Endress and Hauser SE KG FMR2XK Tank Level-probing Radar User Manual Micropilot FMR20
Endress and Hauser GmbH and Co Tank Level-probing Radar Micropilot FMR20
Contents
- 1. User manual FRM10
- 2. User manual FRM20
User manual FRM20
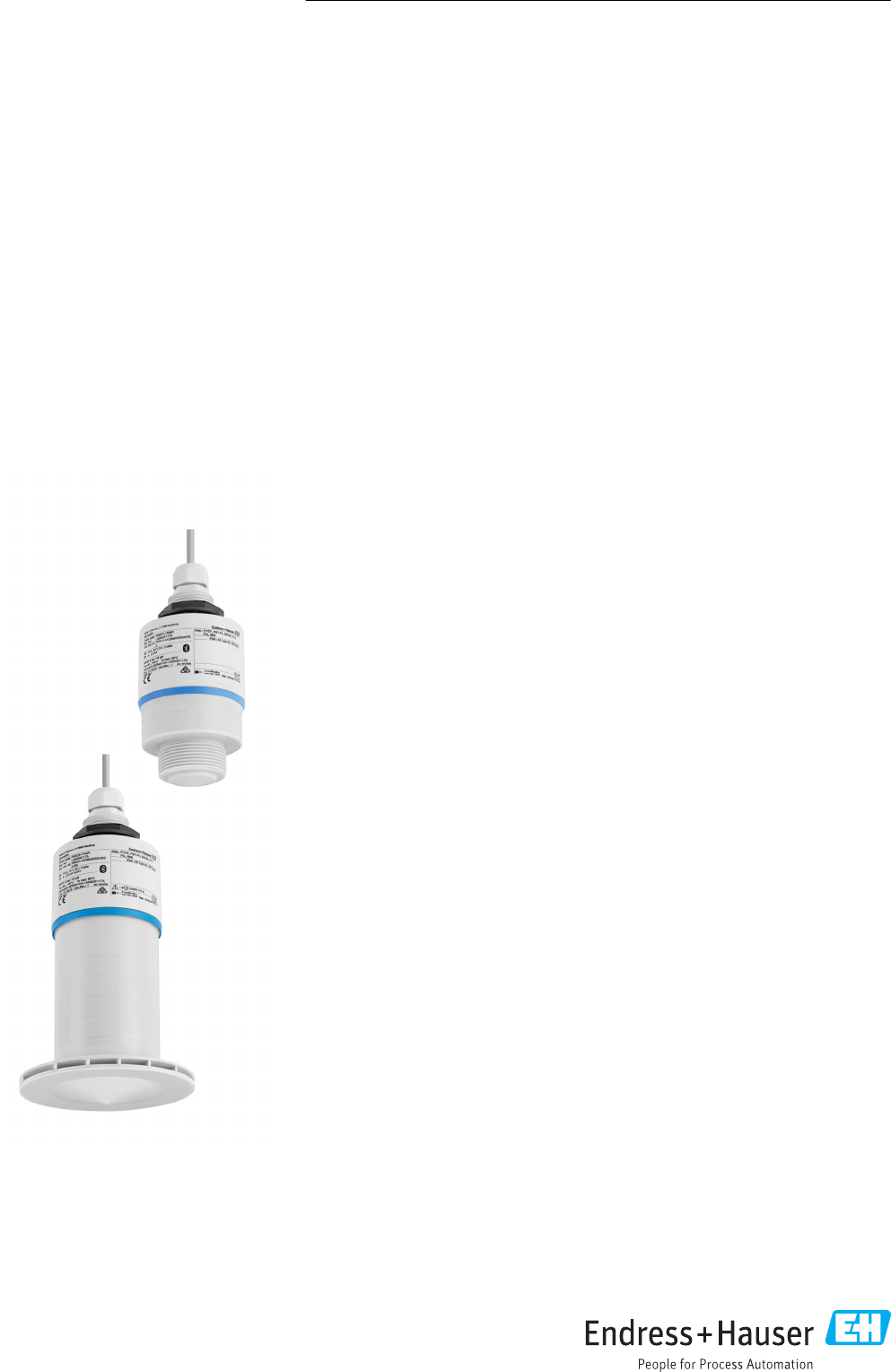
Level measurement for liquids
Application
• Ingress protection: IP66/68 / NEMA 4X/6P
• Measuring range: up to 20 m (66 ft)
• Process temperature: –40 to 80 °C (–40 to 176 °F)
• Process pressure: –1 to 3 bar (–14 to 43 psi)
• Accuracy: up to ± 2 mm (0.08 in)
• International explosion protection certificates
Your benefits
• Level measurement for liquids in storage tanks, open basins, pump shafts and
canal systems
• Radar measuring device with Bluetooth® wireless technology and HART
communication
• Simple, safe and secure wireless remote access – ideal for installation in hazardous
areas or places difficult to reach
• Commissioning, operation and maintenance via free iOS / Android app SmartBlue
– saves time and reduces costs
• Full PVDF body – for a long sensor lifetime
• Hermetically sealed wiring and fully potted electronics – eliminates water ingress
and allows operation under harsh environmental conditions
• Most compact radar due to unique radar chip design – fits in limited space
installations
• Best price-performance-ratio radar
Products Solutions Services
Technical Information
Micropilot FMR20
Free space radar
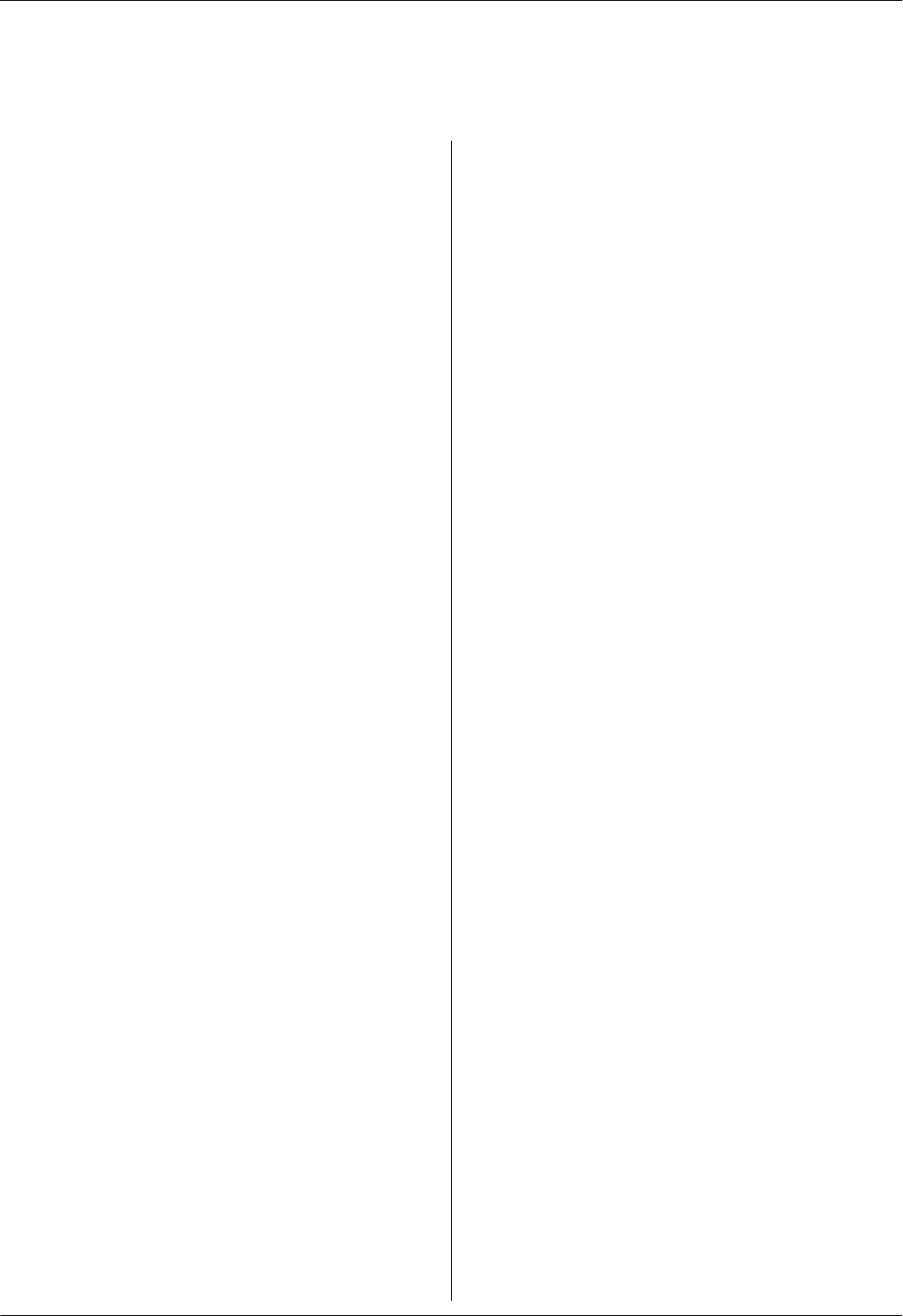
Micropilot FMR20
2 V. 5, Rev. 3, 20-12-2016 Endress+Hauser
Table of contents
Important document information ............... 3
Symbols for certain types of information .............. 3
Safety symbols ............................... 3
Electrical symbols ............................. 3
Symbols in graphics ............................ 3
Terms and abbreviations ..................... 5
Registered trademarks ....................... 5
Product life cycle ............................ 6
Engineering ................................. 6
Procurement ................................ 6
Installation ................................. 6
Commissioning ............................... 6
Operation .................................. 6
Maintenance ................................ 6
Retirement .................................. 6
Measuring principle ......................... 7
Input ...................................... 7
Output .................................... 7
Input ..................................... 8
Measured variable ............................. 8
Measuring range .............................. 8
Operating frequency ........................... 8
Transmission power ............................ 8
Output ................................... 9
Output signal ................................ 9
Digital output ................................ 9
Signal on alarm ............................... 9
Linearization ................................ 9
Protocol-specific data ........................... 9
Electrical connection ....................... 10
Cable assignment ............................ 10
Supply voltage .............................. 10
Power consumption ........................... 10
Current consumption .......................... 10
Starting time ............................... 10
Power supply failure .......................... 11
Connection ................................. 11
Cable specification ............................ 13
Overvoltage protection ......................... 13
Performance characteristics .................. 14
Reference operating conditions ................... 14
Maximum measured error ....................... 14
Measured value resolution ...................... 14
Response time .............................. 15
Influence of ambient temperature ................. 15
Installation ............................... 16
Installation conditions ......................... 16
Environment .............................. 23
Ambient temperature range ..................... 23
Storage temperature .......................... 23
Climate class ............................... 23
Installation height as per IEC 61010-1 Ed.3 ........... 23
Degree of protection .......................... 23
Vibration resistance ........................... 23
Electromagnetic compatibility (EMC) ............... 23
Process .................................. 24
Process temperature, process pressure ............... 24
Dielectric constant ............................ 24
Mechanical construction .................... 25
Dimensions ................................ 25
Weight ................................... 31
Materials .................................. 32
Connecting cable ............................. 32
Operability ............................... 33
Operating concept ............................ 33
Via Bluetooth® wireless technology ................ 33
Via HART protocol ............................ 33
Certificates and approvals ................... 34
CE mark ................................... 34
RoHS ..................................... 34
EAC conformity .............................. 34
RCM-Tick marking ............................ 34
Ex approval ................................ 34
Explosion-protected smartphones and tablets .......... 34
Pressure equipment with allowable pressure
≤ 200 bar (2 900 psi) .......................... 34
EN 302729-1/2 radio standard ................... 35
FCC / Industry Canada ......................... 36
Other standards and guidelines ................... 37
Ordering information ....................... 37
Accessories ............................... 38
Device-specific accessories ...................... 38
Communication-specific accessories ................ 50
Service-specific accessories ...................... 51
System components ........................... 51
Supplementary documentation ............... 52
Standard documentation ........................ 52
Supplementary documentation ................... 52
Safety Instructions (XA) ........................ 52
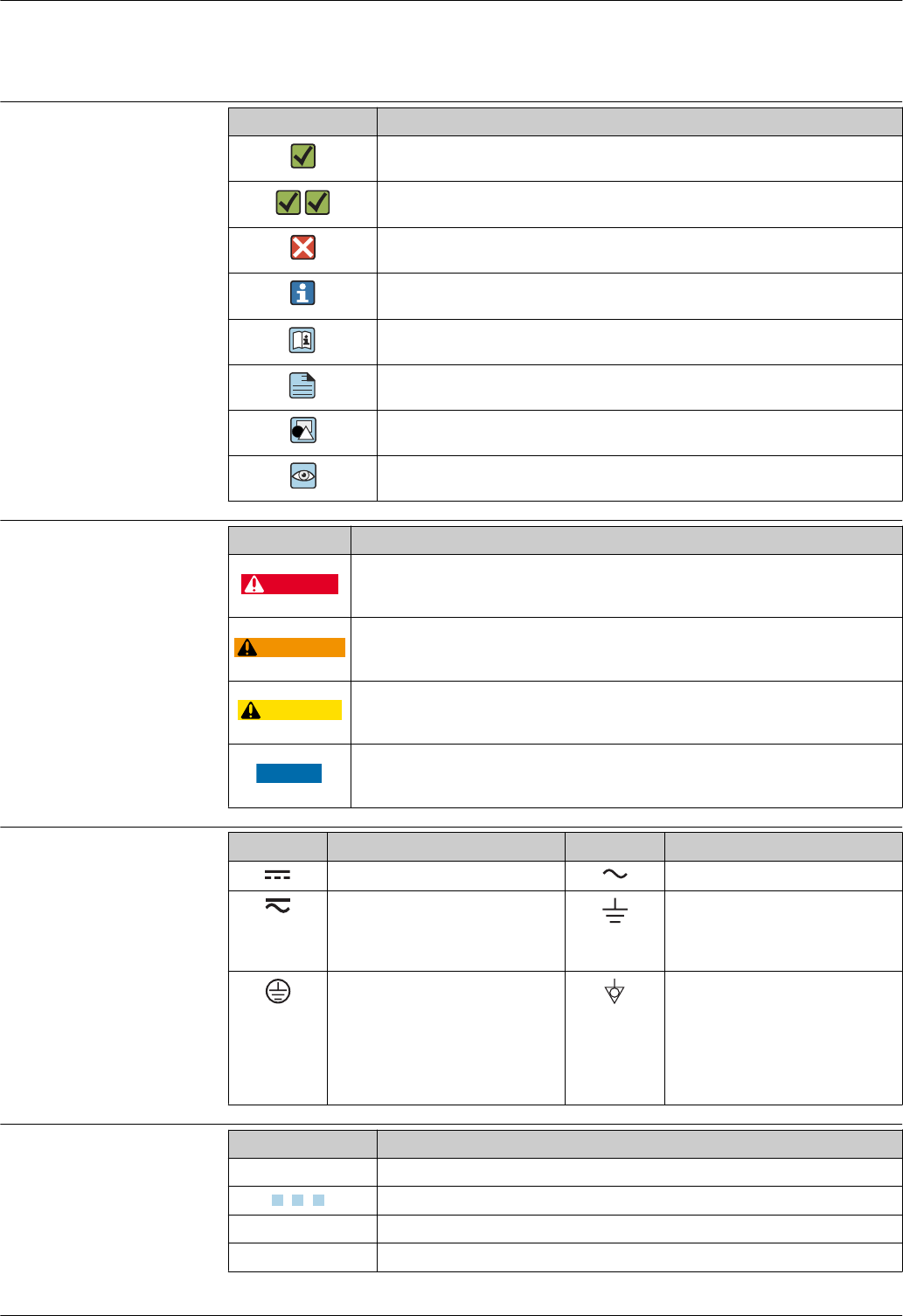
Micropilot FMR20
Endress+Hauser V. 5, Rev. 3, 20-12-2016 3
Important document information
Symbols for certain types of
information Symbol Meaning
Permitted
Procedures, processes or actions that are permitted.
Preferred
Procedures, processes or actions that are preferred.
Forbidden
Procedures, processes or actions that are forbidden.
Tip
Indicates additional information.
Reference to documentation
A
Reference to page
Reference to graphic
Visual inspection
Safety symbols Symbol Meaning
DANGER
DANGER!
This symbol alerts you to a dangerous situation. Failure to avoid this situation will result in
serious or fatal injury.
WARNING
WARNING!
This symbol alerts you to a dangerous situation. Failure to avoid this situation can result in
serious or fatal injury.
CAUTION
CAUTION!
This symbol alerts you to a dangerous situation. Failure to avoid this situation can result in
minor or medium injury.
NOTICE
NOTE!
This symbol contains information on procedures and other facts which do not result in
personal injury.
Electrical symbols Symbol Meaning Symbol Meaning
Direct current Alternating current
Direct current and alternating current Ground connection
A grounded terminal which, as far as
the operator is concerned, is
grounded via a grounding system.
Protective ground connection
A terminal which must be connected
to ground prior to establishing any
other connections.
Equipotential connection
A connection that has to be connected
to the plant grounding system: This
may be a potential equalization line
or a star grounding system depending
on national or company codes of
practice.
Symbols in graphics Symbol Meaning
1, 2, 3 ... Item numbers
1.
,
2.
,
3.
… Series of steps
A, B, C, ... Views
A-A, B-B, C-C, ... Sections
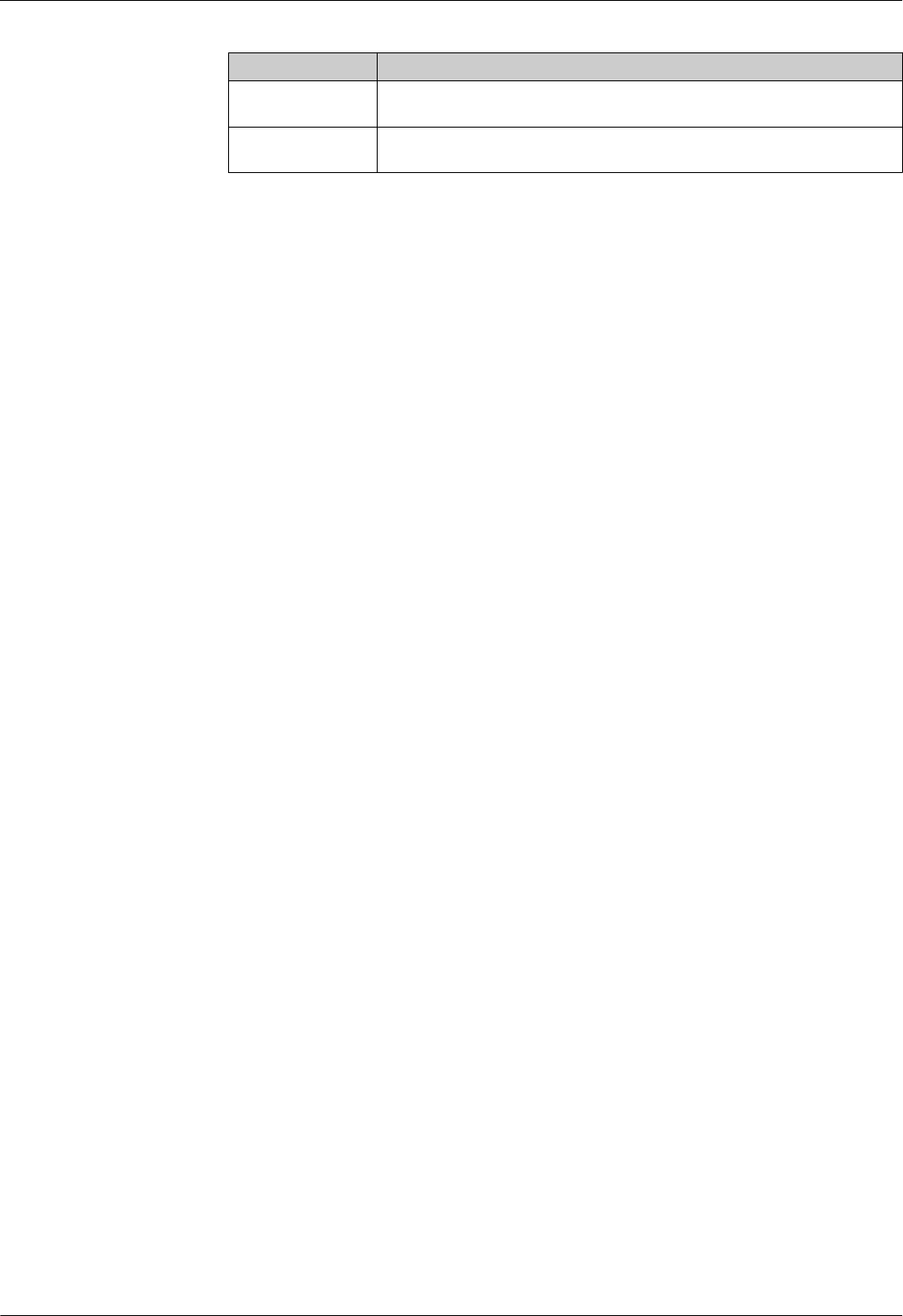
Micropilot FMR20
4 V. 5, Rev. 3, 20-12-2016 Endress+Hauser
Symbol Meaning
-
Hazardous area
Indicates a hazardous area.
.
Safe area (non-hazardous area)
Indicates the non-hazardous area.
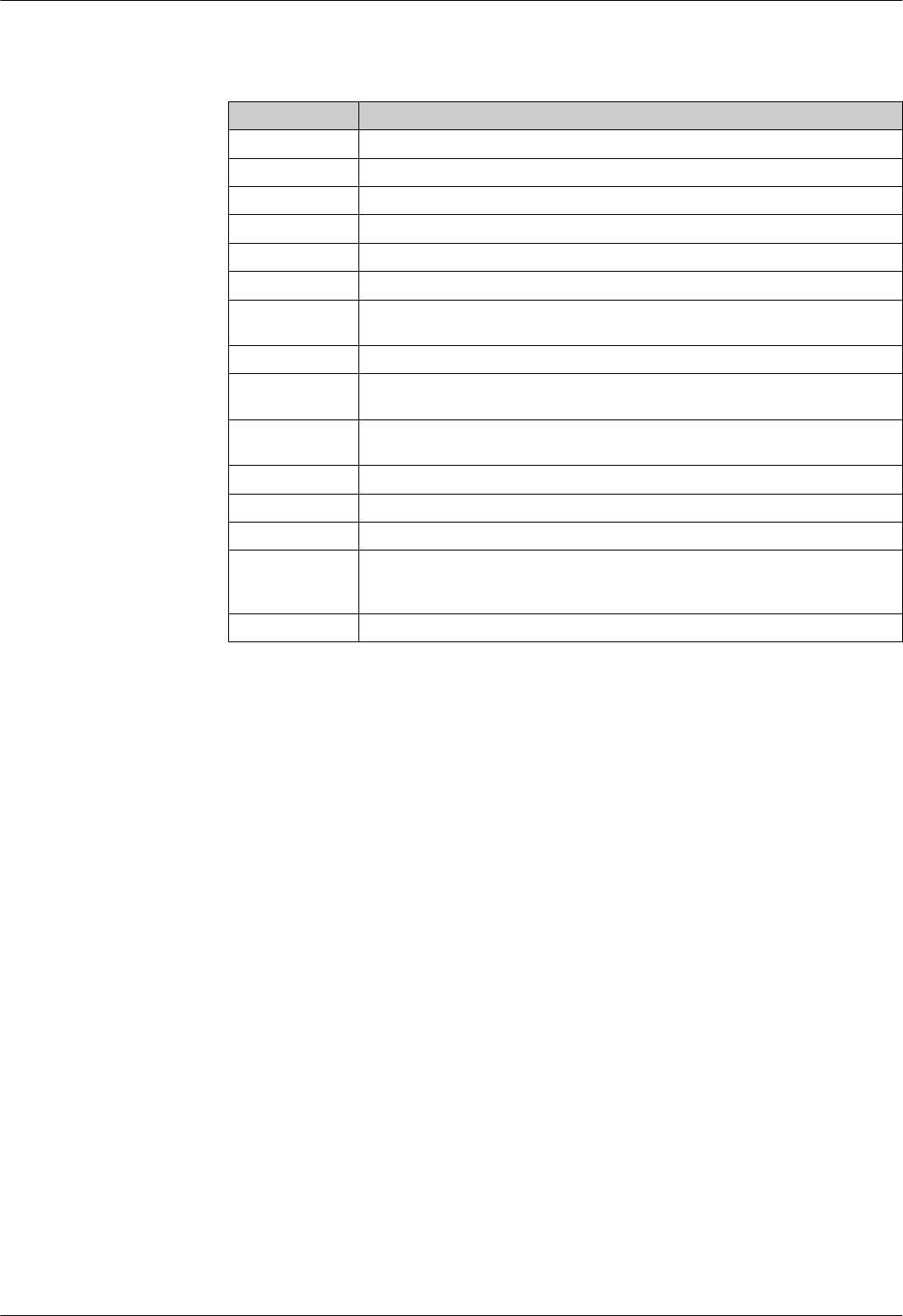
Micropilot FMR20
Endress+Hauser V. 5, Rev. 3, 20-12-2016 5
Terms and abbreviations
Term/abbreviation Explanation
BA Document type "Operating Instructions"
KA Document type "Brief Operating Instructions"
TI Document type "Technical Information"
SD Document type "Special Documentation"
XA Document type "Safety Instructions"
PN Nominal pressure
MWP Maximum Working Pressure
The MWP can also be found on the nameplate.
ToF Time of Flight
FieldCare Scalable software tool for device configuration and integrated plant asset management
solutions
DeviceCare Universal configuration software for Endress+Hauser HART, PROFIBUS,
FOUNDATION Fieldbus and Ethernet field devices
DTM Device Type Manager
DD Device Description for HART communication protocol
DC Relative dielectric constant εr
Operating tool The term "operating tool" is used in place of the following operating software:
• SmartBlue (app), for operation using an Android or iOS smartphone or tablet.
• FieldCare / DeviceCare, for operation via HART communication and PC
BD Blocking Distance; no signals are analyzed within the BD.
Registered trademarks
HART®
Registered trademark of the HART Communication Foundation, Austin, USA
Bluetooth®
The Bluetooth® word mark and logos are registered trademarks owned by the Bluetooth SIG, Inc. and
any use of such marks by Endress+Hauser is under license. Other trademarks and trade names are
those of their respective owners.
Apple®
Apple, the Apple logo, iPhone, and iPod touch are trademarks of Apple Inc., registered in the U.S.
and other countries. App Store is a service mark of Apple Inc.
Android®
Android, Google Play and the Google Play logo are trademarks of Google Inc.
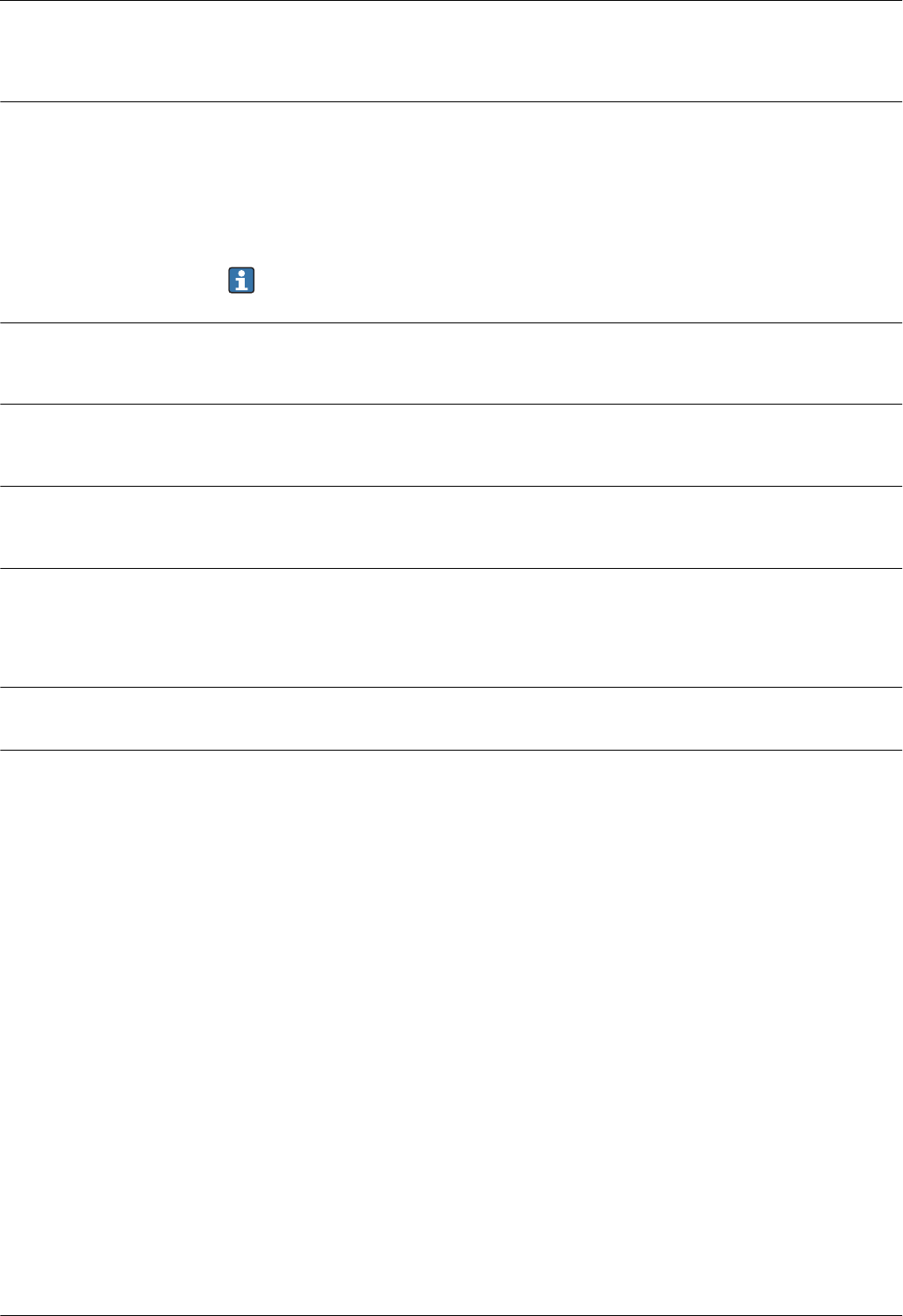
Micropilot FMR20
6 V. 5, Rev. 3, 20-12-2016 Endress+Hauser
Product life cycle
Engineering • Proven radar measuring technology
• Level- and open channel flow measurement for Ex and non-Ex
• Indication of over-flooding situation
• Wide range of installation possibilities and accessories
• Highest degree of ingress protection
• 2D / 3D drawings
• Spec Sheet Producer
• Applicator Selection tool for the selection of the perfect measurement solution
Device not compatible with transmitters and sensors of ultrasonic measurement technology
(e.g. Prosonic FMU9x, FDU9x)
Procurement • Best price-performance-ratio radar
• Global availability
• Order code includes variety of mounting accessories and remote HART indicator RIA15
Installation • Rear- and front side thread for flexible installation
• Slip- on flange for nozzle installation
• Complete measuring point: Including mounting accessory, RIA15 and flooding protection tube
Commissioning • Easy and fast setup via SmartBlue (app) and DeviceCare / FieldCare or RIA15
• No additional tools or adapters required
• Local languages (up to 15)
Operation • Continuous self-monitoring
• Diagnosis information acc. NAMUR NE107 with clear text messages remedy directives
• Signal curve via SmartBlue (app) and DeviceCare / FieldCare
• Encrypted single point-to-point data transmission (Fraunhofer-Institut, third party, tested) and
password-protected communication via Bluetooth® wireless technology
Maintenance • No maintenance required
• Technical experts on-call around the global
Retirement • Environmentally responsible recycling concepts
• RoHS compliance (Restriction of certain hazardous substances), lead-free soldering of electronic
components
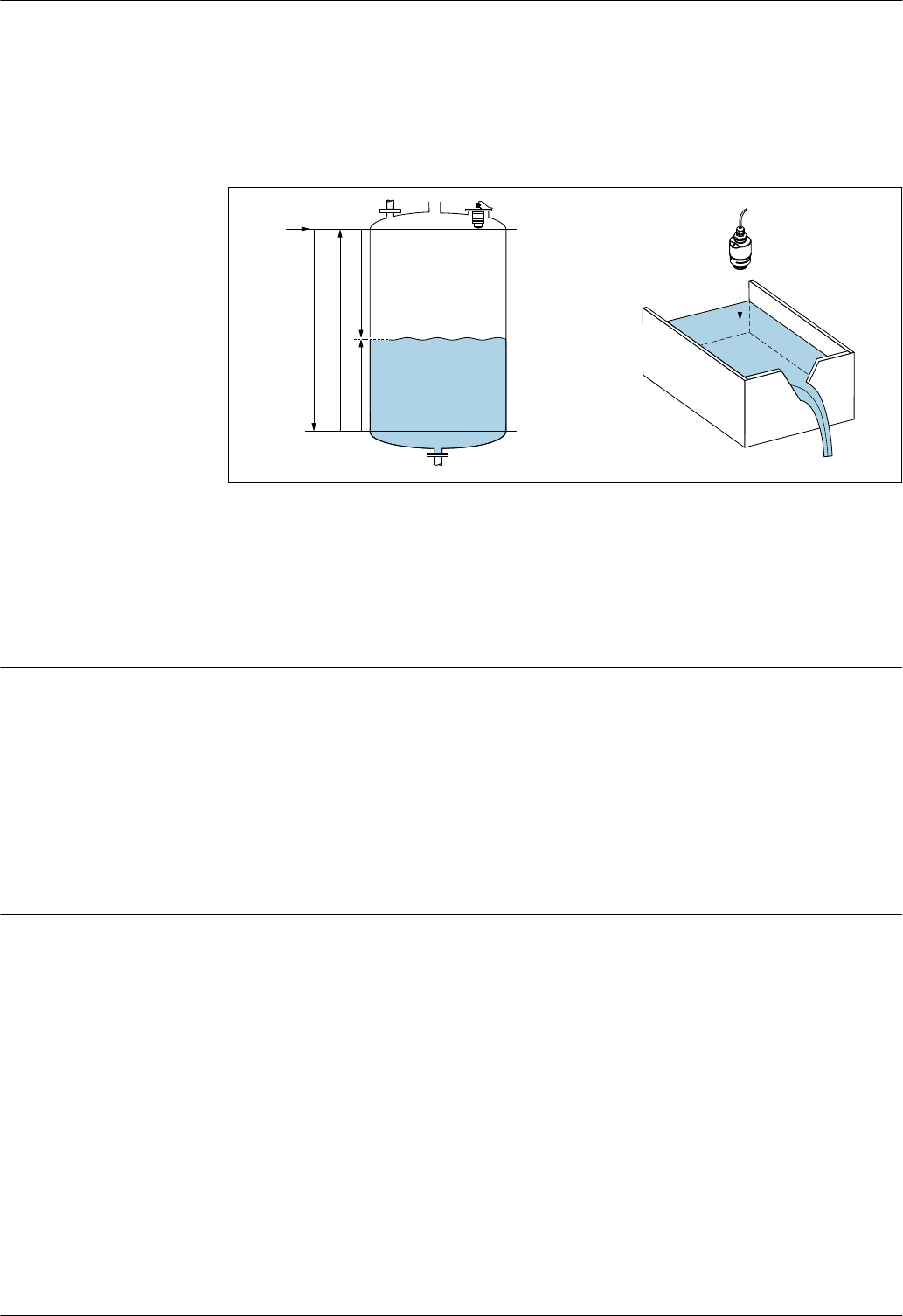
Micropilot FMR20
Endress+Hauser V. 5, Rev. 3, 20-12-2016 7
Measuring principle
The Micropilot is a "downward-looking" measuring system, operating based on the time-of-flight
method (ToF). It measures the distance from the reference point R to the product surface. Radar
impulses are emitted by an antenna, reflected off the product surface and received again by the radar
system.
D
Q
R
100%
0%
D
L
F
E
A0028409
1 Setup parameters of the Micropilot
E Empty calibration (= zero)
F Full calibration (= span)
D Measured distance
L Level (L = E - D)
Q Flow rate at measuring weirs or channels (calculated from the level using linearization)
R Reference point
Input The reflected radar impulses are received by the antenna and transmitted into the electronics. A
microprocessor evaluates the signal and identifies the level echo caused by the reflection of the radar
impulse at the product surface. This clear signal detection system benefits from over 30 years'
experience with time-of-flight procedures.
The distance D to the product surface is proportional to the time of flight t of the impulse:
D = c · t/2,
where c is the speed of light.
Based on the known empty distance E, the level L is calculated:
L = E – D
Output The Micropilot is adjusted by entering the empty distance E (= zero point) and the full distance F (=
span).
• Current output: 4 to 20 mA
• Digital output (HART, SmartBlue): 0 to 10 m (0 to 33 ft) or 0 to 20 m (0 to 66 ft) depending on
antenna version
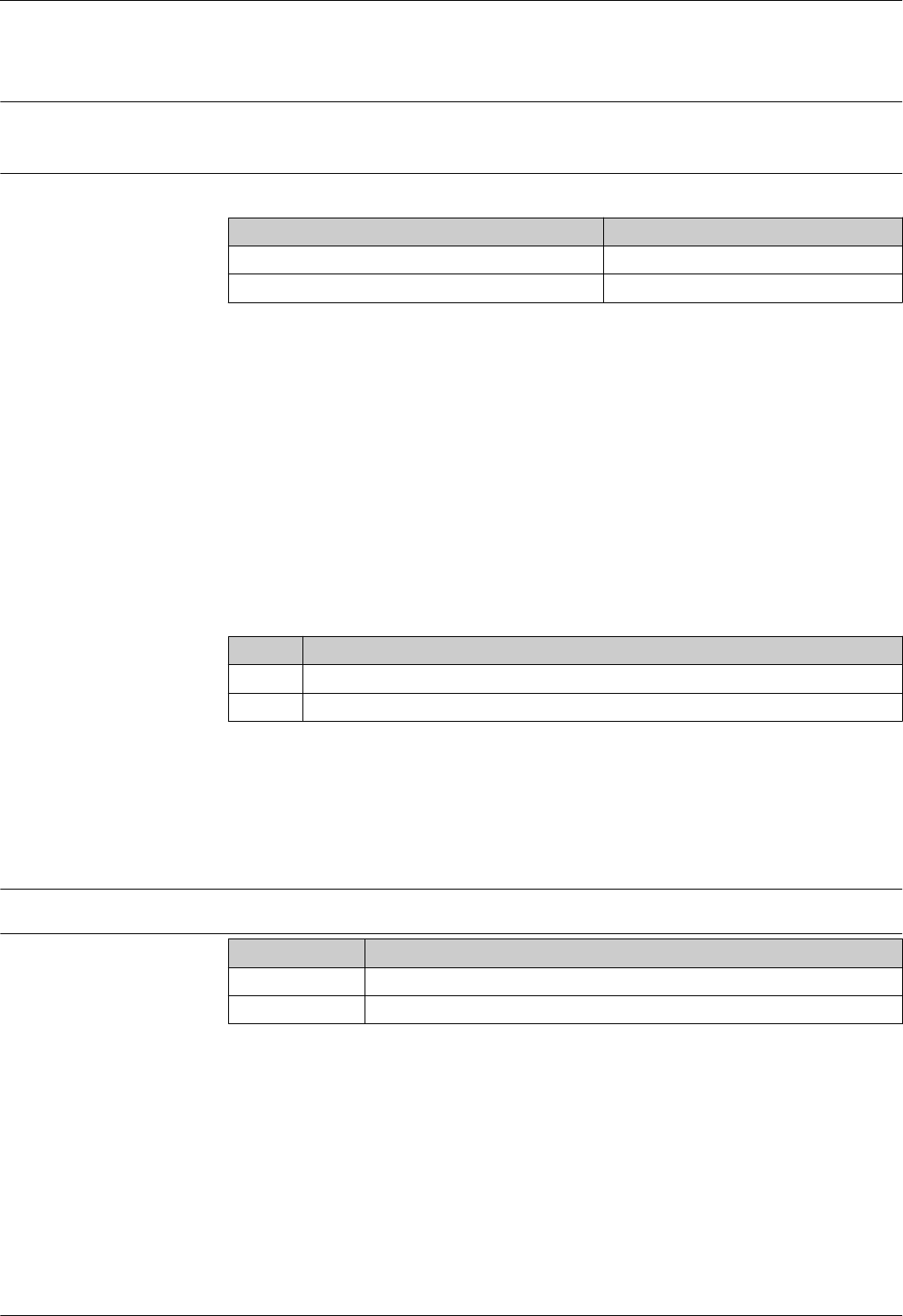
Micropilot FMR20
8 V. 5, Rev. 3, 20-12-2016 Endress+Hauser
Input
Measured variable The measured variable is the distance between the reference point and the product surface.
The level is calculated based on E, the empty distance entered.
Measuring range Maximum measuring range
Device Maximum measuring range
FMR20 with 40 mm (1.5 in) antenna 10 m (33 ft)
FMR20 with80 mm (3 in) antenna 20 m (66 ft)
Requirements of the installation
• recommended tank height > 1.5 m (5 ft) or media with low DC value
• Open channel minimum width 0.5 m (1.6 ft)
• Calm surfaces
• No agitators
• No buildup
• Relative dielectric constant εr > 4
Usable measuring range
The usable measuring range depends on the antenna size, the medium's reflective properties, the
installation position and any possible interference reflections.
The following table describes the media groups.
Media groups
εrExample
4 to 10 E.g. concentrated acid, organic solvents, ester, aniline, alcohol, acetone.
> 10 Conductive liquids, aqueous solutions, diluted acids and bases
Reduction of the max. possible measuring range by:
• Media with bad reflective properties (= low εr value)
• Formation of buildup, particularly of moist products
• Strong condensation
• Foam generation
• Freezing of sensor
Operating frequency K-band (~ 26 GHz)
Transmission power Distance Mean power density in the direction of the beam
1 m (3.3 ft) < 12 nW/cm2
5 m (16 ft) < 0.4 nW/cm2
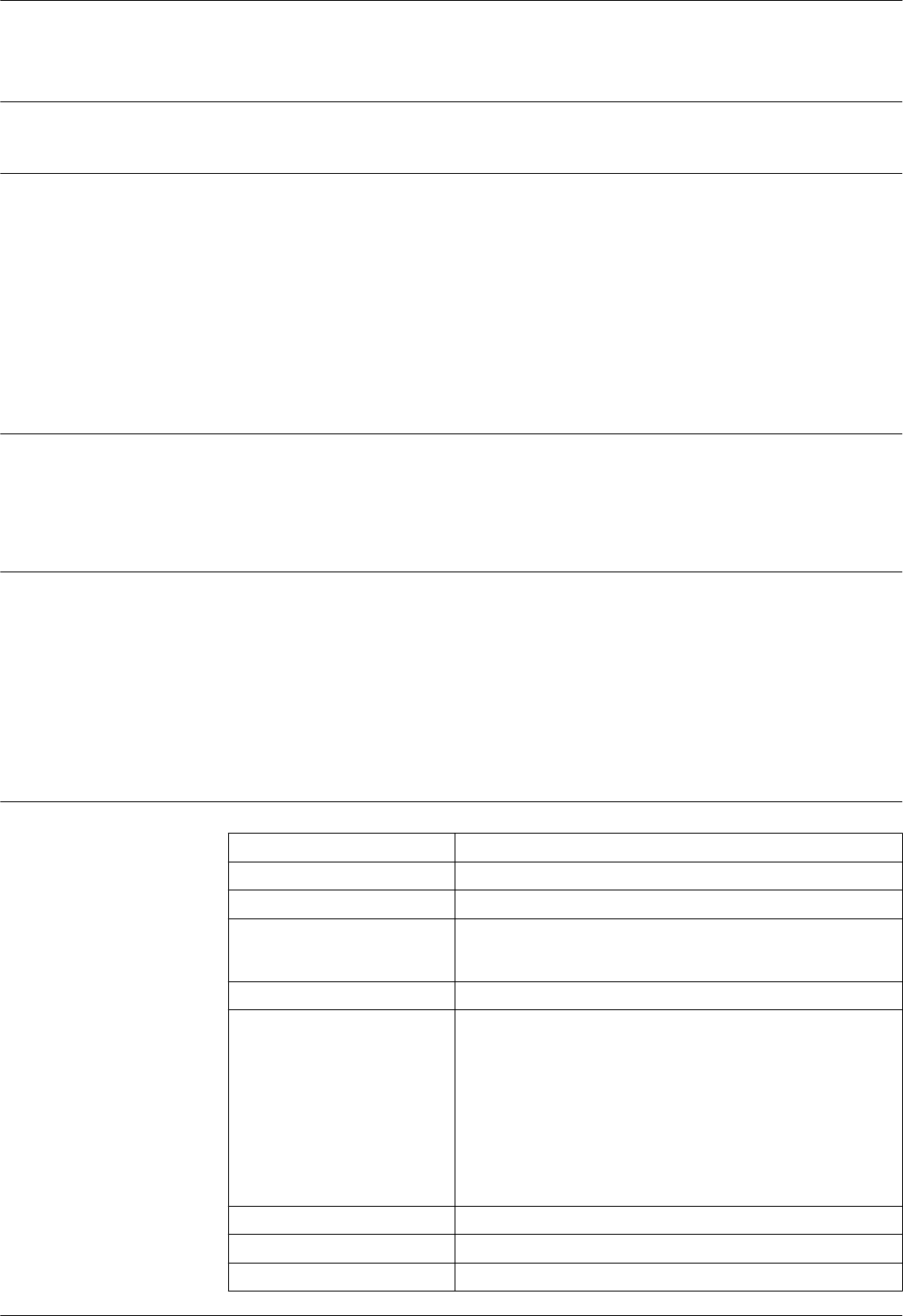
Micropilot FMR20
Endress+Hauser V. 5, Rev. 3, 20-12-2016 9
Output
Output signal 4 to 20 mA
An 4 to 20 mA interface is used for measured value output and to power to the device.
Digital output HART®
• Signal encoding; FSK ±0.5 mA over current signal
• Data transmission rate;1 200 Bit/s
Bluetooth® wireless technology (available as an optional extra)
The device has a Bluetooth® wireless technology interface and can be operated and configured via
this interface using the SmartBlue app.
• The range under reference conditions is 25 m (82 ft)
• Incorrect operation by unauthorized persons is prevented by means of encrypted communication
and password encryption.
• The Bluetooth® wireless technology interface can be deactivated.
Signal on alarm Depending on the interface, failure information is displayed as follows:
• Current output
Alarm current: 22.5 mA (as per NAMUR RecommendationNE 43)
• Operating tool via digital communication (HART) or SmartBlue (app)
– Status signal (as per NAMUR Recommendation NE 107)
– Plain text display with remedial action
Linearization The linearization function of the device allows the conversion of the measured value into any unit of
length, weight, flow or volume. When operating using DeviceCare and FieldCare, linearization tables
for volume calculation in vessels are preprogrammed (see following list).
Pre-programmed linearization curves
• Cylindrical tank
• Spherical tank
• Tank with pyramid bottom
• Tank with conical bottom
• Tank with flat bottom
Other linearization tables of up to 32 value pairs can be entered manually.
Protocol-specific data HART
Manufacturer ID 17 (0x11)
Device type ID 44 (0x112c)
HART specification 7.0
Device description files (DTM, DD) Information and files under:
• www.endress.com
• www.hartcomm.org
HART load Min. 250 Ω
HART device variables Assignment of HART device variables is fixed and cannot be changed.
Measured values for PV (primary variable)
Level linearized
Advanced diag. measured values for SV (secondary variable)
Distance
Advanced diag. measured values for TV (tertiary variable)
Relative echo amplitude
Advanced diag. measured values for QV (quarternary variable)
Temperature
Supported functions Additional transmitter status
Multidrop current 4 mA
Time for connection setup < 1 s
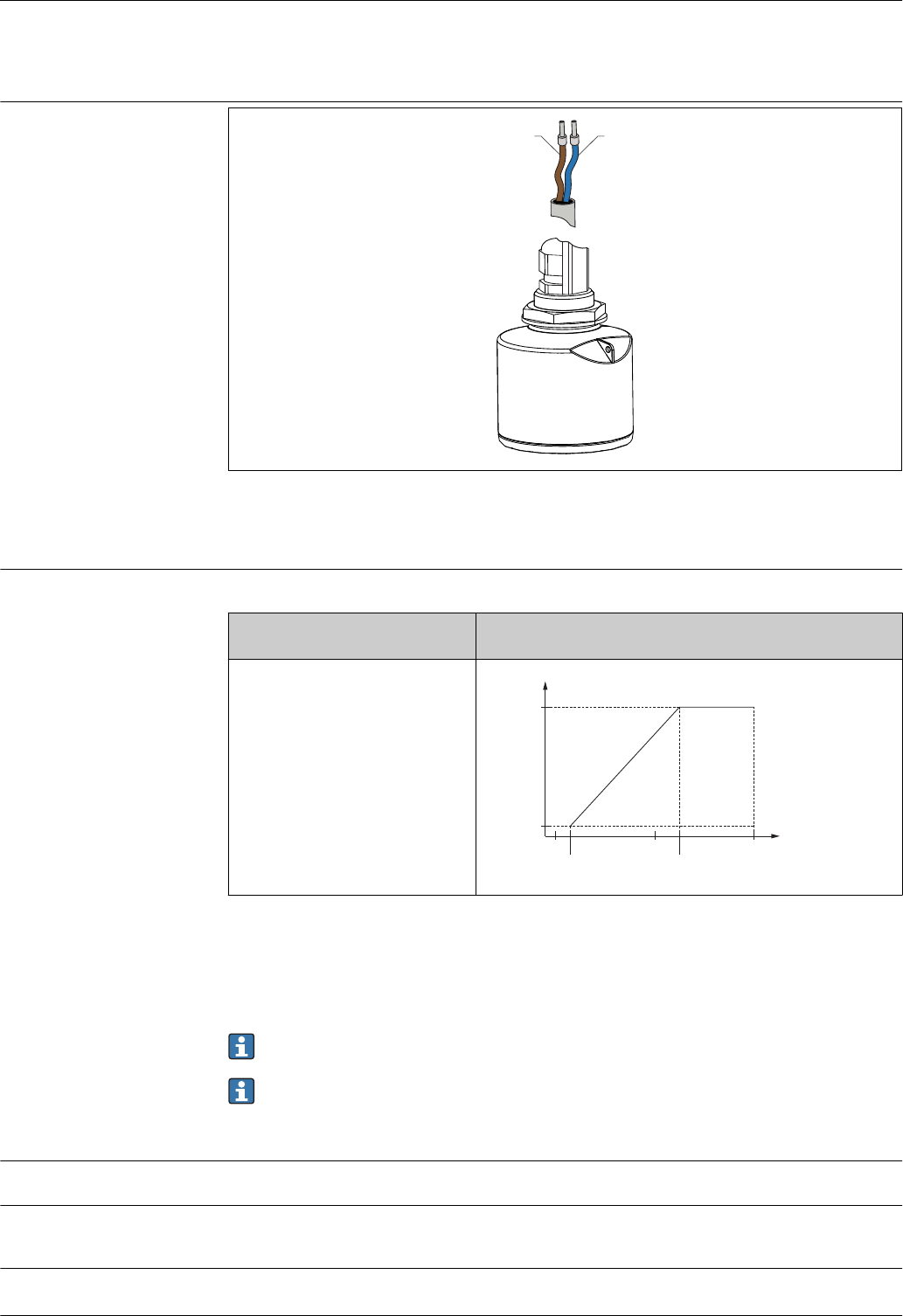
Micropilot FMR20
10 V. 5, Rev. 3, 20-12-2016 Endress+Hauser
Electrical connection
Cable assignment
-
+
12
A0028954
2 Cable assignment
1 Plus, brown wire
2 Minus, blue wire
Supply voltage An external power supply is necessary.
Terminal voltage U at device Maximum load R, depending on supply voltage U0 of power supply
unit
10.5 to 30 VDC 2-wire
R [ ]W
U0[V]
10
10.5 21.75
20 30
0
500
A0029226
Potential equalization
No special measures for potential equalization are required.
In the case of a device for the hazardous area, please comply with the safety instructions in the
separate "Safety Instructions" (XA, ZD) document.
Various power supply units can be ordered from Endress+Hauser: see "Accessories" section
→ 51
Battery operation
The sensor's Bluetooth® wireless technology communication can be disabled to increase the
operating life of the battery.
Power consumption Maximum input power: 675 mW
Current consumption • maximum input current: <25 mA
• Maximum start-up current: 3.6 mA
Starting time First stable measured value after 20 s (with supply voltage = 24 VDC)
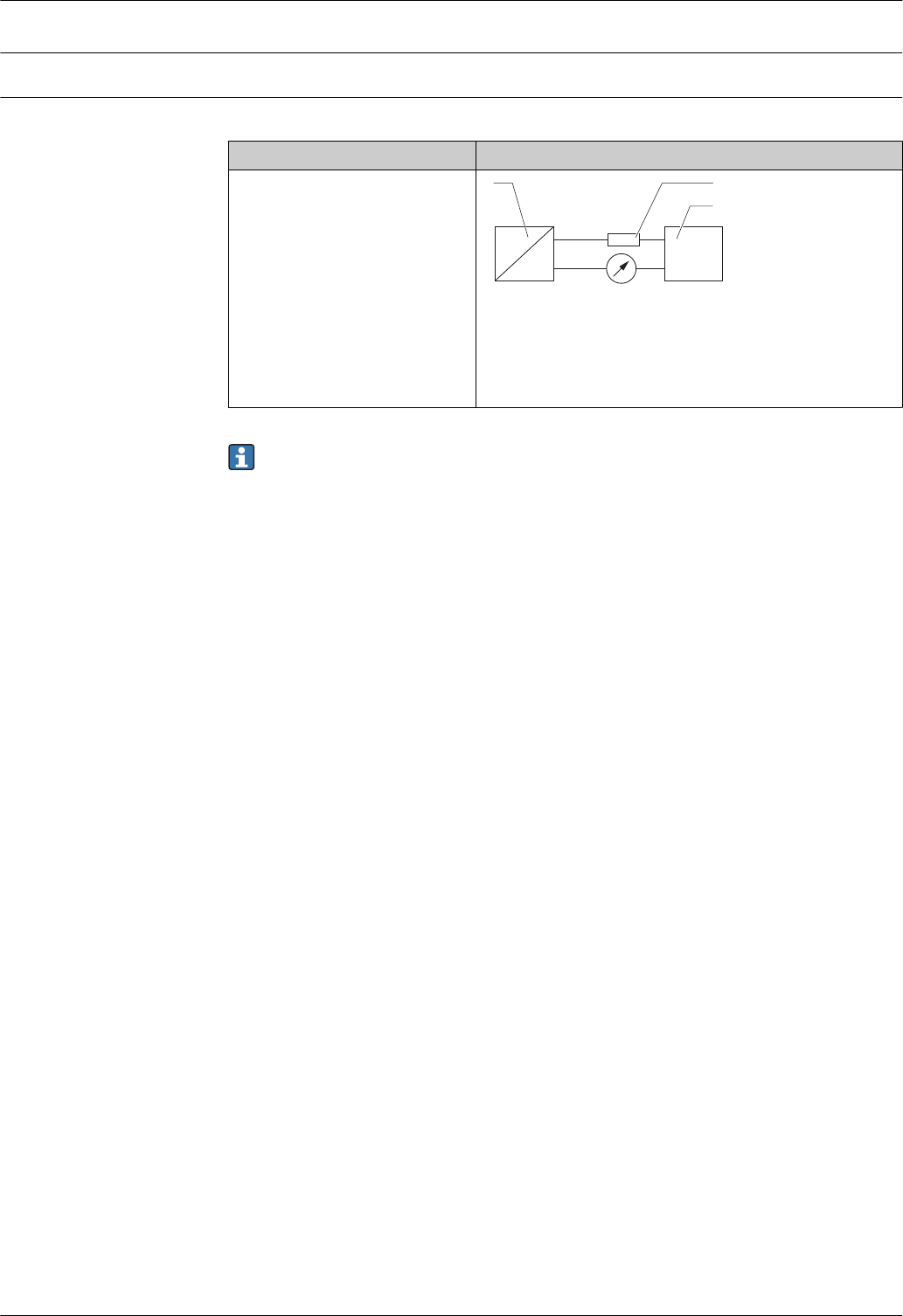
Micropilot FMR20
Endress+Hauser V. 5, Rev. 3, 20-12-2016 11
Power supply failure The configuration remains stored in the sensor.
Connection FMR20, 4 to 20 mA HART
Circuit diagram / Description
FMR20 connection with HART
communication, voltage source and
4 to 20 mA display
2
3
Y+ +
- -
I
1
mA
A0028908
3 FMR20 block diagram, HART
1 Micropilot FMR20
2 HART resistance
3 Power supply
The HART communication resistor of 250 Ω in the signal line is always necessary in the case of
a low-impedance power supply.
The voltage drop to be taken into account is:
Max. 6 V with 250 Ω communication resistor
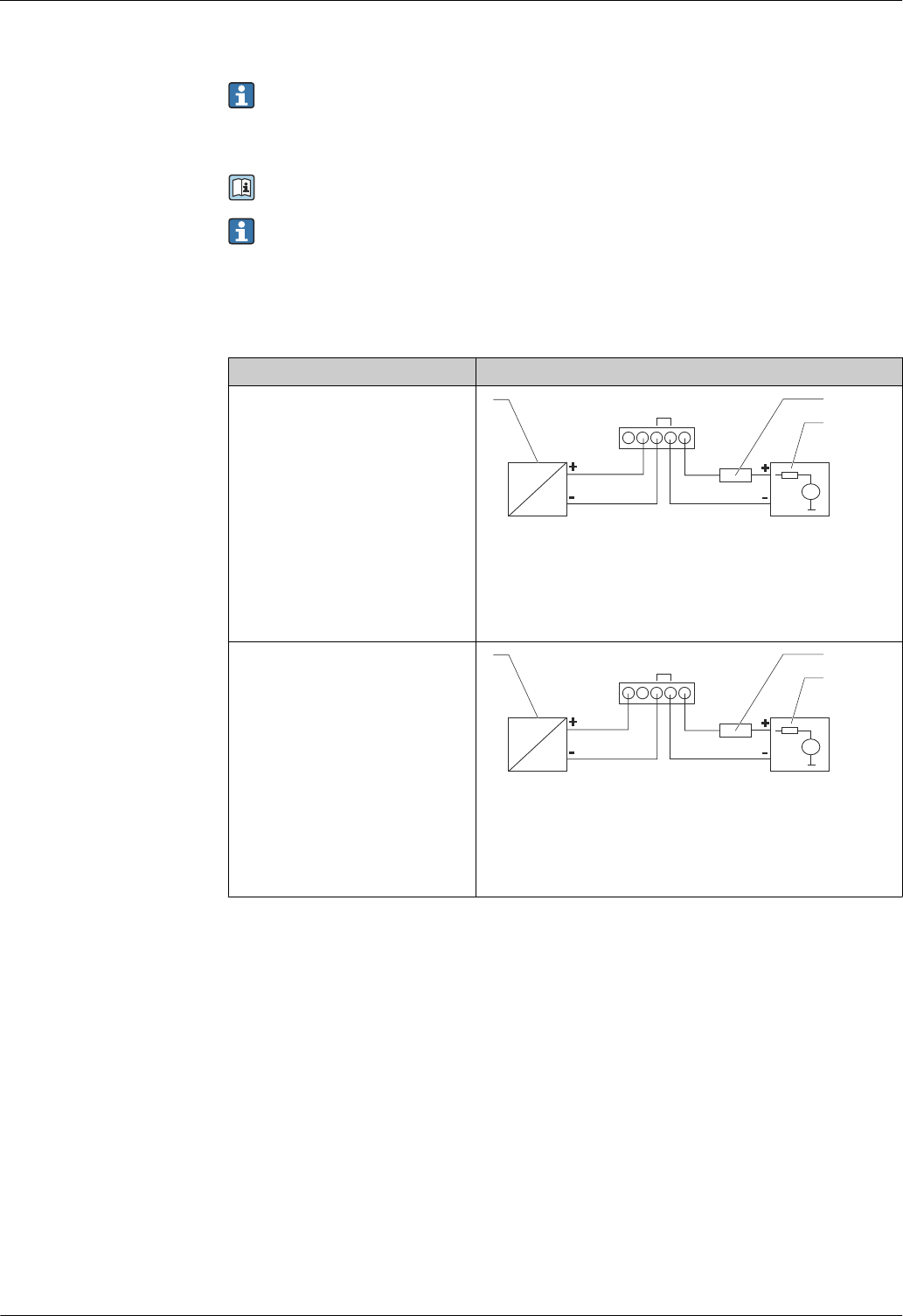
Micropilot FMR20
12 V. 5, Rev. 3, 20-12-2016 Endress+Hauser
FMR20 with RIA15 (incl. option for basic configuration FMR20)
The RIA15 remote display can be ordered together with the device.
Product structure, feature 620 "Accessory enclosed":
• Option R4 "Remote display RIA15 non-hazardous area, field housing"
• Option R5 "Remote display RIA15 with explosion protection approval, field housing"
Alternatively available as an accessory, for details see Technical Information TI01043K and
Operating Instructions BA01170K
The RIA15 process display unit is loop-powered and does not require any external power
supply.
The voltage drop to be taken into account is:
• ≤1 V in the standard version with 4 to 20 mA communication
• ≤1.9 V with HART communication
• additional 2.9 V if display light is used
Circuit diagram / Description
FMR20 connection, HART
communication and RIA15 without
backlight
Y
IRsDC
1
2
3
LED
-
+
A0019567
4 FMR20 block diagram, HART with RIA15 process display unit
without light
1 Micropilot FMR20
2 Power supply
3 HART resistance
FMR20 connection, HART
communication and RIA15 with
backlight
Y
IRsDC
1
2
3
LED
-
+
A0019568
5 FMR20 block diagram, HART with RIA15 process display unit
with light
1 Micropilot FMR20
2 Power supply
3 HART resistance
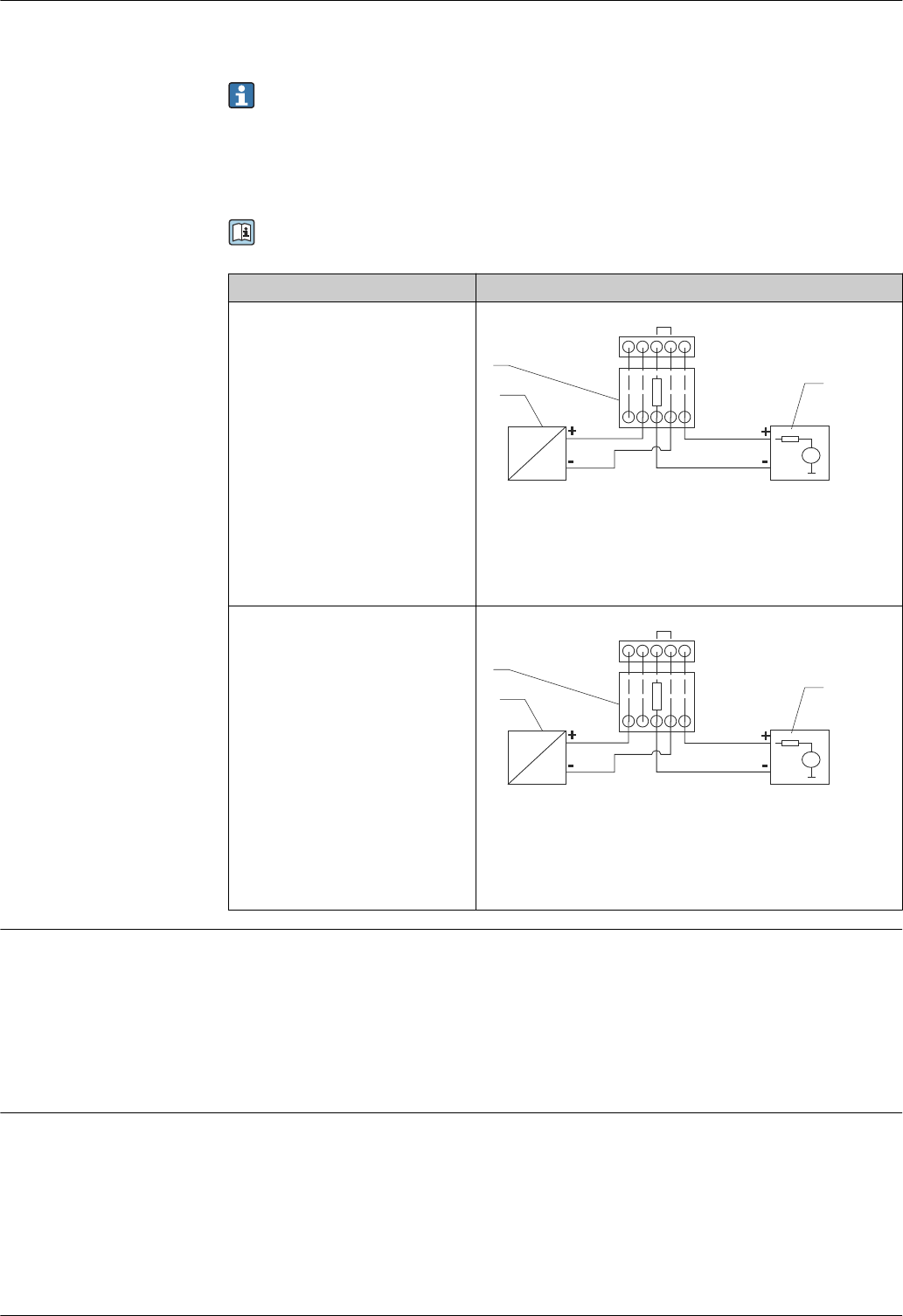
Micropilot FMR20
Endress+Hauser V. 5, Rev. 3, 20-12-2016 13
FMR20, RIA15 with installed HART communication resistor module
The HART communication module for installation in the RIA15 can be ordered together with
the device.
Product structure, feature 620 "Accessory enclosed":
Option R6 "HART communication resistor hazardous / non-hazardous area"
The voltage drop to be taken into account is:
Max. 7 V
Alternatively available as an accessory, for details see Technical Information TI01043K and
Operating Instructions BA01170K
Circuit diagram / Description
FMR20 connection and RIA15 without
backlight
1
LED
-
+
3
2
Y
IRsDC
A0020839
6 FMR20 block diagram, RIA15 without light, HART
communication resistor module
1 HART communication resistor module
2 Micropilot FMR20
3 Power supply
FMR20 connection and RIA15 with
backlight
1
3
2
Y
IRsDC
LED
-
+
A0020840
7 FMR20 block diagram, RIA15 with light, HART
communication resistor module
1 HART communication resistor module
2 Micropilot FMR20
3 Power supply
Cable specification Unshielded cable, 2 × 0.75 mm2
As per IEC/EN 60079-11 section 10.9, the cable is designed for a tensile strength of 30 N (6.74 lbf)
(over a period of 1 h).
The FMR20 is supplied with 5 m (16 ft) cable length as standard. Optional lengths are available with
10 m (33 ft) and 20 m (66 ft).
Lengths can be selected by the user up to an overall length of 300 m (980 ft) and are available by the
meter (ordering option "8") or foot (ordering option "A").
Overvoltage protection The device is equipped with integrated overvoltage protection.
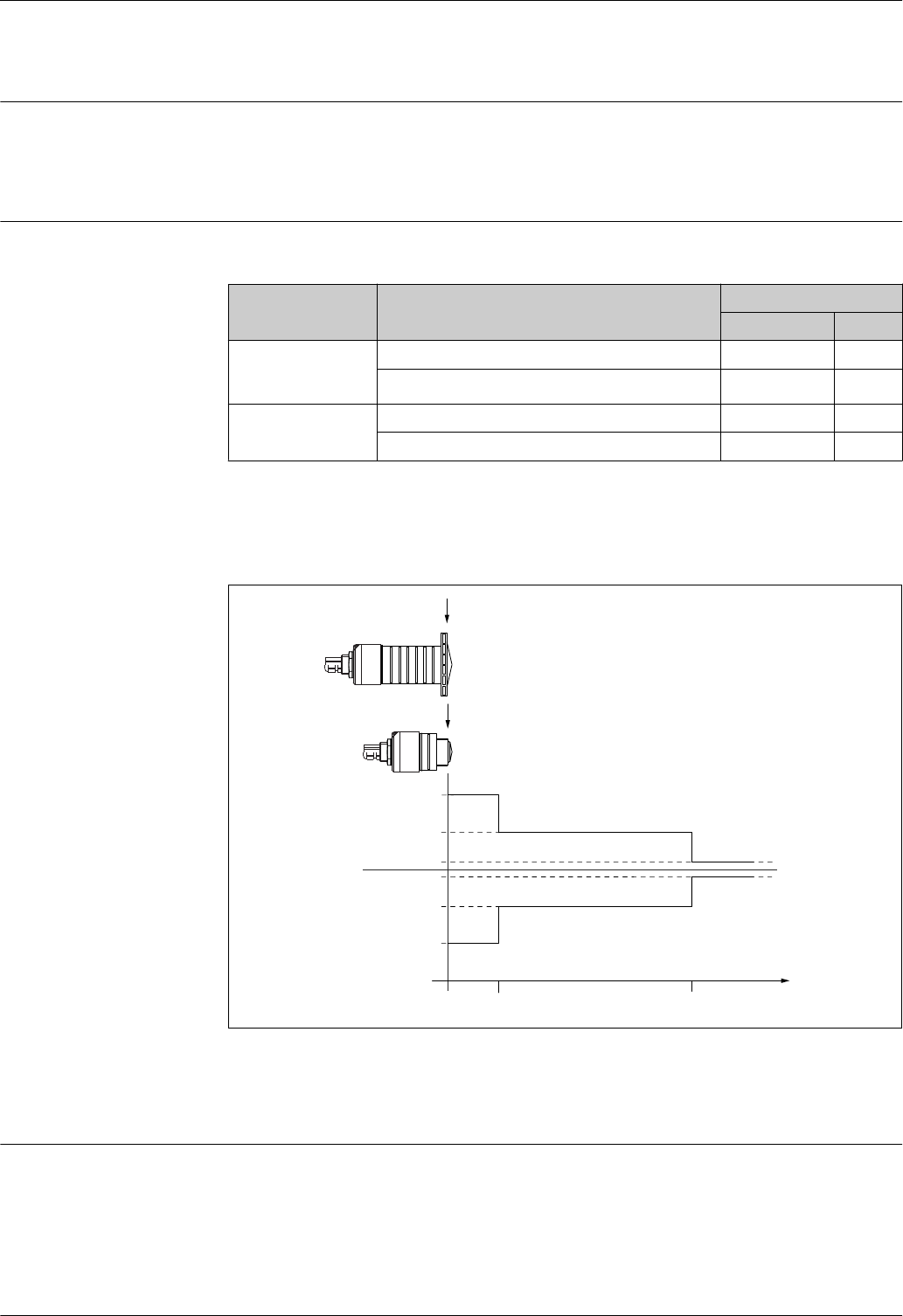
Micropilot FMR20
14 V. 5, Rev. 3, 20-12-2016 Endress+Hauser
Performance characteristics
Reference operating
conditions
• Temperature = +24 °C (+75 °F) ±5 °C (±9 °F)
• Pressure = 960 mbar abs. (14 psia) ±100 mbar (±1.45 psi)
• Humidity = 60 % ±15 %
• Reflector: metal plate with diameter ≥ 1 m (40 in)
• No major interference reflections inside the signal beam
Maximum measured error Typical data under reference operating conditions: DIN EN 61298-2, percentage values in relation to
the span.
Device Value Output
digital 1) analog 2)
FMR20
40 mm
(1.5 in)Antenna
Sum of non-linearity, non-repeatability and hysteresis ±2 mm (0.08 in) ±0.02 %
Offset/Zero ±4 mm (0.16 in) ±0.03 %
FMR20
80 mm (3 in)Antenna
Sum of non-linearity, non-repeatability and hysteresis ±2 mm (0.08 in) ±0.02 %
Offset/Zero ±4 mm (0.16 in) ±0.03 %
1) HART, SmartBlue (app)
2) Only relevant for 4-20mA current output; add error of the analog value to the digital value
Differing values in near-range applications
0
0,5 (1.67) D[m ](ft)
D[mm (in)]
2 (0.08)
10 (0.39)
-20 (0.79)
20 (0.79)
-2 (-0.08)
-10 (-0.39)
R
R
0,1 (0.33)
R
A0029049-EN
8 Maximum measured error in near-range applications; values for standard version
∆ Maximum measured error
R Reference point of the distance measurement
D Distance from reference point of antenna
Measured value resolution Dead band as per EN61298-2:
• Digital: 1 mm (0.04 in)
• Analog: 4 µA
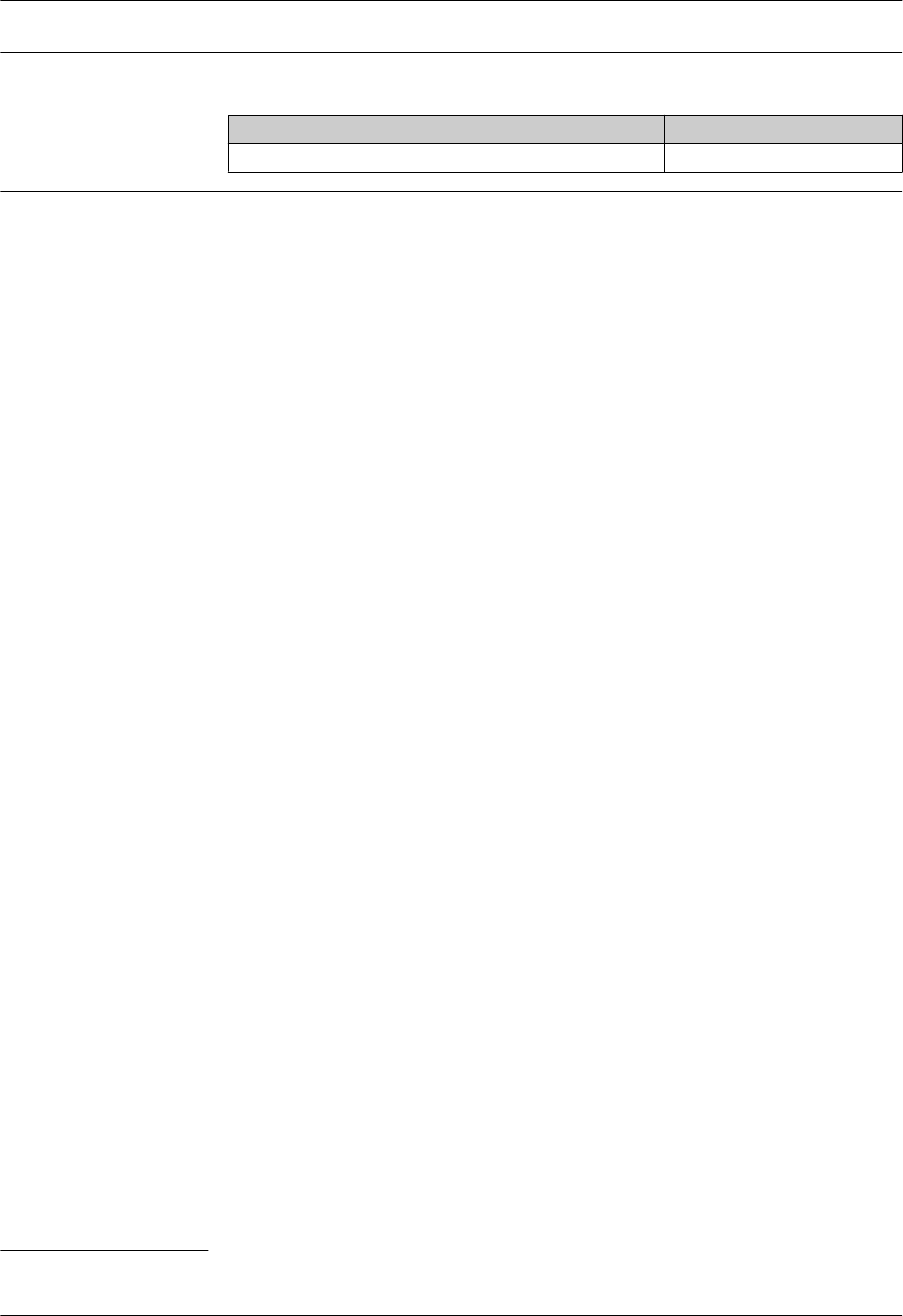
Micropilot FMR20
Endress+Hauser V. 5, Rev. 3, 20-12-2016 15
Response time The response time can be configured. The following step response times (as per DIN EN 61298-2) 1)
apply if the damping is switched off:
Tank height Sampling rate Response time
< 20 m (66 ft) 1 s-1 < 3 s
Influence of ambient
temperature
The measurements are carried out in accordance with EN 61298-3.
• Digital (HART, Bluetooth® wireless technology):
Standard version: average TK = ± 3 mm (0.12 in)/10 K
• Analog (current output):
– Zero point (4 mA): average TK = 0.02 %/10 K
– Span (20 mA): average TK = 0.05 %/10 K
1) According to DIN EN 61298-2 the step response time is the time which passes after a sudden change of the input signal until the output signal
assumes 90% of the steady-state value for the first time.
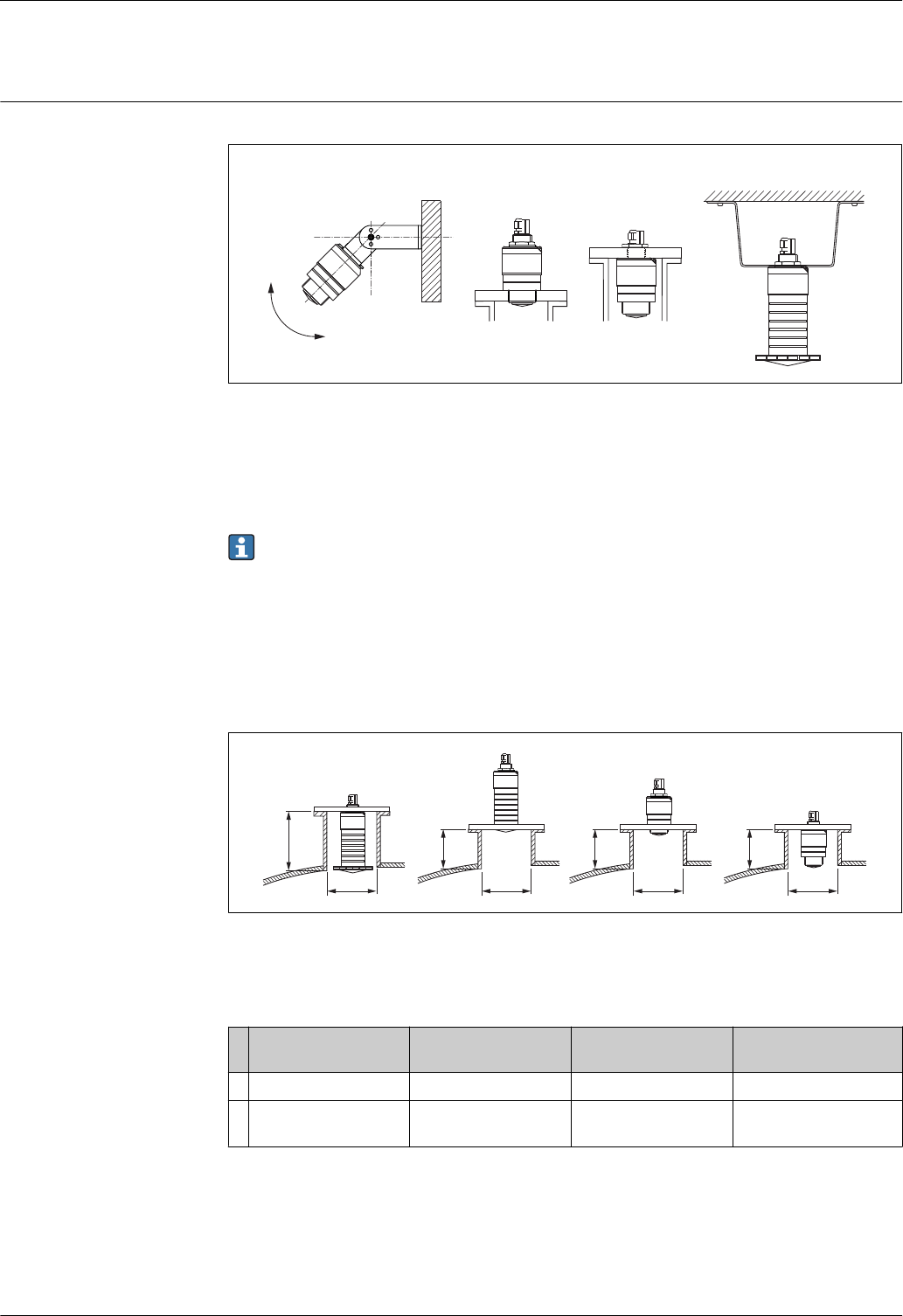
Micropilot FMR20
16 V. 5, Rev. 3, 20-12-2016 Endress+Hauser
Installation
Installation conditions Installation types
B C D
A
A0030605
9 Wall, ceiling or nozzle installation
A Wall or ceiling mount, adjustable
B Mounted at front thread
C Mounted at rear thread
D Ceiling installation with counter nut (included in delivery)
Caution!
• The sensor cables are not designed as supporting cables. Do not use as a suspension wire.
• In the free-field, a vertically downward orientation must be ensured at all times
Nozzle installation
The antenna should be just out of the nozzle for optimum measurement. The interior of the nozzle
must be smooth and may not contain any edges or welded joints. The edge of the nozzle should be
rounded if possible. The maximum nozzle length L depends on the nozzle diameter D. Please note
the specified limits for the diameter and length of the nozzle.
BA
L
D
L
D
L
D
L
D
A0028413
10 FMR20 nozzle installation
A FMR20 80 mm (3 in) antenna
B FMR20 40 mm (1.5 in) antenna
80 mm (3 in) antenna,
inside nozzle
80 mm (3 in) antenna,
outside nozzle
40 mm (1.5 in)
antenna, outside nozzle
40 mm (1.5 in) antenna,
inside nozzle
D min. 120 mm (4.72 in) min. 80 mm (3 in) min. 40 mm (1.5 in) min. 80 mm (3 in)
L max. 205 mm (8.07 in)
+ D × 4,5
max. D × 4,5 max. D × 1,5 max. 140 mm (5.5 in) +
D × 1,5
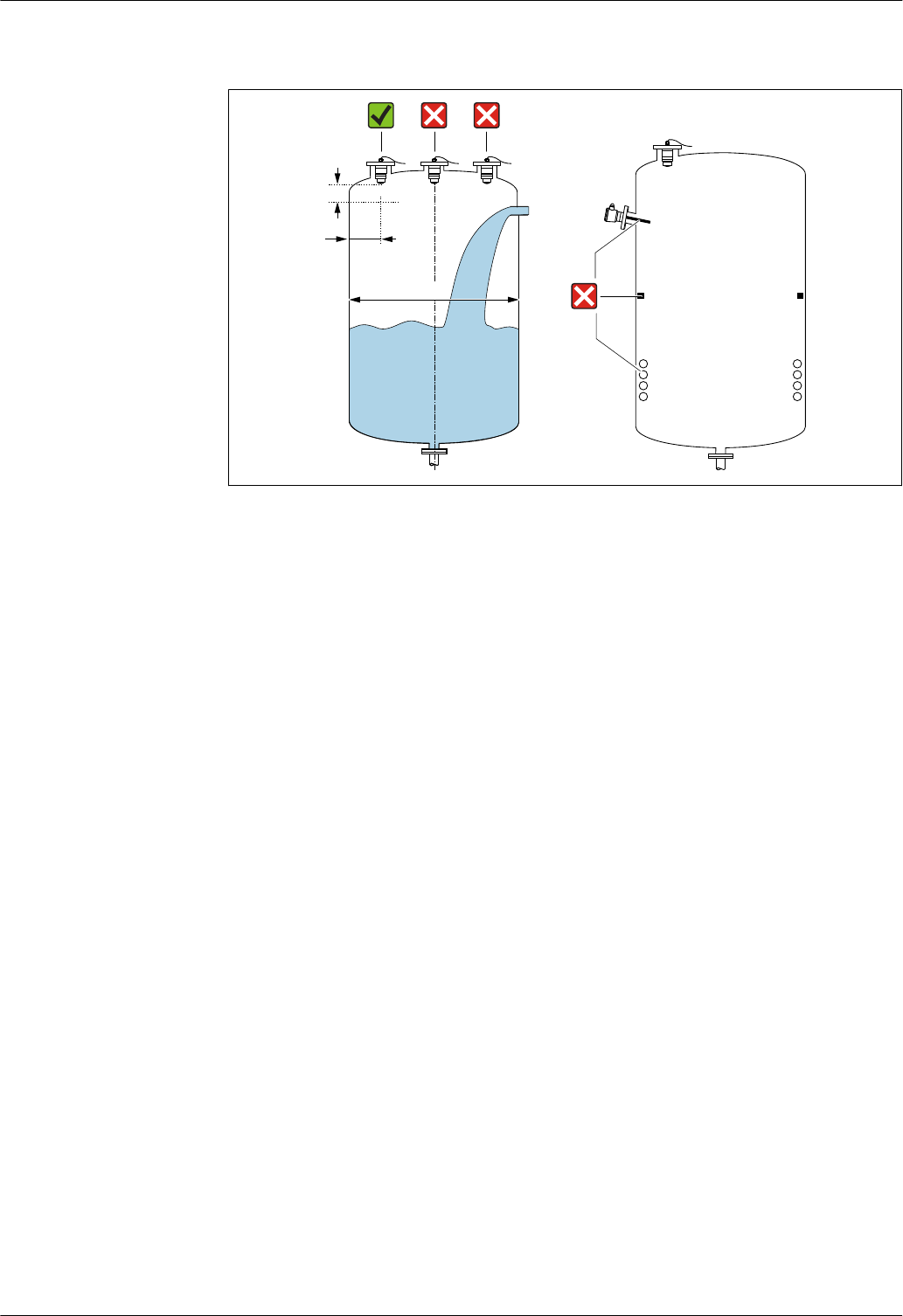
Micropilot FMR20
Endress+Hauser V. 5, Rev. 3, 20-12-2016 17
Orientation
A
BD
D
A0028410
11 Tank installation position
• If possible install the sensor so that its lower edge projects into the vessel.
• Recommended distance A wall - nozzle outer edge: ~ 1/6 of the tank diameter D. However, the
device must not under any circumstances be mounted closer than 15 cm (5.91 in) to the tank wall.
• Do not mount the sensor in the center of the tank.
• Avoid measurements through the filling curtain.
• Avoid equipment such as limit switches, temperature sensors, baffles, heating coils etc.
• Several devices can be operated in a single tank without impacting on each other.
• No signals are analyzed within the Blocking distance (BD). It can therefore be used to suppress
interference signals (e.g. the effects of condensate) close to the antenna.
An automatic Blocking distance of at least 0.1 m (0.33 ft) is configured as factory setting.
However, this can be overwritten manually (0 m (0 ft) is also permitted).
Automatic calculation:
Blocking distance = Empty calibration - Full calibration - 0.2 m (0.656 ft).
Each time a new entry is made in the Empty calibration parameter orFull calibration parameter,
the Blocking distance parameter is recalculated automatically using this formula.
If the result of the calculation is a value <0.1 m (0.33 ft), the Blocking distance of0.1 m (0.33 ft)
continues to be used.
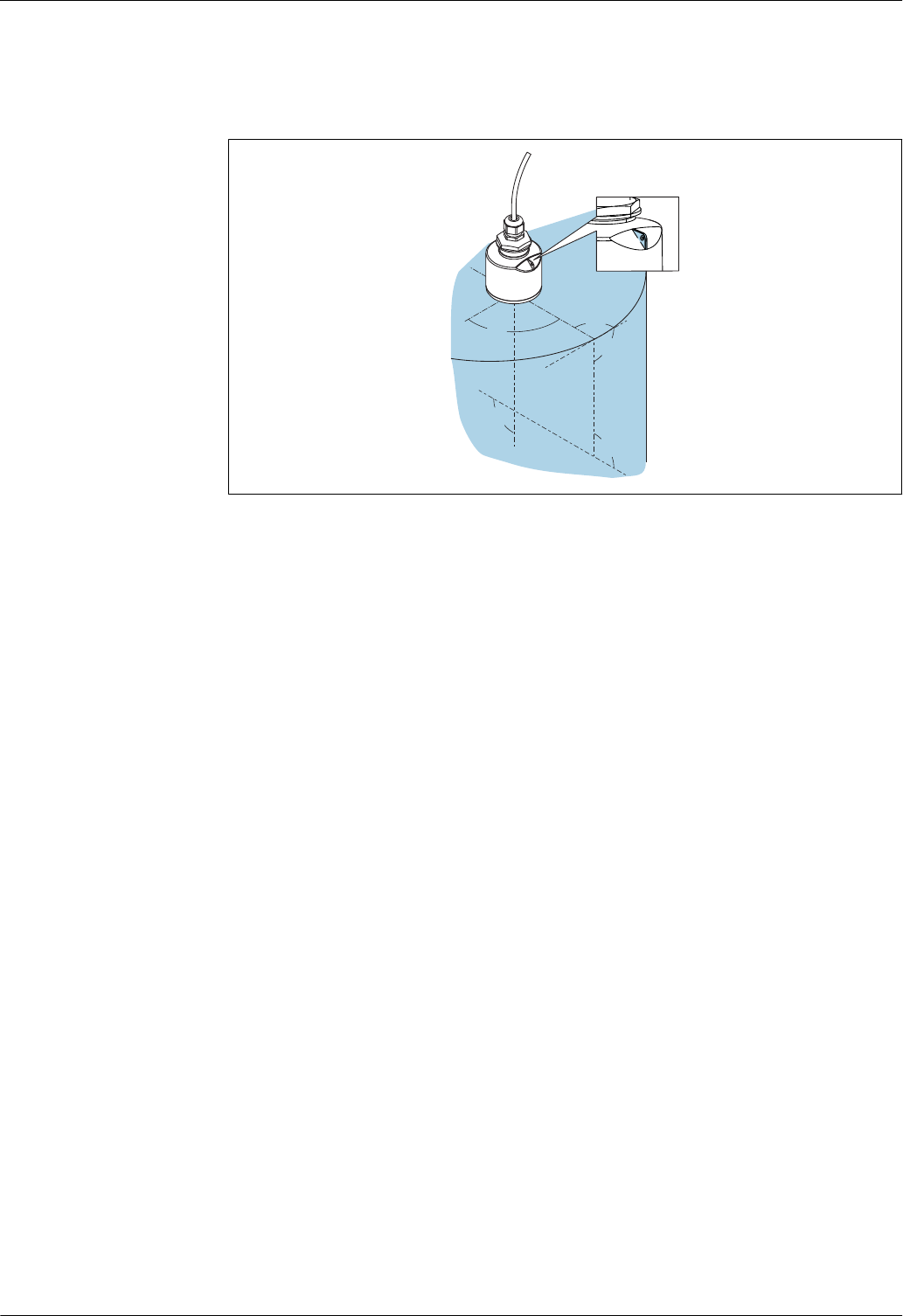
Micropilot FMR20
18 V. 5, Rev. 3, 20-12-2016 Endress+Hauser
Alignment
• Align the antenna vertically to the product surface.
• Align the eyelet with the mounting eye as well as possible towards the tank wall.
90°
90°
90°
90°
90°
A0028927
12 Sensor alignment when mounting in tank
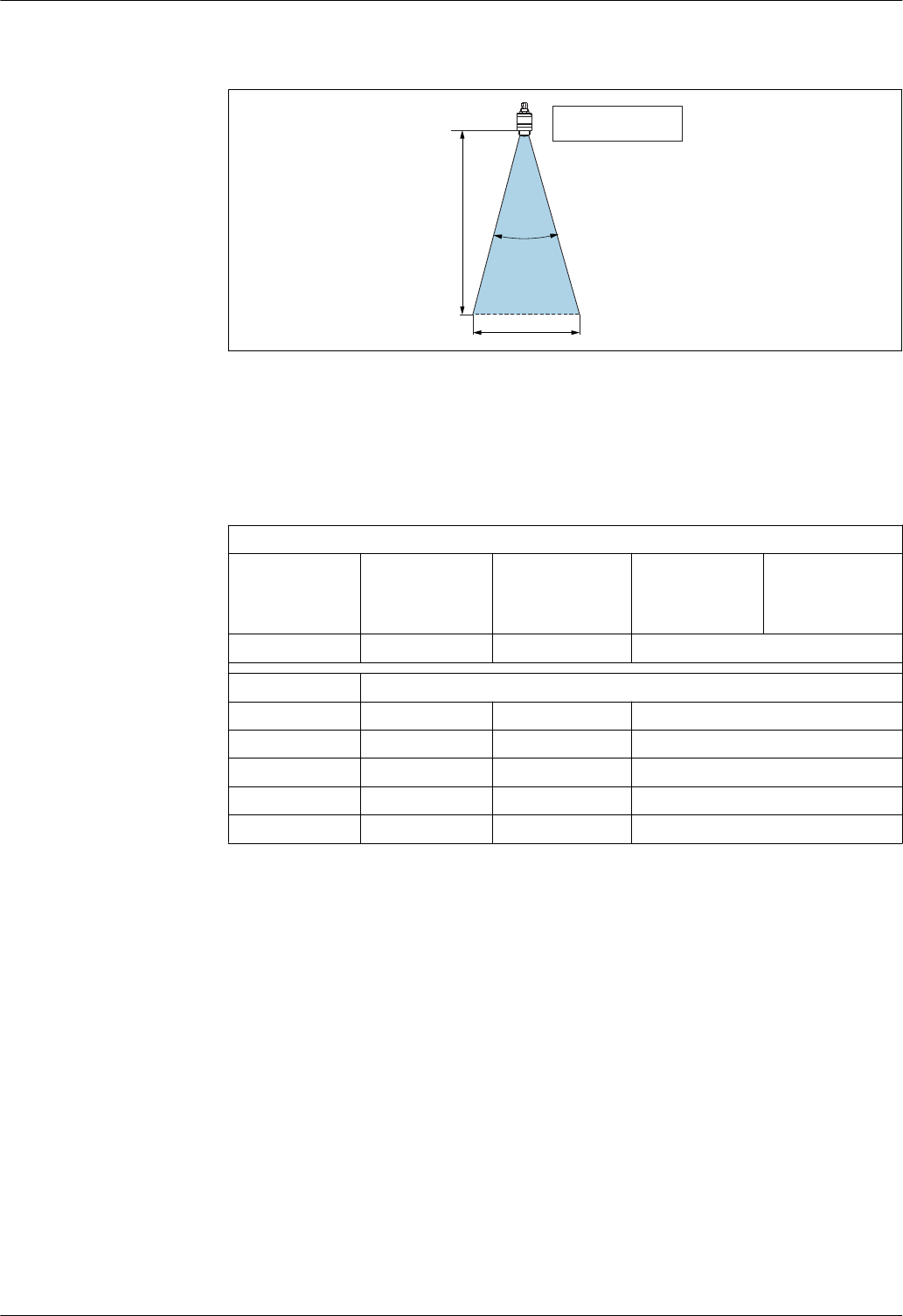
Micropilot FMR20
Endress+Hauser V. 5, Rev. 3, 20-12-2016 19
Beam angle
α
D
W
W = 2 x D x tan
_
2
α
A0029053-EN
13 Relationship between beam angle α, distance D and beam diameter W
The beam angle is defined as the angle α, at which the power density of the radar waves reaches half
the value of the maximum power density (3dB width). Microwaves are also emitted outside the
signal beam and can be reflected off interfering installations.
Beam diameter W as a function of beam angle α and distance D.
FMR20
Antenna size 40 mm (1.5 in) 40 mm (1.5 in)
with accessory
"flooding protection
tube"
80 mm (3 in) 80 mm (3 in)
with accessory
"flooding protection
tube"
Beam angle α 30° 12° 12°
Distance (D) Beam diameter W
3 m (9.8 ft) 1.61 m (5.28 ft) 0.63 m (2.07 ft) 0.63 m (2.1 ft)
5 m (16.4 ft) 2.68 m (8.79 ft) 1.51 m (4.95 ft) 1.05 m (3.45 ft)
10 m (33 ft) 5.36 m (17.59 ft) 2.10 m (6.90 ft) 2.1 m (6.9 ft)
15 m (49 ft) - - 3.15 m (10.34 ft)
20 m (66 ft) - - 4.2 m (13.79 ft)
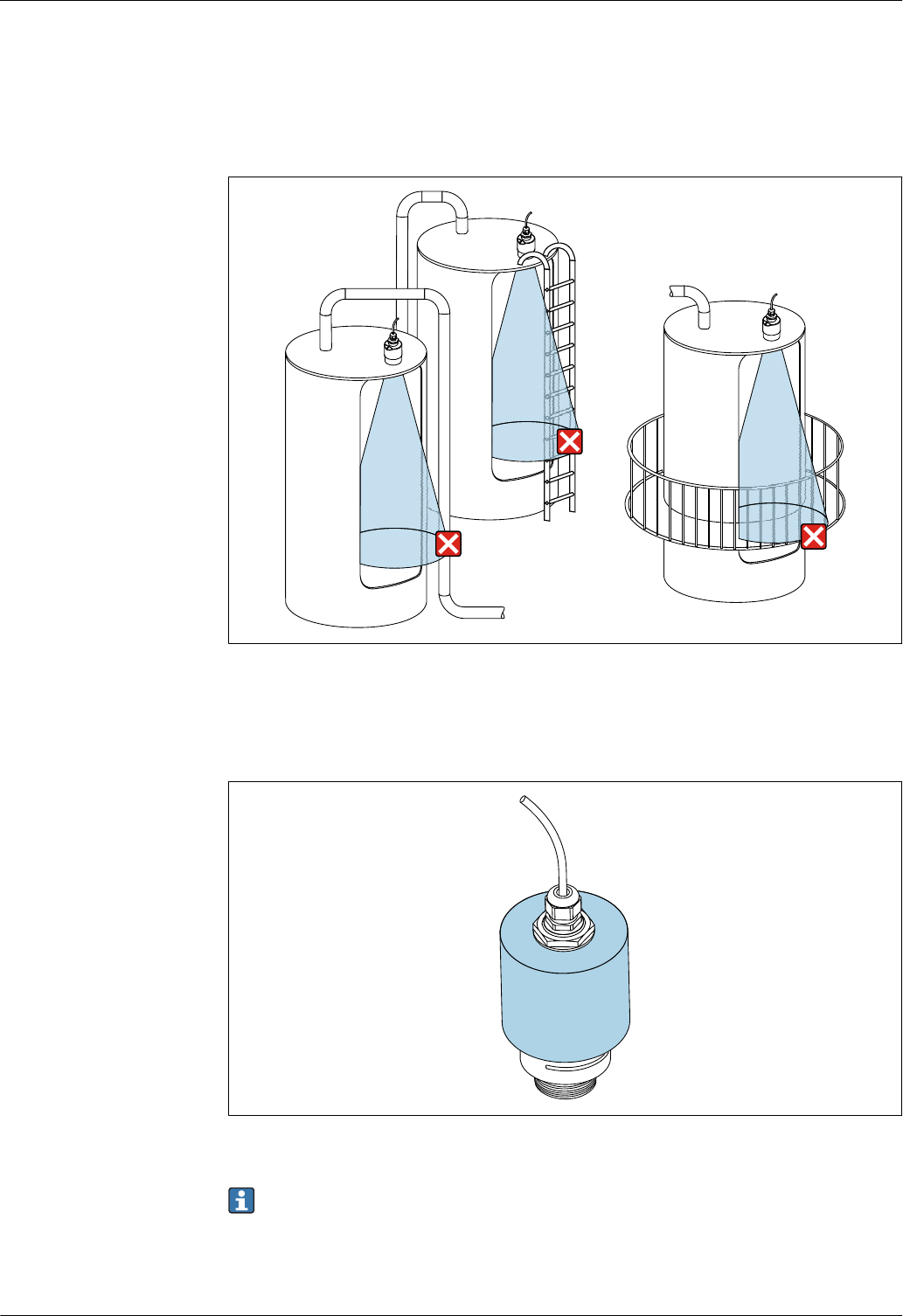
Micropilot FMR20
20 V. 5, Rev. 3, 20-12-2016 Endress+Hauser
Measurement in plastic vessels
If the outer wall of the vessel is made of a non-conductive material (e.g. GFR) microwaves can also be
reflected off interfering installations outside of the vessel (e.g. metallic pipes (1), ladders (2),
grates (3), ...). Therefore there should be no such interfering installations in the signal beam. For
more information, please contact Endress+Hauser.
3
1
2
A0029540
14 Measurement in a plastic vessel
Weather protection cover
For outdoor use, a weather protection cover is recommended.
A0031277
15 Weather protection cover, e.g. with 40 mm (1.5") antenna
The sensor is not completely covered in the case of the 40 mm (1.5 in) antenna or the
80 mm (3 in) antenna.
The weather protection cover is available as an accessory. → 38
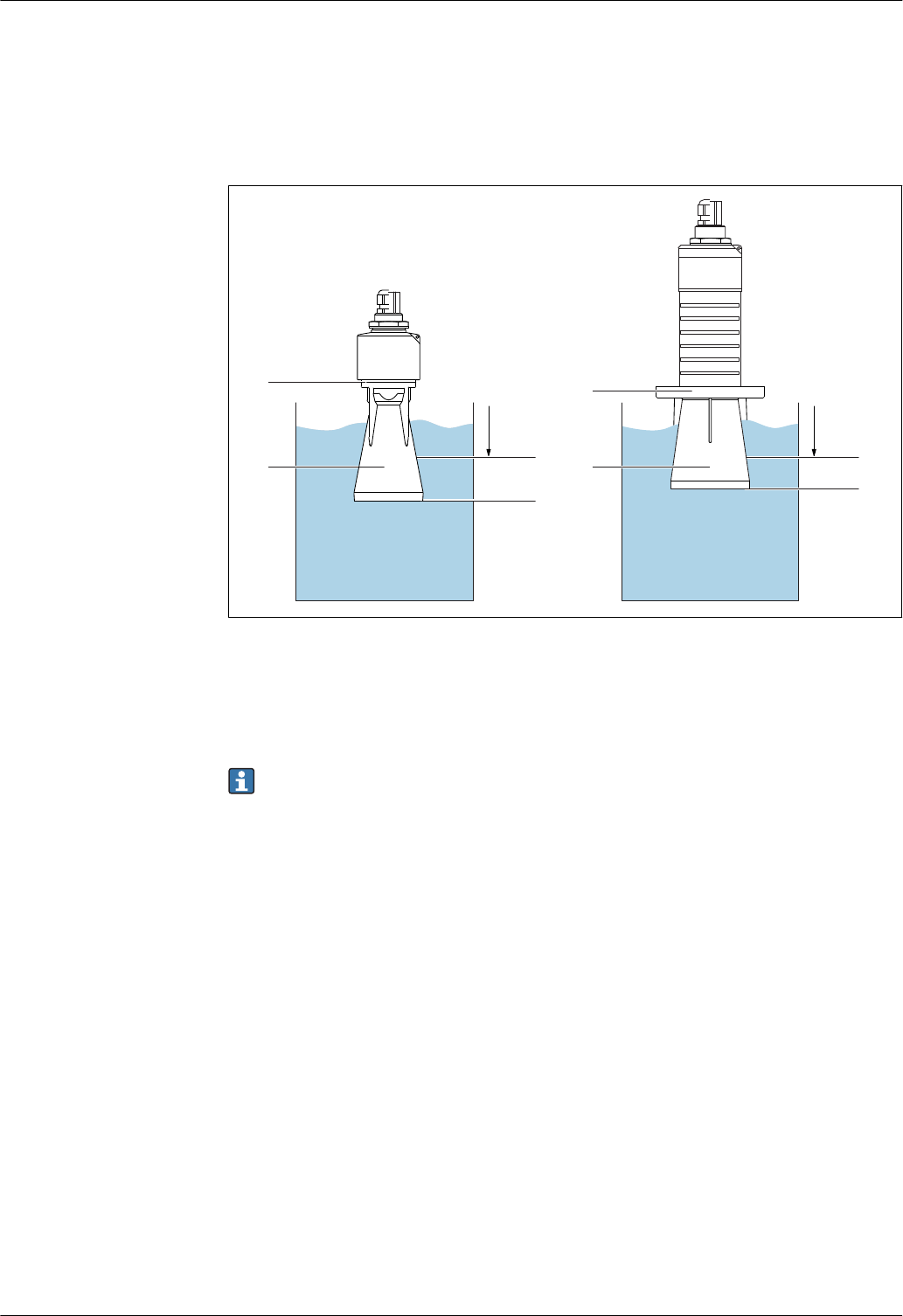
Micropilot FMR20
Endress+Hauser V. 5, Rev. 3, 20-12-2016 21
Free-field measurement with flooding protection tube
The flooding protection tube guarantees a definitive analysis of the maximum level even in the event
that the sensor is completely flooded.
In free-field installations and / or in applications where there is a risk of flooding, the flooding
protection tube must be used.
13
4
1
2
3
4
2
A0031093
16 Function of flooding protection tube
1 Air pocket
2 O-ring (EPDM) seal
3 Blocking distance
4 Max. Level
Flooding protection tube 40 mm (1.5 in) Antenna, metallized PBT-PC:
For use with devices in product structure, feature 100 "Process connection front", option WFE
"Thread ISO228 G1-1/2".
The flooding protection tube can be ordered with the device. Product structure, feature 620
"Accessory enclosed", option R7 "Flooding protection tube, metallized PBT-PC suitable for
40 mm (1.5 in) antenna with G1-1/2" process connection on front".
Alternatively available as an accessory; order number 71325090.
Flooding protection tube 80 mm (3 in) Antenna, metallized PBT-PC:
For use with devices in product structure, feature 100 "Process connection on front", option XR0
"Customer mounting device without flange".
The flooding protection tube can be ordered with the device. Product structure, feature 620
"Accessory enclosed", option R8 "Flooding protection tube, metallized PBT-PC suitable for
80 mm (3 in) antenna.
Alternatively available as an accessory; order number 71327051.
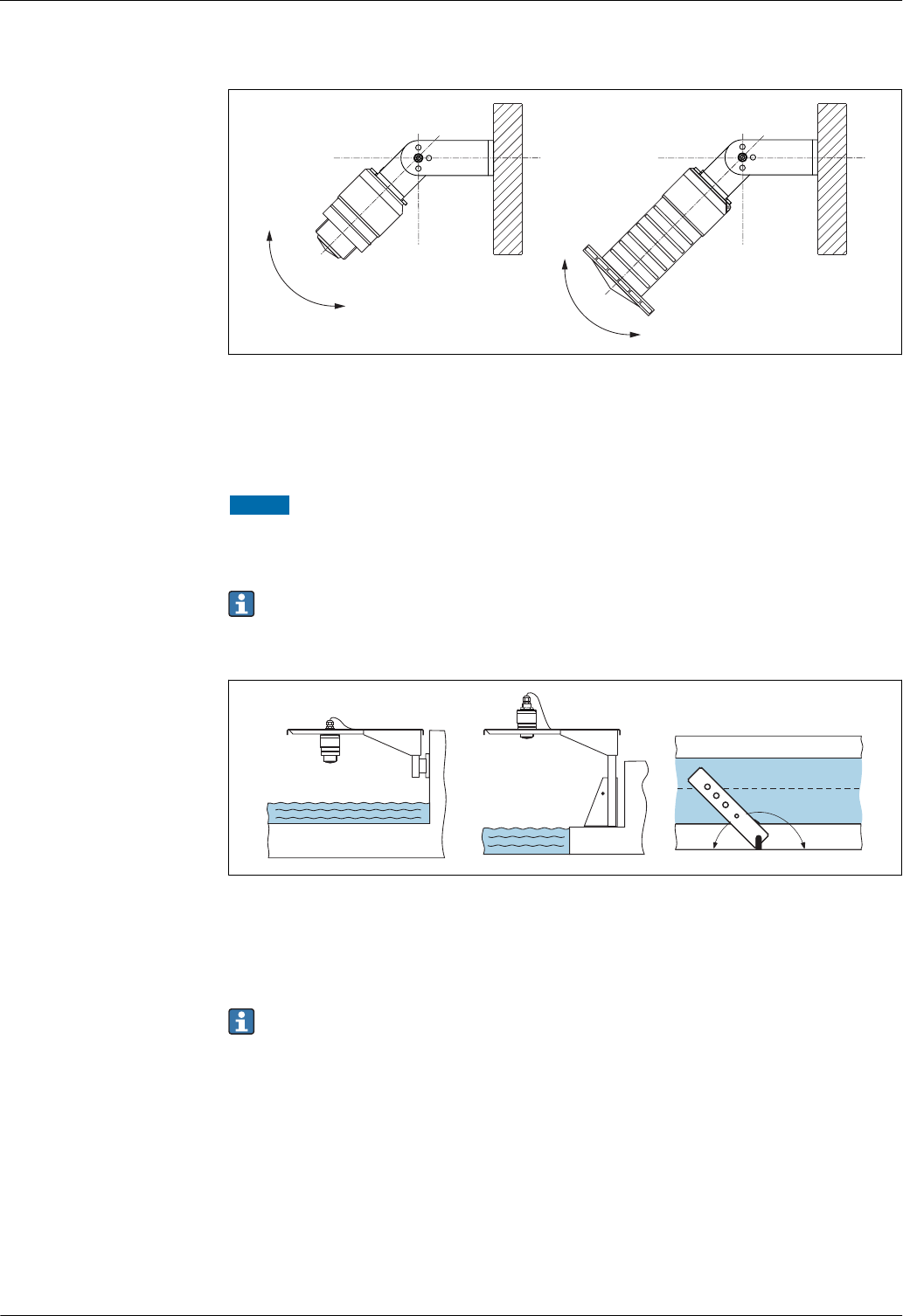
Micropilot FMR20
22 V. 5, Rev. 3, 20-12-2016 Endress+Hauser
Installation with mounting bracket, adjustable
A0030606
17 Installation with mounting bracket, adjustable
• Wall or ceiling installation is possible.
• Using the mounting bracket, position the antenna so that it is perpendicular to the product
surface.
NOTICE
There is no conductive connection between the mounting bracket and transmitter housing.
Risk of electrostatic charge.
‣Integrate the mounting bracket in the local potential equalization system.
The mounting bracket is available as an accessory. → 38
Cantilever installation, with pivot
ABC
A0028412
18 Cantilever installation, with pivot
A Installation with cantilever and wall bracket
B Installation with cantilever and mounting frame
C The cantilever can be turned (e.g. in order to position the sensor over the center of the channel, for example)
The cantilever, wall bracket and mounting frame are available as accessories. → 38
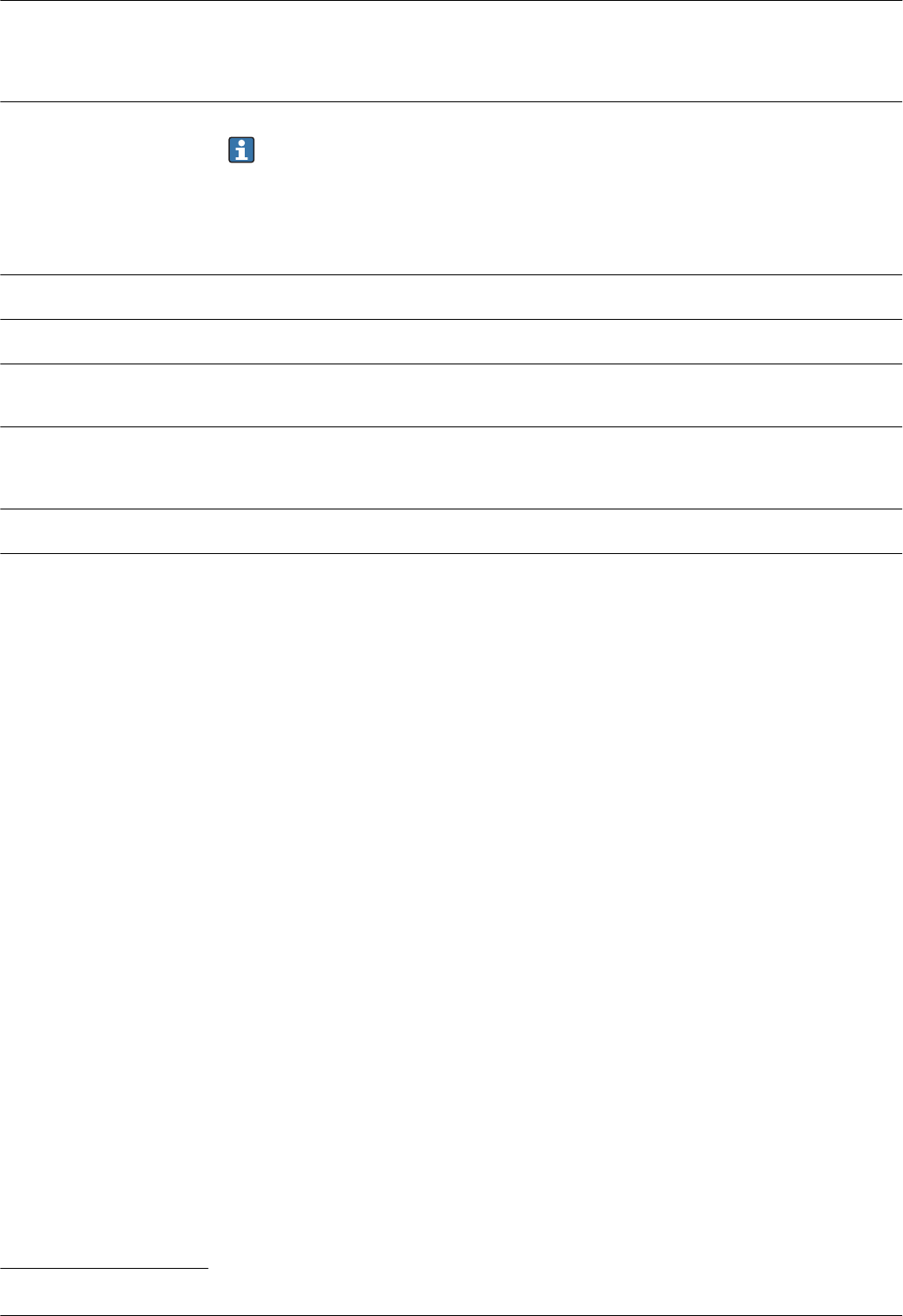
Micropilot FMR20
Endress+Hauser V. 5, Rev. 3, 20-12-2016 23
Environment
Ambient temperature range Measuring device: –40 to +80 °C (–40 to +176 °F)
It may not be possible to use the Bluetooth connection at ambient temperatures
> 60 °C (140 °F).
Outdoor operation in strong sunlight:
• Mount the device in the shade.
• Avoid direct sunlight, especially in warmer climatic regions.
• Use a weather protection cover → 38.
Storage temperature –40 to +80 °C (–40 to +176 °F)
Climate class DIN EN 60068-2-38 (test Z/AD)
Installation height as per
IEC 61010-1 Ed.3
Generally up to 2 000 m (6 600 ft) above sea level.
Degree of protection Tested acc. to:
– IP66, NEMA 4X
– IP68, NEMA 6P (24 h at 1.83 m (6.00 ft) under water)
Vibration resistance DIN EN 60068-2-64 / IEC 60068-2-64: 20 to 2 000 Hz, 1 (m/s2)2/Hz
Electromagnetic
compatibility (EMC)
Electromagnetic compatibility in accordance with all of the relevant requirements outlined in the
EN 61000 series and NAMUR Recommendation EMC (NE 21). For details, please refer to the
Declaration of Conformity 2)
2) Available for download at www.endress.com.
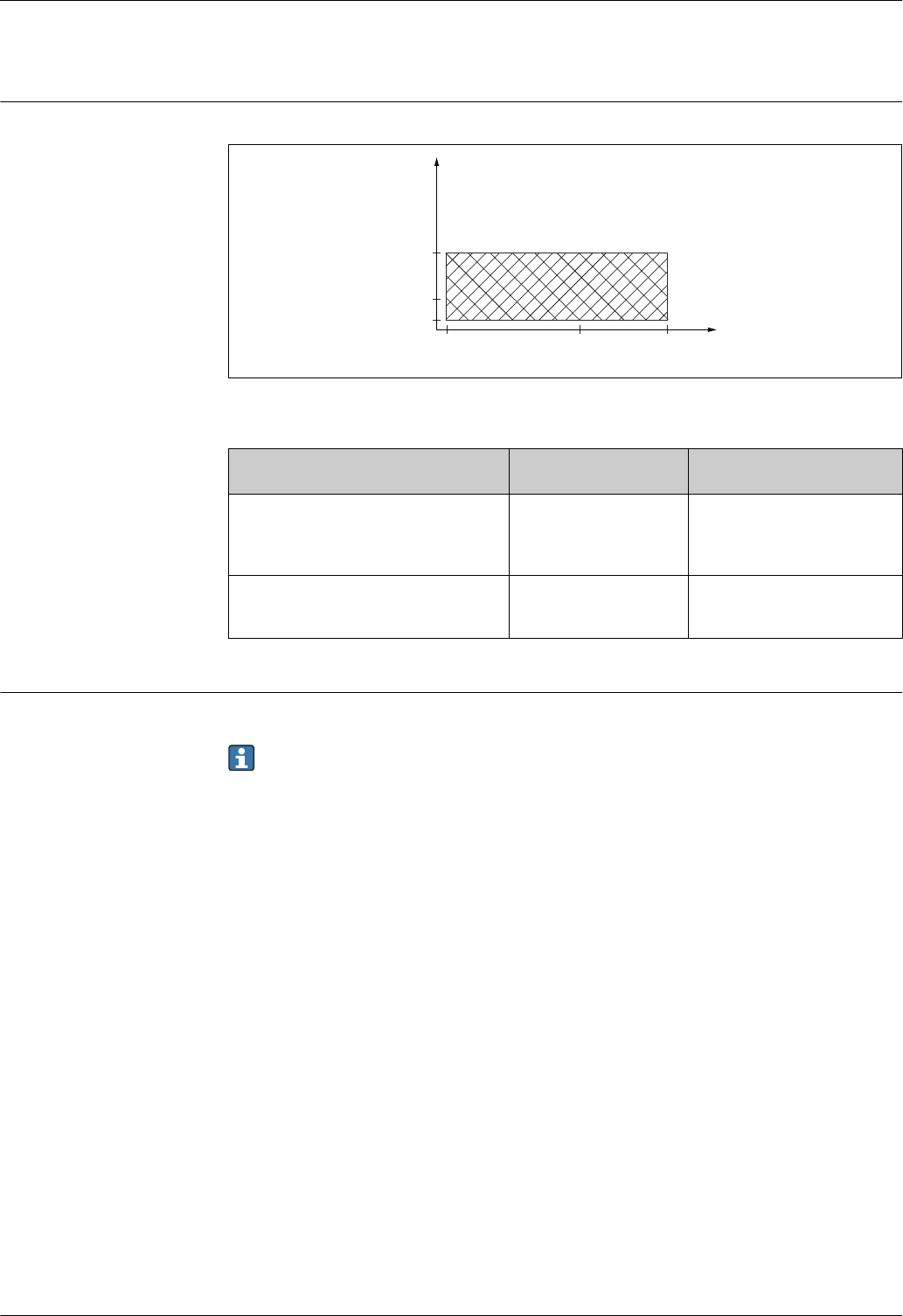
Micropilot FMR20
24 V. 5, Rev. 3, 20-12-2016 Endress+Hauser
Process
Process temperature, process
pressure
FMR20
p
-40 +80 ( 76)+1
0 ( )+32
Tp
[ °F ]°C ( )
-1( )-14.5
0
[bar ](psi)
3 (43.5)
A0029007-EN
19 FMR20: Permitted range for process temperature and process pressure
Feature 100 "Process connection" Process temperature
range
Process pressure range
• VEE: Thread ASME MNPT1-1/2; PVDF
• VFE: Thread ASME MNPT2; PVDF
• WFE: Thread ISO228 G1-1/2; PVDF
• WFE: Thread ISO228 G2; PVDF
–40 to +80 °C
(–40 to +176 °F)
prel =
–1 to 3 bar (–14.5 to 43.5 psi)
pabs < 4 bar (58 psi) 1)
• RPF: UNI slip-on flange 3"/DN80/80; PP
• RRF: UNI slip-on flange 4"/DN100/100; PP
• RSF: UNI slip-on flange 6"/DN150/150; PP
–40 to +80 °C
(–40 to +176 °F)
prel =
–1 to 1 bar (–14.5 to 14.5 psi)
pabs < 2 bar (29 psi) 1)
1) The pressure range may be further restricted in the event of a CRN approval.
Dielectric constant For liquids
εr ≥ 4
For dielectric constants (DC values) of many media commonly used in various industries refer
to:
• the Endress+Hauser DC manual (CP01076F)
• the Endress+Hauser "DC Values App" (available for Android and iOS)
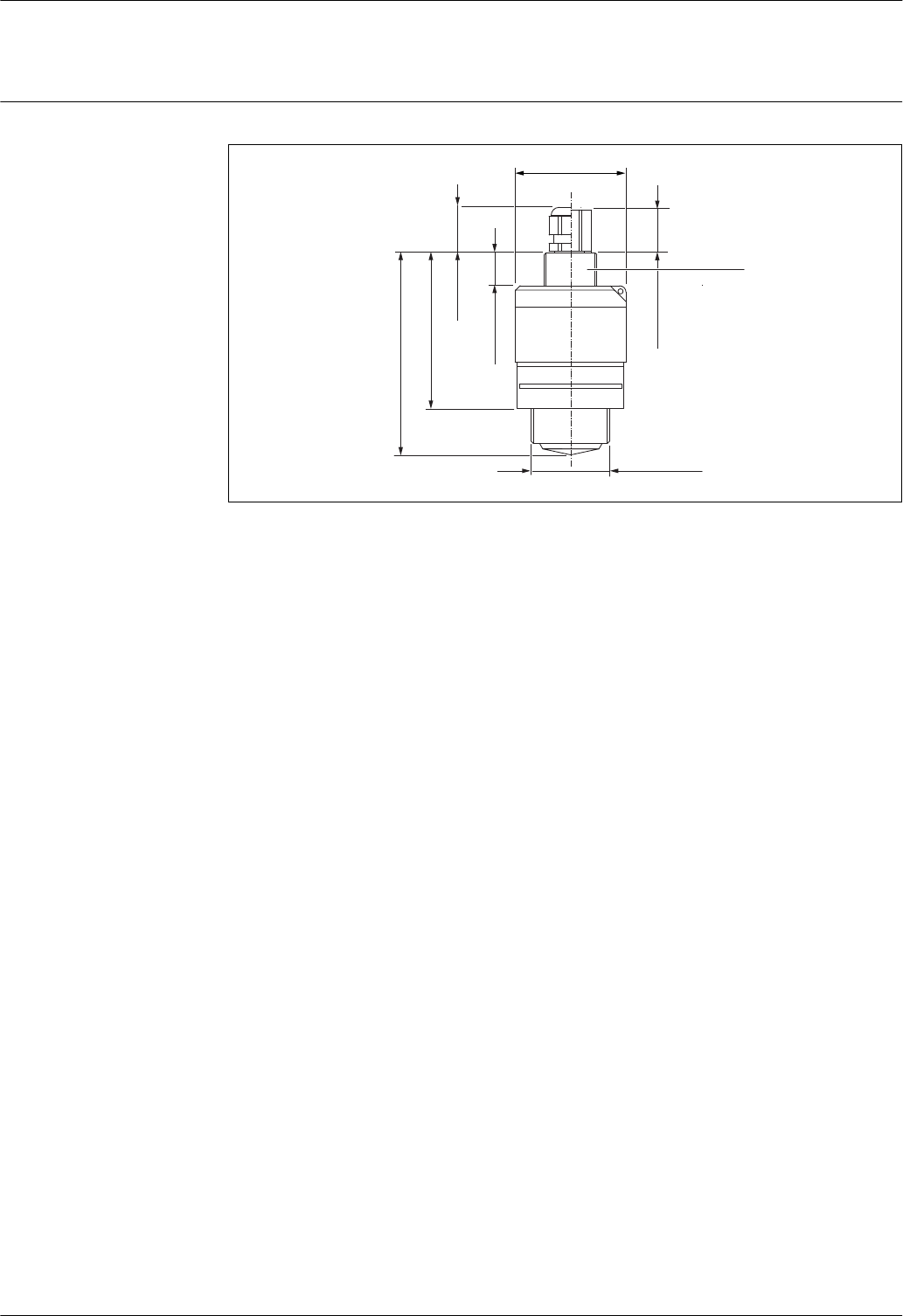
Micropilot FMR20
Endress+Hauser V. 5, Rev. 3, 20-12-2016 25
Mechanical construction
Dimensions 40 mm (1.5 in) antenna with G 1-1/2" or MNPT 1-1/2" thread
G 1 1/2"
20 (0.79)
G 1"
NPT 1"
26 (1.02)
ø75 (2.95)
28 (1.1)
140 (5.5)
112 (4.4)
NPT 1 1/2"
AB
A0028805
20 Dimensions process connection G 1-1/2" or MNPT 1-1/2" thread,engineering unit:mm (in)
A Cable gland
B FNPT 1/2" conduit connection
Applies to the following device versions
•Feature 095 "Process connection rear side"
– VCE: Thread ASME MNPT1; PVDF; FNPT 1/2" conduit connection
– WDE: Thread G1 ISO228; PVDF; cable gland
•Feature 100 "Process connection front side"
– VEE: Thread ASME MNPT1-1/2; PVDF
– WFE: Thread ISO228 G1-1/2; PVDF
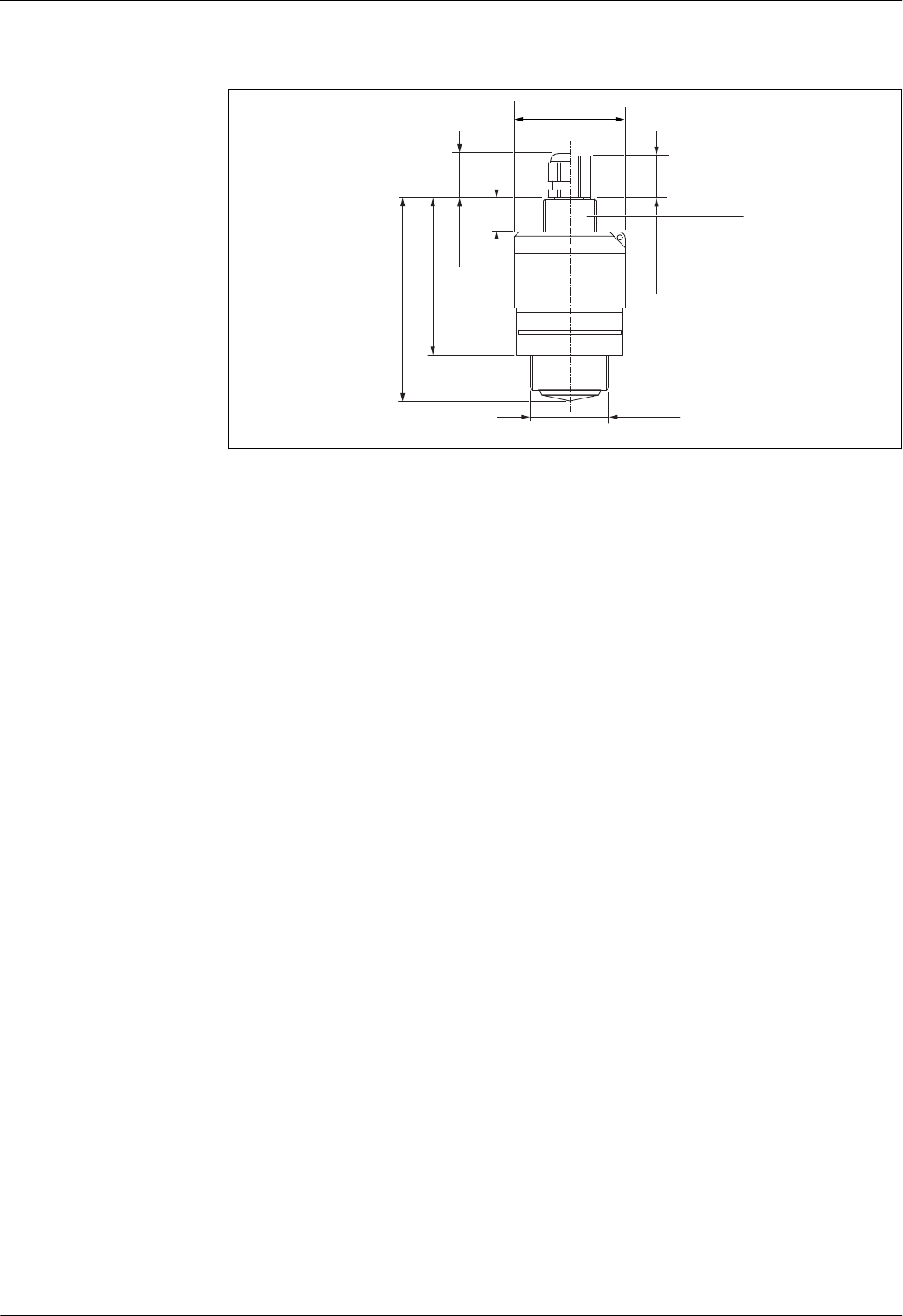
Micropilot FMR20
26 V. 5, Rev. 3, 20-12-2016 Endress+Hauser
40 mm (1.5 in) antenna with G 2" or MNPT 2" thread
G 2"
20 (0.79)
G 1"
NPT 1"
26 (1.02)
ø75 (2.95)
28 (1.1)
140 (5.5)
112 (4.4)
NPT 2"
AB
A0028806
21 Dimensions process connection G 2" or MNPT 2" thread,engineering unit:mm (in)
A Cable gland
B FNPT 1/2" conduit connection
Applies to the following device versions
•Feature 095 "Process connection rear side"
– VCE: Thread ASME MNPT1; PVDF; FNPT 1/2" conduit connection
– WDE: Thread G1 ISO228; PVDF; cable gland
•Feature 100 "Process connection front side"
– VFE: Thread ASME MNPT2; PVDF
– WGE: Thread ISO228 G2; PVDF
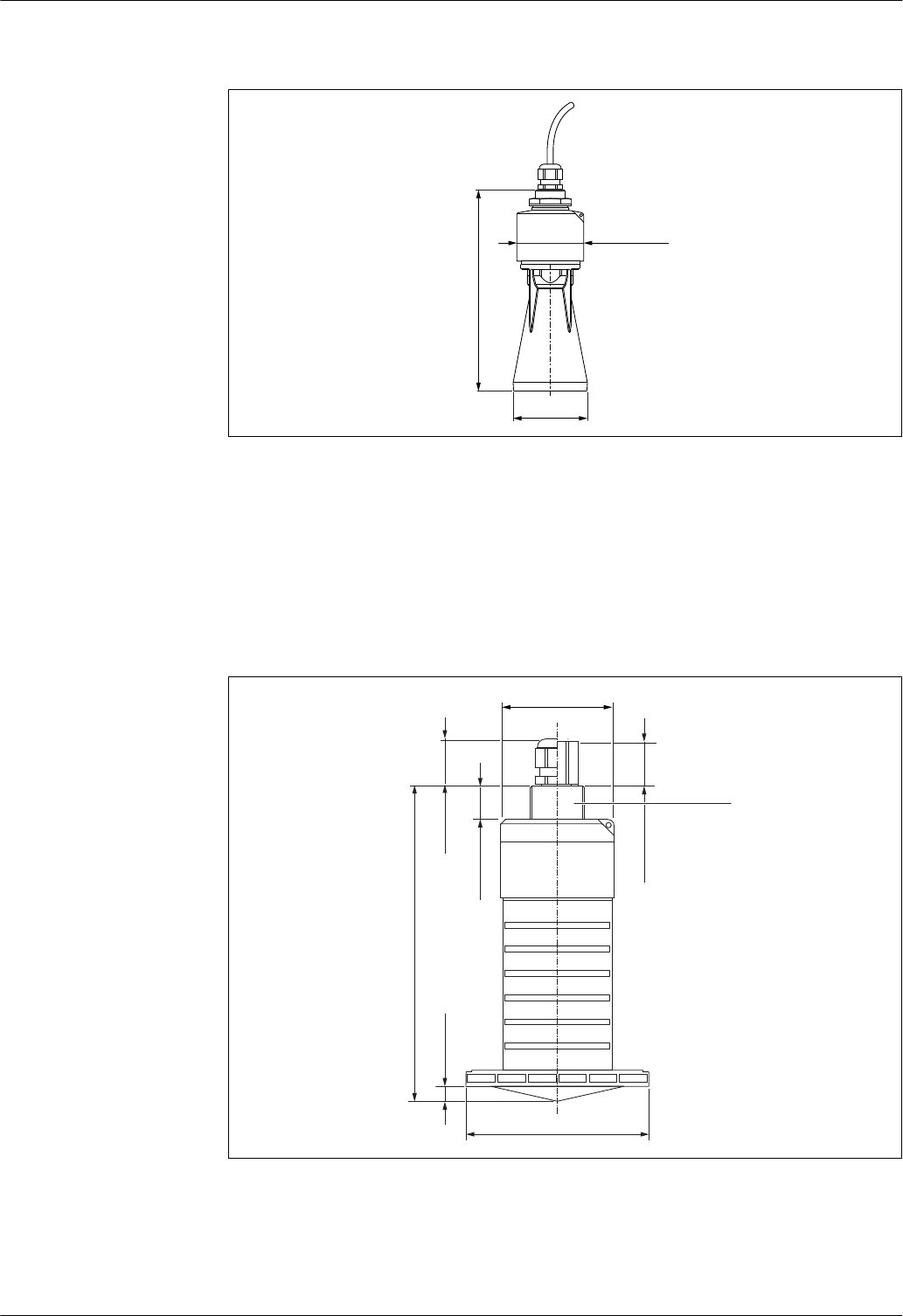
Micropilot FMR20
Endress+Hauser V. 5, Rev. 3, 20-12-2016 27
40 mm (1.5 in) antenna with flooding protection tube
!89 (3.5)
264 (10.4)
!75 (2.95)
A0030266
22 Dimensions 40 mm (1.5 in) antenna with mounted flooding protection tube, engineering unit: mm (in)
Applies to the following device versions
•Feature 100 "Process connection front side"
WFE: Thread ISO228 G1-1/2; PVDF
•Feature 620 "Accessory enclosed"
Option R7 "Flooding protection tube, metallized PBT-PC suitable for 40 mm (1.5 in) antenna with
process connection on front G1-1/2".
80 mm (3 in) antenna
AB
ø115 (4.53)
206 (8.11)
9 (0.35)
20 (0.79)
G 1"
NPT 1"
26 (1.02)
ø75 (2.95)
28 (1.1)
A0028807
23 Dimensions 80 mm (3 in) antenna; engineering unit: mm (in)
A Cable gland
B FNPT 1/2" conduit connection
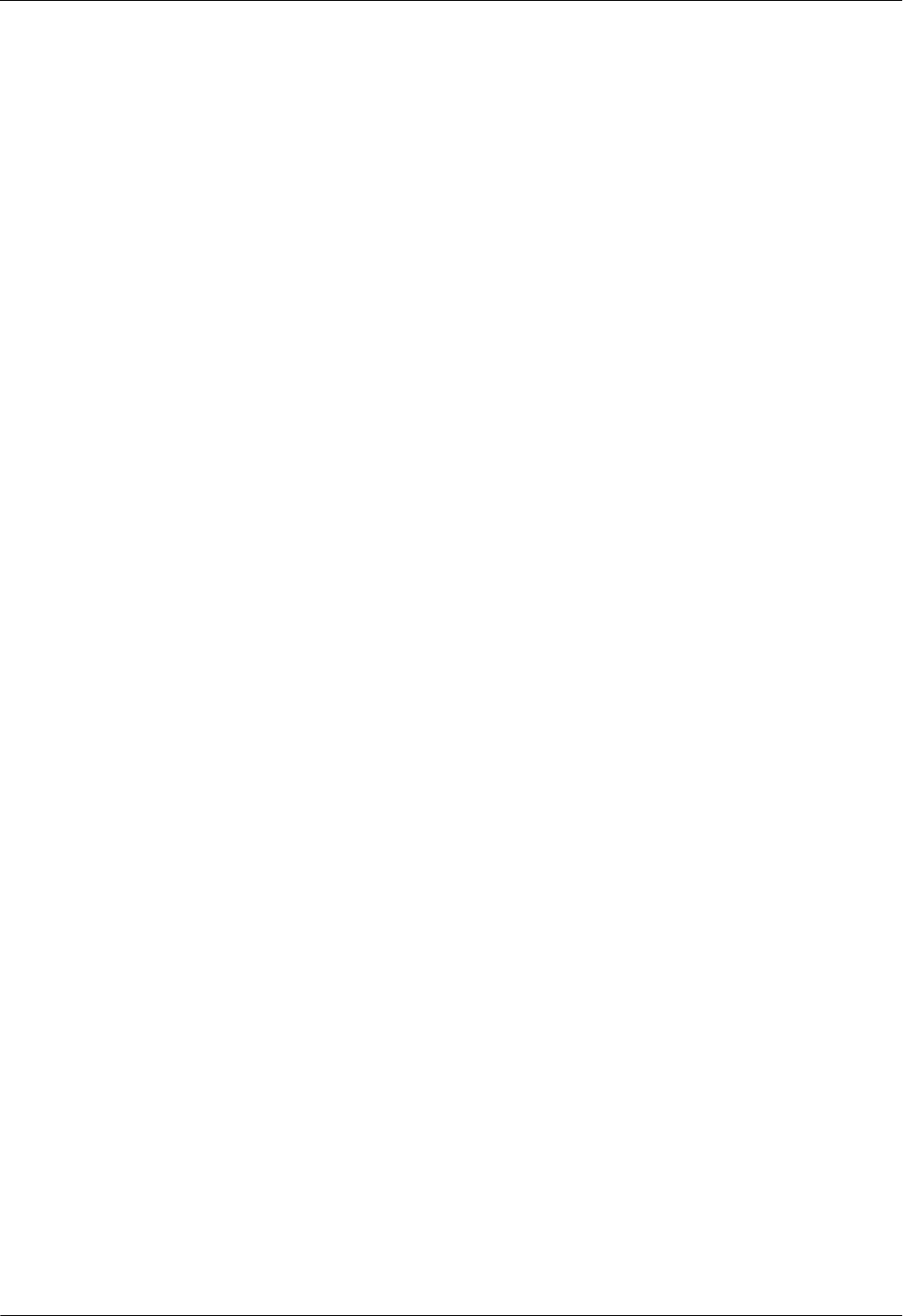
Micropilot FMR20
28 V. 5, Rev. 3, 20-12-2016 Endress+Hauser
Applies to the following device versions
Feature 095 "Process connection rear side"
– VCE: Thread ASME MNPT1; PVDF; FNPT 1/2" conduit connection
– WDE: Thread G1 ISO228; PVDF; cable gland
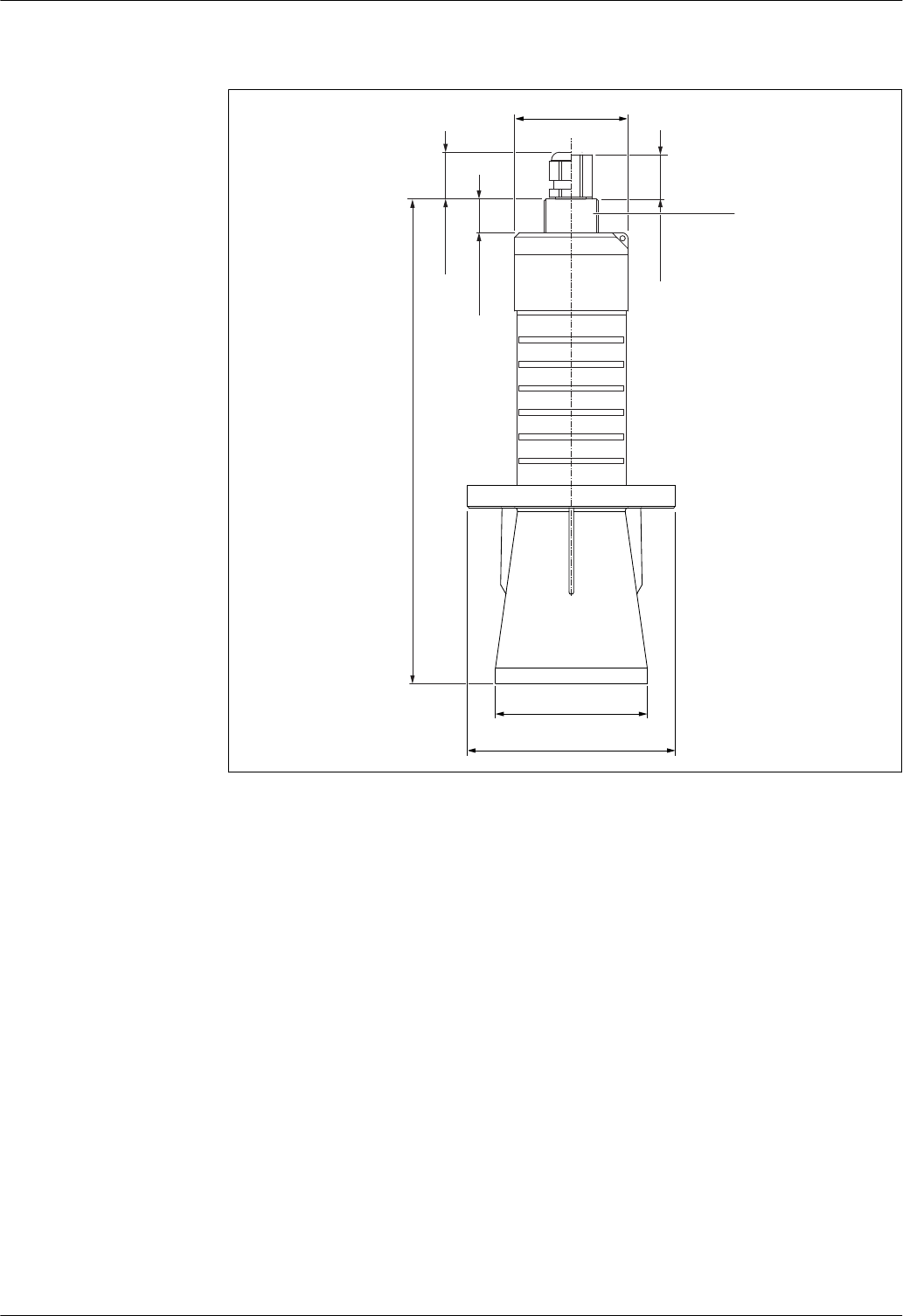
Micropilot FMR20
Endress+Hauser V. 5, Rev. 3, 20-12-2016 29
80 mm (3 in) antenna with flooding protection tube
!97,3 (3.83)
!138,1 (5.44)
322 (12.68)
20 (0.79)
G 1"
NPT 1"
26 (1.02)
ø75 (2.95)
28 (1.1)
AB
A0031095
24 Dimensions 80 mm (3 in) antenna with flooding protection tube; engineering unit: mm (in)
A Cable gland
B FNPT 1/2" conduit connection
Applies to the following device versions
•Feature 095 "Process connection rear side"
– VCE: Thread ASME MNPT1; PVDF; FNPT 1/2" conduit connection
– WDE: Thread G1 ISO228; PVDF; cable gland
•Feature 100 "Process connection front side"
XR0: Mounting customer side w/o flange
•Feature 620 "Accessory enclosed"
Option R8 "Flooding protection tube, metallized PBT-PC suitable for 80 mm (3 in) antenna
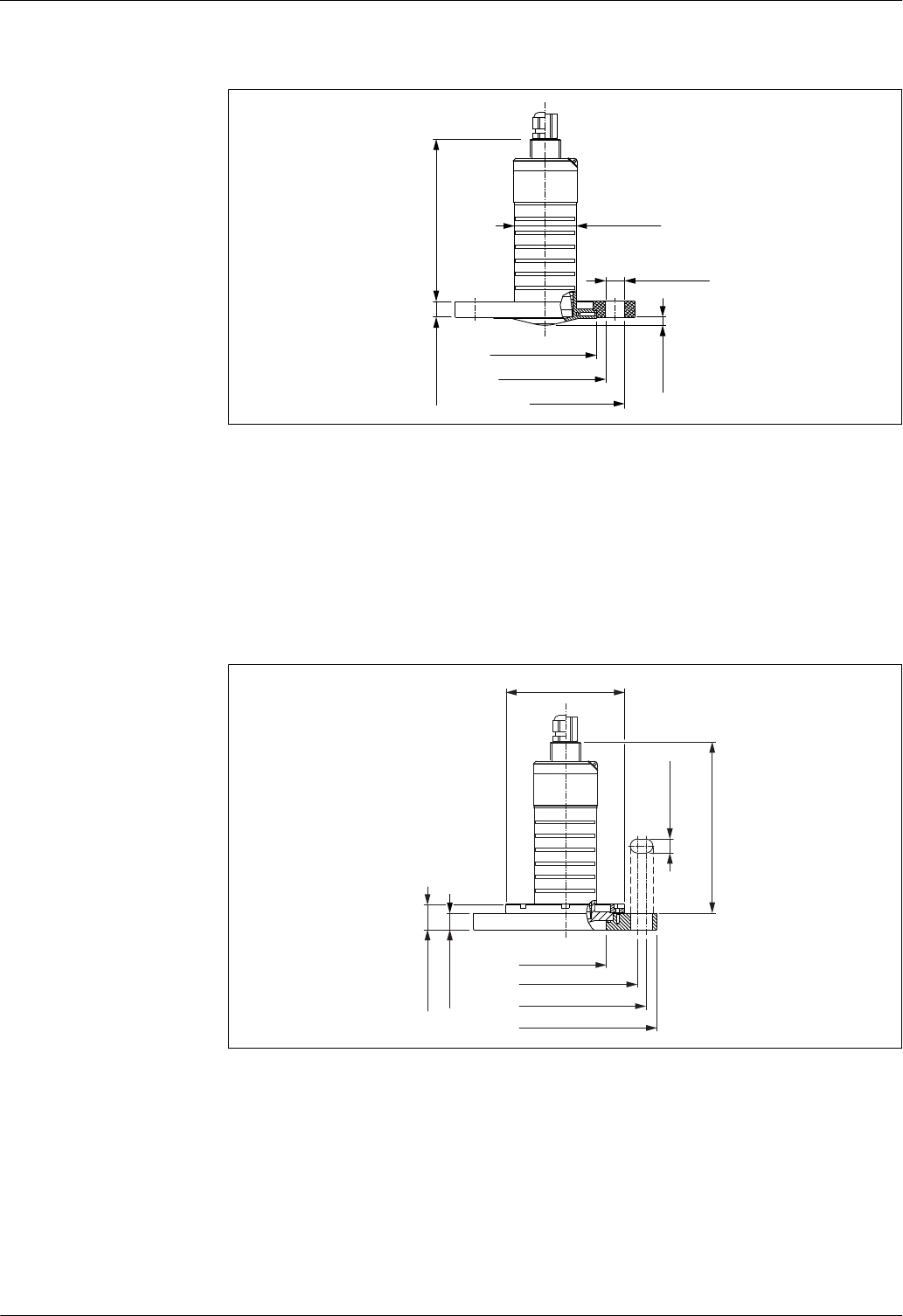
Micropilot FMR20
30 V. 5, Rev. 3, 20-12-2016 Endress+Hauser
80 mm (3 in) antenna with UNI slip-on flange 3"/DN80
ø75 (2.95)
8 x
ø21 (0.83)
ø115.6 (4.55)
ø156.2 (6.15)
ø200 (7.87)
178 (7)
18.5 (0.73)
9 (0.36)
A0028813
25 Dimensions 80 mm (3 in) antenna with slip-on flange 3"/DN80, engineering unit: mm (in)
Applies to the following device versions
•Feature 095 "Process connection rear side"
– VCE: Thread ASME MNPT1; PVDF; FNPT 1/2" conduit connection
– WDE: Thread G1 ISO228; PVDF; cable gland
•Feature 100 "Process connection front side"
RPF: UNI slip-on flange 3"/DN80/80; PP, suitable for 3" 150 lbs/DN80 PN16/10K 80
80 mm (3 in) antenna with slip-on flange 4"/DN100
ø175 (6.89)
ø 98 (3.86)
ø190.5 (5.7)
ø228.6 (9)
188 (7.4)
20 (0.79)
30.5 (1.2)
ø143 (5.63)
8 x
19 (0.75)
A0028816
26 Dimensions 80 mm (3 in) antenna with slip-on flange 4"/DN100, engineering unit: mm (in)
Applies to the following device versions
•Feature 095 "Process connection rear side"
– VCE: Thread ASME MNPT1; PVDF; FNPT 1/2" conduit connection
– WDE: Thread G1 ISO228; PVDF; cable gland
•Feature 100 "Process connection front side"
RRF: UNI slip-on flange 4"/DN100/100; PP, suitable for 4" 150 lbs/DN100 PN16/10K 100
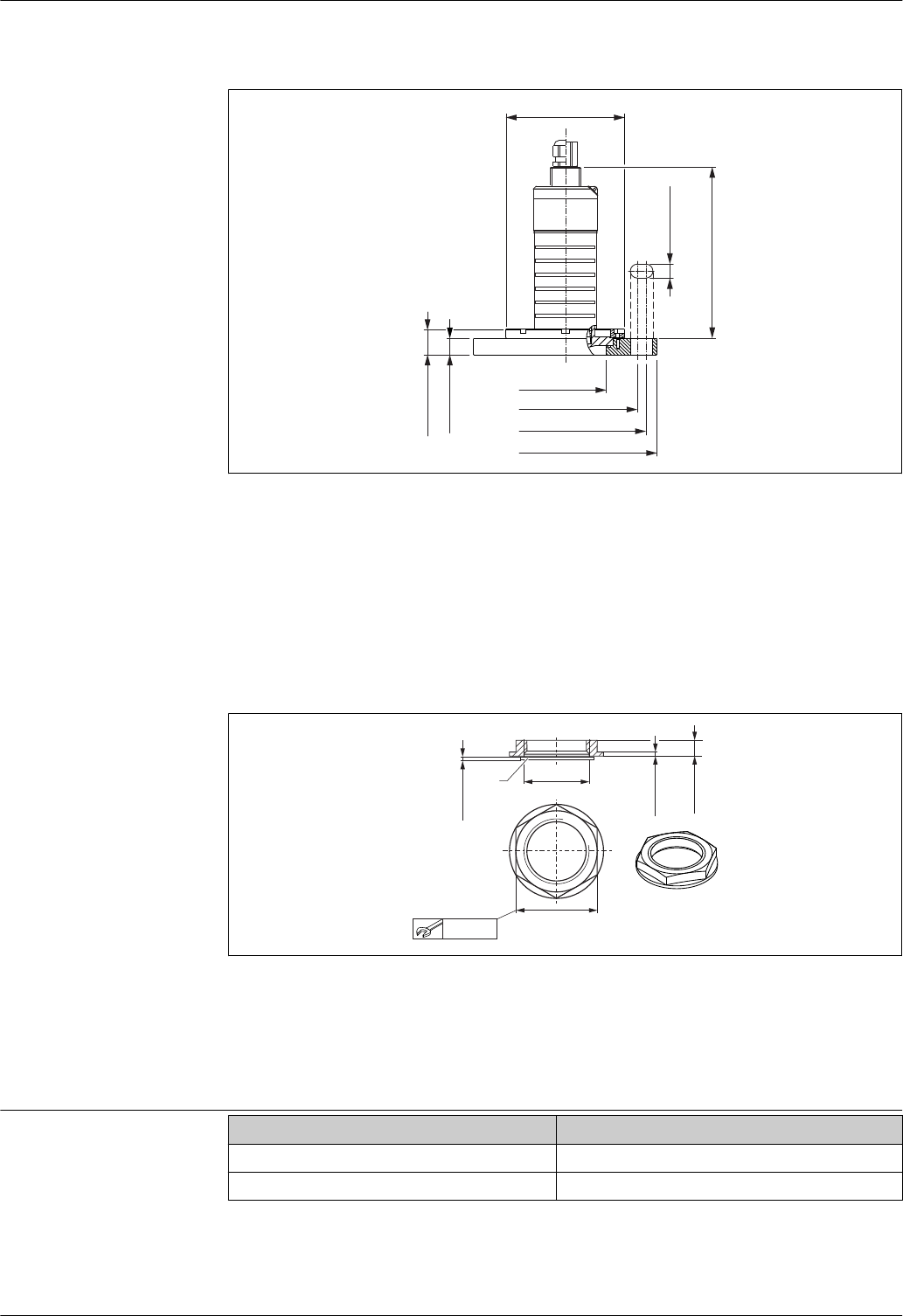
Micropilot FMR20
Endress+Hauser V. 5, Rev. 3, 20-12-2016 31
80 mm (3 in) antenna with slip-on flange 6"/DN150
ø240 (9.45)
ø98 (3.86)
ø241.3 (9.5)
ø285 (11.2)
188 (7.4)
20 (0.79)
30.5 (1.2)
ø163 (6.42)
8 x
23 (0.91)
A0028818
27 Dimensions 80 mm (3 in) antenna with slip-on flange 6"/DN150, engineering unit: mm (in)
Applies to the following device versions
•Feature 095 "Process connection rear side"
– VCE: Thread ASME MNPT1; PVDF; FNPT 1/2" conduit connection
– WDE: Thread G1 ISO228; PVDF; cable gland
•Feature 100 "Process connection front side"
RSF: UNI slip-on flange 6"/DN150/150; PP, suitable for 6" 150 lbs/DN150 PN16/10K 150
Counter nut for process connection rear side
8 (0.31)
G 1"
1
2 (0.08)
41 mm
2 (0.08)
A0028419
28 Dimensions of counter nut for process connection rear side, engineering unit: mm (in)
1 Seal
• The counter nut with seal (EPDM) is included in the scope of supply.
• Material: PA6.6
Weight Micropilot Weight (incl. 5 m (16.4 ft) cable)
FMR20, 40 mm (1.5 in) antenna Approx. 2.5 kg (5.5 lb)
FMR20, 80 mm (3 in) antenna Approx. 2.8 kg (6.2 lb)
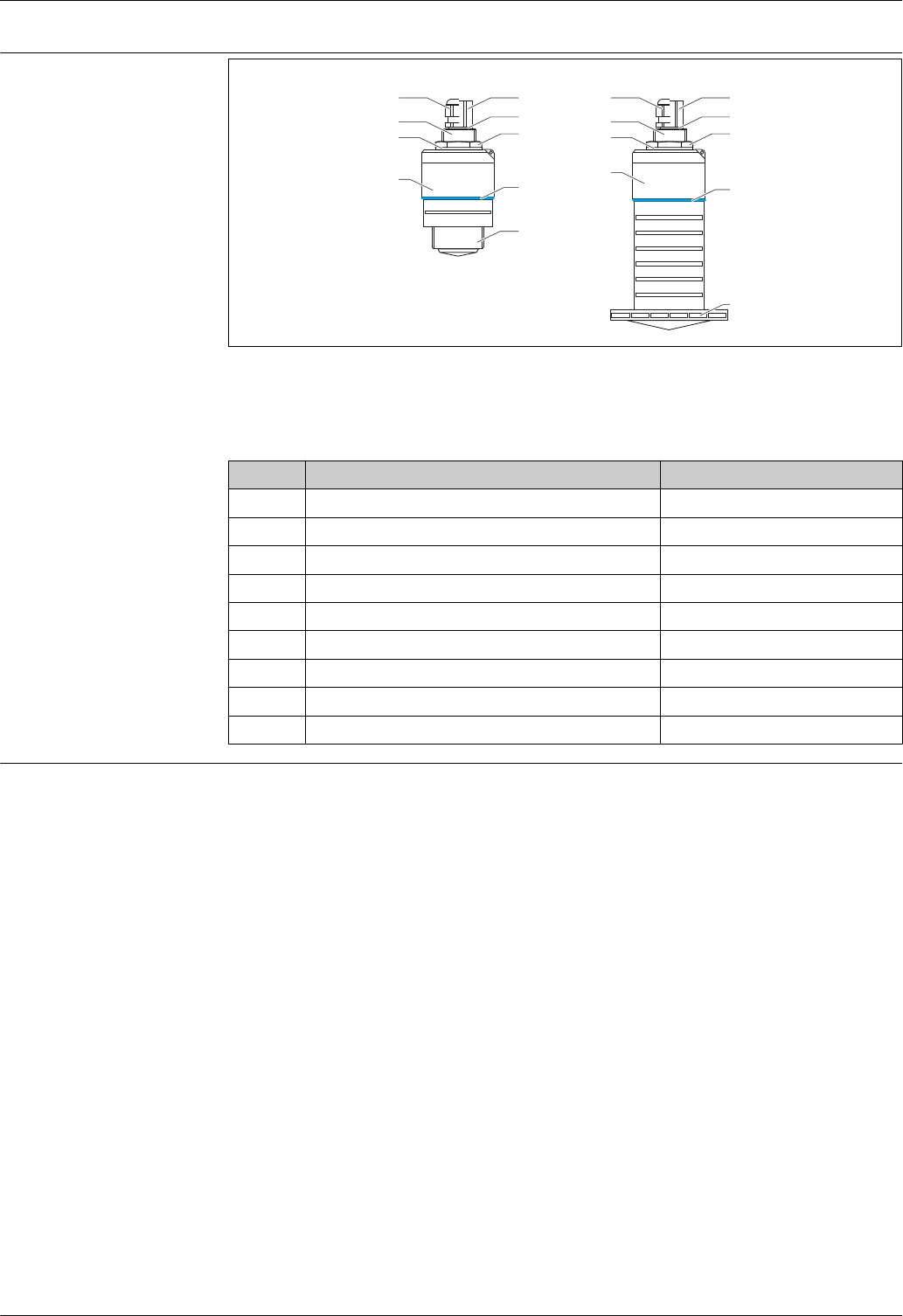
Micropilot FMR20
32 V. 5, Rev. 3, 20-12-2016 Endress+Hauser
Materials
B
1
8
2
3
4 5
6
7
18
9
9
2
3
4 5
6
7
A
A0028416
29 FMR20 materials
A 40 mm (1.5 in) antenna
B 80 mm (3 in) antenna
Item Component part Material
1 Sensor housing PVDF
2 Seal EPDM
3 Process connection rear side PVDF
4 Cable gland PA
5 Conduit connection adapter CuZn, nickel-plated
6 O-ring EPDM
7 Counter nut PA6.6
8 Design ring PBT PC
9 Process connection front side PVDF
Connecting cable Available cable length: 5 to 300 m (16 to 980 ft)
Material : PVC
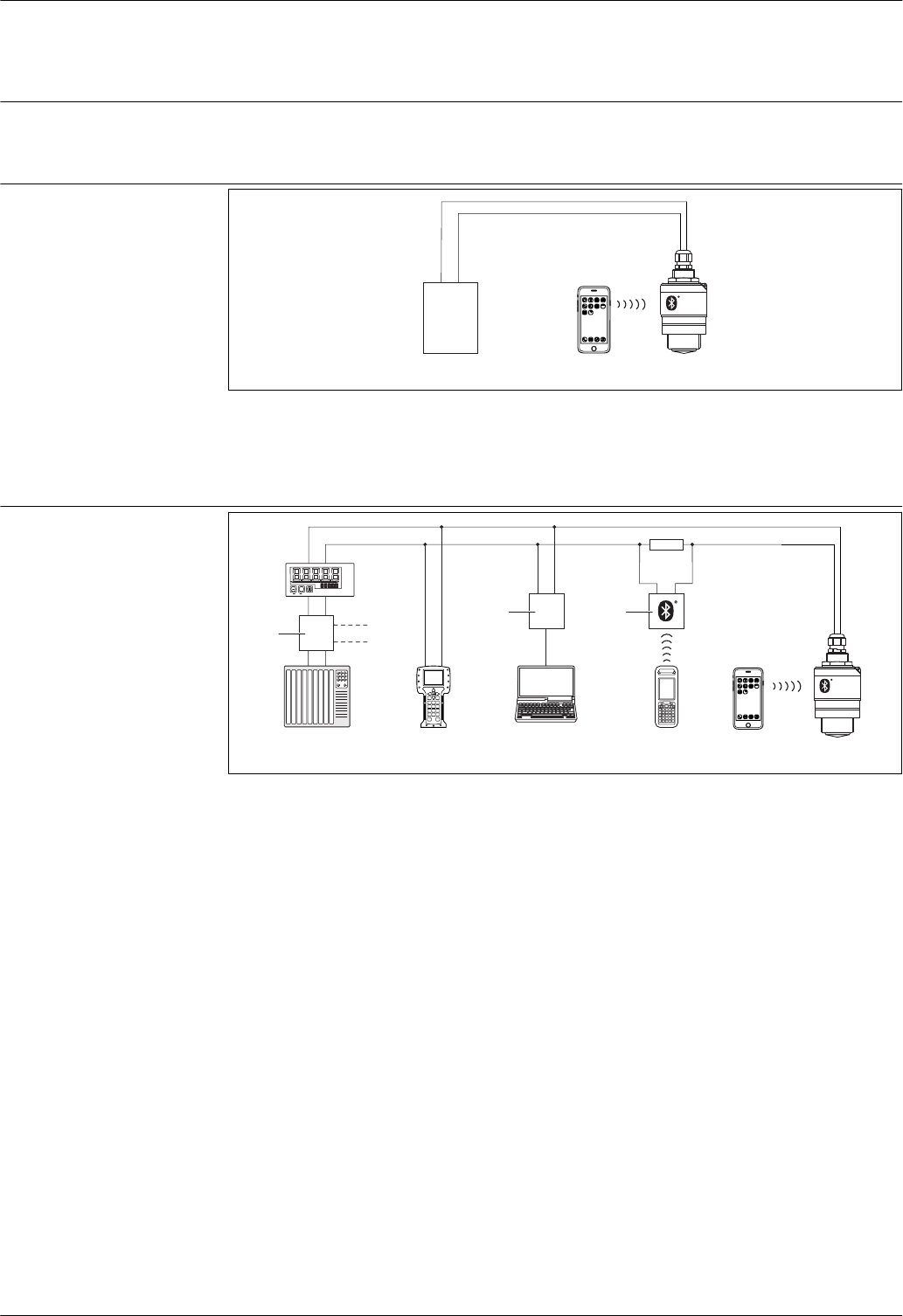
Micropilot FMR20
Endress+Hauser V. 5, Rev. 3, 20-12-2016 33
Operability
Operating concept • 4 to 20 mA, HART
• Menu guidance with brief explanations of the individual parameter functions in the operating tool
• Optional: SmartBlue (app) via Bluetooth® wireless technology
Via Bluetooth® wireless
technology
123
A0028895
30 Possibilities for remote operation via Bluetooth® wireless technology
1 Transmitter power supply unit
2 Smartphone / tablet with SmartBlue (app)
3 Transmitter with Bluetooth® wireless technology
Via HART protocol
1
4
5
79
6 8 10 11
23
ESC
E
+
A0028894
31 Options for remote operation via HART protocol
1 PLC (programmable logic controller)
2 Transmitter power supply unit, e.g. RN221N (with communication resistor)
3 Connection for Commubox FXA195 and Field Communicator 375, 475
4 RIA15 loop-powered process display unit
5 Field Communicator 475
6 Computer with operating tool (e.g. FieldCare, DeviceCare, AMS Device Manager, SIMATIC PDM)
7 Commubox FXA195 (USB)
8 Field Xpert SFX350/SFX370
9 VIATOR modem with Bluetooth® wireless technology
10 Smartphone / tablet with SmartBlue (app)
11 Transmitter with Bluetooth® wireless technology
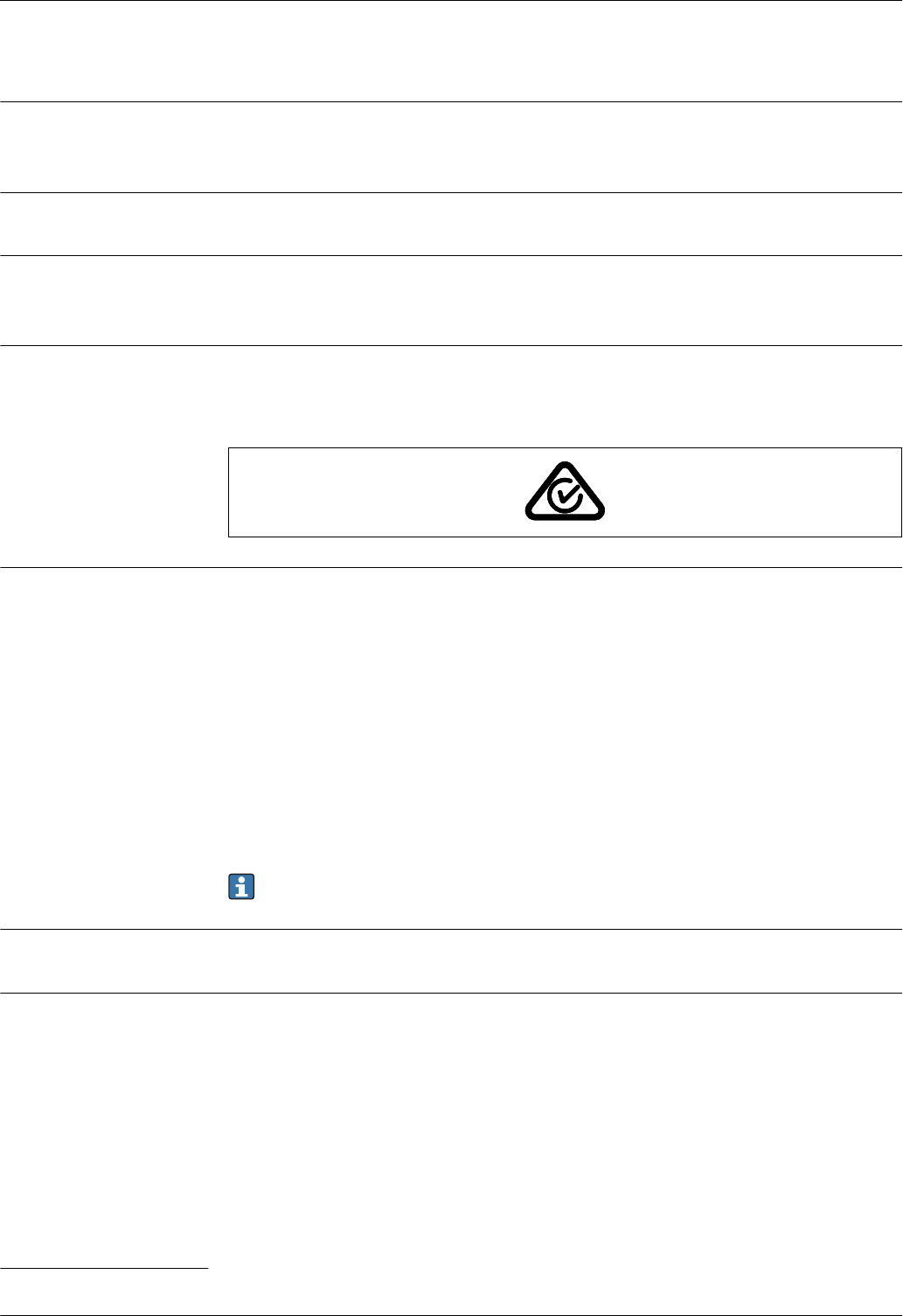
Micropilot FMR20
34 V. 5, Rev. 3, 20-12-2016 Endress+Hauser
Certificates and approvals
CE mark The measuring system meets the legal requirements of the applicable EC guidelines. These are listed
in the corresponding EC Declaration of Conformity together with the standards applied.
Endress+Hauser confirms successful testing of the device by affixing to it the CE mark.
RoHS The measuring system complies with the substance restrictions of the Restriction on Hazardous
Substances Directive 2011/65/EU (RoHS 2).
EAC conformity The measuring system meets the legal requirements of the applicable EAC guidelines. These are
listed in the corresponding EAC Declaration of Conformity together with the standards applied.
Endress+Hauser confirms successful testing of the device by affixing to it the EAC mark.
RCM-Tick marking The supplied product or measuring system meets the ACMA (Australian Communications and Media
Authority) requirements for network integrity, interoperability, performance characteristics as well
as health and safety regulations. Here, especially the regulatory arrangements for electromagnetic
compatibility are met. The products are labelled with the RCM- Tick marking on the name plate.
A0029561
Ex approval • Non-hazardous area
• ATEX II 1 G Ex ia IIC T4 Ga
• ATEX II 1/2 G Ex ia IIC T4 Ga/Gb
• CSA C/US General Purpose
• CSA C/US IS CI.I Div.1 Gr.A-D, AEx ia / Ex ia T4
• EAC Ex ia IIC T4 Ga/Gb
• Non-hazardous area + EAC mark
• IEC Ex ia IIC T4 Ga/Gb
• KC Ex ia IIC T4 Ga/Gb 3)
• INMETRO Ex ia IIC T4 Ga/Gb 3)
• NEPSI Ex ia IIC T4 Ga/Gb 3)
• TIIS Ex ia IIC T4 3)
Additional safety instructions must be followed for use in hazardous areas. Please refer to the
separate "Safety Instructions" (XA) document included in the delivery. Reference to the applicable XA
can be found on the nameplate.
Details on the available certificates and associated XAs can be found in the Additional
documentation section under Safety instructions (XA): → 52.
Explosion-protected
smartphones and tablets
Only mobile end devices with Ex approval may be used in hazardous areas.
Pressure equipment with
allowable pressure
≤ 200 bar (2 900 psi)
Pressure instruments with a flange and threaded boss that do not have a pressurized housing do not
fall within the scope of the Pressure Equipment Directive, irrespective of the maximum allowable
pressure.
Reasons:
According to Article 2, point 5 of EU Directive 2014/68/EU, pressure accessories are defined as
"devices with an operational function and having pressure-bearing housings".
If a pressure instrument does not have a pressure-bearing housing (no identifiable pressure chamber
of its own), there is no pressure accessory present within the meaning of the Directive.
3) Under development at time of going to press

Micropilot FMR20
Endress+Hauser V. 5, Rev. 3, 20-12-2016 35
Note:
A partial examination shall be performed for pressure instruments that are part of safety equipment
for the protection of a pipe or vessel from exceeding allowable limits (equipment with safety
function in accordance with Pressure Equipment Directive 2014/68/EU, Article 2, point 4).
EN 302729-1/2 radio
standard
The Micropilot FMR20 devices comply with the LPR (Level Probing Radar) radio standard EN
302729-1/2. The devices are approved for unrestricted use inside and outside of closed vessels in
countries of the EU and EFTA. that have implemented this standard.
The following countries are those that have currently implemented the directive:
Belgium, Bulgaria, Germany, Denmark, Estonia, France, Greece, UK, Ireland, Iceland, Italy,
Liechtenstein, Lithuania, Latvia, Malta, The Netherlands, Norway, Austria, Poland, Portugal,
Romania, Sweden, Switzerland, Slovakia, Spain, Czech Republic and Cyprus.
Implementation is still underway in all of the countries not listed.
Please note the following for operation of the devices outside of closed vessels:
1. The device must be mounted in accordance with the instructions in the "Installation" section.
2. Installation must be carried out by properly trained, expert staff.
3. The device antenna must be installed in a fixed location pointing vertically downwards.
4. The installation site must be located at a distance of 4 km from the astronomy stations listed
below or otherwise approval must be provided by the relevant authority. If the device is
installed at a distance of 4 to 40 km from one of the listed stations, it must not be installed at a
height of more than 15 m (49 ft) above the ground.
Astronomy stations
Country Name of the station Latitude Longitude
Germany Effelsberg 50°31'32" North 06°53'00" East
Finland Metsähovi 60°13'04" North 24°23'37" East
Tuorla 60°24'56" North 24°26'31" East
France Plateau de Bure 44°38'01" North 05°54'26" East
Floirac 44°50'10" North 00°31'37" West
Great Britain Cambridge 52°09'59" North 00°02'20" East
Damhall 53°09'22" North 02°32'03" West
Jodrell Bank 53°14'10" North 02°18'26" West
Knockin 52°47'24" North 02°59'45" West
Pickmere 53°17'18" North 02°26'38" West
Italy Medicina 44°31'14" North 11°38'49" East
Noto 36°52'34" North 14°59'21" East
Sardinia 39°29'50" North 09°14'40" East
Poland Fort Skala Krakow 50°03'18" North 19°49'36" East
Russia Dmitrov 56°26'00" North 37°27'00" East
Kalyazin 57°13'22" North 37°54'01" East
Pushchino 54°49'00" North 37°40'00" East
Zelenchukskaya 43°49'53" North 41°35'32" East
Sweden Onsala 57°23'45" North 11°55'35" East
Switzerland Bleien 47°20'26" North 08°06'44" East
Spain Yebes 40°31'27" North 03°05'22" West
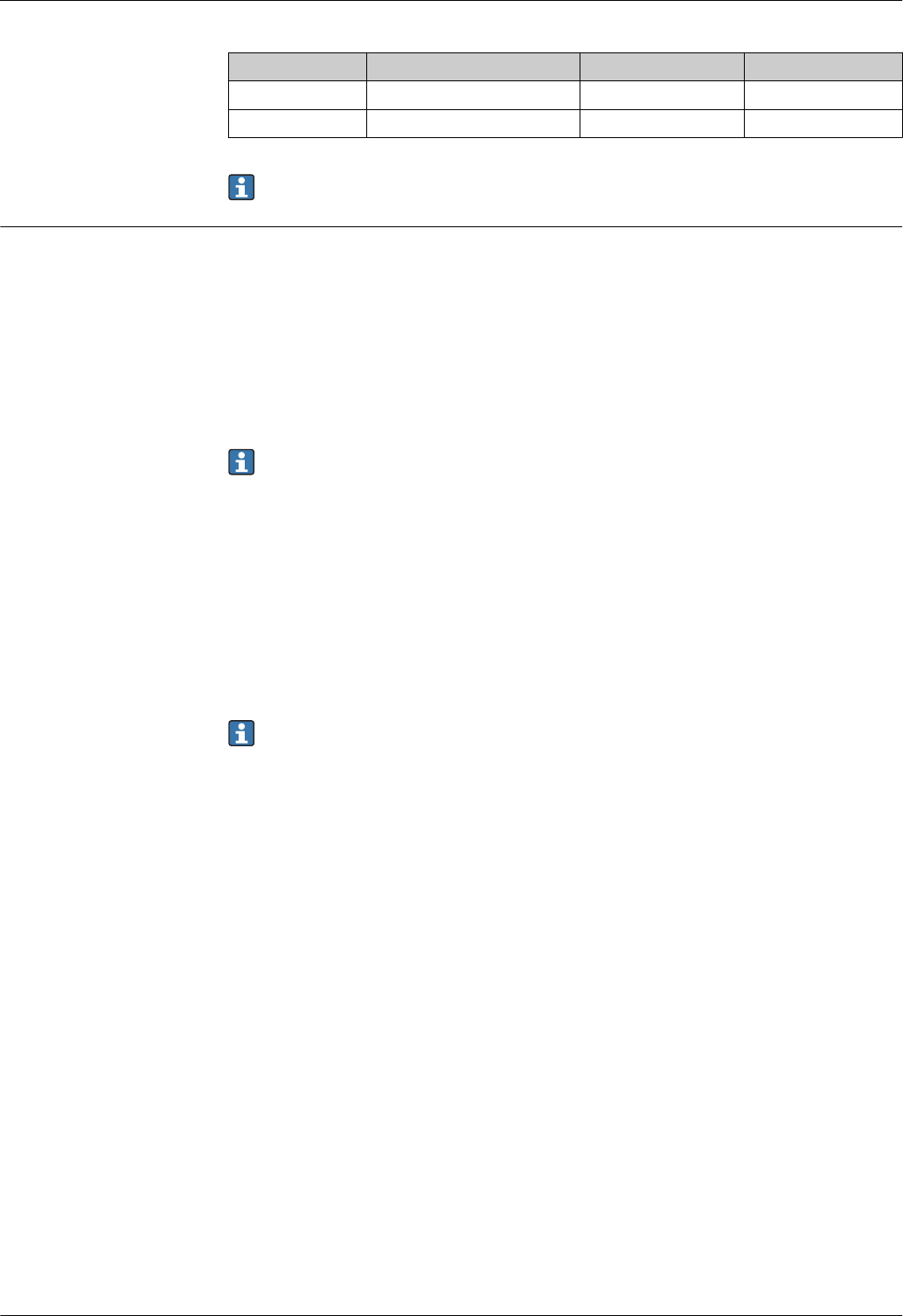
Micropilot FMR20
36 V. 5, Rev. 3, 20-12-2016 Endress+Hauser
Country Name of the station Latitude Longitude
Robledo 40°25'38" North 04°14'57" West
Hungary Penc 47°47'22" North 19°16'53" East
As a general rule, the requirements outlined in EN 302729-1/2 must be observed.
FCC / Industry Canada This device complies with Part 15 of the FCC Rules [and with Industry Canada licence-exempt RSS
standard(s)]. Operation is subject to the following two conditions: (1) this device may not cause
harmful interference, and (2) this device must accept any interference received, including
interference that may cause undesired operation.
Le présent appareil est conforme aux CNR d'Industrie Canada applicables aux appareils radio exempts
de licence. L'exploitation est autorisée aux deux conditions suivantes: (1) l'appareil ne doit pas produire
de brouillage, et (2) l'utilisateur de l'appareil doit accepter tout brouillage radioélectrique subi, même si
le brouillage est susceptible d'en compromettre le fonctionnement.
[Any] Changes or modifications made to this equipment not expressly approved by Endress+Hauser
may void the FCC authorization to operate this equipment.
This equipment has been tested and found to comply with the limits for a Class B digital device,
pursuant to Part 15 of the FCC Rules. These limits are designed to provide reasonable
protection against harmful interference in a residential installation. This equipment generates,
uses and can radiate radio frequency energy and, if not installed and used in accordance with
the instructions, may cause harmful interference to radio communications. However, there is no
guarantee that interference will not occur in a particular installation. If this equipment does
cause harmful interference to radio or television reception, which can be determined by turning
the equipment off and on, the user is encouraged to try to correct the interference by one or
more of the following measures:
• Reorient or relocate the receiving antenna
• Increase the separation between the equipment and receiver
• Connect the equipment into an outlet on a circuit different from that to which the receiver is
connected
• Consult the dealer or an experienced radio/TV technician for help
• The installation of the LPR/TLPR device shall be done by trained installers, in strict
compliance with the manufacturer’s instructions.
• The use of this device is on a “no-interference, no-protection” basis. That is, the user shall
accept operations of high-powered radar in the same frequency band which may interfere
with or damage this device. However, devices found to interfere with primary licensing
operations will be required to be removed at the user’s expense.
• Only for usage without the accessory “flooding protection tube”, i.e. NOT in the free-field:
This device shall be installed and operated in a completely enclosed container to prevent RF
emissions, which can otherwise interfere with aeronautical navigation.
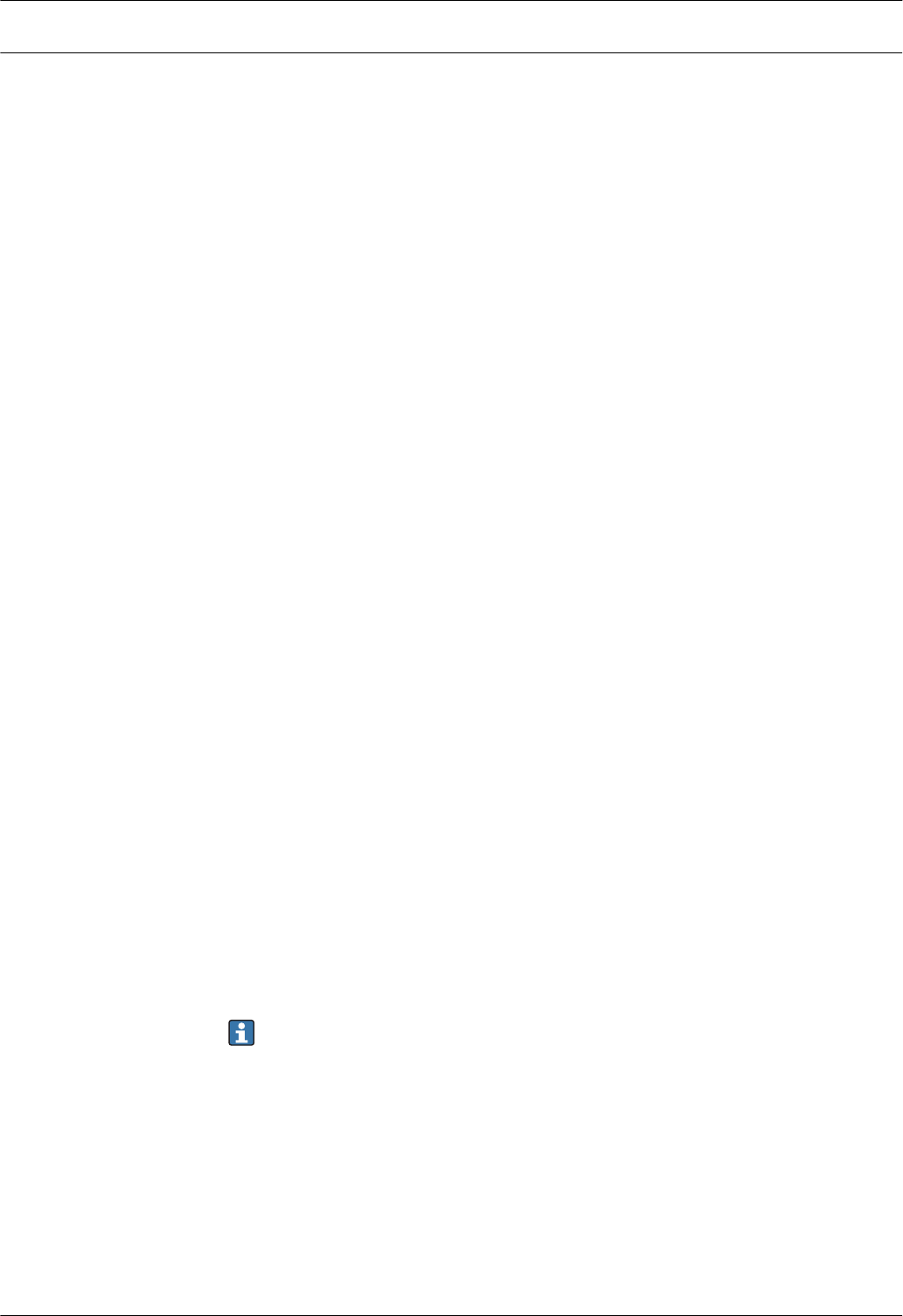
Micropilot FMR20
Endress+Hauser V. 5, Rev. 3, 20-12-2016 37
Other standards and
guidelines
• IEC/EN 61010-1
Safety Requirements for Electrical Equipment for Measurement, Control and Laboratory Use
• IEC/EN 55011
"EMC Emission, RF Emission for Class B". Industrial, scientific and medical equipment –
Electromagnetic disturbance characteristics - Limits and methods of measurement
• IEC/EN 61000-4-2
EMC Immunity, ESD (Performance Criteria A). Electromagnetic compatibility (EMC): Testing and
measurement techniques - Electrostatic discharge immunity test (ESD)
• IEC/EN 61000-4-3
EMC Immunity, RF field susceptibility (Performance Criteria A). Electromagnetic compatibility
(EMC): Testing and measurement techniques - Radiated, radio-frequency, electromagnetic field
immunity test
• IEC/EN 61000-4-4
EMC Immunity, bursts (Performance Criteria B). Electromagnetic compatibility (EMC): Testing and
measurement techniques - Electrical fast transient/burst immunity test
• IEC/EN 61000-4-5
EMC Immunity, surge (Performance Criteria B). Electromagnetic compatibility (EMC): Testing and
measurement techniques - Surge immunity test
• IEC/EN 61000-4-6
EMC Immunity, conducted HF (Performance Criteria A). Electromagnetic compatibility (EMC):
Testing and measurement techniques - Immunity to conducted disturbances induced by radio-
frequency fields
• IEC/EN 61000-4-8
EMC Immunity, magnetic fields 50 Hz. Electromagnetic compatibility (EMC): Testing and
measurement techniques - Power frequency magnetic field immunity test
• EN 61000-6-3
EMC Emission, conducted HF. EMC: Radiated interference - Residential, commercial and light
industry environment
• NAMUR NE 21
Electromagnetic compatibility (EMC) of industrial process and laboratory control equipment
• NAMUR NE 43
Standardization of the signal level for the breakdown information of digital transmitters with
analog output signal.
• NAMUR NE 107
Status classification as per NE107
• NAMUR NE 131
Requirements for field devices for standard applications.
• IEEE 802.15.1
Requirements for the Bluetooth® wireless technology interface
Ordering information
Detailed ordering information is available from the following sources:
• In the Product Configurator on the Endress+Hauser website: www.endress.com -> Click "Corporate"
-> Select your country -> Click "Products" -> Select the product using the filters and search field ->
Open product page -> The "Configure" button to the right of the product image opens the Product
Configurator.
• From your Endress+Hauser Sales Center: www.addresses.endress.com
Product Configurator - the tool for individual product configuration
• Up-to-the-minute configuration data
• Depending on the device: Direct input of measuring point-specific information such as
measuring range or operating language
• Automatic verification of exclusion criteria
• Automatic creation of the order code and its breakdown in PDF or Excel output format
• Ability to order directly in the Endress+Hauser Online Shop
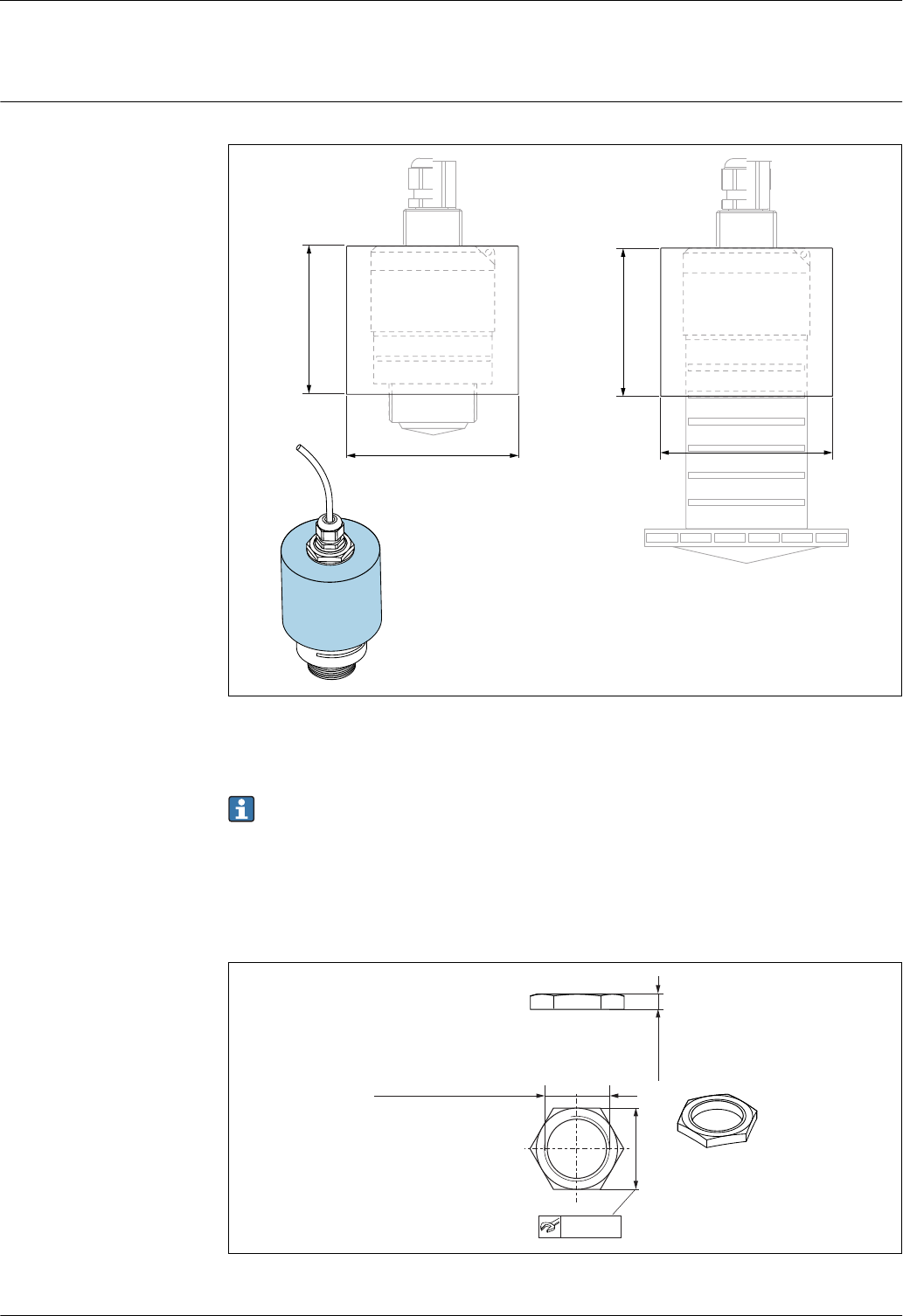
Micropilot FMR20
38 V. 5, Rev. 3, 20-12-2016 Endress+Hauser
Accessories
Device-specific accessories Weather protection cover
90 (3.54)
90 (3.54)
Ø 98 (3.86) Ø 98 (3.86)
A0028841
32 Dimensions of weather protection cover, engineering unit: mm (in)
Werkstoff: PVDF
The weather protection cover can be ordered with the device (product structure, feature 620
"Accessory enclosed", option R1 "weather protection cover").
Alternatively it can be ordered separately as an accessory; order number 52025686.
The sensor is not completely covered in the case of the 40 mm (1.5 in) antenna or the
80 mm (3 in) antenna.
Securing nut G 1-1/2"
G1 1/2" DIN ISO 228
60 mm
10 (0.39)
A0028849
33 Dimensions of securing nut, engineering unit: mm (in)
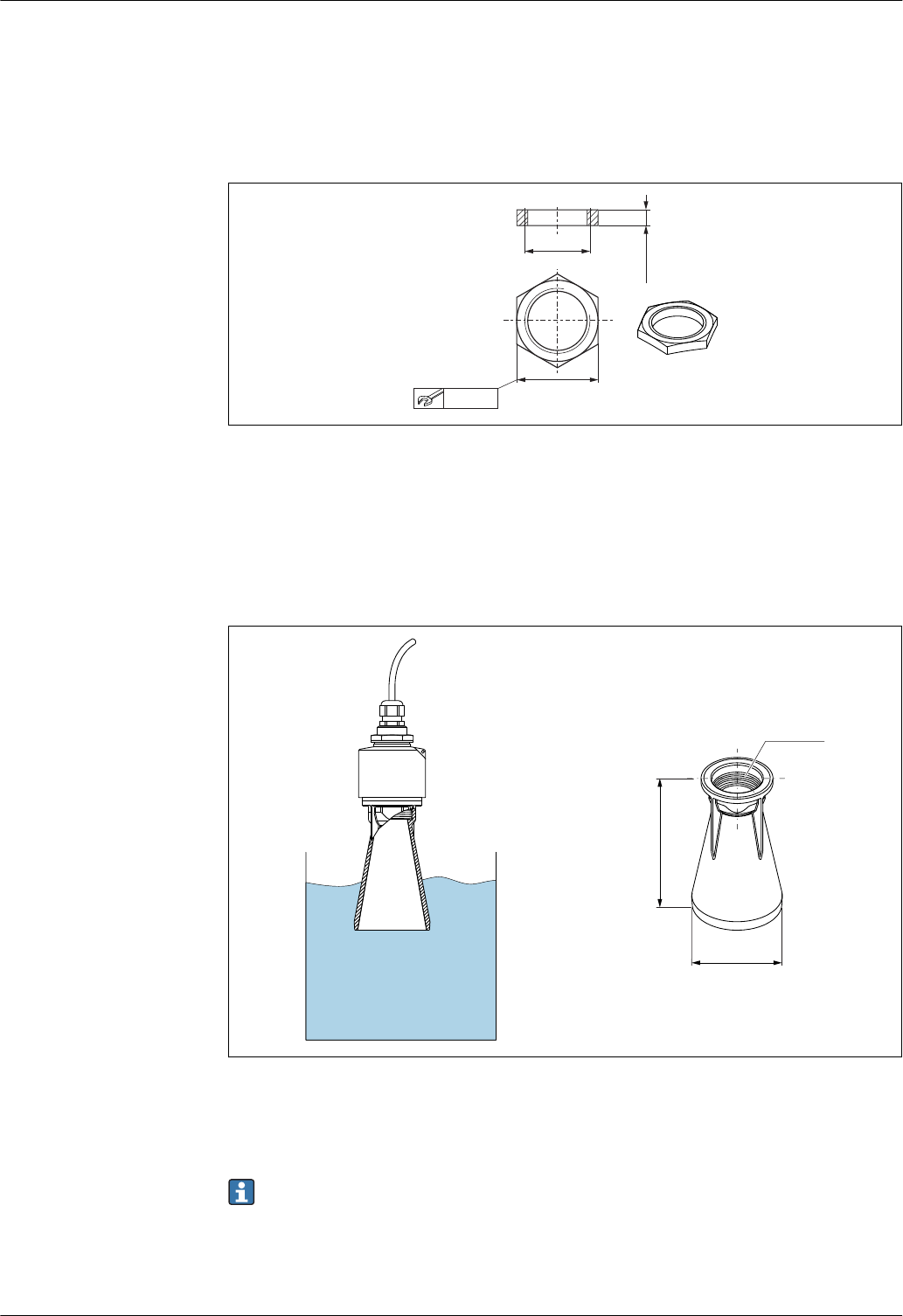
Micropilot FMR20
Endress+Hauser V. 5, Rev. 3, 20-12-2016 39
Suitable for use with devices with G 1-1/2" and MNPT 1-1/2" process connection.
Material: PC
Order number: 52014146
Securing nut G 2"
10 (0.39)
G 2"
70 mm
A0029101
34 Dimensions of securing nut, engineering unit: mm (in)
Suitable for use with devices with G 2" and MNPT 2" process connection on front.
Material: PC
Order number: 52000598
Flooding protection tube 40 mm (1.5 in) antenna, metallized PBT-PC
!89 (3,5)
152 (5,98)
G 1-1/2"
A0028418
For use with devices in product structure, feature 100 "Process connection on front", option WFE
"Thread ISO228 G1-1/2".
Material: PBT-PC, metallized
The flooding protection tube can be ordered with the device. Product structure, feature 620
"Accessory enclosed", option R7 "Flooding protection tube, metallized PBT-PC suitable for
40 mm (1.5 in) antenna with G1-1/2" process connection on front".
Alternatively available as an accessory; order number 71325090.
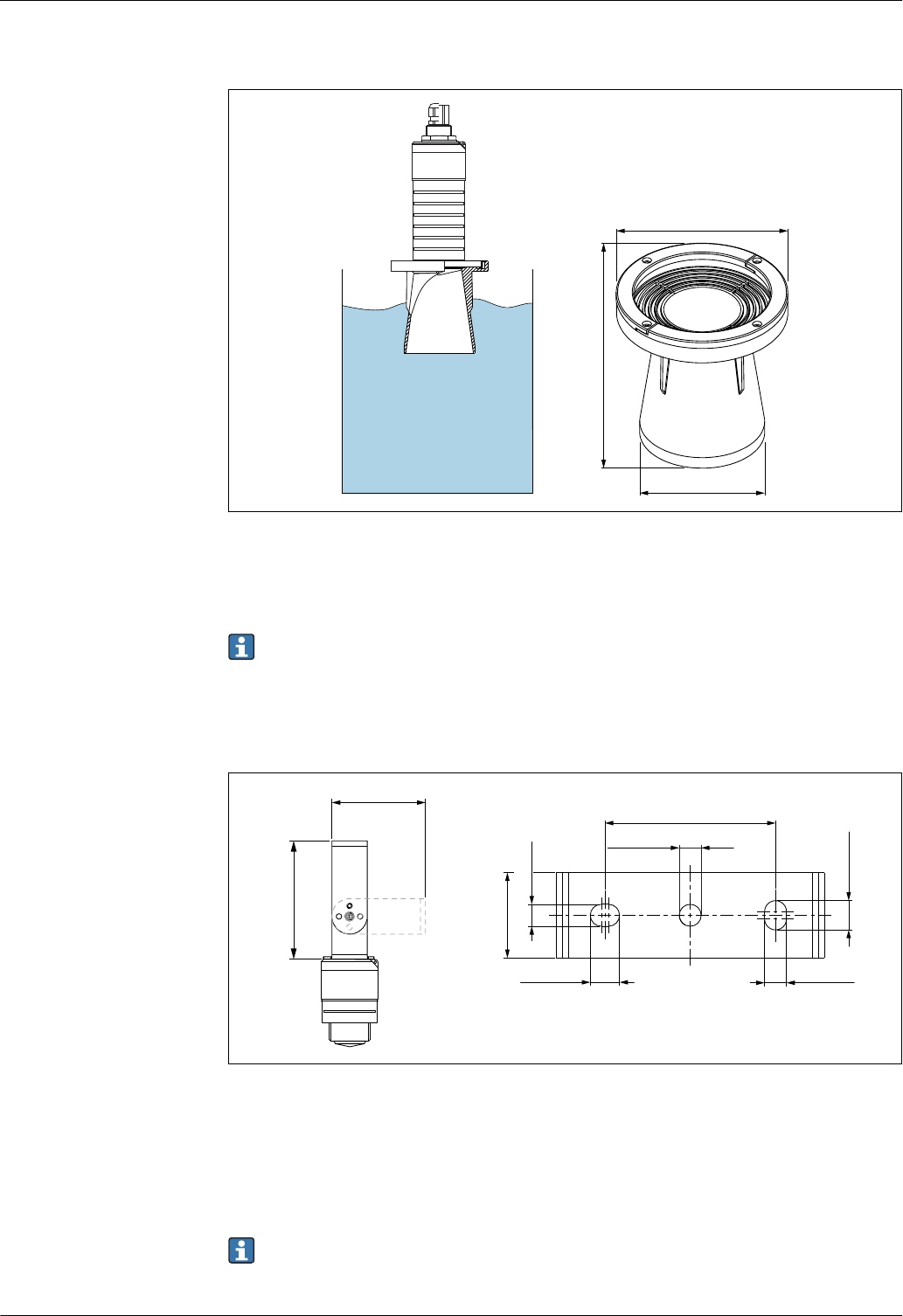
Micropilot FMR20
40 V. 5, Rev. 3, 20-12-2016 Endress+Hauser
Flooding protection tube 80 mm (3 in) antenna, metallized PBT-PC
!97,3 (3.83)
!138,1 (5.44)
136,5 (5.37)
A0031094
For use with devices in product structure, feature 100 "Process connection on front", option XR0
"Customer mounting device without flange".
Material: PBT-PC, metallized
The flooding protection tube can be ordered with the device. Product structure, feature 620
"Accessory enclosed", option R8 "Flooding protection tube, metallized PBT-PC suitable for
80 mm (3 in) antenna.
Alternatively available as an accessory; order number 71327051.
Mounting bracket, adjustable
117.5 (4.63)
92.5 (3.64)
70 (2.76)
!9 (0.35)
12 (0.47) 9 (0.35)
12 (0.47)
9 (0.35)
35 (1.38)
A0028861
35 Dimensions of mounting bracket, engineering unit: mm (in)
Consists of:
• Mounting bracket: 316 (1.4404)
• Angle bracket: 316L (1.4404)
• Screws: A4
• Retaining rings: A4
The mounting bracket can be ordered with the device (product structure, feature 620 "Accessory
enclosed", option R3 "Mounting bracket adjustable, 316L").
Alternatively, it is available as an accessory; order number 71325079.
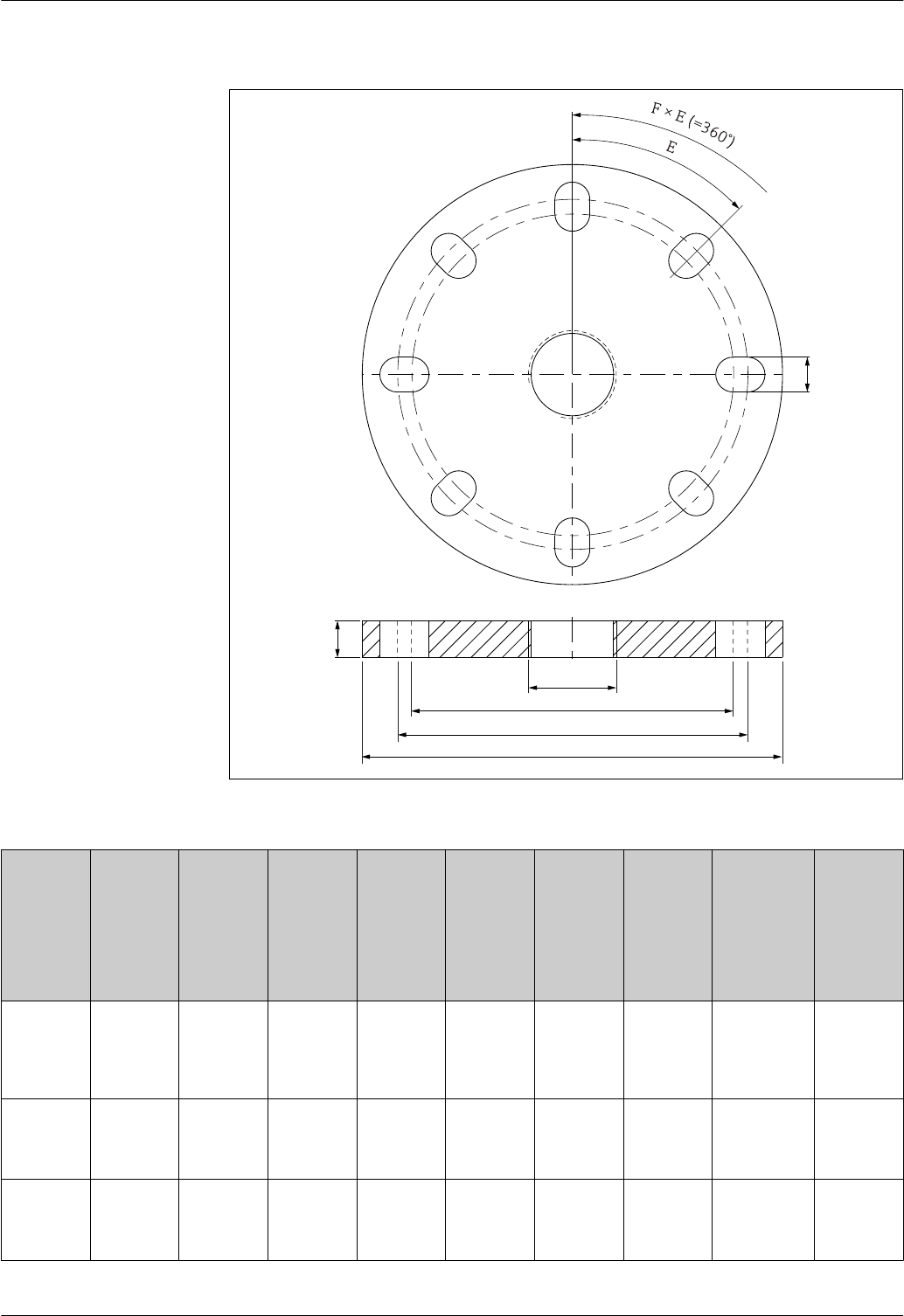
Micropilot FMR20
Endress+Hauser V. 5, Rev. 3, 20-12-2016 41
UNI flanges
20
G
A
D
B
C
A0031103
36 Dimensions of UNI flange, engineering unit: mm
Product
structure
Feature 620
"Accessory
enclosed"
Option:
A
(mm)
B
(mm)
C
(mm)
D
(mm)
E F
Number of
bores
G
Product
structure
Feature 95
"Process
connection
on front"
Option:
G
Product
structure
Feature 100
"Process
connection on
rear"
Option:
Accessory
order code
RA
UNI flange
2"/DN50/50,
PP, on front
120 125 165 19 90° 4 VEE
Thread
ASME
MNPT
1-1/2"
FAX50-XIGG
RA
UNI flange
2"/DN50/50,
PP, on front
120 125 165 19 90° 4 WFE
Thread
ISO228 G
1-1/2"
FAX50-XIGC
RA
UNI flange
2"/DN50/50,
PP, on front
120 125 165 19 90° 4 VFE
Thread
ASME
MNPT 2"
FAX50-XIGH
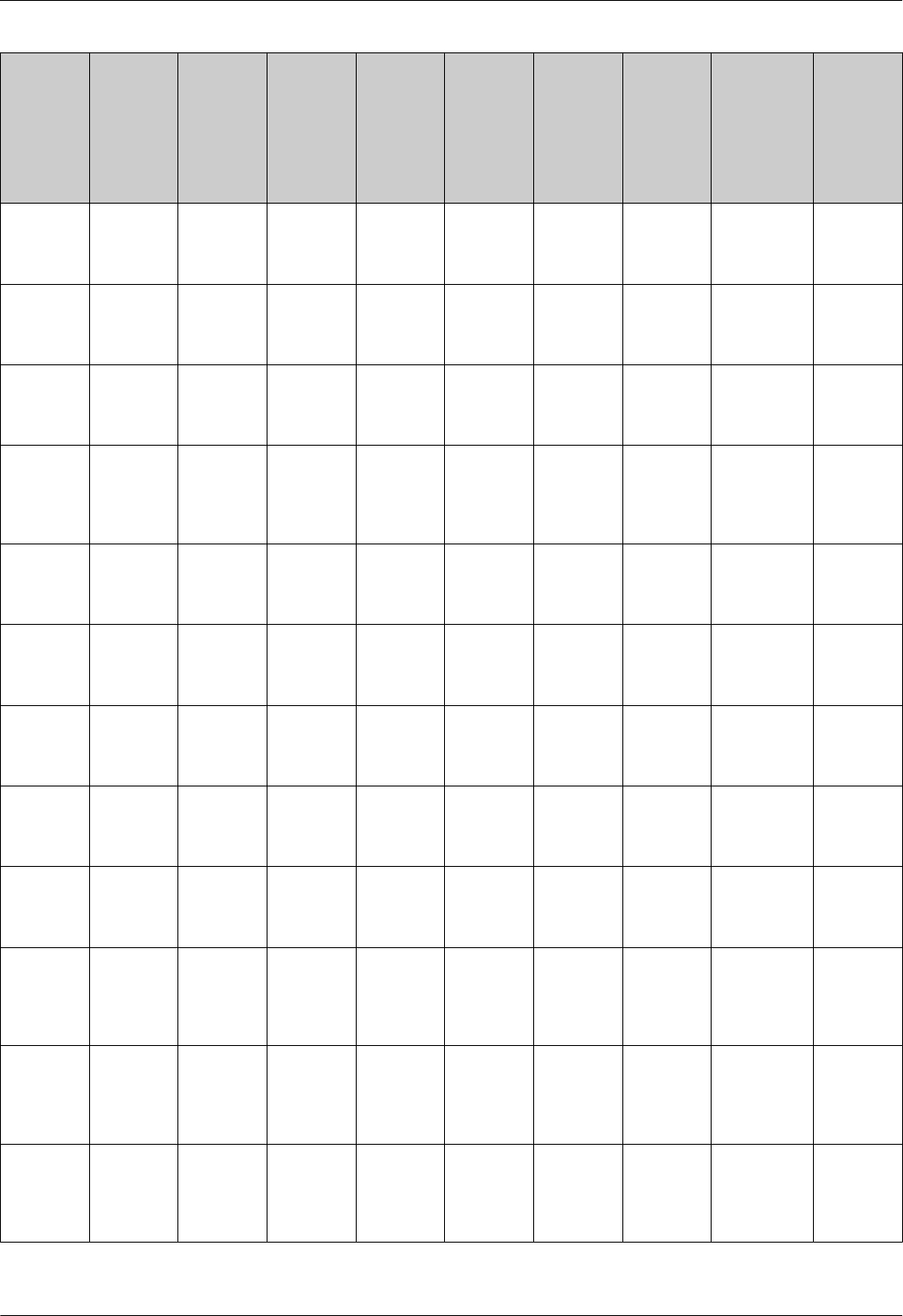
Micropilot FMR20
42 V. 5, Rev. 3, 20-12-2016 Endress+Hauser
Product
structure
Feature 620
"Accessory
enclosed"
Option:
A
(mm)
B
(mm)
C
(mm)
D
(mm)
E F
Number of
bores
G
Product
structure
Feature 95
"Process
connection
on front"
Option:
G
Product
structure
Feature 100
"Process
connection on
rear"
Option:
Accessory
order code
RA
UNI flange
2"/DN50/50,
PP, on front
120 125 165 19 90° 4 WGE
Thread
ISO228 G 2"
FAX50-XIGD
RB
*UNI flange
2"/DN50/50,
PP, on rear
120 125 165 19 90° 4 VCE
Thread ASME
MNPT 1"
FAX50-XIGF
RB
*UNI flange
2"/DN50/50,
PP, on rear
120 125 165 19 90° 4 WDE
Thread G 1"
ISO228
FAX50-XIGB
RD
UNI flange
3"/DN80/80,
PP, on front
150 160 200 19 45° 8 VEE
Thread
ASME
MNPT
1-1/2"
FAX50-XJGG
RD
UNI flange
3"/DN80/80,
PP, on front
150 160 200 19 45° 8 WFE
Thread
ISO228 G
1-1/2"
FAX50-XJGC
RD
UNI flange
3"/DN80/80,
PP, on front
150 160 200 19 45° 8 VFE
Thread
ASME
MNPT 2"
FAX50-XJGH
RD
UNI flange
3"/DN80/80,
PP, on front
150 160 200 19 45° 8 WGE
Thread
ISO228 G 2"
FAX50-XJGD
RE
UNI flange
3"/DN80/80,
PP, on rear
150 160 200 19 45° 8 VCE
Thread ASME
MNPT 1"
FAX50-XJGF
RE
UNI flange
3"/DN80/80,
PP, on rear
150 160 200 19 45° 8 WDE
Thread G 1"
ISO228
FAX50-XJGB
RG
UNI flange
4"/
DN100/100,
PP, on front
175 190.5 228.6 19 45° 8 VEE
Thread
ASME
MNPT
1-1/2"
FAX50-
XKGG
RG
UNI flange
4"/
DN100/100,
PP, on front
175 190.5 228.6 19 45° 8 WFE
Thread
ISO228 G
1-1/2"
FAX50-
XKGC
RG
UNI flange
4"/
DN100/100,
PP, on front
175 190.5 228.6 19 45° 8 VFE
Thread
ASME
MNPT 2"
FAX50-
XKGH
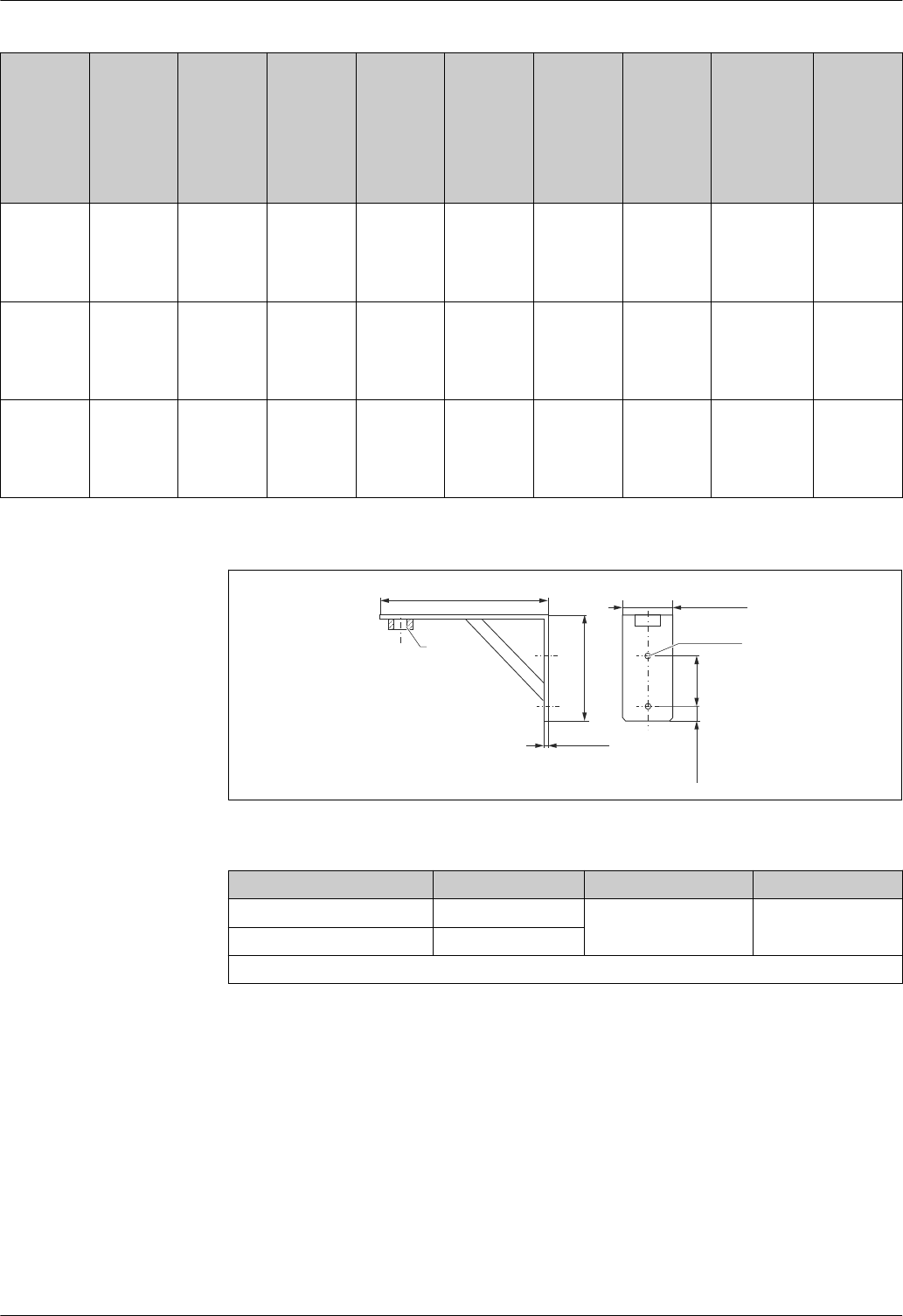
Micropilot FMR20
Endress+Hauser V. 5, Rev. 3, 20-12-2016 43
Product
structure
Feature 620
"Accessory
enclosed"
Option:
A
(mm)
B
(mm)
C
(mm)
D
(mm)
E F
Number of
bores
G
Product
structure
Feature 95
"Process
connection
on front"
Option:
G
Product
structure
Feature 100
"Process
connection on
rear"
Option:
Accessory
order code
RG
UNI flange
4"/
DN100/100,
PP, on front
175 190.5 228.6 19 45° 8 WGE
Thread
ISO228 G 2"
FAX50-
XKGD
RH
UNI flange
4"/
DN100/100,
PP, on rear
175 190.5 228.6 19 45° 8 VCE
Thread ASME
MNPT 1"
FAX50-
XKGF
RH
UNI flange
4"/
DN100/100,
PP, on rear
175 190.5 228.6 19 45° 8 WDE
Thread G 1"
ISO228
FAX50-
XKGB
Angle bracket for wall mount
400 (15.7) 120 (4.72)
120
(4.72)
30 (1.2)
250 (9.84)
Gø16 (0.6)
3 (0.12)
A0019346
37 Dimensions of angle bracket, engineering unit: mm (in)
Process connection Order No. Material Weight
G 1-1/2" 942669-0000 316 Ti (1.4571) 3.4 kg (7.5 lb)
G 2" 942669-0001
also suitable for MNPT 1-1/2" and MNPT 2"
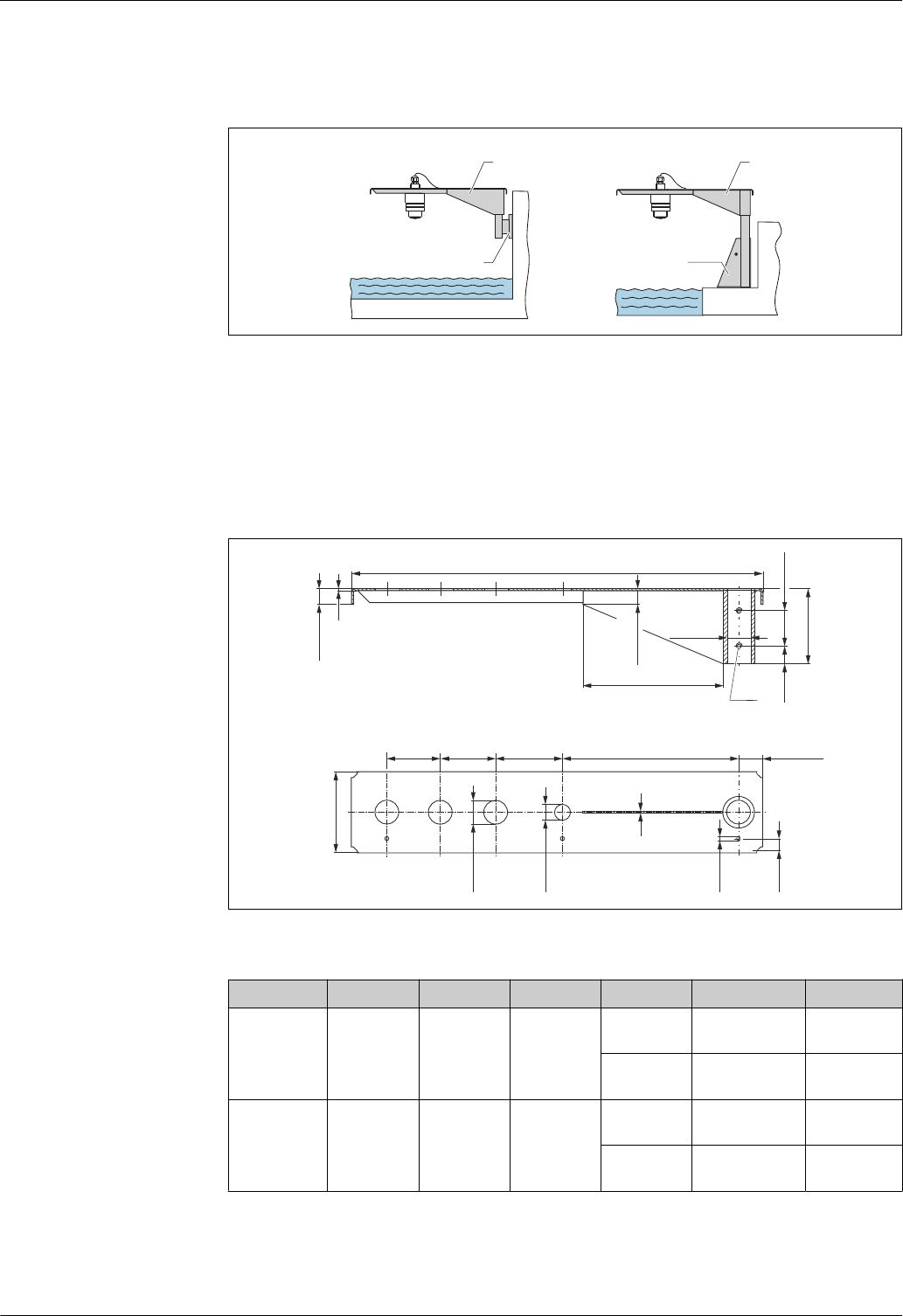
Micropilot FMR20
44 V. 5, Rev. 3, 20-12-2016 Endress+Hauser
Cantilever with pivot
Installation type sensor process connection rear side
3
1
2
A B 1
A0028885
38 Installation type sensor process connection rear side
A Installation with cantilever and wall bracket
B Installation with cantilever and mounting frame
1 Cantilever
2 Wall bracket
3 Mounting frame
Cantilever with pivot, sensor process connection on rear
A
DM8
35 (1.4)
50
(2.0)
20
(0.8)
105 (4.1)
35
(1.4)
22
(0.9)
C
C
6.5
(0.3)
15
(0.6) 100 (3.9)
25
(1.0)
35 (1.4)
100 (3.9)75 (2.9) B
20 (0.8)
75 (2.9)
A0019592
39 Dimensions of cantilever with pivot for sensor process connection on rear, engineering unit: mm (in)
A B C D Weight Material Order No.
585 mm
(23 in)
250 mm
(9.84 in)
2 mm
(0.08 in)
200 mm
(7.87 in)
2.1 kg
(4.63 lb)
Steel, hot-dip
galvanized
919790-0000
2.0 kg
(4.41 lb)
316Ti (1.4571) 919790-0001
1 085 mm
(42.7 in)
750 mm
(29.5 in)
3 mm
(0.12 in)
300 mm
(11.8 in)
4.5 kg
(9.92 lb)
Steel, hot-dip
galvanized
919790-0002
4.3 kg
(9.48 lb)
316Ti (1.4571) 919790-0003
• 35 mm (1.38 in) Openings for all G 1" or MNPT 1" connections on rear.
• 22 mm (0.87 in) Opening can be used for an additional sensor.
Retaining screws are included in delivery.

Micropilot FMR20
Endress+Hauser V. 5, Rev. 3, 20-12-2016 45
Installation type sensor process connection on front
1
2
AB
3
1
A0028886
40 Installation type sensor process connection on front
A Installation with cantilever and wall bracket
B Installation with cantilever and mounting frame
1 Cantilever
2 Wall bracket
3 Mounting frame
Cantilever with pivot, sensor process connection on front
A
DM8
35 (1.4)
50 (2.0)
20 (0.8)
105 (4.1)
50/62
(2.0/2.4)
22 (0.9)
C
C
6.5 (0.3)
15 (0.6)
100 (3.9)
25 (1.0)
35 (1.4)
100 (3.9)75 (2.9) B
20 (0.8)
75 (2.9)
A0019349
41 Dimensions of cantilever with pivot for sensor process connection on front, engineering unit: mm (in)
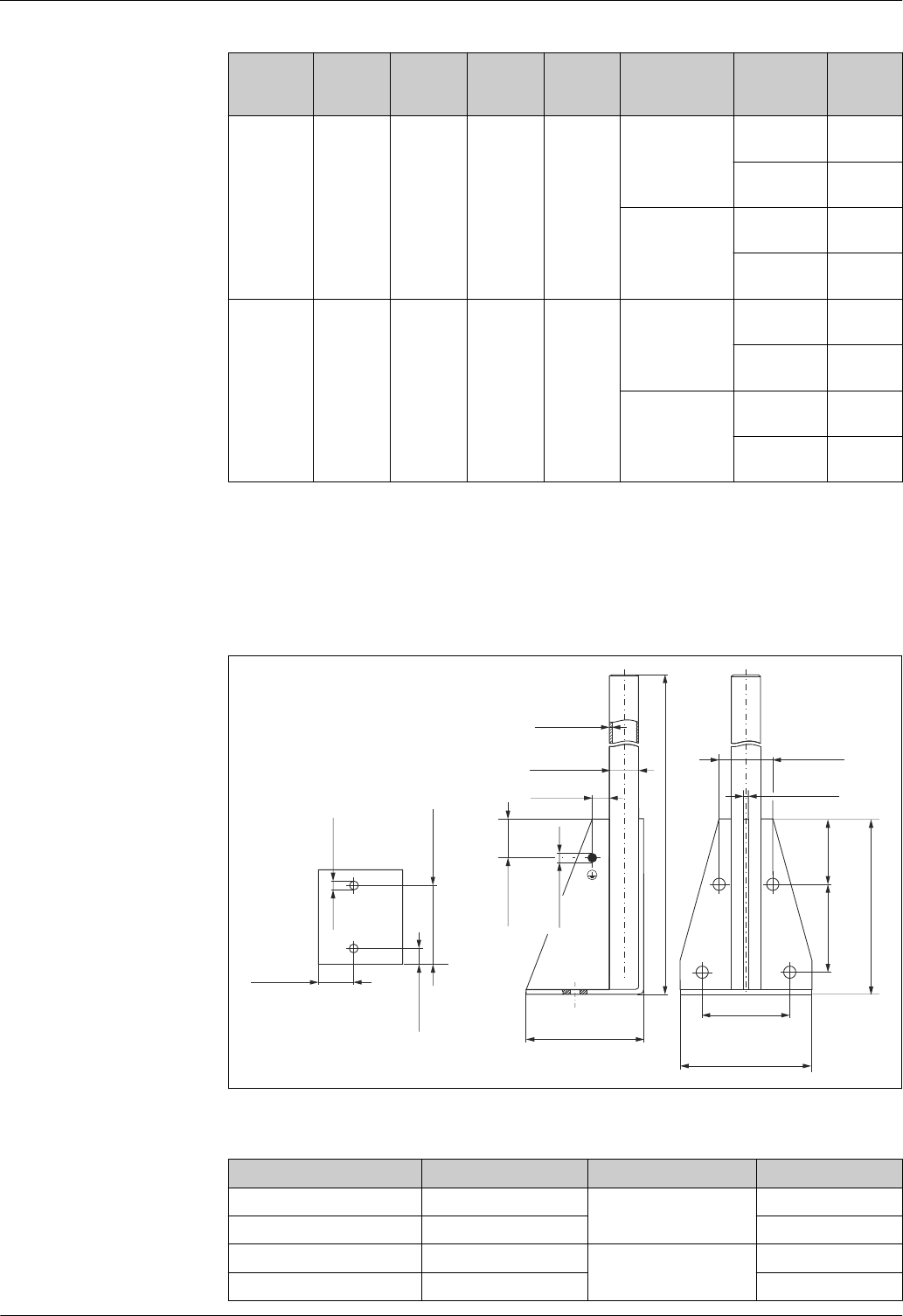
Micropilot FMR20
46 V. 5, Rev. 3, 20-12-2016 Endress+Hauser
A B C D Weight Sensor,process
connection
front side
Material Order No.
585 mm
(23 in)
250 mm
(9.84 in)
2 mm
(0.08 in)
200 mm
(7.87 in)
1.9 kg
(4.19 lb)
1-1/2" Steel, hot-dip
galvanized
52014131
316Ti
(1.4571)
52014132
2" Steel, hot-dip
galvanized
52014135
316Ti
(1.4571)
52014136
1 085 mm
(42.7 in)
750 mm
(29.5 in)
3 mm
(0.12 in)
300 mm
(11.8 in)
4.4 kg
(9.7 lb)
1-1/2" Steel, hot-dip
galvanized
52014133
316Ti
(1.4571)
52014134
2" Steel, hot-dip
galvanized
52014137
316Ti
(1.4571)
52014138
• 50 mm (2.17 in) or 62 mm (2.44 in) openings for all connections on front G 1-1/2" (MNPT
1-1/2") or G 2" (MNPT 2").
• 22 mm (0.87 in) Opening can be used for an additional sensor.
Retaining screws are included in delivery.
Mounting stand for cantilever with pivot
3.2 (0.13)
20 (0.8)
55 (2.17)
100 (3.94)
25 (0.98)
700/1400
(27.6 / 55.1)
45 (1.77)
76
(2.99)
100
(3.94)
200 (7.87)
13 (0.5)
ø33.7 (1.3)
130 (5.12)
150 (5.91)
100
(3.94)
60 (2.36)
4 (0.16)
6.5 (0.3)
A0019279
42 Dimensions of mounting frame, engineering unit: mm (in)
Height Material Weight Order No.
700 mm (27.6 in) Steel, galvanized 3.2 kg (7.06 lb) 919791-0000
700 mm (27.6 in) 316Ti (1.4571) 919791-0001
1 400 mm (55.1 in) Steel, galvanized 4.9 kg (10.08 lb) 919791-0002
1 400 mm (55.1 in) 316Ti (1.4571) 919791-0003
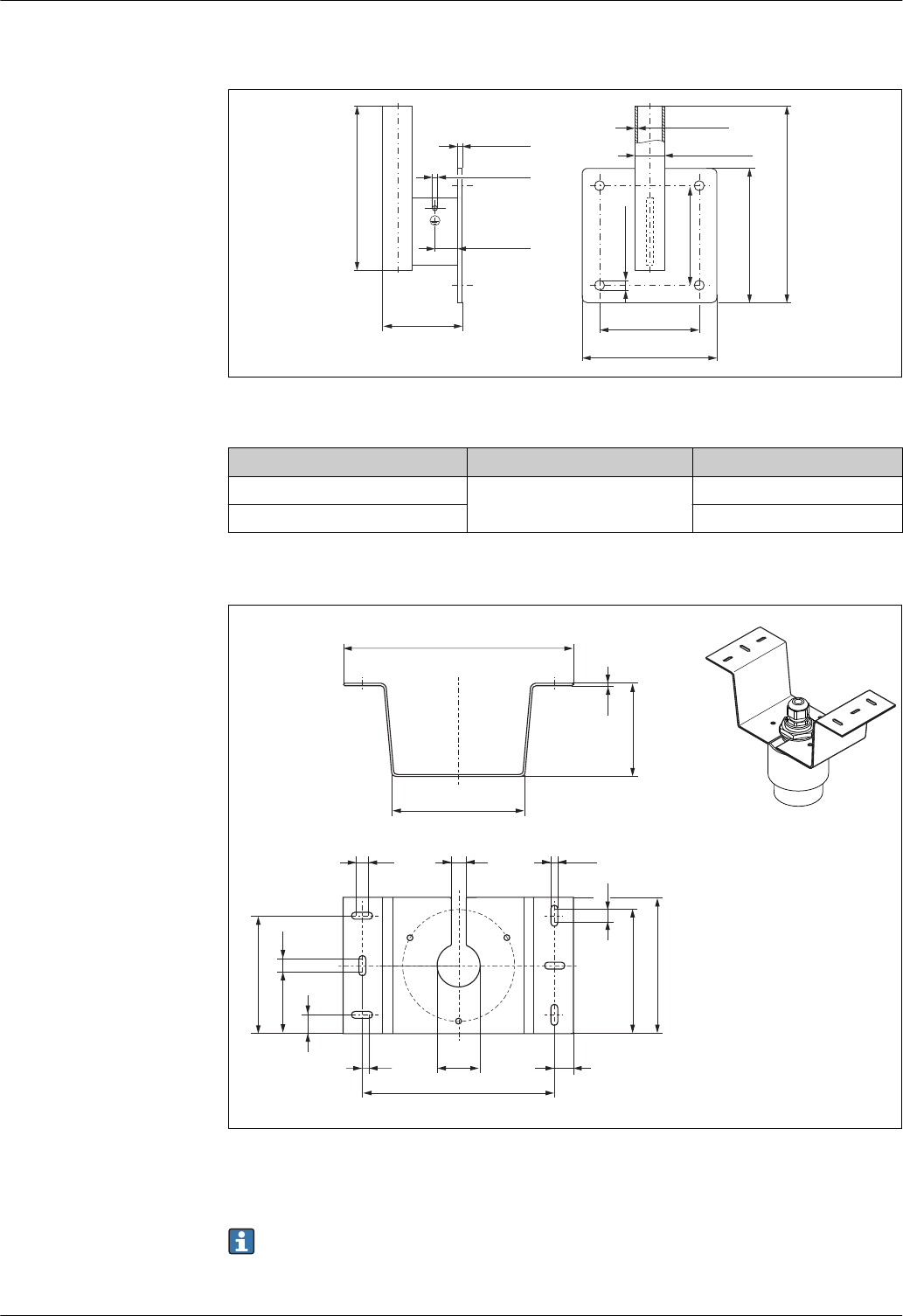
Micropilot FMR20
Endress+Hauser V. 5, Rev. 3, 20-12-2016 47
Wall bracket for cantilever with pivot
110 (4.3)
25 (1.0)
5 (0.2)
6.5 (0.3)
150 (5.9)
ø33.7 (1.3)
3.2 (0.1)
110 (4.3)
13 (0.5)
150 (5.9)
180 (7.1)
~213 (8.4)
~ (3.5)88
A0019350
43 Dimensions of wall bracket, engineering unit: mm (in)
Material Weight Order No.
Steel, galvanized 1.4 kg (3.09 lb) 919792-0000
316Ti (1.4571) 919792-0001
Ceiling mounting bracket
185
5 15
15
50 10
95
ø35
1210 ø5.6
155
1.5
75
100
110±2
105
10
A0028891
44 Dimensions of ceiling mounting bracket, engineering unit: mm (in)
Material: 316L (1.4404)
The mounting bracket can be ordered with the device (product structure, feature 620 "Accessory
enclosed", option R2 "Ceiling mounting bracket, 316L").
Alternatively, it is available as an accessory; order number 71093130.
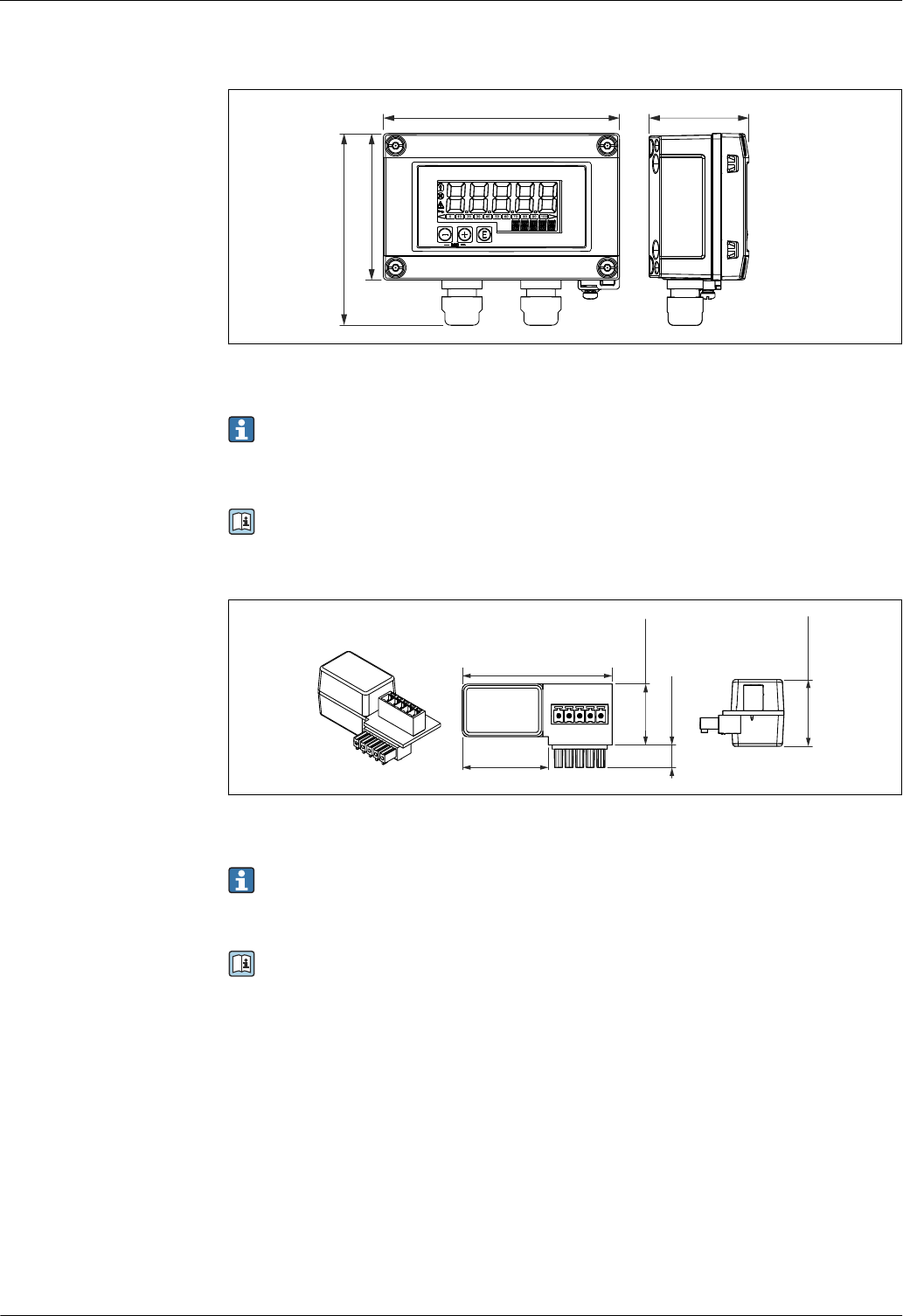
Micropilot FMR20
48 V. 5, Rev. 3, 20-12-2016 Endress+Hauser
RIA15 in the field housing (incl. option for basic configuration FMR20)
131 (5.16) 55.5 (2.19)
106.5 (4.19)
81.5 (3.21)
mm (in)
A0017722
45 Dimensions of RIA15 in field housing, engineering unit: mm (in)
The RIA15 remote display can be ordered together with the device. Product structure,
feature 620 "Accessory enclosed":
• Option R4 "Remote display RIA15 non-hazardous area, field housing"
• Option R5 "Remote display RIA15 Ex= explosion protection approval, field housing"
Alternatively available as an accessory, for details see Technical Information TI01043K and
Operating Instructions BA01170K.
HART communication resistor
54 (2.13)
31 (1.22)
24 (0.94)
22 (0.87)
8.1 (0.32)
A0020858
46 Dimensions of HART communication resistor, engineering unit: mm (in)
A communication resistor is required for HART communication. If this is not already present
(e.g. in the power supply RMA, RN221N, RNS221, ...), it can be ordered with the device via the
product structure, feature 620 "Accessory enclosed": option R6 "HART communication resistor
hazardous / non-hazardous area".
Alternatively available as an accessory, for details see Technical Information TI01043K and
Operating Instructions BA01170K.
The HART communication resistor is specially designed for use with the RIA15 and can be attached
easily.
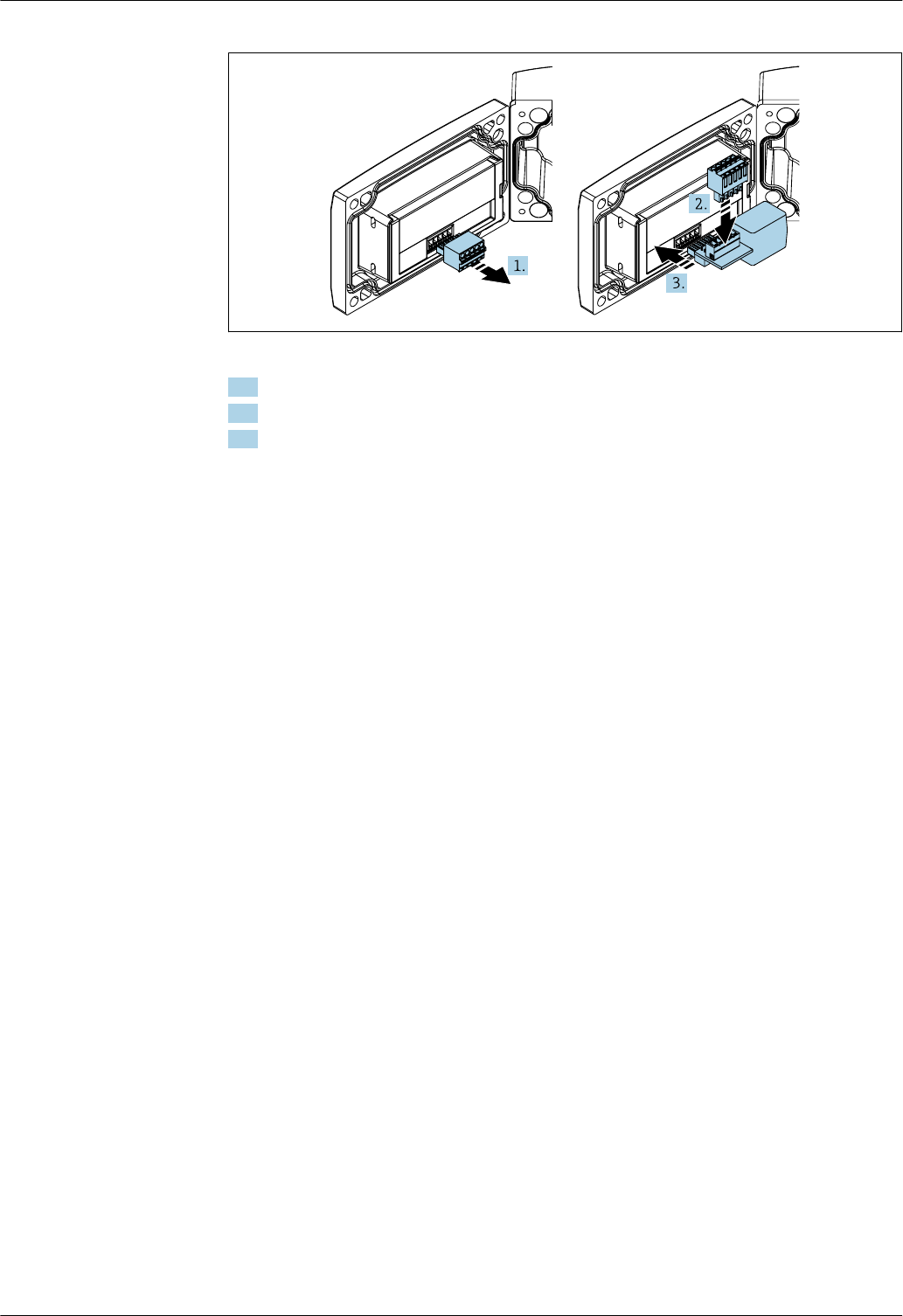
Micropilot FMR20
Endress+Hauser V. 5, Rev. 3, 20-12-2016 49
A0020844
1. Disconnect plug-in terminal block.
2. Insert the terminal block into the slot provided on the HART communication resistor module.
3. Insert the HART communication resistor in the slot in the housing.
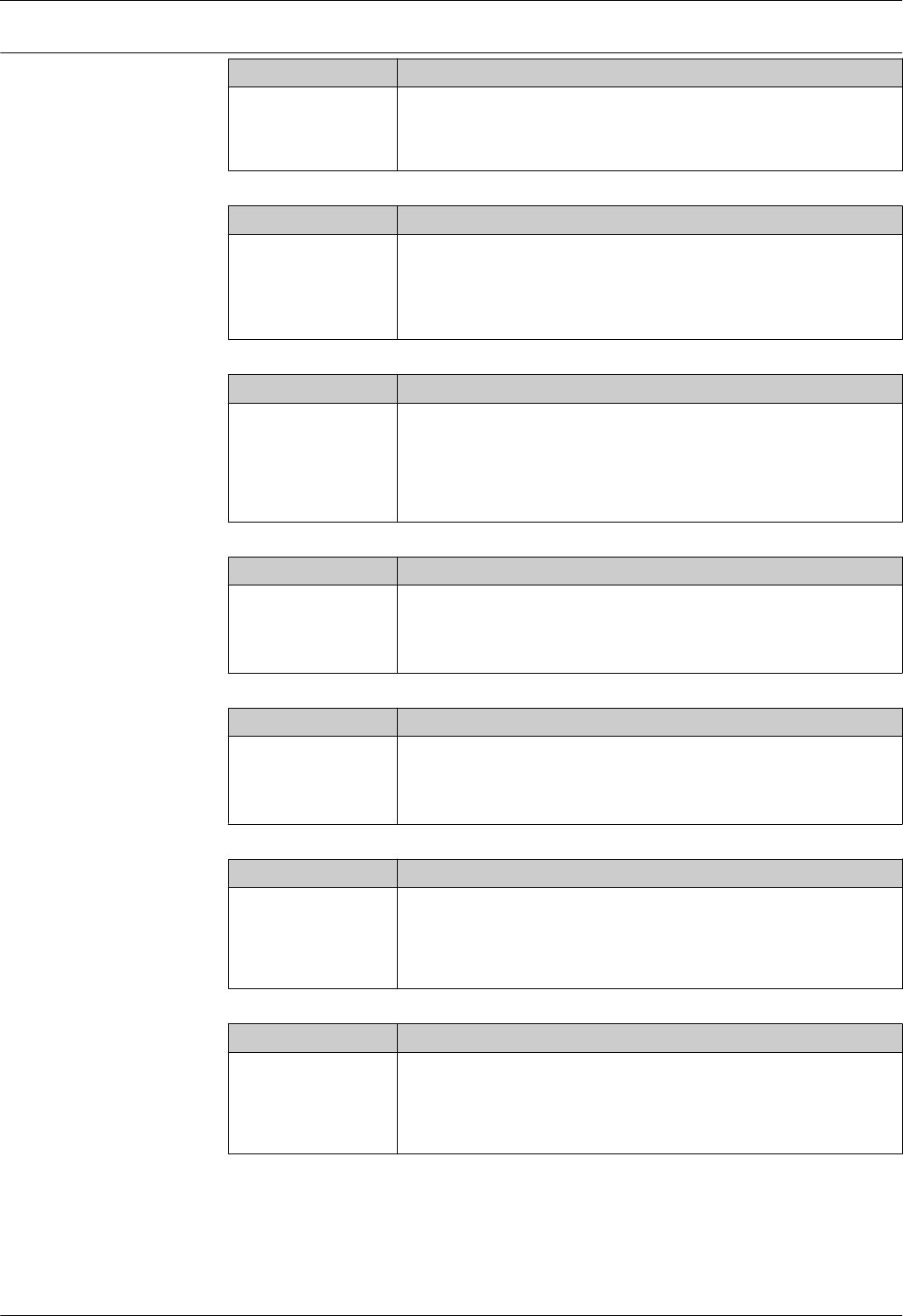
Micropilot FMR20
50 V. 5, Rev. 3, 20-12-2016 Endress+Hauser
Communication-specific
accessories Accessories Description
Commubox FXA195
HART
For intrinsically safe HART communication with FieldCare / DeviceCare via USB
interface.
For details, see Technical Information TI00404F
Accessories Description
HART Loop Converter
HMX50
Is used to evaluate and convert dynamic HART process variables to analog current
signals or limit values.
Order number: 71063562
For details, see Technical Information TI00429F and Operating Instructions
BA00371F
Accessories Description
WirelessHART adapter
SWA70
Is used for the wireless connection of field devices.
The WirelessHART adapter can be easily integrated into field devices and existing
infrastructures, offers data protection and transmission safety and can be operated
in parallel with other wireless networks.
For details, see Operating Instructions BA00061S
Accessories Description
Fieldgate FXA320 Gateway for remote monitoring of field devices with 4 to 20 mA and digital output
signal
For details, see Technical Information TI00025S and Operating Instructions
BA00053S
Accessories Description
Fieldgate FXA520 HART Gateway for remote monitoring of field devices with HART / 4 to 20 mA and
digital output signal
For details, see Technical Information TI00025S and Operating Instructions
BA00051S
Accessories Description
Field Xpert SFX350 Field Xpert SFX350 is a mobile computer for commissioning and maintenance. It
enables efficient device configuration and diagnostics for HART and
FOUNDATION Fieldbus devices in non-hzardous areas.
For details, see Operating Instructions BA01202S
Accessories Description
Field Xpert SFX370 Field Xpert SFX370 is a mobile computer for commissioning and maintenance. It
enables efficient device configuration and diagnostics for HART and
FOUNDATION Fieldbus devices in non-hazardous areas and hazardous areas.
For details, see Operating Instructions BA01202S
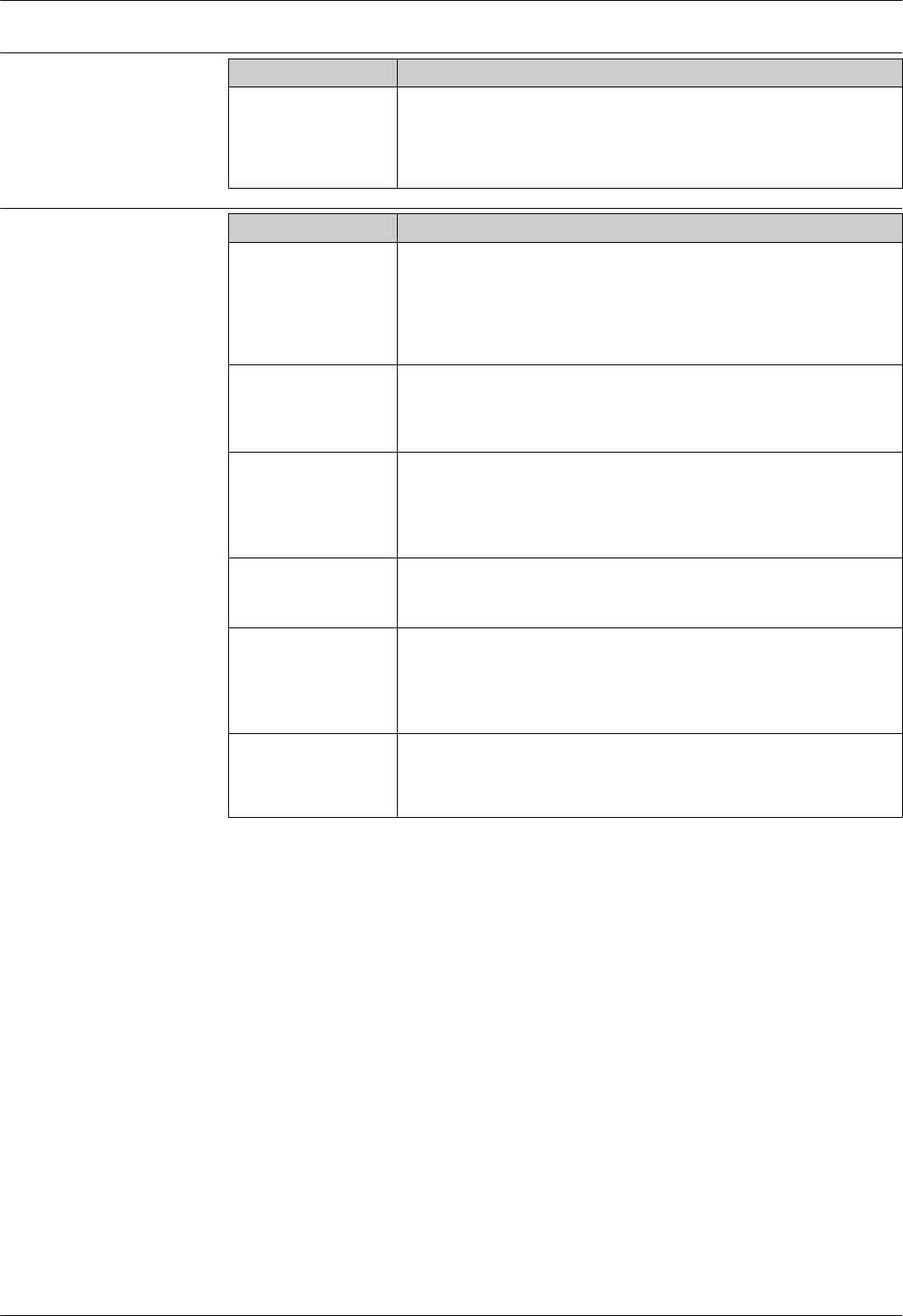
Micropilot FMR20
Endress+Hauser V. 5, Rev. 3, 20-12-2016 51
Service-specific accessories Accessory Description
FieldCare / DeviceCare Endress+Hauser's FDT-based Plant Asset Management tool.
Helps to configure and maintain all field devices of your plant. By supplying status
information it also supports the diagnosis of the devices.
For details refer to Operating Instructions BA00027S and BA00059S.
System components Accessories Description
Memograph M graphic
display recorder
The Memograph M graphic data manager provides information on all the relevant
process variables. Measured values are recorded safely, limit values are monitored
and measuring points analyzed. The data are stored in the 256 MB internal
memory and also on an SD card or USB stick.
For details, see Technical Information TI01180R and Operating Instructions
BA01338R
RNS221 Supply unit for powering two 2-wire measuring devices. Bidirectional
communication is possible via the HART communication jacks.
For details, see Technical Information TI00081R and Operating Instructions
KA00110R
RN221N Active barrier with power supply for safe separation of 4...20 mA current circuits
Bi-directional HART-communication is possible using the built-in communication
sockets (with resistance R=250 Ω)
For details, see Technical Information TI073R and Operating Instructions
BA202R
RMA42 Digital process transmitter for monitoring and visualizing analog measured values
For details, see Technical InformationTI00150R and Operating Instructions
BA00287R
RIA452 Digital process meter RIA452, in panel mounted housing for monitoring and
displaying analog measured values, batch, pump control functions and can be used
as a preset counter and for measuring flow
For details, see Technical Information TI113R nd Operating Instructions
BA00254R
HAW562 Surge arrester for DIN rail according to IEC 60715, used to protect electronic
components from being destroyed by overvoltage.
For details, see Technical Information TI01012K
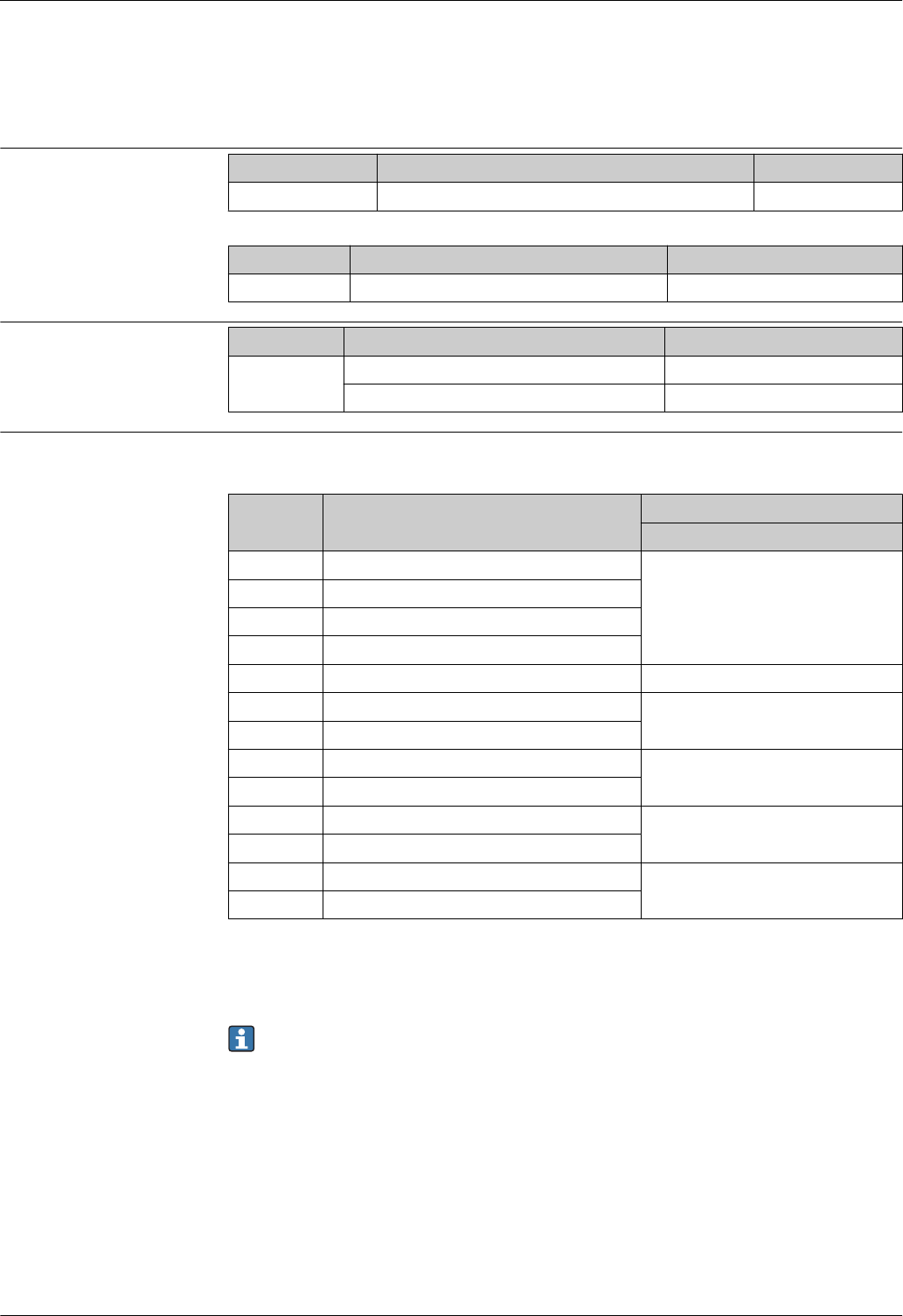
Micropilot FMR20
52 V. 5, Rev. 3, 20-12-2016 Endress+Hauser
Supplementary documentation
The following document types are available in the Download Area of the Endress+Hauser Internet
site: www.endress.com → Download:
Standard documentation Device Document type Document code
FMR20 Brief Operating Instructions KA01248F
Device Document type Document code
FMR20 Operating Instructions BA01578F
Supplementary
documentation Device Document type Document code
RIA15 Technical Information TI01043K
Operating Instructions BA01170K
Safety Instructions (XA) Depending on the approval, the following Safety Instructions (XA) are supplied with the device. They
are an integral part of the Operating Instructions.
Feature 010 Approval Feature 020: "Power Supply; Output"
A 1), P 2)
BA ATEX II 1 G Ex ia IIC T4 Ga
XA01443F
BB ATEX II 1/2 G Ex ia IIC T4 Ga/Gb
IA IEC Ex ia IIC T4 Ga
IB IEC Ex ia IIC T4 Ga/Gb
CB CSA C/US IS CI.I Div.1 Gr.A-D, AEx ia / Ex ia T4 XA01445F
GA EAC Ex ia IIC T4 Ga XA01578F
GB EAC Ex ia IIC T4 Ga/Gb
KA KC Ex ia IIC T4 Ga XA01575F 3)
KB KC Ex ia IIC T4 Ga/Gb
MA INMETRO Ex ia IIC T4 Ga XA01576F 3)
MB INMETRO Ex ia IIC T4 Ga/Gb
NA NEPSI Ex ia IIC T4 Ga XA01577F 3)
NB NEPSI Ex ia IIC T4 Ga/Gb
1) 2 wire; 4-20 mA HART configuration
2) 2 wire; 4-20 mA HART/Bluetooth® (app) configuration
3) At the time of printing in preparation
The nameplate indicates the Safety Instructions (XA) that are relevant to the device.



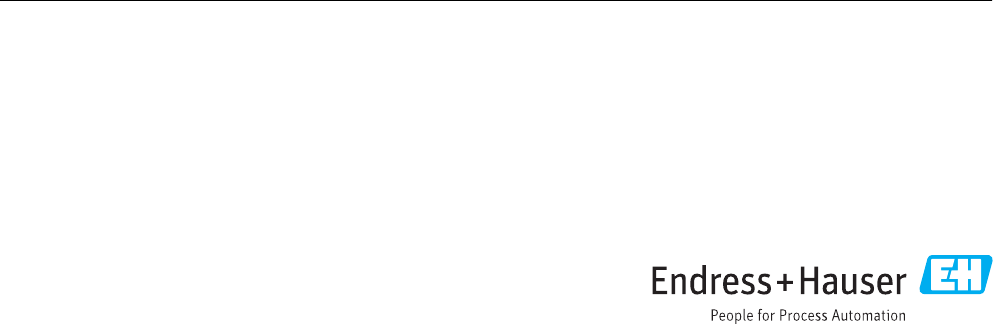
www.addresses.endress.com
*unbekannt*