply anti-seize com-
pound to setscrews and tighten with
hex wrench.
15. Reinstall probe on stack flange.
16. Turn power on to electronics and
monitor thermocouple output. It should
stabilize at 29.3 ±0.2 mV. Calibrate
probe per Instruction Bulletin applica-
ble to your electronics package.
A-13 REPLACEMENT OF CONTACT AND
THERMOCOUPLE ASSEMBLY
Use heat resistant gloves and cloth-
ing when removing probe junction box
and inner probe assembly. Do not at-
tempt to work on these components
until they have cooled to room tem-
perature. Probe components can be as
hot as 800°F (427°C). This can cause
severe burns.
Disconnect and lock out power before
working on any electrical components.
There is voltage up to 115 Vac.
a. Disconnect and lock out power to electron-
ics. Using heat resistant gloves and cloth-
ing, remove probe junction box cover.
Squeezing tabs on hose clamps, remove
hoses from probe junction box, Figure A-21.
Remove four screws in corners of probe
junction box. Pull probe junction box and in-
ner probe assembly free from probe tube.
Set on bench and allow to cool to room
temperature.
b. Disconnect cell extension wire (orange),
thermocouple wire (red alumel), and ther-
mocouple wire (yellow chromel) by cutting
bomb tail connections from the terminal
strip, Figure A-18.
c. Remove two screws, Figure A-21, lock-
washers, and flat washers that connect
probe junction box to inner probe assembly.
Pull heater, V-strut and backplate assembly
away from probe junction box. Inspect all
O-rings and insulating gasket; replace if worn
or damaged.
PROBE JUNCTION BOX
INNER PROBE ASSEMBLY
TO PROBE TUBE SCREWS
PROBE JUNCTION BOX TO HEATER,
STRUT, AND BACKPLATE
ASSEMBLY SCREW
PROBE
JUNCTION
BOX
HOSE
CLAMP
HOSE
21240027
Figure A-21. Probe Junction Box Mechanical
Connections

Instruction Manual
Appendix A Rev. 3.8
July 2002
Rosemount Analytical Inc. A Division of Emerson Process Management Appendices A-21
World Class 3000
d. Use a pencil to mark locations of spring clip
on ceramic rod, Figure A-22.
e. Pry or squeeze tabs on spring clips, and pull
contact and thermocouple assembly out of
probe assembly. Retain spring clips and
spring; replace if damaged.
Be very careful when handling contact
and thermocouple assembly. The ce-
ramic rod in this assembly is fragile.
f. While very carefully handling new contact
and thermocouple assembly, lay old as-
sembly next to new one. Transfer pencil
marks to new rod.
21240010
MOUNTING SCREW
(REAR VIEW)
CONTACT AND
THERMOCOUPLER
ASSEMBLY
V-STRUT
HEATER SCREWS
(NOT SHOWN)
HEATER
CERAMIC ROD
SPRING
CLIP
INSULATING
GASKET
Figure A-22. Inner Probe Replacement
(Heater, V-Strut, and Backplate Assembly)
g. Note wire lengths of old assembly as an aid
for trimming new lengths in step (j). Trim-
ming of wires will not always be necessary.
Throw away old contact and thermocouple
assembly.
h. Carefully guide new contact and thermo-
couple assembly through V-strut assembly
leaf spring (4, Figure A-23), spring (9),
spring clip (10) (held open by squeezing
tabs), and tube supports (11, 13) until
spring clip reaches pencil mark.
i. Reinstall insulating gasket on backplate, re-
place two screws, O-rings, lockwashers and
flat washers connecting probe junction box
to inner probe assembly.
Do not trim new wiring shorter than
existing (old) wiring. Excessive wire
trim will prevent connections from
being properly made and will require a
new replacement kit.
j. Trim wires, if necessary, as noted in
step (g).
k. Connect color coded wires to proper termi-
nals as shown in Figure A-18. Rosemount
recommends connecting the thermocouple
wires directly to the terminal strip. This is
because the junction of different metals at
the wires and lugs and at the lugs and the
134
5
4
8
6
7
8
9
1011
11
2
13
12
1. Heater Ceramic Rod
2. Contact and Thermocouple Assembly
3. Strut
4. Leaf Spring
5. Ring Lug
6. Butt Connector
7. Extension
8. Backplate
9. Spring
10. Spring Clip Assembly
11. Common Tube Support
12. Heater
13. Short Tube Support
Figure A-23. Heater, Strut, and Backplate Assembly
(Inner Probe Assembly)
A

Instruction Manual
Appendix A Rev. 3.8
July 2002
A-22 Appendices Rosemount Analytical Inc. A Division of Emerson Process Management
World Class 3000
terminal strip could act as additional ther-
mocouple junctions. This could produce a
voltage that would affect the thermocouple
output signal.
Do not bend wires closer than 1/4 inch
(6.4 mm) from end of ceramic rod. Dress
wires so they do not touch sides of probe
junction box.
l. Slide assembled probe junction box and in-
ner probe assembly into probe tube. To
align calibration gas tube with correspond-
ing hole in backplate (A, B, Figure A-1), in-
sert scriber through hole in backplate and
into calibration gas tube. Secure with
screws. Reinstall hoses and probe junction
box cover.
m. Power up system. Monitor thermocouple
output. It should stabilize at set point mV
±0.2 mV. Recalibrate probe per Instruction
Bulletin applicable to your electronics
package.
A-14 REPLACEMENT OF HEATER, V-STRUT
AND BACKPLATE ASSEMBLY (INNER
PROBE ASSEMBLY; INCLUDES CONTACT
AND THERMOCOUPLE ASSEMBLY)
Use heat resistant gloves and clothing
when removing probe junction box
and inner probe assembly. Do not at-
tempt to work on these components
until they have cooled to room tem-
perature. Probe components can be as
hot as 800° (427°C). This can cause
severe burns.
Disconnect and lock out power before
working on any electrical components.
There is voltage up to 115 Vac.
NOTE
This replacement may be done without
removing the probe from the duct.
a. Disconnect and lock out power to electron-
ics. Using heat resistant gloves and cloth-
ing, remove probe cover. Squeezing tabs
on hose clamps and remove hoses from
probe junction box, Figure A-21. Remove
four screws and lockwashers (7, 10, Figure
A-24) that hold probe junction box and inner
probe assembly to probe tube. Pull probe
junction box and inner probe assembly free
from probe tube. Set on bench and allow to
cool to room temperature.
b. Disconnect cell extension wire (orange),
thermocouple wire (red alumel), and ther-
mocouple wire (yellow chromel) by cutting
bomb tail connections from the terminal
strip, Figure A-18.
c. Remove two screws, lockwashers, and flat
washers that connect probe junction box to
inner probe assembly. Remove and discard
inner probe assembly (heater, V-strut, and
backplate assembly). Replace with new in-
ner probe assembly. Reinstall screws, lock-
washers and flat washers.
d. Connect color coded wires to proper termi-
nals as shown in Figure A-18. Rosemount
recommends connecting the thermocouple
wires directly to the terminal strip. This is
because the junction of different metals at
the wires and lugs and at the lugs and the
terminal strip could act as additional ther-
mocouple junctions. This could produce a
voltage that would affect the thermocouple
output signal.
Do not bend wires closer than 1/4 inch
(6.4 mm) from end of ceramic rod. Dress
wires so they do not touch sides of probe
junction box.

Instruction Manual
Appendix A Rev. 3.8
July 2002
Rosemount Analytical Inc. A Division of Emerson Process Management Appendices A-23
World Class 3000
124
3
11
5
678 9
10
21240012
1. Snubber Diffusion Element
2. Socket Hd Cap Screw [0.25 in.-28 x 0.063 (16 mm)]
3. Cell and Flange Assembly
4. Corrugated Seal
5. Probe Tube Assembly
6. Gasket [4.0 in. (102 mm) x 4.0 in. x 0.12 in. (3 mm)]
7. Fillister Hd Screw [8-32 x 0.5 in. (12.7 mm)]
8. Cover Head Assembly
9. Hose Clamp
10. Lockwasher (#8 Split)
11. Heater Strut Assembly
Figure A-24. Oxygen Analyzer (Probe), Cross-Sectional View
e. Slide assembled probe junction box and in-
ner probe assembly into probe tube. To
align calibration gas tube with correspond-
ing hole in backplate (A, B, Figure A-1), in-
sert aligning tool (included in probe
disassembly kit, P/N 3535B42G01) through
hole in backplate and into calibration gas
tube, while sliding the heater strut into the
probe tube. Secure with screws. Reinstall
hoses and probe junction box cover.
f. Power up system. Monitor thermocouple
output. It should stabilize at set point ±0.2
mV. Recalibrate probe per Instruction Bulle-
tin applicable to your electronics package.
A-15 CALIBRATION GAS AND REFERENCE AIR
LINES FOR HIGH TEMPERATURE -
CORROSIVE ENVIRONMENT OPERATION
A high temperature, corrosive environment kit is
available when the probe is exposed to these
types of operating conditions. The kit includes
stainless steel tubing and teflon fittings for in-
side the probe junction box. The kit part number
is 4843B93G01.
a. Installation Procedure
Use heat resistant gloves and
clothing when removing probe junc-
tion box and inner probe assembly.
Do not attempt to work on these com-
ponents until they have cooled to
room temperature. Probe components
can be as hot as 800°F (427°C). This
can cause severe burns.
Disconnect and lock out power before
working on any electrical components.
There is voltage up to 115 Vac.
1. Disconnect and lock out power to digi-
tal electronics. Using heat resistant
gloves and clothing, remove probe
cover. Squeezing tabs on hose clamps,
remove hoses from probe junction box
(Figure A-21).
A

Instruction Manual
Appendix A Rev. 3.8
July 2002
A-24 Appendices Rosemount Analytical Inc. A Division of Emerson Process Management
World Class 3000
Do not use sealant when installing the
stainless steel tubes. Gas samples
may become contaminated.
2. First install the stainless steel tubing on
the fitting at the bottom of the probe
junction box. Install the other end of the
stainless steel tube onto the tube going
to the probe (Figure A-25).
NOTE
If abrasive conditions of high ash con-
tent and high velocity exist, an abra-
sive shield is recommended. To
balance out the wear on the shield, ro-
tate the shield 90° every time the
probe is powered down for service.
STAINLESS
STEEL
TUBING
TEFLON
SLEEVES
21240028
Figure A-25. High Temperature - Corrosive
Environment Kit

Instruction Manual
Appendix A Rev. 3.8
July 2002
Rosemount Analytical Inc. A Division of Emerson Process Management Appendices A-25
World Class 3000
REPLACEMENT PARTS
Table A-3. Replacement Parts for Probe
Figure and
Index No. Part Number Description
Figure A-22
Figure A-22
Figure A-22
Figure A-22
Figure A-22
Figure A-23, 2
Figure A-23, 2
Figure A-23, 2
Figure A-23, 2
Figure A-23, 2
Figure A-7
Figure A-7
Figure A-7
Figure A-7
Figure A-20
Figure A-20
Figure A-20
Figure A-20
Figure A-20
Figure A-20
Figure A-20
Figure A-20
Figure A-20
Figure A-20
Figure A-20
Figure A-20
Figure A-20
Figure A-20
Figure A-20
Figure A-20
Figure A-20
Figure A-20
Figure A-20
Figure A-10
Figure A-8
3D39441G061
3D39441G071
3D39441G081
3D39441G091
3D39441G101
3534B56G042
3534B56G052
3534B56G062
3534B56G072
3534B56G082
3D39003G013
3D39003G023
3D39003G073
3D39003G083
4847B61G01
4847B61G02
4847B61G03
4847B61G04
4847B61G05
4847B61G06
4847B61G07
4847B61G08
4847B61G09
4847B61G10
4847B61G11
4847B61G12
4847B61G13
4847B61G14
4847B61G15
4847B61G16
4847B61G17
4847B61G18
3535B42G01
3534B18G01
3535B60G01
Heater, V-Strut, and Backplate Assembly, 18 in. (45.6 cm)
Heater, V-Strut, and Backplate Assembly, 3 ft (0.9 m)
Heater, V-Strut, and Backplate Assembly, 6 ft (1.8 m)
Heater, V-Strut, and Backplate Assembly, 9 ft (2.7 m)
Heater, V-Strut, and Backplate Assembly, 12 ft (3.6 m)
Contact and Thermocouple Assembly, 18 in. (45.6 cm)
Contact and Thermocouple Assembly, 3 ft (0.9 m)
Contact and Thermocouple Assembly, 6 ft (1.8 m)
Contact and Thermocouple Assembly, 9 ft (2.7 m)
Contact and Thermocouple Assembly, 12 ft (3.6 m)
Abrasive Shield Assembly, 3 ft (0.9 m)
Abrasive Shield Assembly, 6 ft (1.8 m)
Abrasive Shield Assembly, 9 ft (2.7 m)
Abrasive Shield Assembly, 12 ft (3.6 m)
Cell Replacement Kit, ANSI, No Lead Wire
Cell Replacement Kit, ANSI 18 in. (45.6 cm)
Cell Replacement Kit, ANSI 3 ft (0.9 m)
Cell Replacement Kit, ANSI 6 ft (1.8 m)
Cell Replacement Kit, ANSI 9 ft (2.7 m)
Cell Replacement Kit, ANSI 12 ft (3.6 m)
Cell Replacement Kit, JIS, No Lead Wire
Cell Replacement Kit, JIS 18 in. (45.6 cm)
Cell Replacement Kit, JIS 3 ft (0.9 m)
Cell Replacement Kit, JIS 6 ft (1.8 m)
Cell Replacement Kit, JIS 9 ft (2.7 m)
Cell Replacement Kit, JIS 12 ft (3.6 m)
Cell Replacement Kit, DIN, No Lead Wire
Cell Replacement Kit, DIN 18 in. (45.6 cm)
Cell Replacement Kit, DIN 3 ft (0.9 m)
Cell Replacement Kit, DIN 6 ft (1.8 m)
Cell Replacement Kit, DIN 9 ft (2.7 m)
Cell Replacement Kit, DIN 12 ft (3.6 m)
Probe Disassembly Kit
Diffuser Assembly
Diffuser Dust Seal Hub Assembly
(For use with Abrasive Shield)
A

Instruction Manual
Appendix A Rev. 3.8
July 2002
A-26 Appendices Rosemount Analytical Inc. A Division of Emerson Process Management
World Class 3000
Table A-3. Replacement Parts for Probe (Continued)
Figure and
Index No. Part Number Description
Figure A-9
Figure A-11
Figure A-4
Figure A-19
Figure A-25
Figure A-1, 2
Figure A-12
Figure A-14
Figure A-13
3535B63G01
3535B62G01
3534B48G01
6292A74G02
1537B70G03
4843B93G01
4843B37G01
4843B38G02
4851B89G04
4851B89G05
4851B90G04
4851B90G05
Flame Arrestor Diffuser Dust Seal
Flame Arrestor Diffuser
Vee Deflector Assembly
(For use with standard or dust seal type ceramic diffusers)
Diffusion Element Replacement Kit
Horizontal and Vertical Brace Clamp Assembly,
9 and 12 foot (2.7 and 3.6 m) probe
High Temperature - Corrosive Environment Kit
Snubber Diffusion Assembly
Dust Seal/Snubber Diffusion Assembly
Cup Type Diffusion Assembly, 5 microns
Cup Type Diffusion Assembly, 40 microns
Cup Type Diffusion Assembly/Dust Seal, 5 microns
Cup Type Diffusion Assembly/Dust Seal, 40 microns
1Heater, V-strut, and backplate assembly includes contact and thermocouple assembly.
2Contact and thermocouple assembly includes platinum pad and inconel wire.
3Abrasive shield assembly includes accessories necessary for its use and a mounting plate and gasket.

Instruction Manual
Appendix B Rev. 2.2
January 1997
Rosemount Analytical Inc. A Division of Emerson Process Management Appendices B-1
World Class 3000
APPENDIX B, REV. 2.2
HPS 3000 HEATER POWER SUPPLY
DESCRIPTION
Read the “Safety instructions for the
wiring and installation of this appara-
tus” at the front of this Instruction
Bulletin. Failure to follow the safety
instructions could result in serious
injury or death.
B-1 DESCRIPTION
The Rosemount HPS 3000 Heater Power Sup-
ply Field Module acts as an interface between
probe and electronics, and supplies power to
the probe heater. The unit allows the use of
probes with a number of different electronics
packages.
The HPS is available in a NEMA 4X (IP56)
non-hazardous enclosure or an optional
Class 1, Division 1, Group B (IP56) explo-
sion-proof enclosure, Figure B-1.
The heater power supply, Figure B-2, consists
of a mother board, daughter board, and a
transformer for supplying correct voltage to the
probe heater. The mother and daughter boards
contain terminal strips for connecting probe,
electronics, and power supply.
The HPS is jumper configurable for 120, 220, or
240 Vac. For 100 Vac usage, the HPS is fac-
tory-supplied with a special transformer. The
100 Vac transformer can also be easily field in-
stalled. Refer to paragraph B-7, Transformer
Replacement for installation procedure; refer to
Table B-2, for transformer part numbers.
35730001
Figure B-1. HPS 3000 Heater Power Supply Field Module
B

Instruction Manual
Appendix B Rev. 2.2
January 1997
B-2 Appendices Rosemount Analytical Inc. A Division of Emerson Process Management
World Class 3000
TRANSFORMER
TRANSFORMER
TERMINAL
COVERS
FRONT
SIDE
TERMINAL STRIP
(FROM ELECTRONICS)
TERMINAL STRIP
(FROM PROBE)
35730002
Figure B-2. Heater Power Supply, Interior

Instruction Manual
Appendix B Rev. 2.2
January 1997
Rosemount Analytical Inc. A Division of Emerson Process Management Appendices B-3
World Class 3000
Table B-1. Specifications for Heater Power Supply
Environmental Classification ..................................................NEMA 4X (IP56) Optional - Class 1, Division 1,
Group B (IP56)
Electrical Classification ..........................................................Category II
Humidity Range .....................................................................95% Relative Humidity
Ambient Temperature Range ................................................-20° to 140°F (-30° to 60°C)
Vibration .................................................................................5 m/sec2, 10 to 500 xyz plane
Cabling Distance Between HPS 3000 and Probe ..................Maximum 150 feet (45 m)
Cabling Distance Between HPS 3000 and CRE 3000 ...........Maximum 1200 feet (364 m)
Cabling Distance Between HPS 3000 and IFT 3000 ............Maximum 1200 feet (364 m)
Approximate Shipping Weight ................................................12 pounds (5.4 kg)
B-2 THEORY OF OPERATION
The HPS 3000 Heater Power Supply may per-
form slightly different functions, depending upon
which electronics package it is used with. Figure
B-3 shows a functional block diagram of the
unit. The HPS contains a transformer for con-
verting line voltage to 44 volts needed to power
the probe heater. The relay, Figure B-3, can be
used to remotely turn the probe on or off manu-
ally. A triac module is used to turn the heater on
or off, depending on probe temperature.
When used with the CRE 3000 Control Room
Electronics or IFT 3000 Intelligent Field Trans-
mitter, the HPS uses a cold junction tempera-
ture compensation feature. This allows for the
use of a less expensive cable between the HPS
and CRE or HPS and IFT. The HPS and elec-
tronics package can be located up to 1200 feet
(364 m) apart.
The standard cable, between probe and HPS, is
thermocouple compensated. This prevents the
additional junctions between thermocouple and
cable from producing a voltage which would af-
fect the thermocouple output signal. A tem-
perature sensor in the HPS monitors the
temperature at the junction and sends a voltage
signal to the CRE and IFT. The CRE and IFT
uses this signal to compensate the probe ther-
mocouple reading for the temperature at the
junction between the compensated and uncom-
pensated cables.
TO HEATER
PROBE TC
STACK TC
CELL
LINE
RELAY
TRIAC
AD590
PROBE TC
STACK TC
CELL MV
FROM
IFT TO
PROBE
686015
Figure B-3. Heater Power Supply Block Diagram
B

Instruction Manual
Appendix B Rev. 2.2
January 1997
B-4 Appendices Rosemount Analytical Inc. A Division of Emerson Process Management
World Class 3000
In operation, when connected to the CRE 3000
Control Room Electronics, line voltage passes
through the relay (when on) and is converted
into 44 volts by the transformer. If the probe
thermocouple indicates that the probe has
dropped below operating temperature, a signal
from the CRE triggers the triac. The triac then
supplies voltage to the probe heater, warming
the cell. Conversely, if the probe thermocouple
indicates that the probe heater has reached the
upper limit of operating temperature, the CRE
deactivates the triac, shutting off power to the
heater.
NOTE
When using the HPS 3000 with an ex-
isting electronics package, such as
Models 218, 218A, 225, or TC200, the
electronics will not have the in-
put/output capacity to support all of
the functions mentioned in this sec-
tion. Refer to Instruction Bulletin IB-
106-300NE.
HPS 3000 TROUBLESHOOTING
B-3 OVERVIEW
The HPS 3000 troubleshooting section de-
scribes how to identify and isolate faults which
may develop in the HPS 3000 assembly.
Install all protective equipment covers
and safety ground leads after trouble-
shooting. Failure to replace covers
and ground leads could result in seri-
ous injury or death.
B-4 HPS 3000 TROUBLESHOOTING
The HPS 3000 troubleshooting may overlap
with the probe in use in the system. Faults in
either system may cause an error to be dis-
played in the electronics package. Figure B-4,
Figure B-5, and Figure B-6 provide trouble-
shooting information.

Instruction Manual
Appendix B Rev. 2.2
January 1997
Rosemount Analytical Inc. A Division of Emerson Process Management Appendices B-5
World Class 3000
HEATER DOES NOT HEAT
UP (DOES NOT INCREASE
IN OUTPUT).
SET METER* FOR 50 VAC.
PLACE PROBES ON
TERMINAL BLOCK J2,
“FROM PROBE”, PROBE
HEATER.
METER INDICATES
PULSATING NOMINAL
44 VAC.
DISCONNECT POWER FROM
HPS & PROBE ELECT. SET
METER ON RX1.
MEASURE RESISTANCE OF
HEATER BY PLACING
PROBES ON TERMINAL
BLOCK J2, “FROM PROBE”,
PROBE HEATER.
RESISTANCE MEASURED
SHOULD BE NOMINALLY
12 OHMS.
SET METER TO 250 VAC.
PLACE METER PROBES ON
J2, “FROM ELECTRONICS”,
ANALOG HEATER.
METER SHOULD REGISTER
A PULSATING NOMINAL
115 VAC.
YES
DISCONNECT POWER TO
HPS AND PROBE
ELECTRONICS. CHECK
ALL FOUR FUSES IN HPS.
FUSES BLOWN IN HPS. NO
NO
CHECK THAT LINE VOLTAGE
IS CORRECT BY SELECTING
CORRECT JUMPERS
ACCORDING TO CHART ON
INSIDE OF HPS COVER.
REPLACE BLOWN FUSES.
HEATER IS OPEN.
REPLACE HEATER.
NO
YES YES
YES
NO
CHECK JUMPER JM2 IS
INSTALLED.
IF FUSES OK, POSSIBLE
PROBE ELECTRONICS TRIAC
FAILURE.
CHECK FUSES IN PROBE
ELECTRONICS.
POSSIBLE TRIAC FAILURE.
REPLACE HPS
MOTHERBOARD.
SYMPTOM
*SIMPSON MODEL 260 OR
EQUIVALENT MULTIMETER.
35730004
Figure B-4. HPS Troubleshooting Flowchart, #1
B

Instruction Manual
Appendix B Rev. 2.2
January 1997
B-6 Appendices Rosemount Analytical Inc. A Division of Emerson Process Management
World Class 3000
HEATER OVERHEATS.
NOTE: ON INITIAL STARTUP THE
TEMPERATURE OF THE PROBE MAY
OVERHEAT TO A NOMINAL TEMP OF
800°C.
CHECK IF THE YELLOW WIRE IS CONNECTED
TO POSITIVE AND THE RED TO NEGATIVE
ON BOTH “FROM ELECTRONICS”AND “FROM
PROBE”TERMINAL BLOCKS. (MODELS 218
AND 225 ONLY)
SET METER* ON 250 VAC SCALE.
CHECK “FROM ELECTRONIC”, ANALOG
HEATER TERMINALS IF THERE IS A
PULSATING NOMINAL 115 VAC.
CHECK “FROM PROBE”, TERMINALS AT
PROBE HEATER IF THERE IS A PULSATING
NOMINAL 44 VOLTS.
CHECK PROBE ELECTRONICS SETPOINT
HAS BEEN CHANGED ACCORDING TO
APPLICABLE ELECTRONICS PACKAGE IB.
SET METER* ON 50 VAC SCALE.
CHECK IF PROBE HEATER VOLTAGE
SELECTION JUMPER JM7 INSTALLED
(REMOVE JM8).
CONNECT THE WIRING
ACCORDING TO THE
DECALS ON THE TERMINAL
COVERS.
IF THE VOLTAGE IS
CONSTANTLY ON, THEN
THE TRIAC IN THE PROBE
ELECTRONICS IS SHORTED.
IF THE VOLTAGE IS
CONSTANTLY ON, THEN
THE TRIAC MODULE IN
THE HPS IS SHORTED.
NO
NO
NO
YES
YES
YES
SYMPTOM
*SIMPSON MODEL 260 OR EQUIVALENT MULTIMETER. 35730003
Figure B-5. HPS Troubleshooting Flowchart, #2

Instruction Manual
Appendix B Rev. 2.2
January 1997
Rosemount Analytical Inc. A Division of Emerson Process Management Appendices B-7
World Class 3000
PROBE HEATER START TO HEAT UP AND
THEN LOOSES TEMPERATURE. (MODEL
TC200 ONLY)
CHECK PARAMETER 35 ON TC200. IF THE
NUMBER IS NEGATIVE THEN SOMEWHERE
THE THERMOCOUPLE WIRES ARE REVERSED.
SYMPTOM
35730005
Figure B-6. HPS Troubleshooting Flowchart, #3
B

Instruction Manual
Appendix B Rev. 2.2
January 1997
B-8 Appendices Rosemount Analytical Inc. A Division of Emerson Process Management
World Class 3000
SERVICE AND NORMAL MAINTENANCE
B-5 OVERVIEW
This section describes service and routine
maintenance of the HPS 3000 Heater Power
Supply Field Module. Replacement parts re-
ferred to are available from Rosemount. Refer to
Table B-2 of this manual for part numbers and
ordering information.
Install all protective equipment covers
and safety ground leads after equip-
ment repair or service. Failure to in-
stall covers and ground leads could
result in serious injury or death.
B-6 FUSE REPLACEMENT
The heater power supply mother board (12,
Figure B-7) contains four identical 5 amp fuses.
Refer to Table B-1 for replacement fuse specifi-
cations. To check or replace a fuse, simply un-
screw the top of the fuseholder with a flat head
screwdriver and remove fuse. After checking or
replacing a fuse, reinstall fuseholder top.
B-7 TRANSFORMER REPLACEMENT
Install all protective equipment covers
and safety ground leads after equip-
ment repair or service. Failure to in-
stall covers and ground leads could
result in serious injury or death.
a. Turn off power to system.
b. Loosen captive screws retaining HPS cover.
Remove cover.
c. Remove hex nut (25, Figure B-7) from top of
transformer assembly. Remove retaining
plate (24) and gasket (22).
d. Disconnect transformer harness plug from
mother board.
e. Remove old transformer. Place new trans-
former in position and reconnect harness
plug as noted in step d.
f. Place gasket and retaining plate on trans-
former.
g. Tighten hex nut only enough to firmly hold
transformer in place.
h. Reinstall HPS cover.
B-8 MOTHER BOARD REPLACEMENT
Install all protective equipment covers
and safety ground leads after equip-
ment repair or service. Failure to in-
stall covers and ground leads could
result in serious injury or death.
a. Turn off power to system.
b. Loosen captive screws retaining HPS cover.
Remove cover.
c. Remove hex nut (25, Figure B-7) from top of
transformer assembly. Remove retaining
plate (24) and gasket (22).
d. Disconnect transformer harness plug from
mother board.
e. Remove screws on either side of terminal
strip covers (2). Remove terminal strip cov-
ers (4 and 8).
f. Unplug ribbon cable from the receptacle on
the daughter board (7).
g. Unscrew stand offs on either side of the
daughter board. Remove daughter board
(7).
h. Unscrew four stand offs that supported the
daughter board.

Instruction Manual
Appendix B Rev. 2.2
January 1997
Rosemount Analytical Inc. A Division of Emerson Process Management Appendices B-9
World Class 3000
i. Making a note of the location and color of
each wire, disconnect wires from terminal
strip on mother board.
j. Remove four screws (9) holding mother
board to stand offs (10) on subplate (14).
k. Remove mother board (12).
l. Position new mother board on stand offs
and reinstall screws removed in step j.
m. Reconnect wires to terminal strip in posi-
tions noted in step i.
n. Reinstall four stand offs removed in step h.
Position daughter board on stand offs and
reinstall stand offs removed in step g.
o. Plug ribbon cable back into receptacle on
daughter board. Reinstall terminal covers.
p. Reinstall transformer, tightening hex nut
only enough to hold transformer firmly in
position. Reconnect transformer harness
plug to mother board.
q. Reinstall HPS cover.
B-9 DAUGHTER BOARD REPLACEMENT
When turning power off at the HPS,
also turn off the respective probe at
associated electronics. When service
on the HPS is completed, restore
power at the HPS and the associated
electronics.
a. Turn off power to system.
b. Loosen captive screws retaining HPS cover.
Remove cover.
c. Remove screws on either side of terminal
strip covers (2, Figure B-7). Remove termi-
nal strip covers (4 and 8).
d. Making a note of the location and color of
each wire, disconnect wires from the termi-
nal strip on the daughter board (7).
e. Unplug ribbon cable from receptacle on
daughter board.
f. Unscrew two stand offs from daughter
board. Remove daughter board (7).
g. Position new daughter board on four stand
offs on mother board. Reinstall the stand
offs removed in step f.
h. Plug ribbon cable into receptacle on
daughter board.
i. Reconnect wires to terminal strip in posi-
tions noted in step d. Reinstall terminal
covers.
j. Reinstall HPS cover.
B

Instruction Manual
Appendix B Rev. 2.2
January 1997
B-10 Appendices Rosemount Analytical Inc. A Division of Emerson Process Management
World Class 3000
35730006
NOTE: NOT ALL PARTS SHOWN ARE AVAILABLE
FOR PURCHASE SEPARATELY. FOR LIST OF
AVAILABLE PARTS SEE TABLE B-2.
Figure B-7. Heater Power Supply, Exploded View

Instruction Manual
Appendix B Rev. 2.2
January 1997
Rosemount Analytical Inc. A Division of Emerson Process Management Appendices B-11
World Class 3000
LEGEND FOR FIGURE B-7
1. Enclosure Cover
2. Screw
3. Lockwasher
4. Terminal Cover
5. Stand Off
6. Lockwasher
7. Daughter Board
8. Terminal Cover
9. Screw
10. Stand Off
11. Hex Nut
12. Mother Board
13. Fuse
14. Subplate
15. Enclosure Box
16. Lockwasher
17. Stand Off
18. Screw
19. Lockwasher
20. Mounting Plate
21. Screw
22. Gasket
23. Transformer
24. Retaining Plate
25. Hex Nut
REPLACEMENT PARTS
Table B-2. Replacement Parts for Heater Power Supply
FIGURE and INDEX NO. PART NUMBER DESCRIPTION
Figure B-1
Figure B-1
Figure B-1
Figure B-1
Figure B-1
Figure B-1
Figure B-7, 13
Figure B-7, 12
Figure B-7, 7
Figure B-7, 23
Figure B-7, 23
3D39129G01
3D39129G02
3D39129G03
1U05667G01
1U05667G02
1U05667G03
1L01293H02
3D39080G02
3D39078G01
1M02961G01
1M02961G02
Non-Hazardous HPS (120 Vac)
Non-Hazardous HPS (100 Vac)
Non-Hazardous HPS (220, 240 Vac)
Explosion-Proof HPS (120 Vac)
Explosion-Proof HPS (100 Vac)
Explosion-Proof HPS (220, 240 Vac)
Fuse, 5A @ 250 Vac, anti-surge, case
size; 5 x 20 mm, type T to IEC127,
Schurter
Mother Board
Daughter Board
Transformer (120, 220, 240 Vac)
Transformer (100 Vac)
B

Instruction Manual
Appendix B Rev. 2.2
January 1997
B-12 Appendices Rosemount Analytical Inc. A Division of Emerson Process Management
World Class 3000

Instruction Manual
Appendix D Rev. 2.4
July 1998
Rosemount Analytical Inc. A Division of Emerson Process Management Appendices D-1
World Class 3000
APPENDIX D, REV 2.4
MPS 3000 MULTIPROBE CALIBRATION GAS SEQUENCER
DESCRIPTION
Read the “Safety instructions for the
wiring and installation of this appara-
tus” at the front of this Instruction
Bulletin. Failure to follow the safety
instructions could result in serious
injury or death.
D-1 DESCRIPTION
The Rosemount MPS 3000 Multiprobe Calibra-
tion Gas Sequencer provides automatic calibra-
tion gas sequencing for up to four probes. The
MPS routes calibration gas to the selected
probe under control of the CRE, IFT, or digital
electronics package. The electronics package
can be preprogrammed by the user for auto-
matic periodic recalibration, or manually initiated
calibration through the keypad on the front of
the electronics package. The calibration pa-
rameters held in the electronics package can be
selected to automatically update after each
calibration.
The MPS is housed in a NEMA 4X (IP56) non-
hazardous enclosure, Figure D-1.
NOTE
A single multichannel MPS cannot be
shared among a number of CRE
electronics.
The MPS, Figure D-2, consists of: an air pres-
sure regulator, a terminal board, a flowmeter
assembly (one for each probe, up to four per
MPS), HI GAS solenoid, LO GAS solenoid, a
manifold, and a power supply. Each flowmeter
assembly contains a probe solenoid.
An optional Z-purge arrangement is available for
hazardous area classification. See Application
Data Bulletin AD 106-300B.
16860013
Figure D-1. MPS 3000 Multiprobe Calibration Gas
Sequencer
D-2 THEORY OF OPERATION
A typical automatic calibration setup is shown in
Figure D-3. The MPS 3000 Multiprobe Calibra-
tion Gas Sequencer operates under the control
of the CRE, IFT, or digital electronics package.
When the electronics package initializes auto-
matic calibration, the solenoid controlling the
selected probe is energized. Next, the solenoid
controlling calibration gas 1 (high O2) energizes
allowing calibration gas 1 to flow to that probe.
After the probe measures the oxygen concen-
tration of calibration gas 1, the gas solenoid is
deenergized. An operator selected time delay
allows the gas to clear the system. Next, the
solenoid controlling calibration gas 2 (low O2)
energizes and allows calibration gas 2 to flow to
the probe. After the probe measures the oxygen
concentration of calibration gas 2, the gas and
probe solenoids deenergize. The automatic
calibration is now complete for the probe
selected.
D

Instruction Manual
Appendix D Rev. 2.4
July 1998
D-2 Appendices Rosemount Analytical Inc. A Division of Emerson Process Management
World Class 3000
POWER
SUPPLY
REGULATOR
TUBE
SOLENOID MANIFOLD HOSE
ADAPTER
CABLE
GRIP
TERMINATION
BOARD
FLOWMETER
27270024
Figure D-2. Multiprobe Calibration Gas Sequencer, Interior
Table D-1. Specifications for Multiprobe Calibration Gas Sequencer.
Environmental Classification ................................................................ NEMA 4X (IP56)
Humidity Range .................................................................................... 95% Relative Humidity
Humidity Range .................................................................................... 95% Relative Humidity
Ambient Temperature Range ............................................................... -20° to 160°F (-30° to 71°C)
Vibration................................................................................................ 5 m/sec2, 10 to 500 xyz plane
External Electrical Noise....................................................................... Minimum Interference
Piping Distance Between MPS 3000 and Probe.................................. Maximum 300 feet (91 m)
Cabling Distance Between MPS 3000 and Electronics Package......... Maximum 1000 feet (303 m)
In Calibration Status Relay................................................................... 48V max, 100 mA max
Cabling Distance Between MPS 3000 and Status Relay Indicator...... Maximum 1000 feet (303 m)
Approximate Shipping Weight .............................................................. 35 pounds (16 kg)

Instruction Manual
Appendix D Rev. 2.4
July 1998
Rosemount Analytical Inc. A Division of Emerson Process Management Appendices D-3
World Class 3000
CALIBRATION
GAS 1
(HIGH O )
2
CALIBRATION
GAS 2
(LOW O )
2
PROBE
(END VIEW)
ELECTRONIC
PACKAGE
CALIBRATION GAS
CHECK
VALVE
PROBE
SIGNAL CONNECTIONS
MPS ELECTRONICS
PACKAGE SIGNAL
CONNECTIONS
NOTE: THE MPS CAN BE USED WITH UP
TO FOUR PROBES AND FOUR
ELECTRONIC PACKAGES. ONLY
ONE PROBE CAN BE CALIBRATED
AT A TIME. PROBE CALIBRATIONS
MUST BE SCHEDULED IN MULTIPLE
PROBE APPLICATIONS.
MPS
INSTRUMENT
AIR IN
REFERENCE
AIR
27270022
Figure D-3. Typical Automatic Calibration System
D

Instruction Manual
Appendix D Rev. 2.4
July 1998
D-4 Appendices Rosemount Analytical Inc. A Division of Emerson Process Management
World Class 3000
REFERENCE PURGE
NOTE: DIMENSIONS ARE IN INCHES WITH
MILLIMETERS IN PARENTHESES.
3
"BEBCO" PURGE WARNING NOTICE
SUPPLIED WITH BEBCO UNIT AND
TO BE INSTALLED ON MPS UNIT
AS SHOWN.
2
WITH ELECTRONICS DOOR CLOSED
TIGHTLY. SET AIR REGULATOR TO
0.25 IN. (65 PA) AS INDICATED ON
REFERENCE GAUGE.
1CUSTOMER SUPPLIED 0.25 IN.
(6,4 MM) OD LINE.
5
USE KROY LABEL, BLACK ON CLEAR,
14 PT. CENTER LABELS UNDER
FITTING HOLES AT DISTANCE SHOWN.
4TO BE CALLED OUT ON
SHOP ORDER.
6
CUSTOMER SUPPLIED INSTRUMENT
QUALITY COMPRESSED AIR SUPPLY
MUST BE EQUIPPED WITH A
TAMPER-PROOF REGULATOR SET
TO 5 PSIG (34,48 kPa) MAXIMUM.
ALARM NORMALLY CLOSED
ALARM NORMALLY OPEN
ALARM COMMON
6
1
2
5
4
1.00
(25,40)
1.00
(25,40)
WARNING NOTICE
3
(2 PLCS)
PARTS LIST
ITEM
01
02
03
04
NOTE
PART NAME
MPS ASSEMBLY
Z-PURGE UNIT
Z-PURGE UNIT
TUBE FITTING
DWG
AML
AML
DWG
DEFINER
SIZE - REFERENCE INFORMATION
GROUP NOTE
MAT'L CODE
PART NUMBER
OR REF DWG
3D39425GXX
1A98474H01
1A98474H02
771B870H05
GROUP
G01
A/R
1
2
G02
A/R
1
2
)
) W/O PRESSURE LOSS SWITCH
) W/ PRESSURE LOSS SWITCH
) 1/4" TUBE TO 1/4", S.S.
PARTS LIST UNITS: INCHES
NOTES:
DETAIL SWITCH CONTACT RATING:
15A - 125, 250,480 VAC
1/8 HP 125 VAC
1/4 HP 250 VAC
CLASS 1, DIV. 1 AND 2 GR. C AND D
CSA, FM AND UL LISTED
ALARM SWITCHING
"A"
COM NO NC
DRILL AND
TAP THRU FOR
1/4" NPT (2 PLCS)
3.00
(76,20)
2.50
(63,50)
1.50
(38,10)
0.75
(19,05)
LEFT SIDE
VIEW LABEL
ORIENTATION
AND HOLE
PLACEMENT
BEBCO MODEL Z-PURGE
REAR VIEW
ENCLOSURE
PRESSURE
INDICATOR
0-125 PA
ATMOSPHERIC
REF VENT
REFERENCE
PRESSURE TO
DIFFERENTIAL
PRESSURE
SWITCH
(SEE DETAIL "A")
1/2" CONDUIT WIRING INLET
EXPLOSION PROOF PRESSURE
LOSS ALARM SWITCH
(USED ON G02 ONLY)
CALIBRATION
SCREW
VENTURI ORIFICE
REDUNDANT PRESSURE
CONTROL VALVE
SYSTEM
REGULATOR
SYSTEM
SUPPLY
27270025
Figure D-4. MPS with Z-Purge

Instruction Manual
Appendix D Rev. 2.4
July 1998
Rosemount Analytical Inc. A Division of Emerson Process Management Appendices D-5
World Class 3000
MPS 3000 TROUBLESHOOTING
D-3 OVERVIEW
This section describes troubleshooting for the
Multiprobe Calibration Gas Sequencer. Addi-
tional troubleshooting information can be found
in the Instruction Bulletin for the electronics
package.
Install all protective equipment covers
and safety ground leads after trouble-
shooting. Failure to replace covers
and ground leads could result in seri-
ous injury or death.
D-4 TROUBLESHOOTING
Table D-2 provides a guide to fault finding fail-
ures within the MPS. The flowchart in Figure
D-5 provides an alternate approach to fault
finding MPS related problems.
Table D-2. Fault Finding
SYMPTOM CHECK FAULT REMEDY
1. Power to solenoid,
calibration gas not
released to probe.
Calibration gas Insufficient calibration
gas Install new calibration gas
tanks.
Solenoid Solenoid failure Replace solenoid.
2. No power to
solenoid. Power supply output Power supply failure Replace power supply.
Fuses in power
supply Fuse blown Replace fuse.
Main power source Main power off Reestablish power.
D

Instruction Manual
Appendix D Rev. 2.4
July 1998
D-6 Appendices Rosemount Analytical Inc. A Division of Emerson Process Management
World Class 3000
YES YES
NO NO
SYMPTOM
SOLENOID IS
OPERATING NORMALLY.
ENSURE THAT A
SUFFICIENT SUPPLY OF
CALIBRATION GAS IS
AVAILABLE.
CALL FOR FACTORY
ASSISTANCE.
SET METER* FOR 50 VDC.
PLACE PROBES ON
TERMINAL BLOCK J2, CAL
RET, AND J1 HI GAS.
INSTALL NEW CALIBRATION
GAS BOTTLES.
SOLENOID IS RECEIVING
24 VDC.
YES REPLACE SOLENOID.
NO
PLACE PROBES FROM
METER ON J11.
METER INDICATES
24 VDC.
YES REPLACE TERMINAL
BOARD.
NO
FUSES BLOWN IN MPS. NO PLACE PROBES FROM
METER ON J1, LINE 1,
AND LINE 2. SET METER
FOR 200 VAC.
YES
REPLACE BLOWN FUSES. METER INDICATES 110
VAC AT J1.
YES
REPLACE POWER SUPPLY.
NO
CHECK MAIN POWER
SOURCE.
*SIMPSON MODEL 260 OR
EQUIVALENT MULTIMETER.
27270023
Figure D-5. MPS Troubleshooting Flowchart

Instruction Manual
Appendix D Rev. 2.4
July 1998
Rosemount Analytical Inc. A Division of Emerson Process Management Appendices D-7
World Class 3000
SERVICE AND NORMAL MAINTENANCE
D-5 OVERVIEW
This section describes service and routine
maintenance of the MPS 3000 Multiprobe Cali-
bration Gas Sequencer. Replacement parts re-
ferred to are available from Rosemount. Refer to
Table D-3 for part numbers and ordering
information.
Install all protective equipment covers
and safety ground leads after equip-
ment repair or service. Failure to in-
stall covers and ground leads could
result in serious injury or death.
D-6 FUSE REPLACEMENT
Power supply (58, Figure D-6) contains two
identical 1 amp fuses (3). Perform the following
procedure to check or replace a fuse.
Disconnect and lock out power before
working on any electrical components.
a. Turn off power to the system.
b. Unscrew top of fuseholder (40) and remove
the fuse. Refer to Table D-3 for replacement
fuse specifications. After checking or re-
placing a fuse, reinstall top of fuseholder.
D-7 POWER SUPPLY REPLACEMENT
Disconnect and lock out power before
working on any electrical components.
a. Turn off power to the system.
b. Loosen two captive screws holding the MPS
cover (15, Figure D-6). Open the MPS
cover.
c. Loosen two captive screws holding the inner
cover (16). Lower the inner cover.
d. Disconnect the 24V connector from J11 on
the termination board (34).
e. Remove two screws (39) and washers (38)
holding the terminal cover (37). Remove the
terminal cover.
f. Tag and remove wires from terminals 1 and
4 or 5 of the transformer in the power supply
(58).
g. Remove two nuts (60) and washers (59)
from the screws holding the power supply
(58). Remove the power supply.
h. Mount the new power supply onto the
screws with two nuts (60) and washers (59).
Make sure the ground wires are connected
to the upper mounting screw.
i. Reconnect the wires removed in step f.
j. Install the terminal cover (37) with two
screws (38) and washers (39).
k. Connect the 24V connector to J11 on the
termination board (34).
l. Close and secure the inner cover (16) with
two captive screws. Close and secure the
outer cover (15) with two captive screws.
D-8 SOLENOID VALVE REPLACEMENT
An MPS 3000 will always have a HI GAS sole-
noid (63, Figure D-6) and a LOW GAS solenoid
(64) mounted to the manifold (11). Each probe
will also have a solenoid valve (9) mounted on
the manifold.
Disconnect and lock out power before
working on any electrical components.
a. Turn off power to the system.
b. Loosen two captive screws holding the MPS
cover (15, Figure D-6). Open the MPS
cover.
c. Loosen two captive screws holding the inner
cover (16). Lower the inner cover.
d. Disconnect the HI GAS (J17), LOW GAS
(J18), or Probe (J13-J16) plug from its re-
ceptacle on the termination board (34).
D

Instruction Manual
Appendix D Rev. 2.4
July 1998
D-8 Appendices Rosemount Analytical Inc. A Division of Emerson Process Management
World Class 3000
49
49
50
53
53
41
31
54
14
34
54
1
17
16
18
15
26
27
42
48 46
42
40
30
30
22
35
36
37
21
32
4
33
58
57
59
60
56
21
44
45
19
20
42
51
43
52
47
62
61
55
2
3
38
39
25 24
23
28
29
5
63
64
6
7
9
8
13
12
11
10
Figure D-6. Multiprobe Calibration Gas Sequencer, Exploded View

Instruction Manual
Appendix D Rev. 2.4
July 1998
Rosemount Analytical Inc. A Division of Emerson Process Management Appendices D-9
World Class 3000
LEGEND FOR FIGURE D-6
1. Enclosure
2. Screw
3. Plug
4. Cable Grip
5. Fitting
6. Hose Adapter
7. Pressure Switch
8. Plug
9. Solenoid Valve
10. Screw
11. Manifold
12. Washer
13. Screw
14. Gasket
15. Outer Cover
16. Inner Cover
17. Flowmeter, 10 SCFH
18. Flowmeter, 2.0 SCFH
19. Bracket
20. Screw
21. Hose Adapter
22. 1/8 in. Hose
23. Nut
24. Lockwasher
25. Washer
26. Washer
27. Screw
28. Nut
29. Washer
30. Washer
31. Cover Stop Slide
32. Screw
33. Washer
34. Termination Board
35. Standoff
36. Mounting Bracket
37. Cover Plate
38. Washer
39. Screw
40. Fuseholder
41. Plastic Nut
42. Bushing
43. Pressure Gauge
44. Bolt
45. Washer
46. Drain Valve
47. 1/8 in. Impolene Tubing
48. Connector
49. Elbow
50. Pressure Regulator
51. Hose Adapter
52. 1/4 in. Tube
53. Screw
54. Washer
55. Inner Enclosure
56. Washer
57. Screw
58. Power Supply
59. Washer
60. Nut
61. Screw
62. Washer
63. Solenoid
64. Solenoid
e. Loosen the retaining ring in the middle of
the solenoid and remove the top part.
f. With a spanner wrench or padded pliers,
remove the remaining part of the solenoid
from the manifold (11).
g. Separate the new solenoid and screw the
smaller part into the manifold.
h. Place the top part of the solenoid into posi-
tion and tighten the retaining ring.
i. Connect the plug to the proper receptacle
on the termination board (34).
j. Close and secure the inner cover (16) with
two captive screws. Close and secure the
outer cover (15) with two captive screws.
D-9 PRESSURE REGULATOR MAINTENANCE
a. Pressure Adjustments
Pressure regulator (50, Figure D-6) is fac-
tory set to 20 psi (138 kPa). Should the
pressure need to be changed or adjusted,
use the knob on top of the pressure
regulator.
b. Condensation Drain
To drain excess moisture from the internal
gas circuit of the MPS, periodically loosen
drain valve (46) on the bottom of pressure
regulator (50). The moisture will flow
through vinyl tubing drain (47) on the bottom
of pressure regulator (50) and exit the bot-
tom of MPS enclosure (1).
D

Instruction Manual
Appendix D Rev. 2.4
July 1998
D-10 Appendices Rosemount Analytical Inc. A Division of Emerson Process Management
World Class 3000
D-10 FLOWMETER ADJUSTMENTS
There are two flowmeters per flowmeter assem-
bly. The top flowmeter is factory set to 5 scfh.
The bottom flowmeter is set to 2 scfh. Should
the flow need to be changed or adjusted, use
knob on the bottom of the respective flowmeter.
D-11 ADDING PROBES TO THE MPS
This procedure is used to add a probe to the
MPS.
Disconnect and lock out power before
working on any electrical components.
a. Turn off power to the system.
b. Loosen the two captive screws holding the
MPS cover (15). Lift the cover.
c. Loosen the two captive screws that hold the
inner cover (16) and lower the cover.
d. From the backside of the inner cover, locate
the flowmeter positions next to the existing
unit(s). Insert a hacksaw blade into the slots
surrounding the positions for two flowme-
ters, and saw out the knockout tabs.
e. From the front of the inner cover, install a
flowmeter (P/N 771B635H01) into the top
hole and a flowmeter (P/N 771B635H02)
into the bottom hole. From the backside se-
cure with brackets provided.
f. Remove four brass screw plugs (CAL GAS
IN, CAL GAS OUT, REF AIR IN, and REF
AIR OUT) for the next probe position in the
manifold.
g. Install 1/8" hose adapters (P/N
1A97553H01) into the empty holes using a
suitable pipe dope. Attach the tubing.
h. Remove a brass screw plug (P/N
1A97900H01) and install a solenoid (P/N
3D39435G01). Make sure the O-ring seals
properly.
i. Attach the hoses to the flowmeter using the
existing installation as a guide. Support the
flowmeter while attaching the hose.
j. Install the solenoid wire connector into the
proper position (J14-J16) on the termination
board (34).
k. Close and secure the inner cover (16) with
two captive screws. Close and secure the
outer cover (15) with two captive screws.

Instruction Manual
Appendix D Rev. 2.4
July 1998
Rosemount Analytical Inc. A Division of Emerson Process Management Appendices D-11
World Class 3000
REPLACEMENT PARTS
Table D-3. Replacement Parts for the Multiprobe Test Gas Sequencer
FIGURE and
INDEX No. PART NUMBER DESCRIPTION
Figure D-6, 58 1A97909H01* Power Supply
Figure D-6, 9 3D39435G01** Solenoid Valve
Figure D-6, 40 138799-004 Fuse, fast acting, 1A @ 250 Vac, size: 1/4" Dia.
x 1-1/4” Lg., glass body, non time delay, Buss-
man part no. BK/AGC-1
Figure D-6, 40 138799-014 Fuse, fast acting, 0.5A @ 250 Vac, size: 1/4"
Dia. x 1-1/4” Lg., glass body, non time delay,
Bussman part no. BK/AGC-1/2
Figure D-6, 17 771B635H01** Flowmeter Assembly - Calibration Gas
Figure D-6, 18 771B635H02** Flowmeter Assembly - Reference Air
1A98631 Probe Adder Kit
Figure D-6, 51 1A97953H01** Hose Adapter
4847B46H01** Tubing Length
4847B46H02** Tubing Length
4847B46H03** Tubing Length
4847B46H04** Tubing Length
Figure D-3 7307A56G02 Check Valve
*Specify line voltage and probe type when ordering.
**These items are included in the probe adder kit.
D

Instruction Manual
Appendix D Rev. 2.4
July 1998
D-12 Appendices Rosemount Analytical Inc. A Division of Emerson Process Management
World Class 3000

Instruction Manual
Appendix E Rev. 4.5
June 1999
Rosemount Analytical Inc. A Division of Emerson Process Management Appendices E-1
World Class 3000
APPENDIX E, REV. 4.5
IFT 3000 INTELLIGENT FIELD TRANSMITTER
DESCRIPTION
Read the “Safety instructions for the
wiring and installation of this appara-
tus” at the front of this Instruction
Bulletin. Failure to follow the safety
instructions could result in serious
injury or death.
E-1 DESCRIPTION
The Rosemount IFT 3000 Intelligent Field
Transmitter (IFT), Figure E-1, provides all nec-
essary intelligence for controlling a probe and
the optional Multiprobe Calibration Gas Se-
quencer. The IFT provides a user-friendly,
menu-driven operator interface with context-
sensitive, on-line help. The IFT may also be
used without an HPS.
The IFT is based on a modular design. There is
a maximum total of four PC boards within the
IFT. Every IFT contains a microprocessor
board, a power supply board, and an intercon-
nect board. In addition to these boards, deluxe
version IFTs also contain a General User Inter-
face/LED display board.
21240002
Figure E-1. IFT 3000 Intelligent Field Transmitter
IFTs with no displays are known as "blind" units.
Blind IFTs also lack a General User Interface
(GUI) and must be controlled with an external
HART communications device.
a. Microprocessor Board
The microprocessor board contains,
EEPROM, RAM, and a timer. The micro-
processor board also controls the probe
heater. The IFT can be used in conjunction
with or without an optional HPS 3000
Heater Power Supply providing power to the
heater depending upon the user's
application.
b. Interconnect Board
The interconnect board is used for all com-
munications from the IFT to the other com-
ponents within the system. These other
components may include an optional HPS
3000 Heater Power Supply, optional MPS
Multiprobe Calibration Gas Sequencer,
World Class 3000 Probe (non-HPS
equipped system), analog output, and relay
outputs.
c. Power Supply Board
The power supply board is user configur-
able for five different line voltages to include
100, 120, 220, and 240 Vac. In addition, the
output voltage for a probe heater is also
configurable if used in a non-HPS equipped
system.
d. GUI/LED Display Board (Optional)
The GUI/LED display board, which is part of
the GUI assembly, has a 4-line by 20-
character liquid crystal display and eight
membrane keys. The board also contains
an LED display which indicates the current
O2 value. The LED display has indicator
LEDs for calibration gas high (TGH), cali-
bration gas low (TGL) and calibrating (CAL).
E

Instruction Manual
Appendix E Rev. 4.5
June 1999
E-2 Appendices Rosemount Analytical Inc. A Division of Emerson Process Management
World Class 3000
e. Heater (optional)
A heater is available for ambient conditions
below 32°F (0°C).
f. Z-Purge (optional)
A Z-purge arrangement is available for ap-
plications requiring hazardous area classifi-
cation. See Application Data Bulletin AD
106-300B.
E-2 THEORY OF OPERATION
A functional block diagram of the IFT, con-
nected to the HPS and probe, is shown in
Figure E-2. In operation, the IFT monitors the
temperature of the cell by means of the probe
thermocouple. The IFT controls the temperature
of the cell. If the temperature of the cell be-
comes too high, the IFT will disable the HPS.
A cold junction temperature compensation fea-
ture ensures an accurate probe thermocouple
reading. A temperature sensor in the heater
power supply monitors the temperature at the
junction between the compensated cable run-
ning to the probe and the uncompensated cable
running to the IFT. The voltage from this sensor
is used by the IFT to compensate the probe
thermocouple readings for the temperature at
the junction.
The cell signal is a voltage proportional to the
oxygen concentration difference between the
two sides of the cell. The IFT receives this sig-
nal and translates it into a user-specified form
for display and/or output.
Table E-1. Specifications for Intelligent Field Transmitter
Environmental Classification ..................................... NEMA 4X (IP56)
Humidity Range......................................................... 95% Relative Humidity
Ambient Temperature Range.................................... -20° to 122°F (-30° to 50°C)
Vibration .................................................................... 5 m/sec2, 10 to 500 xyz plane
Electrical Noise Immunity Standard .......................... EN 50 082-1
Electrical Noise Radiated Emission Standard........... EN 55 011
Installation Category ................................................. Overvoltage Category II (IEC 664)
HART Communications............................................ Modulated on a 4-20 mA analog output, only
Analog Outputs ......................................................... isolated, 0-20 mA, 4-20 mA, 0-10 V, 20-0 mA, 20-4 mA,
or 10-0 V output
O2 Accuracy (analog output) ..................................... 0.1% O2 or ±3% of reading, whichever is greater using
Hagan calibration gases
O2 Range................................................................... Field Selectable 0-40% (linear or logarithmic)
Power Supply ............................................................ 100/120/220/240 ±10% Vac at 50/60 Hz.
Power Requirements................................................. (w/HPS 3000): 30 Watts (VA); (w/Model 218 Probe):
275 VA (w/WC 3000 Probe): 275 Watts (VA)
Output Resolution ..................................................... 11 bits (1 bit = 0.05% of output F.S.)
System Speed of Response (amplifier output) ......... less than 3 seconds
Resolution Sensitivity - Transmitted Signal............... 0.01% O2
Deadman Contact Output ......................................... Form-C, 48 Volt max, 100 mA max
Programmable Contact Outputs ............................... 2 available, Form-C, 48 V max, 100 mA max
GUI/LED Display Board (optional) ............................ 1, with 0.8 in. (20 mm) high, 3-character, alphanumeric
LED display 4-line by 20-character backlight LCD
alpha-numeric display; 8-key general purpose key-
board, or HART device
Approximate Shipping Weight................................... 25 lbs (11 kg)

Instruction Manual
Appendix E Rev. 4.5
June 1999
Rosemount Analytical Inc. A Division of Emerson Process Management Appendices E-3
World Class 3000
PROBE
ZERO
CROSSING
DETECTOR
TRIACRELAY
TO HEATER
COLD
JUNCTION
TEMP. PROBE TC
STACK TC
CELL
LINE
RELAY
TRIAC
AD590
PROBE TC
STACK TC
CELL MV
HEATER POWER SUPPLY
(OPTIONAL)
IFT
TRANSFORMER
21240013
Figure E-2. System Block Diagram
E

Instruction Manual
Appendix E Rev. 4.5
June 1999
E-4 Appendices Rosemount Analytical Inc. A Division of Emerson Process Management
World Class 3000
IFT 3000 TROUBLESHOOTING
E-3 OVERVIEW
The IFT troubleshooting section describes how
to identify and isolate faults which may develop
in the IFT.
Install all protective equipment covers
and safety ground leads after trouble-
shooting. Failure to replace covers
and ground leads could result in seri-
ous injury or death.
E-4 IFT TROUBLESHOOTING
IFT troubleshooting is achieved by determining
the functional status of the microprocessor
board and interpreting status displays on the
front panel.
a. Microprocessor Status LED
The microprocessor board includes an LED
to aid in isolating equipment faults. LED in-
dications are as follows:
1. LED OFF. IFT failure, or power is re-
moved; refer to Troubleshooting Flow-
chart #1 (Figure E-3).
2. LED ON - STEADY. Heater system
failure; refer to Troubleshooting Flow-
chart #2 (Figure E-4).
3. LED ON - FLASHING. Microprocessor
normal.
b. Equipment Status (LCD) Displays
The status line of the GUI equipped IFT will
display one system status display (one at a
time) in priority sequence, as indicated in
the following list. To troubleshoot an equip-
ment fault, refer to COMPONENT FAILURE
indications applicable to the display mes-
sage (SYMPTOM) in Table E-2.
1. Off - The probe has been turned off
because the IFT cannot control the
heater temperature.
2. Param - IFT has been unlocked using
the user’s password.
3. Serv - IFT has been unlocked using
the service password.
4. PrbEr - The probe is disconnected,
cold, or leads are reversed.
5. HtrEr - If HtrEr is displayed, there is a
fault within the heater system.
6. InCal - If InCal is displayed, the system
is currently undergoing calibration.
7. LowO2 - If LowO2 is displayed, the O2
value is below the low alarm limit.
8. HiO2 - If HiO2 is displayed, the O2
value is above the high alarm limit.
9. NoGas - If NoGas is displayed, there is
no calibration gas pressure.
10. CalEr - If CalEr is displayed, an error
was detected during the calibration
process.
11. ResHi - If ResHi is displayed, the cell
resistance is above the high limit.
12. OK - If OK is displayed, the system is
operating normally.

Instruction Manual
Appendix E Rev. 4.5
June 1999
Rosemount Analytical Inc. A Division of Emerson Process Management Appendices E-5
World Class 3000
Figure E-3. IFT Troubleshooting Flowchart, #1
E

Instruction Manual
Appendix E Rev. 4.5
June 1999
E-6 Appendices Rosemount Analytical Inc. A Division of Emerson Process Management
World Class 3000
YES
YES
OXYGEN ANALYZER
SYSTEM IS EQUIPPED
WITH HPS 3000.
CHECK JUMPERS JM6 ON
MICROPROCESSOR BOARD
AND JM1 ON INTERCONNECT
BOARD ARE INSTALLED.
CHECK JUMPERS 9
OR 10 ON POWER
SUPPLY BOARD FOR COR-
RECT CONFIGURATIONS.
REFER TO PROBE
TROUBLESHOOTING,
APPENDIX A, SECTION 2.
CHECK THAT JUMPERS
JM6 ON MICROPROCESSOR
BOARD AND JM1 ON
INTERCONNECT BOARD
ARE REMOVED.
REFER TO APPENDIX B,
SECTION 2, FOR
JUMPER LOCATIONS.
DISCONNECT POWER
AND INSTALL JUMPERS
CORRECTLY. REFER TO
FIGURE 2-5 OF MAIN IB
SECTION.
NO
NO
SYMPTOM - MICROPROCESSOR BOARD LED IS STEADY ON
27270021
Figure E-4. IFT Troubleshooting Flowchart, #2
END OF FLOWCHART #2
SYMPTOM - GENERAL USER INTERFACE OR
LED DISPLAY PANEL DOES NOT FUNCTION
REPLACE GUI BOARD.
STILL NOT FUNCTIONING.
CALL FACTORY FOR
ASSISTANCE.
27270020
Figure E-5. IFT Troubleshooting Flowchart, #3

Instruction Manual
Appendix E Rev. 4.5
June 1999
Rosemount Analytical Inc. A Division of Emerson Process Management Appendices E-7
World Class 3000
Table E-2. GUI Equipped IFT Fault Finding
SYMPTOM COMPONENT FAILURE
1. Display is blank. Possible failure within IFT. Check LED on microprocessor board.
2. CalEr is displayed. Repeat calibration sequence. If error persists, troubleshoot major components.
3. HtrEr is displayed. Ensure jumpers are set correctly on IFT. If system is equipped with HPS refer
to HPS 3000 Troubleshooting in Appendix B for additional troubleshooting
procedures.
4. NoGas is displayed. Possible failure within the MPS. Refer to MPS 3000 Troubleshooting in Ap-
pendix D for additional troubleshooting procedures.
*5. HiO2 is displayed. Possible failure within the probe. Ensure the high alarm level has been en-
tered correctly. Refer to Probe Troubleshooting in Appendix A for additional
troubleshooting procedures.
*6. LowO2 is displayed. Possible failure within the probe. Ensure the low alarm parameter has been
entered correctly. Refer to Probe Troubleshooting in Appendix A for additional
troubleshooting procedures.
7. ResHi is displayed. Cell resistance has exceeded upper limit. Ensure resistance value has been
entered correctly. Refer to Probe Troubleshooting in Appendix A for additional
troubleshooting procedures.
8. Off The probe has been turned OFF because the IFT cannot control the heater
temperature.
9. PrbEr The probe is disconnected, cold, or leads are reversed.
*HiO2 and LowO2 can occur in the system without system failure.
E

Instruction Manual
Appendix E Rev. 4.5
June 1999
E-8 Appendices Rosemount Analytical Inc. A Division of Emerson Process Management
World Class 3000
SERVICE AND NORMAL MAINTENANCE
E-5 OVERVIEW
This section describes service and routine
maintenance of the Intelligent Field Transmitter.
Replacement parts referred to are available
from Rosemount. Refer to Replacement Parts
later in this appendix for part numbers and or-
dering information.
Install all protective equipment covers
and safety ground leads after equip-
ment repair or service. Failure to in-
stall covers and ground leads could
result in serious injury or death.
E-6 FUSE REPLACEMENT
Power supply board (4, Figure E-6) contains
four identical 5 amp fuses.
Perform the following procedure to check or re-
place a fuse. In addition, 2 additional 5 amp
fuses (F1 and F2) are included if the IFT unit
has an internal heater installed.
Disconnect and lock out power before
working on any electrical components.
There is voltage up to 240 Vac, and
could cause personal injury.
a. Turn off power to the system.
b. Open cover door (16) of the IFT by remov-
ing screws (17).
c. Remove protective cover (13) by removing
screws (14) and washers (15).
d. Unscrew fuseholder top and remove the
fuse (5). After checking or replacing a fuse,
reinstall the fuseholder top.
e. Replace protective cover (13) and secure
with washers (15) and screws (14).
f. Close cover door (16) and secure with
screws (17).
E-7 TRANSFORMER REPLACEMENT
Disconnect and lock out power before
working on any electrical components.
There is voltage up to 240 Vac, and
could cause personal injury.
a. Turn off power to the system.
b. Open cover door (16) of the IFT by remov-
ing screws (17).
c. Remove protective cover (13) by removing
screws (14) and washers (15).
d. Disconnect cable (1) from the receptacle on
microprocessor board (11). Disconnect GUI
assembly cable from receptacles on micro-
processor board if IFT is equipped with GUI.
e. Carefully tagging wires, remove the wires
from terminal strip on interconnect board
(12).
f. If unit is equipped with heater option, re-
move thermoswitch assembly (18, 19,
Figure E-8) by removing screws (13) and
washers (14).
g. Remove mounting plate (10) by removing
the necessary screws.
h. Disconnect transformer cable plugs from the
receptacles on power supply board (4).
i. Remove transformer (9) from enclosure (6)
by removing four screws (8).
j. Attach new transformer to enclosure (6) with
four screws (8).
k. Connect the transformer cable plugs from
transformer (9) to the receptacles on power
supply board (4).

Instruction Manual
Appendix E Rev. 4.5
June 1999
Rosemount Analytical Inc. A Division of Emerson Process Management Appendices E-9
World Class 3000
1. Cable
2. Machine Screw, M3 x 8 mm
3. Lockwasher, 3 mm (Note 2)
4. Power Supply Board
5. Fuses, 5 Amp
6. Enclosure
7. Plug
8. Machine Screw, M5 x 8 mm
9. Transformer
10. Mounting Plate
11. Microprocessor Board
12. Interconnect Board
13. Protective Cover
14. Screw, M4
15. Washer
16. Cover Door
17. Screw, M4
18. Pin
19. Nylon Washer (Note 2)
20. O-Ring
21. Nylon Washer
Figure E-6. Intelligent Field Transmitter, Exploded View
1
2
34
6
5
7
11
10
98
2
19
12
2
3
14
15
18
13
16
17
21
20
NOTE 1: NOT ALL PARTS SHOWN ARE AVAILABLE FOR PURCHASE
SEPARATELY. FOR A LIST OF AVAILABLE PARTS, SEE TABLE E-3.
NOTE 2: NYLON WASHER (19) IS USED IN FIVE PLACES ON
MICROPROCESSOR BOARD (11). LOCKWASHER (3) IS USED IN
FOUR PLACES ON BOARD (12) AND IN FIVE PLACES ON BOARD (4).
21240003
E

Instruction Manual
Appendix E Rev. 4.5
June 1999
E-10 Appendices Rosemount Analytical Inc. A Division of Emerson Process Management
World Class 3000
l. Reinstall mounting plate (10) to enclosure
(6) with the necessary screws and washers.
m. If removed, replace thermoswitch assembly
(18, 19, Figure E-8) and secure with screws
(13) and washers (14).
n. Reinstall the wires to the terminal strip on
interconnect board (12) as was noted in
step e.
o. Connect cable (1) to the receptacle on mi-
croprocessor board (11). Reconnect GUI
assembly cable to receptacles on micro-
processor board if IFT is equipped with GUI.
p. Replace protective cover (13) and secure
with washers (15) and screws (14).
q. Close cover door (16) and secure with
screws (17).
E-8 POWER SUPPLY BOARD REPLACEMENT
Disconnect and lock out power before
working on any electrical components.
There is voltage up to 240 Vac, and
could cause personal injury.
a. Turn off power to the system.
b. Open cover door (16) of the IFT by remov-
ing screws (17).
c. Remove protective cover (13) by removing
screws (14) and washers (15).
d. Disconnect cable (1) from the receptacle on
microprocessor board (11). Disconnect GUI
assembly cable from receptacles on micro-
processor board if IFT is equipped with GUI.
e. Carefully tagging wires, remove the wires
from terminal strip on interconnect board
(12).
f. If unit is equipped with heater option, re-
move thermoswitch assembly (18, 19,
Figure E-8) by removing screws (13) and
washers (14).
g. Remove mounting plate (10) by removing
the necessary screws.
h. If unit is equipped with heater option, dis-
connect plug from J2 on power supply
board (4, Figure E-6) by squeezing tabs in
and pulling connector up.
i. If unit is equipped with heater option, re-
move fan assembly (7, 10, Figure E-8) by
removing screws (5) and washers (6).
j. Disconnect the transformer cable plugs from
the receptacles on power supply board (4,
Figure E-6).
k. Carefully tagging wires, remove the wires
from terminal strips J5 and J6 on power
supply board (4, Figure E-6).
l. Remove power supply board (4) from en-
closure (6) by removing screws (2) and
washers (3).
m. Attach new power supply board (4) to en-
closure (6) with screws (2) and washers (3).
n. Reconnect the wires as noted in step e.
o. Connect the transformer cable plugs from
transformer (9) to the receptacles on power
supply board (4).
p. If removed, install fan assembly (7, 10,
Figure E-8) and secure with screws (5)
and washers (6).
q. If disconnected, reconnect plug to J2 on
power supply board (4, Figure E-6).
r. If removed, replace thermoswitch assembly
(18, 19, Figure E-8) and secure with screws
(13) and washers (14).
s. Reinstall mounting plate (10) to enclosure
(6) using the necessary screws.
t. Reconnect the wires to interconnect board
(12) as noted in step e.

Instruction Manual
Appendix E Rev. 4.5
June 1999
Rosemount Analytical Inc. A Division of Emerson Process Management Appendices E-11
World Class 3000
u. Connect cable (1) to the receptacle on mi-
croprocessor board (11). Reconnect GUI
assembly cable to receptacles on micro-
processor board if IFT is equipped with GUI.
v. Replace protective cover (13) and secure
with washers (15) and screws (14).
w. Close cover door (16) and secure with
screws (17).
E-9 MICROPROCESSOR BOARD
REPLACEMENT
Disconnect and lock out power before
working on any electrical components.
There is voltage up to 240 Vac, and
could cause personal injury.
a. Turn off power to the system.
b. Open cover door (16) of the IFT by re-
moving screws (17).
c. Remove protective cover (13) by removing
screws (14) and washers (15).
d. Disconnect cable (1) from the receptacle on
microprocessor board (11). Disconnect GUI
assembly cable from receptacles on micro-
processor board if IFT is equipped with GUI.
e. Remove microprocessor board (11) by re-
moving screws (2) and nylon washers (19).
Pull up very carefully on the micro-
processor board to ensure that none
of the pins in the connection between
the microprocessor board and inter-
connect board are damaged.
f. Connect the new microprocessor board (11)
to the interconnect board (12) by carefully
lining up the pins on the plug.
g. Attach microprocessor board (11) to
mounting plate (10) with screws (2) and ny-
lon washers (19).
h. Reconnect cable (1) to receptacle on micro-
processor board. Reconnect GUI assembly
cable to receptacles on microprocessor
board if IFT is equipped with GUI.
i. Replace protective cover (13) and secure
with washers (15) and screws (14).
j. Close cover door (16) and secure with
screws (17).
E-10 INTERCONNECT BOARD REPLACEMENT
Disconnect and lock out power before
working on any electrical components.
There is voltage up to 240 Vac, and
could cause personal injury.
a. Turn off power to the system.
b. Open cover door (16) of the IFT by remov-
ing screws (17).
c. Remove protective cover (13) by removing
screws (14) and washers (15).
d. Carefully tagging wires, remove the wires
from terminal strip on interconnect board
(12).
e. Remove interconnect board (20) by remov-
ing screws (2) and washers (3).
Pull down very carefully on the inter-
connect board to ensure that none of
the pins in the connection between the
microprocessor board and intercon-
nect board are damaged.
f. Connect new interconnect board (12) to the
microprocessor board by carefully lining up
the pins on the plug.
g. Attach interconnect board (12) to mounting
plate (10) with screws (2) and washers (3).
h. Reconnect wires to the terminal strip as
noted in step d.
E

Instruction Manual
Appendix E Rev. 4.5
June 1999
E-12 Appendices Rosemount Analytical Inc. A Division of Emerson Process Management
World Class 3000
i. Replace protective cover (13) and secure
with washers (15) and screws (14).
j. Close cover door (16) and secure with
screws (17).
E-11 GUI ASSEMBLY REPLACEMENT
These replacement instructions are provided for
GUI equipped systems. Refer to Figure E-7.
Disconnect and lock out power before
working on any electrical components.
There is voltage up to 240 Vac, and
could cause personal injury.
a. Turn off power to the system.
b. Open cover door (43, Figure E-7) of the IFT
by removing screws (5).
1. Screw
2. Washer
3. GUI Assembly
4. Cover Door
5. Screw, M4
6. O-Ring
ENTER
ESC
DATA CALSETUP
HELP
NOTES:
1.
2.
GUI MOUNT AREA IS PART OF COVER DOOR.
GUI FACES INSIDE OF IFT ENCLOSURE WHEN
COVER DOOR IS CLOSED.
3. NOT ALL PARTS SHOWN ARE AVAILABLE FOR
PURCHASE SEPARATELY. FOR A LIST OF
AVAILABLE PARTS, SEE TABLE E-3.
(SEE
NOTE 1)
1
2
3
4
5
6
21240001
Figure E-7. Replacing the GUI Assembly
c. Disconnect GUI assembly cables from mi-
croprocessor board (11, Figure E-6).
d. Remove GUI assembly (3, Figure E-7) by
removing screws (1) and washers (2).
e. Attach new GUI assembly to inside of cover
door (4) with washers (2) and screws (1).
f. Reconnect GUI assembly cables to micro-
processor board (11, Figure E-6).
g. Close cover door (4, Figure E-7) and secure
with screws (5).
E-12 HEATER / FAN / THERMOSWITCH
REPLACEMENT
These replacement instructions are provided for
heater/fan/thermoswitch equipped systems.
a. Heater Replacement
Disconnect and lock out power before
working on any electrical components.
There is voltage up to 240 Vac, and
could cause personal injury.
1. Turn off power to the system.
2. Open cover door (1, Figure E-8) of the
IFT by removing screws (5, Figure
E-7).
3. Remove protective cover (4) by re-
moving screws (2) and washers (3).
4. Disconnect cable (1, Figure E-6) from
microprocessor board (11, Figure E-6).
5. Partially remove mounting plate as-
sembly (15) from enclosure (23) by
removing necessary screws.
6. Remove screws (11) and washers (12)
to free heater mounting plate (20) from
mounting plate (15).
7. Cut wires to old heater (21) close to the
heater; then remove old heater from
heater mounting plate (20).

Instruction Manual
Appendix E Rev. 4.5
June 1999
Rosemount Analytical Inc. A Division of Emerson Process Management Appendices E-13
World Class 3000
8. Splice heater wire to new heater (21)
and attach new heater to heater
mounting plate (20).
9. Attach heater assembly (20, 21) to
mounting plate (15) using screws (11)
and washers (12).
10. Reconnect all cables removed in step
3.
11. Position mounting plate (15) onto en-
closure (23) and secure with the nec-
essary screws.
12. Reinstall protective cover (15) using
screws (2) and washers (3).
13. Close door cover (1) and secure with
screws (5, Figure E-7).
b. Thermoswitch Replacement
Disconnect and lock out power before
working on any electrical components.
There is voltage up to 240 Vac, and
could cause personal injury.
1. Turn off power to the system.
2. Open cover door (1, Figure E-8) of the
IFT by removing screws (5, Figure
E-7).
3. Remove protective cover (4) by re-
moving screws (2) and washers (3).
4. Disconnect cable (1, Figure E-6) from
microprocessor board (11, Figure E-6).
5. Partially remove mounting plate as-
sembly (15) from enclosure (23) by
removing necessary screws.
6. Remove screws (13) and washers (14),
and remove thermoswitch mounting
plate (18) from mounting plate (15).
7. Pull wires free of thermoswitch tabs.
8. Remove old thermoswitch (19) from
thermoswitch mounting plate (18) by
removing screws (16) and washers
(17).
9. Install new thermoswitch (19) to ther-
moswitch mounting plate (18) using
screws (16) and washers (17).
10. Connect wires to thermoswitch tabs.
11. Attach thermoswitch assembly (18, 19)
to mounting plate (15) using screws
(13) and washers (14).
12. Reconnect cable removed in step 4.
13. Position mounting plate (15) onto en-
closure (23) and secure with the nec-
essary screws.
14. Reinstall protective cover (4) using
screws (2) and washers (3).
15. Close door cover (1) and secure with
screws (5, Figure E-7).
c. Fan Replacement
Disconnect and lock out power before
working on any electrical components.
There is voltage up to 240 Vac, and
could cause personal injury.
1. Turn off power to the system.
2. Open cover door (1, Figure E-8) of the
IFT by removing screws (5, Figure
E-7).
3. Remove protective cover (4) by re-
moving screws (2) and washers (3).
4. Remove fan mounting bracket (7) from
mounting plate (15) by removing
screws (5) and washers (6).
5. Remove fan (10) from fan mounting
plate (7) by removing screws (9) and
washers (8).
E

Instruction Manual
Appendix E Rev. 4.5
June 1999
E-14 Appendices Rosemount Analytical Inc. A Division of Emerson Process Management
World Class 3000
1
2
3
4
5
6
7
10
A
11 12
8
9
13 14
19
18
17
16
15
A
B
B
20
21
22
23
NOTES: 1.
2.
LETTERS INDICATE WIRE
CONTINUITY; A TO A AND B TO B.
NOT ALL PARTS SHOWN ARE AVAILABLE
FOR PURCHASE SEPARATELY. FOR A LIST
OF AVAILABLE PARTS, SEE TABLE E-3.
24
21240004
6. Cut wires close to old fan (10).
7. Splice wires to new fan (10).
8. Mount new fan (10) to fan mounting
bracket (7) using screws (8) and wash-
ers (9).
9. Mount fan assembly (7, 10) to mount-
ing plate (15) using screws (5) and
washers (6).
10. Reinstall protective cover (4) using
screws (2) and washers (3).
11. Close door cover (1) and secure with
screws (5, Figure E-7).
1. Cover Door
2. Screw
3. Washer
4. Protective Cover
5. Screw
6. Washer
7. Fan Mounting Bracket
8. Washer
9. Screw
10. Fan
11. Screw
12. Washer
13. Screw
14. Washer
15. Mounting Plate
16. Screw
17. Washer
18. Thermoswitch Mounting Plate
19. Thermoswitch
20. Heater Mounting Plate
21. Heater
22. Electrical Plug
23. Enclosure
24. Nylon Washer
Figure E-8. IFT with Heater Option

Instruction Manual
Appendix E Rev. 4.5
June 1999
Rosemount Analytical Inc. A Division of Emerson Process Management Appendices E-15
World Class 3000
REPLACEMENT PARTS
Table E-3. Replacement Parts for the Intelligent Field Transmitter.
FIGURE and INDEX No PART NUMBER DESCRIPTION
Figure E-6, 9 1N04946G01 Transformer
Figure E-6, 12 3D39120G01 Interconnect Board
Figure E-6, 4 3D39122G01* Power Supply Board
Figure E-6, 11 3D39513G02 Microprocessor Board
Figure E-7, 3 1L04279H01 GUI Assembly
Figure E-6, 5 1L01293H02 Fuse, 5A @ 250 Vac, anti-
surge, case size; 5 x 20 mm,
type T to IEC127, Schurter
Figure E-8, 21 1A97964H01 Heater, 120V
Figure E-8, 21 1A97964H02 Heater, 240V
Figure E-8, 10 1M03255G01 Fan, 120V
Figure E-8, 10 1M03255G02 Fan, 240V
Figure E-8, 19 1M03256G01 Thermoswitch
*Specify line voltage and probe type when ordering.
E

Instruction Manual
Appendix E Rev. 4.5
June 1999
E-16 Appendices Rosemount Analytical Inc. A Division of Emerson Process Management
World Class 3000

Instruction Manual
Appendix J Rev. 1.1
June 1995
Rosemount Analytical Inc. A Division of Emerson Process Management Appendices J-1
World Class 3000
APPENDIX J, REV 1.1
HART COMMUNICATOR MODEL 275D9E
IFT 3000 APPLICATIONS
DESCRIPTION
J-1 COMPONENT CHECKLIST OF TYPICAL
HART® COMMUNICATOR PACKAGE
A typical Model 275D9E HART® Communicator
package should contain the items shown in
Figure J-1, with the possible exception of op-
tions. If a rechargeable NiCad battery pack has
been selected, at least one spare battery pack
(per HART Communicator) is recommended.
J-2 UNIT OVERVIEW
a. Scope
This Instruction Bulletin supplies details
needed to install and operate the HART®
Communicator in relation to the World Class
3000 Intelligent Field Transmitter. Informa-
tion on troubleshooting the communicator is
also included.
12
3
4
5
6
7
o
HART Communicator
FISHER-ROSEMOUNT
TM
MAN 4275A00
English
October 1994
8
9
10
686001
1. Lead Set (with Connectors)
2. Carrying Case
3. Communicator
4. AA Alkaline Battery Pack, or Rechargeable
NiCad Battery Pack (Option)
5. Memory Module
6. Belt Clip (with screws)
7. Hanger (mounts on belt clip, Option)
8. Pocket-sized Instruction Manual
9. PC Interface Adaptor (Option)
10. Load Resistor, 250 W (Option)
Figure J-1. Typical HART® Communicator Package, Model 275D9E
J

Instruction Manual
Appendix J Rev. 1.1
June 1995
J-2 Appendices Rosemount Analytical Inc. A Division of Emerson Process Management
World Class 3000
b. Device Description
The HART (Highway Addressable Remote
Transducer) Communicator is a hand-held
communications interface device. It provides a
common communications link to all microproc-
essor-based instruments which are HART com-
patible. The hand-held communicator contains
an 8 x 21 character liquid crystal display and 25
keys. A pocket-sized manual, included with the
HART Communicator, details the specific func-
tions of all keys.
To interface with the IFT 3000, the HART Com-
municator requires a termination point along the
4-20 mA current loop, and a minimum load re-
sistance of 250 ohms between the communica-
tor and the power supply. The HART
Communicator accomplishes its task by use of a
frequency shift keying (FSK) technique. With the
use of FSK, high-frequency digital communica-
tion signals are superimposed on the 4-20 mA
transmitter current loop. The communicator
does not disturb the 4-20 mA signal, since no
net energy is added to the loop.
The HART Communicator may be interfaced
with a personal computer, providing special
software has been installed. To connect the
HART Communicator to a PC, an interface
adaptor is required. Refer to the proper HART
Communicator documentation in regard to the
PC interface option.
J-3 SPECIFICATIONS
HART Communicator Specifications, Table J-1,
contains physical, functional, and environmental
information about the communicator. Use Table
J-1 to ensure the unit is operated in suitable en-
vironments, and that the proper battery charging
options are used.
Table J-1. HART Communicator Specifications
Physical Specifications
Display ............................... 8-line liquid crystal display with a line width of 21 characters (128 x 64 pixels)
Keypad............................... Membrane design with tactile feedback. 25 keys include:
6action keys
4 software-defined function keys
12 alphanumeric keys
3shift keys
Weight................................ ≈ 3 lbs (1.4 kg) including batteries
Functional Specifications
Memory.............................. Nonvolatile memory. Retains memory when the communicator is not powered.
Program (and Device)
Descriptions ....................... 1.25 MB
Transmitter Data ................ 2 K
Power Supply..................... Five AA 1.5 volt batteries. A rechargeable Nickel-Cadmium battery pack is optional.
Battery Charger Options .... 110/120 Vac, 50/60 Hz, U.S. plug
........................................... 220/230 Vac, 50 Hz, European plug
........................................... 220/230 Vac, 50 Hz, UK plug
Microprocessors ................ 32-bit Motorola type 68331
8-bit Motorola type 68HC05
Connections....................... Lead set: Two 4 mm banana plugs
Battery charger: 2.5 mm jack
Serial port: PC connection through optional adaptor
Memory Module: 26 pin, 0.1 inch Berg connector
Environmental Specifications
Operating Limits................. 32° to 122°F (0° to 50°C)
Storage Limits.................... -4° to 158°F (-20° to 70°C)
Humidity............................. 0 to 95% relative humidity under non-condensing conditions below 104°F (40°C)
without error
Hazardous Locations ......... CENELEC - Intrinsic Safety Certification
Certifications ...................... Factory Mutual (FM) - Intrinsic Safety Approval
Canadian Standards Association (CSA) - Intrinsic Safety Approval

Instruction Manual
Appendix J Rev. 1.1
June 1995
Rosemount Analytical Inc. A Division of Emerson Process Management Appendices J-3
World Class 3000
INSTALLATION
J-4 HART COMMUNICATOR SIGNAL LINE
CONNECTIONS
The HART Communicator can connect to the
IFT analog output signal line at any wiring ter-
mination point in the 4-20 mA current loop.
There are two methods of connecting the HART
Communicator to the signal line. For applica-
tions in which the signal line has a load resis-
tance of 250 ohms or more, refer to method 1.
For applications in which the signal line load re-
sistance is less than 250 ohms, refer to
method 2.
a. Method 1, For Load Resistance > 250
Ohms
Refer to Figure J-2 and the following steps
to connect the HART Communicator to a
signal line with 250 ohms or more of load
resistance.
R 250
L
>
_W
LOOP CONNECTORS USE INTERFACE
00275 0013 ONLY
SERIAL PORT & BATTERY
CHARGER MUST
NOT BE USED IN
HAZARDOUS AREAS
SERIAL PORT
INTELLIGENT FIELD
TRANSMITTER IFT 3000
J1
JM1
JM6
J2 J3
J4
J5 J6 J7 J8 J9
I
V
MICROPROCESSOR
BOARD
CURRENT/VOLTAGE SELECTION SWITCH
TO "CURRENT" POSITION
INTERCONNECT BOARD
ANALOG OUTPUT
4-20mA SIGNAL LINE
ANALOG OUTPUT DEVICE
LEAD SET
HART
COMMUNICATOR
HART COMMUNICATOR
REAR PANEL
LOOP CONNECTORS
686002
Figure J-2. Signal Line Connections, > 250 Ohms Load Resistance
J

Instruction Manual
Appendix J Rev. 1.1
June 1995
J-4 Appendices Rosemount Analytical Inc. A Division of Emerson Process Management
World Class 3000
Explosions can result in death or seri-
ous injury. Do not make connections
to the HART Communicator's serial
port or NiCad recharger jack in an ex-
plosive atmosphere.
1. Program IFT analog output to 4-20 mA.
Select the current mode using the cur-
rent/voltage selector switch on the mi-
croprocessor board in the IFT.
2. Using the supplied lead set, connect
the HART Communicator in parallel to
the IFT 3000. Use any wiring termina-
tion points in the analog output 4-20
mA signal line.
b. Method 2, For Load Resistance < 250
Ohms
Refer to Figure J-3 and the following steps
to connect the HART Communicator to a
signal line with less than 250 ohms load re-
sistance.
Explosions can result in death or seri-
ous injury. Do not make connections
to the HART Communicator's serial
port or NiCad recharger jack in an ex-
plosive atmosphere.
1. Program IFT analog output to 4-20 mA.
Select the current mode using the cur-
rent/voltage selector switch on the mi-
croprocessor board in the IFT.
2. At a convenient point, break the analog
output 4-20 mA signal line and install
the optional 250 ohm load resistor.
3. Plug the load resistor into the loop
connectors (located on the rear panel
of the HART Communicator).
J-5 HART COMMUNICATOR PC
CONNECTIONS
There is an option to interface the HART Com-
municator with a personal computer. Load the
designated Cornerstone® software into the PC.
Then, link the HART Communicator to the PC
using the interface PC adaptor which connects
to the serial port (on the communicator rear
panel).
Refer to the proper HART Communicator docu-
mentation in regard to the PC interface option.

Instruction Manual
Appendix J Rev. 1.1
June 1995
Rosemount Analytical Inc. A Division of Emerson Process Management Appendices J-5
World Class 3000
R
L
< 250 Ω
INTELLIGENT FIELD
TRANSMITTER IFT 3000
LOOP CONNECTORS USE INTERFACE
00275 0013 ONLY
SERIAL PORT & BATTERY
CHARGER MUST
NOT BE USED IN
HAZARDOUS AREAS
SERIAL PORT
NOTE: THE SIGNAL LOOP MUST BE BROKEN
TO INSERT THE OPTIONAL 250 OHM
LOAD RESISTOR
MICROPROCESSOR
BOARD
CURRENT/VOLTAGE SELECTION SWITCH
TO "CURRENT" POSITION
INTERCONNECT BOARD
ANALOG OUTPUT
4-20mA SIGNAL LINE
ANALOG OUTPUT DEVICE
250 OHM
LOAD
RESISTOR
(NOTE)
HART
COMMUNICATOR
HART COMMUNICATOR
REAR PANEL
LOOP CONNECTORS
686003
Figure J-3. Signal Line Connections, < 250 Ohms Load Resistance
J

Instruction Manual
Appendix J Rev. 1.1
June 1995
J-6 Appendices Rosemount Analytical Inc. A Division of Emerson Process Management
World Class 3000
OPERATION
J-6 OFF-LINE AND ON-LINE OPERATIONS
The HART Communicator can be operated both
off-line and on-line. Off-line operations are those
in which the communicator is not connected to
the IFT system. Off-line operations can include
interfacing the HART Communicator with a PC
(refer to applicable HART Documentation re-
garding HART/PC applications).
In the on-line mode, the communicator is con-
nected to the 4-20 mA analog output signal line.
The communicator is connected in parallel to
the IFT, or in parallel to the 250 ohm load
resistor.
The opening menu (displayed on the LCD) is
different for on-line and off-line operations.
When powering up a disconnected (off-line)
communicator, the LCD will display the Main
Menu. When powering up a connected (on-line)
communicator, the LCD will display the On-line
Menu. Refer to the HART Communicator man-
ual for detailed menu information.
J-7 MENU TREE FOR HART COMMUNICATOR/
WORLD CLASS 3000 IFT APPLICATIONS
This section consists of a menu tree for the
HART Communicator. This menu is specific to
IFT 3000 applications.

Instruction Manual
Appendix J Rev. 1.1
June 1995
Rosemount Analytical Inc. A Division of Emerson Process Management Appendices J-7
World Class 3000
Oxygen
Efficiency
Stack
O cell
CJtemp
2
VIEW FLD
DEV VARS
PV is
PV
PV % mge
PV AO
PROCESS
VARIABLES
DIAG/SERVICE
VIEW PV-Aout
VIEW OUTPUT
VARS
VIEW SV
SV is
SV
SV % mge
O cell
Cell TC
Stack TC
CJmV
2
VIEW FLD
DEV mV
Not Applicable
VIEW STATUS
SELF TEST Not Applicable
LOOP TEST Loop test
method... Cal Mode
Optrak TG?
PERFORM O
CAL
CalState
2
PERFORM O
CAL 2
O CALIBRATE
2
CalState
TimeRemain
Present TG
Present O2
O CAL
STATUS
2
Cal slope
Cal const
CellRes
LAST
CALCONSTANTS
Reset
CalConstants
method...
RESET
CALCONSTANTS
D/A trim method
D/A TRIM
O Cal method...
2
DEVICE SETUP
PV
PV AO
PV LRV
PV URV
(CONTINUED ON
SHEET 2)
21240020
Figure J-4. Menu Tree for IFT 3000 Applications (Sheet 1 of 3)
J

Instruction Manual
Appendix J Rev. 1.1
June 1995
J-8 Appendices Rosemount Analytical Inc. A Division of Emerson Process Management
World Class 3000
DEVICE SETUP
PV
PV AO
PV LRV
PV URV
(CONTINUED ON
SHEET 3)
Tag
ASSIGN
PV&SV
SELECT O
RANGE
2
Set O Xfer fn
2
DEVICE
INFORMATION
Manufacturer
Distributor
Model
Dev id
Tag
Descriptor
Message
Date
Final asmbly num
Snsr s/n
Fld dev rev
Software rev
Universal rev
O
efficiency
StackTemp
O cellTemp
ColdJuncTemp
O cell mV
O cellTCmV
StackTCmV
Cold Junc mV
2
2
2
2
PV URV
PV LRV
Xfer fnctn
PV % mge
ANALOG
OUTPUT
HART OUTPUT
RELAY
OUTPUTS
O
2
EFFICIENCY
HighTG
LowTG
Cal Mode
OPtrak TG?
Cal Intrvl
NxtCalTime
TGtime
PurgeTime
ResAirSP
HiAlarmSP
LoAlarmSP
Deadband
SENSORS
SIGNAL
CONDITION
OUTPUT
CONDITION
CALCULATIONS
O
CALIBRATION
2
O ALARMS
2
(CONTINUED FROM
SHEET 1)
BASIC SETUP
DETAILED
SETUP
PV AO
AO Alrm typ
LOOP TEST
D/A TRIM
Poll addr
Num req preams
K1
K2
Slope
Constant
HeaterSP
Eff.enabled?
K1 efficncy
K2 efficncy
K3 efficncy
Loop test
method...
D/A trim method...
K1 state
K1 input1
K1 input2
K1 input3
K2 state
K2 input1
K2 input2
K2 input3
PV is
SV is
O RngeMode
HiRnginCal?
RngeSwtSP
Normal URV
Normal LRV
Hi.mg.URV
Hi.mg.LRV
2
21240021
Figure J-4. Menu Tree for IFT 3000 Applications (Sheet 2 of 3)

Instruction Manual
Appendix J Rev. 1.1
June 1995
Rosemount Analytical Inc. A Division of Emerson Process Management Appendices J-9
World Class 3000
DEVICE SETUP
PV
PV AO
PV LRV
PV URV
(CONTINUED FROM
SHEET 2)
Manufacturer
Distributor
Model
Dev id
Tag
Descriptor
Message
Date
Final asmbly num
Snsr s/n
Fld dev rev
Hardware rev
Software rev
Universal rev
Cal mode
Optrak TG?
Cal Intrvl
Tgtime
PurgeTime
ResAirSP
LowTG
HighTG
Cal slope
Cal const
CellRes
HeaterSP
Slope
Constant
Eff.enabled?
K1 efficncy
K2 efficncy
K3 efficncy
Normal URV
Normal LRV
Hi.mg.URV
Hi.mg.LRV
O RngeMode
HiRnginCal?
RngeSwtSP
HiAlarmSP
LoAlarmSP
Deadband
K1 input1
K1 input2
K1 input3
K2 input1
K2 input2
K2 input3
Poll addr
Num req preams
2
DEVICE
INFORMATION
CAL INFO
DEVICE CONFIG
OUTPUTS
CONFIG
REVIEW
21240022
Figure J-4. Menu Tree for IFT 3000 Applications (Sheet 3 of 3)
J

Instruction Manual
Appendix J Rev. 1.1
June 1995
J-10 Appendices Rosemount Analytical Inc. A Division of Emerson Process Management
World Class 3000
TROUBLESHOOTING
J-8 OVERVIEW
If the HART Communicator fails to function
properly, verify that the unit's battery pack and
memory module are correctly assembled to the
communicator. Check the communicator's
model number. For IFT applications, HART
Communicator model number 275D9E must be
used. If the HART Communicator model num-
ber is correct, and if it is properly assembled,
the troubleshooting flowchart, Figure J-5, may
be useful to find and correct problems.
J-9 TROUBLESHOOTING FLOWCHART.
Refer to Figure J-5.

Instruction Manual
Appendix J Rev. 1.1
June 1995
Rosemount Analytical Inc. A Division of Emerson Process Management Appendices J-11
World Class 3000
DOES
HART UNIT
HAVE
POWER
?
DOES
HART UNIT
INDICATE
BATTERY
POWER
GOOD
?
IS
HART UNIT
BEING USED
"ON-LINE"
?
IS
HART UNIT
CONFIGURED
FOR IFT?
IS IFT
POWERED
?
IS IFT
EXPERIENCING
FAULTS
?
DOES
IFT HAVE
MICROPROCESSOR
BOARD
REV.#
3039513G
?
CLEAR IFT OF ALL FAULT
CONDITIONS.
YES
YES
YES
YES
YES
YES
YES
(GO TO
SHEET 2 OF 2)
REPLACE BATTERIES. IF
APPLICABLE, RECHARGE
NiCad BATTERIES.
VERIFY HART IS
CONFIGURED FOR IFT.
REFERENCE OFF-LINE
CONFIGURATION (HART
POCKET-SIZED MANUAL).
RECONFIGURE HART UNIT
FOR IFT.
CONTACT SERVICE
REPRESENTATIVE.
SUPPLY POWER TO IFT.
NO
NO NO
NO
NO
NO
NO
686004
Figure J-5. Model 275D9E, Troubleshooting Flowchart (Sheet 1 of 2)
J

Instruction Manual
Appendix J Rev. 1.1
June 1995
J-12 Appendices Rosemount Analytical Inc. A Division of Emerson Process Management
World Class 3000
NO
NO
NO
NO
NO
NO
YES
YES
YES
YES
YES
YES
>
IS
LOAD
RESISTANCE
250 OHMS
?
(CONTINUED FROM
SHEET 1 OF 2)
CONNECT THE HART UNIT
TO THE 4-20 mA SIGNAL
LOOP. REFER TO SECTION
2. IF LOAD RESISTANCE IS
<250 OHMS, THE 250 OHM
LOAD RESISTOR MUST BE
USED.
686005
Figure J-5. Model 275D9E, Troubleshooting Flowchart (Sheet 2 of 2)

Instruction Manual
Appendix J Rev. 1.1
June 1995
Rosemount Analytical Inc. A Division of Emerson Process Management Appendices J-13
World Class 3000
RETURNING EQUIPMENT TO THE FACTORY
J-10 If factory repair of defective equipment is re-
quired, proceed as follows:
a. Secure a return authorization number from
a Rosemount Analytical Sales Office or
Representative before returning the equip-
ment. Equipment must be returned with
complete identification in accordance with
Rosemount instructions or it will not be
accepted.
In no event will Rosemount be responsible
for equipment without proper authorization
and identification.
b. Carefully pack defective unit in a sturdy box
with sufficient shock absorbing material to
insure that no additional damage will occur
during shipping.
c. In a cover letter, describe completely:
1. The symptoms from which it was de-
termined that the equipment is faulty.
2. The environment in which the equip-
ment has been operating (housing,
weather, vibration, dust, etc.).
3. Site from which equipment was
removed.
4. Whether warranty service or non-
warranty service is requested.
5. Complete shipping instructions for re-
turn of equipment.
6. Reference the return authorization
number.
d. Enclose a cover letter and purchase order
and ship the defective equipment according
to instructions provided in Rosemount Re-
turn Authorization, prepaid, to:
Rosemount Analytical Inc.
RMR Department
1201 N. Main Street
Orrville, Ohio 44667
If warranty service is requested, the defec-
tive unit will be carefully inspected and
tested at the factory. If failure was due to
conditions listed in the standard Rosemount
warranty, the defective unit will be repaired
or replaced at Rosemount's option, and an
operating unit will be returned to the cus-
tomer in accordance with shipping instruc-
tions furnished in the cover letter.
For equipment no longer under warranty,
the equipment will be repaired at the factory
and returned as directed by the purchase
order and shipping instructions.
J

Instruction Manual
Appendix J Rev. 1.1
June 1995
J-14 Appendices Rosemount Analytical Inc. A Division of Emerson Process Management
World Class 3000

Instruction Manual
IB-106-300NH Rev. 4.2
July 2002
Rosemount Analytical Inc. A Division of Emerson Process Management Appendices 9-1
World Class 3000
SECTION 9
INDEX
This index is an alphabetized listing of parts, terms, and procedures having to do with the Haz-
ardous Area Oxygen/Combustibles Transmitter. Every item listed in this index refers to a location
in the manual by one or more page numbers.
A
Abrasive Shield, 2-7
Absolute Temperature, 1-2
Adapter Plate, 1-1, 2-1
Air Pressure Regulator Valve, 2-22
Analog Output, 2-14, 5-13, 5-14
Annunciator, 2-14
Arithmetic Constant, 1-2
Automatic Calibration, 1-3, 2-23, 4-6, 5-10
B
Blind Version, 5-1
C
Cable Shields, 6-1
CAL, 5-2
CALIBRATE O2 Sub-Menu, 5-4, 5-10
Calibration, 4-1
Calibration Constants, 4-1
Calibration Fittings, 1-7
Calibration Gas, 4-3
Calibration Gas Out, 2-23
Cell Constant, 1-2
Ceramic Diffusor, 2-1
Chart Recorders, 2-14
Check Valve, 1-7, 4-3
D
DATA, 5-2
Diagnostic Data, 5-3
Dust Seal Packings, 2-7
E
Electrical Noise, 6-1
Electrostatic Discharge, 6-1
G
Gas Kit, 4-5
Gas Mixture, 2-8, 4-2, 4-6
Gas Stratification, 2-1
General User Interface, 1-4, 5-1
Grounding, 6-1
GUI, 6-1
H
HART® Communications, 1-2, 5-1
HART® Communicator, 1-1
HART® Interface, 1-4
Heater Power Supply, 1-1, 1-3, 2-14, 2-20, 2-21
HELP, 5-2
High Gas, 2-22
I
Instrument Air, 1-7, 2-8
Instrument Air In, 2-22
Intelligent Field Transmitter, 1-1, 1-2, 5-1
Interconnect Board, 2-16
L
Languages, 1-3, 5-1
Low Gas, 2-23
M
MAIN Menu, 5-3
Manual Calibration, 4-2, 5-10
Microprocessor Board, 2-14
Mother Board, 2-21
MPS Wiring, 2-24
Multiprobe Calibration Gas Sequencer, 1-1, 1-2, 2-
22
N
NEMA 4X Enclosure, 1-3, 2-9, 2-14
O
Orsat Apparatus, 1-2
Oxygen Analyzer, 1-1, 1-2, 1-3
P
Power Cable, 2-10, 2-17
Power Supply Board, 2-12
Pressure Regulator, 4-3, 4-4
PROBE DATA Sub-Menu, 5-3
9

Instruction Manual
IB-106-300NH Rev. 4.2
July 2002
9-2 Index Rosemount Analytical Inc. A Division of Emerson Process Management
World Class 3000
Pushbutton Regulator, 4-5
Q
Quick Reference Chart, 5-3
R
Reference Air, 1-1, 2-8, 2-22
S
Semiautomatic Calibration, 2-23, 4-2, 4-6
SETUP Sub-Menu, 5-4
Status Line, 5-3
Stop Valve, 1-7
T
TGH, 5-2
TGL, 5-2
Troubleshooting, 6-1
V
Vee Deflector, 2-7
W
Wiring Layout, 2-13, 2-18, 2-19
Z
Zirconia Disc, 1-2
Z-purge, 1-7
3573
3656/7-02
ROSEMOUNT WARRANTY
Rosemount warrants that the equipment manufactured and sold by it will, upon shipment, be free
of defects in workmanship or material. Should any failure to conform to this warranty become ap-
parent during a period of one year after the date of shipment, Rosemount shall, upon prompt
written notice from the purchaser, correct such nonconformity by repair or replacement, F.O.B.
factory of the defective part or parts. Correction in the manner provided above shall constitute a
fulfillment of all liabilities of Rosemount with respect to the quality of the equipment.
THE FOREGOING WARRANTY IS EXCLUSIVE AND IN LIEU OF ALL OTHER WAR-
RANTIES OF QUALITY WHETHER WRITTEN, ORAL, OR IMPLIED (INCLUDING ANY
WARRANTY OF MERCHANTABILITY OF FITNESS FOR PURPOSE).
The remedy(ies) provided above shall be purchaser's sole remedy(ies) for any failure of
Rosemount to comply with the warranty provisions, whether claims by the purchaser are based
in contract or in tort (including negligence).
Rosemount does not warrant equipment against normal deterioration due to environment. Factors
such as corrosive gases and solid particulates can be detrimental and can create the need for re-
pair or replacement as part of normal wear and tear during the warranty period.
Equipment supplied by Rosemount Analytical Inc. but not manufactured by it will be subject to the
same warranty as is extended to Rosemount by the original manufacturer.
At the time of installation it is important that the required services are supplied to the system and
that the electronic controller is set up at least to the point where it is controlling the sensor heater.
This will ensure, that should there be a delay between installation and full commissioning that the
sensor being supplied with ac power and reference air will not be subjected to component
deterioration.

Instruction Manual
IB-106-300NH Rev. 4.2
July 2002
© Rosemount Analytical Inc. 2002
Emerson Process Management
Rosemount Analytical Inc.
Process Analytic Division
1201 N. Main St.
Orrville, OH 44667-0901
T (330) 682-9010
F (330) 684-4434
E gas.csc@emersonprocess.com
ASIA - PACIFIC
Fisher-Rosemount
Singapore Private Ltd.
1 Pandan Crescent
Singapore 128461
Republic of Singapore
T 65-777-8211
F 65-777-0947
http://www.processanalytic.com
Fisher-Rosemount GmbH & Co.
Industriestrasse 1
63594 Hasselroth
Germany
T 49-6055-884 0
F 49-6055-884209
EUROPE, MIDDLE EAST, AFRICA
Fisher-Rosemount Ltd.
Heath Place
Bognor Regis
West Sussex PO22 9SH
England
T 44-1243-863121
F 44-1243-845354
LATIN AMERICA
Fisher - Rosemount
Av. das Americas
3333 sala 1004
Rio de Janeiro, RJ
Brazil 22631-003
T 55-21-2431-1882
World Class 3000
World Class 3000 Probe
Part No. ____________________
Serial No. ____________________
Order No. ____________________
HPS 3000
Part No. ____________________
Serial No. ____________________
Order No. ____________________
IFT 3000
Part No. ____________________
Serial No. ____________________
Order No. ____________________
MPS 3000
Part No. ____________________
Serial No. ____________________
Order No. ____________________