Fluke 190 202 Application Note
2015-09-09
: Fluke Fluke-190-202-Application-Note-808703 fluke-190-202-application-note-808703 fluke pdf
Open the PDF directly: View PDF .
Page Count: 2
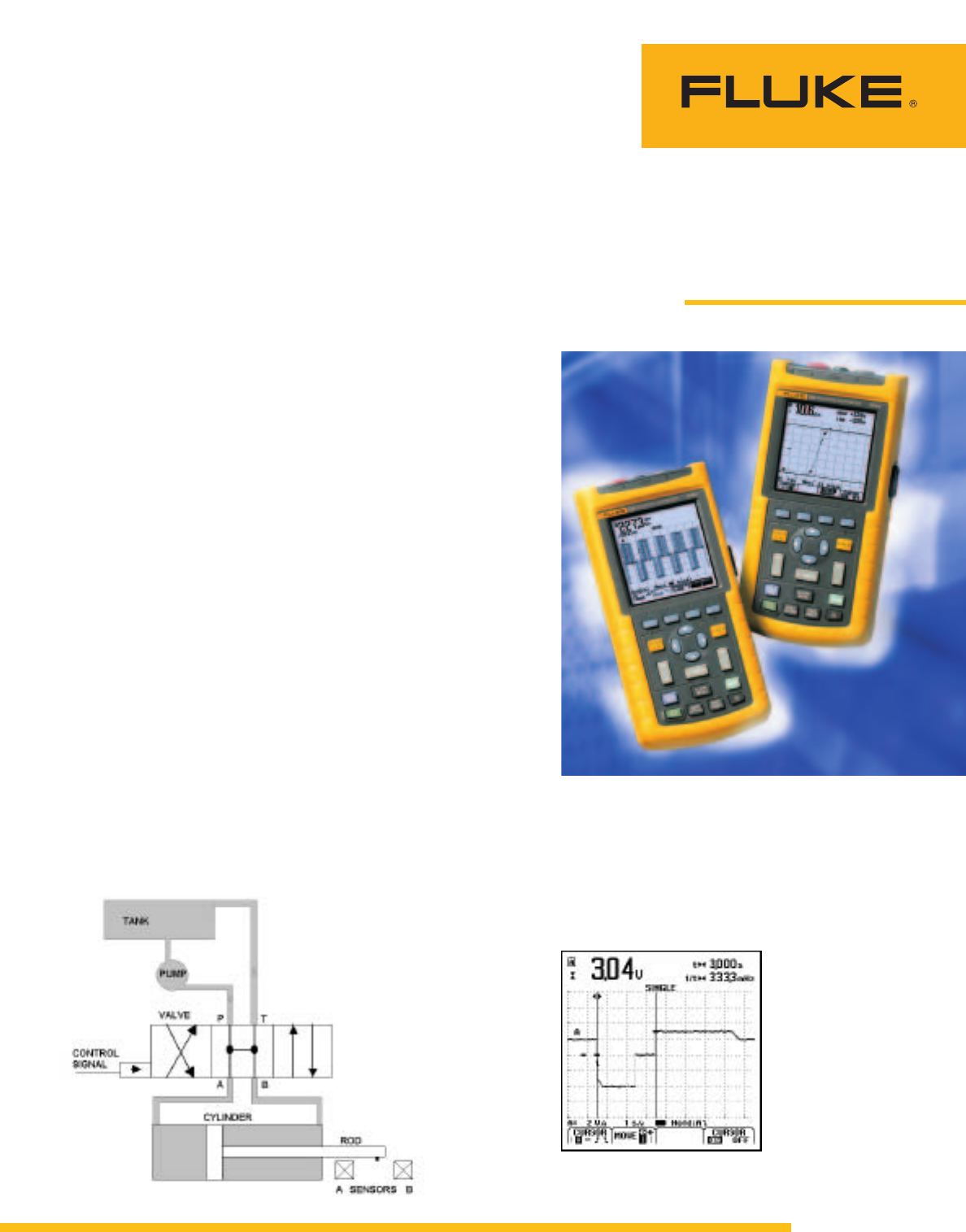
Hydraulic system
principles
An hydraulic system has a fluid
reservoir and a pump that pumps
hydraulic fluid into the various
hydraulic cylinders to create
movement of the cylinder rod. A
controller determines into which
cylinder the fluid is pumped by
opening a valve to that cylinder.
The amount the valve is opened
determines the speed of move-
ment of the cylinder rod.
The valve stays open and the
rod moves until a sensor (or
operator) feeds information back
to the controller, causing it to
close the valve. These feedback
sensors are of three main kinds:
•limit sensors that feed back a
position that has been
reached, for example the “end
of stroke” for the rod
Verifying hydraulic control
system operation with
Fluke ScopeMeter®
120 Series test tools
Figure 2 shows a valve control
signal that has been measured
using a ScopeMeter®test tool.
Initially the signal has a level of
+2 V. This means that the valve
is slightly open, connecting the P
to B (and A to T) and the cylinder
rod is retracted.
From the Fluke Digital Library @ www.fluke.com/library
Application Note
The electronic sensors, controllers and actuators or valves
used to control a hydraulic system enable cranes, presses,
injection molding machines, earth moving equipment and
other “heavy duty” areas to operate faster and more accu-
rately. The service, maintenance and installation of these
electro-hydraulic systems require measurement tools that
provide insight into the system circuit behavior.
Figure 1. Basic diagram.
•position sensors that feedback
the actual position of the rod,
for accurate positioning
•pressure valves that limit the
maximum pressure by venting
fluid to the reservoir
Measuring control and
sensor signals
Control signals
The motion and speed of the
cylinder rod are directly related
to the oil flow regulated by the
valve. Figure 1 shows a
schematic drawing of a cylinder
controlled by a 4-way propor-
tional valve.
This valve has a P for pressure
input that can be fed to either its
A or B outputs depending upon
the control signal, and an T for
Tank (to fluid reservoir) return
which is then connected to the
non-pressurized A or B output. In
this way the cylinder rod can be
moved left or right by controlling
the pressure fed to the A or B
outputs with the control signal.
Figure 2. Valve control.
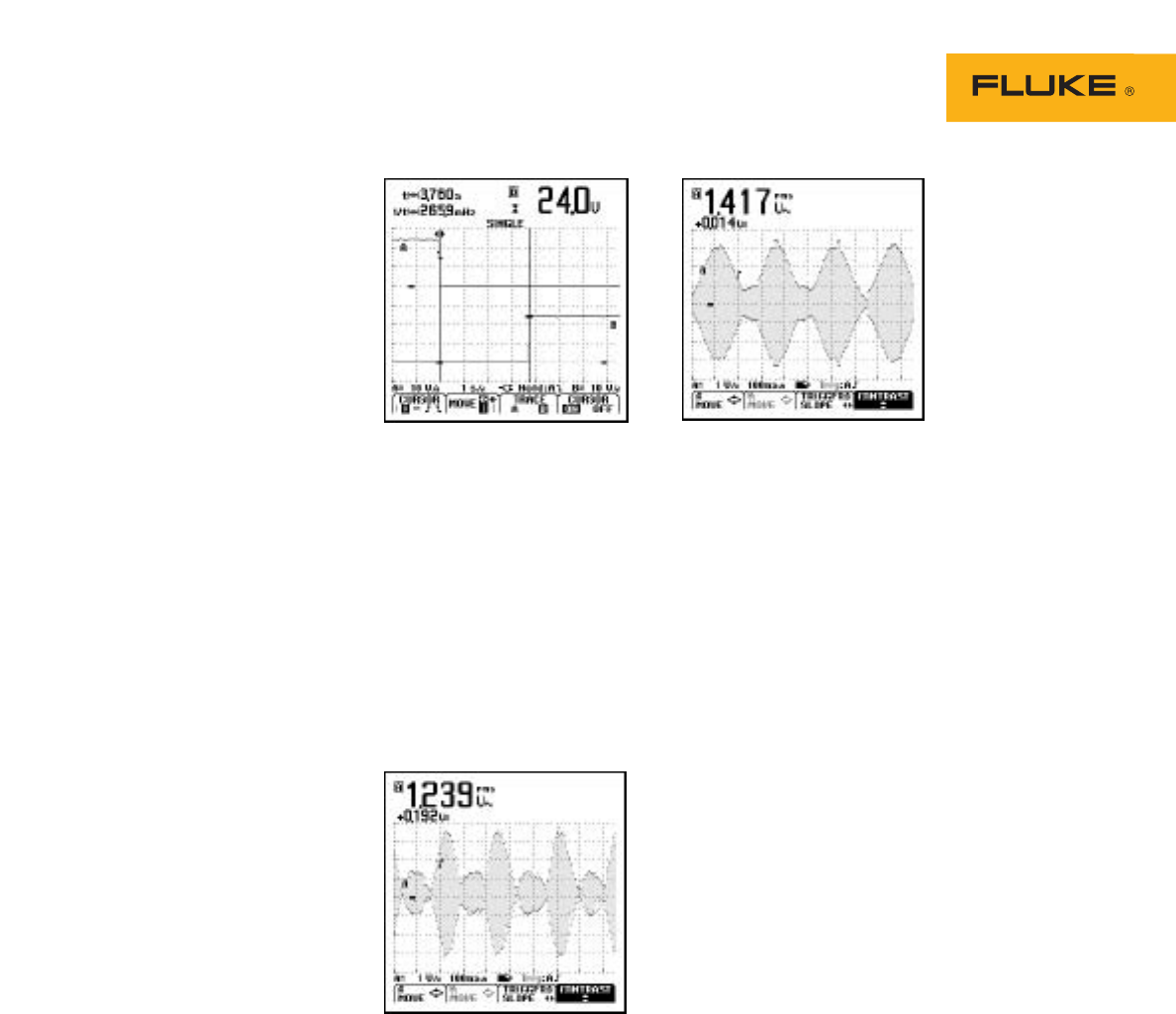
2 Fluke Corporation Verifying hydraulic control system operation with Fluke ScopeMeter®120 Series test tools
When the voltage level
changes to -4 V, the position of
the valve changes and the flow
direction of the oil is reversed (P
to A and B to T), so the rod
moves at high speed to the out-
ermost position. After 2 seconds,
the rod reaches its outermost
position, the valve is closed (0 V)
and the cylinder holds this posi-
tion for about 1 second.
The voltage level then
changes to +3 V to re-open the
valve and retract the rod. Finally,
just before the innermost position
is reached again, the valve open-
ing is reduced slowly by chang-
ing the voltage level from +3 V
to +2 V, so the cylinder rod
moves gently into its innermost
position, where it is slowly
forced to its mechanical limits.
Using the ScopeMeter test tool
cursor function, it is easy to
determine the time taken to
move the cylinder rod from one
position to the other, and to
measure the control voltage lev-
els during the various stages.
From this picture, the engineer
can see which changes he can
make to adjust the behavior of
the system. For instance: he
could increase the retraction
speed by increasing the control
signal voltage from +3 V to +4 V,
or he could reduce the retention
force by decreasing the retention
voltage level from +2 V to +1 V.
Sensor signals
Most systems use sensors to
determine the position of various
moving components, such as an
“end-of-stroke” detector. Figure 2
illustrates how sensors can be
used to detect a “cylinder rod”
end-of stroke position.
The relatively low repetition
rate of the rod movement
requires a storage oscilloscope to
store the measured signal char-
acteristics over a long period of
time. With the ScopeMeter test
tool, signals from the sensors can
easily be measured and stored.
When the measurements are
complete, the cursor function can
be used to measure the time
required for the rod to move from
one sensor the other. Figure 3
shows the signals measured on
sensor A and B. The left cursor is
positioned on the falling edge of
the sensor A signal. This is
where the cylinder rod leaves
the sensor A position. The right
cursor is positioned on the rising
edge of the sensor B signal. This
is where the cylinder rod
reached the sensor B position.
The cursor read-out indicates the
time duration (dt) between both
cursor positions. When position-
ing information is required, a
resistive linear displacement
transducer is often used for short
rod movements. These give an
output signal directly related to
position.
For accurate positioning on
long rod movements, servo cylin-
ders are used. Here a sensor is
mounted in the cylinder head,
where it is protected from water,
dirt and other environmental
influences. The sensor operates
by magnetically sensing a pat-
tern of grooves cut into the base
of the piston rod. The change in
the magnetic field caused as the
grooves pass the cylinder head
generate a signal in the sensor,
which is converted by separate
electronics into a pulse. When
the direction of the rod is
reversed, a phase shift in the
sensor signal output occurs
enabling the direction of the rod
to be determined.
By counting pulses, and with
knowledge of the direction of
travel, highly accurate rod posi-
tioning can be realized.
During initial installation of the
system, or if any of the sensors
have to be replaced when carry-
ing out maintenance, the sensor
output signals must be aligned to
ensure that they are correctly
processed by the system’s elec-
tronics. In particular, the succes-
sive pulses in the output
wave-train must be symmetrical
and of equal amplitude. Figures 4
and 5 show incorrect and correct
alignment of this sensor output.
Conclusion
To verify correct operation of
electro-hydraulic systems, visual
storage of the control signals over
time is essential. The ScopeMeter
120 Series’ test tool’s low-speed
signal display capabilities make
these instruments ideal for meas-
uring and analyzing hydraulic
control signals, and their rugged
battery powered capabilities
enable them to work in all the
environments where hydraulic
systems are employed.
Figure 3. End-of-stroke sensor signals.
(Fluke 124)
Figure 4. Incorrect sensor alignment.
(Fluke 123)
Figure 5. Correct sensor alignment.
(Fluke 123)
Fluke Corporation
PO Box 9090, Everett, WA USA 98206
Fluke Europe B.V.
PO Box 1186, 5602 BD
Eindhoven, The Netherlands
For more information call:
In the U.S.A. (800) 443-5853 or
Fax (425) 446-5116
In Europe/M-East/Africa (31 40) 2 675 200 or
Fax (31 40) 2 675 222
In Canada (800) 36-FLUKE or
Fax (905) 890-6866
From other countries +1 (425) 446-5500 or
Fax +1 (425) 446-5116
Web access: http://www.fluke.com
©2004 Fluke Corporation. All rights reserved.
Printed in U.S.A. 3/2004 2140244 A-ENG-N Rev A
Fluke.Keeping your world
up and running.