Fluke 190 202 Application Note
2015-09-09
: Fluke Fluke-190-202-Application-Note-808713 fluke-190-202-application-note-808713 fluke pdf
Open the PDF directly: View PDF .
Page Count: 6
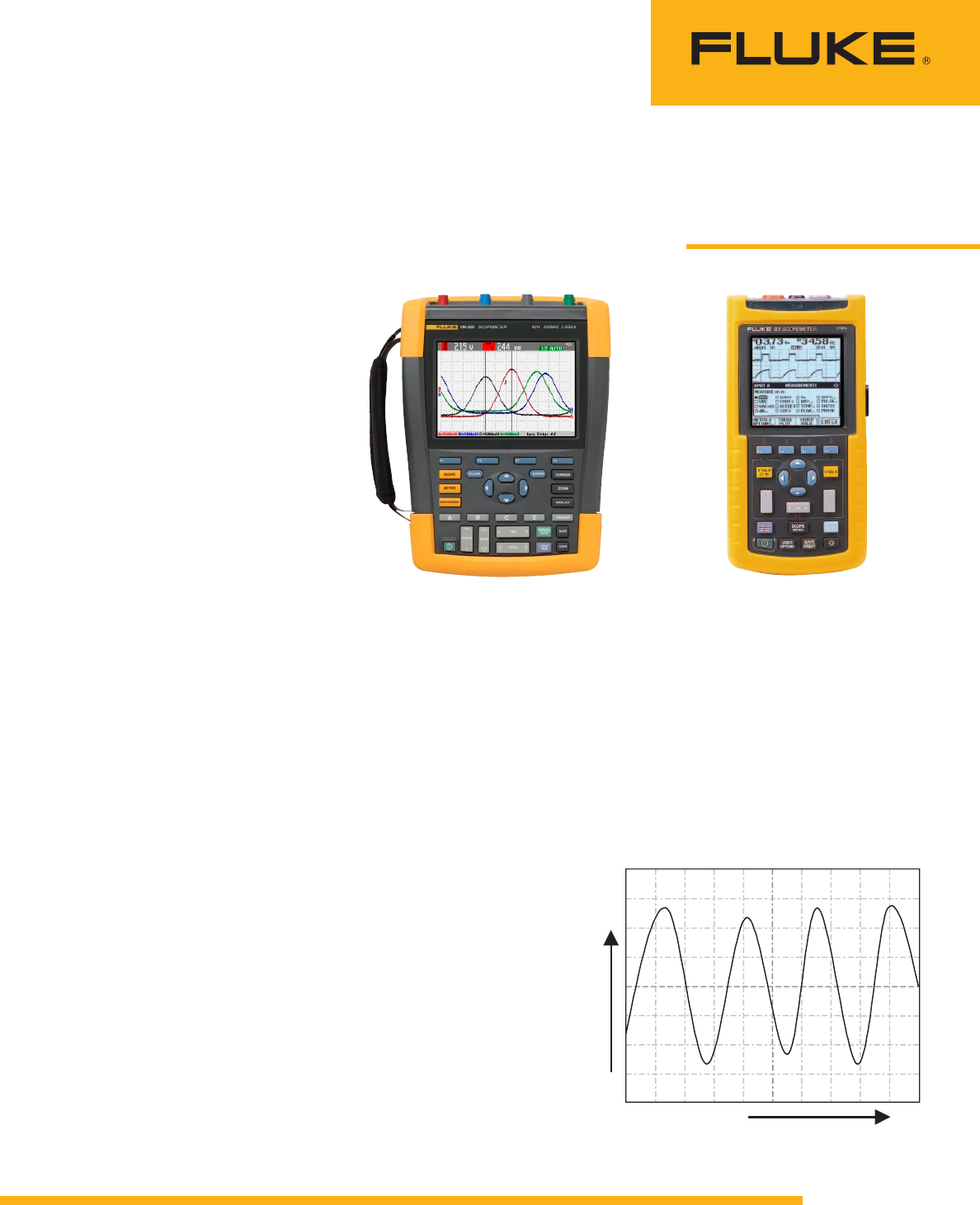
A rst look at DSOs
This introduction to digital storage oscilloscopes
(DSOs) takes you on a quick but comprehensive
tour of DSO functions and measurements.
An oscilloscope measures and
displays voltage signals on a
time-versus-voltage graph. In
most applications the graph
shows how the signal changes
over time: the vertical (Y) axis
represents voltage, and the hori-
zontal (X) axis represents time.
This simple graph can tell you
many things about a signal:
• View the signal for anomalies.
• Calculate the frequency of an
oscillating signal.
• Tell if a malfunctioning compo-
nent is distorting the signal.
• Tell how much of the signal is
noise and whether the noise is
changing with time.
Today’s handheld digital stor-
age oscilloscopes offer two
critical advantages over benchtop
models: they are battery-oper-
ated, and they use isolated,
electrically floating inputs.
These designs make safety-
certified measurements possible
in 1000 V CAT III and 600 V
CAT IV environments—a critical
need for safely troubleshooting
electrical devices in high-energy
applications.
Scopes and DMMs
The difference between an
oscilloscope and a DMM (Digital
Multimeter) can be summarily
stated as “pictures vs. numbers.”
A DMM is a tool for making
precise measurements of discrete
signals, enabling readings of up
to eight digits of resolution for
the voltage, current or frequency
of a signal. On the other hand, it
cannot depict waveforms visually
to reveal signal strength, wave-
shape, or the instantaneous value
of the signal. Nor is it equipped to
reveal a transient or a harmonic
signal that could compromise the
operation of a system.
A scope adds a wealth of infor-
mation to the numeric readings of
a DMM. While displaying instan-
taneous numerical values of a
wave, it also reveals the shape of
the wave, including its ampli-
tude (voltage) and frequency.
With such visual information, a
transient signal that may pose
major consequences to a system
can be displayed, measured and
isolated.
Reach for a scope if you want
to make both quantitative and
qualitative measurements. Use
a DMM to make high-precision
checks of voltage, current,
resistance and other electrical
parameters.
Sampling
Sampling is the process of
converting a portion of an input
signal into a number of discrete
electrical values for the pur-
pose of storage, processing and
display. The magnitude of each
sampled point is equal to the
amplitude of the input signal at
the time the signal is sampled.
The input waveform appears as
a series of dots on the display. If
the dots are widely spaced and
difficult to interpret as a wave-
form, they can be connected
using a process called interpola-
tion, which connects the dots
with lines, or vectors.
Volts
vertical
Y-axis
Time
horizontal X-axis
Figure 1. Time-versus-voltage graph.
The 4-channel Fluke 190 Series II
ScopeMeter has a 200 MHz bandwidth
and 2.5 GS/s real-time sampling rate.
The Fluke 123 ScopeMeter with 20 MHz
dual-input measurement shows both
meter reading and waveform.
Application Note
From the Fluke Digital Library @ www.fluke.com/library
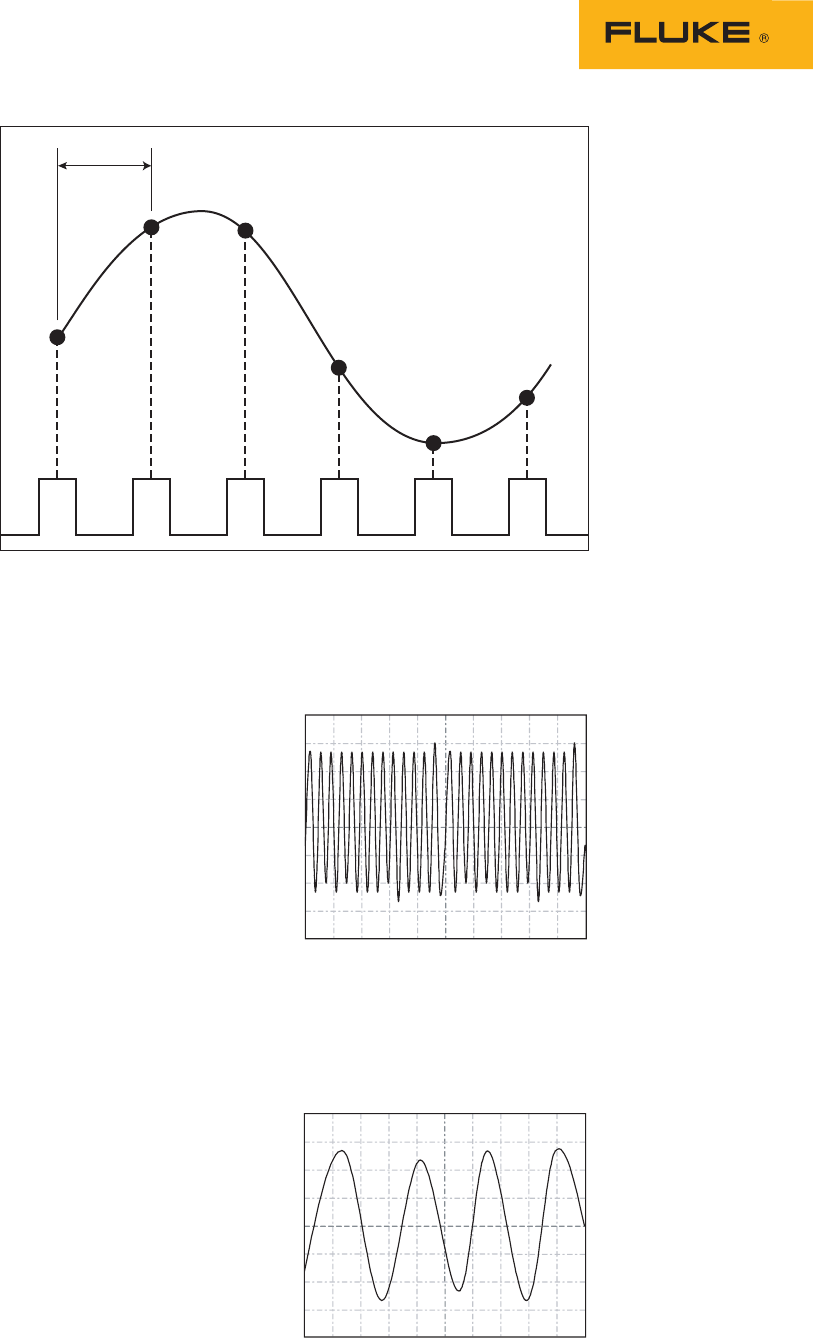
2 Fluke Corporation A first look at DSOs
Triggering
Trigger controls allow you to
stabilize and display a repetitive
waveform.
Edge triggering is the most
common form of triggering. In
this mode, the trigger level and
slope controls provide the basic
trigger point definition. The slope
control determines whether the
trigger point is on the rising or
the falling edge of a signal, and
the level control determines
where on the edge the trigger
point occurs.
For even greater control and
visibility into signal phenom-
ena, you can use the ability of
some DSOs to capture events
leading up to the trigger point
(“pre-trigger”) or after the trig-
ger point (“post-trigger”) on the
input waveform. As an example,
by using pre-triggering or post-
triggering, you may catch a spike
that occurs in between two
occurrences of a signal.
Pulse width triggering trig-
gers on specific pulses within a
series or it can identify one-time
or sporadic problems in a pulsed
signal. In this mode, you can
monitor a signal indefinitely and
trigger on the first occurrence of
a pulse whose duration, or pulse
width, is either outside of or
within set limits. The goal is to
isolate and display a pulse that
meets the predetermined time
criteria.
Single-shot triggering is
useful for capturing a one-time
event—such as electrical arcing
or a relay closure. A DSO with a
single-shot mode waits until it
receives a trigger and then sets
itself in a hold mode to store the
signal at the moment the one-
time event occurs.
Video triggering is a power-
ful feature of advanced DSOs.
Video signals can be extremely
complex, providing no unique
edge that is repetitive and that
can be isolated to stabilize the
signal. With an extensive range
of signaling protocols in use in
today’s electronic video equip-
ment and systems, an effective
DSO is one that recognizes the
predominant video protocols and
provides appropriate triggering
functionality.
Setup
The task of capturing and ana-
lyzing an unknown waveform on
an oscilloscope can be routine, or
it can seem like taking a shot in
the dark. However, in most cases,
taking a methodical approach to
setting the oscilloscope will cap-
ture a stable waveform or help
you determine how the scope
controls need to be set so that
you can capture the waveform.
1) Start with Auto
Connect the ground reference
lead and then connect the probe
tip to the circuit test point. Most
oscilloscopes have the ability to
either perform a one-time auto
setup or continuously analyze the
unknown input signal. Press the
AUTO button or verify that the
scope is already in Auto mode.
Pressing the AUTO button will
typically set up the oscilloscope
to automatically adjust three key
parameters:
Vertical sensitivity. Adjusts
the vertical sensitivity so that the
vertical amplitude spans approxi-
mately three to six divisions.
Horizontal timing. Adjusts
the horizontal time per division
so that there are three to four
periods of the waveform across
the width of the display.
Figure 2. Sampling and interpolation, sampling is depicted by the dots while interpolation
is shown as the black line.
t
Figure 3. Unknown trace adjusted for 3-6
vertical divisions.
Figure 4. Unknown trace adjusted for 3-4
periods horizontally.
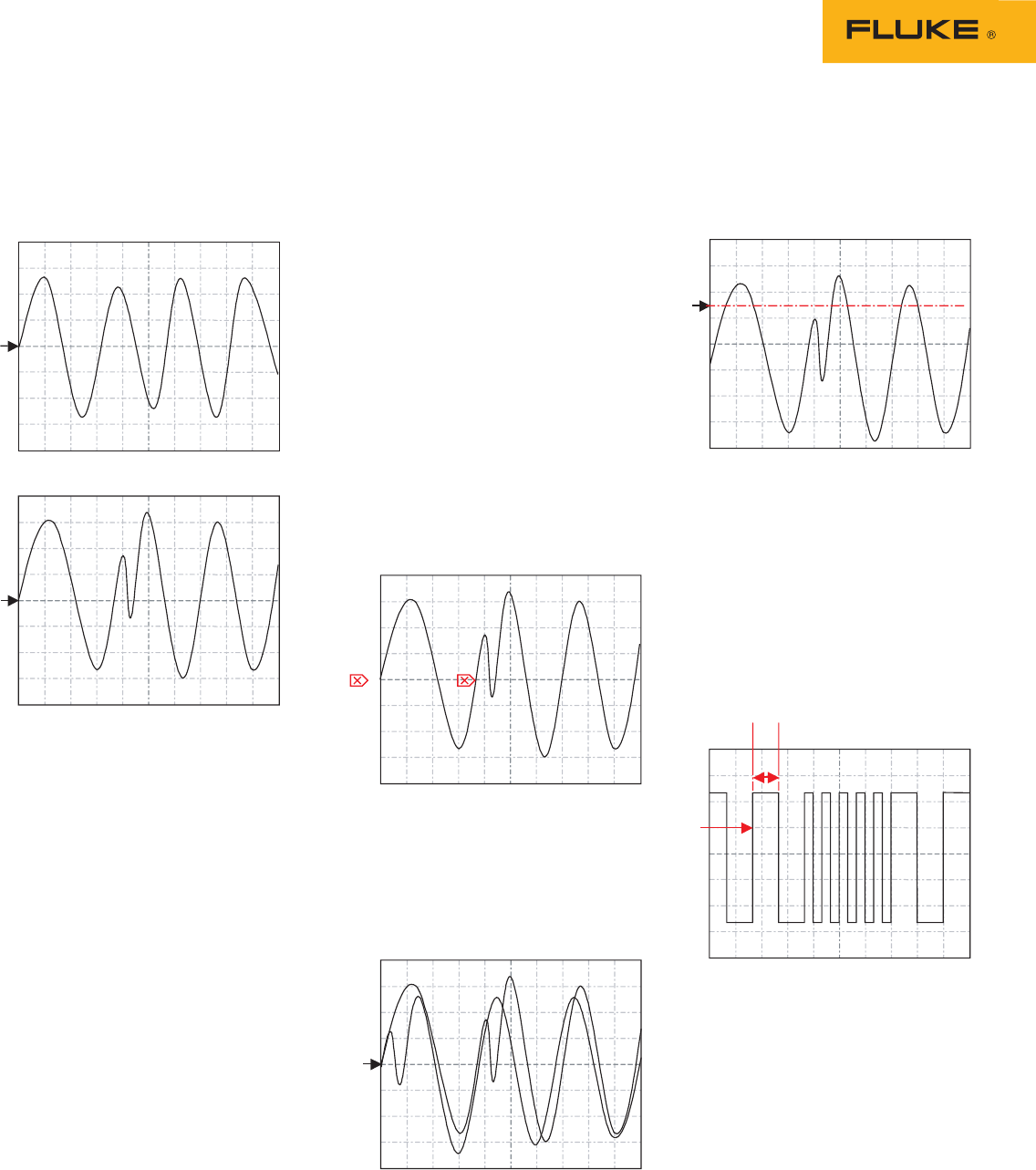
3 Fluke Corporation A first look at DSOs
Trigger position. Sets the trig-
ger position to the 50 % point of
the vertical amplitude. Depend-
ing on the signal characteristics,
this action may or may not result
in a stable display.
At this point you should see
a trace that 1) lies within the
vertical range of the display,
2) shows at least three periods
of a waveform, and 3) is stable
enough to allow you to recognize
the overall characteristics of the
waveform. Next, start fine-tuning
the settings.
2) Adjust vertical and
horizontal settings
Start by adjusting the horizontal
timing, increasing the time per
division so that you see a wide
time span of the unknown wave-
form. From that view, reverse the
adjustment as required to narrow
the view to just what you want
to display.
Now adjust the vertical sensi-
tivity, expanding the waveform
vertically but ensuring that the
high and low points of the wave-
form do not exceed the vertical
span.
3) Adjust trigger settings
If needed, adjust the trigger set-
tings to stabilize the waveform
display. Or, you may want to
adjust the trigger delay to see
pre- or post-trigger details on the
waveform. Always start with the
trigger-level setting, adjusting
it so that it falls on a repetitive,
unique point on the rising or fall-
ing edge of a waveform.
As an example, with the oscil-
loscope trigger set to the rising
edge and the level set to the 50
% point, the following figures
illustrate the cause of an unsta-
ble waveform display.
After two successive updates
based on triggers 1 and 2, the
resultant trace will appear
unstable.
However, simply by manually
adjusting the trigger point to a
repetitive, unique point on the
edge, you can solve this problem
and produce a stable waveform
display.
When working with complex
signals like a series of pulses,
pulse width triggering may be
required. With this technique,
both the trigger-level setting
and the next falling edge of the
signal must occur within a speci-
fied time span. Once these two
conditions are met, the oscillo-
scope triggers.
Another technique is single-
shot triggering, by which the
oscilloscope will display a trace
only when the input signal meets
the set trigger conditions. Once
the trigger conditions are met,
the oscilloscope acquires and
updates the display, and then
freezes the display to hold the
trace.
Trig
Figure 5a. Trigger point set to 50 % point
on trace.
Trig
Figure 5b. Trigger point is set to the 50 %
point but due to the aberration on the lead-
ing edge in the second period, an additional
trigger results in an unstable display.
1st Trig 2nd
Trig
Figure 6a. At the first update, the scope
triggers on the first edge. On the second
update, the scope may trigger on the
second trigger point indicated.
Trig
Figure 6b. Unstable waveform display
caused by incorrect trigger level setting.
Trig
Figure 6c. Trigger level adjusted to a unique
repetitive position, outside the aberration on
the second period.
Trigger
Level (V)
Pulse Width (t)
Figure 7. Pulse width triggering will allow
you to set up the oscilloscope to trigger on a
specific pulse defined by level and time.
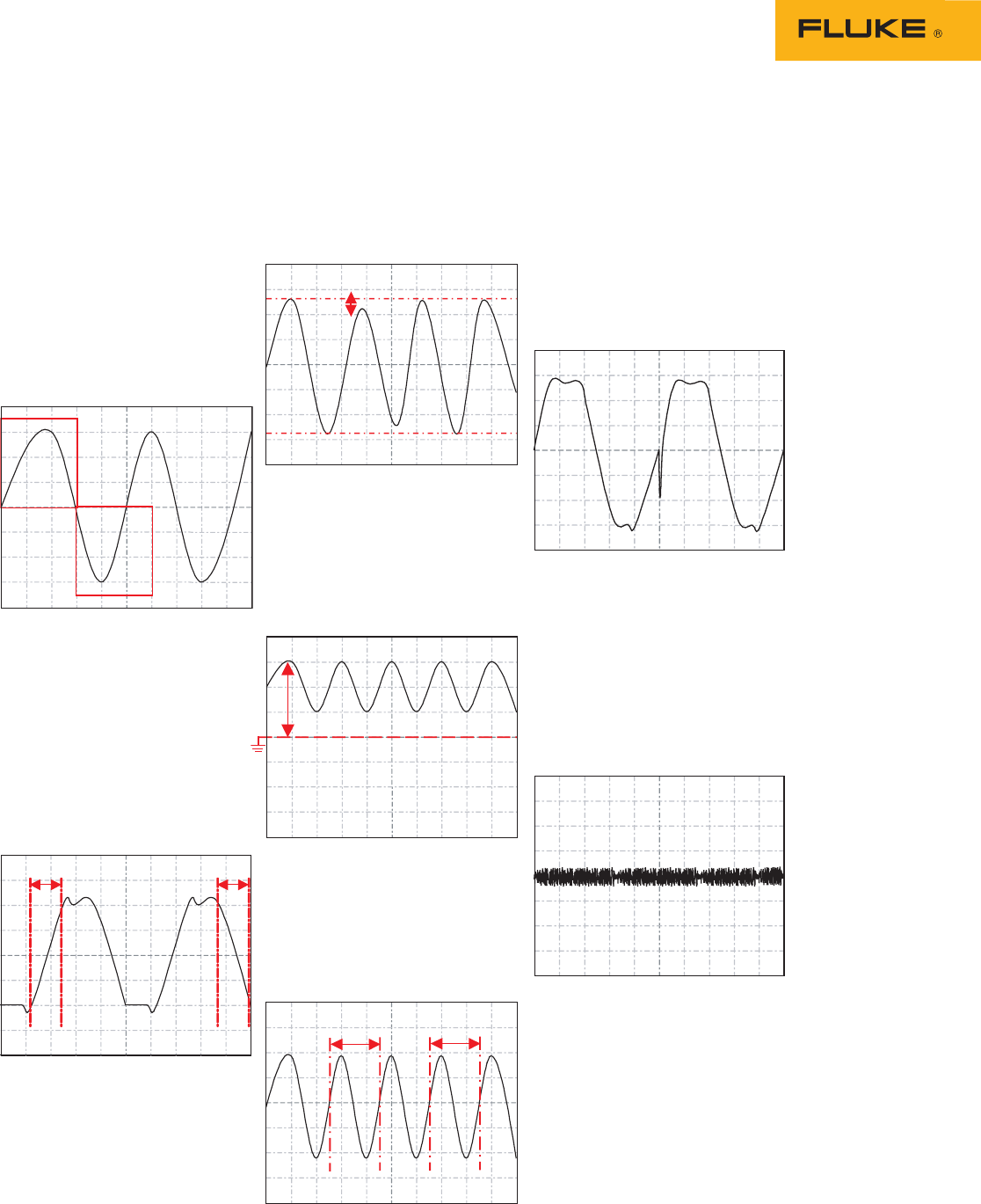
4 Fluke Corporation A first look at DSOs
Understanding and
reading waveforms
The majority of electronic wave-
forms encountered are periodic
and repetitive, and they conform
to a known shape. Here are the
factors to consider in analyzing
waveforms:
Shape. Repetitive waveforms
should be symmetrical. That is,
if you were to print the traces
and cut them in two like-sized
pieces, the two sides should be
identical. A point of difference
could indicate a problem.
Rising and falling edges.
Particularly with square waves
and pulses, the rising or fall-
ing edges of the waveform can
greatly affect the timing in digi-
tal circuits. It may be necessary
to decrease the time per division
to see the edge with greater
resolution.
Amplitude. Verify that the
level is within the operating
specifications of the circuit.
Also check for consistency, from
one period to the next. Monitor
the waveform for an extended
period of time, watching for any
changes in amplitude.
Amplitude offsets. DC-couple
the input and determine where
the ground reference marker
is. Evaluate any dc offset and
observe if this offset remains
stable or fluctuates.
Periodic waveshape. Oscil-
lators and other circuits will
produce waveforms with con-
stant repeating periods. Evaluate
each period in time using cursors
to spot inconsistencies.
1
2
Figure 8. If the two components of the
waveform are not symmetrical, there may be
a problem with the signal.
t t
Figure 9. Use cursors and the graticule
marks to evaluate the rise and fall times
of the leading and trailing edges of a
waveform.
Figure 10. Use horizontal cursors to identify
amplitude fluctuations.
F i g u r e 11. Evaluate waveform DC offsets.
t t
Figure 12. Evaluate period-to-period time
changes.
Waveform anomalies
Here are typical anomalies that
may appear on a waveform,
along with the typical sources of
such anomalies.
Transients or glitches. When
waveforms are derived from
active devices such as transistors
or switches, transients or other
anomalies can result from timing
errors, propagation delays, bad
contacts or other phenomena.
Noise. Noise can be caused
by faulty power supply circuits,
circuit overdrive, crosstalk, or
interference from adjacent cables.
Or, noise can be induced exter-
nally from sources such as dc-dc
converters, lighting systems and
high-energy electrical circuits.
Figure 13. A transient is occurring on the
rising edge of a pulse.
Figure 14. A ground reference-point mea-
surement showing induced random noise.
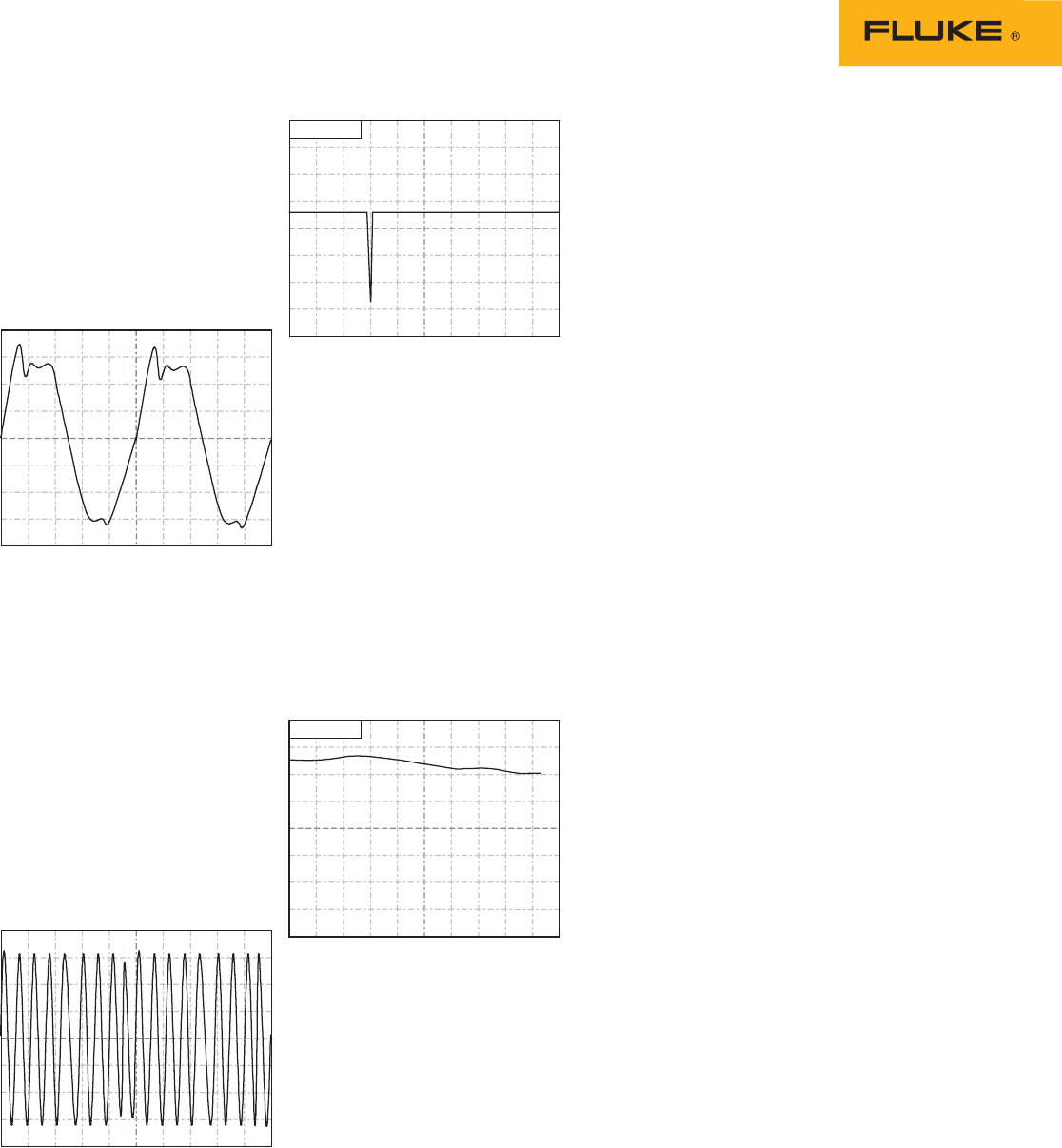
5 Fluke Corporation A first look at DSOs
Ringing. Ringing can be seen
mostly in digital circuits and in
radar and pulse-width-modula-
tion applications. Ringing shows
up at the transition from a rising
or falling edge to a flat dc level.
Check for excessive ringing,
adjusting the time base to give a
clear depiction of the transition-
ing wave or pulse.
Momentary fluctuation.
Momentary changes in the
measured signal generally result
from an external influence such
as a sag or surge in the mains
voltage, activation of a high-
power device that is connected
to the same electrical grid, or a
loose connection. Use the DSO’s
slowest time-base setting or
the paperless recording or “roll”
mode. Start at the input and
watch the acquired waveform
over long time spans to track
down the source of the problem.
Drift. Drift—or minute changes
in a signal’s voltage over time—
can be tedious to diagnose. Often
the change is so slow that it is
difficult to detect. Temperature
changes and aging can affect
passive electronic components
such as resistors, capacitors and
crystal oscillators. One problem-
atical fault to diagnose is drift in
a reference dc voltage supply or
oscillator circuit. Often the only
solution is to monitor the mea-
sured value (V dc, Hz, etc.) over
an extended time.
Figure 15. Excessive ringing occurring on
the top of the square wave.
Figure 16a. A momentary change of
approximately 1.5 cycles in the amplitude of
the sinewave.
110 Vac
Figure 16b. Using an oscilloscope with a
paperless recorder mode allows plotting of
the amplitude (voltage level) over time.
1. 01 kHz
Figure 17. Performing a frequency
measurement on a crystal oscillator that
has been trend-plotted over an extended
period (days or even weeks) can highlight
the affect of drift caused by temperature
changes and aging.
Diagnosing problems
Although successful trouble-
shooting is both an art and a
science, adopting a troubleshoot-
ing methodology and relying on
the functionality of an advanced
DSO can greatly simplify the
process.
Good troubleshooting practices
will save time and frustra-
tion. The time-tested approach
known as KGU, Known Good Unit
comparison, accomplishes both
goals. KGU builds on a simple
principle: an electronic system
that is working properly exhibits
predictable waveforms at critical
nodes within its circuitry, and
these waveforms can be cap-
tured and stored. This reference
library can be stored right on the
DSO as an online resource, or
can be printed out to serve as a
hard-copy reference document. If
the system or an identical system
later exhibits a fault or failure,
waveforms can be captured from
the faulty system—called the
Device Under Test (DUT)—and
compared with their counterparts
in the KGU. Consequently, the
DUT can either be repaired or
replaced.
To build a reference library,
start by identifying appropriate
test points, or nodes, on the DUT.
Now, run the KGU through its
paces, capturing the waveform
from each node. Annotate each
waveform as required.
Get into the habit of always
documenting key waveforms
and measurements. Having a
reference to compare to will
prove invaluable during future
troubleshooting.
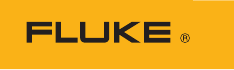
6 Fluke Corporation A first look at DSOs
Troubleshooting
Whichever troubleshooting
scenario below is appropriate
at the time, remember that it’s
important to inspect waveforms
for fast-moving transients or
glitches, even if a spot check of
the waveform reveals no anoma-
lies. These events can be difficult
to spot, but the high sampling
rate of today’s DSOs, together
with effective triggering, makes
it possible.
DUT with KGU. This approach
assumes that you have access to
a KGU and a reference library.
1. Make sure the DUT and KGU
are set up in identical operat-
ing modes.
2. Starting at a high-level point
in the system or block dia-
gram, use the DSO to look
for the presence or absence
of fundamental signals. For
example, look for a line-
voltage supply, as well as
subsequent dc supply voltages
to the various subsystems.
This requires probing the
major input and output signals
at major nodes in the system.
3. Compare signals at key nodes
while changing the operat-
ing mode to see if a failure
occurs. With signals from both
devices available, you have
two options:
• Display the live waveform
from the KGU on Channel 1
of the DSO, and display the
live waveform from the DUT
on Channel 2.
• Capture a trace from the
KGU and overlay it with a
trace from the DUT. Perform
a waveform-compare or
pass/fail test.
• The ScopeMeter 190 Series
II has 4 input channels
which means that 4 signals
from 4 different sources can
be compared.
4. Continue with this process
until you note a variance
between the DUT and KGU
waveforms.
DUT with Circuit Diagrams.
This approach assumes that no
KGU and no waveform reference
library for the DUT are available,
but that circuit diagrams of the
DUT can be located.
1. Review the circuit diagrams to
understand the basic opera-
tion of the DUT.
• Analog circuits such as
oscillators, amplifiers and
signal conditioners (attenu-
ators, filters and dividers)
should exhibit uniform
waveform patterns.
• Digital circuits such as
gates, switches and pro-
cessors should display
waveforms with predictable
amplitudes, pulse periods
and even pulse patterns.
2. Starting at a high-level point
in the system or block dia-
gram, use the DSO to look
for the presence or absence
of fundamental signals. For
example, look for a line-
voltage supply, as well as
subsequent dc supply voltages
to the various subsystems.
This requires probing the
major input and output signals
at major nodes in the system.
3. Use the storage capability
of the DSO to capture and
compare waveforms while
changing the operating mode
of the DUT.
• Visualize a theoreti-
cal “good” waveform and
compare it to the waveform
displayed on the DSO. Try
to identify any obvious
anomalies.
4. Use the horizontal or vertical
cursors to quickly evaluate if
the time or amplitude of the
trace falls within the time or
amplitude ranges suggested
by the circuit design.
Complex DUT, No Circuit
Diagrams. This approach
assumes that the DUT is a fairly
complex system, that no KGU is
available, and that only limited
DUT documentation is available.
1. Study the circuit cards, look-
ing for common components
and circuits, and identify
high-level test points in the
system and check for the
presence or absence of funda-
mental signals. As before, start
at one point and work your
way backwards probing the
major input and output signals
at major nodes in the system.
2. Compare waveforms at key
nodes while changing the
operating modes to see if a
failure occurs. Store these
waveforms.
3. If an examination of the DUT
and analysis of waveforms at
key circuit nodes reveal no
obvious faults, use the DSO’s
storage capability to solicit the
aid of peers.
• Identify “suspect” wave-
forms from the DUT.
• Use the DSO’s Extract or
Output mode to save these
waveform files in a bitmap
(.bmp) format.
• Email the files to a peer or
factory expert anywhere in
the world for aid in trouble-
shooting the circuit.
4. Using outside experts, go
through each key node and
one by one eliminate the obvi-
ous good nodes, eventually
narrowing your focus to obvi-
ous faulty or suspect nodes.
Fluke Corporation
PO Box 9090, Everett, WA 98206 U.S.A.
Fluke Europe B.V.
PO Box 1186, 5602 BD
Eindhoven, The Netherlands
Fluke. Keeping your world
up and running.®
For more information call:
In the U.S.A. (800) 443-5853 or
Fax (425) 446-5116
In Europe/M-East/Africa +31 (0) 40 2675 200 or
Fax +31 (0) 40 2675 222
In Canada (800)-36-FLUKE or
Fax (905) 890-6866
From other countries +1 (425) 446-5500 or
Fax +1 (425) 446-5116
Web access: http://www.fluke.com
©2005-2011 Fluke Corporation.
Specifications subject to change without notice.
Printed in U.S.A. 3/2011 2432735B D-EN-N
Pub_ID: 10882-eng, rev 01
Modification of this document is not
permitted without written permission
from Fluke Corporation.