Fomotech ALPHA510SERIES Industrial Remote Control User Manual Manual
Fomotech International Corp. Industrial Remote Control Manual
Fomotech >
Exhibit D Users manual per 2 1033 b4
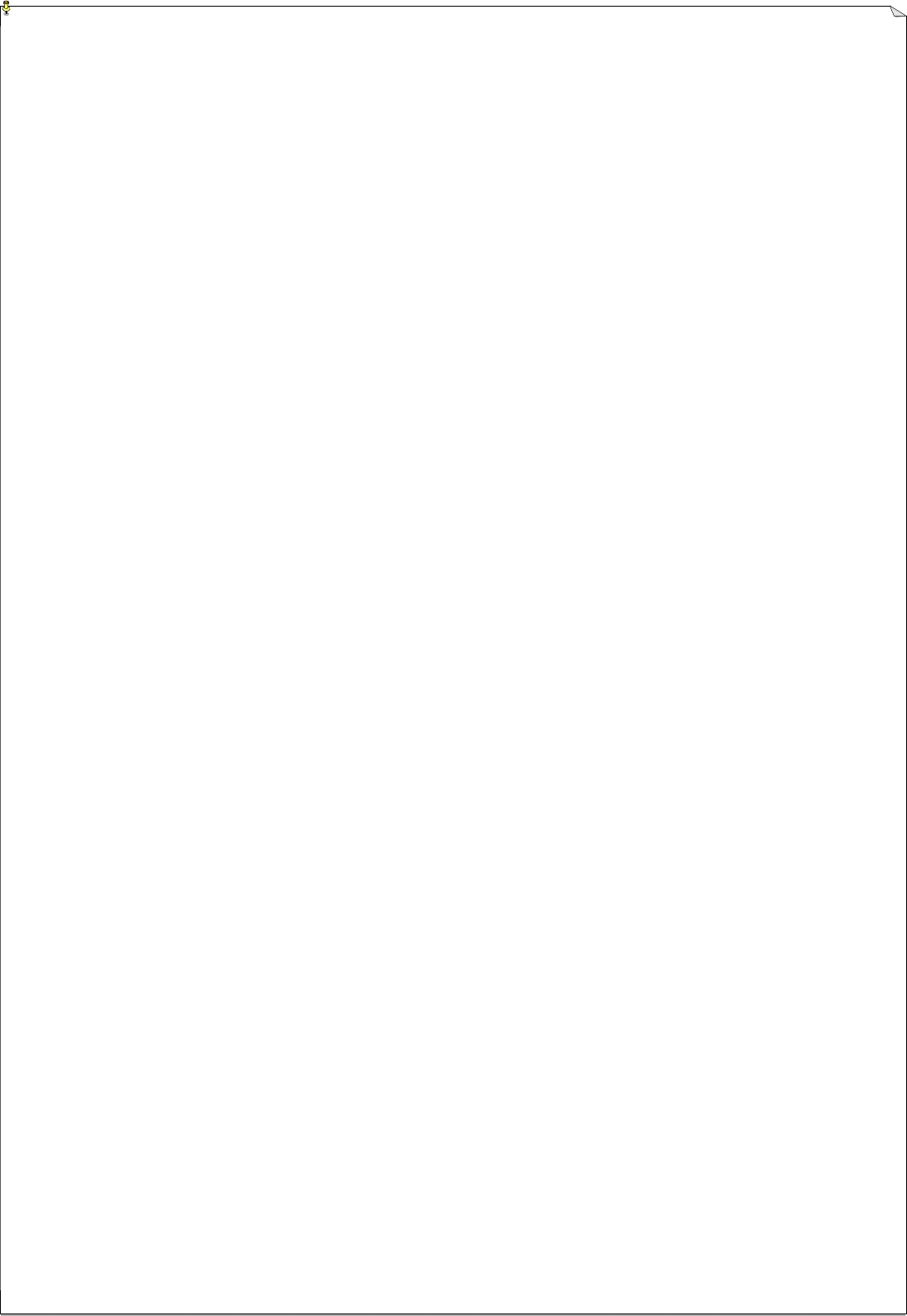
1
T
TA
AB
BL
LE
E
O
OF
F
C
CO
ON
NT
TE
EN
NT
TS
S
Page
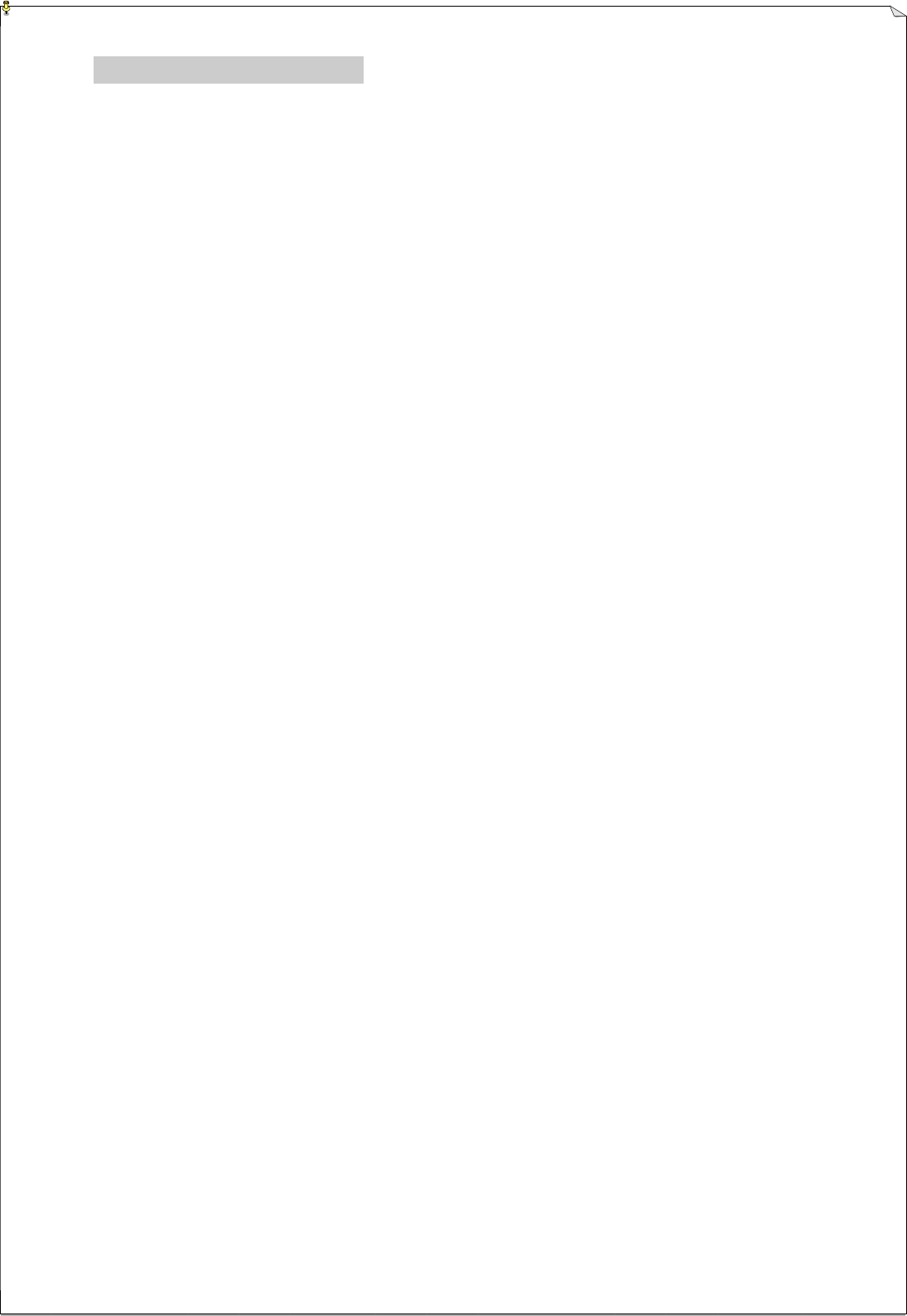
1.
INTRODUCTION
The Alpha 580 is highly reliable industrial remote control system. The versatile features of the
Alpha 580 permit its use in many different remote control applications. The system can be used
to control cranes, hoists, trolleys, mining equipment, building construction equipment,
automatic control systems, and many others.
The Alpha 580 radio control system incorporates numerous redundant safety circuits that
guaranty maximum security and ensure the system is resistant to outside interference. The
major features of the Alpha 580 are as follow:
* The system uses advanced microprocessors which utilizes highly evolved software that
have redundant error checking and correcting capabilities to ensure 100 % error-free
transmission, decoding, and control of the output relays. These highly evolved software
include CRC (Cyclic Redundancy Check codes) and Hamming Codes.
* To insure maximum operating safety, the Alpha 500 series incorporate many safety features.
Some of these safety features include receiver self-diagnosing, transmitter pushbutton
self-diagnosing, transmitter low voltage detection/warning, and transmitter/receiver auto
shutdown after 1 minute of transmitter low voltage warning.
* The encoder/decoder system utilizes advanced microprocessor. The availability of 32,768
sets of unique ID codes will ensure that only commands from the matching control
transmitter can be carried out without any interference from other radio systems. A special
programmable integrated circuit is used to insure the unit can not simultaneously command
conflicting movements.
* Full SMT design for system stability.
The Alpha 580 radio control system consists of a transmitter handheld, and a receiver unit. The
transmitter casing is molded using an industrial strength composite material which is impervious
to dust, water, oil, acids, alkaline, heat, sunlight, and as well as being resistant to deformation
due to long term use in harsh environments. The pushbuttons are also constructed from
industrial strength composite material with a minimum of up to one million cycles. For power
saving, the transmitter unit uses special high efficiency power saving circuits that requires only
two “AA” alkaline batteries (UM-3).
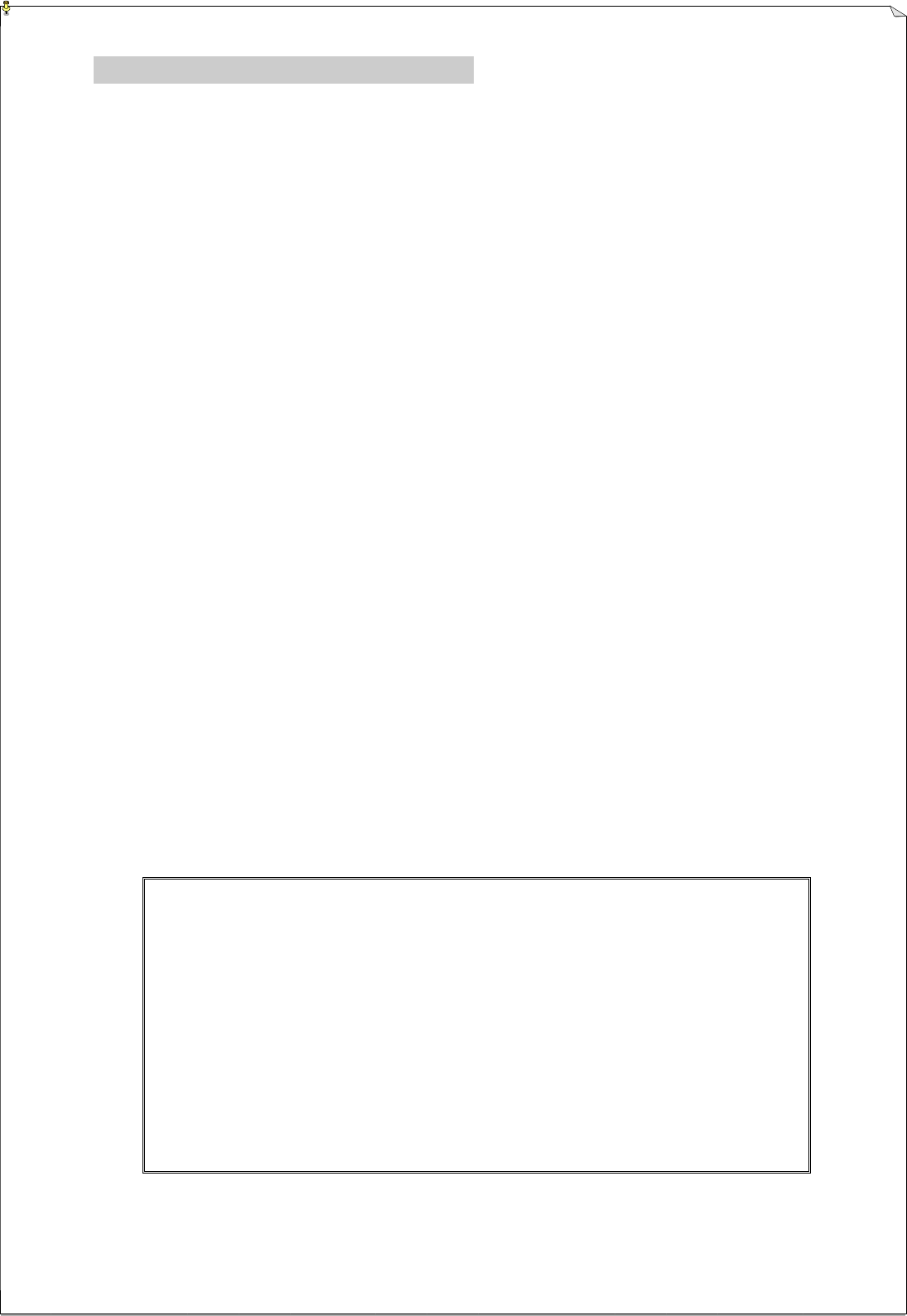
3
2.
SAFETY INSTRUCTION
The Alpha 580 system is relatively simple to use. However, it is very important to observe the
proper safety procedures during operation. When use properly the Alpha 580 system will
enhance productivity and efficiency in the workplace.
The following instructions should be strictly followed:
1. Make a daily check of the transmitter casing and pushbuttons. Should it appear that
anything could inhibit the proper operation of the transmitter unit, it should be immediately
removed from service.
2. The transmitter voltage should be checked on a daily basis. If the voltage is low, the two
"AA" alkaline batteries should be replaced.
3. The emergency stop pushbutton (EMS) should be checked at the beginning of each shift to
ensure they are in the proper working order.
4. In the event of an emergency, activate the emergency stop pushbutton immediately. Then
turned the power “off” from the main power source of the equipment.
5. The power switch should be turned “off” after use and should never left the power “on”
when the unit is unattended.
6. Do not use the same RF channel and ID code as any other unit in use at the same facility.
7. Ensure the wrist strap is worn at all time during operation to avoid accidental dropping.
8. Never operate a crane or equipment with two (2) transmitter units at the same time with
same RF channel and ID code.
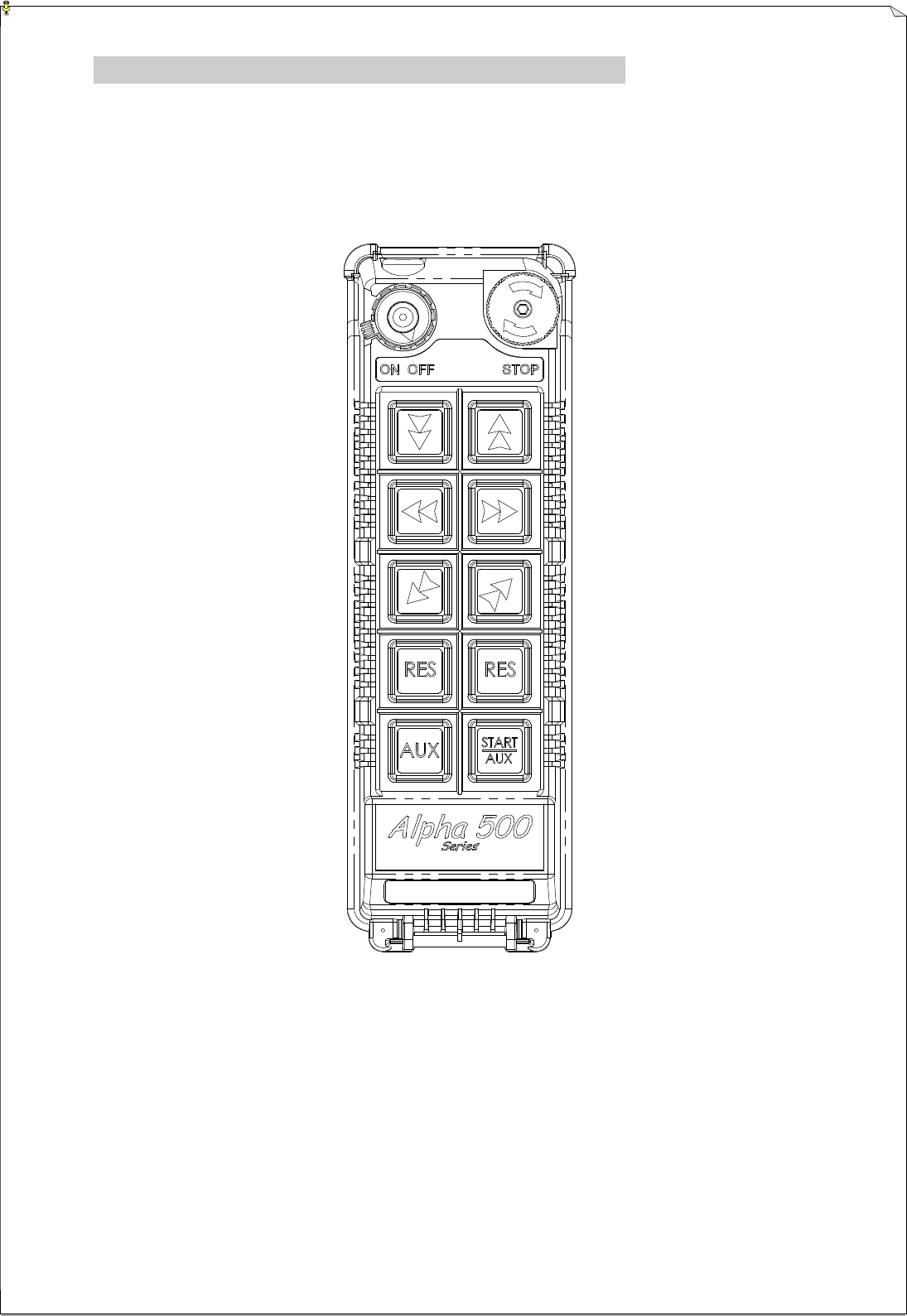
4
3.
PUSHBUTTON CONFIGURATION
The Alpha 580 model can be configured from 3 to 5 motions with 2-speed pushbuttons and an
emergency stop button (EMS).
(Fig. 1) Pushbutton Placements
RES 2-Speed pushbuttons which can be used for the 4th motion or for any other
functions.
AUX 2-Speed pushbuttons which can be used for the 5th motion or for any other
functions.
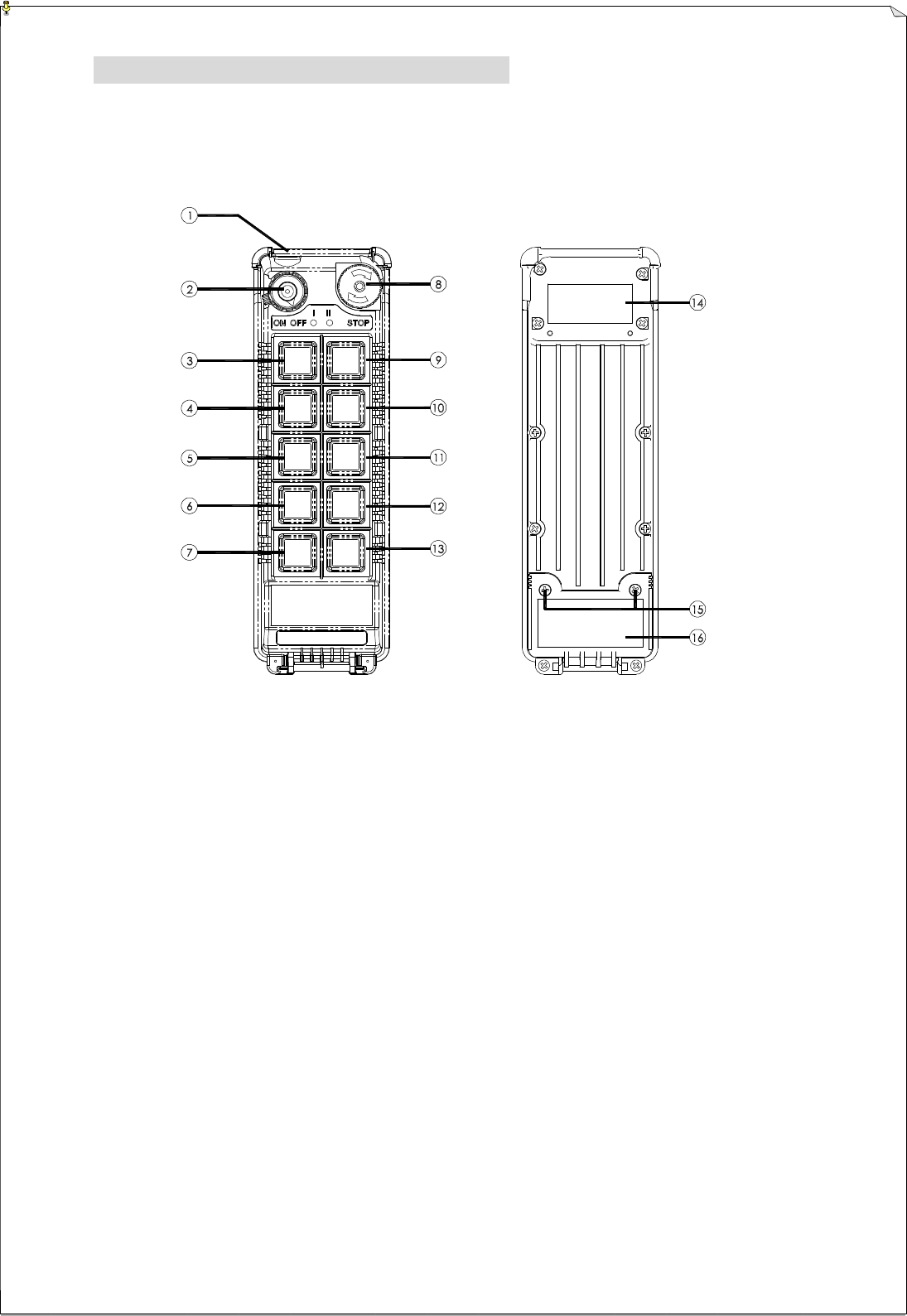
5
4.
TRANSMITTER OUTLINE
4.1 External View
(Fig. 2) Front
View
1) Transmitter enclosure 8) Emergency Stop (EMS) 15) Battery Screws
2) Power switch (ON/OFF) 9) Pushbutton #1 16) Batter Cover/FCC ID
3) Pushbutton #2 10) Pushbutton #3
4) Pushbutton #4 11) Pushbuttons #5
5) Pushbutton #6 12) Pushbutton #7 (A1)
6) Pushbutton #8 (A2) 13) Pushbutton #9 (A3)
7) Pushbutton #10 (A4) 14) System Information
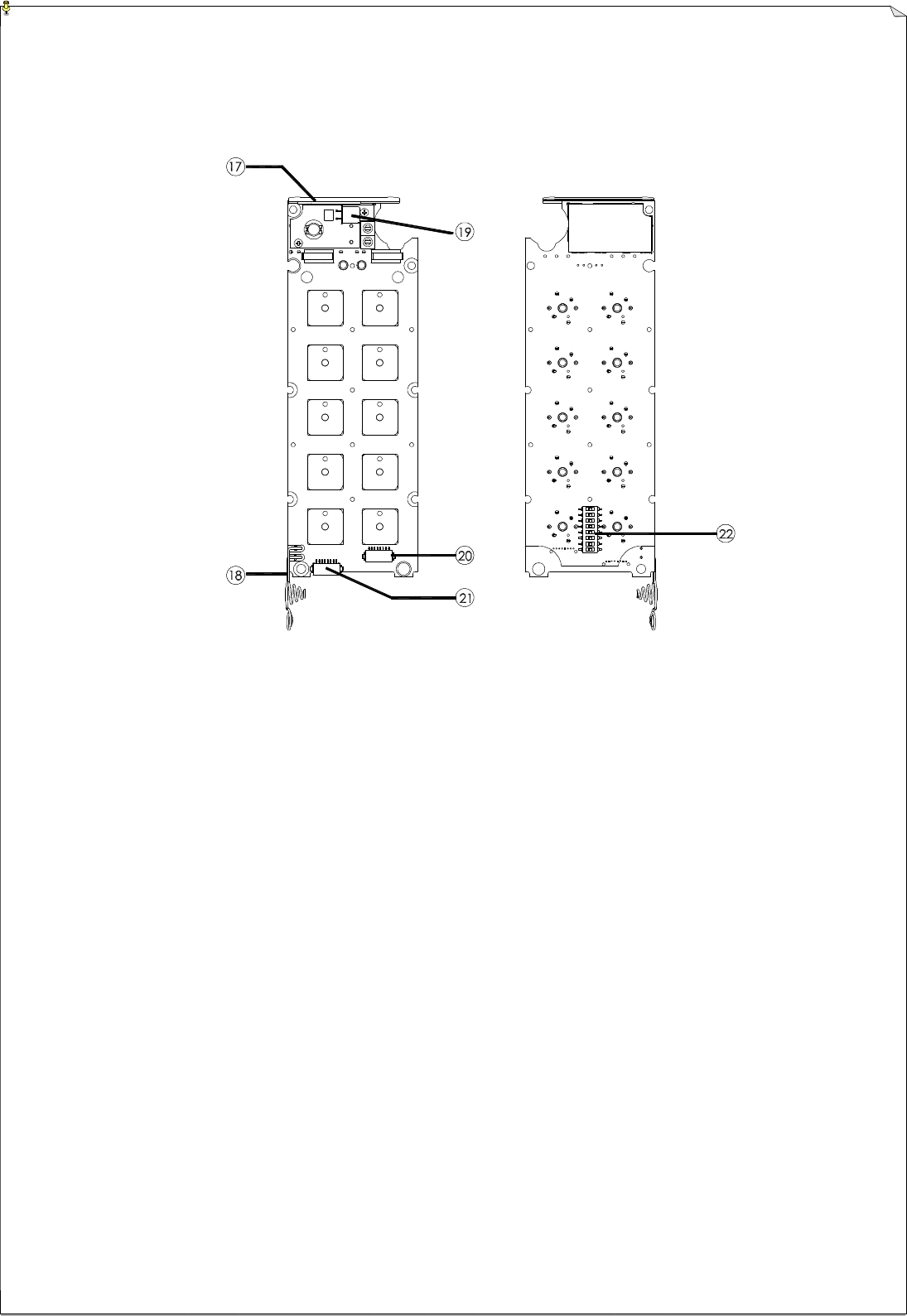
6
4.2 Internal View
(Fig. 4)
Front View
(Fig. 5) Back View
17) TX Module/Antenna 20) Auxiliary Connector
18) Battery Contact 21) Programming Port
19) TX Quartz Crystal 22) ID Code Dip-Switch
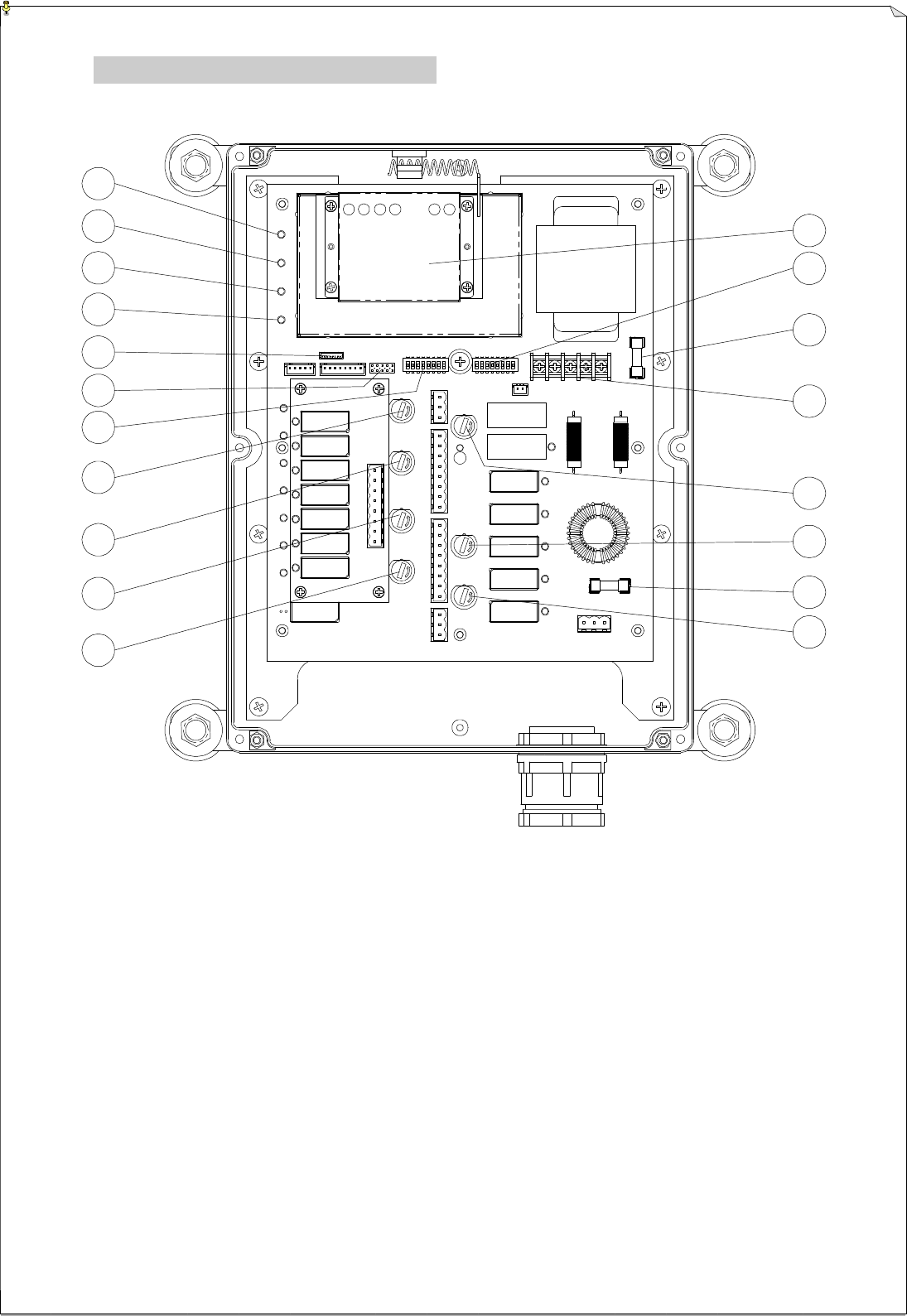
7
18
19
17
16
15
14
12
5
9
7
8
6
1
3
4
2
10
11
13
5.
RECEIVER OUTLINE
(Fig. 6) Receiver Internal Assembly
1) Power LED Display 8) E/W Fuse 15) Voltage Selector
2) SQ Led Display 9) N/S Fuse 16) MAIN Fuse
3) System Status LED Display 10) A1/A2 Fuse 17) A4 Fuse
4) Relay COM LED Display 11) A3 Fuse 18) Primary Power Fuse
5) Programming Port 12) RX Module 19) L/V Fuse
6) Jumper Settings 13) ID Code Dip-Switch
7) Function Settings 14) Secondary Power Fuse
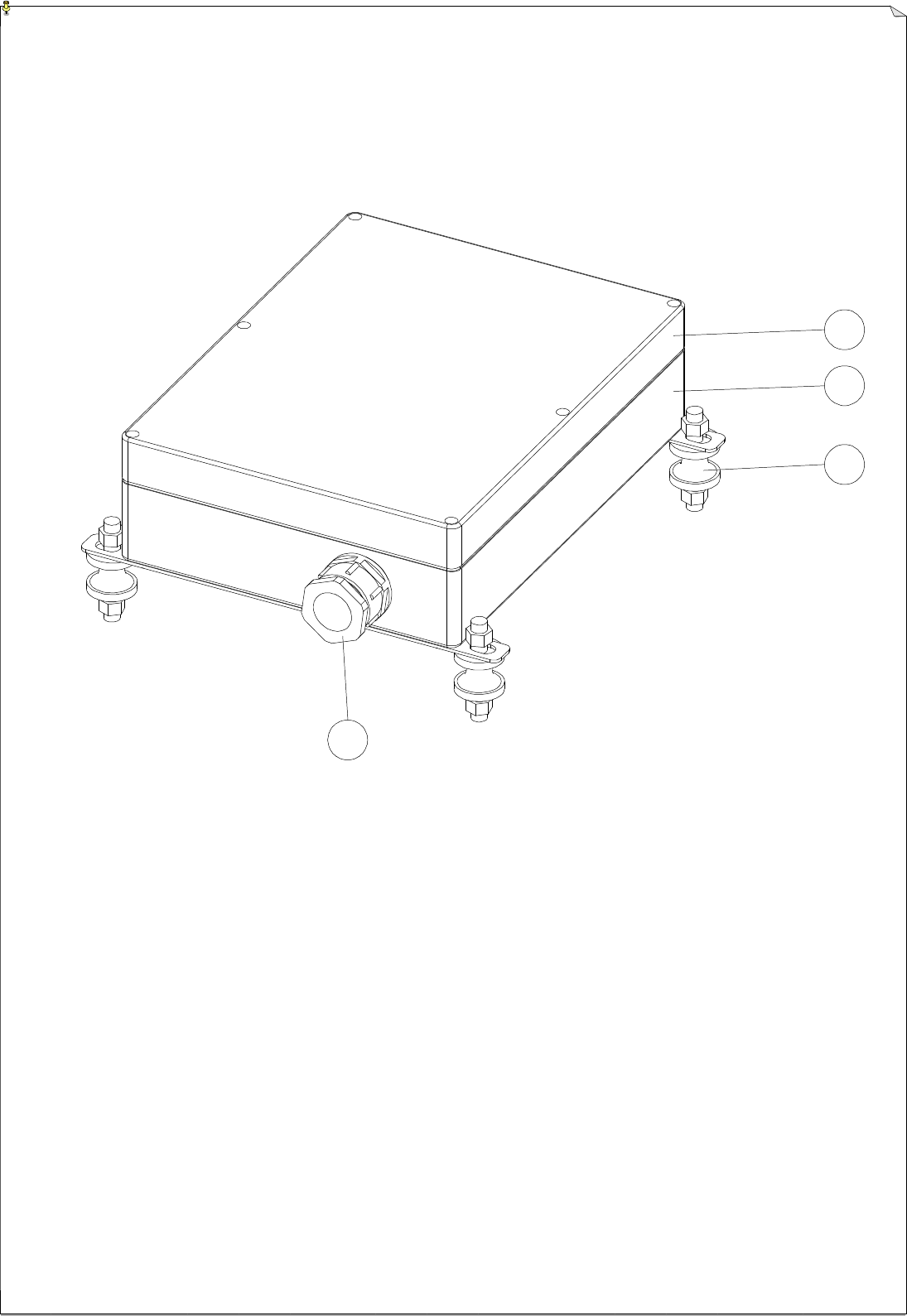
8
1
2
3
4
(Fig. 7) Receiver External Assembly
1) Transparent top cover 3) Mounting bracket with shock absorbers
2) Light-gray colored base 4) Cable gland (PG-29)
* POWER ~ AC Power Source Indicator “On" AC input power supplied.
“Off” No AC input power.
* SQ ~ RF Signal Indicator "On" RF signals received.
"Off" No RF signals received.
* RELAY_COM ~ DC Power Source to Relays “On” DC power to relays.
“Off” No DC power to relays.
* STATUS ~ Receiver System Status LED Display Please refer to page 14.
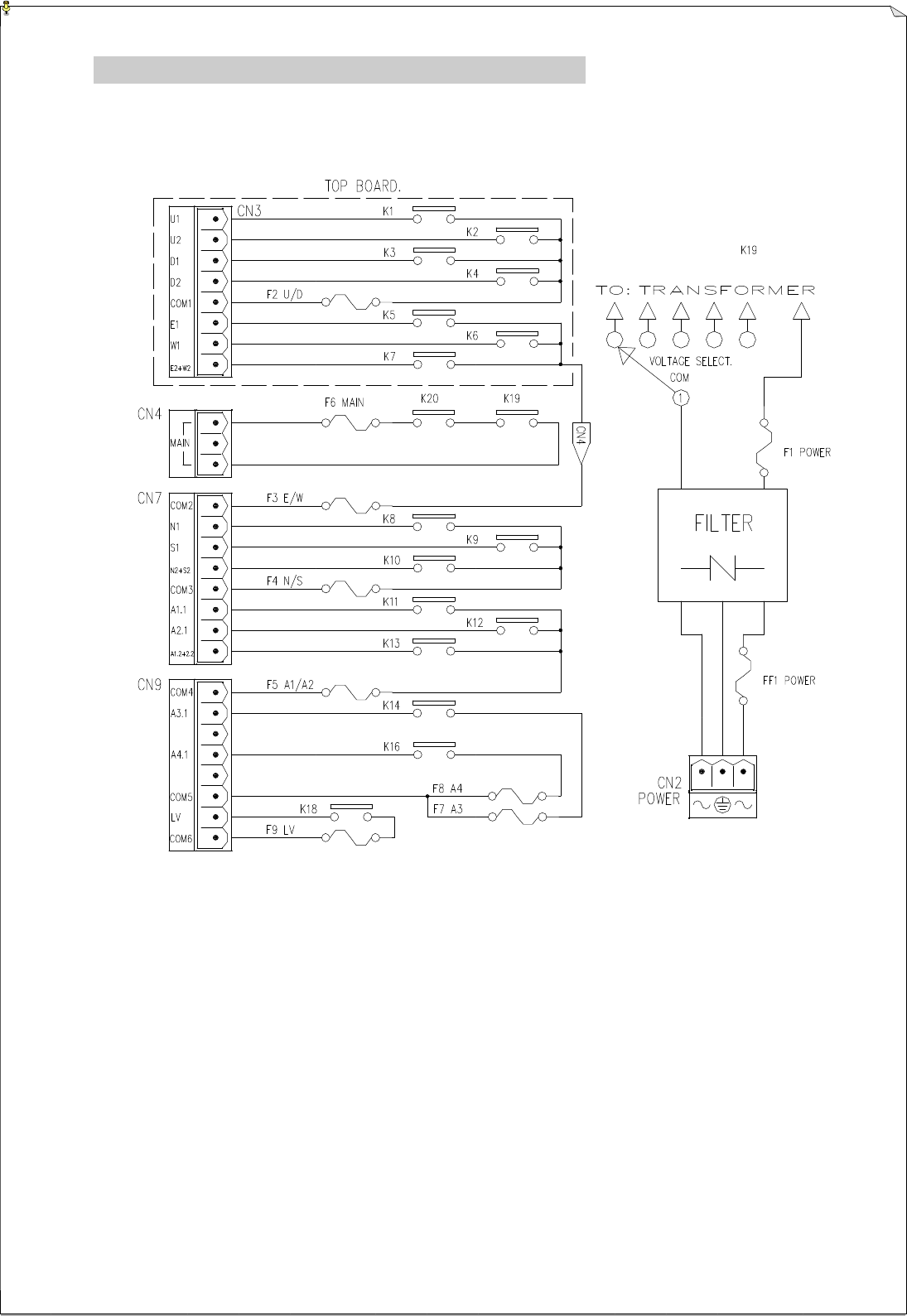
9
6.
OUTPUT CONTACT DIAGRAM
NC No connection
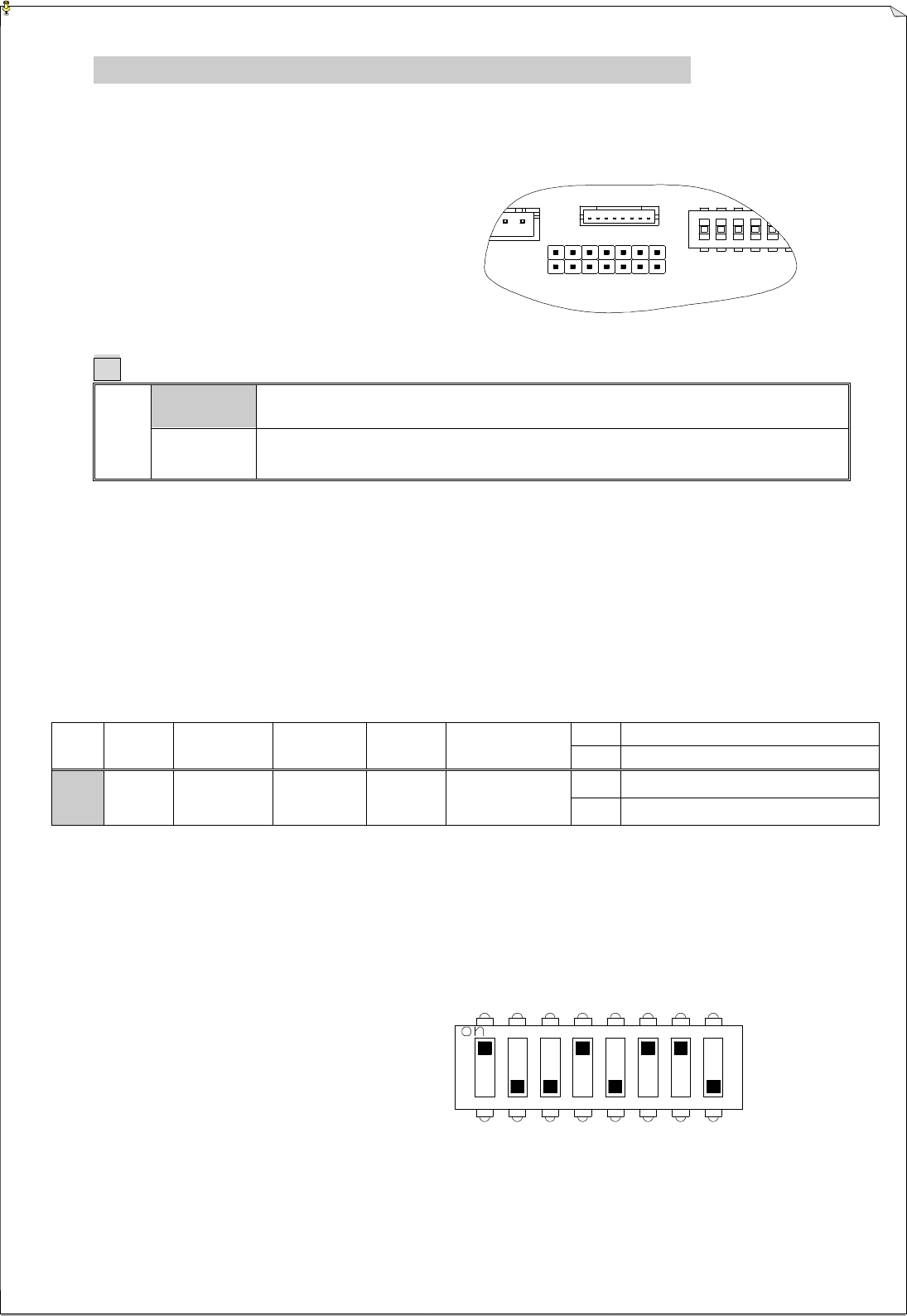
10
JP1
JP2
JP3
JP4
JP5
JP6
JP7
7.
SYSTEM SETTING CONFIGURATION
7.1 Jumper Settings (JP3)
Manufacture settings.
Open Low voltage warning only; receiver MAIN will not be deactivated.
JP3
Short After one minute of low voltage warning, the transmitter
power and
the receiver MAIN will be deactivated. (see note B)
Note A: JP1, JP2, JP4, JP5, JP6, and JP7 not applicable for the Alpha 580 model.
Note B: If transmitter low voltage occurs during operation, other than transmitter itself will display visual
warning, it will also send out a low voltage signal to the receiver to activate its external low voltage
warning device. By connecting a horn, buzzer, or siren to the LV-relay output will ensure that the
operator will clearly notice the low voltage warning even in hard to see or hear environments. After
one minute of low voltage warning, to insure maximum safety, both the transmitter power and the
receiver MAIN will be deactivated. For proper battery replacement, you must first turn “off” the
transmitter power, replace the batteries, and then turn the power switch back “on” again to reactivate
the transmitter and the receiver unit.
YES Work Resumes
JP3
Short System On
Work in Progress
Transmitter Low
Voltage Occurs LV Warning Change Batteries
within 1 Minute NO Transmitter and Receiver MAIN Deactivated.
YES Work Resumes
JP3
Open System On
Work in Progress
Transmitter Low
Voltage Occurs LV Warning Change Batteries
within 1 Minute NO Only Transmitter Unit Deactivated.
7.2 Security ID Code Setting
The ID code dip-switch is located on the back side of the encoder board (refer to Fig. 5 on page
6) and the decoder/relay board (refer to Fig. 6 on page 7).
Example : ID code 10010110
Top location : “1”
Bottom location : “0”
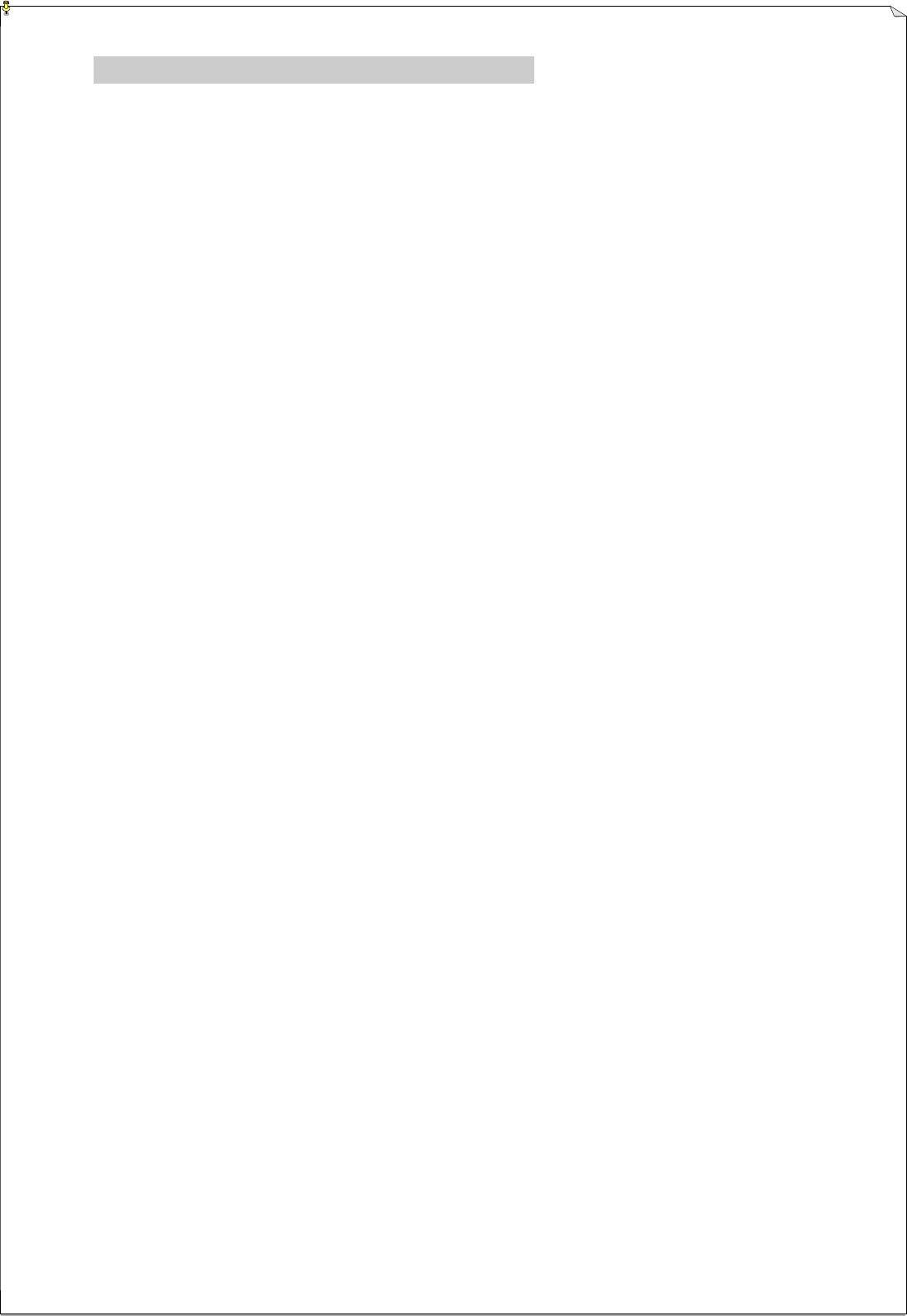
11
8.
RECEIVER INSTALLATION
8.1 Preparation For Installation
1. Required Tools:
(1) Flat Head Screwdriver (-)
(2) Phillips Head Screwdriver (+)
(3) Multi-Meter
(4) 14mm Wrench x 2
(5) 10.5mm Drill-Bit
2. Ensure receiver is not set to the same channel and ID code as any other units in
operation at the same facility.
3. Prior to installation, make sure the equipment itself is working properly.
4. Use the multi-meter to check the voltage source available and ensure receiver voltage
setting is correct for this voltage.
5. Prior to installation, switch “off” the main power source to the equipment.
8.2 Step By Step Installation
1. The location selected should have the antenna visible from all areas where the
transmitter is to be used.
2. The location selected should not be exposed to high levels of electrical noise.
3. Ensure the selected location has adequate space to accommodate the receiver
enclosure.
4. Make sure the receiver unit is in upright position (vertical).
5. The distance between the antenna and the control panel should be as far apart as
possible (see diagram next page).
6. Drill 4 holes on the control panel (10.5mm).
7. Tightened the bolt nuts provided.
8. If the control panel has a plastic surface, extended grounding wire should be used.
9. For system wiring, please refer to the output contact diagram on page 9.
10. Ensure all wiring is correct and safely secured and all screws are fastened.
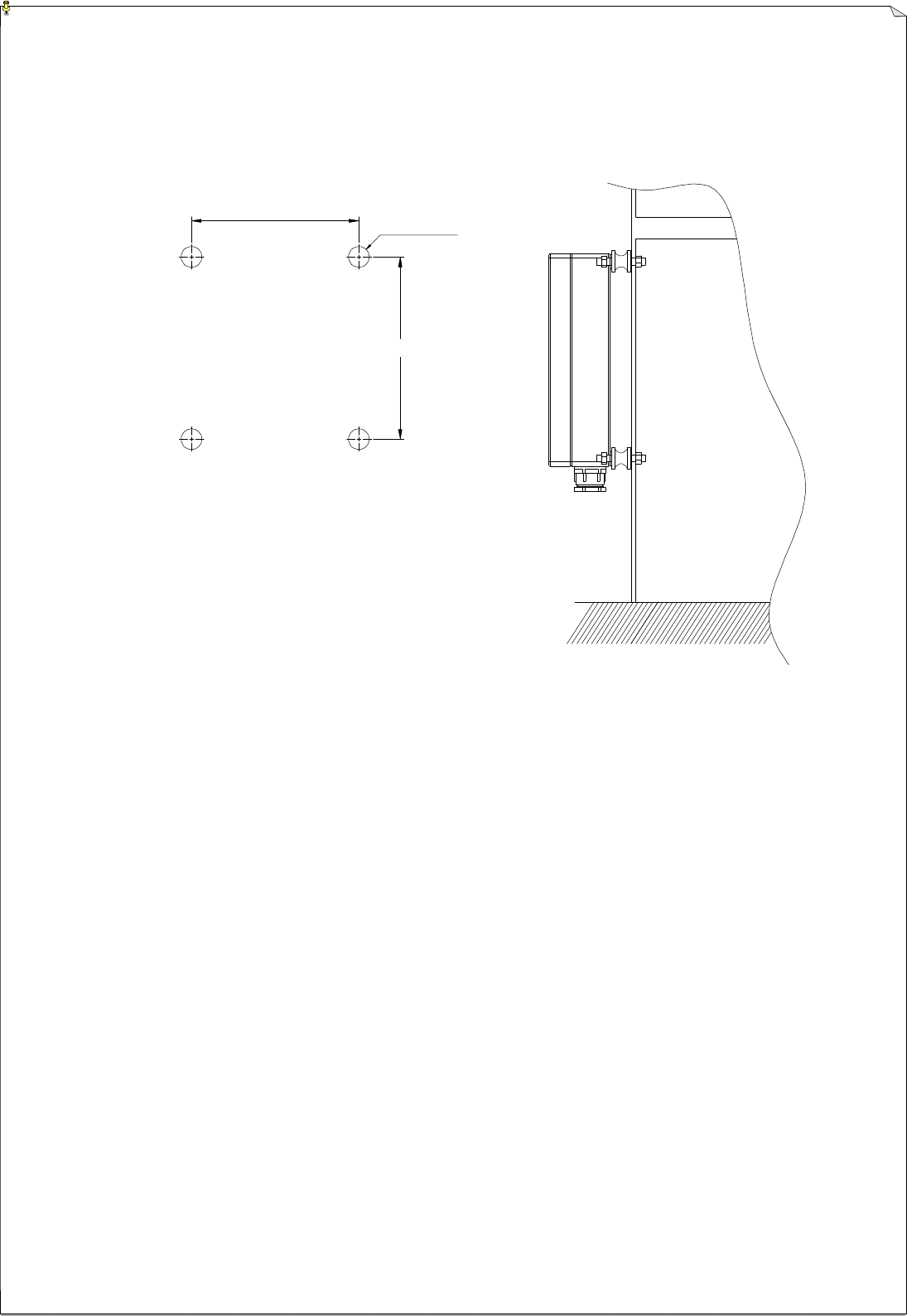
12
255mm
278mm
4-O10.5
8.3 System Testing
1. Connect the power source to the receiver and test the operation of each function to
ensure it operates in the same manner as the pendant controller.
2. Ensure the receiver MAIN can be properly controlled by the remote control.
3. Ensure the limit switches on the equipment that limit all travels are working properly.
4. Ensure the pendant controller is located in a safe location where it would not interfere
with remote operation.
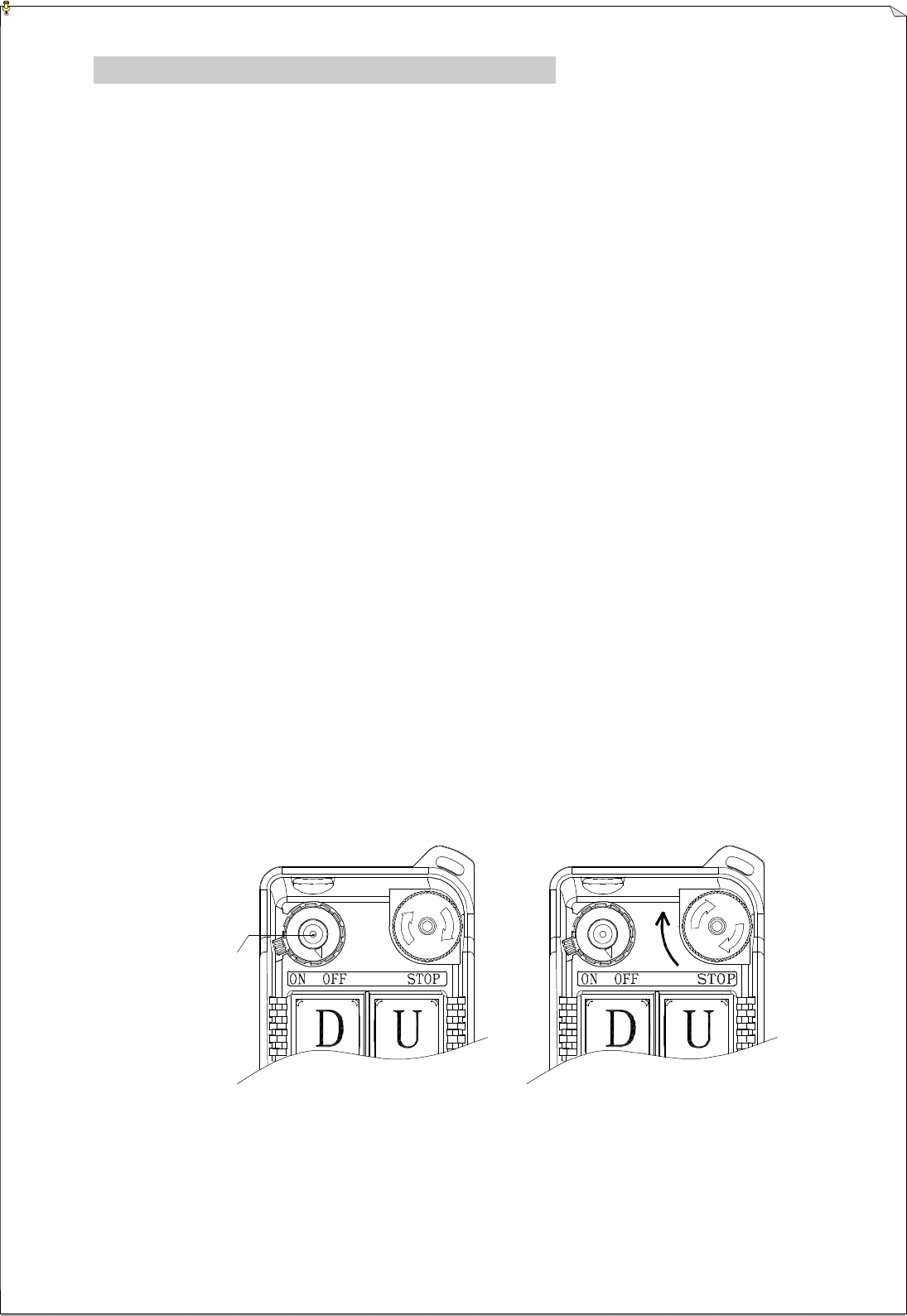
13
LED
9.
TRANSMITTER OPERATION
1. Make sure the two alkaline batteries are installed correctly. Do make sure to use alkaline
type batteries for longer operating time between battery replacements. Rechargeable
batteries can also be used (1,600mA or higher recommended).
2. Turn “on” the power switch located on the top left hand corner of the transmitter unit (refer
to diagram below). The Status LED on the face of the transmitter will display a green light
for up to two seconds when the power switch is turned “on”. Make sure the red EMS
pushbutton is elevated (on), by twisting it 1/4 turn clockwise.
If the Status LED displays a red blinking light with on 0.1 second and off 2.0 seconds
or no light at all, this indicates that the two “AA” batteries in the transmitter must be
replaced. If the Status LED light is blinking red, on 2.0 seconds and off 0.1 second, it
means that the transmitter unit is locked due to a jammed (closed) or defective pushbutton
contact. This important safety feature is designed to prevent any unexpected crane
movement at system start-up caused by a defective or jammed (closed) pushbutton contact.
After turning “on” the transmitter unit, the system will go into self-diagnosing procedure.
After 0.5 second, the transmitter key functions and receiver MAIN will be activated.
3. In case of an emergency, press down the red EMS button will immediately deactivates the
receiver MAIN contact relay. To reset the EMS function and restart the system, just turn
the red EMS button clockwise to enable the red button to elevate to its non-active position.
4. Please note that conflicted movements are interlocked to one another for safety purpose.
Pressing conflicted commands at the same time will result in a non-transmission.
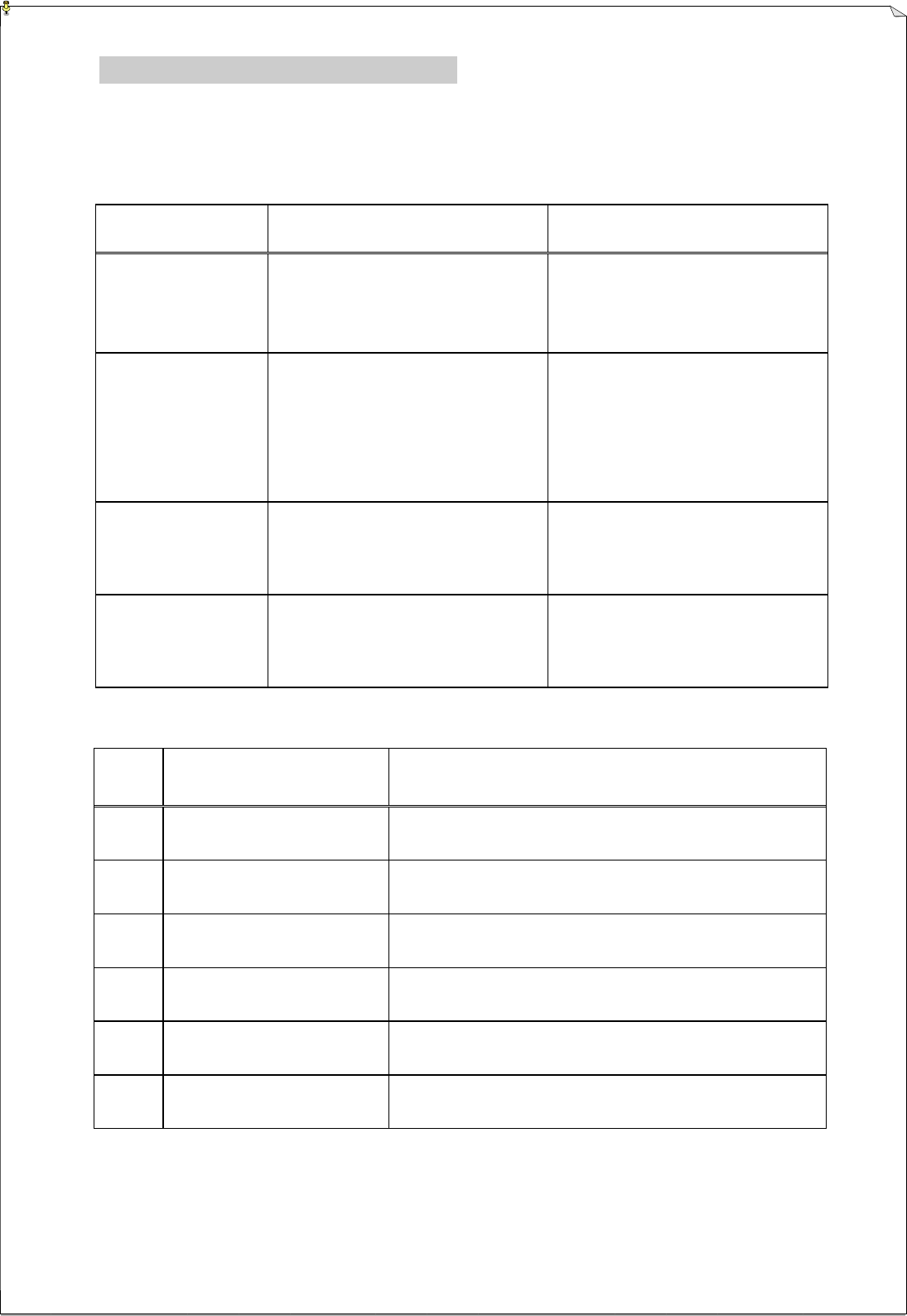
14
10.
TROUBLE SHOOTING
Should the operator find the equipment not operating normally, please check the chart below for
simple trouble shooting steps.
SYMPTOM REASON SOLUTION
Transmitter does not
communicate to
receiver.
Transmitter and the receiver are
not on the same RF channel (SQ
lamp not lit) or ID code.
Ensure the correct transmitter is in
use. The labels on the receiver and
the transmitter
will identify the RF
channel and ID code in use.
Transmitter does not
communicate to
receiver.
Low or no transmitting power
from the transmitter unit.
Turn “on” the transmitter and with
EMS in its elevated position. If
the status LED shows blinking red
light or no light at all, then turn the
power “off” and replace the two
alkaline AA batteries.
No power to the
receiver (AC power
indicator on the
receiver unit not lit).
Blown fuse or no input power
connection.
Ensure power input to the receiver
unit is correct. If power indicator
(AC) is still not lit, please check
the receiver for any burned fuse.
Outputs do not
operate correctly.
Receiver configuration is not set
properly or output wiring is
incorrect.
Please refer to section 6 and 7 to
ensure receiver is correctly wired
and configured for your
application.
Receiver System Status LED Display (please refer to Fig. 6 on page 7).
TYPE
LED INDICATION
(Red) REASON
1 Constant red light. EEPROM error, manufacture reprogramming
required.
2 ON 1.0 second
OFF 1.0 second Incorrect ID code, please readjust accordingly.
3 Dim or no light. Under-voltage, check the main power supply.
4 ON 2.0 seconds
OFF 0.1 second System error, manufacture reprogramming required.
5 ON 0.1 second
OFF 2.0 seconds System normal with transmitter pushbutton either in
neutral or in transmitter power “off” position.
6. ON 0.1 second
OFF 0.1second System normal with transmitter pushbutton in
non-neutral position (pressed).
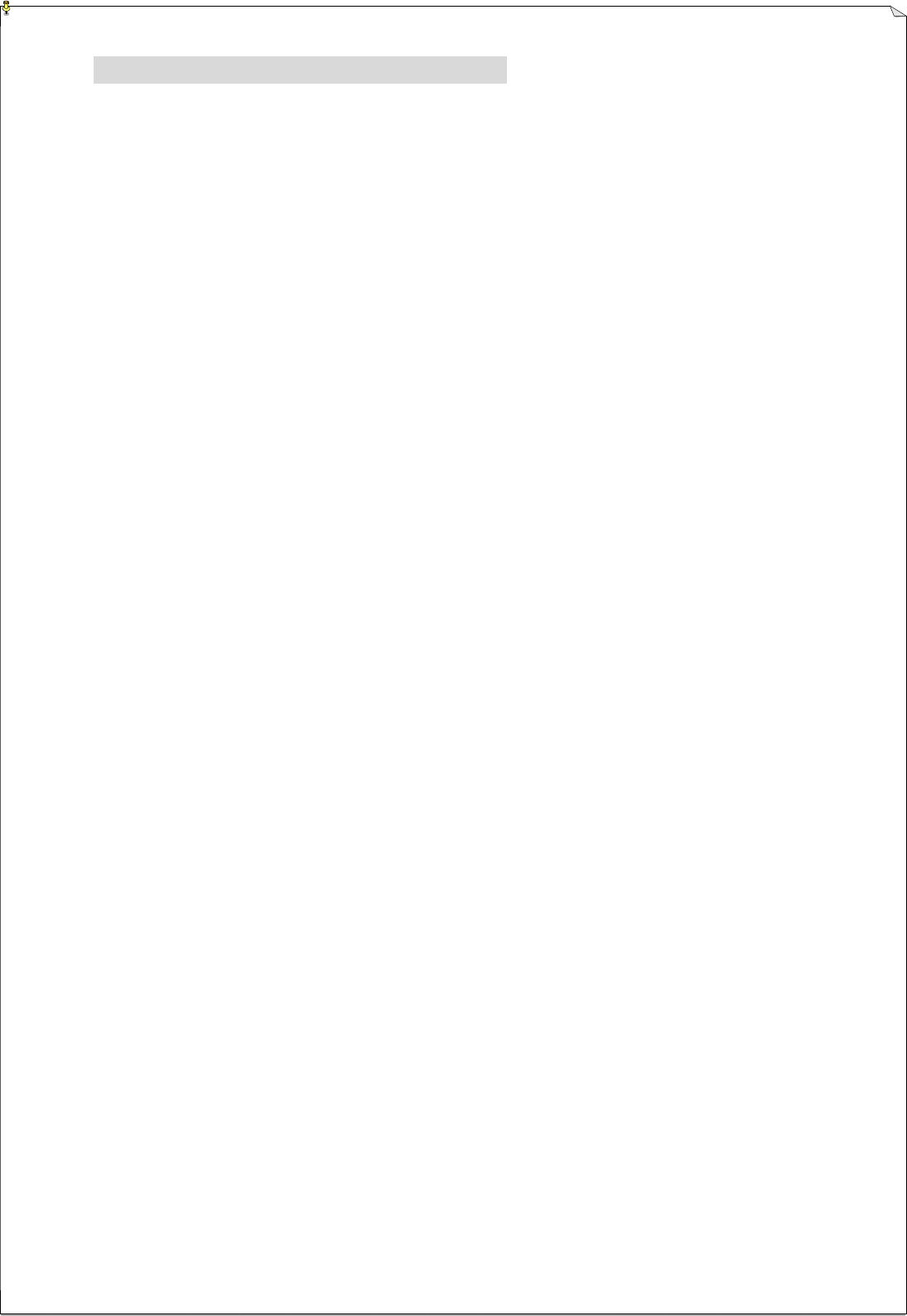
15
11.
SYSTEM SPECIFICATION
Transmitter Unit
Frequency Range : 433 MHz
Transmitting Range : 150 feet
Hamming Distance : 4
Channel Spacing : 25KHz
Frequency Control : Quartz Crystals
Frequency Drift : < 5ppm @ -20 ~ +70
Frequency Deviation : < 1ppm @ 25
Spurious Emission : - 50dB
Transmitting Power : ~.1mW
Emission : F1D
Antenna Impedance : 50 ohms
Enclosure : IP-66
Source Voltage : 3.0 VDC (“AA” alkaline batteries X 2)
Current Drain : 10 ~ 20 mA
Operating Temp. : -20 ~ +70
Dimension : 213mm X 86mm X 33mm
Weight : 290g (include batteries)
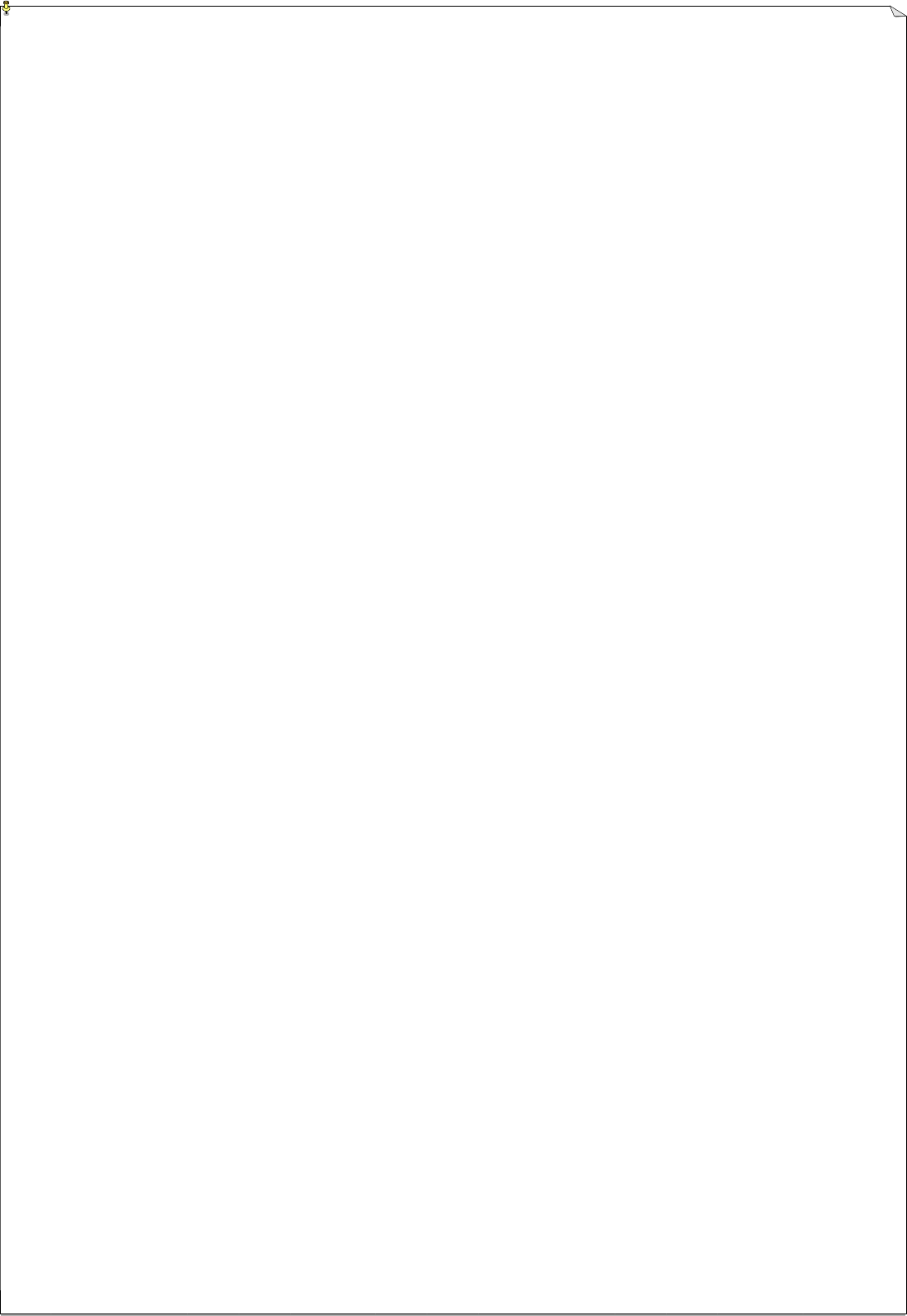
16
Receiver Unit
Frequency Range : 433 MHz
Channel Spacing : 25KHz
Hamming Distance : 4
Frequency Control : Quartz Crystals
Frequency Drift : < 5ppm @ -20 ~ +70
Frequency Deviation : < 1ppm @ 25
Sensitivity : 0.4V
Antenna Impedance : 50 ohms
Data Decoder Reference : Quartz Crystals
Responding Time : 40mS (Normal)
Enclosure : IP-65
Source Voltage : 110 VAC, 50/60 Hz.
Power Consumption : 11VA
Operating Temp. : -20 ~ +70
Output Contact Rating : 250V @ 10A
Dimension : 300mm X 230mm X 86mm
Weight : 3,400g (Include shock absorbers)