Fluke 810 Data Sheet FPG8601™ Forced Balanced Piston Gauge
2015-09-09
: Fluke Fluke-810-Data-Sheet-810347 fluke-810-data-sheet-810347 fluke pdf
Open the PDF directly: View PDF .
Page Count: 2
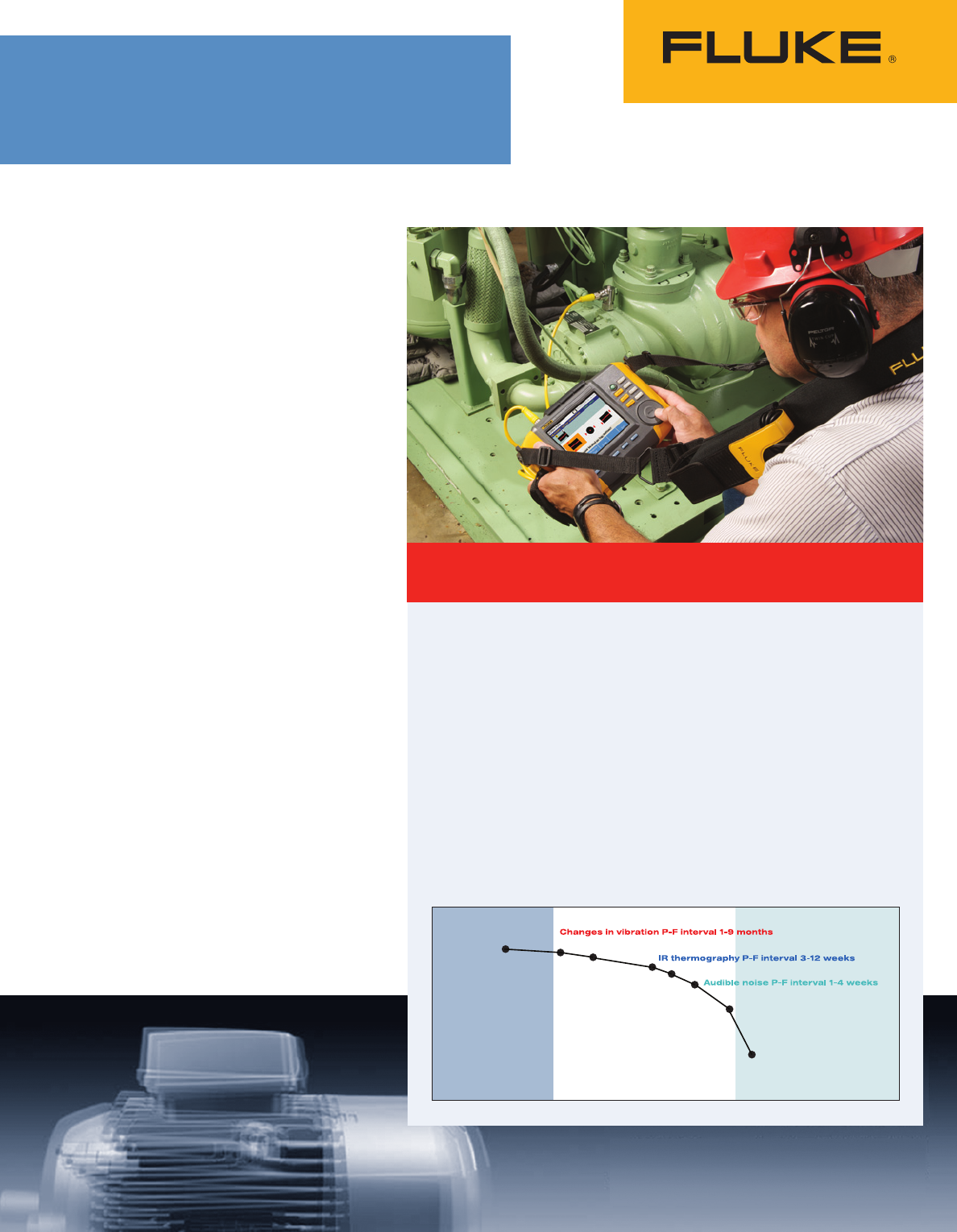
Point where
failure starts
to occur
Heat by touch P-F interval 1-5 days
F= Failure
P= Potential failure
Quantitative PM P-F interval 5-8 weeks
Wear debris in oil P-F interval 1-6 months
PP1 P2
P3
P4
P5
P6
F
The P-F Curve, Adapted from John Moubray’s book “Reliability Centered Maintenance II”
Machine health refers to the overall condition of equipment as
a result of normal use, maintenance and repair actions and/
or external events that impact the operation of the equipment.
Vibration remains one of the earliest indicators of a machine’s
health. Vibration can identify problems before other symptoms—
heat, sound, electrical consumption, lubricant impurities—can
be detected.
Over half of unplanned downtime is attributed to mechanical
failures. While many things can impact the life of a machine,
once the first signs of failure appear a machine generally has
a matter of months before failing completely. Vibration testing
provides a way to determine where the machine is on the failure
curve and react appropriately.
What is machine health and how
does vibration play a role in it?
The Fluke 810 Vibration Tester:
saving money has never been
this easy!
Vibration monitoring is a powerful
maintenance practice which has never
been widely applied. To understand and
gain competence using traditional vibra-
tion monitoring equipment, companies
had to:
1. Make significant investments for initial
setup and training.
2. Change the maintenance culture from
preventive maintenance to predic-
tive maintenance or condition-based
monitoring.
3. Allow two years—or more—for
dedicated resources to be trained and
become proficient in understanding
vibration analysis.
Fluke redefines mechanical
troubleshooting….
Fluke has developed an innovative
solution to help teams take control of
mechanical maintenance by diagnosing
issues before they become real problems.
The Fluke 810 Vibration Tester instantly
identifies mechanical faults, their location
and severity.
Benefits of the Fluke 810
• Anticipate problem areas before
failure and prioritize repair actions
• Reduce spare parts inventories
• Extend the life of existing equipment
• Reduce consulting costs by putting the
expertise in the technician’s hands
Fluke 810 Vibration Tester
Get answers now.
Start saving money now.
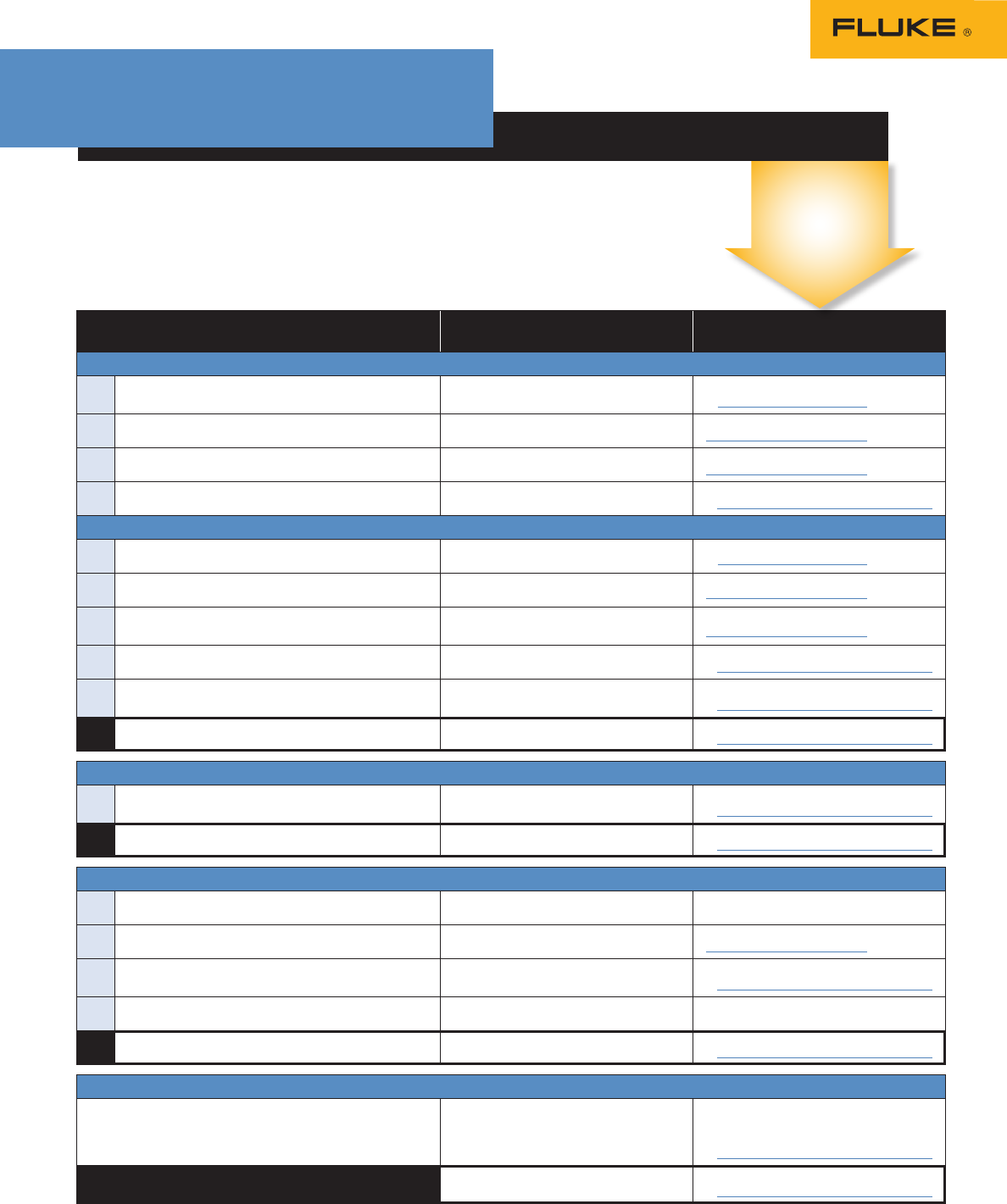
Cost of downtime/repair Example ROI calculation
(Medium size manufacturing facility)
Calculate your ROI savings
Lost production cost
1Average cost of unscheduled downtime due to
mechanical failures $10,000/hr $
2Average downtime for each equipment failure 8 hrs hrs
3Average number of events (failures) per year 5 failures failures
LPC Average annual lost production cost ($10,000 x 8) x 5 = $400,000 $
Labor and spare inventory cost
4Average (regular + overtime) labor cost $30/hr $ /hr
5Average time to repair one piece of equipment 8 hrs hrs
6Average number of technicians assigned for each
equipment failure 2 technicians technicians
7Average equipment and parts cost/failure $5,000 $
TMC Average annual time and material cost to recover
from downtime
($30/hr x 8 hrs x 5 failures x 2 techs) +
($5000 x 5 failures) = $27,400 $
TDC Total downtime cost = LPC + TMC $400,000 + $27,400 = $427,400 $
Outsourcing cost
OC Vibration analysis - annual consultant fee
(based on $8000-$15,000 range) $10,000 $
TOC Total outsourcing costs $10,000 $
Cost of ownership
8The Fluke 810 Vibration Tester $8,000 $8,000
9Number of drive trains to be tested/month 100 drive trains drive trains
10 Average cost of dedicated, experienced technician
for testing (Assume 0.5 hr/motor/month)
0.5 hr/month/motor x 100 drive trains x
12 mos/yr x $30/hr = $18,000 $
11 Training cost $0 $0
COO Initial investment (First year cost of ownership) ($8,000 + $18,000) = $26,000 $
Payback
Annual savings from owning a 810 Vibration Tester
(In the example ROI, it is assumed that 50% of the
annual unplanned downtime cost and 100% of annual
outsourcing costs are eliminated with the 810.)
$427,400 x 0.5 + $10,000 = $223,700
$
Months to payback.
(First year cost of ownership/annual savings x 12) $26,000/$223,700 x 12 ≈ 1.4 months $
Current machine health alternatives do not offer sustainable ROI. They require
significant upfront investment and high ongoing training and support costs.
The Fluke 810 Vibration Tester offers a more practical approach. There is
minimal upfront investment with a positive pay off only months from setup.
No additional training costs. No additional software fees.
Start
saving
money
now!
See for yourself
The Fluke 810 Vibration
Tester ROI worksheet
©2010 Fluke Corporation. Specifications subject to change without notice. 11/2010 3970205A F-EN
Modification of this document is not permitted without written permission from Fluke Corporation.